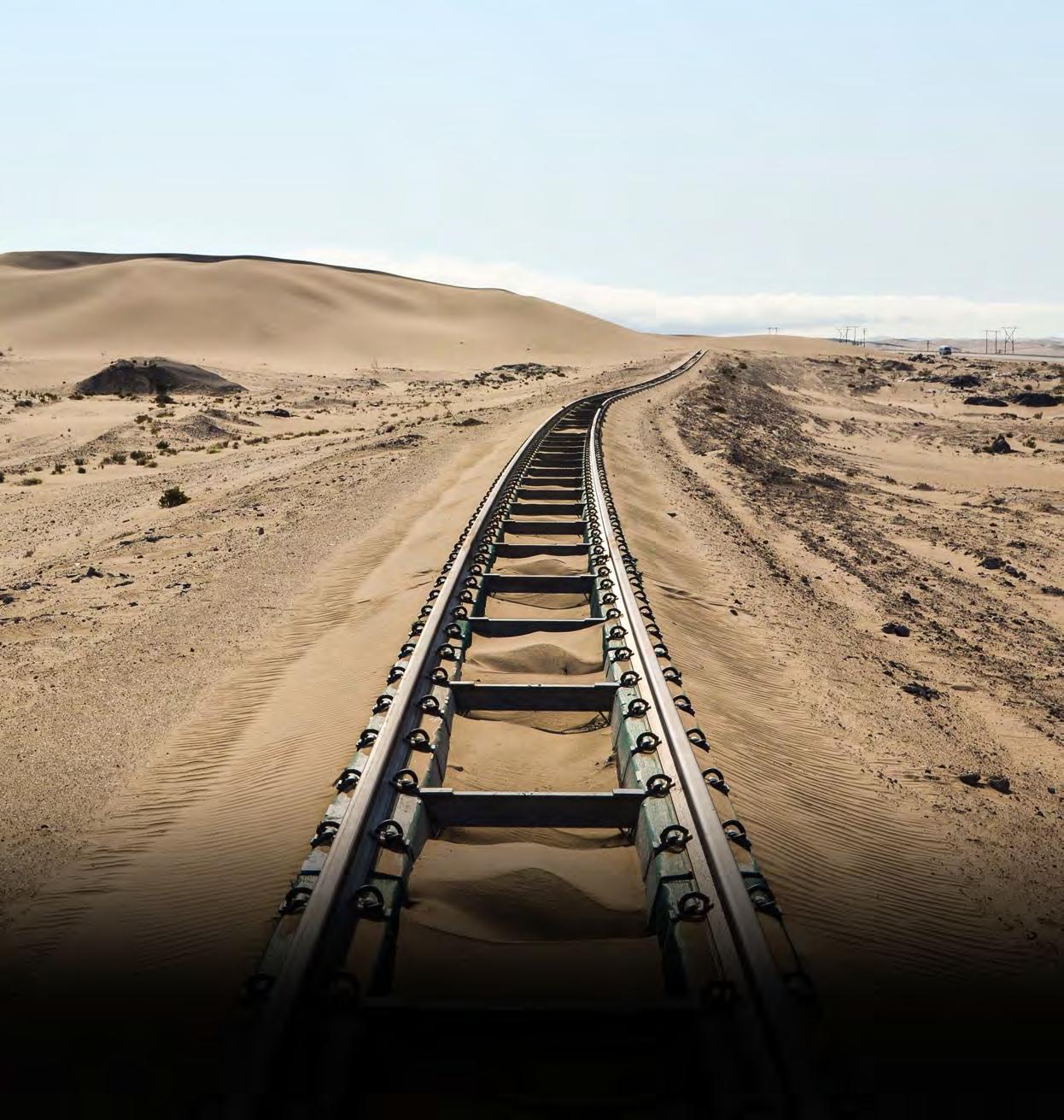
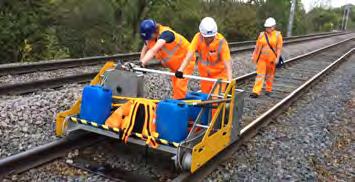

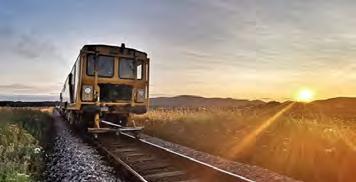
As automation, artificial intelligence and robotics technologies continue to develop, they open up many opportunities to increase railway capacity, performance and reliability, while reducing costs and improving customer experience and safety. Much is also to be learnt about how automation can be introduced effectively and safely.
The speakers involved in this seminar, delivered as a collaboration between four major Professional Engineering Institutions (PEIs), will explore the opportunities and issues involved when introducing automation on existing railways. They will also address the less constrained possibilities in new build railway systems. The contributors will evaluate currently available technologies and their implications for railway capacity, operations and asset management, and discuss options for the future. They will consider the human factors, ethical and stakeholder management issues surrounding automation, and will draw out lessons learnt from projects that have introduced increased automation.
As well as gaining a full systems understanding of railway automation, delegates with an interest in railway infrastructure engineering will learn how automated train operation can affect the physical condition and management of the infrastructure, and how automation of inspection, maintenance and track access can contribute to safer and more effective infrastructure management.
Thank you to Thomas Schmid (Zürich) for this photograph of the GoA 4 metro in Copenhagen.
The seminar will include recorded online content for delegates to view ahead of each of two live seminar sessions (each of duration: 90 minutes inc Q&A).
PART 1
View three and a half hours of prerecorded online content from 28 August ready for the live session on 17 September 2020 09.00-10.30 (UK time)
PART 2 View a further three and a half hours of pre-recorded online content from 18th September ready for the live seminar on 8 October 2020 09.00-10.30 (UK time)
BOOKING OPEN SOON www.thepwi.org/ calendar
1277
It’s always a pleasure to receive feedback over our Journal. Thank you to all those who send in their comments each quarter.
Please contact me if you have any news, both personal and professional, that you’d like us to broadcast in the next edition. It’s great to share our readers’ thoughts and stories.
It’s hard to believe that my term as President is at an end, the last 15 months have flown by. I can clearly recall the day I received a call from the Board asking if I would like to join the Presidential chain and my immediate response was yes, of course. It has been a wonderful experience and I have come to value it more as time has gone on. To have the opportunity to be part of an organisation that is dedicated to knowledge sharing and improving capability of people within the rail industry has been very gratifying.
Throughout the course of my tenure, I visited 14 Sections, including my home city of Belfast, Dublin and Bengaluru. I did have the remainder scheduled in the diary for completion by the end of June but sadly the restrictions of Covid-19 made that impossible. However, the opportunity to complete those visits remains and it’s my intent to do so in my time as Past President. I have thoroughly enjoyed getting to know people throughout the organisation; from the Board and Exec team through to the army of volunteers within the Sections – Secretaries, Chair people, Committee members and Vice Presidents as well as individuals within the membership. Thank you for making me welcome and for your support throughout my term.
I’m delighted I was able to pick up and deliver a project contained within the strategic plan and I put a lot of focus into developing relationships with our Corporate Members. Between October 19 and March 20, we conducted informal interviews with 31 organisations to get their feedback on the performance of the PWI. During the process we lost 3 Corporate Members and gained 4 including Plasser and HS2. We have yet to talk to our 9 Heritage Railway members and their views may be slightly different to those of more mainstream organisations. I fed back the findings of the conversations at the Technical Board in April and the key highlights are mentioned below.
From a strategic perspective our Corporate Members are delighted to be associated with our brand, recognising the importance of the organisation to the Rail Infrastructure community; and the opportunity for networking at both corporate and individual level is highly valued. At a more practical level, there was high praise for technical seminars, the journal, training courses, professional registration and the practical Trackwork challenge; the later viewed as a unique offering relative to other PEIs. On the flip side, areas for attention ranged from improving and modernising our communications through to greater focus on the effects of climate change and helping educate our members on appreciating a whole systems approach. Both the PWI and our Corporate Members are agreed on the need to focus our efforts in engaging more young people. At present only 14% of the current membership is under 30 years old. We have therefore developed a specific plan around this subject including building relationships with certain universities and educational establishments through to the running of a Seminar in 2021 hosted and organised by this group. The PWI cannot drive this on their own and our plea to Corporate Members is they actively engage and encourage their young people to view the Institution as a core part of their learning and development.
As I close this article, I would like to take a few moments to reflect on the role of the President. I was looking at the Presidential badge recently - it contains 75 inscriptions of all the people who have held the office of President, starting with William Meredith in 1884. Some people held the post for one year, others two and through the war years there are gaps as you would expect. Each of those individuals will have taken a different approach to how they spent their time as President and where they chose to put their energy. Some had to focus on the immediacy of the situation as the Institution has not always been in good health and others like me, had the opportunity to take a more active approach in assisting with the delivery of the current initiatives. Irrespective of the area of focus, all share a common thread of doing their best to sustain and grow the organisation due to a deeply held belief in the importance of education and lifelong learning. As I hand over the baton to John Edgeley, I wish him every success in the role and hope he gets as much enjoyment from the post as I have.
These are the demands on modern on-track plant. The infrastructure owner and the maintainer look for high performance machines utilising every available minute of a programmed shift and being able to consistently deliver this throughout its life. By quality we mean the machine design and build, and the condition of the track the machine leaves behind for trains to run over at high speeds. We rely on top quality track being durable for long periods of time and to minimise the frequency of intervention. From the machine itself we expect that it can be relied up to be available and consistently complete all the programmed shifts. Plasser & Theurer as the OEM together with its product support organisations has developed over many years maintenance and repair schemes which guarantee performance, quality, durability and reliability. This coupled with the exclusive use of OEM spares, technical and training support ensures daily operation at highest performance levels. The Plasser UK support organisation should therefore play a vital role in the maintenance and repair regime of ontrack plant to guarantee these demands are met.
www.plasser.co.uk www.plassertheurer.com “Plasser & Theurer“, “Plasser“ and “P&T“ are internationally registered trademarks
A long-time member and supporter of the PWI, Alison has been a cornerstone of our community for many years. Former PWI Marketing Director, Alison’s contribution to the growth of the Institution cannot be understated, and this was very much expressed at her retirement last year by David Packer and colleagues, including those from the London Section that she was a great part of.
Alison remained close to the PWI, lending her skills and deep technical knowledge as PWI Technical Editor, and attending and supporting events. The news of her sudden decline in health came as a terrible shock to all.
Alison passed away peacefully at the end of June, at home, with her family beside her. Words cannot describe our sadness over this loss, nor the high esteem and affection felt for Alison within the PWI and beyond, but we will endeavour to try: the Executive Team are organising a heartfelt tribute to her life and career to be published in the October Journal.
Our Journal Manager Kerrie Illsley, a very close friend to Alison and her family, is also organising a Memorial Book; “I have so many cherished memories of Alison, our friendship, mentorship and our giggles together. I’d like to produce a Memorial Book to gift to her family and so I invite anyone who wishes to contribute written and / or photographic memories of Alison to email me at JournalEditor@thepwi.org“
If you would like any assistance with your contribution, please let us know and we can arrange a call-back to discuss.
From all of the PWI Executive and Board, Alison will be deeply missed and our thoughts are with her family and friends at this time.
VICE PRESIDENT Richard Quigley richard.quigley@networkrail.co.uk
BIRMINGHAM SECRETARY Richard Quigley 07715 132267 richard.quigley@networkrail.co.uk
MILTON KEYNES SECRETARY Kevin Thurlow 07802 890299 kevin.thurlow@networkrail.co.uk
NOTTINGHAM & DERBY SECRETARY John Garlick 07532 071727 jgees01@btinternet.com
VICE PRESIDENT Pat Watchorn pat.watchorn@irishrail.ie
IRELAND SECRETARY Joe Walsh 00 353 872075688 pwiirishsection@gmail.com
VICE PRESIDENT Phil Kirkland philkirkland@btinternet.com
NORTH EAST SECRETARY Phil Kirkland 07899 733276 philkirkland@btinternet.com
WEST YORKSHIRE SECRETARY Martin Wooff 07487 652622 pwi@daelnet.co.uk
YORK SECRETARY Gareth Dennis 07951 918236 york@thepwi.org
VICE PRESIDENT Roy Hickman royhickman@live.co.uk
CHESHIRE & NORTH WALES
SECRETARIES Lynne Garner cheshire@thepwi.org 07494 753652 Alastair Roberts a.roberts@aegis-cert. co.uk 07768 210480
LANCASTER, BARROW & CARLISLE SECRETARY Philip Benzie p.benzie@yahoo.co.uk 01704 896924
MANCHESTER & LIVERPOOL
SECRETARY Richard Wells richard.wells@tonygee.com 07817 302652
VICE PRESIDENT Tom Wilson tom.wilson@wsp.com
EDINBURGH SECRETARY Mark Taylor marktaylor5@networkrail.co.uk 07710 959630
GLASGOW SECRETARY Jim Watson glasgow@thepwi.org 07590 929107
VICE PRESIDENT Paul Ebbutt paulebbutt1@gmail.com
CROYDON & BRIGHTON
SECRETARY Colin White c.white@ chaucerrail.co.uk 07845 316042
LONDON SECRETARY Thomas Utley thomasutley@tfl.gov.uk 07885 732231
SOUTH & WEST WALES SECRETARY Andrew Wilson southandwestwales@thepwi.org 07974 809639
THAMES VALLEY SECRETARY Richard Antliff richard.antliff@gmail. com 07804 329497
WESSEX SECRETARY Kenneth Newell kenneth.newell@btinternet. com 07771 668044
WEST OF ENGLAND SECRETARY Constantin Ciobanu western@thepwi.org 07549 319335
EXETER SECRETARY Mark Woollacott Mark.woollacott@ networkrail.co.uk 07920 509011
BENGALURU SECRETARY Srinagesh Rao sringagesh.rao@ arcadis.com
MALAYSIA Mr K Sukumaran sukumaran@ktmb.com.my
NEW SOUTH WALES Peter Boonstra secretary@pwinsw.org.au
QUEENSLAND Robin Stevens robin. stevens@qr.com.au
SOUTH AFRICA Callie Herselman callie.herselman@transnet.net
SOUTH AUSTRALIA Mark Pronk mark.pronk@sa.gov.au
Brian
LizINDIVIDUAL MEMBERSHIP
Apprentice, Student £0 e-Journal £20 printed Journal
Member £82.00
Member (65 or older at 01.01.20) £33.00 EngTech Member* £82.00 IEng/CEng Member* £131.00 Fellow £110.00
Fellow (65 or older at 01.01.20) £43.00 PWI EngTech Fellow* £110.00 PWI IEng/CEng Fellow* £175.00 CORPORATE MEMBERSHIP
Small enterprise (Turnover up to £17.5m pa) £2,140 Medium enterprise (Turnover £17.5m - £200m
Covid-19 - As I write in mid-June, the country is cautiously navigating its way out of “lock down. We must hope that the application of science, care, and good sense will avoid a threatened “second peak” of infections and any re-imposition of the severest restrictions on work and social activity. We are counting the cost of the pandemic in human and economic terms. The virus has claimed a number of the Institution’s stalwart friends and supporters, though perhaps not as many as we feared: our thoughts go out to their relatives and friends.
I am proud of the way the Institution and its volunteer community have responded to the Covid-19 pandemic. We have expanded massively our programme of online training, lectures, and seminars (all great CPD!) including three SPOLKS (Special Online Knowledge Shares) dedicated to sharing lessons on how to deliver maintenance, renewal and project work in a Covidcompliant way. We’ve ramped up our use of social media to maintain member engagement (making up for the absence of face-to-face contact), and, through our HighVisHeroes campaign, we’re highlighting instances of the great work being done to keep rail systems operational.
FINANCIAL IMPACT - From a railway industry perspective, freight traffic volume is a bright spot: otherwise the industry is suffering from the virus’ specific impact on public transport use and the massive consequential loss of fare box revenue. We really are journeying into unknown territory and will have to wait to see the extent to which the effect on passenger traffic is transient or permanent. Going forward, our industry must consider “pandemic risk” and how it can be mitigated: everything from stairway widths, seating pitches, air-conditioning characteristics, physical methods of work, and use of office accommodation will be under the microscope. Change, whilst inevitable, may be positive too...
The PWI is taking a Covid-driven financial hit: the loss of face-to-face seminars has been particularly damaging. We’re acting to mitigate this whilst maintaining the quality of our output. Discretionary spending has been eliminated and you may notice that this Journal is slightly thinner than recent editions. 2020 and 2021 will be very tight: there’s no doubt that the Institution will endure but development and growth may yet be affected. I’m hugely grateful to our individual and corporate members for their sustained support. Membership is central to the PWI’s purpose and health, and especially in current circumstances I’d ask all members to encourage non-member colleagues and those entering our industry to join the PWI and take advantage of the career-long learning and development opportunities the Institution provides.
INSTITUTION PEOPLE - It gives me great pleasure to welcome John Edgley as President of our Institution for the next year, and Peter Dearman as he joins us as Deputy President: both are senior figures in the world of railway infrastructure and I know they are keen to see the PWI develop and prosper. My heartfelt thanks go to Joan Heery as she steps down from the Presidential role, though I’m very pleased to note that she remains with us on the Board. Joan has been tireless in getting to know and understand our Corporate Members better and in laying plans to better engage with our younger members. Joan’s contribution is invaluable as we seek to improve and expand the Institution’s member services.
I’m very pleased to welcome Michelle Nolan-McSweeney who joins our Board as a Non-Executive Director, and Andy Cooper who continues his support in a similar position. I look forward to working with both, harnessing their extensive rail industry experience and specialist knowledge to help guide the Institution. Colin Wheeler is retiring from the Board: I am hugely grateful for the contribution Colin has made to the PWI’s development. He has been open and generous in sharing a lifetime’s accumulation of railway knowledge and expertise with the Institution and its membership, whilst maintaining a watchful eye on the integrity of the PWI. I wish Colin well, though trust he’ll continue to contribute to the life of the Institution. Finally, I must also thank Colin Cowey who has stepped down from the PWI Sales Manager role: Colin has worked tirelessly for the PWI for many years and he moves into a richly deserved retirement with our very best wishes.
Stephen Barber CEO
Permanent Way Institution stephen.barber@thepwi.org
New members, we’re honoured to have you on board and are thoroughly looking forward to working with you.
We’ll keep you updated on news and events via our monthly newsletter as we don’t want you to miss a thing. We have a thriving social media network and we’d love to see you get involved! We’re here to help, so if you have any questions, then shout out!
ASHFORD: Robin Catt, Craig Collins, Matthew Whiting.
BENGALURU: Deepankar Bhardwaj, Shafique Shaikh, Narasimha Rao Telagamshetty.
BIRMINGHAM: Dionne Bowie-Robinson, Yomil Ravianda, Jonathan Cook, Philip Ponticelli, Jasraj Sarai, Damien Monteith, Henry Bowden, Harvey Hawkins, Gareth Evans, Luke Rowley, Reza Zolfaghari. CHESHIRE & NORTH WALES: James Richards, Dillon Mellor, Phil James. CROYDON & BRIGHTON: Sunny Okpanefe, Derrick Fray, David Shale, Paul Major. EDINBURGH: Grant Morris, Robert Bowden, Andrew O’Donnell, Lino Scaria, Leah Ireland, Hollie Brown, Walter Wood, John Murphy, Peter Breen.
EXETER: Poppy Dixon.
GLASGOW: Paul Cook, Sathish Kumar Manivannan, Alex Hynes, Scott Pirie, Alex Sharkey. INTERNATIONAL: Guglielmo Valente, Dauda Danjuma, Prateek Jayant, Siva Chidambaram, Stephen Hand, Tien Tay. LONDON: Menaz Ahamed, JohnPaul Ohamadike, Robert Buckley, Joseph Njoku, Martin Davies, Hannelore Krausz, Gabriel Yew, Scott Revell,
Dr Tim Arianpour, Scott Smith, Jessal Murarji, Yousuf Charkaoui, Harrison Obayangbona, Keith Davies, Jack Pentland, Nathan Masterson, Jake Morgan, Dr Manu Sasidharan, Karisma Henry, Jonathan Regan, Sumaya Habib, Mark Killick. MANCHESTER & LIVERPOOL: Muhammad Qasim, Jack Wilkinson, Louis Ireland, Jordan Yates, Liam Lyons, Tony Wilcock, Andrew Watts. MILTON KEYNES: Chris Fuller, Dave Dampier, Matthew Henwood. NORTH EAST: Ade Aladejobi, Jennifer Hayton, Kai Bradford, Calum Macdonald, Alex Hill, Salman Muzaffar. NOTTINGHAM & DERBY Harry Willshaw, Kieran Watson, Dipesh Parmar, Jamie Mcmahon. SOUTH & WEST WALES: Lee Brun, Karl Rowland, Jokubas Zagorskis, Leighton Smith, Stuart Fraser. THAMES VALLEY: Ryan Hill, Harrington Stout. WESSEX: Michelle Nolan-McSweeney. WEST OF ENGLAND: Nick Bambridge, Billy Graham, Nicholas Bignell, Alfie Box, Rebecca Brenna, Joshua Friday, David O’Connor, Ben Morris, Gareth Holt. YORK: Daoud Hamdani, William Travers, Graham Carson, Christopher Aplin.
FELLOWSHIPS Chris Binns - London / Michael Winsor - Croydon & Brighton / Jonathan Hayes - Manchester & Liverpool / Colin HedderlyIrish / Peter Fagg - Wessex Jessal Murarji - London / Narasimha Rao Telagamshetty - Bengaluru / Phil James - Cheshire & North Wales / Michelle NolanMcSweeney - Wessex / Alex Sharkey - Glasgow / Mark Killick - London
YEAR!
PWI Section meetings are great places to learn about rail projects and new technical developments, and network with other rail professionals.
The QR Codes on this page will take you directly to the Section page on the website where you’ll find useful meeting information such as locations, meeting details and easy ways to book.
IRELAND The Ashling Hotel, D08 K8P5 / The Prince of Wales Hotel, N37 T2P0 / The Brookfield Suite, BT1 3LP
GLASGOW WSP Offices, 7th Floor, G1 3BX
EDINBURGH The Scots Guards Club, EH12 5DR
CROYDON & BRIGHTON Mott MacDonald House, CR0 2EE
MANCHESTER & LIVERPOOL Manchester Metropolitan University, Room E0.05, M1 5GD
LONDON 10th Floor, London Underground, SW1H 0BD / Transport for London, E20 1JN
WEST YORKSHIRE The Cosmopolitan Hotel, LS1 4AE
NORTH EAST Newcastle College Rail Academy, NE10 0JP
BIRMINGHAM 2nd Floor, Network Rail, Baskerville House, B1 2ND
YORK Network Rail Meeting Rooms 0.1, George Stephenson House, YO1 6JT
THAMES VALLEY
Network Rail Offices, Davidson House Offices, RG1 3EU
SOUTH & WEST WALES Network Rail Offices, CF10 5ZA
WEST OF ENGLAND Engine Room, Atkins, SN1 1DW
WESSEX The Rose and Crown, SE1 8DP / The Eastleigh Railway Institute, SO50 9FE / Network Rail Offices, Waterloo Station, SE1 8SW
NOTTINGHAM & DERBY Aston Court Hotel, DE1 2SL / Jury’s Inn Hotel, NG2 3BJ
MILTON KEYNES Auditorium, The Quadrant, MK9 1EN
LANCASTER, BARROW & CARLISLE Station Hotel, PR1 8BN / Royal Station Hotel, LA5 9BT / Network Rail, CA28 6AX / Network Rail, CA1 2NP
EXETER Network Rail, Training Room, Central Station Buildings, Queen Street, Exeter, EX4 3SB
CHESHIRE & NORTH WALES The Town Crier Inn, CH1 3AE / Crewe Arms Hotel, CW2 6DN
BENGALURU Arcadis Sez Office Bengaluru, Karnataka 560045, India
We welcome corporate members from all sectors of the rail industry.
Corporate members are fully involved in the development of the PWI, ensuring that its products and services meet the needs of the rail industry for technical expertise.
Corporate members benefit from:
• Reserved places at our technical seminars
• Quarterly technical board meetings presenting a unique opportunity to discuss issues and challenges that face the whole industry
• Free copies of the Journal and preferential advertising rates
• Improving technical assurance in the industry by supporting the PWI’s professional registration initiative for rail infrastructure engineers.
In response to Covid-19, technical board meetings will be held online. To attend, please email: secretary@thepwi.org
If you are interested in hosting a technical board meeting or delivering a technical presentation, please contact Brian Counter to discuss: technicaldirector@thepwi.org
PWI corporate membership is a strategic partnership designed to benefit the rail infrastructure industry.
Please refer to the website for the latest updates of event locations and online options utilising user-friendly platforms.
Beating Covid-19 one click at a time!
15 August JOURNAL DEADLINE Please send articles to journaleditor@thepwi.org
17 August COMMUNITY CAMPAIGN PWI Engineering Kids Day
24-28 August COMMUNITY CAMPAIGN PWI International Week
SEPTEMBER 2020
3 September SECTION
MEETING – EDINBURGH Photogrammetry in Rail (Colin McAteer, Programme Manager (BIM), Network Rail).
7-10 September TRAINING - PWI TRACK ENGINEERING DIPLOMA MODULE 1
7-11 September
COMMUNITY CAMPAIGN PWI Careers Week
8 September SECTION MEETING – NORTH EAST Metro Bridge Replacements (Grant Wellford & Duncan Manning, Nexus Renewals Team)
8 September SECTION MEETING – CROYDON & BRIGHTON Track Worker Safety in Rail Accident Investigations (Mark Young, Human Factors Specialist, RAIB)
9 September SECTION MEETING – THAMES VALLEY DLR - meeting challenges, today and in the future (Roger AntoTrack Assurance Engineer, KAD)
9-10 September RAIL LIVE Stand J3, Quinton Rail Technology Centre, CV37 8RP. BOOK HERE: www.raillive.org.uk
10 September SECTION MEETING – BIRMINGHAM The Journey from Asset Management to Maintenance (Rebecca Fasham, ATME Banbury, Network Rail)
14 September SECTION MEETING – SOUTH & WEST WALES Gauging RILA: Rail Infrastructure Alignment Acquisition (Craig Havard, Senior Route Gauging Engineer, Network Rail Wales Route)
16 September SECTION MEETING – GLASGOW UAV Surveying and Modelling (Gerald Brown & Kevin Bryce, Ariel Mapping Solutions)
16 September PROFESSIONAL REVIEW INTERVIEWS 173-177 Euston Rd, London NW1 2BJ (Professional Review Reports must reach us at least six weeks prior to your preferred interview date)
17 September TECHNICAL SEMINAR - AUTOMATED RAILWAYS: Part 1. Online
21-24 September TRAINING - PWI TRACK ENGINEERING DIPLOMA MODULE 2
6 - 8 October TRAININGS&C REFURBISHMENT Part A
7 October SECTION MEETING - THAMES VALLEY In-Possession Approvals of Rail Plant (Sam Barrett, Senior Engineer, Aegis Certification Services)
8 October TECHNICAL SEMINAR - AUTOMATED RAILWAYS: Part 2. Online
8 October SECTION MEETING – EDINBURGH Next generation cast manganese crossings verified by computer modelling and unique physical testing (Hannah Persson, Progress Rail).
12 October SECTION MEETING – SOUTH & WEST WALES Infrastructure Asset Transfer for South Wales Metro (Colin Brading, Transport for Wales).
