

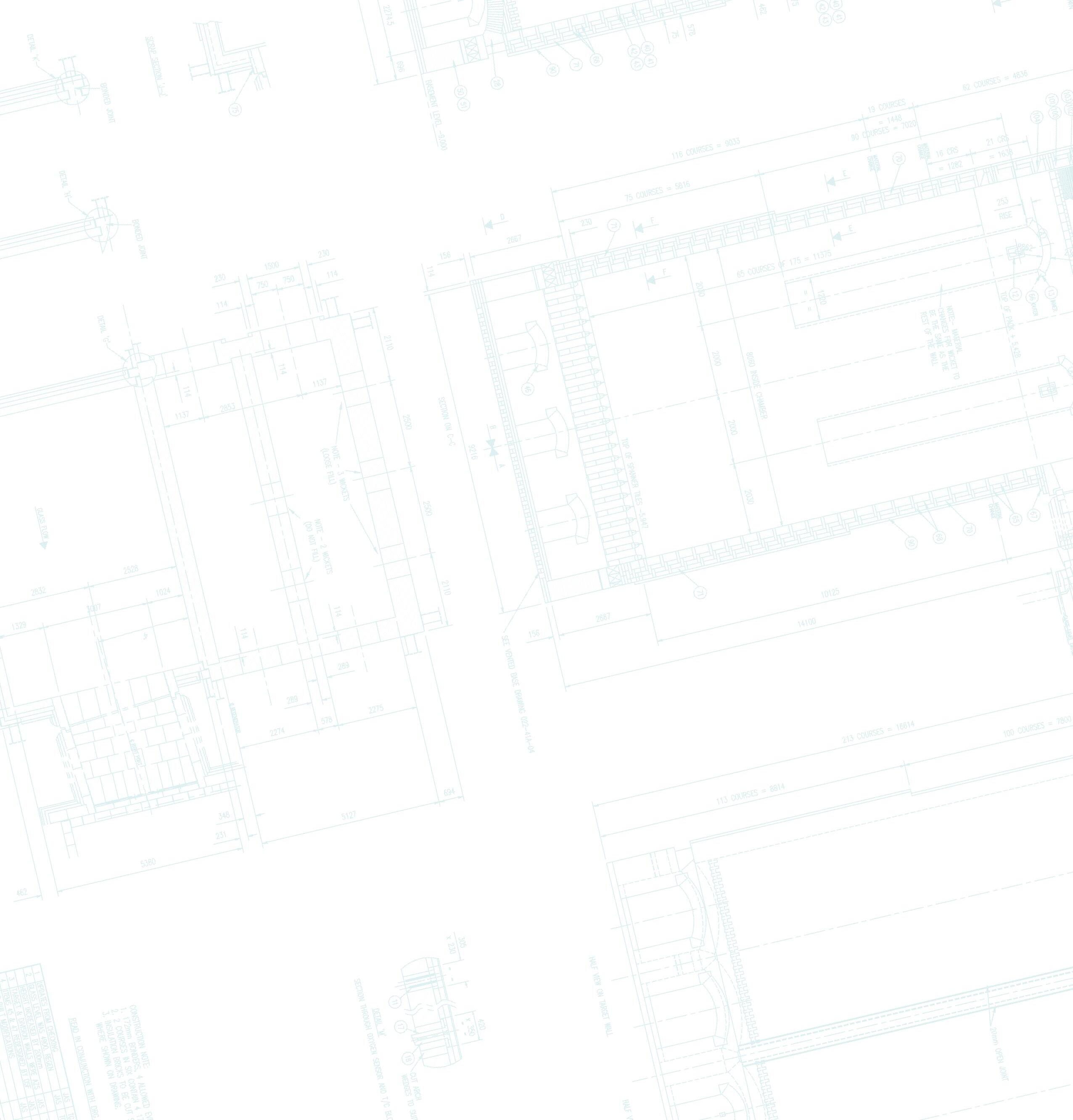
Metpump ® will get you back in operation faster.
Complete MetPump® refractory sets can be delivered in weeks--not months. We’ll get you back in operation faster, reduce install costs and downtime and improve the thermal e ciency of your new furnace. With service life equal or greater than fused cast products in non glass contact areas.
MetPump® colloidal silica refractories are available in precast, prefired, ready to use custom-engineered shapes. MetPump®
conforms to any geometry, allowing consolidation of multiple blocks into single large shapes for faster, safer install. While virtually eliminating all joints, improving furnace operation and reducing your energy costs and carbon footprint.
Delivering the most total value in the industry for over 25 years, MetPump® is the next gen refractory solution. Let us prove it to you.
Tel:
Production
Production:
Sales
Tel:
5 Life of a Furnace News
7 “In-Furnace Thermal Imaging for Hot Refractory Inspection”
11 The rock and roll of continuous furnace aluminium log homogenisation monitoring
17 5 experts on advantages and applications of roller hearth systems
24 Global Furnaces News
26 Environmentally friendly heating without compromise
28 Greener Furnaces News
30 Environmentally friendlier heat: Innnovating the Future of Green Steel
It is with great pleasure that I welcome you to the March issue of Furnaces International magazine.
As we start in this Quarter, I am thrilled to announce that every issue of our publication will now be delivered in both digital and printed formats, catering to the diverse preferences of our international readership.
In this edition, we continue our tradition of delivering a comprehensive digest of global news, events, and statistics, providing you with valuable insights into the ever-evolving landscape of the furnace industry. From market trends to technological advancements, the team has curated a selection of articles to keep you informed and engaged.
In addition to our regular features, this issue takes a deeper look into the technical aspects of furnace technology, with articles exploring the latest innovations and best practices in the field.
Whether you’re a seasoned industry professional or a newcomer seeking to expand your knowledge, we hope you’ll find valuable insights and practical solutions to enhance your understanding and expertise.
Nadine Bloxsome, Editor, Furnaces International, nadinebloxsome@quartzltd.comGRANCO CLARK’S ALL NEW Non-Hydraulic System utilizes servo actuators and pneumatics instead of hydraulics. This includes the Log Lift, Log Pusher, Pullers, Stretchers, Hot Saw, ECS Saw and many others.
Our Hydraulic Free Systems are quiet, quick, powerful and boast incredible new features.
Now that you’re energized, let’s talk! 1-800-918-2600
GAIN INSIGHTS INTO THE THERMAL PROCESSES IN A GLASS MELT TANK WITH ACCURATE REAL-TIME TEMPERATURE MEASUREMENTS.
A unique service for the thermal optimisation of furnaces,the In-Furnace
Thermal Glass Survey produces real-time and recorded images for analysis, supplementing traditional refractory inspections.
A SURVEY HELPS TO:
Improve productivity with optimised pull rates
Increase thermal and combustion efficiency
Lower fuel costs
Protect the refractory from damage
Extend campaign life
Optimise flame pattern to reduce energy consumption
Ensure emissions compliance
Optimised for measuring high temperatures between 1000 to 1800°C (1832 to 3272°F), the NIR-B Glass thermal imager creates detailed and live highresolution images from within the furnace. Dedicated image processing software ensures accurate data analysis. The Lancom 4 portable multi-gas analyser measures up to eight flue gases for the optimisation of combustion and emissions processes.
WWW.AMETEK-LAND.COM | LAND.ENQUIRY@AMETEK.COM
AMETEK Land announces solutions designed to help the steel industry meet global decarbonisation challenges with a range of solutions.
With the steel industry responsible for approximately 7% of global man-made CO 2 emissions, finding a way to meet the ongoing demand for steel while reducing and eventually eliminating carbon emissions, is a major challenge.
AMETEK Land offers steelmakers several temperature monitoring solutions, and the technology, to meet their challenges when transitioning to more sustainable methods of steelmaking, supporting decarbonisation in several ways.
A specially designed solution, the Slag Detection System (SDS) from LAND, leverages the capabilities of mid-wavelength thermal imaging to help deliver improved yields, higher quality steel, and reduce costly downstream processing for EAF steelmaking operations. It is specially designed to withstand the harsh conditions of continuous operation in a steel plant, with minimal maintenance requirements.
