Hyundai must align ops with sustainability claims.
South Korean giant clings to coal dependence.
Foreign steel suppliers starting to feel uneasy. Since 1866
Fuel for decarbonized steel, says SAP’s Stefan Koch.
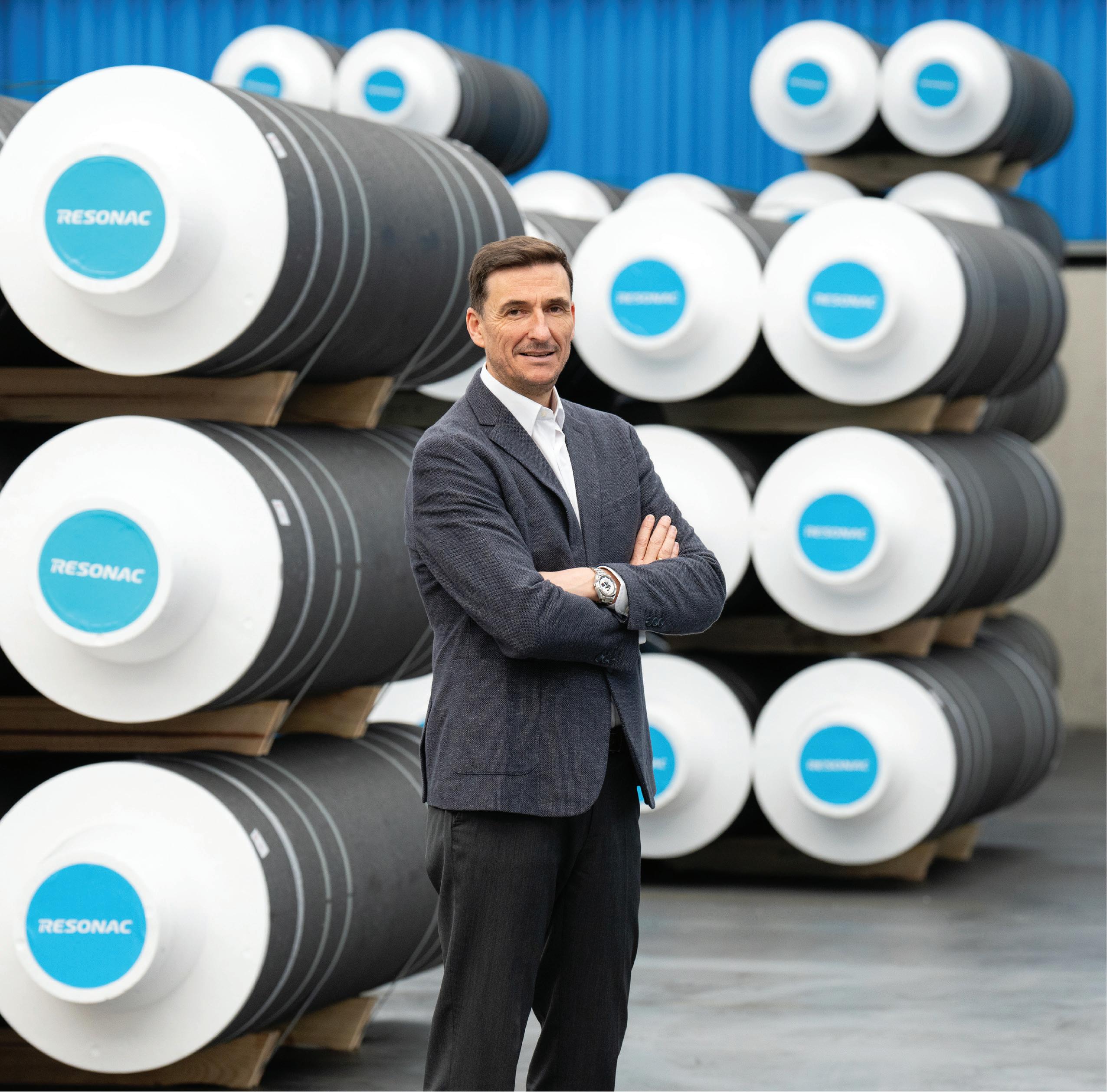
Hyundai must align ops with sustainability claims.
South Korean giant clings to coal dependence.
Foreign steel suppliers starting to feel uneasy. Since 1866
Fuel for decarbonized steel, says SAP’s Stefan Koch.
Metals offers the entire steel value chain an exceptional opportunity for curbing their CO2 emissions.
The unique combination of its historic and recently developed product portfolio, make John Cockerill one of the industry’s most relevant suppliers of equipment for both the hot and cold phase of the steelmaking and processing industry.
Our three distinct business segments are addressing todays and tomorrow’s challenges supporting sustainable and green steel production:
Our new upstream offering related to DRI (Direct Reduced Iron), EAF (Electric Arc Furnaces) technologies and the use of hydrogen in steelmaking. Next to offering indirect electrification (DRI-EAF&H2-DRI-EAF),John Cockerill is also working on Volteron®: A first-of-a-kind iron reduction and steel processing route via direct cold electrolysis. This CO2 free steelmaking process, has been co-developed with the world’s leading steelmaker ArcelorMittal.
Regrouping our historical downstream product portfolio, this segment also includes:
¡ the Jet Vapor Deposition (JVD®) technology set to replace today’s hot-dip or electro galvanizing processes. This novel high-productivity vacuum coating technology provides previously unknown coating flexibility and possibilities, all while offering lower CAPEX and OPEX.
¡ our E-Si® equipment & processing lines specifically designed to produce high-quality Non-Grain Oriented (NGO) steel in response to the need for electrical steel meeting precise metallurgical properties, essential to support the shift towards green mobility.
This segment not only embraces all services and after-sales activities but will be strongly focusing on downstream furnace electrification (reheating and processing line furnaces), as well as hydrogen combustion, and the optimization of plant operations, including energy audits and the modernization of steel production equipment and installations.
EDITORIAL
Editor
Matthew Moggridge
Tel: +44 (0) 1737 855151
matthewmoggridge@quartzltd.com
Assistant Editor
Catherine Hill
Tel:+44 (0) 1737855021
Consultant Editor
Dr. Tim Smith PhD, CEng, MIM
Production Editor Annie Baker
Advertisement Production Carol Baird
SALES
International Sales Manager
Paul Rossage
paulrossage@quartzltd.com
Tel: +44 (0) 1737 855116
Sales Director
Ken Clark
kenclark@quartzltd.com
Tel: +44 (0) 1737 855117
Managing Director
Tony Crinion
tonycrinion@quartzltd.com / Tel: +44 (0) 1737 855164
Chief Executive Officer
Steve Diprose
SUBSCRIPTION
Jack Homewood
Tel +44 (0) 1737 855028 / Fax +44 (0) 1737 855034 Email subscriptions@quartzltd.com
Steel Times International is published eight times a year and is available on
subscription. Annual subscription: UK £226.00 Other countries: £299.00
2 years subscription: UK £407.00 Other countries: £536.00
3 years subscription: UK £453.00 Other countries: £625.00 Single copy (inc postage): £50.00 Email: steel@quartzltd.com
Digital subscription: (8 times a year) - 1 year: £215.00 - 2 years: £344.00 3 years: £442.00. Singe issue: £34.00
Published by: Quartz Business Media Ltd, Quartz House, 20 Clarendon Road, Redhill, Surrey, RH1 1QX, England. Tel: +44 (0)1737 855000 Fax: +44 (0)1737 855034 www.steeltimesint.com
Steel Times International (USPS No: 020-958) is published monthly except Feb, May, July, Dec by Quartz Business Media Ltd and distributed in the US by DSW, 75 Aberdeen Road, Emigsville, PA 17318-0437. Periodicals postage paid at Emigsville, PA. POSTMASTER send address changes to Steel Times International c/o PO Box 437, Emigsville, PA 17318-0437. Printed in England by: Stephens and George Ltd • Goat Mill Road • Dowlais • Merthyr Tydfil • CF48 3TD. Tel: +44 (0)1685 352063
Web: www.stephensandgeorge.co.uk ©Quartz Business Media Ltd 2024
www.steeltimesint.com
2 Leader By Matthew
Moggridge.
4 News round-up
The latest global steel news.
The latest products and contracts.
USA update Fork in the road ahead.
Latin America update From Acesita to Aperam.
India update
Special boost for specialty steel.
Climate crisis
Co(al)-dependent: POSCO dragging its feet
Decarbonization CELSA’s TWINGHY project.
Climate crisis
Hyundai’s tainted steel.
Tube and pipe
New pipes, new prospects.
Digitalization
Smart order dressing explained.
Digitalization
People and technology: fuel for decarbonized steel. 48
Perspectives: Resonac Graphite Radical innovation. 51
History Pioneers of coke smelting part 3: William Chettle and Zachary Downing.
Matthew Moggridge Editor
matthewmoggridge@quartzltd.com
I wonder what Sir Keir Starmer, the UK’s Prime Minister, is thinking right now having publicly brown-nosed President Donald Trump in the White House, touching him here, there and everywhere after his winter greens salad and sea bass and grovellingly handing him a letter from King Charles inviting him on a second state visit. Seriously, I was frantically looking around for a sick bag as I watched such chronic obsequiousness unfold in front of me, knowing full well that tariffs would be applied to UK steel regardless of Starmer’s beggarly behaviour in front of a man the Daily Star, a UK-based tabloid, has labelled the ‘orange man-baby’. I bet King Charles is, at this very moment, standing in front of an ornate mirror practising (with great difficulty) a smile he is hoping will convince Trump that he is welcomed in the UK after publicly humiliating President Zelenskyy of Ukraine (who got to shake hands with our King first!) and then trashing the so-called ‘special relationship’ between the UK and the USA by slapping 25% tariffs on our steel. I just hope that we are as tough with Trump as he has been with us. Let’s hope we respond in kind rather than do nothing in the hope that Trump will see sense and
back track. Let’s face it, he’s not going to, not yet at any rate. Who needs Harley Davidsons and bourbon whisky anyway? Not that we haven’t been here before, it’s like an horrendous Groundhog Day without the humour.
In a BBC News report on the day of the announcement, Gareth Stace, directorgeneral of UK Steel, called the Trump decision ‘hugely disappointing’, adding that some steel company contracts had already been cancelled or put on hold and that customers in the USA will have to pay £100 million per year extra in tax. Stace believes that tariffs will hit the UK hard at a time of rising imports and punitive energy prices.
Oddly, the US only accounts for around 8% of UK exports, according to the International Steel Statistics Bureau, quoted in the BBC report, which rather makes a nonsense of imposing punitive tariffs but, as I’ve said a lot of late, ‘it is what it is’, a phrase that implies a sorry inevitability to a situation I can do little about.
As they used to say in Thunderbirds, ‘anything can happen in the next half hour’ – and it probably will.
Just as athletes rely on their teammates, we know that partnering with our customers brings the same level of support and dependability in the area of manufacturing productivity. Together, we can overcome challenges and achieve a shared goal, optimizing processes with regards to economic efficiency, safety, and environmental protection. Let’s improve together. Do you want to learn more? www.endress.com
www.fivesgroup.com/steel
Norway’s Blastr Green Steel has successfully completed the second round of partnership financing, the company said in a statement. This round involved three of Blastr’s founding investors and three new investors based in Finland. The initial investors who provided additional capital and increased their stake in Blastr are Cargill Metals, the Finnish stateowned venture capital and private equity company Tesi, and Blastr founder Vanir Green Industries.
Source: GMK Center, 4 February 2025
A steel company has announced it could close its only UK plant, putting about 180 jobs at risk. Union Electric Steel has launched a consultation on ending
Tempest Minerals has signed a memorandum of understanding with GreenSteel of WA, a company focused on creating a sustainable steel manufacturing industry for Western Australia. The MOU establishes a framework for Tempest and GreenSteel to explore potential development opportunities for the former’s Remorse magnetite deposit within the Yalgoo project in WA. The collaboration aims to leverage GreenSteel’s production expertise and Tempest’s Remorse deposit to produce high-grade magnetite concentrate for use in green steelmaking processes.
Source: Australian Mining, 7 February 2025
production at its site in Gateshead, which has been making steel for more than 150 years. Bosses said the business had been losing money for the past three years, due to lack of demand for products manufactured in the UK, high energy costs, and the ongoing effects of Brexit.
Source: BBC, 12 February 2025
Indian industrialist Naveen Jindal has submitted a bid exceeding $1 billion to acquire Italian steel manufacturer Acciaierie d’Italia (ADI). The offer, made through his privately held overseas companies, focuses on transforming ADI’s traditional blast furnaces into energyefficient electric arc furnaces, aligning with modern environmental standards.
ADI, with an annual steel production capacity of approximately 10Mt, employs around 10,000 workers, a quarter of whom are currently under a layoff scheme.
Source: Manufacturing Today, 9 February 2025
ArcelorMittal is considering moving some of its European business processes to India as part of its cost optimization strategy. The
Tata Steel UK has selected construction company Skanska to oversee the design and project management of its £1.25 billion new electric arc furnace project, a move aimed at advancing low carbon steelmaking in South Wales. The electric arc furnace initiative is part of a broader strategy to secure the long-term viability of steel production in the region.
Source: New Civil Engineer, 11 February 2025
company emphasized that this decision does not affect production facilities in Europe but is aimed at improving operational efficiency. According to Reuters, citing the company’s official statement, the European steel industry is facing a number of challenges that affect its competitiveness. In response to these challenges, ArcelorMittal is analyzing the possibility of centralizing business functions by expanding its existing service centre in India.
Source: GMK Center, 13 February 2025
SeAH Wind has confirmed it will commence commercial production at its £900 million monopile manufacturing facility at Teesworks in the UK from next month. The company, which rolled the first 7.5-metre diameter steel can in pre-production trials at the factory late last year, said trial production activities and final installations are now fully underway.
Source: ReNews.biz, 13 February 2025
Liberty Steel Georgetown has been hit with a $7 million lawsuit by the South Carolina Public Service Authority for allegedly failing to fulfil an electricity service agreement. According to the lawsuit, Liberty Steel ‘entered into a South Carolina Public Service Authority Service Agreement for Large Power Electric Service’ with Santee Cooper on 1 May 2023. The agreement states Santee Cooper was to sell electricity to the mill for five years, which was to be paid monthly. The filing states Liberty Steel failed to pay for November 2024 service charges of $167,280.50 and December 2024 service charges of $166,942.56, for a total past due balance of $334,233.06.
Source: GAB News, 17 February 2025
South African officials are working with the government to prevent the closure of ArcelorMittal’s Newcastle steel plant, which threatens 1,500 jobs. Acting Newcastle mayor Lihle Mthembu said that the municipality is working with the provincial government to find a way to prevent what local media is referring to as an ‘economic disaster.’ “As the district and our sister municipalities, we will be directly affected by this closure and we are committed in finding more ways of supporting the affected workers and their families,” said Mthembu.
Source: Scrolla, 17 February 2025
Brazilian steelmaker Gerdau may opt to increase its output capacity in the US instead of building a new plant in Mexico, its CEO has said, as tariffs implemented by President Donald Trump shake up global trade. Gerdau announced last year it was considering installing a new special steel mill in Mexico, which would have an annual capacity of around 600kt and require investment of $500$600 million.
Source: Reuters, 20 February 2025
The German Steel Federation is urging the new government to act to sustain the country's steel production, the largest in Europe and seventh worldwide, with a position
British Steel should get an extra £200 million from the government to support it in keeping the UK’s two remaining blast furnaces open until electric replacements are built, according to a proposal put forward by unions.
