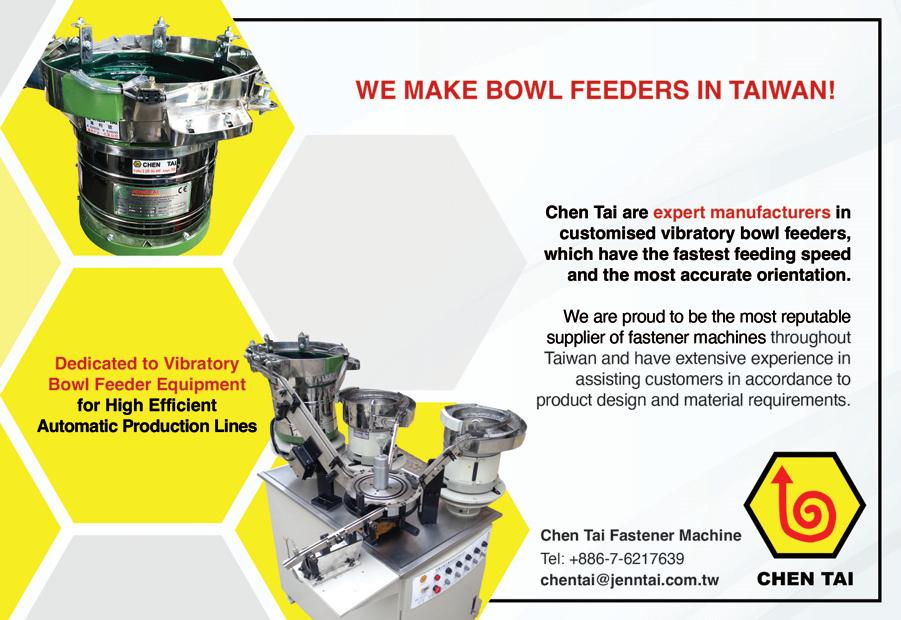
10 minute read
Frédéric Vasseur
from S02
Nationality: French
Born: 28th May 1968
Advertisement
F1 Career:
• 2019-2022 Team Principal of Alfa Romeo F1 Team ORLEN
• 2017-Managing Director & CEO of Sauber Motorsport AG
• 2017-2018 Team Principal of the Sauber F1 Team
• 2016-2017 Team Principal of the Renault F1 Team inclusivity. The team partners with the charity Save the Children to advance children's rights around the world. Support from the team helps Save the Children run projects in Switzerland and globally.
Members of Alfa Romeo F1 Team ORLEN also take an active role in their personal sustainability. “For the last three years, whenever I fly, I always offset my carbon footprint,” explained Mr Bottas. “And I fly a lot, including private flights. However, I offset basically twice the carbon for every flight.”
For all the technological wonders of the latest Alfa Romeo F1 Team ORLEN C42 car to have a wider impact, these sustainable developments in F1 need to trickle down to road cars. “Alfa Romeo F1 Team ORLEN is a good example of this,” Mr Vasseur agreed, “because we are almost on the same path, with the road car division moving to hybrid and fully electric cars.
“Hybrid technology is already here. Some countries are still pushing for fully electric vehicles, but it absolutely makes sense for F1 to stick to this technology. And we have to keep in mind that we will introduce more developments in 2026 with the sustainable fuel.”
The future for F1 and Alfa Romeo F1 Team ORLEN remains sustainable and a source of inspiration for the global audience of motorsport fans. This combination of innovative technology and a motivated team is a winning formula.
“Being able to race against the best drivers,” Mr Bottas said, “the best teams, on the best tracks in the world, that is really, really cool. But also, how innovative F1 is as a sport, how much the technology can help the future of the earth, with a big push for sustainability, that is also pretty cool.”
“I love competition,” concluded Mr Vasseur, “simply the competition! Coming from a racing background, I'm always trying to motivate the company, to show that we need to do a better job tomorrow than we did today.”
PECOL Automotive SA is a specialist in the automotive industry, producing cold formed fixing components. Opening in 2001 under the wing of the PECOL Group, the company has an impressive production capacity, manufacturing 130 million parts per month. Technical Manager Daniel Santos spoke in-depth about PECOL Automotive’s impressive production capacity and discussed the company’s most recent investments, in conversation with Imogen Ward.
The presence of an exceptional inhouse manufacturing process has solidified PECOL Automotive’s market lead in the production of automotive fixings. This extensive range of machinery has ensured the company can supply the highest-quality products to its clients in record time.
