
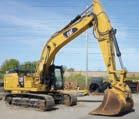





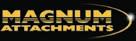
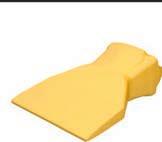





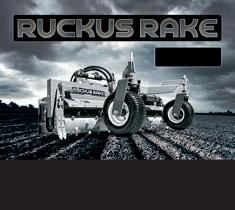



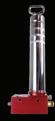
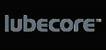





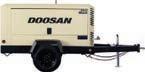
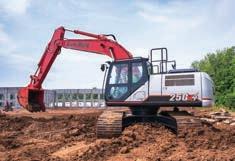

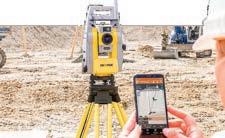



AGGREGATES
End to end washing solutions for wet processing with capacity of producing up to 5 products.
AGG RE GATES RE CYCLING IN DUSTRIA L SANDS WATER
AGG RE GATES RE CYCLING IN DUSTRIA L SANDS MI RECYCLING
AGG RE GATES RE CYCLING IN DUSTRIA L SANDS MI NING MINING
GATES RE CYCLING IN DUSTRIA L SANDS MI NING WATE R MA NA GEME SANDS
AGG GATES RE CYCLING IN DUSTRIA L SANDS MI NING WATE
Vac Truck Waste processing to produce high quality/ high value, saleable products, reducing landfill waste.
Customized solutions to achieve significant efficiencies for your ore processing operation.
Engineered solutions to process contaminated sands with capacity for 3 quality products.
Complete, tailored water management solutions, eliminating the need for settling ponds.
AGGWASH 60-1/60-2 MAIN FEATURES
• Rinsing, Screening, Scrubbing and Sand Processing
• Fully Modular, Pre-Wired & Pre-Plumbed
• Produces 3 Grades of Aggregates and up to 2 grades of sand
• Removal of Trash and Ferrous Metals
• Quick Set up Time
• Twin Shaft Logwasher with an Adjustable Angle
• Heavy Duty, Robust Construction For Rugged Operating Environments
Toll-Free: 1-877-797-7276
LETTER
Opioids are killing construction workers at much higher rates than people in other occupations in Canada.
A recent study by the Ontario Drug Policy Research Network examined opioid deaths in the province between 2017 and 2020. The study found that 428 Ontarians with employment history in construction died of opioid toxicity in that timeframe, representing about 8 per cent of all fatal opioid overdoses. However, construction employment represents about 3.6 per cent of Ontario’s entire population.
Pain was a recurring factor among construction workers that overdosed, with nearly 80 per cent experiencing a pain-related condition or injury in the five years before overdosing.
The report also outlined that opioid deaths among
construction workers are primarily being driven by the illegal drug supply rather than prescriptions.
British Columbia has also reported staggering numbers for opioid deaths in construction. Nearly 20 per cent of overdose deaths in B.C. worked in the trades, transport or as equipment operators.
To reduce fatal opioid overdoses on the jobsite, Ontario is requiring employers to stock a naloxone kit as of June 1, 2023.
Under the Occupational Health and Safety Act (OHSA), all Ontario employers who know, or ought to know, there is a risk of an opioid overdose in their workplace, are required to ensure a naloxone kit is made available in good condition.
The Residential Construction Council of Ontario (RESCON) applauded the
naloxone requirements, noting that kits on hand will also help to reduce the stigma around opioid abuse and raise awareness about the risks of accidental overdoses.
“Most RESCON members are already ahead of the game and have included naloxone kits on site as part of their health and safety protocols,” said RESCON Vice President Andrew Pariser who is chair of the association’s safety committee. “This is an easy best practice that can save lives.”
Naloxone is available at most pharmacies, or through the Ontario government. The drug can temporarily reverse the effects of an opioid overdose, including the use of morphine, heroin, oxycodone, fentanyl, codeine and hydromorphone.
Naloxone is generally considered safe for everyone, and employers are protect-
Bill Tremblay // Editor editor@equipmentjournal.comed from liability available under the Good Samaritan Act for a worker who voluntarily administers naloxone at the workplace in response to an opioid overdose. Regardless of legislation, all jobsites should keep a naloxone kit on hand.
The kits are often free, require minimal space and could literally make the difference between life and death.
CONTACT US
Editor Bill Tremblay editor@equipmentjournal.com
Publisher Mark Baker mark@equipmentjournal.com
Sales Manager Tara Baker tara@equipmentjournal.com
National Account Manager Mona Fahmi mona@equipmentjournal.com
TOLL-FREE: CDN/USA 1-800-667-8541
Creative Director/Creative Services Ryan Chuhaniuk ryan@equipmentjournal.com
Circulation Manager Lisa Bath lisa@equipmentjournal.com
EMAIL US: advertise@equipmentjournal.com
WEBSITE: www.equipmentjournal.com
Vermeer has officially opened its new 29,000-square-metre Global Parts Distribution Center in Pela, Iowa.
At the new facility on the grounds of the company’s corporate headquarters, Vermeer team members will package and ship parts worldwide.
The Global Parts Distribution Center builds on a legacy of customer support, located at the end of the old runway where founder Gary Vermeer once delivered parts to customers by plane.
“Vermeer is focused on optimizing this facility so we can most efficiently deliver the right part at the right time to our customers,” said Tony Briggs, Vice President of the Vermeer Lifecycle product group.
“This facility allows customer support, engineering, procurement and logistics to be co-located. They work in conjunction with our operational team members to make sure we fulfill customer and dealer expectations daily.”
The location of the Global Parts Distribution Center leverages the manufacturing capabilities of the Vermeer mile, where most Vermeer products are assembled.
“Almost one third of the warehouse is filled with parts made by different manufacturing plants on the Vermeer mile. It is very convenient for us to be located near the manufacturing facilities that supply those parts,” Briggs said. “Ultimately, we bundle the Vermeer-manufactured parts with other parts and ship the orders around the world to take care of our customers.”
The new Global Parts Distribution Center provides three times more space than the previous building, and includes 23 dock doors, a warehouse management system and improved warehouse technology. The investment will help drive efficiency by
centralizing parts storage.
“With people at the centre of everything we do, this new facility helps our team members equip dealers and support customers and that ultimately makes a real impact on their ability to get important work done,” said Jason Andringa, Vermeer president and CEO.
The Global Parts Distribution Center is the second facility Vermeer has opened in 2023. Earlier this year, the company expanded its parts manufacturing footprint in Des Moines, Iowa. That facility manufactures horizontal directional drill tooling and utility tractor attachments.
As the number of products and markets Vermeer supports expands, the company continues to invest in its aftermarket efforts to meet the needs of a global economy.
The Scandinavian market leader. Dump trailers produced entirely in high-strength steel Strenx®/Hardox®. The bogie is easily moveable, perfect for wheeled excavators in need of minimizing the ball pressure. Standardly equipped with a vertically adjustable drawbar. For an out-of-the-ordinary outfit, we are happy to match the color of the trailer with the color of your excavator.
A new book by Uxbridge, Ontario author Alanna Allan is helping children of construction workers understand why their parent leaves home for work and the importance of the job.
Using easy-to-read rhymes and colourful illustrations, Where Does Daddy Go All Day? highlights the differences between the typical day of a child and their parent’s role on a jobsite.
“It really parallels what's happening at each stage of the day, like when the little boy is eating breakfast, compared to what his dad might be doing at that time on the jobsite,” Allan said.
During the pandemic,
Allan was at home on maternity leave for her newborn son Benny. At the time, her husband Cam worked as a foreman for a petroleum contracting company, often requiring him to be away from his family for months at a time. (He has since started his own contracting company allowing him to stay close to home.)
Allan wrote the book for her eldest son Brian, who would wake up after his father had left for the jobsite, and often go to bed before his dad returned. Brian would often ask why his father was away, while other parents worked from home.
“It was really challenging
for him to understand where daddy went for five days or more of the week, and then he was magically here,” she said. “It caused him a lot of anxiety. So, I started writing the book to help him understand.”
To comfort Brian, Allen would write short verses explaining why Cam was away from home.
“My dresser was full of these little words and verses on post-it notes that I put together in the middle of the night and then I kind of pieced them together,” she said.
She eventually decided to put the notes together to create a tool to help relieve her son’s anxiety.
“Originally, I made it with pictures of him just on printer paper and I put it in a binder,” Allen said. “He still reads that version, but he likes the book better.”
As a learning tool, the book also draws upon children’s love of construction machinery.
“A lot of children can pick out an excavator from a mile away or a dump truck,” she said.
During the pandemic, Allan and other parents in her community would meet outside of construction sites to allow their children
to watch the machines in action.
“The pandemic was so challenging, but I feel like construction really brought a positive light to the year because every day we would go out on an adventure,” Allen said. “The kids could watch the big drill that was there and the excavators, and we could socialize at a distance.”
Allen hopes the book will teach children to have an appreciation for their parents’ careers.
“And it doesn't even need to be in the field of construction,” she said. “I hope that kids have the opportunity to ask questions of what their mom or their dad do during the day.”
Futura Teeth and adapters are cast from chromium, molybdenum, and nickel to deliver greater strength and durability than any comparable teeth on the market. They feature approximately 20% more usable wear material than other similar systems in the market and 68% of the steel can be used without losing sharpness. That’s Powerful Value. Delivered.
brandt.ca 1-888-227-2638
For a limited time, receive FREE Futura adapters when you purchase three complete sets of Futura bucket teeth. See store for details.
Wacker Neuson employees around the world paused on Monday, May 15, to commemorate the company’s 175th anniversary.
More than 6,000 employees celebrated together, marking this milestone through a global call hosted by the company’s headquarters in Munich, Germany.
The live event travelled around the world with stops in various factories and sales affiliates.
“Taking the time to celebrate 175 years of quality
and innovation reflects the commitment of our company to the many dedicated Wacker Neuson employees who have contributed to our global success throughout our history and those that are now leading us into a bright future,” said Gert Reichetseder, President and CEO of Wacker Neuson America Corporation.
“We originated the compaction industry and that will always be at the heart of Wacker Neuson, even as we grow our product offering into exciting new areas.”
Wacker Neuson was born in 1848 when Johann Christian Wacker set up a blacksmith shop in Dresden, Germany. Since then, the company has introduced numerous innovations that have revolutionized work on construction sites worldwide.
In 1930, Hermann Wacker introduced the electric rammer. The vibratory rammers are used for soil compaction to this day. This was followed by the development of the internal vibrator for concrete consolidation, which captured the market in 1934
and the first reversible plate which set a milestone in soil compaction.
Over the years, Wacker Neuson has continued to enhance its original products and has been responsible for many innovations that have made the construction process more efficient, faster and comfortable for the operator.
In 2014, Wacker Neuson introduced a new skid steer and compact track loader line to the North American market featuring an entirely new design. More recently, the Dual View Dumper changed the view of site material handling. The dumper’s 180-degree rotating seat and control panel allow the operator to always keep the task in the front of the machine, enhancing safety and efficiency.
Always looking forward, Wacker Neuson has intro -
duced an extensive line of battery-powered, zero-emission compaction and concrete consolidation products that are powered by the Battery One modular battery system.
The large selection of eco-friendly, battery-powered products includes the new and industry’s first battery-powered reversible plate, the APU3050e. Future introductions in North America will include the EZ17e zero-emission mini excavator, as well as battery-powered wheel loaders,
dumpers and telehandlers. While Wacker Neuson is often known as the original rammer company, it goes beyond the single product mentality.
The company now manufactures a wide range of light and compact equipment used in construction, landscape, agriculture, utility, residential, municipal and industrial markets. The company’s tradition of countless innovations has changed the way customers work, build and transport goods all over the world.
New Holland Construction is entering the electric equipment market with the launch of the E15X electric mini excavator.
The E15X electric power mini excavator runs on a cobalt-free lithium-ion battery that powers a 21.5 hp motor, making it as powerful as the E14D, its diesel-engine equivalent.
