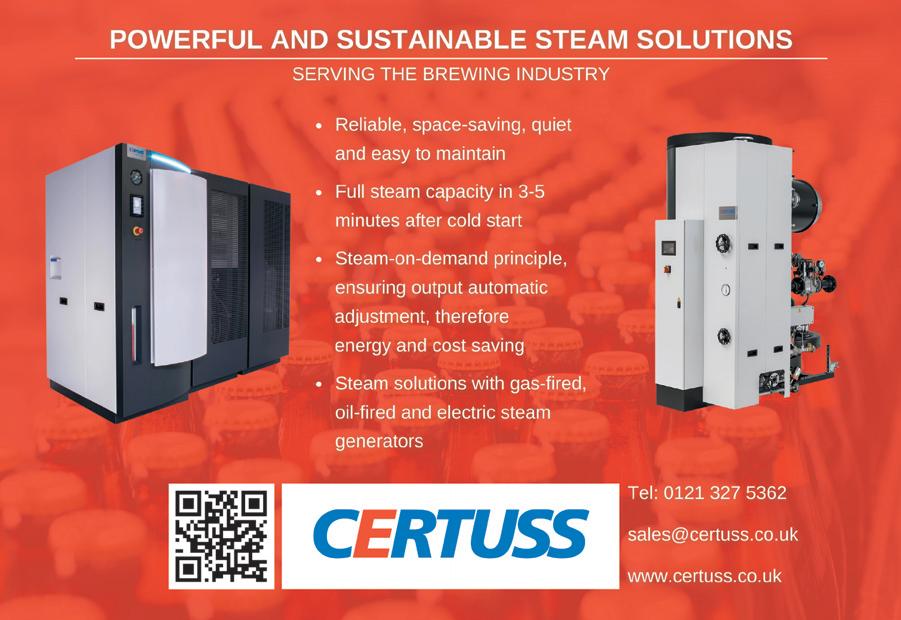
23 minute read
BASF’s Monomers division announces sustainability roadmap
from S02
BASF’s Monomers division has announced an ambitious sustainability roadmap: it will expand its port folio of products with a lower CO2 footprint and is committed to providing a circular option in every major product line by 2025. At the same time, the division will continue to prioritise technical optimisation measures to cut CO2 emissions from operations.
Net zero greenhouse gas emission targets demand a new level of carbon transparency. The product carbon footprint (PCF) is therefore becoming a differentiating factor, even for commoditised products. BASF’s Monomers division is pioneering a certified low-PCF option in all its product lines – applying the company’s mass balance approach.
Advertisement
“ n
BASF’s Monomers division is pioneering a certified low-PCF option in all its product lines ”
Menlo Electric to donate photovoltaic installations to Ukrainian schools and hospitals
The Energy Act for Ukraine Foundation and Menlo Electric, photovoltaic components distributor, will jointly develop solar and storage installations for schools and hospitals in Ukraine. In the first phase of cooperation, the foundation, together with Menlo Electric, will equip up to 10 Ukrainian hospitals and schools with solar plants with a total capacity of 300kW. The projects are intended to ensure electricity supply to critical needs of schools, plus surgery and intensive care units of hospitals through the hybrid solar power and energy storage systems.
The foundation’s first project was completed in November 2022 at the Irpin Academic Lyceum ‘Mriya’. For the second site, carried out jointly with Menlo Electric, the foundation selected Irpin Lyceum Number 1 specialising in arts. The school was damaged during the occupation of Irpin city in the spring of 2022, when it became a shelter for pupils, parents, and teachers during the severe shelling of the city. The installation is expected to be com pleted in the first quarter of 2023.
“Our CSR Energy to Power Your Future charity programme, with the mission to install free of charge PV installations for institutions that take care of children, had seven installations completed until now. Our cooperation with Energy Act for Ukraine increases that number to 17. We will be donating and delivering 300kW of photovoltaic components for schools and paediatric hospitals in Ukraine,” said Bartosz Majewski, CEO at Menlo Electric. n
Briggs of Burton is a process engineering company based in Burton-on-Trent and offers total project solutions for blue chip companies across the globe. With an illustrious history, it was founded in 1732 as a hardware and industrial metalwork manufacturer. These days it has a strong engineering presence across the distilling, brewing, food, and pharmaceutical industries. Head of Marketing Scott Davies explained more to Hannah Barnett.
The company may have been around almost three hundred years, but it is still impressive how many wellestablished brands Briggs of Burton has contributed to.
“You might know Macallan Scotch Whisky, you might know Carling lager, you might know Marks and Spencer’s chilli con carne,” said Scott Davies, Head of Marketing. “All of those have been brought to life through Briggs’ engineering know-how, project delivery expertise and process equipment manufacturing capability. You might even know Diageo, who supply the Johnnie Walker whiskey Keep Walking. But you probably didn't know that Briggs of Burton were the engineering company that built and expanded the distillery for major spirits producers like Diageo.”
The company’s status as a cornerstone in the supply chain of manufacturing is hard to dispute. As it goes through a period of expansion, it is becoming more established still.
Acquisition and growth
Following an acquisition in 2016, Briggs of Burton became part of the Liquid Food Division of CIMC Enric Tanks and Process BV, one of the largest international suppliers of tanks and process technologies.
Joining an international group of companies that provide the design and implementation of turnkey projects, stainless steel process tanks and engineering services has been beneficial for Briggs’ own growth. Mr Davies explained that upon acquisition the company set a target to achieve a £100 million turnover by 2024. “We reached that target by 2022. Two years ahead of schedule,” he said.
