Clearing the water
The tech revolutionising PFAS and mercury treatment

FEATURES
Fit
Sustainability
Australia-first certification
Going the distance for remote clean-ups

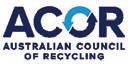
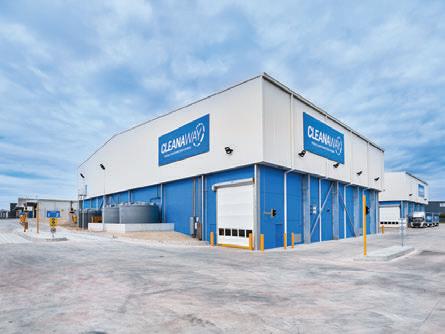

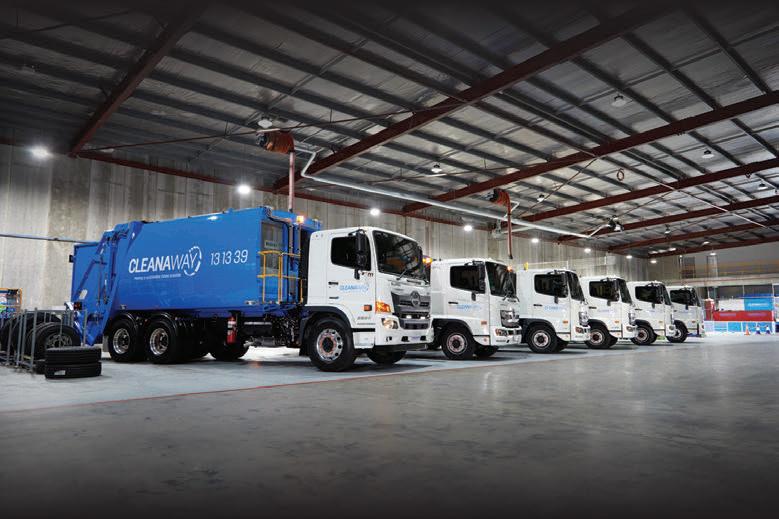
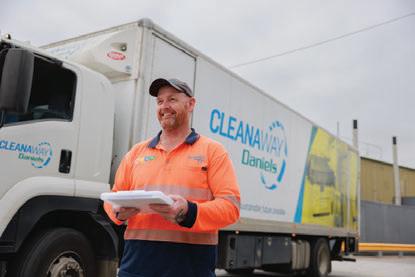

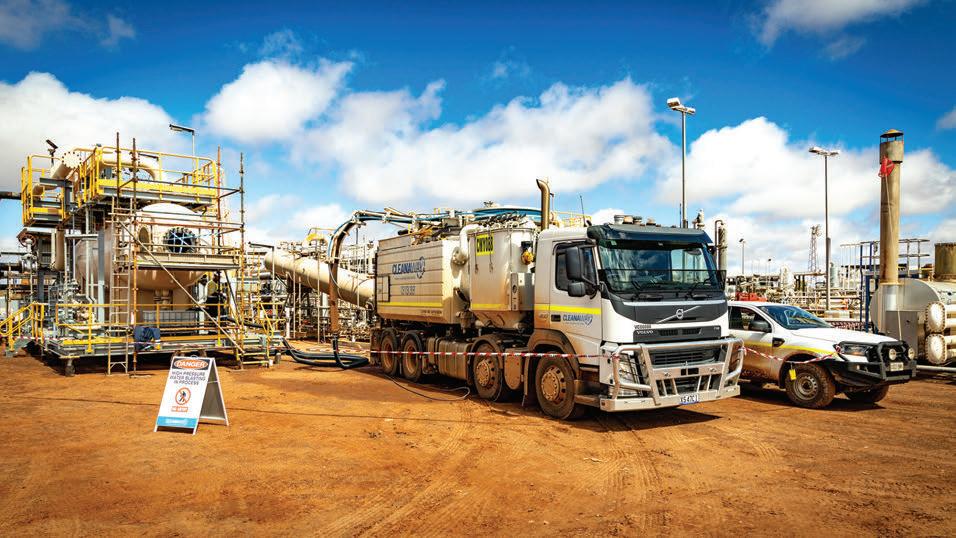
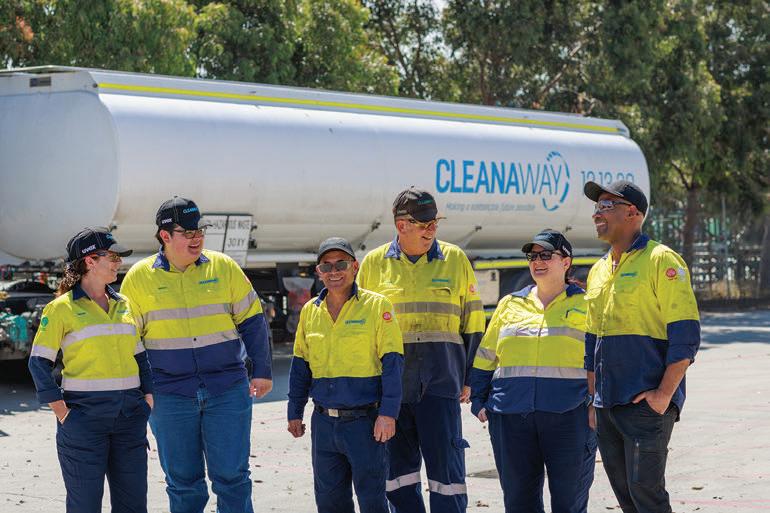
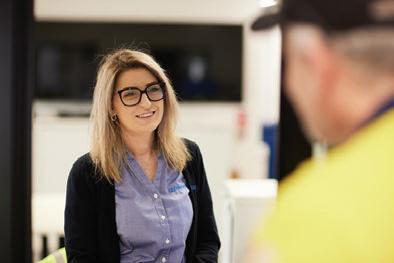
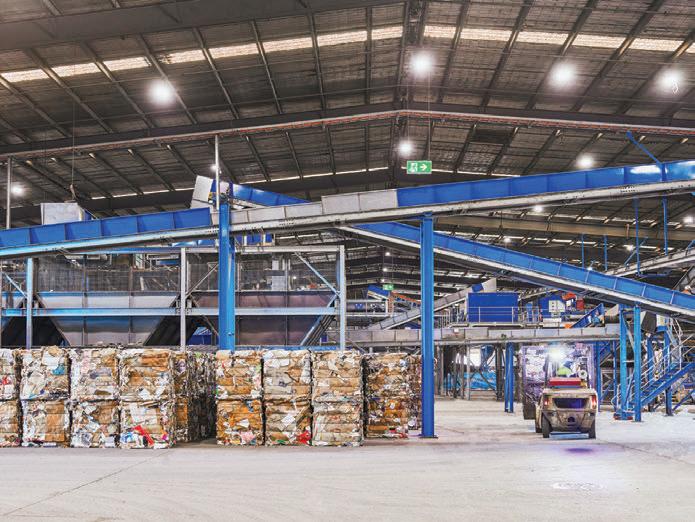

The tech revolutionising PFAS and mercury treatment
FEATURES
Fit
Sustainability
Australia-first certification
Going the distance for remote clean-ups
Australia’s pursuit of a circular economy has gained momentum in recent years.
Businesses and the community are nding innovative ways to use materials more sustainably and e ciently through recycling, renewable energy and designing products for reuse, while most tiers of government have implemented strategies to transition to a circular economy and away from a linear ‘take, make, waste’ approach.
While an interim report of the Productivity Commission’s inquiry into a circular economy says progress has been slow, it also states that by aligning all levels of government, industry and the research sector, Australia can position itself as a global leader in circular innovation.
As this edition of Waste Management Review shows, there are some early adopters who are leading the way, such as waste management provider Cleanaway.
Cleanaway’s new state-of-the-art organics processing facility is enriching the local agricultural industry. e company has also spent more than $70 million on a material recovery facility that will improve the volume and quality of resources recovered from commingled recycling.
We take a closer look at both facilities that are set to fast track New South Wales’ circular economy journey.
We also visit e-waste recycler Ecocycle, which has achieved global certi cation in its pursuit of responsible recycling and resource recovery of dangerous e-waste, and Shred-X, an industry leader with a new division to address the growth of textile waste.
ResourceCo has long been a driver of circular economy outcomes for construction and demolition waste, now it’s providing a tool to support industry and its decision to use recycled products. We discover what’s behind the decision to ‘declare the data’.
We also catch up with Veolia’s new Chief Financial O cer who is hoping to be an enabler of the company’s GreenUp strategy. And in the lead-up to the Federal election, Suzanne Toumbourou, Australian Council of Recycling Chief Executive O cer, outlines why a new government must do better.
Happy reading
CHIEF OPERATING OFFICER
Christine Clancy christine.clancy@primecreative.com.au
PUBLISHER
Sarah Baker sarah.baker@primecreative.com.au
MANAGING EDITOR
Lisa Korycki lisa.korycki@primecreative.com.au
JOURNALIST
Jennifer Pittorino jennifer.pittorino@primecreative.com.au
HEAD OF DESIGN
Blake Storey blake.storey@primecreative.com.au
DESIGN
Laura Drinkwater
BRAND MANAGER
Chelsea Daniel chelsea.daniel@primecreative.com.au p: +61 425 699 878
CLIENT SUCCESS MANAGER
Justine Nardone justine.nardone@primecreative.com.au
HEAD OFFICE
Prime Creative Pty Ltd
379 Docklands Drive Docklands VIC 3008 Australia P: +61 3 9690 8766 enquiries@primecreative.com.au www.wastemanagementreview.com.au
SUBSCRIPTIONS
+61 3 9690 8766 subscriptions@primecreative.com.au
Waste Management Review is available by subscription from the publisher. e rights of refusal are reserved by the publisher
ARTICLES
All articles submitted for publication become the property of the publisher. e Editor reserves the right to adjust any article to conform with the magazine format.
COVER Cover image: OLEOLOGY
COPYRIGHT
Waste Management Review is owned by Prime Creative Media and published by John Murphy.
All material in Waste Management Review is copyright and no part may be reproduced or copied in any form or by any means (graphic, electronic or mechanical including information and retrieval systems) without written permission of the publisher. e Editor welcomes contributions but reserves the right to accept or reject any material. While every e ort has been made to ensure the accuracy of information, Prime Creative Media will not accept responsibility for errors or omissions or for any consequences arising from reliance on information published. e opinions expressed in Waste Management Review are not necessarily the opinions of, or endorsed by the publisher unless otherwise stated.
../ Available in 53L and 62L capacities, these drums are engineered to safely contain new, spent, recalled, or damaged batteries, with a focus on lithium-ion batteries
../ Fire Containment: Proven to contain lithium battery thermal runaways within the drum through extensive testing, ensuring safety under adverse conditions
../ Durability and Transport Safety: Designed to withstand substantial stacking loads, these drums facilitate safe storage and transportation
../ Optional Smart Lid, featuring early heat detection, temperature and fill level monitoring with an automatic notification system.
../ UN Rated to hold up to 100KG .
Revolutionary technology that removes PFAS to non-detectable levels is now being used to clean other problem contaminates from water and gas.
There doesn’t always need to be an evolution. Sometimes, at some point, there should be revolutions.”
It’s an expression that drives the team at OLEOLOGY to continue to develop solutions to recycle and decontaminate water quicker and simpler and stay ahead of regulatory changes.
It’s also why, with more than 20 years in the industry as water and uid experts, OLEOLOGY’s niche area of work is forever expanding.
e company’s technology has proven to remove organics, oils, hydrocarbons and per- and poly uoroalkyl substances (PFAS), to non-detectable levels. It has
also been successful in mercury removal and ammonia reduction, which has led to new Australian-developed patentpending technology.
Saasha Callaghan, OLEOLOGY Technical Solutions Manager, says the ammonia reduction technology has been in development for some time, triggered by working with local government and land ll managers to remove PFAS.
“Ammonia kept rearing its head,” Saasha says. “It’s a real hazard and challenge that is being felt by councils, Australia-wide. We had seen reductions in ammonia using a di erent technology, so we started developing
something speci cally for ammonia. We have developed a process to manage very high ammonia levels, from more than 3500 milligrams per litre down to one milligram per litre.”
A focus on engineering and developing technology that is t for application is not without precedence for OLEOLOGY – its internationally recognised PFAS water treatment process was also driven by industry demand.
