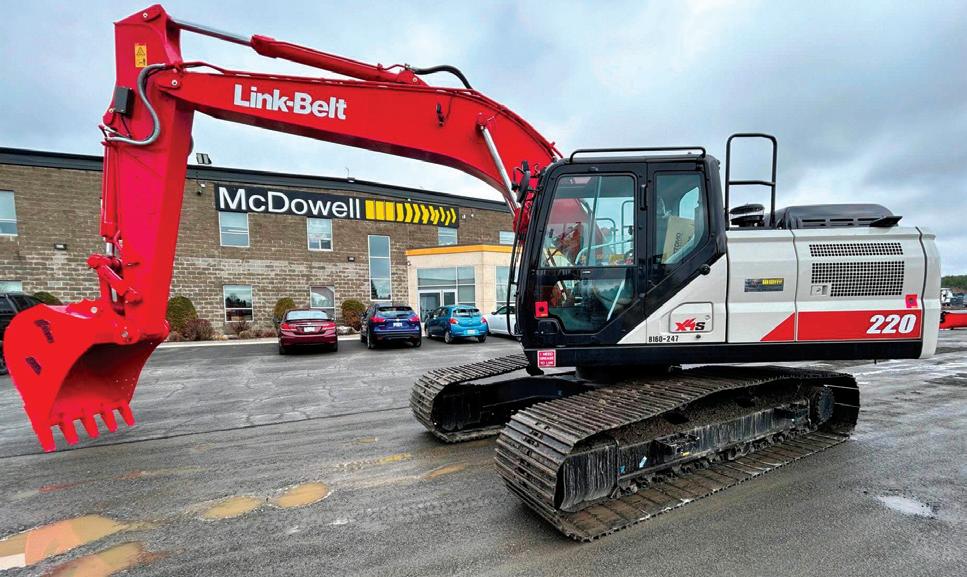

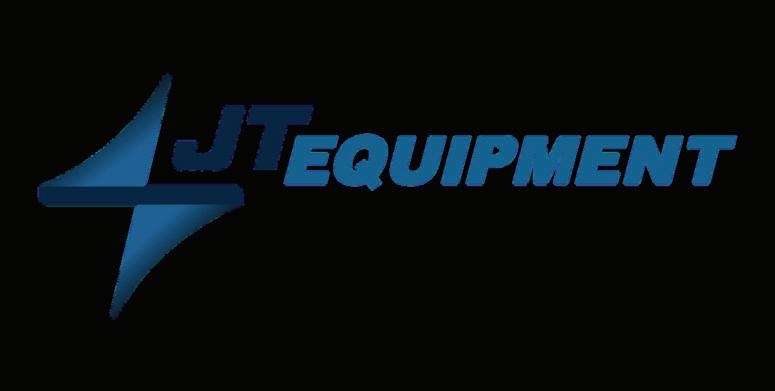


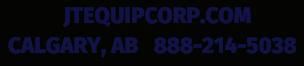
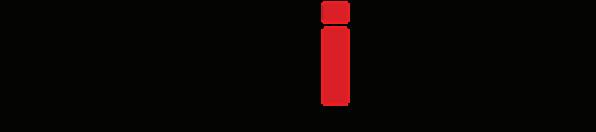

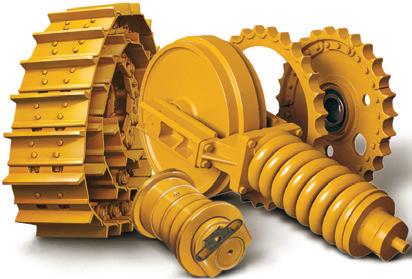


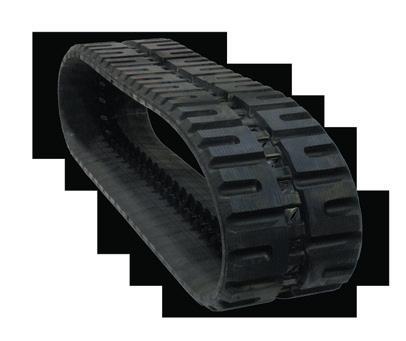
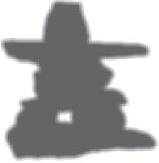
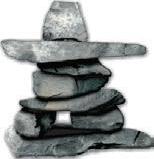
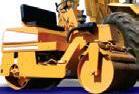
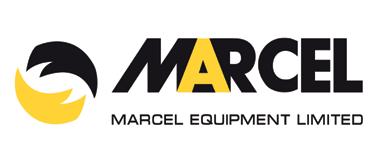

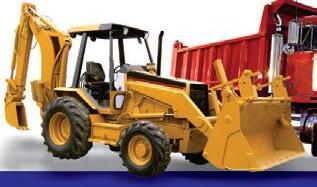



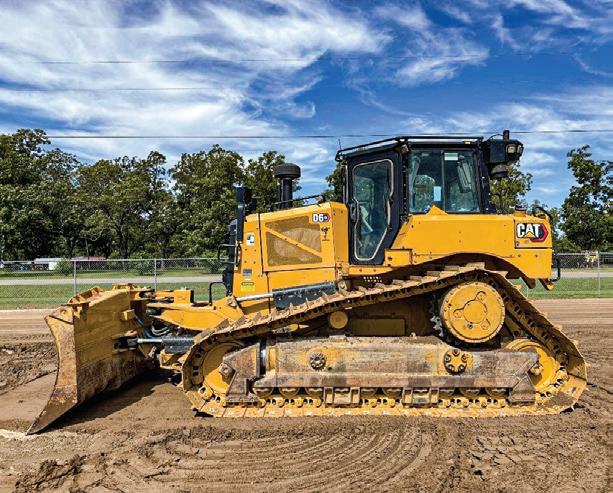
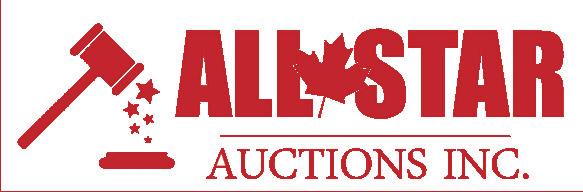
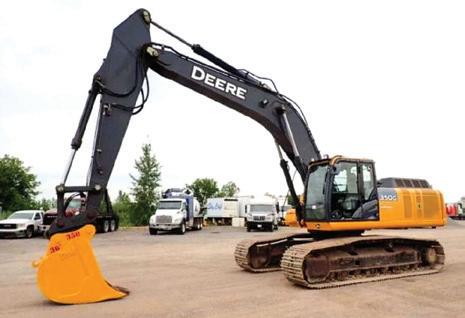
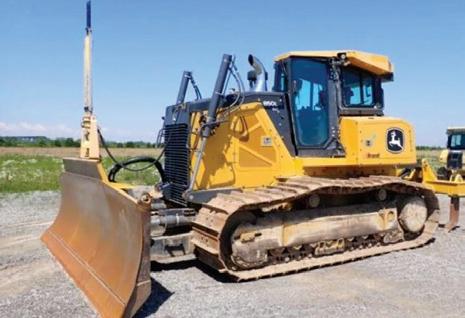
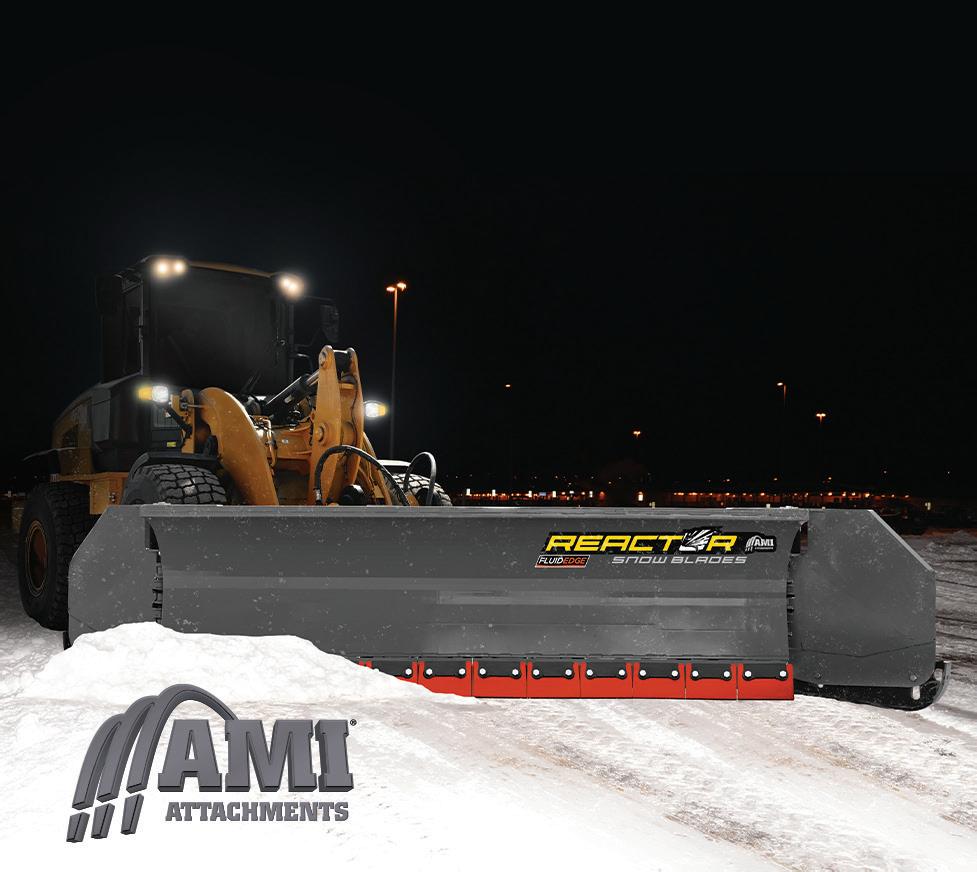

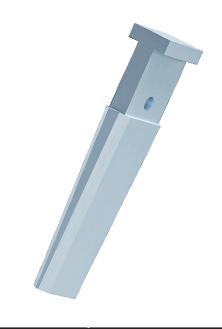
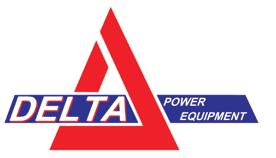
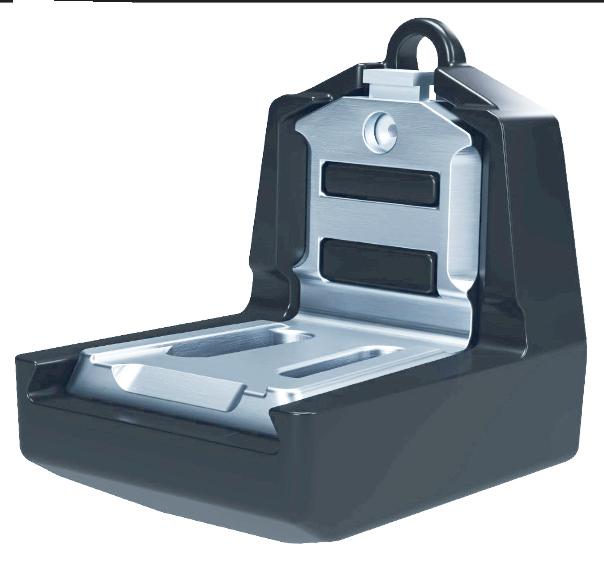
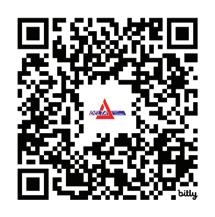
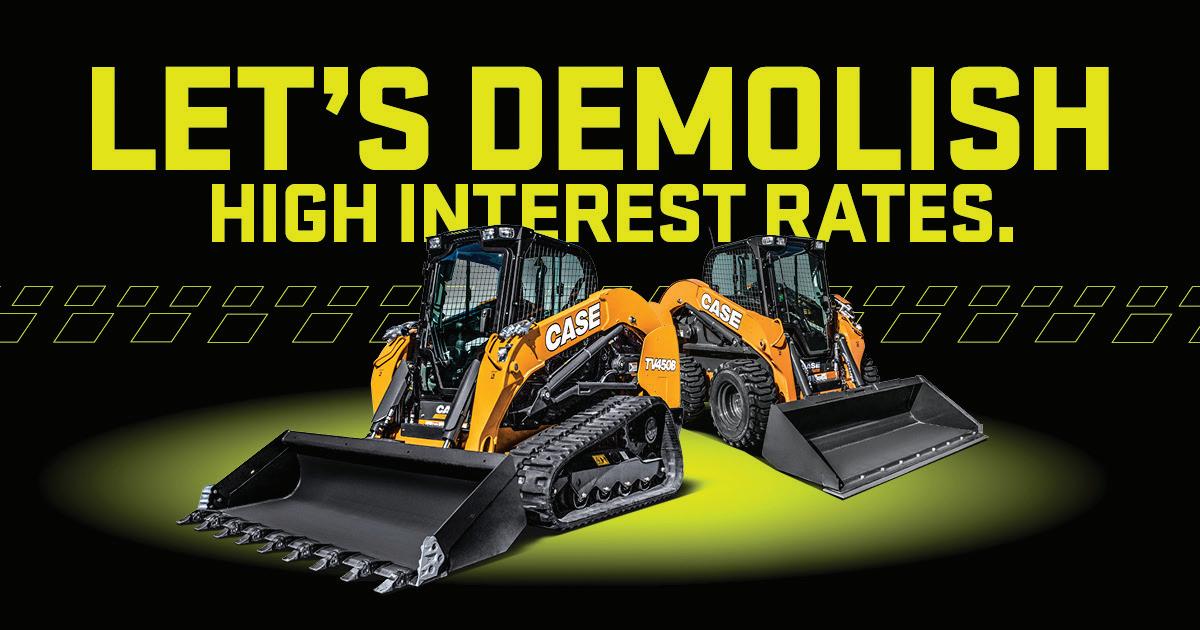
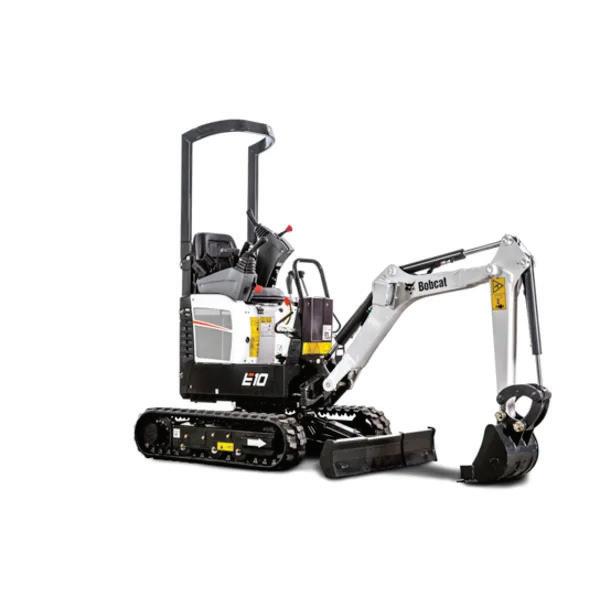
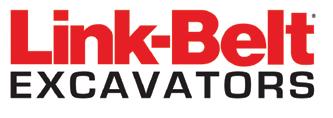

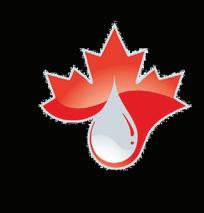
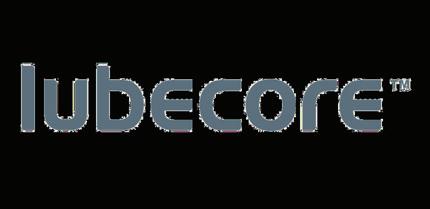
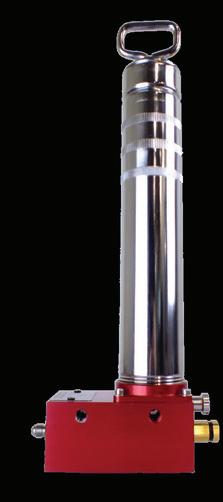
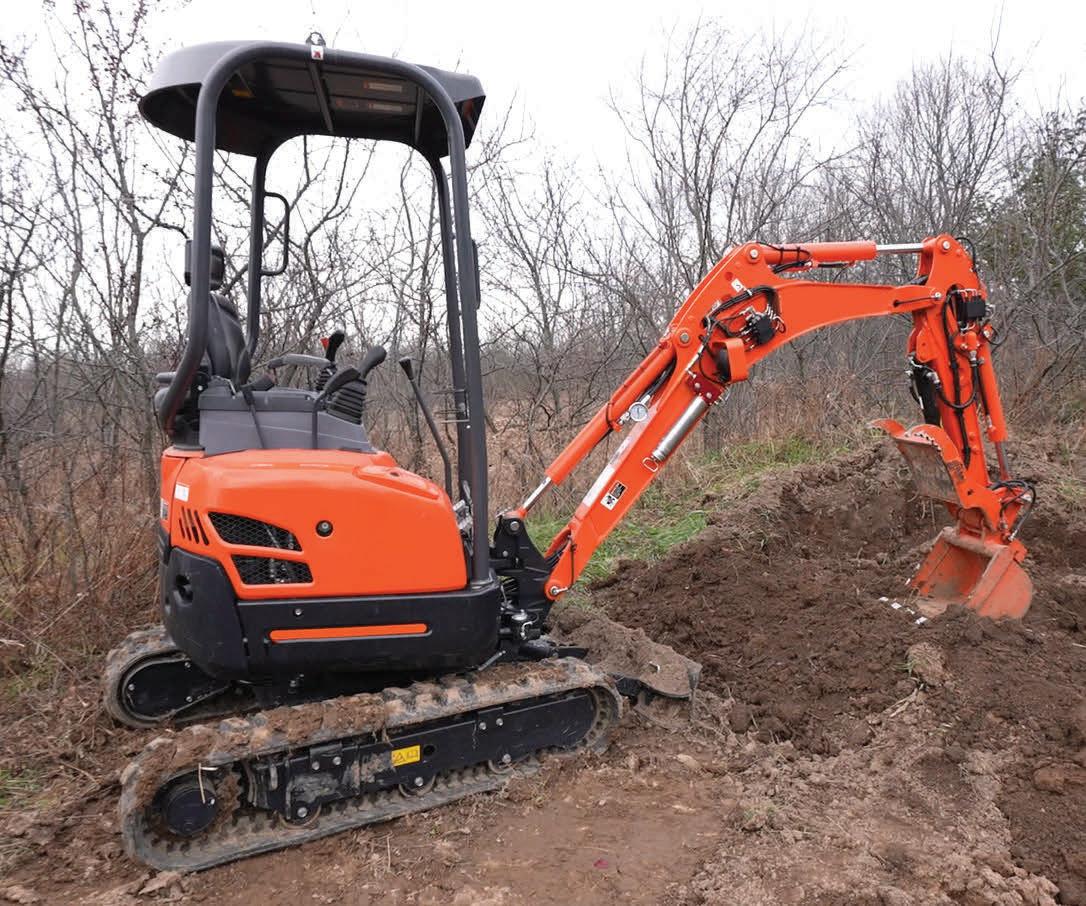
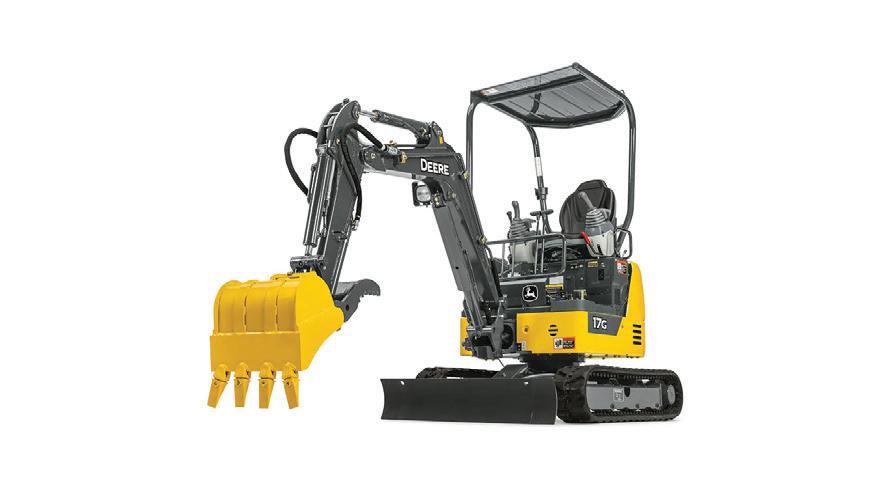
RECOVER, REPURPOSE, AND REUSE
The VacRecover is an innovative modular washing solution specifically designed for processing hydro excavated waste material that was typically a waste material. The washing process converts it into a saleable product, openign up a new revenue stream for many quarries.
The Windsor, Ontario-based Optimotive is expanding its roster of autonomous robots for the construction industry
The notion of “shovel-worthy” needs to carry more weight
Just down the street from my home office, my city is constructing a $50 million expansion to the neighbourhood community centre.
The renovated structure will see the addition of about 6,000 square-metres of space, new aquatic centre and fitness centre etc. Upon completion, the building will be carbon neutral.
In the other direction, dozens of homes are flooded whenever a significant amount of rain falls. The creek that floods has been a growing problem for decades and has started to deliver serious damage to homes in recent years.
The community centre was in a relatively good state of repair pre-expansion, but a bigger facility is needed to accommodate growth.
Unfortunately for my neighbours, containing water in new swimming
pools is politically sexy, while containing water via new stormwater management systems is not.
This month, the Canadian Construction Association (CCA) released a report that highlights the urgent need for increased investment and stronger policies to protect Canadians and infrastructure from the increasing threats of climate change.
The report, titled Climate resilience in construction , stresses the importance of building strong infrastructure that can withstand extreme weather events.
"Canada's infrastructure is the backbone of our communities, but it’s under threats from climate-related disasters," said CCA President Rodrigue Gilbert.
A few key points from the report include the urgent need for investment to protect infrastructure assets and
address the rising strain from increasing population and housing developments.
As well, the construction sector is actively working to reduce its environmental impact, but long-term sustainability requires broader support and collaboration. Incentives to pilot new processes and technologies are also needed.
"The construction industry is making progress in reducing our environmental impact," Gilbert said. "But to reach our net-zero objectives and protect our infrastructure, we need support from both stakeholders and all levels of government."
The report also stresses the need for effective policies to ensure infrastructure is built to last. This includes addressing issues like labour shortages, procurement, alternative delivery models and supply chain challenges.
Gilbert summed up one of the biggest problems Canadians unknowingly face in the following quote: "Too often, infrastructure investment decisions are based on what’s politically expedient, not what’s genuinely needed in a given region of Canada," he said. "We need to focus on projects that are ‘shovel-worthy’, not just ‘shovel-ready’ to ensure Canadians have the infrastructure they depend on."
Bobcat is expanding its North American product lineup with the introduction of the B760 backhoe loader, which offers the most digging depth in its size class, according to the manufacturer.
With a wide range of jobsite solutions built into one machine, the backhoe loader features a lift capacity of about 1,000 kg at full reach, digging depth of 5.6 metres and nearly 180 degrees of backhoe swing for less repositioning and quick cycle times.
As well, the backhoe loader comes with a standard extendable arm that provides up to 20-cm of additional dig depth compared to other machines of the same size.
The B760’s performance and versatility extend throughout the machine, with the front-end loader providing a lift capacity of 3,622 kg with its standard, general purpose bucket.
“The new B760 helps operators accomplish more on the job site with its dig, load and carry versatility,” said Jamison Wood, Bobcat Product Development Specialist.
“The backhoe loader is designed for durability, easy operation, simple maintenance and incredible
performance. Its size keeps it accessible on sites with limited space, while its impressive travel speeds keep operators productive across large job sites.”
Bobcat engine
Powered by a turbocharged 3.4-litre Bobcat engine, the B760 delivers powerful, high-torque performance and efficiency. As well, it achieves emissions compliance without the use of a diesel particulate filter (DPF).
With powerful backhoe and loader breakout forces, operators can confidently tackle job site tasks such as excavation, site preparation, material handling, trenching and snow removal.
The power shift transmission provides quick direction changes while the backhoe loader’s swift travel speeds allow operators to minimize the need for a trailer.
With controls that are thoughtfully laid out and easy to use, new operators can become comfortable operating the machine in less time.
The easy-to-read, 127-mm, colour display panel provides full-featured machine interaction and monitoring capabilities for efficient and productive operation. The operator station and op -
tional cab are designed for all-day comfort, with controls designed for easy use and minimal operator fatigue.
The B760 backhoe loader is also equipped with several other productivity enhancing features, including:
· Ride control for reduced bucket spillage and enhanced operator comfort
· Automatic return-to-dig positioning to maximize cycle time efficiency
· Eight work lights for long days of loader and backhoe operation
· A 1.4-cubic-yard general purpose loader bucket
for greater job site versatility
· Pilot controls for smooth, fast and precise backhoe
workgroup operations
· Auxiliary hydraulics to power attachments from the front and rear
HD Hyundai and Develon are celebrating the grand opening of their new North American Customization Plant in Brunswick, Georgia.
Executives from HD Hyundai, Develon headquarters and North America, HD Hyundai XiteSolution and logistics partner Wallenius Wilhelmsen attended the ceremony held on Sept 4.
Develon opened its first North American Customization Center in July 2019 in collaboration with Wallenius Wilhelmsen. Due to the growth within the company, an expansion was required, and the company moved to
