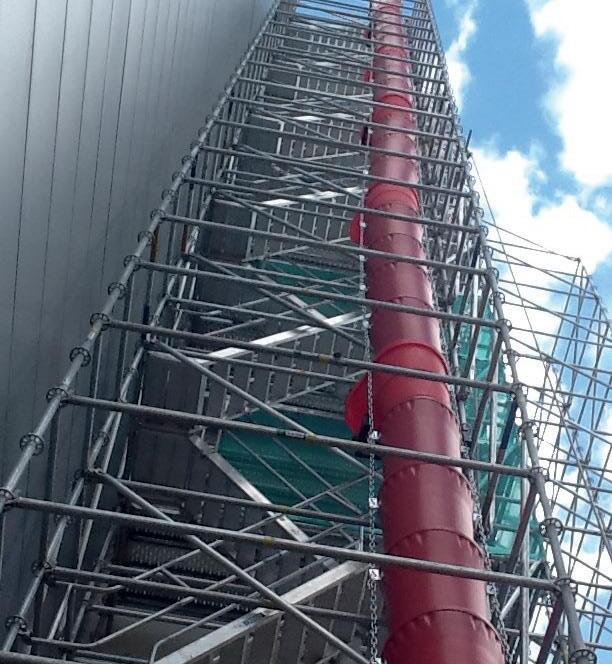
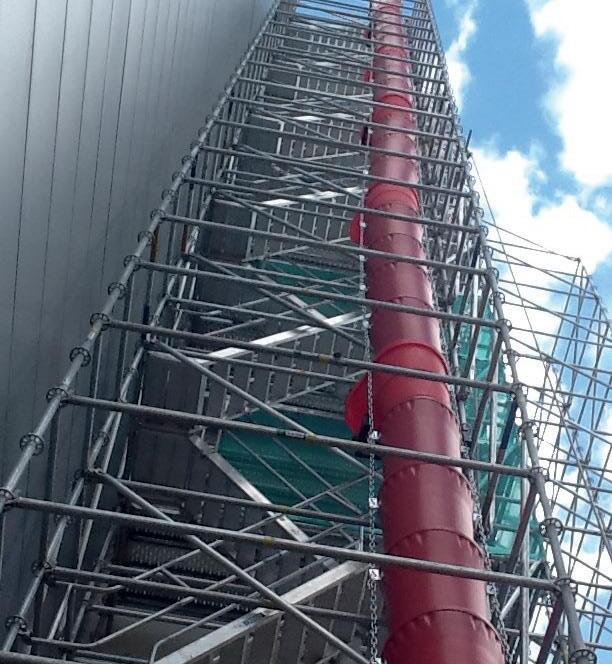
CONTENTS
04 Voice of the Sector: Skills and standards
05 Opinion: Control the Stock –Control the Plan – Control the Results
10 Commercial: Final account applications
12 Feature: Are your vehicles safe and compliant?
14 Scaffold Design: Scaffolding above and around live railways
16 Site Visit: Storm Doris sets challenge for Godiva at University College Hospital Coventry
18 Guidance: Lifting operations – rope inspection and maintenance
19 Health & Safety: Managing Hand Arm Vibration Syndrome in construction
20 Quality Control: Confidence in quality at the centre of responsible sourcing
21 Annual General Meeting Report: Creating a respected voice
22 Association News: Updates from the Scaffolding Association and members
FRONT COVER: Godiva decided on a system-led solution for a fast-moving project for VINCI at University College Hospital Coventry.
Industry reacts to high cost of CPD
Scaffolders across the country are questioning the change in renewing CISRS skills cards.
Contractors allege that from 1 July 2017, the CISRS skills card renewal process will fail to recognise existing continuous training, instead requiring scaffolders wanting to renew to attend a two-day Continuous Professional Development (CPD) course, potentially costing them hundreds of pounds per person.
Ian Redpath at JDM Scaffolding said: “This action has been pushed through by members of the NASC. There has been no consultation with the wider industry. We already TBT (tool box talk) all our staff and give regular training ever year to encourage our staff to gain additional qualifications. So CPD is already happening and there is no recognition of this.
"A Basic Inspection course lasts three days. How can CPD be achieved and a qualification given in only two days? The idea of more training is good, but the way it’s being done is wrong.”
Steven Darren of Synergy Scaffolding said:
Aviva recognises Scaffolding Association’s Audited Membership status
Insurance specialist Amicus has confirmed that the UK’s largest insurer, Aviva, will now regard an Audited Member of the Scaffolding Association as being comparable to an NASC member when looking to provide insurance.
CONTACT US
EDITORIAL
Editor: Adrian JG Marsh
Assistant Editor: Jenny Gibson Telephone: 01926 420 660
Email: newsdesk@accesspoint.org.uk
AccessPoint, Althorpe Enterprise Hub
Althorpe Street, Leamington Spa CV31 2GB
Design: Matthew Glover
SUBSCRIPTIONS newsdesk@accesspoint.org.uk
ADVERTISING
Advertising enquiries: Adam Turner Tel: 01926 420660 adam.turner@campbellmarsh.com
Scaffolding Association
Tel: 01386 764 945 www.scaffolding-association.org
Email: info@scaffolding-association.org
ISNN: 2055-2033 (Print)
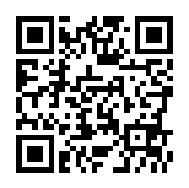
AccessPoint magazine is published on behalf of the Scaffolding Association by Campbell Marsh and the views expressed in this journal are not necessarily those held by the Scaffolding Association or the publishers. The publishers shall not be under any liability in respect of the contents of the contributed articles. The Editor reserves the right to edit, abridge or alter articles for publication.
This significant decision will see Aviva widen its acceptance criteria to include audited Scaffolding Association members and entitle them to discounts on specialist insurance schemes in which Aviva participates – fantastic news for existing Audited Members and those already in the process or considering the audit.
Paul Beck, director at Amicus, commented: “We are delighted that Aviva has recognised the benefits of the Scaffolding Association’s audit process and are confident that with Aviva leading the way, other insurers will soon follow.”
Audited Membership is the Scaffolding Association’s highest level of membership and sits at Level 1 in the PAS 91 Three Assurance Level Model, which is the highest and most comprehensive level.
The Association’s Audited Membership category has been designed to enable scaffolding contractors to demonstrate their high quality operating practices. Members wishing to become audited go through an independent two-stage audit undertaken by a UKAS-accredited certification body.
“I feel this is a decision taken by a few to benefit a few. The course should be aimed at scaffolders who are at management level and who can then relay information to their site level team.”
Des Alexander from Thunderbolt Scaffolding commented: “Looking at the course structure, most of it is already taught by companies who have regular ongoing training. We are now finding we have to pay up to £300 for a two-day course and lose men for two days.”
Responding to criticism about the CISRS CPD Dave Mosely, CISRS scheme manager, said: “There has been a lot of time and effort put into creating the right balance and depth of useful content into the two-day CPD course. CISRS are confident it will only serve to strengthen the safety and knowledge of those attending and help to raise the reputation of the trade amongst the wider industry.”
FIND OUT MORE www.accesspoint.org.uk
Altrad agrees takeover of Cape

