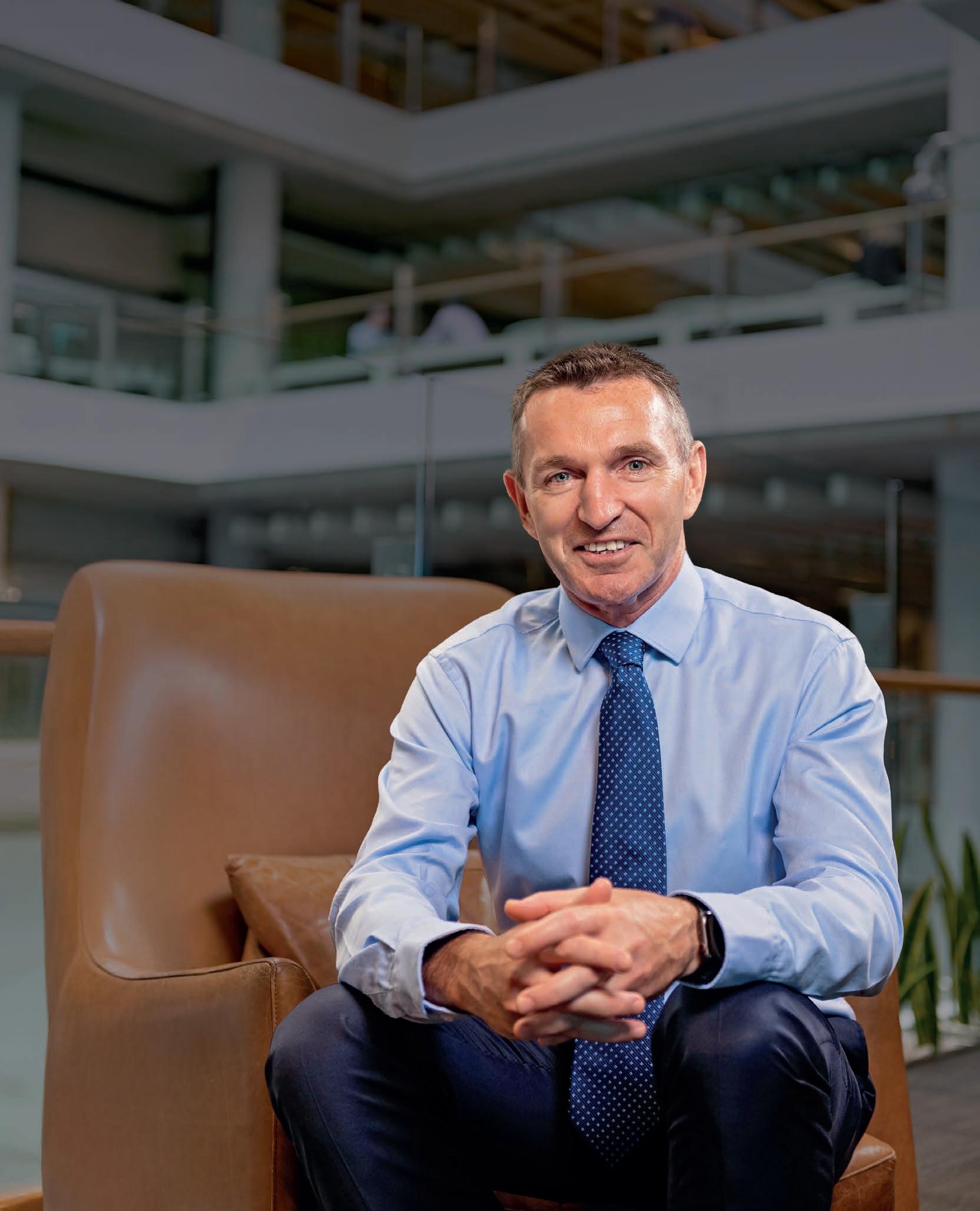
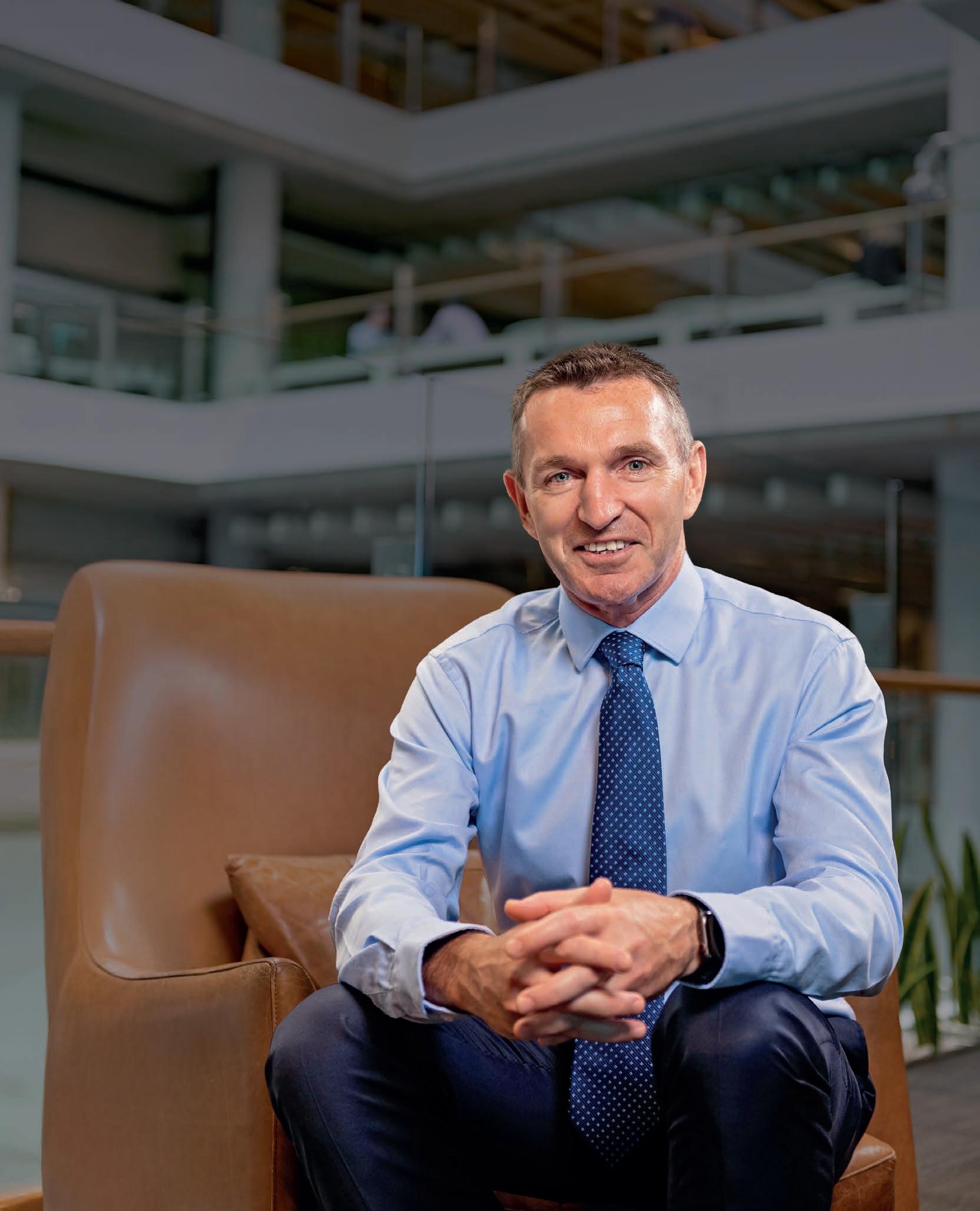
Enhance fleet management through innovation and sustainability
As a global leader in IoT and connected transportation, Geotab processes and analyses data from over 4 million connected vehicles, generating over 75 billion data points per day. It’s a huge amount of data, and it is most powerful when we have the right tools to securely and efficiently manage it. That’s why we have partnered with Google to leverage Google Cloud’s data analytics and machine learning solutions.
