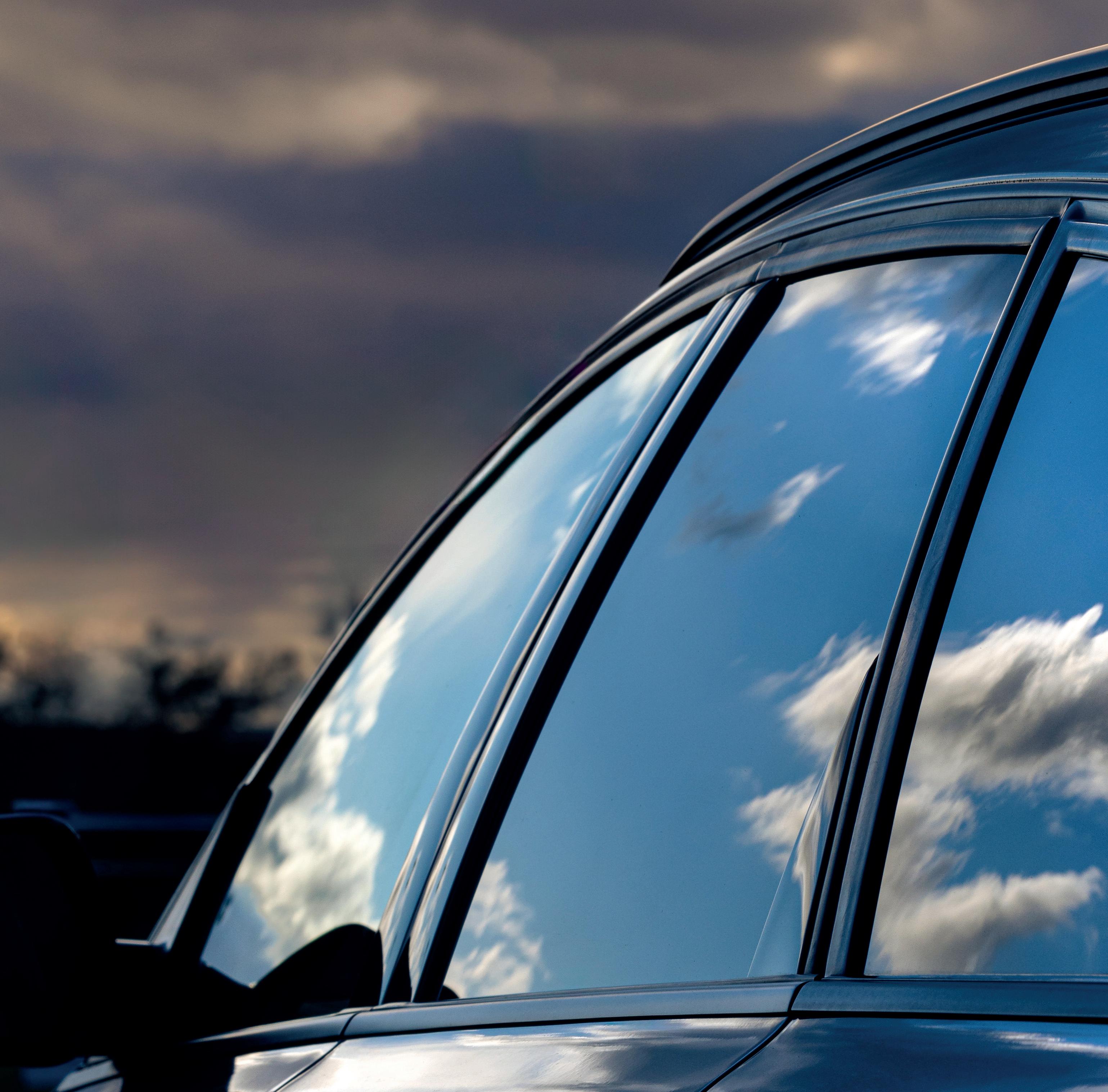
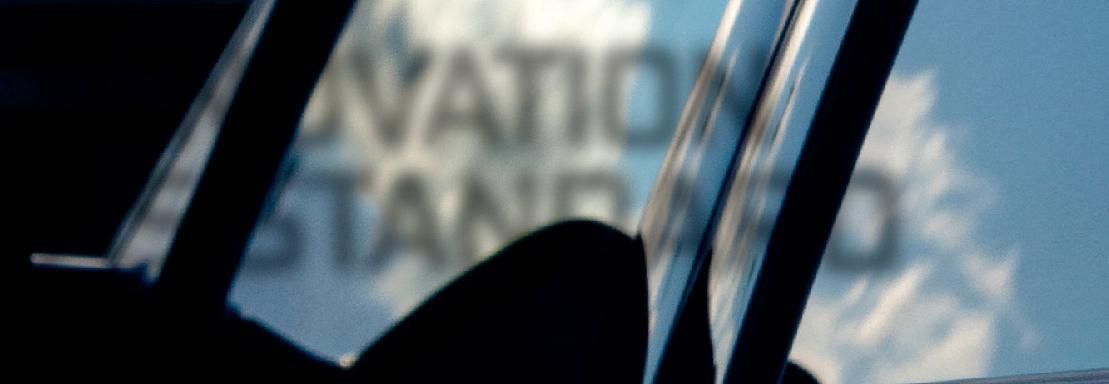
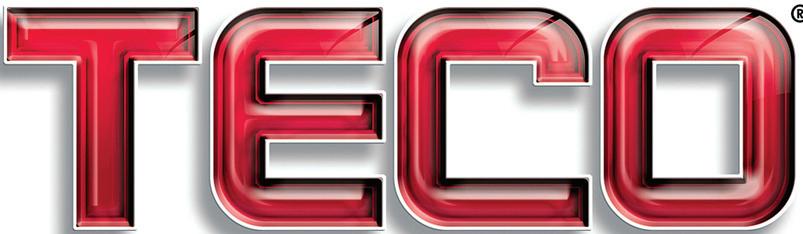
As a true engineering company, we feel confident in providing to our customers, complete Casting & Rolling Lines (for CU & AL), including the Furnace Set and fumes treatment systems.
Group Editor: Greg Morris
Tel +44 (0) 1737 755132 gregmorris@quartzltd.com
Page designer: Annie Baker
Production: Carol Baird
Sales Manager/Advertisement production: Esme Horn esmehorn@quartzltd.com Tel: +44 (0) 1737 855136
Subscriptions: Jack Homewood subscriptions@quartzltd.com
www.furnaces-international.com
Managing Director: Tony Crinion
Published by: Quartz Business Media Ltd, Quartz House, 20 Clarendon Road, Redhill, Surrey RH1 1QX, UK. Tel: +44 (0)1737 855000. Email: furnaces@quartzltd.com www.furnaces-international.com
Furnaces International is published quarterly and distributed worldwide digitally
CelSian
Welcome to Furnace International’s second edition of the year. The past 12 months have generally been marked with a general downturn in business and, in recent months, uncertainty. However, I can cautiously say, there appears to be some green acorns of growth out there. Confidence appears to be increasing after a18-month hiatus. There were a number of reasons for the slowdown: energy price hikes as a result of the Russia/Ukraine conflict, an adjustment after Covid, supply chains reorganising themselves after the pandemic and a general lack of consumer confidence.
But after talking to people in the last few weeks within several of the sectors we cover, there are signs of encouragement. The largest glass manufacturer, O-I, has seen modest sales increase, while the second largest steel company, ArcelorMittal, plans a €1.2 billion electric furnace in Dunkirk, France.
The most notable news is from the USA aluminium sector, where two multi-billion dollar investments have been progressing. Novelis’ $4 billion Alabama faclility is on track for commissioning next year. The second, from Emirates Global Aluminium, will see a $4.1 billion facility open in Oklahoma open by 2030. President Trump has many critics but these investments are a sign of faith in his administration from industry.
Greg Morris, Group Editor, Furnaces International, gregmorris@quartzltd.com
• No trailing thermocouples so quick, safe and effective
• Measure from up to 20 thermocouples with a single data logger
• Ideal for surveying semi-continuous, continuous or modular furnaces
• Live RF telemetry TUS data collection options
• Oil, salt and water quench thermal barrier options
• Efficient real time TUS of static furnaces
• Robust compact external data logger design
• Easy to transport and set-up
• Thermocouple type and plug connection options for quick installation
• Cold junction compensation to give accurate data in changing environmental temperatures
• Fully compliant with AMS2750 & CQI-9
• Full 0.1 °C / 0.1 °F resolution/readability
• Apply accurate data logger and thermocouple correction factors with ease
• Full control over real time data collection and TUS analysis
• Generate your complete TUS reports with efficiency and confidence
Chinese-owned British Steel is now under the control of the British government following an emergency session of Parliament.
It looks likely that nationalisation is the next step to secure a future of sorts for the steel company and the jobs of its 2,700 workers.
Emergency legislation was rushed through Parliament and has been described, by the BBC, as a ‘legislative sprint’ from the First Reading to Royal Assent, something that would normally take months.
Swedish steelmaker Ovako has invested SEK 60 million in a new, energy-efficient furnace at its Boxholm site.
The new furnace reduces energy consumption by 50% and significantly lowers carbon dioxide emissions, says the company. It is also designed to run on fossil-free hydrogen, making it a key part of Ovako’s and the region’s transition towards a more sustainable future.
The inauguration ceremony was attended by Sweden’s minister for climate and the environment, Romina Pourmokhtari, who, together with representatives from Ovako and other key stakeholders, emphasized the importance of investing in energy-efficient and fossil-free industry.
The inauguration ceremony was attended by Sweden’s minister for climate and the environment, Romina Pourmokhtari, who, together with representatives from Ovako and other key stakeholders, emphasized the importance of investing in energy-efficient and fossil-free industry.
‘‘Ovako is a brilliant example of how
Now that the Government is in charge of the company, it is hoped that the raw materials needed to keep the two blast furnaces up and running will be secured although, as a BBC report points out, it’s not like ordering something online, far from it.
Hyundai Steel has unveiled plans for a US$5.8 billion electric arc furnace (EAF)-based integrated steel mill in Louisiana, US.
The facility will focus on producing high-grade automotive steel while significantly reducing carbon emissions compared to traditional blast furnace operations.
A major investment to boost the US steel sector, the project is expected to generate more than 1,300 jobs and contribute to the growth of automotive manufactur-
industrial investments can drive both climate benefits and economic growth. With projects like the hydrogen plant in Hofors and the new furnace here in Boxholm,
Sweden is strengthening its position as a leader in sustainable steel production — setting an example for the entire world,’’ said Romina Pourmokhtari in her speech.
ing in the US.