the new, larger North American Customization Plant.
Develon, HD Hyundai and Wallenius Wilhelmsen have had a long-standing relationship for 24 years and will continue by collaborating in the relocation and operation of the customization plant.
As a result, HD Hyundai and Develon dealers and customers will receive new machines faster and meet stricter quality standards thanks to the company’s larger state-of-the-art customization.
“Our new customization plant in Brunswick will allow us to expedite our services for our dealers and our cus-
tomers,” said Chris Jeong, President and CEO at Develon.
“It’s a much larger facility than the previous customization plant, with dedicated space for our machines, and will better meet the custom needs of our dealers and our customers with an array of final assembly options.”
The 8,640 square metre customization facility in Brunswick is located close to Interstate 95, allowing for convenient transportation once machines are ready to ship, optimizing delivery lead times.
“This state-of-the-art facility will help us reduce the lead time needed to get fully
assembled machines to our customers,” said Stan Park, President and CEO, HD Hyundai Construction Equipment North America.
The HD Hyundai customization team will take machines from shipping to work-ready, for instance fitting excavators with standard or long arms and mass or standard buckets, depending on customer requirements, or equipping them with additional cameras, 2D machine guidance or making them Trimble 3D-ready.
Develon employees with Wallenius Wilhelmsen will manage the final assembly and configuration of construc-
tion equipment, ensuring the highest quality standards are maintained.
The new state-of-the-art facility is 50 per cent larger than the current customization plant in Savannah, Georgia, offering enhanced production capabilities, a dedicated machine storage yard and an
expanded indoor warehouse. Develon maintains its North American headquarters in Suwanee, Georgia, including a parts distribution centre for readily available Develon machine parts. As well, Develon began operating a dedicated warehouse in Georgia in August.
Sampo Rosenlew has introduced its new six-wheel HR56 harvester.
Like the other harvesters in the company’s range, the HR56 is suitable for thinning young forests, so the new model is a natural step in the development of the forestry machine line up.
The HR56 is based on Sampo Rosenlew’s best-selling HR46x four-wheel harvester and includes new features that improve both efficiency and productivity.
The HR56 harvester is an energy-efficient and environmentally friendly choice for thinning and harvesting wood.
The familiar components used in the construction of
the harvester, combined with tested technical solutions, ensure low operating and maintenance costs.
The HR56 is equipped with a Logmer crane with 10-metre reach. Thanks to the six-wheel base, the machine limits harvesting damage while providing more stability.
As well, the HR56 is equipped with a front bogie, so the surface pressure exerted on the ground is low.
The front bogie combined with a low centre of gravity make the machine stable to work with.
The machine is the third harvester in Sampo Rosenlew’s forestry lineup alongside three forwarders.
For your crushing operations, get more options from our versatile and durable GEO series crushers. Designed by our experts in materials science and on-the-ground operations, these premium crushers get 90-95% efficiency and are built to last, meaning you get more, no matter what you throw at it, time and time again.
Primary/Secondary Crushing of Aggregates, Recycled Concrete, Asphalt, and Construction and Demolition Debris | Material Refinement
Easily adjust your feed input angles and tertiary grinding path for fine material output.
Simplified maintenance maneuvers , for less downtime and safer operation.
Get better impact even at lower speeds with our custom rotor and industry-leading wear parts.
A Hydraulic Cylinders
• Shock management springs and block valves for added durability.
• Equipped with an optional sensor controlled hydraulic cylinder adjustment system takes the guesswork out of close side settings.
B Three Adjustable Aprons
• Primary adjustable impact apron allows more consistent feed.
• Primary and secondary aprons allow for more efficient material reduction during the crushing process.
• Retractable tertiary refining apron promotes polyhedral particle shape and increases fine material output.
C Wear-resistant side liners
Available in standard, abrasion resistant, and reinforced steel.
D Breaker Plates
• Breaker plates with threaded holes made in manganese, chrome, or abrasion resistant steel. Cassette style apron weldments which allow operators to safely and easily perform breaker plate change outs on the ground.
E Adjustable Material Inlet Chute
• Allows feed angle adjustments to be made to ensure material contact with the face of the blow bar.
F Rotor (P series, heavy)
• Closed wedge-type rotor complete with rotor protection covers.
• With a rotor diameter of 51 inches the GEO maintains a high peripheral speed even at low RPM's with better inertia and impact force on input material.
This level of innovation is possible because the AMCAST group has been delivering custom premium crusher wear parts for over 65 years internationally, and 25 years in the US. Our team is driven by cutting-edge material science, dedication to durability, and listening to, and working with, our customers. We know what works and we have excellent logistical operations to get your premium parts on-site fast, so you can go faster and crush longer.
THREE SIZES, TO MEET YOUR NEEDS:
GEO 808
Power Input: 175-215 HP
Rotor Speed: 450-650 RPM
Feed Size: 24" minus*
Feed OPG: 33"H X 31.5"W**
Throughput: 100-165 TPH
*for concrete and asphalt feed
**with optional raised feed inlet
B C D E F
GEO 810
Power Input: 215-270 HP
Rotor Speed: 450-650 RPM
Feed Size: 24" minus*
Feed OPG: 33"H X 39.5"W**
Throughput: 100-330 TPH
*for concrete and asphalt feed
**with optional raised feed inlet
GEO 812
Power Input: 335HP
Rotor Speed: 450-650 RPM
Feed Size: 24" minus*
Feed OPG: 33H" X 48"W**
Throughput: 100-495 TPH
*for concrete and asphalt feed
**with optional raised feed inlet
TyBot, the rebar tying robot from Advanced Construction Robotics (ACR), is now available for purchase.
TyBot 3.0, which was previously only available through ACR’s Robot as a Service
(RaaS) model, can now be ordered for delivery in the first quarter of 2025.
"Our success in the pursuit of automating construction equipment is not just an evolution for ACR, it is a
transformative step for the entire construction industry,” said Stephen Muck, Founder and Executive Chairman of ACR.
“Offering TyBot for sale represents our commitment
to creating disruptive solutions that will redefine how the world builds, driving unprecedented efficiency, safety and innovation across a wider range of construction applications."
TyBot 3.0 is capable of tying spans from 20.4 metres to 35.6 metres. The machine includes training by ACR to ensure customers can confidently mobilize, configure, supervise and maintain the rebar tying robot.
ACR’s service platform subscription gives customers access to a live data portal that provides unprecedented insight into rebar installation.
