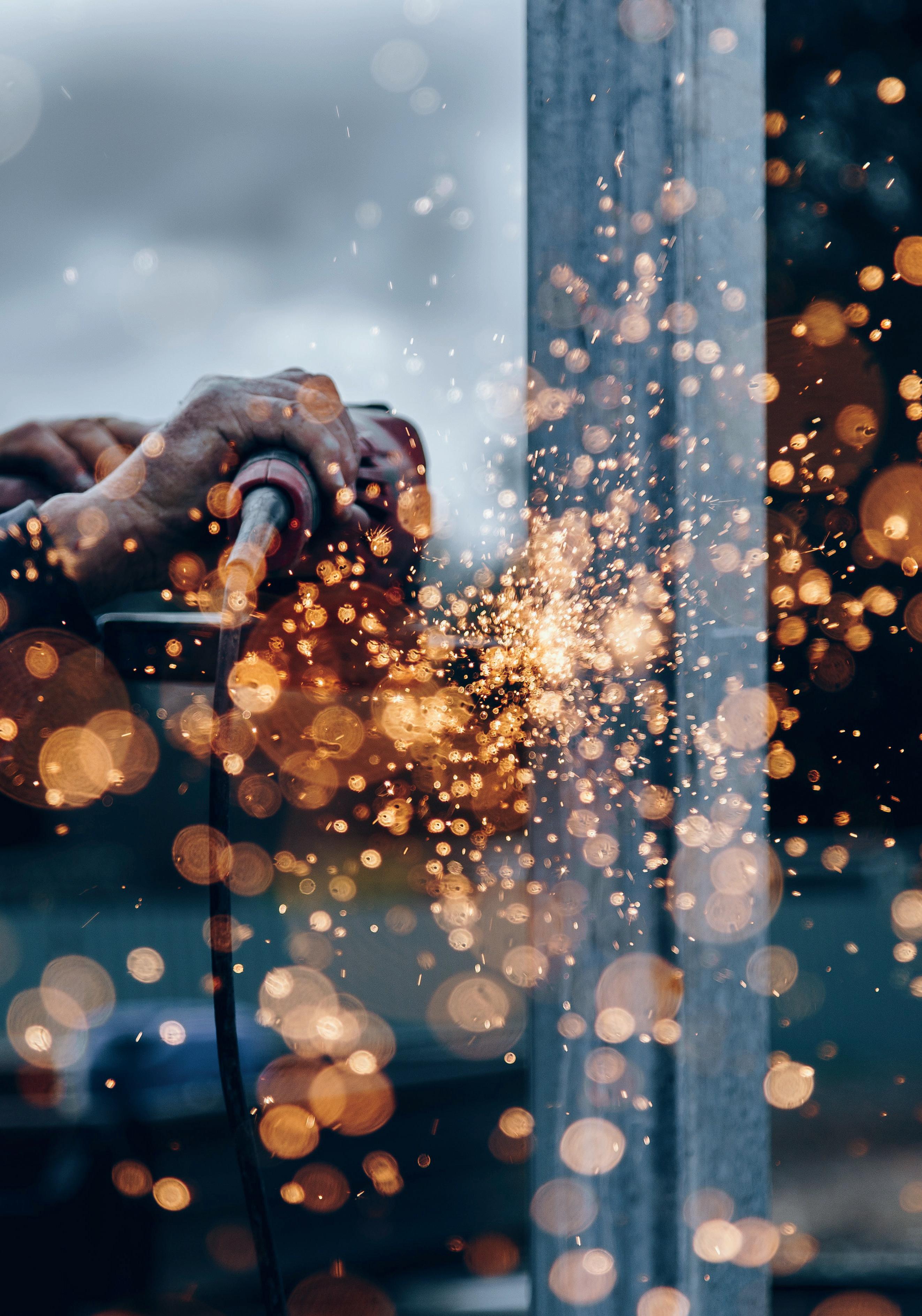
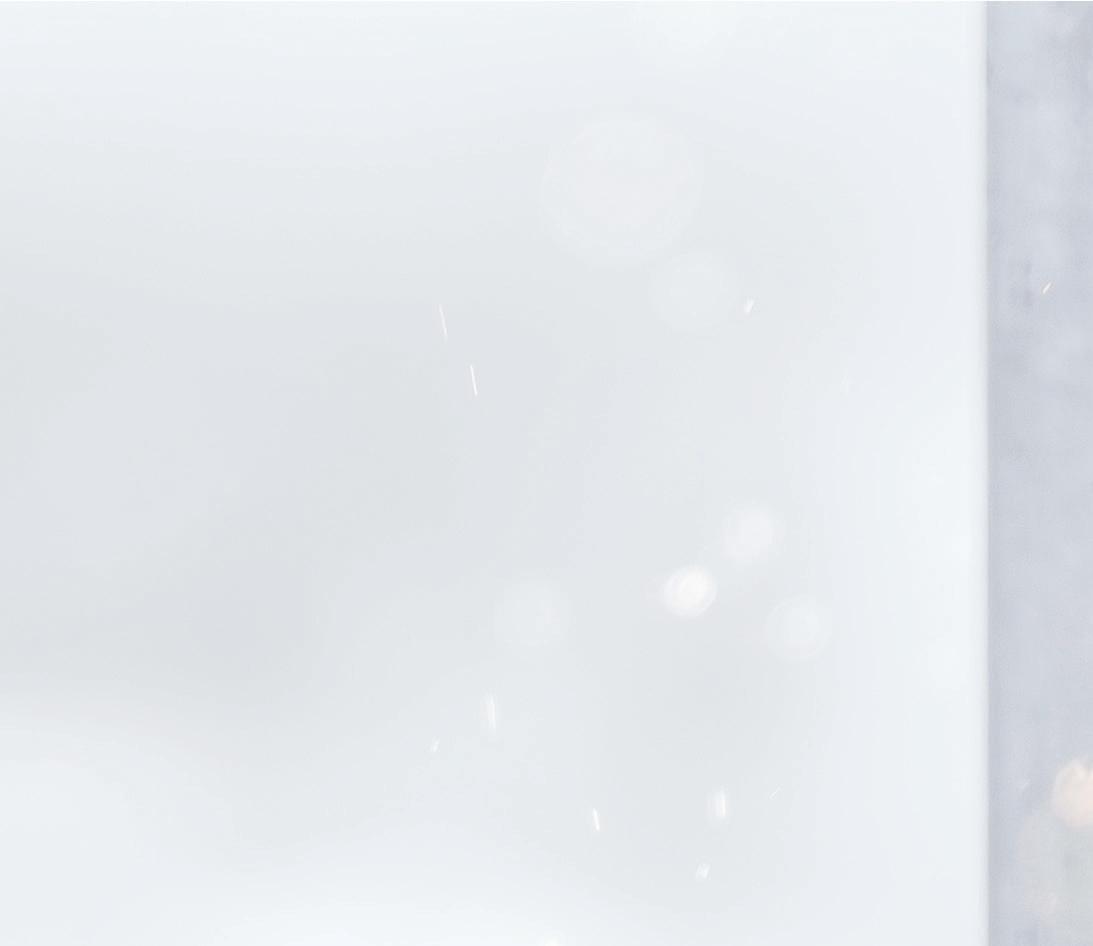
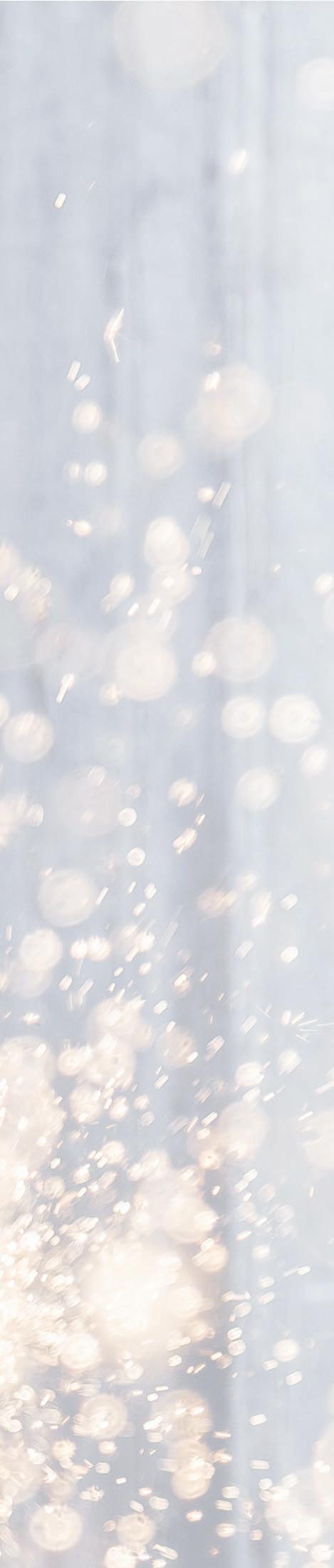
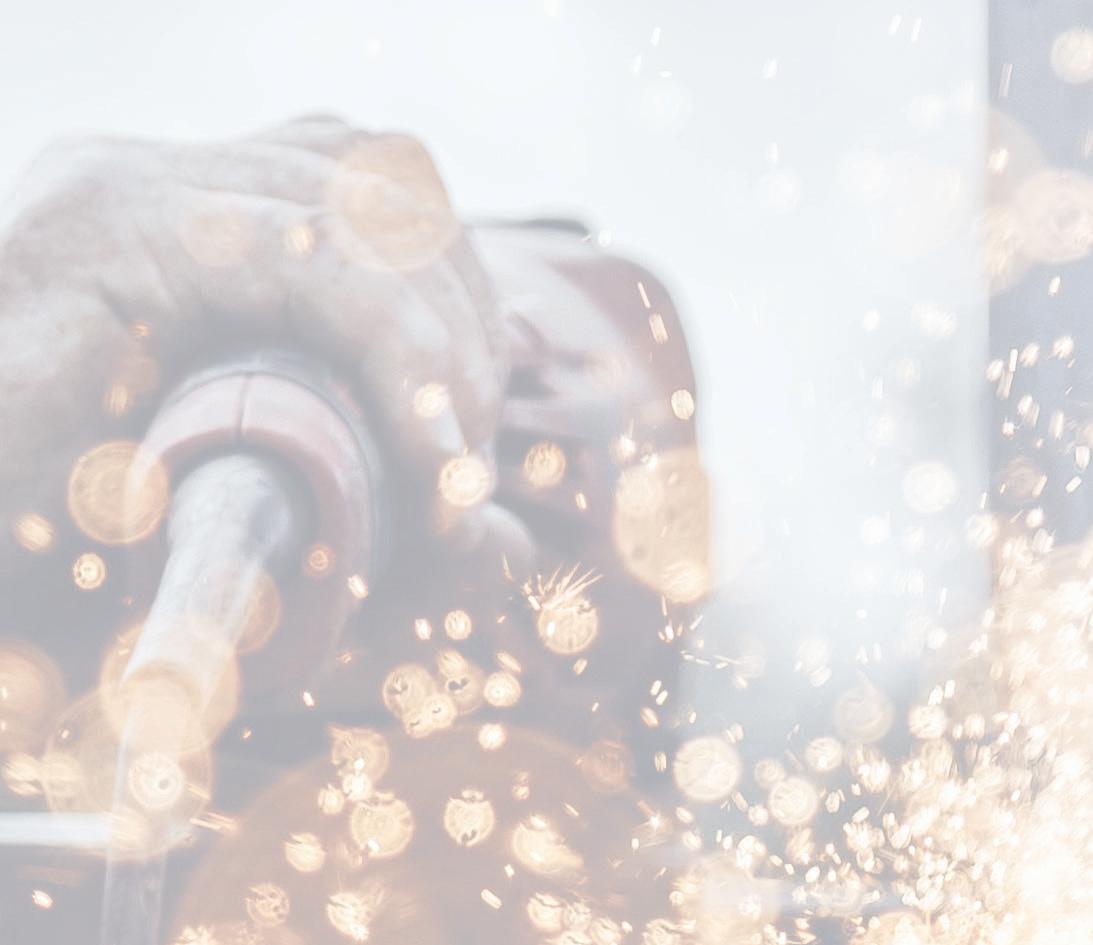
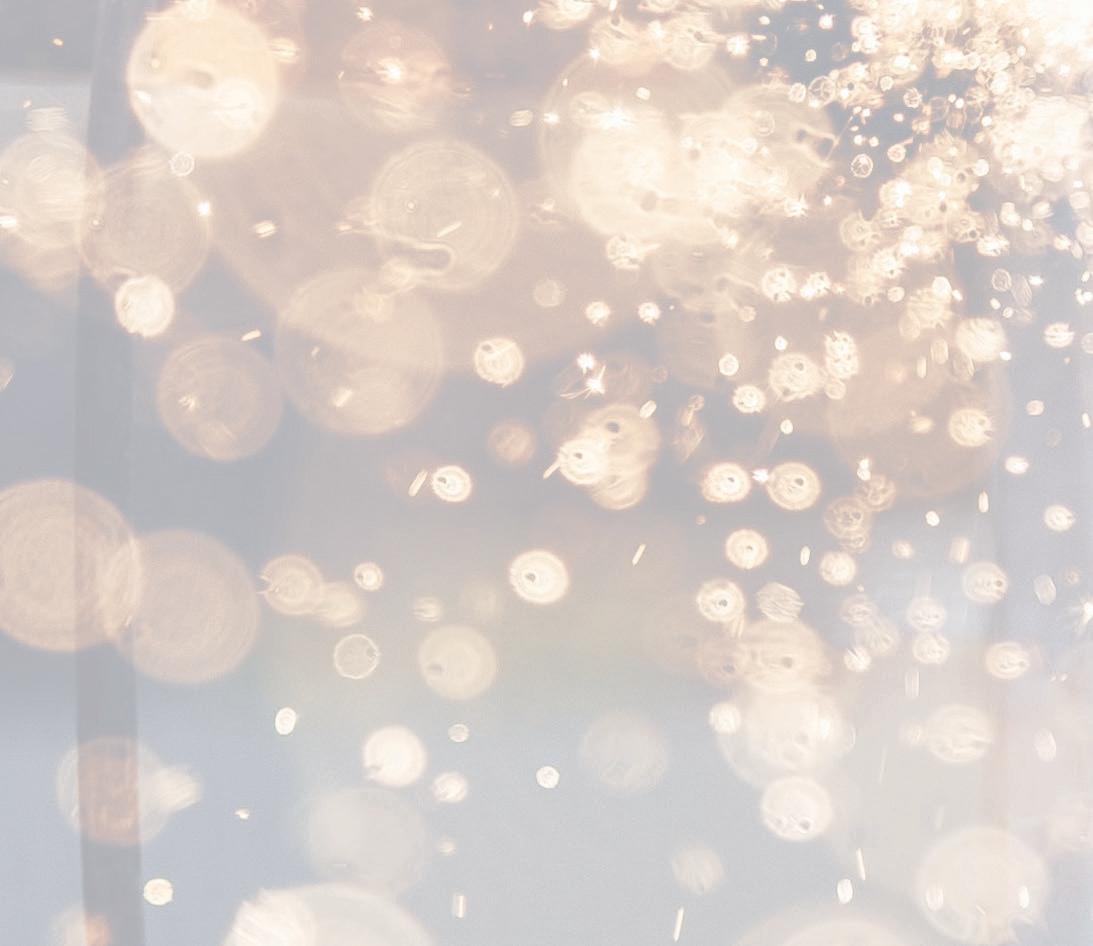

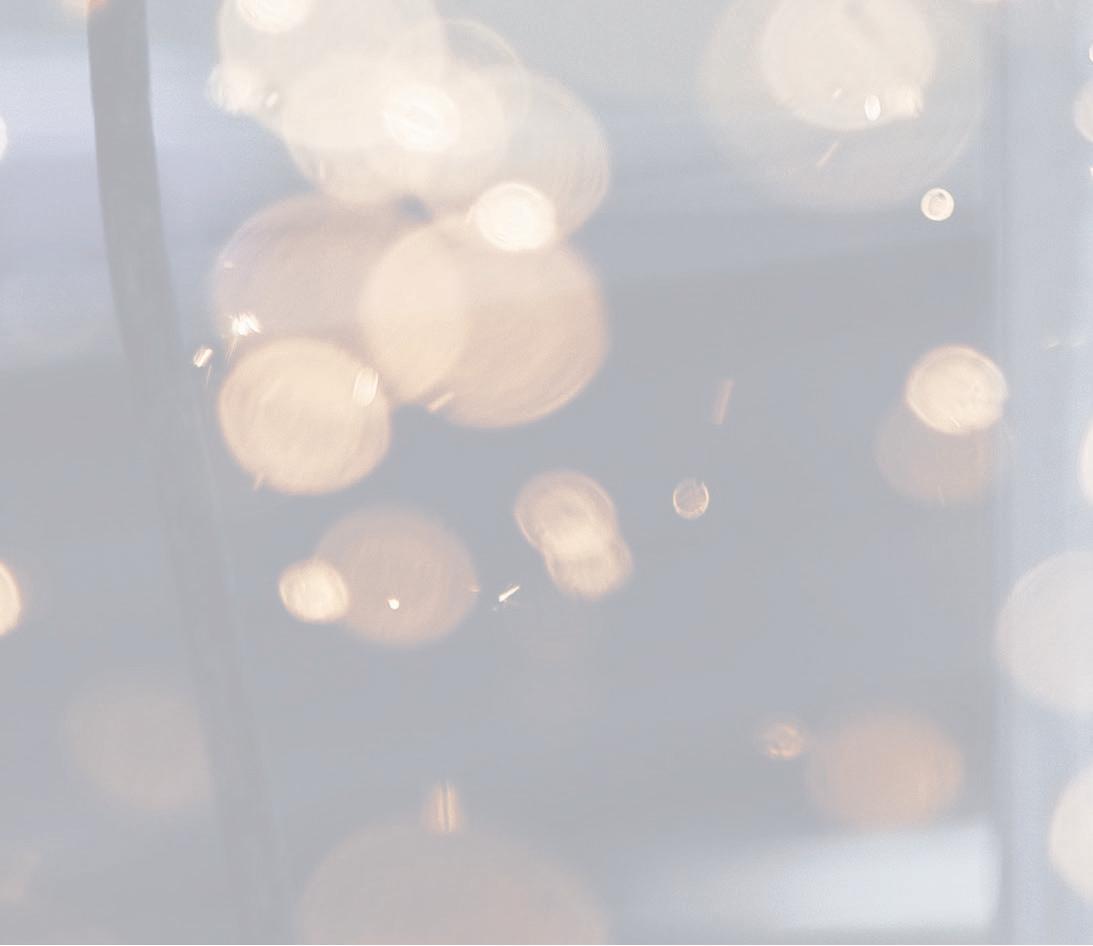
PRIMARY
2.8 million tons OF PRIMARY ALUMINIUM PRODUCED ANNUALLY
Lowest carbon footprint IN THE WORLD
7,500 HIGHQUALITY JOBS
EQUIPMENT SUPPLIERS
1,734 BUSINESSES
29,800 HIGH-QUALITY JOBS
$11.5B TURNOVER PROCESSING
+50 EQUIPMENT AND SPECIALIZED SUPPLIERS SPREAD ACROSS THE WORLD
We had grands plans to host this Future Aluminium Forum in Québec City back in 2020, but as we all know by now, 2020 didn’t quite turn out as we’d expected.