Hyundai Steel president and CEO, Seo Gang-Hyun said: “Hyundai Steel’s investment in an EAF-based integrated steel mill in the U.S. is anticipated to stimulate local economic growth, including the creation of new job opportunities. We plan to supply automotive steel plates not only for Hyundai Motor and Kia’s strategic models but also to expand sales to US automakers in the future.”
The Louisiana mill will have an
annual production capacity of 2.7 million metric tonnes, with commercial operations scheduled to commence in 2029.
The plant will integrate advanced direct reduced iron (DRI) technology, along with hot-rolled and cold-rolled steel plate production.
It represents Hyundai Steel’s first overseas production base, positioning it strategically in a region with strong steel demand.
Source: Manufacturing Digital
Furnotherm has successfully completed a project for SNJ India Glasses’ 230 tpd furnace at its facility in Tamil Nadu, India.
A heating-up ceremony was attended by SNJ India Glasses Chairman Mr S. N. Jayamurugan and Managing Director Ms Anitha Jayamurugan.
The glass draining process, mark-
ing the start of production, was successfully carried out on 7 May 2025.
According to Furnotherm, this is the first container glass furnace to be established in the state of Tamil Nadu. The furnace was designed by Germany’s Horn Glass Industries.
Ardagh Glass Packaging (AGP)Europe has completed an industrial fuel switching trial to produce glass packaging using biofuel.
The £6 million trial, funded by the UK Government’s Net Zero Innovation Portfolio programme, took place at its Knottingley facility in the UK.
The trial, led by Glass Futures, brought together several manufacturers in both the glass and ceramics sectors.
This included AGP-Europe, Encirc, O-I Glass, Pilkington UK, and DSF Refractories & Minerals.
The project’s goal was to evaluate the feasibility of using alternative liquid bio-derived fuels in the glass melting process, with the aim of completely replacing natural gas with lower-carbon biofuel in the furnace.
Over the course of seven days, the AGP-Europe trial successfully
replaced 100% of natural gas with liquid bio-derived fuels.tries.
This produced 4.1 million glass containers, and reduced CO2 emissions by 242 tonnes (compared to carbon emissions from the same furnace using 100% natural gas).
The trial demonstrated that lower-carbon glass packaging can be produced at commercial scale without compromising glass quality or process efficiency.
Dean Butler, Business Development Director, Ardagh Group, said: “This trial validated and supported our existing knowledge and proved that liquid bio-derived fuels can effectively replace natural gas in glass packaging production over an extended period.
“This is an exciting development for the glass industry as we continue to seek innovative solutions to reduce carbon emissions.”
Verallia will begin heat-up of additional Brazilian capacity shortly.
The French-headquartered glass packaging company said heat-up of a furnace at its Campo Bon facility in Brazil will begin shortly, with first production by the end of June.
Its CEO Patrice Lucas said: “This additional capacity will allow us to pursue our growth in the dynamic Brazilian market.
“And this new furnace, a new advanced oxy-combustion technology will operate with an 18% CO 2 emission reduction compared to a traditional furnace.”
India’s Sunrise Glass Industries has ignited a container glassmaking furnace.
The Indian company held an inauguration ceremony for the 225t/ day oven.
The coloured furnace is located in Kosamba, Gujarat, India.
This new furnace is specifically designed to cater to the beer and wine industry, making it the second such facility in Western India. For our customers, it introduces a competitive and reliable alternative in the region.
For Sunrise Glass, this is its first colored glass furnace, marking a strategic expansion into new segments within the container glass industry. The company has four funaces and manmly serves th Indian market, as well as exports overseas.
Aluminium scrap was successfully melted by a hydrogen-powered furnace during recent tests.
Initial tests of a retrofitted a 1.5-tonne capacity furnace using various types of aluminium scrap demonstrated that the quality of the melted metal remained consistently high.
The tests took place as part of the EU-funded HyInHeat project to develop sustainable heat technologies for the aluminium industry.
The furnace was converted at aluminium recycling and rolling group Speira.
“Our early trials have been encouraging,” said Galyna Laptyeva, Senior Scientist and Project Lead at Speira.
“We’ve proven that hydrogen is fundamentally suitable as a fuel for our melting furnaces. This is a major step towards reducing the carbon intensity of our production.”
Launched in 2023, the HyInHeat project brings together 30 partners from 12 European countries to explore hydrogen’s potential for decarbonising heat-intensive processes in the aluminium and steel industries.
With €24 million in funding from the European Union, the initiative aims to develop efficient hydrogen combustion systems that address nearly the entire
process chain of these energy-intensive industries.
To further increase efficiency, Speira has now equipped the test furnace with even more advanced technology. Instead of using normal air, hydrogen is now burned with pure oxygen – a process known as “oxyfuel.”
“Oxygen is a by-product of hydrogen production anyway. By using it for combustion, our calculations show we
can save approximately 30%of fuel,” explains Laptyeva. “This makes the process not only more environmentally friendly but also more economical.”
Another advantage of hydrogen combustion is that, ideally, no harmful nitrogen oxides (NOx) are produced. In practice, however, small leaks and impurities can cause minimal amounts of these pollutants.
Rio Tinto is considering constructing an aluminium smelter in India powered by wind and solar energy.
The global aluminium manufacturer will assess the feasibility of an integrated 1 million tonnes/year low-carbon aluminium project.
It has signed a memorandum of understanding with AMG Metals & Materials to jointly assess the plan.
The proposed site will also produce 2 million tonnes/year of alumina.
Both the smelter and the alumina production will be powered by wind and
solar energy, firmed by pumped hydro storage.
The development will comprise a study to evaluate a potential first phase 500,000 tonnes/year aluminium smelter in a favourable location.
Rio Tinto Aluminium Chief Executive Jérôme Pécresse said: “Partnering with AMG Metals & Materials enables us to assess how we can develop low-cost responsible aluminium production powered by renewable energy.
“With its rapid economic growth and strategic position, India is a compelling
location for this potential project and aligns with our long-term vision for a globally more diverse and resilient aluminium business.”
AMG Metals & Materials is promoted by the two founders of Greenko and AM Green. As part of the study, AMG M&M will examine a firmed renewable energy solution with Greenko, while Rio Tinto will explore a commercial alumina solution.
The study will also assess smelting technology options to determine the most cost-effective solution for the project.
Jeff Remson* outlines how audits and training help ensure the industry’s continued success by passing on knowledge to the next generation of glassmakers.
How do we train a furnace manager? The modern furnace manager often has an engineering degree, but practical glass furnace operation is absent from university curricula. A comprehensive textbook on operating a large industrial glass furnace has not yet been published.
Many times, it seems we take a young engineer and put them in charge of a melting operation and expect them to succeed in the way young albatrosses, abandoned by their parents, dive off cliff faces to fly or die.
One way to improve the odds is to bring students into the factories as college interns and introduce them into the process. This approach will be effective if there is a qualified individual in the factory to mentor and pass on best practices. That’s the ideal, but it assumes that these mentors exist within a company, and these practices are indeed the best. Regrettably, some inherited practices are closer to mythology than effective procedures.
While technology, including automation and computer modelling, has advanced, it cannot fully replace hands-on experience and visual assessment. Technology can only go so far. As long as there have been microcomputers, we have tried to automate every aspect of furnace operation. Although automation and data recording have advanced significantly, a fully automatic furnace has not yet been developed.
Computer model-based controls have come a long way but one of the limits is the furnace itself and the devices we use to measure it. Factors like flame characteristics, batch pile control, and refractory conditions require direct observation. Even using Artificial Intelligence (AI) to assist in decision making would require
input from humans. Therefore, effective training necessitates a combination of technological understanding and practical, in-plant experience.
So, the question remains. How do we train new furnace people? There is no better way than the industry professionals who provide training and audits. We have several important industry meetings, including the Glass Problems Conference, which is now in its 86th year.
There are other meetings from which contact with the best and brightest of the industry is available. For the most part, it’s the discussions with industry experts rather than the content of the presentations which pass along the most practical knowledge. Still, there is no better way to get a young engineer the proper experience than hands-on, in-plant development. This is one of the many benefits of professional plant audits and surveys.
The furnace audit should involve both the engineer and the industry professional. This is a teaching opportunity. The young engineer should be encouraged to ask questions and press the visitor for information. The auditor should share insights to help the plant staff optimise this process to match industry-leading furnaces. This includes glass quality, property control, energy efficiency and furnace life, as well as the key metrics of a well-run furnace.
The audit can be divided into four areas: the furnace condition; the furnace operation; field equipment; and operating procedures.
Are there areas in need of repair? Is the state of condition of refractories expected based on the age and pull rate of the furnace? During the audit, the entire
furnace will be inspected from the crown and superstructure to the glass containment blocks and bottom, to the basement and exhaust systems.
Endoscopy and thermal imaging provide valuable supplementary data for the audit, extending analysis beyond the limitations of human sight (Picture 1).
It is a common practice to perform triage on the areas of the furnace, a three-stage prioritisation in which areas of the furnace are rated:
� Good: No issues currently.
� Of Concern: Minor issues that need to be addressed or monitored.
� Bad: Major concerns that should be addressed at once.
The industry professional will point out condition problems and help the plant develop a repair plan for repairs and remedies. Some are minor and can be done easily while others may require planning and significant capital expenditure (Picture 2).
We need to look at the inputs and outputs of the furnace. The typical inputs are batch materials, combustion gases, and electricity. The outputs are quality glass and environmental emissions. A well-run furnace will maximise glass output and minimise energy inputs and environmental emissions.
Inspection includes combustion analysis by sampling flue gases, observing flame length and alignment to create the thermal conditions to melt the batch as efficiently with the best temperature control possible. If electric boost or bubbling is used, they need to be operated for maximum benefit to the convection of the glass bath.
*Founder, Remsco Glass Furnace Consulting, Delaware, USA https://www.jeffremson.com/
During an audit, equipment is inspected to ensure safe maintenance and operation. The relative energy consumption can be evaluated compared to industry average. If it is subaverage plans, improvements can be planned.
The audit will also critique the batch delivery to the furnace and the dynamic movement of batch on the melt surface.
The melting process necessitates controlled inputs to minimise damage to the furnace and exhaust emissions, thereby ensuring glass quality and prolonging the furnace’s operational life.
