
5 minute read
Start-ups pave the way to new business
Gripping systems modelled on gecko feet, VR goggles for employee training, cloud platforms for fast ordering of CNC components: Ideas from founders help big companies optimise their processes and tap new sources of revenue.
Saturday morning, early shift in the production plant of an automotive supplier. The hectic pace is palpable when suddenly the CNC milling machine goes on strike. Every minute that the machine is at a standstill causes financial loss for the company. The annoyance grows when the technician has to fight his way through heavy rush-hour traffic to get to the site. A situation that the competing company from the neighbouring town does not have to fear. Here, the technician uses the advantages of Industry 4.0: he accesses the CNC milling machine via the internet and identifies the source of the error. After only five minutes, the system shutdown is over.
Advertisement
This rapid response is possible because the machine manufacturer recognised the signs of the times and jumped on the digitalisation bandwagon at an early stage. It equipped the machine with sensors and integrated it into the cloud. In cooperation with a start-up that specialises in sensor technology and Industry 4.0.
This is a path that more and more machine builders are taking in order to become the shapers of disruptive changes in the market. A member survey by the German Engineering Federation (VDMA) shows that 81 % of mechanical enginee- ring companies now use networking platforms to identify partners from the startup scene. Through these collaborations, the often long-established companies gain access to new technologies and process knowledge. They lay the foundation for developing new products and business models beyond the classic core business.
Start-ups that are familiar with the technology topics of the future – such as the Industrial Internet of Things (IIoT), cloud-based services, data analytics and artificial intelligence – are particularly sought after.
Trumpf: „Important building block in the concept of innovation“
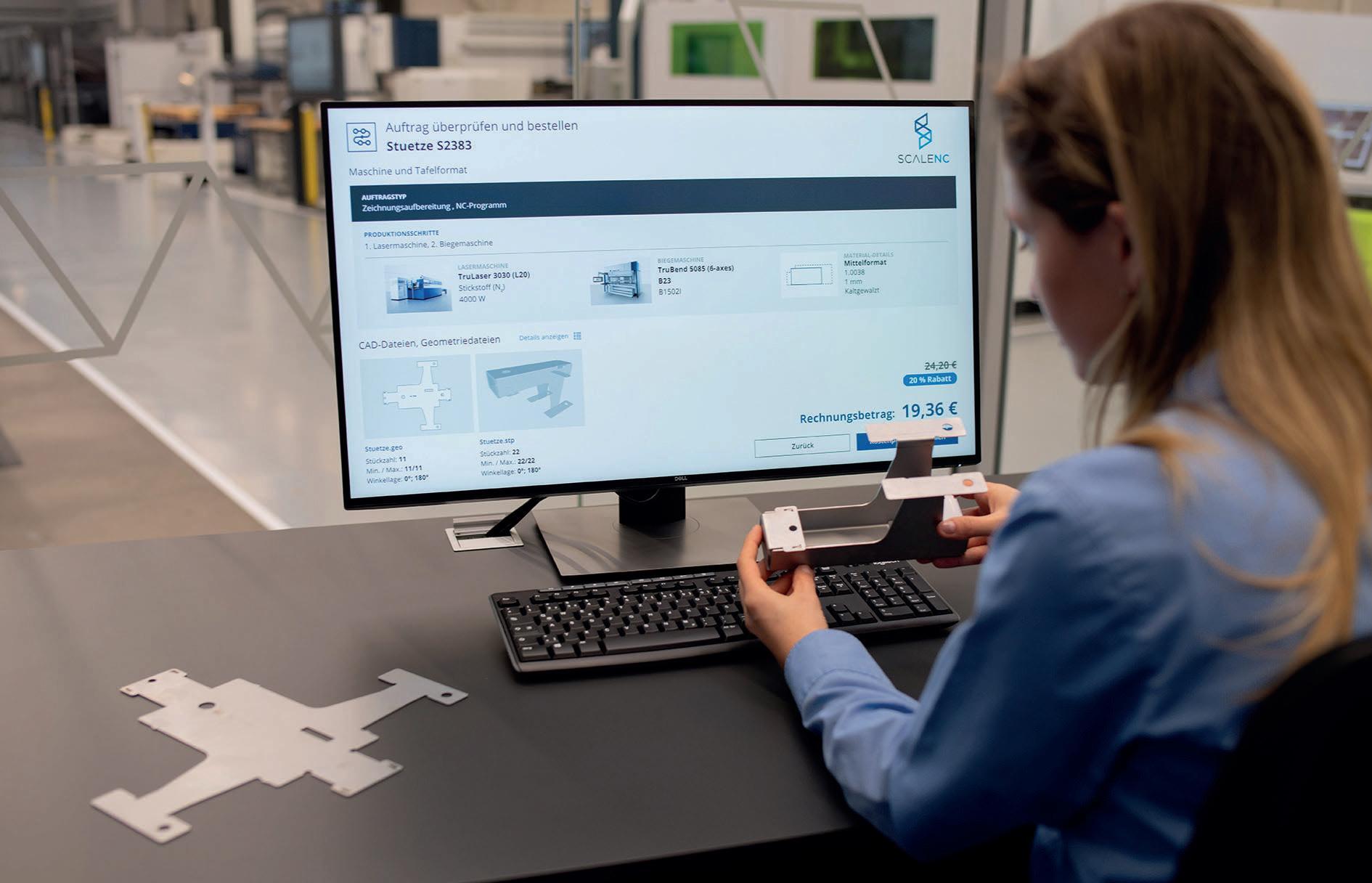
Machine tool manufacturer Trumpf also relies on cooperation with start-ups. „As a high-tech company, we not only have to pick up on the trends of the times, but ideally anticipate them,“ says Niklas Hering, investment manager at Trumpf Venture GmbH. „In this context, close cooperation with start-ups forms an important building block in Trumpf‘s innovation concept and optimally complements our tradition of internal innovation.“
One example of such collaboration is the cooperation with ScaleNC, a young company that has developed a platformbased service package for sheet metal processors. The service works as follows: Customers can upload drawings, sketches and computer aided design (CAD) models of parts to be manufactured to a cloud platform. Computer Aided Manufacturing (CAM) experts then remotely take over the programming of all common Trumpf machines for sheet metal processing, supported by algorithms. This makes it possible to create even demanding CNC programmes in a short time.