Manfred Hayk, Head of Product Management at AMETEK Land, said: “Process parameters are changing throughout the industry in a bid to bring down carbon emissions. We know that there is no single solution to carbon reduction in steelmaking. However, several changes to existing practices can each make a significant contribution to decarbonisation in
the industry.
“We offer accurate, reliable, proven solutions for temperature measurements that support these changes. For example, switching to thermal imagers rather than dip thermocouples helps support decarbonisation efforts by reducing the use of consumables, and delivers more information to support process efficiency.”
A new application note looks at all these processes, and explains the importance of accurate temperature monitoring within each of them, along with expert advice on the best method to use.
Rick Lazarou, Founder and Chairman of Axaeon AG (Axaeon), and Mr. Guanghui Lang, Chairman of Sunstone Development Co, Ltd. (Sunstone), have signed a term sheet initiating a joint venture with the aim of commercialising Lazar Continuous Carbon Baking Furnace (CCBF) technology. Under this collaboration, Axaeon and Sunstone will join forces to
build a facility in China and introduce the Lazar CCBF to the market.
Developed by Rick Lazarou and the team at Lazar Anode Technologies, the Lazar CCBF represents a major improvement in carbon anode baking technology. By addressing the pressing need for energy efficiency and emissions reduction in anode production for aluminum smelting, Lazar’s CCBF is expected to redefine industry standards.
The CCBF technology has undergone extensive process testing and optimisation at a demonstration facility in Hawesville, Kentucky, USA. The result is a process that reduces fossil fuel consumption by eliminating the wasteful cycles of refractory heating and cooling necessary in existing baking furnaces. Consequently, a carbon product is achieved with less impact on the environment - a reduced carbon footprint from lower CO₂ emissions.
Commenting on the partnership,
Mr. Lazarou expressed his enthusiasm, stating, “This collaboration represents a milestone in our journey towards sustainable primary manufacturing. Sectors reliant on carbon products such as those used in aluminum smelting, lithium battery manufacture for electric vehicles, and the primary steel industry are potential applications of the Lazar CCBF technology. Our joint venture with Sunstone has the potential to revolutionise carbon production in these primary industries and set new standards for efficiency and environmental responsibility.”
This article by Philippe Kerbois* and Neil Simpson**, is based on a paper presented by Neil at the 2023 IRE Conference in Sheffield. The IRE conference paper covered the application in refractory in Steel and Cement
Development and Chronology of the Near Infra-Red Borescope [NIR-B]
The Near Infra-Red Borescope [NIR-B] originated from the efforts of AMETEK Land’s Director of Technology, Peter Droegmoeller, more than a decade ago. In 2012, the inaugural NIR installation took place in a Steel Reheat Furnace, followed by the first installation in a Glass Furnace in 2013. In 2014, Neil Simpson established Simpson Combustion & Energy Ltd. Subsequent years witnessed the collaboration between AMETEK Land and Simpson C&E, with notable achievements, such as the Glass Focus
Innovation Award in 2017.
The year 2018 marked the installation of the 50th NIR-B Glass unit, while 2019 saw the launch of the NIR-B thermal survey as a new service, accompanied by a published patent application. The unveiling of the High Definition 2k with dedicated NIR-B IMAGEPro and IMAGEPro Glass occurred in 2020. By 2021, the installation of over 100 NIR-B units in glass, some featuring two per furnace, underscored the technology’s widespread adoption. Recent years have
2017 – Demonstration of Cross-Fired Furnace Optimisation for Unprecedented Pull Records.
The utilisation of in-furnace real-time thermal imaging showcased the potential for optimising the thermal profile of a glass melt tank to achieve energy reduction and increased pull or yield on an unrestrained furnace. Even on a restricted furnace, pull recovery was possible. Through the use of dedicated filter palettes to emphasise peak flame intensity, a correlation was established with NOx formation, offering the prospect of integration into NOx/NH3 reduction strategies. Maintenance-wise, the approach also unveiled opportunities to pinpoint areas requiring sealing or over-coating on weak/thin refractory materials. Moreover, safeguarding furnace assets was attainable with over- and under-temperature alarms, enabling the identification of refractory regenerator restrictions before blockage/deterioration and the detection of NaOH condensation.
*Global Industry Manager –Glass AMETEK Land
**Consultant – Simpson Combustion & Energy Ltd
2018 – Reduction of NOx Emissions
witnessed the NIR B technology in Aluminium reverb and cement applications.
When discussing the unexpected temperature profile on a glass furnace, the customer commented: “Neil, Infra-Red does not lie! We have just never been able to see it before!”. The reality is that this is still just the start of a journey as we start to diagnose thermal data in terms of operation, emissions and refractory inspection.
Building upon the success of the cross-fired furnace optimisation, a case study on a medium-sized end-fired regenerative furnace validated previous findings and emphasised the influence of the thermal profile “engine/pump” on batch patterns. The survey revealed a previously undiscovered regenerator blockage, highlighting the potential to employ target wall temperature modulation to adjust reversal times automatically for potential reductions in energy consumption, emissions, and regenerator protection.
The initial demonstration aimed to identify technologies for reducing NOx to permissible levels, emphasising the ability to achieve compliance by optimising existing equipment through the appropriate filter palette for thermal images, thus avoiding additional capital expenses for the glass manufacturer.
In part of the original sales process, a demonstration thermal imaging camera was inserted into the peephole closest to the proposed camera hole location. The survey was a logical next step where, like a traditional endoscopy, the camera is installed in every peephole.
2020 – Supporting Hot and Cold Furnace Repairs.
This showed how the thermal camera can be used to identify the parts requiring a small repair versus major intervention. Can be used in combination with ceramic welding to ensure the weld is positioned correctly. In addition, the thermal camera can support the cooldown if a refractory is being re-utilised, and the heat-up in all cases.
2021 – In-Furnace Thermal Imaging Survey of a Float Furnace for Combustion Optimisation.
A six-port cross-fired float furnace had a problem with NOx and was out of compliance. The author had used traditional methods without success, so a five-day thermal survey was performed and included for the first time the survey of the regenerators. The camera identified a previously unseen refractory chimney that allowed the combustion air to short-circuit and create a high excess O2 and resulting NOx. Alternative burner nozzle designs were evaluated as part of the NOx reduction.
Since the times of the first Siemens regenerative furnace and patent, the furnace reversals have been approximately every 20minutes. The majority of the end-fired furnaces today operate with 20-minute reveals irrespective of the furnace pull rate or load. By utilising the AMETEK Land NIR-B and the CelSian O2/CO lasers, the paper demonstrated how the furnace reversal firing time and purge can be optimised and potentially automated to meet the changes in furnace operation.
Additional versions of these papers have been presented at Hotbels KY, Glassman, AFGM, and Furnace Solutions. Papers have also been presented at Combustion and Decarbonisation conferences.
While the preceding all relate to glass, the same techniques are replicable in lower-temperature furnace applications.
Melting Furnaces, if the furnace is well-insulated and has a monolithic seal coat, it is often very difficult to see where a hole or “rat hole” is developing. At 1388oC and below, the NaOH in the furnace atmosphere can condense. If it condenses on a silica crown (typical construction in soda lime glass applications), it will corrode the silica and form a hole. The further into the hole, the colder the hole becomes, since it is now closer to the cold face, so there is more potential for the hole to grow. Rarely is the initial path of the hole the shortest route, but the path of least resistance through joints. The first thing that most B&F operators realise is when there is a flame or “sting out” through the cold face insulation. At this stage, it often requires an “archaeological dig” to remove the layers of insulation to find the source or start of the hole. From a refractory maintenance perspective, it is typically easier to fix a small hole than a large one. By utilising a survey camera (figure 1), it is possible to identify where the hole is originating.