In 2006, the company committed in-house research and development to PFAS contaminants and the removal of all analytes and precursors. Since then,
“Our aim has always been to reach non-detectable levels across the board by gaining the knowledge of what else is out there, what is improved, where are the industry and regulators moving toward.”
Saasha Callaghan OLEOLOGY Technical Solutions Manager
its MyCelx technology has been used by some of the top 500 companies for water treatment around the world.
While other oil water separators rely on mechanical separation or chemicals, the MyCelx polymer bonds with oil and other contaminants at a molecular level, removing contaminants in one pass. e system is 1/20th of the footprint of traditional methods and greatly reduces waste volumes. e remaining dry waste is thermally oxidised to ve per cent of its original mass, making it safe to handle and store.
PFAS are referred to as ‘forever chemicals’ because of their resistance to break down, meaning they can persist in the environment for long periods.
Historically they have been used in many products, including re ghting foams, non-stick cookware and cosmetics, leading to growing concerns about the widespread contamination of water sources and health issues.
Saasha says one of the challenges is that while there is a focus on management of more commonly known PFAS, PFOA (Per uorooctanoic acid) and PFOS (Per uorooctanesulfonic acid), there are a lot of other players that fall under the PFAS umbrella. She likens it to doping in sport – as detection technology improves, you start discovering more. OLEOLOGY’s
technology has kept pace with PFAS discoveries.
“We knew the envelope was always going to be pushed, that testing was going to get better, that PFAS limits for environmental discharge would be lower,” Saasha says. “We already knew, based on our want for knowledge and discovery within what was PFAS, that all those chemicals under the PFAS umbrellas would further expand.
“As a technology provider with an innovation focus, our aim has always been to reach non-detectable levels across the board by gaining the knowledge of what else is out there, what is improved, where are the industry and regulators moving toward?
“You have to be ahead of the curve, otherwise you’re going to fall behind very quickly.”
Staying ahead of the curve requires working with regulators, such as environmental protection authorities and industry experts, both locally and overseas, who have experience on advisory boards and government think tanks.
OLEOLOGY’s sister company, OLEOLOGY Consulting, also has a team that is “on the hunt” for new immersive technologies.
“It’s the hard work that nobody else wants to do,” Saasha says. “It’s a
discovery of research or innovation of development, and it is triggered, funnily enough, not by us, but from the market itself.
“We get all sorts of inquiries from people looking for solutions for a problem. It’s not just that we create a widget and go, ‘ is is what the world needs.’ It is driven by a need.”
An example of that need is oil and gas giant Chevron, which operates in Australia and the Gulf of Mexico.
Saasha says Chevron had four major focuses for its water treatment, OLEOLOGY was assigned two of them – to comply with discharge and e uent management requirements and improve operational e ciency and environmental and social governance (ESG) ratings.
Newlands Group, which designs and constructs civil and commercial projects, can also attest to improved operational e ciency and environmental responsibility by partnering with OLEOLOGY.
Grant Campbell, Construction Manager Civil, for Newlands, says working with OLEOLOGY to manage PFAS needs has been a game changer for operations.
He says OLEOLOGY’s PFAS Water Treatment Systems, which ltered the PFAS out of the ground water on one of Newlands’ Department of Transport and Main Roads projects, not only demonstrated exceptional e ciency, but also provided the company with peace of mind that it had e ectively addressed environmental concerns.
“OLEOLOGY’s team impressed us with their expertise and commitment to nding tailored solutions for our speci c requirements,” Grant says.
“ ey guided us through every step of the process, from initial consultation to implementation, ensuring seamless integration and optimal performance. eir dedication to sustainability and environmental stewardship is
evident in the design and operation of their PFAS Water Treatment Systems, which are engineered to minimise environmental impact while maximising e ectiveness.
“ is alignment with our values has made them an invaluable partner in our e orts to mitigate PFAS contamination.”
Grant says the reliability of OLEOLOGY’s equipment – delivering consistent results – coupled with responsive customer support, has given Newlands the con dence to tackle even the most challenging projects.
Which brings us back to ammonia.
Ammonia and PFAS go hand-in-hand at land ll sites.
A lot of waste in land lls is PFAS ridden because of its widespread use.
Leachate, the liquid that drains from a land ll, often contains PFAS and large amounts of ammonia because of the decomposition of waste.
Ammonia can be toxic if discharged directly into waterways and can be
released in high concentrations as a gas, contributing to air pollution. It can also a ect the e ciency of leachate treatment.
“Leachate will build over time. It matures. It grows and builds up in concentration within a land ll cell,” Saasha says.
“So, land ll managers are trying to manage ‘two trouble children’. ey are trying to remove something that is so ubiquitous, like PFAS, and then still have a problem of compliant ammonia levels.
“We’ve been able to create a nonconsumable media, with a life span of a few years, to address the concentrated capture of ammonia.”
OLEOLOGY is conducting extensive ammonia work at a site in Western Australia, to collect performance data of the technology and further push the limits.
Saasha says being focused on improving technology for better environmental outcomes is compelling.
It’s why the team is always looking for the next big thing. One thing that has emerged over the past few years is Australia’s abundance of mercury. As the oil and gas industry decommissions and remediates assets, mercury has emerged as a big concern.
Using a series of di erent medias, similar to the technology used in its PFAS and ammonia removal systems, OLEOLOGY can remove all three forms of mercury – ionic, colloidal and elemental.
Elemental is clean, liquid mercury that most people are familiar with, while ionic and colloidal are a result of weathering.
“For ionic and colloidal mercury, it’s the same premise and concept, we are minimising waste to a point that it is condensed, dry and can be disposed of by third party contractors,” Saasha says.
“For elemental mercury, the lter can last up to ve years or longer in optimal conditions. It’s meant to saturate and when the oil sweats, the mercury drips o and can be collected.”
Further sights are set on the growth for OLEOLOGY Consulting.
“OLEOLOGY sees a huge opportunity to aid improvements in the oil and gas sectors, and the agriculture sector, not just within Australia, but also overseas,” Saasha says.
It is currently working with industry leaders in developing new technology within the waste management and disposal sector.
“We are all about reducing footprint, reducing waste, and improving e ciency,” Saasha says.
“ e team is currently working on a new technology that has always been, in theory, able to work. e practicality of it being used, has only just become a reality.”
For more information, visit: www.OLEOLOGY.com.au
With its multi-rotor design the Genox J-series pipe shredder easily shreds HDPE pipes of all sizes. When combined with a Genox washing plant and Genox pelletising system, you can truly close the loop on HDPE pipes. Pipe to pellets. Pellets to pipe. This is the circular economy in action. Genox make world-class recycling solutions, for real-world recycling applications.
Wastewater treatment is in hot water over PFAS. How can new technology turn the tide on these persistent pollutants?
Per- and poly uoroalkyl substances (PFAS) are the house guests that never leave. Found in everything from re ghting foams to non-stick cookware, these “forever chemicals” refuse to break down, contaminating water sources worldwide.
Australia is no exception, with rising concerns over PFAS levels in land ll leachate, wastewater, and industrial discharge.
Traditional treatment methods often fall short, leaving the waste management industry searching for practical solutions.
One company making waves in this space is ECT2. Its NanoSORB Membrane Bioreactor System combines advanced ltration with biological treatment, promising a more e ective way to remove PFAS from contaminated water.
But how does it perform in the real world?
A Michigan industrial facility faced a signi cant PFAS challenge. Historical site activities had led to groundwater contamination, with per uorooctane sulfonate (PFOS) concentrations averaging 1650 nanograms per litre (ng/L), far exceeding the local publicly owned treatment works (POTW) discharge limit of 28 ng/L.
e facility required an e ective solution to remediate the contaminated groundwater and comply with regulatory standards.
ECT2 deployed its FOAM-X foam fractionation technology to address
the contamination. e system uses air injection to generate a foam layer that captures and concentrates PFAS from the water.
A two-stage foam fractionation strategy was implemented to simulate full-scale continuous ow treatment.
Darrin Stoker, Senior Business Development Manager, says the FOAM-X system demonstrated remarkable e ciency, reducing PFOS concentrations to non-detect levels – an over 99.8 per cent reduction by mass. is level of treatment not only met, but surpassed, regulatory requirements, ensuring the facility could safely discharge treated water.
In addition to high removal e ciency, FOAM-X proved e ective in concentrating PFOS within the generated foam layer. e process
achieved an average concentration factor of 1300 times, reducing the volume of PFAS-laden waste requiring further handling.
Darrin says this represents a key advantage over traditional treatment methods, which often produce large quantities of secondary waste that require costly disposal or incineration.
“By concentrating the contamination into a smaller volume, the facility could streamline subsequent treatment, lowering operational costs and environmental impact while improving long-term sustainability in PFAS remediation.”
To further enhance the treatment process, ECT2 collaborated with Enspired Solutions, integrating ITS PFASigator technology for the on-site destruction of the concentrated PFAS
in the foam layer. is system employs photo-activated reductive de uorination (PRD) to break down PFAS compounds safely and cost-e ectively.
“ e combined approach successfully destroyed more than 99.7 per cent of the PFOS mass, preventing it from re-entering the environment,” Darrin says. “Crucially, this integrated process resulted in a zero-waste outcome, eliminating the need for further disposal.”
Australia’s waste management industry is at a crossroads when it comes to PFAS. Government agencies and environmental bodies continue to re ne PFAS regulations, increasing pressure on land ll operators, wastewater treatment facilities, and industrial sites to implement e ective removal strategies.
However, Darrin says many existing treatment methods either fail to remove PFAS altogether or generate secondary waste that still requires disposal.
“NanoSORB o ers a di erent approach. Integrating biological treatment with adsorptive processes enhances PFAS removal while reducing other contaminants such as total organic carbon (TOC) and chemical oxygen demand (COD),” he says.
“ is dual-action capability is desirable for Australian facilities managing complex wastewater streams. Moreover, its compact design and high removal e ciency mean that facilities with space constraints, such as municipal treatment plants or land ll leachate systems, can implement the technology without major infrastructure overhauls.”
PFAS contamination isn’t going away anytime soon. e waste management industry must stay ahead of regulatory changes and public concerns by adopting proven, scalable solutions.
Darrin says case studies such as the Michigan industrial facility project demonstrate that advanced PFAS treatment is not just possible but practical.
For Australian operators, the challenge now is nding the right approach.
“Whether it’s FOAM-X, NanoSORB, or another emerging technology, the goal is the same: cleaner water, better compliance, and a sustainable way to manage PFAS for the long term.”
For more information, visit: www.ect2.com
+ Heavy-duty cutting table with 8 & 10 knife options.
+ Intelligent electrical control and user-friendly hydraulics.
+ Variable speed main conveyor for efficient operation.
+ 4m tracks for enhanced maneuverability and stability.
+ Cat Tier 3 LRC C13 516HP engine with fuel-efficient hydraulics and double hydrostatic drive.
Unleash the power of the ES-250, the ultimate tracked primary shredder. Designed to tackle a diverse array of materials, this machine features dual asynchronous shafts with rotating knives that prevent bridging and enhance shredding efficiency. Whether dealing with large, tough, or varied inputs, the ES-250 delivers consistent, highperformance results. Perfect for demanding environments, it transforms shredding challenges into seamless operations. Elevate your facility’s capabilities with the ES-250— where power meets precision.
With the support of the Australian Organics Recycling Association (AORA), Repurpose It is proving preschool education can include painting, playtime, and the exploration of organics recycling.
As the peak body representing organics processors and recyclers, the Australian Organics Recycling Association (AORA) is a strong advocate for education about the recycling and organics industries across all age levels and communities.
As such, it supports organisations like Melbourne-based Repurpose It which hosts free sustainability incursions with preschool and school-aged children and has rolled out a ‘train the trainer’ session for teachers focusing on fostering sustainable practices.
Since July 2024, Repurpose It has hosted 45-minute sessions with early childhood centres, in Hume and Whittlesea, covering essential sustainability topics such as waste sorting,
composting, and waste reduction. e aim is to educate children on the work of recyclers such as Repurpose It.
e sessions connect with young people at preschools and primary schools to gauge their level of understanding about waste streams, how they are used and where materials go once they leave the bins at home.
Repurpose It’s Education and Communications Specialist om Fox uses portable worm farms and compost bins as a tangible link between actions at home and the larger scale resource recovery process, to teach young people about sustainable practices.
om says early education about organics is important because it lays the foundation for sustainable practices from
an early age, while instilling a sense of environmental responsibility in children.
“ e early primary school space is such a critical moment for consolidating, understanding and establishing a sense of identity,” says om.