TyBot 3.0 also has optional accessories to further expand cost-saving, including multiple modes of travel for non-bridge projects and a carry function add-on to transport materials efficiently and safely to working crew members.
"With over 65 field deployments nationwide, TyBot has proven that it provides customers at least 25 per cent savings in their installation
operations and is quickly becoming an accepted tool of the trade by rodbusters," said Danielle Proctor, President and CEO of ACR. Proctor added ACR is seeing interest grow in TyBot as well as IronBot, which can augment construction sites by lifting, carrying and placing rebar.
“Our continued planned evolution from product design and adoption through RaaS to offering our bots for purchase reflects our confidence in our team’s ability to quickly provide mature products that reliably solve real-world problems,” Proctor said. “We look forward to customers fully integrating our solutions into their operations, providing enhanced productivity and safety using modern tools for a modern workforce.”
Loved for the features. Trusted for the performance.
Do more without feeling like it in Hyundai’s NEW HX355ALCR compact radius excavator.
• Engineered to redefine efficiency, comfort, and safety
• RH and rear camera (standard)
• AAVM 360° camera with ultrasonic system (option)
• LED lights
• Dozer blade (option)
• 8” touchscreen color LCD monitor (standard) and 2nd monitor (optional)
• Free Hi-MATE mobile telematics for 5 years
Bob Mark Equipment Sales & Rentals bobmark.ca
42 Center St Sunderland, ON LOC 1H0 705-357-3121
1138 County Rd. 41 Napanee, ON K7R 3L2 613-354-9244
551 Grand Road Campbellford, ON KOL 1L0 705-653-3700
2197 Little Britain Rd Lindsay ON K9V 455 705-324-2221
Hood Equipment Canada Inc. hoodequipmentcompany.net 14 Haniak Road Thunder Bay Ontario P7KOC8 888-413-5454
1355 Riverside Drive Timmins, Ontario P4R1A6 705-288-4685
RTI Equipment Solutions, Inc. rtigroup.ca 2528 Bowman St. Innisfil, Ontario L9S 0H9 705-734-3350
Ontario, Canada Hyundai Dealers NEW MODEL
No wonder so many first-time Hyundai users become longtime fans. See the Hyundai difference yourself at your local dealer, or na.hd-hyundaice.com.
In addition to its recently announced 580EV electric backhoe, Case will also make two more EV models available in the coming months.
The Case CX25EV electric mini excavator and the CL36EV electric compact wheel loader will round out the CASE EV lineup for a total of five machines.
The two new machines join the 580EV, the CX15EV electric mini excavator and the SL22EV small articulated loader.
“These new machines set a new benchmark in electrification and sustainable construction, and they’re a testament to our customer-centered approach to practical innovation as we expand our product portfolio,” said Terry Dolan, Vice President, North America for Case Construction Equipment.
“Complementing our diesel lineup, electrification brings real-world solutions to unique jobsite demands, helping urban construction contractors, utility teams,
municipal crews and other contractors further improve productivity, efficiency and their bottom line.”
The 2.5-tonne CX25EV is a bigger, more powerful version of Case’s existing electric mini excavator.
The CX25EV delivers emissions-free performance that is ideal for urban and infrastructure sites with high traffic. The machine includes hydraulic flow settings and up to three aux-
iliary circuits that can be paired with a variety of quick couplers and attachments. It’s also equipped with electrohydraulic controls and a short-radius design, making it easy to manoeuvrer in tight spaces.
The 3.6-tonne Case CL36EV electric compact wheel loader delivers the same power and performance as a diesel-powered loader of a comparable size, along with simplified maintenance and lower life-
time total cost of ownership.
The compact loader can be matched with a full range of attachments and features a hinge-pin height of more than 3 metres, making it an ideal solution for supply yards, large-scale building renovations or projects where indoor operation is required.
The new machines complement the Case portfolio of diesel machines by giving crews more ways to get work done while also minimizing carbon footprints.
“All of these new machines
represent a new benchmark in electrification and sustainable construction, bringing practical solutions to unique demands on the jobsite,” said Brad Stemper, Product Management Lead, North America, Case.
“EVs are new specialized tools that add to the toolbox for unique job site challenges so that workers can get the job done right. It's an exciting time for the industry, as advancements in electrification transform what we can achieve on the job.”
When mounted with the XR Rotator it gives you an overall compact package and equipped with an upper mount to fit any excavator coupler or direct mount to the stick boom. MG Grapples can also be fitted to any Tiltrotator brand and any coupler style that it is equipped with including Pin Grabber, S Style, or Oil Quick options.
From landscaping materials, timber, brush, stones, pipe, or any other materials, the SuperGrip MG Grapples are ideal for a wide range of excavator work. For 6-25 Tonne Excavators
Get new-machine productivity at a used price! Brandt backs all used equipment with unmatched parts & service support.
With the largest used inventory in Canada, chances are Brandt has exactly what you’re looking for.
There’s only one place you’ll find the heavy hitters of concrete and masonry this January: Vegas, baby — at World of Concrete 2025, the largest and only annual international event dedicated to your business. Be here to mix with industry giants. Get your hands on the latest technologies revolutionizing safety, performance and speed. And learn what it takes to not only claim a piece of our industry’s massive projected growth but dominate the field. Join the power players of concrete and masonry.
EXHIBITS: JANUARY 21-23, 2025
EDUCATION: JANUARY 20-23
LAS VEGAS CONVENTION CENTER
Niftylift has launched its first-ever straight boom platform.
The development of the HR22 SE straight boom platform gives customers a new option from the company for fast operation with excellent performance credentials.
“Customers have been asking us for a simplified, lower cost, straight boom option that still features Niftylift’s trademark engineering and manufacturing excellence. So, we’re delighted to introduce our HR22 S,” said John Keely, Managing Director at Niftylift.
“It’s perfect for construction, and other industrial applications, and delivers great reach and control from an all-electric design that ensures lower noise and emissions on site. At Niftylift, we're focused on providing reliable and cost-effective equipment that gets the job done, and we’re excited to see the first units get to work.”
The HR22 SE can cover a large working area with up to 21.7 metres of reach from a platform that extends up to 19.7 metres vertically and with a horizontal outreach of 18.8 metres.
The straight boom platform has a 55 cm tail swing for operation in congested areas and there’s vertical articulation of the basket of up to 150-degrees and equivalent horizontal movement of 170-degrees to access difficult-to-reach areas.
The HR22 SE electric drive means it generates zero-emissions, and there’s a low-noise pump for even
less disturbance.
Power comes from a configuration of 8 x 400 Ah batteries that deliver 48 V and up to five days of consecutive operations, with a 60 A charger for re-powering.
The driving experience is smooth thanks to a rear suspension system and travel speeds can reach up to 5.5 km per hour with a turning radius of 7.7 metres.
Operating is simple via its intuitive, fully proportional controls, while the large 11 cm information screens at the base and basket to provide information on the machine’s status. For safety, the HR22 SE is equipped with SiOPS technology, which prevents sustained involuntary operation.
As with all new models from the company, Niftylink telematics is included for remote monitoring.
The basket on the new HR22SE can accommodate up to 280 kg of personnel and tools inside the 2.4 metre x 0.9 metre basket.
“We’re excited to begin deliveries of the new HR22SE. It’s an addition that expands our offering and allows customers to provide a wider range of services from their Niftylift fleets,” Keely said.
New HR12 4x4
Niftylift has also updated its HR12 4x4. With this new model, the company now has upgraded versions of the full complement of machines in this class, including the HR12LE (low weight), HR12N (narrow) and
HR12NE (narrow, electric).
The modified boom on the latest HR12 4x4 delivers increased horizontal outreach of 6.4 metres while working height is set at 12.1 metres.
The 4x4 performance means there’s a four-wheel drive system for increased confidence across uneven surfaces plus deep tread rough terrain tires to provide extra grip even on soft ground.
Power now comes from Niftylift’s Gen2 plug-in hybrid design to enable operation from an efficient Stage 5-compliant engine or with zero-emissions via its electric-only power mode depending on customer needs and local work environment.
Other new design features include SiOPS and Niftylink telematics for remote monitoring.
“The HR12 range is one of our best-loved and the updated HR12 4x4 means the full line-up now offers the latest Niftylift technology. Our unique parallel hybrid design gives owners a choice of how best to power the machine to suit the application, while technology such as SiOPS and Niftylink deliver added value,” said Simon Maher, Marketing Manager at Niftylift.
“We’re continuing to push the boundaries, giving customers more outreach and better performance from machines that weigh less than competitors. The launch of our new HR22SE and HR12 4x4 underline our commitment to leading the industry in design and innovation.”
ASV has unveiled the new VT-75 Posi-Track compact track loader. Powered by a Yanmar engine, the vertical-lift, 74.3-horsepower machine excels in at-height work, loading trucks and many other tasks in construction and landscaping applications.
Filled with a variety of comfort and productivity features and technologies, the mid-frame compact track loader allows operators to complete more work in more places.
“The VT-75 truly allows our ASV customers to do more,” said Peter Ovrebo, Product Management Director — North America, Yanmar
Compact Equipment North America. “It fits right into the heart of the construction market where operators can make the best use of it.
With the combination of its high rated operating capacity, loading capabilities, reliable Yanmar engine and ASV performance, it’s a valuable asset for operations big and small.”
The 3,770 compact track loader’s Tier 4 Final diesel engine transmits more power and flow directly to the attachment thanks to the machine’s hydraulics and direct-drive pumps. A 3.2metre lift height combined with a 1,043-kg rated operating capacity and 1,043-kg tipping load makes jobs like
loading over the side of high dump trucks an easy task.
ASV’s Posi-Track rubber track undercarriage provides VT-75 operators with traction and mobility all year round. The system includes a suspension made up of two independent torsion axles per undercarriage. These provide a smooth ride over all types of terrain and contribute to a high speed of 15 km per hour.
The flexible track and suspension also mean maximized ground contact and — as a result — more traction and pushing power even in steep, wet, muddy and slippery conditions.
A ground pressure of 4.5
psi minimizes turf damage and contributes to more flotation in tricky conditions. The ability to transit over a variety of conditions is emphasized with a leading 30-cm ground clearance, providing easy passage over large obstacles with less risk of getting stuck.
Operators can do more year-round with the VT75’s superior performance and productivity-enhancing features. An optional work-tool positioner allows access to a preset attachment angle at the touch of a button, enabling operators to set it for repetitive applications. Similarly, optional return-to-position technology allows a preset for the height of the loader arms. Operators can use the features separately or together, depending on the work. Optional self-levelling technology complements this by automatically levelling the load while raising the arms and lowering them.
The VT-75 is highly manoeuvrable thanks to various optional speed and movement-related features. The CTL accomplishes grading and tight-space work with ease thanks to auto 2-speed technology, which provides a seamless transition between low- and high-speed modes. Speed-sensitive ride control
adds to that by improving material retention at higher speeds but switching off automatically when conducting slower-moving tasks.
Efficiency is a key feature of the new model. The efficient hydraulic and cooling systems allow the machine to work in more conditions at maximum power, meaning the VT-75 can operate at 100 per cent load, 100 per cent of the time from minus -40 C to 48 C ambient temperatures.
The MAX-Series VT-75 features a premium operator experience. The cab improves comfort, productivity and safety through a variety of standard features. Premium 360-degree visibility means less effort keeping an eye on the attachment and surroundings, improving both the quality of the work and jobsite safety.
Safety is further enhanced with the model’s roof escape hatch, one of the first included on a compact track loader.
Operators work in comfort during longer days with intuitive and ergonomic electronic controls. A 18-cm colour display consolidates various switches as well as improves access to monitoring tools, the view of the optional backup camera and the ability to keep track of service schedules
and history. Additionally, a fully adjustable and suspended seat accommodates more body types, improving comfort.
ASV offers its Yanmar SmartAssist telematics system as an optional feature to change how operators experience their equipment. Machine owners can make use of features ranging from being notified of errors remotely to real-time operational status updates and daily work reports. Integrated theft protection helps secure owners’ investments, allowing users to set a range from a specific location and trigger an alert if the machine moves outside of that range.
The machine can be serviced from top to bottom by ASV dealers, minimizing hassle when maintenance is needed.
Additionally, operators spend less time trying to service their machine and more time on the job thanks to ease-of-access features. These include a swing-out radiator, top hood and side doors that provide access to all sides of the engine compartment, including filters and other daily checkpoints. The machine’s cooler also swings out with the door, allowing easy access for cleaning.
The energy-saving potential of reduced-temperature asphalt is one of the most important drivers behind the current growth of the road construction material.
Wirtgen Group’s technologies and solutions provide the answer to the growing demand for reduced tem perature asphalt and play an important role in ensuring practical production and use.
Reduced-temperature asphalts — also known as low-temperature asphalt, warm asphalt, or warm mix — are mixes produced at tem peratures of 110C to 130C. Conventional hot-mixed as phalts are produced at 140C to 180C and typically require hot bitumen at a temperature of 160C as a binding agent. As the overall energy balance of these mixes is more favourable, re duced-temperature asphalts deliver financial benefits. Lower energy input translates to fewer emissions, particu larly a considerable reduction of carbon dioxide.
According to the German Asphalt Association, a tem perature reduction of 30C results in saving 900 ml of fuel per tonne of finished asphalt. At a daily production rate of 2,000 tonnes of mix, this corresponds to saving 1,800 litres of oil. The reduction in carbon dioxide amounts to 6,000 kg per day. The figures that can be achieved in the real world are even higher, as the reduction in temperature is frequently 50C or more.
Mixing plants and tech
The major contribution to energy saving and emissions reduction lies in asphalt mix ing plants. As a specialist for the production and recyc ling of all kinds of asphalt mixes, Benninghoven can draw upon years of experi ence and expertise.
The reduction of bitumen viscosity is a basic require ment in the production of asphalt at lower temper atures. Benninghoven has developed — and successful ly implemented — a variety of solutions for temporarily lowering its viscosity. These include high-precision metering systems for the addition of liquid or solid additives and the foamed bitumen module.
Low-cost foamed bitumen also offers advantages dur ing the production process. The binding agent requires only one additive — water, a commodity that is readily available at asphalt mixing plants. Mixing hot bitumen with water increases its volume, which is why this process is also referred to as
bitumen foaming. Due to the surface energy released, the binding agent coats the aggregate extremely well during the mixing process — even at low temperatures —and results in smooth paving
chamber, pipework, injection bars and a water metering system. Thanks to Benninghoven’s Plug & Work concept, the foamed bitumen module can be retrofitted to existing plants at any time. This
Continued on Page A21
Continued from Page A19 -
The use of mobile feeders from the Vögele PowerFeeder series is essential when working with reduced-temperature asphalts due to their ability to offload an entire 25 tonne truckload of mix in 60 seconds. In conjunction with an extra material hopper, it’s possible to bunker up to 45 tonnes of material on the paver. This enables nonstop paving and establishes the basis for the sufficiently broad time-window that is particularly critical when compacting reduced-temperature asphalt. An effective conveyor belt heating system maintains the right temperature of the asphalt mix during transportation to the paver.
The components of all screeds that encounter the material are electrically heated. The use of Vögele’s high-compaction technology has proven to be particularly advantageous during paving. In this context, pressure bars powered by pulsed-flow hydraulics achieve a high degree of pre-compaction, which also extends the window of time for the rollers. Vögele has developed and already implemented specific technologies that play a valuable role in the processing of reduced-temperature asphalts, namely WITOS Paving Plus and RoadScan.
Process reliability
Site logistics plays a particularly important role when working with reduced-temperature mixes. The biggest challenge is the time-window available for compaction. Reduced-temperature asphalts become increasingly resistant to compaction as their viscosity increases, which makes it essential to complete the process at the highest possible material temperature. However, as asphalt is produced at a lower temperature, the gears must mesh perfectly during transportation and on the construction site to ensure the rollers have as much time for compaction as possible.
