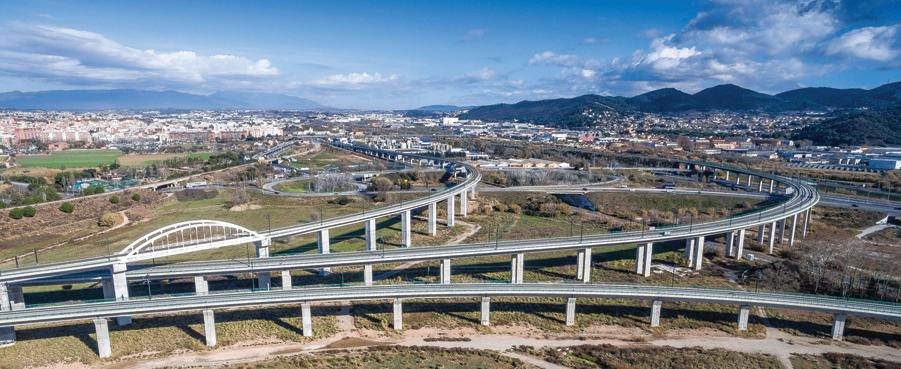
9 minute read
UTURE
from S02
“We know how every project requires a different service; the variety of environments and countries all demand a high level of adaptability, the greatest flexibility and an unswerving commitment to quality.”
Pacadar has developed a highly effective business model establishing temporary manufacturing hubs in the countries it's working in. Mr Dominguez explained how the company uses on-site manufacturing plants close to the construction site: “This gives us competitive advantages as logistic costs are dramatically reduced.
Advertisement
“Once the project is finished, we dismantle the plant and return the site to its former condition. This allows us to move around the globe, using quick-to-assemble tailor-made factories, taking into account the nature and scope of each contract. Our capacity to set up these units in a limited time is the warranty for our clients that project milestones will be accomplished. Closeness to customers is key.”
Projects in the UK
As an example, a large mobile factory used on a completed project in Riyadh, Saudi Arabia was dismantled, with one half erected for a similar job in the UK. Pacadar has enjoyed recent successes in the UK. So much so, it has established a main plant for precast concrete elements in the Isle of Grain in Kent to meet the company’s growing contract footprint.
On the Thames Tideway Tunnel project, ( a key modernisation of London’s ageing sewage system), Pacadar constructed the central and longest section of the tunnel, over 12.7 km long. However, Europe's biggest infrastructure project, HS2, a new high-speed railway line between London and the West Midlands, offers a new benchmark for Pacadar.
Four new contracts have been signed over the last two years. The first was with Balfour Beatty Vinci (BBV JV) for the supply of 1,600 precast concrete tunnel linings for the Long Itchington Wood. Pacadar has completed its production for this project.
Skanska, Costain & Strabag (SCS-JV) HS2’s contractor delivering the London tunnels, awarded Pacadar two contracts to produce 8,400 concrete precast tunnel rings. The contract to supply rings for the Northolt tunnels is the largest contract Pacadar has ever won.
HS2’s London tunnels from West Ruislip to Euston station will have a total length of 26 miles. Construction of the first tunnel will be completed in 2024. More than 160,000 cubic metres of concrete will be used to make the segments, which form a 9.5m outside diameter tunnel, 350mm thick. Each complete ring is made of seven segments, each weighing more than seven tonnes.
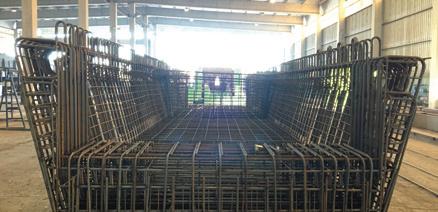
The strict geometrical tolerances required by HS2 are the most demanding that Pacadar has ever faced. A high precision testing system during the manufacturing process was implemented to meet the requested standards. In its commitment to innovation and sustainability, Pacadar uses a concrete mix of 40% GGBS from recycled materials from the steel industry, ensuring a considerable reduction of CO2 emission in the production of each ring.