With plans disrupted and lives changed forever, we have now finally been able to make our return to this beautiful city and engage with the vast aluminium supply chain that encompasses the region.
The timing couldn’t be better. The world is back open for business and with global aluminium demand projected to increase by almost 40 per cent by 2030, the aluminium sector will need to produce an additional 33.3 Mt to meet demand growth in all industrial sectors.
This will only be possible through the inception of streamlined technologies, digital manufacturing and sustainable solutions across the production process.
Originally launched in 2018, the Future Aluminium Forum has focused on the challenges of implementing digitalisation and technologies associated with Industry 4.0 such as Big Data, the Industrial Internet of Things, Artificial Intelligence and Machine Learning.
Today, we are already seeing the industry take huge steps towards digital manufacturing and this goes hand in hand with some of the exciting sustainable solutions we are poised to hear more about over the coming days.
By finally being able to host this Forum in Québec City, I am excited to visit a region where the aluminium industry has existed for more than a century and is now seeing rapid change and collaboration between manufacturers, processors, suppliers and OEMs.
With a dynamic industrial cluster and a number of research centres occupying a special place at the heart of this aluminium sector, Québec City is perfectly positioned to welcome discussions and presentations about what the future of aluminium production looks like.
I hope you have an enjoyable few days, hearing from industry experts and meeting with other colleagues, clients and friends.
Thank you to all of our speakers, sponsors and supporting associations who have helped make this event possible.
Nadine Bloxsome Content DirectorHydro is entering a new development stage for its HalZero production technology. The company will invest in a test facility supported by the Norwegian government. With this step, Hydro claims they are on track to deliver pilot production of zero-carbon primary aluminium by 2030.
HalZero is a brand new process for production of primary aluminium. Instead of carbon dioxide, only oxygen is emitted from the process. If Hydro succeeds in this development, it could revolutionize the aluminium industry.
“The development of HalZero is our most groundbreaking technology initiative ever. This could be the first industrial production of primary aluminum without greenhouse gas emissions in the world. The plan is ambitious, and there is considerable risk. Therefore, we depend on the authorities to join us on the road to make a major investment,” says Eivind Kallevik, Executive Vice President for Hydro Aluminium Metal.
Decarbonizing industrial sectors is one of the most important contributions to reducing global greenhouse gas emissions. Hydro has been working on early phase development of the HalZero technology at Hydro’s Technology Center in Porsgrunn, Norway for seven years. The Norwegian government, via state
enterprise Enova, has granted NOK 141 million for the construction of a test facility. The total investment is expected to be approximately NOK 400 million.
“The technology that Hydro is developing here can contribute to significant emission reductions for the aluminium industry both in Norway and in other countries. Enova supports companies that take a lead in decarbonizing industry, and we believe that HalZero can contribute strongly to reducing emissions from the aluminium industry,” says Kristian Nakstad, CEO in Enova.
Zero-carbon aluminium has properties that are essential in the green shift. The metal is light and is weather resistant, which is significant for, among other things, electric cars, building facades and solar panels.
“We know that demand for aluminium will increase, and aluminium without CO2 emissions will mean a lot for the climate goals. Today, the aluminium industry accounts for 2 percent of the world’s CO2 emissions. We are aware of our responsibility and we want to take the lead in developing zero-emission technology for aluminium production,” says Kallevik.
Development of HalZero is part of Hydro’s technology roadmap to reduce the emissions associated with aluminum production. HalZero is primarily suited for new production capacity.
Hydro is working in parallel to develop carbon capture and storage for its existing aluminum smelters while increasing the use of renewable electricity and testing green hydrogen in the value chain.
“The aluminium industry needs optionality to increase our chances of reaching net zero by 2050. Working on several decarbonization routes in parallel increases our chances of success and the speed at which we will be able to reach our ambitious climate targets,” says Kallevik
Facts about the HalZero project
� HalZero is a new production process for primary aluminum that emits oxygen instead of carbon dioxide (CO2)
� In the HalZero process, alumina is chlorinated and becomes aluminum chloride in a process that also produces carbon dioxide. Instead of releasing the CO2 to the atmosphere, it is sent back into the process and reused in the chemical reaction in a closed loop. This makes the electrolysis process completely greenhouse gas emission free.
� The HalZero process differs significantly from the current production of primary aluminum and is being developed for use in new production facilities.
Gone are the days when premium car buyers simply looked for speed, style, and luxury. Today, there’s increasing interest in the origin, sustainability and emissions profile of the materials used to build their cars.
The new mantra for the high-end auto industry is “green is the new black.” From the leather used for upholstery to the metals used for engine parts, premium car buyers are increasingly demanding vehicles made from responsibly sourced materials.
This fundamental shift in the automotive market has led to the creation of a new, innovative partnership between Rio Tinto and the BMW Group, leaders in their respective industries who share a common goal of developing more responsible, sustainable, traceable and secure supply chains.
Under this new partnership, Rio Tinto plans to provide responsibly sourced aluminium to the BMW Group’s vehicle production plant in Spartanburg, South Carolina, for use in body components from 2024.
Low-carbon primary aluminium from Rio Tinto’s hydro-powered operations in Canada, combined with recycled content, could generate a reduction of up to 70 percent in CO2 emissions compared to the BMW Group’s benchmark for aluminium.
The two companies have signed a Memorandum of Understanding (MoU) which
will see technical experts working together on how to embed these low-carbon solutions into the BMW Group’s supply chain while ensuring the highest standards of vehicle quality are maintained. The partnership provides for the use of aluminium produced using ELYSIS™ on BMW production vehicles. ELYSIS™ is the world’s first carbon free smelting technology for aluminium as it enables the production of aluminium metal without direct carbon dioxide emissions during the smelting process, instead emitting pure oxygen.
Rio Tinto and the BMW Group will also work to deploy START from Rio Tinto. START provides supply chain traceability to customers and consumers with information about provenance and ESG standards.
Rio Tinto Chief Commercial Officer Alf Barrios said: “Rio Tinto’s world-leading position in responsible aluminium production means we can offer innovative solutions to our customers on their decarbonisation journey toward net zero. As global demand for responsibly sourced materials continues to grow, automakers are increasingly looking to partner with suppliers who share their commitment to traceability and sustainability. Rio Tinto is proud to play a role in helping to drive a greener future in the premium car industry through this partnership with the BMW Group and we look forward to deepening our ties with the
automotive industry in the years ahead.”
BMW AG member of the Board of Management, responsible for Purchasing and Supplier Network, Joachim Post, said: “We have clear goals for lowering CO2 emissions in the supply chain. By using innovative materials, we can reduce our vehicles’ carbon footprint – even before handing them over to customers. The agreement to supply low-carbon aluminium is based on several pillars: in addition to hydroelectric power and secondary material, we also want to lead the automotive industry by ramping up our use of aluminium with no direct CO2 emissions from the smelting process.”
The Honourable François-Philippe Champagne, Canada’s Minister of Innovation, Science and Industry, said: “Canada is a global destination of choice for low-carbon investment. This exciting partnership between BMW and Rio Tinto is proof that Canada is well positioned to seize the economic benefits of the clean economy. I am proud to see that low carbon Canadian aluminum will be going into BMW’s vehicles. Canada will continue to enhance our competitive advantages— abundance of critical minerals, skilled labour, clean energy, proximity to markets—to grow our economy and to support made-in-Canada innovation.”
TOMRA Recycling Sorting opened a second test facility at its headquarters in Germany to meet growing demand for material trials. The company now operates one test center each for waste and metal sorting applications at the same location.
From February 28 to March 2, TOMRA welcomed industry partners, customers and media representatives to celebrate the opening of a second test center at its headquarters in Mülheim-Kärlich, Germany. The event took place within the framework of the company’s Integrator’s Conference. More than 200 participants from 26 countries joined the twoday event and enjoyed a diverse conference and event program. On the first conference day, participants listened to numerous presentations detailing the company’s strategic direction, including one held by TOMRA CEO, Tove Andersen. The second day focused on the extension of the test facilities that marked another milestone in TOMRA Recycling Sorting’s long-term goals.
“With more stringent legislation and higher recycling targets, the demand to recover recyclables from waste is at a record high and so is the demand for our sorting solutions and material tests. We’ve observed this situation over the last few years and came close to our test capacity limits in Germany. We had to act to ensure the best service for customers and partners”, states Fabrizio Radice, VP and Head of Global Sales and Marketing at TOMRA Recycling Sorting.
Previously, TOMRA’s test center incorporated both its waste and metal sorting solutions and is one of 8 facilities operated at 7 locations worldwide that give recyclers and plant operators the unique opportunity to test their materials on TOMRA’s advanced sorting machines before making an investment. “Apart from the increasing demand for tests, we are continuously developing new sorting systems that are all installed in our test center. In the last few years, we have introduced multiple new
products into the market and will roll out more in the future. Thus, we needed to make sure that we have sufficient space for our growing portfolio and decided to invest in an additional building”, adds Radice. TOMRA itself will use the extra space for the development of innovations that can be extensively tested and optimised by specialised teams on-site. The company conducts approximately 650
TOMRA’s metal sorting systems recover recyclable metals from mixed metal streams and enable plant operators to create the purest material fractions, such as furnaceready aluminum. As the industry strives for sustainable production and a reduction of CO2 emissions, the global demand for recycled metals continues to surge and so does the need for accurate material recovery
customer and internal trials each year and anticipates the demand to grow in the future. The decision to extend capacities entailed another important change. Ralph Uepping, VP, Head of Technology at TOMRA Recycling Sorting explains: “Until recently, we’ve combined both metal and waste sorting machines in one area. Now, each test hall will be dedicated to one segment only. While waste sorting trials are done in the first established facility, the focus of the new facility is on metal sorting.” TOMRA’s new X-TRACT®, FINDER®, and COMBISENSE®, as well as a soon-to-be release machine for advanced aluminum sorting, have been installed in the new facility measuring 1.000 m2 Equipped with state-of-the-art technology
and processing. “We have a long legacy in the metal industry but given current market trends and our customer’s requirements we will concentrate even more on this area in the future. With our expanded test capacities and the most advanced technology, we are wellequipped to support the industry in processing higher volumes and reaching the required qualities”, explains Radice.
While the new facility allows the company to place a stronger emphasis on the metals segment, waste applications continue to play an equally important role. The original test center started as a mobile test station in Andernach, Germany, moved to MülheimKärlich in 2009, and steadily grew in sophistication. Today, it offers 1.500 m2 for
waste sorting trials. The test possibilities range from the recovery of recyclable polymers from mixed and source-separated waste streams, to flake sorting, the separation of wood by material type, and many more.
Also, deep learning technologies, as a
subset of AI, are part of TOMRA’s product portfolio and can be tested in different sorting tasks. Available as a complementary solution to its core technologies, deep learning is a future-forward tool that helps improve sorting performance by detecting previously hard or impossible-to-detect materials. Summarising the advantages of the new test center setup, Ralph Uepping stresses: “All our products are installed and can be tested in a complete circuit. Together with our expert teams, we can simulate the entire sorting process with eddy currents, magnets, screens and a ballistic separator. This allows us to demonstrate the importance of material pre-treatment and define processes that are stable and economically viable even with changing input streams.”