“This is New Holland Construction’s first step into EV, a segment that’s going to continue to evolve and grow over the next decade not only for the industry, but for New Holland Construction,” said Tyler Mills, head of New Holland Construction North America. “The E15X electric power mini excavator is built to work in a variety of spaces — indoor, outdoor, tight, noise restrictive. It has a place from indoor construction jobs to landscaping, to utility digging and demolition jobs, and beyond.”
On a fully charged battery, the electric excavator can operate for up to 8 hours. The machine can be recharged in 10 hours with a standard 110volt outlet or within an hour with its fast charge option.
“The fast charge times, zero-emission engine and adjustable features make the E15X electric power mini excavator an innovative and
environmentally friendly method to get the job done,” Mills said.
The E15X electric power mini excavator produces zero emissions and uses eco-friendly bio-hydraulic oil to extend service intervals. With zero-emission status, the E15X electric power mini excavator runs noticeably quieter than a similar machine running on a diesel engine, making it optimal for any indoor job or job with low noise level requirements.
The machine features preset eco, standard and power work modes with pre-set precision, normal, produc-
tivity and individual control modes, and all modes can be independently adjusted. Power management software is used to monitor the oil flow and engine speed by detecting joystick movement and setting engine speed to reduce pressure on the hydraulics and battery. Within seconds, the compact E15X electric power mini excavator can become narrow enough to fit through most standard-sized doors. The variable-width undercarriage can be narrowed to 79 cm and the height can be lowered to less than 1.5 metres by rotating the roll bar.
Advanced Construction Robotics (ACR) has launched IronBOT, which is able to augment construction sites by lifting, carrying and placing rebar.
IronBOT is able to manage rebar bundles weighing up to 2,250 kg in a transverse or longitudinal orientation without the need for heavy lifting from crew members.
When IronBOT is combined with TyBOT, ACR’s
rebar-tying robot, the pair can typically provide 50 per cent schedule savings during rebar installation.
“We are confident the combination of TyBOT and IronBOT generates a disruptive technology, meaning the time and cost savings are so significant on a job that it will disrupt the way our industry installs reinforcing steel,” said Stephen Muck, Founder and Executive Chairman of Advanced Construction Robotics.
IronBOT successfully completed its inaugural project in February on the Port St. Lucie West Boulevard Bridge in Port St. Lucie, Florida, alongside Shelby Erectors.
The original estimate for rebar installation was 14 days. By augmenting crews with IronBOT and TyBOT, installation was completed in seven days.
"I am so excited to see our initial prediction of cutting schedules by at least 50 per cent come to fruition on IronBOT’s maiden voyage. This was a perfect example of how field teams working alongside our technology can form a modern crew to unleash disruptive productivity levels,” said Danielle Proctor, CEO of Advanced Construction Robots.
"This robotic revolution provides innovative construction firms the ability to become game-changers by adopting and putting their modern crew to work.”
During the project, IronBOT placed more than 66,500 kg of rebar while TyBOT com-
pleted more than 58,000 ties. Shelby Erectors have been using the TyBOT on jobsites for more than two years.
"We were excited to be able to have IronBOT and TyBOT work together alongside our crews on this project,” said Jack Nix, COO of Shelby Erectors. “We were impressed that we could slash our rebar installation schedule in half. We are actively looking for new projects to incorporate the BOT bundle in our operations.”
Currently, United States contractors Brayman Construction and Advantage Steel & Construction are the only companies certified to provide the BOT bundle solution as part of ACR’s newly launched Certified Innovator Program. Certified Innovators have dedicated crews that have gone through hands-on training to optimize operations alongside the BOT bundle and incorporate the technology in their installation pricing.
"Technology is changing the way we approach construction. It helps contractors like us cope with shrinking labour forces and growing demand. We become more productive, efficient and safer when we pair this technology with an innovative mindset," said Tim Taylor, Vice President of Heavy Civil at Brayman Construction Corporation. "That's why we are proud to be the first Certified Innovator and will continue to work with ACR to weave technology into our company identity."
Equipment Sales & Service Limited (ESS) has been named as one of Canada’s Best Managed Companies for the 12th consecutive year.
The company was recognized for its industry-leading performance, its global business practices, and its sustained growth.
“On behalf of all the people at Equipment Sales & Service, I wish to express our delight at being chosen to be among Canada’s Best Managed Companies again this year,” said Morgan Cronin, President of Equipment Sales & Service Limited.
Canada’s Best Managed Companies program awards excellence in private Canadian-owned companies.
Now in its 30th year, Canada’s Best Managed Companies is one of the country’s leading business awards programs.
Every year, hundreds of entrepreneurial companies compete for this designation. Applicants are evaluated by an independent panel of judges with representation from program sponsors and special guests.
“The Best Managed Company award program and the rigor required to become designated have become ingrained within our entire company and therefore have become part of its culture,” said Peter M Willis, Executive Co-Chairman of Equipment Sales & Service Limited.
“Collaboration and teamwork amongst our dedicated, well trained, experienced employees, across all departments, are hallmarks of our operations with specific focus on serving our customer base in the most efficient and proficient ways possible."
Case Construction Equipment is expanding its mini excavator lineup with the addition of two electric machines.
Each machine complements the existing C Series mini excavators giving Case one of the industry’s most diverse and robust product offerings ranging from 1.5 to 6 tonnes.
“Electric to diesel, true zero to conventional tailswing, cab to canopy, Case now offers a full range of mini excavators to match any need and operator preference, including the ability to access any construction or landscaping
site,” said Brad Mace, Product Manager for Case Construction Equipment.
“Each machine is built with premium features and performance that empower the operator to succeed in the types of jobsites and environments they work in, whether that’s utility work indoors that requires a zero emissions machine, or production-level trenching on a commercial development.”
The new two electric machines include the CX15EV and the CX25EV. The CX15EV is available now, while the CX25EV will be available later in 2023.
The CX15EV is a 1,445 kg mini excavator powered by a 21 hp electric motor. The CX25EV is a 2,190 kg mini excavator running with a 27 hp electric motor.
The lithium-ion battery featured in both machines is charged either by the 110V/220V on-board charger, or via an external rapid charger that can have the machine charged within about 90 minutes. Depending on the type of work, both electric mini excavators will provide enough power to work through a full eight-hour day. All while delivering the core benefits of electrified construction equipment, such as no emissions, reduced noise and less lifetime maintenance thanks to the elimination of the diesel engine.
“Mini excavators are ideal for electrification because they go through varied work cycles throughout the day,” Mace said. “Between access to power and the fast-charging capabilities of the machine with both on-board and external technologies, these machines deliver excellent runtimes and are sure to be ready to take on any task.”
Both electric mini excavators are equipped with a standard colour LCD monitor that delivers easy access to battery information, machine settings and work modes. It also features an electronic pattern changer for switching between ISO and SAE patterns, customizable hydraulic proportional controls and auxiliary hydraulics to let the operator dial the machine into their preferences.
Each machine features three work modes — Power, Standard and Economy — that match electric motor speed to the task at hand. As well, the ability to adjust the sensitivity of the controls allows the operator to control the feel and performance of the machine. This can be done through one of three pre-sets (Precision, Normal or Productivity), or an Indi-
vidual setting that allows the operator to select specific responsiveness for six different bucket and boom actions, as well as swing, travel and blade functions.
A load-sensing hydraulic system further delivers smooth and powerful performance that allows the operator to dial the machine into each task.
“Our focus is on delivering a complete operator experience, even in some of the smallest machines we manufacture, and that attention to detail and operator satisfaction is built into each one of these battery powered units,” Mace said. “Another area where we’ve showcased this is in the ability of these electrical units as attachment platforms.”
Both machines feature standard 1-way/2-way hydraulics with an electronic detent hold to reduce operator fatigue, and an optional second auxiliary circuit (2way only) can be added for more hydraulic options.
The LCD monitor allows flow settings to be set and stored for up to five attachments for convenience and confidence when switching between attachments.
Case also focused on connectivity with the new electrified mini excavators, making SiteWatch telematics standard on each machine for optimal visibility into machine performance, and greater collaborative fleet management with the local Case dealer.
Each model can be outfitted with precision construction technologies to further improve productivity and digging quality.
“These are full featured, fully electric powerhouses built for work in all environments and operations, and operators will recognize that quality when they sit at the controls and dig in,” Mace said.
In 2007 Matthew Elliott started The Northstone Group with his brother and a few years later Vic Bertrand joined. With a focus on design and creating a distinguishable brand The Northstone Group has become an internationally known and awarded landscaping design and build firm.
“It has been challenging for growth but fun,” says Mat. Their projects are high-end averaging from $300,000 to well over a million. Specializing in complex, turnkey design and build. They also do a lot of commercial work for Reliance
Construction in Quebec and Toronto.
What sets Northstone apart is their unique franchise model, which provides franchisees with comprehensive support, including a recognized brand, social media and marketing. “We offer a turn-key service to our customers. All of our plans are done in-house by experienced Landscape Architects and designs which include detailed specifications including materials, plantation and even luxury outdoor furniture. At Northstone we carry exclusive European brands from Spain, Belgium, and Italy. We are a onestop shop for anything outdoor living related.”
YOUR LOCAL AUTHORIZED BOBCAT DEALERS
BARRIE Bobcat of Barrie 705-726-2228 oakenequipment.ca
GREY BRUCE
Bobcat of Grey Bruce 519-372-9100 bobcatoftc.com
PARRY SOUND
Bobcat of Parry Sound Ltd. 705-342-1717
bobcatofparrysound.com
TORONTO WEST Bobcat of Toronto 416-679-4172 oakenequipment.com
BRANTFORD Bobcat of Brantford 519-752-7900 bobcatofbrantford.com
HAMILTON Bobcat of Hamilton 905-643-3177 bobcatofhamilton.com
PETERBOROUGH
Bobcat of Peterborough 705-748-9119
bobcatofpeterborough.com
THUNDER BAY Equipment World Inc. 807-623-9561 bobcat-tbay.com
“In our line of work, it is important to have dependable machinery. We work frequently with Joe Palfy, sales specialist, Bobcat of Toronto. We have bought twelve Bobcat® machines from him,” stated Mat. Joe replied, “these boys are very ambitious, fun, clear on what they want, good guys.” Northstone’s franchise model offers business owners the opportunity to take their enterprise to a new level without giving up their business.
“Three years ago, during Covid, there was no equipment available. Quebec was a dry market, so I called Oaken Equipment in Ontario (Bobcat of Toronto) and talked to Joe Palfy. He said to me, “I don’t have anything now, but I will do everything I can to find you something.” He called me back with five machines, three Bobcat compact skid-steers and two Bobcat compact track loaders. Joe didn’t know me. I didn’t think he was going to call me back. He called me back with even better machines than I asked for. He gave me their financing person and shortly after, we had a deal. Upon delivery, there was even a toy inside for my kid. Under promise, over delivered. I will always use Joe.”
CASSELMAN Bobcat of Ottawa Valley 613-764-2033 bobcatov.com
KITCHENER
Bobcat of Tri-Cities Ltd. 1-866-214-3939 bobcatoftc.com
STRATFORD
Bobcat of Stratford 519-393-6040 bobcatofstratford.ca
SAULT STE. MARIE Bobcat of Sault Ste. Marie 705-949-7379 bobcat-ssm.com
CORNWALL Bobcat of Ottawa Valley 613-932-2034 bobcatov.com
LONDON Bobcat of London 519-455-4900 bobcatoflondon.ca
STRATTON Stratton Equipment 807-483-5505 strattonequipment.com
WINDSOR Bobcat of Windsor 519-737-0120 oakenequipment.ca
When asked why Bobcat machines? Mat replied, “when I was just a one-man outfit, I had one Bobcat. I had received a good deal on a used one. When I was buying more machines, I went to another brand because I was told it was the best. Biggest mistake. Nothing but issues. Couldn’t even lift a pallet. Lesson learned and went right back to Bobcat. When you find gold, keep gold. Parts are easy to get for Bobcat machines and the service is great. Efficiency is important too; all my guys know Bobcat machines. My diesel mechanics love Bobcats. They don’t break. Small and compact machines are the best for what we do. I love the simplicity of the two-finger touch, the light goes green when it’s ready to go. Super simple. We use Bobcat machines to build all our designs but also to clear walkways of snow too.
