TOWARDS GREEN STEEL
The world’s largest & most eco-friendly Acid Regeneration Plant is up and running in China
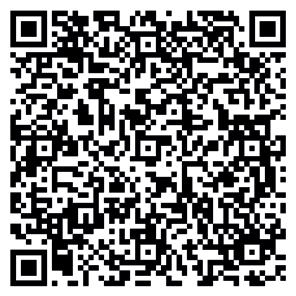
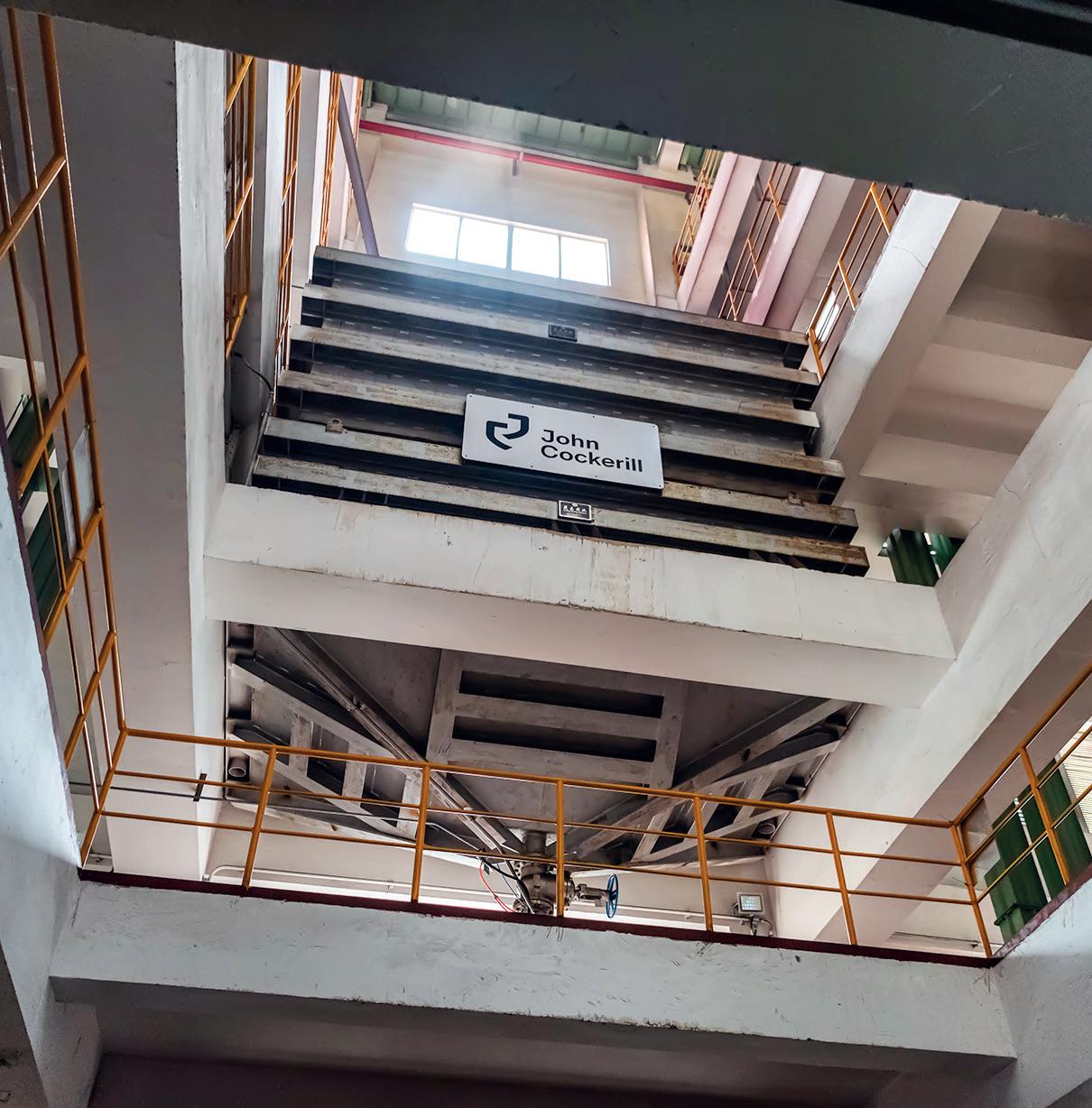
The world’s largest & most eco-friendly Acid Regeneration Plant is up and running in China
Editor Matthew Moggridge Tel: +44 (0) 1737 855151
matthewmoggridge@quartzltd.com
Editorial assistant Catherine Hill Tel:+44 (0) 1737855021
Consultant Editor Dr. Tim Smith PhD, CEng, MIM
Production Editor
Annie Baker
Advertisement Production Martin Lawrence
SALES
International Sales Manager Paul Rossage paulrossage@quartzltd.com Tel: +44 (0) 1737 855116
Sales Director Ken Clark kenclark@quartzltd.com Tel: +44 (0) 1737 855117
Managing Director Tony Crinion tonycrinion@quartzltd.com Tel: +44 (0) 1737 855164
Chief Executive Officer Steve Diprose
SUBSCRIPTION Jack Homewood Tel +44 (0) 1737 855028 Fax +44 (0) 1737 855034
Email subscriptions@quartzltd.com
2 Leader By Matthew Moggridge.The latest global steel news.
New products and contracts.
Dark clouds on the horizon.
18 Latin America update Pecém, Vale, and ArcelorMittal.
21 India update Demand rebounds. 24 Iron ore Gabon intensifies iron ore ambitions.
After the rain, comes the drought.
Building a better America.
In between strength and beauty.
SIP technology and BF operation.
Increasing refractory lifetime 52
Positioned for sustainability
The early days of ironmaking at Scunthorpe Part 2. 1919-1939.
In recent weeks I’ve had the incredible good fortune of being out of the country – twice! Once in Stockholm in Sweden, and then in Buttrio in Northern Italy. On both occasions the relief of not being in the UK – where the current Conservative government under Liz Truss is in freefall and making a mockery of British politics –was palpable. I was in the Swedish capital to meet and interview the great Mark Bula who is the chief commercial officer of H2 Green Steel. Mark and I first met in October 2017 in Osceola, Arkansas, USA. He was working at Big River Steel with Dave Stickler and then, like now, Mark was at the cutting edge of steel manufacturing, working at a facility rammed with hightech manufacturing and digital capability. Today, he commands a leading role in what is arguably THE most important steel project in the world. Mark is the chief commercial officer at H2 Green Steel; he’s relocated from the USA to live the life of an ‘empty nester’ in Stockholm with his wife. While he has travelled further north –to Boden where the hydrogen steelmaking facility is to be located – he’s yet to see the Northern Lights, or rather he has seen them, but, as he put it, ‘not enough to go
wow!’ Well, I’m sure his time will come.
While there are many different decarbonization projects under way around the world, the two most prominent ventures at present are HYBRIT (SSAB, LKAB and Vattenfall) and H2 Green Steel. The former has proved it possible to make green steel using hydrogen and, says Mark, ‘I think they’re making 100kt/ yr’. H2 Green Steel is planning to make an initial 2.5Mt/yr when the Boden facility starts producing green steel in 2025. The key difference between the two projects? ‘We’re skipping the pilot plant,’ says Mark.
Americans are blessed with a good turn of phrase and Mark’s no exception. He refers to Sweden – where both HYBRIT and H2 Green Steel are based – as the ‘Goldilocks location’ for such projects, thanks to an abundance of important natural resources.
Mark and I chatted for around two hours and when I later transcribed the notes back in the UK they ran to 12,000 words. I could have written a dissertation on H2 Green Steel! In the end, however, I settled for around 4,000 words running over six pages in this issue of Steel Times International Go to page 26.
One worker was killed, and five others injured when hot liquid from a furnace spilled on them at a factory manufacturing steel products in the Wada area of Maharashtra's Palghar district in India. The local police registered an offence under relevant sections of the Indian Penal Code against the company for the incident. The accident occurred at Surya Company around 10pm on 22 August, when hot melted steel from a furnace spilled on the workers.
Source: NDTV, 10 September 2022
Tata Power has said that its subsidiary, Tata Power Renewable Energy (TPREL), has collaborated with Mumbai-based stainless steel manufacturer, Viraj Profile, to set up a 100-MW captive solar plant to provide power to its Tarapur plant. According to the official press release, the plant will be located at Tata Power’s Nasik site and will be commissioned by July 2023. It added that the plant would generate about 200 million units of energy and offset 170 million kg of carbon dioxide annually.
Source: ET Energy World, 8 September 2022.
ArcelorMittal, Europe's largest steel maker, has further cut its production in Europe after its Polish subsidiary said that it would idle one of its two blast furnaces. The company will temporarily suspend production at its number 3 furnace at its Dabrowa Gornicza plant in southern Poland. The furnace has a production capacity of 2.2Mt of crude steel. The decision to reduce production is the latest by the Luxembourg-based steel maker as it faces deteriorating market conditions marked by increasing prices for carbon, gas and electricity.
Source: Market Watch, 8 September 2022
POSCO Holdings Inc., the holding company of South Korea’s largest steelmaker, has restarted its blast furnaces at its main plant in Pohang, North Gyeongsang Province, which were idled following damage by Typhoon Hinnamnor. Furnace 3 resumed operations first, while the other two – furnaces 2 and 4 – were restarted afterwards, according to company officials. POSCO’s furnaces at its Pohang plant manufacture heavy plates, hot-rolled steel, cold-rolled steel, iron rods, electrical steel and stainless steel.
Source: The Korea Economic Daily, 12 September 2022
Multinational steelmaker ArcelorMittal and quarried materials group SigmaRoc have entered into a strategic joint venture agreement to create a new company. The company will produce lime, an essential purifying additive used in steel production as well as numerous other industrial applications. The partners will leverage their manufacturing experience to produce 900kt/yr of the material. The operations will be located close to Dunkirk’s harbour and the ArcelorMittal steelworks – which will be the main consumer of the lime produced – allowing for shorter transportation of the finished product.
Source: AggNet, 12 September
British Steel has hiked the prices for some of its structural steel products by a further £150 a tonne, putting more stress on contractors. The Chineseowned steel producer had already increased the price of its steel by £100 per tonne on 15 August. This has followed from a period of relative price stability through the summer following March’s record £250 a tonne rise, which pushed sections towards £1,000 a tonne.
Source: Construction News, 12 September 2022
ArcelorMittal SA has announced it has paid the first tranche of its outstanding penalty set by the Competition Commission six years ago, saying it will settle the full amount by 2028. The steelmaker, which admitted to having been involved in steel and scrap metal cartels, was fined R1.5bn in 2016 for engaging in collusion by fixing prices and discounts, allocating customers and sharing commercially sensitive information.
Source: Business Day, 12 September 2022
Klöckner & Co, the German steel and metal distributor, has launched the new Nexigen® brand bringing together its entire portfolio of sustainable products and services. Under the Nexigen® brand, the company will now provide carbon-reduced solutions in the three categories of materials, processing and logistics. The first quantity of green steel under the Nexigen® brand has been secured by Mercedes-Benz AG.
Source: EQS News, 13 September 2022
Japan's biggest steelmaker Nippon Steel Corp has said that it will start selling steel products next year that are certified as reducing CO2 emissions from the steel manufacturing process. The steelmaker plans to adopt a so-called mass balance method in which the total amount of CO2 emissions that the company has actually reduced by improving manufacturing processes is determined and allocated to any given steel product.
Source: Reuters, 14 September 2022
Prosecutors in the UK say executives of a sincecollapsed steel company falsified documents and created fake trades to defraud five trade finance banks out of $150 million in order to keep the struggling trader afloat. A prosecutor representing the UK’s Serious Fraud Office (SFO) stated on the first day of a criminal trial at Southwark Crown Court in London on 11 September that five executives of Balli Steel Plc told ‘increasingly egregious’ lies throughout 2012 and early 2013 as part of a ‘widespread and systemic fraud’ against trade finance lenders in Europe and Asia.
Source: Global Trade Review, 14 September 2022
Hyundai Steel Co. has announced that it succeeded in the pilot manufacturing of advanced auto steel sheets using an electric furnace. According to the company, thanks to the electric arc furnace, carbon emissions were reduced by more than 30% when compared to a conventional method that used iron ore and coal in furnaces. The steelmaking arm of Hyundai Motor Group is headquartered in Incheon and Seoul and manufactures a range of products – including H-beams, rails, and stainless cold-rolled sheets.
Source: The Korea Economic Daily, 14 September 2022
A steel worker passed away while working at a Tata Steel UK plant, prompting police to launch an investigation. Gwent Police officers were called to a medical emergency at Tata Steel in Newport, Wales on 14 September. The man, 50, from Cwmbran, Torfaen, was pronounced dead at the scene. Tata Steel said it was ‘incredibly sad’ that one of its employees had died. A spokesman added: "The health and safety of our employees, contractor partners and visitors has always been, and will remain, our most important priority. Our thoughts are with our colleague's family, friends and workmates at this distressing time."
Source: BBC, 14 September 2022
The auditor of many of the companies in Sanjeev Gupta’s network of metals companies, which includes UK steelmaker Liberty Steel, has resigned from at least five of them, amid an investigation of its work by UK regulators. London-based King & King has resigned as auditor of the companies in Gupta’s GFG Alliance, a sprawling group of firms under his control. The accountant is under investigation by the accounting regulator, the Financial Reporting Council, for its audits of four GFG companies.
Source: The Guardian, 15 September 2022
NLMK, Russia’s largest steelmaker, has reached an agreement with NLMK Belgium Holdings (NBH), the Belgium-based joint venture with SOGEPA (a Belgian investment fund) to integrate NLMK Dansteel (Dansteel) into NBH. According to NLMK, the consolidation of Dansteel within the NBH perimeter will further optimize European assets' management structure and provide additional strategic flexibility and synergies. The transaction has been submitted for EU merger control approval.
Source: Market Screener, 15 September 2022
Researchers at Imperial College London have developed a new materials design strategy that produces copper-based metal oxides that perform efficiently under high temperatures. Metal oxides are key to greener manufacturing, carbon capture, energy storage and gas purification. These compounds are commonly used in carbon capture, utilization and storage (CCUS), for purifying and recycling inert gases in solar panel manufacturing, thermochemical energy storage, and producing hydrogen for energy.
Source: Mining.com, 16 September 2022
Liberty Galati, the Romanian steelworks, has launched its first GREENSTEEL learning module for Romanian students, in partnership with Dunarea de Jos University of Galati. Starting in October 2022, the
Scania, the Swedish vehicle manufacturer, has announced vast measures in a bid to see its supply chain decarbonized by 2030, with hydrogen looking set to play a key role. As part of its strategy to clean up its materials, Scania has set the target of using 100% green steel, which it has said could be met by replacing coal with green hydrogen in the production of flat steel.
Source: H2 View, 16 September 2022
US Steel Corporation, one of the largest steel producers in the United States, has shut down BF8 at the Gary Works steel plant in Indiana. The blast furnace, with a capacity of 1.5Mt of steel per year, has been idle since 7 September 2022. The date of the units’ restart is not yet known. This is the first closure of rolling plant in the United States in recent times. Local producers point to the constant oversupply of products on the market and the lack of reduction in steel production.
Source: GMK Center, 18 September 2022
Seah Gulf Special Steel has said it has sealed two agreements for its new steel pipe factory in Dammam being built at an investment
University will integrate the GREENSTEEL module, which allows students to learn about climate change and cutting-edge steelmaking technologies, within its academic programme. The initiative is part of the ‘LIBERTY GREENSTEEL Academy project’ that also targets other elite universities, aiming at strengthening the company’s collaboration with the educational and scientific research communities.
Source: The Diplomat, 16 September 2022 worth more than $266.3 million – an EPC contract with Saudi-based Sendan International Company for its construction and a land lease agreement with King Salman Energy City (Spark). Seah Gulf Special Steel is a joint venture between Saudi industrial investments company Dussur and Korean group SeAH Changwon Integrated Special Steel Corporation.
Source: Zawya, 17 September 2022
Asbestos has been found in Tata Steel mills on 35 different times over the past five years, confirms a report by Dutch newspaper, Nordhollands Dagblad. In total, Tata made 1,825 records of factory workers potentially exposed to asbestos at those times. “Asbestos is something that requires our constant attention,” the company stated.
Source: Taylor Daily Press, 17 September 2022
Circular Maritime Technologies International (CMT) has introduced a circular process for the ship breaking industry, aiming to provide a solution to the problem of dangerous ship scrapping. Following a business model, CMT will set up yards with international partners and attract business from shipowners by matching the price paid by South Asian competitors. The CMT yard will run on its own power and produce clean steel, related to green steel production. The yard will reduce the size of the vessel step by step through various automated tools, up to the point where each part of the ship’s steel structure is reduced to many small pieces.
Source: Safety4Sea, 19 September 2022
Dunaferr steel plant, one of Hungary’s largest industrial manufacturing companies, has been forced to shut production, the company said on 18 September. The company said that the immediate reason for the shutdown is the unexpected refusal of Austria-based Donau Brennstoffkontor GmbH, their partner for decades, to supply the essential raw coke. “The forced shutdown now means that there is currently no possibility for pig iron and steel production at Dunaferr,” the company stated.
Source: Euractiv, 19 September 2022
H2 Green Steel and GreenIron H2 have agreed to collaborate to achieve further emission reduction and increased circularity in H2 Green Steel's plant in Boden in Northern Sweden. GreenIron H2 is a Swedish start-up focused on cost efficient CO2-free reduction of metal oxides to pure metals. Its hydrogenbased CO2 reduction process will be used to recycle iron residuals and waste from H2 Green Steel's operations.