The rationale behind the expansion was extensively explained during the three-day conference that took place both at TOMRA’s German headquarters as well as in a hotel nearby to combine theory and practice. On the first conference day, participants listened to numerous presentations to learn more about
TOMRA’s strategy, new ventures, its digital offerings including deep learning, as well as its approach to customer service. On the second day, it got more practical on-site. After a presentation held by Tom Eng, SVP and Head of TOMRA Recycling Sorting, to explain the evolution of the site in Mülheim-Kärlich, the management team guided the participants to the new facility to cut the ribbon an declare the new building opened. Divided into different groups, the conference attendees were guided through the plant and saw live demonstrations for numerous applications. The tour was rounded off by presentations that emphasised how TOMRA and its technology support maximising resource circularity in the plastic, metal and wood industries.
The opening of a new trial hall as well as the conference set the stage for TOMRA’s growth ambition, its commitment toward stakeholders and its mission to enable a world without waste. Customers and partners are invited to take the opportunity to work with TOMRA’s experts to specify the most suitable sorting solution for their requirements.
During the Future Minerals Forum 2023, the Saudi Arabian Mining Company (Ma’aden) announced a major new venture with the Public Investment Fund (PIF). A new, jointly owned company will make significant investments internationally into upstream strategic minerals opportunities, securing value chains critical to industrial development and energy transition in the Kingdom.
Ma’aden has also signed strategic partnerships with leading mining companies, Ivanhoe Electric (IE) and Barrick Gold Corporation (Barrick) to develop globally significant strategic mineral resources in the Kingdom to fuel the development of the sector internationally. These agreements will play an important role in unlocking value from Ma’aden’s extensive exploration and development portfolio, expanding Ma’aden’s international reach and bringing new skills and technology into the sector in Saudi Arabia.
Ma’aden has also signed more than 20 agreements and MOUs with globally leading organizations to increase exploration and technical capabilities in mining operations.
Improving exploration capability through world-leading technology and expertise
Ma’aden also announced that it has entered into an agreement with Ivanhoe Electric that will give Ma’aden an increased international presence and access to cutting edge exploration technology.
IE is a NYSE-listed technology and mineral exploration company that combines advanced mineral exploration technologies, renewable energy storage solutions and electric metals projects. The agreement with IE will see Ma’aden subscribing to new shares in IE resulting in a 9.9% equity interest for $126 million. Ma’aden will obtain the right to appoint one independent director to the Ivanhoe Electric Board of Directors and will be issued with approximately 10.2 million new common shares in IE at a price of US$12.38 per share.
As part of the agreement, Ma’aden and IE will also establish a 50:50 joint venture to explore for copper, gold, nickel and silver in Saudi Arabia. Ma’aden and Ivanhoe
will explore approximately 48,500 km2 of selected licenses areas that demonstrate excellent potential. The joint venture will provide Ma’aden with access to IE’s proprietary Typhoon™ technology, which conducts geophysical surveys using high powered transmitters to detect the presence of sulfide minerals containing copper, nickel, gold and silver. This will help accelerate, de-risk and advance exploration and development activities, enabling Ma’aden to realize value from its exploration assets.
This is a significant investment for Ma’aden giving it strategic presence in a leading international mining company with its own proprietary technology and increasing its
Ad Damar license areas. The close proximity of the new license areas to Jabal Sayid and the associated mine infrastructure will enable the partners to capture synergies between the three areas.
This agreement will strengthen Ma’aden’s copper production and advance its strategic drive for job creation and economic development in remote areas of the country.
A pipeline of agreements to transform the capabilities of the Saudi mining industry
Ma’aden is also entered into more than 20 agreements and memorandums of understanding with a number of high-profile market leading organizations to integrate new
international exposure to critical minerals.
Robert Wilt, CEO of Ma’aden commented:
“Ma’aden’s strategic investment in Ivanhoe Electric is a critically important moment in our journey to becoming a leading supplier of strategic minerals, which will fuel global economic growth over the coming decade. Through Ma’aden Saudi Arabia is making an invaluable contribution to fast-developing new industries across the world characterized by technological advancement.”
Unlocking value from highly prospective copper licenses Barrick Gold Corporation, a world leader in discovering and developing large-scale gold and copper mines, is strengthening its relationship with Ma’aden through two new joint venture agreements to explore and develop the Jabal Sayid South and Umm
technologies and innovation into its exploration and mining operations. These will further reduce energy consumption, improve water and environmental management, advance decarbonization and improved health and safety. Partners include companies such as Nokia, Shell, Bechtel and Eurasian Resources Group (ERG) S.à r.l.
Robert Wilt, CEO of Ma’aden, commented:
“By attracting new partners to Saudi Arabia and increasing the commitment of our existing partners, we are introducing new technologies into our operations, diversifying our upstream product mix and accelerating the development of our exploration portfolio. This will create opportunities for knowledge and technology transfer that will deepen the talent pool in Saudi Arabia and open up new opportunities to develop the Kingdom’s abundant mineral resources.”
Emirates Global Aluminium (EGA) have announced that they are to collaborate on Industry 4.0 and broader digital transformation, aiming to set global best practice for the aluminium industry while improving the sustainability of EGA’s computing operations.
Both Microsoft and EGA are members of the UAE Ministry of Industry and Advanced Technology’s Industry 4.0 Champions Network, which aims to accelerate Industry 4.0 adoption across UAE industry.
Under the new agreement, the two companies will work together to progress EGA’s Digital Roadmap, which is already transforming EGA’s operations through digital capabilities such as artificial intelligence and big data.
EGA and Microsoft will leverage the power of cloud computing to accelerate and scale the development of new digital solutions, shifting a third of EGA’s server infrastructure and applications to Microsoft Azure Cloud.
Through digital transformation and by driving increased efficiencies, Microsoft’s cloud will empower EGA to make substantial energy savings. EGA is estimating to reduce the energy consumption of its overall computing operations by up to 65 per cent and CO2 emissions by more than 80 per cent.
EGA will also develop a private Microsoft
Azure Cloud at its sites, shifting a further third of its computing to this system, unlocking opportunities to deploy data-heavy and timesensitive artificial intelligence and automation solutions within the company’s industrial operations.
EGA will use virtual desktop cloud computers to create a more efficient, flexible, and secure workplace computing experience for employees.
Abdulnasser Bin Kalban (Right), Chief Executive Officer of Emirates Global Aluminium, said: “We are already transforming EGA’s operations, business and employee experience through Industry 4.0 and ourbroader digital transformation. Our collaboration with Microsoft will enable us to further accelerate, scale and sustain this work as a digital lighthouse for the region and our industry.”
Carlo K. Nizam, Chief Digital Officer of Emirates Global Aluminium, said: “Deploying EGA’s and Microsoft’s talent, muscle and technology together will allow us to develop the most advanced digital capabilities and hybrid cloud platform in the aluminium industry. At the same time, we will improve the environmental sustainability of EGA’s computing infrastructure and benefit from seamless security and operations of both our
public and private cloud assets.
Naim Yazbeck, General Manager at Microsoft UAE, said: “We are proud to partner with EGA... to accelerate their Industry 4.0 transformation while also pioneering further improvements in Microsoft’s own cloud for manufacturing services. I look forward to further collaborations between EGA and Microsoft in the future, both locally and globally.”
EGA will provide input to Microsoft on innovations and improvements to the technology company’s products and services. Microsoft will help upskill EGA staff on relevant Microsoft technologies to accelerate adoption within the aluminium giant’s operations. EGA has a bold aspiration to innovate the future of aluminium production. For the decades ahead, the company intends to act as technology pathfinder for the aluminium industry, expanding its position as technology supplier of choice, and establishing a thriving manufacturing innovation ecosystem in the UAE.
EGA has developed technology in the UAE for more than 25 years and is focused on improving the efficiency of the aluminium smelting process. EGA’s latest home-grown technology is among the most efficient and competitive in the global aluminium industry.
GNA specializes in the design and supply of for the primary and secondary aluminum industries...
cast house equipment, technical services and operation strategies
Que votre mission soit de recycler des rebuts d’aluminium ou la production de métal primaire, pour votre opération.
9am WELCOME
Nadine Bloxsome, Editor, Aluminium International Today
9.05am
OPENING ADDRESS
M. Pierre Fitzgibbon, Ministre de l’Économie, de l’Innovation et de l’Énergie
9.15am – 11am
KEYNOTE SESSION: THE FUTURE OF ALUMINIUM
Reinventing the Aluminium Industry for a Sustainable Future
Gaby Poirier, Vice-president of Operations – North America, Alcoa
Partnering for a Responsible and Sustainable Future
Marie-Eve Pomerleau, Specialist Product Advancement, Rio Tinto
Hydro’s Way to Make Aluminium in the Coming Decades
Pierre Rény, Chief Engineer, Primary Metal, Technology and Operational Support
Hydro Aluminium Canada
11am – 11.30am Coffee & Networking Break
11.30am – 12.30pm
SESSION ONE
STATUS, STRATEGY AND CAPABILITIES
Using Digital Modelling to Optimize Business Outcomes
Jean-Denis Carrier, Global Director – Aluminium, HATCH
How to Transform Predictive Intelligence into Valuable Actions
Hilbrand Kuiken, CEO, Quantillion
12.30pm – 2pm Lunch & Networking Break
2pm – 3.30pm
SESSION THREE
SUSTAINABILITY & TECHNOLOGY: A PERFECT MATCH?
Design and Implementation of a CCUS Project Dedicated to a Primary Aluminium Smelter: Focus on Partnerships
Guillaume de Goÿs, CEO, Aluminium Dunkerque
Technology Roadmap – Maximizing the use of Bauxite Residue in Cement
Linlin Wu, Manager Statistical Analysis, International Aluminium Institute
How Becoming Future Ready Means Optimizing Efficient Energy Scheduling to Energy Availability
Gunther Schober, Sales Manager, PSI Metals Non-Ferrous GmbH
3.30pm – 4pm Coffee & Networking Break
4pm – 5.30pm
SESSION FOUR
THE ADVANCE OF AUTOMATION
Digital Transformation Approaches Aluminium Industry
Simone Tadiello, Automation Project Enginee, POLYTEC
The Foundation of a Smart Plant
Mileidy Hernandez, CPI en systèmes automatisés - Informatique industrielle chez WSP au Canada (CPI in Automated Systems - Industrial Computing at WSP in Canada
Haulers’ evolution: From Diesel to Electrification, Autonomous or Semi-Autonomous Solution
Malcolm Caron-Boivin, International Business Development Manager, EPIQ Machinery
5.30pm DAY ONE CLOSE
7.30pm
GALA DINNER HOSTED IN BALLROOM A+B
9.15am – 10am
BREAKFAST BRIEFING:
Aluminium from the Amazon: Lessons for Sustainability
Simon Lobach, Researcher, Geneva Graduate Institute
10am – 11.30am
SESSION FIVE
THE ADVANCE OF AUTOMATION
Waste and CO2 Reductions with Automated Scrap Charging and Skimming
David Roth, Americas Business Representative, Ria Casthouse
Alulibs - Effortless Automated Molten Metal Sampling
Andrew Sauerwald, Product Leader - LIBS at Tecnar
On the way to the Automation of Refractory Maintenance Works for the Aluminium Producers
Jean-Benoit Pineault, CEO, Refraco
11.30am DAY TWO CLOSE
Andrew Sauerwald is an electrical engineer from Drexel University with over 15 years of experience in automation and design. He is the technology and product leader at Tecnar Automation, a company specialising in turning cutting-edge science into industrial products. His role is to oversee and help bring these innovative products to market.
For an aluminium alloy manufacturer to be competitive they rely on recycled aluminium in which the elemental composition may or may not be known. To utilise this material successfully requires constant monitoring through continuous and frequent sampling of the melt to ensure it meets specifications. The sampling process is time-consuming, labour intensive, and a safety risk due to the amount of interaction with the melt.
The Alulibs streamlines the aluminium alloy production by automating sampling by providing 24/7 real-time multi-element chemistry readings in molten aluminium. It enables operations to react faster with additions by understanding how the melt is changing and without the need for sampling it will provide a safer work environment and increased man hours.
The Alulibs will benefit facilities by enabling them to produce the same high-quality aluminium alloys more efficiently and safely, helping to meet customer demands and remain competitive.
Jean-Benoît Pineault is involved in the company since 1997. During his studies, he started as a specialized laborer for the furnace repairs. He learned about the production stages of various products. In 2003, he became project manager, while pursuing his university studies (2nd cycle in metallurgical engineering -specializing in refractories and ceramics). In 2005, he was appointed Director of Product Development, where he assumed R&D responsibilities. Two years later, he managed in addition the department of the works in the customer plants. In 2009, his expertise led him to take on the position of Director of Sales and Operations and in 2012, Jean-Benoît became Vice President and General Manager. He is now the CEO of the company since 2022.
Jean-Benoît has an excellent understanding of the manufacturing processes of different refractory products as well as the various metallurgical processes in the market. In 2003, he patented three refractory processes. In 2004, he jointly published two scientific articles: one at “The Minerals, Metals, & Materials Society” and the other at the “Canadian Institute of Mining, Metallurgy and Petroleum”. Jean-Benoît obtained a Bachelor’s degree in Computer Science - Mathematics in 2004 and a MBA, both at the University of Quebec in Chicoutimi.
We will share the reasons we have started to work on the automation of refractory maintenance work four years ago. We will then present a first industrial unit operating in Canada for six months, materialising an important milestone on our way to fully automated processes. We will finally share our next steps of innovation, including the short term developments we are working on, as well as the global vision we have for a complete automation of refractory maintenance in an aluminium producer.
Gunther Schober, born November 21, 1970 in Leoben, Austria graduated in 1994 as Metallurgical Engineer with focus on industrial and energy economics at the Mining University of Leoben.
After his first experience as sales engineer and sales manager he took over management responsibility as head of sales & marketing for AVL DiTEST an international automotive company.
2007 he joined PSI Metals. As Senior Consultant, Project Manager and Sales Manager his expertise in metals and international experience in process development and Supply Chain Management is much sought-after.
With more than 10 years of experience in the area of Production Management Solutions comprising Supply Chain Management and Planning, Product Design, Quality Management, Production Execution and Logistics he became an acknowledged cognoscente in these fields. PSI Metals known as a very innovative company became metals industries’ partner for Industry 4.0. Gunther Schober’s expertise together with the innovative approach of PSI metals make him a demanded contact for future solutions.
Aluminium has been described as a “miracle-metal” but we also need to admit that with around 1.1 billion metric tons of CO2, aluminium accounts for 2 percent of global man-made emissions. A precious metal that requires a vast amount of energy for production. The abrupt change of the geopolitical situation last year showed us dramatically the fragility of our resources and our energy supply. In Europe, the aluminium industry had to cope with major gas crisis leading also to energy prices skyrocketing. However, that is not all. Global industrial sectors are on a race to achieve green transformation, which entails replacing coal and gas with green and non-fossil energy in the future. One of the consequences would be that energy availability will remain the problem, and increase, as manufacturers strive to get green hydrogen and electricity, creating high demand. To overlook these factors will affect competitiveness. A solution to this current and in-coming challenge is a proactive measure that prepares steelmakers today to forecast and efficiently manage their energy consumption and production scheduling. Our presentation reveals how we can reliably determine energy consumption and successfully adapt production schedules to energy availability. Smart Planning and scheduling supports our customers on their transformation path to green and sustainable production management by significantly increasing energy efficiency, and therefore reducing CO2 emissions.
Hilbrand Kuiken is the CEO of Quantillion. He is an entrepreneur focusing on data intelligence that enables real time autonomous decision making in complex environments. Hilbrand loves working with passionate people in creating real value for the clients. He believes data is not about analytics but about doing!
