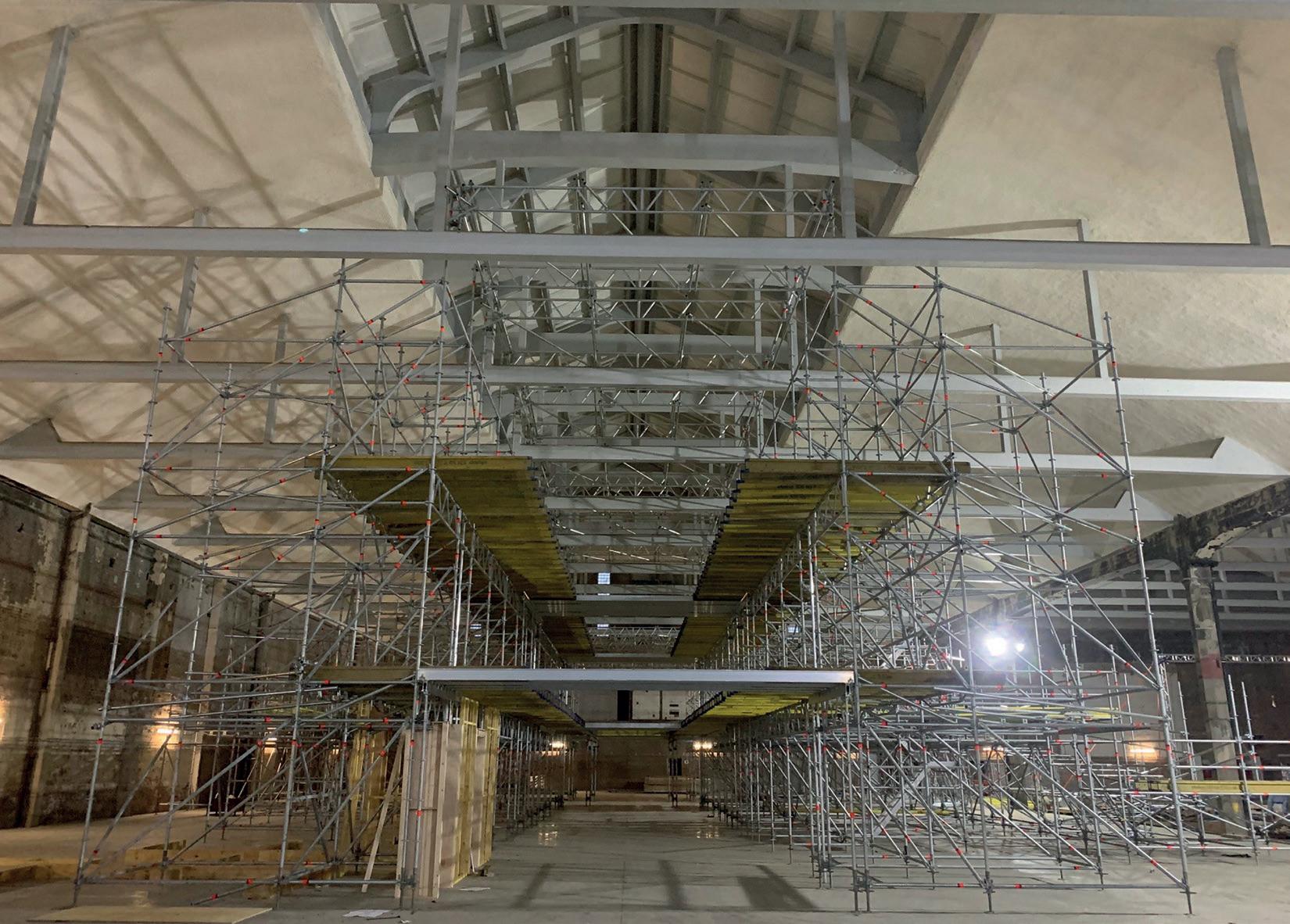
4 minute read
Scaffolding plays starring role in prison drama series
from AccessPoint Issue 22
by AccessPoint
You may have seen the first series of the Channel 4 TV programme, Screw, the drama set in a fictional male prison, Long Marsh. What you may not have realised is that the prison is actually a dressed scaffold structure. Creating a prison from scratch was always going to be a challenge, but with input from multiple sources, that is exactly what was achieved, and with series two about to start filming we took a look into how.
W e spoke to Barry Lawford, Managing Director at Five Star Projects who were approached with the task:
“We were given an original briefing by the Production Team who came to us with a design of a prison from an internal perspective and we had to build the scaffold to match that. We originally took this to Layher to come up with some initial 3D design drawings to utilise their design software to model the initial bones of the model and supply a starting point for both component choice as well as a quants list.
We then went through the tweaking stage, with a lot of forwards and backwards with the designer and various other departments to ensure the structure met all their requirements. Once all parties were satisfied with the concept, we sent this to Scaftec to finalise the design and ensure all the calculations were correct and everything was structurally sound.”