French construction and scaffolding equipment giant Altrad has agreed to buy UK industrial services company Cape Plc for about £332.2 million in cash.
Cape employs 16,000 and provides a multi-disciplinary service offering including the traditional services of access, insulation, mechanical and specialist coatings and fireproofing. In 2016, Cape reported revenue of £863.5m and an annual pre-tax loss of £43.6m with UK margins adversely impacted by weakness in the oil price and reduced demand from the coal-fired power generation market.
Altrad has a global turnover of about €2.3bn (£2bn) and controls a significant part of UK access, hire and scaffolding business, including Beaver, Generation, Hertel, NSG and Trad Group.
Altrad Group chairman Mohed Altrad said: “Altrad and Cape have a strong complementary geographic and product mix enabling the creation of a multi-disciplinary industrial services leader in key markets around the world.”
FIND
Association unveils new President
Russell Maxwell-Smith has been appointed as the first President of the Scaffolding Association.
Mr Maxwell-Smith established Chelmsford-based WellMax Scaffolding in 2008 and has grown the company into a £7 million business that works with leading contractors operating in the London area.
Speaking about his new role, Mr Maxwell-Smith said: “I am delighted to be appointed to the role of President. The Association has a growing reputation for delivering high quality advice and support, and against the backdrop of membership reaching 255, this is an exciting time to be leading the organisation. I look forward to working with the executive team and members to make a positive difference in improving services for access and scaffolding businesses in the UK.”
Robert Candy, chief executive of the Scaffolding Association, said: “We are delighted Russell will be our President. He has extensive experience in the scaffolding sector which will be invaluable to the Association.
“We look forward to working together to develop an exciting, positive future for both the Scaffolding Association and its members.”
www.scaffolding-association.org
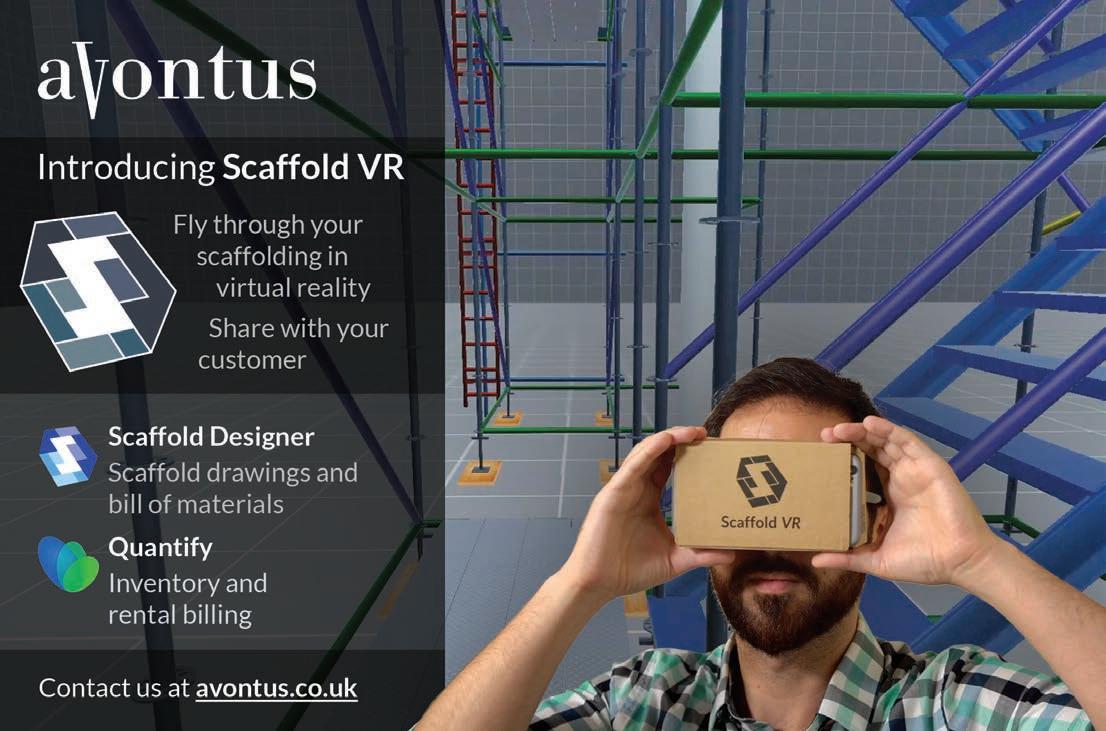
Audit success
London-based Alandale Plant & Scaffolding Limited has announced it is now an audited member of the Scaffolding Association. The 400-strong company made the decision to become audited as it offered the opportunity to take a detailed look at its processes and gain feedback on how they could be further improved.
Matthew Warner, managing director at Alandale Plant & Scaffolding Limited,: said: “This audit is really raising the bar for industry best practice. We pride ourselves on our reputation within the industry for providing a quality service. We became audited members so that we are able to demonstrate to clients that we have a continued commitment to maintaining our high levels of health and safety performance.”
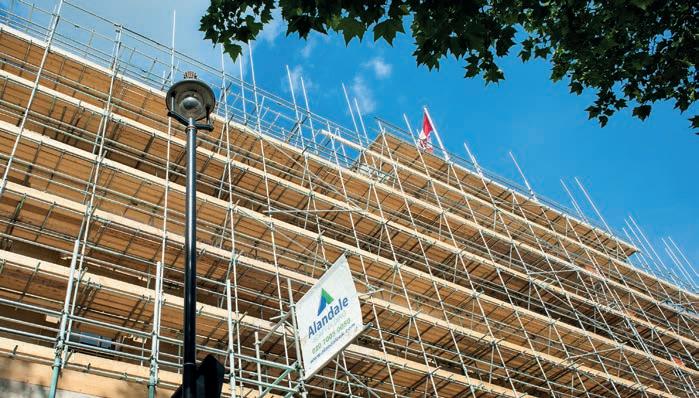
Change is good but safety is critical
I met Jérôme Stubler, chairman of VINCI, during the spring and he talked about how construction was driven by the way we built things in the past but that technology is now shaping the industry for the future. He also talked about how 3D printing is the next revolution and how it offers opportunities to produce components off-site more efficiently than before.
But not for us, I hear many of you scream. Sadly, unless the access and scaffolding sector embraces change and new technology, it will not improve its position in the supply chain. Digitation is here to stay and beginning to seep into our business.
Look at the opposite page and see how more efficient inventory or stock control can raise profitability. We don’t want new technology because it’s new; we want it because it adds value and drives improvements. As confidence increases, it is easier to make effective and sensible decisions that improve performance and profitability.
Innovation is about improving productivity. At a time of rising inflation, clients want to ensure that their supply chain remains skilled, safe and sustainable. The cost burden of the CISRS CPD changes (see page 2) is causing many contractors to ask is it the best way to deliver safer and higher quality or is it just another way to make more money and missing an opportunity to raise standards?
While specialists are focused on their performance on-site, some areas can be missed (see page 12). Out of the 1,000 Public Inquiries into road transport incidents carried out each year, the scaffolding industry appears all too often – and for all the wrong reasons. Being specialists in access and scaffolding doesn’t mean you can’t be inadvertently exposed if you’re not on top of your vehicles.
Take a look at the site report in this issue (turn to page 16) to read how specialist scaffolders remain firmly on the critical path. While many building owners complain about it being a significant fixed cost, what was clear from this work is that safe access is an absolute top priority. Adopting a system, rather than traditional techniques, gives scaffolders the opportunity to respond to a very fast-moving project with the best approach. Best for time, best for quality, but more importantly, best for safety.
Adrian JG Marsh EditorSkills and standards
The Scaffolding Association is steadily gaining greater recognition and respect and playing its part in building a safer environment for our employees, suppliers and clients.
Our first President, Russell Maxwell-Smith, who is the owner and founder of WellMax Scaffolding, was introduced as the Association’s President at our AGM last month.
Russell talked about how our growing reputation for delivering high-quality advice and support, combined with our shared common vision to raise standards, puts the Association in a strong position to bring about positive change in the access and scaffolding industry.
More than 50 members attended the AGM on what turned out to be the hottest June day since 1976! If you want to read a bit more about what we discussed, take a look at our AGM Report on page 21.
We had another opportunity to spend quality time with a cross section of industry professionals at the Safety & Health Expo (SHE) at ExCeL in London. Meeting many members and scaffolding companies at the show gave us a great opportunity to discuss the different health and safety issues that affect their day-to-day operations.
There is perhaps no more important issue within the scaffolding and access industry than health and safety, so keeping abreast of the latest developments in this area is one of the ways that we can serve our membership and the industry as a whole.
Part of our commitment to members is to ensure that our voice is heard and understood by key influencers and stakeholders. We continue to lobby government agencies and other trade bodies to ensure they understand the challenges our members face and capacity we have to respond to their expectations.
We will therefore be returning to UK Construction Week, at the NEC in Birmingham, as part of our plan to improve awareness within the wider construction community.
There have been some really great stories in the press recently about women in scaffolding. We’re all aware that, in percentage terms, very few women work in manual roles in construction and it’s very positive to see a more diverse resource base where the profile of women in scaffolding is rising.
What’s so important for our sector is that we are attractive to new entrants – female and male – and that we are encouraging new people who are passionate, keen to train and get qualified, and committed to working to the high standards that we all aspire to.
We are in discussion with CSCS about a new industry-led skills card scheme. We are working with specialist contractors of all sizes and our key objective is to increase the level and quality of training among scaffolders and reward individuals and businesses that commit to regular training while giving scaffolders another option to demonstrate that they have achieved qualified skills standards.
We’ll be looking to update the industry soon, so keep an eye out for more information on this new scheme for scaffolders.
Robert Candy Chief executive Scaffolding AssociationControl the Stock –Control the Plan –Control the Results
Andrew Smith of scaffolding software specialists
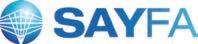
the accuracy of your forecasting and utilisation calculations.
As confidence in your stock control practices is built up, it is easier to make effective and sensible decisions on equipment purchases, cross hiring and the rates of hire you can afford to offer your customers.
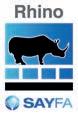
If your idea of scaffolding stock control is a peek out of the window on a Monday morning to check if you need to call a supplier to buy a hundred 21ft tubes (and a basket each of doubles and singles), then you could be missing out on opportunities to increase your bottom line! Achieving bottom-line improvement can be as simple as keeping track of a few key factors in your businesses to ensure equipment is available when you need it, where you need it.
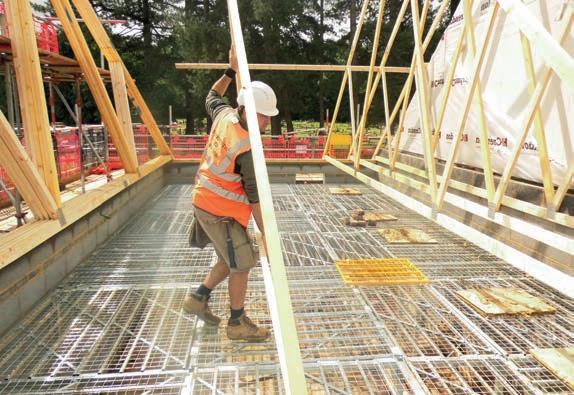
Forecasting
Through forecasting – making predictions of future use based on past and present data – you can plan ahead and understand the future demand for scaffolding equipment. By looking just a few weeks ahead with known or high-probability work, you will be better able to deal with sudden increases in equipment demands. When you look forward to understand future demand, you can plan to make a purchase or choose to cross hire for peak demand for a short period, allowing you to control expenses such as purchase pricing and shipping costs.
Utilisation
When you keep track of equipment utilisation (by comparing equipment owned to equipment in use), it becomes easier to understand the needs of your business and the return on your invested capital. In addition to return on investment (ROI) information, it is often thought that if you are utilising your assets at 75 to 85 per cent, you are in a sweet spot and able to respond to most of the typical jobs you see. As you move beyond 85 per cent utilisation, you approach an area that will not allow you to respond to your immediate equipment needs, resulting in cut-downs and inefficient use of fittings.
Cycle Count
A regular count of your key (fast moving) components – often referred to as a cycle count, where you count a small subset of inventory in a specific location – allows you to identify potential shipment problems, such as un-recorded shipments, returns or transfers. As you find and fix these errors, you ensure
Taking a simple approach to forecasting –through understanding utilisation and verifying though cycle counts – will allow you to plan to succeed and add to your bottom line.
Andrew Smith Avontus Software www.avontus.co.ukCalling all members
Are you working on an interesting project that you’d like to share with AccessPoint readers? Or, are you working on something unusual or quirky that you’d like to shout about to members of the UK’s fastest growing trade association? Then we’d love to hear from you! Send us your story with any relevant images to newsdesk@accesspoint.org.uk
Avontus Software identifies some all-important stock-control concepts that can help meet customers’ needs while adding to your bottom line.
HoloLens app from Avontus brings scaffold designs to life
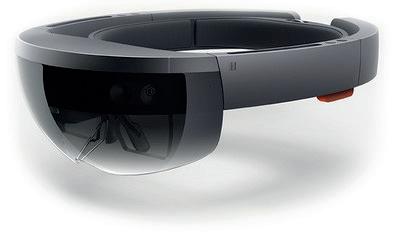
Safelinx Board Retainer reduces trip hazards on the platform
The Safelinx scaffold board retention system, from MS-UK Ltd, is speeding up board retention on sites around the country.
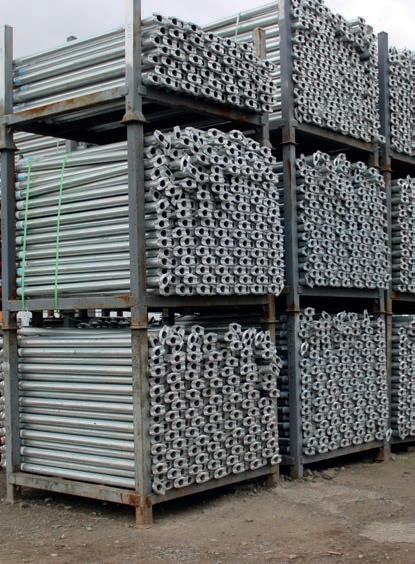
Safelinx secures a whole fleet of boards in one install to combat foot traffic movement and wind uplift, and dramatically reduce the board’s natural tendency to warp, keeping board stock in better condition for longer.
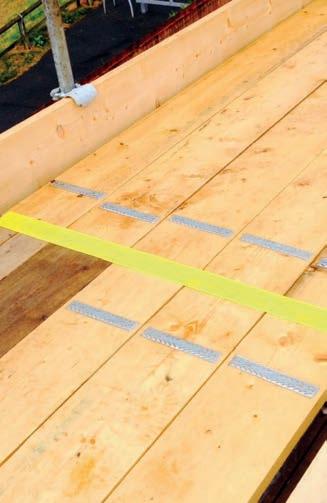
Scaffolding software expert Avontus Software has announced the launch of its new app for Microsoft HoloLens.
The latest launch from Avontus delivers a view of scaffolding in a form being dubbed Mixed Reality (MR). MR projects a 3D scaffold model onto the view of its users’ surroundings to enable interactions to take place. The model can be rotated, scaled and placed anywhere. It can also be viewed 1:1 meaning the scaffolding can be shown at actual scale on the structure it is providing access to.
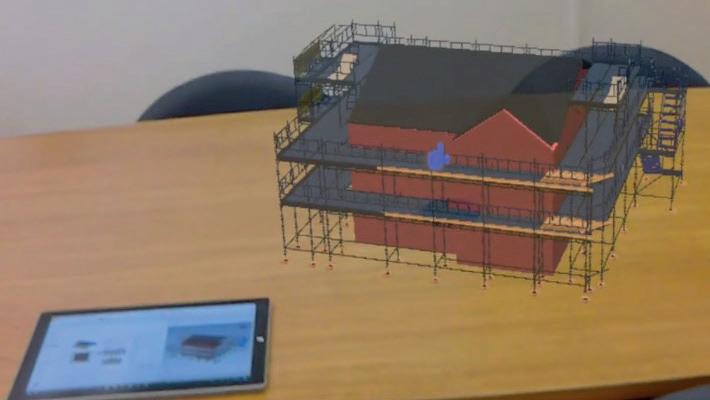
Avontus support specialist Shaun Whyman said: “Even when using traditional 2D and even 3D drawings, a scaffolding company’s customers often don’t understand how scaffolding is supposed to work, let alone what it’s going to look like.”
Andrew Smith, the sales director for Avontus, added: “MR and VR help to bring proposed works to life, without any extra work. As a result, customers are reporting up to a 15 per cent increase in contract wins.”
www.avontus.co.uk
New V-FORM safety harness expands MSA Safety range