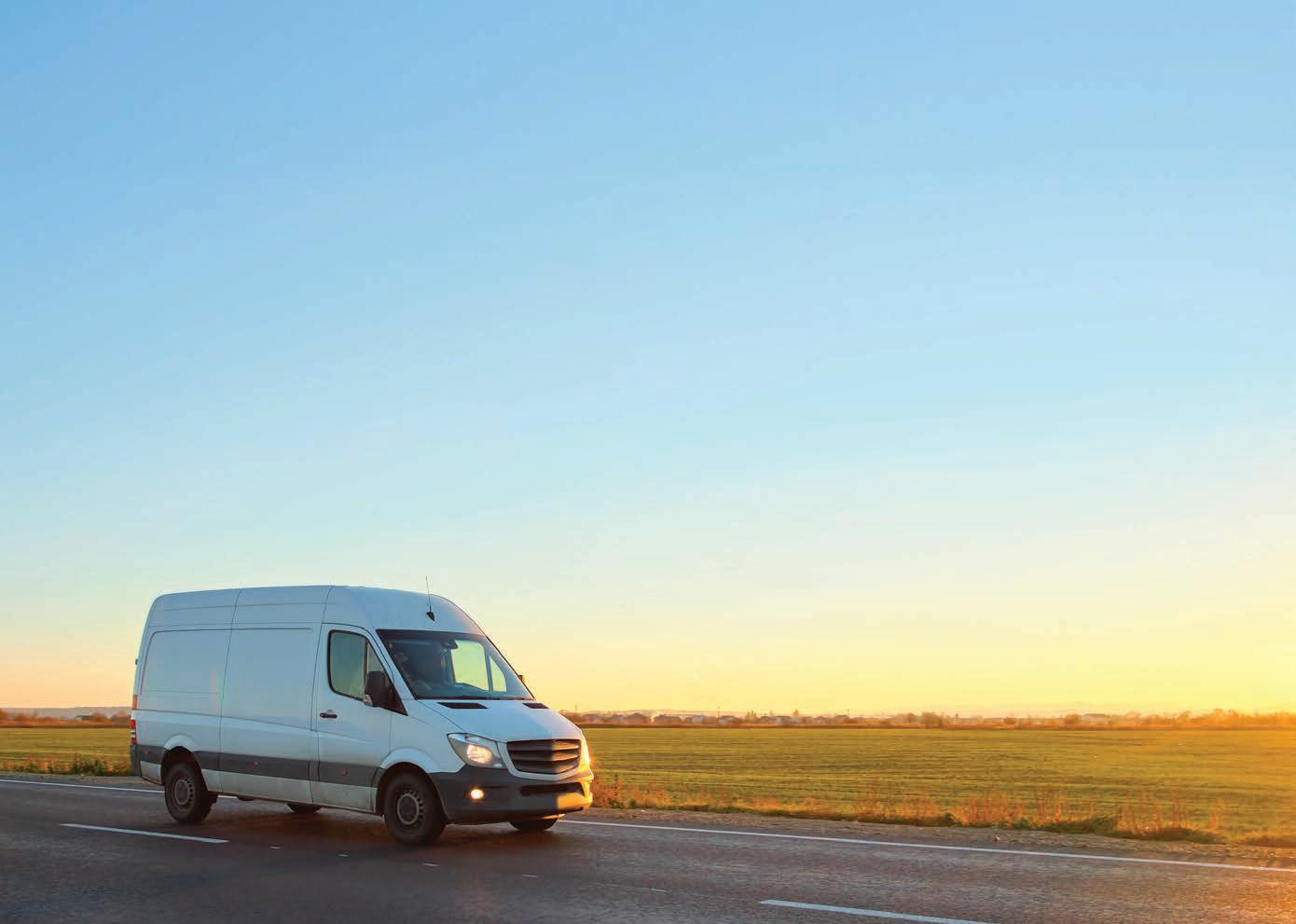
Championing Innovation and Sustainability
Geotab has been awarded two Google Cloud Customer Awards for its achievements in the transportation sector. Recognition in both the Cross Industry and Sustainability categories underscore Geotab’s successful use of Google Cloud’s analytics to innovate and drive sustainable practices in fleet management.
Kirsten Kliphouse, the President of Google Cloud Americas says that the Awards are an opportunity to recognise the most innovative, technically advanced, and transformative cloud deployments across industries globally built on their platform.
In her congratulatory message to Geotab, she acknowledged Geotab’s role in “serving as an innovator for the industry”, which also highlights Geotab’s innovative integration of data to revolutionise the transportation sector, leading to transformative impacts across organisations and customers around the world.

Empowering sustainable transportation
As the world’s premier EV telematics provider, Geotab has demonstrated its commitment to reducing emissions through its Electric Vehicle Self-Assessment (EVSA) tool, which won Google Cloud’s Award for Sustainability.