Barry continued to explain the structure had to incorporate the complete set, including the walkways, cells, toilets, and offices:
“There was a long list of requirements to this project, for example certain cells had to be opposite others for filming purposes. There were a lot of cantilevered walkways and balconies, plus it had to be aesthetically accurate. The walkways had to be a certain depth to make them realistic but also be quite stiff and strong, so ended up using a timber formwork beam to achieve this as scaffold components couldn’t meet the design criteria”
The heavy filming equipment itself created a whole other element to the structure from a loading perspective. With a specified 500kg per square metre load required throughout on all flooring areas, all of the bracings and ballasts etc had to all be engineered to a higher standard than normal construction works.”
The structure needed to be completely free standing and could not be tied in. We spoke to Bill Ferguson, Managing Director at Scaftec Limited, about the design:

“The Production Team had sent the schematics on what they wanted the scenes to look like to Barry, who came to us with a 3D sketchup design proposal, and we then designed and detailed the scaffold frame, producing working drawing and calculations. We also visited the set several times during the construction to discuss changes then alter the designs to suit.
It helped that it was being erected indoors, meaning there were no environmental factors to consider such as wind loads. It wasn’t a hugely technical design to be honest. We went back and forth a few times until we came up with the final design, but it was mainly tweaking things for aesthetic reasons rather than for structural purposes, for example there were restrictions on where we could put standards due to cell doors.”
The structure was mainly made out of Layher System Scaffold, with tube and fittings used to customise specific elements. In addition, both aluminium and steel beams, as well as the timber formwork beams, were all required to complete the structure.


We asked Barry if there were any other challenges to the build:
“One of the biggest challenges we faced was the internal height of the venue, which was not tall enough for the set, we ended up having to build up, over and around the existing roof structure. Using the beams as part of the set was not an option so the final design involved building up & over the beams, with the finished set ceiling only 50mm below the beams and the entire lighting rig and walkways above them. Typically, a lot of the existing structure was not level or square and we had to work around this, but I love an engineering challenge, and I really enjoyed working out how to get all the different systems to work together on this job.”