We wouldn’t hesitate to recommend Joe Palfy, Bobcat of Toronto and Bobcat machines.
Thanks Mat and Vic.
COURTICE Bobcat of Durham East Ltd. 905-404-9990 bobcatofdurhameast.com
MUSKOKA
Bobcat of Muskoka 249-390-7000 oakenequipment.ca
SUDBURY McDowell B Equipment Ltd. 705-566-8190 bmcdowell.com
FRANKFORD John’s Equipment 613-398-6522 johnsequipmentsales.com
OTTAWA
Bobcat of Ottawa Valley 613-831-5166 bobcatov.com
TORONTO EAST Bobcat of Toronto 416-679-4171 oakenequipment.ca
Registration for The Utility Expo 2023 is now open.
In 2021, The Utility Expo took home awards from Trade Show Executive’s TSE Gold 100, including the “Largest Trade Show of 2021” award. This year, the expo returns to the Kentucky Exposition Center in Louisville from September 26 to 28, and organizers are expecting it to be the largest show yet for utility industry professionals, exceeding previous records for size and scope.
“The Utility Expo is the premier trade show exclusive to the utility construction industry. Utility professionals won’t want to miss what we have to offer at this show, and we’re expanding our education program to cover more topics and showcase
hands-on learning,” said John Rozum, Show Director for The Utility Expo.
“And throughout the 1.4 million square feet of exhibits, we will be featuring the latest equipment and technologies that support the massive amount of utility infrastructure work that is happening around us right now.”
The Utility Expo registration
To save 50 per cent on the full cost of registration, use code NEWS50 by June 16. The discount code is the most cost-effective way to attend The Utility Expo.
Attendees are also able to sign up for the various education sessions that take place during the expo. Education topics cover everything from
aerial devices to vegetation management.
This year, The Utility Expo is expanding its education program to offer traffic safety content and certifications from the ATSSA.
This summer, the show will launch its mobile app, which will link to the show planner and include show maps and real-time notifications.
The Utility Expo is the largest event for utility professionals and construction contractors seeking insight into the latest industry technologies, innovations and trends. The biennial trade show, organized by the Association of Equipment Manufacturers (AEM), is known for equipment test drives and interactive product demonstrations.
Skyjack will establish an innovation hub at its headquarters in Guelph, Ontario, as the OEM expands its manufacturing capabilities around the world.
At its P1 and P2 plants in Guelph, the innovation hub will allow Skyjack to increase its advanced engineering structure and coordinate the design and development of new machines.
“The innovation hub gives us the resources we need to focus on product development to address industry trends such as sustainability, new applications that are coming out on machines every day, as well as the new technical integrations that we need to put into our machines,” said Skyjack President Ken McDougall.
The hub will also make more floor space available to test new machines designed by the Skyjack team.
“It doesn't matter how many things we design, if we don't have the space to test them, we can only do two or three projects at once,” said Kurt Atchison, Skyjack’s General Manager of Plant 2 in Guelph. “But this will allow us to do more in parallel. So, we'll be able to innovate a little bit quicker."
As part of Skyjack’s innovation hub, the company has established an advanced engineering team.
“It is kind of a precursor that does new technology and advanced validation prior to going into new product development, which would be integrated into a machine,” Atchison said.
Global manufacturing
To create space at its Guelph facilities, Skyjack is moving production of telehandlers and booms to its new plant in Mexico, as well as reconfiguring its Canadian facilities.
Skyjack’s Mexican plant has two phases. Phase 1 includes an 18,580 squaremetre plant for telehandlers and booms, with the focus of production aimed at the Americas region. In January, the first telehandler was produced at the Mexico facility.
Phase two, which has already been initiated, will see an additional 45,500 squaremetres of space.
The Mexico facility is part of a major transformation of Skyjack’s global manufacturing structure. Alongside Mexico, the company began expansion into Hungary and China in 2022.
In China, the first units rolled off the production line in September, marking the completion of Phase 1, which saw the use of a 3,250 square-metre facility via a partnership with Skyjack’s parent company Linamar. In October, Phase 2 was launched with a ground-breaking ceremony for the development of a 27,160 square metre greenfield facility. With production expected to begin in the third quarter, the plant’s production will focus on DC scissors and booms with output supplying the Asia-Pacific and Australian regions.
“We have had our eye on the Chinese market for some time. The key to success here is the ability to commit to the region and in-turn that means an in-market manufacturing presence,” McDougall said. “We have been lucky enough to benefit from our parent company’s existing infrastructure in the short term and we are now focused on building up sales and distribution networks.”
In Hungary, production of the new SJ45 AJ and SJ60 AJ articulating booms began in October. The 10,500 square-metre facility will
supply articulating booms, telescopic booms, DC and compact RT scissors to Europe.
Combined, the new facilities represent a potential global unit capacity increase of 235 per cent.
“2022 was a busy year and it is great to see how our global team achieved so much so quickly,” McDougall said. “2023 will be even more exciting as this capacity comes on stream. This, and some exciting new products later in 2023, will make it a memorable year.”
Opening new facilities has also enabled Skyjack to increase fabrication and vertical integration at its Canadian plants. Supply
chain constraints triggered by the COVID-19 pandemic encouraged Skyjack to begin fabricating its own components in-house and reduce reliance on a network of suppliers.
“After COVID, we had a lot of struggles getting our supply chain back up and running. So, I guess we want to be masters of our own destiny, and make everything in-house that we can,” said Wayne Decker General Manager of P1. “So now with the extra plants globally, it's actually freeing up more space in the plants to do more value-added work back in house.”
Furthermore, the transition will equal improved working conditions at the Guelph plants. With more
floor space available, Skyjack is improving ergonomics and legroom on its production lines, as well as improving manufacturing efficiency.
“Really, what we needed to do was make some room. So, moving our telehandlers has started a cascading effect that will go on through all of this year and into the next,” McDougall said.
A less crowded and more ergonomic line will also assist Skyjack with recruitment efforts in Guelph.
“We're trying to make it as good an environment as (employees) can have. So, we have some room to do that,” McDougall said. “And that's what we're focusing on that as we move our lines around.”
A granite monument in Fort Kent, Maine, commemorates “America’s First Mile,” the starting point of US Route 1.
Fort Kent isn’t quite the northernmost point in the United States, but it’s pretty far north, located along the Canadian border in northern Maine.
With a population of just more than 4,000, the small town was a great place to grow up, according to Tony Nadeau, owner of TN Nadeau Harvesting.
“Maine has beautiful scenery, wildlife and woods. It’s very quiet and relaxing up here,” he explained.
Today, TN Nadeau Harvesting works for Irving Woodlands, a Canadian company that manages more than 3.2 million acres of forestland, including extensive holdings in Maine.
“They manage over a million acres in Maine, so they’re a big company up here,” Nadeau said.
With a firm commitment to sustainability, Irving Woodlands plans 80 years ahead to ensure healthy forests, biodiversity and bodies of water on the land it owns or manages. This generational commitment includes growing more wood than it harvests. Since 1957, the company has planted more than one billion trees. In 2022 alone, across New Brunswick, Nova Scotia and Maine, the company planted 19 million trees.
Irving Woodlands prides itself on innovation, and invests in the latest best practices for sustainable forest management.
To harvest wood, the company contracts with numerous independent contractors like TN Nadeau Harvesting that run the latest machines and technology.
TN Nadeau runs a John Deere 853MH tracked harvester with a Waratah H425x harvesting head.
“They’re perfect together,” Nadeau said. “The combination is productive, reliable, fast and fuel efficient. It checks all my boxes. It’s everything I ever wanted.”
Nadeau also depends on the hard work of his two operators, who each work 12-hour shifts. “They are awesome. I’m so proud of them taking this operation to the next level. It’s hard to find good operators, so I’m very fortunate.”
About 90 per cent of Maine is forested — the highest percentage of any American state. This includes 12 million acres of forestland in the less-populated northern part of Maine where TN Nadeau Harvesting works. Although hardwood now covers 60 per cent of Maine, pine dominates this region.
TN Nadeau Harvesting is currently working about a two-hour drive south on U.S. Route 1 near the town of Houlton, Maine, not far from the company’s local John Deere dealership, United Construction & Forestry.
“It’s a pure stand of softwood,” Nadeau said. “It’s beautiful. Really nice.”
Nadeau’s father was a diesel mechanic who worked on excavators, dozers and some John Deere forestry machines, including processors and skidders.
“When I was young, I’d help him out on weekends, cleaning parts and getting tools for him,” Nadeau said. “I loved seeing the equipment after he fixed it. He taught me a lot. Being a mechanic was something I always wanted to do.”
At age 22, Nadeau began running a feller buncher for a logging contractor. “I’ve been in the woods ever since,” he said.
Nadeau spent more time
fixing the machine than he did operating it, so the company made him a full-time mechanic.
“I did that for about 15 years,” he said. “I had my own service truck and a lot of experience turning wrenches and repairing equipment out in the field, so I thought, ‘I’m going to have a go at this myself.’”
So, in 2015, Nadeau started his own company.
Today, TN Nadeau Harvesting runs its 853MH 24 hours a day, five days a week to keep up with demand.
“It just runs, all day, every day,” Nadeau said. “The machine is durable and easy to service. I’ve been a mechanic most of my life, and it is awesome to work on. Everything is very accessible.”
As well, the H425x Harvesting Head is perfect for
softwood and mixed-stand harvesting.
“It’s phenomenal,” Nadeau said. “It’s fast and durable. At the end of a 12-hour shift, you want to see a productive outcome, and this head really delivers.”
Ensuring uptime
United Construction & Forestry helps keep the 853MH going.
“When we are working around the clock, we can’t afford to have downtime,” Nadeau said. “It’s a huge expense. The parts support and service we receive from our local dealer are critical. If we have an issue, we’re usually never down for very long.”
Using JDLink, both TN Nadeau Harvesting and the dealer can monitor the machine. Nadeau receives immediate alerts about ma-
chine issues on his phone. Remote diagnostics and programming enable United Construction & Forestry to minimize the time and cost associated with sending out a technician.
“I can call a service technician with the code, and often they can walk me through the steps of repair on the phone,” Nadeau said. “They can also remotely diagnose the machine. If a part is needed, I know they’ll send someone out with the right one the first time.”
JDLink also sends Nadeau reminders about periodic scheduled maintenance. It allows him to track machine location, utilization, idle time and fuel consumption on his phone.
“It helps me to see if everything is running efficiently,” he said. “Fuel cost is another
big expense, so seeing that alone is worth a lot.”
By switching from his old Waratah 622B harvesting head to the new H425x, he is saving about 12 litres of fuel per hour, or about 30 per cent.
“The fuel efficiency from this setup is amazing,” Nadeau said.
“And I’m getting 15 per cent more productivity using the same machine.”
The forestry market is looking good in Maine, but Nadeau doesn’t have plans to expand.
“It’s booming right now, but I’d like to keep my operation to one machine only,” he said. “Operators are hard to come by, so we’ve been making it work. We have a machine and operators we can depend on. It’s been great.”
Machinery Americas has introduced three new to its Dash 7 series.
The ZAXIS-7 ultrashort tail-swing excavators allow operators to efficiently work in congested urban environments without sacrificing performance. The reduced tail swing eases job site maneuverability and increases application versatility.
“As the number of urban projects continues to increase, there is clear demand among operators for larger reduced-tail-swing excavators. These excavators can work in congested areas while keeping lanes open on road projects,” said Patrick Baker, Product Manager for medium and large excavators at Hitachi Construction
The ultrashort tail swing excavators include the ZX135US-7, ZX245USLC-7 and the ZX345USLC-7.
The Hitachi ZX135US-7 excavator weighs 14,500 kg and has a 5.98-metre maximum dig depth and a bucket breakout force of 23,380 pounds. The 25,700-kg Hitachi ZX245USLC-7 excavator features a maximum dig depth of 6.61 metres and a bucket breakout force of 35,520 pounds. As the largest of the three ultrashort tail swing excavators, the ZX345USLC-7 excavator has a 34,900-kg operating weight, a maximum dig depth of 7.57 metres and a bucket breakout force of 45,411 pounds.
