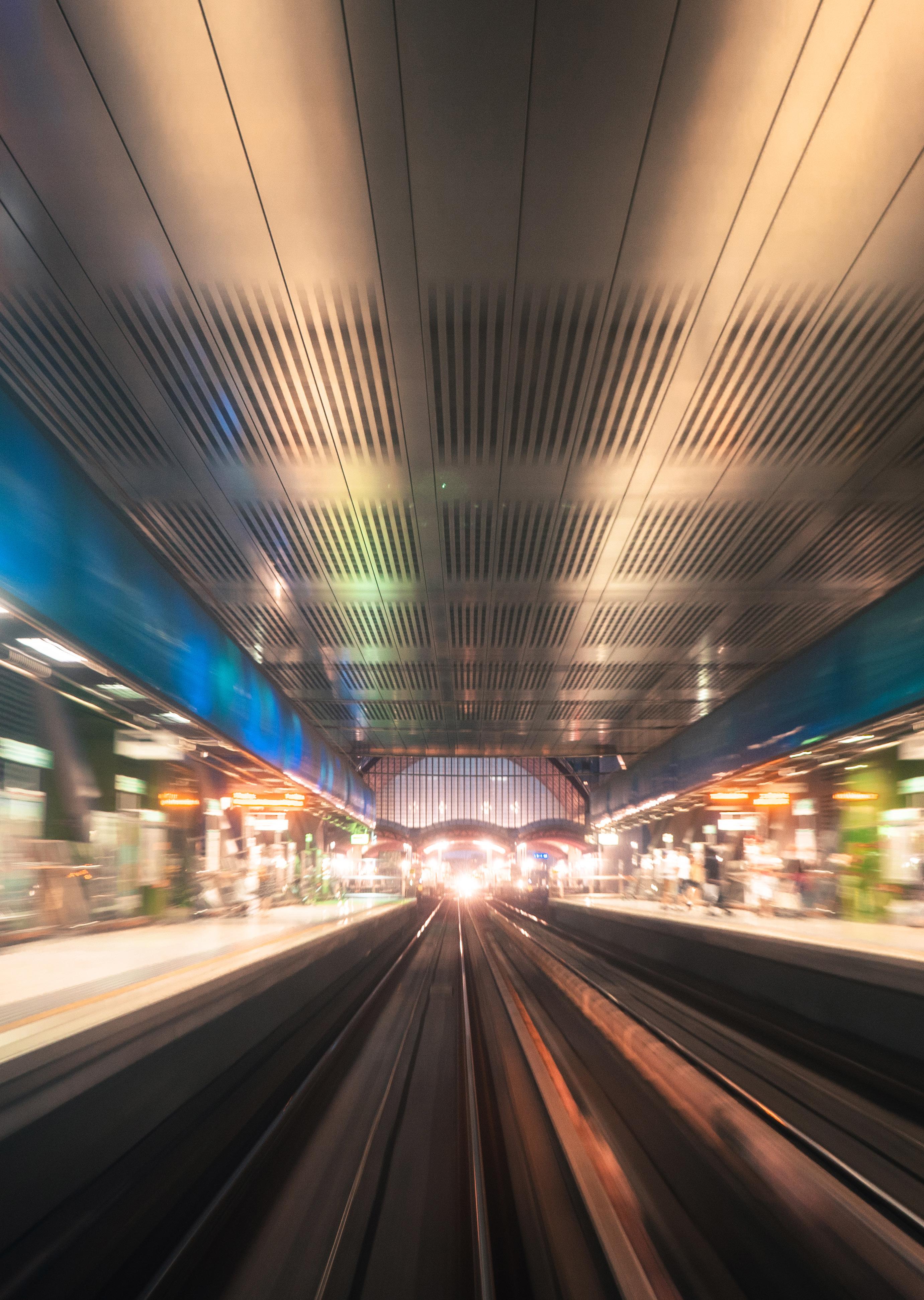
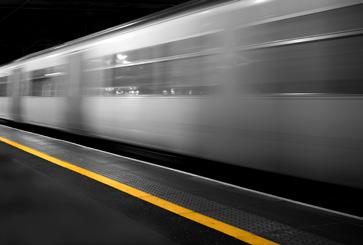
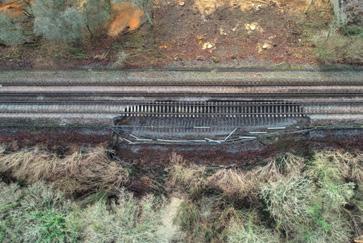
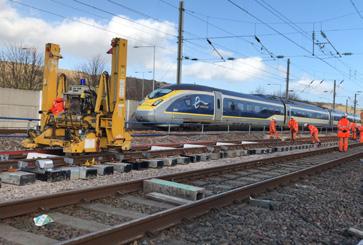
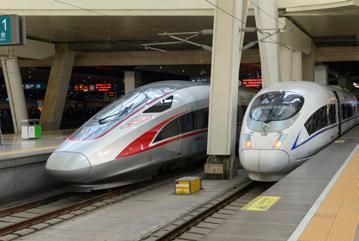
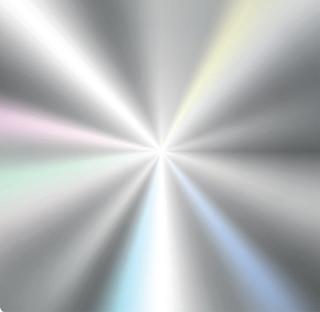
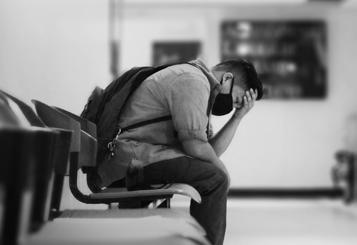
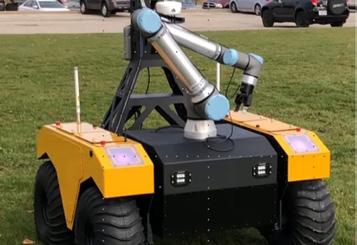

The need to provide high performing railway systems has never been greater. While the outlook for the rail sector is bright, it faces many real threats in the post COVID era.
This autumn, 5 major institutions and the Railway Industry Association are bringing together expert speakers from across engineering and operational disciplines to present a vision of “High Performing Flexible Railway Systems for the Future”.
The seminar will cover factors spanning the operational and engineering disciplines, focusing on how they contribute to increasing capacity, reliability, flexibility and resilience, while delivering the high quality of service that customers demand.
Speakers will set out:
• how technical solutions can empower operators to deliver a resilient service and provide them with the data needed to respond optimally to issues and changes, cascading live information to those who need it;
• how systems are designed to maximise the capacity and reliability of our infrastructure and the tools that can be used to predict and prevent failures before impacting operations;
• how railways respond to urgent challenges such as climate change adaptation and decarbonisation as well as the need to radically reduce the exposure of railway infrastructure workers to hazards while shifting to 7-day operations.
WED 13 OCTOBER & WED 3 NOVEMBER 2021
The seminar will include recorded online content for delegates to view ahead of each of two live seminar sessions (each of duration: 90 minutes inc Q&A).
PART 1 View four hours of pre-recorded online content from 22 September ready for the live session on 13 October 2021 09.00-10.30 (UK time) PART
View a further four hours of prerecorded online content from 13 October ready for the live seminar on 3 November 2021 09.00-10.30 (UK TIME)
Apprentice, Student £0 e-Journal £25 printed Journal
Member £86.00
Member(66 or older at 01.01.21) £35.00
EngTech Member* £86.00 IEng/CEng Member* £137.00 Fellow £115.00 Fellow (66 or older at 01.01.21) £46.00 EngTech Fellow* £115.00 IEng/CEng Fellow* £182.00
Sml enterprise (Turnover up to £17.5m pa) £2,140 Med enterprise (Turnover £17.5m - £200m pa) £5,350 Lrg enterprise (Turnover above £200m pa) £10,700 Heritage railway £150
APPLICATION FEE: New Registrant** EngTech £60 / IEng £225 / CEng £225
APPLICATION FEE: Additional Membership EngTech £40 / IEng £90 / CEng £90
EngCouncil Fee* EngTech £19.90 / IEng £34.70 / CEng £40.90
* If you are professionally registered through the PWI the annual Engineering Council Registration fee will be collected in addition to your PWI subscription and will be paid to the Engineering Council on your behalf. ** Includes the Engineering Council Registration Entry fee.
The Engineering Council has granted a two-year licence commencing June 2021 to the PWI to undertake accreditation and approval of University and College courses that provide exemplifying academic qualifications for professional registration. This licence provides for full participation in the activities of the Joint Board of Moderators (JBM), the body that is licenced to accredit civil engineering qualifications, which consists of the Institution of Civil Engineers (ICE), the Institution of Structural Engineers (IStructE), the Chartered Institution of Highways and Transportation (CIHT), the Institute of Highway Engineers (IHE), and the Permanent Way Institution (PWI).
Dr. Brian Counter said “This puts the PWI up there with the great guns! We want to be the Institution of choice for railway infrastructure engineers in the UK and JBM accredited courses are sought after by school leavers wanting to obtain high level professional qualifications.”
The PWI is delighted to have made another step towards promoting professional registration in the UK and worldwide rail industry by establishing a formal link with colleges and universities through the JBM. The PWI currently has strong links with many colleges and universities who currently have rail-specific curricula and will promote others to develop rail studies, in addition to highway studies, at locations where there is enhanced demand from rail employers.
The JBM currently approves and accredits higher level and degree apprenticeships for working trainee engineers, as well as academic courses, and the PWI will actively support and develop these in the rail industry.
• Our logo will appear on 86 university and college websites and their course documentation, alongside JBM’s.
• The PWI President will sign the certificates posted at educational locations alongside the Presidents of the other JBM Member Institutions.
• We will send our reps to visit selected “railway” universities and colleges and support the civil engineering education in the UK.
• We will vote and approve all relevant bachelor and master’s degree courses as part of the JBM Board.
• PWI Board approval of PWI JBM representatives, Board Members Phil Ransom and Dr. Amer Ali, Visiting staff and Sub Committee members, Dr. Mohammed Wehbi, Dr. Matthew Frost, Prof. Martin Crapper and Neil Raw.
• Presentations to universities and colleges in early 2022.
The institution for rail infrastructure engineers becomes the fifth member of JBM, which sets the standards for civil engineering education in the UK.
The Permanent Way Institution will bring its rail infrastructure expertise to the board. Image credit: Shutterstock
The Permanent Way Institution will bring its rail infrastructure expertise to the JBM. Image credit: Shutterstock
ICE head of qualifications, John Laverty, said: "ICE works in partnership with other institutions through JBM to provide a joined-up approach to engineering education in the built environment.
"The addition of PWI, with its specific interest in railway infrastructure, reinforces JBM’s role in accrediting degrees and approving vocational qualifications for the civil, structural, transportation and associated engineering disciplines."
By joining the JBM, Laverty said he looked forward to PWI joining the JBM on its "mission" to meet the net zero challenge.
"The extraordinary challenge of the climate emergency is becoming a central cultural feature in the education of civil engineering students. Both ICE and JBM want to bring about that fundamental shift in perspective, to help engineers meet the major challenges facing society.
"We look forward to colleagues from PWI joining the JBM in that mission," he said.
The Institution of Civil Engineers (ICE), the Institution of Structural Engineers (IStructE), the Chartered Institution of Highways and Transportation (CIHT), the Institute of Highway Engineers (IHE) and the Permanent Way Institution (PWI) together represent some 100,000 of the world’s leading professional engineers.
These five professional bodies comprise the Joint Board of Moderators (JBM) working to strengthen links with universities and industry, to ensure that formal educational programmes (eg degrees) and workplace programmes are in place to develop professional engineers that will continue to provide a global contribution to sustainability, economic growth and ethical standards.
The JBM assesses and makes recommendations on the accreditation and approval of relevant educational programmes that it accepts as meeting the requirement to register as a professional engineer with the Engineering Council (EngC) the body responsible for regulating the engineering profession within the UK.
The JBM Board will make recommendations on accreditation/non-accreditation of educational programmes, for consideration by the JBM member institutions, to allow them to publish, and keep up-to-date, a list of qualifications which they accept as providing the educational base for different grades of membership and the Engineering Council (EngC) Register: CEng, IEng and EngTech.
The JBM seeks to maintain and strengthen links with educational establishments in the United Kingdom on all matters concerned with first degree programmes and periods of Further Learning in those engineering disciplines of relevance to the JBM member institutions.
If requested, the JBM will also consider the accreditation of programmes overseas provided that no costs are incurred by the sponsoring institutions. Applications for accreditation through individual educational establishments are referred to the Board.
The JBM is appointed by, and answerable to, the Councils/ Executive Boards of the sponsoring institutions and reports through the relevant membership/education committees of ICE, IStructE, CIHT, IHE and PWI.
The Board consists of a Chair nominated by the Presidents of the participating institutions, drawn from the academic, private and public practice sectors, representing a wide range of engineering in the construction industry.
All members involved in accreditation activities are experienced engineers, capable of making balanced judgements on the ability of an educational establishment to create a high standard of graduate output.
Our next PWI theme is S&C and this is becoming a major focus for the PWI. We are encouraging members to write articles and get involved in expanding our knowledge base in this important area.
See page 67 for the PWI S&C Refurbishment courses which are becoming extremely popular for all companies, and we are now doing bespoke courses for Network Rail and TfL at locations to suit the participants.
As I mentioned in the April Journal, it is a challenge for engineers to fully understand degradation of S&C layouts, especially when considering the changes that have occurred since layouts and components were designed to cater for the loadings and stresses around 20-40 years ago. The classic rail engineering concept is the knowledge and understanding of the wheel rail interface.
PWI training does not stand still, and we are continuously improving our knowledge through research based on a theoretical and practical experiential approach.
We need to know more about how modern vehicles approach S&C and travel through the obvious discontinuities associated with switches and crossings, as this is a major subject of debate.
The fragmentation of the industry post 1990s privatisation involved splitting the wheel and rail technology between stakeholders. It has not always allowed us a full and comprehensive understanding of new rolling stock, some of which have varied sprung and unsprung masses. I have had some interesting discussions with experts who indicate that they are especially concerned about some modern vehicles which exert forces in all directions which may be somewhat different from what was expected. We need to work together as an industry to prevent derailments. I am excited about being able to offer more courses in S&C.
Counter TECHNICAL DIRECTOR technicaldirector@ thepwi.org BrianAs I mentioned in April, the Institution was only operating virtually as we went to press. We have really enjoyed meeting online and had some great meetings and another superb Network Rail Track Maintenance Engineers’ Conference with excellent speakers and new insights.
I have good contacts in USA at the University of Illinois, and it was great to hear from William Rothery regarding rail stresses. Also, some of us still worry about long timbers; well done to John Nelson for leading the network Rail working group.
I have to say that the opportunity to speak online at very short notice has given us a unique edge on the ability to conduct business, formulate decisions and make progress. So, it’s not just doom and gloom, its Zoom!
What a change in early May, though. I have been on site in my PPE (images 2&3) at High Marnam, taught face to face at the Derby Conference Centre and Derby University on railway courses and even had mask wearing train trips to London, Worthing and Sheffield.
It is only when experiencing our vastly improved railway that we appreciate the advantages of rail. I was particularly excited by my first proper visit to London Bridge with its amazing concourse and superb track layout. I remember the PWI Section meeting I attended some years ago where the complexity was shown of opening up the underneath. Having remembered the old bleak, dark and dirty platforms, it made me immensely proud of the new station with impressive views of my favourite skyscraper, the Shard. Please go and see what we can do; this station is far better than many in Europe and the rest of the world.
The icing on the cake for me in May was a restaurant meal and a drink with railway colleagues. As we return to normal, our plan for autumn seminars is extensive, so I hope to see many of you in Manchester and Swindon.
We cannot help but anticipate some very positive changes with the long-awaited Williams-Shapps review. A vertically integrated railway will optimise the point that I am always harping on about apart from the obvious performance benefits to the customer, it is the systems approach throughout and for us in permanent way the wheel-rail and train-wire interfaces.
The spring is over and we have had our share of weather surprises with the usual weather records being smashed, the wettest May in Wales since records began! However, on PWI training we talk about how we should continue to monitor our railway neighbours and the surrounding areas to make the railway more resilient, and think big!
Image 4 shows Draycott, south of Derby, on the Midland Main Line. Although a drainage ditch was installed in 1999 to help prevent flooding on the railway, it has still been flooded 19 times in the last 8 years. Why? If we look at when the adjacent canal was infilled in the 1960s, we see the problem. With a reinstated canal, would the problem go away? A joint venture has been worked out between Network Rail and the Canal Trust worth £450,000 that will significantly reduce flooding and create new recreational facilities. A win-win!
Finally…Guess the location! (Image 5)
Images 2&3: Brian Counter (top) and Jacob Fay (bottom) on track on the High Marnham test track, notice the transition!
Image 1: An interesting set of hand points - are we really allowed to have a concrete sleeper there? Please let me know!
Image 4: Draycott, south of Derby, on the Midland Main Line.
Image 5: Guess the location!
How is the PWI seen within the wider railway industry community? And is that perception what we’d wish it to be?
A recent conversation with a (non-PWI member) railway acquaintance led me to answer those two questions respectively: “too narrowly”, and “definitely not”. My friend’s killer question “Why would I join the PWI, my work doesn’t relate to track?” underlines the challenge the PWI still faces in getting over its key messages.
• Railways are an engineered system.
• Railway infrastructure is roundly half of that system.
• The PWI seeks to inform, educate, and represent all those who work in and around railway infrastructure engineering.
In the paragraphs below I’ve expanded on those messages, setting out to answer my friend’s question, and explaining why those who work with railway infrastructure should join the PWI.
Each of the major railway infrastructure subsystems: earthworks and drainage; structures and buildings; track; power supply; signalling and control; data and telecommunications; and electrification is an engineering specialism in its own right. And our industry needs people who are competent in each of those fields. However, railway history has taught us that to work safely, effectively, and efficiently those people must be aware of the critical interfaces between their own specialism and others, and of the risks to be controlled at those interfaces. All should be sufficiently aware of how the railway functions to keep the overall system safe. Fostering that awareness is one of the PWI’s main objectives and we seek to achieve it by offering our members opportunities to grow their knowledge and understanding of interfacing disciplines and of the interfaces themselves. That marks us out from some other professional engineering institutions.
Looking back through previous Journals, browsing the Knowledge Hub, and looking at our programme of Section meetings leaves me in no doubt about the wide scope and excellent quality of the technical information we provide. Bridges; tunnelling; earthworks and soil mechanics; track manufacture, installation, and maintenance; railway plant; data collection, processing, and management; electrification; work management systems; project management; and logistics and planning are all subjects well represented. Importantly, this information is presented in the context of the railway system, and in a way intended to inform those from other disciplines, as well as those working within the subject discipline. Making technical information accessible is very important to us!
To fulfil its mission, the PWI must also offer its members opportunities to develop their understanding of the whole railway system and the way it operates. The Institution offers a storehouse of knowledge covering four of the critical infrastructure-train engineered interfaces: the wheel-rail system; the train-structure system (notably at the train-platform interface and including all aspects of “gauging”); the track-vehicle system (determining the forces and displacements that arise when track geometry and stiffness interact with vehicle suspensions); and the pantograph-catenary system.
Stephen Barber CEO Permanent Way InstitutionThe construction and commissioning of HS2 will add significant capacity to our national railway network and the push for decarbonisation is likely to drive big changes in transport demand too. Infrastructure engineers should be able to engage in technical discussions on how network capacity is to be used, on how transport demands are to be met, and on the consequent impact of traffic changes on the infrastructure.
Train operating disciplines such as timetabling and resource diagramming can be unfamiliar to those involved in railway infrastructure engineering, though those disciplines effectively shape the infrastructure we are called on to provide and determine the level of service offered to passenger and freight customers. Operating disciplines should also work closely with engineering in determining the detail of asset management strategies and plans. It is after all important to provide sufficient time for the maintenance work that is itself driven by the characteristics of traffic on a particular route. The Institution of Railway Operators (IRO) is the home of expertise in timetabling and resource diagramming and the PWI is seeking ways to share discipline perspectives between the two Institutions’ memberships.
Whilst there is work to do on the PWI’s coverage of command and control (including signalling), a 2020 joint PWI seminar with the Institution of Railway Signal Engineers (IRSE), Institution of Engineering Technology (IET), and Institution of Mechanical Engineers (IMechE) covering all aspects of automatic train operations (ATO) gave participants from all four institutions a view of the broader infrastructure issues raised by automation and the application of artificial intelligence (AI) to railways. ATO is in many respects a mature technology. It was pioneered from 1968 on London Underground’s Victoria line where the running tunnels provide a highly constrained and controlled infrastructure environment. It is notable that many of the difficult questions facing ATO in the 21st century are not about train control technology itself, but about how external risks from a more varied and open infrastructure, flooding or escaped livestock for example, are to be identified, assessed, and controlled under automatic operation. This requires input from all infrastructure engineering disciplines!
The presentations from the joint seminar, together with the questions and answers arising are freely available to PWI members. Building on its success and broadening the knowledge available to our members, we intend to hold further joint events with our fellow professional institutions: the next is planned for Autumn 2021.
The broad application of AI to engineering has already been the subject of much research and development, particularly in the field of autonomous vehicles. Frameworks of decision-making principles have been established and the role of ethics in machine-made decisions is certainly better, if not yet completely, understood.
Historically, the identification and control of risks within the railway industry has tended to be “bottom-up” within specific disciplines, and this may go some way to explain the weakness in risk controls at subsystem interfaces that have been exposed by serious incidents over the last 25 years. Whilst the “top hazards” (derailment, collision, and fire for example) that might arise from the use of AI will be those we are already familiar with, the ways in which AI might create real incidents are likely to be very similar across engineering disciplines and subsystems. So, to make best use of experience and learning from the application of AI we will require effective dialogue across engineering disciplines, and a broad commonality of approach in the way AI is evaluated, assessed, and deployed. The PWI is alert to this requirement and is well-placed to facilitate it.
As we look (with hope) to the 2022 opening of Crossrail and continue to lament the cloud cast over English electrification schemes by the Great Western Main Line, it is difficult to argue that all is well in the engineering and management of significant UK railway projects. That said, the success of Thameslink (after some initial operational hiccups) and its underlying approach to systems engineering, the commissioning of Corby to Bedford and several Scottish electrification schemes, the steady progress on East West Rail, HS2s move into its major construction phase, and the success of a series of smaller (though still substantial) projects including the reconstruction of Kings Cross station throat and the construction of Werrington dive-under give cause for some serious optimism!
It is clear that the UK can deliver large, successful railway infrastructure projects on time and within budget, but the jury is still out as to whether this can be done consistently.
Despite “lessons learnt” exercises and informative National Audit Office (NAO) reports on projects from the early 2000s, lessons were not learnt. Looking at more recent reports on Crossrail by both the NAO and the Greater London Transport Authority it is evident that the complexity of railway systems engineering, and the scope of its proper assurance were not well understood by a very senior project team at critical stages in the project’s development and delivery. It is hopefully now evident to all that delivering a modern operational railway system is much more than an aggregation of several smaller engineering projects, and that details (especially at subsystem interfaces) really matter. The complexity and interdependency of railway infrastructure is not due to a single engineering discipline but to multiple disciplines, with many interfaces which are critical for both technical compatibility and construction programming.
