
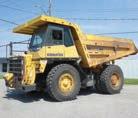






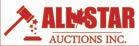

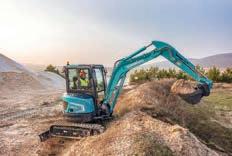




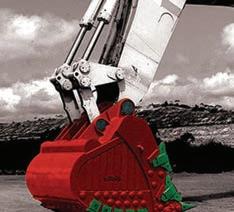







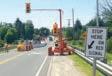



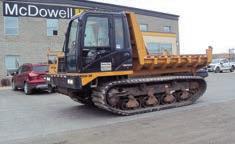
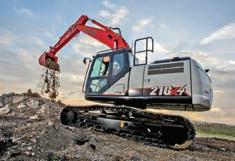


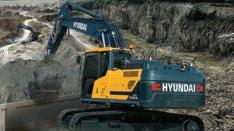

POWERSCREEN |CHIEFTAIN 1700

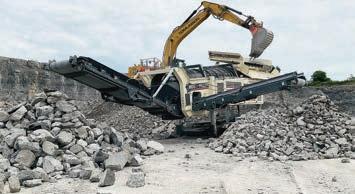
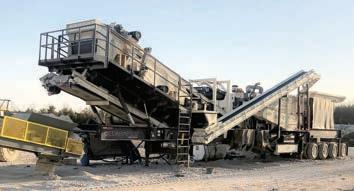
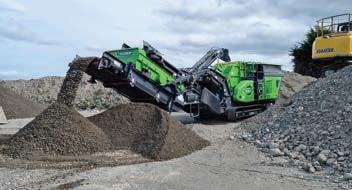
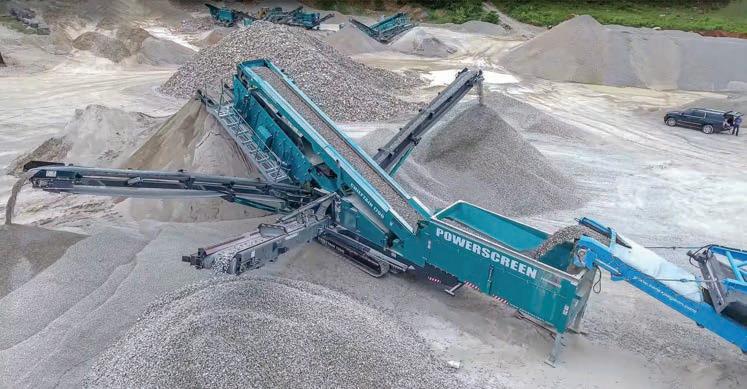
POWERSCREEN |CHIEFTAIN 1700
Closed circuit impactor/screen plan, 6’x16’ 2-deck inclined screen, 450 HP T4F Scania diesel with hydraulic clutch crusher/generator drive, 150KW generator, 48” x 18’ vibrating grizzly feeder with 6’ stepped 2-deck grizzly, high production, high value plant.
CEDARAPIDS |CRS620H
Toll-Free: 1877-797-7276
9’x6’ single screen, Volvo D8 315 Hp, 3.3m3 hopper, integrated pre-screen for fines removal, 40” conveyor, optional 20” side conveyor, Afterscreen system recirculates oversized material, optional wind sifter to remove contaminants, suitable for reinforced concrete, recycled asphalt, construction and demolition waste and natural rock.
MDS HEAVY DUTY TRACK TROMMELS
Complete range of heavy duty track trommels. Over 25 years of experience. Ideal for Gabion Stone, Quarried Rock up to 32”, RipRap/Armour Stone, and cleaning sticky clay from rocks. Visit powerscreencanada.com
CREATES PRODUCT SIZES FROM:
LETTER
I’ve noticed a growing theme in recent issues of Equipment Journal
More and more articles focus on sustainability and zero emission power sources.
In this issue alone, we cover JCB converting a Mercedes Sprinter to hydrogen (Page A13), Strongco’s demo of Volvo CE’s electric compact equipment (Page A7) and how Rokbak’s sustainability efforts are lowering the cost of ownership of their articulated haulers (Page A22) — just to name a few.
It’s not intentional on our part. Demand — and availability — for machines powered by zero, or low, emissions power sources is clearly growing rapidly and naturally represented in our coverage.
“We're getting more and more interest in electric every single month, and the big motivation is sus -
tainability,” Roy Milicevic, Strongco Sales Manager, CE Ontario explained during the company’s recent demo in Milton, Ontario. “We have some customers that want to electrify 40 to 50 per cent of their fleet within the next five to 10 years.”
Despite the growth in demand and development, I’ve heard many comments from people that are steadfast against "green" technology.
Unfortunately, adoption of green tech seems to have become a political wedge issue for some.
Now, I’m not trying to convince anyone to pledge their allegiance to the Paris Accord. Instead, consider the benefits of zero emissions machines beyond mitigating the impact on climate.
With electric for example, the reduction in maintenance, and the time to complete said maintenance,
is an impressive selling point. Without an internal combustion engine, fluid and filter changes are nearly eliminated.
The reduction in noise and vibration is another factor to consider. This opens the door to operation in new locations, as well as outside of normal operating hours. Plus, it equals a more comfortable day for the operator.
The constantly rising cost of fuel is another serious factor to consider.
It’s also important to remember that before the commercial availability of electric or hydrogen powered machines, massive strides were made to reduce construction equipment emissions.
As you will read on Page B9 of this issue, today’s Tier 4 Final engines offer a 96 per cent reduction of oxides of nitrogen as well as a 97 per
Bill Tremblay // Editor editor@equipmentjournal.comcent reduction in particulate matter compared to Tier 1 engines.
Obviously, zero emissions machinery won’t work for every application, and diesel will remain king on many worksites for years to come.
However, if electric or hydrogen can fit into a typical day’s work, it’s probably worth the time to take a
Editor Bill Tremblay editor@equipmentjournal.com
Publisher Mark Baker mark@equipmentjournal.com PACE
Sales Manager Tara Baker tara@equipmentjournal.com
National Account Manager Mona Fahmi mona@equipmentjournal.com
TOLL-FREE: CDN/USA 1-800-667-8541
Creative Director/Creative Services Ryan Chuhaniuk ryan@equipmentjournal.com
Circulation Manager Lisa Bath lisa@equipmentjournal.com
EMAIL US: advertise@equipmentjournal.com
WEBSITE: www.equipmentjournal.com
TECHNOLOGY IS ONE OF OUR GREATEST TOOLS
The stand-on mini track loader market is expected to expand rapidly in the next decade, as demand grows for landscaping, tree removal and other jobs that require travelling over existing turf without causing damage.
To meet growing demand, Case Construction Equipment is introducing the TL100 mini track loader (MTL).
The TL100 features a rated operating capacity of 454 kg (35 per cent of tipping load), and will be available with numerous attachments and premium features.
“We’re entering the MTL market with the weight and power of a global full-line manufacturer who has taken its time, researched the product demand and engineered a machine that is ready to deliver serious performance for landscapers, residential services contractors, utilities and farms. We also expect this to be extremely hot with rental businesses,” said Brady Lewis, Product Manager for Case Construction Equipment.
“The compact size, ease of transportation and excellent attachment compatibility makes this an extremely dynamic addition to the Case product line and dealer network.”
The 25 hp Case TL100 features hydraulic pilot controls (ISO pattern) and a powerful standard 50-litre-per-minute auxiliary hy-
draulic setup (2,700 psi) that delivers excellent attachment performance.
Attachments connect through a Common Industry Interface (CII) compatible with most major manufacturers of mini track loader attachments.
“We’ve also brought our commitment of hip pocket support that’s never more than a phone or tablet away with a five-year Case SiteWatch telematics subscription on each machine,” Lewis said. “Making these technologies available as a standard offering to compact and sub-compact equipment owners bring their fleet management game to another level and opens the door to a deeper collaborative service and support relationship with their Case dealer.”
Optional equipment on the TL100 mini track loader will be a 14-pin front electric connector that includes a hydraulic case drain circuit, multiple track widths, additional counterweights, environmentally friendly hydraulic oil and multiple bucket options.
The TL100 mini track loader will become commercially available this year.
“We are fully committed to this market and are excited to work with our dealer network to share these new, premium MTLs with fleet managers and business owners who thrive with compact equipment,” Lewis said.
Strongco recently showcased the emissions-free power of Volvo Construction Equipment’s compact electric lineup during its demo days across Canada.
Throughout the fall, Strongco held demos in Milton, Ontario, Dartmouth, Nova Scotia, Laval and St. Augustin, Quebec and Acheson, Alberta.
“We're getting more and more interest in electric every single month, and the big motivation is sustainability,” said Roy Milicevic, Strongco Sales Manager, CE Ontario. “We have some customers that want to electrify 40 to 50 per cent of their fleet within the next five to 10 years.”
Volvo Construction Equipment offers the largest lineup of electric equipment in the industry. This includes three electric compact excavators —the ECR25 (2,680 to 2,780 kg), ECR18 (1,790 to 1,870 kg) and the EC18 (1,960 kg) — as well as the L25 (4,900 to 5,270 kg) and L20 (4,550 kg) electric wheel loaders.
Recently, Volvo also announced it will begin production of the DD25 electric compactor at its factory in Shippensburg, Pennsylvania. The mid-size 23-ton EC230 Electric excavator is also expected to arrive in Canada later this year.
While sustainability is a key factor for many contractors that
purchase electric equipment, performance is also a benefit. The specs between a diesel and electric machine are nearly identical. However, electric machines deliver instant torque as there is no delay in rpm.
“In terms of performance, we've seen what they can do. I think they perform above their weight class,” Milicevic said.
Depending on the job, a typical stop-start work pattern will allow operation of an electric machine for four to six hours on a single charge.
“We get the same work hours from the electric compact excavator that we do from a diesel
compact excavator,” Milicevic said.
As well, with diesel construction equipment, engine runtime defines operating time, but many of those hours include machine idling. With electric equipment, as soon as the operator stops working, the motors turn off and operating hours are not accumulated.
The reduction in noise is another important factor. The ECR25 is two times quieter than its diesel counterpart.
“You can literally have a conversation with the operator while he's digging a hole,” Milicevic said.
Noise reduction not only reduces
fatigue for the operator but allows the machine to work in new, sound sensitive environments and for longer time periods in municipalities with restrictions.
As the electric machines do not include engines or cooling fans, maintenance is also greatly reduced. The only services required are grease, hydraulic oil and in some cases coolant for watercooled inverters and drivetrain. On average, an electric machine will save about $3,500 per year compared to a diesel-powered machine.
“If we add that up over the machine’s lifespan, it’s pretty significant savings,” Milicevic said.
Kleemann recently debuted the new Mobibelt MBT 20(i) and MBT 24(i) mobile stackers Mobibelt to enable efficient logistics processes on work sites.
The stackers flexibly extend the action radius of crushing and screening plants to make large stockpiles and improved work site logistics.
To a large extent, modern crushing and screening plants automatically regulate material streams within the
Broderson Carry Deck Cranes are extremely versatile, ideal for lifting material that require a compact, low-profile crane to maneuver in tight spaces and clear overhead obstacles. Multiple sizes and capacities, including optional equipment for customization, ensures your Broderson crane can fulfill all your lifting needs.
•
•
plant. However, machine operators still have a strong influence on the quality of the final product and the daily output. They control the input with their excavators and wheel loaders by the loading of stone or recycling material. Users also play the main role with regard to output, as they co-ordinate the final products by means of building up stockpiles, intermediate storage areas and loading.
