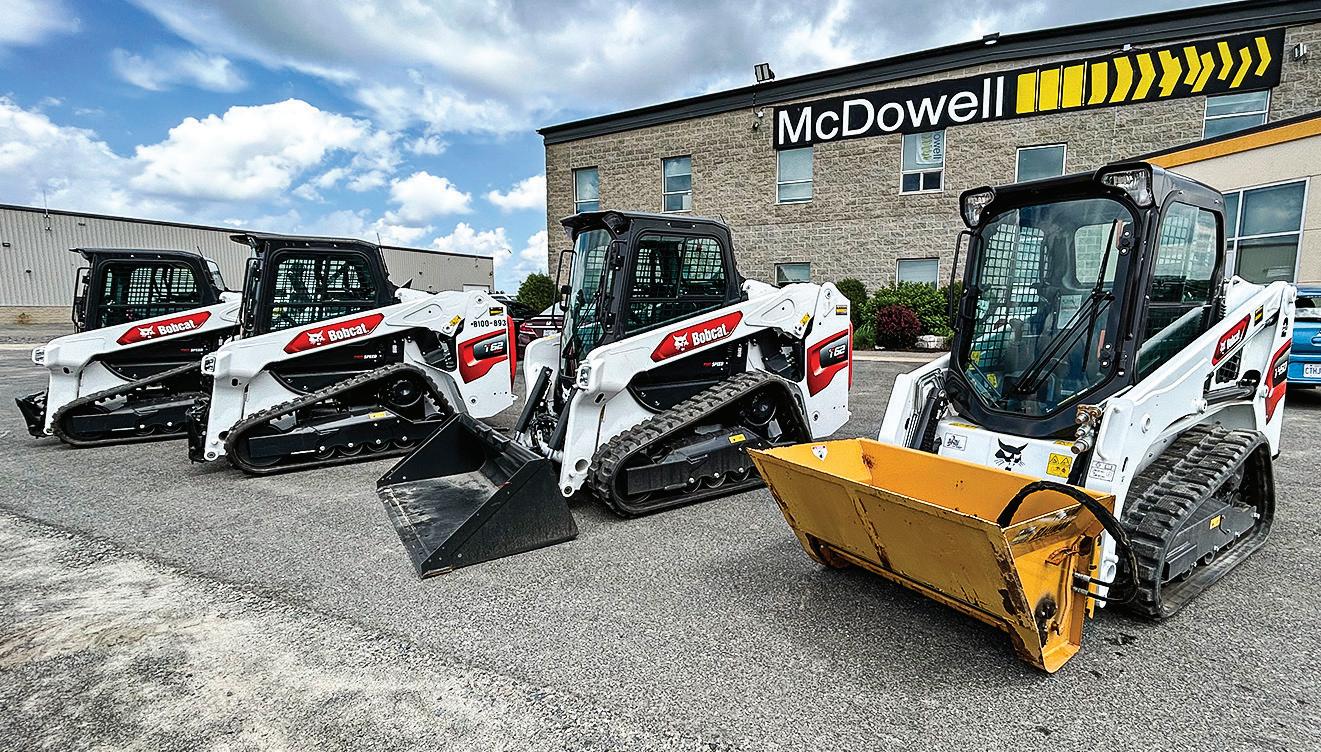
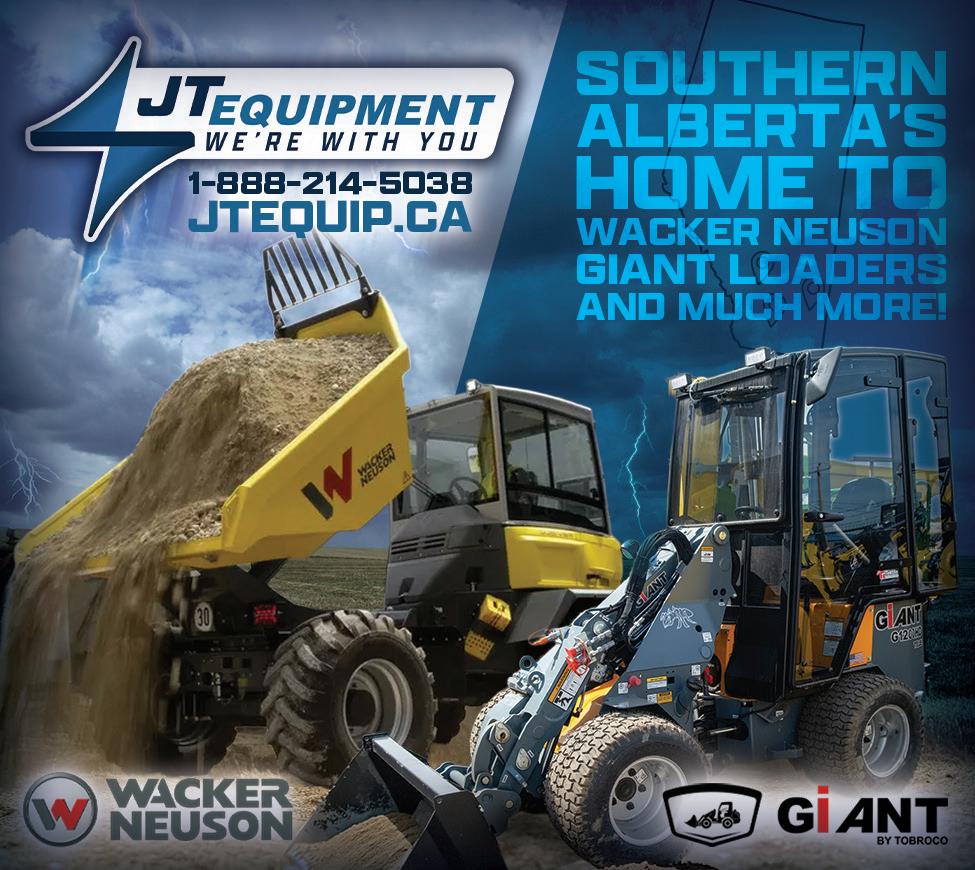
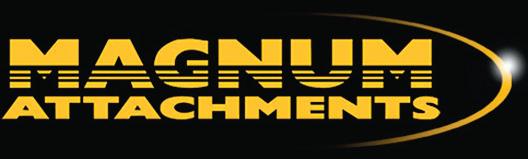
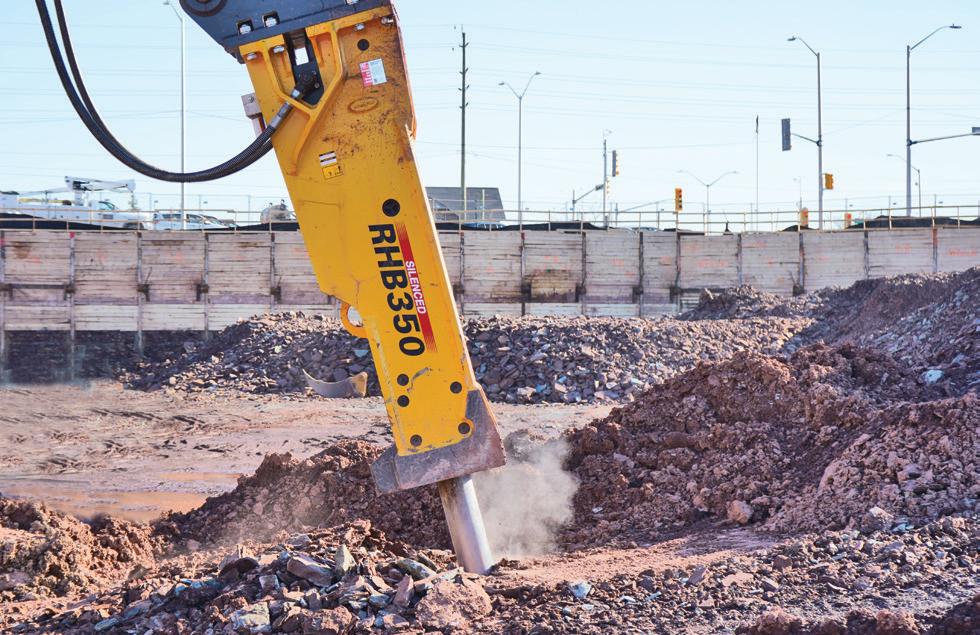
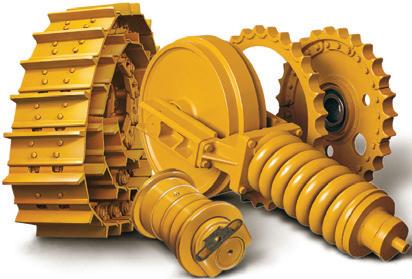
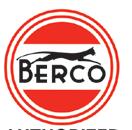
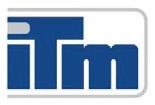
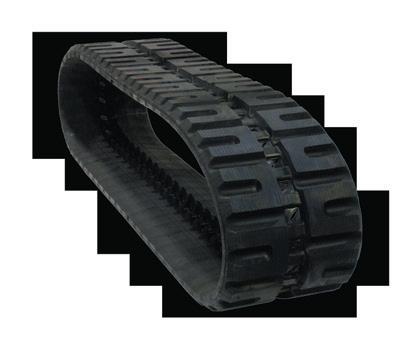
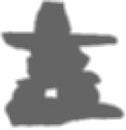
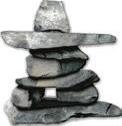
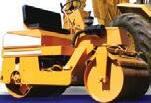
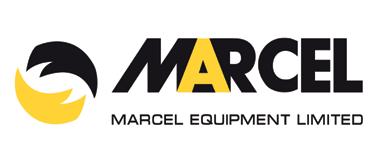

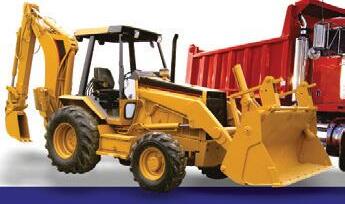

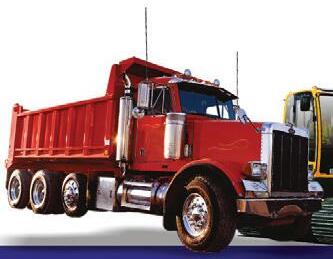
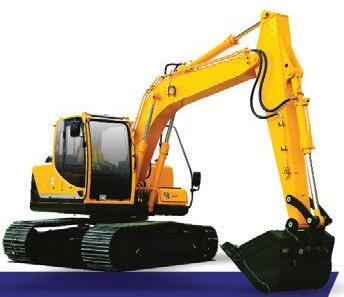
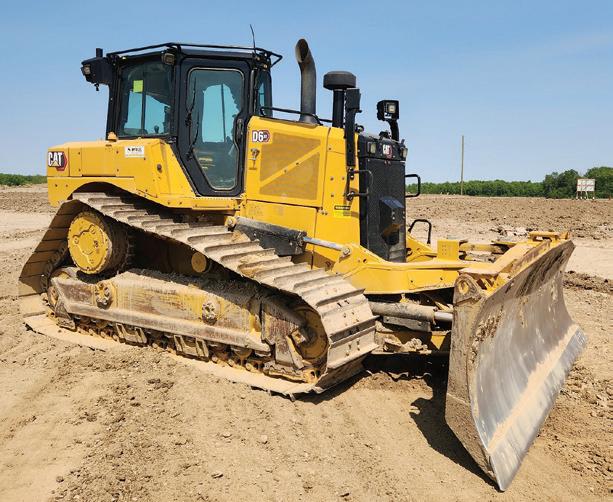
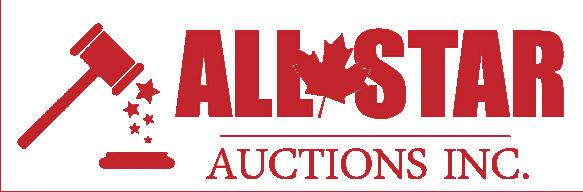
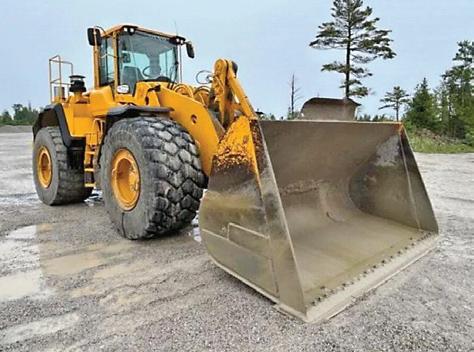