Mr Pastor added: “This is an important contract for Pacadar, and we look forward to working with SCS-JV over the coming years and adding value to the project.”
As one of Pacadar’s key objectives, they signed a contract to supply the precast concrete beams, piers and planks for the Thames Valley Viaduct, within the Eiffage, Kier, Ferrovial and Bam Nuttall (EKFB JV) section for HS2. The precast concrete solution adopted for the beams is based on a proven technique previously implemented by Pacadar on high-speed lines. This agree ment significantly enlarges Pacadar’s port folio in the UK.
Backing up their local approach, Pacadar established two new units and is building a third to meet demand. Mr Dominguez said 130 people are engaged on the UK projects, which “now form the biggest part of Pacadar’s turnover.”
Global Consolidation
From a deep understanding of the precast concrete market, Pacadar is highly active on the international stage, completing iconic projects including the Panama City Metro, Riyadh Metro in Saudi Arabia, and Puebla's Toll Highway in Mexico. It also worked on Kuwait International Airport's new international passenger terminal, which is expected to be completed shortly. One key milestone was manufacturing heavy-weight arches to hold the roof. Pacadar manufactured six pieces in a day, a total weight that exceeded 1,000 tonnes of concrete.
The company is now manufacturing precast structures for the Common Shielding System for the new research infrastructure European Spallation Source (ESS) in Sweden. ESS, built and operated by a European Research Infrastructure Consortium composed of 13 countries, UK and Spain among others, that will be the world's most advanced research facility for neutron science. It will study atomic structures using neutrons, and this facility could yield discoveries that will benefit energy, materials, medicine and the environment.
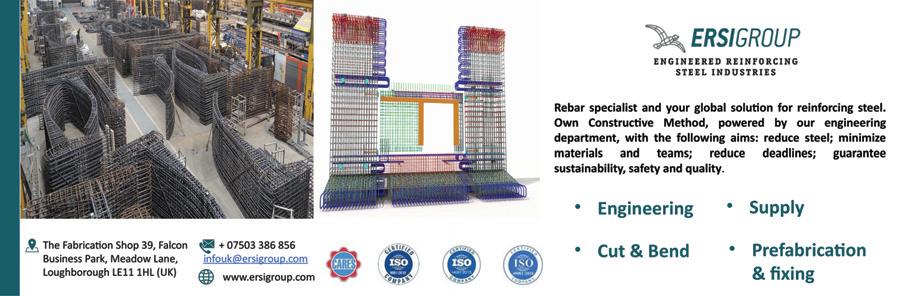
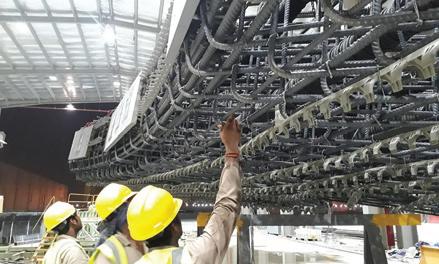
Pacadar contributed to the design and will manufacture the precast concrete shielding blocks under the most demanding requirements of accuracy, tolerances and safety conditions.
“We continue to monitor the international markets as big infrastructure projects come forward,” Mr Dominguez explained.
“High-speed rail networks such as HS2, tunnels and elevated metros are ones we are keen to add to our portfolio. There is also enormous business potential where solutions are sought for large, densely populated cities.”
Sustainable innovation
Pacadar continues to implement innovations – reducing carbon footprint in its production of pre-cast concrete by using more sustainable cement and raw materials. The adoption of temporary facilities to cut logistics and transport on a project is a key strength, while Pacadar's elite design and engineering team takes a lead role in minimising carbon emissions from conception by optimising structural solutions.