Source: Cision, 23 September 2022
Tata group has announced the amalgamation of all metal companies within Tata group into Tata Steel. The company board approved merging its seven metal companies with its parent metal company Tata Steel Limited. The seven metal companies of Tata group that will be merged with Tata Steel are Tata Steel Long Products Limited, The Tinplate Company of India Limited, Tata Metaliks Limited, TRF Limited, Indian Steel & Wire Products Limited, Tata Steel Mining Limited and S & T Mining Company Limited.
Source: Mint, 23 September 2022
The Ethiopian Ministry of Finance has announced that a decision has been made to sell scrap metal and outof-service vehicles to steel manufacturing industries without resorting to a bidding process. The scrap metal and out-of-service vehicles will be collected from federal offices, public development organizations, and state-owned universities, then allocated to companies according to the manufacturing capacity of the factory of each company. The selling price will be set according to market conditions and the type of items.
Redcar's former blast furnace, part of the Teesside Steelworks in northern England, has been demolished. The 365ft structure dominated the skyline for decades, but the decision was made to clear the site for regeneration. The site has been dormant since 2015 when its owner, Sahaviriya Steel Industries, went into liquidation with the loss of more than 2,000 jobs. It is hoped the 4,500-acre site will become home to a range of new industries .
Source: BBC, 20 September 2022
A 100-year-old woman from the UK has been given an honorary degree for her input during World War II to keep an entire steel industry from collapsing. Kathleen Roberts and her female coworkers kept Sheffield’s steel industry afloat with months of ‘gruelling work’ during the outbreak of World War II. Kathleen worked 72-hour weeks with the other women while being paid less than men. For their exemplary determination and hard work,
the group came to be known as 'Women of Steel'. Today, Kathleen is the only surviving member of the group.
Source: Times Now, 25 September 2022
Source: 2Merkato.com, 23 September 2022
Arabian Pipes Company has been awarded a contract worth around SAR 155 million to supply the Saudi Arabian Oil Company (Aramco) with steel pipes. The financial impact of the 15-month contract will reflect on Arabian Pipes’ financials in the second and third quarters of 2023, according to a stock exchange statement. Currently, Arabian Pipes’ existing projects total more than SAR 800 million. Source: Zawya, 25 September 2022
50 local farmland owners near Yekepa, Nimba County, Liberia received $138,188 in resettlement compensations from ArcelorMittal Liberia (AML), due to crops being affected by mining. The ‘Resettlement Programme’ which has been an ongoing focus for the company, focuses on evaluating assets and compensating affected farmers in areas where ArcelorMittal Liberia operates. The AML Community Relations department confirmed that including the recent transaction, the company has now paid more than $18 million in resettlement compensation to farmers and it is expected that the amount will further increase.
Source: GNN Liberia, 25 September 2022
Czech Republic-based steelmaker Liberty Ostrava, a subsidiary of UK-based Liberty Steel, has announced that it will invest $3.45 million to install a new exhaust pipeline at its sinter plant to reduce dust emissions by around 46%. The project on the sinter conveyor paths, which will be completed later this year, is a further sign of progress in Liberty Ostrava’s green steel transformation programme, the company said.
Source: Steel Orbis, 26 September 2022
Rachel Reeves, the shadow chancellor of the UK Labour party, announced that the party would set up a ‘National Wealth Fund’ for the state to invest directly in projects like steel to create a return for taxpayers and rebuild industrial areas. This includes £3 billion of investment for six clean steel plants which would benefit Sheffield, Rotherham and Scunthorpe, to help strengthen the industry.
Source: The Yorkshire Post, 26 September 2022
Tata Steel Europe, a subsidiary of Indian steel producer Tata Steel, has announced that it has signed a contract
with the Netherlands-based transportation service company Hardt Hyperloop for the delivery of Zeremis
Carbon Lite, steel with an allocated carbon reduction of up to 100%. In July this year, Tata Steel delivered the first batch of the new steel product tailor-made for the Hardt Hyperloop.
Source: Steel Orbis, 26 September 2022
ArcelorMittal Poland, a subsidiary of global steel producer ArcelorMittal, has announced that it has received ResponsibleSteel certification, a sustainability certification, as the business fulfilled the criteria required to earn certification against the ResponsibleSteel Standard. The company is the first to be certified in eastern Europe by ResponsibleSteel, the steel industry’s first global standard and certification initiative for sustainability.
Source: Steel Orbis, 26 September 2022
According to the participants of the First British Steel Forum, British steelmakers are pushing for stronger sanctions against imports of Russian origin steel that may have been processed in third countries. The UK imposed sanctions on the import of steel products and semifinished products from the Russian Federation due to the invasion of Ukraine. There is a total ban on steel, while semifinished products are subject to a 35% duty.
Source: GMK Center, 26 September 2022
As part of reducing carbon footprint throughout the equipment supply chain, Swedish sustainable solutions provider Alfa Laval, and Nordic and US-based steel
company SSAB have signed an agreement to collaborate on the development and commercialization of the world’s first plate heat exchanger to be made using fossil-free steel. The goal is to have the first unit made with hydrogen-reduced steel ready for 2023. SSAB is part of the HYBRIT initiative alongside mining company LKAB and power provider Vattenfall.
Source: Offshore Energy, 27 September 2022
Outokumpu, the largest producer of stainless steel in Europe, has launched a new sustainable stainless steel line, Circle Green, with a carbon dioxide footprint 92% lower than the global industry average and 64% lower than Outokumpu’s regular production of stainless steel, the company has stated. The new product line achieves significant carbon reduction by relying on biobased materials — biogas, biodiesel and bio-coke — to produce stainless steel and by purchasing electricity from low-carbon sources.
Source: Fastmarkets, 27 September 2022
Russian vertically-integrated steel producer Severstal will supply large-diameter pipe (LDP) to leading Russian gas producer and supplier Gazprom, the company has said. The 63kt consignment will contain pipes in diameters of 1,0201,420mm, which have have an external anti-corrosion coating and wall thickness of 12-37mm. The product will be manufactured at the company's LDP dedicated Izhora Pipe Plant near St. Petersburg from K52-K65 strength grade steel.
Source: Kallanish Commodities, 28 September 2022
A steel shipment has arrived on Teesside, UK, – marking the first activity of a freeport, anywhere in the UK. The area's freeport is expected to create 18,000 jobs and drive billions into the local economy in five years. Around 100 tonnes of steel were delivered to the South Bank area of Teesworks, designated as part of the freeport. Tees Valley Mayor Ben Houchen said: “Whether it’s pioneering the industries of tomorrow, or innovative initiatives, Teesside is leading the way –and this is yet another UK first as we become the first area to accept goods through our freeport."
Source: Teesside Live, 28 September 2022
ArcelorMittal has submitted an expression of interest (EOI) to acquire Srei Equipment Finance and Srei Infra Finance, which are both undergoing a resolution process under the Insolvency and Bankruptcy Code (IBC). Srei lenders have invited a fresh round of bids for these companies after a dispute with earlier bidders over earnest money deposits (EMDs). The creditors are yet to decide whether they can allow the entry of a new bidder, say various sources.
Source: BQ Prime, 29 September 2022
Immersive digital experience specialist Animmersion has created ‘Steelmaking of the Future’ for the Materials Processing Institute. The app enables users to scan QR codes placed around a purpose-built scale model of a steel plant and enables the Institute to showcase its advances in research and innovation in the steel industry on the road to Net Zero. Chris McDonald, CEO of the Materials Processing Institute, said: “This hi-tech model allows us to explain in an engaging and informative way just what steelmaking will look like in 2050, the year the government has pledged to meet its net zero targets’’.
Source: The Yorkshire Post, 30 September 2022
US-based Latrobe Specialty Steel has seen its workers at odds with their union after a hastily ratified contract. After the United Steelworkers rejected a new contract, employees began to collect signatures for a decertification petition to vote out the union. When union officials heard about the petition, they signed the contract on 28 July. Then, a second vote on the contract was held on 1 August. Workers were unaware the contract had been signed, but the vote was irrelevant to the contract negotiations. The situation ‘is another example of how union bosses put their own power and interests ahead of those they claim to ‘represent,'’ National Right to Work Foundation vice president Patrick Semmens said.
Source: Broad + Liberty, 28 September 2022
India has applied to the World Trade Organization (WTO) for permission to impose additional import tariffs of 15% on 22 British goods. According to a report, this step was taken by the Indian government in response to restrictions on shipping steel products to the UK. The government told the WTO that the safeguard measures taken by the UK on steel products led to a reduction in Indian exports of 2.19Mt.
Source: GMK Center, 29 September 2022
The Global Innovation Lab for Climate Finance, a publicprivate partnership to scale up climate finance, has launched seven innovative financial instruments for climate-related projects in emerging economies. Combined, the new deals seek over $1 billion from commercial, concessional, and philanthropic investors for climate adaptation, food systems, zero-carbon buildings, sustainable energy, and green steel.
Source: Eco Business, 3 October 2022
Tata Steel Mining Limited (TSML) has received the prestigious Responsible Chromium recognition, awarded by the International Chromium Development Association (ICDA) based in Paris. TSML is the first Indian mining company to receive this international recognition. The Responsible Chromium recognition was awarded to the company after a rigorous sustainability assessment, combined with a verified rating from the independent sustainability rating agency Ecovadis.
Source: The Pioneer, 3 October 2022
BHP Group, the Australian multinational mining company, has lifted its long-term demand forecast for steel based on what it describeds as a global shift towards the decarbonization of power generation that will increase the need for steel. The company forecasts surging demand for wind and solar farm equipment to boost steel demand by 2% in 2030 and by 4% in 2050. It expects global steel consumption to increase by 42Mt and 76Mt in 2030 and 2050, respectively, with a sizeable chunk due to demand for solar and wind power equipment.
Source: Reuters, 3 October 2022
Italy-based plantmaker Danieli has announced that it will supply a new rolling mill and reheating furnace to Brazilian steelmaker ArcelorMittal Brazil for the production of profiles including flats, angles, rounds, and squares. The new rolling mill and reheating furnace will be installed at the company's Barra Mansa Works to produce 400Mt/yr of quality bars and medium sections, increasing the production capacity of the plant. The rolling mill and reheating furnace are expected to start operation by mid-2024. This will be the 48th Danieli rolling mill in Latin America.
Source: Steel Orbis, 3 October 2022
ArcelorMittal has announced that it has invested a further $17.5 million in Form Energy Inc. (Form) via its XCarb® Innovation fund. The investment, which is part of Form’s oversubscribed $450 million Series E financing
round, is the second investment ArcelorMittal has made in the company, following its initial investment of $25 million announced in July 2021. Form Energy was founded in 2017 and is developing, manufacturing, and commercialising a new class of cost-effective, multiday energy storage systems that aim to enable a reliable and fully renewable electric grid year-round.
Source: ArcelorMittal, 4 October 2022
Steel Dynamics Inc, the US-based steelmaker, has announced the completion of its acquisition of Mexican recycler ROCA ACERO (ROCA), as part of its North American raw material procurement strategy. The transaction was funded with available cash. ROCA, headquartered in Monterrey, Mexico, operates a ferrous and non-ferrous scrap metals recycling business comprised of five
scrap processing facilities strategically positioned near high-volume industrial scrap sources located throughout Central and Northern Mexico.
Source: Cision, 4 October 2022
The Indian government has set up two advisory committees to iron out the challenges in the steel industry to achieve the target of 300Mt of production capacity by 2030. Members of the steel industry, associations, academia, and senior retired government officials comprise the two separate committees formed for integrated steel plants (ISPs) and the secondary steel sector, according to a steel ministry document. Source: Moneycontrol, 5 October 2022
The official inauguration of the world’s largest acid regeneration installation has taken place at the Chinese BAOWU Steel Group’s Shang hai-based subsidiary, Baoshan Iron and Steel, supplied by mechanical engineering group, John Cockerill Industry.
The world`s largest capacity twin acid regener ation plant (ARP) purifies 2 x 20 litres per hour of spent hydrochloric acid (HCl) that is led back into the client’s manufacturing process. According to the latest monitoring data recorded by John Cockerill, it will reduce the plants carbon foot print by 4.8kt per year, and its dust emissions by 25 tons, all while either reducing or eliminating other waste streams, including wastewater and solid hazardous waste.
Located in the client’s flat steel complex in Shanghai, the two ARPs are based on John Cock erill’s fluidized bed (FB) technology, for highest throughput and plant availability, which the company claims provides operator friendliness, as well as a small footprint and easy oxide handling.
According to the company press release, John Cockerill’s acid regeneration plants allow the re cycling of close to 100% of the generated spent pickling liquor. Additionally, the tank farm guar antees the management of consumable process chemicals and maximizes operating efficiency, but also minimizes the environmental impact.
“There are many ways towards circular econo my in the steel sector, but the fundamental solu tion lies in technology.” said Mr. Gu, Baoshan Iron and Steel’s project manager, adding: “This new installation is yet another element to help
our Group towards circular economy and tackle climate change. One of the strengths of the acid regeneration process provided by John Cockerill is the environmentally friendly design of the twin plant. Thus, the two highly efficient ARPs allow the recycling of close to 100% of the used hydro chloric acid for reuse in our hot-rolled steel strip manufacturing process.”
“John Cockerill’s latest generation of ARPs come with an innovative and environmen tally friendly concept, particularly in terms of emissions and waste energy recovery, combined
with smart manufacturing and Industry 4.0 technologies. We are proud being able to assist premium steel suppliers like BAOWU to face the ever more stringent environmental policies in their country and to deliver a cleaner and more sustainable steel industry by providing future-ori ented high-performance equipment like this Twin ARP installation,” commented Isabelle Widmer, managing director of John Cockerill UVK.
For more information, log on to www.johncockerill.com
The Chinese producer of special bar quality prod ucts, Fujian Sangang Minguang Group Co., Ltd. (Sanming), has successfully modernized its bar mill line and rolled the first bar on its new KOCKS 3-roll Reducing & Sizing Block (RSB).
The government-owned enterprise was found ed in 1958. Today, it is one of the largest steel producers in the Fujian province on the south eastern coast of China, producing around 11Mt of steel every year. As part of a major moderni zation project, the decision was made to invest into an upgrade of the existing mill, including the integration of a KOCKS RSB®
The commissioned RSB® 370++/4 is located as part of a finishing unit after 21 stands in H/V rolling mill arrangement, and will produce bar in coil within a dimension of Ø 16 to 48 mm and
straight bars within a dimension of Ø 20 to 90 mm in a 800kt/yr mill line.
The large-scale modernization through a Chinese EPC contractor required the purchase of additional rolling mill equipment. As well as the KOCKS RSB, the project included the supply of H/V stands, shears, a new bar in coil line with finishing facilities, and the upgrade of the inspection line.
In addition to the mechanical equipment, electrical and automation components have been modernized to ensure minimum down times, maximum transparency and the highest efficiency.
For further information, log on to www.kocks.de
Amid declining steel production the US steel industry braces itself to cope with the climate change challenge. By Manik Mehta*
ONE had been hearing for some time the Cassandra cries about soaring inflation, job cuts and, indeed, a recession ahead of us, though such forebodings were dismissed in the past by some experts as ‘unrealistic’ and divorced from the economic realities. America, they said, had fared not badly despite the Covid slowdown, compared to other developed countries where the confidence level in the steel industry had sunk to a low point. America had jobs for the asking, with employers stretching their hands with a carrot for enticing workers.
But the upbeat mood is increasingly becoming a thing of the past, and many have revised their outlook for the economy but also for specific industries, including the steel sector.
US raw steel production declined by 0.6% to 1.683Mt (net tons) in the week ended 24 September while the capability utilization rate slipped to 76.4%, the lowest since 20 months, according to the weekly data of the American Iron and Steel Institute (AISI) the steel industry’s ‘voice’.
Year-to-date (YTD) raw steel production until 23 September dropped to 66.4Mt (net tons) at a capacity utilization of 79.6%, down from 69.2Mt (net tons) the year earlier at a capacity utilization rate of 81.0%.
The AISI, quoting Census Bureau’s preliminary data, reported that US imports amounted to 2.51Mt (net tons) in August 2022, including 2.08Mt (net
tons) of finished steel (down 6.2% and 8.4% respectively compared to July 2022).
Imports of total and finished steel were up 8.8% and 28.7% respectively, year-to-date compared to 2021 levels.
In August, the largest supplying countries were Canada (589kt NT, up 8% versus July), Mexico (485kt NT, up 5%), South Korea (177kt NT, down 37%), Brazil (176kt NT, down 30%) and Vietnam (107kt NT, up 110%). For the 12-month period September 2021 to August 2022, the largest suppliers were Canada (7.00Mt NT, up 9% compared to the previous 12-months), Mexico (5.77Mt NT, up 50%), Brazil (2.98Mt NT, down 16%), South Korea (2.90Mt NT, up 21%) and Vietnam (1.29Mt NT, up 160%).
Aside from the drop in production and imports, the pundits predict a weakening of the US steel industry accompanied by dark clouds on the horizon that could result in a recession.
The US steel industry has faced a steady decline in demand since the third quarter of 2021 when prices had crossed the highest
mark of $2,000 per ton. This was quite a departure from the previous year’s so-called ‘less pessimistic mood’ prevalent in the market, even as buyers then had begun to experience the low after a cautious return to their business in the aftermath of the Covid lockdowns and restrictions.
