
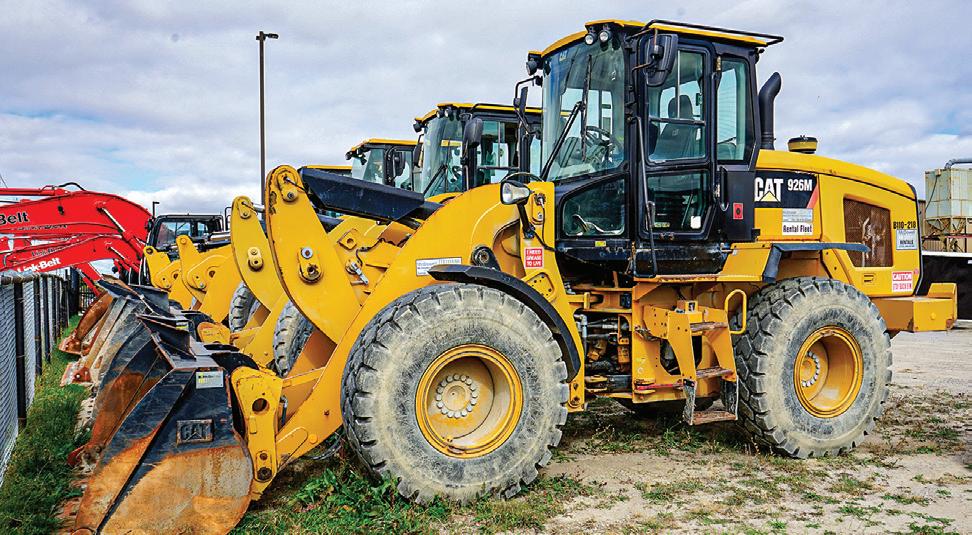
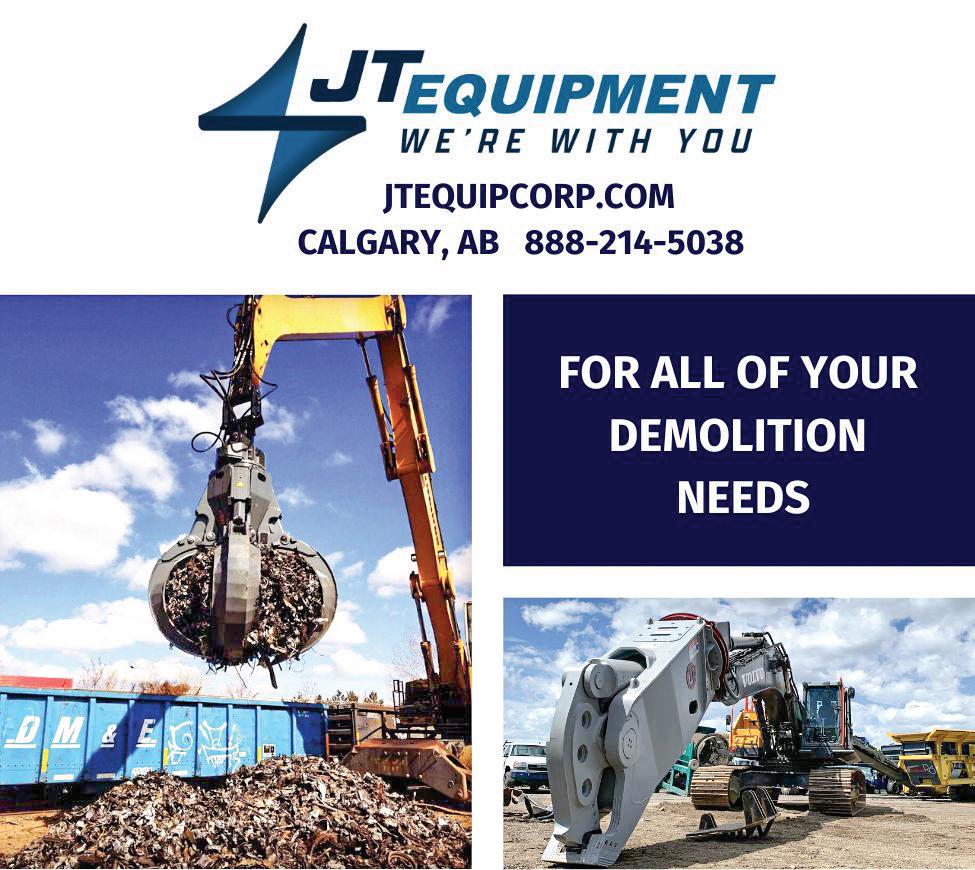
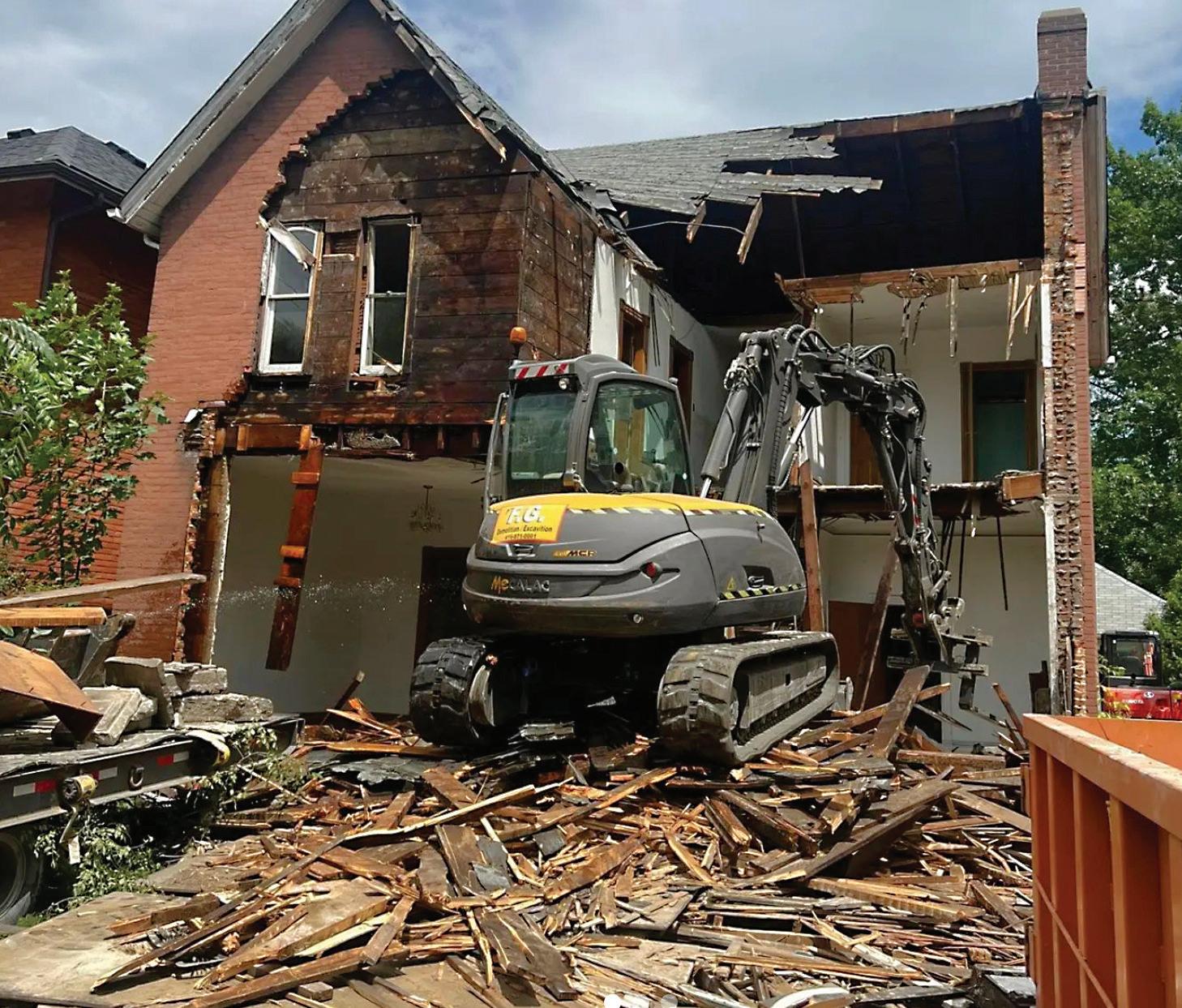
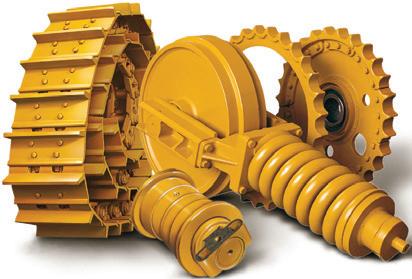
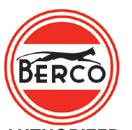
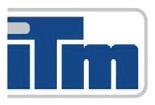
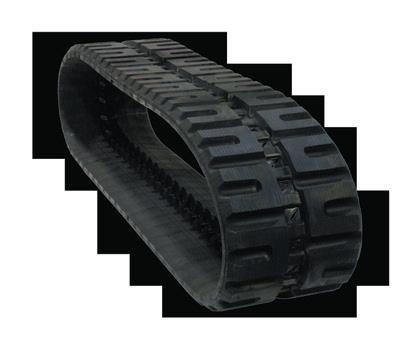
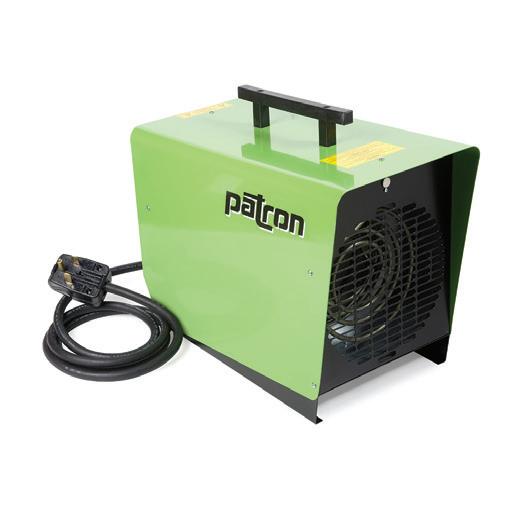
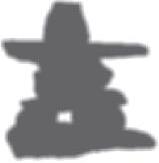
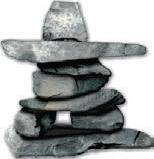
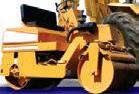
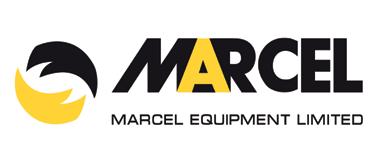

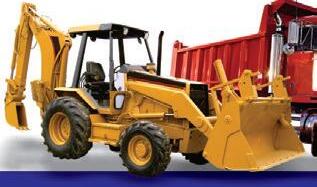

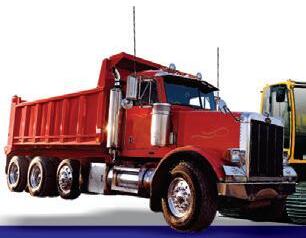
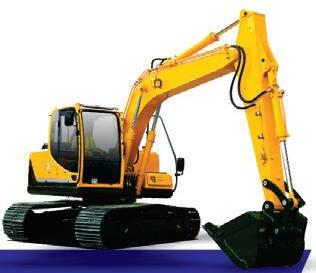
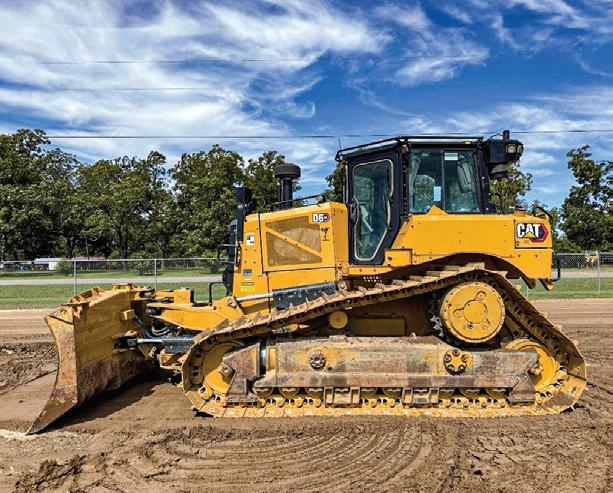
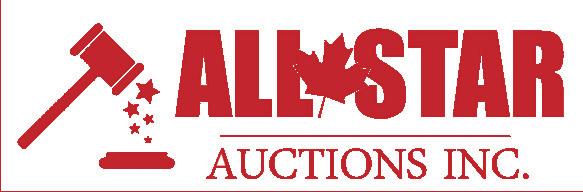
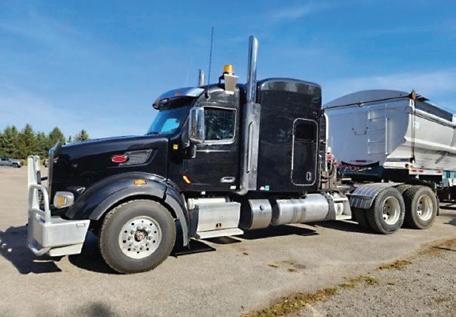
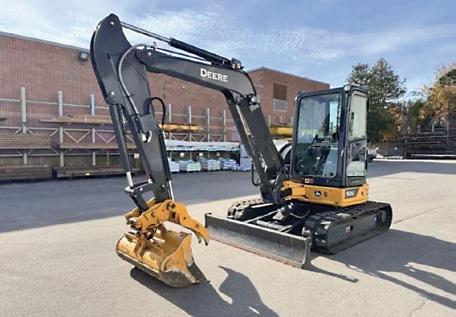
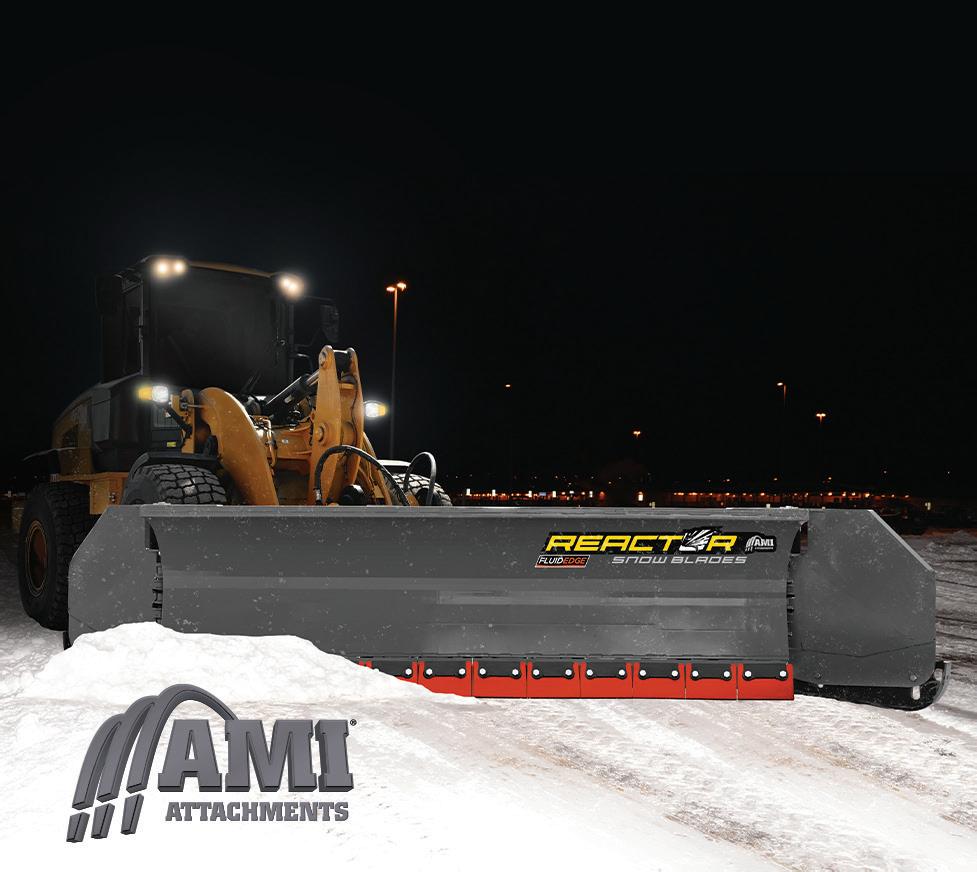
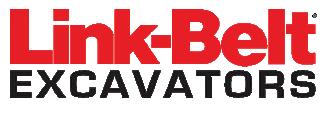


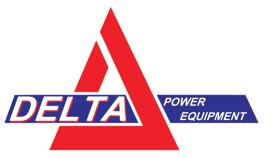
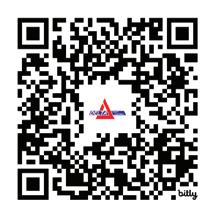
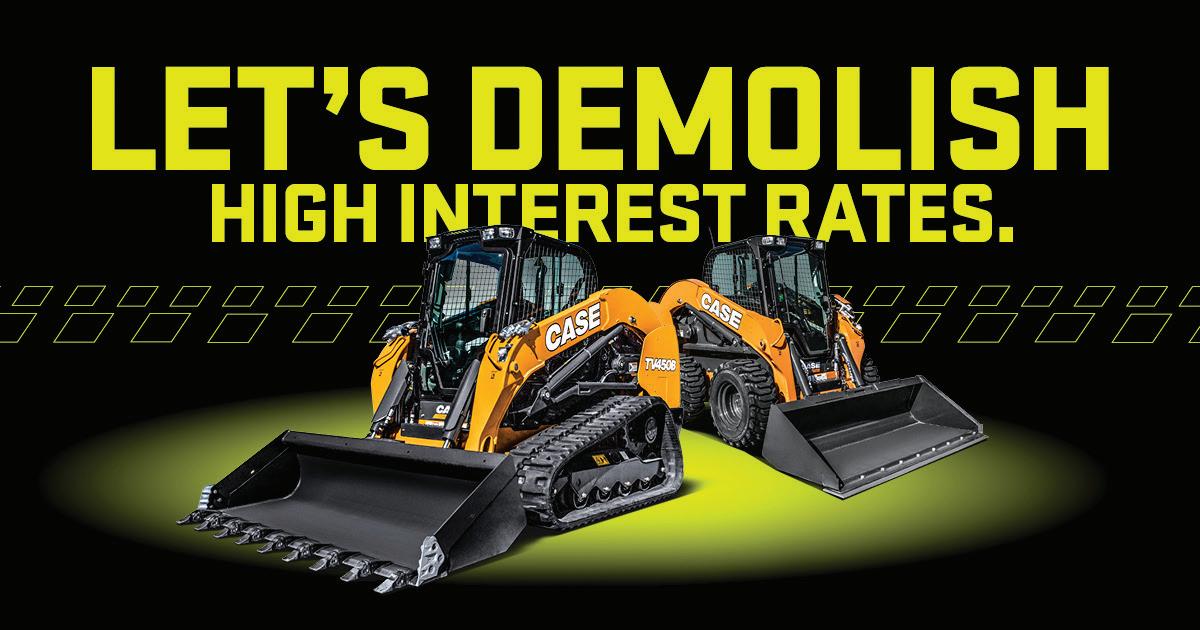
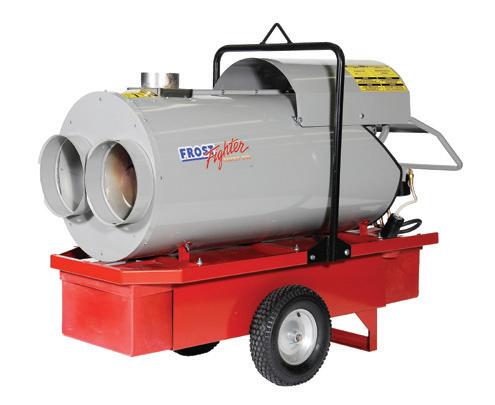
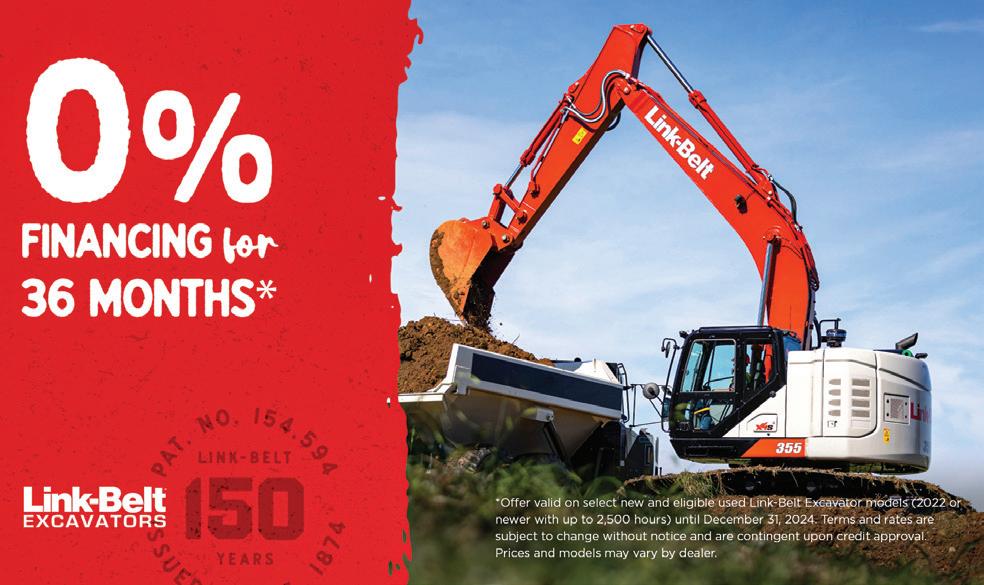
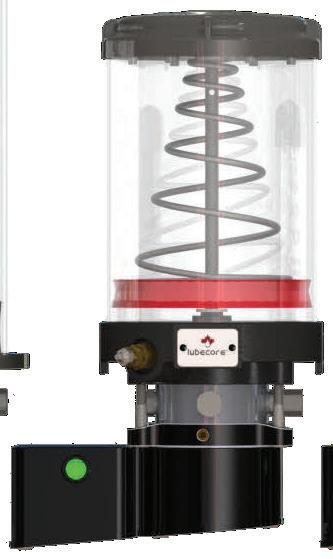
PREMIERTRAK 600 JAW CRUSHER
Designed for large and medium scale operators in quarrying, demolition, recycling & mining applications. 9.3m3 hopper, 47”x 32” crusher
Ideal for creating RipRap and recovering rocks up to 800mm (32”) that are mixed with clay and other sticky materials. The updated model has been redesigned to include new features that will improve transportation, access, and stockpile heights.
GLADIATOR MT1300 OPEN CIRCUIT
Able to operate in both heavy duty scalping and precision screening applications and will manage the most difficult of materials. 3’6” x 4’ - 2 deck screen, variable screen angle, configurable layout/ability to convert to 2-way split, wide range of screen media, quick set-up time, reversible side conveyors, 55kW/74hp @2300rpm CAT engine.
the popular 6’ x 20’ TSV6203 screen, along with a flex shaft screen drive and rollaway blending chutes, make this a leader in the screen plant market. The wide conveyor belts handle peak load conditions easily. The plant is designed to get the most out of the screen so there is plenty of capacity to make the crushers the bottleneck in the circuit, not the screen.
Liebherr
In October, the Association of Equipment Manufacturers (AEM) held its first Hill Day in Ottawa.
During the inaugural event, industry executives held meetings with Members of Parliament, senators and federal government officials to discuss how public policy can positively or negatively affect the challenges facing Canadian equipment manufacturers.
The same month, AEM announced its member count exceeded 1,100 for the first time in its history.
This month, the Associated Equipment Distributors (AED) will also hold their annual Parliament Hill Day, which offers the opportunity to “influence the policymaking process and build relationships with leading lawmakers.”
Their Parliament Hill Day will follow the finalization of
a merger with the Canadian Equipment Dealers Association (CEDA).
In Canada, equipment manufacturers employ more than 152,000 Canadians and contribute $17.6 billion to Canada’s GDP each year.
The strengthening of AEM and AED, whether it’s through new membership milestones or mergers, is important for the heavy equipment industry, and the industries it serves. It’s simply strength in numbers.
The decisions made in Ottawa have a direct impact on the economic health of the industry.
As the equipment manufacturing industry continues to develop new technologies and products for Canada’s construction, mining and forestry sectors, both organizations needs to increase advocacy efforts across Canada to make sure legislative
and regulatory changes do not negatively impact the growth of the industry.
Whether it is changes to right to repair legislation, immigration policy that could limit available skilled labour, infrastructure investment or potential tariffs or trade agreements, the equipment industry needs to have its viewpoints heard, and respected, in Ottawa.
It’s important to remember that every industry, union and advocacy group in Canada is vying for the opportunity to sit down with politicians to plead their case as to why policy should cater to their specific wants and needs. As their priorities likely do not align with equipment, it’s important to have a loud, strong voice.