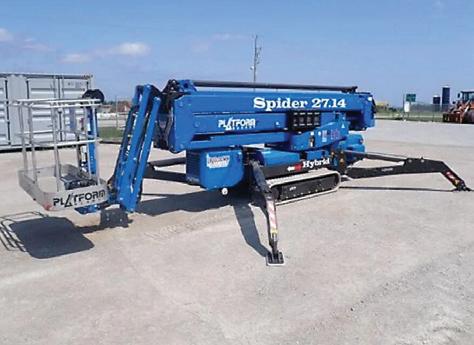
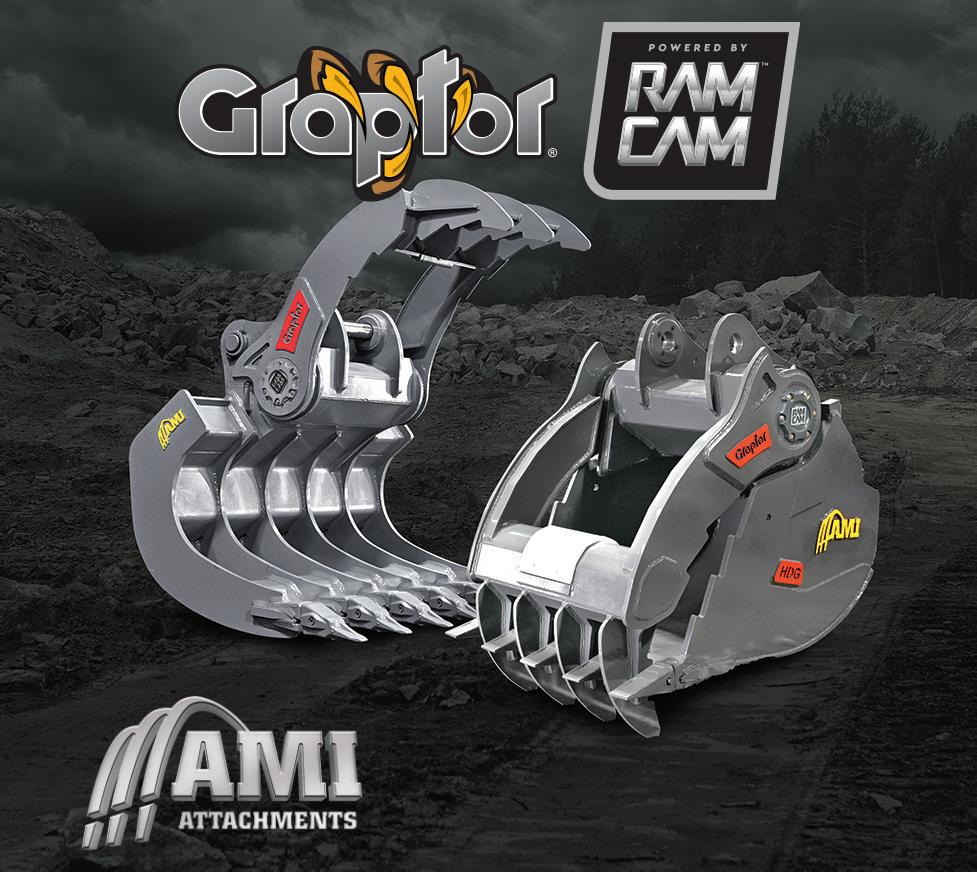
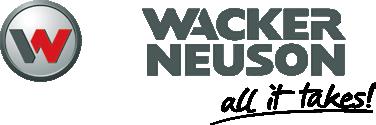
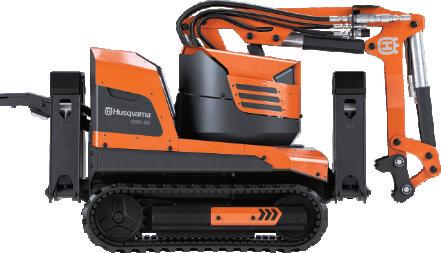
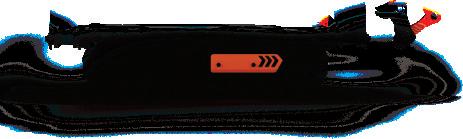

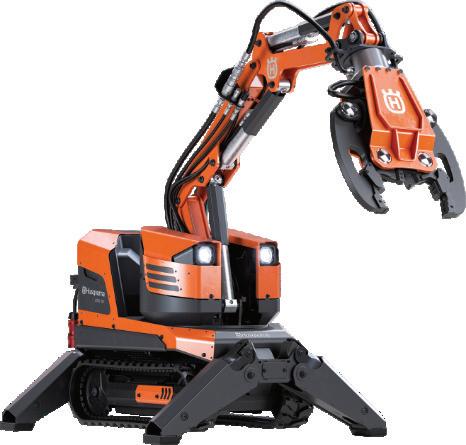
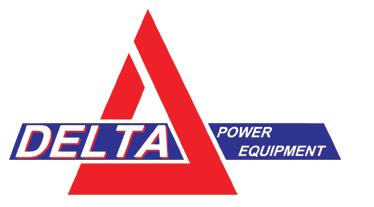
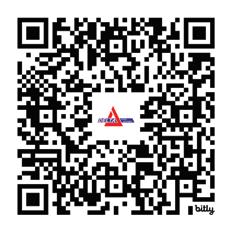
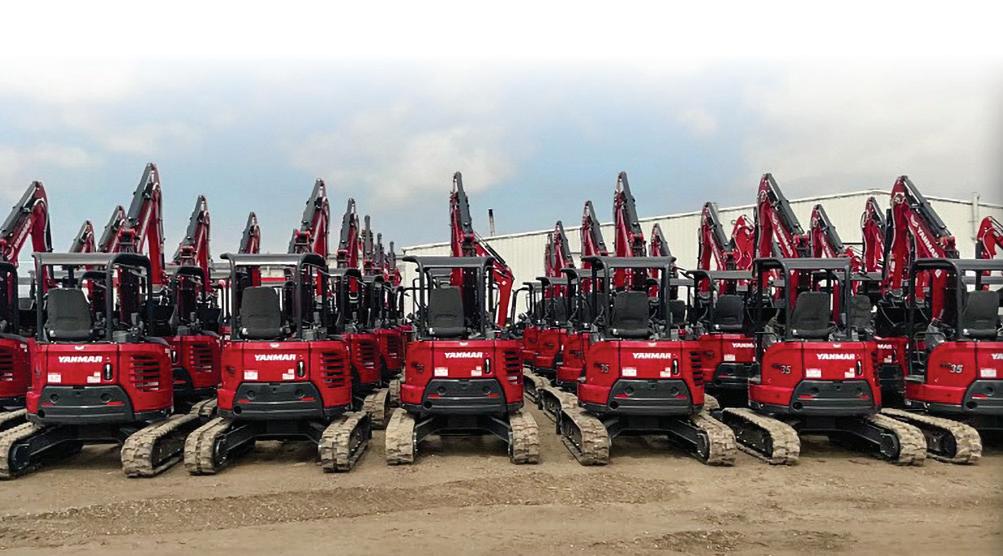
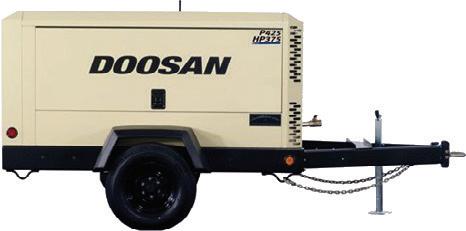
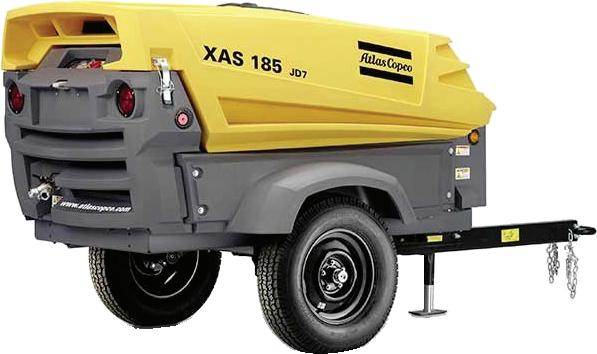
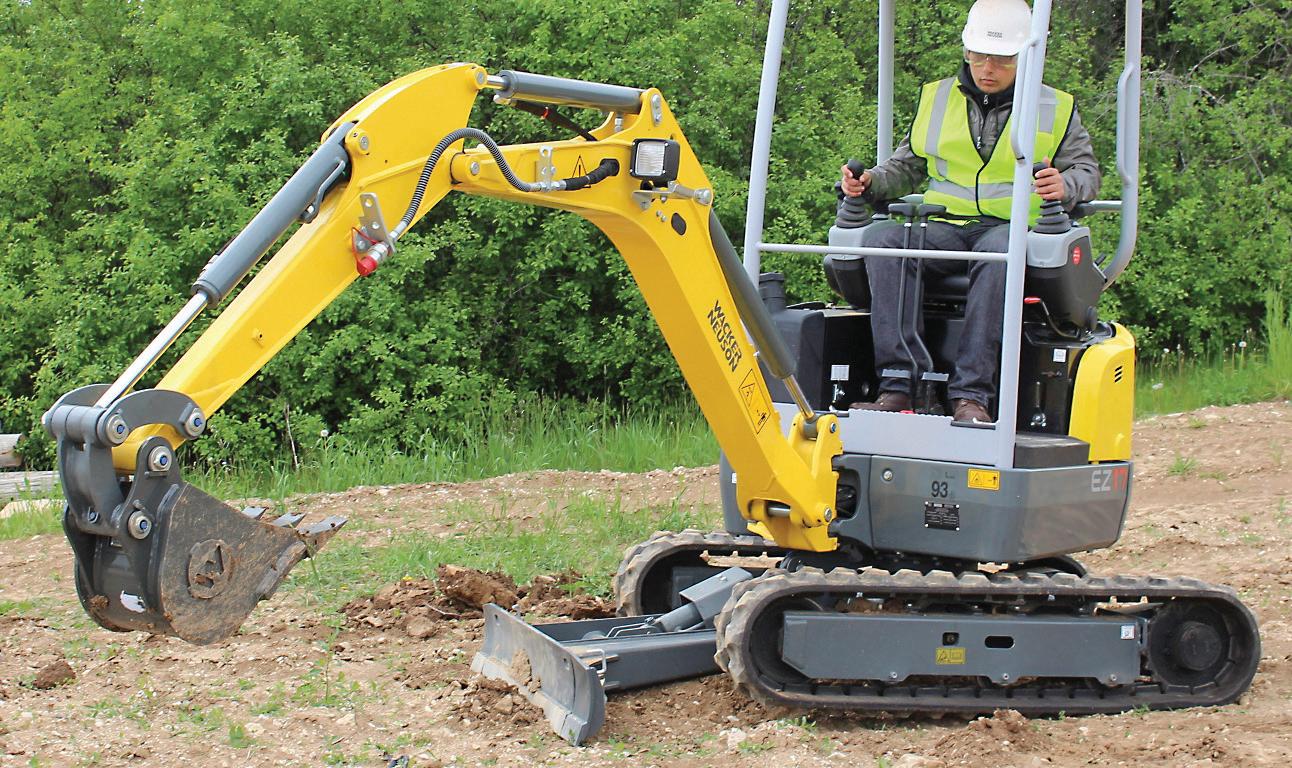
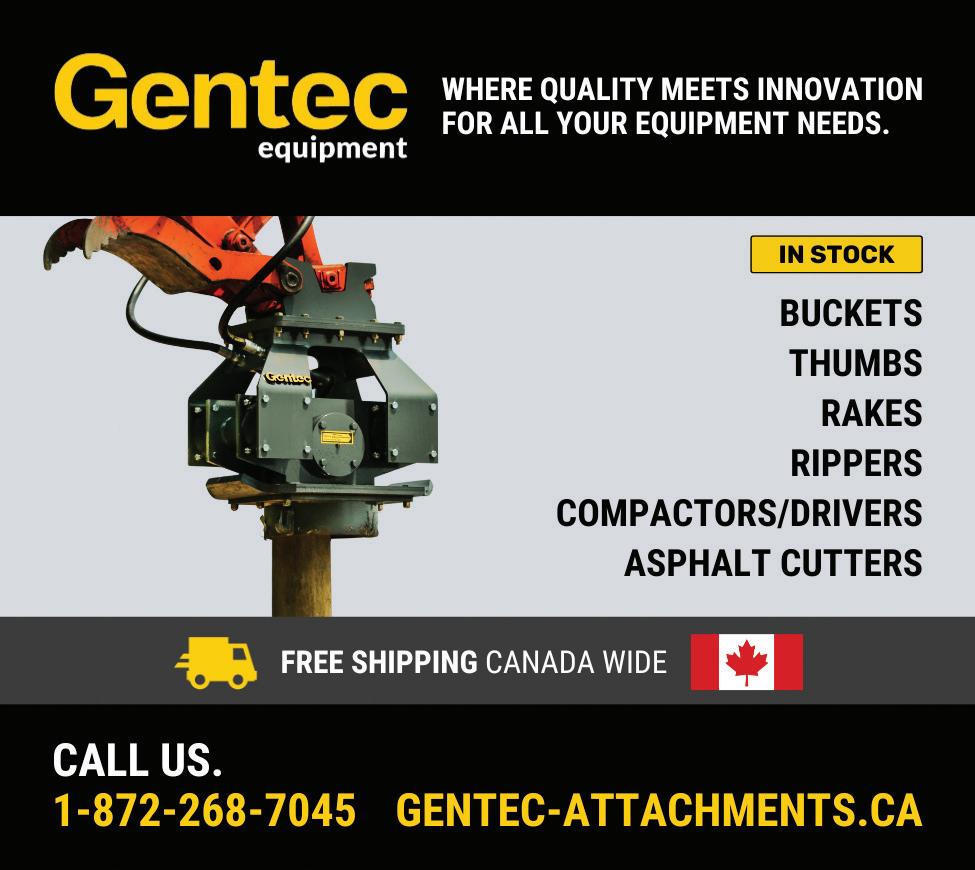
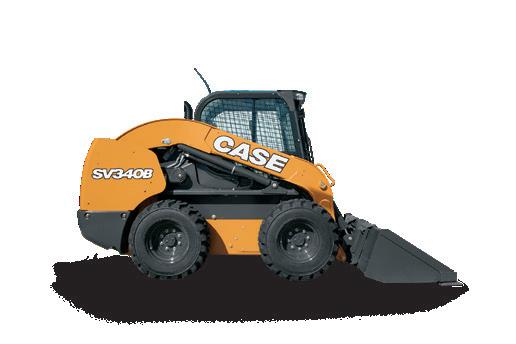
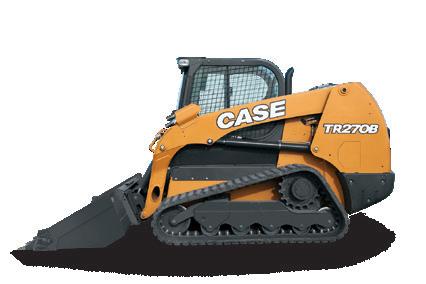
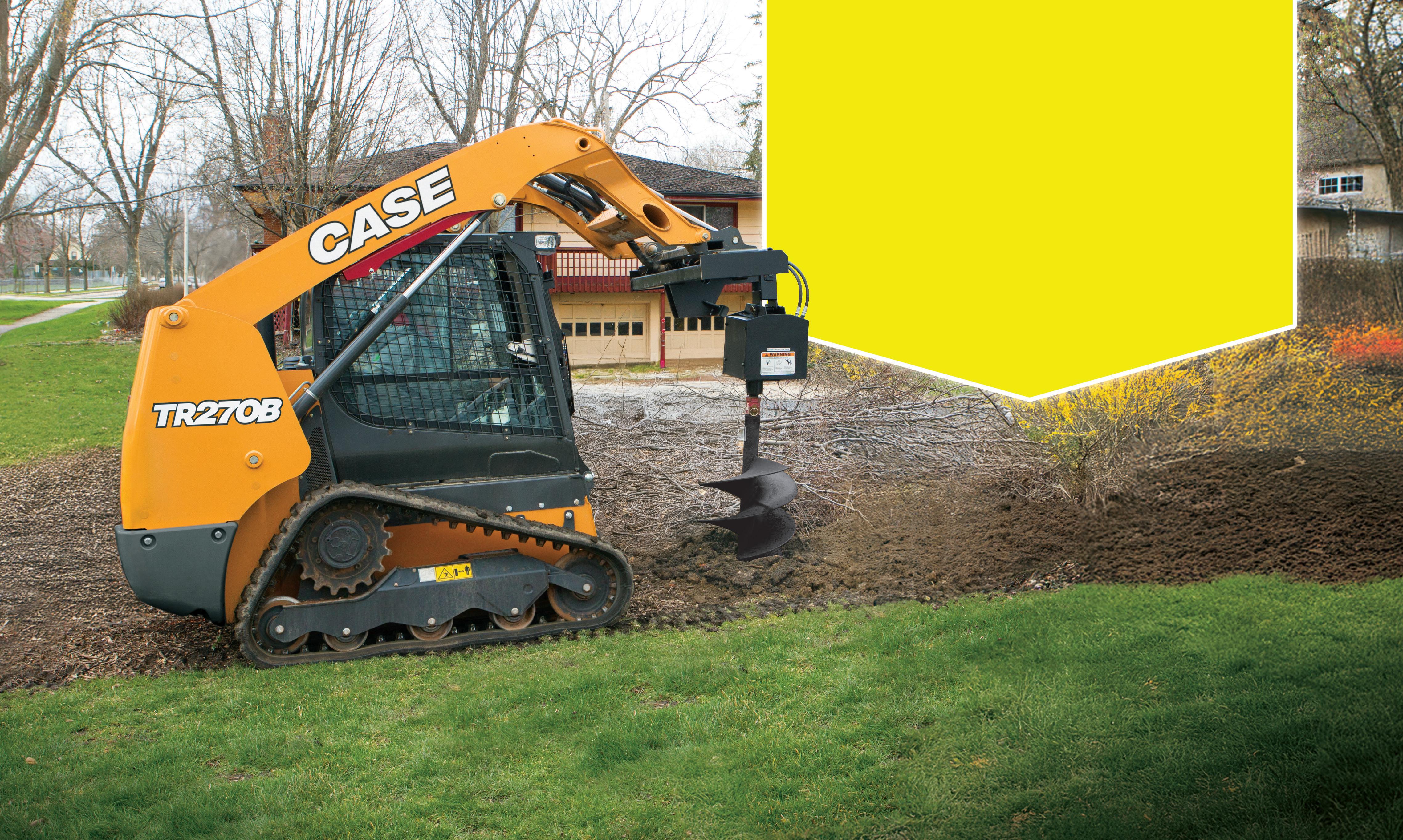
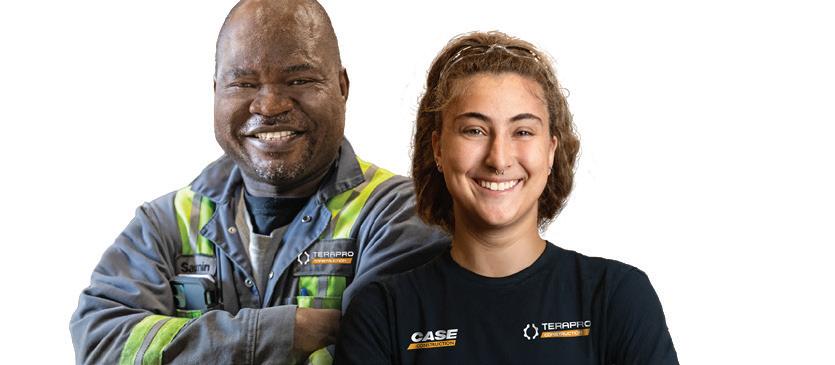
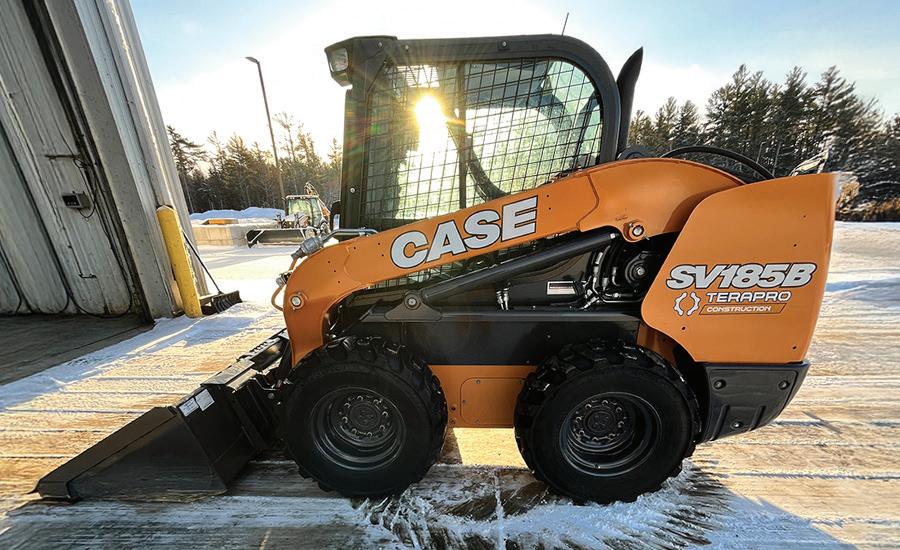
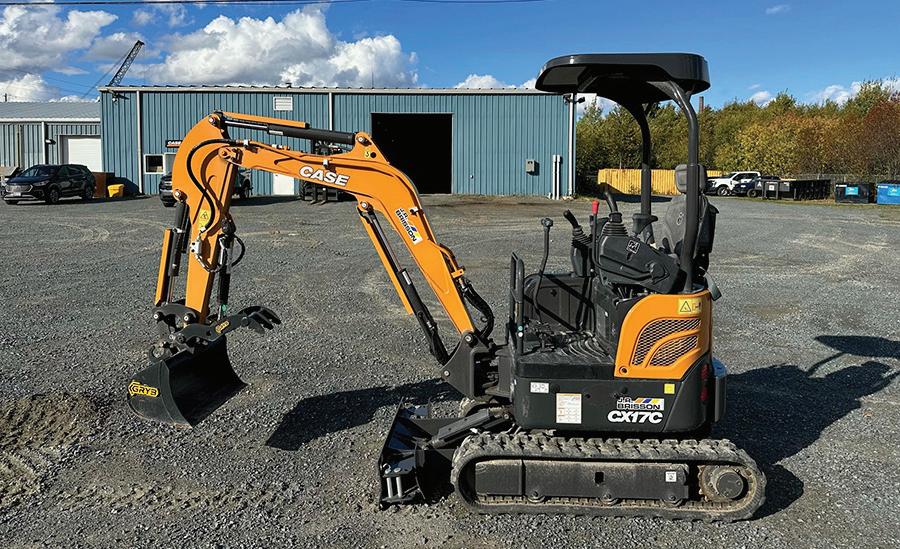