“Kids learn their place within the world, and how their actions have an impact and in uence their community.”
In the sessions, children discover how to make compost and recycle food scraps, and how they can take care of nature.
om says the sessions inspire children to care for the planet by reducing waste, which helps them develop habits that can positively impact the environment throughout their lives, while learning about Repurpose It.
“In the sessions we work to replicate what’s happening on our site in Epping by breaking the process down in ways they will understand,” he says.
Repurpose It produces products from waste that support a number of industries including construction and demolition, and food organics and garden organics (FOGO).
Materials that enter the site are screened and tested. om discusses these steps and how the organic material is broken down into compost at the other end.
“We want to educate the kids about Repurpose It’s mission, but more importantly the sessions are about how to use the waste streams e ectively to reduce contamination,” he says.
“We use real world language like contamination, recycling and mitigation strategies with kids while combining easy
to understand practices like worm farms. is is a great tool for explaining the workings of FOGO, because if the worm cannot eat it, it cannot go in the FOGO green bins.”
om says this tangible learning is a useful tool because the choices made at home do matter.
“Contamination mitigation is best combatted at the incoming feedstock point, which is also known as the residential bin,” he says.
“We want to reduce contamination at the source, rather than trying to innovate and ideate at the back end with milliondollar machinery.”
om says reasons for residential contamination can range from misunderstanding, ‘wishcycling,’ and apathy, to simply not knowing what waste goes in which bin. e sustainability incursions work to demystify the recycling process by highlighting the human element.
“We want community connection between organics and recycling to be second nature,” he says.
“By starting our programs with children at one of their most critical cognitive developmental stages, we’re aiming to foster a strong sense of environmental advocacy and agency. If you start environmental education at this age, you are potentially setting them up to have 13 years of education focusing on some elements of environmental sustainability.
“You also get ‘pester power’ with children who pester their parents and family members to keep up with organics and recycling.”
Since the inception of the program om has sent surveys to all participating centres and is pleased to have always received positive feedback.
“We have visited more than 30 ELCs (Early Learning Centres) and ve schools, allowing us to reach over 1300
families just from the ELC visits alone,” he says.
“Written feedback has been overwhelmingly positive. We nd although the program is targeted to school-aged children, the adults in the room are also listening and learning.
“Our requests for incursions have increased exponentially since schools have returned for 2025. We are fully booked for term one, I am now taking incursion bookings for term two and three.”
Repurpose It collaborates closely with its council partners across Victoria where they take in FOGO, street sweepings as well as hard and soft green waste. om says the team is looking to expand the program to o er excursions on site in Epping.
“Incursions are amazing, and it is wonderful to be able to facilitate them. But there is nothing more visceral and tangible for students and teachers than an onsite excursion,” he says.
om says it is incredible to have a peak body in Australia, such as AORA, representing organics recycling.
“AORA has such a strong community focus and an end goal which aligns with Repurpose It’s views on minimising contamination,” he says.
“ ere are so many approaches that can be taken to share the messaging on contamination from the punitive to informative letters in the mail to initiative-taking social media and face to face campaigns.
“Ultimately AORA and Repurpose It both agree that education is one of the most e ective methods and we enjoy our respectful mutual partnership.”
John McKew, AORA National Executive O cer, says education is critical to eliminate the issues currently facing the recycling industry.
“ e primary issue continues to be contamination, a ubiquitous problem which occurs across all waste streams. If we continue to educate at all levels, then we are not only helping the industry, we are also helping the economy and environment.
“Young children do an excellent job at reminding their closest friends and family members about what they learnt that day and why recycling is important for the planet.
“ e sooner we can embed the right practices the better. If we teach kids how to manage recycling streams, we have a greater chance of success.”
For more information, visit: www.aora.org.au and www.repurposeit.com.au
A new development in Western Sydney is setting the standard for resource recovery in Australia.
Cleanaway has spent more than $70 million to deliver a best-in-class material recovery facility (MRF) in Western Sydney, to cater to the needs of New South Wales’ growing population and the increased awareness of the importance of recycling.
Built in conjunction with property investment and funds management group Charter Hall, and the backing of foundation partners Blacktown City Council, the MRF aims to improve the volume and quality of resources recovered from the state’s recycling. It will process up to 120,000 tonnes of residential and commercial waste a year, achieving up to 99.5 per cent purity of plastics recovery – enabling downstream processing facilities to maximise the quality of new containers.
Danny Lemme, Cleanaway’s Resource Recovery Manager, says purity is one of the biggest achievements within the facility.
“ e more Australia pivots to domestic recycling, the more we must focus on quality and purity,” he says.
“Contaminated material can degrade the quality of a recycled product, making it less valuable and potentially unusable. e cleaner the material, the better it can be reprocessed into new products.
“ e screening and optical technology we have installed will help us achieve our purity rates, ensuring a reliable pathway to market and circularity of the bene cial product.”
Forming part of Cleanaway’s NSW Resource Recovery Network, the Western Sydney MRF recovers cardboard and mixed paper, glass, aluminium and steel, natural and coloured high-density polyethylene (HDPE), coloured and clear polyethylene terephthalate (PET), polypropylene (PP) and mixed plastics.
All recyclables undergo a manual pre-sort to remove oversized, hazardous or incorrect items. ey are then separated into their respective output streams using advanced technologies
such as ballistic separators, optical sorting, eddy currents, magnets and wind sifting.
“While optical sorting is not new, what sets this MRF apart is the installation of the latest TOMRA technology with 2D and 3D shape recognition and colour separation to separate bre from the stream and categorise plastics into HDPE, PET, PP and mixed,” Danny says. “For a circular economy, the input product for recycling has to be of a high quality to achieve the right output product.”
While Cleanaway is leading the way in recycling and resource recovery, it also recognises the importance of safety and protection of the environment. e waste, recycling and resource recovery industry has been rocked by an alarming rise in res primarily caused by incorrect battery disposal.
In 2024, the Australian Council of Recycling released research that suggested there were between 10,000 and 12,000 battery-related res across waste and recycling streams in Australia over the past 12 months.
Fires pose a signi cant risk to workers, as well as damaging or destroying infrastructure, leaving otherwise recoverable product at risk of being land lled.
Cleanaway’s Western Sydney MRF sets the industry benchmark for reresistant infrastructure, featuring a fully compartmentalised building design and a detection, suppression and containment system providing coverage above and below the plant.
Supported by 1.1 million litres of onsite stored water and a sealed
underground containment system, Cleanaway ensures that any water used to extinguish a re cannot leave the site and damage the environment.
“ e industry is trying to respond to the prevalence and intensity of res, particularly lithium batteryrelated res,” Danny says. “It’s important that the industry, where it has the opportunity, builds resilient infrastructure, because ultimately not doing so puts resource recovery outcomes at risk.
“ e resilience of this facility, from a re control perspective, is unparalleled. It’s got VESDA (very early smoke detection apparatus) systems, it’s got AI thermal cameras, it’s even got oversized bunkers to keep material separate from each other.
“ ere are no shortcuts. is facility sets a standard to which future
material recovery facilities should be built.”
VESDA is a sensitive smoke detection system that continuously samples air to detect even minute traces of smoke, providing an early warning of potential re.
Danny says it’s important for Cleanaway to invest in protecting not only the plant and its sta , but the environment and local communities.
Under its 2024 Reconciliation Action Plan, Cleanaway is focused on increasing awareness, understanding and partnerships with First Nations communities of the lands on which it operates.
Recognising the site’s heritage, Cleanaway has partnered with local First Nations artists to include a mural on two re tanks at the new MRF.
e Wawarrawarri Darug people, who lived along Eastern Creek, practiced sustainability and cared for the waterways, recognising the interconnectedness of nature and the need to preserve it for future generations. Danny says the mural serves as a conversation starter and demonstrates a dedication to growing cultural awareness.
“ is was a really great way of partnering with First Nations people and giving them a space in a really important state-of-the-art facility that is our modern-day way of giving back to the land and creating sustainability,” he says.
“We are dedicated to making a sustainable future possible together.”
For more information, visit: www.cleanaway.com.au
• Expert Insights: Hear from leading industry voices on the latest challenges and innovations in waste management.
• Unparalleled Networking: Connect with 700+ waste professionals, including local and state government representatives, industry leaders, and solution providers.
• Cutting-Edge Exhibitions: Explore an extensive indoor and outdoor expo showcasing the latest equipment and technology.
Secure your place today! With a revamped program designed for maximum value, this is the must-attend event for waste management professionals.
Join industry professionals at the premier event for waste and resource recovery. With seats filling fast, don’t miss your chance to be part of Waste 2025!
• Interactive Sessions: Engage in panel discussions, workshops, and four streams of educational content.
• Social Events: Build connections at three exclusive networking events.
Secure Your Spot at Australia’s Leading Waste Management Conference!
• Live Demonstrations: See waste and recycling technology in action.
• Flexible Access: Attend in person or join via live broadcast.
SEQUENCED FILTRATION:
REMOVAL TO "NON-DETECT"
1,000,000 LITRES /DAY (SHOWN ABOVE)
PROVEN REMOVAL ALL PFAS
REMOVES FUTURE LIABILITY
SAFE AND FAST:
INSTALLATION MAINTENANCE
REDUCE SITE COSTS:
DRY WASTE
REMOTE CONTROLLED SAVE OPERATOR TIME
SMALL FOOTPRINT
Australia is among the highest per capita producers of e-waste in the world, generating 511,000 tonnes of e-waste in 2019, according to the Department of Climate Change, Energy, the Environment and Water (DCCEEW).
On average, Australians discard 20 kilograms of e-waste per person each year, nearly three times the global average of seven kilograms per person.
Despite various industry-led initiatives, only 17 per cent of this waste is formally recycled, with the majority still ending up in land ll, contributing to environmental degradation.
Mobile phones, power tool batteries, and e-mobility batteries make up a signi cant portion of this growing waste stream. Without proper recycling, the hazardous materials found in these devices pose risks to both the environment and public safety.
Battery disposal, in particular, has become a national safety concern, with lithium-ion batteries being responsible for an increasing number of res in waste facilities and recycling centres. Victoria’s Metropolitan Fire Brigade (MFB) has responded to more than 100 batteryrelated res in waste facilities over the past ve years.
Nick says that R2v3-certi ed recyclers such as Ecocycle are essential to addressing these challenges.
“As battery usage continues to rise, so do the risks associated with improper disposal,” he says. “We need a clear, certi ed framework that ensures all e-waste, batteries and mobile phones are processed in a way that is safe, e cient, and environmentally sound – and that’s exactly what our R2v3 certi cation provides.”
Nick says Ecocycle’s R2v3 certi cation is a game-changer for businesses, councils, and organisations looking for a trusted, compliant, and sustainable recycling partner.
Clients who work with R2v3certi ed recyclers such as Ecocycle bene t from:
• Enhanced credibility and marketability: Businesses that use certi ed recyclers can demonstrate their commitment to ethical and sustainable waste management, which builds trust with stakeholders and government bodies.
• Regulatory compliance and risk management: Partnering with an R2v3-certi ed recycler ensures full compliance with environmental laws, data security regulations, and workplace safety standards, reducing the risk of nes, legal issues, and reputational damage.
• Guaranteed data security: e safe destruction of IT assets and mobile phones is a concern for businesses. R2v3 certi cation guarantees that data is securely wiped or destroyed, ensuring full compliance with privacy laws and reducing liability risks.
• Sustainability and circular economy support: Ecocycle’s certi cation means that valuable materials are recovered and reused, supporting a circular economy and minimising environmental impact.
• Operational e ciency and cost savings: Best-practice waste management and maximised material recovery help businesses reduce disposal costs while maintaining high sustainability standards.
• Competitive advantage: Many corporations, government agencies, and international organisations require R2-certi ed recyclers. Businesses working with Ecocycle gain access to new markets and opportunities that demand certi ed recycling partners.
• Worker health and safety standards: R2v3 certi cation enforces strict protocols to protect workers from exposure to hazardous battery
materials, ensuring a safer workplace for all employees.
Nick says that choosing an R2v3certi ed recycler is now a necessity, not a luxury.
“Companies that take sustainability and compliance seriously want to know that their waste is being handled responsibly,” he says.
“With R2v3, we provide that assurance – guaranteed compliance, secure processing, and fully transparent recycling practices.”