Again, the PWI’s ongoing role here is to collect and share with its membership knowledge and experience from across engineering and construction disciplines within the railway sector, and from outside the industry where relevant. Previous project review presentations have laid the groundwork and, in addition to Journal articles, we intend to hold a seminar in 2022 presenting experience and understanding drawn from recent railway projects.
I hope I have explained why the PWI is different to some other professional engineering institutions and is of particular value to those working in the railway infrastructure sector. I hope too that you can use my answers, bolstered by your own experience, to persuade colleagues and acquaintances within our industry to join this Institution and to share their varied railway knowledge and experience with other PWI members, for the good of both individuals and the collective industry.
Looking back through previous Journals, browsing the Knowledge Hub, and looking at our programme of Section meetings leaves me in no doubt about the wide scope and excellent quality of the technical information we provide.
One thing I found particularly helpful in my professional life was developing a systems understanding of the railway, its engineering, operations and how these served the needs of its stakeholders. Early in my career, after completing a civil engineering degree I focussed primarily on bridges, structures, geotechnics and track engineering. Looking back, while I had a good level of competence in these specific areas, my horizons were not well developed in terms of understanding fully where these disciplines sat in terms of the smooth functioning of the railway system as a whole, and how the railway system fitted in with the overall needs of society. In other words, in many ways I was siloed within my specific disciplines. It was only in my mid and later career when I took on roles where I managed people from many wider operational and engineering disciplines and when I joined a section committee of the PWI that I developed a much broader perspective. I realised that developing a wider systems understanding earlier on would have been really helpful in terms of my development and in making my contributions and output more effective. I think that nowadays with interdisciplinary reviews etc, more is probably being done to encourage engineers to develop a systems understanding earlier in their careers, but there is always more that can be done…
One brilliant opportunity coming up to help in this area is this year’s Joint Institution online international seminar “High performing flexible railways systems for the future” which takes place this autumn with streamed content and live summary sessions being delivered from 22 September onwards. This Journal includes an advert for the event on page 2 with details of how you can register as a delegate, and I would thoroughly recommend that you do this. The seminar is a joint initiative organised by the PWI, the Institution of Railway Signalling Engineers (IRSE), the Institution of Mechanical Engineers (IMechE), the Institution of Engineering and Technology (IET), the Institution of Railway Operators (IRO) and the Railway Industry Association (RIA). The seminar brings together expert international speakers from across railway engineering and operating disciplines and will give you an excellent systems understanding of the many interesting requirements, challenges and conundrums that the railway system has to overcome and deliver against now and into the future.
Andy Packham Technical Content Manager andy.packham@thepwi.orgMy Presidential year will soon draw to a close and it has been a unique year of great turbulence in the UK, and this has been reflected in many changes in our railway industry.
In January I discussed the challenges of Covid and how we rallied to face and overcome them. I also commented that we need to adjust to this new paradigm, facing the reality that revenue is down and so creating the need for us to consider how we can become leaner and efficient doing the same, and potentially more, with less revenue.
In April I reflected on our need to reconsider our approach to the safety of our workforce as shown through our industry’s recent tragedies where our colleagues, and members of the public, lost their lives. These being at Carmont, Eastleigh, Margham and Surbiton. Whilst the exact root causes of these incidents are being and have formally been investigated, I believe it is fair to say that the themes of the management of asset risk, competence, capacity and capability of our people as well as the processes and system they work within feature as elements in the incidents.
In September 2020 I discussed my chosen Presidential theme, that of industry competency and the case to drive forward with a changed approach. This approach provides many benefits such as clearer career paths, educational opportunities, and also, critically an opportunity to help us identify the areas where we need to strengthen the capability of our community to deal with the changes in our railway environment. This initiative has progressed pleasingly with widespread industry support.
In May the Government released the WilliamsShapps Plan for Rail; ‘Great British Railways’ announcing a major shake-up in the structure of our industry, in many ways bringing the UK Railway back to its roots. This change being intended to simplify industry structure, make decision making more passenger focussed and swifter, and to address a sprawling industry which had evolved layers of complexity since privatisation. It also highlighted the critical points that we must maintain and improve our railway’s reliability, safety and security. Also, that the government intends to grow and invest in our railway and to do so efficiently. Whilst the 113-page document sets out the vision, high-level operating model and initial steps, it is clear that the detail needs to be developed over the coming months. Therefore, we as an industry have the opportunity to support, advise and shape the direction of the new model and take advantage of and harness the opportunities this will bring.
I believe the biggest opportunity and area of importance to us is that of driving and embracing innovation for the ‘new normal’. Specifically, the delivery and implementation of innovation bringing forward new ways of working, new tools, equipment and processes. Ideas that might have been stifled through our current industry operating model might soon have new opportunities to thrive, and through a focus on the whole joined up railway system, we have a new opportunity to tackle the end-to-end system challenges of system performance, system safety, and system cost efficiency.
For instance, we can re-examine and accelerate the industry cases which lever off a single entity operating track and trains such as at TfL. This includes looking again at mounting equipment on trains such as lubrication and friction modification systems or accelerating the systematic installation and use of track geometry monitoring systems.
We’ll also be able to lever off the new operating model to challenge ourselves to work more efficiently, such as accelerating the systematic use all of the data we gather from track and train, using it to help us diagnose problems early and even retire less effective / more expensive systems and ways of working.
We can also challenge ourselves to find simple and effective innovations for cost and efficiency problems such as the example of the invention of robust low conductivity coatings which can be applied to existing structures to reduce required electrical clearances. This particular innovation will remove the need to reconstruct bridges and tunnels where electrical clearance challenges in the past would have made improvements such as the transpennine line electrification upgrade affordable.
I’m confident that through harnessing the skills of our community, through teamwork and collaboration, we can encourage and foster lateral thinking to deliver innovation that will create a more efficient, better performing, and safer railway for our people and the travelling public.
While this year has undoubtedly been very difficult and challenging for us, I see a brighter future ahead, one full of opportunity that we only need to be willing to grasp. It has been a privilege being your President, and I thank you for your support over the last year.
I believe the biggest opportunity and area of importance to us is that of driving and embracing innovation for the ‘new normal’.
Joan is a Chartered Engineer with the ICE and a Fellow of both the PWI and ICE. Her career spans many years of rail engineering leadership working for both a client organisation, Network Rail and within the supply chain. Following her Presidential term, Joan formed and is Chair of the Climate Change and Decarbonisation Advisory Committee. She is honoured to be part of our learned society which seeks to improve knowledge, standards and professionalism throughout industry. One of her core values is around continued life-long learning which sits at the heart of our Institution.
Climate change and the consequent requirement to both adapt and decarbonise global society is the largest and most important issue facing humanity. Engineering and engineers have a critical role to play: in defining the policies and actions necessary to avert physical and societal collapse; and in working with government, other key disciplines (particularly economists and social scientists), and industry to win the arguments so that those actions are taken with the urgency necessary.
The Permanent Way Institution has a strong desire to speak with knowledge and authority on this critical topic, both to its own members and in the wider world of engineering and industry. To this end, during the Autumn 2020 the PWI Board decided to establish the Institution’s own expert advisory committee on decarbonisation and climate change, drawing on the expertise of members from across railway infrastructure engineering.
As Past President, I was asked to take on the role of first Chair of the committee, a role I accepted with great enthusiasm. All Corporate Members were asked if they would like to volunteer staff from within their organisation to become committee members and we were inundated with responses. Following a period of consultation, the following people have been appointed to the committee:
D/Gauge: Colin Johnson Managing Director
Mott McDonald: Jenny Smith Knowledge Manager
Network Rail: Alan Ross – Director of Engineering & Asset Management; Stuart Kistruck Director of Planning and Franchising; Rossa Donovan Head of Environment & Sustainable Development; Richard Quigley Senior Engineer and PWI Vice President
Office or Rail & Road (ORR): Matthew Gillen Civil Engineer
The Permanent Way Institution: Peter Dearman Deputy President; Stephen Barber CEO; Kate Hatwell Operations Director
SNC Lavalin: Mohammad Safari Baghsorkhi Senior Track Designer
Swietelsky: Michael Zeidler Head of Plant
Tensar International: Peter Matthias Design Lead for Rail
Transport for London: Chrisma Jain Senior Project Manager; Elizabeth Lasserre Track Strategy Manager
The Committee’s purpose is to provide advice and guidance to the PWI Board and Executive and it has been specifically requested to monitor and consider the following on an ongoing basis:
1. What the PWI as an Institution can do directly to decarbonise.
2. What PWI members can do in both their personal and professional lives to decarbonise.
3. What the PWI can do to help its members (individual and corporate) to understand and manage decarbonisation and climate change adaptation (eg sharing good practice, holding conferences and workshops, forming special interest groups).
4. What the PWI with its members, other professional groups, and industry partners can do to foster political and public support.
5. What the external organisational topography of decarbonisation and climate change is (who is out there and what they are doing), and what other bodies it would be advantageous for the PWI to engage with.
To date the committee have met virtually on two occasions; the inaugural meeting was held on 19 March and the second meeting on 27 April. Whilst we are very much in the storming/forming stage of our relationship, the committee has started to develop the bones of a forward-looking strategy aligned to the points above.
Aside from introductions, the first meeting was largely an information sharing exercise between myself and other members of the PWI explaining to committee members what the organisation has done to date. We talked about the importance of the PWI’s relationship with the Royal Academy of Engineering, in particular with the National Engineering Policy Centre (NEPC). You may recall reading an article on this subject, authored by Dr Nick Starkey in the April Journal. The NEPC is a unified voice for 43 engineering organisations who give policy makers a single route to advice from across the engineering profession. The PWI is part of that group.
With regard to climate change, decarbonisation and achieving net zero, the NEPC has positioned itself to provide thought leadership, both collating and communicating relevant information to a diverse range of stakeholders. Working with all Professional Engineering Institutions (PEIs), the organisation has produced a five step plan (figure 1) laying the foundations for a net zero recovery1
STEP 1 Ensure recovery packages work together as a whole to pivot the UK within a net zero economy.
STEP 2 Apply outcome based procurement processes for all public sector infrastructure and building projects with a focus on low carbon.
STEP 3 Prioritise diversity and inclusion for jobs and skills to reverse COVID-19 impacts and help build net zero capacity and strengthen long term capability.
STEP 4 Drive digital transformation as an essential enabler of net zero and resilience.
STEP 5 Deploy cross-sectoral systems approaches to policymaking that underline the interconnectedness of different policy areas and economic sectors.
Each of the above steps has a developed plan with actions for government, industry, research funders and the engineering profession and the PWI have a part to play in their delivery along with the other PEIs. Further information can be found in reference 1.
During the course of 2021, the NEPC has also set itself the challenge of looking at the subject of sustainability in Engineering Higher Education and is considering the following:
1. How to design curricula in the UK to give due consideration to net zero.
2. Developing a road map of the skills engineers require to achieve net zero.
3. Building a coalition to work out the practical steps and make the change.
All the above subject matter is very important for the future of the PWI and its members and it is intended that the committee can contribute to this debate as a voice for the Institution.
In addition to looking at the work of the NEPC, the committee also discussed the broad subject of decarbonising transport. The UK Government (DfT) published a policy paper in March 2020 entitled “Decarbonising Transport: setting the challenge” 2 and that identifies six areas of focus (figure 2):
1. Accelerating modal shift to public and active transport.
2. Decarbonisation of road vehicles.
3. Decarbonising how we get our goods.
4. Place based solutions.
5. UK as a hub for green transport technology and innovation.
6. Reducing carbon in a global economy.
The PWI membership can find alignment with at least three of the published areas of focus as both individuals and as a collective and it’s certainly an area the committee are interested in. The transport decarbonisation plan was due to be published in Spring 2021 but, at the time of writing, this has not yet occurred.
Aside from presenting material at the first meeting, the committee talked about the need to join with other industry bodies and associations who are also focusing on the climate change and decarbonisation agenda. Continuing with that theme, we invited David Clarke, Technical Director of The Rail Industry Association (RIA) to join the second meeting to speak about the work RIA are doing in this space. To ensure the subject matter remains prominent, RIA are actively campaigning for a rolling programme of cost effective electrification following on from the publication of the Electrification Cost Challenge Report in March 20193 (figure 3) and their most recent report “Why Rail Electrification?”4 (figure 4) published in April 2021.
RIA and its members are urging the government to develop a ten year rolling programme of electrification that allows the sector to build up expertise and capability, in order to deliver in a cost effective, efficient manner. RIA have obviously been working on this subject matter for some time and have a clear strategy as to the direction of travel (further details can be found on the RIA website). We agreed at the meeting that both organisations would support in each other in this subject area as and when appropriate.
We also heard from Rossa Donovan, Network Rail’s Head of Environment and Sustainable Development at the second meeting who briefed the committee on Network Rail’s Environmental and Sustainability Strategy (2020 2050) 5 (figure 5).
There are four elements to this strategy:
1. A low emission railway.
2. Improved biodiversity of plants and wildlife.
3. A reliable railway service resistant to climate change.
4. Minimal waste and the use of materials.
The wealth of information contained within this document will be excellent material for PWI Section meetings and technical conferences.
Members of the committee have agreed to provide an article on the subject matter in each copy of the Journal as thought leadership pieces to inform, educate and promote debate. In addition, the PWI Manchester and Liverpool Section have committed to organising and running a technical conference on this subject in Spring 2022.
As an organisation, the PWI need to understand their baseline carbon footprint before we can put a plan in place to reduce our impact. Committee members have offered to help us recognise the baseline position, which is much appreciated. In the months ahead, the PWI will be in a position to publish its own carbon reduction strategy which will no doubt make demands of all of us to do things differently.
The subjects covered above are not exhaustive in respect of the conversations that have taken place, but I have tried to give readers a flavour of the content, to reassure our members that our strategy will be both inward and outward facing. It will take some time to mature; each member of the committee brings their own experience and knowledge and at present we are very much learning from each other.
1. “Beyond COVID 19: laying the foundations for a net zero recovery” Royal Academy of Engineering: National Engineering Policy Centre, June 2020. https://www.raeng.org.uk/publications/reports/beyondcovid-19-laying-the-foundations-for-a-net-z
2. “Decarbonising Transport: setting the challenge” Published by Department for Transport, March 2020. https://assets.publishing. service.gov.uk/government/uploads/system/uploads/attachment_ data/file/932122/decarbonising-transport-setting-the-challenge.pdf
3. “RIA Electrification Cost Challenge” Railway Industry Association, March 2019 https://www.riagb.org.uk/RIA/Newsroom/Stories/ Electrification_Cost_Challenge_Report.aspx
4. “Why Rail Electrification?” Published by the Railway Industry Association (RIA), April 2021. Authors David Shirres C Eng MIMech E, Editor Rail Engineer; Gary Keenor CEng FPWI MIET, Group OLE Engineer Atkins; Noel Dolphin, Head of UK Projects Furrer +Frey; Paul Hooper C Eng MIET, Technical Director Atkins. https://www. riagb.org.uk/RIA/Newsroom/Why_Rail_Electrification_Report. aspx?WebsiteKey=dc1927f5-fa2e-4539-97fe-f032f006424d
5. “Network Rail Environmental & Sustainability Strategy 2020 2050”, Not dated. https://www.networkrail.co.uk/wp-content/ uploads/2020/09/NR-Environmental-Strategy-FINAL-web.pdf
It is the intent to devote a specific page on the new PWI website about the activities of the Climate Change & Decarbonisation Committee so please watch out for that. You are also welcome to submit any thoughts or ideas you may have on the subject and the areas you would like to see the PWI focus on. You can contact me directly at joan.heery@thepwi.org or via any of the committee members.
• Help make public transport and active travel the natural first choice for daily activities
• Support fewer car trips through a coherent, convenient and cost-effective public network; and explore how we might use cars differently in future
• Encourage cycling and walking for short journeys
• Explore how to best support the behaviour change required
• Consider future demand and changing consumer behaviour for goods
• Transform ‘last-mile’ deliveries –developing an integrated, clean and sustainable delivery system
• Optimise logistics efficiency and explore innovative digitally-enabled solutions, data sharing and collaborative platforms
• Support the transition to zero emission road vehicles through: regulatory framework strong consumer base market conditions vehicle supply refuelling and recharging infrastructure energy system readiness
• Maximise benefits through investment in innovative technology development, and development of sustainable supply chains
• Consider where, how and why emissions occur in specific locations
• Acknowledge a single solution will not be appropriate for every location
• Address emissions at a local level through local management of transport solutions
• Target support for local areas, considering regional diversity and different solutions
UK as a hub for green transport technology and innovation
• Utilise the UK's world-leading scientists, business leaders and innovators to position the UK as an internationally recognised leader of environmentally sustainable technology and innovation in transport
• Build on expertise in the UK for technology developments and capitalise on near market quick wins
• Lead international efforts in transport emissions reduction
• Recognise aviation and maritime are international by nature and require international solutions
• Harness the UK as a global centre of expertise, driving low carbon innovation and global leadership, boosting the UK economy
Principal, Phase 1&2Data analysis
Matthew is an engineering consultant with ten years of experience in data analytics and its applications in infrastructure asset management, including rail, data centres, oil, gas and water treatment. His focus is on operational data modelling, helping clients make Opex / Capex decisions using their maintenance, inspection and renewal data.
Principal, Phase 1 & 2Client & Technical Direction
Mike is a Principal Engineer in Network Rail’s central Technical Authority. His work focusses on portfolio level asset management of c.200k railway earthworks. Recent initiatives Mike has led include the developments of parametric hazard indices, global stability appraisals and rainfall/soil moisture diagnostics. He plays a key role supporting Network Rail’s operational business, including policy, standards, competence, assurance, IT and R&D. Mike is a Chartered Engineer and Member of ICE.
The failure of earthworks on the UK rail network is associated with train accident risk, where derailments may occur if support to the track is lost due to embankment failure. Table 1 shows that, whilst earthwork attributed derailments and potentially high-consequence failures were reducing by the end of Control Period 5, total numbers of earthwork failures and earthwork-related temporary speed restrictions remained comparable to a decade earlier. Suppressing underlying failure rates and speed restrictions through effective asset management of earthworks is key to controlling train accident risk to tolerable levels.
This article focuses on the key elements of a programme to build an operational asset management tool for the effective management of earthworks that will help to suppress underlying failure rates and speed restrictions and control train accident risk to tolerable levels.
The condition of rail embankments has been primarily monitored through visual inspections by earthwork examiners using electronic handheld devices since the early 2000s2 The last examined state determines both an asset’s examination frequency, and whether the asset is promoted for evaluation by Network Rail asset engineers. Evaluation is where all known data related to an asset is scrutinised and a management strategy for the asset determined.
AUTHOR: David KitePhase 1&2Technical Lead & Project Manager
Dave leads AECOM’s Rail Research & Consultancy team and has worked for a range of global clients to develop track renewal strategies, manage track investigations and has led development of digital tools to give rail clients greater insight into their track data. He is a Chartered Member of the ICE and was technical lead for the first phases of development of the embankment instability analysis.
Network Rail typically examines approximately one-third and evaluates approximately one-tenth of its 190,000 earthwork assets annually.
To better understand performance between examinations, and promote deteriorating assets for evaluation where required, Network Rail is seeking to complement earthwork examination data with data captured through other means.
Track geometry data is collected routinely by Network Rail using specialist measurement trains. Previous research has shown that this measurable track geometry data can be used to give an indication of the performance of railway embankments3
Furthermore, Network Rail’s Earthworks Technical Strategy published in June 20181 expresses a desire to better utilise track geometry data for identification of embankment instability, allowing the root cause to be addressed through deep-seated remediation, rather than continuing to deal with symptoms eg tamping track back to line and level.
The research described herein mostly discusses the second phase of a four-phase programme to deliver an operational tool. The phases of the research can be summarised as follows:
PHASE 1 PROOF OF CONCEPT (2018 2019): Analyse the track geometry data of embankments within Network Rail’s CP6 work bank with the purpose of identifying indicators of embankment instability. Subsequently use this analysis to develop an algorithm capable of generating a metric that can be used to quantify embankment instability. Further details of this research are summarised in Reference 1.
PHASE 2 VALIDATION AND REFINEMENT (2020): Analysis of track geometry for a control group of embankment assets from the Anglia Route, not selected based on current performance. This paper will focus on this phase of this research programme.
PHASE 3 – SCALE UP TO WHOLE ROUTE/REGION AND REFINEMENT (DUE TO FINISH 2021): Analysis of track geometry for all embankments within a single Network Rail Route/Region. This study will include the necessary steps required to elevate the proof of concept to a full prototype capable of analysing the substantial volumes of data at Route/Region level.
PHASE 4 – SCALE UP TO WHOLE NETWORK AND SUPPORT IMPLEMENTATION (EXPECTED FINISH 2022): Analysis of track geometry for all embankments for Network Rail’s entire network. Furthermore, this phase will focus on integrating the analysis technique into Network Rail’s systems for use as an operational tool.
This paper is a summary of outcomes from the validation and refinement phase of the research (Phase 2) and is not exhaustive.
Over the past six years research has been conducted on the use of measurable track geometry data for detecting embankment instability, primarily by AECOM and Network Rail.
In 2014, a pilot study was carried out by AECOM and Network Rail to assess the feasibility of using measurable track geometry data to detect early stages of embankment failure3 In this study, track geometry records between November 2010 and May 2014 were processed for embankments experiencing some degree of instability. It was found that the rate of change of vertical alignment (Top) and lateral alignment, along with a composite parameter referred to as dTop or differential top (equal to Left Rail Top Right Rail Top) were the best indicators of earthwork movements. This concept is shown graphically in figure 1.
In the Phase 1 study, track geometry data was processed for over 1,800 embankments, which were planned to be renewed, refurbished or maintained as part of Network Rail’s Control Period 6 (2019 2024). This process involved calculating SD values for the Lateral Alignment and Top parameters of the track geometry using a 20-yard base length, and then trending the data over the relevant time period. Consideration was also given to alternative base-lengths for the SD calculation which showed that the 20-yard base length was most suited to this assessment, providing the best balance between mitigation of alignment errors and sensitivity to localised instability.
The Phase 1 research showed that the Lateral Alignment and dTop parameters could be used to quantify earthwork instability, which resulted in the development of an algorithm which outputs an Embankment Instability Metric (EIM). The EIM value is a measure of the average annual deterioration of the Lateral Alignment and dTop parameters and calculated for each 10-yard section of embankment. The resulting EIM values (units mm/yr.) are calculated for each year for each 10-yard track segment. The study observes a period from 01-May to 30-Apr to calculate an annual measure of the EIM each year, as an assumed ‘neutral’ point to negate any seasonal variability by taking a full summer-winter season.
A comprehensive summary of the Phase 1 research, along with the criteria for valid track geometry records, can be found in Reference 1.