14 October SECTION MEETING – EXETER The good old days! A look at safety (Mark Woollacott, Project Engineer, Network Rail)
Mid October JOURNAL DELIVERY To members
20 October SECTION MEETING – WEST YORKSHIRE HS2 (Gareth Dennis, Senior Permanent Way Engineer, Arcadis)
21 October SECTION MEETING – GLASGOW Professional Development and Registration (Dr Brian Counter, Technical Director, PWI)
20 - 22 October TRAINING - S&C REFURBISHMENT Part B
SECTION MEETINGS
Please refer to the website
4 November TECHNICAL SEMINAR - PLANT AND MACHINERY: Support to rail infrastructure renewal and maintenance for the 2020s and beyond. Swindon Steam Museum
9-12 November TRAINING – TRACK ENGINEERING DIPLOMA MODULE 3
15 November JOURNAL DEADLINE Please send articles to journaleditor@thepwi.org
1 December TECHNICAL SEMINAR - SAFETY: On track for a safer railway. Institute of Physics, London
16 December PROFESSIONAL REVIEW INTERVIEWS 173-177 Euston Rd, London NW1 2BJ (Professional Review Reports must reach us at least six weeks prior to your preferred interview date)
www.thepwi.org/ calendar/
Our parent companies are leading railway infrastructure specialists.
Together we continue to invest in cutting edge on-track machines which improve safety, reliability and e ciency.
PWI Technical Content Manager’s (TCM) Andy Steele (left) and Andy Packham (right) source interesting high-quality technical papers and content for the PWI Journals, textbooks and other printed and online media.
They also arrange PWI seminars and training courses, packing them with relevant technical content, delivered by presenters who have great knowledge and a passion to share it.
Do get in touch with us if you have a potential Journal paper to contribute or if you would like to present at one of our seminars. We’d be delighted to hear from you! Also, if there are particular subjects you want covered in the Journal or at a seminar, please let us know.
As I write, we are entering the eighth week of lockdown and I sincerely hope that if like me you have been in self-isolation, that you are staying fit and healthy - and just as importantly sane. Those of us who have been working from home have been learning new technology such as Microsoft Teams and Zoom. I have found the online meeting to be a revelation and when this threat has passed, I feel that the way we work will have changed forever.
But of course, for so many of our membership, the lockdown has meant “Business as Usual” and you have been working hard to complete the necessary maintenance and renewals projects essential to keeping the railway operational. Our railways ensure that our shops are filled with food and drink, and that NHS frontline staff and other keyworkers can get to their places of work and protect the public. Many hundreds of you have played your part in this and you should be commended, and in this journal and via our social media channels you will see that we are celebrating your contribution in our #HighVisHeroes campaign.
Whilst many of you are working from home and on-site, many of the agency workers who support our industry have seen a significant reduction in available work. My local foodbank informs me that they are experiencing an increase in the use of their services due to redundancies whilst simultaneously seeing a drop in their donations as we all stay indoors. May
I ask you to consider donating to your local foodbank if you possibly can? Most foodbanks, but by no means all, are connected via the Trussell Trust who can be contacted via www.trusselltrust.org.
A great piece by Andy S and as I write, I have just attended the first of the PWI’s online SPOLKS that he organised. Nice work Andy and all the folks who have shared their experiences at this!
It is fascinating to hear how railway engineers are responding and innovating to meet the current challenges and overcome a new set of constraints, making sure the railway stays operating while at the same time maintaining the safety standards that are vital to us all. It’s interesting that safety challenges can drive innovation and that, in turn, this so often results in improved efficiency. Everything has to be thought out in more detail to be properly joined up, planned and have safety and efficiency built in.
A few years ago, when I was a company Transformation Director, as part of the role, I oversaw the Quality Safety and Environment (QS&E) function. I must admit, I was surprised at how engaged and fervent I became about promoting improvements in these areas. For example, as part of our push on behavioural safety, a system was set up that made it really easy for every person in the company to report the slightest safety risk, near miss or (much, much less often) incident. People really engaged in this, sending in simple one or two-line reports submitted electronically through the company intranet, knowing that at least one senior person within the company would read it promptly and that it would definitely be followed up on. The follow up engagement was brilliant, and most times not only resulted in the safety risk being mitigated, but also led to a more efficient way of working being introduced, suggested by staff members and with full buy-in from the team.
I guess that now, more than ever, this sort of teamwork and engagement is needed to solve problems in how to work and overcome the new challenges posed by Covid-19 that are facing us. In the end, it might just cause improvements we never would have thought of making before!
Andy Packham Technical Content Manager Permanent Way Institution andy.packham@thepwi.orgAfter many months of research, the proposal for a new PWI website was recently approved by the PWI Board. This means that the Operations and Marketing Teams will now be embarking on an exciting web development project with a partner agency, collaborating to build our brand new site.
The project will bring together all of the amazing online activities and resources that the PWI team and community have been involved in over the last few months, creating a more dynamic, modern and user-friendly space.
Andy Packham and Andy Steele, PWI Technical Content Managers, give their viewpoints on all things railway.
OUT AND ABOUT - Well, what a unique and challenging spring and early summer for me as Technical Director through the Covid-19 pandemic. Just as our dedicated railway staff were able to rise to the challenge of keeping railways and tramways operating, we in the PWI Executive Team have done very much the same to support the industry. I would say that we have been blessed with the development of amazing video technology that has enabled us to communicate as well, if not better, than before.
The future will be different, no doubt, so we will make the most of it and enjoy future travelling to well-attended PWI technical seminars to learn, network and socialise.
The PWI code of conduct is all too relevant for us today and as I prepare my ethical session for Module 1 of the PWI Diploma, I will be emphasising how proud I am of the PWI and Engineering Council for its absolute commitment to equality, diversity and inclusion. We have wide open doors internationally and are enhanced by our rich mix of cultures which help us to improve railways.
VIRTUAL MEETINGS TECHNICAL SEMINARS AND EVENTS - We have maintained our technical Section meetings well with great efforts through virtual technology and numbers have been great. Life will never be the same again and we have to consider how we plan a blended approach to local meetings and webinars in the future.
Andy Steele did a great job with the SPOLKS seminars and Joan Heery, Stephen Barber and I chaired the three sessions with three speakers. It is incredible the way organisations have responded to continuing their work in the crisis and finding innovative ways of carrying out essential infrastructure work. I was very impressed by the focus of railway staff to come to work and accept new ways. These are all on the website.
Sadly, we lost 2020’s PWI Glasgow seminar, Infrarail, Rail Live and a number of international conferences, particularly those in Europe and America. Railways 2020 in Spain, supported by the PWI, is the conference organised by Prof. Joao Pumbo from University of Huddersfield and has been postponed to September 2021.
In the PWI, we are working hard towards Autumn 2020 in the hope that positive plans can emerge.
PWI TECHNICAL BOARD - On 29 April we held the Technical Board using the ‘Gotomeeting’ online format with excellent attendance and with very positive feedback. The meeting started on a sad note as the group were informed of a track fatality at Roade, Northamptonshire; further details will follow at the next meeting.
James Andrew from Amey Consulting presented the details of the degree apprentice scheme which they launched in March. They have recruited 30 new starters with A-Levels or equivalent to commence on part time degrees at Sheffield Hallam University. There are over 20 trainee track engineers who have joined as student members, thereby indicating the future. Amey would like these to become PWI IEng.
David Godley from Network Rail talked about registration, capability and competency in the context of rail infrastructure management. He was keen to work with the PWI especially at EngTech level where they had a small number, currently less than 100, and probably three to four times as many chartered engineers. There should probably be four EngTechs for every CEng, which means they could easily have 1000 Engineering Technicians! David indicated that he is keen for us to work with his team to map our training courses against their competency framework.
Joan Heery presented her findings on her discussions with PWI Corporate Members, particularly in the area of their support and requirements. There was a good mention of young people and development, particularly training. One of the most important aspects was a review of the benefits of meetings such as the Technical Board.
A ND FINALLY…l’ll finish with two examples of where we as PWI members can make a difference, working to get new technology right and caring for the environment!
On-site induction welding was demonstrated at Rail Live last year in Stratford-upon-Avon. Trials are developing well and those involved are convinced it will make a difference by speeding up welding on renewal jobs. (Image 1)
Image 2 - Michelle Mabbett, PWI Marketing Consultant, as part of her excellent work on positive themes for the PWI has mentioned the recent Environment day. So, I thought I would include this example of a railway turtle duct, on the right, in the hope that it will deter them from sleeping between the switch and stock rail! Now, who can tell me which country it is? (Image 2)
Please see page 46 - YOUR CAREER - for articles on Degree Apprentice training and Virtual Classroom Training.
Counter Technical Director Permanent Way Institution technicaldirector@thepwi.org
Railway operations in Namibia are provided by TransNamib Holdings Ltd formed in 1998, and wholly owned by the Government. Namibia’s rail network consists of 2,382 route-km of tracks. This number continues to increase as the rail infrastructure continues to grow at a healthy rate. Namibia has a history of more than 100 years of railway service. During the colonialisation by the German Empire between 1894 and 1915, a number of railways were built, of which some are still in service today. See image 1.
In preparing this particularly challenging paper returning again to the African continent, making professional and industry contacts and obtaining any real information has proved to be a particular issue! I am indebted to the Namibian High Commission in London who sourced and secured some excellent support for the PWI and me personally.
I thought it prudent to spend a little time describing Namibia, its location and history, in order to put the subject of railways in context. Namibia is officially a Republic, and a country within Southern Africa. Its western border is the Atlantic Ocean; it shares land borders with Zambia and Angola to the north, Botswana to the east and South Africa to the south and east. Although it does not border Zimbabwe, less than 200 metres of the Zambezi River separates the two countries.
Namibia gained independence from South Africa on 21 March 1990, following the Namibian War of Independence. Its capital and largest city is Windhoek and Namibia is now a member state of the United Nations (UN).
Namibia is a truly spectacular place, with the cool Atlantic breeze to the west and hot deserts to the east. The Namib Desert is an important location for the mining of tungsten, salt and diamonds. The sand dunes, some of which are 300 metres (980 ft.) high and span 32 kilometres (20 mi) long, are the second largest in the world.
Temperatures along the coast are stable and quite unique for these latitudes, generally ranging between 9–20 °C (48–68 °F) annually due to the influence of the cold, north flowing Benguela current of the Atlantic Ocean. Further inland temperatures are variable - summer daytime temperatures can exceed 45 °C (113 °F) while nights can be freezing. The Kalahari Desert is also a large semi-arid sandy savanna extending for 900,000 square kilometres (350,000 sq. mi), covering much of Botswana, parts of Namibia and regions of South Africa. All of this of course truly presents real challenges for railway operations, engineering, construction, inspection and maintenance!
In 1966, South West Africa People’s Organisation’s (SWAPO) military wing, the People’s Liberation Army of Namibia (PLAN) began guerrilla attacks on South African forces, infiltrating the territory from bases in Zambia. After neighbouring Angola became independent in 1975, SWAPO established bases in the southern part of the country. Hostilities intensified over the years. It took, however, until 1990 for Namibia to gain independence. On 1 March 1994, the coastal area of Walvis Bay and 12 offshore islands were additionally transferred to Namibia by South Africa.
Phil Kirkland CEng MICE, FPWI PWI Vice President (North England Sections)Phil is an experienced Railway Engineer of 47 years continuous service, beginning in 1973 with British Rail in Newcastle and more recently retiring as Head of Maintenance Delivery at Nexus Metro (Tyne and Wear PTE).
Phil has worked in the rail industry worldwide, specifically in the areas of track inspection, maintenance, renewal, mechanised maintenance, high output systems, railway rules, regulations, policies, processes and all safety matters.
After the independence of Namibia, the Stateowned enterprise TransNamib took control of the national rail network that operates on 3 ft. 6 in (1,067 mm) track gauge, often referred to as ‘Cape gauge’. TransNamib is headquartered in Windhoek and Namibia is well connected in terms of railway infrastructure.
The Rail network stretches from the South (South African border) to the Northern part of the country (Angolan border) and from the middle of the country to its coast and harbour towns. There are aspirations too for new rail links with neighbouring Botswana and perhaps Zambia.
TransNamib operates 2,382 km of route in a country of 825,000 sq.km (by comparison the UK has approx.15,800 km of route in a country of 250,000sq km). While business focus has been primarily on freight services, passenger services are becoming a growing element of the TransNamib business, with the introduction of the timetabled ‘Starline’ passenger services and the ‘Desert Express’ tourist train in 1998, linking Windhoek and Swakopmund. The privately run Rovos Rail ‘Pride of Africa’ luxury train has also reached Namibian rails. Focus is also now on the possible future provision of commuter services perhaps in the capital Windhoek and surrounding areas, and in the north.
The current railway routes within Namibia (see map at image 1) are:
• Windhoek-Kranzberg: 210 kilometres (130 mi) long and completed in 1902.
• Kranzberg-Walvis Bay: 201 kilometres (125 mi) long. In 1914 an extension to Walvis Bay was commissioned; the rails were laid close to the shore of the Atlantic Ocean. In 1980 this extension was replaced by an alternative route behind the dunes that allowed for higher axle load.
• Kranzberg-Otavi: 328 kilometres (204 mi) long and completed in 1906.
• Otavi-Grootfontein: 91 kilometres (57 mi) long and completed in 1908.
• Seeheim-Aus- Lüderitz: 318 kilometres (198 mi) long. The connection between Lüderitz and Aus completed in 1906. The extension to Seeheim was completed in 1908. Eventually the service between Aus and Lüderitz was decommissioned. The line to Lüderitz was reopened in 2018.
• (Uppington) Nakop-Windhoek: 869 kilometres (540 mi) long. The section between Karasburg and Windhoek was completed by 1912, with the extension to Uppington (South Africa) built in 1915.
• Otjiwarongo-Outjo: 69 kilometres (43 mi) long. The first 26 kilometres (16 mi) were completed under the German colonial administration in 1914/1915. The link to Outjo was completed in 1921 under South African rule.
• Windhoek-Gobabis: 228 kilometres (142 mi) long and completed in 1930.
• Tsumeb - Ondangwa Oshikango, Oshakati: commencing in 2005, a new northern extension railway was built between Tsumeb (the existing terminus) to Oshikango and Oshakati approaching the Angolan Border. The project was delivered in three key stages:
1. Tsumeb to Ondangwa 250 Km
2. Ondangwa to Oshikango 59 Km
3. Ondangwa to Oshakati 58 Km
To complete the project, a connection from Oshikango to a point near Cassinga, Angola is planned on Angola’s southern railway system. This new line will link up with the rail system of Angola, (which still needs to be rehabilitated - another Journal article perhaps!) and would enable Angola to export iron ore mined near Cassinga through Namibia via Walvis Bay to countries abroad.
In more recent and very forward-looking times, Botswana Railways signed a Memorandum of Understanding (MoU) in 2015 with its Namibian counterpart state owned TransNamib to facilitate the joint development of the TransKalahari railway which will cost US$ 9.5bn.
The likely railway line would traverse the vast semi-arid Kalahari Desert and has the potential to accelerate the development of Botswana’s huge coal reserves, currently in excess of 200 billion tonnes. The line would extend east from the current livestock railhead at Gobabis and excitingly, is likely to be electrified.
The investments in Namibia and its railways have attracted significant funding requirements from a range of sources. Examples of these include loans and borrowings from the African Development Bank, Arab Bank for Economic
Development in Africa and the Kuwait Fund for Arab Economic Development. The ExportImport Bank of China signed off a concessional loan for purchasing of locomotives, wagons and infrastructure for the new railway being built in northern Namibia, and China further pledged concessional loans, preferential export buyer’s credit, grants and interest-free loans.
One of the biggest social issues in Namibia is the critical public health issue of HIV/AIDS. While the disease has declined in prevalence, Namibia still has some of the highest rates of HIV of any country in the world. 13.8 percent of the adult population between the ages of 15 and 49 are infected. This is a significant issue and risk for any transient work force (either internal or external) engaged in railway construction works.
There was also a dearth of skills, and the track on much of the network was in poor shape. The railway suffered from archaic systems, embedded in the 60s and 70s. Policies, processes and procedures all needed updating. Computerisation, mechanised maintenance equipment, technical understanding and safety management systems were all very much required, and there is still work in progress. To change would be a slow process and contrary to the current policies as labour in Namibia is so plentiful and inexpensive.
Some of the practices to us as outsiders looking in will seem incredulous and downright unsafe - the fainthearted should look away now! The younger members of the PWI should understand that for many of us here in the UK, when our safety practices were less enlightened, this is how we too actually worked week in and week out! We should not however
Factory-assembled TMT panel showing cable ducting Image: WCM/T-Track Global Ltd. Diagram 1: Comparable construction volumes (image: WCM/T-Track Global Ltd.). TMT (Tubular Modular Track) T-Track system installed on the Aus to Luderitz railway (two images above: WCM/T-Track Global Ltd.).criticise; as professional PWI members we should share our knowledge, techniques and products wherever possible to ensure continuous improvements, especially in safety matters, around the world.
Namibia Rail Construction was established as a joint venture between TransNamib and D&M Rail Construction (Pty) Ltd with the objective to build local capacity for the maintenance, rehabilitation and construction of all railway infrastructure in Namibia. D&M Rail Construction is the leading permanent way inspection, maintenance and renewal contractor in Namibia, and has been at the forefront of track work upgrades for many years now.
There would appear to be four main strands to PWay engineering activities in Namibia:
• Existing track rehabilitation and maintenance
• Existing track complete renewal
• New route construction
• Industrial sidings and facilities installation and maintenance
The railway line from Kranzberg to Tsumeb covers nearly 400 miles and connects the port of Walvis Bay with the north of Namibia where major industries such as Ohorongo Cement and Dundee Precious Metals (Copper) are located. As a by-product of the copper extraction process, 330,000 tonnes of sulphuric acid is produced annually which is then sold to Namibia’s Uranium mines and transported back by rail to the Walvis Bay area. The line was converted from 600 mm
to 1067mm gauge in the 1960s, but built to branch line standards using 30Kg/m jointed flat bottom rails on steel sleepers with through T-Bolt fastening systems and little or no ballast. Rails were anywhere between 12m (40ft) and 36m (120ft), joined by fishplates that allowed for expansion and contraction.
As was standard then in South Africa, expansion gaps up to a maximum of 15mm were applied to allow for thermal movement of the rails. Such rail joints reduced the risk of lateral track buckling at high temperatures, and also reduced the risk of rail breaks during the cold desert nights. As traffic patterns changed and increased, tracks required increased and intensive maintenance which could not be sustained, therefore the quality rapidly deteriorated causing several significant and costly derailments, mostly involving very hazardous materials. Our own experiences with T-Bolt steel sleeper systems here in the UK will testify to this.
By 2011 derailments had reached critical levels. TransNamib then invested in a significant emergency track maintenance and upgrade ‘turnaround’ programme, some of which would be complete renewals. The new track installations would be of an entirely different construction. Properly specified and sourced track ballast was used with an appropriate construction depth. P2 concrete sleepers at 700mm spacings combined with 48Kg/m 36m flat bottom (Lucchini Italy) rails, resilient rail pads and proprietary elastic rail fastenings, all combined to make what we would recognise as quality, maintainable permanent way. The rails would be welded into Continuously Welded Rail (CWR), using both Flashbutt and Aluminothermic processes. The first CWR was actually installed in Namibia in the early 1970s and now covers about 60% of the system. CWR is not installed on radii less than 200m and also not on specific steel bridges.
In Namibia CWR is laid within a predetermined temperature range, which is determined using historical air temperature data for each geographical area along the route. (Obviously Namib Desert conditions are much different to those on the Atlantic Coast or northern areas). Minimum and maximum temperature limits within which CWR can be
laid are calculated by deducting 40*C from the maximum expected rail temperature and adding 50*C to the expected minimum rail temperature. This ensures that CWR laid within this temperature (‘A’) range will not be subject to a temperature change of 40*C in compression and 50*C in tension. Wherever possible the CWR is laid or stressed to a neutral / stress free temperature which of course lies within the A range. In Namibia, the neutral / stress free temperature is generally set closer to the upper limit of the A range due to the high ambient air temperatures for most of the year.
Of course, with the construction of such quality ballasted CWR track, TransNamib is able to implement mechanical maintenance and geometry control techniques hitherto not possible. Previously, it is believed (although the author has been unable to fully substantiate) that Namibian railways had a single Plasser 05/06 series machine, latterly supporting what looks to be a Plasser type 07 series machine in the 1970s. Both have seen hard times and are understood to be out of use now.
Therefore more recently, TransNamib has invested 22MN$ (£2M) in a state of the art tamping machine to mechanically maintain the rehabilitated and newly constructed rail routes to a high standard. The machine manufactured by Plasser and Theurer (SA) is an 08-16SH (Split Head) tamper, capable of attending to both plain line and switches and crossings. The machine replaces the two former, probably much older Plasser machines. It represents the highest standard for compact tamping machines in split-head design and contains the same tamping and measuring technology as its larger counterpart high performance tamping machines, with top technology packed into a small machine frame. The 1067mm gauge, 3-axle basic structure with work units and measuring systems offers sufficient scope for individual equipment chosen from the Plasser modular systems and work units, for maintenance of both plain line and S&C units.
The new machine is equipped with four single sleeper tamping units fitted with 16 tamping tines which can be tilted laterally in pairs and also lifted and lowered independently of each other. These special features enable maintenance to be performed in the tightest areas of the turnouts. The lifting and lining unit is also adapted for these areas with both hook and roller clamp for lifting the track at various stages of the tamping process.
Another innovation is that once placed in working mode, the roller clamps operate and open automatically, which enables higher outputs to be achieved, especially when tamping S&C units, allowing the operators to be more spatially-aware and fully focus on tamping position rather than constantly opening and closing clamps. The choice of a 16 tool single head machine allows for working on a variety of plain line sleeper spacings. The machine is fitted with the same measuring equipment as the high output tamping machines. The WIN-ALC automatic geometry guiding computer controls the machine during operations, in conjunction with the DAR (Data
CBG (Iran) ltd elevated rail seat concrete sleeper (image courtesy CBG (Iran) Ltd).Acquisition Recorder). (In fact the machine very much reminds me of my enjoyable times with the VolkerRail 08-90/4ZW machine and our 08-275NX on the Tyne and Wear Metro system.)
The original railway line to Lüderitz closely followed the Atlantic coast around Elizabeth Bay and Pelican Point with all its inherent consequences. Eventually consumed and corroded by the ocean, operations and maintenance were unsustainable, and the line closed. With an increase in Zinc export traffic through the port in recent years, the line was completely rebuilt, but this time across the desert and through the sand dunes. This called for a really innovative and different approach to permanent way engineering.
And now for something completely different! One of the track form systems used in Namibia, and fairly unique (in my experience) to South Africa, is known as T-Track. A tubular, modular track form construction.
• No ballast, no screening and no installation tamping is required
• No sleepers are required, therefore no further maintenance tamping is required
• With a continuous support and reduced rail stresses, reduced rail sizes can be used
• Resilience is provided by a continuous pad under the rail, no pad creep
• Fixed geometry, vertical and horizontal alignments remain constant
• Integrated system, so formation layers form an integral part of the overall system
• Reduced maintenance (i.e. moving parts)
• Can be custom designed for any axle load or speed
TMT can potentially provide solutions in the following contexts:
• Desert conditions
• Tunnels, platforms, yards and loading facilities (i.e. coal mines etc)
• Turnouts
• Low lying areas
• Where earthwork costs need to be minimised
• Simplicity of rapid construction
TMT railway track is similar to a Mecanno set. Pre-manufactured, twin reinforced concrete beams linked with steel gauge (tie) bars provide continuous support for the rails. The twin beams and the layered formation on which they are laid, are designed as an integral system, and as such the track must only be laid on formations constructed strictly in accordance with that specific system design. The twin beams are tied together using specially designed galvanised steel tie bars, the ends of which encircle the beams and are thus not cast into the beams. This enables easy replacement of the tie bars, and also ensures that the tie bars do not work loose under repetitive dynamic forces. Tie bars are spaced at 3m intervals on straight track, and at lesser intervals on curved track to accommodate lateral forces. Intermediate rail fastenings are provided on stirrups which also encircle the beams. Rails are fixed to shoulders welded onto the tops of tie bars and intermediate straps by means of proprietary (Pandrol / Vossloh) fastenings. Resilience is imparted to the system by means of continuous resilient strip (rubber bonded cork) placed under the rails. The Transition zones at interfaces between Tubular Track and conventional ballasted track require special designs to accommodate the change in stiffness between the two systems. Further research and development into this permanent way system and potential improvements continues at the University of Pretoria in South Africa.
Diagram 1 outlines some of the potential construction savings by deployment of TMT in the appropriate conditions and context.
In the context of locations such as the deserts of Namibia, windblown sandstorms are frequent, variable and often significant (see following images). The deposited sand fills and contaminates the voids between the ballast in conventional track, thus removing the dynamics and the ability to maintain by such as mechanical tamping. The sleepers are not visible and the fines accelerate ballast and sleeper attrition under traffic. Rail corrugations appear and normal maintenance techniques are just not possible. In times of significant storms, conventional ballast is simply blown out of the track and across the desert.
Tubular Modular Track eliminates many of these maintenance problems and allows the railway administration to focus on the operational task of clearing sand deposits elsewhere. On occasion, these sand deposits can however be quite substantial, requiring several days of clearance activity. The subject
of windblown sand on railways is quite a topic and much research has been undertaken, particularly as many administrations are now operating higher speed passenger services across arid desert areas (eg UAE, SAR, Iran). TMT is also currently on trial in Saudi Arabia.
Other solutions such as the elevated rail seat sleepers manufactured by CDG in Iran are now being trialled, both as sleepers and slabs on many routes. (I did challenge tamping tine penetration depths and pressures, especially for elevated sleepers and when transitioning from one sleeper type to another, but have not received any technical response to date.) In very general terms, windblown sand will reach the elevated railway or nearest rail and be deflected upwards. As its velocity decreases, it generally falls into the four foot. Once this begins, a cycle develops whereby the sand builds up and eventually engulfs the railway. Most solutions involve breaking this cycle.
By having an air gap beneath the rails from cess to cess, the windblown sand is no longer deflected upwards, but can pass right through the permanent way in significant quantities, without forcing out ballast or blocking the tracks. Alternatively, specialised lineside fencing can be deployed away from the track which slows down the velocity of the windblown sand and causes it to deposit away from the railway. These deposits can then be removed at leisure with no operational railway impact.
Therefore, Namibia has a requirement for two types of track construction, standard ballasted track in arid areas and Tubular Modular Track in the true sandy desert areas. Uniquely, this calls for differing maintenance strategies, skills and equipment.
In researching and preparing this paper, further contacts and more great friends have been made around the world which I never could have imagined. Therefore I am deeply indebted to the following and others for the assistance and supporting technical information given by: the Namibian Consulate in London, D&M Rail Construction Ltd, TransNamib Holdings, Plasser & Theurer SA, CBG (Iran) Ltd, T-Track Global Ltd, Independent photographers JonErik Munro (SA) and Laurie Mulrine (UK).
This article is aimed at widening understanding of our subject and perhaps inspiring some further research, particularly by our younger engineers and members. With that in mind, here are some research and study points that you may find useful for your CPD and NVQ portfolios, or even discussion at your section meeting!
1. What other types of modular track systems are available to engineers? 2. What are the risks of manually offloading concrete sleepers, and what alternative methods can be used? 3. What are the risks of manually offloading rails and what alternative methods can be used? 4. What is WinALC? 5. What equipment or systems are available to reduce windblown sand from railways? 6. What is the legislation covering the transportation of hazardous materials by rail?
Aberdeen, population 200,000, is Scotland’s third largest city. Inverness is one of Europe’s fastest growing cities. Linking them is the Aberdeen to Inverness line, 107 miles of mostly single line railway with eight additional stations spread along the route, each with their own passing loop.