“For example, we evolved the use of steel fibres in production compared to steel rebar, which helps reduce the overall use of steel,” affirmed Mr Pastor. “The Thames Valley Viaduct is another good example of how an adequate design contributes to this objective. The solution finally implemented, based on previous highspeed experiences, reduces the number of structural elements without compromising the quality, nor the structural requirements or safety.
“The industry is slowly transitioning to more sustainable concrete. But that entails continual research as quality and safety are key concerns. Tolerances, such as on HS2, are stringent and very demanding, which Pacadar can never sacrifice.”
The company continues to develop high-technology practices by investing in innovative materials for the precast sector and collaborating with clients to offer smarter solutions that are more costeffective, efficient, durable and lighter. It also pursues a strong policy on recycling materials such as water, oil, batteries and paper, investing in technologies with reduced carbon emissions within its production facilities.
Mr Dominguez concluded: “As demand increases for infrastructure globally, we envisage Pacadar taking the lead in offering its experience, expertise and know-how.” n
As many industries, transition to renewable energy solutions continues apace, TMEIC Europe is ideally positioned to contribute to the realisation of carbon neutrality with its accumulated experience and know-how. Business Development Manager Mark Newman told Andy Probert how TMEIC’s ground-breaking technologies will play significant roles as a new industrial era dawns.
The July 2022 heatwave that blistered Europe and the UK served as a telling reminder that the greenhouse gas crisis is here. It can no longer be ignored by the majority of the population that sizzled in its wake.
“You can’t say climate change is not happening,” agreed Mark Newman, Business Development Manager of TMEIC Europe. TMEIC as an entity was created in Japan through the 2003 merger of the industrial systems divisions of Toshiba and Mitsubishi Electric.
While some companies have been slow or unwilling to catch the ‘transition train’ to a carbon-zero destination, TMEIC is speeding ahead by developing innovative integrated technologies for industry that promote a more sustainable future.
Renowned for a quality product range of motors, generators, AC and DC drives, controllers, inverters and UPS systems, TMEIC also develops solutions for industrial applications, wrapped around its core power inversion technology and complemented by plant-based equipment utilised via locally-resourced supply chains.
Clients are not confined to traditional industrial sectors, such as oil and gas, metal rolling, pulp and paper, mining, water and desalination: TMEIC is rapidly gaining ground in the power and renewables fields, by supporting the adoption and integration of renewable power generation through various energy storage initiatives.
TMEIC Europe, created in 2006 as a sales and engineering-focused subsidiary backed by its parent’s manufacturing prowess spread across Japan, China, India and the US, has a 40-strong workforce at offices in London, UK, and Puglia, Italy.
Mr Newman asserted: “While we have a global footprint and brand behind us, TMEIC Europe is a smaller but no less dynamic and agile entity. We support our partners’ business ambitions with a more partnership-based approach, rather tha n on a customer-supply commoditised basis.”
This has led TMEIC Europe into the realms of new fields and new partners based on developing projects around hydrogen, batteries, and compressed air as energy storage mediums to support the integration of renewable power generation. These are for commercial power generation for national grid networks , and back into the traditional industries to help achieve carbon-neutral applications and economies.
“Through our learnings on battery energy storage for grid support, we are looking to support, for example, oil and gas partners to integrate renewable power supplies in their industrial applications and decarbonise their emissions.
There’re many significant challenges, so we look to promote our technologies into those traditional industries.”
Flagship project
Indeed, TMEIC Europe’s expertise and technological advances led to the winning of an order to supply two 49.5 MW large-scale battery energy storage systems for UK power grids.
The joint venture, along with Nippon Koei Energy Europe BV, a European subsidiary of Nippon Koei Co, will see the facilities constructed in southeast England and due for commercial operation in 2023.
TMEIC will provide storage battery systems that integrate software and critical equipment such as storage batteries, power conditioning systems for storage batteries and power plant controllers that control power, voltage and frequency.
TMEIC has a proven track record of delivering best-in-class battery energy storage systems in Japan centred on projects with r enewable energy power plants (large- scale solar and wind power).