Chinese-owned British Steel has said it will replace its blast furnaces at Scunthorpe with electric arc furnaces, which can be used to make much cleaner, recycled steel. However, unions are concerned that a rapid closure of the blast furnaces will result in the loss of nearly 2,000 jobs within months.
Source: The Guardian, 20 February 2025
paper aimed at ensuring the sector's competitiveness and sustainability, a WV Stahl spokesperson told Platts, part of S&P Global Commodity Insights. According to the Federation, addressing electricity costs – which account for 20-40% of steelmakers' expenses – is crucial. Source: S&P Global, 24 February 2025
In a recent review published in the Journal of Energy and Climate Change, researchers from IIT Bombay have collated the advances made in the field of hydrogen generation for the steel industry and put forward the best way to decarbonize the steel industry using ‘green’ hydrogen. A team of researchers, Arnab Dutta, Sukanta Saha, Suhana Karim and Santanu Ghorai, from the Chemistry Department at the Indian Institute of Technology Bombay (IIT Bombay) have come up with a set of sustainable catalysts for generating green hydrogen that can be utilised in the steel making process via hydrogen-based direct reduction of iron (H-DRI) method. Source: The Hindu, 25 February 2025
The Trade Remedies Authority (TRA) has published initial findings, proposing that antidumping and countervailing measures on organic coated steel imported from China be maintained for an additional five years, until 4 May 2029. In its Statements of Essential Facts (SEF), the TRA found that dumping and subsidisation would likely recur if the measures were removed, potentially causing injury to UK industry.
Source: GOV.UK, 25 February 2025
Petronas, a Malaysian oil and gas company, has formalized an agreement with Sabah Energy Corporation Sdn Bhd (SEC) for supplying additional natural gas to support Sabah’s industrial and energy needs. SEC will allocate a portion of this to Esteel Enterprise Sabah Sdn Bhd, supporting its steel production operations and efforts to adopt greener and more sustainable practices.
Source: Egypt Oil & Gas Group, 2 March 2025
TOSYALI SULB Steel Industries, which was formed by TOSYALI and Libya United Steel Company, has awarded an order to Midrex and SMS group for a new DRI complex. The company intends to immediately commence the first phase of the project, with the construction of a 2.5Mt cold DRI (CDRI) plant. The Libyan plant will supply CDRI to meet the needs of the nearby region.
Source: Construction World, 26 February 2025
Korean steel giant POSCO has been sued over the climate impact of a blast furnace expansion plan. Youth activists are arguing that POSCO’s plan to extend the life of its Gwangyang coal-based blast furnace violates a human right to a healthy environment. It is the first lawsuit to challenge a company on its climate impact since a constitutional ruling recognised the state’s obligation to protect citizens from climate change.
Source: Eco Business, 2 March 2025
Swedish steelmaker SSAB and Italian crane manufacturer Fassi have reportedly signed an agreement to supply steel with almost zero fossil carbon emissions in the future. Under this agreement, SSAB will provide Fassi with steel made from iron ore and recycled scrap steel. Fassi produces self-propelled hydraulic cranes and crane trucks.
Source: Yieh Corp Steel News, 28 February 2025
ArcelorMittal has announced the appointment of Everton Negresiolo as CEO of its South American long products and mining business and a member of the group management committee, effective 1 April 2025. Everton will report to Aditya Mittal, CEO of ArcelorMittal. Everton succeeds Jefferson de Paula, who is retiring, also effective on 1 April 2025.
Source: Global Newswire, 3 March 2025
HYBRIT, a joint venture between steelmaker SSAB, mining company LKAB, and energy company Vattenfall, has completed a pilot hydrogen storage project, as reported to the Swedish Energy Agency. According to the company, the results of the project show the technical feasibility of storing hydrogen for metallurgical production without fossil fuels on an industrial scale.
Source: GMK Center, 2 March 2025
The Washington-based Steel Manufacturers Association (SMA) is citing a study prepared by a French consulting firm that backs the notion that enough domestically generated ferrous scrap is in the United States for recycled-content electric arc furnace (EAF) mills to supply nearly all of the country's steel needs. The 18-page report, titled A Transition towards Scrapbased EAFs Accelerates the Competitiveness and Decarbonization of the American Steel Industry, has been prepared by French consulting firm Laplace Conseil. According to the SMA, the study helps confirm that EAFs in the US already produce the same high-quality steel as blast furnaces and basic oxygen furnaces.
Source: Recycling Today, 3 March 2025
Liberty Steel Galati has initiated a preventive composition process, designed to stabilise the company, optimise resource allocation, and unlock new investment opportunities. The business claims that its actions will build a sustainable business, protect the company’s future and restart the production operations in Galati, which shuttered in May last year.
Source: BR Magazine, 4 March 2025
Liberty Steel UK’s pipes division in Hartlepool has now started work on creating pipelines for the Net Zero Teesside project after securing work on the bp-led scheme last year. The company will produce 105km of offshore pipeline infrastructure which will be used to transport CO2 to the Endurance carbon capture storage facility in the North Sea – 1,000 metres below the seabed.
Source: Tees Business, 7 March 2025
Rails manufactured by British Steel in Scunthorpe, UK, for Egypt’s first fully electrified mainline and freight network have recently passed inspection and been dispatched from the port of Immingham. The UK-based steelmaker recently hosted representatives from the Egyptian companies F.A.T. and Orascom, who are managing the project, to deliver Egypt’s landmark new rail route. They inspected, and approved rails from a batch of over 4,500 18-metre lengths which were ready for dispatch at both the Scunthorpe site and the Immingham port.
Source: British Steel, 4 March 2025
The UK’s only plate steel mill needs investment to allow it to become a ‘world-leading producer’ of a key component for offshore wind turbines, trade union leaders have said. A new report from the
The European Recycling Industries' Confederation and the Bureau of International Recycling, both based in Brussels, are ‘profoundly concerned’ about the conclusions reached during the Summit on the Future of the European Steel Industry in Paris, particularly with the intention expressed by representatives of Belgium, Italy, France, Luxembourg, Romania, Slovakia and Spain to ‘secure access to raw materials while retaining steel scrap within the EU’ and the proposal to ‘restrict or ban exports to third countries that do not adopt environmental and production legislation similar to that of Europe.’
Source: Recycling Today, 4 March 2025
Ukraine still maintains steel production growth in the first two months of 2025 despite the loss of the sector's key coking coal mine in Pokrovsk in the eastern part of the country, data from the Ukrainian steel producers' union showed earlier this
Fujian Kebao Metal Products, a Chinese silicon steel producer and subsidiary of Sanbao Group, has placed an order with Primetals Technologies for a continuous tandem cold mill (CTCM) at its steel plant in Zhangzhou. According to a press release, the 6-stand CTCM will be used to produce high-quality silicon steel and associated services in China. The machine will be designed to achieve precise thickness and flatness tolerances with high accuracy. It will be equipped with chamfered shiftable work rolls and a multichannel edge drop thickness gauge.
Source: Primetals Technologies, 6 March 2025
month. Ukrainian steelmaker Metinvest has suspended operations at Ukraine's only coking coal mine, citing a deteriorating security situation as Russian forces advanced.
Source: yahoo!finance, 8 March 2025
Community trade union made the case for investment in the Dalzell steelworks in Motherwell, which is currently the UK’s only plate mill.
Source: The Standard, 9 March 2025
DYSENCASTER®
HYDROGEN-READY AND ELECTRIC TUNNEL FURNACES
Performances, operational reliability and quick startups are the result of 30 years of continuous R&D activities, carried out at the Danieli research center and onsite together with partnering customers.
QSP-DUE can make use of more than 20 Danieli patents covering technological layouts, production equipment and Danieli Automation solutions, such as power, instrumentation and intelligent digital controls.
— The most efficient, digitally controlled electric steelmaking with no impact on the power grid.
— 6 m/min casting speed, allowing up to 4.5-Mtpy productivity on a single strand, with dynamic adjustment of slab thickness and width at any speed. In-mould fluidodynamic control with MultiMode Electromagnetic Mould Brake (MM-EMB) for no quality limitation.
— Hydro-MAB burners ready for 100% hydrogen operations and electric tunnel furnaces for carbon-free slab reheating.
— Split mill layout, intensive cooling and dynamic transfer bar reheating for true thermomechanical rolling and endless operation of ultra-thin gauges.
— Danieli Automation robotics and artificial intelligence for zero-men on the floor.
— Least power-consuming process with the lowest carbon footprint.
— The most competitive plant in terms of CapEx and OpEx.
— The highest production flexibility due to three rolling modes available in a single line.
QSP-DUE® ENDLESS CASTING-ROLLING PLANTS
SGJT and Yukun are enjoing their QSP-DUE plants operating in coil-to-coil, semi-endless and endless mode, based on HRC market requests. The Nucor Steel QSP-DUE plant is under construction.
15 QSP PLANTS
The TII Group has ‘set the course for ensuring continued future success’ through the appointment of Filippo Baldassari as managing director of TII GmbH. Together with CEO Dr. Gerald Karch, he has been tasked to strategically develop the group and sustainably strengthen its market position.
Filippo Baldassari has been managing director of TII SCHEUERLE and TII KAMAG since 2020, contributing to the successful development of the group of companies during this time. In his new role as managing director of TII GmbH, he will continue to assume his previous responsibilities as well as working closely with Dr. Karch. Together, they will maintain the TII Group’s course, drive innovation forward, and strengthen customer orientation.
“With the new management structure, we are focusing on continuity and future security and reliability. Dr. Karch and Filippo Baldassari bring extensive experience and strategic foresight to optimally position the TII Group for facing future challenges. In this way, we can ensure that we
For further information, log on to www. tii-group.com
AMADA WELD TECH EUROPE has announced the launching of its IS-Q Series Inverter Resistance Welding Power Supply. With a compact design for optimal system integration, the IS-Q series is designed to be used in combination with mechanical, pneumatical, or motorised weld heads. This technology was created for a variety of applications, including stranded wire to coil, motor fusing, and stranded wire to terminal welds.
The IS-Q Series offers control monitoring with the MG3 and OP-AWS3-A Active Welding Systems. The OP-AWS3-A integrates the process control of all mechanical and electrical parameters. It also integrates static and dynamic process monitoring, as well as quality analysis with an advanced SPC feature and data logging capability.
The integrated process monitoring offered by this series allows for rigorous quality control, says AMADA. With a high output current, the system also leads to short cycle times, it is claimed. With up to 20kHz of feedback, it enables fast
reaction to fluctuations in the weld process, says AMADA WELD TECH EUROPE. The ISQ-Series also offers additional force control via a proportional pneumatic valve and comes in a variety of different versions, each with a different performance range, weld current type, and various other fea-
tures. These versions include the IS-Q3000A, the IS-Q6000A, the IS-Q40A, and the IS-Q500A.
For further information, log on to www.amadaweldtech.eu
Wheatland Tube, a division of Zekelman Industries, has announced a new name for its proprietary, five-step galvanization process. The newly dubbed HDZ Coat™ is used in the company’s standard and fire sprinkler pipe for fluid, water, and gas applications. The hot dip zinc process is completed fully in-house at Wheatland Tube, so that engineers and contractors who specify HDZ
Coat will have full traceability and compliance with updated ASTM standards.
“With HDZ Coat, Wheatland Tube goes the extra mile to eliminate the pain that engineers and contactors feel with every piece of returned inventory or project claims,” said Kevin Kelly, president of standard pipe, Wheatland Tube. “By controlling the entire process for HDZ Coat in-
house, we eliminate those pain points with fully compliant pipe that also prevents early rust and eliminates microbial contamination.”
For further details, log on to https://www.wheatland.com/.
Air Turbine Technology Inc., a manufacturer of high-speed turbine products, has launched its new Air Turbine Spindles® 601 Series Spindle. The spindle combines constant high-speed in cut, energy efficiency and a user-friendly design, says the company.
The compact 601 Series Spindle incorporates Air Turbine Technology Inc.’s patented governor technology, which increases CFM airflow on demand to maintain constant speeds of 40,000 to 90,000 RPM under cutting load on the toolpath through the program. The 601 Series Spindle provides up to 0.2 HP (0.15 kW) power, delivering power for micro-machining applications – although Air Turbine Technology Inc.’s range includes spindles with power to 1.4HP (1kW) for larger tools and hard materials.
This governed turbine maintains the required surface feet per minute (SFM) and chip load for micro and small tools by sustaining high RPM on the toolpath. Air Turbine Technology Inc.’s direct drive 601 spindle generates no heat, delivering accuracy with no thermal growth in the spindle.
Fully automated loading is available using air supply through the machine spindle, a collar and stop block or manual connection through the side air inlet. Easy installation minimizes downtime, claims the company, allowing manufacturers to quickly adapt to changing production demands.
For further information, log on to https://www.airturbinetools.com/products/spindles/ spindle-series/601-series/
Eudmarco S/A Serviços e Comércio Internacional has added two more customized Konecranes reach stackers to its fleet at the Port of Santos terminal in Brazil. The Konecranes SMV 4638 TC6H and Konecranes Liftace 4532 TC5 were ordered in early 2024 and delivered later in the year in November.
Both of the new reach stackers are fitted with the latest driveline or transmission technology, enabling up to 10% fuel savings compared to older models, claims Konecranes. Load-sensing pumps and an automatic acceleration feature for hydraulic movements aim to reduce the need for engine revving – helping to cut carbon emissions. ‘Eco mode’ is designed to further enhance fuel efficiency and extend the lifespan of the equipment.
Built with the same chassis as the top-selling Konecranes SMV 4632 TC6 model, the two new reach stackers come with the addition of power-damping capability. This allows operators to lock the tilt of the spreader, which is useful when the ground is not flat or when loading containers onto a train.
With the new Konecranes SMV 4638 TC6H, Eudmarco’s operators can stack up to six 9’6’’ containers in the 1st row and up to five 9’6’’containers in the 2nd row – significantly increasing
capacity and operational efficiency at the terminal. To increase stability and safety, this crane model comes with larger 18.33 tyres.
“We really appreciate the quality of Konecranes equipment, and the support provided by the company, so we decided to take this next step together. We’re very happy to make our operations more eco-efficient with Konecranes’ new fuel-saving technology,” said José Wenes, administrative manager from Eudmarco’s parent company, ABA Infraestrutura e Logística.
Konecranes TRUCONNECT® telematic solution is also included, so Eudmarco can remotely monitor the performance of the reach stackers through the yourKONECRANES.com customer portal and the Konecranes CheckApp for inspections.
“We are very pleased that Eudmarco is taking Konecranes advanced features and digital tools into use. The powerful technology package we’ve customized for the Port of Santos terminal will enable higher productivity and efficiency, with lower fuel consumption and fewer emissions,” added Andres Ramirez, sales manager, lift trucks, Konecranes.
For further information, log on to www.konecranes.com
Thermo Fisher Scientific has introduced the Thermo Scientific™ Elescan™ XRF-100 Online Multi-Stream Elemental Slurry Analyzer. The analyzer supplies real-time elemental analysis of multiple slurry streams in a centralized multiplexed system configuration by employing the latest Energy Dispersive X-Ray Fluorescence (EDXRF) technology, including low-power, air-cooled X-ray tube. The modular design allows for optimization of the sampling strategy for online analysis, says the company, and incorporates the latest iteration of proven XRF technology, ensuring longevity and serviceability for the years to come.
In base metal and polymetallic ore plants, the analyzer helps enhance recovery rates while increasing product quality. Because the measure-
ments are taken in real-time, the analyzer gives plant operators immediate notification of process upsets, facilitating rapid response and remediation to minimize losses. Additional benefits include optimization of reagent usage, reduction in product grade variability, control of product contaminant levels, and rapid experimentation of operational strategies.
The Elescan XRF-100 features a modular design that allows flexible integration into a wide range of plant set-ups. Its scalability ensures it can adapt to both small and large operations.