Until 2019 the line carried 11 trains from Aberdeen to Inverness per day and the same on the return, with the journey averaging two hours 18 minutes. An additional 15 commuter services ran between Aberdeen and Inverurie and two between Inverness and Elgin per day. The journey times and irregular service between Aberdeen and Inverness meant that the railway line did not offer an attractive alternative to road travel.
As part of a strategic review carried out by Transport Scotland in 2008 a set of key output requirements were established for the Aberdeen to Inverness line:
• hourly service between Aberdeen and Inverness
• half hourly service between Inverness and Elgin including a new station at Dalcross
• half hourly service between Aberdeen and Inverurie including a new station at Kintore
• a circa two hour end to end journey time
• maintain, as a minimum, the ability to deliver existing freight access rights on the route.
Achieving these outputs would require a series of interventions to be carried out along the length of the route.
Over the course of 2015, 2016 and 2017, interventions at Forres and Elgin on the western end of the route were designed and constructed. At completion the following works had been delivered:
• Elgin – extension of existing platforms. Extension of existing loop from 630 m to 1330 m including new F21.5 turnouts at either end allowing simultaneous arrival in to the station. Upgrade of Elgin LX (level crossing) to MCB-CCTV. Closure of Elgin signal box and removal of token exchange signalling system. New signalling system recontrolled to Inverness Signalling Centre.
• Forres – new twin platform station with 1300m passing loop allowing simultaneous arrival in to the station. One new overbridge and one new underbridge installed. Two LX’s closed and two UWC’s upgraded. Closure of Forres signal box and removal of token exchange signalling system. New signalling system recontrolled to Inverness SC.
After completion of the works on the west, attention turned to the eastern end of the line. This section of line was the busiest on the whole route, allowing passengers to travel between Aberdeen, Dyce (Aberdeen airport) and the town of Inverurie. Due to a pressing need for increased commuter services at the eastern end of the line, emphasis had been placed on this section for the greatest extent of proposed redoubling. In addition a new station was proposed at the town of Kintore.
The existing line from Aberdeen to Inverurie was 16.25 miles of single line, with a 0.75 mile section of double track serving Dyce Station and Raiths Farm freight facility. The proposal to redouble this section of line was made more complicated because since the line was singled in the 1960s, the existing track had gradually been renewed and maintained to follow the racing line in six areas (see image 4), removing clearance issues through overbridges, platforms and a tunnel (see image 5).
In addition large sections of the existing single line had track components not suitable for a linespeed increase. This meant that a scheme to redouble 17 miles between Aberdeen and Inverurie, resulted in 60% of the existing line having to be renewed.
Over a period of 18 months, AECOM, Jacobs and Siemens designed the works required for the redoubling, with the output being:
• 40,000 m of new track including 15 new point ends
• 85,000 m3 of earthworks
• 4,300 m of retaining walls
• 30 structures altered (extensions, infill, removal, strengthening)
• 3 level crossing removals, 3 upgrades.
• new station at Kintore
• plus re-signalling throughout along with associated ancillary civils, resulting in the closure of signal boxes at Dyce and Inverurie
AUTHOR Robert McCafferty Technical Head of Track, BAM NuttallRobert started on the railway in December 1995, spending his first six years working with Scott Wilson Railways in Glasgow. The six years were spent in a survey and design environment and gave Robert the foundations for the years and roles to come. Six years followed with Mowlem Railways on the contractor side, followed by three and a half years with Network Rail.
Robert moved to Australia, spending two years in Brisbane with AECOM. Since returning in 2013, Robert has worked in various CRE and CEM roles and is now the Technical Head of Track for BAM Nuttall.
Robert is currently working towards CEng status through the PWI Experiential Learning Route.
These works would be carried out during a series of rules of the route possessions, weekend possessions (54 or 78hrs) and a 14 week blockade in each of the summers of 2018 and 2019.
The 2018 blockade primarily consisted of works between Aberdeen and Dyce. During the 14 weeks, all earthworks, structures work, drainage, ancillary civils and trackworks were completed. During the initial part of the blockade, all the existing track was removed other than two short sections that only required tamping. This allowed the site to be managed as a high street environment, reducing the need for expensive rail mounted plant and allowing earthworks and drainage to be completed quicker (see image 6).
By the end of the blockade, the existing single line had been lifted, slued and renewed to form the down line. Four miles of the new up line had been laid, but not connected at either end and the Kittybrewster sidings area installed to a temporary alignment that maximised the amount of the new layout that could be installed, whilst still retaining the existing signalling and functionality. Image 7 below shows an extract from the Kittybrewster Scheme Plan at the end of the 2018 blockade. Black = existing, red = new track brought in to use, blue = new track not brought in to use.
As part of the 2019 blockade, Don Viaduct, a 103 m long, five span viaduct was to be upgraded to carry a second track. The viaduct carried the existing single track on waybeams over the river Don and its floodplain. The rail bearers span between cross girders supported from 2 outer main girders on a skew angle of 35 degrees. It was recently strengthened and repainted but only for single track loading. There is no deck, apart from an open mesh walkway. Therefore the deck is relatively lightweight (see image 8). The superstructure is supported by eight 2.1 m diameter granite masonry piers and two granite masonry abutments (see image 9).
At early GRIP (Governance for Railway Investment Projects) stages it was established that the superstructure could be strengthened to support a second track. Several options including complete replacement and various strengthening schemes were considered. Key to this was removing the waybeams and installing ballasted track. The existing cross girders needed significant strengthening, so to simplify construction these would be removed and replaced with heavier sections. The main girders needed some straightforward strengthening, and a new steel deck, ballasted track and cantilevered walkway would be
installed.
Proposed superstructure solution:
• replace cross girders
• 85 new cross girders / trimmers
• 164 new stiffeners
• strengthening of main girders
• new cantilever walkway
In order to support the increased dead load of the deck, substructure strengthening would be required.
From ground investigation and record information available at the time, the piers were understood to be approximately 2 m deep. AECOM proposed installing a concrete collar around the base of the piers to strengthen the substructure (see image 10).
Following outline design some additional trial pits appeared to contradict the previous GI, and newly available record drawings seemed to show deeper foundations. This led to specialist survey by seismic ground penetration to confirm the depth of the piers and the depth of rockbed. This found that the piers were between 5-8 m deep (see image 11) which had a significant impact on the proposed solution. A collar around the base of the piers could not be installed without undermining the integrity of the structure and a collar around the pier at 2 m depth would not be effective as the load would still be transferred to the base of the pier.
AECOM found that we would need to install the concrete collar with piles anchored into rock level for the design to work. This would have a significant impact:
• access to install piling would impede the installation of the scaffold needed to carry out steelwork strengthening
• the piling and steelwork strengthening would all have to be carried out in the blockade. Not enough time was available to carry out the works
• piling solution would be much more expensive
Once these issues came to light a focus group was established involving BAM Nuttall, AECOM, Lanarkshire Welding and NR engineers. This was an open collaborative forum which met on a weekly basis to discuss the developing design. The aim was to integrate the requirements of design, construction and fabrication to develop a solution that met Network Rail’s requirements in terms of scope and programme.
The group looked at ways to avoid or reduce substructure strengthening. Finding a way to remove the need for piling in the river would go a long way to allowing the works to be delivered within the required timescales and budget.
The group looked at ways of reducing the deadload by investigating a waybeam solution, removing the weight of ballast and steel deck plates. Using a risk-based assessment, AECOM compared historic loading against new loading to determine the reduction in factor of safety. If the factor of safety could be shown to be close to historic cases, the technical solution proposed could be shown to be feasible. For waybeams, AECOM calculated that the vertical loads only imposed a marginal reduction on the FOS (Factor of Safety). However, the longitudinal traction and braking loads meant that substructure strengthening was still required.
Piling in the river was still the key constraint to the programme so AECOM proposed the use of shock transmission units (see image 12). The shock transmission units lock up when longitudinal loading is applied transferring the load through the structure into new transition slabs behind the abutments. By doing this the longitudinal loading was taken out of the piers, and AECOM were able to demonstrate that the FOS were the same or better than the historic case. This solution took the piling out of the river clearing the way for the superstructure strengthening. The piles could be installed in advance of the blockade and the programme could be met. No substructure strengthening was needed on the piers.
By holding the focus group and including the fabricator in the design process we were able to simplify details and reduce the amount of time needed in the blockade and also improve the safety of the design. As an example, the standard detail was to attach the new cross girder to the main girder then install the u-frame stiffeners. All work that would need to be carried out during the blockade.
By amending the detail to install a stub end and stiffener in advance of the blockade using rules of the route possessions, a lot of preparation work could be carried out in advance. The blockade work then became a simple drop in and connect of the cross girder (see image 13). The focus group was a great benefit to the project, and a truly collaborative approach to resolving a key challenge on the project. Lessons learned will be applied to future
Image 13: History of cross girder detail.Image 17: Track design - setting out - vertical.
complex structure works.
Having solved one problem, the focus group then had the challenge of developing details that allowed the waybeams to be installed effectively. The design of the waybeam was complicated by several factors:
• the structure was on a high skew
• the track was rising at a gradient, and with differing levels of main girders
• the design would need to include packer plates below the waybeams to ensure that the track sat at the correct level across the structure and also limit the variance in waybeam depth and size
• the south end of the viaduct sat on a transition, with the cant varying from 49 mm to 0 mm. This required further packing plates to ensure the 1:20 rail inclination and crossfall were introduced in to the baseplate/waybeam system
• a guard rail was needed as a mitigation to derailment loading as the design only proposed a light GRP deck. This dictated the type of baseplate used and required gathering panels on approach to the viaduct
• finally, the civils element of the work (waybeams and below) had to be ready for the installation of the track to commence in week eight of the blockade. The track installation had a three week window before engineering trains had to cross to access renewal works to the west
On commencement of the detailed design, AECOM proposed the use of Schwihag BCR7 baseplate. The baseplate would be fitted with CEN56E1 running rail and 33C1 guard rails. These would be mounted on a variety of tapered shims and straight shims depending on the location (see image 14).
Once the components were agreed, AECOM then had to produce a Form B design that took all the factors above into account and provided enough information to allow the installer (Babcock Rail) to install the baseplates, shims and rails in accordance with the tolerances set out in Table A.1 of NR/L2/TRK/2102 Design and Construction of Track.
Image 18: Baseplate setting out design.
For a normal track renewal the design is built from a series of known values, rail level, rail type, sleeper type, ballast depth. From these an engineer can calculate what the design rail level, bottom ballast level and formation level are. In the case of Don Viaduct, it wasn’t quite so simple.
Rather than a formation level, we had to work up from the top of cross girder level (see image 15), this being an anticipated level rather than fixed, the anticipated part being explained by the following note on the drawing:
“The anticipated levels to the top of each of the cross girder fixing plates shown on this drawing are derived from the proposed depth of the new cross girder construction and the bottom flange levels for the existing main girders at each of the proposed new cross girder connections obtained from the pointcloud survey completed by Plowman Craven Ltd. in September 2018. These levels include an allowance for the estimated additional deflection of the main girders due to the increase in dead load following.”
The design then worked up from this pointanticipated level of cross girder fixing plate, anticipated depth of bottom packing plates, target level to underside of steel troughing fixing plate then the waybeam itself.
For the waybeams we needed circa 100 m3 of FSC Greenheart and FSC Ekki timbers, 350380 mm x 530 mm of D70 strength (as defined in BS EN 338). Due to these being non stock sizes, the timbers were either imported from a source country (Guyana, Gabon or Cameroon) or sawn from stock in Europe.
The supplier for the timbers, Gilmour & Aitken Timber Merchants, advised the tolerance of the timbers would be -0/+10 mm however with additional planning in Europe this could be
Image 19: Extract from waybeam as built survey.reduced to +/-1.5 mm. Adding more uncertainty to the steps needed to get from cross girder level to rail level. The output from the vertical element of the design is shown in image 17.
As well as the factors noted above for the vertical alignment, the design and installation also had to take in to account the following requirements from NR-L2-TRK-3038 (longitudinal timbers) when positioning the baseplates:
• baseplate centres (max 650 mm)
• Centre of baseplate fixing hole to edge of waybeam (minimum 75 mm)
• centre of baseplate fixing hole to end of waybeam (minimum 150mm)
• max shim depth (30 mm)
• baseplate rotation (+/-2 mm)
• baseplate pair squareness (+/-5 mm)
To enable the baseplates to be installed to the required accuracy, we asked that AECOM produce a table showing the co-ordinate for all three holes on every baseplate, a total of 2112 setting out points (see image 18).
Once the design had sufficiently progressed we were able to order the PWay materials required for Don Viaduct, these consisted of:
• 800 BCR7 baseplates
• 2 x gathering panel
• 2 x run off panel
• 28 x 18.288 m 33C1 guard rails with fishplates and screws
• 800 straight packing plates in range of sizes from 10 mm to 2 mm
• 220 tapered shims
• plus AS screws, LS screws and other smalls required
The first eight weeks of the blockade passed without incident, eventually reaching the point where the waybeams were installed and ready for the track to be installed. Firstly an as built survey was completed of the top of waybeam level. As explained earlier, getting to this point required a build up from the cross girder, including packing plates and the inherent variability of the waybeam itself, so it was no surprise that in some areas the survey was slightly outside the required tolerance. As can be seen from image 19, the majority of the survey points were within the target tolerance (green), some were outside the target tolerance but still within 2102 tolerances (orange) and a small number were outside the allowable installation tolerance (red).
All the areas identified as being outside tolerance were high to design, so the solution proposed was to plane the affected areas of waybeam, reducing the height locally to the affected baseplates (see the RH side of image 20). Once the waybeams were within the required tolerance, the baseplates and tapered shims were laid out and a small piece of slave rail inserted to check the resultant rail level. The Babcock engineers were then able to calculate the depth of packing shim required.
Babcock then installed 30 ft slave rails on the down line and clamped them up using temporary plates and clamps. The down line was then used as a service road to pull long welded rails across the viaduct for installation on the up line. This process required a series of rail rollers to be mounted on cross timbers supported by the waybeams. Once installed and clamped up, the process was reversed and the long welded rails installed on the down line. Once in place, the rails were clipped up and a final check carried out on the rail level, cant and twist. Height adjusting shims were then installed as required to ensure that the installation was in accordance with NR/L2/ TRK/3038, NR/L2/TRK/2102 and the AFC (Approved for Construction) design. The viaduct is 115 m long, so the rails extended beyond the bridge meaning no welds were required on the bridge.
Given the bespoke nature of the installation it was necessary to create a bespoke inspection and test plan (ITP) to check and record that everything had been installed within tolerance. In image 21 you will see the ITP used to check the baseplates centres, offsets from the side and end of waybeams, depth of shims used, pilot hole depths and horizontal and vertical alignment. Image 22 shows the ITP used to record the relationship between pairs of baseplates – gauge, cant and baseplate pair squareness.
The works on the viaduct, both track and civils, were completed as per programme, meeting the reduced tolerances for horizontal and vertical alignment and with minimal snagging work required post blockade. Image 23 shows the track in its final arrangement.
Image 23: Track in final arrangement.As well as Don Viaduct, other major works were undertaken during the 2019 blockade. These included the closure of Pitmedden LX, upgrade of Boat of Kintore LX to MCB-OD, removal of three overbridges, upgrade of six underbridges, renewal of 8,000 m of existing track, installation of 15,000 m of new track and introduction of the new signalling system. The line opened for driver training on Saturday 17 August, with the first passenger trains running as planned on Monday 19 August.
At the end of the blockade we opened 11 miles
of new track at the new linespeed of 75 mph with no requirement for a TSR. Due to the amount of earthworks, structures, drainage and new track installed, we agreed with Network Rail that an amber trolley would be run nightly for the first two weeks. Using two trolleys per night we surveyed 11 miles x 2 lines x 14 nights, a total of 308 miles of recording. No issues were detected in those two weeks or since. Image 24 below shows an extract of the spreadsheet used to compare runs over Don Viaduct.
Over the course of four years, BAM in partnership with Siemens, Babcock, AECOM and Jacobs designed and installed a series of upgrades at Forres, Elgin, Aberdeen to
Inverurie and other locations on the Aberdeen to Inverness line. By the end the following works had been completed:
• 45,000 m of new track including 20 new point ends
• 90,000 m3 of earthworks
• 4,300 m of retaining walls
• 33 Structures altered (extensions, infill, removal, strengthening)
• four Level Crossing removals, six upgrades.
• new station at Forres and Kintore
• closure of four signal boxes
• removal of token exchange signalling and recontrol to Inverness and Aberdeen SC.
The journey from the 2008 Transport Scotland output requirements to now has taken 12 years, but isn’t yet finished. Further works are ongoing and planned on the Aberdeen to Inverness line. A new station is almost complete at Kintore (see image 25) and design has commenced for a new loop and station at Inverness Airport.
I’d like to thank David Herron, Associate Director with AECOM. David and I gave a presentation to the Winter Track Conference in December 2019 and his contribution to that forms part of this paper, particularly the Don Viaduct Civils elements.
NR/L2/TRK/3038 - Longitudinal Timbers –Design, Installation and Maintenance NR/L2/TRK/2102 - Design and Construction of Track
Image 25: Kintore Station.This paper will introduce the concept of low adhesion between train wheel and rail, including why it is so important to the railway, and will show how sand is used to improve low adhesion braking performance. Using sand is not a new concept, indeed steam trains were using sand for traction purposes over 100 years ago. However, by increasing sand delivery it is possible to deliver consistent train braking performance regardless of the underlying adhesion conditions. Solving the braking issue builds driver confidence in poor adhesion conditions and opens the door to using sand in traction to achieve higher performance.
This paper describes how the braking performance of different sanding configurations was quantified in a real railway environment, and how an innovative new analysis methodology was developed (since wheel/rail adhesion cannot be measured directly, the ‘Reference Adhesion ’ provides a method of inferring effective adhesion during a brake event).
In order to accelerate or decelerate normally, railway vehicles rely on adhesion between steel wheels and rail. A typical ‘step 2’ service brake demand (representing a requested deceleration of 0.6m/s2 or 6%g) requires a coefficient of adhesion between wheel and rail of µ ≥ 0.06. Table 1 shows a range of typical braking demands, however please note that some trains have different brake rates and/or more granular control.
For the majority of the year, this level of wheel/ rail adhesion is readily available. However, each autumn, deciduous trees shed their leaves with some being crushed under the pressure of train wheels, bonding to the rail to produce a very hard and smooth layer. When combined with moisture, the resulting coefficient of adhesion between wheel and rail can be as low as µ = 0.01; six times lower than that required to sustain normal braking. During braking, if the demanded adhesion exceeds the available adhesion, the train wheels start to rotate more slowly than the actual train’s speed; the wheels are starting to slide. With a pneumatically actuated friction braking system, the Wheel Slide Protection (WSP) system will intervene to control the slide before any wheel damage occurs.
This is generally done on an axle-by-axle basis by rapidly venting pneumatic pressure in the brake cylinders, thus removing the braking force and allowing the wheel speed to increase back to true train speed. Some slide is beneficial as it can create heat, drying and scrubbing the track, improving adhesion for the following axles. This effect, known as wheelset conditioning, tends to work best at improving medium levels of adhesion - however it is less beneficial at very low adhesion levels.
Low adhesion can cause safety incidents (such as Signals Passed At Danger, or SPADs) and significant performance issues (such as station overruns or delays). In low adhesion, train drivers will naturally drive more cautiously; perhaps resulting in a lower maximum speed between stations and braking early and gently. There are also issues with traction, particularly affecting freight trains with limited motored axles. Each year, approximately 350,000 delay minutes are attributed to low adhesion. The direct impact of low adhesion is estimated to cost the GB railway industry and wider society £345m per year. The cost is made up of delay compensation, as well as the costs to mitigate low adhesion (including rail head cleaning) and the operational and reputational damage which occurs when train reliability and punctuality are degraded. Low adhesion issues are also a significant barrier to maximising future network capacity increases, since predictable and reliable braking is a key requirement for running trains closer together.
Although low adhesion exists mainly on the rail (the permanent way engineer’s domain), it primarily affects the rolling stock (the rolling stock engineer’s domain). There are several types of available mitigations against low adhesion:
• infrastructure-based mitigations include vegetation management (to reduce contaminant getting on to the rails in the first place) and rail head treatments (to clean the contaminant off the rails).
• rolling stock mitigations include sanders (the subject of this paper), as well as braking systems independent of wheel/rail adhesion (magnetic or eddy-current track brakes). There are also potential future technologies being evaluated, including using highpowered lasers or plasma arcs to burn contaminant off the rails, or using frozen carbon dioxide to freeze the leaf film and blow it clear of the track.
This paper focusses on enhancing the use of sanders. Since sanders already have a history of in service use on the railway, the technology is available now and the benefits are proven. Sand is also relatively inexpensive.
Sand, as shown in image 1, has been used on the railway for almost as long as railways have existed; historically steam locomotive drivers could open a valve to activate steam-powered sanders to aid traction. On a modern train, the WSP system controls the sander (automatic sanding) - although the driver often has a manual override button to obtain sand on-demand.
Andrew Lightoller is a Chartered Mechanical Engineer, working for DB ESG, a rolling stock consultancy. Andrew started his career in the rail industry as a graduate engineer at Bombardier where he took over as Brakes engineer on the Classic project. After various experience including a six month placement at Chiltern depot commissioning 168s and EU testing of aluminium foam, Andrew moved to Atkins as a Brakes & Pneumatics Engineer in 2001. In 2014, Andrew moved to DB ESG after their acquisition of WSPER and works as a Principal Mechanical Engineer involved with WSPER, brake testing and other general consultancy work.
Liam Purcell, CEng FICE FPWI
Liam is currently working as a Principal Consultant at Ricardo Rail, and leads the Intelligent Infrastructure team. Liam is a Chartered Civil Engineer and Fellow of the ICE and PWI, with sixteen years’ experience in the railway industry.
After initially joining AEA Technology Rail /DeltaRail as a graduate in 2003, he worked as a track consultant focussing on vehicle-track interaction and derailment investigation. Liam joined Lloyd’s Register Rail (now Ricardo Rail) in 2012 to specialise in wheel-rail adhesion, asset management and independent assurance of infrastructure projects.
Sanders deliver sand to both wheels of an axle either by having a pair of sanders (one for the left wheel and one for the right wheel) or by having two delivery hoses from a single sander. Since sanders are directional, Multiple Units are typically equipped with sanders at axle three in each direction.
When the WSP system detects wheel slide, it calls on the sander to eject sand. A typical sander configuration is shown in image 2; the sand is delivered from a hopper and compressed air carries it along a flexible sand delivery hose, ejecting the sand just ahead of the wheel. The sand is aimed at the wheel/ rail contact point, as shown in image 3. As the sand passes through the wheel/rail interface, the abrasive nature of the sand helps transmit the braking shear forces from the wheel into the rail, and the contamination layer is also damaged by the abrasive sand particles. The sand is crushed and turns to dust (see image 4); the dust probably helping to absorb moisture. Sanders are considered to have a two-fold benefit by:
• Providing a temporary boost to the level of adhesion experienced by the sanded axle (and subsequent axles to a lesser extent), and
• Abrading or breaking down the leaf film, assisting in its removal.
It should be noted that automatic sanders do not predict where to lay sand: they need wheel slide to occur first to trigger the sand delivery. Automatic sanders were initially introduced on multiple units by British Rail Research, starting around 1996. Most modern multiple units
are equipped with fixed rate sanding ahead of the third axle, delivering a nominal 2 kg of sand per minute (to each wheel). The sander is often inhibited at speeds below 10mph, to avoid laying a high density of sand which could cause interference with track circuits. (2 kg / min of sand, deposited at 10 mph, is equivalent to a sand density on the track of 7.5 g/m. At this density, sand is unlikely to interfere with track circuits.) The above configuration, herein referred to as Single Fixed Rate Sanding (SFRS) undoubtedly has low adhesion braking performance benefits. However, by using more sand, there is potential to deliver greater benefits.
A greater quantity of sand could be delivered through:
• Distributed sanding (multiple sanders distributed along the train), and
• Variable rate sanding (speed-dependant sand discharge rate, with higher sand rates at higher speed).
The key benefit of the variable rate sander is that it can deliver a higher rate of sand at higher speeds (4 kg / min at speeds above 20 mph), yet it is able to vary its flow rate at lower speeds to respect the 7.5 g/m guidance. A comparison of sand flow rates for fixed and variable rate sanders is given in image 5. A train equipped with variable rate sanders at axle 3 is referred to as Single Variable Rate Sanding (SVRS), and when two axles are equipped (typically axles 3 & 7) it is known as Double Variable Rate Sanding (DVRS).
Image 5: Comparison of fixed rate (orange) and variable rate (green) sanders; sand flow rate (left graph) and sand density on the track (right graph).
Image 6: Test site for sander testing in low adhesion.
Table 1: Relationship between brake demand and adhesion. Image 1: Railway sand (note coarse grains). Image 2: Typical sander configuration (note sand hopper and flexible delivery hose). Image 3: Sand being ejected from the sand delivery hose, directed at the wheel/rail interface (train is stationary; test button used to eject sand for photograph). Image 4: Sand being delivered at speed (≈ 40 mph) during wheel slide.is derived from tree pulp and is therefore a similar composition to real leaves. This artificial (but representative) low-adhesion zone enables consistent and reasonably repeatable tests. A bespoke trolley was used to lay the paper tape (which is gummed on one side, so it adheres to the railhead), as shown in image 7.
Two brand new four-car Class 387 EMUs were used for the testing, and were modified by:
A working assumption in this was that adhesion would remain constant between individual tests. In reality this was not experienced. After the first few testing sessions, it became clear that the changing environmental and rail conditions produced substantial adhesion changes between consecutive tests, and the planned test strategy was not appropriate. A new approach was needed.
The T1107 project aimed to determine the benefits of enhanced sanding that could be achieved in low adhesion conditions, using a real train running on real track. The test objectives were:
• quantify the benefit of distributed sanding;
• quantify the benefit of variable rate sanding;
• determine if it is possible to deliver ‘assured’ 6%g braking in low adhesion conditions.
Testing was carried out at Network Rail’s RIDC (Rail Innovation and Development Centre) Melton facility; the line used for testing was approximately 7 km in length - an aerial view of the test site is shown in image 6. The site was divided into a 2 km acceleration zone (for accelerating to 55 mph); a 1 km low adhesion zone (to undertake the sander testing) and a 4 km run-off zone (for train deceleration and a safety buffer).
To create the low adhesion zone, 1 km of track was ‘contaminated’ with paper tape. The tape is typically used in the packaging industry and
• provision of variable rate sanders in advance of axles 3, 7, 11 and 19;
• installation of water spray system ahead of axle 1 (to moisten the paper tape to create low adhesion);
• installation of transducers to measure and record parameters including axle speeds, brake cylinder pressures, train speed, etc.
The paper tape was ‘bedded’ by coasting over it and then ‘conditioned’ by undertaking full-service brake applications while using the water spray to moisten the tape. Once sufficient slide was apparent, an un-sanded test was undertaken to verify that a suitable low adhesion layer had successfully been created. Finally, a sanded braking test was undertaken, and the resulting data analysed to determine basic statistics of the test.
Initially, the test methodology was based on quantifying the low adhesion train braking performance without sand (the control test) followed by a sanded test; with the control test effectively providing a benchmark from which to compare the improved deceleration of the sanded test.
A new strategy, Initial Reference Adhesion, was devised whereby the first two (un-sanded) axles of the train were used to estimate the initial underlying wheel/rail adhesion that the train was running over. This novel approach to inferring real-time adhesion was a significant breakthrough for the project because not only did it provide a suitable method of comparing one test with another, but it also removed the need to establish identical rail conditions between tests.