There have been alternative approaches to the method outlined above, such as an approach developed by Network Rail5 , which uses a 220-yard SD base length for processing the Alignment and Top parameters. The benefit of a 220-yard SD base length over a 20yard base length is ease of processing, since the 220-yard SD data is already generated by Network Rail for all available track geometry. Thus, for the 220-yard SD method it was not necessary to align and re-process track geometry data for shorter standard deviations such as in this study. Therefore, the speed in which 220-yard SD data can be analysed is an order of magnitude faster. However, it was shown that the use of this longer base-length meant it was not possible to recognise embankment instability due to the lower resolution masking these more localised faults which are typically less than 100 yards in length.
Both methods described above are looking for gradual embankment movements, which are significant enough to move the tracks and therefore manifesting in the measurable track geometry data. The shallower the embankment movement, the less likely it is to manifest in the track geometry data and other types of embankment failure mechanisms (eg highly localised slips or localised animal burrowing) will also not appear at all in the data as these types of failures are unlikely to impact the geometry of the tracks or result in immediate loss of track support.
Figure 1: Effect of typical rotational slip on track geometry.
Figure 2: Extract of Embankment Instability Metric (EIM) heatmap and EIM aggregation and shrink swell identification modules, where each block represents a 10-yard segment.
Figure 3: Time series plot showing seasonal shrink-swell behaviour, with annual EIM values at the top of the plot.
Furthermore, the research thus far has generally looked at embankments with known instability issues, however the following section describes the second phase of this research project which examined a control group of embankments.
This section details the approach carried out for Phase 2 of this research which largely adopts the methodology described in the initial phase1 The objectives of this phase of research were to further validate and to improve the accuracy of the methodology, thus, several improvements were made to the calculation of the EIM, described in the following sections.
During the first phase of this research it was shown that higher measurement frequencies resulted in calculation of higher EIM values, since EIM values are a function of track geometry, which can change rapidly but is measured infrequently. Since the relationship
between measurement frequency and the resulting EIM value was observed, it follows that normalisation to correct for the disparity in the measurement frequency should be a consideration.
A simulation was therefore completed in Phase 2 to establish the relationship between measurement frequency and calculated EIM value. This simulation used five years of data from 340 10yard embankment segments from different parts of the network. Commencing with the original 10 records per year, the simulation performed a systematic removal of an increasing quantity of geometry records, followed by a recalculation of the EIM value.
The resulting calculated EIM values were plotted against the simulated recording frequency. This showed a very strong linear relationship for segments with lower EIM values, with the relationship becoming less linear and weaker with higher EIM values.
The consistency of this relationship allowed for a normalisation correction factor to be calculated and applied to the EIM values, depending on the frequency of available data for the track segment and year for which it is calculated.
Figure 4: Extract of track rotation metric data.
In order to minimise the amount of adjustment of the EIM values from their original calculated results, the normalisation was carried out to the equivalent of six records per year. This frequency was selected as this is the average number of track geometry records which meet the criteria for calculation of an EIM value.
Aggregation is necessary to reduce the quantity of data for user consideration to a manageable level, and aggregation of all the annual EIM values to a single 10-yard segment EIM value is the first step in this process. In order to provide a single result for each segment, the maximum calculated EIM over the analysed period or following any significant earthwork intervention has been proposed, with a weighting to reduce the influence of older data.
Using the maximum EIM value maintains the variance of the dataset and the preservation of the metric units. This approach also places significance on the calculated EIM during a particular year, regardless of the observed instability during other years. An additional reason for use of the maximum EIM method, is due to the difficulty in accurately measuring the deterioration rate and the tendency to underestimate the true rate of geometry deterioration, as discussed in the previous section.
In conjunction with using the maximum EIM value a historic data weighting is also proposed to compensate for the relative importance of more recent instability. This method weights calculated EIM values from the past three years with a factor of 1.0, with this factor dropping by 0.1 for each year. Further research related to historic data weighting is required and should be carried out as part of any future phases of this research.
One drawback however, of using a single maximum weighted EIM value, is the extent to which erroneous data can influence these Segment EIM results. This is partly addressed through spatial aggregation, which is now discussed.
For Phase 2 of this research 26,889 EIM values, split across 5,591 track segments and covering 595 embankment assets were calculated. For an earthworks engineer, using a tool to assess the performance of their embankment portfolio, this may seem overwhelming. Thus, spatial aggregation of multiple track segments is necessary to allow a rapid first-pass filter, removing the need for the engineer to review every 10-yard segment of data. There were two main objectives in performing spatial aggregation. Firstly, to accentuate spatially clustered high EIM values and reduce the effect of isolated high EIM values, since it has been recognised that isolated values are more likely to be erroneous track geometry data or resulting from misaligned data.
The second objective is to support grouping of segments into larger sections of track which can be reported for further action.
After consideration, a method using a 50-yard rolling average was deployed to smooth and group the segment EIM results, with the chosen base-length seen as a good approximation for an average length of track which might be affected by an earthwork related instability.
A fundamental assumption for trending of track geometry data is that the geometry does not typically improve substantially without maintenance intervention. However, the initial phase of this research identified examples of seasonal cycles showing large but gradual improvements in track geometry, followed by gradual deterioration.
After consideration, this seasonal cycle was attributed to the shrinkswell behaviour of expansive soils in the embankment core material, since the gradual nature of improvements contrasted to the rapid improvement in geometry typically seen with maintenance events. An example of the related worsening and gradual improvement in track geometry is shown in figure 3.
This effect can be clearly seen in figure 3, between 2016 and 2019, most notable in the dTop, Alignment and Worst Top parameters.
Since the deterioration in dTop and Alignment parameters associated with shrink-swell behaviour can appear like the development of a rotational failure, it was recognised that it is important to distinguish this effect, programmatically if possible. Therefore, an algorithm capable of identifying segments of track which exhibit this seasonal shrink-swell behaviour was developed and has been used to analyse all track segments within this phase of study.
The shrink-swell algorithm analyses elements of the dataset, including the length of time between, and the month during which peaks and troughs in the data appear, as well as how gradually the geometry improves and the relative size of the peak-trough amplitude. These factors are required to be satisfied by two out of three parameters analysed, for any three years, for a segment to be identified as exhibiting a seasonal shrink-swell behaviour.
It is acknowledged that this analysis still requires refinement, since the total identified segments is thought to be lower than the prevalence of the behaviour. However, it is recognised that seasonal shrink-swell behaviour will vary with differing climatic conditions and the presence of high-water demand trees.
Since the primary failure modes identified through this analysis of track geometry are shallow and deep rotational movements, it follows that analysing the magnitude and direction of rotation programmatically could assist with identifying potential failure modes for segments. The compound parameter referred to as differential Top is calculated, with a larger value of SD Top assumed to indicate downward settlement related to that rail. Therefore, a positive value of dTop implies the vertical alignment of the left (cess) rail is worse than the right (6ft) rail, more likely to indicate a shallow rotational movement (anti-clockwise looking in direction of travel). A negative value of dTop is therefore more indicative of a deep rotational movement. Figure 1 gives a visual representation of how the movement of the rails is indicative of the movement of the earthwork.
An algorithm was developed to calculate the magnitude and sign of the change in dTop on an annual basis, reporting a sum of the change in dTop in mm SD for each segment-year.
The resulting values are reported along with the EIM values to support interpretation of areas of identified instability by providing an annual measure of the direction and magnitude of measured rotational movement. The track rotation metrics are presented in a similar heatmap to the EIM values with (shallow slip) positive values shaded progressively darker orange and (deep seated) negative values shaded progressively darker magenta. Figure 4 shows an example of the track rotation metric heatmap, with values reported on a per 10-yard per deterioration year basis. Such data can aid, for example, identification of embankments where rotational failure can be seen to be propagating along the track, or where data shows shallow rotation leading to a deep-seated rotational movement, suggesting the slip plane is moving beyond the track centreline.
Research around the track rotation metric is still in its infancy. Thus, the next step will be to validate this analysis with some selected sites known by the client, and additionally to program the algorithm to recognise these sites automatically from the data.
Following recent improvements to the methodology listed above, the updated algorithm was used to calculate a total of 26,889 EIM values, split across 5,591 track segments and covering 595 Embankment Assets. The average EIM value in Phase 2 of this research was calculated as 1.24 mm/year.
In order to assess the validity of the calculated EIM values and segment level values, Network Rail provided the following subsample datasets for correlation: assets with a known desiccation issue, assets with visual signs of distress and assets with a known failure. Average EIM values for these embankment assets averaged 2.06mm/yr., 4.41mm/yr. and 4.41mm/yr. respectively, all significantly higher than the average EIM for all assets (1.24mm/yr.).
An additional dataset provided included the assumed embankment fill type, which originates from a study commissioned by Network Rail to provide an analysis of the fill material used during the original construction of embankments. This assumed fill type was available for 82.9% of the embankments analysed in Phase 2 of this study. Embankments consisting of high potential cohesive soil had an average EIM value of 1.31mm/yr., which was the highest out of all the different fill types. This was expected as embankments consisting of high potential cohesive soil are more susceptible to embankment instability issues than other fill types.
A full breakdown of results will be provided in further publications of this research.
During the initial phase of research, 35 failure sites were analysed to provide understanding of the accuracy of this methodology and insight into the feasibility of using this technique for early failure identification. An additional four failure sites (from winter-2019/20) were considered during the most recent phase of the study and figure 5 shows drone footage from one of these failure sites.
The failure analysis carried out in the most recent phase of this work successfully highlighted embankment instability issues in three of the four failure sites analysed, where the reported failure locations coincided with the highest amounts of geometry deterioration in and around the area, data also showed instability throughout most of the years of available data.
Figure 6 displays the track geometry data along with an EIM heatmap covering the area of an embankment showing signs of instability. The data shows rapid deterioration of the differential Top, with negative values indicating deep rotational failure centred at 72m 375y with EIM values consistently above high risk threshold (4mm/ yr.) between 72m 259y and 289y. The analysis demonstrates that there have been instability issues with this embankment for at least the last four years which this methodology would flag up for further investigation.
An initial study (Phase 1) developed the proof of concept technique and analysed approximately 1800 embankment assets identified for maintenance intervention between 2019 and 2024. Further analysis (Phase 2) has now been completed for a control group of 595 embankment assets in the Anglia Region, consisting of 26,889 EIM values being processed over 5,591 10-yard track segments. These EIM results have been successfully correlated with client provided datasets: sites with desiccation issues, failure sites, assumed embankment fill material and movement indicator data, confirming the validity of the methodology. This control group has also been compared with Anglia embankment assets planned for renewal and refurbishment, showing higher EIM values resulting from analysis of the track geometry for these embankments.
Further developments to the methodology have been completed during this recent phase of work, including: spatial and temporal aggregation of EIM values to aid reviewing of results, normalisation of EIM values to account for varying track geometry measurement frequency, automatic identification of shrink-swell behaviour and development of a metric to indicate the direction and magnitude of rotational movement.
Validation performed on the EIM value has clearly demonstrated that this method of analysis offers the potential to recognise instability of embankments using track geometry data, providing an invaluable quantitative tool to geotechnical engineers giving insight on the timing, rate and location of detected movement. Where rotational movement is taking place, the direction of rotation can be established and propagation along the embankment analysed.
The main remaining challenges in the deployment of this technique are:
• Ensuring sufficient track geometry data coverage and measurement frequency.
• Identifying and allowing for errors in track geometry data measurements.
• Refining the algorithms used in the processing of the longitudinal alignment of the track geometry data.
Future phases of this research plan to address these challenges, conducting further algorithm developments, such as using a variable minimum data measurement frequency and automated detection of track geometry data errors. Additionally, the AECOM team are working on fully automating the alignment of track geometry data to improve the consistency and accuracy of data alignment, allowing this technique to be more easily scaled up to a network level tool. Additionally, it is planned that this technique is trialled using data from in-service revenue vehicles (known as UGMS data by Network Rail) as this dataset offers far greater measurement frequency than the track geometry records. This dataset is however only being gathered for a small fraction of the network currently, and the measurement history is limited at present, however it is envisaged this will change and UGMS will become an increasingly useful dataset for future analysis of embankment stability.
1. Networkrail.co.uk. 2018. Earthworks Technical Strategy June 2018. [online] Available at: https://www.networkrail.co.uk/wp-content/ uploads/2018/07/Earthworks-Technical-Strategy.pdf
2. Power, C., Mian, J., Spink, T., Abbott, S. and Edwards, M., 2016. Development of an evidence-based geotechnical asset management policy for Network Rail, Great Britain. Procedia engineering, 143, pp.726-733.
3. Sharpe, P.; Hutchinson, D. Prediction of Earthwork Failures Using Track Recording Car Data. In Proceedings of the Railway Engineering Conference, Edinburgh, UK, 30 June–1 July 2015.
4. Kite, D., Siino, G. and Audley, M., 2020. Detecting Embankment Instability Using Measurable Track Geometry Data. Infrastructures, 5(3), p.29.
5. Nogy, L. Railway Earthworks Instability Diagnosis Using Track Geometry Measurement Data-CCQ and Top 35m; Permanent Way Institution: Warley, Brentwood, 2016.
Head of Route Engineering and Operations HS1
Robert is a rail industry professional with nearly 20 years’ experience in the rail and transportation sector within highspeed, UK mainline and metro railways. A Chartered Engineer and Fellow of the Institution of Civil Engineers he is currently the Head of Engineering and Operations for HS1 Ltd, the company granted the concession from government to operate, maintain and renew the UK’s only high-speed railway until 2040. He is responsible for providing client leadership to HS1’s supply chain which is supporting HS1 Ltd to protect, evolve and grow its assets.
Director, High Speed Delivery, Network Rail (High Speed) Ltd
Jonathan has worked in the railway industry for over 28 years in operations, maintenance and projects. He has worked in the UK for British Rail, Railtrack and Network Rail as well as internationally mainly in North America. He was part of a joint UK/US team developing the design, build and maintenance of California High Speed rail. He currently leads operations, maintenance and planning for Network Rail High Speed.
High Speed 1 is the only true high-speed railway in the UK and runs between London St Pancras and the Channel Tunnel. It was constructed in two phases. Section 1 between the Channel Tunnel and Fawkham Junction (south of Ebbsfleet) was opened in 2003, with Eurostar services operating on the high-speed and domestic lines through Kent into London Waterloo, continuing an operation that had started in 1994.
Section 2 was opened in 2009 and saw the routing of high-speed services through to London St Pancras at which point international operations ceased into Waterloo. At this time, domestic high-speed services started from London to Ashford, bringing the Kent town within 38 minutes of the capital with Southeastern. International passenger services (Eurostar) operate at up to 300 km/h (186mph) and Southeastern Javelin services at up to 225 km/h (140mph). There are a small number of freight services (around 2% of overall traffic) operating between the Channel Tunnel and Dagenham. Fawkham Junction is no longer used for operational traffic.
Southeastern operate Javelin Class 395 trains (figure 1), Eurostar Class 374’s (figure 2) and Freight Class 92’s.
High Speed 1 was built to international (UIC) high-speed standards and is of a wide W10 gauge, with the French TVM430 ‘Transmission Voie-Machine’ in cab signalling system which extends across many high-speed lines in northern Europe. The railway is twin track and fully bi-directionally signalled with frequent cross overs. This is an in-cab signalling system with lineside markers and is comparable to ETCS level 2. At the complex station layout at St Pancras, Belgian KVB (control voi Balise) is used in conjunction with colour light signals. The system is track circuited throughout and controlled from two dedicated signalling workstations at Ashford Integrated Electronic Control Centre (IECC).
AUTHOR: Ben StrawHead
Ben is an engineering and projects professional with over twenty years’ experience in the design, construction, operation, maintenance and renewals within the infrastructure sector for major UK and overseas projects and high speed rail. A Chartered Engineer and Member of both the Institution of Civil Engineers and Association for Project Management he is currently the Head of High Speed Projects for Network Rail (High Speed) Ltd, which is a wholly owned subsidiary of Network Rail Infrastructure Ltd, that is contracted to manage, maintain, operate and renew the UK’s only high speed line.
Section 1 is characterised by a high-speed line across the countryside of Kent and the track is predominantly constructed on ballast. Section 2 crosses the Thames through a twin bore tunnel just north of Ebbsfleet International station. North of Dagenham, two further long twin bore tunnels traverse east London Long Tunnel 2 between Dagenham and Stratford International which is 10,120m in length, and Long Tunnel 1 between Stratford International and the approach to St Pancras is 7,543m. The entire line has a 25kV overhead line catenary system which is integrated with the tunnel fire life safety systems and controlled from Ashford IECC.
When High Speed 1 was completed in 2009, the concession for the operation, maintenance and renewal of the line was awarded to High Speed 1 Ltd for a 30-year period. At the end of the concession in 2040, either a new concession will be let, or the ownership will transfer back to the Department for Transport. This concession also includes retail, parking and station operation at St Pancras (figure 3), Stratford, Ebbsfleet (figure 4) and the international station at Ashford.
High Speed 1 Ltd contract the operation, maintenance and renewal of the railway, as well as the station management of St Pancras, Stratford and Ebbsfleet, to Network Rail (High Speed) (NRHS), a wholly owned subsidiary of Network Rail.
The funding mechanism of the railway is different to that used on the rest of the mainline network. Train operators are charged a track access fee which incorporates the future cost of renewing railway infrastructure over the next 40 years. The renewals charge is held in an Escrow account and drawn down as renewals are required.
High Speed 1 was designed and built to provide speed and convenience. Through these it has delivered substantial economic benefits to the areas it serves. The reliability of the system plays a
crucial role. Unlike anywhere else in the UK, delays are measured in seconds rather than minutes. Typically, before the pandemic, average delays related to operations and maintenance were consistently under 7 seconds per train. In financial years 2019-20 and 2020-2021, High Speed 1 accumulated over 200 days per year without any delay at all. In 2020-21, there were 335 days with no delays due to infrastructure. Whilst it is recognised that COVID has had a significant effect on train services, the strength of performance has been driven by underlying reliability. High Speed 1’s unique selling points therefore remain its speed, convenience and reliability. These must be maintained to ensure for TOC and FOC customers that train travel is the transport mode of choice, for domestic and international destinations. The chances are if you use the system for either an international or domestic service, it will be delay and fuss free!
However, to maintain this high level of performance has meant a continuing challenge for both High Speed 1 and Network Rail. The system is classed as mid-life by the Office of Road and Rail (ORR) and it is recognised that to keep the system operating at high tolerance levels, more invasive work will need to take place. The system is financed in control periods of five-year duration which are similar to those undertaken by the wider Network Rail across the UK. This is no coincidence, as the ultimate ownership of the system is by the Department for Transport (DfT) and the regulation of the system is undertaken by the ORR, as it is in Network Rail. Control Period 1 started at service operation in 2009 and ran until 2015. During Control Period 2 (CP2) (2015-2020) the system started to show signs of mid-life ageing; some of the switch and crossings required more maintenance and replacement, and other components, particularly in signalling and telecoms, were becoming obsolete, despite being less than 15 years old. As a result, this level of heavy maintenance / light renewals required a re-think in terms of how work is undertaken, and the high level of performance maintained. The workforce had very little experience of this type of work activity and during CP2, experts from outside of High Speed 1 in the wider Network Rail and contracting organisations helped deliver this type of work. However, the aim was to manage the increasing project portfolio in-house, with the maintenance teams learning new skills to undertake some of this work themselves.
We are currently in Control Period Three (CP3) which runs from April 2020 to March 2025. Figure 5 shows the number of schemes within the control period split by discipline.
The delivery of this workbank required the formation of a High Speed project renewals team with a dedicated Project Management Office (PMO) created with functional leads for Development, Delivery, Controls and Planning, Engineering Assurance, Commercial and Finance (See figure 6). The PMO is to project manage the Route and Station works agreed in the 2019 periodic review (PR19) determination from the Office of Road and Rail (ORR). Governance is undertaken in line with a gate process which sets out the control framework for the financial authority and technical assurance. The five-stage gate process draws on Association for Project Management (APM) guidance and aligns well with Network Rails’ GRIP (Governance for Railway Investment Projects) process and the recent changes of the Project SPEED and PACE (Project Acceleration in a Controlled Environment) initiatives now being introduced within the domestic UK rail industry.
Delivery of renewals is either using third-party suppliers or NRHS maintenance engineers depending on the level of complexity of a project. We procure services via a competitive tendering process using existing NR frameworks and RISQS registered contractors, typically appointed under standard forms of contract but we are starting to use target cost options to introduce supply chain incentivisation. In line with an efficient operating model, we are able to use in-house maintenance teams, via an asset management effectiveness strategy, so we have developed a selfdelivery capability and provide construction supervision for safety critical roles. All works are undertaken follow Construction Design and Management (CDM 2015) Regulations and use Active Risk Management (ARM).
Figure 7 shows the renewal costs for CP2 and 3 as we forecast costs for future control periods. As we move into preparations for CP4 and the increasing volume and value of renewals, the High Speed 1 plan is to develop an integrated renewal plan that models the work bank, access and execution of the works. Key principles of this are to ensure we meet stakeholder requirements, with minimal
disruption and deliver value for money. Within CP3 a strategic theme has been developed to minimise disruptive engineering access through use of an integrated planning technique for resources and possessions. This will allow availability and track access charges to be optimised for existing and future service growth whilst ensuring the renewals programme of planned interventions sustains the required levels of safety and performance.
Project work has started from a very low base back in 2017 with this type of work not undertaken before on the route and continues to ramp up apace today. In 2019, the first switch and crossing renewal (figure 8) with signalling design (to a new specification) was undertaken close to the Eurotunnel boundary and there is a campaign underway for changing of switch and crossing components based on wear rates and reliability across the route. In addition, some telecoms equipment has been replaced based on being obsolete and wishing to reduce the risk of non-availability of components as well as mitigating cyber security which was not perceived as a risk when the system was designed back in the late 1990’s. This has meant some new skills being learnt by the team, supplemented by project management to help integrate the work with current inspection and maintenance. These skills will be further developed over the control period to help ensure, where possible, projects can be delivered in-house.
The Coronavirus pandemic has also provided increased focus on the need to provide efficient and effective renewals. Any delay to services as a result of engineering works may be damaging to the recovery from the pandemic. Costs must also be continually challenged to help support customers.
One of the challenges of undertaking renewal work is how to integrate with both the running of trains and the current level of inspection and maintenance work. Unlike the rest of the UK network which has organically grown the planning of work, High Speed 1
has not, so there are no engineering allowances or a long-term strategy for major engineering work agreed many years in advance with stakeholders. These are currently being examined as part of a review of engineering work and it is likely that work will be confined to more intense but less frequent blocks during the working week. Domestic and international operations often have competing aims with Eurostar, for example, seeing the opportunity for growth during Christmas day operation to allow people to move between London and Paris later in the day. At weekends, whilst Southeastern may see a lowering of traffic outside of the peak hours, Eurostar often may want to run later due, for example, to international rugby taking place in Paris. In addition, post pandemic, it appears increasingly likely that operators will prefer engineering disruption during the week rather than at weekends where a recovery in leisure traffic can be sought.