For further information log on to: https://www.thermofisher.com/Elescan
Primetals Technologies has recently received the final acceptance certificate (FAC) for digital assistant systems at SSAB’s Hämeenlinna plant in Finland. These systems mark the first-ever implementation of Primetals Technologies’ digitalization solutions for coil identification and pickling defect detection. The AI-powered systems identify surface quality issues, reducing production interruptions caused by strip breakage and other defects, says Primetals.
For producers in the metals industry, pro-
cessing coils out of sequence or with undetected pickling defects can result in production delays and equipment damage. To address this, Primetals Technologies has developed AI-driven computer vision solutions for automated coil identification and strip surface monitoring. These assistant systems aim to enhance operational efficiency by minimizing downtime and eliminating the risk of processing coils that do not meet end-customer specifications. The solutions are designed to prevent coil mismatches and reduce
scrap, with real-time results visualized through augmented video streams.
A key objective of the assistant systems is to identify coils at an early stage to ensure correct storage in the coil yard. A strategically placed camera detects coil and saddle numbers while the hot-rolled coils are still located on the delivery train, before storage.
The data is transmitted to a coil yard management system to streamline and optimize crane operations. As the coils are loaded onto the entry walking beam, the coil identification number is detected and cross-checked with the production schedule. If a mismatch is identified, the operator is immediately notified to correct the coil sequence, ensuring smooth and accurate processing.
The insights gained from the assistant systems are transmitted to the automation systems for further processing, analysis, and documentation. The results are communicated to subsequent downstream processes, enabling real-time adjustments such as modifying rolling speeds or adapting cutting plans.
At SSAB Hämeenlinna, the system will be continuously optimized, as it can be trained to detect new types of coil marking and pickling defects.
For further information, log on to www.primetals.com
While President Trump’s inauguration speech did not mention tariffs, foreign steel suppliers feel trepidations. By Manik Mehta*
FOLLOWING the inauguration of President Donald Trump on 20 January, many steel pundits are wondering if and when he would impose new tariffs against imports, as he vowed to during his election campaign, since his inauguration speech did not provide any indications of tariffs.
Prior to his inauguration, Trump had vowed to impose more tariffs on imports of Chinese products; imports of Chinese steel products are already subject to 25% tariffs imposed in 2018 under Section 232. However, it remains to be seen if Trump will continue with the existing level of tariffs on Chinese steel imports or if he would impose further tariffs on Chinese steel imports.
Steel industry experts are also wondering about the future of the United StatesMexico-Canada (USMCA) free-trade pact, since Trump had threatened to impose 25% tariffs on exports from Canada and Mexico. Such a move would, invariably, affect trade relations with both these trading partners who are very likely to retaliate by imposing tariffs on US products. Trump is very likely to call for a comprehensive review of the USMCA agreement, a step leading towards imposing tariffs against Canada and Mexico which, so far, enjoyed tariff exemption.
But China exports far less steel to the US – about 32.555kt or 1.67% of the total US imports in November – than the volumes exported by Canada and Mexico. Trump has threatened to impose an additional 10% tariff on all imports from China if the latter did not curb ‘the flow of illegal drugs into
The US domestic steel industry could benefit from tariffs on imports from Mexico and Canada; this was the case when Trump imposed Section 232 tariffs in 2018 which brought US steel companies higher steel prices and margins.
In the six years since the imposition of tariffs in 2018, the average margin for hot-rolled coil production, for example, jumped to over $630 per tonne compared to the average margin of $405 per tonne prevalent in the five years prior to the tariff introduction.
“Keep your fingers crossed,” was the response I got from a New York-based analyst when asked to give his view on when the tariffs could be imposed. But the analyst, preferring to remain anonymous, commented that there was a procedure that would have to be followed, including a review of the industry and market situation as well as studying the implications (by which he meant the possible retaliatory measures from those facing the tariffs) for the US.
Former US President Joe Biden decided to officially block the US Steel/Nippon Steel merger but executives of the Japanese steelmaker are now hoping that President Trump will find a way to accommodate the deal. Japan’s prime minister Shigeru Ishiba had directly expressed his concerns to Biden
*US correspondent, Steel Times International.
during a video conference on 13 January about Biden’s action against Nippon Steel’s planned acquisition of US Steel.
Besides being opposed by domestic steel companies and steelworkers, the $14.9 billion merger deal was also opposed by politicians; during the campaign, both Biden and Trump had opposed the deal but Trump has, lately, maintained silence over the issue, leading some to believe that this could lead to a gradual acquiescing to the merger deal.
American industrialists, steelworkers, and politicians generally disapprove of the idea of the control of a one-time iconic steel business falling into the hands of a foreign company. But Nippon Steel already has operations in the US. Indeed, a large number of Japanese and American automobile manufacturers source their requirements from Japanese steelmakers in the US.
Nippon Steel and US Steel have, meanwhile, initiated a lawsuit against the Biden administration’s decision to block their merger, and also moved a federal court to set aside the review of the Committee on Foreign Investment in the US (CFIUS); the two merger partners argue that the deal would enhance, not threaten, US national security.
Supporters of the merger, including a number of politicians and senior officials, point out that Japan is a staunch ally of the US in East Asia and an effective counterweight to China’s growing
influence. Indeed, the Biden administration had cleared a $3 billion air missile sale to Japan just a day before the merger deal was blocked.
US Steel/Nippon Steel merger has other rival suitors
Somewhat coinciding with Trump’s inauguration, Lourenco Goncalves, CEO of Ohio-based steelmaker Cleveland-Cliffs, was brazenly critical at a press conference of Japan, even making incredulous references to the US bombing of Hiroshima and Nagasaki and harping on the need to save the industry in the Mon Valley.
Despite President Biden blocking the merger, the CFIUS has, meanwhile, extended its own deadline to 18 June for delivering its final assessment. Many see in this date extension a sign that CFIUS will reconsider its original review which
may have been done under pressure from the administration. Besides the lawsuits challenging the CFIUS review and questioning whether due process was followed, the time would also allow President Trump to find a way to reverse his predecessor’s decision.
With his outburst, Goncalves was trying, as many believe, to catch attention of the new administration by toeing the nationalist line, in keeping with Trump’s much-touted MAGA (Make America Great Again) slogan, though many felt that his expression of anti-Japan sentiments were uncalled for. The Cleveland-Cliffs CEO’s remarks did shock Japan and its industry, creating the impression that the US did not welcome foreign investors. Goncalves had been interested in acquiring US Steel which
spurned his first takeover bid. If US Steel had acquiesced in Goncalves’ takeover bid, it would face anti-trust issues whereas in Nippon Steel’s case, the anti-trust question would not arise. US laws encourage competition and discourage any entity from having a monopoly in the industry.
At the press conference, Goncalves also announced his company’s renewed bid to acquire US Steel which had once rejected the former’s bid and accepted Nippon’s offer. Without revealing many details, Goncalves spoke of offering an ‘all-American solution’ to save US Steel by relocating Cleveland-Cliffs to Pittsburgh, retaining the US Steel brand name, and making Cleveland-Cliffs part of US Steel.
Goncalves is also trying to partner with electric arc furnaces (EAF) steelmaker Nucor Corp. of Charlotte, North Carolina, to make a joint bid to acquire US Steel, with Cleveland-Cliffs acquiring most of US Steel and Nucor taking its mini-mill EAF assets, which are based in Arkansas and operate under the Big River Steel brand.
It remains to be seen if the joint bid would materialize and succeed with the acquisition. �
Main advantages:
• Reduces downtime;
• Forms tidier packs;
• Requires rare and limited maintenance;
• Achieves 30 tons per hour with cycle times under 10 seconds per layer;
• Saves energy while producing at peak performance.
The Robotic Stacker is AIC’s new system that automates the process of piling flat and angular profiles.
The system is designed to handle up to 6 bars from 4,5 to 13 m in legth, and the profiles can be picked in a mixed way (straight or reverse).
It integrates perfectly with no mechanical modification to the existing machine.
The system is very flexible and allows to change profile in just 7 minutes.
In the third part of a series of articles analysing the development of Acesita/Aperam, Germano Mendes de Paula* examines the 1990s and the 2000s and the company’s transition from Acesita to Aperam Group.
IN October 1992 Acesita was privatised for $465 million, using Brazilian pension funds and, to a lesser extent, banks as the primary buyers. In the years that followed, the company underwent significant shifts in corporate strategy (STI, Jul-Aug 2002, p. 50).
In 1994-1995, Acesita made several acquisitions, primarily in the special steel and forging sectors. In 1994, it acquired Eletrometal, a small long specialty steel producer specializing in high-alloy steels. In 1995, Acesita purchased a 31% stake in Aços Villares, Brazil’s largest producer of special long steel. The following year, Eletrometal was integrated into Aços Villares, resulting in the formation of Villares Metals. Additionally, Acesita took over Sifco in 1994, the second-largest forging producer in Brazil, which focused on the automotive industry and held around 25% market share. Before this acquisition, Acesita’s forging division had a mere 6% share of the Brazilian market.
In a more significant move in 1996, Acesita acquired a 34% strategic stake in Companhia Siderúrgica de Tubarão (CST) for $518 million. The deal saw Companhia Vale do Rio Doce (CVRD) and Kawasaki Steel, both existing shareholders of CST, purchase additional shares. Two Brazilian banks and the Italian steel company Ilva (part of the Riva group) divested their total shareholdings in this transaction.
However, Acesita’s consolidator strategy was short-lived, as the company’s financial conditions deteriorated. By late 1997,
rumours of a potential sale surfaced, with Usiminas initially seen as the likely buyer, due to logistical synergies. By 1998, competition for Acesita narrowed down to Companhia Siderúrgica Nacional (CSN) and France-based Usinor, with the latter ultimately acquiring 28% of Acesita’s total capital and 39% of its voting capital for approximately $610 million. This agreement also granted Usinor a 49.9% stake in a new special-purpose company that took over Acesita’s interest in CST, making them a stakeholder in CST through two indirect means.
Following Usinor’s acquisition, Acesita underwent another radical shift in corporate strategy, refocusing on the flat stainless steel market. Between 1998 and 1999, Acesita divested several assets:
a) Forjas Acesita (forging producer) to Krupp;
b) a hydroelectric mill;
c) its stake in Atlas, a leading Brazilian lift manufacturer; and
d) various forest holdings.
Regarding production capabilities, Acesita commissioned a new Sendzimir cold rolling mill with a capacity of 160kt/yr in 1998 at a cost of $215 million. Pig iron production increased from 545kt in 1990 to 623kt in 1999 (a 14% growth), while crude steel output rose from 673kt to 786kt (17% increase) (Graph 1). Production of special flats grew only slightly from 410kt to 413kt, while special longs drastically decreased from 118kt to 3kt, indicating a near-total exit from that segment (Graph 2). Notably,
high-value-added products saw significant gains, with flat stainless steel production rising from 97kt in 1990 to 226kt in 1999, and silicon steel output increasing from 72kt to 107kt (Graph 3).
The ‘noughties’
The first decade of the 21st century witnessed a continued focus on flat stainless and silicon steels from an operational standpoint, along with complete ownership by ArcelorMittal from a corporate perspective, as explained below.
In 2000, the Spanish steelmaker Sidenor acquired a majority stake in Aços Villares, diluting previous shareholders’ stakes. Eventually, Acesita divested its remaining interest in Aços Villares. In 2002, Acesita finalised an agreement to sell Sifco, its autoparts forging subsidiary, to welded tubemaker Metalúrgica de Tubos de Precisão (MTP), for a nominal amount.
In 2002, a merger led to the formation of Arcelor, which combined the former companies Usinor (France), Arbed (Luxembourg), and Aceralia (Spain).
As a result, Arcelor inherited Usinor’s shareholding in Acesita. At that time, the controlling shareholders included Arcelor with 38.9% of the voting capital and Brazilian pension funds with 39.3%. The largest investors decided to delegate operational management to Arcelor.
ArcelorMittal was formed in 2006, and by the following year, it held a 57% stake in Acesita. In April 2008, just months before the Lehman Brothers’ bankruptcy,
* Professor in Economics, Federal University of Uberlândia, Brazil. E-mail: germano@ufu.br
ArcelorMittal made a public offering to acquire the remaining 43% of Acesita’s shares that it didn’t already own. The offer culminated in ArcelorMittal purchasing 94% of the shares it sought for approximately $1.66bn. Following this acquisition, the company was rebranded as ArcelorMittal Inox Brasil.
On the operational front, Acesita completed a $100M investment project in 2002, aimed at increasing the capacity of its Steckel rolling mill from 600 to 800kt/ yr. Additionally, the capacity for stainless
steel production was expanded from 350 to 500kt/yr. That same year marked the complete cessation of long steel product manufacturing, allowing Acesita to concentrate entirely on flat steel products.
Throughout the 2000-2008 period, Acesita’s pig iron production varied around a 636kt/yr plateau, but fell to 478kt in 2009 due to the global financial crisis. Crude steel output reflected this downward trend, with figures of 785kt/yr dropping to 607kt (Graph 1). Production of flat steel products averaged 586kt/yr in the first nine years
of the decade but decreased to 461kt in 2009 (Graph 2). For stainless flat steel, the respective production figures were 350kt/ yr, subsequently dropping to 274kt, while silicon steel production saw a decline from 166kt/yr to 144kt (Graph 3).
In 2011, Acesita transitioned into the Aperam group and underwent another rebranding as Aperam South America. However, the evolution of the company from 2010 onward will be explored further in the next and concluding part of this article. �
Dilip Kumar Jha*
FOLLOWING the success of its first edition, the Indian government has reintroduced its popular Production-Linked Incentive (PLI) scheme for specific categories of importoriented specialty-grade steel. This initiative aims to replace imports with domestic production, save foreign exchange, and make India’s steel sector self-reliant within a
specified timeframe.
India has achieved the distinction of being the world’s second-largest steel producer, with a cumulative steel production capacity of 180Mt and actual crude steel production of 144.30Mt, trailing only China. This is against a total steel consumption of 136.29Mt in the financial year (FY) 2023–24 (April–March).
Source: Joint Plant Committee, Ministry of Steel, Indian government; *April-September
imported steel continues to make inroads
Joint Plant Committee (JPC) under the
Despite this significant achievement, imported steel continues to make inroads into the Indian markets. According to the Joint Plant Committee (JPC) under the Ministry of Steel, India’s total steel imports stood at 8.32Mt in FY 2023–24, compared to 6.02Mt in the previous year.
Source: Ministry
The revised PLI Scheme 1.1 targets coldrolled grain-oriented (CRGO) steel, a high-value material used in the production of power transformers for high-tension (HT) electricity distribution. Recognizing the strategic importance of achieving selfreliance in CRGO, the Indian government has consistently engaged with the industry to promote domestic production. However, Indian steel manufacturers have struggled to find a solution due to the unavailability of the required technology to support local manufacturing. High capital expenditure, coupled with a lack of government support, has rendered previous attempts unsuccessful.
Although the earlier PLI scheme covered a wide range of specialized steel products, CRGO steel for HT power distribution remained an untouched area, with no steelmakers showing interest in setting up greenfield projects or modernizing existing facilities to begin domestic production. To address this, the government has reduced the investment and capacity creation thresholds in the revised PLI scheme – from INR 50 billion ($588 million) and 200kt to INR 30 billion ($360 million) and 50kt respectively. The Ministry of Steel hopes that these changes will encourage industry participation. India’s total consumption of electrical steel is estimated at approximately 400kt/yr.
