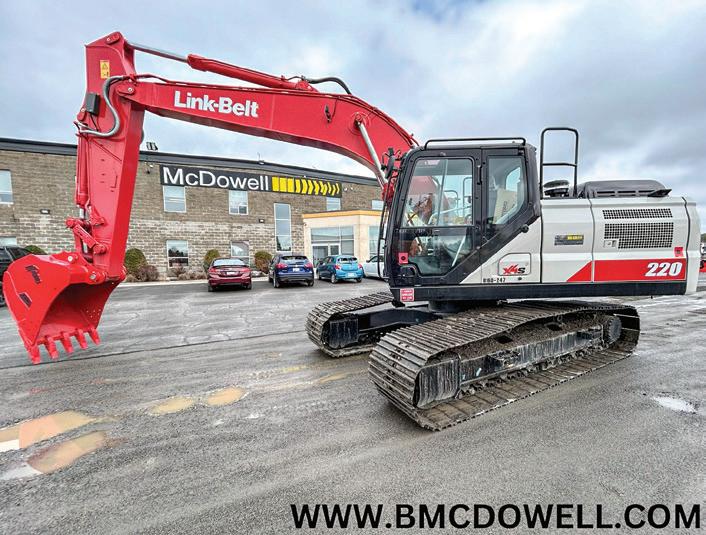
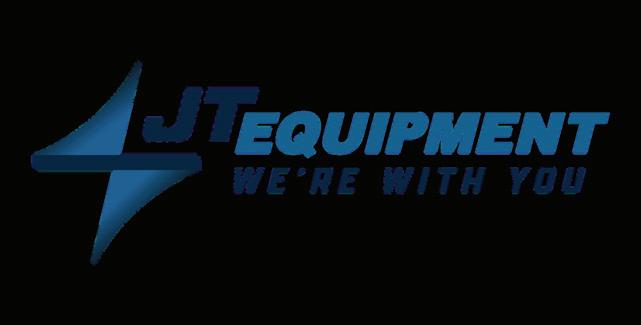
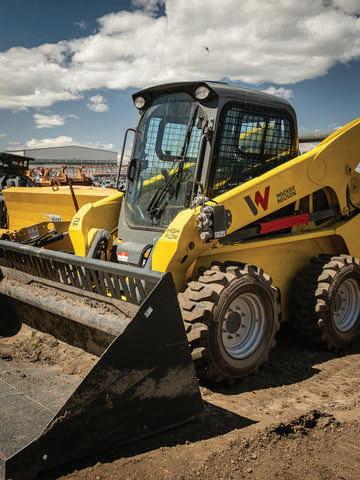
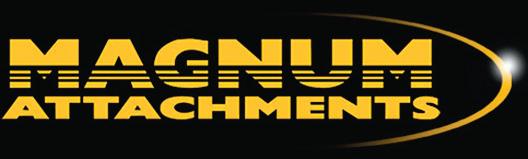

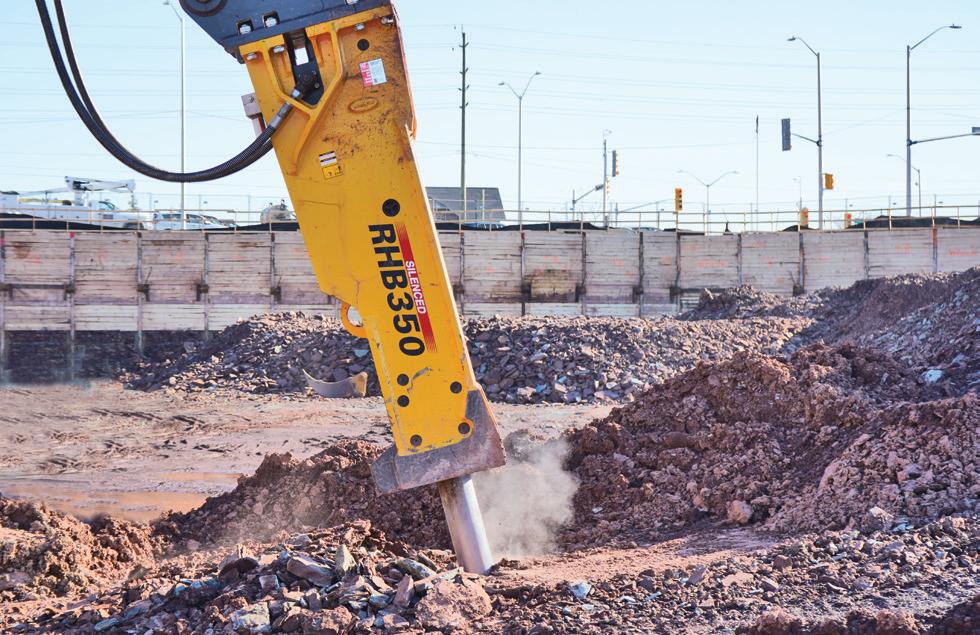
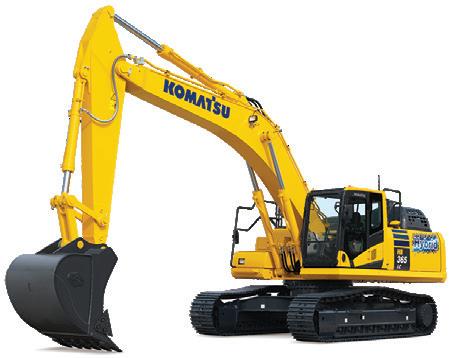
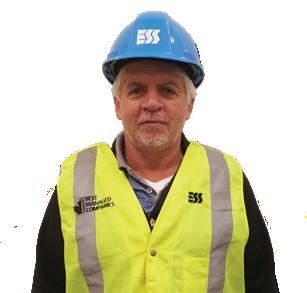
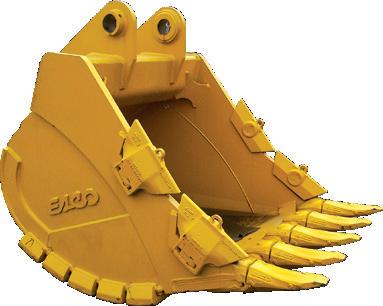
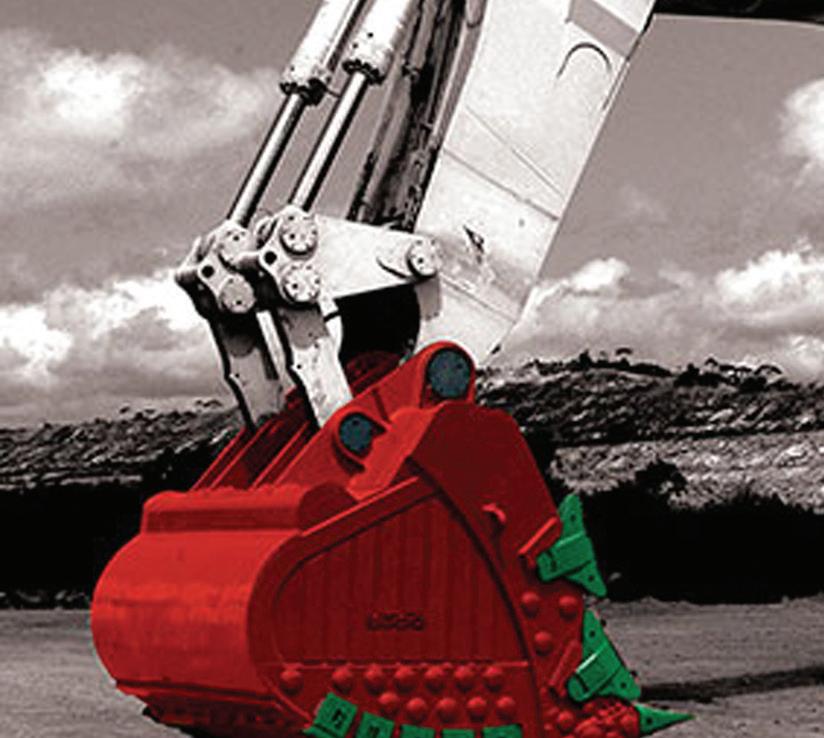
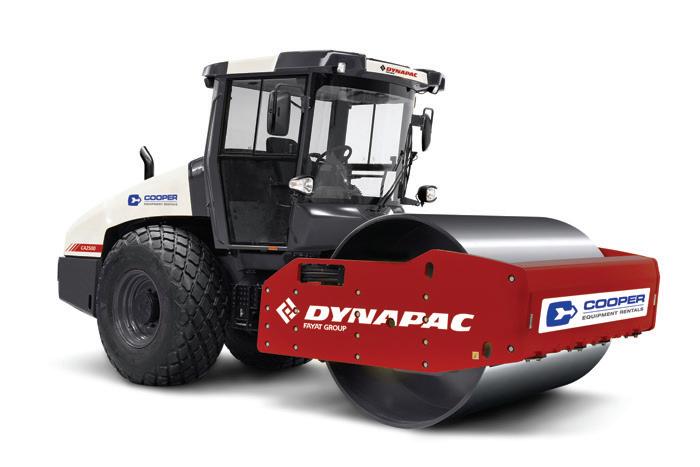
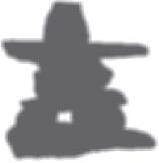
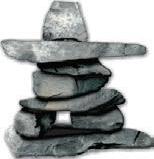
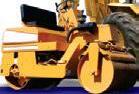
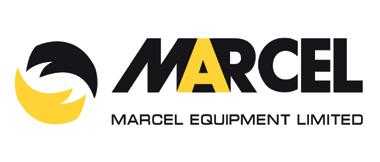

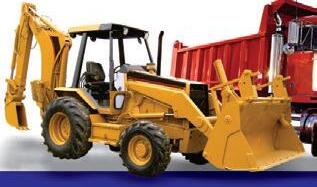
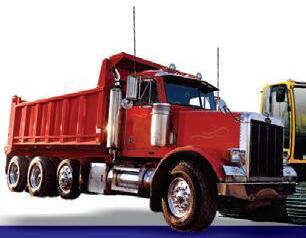
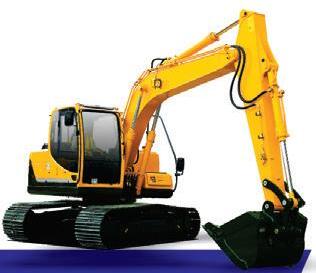
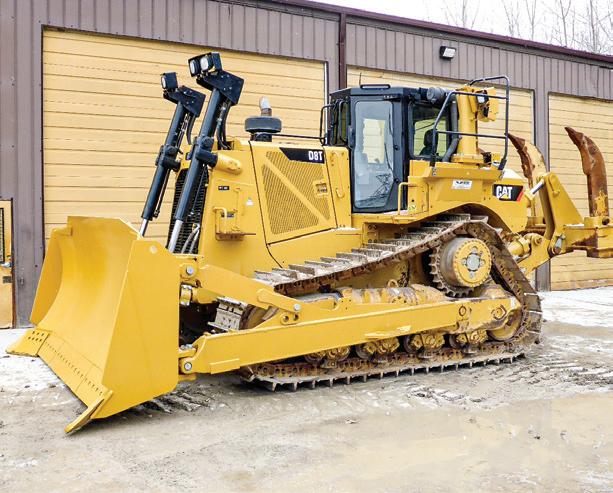
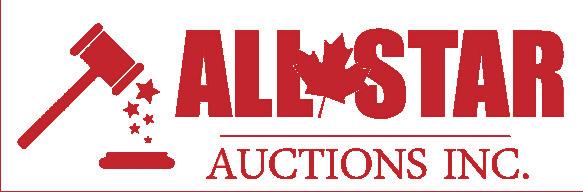
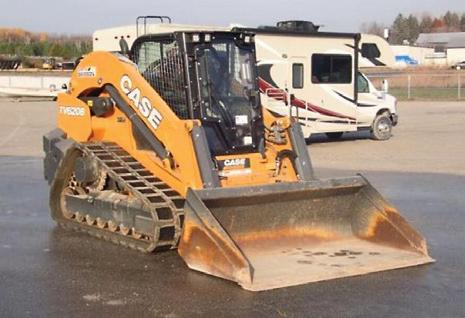
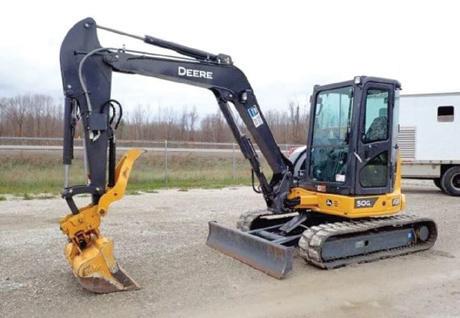
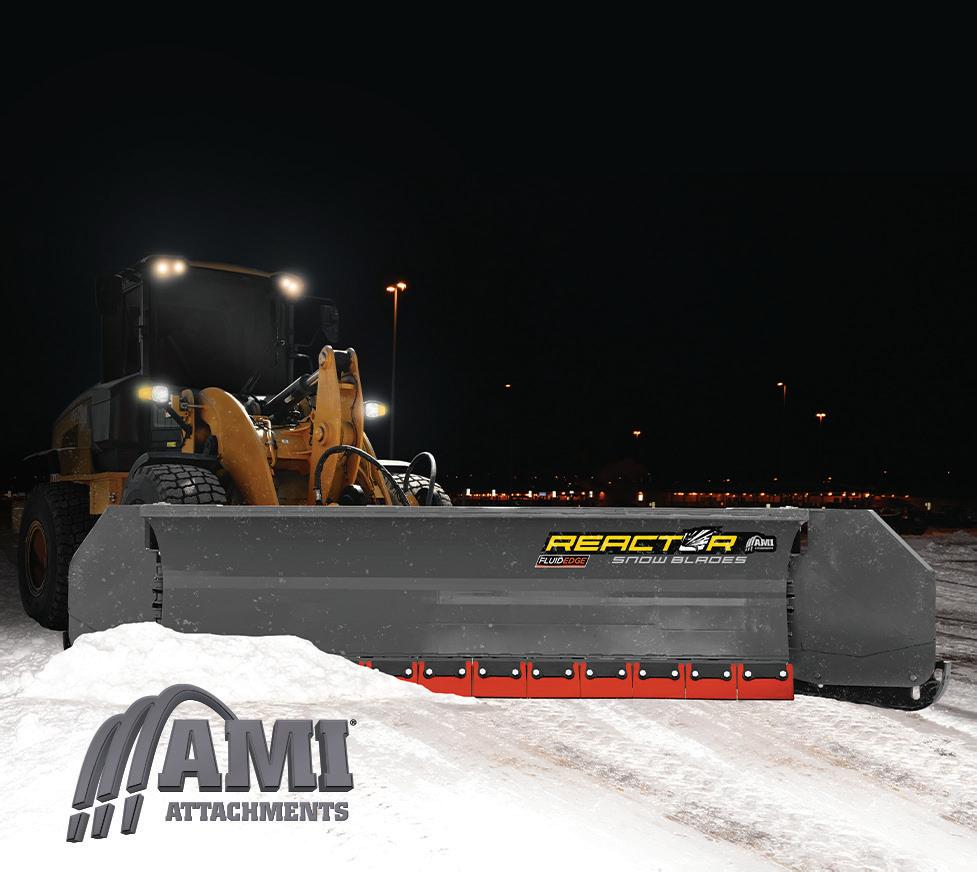
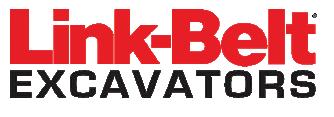
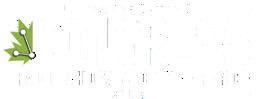
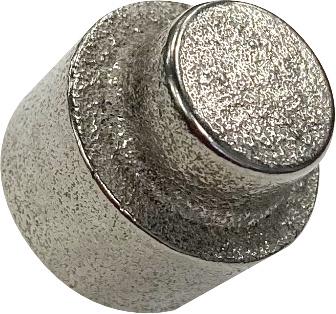
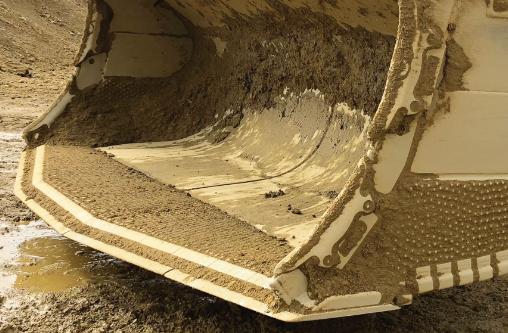
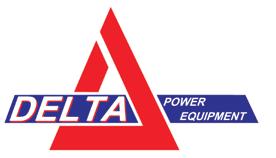
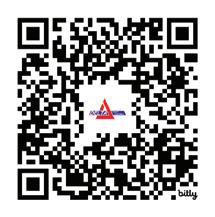
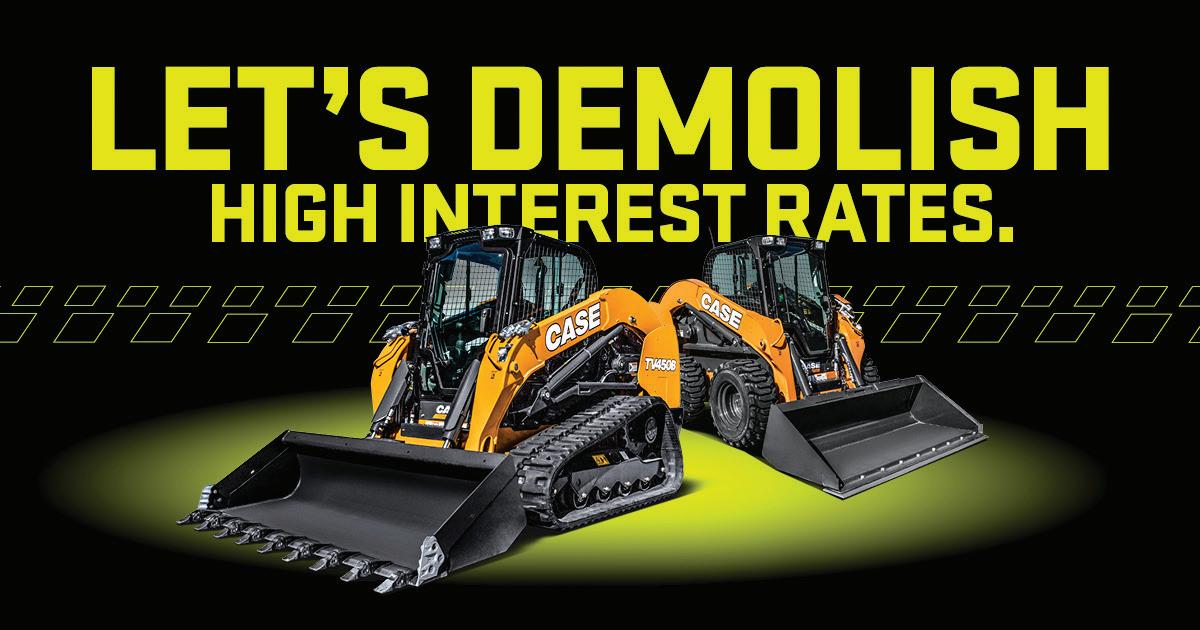
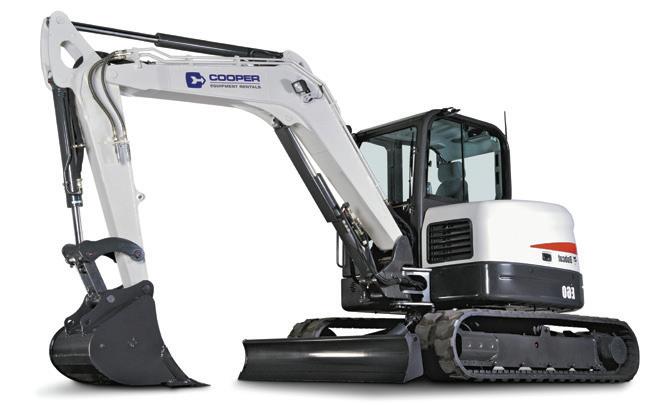
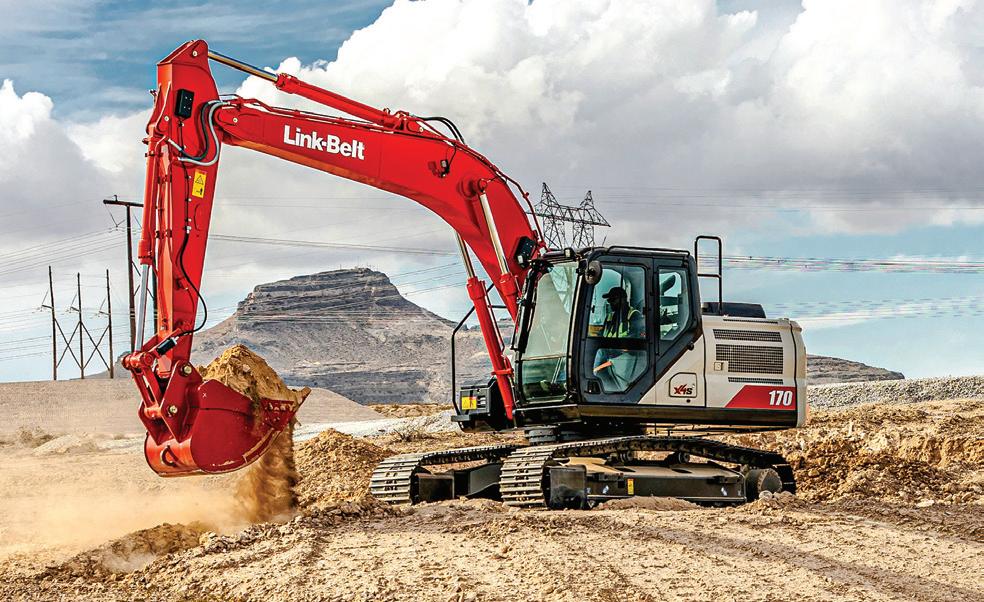
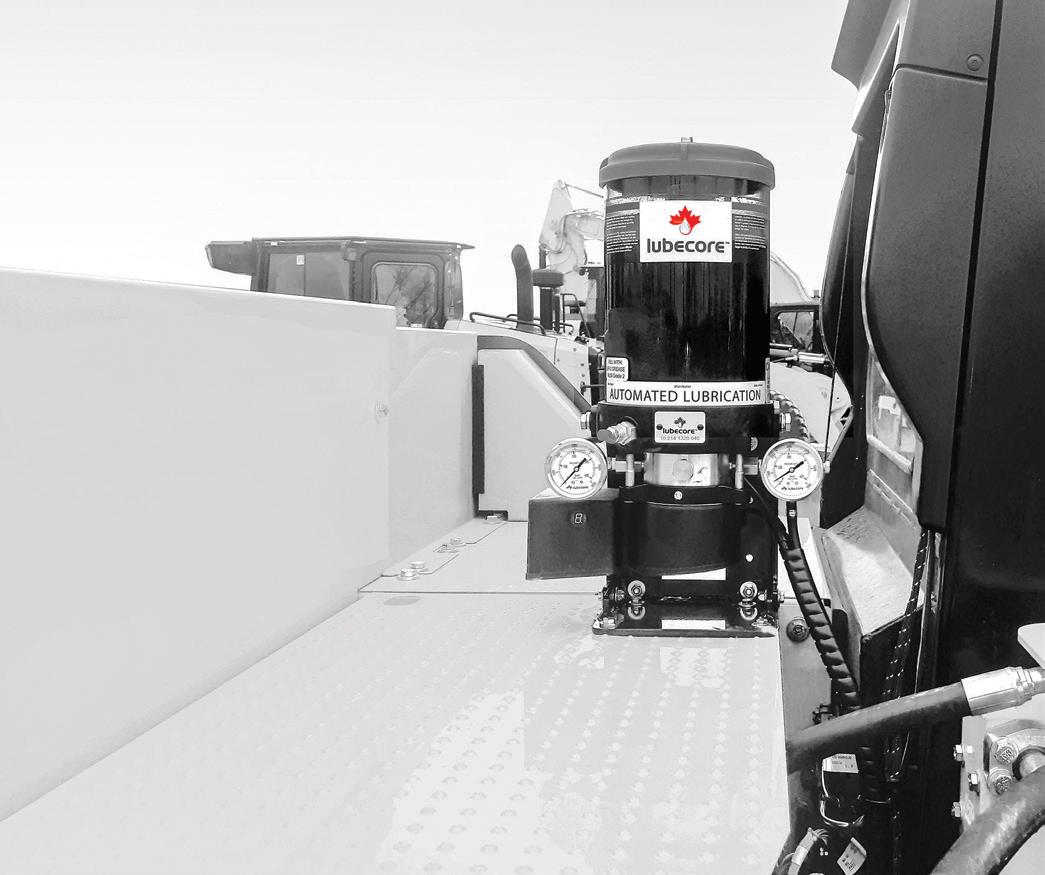
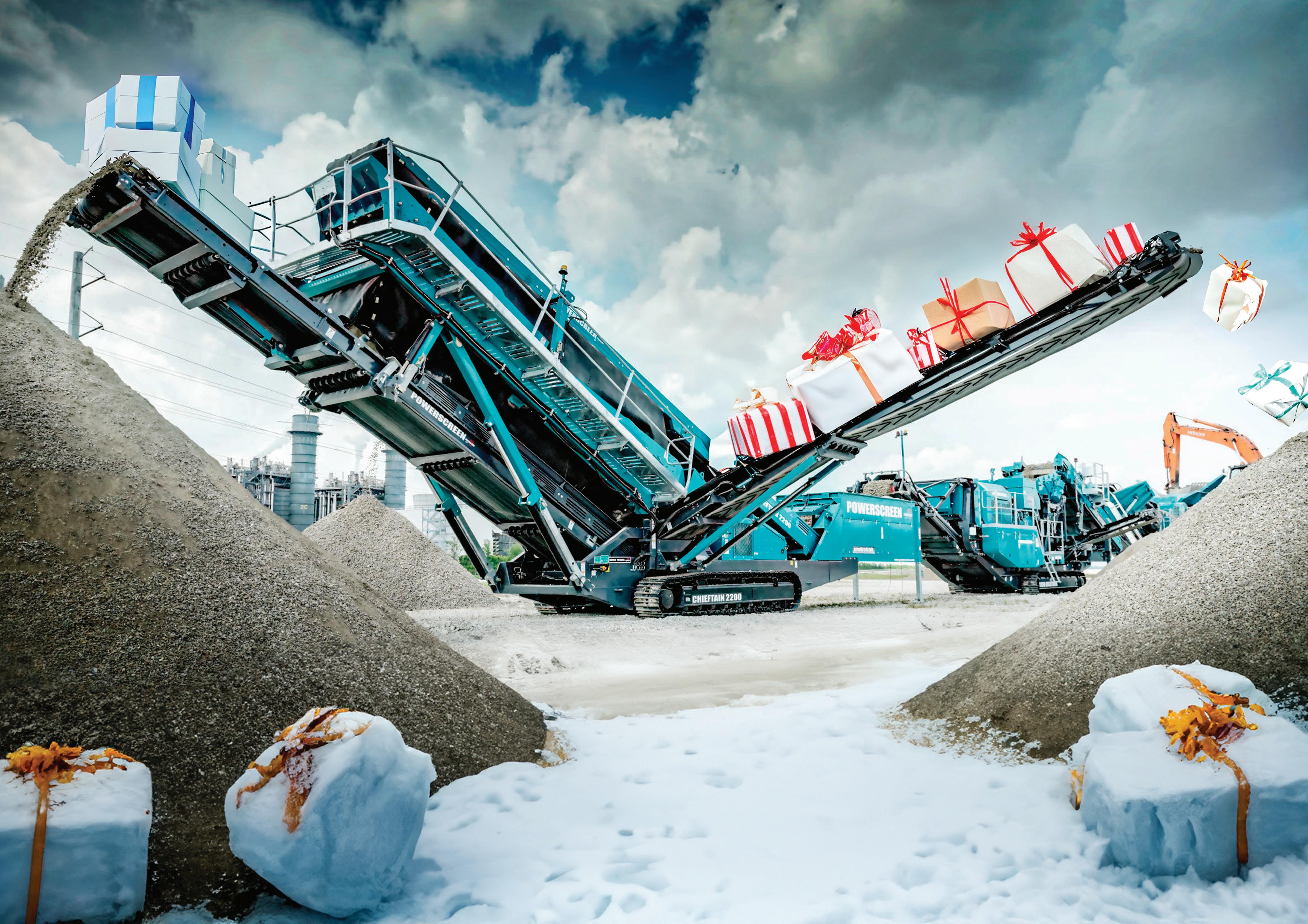
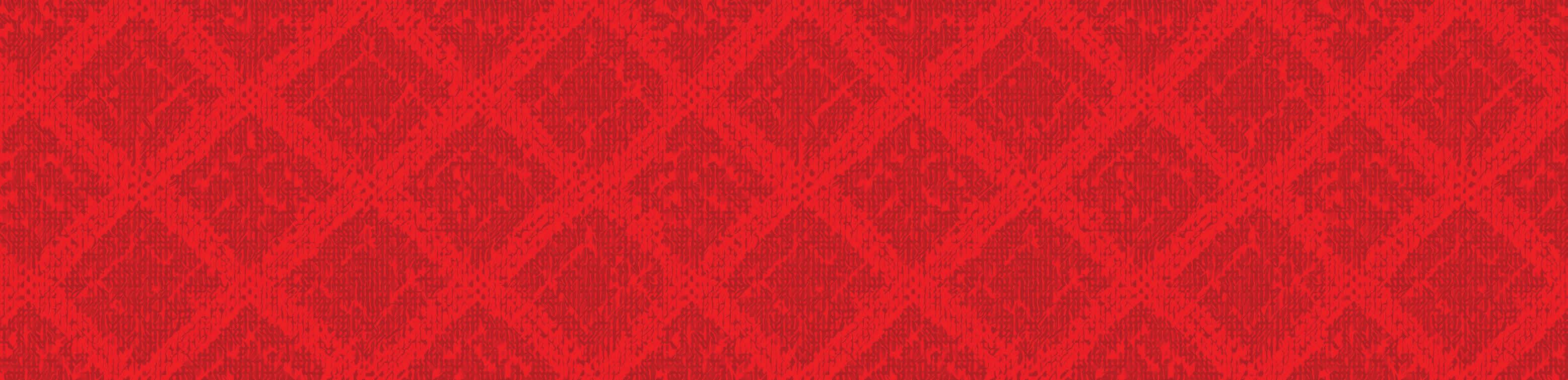
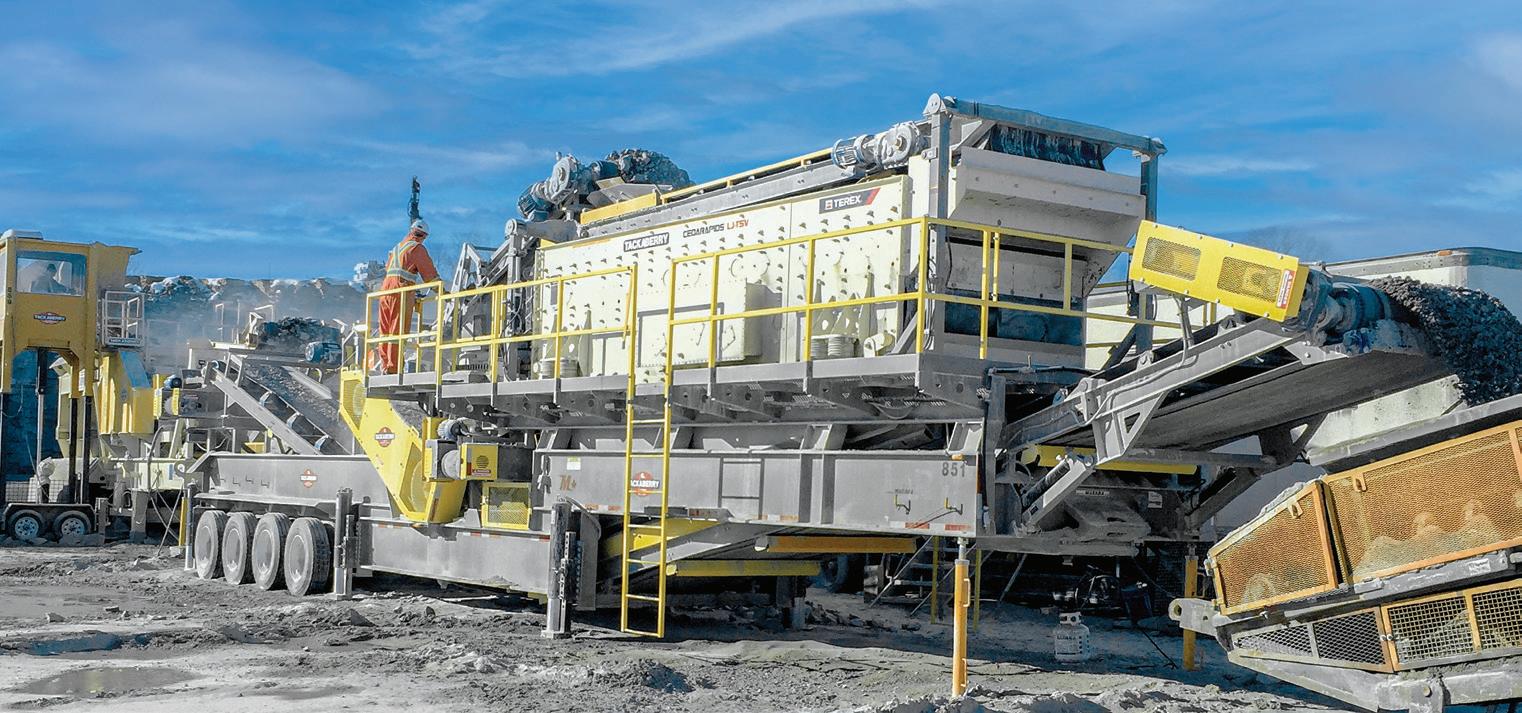
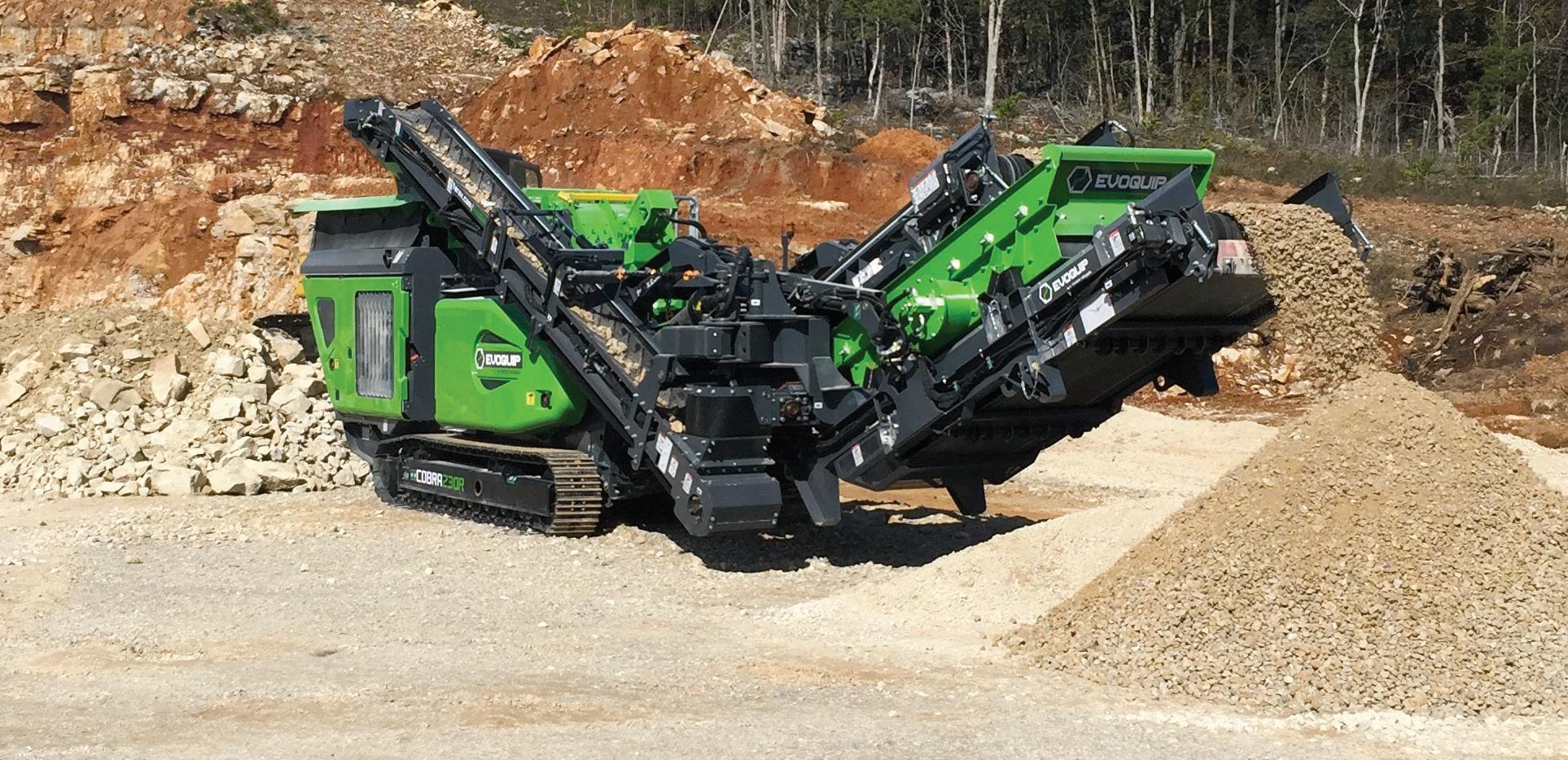
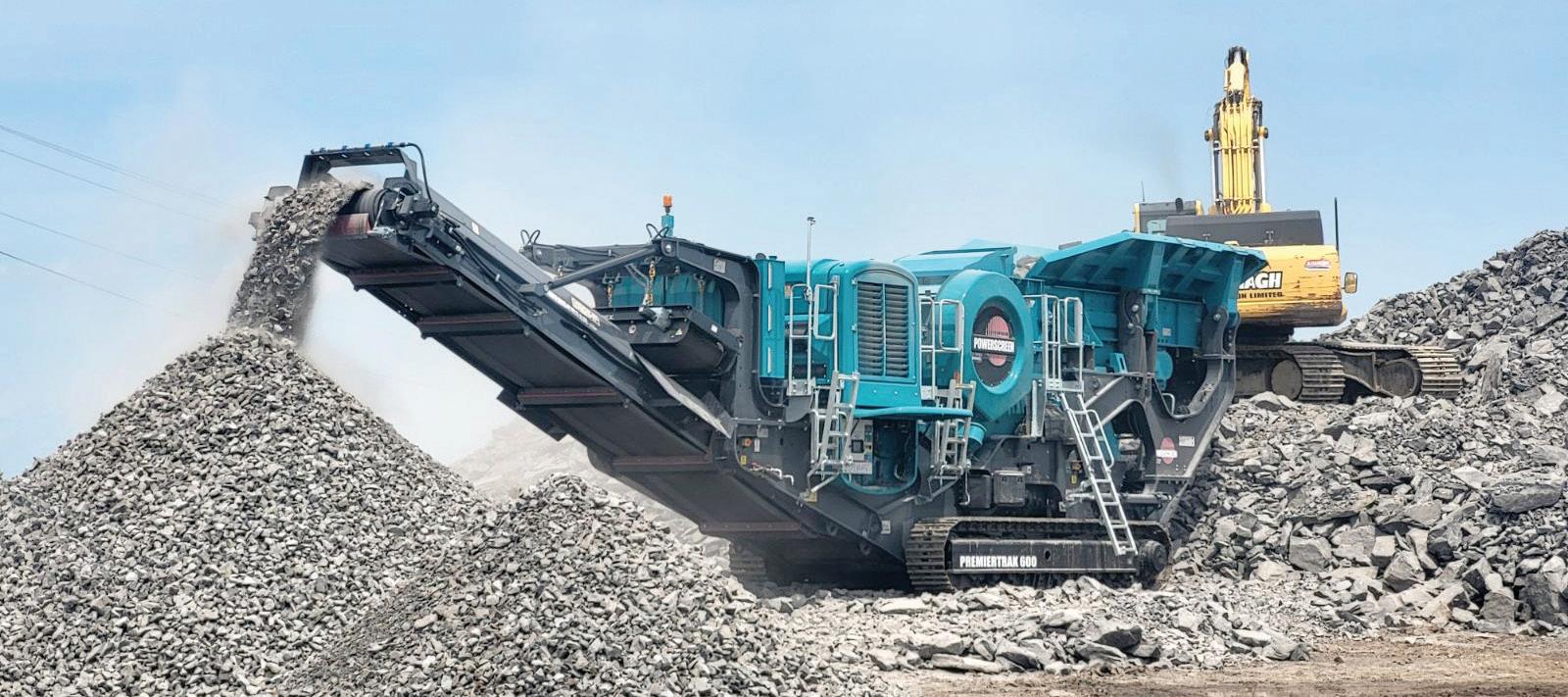
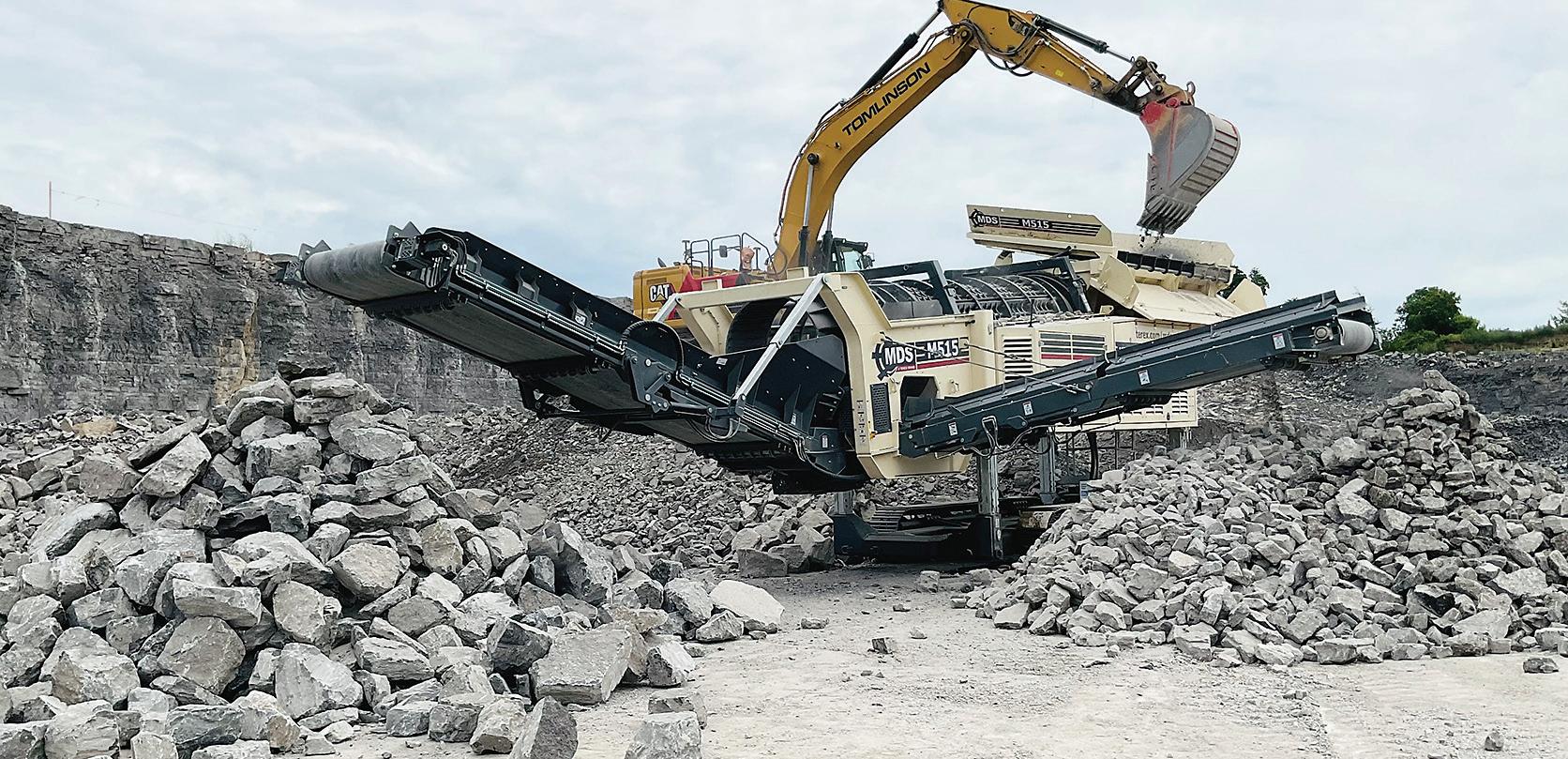
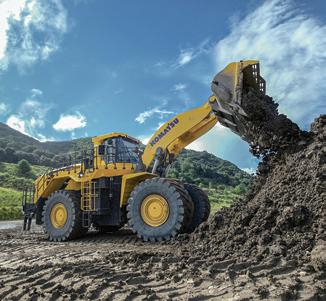
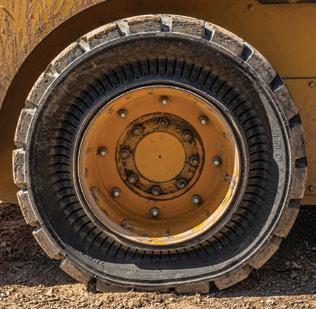
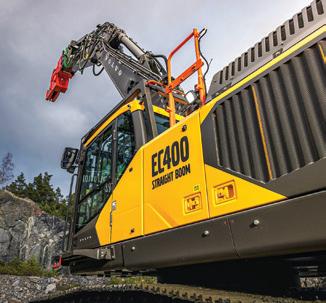
Vermeer enters a new era in utility installation with the introduction of the D24 HDD
Canada’s military veterans are two to three times more likely to become homeless than the general population.
The estimated number of homeless vets across Canada varies from 2,400 to more than 10,000. In the United States, 32,800 vets are homeless, which is closer to Canada's low-end estimates when viewed as per capita figures.
The United States has also made significant progress in ensuring its veterans have a place to live, recording a 55 per cent reduction since 2010. In Canada, however, the number is expected to grow quickly.
In a recent National Post article, Alan Mulawyshyn, Executive Director of Veterans’ House Canada, said a bubble of veterans that served in Afghanistan more than a decade ago is about to
burst onto the streets.
“We’re 10 years later, which experts say is when people start to fall through the cracks,” Mulawyshyn told the National Post. “So, we’re expecting this bubble to burst.”
In Ontario, the provincial government is looking to construction to help ensure veterans have a successful life after leaving the Canadian Armed Forces (CAF).
The province recently announced a plan to spend $3 million over three years to help train 650 active and former CAF members for careers in the construction sector.
The funding will help fill a gap in Ontario’s employment and training resources, while addressing the unique needs and experiences of former military members.
“We owe our veterans, who have put their lives on the
line in defence of our freedom, safety and values, a debt that we can never fully repay,” said Premier Doug Ford.