Hitachi hydraulics
Hydraulic system efficiency on the ZAXIS-7 excavators allows optimized performance while reducing fuel consumption. Each Dash 7 model uses a hydraulics solution to best match its size and application. For instance, the ZX135US-7 includes HIOS IV technology that ensures a responsive boom, arm and bucket. The ZX245USLC-7 uses next-generation TRIAS III technology that provides quick response to all control inputs while minimizing losses in the system.
The ZX345USLC-7 relies on proven TRIAS II technology that ensures efficient use of available power.
The ZX245USLC-7 features a new arm roll-in metering
control valve that allows a reduction in hydraulic pump power when the arm is operated with a low load. When digging, the roll-in metering control valve reduces hydraulic pressure loss to the tank. This decreases the pump power required for digging operations, improving fuel efficiency.
The ZX245USLC-7 and ZX345USLC-7 allow adjustment of attachment or arm priority on the monitor to match the attachment or the operator’s preference. When the attachment and arm are operated at the same time, the operator can adjust whether the speed of the attachment or the arm should be prioritized.
As well the operator can adjust boom raise priority
using the monitor. This can tailor the machine for everything from truck loading to heavy digging.
Isuzu engines
Isuzu engines power all three machines, producing 100 hp for the ZX135US-7, 164 hp for the ZX245USLC-7 and 249 hp for the ZX345USLC-7. Economy, power and high-performance modes match available power to the working conditions, while an auto idle system with auto shut-down control prevents wasted fuel.
Hitachi has equipped the three excavators with a larger cab with increased head clearance. A one-touch adjustable air suspension seat is synchronized to move with the console. As well, noise has been minimized by increasing the thickness of the rear glass. Improved airtightness of the cab keeps the dust out, even when the air conditioner is started.
A 20-cm anti-glare LCD monitor provides visibility, even in bright surroundings, while LED lights provide visibility in challenging conditions.
For operator convenience, switches have been collectively installed on the right side with easy access to those frequently used.
For panoramic visibility, Hitachi created its Aerial Angle peripheral vision camera system. It provides a 270-degree bird’s-eye view of the machine’s immediate environment. The operator can select a view on the monitor quickly and easily that best suits the situation. A rear-view camera allows the operator to see the area right below the counterweight.
The ZAXIS-7 excavators feature enhancements on critical components such as
the undercarriage and boom. On the undercarriage, the lower roller design helps prevent mud compaction, protecting oil seals. The upper and lower rollers also feature improved idler sealing.
Hitachi also strengthened the boom end and boom foot with bushings installed in the brackets.
Design enhancements help protect critical components from the environment. An inner element of the engine air filter protects the engine from dust while cleaning the outer element. Even the air conditioner is protected with an internal filter with a seal that prevents dust from entering the AC unit.
The ConSite full data toolkit, which remotely monitors operational status and alerts owners and operators to upcoming maintenance needs, is making a leap forward.
“ConSite now actively checks engine and hydraulic oil, along with other parameters, so operators can see a problem before its even a fault code. This increases customer uptime,” Baker said.
ConSite OIL is standard on the ZX245USLC-7 and ZX345USLC-7 and an option on the ZX135US-7. It monitors engine and hydraulic oil conditions to proactively catch issues before any fault codes are triggered in the machine. This helps drive uptime by catching oil degradation before damage to critical systems can occur. This allows operators to focus on the work that needs to be done.
ConSite Air allows the excavator to be diagnosed remotely, as well as remote updates of the software.
Not only is JCB the world’s biggest backhoe manufacturer, but we also sell as many backhoes around the globe as all other manufacturers combined. It’s not that big makes us better. Rather, we’re big because we’re better. Buy better at JCB.com.
ALBERTA
Liftboss JCB
Calgary: 403-301-0041
Edmonton: 780-474-9900 liftboss.ca
BRITISH COLUMBIA
Williams JCB
NEW!
NEW BRUNSWICK
A.L.P.A. Equipment
Edmundston : 506-735-4144
Balmoral : 506-826-2717
Fredericton : 506-452-9818
Moncton, N.B. : 506-861-2572
alpaequipment.com
NOVA SCOTIA
A.L.P.A. Equipment
Truro : (902) 897-2717 alpaequipment.com
NEWFOUNDLAND
Harvey JCB
Corner Brook: 709-639-2960 St. Johns: 709-738-8911 harveyco.ca
ONTARIO
Advance JCB
Waterloo: 519-742-5878
Harriston: 519-510-5878 advanceequipment.net
D&W Group Inc.
Doughty & Williamson
Jarvis: 519-587-2273
Brant Tractor
Burford: 519-449-2500
Redtrac International
Vineland: 905-562-4136 dwgroup.ca
ONTARIO
Delta JCB
Dunvegan: 613-527-1501
Renfrew: 613-432-4133 Winchester: 613-774-2273 deltapower.ca
Fulline JCB
Glencoe: 519-287-2840 fullinefarm.com
Hub International Equipment Ltd. Lindsay: 705-324-6136 Port Perry: 905-982-1500 hubinter.com
Jade Equipment Simcoe County and Districts of Parry Sound & Muskoka 705-325-2777 jadeequipment.com
John’s Equipment Sales Frankford: 613-398-6522 johnsequipmentsales.com
ONTARIO
Moore JCB
Toronto, York & Peel Region: 416-747-1212 moorejcb.com
North Rock JCB
North Bay, Sault Ste. Marie, and Sudbury: 705-897-7369 northrockrentals.com
ReadyQuip Sales & Service Ltd.
Timmins: 705-268-7600 readyquip.com
WPE Landscape Equipment - JCB
Hamilton/Halton: 905-628-3055 wpeequipment.ca
PEI
A.L.P.A. Equipment (506) 861-2572 alpaequipment.com
QUEBEC
A.L.P.A. Equipment
Bas-Saint-Laurent : (506) 735-4144
Gaspésie : (506) 826-2717 alpaequipment.com
Bossé Quebec Inc.
Desmaures: 418-878-2241 Saint-Augustin-debosse-frere.com
Moore JCB
Montreal: 514-333-1212 moorejcb.com
SASKATCHEWAN & MANITOBA
Westcon JCB
Regina: 306-359-7273
Saskatoon: 306-934-3646
Winnipeg: 204-694-5364 westconjcb.com
Most TRUSTED in the world doesn’t happen by accident.
We have a new name and a vision to build a better world. As we move forward, your local dealer continues to deliver the expert service and innovative equipment you trust.
Authorized Dealers
Alberta Brown’s Industrial Sales
Cold Lake | 780-826-2399
Lloydminster | 780-875-2339
Rentco Equipment
Grande Prairie | 780-538-0791
British Columbia
Rentco Equipment
Fort St. John | 250-785-1197
Westerra Equipment
Abbotsford | 604-850-7313
Kamloops | 250-314-3600
Nanaimo | 250-716-0443
Williams Machinery Prince George | 250-563-0181
Surrey | 604-930-3300
Terrace | 778-721-0398
Manitoba
AgCon Equipment Springfield | 204-255-4772
C&C Rentals Brandon | 204-728-2699
Ontario
Bobcat of Hamilton Ltd. Stoney Creek | 905-643-3177
C G Equipment
Guelph | 519-826-0550 Zurich | 519-236-4934
Eastrock Equipment Inc. Ottawa | 613-737-3963
Elvaan Equipment Solutions
Mississauga | 647-988-9931
G F Preston Sales & Service
Sundridge | 705-384-5368
Hartington Equipment
Hartington | 613-372-2744
ITEC 2000 Equipment
Rosslyn | 807-768-8584
ReadyQuip Sales & Service Ltd.
Timmins | 705-268-7600
New Brunswick
Paul Equipment and Sons
Balmoral | 506-826-3289
Fredericton | 506-449-3289
Northwest Territories
Ron’s Auto Service Ltd.
Yellowknife | 867-766-6025
Nova Scotia
East Coast International Trucks Inc.
Dartmouth | 902-478-3552
Quebec
Équipements Plannord
Beloeil | 450-464-8000
St-Augustin-de-Desmaures | 418-878-4007
Machinerie St. Pierre Val-d’Or | 819-824-6931
Saskatchewan
Bobcat of Regina, Ltd.
Regina | 306-347-7600
Earthworks Equipment Corporation
Saskatoon | 306-931-7880
Yukon
MacPherson Rentals
Whitehorse | 867-633-4426
Caterpillar is launching two new built-fromscratch models of reclaimer/stabilizers: the RM600 and the RM800.
According to Mark Eiden, Cat’s Global Sales Consultant, the introduction gives the brand the widest selection of choices in this equipment category.
“This is the result of a long validation, and of listening to the voice of the customer,” he said, estimating 10,000 hours of validation. The goals of the two new machines include performance, ease of maintenance and operator comfort.
Both models rely on the Cat C18 engine. The 600 features a single turbo and can produce 17 per cent more power than the RM500B, while the 800 has twin turbos and produces 23 per cent more power than the RM600.
By using cool air, the cooling system maximizes fuel efficiency. Reversible cooling fans enhance efficiency, clean the heat exchangers and extend maintenance intervals.
Cutting tools deliver the desired material sizing. A bolt-on paddle toolholder can be configured on the rotor for reclamation ap plications or switched out for a wedge for soil stabilization.
A hydraulically actuated floating rear rotor chamber door allows the operator to select the appropriate down pressure, and the door can be opened if a lot of material is in the chamber.
Automatic load control maintains rotor mixing depth and machine speed to deliver the accurate mix quality.
Depth indicators on the side and the front leg enable a ground person to guide the leading edge of the rotor. The new models can cut 2.4 metres wide and 50 cm deep.
All about the operator
Operator comfort begins with a new cab and easy-to-learn controls with the latest technology. In addition to the user-friendly controls, the cab provides heat and airconditioning as well as optimized sightlines with floor-to-ceiling glass, including an angled pane on the right side that provides a clear view to the leading edge of the cutting chamber.
improves productivity, but also augments safety.
Operators will appreciate the heated air-ride suspension seat with 180-degree positioning. A 25-cm colour touchscreen display positioned in the headliner comes standard, with an auxiliary display near the armrest. To increase visibility even more, configurable front and rear-mounted cameras are standard, with optional side-mounted cameras. Controls are grouped by function, with a mini wheel on the armrest replacing a central steering wheel to clear sightlines.
“The creature comforts are ergonomic for greater productivity,” said Scott Reynolds, CEO of ARS Companies, one of the Cat customers who helped validate the machines during field testing.
Designed for full-depth reclamation and stabilization projects, both Tier 4 Final machines provide stability through frontto-rear weight distribution and constant
slope cutting.
A belt-driven rotor drive system helps handle heavier cuts. The rotors have no pins, fasteners or setscrews to fuss with. Added weight over the rotor improves stability.
Both the RM600 and RM800 include four steering modes (rear-wheel, front-wheel, crab and coordinated) to aid maneuverability, while wheels at each corner permit the machines to make the tightest of turning radii. Electronically controlled all-wheel drive assists traction and mobility.
Dual hookups are located at the front of the machines for a spray system to dispense water and bitumen emulsion. Eiden explained they’re “very accurate at low flow rates.” In addition to having self-cleaning nozzles, they are available in manual or automatic mode, and can be set up for any mix design: by volume, area or by a percentage of soil density.
Maintenance made easy
Cat promises extended service intervals with the RM600 and RM800. For example,
an auto-reversing cooling fan that prevents debris build-up contributes to longer service
When maintenance is required, convenient access points make it easier. A hood opens for walk-in access. Service doors on each side of the rotor chamber allow access for inspection or changing without reaching inside the rotor chamber. Hydraulically powered turning with a control pendant allows the rotor to be cleaned and the bits replaced.
A standard compressed air system that can power pneumatic tools has two access points, which speeds up rotor bit changes. Controls adjust to allow the operator to exit at ground level and raise for bit service. A rear safety switch has lock-out functions to allow work to proceed safely while the engine’s running. An optional high-pressure wash system enables quick cleanup.
Both machines come with built-in diagnostics to monitor performance and provide troubleshooting information for remote diagnosis.
