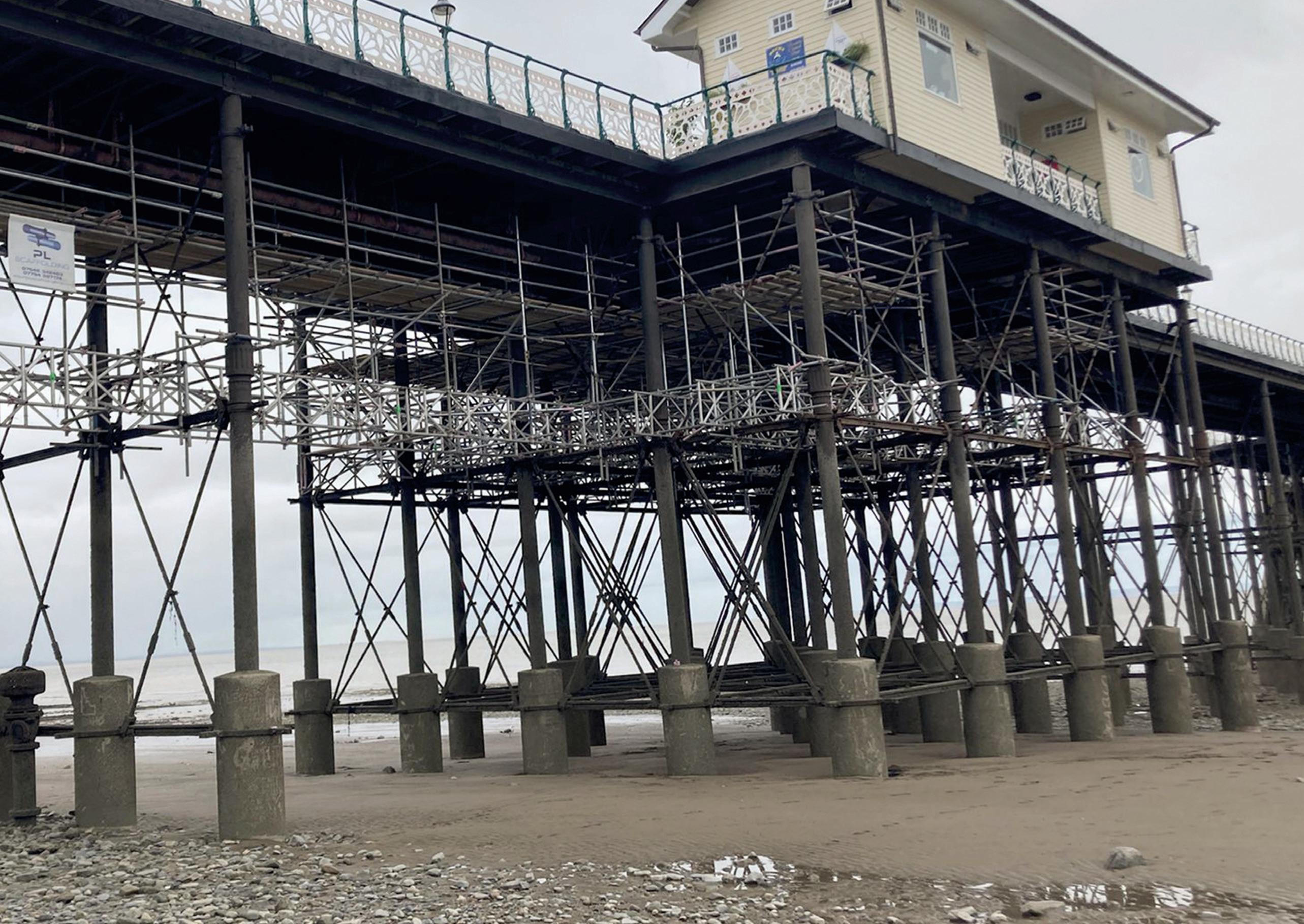

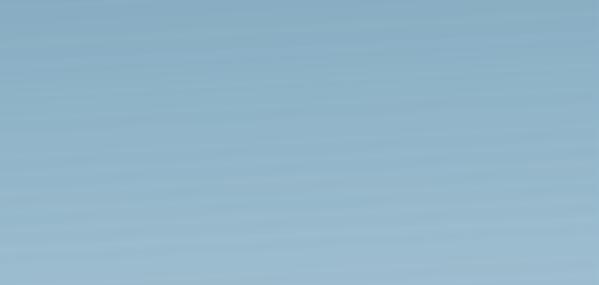

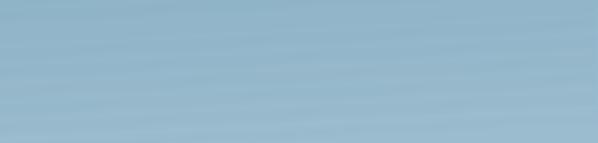

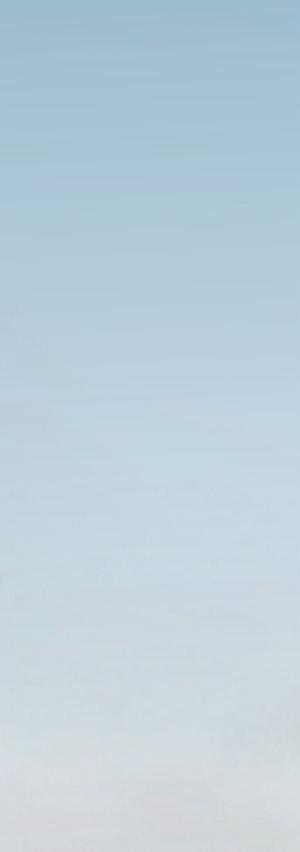

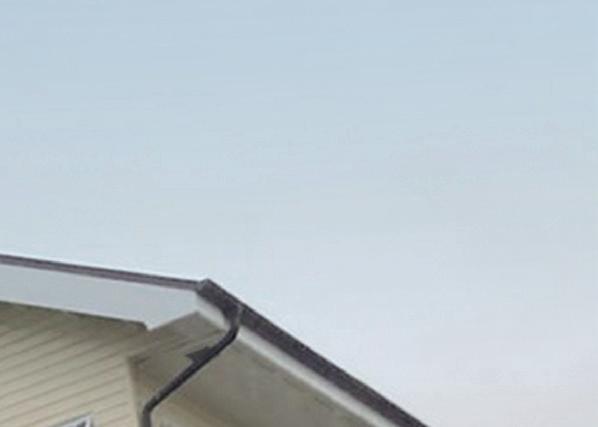
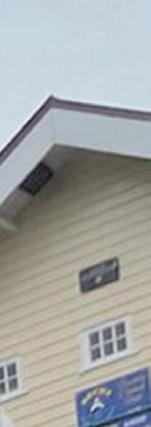

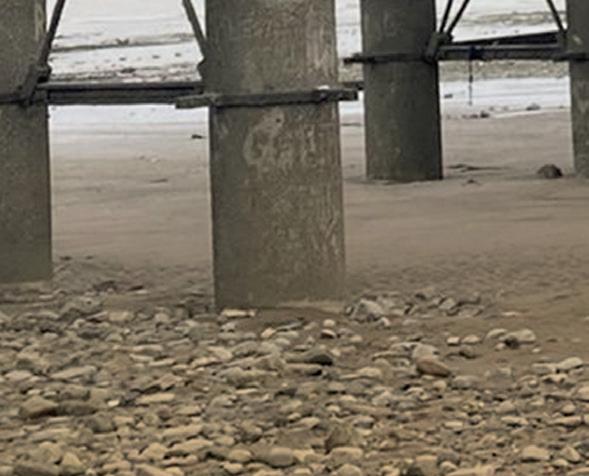
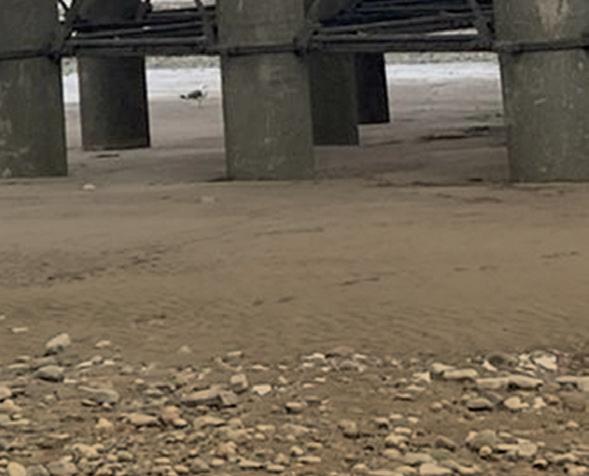
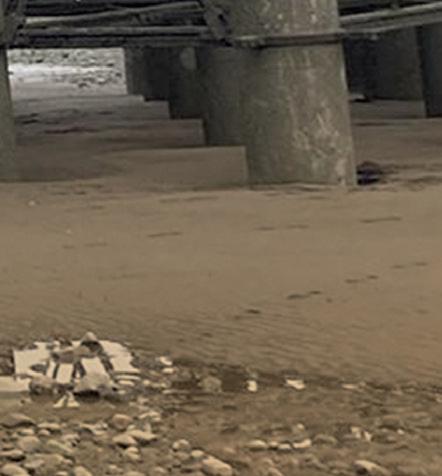

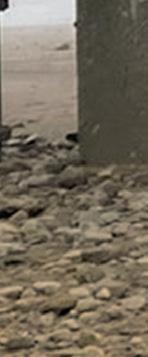
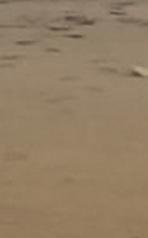
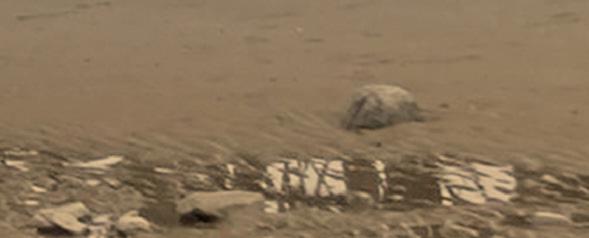
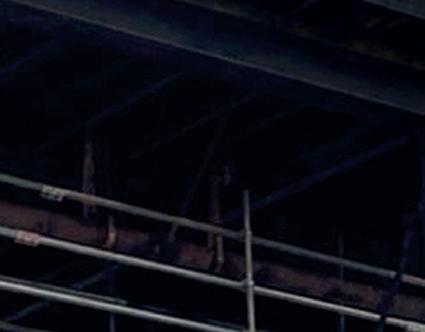

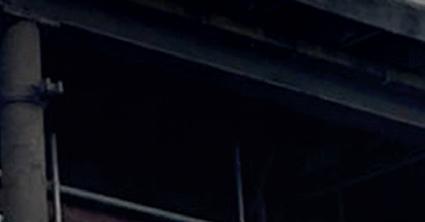
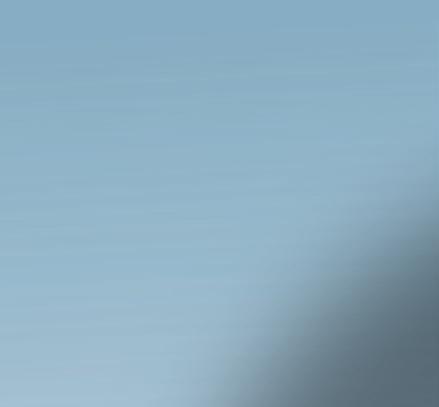
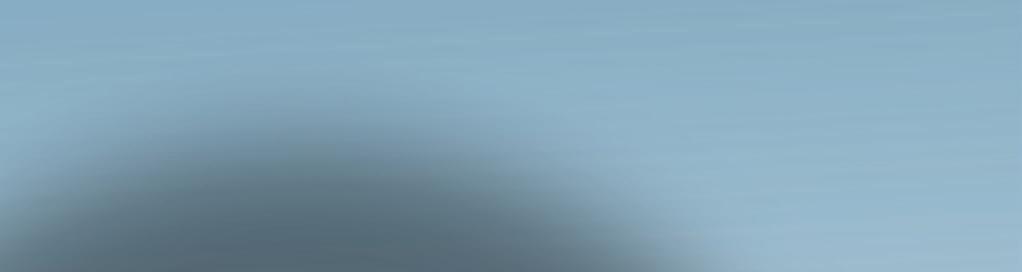
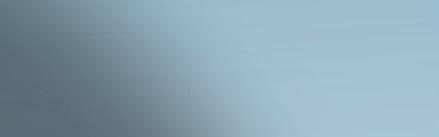
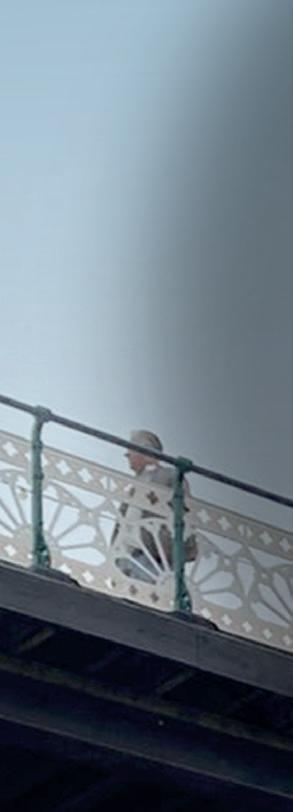
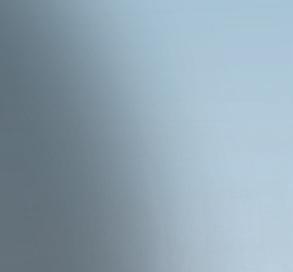


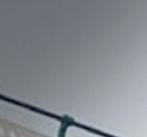
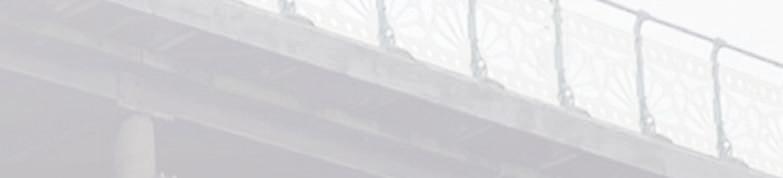
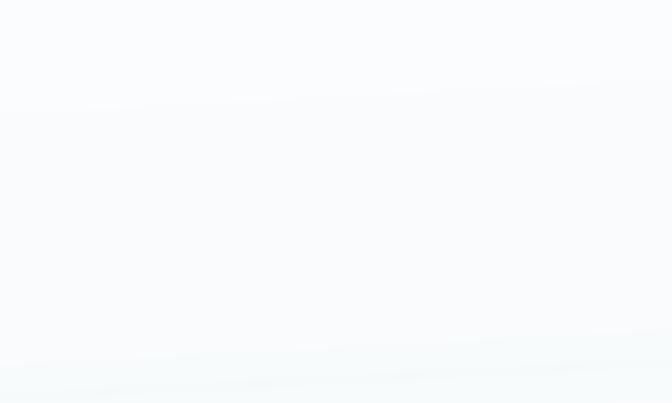
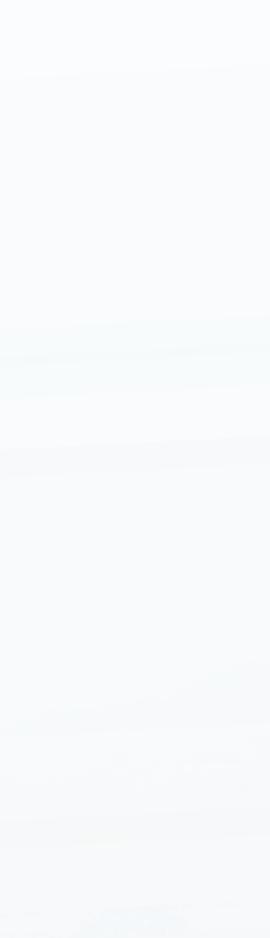


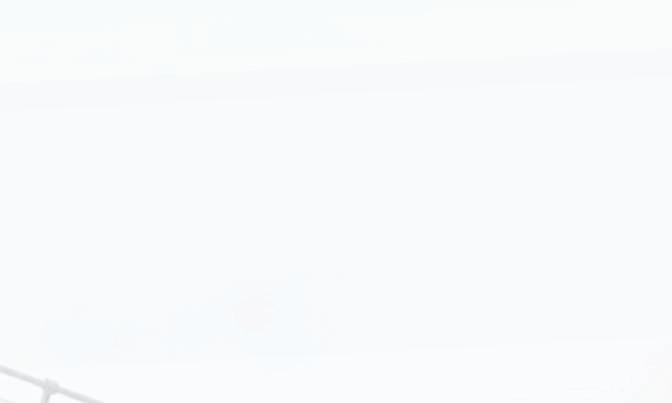
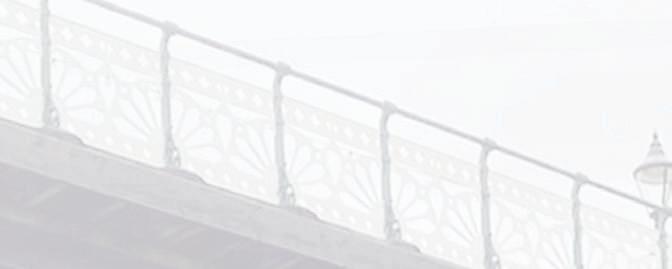

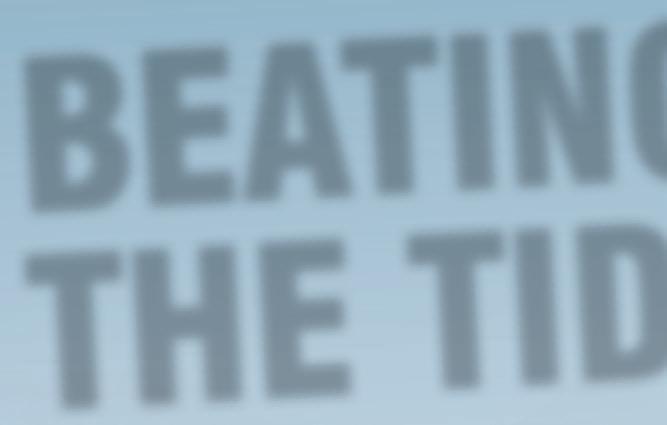
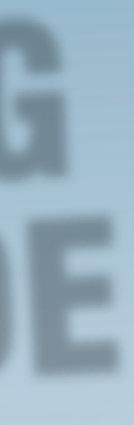

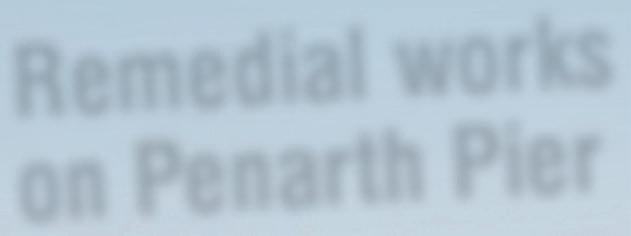