The funding will be used by Helmets to Hardhats Canada to expand job-ready skills training to more veterans and accelerate their pathways from active military service to apprenticeships in construction by two to three months. Helmets to Hardhats Canada will also be able to deliver access to critical safety training and specialized certifications for in-demand careers.
Helmets to Hardhats Canada has referred more than 2,600 clients, including more than 1,500 in Ontario alone, to unionized careers in construction.
There are many occupations that Canadians owe a debt of gratitude. However, what makes the military
unique is most leave the job well before the average retirement age. Only 7 per cent of CAF members are older than 55 years old. Both the lack of housing and skilled labour are credible threats to the lifestyle Canadians enjoy. Who better to train to solve these existential issues than our CAF veterans?
Komatsu has unveiled the new WA700-8, a more powerful and efficient addition to its wheel loader range for quarry operations and aggregate producers.
Equipped with a 12 cubic yard bucket, the 97,000-kg WA700-8 is powered by a 773 hp Komatsu SAA6D170E-7 engine.
The wheel loader is an ideal four-pass match with 70-ton haul trucks such as Komatsu’s new HD605-10.
“The new WA700-8 can help quarry operations hit that sweet spot for 70-ton truck loading, making every pass count,” said Sebastian Witkowski, Komatsu Product Manager. “With a heavier operating weight, greater static tipping load and larger breakout force than the previous model, the WA700-8 is a productive and efficient wheel loader that is ideal for quarry operations.”
The WA700-8 also offers substantial improvements in performance, efficiency and operator comfort compared to its predecessor, the WA700-3.
Compared to the previous model, the WA700-8 delivers up to 8 per cent more gross power and 15 per cent more torque, making it ideal for demanding work environments.
As well, the new loader delivers a 6 per cent increase in lifting force and rated load, allowing operators to handle larger volumes of material with greater ease.
The WA700-8 features a comfortable cab with tech designed to help reduce operator fatigue on long shifts, including a new advanced joystick steering system and electronic pilot control levers for precision and ease of operation.
Automation features such as an automatic digging system, semi-automatic approach and semi-auto dump systems simplify repetitive tasks, helping operators optimize load cycles. These systems are beneficial for less experienced operators, helping to close skills gaps and enhance overall operational efficiency.
On tough terrain, the variable traction control system helps prevent tire slippage, prolonging tire life and improving safety in wet or slippery conditions.
The wheel loader’s modulated clutch system offers precise control for smooth transitions between forward and reverse, which is critical during truck-loading operations.
An available KomVision
For fuel consumption, Komatsu’s WA700-8 is up to 8 per cent more efficient, which helps reduce operating costs while maintaining productivity.
Battlefield Equipment Rentals opens two new locations
Battlefield Equipment
Rentals has announced the opening of new locations in St. Thomas and Pembroke, Ontario.
The expansion brings the company’s total number of locations to 70, reinforcing its commitment to serving the construction and industrial sectors across eastern Canada.