After working in industrial asset management for several years, Hilbrand started his own company. For the past 5 years he and his team have been developing new solutions for the core processes in the aluminium and steel industry making sure they are able to adapt to changing environments and successfully making the bridge between operators and autonomous equipment.
With Quantillion, Hilbrand is enabling the heavy industry with the usage of dynamic multi-agent planning power by AI-algorithms. With the combined integration of separate workflows and agents, Hilbrand aims to support the industry in its transition towards “Collaborative Intelligence”.
Industries are starting to collect more information and create complex models to forecast their supply, production and demand. With these indepth analysis companies gain in-depth knowledge, but only one question remains. How do we act on it? By combining these insights with the current state of the factory, Quantillion transforms predictive models into real-time tangible actions.
4.0
Collaborative Intelligence focusses on the improvements when humans and AI work together.
Based on a study published in Harvard Business Review in 2018, organizations that use machines to displace workers through automation, will miss the full potential of AI. Collaborative intelligence has already proven itself and is now becoming an essential contributor to solving a number of issues that are critical for metal production.
The heavy industry has flexibility at the top of their agenda!
Flexibility provides the industry with the ability to adjust to unforseen events and increase profitibility by optimizing costs.
Improved Quality
Flexible automation and processes enables the industry to achieve increased consistency and the ability to capitalize on opportunities.
Adaptable
Flexible manufacturing increases adaptability, making it easy to react to changes, whether predictable or unpredictable
At Quantillion, we are putting fast and powerful decision-making algorithms at the heart of production processes. Our products make it easy for operators and machines to make smart decisions, fast.
Hilbrand is the CEO of Quantillion. He is an entrepreneur focusing on data intelligence that enables real time autonomous decision making in complex environments. Hilbrand loves working with passionate people in creating real value for the clients. He believes data is not about analytics but about doing!
FAST. SMART. SUSTAINABLE.
At Quantillion we use AI systems and digital twins to optimize smelter operations in the production process. We consider the production environment as a cyber-physical space where humans, machines and equipment need to work together in the most optimal way. By increasing this collaborative intelligence within the process we allow companies to create actions upon valuable data analytics.
We believe that new technology enables world leading industries to increase their flexibility. Translating predictions into real-time actions opens industries up to act on outer change as well as the changes they face in their day-to-day operations. Therefore, we are putting fast and powerful decision-making algorithms at the heart of production processes.
Industry 4.0 is currently one of the most talked about topics in the aluminium industry, with such elements as automation, robotics, IIoT, ML, AI and AR leading the way towards the ‘smelters of the future’. All these smart implementations have provided an increased understanding of current operations and allowed for complex models to forecast supply, production and demand. Identifying trends, risks and opportunities is only the first step, transforming this knowledge into actions is the next!
By making use of our platform, we can combine the power of predictive models with a cyber-physical space and translate insights into executable actions. By doing so we can capitalize on predictions in your core process.
Industry increases human-machine interactions Linlin WuMSc from London School of Economy and Political Science, 2007
Joined the Institute in 2009, is responsible for statistical analysis and environmental impact information; manages the Life Cycle Assessment data collection and analysis; also focuses on sustainable development of the industry.
Primary Aluminium demand is expected to increase over the next 20 years, consequently, the increase of metallurgical alumina production, and the generated bauxite residue. This roadmap provides information and support by addressing technical, legislative and prejudicial barriers. It facilitates bauxite residue valorisation actions of the alumina sector and engages other stakeholders who can help deliver success. Developing standards, frameworks and promoting bauxite residue is critical to all stakeholders in increasing the use of BR in cement and concrete products.
Malcolm Caron-Boivin holds a bachelor’s degree in Mechanical Engineering from Laval University. Owning a private pilot licence, he began his career at CAE in Montreal as a Test Engineer on full flight simulators dedicated to pilot training. He later worked in a paper mill as a Reliability Engineer for Produits forestiers Résolu where he acquired industrial experience and knowledge. Malcolm joined EPIQ Machinery in May of 2021 as a Product Manager for AGV solutions. More recently, he was assigned to the International Business Development Manager position. He will provide frontline support for new MECFOR vehicle opportunities to our international customers. Malcolm shows passion for new technologies and innovation. The industrial haulers’ electrification process, for which is gets highly involved, is a great source of motivation.
Conventional. Electric. Auto guided (AGV). Technological breakthroughs open the door to a range of options for industrial equipment. In this presentation, EPIQ MECFOR will share its experience in designing haulers and its vision of what they could look like in the future. These days, two buzz words are drawn on everyone’s lips: Industry 4.0 and net-zero emissions. How can these be concretely integrated to mobile equipment? What technologies are available to aluminium producers? What type of transition is possible if they want to switch from conventional to semi-autonomous or even full autonomous (aka AGV) haulers equipment? All these questions pop multifaceted challenges across all levels.
The task haulers perform is rather repetitive, but essential to the operation of a smelter. Hauling may seem simple. However, when we take a closer look at the operating environment of aluminium producers, we quickly come to understand the complex challenges that comes with operating haulers in this environment. It requires extreme vigilance.
What ever changes are to be made, the leap centres on two key aspects:
1. Analysis of vehicle usage: Type of driving, accelerations/decelerations, speed management, duty cycle, etc.
2. Analysis of work processes and practices: Defining a transition strategy
The two major challenges of the industry are: net-zero emissions and system optimisation by data management.
On the same token, Aluminium production managers aim to adopt a holistic approach of their operations and processes. The concept of Industry 4.0 implies gathering data that, once managed and processed through proper algorithms, will predict a behaviour and populate an order. Adding software layers with artificial intelligence (AI) will help us grow towards an optimised ecosystem.
EPIQ Machinery strives to be a strong link in this constantly evolving aluminium production ecosystem. Our goal: delivering ‘green’ intelligent equipment.
15 years at Alouette aluminium smelter, Quebec, Canada
1991-1996 Senior process engineer, reduction
1996-2000 Potrooms superintendant, reduction
2000-2006 Reduction manager
17 years for Hydro, Norway
2006-2009 Process and projects manager Kurri Kurri, Australia
2009-2017 Principal engineer, HAL4e Ultra project Årdal, Norway
2017-2018 KTP start-up manager Karmøy, Norway
2018-2020 KTP head of controller team Karmøy, Norway
2020- Chief engineer, Techology and Operational Support, Aluminium Metal
Under the multiple social and political pressures for acceptability, decarbonisation, transparency and sustainability, corporations must keep increasing profitability and returns. Following its mission, Norway’s Hydro has a been engaged in developing renewable and clean energy sources while providing low carbon, high quality aluminium products to its customers for many years.
But in today’s fast changing world, companies like Hydro must compete not only for markets shares, but also for resources, the most important yet volatile being their workforce. In this context, Hydro’s Industry 4.0 initiatives will help making aluminium production safer and easier through robotics and automation, while improving the productivity and the workplace quality for the active force. Furthermore, innovation in Information and Operation Technology convergence, connectivity, remote operations and digitalisation of processes and equipment will help Hydro improve the quality and efficiency of its activities to meet society’s demands in the coming years.
This presentation gives some examples of Hydro’s ambitions and progress in better serving society by improving production and sustainability through decarbonisation and in digitalisation. through decarbonisation and in digitalisation.
Senior figure with over 25 years of experience in the world of Automation and Industrial Machinery in various sectors (Steel, Paper, Plastics, Automatic warehouses, food & beverage, Heavy lifting, motion control). Managerial and Technical Management, combined with solid training in the field of Hydraulic and Pneumatic Controls with a strong aptitude for continuous learning. Able to manage and collaborate with a work team to pursue the objectives and finalise the project focuses. Coordinator of multi-ethnic teams, with good organisational, interpersonal and time management skills as well as solid technical skills. Maximum seriousness and use of the working method for objectives. Problem solving, decisionmaking autonomy, multidisciplinary skills, resilience and profitable interpersonal relationships in the professional field.
The aluminium Industry today is deeply involved in the Green and Digital transitions. The integration of environmental and digital technologies in industrial processes allows us today to achieve not only competitive goals in terms of production efficiency, product quality and sustainability, but also social ones, placing the health and well-being of workers at the centre of the process .
Digital technologies such as artificial intelligence (AI) and intelligent robotics allow to reimage workplaces, safer and less burdensome, optimising human-machine interactions with an added value acquired: the worker’s empowerment. Furthermore, the digitalisation path makes factory work more attractive for new generations.
Innovation always comes at the same time as a cultural renewal. Developing innovation more effectively and quickly is only possible through the synergy between specialisations and with the involvement of all stakeholders.
How can we upgrade traditional aluminium production process?
Through the integration of different digital technologies connected simultaneously to computer systems equipped with artificial intelligence and learning algorithms. Robots can automatically perfect their operations and operators are able to quickly intervene on the production efficiency, making decisions based on objective data, in a path of continuous improvement. The presentation offers an overview on latest technological innovations that turn an aluminium production plant into a “smart” one.
David has over forty years of experience in the aluminium industry. Originally employed by ALCOA and the ARCO Aluminum, David has held various positions within both companies. These positions included Process Metallurgical Engineer, Cast House Metallurgical Engineer, Chief Metallurgical Engineer, Senior Process Engineer, Engineering and Maintenance Manager and Director of Technical Services. David has also been involved in major projects, including plant installations of propriety processes, development of recovery devices for reclamation of aluminium from dross, established technical services for organisations and project engineering on complete recycling facility projects.
Mr. Roth was a founder and with ALTEK for twenty-five years. He was involved in dross handling projects, casting projects and furnace installations. He developed patents in these areas. As a principle and President of the company, David oversaw all aspects of ALTEK dross handling systems and engineering services.
Currently as Americas Business Representative – RiA & President of GPS Global Solutions, he is focused on providing automated scrap and patented dross processing systems to make the scrap melting operations a safer and more efficient working environment.
David has a B.S. in Metallurgical Engineering from the University of Missouri – Rolla, USA.
Automation of the scrap charging and skimming operations gives a set of advantages that are unique, especially in an environment where keeping well trained operators in the cast house can prove difficult in today’s labour market.
This presentation will review the utilisation modern scrap charging systems with In-Furnace cameras, that can optimise scrap loading systems. This can reduce cycle times by up to 50%, while saving up to 30% in energy consumption and subsequently reduce CO2 generation. Automated skimming with video optimisation, has a significant impact on melt yield. Taking the skimming out of the hands of the operator, makes total dross removal a thorough practice every time. Automation of the process allows for no dross to remain in the furnace between cycles, eliminating the generation of more dross and lowering recoveries. Precise skimming operations keeps the free and alloyed aluminium in the furnace where it belongs and not removed due to untrained operators or uneven floors. Automated skimming also shortens skim cycles, further reducing door open time and wasted energy.
Advantages of these areas will be discussed in detail in this presentation.
Mileidy Hernandez is a recent graduate with a bachelor’s degree in engineering who is passionate about the field of automation, specifically in relation to industry 4.0. She is currently working at WSP, where she specialises in working with EDA, a technology developed by the company used in a variety of industries to optimise production processes and efficiency.
During her studies, she completed internships in the automation industry, providing her with a solid foundation in the field and sparked her interest in pursuing a career in automation. She is fascinated about discovering new ways to improve both production processes and efficiency using the latest technologies. At WSP, she has participated in several commissioning projects working with EDA which brought her valuable reallife experience. She is constantly seeking to expand her knowledge and skillset in this area.
Ms. Hernandez’ experience working with EDA will bring valuable insight as speaker at the Future Aluminium Forum 2023 in sharing how automation technology can optimise production and enhance bottom line across a range of industries. She looks forward to sharing her enthusiasm to the audience as well as exchanging on these topics with other experts and learning from their experiences.
Industry 4.0 is quickly changing the way production and maintenance teams operate, and WSP has recognised the need to facilitate this transition. To help with the shift to Industry 4.0, WSP has developed a tool, called ADE, that brings autonomy and insights to all of its users. This tool has two primary goals: from a production standpoint, it aims to minimise alarms during production, provides autonomy to the operation team and centralizes all systems in the same interface. From a maintenance standpoint, it standardises and simplifies controller and HMI programming, reduces programming interventions, gives access to failure analysis tools, reduces calls for minor issues and helps track faulty equipment. We have successfully implemented ADE at ABI aluminum smelter and in various factories across Québec, such as Rio Tinto. where it has enabled more efficient production and maintenance processes, allowing the company to stay competitive in the ever-evolving Industry 4.0 landscape.
With the help of ADE and the modernisation of the equipment in the factories, we can build a solid foundation to continue revolutionising production and maintenance in line with Industry 4.0 principles. ADE is the foundation of a smart plant.
Guillaume de Goÿs is the CEO of Aluminium Dunkerque, the largest primary aluminium smelter in the EU and one of the largest industrial consumers of electricity in France. He chairs the board of Aluminium Duffel, a rolling mill located in Belgium. He has held several management positions in France and abroad, as a senior executive and project manager for various global aluminium, graphite, and tyre companies. He is also President of the French Association of Aluminium Producers and chairs the primary division of European Aluminium where he actively defends the interests of the profession and contributes to decarbonisation and the circular economy.
With less than 4.5 tons of CO2 per ton of aluminium produced (Scope 1, 2 and 3), Aluminium Dunkerque is one of the best performing primary aluminium smelters in the world. AD has reduced its CO2 emissions by 40% over the last 15 years and has developed a roadmap to near zero by 2050.
Carbon Capture, Utilisation and Storage (CCUS) is a key technology to achieve this roadmap and to halve its emissions by 2030. CCUS is a well-known technology, but it is yet not suitable for primary aluminium smelting because the CO2 in the flue gases is not concentrated enough to be economically viable. Therefore, Aluminium Dunkerque has developed several partnerships in order to: i/ adapt carbon capture to primary aluminium smelting ii/ transport and store the CO2 captured in the smelter iii/ offer the CO2 to partners for reuse.
Mr. Jean-Denis Carrier is a chartered Civil Engineer holding an Executive MBA whom has been working for the growth of the aluminium industry in North America, Europe and the Middle East for the past 20 years. He combines his passion for projects and business value creation to support the aluminium industry identify growth opportunities.
Mr. Carrier is currently the Global Director, Aluminium & Alliances at Hatch
In this digital era, data-based decision making is an efficient way to improve business outcomes. Over the past years, Hatch has been developing technical and techno-economic models to improve operational performance and business outcomes across the aluminium.
Marie-Eve Pomerleau is a product specialist in the metals and minerals marketing team at Rio Tinto. In her role, she aims at finding solutions to future market demand and supporting asset investment to meet these needs. She joined Rio Tinto in 2006 after graduating with a bachelor’s degree in Metallurgical Engineering from the University of British Columbia. Her career begun as a metallurgist in aluminum casting operations where she held various roles optimizing processes, monitoring product quality, and enhancing customer satisfaction. She believes in partnership with customers and suppliers to build a better more sustainable world.
Aluminium is a critical material in a decarbonizing world and we expect that demand will continue to grow while supply is more challenged. As an industry leader in responsible aluminium, we’re committed to pioneering responsible and sustainable aluminium. Partnering to provide recycling solutions is key to be ready and able to address the needs and demands of end users and consumers we work for. To be successful, we’ll leverage local scrap availability, our dilution capabilities, and our diverse portfolio advantage.