Premier Access Scaffolding Ltd www.premieraccess.co.uk 01522 542244
MEMBER SUPPLIER
Buildeck Limited www.buildeck.co.uk
01635 914870
Construction Products Direct Ltd
www.constructionproductsdirect. co.uk 0844 4170 1864
T Newman Hire Ltd
www.tnewmanhireltd.co.uk 0121 485 0150
Total Safety Solutions International Ltd T/A TSS International www.tssinternational.co.uk 01473 927373
262449
K2 Scaffolding (NI) LLP www.k2scaffolding-antrim.co.uk 028 9086 1222
Leda Scaffolding Limited www.ledascaffolding.co.uk 01622 873403
MBM Scaffolding Limited www.mbmscaffolding.co.uk 01462 418814
Pipe Scaffolding Limited www.pipescaffolding.co.uk 020 8804 4234
Editorial
Enquiries: Alison Hurman, tel: 0300 124 0470
Email: alison@scaffolding-association.org
Advertising
Enquiries: Trish Meyer, tel: 0300 124 0470
Email: trish@scaffolding-association.org
Scaffolding Association
Telephone: 0300 124 0470
www.scaffolding-association.org
Email: info@scaffolding-association.org
01626 331446
Worksafe Access Scaffolding Limited
www.worksafescaffolding.co.uk 01275 892 125
Subscriptions AccessPoint is distributed to members of the Scaffolding Association and other selected access and scaffolding businesses.