“The opening of our new locations in St. Thomas and Pembroke marks a significant milestone for Battlefield Equipment Rentals,” said David White, Marketing Manager at Battlefield Equipment Rentals.
“These branches will not only enhance our service capabilities but also demonstrate our unwavering commitment to supporting the growth and success of our customers across eastern Canada.”
The new St. Thomas location is expected to become a pivotal branch for both civil and industrial markets. This
hybrid store will offer a range of rental equipment, new and used equipment sales, specialty tools, building products, safety supplies and safety training programs. The inclusion of jobsite industrial rental services at this branch further diversifies Battlefield Equipment Rentals’ capabilities.
Heather Aristone will lead the St. Thomas branch as Branch Manager, supported by General Manager Gary Bidelman, Regional Manager Jason Kudrey, Sales Manager Pat Fox and Service Manager Erik Robinson.
In Pembroke, the new branch (located at 11958 Round Lake Road) will extend Battlefield Equipment Rentals’ reach into the community.
The rental store will operate under the leadership of Branch Manager Dirk Beimers, General Manager Margie Davis, Regional/Sales Manager Tim Sims and Service Manager Liam Ball.
camera system provides operators with a comprehensive view of the machine’s surroundings, and Komtrax Plus offers remote monitoring and data-driven insights that can help reduce unplanned downtime.
•
•
Broderson Carry Deck Cranes are well known for their versatility and reliability. Engineered to work in tight spaces and areas with low clearance, these cranes are perfect for handling a wide range of tasks with ease. Available in multiple sizes and capacities, Broderson cranes provide the flexibility to meet all your lifting and rigging needs.
Broderson Carry Deck Cranes compact, lowprofile design allows them to navigate confined spaces and clear overhead obstacles effortlessly.
Broderson’s booms are designed for durability and precision. With exceptional reach and strength, they handle demanding lifts effortlessly, even in tight spaces and areas with vertical obstructions.
Standard 4-wheel steer, 2-wheel drive, or optional 4-wheel steer, 4-wheel drive coupled with up to four-speed powershift transmission provides industry-leading speed with a tight, turning radius.
Operating a Broderson Carry Deck Crane is straightforward, thanks to intuitive controls and user-friendly interfaces.
Choose the best diesel or dual-fuel engine to power through challenging applications— Cummins diesel (US EPA tier 4F or global) or GM dual-fuel liquefied petroleum gas (LPG).
Broderson offers a range of options to suit your specific requirements.
Broderson’s ergonomically-designed cabin provides operator comfort, safety, accessibility, and ease of entry.
Select models have integrated telematics that empower owners to access location, operating hours, utilization, engine, and maintenance information online via desktop, laptop, tablet, and mobile devices.
When you choose Broderson with us, you’re not just getting a machine—you’re gaining a trusted partner. Our dedicated support team backs every Broderson crane, offering expert advice, troubleshooting, and a vast inventory of OEM parts to keep your equipment running at peak performance.