This new approach relies on the assumption that the WSP system regulates the brake force (in this case brake cylinder pressures) to maximise the use of the available adhesion to stop the train in the shortest distance. As a result of this assumption, differences in WSP system performance may lead to small differences in the results but comparison of stops from the same train (and possibly of different trains using the same WSP system) should be directly comparable.
Reference Adhesion is an approximation of the wheel/rail adhesion that each axle of the train was able to utilise over the course of the brake application. Initial Reference Adhesion is the average Reference Adhesion for the first two axles of the train, and provides a snapshot of the incoming track condition, before it is changed significantly by the train.
Image 8: Mean deceleration achieved for DVRS, SFRS and un-sanded stops.
Image 9: Stopping distance achieved for DVRS, SFRS and un-sanded. stops.
Image 10: Average results from all the sander tests.
Image 11: Average stopping distance chart from 55mph for sander configurations with µ = 0.02
Image 12: Reference Adhesion plots for axles along the train, each grey line indicates an SFRS test run and the orange line shows the mean SFRS.
Image 13: Reference Adhesion plots for axles along the train, each grey line indicates a DVRS test run and the green line shows the mean DVRS result.
Image 14: Range of stopping distance results from 55 mph for differing sander configurations (Initial Reference Adhesion between 0.02 and 0.045).
Equation1.
Calculation of the Reference Adhesion of an axle is relatively simple, as indicated above(equation 1) where,
• ‘Average BCP’ is the mean Brake Cylinder Pressure measured over the brake application for that axle;
• ‘Dry Rail BCP for Brake Demand and Load’ is the BCP pressure in good (nonslide) adhesion conditions after automatic adjustment for passenger loading; and
• ‘Dry Rail Deceleration for Brake Demand’ is the straight & level track retardation rate in ‘g’ for the selected brake demand.
The above calculation assumes that the automatic adjustment of brake cylinder pressures for passenger load assures a similar retardation rate independent of vehicle payload - otherwise the deceleration rate should also be factored for load.
The Reference Adhesion for each axle provides a method of demonstrating how adhesion changes on an axle-by-axle basis along the train. The Initial Reference Adhesion (average of first two axles), provides a benchmark of the starting adhesion conditions and enables comparison of one test with another.
Image 15: Examples of theoretical maximum sand density of 7.5 g/m, if all the sand were to land on the railhead in a narrow bead (left) or more spread out (right).
The T1107 testing project carried out 147 sanded tests and 78 un-sanded tests. The Initial Reference Adhesion methodology provided an understanding of the adhesion levels at each axle and allowed:
• a comparison of achieved deceleration and stopping distances against Initial Reference Adhesion for un-sanded and sanded stops;
• a comparison of adhesion levels axle-byaxle along a train; and
• a demonstration of the benefits of enhanced sanding.
Image 8 demonstrates the effectiveness of DVRS (green squares) over SFRS (orange circles) and un-sanded stops (red diamonds). The smaller amounts of sand from existing sanders (SFRS) may be seen to be reasonably effective at medium adhesion levels (Initial Reference Adhesion >0.05) but its effect is limited and more variable at lower adhesion levels. Increasing the sand output to that of DVRS provides a significant benefit at the very low adhesion levels approaching 0.02. In terms of stopping distance, the vertical axis of the graph can be changed to distance and instantly it can be seen that in very low adhesion, DVRS returns stopping distances that are approaching those of dry rail (image 9).
Looking at the calculated Reference Adhesion along the train enables an understanding as to how the improvement in stopping distance (or deceleration) is being achieved. Image 10 shows the average of all the tests for each sander configuration tested. The red line indicates the average un-sanded adhesion improvement along the train resulting from wheelset conditioning only. The other three results demonstrate the improvement from the existing SFRS (orange) to SVRS (yellow) and finally to DVRS (green). It is the significant improvement in adhesion for all of the axles that creates the significant additional braking force of DVRS and thus reduced stopping distances.
From the above results we can see that the stopping distances with DVRS are significantly reduced when compared to un-sanded and existing SFRS stops. The trendlines shown in image 9 can be used to estimate an average stopping distance for any given Initial Reference Adhesion; image 11 shows stopping distances from 55 mph at adhesion = 0.02.
As well as the significant improvement in average stopping distance, enhanced sanding delivers much more consistency in the stopping distance. The variance in Reference Adhesion along the train and between tests may be
seen with the existing SFRS results (image 12) and the greater consistency of DVRS results (image 13). The variation in stopping distance can be simplified into another graph; image 14 illustrates the shortest and longest stopping distance for each sander configuration. This further demonstrates the benefits of the additional sand that DVRS brings.
The final objective was to determine if it is possible to deliver ‘assured’ 6%g braking in low adhesion conditions (since train timetables are typically designed around 6%g deceleration). The Class 387 brake step 3 results with DVRS, plotted as deceleration (vertical axis) in image 8 show that for every test undertaken, the mean deceleration was greater than 6%g. This result is important for maximising future network capacity, since predictable and reliable braking (regardless of underlying adhesion conditions) is a key requirement to enable future train control systems to run trains closer together.
To reassure the permanent way engineer, sanders only dispense sand during wheel slide events. By this definition, sand is only deposited where low adhesion is present on the track and is causing the wheels to slip. Sanders are designed to discharge a maximum 7.5 g of sand per meter of rail – as seen in image 15. At 60 mph the sand density will be three times lower than this, at just 2.25 g/m (refer back to image 5). The enhanced sanders will help to clean the track, which should improve the track conditions for the following train; this ought to lead to fewer instances of slide and wheel flats which are known to damage the track. The authors are not aware of any evidence that enhanced sanding leads to any higher wear rate of the rail, nor that it will lead to sand-contamination of the ballast.
However, if turnouts are located in braking areas, there is a chance that enhanced sanding could lead to a slightly higher wear rate of switch slide bearing surfaces.
Following the T1107 testing, train operators were interested in realising the potential benefits of DVRS to improve autumn performance; however, the challenges of retrofitting were not clear. To support industry adoption of DVRS, RSSB commissioned a project to implement an in-service pilot of DVRS on the mainline railway. This project aimed to provide dedicated support for the first in service retrofit of DVRS and to verify that the benefits of DVRS demonstrated on the test track would translate into similar benefits for normal in-service running of a passenger train. In early 2018, several train fleets were identified as candidates for the in-service pilot. A feasibility study was conducted for each and it was considered feasible to retrofit DVRS to all the fleets. However, all had some technical challenges to overcome; image 16 shows the main considerations. Equipping a unit with DVRS typically requires upgrading the existing fixed rate sander at axle three to a variable rate sander, and adding an additional variable rate sander at an intermediate axle (typically axle seven or eleven depending on unit formation and available space). West Midlands Trains Class 323 units were selected for the in-service pilot and were equipped with DVRS (image 17); these were introduced into passenger service on the Cross-City Line in Birmingham in 2019. The trial units were also fitted with remote condition monitoring, to capture key performance data.
Following the introduction of DVRS equipped units, a series of low adhesion driver familiarisation sessions were conducted in order to provide an opportunity for train drivers
/ representatives to familiarise themselves with the enhanced low adhesion braking performance afforded by the DVRS equipment. During conversations with the drivers, they were impressed with the performance that the DVRS system gave them. Driver feedback included “anything that stops me a metre quicker, I’m happy with” and “this DVRS system is brilliant, absolutely brilliant, a marked improvement in stopping”. In addition, both WMT’s Operations Director and Network Rail’s Head of West Midlands Operations were very happy with the performance, describing the new way of using sand as a “game changer” and “ground-breaking”.
Enhanced sanding is the simplest technical solution to low adhesion, but the human factors aspect must not be overlooked. It will take time for drivers to become accustomed to the enhanced braking that sanding provides and to gain confidence to let the train deal with low adhesion conditions. A train driver’s primary concern is the safety of the train and its passengers; changing driving style sufficiently to make use of the extra sand will take time.
The standard which controls the use of sanders on multiple units is GMRT2461 ‘Sanding Equipment’. This standard was updated in 2018 to include the results of the T1107 testing work, to encourage the GB rail industry to adopt distributed and variable rate sanding. The work described in this paper represents a significant advancement in the understanding of enhanced sanding. The work has quantified the benefit of different sanding configurations, and has shown how fitting DVRS on a modern four car unit can consistently deliver 6%g braking irrespective of underlying adhesion conditions. The work has also shown how it is feasible to retrofit DVRS to existing multiple units and has provided guidance for those doing so. The general trend is that, as the sand is increased, the stopping distances get shorter but (possibly more importantly) the variation in stopping distances is reduced, indicating a greater predictability and consistency for the train driver. DVRS also has the capability to unlock future network capacity by enabling control systems to run trains closer together.
With thanks to our client Rail Safety and Standards Board (RSSB) for developing, managing and funding the programme of low adhesion work. Thanks to project partners, Great Western Railway, Porterbrook, Network Rail, Freightliner, Serco Rail Technical Services, Knorr Bremse, Bombardier, Bridgeway, West Midlands Trains, AB Hoses and Instrumentel.
T1107 ‘Trial of Sander Configurations and Sand Laying Rates’
IMP-T1107 ‘Class 323 DVRS In-Service Pilot Issue’
COF-BRP ‘Class 323 DVRS Driver Familiarisation’
All reports are available through RSSB’s repository, www.sparkrail.org
The Islamic Republic of Iran is a country in South-West Asia with a territory of 1,648,195 km2 and approximately 83 million of population, with a median age 32. It is the 19th most populated country in the world. Iran is a mountainous country with approximately 30% or 34 million hectares of desert territory. Communities are located in areas where there is water and cities are separated by hundreds of kilometres. The density of population in Iran is 51 persons per km2, which is low, compared to UK with 270.7 person per km2. Iran shares its land border with seven countries: Armenia, Azerbaijan, Turkmenistan, Afghanistan, Pakistan, Iraq and Turkey. Three of them are former USSR countries: Armenia, Azerbaijan and Turkmenistan.
The railway system in Iran is state owned, controlled by the Ministry of Roads and Urban Development. The centre of the railway network is Tehran, which is the capital of Iran and is connected to 19 local regions. One of the outstanding engineering achievements of Iran was a construction of the Trans-Iranian Railway. Construction began in 1927 and was completed in 1938. It is a 1,394 km line with 90 stations along the route. The railway line stretches from the Caspian Sea through the central part of Iran to the border with Iraq. The railway runs along the highlands and reaches 2,000 m above sea level, passing over 3,000 bridges and through 126 tunnels in the Zagros Mountains. This railway played an important role in the Second World War as a route delivering supplies to the Soviet Union. The railways in Iran use standard gauge, electrified at 25 kV 50 Hz AC, which is the same as Turkey and Iraq. The majority of the railway lines are constructed with UIC60 rails on B70 concrete sleepers. Most of the Iranian railway network is a single track, which is approximately
82%, and 18% is double track. A large part of the railway network passes through desert. In these areas, windblown sand on the track reduces the elasticity of the track bed. This leads to degradation of the railway track and rolling stock and increases their vulnerability. It affects reliability, safety and passenger comfort. Maintenance of these lines take lots of effort and puts huge financial pressure on Islamic Republic of Iran Railways (RAI). RAI found that one of the most economically efficient and best long-term solutions for windblown sand mitigation is planting vegetation (Zakeri, 2012).
The RAI network includes 360 stations and 12,998 km of line. It is an approximately 7.89 km railway line per 1,000 km2 of land. In the UK, this figure is almost ten times higher and reaches 66.7 km of railway line per 1,000 km2 of land. On the 1 January 2020, the Iranian Transportation Minister announced that in the next two years the railway network in Iran will be expanded by another 1,500 km and will reach 25,000 km by 2025. There is a total of 45 projects to build new lines and 140 projects to upgrade existing lines (Seyedvakili et al., 2019). Image 2 shows the cost share of Iranian railway projects.
The Iranian railways are working on a demandbased principle. For freight trains, there is no fixed timetable. Railway responds to demand and runs trains when there is enough freight to transport. This causes long delays in the delivery of freight to their destinations. Iranian railway network has 170 terminals with 200 origin to destination demands, which handle around 1,500 wagons every day (Yaghini et al.,2013). In 2006, RAI had 50 depots, 565 locomotives, 16,330 wagons and 1192 passenger coaches (Mirabadi and Sharifian, 2010). Nowadays, lots of rolling stock is manufactured domestically. In 2019, there were 432 new freight wagons, locomotives and passenger coaches commissioned into service. The railway system of Iran is continuously
Inara Watson PhD Researcher PWI member London South Bank UniversityInara was born in Latvia and graduated with a BSc in Mechanical Engineering from Riga Technical University. She has a MSc in Transport Engineering and Planning from London South Bank University and is in her last year studying at London South Bank University for a PhD.
Her research interests are focused on railway engineering and sustainability. Inara is currently involved in two international projects in Australia and Ecuador. Inara is a member of the PWI, ICE, OR and the DMDU society.
Image 2: Cost share of RAI projects (data taken from Seyedvakili et al., 2019).
expanding. Construction of railway lines increased from 120 km per year in 2013 to 180 km in 2017. There are 6,500 km of railway lines under construction. Also, there are several projects for electrification and upgrading existing lines. One of them is the 926 km double track Tehran-Mashhad, the busiest railway line in Iran. The line will be electrified, which will increase the speed of trains from 160 km/h to 200 km/h. It will reduce the travel time by almost half and increase the capacity of the line. Electrification of the line will increase traffic on the route from 17 to 40 trains per day in each direction, which permits an increase of the ridership from 2.7 million to 33 million and freight from 1.5 to 10 million tonnes per year by 2032. The total cost of the project will be around $6bn. This project is partially financed through Chinese loans.
Iran has an ambitious plan to construct one of the largest HSR networks in the Middle East. Iran has 1,336 km of HSR under construction, 177 km planned and 165 km long-term planning with an operational speed of 250 km (Uic.org, 2020). Construction of 410 km HSR Tehran-Isfahan, with operational speed up to 300 km/h is being carried out by the China Railway Engineering Corporation (CRECP). Also, it involves Germany’s Siemens, Italian group Ferrovie dello Stato and Khatam Al-Anbia Construction, owned by Iran’s Revolutionary Guard (Globalconstructionreview.com, 2020). The cost of the project is estimated to be $41.8bn and completion is set for 2021. In 2015, the French consultant Arep signed an $8m deal to redevelop the three largest stations in Iran: Tehran, Qom and Mashhad. It is part of a seven-year programme for upgrading railway infrastructure for which the total cost is $25bn (Rogers, 2015). Qom-Arak HSR line 135 km long and Tehran-Hamadan line 320 km will be built by Italian Ferrovie dello Stato company as part of a €5bn credit promised by Italy (Globalconstructionreview.com, 2020). The use of railway capacity in Iran is heterogeneous. Capacity of most railway lines in Iran is used by no more than 25%, only routes from Andimeshk to Qom, Isfahan to Bafgh and a couple of others where capacity of lines is used
up to 75% (Seyedvakili et al., 2019).
The major reason to build HSR is to increase the capacity of railways. This involves a large financial and carbon investment. Before a decision is taken to construct HSR, there is a need to look for other solutions to improve the capacity of lines, such as upgrading existing infrastructure, implementing an advanced signalling system and upgrading rolling stock. However, some countries when deciding to construct HSR put other reasons first, such as a defence or to affirm the regional leader status or promoting the image of the country (Watson et al., 2019). To build Iranian HSR it will need to have a large financial input and use a large amount of natural resources. Due to the low capacity of existing railways a new HSR will not give sufficient carbon savings.
Iran is located between Europe and Asia and the Iranian network has nine major corridors which cross the country from North to South and from West to East. Iran has 13 rail borders, ten of them in operation and three under construction. Lately, Iran has increased cooperation with Turkish and Pakistan railways, also with parts of the former USSR. Iranian railways have bogie-changing stations on the border with Azerbaijan-Jolfa station and on the border with TurkmenistanSarakhs station. Azerbaijan and Turkmenistan have 1520 mm gauge. Iranian railways have
bogie-changing stations on the border with Pakistan, as Pakistan has 1676 mm gauge. One of the bogie-changing stations is the Zahedan station, which has been in operation since 2007. Iran and Pakistan are working on projects to increase the volume of freight transported by railway and the number of tourists and pilgrims from Pakistan to Iran and Iraq travelling by railway. There is a strong will from Iran and Pakistan to restore the Islamabad-Tehran-Istanbul railway network. Russia is very heavily involved in construction and modernization of Iranian railways. One of the joint projects was the construction of a new 160 km railway line Astara-Astara between Republic of Azerbaijan and Iran. The main feature of the project was to build a railway with a dual gauge 1520 mm and 1435 mm. This line is part of the International North-South Transport Corridor (INSTC) that connects Russia, Iran and India. The 7,200 km long corridor includes different transportation modes, such as shipping, rail and road. Studies have been made for a third railway link between Iran and Azerbaijan and further to Russia, the Ardabil-Parsabad railway. Another large joint project of the Russian and Iranian governments is to electrify 495 km of the Gsarmsar-Ince Burun line near the border with Turkmenistan, with the estimated cost of $1.3bn and construction taking 4-5 years. (Rogers, 2015) This will allow an increase in speed and as a result will increase the capacity of the line to ten million tons per year. Russia and Iran have a long history of technical and military cooperation.
Iran is developing a railway that will connect the Iranian city of Khaf in Eastern Iran to the Afghan city of Herat. In the past, the Afghan government did not encourage the construction of railways for strategic reasons. Iran is enhancing communication and influence on neighbouring countries. The Iranian government has an international project to connect Iran, Iraq and Syria by railway. This will link the railway networks from the Persian Gulf to the Mediterranean Sea. The first step of this project will be the construction of a 32
Image 3: Isfahan railway station. Image 4: Railway Station in Tehran.km link between Shalamcheh city in SouthWest Iran to Basra city in Southern Iraq. All these projects show that the volume of freight and the number of passengers transported by railways in Iran is increasing. The volume of freight transported by Iranian railways in the last year increased by 140% compared to the previous year and reached 31 million tons. The railway’s share in freight transit increased to 14%. Passenger numbers reached 42 million in 2018.
RAI has a vision to transform railway stations into transportation hubs. To do this is a need to enhance many transport options in one place where passengers and freight exchange between different transportation modes. Tehran, with one of the busiest metro systems in the Middle East, or Mashhad, where there is a light rail system, will be good options for a transportation hub, but for other cities, such as Isfahan, it looks unlikely. Many railway stations can only be reached by private car or taxi. Isfahan railway station is located 15 km distance from the centre of the town in the desert and is surrounded by a few buildings. The railway station cannot be reached by public transport, only by private car or taxi. It is a two-storey huge building but most of the time it is deserted, as it has only a few weekly departures for passenger trains. Isfahan, a city with 1.756 million population has only one train to Tehran every two days, to Mashhad two trains every day, to Zahedan one train weekly and to Bandar Abbas every two days. Table 1 shows the ridership of the most important stations in Iran in the period between March 2018 - March 2019.
Apart from providing services for passengers, many stations handle freight trains. At the end of 2019, Iran has exported 19,000 tons of steel products to Turkey and most of it was loaded in Isfahan and Kashan. It was mainly rebars. Iran is planning to transport to Turkey by railway sea salt, coal and tar. The Iranian government is forecasting that by 2041 the freight transportation from Isfahan will increase to 36 million tons, and passenger demand will increase to 26.3 million, from which 2.1 million long-distance passengers and 24.3 million commuters. In recent years, the number of passengers on the railway has increased substantially but not the number of trains. For many destinations, tickets are sold out weeks before departure.
The major railway passenger transportation company is the Rail Transportation Company (RAJA) which was established in 1996. RAJA is responsible for the operation and maintenance of passenger carriages. RAJA transports approximately 60% of the total number of passengers in Iran. Between 2008 and 2016, RAJA supplied around 227 million seats and transported 186 million passengers with an occupancy rate of 82%. To satisfy a continuous increase in demand for travel, the company introduced double-decker trains. In terms of transporting passengers, Iranian railways mainly provide long-distance connections. The average distance travelled by a passenger in Iran in the period of 2008 - 2016 was 521 km. In comparison, travelling
distance on HSR in France was 464 km and in Japan 233 km. Image 4 shows the Tehran railway station.
Safety is a big issue for Iran. Iranian railways have many accidents that are mainly due to human error and sand and dust storms. One of the deadliest accidents happened in 2004 near Neyshabur with 328 deaths and 460 injured (Khademi et al., 2018). One of the reasons for a high accident level can be over-tiredness of railway staff. For example, the average length of a shift for train drivers is 8 hours but the maximum can be 24 hours (Yaghini et al., 2013).
Iran is massively developing their railway infrastructure which will link all major cities in Iran and link the domestic railway infrastructure to neighbouring countries to facilitate trade and movement of passengers. It is undoubtedly true that the Iranian government wants to transform the country into a powerful logistics and transportation hub that will link North to South and East to West. However, Iran railway needs more investment, and it is obvious that the sanctions US Government imposed on Iran dramatically weakened the country. The lack of investment and development can be seen everywhere in Iran.
Alireza Seyedvakili, S., Zakeri, J., Nasr Azadani, S. and Shafahi, Y. (2019). LongTerm Railway Network Planning Using a Multiperiod Network Design Model. Journal of Transportation Engineering, Part A: Systems, [online] 146(1), p.04019054. Available at: https://ascelibrary.org/doi/abs/10.1061/ JTEPBS.0000276 [Accessed 8 Jan. 2020]. Globalconstructionreview.com. (2020). Iran to draw $2.4bn Chinese credit line for Tehran–Isfahan high-speed railway - News - GCR. [online] Available at: http://www. globalconstructionreview.com/news/iran-draw24bn-chinese-credit-line-tehranisfahan-h/ [Accessed 6 Jan. 2020].
Globalconstructionreview.com. (2020). Russia to spend $1.3bn electrifying Iran’s northern railway - News - GCR. [online] Available at: http://www.globalconstructionreview.com/ news/russia-spend-13bn-electri8fy8ing-iransn8orthern/ [Accessed 6 Jan. 2020]. Iranrail.net. (2020). TRAINS OF IRANIAN RAILWAYS. [online] Available at: https://www. iranrail.net/trains.php [Accessed 6 Jan. 2020]. Khademi, N., Babaei, M., Schmöcker, J. and Fani, A. (2018). Analysis of incident costs in a vulnerable sparse rail network –Description and Iran case study. Research in Transportation Economics, [online] 70, pp.9-27. Available at: https://www.sciencedirect.com/ science/article/abs/pii/S0739885917300860 [Accessed 9 Jan. 2020].
Mirabadi, A. and Sharifian, S. (2010). Application of association rules in Iranian Railways (RAI) accident data analysis. Safety Science, [online] 48(10), pp.1427-1435. Available at: https://www.sciencedirect.com/ science/article/pii/S0925753510001657 [Accessed 8 Jan. 2019].
Pakistan Defence. (2020). Iran to double national railway length to 20,000 kilometres.
[online] Available at: https://defence.pk/pdf/ threads/iran-to-double-national-railway-lengthto-20-000-kilometres.238771/ [Accessed 6 Jan. 2020].
Reconnectingasia.csis.org. (2020). [online] Available at: https://reconnectingasia. csis.org/database/projects/astara-astararailway/221e21ff-be21-45d8-aa0313e61d9670b6/ [Accessed 7 Jan. 2020].
Report News Agency. (2020). Astara-Astara railway route officially launches today. [online] Available at: https://report.az/en/infrastructure/ astara-astara-railway-line-to-officially-launchtoday/ [Accessed 7 Jan. 2020].
Rogers, D. (2015). Iran’s railway revolution - - GCR. [online] Globalconstructionreview. com. Available at: http://www. globalconstructionreview.com/markets/howislamic-republic-set-become-land-br8i8d8ge/ [Accessed 5 Jan. 2020].
Shakibayifar, M., Hassannayebi, E., Mirzahossein, H., Taghikhah, F. and Jafarpur, A. (2018). An intelligent simulation platform for train traffic control under disturbance. International Journal of Modelling and Simulation, [online] 39(3), pp.135-156. Available at: https://www.tandfonline.com/doi/ abs/10.1080/02286203.2018.1488110?journalC ode=tjms20 [Accessed 5 Jan. 2020].
Uic.org. (2020). [online] Available at: https://uic. org/IMG/pdf/20191001_high_speed_lines_in_ the_world.pdf [Accessed 6 Jan. 2020].
Watson I., Ali A., Bayyati A. (2019), Sustainability of HSR-Comparative Study, ICE Innovation in Railway Civil Engineering Journal, Available at: https:// www.icevirtuallibrary.com/doi/pdf/10.1680/ jtran.18.00131
Yaghini, M., Karimi, M. and Rahbar, M. (2013). A set covering approach for multi-depot train driver scheduling. Journal of Combinatorial Optimization, [online] 29(3), pp.636-654. Available at: https://link.springer.com/ article/10.1007/s10878-013-9612-1 [Accessed 9 Jan. 2020].
Yaghini, M., Momeni, M. and Sarmadi, M. (2013). An improved local branching approach for train formation planning. Applied Mathematical Modelling, [online] 37(4), pp.2300-2307. Available at: https:// www.sciencedirect.com/science/article/pii/ S0307904X12003356 [Accessed 8 Jan. 2020].
Yaghini, M., Sharifian, S. and Akhavan, R. (2012). Reengineering the Locomotive Operation Management Process in the Railways of Iran (RAI). Procedia - Social and Behavioral Sciences, [online] 43, pp.86-97. Available at: https://www.sciencedirect.com/ science/article/pii/S1877042812009627 [Accessed 9 Jan. 2020].
Zakeri, J. (2012). Investigation on railway track maintenance in sandy-dry areas. Structure and Infrastructure Engineering, [online] 8(2), pp.135-140. Available at: https://www.tandfonline.com/doi/ abs/10.1080/15732470903384921 [Accessed 13 Jan. 2020].
Part 1 of this article was published in the April 2020 Journal. Please visit the website to view.
The design, fabrication, installation and maintenance of S&C involves a complex array of measurements within the layout, all intended to ensure the installed and soon to be maintained article remains as close to its design as possible. This article follows on from Part 1. Design and Fabrication and aims to provide guidance to inspectors, designers, maintainers and those who are generally interested in this topic, on the correct way S&C should be inspected through its intended lifecycle.
The inspection method used for the prefabricated layout (see Part 1 in the April 2020 Journal) can be replicated at installation phase at the same level of detail to provide a direct comparison between the two stages of construction. Whilst it is common practice for the installation of S&C to measure the design alignment, cant, gauge, toe openings, flangeways and check gauge, other areas which require further scrutiny are:
• horizontal alignment variance from 10m in front of the toes up to 10m beyond the heel - ensures the stock rails are to their correct alignment and bearing with as little deviation as possible to help achieve the correct closed switch to stock rail fit.
• vertical alignment variance between 10m in front of the toes and 10m beyond the heel to avoid large variances in switch rail support on the slide plates which lead to high friction or toes/switch tips sitting high. This includes change in super-elevation (cant) in the same area and measuring the slide to underside of switch rail gaps on the closed switch at every slide plate whilst also observing whether the switch is twisted.
• inspection to ensure no obstructions have
been introduced around the moveable switch area. In particular, ballast, concrete over-pour or temporary staging work remaining in-situ.
• inspection of the closed switches to ensure they sit flush against all distance blocks and that any large gaps or heavy contact with the blocks are rectified.
• point machines and POE (Points Operating Equipment) are not causing the switch rails to lift, twist or drag due to incorrect height setting or over driving causing the switch rail to turn into the stock rail. The height relationship between the point machine and rails is important to ensure the design is achieved where multiple pads and plates are used.
• supplementary drive crank and switch opening settings are correct as per the Operation and Maintenance manual.