If you wish to receive a copy of AccessPoint or would like to amend or cancel your subscription, please call 0300 124 0470 or email info@scaffolding-association.org
SERVICE PROVIDER Independent Access Inspections Limited www.iainspections.co.uk 0203 876 0183
Quintessence Safety Consultants Limited www.quin-safe.co.uk 07432 032 443
AccessPoint is published on behalf of the Scaffolding Association. The views expressed in this journal are not necessarily those held by the Scaffolding Association. The Scaffolding Association shall not be under any liability in respect of the contents of the contributed articles. The Editor reserves the right to edit, abridge or alter articles for publication.
ISNN: 2055-2033 (Print)
© All editorial contents AccessPoint 2022
Printed by Tewkesbury Printing Company Designed by Gladstone Design
P3 - P5 News Stories from the sector
P6 Comment
Robert Candy, CEO of the Scaffolding Association: “The skills and labour shortage is a significant issue”
P7 Commercial Builders’ Conference:
“The UK construction sector continues on a positive trajectory”
P8 Legal
Holmes & Hills Solicitors: What is Adjudication?
P10 - P11 Scaffolding Conference 2022
A look at how the UK’s first Scaffolding Conference went ScaffStar 2022
P12 - P13 Take a look at this years nominated ScaffStars
P14 - P15 Women in Scaffolding
Interviews from some inspiring women in the industry
P16 Health & Safety
CHAS: The importance of fairness, inclusion, and respect
P17 Health & Safety
Citation: Advice on taking the hassle out of workplace risk assessments
P18 - P19 Screw TV Set
P20 Penarth Pier
P21 Braemar Castle
P22 - P23 Product News
Members of the Scaffolding Association have been recognised in the prestigious RoSPA Health & Safety Awards - rewarding companies and people around the world for their safety performance.
Accidents at work and work-related ill health not only cause major disruptions to business processes but the effect on the quality of life of the individual cannot be understated. That’s why good safety performance deserves to be recognised and rewarded.
The RoSPA Awards are one of the most prestigious and recognised schemes in the world with almost 2,000 entries every year, across nearly 50 countries and a reach of over seven million employees. The health and safety awards are truly global and open to teams and companies from anywhere in the world.
Members of the Scaffolding Association which have been recognised in the awards include:
Patron’s Award:
• Maintenance Access Company Scaffolding Limited
Gold Award:
• Emcor Group
• Lee Marley Brickwork and Scaffolding
Silver Award:
• WellMax Scaffolding
Assessed Members of the Scaffolding Association, Shaun Hanney Ltd, have won the ‘Most Professional Scaffolding & Construction Company 2022’ Southern Enterprise Award.
The Southern Enterprise Awards, which are hosted by SME News, highlights and rewards the businesses and individuals who show “true excellence, commitment and determination across the southern regions.”
Kimberly Howard, Compliance Manager at Shaun Hanney Ltd commented:
“Another amazing achievement by our Shaun Hanney Ltd team, proving that our hard work, dedication, loyalty and passion is paying off. The past two years have been a ride, trying to navigate the unknown, but we continued and overcame the obstacles to ensure that we could deliver the best quality work for our clients and the awards programme has been designed to seek out the enthusiastic and determined people who lead the way. A massive thank you to those that nominated us, voted for us and continue to work with us on a daily basis.”
CWIC is a unique CITB funded all-Wales training centre with its hub forming part of the University of Wales Trinity Saint David’s in Swansea.
The facility underwent an approximately £1.5million refurbishment, thanks to TRJ Construction, to create an Access Hall of 2,000 m2 including classroom and IT facilities. Since its initial CISRS approval in 2020, the centre has really hit the ground running, welcoming almost 1000 trainees through its doors on a range of courses since that date.
In addition to those undertaking the recognised CISRS Pt1, Pt2 route to qualification, Inspection and Supervisory training, around 50 operatives are currently nearing completion of their Scaffolding Apprenticeships, with another 18 candidates signed up for 2022-23, plus a waiting list of 20 in place for the next cohort.
This is a considerable feat for any new centre but all the more impressive when taking into consideration the COVID pandemic and storm damage to the Academy Roof in the last 18 months.
An employee at LFI Ladders, who are Associate Members of the Scaffolding Association, has celebrated his 50th work anniversary.
Bobby Blewitt has been a one-company man since leaving school at the tender age of just 16, spending his entire professional career as part of the team at LFI.
LFI’s Operations Director, Darren Smart commented:
“Throughout Bobby’s whole career, he has shown a fantastic work ethic. He has consistently delivered to the highest of standards, driven production levels to a new high, and done so with an impeccable safety record. Considering how manufacturing has changed in Britain, with five decades coming and going, it’s a testament to Bobby’s loyalty and longevity that he is still dedicating each of his working days to help produce the high-quality access equipment which we have built our reputation on and seen us become a market leader in Britain.”
When asked about what is the best thing about working at LFI Bobby commented:
“That’s a simple answer! I get satisfaction at the end of every day, from the work I did, and still do currently. Knowing that one more day has passed, and I’ve contributed to the team and produced the best product that I possibly could!”
Bobby is now preparing for his upcoming retirement, which is quickly approaching in October 2022.
Darren concluded:
“Bobby will be greatly missed by the whole of Team LFI, but it will also leave some very big shoes to fill.”
www.britishladders.co.uk
HSE’s Working Minds campaign has added to its partners with the addition of the Lighthouse Construction Industry Charity.
Construction is one of the key focus sectors for the campaign and the Lighthouse Construction Industry Charity provides a new route for Working Minds to raise awareness of how to prevent work-related stress and encourage good mental health.
Bill Hill, CEO of the Lighthouse Club said, “No construction worker or their family should be alone in a crisis and we have a number of ways that people can reach out for support. We provide
JMAC’s MD Luis McCarthy has successfully completed a self-funded gruelling mountain odyssey, raising £15,000 for local charity, the Teesside Family Foundation.
Luis took part in The Big Mountain Challenge, reaching the summits of Mera Peak (21,247 ft) and Island Peak (20,210 ft), both of which stand opposite the majestic Mount Everest. With temperatures plunging to minus 40 degrees, and suffering from acute altitude sickness and
24/7 free and confidential emotional, physical and financial support to our construction community in the UK and Ireland.”
Sarah Jardine, Head of Construction Division HSE, said: “The Working Minds campaign is calling for a culture change across Britain’s workplaces where managing stress and talking about how people are coping is as routine as managing workplace safety. The Lighthouse Club, alongside existing partner Mates in Mind, will help us to talk to businesses and workers in the construction industry.”
Working Minds is aimed at supporting small businesses by providing easy to implement advice, including simple steps based on risk assessment to Reach out, Recognise, Respond, Reflect, and make it Routine.
blinding headaches, brave Luis had to push himself out of his comfort zone to complete his mammoth challenge.
Luis commented: “I’ve always believed in pushing the limits of my own abilities. As a person who is blessed with good health and a supportive family, two weeks of discomfort was more than worth it to raise money to help those in need.”
You can read the full story over on our website and to donate to Luis’ charity fundraising efforts please visit: https://www.justgiving.com/ fundraising/jmac-himalayastrek
SIMIAN’s London Academy for Sustainable Construction (LASC) played host to a dedicated programme for women in London who are looking to enter the construction industry and re-ignite their career.