Galileo Wheel has developed the first airless, but not solid, tire for skid steers.
The new SkidCup, according to the company, is the first major structural change in industrial tire design since the adoption of run-flat tires in the 1970s.
Galileo Wheel claims the tire delivers critical performance improvements that surpass both traditional pneumatic and solid tire designs.
SkidCup's patented air cavity design maintains full operational capabilities without inflation. The technology eliminates puncture-related downtime while demonstrating superior impact absorption and traction compared both to solid and pneumatic tires, with reduced shock and vibration transmission to both machinery components and
operators. This eliminates the trade-off between puncture resistance and equipment preservation.
"Fleet downtime costs can exceed $400 per vehicle daily," said Armin Schon, CEO of Galileo Wheel. "With SkidCup, we're not just introducing a new tire, we're reimagining what a tire can be. Our patented CupWheel technology represents a fundamental shift in tire design, marking a new era in industrial mobility solutions."
At the core of Galileo's CupWheel technology is a proprietary sidewall concave design.
The approach creates a non-pressurized air cavity that delivers shock absorption and traction without vulnerability to punctures.
The development of SkidCup builds on Galileo Wheel's successful track re-
cord, including the IrriCup tire line for irrigation pivots.
"By completely rethinking tire architecture, we've created a solution that transforms performance,” said Avishay Novoplanski, CTO and Cofounder of Galileo Wheel.
The SkidCup launch follows Galileo Wheel's recent $8 million Series C funding round led by Stine Seed Farm, one of the largest privately held seed companies in the United States. The company has also secured strategic investment from the Japanese Marubeni Corporation.
Founded in 2011, Galileo Wheel develops and manufactures tire solutions for agricultural, construction and industrial applications, combining the advantages of radial off-road tires and rubber tracks on a standard rim.
Screencore’s new 470 XGRID provides the benefits of a tracked screener/ scalper with the stockpiling capacity of a 15 metre stacker.
Being able to produce high quality accurately sized ag-
gregates is essential today, whether its materials from a surface mine, quarry or an aggregate plant, or recycled construction materials from highways, demolition or material handling operations.
The 470 XGRID scalps materials via a lively screening action but also delivers high performance in fine screening applications.
Despite the excellence of the individual product ranges, to combine the attributes of precision screening and scalping with large material stockpiles, two pieces of equipment are required: a screener/scalper and a stockpiler.
Now, however, Screencore has combined stockpiling and screening/scalping with the introduction of the new 470 XGRID.
The new machine not only provides an efficient and productive solution, but also helps minimize expensive outlay on machinery, while reducing carbon emissions at the same time.
The new Screencore 470 XGRID combines the benefits of a modern heavy-duty primary scalper screen with the obvious benefits of a 15metre stacker.
Essentially, customers get three machines, — a screener, scalper and stockpiler — in one, resulting in remarkable reductions in carbon emissions, substantial fuel savings and the elimination of the need for double handling fines.
Its vibrating grid is easily fed by an excavator (or crusher or stacker etc) and has an aggressive action for scalping large materials to ensure that only the desired fines product makes it to the stockpile. It is designed to withstand the rigours of handling demanding materials such as rock or demolition concrete, but equally at home when precision screening.
The design of the 470 XGRID further allows the machine to operate in confined spaces while the high tracked mobility factor eliminates set up time.
The 470 XGRID is essentially a versatile and reliable compact scalping, screening and stockpiling machine designed for optimum output and efficiency, while prioritizing simplicity for the user. It possesses a 1,200 mm belt feed hopper and has assorted grid options. Although equipped as standard with a 15 metre stockpiling conveyor, 18 metre, 21 metre or 24 metre options are available on request.
It can also be configured as a mulch unit with chevrons, agitator and mulch hopper and comes with multifunction radio remote for total control.
It is further available in diesel or dual-power configuration to suit modern needs.
Whether it's within the confines of a quarry, construction site, sand and gravel operation or dealing with soil and mulch, its capacity to effortlessly screen, scalp, and stockpile large quantities of fines without requiring double handling, or the creation of a wheel loader stockpile, is beneficial.
Packed with advanced features and technology, the new Vermeer D24 horizontal directional drill (HDD) enables crews to efficiently install utilities, including fibre optic, power cables and water infrastructure in congested urban areas.
Replacing the D23x30 S3 in Vermeer’s HDD lineup, the D24 is a 24,000-lb (110-kN) class drill equipped with a 100 hp, Tier 4 Final Cat 3.6L engine.
Vermeer introduces the D24 HDD during a virtual launch event held in November.
“We know your needs are constantly evolving. You're facing new challenges, longer bore shots, more demanding ground conditions, the need for skilled operators, all with tighter project timelines,” said Jason Andringa, Vermeer President and CEO. “We're taking these challenges head on. I am incredibly proud and excited to introduce the next generation of Vermeer utility drills, a generation designed to help your crews get more done and maximize every minute on the job.”
The D24 delivers a max peak thrust and pullback of 24,700 lb (110 kN) and a continuous thrust and pullback of 22,000 lb (98 kN). It also features 3,080 foot-pounds of rotational torque and a 170-litre per minute mud pump.
"The D24 represents a significant step forward in HDD technology," said Clint Recker, product manager for utility HDD equipment at Vermeer. "We've listened closely to utility contractors and incorporated their feedback into every aspect of this machine, resulting
in a drill that sets new standards for ease of operation and maintenance simplicity."
A standout feature of the Vermeer D24 HDD is the automated rod exchange (ARE) system. ARE increases onboarding velocity for new operators, reduces workload for skilled operators and maximizes wear part component life through highly controlled processes. Using ARE, one button can replace up to 19 manual steps.
“With a single button push, an operator can change out an entire rod sequence. So, whether they're drilling out or pulling back, they'll be able to change that rod out automatically,” said Weston Peters, Vermeer Product Specialist. “Another big piece of it would be that it really saves on the wear parts because it is making up and breaking out the same way every single time.”
Enhanced diagnostics
The D24 features an advanced onboard diagnostic system that is accessible via the machine's touchscreen display. The diagnostics system offers operators and technicians comprehensive information about any issues and provides step-by-step troubleshooting guidance.
For example, if a sensor detects a hydraulic system glitch, the display provides detailed information to minimize diagnostic time. If dealer support is needed, the system equips technicians with comprehensive data, helping them arrive better prepared. This approach
helps keep projects on schedule by getting the machine back to drilling sooner.
“Customers have been asking to be able to do more diagnostic time on their own,” Recker said.
“It basically is like having the dealer technician come out and plug a laptop into your machine. It empowers the customer to better understand what's happening with their machine if an issue arises.”
Throughout the HDD, Vermeer has prioritized enhancing the D24's overall reliability. The machine features premium hydraulic components — typically found in larger pipeline equipment — that help protect the hydraulic circuit and extend its lifespan. These high-quality components improve the machine's durability and allow consistent performance across various drilling conditions.
The D24 is engineered to tackle the unique challenges of urban utility installation. Its compact design allows for efficient operation in confined city spaces while delivering the power and precision needed to handle diverse soil conditions. This balance of size and capability makes the D24 an ideal choice for contractors working in densely populated areas.
“Today's work is happening in congested and tight job sites, but still requires long bores and challenging ground conditions. You need a machine that can deliver the appropriate rotational torque and thrust while maintaining a small footprint, and that drill has to run quietly to keep everyone in
the area happy,” said Doug Hundt, Vermeer’s President of Industrial Solutions. “Our team was up to the task of addressing all of these challenges, but they actually came up with a new generation of drill that delivers even more."
The D24 HDD operates at 88 dB(A) at the operator's ear with a guaranteed sound power level of 100 dB(A). This low noise output minimizes disturbance in sensitive urban areas, enhances on site communication and helps contractors meet noise regulations. As well, the D24’s operational sound levels contribute to a comfortable work environment, which can positively impact crew productivity and job satisfaction.
Efficient operation
Operators can choose between 122 metre or 146 metre of 60-mm Firestick drill rod for the D24, selecting the configuration that best suits their typical job requirements.
The redesigned vise system features sliding open-side vises, enabling easy cleaning and clear joint visibility. This sliding mechanism streamlines the breakout process compared to fixed opentop vises. With enhanced clamp force, the vises help extend the life of the vise die.
The D24's stakedowns feature tiered shark teeth and a rotation speed of up to 60 rpm, which is nearly triple its predecessors. This upgrade improves setup efficiency, especially in harder soils, allowing crews to begin drilling faster. This quicker setup is particularly valuable in urban areas, where
minimizing disruption is crucial.
Contributing to its efficiency on the jobsite, the D24 delivers a rotation speed of 198 rpm and a carriage speed of 55 metres per minute. The drill's 5.3 km per hour tracking speed enables quick relocation between work areas, helping further enhancing productivity.
"We're confident that contractors will see an impact in their operations when they use this machine in the field. It truly sets a new standard for HDD equipment,” Recker said.
“We believe contractors will be impressed when they put this machine to work in the field, as it truly raises the bar for what they can expect from their HDD equipment."
Vermeer has introduced a simplified model numbering system for its new drills.
This system represents each unit's respective drill class, making it easier for customers to understand the machine's capabilities. The D24 replaces the D23x30 S3 HDD in the Vermeer utility drill line, with its name signifying its thrust capabilities.
“Utility contractors work tirelessly to connect our world. Because of the work you do, lights turn on, homes stay warm and people stay connected. Our world needs you and the important work you do every day,” Andringa said.
“At Vermeer, we've always known this. It's why every day we show up to equip you with the machines and tools you need to work efficiently and productively.”
“Bobcat. They are good machines with smooth hydraulics, they are very reliable and dependable. ”
For over 64 years, Ambassador Building Maintenance Ltd. has built its reputation on providing first-rate janitorial cleaning services and building maintenance for industrial, commercial, institutional, health care, and private sectors, 7 days a week/24 hours a day, throughout Ontario. They are a proud third-generation run company. Bill and Karl Taylor have grown the company by adding a security division seven years ago and a full landscape design with both hardscape and softscape landscaping and snow removal division two years ago to service the Windsor area.
The landscaping and snow removal division has led them to purchase all-new equipment from Braedon Lansue, sales specialist for Bobcat of Windsor, including two Bobcat® L95 compact wheel loaders, a Bobcat UW56 Toolcat utility work machine, a Bobcat CT5558 compact tractor, five snow raiders and all new plows and salt spreaders on their trucks as well. They purchased Bobcat ZT6000 and T3500 zero-turn mowers for lawn cutting and are looking to purchase a walk-behind commercial Bobcat mower for next season. The walk-behind mowers are great for slopes, and we are all about safety,” stated Robert.
Ambassador Building Maintenance hired Jon Cooney,
sales associate, as he previously ran a landscaping/ snow removal company, along with Robert Lopez, landscape manager, together with 35 years of experience, to head the landscaping/snow removal division.
When Jon and Robert were asked what they liked about Bobcat machines, Jon replied, “They are good machines with smooth hydraulics, they are very reliable and dependable. Very important in our line of work. We depend on machines 24 hours a day, 7 days a week. Bobcat of Windsor is centrally located. Anything we need, we get it done right away.” Robert adds, “Bobcat technology is very advanced compared to other brands. They are easy to operate. Other brands, for example, is hard to change a belt, but on a Bobcat machine, you can do it quickly and right on site!”
They use the Toolcat for moving materials around in the shop, moving pallets, carrying chemicals/pesticides/sprays, and loading dump trailers with gravel and rock. The Bobcat CT5558 compact tractor is used for field cutting with the Bobcat Brushcat™ rotary cutter attachment and snow removal. The Bobcat L95 compact wheel loaders are brand new, and they will be used for commercial plaza snow removal.
Jon Cooney has been working with Braedon Lansue since he was 15 years old. “You keep your circle small. Work with people you trust. I trust both Braedon and his father, Brian. Brian is known in Windsor for being the snowplow guy; they both know the snow business. We went to Bobcat because of them. Braedon has been professional to work with. His knowledge surpasses the average normal person.” Robert adds, “Braedon is always available. With other people, you can call for weeks and no calls back. He is very knowledgeable. Both Jon and Robert agree, “we would recommend Braedon Lansue and using Bobcat of Windsor for your next purchase.”
Thank you, Jon and Robert.
BARRIE
Bobcat of Barrie
705-726-2228 oakenequipment.ca
GREY BRUCE
Bobcat of Grey Bruce 519-372-9100 bobcatoftc.com
PARRY SOUND
Bobcat of Parry Sound Ltd. 705-342-1717 bobcatofparrysound.com
TORONTO WEST
Bobcat of Toronto 416-679-4172
oakenequipment.ca
BRANTFORD
Bobcat of Brantford 519-752-7900 bobcatofbrantford.com
HAMILTON
Bobcat of Hamilton 905-643-3177 bobcatofhamilton.com
PETERBOROUGH
Bobcat of Peterborough 705-748-9119 bobcatofpeterborough.com
THUNDER BAY Equipment World Inc. 807-623-9561 bobcat-tbay.com
Bobcat of Ottawa Valley 613-764-2033 bobcatov.com
Bobcat of Tri-Cities Ltd. 1-866-214-3939 bobcatoftc.com
STRATFORD
Bobcat of Stratford 519-393-6040 bobcatofstratford.ca
SAULT STE. MARIE
Bobcat of Sault Ste. Marie 705-949-7379 bobcat-ssm.com
CORNWALL
Bobcat of Ottawa Valley
613-932-2034 bobcatov.com
LONDON
Bobcat of London 519-455-4900 bobcatoflondon.ca
STRATTON
Stratton Equipment 807-483-5505
strattonequipment.com
WINDSOR
Bobcat of Windsor 519-737-0120 oakenequipment.ca
COURTICE
Bobcat of Durham East Ltd.
905-404-9990 bobcatofdurhameast.com
MUSKOKA
Bobcat of Muskoka 249-390-7000 oakenequipment.ca
SUDBURY
McDowell B Equipment Ltd. 705-566-8190 bmcdowell.com
WYOMING
Advantage Farm Equipment Ltd. 519-845-3346 advantage-equip.com
FRANKFORD
John’s Equipment 613-398-6522 johnsequipmentsales.com
OTTAWA
Bobcat of Ottawa Valley 613-831-5166
bobcatov.com
TORONTO EAST
Bobcat of Toronto 416-679-4171 oakenequipment.ca
Cedarapids has created the new CRC1350S portable closed-circuit cone and screen plant, which is designed for high production while remaining portable.
The CRC1350S is the largest portable closed-circuit cone and screen plant on the market, according to Cedarapids.
The CRC1350S can deliver high production at lower costs per ton, while remaining permittable with a travel height of 4.27 metres.
“Our focus with the CRC1350S was to address what customers consistently tell us they need: higher production, lower costs per ton and ease of mobility,” said Russ Burns, Cedarapids Sales Director.
“This plant combines power, efficiency and portability to meet those demands head-on."
The 400 hp TC1300X Cedarapids cone crusher is a key component to its ability.
With improved kinematics and a large eccentric throw, this advanced cone crusher produces quality aggregates with superior shape and cubicity.
The 2.1-metre TSV horizontal screen complements the cone crusher, which enhances production and accommodates a wider range of applications. Its high G-force oval stroke motion and variable slope operation allow it to outperform traditional horizontal screens.
The CRC1350S has several standard features to enhance the customer experience and operational efficiency.
These include an oversized cone feed hopper with an overflow chute, a straight-line under-crusher conveyor, a metal detector for improved safety, a hydraulically powered transfer chute and various axle configurations to facilitate plant permitting.
The portable closed-cir-
cuit cone and screen plant is designed for fast setup and operation, with easy-access maintenance platforms, a hydraulic folding walkway and integrated emergency stop stations to ensure operators' quick return to production.
In a recent field test, the CRC1350S was used in a high-production railroad ballast application.
The project involved processing drilled and blasted granite material into 2” minus railroad ballast. Material was fed by a Cat 349 excavator into a Powerscreen 32” x 47” jaw crusher with a 5” closed side setting, reducing the granite to 9” minus.
From there, the material was conveyed to the Cedarapids CRC1350S, which was configured to produce three product variations: railroad ballast at 2” x 7/8”, 3/4” stone and 1/2” minus dust.
The CRC1350S produced an estimated 425 tons per hour, split across the three products.
Although the plant demonstrated excellent performance, there is potential for even higher production rates with the use of a larger excavator and minor adjustments to the circuit.
The customer expressed high satisfaction with the CRC1350S’s performance in the rail ballast configuration, highlighting the plant's significant production capacity and ease of transport.
Yanmar Compact Equipment has introduced a new line of branded attachments that are optimized for use with its compact track loader lineup.
The Yanmar attachments include a full range of buckets, augers, trenchers, stump grinders, soil conditioners, breakers, sweepers, pallet forks, brush mowers, grapple rakes, grapple buckets and snow and grading blades.
According to the company, the introduction of the new attachments streamlines the purchasing process for fleet owners, contractors and rental centres by allowing Yanmar dealers to act as a one-stop shop for Yanmar equipment and attachments.
“We’re excited to offer yet another reliable and versatile set of tools to help fleet customers and contractors be productive right out of the gate and conquer the evolving demands of any construction jobsite head-on,” said Frank Gangi, Product Manager for Attachments at Yanmar Compact Equipment North America. “ Yanmar customers can save time by buying their machine and attachments all from one place.”
The attachments, available through Yanmar’s dealer network, allow for seamless compatibility for use with all Yanmar-branded compact track loaders. This allows operators to simply attach the tool and get to work with the confidence to get the job done.
As well, the attachments are matched and tested to ensure efficiency and performance when used with their Yanmar compact track loader.
When the job demands a serious excavator, rely on the quality of Liebherr. The R 945 is perfect for heavy-duty jobs like mass excavating and truck loading, trenching, demolition, land clearing, and moving large amounts of material in a quarry.