An integrated system solution for process optimization and documentation such as WITOS Paving Plus, which comprises of five coordinated modules for the various individuals involved
in the process can be used as an aid to the successful management of these complex processes. RoadScan has become established as a solution for monitoring and maintaining a constant temperature range of the mix. In the process, an infrared camera precisely measures the temperature of the entire area behind the road paver’s screed across a width of 10 metres. The system makes the quality of paving with reduced temperature asphalt a measurable and verifiable parameter, which can be important in the event of an inspection by the client.
For compaction, the use of reduced-temperature asphalt means the time window available for achieving the required stiffness value is shorter. Operators have a variety of solutions for compaction at their disposal.
The first of these is oscillation, which was developed by compaction specialist Hamm about 40 years ago. The permanent contact of the oscillation drum with the asphalt layer enables rapidly increasing compaction. The more material-friendly compaction in comparison to vibration also ensures the prevention of surface damage during compaction at low asphalt temperatures. The advantages of oscillation also play an important role when processing joints to prevent damage to the already cooled asphalt.
Another solution is the Hamm Smart Compact compaction assistant, which continuously regulates the compaction energy and mode in both drums of HX series tandem rollers under consideration of the cooling behaviour of the asphalt and the momentary stiffness values. For example, Smart Compact shows the operator whether compaction should be carried out statically, with vibration or with oscillation and selects the required compaction energy. The consequence of this is the effective prevention of over-compaction and surface damage and a reduction of the number of compaction passes required. Smart Com-
pact increases the efficiency of the compaction process and makes optimal use of the available time.
A material with potential
The energy saving potential is impressive when paving with reduced-temperature asphalt. The challenges simultaneously arising from the use of this road construction material can, however, be effectively overcome by using perfectly coordinated, state-of-the-art technology. Thanks to these, the low temp asphalt mix can not only be produced, but also paved and compacted with conventional methods.
Oklahoma Governor Kevin Stitt recently helped celebrate the groundbreaking of a new 15,800 square metre paint facility at the Ditch Witch factory in Perry, Oklahoma.
The event was a part of a stop from the Association of Equipment Manufacturers (AEM) Express Tour of manufacturing companies across the country.
The new paint line facility is expected to generate 100 jobs and will help drive greater operational efficiencies and capacity to better serve customers.
The groundbreaking event was kicked off by Ditch Witch Vice President Kevin Smith with welcoming remarks to the nearly 1,000 people in attendance.
“What we do matters.
Within the first 30 minutes of your day, the work that we
do makes a positive impact on people’s lives,” Smith said.
“The first thing you do in the morning might be check your cell phone and look at the weather or social media. We helped bring that into your hands. Then you flip on the light switch. We helped deliver that power to your house.”
As Ditch Witch celebrates its 75th anniversary, the expansion reinforces its long-standing commitment to Perry and Oklahoma and positions the company to support future growth in the underground construction industry.
“This investment in the Perry facility will help expand our manufacturing capacity, reinforces our commitment to the many customers we serve around the world, and ultimately helps us continue to produce the world-class products Ditch Witch is known for
Toromont Industries has acquired the Guelph, Ontario-based Tri-City Equipment Rentals.
Founded in 1988, Tri-City Equipment Rentals started as a one-person company and has grown to include operations across Southwestern Ontario.
The company rents equipment for several applications, from quarries to housing construction to golf courses. Tri-City Equipment Rentals also provides operators for its wide range of equipment inventory.
"The heavy equipment rentals market is a long-term strategic focus area for us," said Mike McMillan, President and CEO of Toromont.
"This acquisition expands our Toromont Cat heavy rents business to better serve and expand our customer base and provides a rental hub in the southwestern Ontario region. We are pleased to welcome the Tri-City Equipment Rentals team to the Toromont family."
Toromont Industries paid for the transaction in cash using available funds and is subject to customary post-closing adjustments. It is not expected to have an overall material impact on Toromont's combined revenue, earnings or balance sheet.
well into the future,” Smith said.
Ditch Witch traces its roots back to 1902 when Carl Malzhan opened a blacksmith shop with his sons in Perry. Its first production trencher came off the assembly line in 1949, and since that time, Ditch Witch has been the largest employer in Perry and has become a global provider of underground construction equipment. Today, the company employs more than 1,700 people in the community.
The new paint facility is scheduled to be completed in early 2027.
Tri-City Equipment Rentals will continue to operate as it does today. It’s President, Jeff Armishaw, will join the Toromont team as a Strategic Advisor.
In a news release, Toromont Cat said it is committed to ensuring a seamless transition for all customers.
“We enter this next phase of our heavy rental business with a great deal of collective excitement and passion,” the company said. “We are confident that the combined rental fleets and teams will deliver industry leading solutions and options for your rental needs.”
Toromont Industries operates through two business segments: the equipment group and CIMCO. The equipment group includes one of the larger Caterpillar dealerships by revenue and geographic territory, spanning the Canadian provinces of Newfoundland & Labrador, Nova Scotia, New Brunswick, Prince Edward Island, Québec, Ontario and Manitoba in addition to most of the territory of Nunavut. CIMCO is a market leader in the
and
For 40 years, Wacker Neuson has engineered, designed and built excavators around the needs of our customers. And because every construction site is di erent, we o er variety and versatility for the job at hand. From rugged and reliable tracked conventional tail machines to minimal tail swing, wheeled, and zero emission models, you’ll find the right configuration, lifting capacity and breakout force to handle the toughest challenges. What’s more, Wacker Neuson excavators are durable, powerful and easy to operate.
See how Wacker Neuson builds solutions for you. Contact your local dealer today!
A.S.E. Equipment
8503 Wellington Road 18, Fergus, ON, N1M 2W5
Access Mining Services 1106 Webbwood Drive, Sudbury, ON, P3C 3B7
Advantage Farm Equipment 6915 Colonel Road, London, ON, N6L 1J1
Brownlee Equipment 332416 Hwy 11 N, Earlton ON, P0J 1E0
Coleman Equipment Inc. 3541 Trussler Rd New Dundee, ON, N0B 2E0
Construction Equipment Co. (Sault) Inc. 1245 Great Northern Rd, Sault Ste. Marie, ON, P6B 0B9
Eastrock Equipment Inc 100 Warehouse St., Vars, ON, K0A 3H0
Frontier Sales & Equipment 7213 Line 86, Wallenstein, ON, N0B 2S0
Hood Equipment Canada 14 Haniak Road, Rosslyn, ON, P7K 0C8
Hood Equipment Canada 1355 Riverside Drive, Timmins, ON, P4R 1A6
Hood Equipment Canada 9 Ferndale Drive N, Barrie, ON, L4N 9V4
Mark McCabe Tractor Sales Limited 708 Centreline Road, Lindsay, ON K9V 4R5
519-843-1161 www.aseequipment.ca
705-419-2602 www.acces-s.ca
519- 652-1552 www.advantage-equip.com
705-563-2212 www.bequip.ca
519-696-2213 www.coleman-equipment.com
705-942-8500 www.cec-ssm.com
613-443-0695 www.eastrock.com
519-669-8709 www.frontierequipsales.com
807-939-2641 www.hoodequipmentcompany.net
705-269-0830 www.hoodequipmentcompany.net
705-503-7732 www.hoodequipmentcompany.net
705-799-2868 www.mccaberepair.com
McGill Equipment 300 Midwest Rd, Scarborough, ON, M1P 3A9 416-751-4455 www.mcgillequipment.com
Oneida New Holland 634 Fourth Line, Caledonia, ON, N3W 2B3
Oneida New Holland 1410 Fourth Ave, St. Catharines, ON, L2S 0B8
Top Lift Enterprises 42 Pinelands Ave, Stoney Creek, ON, L8E 5X9
Top Lift Enterprises 12343 Highway 50, Bolton, ON, L7E 1M3
1-800-201-3346 • www.wackerneuson.com
905-765-5011 www.oneidanewholland.com
905-688-5160 www.oneidanewholland.com
905-662-4137 www.toplift.com
905-857-5200 www.toplift.com
As demand for autonomous construction solutions grows, a Windsor, Ontariobased company is expanding its fleet of robots to meet the evolving needs of the jobsite.
Optimotive recently raised USD$2 million in an oversubscribed seed round to expand its robotics portfolio.
Led by Version One Ventures and supported by Garage Capital and Newlab, the funding allows Optimotive to fulfill pre-orders received earlier this year and accelerate the company's mission to automate the outdoor construction workforce.
The new funding will also help the company launch two new robots designed to enhance efficiency, data capture and safety at outdoor industrial sites.
“This funding not only moves us forward but also marks a significant shift in how industries like construction, mining and oil and gas approach automation,” said
Scott Fairley, Founder and CEO of Optimotive.
“By reducing human exposure to dangerous and repetitive tasks, our robots are setting new standards for safety and efficiency."
Optimotive’s autonomous robots aim to offer a more affordable and efficient solution to traditional methods while reducing the need for constant oversight often required for autonomous machines.
Each one of Optimotive’s robots are built, assembled and tested in Windsor.
“The construction industry wants to innovate, but they have a lack of automation tools available that are suitable for the built world — making it the perfect opportunity for us to build usable, scalable and affordable robotics solutions to tackle mundane tasks with immediate effect on projects,” said Patrick Thompson, Head of Growth at Optimotive.
The company’s current robotic fleet includes Iris and Box, which began working on jobsites about 18 months ago, and have been deployed by several large construction companies including Ellis Don, Pomerleau and Borea.
Iris is a wheeled autonomous robot focused on automating data collection for customers operating in muddy, dusty and unpredictable environments. Iris excels at capturing and delivering large-scale site data, such as inspections, 3D scans and 360-degree photos for BIM/VDC, quality assurance and quality control for
the renewable energy sector, specifically solar.
Box allows Iris to operate with minimal human interaction. Working as a central hub for autonomous robot operations, Box enables data uploads and serves as a reliable home base. Box includes an integrated charger, Starlink antenna, solar panels and more.
Together, they form the foundation of Optimotive’s growing ecosystem of automation solutions.
“As Optimotive continues to grow, the focus remains on delivering scalable, reliable and cost-effective solutions that meet the real-world
needs of our customers,” Thompson said. “This new funding allows us to expand our operations and accelerate the adoption of our technology across various industries. Our goal is to provide companies with the tools they need to adapt to a changing workforce and stay competitive.”
Mule & Scrubbles
Thanks to the funding, Optimotive will introduce the new Mule and Scrubbles robots to its lineup.
"At Optimotive, we're defining what's possible with outdoor automation," Fairley said. "With Mule and
Scrubbles, we're making autonomous systems a vital part of daily operations in challenging outdoor environments.”
Mule is a four-wheel-based robotics platform used to move materials onsite, act as a mobile power station and can tow single-axle trailers. Mule will be available for testing in 2025.
Scrubbles is engineered to tackle site cleanup. The tracked autonomous cleaning robot will focus on clearing nails, small metal objects and debris on large scale jobs sites. Scrubbles is available to start testing immediately.
After 12 years of exclusively offering its rubber tracked crawler series, Terramac has launched its new wheeled dumper product line, marking a significant expansion for the Illinois-based manufacturer.
The new wheeled dumper series offers a versatile, high-speed alternative that complements the tried-andtrue rubber track crawler carrier, catering to a broader range of ground conditions and operational needs.
For more than 10 years, the rubber tracked series has been the go-to solution for challenging terrains, per-
forming in mud, swamp and other difficult ground conditions. The introduction of the wheeled dumper series offers customers an ideal choice when ground conditions are more forgiving, enabling faster cycle times and increased productivity.
"Our customers have come to trust the rubber track crawler carriers for their reliability in the toughest environments, and now, with the wheeled dumper series, we are offering them even more versatility," said Matt Slater, Vice President of Sales and Marketing of Terramac.
"These wheeled dumpers are engineered for speed and efficiency, making them the perfect complement to our existing product line."
The wheeled dumper series is available in a variety of models and sizes. The rear dump, swivel dumper and multi-view swivel dumper each offer unique advantages designed to excel in various construction applications.
The Terramac 120TW articulated multi-view swivel dumper features an 11,793kg maximum payload, a 121 hp Tier 4 Final Perkins engine, heavy duty chassis and 180-degree rotating operator console.
The Terramac DS70 articulated swivel dumper is
powered by a 72-hp Tier 4 Final Yanmar engine and features a 6,985-kg payload. With a maximum speed of 40 km per hour, the DS70 help get jobs done faster.
The D14 rigid-frame rear dumper is the largest machine in the wheeled dumper series with a 13,607-kg payload. The 6,200 kg machine is powered by a 121 hp Tier 4 Final Perkins engine and features three steering modes. Each machine is equipped with a Trackunit telematics system to provide insights into productivity and maintenance.
With this product line expansion, Terramac is positioned to enter new markets and provide customers with more choices tailored to their specific needs.
"Customer satisfaction is at the forefront of everything we do," Slater said. "With the wheeled dumper series, we're not just delivering a new product; we're providing the same level of support and service that our customers have come to expect from Terramac."
K-Tec and SSAB partner to build scrapers with sustainable steel
K-Tec has entered an agreement with SSAB, to become the first Canadian OEM to incorporate fossil-free steel in its earthmoving product line.
Through the partnership with SSAB, K-Tec will have access to pilot deliveries of SSAB fossil-free steel, which has virtually zero carbon dioxide emissions from the steelmaking process. The steel initially will be used in K-Tec's key products serving the construction and mining industries.
"We are thrilled to have our K-Tec earthmoving equipment brand as the first scraper solution to incorporate SSAB Fossil-free steel, continuing our commitment to innovation,” said Dan Pashniak, President and CEO of K-Tek’s parent company K.A. Group.
“It is also an honour for our organization to be the first Canadian manufacturing partner to collaborate with SSAB in this crucial initiative to lead our industry. We are excited to partner with SSAB as they strive to provide environmental steel solutions to advance towards a sustainable future.”
The company currently designs, manufactures
and delivers earthmoving equipment built with SSAB’s Hardox wear steel and Strenx performance steel. The collaboration is K-Tec’s next step in reducing emissions and improving sustainability for its customers.
“This partnership demonstrates the commitment from both companies toward reducing carbon emissions,” said Johnny Sjöström, Head of Special Steels at SSAB.
“Our transformation to change the way steel is made is well underway, and we are proud to already have reached this far in our journey towards a fossil-free future.”
SSAB plans to change the steelmaking process by producing steel with virtually zero carbon dioxide emissions. The pilot deliveries of SSAB fossil-free steel are made using the unique HYBRIT-technology, which was jointly developed by SSAB, iron ore producer LKAB and energy company Vattenfall. It replaces the coking coal traditionally used for iron ore-based steelmaking with fossil-free electricity and green hydrogen. The by-product is water instead of carbon dioxide emissions.
The new Mega Jack 10000 from Mammoet provides 10,400 tonnes of lifting capacity per tower — double the current 5,200 tonnes —without increasing the footprint of the tower base.
This means that less steel is required to support structures as they are lifted, and the heaviest lifts will be able to start closer to ground level.
As the Mega Jack system’s capacity has doubled, fewer towers are required to lift larger loads. This means smaller foundations are needed, which enhances both scheduling and costs.
The Mega Jack 10000 introduces a five-metre jacking beam with three connection points, allowing for load distribution across eight Mega Jack base units: four at the corners of the tower and four at the centre of each side.
Large jacking projects require starter beams, which are used to connect these jacking towers together and distribute the load. For example, if two Mega Jack 5200 towers are connected by a starter beam, they will be able to lift a load of 10,400 tonnes.
As one Mega Jack 10000 tower can lift this weight, lifts that would formerly require starter beams of two towers may now only need one. So, supporting steel can be smaller, thinner and require less engineering to develop.
This also reduces the lift’s starting height, allowing easier access and requiring smaller cranes to complete projects.
“We noticed that loads were growing beyond the capacity of the Mega Jack 5200 and came up with the idea of the Mega Jack 10000.
We designed an early initial concept and now we have upgraded the system to accommodate future projects that require a 10,000-tonne single tower solution,” said Richard Verhoeff, Director Sales Global Special Devices at Mammoet.