At Allied Glass in Leeds in November 2018, there was a significant refractory failure in an end-fired furnace. Whilst a thermal camera was already permanently installed in the furnace, the damage was visible to the “naked eye”.
Figure 2, taken the day before the welding, is from the fixed location in the bridge wall above the throat. By utilising the 2* digital zoom function, the damage to the port end wall is clearly visible. �
The ceramic welding was successful and enabled the furnace to continue to operate for several years.
At a separate Allied site, the furnace was studied in 2018 and 2019, and the furnace cool-down was the subject of the 2020 Glass Problems paper. Figure 4 shows simultaneous images from a static, permanently installed NIR-B in combination with a survey instrument.
At a previous cold repair, the breast wall had been replaced and was in sufficiently good condition to be used after the repair. The NIR-B was installed for several years and was used as part of the furnace cooldown to monitor the refractory temperature and avoid thermal shock.
Figure 5 is during a reversal and partway through the furnace drain. The blue lines highlight the glass level. The wear on the glass contact “Soldier blocks” is clearly evident, with over-coating repair visible.
A little over 28 hours later is a sad moment for a combustion guy since it is THE last figure 6 with the port flame! Immediately downstream of the port flame, below the Region off Interest 1, is a pre-mix burner which was used for the balance of the controlled cooldown. An unusual sight is to see the barrier boost electrodes at the base of the image.
During the presentation at the 2023 Annual Conference in Sheffield, additional slides were shown, which showed recordings and images at 12-hour intervals up to 60 hours beyond the initial image.
While AMETEK land would state that the instrument was below the instrument’s calibrated range, the information is significantly more than would be seen in the visual spectrum. The relevance of this statement is more for the resulting furnace heat-up following the repair/rebuild. The camera was used as part of the heat-up, and while Allied permitted the use of the images, the authors felt that it would reveal confidential furnace design information.
As an alternative, and part of the 2023 Glass Problems Conference, a Long-Wave
Infra-Red [LWIR] camera was used to measure the Rider Arch temperature at the base of the regenerators. Instruments ranging from 0-500 and 500-1000°C are available for inspections and heat-up of low-temperature furnace applications using the peepholes for access. It is proposed that this could be the topic of a future Conference and/or Journal article.
For more information on the AMETEK Ltry-product-managers or contact us at land.enquiry@ametek.com
After casting, aluminium logs/billets undergo a homogenising heat treatment process to ensure uniform distribution of the alloying elements such as Zn, Cu, or Mg2Si and Fe within the structure of the log. This involves heating the log at a controlled rate, soaking at temperature (typically 480 °C to 540 °C / 896 °F to 1004 °F ) for a specific period of time,
and cooling at a specific rate to allow the precipitating elements to become more evenly distributed throughout the material. Each phase of the heat treatment process is temperature critical. An accurate means of monitoring the log internal temperature throughout the whole furnace cycle is, therefore, important to the success of the homogenisation process, material properties and efficiency of the furnace heat treat operation.
When setting furnace conditions for new production batches, monitoring the actual product temperature of the logs throughout the furnace is vital to maximise production throughput, while ensuring the correct metallurgical structure of the product.
Measurement of the product temperature is generally not considered a prob-
lem when the operation is conducted in a batch furnace. In such case thermocouples can be run from the static logs, loaded in the furnace, to an external data logger without significant issues.
However, when homogenising is conducted in a continuous process, such as a walking beam furnace, monitoring the product temperature from a data logger external to the furnace is not possible because the logs generally travel in different directions as they enter, move through the hot zone, and exit the furnace. Also, the logs can slowly rotate due to the action of the walking beam. These factors make external monitoring with long trailing thermocouples impractical and even if possible, will not comply with every increasing safety requirement for technical plant operatives.
The solution is to use a ‘thru-process’ temperature monitoring system where a thermal barrier can be attached to the log protecting a data logger as it gathers temperature data from thermocouples set within the test product. In this way the product temperature profile can be accurately monitored as the test product travels through the process. Short thermocouples are safely contained within the thermal barrier, before running along pre-cut routing channels within the log, eliminating the risk of tangling or being caught during the log movement through the furnace (Figure 3).
The innovative cylindrical thermal barrier design is critical to the success of the temperature monitoring system. The diameter and length of the thermal barrier matches a machined gap at the end of the aluminium log so that loading the log, with the monitoring system attached, can be achieved as if a standard log. No height restriction challenges are faced and most importantly being cylindrical the system can rotate safely with the log as it is transferred through the walking beam furnace.
The PhoenixTM ‘thru-process’ monitoring system to accommodate the size restrictions of the homogenising processes and its long duration (up to 10 hrs) / high temperature (600 °C/1112 °F), employs a phased evaporation method of thermal protection. The data logger in encased in thermally insulated cylindrical water tank employing evaporating water as a phase
The
Furnaces International is an English language journal dedicated to the production of rnaces. Circulated each quarter in March, June, September and December to our database of over 20,000 readers across the Aluminium, Glass, Furnaces and Steel industries, Furnaces International contains a digest of global news, events, and statistics as well as more detailed technical articles, company and country pro les, and regular regional economic brie ngs.
The Furnaces International Buyers' Guide is the essential guide to rnace manufacturers and suppliers of rnace equipment and services to the industrial heating/process industry. Providing comprehensive company listings, product information and key contact details, the guide is published in December each year.
Packed with information on the rnaces industry and continually updated with news for professionals, rnaces-international.com also features special articles and interviews with leading industry gures.
A round-up of the top news stories is sent to more than 44,000 industry professionals every month. You can register online to receive the weekly newsletter and keep up-to-date with the latest news from across the rnaces manufacturing industry.
Sign up at
Aluminium International Today (AIT) is the leading bi-monthly English language journal dedicated to all sectors and regions of the international aluminium manufacturing and processing industry. Subscribe to the free weekly newsletter at aluminiumtoday.com
Glass International o ers readers the latest news from across the hollow, container, flat, and speciality glassmaking industry and is the o cial media partner for Glassman events. Subscribe to the free weekly newsletter at glass-international.com
Steel Times International is the key publication for the steel market, reporting on iron and steel making issues from all corners of the globe. Subscribe to the free weekly newsletter at steeltimesint.com
change medium. As the water reaches its boiling point it changes from liquid to gas (steam) as it evaporates but maintains the operating temperature of the logger at a safe 100 °C/212 °F so prolongs the period it can remain in the furnace. The thermal protection provided by the thermal barrier can be controlled by selecting the volume of the water tank and so water capacity (Litres).
The innovative barrier design must allow the steam to evaporate whilst not losing any water as the barrier rotates. For this type of system, it is also necessary for the data logger to be able to operate at 100°C as it is surrounded by boiling water (Figure 1. PhoenixTM TS57 Rotating Evaporative Water Barrier)
Having established the diameter range of the logs and the process parameters, the size of the system (length and diameter) can be calculated and a piece of the log equal to the length of the thermal barrier can be cut off and discarded. The end of the log is then machined to allow the thermal barrier to be secured directly with steel bolts. Alternatively, a custom mounting plate can be bolted to the end of the cut log to which the barrier can be efficiently fixed and removed from test to test (Figure 2). A slot is machined longitudinally along the log to guide the thermocouples to holes drilled at right angles to the correct measuring depth. This ensures that both the thermocouples and the ‘thru-process’ system are kept within the boundaries of the product (Figure 3).
When this is complete the thermocouples are positioned, the data logger reset and placed in the thermal barrier fixed to the test log, and the trial is ready to run.
Winning solution providing accurate process validation
Requiring a solution to allow process monitoring of their walking beam aluminium log homogenisation furnace Service Center Metals (SCM) located in Prince George, VA, USA approached PhoenixTM.
The resulting ‘thru-process’ temperature monitoring system provided to SCM is shown in Figure 2
Fitted with a RF telemetry module the data logger allowed live ‘Real Time’ product temperature to be monitored through the whole furnace. With such information SCM were able to validate mathematical models used to control the furnace and so optimise the efficiency of the entire homogenisation process.