Run in partnership with Quantum Vantage the course, worth £1995 per delegate, was fully funded with support from Aspire London, part-funded by the European Social Fund and Greater London Authority.
The programme included:
• 2 x one day workshops
• Online learning module
• Comprehensive workbook and materials
• One to one coaching
• Networking with like-minded women
• Gain an accredited Level 4 Project Management certificate
Covering topics such as problem solving, project management, conflict management, decision making, effective communication and much more, the programme aimed to provide attendees with the critical skills required within the construction industry.
Two programmes were held, one in September and one in October.
Find out more: https://simian-risk.com/wpcontent/uploads/2022/08/Re-ignite-CareerQuantum-Vantage.pdf
Construction Sport, a charity that promotes the wellbeing benefits of sport to the operatives within the construction industry, organised Walking for the Workforce, a 40-mile-long trek that visited every Premier League Football stadium in London, to raise money for two construction professionals who are both battling with cancer.
The trek was done in one day and started at 4am at Crystal Palace Football Club and finished 14.5 hours later at West Ham United, having visited the grounds of: Tottenham, Arsenal, Brentford, Fulham and Chelsea.
Richard Stewart, Operations Manager at PDC
Scaffolding Limited, who are Audited Members of the Scaffolding Association, took part in the walk.
Paul Casey: Managing Director at PDC Scaffolding Limited, commented:
“PDC Scaffolding took part in a 40-mile trek organised by Construction Sport, to benefit two lads, Mechanical & Electrical Engineer, Martyn Guest & Site Manager Steve Hall, who play a part in our construction network and have both been diagnosed with cancer.
We are delighted for PDC to have taken part in Construction Sport’s longest walk yet and to have helped such a great cause!”
Steve Kerslake, Director at Construction Sport concluded:
“Not only is this event about raising funds for them and their families, but it is ultimately to show them that we are here as mates, as colleagues and as an industry to give them the morale boost they truly need in these tough uncertain times.”
You can still donate at: www.gofundme.com/f/ walking-4-the-workforce
Find out more: www.constructionsport.com
CITB is investing £90,000 to fund a pilot scheme which will provide mental health support for apprentices from the start of their construction industry careers.
Optima UK Ltd will train further education construction tutors to be Mental Health First Aiders so they can support construction apprentices during their learning. Apprentices will also be given mental health awareness training in bite size four hour sessions. This will mean the apprentices have the knowledge and education during learning, at the start of, and throughout,
their career in construction. There will also be one-to-one support.
The courses will be run by trainers accredited by Mental Health First Aid England and deliver 29 courses, all with 16 delegates, to hubs of colleges across the UK. In the space of a year, they will have trained 464 tutors and 464 apprentices, as well as offered one-to-one support to around 100 apprentices.
The CITB investment comes after a study compiled by the Lighthouse Construction
Industry Charity and CITB, highlighted the toll poor mental health is taking. Research showed 26% of construction workers had experienced suicidal thoughts and 91% felt overwhelmed. Tragically, two construction workers take their own lives each day.
This UK-wide pilot scheme will aim to understand how mental health education and support can contribute to improved retention for individuals during their apprenticeship in construction, as well as reducing their likelihood of experiencing mental health issues.
Construction is not on its own, and over the past 12-months it has become clear that the nation cannot meet labour demand for many other critical sectors and professions from veterinarians to HGV drivers.
There are several reasons which are suggested to have contributed to this problem one of which being the UK’s reliance on non-UK labour, much of which disappeared as the UK left the EU. This coupled with scores returning to their home nations to be with family during extended periods of global lockdown and then not coming back, resulted in the construction sector losing an estimated 50,000 non-EU workers.
It is easy to point the finger at Brexit and a global pandemic. However, they are not the only reasons why this sector and several others find themselves struggling to fill vacancies or attract a new generation of workers.
It’s a problem we need to resolve and fast. ONS figures published in June 2022 indicate that there were 42,000 job vacancies in construction. Compare that with June 2021 when there were 35,000 and with June 2020 when there were only 12,000 and the scale of the challenge becomes clear.
I think government and its agencies have a part to play, to ensure that employers and jobseekers can access fit-for-purpose training that is visible, relevant, accessible, affordable, and scalable. For scaffolding and access specifically, I think there are several gaps here and the association is working hard to address them.
The industry must also do its bit by helping to attract a new generation of workers but also by looking after and retaining those that are already here.
Women make up around 11% of construction workers, far less in scaffolding and access. There are several factors that might explain this enormous gender gap, including unconscious gender bias and negative perceptions of women working in construction. As a sector, we need to work harder to address this gender imbalance and again, this is not something the government will do for us.
As this month’s AccessPoint Magazine lands on doormats, we will have not long finished National Scaffolding Week (NSW) - a one-of-a-kind campaign, facilitated by the Scaffolding Association, which encourages industry stakeholders, fellow trade associations, government departments and scaffolding and access businesses to come together, to bring a much-needed platform to help raise the profile of careers and achievements within this sector.
The campaign is also working to build relationships with schools and colleges so that over time, young people at the point that they are making their career choices, know about the wide range of well-paid jobs and careers our sector has to offer.
Of course, we cannot solve our skills and labour shortages during the course of a week. However, NSW is one of several initiatives that our collective industry can and should be getting behind, to help ease the problem.
Robert Candy CHIEF EXECUTIVE, SCAFFOLDING ASSOCIATION www.scaffolding-association.orgI’ve talked about skills and labour shortages within our sector several times before. This is because it is such a significant issue for scaffolding and access businesses across the UK.
In the midst of political upheaval, escalating energy and materials costs and labour shortages, the UK construction sector continues to deliver results above the expected norm for a traditionally quiet time of the year. How long this will last remains to be seen.
In the midst of the traditionally slow holiday period, August was another upbeat month.
In what is traditionally a quiet month, the BCLive league table hit an impressive and unseasonal £6.2 billion. Kier Group landed an impressive haul of 21 new projects. The largest of these is a £400 million new build of a prison at Full Sutton, York.
Morgan Sindall reported 34 new contract awards worth a cumulative £320 million to take the number two position for August 2022. VolkerWessels secured six new contract awards worth a combined £301 million to take third position in the BC Live league table.
House-building took top spot, reporting 136 new projects for a total of £1.89 billion, the water and sewage sector contributed £505 million to the monthly total, which was further boosted by the factory and education sectors which contributed £325 million and £316 million respectively.
Regionally, London clung on to the top spot, reporting 99 individual projects worth a combined £1.45 billion. But Yorkshire (£666 million) Scotland (£566 million) and the North West (£492 million) all enjoyed a positive month. Sadly, the same cannot be said for Wales which just passed the £121 million mark.
Construction contract awards for June 2022 hit a very healthy £5.9 billion. But with the number of contracts and the number of companies winning contracts markedly down on the previous month, it is difficult to paint this in a wholly positive light.
On the face of it, a monthly BCLive league table total that fell just a whisker short of £6 billion should be cause for celebration. However, the number of contracts recorded in June 2022 was down 19%, and the number of contractors winning work was down by 20%.
Despite this, the team at Winvic bagged the biggest single contract of the month: a £1 billion project for the construction of a mammoth industrial hub in Cannock, Staffordshire for client Oxford Properties. Coming in second place is a joint venture between Wates and Kier. The JV picked up six new contract awards during the month worth a total of £504 million. Kier Group secured third place with 15 new contract awards worth £337 million. The largest of these is a £300 million design and build contract for a new dual carriageway at the A417 in Cirencester.
Regionally, London failed to break the £1.0 billion mark, accounting for just £815 million split across 92 individual projects, and was beaten into third place by the South West (£1.22 billion) and the West Midlands (£1.2 billion). Scotland delivered £223 million in new work while Wales contributed just under £37 million.
Against a backdrop of political upheaval, escalating fuel and materials costs, inflationary pressure and a rise in the number of liquidations, the UK construction sector once again posted monthly results that were above the accepted norm.
July saw more than £5.7 billion in new contract awards. Kier Group took the top spot courtesy of a 23-project haul valued at a combined £679 million. Taking the number two position was Sir Robert McAlpine who secured £567 million in new work split across three individual projects. Lendlease took the number three position with four new projects valued at £503 million.
Regionally, London reported £2.7 billion of new work split across 94 individual projects. The East and West Midlands reported £160 million and £1 billion respectively and Scotland slipped back to just £76 million across 18 projects.
The office sector finally wrestled the top sector crown away from housebuilding with a tally of £1.7 billion compared to housing’s £1.4 billion and the roads sector jumped to £862 million. However, health and education continue to lag behind with just £159 and £326 million. So despite all that is going on in the world, the UK construction sector is looking good well into the Autumn.
Quite how long the UK construction sector can remain removed and unmoved by the wider economic climate remains to be seen. But, for now, at least, the separatist sector continues to bask in positivity while fear and concern gathers all about them.
Never before has Builders’ Conference independent, verified real-time, construction information and research been more important as businesses navigate through COVID-19. Ensure your business has access to evidenced based construction project information from across the UK by becoming a member.
Audited and Assessed membership of the Scaffolding Association includes access to the Builders’ Conference platform, with premium information about 11,000 UK construction projects.
In an industry with tight profit margins, as scaffolding contractors, you can be unfairly targeted with claims of delay, contra charges or reductions in your payment applications.