According to Sandeep Poundrik, secretary at the Ministry of Steel, the revised PLI
scheme 1.1 will be implemented during the production period from FY 2025–26 to FY 2029–30. He noted, “There were no participants in eight sub-categories during the previous round, but we hope for wider participation this time. Certain changes have been incorporated in consultation with the industry to make the scheme more investor-friendly. These include reducing the threshold investment and capacity requirements for CRGO product sub-categories, allowing the carry-forward of excess production to the immediately following year for incentive claims, and lowering the threshold investment under the capacity augmentation mode.”
The steel industry previously perceived the large thresholds for capital investment and capacity creation as unworkable, necessitating a revision. Not all companies need to install new mills. Recognizing the importance of producing high-quality steel, improving energy efficiency, and enhancing other processes, the revised scheme allows companies investing in capacity augmentation to participate. In such cases, the required investment will be 50% of the threshold mentioned in Annexure-III of the guidelines, which were uploaded on the web portal launched by the honourable minister.
HD Kumaraswamy, union minister of steel, stated, “The PLI Scheme 1.1 spans five product categories of specialty steel, consistent with the existing scheme. The revised version aims to encourage further
participation, addressing requests from industry stakeholders for relaxation. Indian steelmakers are expected to actively participate, invest, and contribute to strengthening Brand India, reducing imports, and positioning India as a global steel powerhouse. The changes in the PLI scheme for specialty steel reflect the government’s commitment to bolstering domestic production, fostering innovation, and minimizing imports.”
Under the revised scheme, steelmakers can carry forward excess production to the subsequent year for incentive claims. If a company’s production in a given subcategory exceeds its committed target for the year, the excess can be carried forward to offset shortfalls in meeting the committed production for the immediate next year. This ensures that incentives are distributed optimally and that no company is denied benefits if it falls short of incremental production targets following a strong performance year.
Originally conceived and notified in July 2021 with a budgetary outlay of INR 63.22 billion ($743 million), the first round of the PLI scheme aimed to promote the manufacturing of value-added steel grades within the country. It sought to help the Indian steel industry advance technologically and move up the value chain.
According to the Ministry of Steel, 26 Indian companies proposed setting up 44 projects with a committed investment of approximately INR 2,710.6 billion ($3.19 billion) and a downstream capacity creation of 24Mt. Of these, the investment reached so far is around INR 1,830 billion ($2.15 billion), resulting in the direct generation of approximately 8,300 jobs. The government’s incentive payout under the first PLI scheme is estimated at INR 20 billion ($235.29 million).
The PLI Scheme for specialty steel has highlighted the importance of developing self-reliance in the production of specialty steel.
The country will benefit from a reduction in imports and, it is hoped, will achieve selfreliance through capacity creation, ensuring investments that lead to job creation, and moving up the value chain in the steel business. �
The world’s biggest integrated steel production hub, the POSCO Gwangyang Steelworks, continues to cling to its coal dependence, with the relining of one of the facility’s blast furnaces expected to extend the lifeline of dirty coal-based steelmaking while depleting the global carbon budget. By Yeongmin Kweon*
THE climate crisis is accelerating faster than ever, yet some of the world’s biggest polluters remain locked into coal dependency. According to the World Meteorological Organization (WMO), 2024 is projected to be the first year that global temperatures exceed 1.5°C above preindustrial levels, underscoring the urgency of immediate emissions reduction. This intensifies the pressure on carbon-intensive industries, such as steel, to accelerate their decarbonization efforts. However, POSCO, South Korea’s largest steel producer, continues to extend the lifespans of its coalbased steelmaking facilities, undermining global efforts to limit temperature rise. The steel industry has long been a significant source of carbon emissions due to its conventional production methods. Blast furnaces, the dominant method of steel production both globally and in South Korea, are heavily reliant on coal. In particular, POSCO produces over 97% of its steel through this emissions-intensive process, consistently ranking as the nation’s top industrial emitter for the past decade. In response to growing climate concerns, POSCO has announced its commitment to achieving carbon neutrality by 2050 and reducing carbon emissions by 10% from its baseline (average emissions between 20172019) by 2030.
Despite these commitments, POSCO recently began relining one of the largest blast furnaces at its Gwangyang steelworks. Relining is not a short-term measure – it
is a significant financial commitment to maintain carbon-intensive steelmaking for decades.
Just last year, POSCO completed a similar relining at its Pohang steelworks, spending approximately $360 million to extend operations. The blast furnace can now produce 5.3Mt/yr of steel, which is over 80% of the total annual capacity of US Steel’s Gary Works. Given the scale of these investments, the blast furnaces are likely to operate for as long as possible after relining, meaning the decision to reline effectively commits to massive carbon emissions for another 15 to 20 years. In essence, POSCO continues to pour vast sums into coal-based steelmaking, despite their tremendous cumulative emissions.
These continued relinings are seriously concerning, as they risk accelerating the depletion of the global carbon budget. The carbon budget represents the maximum allowable carbon dioxide emissions required to limit global temperature rise. The United Nations Intergovernmental Panel on Climate Change (IPCC) calculates carbon budgets under various scenarios, offering guidance for setting fair and effective greenhouse gas reduction targets. If the carbon budget were allocated to South Korea’s steel industry, these relinings would rapidly consume a significant share. According to recent research by Solutions for Our Climate (SFOC), the estimated remaining carbon budget allocated to Korean steelmakers as of 2024 is only 550MtCO2e, and to
*Policy analyst, Solutions for Our Climate
align this carbon budget, at least four blast furnaces in South Korea should be shut down by 2030. In other words, the blast furnaces should be shut down as soon as possible rather than having their operational lifespans expanded, given the cumulative emissions from blast furnaces and their ongoing contribution to global warming.
The situation appears even more alarming when the emissions are quantified. Given the scale of annual production and the carbon intensity of steel produced from blast furnaces, the ongoing relining is comparable to building a new facility that would emit approximately 137Mt of carbon emissions over the next 15 years. This is roughly equivalent to the lifetime emissions of 3.68 million passenger vehicles, exceeding the total number of registered cars in Seoul. This decision is a clear contradiction to the urgent need to cut carbon emissions.
Rather than extending the life of coalbased blast furnaces, POSCO has viable alternatives, such as hydrogen-based direct reduced iron (H2-DRI) technology, which has already demonstrated its potential to significantly reduce carbon emissions. POSCO has been developing its own innovative hydrogen-based steelmaking technology, HyREX, but progress on its development and commercialization has been slower than expected. Rather than investing further in carbon-intensive steelmaking, POSCO should prioritize a
more sustainable future by aggressively accelerating the commercialization of H2-DRI technology. This would not only align with the growing global demand for greener steel but also ensure POSCO remains competitive in a rapidly changing market.
Financial considerations also favour a transition toward greener steel production. As carbon pricing mechanisms and trade regulations tighten globally, continued reliance on coal-based steel production exposes companies like POSCO to rising operational costs and regulatory risks. A proactive shift toward low-carbon technologies, rather than sticking to the traditional carbon-intensive methods, could mitigate these risks and secure long-term profitability.
The climate crisis demands bold action from industries responsible for the highest emissions. As a leading steel producer, POSCO is uniquely positioned to drive transformative change in the sector. The company has both an opportunity and a responsibility to lead the way toward low-carbon steel production. By focusing
on innovative, low-emission technologies, POSCO can help accelerate the industry’s shift toward sustainability, and influence global practices.
A commitment to phase out coalbased steel production not only aligns with scientific urgency but also secures a competitive advantage in the evolving global market for green steel. However, POSCO continues to invest in conventional carbon-intensive steelmaking facilities
without any plans to phase them out or explain how carbon emissions could be reduced while continuing to operate the blast furnaces. The ongoing relining of blast furnace no.2 at its Gwangyang steelworks is a prime example of this.
The decisions made today will determine whether POSCO remains competitive in a decarbonizing global market or faces escalating environmental and economic risks. �
• Production Capacity: 600,000 Tons/year
• Input Materials: Billets, Blooms, or Beam Blanks
• Product Range: Beams, Channels, Angles & Flat
Steel Times International travelled to Barcelona to discuss the TWINGHY decarbonization project with Spanish steelmaker Celsa Group and Fives, supplier of a walking beam furnace at the centre of the project. By Matthew Moggridge*
ACRONYMS are funny things. They’re fine if they work, like NATO, meaning North Atlantic Treaty Organization, or ASAP being short for As Soon As Possible, but sometimes, like personalized licence plates, they simply don’t add up. Or rather they do, but you need to be a little flexible in your thinking. Take TWINGHY, for example. Yes, I know it sounds like the name of a new children’s television programme – the Twinghys – but in reality, it means Digital Twins For Green Hydrogen Production. So, where’s the ‘D’ for digital? Call me a pedant, but it matters. Or perhaps it doesn’t.
Despite its rather cute name, TWINGHY is a serious project, as, indeed, is green hydrogen production in the quest for zero-
carbon steelmaking.
One of the project’s industrial partners is Fives Group. The company is developing a new reheating burner capable of injecting a blend of hydrogen and natural gas in a range from 0 to 100% hydrogen. The burner will be tested at leading Spanish steelmaker CELSA’s furnace number three in Barcelona, Spain.
Replacing traditional burners with hybrid technology is a big challenge as the quality of the final products must be guaranteed and NOx emissions reduced while maintaining the same productivity.
The TWINGHY consortium consists of nine partners – Celsa Group in Barcelona (Spain); Swedish steelmaker SSAB; Fives Stein, a Fives Group subsidiary (France);
Nippon Gases Espana (Spain); Barcelona Supercomputing Centre (Spain); RWTH Aachen (Germany); Oulun Yliopisto – Uoulu (Finland); Calderys Iberica Refractarios SA (Spain); and Swerim (Sweden).
The TWINGHY project was started in early 2023 and is one of many initiatives led by Celsa Group that form an important part of the Spanish steelmaker’s decarbonization strategy and will contribute to its ambition of becoming net positive by 2050.
“Which means we need to be at least zero carbon and fully circular by then,” said Celsa Group’s head of innovation, Anna Domenech.
Steel Times International had been planning to visit Celsa to discuss TWINGHY for some time and embarked upon a
natural gas’, said Domenech.
Celsa is a recycler so most of its energy is generated by electricity used to melt the steel.
profiles, wire rod and rebar.
A great deal of research has gone into energy efficiency, ‘which is a critical first step’, says Domenech, ‘and then we will move forward in order to prove that it’s possible to make the switch towards hydrogen’. The timelines are simple: this year [2025] will see the installation of the required pipes and instrumentation, which can only be done after the plant has been shut down – the facility runs 24/7 all year round but closes for maintenance for three weeks in the summer and two weeks in winter. In 2026, the trials with hydrogen will begin.
train journey from London to Barcelona in early December 2024. Editor Matthew Moggridge sat down with Celsa Group’s Anna Domenech, the rolling mill plant manager Ramon Garriga and Gustavo Guzman, CEO of Fives Steel Spain, another subsidiary of Fives Group, involved in this project.
“When it comes to zero carbon, one of the most important things we need to do is to replace natural gas and to do that we currently consider three alternatives,” said Domenech. The options are biofuels, hydrogen and ‘not combusting for induction’, the latter meaning electrification.
“We are not the ones that are going to select which one is happening in the future, what we are doing is trying to keep all doors open. So, we are investing into knowing a bit more about every one of these possibilities,” she said, adding that there are no innovation projects concerning biofuels because their composition is similar to natural gas, but more sustainable. The third option involves electrifying the process of beam reheating ‘because that is the main part of the process where we consume
TWINGHY is a hydrogen project, started in early 2023 and, therefore, almost two years in development. Celsa uses natural gas for reheating and currently has many hydrogen-focused projects underway for reheating furnaces across the group. Domenech highlighted other planned Celsa projects testing the consumption of hydrogen in EAFs and ladle furnaces.
In Spain, however, the challenge is to make the reheating furnace in Barcelona ‘hydrogen ready’ and, according the plant manager, Ramon Garriga, that means making many improvements to the company’s existing reheating furnace, supplied by Fives.
The aim of TWINGHY, according to RWTH Aachen, one of the project consortium’s nine participants, is to ‘demonstrate an optimized heat transfer process based on hybrid burners in reheating furnaces, progressively decarbonizing the reheating process through the increase of H2 in combination with O2 and by monitoring and controlling it through a digital twin’.
Celsa’s Barcelona facilities constitute a true steelmaking hub. It has two electric arc furnaces (EAFs) in the melt shop, three rolling mills and several final transformation plants. The TWINGHY project is focused solely on one of the plant’s rolling mills and a Fives walking beam reheating furnace. “We have three rolling mills in Barcelona,” said Domenech, but only one of them is being used for the project producing merchant bars. The others produce big
Domenech said that energy efficiency was crucial. “You cannot use hydrogen in a process that is not efficient,” she explained, stating that hydrogen will need a lot of energy to be created. “And that’s also the power of the digital twins as they allow us to not only simulate the situations that we will have in the future, but also to find the most optimal situation for every specific moment or scenario”.
The plant will be shut down for around three weeks during the coming summer to install the special burners, which are bigger than the existing ones and, therefore, require new holes to be made. The summer is the only season when it is possible to completely stop the furnace. The rest of the installation procedure (pipes and instrumentation) can be carried out during plant operation. The new burners can run with 100% natural gas and that’s good because when the plant restarts there won’t be any hydrogen available.
The reheating furnace has 24 burners in total, 10 of which will be repurposed for use with hydrogen.
There are also two burners from Nippon Gases, a consortium partner, and these are capable of working in hybrid mode, i.e. natural gas and hydrogen, but they are located in the less efficient soaking zone of the furnace, which comes after the heating zone. Oxy-combustion is generally more efficient since there are no additional air particles to be heated during the combustion process. This is why CELSA is interested in exploring this solution further. However, the furnace was not originally designed for this technology, and when combined with H2 combustion, it could create an imbalance in air pressure. This imbalance may allow cold air to enter the furnace, potentially reducing the overall efficiency of the process, therefore Nippon’s
oxy burners are located in the less efficient soaking zone of the furnace, which comes after the heating zone. The eight burners from Fives are inside the heating zone, which is the most important part of the reheating furnace. In total, including the Nippon burners, there are 10 out of 24 burners being repurposed. All 10 (including the two from Nippon Gases) can handle hydrogen and will not have an adverse effect on the function of the reheating furnace.
Fives Steel Spain’s Gustavo Guzman said that the company’s contribution to the TWINGHY project was the development of the new burners which, he claimed, were fully compatible with all blends of hydrogen from zero to 100%. Fives was brought into the project by Celsa with the express purpose of developing the burners, said Domenech, as they are also the suppliers of the furnace. The two companies have enjoyed a long and fruitful working relationship for many years, she added, and Fives was very much interested in participating in the project.
Fives has up to eight furnaces working within the Celsa Group of companies, the last installation being at Celsa Atlantic’s new rolling mill in Bayonne, France. He said that Fives was working on increasing the efficiency of other furnaces in operation at Celsa, not just the TWINGHY furnace in Barcelona. From Celsa’s perspective, having a trustworthy furnace supplier is important when dealing with a new, disruptive and risky product such as hydrogen. “You need guarantees,” asserted Domenech.
Celsa’s Ramon Garriga said that, when operational, the burners will be the first
industrial-scale hydrogen burners in Europe on a reheating furnace, with a capacity of 180 tons/hr. Each burner will have a capacity of 4MW or 32MW in total across the eight burners developed by Fives. Guzman believes the total useful power of the furnace is around 55MW.
The burners are currently 100% natural gas, but it can be 100% hydrogen or a combination such as 20% hydrogen, 80% natural gas. The burners can be set to work with whatever blend combination is applicable at the time.
The overarching challenge, of course, is hydrogen supply and that, says Domenech, is why the digital twin approach is so good. “Because it will allow us to adapt to different market situations in terms of availability.”