With the new Mobibelt MBT 20(i) and MBT 24(i) stackers from Kleemann, logistics can now be organized flexibly and adapted to the respective situation.
High feed capacity
Both stackers are equipped with a large 1.25 cubic-metre feed hopper made of Kleemann Resistant Steel (KRS), which permits the feeding of material with an edge length of up to 200 mm without complications.
An optional hopper extension up to 2.5 cubic-metres is provided with an additional impact bar that prevents the direct impact of the feed material on the conveyor belt and thus reduces wear.
Thanks to the hydraulically adjustable feed and discharge height, a fast set-up is possible and the stackers can be used flexibly behind screening and crushing plants with different discharge heights. Operating mobile stackers is less complex than crushing plants and it should also be simple and convenient.
The Mobibelt MBT 20(i) and MBT 24(i) include the Spective operating system that makes intuitive operation of the machines possible. During a typical workday, the operator receives support with a central operating position, local operation and the option of troubleshooting help via Spective Connect.
Hy-Brid Lifts has announced it has entered a strategic partnership with the Turkish-based ASKO, who is acquiring a majority stake in the company.
Headquartered in Turkey, ASKO operates in the construction and agricultural machinery, energy and technology sectors through its eight companies and subsidiaries.
ASKO currently owns ELS Lift, who produces a range of scissor lifts, vertical mast lifts and boom lifts; and MST Construction Machinery, who produces telehandlers and earthmoving equipment.
“The next chapter for HyBrid Lifts has started with this partnership with ASKO,” said Jay Sugar, CEO and President of Hy-Brid Lifts.
“We see this as a great opportunity for our customers as we will be bringing new products to the mar-
ket, accelerating R&D and increasing our sales and service support.”
Hy-Brid Lifts is a brand of Custom Equipment. The company manufactures all-purpose lifts in electric, self-propelled and pusharound models.
The partnership will increase the Hy-Brid Lifts product offering and provide working capital for accelerated growth in all areas.
“We are very excited to welcome Hy-Brid Lifts and its skilled employees into the ASKO family,” said Sami Konukoglu, Founder and Chairman of the Board of ASKO.
“With Hy-Brid Lifts’ track record of producing innovative high-quality products and having an established dealer network, this investment fits into ASKO’s strategy to become a global player and expand in North America.”
With the introduction of the LX20 Series, Kubota Canada is adding two new tractor models to its lineup of compact equipment.
The new LX20 Series compact tractors include the LX3520 and the LX 4020 models, available with 35 or 40 horsepower to meet a variety of needs. As well, upgrades include improved comfort and operator controls, noise reduction, premium loader operability and an increased travel speed.
Kubota Canada has also introduced the LX3520 Narrow with a width less than 101 cm, allowing for ease of use between trees, making it an ideal equipment option for orchards, vineyards and nurseries.
“The new L X20 Series models represent the core pillars of Kubota’s compact tractor lineup, built with quality, durability and performance in mind,” said Chris Isaac, Product Manager for Compact Utility Tractors at Kubota Canada.
“Available with a variety of implements, the versatility of the LX3520 and LX4020 make them invaluable property maintenance tools for easy material handling and transport. The size of the equipment is just right in that it allows users to operate in tighter areas and be nimble, without sacrificing power, performance or comfort.”
Kubota’s integrated cab
For operator comfort, the LX20 Series’ integrated cab includes features that prioritize noise reduction. The four-pillar design with rounded glass gives the operator ample space and panoramic views, while the high back suspension seat is designed to absorb shock and reduce operator fatigue.
The large, flat deck provides more legroom, and makes it easier to enter and exit the tractor, as does the door’s wide opening.
Each tractor has ergonomic lever grips and a steering wheel for easy access and smooth low vibration operation during any application, as well as powerful LED work lights to provide strong visibility at night.
The LX3520 and LX4020 include an independent, clutch-less PTO switch for simple engagement and disengagement while in
operation and the Kubota proven three-range HST transmission, which provides optimal speeds that cater to the job at hand.
As well, the LX20 series can be equipped with Land Pride’s Quick Hitch, a feature that improves ease of switching out rear implements and reduces the time it takes to do so. Designed for operators who have more than one rear three-point implement, the Quick Hitch saves time and helps to reduce fatigue.
The 35 and 40 horsepower models meet a variety of needs and boast a new threepoint lift capacity of 893 kg, nearly 136 kg more than the current LX3310 model.
The Kubota four-point quick connect front hitch lets the operator connect and disconnect the front PTO-driven attachments in no time at all, while the dual engine memory switch allows the operator to adjust ideal engine rpm by the press of the button.
The newly adapted brush guard option helps prevent the bonnet and grill from being damaged, and the auto throttle links the engine speed to the travel speed so the operator can control engine rpm with the HST pedal. This allows the operator to set the rpm to a desired level and increase as needed for various applications.
The Kubota designed and built LA545 loader matched to the LX3520 and LX4020 has premium valving, allowing simultaneous boom and bucket operation with a regenerative circuit that makes it comfortable to operate.
The new LX20 Series compact tractors will be available at Kubota dealers across Canada during the winter of 2024.
Hydrema dump trucks are making inroads in Ontario where small dumpers or full-size dump trucks may not fit the application.
Based in Denmark, Hydrema manufactures 7, 10 and 20 tonne compact dump trucks (as well as compact wheel excavators and backhoes).
“Hydrema is a small family-owned business, and because of that, they are a specialist product. They fill a gap in the market. They're smaller than your typical offering in the dump truck range,” said Stephen Cargill, owner of Annagola Iron, the Ontario dealer for Hydrema equipment.
The Hydrema dump truck line is relatively new in Ontario. Cargill sold the first Hydrema truck in the province about three years ago as a standalone piece of equipment. The buyer returned for a second machine and encouraged Cargill to become the Ontario dealer for the dump truck line.
With about 16 dump trucks sold in the province to date, the 10-tonne 912 series is proving to be the flagship model.
“It represents a segment that nobody else is really in. There are other players, but they don't build the type of truck that Hydrema is able to offer,” Cargill said.
The trucks are designed with a unique articulation point with oscillation and hydraulic stabilizers. Equipped with 17.5 R25 EM tires, the 912 is only 2.2 metres wide. Thanks to the articulated joint in the middle, it becomes a narrow and manoeuvrable machine that is ideal for tight construction sites.
“The compact nature of the trucks means you can fit it into an urban area much easier,” Cargill said.
As well, the 912 dump
trucks are approved to drive fully loaded on public roads, enabling the transportation of material between sites or the ability to move the dump trucks to a different construction site.
“They're pretty nippy on the road and can travel up to 50 kilometers an hour depending on the model,” Cargill said.
MultiTip is a popular option for Hydrema dump trucks. Available on the 7 and 10 tonne models, MultiTip allows the dump truck body to turn in a 180-degree radius to unload material.
As well, the optional Auto-Body-Return function automatically lowers the body back onto the chassis with a push of a button. With this feature, the operator can move on to the next task while the body lowers itself.
“MultiTip basically encompasses both sides of the truck or anywhere in between,” Cargill said. “It gives them a good ability for spreading and planting materials that a conventional dump truck wouldn't be known for.”
This summer, Hub Equipment, based in Etobicoke, Ontario, purchased two 912GS and two 912HM models for its rental fleet.
“We think they're going to become a popular rental tool for certain contract -
ors and landscapers who don't require a full-sized truck and want a more versatile, more maneuverable, smaller truck,” said Tom Stevenson, President of Hub Equipment. “One of the key features is how the box can pivot. So, it’s really helpful in certain applications.”
The 912GS is equipped with a suspension system on the front axle. The suspension includes an electrohydraulic spring system with independent suspension cylinders and level control that aligns the machine in the optimal position. This reduces the impact on the operator from vibration during long transport stages or in rough terrain operation.
The Hydrema 912HM (High Mobility) is the same machine as the 912GS, but with higher and wider tires of up to 80 cm, which gives it more ground clearance and minimal ground pressure. Fully loaded, the truck has a ground pressure of 12 psi. This translates to exceptional off-road performance, even in soft and muddy terrain or on sensitive surfaces.
“The low ground pressure makes them ideal for conservation or golf course type work — anywhere where you have to try to protect the turf or environment,” Cargill said. “It’s basically anywhere a triaxle wouldn’t be able to go.”
The latest G Series trucks include an upgraded cooling system, which has a 10 per cent increase in cooling capacity thanks to a fully welded radiator. Furthermore, the new generation of the truck is equipped with an electronically controlled cooling fan that only operates when needed. This saves fuel and reduces noise.
The dump truck is also equipped with an automatic
WE ALSO CARRY:
• Augers
• Breakers
• Brush Cutters
• Buckets
• Compactors
• Demolition
• Forest Mulcher
• Grapples
• Quick Couplers
• Rippers
• Compactors
• Rubber Tracks
• Thumbs
• Screening Buckets
shawbros.ca info@shawbros.ca
battery isolator that shuts down when power is not required, allowing the operator to leave the machine without forgetting to turn off the isolator.
The 912 models are powered by a 145 hp, four-cylinder Cummins
Stage 5 diesel engine. The engine compartment has been reorganized to allow access to all service filters and check points from ground level. Extra drain
QUALITY ATTACHMENTS
valves have been fitted to ensure easy and safe oil draining. The radiator compartment has been fitted with a new easy access panel.
The steps on the 912 G-series have been widened, while maintaining one-step access to the cab.
An optional LED work light package is available to improve visibility while operating in dark conditions.
Barrie, Ontario 1-877-625-9677
Gyru-Star compact screening systems are used primarily for screening soil, compost & aggregates. They bring an affordable, high quality and performance screening solution, with low or zero maintenance, to the compact attachment market.
MACHINE CONTROL
LMC produces after-market cables and harnesses, for machine control and heavy machinery. We also design and manufacture electronic grading solutions specializing in laser and inclinometer machine control systems.
LT-800 FEATURES INCLUDES:
• Fully automatic self-leveling
• Height of instrument alert (HI alert)
• Long 500 feet operating radius
• Machine control compatible
• 20 arc second accuracy
• 635nm visible red beam
GO THE DISTANCE... SAVE ON FUEL.
5-YEAR/ 5,000 HOUR Full Machine Warranty
5-YEAR/ 10,000 HOUR Machine Structures Warranty
•
Largest minimum swing radius exavator in Link-Belt lineup.
•
Power of large machine at lower weight.
•
6-cylinder Isuzu Final Tier 4 engine with fuel efficiency and high productivity without need for DPF.
•
4 work modes, including the new Eco mode.
•
New cab with more head and leg room making this the roomiest cab ever.
•
Optional WAVES® camera system adds a third camera and gives the operator a full 270º view around the machine.
RemoteCARE® GPS-enabled telematics system included with no subscription fee!
Your LINK-BELT Excavators Dealer has all the details!
ALBERTA
Equipment Sales & Service Ltd.
Edmonton (780) 440-4010 essltd.com
BRITISH COLUMBIA
The Inland Group
Burnaby, BC 604-291-6431
Campbell River, BC 250-287-8878
Castlegar, BC 250-365-2807
Cranbrook, BC 250-426-6205
Fort St. John, BC 250-785-6105
Kamloops, BC 250-374-4406
Kelowna, BC 250-769-2933
Langley, BC 604-607-8555
Nanaimo, BC 250-758-5288
Penticton, BC 250-492-3939
Prince George, BC 250-562-8171
Quesnel, BC 250-992-7256
Terrace, BC 250-635-5122
Vernon, BC 250-545-4424
Williams Lake, BC 250-392-7101 inland-group.com
NEW BRUNSWICK
Paul Equipment Balmoral (506) 826-3289 paulequipment.ca
ONTARIO
Itec 2000
Rosslyn (888) 574-8530
Thunder Bay (888) 574-8530 Timmins (705) 267-0223 itec2000.com
McDowell B Equipment Ltd. Sudbury (705) 566-8190
Barrie (416) 770-7706 bmcdowell.com
Stratton Equipment Sales & Service Stratton (807) 483-7777 strattonequipment.com
QUEBEC
Équipement JYL Inc.