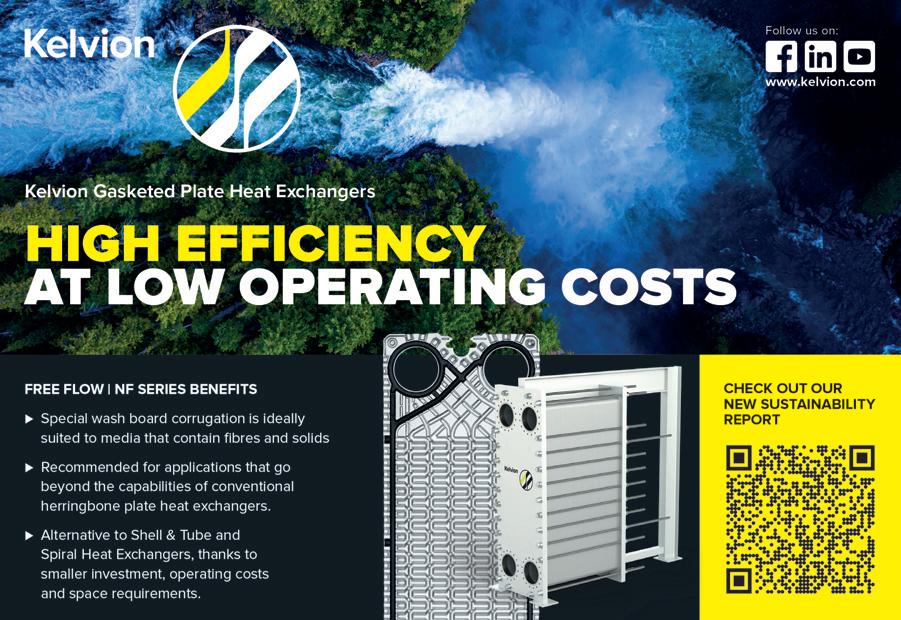
“When the business was acquired, it was turning over about £20 million,” Mr Davies continued. “That used to be made up of a mix of projects, maybe a £10 million Scottish distillery expansion, a £5 million UK brewery project and a mix of smaller pharmaceutical and food projects. In the last couple of years, we’ve been winning £20 million projects, £50 million projects and in Q1 of 2022, a £95 million project.
“We’ve seen huge amounts of internal investments, in terms of employees and their training, and in infrastructure. Through our sales and engineering network we have increased our opportunities to bid, win and execute larger projects around the world. And Briggs acquired McMillan coppersmiths during the Covid pandemic. That whole mix of operations and activity have been a real catalyst of change across the organisation. We’ve seen more growth in the last three years than we have in the last 30.”
International presence
Since acquisition, Briggs has spread its wings internationally. As Mr Davies explained, the company always had a global presence, but it did not have the resource and capability to manage multiple projects overseas before.
It now has a Mexico office, and a large new contract in the tequila industry to match. Briggs also recently opened a sales and engineering hub in Kentucky, alongside offices in upstate New York, China and the Global Technical Centre in Burton-on-Trent.
“Delivering these big projects feeds our appetite for risk, scale and complexity,” Mr Davies said. “Doing enormous projects in Mexico from Burton-on-Trent is one thing. But we’re now setup over there, with a local sales and engineering office, to get closer to customer projects and increase site and after-sales support.
“Immersing yourselves in these locations, languages, and cultures gets you closer the customer. Our North America team are now in Kentucky, the home of bourbon. So having a sales and engineering office setup there to do the work is hugely beneficial. We were doing project work there for several years, but it was remote, we were parachuting in teams of people. Now we have a dedicated team and office, just like Mexico. These sales and engineering hubs provide a huge benefit to our customers around the world.”
Sustainable supply chain
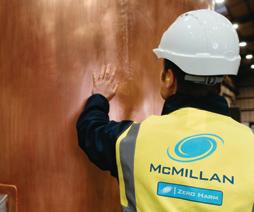
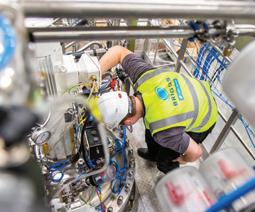
One of the most exciting projects Briggs is involved in is the Ardgowan distillery in Scotland, which has pledged to be carbon negative in its operations, ahead of targets set by the industry. Realising that ambition will be achieved by creating a modular distillery, able to adapt as sustainable technology evolves and matures. Each part of the whisky making process has been designed so that new technologies can be swapped to reflect the latest innovations in energy reduction, heat recovery and CO2 capture, as they become available.
“If you’re building a distillery now you can’t be anything but sustainable and mindful of the environmental impact,” Mr Davies said. “The Scotch whisky industry is on a trajectory to dramatically reduce its carbon intensity. We were focused on exploring a design that would implement the best available technology, that was sufficiently mature and commercially appropriate.”
He added that Briggs is investing in vapour recompression technologies, considering both thermal and mechanical types, which serve as an essential step in becoming efficient: “It’s all about reducing energy usage. The distillation process is quite energy intensive. Vapour recompression technologies can save between 45 to 85% of the steam usage in a still house. And that's significant for a distillery because that’s where most of the energy is.”
Unsurprisingly for a company that has been in operation for so long, Briggs has a large portfolio of suppliers, and that these days sustainability plays a large part in that relationship.
“Over time we’ve chosen a range of key suppliers and evolved and invested with them,” Mr Davies reflected. “I think particularly with sustainability, honesty in partnerships is the most important it’s ever been. Reporting Scope 3 Greenhouse Gas emissions presents a challenge, which is being accelerated by our customers who ask more of us and our suppliers. There is a big pull through the supply chain on capturing and sharing data. Along with specification, health and safety and cost we are considering footprints and metrics associated with carbon, water, and energy. What we used to ask of our supplier was just a quote. But that’s rapidly evolving to the carbon footprint associated with the items transport to its destination.”