In general, one can say that the mood is not exactly upbeat right now, particularly among flat-rolled producers who have faced a number of production challenges and shipment issues, with some not ruling out a major drop in demand in the remainder of the year.
Meanwhile, there have been calls for repealing Section 232 tariffs with the argument that this would generate economic growth and other benefits. A report from the Tax Foundation suggests that the nation’s GDP would gain by $ 3.3 billion and create some 4,000 jobs.
The tariffs of 25% and 10% were imposed on steel and aluminium imports respectively by former President Donald Trump in March 2018, in an effort to support the domestic steel and aluminium industries using national security interests to justify the tariffs. The US also signed agreements with Canada, the European Union and others, replacing tariffs with other restrictions such as quotas.
While the US steel industry supported the tariffs, the opponents have been questioning the relevance of the national security argument for imposing the tariffs; besides, they argue, the benefits to domestic steel producers did not take into account the heavy price paid by the national economy. The Tax Foundation’s
representatives said that several independent studies had concluded that each of the estimated 8,700 jobs protected in the steel industry cost an estimated $650,000; indeed, the tariffs had led to some 75,000 job losses in the general manufacturing sector. The Foundation further concluded that the evidence suggested that the cost of tariffs had been borne, mainly, by the nation’s consumers and companies.
Reacting to the call to revoke the tariffs on steel imports, US Commerce Secretary Gina Raimondo said that the government is considering repealing tariffs on certain goods to curb the highest inflation Americans have had in 40 years.
However, Raimondo was not specific about steel and aluminium tariffs.
“I know the president is looking at that,” Raimondo noted in an interview on CNN’s State of the Nation. “There are … products – such as household goods and bicycles –[where] it may make sense.”
“Steel and aluminium – we’ve decided to keep some of those tariffs because we need to protect American workers and we need to protect our steel industry; it’s a matter of national security,” said Raimondo who had in the past supported Trump’s tariffs on China.
However, the steel industry’s big challenge lies in overcoming the pollution emitted in the course of production. Though US steel production is considered to have the lowest carbon level, the industry is also taking measures to curb carbonization. The Biden administration announced in September new measures to be included in the so-called Federal
Buy Clean Initiative aimed at pushing the development of low-carbon construction materials made in America and, in effect, supporting good paying jobs.
While visiting the direct reduction steel plant of Cleveland Cliffs, Transportation Secretary Pete Buttigieg and some senior officials remarked that the administration would prioritize the purchases of steel, concrete, asphalt and flat glass with reduced emissions.
The US steel industry welcomed the measures. In his reaction, AISI’s president/ CEO Kevin Dempsey said that the announcement was a recognition of the innovation and advancement made by American steel producers, offering to work with government agencies to ensure the use of clean American steel.
As the emphasis on ‘clean and green steel’ grows, the industry is turning, increasingly, to recycling. According to estimates by industry groups, US steelmaking furnaces consume about 70Mt of domestic steel scrap for producing new steel. This is also in sync with the industry’s commitment to sustainability, as the steel industry conserves energy, emissions and resources.
Demand for steel scrap directly sustains and enhances recycling of many products such as cans, cars, appliances and construction materials that consume steel. The physical characteristic of steel allows it to be recycled numerous times without affecting its quality or strength. Indeed, more than 80% of the co-products from the steelmaking process are recycled or used again.
While the fear of cheap imports hangs like the proverbial sword of Damocles over the domestic steel industry, the latter also faces the challenge of drastically cutting down decarbonization.
According to a report by the research firm Wood Mackenzie, decarbonizing the iron ore and steel industries by the 2050 target year, in line with the Paris Climate Agreement, would require a whopping $1.4 trillion in terms of investment and upgrading across every stage of the value chain, creating challenges for the industry but also for the institutions charged with funding.
The US steel industry has its job cut out for it – it must eventually play not only to international public opinion, but may also come under the scrutiny of environmentallyconscious US politicians. �
With ArcelorMittal having recently disclosed its acquisition of Brazilian steelmaker Companhia Siderúrgica do Pecém (CSP), opportunities and impacts from this investment are heading to the surface. It is yet to be seen what strategy ArcelorMittal will utilize to expand to the company, but, says Germano Mendes de Paula*, the effect on the global market in both the short and long-term will be considerable.
ARCELORMITTAL has announced the acquisition of a 100% stake of the Brazilian steelmaker CSP, for a consideration of $2.2bn, in late July 2022. The seller was a consortium formed by Vale (50%) and the South Korean steel producers Dongkuk (30%) and Posco (20%). CSP, the new Brazilian integrated coke mill, started-up in 2016. CSP’s productive and financial performance in its initial years of operations was theme of the article published in STI, Nov-Dec 2021, pp. 20-21.
Vale’s disposal of its stake in CSP cannot be seen as a surprise. In 2016, we discussed the company’s strategy regarding investments in the Brazilian steel industry. It was identified as having three different stages: a) investments for the implementation of coke integrated steel mills during the 1950s and 1970s, aiming to boost iron ore sales; b) participation in the privatised companies, during the period 1991-2009, not only for commercial purposes, but also due to a financial goal: to convert a large amount of Siderbrás’ (a governmental holding for steel assets) debentures, an illiquid financial asset, into steel enterprises’ shares; c) investments in
greenfield projects, from 2004 onward, including ThyssenKrupp CSA and CSP.
It was verified that “Vale’s investments in CSA and CSP share similar characteristics, because they are: a) greenfield coke integrated mills; b) joint ventures with international steelmakers; c) specialised on slab production; d) located on the coast. In this way, the third phase can be considered as almost a reproduction of the first one”. Moreover, “Nowadays, Vale’s participation in Brazilian steel companies is restricted to CSP, prompting one final question: When will it sell its stake in CSP?” (STI, Nov-Dec 2016, p. 12). The answer finally came over five years later. Now, it is the first time in six decades that Vale does not have any stake in a Brazilian steel company.
According to a report released by the Brazilian investment bank Itaú BBA, concerning Vale’s corporate strategy: “Last decade’s diversification strategy comes to an end. CSP was one of the last relatively significant assets that remained to be sold by Vale. In 2022 they had previously concluded the sale of their coal operations. In 2021, they divested from: i) nickel assets in [Vale New Caledonia] VNC; ii) a stake in fertilizer assets at Mosaic; and iii) a 50% stake in CSI’s steel operations in California”.
It is worth noting that a 40% stake in Mineração Rio do Norte, a bauxite mining located in the Amazon Forest, is the only asset that falls in a non-core category that remains to be sold. Indeed, for Vale, CSP was a non-core asset, both in terms of strategy and finance. It sold its participation in CSP for $1.1bn, while its market capitalisation reached $63.3bn, when the transaction was announced.
ArcelorMittal has extensive operations in Brazil, both for flat steel products (Tubarão and Vega do Sul) and long steel products (Monlevade, Juiz de Fora, Piracicaba, Barra Mansa, Resende, and 50% of Sitrel, as well as in the downstream activities through its partnership with Bekaert). In 2021, it produced 11.2Mt of crude steel, which was equivalent to 31% of the country’s output. Consequently, it has substantial expertise in operating in Brazil, and in producing and exporting slabs (in Tubarão).
It should be stressed that from a financial perspective for ArcelorMittal, the acquisition of CSP is more relevant than for Vale, not only because it needs to pay $2.2bn, but also due to its lower market capitalisation ($25.9bn). Thus, the deal was equivalent to
* Professor in Economics, Federal University of Uberlândia, Brazil. E-mail: germano@ufu.br
8.5% of ArcelorMittal’s market capitalisation, whilst only 1.7% for Vale. It should be highlighted that the CSP’s purchase still needs to be approved by the Brazilian antitrust authority, which is expected to happen by the end of this year.
ArcelorMittal justified its considerable investment to purchase CSP by the following reasons. Firstly, it is a first-class 3.0Mt/yr slab producer, installed in a deep-water port. It is capable of producing high quality slab, and its steel shop is already prepared for doubling its installed capacity.
Secondly, it is located relatively close to Carajás iron ore mine, which allows lower logistic costs. In addition, CSP is installed inside an Export Processing Zone and benefits from a special tax regime on the sale of products and purchasing of raw materials. The asset will face a 15% tax rate and has $1.2bn of tax credits to be utilised to offset profits in other operations and to reduce expansion costs.
Thirdly, CSP’s 5-year average EBITDA has been $320M. ArcelorMittal expected to gain $50M of synergies, including selling, general, and administrative expenses (SG&A), procurement, debottlenecking, and improved productivity. In addition, it planned to achieve a normalised EBITDA of $330M, implying that it is paying a 6.7x Enterprise Value (EV)/EBITDA, in the post synergies scenario. As CSP is quite modern, a small maintenance capex (lower than $50M annually) is projected.
Fourthly, CSP’s output can be used to supply slab to other groups, such as for Lazaro Cardenas mill, in Mexico, which is ramping up a 2.5Mt/yr hot strip mill, Calvert mill, in the USA (a 50:50 joint venture with Nippon Steel), and other plants in Europe. It can also serve third parties in the USA, which currently is short of slabs, and in Latin America.
Finally, ArcelorMittal is considering expanding CSP. Two main options have already been mentioned by the company. The first refers to amplifying crude steel capacity, by adding BF/BOF or even DRI/EAF, and the latter is related to higher vertical integration. Despite the fact that Mr Aditya Mittal declared that there are lots of downstream options, on flat and long steel products, no additional information was provided. Considering that many investments were announced for long steel products in Brazil recently and there is just one flat steel amplification project under construction in the country nowadays (an expansion in ArcelorMittal Vega do Sul), there is likely to be more space downstream for flat steel products. In this case, CSP will need to address this investment opportunity with Tubarão.
In any case, CSP’s transaction might have considerable impacts for the global and Brazilian slab market in the short-term- and even for the country’s finished steel market in the medium and long-term. �
With the demand season round the corner, Indian steel mills are preparing to witness a sharp improvement in their operating margin in the second half (October 2022 - March 2023) of the current financial year, after a lacklustre performance reported in the first half (April – September 2022).
By Dilip Kumar Jha*INDIAN steel mills are desperately waiting for the commencement of construction activity which normally begins following the end of the monsoon rainfalls in September. This restores steel demand after nearly four months of drawdown during the monsoon season, between June and September. The second half brings in a lot of optimism, which not only compensates for the weak demand trend of the first half but also sets the tone for the next year.
During the April – June quarter, the operating margin of India’s steel producers slumped on a sharp decline in steel prices despite high input costs pressure. While input prices have started correcting since July, its impact will be felt towards September-end, when the existing pipeline steel inventory exhausts. This inventory was built on expectation of a further price increase.
While the most developed economies talk of economic recession, India is looking to an emphatic 7% GDP growth, with
focus on a consumption-led economy. Meanwhile, the government’s attention is being paid toward the infrastructure development of road and housing construction projects which are set to support India’s steel demand going forward. The upsurge in demand is bound to elevate the operating margin of India’s steel producers which is estimated to report at 25% in the second half, after falling to 14-15% in the first half between April and September 2022. In the previous financial year, the operating margin of Indian steel mills had set a decadal high record at 30%.
Indian steel mills reported a pressure on their operating margin on account of high
* India correspondentinput cost, lower realizations and a 15% export duty levy on finished steel products that impacted overall business sentiment in the first half. Above all, the high input cost emanated after supply disruptions from Russia following Moscow’s invasion of Ukraine and western sanctions on the Kremlin thereafter, hit the global economy, with India’s steel sector not being immune.
According to Seshagiri Rao, joint managing director, JSW Steel, the entire Indian steel industry suffered after 15% of export duty was levied by the government earlier this year. “India’s steel exports declined by 50% in the first half of the current financial year to around
3-3.5Mt from around 7Mt reported in the corresponding half of the previous year because of a slowdown in overseas orders. Indian steel became uncompetitive in the world market after the introduction of a 15% export duty levy. In July this year, the Indian steel industry, in fact, became a net importer. Presently, India’s steel output is higher than demand which translates to lower realization, and eventually a squeeze in profit margins. We have submitted a written memorandum to the government, seeking immediate withdrawal of the export levy, and are now waiting for the decision,” Rao added.
Indian steel producers are losing the opportunity to dispatch more product, even though the market is less competitive due to the sanctions Russia faces, and the Covid cases and lockdowns in China. In 2021-22, India’s steel exports jumped by over 25% to 13.49Mt from 10.78Mt reported in the previous year.
In the second half of this year, the margin pressure is expected to ease and improve as production costs have declined on account of a sharp decrease in raw material prices amid expectations of robust domestic demand. For the full financial year April 2022March 2023, therefore, operating margins are forecast to average at 22-24%, with a decline of 7-8% from the previous year, but an increase from the pre-pandemic average of around 20% logged between financial years 2017 and 2020.
Coking coal is a key raw material comprising around 40% of the production cost and is usually imported by Indian steel manufacturers. Prices, however, dipped from a historical high of around $600 a tonne in March to around $250 a tonne in August due to improved supply from Australian mines and weakening demand from global steel producers. Coking coal prices are expected to remain benign as supply improves. The global demand outlook is forecast to remain weak.
“Iron ore sourced domestically and accounting for 15-20% of the production cost, has also shed more than 50% in price since May 2022 on account of increased domestic supply following the imposition of export duty of 50% on iron ore and 45% on pellets. The lower raw material prices, mainly global coking coal and domestic iron ore, may reduce production costs for Indian steelmakers by around 30% in the second half of this fiscal,” said Ankit Hakhu, director, Crisil Ratings.
Indian steel mills are estimated to have expanded their cumulative installed capacity to 155Mt, for the financial year 2021-22 against 142.91Mt reported the previous year. JSW Steel alone added 5Mt of new capacity at its Dolvi plant in Maharashtra. However, weak demand coupled with high raw material prices in the first half yielded an average total capacity utilization of 77% for the financial year 2021-22. With demand weakened further in the first half, the average capacity utilization of Indian steel mills is projected to have declined to below 70% during the April – September 2022 period.
Strong economic growth coupled with governmental focus on consumption-led demand drivers is set to brighten the outlook for Indian steel producers in the second half of the current financial year, between October 2022 and March 2023.
ARL iSpark. The trusted standard.
Metal is the backbone of our society. It’s in the structures we ride, work and live on every day. That’s why you’ve trusted the detection technology inside every ARL iSpark for over 80 years to ensure every piece of steel and metal you produce is safe. With so much riding on that, why would you choose anything else?
Find out more at thermofisher.com/ispark
*Based on a data comparison, completed by Thermo Fisher Scientific in 2021, of detection limits for OES systems using data published in specifications and applications notes for ARL iSpark and competitors.
©2022 Thermo Fisher Scientific Inc. All rights reserved. All trademarks are the property of Thermo Fisher Scientific and its subsidiaries unless otherwise specified. AD41408 0922
Following STI’s recent review of Genmin’s iron ore activities in Gabon, Fortescue Metals Group Ltd (FMG) has outlined its preliminary investigations of further iron ore activities in that country. This development reflects Gabon’s drive to become a major high-grade iron ore producer.
By Michael Schwartz*FMG has entered into an agreement with the Gabonese Government to study the potential development of the country’s Belinga iron ore project. The company’s CEO Elizabeth Gaines outlined the background to STI: “In December 2021, Fortescue announced it had entered into a binding preliminary agreement with the Government of the Republic of Gabon to study the opportunity to develop the Belinga iron ore project in Gabon, West Africa. If successful, the project would complement Fortescue’s existing product mix by providing a high-grade iron ore.”
Three years will be specifically set aside under the agreement to study and negotiate a mining convention for the development of the Belinga project, which stretches over 5,500 km². A separate Gabonese mining company will be established to enter into the mining convention and to hold the mining tenure over the Belinga project.
In turn, the mining company will be established by an incorporated joint venture which will be owned 80% by Fortescue and 20% by the Africa Transformation and Industrialisation Fund, an Africafocused investment fund incorporated in
Abu Dhabi. The joint venture will initially focus on exploration works to determine the potential size and grade of the Belinga deposit and logistics solutions during the 36-month exclusivity period.
commonly host banded iron formations and itabirites found in other parts of West Africa such as the Simandou project. The Belinga Iron Ore Project has been progressively assessed by Fortescue since 2018.
Elizabeth Gaines stressed that discussions with the Gabon Government on final documentation are progressing and that a technical review recently commenced to assess infrastructure and local geology in Gabon, as well as to conduct community engagement.
In addition, Gabonese president Ali Bongo Ondimba said that ‘following successful completion of the initial exploration and due diligence work with Fortescue, our aim is to put the Belinga project back on track, building the mining sector’s contribution to our economy and delivering training, jobs and skills.’
The Belinga iron ore project is located in the northeast of Gabon. The deposit was initially discovered in 1955, and subsequent exploration in the 1970s identified high iron and low contaminant mineralisation. The deposit sits in Archean aged rocks of the Congo Craton. The lithology and structure are typical of other greenstone belts that
*Iron ore correspondentThe last words are those of Elizabeth Gaines: “Fortescue is committed to its strategic pillars of investing in the long-term sustainability of the iron ore business and investing in growth…We look forward to working with all key stakeholders on this project as we continue to invest in assets to optimise growth and returns in our iron ore business.” �
Ready to invest in carbon capture? Munters has the expertise and equipment to support your project. We have decades of experience in Mass Transfer and Mist Elimination – Clean technologies that are essential to any successful carbon capture project, no matter the industry. You can count on Munters proven solutions to support your carbon capture project.