“We make everything in-house, except steel wire,” Technical Manager Daniel Santos said. “Because we can produce so much in-house, we are very flexible and adaptable. We don’t have to rely on anyone else, resulting in much shorter lead times for our clients.”
PECOL Automotive has been ahead of the manufacturing game since it was first established in 2001. With a plethora of support and knowledgeable experience provided by its parent (PECOL Group), the company has a strategic position within the automotive industry.
Alongside its headquarters, located in Águeda, Portugal, the company is supported by four PECOL Group industrial units located nearby. These units manufacture parts using cold forming, produce tools and special hard-metal parts, have heat treatment facilities and distribute PECOL products. The company also has supporting warehouses in Spain, Italy, Poland and Morocco. In Spain, the PECOL Group company INKATOR manufactures parts through cold forming. These facilities enable PECOL Automotive to manufacture 130 million parts every month – securing the company’s reputation as a steadfast competitor in the automotive industry.
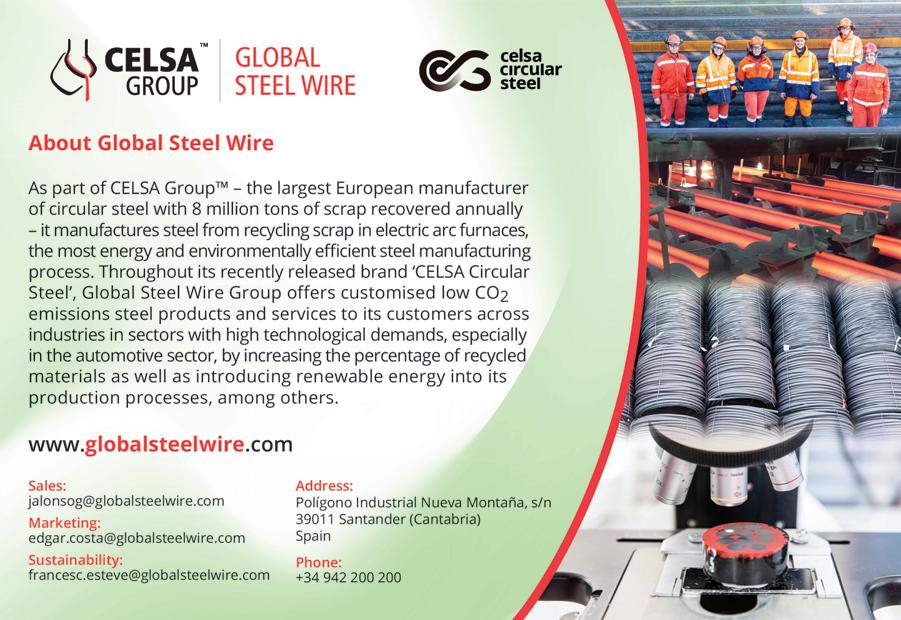
Pecol Automotive I Profile
Integrated investments
After purchasing its first annealing furnace in 2017, PECOL Automotive opted to further invest in growth by acquiring a second furnace. This decision resulted in a successful expansion of the company’s production capacity and will lay the foundations for in-house steel wire p roduction. With this development, 100% of the production process will occur inhouse at PECOL Automotive.
“We have automotive tooling production and raw material annealing,” Mr Santos said. “For setting and conforming products, we have raw material pickling and phosphating. PECOL Automotive invested in a portfolio of machinery so our customers could have products delivered to them quickly and without delay.”
In more recent times, this integration has greatly aided the company. With global supply issues becoming increasingly problematic for many, using its in-house processes, PECOL Automotive has successfully minimised the impact of supply delays.
An investment of €1.5 million was also dedicated to the acquisition of a new in-line stamping machine. This purchase was in response to an increasing customer demand for larger parts. With this new machine, PECOL Automotive can now stamp parts that have a diameter of 33mm and are 180mm in length. This 450-ton machine enables the company to cold form, shear, die and bridge parts – making the whole production process more efficient.
Fixing the planet
To improve its sustainability, PECOL Automotive implemented a forwardthinking environmental management strategy. The company installed on its facilities 3,500 photovoltaic panels, covering an area of 10,000 square metres. To clean these panels, the company collects and stores rainwater (significantly reducing its water usage). This rainwater is also used to supply the factory’s tank for its firefighting system – highlighting the company’s dedication to a safer, more environmentally conscious future.