• the field side stock rail foot is tight against the slide plate housing to reduce gauge widening when thrown by switch or opened to traffic. This can affect switch detection within primary and secondary detection.
• Residual Switch Openings (RSO, gap between closed switch and stock) throughout the complete planed length of the switch. Exceedances greater than 0.5mm at the tip and 2mm towards the head cut are unsatisfactory for new works.
• Free Switch Test – mentioned in Part 1 are integral to ensuring any switch fit or switch rail spring issues as a result of realignment, poor installation or rails being damaged during transportation from Prefab to site have been correctly assessed and remedial measures undertaken. This can be crowing of the switch (using a Jim Crow tool to curve and shape the switch rail), more detailed realignment or adjustment of POE installation.
London Underground Standard T0435 references form F5554 that, in section 5.2 (shown right), captures the installation measurement checks for the switch panel as described above. Note the inclusion of design tolerances, especially those related to the RSO. These tolerances were the outcome of an RSO working group where track and signal engineers agreed the RSO range for new and existing maintained switches in the varying locations within the switch planning. This was dependent upon the location of stretcher bars, primary and supplementary drives and supplementary detection for each switch type.
On LU and other railways where third (or fourth) rail is present the measured inspection of conductor rail within S&C is a safety and operationally critical activity. Measurements are to be undertaken to confirm the longitudinal,
Darren has 30 years experience within Permanent Way Engineering covering design, innovation, manufacture, renewals and maintenance. He has worked for British Rail, Scott Wilson, Jarvis, Transport for London and various consultancies. Darren’s work has mainly concentrated on London Underground for over 20 years, involved with project engineering management and as the Principal Engineer for S&C and more recently working with JBA consulting within New York City Transit and Network Rail Asset Enhancement team.
vertical and horizontal positioning of the ramp ends and contact rail in relation to the running edge, toes and nose. Positioning and measurement of conductor rail within S&C is more critical than plain line. This is due to the additional risks introduced by gaps within the conductor rail that allow for the diverging route and swept path of the conductor rail shoe on converging or adjacent routes. If installed or maintained incorrectly this can lead to loss of shoes, gapping of trains and in some instances derailment due to shoe beams being caught beneath the conductor rail and running rails.
The three critical dimensions, X, Y and Z (as detailed in image 2) and the vertical and horizontal offsets of the conductor rail are to be taken at every ramp end, and at 5m centres thereafter.
X = minimum horizontal dimension of 535mm measured from the diverging running edge to nearest part of the positive conductor rail ramp.
Y = minimum horizontal dimension of 130mm measured from the nearest running edge to the nearest part of the negative splay ramp at the heel.
Z = minimum horizontal dimension of 510mm measured from the nearest running edge to nearest part of the positive conductor rail ramp in front of the crossing.
(See image 2).
The minimum horizontal dimension between adjacent positive conductor rails in the vee of the crossing is 150 mm.
The third rail system on the southern mainline railway has similar critical measurements for lateral and longitudinal positioning.
Other ancillary components within LU, such as point machine ramps and slipper runs are installed to protect against low hanging shoes. The heights and offsets for these are also measured and recorded. A 2m conductor rail exclusion zone is maintained surrounding the point machine to safeguard operational staff against the risk of electrocution.
The introduction of modular tie-plated bearers has introduced additional inspection requirements to ensure the correct installation process for the tie plate assembly has been followed. Torque setting of the screw bolts in the correct order, torque marking to indicate any movement and then recording these activities onto an inspection test plan are all mandated activities required for hand back and handover. Additional gauge and twist checks are undertaken through the tie-plated
sections. This follows into the maintenance inspection where S&C Inspectors check the tightness of the screw bolts, the condition of the coil washers and for signs of voiding or displacement around the tie plate joint.
As part of the track handover process, dynamic geometry recording is used to provide evidence of the track quality post installation and final tamp. The handover process also involves visual inspections with the asset owner/maintainer to ensure visual defects such as missing clips, ballast levels, rail head condition, bearer squareness and any other missing parts are to a satisfactory level for acceptance back into maintenance. This method can be subjective, especially where issues arising from the design or prefabrication cannot be addressed or were not communicated to the maintainer beforehand. This can be improved by the introduction of 3D scanning or drone surveys of the layout to act as a before-and-after comparison and also as a record for ongoing maintenance works. A drone or trolley mounted scanner can be used to survey the layout at prefabrication and installed to check the accuracy of the work.
This can then help form the baseline 3D model for a digital twin.
(See image 4). Fully compiled with the correct data models and process information, the digital twin will form the backbone of the asset management tool.
All data associated with the ongoing management of the system will be stored within the digital twin to provide a one-stop integrated virtual model that is continually mapped to live data sources. This provides an accurate health status of the asset and reduces the need for human intervention to filter through various information, which is not always reliable or recorded. Track, Signals, Civils, Power/Electrification, Drainage, Mechanical and Communications are all asset areas that would benefit from the presence of their own digital twins to connect with their interfacing counterparts.
As part of the project handover process we rely upon MAIDs (Mandatory Asset Information Deliverables) or as previously known, Health and Safety files all presented in a PDF format of drawings and as-built data. Whilst other geographical information system exists that can be overlaid or linked to this information to the GPS location, the data only provides an asset register for the S&C at that point in time. This will hopefully become a thing of the past once the digital twin is in use. Network Rail and other European partners through the In2Track2 project will soon be trialing the use of the digital twin model.
Over the last ten years, there has been a growing trend towards changing the way in which we inspect our track assets by focusing on the root cause of failure that we are
witnessing on our S&C. Whilst inspecting to a safety standard is paramount, inspecting to a reliability level is becoming an important maintenance activity. Standards are based on safety tolerances and on most infrastructure organisations, they do not allow prediction of a potential failure. In addition, the reactive inspections undertaken post failure rarely feed back the root cause and, in most cases, attempts to rectify the fault are made and not recorded. This, coupled with the ineffective interaction between track and signal engineers during inspection or rectification works, leads to a poorly managed asset.
To help reduce switch failures on both DLR and NYCT, a Switch Reliability Inspection process was introduced. This focused on the common failure modes associated with the differing types of S&C and incorporating these into the inspection process to prevent the failure from occurring. New tools were also introduced for measuring residual switch openings, heel joint gaps, slide plate gaps and other voiding or clearance measurements. The inspection form is summarised in image 6:
Water ingress into the tunnel network from the above connected street drains and leaking tunnel walls is a major cause of track and signal failures on NYCT. Water ingress into point machines and around the switch panels causes points failures due to the rapid degradation of the components, the
track geometry and the integrity of the signal wiring and controls. The latent effects of water ingress damage are visually examined as part of the reliability inspection of S&C. An additional inspection process for inspecting the reliability of track circuits was also introduced, focusing on the failure modes of IRJs (Insulated Rail Joints), track wires, bonding and track conditions that lead to earthing of the track circuit. See image 7.
The importance of recognising how and when wheel rail interaction affects the reliability of switches was introduced as part of the switch reliability inspection training to both track and signals staff. The effect of flange back contact on the back of a switch rail on the New York City Transit (NYCT) system differs from the UK due to the presence of the housetop (see image 8). The housetop provides additional wheel guidance for the turnout route reducing wear and flange-climb derailments. The rear of the switch blade is used beyond the housetop extent which can transmit forces back to the POE if not correctly stabilised by the switch stops. This leads to stretcher bar, stock rail braces, detection and locking failures which are inherent failures of the track design.
Data from varying sources exists to enable the maintainer to manage S&C to within the mandated safety thresholds. Geometry data from Track Recording Vehicles measurements provides a dynamic snap-shot of how the S&C performs underload. When combined with rail defect data, switch (signals) failure history, AVI (Audio Visual Inspection) and manual geometry inspections, this will help to provide a more holistic approach for managing the reliability and maintainability of the system. Our next goals within the UK are to achieve an autonomous inspection process for S&C using pattern recognition, laser and optical measurement equipment combined to create a more accurate representation of the asset. The use of drones to cover inspection tasks that cannot be undertaken by automated means, such as items that are obscured or outside of the photogrammetry recording systems view, can assist in filling these gaps to fully automate S&C inspections.
The use of varied data sources from rail flaws, geometry condition, remote sensors and signal
condition monitoring can be combined to create a combined defects diagnostic system. Certain conditions within S&C that on their own do not present a risk of failure, can become an issue when combined with other conditions which then lead to an increased likelihood of failure or rapid deterioration. The various independent condition monitoring systems can be collated and assessed simultaneously using a multiple defect diagnostic tool to predict failure. This will all then become part of the Digital Twin degradation and diagnostics
Gauge within Switch Panel
Flangeway Clearance (FWC)
Y Y
model.
In the meantime, manual measurement techniques are still relied upon until the technology is ready for general use. It is important that we don’t lose sight of why we measure what we measure, and also to consider what else we could measure that we couldn’t before.
Table 1 lists the critical measurements to be recorded within S&C. The table identifies
Dynamic gauge spread, rail roll, RSO and distance block gaps provide a more realistic measurement under load. However, dynamic gauging through the front portion of the switch rail is known to include inaccuracies due to varying rail profiles at the measuring datum.
N Y If the wheel flange back is in contact with the back of the switch rail, a forced and increased flangeway opening will be measured that provides a false indication of the dynamic flangeway measurement. Dynamic flangeways can increase where RSO is present within certain distances of the stretcher bar. Dynamically measured flangeway allows complete length of switch to be measured, rather than defined locations which is an improvement. Current static measurements using a flangeway slider gauge measures at a set height below the rail level. The flangeway gap becomes less when measuring further down the chamfered switch where the wheel flange is at its lowest point. Both methods have their issues. Measuring using photogrammetry may also present a problem when measuring 25 to 30mm below the crown of the rail.
whether they are currently measured in the UK dynamically (train-borne equipment) or statically under standard maintenance inspections. The drive towards autonomous inspection, to help reduce the risk of workforce exposure to unsafe conditions and human error when measuring, is a positive move within the industry and one that should be treated with a high moral standing. Comments have been included to help consider whether the measurement is best taken in a loaded or static condition.
Toe Opening (FWC at Toe)
Residual Switch Opening (RSO)
Slide Plate to Switch Rail Gap
Check Gauge Free Wheel Passage (FWP)
Check Rail Back to Back in Diamond
Gauge within Crossing Area
Switch Profile
Cast Crossing Profile
N Y Differs for each POE type. Minimum values can be set. Does not present a safety risk, critical only for the set-up of the points machine and reliability of the system. Measured level with the top of the switch to the stock rail, stock chamfer can affect reading slightly.
N Y RSO in most cases reduces to zero under load and therefore varies under load. Measured ahead of vehicle is static and when measured within wheel passage is closed up and becomes quasi-static. Therefore difficult to measure dynamically. Switch tip openings can cause tip wear in facing moves leading to derailment.
N Y Whilst not critical it establishes whether high friction of switch hogging is present. In most cases the gap closes under load as the switch is deflected to its supported position. This only occurs passed the contact point and therefore gaps at the toe generally remain under load and can cause high levels of vibration.
N Y Not measured dynamically currently. Dynamic movement is negligible and occurs mainly in the check rail which can role under load.
N Y Not measured currently as part of standard inspection process. Dynamic movement is negligible.
Y Y
N Y
N Y
Fabricated Crossing Profile
Dynamic measurement gives false reading in throat/neck of crossing. These can be filtered as a rule. Dynamic affect is not as noticeable in crossing due to lack ofrail role.
Dynamic will provide correct switch to stock relationship both vertically and horizontally. Static 053 method has known human factor issues.
Static 3D scanning preferred for accuracy. However, dynamic is less time consuming. Dynamic will provide a more coplanar measurement. Current 054 static method is not consistent or repeatable. Discreet profile changes on the nose and relationship between the wing at the transfer point can be measured with far greater accuracy with 3D scanning.
N Y Dynamic provides for movement within components, eg dipped nose.
Cross Level Y Y
Dynamic preferred due to voiding, twist etc.
Table 1: (Blue cells denote preferred measurement).
Certain dynamic track behaviors that cannot be measured on a vehicle, such as voiding, P1/ P2 forces, lateral movement and acceleration/ vibration of the track, are measured using varying methods as part of product trials, or in some cases, where the asset is having reliability problems. The old style void meter has been used for many years for this task, however, as installation tolerances become more accurate and with higher quality being demanded, so must the measuring devices. The use of mobile track behavior measuring devices is becoming more widespread with suppliers now providing solutions to assist the maintainer with accurate information on how the S&C is performing. This can become a useful monitoring tool when used correctly and helps predict a timelier intervention.
Trials of digital void meters and other mobile monitoring equipment such as strain gauges, accelerometers, potentiometers and linear deflectometers are presently being considered for trial for this purpose as part of Network Rail and In2Track2 future enhancements.
To summarise, the two images 9 and 10 show methods of inspecting and measuring S&C throughout its life span comparing the current disjointed process against a future improved data capture process.
To improve reliability of S&C further, the use of specific reliability focused inspections undertaken at a predetermined time to prevent failure should be implemented specifically on legacy systems where known failure modes cannot be managed or controlled. New S&C measurement techniques are being devised as we start to embrace technology that allows us to measure and inspect in a more consistent way. The evolution in photogrammetry measurement inspections, both static and dynamic, coupled with track condition monitoring and embedded sensor technology all assist in prolonging the life of S&C and reducing staff attending site, both of which are the key objectives to a sustainable design.
Nick discussed the mass collaborative efforts needed in order to keep the railway open to the public and touched upon some of the key crisis management strategies that Network Rail have been undertaking in these challenging times. Nick said their focus has been on protecting the people and ensuring the railway key workers were able to safely carry out their duties so that the UK economy was protected. He impressed upon the audience the importance of the railway in the efforts to supply supermarkets, fuel power stations, remove waste from Central London, and most of all; keeping workers working.
Network Rail have been proactive in their response to the Covid situation and have rewritten numerous standards to reflect today’s reality. Changes to work activity risk assessments have been made and Covid Champions appointed to monitor social distancing measures on-site. Thermal imaging cameras have been set up at Network Rail facilities with more than 100 staff members, and smaller handheld versions are in use at smaller sites. Network Rail also responded quickly to the Covid situation by diverting project staff to assist in building the Nightingale hospitals.
New PPE has been introduced for Network Rail staff. Following a collaboration with a lemonade bottle supplier, 30,000 visors have been manufactured to attach to hard hats. Staff members have been allowed to use their own vehicles to travel to work, and where this hasn’t been possible, 3,000-4,000 vehicles have been hired so staff could travel on their own. Where staff do not drive, arrangements have been made with black cab companies to have vehicles on permanent hire with technicians in the back seats and the polycarbonate screens between themselves and the drivers for protection. In-house they have converted approximately 2,000 vehicles with various types of screens to transport colleagues to work sites safely. The sheer numbers of these vehicles suggest this was no mean feat and shows the lengths that Network Rail have gone to, to protect its key workers.
London Underground’s early planning for the Covid pandemic has ensured the key maintenance works have been carried out to schedule with minimal disruptions. Considering 170 members of TfL staff were shielding or furloughed, this was not an easy task. Duncan explained that the management team had been involved in the military planning for SARS and were ready to implement those lessons learned to this situation. He went on to explain the 4 key principles they followed to avoid spreading the disease:
Waterworth CEng MICEAlison is a Chartered Civil Engineer and Project Manager. With a career spanning over 10 years, Alison has worked in many sectors of the transport industry including structures, highways, airports and railways. She has extensive experience leading largescale multidisciplinary engineering teams through all phases of design and construction; from early strategic business case to handover for operational use. Her most notable projects include the M10 Moscow to St Petersburg Motorway Construction, the Forth Road Bridge Cable Band Bolt Replacement project, HS2 Phase 2B ACI JV, and is currently the Project Manager for Northern Powerhouse Rail Manchester to Sheffield corridor.
Alison is an avid promoter of equality and diversity in the industry; speaking at many high-profile events including the Women in Construction Summit and UK Construction Week. She is also the Mott MacDonald Advancing Gender Champion.
1 of 3 SPOLKS - Supporting the industry workforce physically and mentally through the Covid-19 emergency – from an infrastructure management perspective
18 MAY THREE 20 MINUTES TALKS FOLLOWED BY 30 MINUTES OF Q&AS
1. teams were to undertake essential maintenance activities to ensure the safety of the line
2. there would be separate workforces where possible and practical
3. where separation was not practical, teams would be separated from other group and to maintain a 2 m distance
4. masks regardless of tasks.
Jim went on to explain the two main planning elements they considered; the physical measures needed to protect staff and keep trains running, and the psychological measures needed to reassure and support staff. The practical measures implemented included:
• stopping all face to face meetings and using conference calls.
• splitting teams into morning and afternoon shifts (red and blue teams) and the use of cabins was prohibited; staff were to go straight to work and then home again.
• site documents were emailed to staff at home and drop boxes set up with safety critical paperwork to be collected from offices.
• tasks carried out sequentially instead of concurrently.
The psychological measures implemented were:
• addressing concerns in an open manner to keep workers and families safe. Townhall meetings (without the townhall) have been implemented.
• maintaining communications with the
whole team to ensure the personal touch is kept despite no physical contact. • positive messaging to staff. Initial communications focused on what was planned to be done in the immediate term to prevent the spread of Covid, but messages now are about future developments and positive goals.
Jennifer introduced us to the Manchester Metrolink network and the 1,300 services a day this network provides (pre-Covid). The timing of the Covid lockdown wasn’t ideal for Metrolink as the day before lockdown, the new Trafford Park Line route was launched 7 months ahead of schedule and almost immediately began operating at the new reduced Covid frequencies. Operating reduced services and reduced hours has been designed to limit the risk of exposure for Metrolink staff. In order to compensate for this, more double-unit trams have been put into operation to allow for better social distancing for those who do need to use the network. There has been a drop in patronage by 95% currently.
Like TfL, Metrolink understood communication to be crucial for the frontline workers and they set up new engineering updates and all meeting were switched to online calls. As well as to workers, the messaging to the public was important, and special safety signage was made to ask members of the public to respect Metrolink staff and maintain their distance.
Welfare vans have been deployed to enable easy hand washing facilities for staff and antivirus cleaning points have been set up. A local gin distillery provided bottles of hand sanitiser to Metrolink. A security company is currently collaborating with Metrolink to protect the frontline staff from antisocial behaviour.
A Temporary Approved Non-Conformance (TANC) process has been introduced, using ORR coronavirus guidance to document these. Meanwhile, Metrolink are continuing to look ahead and are introducing tram mounted remote condition monitoring kits to gain a holistic view of conditions and assist in moving towards proactive and preventative working instead of reactive working. Unfortunately, the equipment is from an Italian-based company and therefore there has been a slight delay to commissioning this equipment, but hopefully this will be resolved soon.
Joan closes the discussion by surmising that all companies have been very responsive and have embraced change positively. It is clear from the current Covid situation that Railway workers provide essential services to health workers, are key to the movement of goods, and support the day to day business of other industries; all essential elements to continue to support the UK’s economy.
Her final, and most important point is that companies are focusing on health and wellbeing as much as the work itself, and this is a great step in the right direction for the future.
Railways serve as a key sustainable mode of transportation for passengers and freight in urban, suburban, regional, and national contexts. With the rise in road traffic, which is seen as a less green form of transport and associated congestion, there is an increasing demand for railways to expand their capacity, availability and carry goods and passengers at ever higher speeds. Such increases in usage result in faster railway track degradation rates and higher maintenance costs.
As a result, the UK is projected to spend £18.5bn on operation and maintenance during 2019-24, an increase of 25% compared to the previous five years2,3. Since maintenance funding is provided from the public purse, maintenance investments should be made in an equitable and transparent manner which maximises benefits to all stakeholders whilst minimising the costs to the environment.
Railway track condition, and therefore maintenance strategy, directly impacts track use costs, including train operation, accident, environmental and delay costs 4. Therefore, maintenance decisions can only be taken responsibly when the costs and benefits of maintenance alternatives (ie total railway transport costs) are compared on a long-term, whole lifecycle cost (WLCC) basis.
Further, decisions and strategies for renewing, maintaining and operating railway infrastructure need to consider any ambiguities inherent in the data, including future uncertainties. In part due to the segregation of the railway
Dr Manu Sasidharan is an Honorary Research Fellow at the University of Birmingham and Research Associate at the University of Cambridge. He read for his PhD in Civil Engineering at the University of Birmingham by adopting a whole-life and whole-system approach to identifying cost-effective and risk-informed railway track maintenance strategies. Dr Sasidharan conducts research on developing risk-informed approaches and value-based decisions for managing and appraising investments for critical transport infrastructure. He is a recipient of the Prestige Award for Young Researchers from the World Transport Research Society.
Dr Michael Burrow is a Senior Lecturer in the School of Engineering at the University of Birmingham and obtained his MA in Engineering from Cambridge University and PhD from University of Birmingham. He leads the Sustainable Infrastructure and Asset Management theme within the University of Birmingham’s BCRRE Centre of Excellence in Rail Decarbonisation. His research interests are primarily focused on road and railway asset management and he leads the Infrastructure Pole of the European Railway Network of Excellence (EURNEX). He also leads the world renowned team of road specialists at Birmingham which developed a suite of cutting edge road asset management decision support tools, the products of which are used world-wide.
Gurmel Ghataora is a Senior Lecturer in the School of Engineering at the University of Birmingham. He graduated from the University of Wales, Cardiff with a BEng (Hons) and PhD in Civil Engineering. He has a vast experience of working in the industry with Douglas Technical Services Ltd and Ove Arup and Partners. He has undertaken consultancy work for a range of companies including:
DTS Raeburn Ltd., Jackson Contractors (Preston) Ltd., ICI, Ove Arup and Partners and Shropshire County Council. Dr Ghataora’s research focuses on the use of marginal materials in civil engineering, ground improvement and railway track foundations.
industry, in which the management of the infrastructure is apart from the ownership and operation of rolling stock, existing asset management decision support tools in the railway industry tend to focus on particular elements of the system and do not perform such a holistic analysis.
To address this, a unique risk-informed decision support tool that uses a Whole Life Cycle Cost Analysis (WLCCA) approach under uncertainty has been developed to take into account the costs and benefits of track maintenance strategies to track maintainers, train operators, users and the environment. The concept of the approach is summarised in image 1 and the resulting tool, known as RITRAK, provides strategists and asset managers with an equitable and transparent means of evaluating the economics of maintenance strategies.
As illustrated in image 1, RITRAK adapts an approach where the (uncertain) costs and benefits of different candidate maintenance
strategies are compared to achieve the most appropriate maintenance strategy ie the strategy with the lowest total railway transport cost. The WLCCA model at the heart of RITRAK considers the direct and indirect costs to all stakeholders and includes track construction; track inspection; track maintenance (realignment; ballast renewal and cleaning; routine maintenance); capacity loss; spillage; risk of derailments; train operation; environmental costs; transport mode change and end-of-asset-life value.
Changes in track quality over time due to track deterioration or maintenance are determined using a probabilistic based model. Monte Carlo simulation and Fuzzy Logic are used within RITRAK to deal with uncertainty through probabilistic risk assessment allied to expert opinion5
Images 2-5 illustrate a number of windows within the web-based RITRAK tool. The tool features a user-friendly interface to upload datasets associated with track condition,
track maintenance history and the whole lifecycle cost analysis (see image 2). The window showing the track deterioration model that predicts the track behaviour when subjected to different maintenance strategies is seen in image 3. The risk assessment window shown in image 4 captures experts’ opinions regarding the severity and probability of derailments associated with different maintenance strategies. The results are presented in a dynamic interface (image 5) that allows user-interaction and report downloads.
RITRAK can be used to support strategic planning and programming levels of railway asset management. For example, in the cases when there is a shortage in the annual track maintenance budget, RITRAK can be used to inform plausible maintenance strategies that realise the maximum benefit, in terms of minimising total railway transport costs, for the available budget. Senior managers and decision makers can also use RITRAK to improve long-term investment choices. For example, the tool allows the implications of reductions in maintenance budgets on total railway transport costs to be scrutinised and investment to be targeted to the areas of the railway network providing the greatest benefit.
The RITRAK tool was applied to case studies on three different routes on the UK mainline network (commuter, intercity passenger and mixed traffic routes) and demonstrated that economically-beneficial maintenance standards could be adopted if railway track use costs are considered, and by doing so validated the applicability and usability of the developed approach.
The annual train operation costs (fuel consumption and train maintenance costs alone) could rise by up to £500 per metre if the track quality deteriorated from good to poor condition. A sensitivity analysis was carried out to quantify the contribution of maintenance and track use to the total transport costs
Image 2: Data entry-window for RITRAKImage 4: Risk of Derailment model within RITRAK that captures expert opinion
In summary, the whole-lifecycle, whole-system approach encapsulated within the RITRAK decision support tool, enables cost-effective railway track maintenance strategies to be determined which are transparent and equitable through consideration of the costs and benefits to all stakeholders and the environment. It is an essential component of any holistic asset management approach.
Image 5 Interface with results from the WLCCA employed within RITRAK
Image 6: Contribution of different whole-life-cycle cost elements towards the total railway transport costs
of a 200-metre-long track section. Image 6 presents the results of 10,000 possible scenarios generated using Monte Carlo simulations.
The analysis found that the environmental impacts of train operation (associated with CO2, NOX and SO2 emissions) due to deteriorating track quality had the highest contribution to the total railway transport costs
(see image 6).
The analysis also indicated that approximately £6,400,000/year could be saved on the London to Birmingham route if a total railway transport cost approach is adopted to maintenance decision-making. The detailed results of these case studies are given in Sasidharan, Burrow and Ghataora (2020) 4
The authors are grateful for the invaluable inputs from the RITRAK project steering group of Dr Mohammed Wehbi from Network Rail; Prof. Clive Roberts, Prof Nigel Cassidy, Dr Francesco Maria Colaccino, Dr Alan Tibbats and Kate Jermey from the University of Birmingham; and Prof Simon Iwnicki from the University of Huddersfield. The development of RITRAK was funded through an EPSRC Impact Acceleration grant and by Intellex Consulting Services Ltd.
1. ORR (2017a) ‘Network Rail Monitor’Quarters 3-4 Year 3 of CP5 16-17’, London, UK
2. ORR (2017b) ‘UK Rail Industry Financial Information 2015-16’, Available at orr.gov. uk/__data/assets/pdf_file/0020/24149/uk-railindustry-financial-information-2015- 16.pdf
3. Sasidharan, M., Burrow, M. P. N. and Ghataora, G. S. (2020) ‘A whole life cycle approach under uncertainty for economically justifiable ballasted railway track maintenance’, Research in Transportation Economics. Elsevier Ltd, 80 (January), p. 100815. doi: 10.1016/j.retrec.2020.100815
4. Sasidharan, M., Burrow, M.P.N., Ghataora, G. S. and Torbaghan, M.E. (2017) ‘A review of risk management application for railways’, Railway Engineering, Edinburgh, UK
A unique holistic decision support platform for risk-informed infrastructure asset management that considers costs and benefits to track and rolling stock owners and operators, users and the environment
to predict changes in track performance over time
to compare alternative maintenance strategies
to deal with uncertainties and risk in decision-making
of total transport costs associated with track infrastructure, rolling stock, users and the environment
of construction, maintenance, operation and renewal of track assets
to predict track performance, identify maintenance strategies and monitor safety and budgets
www.ritrak.bham.ac.uk
m.sasidharan@bham.ac.uk
Career development with the PWI is for anyone who seeks to further themselves academically or professionally, and we are here to support your aspirations.
Whether it’s achieving your next career milestone, securing a promotion or enhancing your skills for better confidence in a particular area of work, we offer a powerful blend of options uniquely available through our Institution.