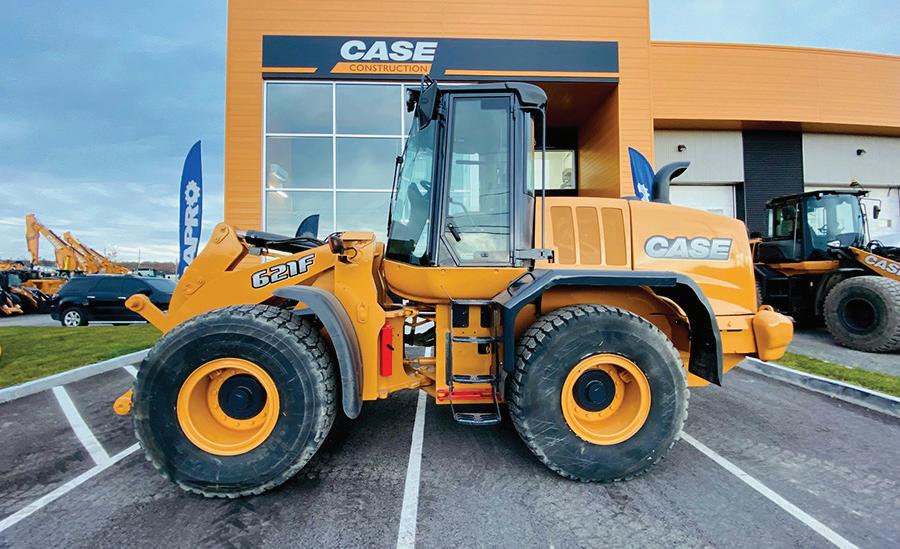
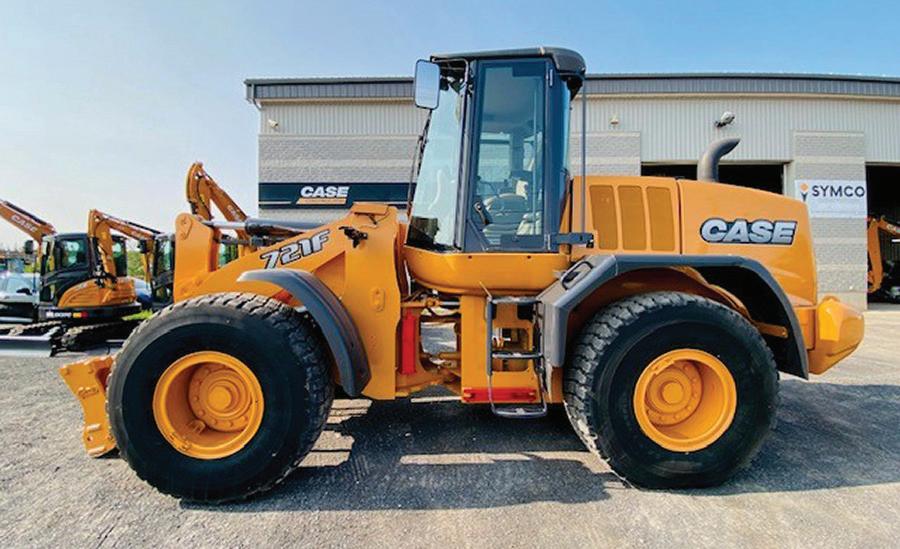
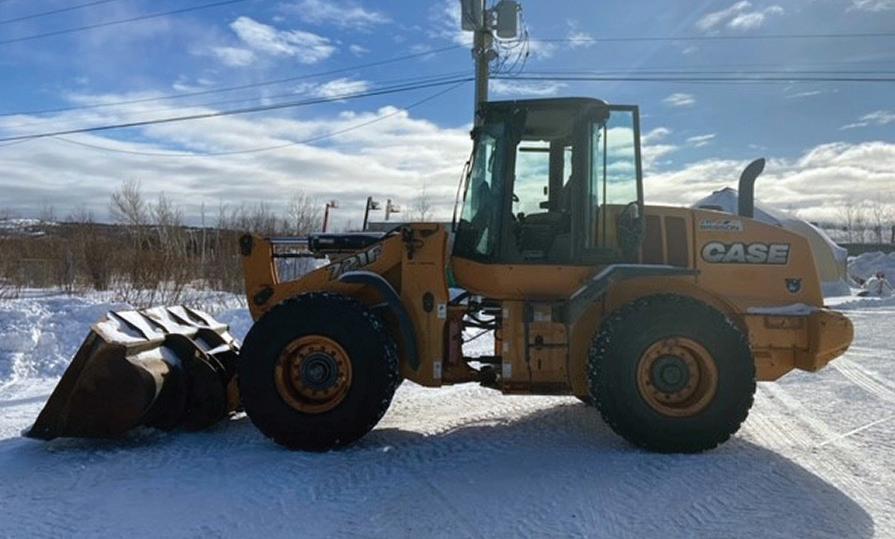
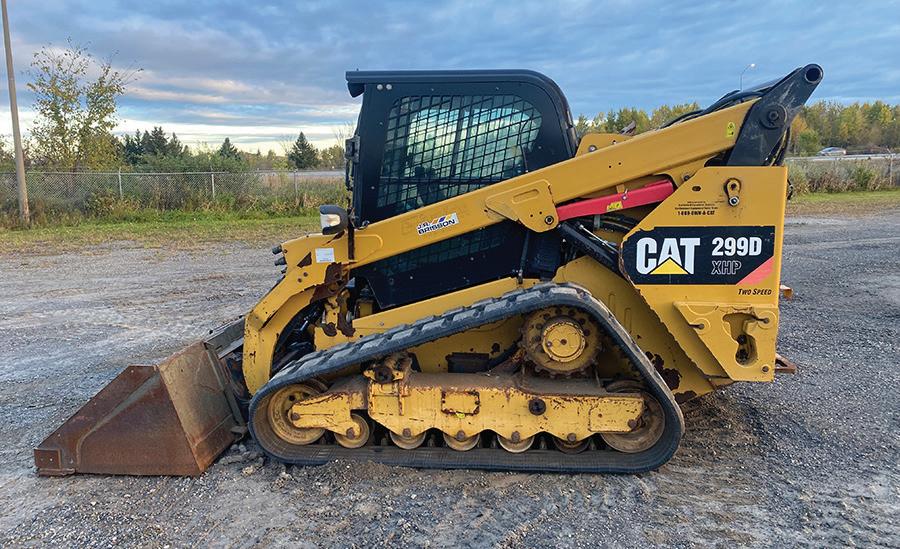
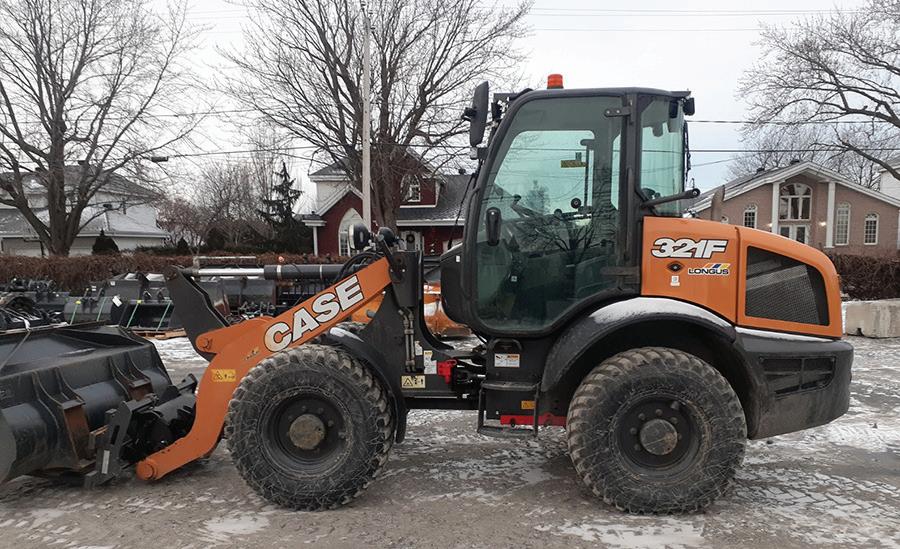
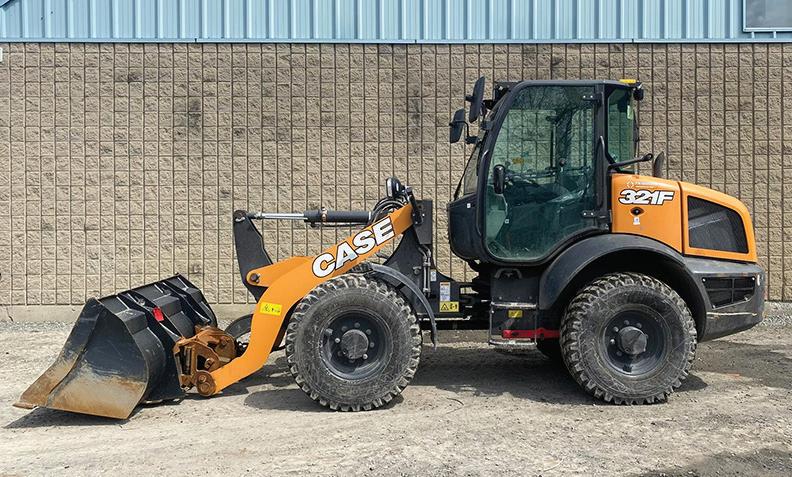
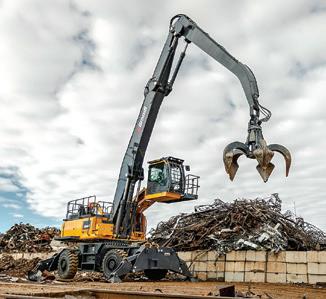
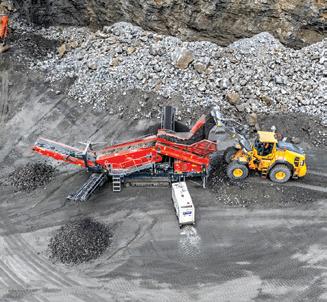
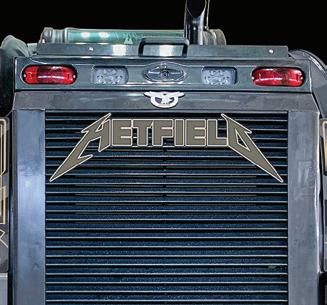
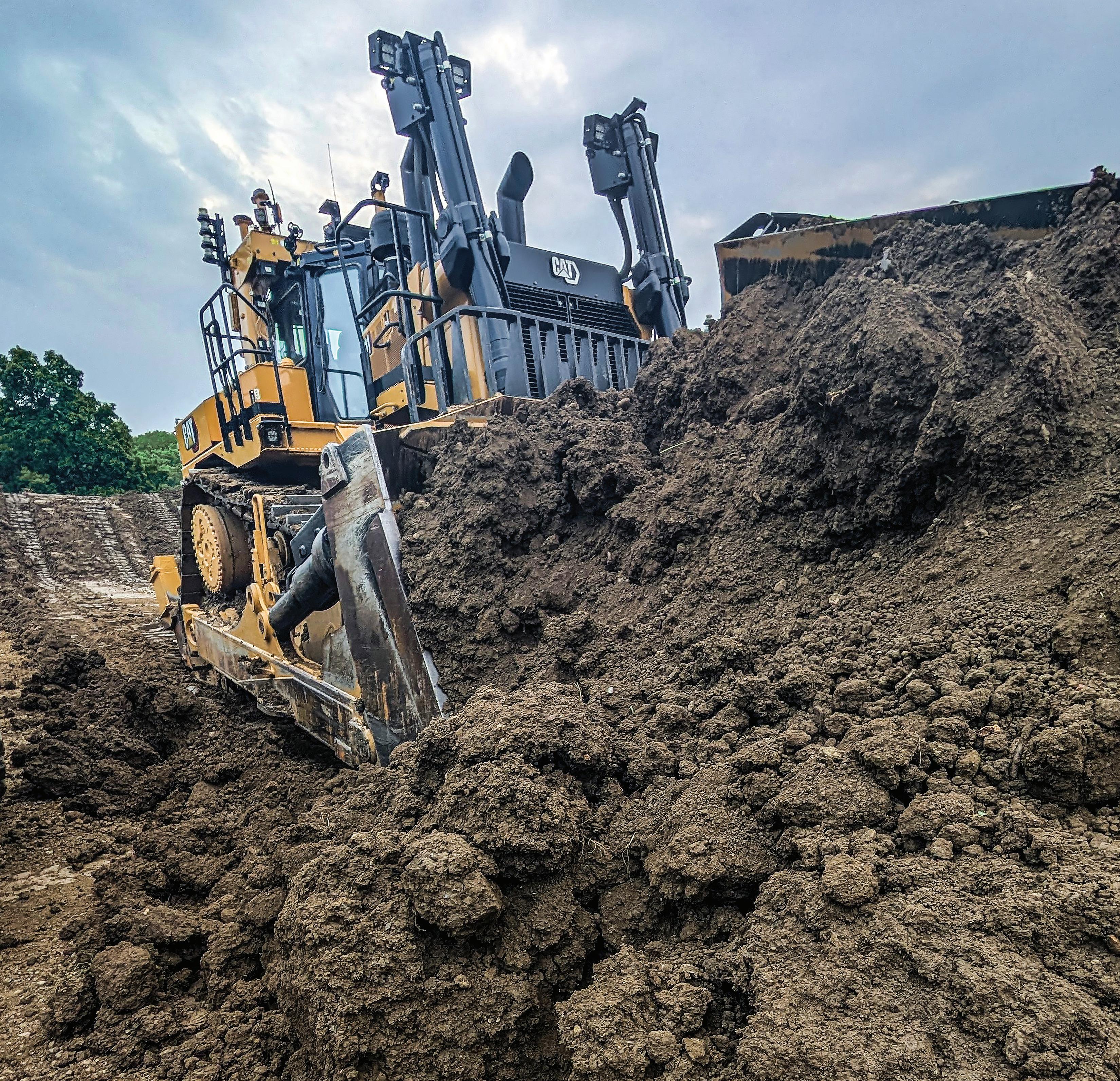
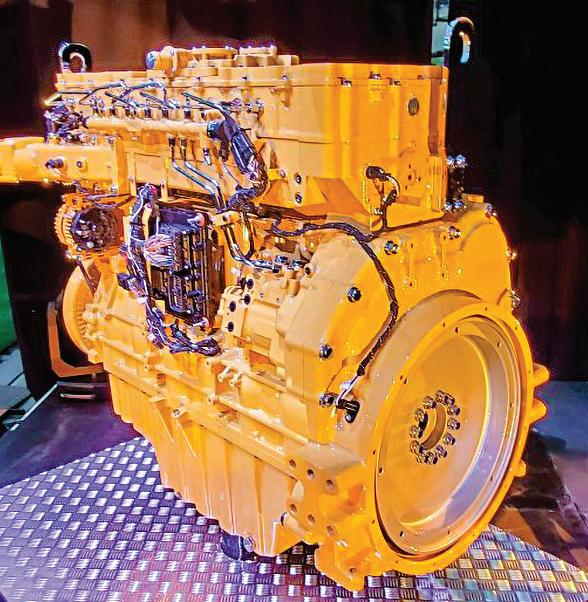
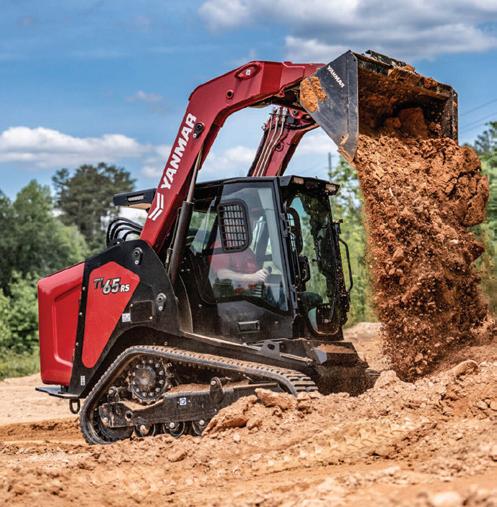
Multigenerational homes are a growing trend in Canada. In the last two decades or so, this living arrangement has grown to represent 6.4 per cent of the population, a 50 per cent increase. This significantly outpaced overall growth of households nationwide.