So what do you do? You could consider court proceedings but are you aware of the dispute mechanism known as Adjudication (not to be confused with mediation)?
This article explores the right to adjudicate which is a statutory right arising from construction contracts.
As a scaffolding contractor, it is likely your contracts fall within the definition of ‘construction contracts’. The only caveat to that is when you are contracting with a residential occupier, then it will depend on whether the contract contains an adjudication provision.
Adjudication is not mediation! Mediation is alternative dispute resolution in which parties voluntarily agree to appoint a mediator. Adjudication is not an “opt in” and an Adjudicator will simply reach a binding decision even if the other party refuses to take part.
Adjudication has strict timelines and is a usually 28-day process (from the Referral Notice) unless extended by agreement. The Scheme for Construction Contracts (England and Wales) Regulations 1998 (“the Scheme”) applies if the contract is silent on the applicable Adjudication rules. Here is a typical Adjudication timeline:
Issue Adjudication Notice
Apply to nominating body
Issue Referral Notice
Issue Response
(Issue Reply)
(Issue Rejoinder)
(Issue Surrejoinder)
(Meeting)
Decision
Enforcement
Day 0
Day 0 Day 7 Day 14 Day 21 Day 24 Day 26 Day 28-35 Day 35-49 Day 35+
Adjudication is particularly suitable for helping to resolve financial disputes relating to, for example, delay and extension of time claims, interim payment disputes and final account disputes and variations (i.e. extra hire!) all of which we have seen arise in relation to scaffolding disputes.
The decision maker in Adjudication is usually someone who has considerable experience in the construction industry, e.g. quantity surveyor or a specialist construction lawyer. Although judges are legally trained, they do not always have specific knowledge of the construction industry. Having someone decide the dispute who has first-hand knowledge of the construction industry can be a benefit to you.
So you have got a dispute, you know what Adjudication is but why would you want to issue an Adjudication to resolve your dispute?
Speed:
You may have heard it referred to as ‘pay now, argue later’. It is a fast-paced process and designed to resolve disputes quickly to keep cash flowing through the industry while disputes are being resolved.
Current pressures mean claims in court can be lengthy. However, there may be times where issuing a claim in court might be more appropriate than Adjudication. It is important to consider the commercial outcome of a dispute for your business; a large complex dispute with years of delay analysis, may be better argued in court. This is all dependent on the facts of the case and it is always best to seek legal advice when settling disputes.
The “Surprise” Factor:
The party issuing an Adjudication, known as the referring party, may take a responding party by surprise providing approximately 7 days to respond. This is an extremely tight turnaround when the referring party may have spent months preparing. It is even more likely for a subcontractor to take a main contractor by surprise as they often do not think smaller businesses will pursue legal action. Adjudication is often considered ‘rough justice’ as it is typically a document only process.
Cost Saving:
No-one wants a dispute hanging over them, nor do they want to throw good money after bad. The advantage of adjudications is that costs are considerably less when compared to Court proceedings. Costs is always something we consider and how to make any legal costs proportionate to the dispute.
Conclusion
If you believe you have been unfairly targeted with claims of delay, contra charges or reductions in your payment applications, consider adjudication. Adjudication is a useful tool when used correctly, but be aware of strict timelines and rules that can be imposed, therefore seek legal advice before proceeding with an adjudication.
In the last 12 months, we have run over 15 adjudications for members of the Scaffolding Association, including 3 enforcements. Adjudication is fast and effective, and we would be happy to discuss the process with you further.
If you wish to discuss adjudication further, contact the Construction Team at Holmes & Hills LLP on 01206 593933.
For more than 75 years, Layher has focused on innovation not imitation. It’s why we remain the past, present and future of system scaffolding.
On the 29th of September 2022 the Scaffolding Association hosted the UK’s first dedicated scaffolding and access conference at the Heart of England Conference Centre in Coventry. Around 150 people attended the day which had an agenda packed full of insightful speakers, here are some of the highlights...
Construction Law Solicitors, Holmes & Hills LLP, delivered a live contract review where Sam Bawden summarised with one key piece of advice: “When it comes to contracts, scrutinise each and every one carefully and look where the areas of risk are.”
The first speaker in this session was David Abraham, the Managing Director of Fulcrum Scaffold Safety & Training Ltd, who spoke about the recruitment of ex-offenders into scaffolding and commented: “We’ve trained 73 people in the last 6 months. The biggest thing for us is social values - giving people a road to go down - a direction in life.”
Next to the stage in this session was Jim Scott, Head of Trainee Recruitment & Development at Alltask Ltd, who discussed ways to address the skills gap, he concluded: “Recruitment is about engagement - talk to as many people as you can and sell the compelling story.”
The last speaker in this session was Danny Heath, founder of Your Game Plan, who delivered a talk on early talent recruitment communications & training, he commented that scaffolders need to know who they’re talking to: “Know your target audience and start talking about what they want to hear!”
Discussion: System Scaffolding - Is this the future?
Des Moore (CEO at TRAD Group), Sean Pike (Managing Director at Layher) & David Abraham (Managing Director at Fulcrum Scaffold Safety & Training Ltd) joined the Scaffolding Association’s Chief Executive, Robert Candy, on the stage to discuss the merits of system scaffold and how it can provide a way forward for the scaffolding industry.
The Chief Executive of the CITB, Tim Balcon, delivered his keynote speech that highlighted the funding available for employers to help train and develop their staff, with his closing sentiment being: “There’s only one way to kill a skills gap, and that’s to train more people.”
Catherine Hare, Professional Support Solicitor from Citation Ltd, delivered a session on employment law and stated “good intentions are not enough” and where shortcuts are available, she advised scaffolders to “use them wisely.”
Alan Roe, MD of Touchstone Underwriting Limited, delivered a session in which he broke down some of the more common insurance claims they see from scaffolding contractors and reminded people that: “If it’s not evidenced, it didn’t happen.”
Keynote: When is a scaffold company not a scaffold company?
Senior Traffic Commissioner, Richard Turfitt, reminds scaffolding contractors of their responsibilities as hauliers and advised them: “To treat their Operators License as an asset.”
Martin Dean, Key Account Manager at the Road Haulage Association, talked about the European truck manufacturers who were found to be operating a price-fixing cartel between 1997 and 2011 and how delegates could get involved with the RHA’s collective claim.
Discussion: What does the future hold for the scaffolding industry?
Russell Maxwell-Smith (Managing Director at WellMax and Scaffolding Association President), Jonathan Greer (Operations Director at Ducker & Young Scaffolding Limited and Scaffolding Association Committee Member) and Ian Pickard (Managing Director at I.D.P. Safety Services Limited and Scaffolding Association Wellbeing Committee Member) all joined the Scaffolding Association’s Chief Executive, Robert Candy, on the stage to discuss what they think the future holds for the industry. Topics such as: procurement, skills shortage and well-being were all discussed with Russell Maxwell-Smith concluding: “We are all in this together, we need to stop looking to others to solve the industries problems, and work on the solutions together.”
The Scaffolding Association would also like to say a huge thank you to their exhibitors and sponsors:
Amicus | Avontus | Citation | CITB | DESSA | G-DECK | Holmes & Hills | ITP | Layher | PERI STAY-SAFE | TRAD UK
As a part of the campaign to inspire a new generation to take up industry roles, NSW asked people to nominate those they felt deserved some recognition for their work within the sector.
The 14 nominees were presented with their Scaff Star award by the Scaffolding Association’s President, Russell Maxwell-Smith, at the Scaffolding Conference.
Derek Wood
Safety Health and Environment Quality Manager
Morrison Energy Services
Derek has been in the scaffold industry 30 years, he has made it his mission to raise awareness of how to build and utilise scaffolds safely to those in the industry and those who use it.
“Derek is charismatic and gets his message across whilst adding a bit of humour along the way. I can’t think of anyone more deserving of this award as he has really raised the profile of the scaffold industry.”
Trainee Scaffolder | Powertherm
Paige is a trainee scaffolder at Powertherm and has come on leaps and bounds and really got stuck in with anything she is asked. Mick Smith, Scaffolding Contracts Manager at Powertherm said: “I was part of the team that interviewed Paige for her role and can honestly say that she was by far the best candidate. She fits right in and gets on great with fellow workers and clients alike.”
“Colin has worked in the scaffolding industry since 1973 and has been instrumental in creating jobs for 100s of people during that time. He helped me set up my company as well as supported his brother and nephew in doing the same. Colin’s knowledge and expertise have meant he has had a major influence in the local area and sector.”
Andrew Nuttall
Andrew has undertaken several charitable projects, the latest being the erecting of a temporary structure at the doctor’s surgery in Ashton to shelter people waiting outside the surgery due to Covid restrictions in place.
As a leader and manager he has turned ex-guardsmen into Class 2 HGV drivers, and unskilled labourer’s into skilled scaffolders. Andy’s greatest skill is bringing out the best in everyone.
Haven Scaffolding
Malcolm and his team enabled an abseil in aid of co-founded charity, My Mito Mission, this summer by building the necessary platform on a locally listed building - Wainhouse Tower, Halifax. Covid really hammered the charity’s income in 2020 and 2021 so this gesture was like gold dust to them as the day managed to raise £10,000+ and lots of priceless awareness too.
Sarah helped to introduce an apprenticeship programme into the business and built great relationships with local schools and colleges to facilitate long-term recruitment plans.