Technology plays a key part in the strategy now and going forward, as well as some challenges. High Speed 1 was built and has continued working as a ‘people-less railway’ which has always meant no red zone working. Much of the work has been undertaken using a fleet of dedicated Multi-Purpose Vehicles (MPV’s) (figure 9) which have the in-cab signalling system, TVM430 fitted. During CP3 they will be overhauled and upgraded, including the consideration of battery operation in tunnel environments with the aim of using the MPV fleet far more for efficient delivery of possessions. The entire route is bidirectionally signalled which gives flexibility in terms of running trains on one line if the workforce and equipment can be safely protected on the line which is blocked, however whilst operating in this format there is a reduction in allowable speed. Due to the wide gauge, in most locations this is far more straightforward than the rest of the UK. High Speed 1 does not have conventional speed restrictions imposed like the rest of the UK; the signalling system has the ability to provide set speed parameters in the event of any speed being required. This is undertaken both on the system and locally, in signalling switch rooms. Pre-set speeds of 80, 160
and 225 km/h are available. The system automatically controls the approach speed to reduce line speed to the target speed throughout the section. However, what this does mean is that there is a challenge to be able to hand back any work that requires a speed to this level. The reduction in speed from 300 km/h to 225 km/h on a long high-speed section is significant and therefore the delay for a sectional running time can be several minutes. If, for example, the 225 km/h parameter after work cannot be met and a 160 km/h speed restriction has to be imposed, this would have a significant effect on train services, with either cancellations or more likely bidirectional running in place.
As part of the determination for CP3 High Speed 1 was awarded £2m of research and development investment that aims to reduce operations, maintenance and renewal cost. Investment is being made in trialling train borne monitoring and inspection of assets, static forms of remote monitoring, advanced analytics and technology enabled ways of working that will improve asset knowledge, extend asset life and help deliver more efficient renewals. The use of 5G networks to facilitate some of these initiatives is also being trialled.
In summary High Speed 1 is now approaching midlife. Its ongoing management requires ever increasing amounts of asset renewal activity. We face ongoing challenges related to maintaining safety, cost, sustainability and maintenance that makes our product affordable to our customers. To ensure the continued exceptional levels of high operational performance that our customers require and realise the efficiencies needed in a post-pandemic world, new technologies will be harnessed, and operations optimised.
Furthermore, not only is high performance expected on High Speed 1, but ensuring it is undertaken in a sustainable and environmentally friendly way as well as providing the flexibility to run passenger and freight services based on the unpredictable demand post pandemic will be a key challenge over future years. In doing so, High Speed 1 working in partnership with NRHS, will continue to increase the value of its asset which is then translated into value for the public purse when the concession is returned.
Figure 5: Breakdown of High Speed 1 schemes by discipline during CP3.
Figure 6: The High Speed 1 renewals team Project Management Office.
Figure 7: Renewal costs over High Speed 1 control periods.
Andrew Benton is a PWI member and has lived, studied and worked in China for 24 of the last 30 years, where he had the opportunity to follow the development of its conventional and Passenger Dedicated Line (PDL) networks first-hand, and to ride the rails to places near and far. He works in the international development sector and is currently “home-based” in Britain, hopeful of a return to China soon.
China’s first experience of high speed rail came a few days before the opening ceremony of the Beijing Olympics in August 2008, with the inauguration of the new Beijing Tianjin 350 km/h Passenger Dedicated Line (PDL). Opening just in time to enable fans to hop to Tianjin where some of the football matches were being played, even the tickets were new style light blue, machine-printed credit-card sized billets, easy to slip in your wallet or purse and easy to find again as you moved through the autoticket barriers and down to the dedicated platforms at the new Beijing South PDL station (figure 1). There was huge interest in the office as my esteemed and venerable professor colleague showed us all his return tickets one lunchtime, excited to be one of the first to travel at the weekend.
The Beijing Tianjin PDL is now one of the most heavily used PDLs in the country, with over 150 pairs of high speed trains making the 30 minute trip each day, about a third of which continue on to destinations further afield. With departures between 6am and 11.15pm there are approximately 65,000 seats travelling in each direction each day, an annual capacity of 27.5 million. And this is just a tiny sliver of the national total there were over two billion rail journeys on the PDL network in 2019, and almost 4 billion in total on both high speed and conventional networks (figure 2).
The People’s Republic of China is a huge country, covering 9.6 million square km, forty times larger than the UK, and with a population that is 20 times greater. The large majority of the populace are concentrated on the eastern, seaboard, side of the country, areas that were the focal points of China’s growth when the country started to open up economically in the 1980s. The far western provinces such as Gansu, Xizang (Tibet) and Xinjiang are very sparsely populated and much less developed. China’s rate of urbanisation has been growing very rapidly and has been crucial to its growth, providing low-cost labour for the manufacturing that has driven production and productivity, and is now driving innovation and the creation of new markets. Sixty percent of China’s people now live in urban environments, up from 50% just ten years ago, 35% at the turn of the millennium, and 25% in 1990. As people continue to move to urban centres, the populace is less dispersed and investment in centre to centre transportation becomes both more necessary and more financially viable. With GDP growing by 7-15% per year in the 1990s, there was plenty of need, opportunity and money available for investment in the country’s transport infrastructure to support and drive its growth and development at the turn of the millennium.
In 2000, a journey by rail from Beijing to Shanghai, a distance of 1,318 km, would take fourteen and a half hours pleasant indeed in comfortable soft sleeper class, with access to the dining car and
a restful night’s sleep, but for business travellers and others for whom time had more financial value, a shuttle flight of two hours or so was proving to be by far the more popular choice, with dozens of direct flights per day. With other major cities spaced out by similarly large distances (36 hours by train from Beijing to Kunming, 22 to Guangzhou and 30 to Chengdu), and booming private car ownership, the days of rail as the preferred means of long distance travel in China seemed numbered.
However, in the meantime the government had been working on developing the railways as an integral part of the future transport mix, and issued the “Medium and Long Term Railway Development Plan” in 2004, which covered national rail network development to 2020. It recognised that to drive and support the nation’s economic growth there would be a pressing need for increased freight and passenger capacity to complement that provided by the growing air and road travel sectors as the nation became more mobile. Crucially, the plan included the development of a passenger-dedicated high speed network.
Up to that point, China had experimented with the production and deployment of high speed motive power units based on existing domestic technologies, but the results had been disappointing and many of these early multiple units ended up relegated to serving conventional routes in the western backwaters of the country until the mid 2010s. The famous Siemens-built maglev line serving Pudong airport in Shanghai opened in 2002 but the system proved too costly to serve as the blueprint for a nationwide high speed network, although discussions and public consultations on a possible maglev line from Shanghai to Hangzhou, a major city 180 km to the southwest of Shanghai, continued until the Shanghai Hangzhou PDL opened in 2010.
China therefore looked for overseas assistance to develop its high speed system, and worked with a range of international suppliers to develop and adapt systems suitable for the China context. The plan was that once these had been proven in situ and seen to be effective, the country could embark on a localisation policy to produce and evolve the whole PDL system without outside expertise, tweaking and pummelling the imported technologies to improve them, and protecting these innovations in a vast series of new national patents a system that has been very successful, and has enabled China to develop a mature home-grown PDL system that has grown to 38,000 km since 2008, and is marketed for overseas connectivity, especially to its near neighbours, under the Belt and Road Initiative.
Bombardier’s Regina EMUs formed the basis for the CRH1 250 km/h series units, Kawazaki’s E2 Shinkansen became the CRH2 series (figure 3), Siemens’s IEC3 became the CRH3 series, and Alstom’s Pendolino became the CRH5. There was no CRH4, possibly because the number 4 is thought to bring bad luck in Chinese culture. Selection of the major global types of EMUs in production thus gave China the opportunity to learn and absorb relevant technologies from each one, whilst comparing their performance on the China network.
It appears that Siemens was able to tap into the China experience of car-maker Volkswagen, (Volkswagen set up the first overseas jointventure car manufacturing plant in Shanghai in the early 1980s and was hugely successful at capturing a large segment of the domestic market in the early 2000s it was said that half the cars on the road were VWs.) and the German company formed the vanguard of overseas involvement in China’s PDL system. Of the four companies originally involved, all but Kawasaki maintain strong partnerships in China today.
Protecting the intellectual property contained within any product is a not-to-be underestimated task in the China context, with matters often biased towards shorter-term national protectionist interests as a default, though in the past few years there have been signs of a more enlightened approach emerging a notable case against the manufacturer of a Range Rover Evoque copy called the “Land Wind” ended on Land Rover’s side a couple of years ago.
The next major line to open after Beijing Tianjin was the Wuhan to Guangzhou line, extending south from Wuhan on the Yangtse river in central China to Guangzhou, 120 km north of Hong Kong, which
opened on 26 December 2009, from where a local connection on the fast commuter line to Shenzhen could take one on to Hong Kong. The Beijing to Wuhan section was connected in 2013 (figure 4), and the Hong Kong Express link to Shenzhen, and connection of the Special Administrative Region to the national PDL network, opened in September 2018. Over the years the network has developed in an apparently piecemeal way, with sections opening here and there when completed, and often not connected to other PDL sections on opening, but this approach has enabled more rapid development of the network as a whole.
The most recent to open is the 192 km Beijing to Chengde section of the Beijing to Shenyang/Harbin PDL which connects the capital to its three north-eastern provinces by a 350 km/h-designated line. Commencing from a new station at Beijing Chaoyang in the eastern part of the city, the line runs via new PDL stations at Huairou south and Miyun south to Chengde, the mountainous summer retreat of emperors and now a tourist destination with its preserved and restored imperial palaces, and many temples and shrines. The fastest service takes just 52 minutes non-stop, a reduction of nearly four hours compared to a journey on the conventional line though PDL passengers miss the lovely meandering ride through the valleys to Chengde for the last 90 minutes of the trip. With the 500 km Chengde to Shenyang section having opened in December 2018, and the 540 km Shenyang to Harbin section in 2012, the entire 1,300 km trip from capital city to Harbin at the heart of what was once known as Manchuria takes five hours and thirty-eight minutes, at a cost of 584 RMB (£65) one way, second class, notably cheaper than by air.
Figure 5: China’s PDL Network.
Source: Author - SS (Own work) CC BY-SA 4.0, https://commons.wikimedia.org/w/index.php?curid=64448527
Today, the backbones of the PDL network are the trunk lines, which form an “8 x 8” network crisscrossing the country (figure 5), with eight broadly north-south, mostly 350kmh trunk routes (eg Beijing to Shenzhen; Beijing to Shanghai), and eight east-west trunk routes (eg Lianyungang to Lanzhou and then on to Urumqi; Shanghai to Kunming) connecting the major centres of population, and an increasingly dense network of regional, connecting and feeder lines (figure 6). In many cities the new PDL stations allow immediate transfer to new metro or tram lines, facilitating rail-based long-distance transport from city centre to city centre. Lines are usually elevated on viaducts where possible, officially to reduce land-take from farmers, but raising the trackbed facilitates the use of standardised modular construction and is likely to be more cost effective than needing bespoke engineering works the full length of a line (figure 7). China’s railway press regularly showcases the newest longest-span PDL bridge or deepest tunnel, and not unusually these break world records.
How fast is high speed? Many of the PDLs are not built for 350 km/h operation, but for 250 km/h, and some are even designated at 200 km/h. These latter lines can be used for non-EMU traffic too. As prices are charged according to speed and class, high speed services are notably more expensive than conventional ones. A trip from Beijing to Xi’an to see the Terracotta Warriors currently costs 515 yuan (£57) in second class by PDL (4.30 hrs) compared with 156 yuan (£17.5) in hard seat by conventional train (15 hours).
And if you want to, you can spend 1,627 yuan (£180) on a fully lie flat seat in business class. Services invariably have a first class (four seats across, compared to five in standard) usually priced at 20 30% more than standard class, except on the Beijing Shanghai line where it is at least 50% more, presumably to maximise returns from the many business travellers on that route. Occasionally, but still rarely compared to more market-based pricing systems in other nations, discounted tickets are offered. Services are classified with prefixes to denote speed/type G for long distance 350 km/h expresses, C for shorter distances with more stops, and D for 250 km/h operation. Sleeper services were introduced on selected PDL routes three years ago using sleeper versions of the latest Fuxing EMU units, whilst sleeper versions of CRH2 units had operated on the network, especially serving the Beijing to Shanghai route, since 2011. The use of the high speed system to transport goods has been trialled in the last few years every year on “singles day” (November 11), which is China’s foremost online shopping day, there are stories in the media of high speed services being used for the rapid delivery of important purchases and now CRC has developed a high speed goods EMU to
into this market.
Despite the huge numbers of people travelling on the high speed network, only the Beijing to Shanghai line is known to make an operating profit. The operator, the state-owned Beijing to Shanghai High Speed Railway Company, listed on the Shanghai stock market in late 2019.
Although maglevs were not pursued in the first decade of the 2000s, in recent years interest has grown again in the technology, in part due to the increase in innovation and high quality manufacturing capacity that the government’s various railway and business policies have supported over the past fifteen years. China is now one of the world leaders at developing both low and high speed maglev systems, having taken the opportunity to quietly innovate, develop and implement reasonable-cost maglev technologies. Domesticallyproduced low speed suburban maglevs now operate as part of the metro systems in Beijing (since 2017) and Changsha (since 2016), and more are under development and construction. More recently, a very high speed system (600 km/h) has been prototyped, and development continues.
This national capacity to innovate is a major factor driving the development of China’s railway manufacturing and supply sector. China is leading the way in autonomous driving technology, with the Beijing to Zhangjiakou PDL that opened in 2019 the first to use driverless operation (though there is a “driver” in the cab for safety reasons), and one that will surely garner publicity from the world’s media during the Winter Olympics next year, as it connects Beijing with the event’s skiing venues in Yanqing and Zhangjiakou. Driverless technologies are also being rolled out on metro lines and suburban EMU-operated systems and are likely to become commonplace within the next five years.
Yet it was only ten years ago that the worst modern rail disaster on China’s railways occurred, in Wenzhou, a city 400 km to the south of Shanghai. Two services on the newly built 250 km/h PDL line from Shanghai to Fuzhou, further south around the coast, collided after one had been unexpectedly held at a signal, and forty people lost their lives. The authorities rapidly buried the affected coaches and encouraged the media to limit reporting, but passenger interest in the new PDL system declined notably over the next period, and confidence in the railways was dented. A review of the accident blamed technical component problems, but also highlighted a lack of appropriate behaviour on the part of some staff, who could have acted to avoid or reduce the severity of the disaster earlier and in more effective ways than they did.
The accident was also clearly a factor in the subsequent restructuring of railway management in the country. For over sixty years, between the establishment of the People’s Republic of China in 1949 and 2013, the Ministry of Railways was builder, operator,
judge and jury of the nation’s railways. It employed about two million people when it was disbanded in March 2013 and was then £200 bn in debt. With corruption charges levelled at the then director in early 2011, the Wenzhou crash, and a very top-down operating model increasingly unpalatable to a country keen to embrace more private sector investment in its national infrastructure, the justification for its dissolution was clear.
The Ministry was split into the National Railway Administration, effectively the railway regulator, which is a component of the Ministry of Transport in the government hierarchy and which has formal responsibility for safety, as well as policy. The remainder of the Ministry’s responsibilities were passed to a new operating and construction company, China Railway Corporation (CRC), which has over 500 subsidiary companies, many of which are involved in building the PDL network. CRC operates the seven regional railway bureaus which do not cover the PDL network except where it intersects with the conventional one and the separate “China Rail High” (CRH) branded PDL network.
Development of the high speed system was achieved by partnering the Ministry, and then CRC once it took over, with the governments of the provinces the lines were designed to serve, often in 5050 partnerships and usually with the province providing funds by borrowing from national and regional development banks.
Do the lines do what they are intended to do? They surely do. Studies show that a notable proportion of network journeys are of middle distances of 300 500 km, not short hops or full length trips from huge metropolis to metropolis, and that about half the passengers on some lines are taking journeys they would not otherwise take by conventional train (figure 8). Thus, the network is creating its own demand and helping to drive increased profitability or perhaps reducing losses!
New lines increasingly adopt the around-the-station development model too, with cities and towns en route investing heavily in developing new residential and business areas surrounding their new high speed railway stations. These are usually built on the outskirts of town where they also serve as components of intermodal transport hubs (figure 9). Shanghai’s Hongqiao PDL station is the most well established and ideally located to provide instant connectivity to Hongqiao international airport. Other mature examples include Zhengzhou East, which is helping drive development of the eastern part of that city, and the now elevenyear-old Wuhan PDL station (Wuhan’s main conventional railway stations are named after two of its component districts, Hankou and Wuchang), which is at the centre of an eastern Wuhan city revival.
China has added 37,800 km to its PDL network since the Beijing Tianjin PDL opened in 2008. The government released its National Transport Outline Plan 2021 2025 earlier this year, incorporating
recommendations by China Railway Corporation that were made public in the middle of last year. This includes the completion of a 70, 000 km PDL network, almost doubling the current length, as well as increasing the conventional network to almost 130,000 route km. The plan builds around five foci to drive the rail sector boosting innovation and innovation capacity, better intermodal integration, improvements in the quality and nature of services, better environmental friendliness and reductions in carbon emissions, and greater international connectivity.
The commitment of resources by government and private sector (often with significant levels of state ownership), the personal professional commitment to the development of the railways of those involved, and the acceptance of the need to build such a system by those who have been directly affected (such as farmers whose land the lines cross and in whose fields stations and slip roads have been built) must be second to none in the development of railways in the modern era. Let’s hope that China’s vision and experience, albeit in very different political and financial environments to the UK, can provide some inspiration for the decision-makers leading Britain’s high speed network as it grows, and a raft of new opportunities for those who will plan, design, build, operate and maintain it.
For an excellent summary of the development of China’s high speed railway network, please refer to:
“China’s High-Speed Rail Development.” International Development in Focus. Lawrence, Martha, Richard Bullock, and Ziming Liu. 2019. Washington, DC: World Bank. doi:10.1596/978-1-4648-1425-9. License: Creative Commons Attribution CC BY 3.0 IGO
https://documents.worldbank.org/en/publication/documents-reports/ documentdetail/933411559841476316/chinas-high-speed-raildevelopment
After the publication in the April Journal of the article: “An introduction to the overhead electric traction system” by Garry Keenor, Paul Hooper and Peter Dearman, the following correspondence was received from PWI Member Anthony Foster:
Dear PWI,I'm pleased to see the beginning of a new article series 'An introduction to the overhead electric traction system' in the April Journal although I wish to question some technical points that it makes.
Within the article, it suggests that three-phase electrification is impractical and also that three overhead conductors are required, which I don’t believe is correct. Admittedly there was a 1901 project with railcars by Siemens & Haske that used three conductors, one above the other that ran for about 14 miles. It is the case that this project was over-complex and was discontinued (See Wikipedia "Experimental three-phase railcar").
Nonetheless, before the days of semiconductor rectifiers, several Swiss and Italian mountain railways used three-phase traction using two overhead wires and the rail to give the three conductors required. They used induction motors and had fixed speeds set by pole-changing motors. The great benefit was the ability to regenerate when descending, much safer than friction braking. It seems that the original system lasted until 1963 but there seems to be a few surviving. Junctions are complex but they work.
The book "Electric Railways 1880 - 1990" by Michael C. Duffy published by the IEE as part of its History of Technology series, Chapter 8 and Wikipedia "Three-phase AC railway electrification" give details of this reasonably successful system.
Later in the article, the 'Traction Return' section talks about the aerial return conductor and mentions that 'some' return current can flow out of the rails to this conductor but no mention is made of how. The presence of the extra conductor would have very little effect and is only used where immunisation is not necessary (there is a length of the ECML North of York like this).
Older systems use transformers with their primary in series with the overhead line and secondary in series with the earth conductor which is connected to the rail at the mid-point of the between-transformer span. These transformers, called 'Booster Transformers' (BT) are mounted at distances of about 1-2 miles, determined by immunisation requirements. An ideal BT system shifts all of the return current from the rails to the return conductor.
Higher power modern systems don't have a true return conductor, the same size of wire is energised at 25kV in anti-phase to the OLE. At intervals of about 10 miles an auto-transformer links the antiphase conductor, the rail and the OLE. This has the effect of reducing the average current in the rail to near-zero and makes the return conductor work for its existence. Power is supplied to the system at 50kV but the train sees 25kV. The main advantage is that Grid feeder points can be much further apart. (We used 40 route miles for the initial GWML calculations).
Yours, Anthony J Foster
The PWI thanks Anthony for his email and has been in touch with the authors, one of whom has provided the following response:
• 3-Phase OLE “Anthony correctly notes that 3-phase traction has proved enduringly practicable for a small number of very specialised railway systems. However, the article’s broad conclusion that 3-phase OLE traction is impractical is undoubtedly correct in the context of modern standard-gauge mainline mixed-traffic and high speed railways, as evidenced by the overwhelmingly predominant modern single phase AC OLE systems used all over the world. The ready availability of software controlled rolling stock traction packages able to regenerate during braking and feed single phase AC power back into the OLE network, together with the use of Static Frequency Convertors at national grid power supply points (which enable traction power supplies to be taken from the grid “balanced” across the 3 grid phases) means it is very unlikely that 3-phase contact systems will be used in any future OLE schemes. The mention of 3 conductors rather than 2 was an unfortunate technical proofing oversight on the PWI’s part.”
• Return currents “Anthony provides a useful expanded description of the legacy booster transformer system (now deprecated in favour of boosterless feeding) and the auto transformer system used in higher capacity AC OLE systems and I have nothing to add at this point. However, the topic of traction power supply (both AC and DC) is a large one and will be covered in greater depth in future Journal articles.”
Dr Özgün Sunar is a Lecturer in the Department of Railway Systems and Technologies at Eskisehir Technical University, Turkey. During his PhD at the University of Sheffield, he conducted research to improve the reliability of overhead line electrification equipment, particularly when short-circuits and arcing occurs. His research interests are fatigue, fracture mechanics, finite element modelling and overhead line electrification.
David Fletcher is Professor of Railway Engineering in the Department of Mechanical Engineering at the University of Sheffield. He leads UK Rail Research Innovation Network (UKRRIN) activity at Sheffield and runs a rail transport MEng module for undergraduates interested to join the industry. His research includes rail-wheel interface, OLE and traction energy modelling, building on 5 years spent on a rail depot conducting large scale test work prior to joining Sheffield.
Arcing in overhead line electrification (OLE) systems becomes a significant phenomenon particularly with the increase in speed of electrified trains or with contamination of the wires, for example by ice. It has been known that arcs cause damage to the pantograph current collectors and often play an important role in limiting their service life. However, in recent years, studies in the literature showed that arc phenomenon can be also a significant problem for contact wires. This study provides new insight into damage to OLE contact wire subjected to arcs. Contact wire samples were extracted from an in-service OLE contact wire, cross-sectioned and analysed with optical microscopy and microhardness tests. The results show that the heat input from arcs influences the microstructure through modification to the metallurgical grains of the contact wire as well as leaving visible surface burns. Additionally, a correlation between arc damage and contact wire softening was identified. These factors are crucial in mechanisms of wear and fatigue in metals, two of the service life determining processes affecting OLE. This study lays the groundwork for future research into examining the role of arc current, number of arcs and feeding system (AC or DC) in arc damage to OLE contact wires.