Looking ahead
The company has broken ground with an expansion to its manufacturing site, which will be dedicated to pharmaceutical systems in Burton-on-Trent. Briggs builds the mixing systems that produce the gases in blue asthma inhalers and Mr Davies explained how this work will contribute to sustainable practices too.
“There’s been a big change in the market,” he said. “Historically, it was chlorofluorocarbons (CFCs) in the asthma inhalers acting as drug propellants, then the market shifted to hydrofluoroalkane’s (HFAs. Now it’s moving to even more environmentally green propellants. Briggs have been at the forefront of supporting the first commercial HFA systems and the first pilot of greener propellants. Alongside distilling, sustainability is growing in the pharma sector through designing and building these inhalant suspension production systems.”
As Mr Davies summarised, the work Briggs of Burton does allows other companies to flourish: “We join the bits, we give clients something bespoke. We have our own technology to meet our customers specific requirements, as opposed to a standard catalogue offering. The sales team dream of selling the same system twice. That isn’t to say we don’t have standards; we have a broad set of engineering standards based on good practice, but its seldom that two jobs are the same. And having existed since 1732, we are incredibly fortunate have vast experience to draw on. We can add value transferring technology and learnings from one sector or region into another.”
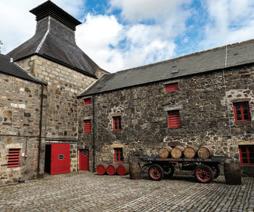
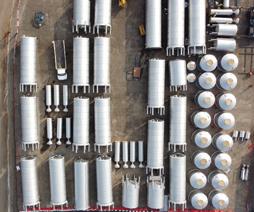
Despite its longevity, the company is focused on the future and maintaining its well-established presence. Mr Davies concluded: “We do amazing things, we invest in people, we're nurturing future generations. And, modestly, we are the brand behind many of the other brands that you, your friends, and your family consume and enjoy.” n
Aritex has over 60 years’ experience serving the automotive industry as a provider of assembly lines and automation. Following its success in the market, the company diversified into the aerospace sector in 2001 and has continued to expand its capabilities ever since. Chief Sales Officer Carlos Mendez has more than 20 years’ experience working for the company and spoke in detail about the company’s vision and plans for the future. Reporting on this topic is Imogen Ward.
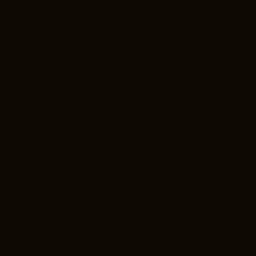
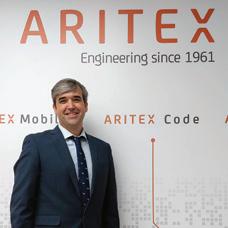
Aritex made several advancements over the past few years, solidifying its position as a market leader in the automotive, aerospace and robotics sectors respectively.
“We want to have a hugely diverse and impressive portfolio,” Chief Sales Officer Carlos Mendez said. “Originally, our company focused on large-scale turnkey projects. Now, more so, we are also developing technology that not only aids these engineering projects, but also can be adapted to work for any industry. We are working hard to keep our roots whilst continuing to evolve and grow – for instance, we are digitalising, with the development of IIoT and Augmented Reality.”
In 1961, Aritex entered the automotive scene and has offered its clients creatively tailored solutions ever since. With pride in its work, Aritex engineers solutions for a diverse range of sectors, and is always on the lookout for new markets to infiltrate.
The company is currently breaking into the renewable energy sector, offering turnkey packages and high-specification tools and equipment using a highly precise manufacturing process.
Airbus, Boeing, Nissan and Volkswagen are just a few of the companies that Aritex has worked hard to supply with innovative and cost-effective turnkey packages. With the help of its evolving supply chain, Aritex has successfully created production lines that simplify the process and make manufacturing more efficient.
Launching into Industry 4.0
After the company’s success with more traditional engineering projects, it decided to focus on Industry 4.0. Following a boost in demand for the product, Aritex realised that digitalisation and robotics were an increasingly lucrative prospect to focus on.
“We have started several new businesses,” Mr Mendez said, “allowing us to diversify our turnkey products. In some cases, we produce complete world data distribution. In other words, we are launching into Industry 4.0. We are achieving this with the development of our robotics solutions, and the more recently launched Aritex Code.”
With an impressive range of knowledge and experience, Aritex decided to sell high-specification solutions under the name Aritex Code. The company exploited its extensive industry knowledge through consulting and implementation services, to enable customers to minimise costs and increase productivity. Merging the digital with the real, the client can access the digital twin as a tool to obtain vital information, including running times and machine restrictions.
Augmented Reality as an accelerator for the learning of operators and machinery maintenance, is consolidated day after day. Augmented Reality-guided assembly instructions ensure frontline workers are equipped with the information they need to complete even the most complex tasks with precision and efficiency, improving ontime delivery and customer satisfaction.
From the #AritexCode unit, Aritex guides companies on their path towards the digitalisation and automation of industrial processes, through complete solutions based on the latest technology, starting from project consulting, to development, implementation and after-sales services.
Revolutionary robotics
After becoming a major shareholder in Loxin in 2012, the company has produced several highly successful patents, including its work in parallel kinematics. Aritex then began offering conventional robotics systems as well as new ones: mobile and col laborative robots.
The advancement of robotics at Aritex is a spectacular feat. Removing the need for isolation provides opportunity for smaller companies to incorporate collaborative or mobile robotics into their production lines. This, therefore, offers more efficient services to smaller companies that previously did not have the space for more conventional robotics systems.