Simon Lobach is a doctoral researcher and a consultant in the fields of sustainability and environment. After a career within the United Nations advising governments on green economy policies, Simon is currently working as a researcher for the Geneva Graduate Institute, where he is obtaining a PhD on his multiple-year research project regarding the aluminium industry in the Amazonian region in South America. Countries where bauxite, alumina and aluminium are produced in Amazonia include Brazil, Guyana, Suriname and Venezuela. In the context of this research, Simon evaluates cutting-edge technologies applied in the aluminium industry in the context of the very particular demands and opportunities of this highly diverse, rich, yet vulnerable region. Elements of this research were funded by the European Research Council (grant 950672).
The Amazon region in South America contains operations of some of the main aluminium producers worldwide, including Alcoa and Norsk Hydro. These companies are among the avant-garde in terms of sustainability, as certified by the Aluminium Stewardship Initiative. They have earned their green reputation thanks to cutting-edge technologies applied in mining as well as in alumina and aluminium production. Examples include the management of bauxite tailings, measures for safer disposal of red mud, the greening of the energy mix used, carbon capture and sequestration, and reforestation programmes at the impacted sites.
Bringing an academic perspective, Simon Lobach has studied the environmental performance of aluminium producers in the Amazon. Besides the actions of the aluminium producers, he has also taken the fragility and global importance of this unique ecological biome into account. Based on a several-year research project on aluminium production in the Amazon, he presents his findings in the form of lessons that can be learned from the aluminium producers in the Amazon in terms of sustainability, but also the lessons that the sector can learn from a wide array of academic and societal actors in the region that were consulted in the context of this project regarding responsible operations in this highly diverse, rich, yet vulnerable biome.
Gaby Poirier is Alcoa’s Vice President of Operations for North America, overseeing the company’s operational facilities in the United States and Canada.
Poirier has deep operational background in diverse industries such as aluminum, iron ore, and copper and has worked in senior leadership roles in the United States, Canada, Europe, and Australia.
Prior to joining Alcoa in 2022, Poirier worked for Rio Tinto for 20 years. Between 2020 and 2022, he was Managing Director of Kennecott copper mining and smelting complex in Salt Lake City, USA. From 2017 to 2020, he served as General Manager of the Greater Hope Downs joint venture in Perth, Australia, part of Rio Tinto’s Iron Ore Product Group. He also served as General Manager of the Dunkerque smelter in France, from 2016 to 2017, as well as General Manager of the Kitimat smelter in British Columbia, between 2013 and 2016. Previously, Gaby occupied management roles at Kentucky’s Sebree smelter, as well as Alma and Arvida smelters in Quebec’s Saguenay region.
He was a member of the Board of Directors of the Salt Lake Chamber, as well as the Copper Development Association and the Copper Club, until 2022.
He holds a bachelor’s and master’s degrees in Chemical Engineering and an MBA in Finance.
Aluminum is essential for modern life, and the metal will play an even larger role in the low-carbon future. It is lightweight, strong, and – most importantly – infinitely recyclable. It is being used to replace plastics and heavier metals in a wide range of applications, and it is vital for the ongoing transition to electric vehicles and renewable energy infrastructure.
Alcoa is working to meet the needs of a more sustainable world, improving its environmental footprint, delivering sustainable products that support its customers’ own sustainability ambitions, and creating shared value in our communities. Alcoa has a rich legacy of innovation, and is leveraging that history with a technology roadmap that has the potential to decarbonize the upstream aluminum value chain.
Alcoa (NYSE: AA) is a global industry leader in bauxite, alumina and aluminum products with a vision to rein-vent the aluminum industry for a sustainable future. With a values-based approach that encompasses integrity, operating excellence, care for people and courageous leadership, our purpose is to Turn Raw Potential into Real Progress. Since developing the process that made aluminum an affordable and vital part of modern life, our talented Alcoans have developed breakthrough innovations and best practices that have led to greater ef-ficiency, safety, sustainability and stronger communities wherever we operate.
Website: www.alcoa.com/global/en/home/
Located in the north of France, Aluminium Dunkerque (AD) started its activity in 1991. Today, with an annual production of 290,000t, it is the largest primary aluminium smelter in the EU. Employing 650 people and located on 65ha, AD is one of the main sites of the Dunkirk industrial port platform.
The electrolysis process which transform alumina into molten aluminium requires significant electrical power. AD consumes an average of nearly 4TWh/year, making it the leading industrial site in France for electricity consumption.
AD uses the AP40 technology, with a consumption of 13,120 kWh per ton of aluminium, AD is among the most efficient in the world. The site manufacture of aluminium rolling plates and ingots with a purity of over 99% for value-added applications in the transportation, automotive, packaging, building and construction sectors. Aluminium Dunkerque’s historical customers include major players in the European manufacturing industry such as Constellium and Stellantis.
With more than 30 years of operations, AD is recognised by its customers as a robust supplier, with a satisfaction level of over 98%. Recently certified to IATF standards, AD is a key supplier to its automotive customers.
Website: www.aluminiumdunkerque.fr
Australia’s leading innovator of technical textile solutions. Bruck is the major manufacturer in Australia of value added, high performance and protective clothing fabric’s, used in end applications such as Metal Smelting, Military, Mining, Oil and Gas, Fire Fighting and General Industrial.
Bruck has proven design capability and integrated product development processes. Our PR97 brand is globally recognised and renowned for its superior protective and comfort benefits. Bruck is committed to product innovation and development of new technologies.
Website: www.brucktextiles.com.au
EPIQ Machinery is a world class equipment designer with the mission to manufacture innovative and effective solutions for the global heavy duty material handling and mobile systems market. The EPIQ team blurs the lines between being a technology company and a machinery manufacturer by bringing new technologies onto its equipment portfolio. The synergies found in the equipment brands; AD, MECFOR, BROCHOT, HYDROMET and EPIQ DTA enable the EPIQ Machinery to take on both large- and small-scale projects while keeping the flexibility and agility to design custom made to order equipment.
The EPIQ team has the ability to analyse current systems and make recommendations of upgrades, equipment additions or the addition of new technologies to a process.
As leaders in their respective primary and secondary aluminium markets, the founding companies, Advanced Dynamics (AD) and MECFOR, make EPIQ Machinery a company capable of supplying and improving processes in all sectors of aluminium production: from the smelter to the finished good area.
With EPIQ Machinery; there is more than meets the eyes.
Website: www.epiqmachinery.com
Equibras is an equipment supplier for the aluminium industry since more than 20 years. With over 5000 equipment distributed worldwide, Equibras is the world leader in Equipment for the potlining of the electrolysis cells.
Our focus is to provide the best products and services to our clients to increase efficiency, safety, profitability as well as reducing operation costs. Our solutions include advanced technologies for operation in potroom and worshops.
At Equibras, client needs are at the center of the design process of the equipment / service. Thanks to its collaborative approach, Equibras is able to offer turnkey products, perfectly adapted to the needs of the aluminium plants. This approach also allows Equibras to be flexible in its offers. Thus, the company is able to meet the needs of various industries. Whether it is for an equipment or consultant need.
Website: www.equibras.com
The Geneva Graduate Institute is an institution for research and higher education situated within the top-50 globally in the field of international affairs. Located in the heart of International Geneva, it produces and shares academic knowledge and expertise on international relations, development issues, global challenges and governance. Within the Geneva Graduate Institute, the Centre for International Environmental Studies is a top academic institution for the assessment and development of environmental policies for the public and the private sector.
Website: www.graduateinstitute.ch
GNA specializes in the design and supply of equipment, technical services and operating strategies for the pot room and cast house in both primary and secondary aluminium industries. Our Cathode Sealing Systems are in operation world-wide and
recognized as industry-leading designs. Different pot room technologies are being processed in our systems daily and they include, AP, DX+, Mitsubishi, Montecatini, and others. Our cathode sealing systems are supported by three decades of experience in designing, fabrication, testing and a continuous improvement program driven by Client needs.
For the cast house, we cover design and technical support services from scrap yard layout through all major process steps to get product to the shipping door. GNA will assist you with raw material segregation, material flow and process management. Furnace charging equipment, melting and holding furnaces, bath skimming and alloying, metal treatment, filtration and casting lines can all be integrated into an autonomous operation. GNA is the leading innovator in modern cast house hands-free technologies. Whether you are melting/casting prime metal, clean or contaminated scrap, GNA can help you to improve metal quality and yield while decreasing energy consumption, melt losses, emissions and operating costs.
Our casting capabilities include technologies for slab, extrusion ingot (continuous and vertical) and continuous casting for sheet, plate and coil using Hazelett Corporation’s Twin-Belt Casting Machine. Hazelett joined the EBNER Group in 2021.
Our heat treatment capabilities include batch and continuous homogenizing, annealing and more using fully integrated and automated production lines.
Website: www.gna.ca/en
Our organisation is passionately committed to the pursuit of a better world through positive change. We embrace your visions as our own and partner with you to develop better ideas that are smarter, more efficient, and innovative. Our global network of 9,000 professionals work on the world’s toughest challenges. Our experience spans over 150 countries around the world in the metals, energy, and infrastructure sectors.
We are employee-owned and independent—free to bring our best thinking to your business. Our exceptional, diverse teams combine vast engineering and business knowledge, working in partnership with our clients to develop market strategies, manage and optimise production, develop new game-changing technologies, and design and deliver complex capital projects.
We work closely with the communities in which we serve to ensure that our solutions optimise environmental protection, economic prosperity, social justice, and cultural vibrancy. We want their businesses, ecosystems, and communities to thrive, both now and into the future.
Our people are passionate about our corporate purpose and values. We believe in long-term relationships with our partners, and are committed to our clients’ lasting success.
We are “entrepreneurs with a technical soul.”
Website: www.hatch.com
Funded in 1905 in Norway by Sam Eyde, Hydro is one of the largest aluminium companies worldwide. It has operations in some 40 countries at 140 locations around the world and is active on all continents. The Norwegian state owns 34.3% of the company. Hydro employs approximately 31,000 people.
First a synthetic fertiliser and power producer, Hydro entered oil and gas production in 1965. The fertiliser business was spun off in 2004 as Yara, while the oil part of the company was sold in 2007. Hydro entered aluminium production in 1986 when it acquired the Årdal aluminium plant from the Norwegian state.
Today Hydro is a fully integrated company with
- High quality bauxite and alumina production in Brazil,
- Primary aluminium production in Norway, Qatar, Slovakia, Germany, Brazil, Canada and Australia
- Production of 13.4TWh of renewable power
- A world leading position in aluminium extrusion ingots, extruded profiles solutions and precision tubing
- Remelting operations in America and a large European recycling network
- Efficient Technology and R&D organisation
In line with its mission of creating a more viable society by developing natural resources into products and solutions in innovative and efficient ways, Hydro aims at lifting productivity drive sustainability - creating value for all stakeholders. Pursuing that goal, the Company is strengthening its position in low-carbon aluminium and recycling, along with diversifying and growing renewable energy.
Website: www.hydro.com
The International Aluminium Institute (IAI) is the only body representing the global primary aluminium industry, aim to promote the sustainable development of the aluminium industry and to increase demand for aluminium products by raising awareness of their unique and valuable properties. Established in 1972, IAI member companies are engaged in the production of bauxite, alumina, aluminium, the recycling of aluminium, or fabrication of aluminium or as joint venture partners in such.
Website: www.international-aluminium.org
Laserax works with the world’s leading manufacturers to implement automated laser marking, cleaning, texturing, and welding solutions. Providing turnkey machines and OEM systems, the driving force behind Laserax is the desire to push the limits of laser technology and establish new standards in the industry.
Founded in 2010, Laserax first developed inline laser solutions for major smelting plants. Building on our reputation, we moved on to conquer casting plants and automotive parts suppliers all over the world.
Laserax is a manufacturer of laser systems that provide fast, reliable, and safe solutions for the most demanding industrial applications. Laserax relies on laser technology experts to offer a complete range of products for leading-edge marking and cleaning applications in the primary metals industry, automotive industry and battery and fuel cell industry.
Website: www.laserax.com
Maestria Solutions’ expertise is recognized by users worldwide. Our tools are used on a daily basis by different teams to detect and improve the performance of their cells, track crucibles for the transfer of molten metal over the road, or manage and deliver status and alarm messages through hall PAS, SMS, or email while creating a history of all the events. Instrumental in increasing Current Efficiency, Better Energy Consommation with proven results.
The mVa Profito solution for anode drop measurement allows quicker incident detection on your cell in order to limit the process degradation or speed up the crisis recovery, limiting the incident cost. Combined with our software, it’s proven to improve the Current Efficiency or get better Energy Consumption. Allow quick detection of problematic anode and cell, watch for potline drift, and help to locate the probable cause. Use big data strategy on measurement. We expect 0.1% CE increase for most smelters and 1% reachable in some cases. No modification on your potline is needed.
CICERO covers the security and plant operation field. This solution meets the needs of communication and transmission of messages, of any event requiring the attention of the staff with an objective to ensure efficiency and safety. This intelligent system, coupled with the pot control systems, pushes their messages to the right staff and location and with efficiency, using multilingual messages, and diffusing them by many means through the hall via PAS (speakers), SMS, or email.
In the primary aluminum business, part traceability protects manufacturers, buyers and sellers by providing a set of authentic and valid data.
By tracking each individual product, the information can be narrowed down to a specific batch or production process.
Laserax’s laser technology is the most widely used marking method to identify and guarantee the origin of sustainable aluminum.
We are proud to work with leading primary aluminium producers around the world to drive a meaningful change for product transparency and sustainability.
APPLICATIONS FOR THE ALUMINUM INDUSTRY
ALUMINUM BILLETS
Serialize products and accurately identify billets to automate extrusion process and meet new extrusion requirements from major automotive OEMs.
ALUMINUM SOWS
Stop spending on expensive labels that fall off. Laser etch a high-definition identifier label directly on the sow’s surface to obtain foolproof traceability and inventory management.
ALUMINUM INGOTS
Ensure heat resistant traceability with laser marking and unlock industry 4.0 features with individual ingot serialisation and bundle automated labeling.
LASERAX.COM
ProMETO is a solution for casting to track crucibles for the transfer of molten aluminium over the road. This solution precisely tracks logistically and geographically molten aluminium move in cradles by trucks for optimal planning and increases risk management, and updates it lives over private internet access with proper mapping. Enable tracking within the plant site access road by easily customizing the mapping.
Website: alu.maestria.ca/en/home
Mössner develops and builds special solutions in the fields of mechanical engineering, automation technology and robotics. With our 140 employees we can handle even larger projectswithout losing the necessary flexibility for your special solutions. At our location in Eschach, Germany we develop, manufacture and assemble your system and commission it for our customers worldwide.
Aluminium Technology
In the field of aluminium technology, we offer precise sawing and milling systems for primary and secondary aluminium production. These enable the processing of rolling ingots, T-bars, blanks, contours, round blanks, samples, ingots and plates.
Foundry Technology
Whether system components or turnkey casting and finishing lines - our special machines stand for reliable and automated system technology. This includes core handling, automation of casting machines, cooling and industrial marking, decoring, sawing, milling and deburring, as well as all necessary sub-processes of your casting production.
Band Saw Machines
For more than 130 years our band saws have been known for their durability, robustness and precise cutting performance on a wide range of materials. The saws are manufactured and assembled exclusively at our location in Eschach. Spare parts supply is guaranteed even decades after the purchase.
Special Machinery
In addition to handling tasks, our machines take over the processing steps of drilling, milling and sawing. As a complete supplier, we supply systems for all areas of quality control, conveyor technology and nuclear decommissioning.
Engineering
Our engineering department supports you in all questions of planning, optimisation, simulation and programming of robot applications. We offer automation in the field of robotics and control engineering as well as image processing for automated inspection stations and the digitisation of workpieces by 3D scanning.
