T Y i
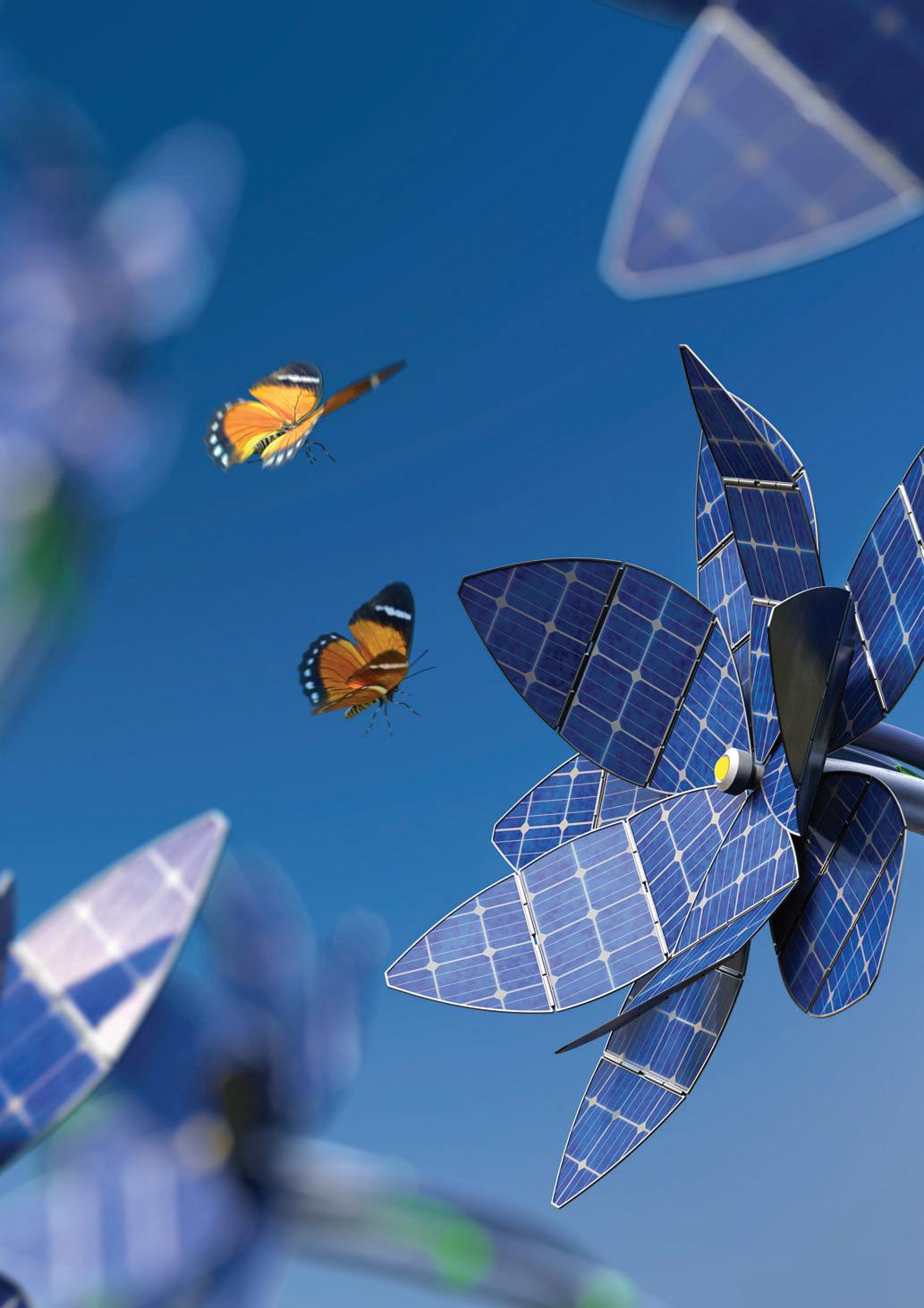
Valtteri Bottas interview
Formula 1 is on a drive to make the sport sustainable. Our Editorial Manager sat down with Alfa
Romeo F1 Team ORLEN Lead Driver
Valtteri Bottas to discuss sustainability and the challenges of racing in a new era of hybrid cars.
Managing Director
John White
Editorial Manager
Phil Nicholls
Editorial Assistant
Imogen Ward
Hannah Barnett
Finance Director
Filomena Nardi
Feature Writers
Andy Probert
Romana Moares
Richard Hagan
Sales Director
Richard Brightmore
Sales Manager
Helen Leisi
Project Managers
Alexander Paterson
Tony Ingrouille
Kym Hamilton
Chris Renicar
David Earl
Connor Doddington
Verity Manning
Lisa Smith
Carl Millican
Business Development Manager
Darren Foiret
Research Editors
Jeff Johnson
Becky Scrivens
Clare Bishop
Dane Coady
Jamie McBride
Mark Simmonds
Art Director
Ian Spencer
Art Editor
Philip White
Webmaster
Michael Stamp
Designers
Sarah Jones
Georgina Harris
Marketing Manager
Daniel O’Malley
Marketing Executives
Adam White
T: +44 (0)1493 445121
+44 (0)1502 566216
E: media@insidepublication.com
W: www.inside-sustainability.com
John White Managing Director
Managing Director John White talks through the exciting changes in this edition for an even more enjoyable reading experience.
Welcome, Dear Reader, to the much anticipated and exciting… well we think it is… edition of Inside Sustainability. We introduced this new-look magazine last year to almost universal adulation. However, we have been busy bees, working hard to further improve things for you.
Therefore, the second issue has a revised layout. Gone, in part, is the traditional part one of the magazine that contained a wealth of information about multiple industry sectors. Our magazine is now essentially split into mini magazines, each having its own theme.
This issue has five sections: Automotive, Engineering & Services, Manufacturing, Packaging and Sea & Air. Ahead of any relevant company profiles and advertising is an outline of the latest industry news, facts, events, special reports or innovations.
For example, our automotive section in this edition commences with automotive focused news, facts, a special report and innovations. This is followed by an Alfa
Romeo F1 Team ORLEN article, that explores sustainability in sport and business, then two more automotive company profiles and complementary advertisements. These themes will change every issue. Importantly, we will continue to accommodate all of you within each edition. The orig inal part one still exists, but with a more general feel.
Our aim is to make the magazine a more engaging experience by enabling you to skip to your most relevant section. Yet, from over 14 years of working with you all, it seems most industry sectors are directly or indirectly linked. Therefore, I believe the whole magazine will interest, regardless of your sector.
Without further ado, let me introduce you to this new-look edition of Inside Sustainability. As always, our job is to provide a media platform with a truly global reach, helping you showcase your business. Please help us to continue to improve by sending in your feedback, new ideas and suggestions for future editions.
n
10-11 May 2023
CHEMUK 2023
CHEMUK 2023 presents over 400 specialist exhibitors and 150 expert speakers, split between three major show zones: Chemical Industries Supply Chain, Chemical, Process & Plant Engineering and (new for 2023) CHEMLAB. The event is free to attend, and visitor registration is now open.
[click here] for weblink
09-11 May 2023
World Hydrogen 2023
The leading global platform for hydrogen business. As hydrogen accelerates into the mainstream energy sector, it’s crucial for policy makers and industry stakeholders to increase collaboration and cross-sector dialogue to ensure the rapid scale-up and delivery of a global hydrogen economy.
[click here] for weblink
04-10
Sus imp suc the region. such as reg lar packagi in packagin
[click h
May 2023
interpack 2023
interpack is a global trendsette the food industry. The focus is packaging machines and relat for the food, beverage, confectionery, b cosmetics, non-food and industrial good
[click here] for weblink
stainability in Packaging Asia is an portant forum to share the value and ccesses of the packaging industry in Hear from key experts on hot topics gulatory landscape, initiatives for circung, new technologies and innovations ng materials.
here] for weblink
NAEM's EHS & Sustainability Management Forum is the largest annual gathering for environment, health & safety, and sustainability decision-makers. Forum23 is the event dedi cated to sharing best practices for those developing and integrating strategic environmental and health & safety programmes.
[click here] for weblink
r for the future themes of on packaging materials, ted process technology bakery, pharmaceutical, ds sectors.
Why not give your event exclusive coverage to thousands of readers and connections globally? Contact us: media@insidepublication.com
Latest developments from the Chinese industry
The Chinese multinational automotive group is the latest partner to join the leading collaborative platform of eleven Original Equipment Manufacturers (OEMs) aimed at improving the social, ethical and environmental performance of automotive supply chains.
ATthe end of 2022, the Chinese multinational automotive group Geely Holding Group (Geely) became a partner of the leading collaborative platform Drive Sustainability, facilitated by CSR Europe. Geely will work together with the other eleven Original Equipment Manufacturers – BMW Group, Daimler AG, Fiat Chrysler Automobiles, Ford, Honda, Jaguar Land Rover, Scania CV AB, Toyota Motor Europe, Volkswagen Group and Volvo Group – to lead the transformation towards a circular and sustainable automotive value chain.
“We are thrilled to welcome Geely Holding Group in CSR Europe’s leading collaborative platform Drive Sustainability,” said Stefan Crets, CSR Europe Executive Director. “The sustainability agenda towards 2030 and 2050 is by necessity both a leadership and collaborative program.
“Only when leading companies like Geely engage within their value chain and work together with their sector-peers and other stakeholders, can sustainability impact at
scale be reached. Geely’s participation will strengthen the common voice of Original Equipment Manufacturers across the world for a circular and sustainable automotive value chain.”
Zhejiang Geely Holding Group (Geely Holding) is a global automotive group that owns several well-known international automotive brands, with operations spanning the automotive value chain, from research, development and design to production, sales and servicing.
Founded in 1986 by Eric Li, the company’s Chairman, in the city of Taizhou in China’s Zhejiang province, Geely Holding launched its automotive business in 1997 and is now headquartered in Hangzhou, China. Today, Geely Holding operates several brands including Geely Auto, Lynk & Co, ZEEKR, Geometry, Volvo Cars, Polestar, Lotus, London Electric Vehicle Company, Farizon Auto and Cao Cao Mobility. n
Latest developments from the American industry
Corvus Energy celebrated the grand opening of its new battery factory in Bellingham WA at the end of January. The ceremony was held with distinguished guests such as the Governor of Washington Jay Inslee, Norway’s Ambassador to the USA Anniken Krutnes and US Representative Rick Larsen, along with customers, industry partners, government agencies and others.
The new battery plant is located in Fairhaven at the Port of Bellingham and is a key step in the expansion of Corvus’ US operations.
“We have seen a significant uptake in opportunities for maritime batteries from the US market,” explained Geir Bjørkeli, CEO of Corvus Energy. “Increased capacity and production flexibility will be key to meeting this anticipated growth. Washington state was a natural choice for Corvus due to the presence of a strong maritime cluster, the state’s focus on green shipping, and the proximity to our Richmond facility in Canada. US presence and close collaboration with shipyards, shipowners, Washington Maritime Blue, as well as other suppliers and service providers, fosters innovation across the entire industry and builds valuable competence and local green jobs.”
Ole Jacob Irgens is President Americas in Corvus Energy and leads the sales and business development. He said: “We see a big change. Ship owners, designers, naval archi-
tects as well as electric propulsion integrators in North and South America are turning to Corvus in record numbers, The US factory, along with a more robust sales and service organisation, will ensure that we can better service our US customers.
“Our customers see great value in Corvus’ investments in North America and our efforts in creating green jobs in local communities such as Bellingham.”
The Bellingham Plant will produce the modules for Corvus Energy’s marketleading and award-winning Corvus Orca ESS. There has been close to 650 Corvus Orca projects with a combined energy storage capacity of 550MWh worldwide since the ESS product revolutionised battery-powered marine propulsion with its introduction in 2016. Since then, product enhancements and continual upgrades have kept Corvus Orca ESS at the forefront of the global movement towards low- and zero-emission vessels and maritime infrastructure. n
Latest developments from the Australian industry
Australian company Squadron Energy (Squadron) recently announced it has acquired CWP Renewables (CWP), in an agreement that takes Squadron’s renewable energy operating portfolio to 2.4 gigawatts with an Australian development pipeline to 20GW.
Squadron, part of the Tattarang group of companies, is 100% Australian owned and operated, and dedicated to accelerating Australia's decarbonisation. Once fully operational, Squadron’s portfolio will provide enough electricity to power 8.5 million homes, more than double the number of homes in New South Wales.
CWP will be integrated into Squadron’s existing business, which includes majority ownership of Windlab, and provide Squadron with the scale it requires on the east coast of Australia to meet the huge demand from large commercial and industrial customers for reliable green energy.
“Squadron is proud to bring a very significant portion of Australia's renewable energy assets home to local ownership,” said Chairman of Tattarang Dr Andrew Forrest. “We share a vision of Australia and the world. We want to look back on the dark era of fossil fuel as an aberration in humanity’s history. One that could have ended with that fuel, but is now powered by cheap, pollution free, democratic inexhaustible energy.
“It is paramount that Australia continues to increase cost-efficient renewable green energy, to economically power homes and industry at pace and rid the Australian consumer of its forced reliance to increasingly expensive, dangerously pollutive fossil fuels.”
CWP is a vertically integrated renewables energy business that spans wind, solar and battery farms, and provides renewable energy to Transurban, Woolworths Group, Sydney Airport, Commonwealth Bank and Snowy Hydro. It has approvals in place to construct four more wind farms in New South Wales, totalling over 750MW, along with a construction ready 414MW wind farm, 180MW solar farm, two battery farms and a firming power station capable of using hydrogen, biofuels and hydrogen gas blends.
“We are realising significant value by combining CWP's wind, solar and battery farm portfolio with Squadron’s existing renewable power and firming assets,” said Dr Forrest.
n
Latest developments from the Dutch industry
Since the start of 2023, Neste MY Renewable Diesel™ is used to run all diesel-powered ground handling vehicles and machinery at Amsterdam Airport Schiphol in the Netherlands.
Equipment Services (KES) is the fuel supplier for all vehicles and machinery on Schiphol with a fuel station at the airport, as well as three fuel trucks operating seven days a week.
There are around 1,900 ground handling vehicles with a diesel engine at Schiphol airport, varying from standard cars, vans, pushback tractors and trucks to more specialised ground support like conveyor belt loaders, pallet or container loaders, catering high lifts, aircraft fuel dispensers, passenger steps and ground power units.
“At the moment, 40% of the motorised equipment at the airport runs on electricity, and that number will increase over the coming years,” said Paul Feldbrugge, responsible for the Zero Emission Programme within KES. “However, for several specialist heavy vehicles, it is a technical challenge to develop a battery with sufficient capacity that can also be charged quickly enough. Using Neste MY Renewable Diesel is therefore a good solution.”
Neste MY Renewable Diesel is produced from 100% renewable raw materials. It is
a drop-in fuel, the use of which does not require any modifications to existing vehicles or machines, energy systems or fuel distribution infrastructures.
one planet – one chance – one voice
An introduction to the automotive sector, with news, innovations, automotive facts and a Drive Sustainability special report, followed by company profiles.
Latest innovations from the automotive industry
Six public bp pulse charging locations with ultra-fast 300kw charge points aimed at E-Trucks have been launched along a 600km stretch of the Rhine-Alpine corridor across Germany. This corridor is one of the busiest road freight routes in Europe, connecting key North Sea ports in Belgium and the Netherlands with the Mediterranean port of Genoa in Italy as part of a 1,300km network of roads.
The new chargers have been installed on Aral retail sites in Germany between the Rhine-Neckar metropolitan area and the Rhine-Ruhr metropolitan region. Aral is bp’s German retail brand. In the next six months, two additional locations are scheduled to open on Aral retail sites to complete the new charging corridor.
Once complete, using the Aral pulse charging corridor, an E-Truck will be able to cover over 600km across Germany along one of European’s major road transport routes. The 300kw charging stations are each capable of charging more than 20 E-Trucks, per charger each day. An E-Truck’s range can reach up to 200km in around 45minutes using the ultra-fast charge points.
The Aral retail sites offer access to hot food, restrooms and showers for drivers to use during a mandatory rest period in addition to dedicated charging in safe, well-lit and convenient locations.
“This is a significant moment for E-Trucks in Europe,” said Nigel Head, EV Truck Director, Europe, bp pulse, “and an important step in our journey towards helping to decarbonise truck transportation.
By electrifying this stretch of the RhineAlpine corridor with ultra-fast charging, bp is enabling EV Truck charging beyond ‘back to base’ whilst rapidly learning customer insights which will directly inform our longerterm European network and proposition.
“By beginning the roll-out of a dedicated charging network for freight operators and fleets, with a focus on major logistics corridors, bp is supporting the electrification of medium and heavy-duty vehicles, decarbonising the movement of goods, as well as people. Ultra-fast charging in the right locations, combined with depot and destination charging, is critical infrastructure to accelerate the electrification transition, unlocking the
economic and environmental benefits of low-carbon commercial road freight and transport.”
“To reduce CO2 emissions in road freight transport significantly, e-trucks will play a central role in regional and long-distance transport,” said Johannes Pallasch, from Germany’s National Centre for Charging Infrastructure, part of the Federal Ministry for Digital and Transport. “As with passenger cars, the switch to electromobility can only succeed with a reliable and needs-based charging infrastructure. With today’s
opening, Aral is taking an important step in this direction.”
By 2030, it has been estimated that approximately 270,000 battery electric medium and heavy-duty vehicles will be in operation in Europe, and they will require up to 140,000 public and destination electric charging points. This transition is already underway; the German truck fleet is now over 3.5 million vehicles and bp pulse launched its first ultra-fast-charging facilities for medium and heavy-duty electric trucks in Schwegenheim, Rheinland-Pfalz. n
Latest innovations from the automotive industry
The fourth model in Audi’s activesphere series has been unveiled. The concept car has an electric drive and quick-charging technology. From Audi’s PPE modular system, the Audi activesphere joins the sphere family of concept vehicles. With no local emissions, a range of over 372 miles, and extremely fast charging times thanks to 800-volt technology, it combines the sustainability, dynamics and long-distance capability of state-of-the-art electric vehicles.
ASa perfect all-rounder, the Audi activesphere concept is ideally suited for the high demands of a future-oriented generation of Audi customers. That is, people for whom individual mobility and sustainability are not mutually exclusive. Also, owners expect their vehicle to deliver the brand’s typical aesthetics and dynamism to the highest degree, combined with future-oriented technology. For these customers, the Audi activesphere concept acts as a fascinating vision of crossing the boundaries between these dimensions.
Due to its dimensions and performance level, the Audi activesphere concept lends itself to the use of Audi’s most innovative electric drive system: the Premium Platform Electric, or PPE for short.
The PPE is designed exclusively for battery-electric drive systems and can therefore take full advantage of all the benefits of this technology, for the benefit of the car’s driving characteristics, economy, and package options.
The key element of the future PPE fleet is a battery module between the axles. In the Audi activesphere concept, it holds around 100kWh of energy. Using the entire car width between the axles makes it possible to achieve a relatively flat layout for the battery.
Electric motors on the front and rear axles of the all-wheel drive Audi activesphere concept together deliver a total output of 325kW and a system torque of 720Nm of torque. The front and rear wheels are connected via a five-link axle. The
concept car features Audi adaptive air suspension with adaptive dampers.
Fast charging with 800 volts
The heart of the drive technology in all future PPE models will be the 800-volt charging technology. Like the Audi e-tron GT quattro before it, this ensures that the battery can be charged with up to 270 kW in a very short time at fast-charging stations. This revolutionary technology will enter the
high-volume mid-range and luxury segments with the PPE for the very first time. PPE technology enables charging times that come close to a conventional stop to refuel a combustion engine car. Just 10 minutes is enough time to charge the battery to a level sufficient to power the car for more than 186 miles. And in less than 25 minutes, the 100kWh battery charges from 5 to 80 percent.
innovations from the automotive industry
Honeywell is expanding its strategic alliance with Nexceris, developer of Li-ion Tamer lithium-ion gas detection solutions, to help make electric vehicles (EVs) safer. Honeywell and Nexceris will co-develop sensor-based solutions to help prevent conditions leading to thermal runaway in EV batteries, a phenomenon that causes extremely high temperatures within the battery cell and can result in a fire. Several industries are moving to electrified power sources, and for the automotive industry specifically, global sales of EVs in 2021 doubled from the previous year to nearly 7 million.
Many of these vehicles use lithium-ion batteries as an energy source, which can pose rare but significant safety risks including fires that impact drivers on the road, homeowners who may have EVs parked in their garages and shipping handlers transporting EVs to their final destinations. To help mitigate these risks, automobile manufacturers are looking to incorporate technology to provide enhanced safety.
Honeywell offers a wide range of lithium- ion battery safety and performance solutions, including sensors used in battery management systems to monitor the health of EV batteries, gas detection solutions used throughout the manufacturing process and electrical safety personal protective equipment, providing protection
to workers and allowing them to operate safely in hazardous conditions.
Nexceris is an energy innovation com pany dedicated to the clean energy transition. Founded in 1994, Nexceris’ vision is to create a better world through clean energy innovations. The company collaborates with global customers and partners to transform powerful ideas to make energy production safer, more efficient, and environmentally responsible.
In 2020, Honeywell and Nexceris formed a strategic alliance to address lithium-ion battery system safety for energy storage applications, combining Honeywell’s very early warning smoke detection and Li-ion Tamer’s leading off-gas detection technology for a safe, redundant way to protect facilities of any scale.
A smart collaboration
“As the world transitions to electric vehicles,” said Victor Verissimo, General Manager of the Transportation line of business at Honeywell Sensing and Safety Technologies, “automakers are faced with the need to provide lithium-ion batteries that function properly and safely during all stages of their lifecycle. At Honeywell, we are supporting this transition with ready-now solutions to help our customers mitigate safety risks as they expand their electric vehicle portfolios.”
The companies will collaborate with leading global vehicle manufacturers to deliver advanced gas detection solutions in EV battery packs to allow for early intervention, helping avoid costly property damage and safety issues.
“Our work with Honeywell will help us empower the global transition to electric vehicles through enhanced battery monitoring,” said Kyle Shen, President and CEO of Nexceris. “Fires from lithium-ion batteries are dangerous and often difficult to contain after they start. By combining our shared expertise in battery sensing and gas detection technology with Honeywell’s extensive manufacturing capabilities, we will be working toward offering our vehicle manufacturing customers a more advanced safety solution and meeting the growing demand for lithium-ion batteries.” n
Drive Sustainability
Supported by CSR Europe, the Drive Sustainability partnership promotes environmental concerns all through the automotive supply chain. Member companies adopt a common approach to these issues and integrate sustainability into their procurement procedures.
The Drive Sustainability partnership is an association of automotive manufacturers. Membership com prises BMW Group, Daimler AG, Fiat Chrysler Automobiles, Ford, Honda, Jaguar
Land Rover, Scania CV AB, Toyota Motor Europe, Volkswagen Group and Volvo Group. The recent addition of the Chinese multinational Geely Holding Group makes a dozen companies.
These 12 manufacturers understand the necessity that the workers building their vehicles, components or delivering supporting services are granted decent working conditions: a workforce should be treated with dignity and respect. These principles run alongside schemes to limit the environmental impact of the automotive industry and promote integrity within the business.
Drive Sustainability is a continuation of work conducted by The European Automotive Working Group on Supply Chain Sustainability. This group began in 2012 as a project to develop and promote sustainability within the automotive supply chain.
The vision of the partnership is to lead the transformation of the automotive sector towards a value chain that is both circular
and sustainable. Member companies seek excellence, innovation and performance within a sustainable framework. Furthermore, it is clear to members that workers and the environment are the most important resources in the automotive industry.
The unified mission is to drive sustainability in the automotive sector by adopting a single voice on these issues. The intent is
to engage with suppliers and stakeholders within the automotive and associated sectors to further push the industry to address sustainability issues.
This single voice within the automotive industry is devoted to expressing the common direction of the partnership. The member companies hold a unified position committed to achieving a sustainable supply chain. This change is driven by the
development of common activities and tools that impact the supply chain.
Membership of the programme supports the unified approach by companies for promoting the sustainability of the automotive supply chain.
Through encouragement, promotion and working together, the Drive Sustainability partners have adopted a common approach and process on supply chain sustainability throughout
the industry. The overall goal is to embed sustainability into the procurement process of every company within the industry.
The establishment of sustainable supply chains will enable Drive Sustainability to reach its long-term ambitions. Impact on the automotive supply sector will be achieved through close collaboration with
existing suppliers to implement the actions necessary to reach the group’s sustainability targets.
Drive Sustainability’s road to its goals is impacted by the inherently complex structure of the automotive supply chain, notably the interwoven relationships within the sector. However, these companies are embedded within this structure, so the group has planned its strategic actions to accommodate the existing supply network.
The action plan to deliver sustainable supply chains has four areas of focus. Firstly, there is the need for sustainable raw materials, including the promotion of standardised tools to manage procurement. Longer-term, this aspect will also achieve an audit of minerals and deliver transparency of origin for materials.
Additionally, the programme aims to deliver workforce wellbeing with common standards to tackle issues affecting workers. Drive Sustainability is promoting carbon neutrality throughout the supply chain, looking ahead to establishing common measurement tools. Finally, the group wants to oversee the creation of a circular value chain.
This strategy is already being implemented. Drive Sustainability is currently engaged with over 19,000 suppliers in more than 100 countries. At least 1,600 suppliers are now involved in capacity-building activities and 20 materials have already been assessed for their importance and associated ESG risks.
The work of Drive Sustainability is guided by three underlying principles. These begin with a focused effort to build stakeholder engagement with the project. While the group represents major manufacturers, the transformation of the automotive supply chain can only be achieved through a partnership with the entire sector.
Secondly, the participants enjoy a shared belief in the benefits to the industry of heightened transparency, through greater communication within the sector. Both stakeholders and partners are expected to share the sustainability information required to deliver the group’s collaborative solutions.
Finally, the Drive Sustainability group plans to adopt existing best practices and make good use of the existing tools for delivering sustainability throughout every stage of the extensive automotive supply chain network. n
Interesting and unusual sustainability facts from around the automotive world
The new Tonale Plug-in Hybrid Q4 from Alfa Romeo achieves 26g/km CO2 emissions and 235mpg consumption in the combined WLTP cycle.
Mercedes-AMG PETRONAS Formula One Team reported a staggering 89% reduction in CO2 freight emissions after Spa-Zandvoort-Monza biofuels truck trial. The team’s 16 Actros Gigaspace trucks used Hydrotreated Vegetable Oil (HVO 100) biofuel – a 100% renewable fossil fuel-free product derived from vegetable oils, waste oils and fats.
In 2021, 7.7 million kilogrammes (17 million pounds) of recycled plastic were used in General Motors vehicles.
Ford Motor Company’s Model T averaged up to 9km/l (21mpg). Today, the average car only achieves around 10km/l (25.2mpg). However, the most fuelefficient cars can reach over 25km/l (60mpg).
BMW Group’s production of almost 2.5 million vehicles per year generates around 780,000 tonnes of waste. In 2021, 99% of this waste was recycled (93.4%) or (thermally) recov ered (5.8%).
Trim levels for the IONIQ 6 from the Hyundai Motor Company include bio paint derived from veg etable oils for the doors and recycled fishing nets used to make the carpet.
Formula Motorsport Limited and Formula 1 Global Partner Aramco will introduce the use of sustainable fuels in both FIA Formula 2 and Formula 3 Championships from 2023.
The fuel revolution has already begun in Formula 1, with 2022’s generation of cars running on ‘E10’ fuel, a blend of 90% fuel and 10% renewable ethanol.
The latest company and industry related developments from the automotive world
With the foundation of Cofinity-X the shareholders BASF, BMW Group, Henkel, Mercedes-Benz, SAP, Schaeffler, Siemens, T-Systems, Volkswagen and ZF initiate the next step in Europe to foster the Catena-X initiative. Cofinity-X strives to be one of the first operating companies which aims to provide products and services for the secure exchange of data throughout the entire automotive value chain.
“As the leading chemical supplier to the automotive industry,” said Markus Kamieth, member of the Board of Executive Directors of BASF SE, “we see tremendous opportunities in operating an ecosystem based on standardised digital services and harmonised data models. This will strengthen
supply chain resilience, improve transparency, and accelerate the transformation towards circularity and net zero carbon footprints across many material categories.”
Future customers will be able to access applications and services to implement use-cases in the automotive value chain such as CO2 and ESG monitoring, traceability, circular economy or business partner data management.
Carbon footprint tracking enables concise, accurate calculation and reporting of CO2 values along the value chain. This will allow Cofinity-X customers to stay ahead in carbon footprint transparency and derive potential sustainability improvements to play an active role in the global effort to reach net-zero. n
TheUK’s leading breakdown service, the AA, has partnered with ScottishPower to help more UK drivers make a move to electric vehicles by giving people with ‘range anxiety’ confidence to switch to a zeroemissions vehicle.
Both organisations are committed to helping people across the UK switch to electric transport. The new partnership will ensure that if anyone who buys an EV charger from ScottishPower is ‘out of charge’ when driving their electric vehicle, the AA will pick them up and take them to their nearest charge point or home, whichever is closer.
Anyone who purchases an electric vehicle home charger with ScottishPower can register for the free service from the AA.
“We are delighted we can offer these additional services to help even more people make the switch to electric vehicles,” said Chris Carberry, Smart Solutions Director at ScottishPower. “We’re on a journey towards Net Zero and by working with a fantastic
organisation such as the AA, we can help make that transition easier and quicker.”
As part of the AA’s ongoing commitment to electric vehicle drivers, the motoring association will provide access to their trusted breakdown service via ScottishPower for the ‘out of charge’ service. This gives drivers confidence to switch to electric vehicles and supports the UK’s transition to zeroemissions transport. n
wiss-based Alfa Romeo F1 Team ORLEN has embraced the sustainability goals of orsport’s governing body the Fédération Internationale de l'Automobile (FIA). The FIA’s tegy meshed with the existing sustainable philosophy at Alfa Romeo F1 Team ORLEN. am Principal Frédéric Vasseur and Lead Driver Valtteri Bottas discussed sustainability and racing hybrid engines, in discussion with Jamie McBride and Phil Nicholls.
The FIA Environmental Strategy for 2020-2030 is embedded in the global environmental and sustainability agenda. This strategy exists within the UNFCCC Sports for Climate Action Framework launched during COP24.
“All the partners of F1 today are talking about sustainability,” explained Team Principal Frédéric Vasseur.
“It's a topic for everybody, including the fans.
I'm very, very pleased with the fact that, collectively, the teams took it as a serious topic.”
The history of Alfa Romeo F1 Team ORLEN began in 1970 when Peter Sauber started racing two-seat cars. After racing sports cars through the ‘80s, the Sauber team entered Formula One in 1993. Over the years, Sauber raced in F1 with various partners, before evolving into Alfa Romeo Sauber F1 Team in 2018.
