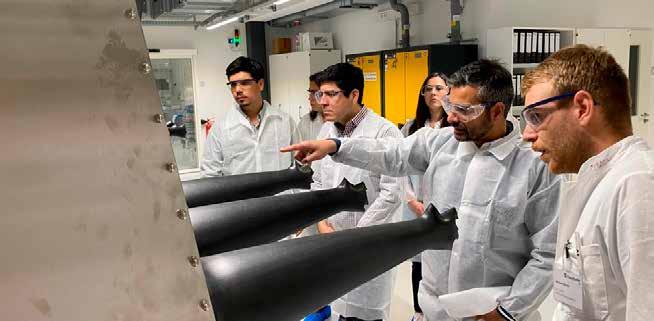
11 minute read
en Cadena de Valor de Baterías de Litio
El proyecto considera cuatro líneas de investigación.
Foto Gentileza Universidad Católica del Norte.
Nace Centro
Como iniciativa que levanta la Universidad Católica del Norte y SQM, y a partir del Polo de I+D en la cadena de valor de baterías de litio, emerge el Centro de Investigación y Desarrollo en Cadena de Valor de Baterías de Litio. El Centro se encuentra en proceso de apertura. “Tenemos áreas de investigación ya desarrolladas y otras que están encadenadas con expertos de instituciones internacionales que nos están apoyando en el proceso. El funcionamiento completo debería concretarse en marzo 2023”, detalla a MINERÍA CHILENA Hernán Cáceres Venegas, decano Facultad de Ingeniería y Ciencias Geológicas en Universidad Católica del Norte.
¿Cómo nace la creación de este Centro de I+D y a dónde apunta? El origen de este centro surge de la necesidad por aplicar investigación y desarrollo tecnológico en la región como parte de la contribución que deben realizar los productores de litio en Chile para el territorio. Sin embargo, también hay que destacar los incentivos que Corfo ha determinado para invertir en I+D dentro de la Región de Antofagasta, ya que su la consolidación de este ecosistema es fundamental para impulsar el crecimiento económico de la región. Además, con la formación de capital humano avanzado y la implementación de infraestructura tecnológica en un sector clave para el desarrollo nacional estamos generando valor económico, social y ambiental.
¿De qué manera proyectan que comenzará a operar? Tenemos distintas iniciativas que tienen relación con el reciclaje de baterías de litio y el desarrollo de diferentes metodologías para poder hacer que el reciclaje sea económicamente viable pero también amigable con el medio ambiente. El proyecto cuenta con cuatro líneas de investigación, entre ellas el reciclaje de baterías que busca desarrollar procesos innovadores y sustentables para recuperar un alto porcentaje de los materiales críticos que componen las baterías de litio, como el níquel, cobalto, manganeso y litio empleando los principios de la economía circular a través de procesos biológicos, aplicación de nanopartículas y de membranas de filtración. Por otro lado, en el área de la creación de nuevos materiales para las baterías planificamos generar baterías de menor costo y con mayor resistencia a la degradación durante el proceso de carga y descarga, como también baterías de tipo botón (CR2030) que permiten obtener sus parámetros operacionales clave y luego escalar los resultados a baterías de mayor tamaño, aplicando procesos menos agresivos con el medio ambiente, evitando así minerales críticos de alto valor. En cuanto al área de análisis y optimización de baterías, se enfocará en desarrollar e implementar métodos y herramientas para la producción y reciclaje de baterías, considerando criterios económicos, ambientales legales y sociales, a través de nuevos modelos matemáticos y el uso de programas e infraestructuras computacionales avanzadas
El lanzamiento de este espacio -que considera cuatro líneas de indagación- está planificado para la primera semana de abril.
para solucionar problemas en torno a la continuidad y crecimiento de esta nueva industria a nivel local, nacional y global.