While Ecocycle’s head o ce in Campbell eld is the rst site to receive R2v3 certi cation, the company has already started the process of expanding certi cation across all its Australian locations. By end 2025, all Ecocycle sites– including its new facility in New Zealand – will be certi ed, creating a nationwide and international network of R2v3accredited battery and e-waste recycling centres.
For Nick, R2v3 certi cation is just the beginning. Ecocycle remains focused on expanding its infrastructure, increasing collection networks, and investing in advanced recycling technologies to further improve e ciency, safety, and sustainability.
“We’re not just meeting industry standards – we’re setting them,” he says. “We will continue pushing the boundaries of what responsible e-waste, battery and mobile phone recycling should look like in Australia.
“ is certi cation is a commitment to doing things the right way. We take this responsibility seriously, and we will continue leading the industry towards a cleaner, safer, and more sustainable future.”
For more information, visit: www.ecocycle.com.au
Shred-X, an industry leader providing secure destruction, recycling and repurposing solutions, has launched its newest division, TeXtura, to address the growth of textile waste in Australia.
Fuelled by trending items, low prices and the ease of online shopping, fast fashion continues to gain traction around the globe, including Australia.
According to Clean Up Australia, the nation is the second highest consumer of textiles per person after the United States, with every Australian disposing of an average 23 kilograms of clothing to land ll each year.
Shred-X is actively pursuing alternative end destinations for textiles. In 2024 alone, the company collected and diverted 1.3 million kilograms of textile waste from land ll.
Re ecting on the company’s “biggest year of collections”, Ben Armstrong, Business Development Manager, says the team launched TeXtura to help ll a gap in Australian recycling.
Ben says that with a myriad of textiles to be recycled in the market, it is TeXtura’s mission to nd sustainable solutions.
“ ere is an urgent requirement for Australia to formulate a plan for recycling unwearable clothes,” he says.
“At TeXtura we regularly face challenges in nding markets for these recycled materials. We are actively working to develop downstream pathways for textile recycling by collaborating with emerging recyclers and we’re excited to see what’s ahead.”
e introduction of TeXtura is a continual evolution of Shred-X. e speciality solutions provider began in 2001 as a secure document destruction provider in response to changing privacy laws and to mitigate potential data breaches.
Shred-X has 11 certi ed facilities and operations located in all states throughout Australia.
e foundation of Shred-X continues to be sustainability with a company goal of diverting waste from land ll wherever possible.
In 2007, the company expanded its
land ll diversion solutions to include IT and data assets, media, uniforms, dated or contraband products, used co ee cups and QSR (Quick Service Restaurant) waste.
In 2024, TeXtura was launched, o ering a comprehensive and sustainable end-to-end solution for the textile industry in Australia, including collection, processing, and recycling services.
TeXtura is primarily business to business, providing customised solutions such as uniform and clothing destruction, fabric and textile recycling and repurposing, and specialised logistics.
Ben says obsolete uniforms and branded clothing should be kept out of the general waste stream to prevent unauthorised use of these materials. Shred-X’s uniform and clothing destruction solutions protect a company’s brand and keep proprietary company material out of public circulation.
“We guarantee the complete destruction of branded, used and unwearable clothing with our industrialgrade shredders,” he says.
rough its national logistics capability and network, TeXtura is the “link” between the market and the recyclers, actively working to ease operations for all parties involved.
“We assist our customers to cost-
A commitment to sustainability and to “refine not mine” is turning a problem waste into an agricultural resource.
Sometimes a product’s end use isn’t where you expected to nd it. at has proven to be the case for Wendy and Rob Howe, Founders of Flinders Agriculture based in Ipswich, Queensland.
After 13 years of extensive research, including three years of desktop studies and eld trials lasting up to ve years, they have developed 11 products and are the only company worldwide recycling bre cement by-product into a soil amendment.
What started out as an idea over a couple of beers has turned into a journey of challenges, new partnerships and has earned the couple an industry award.
“Nothing in recycling is ever standard and our story is no di erent,” Rob says.
“Everything we do on a day-today basis has been invented from scratch. We can con dently wake
up in the morning and say we have developed this market from scratch for a product that we built from scratch, from a material that nobody else wanted.”
Flinders Agriculture diverts about 50,000 tonnes of bre cement byproduct annually from land ll and transforms it into calcium silicate soil amendment.
Wendy says the products deliver proven agricultural e cacy by stimulating plant physiology to strengthen cell wall structure, root systems and improving the uptake of nutrients that would otherwise be unavailable to the plant.
She says that with the addition of locally extracted Dolomite, lime and elemental sulphur (which is a 100 per cent recovered industrial by-product), the products are the
embodiment of the company’s “re ned, not mined” ethos.
Growers across Queensland and Northern New South Wales use it to improve their soil and crop health and crop yields. Flinders Agriculture is now exploring new overseas markets – there are currently commercial trials in Argentina and Fiji where there are similar tropical climates – and new waste streams.
Wendy and Rob can see the results of their labour, but as with many “overnight” success stories, theirs was a long time in the making.
Even before one kilogram of material was received for processing, Wendy, who has a PhD in immunology and vaccine technology, spent almost three years researching the material’s potential.
“ ere are some real apex uses for bre cement by-product being developed in Europe, but the Australian economy doesn’t support it,” Rob says.
“Australia is particularly good at recovering resources, but because we don’t make anything, where those resources go is a problem.
“So, we looked at the properties and material and found that commercially we could make soil amendment stack up.”
e bre cement by-product is produced in di erent forms, and while they are all elementally the same, each form requires di erent handling and processing.
e raw material is initially separated into cured, non-cured, o cuts and pack streams. e non-cured streams have time to cure before progressing in the process. Anything
that is not bre cement by-product, is removed at this point.
It’s then shredded or preprocessed to the desired feed size and then processed through a two-stage custom-built mill designed to reduce the particle gradings and shape.
Everything from wear rates through to optimal mill design was developed from scratch speci cally to process bre cement by-product.
Sizing is then achieved with commercially available screening plant. Wendy says it takes almost twice the amount of energy per ton to deconstruct the raw material as it does to construct it in the rst place.
“Size matters, a lot,” she says. “ e particle grading used is
that will sustain nutrient release for up to ve years, whereby a small crop grower will require a di erent rate of nutrient release over a period as short as 16 weeks.”
e couple went through three di erent crushers to mill the material to the right size. Eventually, they developed their own technology, incorporating techniques from tree grinding and the quarry industry.
Flinders Calcium Silicate products range from 70 per cent re ned bre cement to 100 per cent re ned, dependent on the requirements of the end user.
ey are regularly tested against environmental benchmarks such as National Environment Protection
In 2024 the product was named Best Recycled Product by the Waste Recycling Industry Association in Queensland. It’s huge recognition for Wendy and Rob, but they’re not stopping there.
“We’ve still got so much life to this product,” Rob says.
“It’s quite exciting. We’ve spent 13 years focused on nothing more than bre cement and we can tick o our list of things to do, but now that we’re here, we can see other opportunities that are out there. We’ve got plans on how we develop the products in the future.
“Sometimes, and this is the hard part in the Australian economy, sometimes the end use isn’t where you expect to nd it.”
“Recovering and returning these valuable nutrients back to farmland is helping to enrich soils and support healthier ecosystems,” he says. “I’ve seen the product on the ground and seen the results. It is quite demonstrable. It’s exciting to see a product that you’ve made, doing something bene cial.
“By keeping food waste out of land ll, we’re also reducing methane gases that are produced when organic matter breaks down and helping conserve limited land ll space in Sydney.”
Cleanaway’s Eastern Creek facility has the capacity to process up to 220,000 tonnes of organics annually. It began processing FOGO from several Sydney metropolitan councils in October 2024 and another large western Sydney council is expected to sign on soon.
e compost hall, which houses Biomax composting technology, is complete and running as designed. e hall gives Cleanaway full control of the atmosphere, improving the composting process by reducing maturation time.
Cleanaway’s composting process includes manual screening, sizing, and will include advanced decontamination techniques such as selective automated
sorting, magnetic/non-magnetic separation and wind sifting. is method, followed by secondary screening, allows the facility to handle feedstock with higher levels of contamination but still achieve a compliant, quality compost product.
Contamination is currently about eight per cent, which, Ash says, is to be expected at the early stages of FOGO kerbside collection. Cleanaway continues to work with customers to educate on what can and can’t go in FOGO collections to ensure this rate is maintained or improved in future.
Ash is excited by the opportunity to netune the process at the facility’s new re nery. While the compost meets biosecurity and Resource Recovery Order requirements, the process is not as e cient as it could be.
“Currently, we’re reprocessing about 40 per cent of our nal product to get more out of it,” Ash says. “ e re nery will do all of that in one go.”
Cleanaway made a commitment to reinvigorate the Eastern Creek facility more than two years ago, in anticipation of growing customer demand for organics processing.
Ash says that commitment has put Cleanaway ahead of the curve now that
the New South Wales Government has implemented a statewide mandate for FOGO recycling for households by July 2030 and businesses and institutions in stages from July 2026 and allows Cleanaway to support local councils and customers as they make the transition to FOGO.
“We’re in the middle of Sydney. We’re easy to get to and we have a solution that’s up and running,” Ash says. “We have the ability to take and process FOGO now.”
He says Cleanaway can lean on its experience to help councils and businesses transition to organics collections ahead of the mandate. is makes the transition and communication with communities easier because they can introduce services progressively.
He encourages councils to tour the Eastern Creek facility to see the process rst-hand.
“ ey can come here and see trucks tipping FOGO at one end of the facility and at the other end of the process they can see a good, quality compost,” Ash says. “It really does excite people.”
For more information, visit: www.cleanaway.com.au
industrial wastes, soils, and tyres. At its Lonsdale and Wing eld facilities in South Australia, along with its Brooklyn and Hampton Park sites in Victoria, ResourceCo collects and processes C&D waste into a range of concrete aggregates, drainage aggregates, rubbles, and road base materials, as well as clean, wet and mixed ll.
In 2023 ResourceCo began the rigorous process of developing EPDs for recycled products manufactured at these facilities. EPDs are independently veri ed and registered centrally with EPD Australasia. ey document the cradle-to-gate life cycle of the end-product, and quantify the environmental impacts at each stage.
Environmental impact data can include the consumption of energy, water and renewable resources, emissions to air, water and soil, and contributions to climate change.
ResourceCo’s Environmental Development Manager, Mitchell Bacon said the aim is to build an internal dataset of ResourceCo’s products and their environmental bene ts, enabling end users to seamlessly compare recycled products with their virgin material counterparts.
“Not all recycled products in the market have had the same degree of rigour applied to them to ensure their bene ts stack up,” he says.
“EPDs aren’t just a measure of environmental impact for the enduser. Internally, they help us identify opportunities to address ine cient processes, over consumption, and energy wastage.
“If we have an ine cient process that is consuming a lot of energy or recovering resources in a sub-optimal manner, the sustainability bene ts can be signi cantly diminished. ResourceCo has led the process for EPDs because they are an important way to independently verify and demonstrate credibility within the market.”
Brad says ResourceCo is manufacturing products that are speci ed and certi ed to use in major road projects. e EPD-veri ed products have supported projects managed under road management authorities, including VicRoads and the Department of Infrastructure and Transport in South Australia.
But while the quality of the product is at least as good as its virgin material counterpart, and in some instances superior, one of the historical criticisms of recycled content products is that they don’t deliver on performance and quality bene ts. ResourceCo has developed a rigorous quality assurance program as part of its commitment to demonstrating the capabilities of recycled materials.
“Demonstrating the technical capability and performance reliability of recycled products is one thing. Going a step further and quantifying the associated environmental performance is something else entirely,” Brad says.
“Just like testing the physical properties of recycled products, it’s important to have robust processes behind sustainability data too.
“By developing EPDs, we’re validating those sustainability credentials. We need to be able to show the market, our customers, that they are not only getting a product that meets or exceeds technical performance but also has signi cant sustainability attributes too.” at validation is also helping customers who are increasingly under similar pressures to demonstrate their own sustainability e orts. at became more crucial when the Federal Government introduced Australia’s rst Environmentally Sustainable Procurement Policy on 1 July 2024.
Under the policy, businesses bidding for government construction service projects above $7.5 million must meet agreed sustainability outcomes, such as reducing or repurposing waste
and replacing quarried or single-use materials with recycled materials.
Brad says the procurement policy will propel the use of high-quality recycled content and deliver more innovation. Based on having EPDs in the market, ResourceCo is already receiving inquiries for additional and more bespoke products such as specialist blends or exible pavements.