Mr Calvin Wiggins, Quality Director at SCM, is quoted as saying “The ease of use of the PhoenixTM system allows us to do more surveys per year than compared to feeding thermocouple wires attached to a rigid log. However, its single best-selling point is improved safety by keeping tech’s away from the furnace entry door, where they would otherwise be feeding TC wires to the survey log as it advances through the furnace.”
PhoenixTM service with style!
Recently a TS57 system was successfully commissioned at the Finnish aluminium profile manufacturer Mäkelä Alu Oy who have been in business for over 80 years (https://makelaalu.fi/en/). The PhoenixTM system was ordered to help Mäkelä Alu Oy with the recycling of production scrap into low-emission aluminium billets. PhoenixTM prides itself with not only providing monitoring technology but ensuring that it is fit for purpose and
working to specification on site. Living up to the company tag line “where experience counts!” Managing Director Michael Taake took on the challenge of commissioning the system with the help of Scandinavian partner CalorMet .
Traveling from the PhoenixTM office in Bad Oeynhausen in Germany you would have thought the obvious transport choice would have been by plane. Micheal decided otherwise as he says “Why should I sit on a cramped plane and sleep in overcrowded hotels when I can explore and enjoy the beautiful nature of Scandinavia by motorbike?”. It took him around 2,000 km along the coast of Sweden and the forests of Finland to Mäkelä Alu Oy.
On site, Michael, together with CalorMet conducted a comprehensive briefing on the PhoenixTM temperature measurement system, and witnessed the system being used for the first thru-process temperature profile.
“It is fascinating that Mäkelä is always familiar with the latest technologies, implements improvements precisely and carries out their work in a sustainable and environmentally conscious way,” says Michael Taake.
Employing the ‘thru-process’ temperature monitoring solution from PhoenixTM major key casting plants have been able to measure the temperature profile of their aluminium log in all three stages of the homogenisation process. With such critical information it has been possible to minimise time in the soak zone to increase productivity and optimize fuel efficiency without compromising product quality. �
This article has been provided by Heat Treat Today
For more information, visit www.heattreattoday.com
Roller hearth furnaces are known as the work horses of the heat treating industry. Though they may be common, these furnaces still hold some surprises — namely, their diverse applications, potential to be fully automated, and long life span. Five industry leaders provide insight into the current furnace features and how to optimise them for annealing heat treat. As you read, notice the different emphases each expert addresses.
This type of furnace is highly customizable, and, as Tim Donofrio, VP of Sales at Can-Eng Furnaces International explains, knowing the application will determine furnace features.
What features do you offer on your roller hearth furnace for annealing various materials?
The following is based on roller hearth furnaces operating at or above 1400°F.
Annealing furnace features depend upon the material being processed and the metallurgical process being carried out. They can be provided with a wide variety of features for preheating, annealing, slow cooling, oxidizing or bluing and accelerated cooling.
Preheating features include direct or indirect heating applications, under air
or controlled atmospheres. Preheating in some cases requires features for burn-off of residual blanking fluids prior to entry into the critical anneal chamber and as such, the off-gas must be appropriately addressed.
Annealing can be a direct or indirect heating application, using natural gas, blended hydrogen/natural gas, and electrical energy sources. Process protective atmospheres include N2, Exothermic gas, Endothermic gas, N2 + H2, and H2. In some cases, process atmospheres must be carefully controlled and monitored to very low O2 PPM levels to ensure correct oxides are formed or, alternatively, a bright oxide-free finish is achieved, something very critical when annealing electrical steels for transformer core and motor annealing. Today we see a rise in
the use of roller hearth furnaces for the manufacture of transformer core and motor cores, processing electrical steels and amorphous metals. This is largely a result of the electrification of the world. Image of roller hearth below.
Post-annealing cooling and bluing are paramount to the process success. In most cases, cooling and soaking stages are provided through the integration of direct and indirect cooling methods that include air, water, and externally chilled atmospheres that can be directly injected into the furnace system and recirculated.
How is your rollerhearth system unique?
Roller hearth furnaces are the work horse of the industry; they are used for a variety of other heat treating applications. For example, roller hearth furnaces can
also be used for low temperature curing, tempering, and aluminum heat treating applications. These lower-temperature roller hearth furnaces do not operate above 1400°F and are built with different fabrication and refractory standards. Of course, additional high temperature applications include neutral hardening, case hardening, carbonitriding, isothermal, and spheroidizing annealing and normalising.
Can-Eng Furnaces International offers roller hearth annealing furnaces that meet the stringent demands of today’s manufacturers where safety, product quality, and equipment reliability are at the top of our engineers’ minds during design and development. Can-Eng has developed a strong user base that has benefited from design features that ensure tight temperature control and repeatable thermal profiles while also tightly controlling process atmospheres. This is achieved by integrating some of the best available heating and atmosphere technologies while being combined with state-of-the art automation and robotics to deliver the lowest cost of ownership processing systems to our clients.
What are best practices for training in-house operators on roller hearth annealing?
Our company promotes hands-on and classroom multi-level training of operators, maintenance staff, and engineers. This provides a complete and full understanding of the equipment and the opportunity to train within the company for future talent development.
What are the furnace’s operational advantages?
Can-Eng integrates operator-friendly features that contribute to the reduction in energy and atmosphere consumption while minimising the carbon footprint and emission levels. Combined with on-board system diagnostics, monitoring, and data collection, these allow for minimal operator involvement.
What is the most common heating method?
Today, the most common methods are both natural gas and electric. However, Can-Eng works to integrate features that provide our partners with the benefits of reusing waste heat sources such as flue gases within the system or facility to improve operating efficiencies.
What are the challenges in operating this type of furnace?
These (atmosphere control, maintenance, uptime, and temperature control) are all typical challenges that are addressed
in design. The key is to design flexibility, ease of use, and operator-friendly features to avoid problems in the future when the client wants to process different products in a different way.
Bob Brock, sales engineer at AFC-Holcroft, emphasizes the importance of training and maintenance to best operate the roller hearth system.
What Features Do You Offer on Your Roller Hearth Furnace for Annealing Various Materials?
Roller hearth furnaces are designed to provide greater uptime, ease of maintenance, and trouble-free operation and are always custom-designed to meet our clients’ specific processing requirements. Modular designs are available to accomplish basic heating, holding, and cooling segments but also to incorporate burnoff, cyclic spheroidizing, bluing, fast cooling, and blast cooling under controlled atmospheres ranging from Endothermic to Exothermic gases, nitrogen, hydrogen, and products of combustion. A broad range of material handling automation and control platforms providing total data monitoring, controlling, tracking, and
(Source: AFC-Holcroft)
acquisition capability are also offered. Image of AFC-Holcroft Annealing Roller Hearth Furnace
How is your roller hearth system unique?
AFC-Holcroft has designed, built, and commissioned hundreds of roller hearth furnaces for our clients around the world through our 100-plus years in business. The in-house engineering staff, manufacturing, and field support teams have extensive knowledge and experience with annealing, isothermal annealing, normalising, carburizing, and solution and aging processes for ferrous and non-ferrous applications. This expertise has well positioned us in the roller hearth furnace market.
What are best practices for training in-house operators on roller hearth annealing?
We use a two-step approach when training operators on our equipment. First, hands-on training provides the best opportunity to learn equipment operation, startup and shutdown procedures, as well as maintenance tasks. Second, we follow up hands-on training with classroom discussions to further the operator’s knowledge of equipment and the use of our operating manual. Our twostep approach arms our client operational team with the confidence and knowledge they need to be successful from day one.
What are the furnace’s operational advantages?
Roller hearth furnaces are designed and built with longevity and uptime in mind. From our integrated preventative maintenance reminders, robust construc-
tion, and user-friendly controls, it’s not uncommon to see our equipment still in operation for 50 years or longer.
What Is the Most Common Heating Method?