Housing costs and a need for family support are the main reasons Canadians are choosing to live with other family members. It’s an understandable and cost-effective lifestyle. From a municipal tax collector’s perspective, it should be viewed as a growing impairment to cash flow.
When you take what’s traditionally three taxpaying properties and combined them into one, you’re reducing revenue while still processing the same volume of wastewater, servicing the
same number of library visits and sending the same number of kids to school.
In Ontario’s Peel Region, my home turf, councillors from Brampton and Caledon recently walked out of a council meeting in protest of the idea to reduce Development Charges (DC) on new residential construction.
Mississauga Mayor Carolyn Parrish proposed the DC reduction of 50 per cent, among other incentives, to kickstart construction in the region.
“Without intervention, we risk years of stagnation, lost jobs and worsening affordability,” Parrish wrote in a letter to Peel’s councillors.
“This motion is not about giving away money. It’s about stimulating growth that otherwise won’t happen. If we do nothing, we collect no DCs at all. But if we act, we can unlock thousands of units,
generate new tax revenue, and create the conditions for long-term fiscal health.”
The protesting councillors believe the full fee amount, which has grown from $53,000 in 2020 to $76,000 in 2025 for a single or semi-detached home, are necessary to pay for services to service new residential properties.
With Canadian residential construction deceasing by 4.5 per cent in April, the councillors’ point of view is out of touch with reality, particularly for Brampton where one in four homes is a multigenerational household.
Combined with the Peel Region levy, Brampton homeowners pay an average of $11,000 annually in property tax. By reducing DCs, municipalities encourage an increase in housing supply, which helps to ease demand and provides the opportunity
for multigenerational homes to become several family homes. This can boost the tax base without increasing population. It’s also an added bonus to existing economic benefits of construction.
Maintaining high fees as investment softens is shortsighted, and politicians should remember that DCs are a one-time payment, while property tax is forever.
As part of a significant global investment, Volvo Construction Equipment will begin manufacturing crawler excavators and large wheel loaders in Shippensburg, Pennsylvania.
For crawler excavators, three main sites will see about $261 million invested to expand production to meet growing customer demands, mitigate supply chain risks and reduce reliance on long-distance logistics. The three sites include Shippensburg, Changwon, South Korea and a location in Sweden.
Alongside crawler excavator production, Volvo CE will also expand wheel loader production to include large wheel loaders in Shippensburg. Currently, soil and asphalt compactors and mid-size wheel loaders are manufactured at the Shippensburg factory.
"We must respond to growing demand, and we’re excited to expand our facilities to serve our customers better," said Melker Jernberg, Head of Volvo CE.
"This investment underscores our commitment to quality and innovation, allowing us to deliver even greater value."
Updates will be made to the existing space within the factory to install assembly lines, integrate more automation technologies into the manufacturing process and train employees.
Volvo CE is aiming to begin production of the new lines in the first half of 2026.
“Bringing excavator production to North America and growing the range of wheel loader models built here has always been part of our long-term industrial plan, so it’s exciting to finally share this news with our employees, dealers and customers,” said Scott Young, Head of Region North America.
“This increase in production capacity means that over 50 per cent of our North American machine supply can be built here in Shippensburg, resulting in shorter lead times while also creating opportunities for supplier growth.”
By expanding production capabilities in key markets, Volvo CE will reduce dependency on any single site and become less reliant on long-distance logistics. Supply chain risks will also be mitigated by expanding domestic supplier bases,
Metso is building a new service centre in western Canada to deliver solutions closer to its customers.
On June 4, the company celebrated the groundbreaking of its new service centre in Prince George, British Columbia.
Situated in the heart of a key Canadian mining region, the facility will support growing customer demand, particularly in the copper and gold sectors.
“The investment decision, announced in September 2024, was very well received by our customers. Metso’s strengthened local presence will enable faster repairs, shorter turnaround times and increased sustainability by reducing transportation distances,” said Justin Ayotte, Vice President, Canada Sales and Service at Metso.
“We’re grateful for our customers’ trust, and we remain committed to becoming the preferred service provider in the industry.”
When the new facility opens, Metso will offer OEM-certified on-site inspections, turnkey service solutions and off-site repairs.
The centre will service a wide range of mining equipment from pit to port, including crushing, grind -
allowing the OEM to more nimbly manage any economic or regulatory challenges.
As well, Jernberg said fostering collaboration with local suppliers and customers will better position the company for sustained growth and innovation without compromising standards.
Volvo CE acquired the Shippensburg site in 2007 from Ingersoll Rand and relocated its regional headquarters there in 2012.
On top of recent investments, Volvo CE will invest about $40 million locally in the next five years.
ing, screening, filtration, flotation, slurry handling, thickening, clarifying, loading and hauling solutions, chute lining and more. It will also offer warehousing capabilities for spare parts and wear parts.
Metso has an extensive service centre network with more than 3,700 field services professionals, technical support and more than 140 service locations on six continents.
The new facility will further contribute to creating employment opportunities for skilled professionals, such as service engineers and technical specialists.
The service centre is expected to be fully operational by early 2026.
Metso aims to the continuously develop of its service and repair capabilities to ensure close support for customers worldwide. As part of this commitment, the expansion of the service centre and the opening of a new training centre in Mesa, Arizona, are scheduled for completion in 2026.
Alongside the new facility in Prince George, these investments aim to strengthen Metso’s service footprint across North America.
Volvo Trucks and Putzmeister have partnered to develop one of the world’s largest battery-electric concrete pump trucks.
The zero-exhaust emission battery-electric concrete pump features a reach of 42 metres and will be delivered to the Swedish construction company Swerock.
With the new battery-electric pump truck, Volvo Trucks can offer construction customers a completely electric alternative for the handling,
transporting, mixing and pumping of concrete.
“Volvo Trucks is the innovator when it comes to new technologies in combination with electric trucks. After presenting electric concrete mixers and heavy applications for construction, we are proud to show yet another world-class innovation for the construction segment here,” said Christoph Fitz, Head of Sales at Volvo Trucks in Germany.
“We believe in cooperation
to move forward, and one example of this can be seen here in Germany together with Putzmeister.”
Using the traditional solution for pumping concrete, a diesel truck needs to operate during pumping, which generates emissions and noise. With the all-electric pump truck, it’s possible to drive up to 50 kms and then pump about 50 cubic metres of concrete without charging. For longer distances, or for larger quantities of
concrete, a Combined Charging System (CCS2) charging solution with 63 or 32 A can be installed at the site, and it’s possible to keep pumping the concrete while the truck is being recharged.
“With this battery-electric pump truck, customers can have a zero-exhaust emission solution, low-noise operation and an efficient process thanks to the workwhile-charging capacity,” Fitz said.
The collab is built on a
Volvo FM Electric 8x4 Rigid Tag Tridem.
It features two electric motors to deliver a continuous output of 330 kW. The four-axle truck has a total weight of 32 tonnes.
For power, the system includes four 4 batteries in a specially developed energy storage system with a total capacity of 360 kWh where 250 kWh is usable.
Volvo began series production of electric trucks in 2019, while the company’s
product portfolio enables decarbonization of the entire flow within construction transport including transport trucks, cement mixers, concrete pumps, tippers, cranes and hook lifts. Volvo now holds about 50 per cent of the battery-electric truck segment in Europe, a leading position in North America and deliveries of more than 4,900 electric trucks around the world, many to customers in the construction industry.
Brandt has unveiled its new BMH60A material handler, the third machine in its lineup for the steel manufacturing, scrap metal and recycling industries.
Brandt’s machines are the only North American-designed and built material handlers on the market.
The BMH60A is purpose built for the industry with greater power, uptime and efficiency. It is made with John Deere components that align to North American
standards to make it easier and quicker to source parts.
“Locally accessible parts and service is a real gamechanger for the industry. It will have a huge impact on uptime, because you won’t have to wait for parts coming from overseas,” said Jason Klassen, Senior Vice President Sales — Manufactured Products at Brandt.
“As well, because this material handler is built on proven John Deere components, it delivers exceptional reliability along with those easy-to-find and maintain parts. This is a machine you can truly count on.”
the job done faster, and an energy recovery system coupled with auto-idle/ shutdown that maximizes fuel efficiency, contributing to reduced cost of operation and wear of machine components.
It also delivers greater visibility, ease of use and operator comfort.
The BMH60A, like the 223-hp BMH40A and 367hp BMH80A, was developed through Brandt’s collaborative product design process, which involved extensive consultations with contractors and operators.
The BMH60A is powered by a 9 litre, John Deere PowerTech engine delivering 271 hp. Featuring a 53-tonne operating weight, the material handler delivers an 18-metre maximum reach, 88,500-foot pounds of torque and an 8-rpm swing system.
Additional features of the new material handler include rapid cycle times that allow operators to get
“We collaborated with the people who would be using this machine to ensure it would improve productivity, reduce downtime and provide a lower cost of operation,” said Chris Semple, President — Manufactured Products at Brandt.
“The feedback we have received so far has been overwhelmingly positive, and we are very proud to release the BMH60A to better serve the industry.”
Volvo CE has signed a contract to sell its shares in China-based SDLG (Shandong Lingong Construction Machinery Co).
The company will sell its entire 70 per cent stake in SDLG to the Lingong Group (LGG).
Volvo will sell its shares in SDLG for 8 billion SEK in the second half of 2025, subject to regulatory approvals and other conditions.
In 2006, Volvo CE acquired a majority stake in SDLG, with LGG as a minority shareholder. The strategic investment gave Volvo CE access to the important domestic Chinese construction equipment market.
While the collaboration has been successful, Volvo and LGG now believe it would be mutually beneficial to pursue independent business strategies for strategic reasons.
Therefore, the parties have agreed that a fund predominantly owned by the LGG will take ownership of Volvo’s SDLG shares.
“SDLG has served us well since 2006. However, with increasing competition, and the need to transform to new technologies as well as strengthen interaction with customers, we need to refocus, said Melker Jernberg, Head of Volvo CE.
“China remains an important market for us, and
we aim to capitalize on our opportunities by focusing on sustainable solutions in targeted segments. We also plan to leverage the excellent industrial system in China.”
Volvo CE will maintain its strategic focus on leading the development of sustainable solutions in the Chinese construction industry, targeting key segments such as mining, quarries and heavy infrastructure.
The emphasis will be on providing tailored and comprehensive solutions that address specific customer needs while developing a sustainable distribution roadmap suited to the competitive landscape.
Volvo CE’s operations in China serve as a global production centre. Volvo CE has operated an excavator production facility in Shanghai since 2002 and has recently announced the establishment of new production lines.
Moving forward, China will remain a component of Volvo CE’s value chain and a base for numerous suppliers, both domestic and international.
A key component of Volvo CE's China strategy is to continue to strengthen the Jinan Technology Center (JTC) into the extensive Global Technology System of Volvo CE, which aims to foster innovation and collaboration on a global scale.
5-YEAR/5,000 HOUR Full Machine Warranty
5-YEAR/10,000 HOUR Machine Structure Warranty
Operating Weight: 18,900 lbs || Net HP: 54 hp || Max Dig Depth: 13’9” || Reach at Ground Level: 22’9”
• The 80 X3 Spin Ace is powered by a quiet, EPA-certified Final Tier 4 Isuzu engine that strikes the ultimate balance between power, productivity and fuel efficiency...without the need for a Diesel Particulate Filter (DPF).
• Comfortable and quiet pressurized cab - 8% larger than X2 series cabs, 6% more floor space and 8% stronger climate control system with 8 vents.
• Optimum visibility - sunroof with sunshade, additional mirrors, rearview camera, and wiper blade stores off front glass.
Equipment Sales & Service Ltd.
Edmonton (780) 440-4010 essltd.com
Inland Truck & Equipment
Campbell River, BC 250-287-8878
Castlegar, BC 250-365-2807
Cranbrook, BC 250-426-6205
Fort St. John, BC 250-785-6105
Kamloops, BC 250-374-4406
Langley, BC 604-607-8555
Nanaimo, BC 250-758-5288
Penticton, BC 250-492-3939
Prince George, BC 250-562-8171
Quesnel, BC 250-992-7256
Terrace, BC 250-635-5122
Vernon, BC 250-545-4424
Williams Lake, BC 250-392-7101
inland-group.ca
Itec 2000
Rosslyn (888) 574-8530
• Up to 18% more fuel efficient, up to 8% faster and up to 15% more lift capacity.
• Equipped with the most efficient hydraulic pump layout, keeping engine rpm’s low while producing plenty of hydraulic muscle and conserving fuel.
• RemoteCARE® lets you remotely monitor and track machine location, operational performance, working status and periodic maintenance requirements, providing 24/7 remote monitoring and security with zero subscription charges or fees.
Équipement JYL Inc.
Chicoutimi (418) 698-6656 equipementjyl.com
Thunder Bay (888) 574-8530 Timmins (705) 267-0223 itec2000.com Paul Equipment
McDowell B Equipment Ltd.
Sudbury (705) 566-8190
Barrie (416) 770-7706 bmcdowell.com
Stratton Equipment Sales & Service
Stratton (807) 483-7777 strattonequipment.com
Terapro Rental
Vars (613) 443-3300
Stittsville (613) 836-0654 terapro.ca
Top Lift Enterprises Inc.
Stoney Creek (905) 662-4137
Bolton (905) 857-5200 toplift.com
Micanic
St-Aug-D-Desm (418) 878-2241 micanic.com
Paul Equipment (506) 826-3289 paulequipment.ca
Terapro Location
Val d’Or (819) 825-4299
Plaisance (819) 718-0945 terapro.ca
Top Lift Enterprises Inc.
St-Laurent (514) 335-2953
Balmoral (506) 826-3289 paulequipment.ca
Inland Truck & Equipment
Whitehorse, YT 867-668-2127 inland-group.com
Sherbrooke (819) 612-5438 toplift.com
Potain tower cranes have been instrumental in the construction of Vancouver’s Broadway Subway Project, a $3-billion infrastructure initiative that extends the reach of the city’s SkyTrain service.
The five crane fleet includes one MDT 389 L16 and four MDT 219 J10s, and they are supporting the building of new subway stations and other key infrastructure elements along the route.
In Vancouver, the Mayors’ Council and TransLink identified the Millennium Line SkyTrain Extension to UBC (UBCx) as one of the region’s 10-year priorities to delivering the city’s 30year regional transportation strategy.
The 5.7-km extension of the Millennium Line
promises fast and frequent SkyTrain service to several destinations, including British Columbia’s second-largest job market, major healthcare facilities, an emerging innovation hub and residential communities.
It’s set to open in 2027 and will feature six new underground stations along the Broadway Corridor.
Potain dealer Cropac Equipment provided the cranes, which have been operational since April 2022.
“The cranes’ performance have exceeded expectations, providing the contractor with the confidence and reliability required for a high-visibility project of this magnitude,” said Pavel Jamro, Business Development Manager at Cropac Equipment.
“The project has reinforced Potain’s reputation for solid performance in critical infrastructure projects.”
Both types of Potain cranes on site are topless, enabling a variety of setups along the corridor.
The MDT 389 L16 is a high-capacity crane with a 16 tonne capacity and a 75 metre maximum radius. The MDT 219 J10 is a mediumsized crane that excels in urban lifting and has a 10 tonne capacity with a 65 metre maximum radius.
The CCS (Crane Control System) has enabled ease of use and familiarity for operators, even for complex multi-crane installations. Assembly, erection, transport and maintenance phases are all optimized for productivity.
Cropac selected these cranes for their precision, durability and efficiency.
After nearly three years of
continuous construction, they have performed with almost no downtime. Their seamless operation has been supported by Cropac Equipment’s service team, ensuring uninterrupted progress on the project.
Vermeer’s new MTR516 microtrencher attachment helps contractors install fibre optics with less restoration work.