Challenges presented by hydrogen supply issues have been a constant concern prompting Celsa to consider installing its own electrolyser or to partner with a hydrogen supplier. A third option was to buy hydrogen from the network. “We were in discussions with many stakeholders, we are part of networks in different regions of Europe that are promoting hydrogen including one in Catalonia. We are doing everything we can to push for hydrogen production,” said Domenech. It looks likely that buying from the network will be pursued. “So, we keep being part of these networks at European and national level,” she said. “We expect this to happen at some point, I don’t know when, but it looks like the availability of hydrogen, or the feasibility of producing it, will depend on the geographical location of your plant. Spain seems to be a good country to
produce hydrogen in terms of renewable energy capacity because we can install a lot of it, but I don’t think we considered the issue of water enough. We tend to treat it like an infinite resource and it’s not,” she explained.
Domenech spoke of water shortages in Catalonia and how, at times, Celsa was almost pushed to stop production. There are now, however, many projects funded by the European Commission that are focused on water circularity. Celsa is involved with two projects related to developing membrane technologies for water cleaning.
Where TWINGHY is concerned, however, the premise is simple: is it or is it not valid to reheat billets with hydrogen? Answering that question is the project’s aim, its end game. It’s then a case of being ready for the right market conditions to prevail.
“We need time to make all the trials,” said Ramon Garriga.
Domenech says it’s not so much about what is there, but for plants to invest further into energy infrastructure. “At the end, Celsa is guided by the politicians. Everything is about politics, but the European Commission says we should get ready for hydrogen because they will make it a reality, so we say okay, let’s get ready. Even if hydrogen is not available in the future, TWINGHY will have been a useful project because it has increased the energy efficiency of our furnaces and opened the door to using new fuels,” she explained.
The relationship between the participants of the TWINGHY project is good, says Domenech. “It doesn’t always happen in European projects, but when you have good personal connections, you just learn
more and want to do more,” she said.
Fives is confident about its new burners which have already been tested, qualified in mid-2024 and are ready to go. “We want to be ready for the opportunity that may come,” said Guzman. “There will be other potential clients interested in having these burners when hydrogen becomes available.”
Celsa’s Domenech cites Fives’ burners as one of the two main achievements of TWINGHY so far. “They have developed the burner and proved it in the lab, that’s the first thing. Second, we have the first high-resolution simulations of combustion in this type of furnace in Europe, albeit with natural gas, and we will do the same with hydrogen,” she said.
So, what’s next? This year the burners will be installed and next year trials will be conducted. “The most important thing is that, at the end of the journey, we will know if our furnace can work with hydrogen and for us it’s already a goal which can be applied to other furnaces. Here in Barcelona, we have three reheating furnaces and one of these is the same
[as the TWINGHY furnace] in terms of capacity,” said Ramon Garriga.
Where hydrogen availability is concerned right now, it’s uncertain how things will unfold going forward, says Celsa’s Domenech and Fives’ Guzman, but one thing is certain: the nine participants in the TWINGHY project are working well together. According to Guzman, “The
starting up of such a programme is always a challenge, bringing people together, signing NDAs between us, it’s difficult to put these people together and work for the same objective, but it’s working pretty well,” he said.
Domenech agrees, stating that ‘every partner has a clear role and a clear reason why they are there’. She believes in small consortiums like TWINGHY as opposed to some of the increasingly larger ones being funded by the European Commission.
Celsa’s Ramon Garriga extolls the virtues of the consortium, agreeing with Domenech’s point about exploiting synergies between the partners. “To use the knowledge of all the people in a collaborative team is good, it’s best to be with a group rather than going it alone,” he said.
“It’s been a good experience for us,” said Fives’ Guzman. “Learning from each other and reaching for a target that we set together. I think what will happen will happen. We don’t know the future for hydrogen, but what we agreed to be done with this project is done.” �
Metal is the backbone of our society. It’s in the structures we ride, work and live on every day. That’s why you’ve trusted the detection technology inside every Thermo Scientific™ ARL™ iSpark Plus OES Metal Analyzer for over 80 years to ensure every piece of steel and metal you produce is safe. With so much riding on that, why would you choose anything else?
Find out more at thermofisher.com/isparkplus
As Hyundai expands its global footprint, the company faces a stark choice: stay on cruise control and maintain the status quo or take real action to align its operations with its sustainability rhetoric, says Matthew Groch*
THE steel industry is one of the world’s largest contributors to climate change, responsible for approximately 7% of global greenhouse gas emissions and 11% of carbon dioxide emissions. The vast majority of these emissions come from coal-fired blast furnaces used in primary steel production, a process that remains deeply entrenched in the industry. Automakers, as the third-largest consumers of steel globally, have an opportunity to drive the steel industry to cleaner alternatives. To accomplish this, automakers need to map out their supply chains and ensure that their suppliers and partners are engaged in clean and ethical practices.
Hyundai Motor Company is uniquely positioned to lead the transition to sustainable steel and cleaner supply chains. In addition to being the world’s thirdlargest automaker, Hyundai is the only automaker in the world with its own steel company, Hyundai Steel. In fact, Hyundai Motor Company seems to understand this opportunity by positioning itself as a leader in sustainability, promoting its commitment to carbon neutrality and ethical supply chains.
However, investigations into Hyundai’s steel supply chain suggest a stark contrast between Hyundai’s marketing and reality, revealing significant under-reporting of
emissions, continued reliance on fossil fuels, and serious human rights concerns along its supply chain. A new report published by Mighty Earth, Tainted Steel: The Deadly Consequences of Hyundai’s Dirty Steel Supply Chain, offers a unique look into the automaker’s steel supply chain and the suppliers who have left a trail of environmental destruction and human rights abuses in their wake.
The report maps Hyundai’s supply chain from coal and iron ore mining to steel production. It identifies a range of projects and facilities across many countries (including Brazil, Colombia, South Korea, the USA, Mexico, Vietnam, Australia, Canada, and Russia) producing materials and components within the Hyundai steel supply chain that have been tied to negative impacts on the environment, climate, and human rights. To identify these suppliers, projects, and facilities, Mighty Earth and Sunrise Project commissioned Empower LLC to analyze 57,402 shipments made between January 2018 and October 2024 by 196 companies in Hyundai’s steel supply chain.
Mighty Earth also collaborated with local organizations and CSOs to validate findings, conduct interviews, and review additional
: *Senior director of the Decarbonization Campaign.
documentation related to supplier impacts. The report was able to trace HyundaiKia’s steel supply chain from raw material extraction to vehicle manufacturing, shedding light on the environmental and human rights risks associated with the company’s global operations.
The report found that Hyundai’s steel supply chain is heavily dependent on coal sourced from countries like Australia, Canada, Russia, and Colombia. In Australia, the company relies significantly on the BHP Mitsubishi Alliance (BMA), which operates several large coal mines in Queensland, including Peak Downs and Saraji. These mines are responsible for emitting vast amounts of methane contributing to significant environmental harm. Additionally, BMA’s proposed mine expansions would clear endangered koala habitats, among other ecological impacts. These coal operations have also faced legal and regulatory challenges, such as fines for water contamination and workplace safety violations, underscoring the environmental and human rights concerns surrounding Hyundai’s supply chain.
In Canada, Hyundai’s supply chain is linked to coal sourced from Teck Resources and Conuma Resources. Teck’s Line Creek
mine in British Columbia is a major supplier of pulverized coal injection (PCI) coal for Hyundai, despite the fact the company has faced repeated allegations of environmental violations, including excessive selenium leaching into local waterways. Conuma Resources, another key player, operates the Brule and Willow Creek mines, both of which have been penalized for over 400 environmental violations between 2020 and 2024.
Russia is another significant source of coal for Hyundai, despite the company’s public stance against the Russian invasion of Ukraine. In 2023, Hyundai Steel continued to receive substantial shipments of coking coal from Russian mines, particularly from the Sibirskaya mine in the Kemerovo region. These shipments, valued at $34.2 million, underscore the ongoing dependence on Russian coal, even as geopolitical tensions rise. In addition, one of Hyundai’s suppliers, Formosa, received shipments of coal valued at more than $450 million between 2022 and 2024.
Lastly, in Colombia, Hyundai’s supply chain is connected to Glencore’s El Cerrejón mine, one of the largest coal mines in the world. This mine has been linked to serious human rights violations, including water contamination, forced displacement of indigenous communities, and alleged ties to paramilitary groups. The environmental and social repercussions of these operations highlight the complex and troubling nature of Hyundai’s coal supply chain, with significant implications for both people and the environment in these regions.
Hyundai’s steel supply chain is deeply intertwined with iron ore mining operations that have been linked to serious environmental and human rights violations, particularly in Brazil and Mexico.
In Brazil, Hyundai sources iron ore from Vale, a mining giant responsible for the catastrophic Brumadinho dam disaster in 2019. The collapse of the tailings dam released a massive mudflow, killing 272 people and displacing thousands, including several indigenous communities in the area. Investigations revealed that Vale had prior knowledge of the dam’s vulnerabilities but continued operations, prioritizing profits over safety. Despite legal proceedings and settlements, many victims and their families are still fighting for justice. Additionally, Vale’s operations have contributed to pollution, community displacement, and dangerous railway conditions, further amplifying the negative impact of iron ore mining in the region.
In Mexico, Hyundai sources steel from Ternium, which operates iron ore mines tied to severe human rights abuses and violence. Communities near Ternium’s Aquila and Peña Colorada mines have reported environmental destruction, including water pollution and habitat devastation. Additionally, multiple activists and community leaders opposing the mines have been kidnapped or murdered in recent years. In 2023, Antonio Díaz Valencia, a community leader, and Ricardo Lagunes, a human rights lawyer, were forcibly
disappeared after advocating for local rights against Ternium’s mining practices. Other indigenous activists, including Higinio Trinidad de la Cruz and J. Santos Isaac Chavez, have also been killed after opposing the mines. These incidents highlight the violent repression faced by those challenging mining operations and raise concerns about corporate accountability within Hyundai’s supply chain.
A similar trend emerges when examining Hyundai’s steel suppliers. In Vietnam, Formosa Ha Tinh Steel Corporation has been at the centre of severe environmental and human rights violations. The 2016 chemical spill, in which Formosa released toxic waste into the ocean, devastated fisheries and agriculture in multiple provinces, significantly impacting the lives of nearly 44,000 families in the region. Activists and journalists covering the disaster, such as Pham Doan Trang and Hoang Duc Binh, were imprisoned for speaking out, demonstrating how corporate negligence not only harms the environment but can also undermine human rights and press freedom. Additionally, Formosa’s ongoing pollution, including the illegal disposal of hazardous waste, continues to pose health risks by contaminating underground water sources with toxic substances like cyanide and heavy metals. POSCO and Hyundai Steel’s operations in South Korea have been linked to environmental and labour rights issues, particularly at their coal-fired steel plants in Gwangyang and Pohang. These facilities, major suppliers to Hyundai, have been identified as key contributors to air pollution, which was estimated to cause 506 premature deaths in 2021 alone and increased cases of asthma and premature births. Despite the staggering economic
and health costs, POSCO has chosen to extend the life of its blast furnaces instead of transitioning to cleaner technologies. Additionally, POSCO’s plants have a troubling history of workplace accidents, with 18 worker deaths between 2018 and 2020 due to unsafe working conditions. The company has also been accused of union suppression, as seen in its firing of three activists who exposed POSCO’s efforts to block independent investigations into workplace accidents.
Hyundai supplier US Steel has faced significant criticism for its environmental and labour practices, particularly regarding pollution from its steel plants. The company has been responsible for multiple violations of the Clean Air Act, including major emissions of benzene, sulfur dioxide, and other hazardous pollutants from its Clairton Coke Works in Pennsylvania.
In 2018, a fire at the facility knocked out pollution controls, leading to months of uncontrolled emissions that harmed local communities, particularly in low-income and minority neighborhoods.
Hyundai Motor Company has marketed itself as a leader in sustainability, but the findings of this report reveal a stark contrast between its idealized image and the realities on the ground.
From coal and iron mining operations that contribute to severe environmental destruction and human rights violations to steel manufacturing facilities responsible for hazardous pollution and worker exploitation, Hyundai’s steel sourcing practices undermine its claims of corporate responsibility.
The company’s continued reliance on coal-fired steel production, despite the availability of cleaner alternatives, exacerbates global carbon emissions and places vulnerable communities at risk. If Hyundai is truly committed to achieving carbon neutrality and ethical supply chains, it must take immediate action to eliminate its dependence on destructive suppliers and invest in sustainable steel production methods.
As one of the world’s largest automakers, Hyundai has a unique opportunity to drive
systemic change within the steel industry. By transitioning to low-carbon steel free of coal, implementing rigorous supplier accountability measures, and ensuring transparency in its supply chain, Hyundai can set a new standard for ethical and sustainable manufacturing. Without decisive action, Hyundai risks damaging its reputation and failing to meet the urgent demands of climate responsibility and human rights protection.
As Hyundai expands its global footprint, the company faces a choice: stay on cruise control and maintain the status quo or take real action to align its operations with its sustainability rhetoric. �
The dimensions of the latticed main cross members can clearly be seen next to the workers
The transformation of the Estadio Santiago Bernabéu, home of legendary football club, Real Madrid, owes a lot to high-strength steel supplied by German steelmaker Dillinger
THE Estadio Santiago Bernabéu is a place of legends that attracts many visitors. As home to Real Madrid, one of the most successful football clubs in the world, the arena was first opened in 1947 and regularly plays host to unforgettable sporting encounters. Following multiple phases of reconstruction work and extensions over the past decades, the most exciting project ever seen at the football temple got underway in 2019 – the transformation to become a multi-purpose arena that is unrivaled worldwide. For Real Madrid, only the very best solution was, therefore, good enough when it came to implementing the ambitious stadium redesign. This not only applied to all of the companies involved in the construction, but also the materials used. A good example of this is S690QL1 from Dillinger, a highstrength premium steel for lightweight steel structures. Despite never having been used in such quantities for a project of this kind, this material is what actually made the challenging roof structure of the Estadio Santiago Bernabéu possible.
The spectacular new stadium design is a joint development of Hamburg-based
architecture firm Gerkan, Marg und Partner (gmp), Spanish project partner L35 Arquitectos, Ribas & Ribas Arquitectos, as well as the schlaich bergermann partner (sbp) engineering office and INES Consulting Engineers. Beside the sculptural facade, comprising sweeping diagonal stainless steel ribs with varying degrees of transparency, the retractable pitch, and a 360-degree LED screen that runs along the edge of the roof, the characteristic design elements of the new Bernabéu Stadium also include the seemingly ‘floating’ roof structure with fully retractable inner roof. Spanish steelwork fabricator Horta Coslada was commissioned to perform the construction work for three of these outstanding design elements.
With four plants in Spain and a total production area of 390,000 square metres, Horta Coslada is Spain’s largest steelwork fabricator. The company specialises in large and complex projects such as bridges, stadiums, infrastructure, and high-rise buildings. Among others, the references of the company founded in 1963 include Terminal 4 at Madrid Airport (21kt of
steel), the Cité de la Musique in Paris (3.5kt of steel), the NATO Headquarters in Brussels (6kt of steel), as well as stadium constructions such as the Estadio Wanda Metropolitano of Atlético Madrid (5.7kt of steel) and the Stade Vélodrome of Olympique Marseille (5.8kt of steel).
