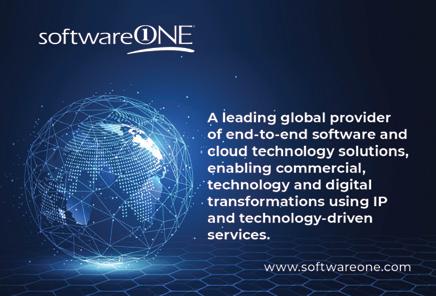
9 minute read
TheRoRo cube ROLLSOUT
from S02
Based in Singapore, with a global network of depots, Goodpack has over 30 years’ experience delivering efficient, integrated supply chain solutions via a network of strategically located global depots and fleets of returnable containers. Chief Operating Officer Peet Leong Kok, Goodpack Korea Country Manager Chul Hee Chun, and Regional President, Northeast Asia and Global Business Director, Synthetic Rubber Chee Heng Sng discussed Goodpack’s news and operations. A report by Phil Nicholls.
Disruptions to the global supply chain remain a challenge for almost every business. Logistics experts at Goodpack have developed the innovative RoRo Cube which enables customers to side-step many of the problems affecting the free movement of global trade.
Advertisement
“We have a partnership with Wallenius Wilhelmsen,” Goodpack Korea Country Manager Chul Hee Chun explained. “They provide us space on their RoRo vessels, we provide them with packaging solutions and transportation equipment. For example, there has been a lot of congestion in US container ports. However, they use their own terminals or contracted terminals which are different from container ship terminals, so once the RoRo vessels arrive, they can quickly release their cargo.”
Goodpack began in Singapore in 1990, focused on logistics for the rubber industry. The company quickly expanded into a global network of supply chain solutions working across multiple sectors. Recent years were dominated by the Covid pandemic and its impact on businesses. Goodpack showed its agility by shifting supply chains to limit the impact on the business, a successful process which enabled growth to continue throughout the pandemic.
As a global operation, Goodpack has 350 associates operating across 80 countries with over 5,000 delivery and collection sites spread through six continents. The company deploys over four million returnable bulk containers and supports close to seven million deliveries each year.
The RoRo Cube
Goodpack delivers efficient, end-to-end supply chain solutions via this worldwide network of depots. At the heart of this provision for customers lies innovative container solutions, such as the RoRo Cube. The business concept of RoRo Cube was developed alongside Wallenius Wilhelmsen, a global market-leader in RoRo shipping with a fleet of over 130 vessels operating on every ocean.
“We realised that a container would be a good solution for a RoRo vessel,” Regional President, Northeast Asia and Global Business Director, Synthetic Rubber Chee Heng Sng said. “So, we looked at ways to work with Wallenius to find a product offering our customers an alternative to how they’re shipping things today. The result is the product we call the RoRo Cube.”
Headquartered in the heart of southeast Asia, Goodpack began serving the rubber industry. As the company expanded, it became involved in the supply chain for a range of industries. Goodpack containers can be fitted with hygienic food- grade packaging. This facilitates transport and storage solutions for food and liquid products.
Another sector for Goodpack is the transportation of chemical products, such as inks, paints and resins. The company’s focus on streamlined transport and storage solutions are also applied to the shipping of components and consumer goods around the world, all customers benefitting from digitisation, payload visibility and speed to market.
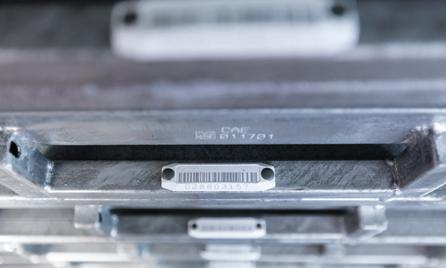
Bespoke shipping solutions
“Goodpack enjoys a close relationship with CEVA, the biggest automotive logistics company,” continued Chief Operating Officer Peet Leong Kok. “We’re working with CEVA in the tyre space, with a programme to develop TYRECUBE TM to transform the supply chain, using our container as the de facto movement medium for everything from intermediates – like compounds, bladders and tubes – to finished tyres.
“Our close relationship with Goodpack in developing innovative solutions for the tyre industry is a key factor for our tyre subsector growth strategy. Our ability to focus on automation, digitalization, and circular economy concepts are gaining the right momentum,” mentioned David Dudek, global automotive and tyre sector leader for CEVA.”
The development of new transportation options such as the TYRECUBE TM is a crucial part of Goodpack’s growth strategy.
Goodpack relies upon its close partnership with the network of third-party logistics, suppliers, depot operators, trucking companies and freight forwarders. “We think of them as our arms and legs, executing our network,” Mr Kok said.