This return of the iconic Italian brand to the pinnacle of motorsport was four years into the FIA’s adoption of 1.6 litre hybrid V6 engines with innovative recovery systems for heat and energy. As a global sport, F1 is perfectly positioned to showcase sustainable technology.
However, the heart of F1 is racing. Lead Driver Valtteri Bottas highlighted the difference between the old 2.4 litre V8 engines and the new hybrid powertrains: “For sure, the sound is very different. The biggest change, in terms of how it feels, is that nowadays the hybrid engine has more power and much more torque.
“The drivability through the different rev range of the engine is super smooth, because of the torque. The new engines
have more things the driver can adjust, in terms of the deployment strategies.”
Hybrid powertrains include a battery pack that the driver can deploy to deliver up to 161 bhp engine boost per lap. This is assuming the driver has previously harvested the required energy for the battery. Managing the harvesting and deployment of this bonus power falls to the driver, who already has many distractions in the cockpit.
“A driver needs to be quite smart with battery management,” continued Mr Bottas. “Some of these processes are almost automatic in a way, but it is still something else the driver needs to manage.”
Fans watching F1 cannot see the immediate consequences of a greater workload on a driver. What they want to see is better
racing. So, has the switch to hybrid engines also brought improved racing to the world’s premier racing formula?
“There are now more things that a driver can mess up,” Mr Bottas explained. “We definitely have more opportunities for racing in the hybrid era, which is beneficial for the drivers, and also for the spectators.”
“The hybrid engines are probably a bit better in terms of overtaking,” agreed Mr Vasseur. “They open doors for new management from the drivers and offer strategic options that the team can play with.”
With hybrid engines improving the spectacle of F1, this is only part of the FIA’s overall strategy for sustainability. “The authorities
Nationality: Finnish Born: 28th August 1989
F1 Career:
• 2022- Alfa Romeo F1 Team ORLEN Race Driver
• 2017-2021 Race Driver for Mercedes-AMG Petronas Motorsport with 10 GP wins
• 2013–2016
Race Driver for Williams
• 2012 Official Reserve Driver for the Williams F1 Team
in F1 took the lead on this,” Mr Vasseur said, “launching a new era in Formula One.
“We had a new version of our engine in 2014, and now the fuel system – the sustainable fuel. The sport can play the role of leader in the system, clearly pushing the development of sustainable technology.”
“The F1 engine is the most efficient hybrid in the world,” Mr Bottas agreed. “The automotive industry is learning a lot from F1. Also, the sport is increasing the biofuel percentage, which is important. I believe biofuel is the future, and F1 has such a big platform to promote it.”
It is this combination of exciting, sustainable technology and a global sport that presents the FIA, and teams such as Alfa Romeo F1 Team ORLEN, with a vital role in promoting sustainability. As Mr Vasseur emphasised, it is not enough to simply adopt the technology, the sport needs to communicate its amazing achievements; these hybrid engines compete at speeds of up to 350 kph.
“For sure, we have taken a major step forward in terms of project ambition,”
he continued, “with sustainable fuel in the new regulations for 2026 and a 50% electric powertrain.”
Fully embracing the FIA’s Environmental Strategy, Alfa Romeo F1 Team ORLEN enjoys impressive green credentials, according to Mr Vasseur: “Firstly, we achieved three-star accreditation from the FIA, which was a big step forward. The second project we put in place was reaching the ISO 14001 certification.”
Alfa Romeo F1 Team ORLEN, as part of the Sauber Group, has sustainability as an integral part of the company. This philosophy focuses on two main elements – the environment and the community.
In terms of the environment, Alfa Romeo F1 Team ORLEN adopts a two-step approach through decarbonisation, along with waste management and recycling. The team also invests in CO2 offsetting via programmes of forest conservation and clean water supply.
Alfa Romeo F1 Team ORLEN’s community strategy concentrates on social development, along with promoting diversity and
Nationality: French
Born: 28th May 1968
F1 Career:
• 2019-2022 Team Principal of Alfa Romeo F1 Team ORLEN
• 2017-Managing Director & CEO of Sauber Motorsport AG
• 2017-2018 Team Principal of the Sauber F1 Team
• 2016-2017 Team Principal of the Renault F1 Team
inclusivity. The team partners with the charity Save the Children to advance children's rights around the world. Support from the team helps Save the Children run projects in Switzerland and globally.
Members of Alfa Romeo F1 Team ORLEN also take an active role in their personal sustainability. “For the last three years, whenever I fly, I always offset my carbon footprint,” explained Mr Bottas. “And I fly a lot, including private flights. However, I offset basically twice the carbon for every flight.”
For all the technological wonders of the latest Alfa Romeo F1 Team ORLEN C42 car to have a wider impact, these sustainable developments in F1 need to trickle down to road cars. “Alfa Romeo F1 Team ORLEN is a good example of this,” Mr Vasseur agreed, “because we are almost on the same path, with the road car division moving to hybrid and fully electric cars.
“Hybrid technology is already here. Some countries are still pushing for fully electric
vehicles, but it absolutely makes sense for F1 to stick to this technology. And we have to keep in mind that we will introduce more developments in 2026 with the sustainable fuel.”
The future for F1 and Alfa Romeo F1 Team ORLEN remains sustainable and a source of inspiration for the global audience of motorsport fans. This combination of innovative technology and a motivated team is a winning formula.
“Being able to race against the best drivers,” Mr Bottas said, “the best teams, on the best tracks in the world, that is really, really cool. But also, how innovative F1 is as a sport, how much the technology can help the future of the earth, with a big push for sustainability, that is also pretty cool.”
“I love competition,” concluded Mr Vasseur, “simply the competition! Coming from a racing background, I'm always trying to motivate the company, to show that we need to do a better job tomorrow than we did today.” n
PECOL Automotive SA is a specialist in the automotive industry, producing cold formed fixing components. Opening in 2001 under the wing of the PECOL Group, the company has an impressive production capacity, manufacturing 130 million parts per month. Technical Manager Daniel Santos spoke in-depth about PECOL Automotive’s impressive production capacity and discussed the company’s most recent investments, in conversation with Imogen Ward.
The presence of an exceptional inhouse manufacturing process has solidified PECOL Automotive’s market lead in the production of automotive fixings. This extensive range of machinery has ensured the company can supply the highest-quality products to its clients in record time.
“We make everything in-house, except steel wire,” Technical Manager Daniel Santos said. “Because we can produce so much in-house, we are very flexible and adaptable. We don’t have to rely on anyone else, resulting in much shorter lead times for our clients.”
PECOL Automotive has been ahead of the manufacturing game since it was first established in 2001. With a plethora of support and knowledgeable experience provided by its parent (PECOL Group), the company has a strategic position within the automotive industry.
Alongside its headquarters, located in Águeda, Portugal, the company is supported by four PECOL Group industrial units located nearby. These units manufacture parts using cold forming, produce tools and special hard-metal parts, have heat treatment facilities and distribute PECOL products. The company also has supporting warehouses in Spain, Italy, Poland and Morocco. In Spain, the PECOL Group company INKATOR manufactures parts through cold forming. These facilities enable PECOL Automotive to manufacture 130 million parts every month – securing the company’s reputation as a steadfast competitor in the automotive industry.
After purchasing its first annealing furnace in 2017, PECOL Automotive opted to further invest in growth by acquiring a second furnace. This decision resulted in a successful expansion of the company’s production capacity and will lay the foundations for in-house steel wire p roduction. With this development, 100% of the production process will occur inhouse at PECOL Automotive.
“We have automotive tooling production and raw material annealing,” Mr Santos said. “For setting and conforming products, we have raw material pickling and phosphating. PECOL Automotive invested in a portfolio of machinery so our customers could have products delivered to them quickly and without delay.”
In more recent times, this integration has greatly aided the company. With global supply issues becoming increasingly problematic for many, using its in-house processes, PECOL Automotive has successfully minimised the impact of supply delays.
An investment of €1.5 million was also dedicated to the acquisition of a new in-line stamping machine. This purchase was in response to an increasing customer demand for larger parts. With this new machine, PECOL Automotive can now stamp parts that have a diameter of 33mm and are 180mm in length. This 450-ton machine enables the company to cold form, shear, die and bridge parts – making the whole production process more efficient.
To improve its sustainability, PECOL Automotive implemented a forwardthinking environmental management strategy. The company installed on its facilities 3,500 photovoltaic panels, covering an area of 10,000 square metres. To clean these panels, the company collects and stores rainwater (significantly reducing its water usage). This rainwater is also used to supply the factory’s tank for its firefighting system – highlighting the company’s dedication to a safer, more environmentally conscious future.
PECOL Automotive also sends all the wastewater from its productions to a dedicated facility where it is subjected to physical-chemical treatments. This process greatly reduces the environmental impact of wastewater disposal. The company is really dedicated to finding unusual and ingenious ways to recycle: one way that PECOL Automotive achieves this eco-friendly goal is through the creation of a continuous oil lifecycle. All the oil used in PECOL Automotive’s stamping machines is processed through a filtration system.
This oil can then be reused in the stamping machines.
“By implementing these processes,” Mr Santos said, “not only do we actively save around €10,000 a month, but we are also helping save the planet too. This is so important to us.”
The company maintains robust relationships with its suppliers, including DIMAC who produce almost all of PECOL Automotive’s machines. “We have successfully maintained this relationship with DIMAC for over 20 years,” Mr Santos said, “relying on them not just for the manufacturing of our machines, but also for the upgrading and maintenance required to keep them in optimal condition.
“We always make sure to give feedback on the work of our suppliers. This client/ customer interaction is extremely important; without that you are not helping the suppliers to upgrade and improve their products.”
Thanks to the flexibility of its in-house manufacturing, PECOL Automotive has extensive product advancement opportunities. To maintain its reputation as a market leader the company also invests heavily in research and development. By monitoring the evolution of technology within the industry, PECOL Automotive can develop
300 new products each year (advancing and evolving alongside the market).
The company’s Engineering Department carries out equally complex and innovative projects, and continuously researches the best solutions for PECOL Automotive’s customers. This dedication ensures the most practical and quality-driven product is available, whilst still meeting client expectations and specifications. In doing so, the company maintains 100% control of the process, from design to production, giving its customers complete peace of mind.
PECOL Automotive also relies heavily on its workforce of over 270 professionals; with trust at the helm, the company prides itself in being internally autonomous when it comes to the development and construction of tools.
This creative freedom gives the company a strong competitive edge. Continuous training and experience also ensure PECOL Automotive’s engineers are some of the most competent tool developers in the industry.
“Our vision for the future will come to fruition with people who have knowledge of new technology,” Mr Santos concluded, “Our continued acknowledgement and investment of advanced technology, as well as our dedicated in-house manufacturing process, secures the future of the company.
“PECOL’s future relies on the people that work here: we will all continue to cooperate, solidifying the very best future for the company.” n www.pecolautomotive.com
Retrac Group, an engineering, design and manufacturing specialist, has positioned itself at the forefront of the revolution in developing lightweight applications for sustainable transport solutions. Having launched its Retrac Future range of sustainable composites to industry approval, Retrac Group CEO Dan Walmsley, CCO Tim Scott and Head of R&D Alan Purves outlined how the company is now set for expansion in its 50th year.
Profile by Andy Probert.
The Retrac name may well be the original owner’s surname backwards; it is, however, fast-forwarding its engineering, design and manufacturing compe tencies in the sustainable bio-composites sphere at full throttle. The Group, which rests 50 years of excellence on its composites-metallics axis, is a leading supplier to blue-chip clients in the Formula One, automotive, aerospace, and motorsport sectors. Based at Swindon, in southwest England, Retrac supplies production components and mould tools, along with design, research and development services.
In alignment with the future transportation supply chain’s trends for sustainable lighter applications and a marked reduction in carbon emissions, the company has devised Retrac Future, a portfolio of sustainable and recycled composite materials.
“This range demonstrates to customers the breadth of what is possible with our various processes,” said Retrac Group CEO Dan Walmsley, “given the world is on the cusp of a lightweighting revolution.”
It is just one of the many exciting elements Mr Walmsley and his team continue to evolve at the company.
Retrac’s half-a-century of business exploits notwithstanding, its paradigm shift to an Employee Ownership Trust (EOT) structure 18 months ago continues to see the company soar. Expansion and further innovation are also around the corner.
“The EOT has been bedding in for over a year,” said Mr Walmsley, “but through hard work from the team, we have not seen any slowdown in company performance. It offers exciting potential for years to come.”
While acknowledging that an EOT essentially places the future of the business into employees’ hands, Mr Walmsley said staff were more engaged than ever to ensure future success. Indeed, their workforce has risen from 115 to 170 personnel in less than a year to cope with an influx of new contracts and con -
tributed to Retrac posting a 45% uplift in turnover.
One such milestone under the new structure is the announcement that Retrac will expand its operations into a new facility, additional to its 50,000 sqft multi-axis machining facility.
Mr Walmsley said the expansion is solely to meet a specific contract to serve the needs of an automotive OEM in the Electric Vehicle (EV) sphere. “It’s an amazing opportunity for Retrac,” he confirmed. “The new facility will give us the adaptability to support all elements of the project, which will have a particular focus on sustainability.
“It is a high-level statement of intent from Retrac’s perspective, bringing additional people to the workforce and placing us firmly within the sustainability space.”
Retrac will focus on a specific component in the cab of a commercial vehicle, with the first production destined for 2023, according to Retrac Group’s CCO Tim Scott: “Sustainability is a key commercial consideration that we need to be involved in and evolving in, given the current market conditions – and certainly, if we want the business to be here in 10 to 20 years’ time.”
The company has developed the Retrac Future range of bio-composite materials. The options, including natural fibres with a positive carbon impact, have been developed to offer greater access to high-performing sustainable materials. Emerging from an extensive R&D project by Retrac’s composites division, the range includes recycled carbon fibre and natural-fibre products suitable for multiple applications across lightweight structures.
Bio-content resin systems enhance the eco-friendly credentials of these composite
materials alongside an energy-efficient production process featuring bespoke compression moulding techniques.
“The options demonstrate what is possible with our various processes using sustainable and recycled materials,” explained Alan Purves, Head of R&D. “These developments have been built on the back of exceptional experience, vision and hard work in-house.
“We have invested in R&D to develop our manufacturing capability using numerous interesting materials. That gives us a great platform to offer clients tailored solutions for their specific requirements in sustainable composites.”
Bio-composites and their positive sustainability are quickly becoming game changers for the transport solutions sector according to Mr Purves: “Our advances are also contributing to starting a conversation with customers and their understanding of sustainability, the future for their applications and what they are trying to achieve. What Retrac offers is the art of the pos sible in today’s world.”
As part of this R&D effort, Retrac Group forged alliances with leading flax natural fibre specialist Bcomp and Composites Evolution, a UK-based prepreg manufacturer and supplier that launched the Evopreg ampliTex prepreg range. The prepregs combine the high-performance Evopreg epoxy resin systems with Bcomp’s ampliTex range of flax reinforcements.
Using Evopreg ampliTex alongside Bcomp’s powerRibs reinforcement system, Retrac produced a demonstrator bonnet panel for a race-bred supercar to form one of the new bio-composites range.
Two thermoplastic materials have been developed from woven carbon and woven glass, which can be manufactured in the company’s compression moulding press system. The 60-tonne bespoke electric servo press is used for product development and allows precise control of position and load at every part of the pressing cycle.
“Making those major inroads in development reflects well on the business,” Mr Purves added, “and on the broader
UK manufacturing sector as a sustainable innovation hub. As globally sustainable transport solutions evolve, Retrac is determined to be central to that.”
Mr Walmsley agreed: “These materials now allow Retrac to positively influence customers’ decision-making, impact their success and futures.”
The new bio-composites range has invigorated the market and focus, with the Retrac Group fielding two to three calls of interest a month from new UK and overseas clients.
“Retrac Group is a relatively small company,” reflected Mr Scott, “but it is taking huge steps in innovation that has caught the attention of larger busi nesses who are approaching us, interested in what we are achieving. The new contract and our expansion is a result of Retrac Future’s innovation.”
Confirming its commitment to being an integral part of the future transportation supply chain, and keeping abreast of customers’ sustainability drives, Retrac Group is signed up to the UK Government’s SME Climate Commitment to halve its greenhouse gas emissions by 2030 and achieve Net Zero emissions by 2040.
“Retrac’s commitment to sustainability and bio-composites innovation demonstrates how far ahead it is in this space,” concluded Mr Walmsley. “It’s apt that we are celebrating our 50th anniversary with such breakthroughs and look forward to a greener 50 years of new materials, tech and innovation.” n
one planet – one chance – one voice
An introduction to the manufacturing sector, with innovations, sustainability facts and a ceramic bearings special report, followed by company profiles
Latest innovations from the manufacturing industry
BASF and MedAccess have accomplished their goal to supply 35 million Interceptor G2 mosquito nets to 16 countries in sub-Saharan Africa by the end of 2022. The agreement to supply the mosquito nets is part of a financing partnership involving both companies and the Bill & Melinda Gates Foundation.
This target was reached ahead of schedule, meaning that 63 million people are now being protected by Interceptor G2 nets. This sees BASF Agriculture contributing to several of its stated Sustainability Goals: the eradication of poverty, improved access to education and a commitment to innovation.
A breakthrough
BASF works with partners and agricultural experts by integrating sustainability criteria into all business decisions to help create a positive impact on sustainable agriculture. A study published in the medical journal The Lancet confirms that Interceptor G2 nets bring additional public health value compared to conventional nets. The results from trials in Tanzania show that over the period of two years, Interceptor G2 reduces malaria incidence by 44% and the number of captured malaria-infected mosquitoes by 85% compared to standard nets.
“Millions more people now have access to a powerful new malaria prevention tool that can help drive down cases in areas with insecticide resistance,” said Trevor Mundel, President of Global Health at the Bill & Melinda Gates Foundation. “We’re proud to be part of this agreement with BASF and MedAccess which was able to deliver on its ambitious goal, demonstrating the ability of innovative partnerships to deploy critical solutions in the fight against malaria.”
According to the World Health Organisation’s 2022 World Malaria Report, there were 247 million cases and approximately 619,000 deaths from malaria globally. Children under five are especially vulnerable and nowhere is the problem more severe than in Sub-Saharan Africa.
Long-lasting insecticide-treated mosquito nets play a vital role in protecting people from malaria, contributing to falling cases in the past two decades. However, mosquitoes have developed resistance to the active ingredient, a pyrethroid, that has been used for bed nets since the 1980s. As a result, since 2017, the number of cases started to rise again.
To combat the insecticide resistance and respond to the call for innovation in the prevention of malaria, BASF developed Interceptor G2 nets. This new generation of nets is treated with a pyrethroid and a pyrrole compound new to public health.
“Accelerating access to innovations like Interceptor G2 mosquito nets is essential if we are to reduce malaria’s burden on communities and eventually beat the disease completely,” said Michael Anderson, CEO of UK-based social finance company MedAccess. “Our partnership with BASF and the Gates Foundation has enabled millions of people to benefit from the additional protection these nets offer more quickly, as well as making the nets more affordable and ensuring reliable supply.”
To successfully continue the fight against malaria, BASF has already begun the development of a third generation of nets. n
Latest innovations from the manufacturing industry
Sybron, a leading UK supplier of cleaning, hygiene, and catering products to some of the largest names in hospitality, has launched its first own brand with SyBio, a range of biotechnology-based cleaning products. Partnering with BioVate Hygienics, Sybron has developed a range of products that has replaced harmful, non-renewable chemicals with adaptive biotechnology that cleans, disinfects and protects.
SyBio is a range of biotechnology-based products that combines probiotic, enzyme and plantbased ingredients to maximise performance with minimal environmental impact. The SyBio products consist of concentrated cleaners, sanitisers and detergents delivered through wall mounted dispensers for optimal dosage control.
“BioVate Hygienics has pioneered the evo lution of biotechnology-based cleaning products and shares our passion and forward thinking for sustainable cleaning and development of green cleaning methods,” said George Mason, Sales & Marketing Director at Sybron. “Our objectives for the range are to deliver environmentally friendly products that provide safer applications and improved performance, along with reduced costs.
“Our partnership with BioVate Hygienics provides the expertise and innovation that has enabled us to develop an extensive and diverse range for our clients,” continued Mr Mason. “Developing our own range has given us more control to deliver specialist products for every cleaning requirement. It also gave us the
opportunity to offer a superior cleaning performance that is cost effective and with minimal impact on the environment. All products are highly concentrated formulas, which, based on cost-in-use figures, provide a 15-20% saving against other ranges.”
SyBio uses plant-based and bio-based surfactants, utilising the latest biotechnology that mixes natural enzymes and bacteria, which has 30 times more actives than any other biotechnologybased cleaning range. What is more, using SyBio provides long term protection for surfaces through a residual clean. After use, SyBio leaves a layer of good bacteria that protects surfaces against dirt and pathogens for up to 30 days.
“The more you use SyBio, the cleaner and safer your environments become,” explained Mr Mason. “Using naturally derived ingredients reduces toxicity compared to traditional chemical-based cleaning products. Using science-based biotechnology increases performance and sustainability across your cleaning protocol. SyBio’s concentrated formula brings the cost efficiencies we all need at this time, along with a huge reduction in plastic.”
Interesting and unusual sustainability facts from the manufacturing world
In 2020, food waste in the EU amounted to an average of 127kg per inhabitant, 70kg of this being household waste.
If used for 12 hours a day, the average LED light bulb will last more than 11 years.
About 36% of all plastic produced is used in packaging. Approximately 85% of this packaging ends up in landfill or as unregulated waste.
If all the jeans owned by UK adults were bought brand new, then the production of those jeans would emit more CO2 than a coal-fired power station running for 18 months.
– Anthony Robbins –“ “
Every problem is a gift, we would not grow without problems
Around 6% of the food sold in the United States was certified organic in 2020.
Glass is 100% recyclable and can be recycled endlessly without loss in quality or purity.
The UK has the highest global recycling rate for cardboard, diverting about 2 million tonnes of waste away from landfill annually.
A 2021 review lists the top three countries with largest reforestation gains as China, Australia and India.
SMB Bearings Managing Director Chris Johnson highlights the different capabilities of bearings and the importance of choosing the right component for the task.
Approximately 27,000 ceramic tiles cover the exterior of the NASA Space Shuttle — a reusable spacecraft that carries astronauts in a low orbit around Earth. Acting as a thermal barrier to the 1,650 degrees Celsius generated by atmospheric re-entry, the tiles illustrate the impressive resistance of ceramic materials. The same impressive properties of ceramics are also being used in bearings. Chris Johnson, Managing Director of ceramic bearings specialist SMB Bearings, explains the specifications, capabilities and differences of full ceramic and hybrid bearings.
Ceramics are primarily used in bearings due to the material’s corrosion and temperature resistant properties. Ceramics are inert, whereas metals are reactive, making ceramics resistant to corrosive materials such as seawater and many chemicals, including acids and alkalis. As ceramic bearings do not corrode, they require less maintenance than their steel alternatives and can be used in highly hostile environments.
Unsurprisingly, these corrosion resistant properties allow for ceramic bearings to be used in many industries, ranging from food and chemical production to marine and underwater applications. However, there is some confusion. Often, what people refer to as ceramic bearings are
actually hybrid bearings. So, what is the difference between full ceramic and hybrid options?
Full ceramic bearings have ceramic rings and balls and either a synthetic cage made from PEEK or PTFE, or no cage at all. They are highly resistant to acids and alkalis and are therefore suitable for use in very corrosive environments. Silicon nitride (Si3N4) bearings can be heated to temperatures of 800 degrees Celsius when used without a cage. Pairing these qualities with their light-weight nature, at 45% of the weight of steel bearings, they are incredible substitutes for tra ditional metal bearings.
An additional feature of full ceramic bear ings is how they are also non-mag -
netic, meaning they can be used in medical devices such as MRI scanners, or any appli cation where there is a strong magnetic field. However, the greater hardness of ceramic bearings also means greater brittleness and as such, they do not tolerate shock loads well.
When most people think of ceramic bearings, they are usually actually referring to hybrid versions. Hybrid bearings sit between full ceramic and steel options. While they use ceramic balls, these bearings are paired with metal inner and outer rings. Using this combination allows for higher speeds than full ceramic options, as the less brittle metal rings are not as prone to sudden catastrophic failure under high speed or load. Despite the small difference in design, hybrid bearings’ requirements differ quite extensively from full ceramic bearings. For example, while full ceramic bearings do not require lubrication, hybrid bearings do. However, although the ceramic
SMB Bearings Managing Director Chris Johnson highlights the different capabilities of bearings and the importance of choosing the right component for the task.
balls will still abrade the steel rings, hybrids will cope with marginal lubrication better than steel bearings due to the low friction coefficient and lightness of the balls.
Lubrication may not be required when using hybrid bearings at very low speeds. As these bearings are often selected for higher speed applications than full ceramics, suitable lubrication is advised. Precision hybrid bearings with a high-speed cage are capable of very high speeds hence their use in, for example, machine tool spindles.
According to research by SKF USA Inc, improper bearing lubrication accounts for up to 50 per cent of machine failures. This comes as machine and equipment manufacturers feel pressure to reduce costs without sacrificing machine performance — a difficult balancing act. Thus, the right choice here
can impact the longevity of machinery and enhance the overall sustainability of a business.
The corrosion resistant properties of the bearing are also affected when choosing a hybrid version over full ceramic. While the ceramic balls are highly resistant, the overall level of corrosion resistance is reduced due to the use of metal rings, even if they are stainless steel.
Decisions on whether to choose ceramic bearings or hybrid bearings will come down to cost, the application and the hostility of the environment in which the bearings are to be used. While an application may not require ceramic bearings with the extreme temperature resistance of the NASA Space Shuttle, a better understanding of the dif ferent types should make this decision a little easier.
SMB Bearings originally specialised in miniature bearings, thin-section bearings and stainless-steel bearings. By natural progression, the company expanded the range to include other corrosion resistant bearings such as plastic bearings, 316 stainless bearings and ceramic bearings. Remaining a specialist business, SMB Bearings provides a high level of product knowledge, providing bearing and lubrication solutions to existing or potential customers, whether individuals or large corporations. SMB Bearings does not just sell bearings, but helps to solve a customer’s problems. n
For further information please visit: www.smbbearings.com
In 1974, Stuga Machinery entered the fenestration industry under the name Thomas Engineering. Pioneers of CNC machine tools and automated machinery, the company became renowned for its ZX series, which is still being produced today. Managing Director Ed Williams discussed the success of this product line and gave insights into the important efforts Stuga is making to improve its sustainability. Reporting on the company is Imogen Ward.
The fenestration industry was revolutionised by the creative heads at Stuga Machinery, seeking ways to overcome huge consumer demand for uPVC products as the industry moved away from traditional steel/aluminium and wooden frames. Since bringing the world-renowned ZX series sawing and machining centres to the market, Stuga has continued to develop its designs to improve the automation of critical fabrication processes and retain its competitive edge.
“Our latest model in the ZX line of machines has an optimisation feature that minimises waste,” Managing Director Ed Williams said. “It does this by looking ahead at the other orders in the programme queue and cutting the plastic profile into required sizes. The designers were working to a clear brief to reduce waste and the response of the industry to the final solution was very positive.”
All Stuga’s machines are designed and developed at the company’s manufacturing centre in the coastal town of Great
Yarmouth, Norfolk. With over 35 years’ experience in the fenestration industry, Stuga continues to bring innovative products to the market. The reputation for reliability and service has not gone unnoticed, and earlier this year the company was purchased by Stürtz Machinery.
After Stürtz’s takeover in February, the parent company highlighted a need for more factory space. This led to the more recent expansion of Stuga’s factory. This resulted in production space doubling and enabled Stuga to substantially increase its manufacturing capacity. As an added bonus of the expansion, Stuga has enough room to display Stürtz machines in-house Although the Stürtz products are manufactured in Germany, having these display models enables Stuga to complete demonstrations for clients, creating additional marketing for these products within the UK.
Stuga is renowned for its ZX series of automated machines. Designed by Gareth Green, the ZX machine innovated the production of windows, reducing labour whilst improving manufacturing times and cost effectiveness.
“Gareth patented and developed a rotary ring system for the machine,” Mr Williams explained. “The ring incorporates multiple tooling stations and is capable of carrying out multiple machining functions simultaneously. This tooling ring improves the speed of machining in an extremely cost-effective way. It would cost our competitors considerably more to achieve the same production levels.”
The most recent model in the ZX line was developed with an optimisation feature. The ZX5-S assesses cutting and sawing profiles using computer-based intelligence,
which results in a more economic process. “Having analysed real production data,” Mr Williams said, “it shows that this system can save up to 5% on the overall consumption of profile, due to the decrease in waste material.
“Plastic profile can cost between seven and twelve pounds per metre, and a company could be using hundreds of thousands of metres per year. If, for example, a large company uses five million pounds worth, a 5% saving of that would be quite substantial. Even a smaller company that only spends 50,000 pounds would make significant savings.”
The company also offers additional machinery, including the entry-level AutoFlow-2 Sawing and machining Centre, an in-line solution designed to appeal more to start-up and lower volume output businesses. The AutoFlow-2 can produce around 400 windows per week.
Just like all Stuga products, this machine is built with high-grade components that increase its reliability. As a result, the company has to replace fewer parts; this
reduction in spare part consumption is better for the environment and helps save customers money too. Stuga’s dedication to the environment is also evident in the company’s ICC SME360X Certification following an environmental impact assessment.
Stuga’s machines are durable and withstand the test of time. The company’s confidence in the products is highlighted through its refurbished machinery programme. This option became available a decade ago and helped improve customers’ environmental impact, offering an alternative option to buying new
“We buy older machines from our customers who purchased them 10-15 years ago,” Mr Williams said, “then we strip the machine down to its chassis and replace all the old electronic and mechanical OEM components. This includes the servos, drive motors, sensors and bearings. Sometimes we even add new functions to the machines, but we are effectively selling customers a refurbished as-new machine. This
means companies can purchase a Stuga machine for considerably less than the list price of a new like-for-like system.
“We are prolonging the lifecycle of these machines, upcycling them and encouraging machinery recycling. New businesses tend to start with very manually oriented production processes, but eventually, they reach a point where the volume of orders is too much to keep good quality control with the workforce they have, whilst maintaining output demand. At that point , automation is the most sensible path to go down, but small businesses don’t have access to unlimited funds; our refurbished machines are the perfect solution, allowing smaller businesses to stay competitive in a huge market.”
As part of this service, the company offers a 12-month warranty for parts and labour. This highlights Stuga’s confidence in these ‘as-new’ machines.
Since becoming a subsidiary of Stürtz, Stuga has set out goals for diversification and expansion of product capabilities. Stuga are already selling and servicing the entire portfolio of Stürtz equipment, including welding and corner cleaning, logistics and handling solutions.
This purchase also benefits existing Stürtz customers – there is already a large instal lbase in the UK market – giving them access to a vast array of first-class engineers who are based across the UK and offer the very best machine maintenance.
“We have 11 engineers,” Mr Williams said, “who carry out planned maintenance and breakdown repairs.