Natural gas continues to be the predominate heating source in North America, although we have seen an increased interest for alternate heating sources like electric, hydrogen, and bio over the last several years. We anticipate this trend to continue as companies invest in minimising their carbon footprint, and can provide clients with carbon footprint analysis and operational costs on our equipment.
What are the challenges in operating this type of furnace?
Routine equipment maintenance is key to operational uptime. AFC-Holcroft offers a wide range of preventative maintenance programs for our clients. The services can
(Source: AFC-Holcroft)
be customised to include hot and cold inspections, thermal imaging, burner tuning, and equipment optimisation analysis.
Given that the roller hearth furnace is a continuous system, understanding how the system works and operating at the correct, consistent rate is crucial for success. Jacob Laird, mechanical engineer at Premier Furnace Specialists, dives in deeper.
Premier Furnace Specialists (PFS) is capable of building annealing furnaces for a wide range of workloads. We have built small batch normalising furnaces with simple manual roller hearths, as well as 120+ foot long fully automated annealing roller hearths with multi-zone control and automatic load staging. We also offer a variety of controlled heating/cooling systems and atmosphere generators and
gas dryers to provide optimal annealed part quality. Controlled cooling systems may include: radiant tube indirect cooling, atmosphere forced convective cooling, and post-process forced convective cooling with ambient air.
How is your roller hearth system unique?
One of the unique uses for annealing furnaces is for soft magnetic steel alloys after they have been cold worked or formed. This is often used for products inside electrical equipment such as electric motors or transformers where grain growth and residual stresses may affect the magnetic properties of the material. The most cost-effective process for this heat treatment is through a continuous
atmosphere with a reducing atmosphere (often provided by a lean Exothermic gas atmosphere). For this process, the atmosphere requires a specific range of hydrogen alongside a controlled heating and cooling recipe with multiple stages.
Premier Furnace Specialists provides the accessory equipment that can be required for a complete annealing operation. We will build the Exothermic gas generators (rich and lean), Exothermic gas dryers (air and water cooled), nitrogen/ methanol/hydrogen (or other bulk atmosphere) gas trains/delivery systems, water recirculation and convective cooling systems, load management equipment/ software, and any other required pre/post processing equipment right here at our
(Source: Premier Furnace Specialists)
facility in Farmington Hills, MI. By building all of the ancillary equipment alongside the annealing furnace, it allows the client to benefit from installation of the entire system at once, identical spare parts across all pieces for easier maintenance, identical control systems with consistent terminology for ease of operator training, a single contact source for all engineering assistance and troubleshooting, as well as a service department capable of quickly responding to requests for both our equipment and any other equipment the customer may already have.
Concerning efficiency, combustion heating systems can be customised with preheat and recuperation systems, recuperative or regenerative burners, or multi-legged radiant tubes to minimise gas train complexity and NOx emissions while maximising efficiency and profitability. Electrically heated systems can be equipped with SCR power controls which minimise temperature swings at setpoint, provide optimum work chamber uniformity by eliminating heat surges, and conserve energy by reducing current draw at operating temperature. Processes can also be equipped with digital atmosphere analyzers, flowmeters, and gauges capable of displaying the remote equipment conditions at localised control stations or on mobile devices. Image of long roller hearth furnace left, below.
What are best practices for training in-house operators on roller hearth annealing?
Specifically for roller hearth furnaces, operators and maintenance personnel must understand the rollers and drive systems to ensure products continue processing at a correct rate. For continuous systems in particular, drive failures may result in the loss of large volumes of product that often cannot be recycled as well as lengthy purge/shutdown/startup times.
As an example, chain and sprocket driven rollers must only be locked down on the drive side of the furnace so that thermal expansion allows them to grow on the idle side. Otherwise, the sprockets may walk out of alignment and cause a multitude of long- and short-term issues such as rollers seizing and warping, drive faults, load crashes, and timing issues between multiple driven segments.
The best practice would be for operators to be trained to understand how major components of the furnace may affect
the part quality. This knowledge will also assist in troubleshooting issues that may arise and correcting them before they become worse.
What are the furnace’s operational advantages?
Roller hearth furnaces can handle a large assortment of part sizes by varying the roller diameters and spacing between them. For small parts, the rollers can be used to drive a mesh/cast belt or convey trays. For long parts, they can rest on the rollers with multiple support points. The bar, pipe, and tubing industries use incredibly long roller hearth furnaces while many industries process heavy wire coils in them. By segmenting the roller drives and utilising VFDs or servomotors, roller hearth furnaces become capable of staging loads, customising processing times, and oscillating at temperature to prevent rollers from warping under heavy loads.
What is the most common heating method?
Premier has seen a steady demand for gas fired roller hearth equipment, but most quotes nowadays also request pricing for an electric alternative to compare against. The end user’s facility location and local utility regulations are typically the deciding factor.
What are the challenges in operating this type of furnace?
A common challenge for any continuous furnace is maintaining consistent production and limiting shutdowns or idle periods. Large continuous furnaces burn up a significant amount of energy even when idling, so any time spent not in production becomes costly. Even when the equipment sits powered down, start-up procedures including insulation dry-outs, inert gas purge requirements, and atmosphere seasoning can take days until production can resume.
However, once consistent production is maintained, part quality, part consistency, and energy efficiency can be noticeably better than batch equivalents.
Issues can be avoided by noting areas of concern as they arise and following routine maintenance procedures until scheduled annual or biannual shutdowns (often around holiday breaks). Then additional time can be given to address potentially major issues with service visits and inspections by OEM service teams.
Reiterating the customizable nature of this style furnace, Ryan Sybo, project manager at SECO/WARWICK USA, comments on the attention on energy usage that clients and suppliers share.
What Features Do You Offer on Your Roller Hearth Furnace for Annealing Various Materials?
We offer a wide variety of options as a custom furnace company. We can tailor the furnace to meet the unique needs of individual clients. On annealing furnaces specifically, we offer a controlled cool chamber and a steam blue chamber.
Individual roll sections can be started, stopped, reversed, oscillated, and run at the same speed or at different speeds for maximum process versatility.
Atmosphere integrity is assured through welded gas-tight shells, sealing doors, and pressure control systems.
Fast and slow heating and cooling rates are possible. Plus, pre-heating can be employed.
Post-heat treating processes like steam blue are possible.
Furnace doors are specially constructed and insulated for operation within the temperature zones in which they are located, minimising stress and warpage caused by temperature differences.
Heating and cooling sections incorporate dependable, high-quality components for long-life operation.
High-speed transfer between sections allows closely spaced workloads or work trays with separation during transfer through doors, assures optimum use of hearth space, and minimises atmosphere mixing. All door openings can be adjusted to workload heights, permitting faster operation and minimising atmosphere mixing
How is your roller hearth system unique?
The controlled cool chamber offers precise control of the cooling rate. The steam blue chamber is used to develop a blue oxide, Fe3O4, for electrical insulation characteristics. Image of Roller hearth annealing furnac, right.
Our company has been designing and manufacturing furnaces for over 123 years, and we have been exploring new refractory materials and more energy-efficient burners and recuperators, as well as offering state-of-the-art atmosphere controls.
What are best practices for training in-house operators on roller hearth annealing?
Our furnaces are all built to the latest NFPA 86 and OSHA standards, however, safety training like HMI is also important.
What are the furnace’s operational advantages?
Several of this furnace’s operational advantages include:
� Continuous Unlimited Work Flow: Provides better efficiency than batch processing since the workload can continuously feed into the furnace.
� Quick, Easy Installation: For SECO/ WARWICK USA, these are normally built at our manufacturing facility and tested, then disassembled into sections to fit on a truck or shipping container.
� Long Life: A 40-year lifespan is typical. Less stress on furnace components from faster or constant temperature recycling when compared to belt, chain, or pusher units.
� Smaller Factory Footprint: Manufacturers can save about half of the floor space than with multiple batch units.
� Flexible Operation: Roller drives can be slowed, sped up, or stopped. Process parameters can be changed, any atmospheres can be used from H2 to air, plus door separations can be used between sections for better separate processing functions.