This breakthrough has helped the industry provide many young people from the local area with employment opportunities and a long-term career path.
The Haven Scaffolding Team Paige Pickering Sarah Jebb Colin BestDuring the lockdown, not only did Ian get 100 scaffolders back to work by putting together a risk assessment and delivering training, but he also kept everyone in the office safe and able to continue working.
Ian has worked in construction for 40 years and is passionate about men’s mental health and has co-founded two charities in construction: Mankind & SWAG, and has personally saved a groundworker’s life from the top of a bridge over the M4.
David is celebrating his 25th year with ITP, an impressive milestone, after starting as a factory operator making elasticated power ties used to attach scaffold sheeting to the scaffold structure.
“David developed himself as an Account Manager within our Scaffold Team, becoming a go-to expert resource for scaffolding clients and construction professionals. He also had a major role in the development of the environmentally-friendly polyolefin temporary keder roof sheeting, widely adopted within the temporary roof industry.”
Keith was diagnosed with Cancer on the 13th November 2020. Keith battled and won meanwhile keeping a positive attitude with his work colleagues and partner, Kelly. Keith returned to work in May 2021and couldn’t wait to get some sort of normality back in his life. Liam, the owner of Speyside Scaffolding, employed another inspector to work alongside Keith for as long as it would take to ensure Keith felt able to continue his role. Keith is a valued member of the team and we are all so happy that he’s all clear
“A brilliant young man with an outstanding attitude to his work. Having reached out to us with aspirations of becoming a scaffolder, Callum was taken on as a yard operative part-time to fit around his college work. Callum would attend college during the day and make his own way to our yard every night and work until 19:00. With a little help from the team, he passed his exams with flying colours and was extremely proud of himself, as were all of us! Callum is well on his way to becoming a scaffolder!”
Freddie has been a monumental driving force behind Teal Scaffold’s success and has helped build the organisation from the ground upliterally! Since Teal Scaffold’s inception into the market, those who have been fortunate enough to work with Freddie often describe him as ‘industrious, amiable and dedicated’.
Freddie is a true leader in which his energy is invested in his dialogue, genuine appreciation, and validation of aligned efforts which had led to immeasurable employee engagement from the team. He is an ambassador not only for Teal Scaffold but for the industry as a whole.
Martyn is an all-around top bloke who continuously champions other people. He has worked tirelessly to support Todd, his employee who has Down’s syndrome, to get recognition and training to help set him up for his career as a scaffolder, he also goes above and beyond with his charity work raising awareness for Down’s syndrome. He selfishly campaigns for other people every step of the way and fully embodies his company motto of #nostigmahere.
Ross is a stellar Commercial Estimator. He has diversified Teal Scaffolds’ portfolio of work immeasurably and consequently provided numerous employment and training opportunities to hard-working scaffolders from the local area.
“Ross has advocated for men’s health campaigns including partnering with the Testicular Cancer Network. Ross has not just opened avenues for our team to talk about their health in an industry that is stigmatised but he also champions opportunities for all within the industry.”
Dave has given lifelong service to the scaffolding trade and will be retiring next year. He is a long-standing contracts manager and is highly professional, conscientious and hardworking at all times and always with a smile on his face and good humour. He is a credit to the company and will be hugely missed when he retires.
Scaffold Manager | Teal ScaffoldThe National Federation of Builders (NFB) awards this year marked the start of real change and progression for the industry. The awards were aimed at showcasing women in the sector in order to make female and non-binary role models more visible and accessible. For this edition of AccessPoint we interviewed some women who are working in different roles within the industry to discuss their experiences.
and Smart scaffolder trained. Currently, I’m progressing through my Business Management degree through Arden University.
I am also currently leading a returning-citizen scheme at Star Scaffolding Ltd, which I hope to roll out over the industry and have recently made the top 100 women in construction voted by the NFB.
Did you experience any challenges getting into the industry?
I was lucky to come into the industry through the family so not really.
How have you found the industry has reacted to you?
I have found it very welcoming, I feel appreciated and valued.
Lydia Chard, the Business Development Manager at Star Scaffolding Limited, who has been short-listed for an award as part of the National Federation of Builders’ Top 100 Most Influential Women in Construction 2022.
How long have you been working in the industry?
I have been in the construction industry for 8 years.
Why did you decide to go into the scaffolding industry?
Growing up, playing with dolls, make up and all things glittering, I never imagined myself ending up in hi vis and steel toe-capped boots trudging through a construction site, however I got into construction through our family business.
What has your career path been?
Working my way from trainee estimator through to my role now as Business Development Manager, I have gained my CSCS card, my Scaffolders Inspectors Card, and I am Strike
Do you think there is anything more the industry can do to encourage more women into the industry?
I think the variety of roles need to be showcased better, there are so many available such as Strategy Directors, Estimators, Business Managers, Apprenticeship Managers etc… there is so much variety of work in the industry.
What is your favourite part about working in the industry?
I love my job, there’s always a challenge and I love finding the solutions. No two days are ever the same!
I have enjoyed meeting some really inspirational characters in construction over the years and enjoy the incredible challenge of being part of building the city around me. Is there any other comments you would like to say?
I hope one day, whether it’s my daughter, my niece, a friend or an apprentice - that one of them will walk into a site office, progress meeting or board room in construction and, instead of being noticed for being female, they get noticed because of their opinion, their input and their knowledge, and I hope one day that they won’t be in the tiny minority of females around the table.
Shannon Phillips, a Trainee Scaffolder at Gold Scaffolding Ltd, who are Assessed Members of the Scaffolding Association.
How long have you been working in the industry?
I started labouring on a building site for Stonewood when I one day took an interest in scaffolding. I started with GOLD in January 2022, so I have only been in the industry about 9 months now but I have remained with GOLD as they have been so supportive from the start and I enjoy working with, and for, them.
Why did you decide to go into the scaffolding industry?
Truthfully the money was my main incentive, I have dreams that are not falling into place as quickly as I’d like and the salary opens up greater opportunities. Already as a trainee what I am putting into my savings each week is liberating. However, that isn’t my only reason, I have learnt as I move my way through professions that I desire a job that allows me to work outdoors all year round and one that keeps me busy and fit also, so scaffolding really ticks all the boxes for me.
I started off originally in childcare when I left school and my path has slowly diverted, although construction originally was going to be a short-term career path, I’ve since come to love everything about the industry and intend to see it through for much longer.
After being told I was too small and weak to become a scaffolder I was more determined than ever to give it a go. GOLD were erecting a scaffold on a site I was labouring for, I reached out to a member of the team and I remember my words were “be brutally honest with me please, am I too small and weak for the job?” To my amazement he told me not at all! And began to tell me about other short scaffolders, women in the industry and more about it in general. He could see I was keen and phoned the directors of GOLD to arrange an interview and well here I am today!
Did you experience any challenges getting into the industry?
Fortunately for me I faced no challenges getting into the industry. I still have physical challenges I wish to overcome for example being able to stand up a 21-foot tube without it touching the ground and always trying to work towards this.I have a great team who encourage me, teach me and take
the time to show my what I want to learn such as technique or exercises to work my way up to my goals.
How have you found the industry has reacted to you?
I think perhaps there may have been some members of GOLD thinking I wouldn’t stick it out or enjoy the work, but they never once said or showed it. I have always received support and guidance from day 1 and the fact I am still here trying every day to be better has only gained more respect from my colleagues.
Do you think there is anything more the industry can do to encourage more women into the industry?
This is a good question and I have thought a lot about it! I can’t think what the industry can do, I feel like a big part of it is women and their mindsets. There are lots that are not interested in such heavy labour and others that don’t like the idea of working in such a male dominated environment. I have been working in male dominated teams for a while now from grounds keeping a school, to labouring on site and now scaffolding and I have to say there is a much more fun and laid-back approach in the work place of male dominated industries. Connecting
with other female scaffolders on my LinkedIn in has been exciting and reassuring for me also. What is your favourite part about working in the industry?
For me every new challenge I face is a step out of my comfort zone, once I have stepped out of that zone and achieved the task at hand, I get such a rush! Similarly, when I notice my strength increasing and can carry more, or lift things I couldn’t before, I love the sense of achievement.
Are there any other comments you would like to make?
I still have a long way to go, I am only a trainee at the moment and have lots to learn and wish to be much stronger, but when I remember where I started and what I couldn’t do/what I didn’t know it’s a boost of confidence every time. Also having a company keen to invest in me is a privilege and I hope any other women that are interested have just as easy and supportive path.
If you are, or know of any women in the industry, or trying to get into the industry we would love to hear more about your story, please contact us on admin@accesspoint.org.uk
As businesses look to drive progress on workplace diversity, they should be prepared to evidence their competence around Fairness, Inclusion and Respect (FIR). Alex Minett, Head of Products and Markets at CHAS, offers guidance on bringing FIR processes in line with industry best practice.
The CHAS Fairness, Inclusion & Respect assessment looks at the following five key topics:
• Commitment - the importance of strategy, leadership and governance
• Employment - how a company incorporates Fairness, Inclusion & Respect when recruiting people
• Working practices - policies and procedures that promote a strong working culture
• Site environment - how sites are set up for everyone’s needs
• Supply chain - how the development of a Fairness, Inclusion & Respect culture can be cascaded down to suppliers
The latest McKinsey & Company diversity report says data from 15 countries and over 1000 large companies shows the most diverse companies are more likely to outperform less diverse peers. It’s little wonder then that many organisations are looking to improve performance in this area. A CIOB report shows in 2019 the workforce was made up of just 5-7% BAME employees and 1 2% female employees. The report also highlighted that fewer than ever 16-24-year-olds are entering the industry.