Large volume of S690 in the Santiago Bernabéu Stadium
Horta Coslada has now also been using steel from Dillinger for around 15 years. Some good examples of this include the Cepsa Tower in Madrid, which is Spain’s tallest highest skyscraper at 249.5 metres, as well as the Pont de l’Assut de l’Or in Valencia. For the roof of the Santiago Bernabéu Stadium, Horta Coslada processed a total of 13kt of steel, some 3.1kt of which were S690QL1 increasedstrength steel from Dillinger in sheet thicknesses of 10 to 120 millimetres. This greater strength means that lighter and more slender designs can be produced that would otherwise simply not be structurally possible. The lower weight of the components not only allows use of larger
Based on estimates provided by Alejandro Otero Gutiérrez, CEO at Horta Coslada, no European project has ever processed such a large quantity of S690 as was used for the roof of the Santiago Bernabéu Stadium. The QL1 grade, which was also ordered by Horta Coslada in thinner sheets, is a particularly sophisticated steel that satisfies the strictest safety standards, as it is in the strongest steel class.
of the new roof structure without access to the interior
The football temple in the heart of Madrid has a long and rich history. The explicit aim of Real Madrid with the remodeling was to lend the legendary Estadio Santiago Bernabéu a completely new face and make it the best stadium in the world. With four new stories in the stands, as well as a shopping centre, hotel, interactive club museum, retractable high-tech roof and lowerable pitch, the home ground of the Spanish record champion heralds the beginning of a new generation of multi-purpose arenas. As a worldwide reference in both sport and architecture,
structural elements, but also opens up completely new architectural opportunities. In addition, the time and money required to weld everything together are significantly reduced. As a premium manufacturer, Dillinger offers a wide range of increasedstrength grades. These also include products such as S690, which is available not only in standard sizes but all the way up to very high sheet metal thicknesses. This steel is commonly used in the field of crane construction. However, it is not used very often in steel construction applications and – even then – only in low tonnages.
the state-of-the-art arena is more than just a place of great emotion, as it now offers ultimate comfort, safety and cutting edge technology. The Santiago Bernabéu Stadium is situated directly on a major transit route in the densely populated centre of Madrid. Accordingly, one particular challenge for all companies involved in the renovation work was the original requirement of Real Madrid for the entire stadium construction works to be performed without disrupting scheduled matches and without any access to the stadium’s interior. The general contractor commissioned by Real Madrid, Fomento de
Construcciones y Contratas (FCC), therefore, collaborated with Horta Coslada to develop a construction strategy involving assembly of the huge cross members required for the roof structure outside the stadium. The core element of this strategy was a sixmetre-high temporary platform, positioned in front of the stadium entrance, on which all components of the roof cross members were pre-assembled. The spectators could then have simply walked through this like walking under a bridge when entering and exiting the ground. Although the COVID-19 pandemic then struck just a few months later, leading to cancellation of all matches, this construction strategy was still maintained.
Four cross members bear the entire roof load
Horta Coslada had already met the strict requirements at the stadiums of Atlético Madrid and Olympique Marseille. This was one of the key motivations behind the decision to go with the same company as the first choice supplier for the steel works in the Santiago Bernabéu Stadium. In 2019, the steelwork fabricator was, therefore, commissioned by FCC for the construction of the new roof at the Santiago Bernabéu Stadium. The original plans of the engineers for the main roof were based on the lightweight spoked-wheel principle. This comprises an inner tension ring that is to be connected via 44 radial cables to an outer pressure ring and rest on steel outriggers of the existing perimeter structure. However, FCC ultimately decided to dispense with this lightweight cable construction and instead replace it with a more conventional system that uses four latticed main cross members made of steel which support the entire stadium roof. The main supports are the north and south cross members, each measuring six metres wide and spanning some 176 metres. These key elements of the roof played a vital role in the entire assembly process. During the construction work, they made it possible to pre-assemble the other roof components on the platform outside the stadium. The two main cross members were produced in full from S690 increased-strength steel in a lattice structure and each weigh almost 1,500 tons. They rest on just four points, or rather columns, two of which were newly constructed. “This structure was only possible thanks to use of the S690 steel grade, a lightweight steel with an extremely high yield point,” explains
Stay
Alejandro Otero Gutiérrez. He goes on to add: “The weight saving, which could only be achieved in this way, was the key to the success of the entire structure. Compared with other solutions, we were able to use around 40% less steel thanks to the properties of this special grade!” Around a third of the entire roof structure at the Santiago Bernabéu Stadium was produced from S690 supplied by Dillinger. “With other steel grades, the roof would have weighed around 20kt more. With the S690 material, we only required around 12kt of steel,” comments Otero Gutiérrez. The steel grades S690 and S460 were combined in roughly equal proportions for the other two supports, the east and west cross members that span some 138 metres.
All individual parts were prefabricated at the Horta Coslada facility in Madrid. Over 100,000 parts were cut and drilled here before being welded together in the stipulated geometry to create transportable elements comprising supports and diagonals. Each support needed to be broken down into 40 parts for transport to the construction site, with the elements measuring a maximum 18 metres in length. To ensure that all of the bolts would fit properly when on the construction site, all of the components were assembled in the production hall at Horta Coslada as a test. The complete support structure above the stadium is fully bolted down
without a single welded seam. A total of 336,500 bolts were needed for this. Following pre-assembly on the platform outside the stadium, the north and south cross members were raised using a 600-ton crawler crane and then bolted together in a step-by-step process while in the air, working from the four corners. The preassembled components of the two other cross members were then raised in pairs, bolted down and – while supported by the main cross members – slid to the opposite side on wheels using electric motors. Using the increased-strength steel S690 not only
allowed the total weight of the roof to be reduced, but also the number of required components and trucks for transport to the construction site. “We managed to save around 300 truck loads,” comments Otero Gutièrrez. In light of the stadium’s location in the heart of Madrid, this not only meant a significant reduction in traffic and associated disruptions on the busy access road, but also a considerable reduction in environmental impact caused by CO2
Clear victory for S690 in the new super stadium
Looking back, the steel fabricator explains: “I can only say that it was one of the most difficult projects in our company history – due to the construction method, the logistics, the extremely tight schedule, and the steel grade.” In his opinion, the steel grade used was one of the greatest challenges. “I only know of two companies in Europe that can manufacture this steel in this thickness. Dillinger is known as probably the best supplier of such thick and high-grade steels in Europe.” His company has already completed many projects with Dillinger. Since the schedule was so tight, the high capacity and delivery reliability of the steel producer also gave the edge to the Saarland-based supplier. “This was a unique project that attracted a great deal of attention among the general public. This is why we decided to work exclusively with the best partners possible. Dillinger was, therefore, also our partner of choice.” �
Future Steel Forum 2025, our seventh live event, unites decarbonization and digitalization in modern steelmaking. With presentations from leading steelmakers including home-grown Spanish company CELSA Group as well as newcomers to the world of green steelmaking like Hydnum Steel, and not forgetting other leading European players and larger Far Eastern businesses, such as JFE Steel, it looks as if the Forum will score big with delegates once again. Secure your spot today!
SPONSOR OR EXHIBIT: For any exhibition or sponsorship opportunities, contact Paul Rossage paulrossage@quartzltd.com +44 (0)1737 855116
WHAT LAST YEAR’S ATTENDEES HAD TO SAY…
“Very well organized event with a good line of speakers focused on digitalization and decarbonization.”
Scan the QR code to preview the conference programme, exhibitor list and to purchase your ticket
“Great immersive atmosphere and excellent platform to learn and network.”
“Unique blend of upcoming technologies, challenges and the latest innovation in digital transformation for the iron and steel industries.”
“A good mixture of high-level presentations, panels and networking opportunities at an excellent location.”
2024 was generally a challenging year for the US energy pipe and tube market with both demand and prices correcting for much of the year from the high post-pandemic levels that it experienced during 2022 and for most of 2023. In recent months, conditions have appeared to stabilize. And there is also increased optimism that, under the Trump administration, which is viewed as being more ‘energy friendly’, that the market will at least moderately improve this year.
Henceforth, barring unforeseen circumstances that would negatively impact the market, 2025 should be a more solid year, Rick Preckel, a partner at Preston Pipe said, adding that it will still be unlikely to see gangbuster growth in either demand or pricing.
In fact, some industry observers question whether energy pipe demand will indeed grow or if there could be further easing.
Kim Leppold, head of Fastmarkets’ steel research, agreed, noting that one of the reasons for the market plateau has been due to an oversupply compared with the level of demand. She noted that it wasn’t surprising for demand to be lower in 2024 with not only the US presidential election, but several other elections elsewhere in the world, coming at the same time as oil prices stagnating at a lower-than-average price –in the $60s to low $70s per barrel for much of the year.
However, given that the average breakeven point is said to be about $56 a barrel, Preckel said that most exploration and production (E&P) operators are still able to be profitable. But Tommy McCartin, a principal economist for S&P Global Market Intelligence, noted that this is because OPEC is somewhat managing the global crude oil supply, holding as much as 4-5 million barrels of production capacity offline – capacity that they could bring back online quickly.
At the same time, natural gas prices have been very low for the last few years. In fact, McCartin noted that in 2024 US natural gas prices fell to $2.17 per MMBtu from $2.54
The
US energy pipe and tube market faced challenges in 2024 with demand and prices correcting from high post-pandemic levels. However, optimism has since increased.
By Myra Pinkham*
per MMBtu in 2023, which he said was already historically low.
Given that drilling is very price dependent, these prices have had a negative impact upon drilling activity, which, in turn means less demand for such energy pipe products as oil country tubular goods (OCTG) and small diameter line pipe.
With the perception that the new US administration is more pro-oil and natural gas than the Biden administration had been, with Trump frequently using the phrase ‘Drill Baby, Drill’ at many of his rallies, and the fact that he has named pro-oil and natural gas individuals to head the Department of Energy and Department of Interior, Trump’s election has generally helped energy pipe market sentiment.
While Trump cannot control oil and natural gas prices as they are global markets, Leppold noted that he can encourage more drilling by accelerating
*North America correspondent, Steel Times International
the permitting process. Trump has signed executive orders reversing Biden’s order which banned offshore drilling on some federal lands and has revoked certain electric vehicle and EV charging infrastructure stimulus measures. He also reversed Biden’s ban of new permits for new liquified natural gas (LNG) export facilities (which opens the door for new transmission pipelines to serve those facilities).
Despite this, the Baker Hughes US rig count has been somewhat flattish over that past six months or so, fluctuating between 580 and 586 rigs. But that, McCartin pointed out, is down from its peak of 780 rigs at the end of 2022 and 623 rigs a year ago.
However, given certain technological advances that have resulted in greater efficiencies, allowing E&P companies to drill more holes with fewer rigs, having
this low of a rig count isn’t as hurtful as it would have been upon OCTG and small diameter line pipe demand as it would have been in the past. A member of the National Association of Pipe Distributors (NASPD) added that this was especially true given that there are less ‘distressed’ pipe inventories on the ground than there had been a year ago.
In fact, Philip Gibbs, a senior equity research analyst for KeyBanc Capital Markets, pointed out that E&P companies are producing more oil than ever before, helped by these new well paid technologies, and the horizontal drilling associated with it.
That, Fastmarkets’ Leppold said, is because with this technology rigs can drill longer distances and, as such, the casing consumption per rig has increased. “So, when the rig count drops it doesn’t necessarily mean that OCTG casing is also going down.”
She said that with these dynamics, 2024
was a big correction year for OCTG and small line pipe, with demand being driven by drilling activity as it tends to be used for gathering lines.
Domestic demand, however, has also been influenced by imports, which the distributor pointed out account for about 50% of domestic OCTG sales and have an even greater percentage share of the US small diameter line pipe market.
This is one area of uncertainty as it is not clear what impact the Trump administration’s policies will have on the market, which by all estimates is oversupplied. In fact, Gibbs pointed out that last year, when overall domestic energy pipe demand was down about 10%, domestic pipe shipments were down less than that in light of a decline in import shipments.
The market dynamics for large diameter line pipe, however, are different than those for OCTG and small diameter line pipe, as it is not so much driven by drilling activity, but
transmission pipeline construction activity. This, Leppold said, has recently been somewhat stalled due to a sluggish market and other regulatory factors. He explained that with it being hard to get new pipelines approved, companies have been largely going on the path of less resistance –repairing and beefing up existing pipelines to increase throughput without putting a lot of extra pipe in.
That said, Preckel pointed out that there are some pipeline projects that are being worked on, but not the big projects like the ones that were seen in the past, rather smaller ones that for the most part have been under the radar.
Leppold pointed out that most of the new pipeline activity is related to new liquefied natural gas (LNG) export facilities that have either recently come online, are under construction, or are expected to be built, mainly in the South along the Gulf coast as a means of transporting natural gas to those facilities. For example, Preckel pointed out that early in February, Kinder Morgan announced that it was going forward with its plan to build its Trident Intrastate Pipeline, which is to transport natural gas from Katy, Texas, for that purpose once it is completed early in 2027.
Preckel pointed out that the two new US LNG export facilities that started up last year are currently ramping up and that several others are either under construction or have the necessary permits to allow them to be built.
In addition to its impact upon pipeline construction and, therefore, line pipe, S&P Global’s McCartin said that these new facilities could support higher natural gas prices. In fact, he is expecting them to increase nearly 90% this year and by another 55% in 2026.
It is important to note that while Biden had placed a ban on new LNG export facility permits, that ban did not impact the facilities that were already under construction or that had permits to be built. Therefore, Preckel pointed out that it wouldn’t have had an impact upon the market up to 2030 or beyond.
In any case, that is now a moot issue as Trump’s executive order declaring a national energy emergency has reversed that permitting ban, as well as reversing Biden’s order to limit oil and gas drilling offshore of the East and West coasts and parts of the Gulf of Mexico (which he renamed the Gulf of America) and on certain national lands.
Clearly the permitting of more LNG export facilities and the resulting construction of new pipelines – as well as the ability to increase drilling on federal land, will have a positive impact, the NASPD member declared. McCartin, however, pointed out that even with Trump looking to speed up the permitting process, it will still be several years before these pipelines are built and for their impact to be felt. In fact, Gibbs and other KeyBanc analysts say that it might not be until the 2030’s that this new wave of LNG export facilities and supporting pipelines come online.
backdrop of energy tubulars – both OCTG and line pipe – being in ample supply when compared with demand, with supply being augmented by imports, Leppold said, adding that while the market was in oversupply for much of 2024, recently it has come into a better balance with inventories.
Due to that better balance, energy pipe prices have gone up somewhat and could potentially continue to inch up further, but Gibbs said that he was doubtful that prices could return to 2022-23 peak levels.
and how the tariffs will be implemented. For example, at this stage it is believed that the planned steel tariffs will not include any exclusions or quotas that were part of the Section 232 tariffs implemented by Trump during his first term.
This comes as about 50% of OCTG and greater than 50% of small diameter line pipe is currently imported, according to the NASPD member. But Leppold questioned whether – at least for energy pipe – the tariffs will have much impact upon that, explaining that if E&P companies need pipe, they will pay whatever is necessary to drill their wells, especially since pipe only accounts for about 13-15% of their overall costs. “If they can’t get it domestically, they will get it from elsewhere,” she declared.
“The energy pipe market tends to be hyper cyclical and that has been the case over the past year,” KeyBanc’s Gibbs said, noting that last year was largely a tough year, marked by oversupply, lower apparent demand, lower prices, and compressed margins.
But Leppold said that as of early February market sentiment had already started to improve, helped by a better balance of supply and demand and the perception that the Trump administration is much more supportive of the traditional oil and natural gas market, which should mean increased drilling, provided market dynamics support that.
Therefore, even with this push, McCartin said that over the next few years, line pipe demand will be lower than it had been several years ago when there had been a boom in the construction of longer pipelines.