“The Mega Jack 10000 not only increases lifting capacity but also enhances safety and sustainability by optimizing the jacking process."
As part of the Mega Jack 10000 development program, Mammoet has also undertaken a root and branch upgrade of its control systems. Towers can now monitor lift positions to one hundredth of a millimetre, reducing stress on structures as they are lifted, improving upon operational safety.
The new system will be utilized by the offshore oil and gas sector, for the manu-
facturing of heavy topsides and the renewable energy industry for the fabricating of converter stations.
In these industry segments, loads can grow to more than 30,000 tonnes, and require heavy lifting solutions that redefine construction methodologies to make them safer, more cost-effective and efficient.
• Augers • Breakers • Brush Cutters
• Buckets
• Compactors
• Demolition
• Forest Mulcher
• Grapples
• Quick Couplers
• Rippers
• Compactors
• Rubber Tracks
• Thumbs
• Screening Buckets
shawbros.ca info@shawbros.ca
Sarens has helped ensure a YMCA social housing complex is safe for its staff.
The company recently installed railings and other safety features on the rooftop of the building, greatly improving working conditions and safety for the building's maintenance staff.
The project was carried out on behalf of YMCA Toronto, a charitable organization that offers a wide range of programs aimed at improving conditions for Canada's underprivileged citizens.
“We have extensive ex -
perience in the construction sector in Canada, which allows us to carry out this type of work, which requires the appropriate equipment to be efficient and agile,” said Mario Carcamo, Project Engineer at Sarens.
“We are also happy to work with YMCA Toronto, a non-profit organization that seeks to improve the lives of the city's residents through various initiatives, especially when it comes to improving safety, one of our core values.”
The installed material weighed about 318 kg, with a height of 51 metres and a radius of 35 metres. To carry out the operation, Sarens' engineering team selected the Liebherr LTM 1070 crane, which, thanks to its eco mode and eco drive system, minimizes fuel consumption and noise generation, important for not disturbing
neighbours in the area during operations.
Thanks to its folding jib, the crane reaches lifting heights of up to 65 metres and has a maximum load capacity of 70 tons.
One of the main points addressed during the execution of the project was the proximity to the Toronto Children's Hospital, especially the access to the emergency parking lot, which was partially blocked by the working position of the crane. Strict traffic control was required to allow the vehicles to enter the hospital. To avoid blocking traffic, the work was carried out in just eight hours, always respecting the pre-established safety measures. The work speed resulted from the versatility of the LTM 1070 crane, which can carry most of its ballast when moving on public roads for greater agility of movement. It also has a quick coupling system for the ballast, speeding up the setup needed to begin lifting operations.
Sarens has extensive experience in the Canadian construction industry and on similar projects internationally. Among others, Sarens has recently worked on Toronto's Finch West Station project, installing 30 precast ceiling panels of 3.25 tons each below ground level, and was also able to contribute to the renovation of Union Station, where the team carried out the lifting and subsequent installation of several 9.4-ton iron girders for the flying garden connecting the station's north and south towers.
SENNEBOGEN’S ELECTRIC EGREEN MACHINES HAVE BEEN PROVEN TO REDUCE COSTS UP TO 50%
MACHINES
Prince Edward Island
Strongco
Prince Edward Island (902) 468-5010
www.strongco.com
Nova Scotia
Strongco
Dartmouth, NS (902) 468-5010
www.strongco.com
New Brunswick
Strongco
Moncton, NB (506) 857-8425
www.strongco.com
Newfoundland and Labrador
Strongco
Mount Pearl, NL (709) 747-4026
www.strongco.com
Quebec
Strongco
Baie-Comeau, QC 1-866-996-3091
Chicoutimi, QC 1-800-323-1724
St-Augustin, QC 1-800-463-2662
Trois-Rivieres, QC 1-855-840-0828
Val d’Or, QC 1-800-561-4192
www.strongco.com
Top Lift Enterprises, Inc.
St-Laurent, QC (514) 335-2953
Sherbrooke, QC (819) 612-5438
www.toplift.com
Ontario
Strongco
Stittsville, ON (613) 836-6633
Sudbury, ON (705) 692-0552
Thunder Bay, ON (807) 475-3052
www.strongco.com
Top Lift Enterprises, Inc.
Bolton, ON (905) 857-5200
Stoney Creek, ON (905) 662-4137
www.toplift.com
Manitoba
Westcon Equipment & Rentals Ltd.
Winnipeg, MB 1-800-453-2435 www.westconequip.ca
Saskatchewan
Redhead Equipment
Estevan, SK (306) 634-4788
Lloydminster, SK (306) 825-3434
Melfort, SK (306) 752-2273
North Battleford, SK (306) 445-8128
Prince Albert, SK (306) 763-6454
Regina, SK (306) 721-2666
Saskatoon, SK (306) 934-3555
Swift Current, SK (306) 773-2951 www.redheadequipment.ca
Alberta
Strongco
Acheson, AB 1-877-948-3515
Calgary, AB 1-800-342-6523
Fort McMurray, AB 1-855-799-4201
Grande Prairie, AB 1-888-513-9919
Red Deer, AB 1-866-950-3473
www.strongco.com
British Columbia
Great West Equipment
Campbell River, BC (250) 286-0123
Cranbrook, BC (250) 426-6778
Fort St. John, BC (250) 785-4223
Kamloops, BC (250) 372-3996
Nanaimo, BC (250) 716-8804
Prince George, BC (250) 612-0255
Surrey, BC (604) 882-5051
Terrace, BC (250) 635-9033
Vernon, BC (250) 549-4232
Williams Lake, BC (250) 392-9599
www.gwequipment.com
The Alberta-based FT Aggregates is on a mission to produce the highest quality aggregates on time, all the time.
Helping the company achieve its ambitions are its trusty Rokbak RA40s and new RA30 articulated haulers.
A symbiotic relationship with Rokbak and local construction equipment dealership Headwater Equipment has formed a
powerful team in the Greater Edmonton Area, and aided FT Aggregates’ consistent service quality.
Last year, FT Aggregates deployed four RA40 articulated haulers. Recently, the company added a RA30 to its fleet.
Each RA40 moves between 100 and 120 loads and 5,000 tonnes of material every day, five or six days a week. The new RA30 has become an operator’s favourite for its comfort and surface handling.
“If our operators had to pick a truck amongst our fleet to run on site, it would be a Rokbak truck,” said FT Aggregates President Shane Smith. “We’ve been very impressed by the fuel economy, the look and the comfort.”
overburden into the RA40’s all-welded body, which has a capacity of 38 tonnes. Each RA40 at Pit 23 transports the overburden, sand and gravel material for production. The truck's body is fabricated from high-hardness steel with a 1,000 MPa yield strength and features a dual-slope tail chute that facilitates material ejection.
FT Aggregates continues to test its Rokbak trucks, showcasing the ADTs’ reliability and performance under the extreme conditions of Western Canada. The company operates in harsh climates, from -40C in winter to 35C in summer, requiring tough equipment and flexible operations.
“The seasons are not kind,” Smith said. “And that means
best places in the world to put trucks through their paces. We’ve found that the Rokbak trucks can be relied upon to operate effectively and efficiently, regardless of conditions.”
Rokbak’s fully automatic transmission ensures smooth gear shifting, reducing fuel consumption and increasing operator comfort, even in tough environments. The pressurized cab with HVAC offers enhanced control and comfort. Key features include excellent traction and a strong power-to-weight ratio, ensuring fast material movement. This maximizes productivity while minimizing costs.
1 million tonnes
FT Aggregates was formed in the mid-2000s with one crusher, one screener and one wheel loader, and a workforce made up of Smith and “just a couple of guys.” Since the company was founded, FT Aggregates has experienced substantial growth, doubling its staff in the last year from 25 to 50, employing 75 to 100 subcontractors and operating six pits across Alberta.
FT Aggregates plans sustained growth by adding new crushing and wash plants to strengthen its market position while maintaining the quality of personal customer interactions.
This year, FT Aggregates is expected to ship more than 1 million tonnes of aggregate into the Greater Edmonton market.
“Being part of FT Aggregates’ success has been a privilege,” said Rokbak Regional Sales Manager Greg Gerbus. “Working with them and seeing their growth has significantly bolstered our own reputation and presence in the Canadian market.”
A family affair
Close relationships are fundamental to FT Aggregates’
framework. Smith’s son Josh runs the operational side of the business, and his nephew Reuben is the production supervisor. As well, Smith’s wife handles the HR, and his two daughters own the coffee shop at the landscape yard. Differentiating itself from larger, more faceless competitors, this personal approach is a key aspect of FT Aggregates’ success and operational model.
“The passion is evident from FT Aggregates,” said Headwater Equipment Sales Manager Scott Letkeman. “FT Aggregates runs 12 hard hours a day, and you see the drive in every aspect of the company. Everything we see at a sales and service level is driven from the top down.”
Sustaining
FT Aggregates’ rapid growth is both a positive development and a challenge, as maintaining personal connections and being approachable despite size and market share increase is crucial.
“We pride ourselves on being able to turn on a dime and build whatever a customer is needing,” Smith said. “Each endeavour is with the intent of helping people. We’re able to respond very quickly to our customers’ needs.” Smith added the company has worked hard to establish its reputation, and its partners must identify with similar standards.
“Our choice of partner has to fit in our operating system. We have an affinity for Rokbak in its similar position as a growing player in a big market,” he said. “The support we have gained from both them and Headwater is incomparable. When I see how they can take care of us, it provides me with a sense of how our customers feel about our ability to take care of them. It’s synchronous.”
The JCB large excavator comes with more standard features than most on the market. That’s the JCB Better way—because when you have your machine, you should have everything you need to get the job done. Learn more at JCB.com
ALBERTA
Liftboss JCB
Calgary: 403-301-0041
Edmonton: 780-474-9900 liftboss.ca
BRITISH COLUMBIA
Williams JCB
Surrey: 604-930-3316 williamsjcb.com
NEW BRUNSWICK
A.L.P.A. Equipment
Edmundston : 506-735-4144
Balmoral : 506-826-2717
Fredericton : 506-452-9818 Moncton, N.B. : 506-861-2572 alpaequipment.com
NOVA SCOTIA
A.L.P.A. Equipment
Truro : (902) 897-2717 alpaequipment.com
Harvey JCB
Corner Brook: 709-639-2960
St. Johns: 709-738-8911 harveyco.ca
ONTARIO
Advance Construction Equipment (Division of Equipment Ontario)
Harriston: 519-510-5878 Waterloo: 519-742-5878 advanceequipment.net
D&W Group Inc.
Doughty & Williamson Jarvis: 519-587-2273
Brant Tractor Burford: 519-449-2500
Redtrac International Vineland: 905-562-4136 dwgroup.ca
ONTARIO
Delta JCB
Dunvegan: 613-527-1501
Renfrew: 613-432-4133 Winchester: 613-774-2273 deltapower.ca
Equipment Ontario
Alliston:705-320-0506 Lindsay: 705-324-6136 Port Perry: 905-982-1500 equipmentontario.com
Fulline JCB Glencoe: 519-287-2840 fullinefarm.com
John’s Equipment Sales
Frankford: 613-398-6522 johnsequipmentsales.com
Moore JCB
Toronto, York & Peel Region: 416-747-1212 moorejcb.com
ONTARIO
North Rock JCB
North Bay, Sault Ste. Marie, and Sudbury: 705-897-7369 northrockrentals.com
ReadyQuip Sales & Service Ltd. Timmins: 705-268-7600 readyquip.com
WPE Landscape Equipment - JCB Hamilton/Halton: 905-628-3055 wpeequipment.ca
PEI
A.L.P.A. Equipment (506) 861-2572 alpaequipment.com
A.L.P.A. Equipment Bas-Saint-Laurent : (506) 735-4144
Gaspésie : (506) 826-2717 alpaequipment.com
Bossé Quebec Inc. Desmaures: 418-878-2241 Saint-Augustin-debosse-frere.com
Moore JCB
Montreal: 514-333-1212 moorejcb.com
SASKATCHEWAN & MANITOBA
Westcon JCB
Regina: 306-359-7273
Saskatoon: 306-934-3646 Winnipeg: 204-694-5364 westconequip.ca
1.99% APR for 48 months
2.99% APR for 60 months OR 6% Cash in lieu of financing
on
tember 30, 2024. Term and rates are
• Largest minimum swing radius exavator in Link-Belt lineup.
• Power of large machine at lower weight.
• 6-cylinder Isuzu Final Tier 4 engine with fuel efficiency and high productivity without need for DPF.
• 4 work modes, including the new Eco mode.
Equipment Sales & Service Ltd.
Edmonton (780) 440-4010 essltd.com
Inland Truck & Equipment
Campbell River, BC 250-287-8878
Castlegar, BC 250-365-2807
Cranbrook, BC 250-426-6205
Fort St. John, BC 250-785-6105
Kamloops, BC 250-374-4406
Langley, BC 604-607-8555
Nanaimo, BC 250-758-5288
Penticton, BC 250-492-3939
Prince George, BC 250-562-8171
Quesnel, BC 250-992-7256
Terrace, BC 250-635-5122
Vernon, BC 250-545-4424
Williams Lake, BC 250-392-7101 inland-group.com
Itec 2000
Rosslyn (888) 574-8530
Thunder Bay (888) 574-8530
Timmins (705) 267-0223 itec2000.com
McDowell B Equipment Ltd.
Sudbury (705) 566-8190
Barrie (416) 770-7706 bmcdowell.com
Stratton Equipment Sales & Service
Stratton (807) 483-7777 strattonequipment.com
Terapro Rental
Vars (613) 443-3300
Stittsville (613) 836-0654 terapro.ca
Top Lift Enterprises Inc.
Stoney Creek (905) 662-4137
Bolton (905) 857-5200 toplift.com
• New cab with more head and leg room making this the roomiest cab ever.
• Optional WAVES® camera system adds a third camera and gives the operator a full 270º view around the machine.
• RemoteCARE® GPS-enabled telematics system included with no subscription fee!
Équipement JYL Inc.
Chicoutimi (418) 698-6656 equipementjyl.com
St-Aug-D-Desm (418) 878-2241 micanic.com
Paul Equipment (506) 826-3289 paulequipment.ca
Terapro Location
Val d’Or (819) 825-4299 Plaisance (819) 825-4299 terapro.ca
Top Lift Enterprises Inc.
St-Laurent (514) 335-2953
Sherbrooke (819) 612-5438 toplift.com
Balmoral (506) 826-3289 paulequipment.ca
Inland Truck & Equipment
Whitehorse, YT 867-668-2127
inland-group.com
The 285 and 285 XE are the largest compact track loaders ever produced by Caterpillar
Caterpillar has unveiled eight new next gen compact loaders, including four skid steers and four compact track loaders.
The new 250, 260, 270 and 270 XE skid steers mark the introduction of the next generation design to the skid steer line.
The new Cat 275, 275 XE, 285 and 285 XE expand the next generation design for compact track loaders,
joining the 255 and 265 announced in 2023.
The 285 and 285 XE compete in a new class size with greater lift height and lift and tilt breakout forces and are the largest compact track loaders ever produced by Caterpillar.
“We are excited to launch the next generation design for our skid steer loader line and expand the performance capabilities to more
compact track loader models,” explained Trevor Chase, Senior Product Consultant and New Product Introduction Lead for Caterpillar.
“Their increased power, lift height, breakout forces, rated operating capacity and multiple high-flow auxiliary hydraulic system options give customers a flexible, high-performance machine to get the job done.”
Maintaining the DNA of
what made the Cat D3 series a leader, the next generation skid steer and CTL models are a redesign that improves upon the features that made the previous series popular.
The machines feature upgrades in engine power and torque, lift and tilt breakout forces, stability, operator comfort and technology.
The new models carry on with Caterpillar’s new machine nomenclature with the elimination of the series letter designation. All next generation Cat skid steers are now identified by an ending model number of 0, while all CTLs have a model number ending in 5. Simplifying nomenclature, the middle number represents machine size with a larger number designating a larger machine.