By the time this issue is published, Americans will have already cast their ballot for the next President of the
United States and Canadians will be heading to the ballot box within a year.
With so many issues requiring immediate attention, or at least presented as life or death, it’s important for associations like AED and AEM to remind our elected officials of the important role machinery plays for those employed in the industry as well as North America at large.
We’ve got attachments for all your needs:
Strongco and Great West Equipment are uniting under the Nors name and branding.
The Portugal-based company is consolidating its portfolio of brands, which includes the former Strongco and Great West Equipment, as one single brand: Nors. Strongco was acquired by Nors in 2020, while Great West Equipment was acquired this year.
Nors now covers more than 80 per cent of the Canadian market, where it has a total of 37 branches and more than 750 employees nationwide.
The Nors name will replace the previous 17 brands of all Nors’ companies located in seven countries and across three continents.
At a launch event, held in Porto, Portugal, and broadcast to about 3,000 employees, Nors unveiled its new brand strategy.
Its purpose is to “improve life and business through reference services and equipment. Creating continuous value for all.”
“Nors’ brand embodies what we have been for over 90 years and our even greater ambition to be recognized
for our exceptional quality service and teams, boosting future growth in all the geographies in which we are present,” said Tomás Jervell, Nors Group’s CEO.
“This brand will be stronger, closer and more sustainable, prepared for the future and for the global transformations that Nors is already accompanying.”
The implementation of the new brand in different locations began at the October 11 launch event, and will be guided by an action plan that meets the needs of the business segments and different geographies.
The brand architecture and identity development were carried out by the Born Portugal agency, while the brand's launch and communication strategy, as well as its implementation, were carried out in partnership with Havas, and will be the subject of an online and offline campaign.
“The Nors brand has existed since 2013 in an institutional dimension," Jervell said.
"As of today, the launch of Nors in its commercial aspect is part of a process of evolution and growth,
The Canadian Rental Association (CRA) recently held its first annual Canadian Rental Week, a new Canada-wide initiative to raise awareness of the rental industry and celebrate its significant contributions to Canada.
The event, held October 15 to 19, aligns with global rental weeks as part of CRA’s collaboration with the Global Rental Alliance. Canadian Rental Week will focus on three key themes aimed at engaging industry professionals, consumers and potential new talent, including: Why Rent, Careers in Rental and Relationships in Rental.
Why Rent is a social media campaign highlighting the benefits of renting, encouraging consumers and businesses alike to embrace rental solutions. Careers in Rental showcased the rental industry as a career path.
The CRA asked individuals to share 30-second videos explaining how they got their start in the industry or offering advice for newcomers.
Through Relationships in Rental, the CRA collected stories of meaningful connections formed between peers and competitors to share on social media and in the association’s newsletter.
where international expansion stands out."
In addition to Great West Equipment and Strongco, the new name and branding includes Auto Sueco Portugal, Galius, Civiparts, AS Parts, Onedrive, Nors Centro Oeste, Agrofito, AgroNew, Auto Sueco Centro Oeste, Auto Sueco São Paulo, Kinlai, Auto Maquinaria, Auto Sueco Angola, Auto Sueco Botswana, Auto Sueco Moçambique and Auto Sueco Namíbia.
Komatsu has introduced two new -10 mechanical haul truck models to its North American lineup.
Offering an upgrade from the previous -8 models, the 60-ton HD465-10 and 70-ton HD605-10 mechanical haul trucks were introduced to the Canadian and United States markets at MinExpo.
The new haul trucks are designed to increase productivity and improve fuel efficiency in quarry, mining and aggregate applications.