This includes helping you become a professionally registered engineer through the PWI, furthering your education with our partner colleges and universities, tracking your CPD, attending our industry renowned training courses and networking with railway leaders at our technical meetings and events.
Enhance your career with us today and see what new opportunities arise.
The PWI has been working on a pilot Level 3 Apprentice Scheme for Rail Engineering Technicians with Colas that leads to EngTech and we are pleased to say we have five successful participants. We are hoping to extend to other companies later this year.
Degree Apprentice training in Railway Engineering has taken an exciting leap with the launch of rail specific high-level apprenticeships with Amey at Sheffield Hallam, and Network Rail at London South Bank University. We are delighted with the enhanced links we have made with these Universities and we are hoping to expand this elsewhere.
Our formal membership of the JBM (Joint Board of Moderators of degrees in civil, structural and highway engineering) is subject to full Engineering Council approval later this year and we have already had interest from usually non-rail institutions such as Brighton University.
We are continuing to work on competence frameworks at all levels of track
and ultimately to professional registration. Apprenticeships at higher level (HNC / HND) and
essential work experience thereby providing all
launch an infrastructure owner approach led
16 September 2020, London
16 December 2020, London We are monitoring our plans to deliver our professional review interviews and are working very hard to ensure they are not interrupted.
Interviews will still take place, whether face-to-face or remotely, dependent on the latest Covid-19 government advice.
Our Professional Development Officers can also deliver virtual professional registration presentations and 1-to-1 conversations.
Please check the website for the most up to date information or contact us: profeng@thepwi.org 01277 230031 (option 2)
Please ensure your completed application form and Professional Review Report reach us at least six weeks prior to your preferred interview date.
This is an amazing achievement.
Kevin Anderson - Engineering Technician
Michael Wainwright - Engineering Technician
Adam Cooke - Engineering Technician
Marc Clarke - Engineering Technician
Liam White - Engineering Technician
engineering that link to training and educational qualifications degree level (Bachelors/Masters) also involve the requirements for professional engineers. Progress has been made and we are about to by Colin Newsome at Network Rail.A huge well done to our members who have become Professionally Registered since the last Journal.
Having worked in the rail industry for more than 10 years, I am very pleased to have been recognised as a Chartered Engineer with the PWI. Attaining chartership has been a goal of mine since studying engineering at university and working at Arup each summer. After graduating with a MEng degree from the University of Leeds I returned to Arup as a Graduate Engineer and became a member of the PWI. I was thrilled to learn that I could become chartered with the PWI and be recognised by peers in my chosen field of Permanent Way design.
I felt proud to have the opportunity to prove my capability to the PWI as part of the application process. Although it took time and effort to collate my report, including a few late nights, reflecting on and summarising my various experiences to date was very fulfilling. Despite feeling apprehensive about the Professional Review Interview, I actually found discussing my report and experience with the interviewers really enjoyable. Their friendly approach was very relaxing and enabled me to fully communicate the answers to their questions. I would like to thank everyone at the PWI for their assistance throughout the application process as well as my Supporter (Heather Ceney) and Sponsor (Simon Tomes) for their support and encouragement.
Accreditation with the PWI is a significant professional and personal milestone leading to further work opportunities and increased responsibility. As well as continuing to progress my own career and the careers of others, I hope to also increase the profile of the PWI within the global rail industry.
TIM DIXONFirst of all, I would like to thank the PWI on their commendable work in conducting and awarding professional registration.
Being in a competitive world we should always keep a step ahead and in a situation like the pandemic and economic fallout, knowledge and experience stands out. I wanted to achieve something where I can demonstrate a professional attitude and commitment in my field, which is valued by employers and clients. The PWI gave me such an opportunity to showcase my skills and achieve Chartership that is recognised all over the world.
The PWI processes, from gaining membership to achieving professional registration, is very smooth and crystal clear as each and everything is clearly mentioned on the website - from fee payment to the interview process. Also, the timely response from the PWI team is commendable.
I would also like to touch upon how smoothly the remote interview was conducted by the PWI, and suggest all to take up the membership from all over the world, and not only from the UK.
Finally, I would say that Chartership has enhanced my career as it gives recognition of my commitment and safety in engineering. It has helped my employer and it will give confidence to my clients. I will become a better engineer, as it helps my continuous professional development through a lifelong journey.
To all rail professionals: “Learn and Gain” by joining the PWI for your selfbetterment.
I have been working in railway research (EngD) and railway engineering for six years and during this period I gained important technical and safety experience. Working in railway engineering requires continuous learning, improvement and facing multiple challenges.
Joining the PWI offered me the opportunity to access a great variety of knowledge, shared through Section events, conferences and the Journal; interact with important people of the industry; and follow recent developments, innovations and best practices in UK railway industry.
Becoming a Chartered Engineer will increase the technical and managerial credibility with my current employer and their clients. It is confirmation of my experience and commitment to the profession and will certainly have a positive impact on my future career goals.
The PWI registration team was really helpful, the guidelines are very detailed, and the registration process straightforward. I am grateful for the mentors I had throughout my career and my Sponsor. The path was not easy, especially in an industry that is dominated by men. I would really encourage and am willing to help other engineers, and particularly women engineers, seek professional registration and career development through the PWI.
MARIA GALLOU CENGIn the early stages of my working life I was mentored by two great figures in BR. It is no exaggeration to say that I owe my career to those men to whom I made a promise to pursue Professional Registration.
I am delighted to say that I have lived up to those promises and recently achieved registration as a Chartered Engineer with the help and support of the PWI. Not having a degree, the professional registration was a two-step process. Step one was demonstrating that my career experience gives me the equivalent understanding of engineering to that of holders of a Masters level degree. Step two was then the application for registration and submission for review interview.
Anyone pursuing registration needs to devote time and attention to produce the written evidence at each of the two steps. But with the help of my sponsors and supporters, and with the superb encouragement and support of the PWI registration team, I found the process very clear and simple to follow.
Sadly, my mentors are both deceased, so I cannot share my success with them. What I can do now is to pass on their sound advice and encourage others to seek registration. Whether you have degree level qualifications, or like me came into our profession by a different route, the PWI process can help you achieve registration and the recognition of your professional standing. I am looking forward now to being able to help with practical support to the next generation achieving the professional registration they deserve.
PETER DEARMAN CENG FPWIENGINEERING TECHNICIAN (EngTech)
APPLICATION FEE £60
Engineering Technicians have a practical understanding of engineering skills and techniques as well as the ability to solve engineering problems. They are the people who turn engineering ideas into reality, playing a key, hands-on role in all aspects of the industry.
Our EngTech application process is open to anyone who meets the EngTech competence and commitment criteria.
INCORPORATED ENGINEER (IEng)
APPLICATION FEE £190
Incorporated Engineers maintain and manage applications of current and developing technology, and may undertake engineering design, development, manufacture, construction and operation. Incorporated Engineers are variously engaged in technical and commercial management and possess effective interpersonal skills.
CHARTERED ENGINEER (CEng)
APPLICATION FEE £190
Chartered Engineers develop solutions to engineering problems, using new or existing technologies, through innovation, creativity and change. They might develop and apply new technologies, promote advanced designs and design methods, introduce new and more efficient production techniques, marketing and construction concepts, or pioneer new engineering services and management methods. Chartered Engineers are variously engaged in technical and commercial leadership and possess effective interpersonal skills.
The PWI is here for your journey and would love to support you in your career aspirations.
www.thepwi.org profeng@thepwi.org
Professional registration is open to any competent practising engineer or technician.
Different levels and pathways to registration are available, depending on your experience, training and qualifications.
If you would like to become a professionally registered engineer, we provide a scheme that has been developed in partnership with the rail industry including, Network Rail and Transport for London, tailored to the requirements of a rail engineer.
As the rail industry’s dedicated infrastructure engineering technical institution, the PWI is committed to ensuring that its process for professional registration adds value to the applicant, their employer and ultimately the rail industry.
Every applicant is assessed against the UK Standards for Professional Engineering Competence (UK-SPEC) requirements as set out by the Engineering Council, but as a PWI applicant, in addition to demonstrating your rail engineering competence, you will also
Engineering degree
accredited with the Engineering Council?
Apply immediately.
need to demonstrate your commitment and contribution to proactively improving safety.
The assessment process, known as a professional review, starts with a written application, which is tailored according to the grade for which you are applying. Once this has been reviewed, IEng and CEng applicants will be invited to attend a professional review interview and providing the registration criteria are deemed to have been met, candidates will be recommended for registration.
Professional registration is open to any competent practising engineer or technician. Different levels and pathways to registration are available, depending on the individual’s experience, training and qualifications.
Hold qualifications that are not listed with the Engineering Council?
Apply for an assessment through our Academic Panel.
No formal qualifications, but an abundance of experience?
Apply through Technical Report Option route.
Open to any rail infrastructure engineer seeking to fill their academic gap.
CPD AUDIT - You find us in the middle of our annual Continuing Professional Development (CPD) Audit. Each year we are required to write out to a sample of our professionally registered members and ask them to submit their CPD records for a 12-month period, together with the underpinning Personal Development Plan and their CV. They must respond and failure to do so could result in removal from the Engineering Council register.
The benefit in them doing this is that – not only does it prove their commitment to professional development – but they also receive individualised feedback to ensure they adopt best practice in planning, recording and reflecting on their learning and development opportunities, and use them to enhance their career aspirations.
We want all our members to access that benefit, so we also invite a sample of our members who are not professionally registered to participate too.
But we don’t stop there. Once the records have been audited and moderated by our Professional Development Committee members (your peers) and feedback provided, we will prepare a ‘good practice’ article for the January Journal, sharing observations and lessons learnt, so that all our members can benefit from the audit.
You don’t need to wait until January though. There’s lots of information on CPD available on our website – overview, a previous Journal article and *a new* presentation dedicated to Personal Development.
Are your objectives a roadmap to your career goals or areas of new knowledge? Do you make use of the development opportunities afforded to you as a PWI member? I do hope so.
PROFESSIONAL REGISTRATION - We now have: 181 registered engineers (111 EngTechs, 28 IEng, 42 CEng), with another 350 in the wings, including 16 approved experiential learning CEng candidates. Experiential learning is still open in its pilot stage, so please contact me for further details.
Virtual professional reviews continue along with the launch of our Professional Development Sub Committee with volunteer PWI fellows and Paul Ebbutt as Chairman. This is the final piece of the jigsaw for our licence as the committee audits CPD and reviews the PWI’s technical seminar strategy.
Paul Ebbutt and Brian Parkinson, our Professional Registration Development Officers, are holding virtual professional registration workshops and can offer 1-to-1 conversations. Would you or your team be interested in this? Let us know!
Liz Turner Professional Registration Manager profeng@thepwi.orgJoin us in our Virtual Classroom Training from your home or office as we deliver the Track Engineering Diploma courses directly to you.
• A four-day course with breaks – just like the classroom, but no travel or hotels
• First class technical training, developed and delivered by experienced rail infrastructure engineers
• Online work materials, tutorials, group discussions, interactive worked examples
• Access to tutors in a 1-to-1 environment to answer any queries or recap any areas of uncertainty
• Small class sizes
• Printed course book and personal workbook posted to your home address
• PWI textbook delivered to you
• Online assessment
• Easy access from home or work.
As well as our Virtual Classroom Training, we offer courses held in Derby. See opposite page.
These courses include all training materials and lunch. Accommodation at the venue includes evening meal, single room and breakfast.
All prices are exclusive of VAT.
Further information and booking www.thepwi.org
secretary@thepwi.org 01277 230031 option 1 technicaldirector@thepwi.org
We are monitoring our plans to deliver our training courses and are working very hard to ensure learning with us is not interrupted.
We are committed to delivering first class technical training, developed and delivered by experienced rail infrastructure engineers.
Please check the website for the most up to date information or contact us:
secretary@thepwi.org 01277 230031 (option 1)
In our April Journal, we were considering virtual classroom training and were delighted by the 13 (unlucky for some) individuals who signed up and became our guinea pigs! They did really well on track design and the feedback was great.
We now have five virtual PWI courses under our belt as we carried on by doing Module 3 twice and are currently in the process of doing Module 1 for a second time.
Lockdown saw Network Rail Graduates lose their first and last PWI Diploma modules, which were due to be held at Westwood in March. The Second Years were disappointed as they had completed Module 1 and 2 and needed 3 to get their Diploma. We managed to include 5 in early May and the rest in late May. The First Year graduates will have completed Module 1 by the end of July. It shows very good partnership between organisations and proves what we can do in a crisis - typical track engineers! The delegates worked through their coursebooks alongside lectures and tutorials with personal questions/answers.
A lot of work was done by the PWI training team who prepared online materials and systems. These were led by me and included Dave Ratledge, Bob Langford, Roy Hickman and Brian Parkinson with fantastic online cameo performances from Richard Johnson, Neil Denton, Jon Graham (RAIB) and Mike McLoughlin (yes, he’s still teaching after spending over 60 years working on the railway!)
We have a full programme of courses, both virtual and in classrooms with increased space for social distancing at Derby Conference Centre from September onwards. These include the Track Engineering Diploma and S&C Refurbishment, see opposite for details. Knowing that training is the key to the future, most companies are committed to providing funding, but please let us know if there are issues that we could help with.
With Covid-19 worries easing and extra tasks reducing, this is a great time to plan for the future, so get your bookings in and join the exclusive band of awardees. Remember, places are limited!
Brian Counter Technical Director Permanent Way Institution technicaldirector@ thepwi.orgPWI training started over 100 years ago providing high level technical training for engineers and professionals operating at all levels. The courses are designed to develop skills and knowledge in all aspects of track repairs, renewals and projects and can help you on your journey to professional registration.
Courses are delivered by industry experts and use the most up to date standards and materials. Awards are made by the PWI upon successful completion of written assessments. These comprise Certificates and a Diploma, which has been professionally validated at university level.
Part A 6 - 8 October 2020 - Derby Part B 20 - 22 October 2020 - Derby
Delegates on this two-part course will gain comprehensive detailed knowledge of S&C and how to undertake refurbishment safely, efficiently and to the required engineering quality. The course will cover both the track assemblies and the trackbed under S&C.
Participants will undertake detailed analysis and inspection of layouts so that they can scope and specify work correctly to provide the necessary life extension of the layout. The course will then ensure that delegates understand the various maintenance interventions suitable for S&C and its components and can plan those required in the correct sequence. Modules include: S&C Components Design and Analysis / Site Survey and Measurement / Scoping and Planning.
Delegates will have to pass a formal assessment at the end of the course and will be awarded a PWI Certificate in S&C Refurbishment on successful completion.
Course cost: £845 Accommodation cost: £300 www.thepwi.org/pwi_training/pages/pwi_s_c_refurbishment_course
The aim of the programme is to give delegates an understanding of the principles, theory and practice of track engineering in the UK. It is comprised of three modules and involves 100 hours of taught study all mapped to HE Level 6. Upon successful completion of all three modular assessments, candidates will be awarded the PWI Diploma in Track Engineering.
This course is aimed both at newly qualified and experienced engineers, and will give delegates the knowledge and skills needed for professionals in track engineering.
MODULE 1: TRACK MAINTENANCE
7 - 10 September 2020 - Derby or Virtual Classroom Training
Gives a basic understanding of track engineering and its theory and context. Develops a knowledge of track types and features, its interfaces with other rail infrastructure including earthworks, structures and clearances, and track maintenance including ballast, drainage, stressing, grinding and welding.
MODULE 2: TRACK DESIGN
21 - 24 September 2020 - Derby or Virtual Classroom Training 7 - 10 December 2020 - Derby
Focuses upon track design for projects and enhancements. Through design case studies and exercises, develop skills in track design of plain line and switches and crossings, component knowledge and configurations, layouts, innovations and life extension, route evaluation and trackbed design.
MODULE 3: ADVANCED TRACK ASSET ENGINEERING AND RENEWALS
9 - 12 November 2020 - Derby 7 - 10 December 2020 - Derby
The study becomes more strategic and delivery oriented with advanced asset management techniques and applications. Gain a deep understanding of UK track renewal planning, plain line, S&C, existing and future methods, rail renewal scenarios and optioneering, and learning from accidents. Understand advanced technical rail management issues, rail sustainability and strategic track asset management.
Module cost: £595 (Virtual or Derby) Accommodation cost: £225 www.thepwi.org/pwi_training/pages/pwi_track_engineering_diploma
Slide from virtual training - Bob Langford explaining the concept of transitions to the class
When the Marketing Team put together the annual schedule for the 2020 PWI journals, we planned to make this edition about important international themes including safety and wellbeing. This was due to the global campaigns that were scheduled to take place this quarter, such as Mental Health Awareness Week, World Environment Day and Rail Safety Week. At the time, we had no idea how heightened these themes would become amidst a global pandemic that was about to unfold.
While Covid-19 has brought major adversity to communities all over the world, it has also united us through technology, showing the human spirit for connectivity at its best. At the PWI, we have felt this daily as our community of staff, volunteers, Ambassadors, Sections, Members, Fellows and friends have stepped forward to overcome physical barriers and stay connected through the virtual world.
Mental Health Awareness Week ran from 18 May, with the organisers shifting the theme from “sleep” to “kindness” to celebrate the way the world has united during these difficult times. In support of this campaign, we took the opportunity to ask our community about the things at work that make you happy, however small, and share these online with fellow rail staff and enthusiasts. We ran this as a photo competition and the winning photo “Dandelion”
by Reza Zolfaghari could not have captured the spirit of the campaign more beautifully. In fact, all entries, including the three runners up, truly demonstrated the positivity and sense of community felt by individuals working in an industry that, like others, has been facing tough conditions and uncertainty during Covid-19. You can read more and see the winning entries on the next page.
Our community’s team spirit and optimism continue to be demonstrated by the HighVis Heroes campaign we’ve been running throughout the pandemic, spreading awareness and paying tribute to those working under difficult circumstances, sometimes as volunteers, to keep essential rail services running. And while Rail Safety Week 2020 remains postponed, continued operation of our rail networks depends on revised working methods to include social distancing and other safety measures protecting against virus transmission.
On 5 June World Environment Day took place and was an opportunity to join in global discussions about the human impact on nature, exploring the cause of Covid-19 and how, as humans, we can interact more empathetically and carefully with the Earth’s ecosystems. We asked our community to share stories, examples, tips and advice on working with nature, exploring what we can do as engineers about this important global topic. An obvious outcome of a global change in behaviour during Covid-19 is the reduction in carbon emissions from traffic, with more people opting to walk and cycle. This is great but maintaining the reduction in carbon emissions after lockdown will need people to feel confident in the safety of public transport before they will leave their cars to take the train. That’s something the
Tech Talk is a private forum where members can discuss, debate and share views on all things related to rail technology. Members can ask questions and make comments about the technical articles that are published in the PWI Journal, as well as react to our technical seminars, Boards and relevant news.
industry is working on - so that traffic shifting to rail coupled with an increasingly electrified railway can continue to play a valuable role in decarbonisation.
At the PWI, we have massively enhanced our digital service offerings, a shift that was implemented in January 2020 as part of the new marketing and communications plan, and that rapidly accelerated as part of the PWI’s operational response to Covid-19. Digital communication reduces resource use compared with in-person events - less travel, less paper, less printing – and is part of the Green Policy we introduced last year. Rest assured though, when it’s safe to do so the PWI will resume inperson events with our intrinsic and invaluable networking opportunities.
We will also be continuing our new digital offerings into the future, including the option of our new virtual classroom for technical training and talks. This immediately enables us to stay connected with our global friends in India, US, Australia and beyond.
As the world works to transition cautiously beyond Covid-19, the PWI can look forward to carrying the skills, experience and lessons during the pandemic into the future with pride and positivity.
PWI International Week from 24 August and PWI Careers Week from 7 September are two opportunities to celebrate the lives and careers of our broad membership base across the globe, which we will be able to do far more effectively with our post-Covid digital and global mindset. What’s more, digital and global fluency is the natural mindset of our youngest demographics today, so being able to speak this language widens our community door to young
people, an essential part of the PWI objective.
Lastly, on 23 June we celebrated International Women in Engineering day, organised each year by the Women’s Engineering Society. We shared stories of some of the inspirational women engineers from our community and reposted stories by our Corporate Members.
Scan
Whenever a technical paper is published and placed in the Technical Hub on the PWI website, a post about the paper will be shared in this group, enabling members to comment or ask questions. This opens up opportunities for great conversations where additional spread of technical knowledge and exchange of ideas can occur in a professional space. We encourage healthy debates and differences of opinions, but ask that contributions remain friendly and respectful at all times.
Thank you to all who participate.
Simply click the Request to join button!
Thank you to everyone who has taken part in the PWI community campaigns we have run so far, and those led by other organisations. And thank you to our Ambassadors, Sections, and guest speakers for continuing to carry our torch - we couldn’t have transitioned through Covid-19 so resiliently without you. Our Ambassador team continues to grow and we would like to appoint at least one Ambassador for every Corporate Member, so if you would like to volunteer, please get in touch, my email address is below.
Michelle Mabbett Marketing Consultant michelle.mabbett@thepwi.orgLife could be tough, workplaces might be rough, but we can find beauties and happiness everywhere, just if we choose the right point of view. This tiny Dandelion was sitting on a cold rail hanging on a stone on a windy and hard-working day, to make me smile and appreciate the beauty of the world. Optimism, happiness and smile are Dandelions, we can spread positivity and encourage railway staff working in rough environments whole around the world, to wear optimism lenses and look at the world from a right angle. We can find reasons for happiness and appreciate life, whoever we are, wherever we are and whatever we are doing. Let's put our hands together and help each other to find our Dandelions to promote mental health awareness in life and work.
Dunkeld & Birnam Railway Station on the Highland Mainline has been around since 1856 and in its time has fought off and survived modernisation, closure and two world wars. A positive for us all to take from the current situation is to remember that life goes on and once it is safe to do so, work and life will return to normal. Working on Scotland’s Railway, I have had the pleasure of working with the maintenance team that looked after this part of the track in this part of the country. On several occasions my favourite journeys and work locations have been those on the Highland Mainline with the wonderful landscape and greenery. As a keen photographer I have taken several photos of this area and find myself looking back to remind me of what’s waiting for us once lockdown is lifted.
This is one of my favourite photos that I have in my time in the rail industry, it features one of my favourite machines, the plain line Stoneblower (80215), in one of my favourite locations, Brora on the Far North Line. Due to my role as a Track Geometry Supervisor I almost always work through the night, and working so far North allows me to work at least part of my shift in the daylight, which always lifts my spirits.
Over the last year a number of suppliers have been supporting Network Rail with some ‘Demonstration Days’ held at various Delivery Units up and down the Country. This picture is an image from our most recent event that was held at the Watford DU. You will probably be able to tell from the photo that it was a very cold day – well it was in February! These events have provided the client an insight into what’s innovative in the market but has also brought about a ‘collaborative approach’ from all the suppliers, as everyone ‘mucks in’ to help each other out. I miss these events guys. Hopefully we can meet up again soon.
I hope that everybody is doing well and staying safe during this hard time. It’s important for us all to work together and stay connected.
Before the lockdown was implemented there was a PWI seminar –“Utilising New Technology on Railways in Manchester”. This was a great day for learning and meeting new people. One section I found interesting was the presentation on the use of technology on TfL. This was due to the wide range of new technologies they were utilising. For example, a lightweight modular trolley that can be separated into smaller and more lightweight parts to allow you to carry it down escalators. This enables easier travel through site thanks to lightweight lithium batteries that power it along the track, which I’m sure must feel like a luxury Another was the new survey technology for Skelmersdale - not just because I live there but because in my job I am involved in doing surveys and so it was interesting to see potential new methods I could use. I look forward to attending other PWI events in the future for opportunities to continue learning about exciting new developments being brought into the
During the lockdown in the last few weeks, myself and the other apprentices within Transpire have been working on a fictional track renewal. Thankfully, due to my past experience with working on renewals, I have found the challenge manageable and interesting and it has been a great refresher as I am helping out the other apprentices with their scenarios; helping them to understand the processes involved in large scale works as they have never been involved in a renewal before. My scenario shows a two track layout which is currently plain line. The details of the existing track include: CEN56 rail on F27 sleepers with level track throughout and an area of contaminated ballast spanning for 40m across both roads. My task (simplistically) is to renew the track with “like for like” geometry but also install a new NR60 E-15 crossover along with a layer of
As I mentioned in the previous article, I have worked on two renewals and so for my scenario I have taken inspiration from the Salford 2016 Christmas works where a Kirow crane was used to install the track in panel form (image 1). I have had to complete a train plan,
detailing the number of different wagons I will need and in what order, for example the order of empty falcon wagons on the trains so as to keep the section of excavated contaminated ballast separate to the non-contaminated spoil wagons. As part of the apprentice renewal challenge I have had to speak to multiple CRE’s about their discipline - including Signalling, E&P, P&D, OLE and Track.
This has been very interesting as I have been able to get a better understanding about how a renewal is seen from a different perspective other than track; more-so how they all integrate together and work cohesively during the time restricted possession. This has gone from hearing about the time and space required for signalling to carry out wheels free testing, to how my compound area will be set up and its layout.
While in lockdown, I have become more involved in a very different part of the railway world: estimating. I have been helping out one of our track estimators with a new system that will use Excel to make the resourcing process much more efficient and easier for staff to use. This has been a very interesting project as I have been able to see how the work we carry out is resourced and the sheer number of different things that may be included. I believe it is a very useful subject to have some knowledge of as it enables planning out works from a different perspective and helps for better understanding of the costing process - this may also help promote development of more cost-efficient methods of completing the task. I have mainly been helping with the background calculations on the Excel file, with things like coding of the virtual buttons to do a million other things when clicked and ensuring that all of the adding up works as it should to produce a correct shift cost summary or week cost summary report to the user.
Due to the obvious situation it is hard to plan in things for the near future, but I will be finishing both the apprenticeship challenge and the estimating project in the coming weeks and hopefully moving on to a new project to help out on. Over the last few weeks I have been involved in Power and Distribution as my rotation as an apprentice and look forward to doing some more on that and hopefully completing a few courses, for example 18th Edition of the IET’s Wiring Regulations and Electrical Equipment (SPWEE) and progress with gaining more practical knowledge on the subject.
Our virtual Section which has been formed on LinkedIn provides a central location for all the younger members of the rail community to engage whilst remaining a member of your regional home Section.
The Young Engineers Section is a place to exchange thoughts, ideas, views and challenges you may be experiencing in your role as a young person working in the rail industry. It’s a place to gain and offer support, to meet likeminded individuals, and to participate in social activities as the group becomes more defined.
Simply click the request to join button!
We are seeking a Section Chair and Secretary, as well as committee members, who will be able to facilitate further structure to this Section. To express an interest in any of these roles, please contact michelle.mabbett@thepwi.org
Ryan Lord, PWI Ambassador and Amey Apprentice Engineer, features his apprenticeship diaries in each issue as a way of sharing the life and journey of a young rail apprentice with our community.Image 1: Kirow Crane lifting a track panel.
Using My CPD will assist you in your career planning and will enable you to demonstrate your professional competency.
My CPD is available to all PWI members www.thepwi.org
CPD (Continuing Professional Development) refers to the learning you do to develop or maintain the knowledge and skills you need to succeed in your career and maintain your professional competency. The most important thing is to focus on its relevance to your current role and your future career ambitions.
CPD demonstrates your competence as you keep yourself up to date. It instills self-confidence, and inspires confidence in those who work with you. And by demonstrating your commitment to learning, you are more likely to be given opportunities to progress in your career.
Don’t leave it until the last minute! You should plan your CPD activity at the start of the year to ensure it is relevant to your development needs.
Read this great CPD guide on our website.