All next generation Cat SSL and CTL models feature a redesigned engine compartment that places the engine and cooling package lower into the frame for improved stability, giving the operator confidence in handling heavy loads. Meeting Tier 4 Final and Stage V emissions standards, the four new CTL models are powered by the Cat C3.6TA engine, while the 250 and 260 skid steers are powered by the Cat C2.8T. The 270 and 270 XE are equipped with the Cat 3.6TA engine.
The new engines maintain horsepower across a wider rpm range compared to the previous engines powering the D3 series.
The engines also deliver significant torque increases, including 13 per cent for the 250 and 260, 35 per cent for the 270, and 50 per cent for the 275 and 285.
With a vertical lift design, these new next generation machines feature significant increases in lift height, breakout forces and rated operating capacity (ROC) to elevate loader flexibility and performance.
The Cat 250 features a lift height of 315 cm, about 7.5 cm more than the 242D3, a 36 per cent increase in tilt, a 26 per cent increase in lift breakout forces and a 21 per cent increase in ROC.
Offering a maximum lift height of 335 cm, the 260 has 19 cm more lift height than the 262D3, a 27 per cent increase in tilt, a 24 per cent increase in lift breakout forces and a 17 per cent increase in ROC.
With 16 cm more lift height than the 272D3, the 270 and 270 XE deliver a maximum lift height of 340 cm plus an 11 per cent and 5 per cent increases in tilt and lift breakout forces, respectively.
The 275 and 275 XE CTLs have a lift height of 341 cm, 20 cm higher than the 299D3, plus a 37 per cent increase in tilt breakout force and 19 per cent increase in ROC.
The 285 and the 285 XE deliver a lift height of 370 cm and tilt breakout force of 6,314 kg. The 285 has an ROC of 2,141 kg with a counterweight while the 285 XE has an ROC of 2,185 kg with a counterweight.
The new closed-centre auxiliary hydraulic system allows the machines to operate all Cat Smart Attachments with the standard hydraulics provided. Standard hydraulic system pressure increases 5 per cent to 3,500 psi in the next generation models. The Cat 250, 260, 270 and 275 machines equipped with standard hydraulic flow are shipped from the factory outfitted as high flow ready. High flow functionality is activated simply via a new software enabled attachment (SEA), permitting on-machine or remote activation of increased hydraulic flow to 113 litres per minute for the 250, 260 and 270 models, and 129 litres per minute for the 275 at standard hydraulic system pressure. Also available, the High Flow XPS factory option increases auxiliary hydraulic system pressure to 4,061 psi for the 250, 260, 270, 275 and 285 next generation models. Along with this, hydraulic flow is increased to 113 litres per minute on the 250, while flow increases to 129 litres per minute for the 260, 270, 275 and 285 models.
John Deere has introduced the 326 telescopic compact wheel loader to its line-up of P-Tier compact equipment.
The new machine has a similar build and design as the 324 P-Tier wheel loader. However, the 326 P-Tier is equipped with purpose-built telescoping linkage, providing effortless operation and extended reach capabilities.
“Providing our customers with jobsite offerings that help boost operator confidence and machine capability are top priorities when introducing new, unique machines to our line-up of compact construction equipment, and the debut of the 326 P-Tier not only emphasizes
that commitment but also helps our customers take their work to new heights,” said Emily Pagura, Product Marketing Manager at John Deere.
The new 326 telescopic compact wheel loader offers nearly 5 metres of reach from its telescopic lift arm, providing lifting power while remaining compact enough to work in tight spaces. The telescopic arm is controlled by the operator’s fingertips, thanks to the mini joystick located on the main control lever.
Now equipped with the Load Torque Indicator System, operators will receive visual and audible alarms if stability limits are exceeded during lifting, lowering or
extension, providing protection against overloading and elevating operator confidence.
Once limits are reached, movements with the telescopic lift arms are only possible if the movement improves the stability of the load. This helps to keep the machine operating at maximum capability and performance.
“This model is perfect for operators of all experience levels and is equipped with easily controllable telescopic arms and an intelligent overload warning system,” Pagura said. “With these features, the 326 P-Tier is a one-of-a-kind machine made for every jobsite needing extended reach.”
The cab in the 326 P-Tier has been strategically engineered with comfort and operator ease of use at the forefront of the design. Optimizing loading and stacking processes, electro-hydraulic controls are conveniently customizable from the 23-cm touchscreen display, offering Auto Return-to-Dig, and Auto Lift and Lower functions to lower cycle times and increase productivity.
The touchscreen display also provides key information including warnings, status and machine-positioning information, all within easy view for further convenience.
In terms of visibility, the 326 P-Tier boasts an overhead window
with dedicated wiper blade and optional boom-mounted lights in addition to LED lights, which provide an increased view, helping ensure operators feel confident in even the most challenging job conditions.
In line with current compact wheel loader offerings, the 326 P-Tier features a standard 37 km per hour top speed, enabling operators to quickly get from Point A to Point B.
For tight job sites, the industry-exclusive Articulation Plus steering system delivers a full 30 degrees of articulation plus 10 additional degrees of rear-wheel steering.
Tilt Buckets, Plate Compactors -Pipeline | Padding Buckets, Rock Grinders, Pipe Handlers -Custom Applications & Conversions
Takeuchi-US has added a new wheeled excavator model to its growing product line in North America.
Formerly available only in select global regions, the TB395W is a versatile excavation option that combines performance with on-road capabilities, making it ideal for fast-paced projects.
“Wheeled excavators have become increasingly common in Europe over the years, and they’re gaining popularity in other regions as well,” said Lee Padgett, Product Manager for Takeuchi. “That’s one reason we’re introducing the TB395W to North Amer-
ica. It’s a high-performing excavator that provides all the unique benefits of a wheeled unit, including higher travel speeds and the ability to handle both on- and off-road applications.”
The TB395W excavator weighs 10,625 kg when equipped with outriggers and a blade. It’s powered by a Tier 4 Final compliant diesel engine that provides 114 hp at 2,200 rpm and up to 339 foot-pounds of torque.
A closed-loop, load-sensing hydraulic system delivers smooth control of work equipment and a wide range of hydraulic attachments.
The TB395W features two steering modes — two-wheel steering and four-wheel with crab steering. A two-piece boom with long arm allows for greater clearance between the bucket and dozer blade due to arm-mount position. This design allows TB395W operators to pull the bucket all the way back to the dozer blade, which is ideal when working in narrow spaces or moving an obstacle out of the way.
An Auto Cruise feature enables operators to set and adjust their travel speeds with a toggle switch. Auto Cruise is also ideal when using attachments that require a consistent, repeatable travel speed, such as a mulcher, mower or trencher.
The excavator delivers a 4.1-metre digging depth and an 8.3-metre cutting height as well as a maximum bucket breakout force of 6,000 kg, a maximum arm digging force of 4,050 kg and a traction force of 5,894 kg.
Takeuchi equipped the TB395W with three auxiliary circuits that cater to different hydraulic requirements. The primary circuit delivers 121 litres per minute ensuring ample power for use with hydraulic attachments. The secondary circuit provides 55 litres per minute, offering flexibility for a wide range of applications.
As well, the third auxiliary circuit is designed for use with a hydraulic quick coupler, enhancing efficiency and productivity on the jobsite.
New cab
Takeuchi equipped the TB395W with a redesigned interior to improve the operator experience. The cab features an easy-to-read, multifunction, 20-cm colour touchscreen monitors with integrated air conditioning and DAB radio functions. Using the machine’s jog dial, operators can navigate and control the TB395W’s monitor, including its HVAC and DAB radio functions.
The TB395W includes a standard 270-degree camera to provide operators with a birds-eye view for greater safety throughout the jobsite.
Furthermore, one-touch control switches operate other machine functions, such as work lights, standard and eco working modes, primary auxiliary detent, low- and high-speed gear box, swing boom/second boom select, differential lock, manual regen/regen inhibit and lift overload alarm.
A deluxe, high-back, air-ride suspension seat, adjustable arm rests, low-effort pilot controls, large flat floor area and integrated footrests help operators remain comfortable and productive throughout the workday. For easier serviceability, Takeuchi designed the TB395W with a wide-opening rear engine service door and a right-side cover, both of which open overhead. Both the service door and right-side cover are also constructed of durable steel and lockable to discourage vandalism and theft.
“We know from experience that machine owners are more likely to properly service and maintain their machines at the correct intervals when those tasks are simpler to perform,” Padgett said. “That’s why the TB395W’s design ensures easy access to key daily inspection points like the engine oil dipstick, engine oil filter, engine oil fill and more.”
Takeuchi’s Fleet Management (TFM) telematics system is standard on the TB395W. TFM reduces downtime and controls costs by providing machine health and condition, run time and machine location, as well as remote diagnostics, scheduled maintenance reminders and customizable alert settings. TFM also gives owners the ability to geofence their machines, helping them protect and secure their investments.
“As the world becomes increasingly urbanized, excavator owners and operators must frequently work on projects near city streets and other developed areas,” Padgett said. “The new TB395W provides the power of a tracked excavator but with less disruption to existing infrastructure and the ability to travel efficiently from Point A to Point B.”
“
Dave Arnold worked with his Father-in-law before establishing his own company in 1984, D. B. Arnold Excavating and Grading that services Southern Ontario (within 1.5 hours from Toronto). “I have built up my business so my son Chris can take it over and hopefully make some money”, Dave remarks and fondly remembers, “When Chris first started working Saturdays for me when he was very young, he said, “Dad how much am I making?” Well, I chuckled and told him, the amount he makes won’t even cover the cost of my training. Chris continued and has proved to excel in his work, and he too has a great passion for what we do.” D.B. Arnold provides excavating, grading, and concrete work for bigger custom homes. We get them out of the ground and provide all the hardscaping, retaining walls, pools, courts, etc. They don’t take on too much at a time, as they want to focus on providing top-quality service to their customers. Their business has always come from referrals and repeat business.
“I have always used Bobcat® machines. Well, we had one other brand once when one of our Bobcat machines was stolen but it kept on breaking down. Never again. We will always buy Bobcat machines. My first one was a Bobcat M610 skid-steer loader, gas with a Wisconsin engine. Then I had a Bobcat 743, then an 843,
then an 863 skid-steer loader and a Bobcat 442 compact excavator. We now have a Bobcat T870 compact track loader and a Bobcat E85 compact excavator. They keep getting bigger and better. Bobcat really puts their money into innovation!”, stated Dave.
When asked why Dave chose Bobcat in the first place, he replied “Dealer network. They were right where we were. For the other brand I mentioned, we had to change chain drives every week. I have never changed one on the Bobcat T870. I am a mechanic by trade. I have had very good luck with Bobcat machines. We work them really hard, and they don’t break as long as you maintain them. Also, for comfort, the new ones are the most comfortable ever made. They have great suspension, overall drive, and no dust in the cab. I also was tired of changing rubbers, now we have metal tracks. We are in them for nine hours a day and it feels like not even an hour. If you can operate a machine all day like this and not feel tired, it does its job. I like the two-stick control, and Chris likes the one-stick, so we both have what we want. These machines are also easy to float and use in downtown Toronto. With 13’4” clearance.”
“I have had a few different sales specialists over the years through the same dealership, Matthews
Equipment/Bobcat of Toronto/Oaken Equipment and I must say I have had no lost time, was worrisome but all of the sales specialists have been great with no problems at all. I now deal with Todd Gill, and he has been fantastic. He answers my phone calls which is rare these days! With us servicing all over Southern Ontario, they have such a great dealer network I can rent attachments or get parts so easily. That variety of attachments is hard to find with other brands. I would 100% recommend Todd Gill, sales specialist and Bobcat of Toronto/Oaken Equipment for your next machine purchase/lease/rent.”
BARRIE
Bobcat of Barrie
705-726-2228 oakenequipment.ca
GREY BRUCE
Bobcat of Grey Bruce 519-372-9100
bobcatoftc.com
PARRY SOUND
Bobcat of Parry Sound Ltd. 705-342-1717
bobcatofparrysound.com
TORONTO WEST
Bobcat of Toronto 416-679-4172 oakenequipment.ca
BRANTFORD
Bobcat of Brantford 519-752-7900 bobcatofbrantford.com
HAMILTON
Bobcat of Hamilton 905-643-3177 bobcatofhamilton.com
PETERBOROUGH
Bobcat of Peterborough 705-748-9119 bobcatofpeterborough.com
THUNDER BAY
Equipment World Inc. 807-623-9561 bobcat-tbay.com
CASSELMAN
Bobcat of Ottawa Valley 613-764-2033 bobcatov.com
KITCHENER
Bobcat of Tri-Cities Ltd. 1-866-214-3939 bobcatoftc.com
STRATFORD
Bobcat of Stratford 519-393-6040 bobcatofstratford.ca
SAULT STE. MARIE
Bobcat of Sault Ste. Marie 705-949-7379 bobcat-ssm.com
Thank you, Dave and Chris. CORNWALL
Bobcat of Ottawa Valley 613-932-2034 bobcatov.com
LONDON
Bobcat of London 519-455-4900 bobcatoflondon.ca
STRATTON Stratton Equipment 807-483-5505 strattonequipment.com
WINDSOR
Bobcat of Windsor 519-737-0120 oakenequipment.ca
COURTICE
Bobcat of Durham East Ltd. 905-404-9990 bobcatofdurhameast.com
MUSKOKA
Bobcat of Muskoka 249-390-7000 oakenequipment.ca
SUDBURY
McDowell B Equipment Ltd. 705-566-8190 bmcdowell.com
WYOMING
Advantage Farm Equipment Ltd. 519-845-3346 advantage-equip.com
FRANKFORD
John’s Equipment 613-398-6522 johnsequipmentsales.com
OTTAWA
Bobcat of Ottawa Valley 613-831-5166 bobcatov.com
TORONTO EAST
Bobcat of Toronto 416-679-4171 oakenequipment.ca
In 1874, William Dana Ewart patented his "link-belt" chain invention and founded the Ewart Manufacturing Company in Belle Plaine, Iowa.
Now 150 years later, LBX employees are celebrating one and a half centuries of innovation since Ewart introduced his invention.
This summer, the company hosted a special event at its Customer Experience Center in Lexington, Kentucky to mark the milestone.
“We at LBX are proud of our Link-Belt heritage and are honoured to be part of a legacy that spans 150 years,” said Eric Sauvage, President and CEO. “We shape our future together with our employees and our business partners, guided by our long-term strategic framework while leaning on our core purpose, living and breathing from our core values, and relying on our strategic anchors to be successful.”
The company was born when Ewart, who was a farm implement dealer, saw a need for a better way to repair farm machinery for the United States’ emerging agriculture sector.
Ewart proposed a solution to the frequent repairs required on chain belt drives on harvesters. He realized the drive chain could be made with several detachable links. When the chain belt would break, his invention would allow the defective section to be replaced in the field, rather than at a metal shop, which eliminated downtime for farmers.
Ewart called his new product the Link Belt.
Soon after, Ewart created the Link-Belt Machinery Company, and the Link-Belt
Engineering Company. Together, his companies would develop the first wide-gauge, steam-powered coal-handling clamshell crane. The machines continued to use the link-belt design as a foundation for all types of machinery.
Throughout the past 150 years, Link-Belt has grown from the invention of a “linked belt” chain drive to a manufacturer of excavators, material handling equipment, and forestry machines.
The company has a long history of innovation, from introducing the first crawler-mounted crane shovels and wheel-mounted excavators to many features that are now standard on excavators, including hydraulic controls.
In 1998, the excavator division of Link-Belt Construction Equipment became LBX Company, headquartered in Lexington, Kentucky.
Within the past 25 years, the Link-Belt Excavator Company and its parent company, Sumitomo, have introduced a robust lineup of equipment encompassing six product series: Quantum, LX, X2, X3, X4 and the recently launched X4S.
Further expanding their lineup, the 40 Series for forestry applications debuted in 2015, followed by the 2024 launch of the 40B Series.