With its new improvements including more engine power, greater productivity, increased safety, and better fuel efficiency, this excavator offers superior performance. www.liebherr.ca
Excavator R 945 G8
Terex Recycling Systems has introduced the new TSD-280 drum screen, which promises to generate higher-quality recyclable material.
Designed for heavy-duty processing, the TSD-280 enhances recycling operations by pre-sorting bulky construction and industrial waste and providing a steady, efficient material flow.
The TSD-280 can handle raw, unsorted construction, demolition and industrial waste of all sizes.
The drum screen also efficiently separates bulky materials from the waste stream, eliminating the need for additional manual sorting. It also improves overall sorting efficiency by preventing jams and providing a more consistent flow of material, reducing downtime, and increasing productivity.
“The TSD-280 drum screen is designed to support recycling facilities by improving operational efficiency and contributing to sustainability efforts,” said Kenny Hull, Product and Commercial Manager for Terex Recycling Systems.
“It is an excellent choice for pre-sorting bulky construc-
tion and industrial waste, which can either be disposed of, sorted or shredded for reintroduction into the process. This results in a more consistent and efficient sorting operation, producing higher-quality recyclables with reduced contamination.”
With less extensive pre-sorting activities, the TSD-280 provides customers with higher capacity and improved material purity.
The screening drum features a heavy duty fourwheel drive with a unique 3D design to avoid blockages.
According to Terex Recycling Systems, the drum screen produces a more consistent material size, resulting in higher-quality recyclables and reduced contamination.
The heavy duty bunker feeder measures 1.8 metres wide with 90 cm high sides, while the oversize conveyor measures 2 metres wide with impact bars.
Additional benefits include reduced labour costs by eliminating the need for additional material handlers and operators, as well as greater environmental sustainability by contributing to a more efficient and sus-
The Association of Equipment Manufacturers (AEM) has set a new record for the largest membership in its more than 125-year history.
In October, AEM’s total member count exceeded 1,100 for the first time in the association’s history, after welcoming 22 new companies in September.
Throughout 2024, 109 companies have joined AEM, helping the association top its previous membership record that was set almost one year ago and achieve an above-average member retention rate of 92 per cent.
“For the second straight year, we’re proud to achieve a record-breaking level of membership as we continue to build on our past successes, serve our member companies and speak with one voice on behalf of equipment manufacturing,” said AEM Vice President of Sales and Membership Paul Flemming.
This year has been an allaround success for AEM. In July, the association launched the AEM Manufacturing Express, a cross-country tour to tell the story of the United States equipment manufacturing industry and celebrate the 2.3 million people who
help build, power and feed the world.
The AEM Manufacturing Express visited more than 20 states and made stops at 80-plus equipment manufacturers in communities across the USA.
As well, AEM hosted a pair of special member events in 2024. The gatherings served as touchpoints between AEM and its members, provided attendees with resources and insights to help drive organizational decision-making, as well as highlighted the benefits offered by AEM.
Member benefits and services support several areas important to members, including bipartisan industry advocacy, safety, environmental and global compliance programs, business/market intelligence, workforce, along with sales and marketing initiatives.
Finally, AEM continues to build upon its reputation as an organizer of industry events that connect member companies with their customers, increase their brand awareness and help them adapt and prepare for future growth. Throughout the year, its events set new attendance records, including World of Asphalt in Nashville.
tainable recycling process.
The TSD-280 is available as a standalone pre-sorting line or integrated into existing and new recycling systems.
The screening drum is available in a 6-metre length for a 45 tonne per hour capacity or a 7.5-metre to handle up to 60 tonnes per hour.
Terex Recycling Systems' largest 9-metre long option has a capacity of up to 90 tonnes.
At SMS Equipment, we’re more than machines from trusted brands like Komatsu. No matter your project, we’re the people beside you—today and every day—bringing industry-leading technology and expertise to your job site.
Because the right partnership makes everything possible.
In response to market demand, Rubble Master has introduced its first mobile jaw crusher, the RM J110X. The primary crusher is ideal for processing hard natural rock in mines, quarries and heavy-duty recycling applications.
With the introduction of the RM J110X, Rubble Master extends its product range to now offer full crusher and screen train solutions that meet the industry’s evolving material processing requirements.
“Launching the RM J110X
in North America is a significant milestone for us,” said Harry Kussegg, Managing Director of Rubble Master Americas. “This machine was built with customer feedback in mind, and we’re confident it will set a new standard in mobile jaw crushing, delivering the durability and flexibility that our customers need for a wide range of materials and working conditions.”
Rubble Master introduced the mobile jaw crusher at a launch event in Texas in October. The event marked
Rubble Master’s entry into a new business segment, marking a significant step forward as it ventures into the competitive market.
"It's like David versus Goliath. With the jaw crusher, we are venturing into completely new territory, but we are convinced this is the right step to take. That’s because we have the support of long-standing customers, whose high demand prompted the development of this machine. With the RM J110X, we are not only entering a new business
field but also demonstrating once again our ability to drive innovation," said Rubble Master Founder Gerald Hanisch.
New Rubble Master HQ
The same day, the company opened its doors to its new headquarters in Alma, Texas.
The expansion is a milestone for Rubble Master’s commitment to its growing customer base across North America.
The new Alma facility, located in an industrial area
with convenient access to major highways, will serve as a regional hub.
The location was strategically chosen to strengthen the company's presence in the southern United States, ensuring faster response times, reduced equipment downtime and enhanced customer service for its partners and customers.
"We are thrilled to expand our footprint in Texas with this new office and service location," Kussegg said.
"Our goal has always been to be close to our custom -
ers, providing them with the highest level of service and support.
"This new facility will enable us to do just that, ensuring that our customers receive the prompt and professional assistance they expect from us."
The Alma location will be fully equipped with stateof-the-art service bays, a large parts inventory and a dedicated team. It will also serve as a training centre for Rubble Master’s North American dealers and customers.
Liebherr has partnered with construction technology company STRABAG to conduct the first test of its L 566 H hydrogen wheel loader.
At the Kanzelstein quarry in Austria, STRABAG is testing Liebherr’s large hydrogen-powered wheel loader over a two-year period.
The prototype machine will be used on site in daily operations during the trial.
As well, a green hydrogen filling station is being built to refuel the wheel loader directly at the quarry.
During a tour of the machine and quarry, Leonore Gewessler, Austria’s Minister for Climate Action, Environment, Energy, Mobility, Innovation and Technology, praised Liebherr’s commitment to reducing greenhouse and other harmful gases and its cooperation with STRABAG on testing hydrogen technology.
“I am pleased to see innovative companies pushing ahead with pilot projects, especially in forms of mobility that are difficult to electrify, such as those in the construction sector,” Gewessler said.
The large wheel loader with a hydrogen engine is expected to save up to 100
tonnes of carbon dioxide annually, equalling the consumption of about 37,500 litres of diesel.
“We want to be climate neutral by 2040. The only way to achieve this is by consistently and comprehensively saving CO2, for example, in the operation of construction machinery,” said STRABAG CEO Klemens Haselsteiner.
The L 566 H from Liebherr is the world’s first prototype large wheel loader with a hydrogen engine.
“The technology also enables large vehicles that are
difficult to electrify due to their high energy demand to be operated without CO2,” said Dr.-Ing. Herbert Pfab, Technical Director of Liebherr-Werk Bischofshofen GmbH.
The hydrogen engine powering the loader is manufactured by the Liebherr components division’s own engine plant in Bulle, Switzerland. These engines will not only make it possible to emit zero greenhouse gases and almost no nitrogen oxides but will also offer excellent efficiency.
With the pilot project,
Liebherr and STRABAG are demonstrating how emissions can be reduced in a sector that is difficult to decarbonize by means of alternative fuels.
Climate-neutral hydrogen produced with wind and water power or solar energy can be a key enabler for achieving emissions neutrality goals.
“Green hydrogen is an indispensable element of our future energy. As an important and valuable energy source, it helps replace fossil natural gas, especially in industry,” Gewessler said.
For 40 years, Wacker Neuson has engineered, designed and built excavators around the needs of our customers. And because every construction site is di erent, we o er variety and versatility for the job at hand. From rugged and reliable tracked conventional tail machines to minimal tail swing, wheeled, and zero emission models, you’ll find the right configuration, lifting capacity and breakout force to handle the toughest challenges. What’s more, Wacker Neuson excavators are durable, powerful and easy to operate.
See how Wacker Neuson builds solutions for you. Contact your local dealer today!
A.S.E. Equipment
8503 Wellington Road 18, Fergus, ON, N1M 2W5
Access Mining Services 1106 Webbwood Drive, Sudbury, ON, P3C 3B7
Advantage Farm Equipment 6915 Colonel Road, London, ON, N6L 1J1
Brownlee Equipment 332416 Hwy 11 N, Earlton ON, P0J 1E0
Coleman Equipment Inc. 3541 Trussler Rd New Dundee, ON, N0B 2E0
Construction Equipment Co. (Sault) Inc. 1245 Great Northern Rd, Sault Ste. Marie, ON, P6B 0B9
Eastrock Equipment Inc 100 Warehouse St., Vars, ON, K0A 3H0
Frontier Sales & Equipment 7213 Line 86, Wallenstein, ON, N0B 2S0
Hood Equipment Canada 14 Haniak Road, Rosslyn, ON, P7K 0C8
Hood Equipment Canada 1355 Riverside Drive, Timmins, ON, P4R 1A6
Hood Equipment Canada 9 Ferndale Drive N, Barrie, ON, L4N 9V4
Mark McCabe Tractor Sales Limited 708 Centreline Road, Lindsay, ON K9V 4R5
519-843-1161 www.aseequipment.ca
705-419-2602 www.acces-s.ca
519- 652-1552 www.advantage-equip.com
705-563-2212 www.bequip.ca
519-696-2213 www.coleman-equipment.com
705-942-8500 www.cec-ssm.com
613-443-0695 www.eastrock.com
519-669-8709 www.frontierequipsales.com
807-939-2641 www.hoodequipmentcompany.net
705-269-0830 www.hoodequipmentcompany.net
705-503-7732 www.hoodequipmentcompany.net
705-799-2868 www.mccaberepair.com
McGill Equipment 300 Midwest Rd, Scarborough, ON, M1P 3A9 416-751-4455 www.mcgillequipment.com
Oneida New Holland 634 Fourth Line, Caledonia, ON, N3W 2B3
Oneida New Holland 1410 Fourth Ave, St. Catharines, ON, L2S 0B8
Top Lift Enterprises 42 Pinelands Ave, Stoney Creek, ON, L8E 5X9
Top Lift Enterprises 12343 Highway 50, Bolton, ON, L7E 1M3
1-800-201-3346 • www.wackerneuson.com
905-765-5011 www.oneidanewholland.com
905-688-5160 www.oneidanewholland.com
905-662-4137 www.toplift.com
905-857-5200 www.toplift.com
John Deere has announced the company will expand its forestry equipment production at its John Deere Specialty Products facility located in Langley, British Columbia.
Manufacturing of the 900-Series models will start later this year, followed by the 800-Series models in early Spring 2025.
“All of us at John Deere Specialty Products are excited about this opportunity to grow at our location and provide customers with even more confidence through our com -
mitment to the highest quality and durable products,” said Alan Tracey, Factory Manager at John Deere Langley.
“We have a long tenure of forestry design and manufacturing experience, and we are passionate about working with our customers.”
The John Deere Specialty Products fa cility will serve as the centre of excellence for manufacturing purpose-built tracked forestry equipment.
Brandt Peterbilt, a wholly owned subsidiary of the Brandt Group of Companies, has been appointed to disperse a major portion of the fleet assets of a Mississauga-based truck leasing firm.
The company filed for bankruptcy protection in late March.
The assets include hundreds of late-model Peterbilt and Kenworth highway tractors, dump trucks and trailers, including dry vans and reefer units, all inspected and with fresh safeties prior to sale.
“We work hard to deliver complete solutions for our customers and giving them access to used units on this kind of scale, along with options for asset liquidation, is an important step as we continue to invest for the long term in our truck dealership business. The addition of these units will increase our new and used catalogue to nearly 1,300 units, the largest in Canada,” said Neil Marcotte, Brandt’s Chief Operating Officer—Transportation.
“This influx of used inventory reflects a core business strategy within our dealership network. It will allow us to grow our used equipment business at an unprecedented rate, better serving our current and future customers while keeping up with the demands of the market.”
Brandt entered the truck market in 2019 with the acquisition of Camex Equipment in Nisku, Alberta.
In 2021, Brandt became the exclusive Peterbilt dealer for Saskatchewan and primary dealer in Ontario with the acquisition of Cervus Equipment.
Brandt was chosen to disperse these units due to its significant service and support infrastructure and nationwide heavy equipment distribution network, including Canada’s largest Peterbilt truck dealership network, with 19 full-service locations in Saskatchewan and Ontario.
The company is a leader in used equipment sales and support with a decades-long track record in multiple industries. The equipment is expected to be available for sale this month at Brandt locations in Mississauga, Ontario; Ayr, Ontario; Winnipeg, Manitoba; Regina, Saskatchewan; Saskatoon, Saskatchewan; Calgary, Alberta; Edmonton, Alberta; Vancouver, British Columbia; and Kamloops, British Columbia.
The production increase will enhance services provided by John Deere to both North American and global customers and strategically position tracked harvesters and feller bunchers in a key forestry region.
The John Deere Specialty Products production facility currently employs about 100
people and produces tracked processors, road builders and tracked log loaders for the global market.
The business has been operating since 1998 and continues to positively impact its local communities and John Deere customers around the world.
By Ontario One Call
In Ontario, the excavation landscape is marked by a sobering statistic: more than 4,200 underground utility damages occur annually, translating to roughly 19 damages every workday.
This high frequency of incidents underscores a critical need for enhanced safety practices among contractors and landscapers, who are often at the forefront of these potentially hazardous situations.
The impact of these damages extends far beyond mere inconvenience. Each incident poses significant safety risks, disrupts services and incurs substantial financial costs. For example, striking a single utility line can result in expenses that spiral into thousands of dollars, alongside severe penalties. More critically, it can lead to serious injuries or even fatalities, making safety compliance not just a regulatory requirement, but a moral imperative.
Despite these clear risks, a significant number of these damages result from failure to secure proper locates before excavation. Skipping this crucial step can stem from various factors, including perceived time savings, cost avoidance or simply a lack of awareness about the consequences of hitting underground utilities and the precautions that are in place to prevent them.
Industry professionals need to understand requesting a locate via Ontario One
Call is more than a formality — it is a legal requirement and a vital safeguard that ensures all underground utilities are accurately marked, thereby minimizing risk of damage. It's a simple yet effective step that not only protects the physical infrastructure, but also safeguards workers on the ground.
Educational outreach is crucial. Industry veterans and newcomers alike must be made aware of the staggering statistics and the real-world implications of neglecting to request locates.
Regular training sessions, workshops and seminars can help reinforce the importance of adhering to safety protocols and staying updated on best practices.
As we advance our infrastructure, the call to action for every professional involved in ground disturbance is clear: prioritize safety, reduce risk and uphold our duty to protect not only our utilities, but also the lives of those who work with them.
Each locate request submitted is a potential disaster averted, a financial burden avoided and a life saved.
Let's make safe digging a cornerstone of our industry standards.
Established in 1996, Ontario One Call is a public safety administrative authority that acts as a communications link between buried infrastructure owners and individuals who are planning to dig in the province.
Ontario One Call spreads dig safe and click before you dig messaging, provides a locate request system that streamlines communications between those who want to dig with the owners of buried infrastructure, and regulates the public locate industry.
In 2012, the Ontario Underground Infrastructure Notification System Act was passed, which stipulates that by law, anyone in the province of Ontario must contact
Ontario One Call before they dig. Though Ontario One Call does not physically mark the lines, pipes or cables, we relay all dig information to the buried infrastructure owners so they can mark (locate) based on the request you submit. Buried infrastructure owners will then deliver locates. Locates minimize the risk of infrastructure damage, loss of service, and injury.
Stellar Industries has acquired Elliot Machine Works, a family-owned manufacturing company based in Galion, Ohio.
The strategic investment is aimed at enhancing Stellar’s growth, expand its product offering and providing greater opportunities for Stellar distributors, customers and
employee-owners.
“This acquisition marks a significant milestone for Stellar and we’re so grateful for this incredible opportunity,” said Dave Zrostlik, President of Stellar. “We are excited to have Elliott’s products as a part of the Stellar product offering. Elliott’s great people and great
products are a natural fit for Stellar.”
Founded in 1948, Elliott Machine Works is recognized for its production of mobile fuel and lube service equipment and is known for its innovative and high-quality products.
Their portfolio includes fuel trucks, lube trucks, water trucks, lube skids, vacuum tanks and other mobile service equipment.
“By incorporating fuel trucks and lube trucks into our existing line of service trucks, we can now serve a broader mission, reach more customers and meet their needs even better by filling gaps in our offerings,” Zrostlik said.
“We anticipate that our customers will start to throw more opportunities our way, and we’re ready to deliver. In addition, this acquisition strengthens our commitment to rural communities, ensuring we are making the biggest impact to the places our employees call home.”
The Elliott manufacturing facility and main office will remain in Galion, Ohio, where it will continue to manufacture the full lineup of specialized service trucks.
“By maintaining operations in Ohio and integrating Elliott’s talented workforce, we are not only preserving jobs but also enhancing economic stability in the region,” Zrostlik said.
“This commitment reflects
our dedication to supporting local economies and the communities we serve.”
Joining the Stellar team opens the door to new opportunities for career development and growth for Elliott employees.
With access to a broader network, expanded roles and additional resources and training, Elliott Machine Works employees will benefit from Stellar’s commitment to professional advancement.
Stellar also employs an Employee Stock Ownership Plan (ESOP) structure that allows employees to become beneficial owners of the company, aligning their interests with the overall performance and growth of Stellar.