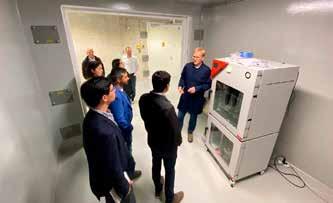
¿Cuántas personas participan en este proyecto? Existe un núcleo ya oficializado, la Universidad cuenta con un proyecto que constituyó un núcleo de investigación y ese núcleo tiene definidas 11 iniciativas de investigación que están en desarrollo. Por cada línea de investigación hay un líder, un equipo de académicos y también personas que son estudiantes de pregrado, magíster o doctorado, además de profesionales de apoyo que se han incorporado a esto. Es decir, hay todo un abanico con alrededor de 40 personas participando.
¿Cuál es el plan a corto plazo que tienen considerado para trabajar? Próximamente tenemos el lanzamiento que será agendado para la primera semana de abril y queremos realizar un seminario internacional o expo del Centro con invitados, como expertos extranjeros desde las instituciones que son nuestros aliados estratégicos, donde también se comunicarán en específico todas las áreas de investigación y sobre cómo estamos trabajando en ellas y cómo lo vamos a trabajar en el futuro. El objetivo es brindar una conversación sobre el ecosistema de baterías de litio y cómo podemos ajustar esto a la realidad chilena. Al mismo tiempo, tenemos
Foto Gentileza Universidad Católica del Norte. Foto Gentileza Universidad Católica del Norte.
acuerdos generales con varias instituciones que ya están firmadas en términos de la creación del centro y estamos avanzando en generar contratos para contar con expertos internacionales en áreas específicas dentro del proyecto, lo que nos va a permitir instalar una nueva capacidad dentro de la universidad, para aquellas áreas del proyecto en donde nuestras capacidades no están tan desarrolladas por ahora. Entonces, por ejemplo, el área de reciclaje y de materialidad ya cuenta con cierto nivel de desarrollo, pero el área de aplicaciones es algo muy incipiente que requiere de contratos específicos para desarrollarla con nuestros con partner internacionales.
¿Cuáles son los planes para ir avanzando en el 2023? ¿han conversado o tienen pensado conversar con empresas de la industria para algún tipo de alianza o relacionamiento? Hemos conversado con empresas, como por ejemplo, las que se dedican al transporte público y que han incorporado buses eléctricos a su recorrido, estos en el mediano plazo entrarán en desuso o en el deterioro de sus baterías y estamos estableciendo alianzas para hacernos cargo de esas baterías en desuso y/o darle un segundo uso dependiendo del deterioro de las baterías, que también será analizado por nuestra universidad, ya que tendremos la capacidad de aplicar un análisis al ciclo de vida de las baterías, con la idea de poder llegar al proceso de reciclaje. Entonces a las baterías en desuso se les puede dar un segundo uso en el mejor de los casos, y si no responden bien, van al proceso de reciclaje y nosotros vamos a tener capacidades de aplicar ambos procesos. Actualmente, estamos avanzando en comprar equipamiento científico para soportar estas líneas, para el próximo año trabajaremos en el diseño de la nueva infraestructura que debería hospedar el centro. En este momento y durante los primeros 2 o 3 años del proyecto transitamos por una etapa de instalación dentro de la institución, adquiriendo los equipos científicos, equipamiento y a medida que se van constituyendo los distintos equipos de investigadores.
De Izq. a Der.: Hernán Cáceres Venegas, decano Facultad de Ingeniería y Ciencias Geológicas en Universidad Católica del Norte.
Actualmente el Centro está adquiriendo los equipos científicos para las líneas de investigación.
ANPLAST DESARROLLA ÁNODOS DE POLÍMEROS
para obtener cátodos de cobre de alta pureza
ESTA INNOVACIÓN, QUE ESTÁ EN ETAPA AVANZADA DE VALIDACIÓN, PERMITE REDUCIR LA CONTAMINACIÓN POR PLOMO, ADEMÁS DE AMINORAR EL CONSUMO DE AGUA Y ENERGÍA CONVENCIONAL EN EL PROCESO.