ResourceCo is rolling out EPDs for its road construction materials and is looking to expand these assessments into other recycled products.
“EPDs are a high bar to get over, it’s not an easy hurdle to clear and not all organisations will be able to deliver. But ResourceCo believes it’s an important mechanism in ensuring there is transparency and accountability,” Brad says.
“We believe this is where the market is going and it’s helping to di erentiate the organisations that can meet those standards.”
For more information, visit: www.resourceco.com.au
Local governments are getting a financial reboot by optimising their waste management and financial processes.
One of the challenges of local government is a tight budget, mixed with an ever-increasing demand for services.
Roads, parking, planning and building approvals. Sport and recreation, waste and resource recovery. ey all demand a piece of the budget pie. en there’s rural councils juggling the metropolitan expectations of residents. So how do councils ensure there is no nancial leakage?
Waste management consultancy Resource Hub is working with councils across Australia to improve e ciency and reduce costs, whether it be optimising opening hours, repurposing sta or investing in coste ective technology.
Lacey Webb, Resource Hub Founder and Director, and former industry Chief Financial O cer, says proactive
management to avoid nancial gaps can improve decision-making and ultimately lead to better services and environmental outcomes.
“Some work we’ve been doing is really highlighting areas where money is disappearing into the ether, and it’s just from a lack of priority or a lack of focus on back-o ce functions. It’s the boring admin stu ,” says Lacey.
“Everybody does well to have a fresh set of eyes now and then, just to make sure things are ticking over. Because sometimes the closeness to a situation, of being constantly in it, means you can’t see the challenges directly under your nose.”
When councils overspend in key areas and are not capturing revenue within others, the thing that often goes by the wayside is investment in waste, education and circular economy
outcomes, says Oscar Gallagher, Resource Hub Senior Consultant.
It’s di cult to deliver recyclable opportunities such as mattress processing or improving textile recycling when there is no spare cash ow to invest in that space.
ose cash ow di culties can come down to a lack of understanding of processes and systems, a lack of resources, including sta shortages, and familiarity.
“It’s a challenge we’re seeing not only in local government, but also in commercial facilities, where you have long-term tenures and long-term positions and there’s a perception that things just work,” Oscar says.
“So, if they’re ‘just working’, we sometimes focus on putting out the res without realising that the thing isn’t actually working as e ectively anymore.
“ ere are often better quality processes and support systems available. Better tools in the market.”
Resource Hub recently undertook a business case for a Far-North Queensland council. With 12 small regional transfer stations and land lls to operate, the council’s waste management department was under resourced with no budget to hire more sta .
Lacey says not investing in sta meant that the transfer stations and land ll were non-compliant, and the council wasn’t capturing data, so it couldn’t make good decisions. It was also failing to meeting its data compliance obligations.
Resource Hub worked through an audit of current opening hours,
looked at how the council could redeploy sta , and the possibility of bringing in additional technology to meet its obligations, without adding another salary.
With some adjustments, the council is now meeting all its obligations, for a once-o $10,000 investment instead of $90,000 annually for a salary.
“Loss area number one is often identi ed by asking – how do we manage our opening hours?” says Lacey.
“How do we manage maximising small changes and small reviews of what we do with our equipment, our people, and our software systems, to make sure that we’re getting the best bang for our buck? Often, we can take a small amount of time to reinvigorate that and save a signi cant amount of money.
“It’s especially important these days for councils because ratepayers want to know where their money’s going.”
She says councils are often surprised by how much opportunity is found.
Case in point. A western New South Wales council was unclear on volumes and visit numbers at its facilities because it had no data. e team wanted support to understand what systems were available and what was t for purpose.
It was also looking at a $50,000 investment in a camera system attached to a movable trailer to suit the size of their site and stockpile locations.
Following a review by Resource Hub, instead of spending $50,000 the council is now looking to invest $8000 and mount the cameras on a plinth, moving it with a forklift that it already owned.
“ eir investment was reduced by $32,000 but with the same outcome,” Oscar says. “And the council is better utilising equipment it already has on the ground. It’s simple, easy and e ective.”
Similarly, a metro regional fringe council wanted to outsource some work entirely. e Resource Hub team is currently managing the council’s weighbridge database and acting as
a ‘call centre’ for its gatehouse team. Lacey describes it as an extra set of hands, eight hours a month, that is already delivering results. e council now has 18 months of data that’s clean and reliable, and is saving a minimum four per cent each month on waste levy returns.
“Four per cent doesn’t seem like a huge number, but when you’re paying $200,000 a month in waste levies, that’s $8000 every month back in your pocket, and the cost of our team member is less than $1100 per month,” she says.
“If you’ve got a four per cent saving every month, that might be something that could be reinvested into another program. In this council’s case, it is reinvesting in targeted training for its team.”
One of the primary functions of local government waste and resource recovery teams is managing kerbside bins. It’s also a common area of revenue loss and one that councils are increasingly addressing.
Oscar and the team have helped Wollondilly Shire Council, a large council on the south-west fringe of Greater Sydney, understand its collection services, including how much residents are being charged, how many bin services are o ered and how many collections council is paying for.
“We are seeing more and more councils where kerbside bin collection contracts have been in place for a long time, and there can be a disconnect between where premises are and where
those bins actually sit,” Oscar says. “Wollondilly has 60,000 bin services. Customers have the option of an 80-litre bin, a 120-litre bin, a 240-litre bin and a 360-litre bin in mixed waste, organics and the yellow-lidded bin. All up, there’s 12 bin types that residents can have.
“Finding the time for a waste coordinator or administrator, who has 45,000 other jobs to do, to audit these systems is near impossible or it’s just not their jam.”
Which begs the question. Why is it Resource Hub’s jam?
“Because we’re data and process geeks,” Lacey says. “All day long we look at process e ciency and good quality data for decision making and we ask the most important question: Why do we do that?
“Once you know the why, you ask the how and could it be more e ective? at’s usually where that nancial leakage occurs.
“Our company slogan is More Business, Less Waste. But a customer recently told us that we should make it Resource Up with Resource Hub. Because both are what we’re about! To help local government get away from being reactive and start to plan, make good decisions and put programs, infrastructure and systems in place to make sure they are delivering the service they’re meant to…with a helping hand from the data and process guru on the behind the scenes magic.”
For more information, visit: www.resourcehub.com.au
Sophie Hager hopes to be an enabler for Veolia to ‘GreenUp’.
The recently appointed Chief Financial Officer shares her first impressions and enthusiasm for environmental sustainability.
Anew job can be daunting. e stakes are raised when that role is a senior leadership position at one of Australia and New Zealand’s leading waste management companies, which plans to be the missing link in the nation’s ecological transformation.
But just months into her new role as Chief Financial O cer, Sophie Hager is driven to bring Veolia’s big picture to life and take stakeholders along for the ride.
As an internal auditor for Veolia in France for more than a decade, Sophie knows the importance of nancial results to fund long-term plans and projects. She also brings a
fresh perspective to the CFO role and a passion for her work.
“It’s an interesting time to be with Veolia now in Australia because we have this big challenge – our GreenUp strategy – to develop all these amazing projects that can help make a di erence for everyone in Australia,” Sophie says.
“For me, it’s fascinating. GreenUp is really a game changer, and I see every day that people are really committed to it. I’m really driven by the enthusiasm and the energy that the team is bringing.”
Veolia’s GreenUp strategy is a three-year plan aimed at accelerating ecological transformation by focusing
on decarbonising, depolluting, and regenerating resources through its waste, water, and energy services.
It aims to position Veolia as a key player in the transition towards a more sustainable future by investing in innovative solutions, expanding into areas such as hazardous waste management, and prioritising sustainable practices across its operations.
Sophie will play a key role in ensuring the company nancials back up the strategy.
“ e environmental outcomes that we want to deliver are dependent on our nancial solidity, as what enables our
“GreenUp is really a game changer, and I see every day that people are committed to it. I’m really driven by the enthusiasm and the energy that the team is bringing.”
Sophie Hager Veolia Chief Financial Officer
projects,” she says. “In order to grow our capabilities and to Green Up at scale, our investments need to be successful. We have a very clear strategy for this.”
Sophie is well placed to help deliver major projects. During her 16 years with Veolia, she has worked across all business groups including water, energy and waste and has a keen sense of the company’s purpose.
While based in France she was part of the team which, in 2024, secured a 12-year contract to manage the public drinking water service for the Greater Paris Water Authority. e contract is the largest water management contract in Europe and will deliver potable water to four million people.
It was a huge achievement, and one that left Sophie searching for bigger challenges. Seeking more international travel, a new culture, and the chance to hone her English, she began her role at Veolia Australia in January.
“I was always very passionate and enthusiastic about protecting the environment and that’s really what drew me to Veolia,” Sophie says.
“It’s a company that has a purpose, that has a meaning, especially now. Ten years ago, people were not really seeing all the implications of climate change, but now it’s really something that is on everybody’s mind and Veolia has a big role to play in combatting that.
“When I tell people I’m with Veolia, they are aware of the projects we’re invested in. It’s no longer ‘okay you work in waste collection’. People understand the meaning behind what we’re doing for ecological transformation. And I’m very proud to be working with Veolia.” ere are many challenges, but also “exciting new opportunities” that come with the role of CFO.
Coming from Europe, one of the challenges is trying to understand Australian regulation and the context. And Sophie’s motivated by Australia’s current shift away from land ll oriented waste disposal.
When talking energy-from-waste, she says Europe is well ahead, but Veolia’s global knowledge has been brought to Australia to support the country on its energy from waste journey.
She adds that Veolia also can have a big impact on treating di erent streams of pollution, such as Per- and poly uoroalkyl substances (PFAS).
“Veolia de nitely has a role to help Australia depollute, and we bring expertise to provide customers with viable waste solutions,” Sophie says.
“We have teams capable of solving almost every waste problem, and my role is to ensure those activities are appropriately invested in. e numbers are an important point of entry to solve environmentrelated problems.”
It’s not just Veolia’s environmental credentials that have drawn Sophie to the role. e company is committed to diversity and setting the benchmark to develop a skilled workforce.
In 2025 Veolia reached a 50-50 gender split in its leadership group and has several programs to support women including Women in Leadership and Women on Wheels.
e Women on Wheels program has resonated with Sophie. e program is as much about bringing a diverse balance to Veolia’s operational teams, which have traditionally been male dominated, as it is to providing women with exibility in the workforce.
e program was adopted from Veolia’s global know-how and is being rolled out across Australia, o ering skills and a pathway to the industry.
“I met some of these women, and kudos to them. ey’re extraordinary,” Sophie says. “ is program would not have existed 30 years ago and I’m extremely touched that now we can give women this opportunity.
“I’m a big advocate for diversity.”
Without an Australian licence Sophie won’t be getting behind the wheel of a Veolia truck any time soon. But she is more than happy to drive the company toward success in other ways. at means achieving nancial targets so that Veolia can continue to grow and implement its long-term plan.
Sophie is part of strategic meetings to work through any ‘blocks’ and ensuring everyone and everything is on track. She hopes she brings fresh eyes, a new perspective and energy to the role.
“I’m passionate about what I do, and about supporting my team. I try to convey that,” she says. “Day-to-day I bring good energy with my peers, my teams and the people around me. I hope I can make a di erence.”
For more information, visit: www.veolia.com.au
FORNNAX Technology has set its sights on strengthening its foothold in Indian and global markets. Construction of a large-scale manufacturing facility has set this path in motion.
FORNNAX Technology, a leading name in India’s recycling equipment manufacturing sector, reached a milestone, breaking ground (Bhoomi Pujan) on its 23-acre manufacturing site in Gujarat, India.
e new facility is poised to be among the largest in the world, with an aim to produce about 250 machinery units annually by 2030.
It’s a strategic step in the company’s bid to bolster its market share, aspiring to become a global leader in the industry.
Jignesh Kundaria, Chief Executive O cer and Director, who along with Kaushik Kundaria, Director of
FORNNAX, is the architect of the ambitious project, says the ceremony marks the beginning of an exciting new chapter for the company.
“ is facility will not only bolster our global presence but also signi cantly contribute to India’s goal of achieving Net Zero emissions by 2070 while driving economic growth,” Jignesh says.
“We are con dent that our advanced manufacturing of high-capacity and heavy-duty machinery, and commitment to quality, will meet the needs of our global clients seeking e cient recycling solutions.”
FORNNAX produces primary shredders, secondary shredders and
granulators for tyres, municipal solid waste, cables, e- waste, aluminium and many other industrial applications.