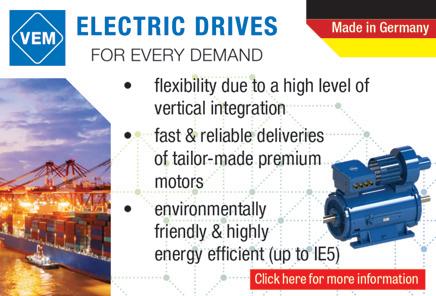
Mr Newman said: “This marks the first time for the company to deliver its systems to the UK market. Compatible with various options in the power market, including grid stabilisation services for the National Grid, the system will help address power grid stability in the UK where the share of renewable energy continues to grow.”
TMEIC has a battery system laboratory at an Indian subsidiary’s power electronics factory. This allows it to conduct state-ofthe-art demonstrations that combine a solar power generation system and battery energy storage system connected to the power grid and factory load, and realtime simulators.
Development and verification of respective control functions required for the project will be carried out at the laboratory to ensure a smooth start-up.
TMEIC, participating as one of five Japanese companies collaborating in the investment and financing of the project, will continue to be involved after the sys tems have been delivered.
It aims to contribute to the realisation of carbon neutrality by deepening its accumulated experience and know-how in power electronics and system control technologies to support the growing use of renewable energy globally and provide solutions to issues and challenges.
Mr Newman confirmed: “The i ntroduction of grid battery storage systems is expected to expand in many countries and regions worldwide.
“What we learn through this project will also be implemented into industrial applications to achieve greater carbon-neutral ambitions in heavy powerconsuming related sectors. This will put us at the forefront in breaking new ground that will have a global impact.”
A change for good
Since its inception, TMEIC Europe’s turnover has grown six-fold, with annual growth rates above 10% per year for the past five years.
“TMEIC Europe is looking to expand further, especially as we grow our business activities in supporting carbon-neutral economies. This underpins our very ambitious growth targets,” stated Mr Newman
“We have projects on the horizon: We are actively growing a pipeline of projects for battery energy storage technologies and developing solutions for industry decarbonisation, including onshore and offshore compressed air energy storage technologies.”
The company is also looking to adopt existing technologies into new areas that may not have been used or considered before and enable their efforts to drive further decarbonisation goals.
Mr Newman disclosed: “We are also developing solutions for the hydrogen economy, including both hydrogen generation and innovative rectifier technology that fits in with adopting renewable power generation.
“Our committed approach to collaborative solutions ensures we are positioned to develop innovative technologies, respond to industry trends and apply solutions to a wide variety of industrial market segments. From concept to installation, we develop lasting relationships by working hand in hand with our partners to ensure challenges are met and business goals exceeded.”
Efforts are being put in to develop and strengthen relations with new and existing clients postpandemic in the collective journey towards a carbon-neutral world.
“If we are to grow as we intend, then we will have to expand our workforce and localise engineering capabilities as we move into new business areas and grasp future opportunities,” Mr Newman outlined. “Managing and growing the supply chain is essential. A recent challenge that we have seen is the shortage of silicon-based components. That will prove a challenge to meeting project deadlines over the next 12 months.”
While TMEIC Europe is backed by a global 4,300 workforce and large corporation backing, the company’s agility, highlighted Mr Newman, enables it to be adaptable.
“We deliver quality products and solutions without sacrifice and follow an exacting Japanese-ethos in all our production, processes and standards.”
These are further propelled in maintaining long-term business relations with loyalty, trust and integrity as key fundamentals. He added: “These ensure we enable our partners get the most ou t of what they are trying to achieve.”
Mr Newman concluded: “Industries are in a state of change and transition. Europe is leading the way globally in decarbonisation efforts by putting in place mechanisms and incentives to achieve those goals.
“TMEIC Europe will have increasing significance in TMEIC globally as new ter ritories follow and learn from Europe as they move towards carbon-neutral economies. We want to support those goals as they are, undoubtedly, a change for good.” one planet – one chance – one voice