Producir un cátodo de cobre de alta pureza con menos impacto en el medio ambiente, reduciendo además el consumo de agua y energía convencional en el proceso, son las principales ventajas de los ánodos de polímeros que desarrolla ANPLAST. La firma, que surgió este año de la asociación de dos empresas proveedoras de la minería, como son Cupper Quim y Pizmor Eirl, busca con esta innovación hacer más sostenible el procesamiento de cobre y eliminar la contaminación por plomo que afecta a Calama y Antofagasta. “En la elaboración de este ánodo para la electroobtención de cátodos de cobre de alta pureza, utilizamos un plástico que es conductor de corriente, reemplazando a los tradicionales de plomo”, destaca Alfonso Gómez, gerente de Operaciones de Cupper Quim.
MATERIA PRIMA El ejecutivo revela que como materia prima utilizan polietileno reciclado, como el plumavit, y que para los procesos recurren a la energía solar. “Para desarrollar este ánodo, tuvimos que implementar una planta semi industrial piloto en Calama para hacer las pruebas y posteriormente las validaciones. Esto, de manera ecológica, ya que no ocupamos combustibles fósiles”, resalta el ejecutivo. Si bien la producción de cobre que se logra con este nuevo método aún es incipiente, Gómez remarca que lo importante es que las grandes mineras comprueben que se puede procesar el mineral de una manera más limpia y con excelentes resultados. “Tenemos pilas de lixiviación, una planta de extracción por solvente y una de electrowinning. Y estamos sacando un cátodo de casi 99,9% de pureza, con la gran diferencia de que en plomo estamos en 0,06-0,07 ppm. Esto porque no ocupamos ánodos de plomo”, asevera.
MENOR COSTO Gómez adiciona que el proceso resulta menos costoso debido al uso de ERNC. “Antiguamente, producíamos lo mismo con los otros ánodos, pero enfrentábamos casi un 40% más de gasto porque utilizábamos petróleo. Con el cambio a paneles solares y el almacenamiento mediante baterías de gel, el costo bajó considerablemente”, dice. Indica que, aunque la inversión inicial fue alta, en un año ya estaba recuperada. “Además de que este ánodo de polietileno reciclado tiene una vida útil mayor y no contamina, no hay desborre de las celdas, no se necesita de un tercero que las limpie, por lo que el ahorro en la obtención de este cátodo de cobre es muy interesante”, sostiene. El ejecutivo de Cupper Quim indica que, con esta innovación, Anplast se encuentra en etapa de TLR casi a nivel 9, trabajando con Inacap-sede Antofagasta en las validaciones a nivel de pilotaje, y en la planta en la validación semi industrial.

MÁS INNOVACIÓN La firma desarrolla, además, junto a Inacap, otra innovación consistente en la lixiviación de los minerales sulfuros, pero utilizando el ánodo plástico. En este caso, la empresa se encuentra aún en etapa 1, que corresponde a I+D. Gómez explica que en el proceso usan una solución con amoníaco al 5% y el resto de agua, sin utilizar ácido clorhídrico, ácido sulfúrico u otro tipo de ácido, obteniendo un concentrado que tiene sobre 75% de pureza y con la diferencia, respecto al proceso habitual, de que se recupera el agua, la que es devuelta a la lixiviación. “Queremos cambiar el paradigma de las plantas concentradoras para lograr menor consumo de agua y de energía. Como los minerales óxidos ya se están agotando, hay que buscar alternativas”, afirma. Recuerda que, mientras más puro sea el cobre, más fácil será de fundir, y con eso se aminora la emisión de gases tóxicos. “Queremos llegar a obtener un lingote de cobre con este proceso, para así entrar a las fundiciones en forma directa, porque como tiene alto grado de pureza, no se necesita una refinación, reduciendo las emanaciones a la atmósfera”, concluye.