Jignesh says the new manufacturing site enables the company to extend its reach into critical markets such as Australia, Europe, and the Gulf Cooperation Council (GCC.)
FORNNAX already has a presence in Australia, operating Tyre Collection Australia Pty Ltd since 2018. In 2024, the company announced an expansion of its operations with a $3.5 million investment in a tyre recycling plant in Melbourne, Victoria.
When complete, the plant will have capacity to process 10 tonnes per hour,
and an annual capacity of 55,000 tonnes, producing 20-25-millimetre steel-free rubber chips.
Jignesh says FORNNAX is actively working to build stronger sales and service partnerships in Australia, Europe, and the GCC to ensure its innovative recycling solutions are readily accessible and supported.
“By collaborating with our dedicated partners worldwide, we aim to set new standards,” he says.
“We are committed to shaping the landscape for sustainable recycling solutions in the future. Because we’re not just selling equipment, we’re building business. at’s what we believe, that’s who we are.
“Our equipment is an evolution of advanced products designed for the challenges of the recycling world.”
Jignesh says the company’s global sales partner network makes it successful worldwide. And as FORNNAX embarks on a new journey, it remains dedicated to leading innovation and sustainability in the recycling technology industry.
A key element to the company’s success is its corporate culture, based on the company history of providing value to customers’ success worldwide. Jignesh says this motivates employees to work together, develop innovative products, and produce quality equipment.
With construction of the new facility, the production department is expected to scale up signi cantly to ensure the seamless manufacture of high-capacity and heavy-duty machinery to meet global demands for solutions for waste tyre, municipal solid waste (MSW), cables, e-waste, aluminium, ferrous metals, and more.
e research and development team collaborates with global research and industrial organisations. It will continue to spearhead cutting-edge technologies and solutions, focusing on both new product development and the enhancement of existing
o erings to meet evolving market needs. Jignesh says the design department is committed to creating e cient and user-friendly machinery that addresses diverse customer needs while the quality and control department will uphold FORNNAX’s commitment to excellence by ensuring that every product meets the highest standards.
Additionally, the after-sales service department will expand its reach to provide comprehensive support and maintenance services, ensuring the longevity and optimal performance of the equipment.
“Our mission is to create a green future by utilising ground-breaking innovation, crafting customised
recycling system solutions that provide unparalleled value to our customers, while also spreading awareness about their economic and environmental bene ts,” Jignesh says.
“With this, FORNNAX is set to push the boundaries of innovation, setting new standards in the recycling industry and paving the way for an ecofriendly future.
“ is initiative will drive economic growth with increased employment opportunities, ultimately creating a greener future for the generations to come.”
For more information, visit: www.fornnax.com
e ET-620 is a tracked trommel designed to meet the needs of recycling plants dealing in soils, compost, light construction and demolition waste, wood and bark.
e ET-620 is equipped with a quickchange drum system which allows a machine to be e ortlessly changed to a di erent feed material, eliminating the need for multiple machines and multiple waste streams onsite.
e trommel is compatible with both diesel and a fuel-e cient hydraulics systems and has been designed to comply with Australian engine standards.
“McCloskey has tailored the ET-620 to the Australian market to suit our tier three engines,” says Paul.
Also new to the Tutt Bryant inventory is the ES-250, a tracked primary shredder capable of shredding
most types of material. Paul says the ES-250 is designed to meet the needs of recycling plants where incoming materials vary greatly in terms of size, composition and di culty to shred.
“ is shredder is compatible in both diesel and electric engines and is a very robust machine compared to other shredders on the market,” he says.
With an aggressive eight and 10 knife, heavy-duty cutting table, variable speed main conveyer and four metre tracks for manoeuvrability and stability, the ES-250 is suitable for any job site, Paul says.
“Tutt Bryant Equipment is excited to have these machines in our inventory, as well as other development projects that McCloskey’s working on which will continue to ll product gaps in the market,” he says.
“ ese machines have simple design and functionality features, making them easy to use on everyday operations.
“ ey are functionally designed for the majority of applications with several di erent options for further operational exibility.”
Tutt Bryant has yards and warehouses in Brisbane, Sydney, Melbourne, Adelaide and Perth, giving customers easy accessibility to spare parts and servicing.
“We have a lot of strength in our network to look after these types of machines, in terms of warehouses and dedicated eld service technicians.”
Tutt Byrant is stocking new machinery in preparation for customer trials later in 2025.
For more information, visit: https://tuttbryant.com.au
The JCB JZ140 tracked excavator embodies power, speed, strength, efficiency and sustainability.
The demanding tasks found on waste management sites require powerful, reliable, e cient and sustainable machinery.
JCB, a global leader in construction equipment, has developed a range of machinery tailored to these tasks.
One of the most popular pieces of equipment within JCB’s waste management portfolio is the JCB JZ140 tracked excavator.
Paul Fairhurst, National Sales Manager Heavy Line Products for JCB CEA, says the JZ140 has become
its largest selling tracked excavator for waste sites because of several key features.
“It has done well because of its stability and reliability, and with proven technology we anticipate the machine will be successful well into the future,” says Paul.
With a dedicated division in the United Kingdom (UK) specialising in waste equipment, JCB knows how to tailor a machine t to handle all types of waste management, he says. e team has created a line of
machinery t for land ll, recycling and composting processes.
e JZ140 is manufactured in the UK and then speci cally tailored for operations in Australia.
At the heart of the JZ140 lies a powerful EcoMAX T4F/Stage IV engine which has been tested for 110,000 hours in 70 machines across a range of environments worldwide.
e JZ140 promises peak torque at low engine revolutions per minute (RMP), meaning the excavator can run under the most stringent environmental regulations while delivering a standout performance. is reduces emissions and requires less fuel.
JCB recently sold its 1,000,000th engine. Paul explained this is a re ection of the longevity of the unit and the bene t of in-house engine manufacturing.
“We are one of the only manufacturers that build their own engine in-house. JCB is proud to have a successful engine made under the supervision of our team,” he says.
e high-strength undercarriage of the JZ140 tracked excavator uses a fully welded X-frame construction, making it one of the heaviest in its class and, according to Paul, one of the most stable.
“Stability in the waste management environment is crucial, because the attachments tend to be quite heavy,” he says. “In every case, JCB knows the more stable the machine, the higher productivity and performance levels will be.”
JCB understands that di erent applications require di erent performance from machines. is is why the JZ140 uniquely provides two slew speeds.
“ ere are applications where operators want to focus on control and accuracy, and there are other applications where operators want to focus on speed and productivity,” says Paul.
“For this reason, the JZ140 is equipped with a standard slew speed and a second, faster slew speed.”
e standard slew speed setting can be used for pre-sorting applications where operators require and value control and accuracy above anything else.
e second speed option will be faster and preferable for operations such as loading material in and out of
a truck. Paul says this option is best suited for times when performance gains are critical.
“To have the option between speed or accuracy is very important and something operators will appreciate when considering what machine to purchase,” says Paul.
Another feature unique to JCB is its cushion control reinforcement for the machine’s boom and dipper.
Paul says the boom and dipper is made of high tensile steel and cushioned hydraulically, ensuring operators remain conformable when sorting materials.
“Most excavators have rod end cushioning, JCB di ers in this eld by providing a custom cushion control through the whole stroke,” he says.
“ e cushioned control means the machine won’t shake and jitter when slewing the arm left or right.
“ is is bene cial when working at both speed and pace as operators won’t feel the machine suddenly jolt. Drivers can operate at any pace while maintaining a smooth arm and accurate results while feeling comfortable and safe.”
JCB CEA is committed to providing the best machines. at is why operators are given the option of additional attachments should the task require.
“We are more than happy to work with a client if they have a certain requirement to suit their applications,” says Paul.
“Our branches are located in every major state, allowing us to tailor speci c builds for special orders.”
For more information, visit: www.jcbcea.com/en-au
RecycleSmart is making the collection of hard to recycle items easier with a new direct service offered to councils around the country.
To expand on its existing pick-up services, on-demand recycling business RecycleSmart is now o ering a new exible solution to better meet councils’ needs.
Currently, RecycleSmart picks up recyclable items that can’t be disposed of in residents’ kerbside bins, including soft plastics, e-waste, batteries, polystyrene, blister packs, mattresses and printers.
With hopes to reduce contamination and hazardous waste dumping, RecycleSmart will slowly roll out two new o erings – small-volume collections and less frequent “clean-up” collections. Roxane Uzureau, Business Development and Council Relationships O cer at RecycleSmart, says the customisable service supports RecycleSmart’s mission to o er a truly
convenient home collection service for hard to recycle items.
“We understand that councils have di erent price points and collection requirements, that is why we aim to provide a completely customisable experience for them when choosing frequency and the size of pickups.
“Councils have the choice of deciding how often they want to o er the pickups in the Local Government Area (LGA) and how much they want to subsidise the pricing for residents,” says Roxane.
“ is o ering allows us to have greater exibility with varying council budgets and their end goals for waste collection.”
Roxane says the service is a selfsu cient system accessible to all residents in an LGA that is o ering the service.
“ rough the RecycleSmart app, residents can order a pickup for their hard-to-recycle items. ey will get advice through the app, based on what size pickup they need and if it is subsidised. If the pickup they select is not subsidised, it will simply show up as a paid option.”
Roxane says the extra-large pickup is ideal for larger items such as bikes, computers and furniture.
“ e process is entirely hands o for the council once they choose to enter this service with us,” she says.
“ ere is very little need for administrative involvement from their end.”
Roxane says RecycleSmart aims to eliminate illegal dumping by providing
the service directly to residents’ doors.
“Currently, to recycle bulky items some residents must drive to charity shops or recycling centres and try their luck at handing it over. If their items aren’t accepted there, residents are then required to store it at home and wait for a hard rubbish kerbside pickup,” she says.
“We get feedback from people who have tried to drop items o but have been turned away, this shows there isn’t great communication about what’s accepted and where.
“If it becomes inconvenient to recycle, people are going to resort to dumping their stu .”
Roxane says the service will not only bene t councils but also residents, such as the elderly, physically impaired, new parents and shift workers, who can’t transport items to a recycling centre or access nine-to- ve services.
“We want to bring the service of the recycling centre to people’s homes,” she says.
Pickup options vary depending on location and population density which, Roxane says, means each council can bene t from the service.
“Some council areas consist of people living in high-rise buildings where
they don’t have as much storage space as those living in housing with large garages,” she says.
“But for regional and remote council areas, where people do have the space to store large items, it doesn’t necessarily mean they are able to dispose of items easily. ere might not be a recycling centre around, they might not be mobile, they might have a small car.
ere are many reasons why this service can help everyone.”
For those who are unsure about what can and can’t be recycled, Roxane encourages the use of the recycling encyclopedia in the RecycleSmart app.
e ‘Recyclopedia’ is an itemised index outlining how to recycle and dispose of a multitude of items. Each participating council has its own tailored version.
“It tells people which bin to use speci c to their residential address,” Roxane says.
“If an item can’t be thrown out in a bin, the app will direct them to a nearby
recycling centre. And not only does it tell you where to take the item, it will give a description of what happens once it is recycled, how it’s done and what is recovered.”
Roxane says it is crucial for people to know why it is important to recycle and how it works.
“We do this to increase transparency on the recycling process, education is important across the board,” she says.
“We have an important role to play with how councils educate their residents, and promoting the Recyclopedia is the rst step.” e new service is currently available to all councils in metropolitan areas that have an existing contract with RecycleSmart.
Roxane says the gradual rollout will allow RecycleSmart to gauge interest in the service and what works best for di erent areas.
For more information, visit: www.recyclesmart.com
A New South Wales-based company is helping regional and remote communities address environmental issues by taking waste solutions to the source.
Tyranny of distance has often been cited as an obstacle for recycling and waste recovery across Australia.
Vast distances between towns and recycling facilities, high transportation costs and a lack of infrastructure can make resource recovery economically unviable.
But Jamie Walmsley is a man on a mission to bring solutions to even the most remote areas.
During the past eight years, the Owner Operator of JLW Operations, based out of Cootamundra in New South Wales, has clocked up thousands of kilometres, travelling to mine sites
and land lls in regional Australia, delivering an onsite shredding service.
In that time, he’s taken on o -theroad mining tyres, green waste, pallets and mattresses. ey’re all challenging materials that, when combined with the harsh climate of remote Australia, can take a toll on equipment. But Jamie has an ace up his sleeve – the Tana Shark.