MSA Safety’s new V-FORM safety harness is the first product available in the company’s new V product range, which is named after the iconic V-Gard safety helmet developed by MSA in 1962.
The new high-specification V-FORM fall-protection harness makes outstanding work-at-height safety accessible to all and is designed to be comfortable, light and easy to use.
V-FORM combines simplicity with safety in a streamlined harness that can be fastened securely and released quickly. It benefits from an intuitive design that ensures correct fitting first time. Specific features include high-visibility alert to show if the equipment has been used in a fall, 3- or 5-point adjustment for a tailored fit and sub-pelvic strap for more even weight distribution.
www.msasafety.com
This new board retention system is a reusable and durable solution with the ability to secure multiple layers of boards at the same time.
Safelinx is available in standard platform widths or custom lengths, subject to minimum order.
www.ms-uk.co.uk
VR Access Solutions invests in quality
VR Access Solutions, which manufactures and supplies access solutions and scaffolding products, has had its Quality Management System audited and accredited to BSI’s latest standard, ISO 9001:2015.
The company is one of the first known in the sector to meet the requirements of this updated standard and has made the investment as part of its continued commitment to delivering customer quality and high standards.
VR Access Solutions’ investment in meeting the requirements of ISO 9001:2015 has also been backed up with the appointment of its first scaffold engineer and designer to provide customers with the latest mandatory design knowledge and technical assistance for the BS EN 12810 and BS EN 12811 trademarked Turnlok scaffolding system. An additional scaffolding system and all-round scaffolding fitting are soon to be made available from VR Access Solutions to provide customers with greater choice.
www.vrscaffold.com
Sayfa Systems’ RhinoDeck provides benefits for scaffolder and house builder alike
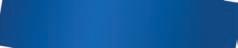
A Barnstaple-based scaffolder and nationally recognised housing developer have kept up with high demand for housing and a need for speed respectively thanks to Sayfa Systems’ RhinoDeck load deck platform and trestle system.
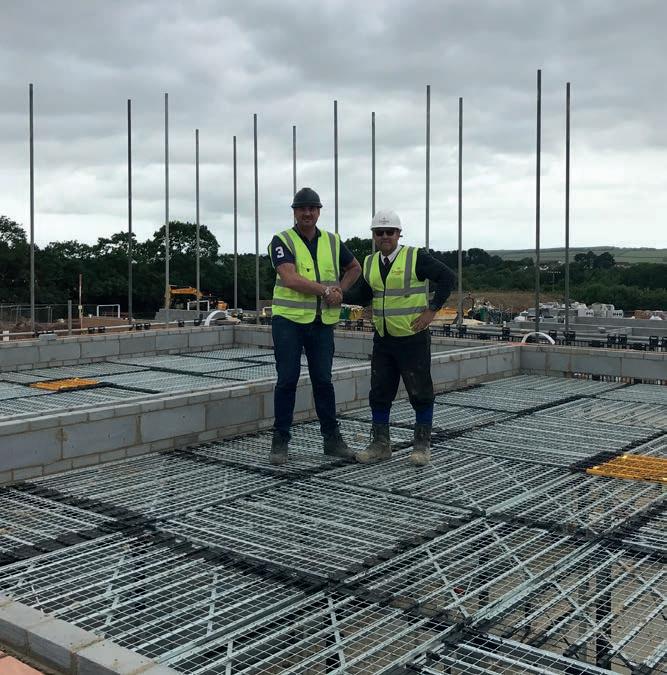
Advanced Scaffolding (SW) had previously used RhinoDeck and already appreciated its benefits of ease-of-use and speed of installation. So, when a surge in general demand coincided with a contract from Linden Homes (Galliford Try), Advanced Scaffolding decided that investing in its own fleet of the Sayfa Systems’ load decks was vital.
Matt Bacon, Advanced Scaffolding’s founder, said: “While it normally takes a minimum of four hours to fit out the average ground floor of a new-build semi with tube and fittings, it takes just over an hour to fit out the same area with RhinoDeck.
“This means we can now fit out between seven and eight plots in a day as opposed to being limited to a maximum of two plots using conventional methods.
“This is not only a massive benefit for us, wanting to make the most of labour, but also provides knock-on benefits for Linden Homes, including added flexibility, productivity and safety on-site.”
www.sayfasystems.co.uk
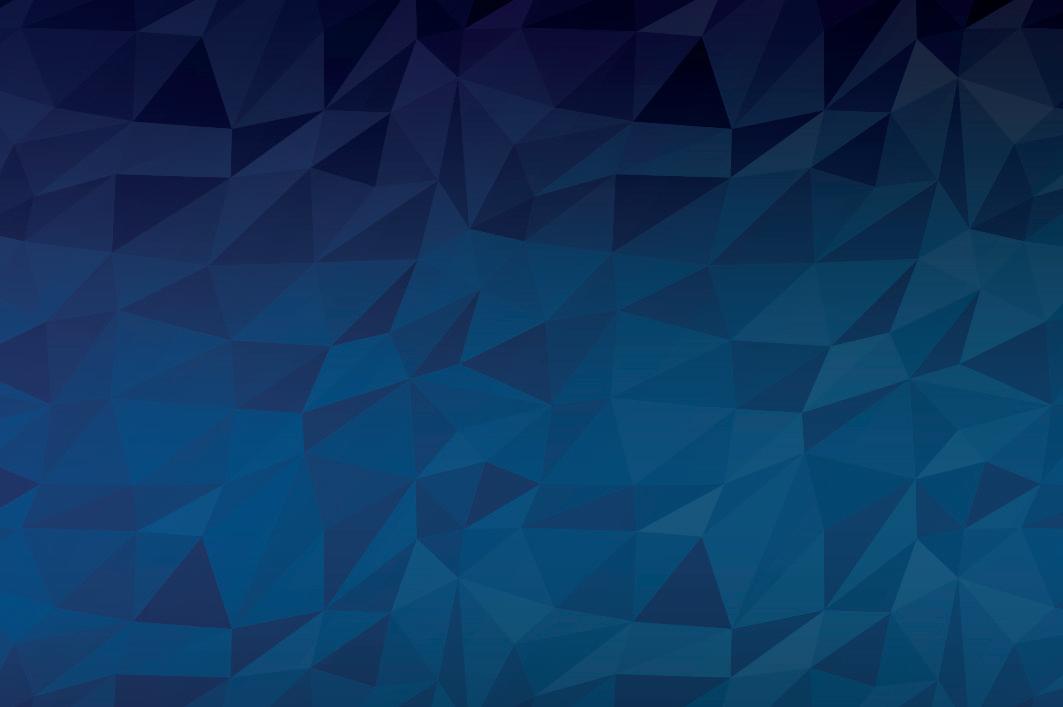
OIL, GAS & CHEMICALS POWER & ENERGY MINING & REFINING PROJECTS