Chicoutimi (418) 698-6656 equipementjyl.com
Paul Equipment (506) 826-3289 paulequipment.ca
Top Lift Enterprises Inc.
St-Laurent (514) 335-2953
Sherbrooke (819) 612-5438 toplift.com
YUKON TERRITORY
The Inland Group
Whitehorse, YT 867-668-2127 inland-group.com
www.lbxco.com/warranty
Link-Belt is expanding its truck terrain crane lineup with the launch of the new four-axle 120|TTLB.
The Link-Belt 120|TTLB truck terrain crane features a seven-section 11.7 metre to 50 metre pin and latch boom with all-wheel steer and a tight turning radius.
The 120-ton capacity truck terrain crane features a 108 metre per minute maximum speed, a max line pull of 105.12 kN and a maximum tipping height of 79.7 metres.
The all-wheel steer capability on the new truck terrain crane makes it an ideal option for crane maneuverability in tight jobsite settings.
As well, a steerable rear axle with super single tires gives the 120|TTLB four steering modes — independent front, independent rear, combination and crab.
Link-Belt Cranes introduced rear wheel steering to the truck crane market on a custom truck crane chassis 21 years ago when it displayed the 60-tonne HTT-8670 at ConExpo. Since then, the performance and agility of Link-Belt HTTs in a variety of applications have remained the benchmark for truck terrain cranes.
The 120|TTLB truck terrain crane comes with an air-ride suspension design, and air disc brakes on a rear-steer
truck crane for advanced braking performance. For added engine performance and fuel economy the 120|TTLB is powered by a Cummins 445 hp EPA emissions compliant X12 Series engine. The 120|TTLB is capable of reaching a maximum speed of 88 km per hour.
The product launch brings Link-Belt’s family of hydraulic truck terrain models to five, including the 75-ton HTT-8675 Series II, 100ton HTT-86100, 110-ton HTT-86110, 120-ton 120|TT, and now the new 120-ton 120|TTLB.
JCB has successfully installed one of its hydrogen engines into a Mercedes Sprinter van, marking an advancement in the utilization of sustainable energy for vehicles.
The Sprinter van was retrofitted in just two weeks and is the second Mercedes vehicle to be modified with a JCB hydrogen engine. Earlier this year, JCB equipped a 7.5-ton Mercedes truck with a hydrogen engine.
The internal combustion engine used in the van is the same as those already powering the JCB construction and agricultural prototype machines.
One of the first test drivers was JCB Chairman Anthony Bamford, who is leading the company’s 100 million hydrogen engine project.
“We retrofitted this vehicle with a JCB hydrogen engine to demonstrate how simple it will be to convert existing vans and to show that it is not only construction and agricultural machines that can be powered by hydrogen,” Lord Bamford said. “While converting vans will not be for JCB to do, it does prove there is something else other
than batteries that can work very effectively.”
JCB has manufactured more than 70 hydrogen internal combustion engines in a project involving about 150 British engineers. The hydrogen engines now power prototype JCB backhoe loader and Loadall telescopic handler machines.
The converted van was previously diesel-powered. The switch to hydrogen is another breakthrough that underlines the power source could represent a quick way to reach global carbon dioxide emissions targets. Another benefit of hydrogen powered vehicles is they can be refuelled in a matter of minutes compared to several hours for recharging batteries.
JCB developed the world’s first working hydrogen-powered construction and agricultural machines. Last year, JCB revealed another industry first with a mobile hydrogen refueller, which provides a quick and straightforward way to refuel machines on site. JCB’s hydrogen internal combustion engines are manufactured at JCB Power Systems in Derbyshire, England.
To meet the critical needs of the electric power generation industry, Perkins has introduced the 18-litre 2806J-E18TAG1 Electropak.
Building on its Stage V power offering and more than 90 years of design experience, the new engine delivers a powerful package and ease of integration to meet the requirements of the electric power sector.
By achieving ISO 85285 G2 performance, the 2806J-E18TAG1 Electropak provides excellent load ac-
ceptance in a wide range of electric power applications. From a stationary prime source of power to a mobile unit serving the rental sector, the 2806J generates dependable power for everything from jobsites to critical installations including hospitals and data centres.
“Reliable electric power is not an option, it’s a fundamental need to keep operations running, whether that’s for standby when the mains power fails or to meet onsite prime power require-
ments,” said Jaz Gill, Vice President of Global Sales, Marketing, Service and Parts for Perkins.
“Our engines are engineered and expertly crafted to provide reliable, stable and sustainable power for our customers, with the new 2806J being the latest in a long line of products that also deliver a low total cost of ownership.”
For generator manufacturers and end users looking to reduce greenhouse gas emissions, the 2806J Electropak
can run with biodiesel up to B20, based on a 20 per cent dilution of biodiesel with standard diesel, or on 100 per cent hydrotreated vegetable oil (HVO).
The 2806J Electropak produces up to 610 kVA at 50 Hz and is switchable to 60 Hz, delivering up to 625 kVA.
As well, the Electropak features the latest electronics with a single, on-engine electronic control module (ECM) that simplifies wiring harnesses, eases installation, supports future diagnostics and is fully capable of integration with customers’ telematics solutions.
The ECM also manages
all aspects of aftertreatment operation and regeneration without operator input. Regeneration occurs automatically with no impact to performance to maximize uptime.
Perkins offers a growing portfolio of connectivity solutions that can help promote the optimal performance of diesel engines.
Available as a standalone service from Perkins or integrated with generator equipment, connected engine capabilities deliver timely insights through a customizable dashboard of performance, fuel and oil consumption, as well as other vital engine data points that assist in boosting
uptime of Perkins-powered equipment.
The connectivity offerings are integrated with expert maintenance and service capabilities from the Perkins global distributor network to prompt the proactive diagnosis and resolution of engine issues, helping technicians provide solutions and minimize downtime and repair expenses.
The new 2806J Electropak joins Perkins' full lineup of Stage V certified engines for electric power generation, including the 400 Series, 904 Series, 1200 Series, 1700 Series, and the 2000 Series, with power ranging from 4 kW at 1500 rpm to 559 kW at 1500 rpm.
•
•
I can’t give enough credit to the SENNEBOGEN service team. They worked through all the ‘interesting’ challenges that came up along the way – there are no better guys out there. Being so new, there weren’t a lot of mechanics anywhere trained on this, but they and our dealer’s mechanics have been great about coming out and working alongside our mechanics.
Barge Terminal Manager, Huger, NC
Read more about how our “Beyond the Machine” aftersale commitment ensures life-long support for SENNEBOGEN customers with the nation’s largest network of factory-trained technicians.
SENNEBOGEN is committed to leading the industry in aftersale support throughout the life of its equipment. We’re thinking “beyond the machine” to deliver dependable uptime and lower Total Cost of Ownership (TCO) for every customer.
Learn more about our commitment to our customers
sennebogen-na.com/beyond-the-machine
Prince Edward Island
Strongco
Prince Edward Island (902) 468-5010
www.strongco.com
Nova Scotia
Strongco
Dartmouth, NS (902) 468-5010
www.strongco.com
New Brunswick
Strongco
Moncton, NB (506) 857-8425
www.strongco.com
Newfoundland and Labrador
Strongco Mount Pearl, NL (709) 747-4026
www.strongco.com
Quebec
Strongco
Baie-Comeau, QC
Chicoutimi, QC
St-Augustin, QC
1-866-996-3091
1-800-323-1724
1-800-463-2662
Trois-Rivieres, QC 1-855-840-0828
Val d’Or, QC 1-800-561-4192
www.strongco.com
Top Lift Enterprises, Inc.
St-Laurent, QC (514) 335-2953
Sherbrooke, QC (819) 612-5438
www.toplift.com
Ontario Strongco
Stittsville, ON (613) 836-6633
Sudbury, ON (705) 692-0552
Thunder Bay, ON (807) 475-3052
www.strongco.com
Top Lift Enterprises, Inc.
Bolton, ON (905) 857-5200
Stoney Creek, ON (905) 662-4137
www.toplift.com
Manitoba
Westcon Equipment & Rentals Ltd.
Winnipeg, MB 1-800-453-2435
www.westconequip.ca
Saskatchewan Redhead Equipment
Estevan, SK (306) 634-4788
Lloydminster, SK (306) 825-3434
Melfort, SK (306) 752-2273
North Battleford, SK (306) 445-8128
Prince Albert, SK (306) 763-6454
Regina, SK (306) 721-2666
Saskatoon, SK (306) 934-3555
Swift Current, SK (306) 773-2951
www.redheadequipment.ca
Alberta Strongco Acheson, AB 1-877-948-3515
Calgary, AB 1-800-342-6523
Fort McMurray, AB 1-855-799-4201
Grande Prairie, AB 1-888-513-9919
Red Deer, AB 1-866-950-3473
www.strongco.com
British Columbia
Great West Equipment
Campbell River, BC (250) 286-0123
Cranbrook, BC (250) 426-6778
Fort St. John, BC (250) 785-4223
Kamloops, BC (250) 372-3996
Nanaimo, BC (250) 716-8804
Prince George, BC (250) 612-0255
Surrey, BC (604) 882-5051
Terrace, BC (250) 635-9033
Vernon, BC (250) 549-4232
Williams Lake, BC (250) 392-9599
www.gwequipment.com
are no better guys out there
The new DD25 Electric compactor will be the Volvo Construction Equipment’s first electric machine manufactured in the United States.
Volvo Ce announced the American production plan during an event at its Shippensburg, Pennsylvania, headquarters in August.
The first DD25 models are expected to deliver in early 2024. The company aims to have 35 per cent of its product line electric by 2030.
“This is a monumental day at Volvo CE,” said Scott
Young, Head of Region North America, Volvo CE.
“Manufacturing electric machines in Shippensburg is good news for the environment, our customers, the local economy and the broader U.S. construction equipment industry.”
The DD25 Electric compactor will be manufactured on the same assembly line as Volvo diesel asphalt and soil compactors. This allows the site to expand production capacity without increasing its footprint or incurring significant costs to retool the factory.
The DD25 Electric compactor originated from a crowdsourcing project within the Shippensburg compaction engineering team, using scrum methodology and building on Volvo CE’s proven electric equipment platform. The first model made its debut in March at ConExpo.
The electric driveline of the DD25 Electric compactor is based on the same architecture and components as the Volvo CE ECR25 Electric compact excavator and L25 Electric compact wheel loader.
Its zero-emission operation makes the DD25 Electric asphalt compactor ideal for sensitive or urban environments with strict emission regulations and for organizations that are looking to meet their own sustainability goals. Zero tailpipe emissions also mean a cleaner and more enjoyable work environment for operators, site teams and the public.
If used alongside other electric powered equipment, the DD25 Electric offers the possibility of a zero-emission jobsite.
The DD25 comes with an integrated on-board charger that enables charging from zero to 100 per cent in as little as three hours, depending on AC power level. With an optional off-board DC fast charger, this can be achieved in just over an hour.