As glass furnaces have evolved, electronic instruments have replaced human inputs. There are instruments to measure internal temperatures, pressure, and glass level. All these devices operating under the extreme conditions of a glass furnace and have the potential to fail or drift calibration. Part of an audit should include checking the calibration of field devices so that the control systems have accurate input.
Glass level can be manually checked optically in the melter and probed in the front end. Furnace pressure can be checked with a manometer and a probe inserted into various locations around the melter superstructure. For every automatic control loop there should be a manual back-up system, and the furnace engineer should be able to use them. No matter how sophisticated a control system is, it is only as good as the data from the field.
Through the audit process, we will also evaluate that standard procedures are being used for both routine and emergency conditions. On a day-to-day basis the conditions of production may alter furnace set-up. There may be composition changes for cullet supply or customer requirements. Some furnaces will make colour changes.
In these cases, the furnace must be managed with the best practices by all department personnel. Every operator should be trained in these standard procedures so that all team members respond to changes in the same way. Furnace history should be reviewed and “best day” operations documented so it can be repeated the same way every time.
Emergency procedures are necessary to ensure the safety of the personnel and the company assets. Glass plant emergencies include glass leaks, power failures, fuel curtailment and extreme weather. The equipment for these emergencies should be in working order and the department personnel should be trained in the standard procedures on a regularly scheduled basis.
Given the rarity of real emergencies, and the potential for operators to go years without one, regular simulated training is necessary. The auditor will inspect records of the training and explain any opportunities for improvement to the young engineer.
Two key deliverables follow the completion of the audits. The first is a closeout meeting which should be used to present initial findings, and help the plant
prepare for any upcoming repairs. The second deliverable is the audit report. This serves as a snapshot of the furnace at one point in its history. From here we can later see changes both in improvements and new issues that occur later.
For our young engineer this report is a training document. The use of triage for furnace conditions can be used to create a prioritised plan to allocate resources as they will be needed. A list of actionable tasks may be created. From the operations critique the engineer now has a reference of what to look for when problems arise.
If glass quality begins to worsen, the engineer can reference back to a time when things were optimal. They can develop routines to manually back up their control systems by validating the field equipment. The furnace engineer who uses this data will find rewards from knowing that the furnace is being operated at peak performance.
Furthermore, in the event of emergency they can rest assured that they and their department personnel are prepared to respond calmly and safely to minimise risk to the safety of people and equipment in the plant.
To summarise, professional audits and training are vital for the glass industry’s continued success. While past furnace managers gained expertise through years of on-the-job experience, today’s younger, more educated engineers require mentorship and specialised training from industry professionals to maximise their potential. �
Steel Times International travelled to Barcelona to discuss the TWINGHY decarbonization project with Spanish steelmaker Celsa Group and Fives, supplier of a walking beam furnace at the centre of the project.
By Matthew Moggridge*
Acronyms are funny things. They’re fine if they work, like NATO, meaning North Atlantic Treaty Organization, or ASAP being short for As Soon As Possible, but sometimes, like personalized licence plates, they simply don’t add up. Or rather they do, but you need to be a little flexible in your thinking. Take TWINGHY, for example. Yes, I know it sounds like the name of a new children’s television programme – the Twinghys – but in reality, it means Digital Twins For Green Hydrogen Production. So, where’s the ‘D’ for digital? Call me a pedant, but it matters. Or perhaps it doesn’t.
Despite its rather cute name, TWINGHY is a serious project, as, indeed, is green hydrogen production in the quest for zero-carbon steelmaking.
One of the project’s industrial partners is Fives Group. The company is developing a new reheating burner capable of injecting a blend of hydrogen and natural gas in a range from 0 to 100% hydrogen. The burner will be tested at leading Spanish steelmaker CELSA’s furnace number three in Barcelona, Spain.
Replacing traditional burners with hybrid technology is a big challenge as the quality of the final products must be guaranteed and NOx emissions reduced while maintaining the same productivity.
The TWINGHY consortium consists of nine partners – Celsa Group in Barcelona (Spain); Swedish steelmaker SSAB; Fives Stein, a Fives Group subsidiary (France); Nippon Gases Espana (Spain); Barcelona Supercomputing Centre (Spain); RWTH Aachen (Germany); Oulun Yliopisto – Uoulu (Finland); Calderys Iberica Refractarios SA (Spain); and Swerim (Sweden).
*Editor, Steel Times International
The TWINGHY project was started in early 2023 and is one of many initiatives led by Celsa Group that form an important part of the Spanish steelmaker’s decarboniza-
tion strategy and will contribute to its ambition of becoming net positive by 2050. “Which means we need to be at least zero carbon and fully circular by then,” said Celsa Group’s head of innovation, Anna Domenech.
Steel Times International had been planning to visit Celsa to discuss TWINGHY for some time and embarked upon a train journey from London to Barcelona in early December 2024. Editor Matthew Moggridge sat down with Celsa Group’s Anna Domenech, the rolling mill plant manager Ramon Garriga and Gustavo Guzman, CEO of Fives Steel Spain, another subsidiary of Fives Group, involved in this project.
“When it comes to zero carbon, one
of the most important things we need to do is to replace natural gas and to do that we currently consider three alternatives,” said Domenech. The options are biofuels, hydrogen and ‘not combusting for induction’, the latter meaning electrification.
“We are not the ones that are going to select which one is happening in the future, what we are doing is trying to keep all doors open. So, we are investing into knowing a bit more about every one of these possibilities,” she said, adding that there are no innovation projects concerning biofuels because their composition is similar to natural gas, but more sustainable. The third option involves electrifying the process of beam reheating ‘because that is the main part of the process where we consume natural gas’, said Domenech.
Celsa is a recycler so most of its energy is generated by electricity used to melt the steel.
TWINGHY is a hydrogen project, started in early 2023 and, therefore, almost two years in development. Celsa uses natural gas for reheating and currently has many hydrogen-focused projects underway for reheating furnaces across the group. Domenech highlighted other planned Celsa projects testing the consumption of hydrogen in EAFs and ladle furnaces.
In Spain, however, the challenge is to make the reheating furnace in Barcelona ‘hydrogen ready’ and, according the plant manager, Ramon Garriga, that means making many improvements to the company’s existing reheating furnace, supplied by Fives.
The aim of TWINGHY, according to RWTH Aachen, one of the project consortium’s nine participants, is to ‘demonstrate an optimized heat transfer process based on hybrid burners in reheating furnaces, progressively decarbonizing the reheating process through the increase of H2 in combination with O2 and by monitoring and controlling it through a digital twin’.
Celsa’s Barcelona facilities constitute a true steelmaking hub. It has two electric arc furnaces (EAFs) in the melt shop, three rolling mills and several final transformation plants. The TWINGHY project is focused solely on one of the plant’s rolling mills and a Fives walking beam reheating furnace. “We have three rolling mills in Barcelona,” said Domenech, but only one of them is being used for the project producing merchant bars. The
others produce big profiles, wire rod and rebar.
A great deal of research has gone into energy efficiency, ‘which is a critical first step’, says Domenech, ‘and then we will move forward in order to prove that it’s possible to make the switch towards hydrogen’. The timelines are simple: this year [2025] will see the installation of the required pipes and instrumentation, which can only be done after the plant has been shut down – the facility runs 24/7 all year round but closes for maintenance for three weeks in the summer and two weeks in winter. In 2026, the trials with hydrogen will begin.
Domenech said that energy efficiency was crucial. “You cannot use hydrogen in a process that is not efficient,” she explained, stating that hydrogen will need a lot of energy to be created. “And that’s also the power of the digital twins as they allow us to not only simulate the situations that we will have in the future, but also to find the most optimal situation for every specific moment or scenario”.
The plant will be shut down for around three weeks during the coming summer to install the special burners, which are bigger than the existing ones and, therefore, require new holes to be made. The summer is the only season when it is possible to completely stop the furnace. The rest of the installation procedure (pipes and instrumentation) can be carried out during plant operation. The new burners can run with 100% natural gas and that’s good because when the plant restarts there won’t be any hydrogen available.
The reheating furnace has 24 burners in total, 10 of which will be repurposed for use with hydrogen.
There are also two burners from Nippon Gases, a consortium partner, and these are capable of working in hybrid mode, i.e. natural gas and hydrogen, but they are located in the less efficient soaking zone of the furnace, which comes after the heating zone. Oxy-combustion is generally more efficient since there are no additional air particles to be heated during the combustion process. This is why CELSA is interested in exploring this solution further. However, the furnace was not originally designed for this technology, and when combined with H2 combustion, it could create an imbalance in air pressure. This imbalance may allow cold air to enter the furnace, potentially reducing the overall efficiency of the
process, therefore Nippon’s oxy burners are located in the less efficient soaking zone of the furnace, which comes after the heating zone. The eight burners from Fives are inside the heating zone, which is the most important part of the reheating furnace. In total, including the Nippon burners, there are 10 out of 24 burners being repurposed. All 10 (including the two from Nippon Gases) can handle hydrogen and will not have an adverse effect on the function of the reheating furnace.
Fives Steel Spain’s Gustavo Guzman said that the company’s contribution to the TWINGHY project was the development of the new burners which, he claimed, were fully compatible with all blends of hydrogen from zero to 100%. Fives was brought into the project by Celsa with the express purpose of developing the burners, said Domenech, as they are also the suppliers of the furnace. The two companies have enjoyed a long and fruitful working relationship for many years, she added, and Fives was very much interested in participating in the project.
Fives has up to eight furnaces working within the Celsa Group of companies, the last installation being at Celsa Atlantic’s new rolling mill in Bayonne, France. He said that Fives was working on increasing the efficiency of other furnaces in operation at Celsa, not just the TWINGHY furnace in Barcelona. From Celsa’s perspective, having a trustworthy furnace supplier is important when dealing with a new, disruptive and risky product such as hydrogen. “You need guarantees,” assert-
ed Domenech.
Celsa’s Ramon Garriga said that, when operational, the burners will be the first industrial-scale hydrogen burners in Europe on a reheating furnace, with a capacity of 180 tons/hr. Each burner will have a capacity of 4MW or 32MW in total across the eight burners developed by Fives. Guzman believes the total useful power of the furnace is around 55MW.
The burners are currently 100% natural gas, but it can be 100% hydrogen or a combination such as 20% hydrogen, 80% natural gas. The burners can be set to work with whatever blend combination is applicable at the time.
The overarching challenge, of course, is hydrogen supply and that, says Domenech, is why the digital twin approach is so good. “Because it will allow us to adapt to different market situations in terms of availability.”