“Having this structure in place is really important for Stuga because, as they say, a sales representative can sell the first machine, but the reliability of the product and the service support provided is what
keeps customers coming back. Previously, Stürtz didn’t have reliable UK representation, so the Stuga acquisition helps tackle this critical challenge.”
As part of its investment into expansion, Stuga is also adding new members to the workforce. Mr Williams is bringing an array of business strategies to the company which will set about delivering sustainable and profitable growth – including the immediate objective to build a sales and technical team that can sell and support the range of Stuga and Stürtz products.
The company hopes to continue working with its long-standing suppliers who are local to the business, Stuga has maintained these relationships since the 1990s, regarding them as critical.
“Stuga has always designed its own parts, but the manufacturing of those –the metal parts anyway – has always been completed by our local supply chain,” Mr Williams concluded. “We like the fact that we have these great relationships with fabricators around the Great Yarmouth area.
“Gareth always liked the idea of working within the community and helping keep businesses alive and afloat, especially during the 90’s when the automotive industry was collapsing. It works both ways, when Gareth approached the local manufacturing companies, they threw their arms around the business and really supported us too, they have ever since.”
Hydra-Perm-Co Ltd is a UK manufacturer and supplier of hydraulic equipment. A large scope of the company’s operations is as distributor for Permco Inc, a US-based hydraulic manufacturer. The two enterprises work closely together, Hydra-Perm-Co being the sole UK manufacturer and European distributor of Permco cast iron gear pumps, motors and flow dividers. Debbie Patrickson, Managing Director, explained to Hannah Barnett how her family’s firm operates so fluidly.
ASPermco’s distributor for four decades, Hydra-Perm-Co has an extensive knowledge of the US company’s products for mobile or industrial applications. The two businesses work synergistically together. The Permco assemblies are manufactured at Hydra-Perm-Co in Leeds for distribution all over the world.
Hydra-Perm-Co’s Managing Director
Debbie Patrickson has been at the company since establishing it alongside her parents in 1991.
Hydra-Perm-Co may have been founded in 1991, but its relationship with Permco stretches back even further.
“My father, Ken Smith, started his business, K.S. Hydraulics in 1974,” Debbie explained, “and he became a Permco distributor in 1982”. So, by 2022, the family have been distributors for 40 years.
Hydra-Perm-Co initially started out supplying Permco products but has increased its range since then. The company is now UK agent for PONAR Wadowice, a Polish company who offers valve components across various sectors. Additionally, they are distributors for Hydreco Hydraulics, and more recently became the UK distributor for Hidrapac, a Turkish manufacturer of piston pumps and motors.
Good relationships with many, longstanding equipment suppliers means Hydra-Perm-Co can offer customers a variety of other hydraulic compon-ents too.
The company may only be small, but Hydra-Perm-Co operates efficiently.
“We have new customers coming on board all of the time,” Debbie said: “I believe we have a good reputation throughout the industry. Manufacturing from kit-form means we are very flexible as well. So, we're not dependant on one particular design; we can produce different variants.
“We can build an assembly in a few hours if the parts are in stock. Some companies are quoting weeks, months and unbelievably , even years. If we have the stock, and the customer needs it quickly, we can do it.
“Having an experienced team, including sales, machining, production and despatch makes the company stand out from its competitors”
Debbie identified other key milestones in the development of Hydra-Perm-Co.
One is being awarded the ISO 9001:2015 quality standard, another is having ATEX approval on Permco products, which means they can be used in explosive atmospheres. This sort of accreditation has helped Hydra-Perm-Co contribute to its sustainability.
Other areas of sustainability have been to reduce our energy consumption by
installing LED lights and motion sensors within the business.
“We’ve invested in oil contamination control equipment to keep the oil in our test rigs clean,” Debbie continued. “This reduces our waste, as we continuously recycle the oil. We recycle around 80% of our packaging, and where we need to buy new, we only use environmentally friendly products”.
The company employs just 11 people currently, Debbie included. She acknowledged that it has been difficult to recruit staff since Covid. Not that this has impacted on the company’s output or productivity; turnover remains healthy. The dedication of all employees is a crucial part of the business.
According to Debbie, the turnover has been increasing at a steady annual rate and the company expects it to reach around £1.5 million at the end of the next tax year. A good supply of parts remains crucial for an operation like Hydra-Perm-Co and a key facet in the company’s vision for continued growth. “We want to increase
stock so we can offer a quick turnaround to meet customer demands,” Debbie explained. “We hope to invest in a new software system too, to streamline our processes.”
Debbie revealed that she wants these various investments to contribute to an expansion of sales of the Permco products across Europe for Hydra-Perm-Co: “We just want to get our name out there as much as possible. Because of Covid, we've not been travelling, but hopefully we can pick that up in 2023. Now things are relaxed with restrictions, we can look
for new customers: maybe even find new distributors that we can help to set up in Europe as manufacturing centres. That’s something I've got in mind.”
The Managing Director emphasised Hydra-Perm-Co’s customer service when reflecting on what makes the company |so good at what they do.
“What keeps us going is the repeat orders from customers,” she said. “We thrive on that. It's nice to get referrals and testimonials. We’re clearly doing something right. Customers keep coming back to us. It’s nice to speak to them and
discuss new applications too. Hopefully, we can grow the business with existing customers and new ones.”
The dependability and efficiency of HydraPerm-Co is difficult to contend, with its 40 years working alongside Permco evidence enough of the company’s dominance as a distributor of hydraulic equipment. It may be a small-scale operation, but its team is clearly infused with knowledge and experience, which takes priority over all else.
When interviewed, Debbie was asked what motivated her to come into work every day and she replied: “Well as it’s still a very male dominated industry, I am faced almost daily with a hesitant caller who is reluctant to discuss their enquiry as they expect me to pass them on to a male colleague.
“However, it’s quite satisfying that I have an extensive technical knowledge and can hold my own.”
UK-based Cadillac Plastic Limited is a supplier of highperformance plastic films and filmic adhesives to various industry sectors. With customers in the UK and Europe, and over 40 years of experience, the company leads the way in providing the most technologically advanced and appropriate solutions. General Manager Simon Jones shared the latest developments and the company’s plans for further growth. Report by Phil Nicholls.
Earlier this year, Cadillac Plastic became the exclusive distributor within the UK and Eire for the Autotex® and Autoflex® hardcoated industrial films from MacDermid Autotype. As so many industries bounce back from the Covid pandemic, this is a welcome development for Cadillac Plastic and underlines the potential for growth within the sector.
“We were very pleased to be appointed exclusive converter and distributor of the MacDermid Autotype range,” explained General Manager Simon Jones, “because it helps us reinforce our position as a ‘one-stop shop’ for our customers. The MacDermid
Autotype range adds a wide variety of materials to our already comprehensive portfolio.”
Cadillac Plastic endured the Covid pandemic thanks to a strong footing in many sectors. When demand fell from one set of customers, another area experienced growth. These fluctuations balanced out, allowing Cadillac Plastic to continue trading during the pandemic and emerge ready to embrace new opportunities, such as this agreement with MacDermid Autotype.
The experienced, 18-strong team operates its warehouse and production facilities in Swindon, Southwest England. Cadillac
Plastic’s comprehensive, in-house conversion capabilities cater for individual sheeting and slitting requirements at no extra cost, enabling customers to save money through the elimination of waste. The company also offers bespoke product solutions, including die-cutting and laminating.“We have a
Cadillac Plastic offers:
• Sabic Lexan TM polycarbonate films
• DuPont Teijin Polyester films
• 3M TM Adhesive films and tapes
• MacDermid Autotype Range of polyester and polycarbonate films
• DuPont Tyvek®
• Nitto Adhesive films and tapes
Major brands including Folex, Toray, Avery Dennison, Transcontinental and Kimoto.
Also, Cadco, TeknekTM clean machines, BoltaronTM , Cadco Jet-MirrorTM , surface protection films and release liners.
strong footing in the aerospace sector,” Mr Jones said, “which is recovering with the relaxation of travel restrictions. Materials required in the manufacture of aircraft are usually specialist, high-value materials such as Lexan Flame Retardant Polycarbonates and Jet-Mirror.
“The largest sector we currently supply continues to be the industrial print market, which feeds into many other sectors and utilises a wide range of materials. Having an extensive portfolio of products is essential and allows us to provide our customers with everything they need.”
The bespoke provision of high-performance plastic films and adhesive products is a critical aspect of Cadillac Plastic’s customer service. The in-house conversion facilities enable the company to convert master rolls of film into precisely cut pieces matching the client’s exact specifications.
The extensive range of films and adhesives at Cadillac Plastic delivered strong growth through 2022. This trend is perfectly illustrated by the recent agreement with MacDermid Autotype.
“A large number of our customers who already used these materials from MacDermid Autotype now benefit from our bespoke services,” said Mr Jones. “This opportunity has also brought new business to Cadillac Plastic, allowing us to start building relationships with an expanded customer base.
“Our customers can expect shorter lead times when ordering from Cadillac Plastic, rather than direct from the manufacturer, because we order stock well in advance, based on expected forecasts. We are better placed in the supply chain to work with customers to identify their needs and convert their specifications into new business. Cadillac Plastic works closely with our key suppliers to give customers technical support, especially on projects where the material has rigorous technical specifications.”
This growth trend is set to continue at Cadillac Plastic, according to Mr Jones: “We will upgrade our central business system in early 2023. Focusing on improving our digital marketing, we are also upgrading our CRM system so we can further build relationships with our customers. To support our forecasted business growth, we are investing in new storage areas and facilities to accommodate our increasing product range.”
Cadillac Plastic’s reputation is based on more than just an extensive portfolio of films and adhesives. “With over 4 decades in the high-performance films and adhesives industry, we are confident that our collective knowledge and experience qualifies us as trusted advisors, and allows us to meet our customers’ needs,” explained Mr Jones.
“Our experienced team has the expertise to assist our customers in finding the most appropriate solution to their needs,
and by providing technical support services which are second to none.
“We work in partnership with some of the industry’s biggest brands such as Sabic, DuPont, 3M, MacDermid and Nitto, along with many others.
Cadillac Plastic provides a source where businesses can buy all their requirements in one place.”
A strong relationship with suppliers plays a huge role in the success of Cadillac Plastic. Maintaining close communication with manufacturer representatives and suppliers enables the company to keep customers up to date with material availability, new products and product changes.
“We recently took some customers to the 3M research and development site, which was a fascinating visit,” Mr Jones said. “Because of our close relationship with major brands, we have access to the best advice and product information for our customers.”
Sustainability has always been part of Cadillac Plastic’s culture, demonstrated by its commitment to upholding the ISO 14001 Environmental Standard since 2006.
“We operate in a responsible and ethical way,” continued Mr Jones. “We are acutely aware of environmental issues and work hard
to reduce the environmental impact of our business.
“We are committed to waste reduction, and monitor our waste output, recycling and energy consumption. Cadillac Plastic always strives to meet, or exceed, environmental regulations and targets. This year, we began recycling more types of waste than ever before, which is another positive move forward.”
Recent events have brought challenges across the industry, notably with regards to the supply of raw materials, but Cadillac Plastic remains optimistic. The experienced team continue to offer high levels of service and the wide range of products that its customers expect.
In conjunction with the expansion into offering the MacDermid Autotype range, Cadillac Plastic plans to consolidate its position as a one-stop shop for customers. The company is continually assessing ways to improve both its facility and services, to
deliver expert advice and quality solutions to customers – where excellent customer service is paramount.
“Cadillac Plastic is the perfect SME,” concluded Mr Jones, “and I feel privileged to be heading a fantastic, highly experienced and motivated team. Every member of staff makes a genuine difference to the business, creating a real buzz and ‘can-do’ attitude within the workplace.
“Many of our customers rate Cadillac Plastic as their best supplier, which brings a great sense of pride, both personally and for the entire team.” n
It seems appropriate that the Ittihad Paper Mill (IPM) started out as a ‘greenfield project.’ That means a business built from scratch, without nearby competitors; a blank sheet of paper, in other words. Slowly but steadily, IPM is making its mark, through innovation, a commitment to sustainable production and a coherent shared vision. Rabih Elassadi, Operations Director at the mill, let Hannah Barnett in on the details.
There were sceptics who did not believe IPM would work. Establishing facilities in 2016 at a 250,000 square metre site in Abu Dhabi, IPM is the first printing and writing paper production facility in the Gulf Cooperation Council (GCC).
Catering to the growing regional demand for paper products, it also serves the international markets, offering a full product range across grammages, shades and sizes.
“The main idea behind it was to produce locally, trade internationally, and try to
diversify the local produce of the country,” said Operations Director Rabih Elassadi. “The UAE has a world-class infrastructure and an integrated transport and utilities network: We simply wanted to utilise these infrastructures, provided by the UAE government, and reach markets worldwide. For many people who are not familiar with the UAE, they think we were crazy for thinking of making paper in the middle of the desert.”
The company’s inception was financed by four banks, along with external funds from the EU. This gave credibility to the project, recalled Mr Elassadi: “They checked our concept model, and the strategy that we have. And it was verified that the concept works well. When we started, the concept was ready to prove itself.”
IPM could not have foreseen what was around the corner after it finished commissioning test trials in July 2019. The mill was poised to begin commercial production in January 2020.
“That was the worst time for us to start because in March 2020 the pandemic hit,” recalled Mr Elassadi. “It was a complete struggle, opening such a facility with all sorts of restrictions especially in the supply chain.”
Of course, it was not merely the restrictions themselves, the demand for paper
also dried up overnight. Mr Elassadi went on to describe the landscape at that time: “Offices were closed, universities, schools, everything was closed. There was a huge struggle on paper demand worldwide. The world’s supply chain was interrupted. There were lots of challenges.”
The long-term impact of the pandemic, however, has proved to be less a fatal wound, more a papercut. Despite the early turbulence, the company is doing well. IPM’s market share is about 35 –40% in the region. “We have reached over 70 countries since we started,” revealed Mr Elassadi. “This year, we expect a total turnover of around $300 million. This is even a conservative estimate, but it will be around that, dependent on the price of paper.” Fluctuation in the currency exchange is one of the primary challenges these days, he added.
How have they done it? The pandemic aside, the question of ‘making paper in the desert’ still loomed. One of the key elements of the company’s success lies in a sincere and far -reaching commitment to sustainability.
“Paper is always seen as the business that is destroying woods and reducing forests around the globe. This is misleading,”
Mr Elassadi said. “We source our raw material only from sustainable resources from suppliers who are FSC certified.”
The paper produced by IPM is designated ‘wood free’, made from pulp sourced from sustainable forests, strictly in compliance with global environmental standards. It is the utilisation of this pulp that gives the company confidence in its environmental credentials.
As Mr Elassadi explained, a huge number of trees are planted in replacement of those
that go into the pulp: “People who are into the production of the wood pulp have to make sure that they will have more trees later on. So that's why you will see the forest is increasing rather than decreasing because the industry must sustain it. Trees are a crop. It's like potatoes; farmers grow potatoes, they harvest potatoes, and then they plant more potatoes, otherwise the farm will be gone. Basically, paper is the same thing.”
Being one of the first paper mills established in an area with a water deficit, IPM has a responsibility to conserve resources. But it wants to do more: this
is where the effluent treatment plant will come in. Efficient water usage, combined with effective effluent treatment plants, ensure the company is using less water and recycling as much of it as possible.
Mr Elassadi elaborated: “We are now in the process of investing in recycling 60-70% of the water that's the discharge from the plant. This is essential for us because water is a scarce resource in our area. We are in the final stages of securing the funding for the effluent plant. Execution should happen very soon. We are negotiating the terms.”
Another path the company look to be heading down is in the field of automation and digitisation. Even though, as Mr Elassadi remarked, ‘paper is paper’ and the end product will be essentially the same, the process can be streamlined to be more efficient and cost effective.
The embracing of automation is especially beneficial when acknowledging the fact that IPM is the only printing and writing uncoated woodfree mill in the GCC and is the largest in the entire MENA area. “There are zero producers in the region,” Mr Elassadi stated. “The companies that are here are basically people who get the paper and cut the paper, but they don't produce it. We refer to them as converters.”
Like any successful business, another key element to its success lies in the network of suppliers, or ‘partners’. “For me they are partners not suppliers” stressed Mr Elassadi. “We have Valmet as the paper machine supplier and BW Papersystems in our converting facility, where we cut the paper. There is also Solenis, our chemical supplier who is responsible for the overall chemistry at our plants.”
Mr Elassadi painted a picture of a mutually beneficial and synergistic partnership,
based on striving to be better: “We don't try to change those guys, but we always like to challenge them.”
He described the rest of IPM’s staff in similar terms: “We have a very experienced and diverse team. We have people from all over the globe, all with the same passion for producing paper. This is what brings us together, irrelevant of colour, irrelevant of background, or religion. We all work together with the same respect. And we are working towards creating our own success story.” IPM may have started with a blank sheet of paper, but the company is now firmly making its mark. n
AstenJohnson has a rich history within the paper industry as a global textile manufacturer. With the acquisition of Eagle Nonwovens and Foss Manufacturing, the company continues to diversify and strengthen its reputation in the speciality fabrics industry. Global Sustainability Manager Anaëlle Roemans and Global Marketing Manager Daniel Hédou discussed this evolution, as well as the company’s goals for sustainability, in conversation with Imogen Ward.
IN1999, AstenJohnson formed from the deeply embedded roots of two varied companies with mutual goals. Dating back to 1790, JWI Group brought world class expertise in wire works and drainage equipment. Similarly, Asten, founded in 1882, entered the merger with world class knowledge in dryer fabrics. This wealth of experience would prove to be fundamental for maintaining AstenJohnson’s leadership in the market.
“In 2014, we entered the nonwovens market with the acquisition of Eagle Nonwovens and soon after, in 2017, of Foss Manufacturing,” Global Marketing Manager Daniel Hédou said. “Those additions demonstrated dynamic organic growth and have lead to our expansion with a new nonwoven greenfield site in Waco, Texas.”
In 2022, AstenJohnson announced the creation of a new division: AJ Nonwovens. AJ Nonwovens combines Eagle Nonwovens
in St. Louis, Missouri, Foss Performance Materials in Hampton, New Hampshire, and the new Waco site as one division.
Working united, AstenJohnson has maintained its place in the market by diversifying its specialties.
With its relentless focus on innovation, AstenJohnson offers a broad and differentiated catalogue of products, all of which directly impact end-users’ consumption of energy and resources.
The AccuFlowTM S2/E2 Press Fabric (exclusive to AstenJohnson) brilliantly exemplifies the company’s endless abilities. The product’s unique single-seam configuration and highly sophisticated base fabric construction is comprised of two layered modules angled upon each other. This structure increases robustness
and durability, which translates to higher water removal capacity, reducing energy used to dry the paper, and longer life which lowers landfill use.
AstenJohnson’s innovations create products that last longer, are more efficient and require less energy. In addition, the expert knowledge AJ field associates share with their customers helps improve outcomes from fabric life to the quality of the end product.
To ensure safety across the company, AstenJohnson implemented a Zero Accident Culture (ZAC) safety system. All associates are trained in workplace safety based on 3 core values: accountability, commitment, and trust. Complemented with AstenJohnson’s Lean 6S system, safety and efficiency have improved business processes while reducing the risk of safety incidents occurring.
“We are ahead of the curve when it comes to safety and safety awareness,” Mr Hédou said. “We used to encourage our sites to pursue local strategies. This changed in 2016, when we involved the overall corporate culture to improve the safety of every site. We continue to accelerate the sharing of these practices so that we can reach our goal of zero accidents.”
Making a difference, AstenJohnson has encouraged its offices worldwide to partake in various green initiatives. Starting in 2021, its office in Eupen, Belgium, has
offered its associates a bicycle leasing programme with different types of bikes available. The office has an impressive bicycle parking lot – featuring solar panelled charging stations for electric bikes and secure bike housing for associate’s peace of mind.
The site in Clinton, South Carolina, has also worked tirelessly to improve its ecooutput. In 2016, the facility set goals to eliminate its air emissions. This was successfully managed a year later and
resulted in the site no longer requiring an air permit.
In China, AstenJohnson Suzhou has implemented a recycling programme for scrap from its monofilament plastic. AstenJohnson sends this waste to a local partner to process the leftover plastic in a pelletiser machine. These plastic pellets are used to produce new items, creating a continuous lifecycle for AstenJohnson scrap material.
AJ Nonwovens in Hampton, New Hampshire, uses a large portion of PET resin from recycled beverage bottles to make the fiber used in their products. Since 2016, AJ Nonwovens has consumed 190 million pounds of resin from bottles.
As an innovator within the paper & pulp and nonwoven industries, AstenJohnson is determined to lead the improvements needed for a greener future. Looking inward to its business processes, the company works hard to accomplish several sustainability-based goals.
AstenJohnson hopes its efforts will help create a greener planet. “In 2020 we developed the Sustainable Procurement Policy,” Global Sustainability Manager Anaëlle Roemans said. “The next step was to develop a supplier risk assessment, based on their geographical location, the annual spend level, and their business sector. This allows us to assess our
supply chain and ensure that the values of our suppliers match our own.
“Based upon the risk assessment, we communicated with our suppliers our sustainable partner expectations. This is an important step in making our supply chain more sustainable. We really believe sustainable progress should be done through the entire value chain.”
The company recently received the EcoVadis Bronze Medal for the second consecutive year. This award recognises AstenJohnson’s Corporate Social Responsibility (CSR) sustainability performance. EcoVadis uses categories including environment, labour and human rights, ethics, and sustainable procurement in its assessment. After analysing current sustainable policies and actions, AstenJohnson was deemed to be in the top 50% of those within its industry with the most advanced CSR approaches.
AstenJohnson has outlined environmental and social KPIs and aims for a 30% reduction of its CO2 emissions by 2030 compared to 2020 (unit CO2/unit sales) and waste free production by 2030. Those KPIs are fully integrated in the five pillared values of AstenJohnson: safety, excellence, integrity, people and sustainability. Most of the company’s actions towards sustainability relate to these pillars.
“These actions include dedication to our social and environmental KPIs,” said Anaëlle Roemans, “our CO2 emission goals, and our efforts to creating waste-free production processes. This means that we won’t send any waste to landfill or to be incinerated.”
Not only is the company working hard to improve its environmental impact, AstenJohnson is also aiming to exemplify a positive work culture. The company provides ample opportunity for individuals to gain experience and supports associates to progress within the organisation.
Additionally, AstenJohnson is focused on mental wellbeing. “The social side of our company is also really important,” Ms Roemans concluded. “The wellness of associates, ensuring they are fairly compensated, and making sure everyone has equal opportunities is monitored. We are determined to maintain an environment free from discrimination, and we do not want anyone to feel judged. We encourage free thinking – everyone’s voice is important to us.
“We want to highlight this aspect of sustainability within the workplace; too often it is ignored. It is much easier to track a reduction in CO2 than it is to monitor associate’s mental health levels.”
Leaning on the roots formed over 200 years ago, AstenJohnson will continue to monitor and improve business practices, to protect the well-being of its associates, the communities in which it operates, the stability of the company, and its overall impact on the environment. This focus has built a solid foundation for AstenJohnson to achieve short-term sustainability goals, as well as favourable long-term outcomes. n
Six generations after the first guitar was produced on Christian Frederick Martin’s workbench in 1833, C.F Martin & Co has earned its place as a leading manufacturer of acoustic guitars and strings. Director of Supply Chain Management Frank Untermyer sat down with Richard Hagan and revealed how the company has forged a unique manufacturing process that combines the best of traditional, time-tested skills with modern machinery and a remarkable commitment to sustainable procurement.
Martin Guitar, headquartered in Nazareth, Pennsylvania in the United States, manufactures a range of high-quality guitars and guitar strings. Founded in the early 19th century by Christian Frederick Martin, the company pioneered various manufacturing techniques and design philosophies that were so effective and successful that they quickly became industry standards.
Martin Guitar’s main facility is also its headquarters, with an impressive footprint of 200,000 square feet, 146,000 of which is dedicated to manufacturing space and the remainder is offices and manufacturing support. Ten minutes from this facility lies the firm’s second property. Designed specifically for the company’s
distribution needs, Martin Guitar occupies about half of this 200,000sqft facility, with the remainder leased out to others.
Finally, its third facility is located in Navojoa, Sonora, in Mexico. This factory is equipped to a similar level as its headquarters and is responsible for manufacturing. Across all three sites, the company employs about 1,000 staff.
Martin Guitar’s manufacturing philosophy is a fascinating blend of artisanal guitarmaking techniques - called luthiery - with ultra-modern machinery and capabilities, as Frank Untermyer, Director of Supply Chain Management, pointed out: “We strongly believe in continuous investment in the latest technology. We have machines that precisely cut a guitar’s dovetail neck joint, as well as CNC buffing machines. We also utilise automated
technology to set a uniform fret height on the fingerboards. Our spray booth is robotic, and we use CNC for precision inlay work.”
The company’s high-tech production capabilities contrast with its deliberate, continued focus on traditional luthiery skills, especially for its higher-end products. Martin Guitar’s custom guitar workshop is said to be the largest of its kind in the music industry, boasting a large number of skilled luthiers.
“We use chisels to hand fit necks to bodies, and hand files to dress the frets on the fingerboards,” said Mr Untermyer. “This workshop cuts inlays and sprays the guitars all by hand. Our capabilities in the custom shop match and exceed those found anywhere else. It’s a focus area of ours and it continues to grow.”
Sustainability is a core value at Martin Guitar, especially given its inescapable reliance on timber and other natural resources for manufacturing its products. For that reason, the company places a high value on the wood that its uses while also ensuring that it is responsibly harvested from sustainable sources.
“Wood is the lifeblood of an acoustic guitar and so we need the tonewoods to exist for generations to come,” Mr Untermyer explained. “Responsible harvesting methods guarantee a high monetary value for those woods, discouraging wasteful usage of such precious resources.”
Martin Guitar developed an ecological policy as far back as 1990 which subsequently saw the company receive Forest Stewardship Council ® (FSC ® Chain of
Custody certification (License code FSCC008304). Consequently, the company strives to procure FSC-certified wood wherever possible. For example, the company sources mahogany for its guitar necks and bodies from a certified source in Guatemala, and its ebony for its fingerboards and bridges from a similar source in the Republic of the Congo.
Additionally, the company utilises the services of a specialist third party to verify the legality of the woods that Martin Guitar procures, and in certain cases, the company dispatches its own teams into the forest to confirm the actual source of the wood. “We are passionate about ensuring the sustainability of the forests and specifi c species that we use,” said Mr Untermyer.
Martin Guitar also actively embraces listings on the appendices of the Conference of International Trade in Endangered Species (CITES) which fosters the legality and traceability of the
Untermyer Director of Supply Chain Management
tonewoods used in Martin Guitar manufacturing processes. To this end, Martin Guitar maintains close relations with the United States Fish & Wildlife Service –responsible for managing CITES in the United States – as well as many other CITES authorities all in addition to the Secretariat based in Geneva.
Reclaimed wood is another sustainable source for Martin Guitar. In Canada, the company routinely travels into the forests and disassembles old, disused logging bridges from which it produces guitar tops. Abandoned logs left behind on the forest floor are also fair game and to date, have gone into the production of 15,000 guitar tops without Martin Guitar having to cut down a single tree.
Martin Guitar’s sustainability efforts extend to a substantial infrastructure investment to reduce its energy
footprint. Several years ago, the company invested $8.85 million in a full retrofit of Martin Guitar’s Pennsylvania facility’s HVAC system. The new system now consists of three water-cooled chillers, while the heating system now includes three, low-temperature condensing boilers. This upgraded system reduced the company’s electrical and natural gas consumption by over 40% and 20% respectively, resulting in an annual cost reduction of $500,000.
Meanwhile, Martin Guitar partnered with guitar string manufacturer D’Addario to support that firm’s Playback world-leading string recycling program. With the aid of
string recycling receptacles at music stores around the country, Playback has recycled over 10.5 million guitar strings.
Looking ahead, Martin Guitar is focused on continuing to innovate the guitar market just as it has done for over six generations; and so in closing, Mr Untermyer explained the company’s vision: “We will continue to set the benchmark for acoustic guitar design, quality and playability. We hope that the instruments that we build, and the music that is made on them, will continue to inspire people. Music is the universal language; it brings people together. We need more people to live harmoniously . We all need more music.”
n
Securely positioned in the field of mechanical engineering, Marcovil –Metalomecânica de Viseu, S.A. is a company with lots going on. Dedicating its operations to the design, manufacture and commissioning of machinery and turnkey solutions, the business works to improve the efficiency of the industry. From lifting equipment to forming technology, to the most innovative and advanced machines for waste separation and recovery of secondary raw materials, all Marcovil’s endeavours are shown the same care and attention. The company cites its ethos as ‘innovation, sustainability, reliability and efficiency.’ Board Advisor Nuno Albuquerque explained how this works to Hannah Barnett.
When Marcovil was established in 1987 at Viseu - Portugal, it was as a manufacturer of overhead cranes and elevation equipment. Board Advisor Nuno Albuquerque explained that the company continues its work in this field to the present day: “We have overhead cranes, we have mobile gantry cranes, we have jib cranes, among others. That is something that we are quite well known for and there is still a lot of demand.” There must be, because the company sold around €2 million of crane equipment in 2021 alone.
These days Marcovil is something of a four-pronged operation.
Alongside the cranes, it also produces ‘movement equipment’, as Mr Albuquerque described: “Acceleration conveyor belts, flat belt conveyor belts, sorting conveyor belts. And there is plenty of demand for it, too.”
The third strand is Marcovil’s roll bending machines. “You have a sheet of metal, and
you can bend it in whatever diameter you wish; we have machines that do that kind of work, and we can also build them,”
Mr Albuquerque said.
The final part of the operation falls within the recycling arena. “We produce individual equipment, but also turnkey solutions, like complete lines to recycle plastic,” explained Mr Albuquerque.
Marcovil’s plastic separation machines are designed to separate plastic e-waste by type and colour so that they can be recycled as a raw material. On average 44.7 million tonnes of e-waste are generated per year, while the potential value of plastic raw material in e-waste is a staggering €15 billion per year. It is clearly both environmentally and economically prudent for the company to capitalise on this.
Alongside the plastic e-waste operation is the fridge compressor, which is a machine designed to recycle the compressors of small, non-industrial fridges.
“We have come up with a machine (patent pending) that can read the different geometries of the compressors, and then make the cut automatically in the compressor,” Mr Albuquerque said. “This will then open the body and you can separate the copper from the plastic. The copper is a highly valuable material.”
Environmental innovation is a significant aspect of what the company does, and it is paying dividends: “We have invested quite a lot in the I&T department. We have spent a lot of time in that area – a good example is the recycling compressor cutting machine. And I can tell you that right now we have various orders for these machines in Europe.”
Around 65% of Marcovil’s core business now comes from its environmental products. The company has an ongoing project in Europe to build three recycling plants.