Overhead line electrification (OLE) systems transmit energy to trains through contact between the pantograph current collectors and the contact wire. Besides being an electrical system, the OLE is also a mechanical system in which the contact wire is subjected to tensioning, uplifting and friction while carrying electrical energy. Contact wire-pantograph interaction presents a challenging tribological system, particularly at higher train speeds1-3 and it’s
optimisation through system design, inspection and maintenance is central to efforts to achieve cost effective electrification4 Although the pantograph is designed to ensure reliable current collection with steady uplift force, the sliding of the pantograph current collectors over the contact wire can result in interruptions due to the surface irregularities of the contact wire and its fittings, or dynamic effects on the pantograph and the uplift force while passing structures. Figure 1 shows a schematic of an OLE system.
The contact wire-pantograph interface plays an essential role in determining the component life for OLE. Besides mechanical wear in the contact wire and pantograph current collector, any current interruption with consequent arcing is also a significant problem. Two forms of arc are relevant here: (i) “Pantograph arcing” caused by momentary loss of contact between the wire and the pantograph, with arcs on the lower surface of the contact wire. (ii) “Flashover” arcing, which can occur due to low electrical clearance between the contact wire and civil structures (bridges, overpass or tunnel). In flashover arcing, arcs are usually focused on the top or side surfaces of the contact wire (facing towards civil structures). The schematic in figure 2 shows arcing types in OLE contact wires.
Arcing is considered one of the most important interaction problems with the potential to cause severe damage both on the pantograph surface and contact wire, likely to shorten the service life of these OLE components 5-7 He et al.8 defined the arc issue between contact wire and pantograph surface as “electrical welding”. Similarly, hot spots due to arcing were identified by Gonzalez et al.9 as microwelding that is significantly detrimental to the contact wire surface. Arcs generate heat exposure on the surface of both collector strip and contact wire, and Kubo et al. found the thermal effects of discharge could lead to melting and evaporation 10
Figure 1: Schematic of OLE.
However, since most of the studies focus on wear mechanisms of the pantograph surface there is a relatively small amount of literature that is concerned with arc damage effects on the contact wire. One study by Zhu et al.11 examined temperature distribution due to arc discharge over the pantograph and contact wire surface with current values between 100-300 A. The results showed that copper on the surface melts and turns into vapour due to the high temperature. An experimental study was carried out to determine the effects of arc discharge intensity by Ding et al.12 and showed that when the intensity of the arc discharge increases, the damage on the materials of pantograph and contact wire becomes more severe.
To build on these studies this paper reports observations from wires removed from service in the UK, focusing particularly on apparently minor arc damage that would not warrant any rectification action, but which does modify the condition of the OLE contact wire. The investigation was conducted using metallurgical examination, optical microscopy and hardness measurements on cross-sections of the wire. It provides an original contribution to exploring damage in the contact wire due to arcing. Conducting the study with naturally arc affected contact wires from service (extracted from a mainline) is intended to represent a benchmark for future studies under more controlled conditions. Actions which may be taken based on the findings include: (i) Increased focus in OLE system and pantograph design in avoidance of even minor arcs. (ii) Placing value on maintenance that avoids introduction of features (splices, twisted or kinked sections, figure 3) which trigger OLE-pantograph dynamics leading to arcing. (iii) Application of improved design and materials at locations such as neutral sections frequently subject to arcing.
A location on the UK West Coast mainline at Milton Keynes (58m 32ch from London Euston) was selected to investigate the OLE arcing phenomenon with a 1 metre length of contact wire (CuAg0.1) extracted from this region. Prior to detailed investigation, visual inspections of the contact wire show that 26 significant burn marks existed on the various surfaces: sides, bottom and top. Figure 4 shows the detected burn marks on the contact wire surface.
After visual inspections were completed, a short length of contact wire was cut off for microstructural investigations. Optical microscope and microhardness tests were chosen to quantify the microstructural and mechanical properties of baseline (worn but not visibly arc exposed) and arc affected contact wires. Samples were cross-sectioned from the burn mark locations parallel to the longitudinal axis. Contact wire specimens were prepared for metallography following cross-sectioning, mounting in a standard 30mm diameter mount, grinding and polishing to a 1μm finish and etching using to reveal the microstructure of the copper alloy. The etching process preferentially attacks grain boundaries within the alloy to reveal the structure using ferric chloride (FeCl3) dissolved in alcohol (5g FeCl3, 96ml industrial methylated spirit and 2ml HCl) applied for 11 s before being rinsed off.
Analysis methods applied following sample preparation were: (i) Optical microscopy to reveal grain structure, and (ii) microhardness tests from the arc damaged surface region to the interior material
Figure
revealed by the cross-sectioning. Examples of surface burn marks, the cross-sectioned interior, and hardness measurement locations and direction are shown in figure 5. Microhardness tests were performed for each of the samples with more than 40 indents, and for three arc exposed regions to verify the results. Control samples with no evidence of arc damage were prepared for two different locations for which the contact wire was worn 0.5 and 1.0 mm. These control samples help to reveal whether the wear at the bottom surface could be responsible for the internal structure and microhardness observed at the arc exposed locations of the contact wire.
To provide a baseline, an arc free control sample microstructure from the overhead line is shown in figure 6. The bottom surface indicates the contact wire to pantograph interface surface. It can be seen that the contact wire grains are elongated in the longitudinal direction. This was because the contact wire was manufactured by the drawing process. Importantly, although the wire has been in service and had undergone wear corresponding to many thousands of pantograph passages there was no evidence of arcing or internal modification to the microstructure relative to that for an unused wire.
The internal microstructure of the contact wire samples cut from below surface arc locations are shown in figure 7. In comparison to figure 6 significant metallurgical modifications were observed in these contact wire samples. The first modification is significant arc damage at the edge of the sample where the arc met the contact wire. Secondly, voids are present internally below the running surface and close to the arc damaged surface. These voids were formed from 50-300 μm below the contact surface of the samples (figure 7a/b/d). Another significant finding was that when moving from the core of the material to the arc damaged surface, the grain size of the copper increases, and the longitudinal shape of the grains imparted during manufacture is lost with them showing a circular/ spherical shape instead in this region. Although there are no voids shown in figure 7c, the grain modification and grain growth remained apparent.
Microhardness tests were conducted using the Vickers method according to British Standard BS EN ISO 6507-1:2018. This requires that hardness indents are positioned at least 2.5 times the mean diagonal length of indent away from the specimen surface in copper
alloys, and it was assumed the same distance also applied from the internal voids. Hardness measurements therefore started from 0.24mm away from the contact wire running surface. Figure 8 presents the Vickers hardness results obtained and shows there was no hardness reduction with distance from the contact surface in the worn wire removed from service with no evidence of arc exposure. However, a significant hardness decrease of up to 60 % was observed in arc-affected samples. As the damage was produced in service, the details of arcs affecting these contact wire samples (current, number of arcs and duration) were unknown, however, these hardness reductions are very similar to those observed in laboratory arc exposure of this contact wire type13 where currents of 100A and 200A where used to simulate AC and DC systems. All the arc spots observed showed a similar hardness reduction pattern across the sectional area of the material.
To link the metallurgical observations on grain modification with the microhardness results these are brought together in figure 9 to establish a link between contact wire softening and microstructural modifications. The colour scale of the figures was set to be in the range 60 and 120 HV in both cases to allow comparison of the results between samples. The coloured area was restricted to the microhardness measured area, so could not describe the area very close to the surface or voids.
In figure 9 a very high hardness reduction is seen at the arc damage regions. As is typical for metals, a positive correlation was found between the reduction in hardness and grain growth produced by the arc heating of the samples. Moving from the damaged surface to the interior it was also seen from the figure that grains change from highly enlarged, then smaller, and then to those unchanged from their original longitudinal shape when moving to the core of the material. In between the regions of grain growth and the material core, a transition region existed. In this region, although the grain shapes did not change, there was an evidence that the hardness of the material dropped to range of 80-90 HV.
The findings of the investigation are of importance for understanding two major service life limiting processes that affect contact wires: wear and fatigue. Fatigue damage typically progresses through a slow initiation phase as a recognisable defect develops, followed by a much more rapid crack propagation phase leading to fracture and complete failure. Internal void formation is relevant to the
initiation phase and may bypass an otherwise slow process of material degradation. Wear damage is typically a visible and clearly progressive process, with mechanical wear rate proportional to material hardness within the design uplift load range. While total wear rate will depend on the sum of mechanical and electrical effects the softening observed here suggests a local acceleration of wear is possible. These processes may interact, for example, on the contact surface accelerated wear in softened material offers the possibility that initiated defects are worn away before cracking can start. The position of the arc event around the wire (flashover arc to structure, or pantograph arc) will also affect the stress cycle experienced in the damaged region as the wire bends and deflects with each subsequent passing pantograph. With these factors in combination it is clear there is considerable scope for further investigation to better understand wire life and failures in service, some of which has begun through laboratory based investigation [13], [14]
The importance of arcing in understanding non-tribological damage in the contact wire is revealed by the results presented here. The initial objective was to identify the significance of arc damage on the contact wire installed in a UK mainline and it was expected this would be in the running surface of the contact wire. The results show that arc spots were seen not only on this lower surface (facing towards the pantograph) but also on the sides and the top surfaces. The findings from visual inspections were important in showing that arcing is a phenomenon that can occur between OLE cables and civil structures (flashover) as well as between contact wire and the pantograph (pantograph arcing).
Having identified that even mild arcing can damage the contact wires the question arises of what can be done about this. To the authors knowledge, there is no viable inspection technique that can find internal damage of the type identified for contact lines in situ. As their long term impact becomes clearer, a more promising direction is in renewed focus on system and pantograph design to avoid even mild arcs. Where maintenance is undertaken the value of avoiding introduction of splices or other features which excite pantograph to contact wire dynamics is perhaps higher than was previously realised. Such repairs have a high potential for generating arcs and further wire damage in the same area. For features such as neutral sections where arc exposure is hard to avoid there may be options with alternative, less damage susceptible, materials [13] that can be deployed locally in high exposure areas.
Figure 8: Hardness survey of arc spots extracted from OLE main line.As the arcs driving damage in the samples occurred naturally on the contact wire in service the parameters of arc duration, current and number of arcs were unknown in this study. To understand the relative importance of these factors and feeding system type (AC, DC) on contact wire metallurgy and mechanical behaviours a laboratory study can give more definite answers. The question of softened contact wire developing accelerated wear local to the arc damage and whether this is significant in the behaviour of the 50-300μm depth of voids beneath the outer surface of the contact wire is also expected to require laboratory investigation as detailed observation cannot be conducted on wires in service and under power. With increased understanding of these microscale events, it is hoped that wire life and planning for maintenance can be improved to avoid sudden failures, and to design the underlying problems out of the system.
This study set out to understand the potential damage from arcs on the contact wire using samples extracted from existing mainline OLE contact wire. Both macroscopic and microscopic inspections of the contact wire revealed that arcing had modified the microstructure and reduced the hardness of the contact wire due to local heating. The study provides important insights that apparently minor arc damage that would not warrant any rectification action actually modifies the condition of the contact wire with potential to influence the failure mechanisms that limit service life. The findings of this study lay the groundwork for future research into detailed analysis of parameters affecting severity of arc damage and how to mitigate this problem.
This project was supported by Network Rail, Furrer+Frey and postgraduate scholarship programme of Turkish Ministry of National Education. Thanks are due to Dr Patric Mak for provision of the contact wire for study.
1. S. Midya, D. Bormann, T. Schütte, and R. Thottappillil, “DC component from pantograph arcing in AC traction system-influencing parameters, impact, and mitigation techniques,” IEEE Trans. Electromagn. Compat., vol. 53, no. 1, pp. 18–27, 2011, doi: 10.1109/ TEMC.2010.2045159.
2. J. J. Shea and X. Zhou, “Contact material and arc current effect on post-current zero contact surface temperature,” IEEE Trans. Components Packag. Technol., vol. 29, no. 2, pp. 286–293, 2006, doi: 10.1109/TCAPT.2006.875881.
3. Z. Yang, Y. Zhang, F. Zhao, and B. Shangguan, “Dynamic variation of arc discharge during current-carrying sliding and its effect on directional erosion,” Tribol. Int., vol. 94, pp. 71–76, 2016, doi: 10.1016/j.triboint.2015.03.012.
4. S. Hayes, D. I. Fletcher, A. E. Beagles, and K. Chan, “Effect of contact wire gradient on the dynamic performance of the catenary pantograph system,” Veh. Syst. Dyn., pp. 1–24, Jul. 2020, doi: 10.1080/00423114.2020.1798473.
5. G. Gao, J. Hao, W. Wei, H. Hu, G. Zhu, and G. Wu, “Dynamics of Pantograph-Catenary Arc during the Pantograph Lowering Process,” IEEE Trans. Plasma Sci., vol. PP, no. 99, pp. 2715–2723, 2016, doi: 10.1109/TPS.2016.2601117.
6. S. Midya and R. Thottappillil, “An overview of electromagnetic compatibility challenges in European Rail Traffic Management System,” Transp. Res. Part C Emerg. Technol., vol. 16, no. 5, pp. 515–534, 2008, doi: 10.1016/j.trc.2007.11.001.
7. G. Wu, Y. Zhou, G. Gao, J. Wu, and W. Wei, “Arc Erosion Characteristics of Cu-Impregnated Carbon Materials Used for Current Collection in High-Speed Railways,” IEEE Trans. Components, Packag. Manuf. Technol., vol. 8, no. 6, pp. 1014–1023, 2018, doi: 10.1109/TCPMT.2018.2811801.
8. D. Hai He, R. R. Manory, and N. Grady, “Wear of railway contact wires against current collector materials,” Wear, vol. 215, no. 1–2, pp. 146–155, 1998, doi: 10.1016/S0043-1648(97)00262-7.
9. F. J. Gonzalez, J. A. Chover, B. Suarez, and M. Vazquez, “Dynamic analysis using finite elements to calculate the critical wear section of the contact wire in suburban railway overhead conductor rails,” Proc. Inst. Mech. Eng. Part F J. Rail Rapid Transit, vol. 222, no. 2, pp. 145–157, 2008, [Online]. Available: http://pif.sagepub.com/ lookup/doi/10.1243/09544097JRRT144.
10. S. Kubo and K. Kato, “Effect of arc discharge on wear rate of Cuimpregnated carbon strip in unlubricated sliding against Cu trolley under electric current,” Wear, vol. 216, no. 2, pp. 172–178, 1998, doi: 10.1016/S0043-1648(97)00184-1.
11. G. -y. Zhu, G. -q. Gao, G. -n. Wu, Z. Gu, J. Wu, and J. Hao, “Modeling pantograph-catenary arcing,” Proc. Inst. Mech. Eng. Part F J. Rail Rapid Transit, vol. 230, no. 7, pp. 1687–1697, 2016, doi: 10.1177/0954409715607906.
12. T. Ding, G. X. Chen, Y. M. Li, H. J. Yang, and Q. D. He, “Arc erosive characteristics of a carbon strip sliding against a copper contact wire in a high-speed electrified railway,” Tribol. Int., vol. 79, pp. 8–15, 2014, doi: 10.1016/j.triboint.2014.05.003.
13. O. Sunar, D. Fletcher, and A. Beagles, “Laboratory assessment of arc damage in railway overhead contact lines with a case study on copper-silver and low oxygen content copper,” IEEE Trans. Power Deliv., pp. 1–1, 2020, doi: 10.1109/TPWRD.2020.3032798.
14. O. Sunar, “Arc Damage Identification and Its Effects on Fatigue Life of Contact Wires in Railway Overhead Lines (PhD Thesis),” The University of Sheffield http://etheses.whiterose.ac.uk/28205/ ISNI:0000 0004 9356 9895, 2021.
Figure 9: Hardness map of samples with microstructure: sample 3 (left), sample 2 (right).Inara was born in Latvia and graduated with a BSc in Mechanical Engineering from Riga Technical University. She has a MSc in Transport Engineering and Planning from London South Bank University. In 2020 she successfully completed her PhD thesis on the topic “Sustainability and Related Factors of High-Speed Railways” and in September 2020 was awarded PhD. Currently she is a lecturer at the School of Engineering, LSBU. Her research interests are focused on railway engineering and sustainability. Inara is currently involved in two international projects in Australia and Ecuador. Inara is a member of the PWI, ICE, OR and the DMDU society.
The American Public Transportation Association (APTA) on 7-8 April 2021 held the High Speed Rail Conference “Connecting America’s Cities”. APTA is a non-profit international organisation which represents all modes of transportation and has more than 1,500 members from public and private sectors. Significantly, the conference coincided with President Biden’s announcement to invest over $2 trillion in the next four years to transform the American infrastructure, in a “New Deal for the 21st Century”. These investments are expected to positively impact all segments of the US economy, fight climate change, and potentially spark a second great railroad revolution in USA.
In 2019, American drivers lost on average nearly 100 hours of their time stuck in congestion, costing the economy circa $88 bn. 43% of US roadways are in a poor or mediocre condition, costing drivers almost $130 bn in extra vehicle repairs annually. Pre COVID, flight delays cost Americans around $31 bn in wasted time annually. One way to reduce congestion and greenhouse gas emissions, and improve safety and reliability of transportation, is to invest in High Speed Rail (HSR).
The “Connecting America’s Cities” conference was presented by SYSTRA and was held virtually. It attracted approximately 170 participants from USA, Canada, and Europe. The conference was opened by Paul P. Skoutelas, President and CEO, American Public Transportation Association. He highlighted that in the plan to deliver post COVID mobility, the railway has a special role as backbone of transportation services, and success depends on integration of new technologies and workforce skills. The two-day conference covered several important topics:
• The Economy and the Environment A Renewed Synergy
• Amtrak’s Vision for a 21st Century National Rail System
• Fast Trains for All
• Y’all Aboard! How to Make “Y’all Mean ALL” When Designing HSR Communication Strategies
• Connecting California - Progress on the Nation’s First HSR System
• Driving the Economy with High-Speed Rail
• Transforming Rail in Virginia
• More of the Village Job Creation Everywhere
• No one left Behind Equity, Access, and Affordability
The two days included several highly perceptive presentations. Gov. Jay Inslee, Governor, State of Washington, spoke of the critical role of HSR in transforming transport, emphasising that it is a great opportunity to make transportation cleaner and more reliable, connecting people and communities and improving quality of life. This investment will help to connect workers with jobs, increase access to affordable housing, provide greater mobility for people and help to mitigate climate change.
The first presentation on balancing the economy and the environment was delivered by Dr Anthony Perl from Simon Fraser University, Canada. He began with a quote by Louis Arman “The 21st century belongs to the railways, if they can survive the 20th century”. Dr Perl talked about the history of development of HSR technology which started in 1964 with Shinkansen, and emphasised that the railway renaissance is coming. HSR will provide mobility that fits increasing globalisation and connectivity while also connecting and intensifying economic and social opportunity.
Celine Fornaro, Managing Director, Head of Industrials, UBS, pointed out the opportunities for nextgeneration technology. Currently in Europe 46% of the mainline network is still served by diesel trains. The number of operators willing to ban these from 2035 is increasing, so they are strongly pushing for developing other options, including hydrogen powered trains for regional use. Alstom is a pioneer in developing hydrogen technology and is involved in numerous projects through Europe. The USA’s first hydrogen train is scheduled to be delivered in September 2022.
Daniel Plaugher, Executive Director, Virginians for High Speed Rail, gave an overview of a $3.7 bn project to transform transportation in Virginia. This includes building a rail bridge over the Potomac River and an additional line in the Washington-Richmond corridor. The project will increase capacity and the number of rail services which, by 2030 will reduce CO2 emissions by 148,200 tons and will generate an economic benefit of $1.25 bn each year.
Caroline Decker, VP, Northeast Corridor Service Line, Amtrak, and Roger Harris, Executive VP, Chief Marketing and Revenue Officer, Amtrak, talked about Amtrak’s vision for a 21st Century National Rail System. Amtrak is a federally chartered corporation owned by the US Government pursuing a public purpose but operating like a business. Amtrak’s current network is shown in figure 1. In the pre-pandemic period, Amtrak operated approximately 300 trains per day with over 32 million passengers per year. In 2019, Amtrak spent approximately $5 bn, from which $3.4 bn was operational expenses and $1.6 bn capital investments. This was funded by $2.4 bn in ticket and ancillary revenue, $1.9 bn in federal appropriations, $300 million in state funding and $400 million in commuter authority’s payments.
Due to COVID 19, Amtrak temporarily reduced services on almost all routes, but returning customers will experience Amtrak like never before. It will introduce new sleeping cars, increase speed on some routes, and improve and open new stations. Amtrak is working on substantially upgraded services in Illinois, along the Gulf Coast, between Chicago and Detroit. It is also working on extending an existing corridor service and adding frequency along existing corridors.
The Washington-Boston 457-mile corridor is the busiest railroad in North America, with over 2,000 daily commuter, intercity, and freight trains. More than 800,000 passengers use this corridor daily, approximately 40,000 travel by Amtrak and around 760,000 by commuter rail. Amtrak offers two types of services: Acela with up to 35 departures per day at speeds up to 150mph and NER with up to 40 departures per day at speeds up to 125mph. In 2022, the new Acela trains with a top speed of 160mph will enter service. The new tilting trains with articulated trainset design are manufactured by Alstom and based on the TGV platform. They will offer greater stability, better fuel efficiency and smoother ride. Also, the northeast corridor will have major asset improvements, including the renewal of a number of tunnels and bridges and major station developments.
Brian Kelly, CEO of the California High-Speed Rail Authority, discussed the progress of the nation’s first HSR system (CAHSR). California is the most populated state in USA, expected to reach 59 million by 2050. Roads and airports are congested, and the infrastructure is struggling with increased demand for travel. The two-line HSR track will have 20 times more capacity than existing roads and railways and will reduce CO2 emissions by 40% compared with the 1990 level. The CAHSR will operate with 100% renewable energy and all its 24 stations will be energy self-sufficient. Building the CAHSR will increase accessibility and connectivity and enhance the economy by creating new jobs and supporting local businesses. CAHSR hire and employ local people and the $2.3 bn investment in construction of CAHSR is going to local businesses. Mr Kelly described the construction of Wasco Viaduct (figure 2), which will be over 600 metres long and will take HSR traffic over
the existing BNSF freight tracks. To reduce noise levels from this structure, sound protection walls over 10 m high will be installed. CAHSR will reduce travel time and remove cars from roads reducing highway congestion and CO2 emissions. The project will improve opportunities and quality of life for everybody.
Joseph Giulietti, Commissioner, Connecticut Department of Transportation, highlighted three major HSR projects: California, Florida, and Texas. In California, a HSR (figure 3) will connect Los Angeles and San Francisco with speeds of more than 200 mph and travel between the two cities will take less than 3 hours. Currently the city centre to city centre journey takes nearly 12 hours by rail, including a bus connection into downtown San Francisco. The project is due to be completed by 2033 and is set to reintroduce a mainline railway station into central San Francisco.
Another project is in Florida, where a private company is working on HSR from Miami to Orlando, scheduled to open in 2022. In Texas, another private company will develop HSR between Dallas and Houston based on Japanese technology. Scheduled for completion in 2026, trains will operate with speeds of around 200mph, and the 240-mile journey will take only 90 minutes. All these projects contribute to creating a national HSR network that will boost the US economy and ultimately benefit the country. They will improve the environment and connectivity, creating many thousands of new jobs, transforming communities, and offering economic benefits in the long term. HSRs will increase opportunities in affordable housing for working families by expanding geographic areas where people can reach employment places.