Challenges presented by hydrogen supply issues have been a constant concern prompting Celsa to consider installing its own electrolyser or to partner with a hydrogen supplier. A third option was to buy hydrogen from the network. “We were in discussions with many stakeholders, we are part of networks in different regions of Europe that are promoting hydrogen including one in Catalonia. We are doing everything we can to push for hydrogen production,” said Domenech. It looks likely that buying from the network will be pursued. “So, we keep being part of these networks at European and national level,” she said. “We expect this to happen at some point, I don’t know when, but it looks like the availability of
hydrogen, or the feasibility of producing it, will depend on the geographical location of your plant. Spain seems to be a good country to produce hydrogen in terms of renewable energy capacity because we can install a lot of it, but I don’t think we considered the issue of water enough. We tend to treat it like an infinite resource and it’s not,” she explained.
Domenech spoke of water shortages in Catalonia and how, at times, Celsa was almost pushed to stop production. There are now, however, many projects funded by the European Commission that are focused on water circularity. Celsa is involved with two projects related to developing membrane technologies for water cleaning.
Where TWINGHY is concerned, however, the premise is simple: is it or is it not valid to reheat billets with hydrogen? Answering that question is the project’s aim, its end game. It’s then a case of being ready for the right market conditions to prevail.
“We need time to make all the trials,” said Ramon Garriga.
Domenech says it’s not so much about what is there, but for plants to invest further into energy infrastructure. “At the end, Celsa is guided by the politicians. Everything is about politics, but the European Commission says we should get ready for hydrogen because they will make it a reality, so we say okay, let’s get ready. Even if hydrogen is not available in the future, TWINGHY will have been a useful project because it has increased the energy efficiency of our furnaces and opened the door to using new fuels,” she
explained.
The relationship between the participants of the TWINGHY project is good, says Domenech. “It doesn’t always happen in European projects, but when you have good personal connections, you just learn more and want to do more,” she said.
Fives is confident about its new burners which have already been tested, qualified in mid-2024 and are ready to go. “We want to be ready for the opportunity that may come,” said Guzman. “There will be other potential clients interested in having these burners when hydrogen becomes available.”
Celsa’s Domenech cites Fives’ burners as one of the two main achievements of TWINGHY so far. “They have developed the burner and proved it in the lab, that’s the first thing. Second, we have the first high-resolution simulations of combustion in this type of furnace in Europe, albeit with natural gas, and we will do the same with hydrogen,” she said.
So, what’s next? This year the burners will be installed and next year trials will be conducted. “The most important thing is that, at the end of the journey, we will
know if our furnace can work with hydrogen and for us it’s already a goal which can be applied to other furnaces. Here in Barcelona, we have three reheating furnaces and one of these is the same [as the TWINGHY furnace] in terms of capacity,” said Ramon Garriga.
Where hydrogen availability is concerned right now, it’s uncertain how things will unfold going forward, says Celsa’s Domenech and Fives’ Guzman, but one thing is certain: the nine participants
in the TWINGHY project are working well together. According to Guzman, “The starting up of such a programme is always a challenge, bringing people together, signing NDAs between us, it’s difficult to put these people together and work for the same objective, but it’s working pretty well,” he said.
Domenech agrees, stating that ‘every partner has a clear role and a clear reason why they are there’. She believes in small consortiums like TWINGHY as opposed to some of the increasingly larger ones being funded by the European Commission.
Celsa’s Ramon Garriga extolls the virtues of the consortium, agreeing with Domenech’s point about exploiting synergies between the partners. “To use the knowledge of all the people in a collaborative team is good, it’s best to be with a group rather than going it alone,” he said.
“It’s been a good experience for us,” said Fives’ Guzman. “Learning from each other and reaching for a target that we set together. I think what will happen will happen. We don’t know the future for hydrogen, but what we agreed to be done with this project is done.” �
Take a good look inside your furnace, you won’t need to see it for over a decade!
Zahra Awan met with industrial leaders at Fives to discuss the company, the decarbonisation of the industry as well as the role of AI in manufacturing technology.
FIVES has an importance presence in Paris, from locomotives to bridges to the Eiffel Tower. In its 213 year-history it has played a part in numerous industrial sectors and projects.
Since starting at Fives in 1989, Pablo Arribalzaga, Managing Director Europe, Fives North American Combustion, has observed considerable growth in the group’s size, with turnover up by 200%.
The differences between North America and Europe are widely recognised, the two regions have different cultures, attitudes, and goals.
But this is also the same for countries within Europe: “We have common rules and techniques, but culturally we are different,” said Pablo.
But one thing that connects both regions is the “mindset of developing new things and improving the quality of the industry today.”
“On both sides [of the pond] we would like to be more sustainable. However, in North America they are most concerned about NOx emissions, whereas in Europe they are more concerned about energy costs,” Pablo said.
But could the agenda shift with the arrival of the Trump administration?
Since Trump took office earlier this year, the world has experienced a series of developments related to trade, tariffs and international relations in particular.
Pablo noted it is too early to predict and understand how the administration will affect the global aluminium industry. While past experiences can offer insights into the future, history is not a fortune teller, he states.
The global industry’s response will vary, but working with both regions, as well as with the Middle East, Pablo is particularly interested in the comparison between the US and Europe.
“It’s complex because what may work for the US side may not work for the European side.
*Former editor, Aluminium International Today
“In Europe, we manufacture our best-selling product, while in the US, we produce the entire product portfolio. We will be affected by local policies but to a lesser extent.”
Fives works throughout North America, with 23 subsidiaries located across Mexico,
Canada, and the US.
Pablo Arribalzaga, Managing Director Europe, Fives North American Combustion
Pablo started his career as an apprentice working in an aluminium foundry, and since then he has spent “all my career in the in the combustion and furnaces industry.” He joined Fives Stein, another subsidiary of Fives group, and became the Managing Director for Europe of Fives North American Combustion in 2011.
“Fives is a company that has a lot of heritage and industrial culture. It is a company that has been in the market for over 200 years. You can imagine that the company has had to evolve dramatically, with each evolution of the industry.” – Pablo
Florent Grumiaux, Managing Director, Fives ECL
Florent started work at ECL in 2000 (before it was bought by Fives). Starting at the company as an apprentice, he “changed role ten times,” and worked his way up from the workshop floor to become the Managing Director of Fives ECL.
“We are a team of passionate guys. We are all driven by this willingness to develop and to improve.” –Florent
One noticeable trend is the support for Trump in the US versus the opposition to his actions outside of the US. Essentially, the US has stepped away from globalisation, raising the question: Could this be the beginning of a significant shift toward deglobalisation?
Pablos states: “Globalisation is something that has been going strong for the last three or four decades, it will be difficult to move away.
“Fives in an international group with a strong local footprint with over 100 locations in 24 countries.
“Our organisation enables us to adapt to the shifts in the industrial and geopolitical worlds. We are global but we act local.”
It is believed sustainability will continue to advance and evolve despite global challenges and Pablo states: “I think the aluminium industry will continue to become greener.”
Fives has a long history in research and development, with many of its current ventures focused on sustainability.
Pablo noted a couple of collaborative projects where Fives is working with companies such as Ma’aden, where it will reduce emissions by 40% in the furnace, or a project in Germany, where it has modified furnaces and reduced emissions by 35%.
Turning the discussion to hydrogen, Pablo states: “Fives North American Combustion was one of the first companies to test with hydrogen on an industrial scale.”
A paper on its hydrogen tests with Hydro was premiered at this year’s recent
TMS show in Las Vegas.
The paper reported the results seen when producing recycled aluminium with hydrogen.
The study detailed the results of combining Fives’ regenerative burners, that recover waste heat from furnace exhaust gases to preheat the combustion air, and hydrogen that reduce carbon and NOx emissions.
Pablo said: “We can make use of 100% natural gas, or 100% hydrogen. We can mix fuels, but the outcome is the same, our customer can reduce their emissions to zero.”
Hydrogen has been a re-occurring theme across the decarbonisation narrative, but is there a future for hydrogen, and if so, where?
Pablo responds simply: “In Europe.”
According to the European Union website, in 2022, hydrogen accounted for less than 2% of Europe’s energy consumption. 96% of this hydrogen was produced with natural gas, resulting in significant CO2 emissions.
That being said, hydrogen plays a huge role in the EU’s plan for a renewable future. The REPowerEU Strategy of 2022 laid out the targets: Producing 10 million tonnes and importing 10 million tonnes of renewable hydrogen by 2030.
There are three EU hydrogen initiatives: the Clean Hydrogen Partnership, The European Clean Hydrogen Alliance and the Hydrogen Public Funding Compass.
Pablo believes hydrogen is a viable fuel for the future.
“Europe is investing. We want to have an independent fuel source that does not rely on external relations.
“The idea is to start producing. Wheth-
er the whole of Europe will use hydrogen is a different question. The likely situation will be that different areas will rely on different fuels, like biomass or nuclear.”
But making these sustainable changes region by region is dependent on the governance of a region. When asked whether he thought that the US will continue to align with the Paris agreement, Pablo answered “yes, because this is not only an environmentally sustainable choice, but also a sensible economic decision.”
Environmental sustainability is not the only agenda on the Fives sustainability roadmap. “Sustainability for Fives also includes working with regions to provide them with local resources and support,” he states.
Digitalisation in industry
Fives’ subsidiary Fives ECL is based in Lille, France. The company (ECL 1947) joined the Fives group in 2015, and predominantly works for primary aluminium smelters.
With almost 300 employees, Fives ECL has a highly robotised and digitalised 18,000m2 manufacturing facility.
Florent Grumiaux, Managing Director, Fives ECL, states it is also working with European companies and countries on carbon capture and storage projects.
Fives also has a huge involvement in the digitalisation of technology. For the aluminium industry the implementation of artificial intelligence (AI) is a huge topic. But how does this link in with Fives?
Florent states: “AI will be a tool used by our team to be more efficient or to reduce the stress on some tasks. It’s something we’re starting to implement. But we are aware we also must be cautious with
how we use it.”
One of the main challenges in implementing digital technologies is building a database. This aligns with the familiar call from the industry for companies to track and record data and share this data so that digitalisation can push forward.
Florent shared an example of data-driven improvements in efficiency and emissions. By collaborating with Aluminium Dunkerque, Fives analysed data to optimise operations, successfully reducing furnace gas consumption by 5%
“Our target is not to trash everything and to redo it. Our target is to optimise and be responsible,” he states.
