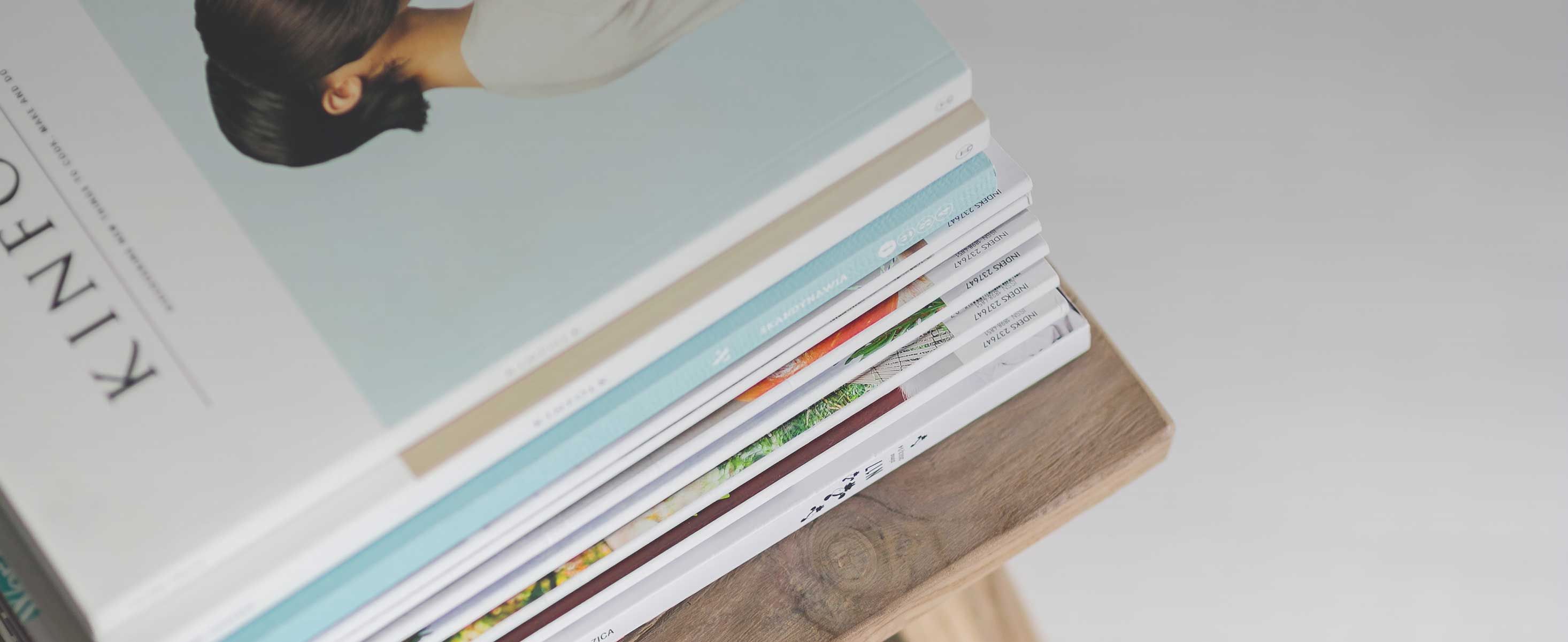
1 minute read
ments
from S02
requirements for a typical eight-hour shift. It compared a base case of an electric machine equipped with a traditional swash plate pump versus an excavator with a Danfoss Digital Displacement system and electric drive.
More efficient systems
Advertisement
The results show that, depending on system complexity and duty cycle, a reduction in energy requirement of up to 24.8% can be achieved. The improved system would require a 314 kilowatt-hour (kWh) capacity battery for an eight-hour shift compared to a 418kWh battery in the base case.
“Today’s excavators are only 30% efficient, with around 70% of the engine’s energy wasted in the fluid power system,” explained Leif Bruhn, Head of Digital Displacement, Danfoss Power Solutions. “Electric drives have much greater efficiency than internal combustion, but with duty cycles needing upwards of 400kWh every day, the cost of batteries can be prohibitive.
“Our research has shown that combining an electric drive with a highly efficient
Digital Displacement system is the most effective way to turn battery energy into hydraulic work,” Mr Bruhn continued. “This paves the way to smaller batteries and longer duty cycles for the electrically powered excavators of tomorrow.”
Danfoss’ calculations show that an electrified excavator utilising Danfoss Digital Displacement technology will have a better total cost of ownership than a standard diesel engine within the next five years.
About Danfoss
Danfoss creates engineering solutions and has a worldwide presence in more than 100 countries. Its work aims to increase machine productivity, reduce emissions, lower energy consumption and enable electrification. The company develops solutions in areas such as refrigeration, air conditioning, heating, power conversion, motor control, industrial machinery, automotive, marine, and off- and on-highway equipment. The company also provides solutions for renewable energy, such as solar and wind power, as well as districtenergy infrastructure for cities. n