“We are thrilled to keep our legacy moving forward with Stellar, a highly esteemed company that shares our values. This partnership is a great cultural fit for our employees, and we’re excited for the new heights we can reach together,” Brent and Brad Ekin, owners of Elliott Machine Works, said in a news release.
“Stellar’s strong distribution network will allow our exceptional products to reach more customers, and we are especially happy that Stellar’s employee-owned structure means our employees will continue to thrive under new ownership.”
As part of Volvo CE’s new generation revamp, the OEM has launched the EC300 and EC400 straight boom demolition excavators, delivering improved performance, safety and strength.
The 40-ton EC400 straight boom crawler excavator is replacing the EC380E, while the 30-ton EC300 straight boom is the enhanced model following the previous generation EC300E.
“These mighty machines embody the very best in demolition strength,” said Martijn Donkersloot, Product Manager for Demolition Equipment at Volvo CE.
“Starting with a solid foundation of a new modern design that provides operators with best-in-class comfort and visibility, we have also packed in a number of outstanding features to ensure the toughest of demolition jobs can be carried out with greater ease, safety and performance.”
Both straight boom excavators are designed to deliver the highest levels of productivity in demolition applications, while retaining the quality and comfort of their standard counterparts.
Standard innovation
Several new features come as standard, including a bigger auxiliary return line for faster attachment movements and an industry first, case drain line that feeds
returning oil back into the tank, instead of a case drain circuit.
Also included in the upgrade are technological advantages such as Auto Power Boost, boom-and-arm bounce reduction, the ability to adjust boom-down speed, and boom-swing and boom-travel priority.
The updated machines offer a height advantage with an increase in reach of about 30 per cent over standard digging-based models.
A heavier counterweight can be easily detached using a hydraulic removal feature when moving from site to site, which also ensures outstanding stability during tall tasks.
Thanks to the new generation machine
base, they also enjoy a 14 per cent improvement in fuel efficiency and a 10 per cent increase in engine power for the EC400 straight boom over the machine it replaces.
The new cab is more spacious and packed with new features, ensuring optimum comfort and visibility. As well, improved controls, an electric joystick and travel pedal allow precise controllability for the operator.
The new cab design doesn’t only focus on comfort and productivity. It also offers the ultimate protection against falling debris with its roll over protection system and frame-mounted falling object guards, which can also be swung out to help clean the front window. With 12 mm thick single-piece high-impact resistant glass, the windows
not only provide a clear view but the best possible protection.
When combining these advantages with the machines’ stability, high visibility and durable design, these excavators are ideal for efficient heavy-duty demolition projects.
Despite their impressive strength across demolition tasks, they are versatile enough to be used across several other tasks, such as digging, site tidy-up and truck loading — even loading high-sided trucks thanks to the extended reach of their longer booms.
Furthermore, maintenance is made easy with hydraulic oil and return filter changes extended to over 1,000 hours.
A reversible cooling fan helps to protect vital machine components from damage through overheating in dusty demolition environments. In addition, the unique factory-fit dust suppression system removes the need for a separate truck for pumping water, with its optimized positioning of water spraying nozzles helping to capture dust at the earliest opportunity.
The EC300 straight boom and EC400 straight boom demolition crawler excavators are the first of the range for Europe and North America to be included in the new generation update.
The EC400 straight boom can be ordered now and the EC300 straight boom can be ordered starting in March 2025.
The Consumer Technology Association has announced Martin Lundstedt, President and CEO of Volvo Group, as one of the keynote speakers for CES 2025.
Volvo Group will highlight its vision for a 100 per cent safe, 100 per cent fossil-free, and 100 per cent more productive transportation and infrastructure.
“Volvo Group is leading the way in mobility to deliver sustainable technologies across trucks, buses, construction equipment and marine and industrial solutions,” said Gary Shapiro, CEO of the CTA.
“We look forward to hearing their ambitious strategy to accelerate climate progress in the next decade.”
Volvo Group will focus its presentation on the urgency to deliver a more sustainable and efficient way of working through the power of electrification, connectivity and automation.
Technology and collaboration are Volvo Group’s most effective tools in achieving its ambitious target to reach net zero value chain greenhouse gas emissions by 2040.
Volvo Group will highlight its unique three-pronged approach to fossil-free transportation, which includes battery electric, hydrogen fuel cells and combustion engines running on renewable biofuels.
The company will explain why a systemic approach across the entire value chain is essential to support the successful adaptation and continued adoption of these technologies.
“We are honoured to take the stage at CES and highlight the impact our technological advancements will have on our industry and society at large,” Lundstedt said.
“Transforming mobility is a full-scale societal issue.”
ALBERTA
Liftboss JCB
Calgary: 403-301-0041 Edmonton: 780-474-9900 liftboss.ca
BRITISH COLUMBIA
Williams JCB
Surrey: 604-930-3316 williamsjcb.com
NEW BRUNSWICK
A.L.P.A. Equipment
Edmundston : 506-735-4144
Balmoral : 506-826-2717 Fredericton : 506-452-9818 Moncton, N.B. : 506-861-2572 alpaequipment.com
NOVA SCOTIA
A.L.P.A. Equipment
Truro : (902) 897-2717 alpaequipment.com
Harvey JCB
Corner Brook: 709-639-2960
St. Johns: 709-738-8911 harveyco.ca
ONTARIO
Advance Construction Equipment (Division of Equipment Ontario) Harriston: 519-510-5878 Waterloo: 519-742-5878 advanceequipment.net
D&W Group Inc.
Doughty & Williamson Jarvis: 519-587-2273
Brant Tractor Burford: 519-449-2500
Redtrac International Vineland: 905-562-4136 dwgroup.ca
ONTARIO
Delta JCB
Dunvegan: 613-527-1501 Renfrew: 613-432-4133 Winchester: 613-774-2273 deltapower.ca
Equipment Ontario Alliston:705-320-0506 Lindsay: 705-324-6136 Port Perry: 905-982-1500 equipmentontario.com
Fulline JCB
Glencoe: 519-287-2840 fullinefarm.com
John’s Equipment Sales Frankford: 613-398-6522 johnsequipmentsales.com
Moore JCB Toronto, York & Peel Region: 416-747-1212 moorejcb.com
ONTARIO
North Rock JCB
North Bay, Sault Ste. Marie, and Sudbury: 705-897-7369 northrockrentals.com
ReadyQuip Sales & Service Ltd. Timmins: 705-268-7600 readyquip.com
WPE Landscape Equipment - JCB Hamilton/Halton: 905-628-3055 wpeequipment.ca
PEI
A.L.P.A. Equipment (506) 861-2572 alpaequipment.com
Bas-Saint-Laurent : (506) 735-4144
Gaspésie : (506) 826-2717 alpaequipment.com Bossé Quebec
Desmaures: 418-878-2241
Saint-Augustin-debosse-frere.com
Montreal: 514-333-1212 moorejcb.com
“EVERYONE HAS THEIR BRAND, AND MY BRAND IS CASE.”
Mark Zammit’s journey began humbly, when he worked with a family friend at a mechanic shop. However, he soon realized that this was different from the path he wanted to pursue. He then took a summer job laying interlock, where he discovered his passion for outdoor work, team collaboration, and creative construction.
At a young age, Mark started knocking on doors, offering his services to repair steps and pathways. Now, 20 years later, he is the proud owner of The Markstone Group“Your Trusted Partner for All Seasons.” The company operates four divisions to serve all outdoor living needs, including pool and landscape construction (95% residential and recently expanded into the municipal sector), snow and ice management for municipal, retail & commercial properties, and a tree farm serving the Burlington and Greater Toronto Area (GTA).
Mark is a proud father of four and ensures a healthy work-life balance. His tree farm, Bella’s Branching Out, is named after one of his daughters, while his pool division, Mayascape Pools, is named after his oldest daughter. Mark takes great pride in his long-standing team, many of whom have been with him since the start of the business. “We prioritize training, whether it’s for DZ/AZ drivers or leadership development for our supervisors. Investing in our people is crucial to both our success and our customers’ satisfaction,” he says.
During the COVID-19 pandemic, Mark decided to make snow removal a more integral part of the business, ensuring that his team remained resilient during uncertain times. With over 200 workers employed across two locations during the winter, spanning the GTA, The Markstone Group continued to thrive.
One of Mark’s key investments in the company’s growth was the purchase of a 2006 Case 430 skid-steer, the first machine he bought. “It took all the money I had, but it lasted 10 years before I decided to sell it. I was able to sell it for nearly the same price I paid, which really helped us grow. The service at Nors, formerly Strongco, in Brampton, has always been top-notch for us,” Mark reflects.
He goes on to explain that buying equipment is much like purchasing a home-the return on investment matters. “I’ve found that my best investments have been in Case machines. I’m an owner-operator, and I find the Case controls to be user-friendly. It’s also easy to train new operators. Everyone has their brand, and my brand is Case.”
Mark’s relationship with his territory manager, Brendan Mooney, has played a pivotal role in his business’s growth. Since meeting Brendan in 2020, Mark has expanded his fleet significantly, purchasing 20 Case wheel loaders in 2021 and, most recently, 31 Case skid-steers specifically for snow removal. His fleet now includes 63 Case machines. “My Case loaders still look as good as new, with only 50-100 hours of use each winter,” he says.
Mark praises Brendan and the entire Nors team for the exceptional support, which provides reliable service and parts. “I can always count on Brendan to take care of us, and if something goes wrong, I know I can get the parts and service I need right away,” he adds. “I wouldn’t hesitate to recommend Brendan, Case, and Nors to anyone looking to buy their next machine.”
Mark’s success is a testament to the dedication of his team and the unwavering support of his wife and family. Their support has been instrumental in his journey, and he looks forward to continuing to grow his business alongside his trusted Case partners, demonstrating the company’s strong values and commitment.
Thanks, Mark.
Highways, arterial roads, airport runways or even railway tracks without ballasts all have one thing in common: concrete.
Wirtgen has offered machines for inset slipform paving of these extremely resilient and hardwearing concrete roads and runways and the production of monolithic concrete profiles for more than 35 years.
Automated construction of these roads that deliver a long service life and resistance to deformation is a persuasive proposition for road construction.
Planned precision
The following workflow is typical for inset concrete paving projects. First, trucks unload the concrete in front of the machine. Depending on requirements, the concrete can also be placed from the side via a belt conveyor or by a placer/ spreader (WPS) in front of the paver. The pre-placed concrete is then evenly distributed by a spreading auger or a spreading plough.
Next, high-frequency vibrators consolidate it directly in front of the paving mould. The integrated hydraulic or electric vibrators also remove excess air from the concrete. As the Wirt-
gen paver moves forward, the slipform mould shapes the profile to the specified width, thickness and form.
Inset slipform pavers offer paving widths of up to 16 metres and can pave thicknesses of up to 45 cm. The machine maintains its forward motion throughout the paving process at a paving speed in the range of 1 to 2 metres per minute. Depending on the paving project requirements, a dowel bar inserter can be integrated in the machine to insert dowels into the concrete parallel to the paver’s direction of travel as specified in the reinforcement plan.
As well, central tie bars or side tie bars can be inserted into the paved concrete at right angles to the paving direction. They serve not only as reinforcement, but also for connecting the slabs that are created by cutting joints precisely above the reinforcing elements. This ensures any cracking that may occur as a result of stress and temperature fluctuations is controlled in such a way that it occurs at the right location within the concrete surface.
The oscillating beam used for smoothing the concrete surface at right angles to
the direction of paving is mounted behind the slipform mould. The grinding movement produces a small roll of concrete in front of the oscillating beam that fills any smaller holes in the concrete surface. After this, a super smoother can be used to smooth the surface again.
The right grip
Texture curing machines begin their work immediately after the smoothing of the concrete road surface by the oscillating beam and the super smoother.
These texture curing machines give the paved concrete the desired texture and apply a solution that prevents premature drying of the surface and edges. The required surface texture is produced by using a brush, a burlap cloth or artificial turf. Automatic crown adjustment and a film unwinder for the application of a protective film round off the equipment of the texture curing machines.
Two layers, one pass Roadbuilders are able to complete two-layer concrete paving with either one or two slipform pavers.
When only one paver is used for two-layer con -
crete paving, the bottom layer concrete and top layer concrete are paved in a synchronous operation by a single machine with two sets of concrete paving equipment. The bottom layer and top layer concrete are paved “wet-in-wet,” regardless of the weather or site conditions.
When two pavers are used for two-layer concrete paving, the bottom layer concrete and top layer concrete are paved by two separate slipform pavers. Synchronous coordination of the two machines for the realization of “wet-in-wet” paving is much more demanding when using this option.
The main advantage of using two slipform pavers rather than one is the machine weight. This is because the distribution of the overall operating weight between two separate machines may be relevant for the paving workflow on the construction site.
Wirtgen slipform pavers are built on a rigid and torsion-free machine main frame. The slipform moulds themselves also have a rigid frame to prevent unevenness of the paved concrete slabs.
The heavy oscillating beam ensures a consistently smooth surface without
ridges or ruts. The super smoother, then produces the final surface evenness by a combination of longitudinal and lateral oscillation. Levelling and steering parameters are communicated to the Wirtgen machine’s control system via a physical stringline or stringless systems like Wirtgen’s smart AutoPilot or 3D systems. The interaction between mature machine technology and equipment configurations precisely tailored to the paving requirements assure perfect evenness of the concrete road surface.
Concrete road surfaces have a long service life of 30 to 40 years, according to Wirtgen.
FAE’s RCU75 remote controlled tracked carrier is entering a new era, as the manufacturer has equipped the machine with an RPL/ SSL-45 asphalt shredder.
The addition of this attachment allows FAE to offer customers a wider range of solutions, capable of addressing specific needs across industries.
The RCU75 can mill up to 17 cm deep, has a working width of 45 cm and the head comes standard with state-of-the-art technological features.
The combination of self-levelling skids and tilt ensures optimal results even on uneven surfaces.
The 3,470-kg remote controlled tracked carrier is powered by a 74-hp Tier 4
Final Kohler engine. As well, the machine can work on grades up to 55 degrees.
The hydraulic drive system helps to ensure operational precision, which makes it possible to work right up against a wall on the right or left side — as well as practical depth and cutting indicators.
The water system with an integrated tank allows for the elimination of dust from machining operations and contributes to cooling the teeth. It also has special teeth, designed for use on asphalt and concrete road surfaces.
FAE’s road planers are based on cold planer technology. With cold planer technology, the road's surface is scraped and cut by the impact of special teeth attached to the rotor.
The RPL/SSL-45 has a specially designed tooth layout to increase performance and reduce vibration, making it the perfect tool to prepare roads for resurfacing, or to simplify excavation operations. Based in Fondo, Italy, FAE is a global designer and manufacturer of heads for tractors, excavators, skid steers, special vehicles and tracked carriers for forestry, agricultural, road and demining work.
With a range of more than 90 products and 400 models, production, sales, after-sales service and parts distribution are handled at its four production sites, the headquarters, seven commercial branches and a network of authorized dealers all over the world.
By HCEA Canada
Pictured here in 1951 is a Barber-Greene Model 879 asphalt spreader in action on the main street of Sarnia, Ontario, under the watchful eye of many a local sidewalk superintendent. Area contractor, Stonehouse & Sons Ltd. was completing a reconstruction project laying down the top asphalt.
The Barber-Greene Model 879 paver, initially developed in the 1930s, underwent many revisions with the Model 879 B being introduced in the mid-1950s commanding a
purchase price of $13,500!
Powered by a Hercules four-cylinder gas engine rated at 45 kW, the paver boasted an 80 tonne-per-hour asphalt placement supplied by single axle dump trucks. With a heated screed, crown control, hydraulics to lift the screed and the ability to handle extensions to pave up to 4.27 metres in width, it was considered state-ofthe-art through the 1960s. Eventually acquired by Caterpillar, the Barber-Greene name was synonymous with
asphalt equipment innovation in roadbuilding.
The Historical Construction Equipment Association (HCEA) Canada's 2025 events include Wheels & Tracks in June and the Last Blast in October. Both events are held the Simcoe County Museum near Barrie. To see more than 60 pieces of vintage construction equipment in action, be sure to attend. HCEA Canada is a proud Heritage Partner of the Simcoe County Museum. Visit hceacanada.org for more information.
U.S. EPA PHASE III / EU STAGE V
The ARX10.1 offers cutting-edge “Side-Free Drums” technology that allows you to experience compaction like never before. The uniquely designed drum consoles installed from a single side provide unmatched precision, control, and performance. Not only that, but you will:
• The safe design = focus on productivity = reducing the time and effort spent on a task
Save on fuel costs
Reduce engine maintenance spending
Ammann is now integrating eMission, its environmentally friendly solution for machines, into new products from the manufacturer.
The strategy starts with reducing carbon dioxide and other particles, and incorporates efficiency, productivity and lower maintenance demands that make job sites healthier, while improving upon the return on investment for business owners.
As well, Ammann is using digital technologies to enhance product performance and job site management, while incorporating alternative power sources, including
electricity today and other sources in the future.
Ammann has also taken efforts to incorporate sustainable improvements across its product line through the ECOdrop initiative, which falls under the eMission umbrella.
ECOdrop starts by maximizing engine efficiency, which trims both emissions and fuel costs. As well, ECOdrop involves reconfiguring key systems and components to minimize the operational fluids required for operation. This
results in lower costs for both acquisition and disposal of the fluids.
A closer look at one specific product, the Ammann ARS 70 soil compactor, highlights the key features and benefits.
With ECOdrop, the ARS 70 has seen a reduction of 22 per cent in fuel consumption, 26 per cent in required hydraulic fluid and 10 per cent in vibratory system fluid.
ECOdrop also incorporates alternative fuels, including hydrotreated vegetable oil (HVO). The fuel has been approved for use in all Ammann diesel-powered machines.