The use of technology to enhance efficiency and sustainability is justification for its implementation, but a slightly less obvious reason is its role in tackling a deindustrialising world.
A shrinking workforce in the industrial sector is a serious issue. Digitalisation has allowed technology to replace human labour, enabling operations to be run by fewer individuals.
A focus on continuous development and upgrading machinery is implemented in Fives’ ECL mindset towards manufacturing itself.
Florent states: “When you compare the past to how things are run in the present, thanks to years of research and development, we have completely changed the way of manufacturing, and our future is also continuing to change.”
Technology is also valuable for preserving knowledge. As skilled employees retire, technology can be used to capture and store their expertise, ensuring it is not lost. But there will always be a limit. Pablo states clearly that technology will never 100% replace humans.
According to data collected by Statista, the number of employees in the manufacturing industry in France decreased by 77,080 employees (-2.5 percent) in 2021 compared to the previous year. In response to this challenge, Fives ECL runs initiatives that engage college students in programmes related to manufacturing.
Florent emphasised the importance of introducing young people to the industry.
“Because they don’t know how the industry works, and they often have a bad image of the industry, we have created a network that works with schools and universities to explain how working in
� Fives designs and manufactures machines, process equipment and production lines for the world’s largest industrial groups in every industry.
� Fives North American Combustion is one of the most trusted names in combustion worldwide, with more than 100 years of experience in thermal process solutions across many markets and applications.
� The Aluminium Division of Fives, which includes Fives ECL, specialises in the design and supply of key process equipment and the management of complete installations both in carbon and reduction sectors of the primary aluminium industry.
industry is rewarding.
“We show them that we are making an impact, we can change things, we can improve and make life easier for people who are using our materials or product.”
Fives ECL has welcomed 20 apprentices this year to the company. Speaking to Pablo and Florent it is clear that bringing new, younger employees to the company is an investment Fives is committed to.
Florent also discussed virtual reality (VR) and simulations that have been produced to assist training. This was a way to “remove people from the danger zone, while exposing them to the knowledge
and equipment.”
When asked about whether the deindustrialisation of Europe will result in no industry in France, Florent answered, “I’m fully convinced that we’ll keep some industry, the aluminium industry in particular, in France and Europe.
“We still have demands here in Europe, which is why Fives ECL is still here.”
When asked what message he would share with the entire industry, Pablo said: “The industry has to continue on the path that we have started on to improve decarbonisation and we must speed up this process.”
Florent added: “We are looking for the last percent [of emissions], everything counts. Even the detail. we are looking for continuous improvement, we don’t expect a huge, big step. But we need to continue to improve, step by step.” �
Benjamin Herout* provides an overview of hot and cold repair options, including case studies of repairs on container glass furnaces.
Production facilities in the glass industry are capital intensive and require long investment cycles, while market and energy prices are volatile.
Glass producers face complex choices in energy sources: using current fossil fuels such as natural gas, oxy-gas, hydrogen and rounding it out with electrical boosting before making a transition to full electric furnaces.
A side effect of reducing GHG emissions by electrical boosting is a higher corrosion rate of materials in contact with glass, especially in melting bath areas.
Exposed to these trends, the glass industry is adapting its industrial strategy to optimise current furnaces, as well as evaluating new furnace technologies to be used in future.
Sefpro Care was developed to propose complete solutions for hot and cold repairs for all glassmakers, which provides customers flexibility and reliability in the management of their industrial assets.
The aim of this article is to give an overview of possibilities offered for hot and cold repairs, illustrated with two real-case scenarios with outcomes from the repair work done on regenerator chamber and container glass furnaces.
Until now, classical products for hot bottom repair exhibit several drawbacks such as limited flowability, strong surface roughness and open porosity, high curing temperature, and limited capability to be drilled. Sefpro Care has developed its solution to perform hot bottom repairs without these issues.
This patented composition provides an alternative to the use of AZS chips (Figure 1).
With self-flow behaviour, a composition purely made of Fused Cast AZS grains, and a sintering stage starting at 1000°C, our composition can be used in low temperature areas such as refiners and forehearths. With ten hours of curing time in the range of 1200/1300°C,
the product sets during the installation process (Figure 2). This creates a high level of mechanical strength in the lower layers.
Thanks to these specific properties, furnace managers can shorten their repair time by having fast sintering after installation compared to traditional solutions. These time-savings can represent up to several days depending on the project size.
Furthermore, it secures the furnace structure by avoiding a long, risky, and costly specific heat up at 1550°C for 72 hours to sinter as the other types of solutions based on zircon/alumina/mullite grains require.
Considering the installation, or re-installation, of electrodes, our Hot Bottom AZS provides sufficient mechanical strength after sintering to be compatible with drilling operations to install or reinstall electrodes, in addition to a smooth surface with closed porosity that protects electrodes from corrosion.
The two next products are monolithics that have been engineered to provide glassmakers with a flexible solution to perform hot and cold repairs with a single type of application.
An example is given for AZS grains obtained from fused cast, but different sets of premix and binders are to be selected depending on the furnace application and
installation conditions.
This product has been designed to propose a versatile castable solution for hot repairs of glass furnaces (Figure 3). Thanks to its special properties, it can be used in a range of applications and gives the best results in terms of duration.
We decided to use our Fused Cast AZS grains to generate this monolithic solution. Thanks to a special packing in bags, our customers can decide to prepare batches from 125kg up to several tons. Its application process is also flexible, as it can be used from a simple casting with buckets to a continuous feeding by double pistons pumping.
The product can take the required shape by using multiple types of forming methods. For example, wooden or metallic moulds can both be used. Its self-flow property is a key strength for filling all cavities and ensuring a good homogeneity in the final block after setting. Starting usage at 50°C all the way up to the highest furnace temperatures, Fused Cast AZS exhibits its best final properties at any temperature within this exceptional range.
This product has been validated across a broad range of applications from glass contact overcoating to crowns or regenerators repairs.
*Sefpro Care and Expendables Manager, Sefpro, Le Pontet, France www.sefpro.com/
This product is the cold version of the one presented previously. It exhibits the same properties in terms of rheology and casting functionality. The main difference is the application temperatures which should not exceed 35°C.
The product sets in cold conditions and is requires a 24-hour maturation period in its mould before release. It is especially advantageous when weak areas are discovered during a cold stop of a glass furnace (Figure 4).
Once casted, an additional curing time of 48 hours is optimal to allow the product to reach its full mechanical strength. Then the heat up process can begin according to the heat up curve specified in product data sheets, or tailored to the specific case if the thickness of the CIP exceeds 250 mm. This product can be used to rebuild glass contact areas, superstructure, tuckstones, port necks and/ or regenerator walls, partially or fully.
These electro-fused tiles are particularly suitable for over-coating tanks and can provide furnace lifetime extension around three or four years.
They can be applied in a furnace with a broad range of temperatures from room temperature to 1500°C. They exhibit premium corrosion resistance properties thanks to Sefpro’s manufacturing process to create void-free homogenous pieces.
The use of electro-fusion process, or fused cast grains for the low-fired version, provides the highest material compatibility with glass baths.
Consequently, patching tiles are of interest as they avoid heat-up, maintain high corrosion resistance, are EHS friendly (no Cr6+), and are easy to recut on site.
They are available in multiple thicknesses, and our supply chain ensures a permanent stock to support urgent repairs with delivery in less than two days.
Sefpro’s Zircon paste is dedicated to filling superstructure joints during hot operations or cracked blocks repair. Initially provided as a pumpable and dust-free sealing solution, this jointing paste is now also available in ready to use applications, such as bucket or specific guns, for smaller repairs. Composed of 63% Zr, this paste is easy to prepare and to apply, fills small cavities from 2 to 20 mm, and does not require any vibration.
Regenerator
The following is an example of a hot repair that kept the furnace in operation to save one of the four regenerator chambers.
A container glass furnace was powered with natural gas and furnace oil around 16 MW and was producing around 340 tpd. The furnace was facing a collapse of the chimney blocks, impacting drastically the regenerator efficiency.
Application of Hot Overcoat AZS within the chimney block kept the regenerator chambers in working conditions and avoided further damages while running production (Figure 5).
Knowing that pre-heated air passing by regenerators provides approximately 2530% of the total heat required for glass melting, estimated consumption savings from this repair is 1 MW that would have been powered from gas if the chimney block was not repaired.
Translated into CO2 emissions, if this furnace would have been operated without this hot repair, approximately 1825 tCO2/year would have been emitted.
As mentioned, classic products developed for hot bottom repairs exhibit several drawbacks such as limited flowability, strong porosity, high curing temperature, and limited capability to be drilled.
For such repairs, our Hot Bottom AZS
composition can provide important energy savings thanks to lower sintering times and temperatures, and consequently a rapid return to production.
Indeed, our composition made purely of Fused Cast AZS grains provides a sintering stage starting at 1200°C and requires only around 10-20 hours of time to apply.
Meanwhile, other hot bottom solutions provide a sintering stage starting above 1500°C and require around 48 up to 72 hours for use. When it comes to electrode boosted furnaces, our Hot Bottom AZS solution also provides a smooth surface with limited porosity that protects electrodes from corrosion and prevents any future leakage in this sensitive area. Feedback from our latest repairs have confirmed an efficient ramp-up after Hot Bottom AZS repair, especially within the quality target (no stones or bubbling were noticed after the glass filling period).
The glass industry is facing external trends such as reduced end-consumer consumption, energy price volatility and regional legislation for GHG emissions. Therefore, all glassmakers need to adapt industrial strategies to use their current furnace in the best way possible, and decide which furnace technology they will use for the next two decades. This is why Sefpro Care has developed and proposed solutions which have been validated. From bottom to regenerators, there is always a solution to repair and extend furnace lifetime without impacting glass quality. �
Pooyan Kheirkhah, Valmiro Sa, and Anand Makwana*
Aluminium production through secondary melting using recycled scrap, requires a fraction (5%-10%) of the energy required in the primary production route.
Combustion of conventional fuels (e.g., natural gas (NG)) in a reverberatory or a rotary furnace is a major source of carbon dioxide (CO2) emissions.
Low-carbon intensity hydrogen (H2) is being considered a key fuel in decarbonising these furnaces.
The use of hydrogen will affect the flame properties (e.g., no soot formation due to the absence of carbon in the fuel), emissions (NOx), and furnace atmosphere, as no CO2 is produced from hydrogen combustion.
The change in flame properties and the impact on the thermal efficiency and NOx emissions can be addressed through specific burner designs.