“Komatsu is committed to developing equipment that supports our customers’
needs and helps them be most effective at the job site,” said Madeline Pearce, Product Marketing Manager for Komatsu. “The fuel efficiency and productivity benefits these products provide — combined with a number of operator-designed features — demonstrate that commitment. We are excited to provide these new models of haul trucks to support our customers across North America.”
HD465-10
The HD465-10 is a rigid frame machine powered by
an 818 hp engine. With a 105,400-kg operating weight, the truck features a capacity of 48.5 cubic yards and efficient hauling capabilities. Compared to the -8 model, the HD465-10 delivers 5.5 per cent more horsepower, a 1 per cent fuel efficiency improvement and is up to 6 per cent more productive when hauling loaded uphill compared to the -8 model.
The HD605-10 mechanical haul truck is also powered by an 818 hp engine and features a 114,400 kg operating
weight and a 56.3 cubic yard capacity.
Compared to its predecessor, the truck delivers a 12 per cent increase in peak torque, an 8 per cent boost to productivity when hauling uphill and a 5.5 per cent increase in horsepower.
Both trucks offer a tight turning radius of 8.7 metres for easy navigation on narrow haul roads and ergonomically designed cabin features for operator comfort during long shifts.
With increased horsepower and higher-strength steel for reduced operating
weight, the machines are built to provide excellent speed on grade.
Additional features include a MacPherson-strut-type independent front suspension that allows the vehicle to traverse uneven road surfaces, the ability to regulate fuel efficiency for lighter work with economy and economy light modes and controlled downhill descent with the automatic retard speed control function.
On both models, the dump body has been re-engineered using higher-tensile strength steel to reduce
weight, increase speed on grade and improve fuel efficiency. Stability is improved due to the lower centre of gravity through a standard V-shape body design.
New operator features include hill start assist, throttle lock, a retractable sun visor and waiting brake.
Beneficial maintenance elements include a full LED light package, plastic resin wheel chocks, maintenance-free batteries, brake performance checks and ground level Komatsu Oil and Wear Analysis (KOWA) sampling ports.
Tilt Buckets, Plate Compactors -Pipeline | Padding Buckets, Rock Grinders, Pipe Handlers -Custom Applications & Conversions
The ORION line of high capacity lift trucks is designed for superior performance and reliability. Engineered with advanced technology, ORION machines offer maximum efficiency and productivity, making them ideal for a wide range of applications. Whether you need powerful lifting capabilities or precise maneuverability, ORION has the right solution for your needs.
LIFTING VERSATILITY
Forks or boom
• Side-shifting carriages/fork locators and optional load placement cameras on select models.
PRECISION CONTROLS
• Advanced precision control systems provide smooth and accurate movements, allowing operators to perform intricate tasks with ease and confidence.
ROBUST CONSTRUCTION
High-strength steel frames and durable components designed to withstand the toughest environments and intense workloads.
EFFICIENT POWER MANAGEMENT
• ORION liquid propane machines optimize fuel use and reduce consumption, lowering operational costs and minimizing environmental impact.
CUSTOMIZED FOR YOU
• Remote control capabilities
• Various frame designs
• Custom mast heights
• Mulitple types of forks and booms
• Rear and front-facing cameras
• Side-shifting carriages
• Diesel engine or liquid propane
• Propane tanks situated in low, easy-to-reach locations
• Ergonomic seating and control placement
• Easy access panels around the engine for quick repairs and maintenance.
Full-power individual fork positioners
• Ability to side-shift maximum capacity loads for near pin-point accurate load placement, improving safety and saving time and money.
• ORION Quick Change System enables operators to switch attachments within 10 minutes
SUPERIOR LIFTING CAPACITY
• ORION machines are calibrated for optimal lifting power, ensuring safety and efficiency on every job site.
The City of Toronto has once again maintained the top spot in Rider Levett Bucknall’s (RLB) biannual crane index.
The RLB crane index counts tower cranes in 14 key markets in North America. In the last six months, Toronto recorded an increase of three cranes for a total of 83 cranes in the core area.
Residential construction accounted for the majority of cranes with 43, an increase of 11, while the mixed-use construction sector accounted for 26 cranes, a decrease from the previous index. Toronto’s healthcare, education, public assembly and transportation sectors also recorded an increase in crane activity.
“This uptick suggests a recovery from the construction slowdown observed in Q1 2024, indicating renewed growth in development activities,” the RLB crane index noted.
The crane index has changed how its counts cranes in the Toronto Area. For the new report, Toronto is using a revised radius for crane counting, prioritizing the downtown core area, which has the highest density of construction projects.
The revised area is a 3.5 km radius from Bloor Street West and Avenue Road. In the first report of 2024, this area recorded 80 cranes, about 35 per cent of the overall crane count.
Los Angeles placed second
on the Crane Index with 42 tower cranes. The city has experienced a decrease in crane activity since the beginning of the year as construction projects reach completion.
Growth in Calgary Calgary has experienced a 20 per cent increase in activity, up to 24 cranes.
The increase in Calgary represents a significant
growth in capital projects.
These major developments include the $1.2 billion Calgary Events Centre and the $1.2 billion Future Energy Park project.
As well, Calgary’s $5.5 billion Green Line LRT project is under construction, and about $550 million in residential projects are underway.
The new SM475 is now the most powerful tractor in the Yanmar America lineup.
The new machine, alongside the SM240 and SM240H tractors, made its debut at Equip Expo 2024 in October.
As well, Yanmar unveiled its first-ever limited-edition tractor, the SA223 Kuro Edition, and a fully electric concept tractor featuring the latest Eleo off-highway battery pack technology.
“At Equip Expo, Yanmar is excited to reveal a broader range of tractors designed
to meet the needs of more types of rural landowners and landscape contractors, including the Kuro Edition SA223 and our most powerful tractor yet, the SM475,” said Jon Richardson, Director of Yanmar America's Rural Lifestyle Division.
With an output of 74 horsepower, the SM475 is Yanmar’s most powerful tractor offering in North America to date, combining advanced technology and luxury design for optimal performance and comfort.
The SM475 also features a clutch-less power shuttle transmission for effortless operation and convenience via adjustable power steer-
SA223 tractor for rural landowners — the Kuro Edition. Meaning “black” in Japanese, the SA223 Kuro Edition trim offers additional rider comfort with a suspension seat and black accents. Featuring dual-range speeds, standard differential lock and three-point hitch position control, the SA223 Kuro Edition is powered by Yanmar’s three-cylinder, liquid-cooled diesel engine paired with a hydrostatic transmission. Available in summer 2025, the Kuro Edition features the design and performance of the SA223 but with added comfort and a sleek new look.
Also at Equip Expo, Yanmar will showcase its fully electric concept tractor powered by the company’s latest in Eleo off-highway battery pack technology. Yanmar expects to release its first electric tractor for rural use in 2026.
“Yanmar is also leading the way with its first battery-powered concept tractor, a crucial step to becoming a fully carbon-neutral organization as part of the Yanmar Green Challenge 2050,” Richardson said. “Taken together, these new tractors continue the Yanmar tradition of producing powerful yet efficient, versatile and comfortable tractors built to last.”
engcon has introduced a new lightweight and agile finger grab to handle twigs, branches and logs.
The finger grab is equipped with EC-Oil as standard, allowing the operator to easily change hydraulic attachments or disconnect the tiltrotator.
Developed in collaboration with Hultdins AB, the finger grab is equipped with arms that are perfect for demanding tasks like handing vegetative debris.
"The finger grab is a good addition to our range of tools," said Martin Engström,
Product Manager at engcon.
"Thanks to our close dialogue with our end customers, we can develop products that we know there is a need for on the market, and the finger grab in combination with ECOil is an excellent example of this.”
The finger grab is able to open smoothly and softly when deployed by the operator.
As well, it can lift material without the problems that often come with handling vegetation that can otherwise make the moment difficult to handle.
The Collingwood, Ontariobased MacLean Engineering has partnered with Fortescue to help rapidly electrify and decarbonize the surface mining industry.
As part of the partnership, MacLean will deliver a fleet of 30 GR8 electric graders to Fortescue’s mining operations in Western Australia.
The electric graders will be powered by a Fortescue Zero battery power system, making them one of the first battery electric graders for surface mining. The first EV grader is expected to be delivered in 2026, with the full battery electric fleet
aiming to be operational in 2029. The partnership was announced at MinExpo in Las Vegas.
“Surface mining vehicle electrification represents the dawn of a new era at MacLean, but it’s one with a deep foundation in our past as a manufacturer of fit-for-purpose solutions for the mining industry,” said David Jacques, Vice President, Surface Mining Vehicles at MacLean. “We’re taking all the learnings from our GR5 Underground Grader commercialization and our years of experience in underground BEV design,
manufacturing and site support, and putting it to good use in the context of surface mining electrification.”
At the launch event, MacLean CEO Kevin MacLean also announced the company's commitment to Fortescue's RealZero2040 initiative. MacLean pledged the company will now work toward achieving real zero emissions by 2040.
“Not long ago, industrial accidents and deaths were considered a standard part of our industry. Tailing ponds were considered a part of the normal cost. People changed that,” MacLean said. “To any-
one who thinks the carbon emissions are a required aspect of mining., Andrew Forrest (Executive Chairman
of Fortescue) stood up and said, ‘no, they're not.’ I'm here to support that statement and further say this is
now our generational challenge. We will solve it.” MacLean added the company plans to become more vocal about the need to decarbonize the mining industry.
“Going green is not a new thing for MacLean Engineering. It has been built into our DNA from the outset. However, I only recently came to realize that being public and vocal about it was also important,” he said. “Following Fortescue’s lead, we are going to be much more public about our intentions.”
MacLean has nearly a decade of experience with its full-fleet electrification program with about 500,000 operating hours logged. The company has electrified 25 machines and sold about 100 electrified units.
Fortescue Metals CEO Dino Otranto said companies like MacLean will help it fulfill its mission to eliminate fossil fuel use across its Australian iron ore operations by 2030.
“We must partner with like-minded companies like MacLean, which has a proud reputation for designing and manufacturing innovative and high-quality products for underground mining. Importantly, they also share our vision for a mining industry, and a world, no longer reliant on fossil fuels,” Otranto said.
“In 2030, we believe Fortescue will be the go-to company for green metals, technology, energy and energy storage globally. When the world needs the ‘how’ to be answered, it will turn to Fortescue.”
During the announcement at MinExpo, Oakville MPP Stephen Crawford, Associate Minister of Mines in Ontario, praised MacLean Engineering as a success story in the province. He added Ontario is the only jurisdiction in the world where critical minerals for electrification can be extracted, processed and manufactured.
“Ontario, over the last five or six years, is truly seeing a renaissance in investment, manufacturing and mining,” Crawford said.
SmartDetect is now available for select utility-class and production-class loaders from John Deere.
Building upon John Deere’s jobsite-proven advanced object detection and vision solutions that utilize a combination of cameras, radar and machine learning tools, SmartDetect technology is designed to enhance overall situational awareness, providing informed visibility to an operator’s surroundings.
“SmartDetect is a crucial addition to our portfolio of precision construction technology solutions, designed to help operators confidently navigate and maximize productivity on busy construction sites," said Katie Voelliger, Product Marketing Manager at John Deere. "Safety is a shared responsibility, and we’re excited to continue developing solutions that empower operators to work more safely and effectively.”
SmartDetect combines cameras and machine learning to help give operators a better view of their surroundings to help prioritize visibility, perception and awareness.
The system utilizes the machine’s integrated digital cameras and a dedicated
rearview high-resolution monitor to supplement jobsite visibility. The stereo camera on the rear of the machine enables depth perception to identify and classify known objects, further improving awareness.
As well, the SmartDetect system alerts operators when an object enters the machine’s projected travel path and provides unique detection alerts for the operator, as well as people in the camera’s field of view. With this advanced perception system, visual cues and bounding boxes are shown to the operator, helping to distinguish and highlight any obstacle type. By identifying fixed or moving objects such as people, poles, structures or other machinery, vision technology provides critical information to the operator.
“Our customers continue to tell us technology solutions that assist operators in identifying the most valued asset on their jobsites, their people, is an area of high importance to them,” said Nathan Demski, Jobsite Safety Product Manager at John Deere.
“Operators work long days and it’s not easy for them to remain at the peak of situational awareness throughout the day.”
Field Kits to incorporate SmartDetect are available for select utility and production-class loader models already equipped with the John Deere Advanced Vision System and Advanced Object Detection technology
“SmartDetect is another tool in the toolbox that they can use to help improve their confidence and be more aware of what's around them on the jobsite,” Demski said.
John Deere and Trimble have entered a new strategic partnership for grade control technology.
In the future, the Trimble Earthworks Grade Control technology will be integrated with the John Deere SmartGrade platform, giving customers access to the expansive Trimble technology ecosystem.
“Our mission is to help our customers maximize their productivity and profitability, especially when it comes to incorporating valuable technology solutions into their equipment fleets,” said Jerred Pauwels, Vice President of Earthmoving Production
Systems and Engineering at John Deere.
“Our partnership with Trimble presents a tremendous opportunity for our customers to access Trimble’s advanced technology ecosystem. Paired with the power and performance of the John Deere construction equipment line-up with SmartGrade, our customers will be able to make productivity gains, at the jobsite and beyond.”
With the addition of Trimble to the John Deere SmartGrade portfolio, Deere customers now have more options to access integrated grade control solutions.
By enabling optionality through SmartGrade, John Deere customers can continue to choose Deere as their machine of choice with the technology preference that best suits their needs.
“Trimble is committed to making it as easy as possible for civil construction contractors on job sites all over the world to benefit from the use of machine control technology, regardless of what type of heavy equipment they use,” said Ron Bisio, Senior Vice president of Field Systems at Trimble.
“Our Connect & Scale strategy enables smarter operations across digital
and physical domains. We are excited to team up with John Deere to advance this mission and better serve their customers’ preferred workflows.”
For more than a decade, John Deere has offered a Trimble Ready option on select machines to simplify installation in the aftermarket.
To simplify adoption for customers, various purchasing options will be available in the future for John Deere SmartGrade with Trimble Earthworks, including factory direct or field installations, and as part of the Trimble Construction One suite of digital solutions.
•
Terex Rough Terrain Cranes have developed two new models for its expanding TRT Series — the TRT 100 and TRT 60.