Our experienced customer driven team provides a seamless service from product development, supply chain management, production, quality control, delivery and local engineering support available for fast, effective solutions where required.
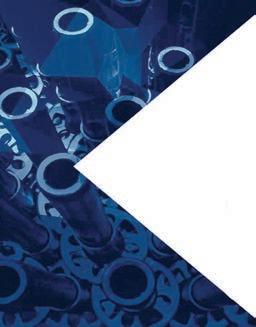
Security is the priority for Scaff Security Alarms
Scaff Security Alarms provides monitored alarms, CCTV and lighting services to secure scaffolding for a variety of buildings, including churches.
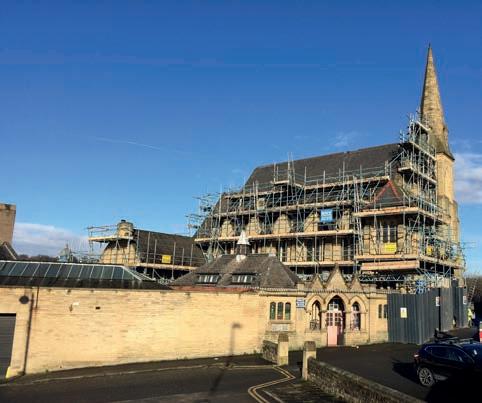
Sheffield-based Scaff Security Alarms uses alarm equipment of the highest standard, include the latest in infrared photoelectric beam sensors and dual tech PIRs. Sensors and beams are installed in the most effective positions and every scaffold alarm installation is supported by large, clear and clean warning signs to inform any opportunists that the scaffold is protected.
Systems are fully monitored and provide many features including mains power failure, siren and strobe upon alarm activation, wireless connection to a 24/7 monitoring station, user-specific codes for user identification and proximity tags for increased security.
www.scaffsecurityalarms.co.uk
New collaboration for Clow Group and StepUp Scaffold
Sayfa Systems takes first Stateside orders
Sayfa Systems is venturing into the US construction market with two orders for its construction site safety systems.
The Los Angeles Police Department (LAPD) and LendLease have both placed orders with Sayfa, which produces a range of solutions to ensure the safety of those working at height. Sayfa’s product concepts are new to the US.
LendLease has ordered 530 units of Sayfa’s AirDeck – a portable air cushion designed to protect those working at first-floor level – for use on its Stateside projects. Meanwhile, following promising results of a trial exploring the use of AirDeck in potential suicide situations, the LAPD has placed a second order to broaden the trial.
This international success has come following support from the Department for International Trade (DIT).
Robert Hall, marketing manager at Sayfa, said: “DIT has been excellent and we have really appreciated their support. They opened our eyes to the possibilities of trading internationally and the additional success it could bring us.” www.sayfasystems.co.uk
Anchor to the ground with Spirafix
Spirafix Ground Anchors provide an alternative to kentledge for securing scaffold to the ground.
Installed using a hand-held petrol post driver, or similar, on the impact setting, these high-load-bearing spiral anchors drive down into position on their own helix. They can then be locked off once installed and easily removed and repositioned if required.
Spirafix provides an ‘Anchors and Accessories for Scaffold Applications’ download from its website. This specifies guidance load ratings per anchor for different soil conditions and provides fixing options for tethering, buttress rakers, and transoms, ledgers and standards. www.spirafix.com
PERI helps take concrete frame contractor in new direction
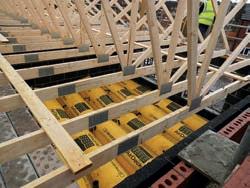
Scaffolding and formwork systems manufacturer PERI has supported major concrete frame contractor Byrne Bros (Formwork) Ltd on London’s Crossrail project.
Clow Group and StepUp Scaffold have formed a strategic partnership to provide scaffolding and access products across the UK from depots in London, the Midlands, Belfast and Glasgow.
Clow Group is the largest independently owned manufacturer of ladders, steps, access equipment and bespoke access solutions in the UK, while StepUp Scaffolding is one of the largest importers and manufacturers of scaffolding and access equipment in the North American market.
A statement from the partnership said they will combine Clow Group’s expertise in full and complete access solutions with StepUp Scaffold’s superior scaffold manufacturing and global distribution capability to deliver quality solutions for today’s increasingly diversified customer needs.
www.clowgroup.co.uk and www.stepupscaffold.com
Working from the Limmo shaft in the Canning Town area, Byrne Bros partnered with PERI for its first tunnelling project, specifying PERI’s VARIOKIT engineering construction system.
PERI engineers designed a bespoke system for Byrne Bros, combining load optimisation, flexibility and functionality, and provided full back-up technical documentation. Using the VARIOKIT system enabled Byrne Bros to move the whole formwork unit without having to remove any formwork elements or parts. This was achieved by means of rails and wheels which allowed the formwork to move along each section.
For PERI, this was a continuation of its involvement in the Crossrail project, having also provided scaffolding systems for the construction of the works on the Farringdon Station project and a system for the construction of the escalator shafts.
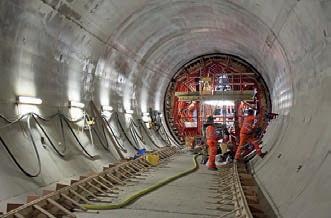
www.peri.ltd.uk
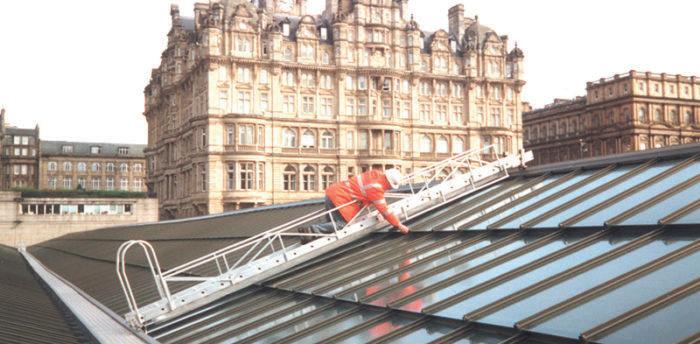
Secures the fleet of boards in one install Designed to store interlocked for longevity
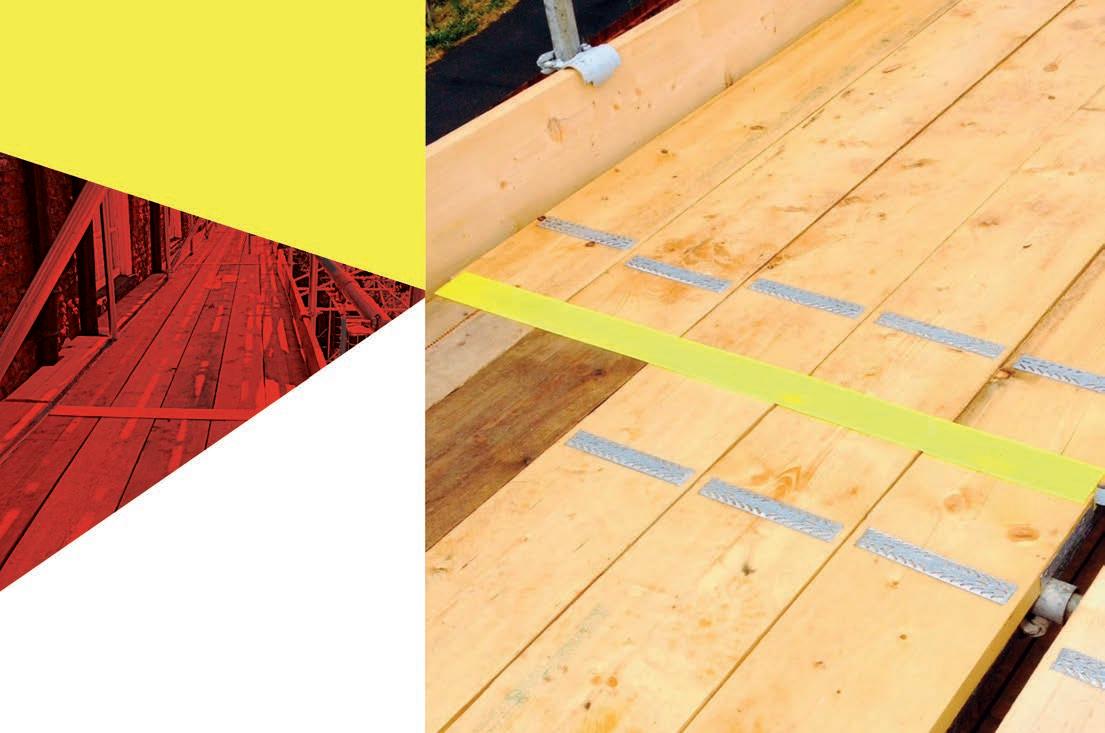
Dramatically reduces the board’s natural tendency to warp
Secures the platform against foot traffic movement and wind uplift
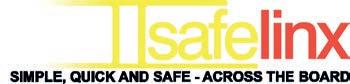
www.ms-uk.co.uk
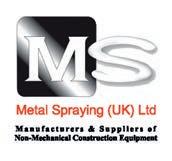
Tel: 0121 568 7831
Installs in seconds
Reusable and durable
The only board retention method suitable for double layers of boarding
Available in a selection of platform widths or custom lengths (subject to minimum order)
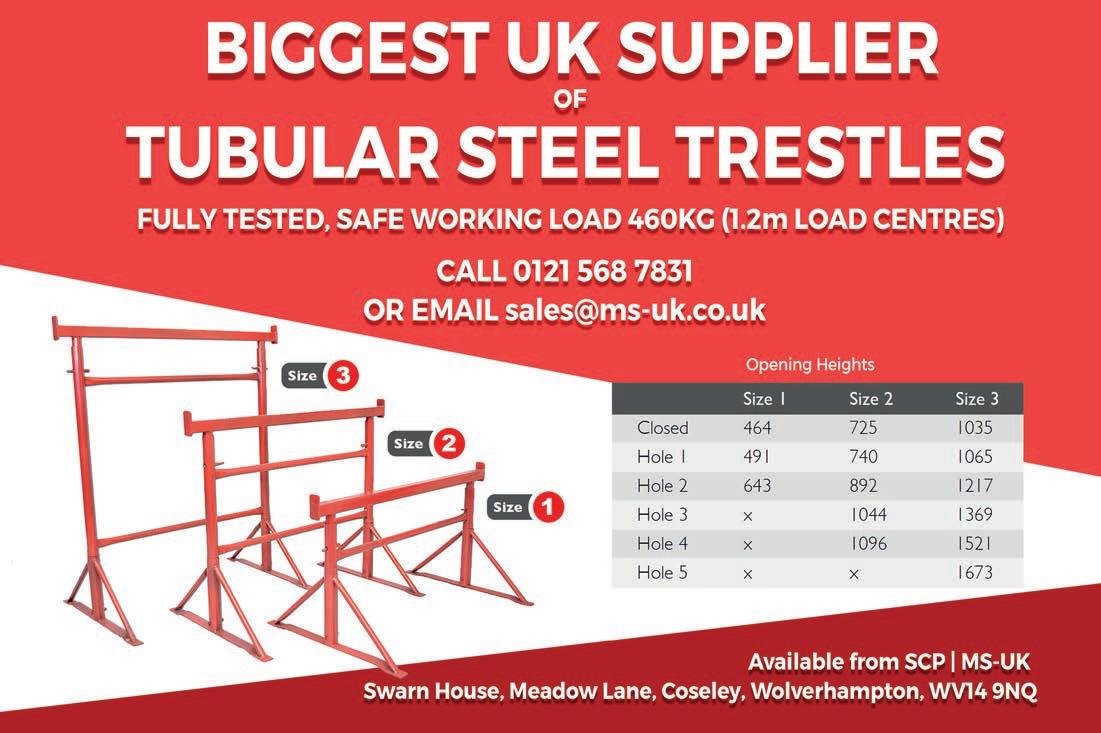
Final account applications and the importance of the payer notice
Professor Rudi Klein Barrister considers the legalities of final account applications.
The setting for the case of Kilker Projects Ltd (Kilker) v Rob Purton t/a Richmond Interiors (Purton) was the palatial splendour of the Dorchester Hotel in Park Lane, London. Purton had entered into an oral, or word of mouth, contract with Kilker for specialist joinery works at the hotel. It should be noted that this was an oral contract for works (including variations) that were ultimately valued at almost £800,000. The dispute between the parties was about the sums due in respect of the final account.
The facts
Purton had submitted its final account application to Kilker. Kilker had not responded with either a valid payment notice or pay less notice, as is required by the Housing Grants, Construction and Regeneration Act 1996 (the Construction Act). Following Kilker’s failure to pay the amount applied for, Purton referred the matter to adjudication. In the absence of valid payment notices and/or pay less notices, the adjudicator decided –in accordance with the amended Construction Act – that the amount applied for had to be paid by Kilker. Kilker duly paid £147,223.00 plus the adjudicator’s fees and expenses.
But Kilker did not leave things there. It felt that it had overpaid Purton. It then launched its own adjudication with the aim of establishing the true value of the final account and securing repayment of any overpaid sums. The adjudicator granted a declaration that the true value of the final account was £745,709 and that Purton would have to repay £55,676 plus VAT. Purton didn’t pay
and Kilker issued proceedings to enforce the decision.
The arguments in court
Kilker’s position was that the statutory payment notice procedure was primarily concerned with improving cashflow. But it was not aimed at deciding contractual entitlement to payment on a conclusive basis. It could go to adjudication at the end of the job to obtain a decision on the other party’s proper entitlement under the contract.
Purton’s defence was that Kilker’s failure to issue a payment notice and/or a pay less notice meant that Kilker had, in effect, agreed the valuation for that payment cycle and must therefore pay the application in full. Such agreed valuation could not be re-opened in a subsequent adjudication, although it could be challenged by Kilker in any subsequent litigation or arbitration.
Purton was relying upon passages in a judgement of one of the earlier cases on payment notices, ISG Construction Ltd v Seevic College in 2014. In that case, the judge held that in the absence of any payment notices, the amount in the contractor’s application is deemed to be the value of the works included within the application and the sum applied for must be paid, and that if the payer fails to serve any notices in time it must be assumed that it has agreed the amount applied for, right or wrong.
Therefore, the first adjudicator must have decided the value of the work included in the application.
In a later case (Galliford Try
Building v Estura Ltd), the same judge decided to clarify his position. A paying party can challenge the value of work by, if necessary, revising it downwards following the next application. In the 2015 case of Matthew Harding t/a MJ Harding Contractors v Paice, the Court of Appeal decided that a payer could determine in adjudication the valuation of the final account following termination of the contract (despite the fact that there was an earlier adjudication in which the adjudicator ordered payment of the contractor’s application because of failure by the payer to serve a valid pay less notice).
The judge’s decision
The judge confirmed that the statutory payment provisions do not affect the ultimate value of the contract sum that the parties have agreed as the price for the work and/or services to be provided. The judge stated: “They are concerned only with cashflow and not the contract sum.” The first adjudication determined that the application had to be paid in the
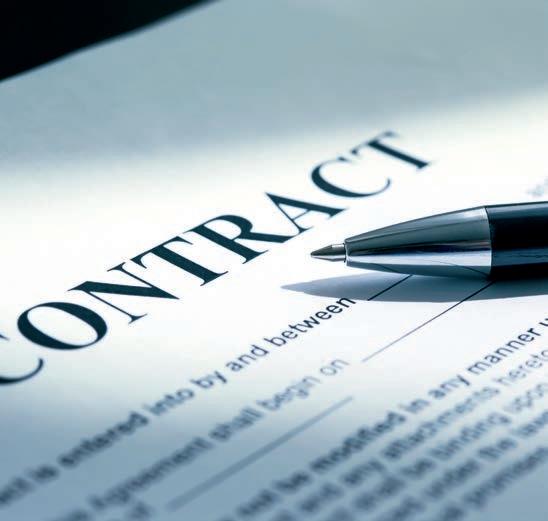
absence of any payment notice. Kilker had to pay the full amount in the application. But that adjudication was not about determining the proper value of the final account. In this case, therefore, the adjudicator had jurisdiction or the power to determine the dispute and his decision should be enforced.
Conclusion
This case reinforces the message emerging from other payment cases that failure by a payer to issue valid payment and/or pay less notices means that the amount applied for must be paid (providing the application is issued in accordance with the contract and sets out the sum due and the basis on which it is calculated). If the payer believes that an overpayment has been made this can be rectified in subsequent payment cycles. As far as final account applications are concerned then, the payer has the right (subject to anything in the contract to the contrary) to refer any disputes for the valuation of the final account to adjudication.
Plans to overhaul payment practices in Scotland unveiled
Representatives from over half of the councils in Scotland attended a seminar in Stirling to hear how they can overhaul payment practices in construction procurement. There is a statutory obligation on all public bodies in Scotland with large construction spends to ensure that supply chain firms are paid within 30 days.
On behalf of Scottish Government, Colin Judge encouraged the local authority representatives to consider setting up project bank accounts (PBAs). These enable all those delivering construction works to receive their payments directly from one bank account. Payments do not, then, have to pass through the different layers of the supply chain (with the result that many SMEs are waiting over 60 days to get paid). PBAs enable small firms to receive payments regularly with protection from any insolvencies at the top of the supply chain.
Hilary Cameron from Transport Scotland, which piloted one of the first PBAs in Scotland, highlighted that the trial use of a PBA had demonstrated that it was feasible for payment to PBA beneficiaries to take place well within the 30 day statutory payment.
Professor Rudi Klein, from the Specialist Engineering Contractors’ (SEC) Group, said that PBAs were the most effective method for ensuring that all in the supply chain were paid. He added that every SME in Scotland would support those public bodies setting up PBAs.
Calls for fundamental change at the CITB
The government’s decision to support the continuation of CITB is the right decision for the construction industry, but only if it is subject to fundamental reform, according to the Federation of Master Builders (FMB).
In response to a letter from Apprenticeships and Skills Minister Anne Milton MP to CITB, the government confirmed that the CITB review will not be published until after the consensus process has come to an end and indicated that the CITB will not be abolished.
The FMB is calling for greater involvement of SMEs in the governance of the CITB which it says is dominated by main contractors who do not train as many people as SMEs. It also wants the concept of the levy changed.
Brian Berry, FMB chief executive, said: “Most people agree that the CITB had lost its way but scrapping it altogether would only make the construction skills crisis worse. What we now want to see is for the CITB leadership to embrace a culture of change until we’ve reformed the organisation from head to toe.
“We are particularly keen to see some recommendations regarding the need for a governance review as the current structure is not fit-for-purpose. When you look at the make-up of our industry, 99 per cent of firms are SMEs but we don’t see that reflected on either the Board or the Council.”
Specialists in Construction Insurance
especially scaffolders, demolition contractors, formwork & concrete suppliers
Amicus is a specialist broker to the Construction and Scaffolding Industries. We have been working with the Scaffolding Association since 2015 and are proud to insure many of the UK’s leading Scaffold companies.
We really understand scaffolding insurance and we love it. We even employ some former scaffolders within our business so you can be 100% confident that we really do talk your language!
All that expertise, enthusiasm and industry knowledge means that you can trust Amicus to not only find the best insurance to protect you, your business and your employees, but that you can also rely upon us to do it at the most competitive price.
Why not give us a try!
• Specialist knowledge with an informal approach
• Quick answers, either yes or no
• Providing policies relevant to your business and within your budget
• No hidden terms and conditions that are not relevant to your business
• First rate claims support (we have our own specialist team)
• No tick box approaches
• No call centres
• Not forgetting about you until renewal time
To discuss your insurance requirements, or to find out how we can help you, contact Richard Evans or Adam Scott on 0208 669 0991 or email us at richard.evans@amicus-insurance.com or adam.scott@amicus-insurance.com
Are your vehicles safe and compliant?
Contractors who consider themselves specialists within the scaffolding industry may have some surprises in store if they find themselves being questioned by either the Driver and Vehicle Standards Agency (DVSA) or the police over matters relating to their vehicles and operator’s licence. Transport consultant Andy Miles considers some of the issues scaffolders may face.
Even though most scaffolding companies hold restricted operator’s licences, this does not restrict the impact of legislation relating to the safe and compliant operation of their vehicles.
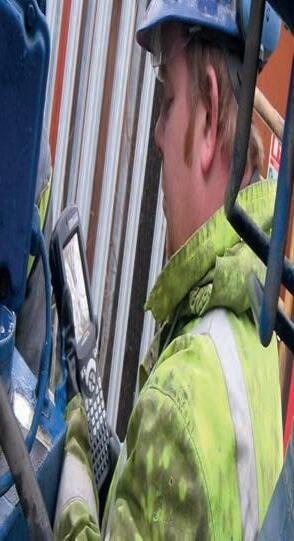
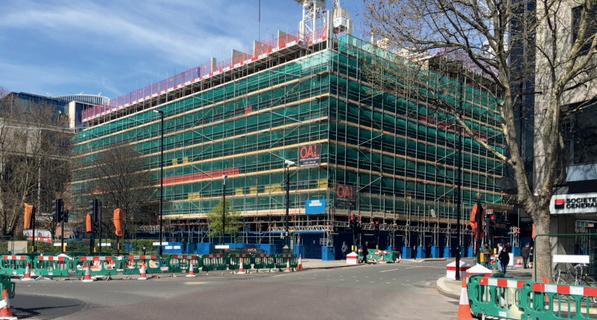
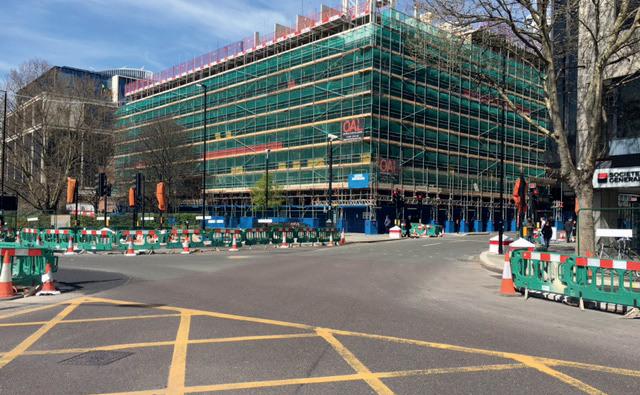
The Occupational Road Safety Alliance’s last available figure for 2015 shows that 541 deaths occurred due to ‘driving for work’ collisions. This figure is over four times the number of people killed in accidents at work in the same period.
Transport Commissioners across the UK carry out around 1,000 Public Inquiries (PI) per year, which is less than 1 per cent of the total number of operator’s licences held by businesses. Out of the 1,000 PIs, the scaffolding industry appears all too often – and for all the wrong reasons.
In a recent survey of the last five weeks of Traffic Commissioner published data for PIs across the UK, 22 scaffolding companies were called to PI. Of those that have been seen in the same period, 11 have had regulatory action taken against them, including five that have had their licence revoked in full and a director disqualified for eight years; one that was refused an application due to previous poor standards; three that have had their licence curtailed (vehicles taken off them); and two that received formal warnings about future conduct.
What is sad about this is that ALL of it was totally avoidable, especially if owners and directors were as serious about their fleet and
drivers as they are about Health & Safety and the industry standards around the scaffolding they erect.
Here are some simple actions to take:
• Make sure that drivers’ daily checks of vehicles are carried out and recorded.
• Check that drivers have the correct licence to drive and whether they have any points or a ban. The answer “Well, they drive to work every day” isn’t good enough and isn’t legal proof.
• Consider whether your vehicles get maintained according to the terms of your operator’s licence or whether they are maintained when it ‘feels like it needs a service’.
• Check your operator’s licence details on the Vehicle Operator Licensing (VOL) system.
• Check what your Operator Compliance Risk Score (OCRS) is.
• Check your drivers’ driving hours and whether there were any infringements.
• Review your company policy on the use of mobile devices in the company vehicles.
• Consider whether you then ring the drivers to give them instructions whilst they are driving.
• Be aware of whether home life is affecting your employees’ ability to perform their job.
Non-compliance
A company operating one vehicle in the West Midlands was stopped by the DVSA in early 2016. The driver was subsequently charged relating to 10 specimen driving hours offences and fined £160 for each offence by the courts. The company was also fined £1,600 for each of the offences. The driver then faced a Driver Conduct hearing in front of the Traffic Commissioner and the company faced a PI where a number of conditions were imposed on the company and the driver lost his vocational driving entitlement for 28 days.
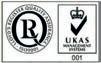