The double-drum DD25 Electric asphalt compactor offers 24 kW of available power, which is 30 per cent more than the conventional Volvo DD25B compactor. The result is a more responsive machine in terms of speed and vibrations. It also performs better on grade thanks to the size of its components and better at high elevations when compared to a diesel machine, which loses power as altitude is increased.
Electric production
Volvo is investing heavily in training for its employees, providing more than 800 total hours of instruction on electric equipment production concepts and processes.
“We have a talented workforce and the perfect space at this location to set ourselves up for ongoing development and production of industry-changing machines,” said Gustavo Casagrandi, Head of Operations at the Shippensburg plant.
“Some of the world’s best engineers and production team members are right here, building the future of construction.”
During the event, Volvo CE also announced it is expected to receive a $1.1 million grant from the United States Environmental Protection Agency (EPA) for a pilot testing project of the DD25 Electric in Southern California.
As part of the same event, Volvo Construction Equipment officially opened its new training centre in Shippensburg, Pennsylvania.
The $7.3 million facility will serve as a training hub of expertise and innovation for Volvo CE service technicians on diesel and electric heavy equipment, machine control technology, connectivity and productivity services.
The new facility includes in-person classrooms, virtual labs and three service bays that can accommodate the company’s largest machines, allowing training to occur inside year-round.
“I’m proud to work for a company that invests in not only the equipment and technology of the construction industry’s future, but also the North American workforce,” Young said.
“The technicians who come through this training centre will be prepared for a more climate-friendly and connected future, supporting our customers in this fastchanging industry.”
Volvo Construction Equipment offers training to dealer service and sales teams from across Canada and the United States. This includes three levels of technical certifications for maintenance, diagnostics and repair of Volvo equipment, plus a new certification to perform commissioning and decommissioning of Volvo electric machines.
The new centre doubles the number of students Volvo CE can train in a year, compared to its former off-site location. The facility also provides hands-on and virtual trainings to Volvo employees globally.
Traditional vendor managed inventory (VMI) programs track part ordering, fulfillment and replenishment in construction equipment manufacturing facilities. But a genuinely automated, end-to-end system is more significant in scope and benefits than just managing parts.
Modern inventory management offers a strategy that elevates supply chain
assurance, increases facility efficiency and positively impacts financial performance. These tech-enabled processes also enhance supplier-distributor collaboration and align both partners by:
· Illuminating and adapting to changes in demand
· Offering visibility into consumption patterns, on-hand inventory and locations
· Providing data to optimize quantity, logistical and delivery decisions
· Automating replenishment based on individual facility requirements
Digitized inventory management ensures you can make data-driven decisions with current inventory numbers that are not vulnerable to mistakes, tardiness, miscommunication or multiple data sources. In turn, automated solutions help accurately anticipate required stock levels and bring your supply chain planning into focus.
Still, some equipment manufacturers cling to legacy inventory management processes. Familiarity breeds comfort but remaining loyal to those routines are likely doing you few favours. Before embarking on a new solution, its best to get more acquainted with what fully integrated inventory management can look like, how a
digitized system reduces cost and some small steps to get started.
Tech-enabled inventory
Managed inventory employs a partner (think full-service distributor) that’s responsible for all things related to inventory. This resource develops a custom program to ensure stocking levels match demand and inventory is delivered when needed. It’s about streamlining your supply chain, reducing costs, having higher visibility into your parts consumption and reallocating human resources away from slow, manual, error-prone work to more quality-focused, value-added responsibilities.
Partner requirements inc lude:
· Digital tools to meet individual plant requirements: The ability to easily implement technology solutions that meet different workflow and space requirements at one or multiple manufacturing facilities.
· RFID and EDI: Proven transmission protocols that assure the partner’s network and support data flows freely and securely to and from manufacturing and distribution locations.
Continued
from Page
· Integration into existing ERP and SCM platforms via web tools — It’s critical to ensure all aspects of production are working with the same data through a single source of truth.
· Security: All data transactions moving between the manufacturer and the partner must be secure and can’t be compromised.
· Accountability: The partner should demonstrate multiple ways to understand and attribute inventory usage.
· Reporting: Visibility throughout the managed inventory process starts with good reporting that is designed to meet a manufacturer’s unique needs.
· Control: The partner needs to demonstrate that manual inventory practices can be moved to automated replenishment processes at a pace that’s comfortable for the manufacturer.
Reduced costs
A recent study found most companies devote 20 per cent to 40 per cent of their overall working capital to inventory alone. Keeping those costs down is critical to maintaining cash flow with such a sizable percentage of funds invested in inventory. Automated inventory management facilitates offer better stocking levels, and less E&O (Excess & Obsolete), greater control over cash flow and fewer people needed to manage fastener stock. A tech-enabled solution can reduce costs in many ways and equipment manufacturers are starting to understand the importance of:
· Better forecasting via technology: Using RFID technology to manually
or automatically submit replenishment orders means that inventory may be monitored in real-time. As a result, procurement and supply chain professionals can manage inventory levels to production requirements.
· Working smarter with business analytics: Technology available today allows you to capture and use data and modelling based on real-time and historical consumption patterns. The best forecasting uses a mix of quantitative and qualitative data to guide more accurate inventory management decisions. This foresight allows you to see where demand and usage comes from and plan accordingly. You can see where fulfillment levels are, and adjusting production up or down based on demand, parts availability and lead time.
· Refocusing human capital: With a manual scanner or an automated replenishment program, it will take less time, teammates and process to maintain appropriate inventory levels. These productivity gains drive soft costs down and offer an opportunity to re-allocate people to roles with greater impact on production.
The first step is to identify the core pain points of your current solution and map them to the benefits a digitized system provides. Here are the top five questions to ask:
1. On a scale of 1 to 10 how accurate are your part counts?
2. How long does it take to go from count to replenishment?
3. Has production slowed or
stopped because of low inventory or stockouts in the last 12 months?
4. Has E&O inventory negatively impacted your company’s balance sheet in the last three years?
5. Is your current supplier doing anything to improve your inventory management process?
Answers to these questions are a first step toward achieving the benefits associated with a modern inventory management solution.
Digitized inventory management can make your supply chain more efficient and resilient to disruptions, develop higher visibility into your part consumption, im-
prove forecasting and help you reallocate resources to more productive responsibilities.
Tech-enabled inventory management has promising benefits for manufactures in the construction equipment arena. Among them are savings in time from a labour and administrative standpoint, increased supply chain assurance and greater confidence in data-driven decisions.
Preventive maintenance and inspection programs can help construction and industrial companies ensure maximum value from their equipment fleets.
United Rentals recently outlined how regular maintenance and inspections are a critical component of equipment operational efficiency.
Under-maintaining equipment, especially high-use compact to midsize machinery, can happen for a variety of reasons. However, failing to conduct fleeting maintenance and required inspections comes at a price that includes higher equipment costs, lost productivity and increased safety risks.
“For too many companies, preventive maintenance tasks and inspections fall through the cracks of busy work schedules and equipment moving from worksite to worksite,” said Bret Kasubke, Director of Customer Equipment Solutions at United Rentals.
“A well-executed maintenance and inspection program delivers great value by ensuring equipment is ready to go. It adds structure and visibility to the maintenance of owned equipment so companies can reduce downtime and improve cost control. The program protects equipment investment and can extend machinery life, possibly reducing the risk of catastrophic equipment failure that can lead to worksite safety issues.”
Preventive maintenance programs and regular inspections provide construction and industrial companies with several safety, productivity and financial benefits.
Over time, wear and tear on equipment can lead to potentially dangerous mechanical failures. Worn chains and cables, broken pedals or levers and malfunctioning safety lights or audio signals can cause worksite accidents.
Creating and following an equipment maintenance plan can mitigate serious hazards that result from faulty equipment and
improve overall worksite safety.
Equipment inspections required by ANSI, OSHA and CSA are equally important. For example, aerial lifts, such as boom and scissor lifts, require inspection by qualified mechanics or technicians every three months or every 150 hours, whichever comes first. As well, aerial lifts must be inspected annually – every 13 months – and every time the equipment has been out of service for more than three months.
It is important to note that only a mechanic or technician qualified to work on the specific make and model of the aerial lift can perform the inspection. If a company does not have this expertise in-house, it should consider outsourcing equipment inspections to a qualified vendor.
Productivity
Poorly maintained equipment is more likely to break down. Companies that follow a preventive maintenance schedule experience less unplanned equipment downtime and better equipment performance, resulting in greater productivity. Inspecting equipment during regular preventative maintenance service can reduce the risk of potentially crippling issues.
Financial benefits
Proper maintenance and inspection of equipment can save a company money in numerous ways, including:
· Reducing downtime: When a single piece of equipment fails, the costs of lost productivity and wasted wages can be considerable. Preventive maintenance and regular inspections help reduce equipment failures.
· Avoiding fines: Failures to perform aerial work platform inspections or inspect other equipment on schedule, such as cranes and derricks, can result in government fines.
· Lowering repair costs: A well-executed preventive maintenance program can lower repair costs more than relying on reactive maintenance – waiting until a machine breaks to fix it. The simplest maintenance tasks can prevent expensive engine breakdowns.
· Reducing overtime: If equipment breaks during a project with a tight schedule, a company may have to pay workers overtime to make the scheduled deadline.
· Extending the useful life of equipment: Well-maintained equipment lasts longer. When regular fleet maintenance is performed, companies can delay the need to purchase new equipment.
Outsourcing can be an attractive option for companies that want to gain the benefits of preventive maintenance and inspections but need more internal capabilities or resources. A third-party provider that offers a
dependable one-stop shop with standardized processes and rates takes the maintenance and repair burden off of fleet owners.
This approach can give companies the peace of mind that comes with knowing equipment will be ready to perform when needed.
“Starting and sticking to a preventive maintenance program isn’t simple or easy, especially when equipment moves from jobsite to jobsite,” Kasubke said. “Outsourcing these tasks to a single vendor with deep experience in equipment maintenance and a large staff of skilled technicians can relieve the burden of fleet maintenance and let companies focus on what they do best.”
The United Rentals Customer Equipment Solutions team specializes in equipment repair and service in the field and onsite, so companies can protect their investment, safeguard employees and meet ANSI, OSHA and CSA requirements.
As part of its sustainability strategy, Rokbak has implemented a set of ambitious goals in operating measures, articulated hauler design and construction that also help to improve the total cost of ownership (TCO) of its machines.
As part of the Volvo Group, Rokbak is aligned to the Science Based Targets initiative (SBTi). Specific aims include a 30 per cent reduction in
carbon dioxide by 2030, a 50 per cent factory operations emission reduction by the same year and becoming net-zero by 2040.
“A lot of work has gone into our sustainability drive over the years,” said Charlie Urquhart, Rokbak Product Manager. “Rokbak’s heritage, knowledge and resources mean that we’re constantly developing and looking to improve the trucks and the
way we operate, in a manner that benefits our customers.”
Sustainable by design
These goals have influenced the design of Rokbak trucks, the daily operation of the Rokbak Motherwell factory and a strict adherence to the Rokbak sustainability roadmap.
The effort to reduce environmental impact has seen Rokbak employ several strategies, including fuel consumption analysis, examining alternative fuels, extending maintenance cycles and reducing maintenance consumables. Furthermore, this research and development in sustainability has led to the reduction of TCO for Rokbak customers.
“We are creating significant steppingstones towards a sustainable future,” Urquhart
said. “And this not only results in less waste being generated, but also benefits the Rokbak customer’s wallet.”
Fuel consumption is the biggest cost of operating a machine and the Rokbak RA30 and RA40 EU Stage V engines produce a fuel consumption saving of up to 7 per cent, compared to the previous engines. This means lower operating costs and less impact on the environment.