The change in furnace atmosphere due to the switch from NG to H2 can potentially impact aluminium melt and dross quality/quantity due to higher furnace water vapour (H2O) and is an area of active study [1-2].
Application of oxy-fuel burners in secondary melting furnaces has demonstrated fuel efficiency gains as compared to cold air-fuel burners, reducing the NG fuel usage by up to 45% [3]
In gas-fired furnaces, the use of oxy-hydrogen burners has the potential to reduce the operational carbon footprint of melting furnaces.
However, it is important to ensure the use of oxy-hydrogen burners will not impact the process or the furnace.
In this study, the effect of changes in the furnace atmosphere, by switching the fuel from natural gas to hydrogen in oxy-fuel combustion, on melting characteristics of aluminium alloy 6061 is investigated.
Melt quality and oxide formation depend on several factors, including the material being melted (% Mg in the material, type of alloy), furnace and melt temperature, melt time, temperature-time history of the melting cycle, melt surface area exposed to the furnace atmosphere, flame type (burner type and fuel or oxidisers used), and furnace atmosphere.
In this study, all these potential parameters that can impact the melt were kept similar across different experiments apart from the fuel type to investigate how a fuel composition change can impact aluminium melt and slag/dross properties.
Air Products’ US Advanced Clean Energy Laboratory has a well-instrumented refractory-lined, custom-designed box
research furnace for conducting batch melting experiments [4] and the study was executed in that test furnace (material placed in removable crucibles placed on the furnace floor).
Subsequent effects of fuel change on the amount and composition of dross formed in the dross layer were studied using X-ray diffraction (XRD) and Scanning Electron Microscopy/Energy Dispersive X-ray Spectroscopy (SEM/EDS).
This study used a pipe-in-pipe oxy-fuel burner to generate furnace atmosphere conditions (gas composition and temperature) similar to what is expected in an actual reverb or rotary furnace.
Air Products has developed a proprietary smart Transient Heating Burner technology that can be used in reverb furnaces.
These burners are fuel-flexible (can operate with NG, H2 or blends), and produce lower emissions (NOx) compared to conventional oxy-fuel burners.
The combustion thermal power and the furnace gases (concentration of O2, H2O, and CO2) are summarised in Table 1 The detailed experiment procedure and analysis process are described in [4]
Figure 1 shows a comparison of
*Air Products and Chemicals, Allentown, Pennsylvania, USA https://www.airproducts.com/applications/melting-non-ferrous
furnace, flue gas, and ‘inside crucible’ temperatures of the NG-O2 and H2-O2 experiments.
Two studies were executed: a ‘short
test’ that achieved melting and peak melt temperature of 1000 deg C and a ‘long test’ that had a hold time of 2.5 hours after melting at 850 deg C.
Table 1. Conditions inside the test furnace during melting operation.
2. The aluminium mass measurements before and after the melting (*initial mass of alloy: 7.21 lbs).
The temperature plots in Figure 1 show a similar temperature-time history for the two experiments, considering a variability of ± 50 °C in the measurement due to spatial distribution of heat and thermocouples position.
In the ‘Short Test’, the crucible temperature shows that the temperature increased first (measured gas temperature) and then dropped from about 700°C to 670°C as aluminium melting began.
The melted aluminium was further heated to 1,000°C before experiment shut-down and the furnace was purged with nitrogen to protect the melt from further oxidation by air that could enter the furnace from outside.
Table 3. Comparison of the compounds detected in the oxide layer of the NG-O2 and H2-O2 melts during the short test (x: detected, - : not detected).
In the ‘Long Test’, after the melting, the melt was held at 850°C for 2.5 hours. The data is not suitable to study melt rate as it depends on several factors (flame type, burner design) and should be studied in an actual furnace.
Dross formation
The mass of the aluminium charge in each crucible was measured post-melting, where a net gain in its mass was noticed due to oxidation.
The results of weight change for the melts are summarised in Table 2
The alloy shows similar level of oxidation for both NG and H2 fuels in both the ‘Short Test’ and the ‘Long Test.’
Chemical composition analysis:
slag/dross and melt
The results of the XRD analysis of the oxidised dross layer for the short test are shown in Table 3
The two major phases present in the XRD spectrum are the MgO (periclase) and MgAl2O4 (spinel), which correspond to the makeup of the oxide dross layer formed over the melt.
The minor phases identified by the XRD analysis includes the silicate Mg3Al2(SiO4)3, the iron oxide (Fe2O3), and a titanium-chromium oxide (Ti0.1Cr0.9O2) phase, corresponding to minor elements present in the alloy.
The results indicate the presence of alumina (Al2O3) in the sample melted with the oxy-hydrogen flame.
The surface samples of the solidified melts from the ‘Short Test’ were examined using an SEM/EDS to determine the
morphology/elemental composition of the dross oxide layer. Details are covered in [4]
SEM/EDS images in Figure 2 show metallic aluminium in the core covered by a layer containing different compounds/ oxides on the sample surface exposed to the furnace atmosphere.
The oxide consists of an MgO outer layer with MgAl2O4 present below the exposed surface. Other phases containing minor elements in the alloy are present below this surface, such as a silicon-containing phase as shown in image (f) of Figure 2 (a) and 2 (b)
The presence of both MgO and MgAl2O4 indicates that breakaway oxidation has started, but the fact that MgO is still detected shows the breakaway oxidation has progressed partially.
Comparison of Figures 2 (a) and (b) shows the structure and composition of the exposed oxide layer formed on the melt from both the NG-O2 and H2-O2 flames are similar and consistent with the pattern described above, an MgO-layer on the exposed surface with a more porous MgAl2O4 phase below the MgO layer.
Figure 2 (b) shows formation of an internal oxidation zone, below the top oxide layer, that contains MgO, MgAl2O4, and Mg-Al-Si oxides.
An aluminium layer separates the internal oxidation zone from the top oxide layer.In some areas of the melt from the H2-O2 flame, SEM/EDS maps show a relatively uniform 3-4 micron MgO layer covering the inner phases and the core aluminium phase (Figure 3).
This phenomenon could potentially protect the aluminium phase against further oxidation, reducing the melting losses.
The impact of changes to the furnace atmosphere from using hydrogen versus natural gas fuel (oxy-fuel combustion) on the 6061-aluminium melting and the melt properties was investigated in Air Products’ Advanced Clean Energy Laboratory facilities.
Both melts (NG fuel and H2 fuel) showed similar mass gains in the range of 0.14-0.28% of the initial charge.
The samples from the ‘Short Test’ were further analyzed and XRD patterns of slag powder samples from two melts indicated the presence of the two major
oxides MgO (periclase) and MgAl2O4 (spinel).
SEM micrographs showed a dross layer (a few microns thick) over an internal aluminium core.
The dross layer consisted of an outermost MgO layer covering a more porous MgAl2O4 phase. Additionally, melt sample from the oxy-hydrogen flame indicate formation of a more uniform MgO layer protecting the melt from additional oxidation.
The experimental results from this study are encouraging for the use of oxy-hydrogen burners as a means to decarbonise secondary aluminium melting.
The total mass gain (dross formed) and type of oxides formed are similar between hydrogen and natural gas fuels for the 6061 alloy, demonstrating that melt yield was not adversely impacted with the fuel switch. Expanding the scope of future testing to include higher Mg-containing alloys will be needed for broader applicability across the secondary melting market.
It is important to note that while the high moisture content in the furnace atmosphere with hydrogen fuel did not result in additional oxidation of the melt pool, proper selection of the refractory material will be needed to understand effects on refractory life.
However, these initial results provide a strong basis for scaled-up testing in a reverb furnace and the continued evaluation of hydrogen as a viable fuel for secondary aluminium melting operations.
1. Syvertsen, M., Johansson, A., Lodin, J., Bergin, A., Ommedal, M., Langsrud, Y., & Peterson, R. D. (2023). Oxidation Study of Al-Mg Alloys in Furnace Atmospheres Using Hydrogen and Methane as Fuel. In: Broek, S. (eds) Light Metals 2023. TMS 2023. The Minerals, Metals & Materials Series. Springer, Cham.
2. Piquard L, Clément E, Adendorff M, Iplik E, Ekman T (2024). Reverberatory Furnaces Decarbonization – The Case of Hydrogen Combustion: Proof of Concept and First Experimental Results on Borel Furnace. In: Wagstaff, S. (eds) Light Metals 2024. TMS 2024. The Minerals, Metals & Materials Series. Springer, Cham.
3. Sane A, Gangoli S, He X, Lawrence M, Hewertson R (2018). Effective Use of Oxy-Fuel Combustion in Aluminum Reverberatory Furnaces. Light Metal Age, August 2018, pp. 36-38.
4. Kheirkhah, Pooyan, Valmiro Sa, and Anandkumar Makwana. “Oxy-Fuel Combustion: Impact of Hydrogen Combustion on Aluminum Melt Quality in Secondary Melting Processes.” In TMS Annual Meeting & Exhibition, pp. 1234-1242. Cham: Springer Nature Switzerland, 2025.
Vacuum-tank degassing offers better performances in desulfurization and nitrogen removal, and allows raw material flexibility, at lower CapEx and OpEx. By Bojan
Vucinic*
*Senior manager, process technology, Danieli, Italy b.vucinic@danieli.it +39 0432 195 5519.
Vacuum treatment is critical to achieving the lowest levels of carbon, sulphur, hydrogen, and nitrogen, together with the highest level of steel cleanliness. One vacuum degassing process based on liquid steel recirculation is the RH process (with/ without oxygen supply). The second most common degassing process is ‘Vacuum Tank Degassing’ (VTD process). The focus of this article is on the ability of both degassing processes to treat steel melted in an electric arc furnace (EAF).
The different capabilities of RH and VTD to remove nitrogen and the impact on overall steel quality and cost control are key drivers for proper selection between the two different vacuum refining techniques.
CO2 footprint reduction in steelmaking and adoption of the EAF in place of the basic oxygen furnace (BOF) process, together with a shortage of clean and suitable scrap, and the limited availability of high-quality DRI and/or HBI needed for EAF melting, are the main variables to be considered when evaluating a degassing project.
Flat-product quality requirements will not change due to adoption of EAF melting. An EAF-based process together with properly selected secondary refining units must fulfil the same quality requirements as BOF-based melt shops.