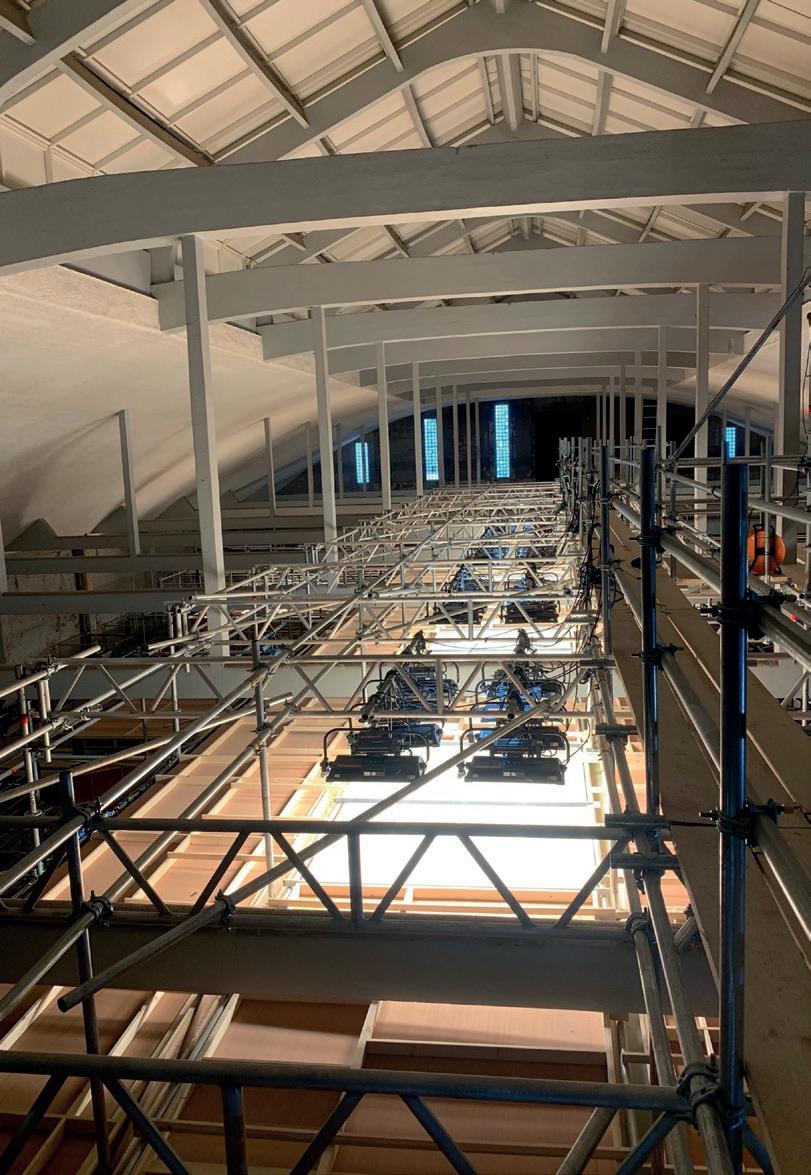
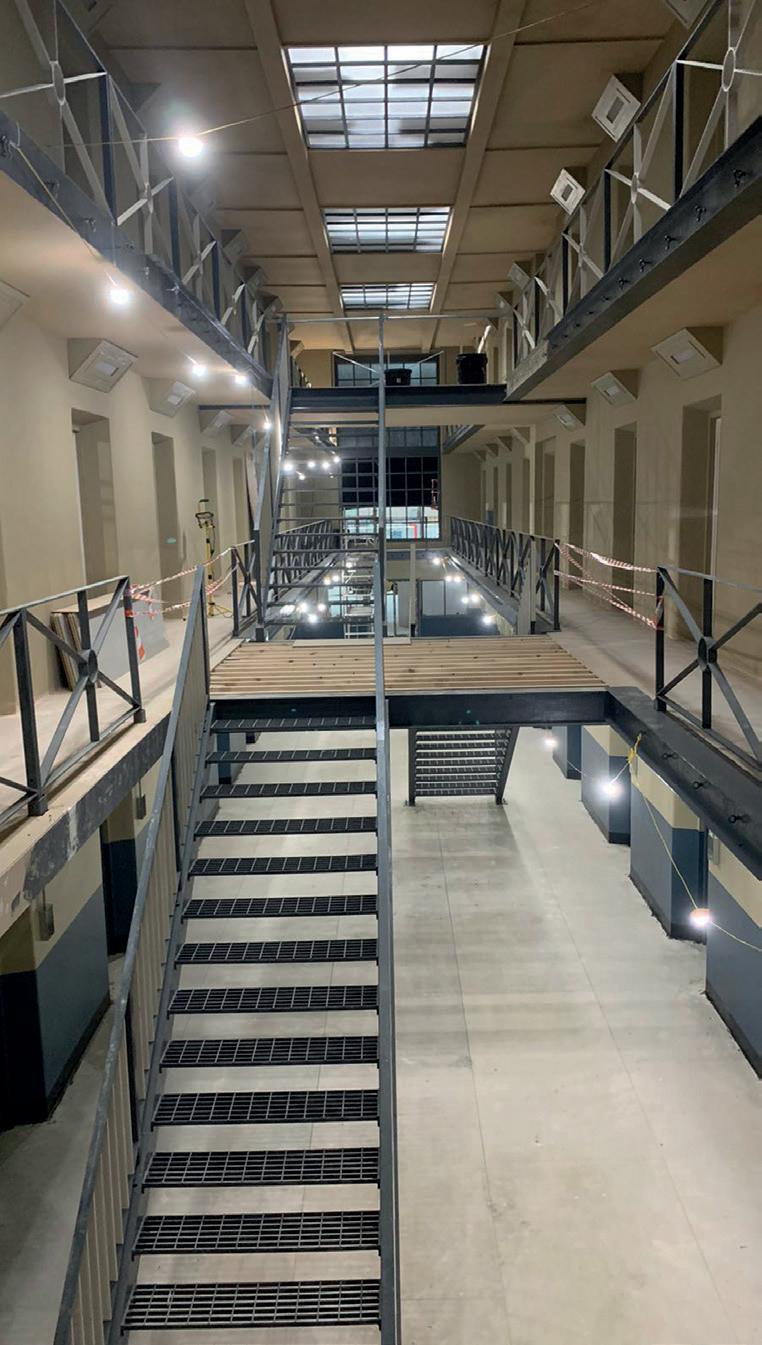
On top of all this, the project was subject to a very tight time schedule, which wasn’t helped by the need to pour a new floor as the existing one wasn’t suitable.
Barry commented:
“The Five Star Projects team had less than a week to build the entire structure ready for other departments to begin the full set build - including construction, set, props, dressing, paint, scenic artists etc etc. These departments had much more work to do than we did, and the final finish & level of detail is testament to this.”
The venue location itself also caused some issues, based in the old transport museum in Glasgow City Centre it meant that the team did not have a straightforward access for trucks to load in either.
To conclude Barry stated:
“It is normal for Film/TV Projects to experience a lot of changes and this one was no exception. From the original brief to what we ended up building, there is quite a difference. Every step of the way we had to keep coming up with engineering solutions that also worked aesthetically as well as taking filming requirements into account, and I thoroughly enjoyed making this happen.
The Production Team were clearly happy with the results because they have kept the structure as it is for series two, which starts filming again in the coming weeks.
It was a challenging project but a thoroughly enjoyable one, I would also like to thank Scaftec for all their hard work on this one, we have worked together for many years, including on multiple other Film & Tv projects both in Glasgow as well as further afield in places like Norway, so I trust their work and I know that they can put a team together and come through with a quick turnaround, which is exactly what we needed for this one.”
Bill concluded:
“It is always nice to work on an interesting project, especially one that you can see on TV where you get to see your work actualised on screen.
We’ve worked with Barry and his team on many different TV and Film projects now, we know how each other work and the standards we all expect, it’s always an enjoyable experience working on projects together.”