The two new rough terrain cranes follow the recent introduction of the TRT 80L, also part of the TRT Series.
With advanced features including the intelligent TEOS operating system, compact design, four steering modes, proportional full power telescoping boom, eco mode function and T-Link telematics platform, the TRT Series has been well-received in the marketplace.
TRT Series cranes also come complete with LED lights, a comfortable, tiltable cab with large glass surfaces and high-quality components throughout.
Combined, these advanced features contribute to the ability and ease of operation of the TRT Series and make these cranes ideal for applications including ports, construction, infrastructure, mining, energy, yard logistics and general lifting.
“We are diligently expanding our product offering to ensure our portfolio possesses the capacity and flexibility to address daily lifting challenges in the modern working environment,” said Giancarlo Montanari, General Manager of Terex Rough Terrain Cranes.
“The marketplace is highly competitive, but I have great confidence in our dedicated team members and the superior Italian craftsmanship behind every crane produced at our Crespellano manufacturing centre of excellence.”
The TRT100 has a maximum capacity of 100 tonnes and main boom length of 47 metres, with a 17-metre jib stowed on the crane’s side that can be attached to the main boom to extend reach.
A self-removable counterweight aids operational efficiency, stability and transportability. The TRT 60 rough terrain crane has a maximum capacity of 60 tonnes and main boom length of 42.5 metres, with a stowable jib of 8 metres to 15 metres. These machines are the first to feature the new IdeaLift from Terex Rough Terrain Cranes, which optimizes load lifting with asymmetric outriggers. Whether fully extended or partially retracted, the crane automatically selects the best lifting capacity based on the specific formation of the outriggers.
“Looking forward, I am excited about the prospect of further expanding our product portfolio, including reintroducing some past product lines that are currently in demand in certain markets,” Montanari said.
“This is an exciting development for our engineering and manufacturing teams, and we eagerly anticipate bringing these innovations to the marketplace in the coming year. I am proud of our team and believe these future advancements will strengthen our value offering and reputation in the lifting industry.”
Making its debuts at MinExpo, the introduction marks Stellar's latest innovation ideal for mining and construction industries and beyond.
“We are so excited to unveil the aluminum version of the TMAX 3T Mechanic Truck,” said Tim Davison, Vice President of Sales and Marketing at Stellar.
“This lighter-weight, corrosion-resistant aluminum model exemplifies our commitment to delivering cutting-edge solutions that minimize downtime and enhance operational efficiency and reliability in challenging environments.”
The TMAX 3T aluminum mechanic truck features increased payload capacity, superior corrosion resistance and an extruded top rail for convenient mounting. It also includes a robust steel crane compartment and a torsion box to withstand tough environments.
With a weight reduction of 720 kg compared to the steel model, the TMAX 3T aluminum mechanic truck maximizes payload and efficiency without sacrificing options or durability.
This product launch underscores Stellar’s commitment to providing mining and construction professionals with a full range of aluminum mechanic truck options.
Ideal for the demanding conditions of mining operations and construction sites, the aluminum variation of the popular steel TMAX tandem axle mechanic truck combines the benefits of lightweight construction with enhanced durability.
(L to R) Enzo Forletta, equipment/yard manager for Eastern Construction and Stu Johnson, sales specialist for Bobcat of Toronto/Oaken Equipment, at one of Eastern Construction’s current jobsites where they are building a new police headquarters in Brampton.
Eastern Construction is a General Contractor based out of the Greater Toronto Area. Eastern Construction was established in 1951 and is one of Canada’s most respected employee-owned construction companies.
Eastern Construction takes pride in its reputation for thinking forward and rising above after seven decades of completing 1000+ significant projects.
Enzo Forletta, equipment/yard manager for Eastern Construction, has been with the company for 15 years. When he was asked why they chose Bobcat® machines for the compact equipment, he replied, “It’s my opinion that they have the better machines. Also, for all their attachments and for the service support I get from Stuart “Stu” Johnson, sales specialist, Bobcat of Toronto/ Oaken Equipment. I love the smoothness more than anything when operating the Bobcat machines, which makes them more controllable and durable. They make the machines second to none. They move forward
BARRIE
Bobcat of Barrie
705-726-2228 oakenequipment.ca
GREY BRUCE
Bobcat of Grey Bruce 519-372-9100
bobcatoftc.com
PARRY SOUND
Bobcat of Parry Sound Ltd. 705-342-1717 bobcatofparrysound.com
TORONTO WEST
Bobcat of Toronto 416-679-4172 oakenequipment.ca
BRANTFORD
Bobcat of Brantford 519-752-7900 bobcatofbrantford.com
HAMILTON
Bobcat of Hamilton 905-643-3177 bobcatofhamilton.com
PETERBOROUGH
Bobcat of Peterborough 705-748-9119 bobcatofpeterborough.com
THUNDER BAY
Equipment World Inc. 807-623-9561 bobcat-tbay.com
so they don’t get left behind. Everyone calls a skid-steer/track loader a Bobcat.”
“Stu Johnson always calls me back and took good care of me on our newest purchase, a Bobcat T740 compact track loader. I am very meticulous about our machines. I make sure our operators take great care of them by keeping them clean and maintained. We have machines 20+ years in the yard and they are still in great condition. The resale value on the Bobcat machines is better as well. You get what you pay for. On the Bobcat machines, you get chrome rods, and their cylinders have patents on them. Some other machines are using cheaper parts.”
“The applications we use the Bobcat machines for on our sites are for site prep, clean up and some street sweeping. We went with the Bobcat track loaders for the mud at new sites. It’s much easier and faster to get through mud, and for flotation purposes, it’s easier.”
“I have been working with Stuart Johnson, Bobcat of Toronto since 2011, and I wouldn’t hesitate to recommend him, Bobcat of Toronto/Oaken Equipment and Bobcat machines for your next compact machine purchases and attachments.”
Thank you, Enzo.
CASSELMAN
Bobcat of Ottawa Valley 613-764-2033 bobcatov.com
KITCHENER
Bobcat of Tri-Cities Ltd. 1-866-214-3939 bobcatoftc.com
STRATFORD
Bobcat of Stratford 519-393-6040 bobcatofstratford.ca
SAULT STE. MARIE
Bobcat of Sault Ste. Marie 705-949-7379 bobcat-ssm.com
CORNWALL
Bobcat of Ottawa Valley 613-932-2034 bobcatov.com
LONDON
Bobcat of London 519-455-4900 bobcatoflondon.ca
STRATTON
Stratton Equipment 807-483-5505
strattonequipment.com
WINDSOR
Bobcat of Windsor 519-737-0120 oakenequipment.ca
COURTICE
Bobcat of Durham East Ltd. 905-404-9990 bobcatofdurhameast.com
MUSKOKA
Bobcat of Muskoka 249-390-7000 oakenequipment.ca
SUDBURY
McDowell B Equipment Ltd. 705-566-8190 bmcdowell.com
WYOMING
Advantage Farm Equipment Ltd. 519-845-3346 advantage-equip.com
FRANKFORD
John’s Equipment 613-398-6522 johnsequipmentsales.com
OTTAWA
Bobcat of Ottawa Valley 613-831-5166 bobcatov.com
TORONTO EAST
Bobcat of Toronto 416-679-4171 oakenequipment.ca
The Perkins 2606 power generation engine offers advanced load acceptance,efficiency and versatility
Perkins has announced the development of the Perkins 2606 diesel engine, which is optimized and purpose-built for electric power generation applica tions.
Initially available for use in currently non-regulated stationary territories, this 13-litre, six-cylinder engine leverages the power density and fuel efficiency of the in dustrial Perkins 2600 Series platform announced last year.
To date, engineers have completed more than 30,000 hours of design validation and have more than 120 pat ents granted or pending, across the entire 2600 Series engine platform.
The 2606 engine for elec tric power is scheduled for commercial production in the second half of 2025.
The latest addition to the comprehensive Perkins elec tric power range delivers a powerful 321 to 523 kW of prime power and 365 to 572 kW for standby require ments.
The 2606 engine provides flexibility by switching be tween 50 and 60 Hz and across a range of voltages, enabling one generator set to satisfy requirements in diverse regions and appli cations. It is ideally suited to the power demands of critic al applications, data centres, power plants, industrial and real estate, among other in stallations. For example, the engine is also suitable for power demands in prime applications, such as those found in remote worksites.
“Generator sets still re main the core foundation for stationary and mobile power generation needs across the globe, especially in places where the electrical grid is not readily available or reliable,” said Jaz Gill, Vice President of Perkins Global Sales Marketing, Service and Parts.
“Diesel engines are still the driving force for these generator sets, so the Perkins 2606 engine takes advantage of our deep investment in the 13-litre engine platform to deliver a dynamic, versatile power plant that provides outstanding performance at low total ownership and operating costs.”
The 2600 Series engine is designed to perform at alti tudes of up to 3,500 metres, and in extreme ambient temperatures as high as 60 C and as low as -40 C with aids.
The engine supports reliability and easier maintenance through numerous design enhancements, including the integration of
The 2606 power generation engine is compatible with renewable liquid fuels such as 100 per cent hydrotreated vegetable oil (HVO),
Exclusive to Cat machines and undercarriages, the proprietary Cat Track Wear Sensor (CTWS) remotely monitors undercarriage wear to predict and plan maintenance and increase machine uptime.
Monitored within the Cat Wear Management System, the new CTWS wirelessly communicates critical track wear information from the machine to the dealer for monitoring.
Timed alert intervals — a 40 per cent wear alert for possible bushing turns, 70 per cent to signal for measuring and replacement part ordering and 100 per cent for required replacement — im-
prove inspection scheduling and streamline ordering of replacement parts.
The real-time track wear status enables no-touch track link measurements, increases fleet coverage by automating inspections, provides visibility to track wear when operating in remote locations and allows for prioritized timing of service visits by optimizing manual inspections.
Field tested for reliability, more than 2,000 Caterpillar machines have been shipped with the sensor technology.
The small electronic sensor installs in a custom pocket in the track link for protection. Each link assembly includes
a smart link, resulting in two sensors on a machine, one on each side.
The CTWS survives high frequency shock loads and meets sensor functional and environmental tests. Subject to operating conditions, sensor battery life has been shown to last up to seven years.
The wear sensor is standard on new Cat D5, D6 and D8 dozers, as well as 953 and 963 track loader models in select regions with planned expansion to models in the dozer line in the future.
The Caterpillar wear sensor can be retrofitted on to eligible dozer undercarriages.
Liebherr has completed its Generation 8 range of mining dozers with the introduction of the new PR 776 G8.
Introduced at MinExpo, the new 768 hp flagship dozer from Liebherr is built to tackle tough mining and quarry operations.
“With the launch of the PR 776 G8, our entire range of mining dozers – which includes models with operating weights from 35 to 73 metric tonnes – is now comprised of Generation 8 machines,” said Dr Jörg Lukowski, Executive Vice President, Sales and Marketing, Liebherr-Mining Equipment. “And all of these machines include our latest product innovations and cutting-edge technology.”
The 70-tonne class PR 776 G8 features a new electronic machine architecture enabling the dozer to use more of Liebherr’s technologies.
“It is a technological enabler for operator assistance systems for the blade and ripper control, as well as for teleremote dozer operation,” said Nico Schuchter, Area Sales Manager at Liebherr Group.
The Generation 8 crawler dozer integrates advanced Operator Assistance Systems (OAS), previously available only on smaller models, that offer two levels of assistance systems. The Free Grade system delivers active blade stabilization during fine grading. Definition Grade enables automatic blade positioning when creating 2D grades.
With the Auto Blade Pitch assistance system, the operator can save and utilize three blade positions at the touch of a button, including:
· Perfect material penetration
· Optimum material transport
· Rapid blade clearing at the end of the push path
The assistance systems of the PR 776 G8 not only increase productivity and efficiency but also enhance operator comfort.
As the only mining dozer featuring a hydrostatic travel drive in the 70-tonne class, Liebherr says the machine offer best-in-class efficiency for customers. On average, the PR 776 will consume 38 litres of fuel per hour.
“The hydrostatic travel drive system provides us with unmatched fuel efficiency and power delivery when operating the dozer,” Schuchter said.
Another benefit of the hydrostatic drive is its ability to boost manoeuvrability and, in turn, productivity.
“Each track side can be controlled individually,” Schuchter said. “It's the only
dozer that's actually capable of turning on a standstill immediately.”
The combination of a Liebherr diesel engine, hydraulic motors and pumps connected by high pressure hydraulic hoses also creates a unique closed loop system reducing wear and tear on components. The standard eco mode allows operators to choose between high performance and maximum efficiency at any time.
LiReCon
The PR 776 G8 is also compatible with the LiReCon (which stands for Liebherr Remote Control) remote operation system. At MinExpo, Liebherr demonstrated the system by operating a dozer in Austria from an operator station at the trade show in Las Vegas.
“LiReCon is a teleoperation system that helps boost productivity while enhancing the safety and comfort of operators,” said Oliver Weiss, Executive Vice President of Research and Development, Engineering and Production, Liebherr-Mining Equipment.
“It allows dozers or excavators to move through hazardous areas while operators are safely ensconced in an office — far away from the danger.”
The system is suitable for all dozer applications. It consists of the Liebherr Remote Control teleoperation stand; an operator workspace including all required controls; and onboard dozer installations such as cameras for all different angles and views, microphones for recording machine sounds, radio link
receiver and transmitter.
LiReCon allows fast shift changes between operators and consequently reduces idle and downtime. As the operator is no longer tied to the machine, it also enables customers to reach new extraction areas in hazardous zones, extending the range of applications for Liebherr mining dozers.
Optimal service accessibility and extended maintenance intervals are key features. Centralized maintenance points, wide-opening access flaps and engine compartment doors, a standard tiltable operator's cab and an optional swing-out fan for cleaning facilitate quick maintenance access and straightforward servicing of the new Liebherr dozer.
As well, the new PR 776 G8 boasts particularly long change intervals for operating fluids such as hydraulic or engine oil.
"The PR 776 G8 offers longer change intervals for operating fluids that can be extended to 8,000 operating hours when Liebherr Plus oils are used,” Lukowski said.
The Generation 8 dozer is equipped with an updated cab. Operators appreciate the convenience and simplicity of a single joystick. Safety is enhanced via 360-degree blade and ripper visibility, provided by large panoramic windows and integrated ROPS / FOPS in the cab structure.