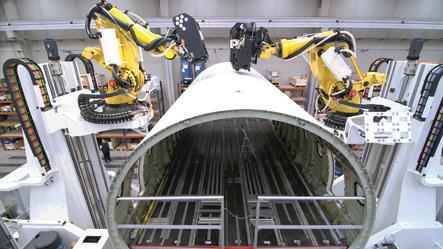
This type of robotics also encourages cooperation between man and machine –ensuring both can work side-by-side, increasing efficiency (in comparison to more conventional robotics that would take up a greater portion of the production line). Another advantage of this robotics range is that it reduces injuries and accidents within the work environment. On top of this, collaborative robots are lightweight and easy to install, making them highly efficient and as stress-free as possible for the customer.
Thanks to Aritex’s advances in Industry 4.0, it is not just customers that have benefitted: due to the increase in efficiency, the reduction in waste materials and the minimisation of rejection rates, Aritex’s turnkey products help the environment too.
Furthering its mission to aid the planet, Aritex also entered the renewable energy sector. During Covid, the company worked on a large wind farm project: “we have been working on manufacturing production lines for wind turbine blades,” Mr Mendez said. “We have recently completed a project with General Electric. After the successful development of this project, we plan to offer our turnkey production line out to other wellknown companies working within the wind energy sector – creating long-term relationships with them.
“Although we are quite new to this sector, it has similarities to aerospace – they are different markets, but we can apply similar solutions to both.”
Ready… steady… GROW!
Aritex’s future is as bright as an aeroplane landing strip. The company is focused on continuing growth, with the aim of expanding its product portfolio. This goal will see Aritex further its work within the automotive industry. Specifically, the company is hoping to meet customer demand for electric cars.
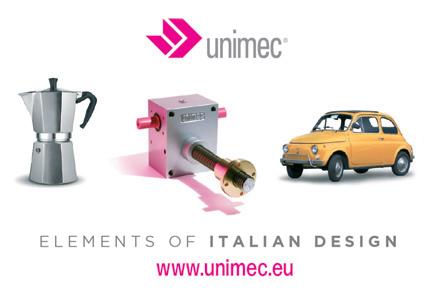
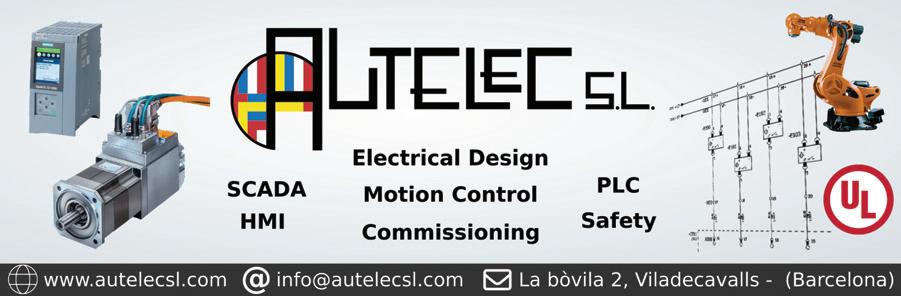
After working on small-scale projects, and a massive new electric vehicle production line, the company hopes to take on even more of these contracts going forward. With extensive automotive experience spanning back over half a century, the company is confident entering this division of the market.
As Aritex increases its production capabilities, it is determined to retain its reputation for excellence. Aritex holds a range of certifications, including the ISO 14001 (which is an international standard of requirements for an environmental management system) and the ISO 27001 (this is the best standard for information security management systems). These accreditations not only ensure quality, but also guarantee customer confi- dentiality – offering customers that extra peace of mind.
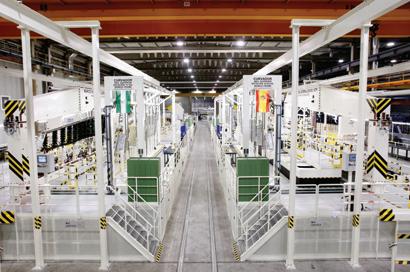
“I have been in the company for 21 years. So, they must be doing something right for me to stay here that long,” Mr Mendez joked. “The company is always working on lots of huge projects and each one brings new challenges. I think those hurdles inspire us; there is no repetition in our work as no two days are the same.
“Aritex achieves a lot of impressive feats that other companies struggle to compete with. The continuous development and business model evolution completed by Aritex ensures the very best for our customers. Going forward, expect to see us continue down the path of digitalisation and robotics; we aim to evolve and grow in this area –opening doors to new markets and allowing us to reach a wider range of customers who need our help.”
Advance Mechanical Services is a technology conglomerate that provides services in automation and engineering to its customers worldwide. The company contains decades of experience within its workforce to provide technology solutions in design engineering, robotics programming, digital manufacturing and many other fields. The work is specifically applicable to the automotive, aerospace and heavy engineering industries. CEO and Director Shashidhar NC explained the nuts and bolts of the operation to Hannah Barnett.
Catering to the needs of clients across the globe, Advance Mechanical Services is a large operation. It has three design offices in Bangalore alone. The company also has marketing arrangements across India with further offices in Pune, and in Delhi. It works closely with partner companies Aut-Tech GmBH in Germany and Aut-Tech-AMS Inc in the USA.
A start in the car business
Advance Mechanical Services certainly seems to be doing well, with a turnover of £2 million in 2021 according to CEO and Director Shashidhar NC. Its illustrious his - tory can be traced back thirty years when it started out in the automotive industry, engineering and designing car factories. Mr Shashidhar recalled: “We must have designed body shops for almost all the OEMs across the globe.”
Mr Shashidhar began his own career at a manufacturing company where he got a taste for robotics: “I was lucky to have the opportunity to work with the first robotic installation in the country. That's when my career in automation and robotics started. And from then on, I've always been in the robotics business. Robots are now used a lot in the automotive industries.”