These massive investments in the US infrastructure make it necessary to think about workforce development in advance. Dr Karen E. Philbrick, Executive Director, Mineta Transportation Institute, highlighted the employment shortage across the transportation sector, which pre-Covid reached 460,000 people annually. An ageing population and workforce means there is a need to attract a younger generation to the railway industry. One approach is to offer apprenticeships and stable employment, maximising the benefits for local communities by creating good jobs.
All the presenters pointed out that building HSRs in the USA will create more sustainable lifestyles, increase connectivity, and create new jobs. Growing and improving railway infrastructure brings economic growth. HSR will provide benefits for today and for future generations, connecting communities in a more sustainable way. It will connect cities, increase capacity for passengers and freight, and will open new opportunities for communities. HSR will contribute to greater population mobility, help to mitigate environmental damage and meet the needs of an aging population. HSR can offer travel time savings and improved capacity as well as reductions in road accidents and road and airport congestion. To maximise the benefits from developing HSR there is a need to integrate all public transport in one seamless transportation system, and do this smarter and better. The conference was very informative and sparked lots of debate. It provided a perfect opportunity for politicians, practitioners, and academics from different parts of the world to exchange experiences and knowledge regarding HSR, and to discuss the next steps for a safer and more efficient transportation network for all Americans.
Figure 2 (left): The Wasco Viaduct.Chris is a Chartered Civil Engineer, and a Fellow of the PWI and ICE. He has worked in the rail industry since 1972 retiring in 2004. His experience covered track and structures, design and maintenance and infrastructure management. After retiring Chris has remained active as a technical writer as well as writing reports for the PWI Journal and other organisations.
This online conference, organised by the Permanent Way Institution on behalf of Network Rail (NR), was introduced by Ian Coleman, Principal Engineer, Track Switches and Crossings, NR. Traditionally this conference has been run annually specifically for Network Rail’s Track Maintenance Engineers. This year, running it online made it possible to open the conference up to the whole maintenance community and beyond. After welcoming everyone, Ian introduced the first speaker:
Gareth commenced with a welcome to the first virtual NR/PWI Track Maintenance Conference. He spoke of the unprecedented times in which we find ourselves, mentioning the pandemic and recent fatalities. Some of the incidents that led to the latter involved passengers, some colleagues, but all were tragic.
He discussed briefly the hazards, consequences and controls relating to track engineering, and things like bow-tie visualisation and other techniques relevant to controlling risks. Such things need to be re-examined in the light of recent events, and Gareth asked everyone to take part in this.
Challenge standards, he said, and be involved in working groups. He reminded maintenance engineers of their responsibilities, including the following:
• Know where the high-risk assets are and have them recorded
• Work with other asset managers on cross-disciplinary issues
• Ensure that teams are trained and competent
• Ensure that assets are being appropriately inspected and maintained
He went on to recognise the challenges and risks of manual track inspection, including safety, health, weather, nights, competence, quality, capacity and efficiency. We are responding to these challenges, with initiatives like train-borne or remote monitoring of assets, risk based principles of inspection and maintenance, and much more.
John began by reflecting on a number of current issues:
• Incidents: the recent poor safety performance, with the deaths of colleagues and members of the public, as referred to earlier by Gareth. Have we lost sight of the challenge? What more should we do?
• Covid-19: whilst the pandemic is not over, we can take pride in the way we have pulled together in the last year. John mentioned such things as the development and application of emergency standards and significant innovation that has been used. However, we have been left a legacy in the value for money challenge created by the disappearance of passengers and their revenue.
• Successes: the annual number of derailments has tumbled, as has the number of rail breaks. The track measure of PIM (Precursor Indicator Model the train accident precursor model) is at an all-time low. The Competence Framework for track has been developed and is coming into use.
• Opportunities: John mentioned a long list including the Competence Framework, redesigned cast crossings, composite materials for such things as timbers and bearers, intelligent infrastructure, review of hot weather patrolling and review of S&S inspections.
Moving on to PWI matters, John began by mentioning the Presidents’ themes. Firstly, his own theme for 2020/21, which is industry competence. His objective is a collective industrywide approach with an agreed framework. This should ensure consistent staff development, knowledge and good practice. He identified the themes selected by future Presidents elect. These are Nick Millington, whose theme for 2021/22 is to be Safety and Performance, followed by Peter Dearman in 2022/23 with Electrification.
He said that the PWI as a whole has a focus on support to its members, both individual and corporate. This has been seen in the successful transfer of many Institution activities from face to face over to online formats, in the new Institution website and in the realignment of the PWI Vice-Presidencies with the NR Regions.
Liam’s theme was the excellent maintenance response to the Covid-19 pandemic. The challenge was to keep freight and essential workers moving on the rails and keeping people safe whilst managing the infrastructure. Teams had to be led remotely and best practice had to be identified and spread effectively.
Nick reminded his audience of the reasons for the setting up of the Task Force in 2019. This was initiated as a result of the upturn in track worker fatalities, a sad reversal of the steady decline that had been occurring over the 10 or 11 years up to 2018.
He emphasised that the clear evidence shows that working on live railways whilst relying upon human lookout protection is by far the riskiest activity for people. He and his team have been leading the business/industry in the effort to reduce such working, and a massive change has been achieved already. However, further deaths have occurred, and more needs to be done. Network Rail is also legally obligated to eliminate human (lookout) warnings by July 2022.
He went on to discuss the work currently taking place. This is strongly based upon analysis of facts and data. For example, he showed analyses of types of near miss in relation to line speeds and types of protection in use. By far the worst statistically is the use of unassisted human lookout protection.
Further analysis considered the times of day when work was undertaken, showing that midweek mornings were the times when incidents were most likely. This is when the railways are most busy, but also when we are most likely to roster track works.
Since Nick first prepared a slide showing the industry people killed at the start of his current role, there have tragically been several more deaths to add to the graphic; three at Margham, one at Roade and
The revised timetables meant fewer passenger trains but more freight. The required level of performance needed to be delivered, but what was that? Delivery of the required response capability meant moving our people about safely and providing them with the necessary support such as welfare facilities and food.
Liam went on to discuss how people were kept safe, whether from Covid or other hazards, how the infrastructure was managed by taking a systems approach to maintenance, how managing people remotely was done and what was done to capture best practice. There are definitely lessons in what he said which are applicable for the future, even after things return to normal.
one at Surbiton. It is not surprising that he intends to spend his year as President of the PWI campaigning to remove people from in front of trains.
Progress is being made, with Scotland having gone lookout free some time ago, Western achieving the same status on Monday 22 March this year and East Midlands following soon after on 31 March. Three clear goals have been set:
• No more lookouts
• 100% use of track safety equipment for protection from trains
• 100% compliance with “019” Safe Working Practices
Nick showed current progress on a complex chart, best seen by looking at his presentation in full. Key points were the fall in open line working from 25% to only 8% and the reduction in the rate of near misses that amounts to almost 50% in 18 months. The Executive Leadership Team (ELT) wish to accelerate the Task Force still further. Six headline risks have been identified and Route plans are being peer reviewed.
RSSB is being very supportive. It has conducted a hazard identification “deep dive”, and Nick showed another detailed slide of the 6 key risks identified.
Finally, Nick talked about the proposed next steps, what engineers need to do now, and offered a free gift! He asked engineers to be leaders, to plan, innovate and challenge and to take pride in what has already been achieved. Lives will have been saved, he said. His free gift was his recommendation of the use of Interflon switch lubricant. Almost 2/3rds of unassisted lookout protection is for switch lubrication. Since using Interflon reduces vastly the required lubrication frequency, this alone would make a significant cut in the reliance on lookouts.
• The MicroDrill
• Composite “timbers”
• Remote cameras to view timbers under load
• Online training, including interpretation of MicroDrill results
NELSON - PRINCIPAL ENGINEER (COMPETENCE & CAPABILITY) PERMANENT WAY NETWORK RAIL (NORTH WEST & CENTRAL)JOHN
John started with some basics about longitudinal timbers; what they are, what the hazards are, the fact that NR has about 13,000 across the network and how they need very careful maintenance, inspection, repair and replacement if things are not to go wrong. He stated that he had an objective to convince everyone that the use of the MircroDrill for condition inspection is worthwhile.
To emphasise the last point, he offered some very scary examples of the incidents that have been caused recently by failures of such timbers. These ranged from a derailment at Paddington Station in 2017 and another very serious derailment at Wanstead Park in 2021, to a couple of cases where unplanned line blockages resulted from inspections revealing very serious problems at Eskmeal Viaduct in 2020 and at the River LLwchr later the same year.
John described the “roadmap” from Paddington to the future. A working group was set up after Paddington and research has been commissioned. New standards are being produced with new track work instructions and training packages. A new competence for examiners is included. Ellipse is being modified to include a longitudinal timber register. Examples of the current support on offer to TMEs John mentioned included:
IAN COLEMAN PRINCIPAL ENGINEER (TRACK, SWITCHES & CROSSINGS)
NETWORK RAILJASON WARDELL, PROGRAMME ENGINEERING MANAGER, NETWORK RAIL (EAST MIDLANDS)
Jason gave an update on the workbank optimisation workstreams and infrastructure forward plan. He spoke about a number of pilot studies such as the Track PLPR Pilot, the Track Geometry Pilot and the Rail Profile Management Pilot.
The new standard NR/L3/TRK/7014 “Inspection and Maintenance of Permanent Way using Risk Based Maintenance (Plain Line CWR Track)” has been published. This focusses on reliability centred maintenance.
CHRISTIAN NICHOLSON, HEAD OF ASSURANCE CHRISTIAN BELL, FUNCTIONAL AUDIT MANAGER NETWORK RAIL (SOUTHERN)
Between them, the two speakers described how a year ago work was begun to improve Management Systems Auditing (MSA) and get away from a culture of box-ticking.
The existing MSA question set was used as the basis, an evidencebased approach was employed, and results were recorded in IRIS (Incident Reporting and Investigation Software).
Audits are quarterly, and feed back to line managers, with autogenerated reports from IRIS to the post holders.
John proceeded to explain more about the MicroDrill, a highspeed drill with a small diameter bit. It is used to drill through a timber in different directions, and during this the resistance to the drill is recorded, both the torque required to turn the bit and the longitudinal force needed to penetrate into the wood.
The recorded data can be viewed graphically, showing the variations as the drilling progresses deeper into the timber, giving an indication of the nature and quality of the material along the length of the drilling. Interpretation requires care and skill, since the resistance of the timber can vary not only due to the presence or absence of decay. Variations also occur due to the orientation of the drill bit relative to the timber grain, for example, or because of the natural variations between different parts of the parent tree such as heartwood.
Future support will come as a result of research projects such as one on timber preservatives like boron gel, from about 15 standardised work instructions including one on use of the MicroDrill, from work modelling timber decay and from examiner training.
John concluded by mentioning the Long Timber Open Forum, which meets regularly to discuss relevant issues and challenges and promotes good practice. He issued an invitation to anyone to attend. They can arrange to do so by contacting John at: john.nelson@ networkrail.co.uk
Ian took the floor himself for this presentation. He began by thanking those that had responded to this survey, about 50 by the time of the Conference, he said. He asked people to continue to participate up until the end of the week of the Conference. A separate open forum was planned to take place on 28 April 2021. He then went into some detail about the responses received to date.
The next standards work will be rewriting the Track 001 modules using reliability-based maintenance philosophies. Jason gave some details of the planned workshop events and identified the people who will be leading these.
He continued by describing various other work, such as that on slide chair lubrication and the lubrication of fishplates, work on train-borne monitoring of S&C, work on curve and switch lubrication work on the uses of drones (UAVs).
He finished by appealing to people to say what else would help them to perform their roles more effectively.
Feedback to: tim.flower@networkrail.co.uk please.
A risk-based question set is under development and staff feedback is welcome.
The presenters reviewed what has been found to date, when they are now in the second round of delivery of the process. Most findings focus on safety, especially management checks on safe working practices (SWPs). Indications were found of wider issues with SWPs, and this has led to an 019 compliance programme on Southern Region.
The MSA coaching pilot has received positive customer feedback, led to an increase in action numbers and quality and the process has been approved by the Route Director and Director Route Asset Management (DRAM). Enhanced audit outputs have resulted, and real value has been added.
LYNNE
GARNER - SENIOR PROJECT ENGINEER RICHARD QUIGLEY - SENIOR ENGINEERNETWORK RAIL (NORTH WEST & CENTRAL)
Ian Coleman gave a brief resume of what professional registration is, described the three levels of registration and discussed why it matters to individuals. He offered a brief review of the routes by which registration may be achieved with the PWI. He considered that registration used not to be a big issue within the rail industry, but that has begun to change significantly, with increasing emphasis on the need to demonstrate that people are professionally competent. Ian’s introduction was followed by each presenter in turn describing briefly their own path to registration: Craig achieved EngTech in 2017 before proceeding to CEng in 2019. He and his whole team got EngTech registration together.
William began with a brief introduction to Network Rail Consulting. The organisation operates in the USA and Canada, the Middle East and in Australasia and Asia. It has several offices in North America and also in Sydney, Australia and in Riyadh.
Moving on to his main topic, he introduced the US railways with a few statistics: the freight network has about 140,000 route miles, owned by 7 Class 1 railroads, 22 Regional and 584 local ones.
The industry turns over about $80bn pa, employing about 167,000 people. It is big business, moving about the same annual tonnages as the road haulage industry.
William described how the industry is regulated by the Department of Transport (DoT) which covers the freight railroads, and the Federal Railroad Administration (FRA), covering the local transit agencies (which include non-rail transport as well). There is also the National Transportation Safety Agency (NTSB).
The railroads belong to a trade body, the American Association of Railroads (ARR), which owns TTCI, the railway research body many will be familiar with. The other rail industry body is AREMA, the American Railroad Engineers’ and Managers’ Association, a close equivalent to the PWI. All of these industry bodies assist their members and also provide feedback from the industry to the regulatory bodies.
Federal Track Safety Standards (known as FRA Part 213) apply particularly to the freight railroads and Amtrak, the passenger rail organisation. These standards are a mix of minimum requirements and prescriptive actions. Reliability centred maintenance and similar approaches have not been encouraged up to now. Change has been slow, William quoting that it has taken 10 years to get the FRA to authorise continuous ultrasonic rail inspection, for example. Some railroads had obtained “temporary” waivers to permit them to apply it, but these had run for years in some cases. William showed example pages from a couple of standards to illustrate their nature. Tracks are categorised by speed alone, for example, with tonnages not mentioned in the standard.
John said that the conference had left him feeling encouraged and proud, thanks to the energy and enthusiasm shown by all. He thanked the PWI, particularly Kate Hatwell, for organising
They found the PWI process simple and valued having mentors/ sponsors. Craig had found registration helpful in his career progression. Lynne achieved CEng registration in 2020. She found the PWI very supportive, with a clearly defined process. She recommended finding a good mentor and remembering that the whole of one’s career may be of use. She has found that registration has opened up for her senior roles where professional qualifications are essential prerequisites.
Richard made very similar comments to the others concerning his progress to IEng registration in 2018 by the Technical Report route in 2018. He briefly described the route. He emphasised the need for self-motivation in completing the registration process. In all this, the first and important step has to be to join the PWI. Go to the PWI website at: www.thepwi.org or contact profeng@thepwi.org Craig, Lynne and Richard all offered their support with the process, and with finding suitable mentors. Network Rail staff were reminded that they should add their professional qualifications to their profiles on ORACLE.
Maintenance delivery is quite different from what we are used to. Trains tend to be very long (up to 2 miles) and heavy, but widely separated in time. This and other factors mean that it is feasible to safely carry out quite significant maintenance works between trains in a way that would be impossible here. This, combined with other factors like union rules and custom and practice, results in the widespread use of long fleets of separate, small, single purpose machines where we would use one or a few multi-purpose ones. Each tends to be worked by one specialised operator/maintainer, and each can be put onto the track, or removed from it, quickly and easily. William described how sleeper (tie) changing is done, as an example.
William noted that plant tends to be quite dated and simple to his eyes, and for example rail cranes tend to be small and few railroads have access to Kirov type machines.
Timber is the almost universal material for ties/sleepers, as the timber sleeper is cheap and readily available. The speed and nature of traffic means that there is no requirement for very high track standards, the emphasis is upon maintaining a safe operational standard and minimising disruption. Timber sleepers are adequate for this, and being lighter than concrete ones, are easier to change with small, simple plant in the windows between trains.
One difference in practice that William considered of possible benefit here was the use on slow speed locations of guarded switches. These have a specially shaped check rail at the switches. The switch tip slides under this in the open position, and so is protected from damage by wheels passing on the adjacent stock rail. The check does make it difficult to inspect the switch tip unless it is practicable to swing it to the closed position, but that was the only disadvantage that he could conceive of.
For the future, he said that the railroads are well funded and appear to have a secure future. The federal agencies are beginning to open up to new ideas, and this is bringing changes to standards, new rolling stock, new components and revised processes. Train borne track inspection methods are beginning to be applied, and the next step, he foresaw, would be to adopt reliability centred maintenance approaches.
the conference, Liam Jackson and Ian Coleman for their major contributions, and everyone else who had been involved, not least the speakers. The strong message he had taken from the event was the message that this is all about people working together, listening, learning and having the courage to speak up when they need help.
An exciting and challenging time is ahead, John said, but we must remember that we have the tools, techniques and talents to succeed.
Gareth is a Chartered Engineer and a Fellow of the PWI.
Gareth’s early career was in the steel industry, manufacturing railway products and delivering technology and asset management projects for heavy and light rail clients. Joining Network Rail in 2009, Gareth has been Head of Track since 2016. He has accountability for Network Rail’s national standards and competence frameworks, and the R&D programme for track engineering. He is focussed on addressing the strategic challenges of improving safety and reliability of track infrastructure, mitigating the effects of weather and climate change and delivering decarbonisation of the railway system.
Our industry is facing unprecedented challenges with recent events triggering a top-to-bottom review of how we inspect and repair the fixed assets that make up our railway infrastructure. The tragic workforce fatalities at Margam in 2019, Roade in 2020 and Surbiton in 2021 have led to enforcement action against Network Rail and an acceleration of changes to the way our frontline teams access their assets safely for inspection and maintenance. The global COVID-19 pandemic has challenged our assumptions about passenger growth and whether the pattern of use will return to pre-pandemic levels. Given the necessary resource put into supporting the UK through COVID, our industry is also now challenged to accelerate innovation and change to deliver a more efficient railway system providing better value for money for UK taxpayers.
Automation of infrastructure inspection and maintenance, when carefully designed and implemented, offers part of the solution to the challenges we face.
So, our first objective is to improve safety for anybody working on the railway. We need to reduce the risk of harm from traffic to trackworkers, as UK data shows we have not made great improvements in this area over the last five years (figures 1a and 1b). We also need to continue to improve the health of our frontline teams by reducing their exposure to risks associated with conventional ways of working, for example manual handling and hand-arm vibration syndrome (HAVS).
Our second objective is to improve the capacity of the railway. Automation allows us to introduce more reliable and reproduceable methods of inspection and repair, as well as increasing the productivity of maintenance of our fixed assets.
Our third objective is to reduce the cost of running the UK railway. Two examples where we’ve done more detailed analysis show the business benefits that could be achieved. By automating the process for repairing rail head defects we could save £91M over a typical five-year funding period. By automating our inspections of tunnels, we can reduce the ‘on track’ examination time by 96%.
Lastly, we need to align with the agreed technical strategy for UK railways, published in autumn 2020. One of the five key objectives of this strategy, reliable and easy to maintain infrastructure, relies on the introduction of greater levels of automation and mechanisation of fixed asset inspection and maintenance to deliver the 2040 vision agreed by wider industry.
Working closely with academia and our supply chain partners (eg via UKRRIN, other UK funded research and EU Horizon 2020 programmes) we have created a cross-asset Autonomous Intelligent Systems (AIS) research and development strategy, comprising of three themes:
1. Smart data collection using state-of-the-art sensor technology, either fixed to the infrastructure or mounted on mobile platforms such as service trains, to collect more and better quality data about our asset, providing that data more quickly to the engineers who need it to make decisions about where and when to intervene.
2. Autonomous planning to support this we are developing tools and techniques to help plan maintenance intervention based on our enhanced knowledge of asset condition and the rate of change of condition.
3. Autonomous robotics to deliver workforce safety and maintenance productivity benefits.
Our vision (figure 2) is to construct scalable architecture that allows us to grow the scope of autonomous intelligent systems, using a wide range of asset data and information sources about the condition of the asset, using commercial off the shelf technology to future proof the system architecture, and to provide us all with the functionality we need to evolve and grow this capability in future years. At the heart of our AIS will be the corporate ‘brain’, the database of all asset information aligned to a single common geospatial referencing system for the location of assets and faults, taking in data collected by frontline teams, rolling stock and unmanned drones/robotic inspection platforms. We will then use our advanced analytics capability to investigate patterns and trends in asset behaviour. Initially this new knowledge will be presented to our engineers and their teams to support decisions about where, when and how to intervene to address faults. Longer term, the vision is for certain forms of maintenance to be scheduled automatically based on the outputs from asset condition data analysis.
So now to some examples of new technology that is being developed to move us towards this future vision. The first of these is development of our Plain Line Pattern Recognition (PLPR) capability. We already run a fleet of trains over 75% of our plain line track that use high-definition video and automated image analysis algorithms to inspect for a small number of failure modes.
Figure 1a: Number of fatalities as a result of trackworkers being struck by trains for each year between 1997 and 2020 (source: RAIB).
Figure 1b: Number of near misses involving trackworkers 2015/16 – 2019/20 (source: RSSB Annual Health & Safety Report 2019/20).
We are enhancing the scope of the algorithms to start automatically detecting a larger range of faults and component types. For example, the introduction of a new algorithm to detect clamped rail joints and present images of missing/loose clamps and/or fishplates to NR inspectors to verify and categorise the severity of the defects. The recent acceleration of our track worker safety programme has prompted another review of how existing PLPR imagery can be used to deliver inspections differently without compromising system risk. For example, figure 3 shows PLPR an image of rail foot corrosion, which when combined with rail depth data collected by our Ultrasonic Test Units (UTUs), could replace our themed manual inspections of rail in tunnels.
Figure 4 shows another PLPR image of a rail running band, in this case the running band exhibits localised widening that could indicate the presence of a vertical longitudinal split defect. By automating measurement of the change in width and location of the running band, and combining this with other rail inspection data we may be able to automate another set of themed manual inspections of rail condition. We are also developing the facility to capture and store the PLPR video images of every S&C unit our PLPR trains travel over, in order to potentially reduce the amount of ‘boots on ballast’ time inspecting our newer, more robust S&C assets.
Another example of improvements to our mobile monitoring capability is in rail flaw detection. Our UTUs inspect running rails for cracks and wear at speeds of up to 35mph, using ultrasonic, eddy current and laser profiling technology. However, the current inspection speed limitations pose challenges when planning the UTUs into the timetable. Through our R&D programmes we are now investigating whether there are new emerging technologies that can do the same job but at higher speed. Longer term this will allow us to introduce a trainborne rail inspection process that is easier to plan, more reliable and less disruptive to our passenger and freight customers.