Mohandas
Arunkumar - Project ManagerExperience - 18 years
Qualifications – Chartered Engineer (India) from Indian Institution of EngineersIndia, Masters in Business Administration (Construction Management) from Indian School for Management & Studies - India, Post Graduate Diploma in Railway Engineering from Institute of Permanent Way EngineersIndia, Degree in Mechanical Engineering from Indian Institution of Engineers - India, Diploma in Mechanical Engineering - Directorate of Technical Education - India.
I joined railway in the year 2006 with Alstom Transport as a designer for P-Way metro tracks for the circle line project in Singapore. From there my journey in P-Way started and my interest towards learning P-Way Engineering increased day by day, even though my education background was mechanical engineering. I found mostly civil engineers working for the P-Way industry. So, I started enhancing my civil knowledge by attending seminars and was fortunately selected for assisting Technical Manager for trackwork maintenance manual preparation and training session to our customer SMRT. This was a gamechanger in my P-Way career.
The right opportunity can change your life for the better and I ensure it doesn’t pass by. When I moved from Singapore to India for Alstom Transport in 2011 to take up the new role in Chennai Metro Rail Project, I was well recognised by the senior railway people in India because of my international metro project experience. At that point in time, Metro track technology was booming in India with limited expertise. After I moved into trackwork, I figured out my passion lies here and considering the volume of upcoming Metro track projects in the region, I decided to pursue a career in track design and installation.
In 2018, I was promoted as Project Manager for trackwork and was told that I was the youngest Project Manager with Alstom Transport in India. I’m very satisfied with some of the projects that I have delivered throughout my career, like Pink Line (60 track KM) of Delhi Metro Rail Project, Waad AL ShamalCTW 320 (200 Track KM) for Saudi Arabian Railway, Appitrack for Nagpur Metro Rail Project and Chennai Metro Rail Project. I am also very proud that we have constructed the first Ballastless Automatic Track laying using Appitrack technology in Nagpur; a first of its kind in India.
WHAT ARE SOME OF THE DIFFICULTIES YOU HAVE FACED IN THE WORKPLACE AND HOW DID YOU OVERCOME THEM?
and freight trains to run safely and efficiently. Rail opportunities are available all around the globe, not just in your own country. If you take up a career in rail, there are plenty of opportunities to work internationally.
around
As Project Manager, I manage and ensure trackwork project delivery in conformity to contract / project scope. I drive project execution to maximise cash and margin, whilst delivering on time with quality and identifying additional opportunities during execution and project closing phase. I lead the Project Team, including the Trackwork Core Team (15 Direct Reporting) and I manage external stakeholders including civil, S&T, OHE and rolling stock for trackwork. In addition to the Project Manager role, I am also responsible for tendering for trackwork projects in India region and implementing Alstom innovation products in trackwork, such as Appi track (Automatic PIN and PLATE Insertion) and HAS (High Attenuation Sleeper).
As mentioned, my graduation was in Mechanical Engineering and the expectations were that people managing P-Way projects should be Civil Engineers. It was really difficult to get my CV approvals and I had many hurdles within our organisation. I overcame these difficulties by demonstrating my knowledge in P-Way by successfully executing some of the more difficult projects. I also enhanced myself by completing my Post Graduate Diploma in Railway Engineering with the Institute of Permanent Way Engineers India and started utilising the PWI-UK online resources and forums.
WHAT ADVICE WOULD YOU GIVE TO THOSE WHO ARE NEW, OR ARE CONSIDERING JOINING, THE RAILWAY INDUSTRY?
Rail infrastructure is a vital component of the rail sector. It involves the construction and regular maintenance of infrastructure assets and equipment including track, tunnels, level crossings, bridges, platforms, land around the track and other facilities which allow passenger
At the moment, my aspiration is to achieve Chartered Engineering status through PWIUK by 2020 end. My next assignment is as P-Way Manager with SMRT-Singapore for the track renewals and maintenance projects. In the longer term I’d like to start my own consultancy in P-Way design and construction for ballastless tracks. I’d also like to keep promoting the railway industry through the PWI and pursue the opportunity to become President of the PWI-India Chapter.
I’m very passionate about promoting railway engineering as a career with younger people by being a part of PWI-UK India chapter. Our first chapter in Bangalore was very successful with the presence of our PWI President Joan Heery. Outside of work, my other interests include listening to music, watching movies and volunteering at local rotary club events.
TELL US ABOUT YOUR JOB ROLE. WHAT ARE YOUR DAY-TO-DAY RESPONSIBILITIES AND TYPICAL TASKS?
Rail opportunities are available all
the globe, not just in your own country. If you take up a career in rail, there are plenty of opportunities to work internationally.
ATTENDEES - Joan Heery, John Edgley (13:00 arrival), Nick Millington (13:35 arrival), Gren Edwards, Andy Cooper (11:20 arrival), Andy Tappern, Colin Wheeler, John Dutton, Steve Whitmore, Stephen Barber, Brian Counter, Kate Hatwell, Michelle Mabbett, Liz Turner, Mark Taylor, Vice-President (13:00 arrival)
WELCOME - JH welcomed all to the meeting. Etiquette briefing provided for the conduct of the meeting virtually.
NON-EXECUTIVE REPORT FOR JOURNALCW agreed to write the non-executive summary for the July Journal.
SAFETY, ETHICS & INTEGRITY - SB noted that the Institution has taken Covid-19 very seriously and adopted government advice. We intend to retain operations consistent with that advice, and until we are convinced that face-to-face operations can be safely resumed. Interesting to note that the advice is beginning to vary according to the four nations, and we are listening to each of them as appropriate.
13 FEBRUARY 2020 BOARD MINUTES & ACTIONS - JH highlighted the AOB item re Terms of Reference (TORs) and enquired whether it should this be an action? SB noted that the Corporate Governance Code 2018 (aka the Cadbury Code) has been adopted as the TORs for Board. TORs for Technical Board have been prepared and are to be presented to Technical Board. This position will be reflected in a revision to the February minutes. Subject to the above, the Board were happy that the minutes were a proper reflection of the meeting and were agreed and approved.
CEO REPORT (STEPHEN BARBER) - SB noted that the past three months have been dominated by the Covid-19 emergency and response. Recently the Royal Academy of Engineers (RAE) asked for help to identify supply chain impacts of Covid-19; this request was passed on to corporate members. RAE maintains focus on long term strategic issues, e.g. climate change and flood risk; it is clear that the engineering challenges facing the country are massive and will affect the railway industry. SB noted that the PWI has moved its activities online and a working assumption is that face-to-face activity can resume in the Autumn for training and seminars, but there is no certainty about that and we continue to watch and tweak the programme. In conjunction with moving online, MM and KI have done a fantastic job in raising the PWI’s social media profile and retaining member engagement despite the loss of face-to-face activities. However, face-toface events are traditionally the prime market for securing new members, so our targets for individual membership growth are highly unlikely to be met and, at best, membership volume is likely to stagnate. Corporate Members (CMs) have been incredibly supportive and involved. The Technical Board in April saw the highest ever number of attendees. The Practical Trackwork Challenge has been deferred to March 2021 (all being well) with a return to Churnet Valley. There will be a focus on better engagement with young engineers and technicians, with an 8-point plan recently adopted by Executive team. The proposal for the new website has been worked up and the team is unanimous that it is critical to our future with the enhanced functionality it brings, and that implementing it sooner will maximise overall benefits. Work on our membership of JBM
continues, and is subject to Engineering Council review and award of a licence to accredit / approve educational programmes.
SB formally registered his thanks to the team who he noted have worked above and beyond to improve and raise the PWI’s online profile. The level of change managed in a 13-week period has been astounding. Without the fantastic team, the PWI would not have been able to implement such a volume of change at the required speed and SB is grateful for their support. JH fully endorsed SB’s comments on the team.
FINANCIAL POSITION (KATE HATWELL)
2020 ACCOUNTS YEAR TO DATE - KH reported on the YTD numbers and the forecast year end-position based upon a number of scenarios. The year to date cash position is strong. Training courses have moved online. We chose to keep numbers small as a sensible step for the first time and to ensure the quality of the teaching was not impaired. The course feedback has been positive, and all delegates have re-booked onto the next Module. The lecturing team are now confident with larger online class sizes.KH expressed disappointment and surprise at the drop off in Professional Registration applications, particularly at EngTech level. This is possibly linked to the weakening of direct line management at that grade consequent on Covid-19. In contrast, LT noted that we are seeing better progress from those applicants who have previously applied. KH noted that she is delighted that three companies wish to be principal sponsor of the Autumn plant seminar and that they are happy to share the position and contribute whether it occurs in 2020 or 2021. AT felt the team was doing a fantastic job with training. Having been involved in a couple of review meetings he was also impressed by the really good work that has gone into pulling together the accounts and financial forecasts.
2020/2021 FORECAST - AT noted that we look to be in a good position for 2020 year-end, however he cautioned we are likely to feel a hit in 2021. Corporate Member and Individual Member retention will be key. AT asked when training might be back in the physical face-to-face classroom? SB explained that our forecast is based on a September return to face-to-face tuition as universities and schools look to be normalising operations then. KH noted that we have identified more weeks to repeat TED Modules 1 and 2 in June-July. BC noted that our lecturers’ availability is good, but we do need be aware of the likely external constraints. BC understood training to be optional for most companies and, as in previous recessions, some companies may not choose to support it. AC noted that we should get companies to think about training in 2021, in addition to the current year, and believed that the PWI should promote this very heavily. The PWI should indicate clearly that it will still be here next year. The financial forecasts and underlying assumptions were unanimously approved. JD thanked KH for the work done in putting the forecasts together. He asked for monthly visibility of the cashflow forecast in correspondence.
TECHNICAL REPORT (BRIAN COUNTER)BC thanked everybody for their support and noted that much of what he reports on has been covered in the preceding discussions. BC noted that Technical Board is generating involvement from the top levels of CMs: Jonathan Graham of RAIB presented at the last Technical Board. Professional registration has moved forward,
carrying out virtual reviews, some of which BC will observe. The PWI’s Professional Development Committee (PDC) has been established, fulfilling an EngC requirement. PDC includes two Fellows and its first meeting has taken place.
REGISTRATION REPORT (LIZ TURNER) - LT reiterated that professional registration has moved into the virtual world with all interviews set to take place by remote means and all candidates content to proceed on that basis. Membership Committee and Academic Panel meetings were convened virtually in March and will run again in that format in July, as well as the meetings of the PDC. The PWI is also using the virtual platform to run workshops on registration, with pleasing levels of interest. One aspect from the annual EngC statistics for 2019 worthy of note is the healthy number of new registrations and that roundly 75% of these are 25 years of age or under. This highlights the importance to the PWI of recruiting and retaining the students and young employees who become early career registrants. This is recognised within the PWI’s plan to improve engagement with young engineers. BC noted that the PWI is focussing on degree apprenticeships with the objective of being the PEI of choice for engineering apprentices and students in the rail infrastructure sector, who will go on to become registrants. CW stated that we should also focus on OLE engineers as there appears to be no natural PEI for them. SB agreed and noted that the PWI has OLE reviewers so can assess registration applications from those within the OLE discipline. Presuming Peter Dearman is elected as Deputy President at the AGM, he will bring to the PWI considerable influence in this discipline area.
- MM summarised the result of the online analytics within her report which showed a significant spike in engagement following launch of the new marketing communications plan in January 2020. This steady performance has been followed by a second huge spike due to the change in our approach consequent on the Covid-19 emergency. The new communications plan and the PWI’s Covid-19 response have coincided and complement each other. The way we have stepped up has made the PWI look very resilient and forced its officers and volunteers to become familiar with and comfortable in the online environment. MM noted that the flip-side to this spike in engagement is risk in two areas: i) that when life returns to normal and “in-person” communication resumes, online engagement will dwindle, and; ii) that whilst engagement is on the up and positive, at the same time our current website is struggling and unable to effectively support the increased engagement generated. The website does not match the standard of our other recent communications and it is potentially why new member figures do not match the reported increase in engagement. MM noted that she did not intend her report to become a pitch for the new website (which is the subject of a later discussion) but made the point that the correlation is clear. JE asked if there was a real risk that the website could become inoperable? MM explained that if we do not soon proceed with the new website, we would have to negotiate a way forward with our current providers. KH agreed that this course of action would be feasible but that a new up-to-date website would make a significant difference. Both MM and KH were of the view that the current website is the PWI’s Achilles’ heel with a negative impact on a large proportion of PWI activities. AC felt strongly that the PWI should now
be developing a full event programme for 2021 and managing the communications around that, making it clear that the Institution will do more of what has been well received as the technology is put into place to support it.
RISK REGISTER REVIEW - SB introduced the up-issued risk and opportunities register ahead of the standing six monthly review, bringing to the Board’s attention the addition of a new “pandemic” risk together with its impacts on the PWI and the mitigation measures already enacted.
WEBSITE / CRM (KATE HATWELL) - KH introduced the item noting that the whole Executive team share that belief that this project is of critical importance to the PWI, even more so in the face of the Covid-19 emergency. KH highlighted that the new website offers a huge opportunity to improve the PWI’s membership service and activity and provide a better experience to all who interact with us. KH explained that, as a key output from the PWI’s 2018/19 Strategic Review, the proposal has been 9 months in development. SB, MM, KI and KH met with three shortlisted suppliers who demonstrated their product. Based on the presentations and follow up Q&As, that panel subsequently identified two preferred partners, both with similar costings. Further detailed analysis and discussion had enabled the Executive to recommend the proposal made by All My Systems Ltd (AMS). KH noted that it had not been practicable to quantify consequent improvements in the PWI team’s productivity against particular system attributes, but explained that productivity gains will be used to generate improved member satisfaction. KH noted that AMS specialise in Microsoft Dynamics for smaller businesses and they meet all the objectives within the PWI’s specification and provide additional functionality. In common with other Microsoft applications, the system is intuitive and integrates with the suite of other Microsoft 365 products. The intensive procurement process has provided assurance that AMS have a clear understanding of the PWI’s requirements and have taken time to understand our business. AMS’ platforms are licensed and payable through a monthly subscription, thus always delivering the most up to date application versions. The product is scalable and the risk of obsolescence is very well controlled. Additional assurance of product support is provided by the large external supply market in Microsoft Dynamics and WordPress specialists. KH concluded by noting that while there are significant current pressures around the PWI and the rail industry, the PWI remains well placed, both financially and in terms of staff capability, to deliver this project and that delivery will provide critical support to the PWI’s growth
It was noted that since the last meeting of the Board in February, a significant amount of work has been completed by the Executive and the Section Leadership which continues to be progressed to ensure that the PWI remains focused on the delivery of its core areas of business. The work completed by the Executive and the Section Leadership has required a
trajectory. The Board noted the comprehensive paper. The issues with the current website were widely acknowledged and following a series of probing questions, it was unanimously agreed that the proposal represents a pragmatic, sensible way forward with industry standard software. JH queried whether AMS had been asked to provide testimonials? JD responded that he had reviewed recommendations for AMS on LinkedIn and then looked at the operation of the British Heart Foundation website (based on the AMS product) when making a donation. He noted the similarities between BHF and PWI and noted that the BHF site appeared to work extremely well. He also noted good feedback on AMS from four or five companies that had worked with the provider since it was set up. MM noted that she has worked with a number of other tech companies in the past. She was of the view that AMS have listened to our specification requirements and concerns, and that their solution places control in our hands and delivers a significant cost saving for the PWI. AT noted that the paper explained all aspects of the project well and that he supported the proposal as an essential element of the PWI’s development. He suggested establishing a benefit tracker for the project so that the Exec can clearly confirm that the five to eight critical capabilities at the heart of the project have been delivered. JD added that the benefit tracker should incorporate all current manual processes that are to be made redundant so that Exec can confirm they have ceased and the potential savings have been realised. KH responded on project timescale that the current support contract takes us through to Feb 2021 with 3 months’ notice to cancel. We will need to be very confident by 1 Nov 2020 that data and test phases are complete and we are ready for go-live. KH and other Exec members were clear that testing must not be rushed and that a successful “glitch-free” go live in 2021 would be a win. The Board endorsed the paper presented and its conclusions and agreed to proceed with the project. JH noted that the decision represented a great milestone against one of the PWI’s strategic objectives.
AGM AGENDA AND FORMAT - SB noted that CW steps down from the Board at the AGM, and wished to place on record the huge debt of thanks that the PWI collectively, and he personally, owe to CW. CW has been a stalwart member of the PWI for many years and, as a Non-Executive Director, has ensured the PWI is fit to remain in the first division of engineering institutions. SB gave his thanks to CW for keeping an eye on where Board has been taking the Institution and keeping it on the straight and narrow. CW’s knowledge and experience will be missed, and his contribution is greatly appreciated. SB’s sentiment
was echoed and endorsed by all present. CW thanked the Board for their kind words but noted that he intends to maintain an overview of where the Board is taking the PWI and promised to alert them to any misgivings he has concerning the Institution’s future direction! SB noted that the Exec is currently working through options for holding the AGM in a Covid-19-compliant manner. Current thinking is that the AGM will be online. KH reported that she had attended a seminar on the management of online AGMs. The current 3 July date may be tight and we may need to take the decision to push the AGM back by a month. Such a decision is consistent with the Articles of Association. SB noted that he would like to retain the traditional timescale if at all practicable and to retain the passing of the Presidency too. SB explained that the election of the full slate of VPs will depend on the approval of AGM Agenda item 7, a small amendment to clause 4(1)(b) of our Articles of Association, to allow Board to determine at its discretion, from time to time, as many VPs as required, with a minimum of six. Since the PWI became a fully accredited PEI, the scope of the VP role has clearly expanded and some VPs have found themselves pressed by the volume of potential tasks. It is particularly important to increase capacity in the South of England where the ratio of members to VPs is comparatively high.
HLM NOMINATIONS - A nomination received from Edinburgh Section for Bob Gardiner was tabled. Proposed by JH, the nomination was approved unanimously.
FELLOWSHIP APPROVALS - Following the recommendation of the Technical Director, Board APPROVED applications for Fellowship from:
• Michael Winsor, Atkins (Sponsor - Mike Ashton)
• Jonathan Hayes, Atkins (Sponsor - Les Fox)
• Narasimha Rao Telagamshetty, Atkins (Sponsor - Mike Ashton)
• Colin Hedderly, Irish Rail (Sponsors - Brian Lucas & Joan Heery)
• Peter Fagg, WSP (Sponsors - Russell Pope & John Lonergan)
• Jessal Murarji, RSSB (Sponsors - John Campbell & Bridgett Eickhoff)
NEXT BOARD MEETING - AT noted that the next Board meeting is scheduled to be at Paddington but enquired as to whether it could be held virtually again. Other Board members agreed that this would be sensible, and it was resolved to hold the next meet online. Thursday 14 July 2020 (11:00 – 15:00), virtual platform.
great deal of effort which has resulted in many aspects of the PWI delivering its business as usual, albeit in a virtual environment. These developments have been progressed swiftly over the last two months – the Board were very grateful for the terrific efforts that the Executive and Section Leadership were providing in these unusual and challenging times. In considering the financial position for the month end of April and the forecast year-end, given the current environment, the Board considered the year-end forecast challenging to deliver, but still achievable given the present situation. It was noted that the forecasts include additional investments
The grade of Fellow is the highest grade of membership that the PWI can confer upon a member. PWI Fellowship will raise your professional standing within the industry, increase recognition of your expertise and enhance your professional networks. The PWI Board must by majority approve all transfers to Fellowship. An applicant for Fellowship must hold or have held a senior or influential position in the railway industry and made a significant contribution to the industry or PWI
required to move the training to an online solution as well as further investments in web-based and CRM developments. However, the Board anticipates that the returns will be forthcoming in the months ahead. It was exciting to see the growing and developing engagement with the Railway Community with the enhanced Marketing that the PWI were undertaking. The AGM Agenda and format were discussed and endorsed, noting that further alteration may arise given the present Covid-19 position – this was agreed to be monitored by the Executive over the coming weeks. John Dutton - Non-Executive Director
TO APPLY
www.thepwi.org/membership/fellow
5
Our Speaker for the evening, Andrew Allen, Senior Engineer within the Aegis Certification Service at Aegis Engineering Systems, set out a comprehensive introduction to the range of railway level crossings in Britain, assessment of their safety and examples of practical improvements. Aegis are an independent consultancy and provide advice, principally to Network Rail but also to other rail and road organisations, through the normal tendering processes.
Differing definitions of user priorities at level crossings prevail. The Collins English dictionary considers that they are places where a railway line crosses a road, whereas the ORR (The Office of Rail and Road) advise that they are where a railway is crossed by a road or right of way on the level and further qualified as being without the use of a tunnel or bridge. The ORR definition reflects the superior legal status, from the earliest days of railway legislation, of the railway over the road or path.
There are some 7500 level crossings across the country of which Network Rail is responsible for some 6000. The balance is on heritage railways, metro systems and industrial lines. NR policy is to close crossings wherever practical, not least in response to increased train frequencies and speed, but also for the obvious principle of minimising direct conflict between rail, road and pedestrian users. About half of all catastrophic accidents on the railway occur at level crossings. It has been possible to close around 300 crossings in recent years and NR has set a target to close the total they manage by 25% by 2022. Not all crossings can be eliminated, and Andrew emphasised that the ORR advocates that safe design, management, and operation reduce user risk and has a positive effect on user behaviour.
Andrew explained the full range of level crossing types, their varying warning and protection arrangements and the factors and process in their risk assessment. Most crossings provide for public roads, footpaths, and bridleways while ‘occupation’ crossings
provide for crossing by a private road and ‘accommodation’ crossings enable access between parcels of private land separated by the railway. Key information is set out in the ORR guidance document ‘Level Crossings - A Guide for Managers, Designers and Operators (Rail Safety Publication 7 December 2011).
Andrew illustrated crossing types ranging from ‘Manually Controlled’, locally by a gate keeper or remotely but monitored by CCTV and/or by object detection equipment, with trains responding to signals, to ‘Automatic’ types, either CCTV monitored, or railway staff operated, or unprotected half barrier. The third main category is ‘User Worked’ for pedestrian, horse or vehicle use, either simply with ‘Stop Look Listen’ signs at fence stiles or gates, or more detailed instructions to observe miniature stoplights or to telephone the signaller. Some gates have a power operated gate opener (POGO) and one type features hand pumped lifting barriers! Diligence of users to observe instructions often depend on their level of inconvenience and perceived relevance through previous experience at the crossing. The Health and Safety Executive sets out general guidance on risk assessment. Whether a risk assessment, in this case of a crossing, is ‘Suitable and Sufficient’, as required in law, should include that a proper check of the case has been made, the right people have been identified and consulted, the obvious significant risks addressed and the precautions in place are reasonable. The meeting could see that ‘suitable and sufficient’ depended greatly on professional judgement. Andrew illustrated the comprehensive process that Aegis follows to achieve an acceptable assessment. This comprises pre-survey data capture, with sources ranging widely, site survey, risk management provisions analysis, cost benefit analysis and discussion with interested parties about options and risks. The Rail Safety and Standards Board (RSSB) have made available a Level Crossing Risk Management Toolkit (see www.lxrmtk.com).
To draw the subject together, Andrew selected as a case study an automatic half barrier unprotected crossing in a semi-rural location equipped with roadside telephones. Encroaching road verges rendered the crossing itself the widest place for vehicles to pass. The telephone was significantly on the
railway side of the vehicle stop line (the legal position of safety). Another railway telephone was confusingly nearby and the closest practical place for large or slow vehicles to park before ringing the signaller was 200m away and out of sight of the crossing. The example showed that despite carefully provided equipment, user discipline was the ultimate influence on user safety at level crossings.
Questions explored the balance between control by the railway and initiative allowed to the user, contrasting UK and continental approaches, the drawbacks of some measures, such as audible warnings in residential areas and the need to take advantage of mitigations in the hands of other parties such as the local highway authority. Members were intrigued to hear that a new level crossing was about to be commissioned on a Trunk Road in Kent! A vote of thanks was proposed by Ray Pocock for a thorough and well-pitched presentation.
This was another in our sequence of contemporary topics. Alan began by telling us that his experience of plant started when driving tractors on a farm as a child. He has worked for many of the well-known firms and said that working in the rail sector is a completely different challenge. He had the courage to explain that this is due to some of the less attractive facets of the industry, such as the last-minute cancellation of works as a result of the railway industry’s failure to make relevant arrangements. Alan then gave details of how such occurrences adversely impact on the finances, investment, and innovation of the plant industry. Ironically, innovation itself can cause problems. As an example, Alan cited Story Contracting’s purchase of cherry pickers with 400kg buckets. These are a development of the version with 300kg buckets that are now ‘suffering from a reduction in demand.’ If someone creates a version with a 500kg bucket, will Story’s fleet of 400kg cherry pickers suffer the same way? Add the need to recruit and train the necessary calibre of staff in addition to increasing demands of legislation and it becomes clear why firms are ‘cautious’ about investing in equipment
that is predictably expensive. Attracting staff is becoming a challenge as more and more people are reluctant to work in poor weather conditions and the antisocial hours that are almost hallmarks of railway engineering works. On a positive note, this is prompting a long overdue improvement in the facilities for the machine operator. Where once the operator was exposed to the elements and other hazards, now many machines have air-conditioned cabs that protect the operator not only from the weather, but such hazards as dust. This fascinating insight into the world of On Track Plant prompted much interest from attendees who were happy to thank Alan in the traditional manner. My thanks to Alan, and to Ian Salisbury who made notes on this presentation.
SECTION MEETING- GLASGOW 19 February 2020. New Zealand Railways: Operational challenges and opportunities - Phil Kirkland, Vice President England (North) the PWI
system. The railway system in New Zealand was founded in 1863 with the opening of the Canterbury Provincial Railway, Christchurch and by 1920 had developed into a 3000-mile system carrying 15 million passengers per year. In 1931 a Transport Licencing Act was introduced which restricted road haulage to 30 miles distance which was of huge benefit to the railway until deregulation of land transport in 1982.
Despite electrification projects, including Wellington suburban routes in 1937 and the 1988 25kv AC electrification of 411km south of Wellington, the railway system was in decline with operating losses and debt of $1.2 billion by 1989.
In 1990 privatisation began with New Zealand Rail Ltd (NZRL) being established as a Crown Company taking over rail transport and shipping activities, including the railway infrastructure. In 1993 NZRL was sold for NZ$400 million to a consortium of Wisconsin Central and renamed Tranz Rail, with suburban trains rebranded Tranz Metro, long-distance passenger trains Tranz Scenic and freight Tranz Link.
In 2008 the Labour Government announced that the rail and sea operations of Toll NZ Limited, less its trucking and distribution operations, was to be purchased for $665 million NZ and the company renamed KiwiRail.
The aftermath of the devastating 2016 earthquakes brought home the national strategic importance of the rail system and Phil described some of the major recovery works. The 2017 new Government Rail Transport Policy plans to:
• Create a rapid passenger rail service linking Auckland, Hamilton and Tauranga...
• Capital investment for commuter rail from Rolleston to Christchurch.
• Retain an electrified network between Hamilton and Palmerston North and work on an evidence-based plan to progressively electrify other key parts of the network.
• Reopen moth-balled railway lines, notably the Napier to Gisborne rail line.
• Reopen a rail line to Marsden Point and Northport and upgrade the North Auckland Line.
Phil introduced his presentation by drawing comparisons between Kiwi Rail and parts of the UK system before discussing the origins, regression, the subsequent growth, and the opportunities facing the New Zealand railway
In 2001 the Auckland and Wellington metropolitan rail networks were transferred from Tranz Rail to the local government authorities under concession arrangements. In 2004 Tranz Rail was purchased by Toll Holdings and renamed Toll NZ, whilst NZRC assumed the Crown’s responsibilities under the rail access agreement with Toll and adopted the trading name ONTRACK. By 2006 ONTRACK and Toll NZ were in dispute about track access fees and an independent arbitrator was called in to resolve the issues. Serious concerns were being expressed regarding the condition and sustainability of the infrastructure.