Link-Belt machine sales extend throughout North and Latin America, with LBX do Brasil as their subsidiary for distribution and support in Brazil and the broader Latin American market.
ALL MAKES ALL MODELS
AUTHORIZED DISTRIBUTOR
POWER TRAIN SPECIALISTS
TRANSMISSIONS - AXLES - STEERING PAR TS - EXCHANGE - REBUILDS
TARTEN EQUIPMENT LIMITED
6199 Shawson Drive Mississauga, ON L5T 1E5
Phone: 905 670 1704 Fax: 905 670 4790
Toll Free: 1 888 670 1704WWW.TARTEN.COM
COMMITTED TO SERVICE EXCELLENCE SINCE 1976
Equipping the 250 skid steer with the High Flow XPS option gives customers auxiliary hydraulic performance not available from Caterpillar before in a mid-size chassis skid steer.
Equipped for maximum hydraulic capability, the High Flow option for 270 XE, 275 XE and 285 XE loaders increases auxiliary hydraulic system pressure to 4,496 psi and hydraulic flow to 150 litres per minute.
The four next gen CTL models feature a new E-bar (equalizer bar) undercarriage that provides increased stability for grading and handling heavier loads. The E-bar undercarriage harnesses Caterpillar’s experience with track type tractors to provide a hybrid undercarriage solution. It delivers the benefits of a rigid-style undercarriage design when lifting heavy loads or using
heavy attachments like mulchers or dozer and grader blades, while simultaneously providing the benefits of an oscillating undercarriage when encountering uneven terrain or obstacles.
Upgraded operator comfort
All next generation Cat SSLs and CTLs feature a larger cab design with 22 per cent more overall volume and 26 per cent additional foot space. With a 7 cm increase in interior width, the new cab expands footwell-to-ceiling height by 46 mm and allows for an additional 4-cm of hip room and 28-mm more width between the joysticks to improve operator comfort.
Next generation loaders are equipped with either a 13-cm standard LCD monitor or a 20-cm advanced touchscreen monitor, depending on the selected technology package. Like the advanced display on the D3 series, the standard monitor features Bluetooth connectivity and supports functionality for rearview camera feed, creep, job clock and maintenance reminders.
The advanced touchscreen monitor provides a higher level of control over standard monitor functionality, offers advanced radio control, and supports side cameras and 32 language choices. The new advanced joysticks enable integrated control of the advanced touchscreen monitor, so all machine function control and adjustments can be made without the operator removing their hands from the controls.
Entering and exiting next generation loaders is much easier thanks to their low entry points. The operator can now open the cab door without the lift arms being fully lowered to the frame stops. A simplified two-step door removal process allows operators to quickly remove it without tools. The machines’ lower engine mounting, 59 per cent larger rear window and bigger top window provide a 15 per cent increase in viewable area to improve operator visibility.
The new skid steers and CTLs offer the next level of integrating machine and technology. Both standard and advanced monitors provide the ability to run Cat Smart Attachments, such as the dozer and grader blades and backhoe. Attachment operation is integrated into the joysticks, and the machine automatically recognizes the type of attachment and the required joystick pattern for controlling it.
Available Cat Product Link Elite tracks machine hours, location and asset utilization, provides fault code details and delivers advanced monitoring and machine health with data remotely accessible via VisionLink. Additionally, Product Link Elite provides Remote Flash and Remote Troubleshooting capabilities and quickly enables the remote activation of the SEA High Flow feature.
By J. Lynn Fraser
Grit, tenacity, innovation and being customer oriented are the necessary characteristics of a successful company.
This year, Kubota Canada is celebrating 50 years of providing compact construction equipment for the Canadian market.
“We are a known market leader for compact equipment,” said Barry Greenaway, Director for Construction, Commercial and Residential Products at Kubota Canada Ltd.
Throughout its half century in business, Kubota Canada has also become known for its dedication to innovation.
“It’s incredibly important to the company,” Greenaway said.
Kubota was founded in Japan by Gonshiro Kubota in 1890 to produce cast iron pipes and evolved into a global construction equipment manufacturer. The Canadian division, Kubota Canada, was founded in Markham, Ontario, in 1975.
Companies survive and grow due to their reputations and their ability to understand and deliver what their customers need. The true grit
of Kubota Canada’s success is based on its reputation for the support it provides to both dealers and customers — it is known for a strong commitment to community.
Its 137 dealers are a part of the communities that buy the company’ diverse products and are dedicated to them.
“We are renowned for being trustworthy,” Greenaway said. He notes the product line is constantly evolving from its mini excavators to compact track loaders to utility vehicles.
Currently the third generation SVL 75-3 and the fifth generation KX080-5 excavator are part of the company’s roster of equipment benefiting from their embrace of innovative technology.
The company’s KubotaNOW Telematics is used in specific equipment and allows users, in real time, to extract data for GPS location, ignition status and hours, battery voltage, operating temperatures and fluid levels, error codes, as well as engine hours, status, and rpm. The user is always up to date on the health of the equipment and can access data through a mobile app or desktop computer.
Hitachi Construction
Machinery Americas has launched two new Super Long Front (SLF) excavators: the ZX250LC-7 SLF and the ZX350LC-7 SLF.
The 25-ton and 35-ton class machines are engineered to meet the needs of specialized construction sites and come equipped with a genuine bucket while offering advanced reach and depth capabilities.
The ZX250LC-7 SLF boasts a ground level reach of 18.19 metres and a digging depth of 14.43 metres, while the ZX350LC-7 SLF extends even further with a ground level reach of 21.92 metres and a digging depth of 17.38 metres.
The 29,300-kg ZX250LC-7 SLF is powered by a 188 hp engine, while the 38,500-kg ZX350LC-7 SLF is equipped with a 282-hp engine.
These capabilities make the new SLF excavators ideal for a range of applications,
including dredging, barge and waterway operations, roadwork, agricultural projects and site cleanup.
Designed with stability, safety and controllability at the forefront, both models feature an enlarged counterweight to provide operators with enhanced control of the super long arm for steady performance during operations.
A dedicated swing motor enhances responsiveness, ensuring precise manoeuvrability in challenging environments. Additionally, the versatile dig end dimensions are compatible with a variety of bucket and attachment types, enabling these machines to tackle diverse tasks with ease. The new SLF excavators are engineered to efficiently cover and reach distant, confined work areas, providing superior adaptability on specialized job sites.
“The machine will intuitively guide the user,” Greenaway said.
Users accessing the myKubota app can keep track of their equipment’s location and “view telematics data, create geofences for determined areas of use and even inhibit the ability to start the equipment,” using Kubota Canada’s keyless operator system where users login using a pin code. This important feature reduces equipment theft, which in Canada was estimated at $1 billion as recently as 2021. The app also allows users to “access digital manuals, model-specific maintenance information and how-to videos for common maintenance tasks.”
Construction monitoring is also part of the trend to interconnectedness found in Internet of Things (IoT) devices, Building Information Modeling (BIM), augmented reality (AR), and virtual reality (VR) that will eventually become standard in the design of construction equipment.
Equipment innovations partially originate from dealer and key customer input by extensive surveys in addition to research done at the Kansas-based engineering
centre of the American division of Kubota, Greenaway points out.
Part of the company’s mission is to present itself as a solution provider for customers. Greenaway comments that Kubota Canada is always at the forefront of innovation.
Kubota Canada’s products and employees are known for reliability. According to Greenaway this is part of the Japanese tradition of reliability that is “legendary.”
This mission extends to the company’s presence in Quebec including the province’s language and culture, where there have been Kubota Canada dealers almost as long as the company has been established in Canada.
“We respect that, and we engage and support them,” Greenway said.
Looking ahead, part of Kubota’s focus will remain upon staying the forefront of sustainability. Greenaway
notes the company’s diesel engines always meet or exceed environmental regulations.
The future, Greenaway promises, will involve “alternative energy sources and a lot of advances including customization of power with reduced emissions.”
“We aren’t done yet,” Greenaway said innovation in construction equipment at Kubota Canada Ltd. “There are exciting times ahead.”
Safety is top of mind for Major Drilling, one of the world’s largest drilling services companies primarily serving the mining industry.
Established in 1980 and based in Moncton, New Brunswick, Major Drilling is a key player in the supply chain for the battery metals and critical minerals that are required for the transition to green energy.
The company is the preferred specialized drilling contractor for all tiers in the mining industry. With offices and operations around the world, Major Drilling has spent years implementing various rod-handling solutions.
The increasing importance placed on keeping workers safe has increased the availability of improved environmental conditions and new safety-oriented tools like RodBot, a hydraulic robotic handler that eliminates manual rod and casing handling.
RodBot is a hydraulic robotic rod-handling system designed specifically for the seamless loading and unloading of drill rods and casing.
RodBot eliminates hand-bombing entirely and avoids obstacles, keeping workers out of harm’s way while handling sections of pipe up to 30-cm in diameter and 10.6-metres long.
Requiring just one operator, the robotic rod handler allows its user to set the drill mast and rod storage positions once, then hit repeat.
RodBot was created by the Collingwood, Ontario-based MEDATech, which has been designing and building custom mobile heavy equipment since 2003 for the mining, construction, waste, transportation and energy sectors. MEDATech’s Borterra division creates drilling rigs, robotic materials handlers and high-pressure water pumps.
MEDATech and Major Drilling began collaborating on the development of RodBot in 2021. The two companies worked together to refine the machine through trial and experimentation. The robotic rod-handling solution now saves time in addition to being 100 per cent hands-free.
“Rod handling is the part of drilling historically most prone to accidents,” said Marc Landry, Major Drilling’s Vice President of Technology and Logistics. “Major Drilling is committed to reducing risk for our employees and so we are pleased to have found a solution that really works — the MEDATech Borterra RodBot.”
Major Drilling provided significant guidance on the development of the RodBot’s grapple, while MEDATech refined everything from the machine’s fine motor control to its software. Major Drilling has recently entered into an agreement with MEDATech for exclusive rights to RodBot for use in exploration diamond drilling, everywhere Major Drilling operates.
“The magic of RodBot is really in the software,” said Robert Rennie, MEDATech President and Chief Executive Officer.
“Thanks to electric-hydraulic operation, it’s very robust and precise, it’s easier to use than most video games. The learning curve is quick in every mode — manual, tip control and auto.”
RodBot is suitable for mining, construction and the oil and gas industry, as it can be adapted to work on virtually any piece of drilling equipment.
The robotic rod-handling solution has three control modes, including:
The operator has manual control of each moving element of the arm through a radio remote.
Computer assistance allows the operator to control the arm moving the drill pipe in a linear motion. Single-axis input on the joystick translates to the pipe, moving in a straight line either vertically or horizontally out from the arm base.
The RodBot moves along a path determined by the operator and/or automatically adapted to the current mast position. The operator has hands-on control and can start or stop at any time if safety is ever in question.
RodBot is also equipped with what robotics engineers call “go” and “no-go” areas. These zones within the rod handler’s reach specify
where it is safe to operate and where it’s not. This includes defining zones where there is equipment in the way and must be avoided. With RodBot, an operator can program a starting point as well as an ending point, and the robot will calculate the most efficient path, including navigating around any defined obstacles, using collision-avoidance software built into the robotic operating software.
The operator can define and modify no-go zones for both the path taken by the robotic arm and exclusionary zones for the drill setup at each new location.
“The rod movements are fast and consistent,” said Borterra Division Manager Taylor Davies.
“The controls are easy to master and RodBot significantly reduces the potential for human error.”
RodBot can be retrofitted onto existing cranes and drill rigs, attached to pipe tubs or mounted on a skid.
Borterra can also supply a dedicated hydraulic powerpack (diesel, gas or electric), help integrate an existing hydraulic system or supply the information required to carry out a retrofit.
The robotic rod handler is available in three standard configurations. Powered off the drill, the RB1000 is skid mounted and has a maximum load of 90 kg and a maximum reach of 4.5 metres. It’s capable of handling rods with a diameter of 63 mm to 127 mm.
The RB2000 is mounted on the drill and has a maximum load of 363 kg and a maximum reach of 4.5 metres.
The RodBot RB3000 is the largest configuration, which is mounted on a pipe tub and powered by a plug-in electric with hydraulic powerpack.
The RB3000 can lift up to 545 kg and has a maximum reach of 9 metres.
By HCEA Canada
Pictured here in the 1960s is a 32 tonne (Model 35) capacity WABCO Haulpak rock truck being loaded by a Bucyrus Erie cable shovel equipped with a 7-cubic-metre capacity bucket at the Bethlehem Copper Company's open pit mine near Highland Valley, British Columbia.
This 15-unit WABCO fleet handled ore hauling in addition to moving a monthly average of 680,000 tonnes of overburden and very abrasive ore.
Powered typically by either Cummins or Detroit diesel engine in the 261-kW range, these rock trucks encountered close to a 10 per cent cut in effective horsepower due to the 1,525-metre elevation of the mine site.
In the mid-1950s WABCO (Westinghouse Air Brake Company) had purchased the
R.G. LeTourneau construction equipment lines and soon after were producing large rear dump quarry trucks. Canadian-built WABCO rock trucks were manufactured at the former Adams grader plant in Paris, Ontario into the early 1970s. A decade later Haulpak had transitioned to Dresser Industries.
The Historical Construction Equipment Association (HCEA) Canada’s 2024 events include Wheels & Tracks in June and the Last Blast on Oct. 19. Both events are held at the Simcoe County Museum, near Barrie. To see more than 60 pieces of vintage construction equipment in action be sure to attend. HCEA Canada is a proud Heritage Partner of the Simcoe County Museum. Visit hceacanada.org for more information.
Volvo Construction Equipment is adding two new rigid haulers to their lineup in North America.
The 55-ton-payload R60 and 65-ton-payload R70 rigid haul trucks are designed to move material at the lowest cost per ton while providing the latest comfort and safety features. Both rigid haulers are now available to order in North America.
The two new machines join the 105-ton payload
Darren Hynnes: 1-807-252-6556
Jeff Marshall: 1-807-628-6300
Trevor Hynnes: 1-807-629-3007
Jason Dennis: 1-705-288-4685
Pete Ferguson: 1-705-734-4507
Steve Dobson: 1-705-816-4806
R100 in the Volvo CE rigid hauler lineup.
The R60 features a gross weight of 100,222 kg while the R60 has a gross weight of 111,624 kg. Both rigid haulers are powered by a 760-hp Cummins QSK 19 engine and have a maximum speed of 60.6 km per hour.
Rigid haulers are known for high productivity with a low centre of gravity, balanced weight and tough yet flexible chassis. The R60 has a body volume of 36 cubic metres and the R70 offers 42.5 cubic metres, which makes them well-matched for the loading abilities of Volvo’s EC950 crawler excavator and L350H wheel loader.
The machines feature a V-shaped haul body for maximum load retention and minimal carry-back post-dumping. The dumping process itself is also quick thanks to a fast-tip system.
Providing real-time insights on payload, the optional onboard weighing system helps operators apply the industry standard 10/10/20 payload policy, where the machine can take 10 per cent overload for 10 per cent of the time but should not exceed 20 per cent.
Speed and stability go hand in hand with rigid hauler operation. Both the R60 and R70 are designed with a new adaptive retarder system that can automatically control the rear braking system when travelling downhill.
For grip, the high-drive axle multiplication ensures maximum traction while the high-torque engine reduces fuel consumption with an automatic adaptive gear selection called Volvo Dynamic Shift Control. The engine also has an eco-mode that defaults to the most efficient gear, while the auto engine idle reduces engine wear. Both features boost fuel efficiency as well.
For long downhauls, the rigid haulers feature gear-dependent speed control and a selectable brake or transmission retarder, which also helps reduce operator fatigue. The gearbox has overspeed
protection and a neutral coast inhibitor for downhill travel. There is fail-safe braking and a secondary steering system to keep the machine safely on track.
The cabs on the R60 and R70 are fully ROPS/FOPS certified, and operators can enter from either side via anti-slip steps. A large windscreen and low raked dashboard provide optimal visibility, supported by the left-positioned operator station and optional Volvo Smart View for 360-degree sightlines.