Described as the most versatile waste shredder on the market, the Tana Shark operates as a pre-shredder, primary shredder and screen in one machine.
“Mine site tyres are big and they’re just so hard to deal with. ey’re di cult to load and transport, costing
valuable time and money,” Jamie says. “ e Tana Shark chews through them and pulls the metal out as you go.
“It’s a machine that can handle anything I throw at it.
“A lot of equipment that comes from Europe hasn’t got the cooling system that you need in Australia. I’ve run the Tana in 40-degree temperatures and never had one give up on me.”
Jamie has seen the Tana Shark process 8000 tonnes of land ll waste at Port Hedland, the second largest town in the Pilbara region of Western Australia, and in 2020 he spent three months at the Santos-operated Moomba gas eld site
“Having a mobile shredder is ideal for customers because they don’t have to invest in machinery, but they know they can reduce their waste when they need it.”
Jamie Walmsley Owner Operator of JLW Operations
in South Australia shredding pallets, large plastic drums and tyres.
e shredding campaign aimed to help extend the cell life of the Moomba land ll and reduce recyclable volumes in preparation for transport.
Shredding the size of waste increases the volume of material that can be transported on one truck, reducing transport costs and carbon footprint by decreasing the number of trucks on the roads.
e Tana Shark gives operators full control over the particle size, from 50 to 500 millimetres. ere are 12 preprogrammed operating programs for di erent types of material and purposes of shredding. Extra customer-speci c programs can also be added.
e programs adjust the machine functions to optimal level for achieving the wanted output. For instance, overcharge pressure limits, rotor revs per minute and conveyor speed can be adjusted.
At Moomba, the Tana Shark recovered 38 tonnes of steel from waste tyres, resulting in a 75 per cent reduction in transport costs for the remaining processed rubber.
Redundant pond liners were another troublesome waste stream at the site due to their size and composition. Shredding them reduced the total volume of the liners by about 80-90 per cent, making transporting and handling
more e cient. Removing them from the land ll also increased the remaining cell life expectancy by about 40 per cent.
Overall, the Tana Shark processed about 80,000 cubic metres of general waste and 2000 tonnes of recyclables at Moomba.
“Having a mobile shredder is ideal for customers because they don’t have to invest in machinery, but they know they can reduce their waste when they need it,” Jamie says. “So, we just travel all over the place.
“When I started, there wasn’t much in the way of tyre recycling, especially out in Western Australia and remote areas. We have shredded a lot over the years, but certainly in the past few years the importance of recovering resources and not just burying tyres on site has grown.
“It’s taken a while but we’re having an impact.”
With weeks spent on the road, it’s important that vital equipment is up to the task. Jamie has put his faith in the Tana Shark and distributor GCM Enviro since the beginning.
Over 10 years, he and GCM Enviro have built a relationship based on trust, exibility, a strong work ethic and a shared vision to sustainably manage Australia’s waste.
As a leading distributor of the latest in waste management and recycling equipment, GCM Enviro maintains constant dialogue between manufacturers and clients to ensure that design is governed by market requirements.
From shredders to land ll compactors, screeners and compost turners, more than 3000 machines sold Australia-wide have earned a reputation for their robust design and reliability.
In February 2025, Jamie’s eighth Tana Shark was loaded onto a trailer bound for Wollongong, Port Kembla and Forbes, New South Wales.
“I’ve been dealing with GCM Enviro and the Tana Shark for 10 years, and I can’t fault them,” Jamie says.
“It’s old school service and backup.”
For more information, visit: www.gcmenviro.com
CJD Equipment recently celebrated its golden jubilee, marking a major milestone in its journey.
In 2024, CJD Equipment proudly celebrated 50 years as a leading player in Australia’s heavy equipment industry.
With a steadfast commitment to innovation and exceptional service, the company continues to empower businesses with a diverse range of products.
Founded in 1974 by visionaries Ron Ra erty and Rob Jowett, CJD has transformed from a modest family business into one of Australia’s leading heavy equipment suppliers.
Its journey began in Guildford, Western Australia, with a passionate team of just 28 sta members.
Ron and Rob, who initially connected as part of the sales team at Chamberlain Industries, recognised a unique opportunity to serve as the Western Australia dealer for Chamberlain John Deere construction equipment.
With a customer- rst mindset and an emphasis on sta development, they laid the groundwork for what has become a remarkable national success story.
roughout its storied 50-year journey, CJD Equipment has celebrated numerous milestones highlighting
its signi cant impact on the heavy equipment sector. e company’s growth trajectory is re ected in its impressive nancial performance.
CJD’s transport o ering started gathering momentum in 1984 when it was appointed the Kenworth Truck Dealer for Western Australia.
In 1992 CJD partnered with Volvo Construction Equipment and a few years later, in 1999, opened branches in Melbourne, Brisbane, Launceston, Bunbury and Mackay. CJD Equipment became the national distributor for Volvo Construction Equipment in 2001.
Alan Barnett’s arrival in 2001 marked a signi cant turning point for CJD Equipment.
Initially joining in a commercial and marketing capacity, Alan quickly progressed through the ranks, eventually becoming Managing Director and a key gure in the company’s ownership structure.
His leadership has been instrumental in steering CJD through a rapid national expansion, particularly following the company’s appointment
as the national distributor for Volvo Construction Equipment.
Innovation has always been at the heart of CJD Equipment’s strategy. e company’s dedication to sustainability is exempli ed by the recent launch of Volvo’s zero-emission construction equipment, showcasing its commitment to environmentally friendly practices.
Alan says CJD continues to grow.
“We are a growing business, we will always want to be a growing business, and at our core, we are a sales business,” he says.
CJD Equipment’s success is built on strong relationships with customers and suppliers. Many of these partnerships have endured time, including a 32-year collaboration with Volvo Construction Equipment and a 40-year relationship with PACCAR Australia (Kenworth and DAF). e company’s ethos is encapsulated in its mantra: “Big enough to trust, small enough to care.” is philosophy has allowed CJD Equipment to maintain a personal touch, even as it has grown over the past ve decades.
As CJD Equipment moves forward, it remains steadfast in its commitment to delivering exceptional products, customer experiences, and support.
With a rich history, strong partnerships, and a focus on innovation, CJD Equipment is poised to continue shaping Australia’s heavy equipment landscape for future generations.
For more information, visit: www.cjd.com.au
A recent visit to LiuGong’s Global Research and Development Centre in southern China by the company’s Australian distributor has further reinforced the manufacturer’s market lead for the introduction of a wide range of electrically powered equipment Down Under.
LiuGong was one of the rst equipment manufacturers to identify the potential of battery electric vehicle (BEV) technology and has since launched more than 90 products, o ering solutions for almost every application and segment, including mining machinery, industrial and port equipment, agricultural machinery and various other products.
ere are 11 product lines, including loaders, excavators, mining trucks, aerial work platforms, industrial vehicles and agricultural equipment.
A wheel loader was the rst electric machine to be released in LiuGong’s striking green livery and there are now more than 6000 of the loaders operating globally through Asia-Paci c, Europe,
North America and Latin America. And they already have helped to save hundreds of thousands of tonnes of greenhouse gas emissions.
LiuGong’s Global Research and Development Centre is located in Liuzhou, situated within the Guangxi region in southern China. Some of the top brass from Australian distributor, McIntosh Distribution, were taken aback when they visited the site recently.
“ e sheer scale of the facilities is highly impressive and the level of automation and speed in which equipment is manufactured due to the automated assembly lines feeding from the sides, above and below is world class,” says Digby Moullin, General
Manager with McIntosh Distribution. He says the technical processes and systems operating at the facility are amazing.
“LiuGong’s research and development work is quite incredible. ey run every test imaginable, from acoustics through to dirt, dust and water ingress, plus stress testing of steel items, thermally stressing components and assessing electrical circuit durability.”
Digby said LiuGong was well placed to have a signi cant impact across numerous Australian industries with its electric equipment lineup.
“LiuGong has been at the forefront of battery electric machines for over 15 years and has amassed more than 11 million hours on BEV products around the world.
“It now has a very broad range of equipment, including dump trucks, graders, loaders, excavators and rollers, and we have seen rst-hand that LiuGong has an extensive product development road map to further complement its existing range.”
He says the potential for LiuGong’s wide range of commercially available equipment in Australia is enormous, with several key factors set to drive its adoption.
“ e upfront capital cost of the machines is invariably lower than most competitor’s equivalent diesel options; the
fact they are electric means they are more responsive; the absence of any engine noise and diesel fumes makes them ideal for indoor and night-time applications; and the operational costs are signi cantly cheaper than diesel machines.”
LiuGong’s rst electric wheel loader in 2018 delivered energy savings of about 20 per cent thanks to the optimised electric drive, hydraulic and transmission systems. Variable hydraulic and energy recovery systems added a further 15-20 per cent energy boost.
“ e operational cost savings are signi cant,” Digby says.
“Based on a 20-tonne operating weight loader being used for 2000 hours per annum (pa), the savings are upward of $50,000pa.”
He says organisations seeking to decarbonise had typically been some of the early users of LiuGong’s electric
machines in Australia, however the favourable economic and operational bene ts are now increasing the adoption of the BEV technology across a range of industries.
“BEV machines create a fraction of the carbon dioxide emissions from diesel machines, but the cost savings also are now becoming just as attractive,” Digby says.
“ e transition to electric machines in Australia is progressing and once industry realises the full range of equipment now commercially available and its signi cant bene ts, the speed of the transition will increase exponentially.”
For more information, visit: www.mcintoshandson.com.au
The benefits of Calcium Silicates include:
• The enhancement of soil fertility and structure
• Improved plant resistance to disease and pests
• Increased micro and macro nutrient uptake by plants
• Boosting a plants natural ability to tolerate abiotic stresses such as frost, drought and salinity.
Calcium silicates are also a beneficial soil amendment for use in soil rehabilitation and revegetation projects. They present an economical and viable substitute for Gypsum and Lime to condition and improve the soil.
To continue its legacy in scrap metal recycling, Manhari Recycling has acquired a new material handler from Liebherr.
As one of the biggest exporters of steel and aluminium in Victoria, with established markets for
Victoria to provide local business and councils an opportunity to recycle metal waste.
Spanning decades, Liebherr material handlers have become one of the masters in the metal processing, scrap handling industry because of their robustness and reliability.
Whether the task is sorting, collecting or loading of mixed scrap metals to the feeding of shredders, shears and presses, Liebherr material handlers like the LH 40 M ensure the job is done quickly and e ciently.
Maddy Gupta, Founder and Chief Executive O cer of Manhari Recycling, said the LH 40 M will improve further e ciency of material handling within Manhari facilities.
“In a few months Manhari has used the LH 40 M, the team has reported easy operating and great sustainability on site, in comparison to other machines in the market,” says Maddy. e handling of scrap steel and other metals can be one of the toughest applications in industrial material handling because of heavy loads, sharp edges and bulky or long materials.
Liebherr meets this challenge by designing specialised machines that combine durability with performance and e ciency. By producing many components in-house, Liebherr ensures its machines are built to withstand tough tasks while remaining powerful and economical, with every part carefully developed to meet operational demands.
THE MACHINE OF THE HOUR
Liebherr material handlers, including the LH 40 M, have been developed for the highest productivity.
e optimum interplay between the hydraulics and electronics guarantees powerful, fast movements during handling, while having the precision for di cult sorting tasks.
Safety features include cab guards and laminated safety smash resistant glass, developed to withstand tough scrap handling operations.
e cab has been designed to give operators the necessary space to make the best possible use of the machine’s capability. It features a comfortable driver’s seat, intuitive touchscreen colour display, and central lubrication systems.
Large glass panels, cab elevations and rear and side area monitoring allow the operator to have an optimal view of the working area and around the machine at all times.
Maddy says safety for sta and machine is important.
“ e safety features of the LH 40 M are in line with our best practice around safety and something we appreciated when searching for a new machine,” he says.
“ e material handler o ers the necessary safety and innovative technologies that optimise our work in scrap handling.”
e high-performance LH 40 M is considered a top performer in its class.
Liebherr material handlers come equipped with a patented energy recovery (ERC) system, designed to reduce fuel consumption while increasing the machine’s handling capacity. is enables faster and more powerful work cycles.
e LH 40 M is equipped with Liebherr-Power E ciency (LPE), a system that helps reduce fuel consumption and greenhouse gas emissions. is enables e cient machine operation in the area of the lowest
“The safety features of the LH 40 M are in line with our best practice around safety and something we appreciated when searching for a new machine.”