Mr Albuquerque explained how the company works closely with each customer to create a bespoke recycling system suitable for their specific needs.
“The client tells us about the tonnage per hour that they want, based on their input and output, and it is up to us to come up with a solution,” he said. “After that, we discuss the layout, we discuss the implementation area, and then we start working on the machine and its components. We produce most of the equipment internally. Overall, it's our responsibility to make sure that the line will work properly, and we will achieve the goals the client wants.”
The company, Mr Albuquerque said, is fastidious in its attention to the highquality of the products it produces. This is one of the key features that sets Marcovil apart from competitors.
“Even though it's a little bit more expensive, it's important that the equipment has the right thickness and robustness,” he e xplained. “That is a key feature for us. We prefer to have concrete solutions and good, thick, strong stainless steel. We firmly believe that those kinds of materials will improve not only the efficiency but also the life expectancy of the product. That’s one of our signature moves. We prefer to spend a little bit more money on things like stainless steel, rather than using other materials that are not as robust.”
It is not just around Europe that the Portugal-based business operates. It has an impressive international reach. “We have had partners in the five continents
since 2000. We dispatch equipment for Australia, Africa, Asia, Europe and America, both South America and Central America.”
It is the concept of a global operation that is intrinsic to Marcovil’s ethos. The company positions itself as part of the ‘circular economy’, the economic system of closed loops in which raw materials, components and products lose their value as little as possible, with the emphasis placed on renewable energy sources.
Mr Albuquerque explained what the circular economy means to Marcovil
specifically: “We don't just want to extract, use and dispose; we also want to produce, use and recycle. We are trying to be part of a global network where we can retain valuable raw materials, reduce the risk of losing our supply of primary raw materials; where we can preserve the environment, reduce carbon emissions and reduce waste disposal.”
The company lives up to its promises: installation of solar panels at its site in January 2022 allowed Marcovil to be on the front foot when it came to the later challenges of the year.
“Obviously, solar panel systems allow us to save on our energy consumption from the grid,” Mr Albuquerque said. “But they also work as a kind of insurance against an increase in energy prices, as well as reducing the ecological footprint. We have 490 solar-power modules with a total of 184,000 kWp. We can also sell the energy. It's a win-win situation for everyone involved and it’s an investment that came at the right time, given the latest spike in the electricity prices since the Russia-Ukraine conflict.”
Marcovil estimate that it has produced 5,000 machines and
turnkey solutions since 1987. This is not hard to believe for a company that not only sets objectives like ‘innovation, sustainability, reliability and efficiency’, but also effectively puts them into action. n
When major events and memorable occasions unfold around Europe, the Samlerhuset Group is the first to focus on memorialising the day, person or event with commemorative medals, coins an d /or other collectables.
As one of Europe’s largest coin companies with a presence in 15 different markets, its importance in the numismatics market cannot be overstated. Social Responsibility Manager Zdenka Mulon took Richard Hagan behind the scenes of the intricate business of minting Europe’s milestones.
Headquartered in The Netherlands, Samlerhuset Group was established in 1994 by partners Ole Bjørn Fausa and Reidar Nilsen. From humble beginnings, the company now has a presence in 15 different countries and markets across Europe, operated by a total of 750 staff.
Equally impressive is the fact that Samlerhuset Group also owns the famous Mint of Norway, where a large part of its production takes place. The Mint of Norway, situated in the former mining town of Kongsberg, is the country’s second-longest running manufacturing entity, having been
founded as far back as 1686. In 2003, the Central Bank of Norway sold a 50% stake in the mint to the Samlerhuset Group which later bought the remaining shares in the Mint in 2015.
The Mint of Norway still produces all of the legal tender coinage for Norway as well as several other countries, but a substantial part of its work today is in striking the medals, commemorative coins and other collectables commissioned by Samlerhuset Group.
As one of Europe’s largest coin companies, Samlerhuset Group specialises in the direct marketing of coins, commemorative medals and related collectables to all of its markets across the continent. The company prides itself on superior products made to the
highest quality standards and delivered with its trademark first-class service to customers.
Outside of its own manufacturing capacity at the Mint of Norway, Samlerhuset Group also boasts an extensive network of some of the top mints around Europe who together ensure that Samlerhuset Group can accommodate almost any product specification required by a customer.
Samlerhuset Group’s project portfolio is the best example of the company’s manufacturing versatility. Past projects span some truly epic events, celebrations and milestones including minting the Nobel Peace Prize medals, and selling various medals and collectables for the Olympic Games.
Notable recent projects include Samlerhuset’s substantial donations and participation in significant projects alongside non-profit companies such as Waterloo 200, The Imperial War Museum and the In Flanders Fields Museum.
While these projects are impressive, Ms Mulon took us behind the scenes of the even more impressive amount of background work required to bring them to life, owing to the surprising number of moving parts involved.
“From the conceptualisation of the product until its final stage of readiness for shipping to the customer, takes about six months,” Ms Mulon explained. “The process includes dozens of partners, established processes, highly experienced employees, top-notch creative designers, effective production and logistics and of course, great sales and marketing.
“I don’t think many people outside of the industry realise how demanding the process is.”
A critical part of Samlerhuset Group’s mission is social and environmental responsibility, not only in its local markets but also globally. To this end, Ms Mulon highlighted two social responsibility programmes that the company is involved with.
The first is Samlerhuset Group’s partnership with the Alliance for Responsible Mining (ARM). ARM is a non-profit organisation that supports artisanal and small-scale mining operations and organisations, to become Fairmined certified mines.
Within this partnership, Samlerhuset Group sponsors the Minas y Cuevas mine in Honduras in its journey to becoming certified.
“Certification will make a huge impact on the miners’ lives, financially, socially and in terms of the environmental conditions in which they live and work,” Ms Mulon noted.
The other programme is Samlerhuset Group’s partnership with Swedish NPO Humanium Metal, whose mission is the
promotion of peace by ending the violence caused by illegal firearms.
“There are a lot of illegal guns worldwide causing death and misery every day,”
Ms Mulon lamented. “Even once they’re confiscated, it can be difficult to prevent them from falling back into criminal hands. Humanium Metal assists local governments to solve that issue by melting down illegal guns.”
The metal recovered from the melted guns is turned into a special powder from which a new metal, called Humanium, is produced.
“We’re now in the process of using this metal to create coins instead of our traditional raw materials such as Gold, Copper and Silver,” Ms Mulon revealed. “Production of coins using Humanium is difficult as it’s a new metal, but it’s an initiative that we’re proud to be involved with.”
In closing, Ms Mulon reiterated the company’s competitive qualities. “There are no other companies in Europe or worldwide with a story like ours and products like ours. We have a reach that nobody else has.
“I’m proud to work for Samlerhuset Group; I enjoy the fact that it’s a responsible company that thinks about its responsibilities and the future, and which likes to make a big impact on the key issues within its industry. And of course, I love the product: It’s small, intricate artwork on small pieces of metal!” n
Hubbard Products has over 50 years’ experience designing, manufacturing and supplying the commercial and industrial sectors with cooling equipment. Having recently invested in a new facility, the company is working hard to expand its production capabilities. Sales Manager Alec Stilling and Head of Design and Engineering Ashwaq Mohammed spoke in-depth about the company’s current work scope and its amazing efforts towards improving its customer’s sustainability, in conversation with Imogen Ward.
Hubbard Products has developed highly efficient CO2 refrigeration units to reduce emissions within the industrial and commercial sectors. Using its first-class R&D department, and with the support of its parent company (Daikin), Hubbard Products developed innovative products targeted towards the carbon footprints of its clients.
“We build sustainable products,” Sales Manager Alec Stilling said, “examples include Hubbard Products’ CO2 Refrigeration Packs, A2L Packs and heat pumps.
Our customers have different expectations and aspirations – they’re at varying points in their sustainable journeys.
“Some customers are very far advanced and in tune with what they need to do by 2030, whereas others haven’t even begun to work out where they are headed. Our job is to help them get their foot on the ladder. Energy efficiency is in the DNA of Hubbard Products; it’s what we do best.”
Founded in 1968 by Geoff Hubbard, the company began developing small commercial refrigeration applications. In 1984, the company built its first commercial refrigeration multi-compressor pack for food retail; this project opened the doors to an entirely new market. From this point onwards, Hubbard Products manufactured an array of refrigeration and heat pump equipment, always
ensuring the highest quality for the best price.
In 2016, Hubbard Products made the decision to introduce CO2 Refrigeration Packs to the market. These products were aimed towards commercial companies, including big-brand names Asda and Marks and Spencer, to help them reduce their carbon footprint. These products have extremely low GWP refrigerant levels – the CO2 Rotary Condensing Unit which uses natural refrigerant, has a highly efficient GWP level of one. This refrigerant figure is impressively marginal compared to the legal requirements of refrigeration units in commercial settings. In 2017, Daikin purchased the company, considerably expanding Hubbard Products’ global reach.
“When I started 15 years ago,” Head of Design and Engineering Ashwaq
Mohammed said, “we used to build units with GWP levels of around 4,000. In 2016, we significantly reduced that amount to 2,000 GWP. We then turned to synthetic refrigerants which remain between 150239 GWP. We still use this type of refrigerant now. We also build systems using natural refrigerant. For these products we incorporate CO2 which is gas that is naturally available.”
T he company also produces a range of heat pumps. This product has seen a surge in demand from companies looking to further offset their carbon emissions. Included in this range is the Hubbard Heat Pump, this pump captures waste heat from conditioning compressors and condensers and converts it into a viable
source of hot water. This process effectively reduces the users’ heating costs through its recycling system – making it both efficient for the environment and extremely cost effective.
The most popular applications of all the Hubbard Products’ range are the Blast Chiller and Blast Freezer. These products can be adapted to fit different size specifications and use R448A/R449 A refrigerant. The company also offers
a heat pump module alongside its blast freezers, that utilises the product’s waste gas as a viable source of heat.
As business boomed, new ventures appeared on Hubbard Products’ radar. During the Pandemic, the company offered highly efficient solutions for the safe transportation of pharmaceuticals and medicines. The R&D department at Hubbard Products researched heavily into cold room solutions for monotherap y
and vaccine storage, resulting in three refrigeration units that are GDP compliant These options include the Invisible unit, SFZ2009 (installed beneath the chassis to preserve vehicle height and reduce bodywork); and the SFZ238 nose-mounted unit (designed with energy efficiency in mind).
“We are helping our customers and providing them with a portfolio of solutions that fit their specifications and engineering designs,” Mr Stilling said. “We can provide our customers with multiple options to find the most efficient product for the job. We are also highly flexible when it comes to customer requirements and will engineer a specific solution, putting us ahead of our competitors who have a more standardised range of products.”
The exploration into the pharmaceutical sector enabled Hubbard Products to strengthen its presence as a market leader in sustainable refrigeration units and cre ated potential for future expansion into other areas of the market. The company intends to double its turnover – using its increased production capabilities as a springboard towards success.
Committing to a five-year plan for growth (named Fusion 25), the company’s strategy merges with the goals of parent company, Daikin: contributing to a more sustainable society and achieving growth, Daikin has committed to nine themed strategies. Daikin wants its subsidiaries (including Hubbard Products) to achieve carbon neutrality, improve customer relations, and continue strengthening their technology development capabilities.
Hubbard Products is on target for 2025. Having moved to its new facility in 2021, the company took advantage of the larger space – successfully doubling its factory capacity. To meet its goals of carbon neutrality, the company ensured its state-of-the-art facility in Ipswich was highly efficient.
With a brand-new R&D lab under commission, Hubbard Products is also strengthening its R&D capabilities. “The commissioning of a new R&D lab means that we will have control of our own environment,” Mr Stilling said. “It will enable us to further develop our products and push the boundaries of what we can achieve. We have also recently taken on an R&D manager who will help meet our Fusion25 targets. On top of that, she also has her own plans for improving the business.”
Products has already had a positive impact on the company, having developed and manufactured most of its product components in-house. This integration meant that Hubbard Products avoided the brunt of the global supply issues. The company is, however, reliant on its suppliers for several key components. To avoid delays in production over the past few years, Hubbard Products has adapted its business model. The company is constantly assessing its supply chain to ensure operation is optimised, which has resulted in an ever-evolving supply chain.
“ We have concrete suppliers across all line items,” Mr Stilling concluded. “We had to adapt during Covid and now depend on multiple suppliers for everything. We always do background checks, making sure our suppliers are ethical and align with our sustainable ethos. It is important to us that we can continue to provide the best quality products to our clients, for the best value.” n
Pacadar, the Spanish pioneer in precast concrete solutions, has continued its expansion, picking up important project 'wins' from HS2 in the UK to Kuwait International Airport. Jose Luis Dominguez, International Commercial Director, and David Pastor, Commercial Director UK, reflect on the company's global presence and industry pressures to embrace sustainability. Profile by Andy Probert.
Pacadar, the world's oldest precast concrete manufacturer, remains both international and as close to customers as possible. "We pride ourselves on being immensely agile worldwide to meet demand as precast concrete is a notoriously bad traveller,” reflected Jose Luis Dominguez, Commercial Director Europe. “Being global and local is in our DNA.
“We know how every project requires a different service; the variety of environments and countries all demand a high level of adaptability, the greatest flexibility and an unswerving commitment to quality.”
Pacadar has developed a highly effective business model establishing temporary manufacturing hubs in the countries it's working in. Mr Dominguez explained how the company uses on-site manufacturing plants close to the construction site: “This gives us competitive advantages as logistic costs are dramatically reduced.
“Once the project is finished, we dismantle the plant and return the site to its former condition. This allows us to move around the globe, using quick-to-assemble tailor-made factories, taking into account the nature and scope of each contract. Our capacity to set up these units in a limited time is the warranty for our clients that project milestones will be accomplished. Closeness to customers is key.”
As an example, a large mobile factory used on a completed project in Riyadh, Saudi Arabia was dismantled, with one half erected for a similar job in the UK. Pacadar has enjoyed recent successes in the UK. So much so, it has established a main plant for precast concrete elements in the Isle of Grain in Kent to meet the company’s growing contract footprint.
On the Thames Tideway Tunnel project, ( a key modernisation of London’s ageing sewage system), Pacadar constructed the central and longest section of the
tunnel, over 12.7 km long. However, Europe's biggest infrastructure project, HS2, a new high-speed railway line between London and the West Midlands, offers a new benchmark for Pacadar.
Four new contracts have been signed over the last two years. The first was with Balfour Beatty Vinci (BBV JV) for the supply of 1,600 precast concrete tunnel linings for the Long Itchington Wood. Pacadar has completed its production for this project.
Skanska, Costain & Strabag (SCS-JV) HS2’s contractor delivering the London tunnels, awarded Pacadar two contracts to produce 8,400 concrete precast tunnel rings. The contract to supply rings for the Northolt tunnels is the largest contract Pacadar has ever won.
HS2’s London tunnels from West Ruislip to Euston station will have a total length of 26 miles. Construction of the first tunnel will be completed in 2024. More than 160,000 cubic metres of concrete will be used to make the segments, which form a 9.5m outside diameter tunnel, 350mm thick. Each complete ring
is made of seven segments, each weighing more than seven tonnes.
The strict geometrical tolerances required by HS2 are the most demanding that Pacadar has ever faced. A high precision testing system during the manufacturing process was implemented to meet the requested standards. In its commitment to innovation and sustainability, Pacadar uses a concrete mix of 40% GGBS from recycled materials from the steel industry, ensuring a considerable reduction of CO2 emission in the production of each ring.
Mr Pastor added: “This is an important contract for Pacadar, and we look forward to working with SCS-JV over the coming years and adding value to the project.”
As one of Pacadar’s key objectives, they signed a contract to supply the precast concrete beams, piers and planks for the Thames Valley Viaduct, within the Eiffage, Kier, Ferrovial and Bam Nuttall (EKFB JV) section for HS2. The precast concrete solution adopted for the beams is based on a proven technique previously implemented by Pacadar on high-speed lines. This agree ment significantly enlarges Pacadar’s port folio in the UK.
Backing up their local approach, Pacadar established two new units and is building a third to meet demand. Mr Dominguez said 130 people are engaged on the UK projects, which “now form the biggest part of Pacadar’s turnover.”
From a deep understanding of the precast concrete market, Pacadar is highly active on the international stage, completing iconic projects including the Panama City Metro, Riyadh Metro in Saudi Arabia, and Puebla's Toll Highway in Mexico. It also worked on Kuwait International Airport's new international passenger terminal, which is expected to be completed shortly. One key milestone was manufacturing heavy-weight arches to hold the roof.
Pacadar manufactured six pieces in a day, a total weight that exceeded 1,000 tonnes of concrete.
The company is now manufacturing precast structures for the Common Shielding System for the new research infrastructure European Spallation Source (ESS) in Sweden. ESS, built and operated by
a European Research Infrastructure Consortium composed of 13 countries, UK and Spain among others, that will be the world's most advanced research facility for neutron science. It will study atomic structures using neutrons, and this facility could yield discoveries that will benefit energy, materials, medicine and the environment.
Pacadar contributed to the design and will manufacture the precast concrete shielding blocks under the most demanding requirements of accuracy, tolerances and safety conditions.
“We continue to monitor the international markets as big infrastructure projects come forward,” Mr Dominguez explained. “High-speed rail networks such as HS2, tunnels and elevated metros are ones we are keen to add to our portfolio. There is also enormous business potential where solutions are sought for large, densely populated cities.”
Pacadar continues to implement innovations – reducing carbon footprint in its production of pre-cast concrete by using more sustainable cement and raw materials. The adoption of temporary facilities to cut logistics and transport on a project is a key strength, while Pacadar's elite design and engineering team takes a lead role in minimising carbon emissions from conception by optimising structural solutions.
“For example, we evolved the use of steel fibres in production compared to steel rebar, which helps reduce the overall use of
steel,” affirmed Mr Pastor. “The Thames Valley Viaduct is another good example of how an adequate design contributes to this objective. The solution finally implemented, based on previous highspeed experiences, reduces the number of structural elements without compromising the quality, nor the structural requirements or safety.
“The industry is slowly transitioning to more sustainable concrete. But that entails continual research as quality and safety are key concerns. Tolerances, such as on HS2, are stringent and very demanding, which Pacadar can never sacrifice.”
The company continues to develop high-technology practices by investing in innovative materials for the precast sector and collaborating with clients to offer smarter solutions that are more costeffective, efficient, durable and lighter.
It also pursues a strong policy on recycling materials such as water, oil, batteries and paper, investing in technologies with reduced carbon emissions within its production facilities.
Mr Dominguez concluded: “As demand increases for infrastructure globally, we envisage Pacadar taking the lead in offering its experience, expertise and know-how.” n
As many industries, transition to renewable energy solutions continues apace, TMEIC Europe is ideally positioned to contribute to the realisation of carbon neutrality with its accumulated experience and know-how. Business Development Manager Mark Newman told Andy Probert how TMEIC’s ground-breaking technologies will play significant roles as a new industrial era dawns.
The July 2022 heatwave that blistered Europe and the UK served as a telling reminder that the greenhouse gas crisis is here. It can no longer be ignored by the majority of the population that sizzled in its wake.
“You can’t say climate change is not happening,” agreed Mark Newman, Business Development Manager of TMEIC Europe. TMEIC as an entity was created in Japan through the 2003 merger of the industrial systems divisions of Toshiba and Mitsubishi Electric.
While some companies have been slow or unwilling to catch the ‘transition train’ to a carbon-zero destination, TMEIC is speeding ahead by developing innovative integrated technologies for industry that promote a more sustainable future.
Renowned for a quality product range of motors, generators, AC and DC drives, controllers, inverters and UPS systems, TMEIC also develops solutions for industrial applications, wrapped around its core power inversion technology and complemented by plant-based equipment utilised via locally-resourced supply chains.
Clients are not confined to traditional industrial sectors, such as oil and gas, metal rolling, pulp and paper, mining, water and desalination: TMEIC is rapidly gaining ground in the power and renewables fields, by supporting the adoption and integration of renewable power generation through various energy storage initiatives.
TMEIC Europe, created in 2006 as a sales and engineering-focused subsidiary backed by its parent’s manufacturing
prowess spread across Japan, China, India and the US, has a 40-strong workforce at offices in London, UK, and Puglia, Italy.
Mr Newman asserted: “While we have a global footprint and brand behind us, TMEIC Europe is a smaller but no less dynamic and agile entity. We support our partners’ business ambitions with a more partnership-based approach, rather tha n on a customer-supply commoditised basis.”
This has led TMEIC Europe into the realms of new fields and new partners based on developing projects around hydrogen, batteries, and compressed air as energy storage mediums to support the integration of renewable power generation. These are for commercial power generation for national grid networks , and back into the traditional industries to help achieve carbon-neutral applications and economies.
“Through our learnings on battery energy storage for grid support, we are looking to support, for example, oil and gas partners to integrate renewable power supplies in their industrial applications and decarbonise their emissions.
There’re many significant challenges, so we look to promote our technologies into those traditional industries.”
Indeed, TMEIC Europe’s expertise and technological advances led to the winning of an order to supply two 49.5 MW large-scale battery energy storage systems for UK power grids.
The joint venture, along with Nippon Koei Energy Europe BV, a European subsidiary of Nippon Koei Co, will see the facilities constructed in southeast England and due for commercial operation in 2023.
TMEIC will provide storage battery systems that integrate software and critical equipment such as storage batteries, power conditioning systems for storage batteries and power plant controllers that control power, voltage and frequency.
TMEIC has a proven track record of delivering best-in-class battery energy storage systems in Japan centred on projects with r enewable
energy power plants (large- scale solar and wind power).
Mr Newman said: “This marks the first time for the company to deliver its systems to the UK market. Compatible with various options in the power market, including grid stabilisation services for the National Grid, the system will help address power grid stability in the UK where the share of renewable energy continues to grow.”
TMEIC has a battery system laboratory at an Indian subsidiary’s power electronics factory. This allows it to conduct state-ofthe-art demonstrations that combine a solar power generation system and battery energy storage system connected to the power grid and factory load, and realtime simulators.
Development and verification of respective control functions
required for the project will be carried out at the laboratory to ensure a smooth start-up.
TMEIC, participating as one of five Japanese companies collaborating in the investment and financing of the project, will continue to be involved after the sys tems have been delivered.
It aims to contribute to the realisation of carbon neutrality by deepening its accumulated experience and know-how in power electronics and system control technologies to support the growing use of renewable energy globally and provide solutions to issues and challenges.
Mr Newman confirmed: “The i ntroduction of grid battery storage systems is expected to expand in many countries and regions worldwide.
“What we learn through this project will also be implemented into industrial applications to achieve greater carbon-neutral ambitions in heavy powerconsuming related sectors. This will put us at the forefront in breaking new ground that will have a global impact.”
Since its inception, TMEIC Europe’s turnover has grown six-fold, with annual growth rates above 10% per year for the past five years.
“TMEIC Europe is looking to expand further, especially as we grow our business activities in supporting carbon-neutral
economies. This underpins our very ambitious growth targets,” stated Mr Newman
“We have projects on the horizon: We are actively growing a pipeline of projects for battery energy storage technologies and developing solutions for industry decarbonisation, including onshore and offshore compressed air energy storage technologies.”
The company is also looking to adopt existing technologies into new areas that may not have been used or considered before and enable their efforts to drive further decarbonisation goals.
Mr Newman disclosed: “We are also developing solutions for the hydrogen economy, including both hydrogen generation and innovative rectifier technology that fits in with adopting renewable power generation.
“Our committed approach to collaborative solutions ensures we are positioned to develop innovative technologies, respond to industry trends and apply solutions to a wide variety of industrial market segments. From concept to installation, we develop lasting relationships by working hand in hand with our partners to ensure challenges are met and business goals exceeded.”
Efforts are being put in to develop and strengthen relations with new and existing clients postpandemic in the collective journey towards a carbon-neutral world.
“If we are to grow as we intend, then we will have to expand our workforce and localise engineering capabilities as we move into new business areas and grasp future opportunities,” Mr Newman outlined. “Managing and growing the supply chain is essential. A recent challenge that we have seen is the shortage of silicon-based components. That will prove a challenge to meeting project deadlines over the next 12 months.”
While TMEIC Europe is backed by a global 4,300 workforce and large corporation backing, the company’s agility, highlighted Mr Newman, enables it to be adaptable.
“We deliver quality products and solutions without sacrifice and follow an exacting Japanese-ethos in all our production, processes and standards.”
These are further propelled in maintaining long-term business relations with loyalty, trust and integrity as key fundamentals. He added: “These ensure we enable our partners get the most ou t of what they are trying to achieve.”
Mr Newman concluded: “Industries are in a state of change and transition. Europe is leading the way globally in decarbonisation efforts by putting in place mechanisms and incentives to achieve those goals.
“TMEIC Europe will have increasing significance in TMEIC globally as new ter ritories follow and learn from Europe as they move towards carbon-neutral economies. We want to support those goals as they are, undoubtedly, a change for good.”
one planet – one chance – one voice
An introduction to the engineering and services sectors, with news, innovations and a special report about pumps for Carbon Capture and Storage, followed by company profiles.
Carbon Capture and Storage
Pumps play an important role in Carbon Capture and Storage (CCS). Selecting the most effective pump is the key to achieving low operating costs, cutting CO2 emissions, and limiting the global temperature increase. Senior Product Development Manager Jens Peter Hansen and Key Account Manager Marius Berg Rygvold from DESMI outlined the options.
For nearly three decades, the UN has organised global climate summits. The final text of the latest summit, the COP27 in Sharm El-Sheikh, Egypt, includes a provision to boost low-emissions energy. This requires the combination of many different technologies to help cut emissions – including Carbon Capture and Storage (CCS) systems.
The International Energy Association (IEA) provided an excellent overview of the potential of capturing, storing and utilising CO2. It estimates that 45 Mt/year is currently being captured, but this must increase to 1,300 Mt/year in 2030 to meet the net zero emission scenario (NZE). Around 35 facilities are already in operation, and over 200 new facilities are planned for 2030. However, this corresponds ‘only’ to 220 Mt/year of CO2 being captured, so facilities for at least another 1,000 Mt/year will be required soon to meet the NZE target.
Today, most facilities are installed to capture CO2 emitted from natural gas and hydrogen processing plants. Ironically, the captured CO2 is mainly used for enhanced oil recovery (EOR). However, as oil production must decrease in the future, most of the planned facilities are aimed at power plants, plus the cement and steel industries, as these sectors are impossible to electrify completely due to the nature of their raw materials. Furthermore, captured CO2 should not be used for EOR but stored permanently underground.
Capturing the CO2 in a scrubber or absorption tower is the most common and well-known method for Carbon Capture. A liquid mixture of water and an organic amine is circulated between an absorber and desorber unit.
The inlet flue gas is brought in direct contact with the liquid in the absorption or scrubber tower. The scrubber is usually
a packed-bed type and typically 20-40 metres. A relatively high tower is needed if the concentration of CO2 is low in the flue gas, or if high removal efficiencies are required.
The lean amine is fed into the top of the scrubber and is enriched with the CO2 by flowing downwards in counter-current with the flue gas. A first pump is used to force the solution through a plate heat exchanger and to the desorption or stripping tower. The CO2 is released in pure form by heating the liquid in the reboiler section. A second pump is used to force the liquid through the hot side of the plate heat exchanger and back to the absorption tower again. An additional cooler is often required to reduce the evaporation of water in the absorption tower.
The simulation results are based on many preliminary assumptions which must be further validated and adjusted as more experience with the process is gained. However, it is interesting to relate the calculated pump power to the amount of CO2 captured, thus reaching an initial estimate of the operating expenses.
1,061kW of electrical power (496kW + 565kW) is used by the two pumps catching 20kg/s of pure CO2. This is equivalent to
52kJ/kg of CO2 or 14kWh/ton of CO2. At an electricity cost of €0.15/kWh, the operating expense for the two pumps will be €2.1/tonne of CO2.
As CCS plants become more widespread and operate with increased capacity, selecting the most appropriate pump(s) for a certain scrubber installation is a major task; particularly considering that two or three pumps are often installed in parallel to provide redundancy in the scrubber system. At a CCS plant capable of processing 5Mt/year, for example, annual operating expenses with the pumps used in the example above would be €2.1 million. At this scale, even small power consumption reductions make a significant differ ence to the costs. Selecting pumps that are sized correctly and operate at, or near, their best efficiency point (BEP) is an effective way of reducing expenses.
Too much of a safety margin is often added in the design phase, meaning that the pump will typically operate far from its BEP. In the worst cases, the pump may even run outside the recommended operating area, which is between 70 and 120% of its BEP. It is usually better to add a safety margin in the frequency converter so the pump can
Click here to see the range of centrifugal pumps from DESMI for CCS and other applications
run at higher RPM in extreme cases where max flow and head might be required. This will save both CAPEX and OPEX as smaller pumps can be installed, and it will be easier to operate them efficiently. The pumps will also run with fewer vibrations and generate less heat, meaning there will be less potentially damaging excess energy.
A low NPSHr value is often required. For the rich amine, the solution is almost saturated with CO2 and therefore has a relatively high vapour pressure. For the lean amine, the solution will contain little CO2, but the temperature will be higher and therefore will also cause a relatively high vapour pressure.
DESMI has developed more than 60 centrifugal pumps for the scrubbing industry, generally designed for low NPSHr values. Most of the pumps are available in highgrade stainless steel or super duplex steel. The Dual Cartex seal is recommended due to the toxicity of the MEA. The sealing system can also be connected to an external barrier fluid to ensure that the gaskets will not exceed their maximum temperatures. For projects using a less toxic solution of water and potassium carbonate instead of an amine, cheaper pump materials and standard balanced sealing systems can be used; the potassium acts as a buffer to ensure an almost neutral pH-value.
If CCS is to make a significant contribution to reaching the world’s climate targets, the technology needs further development. Researchers worldwide are intensively searching for more efficient liquids that require less energy for regeneration. However, this may be at the cost of reduced reactivity, meaning larger scrubbers, or more liquid must be circulated to catch the same amount of CO2. These challenges will be overcome, and future CCS solutions will become more effective, capturing ever larger amounts of CO2 using minimal energy. Pumps are not the only important component of a CCS plant. Components such as compressors and reboilers consume far more electricity. However, given the number and scale of future CCS plants, and the fact that succeeding at the green transformation will require us to lower energy consumption in all industrial sectors, selecting energy-efficient pumps for CCS applications makes good financial sense. This is also an effective way of contributing to reaching current and future climate targets.
The €10 million project – funded by the European Union and UK Research & Innovation – aims to deliver a range of innovations to improve the performance of tidal turbines and reduce costs. MAXBlade will investigate the full lifecycle of tidal turbine blades, from materials, manufacture and operation, to decommissioning and recyclability. The project’s long-term aim is to ensure the European composite sector becomes the international leader in tidal blade manufacture.
The project plans to increase the area harnessed by Scottish tidal technology company Orbital Marine Power to generate power – known as the rotor swept area – by 70 per cent, to more than 1,000 square metres.