Having acquired the equipment line in the late 1950s, Cat has a “long design history,” that Eiden believes these new models build upon.
Caterpillar is changing the nomenclature of its vibratory soil compactor range to feature weight-based names.
To correlate with the GC models in the compaction product line, all soil compactor models will feature weight-based names derived from the metric tonnage class in which the model competes. As well,
the model series descriptor letter suffix will be removed.
The Caterpillar vibratory soil compactor line includes smooth and padfoot drum designs offering compaction widths ranging from 127 cm to 213 cm. Durable and reliable, the rollers deliver high compaction performance, speed and gradeability to maximize productivity on a range of
soil types and applications.
The updated vibratory soil compactor models include:
Small soil compactors
· The Cat CP34 becomes the Cat CP5
· The Cat CS34 becomes the Cat CS5
· The Cat CP44B becomes the Cat CP7
· The Cat CS44B becomes the Cat CS7
Medium soil compactors
· The Cat CP54B becomes the Cat CP11
· The Cat CS54B becomes the Cat CS11
· The Cat CP56B becomes the Cat CP12
· The Cat CS56B becomes the Cat CS12
· The Cat CP12 GC becomes the Cat CP13 GC
· The Cat CS12 GC becomes the Cat CS13 GC
· The Cat CS66B becomes the Cat CS13
· The Cat CP68B becomes the Cat CP14
· The Cat CS68B becomes the Cat CS14
Large soil compactors
· The Cat CP74B becomes the Cat CP16
· The Cat CS74B becomes the Cat CS16
· The Cat CP76B becomes
the Cat CP17
· The Cat CS76B becomes the Cat CS17
· The Cat CS78B becomes the Cat CS19
· The Cat CS79B becomes the Cat CS20
The Caterpillar CS10 GC, CS11 GC and CP11 GC vibratory soil compactors retain their current nomenclature.
Pictured here in the mid-1930s is a paving crew at work in Southern Ontario.
Self-propelled asphalt pavers were in demand due to the amount of highway expansion in the era. Several equipment manufacturers built asphalt finishers, such as the Jaegar Co. Ltd. machine that was more concrete oriented.
In addition to asphalt spreaders, Jaegar manufactured concrete pavers, mixer trucks, pumps and compressors in their Ohio-based plant. In the 1950s, Jaegar established a plant in St. Thomas, Ontario to service the quickly expanding Canadian equipment market. This paver, powered by a four-cylinder Hercules gas engine, also featured a vibratory screed for initial asphalt mat compaction. The cumbersome looking paver was based on Jaegar’s slip-form concrete paver design as can been seen in the photo.
By the late 1930s, rival Barber-Greene Ltd. had introduced their Model 879. With upgrades, the asphalt finisher would become the predominant asphalt equipment manufacturer well into the 1970s.
Barber-Greene built asphalt plants, ditching machines, conveyor aggregate systems, snow loaders and crushers. Barber-Greene was acquired by Caterpillar in 1991.
The Historical Construction Equipment Association (HCEA Canada) 2023 event ‘Wheels & Tracks in Motion’ will be held on June 10 and 11, while the ‘Last Blast’ event is on October 14. Both events are held at the Simcoe County Museum near Barrie. To see more than 60 pieces of vintage construction equipment in action be sure to attend. HCEA Canada is a proud Heritage Partner of the Simcoe County Museum. Please visit our website hceacanada.org for updates.
Do you know? We are the industry’s specialist for new, used and rebuilt parts for Volvo, Champion and John Deere motor graders; for used reconditioned sales and rentals of motor graders, wheel loaders, excavators and other road equipment; and we carry a vast inventory of used and new attachments for your machines but we’re more than motor graders?
Jade Equipment JCB is proud to be part of the JCB dealer network, serving Simcoe County and the Districts of Muskoka Parry Sound, Ontario.
JCB is the world’s largest privately-owned manufacturer of construction, agricultural and defence equipment. From its North American headquarters in the USA and at other facilities in the United Kingdom, China, India and Brazil, JCB manufactures a range of more than 300 products for customers in 150 countries.
Wille is the most popular machine on the market for the environmental management and maintenance of urban areas.
It is designed to operate through all four seasons. The articulated steering & location of the cabin in the front frame provide the operator with excellent working conditions. Wille attachments include a multi-function bucket, rotary brush, snow blower & rear spreader, leaf collector, lawn mower, pressure washer, collection sweeper & more.
For over thirty years Spaulding has been dedicated to manufacturing the highest level of quality asphalt equipment, including asphalt hot boxes, asphalt recyclers and chassis-mounted hot boxes. The Spaulding Roadsaver hot box, designed to save time and operational money for the end user, is an asphalt recycler and hot box combo ranging in size capacities of 2–4 Ton, that can be trailer mounted or slip-in style.
From its facility located in Springfield, NB, Forax Equipment Ltd. specializes in fabricating high quality brush cutter and mulcher heads, including attachments for road graders, excavators, tractors, skid-steers, UTVs, loaders, backhoes and groomers. Forax is committed to providing quality, efficient, and reliable products, built to meet their highest standards.
Easi-Pour has been the leader in production, speed and quality in the curb and gutter paving industry since 1967. The Easi-Pour was designed and built with ease of operation and efficiency to give decades of dependable and safe service. From nicely equipped base models to an extensive list of optional equipment, we are confident you will find an Easi-Pour to fit your needs.
Family owned since 1946, Craig Manufacturing has a long history of producing custom manufactured solutions for heavy construction equipment. With three locations in Canada and one in the USA, Craig Manufacturing provides extensive support and service to help you get the most out of your heavy construction equipment.
Bomag’s BOMAP Connect provides networked control and documentation of all rollers working on a jobsite, regardless of brand.
All compaction data col -
lected by BOMAP Connect is cloud-based, allowing quick access to compaction documentation from a computer or mobile device anywhere an internet connection is available.
An operator simply activates the BOMAP app from an Android tablet or smartphone from a BOMAG roller, and the app connects with the machine’s interface and
registers its parameters. All compaction passes are then automatically recorded.
If required by job specification, the interface can connect with BOMAG’s Job-
link via Bluetooth, and in addition to roller passes, the system also records asphalt temperature, vibration frequency and amplitude of the Bomag rollers and adds the data to the documentation.
For other roller brands in the fleet connected to the networked jobsite, BOMAP Connect logs and transmits the number of passes, generating a pass map for the entire site.
GPS reception is maximized by equipping rollers with an optional high-precision antenna to further increase documentation accuracy, which is especially helpful when working in urban areas or in poor weather conditions.
Real-time map display
BOMAP Connect enables all roller operators to achieve optimum compaction in the minimum number of passes. This helps to reduce fuel consumption, lower operating costs and increases roller efficiency.
BOMAP Connect enhances parallel planning of different projects within BOMAP, including construction site planning. Using 3D planning data combined with online map services, the system makes it possible to specify all relevant core project parameters and to plan the construction process in detail.
Project planners can input compaction specification details, such as the number of roller passes or
5-YEAR/5,000 HOUR
Full Machine Warranty
5-YEAR/10,000 HOUR Machine Structures Warranty
•10% cycle time improvement to get your work done quicker.
•5
% better fuel consumption without a Diesel Particulate Filter (DPF) to maintain or replace.
•X4’s all new hydraulic system features electronically controlled pumps that take hydraulic efficiency to the next level.
•Isuzu engine that utilizes a cooled EGR system with minimal maintenance in mind and with minimal
DEF consumption.
•Cab designed for shift-long comfort.
•Equipped with
RemoteCARE® (GPS fleet management system). Free lifetime coverage to original owner.
•WAVES (Wide-Angle Visual Enhancement System) option for a 230° visual.
•X4’s have a beefed up undercarriage.
ALBERTA
Equipment Sales & Service Ltd
Edmonton (780) 440-4010 essltd.com
BRITISH COLUMBIA
The Inland Group
Burnaby, BC 604-291-6431
Campbell River, BC 250-287-8878
Castlegar, BC 250-365-2807
Cranbrook, BC 250-426-6205
Fort St. John, BC 250-785-6105
Kamloops, BC 250-374-4406
Kelowna, BC 250-769-2933
Langley, BC 604-607-8555
Nanaimo, BC 250-758-5288
Penticton, BC 250-492-3939
Prince George, BC 250-562-8171
Quesnel, BC 250-992-7256
Terrace, BC 250-635-5122
Vernon, BC 250-545-4424
Williams Lake, BC 250-392-7101 inland-group.com
NEW BRUNSWICK
Paul Equipment
Balmoral (506) 826-3289 paulequipment.ca
ONTARIO
Itec 2000
Rosslyn (888) 574-8530
Thunder Bay (888) 574-8530
Timmins (705) 267-0223 itec2000.com
McDowell B Equipment Ltd.
Sudbury (705) 566-8190
Barrie (416) 770-7706 bmcdowell.com
Stratton Equipment Sales & Service Stratton (807) 483-7777 strattonequipment.com
Top Lift Enterprises Inc. Stoney Creek (905) 662-4137
Bolton (905) 857-5200 toplift.com
Équipement JYL Inc.
Chicoutimi (418) 698-6656 equipementjyl.com
QUEBEC Micanic St-Aug-D-Desm (418) 878-2241 micanic.com
Paul Equipment (506)826-3289 paulequipment.ca
Top Lift Enterprises Inc.
St-Laurent (514) 335-2953
Sherbrooke (819) 612-5438 toplift.com
YUKON TERRITORY
The Inland Group
Whitehorse, YT 867-668-2127 inland-group.com
Dynapac has launched the new D17 C commercial paver, the successor to its FC1700 C.
The key enhancements include a direct drive 16kW generator to the engine along with a fail-safe heat management system for increased efficiency and reliability. The newly designed proportional auger conveyor system further increases flexibility to control the material flow to the screed.
With paving width of 2.43 to 4.72 metres, the D17 C is an ideal solution for medium to large parking lots and county roads. As well, optional bolt on extensions allow the paver to tackle widths of up to 5.5 metres.
Dynapac’s product range is built on the principle of “designed to perform and built to last.” The D17 C is built with heavy duty structural components and rebuildable wear components. Thanks to bolted conveyor floor plates, segmented auger flights and screed plates, all wear parts are designed for easy replacement and they are rebuildable time and time again.
Unique feed system
When digging is on your to-do list, Wacker Neuson is ready for action. From excavators with bestin-class breakout force to powerful skid steers and compact track loaders, and even a groundengaging telehandler, we have the equipment you need to really dig into the task at hand.
The D17 C’s screed heating delivers next level technology for commercial class pavers. A newly designed direct drive 3 phase 16 kw engine mounted generator increasing the efficiency and reducing the heat up time. The heating system includes multi zone heat monitoring for even temperatures across the entire width of the screed. The reliability of the heat control system is further enhanced by having redundant sensors combined with smart fail-safe heat management technology.
The screed features include auto screed temperature control, hydraulic crown, hydraulic sloping extensions, hydraulic match height and a heated end gate.
The tractor features include hydraulic auto track tension, hydraulic tow points and an automatic proportional feed system.
www.hoodequipmentcompany.net
Dynapac’s quad auger system is a unique design that includes screed mounted augers on both main and extensions. This allows the material to feed with a smoother process for pavement width of 2.43 to 4.72 metres without requiring excess manual work to get the material to the wider paving widths.
The independent conveyor system, along with reversible conveyor capability, allows for easy operation while paving and eliminating material spill on to the ground when transporting the paver between jobsites.
The proportional feed system offers precise control of the head of material in front the screed. Operators can personalize various material pile height settings from the display and simplify the paving process.
The Dynapac D17 C paver is paired with the VF0816 front extension screed for high quality paving results. Weighing 2,041 kg, the VF0816 screed is the heaviest in its class delivering impressive pre-compaction.
The Dynapac D17 C paver is designed for simplicity in operation. The dual consoles deliver all required functions for both tractor and screed. As well, the two-operator set up is standard and customers can select a three-operator road crew kit, which will include a raised operator platform and screed remotes. The layout of the console is based on the frequency of use and functionality enables experienced or new operators to easily adapt and perform.
The paver provides all the necessary premium functions as standard to reduce overall investment and increase the readiness to tackle demanding job site needs.