“We have a sleek and updated cab design with integrated ROPS / FOPS
protection, so there's no additional bulk around the cab,” Schuchter said.
PR 776 electrified
As part of its work with the Australian-based Fortescue, Liebherr is developing a battery-electric dozer, which is expected to enter series production in 2029. The battery power module for this PR 776 BEV will also be supplied by Fortescue Zero.
The PR 776 BEV is part of the $2.8 billion USD deal to deliver 475 zero emissions mining machines. Through the partnership, Liebherr will deliver 60 PR 776 electric
dozers by the end of 2030.
“As an OEM within the mining industry, decarbonization is a vital part of our work,” Weiss said. “We take our environmental, social
and corporate governance responsibilities very seriously and have incorporated these into our strategies for meeting the goals of our zero emission mining program.”
Bobcat’s new TL623 telehandler is a telescopic tool carrier loaded with performance and comfort features not found on other machines as standard equipment.
The TL623 offers the extended reach and lift capacity of a heavy-duty telescop -
ing boom combined with Bobcat’s multi-attachment versatility enabling operators to go beyond pick-and-place tasks.
“The TL623 gives operators the flexibility to accomplish a variety of demanding tasks with superior precision and efficiency,” said Jamison
Wood, Bobcat Product Development Specialist.
“It’s ideal for agriculture, construction, landscaping, snow removal and many other applications that require a high-performing and versatile tool carrier.”
The TL623 has a lift capacity of 2,721 kg and a lift height
of 7 metres to deliver power and productivity with every demanding lift cycle.
The advanced Tier 4, turbo-charged engine is emission compliant without the use of a diesel particulate filter (DPF) or selective catalyst reduction (SCR). Operators will also appreciate the engine’s reliable cold weather starting, along with a variety of features that make maintenance and service more convenient.
Five operation modes
Five operation modes give operators the flexibility required for a wide variety of applications. These modes include:
· Eco mode allows operators to maintain hydraulic performance without using the engine’s full power — working with lower rpm, less noise and lower fuel consumption.
· Smooth drive mode is ideal for manoeuvring across job sites with mild acceleration and deceleration while carrying loads.
· Dynamic drive mode in-
creases responsiveness of the telehandler’s acceleration and deceleration for traveling between tasks.
· Flex drive mode allows the operator to manage the engine speed independently from travel speed.
· Advanced attachment control mode allows for full auxiliary hydraulic performance.
More standard features
The TL623 is loaded with performance and comfort features designed to increase productivity. Along with the five operation modes, the telehandler also comes standard with the following performance-enhancing features:
· Four steering modes for application-matched manoeuvrability.
· The Bobcat Smart Handling System for tailored boom movements via controls on the joystick.
· Power Bob-Tach mounting system for quick and easy attachment changes.
· A spacious, high-visibility cab with an efficient HVAC system, an easyto-read control panel, intuitive controls, an air-suspension seat and an LCD screen that provides full-featured machine interaction and monitoring capabilities.
· Automatic Ride Control for reduced material spillage and faster travel speeds.
· Seven-Pin Attachment Control Device (ACD) for additional control and functionality in select attachments.
Telehandler comfort and operability
The cab features excellent ergonomics, a comfortable air-suspension seat, efficient HVAC system and an easy-toread 127-mm LCD display panel. Bobcat telehandler cabs are designed and tested to Roll-Over Protection Structure (ROPS) and Falling Object Protective Structure (FOPS) Level 2 standards.
A single, intuitive joystick controls the travel direction, lift and tilt functions, boom
extension and auxiliary hydraulics. This gives the operator fine adjustment for lifting loads with care. It also allows operators to manage several machine functions at the same time, enabling more precise control and higher productivity without having to remove their hand from the joystick.
Fingertip control access makes operation comfortable and easy. On the front side of the joystick, the directional switch for forward, neutral and reverse can be operated with the index finger. The 2-speed travel switch, lift-arm float, boom extension, machine function settings and auxiliary hydraulics are located on the rear of the joystick. The telehandler’s low-profile boom sits below operator eye level to provide an open view of the surroundings. Front, top and rear window wipers help keep windows free of debris and precipitation. Mirrors on the operator’s left and right provide added visibility when working in confined areas. An optional rear mirror kit, rear view camera kit and boom work light kit also are available.
The TL623 telehandler is built with a robust box-welded frame for enhanced rigidity, plus a low centre of gravity for optimal stability. The shielded bottom plate protects vital components, while the engine, cooling system and critical components are protected within the centre of the chassis, minimizing wear and tear due to job site obstacles or harsh terrain. Engine compartment accessibility puts routine maintenance checks, filters and other engine components in easy reach, as well as the oil filter and other service points. Thanks to the Bob-Tach mounting system, telehandler operators can share select attachments with other Bobcat equipment for even greater versatility. The TL623 telehandler will be available across North America in the fourth quarter of 2024.
• FT4 Isuzu AQ-6HK1X engine with design improvements to increase durability, performance, serviceability, and operator comfort from the previous model.
• Superior fuel efficiency
• Additional options such as HD arms, WAVES +, reversible engine fans, and Precision Grade on select models add to the perks of owning and operating a Link-Belt excavator.
• WAVES (Wide-Angle Visual Enhancement System) with 270° birds-eye view standard, therefore improving site.
Equipment Sales & Service Ltd.
Edmonton (780) 440-4010 essltd.com
BRITISH COLUMBIA
Inland Truck & Equipment
Campbell River, BC 250-287-8878
Castlegar, BC 250-365-2807
Cranbrook, BC 250-426-6205
Fort St. John, BC 250-785-6105
Kamloops, BC 250-374-4406
Langley, BC 604-607-8555
Nanaimo, BC 250-758-5288
Penticton, BC 250-492-3939
Prince George, BC 250-562-8171
Quesnel, BC 250-992-7256
Terrace, BC 250-635-5122
Vernon, BC 250-545-4424
Williams Lake, BC 250-392-7101 inland-group.com
Paul Equipment
Balmoral (506) 826-3289 paulequipment.ca
ONTARIO
Itec 2000
Rosslyn (888) 574-8530
Thunder Bay (888) 574-8530
Timmins (705) 267-0223 itec2000.com
McDowell B Equipment Ltd.
Sudbury (705) 566-8190
Barrie (416) 770-7706 bmcdowell.com
Stratton Equipment Sales & Service
Stratton (807) 483-7777 strattonequipment.com
Top Lift Enterprises Inc.
Stoney Creek (905) 662-4137
Bolton (905) 857-5200 toplift.com
• The spacious cab offers unprecedented ergonomics and comfort. A high-back seat with air, tilt, and heat features is standard. Adjustable pivoting armrests, headrests, seat height, and lumbar support provide operators comfort on long workdays.
• RemoteCARE® comes standard with a new dualband modem to improve RemoteCARE communication and functionality with greater range and real-time data capabilities - providing 24/7 remote monitoring with zero subscription charges or fees.
Équipement JYL Inc.
Chicoutimi (418) 698-6656 equipementjyl.com
St-Aug-D-Desm (418) 878-2241 micanic.com
Paul Equipment (506) 826-3289 paulequipment.ca
Top Lift Enterprises Inc.
St-Laurent (514) 335-2953
Sherbrooke (819) 612-5438 toplift.com
Inland Truck & Equipment
Whitehorse, YT 867-668-2127 inland-group.com
The Wirtgen Group has introduced the WRC 240i rock crusher— a complete in-motion machine — to the North American market.
Wirtgen wanted to offer a solution for contractors that are tackling downsizing or crushing of large in-place stone without the need for multiple touches.
The technology of the current WR series, Wirtgen’s recycler and soil stabilizer lineup, is capable of pulverizing asphalt and small stone but, the machines had limitations when dealing with larger stone. This led Wirtgen’s engineers to redesign the WR into a complete in-motion rock crusher.
Equipped with new crushing and mixing rotors, to its adjustable and interchangeable screens, coupled with the newly designed reinforced housing, the WRC was launched in 2023.
The WRC 240i’s first test was to tackle deteriorating cobblestone streets in Germany. Putting the
equipment to test was crucial as Wirtgen needed to collect as much data as possible on various stone types across Germany to test its limits.
The WRC proved capable of downsizing concrete cobblestone, asphalt with granite bases, 3-cm thick non-reinforced concrete pavement and packed layers of limestone.
After months of testing, it was assumed the WRC was well on its way to proving it could downsize in-place stone with one touch.
Once the WRC completed its testing on Germany’s infrastructure, Wirtgen engineers set their sights on larger and more abrasive stone.
In January, the first and only WRC in North America arrived in Texas to further the data collection on its capabilities. With Texas’ variety of stone blends, it proved to be the ideal proving ground for the WRC’s new technology.
As the WRC 240i has made its way
around the state, it’s been used to downsize, and in many cases pulverize in-place limestone, dolomite and granite. It was also tested at a calcium chloride byproduct plant where it proved to be “too good” and created a size too small for use.
In every demonstration the WRC has proven it can not only downsize the in-place stone, but it has outperformed traditional methods.
In a recent demonstration, the WRC was put up against a dozer using a ripper with a bucket following for cleanup. This process proved to leave many large stones still in place on the mountain road rehab, which were then dragged by the motor grader. The WRC was able to pulverize at a 25-cm depth of 7,500 square metres of the existing substrate, which was a blend of limestone and granite, to a material that was then used as the base course.
In another demonstration, the WRC was compared to a milling
head attachment on a 23-tonne wheel loader. A total of 1,100 square metres were pulverized at a 20-cm depth using the WRC in 2 hours. This same process took the wheel loader 6 hours and was only able to pulverize 15 cm deep. At another construction site, the WRC was used to downsize heaping stockpiles of large stone to usable fill. This customer ran the math afterwards and calculated a $9,000 daily saving by using the WRC.
When factoring in the WRC’s ability to relieve other fuel consuming processes, the machine can reduce overall fuel consumption on site. In most situations, a typical greenfield site will require the removal of in situ material to achieve the desired profile, grade and pavement layers. In that case, several pieces of equipment are mobilized to clear the land and possibly remove large amounts of stone. It is likely the
stone will be blasted or fractured with a hydraulic hammer, but depending on the size of the stone, it might be processed again through a large, fixed crusher and will again be piled up and moved using a loader and a dump truck.
Fuel consumption is a major contributor in producing carbon emissions and looking at ways to eliminate some of the fuel usage has been a goal of The Wirtgen Group. If on any site, a contractor could effectively remove large in-place stones with fewer touches, it would not only reduce carbon emissions but also increase daily production and profit. Through the many demonstrations Wirtgen has completed, the data supports a reduction of time on site, cost of operation and carbon emissions.
The new WRC is evidence that advanced technology can not only preform as per design but can positively impact the customer’s bottom line.
The JCB large excavator comes with more standard features than most on the market. That’s the JCB Better way—purpose-built innovation that lets you take control of every job. No matter how tough. Learn more at JCB.com.
ALBERTA
Liftboss JCB
Calgary: 403-301-0041 Edmonton: 780-474-9900 liftboss.ca
BRITISH COLUMBIA
Williams JCB
Surrey: 604-930-3316 williamsjcb.com
NEW BRUNSWICK
A.L.P.A. Equipment
Edmundston : 506-735-4144
Balmoral : 506-826-2717
Fredericton : 506-452-9818
Moncton, N.B. : 506-861-2572 alpaequipment.com
NOVA SCOTIA
A.L.P.A. Equipment
Truro : (902) 897-2717 alpaequipment.com
Harvey JCB
Corner Brook: 709-639-2960
St. Johns: 709-738-8911 harveyco.ca
ONTARIO
Advance Construction
Equipment (Division of Equipment Ontario)
Harriston: 519-510-5878 Waterloo: 519-742-5878 advanceequipment.net
D&W Group Inc.
Doughty & Williamson Jarvis: 519-587-2273
Brant Tractor Burford: 519-449-2500
Redtrac International Vineland: 905-562-4136 dwgroup.ca
ONTARIO
Delta JCB
Dunvegan: 613-527-1501
Renfrew: 613-432-4133 Winchester: 613-774-2273 deltapower.ca
Equipment Ontario
Alliston:705-320-0506 Lindsay: 705-324-6136 Port Perry: 905-982-1500 equipmentontario.com
Fulline JCB
Glencoe: 519-287-2840 fullinefarm.com
John’s Equipment Sales
Frankford: 613-398-6522 johnsequipmentsales.com
Moore JCB
Toronto, York & Peel Region: 416-747-1212 moorejcb.com
ONTARIO
North Rock JCB
North Bay, Sault Ste. Marie, and Sudbury: 705-897-7369 northrockrentals.com
ReadyQuip Sales & Service Ltd.
Timmins: 705-268-7600 readyquip.com
WPE Landscape Equipment - JCB Hamilton/Halton: 905-628-3055 wpeequipment.ca
PEI
A.L.P.A. Equipment (506) 861-2572 alpaequipment.com
QUEBEC
A.L.P.A. Equipment
Bas-Saint-Laurent : (506) 735-4144
Gaspésie : (506) 826-2717 alpaequipment.com
Bossé Quebec Inc.
Desmaures: 418-878-2241 Saint-Augustin-debosse-frere.com
Moore JCB
Montreal: 514-333-1212 moorejcb.com
SASKATCHEWAN & MANITOBA
Westcon JCB
Regina: 306-359-7273
Saskatoon: 306-934-3646
Winnipeg: 204-694-5364 westconequip.ca
Assinck creates a tilting boom grab dredge for underwater aggregate extraction
The Assinck tilting boom grab dredge is allowing aggregate producers to reach new depths of extraction.
The new floating dredge transforms how aggregate producers maximize their reserves. It creates the opportunity to extend the life of existing pits without the lengthy land acquisition and permitting phases for aggregate extraction, which can take years to finalize.
On Oct. 3, Assinck unveiled the first machine of its kind at James Dick Construction’s Caledon Sand & Gravel pit in Caledon Village, Ontario. The tilting boom grab dredge is set up on a manmade lake that was created using a drag line.
“Drag lines just don't get deep enough. They realized they had left a lot of material behind in various depths in different areas, and they didn't get as deep as they thought,” said Dean Glenn, Vice President of Assinck.
“With the value of land today, it just made complete sense to design a machine that can go down 80 to 100 feet and extract all that material.”
The Assinck floating grab dredge is outfitted with a 7-yard hydraulic clam shell bucket and it has the capacity to process 400 tons of
7” minus material per hour.