Clean technologies by Munters
more at www.munters.com/cleantechnologies
SOME people say that if you want to get ahead get a hat. Mark Bula, chief commercial officer of H2 Green Steel based in Sweden, would probably beg to differ. He would argue that if you want to move on up, work for somebody who is tough, demanding, and opinionated. There are many people in Mark’s world who have fitted the bill and when he mentions them it’s like a roll call of the US steel industry’s great and good.
“You learn in this industry in general that you’ve got to have a strong backbone and a tough skin,” said Bula, sitting in a bright meeting room in H2 Green Steel’s Stockholm offices. Bula looks the part, he always has, he’s one of two people I know who looks good in a pair of jeans and can carry off ‘smart casual’ with aplomb.
He had emailed explaining how the guys at H2 Green Steel are pretty relaxed and, therefore, there was no need to dress formally, which set alarm bells ringing. Unfortunately, when it comes to sartorial elegance, I have but two settings: smart and utterly derelict, so I opted for a suit. I couldn’t very well arrive in my unpressed ‘I bring nothing to the table’ tee-shirt, which I always pack for emergencies.
I’d been up early figuring out how to get across town from my hotel in the south of the city to where H2 Green Steel was located. I arrived early, very early, 0730hrs early – my appointment wasn’t until 0900hrs – and decamped to a small bakery where cappuccino and almond croissants prepared me for my first meeting with Mark since June, when he kindly
*Editor, Steel Times Internationalpresented the opening keynote at Steel Times International’s Future Steel Forum in Prague. Prior to that I hadn’t seen him for almost five years when he was working for Dave Stickler at Big River Steel in Osceola, Arkansas, USA.
That strong backbone, Mark admitted, had eluded him for many years. “I had to work when I was 14 just to have money to help the family,” he said, referencing humble beginnings. “I was picked on a lot as a kid. I was raised a Catholic, I used to get stuck in trash cans, I was the skinny, scrawny kid with no sports, I wasn’t super smart, I didn’t fit in anywhere and I was an easy target.”
Workplace advice was blunt: “You need to get a tougher skin.” It was one of many ‘valuable lessons’ he learned from the likes
Hydrogen steelmaking has been a big talking point in the global steel industry for many months – and for good reason. Two leading businesses involved in the development of such C02 reduction technology – HYBRIT and H2 Green Steel – are both based in Sweden which is viewed as a ‘Goldilocks location’ in terms of its renewable energy resources. While the former has kept its progress fairly close to its chest – but has proved that it’s possible to produce green steel using hydrogen – the latter has been open enough to offer Steel Times International an exclusive interview. Matthew
Moggridge* flew to Stockholm to meet Mark Bula, the company’s chief commercial officer
Stockholm where they are now looking to buy a place.
Mark described those early days in the US steel industry working for National Steel (which was eventually absorbed into US Steel) as a ‘grunt role’ in sales as opposed to a place on the management training programme, but eventually Nucor came calling and while he was advised that working for what is now the biggest US steelmaker was ‘a little cult-like’ he was assured that if he fitted in, it was a great company. And fit in he did. “I thought Nucor was the greatest thing ever,” he said, explaining how his career path was sales-driven, he was sent to problem territories where profitability wasn’t high enough, there were difficult customers, or the business needed to be expanded. “I was identified as the guy sent in to fix things,” he said, adding that when boredom eventually crept in, he was moved. And when he was bored of moving – and not wishing to jeopardize his second marriage – he resigned despite protestations from one John Ferriola who wanted him to stay. “I think maybe I could have been one of John’s guys,” he said, but not in a Brandolike On the Waterfront manner as Bula would soon be a contender in his own right.
January 2021 when he was working as chief strategy officer for the US-based AI start-up Everguard where he still sits on the board of advisors. The journey started with a random Linkedin message from Harald Mix, chairman and co-founder of H2 Green Steel and subsequent chats with him and his business partner Carl-Erik Lagercantz of Northvolt, a leading manufacturer of lithium-ion batteries. “I’m not here to be the front and centre guy. I’m here to mentor for the first time in my life,” he said. “I am in a role that yes, I have to deliver results, but this is more about me helping build behind the scenes…and that’s a role that I’ve never played before.”
And so he moved to Sweden with his wife and son, his daughter Kathleen had already begun college at the Citadel military college in Charleston, South Carolina, and currently plays Division 1 volleyball for them. His son, Tim, is also back home studying economics at Purdue, leaving Mark and his wife to learn Swedish and live the Scandinavian life. Does he miss his kids?
“The kids don’t miss us right now, they’re in college working out who they are; it’s easy not to miss them when they want to be on their own,” he said.
of National Steel’s Jim Bender – ‘the first one to toughen my skin a little’ – and then from Dave Stickler at one of the start-ups they both worked on, probably Severcor, he said.
Why was he constantly advised to toughen up? “I think probably I took a lot of things personal, and I think it’s pride,” he said, wondering whether he could have done things differently and accepting that he’s always wanted to be liked and recognized as somebody who worked hard and delivered results.
During his early career he was expected to move around a lot and it cost him his first marriage. “I was too focused on myself, and my career and it was my fault,” he confessed, but has since remarried and now has two grown-up kids both of whom remain in the USA, leaving Mark and his wife as ‘empty nesters’ enjoying life in
Joining the late, great John Correnti and Dave Stickler at Big River Steel in Osceola, Arkansas, proved a turning point as it took Bula out of, if you like, ‘traditional’ steelmaking circles and into the world of Industry 4.0, digital manufacturing, artificial intelligence and, strangely, perhaps, the premise that steel as a material wasn’t the beginning, middle and end of what he was doing. Big River Steel, for example, liked to stress that it was a technology company that ‘just happened to make steel’.
Correnti put Mark out front, but when he suddenly (and tragically) passed away while on a business trip to Chicago with Mark, Dave Stickler took centre stage, taking on the role of raising money for the business. But not before Mark had established himself as a man who could develop an excellent rapport with the banks, a rare quality that would soon appeal to those in the early stages of setting up a groundbreaking hydrogen steelmaking business, something Mark described as ‘transitional in our industry’.
He was approached by the founders of the H2 Green Steel Project on, of all things, social media. It happened on 2nd
H2GS AB consists of three operating divisions – hydrogen, DRI/HBI and virgin iron – and ultimately, it’s all about flexibility. “We could just build a hydrogen plant somewhere, we could just build a DRI tower somewhere, we could just build a steel plant somewhere,” said Mark using repetition to drive home his point. “We don’t necessarily want to be in the steel business,” he said referring to the company’s tagline (or mission statement): ‘we decarbonize hard-to-abate industries’, meaning the technology could reduce the carbon footprint of other industries, like cement and fertilizer. “We’re very particular in that; there is a way to decarbonize those industries and to be the leader that takes the risk,” he said, adding that the risk can be ‘de-risked’ by having the hydrogen know-how. He spoke of the three different hydrogen processes that will be married into one hydrogen facility.
According to Mark, the amount of energy needed is enormous and that alone will be a limiting factor for the growth of hydrogen steelmaking generally, particularly for hydrogen to feed DRI and steel plants.
“If we can figure out how to manage all three [hydrogen production technologies] together and use computer learning, that’s
“H2 Green Steel’s purpose is to decarbonize hard-to-abate industries, starting with steel.” The company aims to build a large-scale green steel plant, with production up and running as early as 2025.
GIGA-SCALE ELECTROLYSIS: decomposing water into hydrogen using electricity, the starting point. Using fossil-free electricity to produce enough hydrogen to bring 5Mt of highquality steel to the market by 2030.
THE DR REACTOR: this equipment refines iron ore to direct reduced iron or DRI: iron ore exposed to hydrogen, which reacts with oxygen in the ore to form steam as a residual. Green hydrogen produced through electrolysis is used to reduce the ore instead of coal, reducing CO2 emissions by more than 95%.
ELECTRIC ARC FURNACE: fossil-free electricity used to heat the DRI and steel scrap to a homogenous melt of liquid steel. In the melting process, carbon plays an important role in lowering electricity consumption, forming the protective properties of the slag on top of the melt and enabling the transformation of iron to steel.
where our intellectual property resides,” he said, adding that patents have been filed and suddenly ‘you’re talking about H2GS AB as a parent company with an energy division’.
When I brought up the complex subject of how to define green steel, Mark admitted it was not a topic he or anybody else at H2 Green Steel had considered in any great detail – yet. “We’re still a project, we’re not a company,” he said, telling me that the World Steel Association has said that green steel doesn’t exist, again
prompting the use that word ‘yet’. But there is an official H2 Green Steel definition which reads as follows: ‘Green steel must be produced from a combination of a significant amount of green virgin iron and scrap in a production process which uses electricity from renewable energy sources. The total C02 emissions in such a process must be more than 90% lower than that of traditional steelmaking in a blast furnace process.’
“We’ve defined it less from a marketing and messaging standpoint and don’t
tout it a lot. I think it will evolve into something and maybe it will become the gold standard. The reason we have that definition [above] is we have commercial agreements that we’re closing to help us get finance and when you have a commercial agreement to provide ‘green steel’ or decarbonized steel you need a definition,” he explained.
“We don’t use the words ‘zero carbon’, we don’t use the phrase fossil-free steel because we know that carbon steel inherently has carbon in it, so I don’t
“I think a lot of people believe it’s too complex to get done, particularly for an inexperienced steel team. We have some good people involved, but we need to add more, and I hope this article gets people to realise that we need more experienced, start-up, minimill, DRI, EAF people. We have a really strong DRI team from the Middle East.”
CONTINUOUS CASTING AND ROLLING: Integrated process enables H22 Green Steel to reduce energy consumption by 70% and replace natural gas used in the traditional process.
LINES: for cold rolling to change thickness, annealing (to create the right mechanical properties); hot dip galvanizing: for desired corrosion resistance.
product just like other people, but for now that has not been a primary focus,” Mark said, stressing that the definition is there purely for commercial purposes. And then things took a complicated turn, or perhaps it was just me. Mark said that hydrogen was needed to make ‘green steel’ because natural gas was a fossil fuel. So hydrogen is an essential ingredient to reduce the iron ore to make a virgin iron product. In other words, you need a certain percentage of virgin iron in your EAF along with scrap, to make some of these high-quality steel products, but if the scrap does not have any C02 attached to it, it’s a lower footprint than if virgin iron from a hydrogen facility is added. For Mark, therefore, the ‘funny thing’ is that the automotive sector is leading the charge for ‘green steel’ but automotive grades cannot be made without virgin iron products so there must be a balance. “That intellectual property of the balance of the charge mix that goes into the EAF (and what happens afterwards) that’s what we will retain,” he said, bringing up the possibility of a C02 accounting system. “So, when you have a financial invoice, you should also have a C02 invoice, that’s what creates the value and so in my simple mind it comes down to the C02 footprint of that coil and I don’t think the industry is complex or good enough to know exactly how to put a value on that yet.
“It’s one thing to do these agreements today. I believe that what we’re charging for a green premium now will be considerably higher in the future. The difficult part is that higher grades will have a higher C02 footprint than scrap-based lower grades and that will be a commercial decision.
know that you can make a carbon-free steel but what you can do is decarbonize a significant portion of the traditional C02 intensity footprint of a coil which is 90-99% accomplished by this plant,” asserted Mark.
Mark says that the technology for the three hydrogen-making methods to be employed by H2 Green Steel exist and have been proven, the DRI towers are proven technology – Midrex was recently announced as the DRI partner in the project – and the steel mill, says Mark, is largely a duplicate of the last SMS mill that was
built, so all the technologies are used, but nobody has put them together and that’s what H2 Green Steel is doing. Mark believes H2 Green Steel will be able to achieve a 90-95% reduction in scope one and two emissions. Beyond that, he said, you consider things like carbon storage, carbon capture, bio-diesel. “All those things are incremental to try and get you as close to zero as you can,” he said.
“We’ll figure out how to market it and how we position it and I’m sure we’ll have a trademark name for our green steel
Series A funding was completed a year ago and while it looked as if the facility could be built for 2.5 billion Euros, it now looks as if the final figure will be close to double that, thanks to geo-political headwinds, notably Russia’s illegal invasion of Ukraine, which has increased opex and capex, but Mark believes it can still be financed. The ‘first close’ of series B funding was announced on 29 August 2022 with a ‘selected group of investors’ showing strong support for the company.
H2 Green Steel, says Mark, is one of the biggest projects in Europe but it’s going to take longer than originally anticipated. “Everybody wants to build a new green steel mill so to lock in the DRI tower, the
three different hydrogen processes and the steel plant equipment you need to put money down, so the series B round [of financing] allows for us to do that,” he said.
When it comes to the supply of steel
production equipment, it was recently announced that SMS group has been selected to provide a broad range of technology and equipment for H2 Green Steel’s Boden production facility and that
H2 Green Steel equipment operators will be trained by the German plant builder. But to start talking about equipment now would be premature, Mark suggested. “We’re a long way from that, we don’t have all our
“H2 Green Steel, is one of the biggest projects in Europe but it’s going to take longer than originally anticipated. ”Mark Bula with Maria Persson Gulda, CTO
20 years of experience and over 40 installed plants make Steuler the Refractory Technology Partner for tomorrows DRI Processes.
finance yet,” he said.
In total, across all three business units, there is likely to be between 1,200 to 1,400 employees at the Boden facility in Northern Sweden to deal with the planned initial capacity of 2.5Mt/yr (metric tonnes) – ‘and then we’re going to 5Mt’.
It goes without saying that there’s going to be a lot of eyes on this project. According to Mark it’s becoming a big topic at steel conferences where it comes up a lot in ‘sidebar conversations’.
“I think a lot of people believe it’s too complex to get done, particularly for an inexperienced steel team. We have some good people involved, but we need to add more, and I hope this article gets people to realise that we need more experienced, start-up, minimill, DRI, EAF people. We have a really strong DRI team from the Middle East,” he said.
Cost is a big issue as the plan is to electrify the whole process. “We’re using induction heating and green electricity, and this is the Goldilocks location to try it. I’m not sure you could do this project anywhere else in the world today and we’re going
to prove it can be done, we’re going to do it on a large scale,” said Mark, adding that there are lots of hurdles. He said it wasn’t going to be easy but having all the ingredients – iron ore and renewable energy – in one spot – made it a no brainer.
There will be winners and losers, according to Mark. “The people who can do it and the places where there’s no way you’ll ever be able to do it,” he said. In continental Europe there is limited fossilfree or renewable energy and, therefore, the cost is two or three times that of the Nordic countries. “When your energy rates are that high and you need 800-850MW, it’s a massive project,” Mark said.
There is an abundance of iron ore in the region surrounding H2 Green Steel’s Boden facility and Mark is keen to point out that the company found itself ‘in a little bit of trouble’ when it claimed a supply agreement was in place with LKAB, one of the founding partners of rival hydrogen initiative HYBRIT. “We don’t have an agreement yet,” he said but negotiations are taking place and if they fall through there are plenty of other places around the
world, such as Brazil, where the company could source its key ingredient even if sourcing raw materials from the other side of the world isn’t considered particularly ‘green’. “That is absolutely a concern for us and that is the complexity of Scope 3 upstream for any steel mill, right? We have done it in our modelling where we would have a certain percentage of direct reduction iron from Brazil, Australia and Canada. The real issue is where are the direct reduction pelletizers because you’ve got to have the pellets. We want to buy the pellets, so it makes sense for us to be in Sweden.”
Mark introduced the phrase ‘a rising tide raises all boats’ in relation to Sweden’s natural resources. “Sweden could be the leader, it’s the lighthouse. We’re not talking about SSAB or H2 Green Steel, it should be about Sweden. We think there are ample natural resources for us all to be successful and be the leader of it,” he said.
Jumping the gun a little I wondered what the expansion potential was for a concept such as H2 Green Steel. Are we likely to see more Bodens cropping up?
It was a naïve question as development of such a massive project depends on the availability of renewable resources which, as discussed above, not every country possesses, but Mark believes that elements of what is being built in Northern Sweden can be duplicated elsewhere, certainly in collaboration with like-minded businesses such as the Spanish renewable energy business Iberdrola, which has an established partnership with H2 Green Steel.
“Could we just build a hydrogen unit? Could we build a hydrogen DRI tower? A slab mill? A semi-finished mill? I think all those things are things we’re looking at as a business. We are looking at the world and saying ‘where can we take what we hope to learn here and put it somewhere else to decarbonize the steel industry, to decarbonize the fertilizer business, to decarbonize the cement business? This is the model; we have three business units, and we will look to build and leverage them and the intellectual property that we’ve learned from this and try to duplicate it elsewhere in different configurations.”
Mark isn’t saying that H2 Green Steel is the be all and end all, but purely one option in a location that will work in central Europe. Blast furnaces with carbon capture might still be an option elsewhere in the world. “But we don’t want to carbon capture, we want to eliminate,” he said.
The question of scrap availability raised its head, and I was keen to understand the situation at H2 Green Steel. Mark believes that the availability of prime scrap – as opposed to obsolete scrap – is going to be a problem bearing in mind that the UK, USA, and Europe are all net exporters of scrap metal.
Outside of that, there are quality issues. “That is why we’re building a hydrogen DRI facility because you’ve got to have that high quality virgin iron product so you can mix
it with lower grade scrap, which also helps with your opex, that’s the whole beauty of this process and that’s the value of what we’re trying to do,” he said.
Mark says there must be a partnership for scrap return. He cited BMW as a forward-thinking company where life cycle assessment was concerned, highlighting the car maker’s agreement with H2 Green Steel to return 40% of the volume of steel sold to them as scrap. “Green steel scrap will be more valuable than non-green steel scrap because if there is a backpack value, our backpack value will be considerably less than blast furnace scrap.”