• Immediate order for 100 new locomotives and 900 new container wagons.
The planned investment for 2018 -2020 is c NZ$2,520 billion: signalling a bright future for Kiwi Rail.
4 March 2020. PWI Trackwork ChallengeMalcolm Pearce, Honorary Life Member, PWI
Thermit Welding is part of the Goldschmidt Group –the unique, global network of experts for the railways. Together we lead your rail infrastructure into the future – with smart solutions, services and products.
gives such engineers the opportunity of handson participation and observation of PW works on an operational site. Track renewal and maintenance projects on heritage railways are selected so as to provide live sites, where work to the standards expected on Network Rail and TfL sites can be undertaken, but without the pressures and restrictions necessarily present on the main networks.
Delegates, perhaps only experienced in specific PW planning functions, gain an insight of how to set out work on-site and use machinery, observing specialist OTP, OTM and other equipment carrying out a wide range of track and formation processes. They work in teams and are managed, supervised and mentored by experienced supervisors and PWI representatives throughout the full two days of the site work. There are, in addition, two evenings of theory and discussion. Delegates are encouraged to take full advantage, either in groups or individually, at any time throughout the event, of the expertise available to them.
Event planning begins with identification of heritage railways with the potential to meet the event criteria and, subsequently, dates, work specification, provision of materials by the host, welfare facilities, logistics and constraints. Details are sent to Corporate Members with an invitation to nominate up to two employees to attend and for support through provision of resources such as survey, design and site management, OTP, OTM, SPP and hand tools, site access control, welfare, first aid, review and monitoring of site safety and risk assessment plans, and provision of overnight security.
PTC 2019, held at the Churnet Valley Railway, Staffordshire, was the third such annual event that the PWI had arranged for its Corporate Members and their staff.
Particular thanks were owed to 2019 supporting Corporate Members who comprised Babcock, Balfour Beatty, Churnet Valley (host), Cleshar, Network Rail, Quattro, RAIB, Shannon Rail, TXM and TfL, delegates from Corporate Members coming additionally from AECOM, Costain, Jacobs, ORR, SNC/ Lavalin, Stobart, Story and Volker Rail.
Malcolm completed the presentation with images of all the main operations on the site during the event, culminating with images of the PWI CEO Stephen Barber presenting certificates to the participants and of the first train running over the new track. Questions and comments from the floor provoked discussion both during and after the presentation. A vote of thanks was proposed by Jeremy Smith for a thorough summary of the whole process necessary, from project design to completion and hand back, to achieve the event objectives.
SECTION MEETING – EDINBURGH 5 March 2020. Composite Components at Newark Flat Crossing - Phil Winship, Principle Engineer, Network Rail
Phil delivered the paper titled “Composite Components at Newark Flat Crossing”. For those not familiar with the concept or location; Newark flat crossing is the last remaining flat railway crossing on Network Rail’s network where two standard gauge lines intersect. It is located north of Newark North Gate station, at the point where the Nottingham to Lincoln Line intersects with the East Coast Main Line (ECML). The layout has some 16 crossing noses with the ECML route running at 100mph.
The renewal of the crossing baulks using traditional materials such as 16m long greenheart timbers was no longer sustainable or in line with the Forest Stewardship Council (FSC) requirements, so the use of alternative
artificial materials for the baulks bearing the steelwork was investigated. This included fibre-reinforced foamed urethane (FFU) made from plastic foamed urethane resin reinforced by long glass fibres. These materials have been used as an alternative to timber sleepers in Japan since the 1980s and in Europe over the last 15 years, including 230kph running in Germany. These applications have proved to have greater service lives and resistance than traditional sleeper materials. Indeed, the design life of the baulks at Newark have now increased from the previous 15 to 20 years to an estimated 50 years. Although the material has the increased life expectancy of plastic, it retains remarkably similar characteristics to natural wood, such as weight and workability. To date, the manufacturing facility in Japan had been producing up to 10.000m long elements for export; however, for Newark, Network Rail required elements up to 16.000m in length, which would be the longest ever FFU synthetic rail bearers. This challenge resulted in the process being carried out in the UK for the first time by Sekisui in collaboration with Progress Rail Services.
Whilst the principles of the scheme were developing quickly, the less exciting but equally important issues of internal product approval and CSM legislation (considered ‘significant’ by NRAP) were a key part of Phil’s daily challenges to make the application of new system work at Newark.
Although explosive depth hardening (EDH) crossings were originally intended to be used, after discussions with STE and the LNE RAM team on potential risks to not meeting the required deadlines, it was decided to install non-EDH crossings. The layout also features steel top bearer plates, underbearer pads and a Geocell formation. Whilst the twin density FFU bearer arrangement was some 30% lighter than traditional timber, it
TENCONI plastic division is the only manufacturer of the high quality insulated rail joints also called ‘BENKLER’ joints. The pieces are produced also in small batches, according to customers’ specifications and needs.
TENCONI steel construction department has a reputation of excellence also for the manufacture of special hollow sleepers, low friction slide chairs, insulated base plates and many other railway products.
life: more than 8 years
Colours: yellow, red, white, green, blue (two per cover possible)
LED configuration: one-sided and two-sided reflectors
Charging time: approx. 3 hours on a sunny day
still weighed 52 tonnes. For Installation this meant additional cranage provided a sufficient level of contingency, should there be any plant issues. On the late August 2019 bank holiday weekend, the layout was successfully replaced with a graduated speed increase from 50mph to 80mph, then back to 100mph line speed once the other associated works were also completed.
Phil did remind the audience that even whilst this was a ‘game changing’ project, it still experienced the traditional challenges, such as a lack of original layout drawings and the obligatory negotiations with land owners over access / holding areas.
Edinburgh Section Vice Chairman, Forbes Prentice, gave Phil a vote of thanks for a fascinating presentation, which was warmly seconded by the members present.
SECTION MEETING – SOUTH & WEST WALES 9 March 2020. Acton Dive Under: Slab Track and Yard Remodelling (Phil Holbourn, Holbourn Engineering Ltd & Network Rail)
In a further last-minute change to the programme, the scheduled presentation by Phil Holbourn on ‘Cardiff Intersection Bridges Part 2’ was postponed to a later date. However, Phil was able to make a substitute presentation on an earlier project ‘Acton Dive Under – Slab Track and Yard Remodelling’.
Introduced by Andy Franklin to an audience of 13 members and guests, Phil recalled the events of 2013 to 2016 in the construction of the Dive Under in West London, which now allows Crossrail/TfL trains towards London to
pass underneath freight trains accessing Acton Yard. A vote of thanks was proposed by James Hepburn and carried unanimously with a round of applause. Subsequently, Phil’s presentation became one of the first ‘online’ virtual meetings (25 March; West of England Section) due to the pandemic restrictions. This presentation is available to view on the PWI technical hub.
SECTION MEETING – LONDON 9 March 2020. Network Rail Asset Protection and Optimisation (ASPRO) – David Ollerhead and Peter Barron
Sean Tarrant, Chair of the London Section, welcomed a large turnout to the March London Section meeting. The meeting commenced with the Section Annual General Meeting. At the meeting, the following officers were elected for the next 12 months. Chair – Tom Utley, Vice Chair – Mike Brain, Secretary – Sean Tarrant and Treasurer – Alberto Carrera. After the presentation and acceptance of the accounts, the meeting moved on to the main event for the evening.
Sean introduced David Ollerhead, Programme Director, Open for Business and Peter Barron, Head of Asset Protection and Optimisation, Wessex Route, both of Network Rail. David started by giving the background to the formation of Network Rail’s Asset Protection and Optimisation, commonly referred to as ASPRO arising from the Hansford review of the industry in December 2016. The review had highlighted the necessity for Network Rail to unlock rail investment, build confidence and at the same time reduce costs. The whole was summarised as ‘Open for Business’ and the first phase had 3 main drivers:
1. Easier to work with – this involved the creation of a new organisation within Network Rail for ASPRO together with associated new framework and standards.
2. Easier to invest – this involved working with business development teams at Route level, increasing Network Rail’s visibility to potential suppliers and developers
3. Easier to get involved – this involved challenging and updating standards with a view for increasing possible competition for work and delivering better value for money on schemes.
Some examples of successes for Network Rail included; an award winning collaboration with British Steel driving down the costs associated with manufacture, supply and installation of OLE masts, and the increase in rail capacity at the Port of Felixstowe by doubling the previous single track bottleneck allowing 10 more trains a day to service the port.
Peter then spoke about some of the works of his team on the Wessex Route. He shared an excellent short video which is used by Network Rail to brief potential new customers, suppliers, and developers on how they can become involved with Network Rail. Peter stressed the importance of the new Professional Head for ASPRO providing a central voice for guidance, including policy, standards, and consistency between the Routes. Peter’s team works closely with Business Development, Sponsors, the Capital Works team, and Property on the Wessex Route. The mantra is ‘passengers first’ and an enriched customer experience for outside parties to encourage return business.
Some examples from the Wessex Route included the trialling of new lineside solar panels, the developments of stations such as Guildford and Reading Green, the whole development around the new football stadium for Brentford and the prestigious Elizabeth House development at Waterloo.
There followed a lively Q&A session which included topics like; the challenge of writing standards and achieving the balance between being over prescriptive and being too vague, the issue of ambiguous maintenance boundaries between neighbours, and consistency of application of ASPRO by the different routes with the same supplier. Paul Ebbutt then proposed the vote of thanks which was warmly endorsed by all present.
VIRTUAL SECTION MEETINGGLASGOW 18 March 2020. Glasgow Subway: A History, Modernisation and Why You Don’t Want to Look Under Stones - John Campbell, Head of Engineering at Strathclyde Partnership for Transport
As a consequence of the Covid-19 outbreak, the planned Section AGM and Technical Meeting were cancelled. However, through collaboration with WSP, we were able to provide a platform for John to make his presentation by webinar.
John began his presentation by describing the history of the Subway, which is the third oldest in the world. The system was built in the 1890s, modernised in the 1970s and is now undergoing a transformation to embrace new automated rolling stock. 12.7 million journeys are made annually on the 10.5km circular loop.
The current upgrading embraces station refurbishments to enhance access, wayfinding and provide consistent branding. A new control centre is being established. PRM issues are
being addressed, however, one problem area is that of train evacuation via end doors. New trains, built by Stadler, are currently undergoing acceptance testing on a reinvigorated test track at Broomloan Depot. The trains are capable of unattended operation. The trains will run in four-car formations and have increased articulation to reduce end throw when compared with existing three-car sets; they will run with a 90 second headway. Platforms are being fitted with screen doors. John went on to describe the various grades of automation and the attendant control and communications systems.
John discussed the issues of maintaining the aging infrastructure, highlighting issues relating to the varied ground conditions surrounding the twin bore tunnels with predominantly rock north of the river Clyde and alluvial sands to the south. North of the river rock falls have been an issue with the brick arch being punctured at a number of locations requiring remediation to fill voids and improve the integrity of the lining. Water ingress and its subsequent management is the major problem south of the river leading to accelerated rail foot corrosion. In recent years 68,000 litres of resin and 180,000 x 25kg bags of grout have been used in the remediation works.
Rail corrugation has proved to be an issue. The railway’s nonstandard 1219mm track gauge and tunnel profile means that the railway has no ability to grind rails. There are issues of developing heavy grooving of wheel treads which are not yet fully understood.
Other innovative projects currently under development include one to transform ingress water in the Subway into a sustainable heat source. As well as ways of recycling the water into the system, SPT and Glasgow Caledonian University are looking at ways to recycle the air from the tunnels as another viable energy source for stations. Bridge Street, Buchanan
Street, Govan Interchange and Kelvinbridge are all heated from recycled air from the tunnel network using an Air Source Heat Pump (ASHP), and St. George’s Cross Station is heated using recycled water from the tunnel network with a Water Source Heat Pump (WSHP).
VIRTUAL SECTION MEETINGGLASGOW 15 April 2020. Sustainable Infrastructure Renewals - Brian Beck, Network Rail
As a consequence of the Covid-19 outbreak, the planned Technical Meeting was cancelled. However, through collaboration with WSP we were able to provide a platform for Brian to make his presentation by webinar.
Brian described the (Scottish) Government’s aspirations for decarbonisation and how infrastructure renewals can play a part in the process. He discussed two specific sites; the Aberdeen – Inverness redoubling works and the Glasgow Queen Street reconstruction where material recycling and reuse has been developed and demonstrated.
Brian discussed how the process of optimising sustainability through the reuse and recycling of materials started at the development stage and was subject to adherence to basic engineering specifications. Not every site was suitable and requires assessment through scrutiny of track bed investigation and formation assessments. There is an adverse consequence of not achieving engineering compliance. Also, the risk of over run or production shortfall must be considered.
Brian explained the elements to be considered in the assessment not only in terms of carbon reduction but in costs. The process of quarrying, processing, and transportation of material to site and the process of transportation and disposal of ballast spoil all involve fuel and energy incurs a tax penalty.
Brian reviewed the redoubling element of the Aberdeen to Inverness improvement works where 10,000t of ballast spoil was proved to be suitable for reuse at the point of origin. This was calculated to have saved 27t of CO2 in the extraction and processing of the ballast and 168t of CO2 in transportation savings. For the first phase of the works, ballast was brought to site by rail from the nearest LDC (Kingmoor) but for the second phase a local quarry was used to supply granite ballast, resulting in a saving of 500t of CO2. Significantly, these initiatives also saved the project around £200k in costs.
For track renewals sites, the reuse of a proportion of the ballast spoil brings several factors in to play, including savings in resources and train paths. Even reuse of spent ballast is purely for cess and shoulder enhancements. Engineering fill is a legitimate reuse of ballast spoil.
The redevelopment of Glasgow Queen Street Station has been a major flagship project for Scotland’s Railway. 100% of inert demolition materials were recycled while 94% of mixed waste generated on the project was diverted from landfill. This was a good news story for the industry, particularly with local reprocessing.
The disposal of other materials was discussed, including the benefits of reuse of concrete sleepers for roadways and hard standings rather than crushing and landfill. While the reuse of steel scrap in new steelmaking was a positive, the export of scrap to China was seen as having a negative impact.
VIRTUAL SECTION MEETING- WEST OF ENGLAND 22 April 2020. Using Technology to Reduce Risk - Nick Millington, Safety Task Force Leader, Network Rail
This second online presentation of the Western Section had the greatest audience, with a maximum of 120 attendees. The meeting was chaired my Gilles Moullec, Section Chair, who made the general announcements for the Section and introduced the speaker of the day, Nick Millington, Safety Task Force Leader for Network Rail.
Nick started his presentation with a safety moment, briefly discussing the Roade track worker fatality. He continued by presenting a series of statistical data on the potential fatalities on the Network Rail infrastructure and their distribution on the network. He referred also to the tragic event that took place on 3 July 2019 at Margam East Junction, where Gareth Delbridge, 64, and Michael Lewis, 58, were struck by train and fatally injured. The presentation continued with the current priorities of the Safety Task Force to comply with the ORR improvement notices.
One of his priorities is to increase track worker safety - aiming for 0% unassisted lookout working, 100% additional protection and 100% standard 019 compliance, without transferring the risk.
Another key element is to plan safer interventions by using a predict and prevent strategy, in which more unmanned monitoring technologies of the network are used - eddy current, plain line pattern recognition trains and the remote condition monitoring without the need for track access.
The accelerated deployment of the Intelligent Infrastructure project will allow the implementation of these monitoring technologies.
Modern technologies are also implemented to allow the planning of safer access and the implementation of additional protection in line blockage and of the Planning4Delivery technology.
Nick also presented the Network Rail Spring Safety Standard Challenge, focused on receiving feedback on the standard no longer fit for purpose and to receive ideas to update and improve standards, improving safety on the network.
Nick finished his presentation with a summary of the main points of focus for the Safety Task Force - planning, technology, supply chain partnership, assurance and verification, and safe behaviour.
VIRTUAL SECTION MEETING – JOINT LONDON & SOUTH & WEST WALES 28 April 2020. Wear and Derailment Risk at Facing Points - Andy Franklin, Principal Project Engineer, Track & Lineside, Network Rail
Since this was the first attempt for both these Sections not only to have a joint meeting but also an online meeting under the PWI GoToMeeting banner, a rehearsal had taken place on Wednesday 22 April. At the rehearsal, the main participants, with oversight from Kate Hatwell, PWI Operations Director, and Sara Green, PWI Membership Secretary, had ironed out the anticipated snags and pitfalls and agreed that the meeting would be chaired by Sean Tarrant, Chairman of the London Section.
As a result, the meeting kicked off on schedule at 16.30hrs on Tuesday 28 April, when, after a few introductory remarks by Sean, Andy commenced to present his paper on ‘Wear and Derailment Risk at Facing Points’. Andy preceded his paper by explaining that it was aimed at frontline track maintainers to give them a better understanding and background to Network Standard NR/L2/TRK/053, which was introduced in 2017 and had been updated recently. The emphasis was on flange climb derailments and their prevention. Whilst explaining the 1908 established famous Nadal derailment formula, Andy adequately illustrated the various factors that influenced the constituent components in the formula.
The various influencers were:
• Similar flexure turnouts on curves
• Track geometry on the approach to switches
• Lack of lubrication
• Track faults that could cause wheel unloading at or on the approach to switches
And of course, there are the Rolling Stock contributory factors:
• Broken springs
• Missing shims
• Twisted bogie frames
• Unequal vehicle loading
• Long rigid wheel-based vehicles
In terms of switch maintenance, a table of the five principal combinations of wear that increase the risk of flange climbing was illustrated (also contained in the 053 standard).
Several recent derailments were instanced and one of the lessons to be learned was that any maintenance work on facing points must
be carefully planned in advance to ensure adequate time is available to complete the task and that a careful check on the integrity of the finished work is carried out before returning to traffic.
At the end of Andy’s presentation there followed the usual Q&A session, some of which had been registered via the GoToMeeting slot for that purpose, which Sean read out and a few others via the microphone facility from as far away as Newcastle.
In the end, the approximate 120+ participants in the online meeting were treated to an excellent and informative presentation by Andy. A short vote of thanks was made by Jim Donald and the appreciative clapping echoed around the microphones from all airts and pairts.
VIRTUAL SECTION MEETINGGLASGOW 20 May 2020. The Bo’ness and Kinneil Railway: 40 Years in the Making - Jim Watson and Andrew Anderson
To replace the planned technical visit to the Bo’ness & Kinneil Railway, a webinar presentation was held detailing the development construction and maintenance of the 8.5km long standard gauge heritage railway by the Scottish Railway Preservation Society. Presented by Jim Watson, the railway’s Civil Engineer from the 1980s to 2005 and Andrew Anderson the current Civil Engineer.
Jim explained the background to the formation of the SRPS, its development and need to find a permanent home for its collection. Due to the difficulties in raising large capital sums to purchase an in-situ branch line, the Society took the bold step of constructing a railway on a brownfield site at Bo’ness, West Lothian. The development had support from central and local government bodies and was seen as a catalyst for the regeneration of the town. Work commenced on-site in May 1979 with progressive extension of the operating railway and of storage and workshop facilities based on the availability of funding and resources.
Track maintenance: the Bo’ness & Kinneil Railway Operator training: the Bo’ness & Kinneil RailwayOperations over the new build 11/2-mile section of line to Kinneil commenced in 1985. Here the new railway joined the former Colliery branch line which was part purchased in situ. The first three miles were refurbished, and a new station established at Birkhill in 1989. 11/2 miles of track was re-laid over the remainder of the branch, joining the main line in 1990 with a new main line connection installed by ScotRail. This section of line was not brought into public use until 2010.
The majority of the trackwork was undertaken by volunteers. Track materials were predominantly serviceable (or rather scrap) materials from both mainline and industry, requiring significant refurbishment. Some new material was incorporated, where appropriate, including a section of CWR on steel sleepers. The CWR was created by Thermit welding 60’ 98lb rails.
As the railway has been built on a brownfield site, the infrastructure has either had to be recovered and rebuilt, or newly built in traditional style. Several of the buildings and structures on the
railway have been recovered from operational railway locations including the grade A listed Haymarket train shed.
Andrew described the maintenance challenges facing the current operation and discussed the plans for a renewals programme. The maintenance of off-track estates and structures was discussed, as were the issues of soft skills specific to working with volunteers with mixed skillsets and backgrounds.
The current project to enable two train running was described by Andrew which revolves around the creation of a second platform and signalling system at Birkhill.
The railway is utilised by many industry partners for training and development and is home to the Museum of Scottish Railways which is formally registered and regarded as a nationally significant collection.
From all of the PWI Executive and Board, Alison will be deeply missed and our thoughts are with her family and friends at this time. Please see page 3 for more information.
Sheffield and Doncaster and later West Yorkshire Sections
1944 – 2020.
Denys always had an interest in railways, and after leaving school in 1958, started work as a Signal Engineering student, out on the track. In 1962 he moved down to the Signal Engineering School in London. After finishing his training, he was employed in the Drawing Office at Sheaf House, Sheffield, where he stayed until moving to Doncaster in 1975 as S&T Engineer, first at Marshgate, then Gresley House.
Denys took early retirement when British Rail was privatised, but after a few months was asked to undertake an Automatic Warning System project on the Settle – Carlisle Railway. This was followed by a few days work each week at Hudson House in York, until retirement in 2007.
Denys was a valued member of the Sheffield and Doncaster and later West Yorkshire Sections of the PWI, for a total of 46 years. A PWI Fellow, and lovely man who was always willing to help, he will be much missed. A few years ago, he was kind enough to lend me a then new book on the Woodhead Route. Denys was also a member of the Institute of Railway Signal Engineers (IRSE), serving as Chairman of the York Section on two occasions. In addition, he attended meetings of the Retired Railway Officers’ Society (RROS) in London once a month, where he enjoyed meeting former colleagues.
Denys, Kath and their two daughters enjoyed many holidays travelling by train. Denys also enjoyed walking, especially in Derbyshire, and Bird Watching. I am confident that other members will join me in extending our condolences and best wishes to Kath and their daughters. I would also like to record my thanks to Kath for the above information and wish her well with planned railway excursions.
John Keates died on 18 February 2020 after a period of deteriorating health. John was an enthusiastic PWI member during his railway career, joining the institution as a track machine man in the early 1970s.
He particularly enjoyed the various overseas trips organised at that time to places as distant as Berlin, Venice and Poland. Always adventurous, once on a diving expedition from a cruise liner he went missing and was picked up by a passing yacht before transfer back to the liner. Fortunately, nothing quite so drastic happened on the PWI visits!
John was born in Lancaster and spent all his life in the Carnforth area. Joining British Railways from school as a signalman, he worked boxes at Brock, Bay Horse and Oubeck. In 1966 he married Ann who he had known since his teens. They were together for 54 years and had three sons. A short period working away from the railways was followed by a return to work on the newly introduced on track machines. John always had a love of things mechanical, especially motorbikes, so was ideally suited to working with initially a Plasser lining machine and later the Plasser 07 tamper when they were introduced in the late 1970s.
Former technical staff will however remember him from the days of the old Matisa track recording trolly that he operated all across Preston Area. Following privatisation John was promoted to TQS (Track Quality Supervisor) back with the machines he was so familiar with. He carried out these duties and remained a PWI Member until retirement. Following retirement John kept in contact with his old railway friends and colleagues via the Carnforth platelayer’s association. John touched the lives of all who met him and he will be fondly remembered by all who knew him.
John Parker. LB&C Section Chairman.
It is with great sadness that we announce the loss of our dear friend and colleague, Alison Stansfield.
Specifically designed for use in a railway environment.
Specifically designed for use in a railway environment.
Specifically designed for use in a railway environment. Will remove/fit Chairscrews and Fishplate Nuts in under seven seconds and with our Safety Quick Release Auger Attachment can be easily converted into a Wooden Sleeper Drilling Machine.
Switch tip alignment
Track Slewing Switches
Will remove/fit Chairscrews and Fishplate Nuts in under seven seconds and with our Safety Quick Release Auger Attachment can be easily
Will remove/fit Chairscrews and Fishplate Nuts in under seven seconds and with our Safety Quick Release Auger Attachment can be easily converted into a Wooden Sleeper Drilling Machine.
in under seven seconds and with our Safety Quick Release Auger Attachment can be easily converted into a Wooden Sleeper Drilling Machine.
Crossing Nose Alignment
Hand held stoneblowing has been used for over twenty years. It provides a quick and efficient way to correct settlement by filling the voids caused by train movements, track instability, climatic conditions and wet spots
Hand held stoneblowing has been used for over twenty years.
It provides a quick and efficient way to correct settlement by filling the voids caused by train movements, track instability, climatic conditions and wet spots
Designed
Designed for Green Zone working to remove seized ‘P’ and ‘E’ type Clips from their housing.
Useful in tunnels, under bridges, level crossings, coastal areas where it is difficult to remove Rusty Clips
Useful
SUPPORT TO RAIL INFRASTRUCTURE RENEWAL AND MAINTENANCE FOR THE 2020s AND BEYOND
4 NOVEMBER 2020 SWINDON STEAM MUSEUM
European railway networks are booming and the demand for rail travel continues to increase. As the train services to meet this demand are added to the network, access to carry out maintenance and renewal work is at a premium. The pressure to do more work in shorter possessions drives a requirement for more productive, mechanised, work delivery methods. Effective, safe, and highly productive plant is an essential component of this. Plant and the methods and strategies to deploy it that can together deliver high quality, durable infrastructure at lower unit costs is crucial to meeting industry challenges: along the way it must play its part in reducing rail sector carbon emissions and other environmental impacts, and in improving the performance and reputation of the railway. This seminar will provide delegates and speakers with an opportunity to understand and debate the requirements for plant to meet these challenges, and the solutions that are being deployed and developed to deliver them.
04/11/2020 09:00-16:30 £70 MEMBER / £120 NON-MEMBER / £10 STUDENT
Sponsored by
For infrastructure engineers, delivering a railway that is safe for the people who use it, work on it and interact with it will always be a paramount responsibility. Welcoming guest speakers from RAIB, CIRAS, Plasser and Network Rail’s Safety Task Force, this seminar will provide delegates and speakers with an excellent opportunity to understand and discuss important aspects of railway safety, helping them to discharge this responsibility effectively. The seminar will include topics such as: worker safety and the current actions and programmes in place to ensure people go home safe everyday, particular safety considerations within the railway environment eg electrification systems, working with plant, the importance of reporting and building safety into everyone’s behaviour, reviewing significant historical railway accidents to understand root causes and reinforce the lessons learnt.
1/12/2020 12:00 - 17:00 £40 MEMBER / £70 NON-MEMBER
Sponsored by
YOU CAN ALSO WATCH THIS SEMINAR ONLINE! STAY TUNED TO THE WEBSITE FOR DETAILS.
The Scottish Government has recognised the benefits of a rolling programme of electrification and Network Rail Scotland is developing those plans. Electrifying an existing railway requires the electrification system to be integrated into the broader railway system: the configuration of the traction system and its constituent parts has implications for the operation, maintenance, and performance of the railway. The challenge facing engineers of all disciplines is to simplify the systems integration task so that it supports a rolling programme of electrification rather than impedes it. This seminar will help engineers across the railway disciplines understand the implications of converting a route to electric traction, and explore ways in which system specification, design, and implementation can support a rolling plan.
27/04/2021 09:00 - 16:30 £70 MEMBER / £120 NON-MEMBER / £10 STUDENT