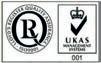

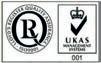

You could find yourself in this position if you are not keeping on top of your operator’s licence. If as a result of your vehicles’ and drivers’ actions there is a collision, especially where there is either a death or life-changing injuries are caused, you can expect a very in-depth and searching investigation into your company’s activities, including its policies and your adherence to them.
Employees, including drivers, look for leadership from managers, directors and owners. If the people in these positions do not give that leadership, they cannot complain if those employees do as they please. As we have covered in this article, so much can be rectified with simple systems that are used daily, weekly or monthly and keep you, your employees and the public at large, safe.
GET IN TOUCH
Andy Miles FCILT, MInstCPD
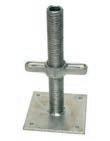
Midlands: 01455 389053 or London: 0208 183 4320 helpme@asmilesconsulting.com


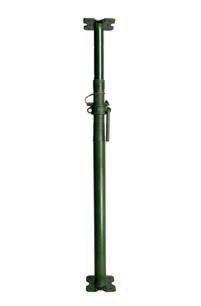



Construction-related deaths fall

The Health and Safety Executive (HSE) annual figures for work-related fatalities show that construction-related deaths have fallen to 30.
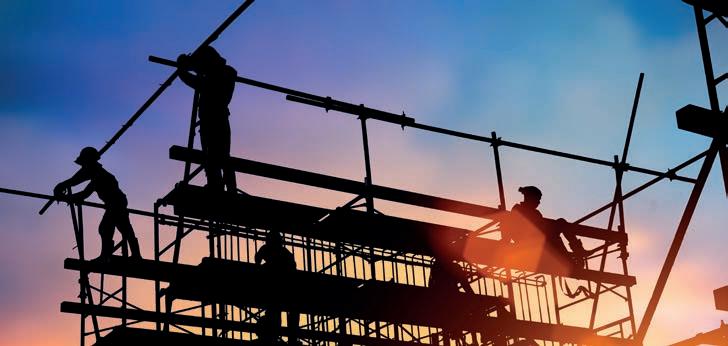
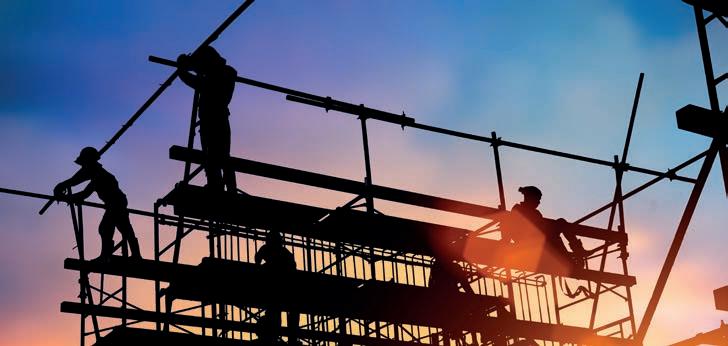
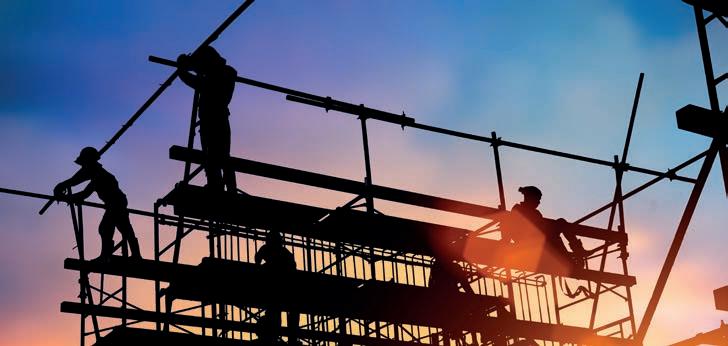
The provisional annual data for work-related fatal accidents revealed that 137 workers were fatally injured between April 2016 and March 2017 (a rate of 0.43 per 100,000 workers), the second lowest year on record.
The new figures show 30 fatal injuries to construction workers were recorded. While this accounts for the largest share, this is the lowest number on record for the sector. However, over the last five years the number has fluctuated. The annual
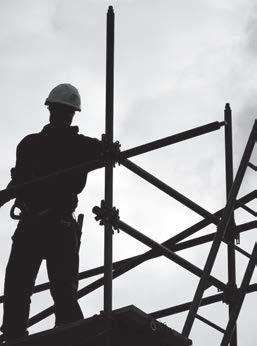
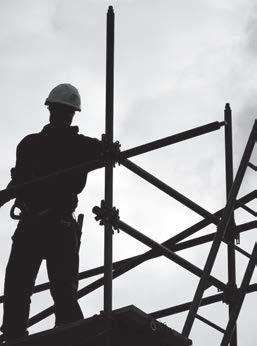
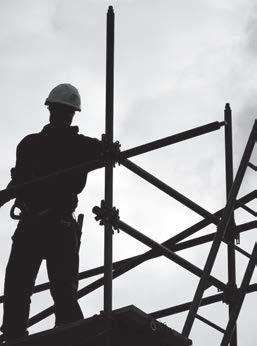
average for the past five years is 39, with the annual average rate over the last five years in construction being around four times as high as the all-industry rate.
There has been a long-term downward trend in the number of fatal injuries to workers – they have halved over the last 20 years – although in recent years the trend shows signs of levelling.


HSE chair Martin Temple said: “Every fatality is a tragic event that should not happen. While we are encouraged by this improvement on the previous year, we continue unwaveringly on our mission to prevent injury, death and ill health by protecting people and reducing risks.”

Scaffolding above and around live railways
Increased infrastructure spending is creating new opportunities and challenges for the access and scaffolding sector. Ivik Masek, from design consultants 48.3, offers guidance about scaffolding design close to railways.
When designing a scaffold structure in the vicinity of railway tracks, aerodynamic actions (buffeting loads) from passing trains are a critical consideration. This guidance compares the methods used in BS EN 1991-21 and GC/GN56122 to determine the pressures on a scaffold bridge over railway tracks.
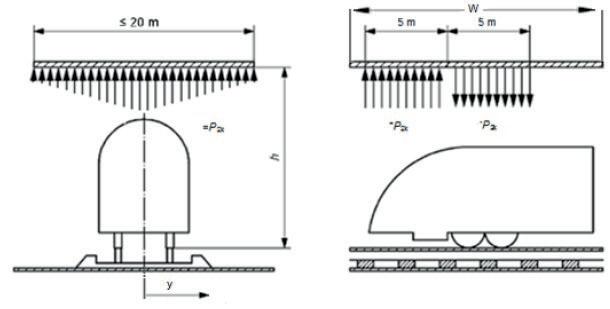
Aerodynamic actions from passing trains
A train traveling at a speed of 120 km/h generates an aerodynamic pressure field which it imposes on scaffold structures alongside and over the track. The graph shown in Figure 1 is limited to line speeds between 120 km/h and 300 km/h. It is important to note that line speeds below 120 km/h also generate pressures on scaffolds and the vertical distance hg is often < 4.5 m. The imposed loads defined in BS EN 1991-2 are intended to be used for the design of new bridges and not temporary bridges that encroach the minimum required headroom of 4.5m. The designer therefore must extrapolate the graph to determine the pressure loads ±q2k
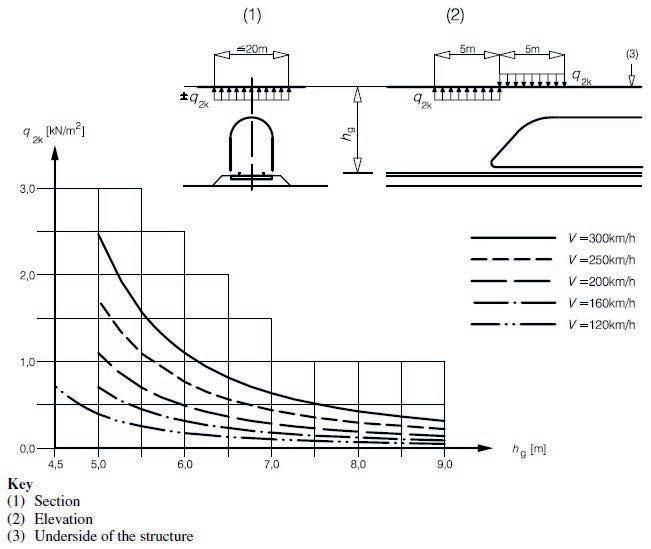
Difference in values between methods
Method A – BS EN 1991-2 clause 6.6.3
a dynamic amplification factor. The value of ±q2k should be multiplied by 2.0 in the 5.0 m zones.
For trains passing each other in opposite directions, the actions should be added, i.e. the total of both calculated values of ±q2k for each train.
The values in Figure 1 apply to trains with an unfavourable aerodynamic shape where k1 = 1.0. The Eurocode states the following reduction factors may be used: k1 = 0.85 for trains with smooth-sided rolling stock and k1 = 0.6 for streamlined rolling stock.
The k values are derived from test results for each structure type and typical examples are given in Figure 2.
k1 = 1.0 Class 66 locomotive
k1 = 0.85 Class 158 leading vehicle
k1 = 0.6 Class 390 leading vehicle
Figure 2: Typical examples of train types and related k values.
Method B – GC/GN5612 clause G 3.5
The values of ±q2k are determined using a graph shown in Figure 1. Note that the loaded width for the structure considered extends up to 10.0 m to either side of the track.
The elevation (2) in Figure 1 shows the pressure field caused by a moving train which it imposes on structures above the tracks for a length of 5.0 m. It is applicable at the start and end of a structure and defined as
Key differences: The actions ±q2k in the Rail Safety and Standards Board (RSSB) guidance are determined using an equation. The equation contains three variables, h, W and y, which allow the designer to identify pressure loads below the 4.5 m vertical distance and on structures < 10.0 m wide. The pressures over the track can also be reduced by the lateral distance y either side of the track.
The shape parameter of the train k2 used in this method are 1.0 for bluff trains (unfavourable aerodynamic shape) and 0.432 for intermediate (smooth-sided rolling stock and streamlined trains).
Design example
We consider the aerodynamic actions on a temporary 1.85 m wide pedestrian footbridge over two tracks with a line speed of 75 mph (120 km/h). Both trains are Class 158 and the vertical distance hg from the running surface of the track to the underside
References
1) British Standards Institution (2010) BS EN 1991-2:2003 – Eurocode 1: Actions on structures – Part 2: Traffic loads on bridges, London, UK, BSI.
2) Rail Safety and Standards Board Limited (2014) GC/GN5612 – Guidance on Loading Requirements for the Design of Railway, London, RSSB.
Worked example using Method A
The value of the action ±q2k is given in Figure 1 where:
V = 120 km/h. The Maximum Design Speed and should be taken as the maximum line speed at the site.
hg = 4.5 m. Dynamic amplification factor = 2.0.
Reduction factor k1 = 0.85 for trains with smooth-sided rolling stock. For trains passing each other in opposite directions (±q2ak) + (±q2bk).
±q2k from Figure 1 = ±0.7308 kN/m2
Therefore, the vertical design load for aerodynamic actions (±q2ak) = 0.73 kN/m2 x 2.0 x 0.85 = ±1.24 kN/m2
Total design load (actions added) = ±2.48 kN/m2 .
The worked examples shown in Box A and Box B illustrate the difference in magnitude of the design loads. Although Method B offers many design advantages associated with reduced live loads, the designer should consider the risks associated with this method. The aim is to design economical scaffold structures with sufficient safety against collapse.
The reader is advised to refer to the full Standard/Guidance for further information.
FIND OUT MORE
Ivik Masek Principal engineer and director
48.3 Scaffold Design Ltd
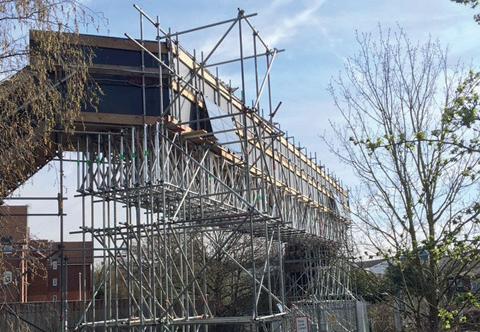
www.483scaffolddesign.com
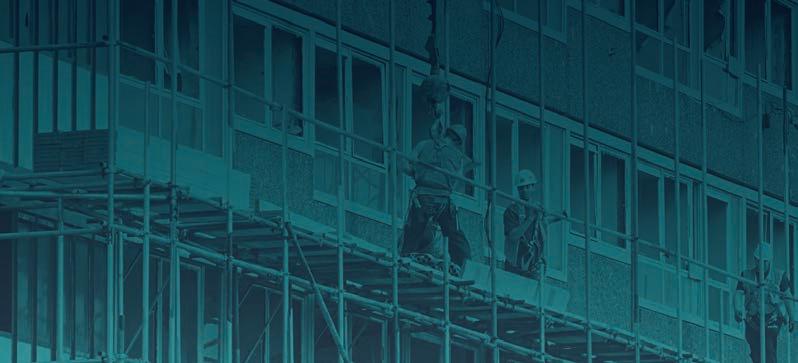
Worked example using Method B
The pressure loads are determined from equation p2k=0.5ρv2k-
2Cp2(h,W,y) where:
Cp2 = characteristic pressure coefficient
Cp2(h,10,0) = ±((5.5/(h−1.9)2)+0.1)
h = 4.5 m. Distance from top of rail to structure over the railway.