Rokbak’s articulated haulers both have lean burning engines and a confirmed low-fuel consumption. The RA40 has a class-leading transmission fluid change interval of 6,000 hours, while the RA30 offers 4,000 hours.
HVO
As well, both the RA30 and RA40 are compatible with hydrotreated vegetable
oil (HVO), a fuel that allows customers a ‘quick-hit’ on their individual net-zero targets. HVO, also known as renewable or green diesel, is a paraffinic bio-based diesel fuel originating from animal fats or multiple vegetable oils, such as waste cooking oil, rapeseed oil or palm oil. HVO fuel has similar chemical and physical properties as diesel fuel, however, its fossil-free composition and low carbon content differentiate it from diesel and make it an option to those seeking a sustainable fuel.
It is a modern way to produce high-quality biobased diesel fuels without compromising fuel logistics, engines, exhaust aftertreatment devices or exhaust emissions. HVO can provide up to a 90 per cent reduction in carbon dioxide emissions on a well-to-wheel analysis. Extensive periods between scheduled maintenance, with infrequent parts and fluid changes, translates to less material going to landfill. Maintenance and fault alerts allow customers to keep on top of the truck and be informed of the machine’s next required servicing. Instigating the ordering of parts in advance and getting the labour in place increases operational efficiency, not only improving sustainability
measures but also reduces TCO.
“When the customer buys a Rokbak hauler, they are acquiring a hauler that has been developed with sustainability in mind,” Urquhart said.
“It is a hauler that has been manufactured on a site powered by green energy and redirects waste away from landfill.”
Rokbak factory
Today, the Rokbak factory is completely powered by sustainable sources. Working towards accreditation on a zero-waste-to-landfill policy, 95 per cent of generated waste is now diverted away from landfill. Within the facility, everyone from the factory floor to the head office has an eye on energy reduction. Internal trackers inform Rokbak employees how much energy has been used in comparison to the previous week and “green champions” are recruited from throughout the business to promote sustainable practices in their respective work areas.
“It’s to make sure everyone’s doing their bit,” Urquhart said. “Whether you’re monitoring power tools usage or remembering to switch off the lights and air conditioning, you’re part of a united drive.”
THE MOBISCREEN EVO S CR EE NIN G PL ANTS –4 TI ME S MOR E P OWER.
HIGH FLEXI B IL ITY AND FIRST C LASS SCR EEN ING RESULTS. Th e MO BISCREEN MS C EVO s cree ning plan ts are charac terise d b y hi g h application ver satility, excellen t tran sport chara cterist ic s and fa st set -up times. Precise resu lts with a ver y wide vari ety of fee d mater ials and lo w consumption are g uaran tee d –where flexib il ity meets preci sion. Th e effic ie nt MSC EVOs t hu s impress wi th top p er forman ce v alu es across the board.
www.kleemann.info
You can meet expectations. Or you can crush them. The JCB Telehandler is the ultimate material handling machine. So, while everyone else is getting the job done, you can get it done better. Learn more at JCB.com.
ALBERTA
Liftboss JCB
Calgary: 403-301-0041
Edmonton: 780-474-9900 liftboss.ca
BRITISH COLUMBIA
Williams JCB
Surrey: 604-930-3316 williamsjcb.com
NEW BRUNSWICK
A.L.P.A. Equipment
Edmundston : 506-735-4144
Balmoral : 506-826-2717
Fredericton : 506-452-9818
Moncton, N.B. : 506-861-2572 alpaequipment.com
NOVA SCOTIA
A.L.P.A. Equipment Truro : (902) 897-2717 alpaequipment.com
NEWFOUNDLAND
Harvey JCB Corner Brook: 709-639-2960 St. Johns: 709-738-8911 harveyco.ca
ONTARIO
Advance JCB
Waterloo: 519-742-5878
Harriston: 519-510-5878 advanceequipment.net
D&W Group Inc.
Doughty & Williamson
Jarvis: 519-587-2273
Brant Tractor
Burford: 519-449-2500
Redtrac International Vineland: 905-562-4136 dwgroup.ca
ONTARIO
Delta JCB
Dunvegan: 613-527-1501
Renfrew: 613-432-4133 Winchester: 613-774-2273 deltapower.ca
Fulline JCB
Glencoe: 519-287-2840 fullinefarm.com
Hub International Equipment Ltd. Lindsay: 705-324-6136 Port Perry: 905-982-1500 hubinter.com
Jade Equipment Simcoe County and Districts of Parry Sound & Muskoka 705-325-2777 jadeequipment.com
John’s Equipment Sales Frankford: 613-398-6522 johnsequipmentsales.com
ONTARIO
Moore JCB
Toronto, York & Peel
Region: 416-747-1212 moorejcb.com
North Rock JCB
North Bay, Sault Ste. Marie, and Sudbury: 705-897-7369 northrockrentals.com
ReadyQuip Sales & Service Ltd.
Timmins: 705-268-7600 readyquip.com
WPE Landscape Equipment - JCB
Hamilton/Halton: 905-628-3055 wpeequipment.ca
PEI
A.L.P.A. Equipment (506) 861-2572 alpaequipment.com
QUEBEC
A.L.P.A. Equipment
Bas-Saint-Laurent : (506) 735-4144
Gaspésie : (506) 826-2717 alpaequipment.com
Bossé Quebec Inc.
Desmaures: 418-878-2241 Saint-Augustin-debosse-frere.com
Moore JCB
Montreal: 514-333-1212 moorejcb.com
SASKATCHEWAN & MANITOBA
Westcon JCB
Regina: 306-359-7273
Saskatoon: 306-934-3646
Winnipeg: 204-694-5364 westconequip.ca
Brandt’s first entry into the hydrovac market delivers maximum legal load weights, lower noise levels as well as quick loading and unloading.
Introduced earlier this year, the HX120 was developed in response to the increasing need for a hydrovac that combines full-sized capacity with maneuverability in tight urban spaces.
The hydrovac features a water tank capacity of 4,353 litres and an 11.6 cubic yard debris tank capacity, as well as an 8.5 metre boom reach with 340-degree rotation.
As Brandt is both a dealer and a manufacturer, the company is able to gather input from technicians at its 138 locations around the world, as well as its more than 200,000 customers, to design new machines.
“We're not designing our products from a boardroom far away from the market. We're designing them from a jobsite in collaboration with our dealership partners,” said Matt Semple, Senior Vice President of Marketing at Brandt..
“It also means we have over 1,200 technicians fixing machines every single day. So, we tend to know what goes wrong. That goes back to our design team to make sure that we're beefing up those areas or swapping out components before failures happen.”
Brandt decided to develop the hydrovac to meet the growing needs of the utilities industry.
“Hydrovacs are an industry that's been growing across the North American market due to infrastructure upgrades, increasing
amounts of telecom expansions and pipeline infrastructure that's going into the ground every year,” said Curt Borys, Director of Product Marketing at Brandt.
To understand the features required by hydrovac end users, Brandt was able to work with its existing customers throughout the product development process.
“The foundation of Brandt’s approach to any new product development is how we understand our customers, and how their needs can become our objectives,” Borys said. “We want to understand the benefits that we're going to bring to a customer, not just a list of features.”
The HX120 helps underground excavation contractors work efficiently with maximized legal load weights and the capacity to take on larger jobs without load weight concerns.
The real-time measurement of water and overall truck weight enables operators to make quick, informed decisions, which reduces the risk of damage or overweight penalties.
“Every part on this truck has been engineered to perform while reducing weight,” said P. Eng Evrhetton Gold, Brandt’s Lead Engineer for the hydrovac.
A unique feature included in the design of Brandt’s hydrovac is the ability to set local legal requirements for the chassis as well as its tare weight.
“The truck will tell you from zero
to 100 per cent how close you are to your legal road limit, giving the operator as much information as possible so they can make the best decisions,” Gold said.
It is also the quietest hydro excavator in its class, a benefit in urban settings.
“We delivered an enclosed cyclone filter and sheltered lower design. This drastically reduces the noise around the unit,” Gold explained.
As well, the vacuum pump exhaust is exported above the truck, while a dual PTO design allows the truck to deliver maximum performance at lower rpm levels.
“This helps reduce the overall noise of this truck by up to 15 per cent versus our competition,” Gold said.
The rear-door lockout ensures safe servicing and allows operators to wash down the inside of the debris tank with ease. As well, the system requires less water to wash out after unloading than slope-unload designed units.
The hydrovac also includes an emergency shut off with multiple access points around the vehicle.
“The system will break back instantly protecting the operator, but then brings the truck down in stages to also protect not only our backend equipment baggage, but the chassis itself,” Gold said.
In case of loss of signal from the remote, the truck’s air and wash
systems will turn off until the remote is reconnected.
“They do not need to come back to the truck to do that now. The last thing we want is an operator to be hung up on a nozzle or a valve and go to reach the remote and not be able to access emergency software,” Gold said.
The automatic transmission, low overall height and compact wheelbase improve maneuverability, making the truck easier to operate.
“We delivered the shortest wheelbase in its class. It's 20 inches shorter than a lot of our competition,” Gold said.
Reducing downtime was a common request Brandt heard from its customers. To boost uptime, the hydrovac features quick clean out with a full open rear door and vibration assistance.
The fully powder-coated debris tank unloads quickly and has the
ability to pressure offload into another truck, bin or land spread for fast turnaround.
The boom turret, constructed of AR steel, is designed with a removable access plate for cleanout and a shut-off plate that allows the operator to shut down the boom suction without shutting down the blower.
As well, the hydrovac is designed with easy access points for service and maintenance allowing for quicker on-site servicing.
“You ask for reduced downtime caused by inefficient operating procedures. So, what we've delivered here is the quickest and easiest truck to get digging,” Gold said.
To improve efficiency at the end of the hose, the boom is built with a progressive diameter from the dig tube to the turret to reduce plugging while acting as a secondary vacuum chamber.
“Anything that goes up the uptake tube is getting to the chassis,” Gold said.
CM Labs will introduce new training simulators for wheel excavators, walkaround inspections and support training programs at The Utility Expo, held Sept. 26 to 28 in Louisville, Kentucky.
CM Labs’ latest scalable simulation solutions train for high-risk procedures in a safe environment, improving technical expertise and increasing line operator productivity.
The simulation training for wheeled excavators focuses on situational awareness and reducing safety risks within a dense urban environment.
As well, the new training pack for excavators includes heavy duty bucket and narrow tiltrotator with a live attachment change exercise.
The walkaround inspection simulator will feature training for excavator operators to identify issues on equipment to help improve jobsite safety and productivity.
As well, CM Labs’ support training programs with instructor operator
station enables trainers to monitor, assess and engage trainees via tablet or single workstation, personalized learning paths, updated metrics reporting and new administrator functionalities.
“With the ongoing need for qualified labour, now, more than ever before, CM Labs’ customers need the best possible operator learning outcomes,” said Lisa Barbieri, CM Labs' Vice President of Marketing and Strategic Relations.
“The ultra-realism of our simulation and advanced reporting insights will future-proof utility training programs and recruitment needs by addressing longterm training needs.”
Comprised of proprietary and patented algorithms, CM Labs’ simulation training is based on real data and authentic machine behaviour that interacts with its environment and materials just as they do in the real world.
“Our simulations ensure training teams have the
flexibility to mobilize line workers efficiently. With hot swappable controls, and quick jump starts between all simulated equipment, there is less time away from the worksite and no need to take equipment off contracts,” said Davis Siu, CM Labs’ Product Manager. “The authentic replication of equipment and simulated risky situations means line operators can train for safety, in safety.”