The attachment cuts trenches up to 43.2 cm deep, and helps crews quickly connect neighbourhoods to high-speed Internet, especially in urban areas, by helping to reduce impact on surrounding property and infrastructure.
The MTR516 microtrencher works with Vermeer’s RTX550 and RTX750 ride-on tractors. Its design focuses on a clean, precise cut while reducing impact on surrounding properties.
"Contractors need to get
fibre in the ground fast and keep the jobsite clean, and the MTR516 microtrencher is built for that," said Nick Olsen, Product Manager at Vermeer. "We've packed it with features that directly impact cutting performance and jobsite cleanliness, all backed by the reliable service and support our customers expect from their local Vermeer dealer."
Vermeer equipped the microtrencher with a fully shrouded cutting wheel that covers the blade during operation, contains debris and optimizes vacuum suction. This keeps the jobsite cleaner and helps reduce cleanup time. The attach -
ment's durability is also key for consistent performance.
"We leveraged our experience with rockwheel durability when designing the MTR516 microtrencher," Olsen said.
"Contractors need equipment that can handle tough conditions day after day. By incorporating principles from our rockwheel designs, we built this attachment to offer enhanced durability and maintain cutting performance, even in challenging ground like cobble."
Serviceability is straightforward.
The MTR516 microtrencher has a replaceable spoil outlet for 10.2-cm or 15.2-
cm vacuum hoses that can be swapped out in the field. Multiple bolt-in wear plates
are field-serviceable, and a dual-hinged access panel gives unhindered access for blade servicing and replacement.
These design choices help reduce trips to the shop and keep crews working.
ive in concrete and rock. The attachment can also be offset up to 61 cm to the right, making it easier to cut next to curbs.
For cutting versatility, the MTR516 microtrencher handles trenches from 2.5 cm to 5 cm wide and down to 43.2 cm deep.
Operation is made simpler with features like single-lever depth control. The design also optimizes airflow for spoil discharge across all cutting depths, meaning less spoil left behind.
Contractors can choose wheel options with welded polycrystalline diamond cutter (PDC) teeth for fast, clean cuts in asphalt or rotary carbide teeth that are effect-
For contractors expanding fibre optic networks, the MTR516 microtrencher attachment is a practical tool. It cuts a narrow, shallow trench, which means less cutting and less backfill.
To gauge the benefits of its technology suite, Caterpillar conducted a roadbuilding production study.
The experiment included building two identical 120-metre-long stretches of road. One road was construction using traditional, low-tech methods, while the second road incorporated telematics, grade control, payload control and compaction control.
“We took the same operators, the same fleet of equipment, the same road design and we built identical roads,” Mike Lenzie, Marketing Manager at Caterpillar, explained during a
recent Technology Days event at the company’s Edwards Demonstration & Learning Center in Illinois.
The end results were night and day. The road built using Cat’s tech suite required 34 per cent fewer equipment hours, consumed 37 per cent less fuel and required 31 per cent less manhours.
Overall, the road built using technology required 46 per cent less project hours.
“At 46 per cent fewer project hours, you could use that same fleet of equipment to go out and do almost the entire same project a second
time,” Lenzie said. “Using that same fleet, you’re getting a much higher ROI on your equipment and capital investment.”
In terms of productivity, construction is lagging behind other sectors in the economy. A study by McKinsey & Company examined productivity over two decades. Construction productivity improved by 0.4 per cent year over year, while the economy in general improved by 2 per cent each year.
“We're trying to create solutions that solve some of that challenge,” Lenzie said.
The right machinery. The right supplier. Right when you need it.
Machines Italia connects Canadian manufacturers with leading Italian equipment suppliers through a free B2B matchmaking service. Whether you’re upgrading, automating, or expanding, we help you find the best-fit solutions — quickly and confidentially.
From food tech to metalworking, and equipment to packaging, Italian machinery is Engineered with Passion and built for performance, precision, and reliability.
• Food Processing
• Plastics & Rubber
• Ceramics
• Foundry & Metallurgy
• Glass
• Hydraulics & Pneumatics
• Textile
• Construction & Earthmoving
• Marble & Stone
• Metalworking
• Packaging
• Woodworking
• Agricultural Machinery
• Printing
• Footwear, Leathergoods and Tanneries
One of those solutions is Caterpillar’s VisionLink, which now consolidates My.Cat.Com and the Cat App into one centralized solution for fleet management. The latest version of VisionLink provides an integrated full-fleet management solution for asset tracking to maximize machine uptime and optimize utilization.
The platform’s refreshed interface helps customers efficiently manage their entire fleet, regardless of manufacturer. Improved asset insights retrieve a broader
range of data from owned, leased or rented equipment and attachments, allowing companies to make better informed asset management decisions.
The new mobile app allows users to stay up to date on key metrics, location of assets, fuel level, idle time and more, all through a smartphone.
Fuel usage alone can account for a third of operating costs in the field. VisionLink can help owners determine where they can reduce excess fuel consumption.
Continued on Page A15
“More than 50 per cent of the time, machines we track through telematics are idling,” said Chih Liang, Vice President of Caterpillar, noting idling also impacts maintenance and resale value. “When the machine idles, obviously it is not doing productive work.”
VisionLink’s new “Needs Review” feature allows customers to focus on critical items, bringing to focus areas where actions need to be taken and providing a workflow to schedule tasks. Within “Needs Review,” the new “Task Management” function allows customers to create quick tasks or a task from scratch. It allows for task assignment and ensures task progress and completion are documented. With fleet management unique to every operation, customers can assign machines the
in-app name of their choosing. Easy-to-use dashboards allow for asset management by projects, groups and geofences. Additionally, customers decide who can and cannot access VisionLink by defining access levels for personnel. Customized reports can be generated and sorted automatically to facilitate tasks such as identifying underutilized equipment.
To make it easier for owners to manage their assets and increase productivity, Cat has rebranded Cat Productivity to VisionLink Productivity. Renaming Cat Productivity is the first step in integrating it with the new enhanced VisionLink.
VisionLink Productivity is a cloud-based application that can help customers analyze jobsite performance and improve productiv-
ity based on actionable information, making their businesses more efficient and ultimately more profitable. It is scalable to any size operation, regardless of asset brand, and can be accessed anywhere via mobile, tablet or desktop.
Today’s VisionLink also offers customers streamlined subscription levels to provide the right combination of features. As well, the new VisionLink continues to offer core telematics data standard with every machine to answer questions about assets, including daily machine location, utilization, fuel usage, maintenance reminders and integration with Caterpillar’s extensive digital ecosystem.
“When you take all information off the machine, you get a lot of data. But being data rich doesn't make you rich,” Lenzie said. “It's all about the information that is perceived to allow you to take actionable steps.”
VisionLink Productivity now incorporates Cat Grade 3D and Cat Compact data into its reporting platform. Leveraging Cat Grade Connectivity, the platform enables 3D design files and updates to be distributed to all machines at the jobsite, eliminating the need for USB uploads. VisionLink Productivity further improves accuracy through GNSS corrections for position validation rather than installing a base station with high set-up costs for short projects. Grade Connectivity also minimizes machine downtime by reducing the need to send a technician onsite to diagnose Grade related issues, improving overall jobsite productivity.
Cat Compact summary dashboards show the amount of work completed for each day and calculate the fill volume. Using the Cat Compaction Algorithm (CCA) or Landfill Compaction Algorithm (LCA), it will also show the per cent of covered area at target compaction. Landfill material compaction density can be viewed when operators enter weights per day.
The new e-Ticket feature eliminates the need for manual or printed tickets generated by onboard Cat Payload systems. Key personnel can now receive an electronic copy of the tickets via email, including detailed information on individual buckets, total payload, truck and material type. Tickets can be quickly recalled using ID or number or filtering based on material type or truck name. Key performance indicators tracked by e-Ticket include ticket count, average truck rate, pass count per ticket and total ticket payload.
Operator Coaching is another new tool to empower operators of all experience levels to enhance their skills, efficiency and productivity. Two categories of operator coaching tips – Operating Efficiency and Machine Health – are tracked. During machine operation, the operator receives an onboard notification when an action with a corresponding tip is detected. This helps to improve operational efficiency and increase machine longevity.
When paired with the offboard VisionLink Productivity, managers can remotely view what coaching tips their operators have activated. This enables site managers to track improvements over time and focus training on areas specific to the operator's needs and overall operations. Dashboards, lists and maps allow quick views of each coaching tip's count, time and location.
Caterpillar often hears from its customer base about the need to address the growing skilled labour gap as veteran operators retire.
“For those operators that are coming in, they may not have the skill levels immediately that more seasoned operators have. So, our technology will try to improve on that,” Liang said.
It’s not just a compact machine, it’s a Cat. That means legendary reliability, intuitive commands, integrated technology that boosts productivity and improves safety, plus the most comfortable cab on the market.
Owning a Cat comes with unmatched parts availability and outstanding service from Toromont Cat, with over 2,000 trained technicians to have your back. What are you waiting for? Once you go Cat, you’ll never look back.
SCHEDULE A DEMO TODAY AND EXPLORE THE FULL LINE-UP! 1-866-720-3001 | toromontcat.com
Finlay is taking a step forward in sustainable screening technology with the introduction of the electric-powered 883+ heavyduty scalping screen, an addition to its flagship 883+ model.
Designed for a range of primary and secondary screening applications, the 883+ Electric scalping screen is ideal for industries such as quarrying, mining, iron ore processing, construction and demolition waste, sand, gravel, compost, topsoil and coal.
“As our flagship model,
the 883+ has always set the standard for performance and versatility,” said Matt Dickson, Business Line Director for Finlay.
“The 883+ Electric scalper represents a forward-thinking solution for businesses looking to reduce their environmental impact, while continuing to benefit from the superior performance and flexibility that Finlay equipment is renowned for.”
The scalper has been developed to meet the increasing demand for efficient, environmentally friendly equipment.
With an intelligent and flexible power pack, the scalper can be connected directly to the grid or powered by a genset, allowing for intuitive operation without compromising performance or application versatility.
The electrical drive system powers the feeder, screenbox and conveyors, making it an excellent solution for customers seeking to reduce their carbon footprint while maintaining high productivity.
As part of Finlay's effort to develop adaptable and user-focused solutions, the
883+ Electric scalper features several upgrades designed with the operator’s needs in mind.
One such improvement is the redesigned feeder, which was developed after receiving valuable feedback from Finlay’s customers and distribution network.
The new feeder offers hydraulically folding and locking extensions, allowing for rear feeding with a wheel loader for added flexibility in material handling.
As well, the hopper is manufactured from wear-resistant steel, with the option
for hopper linings, providing enhanced durability in tough operating environments.
In response to evolving industry demands, the 883+ Electric scalper is also engineered with mobility in mind.
The machine is equipped with an onboard engine that powers the tracks, allowing for relocation across job sites. This ensures customers can continue to move and position their equipment with minimal effort, regardless of power source availability.
The electric variant of the 883+ scalper delivers sev-
eral key benefits, including significant reductions in operating costs through grid electricity use, a smaller carbon footprint thanks to the elimination of carbon dioxide emissions, and reduced engine noise, which is ideal for operations in urban and indoor settings. Furthermore, the shift to electric power typically results in lower maintenance requirements than their diesel counterparts, leading to reduced costs and longer service intervals, ensuring maximized machine uptime and productivity.
Hills Machinery is now upfitting Hydex articulated water tanks on Rokbak articulated truck chassis for the North American market.
Hydex Solutions Ltd. is based in the United Kingdom. The South Carolina-based Hills Machinery will equip Rokbak Trucks with the water tanks for the United States and Canada under the name Hydex USA.
“Dust suppression and access to water is a growing demand throughout North America as jobsites get bigger, mines and quarries get busier, and as local regulations become more restrictive,” said Jim Hills, President of Hills Machinery and Hydex USA. “The combination of the wildly popular Rokbak articulated truck chassis and the engineering excellence of the Hydex water tanks repre-
sents the premium off-road dust suppression and water delivery solution available to the North American construction and mining markets today.”
The Hydex articulated water tanks are designed for integration with Rokbak articulated truck chassis and will also be upfit on the articulated truck chassis of a customer’s choice — including used trucks.
Hydex offers two water tanks matched specifically to Rokbak articulated dump trucks: a 22,700-litre water tank (AWT6) matched to the 370 hp RA30, and a 34.000-litre water tank (AWT9) matched to the 444 hp RA40.
Each tank will also be outfit on the truck chassis of each customer’s choice, as the design allows for upfit and integration with all major manufacturers of articulated trucks.
“We work with Rokbak on a daily basis and believe those to be the two best trucks to outfit these tanks with, and we also recognize that some contractors will want to keep their fleet standardized with other brands of trucks — we’re happy to work with everyone to solve their dust suppression and water access needs,” Hills said.
Outdoor power equipment manufacturer Echo has incorporated Shindaiwa mobile, diesel generators and welders into the Echo brand family under the new Echo Industrial Power Equipment (IPE) name.
While the ECHO IPE name is new, the generators and welders have 20 years of proven performance in North America and with more than 800,000 units sold globally across construction, oil & gas, mining, telecom, disaster re-
sponse and entertainment industries.
“ECHO IPE is engineered with the realities of industrial work in mind, where professionals need power that performs every time,” said Wayne Thomsen, Vice President of Marketing and Product Management at Echo.
“For decades, the performance of these generators and welders has been trusted for some of the world’s most challenging environments.
Now, it’s backed by Echo’s U.S. support, well-established distribution and deep investment in product innovation.”
Echo IPE offers generator models ranging from the compact DGK7F (7 kVA) to the high-capacity DGK180F/P (180 kVA).
Key features of Echo IPE work in tandem to maximize uptime. A compact enclosure features heavy-gauge panels that reduce vibration, resist damage and hold up to the harshest job site conditions.
Built-in overload protection and efficient engines also help optimize fuel use under variable conditions.
Echo IPE generators deliver simultaneous access to dual-voltage, single-phase and three-phase current, with no external transformers required. This Simul-Phase technology assists job sites juggling multiple power needs, from remote construction sites to emergency disaster zones.
•
Hydex water trucks use a Elkhart water cannon that projects water to more than 65 metres.
A front bumper sprayer, vertical side sprayer and rear spray bar with more than 25-metres of coverage gives the operator extreme water spraying versatility and customization.
Noise is controlled thanks to insulated panels, a tuned muffler and airflow design that reduces sound. The DGK180F/P (180 kVA) generator models run at just 65 dBA under full load — quiet enough to hold normal conversation.
An included auxiliary tank compatibility extends runtime for longer shifts and remote deployments. The DGK125FP and DGK180FP models offer paralleling capability to ensure redundancy in critical applications and enable scalable power delivery.
For safety, built-in ther-
mal relays, lockable voltage selectors and engine protections safeguard people and equipment.
All models meet EPA Tier 4 Final standards. The DGK70F, DGK125F and DGK180F models feature S.E.T. Smart Emissions Technology for added protection during light or underloaded operation.
Topcon Positioning Systems has signed a Memorandum of Understanding (MOU) with Vemcon GmbH, a specialist in smart excavator attachments and 2D assistance systems.
The MOU defines a collaboration to expand the availability of advanced excavator technology solutions across the EMEA regions and additional global markets.
The collaboration brings together strengths from both organizations: Vemcon’s expertise in 2D assistance systems that work with smart attachments, and Topcon’s advanced 3D machine control technology and global GNSS network.
The arrangement lays the foundation to create a fully compatible upgrade path from Vemcon’s 2D solutions to Topcon’s 3D systems.
“Strategic cooperation with Vemcon will allow us to provide contractors with a more comprehensive excavator technology solu-
tion,” said Murray Lodge, Executive Vice President at Topcon.
“By integrating our technologies, we will be able to offer customers a clear advancement path from 2D to 3D systems while maintaining their existing investment in smart attachments.”
The arrangement also presents opportunities for data integration between the two companies’ systems, with potential for future development of cloud-based solutions. This data exchange capability could provide contractors with enhanced insights into machine performance and project progress, further improving operational efficiency.
Both companies are exploring opportunities to expand availability across additional markets.
For excavator operators and contractors, the collaboration delivers the established benefits of 3D machine control, including reduced staking costs, minimized rework, increased productivity, improved material management, enhanced operator capabilities, and simplified compliance with design specifications.
“Our platform combines tool recognition, quick coupler control, and assistance features like 2D and scale — and it’s 3D-ready by design,” said Dr. Holger Quast, COO of Vemcon.
“Together with Topcon, we offer OEMs a smart, modular control stack that makes integration easy and opens the door to MiC 4.0.”
“With Vemcon’s 2D system already installed, upgrading to Topcon’s 3D control is fast and cost-effective — the sensors are there, the machine is calibrated. This allows contractors to scale their digital capabilities step by step, project by project, without locking themselves in,” said Jan Rotard, CEO of Vemcon.