The D17 C paver features extra reserve power to tackle demanding job site conditions. On the power pack side, there is up to 20 per cent more power available thanks to a 120 hp engine. With 35-cm track pads, the tractive effort is increase by an additional 20 per cent as well.
Pushing a truck on a steep hill on a housing project or emptying a large truck quickly to complete the paving job on a county road is easily achieved with the extra reserve capacity.
Wirtgen Group machines have helped rebuild the Formula 1 Circuit de Spa-Francorchamps racetrack in Belgium.
The rehabilitation of the Formula 1 racetrack posed distinct challenges, as the track has been in existence for more than a century and includes everyday roads.
Dromo Circuit Design delivered the project. The company’s CEO Jarno Zaffelli emphasized the difficulty of the rehabilitation task due to the undulating nature of the circuit.
“For years, we have been working with contractors who use Wirtgen Group machinery. We know the machines very well and are familiar with what they deliver in terms of quality and reliability,” explains Zaffelli.
The Formula 1 track includes extreme sections featuring gradients of 20 per cent, such as the legendary combination of the Eau Rouge and Raidillon corners. The hairpin bend known as “La Source” is also often saturated with spring water. To ensure driver safety on the Circuit de Spa-Francorchamps, extremely stringent conditions in terms of evenness and grip were applied to the asphalt surface course.
Belgian contractor Bodarwé was hired to complete the asphalt paving for the Formula 1 racetrack. While the variations in level around the winding track present a challenge to Formula 1 drivers, the paving team faced similar difficulties.
The project was to pave a new surface course on a section extending to 505 metres from the Eau Rouge valley
up to the famous Formula 1 corner at Raidillon.
Another 206-metre section was to be paved in the T9Car Formula 1 corner to the north, as well as 701 metres for the new T8Moto and T9Moto motorcycle race corners. Paving had to proceed nonstop, at a rate of between 3 and 4 metres per minute. The temperature of the asphalt material was set at 180 C to maintain a sufficiently large compaction window. A further requirement was for the temperature of the paved surface course to be monitored and documented continuously.
The composition of the material plays a key role in the quality of a Formula 1 track surface. The formula, in this case code-named "Le Noir," was developed by Dromo for Spa-Francorchamps in accordance with the regulations of the Fédération Internationale de l'Automobile (FIA). This formula is a well-kept secret.
The material was mixed in a Benninghoven TBA 4000 asphalt mixing plant belonging to Bordarwé.
Once the surface course in the relevant sections had been removed by a Wirtgen W 220i cold milling machine complete with Level Pro Active milling depth regulator and 3D controller, three Vögele Super 1800-3i machines were deployed. The task was to pave three 4.1 to 4.3 metre strips without joints using the tried-and-tested hot-to-hot method.
The three pavers were each equipped with an AB 500 TV Extending Screed and a Big MultiPlex Ski to ensure maximum longitudinal evenness.
Three multi-cell sonic sensors were fitted to the variable carriers of the Big MultiPlex Ski, each scanning the binder course/the adjacent surface course and ensuring precision paving.
Machines and people worked together to ensure the highest standards on the legendary racetrack in Belgium’s Ardennes mountains.
The demands of the project were intense, but operators used the machinery and technology to overcome every challenge they faced.
Ontario doesn’t require two levels of government to complete Environment Assessments (EA) when it comes to roadbuilding, according to Premier Doug Ford.
At the recent Ontario Good Roads Association conference, Ford explained a single EA would streamline construction.
“Nothing drives me more crazy than when there's duplication of government, no matter if its federal, municipal or provincial,” Ford said. “We need to get shovels in the ground. We need to start building those roads.”
The premier used the proposed Highway 413 as an example of duplicating government process. In 2021, the federal government announced it would conduct its own EA following criticism from environmental advocates.
“The Environmental Assessments in Ontario are second to none, anywhere in the world,” Ford said. “We don't need the federal government to do an EA on top of our EA.”
Highway 413 would span 52 km, and extend from Highway 400 (between Kirby Road and King-Vaughan Road) in the east to the Highway 401 and 407 interchange in the west. The 413 will connect York, Peel and Halton regions upon completion. The project also includes a 4 km extension to Highway 410 and a 3 km extension to Highway 427 for a total of 59 km for the corridor.
“With all the people coming down the 400, you see how jammed it is,” Ford said, stressing the need to build 413.
Ford noted the 2023 budget confirms the government’s commitment to building new roads, as well as expanding or maintaining existing infrastructure. The budget will invest $184 billion in the next decade for infrastructure, including nearly $28 billion dedicated to roadbuilding.
“When we say we're talking about building roads and building transit and building schools, we are building it for tomorrow. We're building it for the next 50 years,” Ford said. “Our plan to build includes the most ambitious capital plan in Ontario's history.”
Alongside Highway 413, Ontario is building the Bradford Bypass, the new Highway 7 between Kitchener and Guelph and widening Highway 3 in Southwestern Ontario.
“And there's a whole list of other projects we're doing but I'd be here until tomorrow if I tell you all 600 of them,” Ford said.
Through the Ontario Community Infra -
structure Fund, the province will spend $400 million this year to repair critical infrastructure in 425 small, rural and northern communities.
As well, the province will build an all-season roadway connecting First Nations communities around the Ring of Fire.
“It’s not only to support development, but also improve access to everyday essentials that we take for granted,” Ford said. “We're getting shovels in the ground, from Thunder Bay to Kitchener to Windsor and everywhere in between.”
The province also aims to build roads faster by improving procurement strategies, make use of new technologies and enhance the Ontario One Call system.
“Let's work together to build a stronger Ontario,” Ford said.
“Let's work together to build and improve our roads and highways and keep people and goods moving.”
For the North American market, Hamm has developed the HP 100i articulated pneumatic-tire roller based on the HD+ series.
The new pneumatic-tire roller was designed primarily for the chipseal process. With five wheels on the front axle and four wheels on the rear axle, the machine meets the requirements of relevant jobsites.
The working width is 1.7 metres, and the generous overlapping of the tire tracks ensures consistent compaction. The roller is driven by a 55.4 kW Deutz engine.
To match the application, the HP 100i is offered with 6 tonne, 8 tonne or 10 tonne operating weights. Weight is adjusted using ballast kits that use individual modules that may be attached or detached as needed. Furthermore, the 700-litre capacity water tank can be used for ballasting. As an option, the roller can be equipped with a water-sprinkling system, scrapers for the tires, thermal aprons and the HTM (Hamm Temperature Meter).
Cab or platform
Hamm offers the pneumatic-tire roller with open operator's platform, including ROPS, with protective roof or with a ROPS cab.
Depending on the configuration, cup holders, heating and air-conditioning system, as well as a 12 V power socket, are standard equipment.
The seat height, tilt and the degree of hardness of the suspension are adjustable. The tilt and height of the armrests can also be adjusted at any time. Options such as a comfort exit with tiltable steering column, a backrest extension, seat belt monitoring device, an additional driving lever and comfort armrests on the left and right, as well as a radio,
round off the operator comfort features. Operation is simple and easy to understand even without language skills.
For optimum visibility, the seat operating unit can be rotated 90 degrees to the left and right.
In addition, the seat position offers a good view of the tire edges from the cab.
For the cab version, a camera for monitoring the rear space is available as an option.
For operation on public roads, Hamm offers a lighting package that is adapted to national specifications. As well, the roller can be supplemented with four-way work spotlights, available as halogen lights or as highpower LEDs, and by LED tire lighting.
The working speed of the roller can be increased up to 19 km per hour, while an intelligent travel control system supports smooth and precise reversing behind the paver. Anti-slip control (ASC) is also available as an option for improved traction on rough terrain.
Thanks to a steering angle sensor and the associated speed control, the speed is automatically reduced during fast cornering, adding an additional layer of safety. The operator can then conveniently return to the preset speed at any time via a rocker switch on the driving lever.
The Hammtronic machine control system also guarantees energy efficiency in the on-board load management. It reduces the engine speeds in such a way that maximum power is always called up while fuel consumption remains low. The optionally available engine stop system, which automatically shuts down the engine during prolonged
inactivity, also ensures low fuel consumption and low operating hours.
For maintenance, all ser-
vice points are quickly and easily accessible. The scrapers on the pneumatic tires are also easy to change.
Hamm has developed an innovative solution for changing the center tire. The tire can be quickly re -
does
Terex
2023
The unique skill sets of Canada’s mining industry may someday help propel space exploration beyond the Earth’s moon.
Recently, the Sudbury, Ontario-based Centre for Excellence in Mining Innovation (CEMI) hosted a webinar to explain the opportunity and challenges in extracting resources on the moon.
“Mining and mineral resource exploration and taking advantage of resources on the moon is going to happen for sure in the very short term,” said Chamirai Nyabeze, Vice President of Business Development and Commercialization at CEMI.
Artemis Accords
In 2020, Canada signed the Artemis Accords, a set of principles for cooperation in deep space exploration, including In-Situ Resource Utilization (ISRU) activities. As part of the Artemis II mission, Canadian astronaut Jeremy Hansen will join a crewed lunar fly-by mission in late 2024.
The following year, the Artemis III mission will land astronauts on the moon as part of an initial plan to eventually establish an Artemis Base Camp on the lunar surface.
“ISRU is really expected to use local resources to extend those missions and it will also reduce the cost of the missions by reducing the need for resupply from Earth,” said Mathieu Giguère, Planning Analyst with the Canadian Space Agency.
Water extraction
The prevalent plan is to extract water from the fine dust deposits found in the moon’s north and south poles and separate it into hydrogen and oxygen.
The hydrogen would be used as fuel to allow space travel beyond the moon, while the oxygen would be utilized to sustain life.
At the moon’s north pole alone, an estimated 60 million tonnes of water is available for extraction.
“If we convert all of that water into shuttle
fuel, we could launch a shuttle per day for more than 2,000 years, just with the water that's at the north pole,” said Dale Boucher, ISRU and Space Mining Consultant. “There's a lot of water on the moon. It's not as dry as we thought it would be.”
The process for separating water into hydrogen and oxygen is simple. Known as electrolysis, the process uses DC voltage for the separation.
“I did it as a high school experiment, most of you probably have seen that done. It's a very simple process to crack water into hydrogen and oxygen,” Boucher said.
The challenge lies within the scale of extraction required to produce the required amount of hydrogen as the dust has an average water concentration of about 5 per cent.
“It cannot be done with just one little science experiment,” Boucher said. “It really needs some well thought out process to be able to achieve these results.”
Giguère explained there is potential for mining companies to adapt their current technologies for use in extracting lunar ice.
“There are similarities between terrestrial mining and lunar ISRU,” he said. “Canada's particular expertise in remote and isolated mining supports increased potential for this crossover.”
While mining companies willingness to contribute to the ISRU plan is critical to boosting Canada’s leadership role in space exploration, Giguère explained developing the methods for lunar extraction would also increase mining competitiveness through innovation and create opportunities for new markets and collaboration.
“Those should be words that are very appealing to the mining sector,” he said. “We tend to believe that Canada is well positioned to seize those future opportunities because of its long-standing heritage of its mining industry.”
When talking about the moon’s resources, CEMI CEO Douglas Morrison said he puts the word “mining” in quotes.
“I think it's very unlikely that we're actually going to use the kinds of mining techniques that I'm familiar with,” Morrison said. “We will certainly be using extraction efforts, but the kind of equipment that we use on Earth today is almost certainly not going to be what we use on the moon.”
Temperatures on the moon’s surface is one of several barriers. Depending on location, the moon’s temperature varies from 120C to -250C. Cost is another factor. During the Apollo missions in the 1970s, an astronaut cost about $1 million an hour.
“Unlike some of the movies that we've all seen, we're not sending miners, and we're not sending drillers to go do drilling and extraction techniques,” Morrison said. “As we do know, that is a fantasy. And we shouldn't be at all misled by that fantasy.”
Cost, and a lack of oxygen, also eliminates the potential for diesel equipment as an option.
“We're not going to put a D8 on the moon, it's just too big and it won’t operate. We're not going to put a three-yard scoop or even a one-yard scoop on the moon. It just weighs too much, and the support required to keep it running is just too big,” Boucher said.