Based in Montreal, Quebec, CM Labs builds simulation-based solutions to help clients design advanced equipment and prepare for skilled operations.
Through its Vortex Studio platform, CM Labs provides capabilities for training simulators, mission rehearsal, virtual prototyping, and testing.
CM Labs wide range of earthmoving and lifting simulation training packs include digger derrick, boom truck, telehandler, compact track loader, rough terrain crane, backhoe, forklift, and the newly released wheeled excavator.
Pictured here in 1960 is a new Massey Ferguson tractor backhoe having been just delivered to the St. Thomas, Ontario, works department. With the introduction of the tractor mounted backhoe in the 1950s many contractors and public utilities realized the obvious advantages of such a highly mobile and versatile unit. Most agricultural equipment manufacturers such as Case and John Deere were quick to adapt their ag tractors with backhoe and front loaders attachments built by Wagner, Wain-Roy & Hopto (an acronym for Hydraulic Operated
This Massey Ferguson Model 65 tractor, equipped with a model 220 backhoe attachment, had a rated digging depth of 4 metres and was powered by either a Continental gas engine or a Perkins diesel engine, both in the 30 kW range. The backhoe had vertical stabilizers and was available with a side-shift option. The operator station swung with the boom, which fortunately for operators was a shortlived design feature.
Produced from 1958 to 1964, the base Massey Ferguson 65 tractor had a
purchase price of $3,900. The town operator appears to be keeping a necessary keen eye on the town council dignitaries inspecting his new machine!
The Historical Construction Equipment Association’s (HCEA Canada) 2023 event the ‘Last Blast’ takes place Oct. 14 at the Simcoe County Museum, near Barrie, Ontario. To see more than 60 pieces of vintage construction equipment in action be sure to attend. HCEA Canada is a proud Heritage Partner of the Simcoe County Museum. Visit hceacanada.org for more information.
16
At The Utility Expo, Bobcat will showcase an expansive product lineup including its latest technological advancements for compact equipment.
Now in concept form, Bobcat will demonstrate the capabilities of its collision warning and avoidance system designed to assist operators’ jobsite awareness.
Compatible on select Bobcat compact track loaders and skid-steers, the technology tracks an objects’ position, direction and speed relative to the machine. Using either the active or passive setting, the operator can receive an audible alert or enable the machine to automatically stop upon detecting an object in its path.
While still in product development, the collision warning and avoidance system is expected to be available to customers in 2024. Customers at The Utility Expo can take part in a guided demonstration of this technology through an interactive display.
Advanced display technology
Attendees can experience Bobcat’s advanced display technology concept with a transparent, touch display. The tech allows operators to look through display information to seamlessly view both the jobsite and operation information. The concept display can be positioned on the front windshield or on a cab side window on a variety of Bobcat machines, including compact excavators, telehandlers and loaders. The display was designed to enhance operator productivity, focus and efficiency for the task at hand.
Depth check
Bobcat will also display its depth check system on an E35 compact excavator. The system allows operators to accurately meas-
ure depth and grade without exiting the machine. The technology allows for precise digging performance with an accuracy of about 1 cm, which helps reduce over-digging. Depth check is available on several Bobcat compact excavator models with standard or long-arm configurations.
Platinum packages
Bobcat’s latest Platinum machines will be on display at The Utility Expo. Bobcat’s Platinum equipment combines technology options with comfort features to offer operators a premium experience.
The Platinum package is available on select loaders and compact excavators with new, limited-edition models introduced annually.
Franna is expanding into the North American market with the introduction of the AT24 US.
The new model from Franna is a mid-sized, mobile pick and carry crane.
The AT24 US model is designed to meet the specific needs of customers in the United States and Canada. The AT24 US combines the proven reliability and versatility of Franna's pick and
carry cranes with advanced safety features tailored to the North American market.
Franna Pick and Carry is a manufacturer of mobile cranes based in Australia. With more than 40 years of experience, Franna, a Terex company, is known for its innovative pick and carry cranes that excel in maneuverability, lifting capacity and ease of operation.
Range of applications
The AT24 US model boasts a powerful lifting capacity of 24 tons, making it suitable for a wide range of applications across industries such as construction, oil and gas, mining and infrastructure development.
"We are thrilled to bring our renowned Franna cranes to the United States market," said Andrew Pritchard, Sales Director at Franna.
"The AT24 US model sets a new standard in safety, combining cutting-edge technology, superior lifting capabilities and our signature manoeuvrability. We are confident that it will not only exceed the expectations of American customers in terms of performance and reliability but also provide a safe working environment for their operators."
Franna cranes are engineered with safety as the Number 1 priority. The AT24 US model incorporates advanced safety technologies to ensure secure lifting operations to protect both personnel and the surrounding environment. With features such as overload protection, Franna’s own Dy-
namic LMI, external E-stop and an ergonomically designed cab, Franna cranes allow operators to focus on their tasks without compromising safety.
The wide stance boom lift cylinders enhance the operator’s vision, while the modern cab design ensures maximum comfort for the operator.
As well, the pick and carry crane is designed to provide easy access to all key maintenance points.
AT24 specs
• Max boom length: 17.9 metres
• Max hook height: 17 metres
• Max line pull: 4.4 tons
• Engine: 228 hp
• Max travel speed: 80 km/h
Expansion plan
Franna's expansion into the United States and Canada is a strategic move in line with its vision to become a global leader in the pick and carry crane segment.
To support its expansion efforts, Franna has established a dedicated distribution network across the United States, comprising of authorized distributors and service centres strategically located to provide support. This network will facilitate delivery, after-sales service, and availability of Franna parts.
The Franna AT24 US pick and carry crane will make its North American Debut at the Utility Expo is Louisville, Kentucky from September 26 to 28.
The Australian pick and carry crane manufacturer will launch its first North American model at The Utility ExpoBy The Utility Expo
As sustainability initiatives, new regulations and technological advancements open a world of possibilities for the utility industry, The Utility Expo will highlight alternative power throughout the show, held September 26 to 28 in Louisville, Kentucky.
With global initiatives to reduce carbon emissions, equipment manufacturers are exploring ways to reduce the carbon impact of
their machines. A range of alternative power solutions are being considered, from replacing the diesel engine to reconfiguring the engine to run on alternative fuels to improving engine efficiency.
The utility industry is well on its way to lessening its carbon footprint with efficient diesel engines. Compared to Tier 1 engines, today’s Tier 4 Final engines offer a 96 per cent reduction of oxides of nitrogen as well as a 97 per cent reduction in particulate
matter. The proposed Tier 5 emissions regulations will reduce emissions even more. The gradual retirement of an aging fleet will also reduce emissions, especially considering the significant reduction in emissions that occurred between Tier 3 and Tier 4. Modifying conventional engines allows them to burn alternative fuels, which doesn’t typically require widespread changes in jobsite practices, machine
componentry or fuelling infrastructure. Manufacturers are also beginning to produce fuel-agnostic engines and explore the usage of various low-carbon fuels, including hydrogen, natural gas and ethanol.
Hydrogen can be used as both a low-carbon fuel and a fuel cell to charge a battery-electric machine. A clean and renewable source of high-density energy with good energy efficiency, manufacturers are work-
ing alongside the United States Department of Energy (DOE) in the early stages of hydrogen fuel cell implementation.
Much of the alternative power conversation has centered on electric, particularly in the compact and utility equipment industries. Commercially available electric machines feature varying degrees of electrification, offering zero emissions, less noise and instant response while delivering the same breakout force as a diesel-powered engine. Battery power density continues to increase as manufacturers utilize technologies to make better use of battery energy.
The instant response of electric machines also correlates directly to real-time efficiency, minimizing idle time and reducing wear and tear on the machine. With fewer components and
moving parts than internal combustion engines, electric machines typically require less overall maintenance, reducing downtime and operating expenses. As the reliability of these electric machines is validated in the market, the utility industry will begin to meet regulatory and societal pressures to reduce carbon emissions while seeing operational gains.
There won’t be one singular solution to reduce carbon emissions.
The utility industry will adopt a variety of alternative power solutions over the next handful of years. It all comes together at The Utility Expo.
The Utility Expo is the largest event for utility professionals and construction contractors seeking comprehensive insights into the latest industry technologies, innovations and trends.
The construction industry is one of the most dangerous industries to work in. It has the second highest number of occupational deaths, and recent data identifies vehicle collisions as the second most common cause of fatal construction injuries.
However, video telematics is providing construction professionals with the visibility and data insights to ensure high levels of safety are always maintained, revolutionizing construction health and safety.
While there are safety protocols in place to minimize the risks involved with heavy equipment, it’s hard to eliminate risk altogether. This is especially the case when regularly dealing with moving parts that create a heightened possibility for unforeseen risk, which in turn places additional burden on operators and construction professionals to manage these effectively.
Video telematics’ ability to provide real-time data for analysis, offers enhanced visibility to support risk detection and prevention, as well as aiding future risk planning.
When it comes to complex and heavy machinery that require advanced maneuvering, even the most experienced operator can find it difficult to detect a sudden, unforeseen or previously unknown risk and respond quickly and efficiently in the moment.
Here, a combination of cameras and sensors give drivers a complete 360-degree view around the machine via an in-cab monitor, a view they would not previously have had. Front, side and rear cameras ensure equipment is covered from all angles, while corner, side and rear sensors warn of nearby people – such as workers, pedestrians or cyclists – especially in blind spots. This system can also be linked to specific driving maneuvers, so a driver can view the appropriate camera when turning, for example, the left-hand indicator or reverse gear links to the correct camera angle when engaged.
Going forward, artificial intelligence (AI) is what will set the next generation of video telematics apart as it becomes increasingly embedded in camera hardware.
The latest intelligent detection cameras adopt deep learning technology to provide real-time insight. This enables the cameras to identify and track vulnerable people, making it possible to trigger an alert to the driver, especially when manual detection is difficult due to blind spots. The technology can even activate an external, audible alarm when someone enters virtual exclusion zones around the machine, thereby supporting the operator by alerting those around of the risk while preventative action is taken.
With traditional proximity sensors, alerts can be triggered by inanimate objects, so there is a risk that drivers become complacent and take less notice of an alarm because of false positives. Here, AI-enhanced smart cameras make all the difference. The AI-powered detection camera can locate people up to 20 metres away in real time, establishing the severity of risk depending on their proximity to the equipment. With such high levels of accuracy and range, it provides the driver with increased reaction time and reduces the possibility of collisions.
Vehicle and plant camera technology is no longer a simple driving aid. To get the most value out of the data captured, forward-facing cameras and mobile digital video recorders (MDVRs) can now be connected 24/7 to a cloud-based platform, such as VisionTrack’s NARA (Notification, Analysis and Risk Assessment) platform. Recorded footage and supporting data of any collision, near miss or harsh driving event is uploaded and can be viewed almost instantly. This provides plant or fleet managers with virtual eyes on the ground, enhancing visibility and control of equipment on site or on the road.
The NARA platform uses deep learning algorithms to process hundreds of hours
of driving footage produced by typical construction operations to remove false positives with precision accuracy within a matter of seconds. This means action can be taken immediately, and when it comes to safety every second counts.
Cloud platforms such as NARA can improve safety compliance with additional safety features like the occupant safety rating that monitors the wellbeing of the driver and can even alert emergency services to severe distress or injury following a collision – providing life-saving minutes to operators.
Everybody in the telematics industry talks about driver behaviour and being able to determine how a piece of equipment is used or treated effectively. However, with traditional telematics you might see that one piece of equipment has had three harsh breaking events, but without more information this is just general trend information.