HVO reduces carbon dioxide emissions by up to 90 per cent, with no additional costs. It is a biofuel made from waste, such as animal fat or processed vegetable oils. It is classified as a renewable diesel and known for having a longer shelf life than other biodiesels.
Every 1,000 litres of diesel fuel burned produces
of legs, integrated battery. made in Germany, 3 year warranty.
Pipe Laser - 5 year warranty
2,640 kg of carbon dioxide, compared to just 260 kg of carbon dioxide for every 1,000 litres of HVO burned.
Operator protection
The most important sustainability efforts are those that provide safety. All machines feature intuitive controls that help keep operators safe. The standard guide handle on many Ammann plates is isolated to minimize handarm vibration. According to Ammann, the vibration levels are so low that safety codes do not require documentation of operator hours.
Extending machine life
Ammann machines are built with components that extend life, once again making the most of the resources used to manufacture them. Their advanced engineering also reduces the wear that can result from less efficient machines.
A first for the aggregate processing and roadbuilding industries, Astec Industries has joined the United States Environmental Protection Agency’s (EPA) Energy Star program.
Through its voluntary partnership with the Energy Star program, Astec Industries will continue manufacturing energy efficiency solutions that minimize environmental impacts throughout the heavy manufacturing industries, by helping its customers and stakeholders implement proven energy-saving strategies designed to enhance their organization’s financial health and preserve the environment.
"Astec is pleased to become an Energy Star partner," said Jaco van der Merwe, Astec President and CEO. "Through this partnership, we further our commitment to en -
vironmental stewardship by formalizing the delivery of energy performance improvements and financial value to our rock to road customers."
In partnership with Energy Star, Astec Industries will help its customers to embed energy management as a fundamental principle in its customers’ cultures and business operations. As well, the program helps take action to realize cost savings through the implementation of energy efficiency projects in their operations and increase an organization’s value, lower risk and deliver other business benefits.
Astec Industries will also encourage corporate staff and the larger community to learn about the benefits of energy efficiency and to look for and purchase Energy Star products.
Volvo Construction Equipment is expanding its North American compaction equipment lineup with a new model for medium to heavyduty compaction jobs.
The new SD125 soil compactor is designed to deliver low operating and ownership costs, making it a fit for both rental houses and highway contractors.
The 12-ton machine becomes the largest model in the Volvo CE soil compaction portfolio with a 2.1-metre smooth-drum and operating weight of 12,050 kg.
The soil compactor will be available for order in North America during the first half of 2025.
"The SD125 is a direct response to dealers and customers who have asked for a machine that combines the quality and performance of the SD115 with the heavier weight of a 12-ton machine,” said Justin Zupanc, Compaction Product Manager. “We take feedback seriously, and I think this model shows that.”
The compactor’s specs are like the existing SD115 but with a 5 mm thicker drum shell and a heavier outer eccentric weight. This results in an additional 424 kg of mass on the drum, increasing the static load and eccentric force
for a different amplitude profile.
As terrain and material depths change, the ability to adjust dynamic drum forces is as simple as the flip of a switch on the new SD125.
Another switch adjusts the two drum frequencies to compensate for changing conditions, and a five-frequency feature is available as an option to further boost versatility and performance.
The centre joint provides 35 degrees of articulation and 12 degrees of drum oscillation for stable yet flexible performance and greater operator comfort over rough terrain.
The drum is in constant contact with the ground, which ensures compaction is smooth and uniform.
The additional static weight on the drum frame enhances stability and performance with the ability to negotiate 35 per cent slopes for better gradeability. The angled frame allows higher clearance in the approach to steep slopes and while loading, eliminating the possibility of damaging the surface or the machine.
A heavy-duty axle is integrated into the drivetrain for an efficient rear wheel drive
system. The no-spin differential increases traction and eliminates tire slippage and improves gradeability, performance and productivity.
As well, a high-traction variant is available for demanding applications where additional torque is needed to tackle extreme slopes or thick lifts of loose material.
All three levels of Compact Assist software are available on the in-cab Volvo Co-Pilot tablet, allowing users to determine the visibility, mapping and reporting features that are most important to them.
The SD125 features a Tier 4 Final four-cylinder Volvo engine with 147.5 hp. Active DPF regeneration eliminates material build-up, further reducing emissions. Additional features include a hydraulically operated engine cooling fan that runs only when needed, reducing fuel consumption as well as an optional fan reverse for cleaning out the coolers.
Remote hydraulic test ports can be configured to enable quick and easy hydraulic checkpoints without having to open the system.
In line with the Volvo commitment to safety, the emergency stop system
shuts down the engine, applies the brakes and stops the machine’s movement if the operator rises from the seat for more than five seconds
during operation.
The SD125 is designed and built at the Volvo CE North American headquarters in Shippensburg, Pennsylvania,
along with all Volvo asphalt and soil compactors. This year marks 50 years of compaction engineering and manufacturing at the site.
Prince Edward Island
NORS
Prince Edward Island (902) 468-5010
www.nors.com
Nova Scotia
NORS
Dartmouth, NS (902) 468-5010
www.nors.com
New Brunswick
NORS
Moncton, NB (506) 857-8425
www.nors.com
Newfoundland and Labrador
NORS
Mount Pearl, NL (709) 747-4026
www.nors.com
Quebec
NORS
Baie-Comeau, QC 1-866-996-3091
Ontario
NORS
Stittsville, ON (613) 836-6633
Sudbury, ON (705) 692-0552
Thunder Bay, ON (807) 475-3052
www.nors.com
Top Lift Enterprises, Inc.
Bolton, ON (905) 857-5200
Stoney Creek, ON (905) 662-4137
www.toplift.com
Manitoba
Westcon Equipment & Rentals Ltd.
Winnipeg, MB 1-800-453-2435
www.westconequip.ca
Saskatchewan
Redhead Equipment
Estevan, SK (306) 634-4788
Lloydminster, SK (306) 825-3434
Melfort, SK (306) 752-2273
North Battleford, SK (306) 445-8128
Prince Albert, SK (306) 763-6454
Regina, SK (306) 721-2666
Saskatoon, SK (306) 934-3555
Swift Current, SK (306) 773-2951 www.redheadequipment.ca
Alberta
NORS
Acheson, AB 1-877-948-3515
Calgary, AB 1-800-342-6523
Fort McMurray, AB 1-855-799-4201
Grande Prairie, AB 1-888-513-9919
Red Deer, AB 1-866-950-3473
www.nors.com
British Columbia
NORS
Campbell River, BC (250) 286-0123
Cranbrook, BC (250) 426-6778
Fort St. John, BC (250) 785-4223
Kamloops, BC (250) 372-3996
Nanaimo, BC (250) 716-8804
Prince George, BC (250) 612-0255
Surrey, BC (604) 882-5051
Terrace, BC (250) 635-9033
Vernon, BC (250) 549-4232
Williams Lake, BC (250) 392-9599
www.nors.com
By Cornelius Morgan, Senior Director of EH&S North America at AWP Safety
In highway work zones, safety isn’t just a box to check, it’s a serious responsibility.
Traffic is getting faster, and roads are busier, making strong, adaptable safety measures essential.
For construction managers, raising the bar for safety means working to protect workers and ensuring smooth travel for drivers. At AWP Safety, North America’s leader in traffic management, we strive to translate this commit -
ment into a multi-layered approach, from detailed pre-planning and strategic partnerships with law enforcement to the use of advanced safety equipment and real-time data.
Taking a closer look, we see these methods are designed not only to meet today’s demands but to set new standards for what safe and effective highway work zones should be.
Work zone setup
Effective highway work zones are the result of careful planning and teamwork well ahead of time. At the core of every successful project is a tailored traffic
control plan that considers the site’s unique challenges and addresses every detail, including lane closures, barriers, detour paths and escape routes, to help crews and motorists stay ahead of risks.
From work zone setup to daily operations and final takedown, a traffic management specialist can help you design plans that keep safety a priority at every stage of the project and align with best practices laid out in the Federal Highway Administration’s (FHWA) Manual on Uniform Traffic Control Devices (MUTCD).
Involving law enforcement from the start also boosts security by helping to keep speeds down and preventing dangerous driving near the work zone. A partnership with local agencies also makes sure the setup complies with regional standards and considers local issues, like heavy traffic times or complex intersections, so the zone works smoothly with community needs.
Quality safety equipment also plays a crucial role in work zones. Beyond traditional traffic calming measures such as cones, barrels and signage, truck-mounted attenuators (TMAs) can be positioned to absorb crash impacts, providing an extra measure of protection between motorists and work crews. Automated portable changeable message signs can also be deployed to give drivers up-to-date information on current traffic conditions, thereby reducing confusion and improving flow.
Training and tech
Effective safety in work zones includes rigorous
training for all workers that is centered on achieving zero harm. At AWP Safety, this approach includes an Environmental Health and Safety (EHS) Management System that helps to facilitate regular, data-driven training sessions. Team members cover essentials like PPE compliance and emergency signalling, for example, with on-site pre-job safety briefings reinforcing awareness and helping people keep their skills sharp where quick responses matter.
Meanwhile, the addition of wearable technology and vehicle telematics is adding new layers to training and monitoring security. Wearables like sensor-equipped safety vests can track workers’ locations and even issue alerts if they stray outside designated safe zones. And for added work zone protection, including travel to and from the site, advanced telematics and fleet management systems are giving fleet managers the ability to monitor vehicle speed, location and driver behaviour in real time.
These systems provide supervisors with live updates, alerting them to any unsafe driving and allowing for immediate adjustments that help keep both workers and drivers safe. The data collected also plays a part in supporting ongoing improvements to training programs, highlights trends and helps to reduce risks across the fleet.
Increasingly, this combination of tech and hands-on training is observed in active work zones and, for AWP Safety in particular, has been effective in reducing near misses and fostering an even stronger culture of
safety awareness. Leveraging Samsara’s real-time data, AWP Safety has been able to improve safety in measurable ways.
Over the past year, harsh events are down 37 per cent while crash rates have fallen by 50 per cent, helping save about USD$850,000 in accident-related expenses.
Stop Work Authority is another critical aspect of work zone safety that gives each team member the right to halt operations the moment they notice a risk, such as a vehicle entering the zone unexpectedly or equipment malfunctioning.
This policy underscores the priority of worker safety over deadlines or project timelines. Once work is stopped, supervisors should perform a rapid assessment of the issue, identifying the root cause and determining necessary adjustments. At the same time, clear and direct communication is critical to ensuring that everyone understands the changes before resuming work.
In high-traffic zones, Automated flagger assistance devices (AFADs) offer a safer alternative to traditional flagging by controlling vehicle flow without putting workers at risk. AFADs reduce the need for direct human involvement in managing cars and trucks passing through work zones, especially in areas with high speed or heavy traffic. This automated system allows for safer, more efficient work zone management.
Building safe and efficient work zones takes more than just following the basics—it
requires thorough planning, intensive training, technological assistance and teams empowered to make crucial safety calls.
Every highway construction site should be uniquely designed with tailored strategies and tools to address specific hazards, traffic flow and local community needs. Partnering with a traffic management expert can help ensure that every team member has the training and tools needed to manage the challenges they face, from setup to quick responses during unexpected events. These forward-thinking practices don’t just solve present challenges; they redefine highway work zone safety. Over time, these efforts will help make work zones models of innovation, leading to a future of safer, smarter roads.
Cornelius Morgan is the Senior Director of EH&S North America at AWP Safety, where he leads comprehensive safety and environmental health initiatives across the organization. Morgan holds multiple respected industry certifications, including Certified Safety Professional (CSP), Master Safety Professional (MSP), Certified Tree Safety Professional (CTSP), Associate Safety Professional (ASP), Construction Health and Safety Technician (CHST), Occupational Hygiene and Safety Technician (OHST) and Associate Safety and Health Manager (ASHM). His expertise spans regulatory compliance, hazard analysis and safety training, making him a trusted voice in advancing workforce protection and implementing best practices across industries.
1.99% APR for 48 months 2.99% APR for 60 months
• Largest minimum swing radius exavator in Link-Belt lineup.
• Power of large machine at lower weight.
• 6-cylinder Isuzu Final Tier 4 engine with fuel efficiency and high productivity without need for DPF.
• 4 work modes, including the new Eco mode.
Equipment Sales & Service Ltd.
Edmonton (780) 440-4010 essltd.com
Inland Truck & Equipment
Campbell River, BC 250-287-8878
Castlegar, BC 250-365-2807
Cranbrook, BC 250-426-6205
Fort St. John, BC 250-785-6105
Kamloops, BC 250-374-4406
Langley, BC 604-607-8555
Nanaimo, BC 250-758-5288
Penticton, BC 250-492-3939
Prince George, BC 250-562-8171
Quesnel, BC 250-992-7256
Terrace, BC 250-635-5122
Vernon, BC 250-545-4424
Williams Lake, BC 250-392-7101 inland-group.com
Itec 2000
Rosslyn (888) 574-8530
Thunder Bay (888) 574-8530
Timmins (705) 267-0223 itec2000.com
McDowell B Equipment Ltd.
Sudbury (705) 566-8190
Barrie (416) 770-7706 bmcdowell.com
Stratton Equipment Sales & Service
Stratton (807) 483-7777
strattonequipment.com
Terapro Rental
Vars (613) 443-3300
Stittsville (613) 836-0654 terapro.ca
Top Lift Enterprises Inc.
Stoney Creek (905) 662-4137
Bolton (905) 857-5200 toplift.com
• New cab with more head and leg room making this the roomiest cab ever.
• Optional WAVES® camera system adds a third camera and gives the operator a full 270º view around the machine.
• RemoteCARE® GPS-enabled telematics system included with no subscription fee!
Équipement JYL Inc.
Chicoutimi (418) 698-6656 equipementjyl.com
St-Aug-D-Desm (418) 878-2241 micanic.com
Paul Equipment (506) 826-3289 paulequipment.ca
Terapro Location
Val d’Or (819) 825-4299 Plaisance (819) 825-4299 terapro.ca
Top Lift Enterprises Inc.
St-Laurent (514) 335-2953
Sherbrooke (819) 612-5438 toplift.com
Balmoral (506) 826-3289 paulequipment.ca
Inland Truck & Equipment
Whitehorse, YT 867-668-2127
inland-group.com
In 1949 in Dubuque, Iowa, the first John Deere MC dozer entered production. Since its entry into the dozer business, John Deere has focused on meeting customer needs to improve jobsite efficiencies.
This year, Deere commemorates its 75th year as a leader in the dozer market.
“This important 75-year milestone of dozer manufacturing recognizes the tremendous teamwork of everyone involved including our factory teams, engineers and our dealers that support our customers every day,” said Matt Costello, Product Marketing Manager for Dozers at John Deere.
“We’re incredibly proud that this lineup has continued to provide the durability and performance that our customers rely on to work smarter and more efficiently getting the job done right the first time.”
In recognition of its 75th year in the dozer market, John Deere will begin adding a commemorative badge to its dozer line-up. This badge will be available on all dozers built for the remainder of 2024 and 2025.
Deere’s dozer history
Looking back at key milestones for its dozer family, John Deere has introduced numerous
industry-leading solutions and breakthrough designs that paved the way for today’s powerful and tech-packed models.
In 1958, Deere debuted the 440 crawler dozer as the first all-yellow machine built specifically for industrial applications. This model stood out as the industry’s first all-hydraulic bulldozer with a six-way power-angle-tilt blade, leading the charge with its ground-breaking design.
Deere introduced dozer T-Bar blade controls, as well as the first integral machines with the new industrial model numbers in 1965. These models included the JD350 and JD450 crawlers, which were configured distinctly as dozers or loaders.
By 1976, Deere became the first North American manufacturer to utilize dual-path hydrostatic drive on its dozer line-up.
In the late 80s, new full powershift transmission models were introduced, including the 400G, 450G, 550G and 650G models, which offered four forward and four reverse speeds, expanding capability on the jobsite. Dual path hydrostatic drive was introduced on the 450H, 550H, 650H models in 1999, and continues to date in the full John Deere dozer lineup.
Two years later, Deere introduced its largest dozer ever with the rollout of the 1050C. The 1050C led the way for the updates and innovations you see in the 1050 P-Tier today.
In 2010, Deere unveiled the industry’s first 764 high speed dozer the first new machine form in decades, boasting travel speeds of up to 25 km per hour.
This decade in dozers
In the last decade, John Deere has elevated its dozer line-up with innovations that have helped shape the current state of the construction industry. Through its investments and developments in productivity-enhancing technologies, jobsite safety solutions and comfort improvements for operators, the current state of the dozer market has been strongly influenced by the milestones met in recent years.
In 2016, John Deere introduced its factory-integrated 3D grade control, SmartGrade, on the 700K model. This factory integrated solution is equipped on more than 20 models in the Deere lineup today.
The 950K with SmartGrade became the industry’s largest power-angle tilt (PAT) blade configuration in 2017.
To assist operators in maintaining the mainfall and cross slope while
grading, Deere launched its Slope Control feature in 2020. The following year, the manufacturer debuted a new suspended double-bogie undercarriage on the 1050K, offering a reduction of peak vibrations in the cab by up to 75 per cent.
Last year, Deere rolled out its innovative EZGrade feature, which aids operators in manually grading smooth finish passes by making small blade corrections automatically.
This year, the 1050 P-Tier model was upgraded to feature the new 13.6 litre JD14 engine, enabling enhanced power and operation on the job.
Deere also expanded its dozer SmartGrade offerings into the 450 P-Tier and 550 P-Tier and updated on the 650 P-Tier. This will provide SmartGrade offerings on the 450 to 950 size dozers going forward.
The next generation of SmartGrade is John Deere designed and supported and can soon be equipped with either Topcon or Leica.