The final example of improvements to our mobile monitoring technology is research we are doing to measure, from a train, the rate of change of track stiffness on our network. This would allow us to identify locations where we have underlying design and construction issues that lead to repeat rail and geometry faults, so we can start to address the root causes of these faults. We have fitted sensors to our NMT infrastructure monitoring train, to both the power car and measurement car. Since each vehicle has different axle loads, it is possible to measure the difference in vehicle response to the same track geometry and from this calculate the dynamic stiffness of the track system.
Initial trials have been completed, we are now at the stage of analysing the data collected and planning the next phase of development.
Of course, with all the new exciting data streams from mobile monitoring, it is vital we can integrate the data in order to convert it to knowledge and understanding about the condition of our assets. Our Intelligent Infrastructure programme is building a decision support tool for track engineering that does just that. We have already aligned all of our track geometry data and traces (figure 5) and have developed algorithms for calculating and then predicting the rate of change of track geometry deterioration. We’ve introduced a cyclic top dashboard (figure 6) providing users with visualisation of existing cyclic top faults as well as geometry features that could develop into future cyclic top defects. As reported by authors in this edition of the PWI Journal, we are also investigating how to exploit the track geometry data we already collect to monitor the condition of earthworks, specifically embankment stability. Combined with use of satellite monitoring technology this has the potential to significantly enhance our understanding of the behaviour of these assets, again allowing us to target investment and treatments at the highest risk locations.
Over the next two years we will increase the functionality of this tool to include all of our rail condition data (ultrasonic defects, eddy current RCF measurements, rail side wear and head wear measurements). The addition of track geometry and
Figure 5: Example of track geometry trace-on-trace alignment capability in the Network Rail Insight decision support tool. This shows alignment of 35m top measurements for a single rail collected over a twelve month period.
Figure 6: Example of cyclic top data visualisation in the Network Rail Insight decision support tool. This shows data for a single rail in the 13.5m wavelength band, highlighting vertical deviations that exceed the threshold (denoted by the red horizontal line) for cyclic top and which trigger Network Rail geometry data analysis algorithms to start summing up the effect of a sequence of these features. The level of corrective maintenance action required depends on the number and severity of sequential features that exceed the threshold value.
track quality data from inspection systems mounted on service trains, structure gauging data, and S&C inspection data will create a tool that provides our track engineers with a metre-by-metre insight into the health of their asset, and the condition of other assets such as drainage and earthworks, for a full system view of the root causes of track degradation.
Moving on to fixed sensors, we are researching the potential of our fixed fibre optic cable infrastructure to monitor the health of track, converting it to 20,000km of continuous, network-wide, remote condition monitoring. The focus initially is to demonstrate if this technology can be used to monitor train position, vehicle type, speed and direction of travel.
As we gain more confidence in the data, we intend to apply the technology to understanding the rate of deterioration of the track. A high priority use case is whether we can detect wrong side failure events such as broken rails and track buckles, to reduce the risk of trains travelling over these hazards. We’re also interested in
whether we can monitor wheelset condition and deterioration, for example how quickly wheel flats develop. If so, then we will be able to update the way we respond as an industry to changes in wheelset condition, introducing a greater degree of predictive analysis and less disruptive corrective actions.
Now for the third strand in our AIS strategy; the autonomous inspection/maintenance vehicle itself. We have determined through extensive stakeholder consultation that we require a more agile approach to inspection and maintenance, for example other delivery platforms to complement our existing trainborne inspection fleet. We are building the system architecture to allow us to ‘plug and play’ a number of options for the automated inspection and maintenance vehicle.
We have research looking at the command-and-control systems that will be required, including navigation to and from worksites. We are looking at the options for the vehicle chassis itself, so it provides the right level of flexibility in terms of the tasks that can be delivered.
The principles and platforms we develop will be applied across a range of use cases and assets, including:
• Automated rail head inspection and repair
• Wet bed treatment and drainage installation
• Stretcher bar installation
• Automated tunnel inspection
• Drones to inspect enclosed spaces, for example mine workings
• Overhead line equipment inspection
But when we talk about autonomy, how much autonomous operation are we looking to build into our technological developments?
Network Rail is basing its requirement specifications on the NASA FLOAAT (Function-specific Level of Autonomy and Automation Tool) scale (figure 7). Network Rail’s research is focussing on projects with Level 2 or 3 autonomy, with the operator very much in the loop for carrying out the task. In the future we’re aiming to migrate to Levels 4 and 5, with systems carrying out initial elements of analysis and ranking, for confirmation by the operator.
We have developed a web-based operator interface used to control an autonomous vehicle system, in a simulated environment (figure 8). The operator selects tasks from a pre-existing job list, reviewing the details of the work before confirming this is the correct job. The location of the autonomous vehicle and the location of the worksite are displayed, and the operator requests the vehicle to move to the worksite, monitoring its progress. The vehicle is capable of obstacle detection, with operator verification of whether certain features can be passed safely. The vehicle automatically regulates its own speed on the approach to the worksite. On reaching the worksite the operator selects from a predefined set of robot arm operations to complete each stage of the inspection and/or repair task.
To build this concept in a live railway environment Network Rail has purchased a Warthog all-terrain remotely operated vehicle (ROV) as the platform for specific use cases (figure 9). The first use case being developed is automated ultrasonic rail inspection, coupling existing ultrasonic inspection trolleys with the Warthog ROV. The prototype autonomous vehicle will receive a ‘Start’ instruction and will then inspect a length of track, analyse the inspection data using artificial intelligence to classify the type and severity of rail defects, and then return down the same track accurately marking defects that have been identified. When all defects are marked the vehicle will return to its start position.
The next steps to achieving the working technology demonstrator are:
• Conversion of the autonomous road vehicle to run on railway track
• Addition of ultrasonic inspection capability (proven technology)
• Develop communications between ultrasonic inspection trolley systems and the autonomous vehicle
• Develop artificial intelligence (AI) for analysis of ultrasonic inspection data (using Sperry system Elmer ®)
• Develop communication between AI and the autonomous vehicle
• Develop enhanced positional information and control systems to ensure defects are accurately identified.
We are aiming to demonstrate the prototype arrangement during 2021. However, the future concept is actually fully automated inspection and weld repair of the rail running surface and restoration of damaged crossings in S&C, including laser scanning of damaged areas to correctly size and define the level of weld repair required, and automated re-profiling of the weld-repaired rail/crossing surface.
Our objective is to develop the system to Technology Readiness Level 7 by December 2022, operating a full-scale technology demonstrator in the railway environment. The Discrete Defect Repair technology (figure 10), developed in partnership with ARR RailSolutions Ltd, is currently a working prototype which includes CNC milling for rail defect excavation, preheating of the area to be welded, CNC flux-cored arc welding, automated weld surface cleaning and final CNC weld re-profiling and measurement, restoring the original profile of the rail head or crossing. The process delivers a high integrity rail surface repair which has been fully tested by laboratory fatigue testing.
For one final example of automation in track inspection, we are developing equipment to automate the TRK053 detailed examination of switches, used to identify potential derailment hazards at the wheel-rail interface. Italian company Loccioni originally developed their ‘Felix’ technology for RFI, the company managing the Italian Railway Infrastructure (figure 11). Over the last two years we have worked with Loccioni to make sure the system has the full range of reference data for Network Rail assets, building the capability to inspect our most common S&C types including full depth vertical, NR56V, RT60, NR60 Mk1 and NR60 Mk2 designs.
Current methods of checking for switch derailment hazards are based on manual checks using a standard set of track gauges the process has an inbuilt level of repeatability and reproducibility. Moving to the Felix system will introduce a greater level of consistency and accuracy into switch derailment hazard inspections. It also speeds up the process, with full recording of a single turnout taking approximately 10 minutes (depending on turnout length).
Felix records laser rail profiles of all parts of the S&C as well as static gauge and cross level, matching measured profiles to wheel and rail profiles.
We have been working with Loccioni to modify the system hardware and software in order to be able to measure the following parameters required by Network Rail switch inspection standards:
• Switch rail seating gap
• Squareness of switch toes
• Residual switch opening
• P8 profile measurement
• Gauge 1 & 2 assessment
• Back-to-back gauge measurement
While COVID has delayed some of the site-based activity required to program Felix for use on Network Rail infrastructure, we are hoping to begin full operational trials with our maintenance delivery units from autumn 2021.
So, there is a lot of very exciting work going on, new ideas and technology that Network Rail is looking to bring to the railway infrastructure. BUT there are a number of challenges we must address if we are going to successfully introduce the technological change.
Our first challenge is to bring our workforce with us on this journey introducing automation is a significant step change. We’re going to have to make sure our people have access to the skills, knowledge, and expertise they are going to need to work with the new technology with confidence. We should not underestimate the scale of this task, but we need to make a start.
Our next challenge is how we manage the data that these systems produce. As we fit more and more sensors and increase the scope and scale of mobile monitoring, we will generate an order of magnitude more data. We have to create a system architecture that allows us to store, process and share this data.
Figure 8: Example of prototype operator interface (top) for control of an autonomous vehicle system in a simulated environment (bottom).More importantly, we have to build the algorithms and tools that convert the raw data into more valuable information and knowledge to support our frontline teams as they make safety-critical decisions about where, when and how to intervene to prevent or correct asset faults. We also have to make sure that the systems which store, record and analyse all of this data are secure, have the appropriate controls and governance associated with managing the data and systems, and are future-proofed so they are scalable and can be enhanced without requiring costly ‘big bang’ IT upgrade projects.
A further challenge that affects us all is climate change. Not only will our assets need to be more resilient to the predicted changes in weather patterns as our climate warms but all of the systems we use to remotely monitor asset behaviour and condition also need to be
reliable in the same operating conditions. So this is an important part of the specifications we develop for the technology changes outlined in this article.
And finally, all of these developments and challenges need to be wrapped up in the safety case for the wider business change. This is where we can apply the Common Safety Method Risk Assessment to make sure we have reviewed all of the hazards, have designed, agreed and implemented suitable mitigations, and all of the governance and regulation that needs to surround the use of more autonomous asset inspection and repair vehicles is carefully considered and constructed as part of the wider programme.
Figures 10 A - D: The three stages in the fully automated Discrete Defect Repair process for weld repair of rail and crossing surface defects. All images courtesy of ARR RailSolutions Ltd.
A: Pre-repair laser rail head profile measurement. Examples of measured profiles (overall and gauge corner detail) are shown on the right.
B: CNC milling tool to remove the rail or crossing defect. Right hand image shows completed defect removal ready for welding.
I recently hosted a panel session discussing the role of technology in keeping trackworkers safe. Technology has an important role to play, but it was fascinating that time and time again the conversation came back round to how it is only any use if the interactions between people and technology are working well. In the case of trackworkers, the most advanced protection system in the world is rendered useless if people are not where the technology thinks they are. The railway system is a complex interaction of fixed and moving assets, and the people who design, build, maintain and operate it. The system is the product of decisions over generations, together with those being taken every day, all by professionals in their own fields. How can we be sure that those decisions are not also being undermined by a view of reality that turns out not to be accurate?
As professionals, we take our responsibilities seriously so that our actions have a positive impact on our world. We wrap these up into codes of conduct and endeavour to take ethically sound decisions which are balanced and well informed by objective evidence. But is there more to this than our training and experience suggest?
Let’s unwrap the phrase ‘objective evidence’. We are rarely gifted with having complete, perfect information to inform a decision. That’s the nature of professional judgement. Wrapped up in that judgement is a choice about what input information matters, and what doesn’t. This may be conscious, but the danger zone is when our unconscious starts to classify information for us. However objective we think we are, we see the world through the filters of our own experience. Psychology meets engineering when quiet voices, unexpected information or weak signals are not picked up on, sometimes with devastating consequences.
The recently published RAIB annual report for 2020 included the following line; “An underlying theme in many of the investigations this year has been the divergence between what the management system said should be happening, and what was actually going on.”
Just like a technically advanced trackworker protection system, an engineering decision can be rendered useless if the inputs don’t reflect all aspects of reality.
How far would you take your concern if decision makers don’t seem to get it?
Whichever part of the infrastructure lifecycle you are involved in, are you listening out for the unexpected? This is true whether it is unusual data from a new remote condition monitoring system, or an off-the-wall question from a new apprentice. Both could be easily dismissed but if you stop and listen, really listen, it could open your eyes to a whole new perspective on your work.
At CIRAS, we listen every day to people from across the transport sector who raise concerns and suggestions that could lead to improvements in health, wellbeing and safety. Most are passionate about wanting to see improvements that will benefit themselves, their colleagues and passengers. Some call because fear prevents them speaking out openly, but the most common reason given is not feeling they would be listened to by raising issues internally.
It is noteworthy that in the last year, over half the concerns that have been raised with us relating to assets and infrastructure have been third party reports. This means they are raised by an employee of a company other than the one responsible for the asset. Listening to inputs from across the many interfaces in our industry is critical if we are to understand, to use the RAIB’s phrase, ‘what is actually going on’.
The NHS recently undertook a survey which included a question about whether staff felt safe to speak up. In response, the NHS National Guardian urged leaders to ‘listen to the silence’, to think about voices not represented in the survey, particularly where those voices might be in vulnerable groups who feel unable to speak up, perhaps because of their role, ethnicity, or contract terms. Listening to the silence can prompt us to think about the voices we are not hearing from, and the inputs we are therefore missing to our decisions.
The work of mathematician Abraham Wald during World War 2 provides a technical example of listening to this silence. Faced with the problem of how to improve the survival of bombers under attack and lots of data about where the returning aircraft had sustained damage, the military reached a natural conclusion that the parts of the plane sustaining most damage were those in need of reinforcement. Wald however was more interested in the data gaps. There was no data for the planes that did not return, and returning planes consistently had little or no damage to the cockpit or tail. Focussing on the data silences enabled him to save planes by pointing out that it was the cockpit and tail that needed reinforcement.
Whether missing data or missing voices, can we really claim that our decisions are ‘sound’ and ‘ethical’ if we have not actively sought to listen to the silence?
What about if the shoe is on the other foot and you are the one with the information rather than the decision maker? It is right there in the PWI Code of professional conduct at 3.6:
Members shall raise any concern, either within the workplace or externally, about a danger, inadequately quantified or managed risk, malpractice or wrongdoing which affects others. Any such concern shall be reported to their employer or manager. If this does not address the concern, they should be aware and make use of existing company and industry sector regulatory reporting systems.
‘Of course I would speak up!’ is easy to say, and we really mean it. But what if you are the junior faced with experts who seem to be dismissive of the issue? Or you are unnerved that something is not quite right with a system, but it is outside of your competences so you could be mistaken. How far would you take your concern if decision makers don’t seem to get it? Internationally, there are major disasters where failure of the connection between those who knew and those who could act is cited in the investigations Challenger and Deepwater Horizon are just two.
Closer to home, you will not have heard about the train accident caused by a warning system error last year, because it didn’t happen. System users reported through CIRAS that the warning sounds were not working as expected. Although it was an established system widely in use, the company owning the system listened and investigated to discover an unexpected compatibility problem in certain use cases.
When speaking up and listening are aligned, early warnings can prevent accidents. System owners may be experts, but if they don’t have access to the critical information that you hold, their decisions too are rendered ineffective.
A phenomenon that we saw more starkly than usual last year was the impact of communication about decisions. During March and April 2020 companies were implementing new risk controls relating to the pandemic so fast that keeping their people up to speed was a challenge. Someone might call us at the end of a shift with a concern they did not think was being heard, only to find that the company already had new controls planned that were implemented by the time they started their next shift.
In more normal times we have picked up concerns that asset faults are not being fixed, again only to find they were in hand but the people on the ground were out of the loop so
did not feel they were being listened to. In one example this led to a whole new approach for providing visibility of how fixes were progressing.
If we want our decisions to be well informed by all the relevant voices, we need to tap into the virtuous circle of people knowing they have been listened to and therefore choosing to speak up again next time. The RAIB Annual Report 2020 states that ‘a positive, open and honest culture is also needed if leaders are to be properly informed, and protected from wishful thinking’. Closing the loop so people know they are being heard is critical.
The confidential reporting service provided by CIRAS is one tool in your toolbox for ethical decision making. If you find yourself in a position of needing to be heard but can’t do so internally, do call our hotline.
If you are the decision maker, where are your silences? Are you encouraging those voices to be heard through any one of the available industry channels?
Don’t forget if you want to know whether someone has raised a concern confidentially on a topic you are working on, you can search reports and company responses on our website www.ciras.org.uk*.
Take a look, it’s your decision.
* We are soon launching an upgrade to our website that will enable all staff of member companies to log in directly to view reports. Until then, you can access the reports via your CIRAS rep.
About the AUTHOR: Catherine Baker - Director CIRAS
Catherine heads up CIRAS, the Confidential Incident Reporting and Analysis Service, a not-for-profit organisation which has provided a confidential health, wellbeing and safety reporting line for workers in the transport and infrastructure sectors for the last 25 years. Starting from a science and analytical background, Catherine has held a range of senior roles in the transport sector, spanning policy, risk management and research, all connected by the thread of working to deliver better outcomes for businesses, their customers, and their people particularly for health, wellbeing and safety. Having spent much of her career working with those taking decisions that impact safety outcomes, it is now a privilege to be enabling people on the front line, who often have the best first-hand knowledge of the hazards, to have their voices heard when they might otherwise stay silent. Hence helping the companies they work for to take better informed decisions.
ROLE Part-time (2 days a week, 40% of Full-time)
LOCATION Remote (home) working with some UK travel
SALARY c£300/day as contractor or c£60k Full Time Equivalent as employee (dependent on skills and experience)
HOW TO APPLY To register an interest in this role, in the first instance please contact: technical.director@thepwi.org
CLOSING DATE 9 August 2021
The Permanent Way Institution (PWI) is the professional institution for the world of railway infrastructure engineering. Working closely with leading organisations from across the industry, including Network Rail, Transport for London, HS2 and Transport for Wales, we provide a range of services to develop the knowledge and competence of all those working in the UK rail industry. Our members, both individual and corporate, benefit from our specialist technical courses and diplomas, our routes to professional registration, the technical meetings and seminars we host, our vast suite of learning resources including our highly respected quarterly Journal, and being part of a unique knowledge community.
We are growing our suite of technical resources and are looking to appoint a Technical Manager who’s duties will include:
• working with the other members of the technical team to create and maintain a plan for the sourcing, validation, and publication of relevant technical material;
• technical editorship of the PWI’s quarterly Journal;
• sourcing technical content for the PWI’s Journals, seminars, technical hub (website), technical courses, and text books;
• carrying out and/or sourcing reviews of technical content to ensure it is and remains accurate, valid, and appropriate;
• overseeing the Journal awards process;
• member of the Professional Development Committee, overseeing the CPD activities of the PWI;
• responding to technical queries from members and nonmembers;
• attending internal meetings and supporting at Rail Industry events and exhibitions eg Rail Live, Railtex.
• Sound technical background in railway infrastructure engineering at degree or equivalent level;
• Significant railway engineering experience in a range of engineering and delivery roles;
• Good understanding of the structure of the UK railway infrastructure industry and its supplier base;
• Ability to motivate and work with Institution volunteers undertaking technical work for the PWI;
• Proactive and results driven.
We are looking for an all-rounder with a passion for rail infrastructure engineering and a proactive, can-do approach. A team player with good people skills who can hit the ground running.
You must be able to self-manage and work autonomously from home, with the flexibility to travel within the UK and attend meetings and events when required.
Professional Registration is an important step in pursuing a career in engineering and it lends itself to a ready-made career path, progressing through the grades as your experience broadens and deepens.
Putting those letters after your name (EngTech, IEng or CEng) instantly tells employers, clients and wider society that your competence and understanding of engineering principles has been independently assessed, that you have the knowledge, skills and professional attitude they value, and that you are committed to developing and enhancing your competence. It sets you apart from your non-registered colleagues.
The right professional registration title for you is based on your academic and professional competence: here’s a general guide…
We reached 234 PWI registered engineers last month with 140 Engineering Technicians, 35 Incorporated Engineers and 59 Chartered Engineers. Other interesting data is that nearly 10% are female, the majority being EngTech, and we are reporting a 23% increase in PWI registrants year on year with the PWI interview pass rate at 87.5%. Our last interviews in March achieved 100% pass and there was another special achievement of note to the members: IEng for an electrification colleague via the Technical Report route.
We have also completed our Track Apprentice “EngTech ready” work for the current TfL and Colas cohorts which means 35 are now able to be registered as EngTech MPWI, which is great for them and the industry. We are working towards offering the full service to employers including Network Rail, to carry out End Point Assessments which link occupational competence with professional competence.
We trained 33 PWI Reviewers in April and for the first time, we had a blend of levels; 13 CEng, 9 IEng and 11 EngTech. It was great to see so many come forward to “give something back”. This is a major achievement, particularly for EngTech as this is our strategic focus for enhanced membership particularly associated with registration, which we know is the right thing for hundreds of rail infrastructure technicians.
Regarding the development of new routes, I can now formally announce that the CEng Experiential Learning route for degree holders is fully open, and we are piloting an IEng route for HNC and HND holders. For information please contact Liz Turner, PWI Registration Manager.
Our Professional Development Officers are working well to promote industry links through more workshops offered to Corporate Members.
It is good to see that in the PWI, people can progress right up the higher professional levels and I get great pleasure in seeing them achieve what sometimes seem impossible goals.
Engineering Technicians apply proven techniques and procedures to the solution of practical engineering problems.
They hold Level 3 engineering/ technology qualifications and 2-3 years industry experience, OR 3-5 years industry experience.
Incorporated Engineers maintain and manage applications of current and developing technology, and may undertake engineering design, development, manufacture, construction and operation.
They hold Level 6 (Bachelors) engineering/ technology qualifications and 3-5 years industry experience, OR 5-10 years industry experience.
Chartered Engineers develop solutions to complex engineering problems using new or existing technologies, and through innovation, creativity and technical analysis.
They hold Level 7 (Masters) engineering/ technology qualifications and 3-6 years industry experience, OR 10-15 years industry experience.
Determination pays off, and help and support from PWI members pays dividends.
Brian Counter TECHNICAL DIRECTOR Permanent Way Institutiontechnicaldirector@thepwi.org
The PWI is here for your journey and we would love to support you in your career aspirations.
Professional registration is open to any competent practising engineer or technician.
Different levels and pathways to registration are available, depending on your experience, training and qualifications.
FIND YOUR ROUTE TO REGISTRATION ON THE WEBSITE www.thepwi.org profeng@thepwi.org
PROFESSIONAL REGISTRATION WITH THE PWI IS SUPPORTED BY NETWORK RAIL AND TRANSPORT FOR LONDON
You may hear from us soon!
Participation is optional for members, but mandatory for registrants.
over
d equipment specifically used for working on, or assisting in, the maintenance and r enewal of the railway infrastr uctur e in Gr eat Britain. It is a har dback, 360 page, full colour thr oughout, thr ead sewn publication with extensive colour illustrations. Included within it ar e compr ehensive details of:
The 2021 North West Technical Seminar will review the proposed upcoming developments in the North of the UK and the latest innovation and technology advances in the rail industry to support these programmes.