Solar is also not an option, as the potential mining sites are in permanently shadowed regions and receive about two days of indirect sunlight per month.
“How do you put megawatts of energy into this kind of operation without solar cells? We haven't figured out if that’s possible,” Boucher said. “But it's kind of the same problem that have here in the mining industry. How do you get a significant concentration of power into something like the Ring of Fire?”
Boucher and Morrison agree the equipment that will be developed for lunar extraction will be small, effective and completely autonomous.
“We need to think about the basic principles of the mining aspect, the geotechnical and the geochemistry, that we understand in the mining industry very well. And how do we start adapting this to work in space?” Boucher said.
Canada’s
sector is brainstorming
MacLean is expanding its elevated work platform lineup with the launch of the ML5 multi-lift.
The newest addition to the MacLean utility vehicle product line was initially designed as a safe and purpose-built alternative to the use of integrated tool carriers in underground operations across Australia.
The purpose-built machine was created for mine services installation and repair work from an elevated work platform with a 6.5 metre working height and
a 4.5 tonne payload. This became the foundation of the ML5’s design, engineered for safety, productivity and versatility. The design principles are relevant to underground mines around the globe and particularly in Australia.
“MacLean product design has always been about safety and productivity, and this new ML5 multi-lift continues in that tradition of solving a specific problem, in a way that engineers the protection of the worker in the real underground
environment, while also enhancing productivity,” said Bryson Lehman, Product Marketing Manager for elevated work platform at MacLean. “‘Safety is our veins, innovation in our DNA,’ isn’t just a slogan, it’s the how and the why of MacLean product development.”
Safety and versatility are embedded in the ML5 design from the ground up.
The slew boom range of motion delivers best-inclass coverage, along with in-basket operator controls
and remote drive.
The boom’s hydraulic and mechanical linkages are also doubled-up for contingency, to increase operator safety. And a quick hitch design allows for easy switch-out between multiple baskets, as well as the use of forks or a jib boom for material handling and general underground construction.
“We’re also excited to launch this new product because of how it complements our elevated work platform product suite - the
SL2 and SL3 scissor lifts, and the LR3 boom lift for high reach and heavy load mine services applications,” said Maarten van Koppen, MacLean’s Vice President of Product Management. “We are now able to offer a range of mine services installation and repair solutions to mines around the world.”
The mining vehicle is now commercially available for mining customers worldwide.
The first unit, a battery electric model, was shipped from the MacLean produc-
tion facility in Collingwood, Ontario, to its eventual destination and deployment in Australia.
“This continues the MacLean tradition of designing mobile equipment solutions for one particular part of the underground mining world, which are then taken around the globe to solve similar problems at different operations. Each mine site is unique, but safety and productivity requirements are universal,” said Jari Tuorila, General Manager, Australasia, for MacLean.
Epiroc has upgraded the Minetruck MT65 S, its highest capacity model for large underground operations.
The 65-tonne mine truck now delivers an 18 per cent increase in productivity compared to the previous model. Via the new updates, Epiroc improved reliability and increased safety for underground operation.
“The close collaboration with our customers has been key during this project development and outcome,” said Daniel Sandström, Global Product Manager for minetrucks at Epiroc’s Underground division.
The new updates on the
Minetruck MT65 S have been verified in the field at Epiroc customer sites, safeguarding the improvements work as intended in real mining applications and environments.
“We are excited to see the new Minetruck MT65 S continuing to support our customers even more in their underground operations,” Sandström said.
One notable improvement for the new Minetruck MT65 S is an increase in travel speed. This has been increased by up to 10 per cent going up the ramp and 18 per cent going downhill. The speed increase is
achieved thanks to the optimized drivetrain and a new software feature that allows the machine to recommend and hold a certain speed depending on conditions.
Reliability has also been addressed in the new update. Several of the machine’s main components have extended life as well as a more protected component location. This provides customers with a reduced lifecycle cost and increased availability of the Minetruck MT65 S.
“We aim to push the mining boundaries even further with the new updated Minetruck MT65 S offering customers smart and effective material haulage solutions," said Martin Wallman, Global Portfolio Manager for Minetruck at Epiroc’s Underground division.
The Minetruck MT65 S is part of the Epiroc Smart series, which makes it prepared for Sixth Sense functionality such as automation and remote control.
The mine truck also features Epiroc’s Rig Control System (RCS), offering data monitoring possibilities for the best underground operations optimization.
Komatsu and Toyota Motor Corporation have announced a joint project to develop an autonomous light vehicle (ALV) for the mining industry.
The ALV aims to improve safety and productivity in mines by running autonomous haul trucks and automated ALVs controlled by Komatsu’s Autonomous Haulage System (AHS).
cept at a customer site by early 2024.
“Minerals and energy resources are essential in our lives and industries. Autonomy offers the opportunity to remove people from harm's way and enhance safety,” explained a joint news release by Toyota and Komatsu. “It can allow our mining customers the ability to continue the hard work of providing critical minerals despite the ongoing challenge of labour shortages in the mining in-
Since the launch of the world's first commercial application of an AHS in 2008, Komatsu has proven the system’s performance in various mine environments and has earned a reputation for safety and productivity.
More than 650 AHS-enabled trucks have been deployed to 22 sites in five countries and have moved a combined 6.2 billion tonnes of material.
Currently, when AHS-enabled haul trucks and manual light vehicles used for maintenance or transport are running on haul roads at the same time, autonomous haul trucks may decrease their speed or stop when passing light vehicles to avoid possible collisions caused by human error. On the other hand, customer demand for improved productivity in mine operations when it comes to autonomous haul truck operating efficiency remains an issue.
Considering those circumstances and to quickly solve those issues, the Komatsu and Toyota partnership aims to accelerate autonomy in mines. Komatsu will develop a new management program for ALVs on its AHS supervisory system, and Toyota will develop ALVs running automatically under AHS
By operating Komatsu's autonomous haul trucks and Toyota's ALVs in mine sites utilizing a common AHS, the following safety and productivity improvements will be realized across the mining operation:
Safe operation of ALVs on haul roads
· Prevent accidental contact caused by drivers
· Minimize speed reductions or brief stops of autonomous haul trucks
As well, Toyota's ALV autonomous operation accelerates further improvements and adds functions that contribute to safety and productivity. For example, the ALV enables autonomous transfer of parts for other mining equipment working in the field. As well, the vehicle will allow autonomous transfer of equipment operators for other machines such as loading equipment or dozers.
Komatsu mining customers were given a sneak peek of the ALV at the recent Automation Global User Forum at the company’s Arizona Proving Grounds in Tucson, Arizona.
With an emphasis on Komatsu’s interoperability strategy, the event highlighted the company’s equipment automation and system technology roadmaps. As well, customers presented case studies illustrating the high value autonomous haulage has delivered to their mining operations and their potential paths to an automated mine site.
The event was attended by customers representing more than 20 mine sites around the world, including mines focused on the production of copper, iron ore, metallurgical coal and oil sands.
"Interoperability is the cornerstone of our mining automation strategy,” said Martin Cavassa, Manager of Automation Business Development for Komatsu.
"This forum was an excellent opportunity to showcase our developments in automation as well as what we envision for the future of mining.”
Komatsu’s concept for the automated mine of the future includes a range of options from teleoperation and tasklevel automation to a fully autonomous mine, including automation of loading, hauling, drilling, dozing, grading and watering.
Caterpillar has developed its first diesel electric underground load-haul-dump (LHD) loader.
The new Cat R2900 XE LHD meets the underground mining industry’s needs for bigger payloads, faster loading and reduced emissions. Built on the platform of Caterpillar’s most popular underground loader, the R2900 XE features an optimized lift arm and component geometry as well as load-sensing hydraulics to improve breakout force by 35 per cent, compared to the Cat R2900G.
The R2900 XE delivers 52 per cent faster acceleration and improved machine response compared to the R2900G. The LHD accelerates from 0 to 24 km/h in 6.4 seconds and achieves a 7 per cent higher speed on grade.
Variable piston pumps deliver higher flow rates for faster hydraulic cylinder cycle times and powerful lift forces. Boasting an 18.5-tonne payload for faster load times, the new LHD model offers a three to four-pass match to the Cat AD63 truck. Combined, these features deliver a 20 per cent increase in productivity for the R2900 XE.
The loader’s redesigned buckets are available in four sizes with capacities ranging from 7.4 to 9.8 cubic metres. Offering an optimized balance between productivity and bucket life, the full range of Cat ground engaging tools includes modular weld-on, bolt-on half Aarrow and Durilock mechanically attached shrouds. To further protect the bucket, a range of heel shrouds, wear plates and bars are available in weldon or mechanically attached designs.
The R2900 XE is powered by the Cat C15 engine, which offers a variety of emission reduction and aftertreatment options, including Stage V and EPA Tier 4 Final configuration and diesel particulate filter. It delivers up to 449 hp with a 31 per cent increase in fuel efficiency. Its lower engine rpm results in reduced fuel burn, heat, noise, vibration and exhaust emissions, while offering an increase in power and productivity.
The new R2900 XE LHD features a proven switch reluctance electric drive system designed by Caterpillar. Its continuously variable speed control delivers improved power and cycle times. With no driveline or powertrain shock loads, it offers smoother directional changing and implemented virtual gears for machine controllability. As well, the drive system prevents coasting in neutral and combines with the anti-rollback feature to further increase operating safety.
Its new axle design offers increased component size, and together with the fourgear planetary final drive groups, provides greater strength and longer life.
Larger wheel bearings and increased brake sizing further increase final drive life.
Built to withstand the forces of high torque and impact loads, the differentials and final drives provide high torque multiplication to reduce drivetrain stress.
The traction control system reduces tire spin in difficult underfoot conditions to improve productivity, increase
tire life and reduce consumable costs.
Next-gen
The next-generation operator environment is built on the successful R1700 platform. The cab’s enclosed design provides fresh, pressurized, temperature-controlled air circulation. Mounted to the frame, the ROPS/FOPS structures isolate the operator from vibration for a more comfortable ride.
Combining selection of direction, virtual gears and steering into a single lever, standard STIC steering and transmission integrated control delivers maximum responsiveness and machine control. Low-effort, electric-over-hydraulic joystick controls feature simultaneous lift and tilt functions to optimize operating efficiency.
The new R2900 XE ships from the factory ready for Cat MineStar solutions, the industry’s most comprehensive suite of technology. From machine health monitoring to fully automated haul and dump cycles, scalable levels of technologies can
be tailored to meet each mine’s requirements. Standard Product Link Elite boosts machine connectivity by enabling the loader to collect and transmit health and condition monitoring information into locally or cloud-hosted applications. Mines can also select a range of available MineStar technologies, including:
· Command for underground: enables remote operation of LHD machines, from line-of-sight to full autonomy.
· Detect for underground: uses peer-to-peer proximity detection to reduce the risk of unintended interactions between people and machines by “seeing” in the dark.
· Fleet for underground: gives real-time access to accurate informa -
tion such as cycle time, payload and machine position, and automatically tracks and records data up and down the value chain.
· Health: collects and transmits equipment data necessary for proactive maintenance services and predictive equipment analysis.
Caterpillar’s new Autodig technology optimizes loading by automating crucial parts of the digging cycle. When combined with Command for underground, Autodig offers a true automated machine, providing high-speed auto tramming and full cycle autonomy.
Built for the long haul
With more robust structures, increased powertrain
durability, longer lasting components, improved maintenance and extended service intervals, the new R2900 XE can be maintained in less time, helping to lower cost-perton operation.
The machine’s electric drive reduces the number of moving parts compared to traditional mechanical drive systems. Extended oil change intervals, together with the electric drivetrain, reduces the number of oils used.
As well, sight gauges are visible from ground level to simplify fluid level checks, and all filters are positioned vertically to provide spillfree servicing. Electrical connectors are sealed to lock out dust and moisture, while harnesses are covered for protection.
1.866.488.0878
Transporting large crawler excavators — machines in the 80- to 100-tonne size class — is no easy task. These large machines are built for big challenges, like digging, lifting and loading heavy materials for infrastructure work and stone, sand and other aggregates in quarry production facilities. Often, the excavators have a longarm configuration and heavy attachments for these rugged tasks.