Website: www.moessner-kg.de/en
Polytec is the merger of two leading companies in automation, robotics, renewable energy and plant engineering, an internationally renowned company operating in the field of system integration, specialising in solutions and platforms that combine robotics, artificial intelligence, process automation and software to help manufacturing companies achieve the technological transformation they need to become smart factories.
Polytec provides digital technologies, to allow aluminum producers a significant leap in productivity, while offering a better control over the production process and customer reach. This also provides better safety and environmental sustainability.
Our expertise in plant upgrading and retrofitting:
Automation and Process Control, Electrical Engineering, Distribution Systems HV/MV/LV, MCC and Drive Panels, Safety Management, PLCs & Drives, DCSs, HMIs & SCADA, Data Management, Cloud & IIoT
We design and supply tailor-made robotic solutions for:
� Plate removal and replacement in the ceramic foam filter
� Coil waste removal from the rolling mill unwinder
� Strap cutting and removal
� Machine tending for aluminum components
� Ingots handling and palletising
� Coils and products marking and tagging Website: www.Polytec.bmgroup.com
PRECIMETER specialise in premium products and technology for molten metal level and flow control solutions. We have been active within the molten metal industry for more than 25 years. Our products are specifically designed to withstand the harsh conditions in a casthouse environment.
We continuously improve and develop both current and new technology in order to offer our customers intelligent and modern solutions to safely make casthouse operations automatic for quality assurance. Our extensive industry expertise and knowledge lays the foundation of our continued work and product development. We work with the major corporations in the business and value a longlasting cooperation together with our customers for a definite future success.
We are fully committed to our customers worldwide and are able to offer our onsite assistance and support for service and support requirements in any of our installations. A hands-free casting process enables various advantages such
Mössner
Vertical saws
Horizontal saws
Saws for the aerospace industry
Saws for T-bars, rolling ingots, slabs, billets
Contour saws
Automation technology
Conductivity measurement
www.moessner-kg.de
as increased productivity due to automation, optimised safety for casthouse personnel, by a repeatable and traceable production the sustainability of the process as a whole is enhanced due to less scrap and remelting procedures.
Webiste: www.precimeter.com
WORLD-CLASS TECHNOLOGIES FOR ALUMINIUM ROLLING
Primetals Technologies provides metals producers with cutting-edge, custom-tailored plant equipment and services.
With over 90 years’ experience in the aluminum industry, Primetals Technologies is your single source supplier for aluminum rolling solutions;
� Fully integrated hot and cold rolling mills
� Mill modernisation projects and equipment upgrades
� Specialist shape measuring and process control technology
� Comprehensive spares and servicing support
� Extensive process knowhow to ensure your plant is fully optimised
Our rolling mill technologies focus on enabling customers to roll faster, thinner, and wider, with the included benefits of higher outputs, tighter product tolerances, enhanced operational flexibility and efficiency, increased plant availability, reduced costs, and maximum environmental compatibility. After the successful completion of more than 350 aluminum rolling mill projects, Primetals Technologies is ideally positioned to offer expert advice and to implement the optimum rolling solutions for both new and existing plants. Website: www.primetals.com
PSI Metals is the leading provider of innovative production management software for the metals industry, by combining Supply Chain Management, Advance Planning Scheduling and Manufacturing Execution System within one Service Platform (SP). It also specialises in business consulting studies that provides strategic information services. This helps metal producers define their digitalisation framework and assists their decarbonisation mission. Our end-to-end solutions enables aluminum and steel producers to stay competitive by delivering tailored and configurable solutions. PSImetals Service Platform allows the integration of these solutions. Our solutions also support all processes such as planning, production, quality, and logistics. By considering the latest developments in the field of digitalisation and user empowerment, PSImetals FutureLab investigates and develops the solutions of
tomorrow, based on the PSImetals Service Platform.
PSI Metals is a subsidiary of PSI Software AG, a publicly traded company that focuses on software for energy, mobility and production management. With our global presence in four continents and headquarters in Duesseldorf, Germany, PSI Metals employs more than 300 committed experts that ensure smooth operations of the company in 10 countries.
www.psimetals.com
Quantillion’s mission is to empower Smarter, Greener and Safer industrial operations. We do this by combining high tech equipment, our unique integration layer and process optimisation techniques. Through this we are able to deliver flexible, profitable, and sustainable logistics for the heavy industry.
We believe that new technology enables world leading industries to become more agile. Not only will industries be able to adapt to outer change, but also to the changes they face in their day-to-day operations. Therefore, we are putting fast and powerful decisionmaking algorithms at the heart of production processes. Our products make it easy for operators and machines to make smart decisions, fast.
Quantillion originally started with automating logistics within primary aluminium. Since then we have grown to be a strong integration provider acting as a key link between the smelters and their numerous equipment suppliers.
For the past 5 years Quantillion has developed and deployed autonomous decision systems. With our order management system and traffic management system we are using Artificial Intelligence to streamline logistical decisions within the heavy industry. We support the industry with the autonomisation of core operations by connecting all separate workflows and agents, either human or machine. By integrating our software with our client’s business operations and IT, we create more profitable, more efficient, and more responsive operations. All of this is done in one environment, with a layer of business logic and artificial intelligence. This results in an easy-to-use user interface for precise control and process management.
Due to our strong focus on primary aluminium, we have a deep understanding of the industry and of the logistical operations that are at the heart of the numerous processes in a smelter. We have become specialised in bringing new data technology to aluminium smelters as a pioneer in autonomising industrial operations. Quantillion contributes to Industry 4.0 through revolutionising the way equipment and operators collaborate and how workflows are optimised. At Quantillion we enable the heavy industry to capitalise on these improvements with our Navigation Kit, Traffic Management System and Order Management System.
By having both humans and machines inter-connected, our
execution system allows for a more efficient and intelligent way of working. Through this we create fully autonomous processes instead of single implemented automated (mobile) equipment. With our centralised system we automatically find the most optimal scenario given any circumstance.
We call this approach “collaborative intelligence”. “Prediction and intelligence is only valuable if you can act on it.” Headquartered in Amsterdam, our highly skilled and passionate people make sure to introduce new technology to the industry and put the data to work!
Website: www.quantillion.io
Since its foundation in 1995, Refraco has offered refractory manufacturing, maintenance, engineering, and research services to clients primarily in the aluminium, steel, cast iron, pulp and paper, cement and mining industries.
Through its innovation and initiative, it has built a reputation for excellence and proven itself to be an invaluable source for refractory solutions.
Refraco is located in the province of Quebec in Canada, in the middle of North America’s largest aluminium producing region and one the leading areas in the world in terms of research centres and product development facilities.
Refraco has partnered with some of the most technologically advanced primary and secondary aluminium producers in the world for over 30 years, providing high-performance refractory products for all aspects of the aluminium transformation process.
Refraco is recognised in the industry as a trusted supplier of innovative refractory products and services, providing value, support and a comprehensive solution package to its valued long term clients.
Refraco is proud to contribute to its clients and partners’ prosperity by providing a solid long-term partnership and unique world-leading solutions.
Our clients benefit from our experience in the refractory industry in order to create new added value offers and more cost-effective solutions to their stakeholders.
The personalised, cordial, open and enduring relationships that Refraco builds and maintains with its clients and partners are at the heart of its success. The resulting atmosphere of trust promotes a high level of collaboration that allows effective and efficient solutions to be found.
Website: www.refraco.com
Efficient furnace practices with low-cost production standards, start with automated charging and skimming. Using the right technology enables a significant reduction of energy consumption, minimum cycle times, reduced furnace maintenance and most importantly a safer environment for the operators. RiA has been focusing on the development and manufacturing of charging and skimming equipment since 1997 and in particular, is now focused on innovative automation and process optimisation solutions and the safest and most efficient systems possible. RiA charging and skimming machines utilise full artificial intelligence (AI) to make charging and skimming cutting-edge technology, without operator interaction. The latest innovation in skimming is In-Furnace Dross Processing (IFDP), squeezing the dross whilst still in the furnace, releasing liquid aluminium which remains with the bath, increasing recoveries. Recent additions to the product portfolio include Fioscope air-cooled smart In-Furnace cameras and laser bath height measurement systems.
Initially established as a local maintenance service and special equipment supplier for the German aluminium industry, over the last two decades RiA became an important International partner for aluminium remelt cast houses worldwide, now with more than 75 charging and skimming machines supplied to major aluminium companies around the globe. Building on high quality standards and continuous improvement has resulted in the most reliable, robust, maintenance friendly and custom-made furnace tending equipment on the market.
RiA charging machines can charge up to 30 tonnes of material in one push in under two minutes, deep into the furnace and evenly distributed to ensure maximum melt rates. RiA skimming machines can skim, stir, mix and clean the furnace with precise position-controlled contact, hence minimal refractory wear. RiA/Fioscope air cooled cameras allow a view into the furnace 24/7 from a safe location with the door closed. RiA bath height measurement systems allow accurate determination of liquid heels ensuring on spec alloying first time and also prevent short cast rejects. RiA systems achieve the lowest possible operational cost and the safest operating environment for all important stages of the cast house process.
Website: www.ria-casthouse-engineering.de/en
Rio Tinto, a global leader in metals and mining, is finding better ways to provide the materials the world needs. A fully integrated mining company, Rio Tinto has a unique vantage point in transparency and traceability. Positioned to meet evolving global trends, they have put climate change and the low-carbon transition at the heart of their business strategy. Now, Rio Tinto has taken their technological knowledge and pioneering spirit to the digital space. Powered by blockchain technology, START provides transparency, traceability, and provenance across value chains so customers and end users can see key environmental, social, and governance (ESG) information. START tells the entire story—from mine to market— of sustainable materials from Rio Tinto, allowing users to prove to their stakeholders and customers that they share a commitment to sustainability. Rio Tinto is helping empower consumers to make sustainable choices.
Website: www.riotinto.com
Proudly Canadian, Royer is a global leader in designing and manufacturing safety footwear for the world’s toughest conditions, since 1934. We continually develop industry leading products by using cutting edge technology and high-quality materials to produce the world’s best collection of safety footwear. We are innovators and change-makers, but it’s our experience that inspires and shapes our future. Our relentless pursuit of perfection is what fuels our passion and dedication to provide our customer with the best possible product.
Website: www.royer.com
STAS Inc. is a Canadian based company specialised in the development, fabrication and commercialisation of process equipment for the global aluminium industry. Since 1989, we have been providing aluminum producers around the world with innovative and technologically advanced solutions
that meet the highest demands of the industry.
We are a world leader in providing various equipment to improve productivity and the quality of molten aluminium in several areas of the aluminium production: carbon, electrolysis, casthouse, crucible shop and SEED rheocasting.
We have delivered more than 1500 equipment units and thousands of projects in more than 40 countries, making us a key supplier.
STAS employs more than 160 persons–half of which are engineers and technicians – with a broad expertise in processes and engineering. Our work is guided by the values of respect, creativity and fun and are customer and family-oriented.
Website: www.stas.com
Based in St. Bruno, Quebec, Canada, Tecnar designs, develops, manufactures and markets novel systems and sensors for industrial process monitoring and control. Founded in 1989, Tecnar has used its expertise to bring cutting-edge technology to the plant floor. Over the past decades, Tecnar has diversified into four highly specialised divisions: Automated pipe and vessel welding, thermal and cold spray in-situ monitoring, molten metal analyser for galvanising and aluminum manufacturing and non-contact ultrasonic gauging for the seamless tube industry.
Website: www.tecnar.com
Question today - Imagine tomorrow - Create for the future WSP is one of the world’s leading professional services consulting firms. We are dedicated to our local communities and propelled by international brainpower. We are technical experts who design and provide strategic advice on sustainable solutions, engineering projects in the Transportation & Infrastructure, Property & Buildings, Earth & Environment, Power & Energy, Resources and Industry sectors that will help societies grow for lifetimes to come.
We value our people and our reputation.
We make extraordinary efforts to attract, develop, engage and retain the best professionals in our fields of expertise because this is what makes us great. We put the highest ethical standards at the centre of all we do. Professionalism is inherent in our offering. We are humble and act with moral and intellectual integrity, keep our word, treat everyone with respect, support our colleagues, and embrace diversity. We care about individuals and their progress and
We see the future more clearly and design for it today. We’re addressing complex challenges and designing solutions that will yield a sustainable, prosperous, and resilient society. Through our global Future Ready® program, we enable, challenge and inspire our people to deliver projects for today, and tomorrow.
wsp.com
offer the most fulfilling career development for our professionals. We promote our young recruits because we believe fresh perspectives bring great ideas and new energy.
We are locally dedicated with international scale. Our strength is our ability to adapt to our client’s culture and local markets. We provide them with the same personalised services as a specialist firm while leveraging our worldwide expertise to undertake the most complex projects and assist them attain their ambitions. We achieve this by remaining agile, with a commonsense approach, and by keeping our structure and business model simple and lean. Our focus on growth also allows us to better serve our clients by expanding our offering, expertise and geographical reach.
We are future-focused and challenge the status quo. We anticipate trends in order to propose innovative ideas for our clients to meet their business objectives. We ask questions, look at complex problems from different angles and find solutions that break paradigms. We are problem-solvers who evolve, improve, modernise and excel. We know our solutions will shape the communities of tomorrow and help societies thrive sustainably. We
embrace change and have an uncompromising determination to achieve excellence.
We foster collaboration in everything we do.
Our international agility is founded on our collaborative working environment. Our devotion to teamwork creates unique networks of outstanding professionals who understand great achievements come from collaboration. We embrace and support a high-performing culture, always strive to learn from others, and foster a stimulating work environment. We put the interest of our team ahead of our own. Joining us is the best way to fully understand the collegiality that defines our firm.
We have an empowering culture and hold ourselves accountable. We are empowered to turn challenges into opportunities while being held accountable to standards beyond the norm. Our proactive leadership empowers us to be client-focused, agile and responsive, while being accountable to our clients, peers and shareholders. The profitability of our firm is essential to our future and this is why we manage our business responsibly as if it were our own.
Website: www.wsp.com
Aluminium International Today (AIT) is the leading bimonthly journal dedicated to all sectors and regions of the international aluminium manufacturing and processing industry.
With more than 30 years’ experience, AIT is committed to delivering up-to date global news, events, and statistics, as well as more detailed technical articles, company and country profiles, conference reports and regular regional economic briefings.
The journal has changed dramatically since its formation and now publishes news regularly on its website: www. aluminiumtoday.com as well as a free weekly newsletter, which is sent to the inbox of more than 24,000 industry professionals.
For more information visit: www.aluminiumtoday.com
Furnaces International is an English language journal dedicated to the life, sustainability and global developments of furnaces, and heat treatment, across the heavy manufacturing industry.
With advanced knowledge and experience in the glass, aluminium, and steel industries; working closely with its sister publications in the respective industries, Furnaces International provides a unique perspective into the industries place within manufacturing and advanced technical knowledge to its readers.
Published quarterly, as a digital issue accompanied by an exclusive once a year print publication and website, the journal contains a digest of global news, events, and statistics as well as more detailed technical articles, company and country profiles, conference reports and regular regional economic briefings.
www.furnaces-international.com
With 50 years of operation and continual innovation under its belt, the Air Bearing ShapeMeter offers market leading levels of continuous measurement feedback for flatness control.
• Low maintenance and maximum equipment reliability.
• Aerospace precision product designed to withstand heavy industrial environments.
• Modular design enables easy installation with minimal downtime.