And then there were the C02 emissions implications of shipping scrap, which Mark insisted were not a huge part of the equation despite the perceptions in some people’s minds. He said that Maersk was part of series B equity funding – “so there’s going to be synergies across all facets of this,” he said.
“It’s why you have automotive companies involved, it’s why you have furniture companies involved, it’s all inter-related, it’s this total life cycle circularity of the entire business model, that’s what we’re trying to form here, it’s all about building a better mousetrap together that benefits the entire supply chain and that’s really important.”
For Mark the whole project is ‘a really cool thing’ that gives him the chills when he thinks about it. “I’m not here as part of the steel company, I’m here as part of a transformation company,” he said alluding to a possible rebrand going forward with the word ‘steel’ coming out. “We’re an energy play, we’re a decarbonization play, steel is just part of it,” he said, reminding me again of the line, ‘we just happen to make steel’.
Going back to that phrase ‘a rising tide raises all boats’, Mark applauds the Hybrit initiative for showing that hydrogen
steelmaking is possible. He says the difference between them is that Hybrit is a pilot plant and H2 Green Steel is skipping that stage. “I think they’re making 100kt/ yr, we’re going to make 2.5Mt/yr and so we applaud what they’ve done. We want to be good neighbours, we think there’s room for all of us.”
Greenfield sites bring new technology, new entrepreneurial talent, new spirit, new ideas, more passion; that’s what Mark’s mentor, the late, great, John Correnti, believed and now Mark was at the very heart of it.
The Boden site is 45 miles south of the Arctic Circle and big enough to expand capacity to 5Mt/yr, up from the initial planned output of 2.5Mt/yr. The company has been given a site permit, as opposed to an operating permit, meaning that the site can be prepared. “All we’re trying to do before winter (2022) is to build the roads and level areas for offices and temporary housing for our construction workers, so that when we get fully financed we can put trailers down and get going, get the workers in there immediately to start working,” he said.
There will be a direct rail line from the plant to the port of Lulea, which is currently being expanded and, bearing in mind the artic location, ships with ice-breaking capability are also under consideration.
Mark has come a long way from the days of National Steel. Along the way he’s met some inspiring people, legends most of them in their own right: – John Correnti, Dave Stickler, John Ferriola – and now he finds himself playing a crucial role in the development of what will arguably be the most advanced and environmentally friendly steelmaking facility in the world, a plant that will transform the way steel is made and make the planet a safer and greener place to live. �
After decades of economic prosperity, Australia’s iron-rich land has been mined to exhaustion. To sustain its industry, lower grade ore may need to replace its high-quality export, but pressure from global competitors, net-zero targets, and a complex socio-political background make the transition even more insurmountable. By Catherine Hill*
LESS than 70 years ago, Australia and iron ore were two incongruent terms: with the former’s economy relying on the export of textiles, and a post-war transformation in policy, which had quickly escalated employment rates, and productivity. The belief that mining was an outsider industry was held so strongly that a national embargo existed on the export of iron ore, as well as a state blanket on the issuing of mining titles. However, in the early 1960s, huge deposits of ore were discovered in the Pilbara region, sky-rocketing an industry that had previously gone unnoticed.
Australia today has the world’s largest reserves of iron ore, with 52 billion tonnes; 30% of the world’s estimated 170 billion tonnes. In volume terms, only China produces more ore, but the material is often lower grade, leaving Australia as the largest supplier to the seaborne iron ore trade. Despite its discovery being only decades ago, the production of iron ore is an integral money-maker for the country, which its economy has grown increasingly reliant upon.
In the face of what has now been consistent years of industrial success, these days, trade is complicated. There is a rapidly growing pressure to decarbonize, competition from China’s emerging economy, and socio-political criticism from the destruction of Aboriginal land in the quest to mine deeper, and further. Steelmakers are increasingly more discerning as net-zero targets loom large, and less sustainable iron ore producers’ risk being ‘left out in the cold’ if they don’t make alterations. These alterations, however, come at a hefty price tag; a so called ‘green premium’, with solutions such
as hydrogen being highly flammable and difficult to transport and store. China, one of Australia’s main competitors in terms of iron ore output, has already signed contracts with a green pellets producer, which has added digital solutions to the process to reduce energy consumption. Australia, however, hasn’t gained its title as the ruler of the industry for no reason. Australian iron ore is enriched by the action of water, which washes away waste minerals, leaving concentrated bands of iron oxide. According to Jonathan Law, an expert in locating and managing mineral deposits at the Commonwealth Scientific and Industrial Research Organisation, ‘‘banded iron formations in their own right are not great iron ore deposits. The ones that have made the Pilbara great are secondary enrichments of banded iron ore. All the major resources that have been
*Editorial assistant, Steel Times Internationalmined in Western Australia fall into this category.’’
Geoscience Australia calculates that the country’s ‘economic demonstrated resources’ of iron – an estimate of what is likely to be available for mining in the long term – currently amounts to 24 gigatonnes, or 24 billion tonnes. According to the Australian Bureau of Agricultural and Resource Economics, that resource is being used up at a rate of 324 million tonnes a year, with rates expected to increase over coming years.
“If you extrapolate that out, then it’s pretty easy to see that within 30 to 50 years, the high-quality ore in the Pilbara will be essentially mined out,” said Dr Gavin Mudd, a lecturer in Monash University’s department of civil engineering and author of a report into the sustainability of mining in Australia. Law, while being slightly more
optimistic, agreed. “My calculation is 56 years if you take the current production rate and what we know about in that economic demonstrated resource basket.” The high-grade of Australian iron ore has, in many ways, caused it to be mined into close inexistence. Australia’s foothold in the market is largely defined around the purity of the product – so any alternatives, such as seeking out lower grade ore, will also threaten the competitive edge it has historically held.
That’s not to say that finding further deposits is impossible. It is just, according to Mudd, highly unlikely. “Banded iron formations are extremely easy to find because they are magnetic, and the deposits we’ve found so far have been discovered on the surface, so it was literally
buried deposits that will almost certainly be more expensive to produce, or whether the big companies just move to use the equivalent easy deposits in Africa or South America.” Particularly given that China is hot on the heels of sustainable iron-ore mining, an attempt to revive the industry through unsustainable measures would place Australia in a poor position looking forward to a future that doesn’t just hope for greener industries, but demands it.
It’s not only a growing lack of deposits that troubles Australia. United Australia Party chairman Clive Palmer has claimed that China is ‘hell-bent on getting Australia’s resources’ and called for higher tariffs on Australian iron ore. “They’ve invested $50 trillion in the manufacturing industry in China so they can dominate the
introducing further sustainability solutions to its iron ore mining, Australia is now victim to its own success; having established itself in a position, that is ontologically unsustainable if it continues at its current rate, and environmentally unsustainable if it adapts to a lower grade.
There are also questions of whether the land should be mined at all. In Western Australia, there are hundreds of indigenous heritage sites; such as caves, springs, and national parks. Aboriginal land in Australia has been mined for over 40,000 years – first by the aborigines themselves, who mined ochre, a form of iron oxide, for cave painting and artefacts. Once Australia was colonised by the British in 1788, rapid economisation took place, weaponizing the Aborigines as an unpaid workforce until the 1970s, when widespread protest catalysed legislative change that is still in place today. One of these such laws was the Aboriginal Heritage Act of 1972, which protected all Aboriginal heritage sites in Western Australia, whether they were registered with the Department of Planning, Lands, and Heritage or not.
The law was harked as a significant victory in reconciliation between indigenous and non-indigenous Australians, and in reconstructing indigenous identity that had been written over with colonial equivocation. Forty eight years later, in May 2020, mining company Rio Tinto blew up 46,000-year-old Aboriginal caves in Juukan Gorge, which was legal under the Section 18 exemption of the Act.
a case of walking along, finding them and then drilling them out.” On the other hand, if the industry doesn’t discover other big deposits, we may need to begin mining lower quality deposits, Mudd noted. In which case, the environmental costs of the industry will grow. “It’s not just a matter of what’s there, but what the environmental cost is of extracting it.”
In fact, the energy and water-use implications might mean that mining lowgrade iron ore deposits is not feasible, said Law. “While these enormous resources are out there, they’re probably not the ones you want to use unless you absolutely have to. I guess the challenge for the future is to see whether or not Australia remains an attractive place to explore for these
world, export to Europe and export to the United States,” Palmer said. “Now what we need is a 15% export license on our iron ore which will repay the debt for us without Australians having to repay it. And if they don’t pay it, they don’t get our iron ore.’’
Regardless of whether it is ‘hell-bent’ or not, China’s rapid mobilisation into a global centre of economy has escalated industrial pressure on Australia, as both compete to dominate the same resource. Prior to 1978, most of China’s output was produced by state-owned enterprises, however, private investors and owners have since taken a large hold of the market, as well as China introducing a free-market system allowing output to grow exponentially, without slowing. Given that China is now
Rio Tinto told the inquiry in August it considered three options for the mine that would have avoided damage to the rock shelters but chose a fourth to pursue an additional $134m in high-grade iron ore. Its CEO and two other executives have since resigned over the incident. The Section 18 exemption under which Rio Tinto was able to load explosives around the caves, allows ministers to approve any application which involves the destruction of a heritage site, regardless of Aboriginal protest.
According to Professor Jon Altman from the Australian National University, there have been 463 applications under Section 18 to impact Aboriginal heritage sites on mining leases over the past 10 years. None have been rejected. “The disaster has now left a gaping hole in our ability to pass on our heritage to our children and grandchildren,’’ said Burchell Hayes, a member of the Puutu Kunti Kuurama
Let’s go beyond refractories and dive into our customized solutions for clean steel, safety, productivity, and green steel that will support you in achieving all your goals. beyond-refractories.com
and Pinikura people. “When I heard, I was driving to Port Hedland with two of my grandsons. It felt terrible as a grandfather that I was not able to preserve the heritage that was on loan to me.” There is a marked difference in attitude, between that of Hayes, and that of the mining industry; in that Hayes interprets the land as ‘loaned’, rather than a quantifiable opportunity for profit. The significance of damage to
Aboriginal sites is not only to their cultural identity; land has a fundamental social and economic importance to indigenous societies, one that can be disrupted and substantially transformed by mining operations.
Any interruption to living traditions carries political and financial repercussions; as indigenous wealth is generated from traditional sources, access to common
resources, food security, social articulation, spiritual certainty, and mutual support in times of need. Threats to wealth are greatly exacerbated if the group is faced with mining-induced displacement or resettlement.
Change is demanded, but the pull is in many different directions. In order to prevent the end of the Australian mining industry; lower quality ore must be sought, but to prioritise the urgency to decarbonize, greener methods are required. A total shift in industrial structure would be needed to compete with China’s super-economy; which in turn demands embracing further change, while avoiding the destruction of land of which the ownership is increasingly contested, and industrial activity criticised. There is a surprising source of respite within the industry, however, as Russia’s invasion of Ukraine wages on, giving Australia more space in a market that is becoming increasingly claustrophobic. Yet, stability that relies on instability is – unsurprisingly – unstable. Once the war concludes, gaps will begin to close, and Australia’s decade long stronghold on iron ore may begin to falter. �
Prior to the COVID-19 pandemic, the US construction sector was booming – but supply chain issues, weak demand and high costs have driven ‘flattish’ conditions. In the eyes of industry experts, opinion varies as to the predictability of the market; but one thing remains clear: increased demand, if possible, will drive success. Myra Pinkham*reports
THERE is no question that thus far 2022, while mixed, has been a better year for the US construction market than the past few years. While overall activity has been moderating somewhat over the past few months, it is expected to remain fairly resilient, especially as the impact of certain recent legislation starts kicking in. That, however, is assuming that the US economy doesn’t fall into a recession.
The performance of the construction sector is very important to US steelmakers, particularly producers of such long products as reinforcing bar, structural steel and wire rod, given that, according to Philip Bell, president of the Steel Manufacturers Association (SMA), it accounts for about 35-40% of all US steel consumption.
“It is very difficult to forecast what will happen in the US construction market over the next several years,” Scott Hazelton, director of S&P Global Market Intelligence’s construction service said, explaining, “There are definitely some clouds on the horizon, but no one knows how severe their impact will be.”
Even though it is likely that over the near term the construction market will be much more moderating and challenging, Bell said he believes that the US steel industry will be able to adapt. “Steelmakers will continue to make investments to prepare for the future,
modernizing their portfolio and preparing for the eventual uptick in infrastructure spending, as well as any rebound that will occur in residential and nonresidential construction.”
As far as this year as a whole, Hazelton said that with the combination of rising interest rates, high inflation, and decreasing business and consumer confidence, US construction spending will likely be down about 5.5%, although it could actually be up about 9.3% in nominal terms because of the still very high inflation.
The US Census Bureau recently reported that in July, US construction spending (not adjusted for inflation), while up 8.5% year
*North America correspondentover year, was down 0.4% from June.
However, Ken Simonson, chief economist for the Associated General Contractors of America (AGC), admitting that he is more optimistic than many other market observers, said that, given he doesn’t expect the US economy to fall into a recession in the next year, he is actually pretty bullish about the US construction market.
This is even though, according to AGC’s annual workforce survey, 58% of the respondents said that they have cancelled, delayed or scaled back at least one project because of high costs while a third said they have done so due to lengthening or uncertain completion times because of supply chain issues. He also noted that some contractors had turned down work either because of their inability to hire enough workers or to get subcontractors to bid on projects.
Simonson said he is particularly bullish
about the construction of non-residential buildings and infrastructure – two sectors that are much more steel-intensive than both residential construction or the housing sector, which has been seeing a sharp decline over the past few months (particularly as it relates to single family homes) and of which he doubts will see ‘good times’ until mid-2023 or so.
That, Simonson said, is due to a combination of factors. First of all, on the back of low inventories of homes for sale, single family home prices have gotten way out of line. At the same time, on the back of the Federal Reserve’s aggressive interest rate increases, the average 30-year fixed mortgage rate climbed to 6.02% in midSeptember – the highest it has been since the 2008 financial crisis.
While single family homes use a limited amount of steel directly, the sector does have an indirect impact on steel consumption, relating to certain things that go into homes such as appliances and ductwork, Phil Gibbs, a metals equity research analyst for KeyBanc Capital Markets, pointed out. He, however, noted that not only has the boom in housing started to reverse, but remodeling activity has now stabilized and could ease.
On the other hand, Hazelton maintained that multi-family residential construction, which uses a lot more steel than single family homes, is plateauing after having been up about 10% last year. But, the National Association of Home Builders said that its recent Multi-family Market Survey indicated that in the second quarter, confidence for new multi-family projects was mixed with its Multi-family Production Index down six points from the first quarter,
while more builders reported stronger rather than weaker conditions. That is even though overall housing builder confidence fell for its ninth consecutive month in September.
Simonson described future multi-family construction activity as being vulnerable, explaining, “If the Federal Reserve continues to raise interest rates, or even keep them at current levels, the multi-family market could be weak for some time.”
The dynamics are a bit more encouraging for US non-residential construction, Tim Gill, chief economist for the American Iron and Steel Institute (AISI) said, referring to non-residential construction as being a mixed bag by sector and stating that traditional infrastructure construction, including highway and street, bridge, water and sewer projects, while currently in ‘a calm before the storm,’ is poised to see double digit increases over the next few years beginning in 2023.
Several recent bills – particularly the $1.2 trillion Infrastructure Investment and Jobs Act (IIJA), the CHIPS and Science Act and the Inflation Reduction Act – have been very supportive of non-residential construction, particularly infrastructure, power, energy and manufacturing projects, given the federal funds that they will eventually make available, Simonson said, noting that they also provide a number of incentives for investment including tax credits and loan guarantees.
Certain forward-looking indicators, such as the American Institute of Architects’ Architecture Billings Index (ABI), support the view of future non-residential construction
growth. While easing downward for the past few months, the ABI saw a month-onmonth increase to 53.3 points from 51.0 points in July, indicating an expansion in non-residential construction activity. It has remained above 50 points for the past year and a half.
SMA’s Bell observed that there is not only a lot of variability according to different construction sectors, but also by region of the country, particularly with southern states such as Florida, Texas, North Carolina and Virginia, but also some in the Mountain West region. But the largest amount of diversity is in the building sector – which has recently seen changing demand dynamics, with more change to come in the next few years.
The best news is coming from the infrastructure sector, which is a big consumer of steel. Simonson said that while a lot of infrastructure and power-related projects have not hit yet, they are imminent, thanks to the IIJA and the other recent federal legislation providing additional funds.
Simonson said that while the pickup in infrastructure investment is already off to a selective start, the federal moneys are still working their way through the regulatory, design and permitting process, so it will be more of a 2023 and beyond story.
He said that is even the case for the portion of the IIJA that involved reauthorizing the surface transportation bill for another five years, explaining, “While the bill was passed last November, it is a long path from the president’s pen to actual construction.”
Hazelton agreed with Simonson’s assessment of how infrastructure activity is progressing, stating that while it is fairly flattish this year, he is forecasting that in 2023, US infrastructure construction spending could increase about 20% in real terms.
Gill said that while the AISI is still digesting what the exact impact of the IIJA will be, money should start flowing later this year, before peaking in the middle of the decade.
Even with expectations of an overall 40-45 million short ton pickup in steel use over the next eight to 10 years associated with the IIJA, Robert Wills, vice president of AISI’s construction programme, said US steelmakers are confident that they will have the capacity to produce the steel needed to meet that demand, including for
the new infrastructure projects.