Due to their size, crawler excavators require special handling to be transported from one jobsite to another or from a dealership to a quarry.
Thomas Lee, Director of Product Management at Develon, discusses several ways to improve the transportation process.
1. Know the weight and height of your machine
Before transporting crawler excavators, understand the dimensions and weight of your equipment. Also, consider the attachments you need to haul. Match the transport vehicles, like trailers or heavy haulers, to the equipment, and follow regulations on gross vehicle weight ratings. Remember to account for the weight of the trailer when calculating total weight.
2. Determine the need for permits
If you are transporting oversized machinery, you will likely need a larger trailer with a larger weight rating. Special approval or trans -
portation permits may be needed for oversize loads along your route. The permit may also require you to have escort vehicles that drive with you to alert other drivers of your load on the road.
Plan your transportation route ahead of time. Watch for narrow roads and bridges with weight restrictions. Make sure your trailer and the excavator can pass under bridges and overpasses. Try to pick a route that’s easy to drive. Oversize loads should have proper banners, signs and lights.
3. Follow basic loading procedures
Before loading your crawler excavator and attachments to a trailer, understand basic operating and loading guidelines as outlined in the owner’s manual. Here are a few loading and safety procedures:
· Park the trailer on firm, level ground
· Ensure ramps can handle the weight of the excavator. Add blocking under the ramp for support, if required
· Remove grease, debris or mud from the ramp and equipment that could cause the excavator to slip or slide
· Travel up the ramp with the heaviest end first when loading the excavator on the trailer
· Run the engine at the lowest speed setting. Travel at the slowest speed possible when loading or unloading the excavator
· Distribute the weight of your excavator on the transport vehicle. Improper weight balance increases the pull on the transport vehicle and tire wear “The best way to determine if the load is distributed is to look at the transport vehicle’s suspension and make sure it is balanced,” Lee said.
4. Properly secure your equipment
Secure your crawler excavator according to regulations in a manner that prevents it from tipping or rolling off the trailer while travelling. Your equipment must not be able to shift in a way that affects the stability of the transport vehicle.
Once your crawler excavator is on the trailer or transport vehicle, follow these steps:
· Lower the bucket or attachment to the floor
· Stop the engine and engage the parking brake. Turn the battery disconnect switch to the “off” position
· Lock all doors and covers before transport
· Place chocks, cradles or wedges in front of and behind each track. This will help prevent any rolling or shifting during transport
· Install tie-downs at the front and rear tie-down positions as identified in your owner’s manual
Most manufacturers recommend at least four tie-downs to prevent any
movement. Some transport devices have D-rings, chain slots or built-in strap rails.
“These allow you to easily connect your equipment to the transport vehicle,” Lee said. “Always use the recommended connection points and securements. It will help minimize damage and maximize the effectiveness of transporting your excavator.”
Before hauling your crawler excavator, inspect the tie-down points and tiedown equipment used to secure the machine.
“All pins and connection points should be secure and the hooks still functional,” Lee said.
“If any cracks, stretches or fatigued links are found, remove the tie-down equipment from service. All tie-down equipment should be able to meet or exceed the machine’s weight rating.”
Secure the attachment or accessory to the crawler excavator during transport. If that isn’t possible, secure the attachment with chain straps. Don’t forget about hydraulic attachments. Route the hoses so they are not interfering with the excavator on the trailer.
“Hoses should not be lying underneath the machine, located in the way of a tie-down or connected in a manner where they could become disengaged,” Lee said. “Secure all hydraulic hoses according to the owner’s manual.”
Some heavy equipment manufacturers, including Develon, offer a removable excavator counterweight that can be hydraulically lowered to its own trailer for
easy transport to the jobsite. This option, available on the Develon DX800LC-7 and DX1000LC-7 crawler excavators, may reduce the overall machine weight and
allow owners and transportation companies to use a standard-size trailer to transport their excavator and a second trailer for the counterweight and any
attachments. This can help reduce hauling costs and avoid additional permits. Refer to the owner’s manual for proper counterweight installation and removal.
Once you have loaded and secured your crawler excavator and attachments, make sure that you or the driver can see out of the front and sides of the transport vehicle.
6. Safely unload your excavator & attachments
Once you’ve reached your destination, safely unload your crawler excavator and attachments. Here are a few things to keep in mind:
· Clear the unloading area of large debris and make the ground as even as possible
· Walk around the machine while it’s on the trailer or transport vehicle. Make sure nothing looks out of place
· Free the load, releasing the chains and ties one at a time
· Slowly back your excavator down the ramp
· Complete a final inspection. Check the crawler excavator and attachments to make sure they’re ready to operate at full capacity
Depending on the size of your excavator and transportation requirements, you may need to disassemble the machine before transporting it. Work with your local equipment dealer for the correct procedures to disassemble the machine and reassemble it at your jobsite. Transporting heavy equipment, like crawler excavators and attachments, requires attention and planning. But it doesn’t have to be difficult or unsafe if you follow proper techniques and local transport regulations.
Since 1983 Central Diesel Service has specialized in DEUTZ. In fact, we’re proud to say “Nobody knows Deutz products better,” and we can prove it!
RE-SEAL YOUR ENGINE WITH THE PROPER DEUTZ GASKETS & SEALS!
LIFE INTO YOUR EQUIPMENT WITH
INJECT
Sandvik Mining and Rock Solutions has introduced the new Ranger DX910i, the OEM’s flagship model of the updated Ranger DXi drill rig family.
The Ranger DX910i delivers the largest coverage area, superior hole size range, advanced automation, a versatile range of rock drills as well as completely new and
efficient rock tools.
The Ranger DXi family is known for its drilling coverage area of 55 square metres as well as mobility, simple controls, fuel economy and advanced automation options.
Sandvik’s Ranger drill rigs, paired with their RD900 rock drills, have created a next-generation optimized drilling system.
New drilling system
The RD925 and RD927 are the ideal rock drills for the
most common hole sizes of 89 and 102 mm. The rock drill range is now completed with a new, larger RD930C model with a patented long piston structure.
The long piston generates optimized, long shock waves and expands the hole size range up to 140 mm in hard rock conditions. Previously, this hole size was only possible in soft rock.
Thanks to simultaneous optimization and trialling, the upgraded Ranger DXi drill rigs are now positioned
to harness the full potential of the rock drills.
The newly launched rock tool families, CT55 and CT67, offer up to 20 per cent higher penetration rates.
Their unique curved thread system provides a robust coupling to match the higher drilling power and still maintains low stress levels in critical thread sections.
The results of extensive field trials recorded up to 15 per cent higher productivity, 30 per cent longer tool life and 15 per cent lower fuel
consumption.
The new Ranger DXi family’s faster drilling means higher penetration rates and more drilled metres in each shift without increasing energy consumption. The innovative power pack and compressor pressure management system reduce average fuel consumption by 23 per cent, translating into a significant reduction both in emissions and in the total cost of ownership.
The rig’s productivity is boosted by advanced connectivity features. The Ranger DXi is the first surface drill compatible with My Sandvik Productivity telematics solution, securing equipment efficiency with detailed health and utilization data.
Fleet performance can be monitored through easyto-use dashboards, or by integrating with external systems through an API.
As well, wireless transfer of drilling plans and hole data are included for precision drilling with Sandvik TIM3D navigation system.
In addition, a new Open Drill Interface will allow third party navigation or fleet management systems to work seamlessly with Ranger DXi drills.
Stephen Roy has been appointed President of Mack Trucks and a new member of Volvo Group´s executive board.
Roy will take on his new position as of June 1, and he will succeed Martin Weissburg, who will retire after a long and successful career within the Volvo Group.
Weissburg has served as a member of the Volvo Group executive board for more than a decade and has been leader of Volvo Financial Services, Volvo Construc -
tion Equipment and Mack Trucks. He will now join the Board of Nova Bus.
As a member of the Volvo Group executive board, Roy will report to Volvo Group President and CEO Martin Lundstedt.
Roy began his Volvo Group career in 1996 and currently holds the position of Head of Region North America for Volvo Construction Equipment.
He has served in leadership positions since September 2016 with Volvo
Construction Equipment (VCE). Before joining VCE, Roy had extensive experience with the Volvo Group’s North American truck organization, including serving as President of Mack Trucks North America, and as the executive leader of Uptime, Aftermarket and Soft Products, and Parts Sales and Marketing for Mack and Volvo Trucks North America.
Prior to joining the truck organization, he spent more than 11 years with Volvo and Mack Financial Services in
various positions, including Vice President of Business Development and Vice President of Sales. Before joining the Volvo Group, Roy was responsible for direct sales of leasing services and niche market development for Cargill Leasing Corporation’s Vendor Transportation Group.
Roy earned a Bachelor of Science degree from the University of Georgia, and a Master of Business Administration degree from Wake Forest University. He
Roy
serves on the Board of Directors of the Association of Equipment Manufacturers (AEM), and chairs AEM’s
Construction Equipment sector board. He will be located in Greensboro, North Carolina.
Mecalac North America has hired Amer Ascic as Aftersales Manager and Diana Lacaire as Controller. In their roles, Ascic and Lacaire will help streamline processes both internally and externally at Mecalac.
“As a company, our goal has
always been to inspire a whole new way of working for our customers. That is reflected in the design of our equipment and our approach to service and support,” said Peter Bigwood, General Manager of Mecalac North America.
“Effectively carrying out that vision begins with the Mecalac team. Diana and Amer fit right into this culture. Their experience and enthusiasm for Mecalac, our customers and partners ensure that vision is carried out in every facet of our business.”
Ascic spent more than 20 years working at Caterpillar
dealers in a wide range of positions, providing a broad base of knowledge and understanding of compact equipment and its applications. He also worked as a service manager for a Mecalac dealer in the northeast United States.
In his new role, Ascic’s primary responsibility is providing after-sales support to Mecalac dealers, such as assessing their needs for training, support and other resources.
As Mecalac adds new dealers in 2023, Ascic will be responsible for a smooth onboarding process on the
technical side of the business. Lacaire brings more than 30 years of accounting experience to her new role as controller, offering valuable insight into streamlining internal processes and analyzing business data.
In her previous role, Lacaire oversaw the integration of three companies into one unit, streamlining and standardizing processes and rules. She built on the success by documenting and adding policies and procedures to grow the company and drive efficiency both internally and externally.
RMT Equipment is welcoming Tino Lepore to its team in the role of Service Manager. Lepore has been evolving with the company for more than 12 years.
“Customer experience and satisfaction are very important at RMT Equipment. With this new position, I will focus on these elements, as well as the training of our technicians and the follow-up with our customers,” Lepore said.
He started at RMT as a
Technician and then worked his way up to become Technical Support Manager. He is an expert in RMT products and his background will allow him to be successful in his new role.
“I strongly believe in the development of our employees and Tino is a fine example of this success. Our customers as well as our technicians gain a person with incredible knowledge of our products.
Congratulations Tino for this
new challenge worthy of your skills,” said RMT President Marc-André Lefebvre.
Ridewell Suspensions has announced that its President John E. Millsap will be retiring after 28 years of service.
"Ridewell is an outstanding company, and I could not have asked for a better place to be," said Millsap about his career at Ridewell. "And this company just gets better every day."
Justin Cravens, who is
currently the Vice President of Sales at Ridewell is set to move into the President position upon Millsap’s departure. The leadership change will take place on June 30.
"Justin has been a great asset to Ridewell for over 20 years, and he is well positioned to take this company to the next level," Millsap
said. "With him at the helm, they will enjoy tremendous success."
Ridewell Suspensions manufactures air ride suspensions for the truck, trailer, and bus industries. The company was founded in 1967 by John Raidel and continues to be a family-owned corporation now in its third generation.
Medium-size, top class: the L 526, L 538 and L 546 wheel loaders score top marks across all performance parameters. With the new, optimised Z-bar linkage, Liebherr has opened up unlimited application possibilities aligned to even better productivity. Generation 8 is bigger, tougher and more powerful than its predecessors – but with consistently low fuel consumption. www.liebherr.com