Sustainable shipping
The company is proud of its sustainability credentials, according to Mr Kok: “Our container solutions have been tested by independent valuers and verification bodies; these containers will last more than 35 years. When compared with a singleuse packaging solution, the Goodpack method is definitely much more sustainable in terms of carbon emissions.”
In parallel with the inherent benefits of reusing the containers, often shifting them between industry sectors to meet fluctuations in demand, Goodpack is also investing in eco-friendly improvements within the company. The network of depots is steadily switching over to energy-efficient LED lighting.
From an operational perspective, the greatest challenge facing Goodpack has been the Covid pandemic and the restrictions this imposed on international shipping. Similar limitations also reduced the opportunities for face-to-face meetings with clients, an important part of building strong partnerships. As these restrictions are now steadily lifting, Goodpack can return to normal business practices, meeting clients and colleagues around the world.
Viewing these signs of the world steadily returning to normal, Mr Kok gave a cautiously optimistic assessment: “Economically, the world may be in a soft slowdown. We see good growth in food logistics, as people always need to eat. Goodpack is also looking at EV batteries as a growth market, at least in terms of sustainability and the automotive industry, as announced recently with Wallenius Wilhelmsen. We’re looking into that segment to see how we
The Goodpack RoRo Cube
A returnable Intermediate Bulk Container made from galvanized metal. RoRo Cubes are suitable for many products, can be stacked safely on RoRo ferries, and are collapsible when not in use.
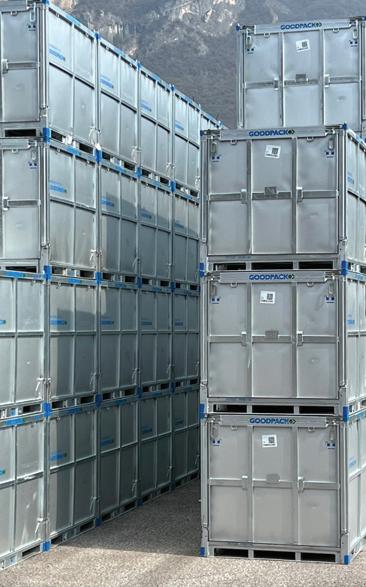
• Dimensions: 1.46m x 1.15m x 1.09m
• Capacity: Up to 1,500 litres
• Unladen weight: 131kg can be the industry-standard for the supply chain of EV batteries to our automotive customers.”
Alongside this expansion into the distribution of EV batteries, Goodpack is also investigating how to harness the accumulated data from seven million voyages annually. Every year, customers demand better service from their logistics partners and Goodpack believes this wealth of data can add value for its customers.
Goodpack continues to enjoy the strategic benefits of its location in Singapore. “This part of the world remains very exciting,” concluded Mr Sng. “China has been a growth engine for us in the region over the better part of ten years as it continues to grow. Goodpack is excited about the future, helped by being so close to China, Japan and Korea. These three countries continue to be at the leading edge of the constant innovation and industrialisation that drives EV technology.”
Greener Packaging originated in Sweden in 2013. Established as a solution to high costs and CO2 levels when packaging products, Greener Packaging’s container supply systems make it easier than ever for companies to simplify their product packaging operations. CEO and Sales Manager of Greener Packaging UK Julie Checkley discussed the company’s latest investments, in a report by Imogen Ward.
All companies are catered for at Greener Packaging, no matter their size or production capabilities. The company’s compact and innovative packaging supply systems ensure that even smaller clients can benefit from manufacturing packaging in-house.
“We use the smallest, most compact blowing machines on the market,” CEO and Sales Manager of Greener Packaging UK Julie Checkley said. “This enables us to be extremely flexible, because we can change from one container design to another in 15 minutes. This means customers can adjust bottle colour, material and production additives whenever they require it. If the company has a limited production line space, our systems accommodate this and enable them to switch quickly to alternatives. This feature is something a lot of clients haven’t had before, and our system offers extremely competitive pricing too, often lowering our customers’ costs by about 20%.”
Greener Packaging’s supply systems have been revolutionising customers’ production lines since it was first established in 2013. From there, the company expanded beyond Sweden, targeting the wider Scandinavian market. Currently, the company is emerging in the UK and Ireland, with plans to target the USA in 2024.
“We serve customers worldwide from our 24 manufacturing locations,” Ms Checkley said. “For our larger customers, we supply bottles and jars from directly within their sites. This is an entirely in-house process that is incredibly sustain able and cost-effective for clients. They also have the option to sell their surplus manufacturing time to neighbouring companies. We automate and digitise the process to maintain optimum efficiency, and we are a very streamlined company, which allows us to remain fast-paced and dynamic.”