One of the company’s key strengths comes from the variety of work it does. It offers end-to-end services in engineering design, controls, automation and robotics programming.
“Most of the automotive companies globally know us and we continue to work with them in engineering body shops,” he said. “We have been doing design work for many OEMs such as GM, Ford, VW and Volvo factories across Europe and the USA through various line builders such as ABB, Kuka, L&W, Gonzalez, Chropynska and many others. We are lucky to be a part of some portion of their design process.”
As Mr Shashidhar put it: “We're only mechanical engineers, but about seven years ago I decided to diversify. And that was a milestone, because that really helped us a lot to move up the value chain in automation and provide end-toend services.”
The R&D Machine
One of the cornerstones of Advance Mechanical Service’s diversification programme is the innovative ‘R&D machine’.
The company started manufacturing specialised 3D printers about six years ago, Mr Shashidhar recalled. The unique selling point of these machines is how they are used, as he explained: “Unlike normal 3D printers, these are designed to help in doing research and development (R&D) which is very evident in the hundreds of papers that are published using our machines. It brought us from engineering into the manufacturing area, and we now have five verticals.”
The operation is a collaboration with Hyrel3D in the USA to provide multiple operations such as additive, subtractive and laser operations on the same machine. Additive manufacturing refers to creating an object by adding multiple layers. Subtractive manufacturing removes or cuts away material to create parts.
The manufacturing facility for the machines is located in a 2,500 square-foot area in the industrial area of Peenya in Bangalore. The company manufactures four different models and 60 different heads that can print at up to 450 degrees centigrade. The machines can also print a variety of materials including liquids, gels and resins using its modular heads categorised under hot, warm and cold flow extruders.
Mr Shashidhar explained how the R&D machine sets Advance Mechanical Services apart from its competitors: “So many people make 3D printing machines, but this is a unique machine, because it’s purely for people who want to do research and use different techniques, different trials, use different type of materials, make composites.”
Mr Shashidhar explained how innovative work on this machine has allowed the company to build a strong relationship with its network of partners and suppliers.
“We are registered as an R&D company in the GEM portal of India, and we have a good sales network, most of our customers are scientists or professors or PhD holders. They understand our machine. It’s a unique sale to them in the Rapid Prototyping area”
Recognised for excellence
For a company which positions itself at the cutting-edge of the international mechanical engineering business, it was fulfilling to win an MSME award for export service and technological innovation. The awards celebrate India’s top micro-, small- and medium-sized enterprises, looking for exceptional achievement in business performance and contributions to the country’s socio-economic growth.
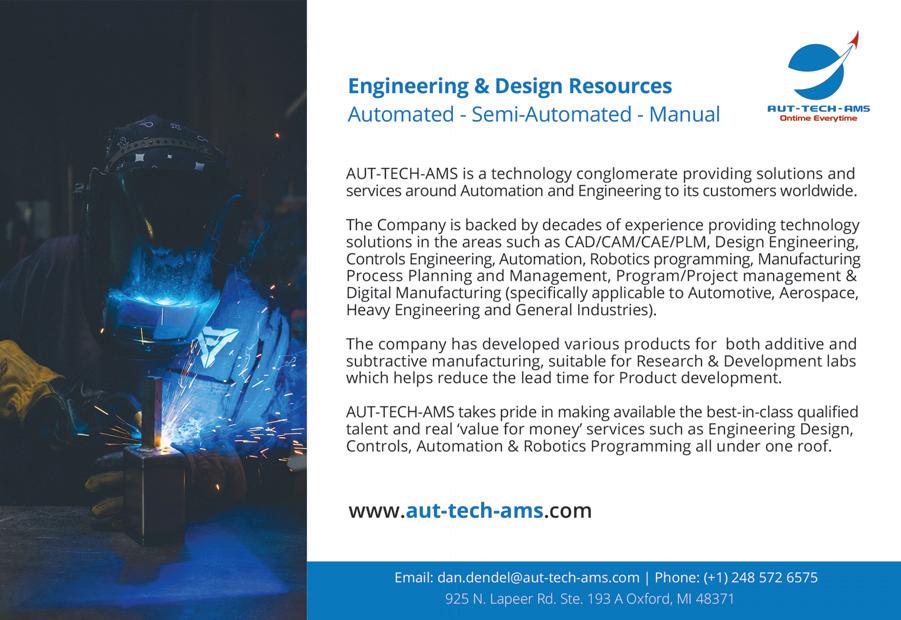
Mr Shashidhar was pleased to receive the award from the Indian Prime Minister: “It was exciting because it was given by Mr Narendra Modi,” he said. “That motivated everyone in our company. After 30 years of working in this business, this is something to be proud of. And it gives our customers the confidence that a project will be executed properly.”
Though recognition and awards are significant, as Advance Mechanical Services continues to expand and develop as a modern company, so too is its commitment to sustainability
The procedures that the company is undertaking to implement appropriate sustainable standards, according to Mr Shashidhar: “It's the whole ZED process, to make the system sustainable.
This encompasses basically about seven or eight different standards. For example, ISO 9001 is a process standard. And there are three different levels: bronze, silver and gold. We're trying to go for the gold standard.”
Mr Shashidhar was enthusiastic about what adoption of these guidelines might mean: “We are implementing these standards and it will make the foundation of the company much stronger.”
A future in education
The future looks bright for Advance Mechanical Services. That is why the CEO is now keen to share the wealth of his knowledge and experience with the engineers of tomorrow.