� Lower Production Costs: Each furnace is custom-designed for continuous operation at the desired operating temperatures. Less waste from heat-up and cool-down cycles used in batch sys-
tems and in-line processing makes energy recuperation easier to integrate.
What is the most common heating method?
Gas fired is the most common, however, we have been seeing a lot of inquiries for electrically heated roller hearth furnaces. Geographic location is also a big determining factor because some areas have more access to natural gas that can offer reduced operating costs. Image of roller hearth furnace system for annealing (left)
What are the challenges in operating this type of furnace?
There are no challenges in operating this type of furnace due to our custom-engineered, user-friendly automatic furnace controls. Preventative maintenance can be included in our control systems to remind operators and maintenance personnel to service the equipment. Furnace data and alarms are logged and ready for download and review.
Kelley Shreve, general manager at Lindberg/MPH, hones in on the significance of roller hearth furnace workload capacity as a lynchpin to heat treat operations.
Kelley Shreve, General Manager, Lindberg/MPH
What features do you offer on your roller hearth furnace for annealingvarious materials?
Our roller hearth furnaces are designed to meet the need for accurate, consistent, and efficient processing of heavy workloads. Features include a sturdy roll design for smooth load motion, high-efficiency heating systems for rapid heat transfer, integrated control systems for accuracy of operation and ease of troubleshooting, and material handling systems that simplify operation. Together, these features provide furnaces that will make operations more competitive.
How is your roller hearth system unique?
What separates Lindberg/MPH from competitors is our ability to take standard designs and customise them so they are tailor-suited to meet the exact client specifications and floor plans.
Extensive experience in ultra-clean heat treating helped us improve roller hearth equipment as well. Traditionally designed furnaces have transfer sections open to air, which allows rapid heat loss and causes scaling or discoloration of the work. Our proven design shields the work with a directed flow of protective atmosphere through double-door transfer sections. This also ensures
isolation of furnace zones that must not be cross-contaminated. An independent, high-speed roll system minimises transfer time and heat loss. The sight-ports allow direct viewing of work-in-process for easy troubleshooting. The result is clean, consistent work. Image of roller hearth installed, right.
What are best practices for training in-house operators on roller hearth annealing?
Lindberg/MPH offers complete installation packages which include installation, startup, and training. In-house operators are fully trained on all aspects of operations while our service technician is present.
What are the furnace’s operational advantages?
Our roller hearth furnaces combine the latest technology in process controls, atmosphere systems, and material handling systems. These furnaces are designed to carry very heavy workloads at high production rates at the lowest possible operating cost. Other advantages are that a roller hearth can be designed to
•
•
Annealing produces parts with reduced hardness and a uniform microstructure as a preparation for further processing. The furnace has a high-heat section followed by a controlled cooling module. Endothermic, Exothermic, and nitrogen-methanol atmospheres are typically used.
(Source: Lindberg/MPH)
run a multitude of different processes as required.
What is the most common heating method?
Roller hearth furnaces can be supplied with either gas fired or electric heating. Gas fired Single End Recuperated Tubes (SERT) provide economical, rapid heating. Electric heating offers reliable, low-maintenance operation using elements tailored to atmosphere application.
What are the challenges in operating this type of furnace?
A challenge for this type of furnace is proper maintenance. Operators should manage this challenge by monitoring the preventative maintenance (PM) features and indicators that are available. Setting in place and following a regular PM schedule is going to help ensure the equipment operates dependably and problem free.
In a groundbreaking move towards global sustainable industrial decarbonisation, MCi Carbon, an Australian clean technology platform, have commenced preliminary engineering work for their first industrial large-scale plant in collaboration with world-renowned refractories leader RHI Magnesita. Alongside an additional multi-million-dollar investment from RHI Magnesita, this accelerates MCi Carbon’s mission to scale-up and commercialise their carbon capture and utilisation technology.
“This investment marks a pivotal moment for MCi Carbon and underscores the trust our partners place in our transformative technology. With RHI Magnesita’s support, we are poised to accelerate our global commercialisation efforts and address the challenges faced by heavy industries in achieving decarbonisation,”
said Marcus Dawe, Founder and CEO of MCi Carbon.
“The partnership with the Australian cleantech startup MCi Carbon is forward-looking and their technological approach is particularly interesting because it combines carbon capture storage and carbon utilisation. This is currently the most promising way for the refractory industry to reduce process emissions,” says Stefan Borgas, CEO of RHI Magnesita.
Previously, RHI Magnesita signed a long-term strategic cooperation agreement with MCi to decarbonise components of their operations. This partnership was formed alongside an initial multi-million-dollar investment made in February 2023 in MCi’s carbon capture and utilisation technology. RHI Magnesita will be MCi Carbon’s first global commercial customer.
The investment will facilitate completion of the Myrtle facility, which is currently being constructed in Newcastle, Australia. Once complete, Myrtle will abate over 1000 tonnes of CO2 annually through customer-focussed trial campaigns. The company is scaling its technology to provide decarbonisation pathways for hard-to abate sectors including steel, cement, lime, mining, chemicals, and manufacturing.
This week, MCi Carbon’s co-founder and Chief Operating Officer Sophia Hamblin Wang is attending the World
Economic Forum Annual Meeting in Davos, Switzerland. Ms Hamblin Wang is urging global leaders to shift from rhetoric to tangible action to combat climate change, calling for courageous climate capital to propel industries towards a net zero emissions future.
“Attending the World Economic Forum Annual Meeting in Davos presents a unique opportunity to advocate for climate action and promote our mission. We call on global leaders to move beyond rhetoric and embrace tangible actions, fostering a climate-conscious, prosperous future,” said Ms Hamblin Wang. “MCi Carbon’s technology proves that it is possible to decarbonise and create profitable business models at the same time. The support of RHI Magnesita accelerates our impact, amplifies our voice and solidifies our position as leaders in carbon capture and utilisation.”
SeAH Changwon Special Steel has placed an order with global technology company ABB for a second ABB ArcSave® electromagnetic stirrer for use on an electric arc furnace (EAF) at the SeAH Changwon Integrated Special Steel plant in South Korea.
ABB ArcSave will be installed on an EAF that produces carbon and stainless steel and has a steelmaking capacity of
100 tons. The technology is expected to improve furnace efficiency, reduce energy consumption and overall operating costs on the continuously operated EAF at Changwon. Steelmakers have typically reported yield improvements of up to one percent, productivity increases of five to seven percent and electrical energy savings of three to five percent when deploying the equipment.
“We have experienced the benefits of the ABB ArcSave first-hand and look forward to further improving the efficiency of our electric arc furnace steelmaking operations with a second installation,” said Eung-Sou Lee, Director, Production Division, SeAH Changwon Special Steel.
“We are very pleased that SeAH Changwon Special Steel has once again chosen ABB to provide this unique technology,” said Zaeim Mehraban, Global Head of Sales, ABB Metallurgy. “It underlines the positive effect that ABB ArcSave has for high-alloy steel producers, including overcoming the challenge of bottom skull formation which can impact steel yield, furnace volume capacity, maintenance costs and downtime.”
The new order, which will be commissioned in late 2024, is the second from SeAH Steel and follows the installation of an ABB ArcSave electromagnetic stirrer on an EAF with a 70-tons production capacity in 2018.
OTTO JUNKER presents two pioneering products which will help shape the future of metal processing: EcoJet, the latest product on the market, and JuDy, a proven solution which, together with EcoJet, will be an unbeatable combination. These future-oriented solutions allow an extremely efficient preheating of bars and billets and environmentally friendly heating without using fossil fuels while at the same time minimizing costs. With these furnace solutions, OTTO JUNKER offers a sustainable and cost-efficient alternative for the industry.