These dynamics all occurred on the
There continues to be a great deal of uncertainty as to what impact the Trump administration’s proposed tariffs could have upon the energy pipe market. The NASPD executive said that, at least for the time being, it has made companies somewhat leery of ordering many imports.
This is especially the case given that it is uncertain if they are just a negotiation tool
“While I don’t believe that 2025 will be a gangbuster year for energy pipe and tube, it should be a solid year,” Preston’s Preckel said, adding that the tariffs should also help lower the import market share somewhat, which would be good for the domestic producers. �
Smart order dressing purposes a higher abstraction level in which the product specialist shall focus on the business rules required to manufacture the product rather than on the product itself.
By Eric Meta1, Scott Miller2, Carlos Olmos1, Kurt Pressberger1, Gunther Schober1
ORDER Dressing is the process that creates a production order (PO) to satisfy a given customer sales order item (SOI) defined, at least, by a product, a steel grade (referenced to by a standard or specification), dimensions and quantity. Technical inquiries and offers can also be dressed as special PO types. The creation of a steel production order means the determination of production route, material demands, quality requirements, instructions for the L2 automations (like production process parameters and sampling requests) and the calculation of time (cost) pattern.
Steel production is not an assembly process, it cannot be described by a list of components and their assembly sequence and rules. Every piece of information in the PO is the result of the evaluation of complex rules that must consider the product requirements specific to each SOI and the capabilities and restrictions of the production lines as well as efficiency demands. Often, interdependencies between the subsequent production steps need to be considered.
For these reasons, a bill of material (BOM) approach is not best suited for the generation of steel production orders. BOM-based dressing systems react to the entry of a new SOI by searching for a match with previously calculated orders.
However, it is not always possible to find a good match so that, consequently, the intervention of an expert is required to create a new entry in the system (i.e. a new combination of parameters for the description of the product and process). This will happen every time that an order was not anticipated. Therefore, the BOM catalogue progressively grows with the result of increasing maintenance complexity and poor efficiency.
To enable the PO calculation every time a new SOI is received, an approach based on dynamic rules and business knowledge is required (Fig 1).
Smart order dressing calculates production orders by executing a set of rules configured in the knowledge base.
*1. PSI SE 2. NLMK USA.
The PO calculation, also known as technical elaboration, starts with the determination of the product and the production route. This is followed by material demand for each production step. Then sampling, test instructions and targets are determined, as well as the production instructions for each specific production step and line. Finally, standard production time and costs are calculated. When certain (calculated) conditions configured by the user are reached, alarms can be optionally triggered. A specific authorization might then be required to release the affected order.
Fig 2 shows the technical elaboration process. For the sake of simplicity, the process is depicted as linear, although often the elaboration is iterative. For example,
the selection of specific production lines might depend on a specific quality requirement, so that the precise finalisation of the production route will happen only after quality instructions and targets are determined. This is an example that shows why the iterative ability to determine PO parameters depending on the results of other parameters, which are calculated at a later stage, is needed for the dynamic generation of steel production orders. In the following, more detailed explanations about the elaboration of a production order are provided.
process instructions
In order to calculate the production route, smart order dressing uses stored data such as plant production capabilities and product description. Plant production capabilities include a list of production lines (resources), processes and sub-processes (operations) and technical restrictions for each resource/operation combination. For each product, feasible alternative production routes consisting of a sequence of operations to be performed on specific production lines can be proposed. Business
rules are then applied for the selection or ranking of alternatives. Associated to every production step are the input and output material(s) and the rules that govern the transformation, described by parameters, formulas and decision tables. The required material demand (weight, dimensions) for each production step is calculated, along with the whole production flow. Fig 3 represents a diagram of the objects and their relations.
Using conditions in the knowledge base, it is possible to define different processes and sub-processes of a production step for the same resource and product type, depending on more specific characteristics. As a result, Smart Order Dressing requires the analysis of the business rules from a higher abstraction level. As the product definition covers a wide range of options, it is necessary to have a clear business definition of what a product means. Nonetheless, the system does not limit the definitions of any object, as usually occurs with BOM-based systems.
The quality data model describes the quality requirements of the final product. Fig 4 shows how a steel standard (external quality), a customer-specific standard and a plant standard (internal quality) are linked to the chemical analysis (i.e. the melt shop ‘recipe’ for the chemical composition) and the test instructions in order to meet and certify all the quality requirements. Notice that revisions of the same standard can be available in parallel.
In multi-site company scenarios, a global quality data repository can be used to allow several local instances of order dressing to download the globally managed quality specifications. This harmonized quality model improves teamwork and transparency.
In case of overlapping quality requirements, smart order dressing can track the rules applied, so that the final requirements can be re-enacted. The calculation rules can be nested, allowing the definition of complex decision algorithms.
For example, a product may have more restrictive, internally-specified quality requirements for a certain customer but when a more demanding dimension is ordered an exception will restore the requirement according to the standard. Additionally, smart order dressing can
manage multi-quality certifications.
The dynamic rules-based knowledge base enables many products to use the same quality specifications, i.e. it minimises the maintenance effort in comparison to the BOM approach. When a certain rule is about to be modified it is also possible to highlight all the products affected.
Process duration and cost
In steel manufacturing, process durations and costs depend not only on the production lines used, but on how these resources are used. The definition of detailed processes and sub-processes enable a more precise duration and cost calculation.
Fig 5 shows a schematic diagram of the time and cost model.
Smart order dressing can calculate the fastest or least expensive route, without the need of another product specification. Defining the route during the PO calculation allows the evaluation of the cost of alternative routes and the final selection within one technical elaboration.
Fig 6 shows an example of a time calculation for a lot of two material units. This calculation is based on the standard defined by customer-specific master data. A process consists of main and secondary process time and the time range between two production steps defined as interoperation time. The model can take into account set-ups, overlaps and loading time related to an availability factor.
Beyond time, cost calculation depends on additional variables like material, material demand and employed resources. Smart order dressing allows configuring such a cost function and integrating it in the iteration of the technical elaboration with the goal of delivering the less expensive PO.
As a conclusion, the advantages of smart order dressing compared to traditional, BOM-based methods shall be highlighted: the possibility to automate technical queries; the reduced maintenance effort; the capability of dressing first time inquiries, which give a competitive advantage to the steel manufacturer.
Smart order dressing purposes a higher abstraction level in which the product specialist shall focus on the business rules required to manufacture the product rather than on the product itself. �
Much of the buzz in the metals business these days is about how the combination of data and technologies like artificial intelligence can give companies a competitive edge in the decarbonization era. And justifiably so, because in working closely with metals companies around the world, I see firsthand how digital capabilities are helping them operate more intelligently, efficiently, sustainably and profitably. By Stefan Koch*
AS the consulting firm Roland Berger asserts in findings from a 2024 analysis based on a survey of steel industry executives, “AI use cases exist across the value chain. Used in combination, they will have a massive impact on [steel company] competitiveness, from performance improvement and safety to innovation and sustainability.” That impact could amount to an estimated 1015% overall cost advantage, according to the report.
Climate change and the resulting
aggressive global push to decarbonize is one big factor that is rapidly reshaping steel markets and the business landscape for steel companies. Technological advances, and the rise of cloud computing and AI in particular, are another. The huge volume of data to which companies now have access is also prompting them to re-examine their business processes and decision-making on a broad scale. And let’s not overlook how issues like the global population redistribution and geopolitical instability
impacts markets and businesses. All this adds up to unprecedented uncertainty for steel companies.
What is certain is that they must behave more sustainably and decarbonize. There is no discounting the vital and expanding role digital technologies in general, and AI in particular, have in helping steel companies do so. Yet smart companies know that prospering in this era is going to take more than just an embrace of intelligent digital technology. It’s also going to depend to
a large degree on their ability to manage three factors: data, energy, and people.
Mounting reporting requirements, looming tariffs
Flourishing industry that it is, the steel industry is not without its well-documented challenges. Most prominent, perhaps, is mitigating the environmental impact of steel production. According to various sources, steel accounts for an estimated 7-9% of annual global greenhouse gas emissions (GHG) and an even larger share of global carbon emissions. In an effort to reduce the industry’s carbon footprint and thus slow the pace of climate change, countries and regions are implementing a wave of new regulations, from tariffs to carbon pricing mechanisms to extended producer responsibility requirements. Among the strongest are coming from the European Union, where policies such
as CBAM (the carbon border adjustment mechanism) will soon impose tariffs on companies involved in carbonand resource-intensive industries like construction, mining and mill products, and building materials, including iron, steel, cement, and more. Companies responsible for exporting or importing emission-intensive products or materials into the EU will be responsible for tracking and reporting on the carbon emissions associated with those products, and for paying tariffs on those products or materials based on their carbon footprints.
Many of the same companies, including some from the steel industry, are subject to another EU initiative, the Corporate Sustainability Reporting Directive.
The CSRD will require an estimated 50,000 companies that operate in the EU (including US companies with EU subsidiaries) to report on their effect on people and the environment, and on financial risks associated with their social and environmental impacts. While Europe moves forward decisively with carbonreduction policies, uncertainty clouds the future of new state and federal policies in the United States. With all the recent policy upheaval in Washington, D.C., it’s unclear what exactly will become of GHG reporting requirements enacted by the state of California, and the US Securities and Exchange Commission.
Regardless of what happens in the US, complying with the responsibilities that policies in the EU and elsewhere put on steel companies and entire steel value chains is going to require high-end technological capabilities, along with new energy sourcing approaches that emphasize low-cost renewables, in tandem with human-powered innovation and collaboration.
As Columbia Business School climate researchers assert, “It is both technically possible and economically feasible to eliminate almost all the CO2 from iron- and steel-making by mid-century, thus cleaning up an industry that accounts for 10% of global emissions.”
Getting there will depend as much on people as it will on technology.
How technology can help
Staying profitable in the era of decarbonization depends on companies finding ways to capture value with greener products and processes. That’s going
to require a heightened level of human collaboration and ingenuity, aided, of course, by data and digital technology. On the compliance front, for example, meeting the responsibilities associated with CBAM and other decarbonization policies requires steel companies to collect and calculate actual (not just estimated) Scope I, II and III emission data produced by their own operations and by others across the value chain, then share it with supply chain partners and regulators. To do so, they’ll need a business platform capable of readily sourcing trusted data internally, from connected processes across business domains and systems, as well as data sourced outside company walls, from the supply chain.
AI can be immensely helpful in this regard. It can help gather all this information, and manage carbon certificates and customs declarations, as required by the CBAM system and the EU’s emissions trading scheme. It also can help companies develop so-called ‘digital passports,’ a comprehensive and definitive record of a material or product’s origin, physical attributes, content, carbon footprint, etc., that be used for the purposes of reporting, regulatory compliance and company comparisons.
With a growing emphasis on ESG, sustainability and decarbonization along the steel value chain, steel companies can use this data to their advantage. There’s an opportunity for them to use a positive GHG profile to earn more business. There’s also an opportunity to gain purchasing leverage and pricing advantages over slower-moving and less-prepared competitors by aligning with suppliers whose products or materials have the most favourable GHG profiles. To realize these competitive advantages, steel companies must be able to factor the ‘green line’ – sustainability-related KPIs –into all their business processes, including design, manufacturing, logistics and supply chain.
When companies can clearly and accurately express the value of ‘green,’ then customers can begin to understand, accept and base their decisions on the extra value associated with greener products and services – and the companies that provide them. When the value associated with EU carbon certificates or green steel is clear, for example, that creates the financial motivation for stakeholders to engage in these markets.
• Preparation of pellets and micropellets
• Sinter mix preparation
• Recycling of valuable residues like dusts, ashes, sludges, slurries
• Fine grinding
• Preparation of carbon paste for graphite electrodes, anodes, cathodes
• Coal preparation
eirich.de
Automated material handling between process lines and warehousing results in minimum lead times and shipment turnaround.
Pesmel - The Material Flow How® company
Data’s value to steel companies in the decarbonization era extends well beyond compliance and developing markets for green products and services. The more connected data-collection points that companies deploy across their business, the more information they will have to analyze and gain insight to run their business more efficiently and intelligently. By feeding data into the modeling construct known as a digital twin, a digital representation of a physical asset or system, they can create 3-D models not just of physical equipment but of processes in areas of the business, like sales, logistics, and finance. The insights these digital twins produce can lead to profound, measurable improvements in those areas.
insight and value
Data also serves as the raw material from which machine learning tools can generate insights and value. We’re already seeing steel companies put ML to work by optimizing scrap loading, identifying quality issues, and better managing energy consumption for example.
Further down the road, data will also function as the grease that makes the circular economy engine work for steel companies, providing the documentation required to track the journey of materials and products (the digital passport again), not just for reporting purposes, but also to verify and justify the request for a premium
on recycled/circular products. Digital twins also have an important role to play in the circular economy, modeling data to uncover pathways for designing products that are easier to disassemble for recycling or reuse, for example.
Another form of artificial intelligence, generative AI (genAI), also shows great promise in supporting the human side of the steel business. GenAI can create solid content for marketing and promotional purposes, and for repair manuals, for example. It can make highly technical language more understandable to technicians working on an asset and, via a digital assistant, even suggest actions for technicians to take in servicing a piece of equipment. It can reshape workforce management and skills training by removing language barriers with automatic simultaneous translation, converting safety information, manuals and other important information from one language to another. It can create documentation for products, loading procedures, and IT programming. Generative AI improves how people interact with any kind of software, replacing traditional IT interfaces with more Googlelike prompt-based interactions where a user asks or tells the genAI tool in text or by voice what they want to accomplish or what kind of information they seek, then receive an answer and an explanation.
What lies ahead?
These technologies point to a future wherein technical steel production operates with a new level of precision in processes and in keeping assets healthy, the result of better data and predictive capabilities. This will reduce resource needs and costs.
Also part of that tech-enabled future is the ability to manage a steel plant as a strand of a broader supply chain or network, where physical locations can be decoupled from worker locations. This could lead to the creation of global centres of excellence for operations, repairs, and so on. The same concept could apply to sales, logistics, and other processes like sustainability. The physical business will get a digital twin and processes can run alongside them.
Returning to the issue of energy, the groundwork also is being laid for development of new green steel production centres, a concept touted by McKinsey in a recent report. These centres could be located in areas with ‘favourable access to low-cost energy and the right metallics feedstock’ to supply green steel for automotive, machinery, construction and other uses. McKinsey notes that DRI (direct reduced iron) production could be located in regions where low-cost natural gas or hydrogen and iron ore are available, while raw-steel production could be sited in regions where renewable energy is accessible and cost-efficient. The Middle East, Oceania, and South America are good candidates to house these hubs, it says.
As reliant as concepts like these are on data and technology, making them a reality will depend, in the end, on people. The standards and structures to guide the application of these technologies must come from human beings. Only through human innovation will we develop the infrastructure for hydrogen production to support green steel manufacturing, for example. Similarly, it’s going to take a great deal of human collaboration to reach consensus on a common, standard definition for green steel, a critical step in the effort to decarbonize the steel industry. Due in large part to data and technologies like AI, steel companies have already made solid progress in finding new ways to drive profitability in the decarbonization era. But technology and data can carry you only so far. Ultimately, the future of the steel industry depends on the ingenuity of human beings. �
As companies continue to drive towards a decarbonized future and hit efficiency targets, Resonac Graphite takes on the challenge of navigating through complex market conditions, while continuing to propel innovation in electric arc furnaces. We talk to César Castiñeira.*
1. How are things going at Resonac Graphite?
The graphite electrode market is heavily dependent on the steel market, so it is also quite cyclical in nature. The peaks and valleys for electrode demand affect our business significantly. At present, we find ourselves in a period of depressed demand and oversupply. We have multiple production sites worldwide, and we are working diligently to mitigate the effects of this cyclicality on our business. Part of that mitigation is through diversification of our product lines.