A recent MoU with Alliance University created the MBA in Digital Transformation programme; a unique two-year, full-time course. Students will have resources and equipment provided by ABB Robotics, Adroitec Engineering, Systema, Hyrel 3D and Siemens, all under the aegis of Advanced Mechanical Services. Students learn various technologies including Additive Manufacturing, SAP, AR/VR, IoT/IIoT and Digital Manufacturing, helping students transform the manufacturing sectors and be more competitive globally.
The curriculum is futuristic and based on the principles of progressive learning with enhanced focus on the contemporary disciplines. Jointly delivered by seasoned industry practitioners and technology experts from Alliance University, this programme equips graduates with the necessary skills to drive business of the future.
“Most college students today are moving away from mechanical and civil engineering,” Mr Shashidhar said. “Everybody wants to go into computer science. But the world will have many problems without good mechanical engineers. To construct houses, we need mechanical and electrical engineers, they can't do everything on computers.
“We add value by working with educational institutions, sharing our experience. We have decades of combined knowledge, so we could train them in these technologies. I want to increase the spirit of research and support education departments, institutions and students with knowledge of mechanical engineering.” n
Every year, ACCIONA goes to great lengths to improve the lives of those in underserved areas. The WATER division specifically, works hard to design, fund and construct vital desalination projects and water scarcity solutions worldwide. WATER Sustainability Manager Mercedes Bengoechea Crespo discussed the company’s innovative strategies for providing global water equality, in a report by Imogen Ward.
Since its origins in 1997, ACCIONA has developed and maintained sustainable infrastructure across the globe. Thanks to this progress, ACCIONA WATER has the capacity to manage water for more than 100 million people in 30 countries. This impressive feat is achievable due to ACCIONA’s EBITDA of €323 million and its implementation of state-of-the-art reverse osmosis technology.
“ACCIONA carries out activities in the integral water cycle,” WATER Sustainability Manager Mercedes Bengoechea Crespo said, “not only in the production of safe drinking water, but also in the development of different tools to analyse and diagnose opportunities for regeneration. We evaluate all our projects with respect to local sustainable development goals, designing vital solutions that have a positive impact.”
While these projects often deploy renewable energy, there can be more value through efficiency. The expertise of the ACCIONA team brings extensive knowledge regarding the optimisation and effectiveness of processes. Not only in the energy aspect, where ACCIONA is a technological leader, but also in innovations that exponentially increase the company’s sustainable contribution, such as the recovery of critical materials or brines.
Life-changing projects
ACCIONA’s work in the Middle East has had a major impact. Shuqaiq 3 in Saudi Arabia is one of the largest desalination plants in the country, providing safe water for 2 million people. As an industry leader in the technology, ACCIONA incorporated reverse osmosis technology to reduce the pressure on conventional water resources and promote the most water- and energyefficient option.
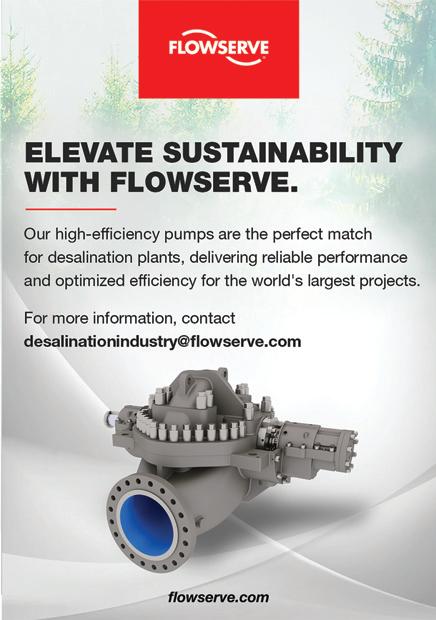
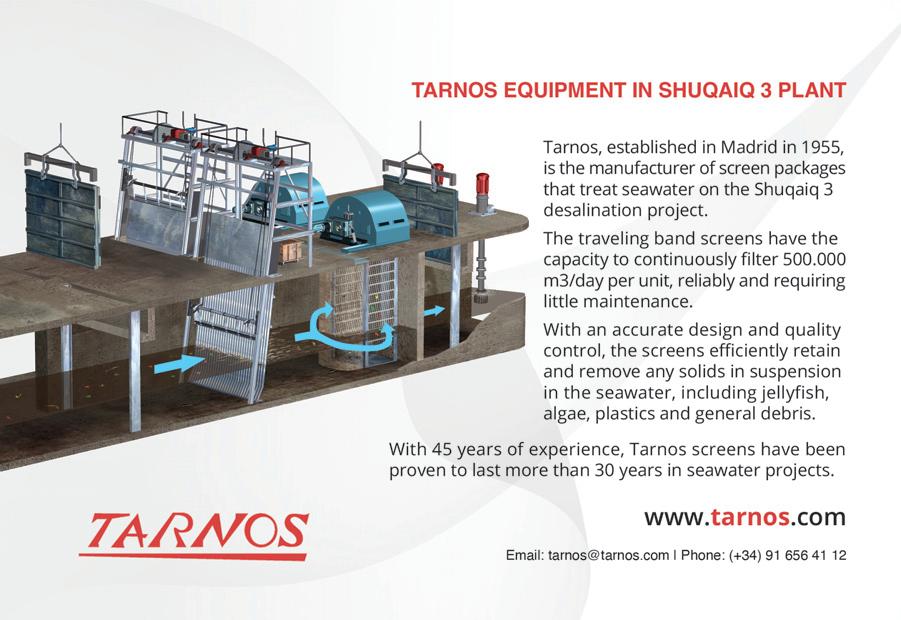
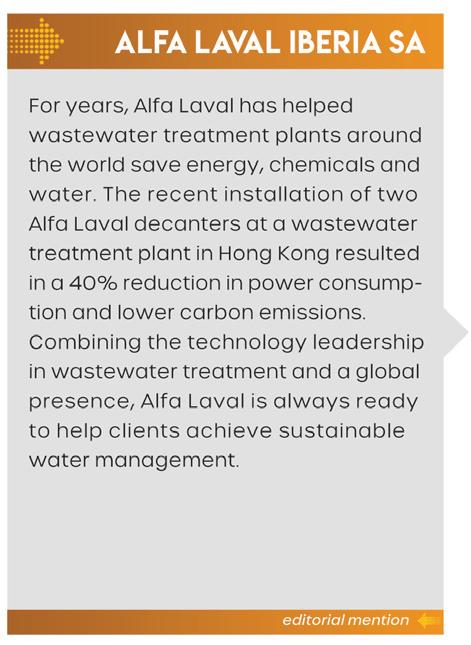
This project benefits the community in more ways than one: as part of its social outreach measures, ACCIONA’s Shuqaiq 3 is also providing training for local residents to solidify the development of industry professionals.