“Orbital is delighted to be involved with so many great partners on this truly cutting-edge project,” said Andrew Scott, Chief Executive Officer at Orbital Marine Power. “MAXBlade will deliver tidal energy into a future, low-carbon energy mix at lower costs while, at the same time, benefit UK and European businesses from long-term industrial opportunities that will come from this new, sustainable industry.”
MAXBlade will increase the length of the turbine blades from 10 to 13 metres –making them the longest of their
kind in the world. The team believes that boosting blade length will have the single greatest impact on reducing the cost of tidal energy. Modelling by the University of Edinburgh’s Institute of Energy Systems estimates £40billion could be generated for the UK economy by harnessing wave and tidal energy. The project will involve a two-year design and development phase, followed by an 18-month build, during which blades will undergo advanced structural testing at FastBlade.
The technology will then undergo two years of real-world testing at the European Marine Energy Centre in Orkney. Two of Orbital Marine Power’s O2 floating platforms – the world’s most powerful tidal turbines – will each be fitted with four of the newly developed blades. n
Latest innovations from the engineering industry
New research published by Danfoss shows that combining an electric motor with its Digital Displacement pump in an excavator is the most efficient way to turn battery energy into hydraulic work. The combination can reduce the energy required, and therefore the battery size, for a typical day’s work by 24.8%.
The analysis, first presented in 2022 at the prestigious International Fluid Power Conference (IFK) in Aachen, Germany, paves the way to smaller batteries and longer duty cycles for hard to decarbonise off-highway machines. The study was supported by the UK Advanced Propulsion Centre, which developed a simulation model of a 16-ton tracked excavator and calculated the energy
requirements for a typical eight-hour shift. It compared a base case of an electric machine equipped with a traditional swash plate pump versus an excavator with a Danfoss Digital Displacement system and electric drive.
The results show that, depending on system complexity and duty cycle, a reduction in energy requirement of up to 24.8% can be achieved. The improved system would require a 314 kilowatt-hour (kWh) capacity battery for an eight-hour shift compared to a 418kWh battery in the base case.
“Today’s excavators are only 30% efficient, with around 70% of the engine’s energy wasted in the fluid power system,” explained Leif Bruhn, Head of Digital Displacement, Danfoss Power Solutions. “Electric drives have much greater efficiency than internal combustion, but with duty cycles needing upwards of 400kWh every day, the cost of batteries can be prohibitive.
“Our research has shown that combining an electric drive with a highly efficient
Digital Displacement system is the most effective way to turn battery energy into hydraulic work,” Mr Bruhn continued. “This paves the way to smaller batteries and longer duty cycles for the electrically powered excavators of tomorrow.”
Danfoss’ calculations show that an electrified excavator utilising Danfoss Digital Displacement technology will have a better total cost of ownership than a standard diesel engine within the next five years.
Danfoss creates engineering solutions and has a worldwide presence in more than 100 countries. Its work aims to increase machine productivity, reduce emissions, lower energy consumption and enable electrification. The company develops solutions in areas such as refrigeration, air conditioning, heating, power conversion, motor control, industrial machinery, automotive, marine, and off- and on-highway equipment. The company also provides solutions for renewable energy, such as solar and wind power, as well as districtenergy infrastructure for cities. n
The latest company and industry related developments from the engineering and services world
BASF’s Monomers division has announced an ambitious sustainability roadmap: it will expand its port folio of products with a lower CO2 footprint and is committed to providing a circular option in every major product line by 2025. At the same time, the division will continue to prioritise technical optimisation measures to cut CO2 emissions from operations.
Net zero greenhouse gas emission targets demand a new level of carbon transparency. The product carbon footprint (PCF) is therefore becoming a differentiating factor, even for commoditised products. BASF’s Monomers division is pioneering a certified low-PCF option in all its product lines – applying the company’s mass balance approach. n
“ BASF’s Monomers division is pioneering a certified low-PCF option in all its product lines ”
The Energy Act for Ukraine Foundation and Menlo Electric, photovoltaic components distributor, will jointly develop solar and storage installations for schools and hospitals in Ukraine. In the first phase of cooperation, the foundation, together with Menlo Electric, will equip up to 10 Ukrainian hospitals and schools with solar plants with a total capacity of 300kW. The projects are intended to ensure electricity supply to critical needs of schools, plus surgery and intensive care units of hospitals through the hybrid solar power and energy storage systems.
The foundation’s first project was completed in November 2022 at the Irpin Academic Lyceum ‘Mriya’. For the second site, carried out jointly with Menlo Electric, the foundation selected Irpin Lyceum Number 1 specialising in arts. The school was damaged during the occupation of Irpin city in the spring of 2022, when it became a shelter for pupils, parents, and teachers during the severe shelling of the
city. The installation is expected to be com pleted in the first quarter of 2023.
“Our CSR Energy to Power Your Future charity programme, with the mission to install free of charge PV installations for institutions that take care of children, had seven installations completed until now. Our cooperation with Energy Act for Ukraine increases that number to 17. We will be donating and delivering 300kW of photovoltaic components for schools and paediatric hospitals in Ukraine,” said Bartosz Majewski, CEO at Menlo Electric. n
Briggs of Burton is a process engineering company based in Burton-on-Trent and offers total project solutions for blue chip companies across the globe. With an illustrious history, it was founded in 1732 as a hardware and industrial metalwork manufacturer. These days it has a strong engineering presence across the distilling, brewing, food, and pharmaceutical industries. Head of Marketing Scott Davies explained more to Hannah Barnett.
The company may have been around almost three hundred years, but it is still impressive how many wellestablished brands Briggs of Burton has contributed to.
“You might know Macallan Scotch Whisky, you might know Carling lager, you might know Marks and Spencer’s chilli con carne,” said Scott Davies, Head of Marketing. “All of those have been brought to life through Briggs’ engineering know-how, project delivery expertise and process equipment manufacturing capability. You might even know Diageo, who supply the Johnnie Walker whiskey Keep Walking. But you probably didn't know that Briggs of Burton were the engineering company that built and expanded the distillery for major spirits producers like Diageo.”
The company’s status as a cornerstone in the supply chain of manufacturing is hard to dispute. As it goes through a period of expansion, it is becoming more established still.
Following an acquisition in 2016, Briggs of Burton became part of the Liquid Food Division of CIMC Enric Tanks and Process BV, one of the largest international suppliers of tanks and process technologies. Joining an international group of companies that provide the design and implementation of turnkey projects, stainless steel process tanks and engineering services has been beneficial for Briggs’ own growth. Mr Davies explained that upon acquisition the company set
a target to achieve a £100 million turnover by 2024. “We reached that target by 2022. Two years ahead of schedule,” he said.
“When the business was acquired, it was turning over about £20 million,” Mr Davies continued. “That used to be made up of a mix of projects, maybe a £10 million Scottish distillery expansion, a £5 million UK brewery project and a mix of smaller pharmaceutical and food projects. In the last couple of years, we’ve been winning £20 million projects, £50 million projects and in Q1 of 2022, a £95 million project.
“We’ve seen huge amounts of internal investments, in terms of employees and their training, and in infrastructure. Through our sales and engineering network we have increased our opportunities to bid, win and execute larger projects around the world. And Briggs acquired McMillan coppersmiths during the Covid pandemic. That whole mix of operations and activity have been a real
catalyst of change across the organisation. We’ve seen more growth in the last three years than we have in the last 30.”
Since acquisition, Briggs has spread its wings internationally. As Mr Davies explained, the company always had a global presence, but it did not have the resource and capability to manage multiple projects overseas before.
It now has a Mexico office, and a large new contract in the tequila industry to match. Briggs also recently opened a sales and engineering hub in Kentucky, alongside offices in upstate New York, China and the Global Technical Centre in Burton-on-Trent.
“Delivering these big projects feeds our appetite for risk, scale and complexity,” Mr Davies said. “Doing enormous projects in Mexico from Burton-on-Trent is one thing. But we’re now setup over there, with a local sales and engineering office, to get closer to
ngineer working on aceutical system during Acceptance Testing (FAT); designed to help greener nts for producing pMDIs.
customer projects and increase site and after-sales support.
“Immersing yourselves in these locations, languages, and cultures gets you closer the customer. Our North America team are now in Kentucky, the home of bourbon. So having a sales and engineering office setup there to do the work is hugely beneficial. We were doing project work there for several years, but it was remote, we were parachuting in teams of people. Now we have a dedicated team and office, just like Mexico. These sales and engineering hubs provide a huge benefit to our customers around the world.”
One of the most exciting projects Briggs is involved in is the Ardgowan distillery in Scotland, which has
pledged to be carbon negative in its operations, ahead of targets set by the industry. Realising that ambition will be achieved by creating a modular distillery, able to adapt as sustainable technology evolves and matures. Each part of the whisky making process has been designed so that new technologies can be swapped to reflect the latest innovations in energy reduction, heat recovery and CO2 capture, as they become available.
“If you’re building a distillery now you can’t be anything but sustainable and mindful of the environmental impact,” Mr Davies said. “The Scotch whisky industry is on a trajectory to dramatically reduce its carbon intensity. We were focused on exploring a design that would implement the best available technology, that was sufficiently mature and commercially appropriate.”
He added that Briggs is investing in vapour recompression technologies, considering both thermal and mechanical types, which serve as an essential step in becoming efficient: “It’s all about reducing energy usage. The distillation process is quite energy intensive. Vapour recompression technologies can save between 45 to 85% of the steam usage in a still house. And that's significant for a distillery because that’s where most of the energy is.”
Unsurprisingly for a company that has been in operation for so long, Briggs has a large portfolio of suppliers, and that these days sustainability plays a large part in that relationship.
“Over time we’ve chosen a range of key suppliers and evolved and invested with
them,” Mr Davies reflected. “I think particularly with sustainability, honesty in partnerships is the most important it’s ever been. Reporting Scope 3 Greenhouse Gas emissions presents a challenge, which is being accelerated by our customers who ask more of us and our suppliers. There is a big pull through the supply chain on capturing and sharing data. Along with specification, health and safety and cost we are considering footprints and metrics associated with carbon, water, and energy. What we used to ask of our supplier was just a quote. But that’s rapidly evolving to the carbon footprint associated with the items transport to its destination.”
The company has broken ground with an expansion to its manufacturing site, which will be dedicated to pharmaceutical systems in Burton-on-Trent. Briggs builds the mixing systems that produce the gases in blue asthma inhalers and Mr Davies explained how this work will contribute to sustainable practices too.
“There’s been a big change in the market,” he said. “Historically, it was chlorofluorocarbons (CFCs) in the asthma inhalers acting as drug propellants, then the market shifted to hydrofluoroalkane’s (HFAs. Now it’s moving to even more environmentally green propellants. Briggs have been at the forefront of supporting the first commercial HFA systems and the first pilot of greener propellants. Alongside distilling, sustainability is growing in the pharma sector through designing and building these inhalant suspension production systems.”
As Mr Davies summarised, the work Briggs of Burton does allows other companies to flourish: “We join the bits, we give clients something bespoke. We have our own technology to meet our customers specific requirements, as opposed to a standard
supporting new distilleries and existing distilleries with exploring energy and water reduction technologies.
catalogue offering. The sales team dream of selling the same system twice. That isn’t to say we don’t have standards; we have a broad set of engineering standards based on good practice, but its seldom that two jobs are the same. And having existed since 1732, we are incredibly fortunate have vast experience to draw on. We can add value transferring technology and learnings from one sector or region into another.”
Despite its longevity, the company is focused on the future and maintaining its well-established presence. Mr Davies concluded: “We do amazing things, we invest in people, we're nurturing future generations. And, modestly, we are the brand behind many of the other brands that you, your friends, and your family consume and enjoy.” n
Aritex has over 60 years’ experience serving the automotive industry as a provider of assembly lines and automation. Following its success in the market, the company diversified into the aerospace sector in 2001 and has continued to expand its capabilities ever since. Chief Sales Officer Carlos Mendez has more than 20 years’ experience working for the company and spoke in detail about the company’s vision and plans for the future. Reporting on this topic is Imogen Ward.
Aritex made several advancements over the past few years, solidifying its position as a market leader in the automotive, aerospace and robotics sectors respectively.
“We want to have a hugely diverse and impressive portfolio,” Chief Sales Officer Carlos Mendez said. “Originally, our company focused on large-scale turnkey projects. Now, more so, we are also developing technology that not only aids these engineering projects, but also can be adapted to work for any industry. We are working hard to keep our roots whilst continuing to evolve and grow – for instance, we are digitalising, with the development of IIoT and Augmented Reality.”
In 1961, Aritex entered the automotive scene and has offered its clients creatively tailored solutions ever since. With pride in its work, Aritex engineers solutions for a diverse range of sectors, and is always on the lookout for new markets to infiltrate.
The company is currently breaking into the renewable energy sector, offering turnkey packages and high-specification tools and equipment using a highly precise manufacturing process.
Airbus, Boeing, Nissan and Volkswagen are just a few of the companies that Aritex has worked hard to supply with innovative and cost-effective turnkey packages. With the help of its evolving supply chain, Aritex has successfully created production lines that simplify the process and make manufacturing more efficient.
After the company’s success with more traditional engineering projects, it decided to focus on Industry 4.0. Following a boost in demand for the product, Aritex realised that digitalisation and robotics were an increasingly lucrative prospect to focus on.
“We have started several new businesses,” Mr Mendez said, “allowing us
to diversify our turnkey products. In some cases, we produce complete world data distribution. In other words, we are launching into Industry 4.0. We are achieving this with the development of our robotics solutions, and the more recently launched Aritex Code.”
With an impressive range of knowledge and experience, Aritex decided to sell high-specification solutions under the name Aritex Code. The company exploited its extensive industry knowledge through consulting and implementation services, to enable customers to minimise costs and increase productivity. Merging the digital with the real, the client can access the digital twin as a tool to obtain vital information, including running times and machine restrictions.
Augmented Reality as an accelerator for the learning of operators and machinery maintenance, is consolidated day after day. Augmented Reality-guided assembly instructions ensure frontline workers are
equipped with the information they need to complete even the most complex tasks with precision and efficiency, improving ontime delivery and customer satisfaction.
From the #AritexCode unit, Aritex guides companies on their path towards the digitalisation and automation of industrial processes, through complete solutions based on the latest technology, starting from project consulting, to development, implementation and after-sales services.
After becoming a major shareholder in Loxin in 2012, the company has produced several highly successful patents, including its work in parallel kinematics. Aritex then began offering conventional robotics systems as well as new ones: mobile and col laborative robots.
The advancement of robotics at Aritex is a spectacular feat. Removing the need for isolation provides opportunity for smaller companies to incorporate
collaborative or mobile robotics into their production lines. This, therefore, offers more efficient services to smaller companies that previously did not have the space for more conventional robotics systems.
This type of robotics also encourages cooperation between man and machine –ensuring both can work side-by-side, increasing efficiency (in comparison to more conventional robotics that would take up a greater portion of the production line). Another advantage of this robotics range is that it reduces injuries and accidents within the work environment. On top of this, collaborative robots are lightweight and easy to install, making them highly efficient and as stress-free as possible for the customer.
Thanks to Aritex’s advances in Industry 4.0, it is not just customers that have benefitted: due to the increase in efficiency, the reduction in waste materials and the minimisation of rejection rates, Aritex’s turnkey products help the environment too.
Furthering its mission to aid the planet, Aritex also entered the renewable energy sector. During Covid, the company worked on a large wind farm project: “we have been working on manufacturing production lines for wind turbine blades,” Mr Mendez said. “We have recently completed a project with General Electric. After the successful development of this project, we plan to offer our turnkey production line out to other wellknown companies working within the wind energy sector – creating long-term relationships with them.
“Although we are quite new to this sector, it has similarities to aerospace – they are different markets, but we can apply similar solutions to both.”
Aritex’s future is as bright as an aeroplane landing strip. The company is focused on continuing growth, with the aim of expanding its product portfolio. This goal will see Aritex further its work within the
automotive industry. Specifically, the company is hoping to meet customer demand for electric cars.
After working on small-scale projects, and a massive new electric vehicle production line, the company hopes to take on even more of these contracts going forward. With extensive automotive experience spanning back over half a century, the company is confident entering this division of the market.
As Aritex increases its production capabilities, it is determined to retain its reputation for excellence. Aritex holds a range of certifications, including the ISO 14001 (which is an international standard of requirements for an environmental management system) and the ISO 27001 (this is the best standard for information security management systems). These accreditations not only ensure quality, but also guarantee customer confi-
dentiality – offering customers that extra peace of mind.
“I have been in the company for 21 years. So, they must be doing something right for me to stay here that long,” Mr Mendez joked. “The company is always working on lots of huge projects and each one brings new challenges. I think those hurdles inspire us; there is no repetition in our work as no two days are the same.
“Aritex achieves a lot of impressive feats that other companies struggle to compete with. The continuous development and business model evolution completed by Aritex ensures the very best for our customers. Going forward, expect to see us continue down the path of digitalisation and robotics; we aim to evolve and grow in this area –opening doors to new markets and allowing us to reach a wider range of customers who need our help.” n
Advance Mechanical Services is a technology conglomerate that provides services in automation and engineering to its customers worldwide. The company contains decades of experience within its workforce to provide technology solutions in design engineering, robotics programming, digital manufacturing and many other fields. The work is specifically applicable to the automotive, aerospace and heavy engineering industries. CEO and Director Shashidhar NC explained the nuts and bolts of the operation to Hannah Barnett.
Catering to the needs of clients across the globe, Advance Mechanical Services is a large operation. It has three design offices in Bangalore alone. The company also has marketing arrangements across India with further offices in Pune, and in Delhi. It works closely with partner companies Aut-Tech GmBH in Germany and Aut-Tech-AMS Inc in the USA.
A start in
Advance Mechanical Services certainly seems to be doing well, with a turnover of £2 million in 2021 according to CEO and Director Shashidhar NC. Its illustrious his -
tory can be traced back thirty years when it started out in the automotive industry, engineering and designing car factories.
Mr Shashidhar recalled: “We must have designed body shops for almost all the OEMs across the globe.”
Mr Shashidhar began his own career at a manufacturing company where he got a taste for robotics: “I was lucky to have the opportunity to work with the first robotic installation in the country. That's when my career in automation and robotics started. And from then on, I've always been in the robotics business. Robots are now used a lot in the automotive industries.”
One of the company’s key strengths comes from the variety of work it does. It offers end-to-end services in engineering design, controls, automation and robotics programming.
“Most of the automotive companies globally know us and we continue to work with them in engineering body shops,” he said. “We have been doing design work for many OEMs such as GM, Ford, VW and Volvo factories across Europe and the USA through various line builders such as ABB, Kuka, L&W, Gonzalez, Chropynska and many others. We are lucky to be a part of some portion of their design process.”
As Mr Shashidhar put it: “We're only mechanical engineers, but about seven years ago I decided to diversify. And that was a milestone, because that really helped us a lot to move up the value chain in automation and provide end-toend services.”
One of the cornerstones of Advance Mechanical Service’s diversification programme is the innovative ‘R&D machine’.
The company started manufacturing specialised 3D printers about six years ago, Mr Shashidhar recalled. The unique selling point of these machines is how they are used, as he explained: “Unlike normal 3D printers, these are designed to help in doing research and development (R&D) which is very evident in the hundreds of papers that are published using our machines. It brought us from engineering into the manufacturing area, and we now have five verticals.”
The operation is a collaboration with Hyrel3D in the USA to provide multiple operations such as additive, subtractive and laser operations on the same machine. Additive manufacturing refers to creating an object by adding multiple layers. Subtractive manufacturing removes or cuts away material to create parts.
The manufacturing facility for the machines is located in a 2,500 square-foot area in the industrial area of Peenya in Bangalore. The company manufactures four
different models and 60 different heads that can print at up to 450 degrees centigrade. The machines can also print a variety of materials including liquids, gels and resins using its modular heads categorised under hot, warm and cold flow extruders.
Mr Shashidhar explained how the R&D machine sets Advance Mechanical Services apart from its competitors: “So many people make 3D printing machines, but this is a unique machine, because it’s purely for people who want to do research and use different techniques, different trials, use different type of materials, make composites.”
Mr Shashidhar explained how innovative work on this machine has allowed the company to build a strong relationship with its network of partners and suppliers.
“We are registered as an R&D company in the GEM portal of India, and we have a good sales network, most of our customers
are scientists or professors or PhD holders. They understand our machine. It’s a unique sale to them in the Rapid Prototyping area”
For a company which positions itself at the cutting-edge of the international mechanical engineering business, it was fulfilling to win an MSME award for export service and technological innovation. The awards celebrate India’s top micro-, small- and
medium-sized enterprises, looking for exceptional achievement in business performance and contributions to the country’s socio-economic growth.
Mr Shashidhar was pleased to receive the award from the Indian Prime Minister: “It was exciting because it was given by Mr Narendra Modi,” he said. “That motivated everyone in our company. After 30 years of working in this business, this is something to be proud of. And it gives our customers the confidence that a project will be executed properly.”
Though recognition and awards are significant, as Advance Mechanical Services continues to expand and develop as a modern company, so too is its commitment to sustainability
The procedures that the company is undertaking to implement appropriate sustainable standards, according to Mr Shashidhar: “It's the whole ZED process, to make the system sustainable.
This encompasses basically about seven or eight different standards. For example, ISO 9001 is a process standard. And there are three different levels: bronze, silver and gold. We're trying to go for the gold standard.”
Mr Shashidhar was enthusiastic about what adoption of these guidelines might mean: “We are implementing these standards and it will make the foundation of the company much stronger.”
The future looks bright for Advance Mechanical Services. That is why the CEO is now keen to share the wealth of his knowledge and experience with the engineers of tomorrow.
A recent MoU with Alliance University created the MBA in Digital Transformation programme; a unique two-year, full-time course. Students will have resources and equipment provided by ABB Robotics, Adroitec Engineering, Systema, Hyrel 3D and Siemens, all under the aegis of Advanced Mechanical Services. Students learn various technologies including Additive Manufacturing, SAP, AR/VR, IoT/IIoT and Digital Manufacturing, helping students transform the manufacturing sectors and be more competitive globally.
The curriculum is futuristic and based on the principles of progressive learning with enhanced focus on the contemporary disciplines. Jointly delivered by seasoned industry practitioners and technology experts from Alliance University, this programme equips graduates with the necessary skills to drive business of the future.
“Most college students today are moving away from mechanical and civil engineering,” Mr Shashidhar said. “Everybody wants to go into computer science. But the world will have many problems without good mechanical engineers. To construct houses, we need mechanical and electrical engineers, they can't do everything on computers.
“We add value by working with educational institutions, sharing our experience. We have decades of combined knowledge, so we could train them in these technologies. I want to increase the spirit of research and support education departments, institutions and students with knowledge of mechanical engineering.” n
Every year, ACCIONA goes to great lengths to improve the lives of those in underserved areas. The WATER division specifically, works hard to design, fund and construct vital desalination projects and water scarcity solutions worldwide. WATER Sustainability Manager Mercedes Bengoechea Crespo discussed the company’s innovative strategies for providing global water equality, in a report by Imogen Ward.
Since its origins in 1997, ACCIONA has developed and maintained sustainable infrastructure across the globe. Thanks to this progress, ACCIONA WATER has the capacity to manage water for more than 100 million people in 30 countries. This impressive feat is achievable due to ACCIONA’s EBITDA of €323 million and its implementation of state-of-the-art reverse osmosis technology.
“ACCIONA carries out activities in the integral water cycle,” WATER Sustainability Manager Mercedes Bengoechea Crespo said, “not only in the production of safe drinking water, but also in the development of different tools to analyse and diagnose opportunities for regeneration. We evaluate all our projects with respect to local sustainable development goals, designing vital solutions that have a positive impact.”
While these projects often deploy renewable energy, there can be more value through efficiency. The expertise of the ACCIONA team brings extensive knowledge regarding the optimisation and effectiveness of processes. Not only in the energy aspect, where ACCIONA is a technological leader, but also in innovations that exponentially increase the company’s sustainable contribution, such as the recovery of critical materials or brines.
ACCIONA’s work in the Middle East has had a major impact. Shuqaiq 3 in Saudi Arabia is one of the largest desalination plants in the country, providing safe water
for 2 million people. As an industry leader in the technology, ACCIONA incorporated reverse osmosis technology to reduce the pressure on conventional water resources and promote the most water- and energyefficient option.
This project benefits the community in more ways than one: as part of its social outreach measures, ACCIONA’s Shuqaiq 3 is also providing training for local residents to solidify the development of industry professionals.
“This project, which offers one of the world’s most competitive rates for desalinated water,” Ms Bengoechea Crespo said, “is part of Saudi Arabia’s plans to transform and modernise its water industry – adapting and renovating all freshwater production facilities to international quality and efficiency standards.”
Of course, these efforts are not limited to Saudi Arabia; ACCIONA WATER is reaching
milestones in other countries too. The Ras Abu Fontas 3 was the first of its kind in Qatar, a country which previously used evaporation technology to desalinate water. Now serving an estimated 1.1 million people, this breakthrough plant is an excellent example of the company’s capabilities.
An ongoing development in Spain, lead by the I+D+I area, is the LIFE PRISTINE project (funded by the European Union as part of its goals for climate action). With an expected completion date of 2026, this project will reduce water contamination significantly.
“The aim is to develop an integrated solution to remove various water contaminants,” Ms Bengoechea Crespo said. “These substances are of growing concern due to their potential to effect environmental, human and ecological health. The presence of most of these substances is not yet regulated, which makes it increasingly
difficult to take adequate measures to protect human health. Therefore, with the LIFE PRISTINE project, we aim to remove 80% of these emerging contaminants.”
All ACCIONA projects are highly sustainable: from concept to production, the company goes to every effort to ensure it meets the rigorous requirements of its green financiers, both for the good of the project and for the planet more generally. Indeed. ACCIONA is a pioneer of sustainable financing.
The ISTP projects – which are currently in development – consist of three sewage treatment plants in Saudi Arabia. These will utilise typically wasted elements of the wastewater treatment process. ACCIONA successfully raised €450 million in green finances to fund these plants.
In 2020, with its sustainability goals in mind, the company opted for an adaption of its corporate model, creating an entire sustainability department to further improve the efficiency of all current and future projects. Under the new approach, the
ACCIONA strategy focuses on the global transformation through a regenerative infrastructure approach. The company thus promotes the development of a more sustainable society through a resilient and balanced portfolio.
As part of these objectives, ACCIONA repeatedly assesses social and environmental areas requiring improvement.
“ACCIONA is not only focused on achieving
water equality,” Ms Bengoechea Crespo said, “but we also have additional projects on the go. These focus specifically on the social and environmental gaps in the geographical locations of our infrastructures.”
The company works closely with key suppliers and partners to ensure the success of each and every project. To source this aid, ACCIONA has an in-house procurement department who develop these relationships.
“We have developed framework agreements with the purpose of focusing in on a few well-managed suppliers,” continued Ms Bengoechea Crespo. “In terms of innovation and sustainability, our suppliers, subcontractors and partners are the main source of new ideas and developments. We always aspire to share our knowledge with them, to give them the opportunity to successfully develop new solutions for our plants and services.”
Reducing social and environmental harm caused by economic activity is no longer sufficient to secure the long-term viability of businesses. Since 2021, ACCIONA has evolved its Social Impact Management Methodology. Going forward, the company aims to further develop this because it knows that the local context is key. “We want to go beyond minimising the negative impacts and enhancing the positive social aspects that our projects could influence,” Ms Bengoechea Crespo explained. “ACCIONA drives towards creating a positive impact through each project. We are currently designing high impact solutions, regenerative projects; which will contribute to improving the living conditions of the population and the environment close to our projects.”
“One example includes the development of a high-impact solution at our Atotonilco Wastewater Treatment Plant in the state of Hidalgo, Mexico. We found that there were high levels of unemployment and low training rates within the community. Seeing this as an opportunity to substantially improve quality of life, we began providing certified training that contributes to the generation of local and long-lasting jobs in the area. The training consists of six months of the oretical and
practical elements that will increase levels of specialisation and employability.”
Another important element of ACCIONA’s humanitarian work is the Foundation Acciona.org. Originally created in 2008, the organisation was implemented to provide communities with sustainable access to basic services, including energy, water and infrastructure. This focused particularly on underserved and vulnerable communities and is now providing for more than 50,000 people in Peru, Mexico and Panama, for example.
“We are currently working with the Foundation in Panama,” Ms Bengoechea Crespo explained, “where we are trying to start a project to further aid the communities who rely on our drinking water treatment plant of Ingeniero José G Rodríguez. We want to develop access to education for children under three, because schools in the area are sparse.
“Currently,” she concluded, “our priority is to help construct a nursery that facilitates education for young children – helping generate better physical, intellectual, affective and social development of the children, giving them greater autonomy in terms of food, hygiene, sleep and general well-being. It is my challenge to make this project come true.” n
Enviroclean has 25 years’ experience delivering specialist waste management and industrial services advice to domestic, commercial, and industrial customers throughout the UK. Operations Manager Mark Donaghy highlighted the company’s operations and steady expansion, in discussion with Phil Nicholls.
Enviroclean is enjoying a period of steady growth with its broad portfolio of cleaning services. Enviroclean’s fleet of specialist vehicles service all of the UK, with a focus on Scotland and the north of England.
“We have won a four-year contract with an extended additional four years,” explained Operations Manager Mark Donaghy, “for all sludge tankering movements in Scotland for the local authorities, and have invested over £8 million on new trucks and trailers.”
Enviroclean was the brainchild of Jim McLuskey and founded in 1997 as an industrial drain cleaning company. The company steadily expanded with repeat business and a growing team of professional engineers. Today, Enviroclean deploys a fleet of over 120 vehicles and more than 160 staff to deal with any waste management or industrial cleaning job.
“We operate from our main office in East Kilbride, just outside Glasgow,” Mr Donaghy said, “which we have expanded over the years to accommodate the growing fleet of innovative plant and equipment.”
It is this growing fleet of distinctive green and yellow trucks that underpins the extensive range of services offered by Enviroclean. For industrial customers, Enviroclean’s services include vacuum excavation using RSP ESE 6 Vacuum Excavators manufactured in Germany, vehicles that are widely recognised as being cutting-edge technology.
Enviroclean operates a fleet of 20, eightwheeled tippers and two articulated tippers capable of carrying up to 30 tons of material. All new tippers delivered since September 2015 are FORS compliant, to meet the growing demand for safer HGVs on British roads. Enviroclean is the first
Scottish company to achieve this accolade. Indeed, Enviroclean recently won the award Scotland’s Top Road Safety Operator 2023, organised by Transport News.
The incredible Enviroclean fleet is rounded off with unusual vehicles such as a 22 metre Hitachi Super Long Front excavator, an allterrain Trac Vac and the CD Enviro D-Max mobile grit and screenings separation unit.
Alongside this impressive portfolio of industrial services, Enviroclean also offers a selection of cleaning services to domestic customers. The company has been desludging septic tanks since its very first day of business in 1997. Additional services include
drain cleaning and unblocking, drainage repairs and pipe lining. Enviroclean also provides CCTV surveys for pipes with diameters from 50mm up to 2.5 metres.