Ready to do more and do it with more power and efficiency? You can count on Wacker Neuson Compact and Utility Track Loaders for the flexibility, reliability and performance to tackle the jobsite challenges you face every day. Ergonomic controls, comfortable work platforms, durable construction and excellent serviceability provide all you need to keep your projects on the right track.
Visit us online or contact your local Wacker Neuson dealer today. 1-800-201-3346 • www.wackerneuson.com
A.S.E Equipment
8503 Wellington Road 18, Fergus, ON, N1M 2W5
519-843-1161 www.aseequipment.ca
Access Mining Services 1106 Webbwood Drive, Sudbury, ON, P3C 3B7 705-419-2602 www.acces-s.ca
Advantage Farm Equipment 6915 Colonel Road, London, ON, N6L 1J1 519-652-1552 www.advantage-equip.com
AR Equipment 9092-B Rd 51 NE, La Salle, MB, RG4 0B2 204-261-1800 www.wackerneusonmb.ca
Coleman Equipment Inc. 3541 Trussler Rd New Dundee, ON, N0B 2E0 519-696-2213 www.coleman-equipment.com
Construction Equipment Co. (Sault) Inc. 1245 Great Northern Rd, Sault Ste. Marie, ON, P6B 0B9 705-942-8500 www.cec-ssm.com
Eastrock Equipment Inc 100 Warehouse St., Vars, ON, K0A 3H0 613-443-0695 www.eastrock.com
Frontier Sales & Equipment 7213 Line 86, Wallenstein, ON, N0B 2S0 519-669-8709 www.frontierequipsales.com Hood
Maximizing uptime and minimizing costs are essential when managing an articulated dump truck (ADT) fleet.
In today’s competitive industrial landscape, articulated haulers are expected to do more than move material. They must operate efficiently, reliably and safely for the long haul.
Scott Pollock, Senior Product Manager for Rokbak, shares strategies — from smarter maintenance and operator training to cutting-edge onboard technologies — that help
boost efficiency, cut expenses, keep your haulers moving and leave you stress-free.
At Rokbak, the focus is not just on manufacturing articulated dump trucks, but on helping customers get the most out of them throughout their operational life.
Unplanned breakdowns are a costly disruption in any fleet. The best defence against them is a solid strategy for planned, proactive maintenance. This goes far beyond routine filter and oil changes. Rokbak encour-
ages regular inspections that can catch issues early, from worn suspension to minor leaks that could become major headaches.
Like a good vehicle checkup, effective servicing looks for both current faults and potential problems on the horizon. A vigilant approach to diagnostics and servicing can keep trucks on-site and earning, rather than waiting on repairs.
No truck is better than the person operating it. Welltrained operators not only maintain productivity but the health of the hauler it-
self. Pre-start checks, basic diagnostics and awareness of operational anomalies make all the difference.
Rokbak invests in training programs that help operators and service personnel. When everyone understands the “why” behind truck care, the result is longer-lasting equipment and a safer, more efficient worksite.
Today’s articulated haulers are smarter than ever. Rokbak integrates automation and safety features that actively prevent misuse and mechanical stress. Technologies such as anti-tip body controls and downhill retardation systems protect the hauler and the operator.
Load monitoring and productivity tracking also ensure trucks are operating within their optimal range, saving fuel, reducing wear and avoiding costly errors. These built-in tools support smarter, more cost-effective operation.
Smarter fleet decisions
Every Rokbak articulated hauler comes fitted with Haul Track as standard, an intuitive telematics system that gives fleet managers real-time access to perform-
ance data. This connected technology uses onboard diagnostics, GPS and wireless communication to track and improve truck performance across multiple sites.
From any Internet-connected device, fleet managers can monitor fuel consumption, idle time and machine usage. This helps them develop more effective maintenance schedules, reduce operating costs and avoid unexpected breakdowns.
Maintenance alerts and fleet activity reports highlight potential issues before they become downtime-inducing problems.
Haul Track also helps identify operational inefficiencies. By detecting patterns like harsh braking or excessive idling, it allows for corrective actions such as targeted operator training or rerouting, improving driving habits, protecting uptime and extending machine lifespan.
Using non-OEM components might save money in the short term but often leads to long-term losses. Rokbak haulers are designed with precision, and only genuine parts offer the fit, compatibility and tested durability the trucks demand.
Every part plays a role in maintaining uptime and performance. By using OEM-approved components, operators gain the assurance of full compatibility with the truck’s systems and sensors.
Understanding that no two job sites are alike, Rokbak works closely with a global dealer network to tailor parts strategies and service support for each application – whether it’s a construction site in North America or a quarry in Australia. Strong local support, combined with a robust global network, is key to keeping haulers running and delivering value.
Efficiency is a team effort Ultimately, achieving long-term ADT efficiency is not about a single factor ; it’s a combination of great equipment, smart technology, reliable parts and skilled and committed people. At Rokbak, there is a focus on this full ecosystem because we know that our customers depend on it. By partnering closely with operators, technicians, customers and dealers, we’re helping to ensure that every Rokbak hauler delivers maximum productivity, minimal downtime and lasting value.
• Cummins B4.5, 140HP engine, EPA certified
• Full hydraulic steering for precise control
• Double-pump confluence system and pilot control
• Multi-power fuel-saving switch and three-level power modes
• 15T heavy duty machine with high strength low alloy steels
• Dual pump double circuit power control hydraulic system
• Cummins QSF3.8 engine
• 3-stage air & fuel filtering system
Case Construction Equipment is releasing a Heavy Metal Hetfield Limited Edition TV450B compact track loader.
The CTL is based on the unique machine designed for Metallica frontman James Hetfield. Case will manufacture just 25 Heavy Metal machines features a unique design that celebrates the fusion of heavy equipment and heavy metal.
“The Hetfield Limited Edition TV450B compact track loader is a showcase machine that’s outfitted to be as distinctive as James Hetfield’s legendary voice,” said Terry Dolan, Head of CNH Construction Brands, North America.
“And, just like his unique ability to bring both force and finesse to every riff, this special edition CTL brings power and precision to the jobsite, in signature fashion, so operators can be more productive, and crews can be more competitive.”
The CTL includes a custom wrap based on one of Hetfield’s famous guitars over the Hetfield Limited Edition TV450B’s gray base paint.
The sides and back of the machine showcase exterior decals and badging that include a font reminiscent of Metallica’s iconic graphics and a skull with wings inspired by one of Hetfield’s tattoos.
On the rear grill, a Hetfield decal is overlaid on a laser-cut steel nameplate secured with anti-tamper fasteners. The cab’s interior features a distinctive guitar-shaped, sequentially numbered serial badge and a Hetfield/Case decal on the seat.
The Hetfield Limited Edition TV450B is a workhorse with a 90-hp engine, 2,045 kg operating capacity and low ground pressure, allowing operators to lift more without disturbing existing turf.
The machine is equipped with high-flow hydraulics so operators can easily power demanding attachments, such as cold plan -
ers, mulching heads and stump grinders. Its operator-first design includes a comfortable, roomy cab and easy-to-use controls.
This special edition TV450B also comes equipped with maintenance-free Case EZ Trac, which helps extend track life and offers superior traction, enhanced stability and greater productivity through a rigid-mounted undercarriage with rollers on pivoting bogeys.
The Hetfield Limited Edition TV450B is available to qualified buyers on a first-come, first-served basis.
Case will also create a diecast version of the Hetfield Limited
Edition TV450B compact track loader to its collectibles line in the fall of 2025.
Show Us Your Metal Case also announced a “Show Us Your Metal” contest, which gives Case and Metallica fans the chance to win exclusive Hetfield-inspired Case merchandise. Case and Metallica fans are encouraged to submit a photo of themselves striking their best heavy metal pose for a chance to win exclusive prizes, including a special hat. One grand prize winner will receive a full merchandise package.
Kioti Tractor’s newly developed Flow+ technology delivers an advancement in hydraulic performance for its compact construction equipment lineup.
Now available, the Flow+ TL750 compact track loaders and SL750 skid steer enhance hydraulic capabilities for operators, who need more power than standard flow, without the excessive cost or fuel consumption of full high-flow systems.
“At Kioti, we’re committed to developing solutions that maximize the performance of our equipment,” said Justin Moe, Product Manager for Compact Construction at Kioti.
“Flow+ bridges the gap between standard and highflow systems, providing operators with the hydraulic power needed to handle more demanding tasks, while improving engine functionality, fuel savings, and overall versatility.”
Designed for light to medium-duty hydraulic requirements, Flow+ allows operators to seamlessly run attachments – like rotary cutters, trenchers, and snow blowers – while supporting standard-flow attachments for everyday tasks. This ability makes the machine more
versatile across job types.
Flow+ optimizes performance and long-term durability by providing more power than standard flow systems, while reducing heat and wear compared to high-flow alternatives. It enhances productivity by enabling quick attachment changes and minimizing job downtime.
As well, its optimized hydraulic power management conserves fuel, extending operational hours without unnecessary consumption.
Built with a five-port coupler block, dedicated Flow+ tube lines and valve, and an added gear pump, the system ensures seamless hydraulic operation.
With Flow+, operators can tackle a wider range of
job-site applications, while keeping their compact loaders running smoothly and efficiently.
The new Flow+ models offer a significant upgrade in hydraulic performance compared to the standard models. While the standard models operate at 3,335 psi with a hydraulic flow of 82.9 litres per minute and 41.80 hp, the Flow+ models operate at a lower pressure of 2,900 psi but provide a higher hydraulic flow of 128.8 litres per minute and deliver 65.7 hp. This increased flow and horsepower in the Flow+ models translates to greater attachment versatility, improved operational efficiency, and the ability to handle more intensive applications with ease.
ALBERTA
Liftboss JCB
Calgary: 403-301-0041 Edmonton: 780-474-9900 liftboss.ca
BRITISH COLUMBIA
Williams JCB
Surrey: 604-930-3316 williamsjcb.com
NEW BRUNSWICK
A.L.P.A. Equipment
Edmundston : 506-735-4144
Balmoral : 506-826-2717
Fredericton : 506-452-9818 Moncton, N.B. : 506-861-2572 alpaequipment.com
NOVA SCOTIA
A.L.P.A. Equipment
Truro : (902) 897-2717 alpaequipment.com
When it comes to reaching higher, even giraffes are taking notes. The JCB Teleskid, the only skid steer with a telescopic boom, gives you unmatched lift and reach for everything from hay bales in the barn to lumber on the jobsite. It’s rugged, reliable, and built for those who don’t settle for average. Snow, sleet, or sunshine—this machine’s got your back.
Harvey JCB
Corner Brook: 709-639-2960
St. Johns: 709-738-8911 harveyco.ca
ONTARIO
Advance Construction Equipment (Division of Equipment Ontario)
Harriston: 519-510-5878 Waterloo: 519-742-5878 advanceequipment.net
D&W Group Inc.
Doughty & Williamson Jarvis: 519-587-2273
Brant Tractor Burford: 519-449-2500
Redtrac International
Vineland: 905-562-4136 dwgroup.ca
ONTARIO
Delta JCB
Dunvegan: 613-527-1501 Renfrew: 613-432-4133 Winchester: 613-774-2273 deltapower.ca
Equipment Ontario
Alliston:705-320-0506
Lindsay: 705-324-6136 Port Perry: 905-982-1500 equipmentontario.com
Fulline JCB
Glencoe: 519-287-2840 fullinefarm.com
John’s Equipment Sales Frankford: 613-398-6522 johnsequipmentsales.com
Moore JCB Toronto, York & Peel Region: 416-747-1212 moorejcb.com
ONTARIO
North Rock JCB
North Bay, Sault Ste. Marie, and Sudbury: 705-897-7369 northrockrentals.com
ReadyQuip Sales & Service Ltd. Timmins: 705-268-7600 readyquip.com
WPE Landscape Equipment - JCB Hamilton/Halton: 905-628-3055 wpeequipment.ca
PEI
A.L.P.A. Equipment (506) 861-2572 alpaequipment.com
A.L.P.A. Equipment
Bas-Saint-Laurent : (506) 735-4144
Gaspésie : (506) 826-2717 alpaequipment.com
Bossé Quebec Inc.
Desmaures: 418-878-2241
Saint-Augustin-debosse-frere.com
Moore JCB
Montreal: 514-333-1212 moorejcb.com
SASKATCHEWAN & MANITOBA
Westcon JCB
Regina: 306-359-7273
Saskatoon: 306-934-3646
Winnipeg: 204-694-5364 westconequip.ca
1.5
John Deere Power Systems (JDPS) is investing in diversified solutions to help its customers meet varied sustainability and efficiency goals.
As a global manufacturer, JDPS is carefully analyzing regional application differences and how they impact the adoption of renewable fuels as well as hybrid and battery electric solutions.
The off-highway equipment market continues to evolve when it comes to how it is approaching sustainability. A challenge as complicated as efficiently powering most important industries requires proven expertise and a commitment to testing and investing in the right solutions.
“John Deere is developing technologies that not only meet today's needs but also anticipate the challenges our industry will face in this next era,” said Nick Block, Director of Global Marketing and Sales of JDPS.
“The demand for sustainable, efficient power solutions is increasing, and we're committed to meeting that demand with a diverse portfolio of technologies that address these evolving needs. We believe the future of power is not defined by a single solution but by a range of options that empower our customers to choose the best fit for their operations.”
Electrified options In 2022, Deere acquired a majority ownership in Kreisel Electric, a battery technology provider based in Austria. Kreisel develops high-density, high-durability electric battery modules and packs.
The following joint partnership between the two companies has led to several innovations for powering off-road equipment, including a prototype battery pack designed for seamless integration with off-highway machinery.
The prototype battery features a flexible, modular architecture and Kreisel's patented immersion cooling technology, which provides active thermal management for optimal performance, safety and lifespan.
With a focus on meeting the evolving needs of customers across equipment segments and applications, Deere is engineering highly energy-dense batteries that deliver significant power. Kreisel battery technology is actively being used in the field across a range of applications and industries, including, agriculture, road building, construction, onroad and marine.
At bauma in April, JDPS displayed its 60 kilowatt-hour KBP63 battery
pack. Compared to the previous 60 kwh battery displayed at bauma in 2022, the KBP63 delivers the same power but in a much smaller package.
“One of the things we're continuing to learn in our joint venture with Kreisel is the development cycles of batteries are on a much shorter timeline than what we have in engines,” said Michael Lefebvre, Manager of Global Marketing and Product Strategy for John Deere Power Systems.
While engine development may take upwards of two decades, battery packs are being developed in as little as three years.
JDPS is also offering 20 kwh and 40 kwh high voltage battery packs delivering between 400 volts and 750 volts.
Now, the company is working to determine the ideal packaging shapes and sizes for batteries to assist the most machines.
“Different vehicles need different things,” Lefebvre said. “We're trying to gather customer needs of all the different internal and OEM customer to come up with the least number of building block shapes that make sense to be able to work in the maximum number of vehicles.”
John Deere is also de -
veloping a comprehensive charging ecosystem featuring Kreisel's battery technology to provide versatile charging options with both stationary and mobile solutions for a variety of jobsites.
With the increasing emphasis on renewable fuels, JDPS is providing, and developing, efficient and optimal solutions. The company's advanced engine technologies are designed to support the use of renewable diesel fuels and biodiesel blends.
“We’re fully certified for renewable diesel and HVO. At this point, we're continuing to work on higher and higher levels of biodiesel blends,” Lefebvre said.
“So, we're approved for B20, and we’re always talking about increasing those levels as the fuel standards improve and as that area develops.”
JDPS is also researching and developing solutions for ethanol, bio-methane and hydrogen.
“There is development work ongoing to ensure that we understand the pros and cons of hydrogen use in our vehicles and in potential OEM space as well,” Lefebvre said.
However, Lefebvre explained the missing infra-
structure to deliver the fuel and the ability to meet the needs of high-power equipment are challenges for the use of hydrogen.
“I think we see it coming on in Europe, especially in carbon zero zones. I think it's something that will be hitting the marketplace, and we're trying to keep an eye on it for our equipment and our customers,” Lefebvre said.
The future of ICE
While electrification and renewable fuels represent new avenues to power equipment, internal combustion engines obviously continue to power most equipment in the field.
JDPS’s next generation engines — the JD4, JD14, and JD18 — are engineered to meet the evolving needs of the off-highway industry.
The engines offer increased power density and improved fuel efficiency.
“You're going to see a lot around renewables and reducing carbon footprints, and all of that is extremely important, but it doesn't leave behind the necessity for diesel engine development,” Lefebvre said.
“We're spending millions in diesel engine development, but not just the same old diesel engines. They need to be more efficient.
They need to be smaller. It needs to contribute to our carbon footprint reduction.”
The JD4, which will be released in the next couple of years, is designed to excel in diverse applications with its compact size and high torque output. The engine features a 20 to 25 per cent reduction in size and weights more than 50 kg less than the John Deere single turbo 4.5-litre engine.
“This is a clean sheet engine coming out in a couple of years that’s much smaller and much more fuel efficient,” Lefebvre said.