The UK government has recently invested £589m to kickstart rail upgrades as part of the Transpennine Route Upgrade programme driving rail improvements across the North of England. The seminar will review the upcoming multi-billion pound rail programmes including Trans-Pennine Route Upgrade, Northern Powerhouse Rail and High Speed 2 which will Hit the North over the forthcoming decade and beyond, providing generational change and legacy benefits of capacity and connectivity to supporting growth of the economy.
Delegates will hear about latest developments, collaboration and integration of these programmes which will provide insight into the future workload pipelines, highlighting the skills and resources needed.
The seminar will explore how the latest innovation and technology advances in the rail industry are being used to support these programmes to provide value for money, cost effective solutions whilst also addressing the traction decarbonisation climate change challenge. Lessons learnt will be shared from previous programmes that are applicable to all upcoming rail works.
David Woods - Chair, PWI Manchester and Liverpool Section
PWI training started over 100 years ago and has been providing high level technical training for engineers and professionals operating at all levels ever since. Our courses are designed to develop skills and knowledge in all aspects of track repairs, renewals and projects and can help you on your journey to professional registration.
Join us in person or in our virtual classroom from your home or office as we deliver our industry revered, first class training directly to you. All PWI courses use the most up to date content and standards; both attendance options provide the same high quality materials, tutorials, group discussions, interactive working examples and access to tutors in a 1-to-1 environment to answer queries or recap areas of uncertainty. A printed course book, personal workbook and PWI textbooks will be made available in class, or posted to your home address ahead of your start date for virtual candidates.
Awards are made by the PWI upon successful completion of written or online assessments. These comprise Certificates and a Diploma, which has been professionally validated at university level.
I recently attended the final module of the PWI Track Engineering Diploma course, and want to say I found the three modules thoroughly enjoyable and valuable in developing my understanding of railway maintenance and its interdependencies. Thank you for putting together a brilliant course which was well presented. I am now interested in becoming an Incorporated Engineer.
NEW DATES ARE TO BE ANNOUNCED SOON PLEASE CHECK THE WEBSITE.
The aim of the programme is to give delegates an understanding of the principles of the theory and practice of electrification engineering in the UK. Gain an understanding of the theory and practice of overhead electrification engineering in the UK, including history and context, interfaces, inspection and maintenance.
Further modules are under development and will include design, construction, asset management, 3rd/4th rail and side contact systems. These will lead to a qualification which is mapped to HE Level 6 and provides further learning from HNC, HND and Foundation Degree towards IEng level.
Course cost: £645 Accommodation cost: £245 See www.thepwi.org for full details
27 September 01 October 2021 Derby
Delegates on this course will gain comprehensive detailed knowledge of S&C and how to undertake refurbishment safely, efficiently and to the required engineering quality. The course will cover both the track assemblies and the trackbed under S&C.
Participants will undertake detailed analysis and inspection of layouts so that they can scope and specify work correctly to provide the necessary life extension of the layout. The course will then ensure that delegates understand the various maintenance interventions suitable for S&C and its components and can plan those required in the correct sequence. Modules include: S&C Components Design and Analysis / Site Survey and Measurement / Scoping and Planning.
Delegates will have to pass a formal assessment at the end of the course and will be awarded a PWI Certificate in S&C Refurbishment on successful completion.
Course cost: £895 Accommodation cost: £325 See www.thepwi.org for full details
The aim of the programme is to give delegates an understanding of the principles, theory and practice of track engineering in the UK. It is comprised of three modules and involves 100 hours of taught study all mapped to HE Level 6. Upon successful completion of all three modular assessments, candidates will be awarded the PWI Diploma in Track Engineering.
Top-up qualification to IEng for HND / Foundation Degree Holders
This course is aimed both at newly qualified and experienced engineers, and will give delegates the knowledge and skills needed for professionals in track engineering.
Gives a basic understanding of track engineering and its theory and context. Develops a knowledge of track types and features, its interfaces with other rail infrastructure including earthworks, structures and clearances, and track maintenance including ballast, drainage, stressing, grinding and welding.
25
Focuses upon track design for projects and enhancements. Through design case studies and exercises, develop skills in track design of plain line and switches and crossings, component knowledge and configurations, layouts, innovations and life extension, route evaluation and trackbed design.
8 11 November 2021 Derby
6 9 December 2021
Well, Summer 2021 is finally here, and we’ve just finished our first half of this new exciting year of transitions, and this, of course, applies to PWI training. Congratulations to those who have been awarded their Track Engineering Diploma, some individuals and a large cohort of Network Rail Graduates who started their railway training journey in September 2019. Also, well done to those with the latest S&C Refurbishment certification.
July is a good time to reflect before the holidays and put yourself down for training that will boost your confidence and improve your performance in current and future career paths. We offer the Track Engineering Diploma both virtual and face to face at Derby and there are still places available.
If S&C Refurbishment is of interest to your current role or something you want to get into, there is massive growth in this highly specialist area, so take a look at our new offer: a single full week residential with a practical site visit, demonstration and survey alongside the best UK S&C trainers for only £895.
Finally, following the success of our first electrification training module in June at Derby, we will be delivering further modules in the Autumn and in Spring 2022. The first module was Overhead Line Systems and Maintenance and the next will be OLE Design, OLE Asset Management and Construction. Our future plans include 3rd rail and power and distribution. These will all lead to another validated award, the PWI Electrification Engineering Diploma.
The study becomes more strategic and delivery oriented with advanced asset management techniques and applications. Gain a deep understanding of UK track renewal planning, plain line, S&C, existing and future methods, rail renewal scenarios and optioneering, and learning from accidents. Understand advanced technical rail management issues, rail sustainability and strategic track asset management.
Module cost: £645 (Virtual or Derby) Accommodation cost: £245
See www.thepwi.org
WWW.THEPWI.ORG secretary@thepwi.org 01277 230031 option 1 technicaldirector@thepwi.org
COVID-19 INFORMATION
We are monitoring our plans to deliver our training courses and are working very hard to ensure learning with us is not interrupted. We are committed to delivering first class technical training, developed and delivered by experienced rail infrastructure engineers. Please check the website for the most up to date information or contact us: secretary@thepwi.org 01277 230031 (option 1).
Due to the overwhelming support for our Practical Trackwork Challenge, the PWI have confirmed that we will be running two events this year. Both challenges will take place at the Churnet Valley Railway near Stoke on Trent; the first will run on 13-14 October and the second will take place the following week on 20-21 October. This is a superb opportunity for those new to the rail industry or lacking practical experience, to see the “coal face” of track engineering in a safe and supportive environment.
The Practical Trackwork Challenge is an event where the PWI undertake a track renewal on a heritage railway. The heritage railway provide the materials and our Corporate Members provide the equipment and expertise. PWI Corporate Members get to send two delegates free of charge to participate in this track renewal.
The event is open to anybody who works for a Corporate Member, however we encourage delegates who are either junior or backroom staff working in the industry who don’t normally work on site in renewals environments.
At our last event, we welcomed delegates from a diverse range of roles and responsibilities, which included a Phd geotechnical engineer, a signaller, team organiser, project planner, junior project managers and railway inspectors to name but a few. It was also great to see that half of our delegates were women.
The renewal work will consist of the installation of a new Bv 8 Left Hand turnout and twist panels on the through route. Additionally, we will be installing 323m (18x 60’ panels) of plain line adjacent to the through route from the turnout along a new track bed to connect to an existing siding. All of the new rail and sleepers will be laid on over 100 tonnes of new ballast cut to the appropriate cross fall.
Our delegates work in groups and rotate around the site to gain experience in everything involved with a track renewal. They get to work in gangs changing sleepers and lifting and packing joints. They will also undertake some basic training in smallpowered plant and participate in tasks such as changing fishplates and fixing baseplates under skilled supervision.
They get to observe the renewals process, reballasting/re-railing using road rail vehicles and on track plant, and participate in the setting out using theodolites/total stations.
Our Corporate Members are also encouraged to participate in the event. This can be at any level they choose, but typically involves providing a service or a specific skill set. We are always looking for help in some capacity during the prep works before and during the event, but as well as the demonstration/training we also have to keep everybody safe as well as making it fun. I guess that’s the challenge in the title of the event!
If you are a Corporate Member and want to get involved in some capacity then please get in contact with me: andy.steele@thepwi.org
Steele PWI Technical Content ManagerThis was an incredible opportunity to be handson and experience the physicality involved in renewing a railway.
We’re honoured to have you on board and are thoroughly looking forward to working with you. We’ll keep you updated on news and events via our monthly newsletter as we don’t want you to miss a thing. We have a thriving social media network and we’d love to see you get involved! We’re here to help, so if you have any questions, then shout out!
ASHFORD: Greg Harrison, Ben Hamilton, Paul Fleming. BENGALURU: Dhan Singh, Nishanth Dharan. BIRMINGHAM: Richard Briggs, Adam Collett, Axcel Simmonds, Daniel Privett, Alexander Rushton. CHESHIRE & NORTH WALES: Lee Coleman, Daniela Cardoso. CROYDON & BRIGHTON: Nicholas Bayley, Daniel Harman, Horace Kennedy. EDINBURGH: Jon Gill. GLASGOW: Andrew Simpson, Reece Fenton, Alistair Hardie, Jamie MacPherson, Jason Robertson, Andrew Gardner. INTERNATIONAL: Sukumar Bhowmick, Alexandros Tsiachris.
LONDON: Peter Johnson, Anthony Smith, Paul Reed, Placide Mbatika, Seron Williams, Arshya Jeadri Salehpour, Jamie Lovegrove, Phil Dutton, Kawsar Ahmed, Thomas Scott, Attia Aslam, Ali-Rezaur Eslami, Gyan Rai, Sany Uddin, Sikandar Ali, Ruben Saayman, Phil McCusker, Charlotte Prommel, Tunji Adedokun. MANCHESTER & LIVERPOOL: Paul Topping, Mohammmed Abbas, Matthew Quegan. MILTON KEYNES: Richard Stainton, Kester Bates, Colin Hodgson, Panashe Mandimutsira, Philip Doughty, Andrew Wyant, Steven Hayden. NORTH EAST: Eleanor Meakin, Christopher Dunn, Claire Blyth, Dean Douglas, Robert Dunn. NOTTINGHAM & DERBY: Hamzah Khan, Andy Batters, Ismail Ismail. SOUTH & WEST WALES: Philip Rawlings, Daniel Matthews, Bradley James, Rhys Giles. THAMES VALLEY: Joseph Tidy, Matt Farmer, Jonathan Scott. WESSEX: Steffan Murray, Connor Hughes, Alexander Johns, Andrew Malcolm, Julian Rowe. WEST OF ENGLAND: Peter Savidge, Steven Farley, Russell Jackson, Lenuta Ionescu. WEST YORKSHIRE: Dr Faris Al-Naemi, John Southgate, Matthew Thompson, Daniel Wilders. YORK: Peter Mitchell, Thomas Williamson.
“Bobby
A huge well done to our members who have gained a professional title since the last Journal. This is an amazing achievement.
Patrick Dickinson - Engineering Technician
Jonathan Regan - Engineering Technician
Ciaran Brown Engineering Technician
Thomas Shaughnessy Engineering Technician
Dominic Kisz Engineering Technician
Karisma Henry Engineering Technician
Matthew O’Connell Engineering Technician
James Field - Engineering Technician
Jake O’Hagan - Engineering Technician
Damel Clarke - Engineering Technician
Kieran Griffiths Engineering Technician
Toby Knight Engineering Technician
Venantas Krasauskas Engineering Technician
Fraser O’Connor - Engineering Technician
Ian Gregory Engineering Technician
Elliott Johnson - Engineering Technician
Christopher Jackson - Engineering Technician
Jake Rowan Incorporated Engineer
John Hyde Chartered Engineer
Richard Wood - Chartered Engineer
Robert Gaylor Chartered Engineer
Grant Hobbs, Julian Leak, Lee Clifton, Joan Heery, Mark O’Callaghan, Adam Haigh, Chris Doig, Chris Fuller, Stephen Clark, David Robb, Anna Kopyto, Alex Charter, Valerie Craig, Alan Whiston, Ong Chin How.
Major Poyntz was a long standing member of the PWI having joined us 1 November 1965.
“His enthusiasm for anything on the railways was unparalleled and he would often be seen with a notebook in hand, while looking from a train window.” Ian Prosser, HM Chief Inspector of Railways at ORR.
Read John’s full obituary on the ORR website: https://www.orr.gov.uk/search-news/life-former-inspectorrailways-celebrated-freight-train-named-his-honour
John Edgley President president@thepwi.org
Peter Dearman Deputy President dearman745@btinternet.com
Nick Millington Deputy President nick.millington@networkrail.co.uk
Technical Director technicaldirector@thepwi.org
Andy Packham
Technical Content Manager andy.packham@thepwi.org
Andy Steele
Technical Content Manager andy.steele@thepwi.org
Joan Heery
Past President Chair of the Advisory Committee on Climate Change and Decarbonisation joan.heery@aecom.com
Andy Cooper
Non-Executive Director mrandrewjcooper@gmail.com
John Dutton
Non-Executive Director jcdutton@btinternet.com
Michelle Nolan-McSweeney
Non-Executive Director michelleusrm@aol.com
Andy Tappern
Non-Executive Director andy.tappern@networkrail.co.uk
Liz Turner
Registration Manager profeng@thepwi.org
Paul Ebbutt
Professional Registration Development Officer (South) 07887 628298 developmentofficersouth@thepwi.org
Brian Parkinson
Professional Registration Development Officer (North) 07876 578905 developmentofficernorth@thepwi.org
Stephen Barber
Chief Executive Officer stephen.barber@thepwi.org
Kate Hatwell
Operations Director kate.hatwell@thepwi.org
Sara Green
Membership Secretary secretary@thepwi.org
Michelle Lumiére
Head of Marketing michelle.lumiere@thepwi.org
Kerrie Illsley
Creative Manager kerrie.illsley@thepwi.org journaleditor@thepwi.org
Tech Talk is a private forum where members can discuss, debate and share views on all things related to rail technology. Members can ask questions and make comments about the technical articles that are published in the PWI Journal, as well as react to our technical seminars, Boards and relevant news.
We encourage healthy debate and differences of opinion, but ask that contributions remain friendly and respectful at all times. Simply request to join!
www.linkedin.com/groups/8862498/
This virtual Section has been formed on LinkedIn and provides a central location for all the younger members of the rail community to engage whilst remaining a member of your regional home Section.
The Young Engineers Section is a place to exchange thoughts, ideas, views and challenges you may be experiencing in your role as a young person working in the rail industry. It’s a place to gain and offer support, to meet likeminded individuals, and to participate in social activities as the group becomes more defined. Simply request to join!
www.linkedin.com/groups/8865220/
This forum connects PWI Ambassadors to discuss ideas, suggest collaborations and to receive updates and announcements from the central team.
PWI Ambassadors are free to post comments, ideas and suggestions to fellow Ambassadors or for the attention of the PWI central team. We continue to seek new Ambassadors and Young Ambassadors, and aim to appoint at least one Ambassador for every Corporate Member. If you wish to volunteer or nominate a colleague, please contact: michelle.lumiere@thepwi.org
www.linkedin.com/groups/8913254/
This group is for all those embarking on their Professional Registration journey, as well as those who have already completed the process. Connect with each other, raise questions, discuss challenges and gain support from your peers.
We encourage members to treat this as an alumni network for PWI Professional Registration, allowing you to make friends and stay engaged with others who have undertaken the same journey, and to offer your experiences and mentorship to others when possible. Simply request to join!
www.linkedin.com/groups/8976547/
Brian CounterDespite the recent falls in passenger traffic consequent on Covid-19, over the longer term the climate change and decarbonisation agendas remain set to drive growing volumes of freight and passenger traffic onto rail networks. As the demand for rail transport bounces back and as train services are added to the network to meet growing demand, access to carry out maintenance, renewal, and project work will remain at a premium.
The pressure to do more work in shorter possessions drives a requirement for more productive, mechanised, work delivery methods. Effective, safe, and highly productive plant is an essential component of
this. Plant and the methods and strategies to deploy it that can together deliver high quality, durable infrastructure at lower unit costs is crucial to meeting industry challenges: along the way it must play its part in reducing rail sector carbon emissions and other environmental impacts, and in improving the performance and reputation of the railway.
This seminar will provide delegates and speakers with an opportunity to understand and debate the requirements for plant to meet these challenges, and the solutions that are being deployed and developed to deliver them.
VICE PRESIDENT Richard Quigley richard.quigley@ networkrail.co.uk
BIRMINGHAM SECRETARY Richard Quigley 07715 132267 richard.quigley@networkrail. co.uk Venue: 2nd Floor, Network Rail, Baskerville House, B1 2ND
MILTON KEYNES SECRETARY Kevin Thurlow 07802 890299 kevin.thurlow@ networkrail.co.uk Venue: Auditorium, The Quadrant, MK9 1EN
NOTTINGHAM & DERBY SECRETARY John Garlick 07532 071727 jgees01@ btinternet.com Venue: Aston Court Hotel, DE1 2SL / Jury’s Inn Hotel, NG2 3BJ
VICE PRESIDENT Cathal Mangan cathal.mangan@ irishrail.ie
IRELAND SECRETARY Joe Walsh 00 353 872075688 pwiirishsection@gmail.com Venue: Wynn’s Hotel, Dublin 1, Ireland, D01 C9F8
VICE PRESIDENT Phil Kirkland philkirkland@ btinternet.com
NORTH EAST SECRETARY Phil Kirkland 07899 733276 philkirkland@btinternet.com Venue: Newcastle College Rail Academy, NE10 0JP
WEST YORKSHIRE SECRETARY Martin Wooff 07487 652622 pwi@ railrace.co.uk Venue:The Cosmopolitan Hotel, LS1 4AE
YORK SECRETARY Vacancy 07951 918236 york@ thepwi.org Venue: Network Rail Meeting Rooms 0.1, George Stephenson House, YO1 6JT
VICE PRESIDENT Roy Hickman royhickman@live. co.uk
CHESHIRE & NORTH WALES SECRETARY Lynne Garner cheshire@thepwi.org 07494 753652 Venue: Crewe Arms Hotel, CW2 6DN
LANCASTER, BARROW & CARLISLE SECRETARY Philip Benzie p.benzie@ yahoo.co.uk 01704 896924
Venue: Station Hotel, PR1 8BN / Royal Station Hotel, LA5 9BT / Network Rail, CA28 6AX / Network Rail, CA1 2NP
MANCHESTER & LIVERPOOL SECRETARY Richard Wells richard.wells@tonygee.com 07817 302652 Venue: Manchester Metropolitan University, Room E0.05, M1 5GD
VICE PRESIDENT Tom Wilson tom.wilson@wsp.com
EDINBURGH SECRETARY Mark Taylor marktaylor5@ networkrail.co.uk 07710 959630 Venue: The Scots Guards Club, EH12 5DR
GLASGOW SECRETARY Angus MacGregor glasgow@ thepwi.org 07775 544509 Venue: WSP Offices, 7th Floor, G1 3BX
VICE PRESIDENT Paul Ebbutt paulebbutt1@gmail.com
LONDON SECRETARY Sean Tarrant seantarrant@tfl.gov. uk 07764429211 Venue: Transport for London, SE1 8NJ / Transport for London, E20 1JN
THAMES VALLEY SECRETARY Richard Antliff richard.antliff@gmail. com 07804 329497 Venue: Network Rail Offices, Davidson House Offices, RG1 3EU
WESSEX SECRETARY Kenneth Newell kenneth. newell@btinternet. com 07771 668044 Venue: The Rose and Crown, SE1 8DP / The Eastleigh Railway Institute, SO50 9FE / Network Rail Offices, Waterloo Station, SE1 8SW
SOUTH EAST ENGLAND
VICE PRESIDENT Jonathan Bray Jonathan.bray@ keolisameydlr.co.uk 07976 199011
ASHFORD SECRETARY Colin Burnikell colin.burnikell@hilti. com 07801 913562 Venue: Online until further notice
CROYDON & BRIGHTON
SECRETARY Colin White c.white@ chaucerrail.co.uk 07845 316042 Venue: Mott MacDonald House, CR0 2EE
LONDON SECRETARY Sean Tarrant seantarrant@tfl.gov. uk 07764429211 Venue: Transport for London, SE1 8NJ / Transport for London, E20 1JN
VICE PRESIDENT Andy Franklin andy. franklin@networkrail.co.uk 07901512293
WEST OF ENGLAND
SECRETARY Constantin Ciobanu western@thepwi.org 07549 319335 Venue: Engine Room, Atkins, SN1 1DW
EXETER SECRETARY Mark Woollacott Mark.woollacott@ networkrail.co.uk 07920 509011 Venue: Mercure Exeter Rougemont Hotel, Queen Street, EX4 3SP
SOUTH & WEST WALES
SECRETARY Andrew Wilson southandwestwales@thepwi. org 07974 809639 Venue: Network Rail Offices, CF10 5ZA
VICE PRESIDENT Tom Wilson tom.wilson@wsp.com
BENGALURU SECRETARY Srinagesh Rao sringagesh. rao@arcadis.com Venue: Arcadis Sez Office Bengaluru, Karnataka 560045, India
MALAYSIA Mr K Sukumaran sukumaran@ktmb.com.my NEW SOUTH WALES Peter Boonstra secretary@ pwinsw.org.au QUEENSLAND Robin Stevens robin. stevens@qr.com.au SOUTH AUSTRALIA Mark Pronk mark. pronk@sa.gov.au
The Scottish Government has recognised the benefits of a rolling programme of electrification and Network Rail Scotland is developing those plans. Electrifying an existing railway requires the electrification system to be integrated into the broader railway system: the configuration of the traction system and its constituent parts has implications for the operation, maintenance, and performance of the railway.
The challenge facing engineers of all disciplines is to simplify the systems integration task so that it supports a rolling programme of electrification rather than impedes it. This seminar will help engineers across the railway disciplines understand the implications of converting a route to electric traction, and explore ways in which system specification, design, and implementation can support a rolling plan.
Replacing broken and worn fishplates using Master 35® Impact Wrench.
Expert supplies for every job 78
Will remove the toughest of T R A C K M A I N T E N A N C E E Q U I P M E N T For more information, contact us: e: tracksupplies@balfourbeatty.com t: 0114 241 5000
Use on outside track and inside the MMT in conjunction with Floating Trolley Fastclip Remover Will install and remove Clips quickly using our quick change Jaws Battery, Diesel & Petrol Trackpack Balfour Beatty offers a wide range of components for rail construction and maintenance projects. Our products include: – Rail sections – Sleepers and timbers – Track smalls – Industrial switches and crossings To find out how we help our customers find the right part for their job, visit: www.balfourbeatty.com/tracksupplies
The Technical Board continues well in a virtual format with excellent attendance and lots of mutual interest.
In April, we had a vibrant and very responsive interactive meeting with 37 Corporate Members.
John Edgley, PWI President, and Colin Newsome from Network Rail updated progress on the competence framework following work done by partner Corporate Member companies.
Stephen Clark from the Gloucestershire and Warwickshire railway presented a paper on the challenges of trackwork.
This was the first presentation from a heritage railway and was the start of a future partnerships approach towards these organisations.
Joan Heery, Chair of the Advisory Committee on Climate Change & Decarbonisation and Past President, updated the board on recent activity of this group.
Corporate Members are fully involved in the development of the PWI, ensuring that its products and services meet the needs of the rail industry for technical expertise.