Video footage combined with telematics data provides important context to the recorded incident, unlocking new value from the telematics data. This allows construction
managers to gain true visibility into the data to take targeted and effective action. If a video shows someone doing something risky that is linked to the event, then a more meaningful intervention can be made to improve safety. It also allows driving styles to be measured and analyzed, so steps can be taken as part of a wider safety strategy and training initiative.
Construction businesses can also monitor compliance using captured video and data. Almost any activity can trigger a recording by combining video telematics with event tracking on the equipment.
There can be no doubt the adoption of a compliant video telematics solution has an important role to play in meeting construction industry safety requirements. Telematics alone can only go so far to prevent safety risks, as it offers only a vague image of the level of safety, with out-of-context incidents and potential false alarms. When real-time video and telematics data are combined in AI-powered video telematics, we have 360-degree visibility not only into activity on the ground but more importantly, into the digital data, to make telematics data more actionable.
Skyjack has updated its Elevate Live telematics system with the launch of Elevate Live 2.0.
The mobile-first solution was first introduced in 2018 to provide operators with access to critical machine information including the machine’s current state of health, pre-use inspection guides and familiarization materials through a QR code.
For Elevate Live 2.0, updated navigation allows straightforward access to features, including live metrics as they pertain to the
machines, including battery details, engine faults and controller alarms.
As well, Elevate Live 2.0’s new user interface includes an additional two screens, enabling live metrics, documentation and technical information feeds are available.
"Elevate Live has always promoted equipment longevity and the latest version strengthens that even further,” said Skyjack Project Manager Greg Virgo.
“Easy to navigate design and enhanced interface with data puts even more crucial
information into the operators’ hands to give them more resources than ever before, reducing the workload for rental companies.”
Via Elevate Live 2.0, electric machines can deliver a live battery percentage, extensive charge information and actions required on how to proceed based on battery percentage. As well, controller alarm data also presents any issues with corresponding codes and timestamps, battery voltage and total hours of battery usage.
For engine powered ma-
chines, users can see issues complete with codes and timestamps, fuel amount and consumption data, total hours and battery voltage among other metrics.
For telescopic and articulating booms tracking of secondary guarding features instances of overload and tilt alarm triggering can be tracked.
Available in seven different languages Elevate Live also includes model information, serial number and operational status.
In addition to the live data, Elevate Live 2.0 provides
in depth, machine-specific documents and five button navigation including:
· Quick start guide
· Familiarization video
· Pre-use checklist
· Manuals
· Emergency lowering procedure
“Our Elevate Live telematics system provides critical alerts and actionable insights into machine operations that help rental companies save time and money,” Virgo said. “The data obtained through Elevate promotes equipment
longevity and on site efficiency.”
Elevate Live is available on all Skyjack equipment, whether or not Elevate telematics is installed. Information is accessed through a QR code eliminating the need to download apps and remember login details. If a machine has the telematics system installed, the operator will see more detailed information like the machine’s state of health including battery life percentage, last charge date and recommended charging instructions.
JLG Industries has developed ClearSky Smart Fleet, a new Internet of Things system for its equipment that digitizes daily processes, streamlines logistics and provides on-demand machine insights.
ClearSky Smart Fleet connectivity is now standard on most new JLG equipment.
The Internet of Things (IoT) technology combines 25 unique features, including analyzers, telematics and productivity applications, into a single connectivity
beacon on JLG machines for seamless back-andforth interaction through the ClearSky mobile app, a user-friendly web portal or an advanced API.
Equipment owners and operators can send a prompt to the beacon to identify a machine’s status or perform diagnostics wirelessly through the mobile app.
“ClearSky Smart Fleet is a bold, new frontier in fleet connectivity,” said Ara Eckel, Director of Product Management for JLG’s connected solutions.
“It’s a true, two-way fleet management and communication platform that turns yesterday’s one-way data transmission into two-way interactivity that gets JLG equipment fleets talking like never before.”
According to Eckel, ClearSky Smart Fleet is built as a constantly evolving IoT platform capable of delivering new functionality, new insights and new ways to run more efficient, cost-effective operations.
The all-new ClearSky Smart Fleet app provides a modern mobile experience to manage data and machine interaction, even when cellular data and Wi-Fi are not available.
The Find my Machine feature activates audible and visual cues from the machine to make equipment identification and location effortless.
“With ClearSky Smart Fleet, equipment owners and operators can light a specific machine’s beacon or honk its horn with the tap of a screen,” Eckel said.
As well, Machine Status
Indication provides visual cues from the machine allowing equipment owners and operators to wirelessly identify a machine’s status, such as active diagnostic trouble codes, battery or fuel level, ignition and more.
Information is also digitized to provide access to targeted information, such as parts and technical manuals, to help solve service issues.
The Digital Analyzer performs wireless diagnostics via a built-in analyzer to replace the JLG wired handheld device. JLG also plans to introduce a digital analyzer reader that will provide a one-page summary of a machine’s set-up, personalities, diagnostics and fault log data, which can be downloaded and shared.
The ClearSky Smart Fleet web portal delivers efficient navigation and features for immediate visibility into a fleet’s health and performance data.
To help digitize daily processes, the web portal’s dashboard displays as much data as needed through a dynamic, action-oriented dashboard.
“Whether a fleet view or individual model view is wanted, powerful filters and tailored customization, including drag-and-drop window widgets, allow any role to prioritize the actionable insights necessary to maximize productivity and ROI,” Eckel said.
Machine level data provides access to specific serial number and asset ID data, such as interactive schematics, knowledge articles, technical manuals and parts information, can be done in seconds.
ClearSky Smart Fleet is also now part of Online Express, allowing for single sign-on and access using Online Express credentials.
“By integrating ClearSky Smart Fleet into JLG’s Online Express service, equipment owners and operators can manage a fleet, troubleshoot machine issues or order parts — everything they need to keep a fleet in top shape — with a single login,” Eckel said.
JLG plans to expand the web portal with the addition of automatic site networks so users can receive notifications when a machine arrives at or leaves a job site using the site network feature.
“Site Networks act like automated geofences,” Eckel said. “When two or more machines are within range of a local connection, a site network is formed automatically, simplifying equipment tracking and reporting.”
Advanced API
Equipment owners and operators can effortlessly combine actionable, JLGrich, ClearSky Smart Fleet data into a current telematics solution to manage an entire mixed fleet from a single screen, no matter where they are.
“Our next-generation IoT platform offers an integrated, enhanced data feed to combine actionable, JLGrich data into our customers’ in-house solution to manage their entire mixed fleet from a single screen, maximizing efficiencies and improving ROI,” Eckel said.
To optimize drill and blast operations, Sanvik has introduced My Sandvik Onsite, which delivers numerous production management, operational efficiency and maintenance and availability benefits for open pit mines and large quarries.
Built on OptiMine technology, the My Sandvik Onsite solution provides and analyzes data for drilling optimization with Sandvik i-series surface drill rigs. The rigs are capable of drilling hole sizes ranging from 64 to 406 mm and includes the Ranger DXi, Pantera DPi and Leopard DI650i, as well as the DR410i, DR412i and DR416i rotary blasthole drill rigs.
The system provides customers with real-time visibility at the shift level, immediate reporting and the ability to keep or utilize data in their own network.
“We’re now able to offer this powerful on-premise data solution to our surface drilling customers,” said Tuomo Pirinen, Head of Digital Solutions, Surface Drilling at Sandvik Mining and Rock Solutions. “Data can remain in the mine network on a local server with an optional extension to the cloud.”
Production management benefits include the ability to analyze shift performance and monitor fleet operations in real-time. Users can also follow up on drilling targets and identify areas of improvement through deep dives. Wireless drill plan transfer and drill navigation improve hole precision while wireless pattern updates and pattern feedback save time and effort in drilling follow-up. Users can monitor hole quality using as-drilled and measurement-while-drilling (MWD) data and track pattern progress and completion.
“Each surface drilling operation has its own unique priorities and targets for improvement and optimization,” said Demetre Harris, Product Line Manager, Surface Drilling Automation at Sandvik Mining and Rock Solutions.
“Whether the main focus is maintenance, productiv-
ity or efficiency, our new My Sandvik Onsite solution is the gateway to help any customer achieve their goals. Having production management data, drill plans and equipment health data in the same system eliminates the need to visit multiple portals.”
My Sandvik Onsite also helps to improve process and operational efficiency. The system visualizes bottlenecks and assists in optimizing drilling cycles and resources to efficiently meet production targets. The solution analyzes work sequences for each hole and monitors time used for drilling and tramming in detail. This enables maximum utilization and improves performance through detailed tracking and analysis of in-seat operational time against idle time and downtime.
My Sandvik Onsite helps maximize uptime through equipment monitoring, enabling prompt reaction to deviations and planning of preventive maintenance based on actual data. It provides insights into major onboard component signal data to reduce troubleshooting time. The solution also provides alert reports to help customers identify and address recurring issues and plan ahead for maintenance and spare parts needs.
“Sandvik drills are capable of providing a wealth of data,” Pirinen said.
“Our customers can now utilize and display that data to enable a range of improvements. Customers can finally integrate drilling into the rest of the mine operation, as our new solu tion seamlessly connects with other third-party re porting systems.”
As well, My Sandvik Onsite can be integrat ed with existing systems for planning, production, maintenance and fleet management. Users can complement various readymade productivity, fleet utilization, work mode, alert and signal reports with tailored views using My Sandvik Onsite data feeds.
My Sandvik Onsite seamlessly integrates
with Sandvik’s AutoMine Surface Drilling remote operation and autonomy solution and extends the functionality further with in-depth reporting.
The solution is also compatible with the cloud-based My Sandvik Productivity offering, providing a telemetry data connection to My Sandvik Productivity dashboards.
Kleemann’s Smart Job Configurator enables its users to match machine settings quickly and easily to the task at hand.
Often, finding the ideal machine parameters takes time and requires experience. The various applications for crushing plants are diverse and machine settings vary depending on the feed material and the desired end result.
Kleemann’s Smart Job Configurator is part of the Spective Connect app. The Spective touch display supports operators in the selection and entry of the correct settings. This ensures the desired high-quality final product is achieved with the lowest possible wear and fuel consumption.
The operator is guided step by step through the menu of the Smart Job Configurator of the Spective Connect app and enters the necessary data of their planned application, such as details about the machine, material and its processing. The Smart Job Configurator suggests a suitable final product as well as the tools required. When all parameters are entered, the tool creates an overview of the ideal machine configurations. The result of the calculations can be exported as a PDF and distributed as required.
On the Spective touch panel the suggested settings can be applied quickly and simply via the Smart Job Configurator menu. The ma-
chine now works exactly with the applied setting and delivers the planned result.
The Smart Job Configurator can also be used without Spective Connect via the QuickStart option on the touch panel. The operator is guided step by step through the machine configuration, which accelerates the set-up. The operator receives the same setting options that are offered in the app.
Sample applications
The Smart Job Configurator is fed with various application scenarios, which were created by the Kleemann application technology. Kleemann is also gradually adding more recipes to the system, and
operators will find an ever-expanding range of various applications.
The customers can also contact Kleemann directly if special applications are required.
With this support for machine
settings, employees with less experience also find the appropriate solution and experienced users benefit from time savings. The material processing is simple and efficient for all users.
Following comprehensive internal validation of its Autonomous Haulage Solution (AHS) at Liebherr’s Mining Technology Development Centre in the United States, Liebherr Mining has deployed a fleet of four T 264 trucks to support onsite validation.