To choose a single project to highlight from Enviroclean’s substantial workload is not easy, but Mr Donaghy selected a personal favourite: “We have been carrying out cleaning works at Grangemouth, working on SBR tanks which has amounted to a project worth over £1 million. This extensive contract includes PLANT DISAB Q20, D-Max screening / treatment plant, Muller water jetting recyclers, Whale and RTN
6000-gallon tankers and ERT teams, all working together.”
Enviroclean enjoys ‘continual and consistent’ growth in its position as the biggest industrial drain cleaning company in Scotland and one of the largest employers in the area. This growth trajectory continues with a new four-year contract for all sludge tankering movements in Scotland. This project alone led to Enviroclean investing over £5 million on new trucks and trailers with more investment for 2023 /2024 already underway.
The latest investment is part of Enviroclean’s rolling project to operate sustainably by rejuvenating its fleet of
vehicles. All of the company’s new trucks have Euro 6 engines and Enviroclean is also exploring the options for upgrading the vans in the fleet, notably the potential to switch to electric vehicles.
Alongside these fleet upgrades, Enviroclean also has a broader programme to increase sustainability across the business. For example, investment in the in-house screening plants has improved the efficiency of treatments of all grit and
rags from sewage treatment works with a lower carbon / CO2 footprint on vehicle movement across the country.
It is this innovative plant and equipment that helps set Enviroclean apart from the competition. By investing in the best machines avail able, the company delivers a first-class service to clients. This investment programme runs alongside extensive Health and safety training for all employees to ensure the best possible outcome for the client.
To deliver services to this required standard, Enviroclean draws from suppliers across the UK and Europe. Enviroclean takes particular care to pay small business suppliers promptly, in appreciation of the importance of cash-flow to these smaller operations. In this way, the company builds up the strong relationships with suppliers that are so necessary for a successful business.
Health, Safety, the Environment and Quality are the four cornerstones of Enviroclean’s business. These principles provide the solid foundation for the company’s business philosophy and keep it as the first choice for customers.
As part of its robust fleet renewable programme, Enviroclean felt the impact of recent disruptions to the global supply chain. “The issue we have is with the supply of new trucks,” Mr Donaghy explained.
“There has been a backlog on all new orders. We were quite fortunate because we invested in the fleet before Covid, to acquire as many vehicles as possible and stay ahead of the competition.”
Additional issues include equipment price increases across the board. Yet, despite these assorted challenges, Enviroclean remains optimistic and committed to its plans for growth. The company feels the responsibility of being a major employer in the area, so is committed to continued employment and training for its knowledgeable team.
The existing Enviroclean fleet of vehicles and machinery gives the company an edge when tendering for new contracts. Not only is Enviroclean equipped for a broad range of services, but the company also has the expertise and depth to chase the larger contracts available in the market.
“I have been in the industrial drain cleaning business for 30 years with different companies,” concluded Mr Donaghy, “but with
Enviroclean I have watched the company grow for the last 16 years. This is a business model which Jim continues to grow, along w ith the management team and all the operational staff.
“I always enjoy the various jobs we undertake, especially assessing the works for the clients, to ensure all elements of the task are covered for the health and safety elements and the client receives the correct machines to carry out the contract. Enviroclean invests in different machines which makes the work easier on the operators and the company is fully committed to safety.” n
Offering environmentally friendly solutions in the hydrocarbon processing industry, GTC Vorro Technology aims to simplify and improve the process of sulphur removal. Phil Walsh, Vice President of the Environmental Services division, and Joseph Gentry, Vice President of the Technology Licencing division, explained how the company has established its presence in the sector. Report by Hannah Barnett and Phil Nicholls.
GTC Vorro Technology is a turn-key environmental services and technology provider to oilfield, refining, petrochemical and chemical companies around the world. The company focuses on the areas where hydrogen sulphide is not being properly removed, or where there are consequential environmental costs for doing so.
Formed a decade ago, GTC Vorro began life as an offshoot of GTC Technology, a technology licencing company. Its core business provides Hydrogen Sulphide (H2S) removal associated with natural gas production typically utilising solid adsorbent scavengers, as well as options to address redundant sulphur plant capacity in refineries. It has since incorporated additional technology to cover higher sulphur loadings that apply to a broader range of the market.
Joseph Gentry, Vice President of the Licensing Division, explained how the com -
pany identified a gap in the market when it brought different parts of the industry together: “We found synergies between the different divisions and between the different segments that had not been explored. The Midstream people don't talk with the Downstream people and viceversa. And there are a lot of inno vations in one area that could be applicable to the other. One of the things that we're doing is bringing those together.”
The company is focused on expanding the business significantly, as Phil Walsh, Vice President of the Environmental Services division, acknowledged: “Our employees, combined with certain other consultants coming in and out as we need, are dedicated to the company’s development. And we are in a growth mode.”
Headquartered in Houston, Texas, GTC Vorro conducts many of its operations remotely, closer to the oil wells themselves. Mainly this means in West Texas, around the
“
GTC VORRO’S METHOD OF SULPHUR REMOVAL HAS SIGNIFICANT ENVIRONMENTAL BENEFITS. THIS IS BECAUSE IT IS AN OPTIMISED PROCESS DESIGNED FOR MAXIMUM EFFICIENCY ”
Permian Basin which as Mr Walsh explained: “Tends to have a relatively high concentration of hydrogen sulphide that needs to be removed.” Going forward, the company is planning to enter into Canada and other international markets.
‘Growth mode’ seems an accurate assessment of GTC Vorro’s current status. The company is developing in exciting ways, recently announcing a partnership with Rameshni & Associates Technology and Engineering (RATE), a global speciality engineering firm providing state-of-the-art process technologies for sulphur processing and acid-gas removal. Described by Mr Gentry as ‘mutually beneficial’, the partnership will offer process technology solutions to customers along with full-service sulphur removal.
“It is a convenient way to deploy first rate technology without having to go to
multiple parties,” Mr Gentry continued. “RATE is a single entity, covering a broad range of technical aspects focusing on sulphur. We can combine our innovations with their engineering skill set to deploy and commercialise, thus providing synergy and convenience for both parties.”
GTC Vorro’s method of sulphur removal has significant environmental benefits. This is because it is an optimised process designed for maximum efficiency. Mr Walsh explained how the company, ‘provides a full ser vice’, which is unique in the US market, and possibly across the world.
The Environmental Services Division works to simplify the H 2S removal process and enhance real-world performance with minimal adsorbent volumes consumed. It does not sell H 2S removal chemistries but rather a turnkey, customised approach to the client’s specific needs, utilising the right
process, product, equipment and people for each application.
Mr Walsh elaborated on this: “We are taking responsibility and ultimately the financial risk for how well the overall system performs. We are not selling chemistry to a customer who then has to work out how best to apply that chemistry, manage and measure the process, and sort out waste disposal etc. GTC’s focus on the end result allows us to become the experts, and fine tune things to improve the performance of the whole system.”
As a result, the company utilises resources in a conscientious manner and the business model is inherently more economic and environmentally friendly. Additionally, the company is moving the industry towards a non-hazardous method for sulphur removal.
Mr Gentry expounded on the benefits of GTC Vorro’s approach to sulphur removal: “Petrochemical plants may use caustic trading to remove the sulphur,” he said, “but then you have waste caustic which is a waste problem; and from that you have a high cost. If we can treat by different means, then you can avoid the use of the caustic treatment or greatly diminish it. We’re solving two problems: we're using a cheaper method, plus we're avoiding a waste stream that needs disposal.”
It is an exciting time for GTC Vorro, as new possibilities for growth emerge. Mr Walsh explained that though the company is not immune to the international supply chain issues being felt across all industries,
it is currently sourcing, developing and evolving new options to foster security of supply both in respect of availability and commercial stability.
Opportunities to move into different markets are presenting themselves all the time, according to Mr Walsh: “One of the areas we're looking at is Liquefied Natural Gas. They are also having to deal with hydrogen sulphide in very high volumes of gas, but relatively low H2S.” The company is also investigating the use of hydrogen sulphide to make a high-end fertiliser.
Mr Gentry and Mr Walsh agreed that the strength of GTC Vorro’s customer base is one of the highlights of what they do, along with the sense of fulfilment they both seem to get from doing it. “It’s really solving problems,” Mr Gentry said, “I’m a process technologist at heart, and there are a lot of opportunities in which you can have an engaging discussion and find some solutions: and then we can bring together something that will make an improvement for their operation.”
Mr Walsh finds satisfaction in interactions with clients too, and in working at the cutting-edge of industry: “It feels almost like being a missionary into the market, trying to get that message out. And then the satisfaction of developing those relationships. Our model is not ‘an independent sale, and then then we move on to the next sale’. We are developing strong, ongoing relationships with a lot of customers. And it's very satisfying to see those grow as we become embedded as their H 2 S removal experts.” n
Amidst the global effort to reduce the impact of climate change, countries around the world are turning to renewable energy solutions to supply their energy needs. In the Caribbean, Sol Ecolution has positioned itself to be the leading regional supplier of commercial-scale solar power systems to governments, businesses and other entities. Regional Manager Dami Adesegha spoke to Richard Hagan about the company’s surging rollout of solar power technology in the region.
Sol Ecolution, based in the Cayman Islands, is the low-carbon and renewable energy division of The Sol Group, a member of Parkland Corporation.
As the largest supplier of energy solutions in the Caribbean, with operations spanning 23 countries, The Sol Group has deep relationships within the energy sector in the region. But also, as with its peers around the world, The Sol Group is actively planning for its continued involvement in the energy market as the world gradually shifts away from fossil fuels.
Sol Ecolution is the vehicle that will drive that energy transition, as Regional Manager Dami Adesegha explained: “In 2019, The Sol Group began to think about the future and what the next 10, 20 or 30 years will look like for us. Thinking long term, it was clear that
the Caribbean region’s energy mix will substantially change towards renewables.
“Rather than just allowing that to happen while we’re stuck trying to defend the past, we decided to use our position, capabilities and experience in the region to become actively involved in driving that change, not only for ourselves but also for the benefit of our customers, stakeholders, utilities and others. We’re uniquely placed to do that given our relationships within the energy ecosystem.”
Sol Ecolution was formally established in January 2021, with the simultaneous appointment of Mr Adesegha. He has since moved quickly to build a dynamic team of experienced energy industry
professionals. And as he confirmed, the Sol Ecolution team has wasted no time in executing on The Sol Group’s mandate, with an initial focus on rolling out systems to The Sol Group’s existing properties. “By the end of 2022,” he said, “30 of our own sites will be fully operational with solar energy solutions. We expect that number to accelerate substantially between 2023 and 2024.”
By late November 2022, Sol Ecolution’s team comprised ten professionals organised into three units. Its two technical units include electrical and mechanical engineers, while its business team deals with financial and sourcing opportunities. The whole team is geographically spread across several islands, including Puerto Rico, Bermuda and the Cayman Islands.
Through local partnerships, Sol Ecolution can install solar at the utility and commercial scales for governments, utilities and
the private sector. The team also benefits from the Sol Petroleum presence on each island, generally consisting of people who are local to that island, often having spent t heir whole lives there. They’re consequently able to leverage their relationships and cultural insight within the island, for the benefit of the company.
“That’s how we know that the Caribbean is really ready for this solar rollout,” said Mr Adesegha. “Our conversations prove that the appetite for solar is there; I can’t emphasise that strongly enough. So, our mission is to find a way to facilitate these projects. I’ve been pleasantly surprised by the positive reception we’re getting from our stakeholders in the islands.”
Sol Ecolution pursues opportunities to add value across the Caribbean’s renewable energy landscape. Leveraging the
market knowledge, experience and presence gained from solarising the company’s existing properties, Sol Ecolution offers solar PV systems to commercial customers at no upfront cost. “Installing solar at no upfront cost reduces a significant barrier to entry and allows more businesses to move to renewables,” said Mr. Adesegha. “Businesses can reduce their carbon footprint and save on energy costs while prioritising other investments – it’s a win-win.”
Sol Ecolution’s commercial strategy aims to increase opportunities for customers to participate in sustainable activities. The company rolled out its carbon credit program in 2022. Customers can purchase internationally verified carbon credits through Sol Ecolution to offset their emissions. In addition to selling credits, Sol
Ecolution is further developing this program through several eligible greenhouse gas reduction initiatives.
The Sol Group places a huge emphasis on being a good neighbour to the communities amongst which it operates. Within each of the markets in which it operates, The Sol Group supports and sponsors a number of community activities and events, ranging from school projects to environmental groups, sporting events and general community initiatives. A particular highlight is the annual Sol Rally Barbados, for which the Group would sponsor a car and a driver.
“It’s important to us to be a good, productive social citizen, to earn our right to operate within these communities,” Mr Adesegha said. “We take it extremely seriously. An important part of this is our commitment to safety.
“We’re dealing with volatile substances. They’re products that can be very unsafe if not handled carefully. We’re handling a lot of fuel every day, so it’s a big part of being a responsible citizen and historically, our safety record has been very positive.”
While Sol Ecolution is still a relatively young business, and also a new category for The Sol Group, the company is extremely
enthusiastic about the work that it’s doing and the future it’s creating for the Caribbean. “We have an opportunity to make a significant difference for entire countries in the Caribbean. That’s incredibly inspiring,” Mr Adesegha explained. “Sol Ecolution makes financial sense for the group, but it also makes a positive difference in the world.
“When I look at our four operational solar energy sites in Barbados, I see the positive impact that it’s having on the environment. Energy is a critical resource that the entire world relies on. We’re playing an important role in making that resource more sustainable and that, to me, is a cause as worthy as any other.”
In 2022 alone, with its rollout of solar systems across its own properties, Sol Ecolution has line of sight to a significant pipeline of over 100 solar projects. “The business opportunity is massive,” he concluded. “We’ll continue to go out there and capture those opportunities.” n
one planet – one chance – one voice
An introduction to the sea and air sectors, with news, innovations and a photo feature, followed by company profiles.
Latest Innovations from the sea and air sector
The first ever net zero transatlantic flight will take off from the UK this year, with Virgin Atlantic receiving government funding to fly across the pond using solely sustainable aviation fuel (SAF).
When fully replacing kerosene, SAF can slash lifecycle carbon emissions by more than 70% compared to conventional fossil jet fuel. This flight is expected to be fuelled by SAF made primarily from waste oils and fats, such as used cooking oil. The use of 100% SAF on the flight, combined with carbon removal through biochar credits will make the flight net zero.
“As an airline founded on and committed to innovation, we’re proud to lead a cross industry consortium of partners to make aviation history by operating the first ever 100% SAF flight across the Atlantic,” said Shai Weiss, CEO of Virgin Atlantic. “Virgin Atlantic’s inaugural flight in 1984 was to New York and today it continues to be one of our most popular routes. It will be an honour to pave the way for this important business and leisure route to become even more sustainable.”
Aviation is one of the hardest sectors to decarbonise and without urgent collaborative action it could be one of the highest emitting sectors for greenhouse gases by 2050. To tackle this, the UK government published the Jet Zero Strategy in July 2022 which sets out the approach for decarbonising the sector and champions SAF as one of the main tools for achieving Jet Zero.
Challenges remain, however, including the need to scale up SAF production and the existing limit on how much SAF is permitted in jet engines by current fuel specifications. Today, a maximum of 50% SAF blended with kerosene can be used in commercial jet engines. By using 100% SAF, the consortium will demonstrate the potential to decarbonise long-haul routes and bring us a step closer to net zero aviation.
The Trent 1000 delivers exceptional fuel efficiency and environmental performance. It has been optimised specifically to power the Boeing 787 Dreamliner family of aircraft, applying latest technology whilst drawing on the experience of four previous generations of Trent engines n
Latest Innovations from the sea and air sector
The rapid development in the shipping industry demands constant updates of on-board routines and seafarer skills. Greener shipping and the adoption of newer and smarter technologies pose a huge skilling challenge to shipping companies. In tanker shipping, the upcoming launch of an updated ship inspection report program, SIRE 2.0, will increase demand even further for company-specific courses and skills development.
When moving into new and larger offices, Furetank saw the opportunity to turn the old building into a training centre on the island of Donsö out side Gothenburg. A simulator complex equipped with the most sophisticated technology available will service all the shipping companies operating from the island, as well as other external parties.
The simulator complex has been designed by Wärtsilä, one of the world's leading maritime simulator manufacturers, and holds 14 students at a time. Physical simulation bridges are combined with virtual, augmented and mixed reality applications. Together they create highly realistic learning environments for navigation, manoeuvring, eco driving, docking, cargo handling, safety procedures as well as proper use of new ship technology like shore-power connection or LNG/PBG bunkering.
The equipment includes a full-size class A navigational bridge simulator using eleven
portrait-mounted 75” displays, giving a 240 degrees horizontal field of view and good vertical height. In addition, there will be a virtual reality bridge / bridge wing and TUG simulator as well as an engine room simulator including a virtual machinery space.
A multi-player feature allows interaction between captain/pilot, bridge/engine room etc, for training communications skills required in real-life scenarios. An awardwinning cloud simulation solution allows connecting to other training centres and performing remote joint exercises.
“We can simulate 50 ship models ranging from pilot boats and cruise ships to tankers and towboats,” said Jonas Gunnarsson, Personnel Manager at Furetank. “You can navigate several fairways, going into the ports of Gothenburg, Rotterdam, the Oslo Fjord etc. We can also simulate moving through ice or rough sea. Only our imagina tion sets the limits for what shipping companies can do in this simulator.” n
Following nature's example, Lufthansa Technik and BASF have jointly developed the functional surface film AeroSHARK for commercial aircraft. The film is modelled on the microscopic structure of shark skin and is applied to the aircraft's outer skin.
AeroSHARK directly reduces aircraft drag, cuts kerosene consumption and thus CO2 emissions. The Lufthansa Group will be the first airline group in the world to equip more than 20 long-haul aircraft in its fleet with aerodynamic sharkskin film. Following extensive testing and a certification process lasting several months, the European Union Aviation Safety Agency has granted Lufthansa Technik a Supplemental Type Certificate for the application of this technology on two Boeing 777 models.
In the future, all 12 long-haul B777-300ER aircraft at SWISS will fly with the fuel-saving surface technology. The same applies to Lufthansa Cargo's current fleet of 11 Boeing 777F freighters. The first SWISS aircraft equipped with AeroSHARK (registration HBJNH) has already been in scheduled service since October 2022. This aircraft had also completed the flight test programme for the certification it has now received.
“For a more sustainable future in aviation, we are consistently driving change in our industry. Our ambitious goal: a neutral CO2
balance by 2050,” said Christina Foerster, Member of the Lufthansa Group’s Executive Board, responsible for Brand and Sustainability. “With the broad rollout of the AeroSHARK surface technology developed by Lufthansa Technik together with BASF, we are once again underlining our innovation leadership. We are the first airline group worldwide to use this new technology. By covering more than 20 aircraft with the new sharkskin film, we will reduce the Lufthansa Group's CO2 footprint by more than 25,000 tonnes annually.”
AeroSHARK consists of millions of ribs around 50 micrometres in size, known as riblets. They imitate the properties of sharkskin and thus optimise aerodynamics at flow-relevant points of the aircraft such as the fuselage or the engine nacelles. As a result, less fuel is required. By covering 950 square metres of a Boeing 777-300ER’s outer skin, for example, annual savings of around 400 tonnes of kerosene and more than 1,200 tonnes of CO2 can be achieved. n
latest innovation from Veer
Veer is developing an innovative wind-powered solution for cargo shipping. The high-performance sailing rig will be able to power 100% of the propulsion requirements of these 100 metre vessels when there are prevailing good conditions
For more information please visit: www.veer.voyage
mething interesting to show the business world? We are always looking for beautiful and interesting visuals of ducts, innovations, buildings and technology. Get in touch and start promoting your company to the global market. media@insidepublication.com
The latest company and industry related developments from the sea and air world
Calling world leaders to act, ensuring the conservation of the ocean and the continent, Bárbara Hernández will defy nature by swimming more than 1,000 metres in the Southern Ocean in temperatures below 1°C. She will do this without a neoprene suit or
protective grease. During the expedition, which is supported by the Chilean Navy, the swimmer will visit the Antarctic Peninsula and the Chilean Antarctic research bases on King George Island. She will record the experience in a documentary piece, highlighting the value of Antarctica’s territory and its wildlife.
With the support of the Antarctic Southern Ocean Coalition, and following in the footsteps of extreme swimmer Lewis Pugh, Bárbara Hernández is urging the Commission for the Conservation of Antarctic Marine Living Resources to back the creation of new marine protected areas in its waters.
Hernández just recently joined Antarctica2020, a group made up of leaders from the world of politics, science, media, and sport who are working together to promote protection of Antarctica’s waters. It includes prominent personalities such as oceanographers Sylvia Earle and Philippe Cousteau, plus South African extreme swimmer and United Nations Patron of the Oceans, Lewis Pugh.
Boskalis has acquired a contract from the Ministry of National Planning, Housing and Infrastructure of the Republic of the Maldives relating to the further development, including climate adaptive measures, of Gulhifalhu.
The contract carries a value of approximately €120 million. This project concerns the second phase of the expansion of the island of Gulhifalhu.
The development of Gulhifalhu, which is located approximately four kilometres from the capital Malé, is part of the Ministry of National Planning, Housing and Infrastructure’s strategic plan to improve and develop the port infrastructure, and will serve as a climate adaptive solution, making this part of the Maldives resilient to rising sea levels.
For the second phase of the island’s expansion, Boskalis will deploy a large trailing suction hopper dredger to reclaim new land using approximately 18 million cubic metres of sand. Boskalis’ activities
also include rock revetment work for shoreline protection.
To manage the environmental impacts of the dredging and land reclamation activities, a comprehensive environmental impact assessment was conducted in accordance with the highest international standards. To mitigate possible adverse effects, Boskalis is implementing various measures, including coral relocation and measures to limit the spread of sediments in the water in combination with regular monitoring of the water quality.
Over the past two decades, Boskalis has successfully executed several climateadaptive dredging and land reclamation projects in the Maldives, including reconstruction work on the islands of Vilufushi and Villingili following the devastating tsunami in late 2004. In addition, Boskalis was responsible for the successful execution of the first phase of the expansion of Gulhifalhu in 2019 and 2020. n
The latest company and industry related developments from the sea and air world
Deltamarin and Socatra have signed a contract for a conversion basic design package for installing two Norsepower rotor sails onboard the 50,000DWT Chemical/Product tanker Alcyone.
The Medium Range chemical tanker built in 2022 will be retrofitted with two 35 x 5 metre Norsepower rotor sails. Deltamarin will carry out a full class approval design package for the conversion, including naval architectural, structural, deck outfitting,
machinery and electrical works. All the necessary modifications to the existing vessel will be carried out with the aim of class approval from the selected class society.
“We are delighted to execute this project together with Socatra and Norsepower, and we look forward to seeing the vessel with installed sails in operation early next year,” said Kristian Knaapi, Sales Manager at Deltamarin.
“Wind is definitely a good technology for decarbonisation in both segments, in existing ships and new builds.”
The signed contract is a good continuation of previous similar projects that Deltamarin has done for both existing ships and new constructions. The increase in decarbonisation technologies and clean technology solutions indicates a clear shift towards efficient and environmentally friendly operations, and enables progress towards emissions reduction goals, such as minimising fuel costs, enabling carbon regulatory compliance and improving IMO Carbon Intensity Indicator ratings. n
Low carbon energy storage company
GES and independent storage and logistics company GPS have announced they have combined both businesses to create a major player in the energy storage sector.
The combined business will take on the name Global Energy Storage Group (GES) and the merger further strengthens GES’ position in the market. This merged company will explore substantial growth opportunities across all markets internationally.
The new structure is being created to put greater focus on the development of the next generation of energy storage assets. This will help facilitate the growing use of low carbon energies, with an emphasis on cryogenic storage for products such as LPG, LNG and ammonia, which is a promising hydrogen carrier. In addition, biofuels and logistics solutions for the transhipment of CO2 are being pursued.
The new GES group will feature the following four storage assets, with additional business and project developments being pursued globally:
• Port of Rotterdam - Europe's main port where GES is pursuing the development of storage and logistics infrastructure designed to facilitate energy transition.
• Port of Amsterdam - Substantial hydrocarbon and biofuels storage capacity, supported by a rail link giving access to continental Europe.
• Port Hamriyah - A recently completed storage facility for fuels and petrochemicals located in the Hamriyah Free Zone in Sharjah, UAE.
• Port Klang in Malaysia - Southeast Asia’s largest independent LPG storage terminal, commissioned in May 2022, with refrigerated storage and VLGC capability.
The corporate management team will consist of: Eric Arnold as Chairman of GES, Peter Vucins as Group CEO, Alan Hyslop as CFO and Mark Synnott as Chief Technical Officer. Combined, the group will have over 140 employees. n
The latest company and industry related developments from the sea and air world
Swiss marine power company WinGD and Belgian shipping and cleantech group CMB.TECH have signed an agreement on the development of ammoniafuelled two-stroke engines. The companies aim to install the ammonia dual-fuel X72DF engine on a series of 10 x 210,000DWT bulk carriers to be built at a Chinese shipyard in 2025 and 2026.
Under this joint development project, CMB.TECH will support WinGD in establishing its ammonia-fuelled engine concept for a large bore engine. CMB.TECH has significant insight into alternative fuels, and it builds, designs, owns and operates large marine and industrial applications that run on hydrogen and ammonia.
The large bulk carriers powered by WinGD’s ammonia engines will be the first of their kind and proof that large sea-going vessels can be powered by zero-carbon fuels.
“We believe that ammonia is the most promising zero-carbon fuel for deep sea vessels,” said Alexander Saverys, CEO at CMB. “Our intention is to have dual-fuel ammonia-diesel engines on our dry bulk
vessels, container vessels and chemical tankers. Collaborating with WinGD on the development of the first ammonia-fuelled two-stroke engines for our fleet is a pioneering partnership on the road to zero emissions in shipping.”
The development project with CMB.TECH is one of several projects WinGD is carrying out with shipowners and engine builders to ensure that dual-fuel ammonia two-stroke engines will be available as the global fleet prepares to adopt green fuels to meet longterm decarbonisation targets. n
Around the world, the development of wind and solar power is in full swing, even if these still account for a small share of total energy generation. But the contribution from wave power is essentially non-existent so far. CorPower Ocean intends to change that with its innovative solution that, crucially, can withstand storms and efficiently generate electricity. CEO Patrik Möller gave Hannah Barnett an insight into how the company is making wave power work.
Akey characteristic of wave energy is that it delivers a consistent and predictable generation profile. This means it can be combined with wind and solar to deliver a stable mix of clean energy. Swedish-based CorPower Ocean is utilising this potential. Patrik Möller, CEO, explained that though there are many companies attempting to harness wave power, ‘the
jury’s still out’ on the design, and none have made it work quite yet.
“I believe there will be one or two winning design principles for offshore and nearshore,” Mr Möller said. “Offshore, I think that the point-absorber type we are developing is the leading one. It’s certainly the one you see the most investment and commercial traction in.”
Several leading companies are using point absorbers. What makes CorPower Ocean stand out, is how its design withstands stormy conditions while amplifying the power generation in regular wave conditions.
“Our distinction, compared to the others, is that our devices are designed to be naturally protected in storms,” explained Mr Möller. “Unless we actively control them, they don't react to ocean waves. They sit still and let the waves sweep by. It’s the same function as pitching the blades of a wind turbine. Every commercial wind turbine has this function of placing the blade horizontally when it's too windy, to avoid overloading. And then you pitch it back up when more regular winds are blowing. That has been missing in wave energies, so we've added that function.”
To amplify the generation in regular ocean conditions, CorPower uses an innovative technology called phase control. Mr Möller explained the theory behind how it works.
“It's like pushing a child on a swing,” he said. “If you're pushing a bit too early, or a bit too late, the pushing has little effect. But if you get the swing just right, you get a good momentum. It's the same with wave energy.”
The design of the equipment was inspired by the pumping principle of the human heart. It was CorPower Ocean co-founder, and medical doctor, Stig Lundbäck, who came up with the initial ideas.
“We have a pre-tensioning system that Stig invented, that allows us to extract the same amount of energy going up as going down,” Mr Möller explained. “Even
though the wave does not pull down, it just lifts. There is an analogy with a heart, which has muscles that pump the blood outwards. Then in the return motion, when you refill the chamber with new blood, there is no muscle that pulls the heart backwards; it's just hydraulically stored under pressure. This is also the principle that makes us protected in storms.”
With four stages of technology demonstration completed, CorPower Ocean now intends to bring wave energy to a bank able product offering scale-up deployments to make wave energy competitive with wind and solar by 2030.
One decade of product development, and four of research have built towards the flagship HiWave-5 Project. Approaching completion by 2025, its purpose is to demonstrate wave energy products
to the market and get additional major customers to invest in wave farms.
“Making wave energy bankable in our world involves a very structured demonstration and proof points,” Mr Möller reflected.
In August 2022, the company finished the dry test for its electromechanical drivetrain programme in Stockholm, at the world's largest facility for testing wave energy converters on land. The equipment then shipped to Portugal for ocean deployment.
“We are confident that we have stable, robust equipment. We developed a factory in Viana do Castelo in Portugal, where we have developed fully automated additive manufacturing technology to fabricate the composite hulls,” said Mr Möller.
Why Portugal? According to Mr Möller: “There's a big need for consistent power there, for finding solutions to combine with wind and solar to bring stability to the
energy system. It’s a great industrial environment, both in terms of the port facilities and the infrastructure around it, to start our operational base for composite manufacturing and maintenance.
“The talent base is important too. In the same region, we found several big manufacturers doing wind turbine blades. And we managed to hire Miguel Silva, who was previously the plant manager of one of the largest blade factories in Portugal. We've been able to attract very clever engineers into composite manufacturing here. That was important.”
Aside from HiWave-5, the company offers what it calls ‘CorPack’ clusters of 10 to 20 megawatts per unit for energy companies to build their own wave farms.
“We are turnkey suppliers of wave energy systems,” said Mr Möller. “We deliver the wave energy converter, the mooring system,
the anchoring and electrical connectivity kit
Our main revenue source is one of an OEM: we’re the technology provider selling the equipment . We can also operate and maintain the devices for the customer. And when we do that, we can offer a warranty on the availability and performance.”
Working closely with suppliers has proved crucial in developing technology for this innovative .
“Everything is optimised for the specific load cases of ocean waves, which are quite extreme,” acknowledged Mr Möller.
“The equipment needs to survive 100 million cycles of waves going up and down over 20 years. Which means we are tailoring the designs of all parts, whether it's gearboxes, pneumatic cylinders, structural components. The steel mill we work with has adjusted its process to our specific product. We go deep into integration with the supply chain and that takes a lot of effort in the proto typing
stages. It's the key to cost efficiency and reliability in volume.