Sustainable preheating with EcoJet
EcoJet is a preheater which combines maximum efficiency and environmental protection. With an efficiency of more than 95 %, EcoJet sets new standards in the emission-free preheating of bars and billets. Thanks to decades of experience in resistance and convection heating and by using state-of-the-art technologies including cutting edge flow simulation and calculations, OTTO JUNKER can offer specially-designed heater banks with a high power density for a wide range of applications. Temperature monitoring is by means of thermocouples in order to ensure optimum heat transfer. All the components of the EcoJet preheater are the result of in-house developments, engineering and manufacture guaranteeing maximum quality and reliability.
By using the EcoJet preheater, companies can not only improve their ecological footprint but also ensure their productivity in times of fluctuating gas supplies. With rapid heat-up times and precise temperature control, the furnace offers a sustainable solution combining environmental protection and economic efficiency.
JuDy: Precise temperature control with taper
JuDy (JunkerDynamicHeater®) is an induction-heated furnace which revolutionizes the final heating of billets. With an efficiency of approx. 58 % and its ability to produce a precise temperature
“ Our innovative strength and the high efficiency of these furnaces are the result of our efforts over the course of several decades. ”
Krieger,
profile in the billet across individual zones, JuDy offers a highly efficient production. The use of a ceramic melting protection tube considerably reduces energy consumption. Thanks to the OTTO JUNKER trough conveyor system, marks and scratches on the billet surface are avoided. By using the mathematical “Billet Pilot” process model, the heat can be applied in an optimized manner and the heat-up time can be reduced. Both the IGBT converter and the coils are core components produced in-house which are extensively tested and fine-tuned before shipment.
JuDy offers the flexibility required for special applications while at the same time guaranteeing a reproducible temperature profile. This solution complements electrically-heated preheating furnaces - as “stand alone”, parallel and in-line.
The best thing, however, is the combination between EcoJet and JuDy which, together, achieve an impressive efficiency.
EcoJet and Judy are not only technological milestones but also offer a wide range of options for various branches of industry. The furnaces can be used for a huge number of applications in order to improve efficiency, minimize environmental impact and lowering costs.
Examples of branches where a significant additional value can be achieved:
Metal processing and foundries: In the metal industry, EcoJet and JuDy can help optimizing energy consumption, speeding up production processes and improving the quality of the final product. This is of particular importance for the production of aluminium and copper.
Renewable energies: Precise heating processes are of major importance in the solar energy, wind energy and battery production fields. EcoJet and JuDy offer sustainable solutions for the production of components for these fast growing sectors.
Automotive industry: The automotive sector can benefit from the advantages offered by these innovative furnaces by the precise heating of billets and other metal parts, making the manufacture of automotive components more efficient and environmentally friendly.
“The introduction of EcoJet and JuDy represent an important milestone in our continuous technological evolution. With almost 100 years of experience in the design and manufacture of industrial furnaces, we have developed these products in order to fulfill the increasing demands of our customers. Our innovative strength and the high efficiency of these furnaces are the result of our efforts over the course of several decades.” �
Stefan Krieger, Sales Engineer - Sales Services Foundry Plants - Billet HeatingOTTO JUNKER.
Calderys announces its participation in HYDREAMS, a project coordinated by French firm UGITECH, part of the Swiss Steel Group. HYDREAMS aims to remove carbon emissions from steel treatment thermal processes by using green hydrogen made from renewable energy sources. Its stated objective is full decarbonisation of thermal processes for steel reheating and heat treatment by means of clean hydrogen oxyfuel combustion. The process will also improve the energy-efficiency of the thermal treatments, and simultaneously cut nitrogen oxide (NOx) emissions.
By replacing natural gas with green hydrogen as a fuel source in reheat furnaces, steelmakers may have to adapt their industrial processes and their plant. As the only refractory maker involved in the project, Calderys will study how modifications made to the furnace - to allow the use of hydrogen in the combustion process - affect the refractory lining. Based on the data obtained, Calderys will re-engineer, or manufacture new refractories, as necessary, to withstand the conditions inside the modified, green hydrogen powered furnace.
Bruno Touzo, Global Vice President, Innovation & Technology Calderys, said “I’m excited to see our teams of experts entering international research projects and placing their refractory expertise at the service of steelmakers making the energy transition. These projects are perfectly aligned with the journey on which we have embarked as a company: to strengthen our innovation at the service of our customers, their industries
and the planet.”
It is expected that successful completion of the HYDREAMS project will lead to investment decisions for deployment of green hydrogen reheating furnaces in at least 5 steel plants in Europe. Calderys has also announced other sustainable projects aimed to decarbonise industry.
Bruno Touzo: “We’ll be involved in many more hydrogen green-steel projects in coming years, as the industry moves towards the EU’s targets for zero emissions. What we’re learning with HYDREAMS and TWINGHY will eventually bring operational and cost benefits to all of our customers, and sustainability, not just in Europe, but worldwide.”
POSCO has announced it has opened a Hydrogen Reduction Steelmaking Development Center at Pohang Works and restructured its carbon-neutral organisation.
The Development Center, which opened on January 26, plans to play a pivotal role in constructing test facilities for HyREX (Hydrogen Reduction Steelmaking), a proprietary process developed by POSCO, encompassing all stages from technology research to facility construction and test operations.
Hydrogen reduction steelmaking technology has been designated as a national strategic technology. POSCO’s Hydrogen Reduction Steelmaking Development Center plans to complete a HyREX test facility with an annual capacity of 300,000 tons by 2027 and validate
Encirc Managing Director Sean Murphy (pictured) has welcomed the news that Cheshire West and Chester Council has approved plans for the first large scale hydrogen production facility and carbon capture plant in the UK which will supply low carbon hydrogen to Encirc’s Elton factory.
Sean said the decision is another step closer to making the decarbonisation of their furnaces a reality.
Sean explained: “This is another important milestone in bringing low carbon hydrogen to the North West. At Encirc we are looking forward to ensuring glass is the most sustainable packaging of choice for generations to come. With access to low carbon hydrogen, we can decarbonise our furnaces and make that future a reality.”
EET Hydrogen, a joint venture between Essar Oil UK, owner of the refinery, and low carbon energy firm Progressive Energy, is behind the proposal. They revealed in September 2023 that engineering and design work had started on the project.
It forms part of the wider Hynet hydrogen project which aims to create a low carbon future across the north west of the UK
The facility will eventually supply up to 1,000MW of hydrogen to glass manufacturers Encirc and Pilkington, as well as soda ash producer Tata Chemicals.
It is estimated that the hydrogen hub will enable local industrial and power generation businesses to switch from fossil fuels to low carbon
energy, helping to reduce the North West’s carbon emissions by 2.5 million tonnes every year.
‘At Encirc we are looking forward to ensuring glass is the most sustainable packaging of choice for generations to come. With access to low carbon hydrogen, we can decarbonise our furnaces and make that future a reality.’
- SEAN MURPHY, Managing Directorthe commercial viability of HyREX technology.
Si-woo Lee, who attended the center’s inauguration, said, “Let’s strive to become the first mover in the new Iron Age by developing hydrogen reduction steelmaking technology, replacing carbon with hydrogen. I hope you will take on a new challenge as the first treasure of the new carbon-neutral economy*, successfully implementing HyREX technology based on our experience in commercialising FINEX fluidised bed technology and developing SNNC electric melting furnace technology.”
In addition, POSCO has upgraded its Carbon Neutral Strategy Sector to a departmental level and appointed Hee Kim, the first female engineering executive, as Head of Carbon Neutral Strategy Department.
Furthermore, to complete and operate the electric furnace planned for Gwangyang Works,
POSCO is actively pursuing the implementation of its carbon-neutral roadmap through the expansion and restructuring of its Electric Arc and Smelting Furnace Project Team).
Iron and steel demand is rising for many reasons, not least because of the increase in urbanization and industrial expansion, which in turn drives the construction of infrastructure. Additionally, as developing countries grow wealthier, the demand for personal and public transportation increases - and the automotive and manufacturing sectors rely heavily on steel. Economic growth, particularly in emerging markets, is pushing demand, and technological advancements in steel are leading to new applications, which also boosts consumption.