It is a more variable story for the construction of non-residential buildings or structures, but with more downside than upside, Gill said, with overall annualized real spending expected to decline about 5-6% given the fact that there is still a certain amount of pandemic hangover effects upon several non-residential construction subsectors. In fact, such sectors as office, lodging and retail are seeing double-digit declines, while others, like manufacturing and warehousing, are seeing improved activity.
Simonson attributed this to the fact that building construction has been vulnerable to some of the changes that have already been occurring in the US economy and that it could be even harder hit if the economy continues to weaken.
The decline in office construction spending has been particularly notable, according to Hazelton down about 18% year-on-year. Simonson said that comes as workers have been reluctant to go back to their offices, especially not full time. Some employers are looking to call their workers back in, at least on a flexible schedule, while others are delaying opening offices all together or even moving into a new building, leasing as little as half the space they had previously. “While there will be some renovations, with the high vacancy rates, there will be limited new office construction for a long time,” Simonson said.
Warehouse construction, as well as data centre construction, had been very strong with the pandemic-related push for e-commerce, KeyBanc’s Gibbs noted. Although Amazon (which had been involved in a once-in-a-generation buildout) has announced that it will be pulling back some of its warehouse investments and would start to sell off and sub-lease space and this is expected to have a dampening effect, assuming that other companies follow Amazon’s lead. Currently warehouse construction activity is described as being flattish.
Meanwhile, Gill said that construction of transportation facilities, such as airports and railway stations, is doing surprisingly well and is expected to see growth in both 2022 and 2023, partly because of the flow, or expected flow, of federal infrastructure monies.
Another contributing factor could be the pickup in both personal and business travel, which Simonson said is somewhat supportive of hotel and convention centre occupancies. “But I think it is too early to say when there will be a resumption of the boom in hotels, amusement and convention centre construction that we had late in the past decade,” he said. Hazelton said that currently real construction spending for lodgings is down about 20%.
Manufacturing construction spending is currently up about 4% in real terms, Hazelton said, noting that there is potential for that growth to accelerate in some of its sectors, particularly those that will be benefiting from the CHIPS Act. One obvious impact of the legislation is the building of US semiconductor production plants, although Hazelton noted that it will likely have a positive impact upon the transportation and electronics industries, which have been hampered by supply chain issues, including a shortage of chips.
While there are some weak areas, such as food processing, Hazelton said there has also been, or is expected to be, a pickup in certain other manufacturing sectors including the steel and energy industries. For example, Becky Hites, president of SteelInsights LLC, said in a recent presentation that over the past decade US steelmakers announced $33.5 billion worth of expansion projects.
Considering these construction market dynamics, both US steelmakers and steel distributors that sell into the industry are being somewhat cautious, John Anton, director of S&P Global Market Intelligence’s steel service, said, noting, that while they are currently handling the situation, and
making good profits, they don’t want to over-produce or build up excess inventories given the uncertainty over future demand.
“Companies are buying all of the steels used in construction – including rebar, beams, plate and wire rod,” he said, “But just not more than they have to.”
Even once demand from the infrastructure sector picks up, aided by the IIJA, the mills are confident they will be able to meet that demand, AISI’s Wills said, especially as investment projects that will increase their capacity to produce construction-related steel come online. For example, both Nucor and Commercial Metals are not only currently constructing new bar micro-mills, but have announced plans to build additional plants.
Nucor is also building a greenfield plate mill that is expected to come online later this year.
The only challenge, Bell said, is getting steel where it needs to be, given certain supply chain and logistics issues.
Overall, this year has been a relatively good year for the US construction industry and the steelmakers and distributors selling into that sector, but Gibbs said that it could be peaking with some contractors delaying or pulling projects due to higher costs, rising interest rates, and labour issues. He said that the momentum could continue to slow into next year, depending upon how much infrastructure projects – and strength in certain other construction sectors – will be able to take up that slack.
As far as the situation exists for steel suppliers in the context of the construction sector, Anton said they should continue to be profitable as long as they continue to match their supply with demand. �
Steel is a thing of beauty, says Barbara Rossi*, with its striking lines that don’t overwhelm the landscape, but work with its inclines and slopes. It is also, in her eyes, deeply undervalued in terms of its potential to transform domestic industry, and help, rather than hinder, urgent decarbonization targets. Having recently spoken to the British parliament, submitting evidence on the irreplaceability and recyclability of the material, Rossi is politicizing the fight for funding research, and an increased public conscience of a material used and seen every day, but often misrepresented. By Catherine Hill**
‘‘I’M terrible at making coffee’’, Rossi is telling me, as she apologetically pours milk into a three quarters full cup, ‘‘I hope this is okay’’. I assure her it is, and we take a seat in two nearby velvet armchairs, in an
intimate room covered in wooden paneling, and chequered jacketed professors.
For someone who feels so underconfident in making hot drinks, her skills and knowledge in other reactive processes is
defining. Prior to being appointed as a tenure-track associate professor at the University of Oxford in 2019, she was an associate professor at KU Leuven in Belgium, and now runs the Sustainable
Metal Structures Research Group at the University of Oxford, which conducts experiments on structures to perform ‘fundamental and applied research’. It is a striking combination on intense academic research, and sheer physical graft.
Once our coffees have settled into a drinkable temperature, I begin by asking what drew her to steel, and she tells me; ‘there is a history behind steel. I’m from Belgium, my grandfather was a coal miner…Belgium, just like the UK, has a long history of steelmaking and coal making, which has inevitably declined…I also come from a city where coal and steelmaking was very much present.’
Rossi studied under Professor René Maquoi of Belgium University – who received among other awards, the Charles
Massonnet Award from the European Convention for Construction Steelwork, the Gold Medal Gustave Trasenster, and the Medal of the Institute for Theoretical and Applied Mechanics from the Czech Academy of Sciences. I look impressed –and I am.
I ask if she has always been passionate about steel. She nods vigorously. ‘‘It’s impossible not to be passionate about steel’’, she says, ‘‘when you look at structures that have been built, like Norman Foster’s viaduct of Millau’’.
‘‘I won’t even use the word beautiful, because the word is subjective…but most of these bridges which do not disrupt the landscape too much…. they look like pencil lines – and they could only be made with high strength materials like steel.’’
As René Maquoi did in the past, she wants to leave a ‘footprint’ in the mind of her students and inspire them to use more steel as civil engineers.
I ask her what challenges this footprint requires, if there are perhaps misconceptions about steel.
‘‘There isn’t a misconception, there are just wrong messages. Some messages say concrete is 100% recyclable, and steel is not easily recyclable – it’s greenwashing – a certain way of describing materials that is misleading and inaccurate.
“The lobby of the cement industry is a powerful one – the steel industry is fairer; they tend to want to support their own industry without saying anything inaccurate about other materials which I respect very much. But in the current context, I find it rather important to communicate more about this material even if that means to be sending negative messages about concrete’’.
She pauses for a moment, as if she is catching a breath.
She tells me another big issue steel faces is that the industry is ‘slower’; ‘‘[the steel industry] is not responding as quickly to today’s society challenges. If you look at SSAB for instance; when they announced they were going to produce fossil-free steel a few years ago, they were laughed at. The industry regarded it as money thrown out of the window. And they were wrong, this is now the biggest change in steel production in over 100 years. Sweden is revolutionizing the industry and everybody else is just late.”
Some would call a lack of pace a sign of passivity, but Rossi disagrees, saying
that it is ‘not that they’re not open to change; it is just a complicated industry facing enormous technical and financial challenges.’
There is a small pause, I sense she has more to say on this note, and I am proved right – as she continues; ‘‘In the UK, there is also,’’ Rossi tells me, a ‘‘national nostalgia’ that exists – the ‘greatness of the UK’s history is printed in its citizens’ hearts, and the steel industry is included in that.’’
And so we move on to the topic of UK steel, which is frequently in domestic headlines, and more than often sandwiched between adjectives like ‘dying’, ‘ailing’ and ‘in decline’. In a quick internet search, the portrait that is painted is one of an industry that was once paramount to the British economy and is now struggling to survive.
‘‘The UK is facing huge competition’’, Rossi says, ‘‘but in this race against the largest steel producers, we tend to forget our own strengths, that we produce enormous quantities of high value scrap, but what is happening here is incredible because more than 2/3 of it is exported! I see that as grains of gold slipping through our hands.’’
I make a note on my laptop, writing ‘angry’, because that is how she sounds – in this moment, or perhaps it is more complex than that. Anger doesn’t often stew as long as she has had to live with the knowledge that the UK is doing things very (obviously) wrong. It is a keen frustration at the solution being in graspable reach, but repeatedly being overlooked.
‘‘With all the scrap we produce each year,’’ Rossi tells me, ‘‘and knowing that there will not be a shortage in the future, we could build a more sustainable industry. In the US, more than 50% [of steel production] is based on EAFs fed on domestic scrap; they don’t export scrap, they guard it jealously. We should look at the US as a terrific example!’’
The potential – and opportunity – is still there, according to Rossi, ‘but we [the UK] should catch the train now’.
‘‘We should,’’ she says, ‘‘stop leaking scrap, make strategic acquisitions to secure supplies, increasing our efforts to have better control of contaminants. Steel is truly indefinitely recyclable. There is no other material that better fits a sustainable circular economy.
‘‘The life cycle of steel is 40 years on average – concrete is at its maximum down-cyclable. That is not as strong as
“
Sustainability and climate change is an important part of our educational offer, and that did not come from us. It’s a community demand, birthed from the teachers and students.”
the original product made from virgin materials” she tells me. “If you ask someone in the street if steel is recyclable they will say yes, we know we never throw it in the bin!’’
This is a message Rossi desperately wants to spread. ‘‘This should be pink flashing on websites!’’, she exclaims, as she frenziedly clenches and unclenches her fists, mimicking flickering lights.
‘‘It should be the message.’’ Is she hopeful about passing this message on?
important aspect; the bottom line for the construction sector is how we reduce material consumption to its bare minimum and guarantee environmentally friendly production means.’’
The conversation shifts to UK politics, and their effect on the industry.
‘‘Tax-payer money is not being used strategically with regards to the steel industry”, Rossi says, shaking her head emphatically. “We should use that money to help build a better [steel] industry rather
but sometimes it’s important to take a step back and think, what have we achieved so far and how can we further support smaller research increments towards more tangible solutions with greater and faster impact? It does sound less exciting, I’ll give you that, and I suspect that’s why government funding isn’t actively supporting my research’’ she smiles.
Before things began to take the same melancholic turn as an Ingmar Bergman movie, I ask Rossi about her current projects. She tells me she is looking into ‘new production methods and new design formulae for highly sophisticated steel structures.’ ‘‘There are’’, she says, ‘‘a number of essential problems – such as fatigue in hybrid structures – that need to be solved. That is where research is needed for the moment, we need to know the technical constraints of certain materials and manufacturing processes to be able to employ them to make structures more sustainable.
“What I’m trying to achieve is a point where we use the exact minimal quantity of the best material at the right place.’’
I ask Rossi to summarize steel in three words, and symbolically of her passion for the material, she proceeds to say four, six, nine, and I begin to lose count.
She then manages to transform my somewhat pithy question into a more powerful statement, saying that steel is ‘both old and new’- ‘‘a future without steel is…’’, she pauses, grasping into her memory for the suitable turn of phrase.
‘‘Vouer à l’échec.’’ There’s a sense of a different language, not French, nor English – but of the industry itself – it’s only when she breaks off into smaller talk, that her vocabulary falters, and she has to search for a word. Within the language of steel, she is perfectly versed.
She smiles, trying to find the English equivalent.
‘‘Sustainability and climate change is an important part of our educational offer, and that did not come from us’’, she says, ‘‘it’s a community demand, birthed from the teachers and students.
‘‘The younger generation…’’, she pauses, perhaps reflecting on students she may even be lecturing after our interview, ‘‘we don’t have to teach them about sustainability, its already there – they tell us! They already know, and they see themselves in that larger context.
‘‘Whatever the subject, this is the
than keep this war horse from the industrial age at all costs.’’
In her eyes, it is a case of stratifying the sentiment into actionable solutions; better placed funding, greater dialogue between government and industry, and overall, a recognition of the power the steel industry holds in building a sustainable future.
There is a small pause, as she looks down briefly, and then continues; ‘‘what I regret, sometimes, is the way our government is funding research… we tend to want to fund innovations, fundamental innovation,
After a moment, she resurfaces, and tells me it means ’doomed to fail’, or more literally, ‘dedicated to lose.’ I tell her I prefer the second definition, in my mind, it takes away less culpability that from what Rossi has been saying for the last hour, is a salvageable set of conditions. If we are ‘doomed to fail’, the failure is already set – but if we are ‘dedicated to lose’, the enterprise exists – it simply needs to be redirected to fight for a world that advocates both for its industry, and its own life.
“What I’m trying to achieve is a point where we use the exact minimal quantity of the best material at the right place.”
The Sequence Impulse Process (SIP) is a new blast furnace technology that first began full operation at Schwelgern blast furnace 1 at the end of 2020. The blast furnace is a large 4,400m3 inner volume blast furnace, operated by thyssenkrupp Steel Europe AG at their Duisburg plant in Germany. The SIP technology has demonstrated an impressive impact on blast furnace operation to date, during production campaigns either side of the recent blast furnace reline in 2021. By William Edmond*
SIP is an oxygen pulsing technology that serves to prevent problems of low permeability occurring in the lower regions of a blast furnace. It does so by injecting small quantities of high energy oxygen, through regular pulses, deep into the blast furnace raceway at each tuyere. The oxygen targets fine carbon material deposited within voids at the transition zone between the raceway and the ‘deadman’, the stationary packed bed of coke present in the hearth of a blast furnace. The deposits can accumulate and reduce permeability into this region if they are not adequately removed.
Under low permeability conditions, important gas and liquid flows are impeded from travelling into and across the deadman toward the centre of the blast furnace. This can have a negative impact on the overall blast furnace process. Permeability here is improved by SIP because it targets the place where the foundations for efficient blast furnace operation, gasification, and effective liquids drainage, are all set out. At its heart, SIP technology works to enhance raceway characteristics and enables oxygen to reach an area of the blast furnace where it is not normally found. The oxygen profile does not usually extend very far into the raceway under normal circumstances. It is rapidly consumed on leaving the tuyere, supplied through conventional means as part of the blast, with or without oxygen enrichment. But with SIP, an amount of oxygen becomes available for reaction with the fine carbon found at the back of the raceway and into the transition zone outside it. It is a key feature of the SIP effect. Permeability becomes improved by removing carbon deposits through the effective mechanism
of oxidation. Gas and liquid flows are no longer impeded and can move more freely to reach the centre of the blast furnace. As paths open to improve the distribution of ascending gases, and the drainage of liquid phases through the blast furnace hearth, process benefits are consequentially realised.
The application of this technology becomes very effective at high pulverized coal injection (PCI) rates, where char particles, formed from unconverted coal in the raceway, are a known contributor of fine carbon deposits. SIP also has a positive effect on raceway reaction kinetics and ignition conditions such that it is also credited with improving the coal conversion
* Senior engineer, Primetals Technologiesbehaviour [1, 2]. SIP, therefore, can play a role in mitigating both the cause and effect of problems arising from unconverted coal at high PCI rates or where a coarser coal is injected.
Set against the backdrop of a requirement for operators in modern blast furnace ironmaking to lower their consumption of reducing agents, improve efficiency and deliver decarbonization improvements, SIP is particularly relevant. This necessary focus is from both an OPEX and legislative perspective. In addition, the continued outlook of uncertainty for securing high-quality and keenly sought after raw materials, means it is no easy task for operators to manage production
schedules and the blast furnace process, to ensure that a stable and high productivity operation results.
At Schwelgern blast furnace 1 the SIP technology has already demonstrated a positive influence on blast furnace performance and assisted with such challenges it has become a welcome addition to the set of operational tools available. Positive changes attributed to operation with SIP, such as enabling a higher cost effective PCI rate with a stable operation, while at the same time, lowering the total reducing agent rate (RAR) requirement, are high among the many reasons why.
SIP is an innovative technology that is available now to improve operation and provide incremental change aligned to reducing carbon emissions. It can readily be incorporated into existing blast furnace plants. This pioneering and exciting new
technology was developed in partnership between thyssenkrupp Steel Europe AG and thyssenkrupp AT.PRO tec GmbH. It is now accessible to blast furnace operators worldwide, through the new exclusive co-operation agreement with Primetals Technologies.
The oxygen used by the SIP plant takes quantities of oxygen previously used by the blast furnace through either hot stove blast enrichment or oxy-coal addition. The oxygen is effectively re-purposed from these routes, with the total flow used consistent with the desired level of total enrichment for the blast furnace operation.
The oxygen is supplied via a connection to the site’s high-pressure network and is delivered to the SIP plant. An associated pressure control station, buffer vessel and
oxygen ring main around the blast furnace service the key plant components within specialist SIP boxes. One SIP box is used for each tuyere of the blast furnace, and they are located just above the tuyere platform. The boxes ultimately send oxygen to the SIP injection lances inserted through the blowpipe at each tuyere. The use of highpressure oxygen (typically > 20 bar g) is a requirement of SIP technology.
The principal function of each SIP box is to provide the means for generation of a shockwave in the supply pipe that leads to each injection lance. The high pressure supply is necessary to produce this phenomenon. Immediately after the shockwave, a free jet is formed travelling at supersonic speed, it is the source of the high energy oxygen pulse that enters into the blast furnace raceway. Proprietary equipment within the SIP box is responsible for inducing the shockwave by releasing a volume of high pressure oxygen in a rapid but controlled manner. Each pulse lasts for only a very short duration (typically 0.5s) but the frequency of them is set to be at regular intervals by virtue of the dedicated control system.