PECOL Automotive also sends all the wastewater from its productions to a dedicated facility where it is subjected to physical-chemical treatments. This process greatly reduces the environmental impact of wastewater disposal.
The company is really dedicated to finding unusual and ingenious ways to recycle: one way that PECOL Automotive achieves this eco-friendly goal is through the creation of a continuous oil lifecycle. All the oil used in PECOL Automotive’s stamping machines is processed through a filtration system.
This oil can then be reused in the stamping machines.
“By implementing these processes,” Mr Santos said, “not only do we actively save around €10,000 a month, but we are also helping save the planet too. This is so important to us.”
Forming strong connections
The company maintains robust relationships with its suppliers, including DIMAC who produce almost all of PECOL Automotive’s machines. “We have successfully maintained this relationship with DIMAC for over 20 years,” Mr Santos said, “relying on them not just for the manufacturing of our machines, but also for the upgrading and maintenance required to keep them in optimal condition.
“We always make sure to give feedback on the work of our suppliers. This client/ customer interaction is extremely important; without that you are not helping the suppliers to upgrade and improve their products.”
Thanks to the flexibility of its in-house manufacturing, PECOL Automotive has extensive product advancement opportunities. To maintain its reputation as a market leader the company also invests heavily in research and development. By monitoring the evolution of technology within the industry, PECOL Automotive can develop
300 new products each year (advancing and evolving alongside the market).
The company’s Engineering Department carries out equally complex and innovative projects, and continuously researches the best solutions for PECOL Automotive’s customers. This dedication ensures the most practical and quality-driven product is available, whilst still meeting client expectations and specifications. In doing so, the company maintains 100% control of the process, from design to production, giving its customers complete peace of mind.
PECOL Automotive also relies heavily on its workforce of over 270 professionals; with trust at the helm, the company prides itself in being internally autonomous when it comes to the development and construction of tools.
This creative freedom gives the company a strong competitive edge. Continuous training and experience also ensure PECOL Automotive’s engineers are some of the most competent tool developers in the industry.
“Our vision for the future will come to fruition with people who have knowledge of new technology,” Mr Santos concluded, “Our continued acknowledgement and investment of advanced technology, as well as our dedicated in-house manufacturing process, secures the future of the company.
“PECOL’s future relies on the people that work here: we will all continue to cooperate, solidifying the very best future for the company.” n www.pecolautomotive.com
Retrac Group, an engineering, design and manufacturing specialist, has positioned itself at the forefront of the revolution in developing lightweight applications for sustainable transport solutions. Having launched its Retrac Future range of sustainable composites to industry approval, Retrac Group CEO Dan Walmsley, CCO Tim Scott and Head of R&D Alan Purves outlined how the company is now set for expansion in its 50th year.
Profile by Andy Probert.
The Retrac name may well be the original owner’s surname backwards; it is, however, fast-forwarding its engineering, design and manufacturing compe tencies in the sustainable bio-composites sphere at full throttle. The Group, which rests 50 years of excellence on its composites-metallics axis, is a leading supplier to blue-chip clients in the Formula One, automotive, aerospace, and motorsport sectors. Based at Swindon, in southwest England, Retrac supplies production components and mould tools, along with design, research and development services.
In alignment with the future transportation supply chain’s trends for sustainable lighter applications and a marked reduction in carbon emissions, the company has devised Retrac Future, a portfolio of sustainable and recycled composite materials.
“This range demonstrates to customers the breadth of what is possible with our various processes,” said Retrac Group CEO Dan Walmsley, “given the world is on the cusp of a lightweighting revolution.”
Exciting times ahead
It is just one of the many exciting elements Mr Walmsley and his team continue to evolve at the company.
Retrac’s half-a-century of business exploits notwithstanding, its paradigm shift to an Employee Ownership Trust (EOT) structure 18 months ago continues to see the company soar. Expansion and further innovation are also around the corner.
“The EOT has been bedding in for over a year,” said Mr Walmsley, “but through hard work from the team, we have not seen any slowdown in company performance. It offers exciting potential for years to come.”
While acknowledging that an EOT essentially places the future of the business into employees’ hands, Mr Walmsley said staff were more engaged than ever to ensure future success. Indeed, their workforce has risen from 115 to 170 personnel in less than a year to cope with an influx of new contracts and con - tributed to Retrac posting a 45% uplift in turnover.
One such milestone under the new structure is the announcement that Retrac will expand its operations into a new facility, additional to its 50,000 sqft multi-axis machining facility.