Greener Packaging has an easy-to-use customer interface, giving customers complete freedom to control their orders and track the bottle production performance (order fill rate OFR). An OFR of 99% is consistently achieved. “Our customers have full access to the customer interface at all times,” Ms Checkley explained. “They can upload their forecasts for production schedules, place orders and review invoices on the same platform. A forecast ensures we provide them with enough preforms for their requirements and helps reduce their dependence on complex supply chains.”
Recent additions
The company recently invested over €1 million into improving its prototyping process. “We can make a bottle from concept to working prototypes within seven weeks,” Ms Checkley said. “We are one of the fastest packaging developers on the market. We have also successfully introduced a new concept to the market: a dedicated Greener Packaging Container supply system with integrated autoquality control.”
This system produces highquality, cost-effective packaging. The auto-quality machine relies on AI technology to automatically assess the quality of the produced bottles. This saves time, as it removes the need for manual quality control at each stage of the produc tion process.
“The auto-quality machine checks several different areas of the bottle,” Ms Checkley said. “It automatically checks wall thickness and cools the bottles to make the process of leak inspection more time efficient. This guarantees quality and consistency across the manufacturing process.”
Compact capabilities
Greener Packaging’s container supply systems are one of the smallest, most compact options currently available on the market. Remarkably, the machines are about three-times smaller than the industry standard and have opened doors for several small businesses.
Previously, packaging supply systems were a luxury only granted to large-scale c ompanies; Greener Packaging, however, is working hard to change that. The company recently installed a highly-versatile compact PET packaging production line at Maustaja –a private-label manufacturer of condiments and seasonings. The customer had specific spatial requirements that Greener Packaging was more than happy to accommodate.
“ As part of our agreement with Maustaja, Greener Packaging is responsible for the full-bottle production on the site and maintenance of the equipment, including new bottle development and technical upgrades,” Ms Checkley said. “This solution resulted in a reduction in Maustaja’s transportation and packaging costs, because it removed the requirement to ship empty bottles before the filling process.
“Another positive outcome of our inhouse bottle supply system is the removal of customers’ reliance on complex multiple supply sources. As a result, there are fewer disruptions in our clients’ supply chains, and they have witnessed a reduction in lead times and a simplification of their buying process, saving time and money.”
Greener Packaging is a platform business and allows customers to receive an instant online quotation for their container requirements directly on Greener Packaging’s website, for both readymade container deliveries and in-house operations The company also works in partnership with a large combination of cap suppliers, offering the complete packaging solution to all clients directly from its website. These suppliers are vital to Greener Packaging’s operation. Developed from customer service and the desire to build long-term relationships, the company maintains meaningful partnerships with businesses that match its values and high-quality standards, making Greener Packaging customers' lives easier.
rPET to the rescue
2022 saw Greener Packaging help convert more customers’ bottles from glass to rPET than ever before. This increasingly popular option has several benefits for both the client and the environment.
Greener Packaging uses rPET as its preferred medium – the material’s recyclable nature makes it kinder to the planet and more cost-efficient. “There are several r easons why our customers are choosing to move away from glass production,” Ms Checkley said. “There is the glass shortage for starters, sending costs soaring. Glass production also requires a lot of energy; with gas prices skyrocketing, glass bottles are highly inefficient in terms of both price and sustainability.
“Customers are also concerned about glass breakage on their filling lines causing difficulties in the production process. rPET not only prevents this issue, but also opens new opportunities within export sales due to the durability of rPET.
We are currently undertaking a lot of conversions for companies who produce jams, peanut butters or alcohol.
“Another trend we are witnessing is the transition from HDPE bottles. These are much heavier than rPET; as a result, conversion to rPET helps reduce our customers’ carbon footprint and lowers their costs. Another issue with HDPE bottles is their tendency to leak. This doesn’t happen with rPET, so wastage levels are significantly reduced.” rPET also offers more freedom in design and makes the customer's product stand out on the shelves.
No two days are the same at Greener Packaging: “Every day we speak to new people and work to solve different scenarios,” Ms Checkley concluded. “Each company’s needs are very diverse, which is part of what makes the job so worthwhile. On top of that, the knowledge that we are helping protect the environment is a huge factor. Our in-house design team works extremely hard to minimise the amount of non-recycled plastic used for our bottles and jars – in the design phase alone they can remove 20% of the plastic.
“We think it’s really important for our customers to be given the opportunity to see the benefits of plastic when it is used properly.”