2. What is your view on the current state of the global steel industry?
The steel industry, like all industries and society at large, has embarked on a path towards decarbonization. Given what we have learned so far, I believe there is no turning back. Some companies, groups and countries are at different places within that journey, but it has begun for all. Our future – for it to remain ‘our future’ – must be environmentally, economically and socially sustainable.
3. In which sector of the steel industry does Resonac Graphite mostly conduct its business?
Resonac Graphite is a global leader in the manufacture of graphite electrodes for electric arc furnaces (EAFs). As I mentioned earlier, the global steel industry has begun its journey toward decarbonization. Currently, two of the most popular solutions for CO2 reduction in steelmaking are through EAFs and the use of hydrogen. Graphite electrodes are an essential part of the EAF production method, and EAFs produce 80% less CO2 than traditional steelmaking methods. Steel is the most recycled material on the planet, and steel is infinitely recyclable – meaning it can be remelted infinitely without losing its properties.
4. Where in the world are you busiest at present?
We are a global company, but we service our customers regionally and locally. In this way, we share challenges as well as successes. My leadership team is spread across three geographical regions – and in each of which we have at least one production facility. We view the world as Asia-Pacific, the Americas, and EMEA (Europe, Middle East and Africa). I can fully rely on the regional presidents to manage the day-to-day operations of their regions. Needless to say, there are unique challenges to overcome everywhere, but we make investments and specific projects based on regional needs. For example, we have a pilot project to study the technical and economic feasibility of graphite production for battery anodes for electric vehicles at our facility located in A Coruna, Spain.
5. Can you discuss any of your major steel contracts?
At the Resonac Graphite business unit, co-creation is in our DNA. We strongly and sincerely believe in stable, longterm relationships. We know that these relationships must be based on mutual trust
*President and CEO, Resonac Graphite Business Unit.
and win-win partnerships. As a company with an 80+ year legacy of serving electric steelmakers, we have several industry partners that share our vision and values. As part of these partnerships, Resonac has developed specific, long-term solutions to solve some of the challenges created by cyclicality.
6. Where do you stand on the aluminium versus steel argument? As a supplier of electrodes for electric arc furnaces, I can only say that we are strongly committed to steel. It is an essential material for the economy of the future. The technological advances in steel have helped improve properties (strength vs. weight), making it more viable as a solution to automotive decarbonization. As I said, steel is a sustainable, versatile and resistant material. This is how I want Resonac to be…sustainable, versatile, and resistant!
7. What are your views on Industry 4.0 and steelmaking?
In today’s world, digitalization is no longer an option. It is mandatory. To be efficient and profitable, one must be automated. This is not possible without the right technology and digitalization. At Resonac, we have taken a definitive step by acquiring AMI, an automation company headquartered in Mexico, and integrating it into our electrode business. We do not want to offer our customers just a consumable product; we want to give them the option of benefiting from an industryleading technology that will help them optimize the performance of their EAFs and make their operations more profitable.
8. What is your view on hydrogen steelmaking?
The production of green steel, whether with green hydrogen or another clean energy, undoubtedly marks the future of the industry. It is true that green
hydrogen is a vector that is still at an early stage of development, but the road to decarbonization and a sustainable steel industry goes through the evolution from fossil to renewable energy.
9. Are steelmakers looking to companies like Resonac Graphite to offer solutions in terms of energy efficiency and sustainability? If so, what can you offer them?
Steel producers are heeding the messages that the industry is sending, and they are aware that energy efficiency is a crucial factor for the overall sustainability of a company. This means they must be efficient, environmentally friendly, and socially responsible at the same time. This is one place where Resonac is leading the market by offering access to AMI’s proprietary products and services –especially in EMEA and Asia, where AMI was not easily accessible.
10. How quickly has the steel industry responded to making its production processes greener?
Sustainability is not a battle that any steel producer can afford to lose; indeed, I would say that no player in any industry sector can afford to lose at this stage. In the steel sector, the main players in the market are moving in this direction and investing in very interesting decarbonization projects. It is true that not everyone is on the exact same path, but I think it is more a question of conviction than guaranteed success on a particular path.
11. Where does Resonac Graphite lead the field in terms of steel production technology?
The acquisition of AMI gives us a competitive advantage that no other manufacturer of graphite electrodes has. We have the technology, the experience, the people, and the products to help any EAF steelmaker optimize their operations. AMI’s products and services can improve shop safety, increase efficiency, lower costs and help on the path to CO2 reduction.
12. How do you view Resonac Graphite development over the shortto-medium term?
Resonac Graphite Business Unit not only offers quantity, but also guarantees quality, reliability, product supply, Resonac+AMI bundled product service portfolios, and
a respect for the environment. We are committed to making investments in safety, technology, R&D and more sustainable uses of graphite. Like us, there are many steel producers in the market that do not want to compete only on price, but on performance and guarantees. I believe that we must all be aligned around this aspiration.
13. How should the industry react to China?
As I said, we should be united to protect what we want most – our future. The way we do business impacts our company, our communities, our families and our future. Our vision, values, and actions matter. We cannot allow different countries, regions or organizations to impose tariffs or regulations that limit our ability to operate, while others do not have to play by the same rules. My concern, especially for Europe, is that the day will come when it will be too late to react.
14. What is Resonac Graphite’s experience of China?
downstream. The opportunities for artificial intelligence and machine learning in today’s steel mills are truly exciting.
16. How optimistic are you for the global steel industry?
There is no future that does not involve steel. Mobility, construction, energy, machinery…you name it, and it contains steel. The future question lies more in ‘WHO will be making it,’ not ‘IF it will be made.’ We must take advantage of the opportunities we are presented and keep working on continuous improvement.
17. What exhibitions and conferences will Resonac Graphite be attending over the next six months?
We typically have commercial and technical Resonac and AMI colleagues at many of the major steel industry shows, such as Made in Steel (Italy), EFRS (Turkey), Future Steel Forum (Spain), AISTech (USA), Expo Acero (Mexico) and SEASI (Indonesia).
18. What keeps you awake at night? Radical innovation! We must always be
Our experience is probably the same as other graphite electrodes manufacturers. We don’t have the lobbying power that the steel industry has, but we believe in a sustainable steel and a sustainable graphite electrode industry. Creating this reality is only possible by working to achieve it.
15. Where do you see most innovation in terms of production technologies?
Mainly in primary, but AMI, for example, offers solutions in both secondary and
moving forward. I love challenges and thrive on pursuing ambitious goals.
19. If you possessed a superpower, how would you use it to improve the global steel industry?
I would like to have the superpower to help people see what I see and feel a sense of urgency for positive change. I would certainly use it to help convince others we must continue to work hard to provide a sustainable industry and a sustainable future. �
Stay ahead with Steel Times International, delivering 12 issues annually. With 8 printed and 4 digital editions, our magazine provides expert insights, the latest developments, and key innovations in steel manufacturing.
Stay in the loop with our Weekly Newsletter—bringing you up-to-the-minute news straight to your inbox, featuring the most crucial updates impacting the global steel industry.
Join us for exclusive webinars each year! Focused on critical topics shaping the ture of steel manufacturing, our webinars o er expert panels, industry discussions, and real-time insights.
The ultimate Steel Industry Directory—your go-to resource for steel manufacturers, producers, and suppliers of plant equipment and services. Whether you're looking for the best in steel production or the latest technology, nd what you need at your ngertips.
Explore steeltimesint.com - a hub for breaking steel industry news, industry trends, and upcoming events. Bookmark the latest key dates and never miss an opportunity to engage with the steel community.
Meet the brightest minds in the industry at the annual Future Steel Forum. A premier event where thought leaders discuss cutting-edge technologies and innovations shaping the ture of steel manufacturing.
Abraham Derby, a Quaker, is credited with developing the casting of iron pots in sand moulds as a cheaper alternative to the established method of casting brass in loam moulds. By Peter King*
DERBY was looking for a way to supply cheaper pots to the poor. To achieve this, he ‘poached’ an expert pot founder, who was to carry out this work for the ironmaster, Zachary Downing, this change of allegiance requiring the clandestine removal of pot moulds from Downing’s warehouse.
The previous article in this series, published in the Jan/Feb issue of STI, described the activities of Shadrach Fox and the Company for ‘Making Iron with Pitcoal’ and coke-smelting at Coalbrookdale in the 1690s to make round shot (for great guns) and hollow grenado shells. This did not end well for Fox when the Nine Years’ War (1688 – 1697 between France and the Grand Alliance) came to an end, causing demand for ordnance to all but vanish. To compound matters, an explosion at the
*Dr
Coalbrookdale furnace when water flooded in left Fox too despondent to continue. He ‘broke and went off leaving all’.
Zachary Downing’s father, John, had long worked for the Foley family (ironmasters making charcoal iron – see Part 1 STI Nov 2024 p 52) as clerk of Hales Furnace (at Halesowen, in England’s West Midlands).
Philip Foley stopped making iron in 1678 and, in 1681, John Downing became a partner with two of Philip’s managers in operating the furnace. A contract made in 1682 involved a regular supply of pig iron of 120 tons per year (perhaps a quarter of the annual output) to Humfrey Jennens for his forges a few miles away. They agreed a boundary between them for buying wood (for charcoal). Hales Furnace appears in the accounts of the Foley partnership in 1692
and again in 1703-5, but not in the years between this.
John Downing (until his death in 1699) and his son, Zachary, were tenants of Hales furnace in this intervening period and renewed the contract to supply iron with Jennens in 1692. In 1695, the Downings also took over Cradley ironworks (where only a forge was at work), and the next year they added a rolling mill, which they later converted to a slitting mill. Following his father’s death in 1699, Zachary took over the running of the business. In 1704, he was in dispute with Jennens, because Zachary had not sent as much pig iron from Hales as had been agreed. Britain was at war fighting the French and Bavarians at this time which had increased the price of iron and wood to make charcoal. Zachary
was tied into a fixed price contract with Jennens and was losing money as the price of iron (and with it the price of wood) had risen, due to the higher cost of importing iron in wartime. Zachary complained about the high price that he was having to pay for wood, but Jennens said it was no better his side of the agreed boundary.
Roger Downes, a founder of pots, came to Zachary Downing in about 1699 to offer his services. Zachary and his father had previously employed potters to make moulds in loam or clay and he had heard that Shadrach Fox (see Part 2 Jan Feb STI) had employed a person to successfully cast pots and utensils in sand, putting these into flasks or boxes for support. Fox (allegedly) had not succeeded to ‘bring the same to effect’. Downes said he was that very person, but that Fox had left him to fend for himself and there was no one to carry on casting in sand, and so Downes offered to do so for Zachary. Here it must be explained that castings can be made in pre-heated loam moulds, but the mould must be broken open afterwards to extract the casting. An alternative was to form the mould in sections in green (damp) sand around a pattern, the mould is then split, and the pattern removed and can be reused. The sections making up the mould are reassembled in a box for support and a ‘gate’ installed through which the metal is poured. This makes mould-making much simpler, and cheaper, but the mould needs to be at ambient temperature. This means that the molten pig iron must be more fluid than is necessary for filling a loam mould, and this requires a source of grey pig iron, with a significant silicon content. This normally means coke pig iron, rather than iron made from charcoal, as much of the silicon is derived from the coal. The production of pots cast in green sand thus implies a source of high silicon pig iron, derived from a coke-fired furnace at Coalbrookdale.
Later Zachary Downing sent Downes to Gwendraeth in Carmarthenshire, South Wales, where Downing was a partner with Peter Chettle, as there would be ‘better vent where no such goods had been made before’. Gwendraeth Furnace was a significant location. The furnace there had been built (or rebuilt) in 1696 by a partnership consisting of Thomas Chettle (a Worcestershire gentleman), his son Peter, and Zachary Downing. Thomas Chettle had obtained a patent in 1695 for smelting
A three-gallon iron-bellied pot weighing 5.58kg cast at Coalbrookdale in grey iron after a patent held by Abraham Derby I. The vertical seam and the horizontal seam above the section adjacent to the legs indicates the pot was cast in a sand mould split to remove the pattern. The two higher horizontal lines are strengthening ribs. Wall thickness 4-5mm, rim diameter 276mm. Pic courtesy R Williams.
iron with ‘pitt coals or sea coals charked or with peat or turf’. (This patent seems to have been omitted by mistake from the numbered series compiled in the mid-19th century but might be called No. 346A.) This suggests that Gwendraeth Furnace (also called Ponthenry or Kidwelly Furnace) was at least sometimes used with coke as fuel, rather than charcoal. Downing supplied pig iron to restart Kidwelly Forge in 1697 and Peter Chettle was later a partner in Whitland Forge, also in Carmarthenshire, suggesting that he primarily operated as a charcoal ironmaster, as he continued to do until 1729.
John and Zachary Downing’s furnace at Cradley seems to have been built by Richard Foley in the late 1630s, but in 1662, when his son Thomas (Philip Foley’s father) renewed the lease, he was authorised to remove the bellows, implying that the furnace was not in use, and it probably lay derelict.
Following the death of his father, Zachary did not renew his lease of Hales Furnace in 1703 but would have needed a furnace to supply his forge. It thus seems that he brought Cradley Furnace back into use in the early 1700s, presumably partly to provide grey iron for Downes to cast in sand, which implies it was used with coke, as Downes was back at Cradley by 1707. Cradley Furnace was blown out at Christmas 1707. Downes then made loam moulds ready for the next blast, drying them with charcoal. He then went to work as a brass founder in Birmingham until Downing was ready to restart Cradley furnace.
Downes happened to meet Abraham Darby, at Stourbridge. Derby had trained as a builder of malt mills but had moved to
Bristol to cast pots in brass. He had a patent for casting iron-bellied pots, a cheaper alternative to brass, and, as a Quaker, wanted to supply iron pots at an affordable price to the poor. Darby paid Downes £100 to work for him and promised £650 more (apparently a salary). The £100 was partly for Downes’ tools, which were in Downing’s storehouse at the Cradley Works, under the charge of Downing’s clerk and his stocktaker. After they had gone home, Downes came at night to the storehouse and removed ‘moulds both of iron and brass’ (presumably patterns) and carried them to an alehouse at Cradley and ‘thence early next morning sent them to Stourbridge to the house of one Harvey, where Darby was.’ (This must refer to Thomas Harvey, Darby’s brother-in-law and a fellow Quaker.)
Downing pursued his goods and demanded them back from Darby, but he claimed to have bought them from Downes and openly declared it was to prevent anybody using them. He claimed ‘he had not else any occasion for them, having better of his own.’ Downes was arrested and brought before a Judge, who granted bail, and suggested a civil action should be brought. The question concerned what patterns Downes had paid for and what had been paid for by Downing. Downes agreed to pay for the goods but never did, and ‘roved abroad to London, Bristol and other places.’
The outcome of the litigation is unknown. Pot-founding is likely to have been a minor activity for Zachary Downing, who now had interests in forging, having converted a mill at Lye to a forge in 1697. He also had a mill upstream from Cradley Forge, which he rebuilt in 1697 and let out as a blade mill.
He rented Ipsley Forge between 1698 and 1700, but the landlord failed to provide as much wood for charcoal as promised. Zachary Downing became bankrupt in 1710, leading to the sale of his works. Apparently, after bankruptcy, he started to build a forge at Blackden (now Blackdown) near Warwick but died before finishing it.
This article is largely based on the author’s ‘Innovation in the Iron Trade’, International Journal for the History of Engineering and Technology 94(1) (2024), 12-41. https://doi.org/10.1080/17581206 .2023.2299493; but with some additional material from his A Gazetteer of the British Iron Industry 1490-1815 (2 vols., BAR British Series 652, 2020). �