“The three commercial partners that we are working with in Portugal are EDP, Enel Green Power and Simply Blue Energy. They are very important to us. On the drivetrain , there are many big suppliers that we collaborate with. We're working with ABB, Siemens on electrical systems, SKF and Trelleborg on bearings and seals. Autonational Composite Machinery supplied and designed the winding equipment and we're working on steel with SSAB, and many others.”
The company plans to instal 600MW of wave technology by 2030, initially off the European Atlantic coast, with the intention of expanding to the West Coast of the US and then further across the globe According to the CEO, this would achieve a €70 per MW/h cost, adding a stable component to the clean energy mix that has high value per MWh.
There seems little doubt that CorPower Ocean has established its groundwork and come up with a truly innovative design solution. Mr Möller is sincerely confident in what the company could achieve: “Wave energy is one of the few clean energy solutions that can fully take on the role of stabilising renewable energy so that we can end our dependency on fossil fuels. Ultimately, that is why we are around.” n
St Helena Airport is located somewhere unique – and remote. The tiny island in the mid-Atlantic is 1,210 miles off the coast of south-west Africa and 2,500 miles from Rio de Janeiro in Brazil. Following its opening in 2016, the airport has gained access to the rest of the world. With the commencement of a small schedule of weekly flights, alongside other services, it has grown steadily in the last five years, only slowing down during the height of the Covid pandemic. CEO Gwyneth Howell and Business Manager Tavonga Chikwenhere gave Hannah Barnett a taste of what goes on behind the scenes at one of the most remote airports in the world.
The opening of the St Helena Airport provided the island with a more efficient link to the rest of the world and, as a result, it is not immune to the challenges facing any airport. “We term ourselves the ‘big-small airport’, having to meet international standards and regulations while operating with very low staff numbers and weekly flights,” said Gwyneth Howell, CEO.
Alongside the weekly commercial departures and arrivals, the airport accommodates frequent private and charter flights. It is also beneficial to aircraft needing technical stops, such as those who use St Helena as a layover between South America and southern or western Africa. Most crucially, the airport supports medevac services to take seriously ill patients to the African mainland to receive treatment. Undertaking these bespoke operations requires considerable flexibility and commitment from staff working at the airport.
The contribution to medical services, via medevac flights, has been a great success and proved the airport’s worth over the last five years. Partly because it has also been able to link up with Ascension Island, relatively close at 800 miles away.
“In 2021 we had 22 Medevacs taking critical patients to South Africa for urgent medical treatment,” explained Mrs Howell. “In 2022, we have had 17 Medevacs, however four of these being Medevac flights for Ascension Island. The operator Awesome Air uses St Helena as a technical stop to and
from Ascension.” Mrs Howell added that the contribution to medical services, via medevac flights, has been a great success for the airport over the last five years.
Mrs Howell also noted that the Airlink weekly flights were a ‘silent Medevac’ as it has made it possible for less critical patients who require specialised and critical treatment not available locally to get off and, on the island without any hassle. The airport is an important lifeline to the community in need of critical medical attention.
Like the rest of the world and stakeholders in the global aviation industry, the ‘big-small’ airport felt the negative impact brought on by the Covid pandemic. St Helena Airport saw a major decrease in passenger numbers and flights. Mrs Howell noted that “We saw pax numbers decreasing dramatically, from 9,462 at our peek in 2019 to 3,048 by 2021”.
Due to the travel restriction put in place by local authorities and the South African authorities at the height the Covid pandemic, “Airlink fights to the island were
suspended on the 22 March 2020,” recalled Mrs Howell. “The St Helena Government then put in place charter flights which were operated by Titan Airways. These flights then ensured that we continued to provide our service as the gateway to the island throughout the whole period.”
The island travel restrictions were completely eased back on the 8th of August and that same month Airlink scaled back flights. “The easing of restrictions and the resumption of Airlink flights have brought about a great sense of optimism for us as an airport, we have recorded passenger number of 5,924 to date and this is passengers before 2022 was out.”
The ‘big-small’ airport is fiercely proud of its commitment to the environment, for example, the airport has a Carbon Management policy. “The main aim of that policy,” said Mrs Howell, “is to assess, reduce and mitigate greenhouse gas emissions under its direct control. All the while guiding aviation stakeholders and users of the airport to assess, reduce and mitigate their emis -
sions, with the ultimate aim of achieving carbon neutrality.”
Mrs Howell went on to explain that this commitment supports UN-defined Sustainable Development Goals and is another way St Helena is connected to the rest of the world. St Helena must keep its carbon footprint in mind. And it does, with a host of sustainable initiatives.
“We achieved the ACI Airport Carbon Accreditation Level 1 on the 3rd of December 2020,” said Mrs Howell. “ACI conduct a desk top remote APEX (Airport Excellence Programme) Safety Audit. The APEX Programmes combines the mandate for regulatory compliance with day-to-day operational needs to maximise operational efficiency and safety standards.”
The airport has also committed to supporting the vision of the wider St Helena Island 10-year plan under the ‘Altogether Greener’ heading. The goal is to safeguard the environment for future generations by minimising pollution and the use of resources.
‘Altogether Greener’ objectives:
• Minimise the impact of airport activities on biological diversity in the airport area.
• Minimise the risk of introducing nonnative species of plants and animals to the island.
• Minimise the use of resources without affecting aircraft and passenger safety.
• Adopt the waste mitigation hierarchy of Reduce – Re-use – Recycle – Recover.
Mrs Howell was enthusiastic about what can be accomplished through adopting these objectives. “We will minimise noise, vibrations and the visual impact on local communities,” she said. “Maximise the social and economic benefits of the air -
port through preferential employment of St Helena citizens and outsourcing to local suppliers. Ensuring the requirements of the Environmental Management System are extended to all suppliers.”
As Mrs Howell acknowledged, the airport has a strong relationship with its partners, and a close network of local suppliers across the island. “We have worked very hard to maintain the same suppliers for most of our goods and services,” she said. “Additionally, we use a select bunch of freight forwarders for goods coming from the UK and South Africa.
“Environmental and economical awareness and the inward freight schedule are important. The inward flight has limited
freight capacity, especially when it comes in with a full load of pax. So, you will note in peak season the freight loads are low, in low season the freights loads are high. However, we also rely on the cargo vessel to transports goods to the island for the airport.”
Unsurprisingly, the ‘big-small’ airport’s vision for the growth and development over the next few years is large in scope but realistic in content.
“I want us to keep the airport open and operational, grow the commercial flights and look for other partners,” said Mrs Howell. “We plan to develop a customer engagement strategy post Covid-19 with other players on the island. We would like to see an increase in Airlink flights during the diving and whale shark season of 2023-2024.”
Mrs Howell sees collaboration as the essential element of the success stoking the fires of this distinctive and intriguing ‘big-small’ airport. “My entire career, I have believed hard work and dedication is key to all working towards a common goal,” she reflected. “Every day at work is an opportunity to contribute to the growth of the company. It brings satisfaction knowing that I have done my best to improve something or create something great.”
The Port of Milford Haven is a leading UK port handling over 30 million tonnes of cargo annually. That’s not all though; the bustling site in Pembrokeshire, South Wales provides expert solutions in marine renewables, freight and passenger ferry services, fisheries, leisure and retail. Commercial Director Steve Edwards and Tam Bardell, Energy Development Manager, described some of the most exciting enterprises the company is involved in. Report by Hannah Barnett.
Though the Port of Milford Haven was officially founded 65 years ago in 1958, the history of commerce and shipping in the Milford Haven waterway stretches back centuries. These days much of the focus at the port is dedicated to how it can contribute to a greener future. There are multiple sustainability initiatives on the go, set to benefit not only the port, but the wider Welsh community too.
Leading by example, the Milford Haven Waterway Future Energy Cluster wants to strengthen the UK’s energy independence. This is a local coalition of energy companies, renewable developers, green technology innovators, the council and the Port of Milford Haven. The initiative has set a lowcarbon vision for the area by backing a South Wales Celtic Freeport bid and a South Wales Floating Offshore Wind proposition. One of the aims of the cluster is to help increase the region’s renewable energy capacity by 10 GW by 2030.
Steve Edwards, Commercial Director for the Port of Milford Haven, explained the main objective of the cluster: “I thought it was important that we galvanised a collaborative energy vision for the Haven. There is vast potential for marine renewables to decarbonise not only the industrial sector across South Wales, but also the UK more generally. The launch of the cluster is a pivotal moment for us.”
Mr Edwards said he hopes the project will help the decarbonisation process of the region’s largest emitters through the South Wales Industrial Cluster. “You’ve got Tata Steel, Valero, RWE, all in South Wales. The port has been part of that industrial group from its early stages as well.”
As Mr Edwards acknowledged, the Port of Milford Haven is known as the UK's largest energy port. This is partly because the port has certain strategic advantages such as the ability to handle vessels with draughts of up to 22 metres. It also has valuable proximity to Atlantic trade routes.
The port has transported LNG since 2009. Mr Edwards identified this as a ’significant milestone’ because the Port of Milford Haven now carries, on average, 20% of the UK’s LNG, serving the South Hook LNG and Dragon LNG companies.
To give a sense of the scale of activity, Mr Edwards added: “In 2020, Milford Haven transported around 65% of all the freight passing through Welsh ports – 33.5 million tonnes. That’s dominated by LNG and oil cargoes. And in 2019, pre-Covid, our twicedaily ferry service saw 327,000 passengers travel between Ireland and Milford Haven. We've already supported over 1,000 vessels into the Haven over the last nine months. I think these are extraordinary stats.”
It is no surprise that as the UK’s largest energy port, the company was a significant player in the Milford Haven: Energy Kingdom Project, a £4.5 million initiative completed in 2022.
The project explored what a decarbonised local energy system could look like for the Milford Haven area and the potential of producing zero-carbon hydrogen alongside other renewables.
Central to the project is a commitment to engage with the community and local industry, providing insight and opportunities for economic growth.
Tam Bardell is Energy Development Manager and played a key role in the project. He explained how it came about:
“We are the UK's largest energy port and we have some very significant energy infrastruc ture here. We need to think about how it’s all going to be used to decarbonise and transition to a net-zero future in all energy vectors – heat, power and transport.
“The technology is already there to decarbonise; it's more about creating
market levers, investment and infrastructure to do so. That's what this project sets out to do: to explore how you create that seed demand for renewables and hydrogen, and how that will aid a larger scale transition to net-zero within the region. It's clearly established the vision to redefine the Port of Milford Haven as a hydrogen hub. It’s also identified local investment propositions to catalyse the market.
“As part of the project, we demonstrated the world's first smart hydrogen hybrid heating system. That's an air-source heat pump paired with a boiler and smart controls which can react to local conditions. We put a hydrogen boiler in and tested hydrogen combustion through the heating system. We believe we are the first in the world to do that with a hybrid system. We also put in a hydrogen-electrolyser and refueler right down in the front of Milford Waterfront, where we get a lot of footfall including school visits. So, it’s really in the public's eye there.”
The port had this world-class marine engineering recognised, along with its potential for further innovation, when it was awarded over £28 million in funding from the Swansea Bay City Deal in June 2021.
The funding is to create a base for decarbonised energy production and marine renewables like offshore wind, wave and tidal, all as part of the Pembroke Dock Marine project. It also provided a substantial upgrade to the port infrastructure, with £13m invested directly by the Port of Milford Haven.
The deal has been ‘ground-breaking’ Mr Edwards said: “Having the LNG facility,
then this funding, not only secured our role in the energy system today, but started to lay the groundwork for us becoming a major marine energy hub.”
The Swansea Bay City programme is expected to generate £73.5 million a year for the regional economy, across all its nine recipients.
With so much sustainable activity already ongoing, a recent pledge by the Crown Estate to deliver a new leasing opportunity for floating offshore windfarms in the Celtic Sea provided an ideal opportunity for Milford Haven.
“We are the closest UK port to the Celtic Sea,” Mr Edwards said. “By 2050, we hope to have put more than 1,000 wind turbines there. There are estimates that the supply chain value of that could be upwards of £80 billion.”
Mr Bardell added: “We are looking at the supply chains capability to support new and emerging industries around the Celtic Sea. We’re involved in project mapping the skills gaps here in the local community and thinking about how we can engage local people to move into the sector.”
Paving the way for a renewable future is evidently essential at the Port of Milford Haven. The company is conscious of its place in the wider community. In recognition of that, it recently won an award
for its sustainability from the British Ports Association.
Mr Edwards reflected on the wider significance of investing so much into sustainability: “We are at the beginning of introducing a brand-new sector of energy that can help deliver Wales' ambitious net-zero plans. Under the energy cluster that we’ve now formed, I think our vision is the most exciting opportunity facing not only the port of Pembrokeshire, but also Wales.” n
Dale Aviation Ltd is a privately owned company, serving aviation industry as a Maintenance Repair Organisation (MRO), offering its customers in-house support to their aircraft. The company has administrative headquarters in Haywards Heath, West Sussex and maintenance sites in France. It is UK.PART145, EASA PART145, 2-REG, BDA, Cayman, Senegal, Qatar and Madagascar approved. Managing Director Matko Dadic explained what keeps the company in the air to Hannah Barnett.
With a healthy turnover exceeding €10 million, Matko Dadic, Managing Director explained what it took to shape Dale Aviation into the successful business it is today. “Love and passion for the aviation industry keeps us going,” he said. “As well as the large range of requirements in the market for various types of support and assistance.
This could be anything, from simple ideas and guidance to full maintenance support.”
Dale Aviation offers a wide range of services to ensure that an aircraft is fit for flight. The approved scope of work covers, but is not limited to, the following: arrival and departure checks, transit checks, other routine and non-routine line maintenance tasks as part of a maintenance program, defect rectification, component replacement, minor repairs and modifications, and more. The company is highly flexible and provides services 24/7 if required.
The company have been running its main site at an old airport, based in central France, for 10 years. It offers a huge range of facilities.
“We provide many different services from here,” explained Mr Dadic, “such as base maintenance, storage and parking,
painting support, modifications, and dismantling. Other sites we have in France, and across Europe, are created to provide line maintenance service to different customers. At the moment, we have around 80 employees, and we are actively recruiting.”
It is clear that Dale Aviation is not a company prone to standing still and is always looking for opportunities for growth. For example, Mr Dadic revealed that the company works on opening line stations outside of the EU soon. As well, Mr Dadic explained that at the end of last year, Dale Aviation started its first official C-Check. A C-Check is the inspection required to be performed on each aircraft every 18 to 24 months. Though the company has a lot going on, Mr Dadic pointed out that parking service has been the company’s busiest activity on offer, currently. “We mostly provide a parking service to a few operators for their aircraft when they are not on the ACMI contract and, at the same time, we
“And at the end of last year, we proudly started our first official C-Check”
prepare them for the next planned ACMI,” he explained. “This service has been active for the last four years.”
Also known as wet or damp leasing, ACMI leasing is an agreement between two airlines, where the lessor agrees to provide an aircraft, crew, maintenance and insurance (ACMI) to the lessee, in return for payment on the number of block hours operated.
According to Mr Dadic, the company distinguishes itself from its competitors in the MRO marketplace simply by the high quality of its work.
“The so-called advertising model we are using is word of mouth,” he said. “Although it is an old marketing strategy, it has not lost its effectiveness. We offer to our present, or future, customers quality services
and assistance. Customers are satisfied. They recommend us to their peers, who will do the same, and those peers to theirs, and so on. Yes, competition is increasing but I see this as a positive trend. We remain strong in our market.”
Indeed, no company can be successful for long without a strong relationship with its chain of partners and suppliers. Dale Aviation is no different. Among many others, the company works with Lufthansa Technik (LHT), Magnetic MRO in Estonia, Croatia Airlines Technical Services and the Italian Aermeccanica.
Mr Dadic explained that strong partnerships take time and loyalty to develop, but in the long run can pay dividends on both sides. “In the beginning, building a network of suppliers and partners was quite a hard and painful journey,” he reflected, “but the moment we increased our presence in the market and our name become known,
things started to change. Now, we are the ones choosing our suppliers and partners in business. It’s fundamental to build an open and trustworthy relationship, where we can rely on each other and mutually support each other’s business, as well as profitability.”
Though it is not the company’s core business, Dale Aviation sometimes has a hand in dismantling and recycling aircraft. “We are currently discussing the possibility of dismantling a couple of aircraft within the next six months,” said Mr Dadic. This, of course, improves Dale Aviation’s sustainable credentials.
Communication is important when it comes to customers, too. And, according to Mr Dadic, that it is one way Dale Aviation keeps ahead of trends in the market. “We are constantly following
market requirements,” he explained.
“This means complying with regulatory changes and investing in tooling and staff training. This is not a fast process as we have a limited budget for investment. But we keep up regular lines of communication with our customers and adapt ourselves to their needs. That keeps us afloat in the marketplace.
“A lot of our customers are increasing their fleet, which prompts us to seek partnerships with operators who need maintenance service providers like us. At the same time, there is a lack of base maintenance facilities and base maintenance providers. So, if we focus on keeping the quality of service at a good level, the future looks bright.”
Complementing this cloud-free horizon, Dale Aviation intends to invest in a new
hangar for a wide-body aircraft, in order to fully develop its activities and services. The company remains committed to helping customers. And in Mr Dadic’s words, though challenges exist, they are what keep the job interesting: “Each day, I solve puzzles in the workplace. It keeps my mind sharp and makes me excited to get up every morning.”n
one planet – one chance – one voice
An introduction to the packaging sector, with an innovation, event previews and a special report about plastic packaging, followed by company profiles.
Special focus on packaging events
The focus at interpack is on packaging materials, packaging machines and related process technology for the food, beverage, confectionery, bakery, pharmaceutical, cosmetics, non-food and industrial goods sectors.
interpack is a global trendsetter presenting the future themes of the food industry. From sustainability to digitalisation: what will be reality tomorrow is presented at interpack. Important growth topics and global trends in the processing and packaging industry on the agenda in 2023 include product safety, the circular economy, resource management and digital technologies.
Germany
2023 4-10th May
The 2023 event features over 2,800 exhibitors from 55 countries. At the previous event, 170,000 visitors attended from 169 countries. 58% of these attendees acquired new suppliers and a staggering 98% of visitors achieved their trade fair objectives with interpack.
interpack alliance spans all international events staged by Messe Düsseldorf under its Processing & Packaging portfolio.
Successful special topics such as SAVE FOOD and components will also be represented at the trade fairs making up the interpack alliance.
The components supplier trade fair is also an integral part of interpack. This second trade fair takes place concurrently at a central location on the site and has long become a destination in its own right. Visitors can attend two trade fairs with just a single ticket. n
www. interpack com
Sustainability in Packaging Asia is an important forum to share the value and successes of the packaging industry in the region. Hear from key experts on hot topics such as regulatory landscape, initiatives for circular packaging, new technologies and innovations in packaging materials.
Last year's online event offered attendees an unparalleled mix of actionable insights, collaborative case studies, leading panel discussions, latest trends, and emerging developments in the sustainable packaging marketplace.
This event included over 40 expert speakers and panellists. There were
presentations on key topics such as case studies of recycling and reusing, designing with climate in mind, sustainable soft plastic packaging and responsible packaging – a way forward with the 3Rs. Further discussions explored opportunities and challenges for realising a circular economy for plastic in Asia, and more.
Finally, there were two live panel discussions covering a wide range of issues, plus real-time networking opportunities for attendees. n Singapore 2023 6-7th June
Latest innovation from the packaging industry
BASF SE in Germany and StePac Ltd in Israel have joined forces to create the next generation of sustainable packaging specifically for the fresh produce sector. Supplying StePac with its Ultramid® Ccycled™, a chemically recycled polyamide six, BASF will provide its partner greater flexibility to advance contact-sensitive packaging formats to a higher sustainable standard within the circular economy.
StePac specialises in developing advanced functional packaging solutions and is pioneering the use of chemically recycled plastics for the packaging of fresh perishables.
Its two brands XgoTM and Xtend are based on MAP technology with built-in
humidity control which effectively slows respiration inside the packaging, delays the ageing processes, inhibits microbial decay, and preserves the quality and nutritional value of the produce during prolonged storage and long-haul shipments. Ultramid Ccycled will make up 30% of the packaging material, with options for integration at a higher percentage.
“This alliance will help strike a balance between creating plastic packaging that is as eco-friendly as possible to keep fresh produce longer through more prudent use of lean plastic films,” said Gary Ward, Business Development Manager of StePac. “These upgraded packaging formats will continue to maintain their role of significantly reducing food waste, a most important task considering that global food waste is responsible for about 8% of anthropogenic greenhouse gas emissions.”
With ChemCycling, BASF has been breaking new ground in the recycling of plastic waste. Chemical recycling primarily involves plastic
waste that would have been used for energy recovery or landfilled. It complements mechanical recycling, accelerating a circular economy by yielding food-grade recycled plastic. In a thermochemical process, the partners obtain recycled feedstock from these endof-life plastics, which is then fed into the BASF Verbund.
Colombian passion fruit exporters
Jardin Exotics SAS will be the first to use the new packaging brand Xgo Circular. Supplied as film for horizontal
form fill-and-seal, the packaging’s MAP properties will slow the ripening process and preserve the quality of the fruit during the long sea voyage from Colombia to Europe.
Packing at-source in the final retail packaging format also eliminates the need for repacking after arrival. For passion fruit, the combination of the produce specific modified atmosphere properties of the film, together with its high-water vapour transmission rate are what makes this film unique in its performance. n
Roger Wright, Waste Strategy & Packaging Manager at Biffa, explores the issues surrounding the recycling of plastics.
Biffa is a leading sustainable waste management company, that annually recycles 151kt of plastic into material which is used to make new products.
Report written by Roger Wright, Waste Strategy & Packaging Manager of Biffa.
The unpalatable fact is that the UK still produces too much waste and does not recycle enough of it. Currently the UK is falling short of its 2050 target to prepare 65% of municipal waste for reuse and recycling, and plastic packaging is an important part of this story. As of 2021, the UK has a recovery/recycling rate of 44% for plastic packaging, while materials such as aluminium (75%) and paper and cardboard (70%) are much higher.
It is easy to point at plastic packaging to say the material is a problem, to get caught up in the good-bad debate that polarises public opinion and media commentary. However, when items are made from reusable and recyclable plastics and managed correctly, they provide sustainable, cost-efficient, and durable packaging solutions.
The five best ways to create a more positive future with plastics involve utilising recyclable plastics, increasing capacity and infrastructure, reducing contamination,
replacing single-use plastic, and simplifying packaging.
WRAP's 2022 update to its annual recycling tracker shows that 90% of UK citizens regularly recycle when asked about all types of materials. However, the recovery rate of plastic packaging is 44% because much of it (flexible plastics or pouches) is not recyclable or reusable. While recycling is part of the nation’s day-to-day activities –and the motivation and behaviour are clear – the packaging used for many products does not support recycling.
What can be done about this? People and businesses need information to guide and support their choices. From businesses’ product design and packaging decisions to consumers’ purchase choices, understanding is needed at every stage of the process. If people know more about the dif ferent types of plastic and the environmental and economic impact of their choices, then a change in behaviour would be more likely, all the while increasing the quality of recyclable material by creating separate waste streams.
When recyclable plastic packaging leaves the UK, the carbon cost of transportation leads to more emissions compared to onshore recycling. There is a clear argument for more plastic to be recycled in the UK; to support green investment, infrastructure, economic growth and jobs.
An end to the export of plastic packaging would mean the UK must recycle the 0.7mtpa of plastic packaging waste a year currently exported. This would take at least 12 polymer plants with a minimum 55,000tonne processing capacity. Biffa’s 57,000tonne capacity recycling plant in Seaham brought 100 full-time jobs to the local region. Investment in infrastructure benefits both the economy and local communities in addition to the environment.
The Deposit Return Scheme in Scotland, launching 16th August 2023, is an example of how bold legislation can drive investment in and improvements to recycling infrastructure. As the logistics provider for the Scottish scheme, Biffa is developing new facilities to handle increased volumes of materials. The consultation for England, Northern Ireland and Wales is now complete, with the launch date set for 1st October 2025.
Last year, Biffa highlighted that nearly a fifth of all recycling is lost due to contamination. Food contamination on or inside packaging is one of the major issues hin dering our recycling efforts, but it doesn’t have to be this way. Increased awareness around the recycling process and the impact of contamination will help change behaviour for consumers and businesses.
There are plans for legislation to make the current voluntary, on-package labelling system mandatory. This needs to be realised for both consumer and business packaging, with the clearest messaging possible, to drive awareness of what the recycling symbols mean and the condition a container needs to be in to be recycled. This will reduce the amount of unrecyclable material in the UK collection and processing systems,
Roger Wright, Waste Strategy & Packaging Manager at Biffa, explores the issues surrounding the recycling of plastics. You can learn more about Biffa and its efforts towards sustainability here: www.biffa.co.uk/sustainability
improve the quality of our recycled materials and lower the carbon emissions output.
Our industry, regulatory bodies and government need a greater understanding of the packaging materials in circulation. Extended Producer Responsibility begins this year, obligating businesses to report greater detail on the packaging they pro duce and in what quantity. This will provide valuable insight to support customer choice and promote better packaging design for recycling.
The UK government recently announced its intention to ban certain single-use plastics, including plates and cutlery. While this is a welcome step in the right direction, the plastics themselves are not the problem; it is that they are single use. As single-use plastics are phased out, they need to be replaced by more multi-use or reusable options.
From bamboo cutlery to plant-based plastic alternatives, any material in a singleuse and on-the-go context presents a unique challenge. For example, it doesn’t matter if something is compostable if it ends up in general waste or if non-recyclable materials are put in the recycling bin. Both result in resources being lost and emissions being created.
The ban on single-use plastics will help increase the use of readily recyclable
packaging solutions, however, it is just one piece of the puzzle that will help the UK circular economy.
Brands are operating in highly competitive markets, working with tight margins. Packaging needs to be easy to fill, protect the contents and catch the eye of consumers in a split second in saturated environments. Often this leads to choices in colour and materials that render the container unrecyclable. It does not have to be one or the other; it is possible to create sustainable plastic packaging that speaks to the consumer.
Commonality and consistency are key to creating simple, sustainable packaging. If materials or different types of plastic are mixed, then it becomes harder to separate these materials and recycle them.
Packaging such as laminated material, plastic wrapping and big sleeves need to be separated or recycled at specialist facilities; this is often impractical and unsustainable at scale.
This is also true of packaging that contains more than one colour of plastic. No food-grade coloured plastic can be recycled back into natural-coloured food-grade packaging as the pigment
remains in the polymer. When mixed pigments are recycled together, the material becomes grey. Adopting clear plastic wherever possible will help move towards more sustainable packaging. Improvements can also be made by shrinkwrapping labels rather than gluing and tethering bottle tops to bottles (ideally the same colour).
Plastic packaging is unlikely to lose its edge if it is clear, homogenous and con sistent. Eye-catching designs can still be used, provided the components are easily removed and recyclable.
Increasing public awareness will support positive changes in consumer behaviour. People want to do the right thing, and those brands which explore sustainable options first will catch the eco-conscious eye and achieve cut-through. The time to start is right now.
Biffa supports some of the UK’s leading brands through this process. Its Blueprint for Waste Net Zero outlines the role of recyclable plastic packaging within the future carbon hierarchy and what further changes are needed to deliver a truly cir cular economy. n
Award-winning CJ Sheeran is an experienced manufacturer of timber packaging. Incorporated in 1994, and with a long history in the industry dating back to the 1960s, the company has been on a continuous mission to aid the planet and minimise its environmental impacts wherever possible. Group Compliance Manager Brian Fingleton discusses the company’s sustainable efforts, as well as the processes it aims to implement soon, in a report by Imogen Ward.
CJ Sheeran recently won the Pakman ‘ Business Recycling Champion’ award as part of its efforts to lead by example and maintain a sustainable operation. This joins the company’s collection of impressive accolades throughout its history.
“The Pakman award is a national environmental award that recognises excellence in recycling and waste management,” Group
Compliance Manager Brian Fingleton said.
“It’s a brilliant accolade for the business; it’s also a great acknowledgement of the hard work and continuous efforts the CJ Sheeran team put in daily.”
Ireland’s leading manufacturer of timber packaging, CJ Sheeran, creates premium wood packaging timber products. With headquarters located in Mountrath, and a further seven sites dotted throughout the
Republic of Ireland, the company is perfectly situated to serve all its customers’ needs.
As the only pallet manufacturer in Ireland to possess separate manufacturing plants, CJ Sheeran is fully prepared for any eventuality.
Focusing on the planet, the company has worked hard to reduce its carbon footprint. As a result, it has been shortlisted for three categories in the 2022 Green Awards (The Excellence in Waste Management Award, The Sustainable Energy Achievement award and The Green Manufacturer Award).
Recycling is an essential for this packaging manufacturer. Having set up a pallet recycling programme to help minimise consumer waste, the company successfully recycles 3 million pallets each year.
CJ Sheeran has a fleet of 80 trailers and would position them across Ireland to act as collection points at customer sites. These trailers are then brought back to the main recycling centre in Mountrath and sorted by a team of professionals into four categories: no repairs required, boards or block replacement required, dismantlement for reuse and irreparable.
All pallets in good condition, and those that were repaired by the company, are then stacked up by type ready for reuse. The dismantled pallets are used as part of the repair process for damaged pallets,
and the remaining stock of irreparable pieces are shredded. Residue and offcuts from the pallet recovery operations are shredded into woodchip, which can be used as biomass fuel and is WFQA certified.
Under the CJ Sheeran name is ComfyBed: the company’s brand of equine bedding.
Again, produced from offcuts and residue from the pallet manufacturing operations, ComfyBed is the official sponsor of RDS Dublin Horse Show and is used to bed some of the world’s best show jumping horses. This effectively highlights the premium quality of this recycled material.
As part of the company’s valiant efforts towards energy sustainability, a biomass boiler was purchased to minimise CJ
Sheeran’s carbon footprint. The group now uses 4,000 tonnes of woodchip to generate the energy required for the 10 kilns to both heat treat and dry their pallets, carried out under the ISPM15 licence. These kilns are crucial to the operation: by heat-treating the wood, CJ Sheeran ensures quality control and optimum safety for clients.
“The company plans to be carbon neutral by 2025, or sooner,” Mr Fingleton said. “Our biomass boiler is helping us get to that stage; 62% of the energy used by CJ Sheeran is produced by our biomass boiler. As a result, we successfully displace 1.5 million litres of kerosene every year, which equates to approximately 3,800 tonnes of carbon.
“Heat-treatment prevents wood-boring insects, which involves a process of bringing
the kilns to 56 degrees and then maintaining this temperature for a total of 30 minutes,” Mr Fingleton said. “The other important process is kiln-drying, which is used when customers require dry pallets for deliveries. The overall moisture content of a pallet after this process will be around 19% (depending on the client’s request) compared to pre-kilning.”