With demands for construction work on an upward trajectory, an ageing workforce, and national skills shortage, attracting new workers and retaining talent is now more vital than ever.
An employer renowned for equality and respect for its employees will almost certainly have an advantage in the recruitment market. Moreover, a valued workforce leads to increased employee engagement leading to better productivity.
Creating a culture of FIR begins with good leadership and a clear vision. A specific FIR strategy should offer a set of core company values on workplace equality and pave the way for actions to ensure all employees feel respected.
A company that routinely tracks and reports on its inclusion data, such as diversity recruitment, shows it is taking its responsibilities seriously.
FIR policies and procedures could benefit from being developed with employee feedback, e.g. through staff surveys. At the same time, staff wellbeing schemes are crucial to supporting staff health and retention. Toolbox talks, FIR steering groups, and FIR champions are all important for driving FIR. It’s increasingly common to see Heads of Equality, Diversity and Inclusion being recruited to HR teams across the industry.
Clients are increasingly looking for assurances that contractors are embedding Fairness, Inclusion & Respect in line with industry best practice. In response, CHAS, the recognised experts in providing third party accreditation, have partnered with the Supply Chain Sustainability School (SCSS), a built environment collaboration dedicated to upskilling those working within, or aspiring to work within, the built environment sector. Together they have developed the Fairness, Inclusion & Respect Growth Assessment to offer an accredited evidence-based assessment that offers third-party assurance that Fairness, Inclusion & Respect is being embedded effectively. The assessment involves a range of online questions and in-person interviews.
What evidence needs to be provided?
The assessment requests evidence of how an organisation complies with their legal obligations relating to the key topics. The assessment then looks for evidence of good practice.
What are examples of best practice?
The assessment offers guidelines on developing and embedding the key topics of the Fairness, Inclusion & Respect framework. Examples could include organisational data that shows how diverse recruitment is tracked or a demonstration of what proactive measures have been taken to reach out to minority-owned businesses to promote supplier diversity.
Industry is making great progress in becoming more diverse, but there is still work to be done. This new accreditation will enable businesses to move from showing they are committed to Fairness, Inclusion & Respect to proving they are making progress to promote a fairer, more inclusive and respectful industry for all.
To find out more about the Fairness, Inclusion & Respect Growth Assessment, call CHAS today on 0345 521 9111 or visit www.chas.co.uk
The Health and Safety Executive (HSE) describes a risk assessment as a step-by-step process for controlling Health & Safety risks caused by hazards in the workplace. If not regularly reviewed, you end up putting your employees, business, and reputation at risk.
Why are workplace risk assessments so essential?
As an employer, you have a legal duty to assess the risks to Health & Safety in your workplace and then take steps to either entirely remove or take steps to reduce the risk of those hazards.
The Management of Health and Safety at Work Regulations 1999 make it clear that employers need to assess not only the risks to the Health & Safety of their employees but also anyone “not in his employment arising out of or in connection with the conduct by him of his undertaking.”
It’s also important to consider the competence of your employees, this will help you understand the level of information, instruction, training and supervision you need to provide
That’ll come in handy when deciding who to appoint as your ‘competent person’, too. Your competent person needs to be someone suitably qualified to meet the Health & Safety requirements of your business. Their role in this context is to support you with the five steps to risk assessments, which are:
1. Identify hazards
2. Assess the risks
3. Control the risks
4. Record your findings
5. Review the controls
Not having a solid risk assessment can lead to accidents, injuries, fines, and even prosecutions, putting your employees’ safety and your business’ reputation on the line.
In terms of severity, illness, injury, and death are some of the most disastrous consequences of a poor risk assessment. The legal implications of poor risk assessments include enforcement notices, prosecution, huge fines, and even imprisonment. These can lead to irreversible financial and reputational damage.
One of the most common causes of accidents, according to HSW annual statistics, is slips, trips and falls – accounting for 33% of non-fatal injuries at work. Similarly, one of the top reasons for fatalities is falls from height. A strong risk assessment is key to preventing them
Since the pandemic, work-related stress has skyrocketed, accounting for 50% of all new cases of work-related ill health in 2020/21. Stress risk assessments are a legal responsibility, and vital for managing the risk of work-related stress in the workplace.
Our risk assessment support helps keep your employees safe, with over 1000 risk assessment templates and 24/7 advice covering everything from COSHH to stress risk assessments. If you’d like to chat about how we can help, call 0345 844 1111 and quote “The Scaffolding Association’ to access preferential rates.
Workplace risk assessments are a legal necessity, but creating them, updating them and storing them can be a headache. The Health & Safety experts at Citation offer advice on taking the hassle out of workplace risk assessments.
You may have seen the first series of the Channel 4 TV programme, Screw, the drama set in a fictional male prison, Long Marsh. What you may not have realised is that the prison is actually a dressed scaffold structure. Creating a prison from scratch was always going to be a challenge, but with input from multiple sources, that is exactly what was achieved, and with series two about to start filming we took a look into how.
W e spoke to Barry Lawford, Managing Director at Five Star Projects who were approached with the task:
“We were given an original briefing by the Production Team who came to us with a design of a prison from an internal perspective and we had to build the scaffold to match that. We originally took this to Layher to come up with some initial 3D design drawings to utilise their design software to model the initial bones of the model and supply a starting point for both component choice as well as a quants list.
We then went through the tweaking stage, with a lot of forwards and backwards with the designer and various other departments to ensure the structure met all their requirements. Once all parties were satisfied with the concept, we sent this to Scaftec to finalise the design and ensure all the calculations were correct and everything was structurally sound.”
Barry continued to explain the structure had to incorporate the complete set, including the walkways, cells, toilets, and offices:
“There was a long list of requirements to this project, for example certain cells had to be opposite others for filming purposes. There were a lot of cantilevered walkways and balconies, plus it had to be aesthetically accurate. The walkways had to be a certain depth to make them realistic but also be quite stiff and strong, so ended up using a timber formwork beam to achieve this as scaffold components couldn’t meet the design criteria”
The heavy filming equipment itself created a whole other element to the structure from a loading perspective. With a specified 500kg per square metre load required throughout on all flooring areas, all of the bracings and ballasts etc had to all be engineered to a higher standard than normal construction works.”
The structure needed to be completely free standing and could not be tied in. We spoke to Bill Ferguson, Managing Director at Scaftec Limited, about the design:
“The Production Team had sent the schematics on what they wanted the scenes to look like to Barry, who came to us with a 3D sketchup design proposal, and we then designed and detailed the scaffold frame, producing working drawing and calculations. We also visited the set several times during the construction to discuss changes then alter the designs to suit.
It helped that it was being erected indoors, meaning there were no environmental factors to consider such as wind loads. It wasn’t a hugely technical design to be honest. We went back and forth a few times until we came up with the final design, but it was mainly tweaking things for aesthetic reasons rather than for structural purposes, for example there were restrictions on where we could put standards due to cell doors.”
The structure was mainly made out of Layher System Scaffold, with tube and fittings used to customise specific elements. In addition, both aluminium and steel beams, as well as the timber formwork beams, were all required to complete the structure.
We asked Barry if there were any other challenges to the build:
“One of the biggest challenges we faced was the internal height of the venue, which was not tall enough for the set, we ended up having to build up, over and around the existing roof structure. Using the beams
as part of the set was not an option so the final design involved building up & over the beams, with the finished set ceiling only 50mm below the beams and the entire lighting rig and walkways above them. Typically, a lot of the existing structure was not level or square and we had to work around this, but I love an engineering challenge, and I really enjoyed working out how to get all the different systems to work together on this job.”
On top of all this, the project was subject to a very tight time schedule, which wasn’t helped by the need to pour a new floor as the existing one wasn’t suitable.
Barry commented:
“The Five Star Projects team had less than a week to build the entire structure ready for other departments to begin the full set build - including construction, set, props, dressing, paint, scenic artists etc etc. These departments had much more work to do than we did, and the final finish & level of detail is testament to this.”
The venue location itself also caused some issues, based in the old transport museum in Glasgow City Centre it meant that the team did not have a straightforward access for trucks to load in either.
To conclude Barry stated:
“It is normal for Film/TV Projects to experience a lot of changes and this one was no exception. From the original brief to what we ended up building, there is
quite a difference. Every step of the way we had to keep coming up with engineering solutions that also worked aesthetically as well as taking filming requirements into account, and I thoroughly enjoyed making this happen.
The Production Team were clearly happy with the results because they have kept the structure as it is for series two, which starts filming again in the coming weeks.
It was a challenging project but a thoroughly enjoyable one, I would also like to thank Scaftec for all their hard work on this one, we have worked together for many years, including on multiple other Film & Tv projects both in Glasgow as well as further afield in places like Norway, so I trust their work and I know that they can put a team together and come through with a quick turnaround, which is exactly what we needed for this one.”
Bill concluded:
“It is always nice to work on an interesting project, especially one that you can see on TV where you get to see your work actualised on screen.
We’ve worked with Barry and his team on many different TV and Film projects now, we know how each other work and the standards we all expect, it’s always an enjoyable experience working on projects together.”