“This project, which offers one of the world’s most competitive rates for desalinated water,” Ms Bengoechea Crespo said, “is part of Saudi Arabia’s plans to transform and modernise its water industry – adapting and renovating all freshwater production facilities to international quality and efficiency standards.”
Of course, these efforts are not limited to Saudi Arabia; ACCIONA WATER is reaching milestones in other countries too. The Ras Abu Fontas 3 was the first of its kind in Qatar, a country which previously used evaporation technology to desalinate water. Now serving an estimated 1.1 million people, this breakthrough plant is an excellent example of the company’s capabilities.
An ongoing development in Spain, lead by the I+D+I area, is the LIFE PRISTINE project (funded by the European Union as part of its goals for climate action). With an expected completion date of 2026, this project will reduce water contamination significantly.
“The aim is to develop an integrated solution to remove various water contaminants,” Ms Bengoechea Crespo said. “These substances are of growing concern due to their potential to effect environmental, human and ecological health. The presence of most of these substances is not yet regulated, which makes it increasingly difficult to take adequate measures to protect human health. Therefore, with the LIFE PRISTINE project, we aim to remove 80% of these emerging contaminants.”
Sustainable local development
All ACCIONA projects are highly sustainable: from concept to production, the company goes to every effort to ensure it meets the rigorous requirements of its green financiers, both for the good of the project and for the planet more generally. Indeed. ACCIONA is a pioneer of sustainable financing.
The ISTP projects – which are currently in development – consist of three sewage treatment plants in Saudi Arabia. These will utilise typically wasted elements of the wastewater treatment process. ACCIONA successfully raised €450 million in green finances to fund these plants.
In 2020, with its sustainability goals in mind, the company opted for an adaption of its corporate model, creating an entire sustainability department to further improve the efficiency of all current and future projects. Under the new approach, the
ACCIONA strategy focuses on the global transformation through a regenerative infrastructure approach. The company thus promotes the development of a more sustainable society through a resilient and balanced portfolio.
As part of these objectives, ACCIONA repeatedly assesses social and environmental areas requiring improvement.
“ACCIONA is not only focused on achieving water equality,” Ms Bengoechea Crespo said, “but we also have additional projects on the go. These focus specifically on the social and environmental gaps in the geographical locations of our infrastructures.”
The company works closely with key suppliers and partners to ensure the success of each and every project. To source this aid, ACCIONA has an in-house procurement department who develop these relationships.
“We have developed framework agreements with the purpose of focusing in on a few well-managed suppliers,” continued Ms Bengoechea Crespo. “In terms of innovation and sustainability, our suppliers, subcontractors and partners are the main source of new ideas and developments. We always aspire to share our knowledge with them, to give them the opportunity to successfully develop new solutions for our plants and services.”
Making a difference
Reducing social and environmental harm caused by economic activity is no longer sufficient to secure the long-term viability of businesses. Since 2021, ACCIONA has evolved its Social Impact Management Methodology. Going forward, the company aims to further develop this because it knows that the local context is key. “We want to go beyond minimising the negative impacts and enhancing the positive social aspects that our projects could influence,” Ms Bengoechea Crespo explained. “ACCIONA drives towards creating a positive impact through each project. We are currently designing high impact solutions, regenerative projects; which will contribute to improving the living conditions of the population and the environment close to our projects.”
“One example includes the development of a high-impact solution at our Atotonilco Wastewater Treatment Plant in the state of Hidalgo, Mexico. We found that there were high levels of unemployment and low training rates within the community. Seeing this as an opportunity to substantially improve quality of life, we began providing certified training that contributes to the generation of local and long-lasting jobs in the area. The training consists of six months of the oretical and
practical elements that will increase levels of specialisation and employability.”
Another important element of ACCIONA’s humanitarian work is the Foundation Acciona.org. Originally created in 2008, the organisation was implemented to provide communities with sustainable access to basic services, including energy, water and infrastructure. This focused particularly on underserved and vulnerable communities and is now providing for more than 50,000 people in Peru, Mexico and Panama, for example.
“We are currently working with the Foundation in Panama,” Ms Bengoechea Crespo explained, “where we are trying to start a project to further aid the communities who rely on our drinking water treatment plant of Ingeniero José G Rodríguez. We want to develop access to education for children under three, because schools in the area are sparse.
“Currently,” she concluded, “our priority is to help construct a nursery that facilitates education for young children – helping generate better physical, intellectual, affective and social development of the children, giving them greater autonomy in terms of food, hygiene, sleep and general well-being. It is my challenge to make this project come true.” n
Enviroclean has 25 years’ experience delivering specialist waste management and industrial services advice to domestic, commercial, and industrial customers throughout the UK. Operations Manager Mark Donaghy highlighted the company’s operations and steady expansion, in discussion with Phil Nicholls.