W = 1.85 m. Along track width.
Y = 0.0 m. Lateral distance from the track centreline.
k2 = 0.432. Shape parameter of the train.
ρ = 1.225 kg/m3. Density of air.
v = 33.33 m/s. Train speed of 120 km/h.
Therefore, Cp2(h,10,0) = ±((5.5/(4.5−1.9)2)+0.1) = ±0.91 kN/m2
Using the calculated value for Cp2(h,10,0), the variation with structure width, W, for bluff, intermediate, and streamlined trains is respectively given by:
Cp2,bluff(h,W,0) = (0.025W+0.75)Cp2(h,10,0) = (0.025 x 1.85 + 0.75) x 0.91 kN/m2 = 0.72 kN/m2
Cp2,int_str(h,W,0) = 0.51Cp2,bluff(h,W,0)), for 1.5 m ≤ W ≤ 3.0 m = 0.51 x 0.72 kN/m
Apply dynamic amplification factor 2.0 and combine actions for trains passing.
Total design load = ±0.44 kN/m2 .
An assurance of quality and performance
Regulating quality and high safety standards Independent audit regulates members Audit exceeds PAS 91
Matching members with new clients
Storm Doris sets challenge for Godiva
It’s not uncommon for specialist contractors to be called in at a moment’s notice to provide emergency support. When Storm Doris battered the UK in February, uprooting trees and damaging buildings, railways and roads, the huge University College Hospital Coventry in Walsgrave, on the north side of the city, was caught in the wake of winds gusting over 80mph. Coventry-based Godiva Group responded and Adrian JG Marsh reports on their work.
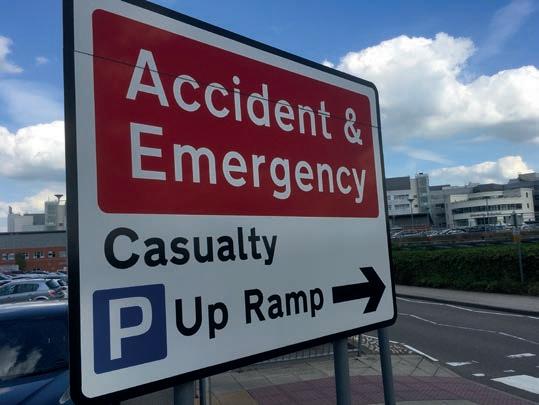
Innisfree, Skanska, VINCI, GE and ISS Mediclean. The hospital is equipped with 1,250 beds, 27 operating theatres and employs more than 6,000 staff.
Karl DeGroot, general manager at Godiva, said: “This was a very fast-moving project and we decided that adopting a system-led solution was the best approach. Because of the connections and the way the node systems work, we knew that we’d be able to have a system designed and erected much faster than if we used tube and fitting.
and knew that the AT-PAC Ringlock System would provide sufficient strength to complete the job with the minimum components. We used our in-house technical draughtsman to draw the required scaffold and then forwarded this to Godiva for approval. Our engineering team and Godiva then worked as a team to complete the design in the time available, allowing equipment to be delivered on the day the job had to start.”
Godiva and AT-PAC had to take account of some operating challenges that meant no ties were permitted into the building fabric due to it being rendered and patching difficulties, as well as a lack of through-tie opportunities.
“After the hurricane damaged some facade panels at the hospital, we were approached by VINCI who asked us to erect scaffolding urgently so that the hospital’s facilities team could inspect and repair the
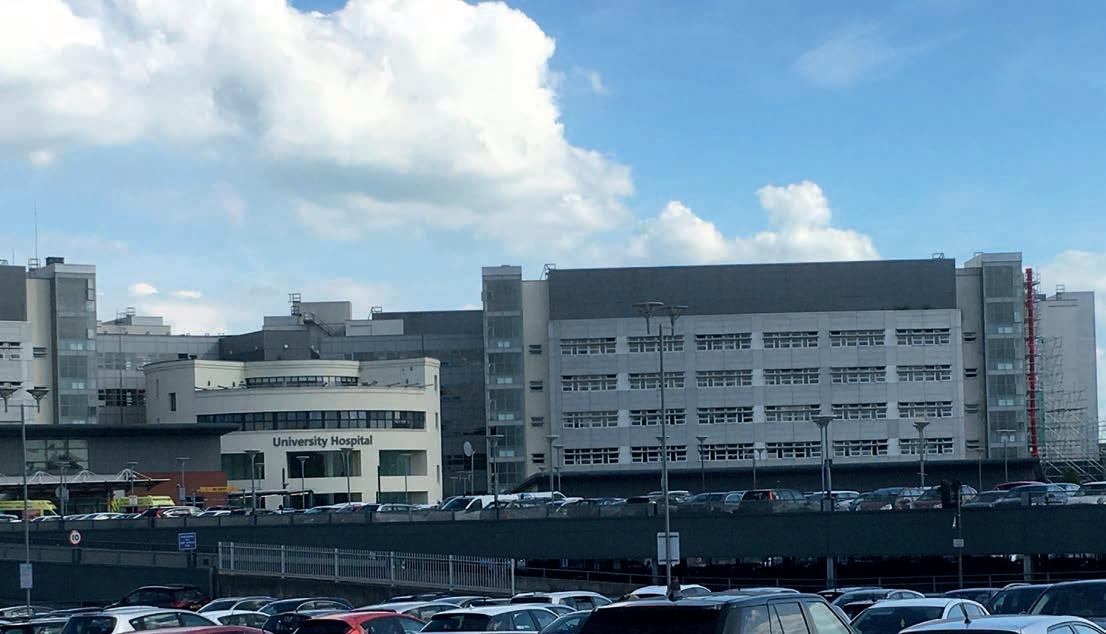
University College Hospital
“The design benefits and speed in getting it up meant system was the best choice. So, we teamed up with AT-PAC to devise a system design. I sketched up how it could work and then it was drawn and calc’d by the engineers at AT-PAC.”
John Brocklehurst from AT-PAC said: “We acknowledged that this was a fast turnaround contract
The design was submitted within 12 hours and Godiva commenced construction following approval the next day. The structure was erected by a team of four specialists within seven working days, reaching to a height of 28 metres with a fully buttressed supporting scaffold.
Mr DeGroot continued: “The system is a ring scaff and we briefed all our fitters who were system qualified in advance at a series of tool box talks. There is less manual handling, fewer components and less tonnage.”
The free-standing structure incorporated two public protection gantries, a full-height system staircase for operative access, both during erection and for the client, and a fully decked facade access scaffolding. A full-height rubbish chute was then added as a designed item a few days later for material removal from high level.

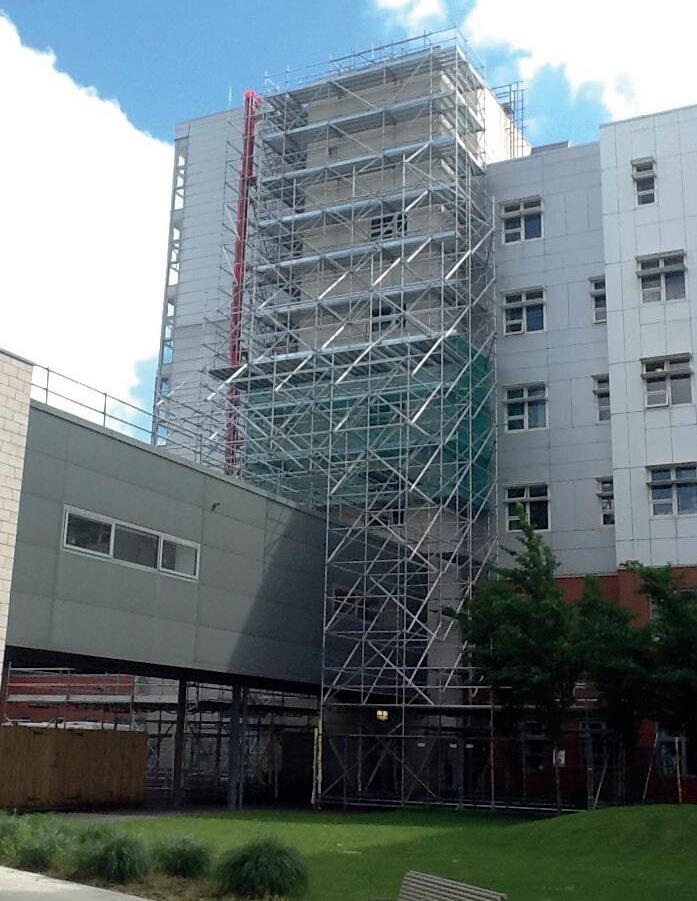
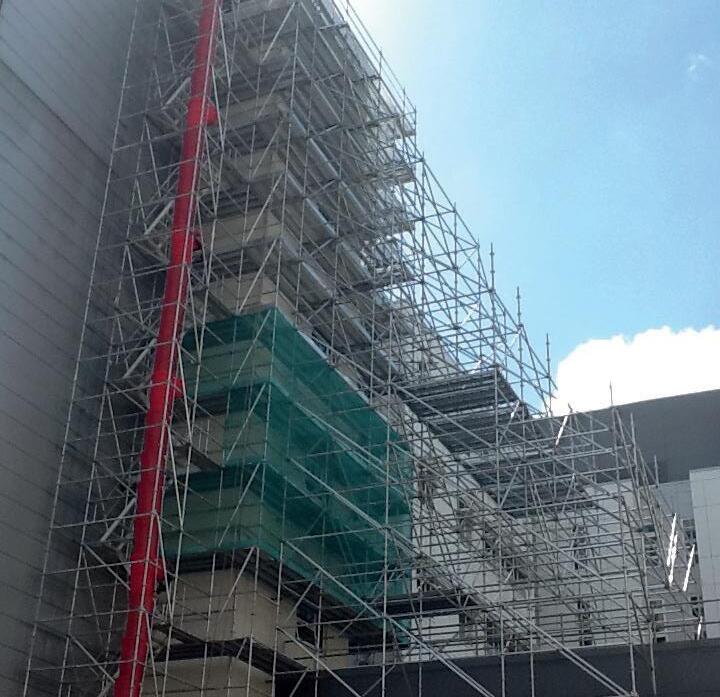
Mr Taylor summed up Godiva’s experience, commenting: “This was our first experience utilising the
AT-PAC system and from the initial design through to project completion, we’ve been impressed with both the response and overall level of service provided.
“The system provided an increased level of safety and reduced manual handling while increasing output levels, which all resulted in a delighted client and a quality finish. It was a great effort all round – a real platform for success for all concerned.”
Maintaining performance and quality
By using a Scaffolding Association Audited Member, employers can be confident that they are prequalifying and awarding work to contractors who have undertaken a rigorous independent assessment of their experience and capabilities and bring greater choice to employers.
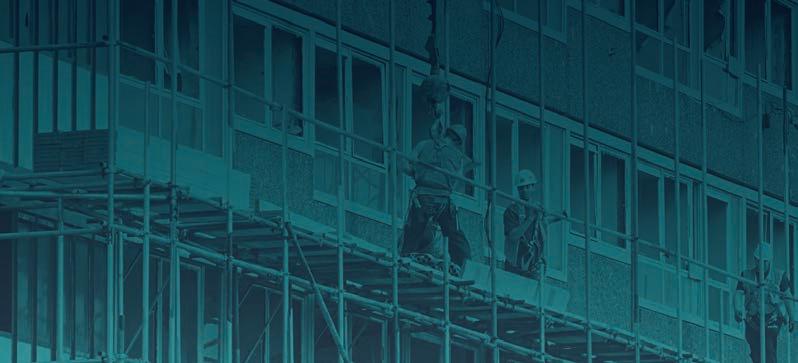
Lifting operations: rope inspection and maintenance
Safe and successful lifting operations largely depend on the continued safety of the lifting equipment and accessories used, with failures from this sort of equipment often resulting in significant or fatal injuries. Health and safety legislation places specific obligations on those providing, controlling and using lifting equipment to properly manage these risks. In addition to the requirements for safe design and construction, all lifting equipment should be checked and maintained as necessary to keep it safe for use. Stacey Underhill, from the Scaffolding Association, highlights some key checks and points for ropes.
Ropes are often a key component in a scaffolding contractor’s lifting operations, and there is a wide range of British Standards in place that specify their physical properties and specific inspection and retirement criteria. Here, we look at what a suitable and thorough examination and inspection process could look like:
Marking and identification
Ropes should be individually identifiable in such a way that their history from manufacture can be clearly followed. It should also be possible to trace and identify on which site each item of equipment is being used, to prevent the use of any equipment that hasn’t been thoroughly examined. Best practice would be to allocate a unique identification number which is marked on the ropes. Alternatively, the use of different colour spots could be implemented to indicate when they were last examined.
Storage
When not in use, ropes should be stored correctly to avoid them undergoing any significant deterioration through excessive bending, gnawing from rodents, or exposure to damp or extreme temperature changes. Textile materials should be stored in the dark within a bag or container. To avoid incorrect items being used, it is important to store those of significantly different ages, performance abilities or sizes separately in clearly labelled positions.
Inspection before dispatch
Even with careful storage, ropes can suffer deterioration. Therefore, ropes should always be thoroughly inspected by someone who is competent to recognise significant faults and ensure that the rope has adequate strength and is in good condition before it is dispatched to site. Ropes should be manufactured to a known standard, of the required length and size, free from damage and contamination, and compatible with the other components in use for the lifting operations.
Pre-use checks
Ropes are often used as a temporary and lightweight component of lifting equipment, therefore the loads to be applied must be carefully assessed to ensure that the support points are capable of supporting them. This assessment should be undertaken by the scaffold designer, or another person competent to assess the impact of the load and strength of the scaffold in line with industry best practice guidance.
Before use, all lifting equipment should be examined and tested by a competent person who will then issue a Handover Certificate confirming the performance capabilities of the equipment in use. This certificate should be signed by both the person checking the structure and equipment and the client to ensure they know the limitations of use.
Weekly inspections
Ropes should be inspected at the same time as the weekly scaffold inspection. This visual inspection should consider:

• Are they of a suitable length?
• Are they properly seated in the pulley?
• Are they free from cuts and abrasions?
• Are there any areas of significant discolouration or localised melting? Defects, including any suspected defects, should be reported immediately and the rope’s use prohibited.
Annual inspections
Ropes used for lifting operations must be thoroughly examined every 12 months. However, it is good practice to inspect them for signs of damage or misuse each time they come back from site. Where ropes remain on-site for periods exceeding 12 months, arrangements should be put in place for them to have a thorough inspection before the 12-month period ends. This inspection should be carried out by a competent person who has experience of the performance limitations and understands the function of the rope so that they will be able to properly judge the significance of wear or damage.
Record keeping
Records must be maintained for the rope’s lifespan and linked to the original manufacturer’s certification and warranty. Comprehensive records and certificates issued concerning the performance capabilities of a rope should be kept and signed and dated by the person making the inspection. Records of weekly inspections should be kept as part of the general scaffold inspection.
A range of substances can quickly and adversely affect textiles, and it is important that the usage history of ropes is kept to help identify the reasons for any discolouration or deterioration. The information gathered from inspections should be monitored periodically to note the rate of deterioration and to help predict when the ropes should be taken out of use.
Disposal
A rope should be disposed of before its rate of deterioration reaches a point where it will not remain fit for use for the forthcoming 12-month period. Ropes deemed no longer fit for purpose must be cut in pieces or otherwise made incapable of reuse.
Managing Hand Arm Vibration Syndrome in construction
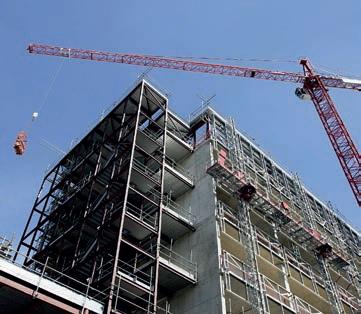
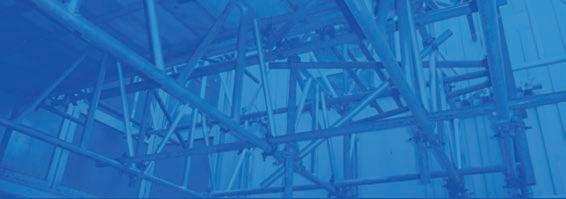
drawn up the ISO 5349-1:2001 standard (Mechanical vibration. Measurement and evaluation of human exposure to hand-transmitted vibration. General requirements) to help calculate the risk posed by machinery to workers.
Defined safe limits
The HSE has given construction tools an Exposure Action Value (EAV). The EAV indicates how long a machine may be used before vibration exposure reaches harmful levels, and action needs to be taken. The HSE also provides an exposure points system and ready-reckoner for calculating daily vibration exposure limits where only the vibration frequency is known. Take a look at www.hse.gov. uk/vibration/hav/readyreckoner.htm

HAVS – which also goes by the name of dead finger, vibration white finger and VWF – is caused by extended use of vibrating machinery, such as impact wrenches. Over time, the vibration causes damage to blood vessels, nerves, muscles and joints, which is typically felt in the hand, fingers and wrist.
The effects of HAVS are relatively mild in the early stages: at the end of the day, workers may notice a slight tingling in their fingertips, and possibly some whiteness. Left unchecked and these symptoms can become more severe: the whole finger can become white and the sense of touch dulled.
As the condition progresses, the symptoms become more like Reynaud’s syndrome. Sufferers will find that damage to the blood vessels in their hands causes their fingers to change colour, particularly when cold. Because blood flow is restricted, the fingers turn white, but when blood flow is restored, the fingers turn an intense red. This is accompanied by uncomfortable throbbing.
At its worst, HAVS can affect the nerves and muscles of the hands and arms, with affected workers experiencing a temporary loss of manual dexterity accompanied by excruciating pain. These attacks can last several hours, during which
time those affected will be unable to work or even carry out many basic tasks at home.
In extreme cases, there is a risk that damaged blood vessels and reduced blood flow could lead to the loss of fingers.
Prevention is essential
Hand Arm Vibration Syndrome is a progressive disease. When left unchecked, the symptoms can become debilitating for the affected person to the point that they can’t work at all. As an employer, it is your legal duty to reduce the risk of your employees developing conditions such as HAVS at work.
To date, the UK government has paid over £100 million to former coalminers who have developed HAVS as a direct result of their work activities. One case saw seven miners awarded £127,000 each in compensation – and private employers face similar fines where their negligence causes workers to develop this condition.
HAVS is completely preventable, but once the damage is done, it is permanent.
Practical safeguards
HAVS injuries are caused by vibrations at frequencies within the range of 50 to 300Hz. The International Standards Organisation has
When drawing up a site risk assessment plan, these figures can help you allocate work and ensure employees are not exposed beyond the acceptable limits. You can also plan how best to share workloads and provide workers with regular breaks – all of this further reduces risks.
Low hand or body temperature increases the risk of finger blanching because of the reduced blood circulation. You should therefore make sure employees working outdoors in cold weather have adequate protection. You should also ensure that gloves or other clothing you provide do not stop employees working safely and do not present a risk of entanglement with moving parts of machinery.
HAVS is a life-changing industrial disease –but one that is completely preventable.
Just as extended exposure to dust can cause all manner of respiratory illnesses, use of heavy industrial machinery and even hand-held power tools has its own risks. By far the most common of these is Hand Arm Vibration Syndrome (HAVS), as Jenny Gibson reports.
Confidence in quality at the centre of responsible sourcing
The term ‘responsible sourcing’ has rapidly become a widely discussed issue within the construction industry, and even when it comes to sourcing tube, fittings and system in the scaffolding sector. Having confidence in the supply chain is a critical component to ensure performance and quality, as Adrian JG Marsh reports.
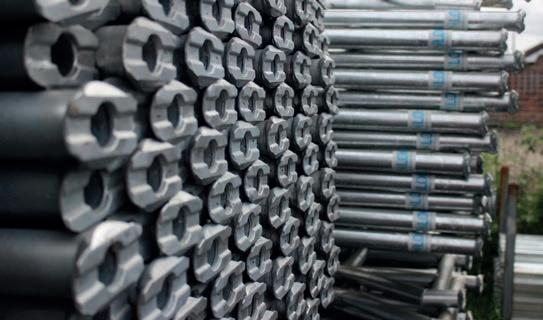