Lack of sulphur removal and limited nitrogen removal during the RH vacuum process cannot be considered a disadvantage for a BOF-based melt shop as the BOF process can achieve very low nitrogen contents due to high carbon-removal rates, and very low sulphur contents based on deep sulphur removal from hot metal. The ability of the RH technique to achieve ultra-low carbon contents needed for non-stabilized, interstitial-free grades is the main reason to select such a degassing unit as part of a BOF melt shop.
An EAF’s ability to produce high-quality long products is an established fact. Over the last 10 years, EAFs have become the melting units for flat products, including automotive grades. Continuous improvements in the EAF process, different furnace designs supported by customized chemical packages, and sophisticated process controls are reasons to believe in the future of EAFs for producing low-carbon grades with ultra-low levels of non-metallic impurities.
The possibility to achieve low carbon contents at the end of steelmaking with reduced carbon versus oxygen ratio, together with low final phosphorus content, is already confirmed (1)
Is it enough just to replace the BOF with an EAF? How challenging is it to manage limited availability of raw materials and at the same time keep melt shop flexibility as
high as possible? Those are key questions during the evaluation of the best technique.
Quite often the optimal degasser choice is obvious. This choice is typically based on the type of melting furnace, the production programme, the metallurgical operations, design of existing equipment, and according to the metallurgical background and experience of the steelmaker. In a scenario where both types of degassers may be applied, all the individual characteristics like material flow, productivity, the share of vacuum-treated steel
in the total production, the melt shop layout, or the location of the steelmaker’s plant must be discussed in correlation to arrive at an optimal solution.
Nitrogen removal during RH degassing, as part of a BOF-based melting process, has never been extensively monitored, mainly because of already low nitrogen content prior to tapping from the BOF. As the steel outputs and the nitrogen and sulphur contents are different than for EAF melting, nitrogen removal during degassing became important.
To understand better the reasons for different nitrogen patterns for two different degassing units, we should understand the impact of equipment design on metallurgical performances and process behaviour as well. The RH vacuum degassing unit has much higher ‘free volume’ above the treated steel as compared with the VTD degassing unit. The best way to reduce partial pressure of nitrogen and achieve low final-nitrogen content is to control the amounts of oxygen, nitrogen, and argon content in the off-gas.
During the VTD process, three distinct phases shall be considered:
> Phase 1: Impact of inlet nitrogen amount; higher nitrogen content before degassing will promote higher nitrogen-removal rate;
> Phase 2: Strong impact of argon bubble geometry;
> Phase 3: Low nitrogen level; to be able to have deep nitrogen removal, partial pressure of nitrogen must be reduced.
Grades for automotive applications, home appliances, and tinplate grades (grades without any carbon removal under vacuum), usually have low, maximum-allowed nitrogen content and high cleanliness requirements. To be able to achieve low final nitrogen content (below 40 ppm after degassing process), the final phase (phase 3) of nitrogen removal under vacuum is crucial. Figure 1
There is a clear difference between the VTD and RH processes regarding the ability to remove nitrogen, with typical nitrogen content before degassing in a range of 70÷100 ppm, and with sulphur content less than 40 ppm, as shown in Figure 2
As explained above, to achieve extremely low final-nitrogen content, partial pressure of nitrogen must be reduced by increasing the argon content in off-gas. Nitrogen removal based on vacuum tank degassing is higher compared with nitrogen removal based on liquid steel recirculation under vacuum. The reasons for this difference could be:
> RH – Higher ‘free volume’ above steel level, as compared with VTD equipment design;
> Higher leak rate, in the case of RH.
The impact of leak rate on lower nitrogen removal during the RH degassing process is already recognized and confirmed (2)
During production of high-quality flat products, it is unlikely to encounter nitrogen contents more than 80÷100 ppm at the end the LF process. Most flat products could have an even lower nitrogen content prior to degassing mainly
Nitrogen content after degassing vs. different inlet nitrogen content (note: considered sulphur content for RH treated grades is lower than sulphur content for tank degassed grades).
Nitrogen removal for different range of inlet nitrogen content (VTD vs. RH, based on low-sulphur grades only).
due to a higher application of clean and carbon-based raw material during EAF melting. Figure 3
With nitrogen content prior to the vacuum process in the range of 50 ppm, nitrogen removal during the RH process is negligible.
Nitrogen removal during vacuum tank degassing is better than nitrogen removal during the RH process. This is especially valid for steel grades with low final nitrogen requirements or for grades where inlet nitrogen content at the vacuum degassing unit is lower than 70÷80 ppm. It is possible to achieve low metallic residual contents for most flat products based on a proper ratio of carbon-based clean material and selected scrap during the EAF process. By increasing the contribution of clean material during EAF melting, nitrogen content before tapping is lower.
With BOF melting, low sulphur contents are possible prior to tapping thanks to the possibility for high levels of sulphur removal from hot metal. With the EAF
5. Impact of effective surface and inlet nitrogen content on nitrogen removal after vacuum tank degassing. Danieli experience: 257 evaluated heats The purpose of this chart is to demonstrate trend only.
as the primary melting unit, low sulphur content is obtained during secondary metallurgy. The influence of sulphur on nitrogen removal during different vacuum degassing processes is reported below. Another, important indication from the chart below is the need for ultra-low sulphur content prior to RH degassing. However, nitrogen removal during vacuum tank degassing is better with higher sulphur content prior to vacuum treatment. Figure 4
Nitrogen removal under vacuum for VTD is easier to control than nitrogen removal during the RH process. At the same time, the VTD equipment is less complex and more ‘user-friendly.’ The removal rate for nitrogen can be described by a first order differential equation:
where [%N] is the concentration of nitrogen in the steel, k is the mass transfer coefficient, ρ is the density of the steel, Aef is the effective reaction area,
and [%N]eq is the theoretical equilibrium content of nitrogen.
The effective reaction area is influenced by the exposed surface and the concentration of active surface elements, like sulphur and free-oxygen content. Slag viscosity, slag conditions with the argon-stirring pattern defined by the number of porous plugs, and the argon-stirring flow rate all have a direct impact on the exposed steel surface. The impact of the effective surface together with nitrogen content are reported in Figure 5. The chart shows the nitrogen removal rate with fixed temperature, fixed vacuum time, and with different sulphur content prior to the vacuum process (as part of ‘effective surface coefficient’)(1)
RH vs. VTD – hydrogen removal
There is no difference between the RH and VTD processes in regard to hydrogen removal. Both are highly efficient. Hydrogen removal is driven by pressure, circulation rate (for RH) or exposed surface (VTD process), and duration of deep
vacuum time. However, Figure 6 shows a statistical evaluation of hydrogen content before and after degassing for both vacuum processes.
Low hydrogen content is achievable with RH and VTD as well. The chart makes clear that inlet hydrogen content is lower before the RH process compared with inlet hydrogen content for evaluated VTD grades. The main reason for lower hydrogen content in evaluated RH treated heats is that the associated steelmaking process is based on hot metal and an average 20% scrap charge (BOF process). At the same time, the evaluated results from the VTD process are based on EAF melting profiles for charges of at least 70% scrap or more.
Nitrogen content before tapping from the EAF could be in the range of 25÷100 ppm. Based on the ability to refine steel during the secondary metallurgy process (nitrogen, hydrogen, and sulphur pattern), and based on the type of EAF chosen, a proper charge mix must be evaluated for each grade of steel.
The best way to reduce nitrogen content in steel before tapping from the EAF is to apply carbon-based and clean raw materials(3). For high-quality grades, the use of direct reduced iron (DRI) pellets for EAF steelmaking is limited mainly because of the impact of splashing during the process, and these pellets are usually the source of high sulphur content.
As shown in Figure 7, the results of hot DRI in the charge mix are:
> Higher amount of CO2 emitted (scope 1 – process) is caused by higher carbon content in charge mix;
> Generated amount of slag is linked
to higher amount (kg/tls) of charged non-metallic compounds with DRI;
> Energy balance is more on the chemical than on the electrical side;
> Process yield reduction is linked with the amount of gangue content in the raw materials.
The difficulty for secondary metallurgy processes to remove nitrogen (example: RH vs. VTD) consequently makes it necessary to reduce nitrogen contents before tapping from the EAF. This is possible by increasing the amount of DRI in the EAF charge mix.
Nitrogen content reduction during EAF melting has its own pros and cons. Figure 7 shows the results of simulated EAF processes for a fixed heat size, fixed tap-to-tap time, and with the same requirements for steel quality (same tapping temperature, same slag basicity, and same carbon and phosphorous content before tapping).
Increasing carbon-based raw material in the charge mix is common practice for high-quality steel grades (e.g., grades based on free-tapping practice followed by carbon removal under vacuum), and higher production costs during the primary steelmaking process route are
usually justified by higher added-value of the final product. Increasing EAF cost caused by reduced refining capability of secondary metallurgy shall be covered by a proper market forecast.
The choice of RH or VTD for a steel plant is determined by the steel grades to be produced.
As demonstrated, overall, VTD process wins versus RH. In fact, desulfurization by VTD reduces total LF process time, increasing overall meltshop productivity, and also improving steel cleanliness and nitrogen removal under vacuum. Furthermore, VTD allows higher flexibility in the selection of raw materials for the EAF. CapEx for VTD stations is much lower as compared to that for RH; production costs are also more competitive because of different process patterns and energy/ steam consumption.
The RH process is only recommended for ultra-low carbon, ‘non-stabilized’ grades with production rates above 20÷30%. �
B. Vucinic: “High-quality low-carbon flat grades based on EAF-LF-VD process route,” EEC 2024.
Yoshiei Kato, Tadasu Kirmara, Koji Y. Amaguchi, Tetsuya Fujii and Shigeru Ohmiya: “Air leak from the immersion tube in an RH vacuum degassing unit and the behaviour of nitrogen in steel;” Iron and Steel Vol. 83 (1997) No. 1. R. Lule, F. Lopez, J. Espinoza, R. Torres and R.D. Morales: “The Production of Steels Applying 100% DRI for Nitrogen Removal: The Experience of ArcelorMittal Lazaro Cardenas Flat Carbon”; AISTech 2009 – Volume 1.
Is carbon capture an ‘essential tool’ in the fight against climate change, or a distraction from the reality of its true potential?
By Stefan Erdmann*
Last year was the planet’s warmest year on record. Global average temperatures reached 1.46°C above pre-industrial levels. Scientists warn that if greenhouse gas emissions continue at current levels, we could see temperature increases of up to 5°C in the coming decades.