Scottish waste management company
Enviroclean is enjoying a period of steady growth with its broad portfolio of cleaning services. Enviroclean’s fleet of specialist vehicles service all of the UK, with a focus on Scotland and the north of England.
“We have won a four-year contract with an extended additional four years,” explained Operations Manager Mark Donaghy, “for all sludge tankering movements in Scotland for the local authorities, and have invested over £8 million on new trucks and trailers.”
Enviroclean was the brainchild of Jim McLuskey and founded in 1997 as an industrial drain cleaning company. The company steadily expanded with repeat business and a growing team of professional engineers. Today, Enviroclean deploys a fleet of over 120 vehicles and more than 160 staff to deal with any waste management or industrial cleaning job.
“We operate from our main office in East Kilbride, just outside Glasgow,” Mr Donaghy said, “which we have expanded over the years to accommodate the growing fleet of innovative plant and equipment.”
A neat fleet
It is this growing fleet of distinctive green and yellow trucks that underpins the extensive range of services offered by Enviroclean. For industrial customers, Enviroclean’s services include vacuum excavation using RSP ESE 6 Vacuum Excavators manufactured in Germany, vehicles that are widely recognised as being cutting-edge technology.
Enviroclean operates a fleet of 20, eightwheeled tippers and two articulated tippers capable of carrying up to 30 tons of material. All new tippers delivered since September 2015 are FORS compliant, to meet the growing demand for safer HGVs on British roads. Enviroclean is the first
Scottish company to achieve this accolade. Indeed, Enviroclean recently won the award Scotland’s Top Road Safety Operator 2023, organised by Transport News.
The incredible Enviroclean fleet is rounded off with unusual vehicles such as a 22 metre Hitachi Super Long Front excavator, an allterrain Trac Vac and the CD Enviro D-Max mobile grit and screenings separation unit.
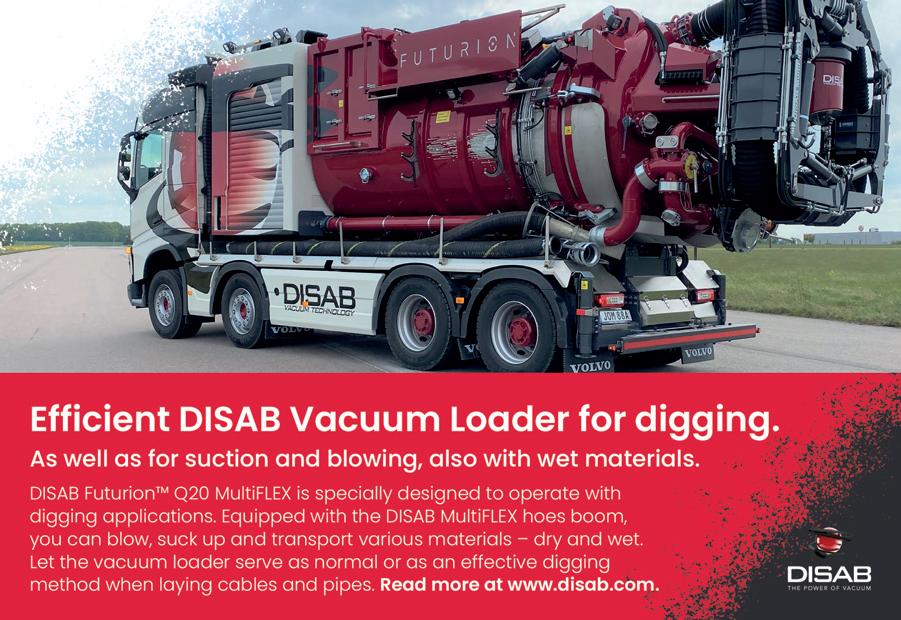
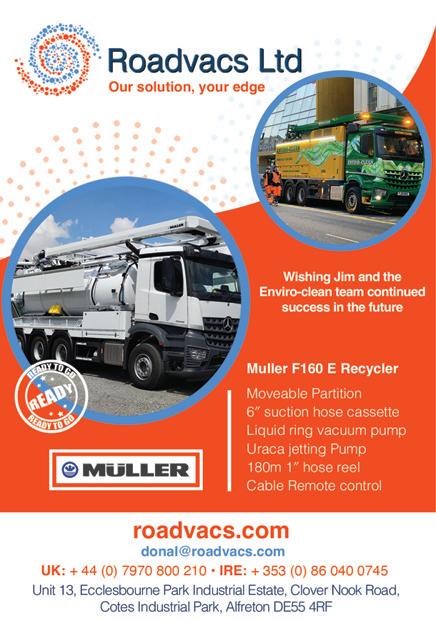
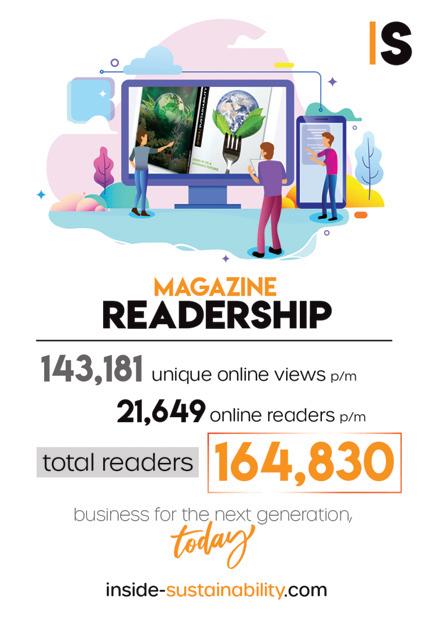