Specialist contractors are increasingly more aware of sourcing and origins of their building products, and while market pressures call for competitive pricing, clients are specifying rigid quality standards within their procurement policies.
Access and scaffolding products demand the highest integrity. Having trust in component quality gives contractors the confidence to use those components that they know are fully tested and manufactured to a safe standard.
Mark Burgess at Springfield Properties said: “With millions of individual components in use across the sector, it is critical that steps have been taken to ensure that tube, fittings or system are fit for purpose.
“Companies spend many thousands of pounds on auditing and testing to demonstrate that what they are manufacturing and erecting meets the standards required. A substandard component, or a poorly fitted one, can lead to catastrophic results.”
Demonstrating that suppliers’ products have been manufactured to the correct standard demands rigid quality control procedures and constant checking and verification.
Jeff Wood, the quality manager at VR Access Solutions, is responsible for monitoring production standards for the company’s Turnlok brand. He said: “Every month, we take delivery of thousands of system components from our production plant in China. It’s essential we can prove to our customers that what they are buying meets the appropriate standard.
“We’ve established a rigid quality control procedure that means we
can trace every component from when it was manufactured through to who it was sold to. Critical features are inspected and tested on a random selection of products at our UK and Chinese testing facilities.
“During manufacture, we mould into each product the product code, EN standard number it covers and a batch production code. This gives onsite personnel extra assurance that they are using a real product and not a fake.
“We also commission independent test engineers to analyse a selection of products. Each test lists every aspect that is tested and the results are available to our customers if they want to review them.”
Mr Wood went on to explain how products are tested to beyond a safe working load, commenting: “Although the design load for, say, a drop forge double is 9kn, we test it to 15kn, well above the recommended load shown in our user guide.
“If a slip is reported, there’s a fair chance the product has been overloaded. If we do have to investigate, we ask for the product and batch number of each component. The failed product is then inspected and tested independently, which means we can find out if a product was overloaded at installation or during operations.”
Mr Wood feels that traceability and testing are at the centre of what VR Access Solutions does to make sure that its fittings and systems are manufactured to the correct British Standard. As Mr Wood concluded: “We know our product is tested fully and we can demonstrate quality
control throughout the whole production process.”
Actavo is one of the largest suppliers of scaffolding equipment into the sector with 27 branches across the UK. It has been using VR’s Turnlok products for more than two years.
Roger Hastie, chief executive of Actavo’s Structural Division in the UK, said: “Quality of products is an absolute top priority to us. When we look at products we stock, we want to know that they are manufactured to the highest standard. Clearly being able to rely on independent test data gives us confidence and is something we can trust and also our customers can trust. Having the necessary guidance for scaffolders
and technical support also helps us to speak with confidence about any of the products we use.
“We’ve successfully introduced the Turnlok system to our fleet where it has been well received; it’s a quality product and it’s proved extremely popular. We like the ability to trace any product back to its origin should we need to.”
In today’s litigious world, having access to such a high level of traceability and testing enables wholesalers and contractors can provide additional assurance in the quality of the tube, fittings and system they’re using.
Creating a respected voice
members to participate. Special Interest Groups will include Commercial, Training, Technical Standards and Offshore.
Concerns were raised among members around commercial issues and the validity of tendering and procurement processes. Members were urged to carefully review terms and conditions of contracts to ensure that they are not signing up to disadvantageous conditions that could cost them dearly.
The Scaffolding Association introduced its first President at this year’s Scaffolding Association Annual General Meeting as tackling skills and addressing procurement issues featured strongly.
More than 50 members attended the Association’s third AGM, held in central London last month, to hear the Scaffolding Association’s chief executive, Robert Candy, report that membership levels are continuing to grow and that enquiries were being regularly received.
Mr Candy said: “We have a growing membership that is committed to raising standards of safety and technical excellence. Our membership represents a broad cross section of specialist contractors, manufacturers and distributors.”
Russell Maxwell-Smith, founder and owner of Chelmsford-based scaffolding contractor WellMax, was introduced as the Association’s President. Mr Maxwell-Smith said: “The Association has a growing reputation for delivering high quality advice and support, and against the backdrop of membership reaching 255, this is an exciting time to be representing the organisation. I look forward to working with the executive team and members to make a positive difference in improving services for scaffolding businesses in the UK.
“We all share a common vision to raise standards and improve skills across the access and scaffolding sector. We also want to challenge our peers to create an even stronger commitment to training and skills development and leave a true legacy of continuing commitment and worthwhile careers for everyone that we work with.”
Membership now includes more than 100 assessed and audited members and 146 associate members. The Association now has more than 200 contractor members.
During the last 12 months, the Association has actively engaged with other trade bodies, clients and government agencies. Stacey Underhill, the head of public affairs, said: “More industry bodies recognise that our members deliver a significant part of the access and scaffolding supply chain.
“We’ve had regular meetings with groups representing major contractors and private housebuilders. The result is we’re now finding that when client groups learn more about our standards, they then recognise the benefits our members bring to the supply chain and invite them onto prequalification and tender lists.”
Adrian JG Marsh introduced members to the new AccessPoint magazine and encouraged everyone to submit examples of best practice so that specialist contractors can gain recognition for high standards of workmanship. Mr Marsh reported: “The new magazine has been well received but there is more to be done to raise the sector’s profile.”
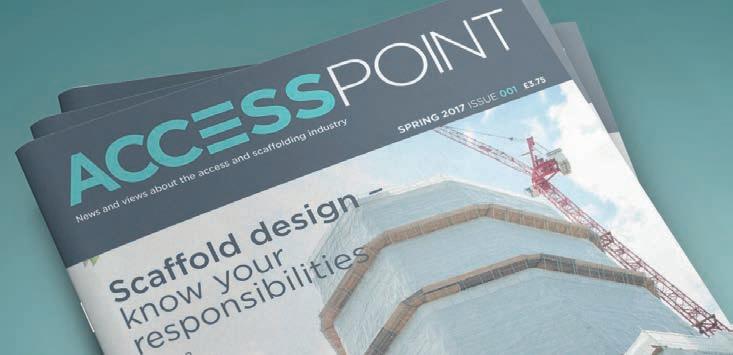
Plans are also in place to expand the committee structure and encourage more
The executive team was also asked to consider the lack of scaffolding detail in the RICS Standard Methods of Measurement given the importance of a uniform basis for measuring scaffolding works in order to facilitate industry-wide consistency and benchmarking, and to encourage the adoption of best practice and help avoid disputes.
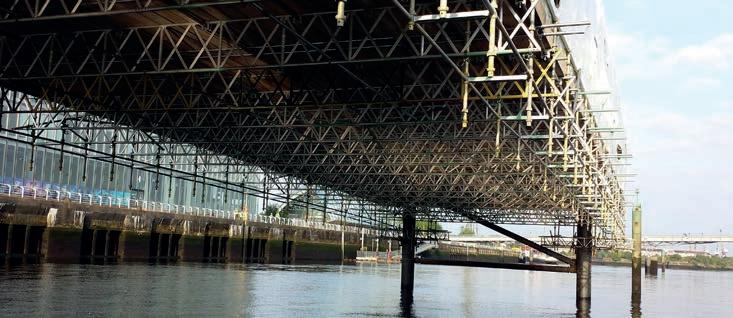
Ms Underhill then went on to outline the implications of the proposed new skills card, which the Association is in discussion with CSCS about. This new initiative is an industry-led response to raising standards and advocates more training on a regular basis while recognising and rewarding those who train regularly.
Mr Candy thanked everyone for attending and said: “We are a new and respected voice in the sector, here to represent the views and opinions of the access and scaffold industry. We need to continue to educate clients because there are misunderstandings and we will challenge policies and proposals that weaken safety and quality. We’re committed to raising levels of performance.” FIND
“We have a growing membership that is committed to raising standards of safety and technical excellence.”
www.accesspoint.org.uk
CALENDAR OF EVENTS
Check www.scaffolding-association.org/
events for updates
Manufacturer Meeting and Executive Committee
Scaffolding Association, Evesham
30 August 2017
Protrack Annual Showcase
Gloucester Rugby Club
6 September 2017
Training Committee
September 2017
UK Construction Week
NEC, Birmingham
10–12 October 2017
London Build
Olympia, London
25 & 26 October 2017
Health & Safety Committee
November 2017
WELCOME TO NEW SCAFFOLDING ASSOCIATION MEMBERS
SCAFFOLD ERECTION
A-Team Scaffolding www.a-teamscaffolding.co.uk
Alliance Intelligent Scaffolding Limited www.alliance-scaffolding.co.uk
Apollo Scaffolding Southern 07956 073423
Aylesbury Scaffolding Limited www.aylesburyscaffolding.co.uk
Contract Scaffolding Midlands Limited www.contractscaffoldingltd.co.uk
Croydon Scaffolding & Cradles Limited www.croydonscaffoldingltd.co.uk
G & D Scaffolding Services Limited 01383 738783
Giraffe Scaffolding Limited 0207 622 2777
WELCOME TO NEW SCAFFOLDING ASSOCIATION MEMBERS
Globe Scaffolding (Cambridge) Limited www.globecambridge.co.uk
Griffin Scaffolding (London) Limited www.griffinscaffolding.co.uk
JAS Scaffolding Limited www.jasscaffolding.co.uk
Knight Scaffolding Limited 07590 040235
Martin Scaffolding Limited www.martinscaffolding.ie
Mercer Scaffolding & Plant Hire Limited www.mercerscaffolding.com
Powell Scaffolding Services Limited www.powellscaffolding.co.uk
Raynes Scaffolding & Groundworks Limited www.raynes.uk.com
Scaffolding Access Limited 01708 555540
Scaffolding City Limited 01536 201335
SEA Scaffolding Limited www.seascaffolding.com
Shadow Scaffolding Limited www.shadowscaffolding.co.uk
Skyline Scaffolding Solutions Limited 01495 244295
Southcoast Scaffolding Limited www.southcoastscaffolding.co.uk
Spear Scaffolding Services Limited www.spearscaffolding.co.uk
Straight Edge Scaffolding Limited www.straightedgescaffolding.com
Talk Access Limited 0113 253 9090
Technique Scaffolding 07803 766719
Thirsk Scaffolding Limited www.ryedaleroofing.com
TSE Scaffolding Limited www.tsescaffolding.co.uk
HIRE AND SALES
NonMech Ltd www.nonmech.com
SCAFFOLDING DESIGN
RDG Engineering Limited www.rdgengineering.co.uk
Avontus adds virtual reality to roadshows
Scaffolding and formwork software specialist Avontus brought a touch of virtual reality (VR) to the recent Scaffolding Association Roadshows in Scotland.
The free events provided a great opportunity for visitors to experience the very latest in virtual reality technology for scaffold design and build and learn more about the industry’s fastest growing trade association.
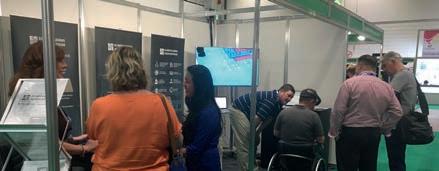
Robert Candy, chief executive of the Scaffolding Association, said: “It was fantastic to get out on the road and meet both members and potential members who we wouldn’t usually get a chance to spend time with.
“Our roadshows took us to Aberdeen, Edinburgh and Glasgow and the sessions provided us with another opportunity to touch base with the industry and talk about issues that are important to scaffolders across the border.
“Having the virtual reality software available for visitors to experience during the sessions provided an interesting twist on a usual conference format so a big thank you goes to the team at Avontus for all their support.”
Scaffolding Association gets stuck in at Safety & Health Expo
The Scaffolding Association team were delighted to bump into a number of members at the Safety & Health Expo (SHE) last month at ExCeL in London.
The event is the largest of its kind in the UK and saw visitors provided with CPD accreditation education, previews of the latest health and safety products, and information on safety-first services. Attending the event also provided the Association with another welcome opportunity to meet up with members and non-members alike, discuss their operations and learn more about the health and safety issues that are most prevalent in the industry today.
Event visitors were also treated to talks by high-profile speakers on the topics of strength, resilience and defying odds. Speakers included Dame Kelly Holmes, Professor Brian Cox OBE, Nigel Owens MBE and Simon Weston CBE.
Robert Candy, chief executive of the Scaffolding Association, said: “We welcome any opportunity to meet with our members and discuss any issues that affect their day-to-day operations.
“There is perhaps no more important issue within the scaffolding and access industry than health and safety. This event is a great way for us to speak directly to members and keep abreast of the latest developments in this area so we can best serve our membership and the industry as a whole.”
Creator brings the fun factor to Framlingham Castle
It’s not every day you get to create something a little bit out of the ordinary when working on a scaffolding project. But, this is exactly what Creator did when they added a huge slide to their existing scaffolding erection at the English Heritage site at Framlingham Castle.
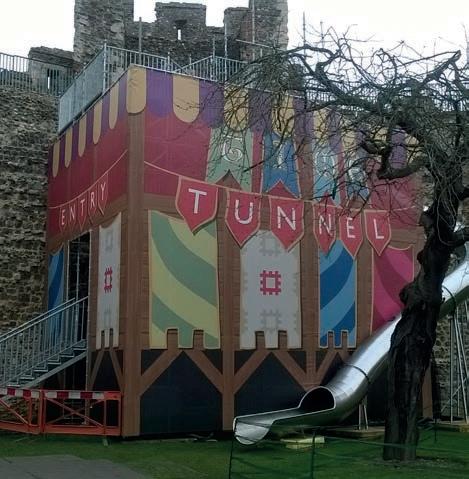
The slide was designed and added to the scaffolding by Creator to keep children entertained while building works were ongoing. And it has proved to be extremely popular with hundreds of visitors marvelling at the unexpected creation and putting their adventurous hats on to give it a go. The structure has also featured on ITV news and appears in the music video for Ed Sheeran’s hit Castle on the Hill.
Bradley Berry, director at Creator, said: “It was fantastic to be able to put our skills to the test on such an unusual project. To find fame in the process has been a bonus!
“The Framlingham Castle site is an interesting building with a rich history. Slide aside, we’ve thoroughly enjoyed the extensive work we’ve carried out on the whole project, which has been extended to the internal design for the castle, including for the prison block, moat bridge and the refurbishment of the original pillars.”
FIND OUT MORE
www.creator-scaffolddesigns.co.uk
Calling all members
Are you working on an interesting project that you’d like to share with AccessPoint readers? Or, are you working on something unusual or quirky that you’d like to shout about to members of the UK’s fastest growing trade association? Then we’d love to hear from you! Send us your story with any relevant images to newsdesk@accesspoint.org.uk
Advanced NI tackles Aberdeen Museum and Art Gallery contract
Scaffolding Association member of three years Advanced NI has been appointed to provide scaffolding support for works at the renowned Aberdeen Museum and Art Gallery. The works include scaffolding to all external walls, birdcages, edge protection, cantilevered scaffolds, crash decks, loading bays, shoring works and the erection of an advertising banner to the front of the building for Aberdeen City Council.
The project, which is part of a £30 million contract for Advanced NI’s client, McLaughlin and Harvey, began in September 2015 and is due for completion this summer.
Robert Andrews, director at Advanced NI, told AccessPoint that the brief for the project initially covered the erection of a temporary roof over the whole site so that all roofs could be removed and steel work be erected for the additional floors and extension at the same time. However, after meeting the project manager and planners, changes were made. “We thought it would be more cost-effective and efficient to erect birdcages inside the building as crash decks which could then double up as temporary roofs for each section as and when the client was ready for them,” he said.
“We came up against many challenges along the way due to the building being listed, and we had to work closely with the respective agencies to ensure all works were signed off along the way. We’ve also kept our engineer, Ricky, from Highland Temporary Works very busy with him designing upwards of 40 scaffolding designs for this one project alone!
“We do a lot of works for McLaughlin and Harvey and have been told it’s our willingness to go the extra mile that keeps us working together. We relish the challenge of finding a solution to any problem,” Mr Andrews concluded.
FIND OUT MORE
www.advancedniscaffolding.com
JLP Scaffolding awarded multi-million-pound contract
Hull-based JLP Scaffolding has been awarded the scaffolding contract on the high-profile renovation of the city’s Holy Trinity Minster, formerly Holy Trinity Church, following a competitive three-way tender.
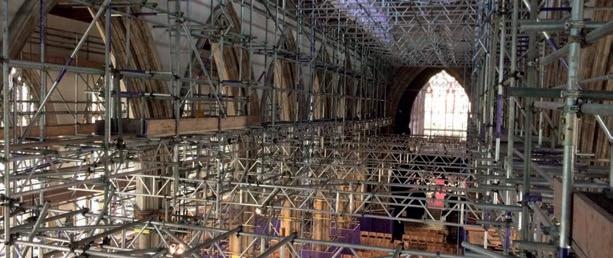
The contract sees JLP, which is only in its second year of trading, providing scaffolding to aid both internal and external renovations.
Jordan Precious, JLP Scaffolding’s managing director, said: “I’m extremely proud of the 20-strong team that’s been working on this project since it started in November last year. It’s a complicated contract due to the delicate nature of the building but we’ve worked hard to solve any issues that have cropped up along the way.”
Scaffolding has been erected to be freestanding and allow access to the external fascias. Then, additional structures have been created to allow access to the roof. Internally, the scaffolding had to be built around the building’s existing columns because the floor in some locations is only four inches thick – crypts are located underneath.
Half the building has remained in use throughout the renovation works so a secondary structure has also been created to allow for the erection of a screen to stop dust and debris affecting day-to-day operations.
Mr Precious added: “With Hull being the UK’s current city of culture, there’s a buzz in the area and we’re proud to be part of that by securing this contract. The client, Houlton, has been delighted with our work to date and we’re looking forward to working with them on more exciting projects in the future.”
SYSTEM SCAFFOLDS
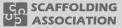

LATTICE BEAMS
ACCESSORIES
TEMPORARY ROOFING PROPS-STRUTS
FALL PREVENTION
TRADITIONAL SCAFFOLD READYLOKS
LADDER BEAMS
Setting
safety standards in aluminium scaffold beams

VR Access Solutions is a manufacturer and supplier for access solutions and scaffolding products. VR Access Solutions has established a strong market position and it is committed to delivering quality and innovation.
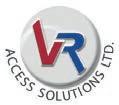

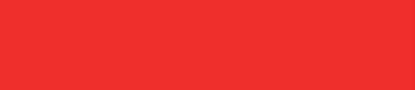
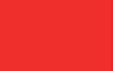
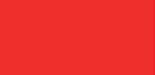
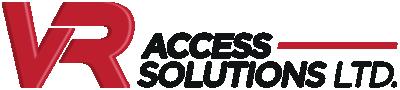