Mr Walmsley said the expansion is solely to meet a specific contract to serve the needs of an automotive OEM in the Electric Vehicle (EV) sphere. “It’s an amazing opportunity for Retrac,” he confirmed. “The new facility will give us the adaptability to support all elements of the project, which will have a particular focus on sustainability.
“It is a high-level statement of intent from Retrac’s perspective, bringing additional people to the workforce and placing us firmly within the sustainability space.”
Retrac will focus on a specific component in the cab of a commercial vehicle, with the first production destined for 2023, according to Retrac Group’s CCO Tim Scott: “Sustainability is a key commercial consideration that we need to be involved in and evolving in, given the current market conditions – and certainly, if we want the business to be here in 10 to 20 years’ time.”
Retrac Future
The company has developed the Retrac Future range of bio-composite materials. The options, including natural fibres with a positive carbon impact, have been developed to offer greater access to high-performing sustainable materials. Emerging from an extensive R&D project by Retrac’s composites division, the range includes recycled carbon fibre and natural-fibre products suitable for multiple applications across lightweight structures.
Bio-content resin systems enhance the eco-friendly credentials of these composite materials alongside an energy-efficient production process featuring bespoke compression moulding techniques.
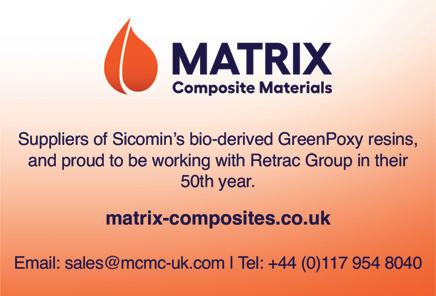
“The options demonstrate what is possible with our various processes using sustainable and recycled materials,” explained Alan Purves, Head of R&D. “These developments have been built on the back of exceptional experience, vision and hard work in-house.
“We have invested in R&D to develop our manufacturing capability using numerous interesting materials. That gives us a great platform to offer clients tailored solutions for their specific requirements in sustainable composites.”
Bio-composites and their positive sustainability are quickly becoming game changers for the transport solutions sector according to Mr Purves: “Our advances are also contributing to starting a conversation with customers and their understanding of sustainability, the future for their applications and what they are trying to achieve. What Retrac offers is the art of the pos sible in today’s world.”
As part of this R&D effort, Retrac Group forged alliances with leading flax natural fibre specialist Bcomp and Composites Evolution, a UK-based prepreg manufacturer and supplier that launched the Evopreg ampliTex prepreg range. The prepregs combine the high-performance Evopreg epoxy resin systems with Bcomp’s ampliTex range of flax reinforcements.
Using Evopreg ampliTex alongside Bcomp’s powerRibs reinforcement system, Retrac produced a demonstrator bonnet panel for a race-bred supercar to form one of the new bio-composites range.
Two thermoplastic materials have been developed from woven carbon and woven glass, which can be manufactured in the company’s compression moulding press system. The 60-tonne bespoke electric servo press is used for product development and allows precise control of position and load at every part of the pressing cycle.
Innovations hub
“Making those major inroads in development reflects well on the business,” Mr Purves added, “and on the broader
UK manufacturing sector as a sustainable innovation hub. As globally sustainable transport solutions evolve, Retrac is determined to be central to that.”
Mr Walmsley agreed: “These materials now allow Retrac to positively influence customers’ decision-making, impact their success and futures.”
The new bio-composites range has invigorated the market and focus, with the Retrac Group fielding two to three calls of interest a month from new UK and overseas clients.
“Retrac Group is a relatively small company,” reflected Mr Scott, “but it is taking huge steps in innovation that has caught the attention of larger busi nesses who are approaching us, interested in what we are achieving. The new contract and our expansion is a result of Retrac Future’s innovation.”
Confirming its commitment to being an integral part of the future transportation supply chain, and keeping abreast of customers’ sustainability drives, Retrac Group is signed up to the UK Government’s SME Climate Commitment to halve its greenhouse gas emissions by 2030 and achieve Net Zero emissions by 2040.
“Retrac’s commitment to sustainability and bio-composites innovation demonstrates how far ahead it is in this space,” concluded Mr Walmsley. “It’s apt that we are celebrating our 50th anniversary with such breakthroughs and look forward to a greener 50 years of new materials, tech and innovation.” n one planet – one chance – one voice