“We located a company in Germany that specializes in underwater dredging. That's all they do is make dredging buckets,” Glenn said.
The dredge includes an advanced hydraulic tipping self-cleaning grizzly screen that discharges rocks that are too large for processing back into the lake. As well, the system features a robust scalping screen and a modern fines recovery system that utilizes hydrocyclone technology for peak efficiency.
“There's a 6x20 triple deck screen in there and then there's a vertical worm and pump that picks up all the sand through the bottom deck pass on the primary scalping screen,” Glenn explained.
The pump then delivers the material into a hydrocyclone that completes s cut at 40 microns.
“We're recapturing the sand product, and it's discharged onto a high frequency dewatering screen. So, we're drying the product out before we put it back on the conveyor belt, and then everything's brought to shore after that,” Glenn said.
The dredge is also equipped with a sophis -
ticated control system. The advanced programmable logic controller (PLC) system and user-friendly human machine interface (HMI) control the machine. The configuration provides operators with control and flexibility, enabling them to make instant changes and effortlessly navigate difficult deposits. An automated positioning system controlled by a PLC and operated with a joystick controller includes four electric winches with self-spool fairleads, allowing for easy adjustments to the dredge's position in the lake when mining locations shift.
“With the onboard positioning system, it is super user friendly,” Glenn said.
“You just simply turn on the positioning system, move the joystick control, and you move.”
The dredge’s material processing plant is integrated into the machine itself and includes a floating conveyor system that delivers material to shore for further processing.
This system is designed with an elaborate slew bearing to accommodate intricate operating angles and is built to be exceptionally robust.
Constructing the dredge
Engineering the tilting boom grab dredge required about a year of work by Assinck.
Procurement and fabrication required another year followed by a six-month assembly period.
When it came time to assemble the system, Assinck dredged an area of the lake to get the required barges into the water.
“For the barges that it's sitting on, we contracted a company in Cornwall, Ontario to build those for us. It took them a year to build,” Glenn said, noting the barges weigh about 113,400 kg.
Assinck then built a dike and dewatered the area to assist with construction of the material processing plant and floating conveyor system.
“As soon as we had the machine built, we opened the dike, let the water flood in, and we floated it up, and we kind of moved it out,” Glenn said.
Based in Toronto, Assinck has been providing complete solutions for industries
such as aggregate, mining, environmental and industrial since the company was founded in 1952. The Assinck Tilting Boom Grab Dredge was created and produced in Canada by engineers and millwrights, and the dredge is the first of its kind for Canadian aggregate operations. Glenn explained the goal of creating the system was to maximize the lifespan of existing properties with aggregate licenses.
“You own the property, and you own everything. If you can go down and get another 60 feet out of that area, you can expand and extend the life of a pit by 10 or 20 years,” he said.
heavy, to withstand abusive quarry applications. Works well in hard/ abrasive stone. Easy to set up, and move around any job site, pit or quarry. Works great as a stand alone crusher, or as the primary in a crushing spread.
By HCEA Canada
Pictured here in the late 1950s is a portable crusher/ screening plant operated by Franceschini Bros. Construction based in the aggregate-rich area of Caledon, Ontario. They had been in the aggregate supply business since the mid-1940s and used several pits in the area as well as the Greater Toronto Area.
Typical of the era, a cable shovel was used to feed the gravel/screening plant. Wheel loaders with their multi-purpose use in pit applications, were on the horizon, but not readily accepted by contractors. Cable
machines still had several years of production ahead of them.
While the NCK cable shovel seen here was a British-made machine, several units found their way to Canada. Based on the well-known US-built Koehring machines, NCK’s were built under license by Newton-Chambers Ltd. of England from the late 1940s to the mid-70s hence the brand name NCK.
The late Buck Franceschini donated several machines to HCEA Canada in our early years. A Koehring 305 cable hoe, an International TD 14 bulldozer and TD 9 were
some of the machines. Buck would come to the events and operate every machine he donated to make sure we were operating it right!
The Historical Construction Equipment Association (HCEA) Canada 2025 events include Wheels & Tracks in June and the Last Blast in October. Both events are held at the Simcoe County Museum, near Barrie. To see more than 60 pieces of vintage construction equipment in action, be sure to attend. HCEA Canada is a proud Heritage Partner of the Simcoe County Museum. Visit HCEACanada.org for more information.
In 2015, Caterpillar engineers enhanced the Cat Water Delivery System (WDS) for water trucks by developing an automated delivery feature to increase safety and efficiency compared to traditional manual watering operations.
Independent of engine rpm, the software adjusts
water flow based on truck speed and automatically turns the water off when stopping at intersections. This feature reduces overwatering that can lead to poor traction and subsequent haul road damage.
Designed using customer input, the first fully integrated Cat Water Solution was
introduced in 2021, connecting a Cat truck, water delivery system, tank and telematics. This ushered in a new era of intelligent watering using Cat MineStar to provide important data for mining and quarry operations to make informed decisions.
“Our spray nozzles, which
are exclusive to Caterpillar, are hydraulically controlled pucks that are operating inside the nozzle with a spray head, and it's adjusting to output,” said Brent Dyche, Account Manager for Caterpillar. “So, what we're really doing is making this deposit of water to the ground as consistent as we possibly can get.”
At MinExpo 2024, Cat debuted WDS 2.0, which delivers more power and efficiency while improving upon integration and installation.
With more than two years of testing and validation at the Caterpillar Tucson Proving Ground, the system’s new water pump and Cat hydraulic motor provides a 25 per cent increase in water output compared to WDS 1.0.
“The Cat Water Delivery System is the culmination of nearly 20 years of collaboration with our dealers and customers,” said Dave Freeman, WDS engineering manager. “Cat WDS 2.0 is a continuation of that journey, showing our dealers and customers we’ve listened.”
The water flow increase enables water trucks equipped with the new system to achieve accurate water application rates at 45 km per hour, keeping pace with autonomous fleets.
Cat WDS 2.0 delivers increased water cannon output and spray distance. Depending on the cannon nozzle orifice and pipe size, maximum output at high idle is 7,192 litres per minute, a 15 per cent increase. It also provides a maximum 73metre spray distance, a 20 per cent increase.
“If you have to keep up the water truck with fast paced haul trucks, the water truck can run right along with
the haul trucks at full speed and still have the capacity of water to handle your dust control needs,” Dyche said.
Streamlined integration
WDS 2.0 is engineered with a high output Cat hydraulic motor connected with a new water pump assembly. The motor is optimized to work with the hydraulic output of Cat rigid frame trucks. The water delivery system is now integrated into the truck’s hoist controls to regulate the optimal amount of hydraulic power from the hoist pump to the hydraulic motor. This design helps provide precise water output while eliminating the need for a separate hydraulic tank, reducing service and maintenance costs. The motor and pump assembly use a dry coupling that reduces the need for lubrication, eliminating leaks and failures associated with wet couplings.
Auto mode uses software to automate the watering process, while allowing operators to deliver a more efficient watering technique with enhanced precision and control. Caterpillar engineers designed this feature to solve issues common with traditional watering systems that deliver water at a constant rate and require operator adjustments. Guided by automation, WDS 2.0 can help junior operators perform at a higher experience level to increase sitewide production.
Patented self-cleaning spray heads produce larger, heavier water droplets designed to reach the ground, losing less spray to wind and evaporation. Caterpillar-designed hydraulic controls regulate water pump starts and stops to increase system
life. The WDS 2.0 software provides additional protection against damage, shutting down when water is no longer pumping. This allows the operator to use all available water in the tank, reducing carryback when returning to the refill station. An in-cab touchscreen allows the operator to view critical water delivery system information like tank level, spray head selection and water application rate. An easy-to-reach keypad allows the operator to select and control the spray heads. The new water camera system provides visibility to the back of the spray bar and top of the refill chute. Reducing the potential for slips and falls, the operator can remotely fill the water tank while remaining inside the cab. Cat WDS auto shutoff integrates with fill points to prevent overfilling.
Scalable tech
The new WDS 2.0 connects with cloud-based Cat MineStar telematics, allowing customers to collect data to measure key performance indicators like operator watering procedures, cycle duration, fuel utilization, volume of water distribution and tank level when reaching the fill station.
To help manage the site more safely and productively, Caterpillar offers a choice between two connectivity options. Cat WDS MineStar Basic uses Equipment Tracking to monitor the water truck and tracks how it is being utilized. Cat WDS MineStar Premium adds Production Recording, helping address sitewide watering needs in conjunction with other water trucks and equipment.
For your crushing operations, get more options from our versatile and durable GEO series crushers. Designed by our experts in materials science and on-the-ground operations, these premium crushers get 90-95% efficiency and are built to last, meaning you get more, no matter what you throw at it, time and time again.
Primary/Secondary Crushing of Aggregates, Recycled Concrete, Asphalt, and Construction and Demolition Debris | Material Refinement
Easily adjust your feed input angles and tertiary grinding path for fine material output.
Simplified maintenance maneuvers , for less downtime and safer operation.
Get better impact even at lower speeds with our custom rotor and industry-leading wear parts.
A Hydraulic Cylinders
• Shock management springs and block valves for added durability.
• Equipped with an optional sensor controlled hydraulic cylinder adjustment system takes the guesswork out of close side settings.
B Three Adjustable Aprons
• Primary adjustable impact apron allows more consistent feed.
• Primary and secondary aprons allow for more efficient material reduction during the crushing process.
• Retractable tertiary refining apron promotes polyhedral particle shape and increases fine material output.
C Wear-resistant side liners
Available in standard, abrasion resistant, and reinforced steel.
D Breaker Plates
• Breaker plates with threaded holes made in manganese, chrome, or abrasion resistant steel. Cassette style apron weldments which allow operators to safely and easily perform breaker plate change outs on the ground.
E Adjustable Material Inlet Chute
• Allows feed angle adjustments to be made to ensure material contact with the face of the blow bar.
F Rotor (P series, heavy)
• Closed wedge-type rotor complete with rotor protection covers.
• With a rotor diameter of 51 inches the GEO maintains a high peripheral speed even at low RPM's with better inertia and impact force on input material.
This level of innovation is possible because the AMCAST group has been delivering custom premium crusher wear parts for over 65 years internationally, and 25 years in the US. Our team is driven by cutting-edge material science, dedication to durability, and listening to, and working with, our customers. We know what works and we have excellent logistical operations to get your premium parts on-site fast, so you can go faster and crush longer.
THREE SIZES, TO MEET YOUR NEEDS:
GEO 808
Power Input: 175-215 HP
Rotor Speed: 450-650 RPM
Feed Size: 24" minus*
Feed OPG: 33"H X 31.5"W**
Throughput: 100-165 TPH
*for concrete and asphalt feed
**with optional raised feed inlet
B C D E F
GEO 810
Power Input: 215-270 HP
Rotor Speed: 450-650 RPM
Feed Size: 24" minus*
Feed OPG: 33"H X 39.5"W**
Throughput: 100-330 TPH
*for concrete and asphalt feed
**with optional raised feed inlet
GEO 812
Power Input: 335HP
Rotor Speed: 450-650 RPM
Feed Size: 24" minus*
Feed OPG: 33H" X 48"W**
Throughput: 100-495 TPH
*for concrete and asphalt feed
**with optional raised feed inlet
Early next year, Volvo Construction Equipment is planning to release its new A40 articulated hauler.
Volvo CE recently offered a sneak peek of the machine during its Volvo Days event, held at its headquarters in Shippensburg, Pennsylvania.
One of the most noticeable changes to the articulated truck is a redesigned, narrower front end compared to the current A40G.
“We have improved the visibility significantly. We're actually exceeding the ISO standards,” said Fredrik Jonsson, Project Manager, Market & Launch for Volvo CE.
At the back of the truck, Volvo CE has also redesigned the tailgate with longer arms allowing it to open wider and more quickly than the previous generation.
The articulated hauler’s new cab has a larger floor area, new hanging pedals and steering wheel, as well as a heated or cooled box on the right-hand side and an integrated display for Volvo Co-Pilot.
“The cab is entirely, totally redeveloped from scratch,” Jonsson said.
Volvo also relocated the cab door from the corner to the lefthand side and in-
cluded a larger platform for access. At ground level, the A40 now includes a startup button that illuminates the stairs to the cab and begins preparation for startup.
“That button boots up all the ECUs and gets it ready for startup. Of course, you need to start the machine with a key, but the (boot up) takes roughly 20 to 25 seconds,” Jonsson said.
Buttons on the truck, as well as the access platform, are all illuminated. Volvo added numerous lights around the truck to improve visibility.
“That’s kind of the concept, we wanted to illuminate all around the tractor to make it safer to walk around the machine,” Jonsson said.
Volvo CE will also offer more options for suspension on the A40, offering hydraulic suspension in addition to rubber suspension.
“You have a choice as a
customer to choose the hydraulic suspension on the tractor only. It will still be the rubber suspension on the boogie beam on the rear,” Jonsson said.
For maintenance, a new access ladder is hidden under the hood. As well, the hood is raised or lowered at the push of a button and the entire engine compartment is illuminated to boost visibility. Furthermore, the condenser package has moved to the righthand side of the cab.
“A lot of customers are really impressed by the room and how easy it is to get in there and work on the machine,” Jonsson said.
Volvo CE also aimed to simplify the end of the workday. On the new articulated hauler, the main switch no longer needs to be switched off to power down the truck.
“Just turn the key off and the operator goes home,” Jonsson said.
Loved for the features. Trusted for the performance.
Do more without feeling like it in Hyundai’s NEW HX355ALCR compact radius excavator.
• Engineered to redefine efficiency, comfort, and safety
• RH and rear camera (standard)
• AAVM 360° camera with ultrasonic system (option)
• LED lights
• Dozer blade (option)
• 8” touchscreen color LCD monitor (standard) and 2nd monitor (optional)
• Free Hi-MATE mobile telematics for 5 years
Bob Mark Equipment Sales & Rentals bobmark.ca
42 Center St Sunderland, ON LOC 1H0 705-357-3121
1138 County Rd. 41 Napanee, ON K7R 3L2 613-354-9244
551 Grand Road Campbellford, ON KOL 1L0 705-653-3700
2197 Little Britain Rd Lindsay ON K9V 455 705-324-2221
Hood Equipment Canada Inc. hoodequipmentcompany.net 14 Haniak Road Thunder Bay Ontario P7KOC8 888-413-5454
1355 Riverside Drive Timmins, Ontario P4R1A6 705-288-4685
RTI Equipment Solutions, Inc. rtigroup.ca 2528 Bowman St. Innisfil, Ontario L9S 0H9 705-734-3350
Ontario, Canada Hyundai Dealers NEW MODEL
No wonder so many first-time Hyundai users become longtime fans. See the Hyundai difference yourself at your local dealer, or na.hd-hyundaice.com.