The Iron and steel industry accounts for around 8% of the global CO2 ** footprint. If companies and nations are to make meaningful progress towards lowering emissions, iron and steel production powered by coal and natural gas must be re-engineered for zero-carbon, sustainable alternatives.
To meet emission targets, the future of iron and steelmaking will employ green hydrogen as an energy source in place of fossil fuels.
Hydrogen is produced using industrial electrolysis. For hydrogen production to be green, the electrolysis must be powered by electricity from renewable sources, such as wind, wave, and solar.
Green hydrogen is a key constituent of the EU’s plan to speed up the green transition and promote massive investment in renewable energy in the region. As well as increasing Europe’s energy security, green hydrogen is important in the EU’s push for net zero CO2 emissions. The target is to achieve 55 % reduction of CO2 emissions by 2030, compared to levels measured in 1990.
Steelmakers are progressively adopting hydrogen and natural gas based technologies as alternatives to their traditional blast furnace and basic oxygen furnace route. The two most promising hydrogen-based technologies are Injection of hydrogen into existing blast furnaces, and hydrogen and natural gas based direct reduction of iron ore,
coupled with an electric melting furnace.
However, introducing green hydrogen as a fuel source in furnaces and other stages of the iron and steelmaking process isn’t completely straightforward, and significant engineering challenges need to be addressed, as well as the cost and reliability of production. For a start, the process is energy intensive and the supply of renewable electricity must be cost-effective, consistent and reliable. Hydrogen also requires more energy to compress than natural gas and, as hydrogen is the smallest and lightest of the elements, it is difficult to store and transport without leakage, and it can react to metals used in plant equipment, causing corrosion.
Designing refractory linings for iron and steelmaking processes using hydrogen and natural gas is also challenging because of the high diffusivity of H2 in the refractory material, and the reactivity of hydrogen with silica and iron oxide from the refractory at high temperature, which, with the increase in H2 concentrations, decreases the physico-chemical properties and the load-bearing capacities.
In order to tackle these challenges, Calderys is developing adapted refractory solutions for its customers, and is going
even further by partnering with a number of laboratories and research projects.
Refractory companies play a crucial role in assisting the iron and steel industry in reducing CO2 emissions due to their significant impact on the efficiency and environmental performance of steelmaking processes. By developing and supplying advanced refractory solutions, Caldeys’ products help improve the energy efficiency of steel production, leading to reduced CO2 emissions per ton of steel produced. Additionally, innovative refractory materials can enable the adoption of alternative, lower-carbon iron and steel production methods, such as open slag bath furnace OSBF.
Below are some of the hydrogen research projects in which Calderys is actively involved, and which are co-funded by the EU.
TWINGHY is a project testing hydrogen as a fuel to replace natural gas in reheating furnaces. The project kicked-off in the summer of 2023 and is scheduled to conclude in 2027.
Based at the CELSA Group plant in Barcelona, Spain, the project is evaluating and demonstrating an advanced heat transfer process, utilizing hybrid burners in order to increase the introduction of hydrogen for direct combustion with oxygen. Key activities include H2/O2 combustion in rolling mill furnaces, trials with new H2 burners, and assessment in terms of product quality, safety, environmental, and effects on refractories.
The process is being controlled by a digital twin of the furnace, incorporating machine learning. Hence the name: (digital) TWIN for Green HYdrogen.
Calderys is the only refractory maker
chosen to participate in this project, and its team of experts is studying how modifications to the furnace affect the refractory lining. Based on these findings, Calderys is adapting refractories, or will develop new refractories, suitable for the working conditions of furnaces burning mixes of natural gas, hydrogen, and oxygen. At this stage in the project, refractories are currently being tested by RWTH Aachen University. Design of the new burners is complete, as is design of the plant modification for hydrogen Integration, and the planned trials with hydrogen.
HYDREAMS is an innovation project also co-financed by the EU, and coordinated by French firm UGITECH, part of the Swiss Steel Group.
The project’s stated objective is the decarbonization of thermal processes for steel reheating and heat treatment by means of clean hydrogen oxyfuel combustion. The process will also improve the energy-efficiency of the thermal treatments, and simultaneously cut nitrogen oxide (NOx) emissions. It is expected that successful completion of the HYDREAMS project will lead to investment decisions for deployment of green hydrogen reheating furnaces in at least 5 steel plants in Europe.
As a key partner in the HYDREAMS project, Calderys will develop innovative and tailored refractory solutions to enable steelmakers to optimize their energy usage, reduce emissions, and enhance overall efficiency in all stages of steel production.
Also in Spain, Calderys is supplying
equipment, refractories and expertise to steel plant manufacturer, Sarralle, to put into operation the world’s first ladle preheating station running on 100% green hydrogen as fuel.
The purpose of this project is to improve the operation of the existing ladle preheater and to replace the natural gas as fuel with green hydrogen, reducing CO2 emissions to a minimum. Additionally, thanks to the installed oxycombustion burner technology, NOx emissions have been reduced to near zero as well. Using 100% green hydrogen as fuel, the different heating/drying curves have been satisfactorily reproduced and the required temperatures for ladle casting have been reached, confirming a homogeneous heating of the refractory.
Hydrogen is increasingly being used in the Direct Reduced Iron (DRI) process as a clean and efficient alternative to natural gas or coal, a process that has a very real potential to help iron and steel industries become carbon neutral.
Calderys is an experienced player in supplying refractory solutions, engineering and installation services to new DRI
projects, as well as revamping and relining existing units.
The DRI process involves reducing iron oxides (usually in the form of iron ore pellets or lump ore) to metallic iron without melting.
In the process, hydrogen acts as a reducing agent, reacting with the iron oxides to produce metallic iron and water as byproducts. This reduction reaction is endothermic and occurs at elevated temperatures typically ranging from 800°C to 1000°C.
This reaction forms the basis of the direct reduction process, where hydrogen serves as the primary reducing agent.
Hydrogen also serves as an energy source in the DRI process. The heat required for the reduction reaction is often provided by burning hydrogen. This ensures that the process remains energy-efficient and environmentally friendly, as hydrogen combustion produces only water vapor as a byproduct.
Calderys’ experts have carried out a full turnkey DRI project, including design, engineering, material supply, relining and installation. A number of technical challenges encountered during the relining and installations were resolved, making the project a success.
For more information, visit www.calderys.com
Compared to traditional reducing agents like coal or natural gas, hydrogen offers environmental benefits. When hydrogen is used as the reducing agent, there is minimal or no emission of greenhouse gasses or pollutants such as CO2, CO, and SOx, which are typically associated with the use of fossil fuels. This makes hydrogen-based DRI processes more environmentally sustainable all round, and aligns with efforts to reduce carbon emissions in steel production.
The shift towards greener furnaces and processes powered by hydrogen represents an important step in the iron and steel industry’s sustainability journey. With initiatives like TWINGHY and HYDREAMS leading the way, supported by teams of innovative partners, including Calderys, the path to decarbonization is becoming clearer. By employing innovative refractory solutions and leveraging the potential of green hydrogen, steelmakers can not only reduce their carbon footprint but also enhance cost-effectiveness and competitiveness. With ongoing research and development, coupled with collaborative efforts across industries and regions, the prospect of a low-carbon future for iron and steel production is within reach. �
• No trailing thermocouples so quick, safe and effective
• Measure from up to 20 thermocouples with a single data logger
• Ideal for surveying semi-continuous, continuous or modular furnaces
• Live RF telemetry TUS data collection options
• Oil, salt and water quench thermal barrier options
• Efficient real time TUS of static furnaces
• Robust compact external data logger design
• Easy to transport and set-up
• Thermocouple type and plug connection options for quick installation
• Cold junction compensation to give accurate data in changing environmental temperatures
• Fully compliant with AMS2750G &
• Full 0.1 °C / 0.1
• Apply accurate data logger and thermocouple correction factors with ease
• Full control over real time data collection and TUS analysis
• Generate your complete TUS reports with efficiency and confidence