The optimized 460-hp JD9 builds on the proven performance of the existing 9-litre engine to provide reliable performance and streamlined integration, while the JD14 boasts exceptional power per litre and an aftertreatment system with or without a particulate filter based on emissions tier.
For heavy-duty demands, JDPS has released the JD18, which delivers up to 908 hp without the use of an exhaust aftertreatment system, which helps to simplify maintenance.
“This is a whole new power space for us. The JD18 is taking us into much larger equipment, especially mining equipment, and it's going gangbusters,” Lefebvre said.
Perkins has developed a plug and play battery electric power unit designed to help off-highway equipment manufacturers seamlessly transition from a diesel engine to a battery electric powertrain.
The battery electric power unit made its debut at bauma as the power source for a McElroy TracStar 900i pipe fusion machine.
“We’re actively helping customers navigate the shift in power system requirements, with a range of advanced power systems including elec -
tric, diesel-electric and alternative fuel compatible engines,” said Jaz Gill, Perkins’ Vice President, Global Sales, Marketing, Service and Parts. “When it comes to the innovative fully integrated battery electric power unit, it can be ‘dropped in’ to a machine to replace a diesel engine.”
The Perkins power unit has been put to the test in a McElroy TracStar 900i pipe fusion machine as a commercial demonstrator; with the battery electric power unit replacing a 3.6 litre 904 Series (134 hp) diesel engine.
The power unit includes a Perkins battery along with inverters, motors and onboard chargers.
It’s packaged in a compact drop-in system, which fits within the same chassis space as the 904 Series engine, to support seamless transition from diesel to electric.
“One of the unique selling points for this concept is it has the same mounting face, the same interface in the flywheel housing and the interconnectivity is the same. It fits within the same box, within the same
envelope, so it literally is plug and play,” said Luke Bennett, Technical Sales for Advanced Power Systems at Perkins. “It gives the OEM that flexibility to have very minimal changes to their machine design."
They could have a battery electric machine, and then also the traditional diesel.
So, it's a really great concept.”
To boost the plug-and-play usability, Perkins equipped the power unit with patented software that allows the power unit to mimic a diesel engine.
“The machine actually
thinks it has an engine running. It's getting oil temp readings and it's getting oil level readings,” said Chris Goggin, Product Marketing Manager at Perkins.
Equipping the TracStar 900i with an electric, emissions-free power unit opens new application opportunities for the OEM.
“They're seeing huge opportunities within the mining sector, because they can now sell these machines into underground applications with zero emissions at the tail pipe,” Goggin said. “What that does is really
help the customer to explore battery electric and electric solutions without having to invest in a whole new team of electrical engineers and integration engineers.”
Development of the battery electric power unit specifically for the pipe fusion machine was completed in about nine months.
“This has been a really fast project. We were able to do that by having already launched our battery technology and already having gone through the validation of the battery technology,” Bennett said.
Cummins has commissioned a new alcohol fuel test cell as part of its joint project with Komatsu and Vale.
The commissioning marks a significant milestone in its joint project to develop an ethanol/diesel-powered surface mining haul truck aimed at reducing greenhouse gas emissions.
Announced in July 2024, the dual fuel program aims to retrofit existing diesel engines in Komatsu haul trucks to operate on both ethanol and diesel. The modified 230-ton to 290-ton haul trucks will be able to use up to 70 per cent ethanol, potentially lowering carbon dioxide emissions by as much as 70 per cent.
“Ethanol/methanol diesel dual fuel systems offer significant benefits to the mining industry, including the realization of up to 70 per cent decarbonization – lowering carbon dioxide, nitrogen oxides and particulate matter –while continuing to meet comparable productivity and performance requirements,” said Luke Mosier, Cummins Innovation Program Leader. “More than that, miners who utilize alternative fuels can utilize their existing infrastructure and leverage their current fleet, facilities and personnel.”
When operational, the haul trucks would be the first vehicles of this size to run on ethanol in the tank.
“At Cummins, we’re committed to advancing practical, sustainable solutions that support the energy transition,” said Gbile Adewunmi, Vice President of Industrial Markets – Power Systems Business.
“Our work in enabling low-carbon fuel pathways — like ethanol dual-fuel technology — demonstrates our dedication to reducing emissions while delivering reliable performance for our customers and partners.”
The Cummins QSK60 Engine testing is expected to run until 2026 before field tests begin at Komatsu's facilities.
"Our ongoing dual fuel project, developed in close collaboration with Cummins and utilizing a blend of ethanol and diesel, is an important bridge technology aimed at supporting Vale’s near-term decarbonization goals," said Dan Funcannon, Senior Vice President, Surface Haulage, Komatsu. “This initiative reflects our shared commitment to practical, scalable solutions that advance sustainable mining. The launch of the dedicated test cell is an exciting milestone as we continue to develop and deploy low-carbon technologies for the future of haulage."
The Brazil-based Vale is one of the world's largest producers of iron ore and nickel and a major copper producer. The company has set a target of reducing its scope 1 and 2 greenhouse gas emissions by 33 per cent by 2030. Among mine equipment, the haul truck is one of the biggest consumers of diesel. Ethanol is already a widely adopted fuel in Brazil, with an established supply network.
“We continue to make progress on our decarbonization projects, reinforcing Vale's commitment to this issue,” said Carlos Medeiros, Vale's Executive Vice President of Operations.
“Ethanol is a priority input to achieve our goal of reducing the use of diesel in our operations while keeping reliability and operational excellence.”
The new advanced low carbon fuel test cells at Cummins’ Seymour, Indiana Engine Plant showcase continued investments in fundamental research facilities and internal capabilities designed to support its decarbonization programs and drive advancements in carbon-reducing technology and innovations that move the industry closer toward carbon neutral power systems.
"We are excited to bring this dual fuel test cell online, as part of our Dual Fuel Engine Development Program that reinforces our commitment to collaborating with OEMs and mining companies in the development and testing of bridge technologies,” Adewunmi said.
“By leveraging advanced technologies like low carbon test cells and our versatile test asset for power electronics, batteries, fuel cells and hybrid systems, Cummins remains at the forefront of guiding miners toward carbon reduction both now and in the future."
Cummins low carbon fuel test cells accommodate a wide range of high horsepower engines — from 38-litre to 95-litre fuel capacity — and ensure seamless transition of a variety of alternate fuel types for varied testing scenarios.
The specialized facilities also maintain a high precision environment to deliver accurate emissions with reliable data and provide safe storage conditions to prevent contamination and maintain fuel quality.
JCB’s hydrogen engine technology has reached another milestone after securing the first full EU type approval for use in off-highway mobile machinery.
The approval means JCB’s hydrogen engine is approved for sale and use in machines and third-party OEM equipment in all 27 European Union member states.
“This is another very significant moment for JCB’s hydrogen program. It was not so long ago that some said that it was ‘game over’ for the internal combustion engine in Europe,” said JCB Chairman Anthony Bamford, who has led the company’s hydrogen engine project.
“For JCB to have secured full EU type approval is proof positive that the combustion engine does indeed have a promising future in pursuit of a net zero world if hydrogen, a zero CO2 fuel, is used instead of fossil fuels.”
The EU type approval fol-
lows earlier approvals by licensing authorities in nine countries in mainland Europe, allowing the engine to be used commercially in machines in those countries under “new technology” provisions.
“I could not be more delighted for the JCB team that put so much work into getting
us to this stage. Now our focus will be on bringing our hydrogen technology to market,” Bamford said. “JCB’s customers are patiently waiting for our hydrogen-powered equipment to make a difference on their jobsites. They won’t have much longer to wait.”
Great Britain type approval was granted rapidly, initially for the “new technology” and now as full type approval.
JCB is the first construction equipment company to develop a fully approved combustion engine fuelled by hydrogen, and a team of 150 engineers has been working on the £100 million development for nearly four years.
Industries worldwide are under pressure to becoming more efficient, sustainable and safer.
But how can these goals be achieved?
Often, the answer lies in the hidden champions of heavy equipment: slewing bearings and slew drives.
These components are the heart of machines for a wide range of applications, including excavators, cranes and tunnel boring machines.
To meet changing demands, Liebherr focuses on innovation. The advanced slewing bearings and slew drives are designed to seamlessly adapt to modern standards, making operations more efficient, safer and environmentally friendly.
Digital wear monitoring
Bearing clearance monitoring (BCM) provides a digital solution for measuring wear in slewing bearings. Built-in sensors allow precise measurements of axial and radial wear without requiring technicians to perform manual checks in hard-toreach areas. This improves safety as well as speeds up the monitoring process.
Permanently installed sensors enable quick wear measurement via a web app, which can reduce downtime by up to 75 per cent.
An upgrade to the BCM can be seamlessly integrated in the customers’ system without the need for additional measuring devices or gateways, reducing system complexity and allowing users to analyze measurement data within your own systems.
Electrifying slew drives
Liebherr’s slew drives can be powered electrically, which reduces noise emissions while eliminating the requirement for hydraulic
oil, which prevents the risk of oil leaks.
Electrically driven slew drives are ideal for applications, where no hydraulic systems are used. They offer a clean solution, especially in sensitive environments. The electric motors are also adaptable and can be combined with various gears. Thanks to intermediate flanges, motors can be easily integrated and installed in a space-saving manner.
Electrically powered slew drives excel in precise positioning tasks, as their power control allows for accurate movements.
Lifinity solid lubrication
Liebherr’s innovative solid lubrication, Lifinity, eliminates the need for regular relubrication. In this process, a heated polymer-oil mixture is introduced into the heated bearing.
As it cools, it forms a stable layer that provides long-term lubrication for the bearing. A major advantage is the significant reduction in maintenance, as regular relubrication is no longer necessary, leading to considerable savings in operating costs and time. This increases productivity, as equipment requires less downtime for maintenance, thus extending the lifespan of machines and boosting overall operational efficiency. Lifinity also reduces the risk of corrosion, enhancing the longevity of the bearing. Lifinity is also environmentally friendly. Conventional greases and oils can leak and pollute the environment, but with Lifinity, there’s no such risk. This technology also meets strict NSF/H1 standards, making it suitable for food-related environments.
By implementing digital measurement, electrification and maintenance-free technologies, Liebherr’s component product segment offers advanced solutions for slewing bearings and slew drives that meet the rising demands across a variety of applications and industries. All the components are future-ready and play a vital role in making operations more efficient, safer and environmentally friendly.
Aldershot Equipment Inc.: A Trusted Partnership with Bobcat
Founded in 1949 as a Heavy Equipment Contractor, Aldershot Equipment Inc. has long been a key player in Canadian construction, particularly in MTO and general contracting projects involving foundries and gas plants. When President John Steeves purchased the company in 1998, he guided it through a pivotal transformation. Roughly 25–30 years ago, the company shifted its focus exclusively to power, hydro, oil & gas, civil work, and equipment rentals across southwestern Ontario. Today, Aldershot services hydro sites and power lines from Windsor to Niagara, and Oshawa to Parry Sound.
Vice President Jeff McGregor, who’s been with the company for 22 years, shared why Bobcat® remains their brand of choice:
“We chose Bobcat for several reasons. We’ve grown alongside the brand, starting with compact skid-steers and transitioning to compact track loaders as they became more widely used. Their adaptability with the extensive range of attachments we use on site is one of the biggest reasons we choose Bobcat. Augers, packers, drum brush cutters, sweepers, salters, sanders, plows, you name it. They have an endless list we can rent at any time and/or buy. Our service techs are well-trained to maintain these machines, and their overall versatility sets the standard in the industry. Ryan Hancock, Product Support
Manager, consistently has what we need in stock, while Andrew Quast, Rental Manager, plays a key role in supplying us with rental equipment and attachments, making it possible for us to serve such a large region effectively.
One underrated feature? Fuel tank capacity. Our Bobcat machines run continuously throughout the day without needing constant refuelling, which is essential when operating in remote areas. Not all brands offer a large fuel tank like Bobcat does. Moreover, the Bobcat telematics system is invaluable. From any laptop, we can check machine locations, monitor performance, and even receive maintenance alerts or request remote support.
What started with one Bobcat track loader quickly grew due to rising demand. Clients appreciated how the machines minimized lawn damage, while operators preferred their superior visibility, power, and weight distribution. The ability to switch between hand and foot controls was another advantage. Recently, Aldershot invested in eight new Bobcat T770 compact track loaders and three Bobcat E88 compact excavators. The T770s handle everything from soil removal to gravel laying and moving material, while the E88s, equipped with thumbs, are ideal for lifting armour stone, duct banks, cable locates, and excavation work. Our sites are congested, and these machines are a huge benefit to us.”
The relationship with Bobcat of Hamilton spans three decades and is built on trust and exceptional service. They bend over backwards for us. Brand loyalty also comes with the service we receive from Bobcat of Hamilton.
“They go above and beyond. It’s a great partnership between John Steeves, Aldershot Equipment and John Quast, Bobcat of Hamilton. Their location is also very convenient for us. The stock they have is impressive. They are always on it, even during the busiest of times. Their pricing is also reasonable, which is another significant factor. If a hose is accidentally cut, they’re out to fix it right away. Ryan Hancock, product support manager, consistently has what we need in stock, while Andrew Quast, rental manager, plays a key role in supplying us with rental equipment and attachments, making it possible for us to serve such a large region effectively. Our sales specialist, Derek Brooker, has been a tremendous asset to us. Knowledgeable, responsive, and a true problem solver who kept us informed every step of the way as our new equipment arrived.
As long as you upkeep the maintenance on your Bobcat machines, you are golden. We currently run 65 Bobcat units and wouldn’t hesitate to recommend both the brand and Bobcat of Hamilton, and Derek Brooker.”
BARRIE
Bobcat of Barrie
705-726-2228 oakenequipment.ca
GREY BRUCE
Bobcat of Grey Bruce
519-372-9100 bobcatoftc.com
PARRY SOUND
Bobcat of Parry Sound Ltd. 705-342-1717 bobcatofparrysound.com
TORONTO WEST
Bobcat of Toronto
416-679-4172 oakenequipment.ca
BRANTFORD
Bobcat of Brantford 519-752-7900 bobcatofbrantford.com
HAMILTON
Bobcat of Hamilton 905-643-3177 bobcatofhamilton.com
PETERBOROUGH
Bobcat of Peterborough 705-748-9119 bobcatofpeterborough.com
THUNDER BAY
Equipment World Inc. 807-623-9561 bobcat-tbay.com
CASSELMAN
Bobcat of Ottawa Valley 613-764-2033 bobcatov.com
KITCHENER
Bobcat of Tri-Cities Ltd. 1-866-214-3939 bobcatoftc.com
STRATFORD
Bobcat of Stratford 519-393-6040 bobcatofstratford.ca
SAULT STE. MARIE
Bobcat of Sault Ste. Marie 705-949-7379 bobcat-ssm.com
CORNWALL
Bobcat of Ottawa Valley 613-932-2034 bobcatov.com
LONDON
Bobcat of London 519-455-4900 bobcatoflondon.ca
STRATTON
Stratton Equipment 807-483-5505 strattonequipment.com
WINDSOR
Bobcat of Windsor 519-737-0120 oakenequipment.ca
COURTICE
Bobcat of Durham East Ltd. 905-404-9990 bobcatofdurhameast.com
MUSKOKA
Bobcat of Muskoka 249-390-7000 oakenequipment.ca
SUDBURY
McDowell B Equipment Ltd. 705-566-8190 bmcdowell.com
WYOMING
Advantage Farm Equipment Ltd. 519-845-3346 advantage-equip.com
FRANKFORD
John’s Equipment
613-398-6522 johnsequipmentsales.com
OTTAWA
Bobcat of Ottawa Valley 613-831-5166 bobcatov.com
TORONTO EAST
Bobcat of Toronto 416-679-4171 oakenequipment.ca
Canada is growing at an estimated 1.8 per cent annually. And while there’s lots of space to go around, there isn’t necessarily the infrastructure in place to support this continued population growth. Which is why pretty much every Canadian city or town from east to west has one thing in common –construction.
As our country’s population continues to climb, the number of development projects — residential homes, apartment complexes, retail spaces, etc. — is increasing exponentially. This requires a need for more efficient and versatile tools and machinery on every jobsite, not only to move things along quicker and in a more cost-effective way, but also to adopt a more future-focused approach to infrastructure.
Navigating urban jobsites
Building projects that take place within city landscapes present many challenges that aren’t found in a larger, more secluded area. Think about the sheer number of people moving around on foot or in vehicles navigating within a space often less than the size of one city block. This is where compact equipment comes into play.
With significantly smaller footprints, the ability to turn on a dime, and even pivot in place, compact equipment, such as mini excavators, compact track loaders and skid steer loaders, can navigate the confined spaces that are urban jobsites, without disturbing surrounding properties or interrupting traffic.
In addition to increased access-
By Jonathan Gardner, Product Manager for Construction Equipment at Kubota Canada
ibility to tighter spaces, compact machinery is unmatched in its versatility compared to its larger counterparts, as one machine can be fitted with a variety of attachments to complete various jobsite tasks.