A pulse pattern, cycle time and the total oxygen flow necessary, can be adjusted accordingly to match the production requirements or to impact upon a particular blast furnace operational strategy. Normal practice at Schwelgern blast furnace 1 has been to deploy a pattern which achieves a form of circumferential symmetry around the blast furnace. However, the operator is provided with a great flexibility in how to use the system. For example, the admission of individual tuyeres is freely selectable and specific tuyeres can easily be targeted for additional oxygen should it be deemed necessary. An option currently not possible for all blast furnaces.
In addition to the periodic pulses of high energy oxygen, each lance receives
a continuous flow of a small so-called ‘base load’ of oxygen. The SIP pulses are in effect superimposed on top of the base load which is designed to ensure adequate lance cooling between pulses. Nitrogen is also available for this purpose via the SIP box supply and the system automatically switches to nitrogen cooling in the event of oxygen being unavailable while the lance is inserted into the blast furnace.
The plant is equipped with fast-acting safety functionality which when required, quickly diverts stored oxygen away from the blast furnace via a vent pipe and nitrogen purge. The plant was designed with the highest consideration for high pressure oxygen safety in both equipment selection and inherent operational safety.
The installed SIP plant at Schwelgern blast furnace 1 has the capacity to supply the blast furnace with up to 25,000 Nm3/h of oxygen in total.
The SIP process for blast furnace application was originally conceived by building on knowledge and experience gained successfully using oxygen pulsing on smaller cupola furnaces. A joint research project between several partners under the framework of the German Federal ministry created the scientific and technical basis to convert the technology for use with blast furnaces. Further research and development activities widened the scope of investigation, leading to a strategic cooperation between the two thyssenkrupp companies for the ‘development, construction and operation of an oxygen impulse system on the Schwelgern 1 blast furnace’ [3]
Before this end goal was reached,
by SIP has also varied somewhat since SIP start-up. However, several suitable evaluation periods comparing SIP operation against non-SIP operation, have been made possible by identifying otherwise similar blast furnace operating points and are detailed within the papers.
encouraging results were found along the SIP developmental path, as evidence grew of its potential impact and influence.
Operating tests using one tuyere at Schwelgern blast furnace 1, equipped with a SIP test facility compared its performance against reference tuyeres. Various investigations in operation such as tuyere core drillings with detailed material sample analysis, helium tracing and thermovision measurements, all gave indications of enhanced results at the tuyere using SIP.
They showed that the raceway length was increased and a shift in the temperature profile towards the centre of the blast furnace took place. Also, a corresponding change in the proportion of liquid phases towards the centre of the blast furnace as well as a significant change of the gas flow distribution toward the centre were observed [4]. These studies clarified the temporary local effect of using SIP oxygen.
Following conclusion of the extensive research and development work, the world’s first blast furnace SIP plant was constructed, then successfully commissioned, and brought into full operation at Schwelgern blast furnace 1 at the end of 2020.
The results seen by thyssenkrupp Steel Europe AG and the future
Understanding the impact of the full SIP system using all the 40 tuyeres at Schwelgern blast furnace 1 has been made possible through analysis of the operating data of thyssenkrupp Steel Europe AG.
The results and findings to date have been quantified and published in recent technical papers [5, 6]. Due to changing production schedules, the desired level of oxygen enrichment in use on the blast furnace has varied. Consequently, the oxygen delivered
The consistent headline findings in using SIP include an ability to support a stable, higher PCI rate. At the same time, it has provided an improvement in the efficiency of operation to such an extent that a significant reduction in the total fuel rate – and consequently, the CO2 emissions generated – have been made possible. These headlines are a direct result of positive changes which occur to the operational state of the blast furnace when SIP is in use. Many of them can be attributed to an improved distribution of the reducing gas, across the full blast furnace cross section, as it ascends upwards from leaving the raceway. Descending burden materials contact with the gas and interact more effectively. This has been evidenced by changes seen in the properties of the sampled gas profiles from in-burden probe measurements, as well as the determined overall gas utilisation of the process.
Further indicators to operators of improving process conditions under SIP have been found with a reduction in the total pressure drop and permeability resistance across the blast furnace recorded. In addition, the variability of wall temperatures and the energy losses experienced in the high heat load areas of the blast furnace also fell when using SIP. This was without any operator intervention to adjust another operating parameter, for example the burden distribution pattern. In general, a greater stability of blast furnace operation has been established when using SIP. This became especially evident during an enforced period of operation where the raw materials used were of very low quality. In the past, use of such feedstocks has led to process upsets and instability being encountered regularly on the large Schwelgern blast furnace 1. For the recent experience, under similar circumstances but with SIP now operating, the outcome was quite different. The additional permeability created by SIP helped to soften the problematic impact on production.
By addressing the issue of low permeability
and enhancing the raceway characteristics, SIP appears to be a technology ready to change the game. For the future, this opens up the potential for blast furnaces to operate at new set points. The improved permeability enables an increase in gas acceptance by the blast furnace that can allow the blowing rate to be raised and production potential increased. Positive economic adjustments, such as exchanging the use of expensive metallurgical coke for more, less expensive PCI but at the same time generating noticeably lower CO2 emissions, are equally beneficial. �
[1] C. Gruening and F. Mayinger, “Experimental investigations of supersonic flame stabilisation based on fuel self-ignition” Chemical Engineering & Technology No. 10, 2000, pp. 909-918.
[2] A. Ben-Yakar and R. Hanson, “Cavity flame-holders for ignition and flame stabilisation in scramjets: an overview”
Journal of Propulsion and Power 17, No.4, 2001, pp. 869-877.
[3] R. Klock, T. Mölleken, M. Peters, H.-H. Heldt, G. König and W. Langkabel, “thyssenkrupp introduces a new oxygen technology for the blast furnance process” Stahl und Eisen 138, pp. 103-107, 2018.
[4] R. Klock, A. Johnen, H.-H. Heldt, M. Kannappel, C. Thiede, M. Feldhoff and D. Senk, “Automatisierter Sequenz Impulsprozess für Großschachtöfen,”
BMBF Final report, 2011.
[5] R. Edmond, R. Klock, B. Smaha and H. Bartusch, “Improving blast funance efficiency and reducing carbon emissions with blast furnance oxygen pulsing technology,” AISTech 2022, Pittsburgh, 2022.
[6] R. Edmond, R. Klock, B. Smaha and H. Bartusch, “Improving of blast furnace operation and carbon footprint using the state-of-the-art Oxygen Pulsing Technology” ECIC ICSTI 2022, Bremen, 2022.
The average campaign life of the RH-OB vessel at SAIL’s Rourkela Steel Plant was almost doubled from an initial average of 88 heats, then 106 heats to 130 by greater attention to the weld joints between the snorkel legs and lower vessel, and by increasing the position of the refractory retainer plates 300mm higher up the vessel. By S Roy1, A Bhattacharyya2, P Kumar Pedapudi1, and P R Padhee1
A number of steel vacuum technologies for secondary refining were developed for degassing in the 1950s. These included RH (Rurhstahl Heraeus) degassing, Vacuum Tank Degassing (VTD), Vacuum Arc Degassing (VAD), and Vacuum Induction Melting (VIM). Today, the demands of clean steels require even lower hydrogen and nitrogen content, ultra-low carbon and sulphur, and lower total oxygen. Vacuum treatment facilities play a crucial role in achieving this. The chosen vacuum degassing technique is dictated by the steel grade to be produced. The use of RH vacuum degassing is the most common, especially for large heat sizes. RH processing is an important tool for various metallurgical functions such as decarburisation, vacuum degassing and inclusion removal. It is also used successfully to produce ultra-low carbon steels, auto grade steels, pipeline steels, and silicon steels. RH degassing starts with sucking up the liquid steel from the ladle into a vacuum chamber via two snorkels (up-leg and down-leg)[1]. Then, a flow of steel is circulated between the vacuum chamber and ladle by blowing an inert gas into the liquid steel. The degassing process involves both a chemical reaction and a transport phenomenon in the liquid steel[1], inside splashes of metal in the vacuum chamber and at the surface of bubbles as they form[2,3]. Liquid steel flow characteristics play an important role in controlling the rate of degassing, decarburisation and inclusion removal. This complex process involves thermodynamics, kinetics, and multi-phase flow and mass transfer[4]. It has been proved that a lower vacuum pressure[5, 6], a deeper insertion depth of the snorkel[3, 7] and a higher gas flow rate[8-12] favour
optimisation of the fluid flow within the RH vessel, although the circulation rate will reach a saturated value with the increasing gas flow rate[7, 13]. The RH-OB degasser is categorised as a ‘Re Circulation Degassing’’
characterised by very high decarburisation and degassing with relatively little temperature loss, as compared to other degassing techniques. Further, the ability to blow oxygen in the RH-OB process
1 Rourkela Steel Plant (RSP), Steel Authority of India Limited, Rourkela, India
2 R & D Centre for Iron and Steel (RDCIS), Steel Authority of India Ltd, Ranchi, India Corresponding Author
compensates for any temperature loss during recirculation of the steel. No special slag measures and no additional ladle freeboard are required. Fast vessel changes and efficient ladle transport concepts increase the capacity and productivity of a plant.
The RH degasser consists of a refractory lined vessel with two snorkels at the bottom and a gas off-take at the top along with a vacuum pumping system. Treatment starts by immersing the snorkels into the molten steel contained in a ladle either by lifting the ladle or by lowering the RH vessel. The steel rises into both snorkels by suction. One of the snorkels is equipped with argon or nitrogen gas injection pipes. This lift gas creates the steel circulation through the vessel back into the ladle via the outlet snorkel. The treatment time is defined as the duration between submersion and removal of the snorkels into the melt and varies between 15 and 45 minutes depending on the steel grade required.
Usually, the lifetime prognosis for the refractories is based on operational experience and on the close co-operation with the refractory supplier. However, there is the risk of unplanned shutdowns that lead to low productivity and higher costs. The demand for RH-treated steel grades is increasing, which necessitates high plant availability and, therefore, high refractory lifetime. The reliability of the refractory is especially important when operating with a single RH degasser as a vessel change takes considerable time. To achieve a high refractory lifetime, it is essential to determine the main factors influencing refractory wear. This enables the
bonded mag-chrome bricks of 250mm lining thickness and has a total height of 2000mm. There is a steel brick retainer plate 25mm thick between the lower vessel and middle vessel which supports the entire load of the latter. The brick retainer plate is covered with a special L-shaped brick[15] to prevent erosion of the retainer plate. The entire vessel is lined with mag-chrome bricks due to their high-volume stability, high hot strength to resist erosion by steel flow, high thermal shock resistance, high resistance to corrosion by steel and slag, high resistance to iron oxide attack and no carbon pick up of the steel from the refractory.
bearings and so forth can be produced. The following metallurgical benefits characterised in the RH-Treatment at Rourkela Steel Plant:
• Optimum decarburisation to less than 20ppm carbon;
• Rapid reduction of hydrogen content to less than 1.5ppm;
• Removal of nitrogen under vacuum to less than 30ppm;
• Achievement of exact compositional values;
• Chemical heating of the melt is possible;
• Improved overall steel cleanliness.
As illustrated in the refractory lining depicted in Fig 1, the vessel along with the snorkel is lined with refractory bricks and castables. The snorkel is relined with bricks of 165mm thickness on the inside while the outer shell is covered with castable of 90mm thickness (Fig 2). The lower part of the leg consists of mag-chrome bricks 175mm thick and the upper part lined with bricks of 200 mm thickness. The lower vessel has 12 courses of direct
Initially, the life of the snorkel and lower vessel was approximately 88 heats and this increased to 130 heats after the first modifications. In the RH-OB vessel, gunning is carried out after every heat to minimise the erosion rate of the snorkel and to increase lifetime. Bricks in the lower vessel are changed after each campaign along with the snorkels.
The RH-OB was a new addition and the challenge, therefore, was to increase the life of the refractory to improve productivity, reduce the specific cost of refractories and, in turn, the cost of steel. In the present study, the abrupt failure of the snorkel and vessel refractory have been addressed which was adversely affecting steel processing in the RH-OB unit.
Since its inception, the RH-OB operation had proved to be a bottleneck, due to the short campaign life of the snorkel and lower vessel refractory. Moreover, during the initial 50 campaigns, the vessel was down 15 times due to the shell being punctured
and metal breakout from the snorkel and bottom junction, and once due to metal breakout from the lower and middle vessel retainer plate area. Also, during these 50 campaigns, the retainer plate had to be changed five times, leading to increased downtime of the vessel. This was adversely affecting productivity and the cost of production at the steel melting shop of RSP. To improve the campaign life, the two most vulnerable areas were identified after several case studies. These were:
a) The weld joint between each snorkel and the vessel and;
b) The retainer plate of the lower vessel.
Detailed inspection after every heat for three months, failure analysis and refractory post-mortem analysis led to identifying these main causes.
The snorkel consists of a metal cylinder lined with refractory inside and out. The metal part is welded to the lower vessel before the start of each campaign. This requires in-situ welding around the circumference of the cylinder from both inside and outside the joint after aligning the snorkel to the lower vessel. The weight of the snorkel and lack of space resulted in a poor weld quality which sometimes led to the creation of pinholes and cracks in the weld during operation (Fig 3). These small pin holes were sufficient for high velocity air ingress into the vacuum chamber which was evacuated to 1-2 mbar. The impact of this high velocity air on the refractory could cause sudden collapse of refractory in the impacted area. Falling refractory further exposed the steel heat being treated and the hole gradually became larger ultimately leading to metal breakout as depicted in Fig 4. As a result, the vessel had to be
taken out of service for repair frequently.
Apart from this, severe turbulence of liquid steel was occurring within the vessel during very low vacuum operation. This was aggravated when the temperature of the steel charged was high – above 1640°C – and this elevated temperature decreased the density of the liquid steel (to around 6.9kg/cm3 Fig 5)[14] which caused a sharp rise of the height of the liquid steel above the recommended 1.47m design level required to produce steel splashing within the vessel during the deep degassing stage. This thermo-mechanical impact resulted in rapid erosion of the thin refractory lining on the bottom retainer plate area, which was only 140mm thick. Once erosion of this refractory was complete, the steel retainer plate was exposed and eroded due to the high velocity and impact of liquid steel. This resulted in the sudden collapse of refractory bricks once the retainer plate, which supported the refractory, failed and this in turn led to hole formation in the lower vessel, which resulted in a loss of vacuum and stopped the operation.
The problem was verified using Bernoulli’s equation. The velocity of the air ingress into the vessel was calculated with real-time
For vacuum pressures of 1 & 10mbar
ρ1 = 1 atmosphere= 101325 Pascal
ρ2= 1 mbar = 100 Pascal (Case 1)
ρ2= 10 mbar = 1000 Pascal (Case 2)
data and found to be above supersonic speed. According to Bernoulli’s equation:
p + 1/2ρV2 +ρgh = constant (1)
where p is the pressure, ρ is the density, V is the velocity, h is the elevation and g is the gravitational acceleration. Now considering that the height is similar we get:
P1–P2= 1/2(ρ2V22–ρ1V12) (2)
and, A1V1 = A2V2 (3)
Therefore, from equations 2 and 3, it shows that decreasing the area of the hole or decreasing the pressure of the vacuum will increase the air velocity.
A2< A1, V2> V1
V2> V1, p2< p1
From the real time data, the air velocity with decreasing pressure is calculated for vacuum pressures of 1mbar and 10mbar, as shown in the box below, indicating that the velocity of air through a pin hole is much higher than supersonic speed and has sufficient momentum to dislodge the refractory lining resulting in leakage of metal.
Several steps were taken to eliminate the
V1 = density of air at room temperature, atm pressure = 1.09 kg/m3
V2 = density of air at 500°C at 1 mbar/10 mbar pressure = 0.0045 kg/m3
V1= velocity of air at room temperature = 0.3 to 0.9 m/s = 0.6 m/s (as an average)
V2= velocity of air when air is entering the orifice 101325 – 100 = 0.5 (0.0045xV22–1.09x0.62)
V2= 6707 m/s (Mach 19.55, Case 1)
V2 = 6677 m/s (Mach 19.47, Case 2)
weld joint problem. First, a channel in the form of a ‘V’ was prepared only on the outside joint of the snorkel to the lower vessel, as inside is covered with refractory. The ‘V’ was prepared with a 45° angle following the recommended procedure of the supplier.
Proper grinding was also ensured in the area. The root run weld and final sealing weld run was made using Tungsten Inert Gas (TIG) welding. Furthermore, in place of random ultrasonic testing of the weld, 100% ultrasonic testing was carried out to detect any weakness of the weld which was then repaired.
To address the increase in height of liquid steel inside the vessel because of a lower steel density at increased temperature, the inside of the vessel was inspected thoroughly after each campaign for five subsequent campaigns to ascertain the maximum height up to which metal splashing ocurred.
The higher level of steel resulted in increased steel splashing inside the vessel and thereby eroded the refractory and subsequently the brick retainer plate. To take care of the unacceptable high rise of liquid steel, the height of the retainer plate was increased by 300mm. Height increase protected the brick covering of the plate from becoming eroded which, in turn, increased the life of the retainer plate as well as that of the lower and middle vessels as shown in Fig 6. HA 90 dense castable was also used to patch the area to retard brick erosion in this vulnerable region.