Mobile crushing and screening plants powered by electricity rather than diesel fuel are particularly environmentally friendly because they do not emit carbon dioxide on site.
Electric plants are also beneficial to the owner in terms of cost-effectiveness in the long term. Sustainable, low-emission solutions are in demand, and companies can position themselves on the market as future-oriented providers with electrically operated mobile plants.
Although initial investment costs are higher, they are quickly amortized due to the fuel savings. A sample calculation for the German market shows this is already possible after about six years.
“Our mobile plant train in the sample calculation consists of a jaw crusher Mobicat MC 120 Pro, cone crusher Mobicone MCO 110 Pro as a secondary crusher and a downstream screen machine Mobiscreen MSC 953 EVO. The plant train consumes an average of approximately 77 litres of diesel per operating hour. In the electrified version, it has an average current consumption of 302 kW per operating hour. The maximum power requirement is 542 kilowatts,” said Tobias Böckle, Head of Product Management at Kleemann.
“The energy requirement must first be provided by the infrastructure and is ideally met by electricity from renewable sources.
A sustainable and quickly cost-efficient solution is to use an in-house photovoltaic power supply.”
Infrastructure design
A suitable advanced design of the infrastructure is important for efficient use of electric crushing and screening equipment. Tobias Möß from Wolff & Müller GmbH explained the actual energy requirements of the plant and the demand of all already existing consumers should be determined.
“How much power is needed on the entire company premises?
The load profile must also be taken into account. When are the power peaks, when are the times with lower consumption? The individual load profile can be obtained from the energy supplier or network operator,” Möß said.
Many companies already have a transformer on their premises that adapts to the required voltage and provides low voltage for systems.
Once the required power has been calculated, it is necessary to check whether the available transformer is sufficiently dimensioned. The amount of power that can be drawn from the transformer is indicated on the type plate.
It is also important to consider where the main distribution is located on site and where the system will be used.
Good planning is a precondition for efficient operation. For example, the electrical energy
required to supply the plant is not transformed to low voltage directly at the transfer station but is instead routed over the medium-voltage level across the site to the plant. The cable cross-section can be much thinner, making the cable easier to handle and significantly cheaper.
At the mobile plant, a second transformer converts the current into low voltage to operate the mobile crushing or screening plant. The aim here is to develop a suitable individual concept.
With a solid foundation, the investment costs are amortized after around six years – or even sooner, depending on how energy is provided.
From this point on, all-electric operation will save considerable
operating costs year after year.
As an example, with the diesel-powered plant, there is no need for additional investment in the infrastructure apart from the fuel costs.
The cost of diesel fuel varies greatly depending on the country and region, so any savings depend on the difference in price between electricity and diesel.
Electrically operated crushing and screening plants are initially more expensive due to their special equipment, plus the cost of cables and a transformer.
All-electric operation incurs initial investment costs, but these pay off for the operating company in the medium term.
On closer inspection, the onetime costs quickly turn into a worthwhile investment. In many cases, climate protection regula-
tions lead to stricter requirements. The electric drive is a decisive competitive advantage, for example when local authorities demand emission-free operation in city centres.
“Especially in combination with your own PV system, electrical operation becomes a climate-friendly, cost-efficient concept in just a few years, which not only provides the operating company with financial benefits, but also reflects the company’s efforts to achieve greater sustainability,” Böckle said.
Environmentally friendly operation is also possible at locations where electricity cannot be supplied due to a lack of infrastructure. The electric version of Kleemann plants can also be operated autonomously with sustainable HVO diesel.
The X70GO is a real-time 3D model reconstruction device which integrates inertial navigation module, high performance computer and storage system. It is equipped with a 360° rotating head, which, combined with the SLAM algorithm, generates high-precision point cloud data.
A 12 MP visible-light camera provides texture information, while a visual camera guarantees stronger real time preview with GOapp.
GOapp is dedicate mobile application for X70G0, to manage projects, real time point cloud display, image preview, firmware upgrade and other operations. The APP runs on Android/iOS operating system.
XFLY series integrates high performance Inertial Navigation System with camera and LiDAR for point cloud generation.
The processing platform contains a Wi-Fi interface, an embedded cellular modem for RTCM corrections, data logging software and a gigabit Ethernet network.
Equipped with a high-performance INS, it delivers clean point clouds even at high AGL. As a small, lightweight and low-power system, it allows the user to fly longer, adapting to the needs of any project. The post-processing software provides fully automatic point cloud generation.
Prince Edward Island
NORS
Prince Edward Island (902) 468-5010
www.nors.com
Nova Scotia
NORS
Dartmouth, NS (902) 468-5010
www.nors.com
New Brunswick
NORS
Moncton, NB (506) 857-8425
www.nors.com
Newfoundland and Labrador NORS
Mount Pearl, NL (709) 747-4026
www.nors.com
Quebec
NORS
Baie-Comeau, QC
Ontario NORS
Stittsville, ON (613) 836-6633
Sudbury, ON (705) 692-0552
Thunder Bay, ON (807) 475-3052
www.nors.com
Top Lift Enterprises, Inc.
Bolton, ON (905) 857-5200
Stoney Creek, ON (905) 662-4137
www.toplift.com
Manitoba
Westcon Equipment & Rentals Ltd.
Winnipeg, MB 1-800-453-2435 www.westconequip.ca
Saskatchewan Redhead Equipment
Estevan, SK (306) 634-4788
Lloydminster, SK (306) 825-3434
Melfort, SK (306) 752-2273
North Battleford, SK (306) 445-8128
Prince Albert, SK (306) 763-6454
Regina, SK (306) 721-2666
Saskatoon, SK (306) 934-3555
Swift Current, SK (306) 773-2951 www.redheadequipment.ca
Alberta NORS
Acheson, AB 1-877-948-3515
Calgary, AB 1-800-342-6523
Fort McMurray, AB 1-855-799-4201
Grande Prairie, AB 1-888-513-9919
Red Deer, AB 1-866-950-3473
www.nors.com
British Columbia
NORS
Campbell River, BC (250) 286-0123
Cranbrook, BC (250) 426-6778
Fort St. John, BC (250) 785-4223
Kamloops, BC (250) 372-3996
Nanaimo, BC (250) 716-8804
Prince George, BC (250) 612-0255
Surrey, BC (604) 882-5051
Terrace, BC (250) 635-9033
Vernon, BC (250) 549-4232
Williams Lake, BC (250) 392-9599
www.nors.com
Contractors know hydrodemolition projects come in all shapes and sizes. Some jobsites provide a decent amount of workspace in more open areas, allowing contractors to utilize larger equipment. Other projects take place in confined spaces, such as building interiors, that limit the size of equipment.
For these applications, contractors require a machine that still provides adequate power but has the compactness to go where larger equipment is unable to access.
Tight spaces are where the Aquajet Ergo shines. Its compact size allows it to work in cramped spaces while delivering four times more power than a hand lance. Its remote-control functionality also increases safety, allowing the operator to work out of harm’s way. With its safety and versatility offerings, the Ergo is ideal for contractors with close-quarter projects.
Limited access
A unique project occurred in the basement of an industrial building in Montreal. The building required a new layout for tanks, each of which requiring a drain line. The contractor tasked with the job needed to create trenches in the basement’s concrete to install the new drainpipes.
The building owner didn’t want jackhammers or saws to be used because they wanted to keep the rebar intact. The concrete slab couldn’t be damaged because of water pressure from the ground water under the building. Furthermore, the basement setting offered limited access that restricted larger equipment from entering.
Montreal-based Groupe MGC took on the project. Groupe MGC purchased an Aquajet Ergo in summer 2021 that was the ideal machine to tackle the job.
“Based on the space we had to work in, the compactness of the Ergo was an advantage,” said Carl Henri, Groupe MGC President said.
“We could have used larger equipment in the work area itself, but limited access made it impossible to get the equipment into the building. One of the main reasons we invested in the Ergo is for projects that require us to work in tighter spaces where we can’t bring larger machines.”
The crew removed 20 cubic metres of concrete at a depth of about 60 cm for the challenging project. Groupe MGC completed the job in about 22 days using a crew of four to six people. Handling wastewater was particularly challenging given the location of the job, where only compact equipment could access the
work area. The crew collected water and debris from the work zone with a vacuum truck and transferred it to a holding tank for treatment.
During the winter in northern Alberta, a pulp and paper plant removed a pump from a below-grade chamber for maintenance. After pulling the pump, they discovered the surrounding concrete was deteriorated to the point of having exposed rebar. The concrete walls were about 30-cm thick with about 10 cm of the concrete chewed away. The ceiling was in a similar state.
The plant engineer worked with the Edmonton-based Restocrete, Inc. in the past and was impressed with their execution of a previous contract. Restocrete managers Nick and Justin Downar needed an efficient hydrodemolition machine that could be operated from a safe distance above the chamber, so they turned to the Aquajet Ergo.
“Once we decided to make the jump and invest in the equipment, we saw the ROI. The equipment was smooth and the relationship with Aquajet has been great,” Nick Downar, Restocrete’s General Manager said.
“It requires less workers, gets rid of silica dust, keeps time off tools
reducing opportunities for injuries and has been easy to take care of.
The Ergo also allowed Restocrete to remove deteriorated concrete without vibrating the existing structure, which was mandated by the client. It was a big win for us.”
The environment presented multiple challenges, beginning with the area for removal. The pit with the damaged concrete was below the water table and a confined space at about 4.9 metres deep, making traditional removal methods difficult and potentially dangerous. However, thanks to the Ergo’s remote-control capabilities, the Restocrete crew could operate the equipment safely from above, with significant reduction of time in the pit for removal.
The weather presented another hurdle. Temperatures during the project dropped as low as -30 C.
The Restocrete crew constructed insulated hoarding for the Ergo and Jetstream pump with heaters running throughout the project. The tent provided some protection from the elements but couldn’t be entirely sealed, allowing a freezing wind to flow through at times.
Visibility also became an issue as the temperature difference between the air in the pit and inside of hoarding produced a great deal of steam when 40,000 psi was used.
This hindered visibility and forced the crew to halt work at various points to let the air clear and ensure operation in the pit was running smoothly.
At project end, Restocrete completed concrete removal and repair on three of the five chambers at the plant, taking out all deteriorated concrete, extending behind the rebar, at a depth of up to 15 cm. The hydrodemolition portion took about a week. Then, they had to go back, form and pump the concrete, then coat it.
“Even with the timeline slightly drawn out due to pausing at points because of the steam, this project was significantly faster, leaving better quality surface profile and overall concrete condition with Hydrodemolition than what it would’ve been with jackhammering,” said Justin Downar, Restocrete’s Commercial Manager.
Whether it’s an industrial building or an underground pit, using an Ergo for hydrodemolition provides an efficient, versatile solution for contractors.
The heightened safety, remote-control operation in confined spaces and efficiency has made it an appealing replacement for traditional concrete removal and repair methods.
Edge Innovate says its new VS750i primary waste shredder represents a leap forward in waste management.
The VS750i primary waste shredder is engineered to handle a broad range of materials and to meet the various needs of modern waste processing facilities.
“Edge Innovate continues its tradition of producing robust, high-performance equipment with the launch of the VS750i,” said Tom Connolly, Global Sales Manager for Edge Innov -
ate. “This latest product is the ultimate high-capacity twin-shaft primary shredder for diverse and demanding waste processing. The VS750i reaffirms Edge’s commitment to leading the recycling industry with advanced processing solutions that meet the evolving demands of waste management.”
The powerful VS750i is engineered to process bulky, industrial and various other materials with ease, reducing them to manageable piece sizes. This capability significantly lowers the volume of shredded material, reduces transportation costs and allows for greater extraction of commodities.
With its ability to be positioned near collection points in plants and landfills, the shredder is convenient and offers operational efficiency.
The machine excels in environments where incoming materials vary greatly in size, composition and shredding difficulty. It features dual 2.5-metre-long rotors made from solid steel and equipped with Hardox manufactured rotating knives that run asynchronously in both directions. This design ensures constant material movement, preventing bridging and maximizing processing efficiency.
“The VS750i is equipped with our advanced intelligent operating system, which includes tramp metal protection,” said Kevin Kelly, Product Development Manager for Edge Innovate.
applications. Capable of shredding a wide range of materials such as, household waste, construction debris and compacted waste bales, it’s ideal for use in recycling plants, refuse-derived fuel (RDF) production, incinerators and large hazardous waste plants.
The shredder's 755 hp Caterpillar engine, open cutting table, hydraulic hopper extensions, automatic tipping hopper and onepoint service area for easy maintenance underscore its user-friendly design.
Delivering consistently high throughput — up to 150 tons per hour depending on the input type, knife configuration and loading procedure — the VS750i ensures maximum uptime and smooth operation.
Edge Innovate’s intelligent load management system further enhances its performance, making it a reliable choice to keep production lines moving efficiently.
Combining Edge Innovates Intelligent Load Management System and the VS Status Alert ensures the efficient loading of the shredder leading to consistent high throughputs with minimal downtime. Edges “track and shred” functionality compliments this combination, allowing the VS750i to be repositioned without the need to stop shredding.
“This system safeguards the shredder from contaminants, preventing asset damage and allowing it to process a wide array of materials swiftly and safely, including municipal solid waste, industrial, commercial and bulky waste. Its multiple chamber configurations enable customization to meet specific product sizing with huge production capacity requirements.”
The VS750i is constructed to withstand the toughest
The VS750i is also available as a static electric unit, offering lower operating costs, less servicing and no refuelling time.
Ideal for markets with environmental, legislative or noise constraints, the VS750i static electric matches the production capacity of its diesel and hydraulic counterpart. Its reduced maintenance needs and higher uptime ensure dependability with operators being able to customize the unit to meet specific application requirements or retrofitting into an existing waste processing plant.
Rotochopper has completed its new facility expansion, marking a significant milestone in the company’s history.
The new Research and Development Innovation Center is a 1,115 square metre expansion that includes a state-of-the-art production space. This significantly increasing the company’s manufacturing capabilities, while the new office area enhances collab-
oration and efficiency.