Steel production accounts for 10% of global greenhouse gas emissions. On average, for every ton produced, 1.89 tons of CO2 are released. In 2023, the steel industry reached a market value of $928 billion, producing nearly 2 billion tons of steel. By 2050, we need to cut emissions by 90% compared to 2022 levels to meet global decarbonization targets.
Innovation, then, is imperative – but where should the focus be? One of the critical debates today is the role of carbon capture and storage. Is it an essential tool in the fight against industrial carbon emissions? Or could it be a distraction that diverts attention from deeper systemic change?
right
At Outokumpu, despite the high alloying content of our stainless steel, we have
managed to lower our emissions to 1.52 tons of CO2 per ton of crude steel (2023). This progress highlights the importance of tackling carbon reduction at every stage of production.
Direct emissions are primarily from fossil fuels used in ferrochrome production. Switching to bio-based alternatives or moving towards a carbon-free reduction process could dramatically cut emissions.
Buying in carbon-free electricity sources – wind, solar, nuclear and hydro – can address indirect emissions. That shift is speeding up thanks to regulatory pressures like the European Union’s Emissions Trading System.
Low-carbon raw materials might not yet be viable at scale – but we can’t afford to wait for the perfect solution. So that’s an area where carbon capture can come into play.
In my view, we should always prioritize carbon reduction where it’s feasible and economically viable. Carbon capture can play a part only where deep reductions are currently unachievable. Economic realities, advances in technology and indus-
*Chief technology officer, Outokumpu
trial collaborations will ultimately dictate the optimal balance between the two.
Repurposing captured carbon presents a strategic opportunity
Critics argue that carbon capture risks becoming a costly excuse for maintaining business-as-usual operations, rather than driving necessary systemic change. Others see it as a vital technology that complements other decarbonization efforts.
For instance, in sustainable fuels and green chemicals manufacturing, captured CO2 and CO can serve as essential feedstocks –helping other industries to decarbonize in the process.
At Outokumpu, we are actively exploring carbon capture for both utilization and storage as part of our broader decarbonization roadmap. As we increase our use of biocoke, these carbon gases will transition from gray to green - creating new industrial opportunities while reducing emissions.
So why isn’t carbon capture scaling up faster?
It’s a sizeable upfront investment to build the infrastructure for storing or utilizing captured carbon. Businesses will
hesitate to make large-scale commitments without strong economic incentives, and dedicated infrastructure for CO2 transportation and storage is not yet widely available in many key steel-producing regions.
Captured carbon must also have viable market applications, for which we need more cross-industry collaboration. Industrial symbiosis, where companies share resources and infrastructure, is still in its infancy.
Expanding global carbon pricing mechanisms and trade policies to encourage decarbonization could also make capture and storage more viable, while regulatory support and green procurement policies –along with private investment – can drive stable demand for low-emission steel.
We need a coordinated policy framework for carbon capture
We can make carbon capture a meaningful part of the decarbonization toolkit. To do that, we need:
� regulatory frameworks to encourage industries to share CO2 resources and infrastructure, creating viable carbon markets
� government investment in zero-emission energy, prioritizing grid decarbonization and energy storage solutions
� expanded emissions trading systems and harmonized carbon border adjustment mechanisms to drive investment in low-carbon steel production
� regulatory alignment with clear, long-term incentives for decarbonization
technology investments, rather than short-term subsidies.
Let’s embrace carbon capture as a tool, not a support
At Outokumpu, we are driving the next generation of low-emission stainless steel by investing in both direct reductions and smart carbon capture applications. As the transition speeds up, steelmakers cannot wait for regulations to force change—we must create scalable, economically viable solutions now.
The green transition is not just a necessity – it is an opportunity. But to seize it, industry players must act decisively and collaboratively. The time for debate is over; the time for large-scale implementation is now. �
The Furnaces International Directory is the essential guide to furnace manufacturers and suppliers of furnace equipment and services to the industrial heating/ process industry. Providing comprehensive company listings, product information and key contact details, the Directory can be found both online and as a printed edition in January each year.
OR
Neil Simpson* provides an overview of CelSian’s first training course dedicated to oxy-fuel, which was held at the University of Toledo, Ohio, USA.
In June 2024, while supporting Scott Cooper in delivering the CelSian General Glass Training Course in Toledo, USA, I learned that Jeff Watts, with 18 years of experience in global furnace operations at O-I and other glass companies, would be joining the CelSian team.
Having previously collaborated with Mr Watts on several combustion projects, I recognised an opportunity to develop a dedicated two-day oxygen training course.
The first training course was held on April 28 and 29 at the University of Toledo campus, where the CelSian US team is based. Attendees represented float, fibre, tableware, industrial gas and combustion suppliers.
As part of the initial introduction and networking, we established that the oxy-fuel experience of attendees ranged from 3 months to 33 years.
Mr Watts covered the essential safety aspects of oxy-fuel, while I gave a two hour introduction to oxy-fuel. This introductory talk will be presented at the evening before the Furnace Solutions Conference in June, which will take place in St Helens, UK.
Part of the breakout sections of this module were considering where oxygen
JEFF WATTS
Attended Ohio State University, majoring in ceramic engineering. Worked in PPG Industries as a production engineer. At Anchor Hocking, he researched raw materials to improve glass quality and reduce costs. Spent 18 years at O-I, starting as a senior global furnace operations engineer. He was promoted to global furnace operations leader. In this role, he led an international team and oversaw the development and implementation of a global standard for furnace operations. In 2024, he joined CelSian as Operations Project Leader.
is used successfully in non-glass segments and where it is not. For example, oxygen-hydrogen combustion would not be a suitable method for drying since the products are 100% water.
Thanks to the support from the majority of the industrial gas and burner companies, Mr Watts was able to review the current commercially available conical and flat flame burners. With the diversity of the attendees and presenters, everyone had some experience with each technology presented. The final session on Day 1
was the basics of oxy-fuel burner design, which I prepared.
Considering blends of hydrogen and natural gas from 0-100%, the respective volumes of fuel, oxygen and products were addressed in terms of burner fuel inlet and nozzle diameters with corresponding oxygen anulus. It was all hard work and justified an evening at the Maumee Bay Brewing Company, demonstrating that beer is the drink of glassmakers.
Day 2 started with the longest Q&A session I have ever experienced. It started with a question of whether anyone had awoken with an oxy-fuel concern. It was the first time we had a coffee break before the first training module of the day! I ran the first session, which covered the application of oxygen and oxy-fuel to air fuel furnaces to lower NOx, recover lost production/quality due to the regenerator, boost production, and on-the-fly oxy conversion for regenerator rebuild with 100% production. It was timely since I had recently supported a regen rebuild in the USA.
*Independent Consultant, Simpson Combustion and Energy, Scotland, UK neilsimpsonfsgt@btinternet.com
*CelSian, Eindhoven, Netherlands https://www.celsian.nl/academy/oxy-fuel-eu-2025/
Mr Watts focused on the theory/ practice of furnace operations, furnace construction and refractory materials. My final session was considering furnace exhaust location(s), foam generation in oxy-fuel vs air fuel, and practical methods to suppress foam.
The final session by Mr Watts was reviewing new technology that is being
NEIL SIMPSON
Neil Simpson graduated in Energy Engineering from Edinburgh Napier University. He developed burners for the glass industry with Laidlaw Drew and BOC, was a glass industry specialist at Eclipse and became an independent consultant in 2014. With over 20 published patent applications, Neil is a Chartered Engineer and Fellow of the Society of Glass Technology. He became a CelSian registered trainer in 2015 and has organised multiple UKbased courses since then.
developed. Presentation materials on hybrid furnaces had been provided by many of the major furnace OEMs on the current hybrid oxy-electric furnace designs being evaluated to reduce emissions. Mr Watts covered heat recovery techniques from oxygen and gas preheating, batch and cullet preheating, waste heat steam boilers, and Organic Rankine Cycle (ORC)
for electricity generation.
The break-out sessions, a cornerstone of our training approach, provided an opportunity for participants to engage in hands-on discussions. We mixed up the groups each day to encourage networking, collaboration, and the sharing of knowledge between suppliers, manufacturers, and industry experts. �
The first Oxy-Fuel Advanced Training course was a success, and we look forward to continuing to enhance the expertise of those working with oxy-fuel technologies in the glass industry.
Our next training session will be on October 1- 2, 2025, in the UK, and we are excited to build on the foundation established in this course to provide even more in-depth knowledge and practical experience.
You can find more details about the course via the link below or contact academy@celsian.nl for more details.
Don' t miss the latest issue of Furnaces International - your essential guide to furnace technology and innovation. Available at the following upcoming events!
FURNACES JUNE ISSUE:
Future Steel Forum 26-27 June
Furnace Solutions 4-5 June
ALUMINIUM China 9-11 July
UK Metals Expo 10-11 Sept
FURNACES-INTERNATIONAL COM
CONTACT US TO FIND OUT MORE:
Esme Horn
tzltd com
FURNACES SEPTEMBER ISSUE:
ASM Heat Treat 21-23 October
FURNACES DECEMBER ISSUE:
Glassman Italy 4-5th February 2026
Furnaces International is an English language journal dedicated to the production of rnaces. Circulated each quarter in March, June, September and December to our database of over 38,000 readers across the Aluminium, Glass, Furnaces and Steel industries. Furnaces International contains a digest of global news, events, and statistics as well as more detailed technical articles, company and country pro les, and regular regional economic brie ngs.
The Furnaces International Directory is the essential guide to rnace manufacturers and suppliers of rnace equipment and services to the industrial heating/process industry. Providing comprehensive company listings, product information and key contact details, the directory is published in January each year and also online at rnacesinternationaldirectory.com.
Packed with information on the rnaces industry and continually updated with news for professionals, rnaces-international.com also features special articles and interviews with leading industry gures.
A round-up of the top news stories is sent to more than 38,000 industry professionals every month. You can register online to receive the monthly newsletter and keep up-to-date with the latest news from across the rnaces manufacturing industry. Sign up at rnaces-international.com/subscribe
Aluminium International Today (AIT) is the leading bi-monthly English language journal dedicated to all sectors and regions of the international aluminium manufacturing and processing industry. Subscribe to the free weekly newsletter at aluminiumtoday.com
Glass International o ers readers the latest news from across the hollow, container, flat, and speciality glassmaking industry and is the o cial media partner for Glassman events. Subscribe to the free weekly newsletter at glass-international.com
Steel Times International (STI) is the key publication for the steel market, reporting on iron and steel making issues from all corners of the globe. Subscribe to the free weekly newsletter at steeltimesint.com