Maddy Gupta Founder and Chief Executive Officer of Manhari Recycling
speci c fuel use. Combined with the Liebherr energy recuperation system, a standard feature on the LH 40 range and above, fuel consumption is reduced to a minimum.
e LH 40 M has an operating weight of 36,400 to 38,700 kilograms and a reach of 16 metres, making the material handler suitable for a range of applications.
A variety of machine attachments are available and are optimally matched to an operator’s application.
Maddy says the customisable attachment provides ample opportunity for operational exibility and improved e ciency with easy and e cient changeover.
“Liebherr equipment is always reliable, and its technical support is always available to assist with not only service but also training,” he says.
For more information, visit: www.liebherr.com.au
Perennial favourites, landscape architect Costa Georgiadis and TV producer Cate McQuillen, will also return, bringing their vibrant perspectives to rethinking communication for deeper community engagement. Further presenters will be announced in the lead-up to the event.
Four interactive expert panel discussions will focus on accelerating progress towards 2030 resource recovery targets, leveraging textile waste, e ective product stewardship, and mitigating the risk of battery-related res. e conference is also o ering a diverse program of interactive workshops, covering issues such as local government waste procurement, optimising waste levy exemptions, illegal dumping investigation, composting and more.
“ e social aspects of the conference are a central and much-loved part of the event, with ample networking opportunities and highly anticipated social events,” omas says. “Attendees look forward to this once-yearly opportunity to connect in person with their peers from across the full spectrum of the industry, at all levels, to share
ideas and experiences and build community. Coming together as an industry to learn, connect, collaborate and lead change is vital in shaping a sustainable future – for the Australian waste sector and the planet.”
For more information, and to register, visit: www.co swasteconference.com.au
The team behind ReGen – Australia’s Circular Resource Expo, is taking steps across its events to minimise environment impact.
Large events can generate signi cant waste and consume large amounts of energy – something not consistent with an event that is aimed at propelling Australia’s resource recovery and circularity.
Which is why the team behind ReGen – Australia’s Circular Resource Expo, is walking the talk.
“Sustainability is at the core of everything we do,” says Ali Lawes, ReGen Event Director.
“We recognise that as an industry, we have a responsibility to reduce our environmental impact and drive meaningful change.
“ at’s why we are taking action through a range of initiatives that promote resource e ciency, waste reduction, and responsible business practices.”
ReGen is the reimagination of the Australasian Waste and Recycling Expo (AWRE) which has been a
premier business trade event for the waste, recycling and resource recovery sectors for 15 years.
e rebrand re ects the expo’s expanded scope and emphasis on the circular economy.
is year’s expo, at ICC Sydney from July 23-24, will encompass all aspects of the circular economy, including circular product design, reuse, repurposing, remanufacturing, and repair ideas and solutions across a wide range of industries.
It will also welcome an array of innovative exhibitors, experts, and emerging professionals committed to reducing waste and promoting resource e ciency.
New for 2025, the Sustainable Exhibitor Awards will celebrate exhibitors who are leading the way in reducing their environmental footprint, from using recycled materials and energy-e cient lighting to minimising waste and adopting carbon-conscious practices.
Ali says the awards are a chance for exhibitors to lead by example and showcase sustainable practices to industry leaders, potential clients and the wider community.
“We aim to inspire and recognise those making a tangible impact,” she says.
e inaugural awards will include Most Sustainable Space, Most Sustainable Stand Package and Overall Outstanding Commitment to Circular Initiatives.
Winners will receive a trophy, crafted from recycled materials
by Defy Design, at the industry networking drinks on day one of the expo.
Understanding that little steps can go a long way and every change can make a di erence, ReGen is using lanyards made from recycled bottles and food packaging, and will recycle the lanyards at the completion of the event; registration badges are printed on recycled materials; and attendees are encouraged to bring reusable drinking bottles that can be re lled at water lling stations.
Separate waste bins will encourage visitors to use appropriate bins for waste disposal, where possible food has been sourced using local food producers and all food waste and co ee grounds will be composted.
ReGen’s commitment to sustainability extends beyond the show oor through partnerships with industry leaders in sustainability. e global convention and exhibition industry is among the largest producers of waste in terms
of industry size, second only to the construction industry.
In recognition of this, ICC Sydney has developed a waste reduction program for all exhibitions and events it hosts, including a 75 per cent waste diversion from land ll and zero captured organic waste to land ll.
Since the strategy was introduced, 567 tonnes of exhibition waste material have been diverted from land ll.
“ICC Sydney has a range of new sustainability initiatives and is working with all Diversi ed events to ensure everything is reused, recycled, and repurposed,” Ali says.
“But most importantly they are partnering with ReGen 2025 to ensure the use of everything at the event has a life cycle.”
Other industry partners include Harry the Hirer, a sustainable contractor partner, providing hire solutions that prioritise reuse and circularity, the CN Agency will measure and reduce the expo’s environmental impact, while
reusable cup partner Huskee Cups will help reduce single-use waste.
ReGen is also collaborating with environmental services Global GreenTag and GECA (Good Environmental Choice Australia) to highlight exhibitors whose products meet high sustainability standards.
“From encouraging digital signage and reusable materials to composting food waste and investing in green energy, every decision we make is guided by our goal of creating a more sustainable future,” Ali says.
“By working together – exhibitors, visitors, and partners – we are not only shaping the future of events but also contributing to a broader movement towards a circular economy.
“At ReGen, sustainability isn’t an ambition, it’s a commitment in action.”
ReGen will be held at ICC Sydney 23-24 July.
For more information, visit: www.regenexpo.com.au
Peterson D-series grinders offer industry-leading features and innovations that allow operators to produce quality product at the lowest cost per ton.
A powerful upturn three-stage grinding process provides better fracturing of material and a consistent product.
The 5710D horizontal grinder is a tracked horizontal grinder designed for high-volume producers with demanding end-product specification. Grinders are specifically designed for recycling waste and green wood material.
Powered by Caterpillar C27 Tier II or IV 772kW engine, or optional C32 838kW engine, the 5710D provides the highest power to weight ratio of any Peterson grinder. At 43,091 kilograms, the 5710D is designed for operations requiring high production and frequent moves between jobs.
A feed opening of 152 centimetres x 102 centimetres, combined with Peterson’s high lift feed roll, means it can readily produce a wide range of material.
The Terex Ecotec TDS820 Slow Speed Shredder processes more types of material than any other machine in its class including green waste, root balls, recycled timbers, tyres, mattresses, kerbside pick-up, black bag waste and anything else, while giving superior fuel efficiency.
This is due to the machine being a twin shaft independent drive which means operatorss can set the shaft rotation, speed and how long each shaft turns in any direction. This feature allows operators to either campaign shred or change settings on the go without stopping production.
The Scania 440HP engine ensures that 100,000Nm of torque is delivered to each shaft and a smart hydraulic system ensures that enough power is delivered to the shafts, even in the most demanding applications, while still delivering excellent fuel economy.
The shafts are two metres long with nine rows of cutting teeth. Each tooth has a cleaning tooth on the other side of the hammer, allowing shredding to occur when each shaft is reversing.
The Peterson horizontal grinders are more productive because less energy is required to reduce waste. The difference in profitability at the end of the year can be dramatic with lower fuel consumption, and higher yield.
Contact - Komatsu Forest Pty Ltd P +61 2 9647 3600 E info.au@komatsuforest.com
hopper extensions, reversable fan, chamber camera and monitor and operational remote control.
One of the most lauded features of the TDS820 is its design. Engineers have made sure that daily checks are simple and easy while the internal layout has been carefully planned.
The Ecotec TDS820 features include extended product conveyor, overband magnet, auto greaser, tipping feeder,
Finlay has both new and demonstration machines in stock available for sale or hire.
Producing circular aggregates
With our state-of-the-art technology, we prevent the negative impacts of extracting virgin raw materials by recovering metals from IBA and producing a secondary aggregate for civil construction work in Australia.
We close the loop on the Energy-from-Waste sector and accelerate the circular economy in Australia, assuring proper use of aggregates
With election 2025 looming, Suzanne Toumbourou, Australian Council of Recycling Chief Executive Officer, says a new government must do better.
Anyone working in the recycling industry knows the sector delivers enormous bene ts to Australia, contributing almost $19 billion of economic activity, and supporting 95,000 jobs.
It also plays a vital environmental role by driving resource e ciency, cutting carbon emissions, reducing land ll, and driving innovation in sustainable manufacturing and technology.
e Australian Council of Recycling (ACOR) is the peak industry body for the resource recovery, recycling, and remanufacturing sector in Australia. It represents enterprise across the recycling value chain, including Container Deposit Scheme (CDS) operations, kerbside recycling, recovered metal, glass, plastic, paper, organic, tyre, textile, oil and e-waste
reprocessing, and construction and demolition recovery.
With the imminent election, now is the time for robust federal policies that boost productivity, enhance Australia’s sovereign capability in resource recovery and remanufacturing, and maximise the impact of recycling infrastructure investments. Here are our asks for our national leaders:
for Australian recycled material: Australia imports more nished goods than we export, and much of this material ends up in our recycling streams.
Recovered glass, tyres and plastic must be processed into new products here in Australia. One catch? Domestic markets
for these goods are often limited. For example, it is cheaper to import virgin plastic than buy locally sourced recycled material.
Without robust and enduring markets for the materials we produce, recycling is not viable.
e solution? Governments can show the way forward by prioritising procurement of Australian recycling content.
Victoria’s ecologiQ program does this at state level by driving purchase of locally produced recycled material in government projects. A national version of this initiative would make a signi cant di erence.
Clear traceability of materials would also help to ensure no one could pass o materials with uncertain origins as legitimate recycled content.
We also need to streamline export licensing for our recycled products, making it simpler for Australian recyclers to access both domestic and international markets for their products.
A key priority for Australia’s circular economy is a uni ed, national approach to packaging. e current system of state-based schemes and regulations is ine cient and costly for both businesses and consumers.
e Australian Government must accelerate the implementation of national packaging regulations,
focusing on design standards that support recyclability and ensuring Australian recycled materials are prioritised.
is should include setting mandatory minimum recycled content thresholds and ensuring traceability to verify recycling claims.
In addition, a mandatory extended producer responsibility scheme with eco-modulated fees is needed to hold producers accountable for the full life cycle of their products, supporting both recycling and the circular economy.
Urgent action to address the hazard of batteries and consumer electronics:
Everyone in the sector knows the huge issues that batteries are causing to recycling. In just the past year, there were more than 10,000 battery-related re incidents across the waste and recycling system.
e costs are staggering, including over $60 million to replace a major materials recovery facility, and soaring
insurance premiums. But the biggest concern is the risk to our workers, who face the daily threat of these combustible and hazardous products.
e only solution is to make all producers of consumer electronics, including loose batteries, responsible for the entire life cycle of their products.
Government also needs to ensure a comprehensively accessible system of safe disposal options for all consumers, with strong incentives to do the right thing.
Community education is also essential. Many people simply don’t understand which products contain batteries, or the risks batteries pose to recycling systems and our workers.
ACOR has the perfect vehicle for this: the Recycle Mate app, which directs consumers to the correct place to dispose of all their household waste appropriately.
Product stewardship that ensures genuine recycling: Product stewardship, where producers take responsibility for their products
through their entire life cycle, is a crucial part of reducing waste and strengthening the circular economy.
But the Recycling and Waste Reduction Act 2020 has failed Australia’s recycling sector. Despite its intentions, the Act has fallen short by failing to incentivise genuine recycling outcomes and it doesn’t support demand for domestically produced recycled materials.
We need the Australian Government to strengthen governance and set clear metrics to measure the impact of product stewardship schemes. A ‘trigger framework’ should be established to de ne when a scheme should be initiated or expanded, improving e ciency, reducing duplication, and fostering market con dence.
e patchwork of rules across our states and territories is hindering Australia’s e orts to build the circular economy – in turn risking the potential economic and job creation bene ts it can bring.
We urgently need a nationally harmonised resource recovery framework to boost our circular economy productivity.
An independently governed Australian Recyclers Accreditation Program would also help ensure credibility, accountability and quality within the recycling sector.
If the Australian Government urgently acts on these asks, our recycling sector – and the economic, environmental, and social outcomes it delivers – can be supported and nurtured, for the good of us all.
ACOR’s detailed Federal Election platform can be viewed online.
For more information, visit: www.acor.org.au