This space will allow Rotochopper’s engineering and R&D teams to continue driving innovation, ensuring they remain at the forefront of technological advancements.
As a factory-direct company, Rotochopper has a deep understanding of the unique challenges its customers face, and the R&D space is essential in creating the tailored solutions that businesses need.
At SMS Equipment, we’re more than machines from trusted brands like Komatsu. No matter your project, we’re the people beside you—today and every day—bringing industry-leading technology and expertise to your job site.
Because the right partnership makes everything possible.
Epiroc has expanded its DP 2320 and DP 4220 demolition pulverizer range with two new models that feature performance booster. The DP 2320 is suitable for
18-ton to 29-ton machines and comes with a service weight of 2,350 kg. The larger DP 4220 fits the 38 ton to 57 ton carrier class and has a service weight of 4,220 kg.
Epiroc’s demolition pulverizer range stands out as the performance booster can be retrofitted onto existing attachments. Unlike other pulverizers on the market that require different bodies to withstand the load of a performance booster, the slim, modular design can cope with the additional power.
The Epiroc performance booster elevates the demolition pulverizer performance by up to 20 per cent, helping to complete jobs faster and more efficiently.
The performance booster not only boosts power but
carrier fuel consumption up to 35 per cent, making the demolition pulverizers a sustainable and cost-effective solution. Both new models deliver precise handling and an impressive crushing force. Their slim, modular design eliminates the need for cylinder rod protection, and the 360-degree endless hydraulic rotation ensures optimal positioning and precise handling on the job site.
Epiroc’s demolition pulverizers are highly versatile attachments capable of handling both demolition tasks and secondary breaking
By Tony den Hoed, Director of Strategic Accounts — Demolition, Volvo Construction Equipment
Researching and selecting the right demolition excavator for your fleet is no simple task. I’ve shared tips for this process before in Equipment Journal, but it’s worth diving a little deeper into one specific area: factory-fitted machines versus converting a standard excavator with aftermarket options to do demolition work.
First things first: I always encourage keeping a machine’s total cost of ownership (TCO) at the front of your mind as you shop, and aftermarket versus factory-fitted decisions contribute to almost every aspect of that calculation.
Let’s start with one of the most critical features for demolition excavators: guarding. This protects the cab, tracks, cylinders and other key components — increasing crew safety and reducing machine damage. A guarding package from a purpose-built demolition excavator is the best choice here because it will be designed for that specific model and remain sturdier than something that gets added on later.
It’s also a smart financial decision. Aftermarket guarding packages can cost $40,000 USD or more. They also involve working with a third party, and support
could be limited. A factory-fit machine, however, should be backed by the OEM’s warranty. Another consideration is that aftermarket modifications could affect your factory warranty, so be sure to do your research.
While I’m speaking of third parties, keep in mind that the more modifications you make from different vendors, the more parties you may have to deal with should an issue arise, and I’ve seen time and again where companies blame each other for problems.
The difference a pin can make
Here’s an example of how design decisions — even something as seemingly simple as a pin — can add up to a big difference.
Almost every demolition excavator will have a modular joint boom concept, but the pins that hold the joint to the boom can differ.
Some manufacturers and aftermarket companies use a half hook for the top pin and short pins on the bottom.
A well-designed, purpose-built demolition excavator should include full-length hydraulic pins that an operator can pull out without leaving the cab. The less an operator must leave the cab to accomplish a task, the safer and more efficient they’ll be. Also, fulllength hydraulic pins are simply more reliable than short pins.
The manufacturers of a purpose-built demolition excavator will put extra thought and effort into elements that may not be as much of a focus on a standard excavator. That means larger boom cylinders, additional frame reinforcement, appropriate counterweighting, a high-visibility and demolition specific cab
that tilts, a dust suppression system with pressure washer and hydraulically extendable tracks for ease of transportation and increased stability.
While some of these features can be added after the fact, they may cause a delay in getting the machine incorporated into your fleet, add more parts for your technicians to maintain or cause you to have to take it into the dealer more often, and have a bigger impact on your bottom line.
For example, you may spend $7,500 per boom cylinder, $21,000 for a counterweight, $60,000 for a tilting cab, $15,000 for a dust suppression system and $75,000 on the hydraulic extensions (All amounts are in US dollars).
The choice is clear
When jobsite safety is the number one goal, the stability, visibility, strength and intentional design of a demolition-specific excavator just can’t be matched. Plus, there’s the expense of adding various components built by multiple manufacturers, including warranty considerations and the potential demands on your time to sort things out if there’s a claim.
Having your demolition excavator built properly from the beginning will save you a lot of time, hassle and money on top of keeping your operators and machines as safe as possible.
There’s only one place you’ll find the heavy hitters of concrete and masonry this January: Vegas, baby — at World of Concrete 2025, the largest and only annual international event dedicated to your business. Be here to mix with industry giants. Get your hands on the latest technologies revolutionizing safety, performance and speed. And learn what it takes to not only claim a piece of our industry’s massive projected growth but dominate the field. Join the power players of concrete and masonry.
EXHIBITS: JANUARY 21-23, 2025
EDUCATION: JANUARY 20-23
LAS VEGAS CONVENTION CENTER
The new Brokk SmartPower+ line of demolition robots boosts endurance, intelligence and operability for the remote-controlled machines.
The new range includes the Brokk 70+, 170+, 200+, 300+ and 500+ demolition robots.
“We are thrilled to introduce SmartPower+, a new generation of demolition robots that redefine the demolition landscape. This innovative advancement reflects Brokk’s dedication to pushing the limits and providing operators cutting-edge machines that surpass expectations,” said Martin Krupicka, CEO of Brokk Group.
SmartPower+ robots increase operational uptime with consistent power delivery over time. Engineered with rugged components, Brokk’s newest generation is resistant to shock, temperature and vibrations. As well, all new robots and control boxes are dust and water protected to an IP65 equivalent improving reliability regardless of the work conditions.
Brokk’s SmartPower+ gen-
eration also includes an 87 per cent reduction in cables and connectors, reducing weak points while facilitating servicing and troubleshooting and increasing the lifespan of the robot.
To improve upon the operating experience, SmartPower+ provides more precision, better response times and ease of operation.
A new and improved lightweight control box weighing less than 3 kg also contributes to more enjoyable and comfortable work shifts.
The new ergonomically designed control box features tilted joysticks, easier-to-reach features and faster dual charging. Brokk’s SmartPower+ control box includes the innovative Brokk QuickSwitch and intuitive settings for an improved operating experience, making it easier than ever to operate a Brokk robot, and in turn, easier to find and train operators. With Brokk’s new range of SmartPower+ robots, operators can perform demolition tasks without shifting their gaze from the machine be-
Frontline Machinery has expanded its distribution network to Eastern Canada.
The company is now the authorized distributor of CBI grinders and chippers in Quebec, Newfoundland and Labrador, Prince Edward Island, Nova Scotia and New Brunswick.
"Frontline Machinery has built a solid reputation for delivering and supporting our products and customers. In 2019, they were recognized as CBI's North American Dealer of the Year," said George Wilcox, Sales and Marketing Director of CBI and Ecotec. "We are confident they will continue to provide excellent service in these regions."
CBI grinders and chippers are known for their design and technology, ensuring reliable and efficient processing of wood, green waste, organic and C&D materials for biomass production — a key industry in Eastern Canada.
CBI (Continental Biomass Industries) is a brand under the Terex Corporation umbrella. It specializes in manufacturing equipment
tween commands, according to the company.
“With nearly five decades of experience, Brokk understands the challenges many industry professionals face in finding skilled operators to get the job done right,” Krupicka said. “This is precisely why we are committed to creating solutions for both seasoned professionals and new operators alike, setting a new benchmark in the demolition landscape.”
The new generation of machines also features added intelligence for the operator. Visual status updates through incremental light
indicators allow the operator to focus their attention on the demolition work at hand while monitoring the status of the machine.
A two-way communication system communicates the status back to the operator in real time, while customized features enhance the operating experience.
Brokk’s SmartPower+ generation is smarter too, alerting the operator about any unwanted power supply or machine status, further contributing to an increase in uptime and overall reliability. SmartPower+ is enabled for future over-the-air upgrades.
for processing biomass and other wood-based materials. CBI is known for its high-performance machines, particularly designed for the forestry, biomass, recycling and construction industries.
Quebec is a leading province in forest biomass energy, with more than 40 biomass heating systems. The province aims to increase bioenergy production by 50 per cent and reduce greenhouse gas emissions by 37.5 per cent by 2030.
"We are very excited to bring CBI and Frontline Machinery to Eastern Canada. This expansion means businesses from all corners of our country will have access to our CBI fleet and, just as importantly, our experienced and professional team," said Daryl Todd, President of Frontline Machinery. "Our roots began in Western Canada, a region with a rich and deep history in forestry. Wood recycling has always been a key part of what we do, and we are proud to do it well, contributing to the region's bioenergy goals."
Metso’s board of directors has appointed Sami Takaluoma as Metso’s new President and CEO, effective November 1.
Takaluoma has been with Metso since 1997 and has led Metso’s Services business area since 2021.
“I would like to warmly thank the board for the opportunity to lead this great company. Having had the privilege of working for Metso for 27 years, I can confidently say that I know the company and understand our potential,” Takaluoma said. “With Metso’s long history and strong foundation in the aggregates and mining
markets, we are excellently positioned to achieve industry leadership. I eagerly anticipate embarking on this journey to deliver even greater value to our customers and stakeholders, alongside my talented and dedicated colleagues.”
Takaluoma has held several management positions with Metso since 2003, becoming Vice President of the Nordic Market area in 2014 and President of Minerals Consumables in 2017. He has been a member of Metso’s leadership team since 2017.
“Sami has done an excellent job in leading the businesses and as a member
of the leadership team over the past seven years,” said Kari Stadigh, Chair of Metso’s board of directors.
“Under his leadership, Metso’s services and consumables businesses have grown and created significant value, especially after the merger of Metso and Outotec. The board is convinced that Sami is the right choice to lead Metso into its next phase.”
Metso’s current President and CEO, Pekka Vauramo, will continue with the company as per his contract until the end of 2024, ensuring a smooth transition of responsibilities.
“On behalf of the entire board, I would also like to extend our thanks to Pekka Vauramo, who is now stepping down from his role as President and CEO of Metso as earlier agreed,” Stadigh said.
Vauramo is credited with helping Metso evolve into a stronger company with an enhanced culture, improved customer satisfaction and a new level of profitability.
“I want to thank all my colleagues and Metso’s board for the past six years. We have achieved a lot, and the company is in a strong position to succeed in the future. I wish Sami and all Metsonites
best of luck and continued success for the years ahead,” Vauramo said.
“I would like to warmly thank the board for the opportunity to lead this great company. Having had the privilege of working for Metso for 27 years, I can confidently say that I know the company and understand our potential,” Takaluoma said. “With Metso’s long history and strong foundation in the aggregates and mining markets, we are excellently positioned to achieve industry leadership. I eagerly anticipate embarking on this journey to deliver even greater value to our customers and stakeholders, alongside my talented and dedicated colleagues.”
Raimondi Cranes is welcoming the return of Mauro Masetti to the company.
Masetti, in his role as Director of Sales, has rejoined Raimondi Cranes to strengthen the company’s commercial roadmap with the guidance of Group CEO Luigi Maggioni.
Masetti’s recruitment underscores the company’s commitment to its
Creighton Rock Drill Ltd. is currently looking for: TERRITORY MANAGER, BUSINESS DEVELOPMENT, USA
Creighton Rock Drill Ltd. is seeking a dynamic Territory Manager, Business Development, to oversee sales operations across the U.S. The role involves extensive travel, developing sales strategies, building strong customer relationships, and driving business growth.
Qualifications: 10+ years of sales experience, strong communication and negotiation skills, and a background in construction or mining (preferred).
Benefits: Competitive salary with commission, vacation package, company paid health benefits, and Group RRSP.
Please contact: Ansa Siddiqui at ansa@creightonrock.com or call: 905-673-8200 for more details.
international commercial operations, and expanding the Raimondi global footprint.
Based in Milan, Masetti will reinforce Raimondi’s sales division, while masterminding sales growth by building on a strategy that aims to see the company expanding into Canada, as well as Northern Europe.
“I am delighted to return to Raimondi, a company I always considered my second
home. Remarkable steps forward have been achieved in recent years, including an impressive new production facility and the introduction to the market of new products,” Masetti said.
“My goals align with the company’s vision and the leadership team, in which I firmly believe.”
With more than 25 years of experience in the heavy lifting sector, Mauro brings a wealth of knowledge to
the entire organization. His extensive career has seen him hold pivotal positions across key heavy lifting players, allowing him to build a robust network and develop a deep understanding of the global market needs.
“Mauro’s values and strategic vision align with the group mission of expanding our global market share.
His demonstrated industry commercial savvy, matched with his ability to adapt to
dynamic conditions, will be instrumental in guiding Raimondi towards a more aggressive commercial strategy and taking decisive steps forward,” Maggioni said. Masetti emphasized his immediate priorities will include optimizing the product rage, primarily the luffing jib segment, driving international sales in strategic markets and reinforcing the sales department.
Priestly Demolition has announced that two new Vice Presidents have been added to the PDI Executive team.
Connie Clearwater will move into the position of Vice President Marketing, Communications & Business Development, and Justin Olthof becomes Vice President Sales & Estimating.
Olthof started his career with PDI as a summer student in 2011, while studying finance. During that time, he learned about the demolition industry under the mentorship and guidance of Ryan and Brian Priestly. In 2012, Olthof was hired as an Estimator, playing a key role in the expansion of PDI's portfolio of projects in Ontario.
In 2021, Olthof was promoted to Chief Estimator and has since lead the estimating team on several large, award-winning projects, helping to drive PDI's growth across Canada and the United States.
In his new role, Olthof will continue to serve PDI’s customer base while leveraging his project experience to create strategic partnerships and expand the sales and estimating department across North America.
Prior to joining the PDI team in 2021, Clearwater ran a graphic design and branding studio for 17 years. Her client portfolio ranged from industrial and global corporations to national brands, government agencies, start-ups and not-for-profit associations. Clearwater is a dedicated leader with over 25 years of industry experience. She has a track record of developing successful brands and implementing marketing strategies.
Versatile,