The company has an ISO 14001 Environmental Management System in place, making it the only pallet manufacturer to be certified with this. As part of its continuous improvement, the company was also accredited the ISO 50001 (energy management system) in April 2022. “We put systems and procedures in place to better understand the company’s energy consumption,” Mr Fingleton explained, “this also enabled us to measure our use and reduce it, which is better for the environment and much more cost effective.
“This not only helps us better understand our carbon footprint, but it has also encouraged us to have important conversations with our customers regarding our sustainability.”
There is only room for FSC approved suppliers at CJ Sheeran. Following its Green Procurement Process, the company only purchases timber from FSC approved suppliers. The company also prefers to partner with local suppliers where possible, which helps to reduce the carbon footprint of all CJ Sheeran’s operations.
This FSC approved timber is used in the production of all new pallets.
When manufacturing, there is a perfect balance of manual and automated production lines at the company. The automation lines at CJ Sheeran can make 80,000 standard sized pallets a week. With a flexibility to produce bespoke pallets and wood packaging products to meet a customer’s size requirements, the company makes these larger pallets manually, manufacturing around 4,500 a week.
Passion is prevalent in the individuals who make these products. The company operates an employee development and training programme under the brand name Talent Tree, giving workers the skill set needed to progress within the company.
“Here at CJ Sheeran there is a vibrant team who always maintain a can-do attitude,” Mr Fingleton said. “Our work is very customer-focused, and our training programme, Talent Tree, ensures employees have the best tools to provide excellent
customer service and care. We also provide access and support to programmes including the green belt and black belt training, apprenticeships and college courses too.”
With a new year comes the opportunity to implement new objectives. A major task CJ Sheeran is undertaking in 2023 is “implementing digitisation across the Group”. Mr Fingleton concluded, “we will be assessing our current capabilities and creating a future state map, where we
expect to deliver KPI dashboard screens, labour efficiencies derived from leaner systems, achieving savings on paper and data inputting which will make our company even more competitive.
“Ultimately, our goal is to continue expanding and the recent addition of our Coolrain and Cavan sites will aid this objective. Implementing digitisation is just another step towards achieving our company goal of carbon neutral by 2025 or sooner.”
n
Fibrestar Drums is the largest supplier of fibre drums in the UK and delivers its innovative, high-quality, industrial packaging solutions across the world. For the last 90 years, the company has produced economical, high-quality, versatile packaging drums in various forms. Product Manager Giulia Bonito explained to Hannah Barnett how they do what they do so successfully.
Innovative, customisable and environmentally friendly, Fibrestar’s drums are made from natural, renewable paper and board that is 100% recyclable and 100% biodegradable. The company uses 1000 tonnes of paper per year, taken from
sustainable, purpose-grown forests; so for every tree used, another three are planted. If stored and handled correctly the drums can be re-used multiple times. Drums that reach the end of their life cycle can be easily reconditioned or recycled back into paper production, used as fuel or as compost material. As Product Manager
Giulia Bonito explained, the company is in demand across multiple sectors, and well equipped to serve them.
“The main markets we sell to are chemical and pharmaceutical, as well as food ingredients and welding wire,” she said. “We have an annual turnover of around £8 million. Our machines can produce 800 drums per hour. We make six different specs at capacities between ten to 250 litres. Drums can be up to a metre tall. All specifications are bespoke. It depends on the product, the viscosity, bulk density and storage conditions. We tailor products to meet the customer’s needs.”
A significant milestone
Fibrestar Drums began life in 1932 as the ‘3 Ply Barrel Co’. Originally located in Trafford Park, Manchester, the company specialised in making plywood kegs, the 1930s equivalent of the state-of-the-art drums it manufactures today.
A key moment in Fibrestar’s later history was its move to Hazel Grove in Stockport in 2013. “It took about a year’s worth of planning to orchestrate the move,” said Ms Bonito, “but despite all the difficulties, we did not fail any customers and we did not lose any employees. Everyone decided to come with us, and we are proud of that.”
The specially designed production site allows the company to provide the very best in up-to-date packaging products and services. Stretching across 10,100 square-metres, the facility is divided into 50% production and 50% storage and is serviced by 60 employees.
The other reason the move marked a significant milestone is that it coincided with a shift in ethos that has gone on to define Fibrestar for the last decade.
“After we moved to our new premises, we put a lot of effort into the development of new paper-based products,” Ms Bonito explained. “Before the move, a lot of our production was of plastic drums. By 2013, things were starting to change in the world; there was more awareness about plastic pollution and climate change. It was then we realised that, for us, the future was fibre drums. So, we decided to put all our efforts into developing new specifications to build our range. Since then, we've been promoting fibre as a sustainable material to be used as an alternative to plastic.”
The Hazel Grove headquarters and sustainable ethos provided ideal conditions for the development of the company’s newest and most innovative product, Nestub. It is a fully biodegradable, durable and stackable paper-based tub made from recycled and virgin kraft paper, designed to compete and eventually replace its plastic counterpart. Nestub creates 66% less CO2 in its production than equivalent plastic pails and can withstand 60 kilos in weight. The product was developed by first understanding the weaknesses of its competition.
The Fibrestar team reverse-engineered the process, highlighting and addressing the weaknesses individually.
“For many years, the agriculture sector has been using plastic tubs,” Ms Bonito explained. “And a couple of years ago, we got an enquiry from one of the biggest manufacturers of animal feed in the UK. They told us that they were looking for an alternative to plastic tubs because the disposal of plastic is an issue for farmers. A recent UN report stated most plastics in fields are burned, buried or lost after use. Speaking with the farmers in the community, we were told that it is possible for animals to suffer injury from broken plastic shards whilst feeding. So, we agreed that we needed something different.”
‘Something different’ is what Fibrestar exists to provide, and the company seized the chance to create something totally new. “We had some options to offer them back then, but they didn't really tick all the boxes,” recalled Ms Bonito. “All the fibre drums were parallel sided, but they needed something conical so that they could minimise transport costs and warehousing space. With the help of The Growth Hub, we managed to come up with a process that allowed us to replicate the conical shape of the buckets, making our containers nestable and stackable.”
Nestub shines a light on the benefits of paper as a renewable and sustainable raw material with a low carbon footprint. And, as Ms Bonito revealed, the development of the protype unveiled some exciting findings: “After we sent out the first few samples, we realised we had basically created a whole new concept for agriculture, because the animals were not only eating the feed inside the tub, but also eating the tub.
“The benefit of using virgin kraft paper is that it is durable but at the same time, it is biodegradable, and it can safely be consumed by the animals. When the tub starts to biodegrade and becomes weakened around the sides, the animals eat it. It's safe because the tub is cellulose based, it’s fibre, and you have no more waste in the fields as the packaging gets eaten too.”
The company has put itself behind this product, set to launch in 2023. “All our resources have been invested in new machinery for the product development of Nestub, to meet the leanest price currently offered by the plastic guys,” said Ms Bonito.
Alongside this, the rest of the Fibrestar range remains innovative and significant, too. “We're continuing to invest in new tooling to improve the performance of our existing kit,” said Ms Bonito, “to get more efficiency out of what we've got. And in new materials.
As Ms Bonito acknowledged, a higher price point is often one of the issues cited by clients when it comes to switching to sustainable products. “Though we do have a lot of customers who value sustainability,” she said. “Ultimately, we're running out of time and resources, so I think soon everyone will have to look for an alternative.
“There's a motto that we love from one of our suppliers: ‘plastic, when necessary, paper when possible’. There are limitations to what paper can do versus plastic. But paper is a resilient and sustainable material, and one of the easiest and most frequently recycled raw materials in the world.
“At this moment, we are at a crossroads,” concluded Ms Bonito, “where we are faced with environmental collapse or a sustainable future. A recent article shared by The Guardian showed how our soils contain more microplastics than the oceans. Change at this point is not only necessary, but it is our only hope. ’’ n
CapsCases manufacturesqualitycardboardpackagingat competitiveprices anddeliversacrossmuchoftheUK.The companyoffersawiderangeofproducts, includingdrinkspackaging,e-comdelivery boxes,subscriptionpacks,cardboardboxes, RetailReadyPackagingandapatented rangeofarchivestorage solutions.There areavarietyofdigitalprintingandin-house designservicesonoffer,too.TrevorBissett, ManagingDirector,explainedmoreto Hannah Barnett.
According to Caps Cases Managing Director Trevor Bissett, the Covid pandemic and subsequent lockdown had a significant impact on the packaging sector; the requirements that have developed as a result have both driven and enabled the company to develop its sustainable ethos.
“It supported and strengthened a lot of the trends we were already seeing,” he said. “The moving away from the high street towards e-commerce, the push for more branding and on-box advertising, a greater requirement for personalisation and a desire to communicate brand messaging through an enhanced unboxing experience.
“All of these things were accelerated by the events of 2020 tenfold. We jumped from a £20 million business to becoming a £30 million business in two years.” As demand has soared, Caps Cases has seen a 30% increase in the square meterage of boxes and packaging it produces.
Mr Bissett stated that the company is targeting sales of £35 million in 2023.
A family-run business, Caps Cases is one of the largest independent, multi-site manufacturers of corrugated cardboard packaging in the UK. It was founded in 1982 by Charlie Bissett, Trevor’s father, and his partner Peter Bush. Their forenames make up the ’C’ and ’P’ of Caps Cases, respectively. And the close-knit, family ethos
remains. “Currently, 18 of our employees have over 25 years of service with us. That’s over 500 years of combined experience,” said Mr Bissett.
With manufacturing sites in Newmarket, Suffolk, a newly established factory in Northampton and one in Baillieston, near Glasgow, Caps Cases supports customers nationally and locally.
The shift towards a modern and sustainable workforce is reflected by the company’s investment in new machinery. In March 2022, Caps Cases became the first business in the world to acquire the EFI Nozomi 14000 LED Digital Corrugated Press, a 1.4-metre-wide, ultra-high-speed digital press designed for mainstream,
high- volume packaging production. The newly launched single-pass UV LED inkjet press brings enhanced productivity, reliability, value and flexibility to the industrial packaging segment.
“It’s helped us produce high-quality printed packaging digitally, so the turnaround speed is much faster than via older technologies,” explained Mr Bissett.
“You don’t have to wait for printing plates, there’s no need for colours to be signed off; it’s enabled us to move straight from being sent a digital file electronically to printing directly onto the box. There’s no wastage, and so in that respect, it’s also a more sustainable process.”
That is not the only thing about the Nozomi 14000 that makes it an environmental step forward. “We don’t have to
buy in printing plates, and it’s very efficient in terms of its power consumption,”
Mr Bissett said. “The ink is cured via an LED lamp, meaning our machine consumes a fraction of the power of others that are currently available.
“It’s helped us become more effective with our older equipment, which we now use to manufacture the higher volume elements of our work mix. It takes away the pain of spending hours setting up highquality graphic work on our flexo printing presses and allows our cus tomers to change design from one run to the next with no extra costs associated.”
Another way the company is making its mark as a sustainable business is with its focus on bespoke packaging, which means using the minimum amount of material, avoiding shipping fresh air and doing away with the need for unnecessary void fillers used for filling wasted space inside the pack.
“Instead of pigeonholing customers into something that is off the shelf, we are able to design packaging to fit the product they’re trying to sell,” explained Mr Bissett “We try to make sure that everything we do is sized suitably and we encourage customers not to buy huge inventories of one particular size.”
Alongside that, Mr Bissett stressed that maintaining a sustainable supply chain is a key facet of Caps Cases’ company ethos. “All of our suppliers use FSC certified materials. And we’re FSC certified ourselves. We’re also ISO 140001 accredited, and members of the ethical trading platform Sedex,” he said.
The company’s established presence in the packaging industry means it can take a discerning approach to its key
partner ships. “We are one of the largest buyers of corrugated sheet board in the country,” Mr Bissett said. “As an independently owned company, we’re able to choose who we work with to an extent We’ve worked very closely with our suppliers over a long period of time. We are very loyal to them, and I think we have excellent relationships with them all because of that.”
There are other small, practical, steps the company is taking to become more sustainable. For example, by switching the type of waste compactor it uses to a larger one, the number of waste collections has reduced by 50%.
As Caps Cases has sites across the UK, the amount of mileage its lorries cover is high, (320,000 miles in 2021), so the
company has taken steps to decrease that, too. “We’ve invested in a case machine in our Scottish factory, to make the prod ucts the customers in Scotland buy locally As a result, we’ve taken more than 100 artic loads that were previously travelling from Newmarket to Scotland off the road,” said Mr Bissett.
The company is also pioneering renewable ink, which replaces solvents with plant-based alternatives. “We actually mix our own inks on site and treat all of the waste back to water, so we’re having minimal by-products collected from the site as a result of that,” Mr Bissett said.
Working in close partnership with the local authority, the Newmarket site now has a total of 1,802 solar panels affixed to its roof. This generates 30% of the overall power consumption for Caps Cases.
While the present seems to be going smoothly, what does the future have in store for this innovative, sustainable company?
“We want to establish ourselves as a point-of-sale provider with our new digital technology and continue to grow in the e-commerce and subscription packaging sectors, whilst still providing high- quality products and an excellent level of attention to detail and customer service,” Mr Bissett reflected.
“Personally, I think I’ll always enjoy finding new ways of doing old things. Then it’s all about trying to make sure that our team has a clear sight of our shared objectives and goals, which we hope helps keep everyone here engaged and motivated. If we can continue to do this sustainably, then I believe the future is bright for Caps Cases.” n
Diageo is responsible for a world-leading package of over 200 premium brands of drinks. Alongside managing the steady growth of this portfolio, Diageo is pushing forward with sustainable packaging options and a broad ESG programme. Report by Phil Nicholls.
The Diageo Sustainable Solutions programme asked innovators for ideas to achieve sustainable growth. Launched in 2020, the programme has launched three different rounds of creative challenges.
Of particular note, the second round focused upon sustainable packaging technologies. The process began in November 2021 and has now reached the pilot stage. Ideas under consideration include the use of sustainable containers, increased refilling or returning of bottles and updated packaging for shipping.
Diageo was formed in 1997 as a merger between Grand Metropolitan and Guinness. However, the brands within the Diageo portfolio stretch back a lot longer, with some reaching down into the 17th Century.
At the turn of the millennium, Diageo consolidated its assets with a focus on premium drinks. As the company progressed through the new century, it steadily expanded its range of brands with additions such as Captain Morgan, United Spirits Limited and Chase Distillery. In 2022, Diageo moved its global headquarters to Great Marlborough Street in London, within the heart of Soho.
Diageo currently has over 200 brands within the premium drinks sector, with sales in more than 180 countries. The company operates 132 production sites and employs around 28,000 people globally. 2022 brought a 21% growth in new sales to £15.4 billion, delivering an operating profit of £4.4 billion.
“Diageo has, again, delivered strong performance, despite the challenges that all consumer goods categories have faced this year,” said Chairman Javier Ferrán in a statement summarising the company’s 2022 annual report. “We continue to invest for the future to sustain the momentum in our brands and deliver a positive impact on society.”
The extensive Diageo portfolio features two of the top four international spirits brands by retail sales value: Johnnie Walker and Smirnoff. The Johnnie Walker range of blended Scotch Whisky has pushed boundaries for 200 years. Available varieties include Black Label, Red Label and Gold Label. Diageo’s most popular blend is the Johnnie Walker Blue Label, hand-selected from rare Scotch Whiskies with a remarkable depth of flavour. Only one in 10,000 casks makes the cut.
Smirnoff holds the position of the world's number one vodka. Established in 1864, Smirnoff is created through a unique process involving three distillations and ten separate stages of filtration. The brand is also offered in flavours such as Raspberry Crush or Mango & Passionfruit Twist, plus a range of seltzers and ready-to-drink cocktails.
The extensive Diageo portfolio also holds iconic brands such as Guinness, the world-leading stout, established in 1759. This classic black beer continues to innovate with the launch of the alcohol-free Guinness 0.0% and Guinness Cold Brew Coffee Beer. Another iconic line is Baileys, the world’s first cream liqueur created in
1974 and now a much-loved spirit across 160 countries.
Other highlights of Diageo’s package of 200 premium drinks include Tanqueray, the world's number one premium gin, Captain Morgan, a spirit made with the finest Caribbean rums, and Gordon’s, the world’s number one international gin.
As part of Diageo’s drive to ‘deliver a positive impact on society’, the company is running the Sustainable Solutions programme.
The Cohort 2 challenges from Diageo focused on the development of sustainable packaging technology for its extensive portfolio of drinks. The pilot stage of this challenge draws together an exciting selection of schemes.
One such project addresses the challenge of glass bottles, which are energy intensive to manufacture, move and recycle. To solve this problem, Diageo is exploring the use of renewable content alternatives and the possibility of innovative metal container formats. The goal is to find a low-carbon solution with minimal associated waste.
A second strand of Cohort 2 investigates a circular business model for reuse and refill archetypes, with an emphasis on consumer-focused sales. This concept requires both containers adapted to a number of reuse/refill cycles, plus an innovative scheme to engage customers and ensure their participation.
Additional challenges being addressed in Cohort 2 concern the implementation of decoration techniques on glass bottles which do not hinder the sustainability credentials of the glass. Diageo is also exploring solutions to optimise glass bottles and other container formats with the associated packaging for shipping. The standard 6- and 12-pack formats were
Diageo’s pioneering grain-to-glass Sustainability Targets for 2030 compel the company to:
• Become sustainable by design
• Preserve water for life
• Accelerate to a low carbon world
designed for bulk palletised loads, but alternate packaging options could reduce waste.
Further evidence of Diageo’s commitment to sustainable business was the recent announcement of a hydrogen-powered furnace together with Encirc to change the face of the UK glass manufacturing industry. This partnership aims to create the world’s first net zero glass bottles at scale by 2030. Encirc will build a new furnace at its Elton plant, Cheshire, that will use an energy mix of green electricity and low carbon hydrogen. It is expected that carbon capture technology will deal with the remaining emissions by 2030.
“We are really excited to be a part of this world leading announcement,” said Ewan Andrew, President, Global Supply & Procurement and Chief Sustainability Officer at Diageo. “This forms part of our commitment to halve our Scope 3 carbon emissions by 2030. We look forward to a world where people can enjoy their favourite drinks from zero carbon glass bottles.”
The use of the zero-carbon furnace will contribute towards Diageo’s commitments in its ESG action plan ‘Society 2030: Spirit
of Progress’ to reduce emissions across its supply chain by 2030. Under this 10-year ESG action plan, Diageo is working towards creating a more inclusive and sustainable world.
The multi-strand ESG plan includes projects to promote a positive drinking culture and champion inclusion and diversity at every level of the business. Society 2030 also features Diageo’s pioneering grain-to-glass sustainability work with three major goals.
Alongside these assorted enviromental projects, growth continues. At the start of 2023, Diageo reached an agreement to acquire Don Papa Rum, a super-premium, dark rum from the Philippines. The initial consideration was €260 million, with a second possible con sideration of up to €177.5 million through to 2028 subject to performance, reflecting Don Papa Rum’s current growth potential.
Diageo remains committed to its position as a global leader in the premium drinks sector, leadership in terms of both portfolio size and driving the sustainable agenda within the industry.
“Our people are engaged and proud of Diageo,” concluded Mr Ferrán in the company’s 2022 annual report. “We continue to invest for the future to sustain the momentum in our brands and deliver a positive impact on society. We have consistently shown resilience in the face of volatility in recent years and proven our ability to emerge stronger in these circumstances.”
n
Based in Singapore, with a global network of depots, Goodpack has over 30 years’ experience delivering efficient, integrated supply chain solutions via a network of strategically located global depots and fleets of returnable containers. Chief Operating Officer Peet Leong Kok, Goodpack Korea Country Manager Chul Hee Chun, and Regional President, Northeast Asia and Global Business Director, Synthetic Rubber Chee Heng Sng discussed Goodpack’s news and operations. A report by Phil Nicholls.
Disruptions to the global supply chain remain a challenge for almost every business. Logistics experts at Goodpack have developed the innovative RoRo Cube which enables customers to side-step many of the problems affecting the free movement of global trade.
“We have a partnership with Wallenius Wilhelmsen,” Goodpack Korea Country Manager Chul Hee Chun explained. “They provide us space on their RoRo vessels, we provide them with packaging solutions and transportation equipment. For example, there has been a lot of congestion
in US container ports. However, they use their own terminals or contracted terminals which are different from container ship terminals, so once the RoRo vessels arrive, they can quickly release their cargo.”
Goodpack began in Singapore in 1990, focused on logistics for the rubber industry. The company quickly expanded into a global network of supply chain solutions working across multiple sectors. Recent years were dominated by the Covid pandemic and its impact on businesses.
Goodpack showed its agility by shifting supply chains to limit the impact on the
business, a successful process which enabled growth to continue throughout the pandemic.
As a global operation, Goodpack has 350 associates operating across 80 countries with over 5,000 delivery and collection sites spread through six continents. The company deploys over four million returnable bulk containers and supports close to seven million deliveries each year.
The RoRo Cube
Goodpack delivers efficient, end-to-end supply chain solutions via this worldwide network of depots. At the heart of this provision for customers lies innovative container solutions, such as the RoRo Cube. The business concept of RoRo Cube was developed alongside Wallenius Wilhelmsen, a global market-leader in RoRo shipping with a fleet of over 130 vessels operating on every ocean.
“We realised that a container would be a good solution for a RoRo vessel,” Regional President, Northeast Asia and Global Business Director, Synthetic Rubber Chee Heng Sng said. “So, we looked at ways to work with Wallenius to find a product offering our customers an alternative to how they’re shipping things today. The result is the product we call the RoRo Cube.” Headquartered in the heart of southeast Asia, Goodpack began serving the rubber industry. As the company expanded, it became involved in the supply chain for a range of industries. Goodpack containers can be fitted with hygienic food- grade packaging. This facilitates transport and storage solutions for food and liquid products.
Another sector for Goodpack is the transportation of chemical products, such as inks, paints and resins. The company’s focus on streamlined transport and
storage solutions are also applied to the shipping of components and consumer goods around the world, all customers benefitting from digitisation, payload visibility and speed to market.
“Goodpack enjoys a close relationship with CEVA, the biggest automotive logistics company,” continued Chief Operating Officer Peet Leong Kok. “We’re working with CEVA in the tyre space, with a programme to develop TYRECUBE TM to transform the supply chain, using our container as the de facto movement medium for everything from intermediates – like compounds, bladders and tubes – to finished tyres.
“Our close relationship with Goodpack in developing innovative solutions for the tyre industry is a key factor for our tyre subsector growth strategy. Our ability to focus on automation, digitalization, and circular economy concepts are gaining the right momentum,” mentioned David Dudek, global automotive and tyre sector leader for CEVA.”
The development of new transportation options such as the TYRECUBE TM is a crucial part of Goodpack’s growth strategy.
Goodpack relies upon its close partnership with the network of third-party
logistics, suppliers, depot operators, trucking companies and freight forwarders. “We think of them as our arms and legs, executing our network,” Mr Kok said.
The company is proud of its sustainability credentials, according to Mr Kok: “Our container solutions have been tested by independent valuers and verification bodies; these containers will last more than 35 years. When compared with a singleuse packaging solution, the Goodpack method is definitely much more sustainable in terms of carbon emissions.”
In parallel with the inherent benefits of reusing the containers, often shifting them between industry sectors to meet fluctuations in demand, Goodpack is also investing in eco-friendly improvements
within the company. The network of depots is steadily switching over to energy-efficient LED lighting.
From an operational perspective, the greatest challenge facing Goodpack has been the Covid pandemic and the restrictions this imposed on international shipping. Similar limitations also reduced the opportunities for face-to-face meetings with clients, an important part of building strong partnerships. As these restrictions are now steadily lifting, Goodpack can return to normal business practices, meeting clients and colleagues around the world.
Viewing these signs of the world steadily returning to normal, Mr Kok gave a cautiously optimistic assessment: “Economically, the world may be in a soft slowdown. We see good growth in food logistics, as people always need to eat. Goodpack is also looking at EV batteries as a growth market, at least in terms of sustainability and the automotive industry, as announced recently with Wallenius Wilhelmsen. We’re looking into that segment to see how we
A returnable Intermediate Bulk Container made from galvanized metal. RoRo Cubes are suitable for many products, can be stacked safely on RoRo ferries, and are collapsible when not in use.
• Dimensions: 1.46m x 1.15m x 1.09m
• Capacity: Up to 1,500 litres
• Unladen weight: 131kg
can be the industry-standard for the supply chain of EV batteries to our automotive customers.”
Alongside this expansion into the distribution of EV batteries, Goodpack is also investigating how to harness the accumulated data from seven million voyages annually. Every year, customers demand better service from their logistics partners and Goodpack believes this wealth of data can add value for its customers.
Goodpack continues to enjoy the strategic benefits of its location in Singapore. “This part of the world remains very exciting,” concluded Mr Sng. “China has been a growth engine for us in the region over the better part of ten years as it continues to grow. Goodpack is excited about the future, helped by being so close to China, Japan and Korea. These three countries continue to be at the leading edge of the constant innovation and industrialisation that drives EV technology.” n
Greener Packaging originated in Sweden in 2013. Established as a solution to high costs and CO2 levels when packaging products, Greener Packaging’s container supply systems make it easier than ever for companies to simplify their product packaging operations. CEO and Sales Manager of Greener Packaging UK Julie Checkley discussed the company’s latest investments, in a report by Imogen Ward.
All companies are catered for at Greener Packaging, no matter their size or production capabilities. The company’s compact and innovative packaging supply systems ensure that even smaller clients can benefit from manufacturing packaging in-house.
“We use the smallest, most compact blowing machines on the market,” CEO and Sales Manager of Greener Packaging UK Julie Checkley said. “This enables us to be extremely flexible, because we can change from one container design to another in 15 minutes. This means
customers can adjust bottle colour, material and production additives whenever they require it. If the company has a limited production line space, our systems accommodate this and enable them to switch quickly to alternatives. This feature is something a lot of clients haven’t had before, and our system offers extremely competitive pricing too, often lowering our customers’ costs by about 20%.”
Greener Packaging’s supply systems have been revolutionising customers’ production lines since it was first established in 2013. From there, the company expanded beyond Sweden, targeting the wider Scandinavian market. Currently, the company is emerging in the UK and Ireland, with plans to target the USA in 2024.
“We serve customers worldwide from our 24 manufacturing locations,” Ms Checkley said.
“For our larger customers, we supply bottles and jars from directly within their sites. This is an entirely in-house process that is incredibly sustain able and cost-effective for clients. They also have the option to sell their surplus manufacturing time to neighbouring companies. We automate and digitise the process to maintain optimum efficiency, and we are a very streamlined company, which allows us to remain fast-paced and dynamic.”
Greener Packaging has an easy-to-use customer interface, giving customers complete freedom to control their orders and track the bottle production performance (order fill rate OFR). An OFR of 99% is consistently achieved. “Our customers have full access to the customer interface at all times,” Ms Checkley explained. “They can upload their forecasts for production schedules, place orders and review invoices on the same platform. A forecast ensures we provide them with enough preforms for their requirements and helps reduce their dependence on complex supply chains.”
The company recently invested over €1 million into improving its prototyping process. “We can make a bottle from concept to
working prototypes within seven weeks,” Ms Checkley said. “We are one of the fastest packaging developers on the market. We have also successfully introduced a new concept to the market: a dedicated Greener Packaging Container supply system with integrated autoquality control.”
This system produces highquality, cost-effective packaging. The auto-quality machine relies on AI technology to automatically assess the quality of the produced bottles. This saves time, as it removes the need for manual quality control at each stage of the produc tion process.
“The auto-quality machine checks several different areas of the bottle,” Ms Checkley said. “It automatically checks wall thickness and cools the bottles to make the process of leak inspection more time efficient. This guarantees quality and consistency across the manufacturing process.”
“Previously, packaging supply systems were a luxury only granted to large-scale companies; Greener Packaging, however, is working hard to change that”
Greener Packaging’s container supply systems are one of the smallest, most compact options currently available on the market. Remarkably, the machines are about three-times smaller than the industry standard and have opened doors for several small businesses. Previously, packaging supply systems were a luxury only granted to large-scale
c ompanies; Greener Packaging, however, is working hard to change that. The company recently installed a highly-versatile compact PET packaging production line at Maustaja –a private-label manufacturer of condiments and seasonings. The customer had specific spatial requirements that Greener Packaging was more than happy to accommodate.
“ As part of our agreement with Maustaja, Greener Packaging is responsible for the full-bottle production on the site and maintenance of the equipment, including new bottle development and technical upgrades,” Ms Checkley said. “This solution resulted in a reduction in Maustaja’s transportation and packaging costs, because it removed the requirement to ship empty bottles before the filling process.
“Another positive outcome of our inhouse bottle supply system is the removal of customers’ reliance on complex
multiple supply sources. As a result, there are fewer disruptions in our clients’ supply chains, and they have witnessed a reduction in lead times and a simplification of their buying process, saving time and money.”
Greener Packaging is a platform business and allows customers to receive an instant online quotation for their container requirements directly on Greener Packaging’s website, for both readymade container deliveries and in-house operations The company also works in partnership with a large combination of cap suppliers, offering the complete packaging solution to all clients directly from its website. These suppliers are vital to Greener Packaging’s operation. Developed from customer service and the desire to build long-term relationships, the company maintains
meaningful partnerships with businesses that match its values and high-quality standards, making Greener Packaging customers' lives easier.
2022 saw Greener Packaging help convert more customers’ bottles from glass to rPET than ever before. This increasingly popular option has several benefits for both the client and the environment.
Greener Packaging uses rPET as its preferred medium – the material’s recyclable nature makes it kinder to the planet and more cost-efficient. “There are several r easons why our customers are choosing to move away from glass production,” Ms Checkley said. “There is the glass shortage for starters, sending costs soaring. Glass production also requires a lot of energy; with gas prices skyrocketing, glass bottles are highly inefficient in terms of both price and sustainability.
“Customers are also concerned about glass breakage on their filling lines causing difficulties in the production process. rPET not only prevents this issue, but also opens new opportunities within export sales due to the durability of rPET.
We are currently undertaking a lot of conversions for companies who produce jams, peanut butters or alcohol.
“Another trend we are witnessing is the transition from HDPE bottles. These are much heavier than rPET; as a result, conversion to rPET helps reduce our customers’ carbon footprint and lowers their costs. Another issue with HDPE bottles is their tendency to leak. This doesn’t happen with rPET, so wastage levels are significantly reduced.” rPET also offers more freedom in design and makes the customer's product stand out on the shelves.
No two days are the same at Greener Packaging: “Every day we speak to new people and work to solve different scenarios,” Ms Checkley concluded. “Each company’s needs are very diverse, which is part of what makes the job so worthwhile. On top of that, the knowledge that we are helping protect the environment is a huge factor. Our in-house design team works extremely hard to minimise the amount of non-recycled plastic used for our bottles and jars – in the design phase alone they can remove 20% of the plastic.
“We think it’s really important for our customers to be given the opportunity to see the benefits of plastic when it is used properly.”
n