The onsite validation, taking place at a mine in Western Australia, marks a new stage of Liebherr’s strategy to accelerate development of a new autonomy product for the mining industry.
“After significant research, development and program planning, Liebherr is excited to
announce the commencement of onsite Autonomous Haulage Solution validation as we move to deploy the next generation of autonomy technology for mining equipment,” said Scott Bellamy, Divisional General Manager of Product Management for Liebherr Mining.
“This deployment not only represents Liebherr Mining’s market introduction of the AHS, but also highlights Liebherr’s continued expansion as a technology solution provider for the mining industry.”
Liebherr’s supply solutions provide customers with scalable
options, from autonomy ready haul trucks through to the fully integrated Liebherr AHS, also including a fully integrated Fleet Management System.
Liebherr’s philosophy is to provide open architecture solutions, allowing customers the freedom to select which base machines, automation, traffic management and fleet management systems will work best for their specific applications.
“Along with the first deployment of the autonomy solution, Liebherr has expanded its autonomy project team to include onsite support for the duration
of the AHS validation program,” Bellamy said. “However, our focus is to ensure the organization can support in the future not only this exciting project, but also future AHS deployments across multiple customers and regions.”
The 416-tonne Liebherr T 264 mining truck is part of the 240-tonne size class, matching ultra-class hydraulic excavators, as well as electric shovels and wheel loaders.
Its unique combination of a 2,700 hp engine, an efficient Litronic Plus AC drive system and 4,425 hp electric wheel motors allow for faster cycle times.
Volvo Construction Equipment has appointed Scott Young as its Head of Sales Region North America.
Most recently Young was Head of the Volvo CE Uptime Center of Expertise and he has held several other roles in strategy, technology and other functions within Volvo CE.
As the new Head of Volvo CE Region North America, Young will continue to oversee the strategic direction of one of the largest markets for construction equipment and will be responsible for meet-
ing its customers’ needs.
He has assumed the role from Stephen Roy who recently took on a new position within the Volvo Group Executive Board as President of Mack Trucks.
As well, Volvo CE announced Mats Sköldberg will take on the role of Head of Technology. Most recently Sköldberg was Head of Technology for Volvo CE in China and has held several other senior technology roles in recent years.
Jay Parker is appointed to the newly created EMT
role of Head of Digital and IT. According to Volvo CE, the creation of the new role at EMT level reflects the importance of digital in its overall transformation journey.
All three appointments will support the company’s leading cultural, sustainable and technological transformation, while demonstrating the expertise and dynamism that is already embedded across all regions of Volvo CE.
“Our leadership team will be greatly strengthened with
the addition of Scott, Mats and Jay, as they join during a significant time of change for our industry,” said Melker Jernberg, Head of Volvo CE.
“With their diverse experience, cross-functional understanding and genuine passion, I have no doubt we will continue to lead our company´s sustainable transformation going forward.”
In addition, Joakim Arndorw has been appointed the new Head of Volvo CE Sales Region International. Joakim is currently Managing Director for Swecon Anläggningsmaskiner, the
CE in Sweden.
MacLean Engineering has promoted Stella Holloway to the role of President of the mining equipment company.
Holloway has had a 15year tenure at MacLean Engineering, where she has held various positions in sales and management. Her journey within the company led her to her current role as Vice President of Sales and Operations for Ontario, Central and Western Can -
Superior Industries has added another industry veteran to its team.
After 17 years at Haver & Boecker Niagara, Kristen Randall joins Superior Industries as the company’s first official training coordinator.
“Many of us at Superior have developed strong relationships with Kristen due to her active involvement in our industries,” said Mary Erholtz, the manufacturer’s Vice President of Marketing. “All who know her here whole-heartedly agree that we hit the jackpot.”
In the new training role, Randall will lead the build out and launch of Superior's Learning Management System (LMS). She and others will create, manage and distribute modern learning content for Superior dealers, distributors and employees that aims to be fun and rewarding.
“There’s lots of action at Superior and I’ve always seen it as such an exciting place to work,” Randall said. “The culture endorses new ideas, encourages sharing without fear and everyone genuinely wants to support each other and the customer.”
ada where she oversees sales and support operations at the MacLean branch in Sudbury, Ontario. With her strong leadership skills and customer-centric approach, she consistently achieved positive outcomes in Canada. Now, she is poised to take on a broader role that aligns with MacLean’s expanding global presence in sales and support.
Tony Caron, formerly the Vice President of Sales for
Fecon has announced Ray Dalton will serve as its new Vice President of Aftermarket Sales. In the newly created role, Dalton will focus on growing the company’s aftermarket business while developing new solutions and products based on customer and dealer input.
“Fecon clearly understands the importance of aftermarket sales and support to become a preferred brand,” Dalton said. “It’s what attracted me to Fecon.”
As the vice president of
aftermarket sales, Dalton will manage Fecon Connect, the company’s online parts-ordering site, and lead the procurement and management of parts inventory levels, including developing packages for key wear items.
Dalton will also work directly with dealers to make sure inventory levels are stocked appropriately, and to develop aftermarket solutions that enhance Fecon’s products.
“Ray’s background gives him an incredible understanding of the aftermarket
business and what is required to ensure customers have what they need, when they need it,” said Mark Middendorf, Fecon’s Senior Vice President of Sales.
Dalton gained aftermarket experience in a previous role with The Shyft Group, where he developed the Red Diamond Aftermarket Solutions brand. Dalton’s career began at the rental division of Carter Machinery in Virginia, which at the time was the only Catowned dealer in the United States.
Quebec and Latin America, has been promoted to Vice President of Global Sales.
Kevin MacLean will retain his position as Chief Executive Officer and Don MacLean will retain his role as Chairman of the board.
“I am very pleased that these internal promotions will allow us to create a foundation for change and growth, while at the same time ensuring a continuity of our culture that has been
built on 50 years of customer-focused innovation, safety and productivity improvements in mining,” said Kevin MacLean.
“The next 50 years of MacLean mining equipment will continue this tradition and we will do it with new products in new geographies, always with an unrelenting focus on our day-to-day contribution to making the world a better place over the long term.”
CZM Foundation Equipment has hired Fabiano Jorg e as its Rental Fleet Manager.
In the role, Jorge will oversee the CZM rental fleet, its preventive and corrective maintenance as well as field staff.
Jorge has more than 25 years of experience in the foundation equipment field. He previously held positions in operational and maintenance management for piling and equipment companies in Brazil. He implemented several systematic applications for fleet management and maintenance within his
previous positions.
“Our rental fleet is growing, and we are happy to have Fabiano join us. His expertise and attention to detail will make our customer experience better. He has the leadership skills along with operational foresight to advance our fleet,” said Giuliano Clo, President of CZM.
CZM Foundation Equipment offers a comprehensive line of drilling rigs engineered for various foundation applications. CZM’s machines are manufactured at its 7,000 square metre facility in Georgia.
Eric Lafleche began working in the fencing industry at a very young age, 20 years ago. In 2015, he and his partner Joe Majic, sales director, officially trademarked FenceScape. FenceScape has exceptional knowledge and expertise in all types of fencing and decking. They are a certified distributor of Bufftech PVC fence, SIMTEK fence, Homeland products, Tuf-fence PVC, Gorilla fence and Gorilla decks for the Ottawa-Gatineau and surrounding areas. They offer a wide variety of top-quality wood, iron aluminum, hybrid, chain link and PVC fencing. This gives their customers many options to fit their tastes, needs and budget. They are extremely passionate about what they do and treat their customers as part of the FenceScape family, not a number. They do the installation themselves so there’s no waiting around for subcontractors. FenceScape takes pride in offering its customers the highest quality materials, creative and unique designs and warranty-backed installation. They have grown to three locations and plans to open further West and to Quebec.
FenceScape owns a Bobcat® MT52 and MT100 mini track loaders, an L85 compact wheel loader (plus another one on the way), 2x E35 compact excavators, a T64 compact track loader and a ZT3500 zero-turn mower. When Eric was asked why they chose Bobcat machines, his
YOUR LOCAL AUTHORIZED BOBCAT DEALERS
BARRIE Bobcat of Barrie 705-726-2228 oakenequipment.ca
GREY BRUCE
Bobcat of Grey Bruce 519-372-9100 bobcatoftc.com
PARRY SOUND
Bobcat of Parry Sound Ltd.
705-342-1717
bobcatofparrysound.com
TORONTO WEST Bobcat of Toronto 416-679-4172 oakenequipment.ca
BRANTFORD Bobcat of Brantford 519-752-7900 bobcatofbrantford.com
HAMILTON
Bobcat of Hamilton 905-643-3177 bobcatofhamilton.com
PETERBOROUGH
Bobcat of Peterborough
705-748-9119
bobcatofpeterborough.com
THUNDER BAY Equipment World Inc. 807-623-9561 bobcat-tbay.com
response “I have always used Bobcat machines but when I was looking for new machines, I got convinced to try a different brand, and shortly after I switched back to Bobcat machines. Bobcat machines are by far, better machines. They have better hydraulics, more power, better functionality, have a keyless start, the reaction of controls is better, and they are fully loaded. Generally, the price is all around the same but truly what matters the most to us, is the service. We get awesome service from Marc-Antoine Castonguay, sales specialist for Bobcat of Ottawa Valley and his dealerships. Marc gives us the true story, no runaround. I want to shop for one day, not 15 days in a row because of getting the runaround. Every minute counts. He always checks up on us and makes sure everything is working okay, thereby giving us extra service and value. They also have three locations to serve us!”
They use the Bobcat machines for fence post digging using a Bobcat auger attachment, lawn maintenance, snow removal and specifically the track loaders for unloading materials and grading. They are meticulous about keeping their equipment as new as possible so they felt going with the Power Lease with Bobcat to be the best option so they can always trade up for a newer model when it is released. “Brand new, clean machines, trucks, and trailers are good
CASSELMAN Bobcat of Ottawa Valley 613-764-2033 bobcatov.com
KITCHENER Bobcat of Tri-Cities Ltd. 1-866-214-3939 bobcatoftc.com
STRATFORD
Bobcat of Stratford 519-393-6040 bobcatofstratford.ca
SAULT STE. MARIE Bobcat of Sault Ste. Marie 705-949-7379 bobcat-ssm.com
for our company image but more importantly, we can’t have our stuff break down, we have no time for that. We want to keep our job on time for our customers. You want a brand you can trust that when you go to use it, it will work. When we got the new MT100 mini track loader, it had twice the loading capacity of the MT52, the same width and double the power than anything else on the market!” exclaimed Eric.
“I wouldn’t hesitate to recommend Marc-Antoine Castonguay and Bobcat of Ottawa Valley for your next machine purchase, rental or service.”
Thanks Eric.
CORNWALL Bobcat of Ottawa Valley 613-932-2034 bobcatov.com
LONDON Bobcat of London 519-455-4900 bobcatoflondon.ca
STRATTON Stratton Equipment 807-483-5505 strattonequipment.com
WINDSOR Bobcat of Windsor 519-737-0120 oakenequipment.ca
COURTICE Bobcat of Durham East Ltd. 905-404-9990 bobcatofdurhameast.com
MUSKOKA
Bobcat of Muskoka 249-390-7000 oakenequipment.ca
SUDBURY McDowell B Equipment Ltd. 705-566-8190 bmcdowell.com
FRANKFORD John’s Equipment 613-398-6522 johnsequipmentsales.com
OTTAWA
Bobcat of Ottawa Valley 613-831-5166 bobcatov.com
TORONTO EAST Bobcat of Toronto 416-679-4171 oakenequipment.ca