“Since its introduction to the construction market in 2016, SmartGrade has been a proven solution that enables our customers to get jobsites to grade quickly and accurately,” said Matt Costello, Product Marketing Manager at John Deere. “Now, as we build
upon this technology with the rollout of the next generation of SmartGrade, starting with our small dozer line-up, customers will benefit from improved and expanded capabilities that help increase user confidence and productivity. We are confident that any customer looking to improve their day-to-day operations will greatly benefit from implementing SmartGrade on the jobsite.”
The next generation of SmartGrade helps customers easily complete grading tasks and supports new operators to hit target grade more quickly and efficiently. Customers can get to work sooner, as no daily setup or calibration is needed at the start-up of the machine. When issues arise, customers and dealers can easily troubleshoot their machine with Wireless Data Transfer and Remote Display Access integration through the John Deere Operations Center.
The split screen capabilities on the new G5 25-cm touchscreen display allows the operator to see jobsite plans and the selected grade management option simultaneously, helping enhance operator flexibility. In addition, machine calibrations can be done easily through the monitor in the cab.
HD Hyundai Construction Equipment North America
has introduced the new 146 hp HD130 crawler dozer the second machine in its dozer line.
The HD series, introduced earlier this year with the launch of the HD100, broadens the Hyundai line of earthmoving equipment, which already includes wheel loaders, crawler excavators, wheeled excavators, articulated dump trucks, skid steers and compact track loaders and equipment designed for material handling in specialized applications.
“The new Hyundai HD130 dozer gives our customers the choice of a heavier-duty model that delivers higher productivity for larger jobs,” said Dale McLemore, Director of Sales for HD Hyundai Construction Equipment North America.
“An expanded dozer product line helps demonstrate Hyundai’s commitment to providing the right solution for a wide range of earthmoving and material-handling applications.”
Two configurations
The HD130 is a 15-tonclass machine equipped with a four-cylinder Perkins
1204J engine that meets Tier 4 Final emissions standards.
The dozer is available in two configurations. Hyundai offers the HD130 as either an LGP (low ground pressure) model or in an XL configuration.
The LGP model has an operational weight of 15,300 kg and ground pressure of 4.98 psi, while the XL configuration weighs 14,500 kg with a ground pressure of 6.16 psi.
Both dozer configurations feature a track length of 2.7 metres. A hydrostatic transmission provides smooth control of speed and torque while enhancing ease of operation.
Other key specs include maximum travel speed of 9 km per hour, eight lower track rollers, and a 76-cm shoe width with LGP blade.
The HD130 provides excellent visibility for enhanced operator confidence and productivity. The cooling system is in the rear of the machine, and the in-line pre-cleaner is under the hood for an unobstructed view to the blade. Fulllength doors help enhance visibility to the sides. As well, four high-illumination LED
lights are included as standard to improve visibility in low-light working conditions.
The Hyundai HD130 dozer comes standard with a 2D grading system that simplifies precision grading for novice operators. The system controls the blade functions, enabling faster and more accurate grading without the need for GPS or lasers.
Standard electrohydraulic controls enhance ease of operation and accur -
acy, and the ergonomically designed joystick helps reduce operator fatigue. Blade movement, slope and tilt can be adjusted to three different levels of control via the monitor.
Standard features include a ROPS/FOPS cab, sixway dozer blade, rearview camera, a 20-cm display, high-illumination LED lights, rotating beacon and track guard, seat belt warning and piping for a ripper. An oscillating track system for stable ground contact and improved operator com-
fort is also standard on the dozer.
Available options include full track guarding, forestry cab guard (top and front) additional work lamps, parallel ripper and a towing draw bar.
Grading precision
The standard six-way, variable-angle-pitch dozer blade — with a maximum angle of 25 degrees — delivers more precision when grading or moving dirt, clay and other materials.
The standard blade float
function is ideal for fine finishing or smooth back-grading. The HD130 is compatible with grading technologies that help even novice operators work faster and more precisely, save time and fuel, and maximize productivity. The HD130 dozer comes Trimble-ready from the factory, offering enhanced precision and guidance for complex designs and construction projects. This feature allows for more accurate and efficient operation in challenging work environments.
Yanmar Compact Equipment’s new ViO35-7 mini excavator delivers significant improvements to productivity, configuration and operator experience.
The 24.4-hp zero tail swing excavator includes 360-degree visibility, a 25 per cent increase in travel speed under load and a 7 per cent improvement in excavator efficiency.
According to Yanmar, the ViO35-7 provides an excellent power-to-size ratio and is easy to transport and simple to maintain.
“This new iteration of the ViO35 elevates both what operators can do and their experience while doing it,” said Zac Evans, Mini Excavator Product Manager, Yanmar Compact Equipment North America. “Yanmar listened to customers and delivered an upgraded model that’s easier to use and move around the jobsite. The ViO35-7 brings new levels of productivity while maintaining unbeat-
able reliability.”
The 3,650-kg machine has increased excavation capabilities thanks to greater breakout forces and improved cycle times under load. As well, a higher torque swing motor boosts power for backfill work involving swinging and usability on slopes.
This is powered by a threepump hydraulic system and 24.4-hp Yanmar engine. The three pumps improve performance and lead to less risk of slowing down during simultaneous operations, such as with the boom, stick, swing and curl functions. With 25 per cent faster travel speeds under load, operators can move quickly from task to task around the jobsite. It’s also easier to transition to slower tasks thanks to the auto kickdown feature built into the twospeed operation.
The new model includes additional serviceability features, including simplified
fan belt tension adjustment thanks to the rearward location of the alternator. Its engine also doesn’t require a Diesel Particulate Filter (DPF), allowing for simple operation and service. Yanmar configures the ViO35-7 for convenient maintenance, including easy access to grease points and filter locations.
Efficiency
Yanmar designed the ViO35-7 for efficient operation in tight spaces. Operators benefit from the zero tail swing aspect of the machine, which protects the equipment and nearby structures by keeping the rear of the mini excavator from extending beyond the track width during rotation. Design improvements to the boom swing angle make confined-space operation easier. The compact nature of the ViO35-7 makes it easier to transport.
The mini excavator in -
cludes a standard hydraulic quick coupler. The coupler is upgraded on the ViO35-7, providing easy attachment switching by allowing operators to engage or disengage attachments without leaving the operator seat. The pin grabber style, double locking quick coupler accommodates a wide range of attachments, from buckets to breakers.
Yanmar CE offers several configuration options to allow owners to select the most efficient machine possible for their intended applications. Buyers can add a second auxiliary circuit for attachments that provide multiple functions such as a rotating grapple or tiltrotator. Straight and angle blade options allow additional ways to customize the machine.
Operators can work in greater comfort with an adjustable suspension seat, ergonomic joystick controls and switch positions, re -
duced cab noise, improved HVAC distribution and more foot space with an updated pedal layout. As well, the model includes comforts such as a cup holder, phone holder and tablet holder for convenience in the cab.
Tech
Yanmar outfits the ViO357 with an advanced 11-cm colour display. The display puts a variety of options at the user’s fingertips, including flow rates for the primary and optional secondary auxiliary circuits, customizable attachment settings, auto
idle, service readouts and maintenance tracking. Additionally, the screen connects to the optional rear-view camera.
A subscription to Yanmar’s SmartAssist Remote telematics system comes standard on new excavators for free for the first five years. The system offers diagnostics and theft protection through GPS tracking. Machine owners or fleet managers can view the operational status of the equipment in real time along with reports to track the machine’s use and service intervals.
With the A 922 Rail excavator, Liebherr has created a machine that is suitable for work on both railway tracks and road construction that quickly navigates jobsites thanks to its mobile undercarriage.
Liebherr presented the A 922 Rail Litronic at the recent Innotrans 2024 in Berlin.
The excavator is equipped
safety systems developed by Liebherr, all customized for the machine.
Powered by a 163 hp engine, the A 922 Rail achieves a fast-working speed with smooth working movements. The innovative hydraulic concept of the A 922 Rail consists of a Liebherr variable displacement double pump with independent control circuits.
litres per minute to boost performance. The heavy ballast was also redesigned to yield the best bearing load values with improved weight distribution and a more compact rear dimension of 2 metres.
Liebherr undercarriage
The A 922 Rail is available with various undercarriage versions with different track
both the lowered and elevated position, enhancing safety.
Double cab
The spacious double cab features a standard roll over protection structure (ROPS) and a modern interior design for comfortable, focused and productive work. Entrance lighting is provided to make accessing the cab easier.
Liebherr designed the cab with a generous use of glass and standard rear and side cameras to provide an exceptional view of the working area and swing range. The touchscreen colour display, as well as the other control elements on the console, are all perfectly matched to one another to form the perfect
Occupational safety is extremely important in track construction, so Liebherr offers its own safety systems, which are tailored to the machine requirements. The safety technologies include load torque, height and sway limitation and the virtual wall.
To meet construction site requirements economically and reliably, Liebherr offers an extensive portfolio of attachments for the A 922 Rail. The new rail tongs are specially designed for the proven gripper mechanism of the GMZ 22. The attachment was developed for Liebherr's railroad excavators in close collaboration with machine operators. It enables efficient work with the track strand. The A 922 Rail exhibited at the Innotrans was equipped with a Solidlink 33-9 quick coupler. The new Solidlink 33-9 model adds more couplings to the fully automatic quick coupling system, with all the advantages. The expansion of the couplings to include a second high pressure circuit also allows the use of hydraulic attachments such as tamping equipment in rail construction, mulchers with flaps or Liebherr stick extensions. The Solidlink fully hydraulic quick coupling system allows attachments to be changed quickly and safely from the operator's cab.
The service-orientated machine design of the A 922 Rail guarantees short maintenance times and minimizes the associated maintenance costs, according to Liebherr. All maintenance points are easily accessible from the ground. The new generation has simplified access to important components even further, including air, oil and fuel filters, the main battery switch, the central lubrication point for the undercarriage and the pilot valves for the
Cat Command for Loading is expanding to all Caterpillar medium wheel loaders, excluding the GC models.
Command for Loading removes the operator from the machine and offers semi-autonomous remote control of next generation Cat 950 to 982 wheel loaders.
The Caterpillar technology allows easy switching between remote and manual in-cab operation.
By allowing the wheel loader operator to comfortably control the machine from a safe location, Cat Command maintains high machine productivity in
operating environments like demolition, environmental remediation, stevedoring and the handling of fertilizer, chips, and sawdust.
Integrated with the loader’s electronic and hydraulic systems for quick response and smooth control.
The hardware required for Command for Loading comes complete in a dealer-installed package that includes a low-profile design on the roof of the loader, requiring no welding or wire splicing.
Basic machine controls
such as wheel loader startup/shutdown, bucket rack/ dump and lift/lower are easily accessed through the ergonomic console control layout. Operator inputs are sent directly to the machine’s electronics from the Command console.
Integrated safety features stop all wheel loader movements when the A-stop or remote shutdown switch is pressed, wireless communication is lost, a severe fault is detected, or the Command console is tilted more than 45 degrees from normal operating position.
Cat Command for Loading
is available in both line-ofsight and non-line-of-sight configurations.
For non-line of sight operation, the Command for Loading station connects to multiple machines at the
same job site or different sites. The user can operate one machine at a time either onsite or from miles away.
As well, it is compatible with other Command offerings for Cat equipment, including
LBX Company has announced the new 370 X4S hydraulic excavator, equipped with several new advanced technology features, including digital level, dynamic stability assist, height and depth alarm and payload.
The 38,000 kg excavator features a 7.36 metre maximum digging depth and a maximum reach of 11 metres.
The heart of the excavator lies in its electronically controlled hydraulic pump system and the industry-recognized spool stroke control (SSC). The combination enhances efficiency and control,
while the 268 hp Isuzu AQ6HK1X Final Tier 4 engine, known for its fuel economy, powers the machine.
The 370 X4S excavator achieves up to 7 per cent improved fuel consumption without requiring a Diesel Particulate Filter (DPF), eliminating the need for maintenance or replacement.
As well, operators can select four power modes, including speed priority, power, eco and lift, allowing the machine to optimize power, precision and fuel savings depending on the task at hand.
Designed for extended operation with minimal
maintenance interruptions, the 370 features a lengthy 500-hour fuel filter service interval, enabling operators to work longer between filter changes. Additionally, the DEF tank has a consumption rate of 2 to 3 per cent compared to diesel fuel, allowing for extended operation between refills. All service points are accessible at ground level and easily opened by hand.
Inside the cab, a high-definition, 25-cm LCD monitor features an anti-glare coating to assist visibility in all lighting conditions. The monitor can be customized to display essential information, including custom hydraulic work tool names, system and machine warning messages, SCR auto regeneration status and incab pressure controls. The WAVES (Wide Angle Visual Enhancement System) provides a seamless 270 degree view around the machine.
The 370 provides a spacious cab with ROPS and FOPS Level 1 certification. Ample legroom, a high back, tilting and a heated seat contribute to a work environment that promotes relaxation and focus for operators working long hours.
There’s only one place you’ll find the heavy hitters of concrete and masonry this January: Vegas, baby — at World of Concrete 2025, the largest and only annual international event dedicated to your business. Be here to mix with industry giants. Get your hands on the latest technologies revolutionizing safety, performance and speed. And learn what it takes to not only claim a piece of our industry’s massive projected growth but dominate the field. Join the power players of concrete and masonry.
EXHIBITS: JANUARY 21-23, 2025
EDUCATION: JANUARY 20-23
LAS VEGAS CONVENTION CENTER
Jeffrey Ratliff is the new Director of Sales and Marketing for Takeuchi-US. Ratliff replaces Henry Lawson, who is retiring after six years with the compact equipment manufacturer.
A resident of Buford, Georgia, Ratliff will be responsible for dealer sales development and national account business and activity in North America.
“Jeffrey has spent his career implementing solid marketing and sales principles within the equipment industry,” said Jeff Stewart, President of Takeuchi-US.
“He has a proven track record
of building excellent teams who understand customer challenges and how to help those customers find the products that will best help them in their everyday lives. We’re pleased to have him join the Takeuchi family, and I’m excited to see his positive impact on market share and overall growth.”
His role includes helping Takeuchi-US achieve company market share objectives, including dealer sales, budgeting, asset management and inventory audits. Ratliff will also direct and manage Takeuchi’s national rental accounts.
“I’m very pleased to be with a company that’s so focused on delivering the best possible value to its customers,” Ratliff said. “All over our office, you see signs saying to ‘Do what’s right – the Takeuchi Way,’ and that’s the mindset our entire team embraces every day. Our motto for 2025 is ‘Make Our Best Better.’ We’re focused on continuous improvement, and that’s something I’m excited to be a part of.”
Ratliff comes to Takeuchi-US with nearly 25 years of experience helping teams deliver new products and services to the market
while simultaneously driving revenue growth, margin improvement and market share growth.
Over the past two decades, Ratliff worked in the agriculture equipment industry, taking on increasing responsibilities in sales and product management, eventually becoming the Marketing Director for an international machinery manufacturer.
Ratliff holds a bachelor’s degree from the University of Missouri — Columbia, where he majored in agricultural systems and minored in agricultural economics. He has also actively pursued continuing education, including such programs as Dardis Communications Leadership Presentation and Image, Fundamentals of Leadership, Purdue University Agronomy Essentials, The Project Success Method and Change Management.
Hy-Brid Lifts has announced Charlie Haskin as its new Director of Sales covering the western United States.
Haskin’s responsibilities include providing customer
support as well as continuing the growth and channel development of the Hy-Brid Lifts line of low-level scissor lifts.
“I’m excited to join this team and to be part of the
growth for the western region by building upon my existing customers and boosting new relationships,” Haskin said.
“After visiting our manufacturing facility in Wisconsin, I’m confident in the quality of our equipment and solid support of our service and leadership teams.”
Haskin brings 20 years of industry knowledge and
experience to his new role, largely derived from his time in equipment sales, dealerships and the equipment rental industry. During his time in these sectors, he had a strong emphasis on customer relationships.
"We're thrilled to welcome Charlie to the Hy-Brid Lifts team as he takes on the western United States
region. His extensive knowledge in sales and the rental industry will enhance our ability to serve our customers," said Eric Liner, CEO of Custom Equipment LLC.
"Charlie Haskins is a great addition, and we're excited about the valuable contributions he will make toward our company's continued growth."
Caterpillar has appointed Nazzic S. Keene, the former Chief Executive Officer of Science Applications International Corporation (SAIC), to its board of directors, effective November 1. Keene will serve on Caterpillar's Nominating & Governance Committee and Compensation & Human Resources Committee.
"We are pleased to welcome a leader of such high calibre to our board," said Caterpillar Chairman and
CEO Jim Umpleby. "With Nazzic's leadership history of driving growth and change in the information technology industry, Caterpillar is well positioned to help our customers build a better, more sustainable world and deliver long-term profitable growth."
Keene, 63, retired in 2023 after four years as CEO and a director of SAIC, a multi-billion-dollar global company engaged in integrating information technology systems that manage engineering,
Henri Kinnunen is joining Tana as Vice President of Product Management and Business Development. Kinnunen has a strong international business background with WOIMA Corporation, where he served as a Chief Executive Officer and oversaw more than 700 sales projects. He also worked for several years at the Finnish technology company Wärtsilä, both in Finland and abroad.
“I am thrilled and proud to join the Tana team especially in this moment of growth and as I can remain in the circular economy industry working for greener future,” Kinnunen said. “I am grateful and excited for this opportunity which fits my values and ambition levels perfectly. So, let’s roll up the sleeves and start making an impact.”
large-scale IT modernization and security, logistics, simulation and data analytics for government bodies. She was appointed to the position of CEO and elected as a director after having served as Chief Operating Officer of SAIC from 2017 to 2019 and as the President of Global Markets & Missions from 2013 to 2017.
Keene is currently a director of Automatic Data Processing Inc. and ITT Inc.
Kinnunen has a master’s degree in both Mechanical Engineering and in Industrial Management and Economics. Through his previous work experience, Kinnunen has a comprehensive understanding and strategic foresight of the global waste management industry.