For comfort, the rigid haulers are also equipped with an ergonomic, air-suspended seat, independent suspension and vibration-damping viscous mounts to create a smooth experience for the operator.
The steering is low effort, the wheel is adjustable and the operator will enjoy a powerful air conditioning system, ample storage space and Bluetooth radio.
Both the R60 and R70 have 500-hour service intervals, and maintenance can be completed swiftly thanks to a straightforward machine design that includes grouped maintenance points located within reach either from the ground or the service platform. Common-sized bearings keep parts stocking simple and cost-effective. On-board diagnostics provide insights into system pressures and temperatures and fault reporting to facilitate and speed up troubleshooting.
The choice between a rigid and articulated hauler in quarrying and mining depends mostly on the conditions of the site. While rigid haulers thrive on sites with wide, firm, well-maintained haul roads where they can travel quickly over long distances, articulated haulers are better on uneven, narrow, slippery and/or steep haul roads with shorter haul cycles.
The Volvo Site Simulation service can recommend the optimal site setup and machine fleet to help fleets meet production targets, reduce emissions and boost profitability.
To offer more reliable and durable operation, Caterpillar has outfitted its 6020 hydraulic mining shovel with the new Cat C32B engine, replacing the previous Cat 32.
To align with the Cat hydraulic mining shovel lineup, the machine’s nomenclature has been updated from the Cat 6020B to the 6020.
The updated 6020 shovel offers the same features, cycle times and reliability as its predecessor. However, the next generation engine powering the machine delivers improved reliability. As well, the 6020’s hydraulic optimization dynamically assigns individual pumps or groups of pumps to deliver the exact flow pressure that each hydraulic function requires. This reduces waste and heat, prolongs component lives and improves fuel consumption.
With designs certified to meet emissions standards worldwide, the new C32B engine is a direct replacement for the C32. The C32B offers the same 776 kW rated power as its predecessor and no additional hardware is required for engine replacement to upgrade existing machines in the field.
Higher flow oil and baffles in the oil cooler keep the engine core cooled and lubricated, while the engine’s new cylinder head with optimized water jacket maximizes heat transfer.
The C32B’s ability to deliver higher power in certain applications comes from increased piston compression height.
An updated crankshaft and connecting rods with larger journals increase durability by reducing contact pressure and optimizing bearing performance, while
a new cylinder block helps increase structural capability. All valves are equipped with oil metering stem seals and reduced contact pressure geometry for maximum life.
As well, a thicker shim gasket reduces the risk of head-to-block oil leaks, while more durable exhaust valves, especially when operating at high power, reduce the chance of exhaust valve failures.
Dual sensor coolant protection detects potential coolant leaks sooner than
the previous capabilities to avoid costly downtime.
Hydraulic
Hydraulic optimization for the 6020 shovel dynamically assigns individual pumps or groups of pumps to deliver the exact flow and pressure required by each hydraulic function.
Hydraulic optimization provides efficient use of the engine for greater productivity, less energy and fuel consumption and reduced component wear. With its
22-tonne payload, the 6020 efficiently loads the Cat 775 truck in three passes, 777 in four passes, 785 in six passes and 789 in eight passes.
The next generation operator cab on the 6020 offers class-leading visibility for operating productively, safely and efficiently. Electronic-hydraulic servo joystick control delivers fast and precise machine movements with less operator fatigue, while five-circuit hydraulics allow for simultaneous control of two-cylinder motions, two
travel motions and swing. The large 25-cm high-definition colour touchscreen puts all vital machine and diagnostic data at the operators’ fingertips. A safer training environment is facilitated by unobstructed views of the digging environment and emergency stop button easily accessible from both training seats.
A range of onboard and optional technology offerings boosts productivity, efficiency and health of the 6020 shovel.
The machine’s board control system employs multiple sensors to monitor operating data, record faults and notify the operator audibly and visually for early detection of faults.
Factory-ready for Cat MineStar Solutions, MineStar Health is fully integrated as an option to deliver critical event-based and operating data. Also available are MineStar Fleet for real-time machine tracking, assignment and productivity management; Terrain that enables guidance technology and high-precision management of shovel operators; and Detect to increase operator awareness and enhance safety.
Hitachi Construction
Machinery has started a technological feasibility trial of the world’s first ultra-large full battery rigid frame dump truck by an original equipment manufacturer.
The technological feasibility trial began this summer at First Quantum’s Kansanshi deep open-pit copper-gold mine, one of the company's largest mines in Zambia.
The trial aims to verify the basic performance of operations required of a battery-powered dump truck — such as travelling, turning, and stopping — under actual operating loads, as well as the verification of the trolley battery charging and discharging cycles.
“Mining companies around the world are working to re-
duce emissions. As an original equipment manufacturer, it is our vision to provide solutions that can reduce our customers’ environmental footprint,” said Eiji Fukunishi, Hitachi Construction Machinery’s Vice President, Executive Officer and President of the Mining Business Unit.
“The battery dump truck represents the future, not only for the Hitachi Construction Machinery Group but for the mining industry as a whole.”
Hitachi began collaborating with ABB in 2021 to develop the full battery dump truck.
On March 1, 2023, Hitachi signed a letter of intent with First Quantum to establish a zero-emission partnership. Hitachi Construction Machinery completed the test machine version of a full battery dump truck and shipped the test machine to First Quantum in January.
The full battery dump truck was jointly developed with ABB Ltd. Based on Hitachi’s experience with dump trucks equipped with trolley dynamic charging systems, the full battery dump truck can continuously operate on sites by directly charging from the overhead lines and a regenerative braking system. Using a battery system developed by ABB, the truck does not need to stop to charge. As well, limiting the battery volume reduces the battery weight as a percentage of the overall vehicle weight and helps maximize the load capacity to display a high level of cost performance.
Sandvik Mining and Rock Solutions has introduced the electric Sandvik DR416iE, the next generation i-series rotary blasthole drill.
The electrified machine is based upon Sandvik’s popular DR416i. The Sandvik DR416iE joins the Sandvik DR410iE, Sandvik DR412iE and Sandvik DR413iE as the fourth and largest electrified rig in Sandvik’s intelligent rotary blasthole range.
The electric drill is designed to deliver sustainable performance while operating in demanding mining conditions.
"Sandvik DR416iE rep -
resents a significant leap forward in electric blasthole drill technology and delivers rotary customers the option of a seamless transition from diesel to electric," said Nellaiappan Subbiah, Product Manager, Rotary Drills at Sandvik Mining and Rock Solutions.
The drill is ideal for iron ore and copper applications, as the rotary blasthole drill can drill a hole diameter range of 270 mm to 406 mm.
Powered by a 1,400 hp electric power group to meet the demands of high-altitude applications, the Sandvik DR416iE boasts a sophis -
ticated electric system that incorporates a soft starter to help reduce impact on the mine's power grid, preventing disruptions to other equipment.
The multi-voltage and multi-frequency electric motor offers outstanding flexibility, while the optional 420-metre cable reel ensures ample capacity for connecting to the mine substation.
Operators will appreciate Sandvik’s familiar and intuitive DRi control system. This common system, featured across all Sandvik i-series surface drills, pro -
vides a consistent operating experience and simplifies operator training.
For tackling hard rock formations, the rotary blasthole drill is equipped with a heavy-duty feed system. This hydraulic motor-driven chain feed system delivers superior pulldown force and
increased weight on bit, resulting in significantly faster penetration rates.
“Sandvik DR416iE uses the same modular platform as our largest diesel-powered rotary rig but with the added environmental benefits of electrification,”
Subbiah said. “We now offer
customers the ability to convert a diesel-powered unit to a fully electrified version in the field. This innovative drill delivers unmatched performance, reliability and sustainability, making it an ideal choice for forward-thinking mining operations.”
With a new carousel design and automation features, Epiroc’s new Simba SM60 S long-hole production drill rig for small to mediumsized drifts is built to deliver optimal performance without compromising on safety.
As part of Epiroc’s Smart series, the new production drill rig is equipped with a wide range of automation options, designed to increase operator safety, drilling quality and productivity.
Epiroc has equipped the machine with automation
software such as Feed Speed Control Impact (FSCI), used to control the rock drill and automate positioning to hole toe, which ensures correct utilization of the machine and improves drilling performance.
The updated electrical control system and the automation software features can significantly contribute to safe productivity by removing the operator from hazardous areas.
“Epiroc’s advanced technology enhances our customers’ operations by boosting productivity, and more importantly, by improving safety standards. We are proud to be at the forefront of accelerating the transformation to safer min-
ABB and Komatsu have signed an agreement to collaborate on the development of net zero emissions for heavy industrial machinery.
The collaboration will combine Komatsu’s and ABB’s industry expertise and products to create solutions ranging from renewable energy generation to fully electrified mining equipment.
Decarbonization of mobile mining equipment is required to help mine operators achieve their greenhouse gas reduction targets. ABB and Komatsu's collaboration is geared towards reducing diesel consumption and ultimately eliminating it through the electrification of mine operations.
"We're pleased to embark on this collaboration with ABB and are excited to leverage one another's industry leading products and technological expertise to help move mining operations toward net zero emissions, empowering a sustainable future where people, business, and the planet thrive together,"
ing practices," said Rickard Johansson, Vice President of Marketing at Epiroc’s Underground division.
The newly developed RHS 17 single-layer carousel ensures seamless rod handling. With the gripper arms placed inside the carousel, it can easily and quickly move the rods between the carousel and the drill centre, significantly improving operation productivity and drilling performance.
“With the gripper arms placed inside the carousel, each rod handling can save more than 20 seconds, compared to the previous carousel model,” said Mikael Larslin, Global Product Manager for
Production Drilling at Epiroc’s Underground Division.
The Simba SM60 S drill rig has one of the lowest transport heights in Epiroc’s fleet of Simba production drills. The new horseshoe-mounted drill unit frame and low-built drill unit are designed to be positioned at the very lowest point, placing the drill unit below the cab roof at a height of 2.8 metres.
“The new horseshoe drill unit frame provides great stability and robustness during drilling, and minimizes the transport height during transportation,” Larslin said. “This makes the Simba SM60 S an ideal rig in smaller drift mines.”
said Dan Funcannon, Senior Vice President of Surface Haulage for Komatsu.
With the collaboration, ABB and Komatsu are deeply committed to providing customers with a portfolio of interoperable solutions to meet their specific needs. Recognizing the varying stages of electrification standards across the mining industry, ABB and Komatsu are focusing on haulage, loading and auxiliary equipment. This approach aims to build a comprehensive portfolio of production and support equipment to accelerate adoption into operations.
“By working together, we will tackle electrification and make a revolutionary difference to the way mining companies operate their sites in the near future,” said Joachim Braun, Division President of ABB Process Industries.
“We recognize the strategic importance of this agreement and believe there will be mutual business benefits and potential technology solutions for the mining market. Collaboration across the industry has already been proven to enable real and faster progress and we look forward to driving what happens next.”
Ecolog International has announced the appointment of Mel Brooks as Chief Executive Officer.
Brooks’ career has spanned more than three decades, and he brings extensive leadership experience and a track record of driving growth and delivering exceptional results.
“I am very pleased to join Ecolog International, an organization renowned for its commitment to improving the lives of the people it serves
across diverse sectors,” Brooks said. “Ecolog's dedication to excellence and innovative approach to solving complex challenges are truly impressive, and I look forward to working with the incredible team to drive further growth and success.”
Prior to joining Ecolog, Brooks held leadership roles at G4S, including Group Strategy and Technology Director, Group Commercial Director, CEO of India and South Asia and CEO of Africa and the Middle East. Dur-
ing his tenure, he spearheaded the growth of the business, elevating operations, enhancing client service and driving sales. His strategic vision and handson approach were instrumental in achieving success in these regions.
His background also includes senior positions in the defense and technology industries.
Brooks’ appointment comes at a pivotal time as Ecolog progresses with expanding its service offerings in government and
defense, oil & gas and mining, as well as humanitarian, NGOs and international development organizations.
“Ecolog is achieving significant growth and actively expanding into new markets,” Brooks said. “I am excited to lead the company into its next phase. By leveraging our team's extensive expertise, we will enhance our service capacity and continue to deliver exceptional value to our clients and the communities we proudly serve."
Bomag Americas has promoted Christoph Thiesbrummel to Vice President of Sales and Marketing for its North American operations.
In his new position, Thiesbrummel will lead Bomag Americas’ dealer channel sales, rental channel sales, sales administration, product management and marketing activities.
Thiesbrummel brings more than a decade of industry experience to his new position, all within the Bomag organization.
“I am excited for this
new opportunity to grow the Bomag brand in North America, working together with our strong network of partners across all sales channels and the Bomag team in the US and Canada,” Thiesbrummel said.
“Our entire team is committed to a customer-first approach and will continue to find innovative solutions for our customers’ individual needs.
"Let’s grow together!”
After receiving his doctorate in marketing & business management, he began his career with Bomag at the
Brokk has hired Taylor Chatterton as a Service Technician for the West Coast.
Chatterton, based in Monroe, Washington, will provide service for rental customers as well as on-site service and support for Brokk and Aquajet machines.
“Our customers on the West Coast now have ac -
Boppard, Germany, headquarters as Pricing and Business Analytics Manager. He then moved to Bomag Americas to assume the role of Sales Administration Manager, where he oversaw the inside sales team.
He also worked with the field sales team, managing market and new dealer development for Bomag Americas.
For the last two years, Thiesbrummel served as Bomag Americas’ Director of Sales, dealer channel for the eastern United States.
“Christoph is incred -
ibly talented, has deep knowledge of the Bomag organization and equipment, and has delivered successful results at every level within the organization he has worked,” said Brian Bieller, President of Bomag Americas.
“He recently completed Fayat’s one-year advanced program for high-potential personnel, the Global Fayat Road Academy management training program. His knowledge, dedication and in-depth experience with Bomag make him the right fit for the position.”
Patrick Sexton has joined OTR Engineered Solutions as the company’s new Global Vice President of Engineering and Innovation.
In this role, Sexton will oversee OTR’s engineering team worldwide, ensuring all activities align with strategic goals.
“It’s an exciting time at OTR, as we’re not only investing heavily in product development, but also advancing technology and building global infrastructure,” said Tom Rizzi, OTR President and CEO.
“Patrick will be a great addition to OTR’s executive team, and he’ll help us continue to innovate and grow.”
Sexton offers vast experience in energy, electrification, automotive and similar industries. He has led the development of various products and solutions for leading technology companies, serving in both engineering and executive-level
positions. He also has a background in providing technical and strategic consulting. Throughout his career, he has been awarded 10 patents, with others currently in process.
“OTR has a proud history of innovation in off-the-road tire, wheel and track technologies, dating back to 1987,” Rizzi said.
“With 32 facilities and more than 1,400 employees worldwide, we’re only getting started. Sexton will be instrumental in further developing our premium solutions for OEM and aftermarket customers in numerous industries, leading to future growth globally.”
A native of Ireland, Sexton earned a degree in mechanical and manufacturing engineering from Munster Technical University in Cork, Ireland. After spending some of his career in the United Kingdom, he moved to the United States, where he recently became a citizen.
cess to a dedicated service technician for both Brokk and Aquajet products,” said Lars Lindgren, President of Brokk. “Taylor brings unique experience as someone who has been both an operator and mechanic during these heavy equipment projects.
As an operator of heavy equipment, he knows what
types of challenges our customers are facing. This allows him to help them decide on the best machine for the job while also providing onsite service for our machines.”
Chatterton will also provide basic training to operators, including showing them machine
capabilities, how to operate the Brokk and how to complete routine maintenance items. Chatterton will consult with operators to assess jobsite conditions and make recommendations on machines, attachments and other equipment for the job.
“Brokk customers face some of the most challen -
ging jobs in their industries,” Chatterton said. “Brokk and Aquajet have some of the most cutting-edge technology on the market, which makes these jobs easier and safer. I’m excited to help train operators on their machines and offer service and support to maximize our customers’ uptime.”