los tradicionales de plomo”, Alfonso Gómez.
www.cupperquim.com
Indimin y universidad peruana firman alianza que
potenciará minería digital de la región
à
La Pontificia Universidad Católica de Perú y la empresa chilena dedicada a crear hábitos productivos y sostenibles habilitados con inteligencia artificial en la industria minera, Indimin, crearon una alianza con miras a la creación del Laboratorio de Minería Digital. Álvaro Díaz, CEO y fundador de Indimin, señaló que “esta alianza es fruto de una búsqueda colaborativa entre la PUCP e INDIMIN y permitirá reforzar y potenciar el desarrollo minero digital con profesionales con nuevas capacidades en ciencia de datos y generar proyectos de analítica avanzada en Perú y en la industria regional”. En tanto, el doctor Adolfo Pillihuaman, coordinador de la Sección de Ingeniería de Minas de la PUCP, indicó que «el desarrollo de profesionales con mirada y capacidades digitales -como la analítica avanzada- permitirá acelerar la madurez digital de la industria, así como también potenciar y realizar nuevos proyectos dentro de la industria minera”.
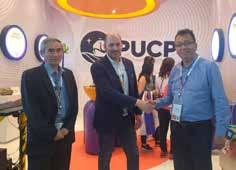
USM inaugura
à
Con la presencia de representantes de la industria, académicos, investigadores y estudiantes de la Casa de Estudios, la Universidad Técnica Federico Santa María inauguró las dependencias del nuevo Laboratorio de Innovación Nanotecnológica en Campus San Joaquín. El espacio busca contribuir al fortalecimiento de un foco de desarrollo de ciencia, tecnología e innovación en las dependencias de la USM en la Región Metropolitana, con una marcada presencia femenina en su equipo de trabajo y el desarrollo de investigación a nivel nacional e internacional, a través de la existencia de redes de colaboración tanto con entidades del ámbito académico como de la industria.
Expertos presentan avances tecnológicos para estabilización del arsénico en la minería
à
Convocado por la Agencia Nacional de Investigación y Desarrollo de Chile (ANID), el Centro Nacional de Pilotaje (CNP) y Departamento de Ingeniería en Minería UC, se realizó el webinar “Tratamiento y disposición de arsénico en la minería”, instancia en que se dieron a conocer los alcances del estudio sobre estabilización de efluentes mineros arsenicales; así como también la
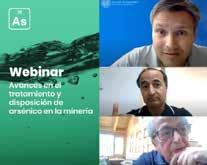
disposición adecuada de arsénico en efluentes de plantas de ácido de sulfúrico, el nivel de peligrosidad de estos residuos, su volumen y posibilidades de recuperación de subproductos. Juan Carlos Salas, director del Departamento de Ingeniería en Minería UC, explicó que la disposición de los residuos arsenicales en la minería es un problema que tiene una larga data en el país y que se ha avanzado en este ámbito, pero aún quedan grandes desafíos respecto de la disposición y encapsulamiento de los residuos de arsénico. Álvaro Videla, director Centro de Energía UC y director del proyecto Fondef, abordó la oxidación electroquímica del arsénico V en efluentes mineros mediante un sistema que utiliza ánodos dopados BDD (Boro Doped Diomond, por sus siglas en inglés) y cátodos de titanio, evitando así la importación, transporte y almacenamiento de H2O2 (agua oxigenada), actual oxidante del arsénico que utiliza la industria minera. En tanto, Juan Cornejo, jefe de Proyectos Sustentables de Ecometales, presentó el “Tratamiento y disposición de arsénico en efluentes de plantas de ácido de sulfúrico”, en la que mostró la evolución histórica que han tenido las leyes de cobre y arsénico de los minerales explotados en las minas chilenas. “En la proyección a futuro disminuyen las leyes de cobre y, a su vez, se incrementan las leyes de impurezas tales como la de arsénico”, puntualizó Cornejo.