Compact equipment provides operators with the agility to handle multiple types of infrastructure projects — big and small — including driveway paving, housing development, foundation repairs and fence installation.
When beginning a project, look to a skid steer loader to support in land-clearing and grading operations, as well as hauling material and debris from one place to another. Compact track loaders are also extremely helpful in moving dirt, rocks and other material with a traditional bucket attachment, and when paired with blades or grapples, can even be used to tackle more of the heavy lifting in levelling and excavating. But when you’re ready to dig, mini excavators are irreplaceable on urban jobsites. They can fit in places most equipment can’t, and with the right attachments, can tackle jobs such as the digging of foundations, removing existing concrete pads and more.
The cost benefits
As companies look to decrease input costs and increase profits in the current economic landscapes, compact equipment is a valuable tool for urban developers for many reasons.
First is the lower capital investment. With a smaller size comes a smaller price tag, making it a
more affordable option for smaller, more limited-access or specialized development projects.
Compact machinery also requires less storage space and can be transported with greater ease than larger models, not to mention the added versatility that allows for quick application and attachment changes, much like a Swiss Army Knife for construction, on urgent jobs.
Equipment that allows for attachments like augers for drilling holes, power rake for ground prep, grading box blades for driveway preparation and plate compactors for soil compaction, are prime examples of the highly versatile nature of compact models. The more projects that can be completed using a single machine, the greater income business owners can expect.
The future of excavation
Productivity goes hand-in-hand with performance, which is another area in which compact machinery excels. Tiltrotators are becoming more popular in the Canadian market, as owners and contractors are realizing they can be more productive and improve efficiencies when building a retaining wall or completing various excavation jobs.
Many compact machines now have telematics systems built-in as standard, to help monitor critical performance metrics, including hours worked, fuel levels and key maintenance intervals, supporting in anticipating operational issues before they arise. In some instances, it can even record when and
where machinery was used, allowing project managers and leads to know when their team completed certain tasks in a development timeline.
When considering compact machinery equipped with telematics for urban jobsites, there are several benefits to keep in mind to ensure that business owners are getting the best investment for their purchase:
· Monitor operational performance and efficiency: Route information, fuel consumption, GPS location and engine status become actionable insights that users can plan around.
· Check equipment health: This allows users to identify and correct issues before they become ongoing problems. A condition-based monitoring system allows technicians access to valuable data ensuring they are responding with the right tools and replacement parts.
· Enhance user safety and security: Users can always know
where their machines are located on large-scale worksites while remotely preventing unauthorized equipment access to untrained operators.
· Improve fault identification: Pre-telematics, a check engine light could be received, but not remotely, and indicated a problem, but no solution. Sensor data now provides detailed remote information about equipment fault status and how operators can streamline the fix.
· Always know how and where machinery is operating to better plan diagnostic and maintenance work.
When it comes to city-based landscaping, development and construction jobs, compact machinery provides more than an essential service.
To navigate urban jobsites of all shapes and sizes, companies are not only doing better work faster; they are also fuelling the future of Canadian infrastructure.
Case CE has introduced two new compact, but featurepacked, midi excavators.
The new CX85E and CX90E midi excavators offer heavy-duty performance without sacrificing manoeuvrability.
Both machines are ideal for construction crews working in residential or commercial
construction sites, landscapers who are trenching, lifting, grading and digging, or rental companies seeking to offer a wider range of excavator options.
“Meeting modern worksite challenges takes innovative equipment that can help crews achieve more with less,” said Terry Dolan, Head
of CNH Construction Brands, North America. “Listening to what contractors need is what drives our ingenuity-obsessed mindset, and it’s why we built our newest Case midi excavators to deliver big-machine performance in a smart, space-efficient design. It’s all about empowering crews to be more
productive than ever in the most challenging environments.”
The CX85E and CX90E midi excavators are powered by a 72-hp engine that provides ample power for digging, land clearing, craning, loading or using high-performance attachments. Operating weight on the CX85E is 8,830 kg while the CX90E operating weight is 9,210 kg.
Both machines come with a comprehensive hydraulic package with standard auxiliary, drain-to-tank functionality and quick coupler circuits to drive an array of advanced attachments. These features eliminate the need for aftermarket modifications and make these machines suitable for tackling various tasks across diverse jobsites, whether running hammers, rippers, augers, thumbs, buckets or grapples.
The new midi excavators are also designed to maxi -
mize output in confined work zones where larger excavators can’t fit but would otherwise be right for the job.
The fixed-boom CX85E delivers maximum performance in tight spaces with zero tailswing, which allows operators to work up against walls, fences or other structures.
The optimized swing boom on the CX90E provides 180 degrees of movement with superior reach and dig depth for trenching and confined-space excavation.
Both midi excavators take an operator-first approach to design, offering a wide range of features that boost comfort and control.
Both midi excavator models feature one of the most spacious cabs in the industry, complete with automatic climate control and a standard heated air-suspension seat.
Superior visibility and an 18-cm LCD touchscreen display improve situational awareness, while ergonomic joystick-controls reduce operator fatigue during long days of operation.
Precision and adaptability come standard on both machines with adjustable electro-hydraulic controls, which let operators set lift and tilt responsiveness to match specific jobsite requirements or operator preferences.
The customizable controls also make it easier to run advanced Case attachments for more versatility.
The new Case midi excavators pack a range of advanced features and options that deliver the capabilities and efficiency crews need to meet the challenges of demanding worksites. With options for full rubber tracks, steel tracks in multiple widths or steel tracks with rubber pads, contractors can customize and optimize their machines to match the terrain of their applications. As well, an optional LED light package delivers industry-leading light coverage, letting crews maximize visibility for working day or night.
The CX85E and CX90E also simplify maintenance. A tilting cab gives operators fast and easy access to hydraulic components, while wide compartments, swing-out side panels and ground-level service points make routine maintenance and daily checks more efficient.
“Our goal at Case is to help increase efficiency, productivity and profitability for contractors with swift, smooth and smart machines that meet today’s evolving jobsite conditions,” Dolan said.
“The latest additions to our midi excavator lineup are a big step forward to provide crews with the power, versatility and precision they need to succeed in an increasingly competitive industry.”
Pictured here is a mid1940s LeTourneau Model D4 Tournapull scraper that was developed by the United States military for use in the Second World War.
Dubbed the ‘Flying Scraper,’ this 1.53 cubic metre unit was powered by a 34 kW (45 hp) four-cylinder Continental gas engine coupled with an off-the-shelf Borg & Warner four-speed transmission.
In the early years of the war, the military realized the need for a lightweight, compact unit that could be air-lifted and deployed initially in runway construction overseas.
Engineered to be transported by the United States C-47 D Dakota transport military aircraft, more than 600 units were produced by
LeTourneau by the end of the war.
Steering an Airborne scraper was accomplished by the popular ‘clutch and brake’ method, which confounded many an army private turned operator.
Note that the unit pictured here has had its steering modified by use of hydraulic cylinders during restoration.
This Airborne scraper and International TD 6 crawler pusher was part of an HCEA Canada event during the 2010 International Plowing Match held near St. Thomas, Ontario.
Fortunately, long-time HCEA Canada members, Bob and Doug Davis, also have an Airborne scraper in excellent operating condition they demonstrate during
events held at the Simcoe County Museum.
In fact, the Davis brothers have two LeTourneau D-Pull scrapers from the early 1950s that are powered by GM 4-71 diesel engines, manual transmissions and a generator to supply all scraper functions electrically, including the steering.
To see more than 60 restored pieces of vintage construction equipment in action, be sure to attend Historical Construction Equipment Association (HCEA) events. The Last Blast event returns this October at the Simcoe County Museum near Barrie, Ontario.
HCEA Canada is a Proud Community Heritage Partner of the Simcoe County Museum.
FAE is expanding the applications for its RCU75 remote-controlled tracked carrier.
The company has developed a universal attachment plate, which makes the RCU75 compatible with a range of equipment that was previously exclusive to compact loaders. This universal attachment plate allows FAE’s RCU75 to be equipped not only with FAE attachments — such as forestry mulchers, swinging hammer mulchers, stump cutters, stone crushers and road planers — but also with third-party equipment designed for skid steers, such as chippers, sprayers, forestry winch
es, sweepers, mixing buckets, lifting forks, dozing blades, disc trimmers and trenchers.
FAE created the RCU75 to work in hard-to-reach areas or on steep, sloping terrain where operator safety and operating efficiency are a concern. This vehicle is ideal for working in hilly and wooded areas and near railroad tracks, power lines, gas and oil pipelines, gardens, roads, highways, canals, rivers and lakes.
The FAE tracked carrier relies on the compact Rehlko 74 hp common rail electronic fuel injection engine, a fuel-efficient option that complies
The heavy-duty undercarriage has a variable hydraulic design with independent rollers and an automatic tensioning system. High profile rubber tracks, with 86 mm spacing and 320 mm width, and idler wheels, enable the RCU75 to handle challenging conditions.
High-tech solutions give the RCU75 impressive traction, making it possible to work on steep slopes up to 55 degrees.
As well, a steel track option is available, ensuring outstanding traction on particularly challenging terrain.
To maintain performance while using the tracks and the attach -
ment simultaneously, the RCU75 makes use of a dual hydrostatic transmission. This integrated technological system consists of electronically controlled piston pumps combined with a dedicated electronic control unit.
The result is high performance, plus simple and intuitive operation. The RCU75 is operated using a remote control, with a large 11-cm display and customizable function keys for superior management of all vehicle and head functions.
A 2.4 GHz transmission frequency ensures reliable communication. Optimally laid out
and comprehensive controls, together with a balanced shoulder strap, make the FAE remote control unit ergonomic and easy to use.
The FAE RCU75 can be paired with the FAE app, allowing access to real time operational data, diagnostic notifications, and scheduled maintenance indications on your smartphone.
The RCU75 will not be the only product to benefit from the new universal attachment plate option. The plate will also be available for FAE’s most powerful remote-controlled tracked carrier: the RCU120.
July 17, 2025
Kioti Tractor has announced two key leadership changes to strengthen its growth strategy in North America.
The company welcomes Don Lowe as Vice President of North American Sales and has promoted Tim Phillips to the Vice President of Sales Operations role.
With more than 30 years of experience in sales, dealer development and strategic growth within the agricultural and compact construction equipment industries, Lowe will play a key role in expanding Kioti’s market presence.
Phillips, a 20-plus year veteran of Kioti, will leverage his knowledge of the company’s sales operations and dealer
network to drive efficiency and growth in his new role.
“We are excited to welcome Don to the Kioti team and recognize Tim’s well-deserved promotion,” said Ryan Kim, Executive Vice President and Chief Operating Officer at Kioti Tractor.
“Don brings fresh ideas and a strategic mindset that will help drive dealer expansion and market growth, while Tim’s deep expertise and long-standing commitment to the brand will ensure operational excellence and continued support for our dealers and customers. Together, their leadership will be instrumental as we strengthen our presence
across North America.”
In his new position, Lowe will oversee the Kioti market expansion strategy, working closely with the sales team to drive growth, improve customer engagement and strengthen the brand’s position as a market leader.
His expertise in sales operations, dealer relations and market development will support Kioti’s expansion across its product portfolio including tractors, compact construction equipment, utility vehicles and zero-turn mowers.
Prior to joining Kioti, Lowe held various leadership roles at Kubota Tractor Corporation, where he managed
national sales teams, dealer programs and strategic initiatives that increased market share and customer reach. His deep understanding of the equipment industry and commitment to dealer success make him a valuable addition to the Kioti leadership team.
Since joining Kioti in 2003, Phillips held several key positions including Territory Manager, Eastern Regional Manager, and most recently, National Sales Manager. His extensive experience across these roles provide him with a deep understanding of Kioti’s dealer network, customer needs and operational priorities.
Advance has appointed Phil Vierno as the new Regional Sales Manager for the Northeast territory.
A seasoned professional with a strong technical foundation, Vierno brings a wealth of experience to the role, offering expertise and a commitment to exceptional client service.
Vierno takes over the position previously held by Sam Cimilluca, a respected industry veteran known for his hands-on approach and extensive knowledge.
“I'm excited to be joining the Advance team and continuing the work of someone as well-regarded as Sam Cimilluca,” Vierno said. “I’m committed to maintaining the high standards of service and expertise that Advance is known for, and I’m eager to work alongside clients to meet their needs with integrity and technical know-how.”
Born and raised in New Jersey, Vierno earned a degree in Mechanical Engineering from Rutgers
University, before beginning a career in technical fields. His career includes experience in medical device manufacturing, where he developed a deep understanding of product innovation and quality control. For the past five years, Phil has honed his expertise in heavy-duty truck sales, where he became well-versed in industrial equipment and cultivating strong client relationships.
While Cimilluca's legacy remains a standard of excellence, Vierno is eager to build on that foundation, bringing his own blend of technical expertise and commitment to open communication. Vierno lives in Bethlehem, Pennsylvania.
Superior Industries has announced the promotion of Kathy Johnson to the role of Vice President of Aftermarket.
In her new role, Johnson will continue leading the company’s aftermarket services team, which supports dealers and end users with everything
from parts sales and technical documentation to hands-on customer service.
“Kathy has a way of bringing people together to solve problems and make things better,” said Superior Industries President Jason Adams. “She’s a leader who listens first, isn’t afraid to get her
hands dirty, and never loses sight of what really matters — serving customers.”
Johnson has been with Superior for 13 years, bringing valuable experience from her background in technical publications. She has played a key role in shaping the company’s aftermarket efforts by
At its most recent meeting, the Supervisory Board of Bauer AG appointed Lena Effinger as a member of the executive board, effective June 1, 2025. She will take on responsibility as Chief Financial Officer of Bauer AG.
Effinger has been with the Bauer Group since 2006 and has headed the group finance department since 2016, where she was most
recently responsible for financing and treasury.
“I would like to thank the supervisory board and the executive board for their trust and look forward to working closely with the entire management team,” Effinger said.
Following the appointment of Lena Effinger, Hartmut Beutler will step down from the executive board. After leaving the executive board
at the end of 2021, Hartmut Beutler had been reappointed as interim member of the executive board of Bauer AG.
"I am delighted to continue our long-standing collaboration with Lena Effinger on the executive board. She is an experienced finance professional who has been responsible for coordinating with our banks for many years and has significantly
improving support systems and finding new ways to make life easier for everyone.
developed Bauer's treasury in recent years,” said Peter Hingott, Member of the Executive Board of Bauer AG.
During his tenure, Phillips successfully led the launch of new product segments, including zero-turn mowers in 2019 and compact construction equipment in 2023. His time in the field as a Territory Sales Manager from 2003 to 2017 earned him valuable market and dealer insights, which continue to inform his
strategic leadership. Phillips also spearheaded the implementation of Kioti’s sales and operations planning process and played a leading role in expanding the dealer network. In his new role, Phillips will oversee sales operations, market intelligence, marketing and inside sales.
Lintec & Linnhoff has appointed Jeffrey Ma as Chief Technology Officer (CTO). Based at the company’s global headquarters in Singapore, Ma will report directly to Group CEO Peter Chan and lead the group’s global technology operations.
Ma will lead the group’s engineering operations, supply chain and operational excellence across the company’s international facilities.
He brings more than 30 years of leadership experience across several industries including most recently one of the largest asphalt plant manufacturers in Europe. He has held senior management roles at a range of multinational organizations and is known for his ability to lead teams, implement continuous improvement initiatives and manage complex global operations.
“We are excited to welcome Jeffrey to Lintec & Linnhoff. His expertise in operations and international business development will play a key role in advancing our technology roadmap and supporting our growth ambitions globally,” Chan said.
Ma graduated in engineering management from Henan University of Science & Technology. He holds an MBA in strategy development from Nanjing University in China, and
studied strategy and international business in Vlerick Business School in Belgium.
“I’m honoured to be joining Lintec & Linnhoff at such an exciting time for the company," Ma said. “I look forward to working with the team to further enhance our technology capabilities, deliver innovative solutions for our customers and support the company’s long-term success across all markets.”
Ma’s appointment reinforces Lintec & Linnhoff’s ongoing commitment to investing in world-class talent to support its innovation-driven growth strategy.
Lintec & Linnhoff is a global manufacturer and distributor solutions for the asphalt and concrete industries under the Lintec and Linnhoff brand names. Its products include asphalt mixing plants, concrete batching plants, pavement related technologies, and specialist concrete cooling solutions.
Loved for the features. Trusted for the performance.
Do more without feeling like it in Hyundai’s NEW HX355ALCR compact radius excavator.
• RH and rear camera (standard)
• LED lights
• Dozer blade (option)
• Engineered to redefine efficiency, comfort, and safety
• AAVM 360° camera with ultrasonic system (option)
• Free Hi-MATE mobile telematics for 5 years
• 8” touchscreen color LCD monitor (standard) and 2nd monitor (optional)