Audited Members of the Scaffolding Association, PL Scaffolding Solutions Ltd and TAD Scaffold Designs, who are Associate Members, have been working together to provide access for remedial works on the Victorian heritage landmark, Penarth Pier.
Penarth Pier originally opened in 1898 with the now Grade II listed Art Deco pavilion being built in 1929. It has gone through some major changes and challenges in its time and a structure of this age naturally requires remedial works.
Recently access was required to change a waste pipe from steal cast to plastic. This would have been a simple job, however the waste pipe that needed changing goes to the toilet block halfway along the pier, meaning the tides played a huge part in how the project could be achieved.
Robert Pearce, Director at TAD Scaffold Designs, explained:
“The biggest problem that we faced with this design was that we couldn’t quantify the tidal flow. Because we couldn’t calculate the pressure of the waves the scaffold had to be elevated above the predicted high tide line
FIND OUT MORE:
for the specific time that it was going to be in place.
Therefore after a few site visits we came up with a bridged scaffold design that spanned the existing trestles of the pier.
It also meant that it had to be erected during a low tide period to ensure the tide wouldn’t breach the scaffold. Around the dates that were chosen to undertake the work the tide gave them an approximate window of 3 to 4 weeks to erect the scaffold, complete the required work and dismantle everything. This meant that we had to design a scaffold that was as streamlined as possible to make sure there was enough time for all that was necessary before the water levels rose again.”
Joshua Penberthy, Operations Director at PL
National Piers Society: www.piers.org.uk/piers/penarth
PL Scaffolding Solutions Ltd: www.linkedin.com/company/pl-scaffolding-solutions-ltd
TAD Scaffold Design: www.tad-designs.co.uk
Scaffolding Solutions, agreed that the tides created the biggest test:
“We had to work within the tidal times which was a big challenge, we had to check the times and work around them.
The streamline design meant we had it up in plenty of time to change the waste pipe and they also did some further testing to determine whether further work on the brackets, and possible strengthening works, are required. We have taken it down now as we could not leave it up past the window we had been originally given due to the tides.”
The pier remained open to the public at all times, including a very busy Bank Holiday, the PL team accommodated this by creating a handrail between the public and the works to ensure a safe environment for all.
Garyn Lucas, Director at PL Scaffolding, concluded:
“Seeing it complete was a proud a moment for us. As expected, this project threw plenty of challenges our way such as working to the tidal times and the pier remaining open to the public, but our dedicated team of scaffolders were not fazed by this and conducted themselves brilliantly once again. We would like to say a big thank you to TAD for their design input on this one once again and also to the Local Authority for continuing their trust in us.”
Abscaff Limited, who are Assessed Members of the Scaffolding Association, and Highland Temporary Works Ltd, who are Associate Members, have been working together to provide access to the iconic Braemar Castle.
T he castle, which was constructed in 1628 by the then Earl John Erskine, and later became the home to the Clan Farquharson, is currently undergoing a £1.6m restoration project. As part of this a scaffold was commissioned by Harper and Allan, who are undertaking the restoration works of behalf of Braemar Community Ltd, the local community who has operated the castle since 2007.
The building is a five-storey L-plan castle with a unique star-shaped curtain wall of six sharp-angled salients, and with three storey angle turrets.
The unique shape was not the only challenge faced in this project as Ricky Mair explained:
“Highland Temporary Works were involved in this project from initial concept scaffold design drawings to full working design package including structural calculations and ‘as-built’ amendments.
Wind loading was a particular challenge due to exposure and location of site which is 332m above sea level.
Cuplok system scaffold was utilised which proved versatile to deal with turret overhangs and recesses in the building. The sheer height of the scaffold is 20m high with 10 fully boarded lifts and induced high leg loads of nearly 25 kN.
2 layers of cruciform 63mm thick timber batten soleboards were also required to satisfy the ground bearing pressure on site.” Over 90 tons of equipment were utilised for the structure which took 8 weeks to build, with over 1000-man hours needed to complete the scaffold.
It is expected that the scaffold will be standing until winter 2022 when works will be completed, with the aim of reopening the castle in July 2023.
Garry Butcher, Operations Director at Abscaff concluded:
“It is always very challenging when working on such an iconic castle, thanks to the client and our team the project was delivered on time and budget.”
You can find out more about the project by searching YouTube for Braemar Castle’s Meet the Builders Tour.
Abscaff Limited: www.abscaff.co.uk
Highland Temporary Works Ltd: www.htwdesign.co.uk
G-DECK’s DUAL is a hybrid safety decking system that enables existing birdcage equipment such as tube & fittings to be upgraded and used with G-DECK’s robust metal decks.
G-DECK’s metal decks have a 600kg/m2 load bearing, making them the strongest load deck system on the market. They are robust and do not warp like traditional materials.
The DUAL brackets are designed to fit perfectly over tube to create the leg that the decks sit on, and tubes can also be fitted at the top of the bracket that allows a further run to allow handrails to be created with ease. The legs can then be braced using standard tube and fittings if needed. Being able to utilise existing equipment keeps investment costs lower.
The main benefits of G-DECK DUAL are:
• 600kg/m2 load bearing
• Fast to erect/dismantle
• Re-use existing scaffold tubes & fittings
• Can be branded with your colours for ownership
• Easily create handrails with tube & fitting
• Can go up to 4 metres in height
• Less storage needed
• 100% repairable to maintain long life span
• Manufactured in Britain
DUAL is fully tested to BSEN 12811 standard. G-DECK also provide full installation training which includes certification with every system sold.
It came about after an in-depth exploration of demands, collecting data and feedback from people involved in lifting operations, which led to a conclusions on how to enhance the tools and techniques involved in lifting.
The Bucket Strap is made from 100% polyester, a strong durable material which also has many benefits. Fabric slings are much softer and lighter than chain or wire rope. This type of sling can also minimize the damage to items being lifted as it will not scratch or dent the load, neither will it rust or weaken with age and are very cost effective.
The main benefits of Bucket Strap are:
• Strength - can lift heavy load with ease
• Durable - it will not decay as natural fibres do, will not rust as chain slings often do, is resistant to acidic chemicals
• Abrasion and cut resistant - protects load from scratching and denting
• Easy to use - quick to deploy, provides effective and fast way of lifting materials
• Affordable – inexpensive when compared to chain slings
• Economic solution - low cost but long service
• Sustainable - due to longevity reduces harm to environment
• Lightweight and easily portable
“Over the last few years there has been a massive adoption of using safety decking over traditional birdcages, this has mainly been led by developers on new build sites who are requesting it as part of the tender process.
The system requires much less labour to install which means payback on investment is achieved quickly, there is a saving of at least £10 per m2.”
Ty Wilson: G-DECK, Sales DirectorFOR MORE INFORMATION HEAD OVER TO: www.gdecking.com or email office@gdecking.com
Whilst developing the Bucket Strap, Focus Factory also tried to tackle the issue of pulling buckets on a rope by attaching the line to the bucket handles, a practice that should never take place as bucket handles are not Safe Working Load tested. Making it an unsafe lifting method that poses a great risk to those involved in lifting operations.
The Bucket Strap creates a faster and safer alternative to traditional handling and makes it easier to balance the load.
Hiab has teamed up with five firms across the UK to develop the next generation of drawbar vehicles for crane offload of building products, with two prototype construction vehicles now in operation at the H&H Celcon Borough Green site.
RT Keedwell Group and H & H Celcon, together identified a need to reduce environmental impact of their vehicles operating inside the M25 specifically.
Working with specialist vehicle manufacturer, Massey Truck Engineering, who oversaw the entire build, the firm enlisted specialist help in each area, including international truck manufacturer, Renault Trucks and local dealer Renault Truck Commercials, and world leading provider of on-road handling equipment, Hiab.
The first-of-a-kind trucks, known as the ‘Borough GREEN machines’, use a Renault Trucks C380 x2 lift axle rigid drawbar combination equipped with lighter-weight day cab for this payload-sensitive sector. Additional weight reduction modifications undertaken at the bodybuilders, including the removal of the passenger seat, successfully achieved a 28t payload for the first time in a construction brick truck using a 26t drawbar combination.
The new LYNCH ADVANCED Guardrail System works with tube and fitting scaffolds and is installed and secured in place from the lower-level position.
Hiab’s remote-controlled X-Hiduo 158B-2 loader cranes were selected thanks to their speedy operation and innovative Hiab HiConnect technology, which provides real-time insights into equipment utilisation, operation, and condition.
HiConnect provides data that can be used to actively optimise performance and safety and avoid unnecessary
downtime, while web-based dashboards with clear and simple overviews provide status monitoring, service planning, and help improve the operation of each unit and operator.
The LYNCH ADVANCED Guardrail System is secured in position by tightening of the upright guardrail bottom fitting to the outside ledger, without the need of using podium steps, therefore providing safer working practices.
The patented design of one fitting connected on top of the other allows for guardrails to be installed level over any required lengths.
Benefits of the LYNCH ADVANCED Guardrail System include:
• Adds to current stock, releasing current guardrail tube and fitting to be utilised elsewhere
• Installed from scaffolders safe zone
• Increases strength in scaffold structures
• No protruding bolts or holders
• Lighter in weight to handle
• Folds down for easier transportation
• Provides safer working practices
• Single bay upright sections
• Collective protection