In conclusion, during the initial 50 campaigns the average life was only 106 heats and there were 15 cases of metal breakout from the snorkel welded joints. After the necessary modifications, in
the next 50 campaigns, metal breakout occurred on only three cases and that too after a high snorkel life. The average life was increased to 130 heats and there was no damage to the brick retainer plate as a result of a marked reduction in erosion of refractory in the area. Vessel down time was dramatically reduced as a result of the significantly fewer shell repairs required. �
J Pieprzyca, T Merder, M Saternus et al , ‘Physical Modelling of Steel Flow in RH Apparatus,’ Archives of Metallurgy and Materials, vol 60, No 3, pp 1859–1863, 2015
M Takahashi, H Matsumoto, and T Saito, ‘Mechanism of decarburization in RH degasser,’ ISIJ International, vol 35, No 12, pp 1452–1458, 2007
Y G Park, K W Yi, and S B Ahn, ‘Effect of operatingparameters and dimensions of the RH system on melt circulationusing numerical calculations,’ ISIJ International,vol 41, No 5, pp 403–409, 2001
Y Luo, C Liu, Y Ren, and L Zhang, ‘Modeling on the fluid flow and mixing phenomena in a RH steel degasser with oval down-leg snorkel’ Steel Research International, vol 89, No 12, Article ID 1800048, 2018
L Lin, F Bao, L Q Zhang, and H L Ou, ‘Physical model of fluid flow characteristics in RH-TOP vacuum refining process ‘ International Journal of Minerals, Metallurgy, and Materials, vol 19, No 6, pp 483–489, 2012
H Ling, C Guo, A N Conejo et al , ‘Effect of snorkel shape and number of nozzles on mixing phenomena in the RH process by physical modelling’ Metallurgical Research & Technology, vol 114, No 111, pp 1–13, 2017
J H Wei, N W Yu, and Y Y Fan, ‘Study on flow and mixing characteristics of molten
steel in RH and RH-KTB refining processes’ Journal of Shanghai University (English Edition), vol 6, No 2, pp 167–175, 2002
D Q Geng, H Lei, and J C He, ‘Numerical simulation of the multiphase flow in the Rheinsahl-Heraeus (RH) system’
Metallurgical and Materials Transactions B, vol 41, No 1 pp 234–247, 2010
X G Ai, Y P Bao, W Jiang, J H Liu, P H Li, and T Q Li, ‘Periodic flow characteristics during RH vacuum circulation refining’
International Journal of Minerals, Metallurgy, and Materials, vol 17, No 1, pp 17–21, 2010
L Zhang and F Li, ‘Investigation on the fluid flow and mixing phenomena in a RuhrstahlHeraeus (RH) steel degasser using physical modelling’ JOM, vol 66, No 7, pp 1227–1240, 2014
X G Ai, S L Li, N Wang, and N Lv, ‘Simulation of inclusions removal influenced by snorkel and blowing parameters in RH refining’ Advanced Materials Research, vol 291, No 294, pp 155–158, 2011
P H Li, Q J Wu, W H Hu et al , ‘Mathematical simulation of behaviour of carbon and oxygen in RH decarburization, ‘Journal of Iron and Steel Research International, vol 22, No S1, pp 63–67, 2015
V Seshadri and S L Costa, ‘Cold model studies of R H degassing process’ Transactions of the Iron and Steel Institute of Japan, vol 26, No 2, pp 133–138, 1986
January 2014 Archives of Metallurgy and Materials 59(2):487-492, DOI:10 2478/ AMM-2014-0080
S Roy, P R Padhee, A Bhattacharyya and R K Singh, ‘Improving health and productivity of calcining kiln through several innovations in refractory maintenance practices at Rourkela Steel Plant’ Processing and Characterisation of Materials, vol 13, pp 245–254, 2021
In a world of increasing costs, the challenges of decarbonization are no different; if the price is too high, steelmakers will struggle to produce cleaner steel. However, the willingness is there, says Dr. Alexander Fleischanderl*, it just requires investment in a greener future to put the technologies in place, ensuring the transition happens right on time.
1. How are things going in your new role as head of green steelmaking? Is the steel industry keeping you busy? Things are going well, and I am proud of my role as the head of green steel at Primetals Technologies. It’s a real gamechanger for the business and how we’re able to speak to our stakeholders. I’ve had many conversations and while today there’s much talk about the willingness of customers to pay a green steel premium, I am convinced that in about 10 years it will be the other way around: it will be hard to fetch a good price for non-green steel.
2. What is your view on the current state of play with decarbonization of the steelmaking process? Are the 2030 and 2050 deadlines realistic and achievable?
It’s important to manage expectations. What we are looking at realizing by 2030 is a small market share for emissions-free steel production, rather than transitioning fully. Take-up of green steel will also vary between regions, for instance, steel producers in countries such as India and China, where they have heavy investments in new blast furnaces that have long life spans, will likely be slower to switch. This framework must include three main pillars: first, a realistic carbon pricing system that makes hydrogen-based steel production more competitive. Second, the creation of a premium market for green steel to encourage different stakeholder groups to make buying decisions based on sustainability, despite higher costs. And lastly, sustainable funding instruments that drive low-carbon initiatives, such as those in the European Green Deal and in tax incentives like the 45Q system in the US. If policymakers can provide this support, then the market will do the rest.
3. Explain in simple terms the nature of your new role within Primetals Technologies
As head of green steel, I lead Primetals Technologies’ Green Steel vision, strategy and technologies which support the steel industry’s transition to net zero greenhouse gas emissions by 2050. We’ve hand-picked leading experts from around the Primetals Technologies’ business to work together to push forward our efforts on green steel, while actively developing synergies within the business as well as within the larger Mitsubishi Heavy Industries Group, which includes Primetals Technologies.
5. Can you discuss any major decarbonization projects you are currently working on?
We are working with multiple projects and development opportunities around the globe. Hydrogen Based Fine Ore Reduction (HYFOR) is a game-changing technology for reducing iron ore, and it is fully based on hydrogen. Primetals Technologies is developing this technology at a pilot plant in Austria. The plant was installed last year and is delivering excellent results with multiple different iron ore feed materials from all over the world.
Another important project is GravitHY, a green steel project development in France. As a partner, we are working closely with a consortium to develop this Direct Reduction plant which includes an electrolysis plant and is based mainly on hydrogen. There are many more ongoing major decarbonization projects, for example, Quantum EAFs in China and Turkey, and Arvedi ESP’s in China and the US, just to name a few.
6. Can digital manufacturing aid the decarbonization of steelmaking?
4. In terms of the global picture on decarbonization of the steel industry, where in the world is the drive for a greener steel industry most intense? Europe has taken a leading role, even though it faces extremely high energy prices recently that make the challenge even harder. When considering boundary conditions, like the political framework that has been set, it is definitely driven by Europe.
*Head of green steel, Primetals Technologies
Digital manufacturing has led to higher levels of speed, efficiency, and precision than ever before. Digital technologies play an important role in our decarbonization efforts. As an example, digital twins can help to optimize production processes by increasing energy efficiency, reducing yield loss throughout the production chain, easing the development of new steel grades, and by calculating carbon emissions per production unit and per produced coil. All-in-all, digitalization allows us to finetune and orchestrate all production and maintenance related aspects.
7. Hydrogen steelmaking appears to be the next big thing. Thoughts?
Hydrogen’s potential to largely decarbonize the steelmaking industry has long been understood in principle.
The real roadblock for green steel now is simply the availability of low-carbon hydrogen. These technologies need to operate at scale to reduce costs which would require a substantial increase in hydrogen. We have calculated that converting all current carbon-based ironmaking to hydrogen would take an annual 72Mt of green hydrogen, requiring 500 gigaWatts of electrolyzer capacity and, by extension, about 4,000 teraWatt hours of electricity per year. So the scale of the undertaking is massive. But it’s going to happen – there is simply no alternative.
8. In your dealings with steel producers, are you finding that they are looking to companies like Primetals Technologies to offer them solutions in terms of energy efficiency and sustainability? If so, what can you offer them?
This is definitely something steel producers are looking for and we’re having these conversations with them. Steel producers will have to switch from methods involving carbon-based production to production methods that involve less carbon such as natural gas and eventually to routes that involve no carbon at all, such as green hydrogen.
9. How quickly has the steel industry responded to ‘green politics’ in terms of making the production process more environmentally friendly and are they succeeding or fighting a losing battle?
Global climate action has become a top priority in many of the world’s societies, prompting the steel industry to channel even more resources toward greater sustainability. In my view, players in the industry have not so much fought a battle against tighter regulation as they have called for clarity, predictability of regulatory measures, as well as a level playing field on international markets.
Over the past couple of years, policymakers have made progress in some important areas — particularly in Europe, looking at things like contracts for difference (CfD), funding mechanisms like EIF and IPCEI, and the carbon border adjustment mechanism (CBAM) in connection with an adapted ETS
mechanism that will put to an end any free-allocations for the steel sector by 2035 Now more than ever, I feel that the political establishment here appreciates the value of an industrial base – policies need to be calibrated in such a way as to retain and strengthen that base while also achieving rapid decarbonization.
10. Where does Primetals Technologies lead the field in terms of decarbonization technologies for steelmaking?
Since different regions in the world have their own different environmental objectives, we strive to provide steel producers with the ideal combination of green production technologies for their particular situation. The green production solutions of Primetals Technologies are designed to enable producers to achieve long-term sustainability, and these technologies ensure that all environmental targets are fully met in those regions.
Looking at currently available technology, one with a particularly competitive carbon footprint is Arvedi Endless Strip Production. This technology combines continuous thinslab casting and rolling in one compact plant layout and is the only solution on the market that offers real endless operation. Compared to a standard production line, Arvedi ESP delivers unparalleled performance at 39% lower CO2 emissions. Energy consumption is also reduced, by a staggering 45%.
11. Since your appointment as head of green steel where would you say Primetals Technologies stands in terms of its abilities to transform the steel industry into something greener and more efficient?
Primetals Technologies’ Green Steel organization has been set up to lead the transformation of the steel industry. That translates into being a driving factor in supporting steel producers on their way to decarbonization.
12. While everybody is focused on hydrogen as the saviour of the steel industry, it has been said that there are ‘several pathways’ towards decarbonization, ie, several different technologies that, ultimately, can achieve the same goal. What’s your view?
Today, fossil fuels remain the only viable
way to process iron ore at scale to get the iron needed to make steel. Steelmakers around the world are racing to deploy new technologies aimed at reducing the sector’s carbon intensity. Such efforts include energy efficiency measures such as waste heat recovery, switching to cleaner electric arc furnaces, and swapping coal for natural gas as a reduction agent.
So, there is hydrogen in the long run, energy efficiency, electrification and natural gas in the shorter term. An area that deserves more attention in the industry is carbon capture. As a part of Mitsubishi Heavy Industries Group, we’re having lots of conversations on leveraging this technology, which is particularly interesting for plants that are part of industrial clusters involving multiple sources of carbon, thus being able to share the necessary infrastructure.
However, while these developments all have a role to play in contributing to a sustainable transition, until 2050, adopting hydrogen will indeed be the key to the long-term, drastic reduction in its environmental impact.
13. What are the key challenges facing global producers in their quest to decarbonize?
There are several challenges facing steel producers, including large investments, higher operational costs, and availability of renewable energy and low-carbon hydrogen.
However, it is important to highlight the fact that the technologies to produce net-carbon steel are basically in place; some of them are just about to be finalized and have to be commercialized. Therefore, the pathways to net-zero steel are defined. What remains an open question is the availability and price of renewable energy.�
We are indeed proud to look back upon more than sixty years of research and development in the field of cokemaking. DMT providing state-of-the-art investigation methods for stamp and top charging supported by
Pilot-scale testing in a 10kg-retort Semi-industrial movable coke oven 60-year experience of coal blending Generation of coal blends with coals from different origin to perform reference tests
DMT use international standards to determine coal properties and coke qualities DMT assists coal merchants and assess their product for the marketing DMT supports coke plants in their continuous quality control of the used coal and the produced coke
In the second part of a threepart feature on Scunthorpe ironmaking, Tim Smith* discusses the expansion, technology, and socio-political impacts on the ironworks between the years 1919-1939.
PART one of this article addressed the establishment of the first ironworks in the Scunthorpe area of North Lincolnshire, UK in 1860 and was published in the September issue of STI. Six iron works were established between 1860 and 1912 using the vast deposits of locally available ore, but all experienced problems with this ore due to its high lime content and low iron, which averaged at 25%. Eventually, it became clear that blending local ore with siliceous ore transported from Northamptonshire enabled efficient iron production.
With little investment during WWI, three integrated works remained in 1919. Appleby-Frodingham, Redbourn, and Lysaght. Each was destined to become part of a larger group; Appleby-Frodingham became part of the United Steel Companies in 1919, Redbourn joined Richard Thomas & Co, of South Wales in 1925 – later to become Richard Thomas and Baldwins, and Lysaght, headquartered in Bristol with works there and in Newport, South Wales and Wolverhampton, became part of Guest Keen & Nettlefolds in 1920.
Appleby-Frodingham Steel Co Ltd was formed by the take-over of Appleby Iron & Co by Frodingham Iron & Steel Co in 1912. Both companies had long histories of ironmaking at Scunthorpe, with Appleby having been established in 1875 and Frodingham in 1864. Redbourn had started as the Redbourn Hill Iron & Coal Co Ltd in 1875. Lysaght established iron and steel production at Normanby Park, Scunthorpe at the turn of the 20th century to provide
Table 1 Average annual pig iron output of blast furnaces (kt)
Year
Table 2 Reduction in coke consumption at Scunthorpe works 1871 to 1974
steel for its mills at Wolverhampton and Newport.
All three works were integrated works, operating blast furnaces and steelmaking using open hearth (Siemens Martin) furnaces. Coke ovens had been built at the Lysaght works in 1912 and at Redbourn in 1919. Until 1939, Appleby-Frodingham brought in coke from its Yorkshire batteries at Silkstone, but eventually built a coke-
oven plant at Scunthorpe.
Ore preparation plants were also added to improve output. The average output from Scunthorpe’s blast furnaces was better than the national average (Table 1) leading to the Scunthorpe works becoming the lowest cost producer in the UK. The output of pig iron as a proportion of UK production increased from 6% to 16% and steel from 3% to 10% in the 1920s.
Nearly all the iron produced by the blast furnaces was used in steel production and the scrap-to-pig iron ratio was very low, ensuring a good quality steel. By 1930, pig iron production from Scunthorpe furnaces reached 8.5Mt and steel output was 7.0Mt.
The coke rate improved from 1.57 tons of coke per ton of pig in 1922 to 0.58t in 1974 (Table 2).
Crushing and screening of both local limey ore and Northamptonshire salicaceous sands had been introduced during WWI but as this increased, the amount of fines produced increased, requiring sintering to be introduced. Sinter plants were erected at Appleby-Frodingham in 1934 with additional lines in 1939 and 1951. Lysaght and Redbourn did not follow this trend until 1962. From this date, no raw ore was charged to the furnaces, a factor only dreamed of by the 19th century ironmakers who suffered a number of explosions in their furnaces as a result of charging uncalcined lime-rich local ore. By 1938, iron-rich foreign ore was being added to the blend imported via the port of Immingham on the River Humber, some 20 miles (32km) to the East. Table 3 shows the evolution of ore sources.
Ore dressing and the charging of sinter had a dramatic effect on the output of the blast furnace. Between WWI and WWII, output per furnace nearly doubled while post 1945, a four-fold increase was achieved, mainly after 1950.
No investment had taken place during WWI but major improvements were made during the inter-war period. By 1921, the steelshop at Frodingham was extended and modernised and, in 1927, the Appleby site commenced steelmaking with three 250ton tilting open-hearth furnaces, unlike the earlier fixed furnaces. In addition, a 500-ton mixer was installed and two plate mills, one 7 ft (2.13m) wide and the larger being 10 ft (3.04m) wide. Two more blast furnaces were added, bringing the total to five. In 1930, a larger 300-ton tilting open-hearth furnace was added, with another in 1937 and again in 1939, as well as a 600-ton active mixer – to blend and partially refine the blast furnace iron – while awaiting transfer to the open-hearth furnaces.
Redbourn commissioned new rolling mills, and Lysaght built a new blast furnace – bringing its total to five. Lysaght undertook a large programme of
reconstruction during the 1920s, building new coke-ovens, reconstructing two of its open-hearth furnaces, and erecting an iron-ore crushing and screening plant.
Equipment was also installed to collect and use blast furnace and coke oven gas. This investment paid off; with Lysaght being ready to meet an upturn in demand in 1930 after the economic depression of the 1920s which had seen demand, and therefore
output, drop dramatically in 1920-21 and 1926. A second 500-ton active mixer was installed in 1937 and output reached 330kt of ingot steel.
At Appleby-Frodingham, in 1939, two new blast furnaces were built at a new site, South Ironworks, bringing the total to eight. These were the first of the four ‘Queens’ and were named Mary and Bess. A battery of coke ovens and two continuous sintering strands were built to supply them.
The outbreak of WWII prevented any further major expansions at any of the three companies. All escaped any serious damage by enemy action. In preparation for post war demand, plans, known as the Anchor scheme, were drawn up by ApplebyFrodingham for future developments.
Part three will follow these developments and those of Redbourn and Lysaght which eventually led to the introduction of tonnage oxygen in steelmaking, which enhanced open hearth steelmaking via the Ajax process, and later led to the introduction of the basic oxygen steelmaking converter, which heralded continuous casting. These processes are the legacy of the present-day Scunthorpe works, British Steel. �
With over 50 years in the Steel Industry, we have a wide variety of solutions to keep your mill rolling.