950 INSTALLED GLOBALLY
Like many other industries, the aluminium industry is in transition. Efforts are underway by a number of firms to reduce carbon emissions, enhance sustainability, improve logistics and supply-chain operations, and utilise tools and technologies that reduce costs.
“In an effort to streamline production, many metals manufacturers have recently found significant value in re-examining their core business processes and fundamental operations for inefficiencies, vulnerabilities, and redundancies to align with industry best practices,” said Joe Velez, Managing Director of Client Services at Ultra Consultants. “We’ve seen aluminium refineries, smelters, and fabricators roll out sweeping changes that are supported by industry-specific enterprise resource planning (ERP) software with updated shop-floor technology. This inside-out approach creates a foundation on which new tech can be supported and innovation encouraged and tracked.”
Mr. Velez began his career at ALCOA, according to his biography, and then worked at Rio Tinto’s ALCAN division. For the past eight years, he has worked for Ultra Consultants, a firm focused on ERP consulting and implementation services. The business indicated that it “…works with aluminium manufacturers headquartered in North America, whose operations are often global.”
“Many aluminium manufacturers are on a system they’ve been patchworking for
twenty-plus years, and they have no idea what they’re missing out on,” noted Mr. Velez. “Today’s cloud-based ERP solutions with advanced analytics, machine learning, and statistical models provide always-on transparent oversight of the entire supply chain and shop floor, predicting when shipments will be late and when equipment is likely to fail, whilst digital imaging, spectroscopy, and non-destructive testing techniques provide seamless quality control.”
“Aluminium refineries, smelters, fabricators, manufacturers, distributors, and recycling facilities all benefit by the increased efficiencies and advanced data integration of ERP systems,” Mr. Velez continued. “…We’ve seen three main external forces that have affected companies’ decisions to optimise technologies: raw material cost fluctuations, increased environmental regulations, and the globalisation of competition in the aluminium industry. Each of these has played a role in companies’ decisions to adopt digital transformation initiatives to increase redundancies and visibility in the supply chain, adopt more energy-efficient and environmentally friendly practices, and optimise their production processes to stay ahead of the competition.”
Throughout the world, a number of businesses are working on technology innovations in the aluminium production processes. This news columns highlights efforts by several of these firms, including Fives, PSI Metals, RIA Cast House Engineering, and
Fives
“As a pioneer in decarbonising industry for over 15 years, Fives now has a clear technical edge when it comes to the energy transition,” said Sébastien Gauguier, President of Fives – Aluminium Division. “The energy crisis only confirms the daring choices we made: working towards an industry that combines performance with energy and environmental efficiency.”
“We must continue to innovate to reduce aluminium industry’s carbon emissions and ensure its digital transformation: 80% of the patents we file concern solutions aimed at reducing our customers’ environmental footprint,” Mr. Gauguier continued. “More than ever, Fives is committed to a mutually responsible and virtuous industry.”
Fives indicated that given the goals of many to increase aluminium production and the tendency to be carbon neutral, the firm expects an increasing demand over the next few years for production “creeping” projects on existing aluminium smelters.
“Investment profitability, time to market, and performance risks being the key drivers,” stated Frederic Pereira, Head of Marketing at Fives Aluminum. “For several years, we have been working on solutions to assist aluminium smelters in their net-zero programmes.”
“At Fives, we are convinced that Industry 4.0 will play a central role in the transformation of the global aluminium
*Do you have questions about the aluminium industry? Governmental regulations? Company operations? Your questions may be used in a future news column. Contact Richard McDonough at aluminachronicles@gmail.com.
© 2023 Richard McDonough
industry in the years to come and will support their road map to net-zero,” continued Mr. Pereira. “That’s why to support our customers in their transition towards green production of aluminium we have introduced successful innovative solutions aiming at optimising CO2 emissions per tonne of aluminium produced, reducing energy consumption and polluting emissions whilst improving working conditions.”
Mr. Pereira said that “in the carbon sector, digitalisation across the whole anode production process with Amelios Suite allows optimised carbon consumption and better monitoring of anode quality. It potentially reduces the amount of CO2 emitted per tonne of aluminium produced by 35 to 70 kg, whilst also reducing anode production costs by 2.5%. Consequently, our Amelios Suite solution has been selected by the Solar Impulse Foundation as one of the #1000 Solutions to change the world.”
“The Helios Advanced Firing Control System (FCS) offers clean and efficient combustion in the anode baking furnace,” Mr. Pereira continued. “When converting plants to natural gas, Fives supports its customers in the modernisation of their anode baking systems
by providing an optimised injection system to reduce NOx emissions at the source. The integration of the anode baking module of the Amelios suite also allows data analysis and provides key performance indicators to monitor and optimise the baking process.”
He also indicated that “in the reduction lines, CAFD Eco2 (Crust Alumina and Feeding Device) contributes to reducing anode effect and the compressed air consumption of the smelter. The Fives’ SMART GTC (Gas Treatment Centre) allows for enhancing smelter environmental performance and reducing operating costs through constant monitoring of emissions and equipment. The Ozeos filtering unit together with Cascade feeding system offers to Fives’ GTC a level of HF (Hydrogen Fluoride) emissions and energy consumption unmatched on the market.”
“In addition, the 4.0 road maps of our customers will drive the demand for control platforms, connectivity, and automation,” explained Mr. Pereira. “We are already in these different digital segments, with machine monitoring software, online advanced scoring sensors and advance control, and a range of remote service mobilising a comprehensive set of technologies and experts.
“That’s why our main target is to continue to develop innovative digital tools to help our customers to improve their productivity,” stated Mr. Pereira. “These include easy access to operational information, everywhere at any time, preventing security concerns with their IT systems, improving operational efficiency thanks to data mining and analytics, switching maintenance from reactive to predictive, and elimination of physically demanding tasks (generating heat stress for example).”
“We also have deployed OEM to customer interfacing tools such as the online portal Fives Connect providing privileged access to numerous digital services,” continued Mr. Pereira. “We continue to expand the functionality of our machine health monitoring system, SMARTCrane, which following its successful introduction continues to be connected to increasing numbers of special process cranes across smelter sites. We have recently launched SMARTVibro for the vibro compactor unit (anode forming) within the green anode plant, and developments continue on the SMART filter for GTC. And we anticipate expanding our portfolio applications such as virtual reality applications for PTM (Pot Tending Machine)
training as we are also leveraged by multiple stakeholders to provide it.”
PSI Metals
“Sustainability and digitalisation are two factors that are key in the coming years,” stated Gunther Schober, Sales Manager at PSI Metals Non Ferrous GmbH. “Our generation has the responsibility to pass on an ecologically-friendly environment to the future generations. This makes sustainable production indispensable.”
“Digitalisation offers huge potentials,” Mr. Schober continued. “AI-based software solution powered by a Service Platform (SP) optimises production plants, using smart services that network like a team of agents. An SP enables a collaboration of local and global optimisation tools. But it is not just the planning solutions that work together; the supply chain is equally optimised and becomes fully transparent, with additional flexibility.”
His biography detailed that “Gunther Schober, is a global expert in aluminium with a background in Metallurgical Engineer, focusing on industrial and energy economics. He has held diverse roles as a Senior Consultant, Project Manager and Sales Manager. His expertise in metals and international experience in process development and supply chain management is highly sought after. With more than fifteen years of experience in production management solutions encompassing supply chain management and planning, product design, quality management, production execution and logistics, he has become a recognised expert in these areas.”
PSI Metals describes itself as combining “…the metals expertise within the PSI Software
AG and is the world’s largest provider for software solutions in production management for the metals industry.” The firm indicated that it has its solutions running at more than 260 customer plants.
Mr. Schober said that the “efficiency of the production plants is also a core of digitalisation as our solution allows aluminium producers to structure how best to produce, the ideal time to produce, the optimised yield, and reduced material movements. The result is savings in cost across all levels – production costs, energy costs, material costs, handling costs, and increased overall equipment effectiveness. Digitalisation of the production plant has a direct impact on sustainability. We promote sustainability by even decreasing material usage and optimising energy. Put simply, save costs in order to save the environment.”
One of the key facets cited by Mr. Schober are smart and collaborative pieces of software.
“Smelting aluminium consumes a vast amount of energy,” stated Mr. Schober. “Software will not change the process, but it can optimise the energy consumption and thus help reduce CO2 emissions. Even if aluminium producers have a CO2 – neutral power supply, energy peaks may have to be met by fossil fuel-based electricity. These peaks may not originate in their plant only. There are waves of electric energy consumption. Intelligent software can predict such events and flatten power consumption in a broader perspective. Further, wind, hydro, and solar power depend on weather conditions. Smart software can integrate the weather forecasts and the anticipated wind force for example to balance the estimated consumption with the predicted supply of energy.”
“There is giant potential to use the flexibility of the process,” he continued. “The technology to use the aluminium bath as a battery is already there. With intelligent software solutions, producers can make the most out of it and optimise the entire production process.”
Mr. Schober said that an important software service is alloy optimisation.
“Aluminium producers use it to optimise the input for their casters,” he said. “The system knows all available input and alloying materials and the corresponding costs. The result is an optimised use of scrap, that is ideal from an energy standpoint as well as from the CO2 perspective.”
“Aluminium producers may want to support the use of a particular material and hold their own scrap sale, or they want to limit a popular material and avoid cherry-picking,” Mr. Schober continued. “Liquid material and the sump can be considered like any other material. They set the target and the system finds the best way there.”
He noted that moving to the next steps downstream – towards extrusion or rolling, “dynamic order dressing (rule-based and characteristic-based) give aluminium producers the required flexibility. In a matter of seconds, they have all the details on qualitative and quantitative material requirements, test and sampling instructions, process instructions and time demand for planning and costs. Further, they can calculate the carbon footprint for each production step and later compare with the actual. A production order optimised and designed for their customer’s request. The time for defining a new article can be reduced from two weeks to two hours.”
In the area of predictive quality, Mr. Schober stated that “intelligent software can
“Sustainability and digitalisation are two factors that are key in the coming years,” stated Gunther Schober.Gunther Schober, Sales Manager at PSI Metals Non Ferrous GmbH. (The photograph was provided courtesy of PSI Metals.)
predict defects and thus help to avoid them. We’re not there yet to avoid them completely – at least not yet. Nevertheless, the results of existing projects show a 50% reduction in defects. This is, based on our experience, equal to an increase of production output by 2% with no additional CO2 emissions.”
“Software would not only predict errors; it can also help aluminium producers find the root cause,” Mr. Schober continued. “If they want to avoid an error, they must first find the cause, then they can determine the measures. Another step towards reducing CO2 by increasing the first time right rate.”
He indicated that an additional option to reduce excessive material is dynamic order combination.
“Based on the existing order book and material units – planned and real – an order/material combination tool will nest different orders optimised into the material units,” according to Mr. Schober. “Multilevel combinations become reality and the smart software fully supports a ‘Make to Stock, Finish to Order’ strategy to optimise production and material requirements. Combined with order dressing, they get the optimised route along with the specific production instructions for emissions by eliminating defective material, right the first time.”
“Collecting a lot of data together with smart analytics can offer a prediction of maintenance too,” Mr. Schober continued. “Producers can change parts including anodes right on the spot. They don’t waste money by replacing parts that have not reached the end of their live cycle nor do they risk production stops or quality issues by worn out parts. This increase of productivity has a significant impact on the sustainability of production.”
Whilst technological innovations will be important as the aluminium industry moves into the future, Mr. Schober stated that “… experienced human operators still make most critical production decisions. These operators launch fully automated procedures that have a predefined mostly rule-based non-adaptive behaviour. If this automation behaviour needs adaption, it will require ‘reprograming’ or ‘re-configuring.’ Unfortunately, production conditions evolve, requiring regular adaptions. This adaptability is one of the main challenges for the next generation
of Production Management Systems (PMS) solutions. We will need production automation that will be able to self-adapt its behaviour to changing production conditions. To this effect, PSI Metals is taking the lead in finding the solution to this current and futurist challenge and deeply involved in research projects.”
Among on-going research projects cited by Mr. Schober, some focused on the future of PMS automation; decarbonisation and CO2 tracking; optimising efficient energy scheduling to energy availability; and online heat scheduler and cast house scheduler for the upstream production and order scheduler for the downstream production.
RIA Cast House
“RIA Cast House Engineering (RIA) provides rail-mounted precision cast house-proven charging and skimming machines for aluminium cast houses worldwide,” said James Tomkinson, Sales and Marketing Manager at RIA Cast House Engineering GmbH. “The design and development of all RIA machines take reliability, durability, maintenance, and occupational safety into account. RIA has supplied over seventy-five furnace charging and skimming machines, all rail-mounted and capable of charging up to 30 metric tonnes in less than 90 seconds or skimming a furnace faster than a traditional forklift truck or wheeled furnace tending vehicle, but with more repeatable results and without damaging the refractory lining.”
He indicated that key customers of RIA include Hydro, Constellium, Kaiser, and Matalco, among others: “Several clients have multiple machines in the same cast house or across multiple sites and territories. One client alone has implemented more than thirty RIA machines in ten different countries.”
“In recent years, in conjunction with our exclusive partner Fioscope GmbH, RIA added the innovative capability of AI [Artificial Intelligence] smart camera-based decision making to our machines to offer fully autonomous operation and therefore removing the requirement to have operators on or even near our machines,” noted Mr. Tomkinson. “RIA’s Managing Director, Michael Rockstroh, also became Managing Director of Fioscope GmbH in February 2022, helping to drive the continuous development of RIA’s AI enabled autonomous
machines and assuring our growing customer base that RIA equipment is not only suitable for today, but also tomorrow and beyond.”
Mr. Tomkinson stated that “in typical operations, melting and holding furnaces are skimmed by either a wheeled vehicle or a rail mounted machine. Typically, both are driven by an operator present on board the machine to give them a direct view in to the furnace to locate the dross to skim from the melt surface.”
“The above process presents two main concerns for the aluminium cast house,” he continued. “The first concern being that operators have to be on board the machine, exposed to the heat and potential dangers of molten aluminium. Secondly, operator-driven wheeled vehicles typically have long skim booms that move with little control or precision when skimming the furnace. Often, this causes unnecessary damage to the refractory lining within the furnace leading to the earlier replacement of refractory walls and the furnace sill and lintel. Not only does this incur the cost of replacing the refractory lining more frequently, but also the lost production time with the furnace being down to conduct the necessary repairs, often for several weeks.”
He said that Fioscope’s air-cooled smart cameras that RIA has installed on board its skimming machines help to manage the radiant heat from furnaces, thus reducing the exposure to operators.
“Camera images are relayed to the operator pulpit and the operator can watch the skimming cycle from a safe location, away from the furnace,” Mr. Tomkinson stated.
“Through precise position measurement and control, it is possible to follow a predetermined skimming pattern, lane-by-lane, to remove the dross from the furnace, without contacting or damaging the refractory nor the need for an operator to be onboard the machine. However, the machine will skim the entire surface of the bath regardless of the location of the dross, or if the dross moves into an already clean and previously skimmed lane, the machine was effectively blind and would not react. The solution was to install smart cameras on the skimming machine that have a view of the bath surface. The cameras identify the difference between dross and a clean surface and drive the skim blade to the location of the dross and remove it from the furnace.”
Mr. Tomkinson summarised the benefits of
using this technology: “Smart cameras reduce unnecessary door openings, shortening cycles, and saving energy. These systems can increase safety and potentially avert accidents. Smart cameras also allow the melt cycle to be optimised, ensuring charging can take place safely, at the first opportunity. Furnace monitoring systems allow playback, trouble-shooting and diagnostics. It is believed that in the future all new furnaces will incorporate in-furnace cameras.”