„ScaleNC is the answer to the shortage of skilled workers. Many of our customers have difficulty filling vacancies,“ says Tom Schneider, Managing Director Research & Development at Trumpf Werkzeugmaschinen. „In addition, ScaleNC provides cost advantages and helps our customers strengthen their competitive position.“ It is a service that is finding favour around the world. „The need for cloud-based services is growing in the industry and we look forward to making our solutions available to even more customers,“ says Holger Röder, founder and CEO of ScaleNC. The startup is currently preparing to enter the US market.
Festo: „Good scouting is the first step“
Festo AG, a manufacturer of control and automation technology from Esslingen am Neckar, also knows how important start-ups are for the future of machine builders. „Start-ups are also taking on an increasingly important role in the field of mechanical and plant engineering, especially for medium-sized companies,“ says Jochen Schließer, Head of Innovation Projects and Networks at Festo. „Good scouting on defined topics is the first step towards cooperation.“ Since 2014, the company has been working with start-ups to make its own processes more efficient.
One example is the cooperation with Holo-Light, a German-Austrian tech startup from Innsbruck that specialises in Industry 4.0 solutions with augmented reality (AR) devices. These include the Microsoft Holo-Lens, AR glasses that add digital content to the user‘s vision. This makes it possible, for example, for a technician to draw repair or assembly instructions remotely in real time in the field of vision of the person wearing the glasses. Holo-Light was able to demonstrate the other advantages of this augmented reality in a pilot project at Festo‘s plant in Rohrbach. Normally, employees there learn how to handle technology on the machines in the factory itself. The disadvantage: during this time, the machines cannot produce. The alternative: data glasses that use holographic images and voice instructions to guide employees step by step through operating processes in a training room. This way, the new employees can learn assembly processes and safety rules virtually. Without interrupting the production flow.
CAD data becomes a component – at the click of a mouse
Among the young companies in the field of mechanical engineering is Spanflug Technologies GmbH, a Munich startup, spun off from the Institute for Machine Tools and Industrial Management (IWB) at Munich Technical University (TUM). The founders are addressing the following problem: when companies want to commission a CNC-manufactured component, they often find themselves sweating. Especially with complex geometries, the calculation for turned and milled parts is complicated and requires a lot of time and expertise. So does the search for a supplier who has sufficient capacity. Thus, according to Spanflug, the conventional procurement process causes costs amounting to 20 % of the component costs on average. The founders have therefore set themselves the goal of automating the parts procurement process in the manufacturing industry.
To this end, the start-up has launched an online platform that has already been joined by over 200 CNC manufacturing partners from Germany and Austria. More than 3000 customers are already using the platform to procure turned and milled parts. They can upload information about the desired components there. „Our software automatically calculates the price based on a CAD model and a technical drawing,“ explains Markus Westermeier, co-founder of Spanflug. In addition, the platform also immediately finds a qualified CNC supplier. Thus, customers could shorten the ordering process from days to a few minutes and reduce the ancillary costs in procurement. Thanks to the digital and lean process, CNC companies are able to deliver the components in as little as six working days.
One of the start-up‘s investors, the German Machine Tool Builders‘ Association (VDW), is correspondingly enthusiastic. „The investment offers great potential, both for our member companies and their customers, as well as for the entire mechanical and plant engineering sector in Germany,“ says Wilfried Schäfer, co-managing director of the VDW. „The aim is to secure the competitiveness of the manufacturing industry in Germany in the long term through the use of the Spanflug technology and the associated efficiency gains.“

Fine hairs carry small parts and heavy loads
Another example of the innovative power of start-ups in machine tool manufacturing is provided by Innocise from Saarbrücken, which emerged from the Leibniz Institute for New Materials. The engineers are developing innovative industrial holding systems. And they take nature as their model. Geckos, to be precise. Their feet are covered with microscopically fine adhesive organs which allow the scaly crawlers to hold on to smooth surfaces.
Weak attractive forces, the so-called Van der Waals interactions, are responsible for this. Innocise uses these temporary forces for holding systems that can hold components without negative pressure, magnetic fields or adhesives.
The heart of the so-called Gecomer technology is a patented surface structure consisting of thousands of fine hairs made of special polymers. It makes it possible to lift heavy automotive or mechanical engineering components.
But it also opens up new possibilities in micro-assembly. Thanks to the tiny polymer hairs, grippers can even handle objects smaller than 0.01 mm – such as components on printed circuit boards, micro-optical components or glass fibres. The objects adhere when the holding system gently presses on the hairs. And they release when pressed or pushed again. A technology that has also convinced Schunk, an expert for gripping systems and clamping technology from Lauffen am Neckar. Together, the companies have developed an adhesive gripper called „Adheso“, which can lift thin films or porous sheets, among other things.

Model-based identification of process instabilities based on process-parallel data