“Aluminium companies need to adapt to an ever-changing environment,” stated Steffen Zendler, Europe, the Middle East and Africa (EMEA) Strategy and Marketing Manager – Heavy Industry at Rockwell Automation. “Current market conditions are characterised by excess production capacity, oversupply of raw materials, constantly changing raw material and energy costs, growing demand for new products, and evolving workforce demographics.”
“Considering that energy costs can account for up to 50% of costs associated with aluminium production, the global energy crisis contributes to the challenges for this industry,” Mr. Zendler noted. “Rockwell Automation’s powered end-to-end systems integration and scalable analytics facilitate better decision-making thanks to both supply chain and smelter-to-market visibility. The Connected Enterprise provides real-time
guidance on the digital way forward, whilst prioritising secure networks and workforce safety simultaneously, creating an infrastructure that enables operators to reduce downtime and maximise efficiency, with the help of predictive and prescriptive maintenance across processes and infrastructure.”
“Smart data analytics and insights help to improve process efficiencies, quality of end products, and timely management of supply chains,” he continued. “In the context of smelter digitalisation, smart sensor technology enables the tracking of materials, manpower, consumables, and emissions. Further, the application of the relevant layers of technology such as digital twins and simulation models helps drive operational efficiency, better throughput and higher profitability by managing validation costs using simulation and allowing for the testing of engineering ideas before implementation.”
Mr. Zendler stated that “artificial intelligence and machine learning offerings facilitate the seamless transfer of knowledge and skills, where augmented reality and virtual reality are useful in improving collaboration across different project locations and making operations safer, where new talent and workers are onboarded.”
Rockwell Automation is engaged in a number of efforts to streamline production in the aluminium industry.
“Our solutions for the metals and mining
industries employ data capture, integration and processing capabilities of the Connected Enterprise, leveraging analytics for better and faster decision-making,” explained Mr. Zendler. “Streamlining production in the aluminium industry is one of the many benefits of the Connected Enterprise. A connected aluminium smelter converges plant-level and enterprise networks, securely connecting people, processes, and technologies.”
“The information revolution has created a huge opportunity for metals companies to fundamentally change their business – to become more productive, agile, profitable and safe,” he continued. “Across the globe, Rockwell Automation technologies are focused on driving effective outcomes with solutions built for optimisation, by helping aluminium producers harness their manufacturing and production data to improve operations and influence business decisions.”
Rockwell Automation has operations, Mr. Zendler stated, in 44 manufacturing units across 11 countries on four continents, with a multi-cultural workforce of approximately 36,000 across the globe.
He cited a few challenges facing the aluminium industry in the years ahead: “The need to upskill new workers against the backdrop of retiring workforce and the advent of new technology offerings; increased capital and operational costs; limited access to resources or pricing instability (raw material, water, energy); market volatility as a new normal (energy and other commodities pricing); and the need for all industries to transition to sustainable models.”
To meet some of these challenges, Mr. Zendler stated that “Rockwell Automation is committed to working with aluminium companies, and the wider metals industry, helping them achieve their business and sustainability objectives, bringing the Connected Enterprise to life. With this integrated and holistic solution, producers can gain situational awareness of single or several operations from any location; deep contextual insights across the value chain, including energy, emissions, and asset efficiency; the ability to benchmark operations from different sites for operational improvement; and realtime operational plant-control systems whilst providing an enhanced user experience.” �
Aluminium companies need to adapt to an ever-changing environment,” stated Steffen Zendler
Equibras is an equipment supplier for the aluminium industry for more than 20 years. With over 5,000 products distributed in nearly 30 aluminium plants worldwide, the company is the world leader in equipment for the potlining of the electrolysis cells.
SECTORS OF ACTIVITY
Various industrial sectors, including the aluminium sector.
CONTACT US TODAY.
PRODUCTS
Turnkey tools and equipment for:
• Potlining of electrolysis cells
• Cells & superstructures repair
• Lifting and handling
• Safety and access
• Customized equipment
• Heating SERVICES
• Equipment supply
• Equipment rental
• Design, optimization and manufacturing
• Technical consultation for enigneering firm
YEARS
In July 2022, PSI Metals signed a strategic partnership with Seresco, a Spanish software company. Within this partnership, Seresco will support the distribution of the PSImetals products and will launch them into new local markets.
Following months of roundtable discussion, the partnership was announced in September, 2022.
When it comes to adoption of new digital transformation technologies, the metals sector is cautious compared to other industries. However, in recent years, the trend has begun to pick up. The metals industry is witnessing significant changes in digitalisation and process automation with widespread applications covering the entire production chain. This strategic deal could accelerate the digital transformation journey of producers in both global and underserved local markets.
PSI Metals is a German-based, globally operated company and the leading provider of production management software for the metals industry. Their unique solutions cover the whole production flow from Supply Chain Management, Advance Planning & Scheduling, Manufacturing Execution System, Quality Management to Logistics Management in an integrated but serviceoriented way.
“PSI Metals has remained the best choice of metals producers when deciding for solutions for automating their steel production process. However, we want to democratise our software solution both locally and globally by providing available options for all metals producers. This means that, once the Seresco team will be ramped up and trained, the customers will be able to choose either to acquire the solutions either from PSI Metals or from our partner company, Seresco,” says Thomas Quinet, Managing Director of PSI Metals.
Seresco and PSI Metals have a shared business culture that shows that the partnership between them will successfully yield results.
Seresco has been, amongst ofther, focusing on the metals business for some years and understands the technicalities in metals production generally and in software for metals production specifically. This is indeed critical to deliver added value to customer on the basis of PSImetals software.
According to Rubén Pérez Sobrino, Head of Business Development at Seresco: “Seresco wants to specialise in the steel sector, taking advantage of the functional knowledge it has acquired over the years. PSImetals is the solution we were looking for- a leader with a global presence that allows us to specialise and aspire to become a preferred supplier in those geographies where we operate.”
The partnership is a journey with many expectations. The two parties have already met to decide the next steps to follow in making the partnership a success. Some of these steps include Seresco setting up a center of excellence with the support of PSI Metals. This would include PSImetals Academy delivering trainings and certification programs to Seresco experts to enable them work on projects independently in the future. Metal producers face enormous challenges in digitalising and decarbonising their steel production while reducing production costs. They need software to increase their product quality and volume, improve efficiency, reduce energy consumption while minimising CO2 emissions. PSImetals solutions will help steel makers to achieve their digitalisation and decarbonisation targets. They need close support and collaboration to navigate the digital transformation journey.
To support metal producers in their
digital transformation and decarbonisation journey, it is important to have experts who have experience in the metals business and understand the complexities that is metals production. Seresco is a multilingual company with the language capacity to support and provide better service within the Spanish and French markets specifically and the global markets generally.
“Seresco has a reputation for their highly professional commitment in the industry. To this end, PSI Metals will support Seresco to build a center of excellence where they will constantly have PSImetals resources, including trainings from our Academy to serve and satisfy the demands of PSI Metals global customers,” adds Thomas.
The PSImetals Academy supports project implementation by offering various courses that enable customer to understand and use PSImetals products in an optimal way. “PSImetals Academy will onboard Seresco by giving them trainings and certification courses on both associate and professional levels. On the associate level, Seresco will be exposed to the PSImetals solutions as a whole, which will allow them to be key users of the PSImetals software. After that, they will proceed with the professional level where they will collaborate on PSI Metals projects and master how to launch them,” adds Roger Becker, Head of Training Certification at PSI Metals, Berlin.
The partnership emphasises PSI Metals’ commitment to providing customers with state-of-the-art and sustainable production management solutions. They want to strategically adapt and grow in local and global markets while strengthening their resilience to support their customers. �
With so much ongoing buzz around AIbased solutions in business planning, what can we expect to change in the coming years for the aluminum industry? More importantly, how will we be required to change with it?
By 2023, organizations across all sectors are predicted to invest close to $6.8 trillion in digitalization efforts. The initial reason for this push is quite obvious: automation of business operations leads to higher accuracy and saves time. Zeroing in on the nuance of these motivations, however, can tell us a much more detailed story–one that can help us discern effective targets to aim for when undergoing the digital transformation process.
Because businesses are made up of many variables, ensuring that any upgrades you make are worth the investment requires consideration of more than just the end result. To discover what will work best for your manufacturing business, there are a few questions that will help shed light on some of the overall aspirations that drive the digitalization mindset as well as a few of the biggest foreseeable challenges that can hinder maximum potential. By exploring these facets of such sizable business decisions, gauging where your company lies in the process will become clearer. This assures your organization can take confident and decisive next steps.
The digital transformation journey is already underway in countless businesses around the world. It is on even many more executives’ minds who, for many valid reasons, have yet to execute their plans to embrace
digitalization. In fact, 72% of over 1,300 manufacturing executives that were surveyed by BCG in 2022 have said they consider advanced analytics to be more important now compared to how they felt just three years prior. With continually increasing uncertainty, this change in outlook has happened–and continues to happen–at an extraordinary pace.
Depending on the size and maturity of your company, you have probably considered going digital because operations have simply become too complicated and dynamic to sustain them manually. Perhaps they have even started to occur at a larger scale. Such cases necessitate technological solutions, not just for profit, but simply to keep the motor running.
Others may find that their goals are standing just out of reach and just need to find the right stepping stool. This is true even for many who have already started their digital journey. McKinsey’s latest Global Survey provides us with a reliable framework for where attention in the transformation process should be given. The greatest loss of maximum potential benefits when undergoing a digital transformation occurs most often in the implementation stage. Understandably, fear of making costly mistakes is why many are still seeking useful guidelines to achieve transformation and optimize value creation across the enterprise.
In addition to these motivations, another major impetus for digitalization is harnessing the power to face unpredictability. Businesses have had to make peace with the fact that supply chain disruptions aren’t ending any
time soon. For example, among some of the top supply chain threats manufacturers are expected to face in 2022 are demand unpredictability and supplier risks and delays. To address the difficulties that companies are facing with regard to planning and forecasting, many have begun to implement AI-based solutions for these reasons alone.
The Case of Heiniger
Heiniger, a leading metalworking manufacturer focused on high-quality animal sheering equipment, faced a challenge in its sales planning due to scattered data and cumbersome manual, repetitive processes. In the span of a mere eight weeks, Heiniger implemented a mobile-based data integration solution that both digitized its sales planning efforts as well as allowed multiple departments to perform self-service analysis with instant mobile access to customer data any time of day or night. Their seamless sales planning process has greatly reduced time while supporting improved profitability.
What’s on your digital transformation checklist (so far)?
Clearly, optimization of time management and accuracy of data is one of the main driving forces that has drawn so many towards automated solutions. Some may strive for more robust collaboration potential between departments by improving lines of communication between decision makers and those with necessary information. Other times, businesses may prioritize flexibility in decision-making when daily fluctuations influence their large-scale operations. These
motivations are inextricably linked to each other, particularly in optimizing the ability to collaborate with accurate, real-time data. From this particular angle, we can observe how taking an integrated approach to building your digital transformation checklist can be beneficial in the search for a solution that will lift your company’s operations and improve business performance.
Whatever may be sitting on your checklist as of today, ask yourself how these goals coincide with each other. In doing so, you may discover that the digitalization process does not necessarily require dramatically expanding your resources. Quite the contrary, it may even unveil new ways of condensing existing systems or processes. The advantage to this method is, of course, augmenting the power of the resources you already have without having to trade valuable, straightforward usability for those who will be transforming alongside the company itself.
Will your solution be ‘onesize-fits-all’ or something more personalized?
Unique circumstances come with unique demands. In addition to the external factors that influence the day-to-day operations of your business–think supply chain disruptions, for example–there are just as many internal factors that should be considered as you are making the digital leap. Your industry, type of workplace–whether it is a traditional office space, completely remote, or more often than not, a hybrid of the two–and all the personalities and skill sets that make up your workforce are some of the key determinants in deciding how best to move forward in the digital transformation journey.
Consider the success of Steinert, a leading mechanical engineering firm in magnet and sensor sorting solutions. As the world’s only full-range provider of sorting and separation technologies, they needed to undertake a more granular search for ways to accommodate business growth. Recognizing where operations became increasingly more complex, they set out for a new method of monitoring a wide range of long-term projects that require close, accurate supervision. With the implementation of a new, integrated solution that can draw from a centralized
pool of data, Steinert’s management accountant can now adapt to new business developments swiftly and independently. By seeking to replace unnecessary complexity with an easy-to-use integrated system, they were also able to increase the speed of their global reporting by five times.
Companies that are diverse in functionality and require vast amounts of flexibility may need to look into prioritizing accessibility of information that can, in turn, enhance both the output and the experience of its workers. Steinart’s example illustrates how taking a personal inventory and developing deeper awareness of your unique situation can lead to simplicity without sacrificing sophistication. One-size-fits-all models for automated solutions can absolutely serve an adequate role in business enhancement and should be considered as part of the transformation process. Once your company is enabled by the gains it has already made, then it may be time to reassess if more fine-tuned updates are necessary to meet your needs.
For those that have already waded into the waters of technological advancement and have found themselves treading in the deep end, it is important to reevaluate the perspectives that have informed their transformation journey. While this sounds like you may want to know what is going on at the top, oftentimes it is the opposite. You need to look at your processes from the ground up.
A common stumbling block businesses encounter in the digital transformation process is prioritizing power over implementation. To reiterate, McKinsey’s Global Survey has indicated that the implementation phase is where most of the maximum potential benefit is lost. Without understanding the human cost of implementation, e.g. the time and effort required of all workers who will be using the new systems, there will be additional roadblocks that delay or minimize success. The carrot dangling in front of us can block what is up ahead if we don’t take a holistic approach to systemic change.
If companies are singularly focused on day-to-day output as opposed to the big picture, they may discover not long after implementation that the new tools are not as intuitive as they thought for their users. This
means that for any company-wide changes, it is important to prioritize user-friendly options that are, at the baseline, easy to navigate and learn. Not only will this approach lead to the immediate gains that one expects with automated processes, but ensure smooth business continuity during the transformation.
At times it can be overwhelming not only to parse out what solutions are out there, but also which of the many options offer the greatest value-add Sometimes it is important to take a step back and remind ourselves that planning for something as wide-ranging as a complete digital transformation takes time and requires patience. Discussing is progress. Research is progress.
The results from the aforementioned McKinsey Global Survey reflect this truth very well. It reports that companies experience success in correlation with the number of actions that comprised its transformation process, not by following a specific subset of actions. Such a finding should empower executives to take any plans they have for change out of storage and bring them to the forefront of their business planning. By extrapolating personal insights from this list of questions, you can feel confident exploring new terrain in your digital transformation journey, with no hiking gear required.
Orienting your company’s mindset towards digital transformation through even the smallest steps you can take will bring you closer towards adaptable and scalable processes that simply your business complexities. The hype and buzz around digital transformation may try to push you in specific directions. Delve into a personal inventory of what is benefiting your company today and what will add value tomorrow. Those answers will be what successfully advances your digital transformation journey.
Christian Ritter is the Regional Vice President, Channel for Jedox, Inc., an awardwinning provider of Enterprise Performance Management solutions. With more than 20 years in supply chain and technology, he brings a unique expertise to helping organizations understand how to achieve a culture of decisiveness and confidence and outperform expectations again and again. � http://www.jedox.com