The tool provides tailored EV recommendations to support businesses and governments in transitioning to electrified fleets. For two consecutive years, Geotab was also identified as a Cross-Industry winner impactful transformation facilitated by Google Cloud. The award also acknowledges the launch of the Intelligent Transportation Systems (ITS) and its flagship transportation analytics platform Altitude.
Altitude has been pivotal in supporting government agencies by offering actionable, privacyconscious data insights for city planning and transportation network enhancements.
Strong synergy of Geotab and Google Cloud show great potential
As a valued partner in the Google Cloud Ready - Sustainability validation program, Geotab plays a crucial role in accelerating sustainability programs and informing strategic decisions for future developments.
Geotab’s collaboration with Google Cloud delivers significant benefits, including real-time improvements in driver safety and behavior, advancement of sustainability goals, enhanced productivity and significant cost savings.
This partnership not only redefines fleet management standards but also illustrates the impactful role of technology in fostering a more sustainable and efficient transportation industry.
An industry-leading solution
Geotab’s partnership with Google demonstrates the company is at the forefront of leveraging data analytics and machine learning to enhance fleet management, drive sustainability and create safer transportation systems worldwide.
By integrating Google Cloud’s advanced analytics with its telematics expertise, Geotab is confident of continuing its lead in the development of sustainable transportation solutions, demonstrating the profound impact that innovative technology can have on the transportation system today.
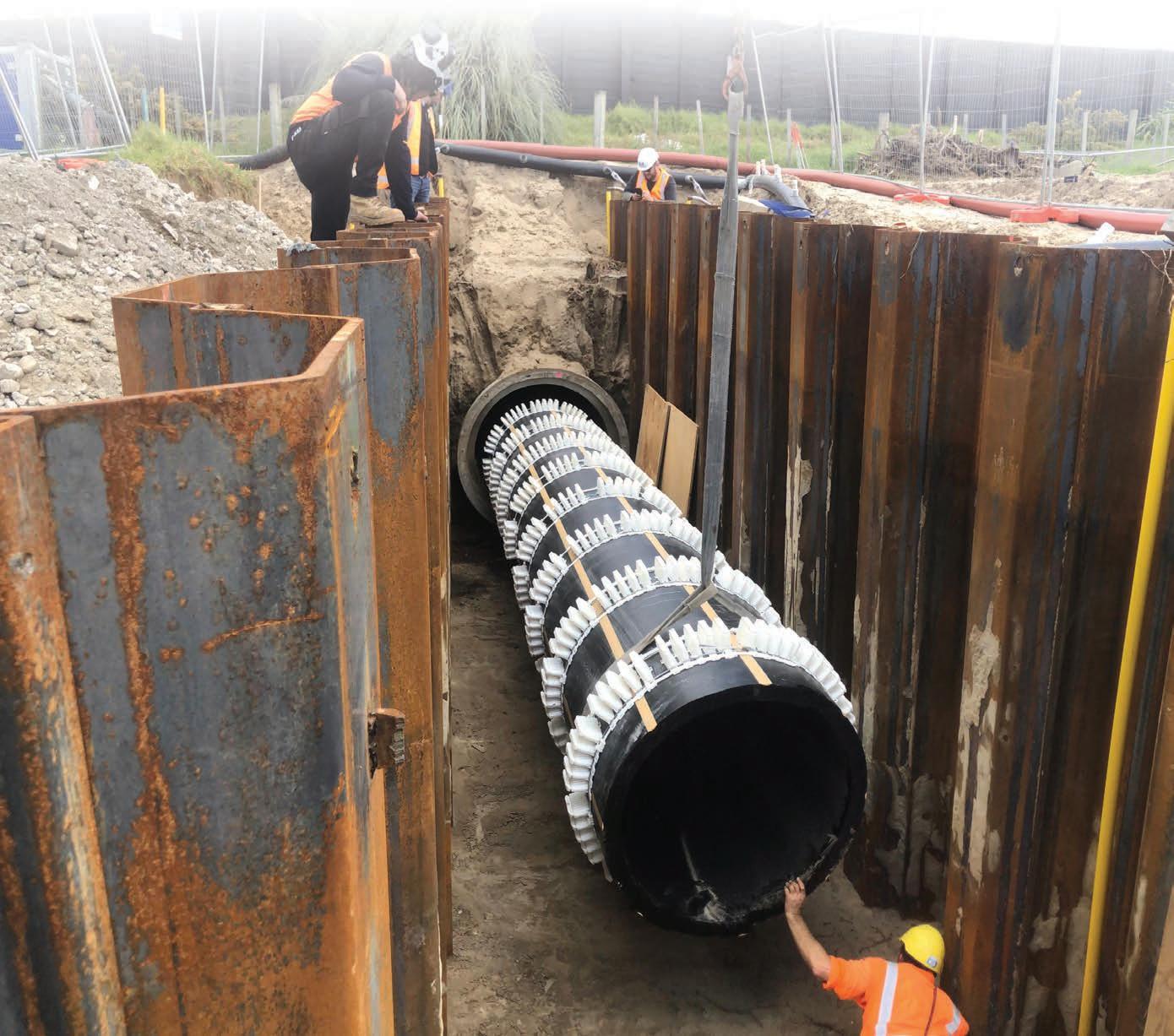
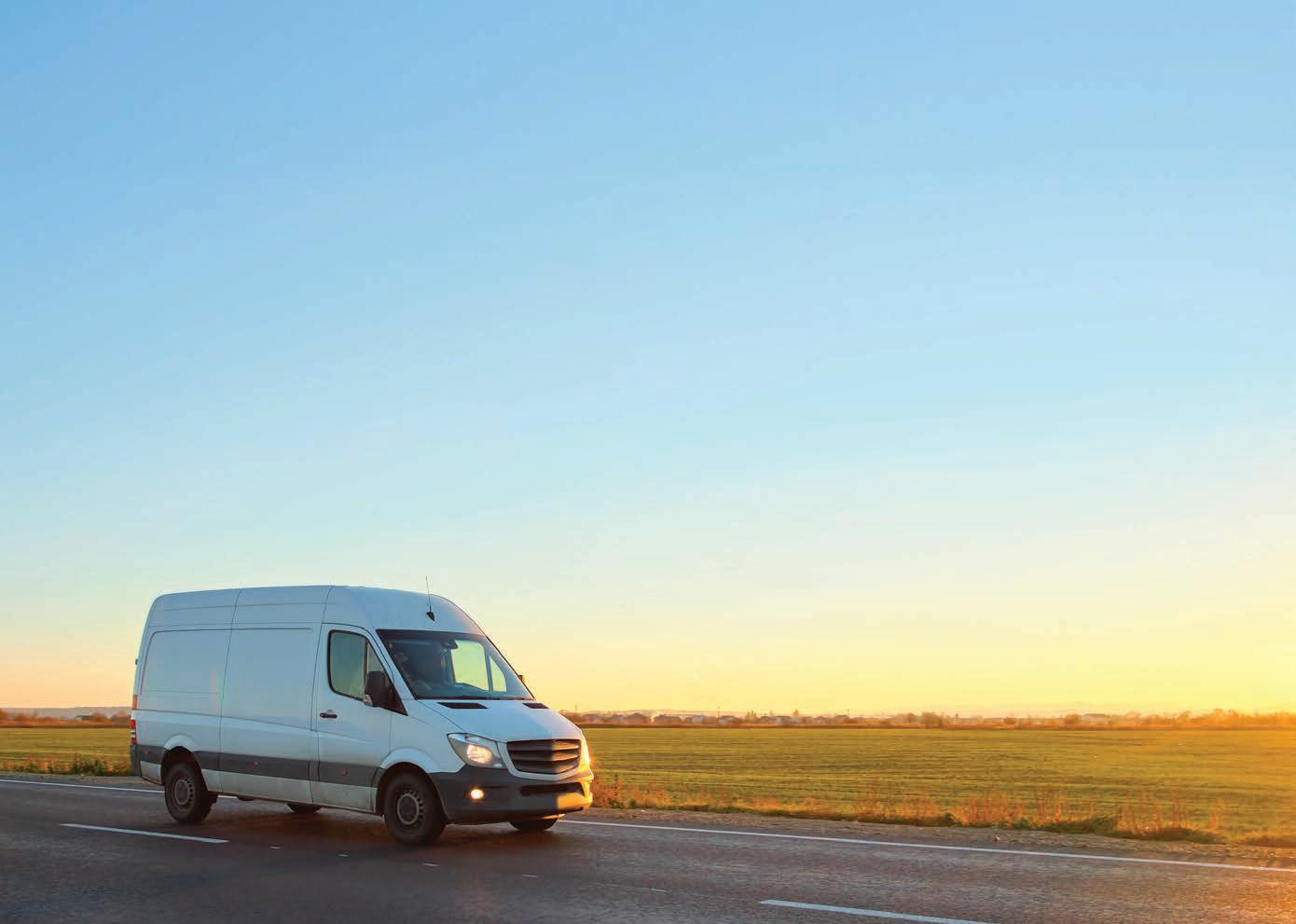
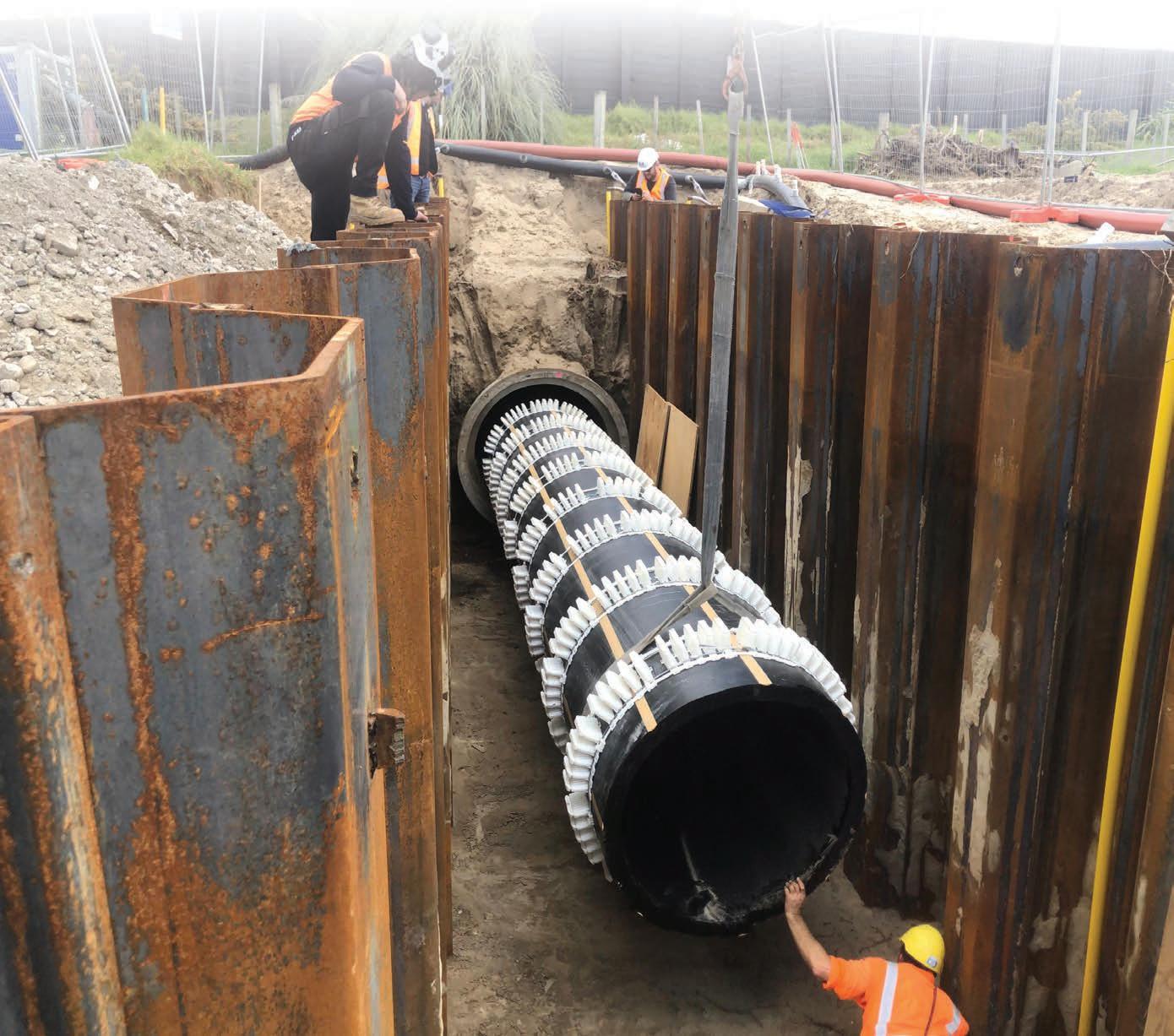
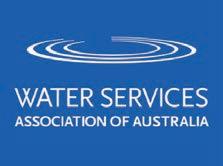
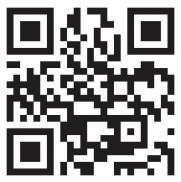
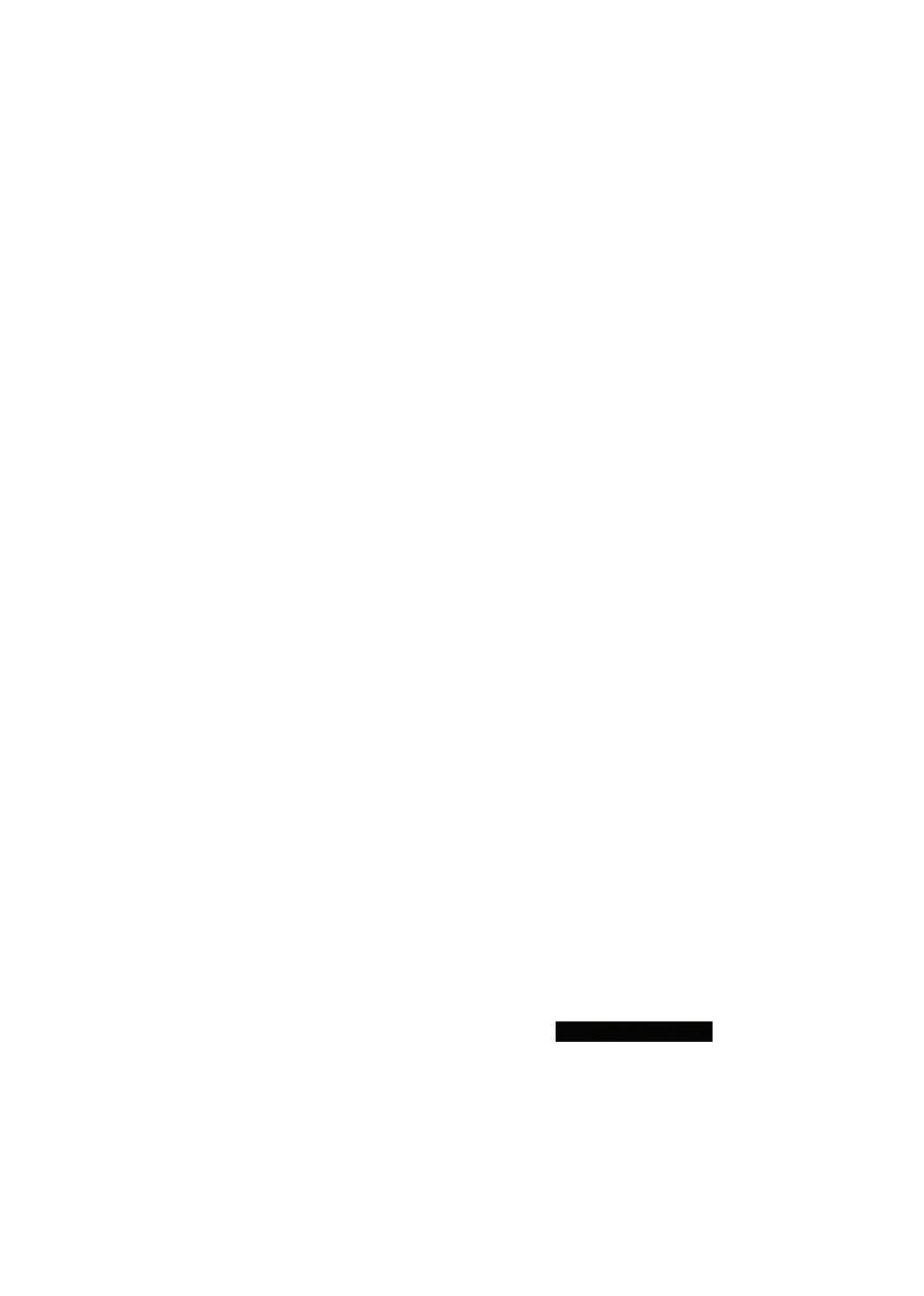

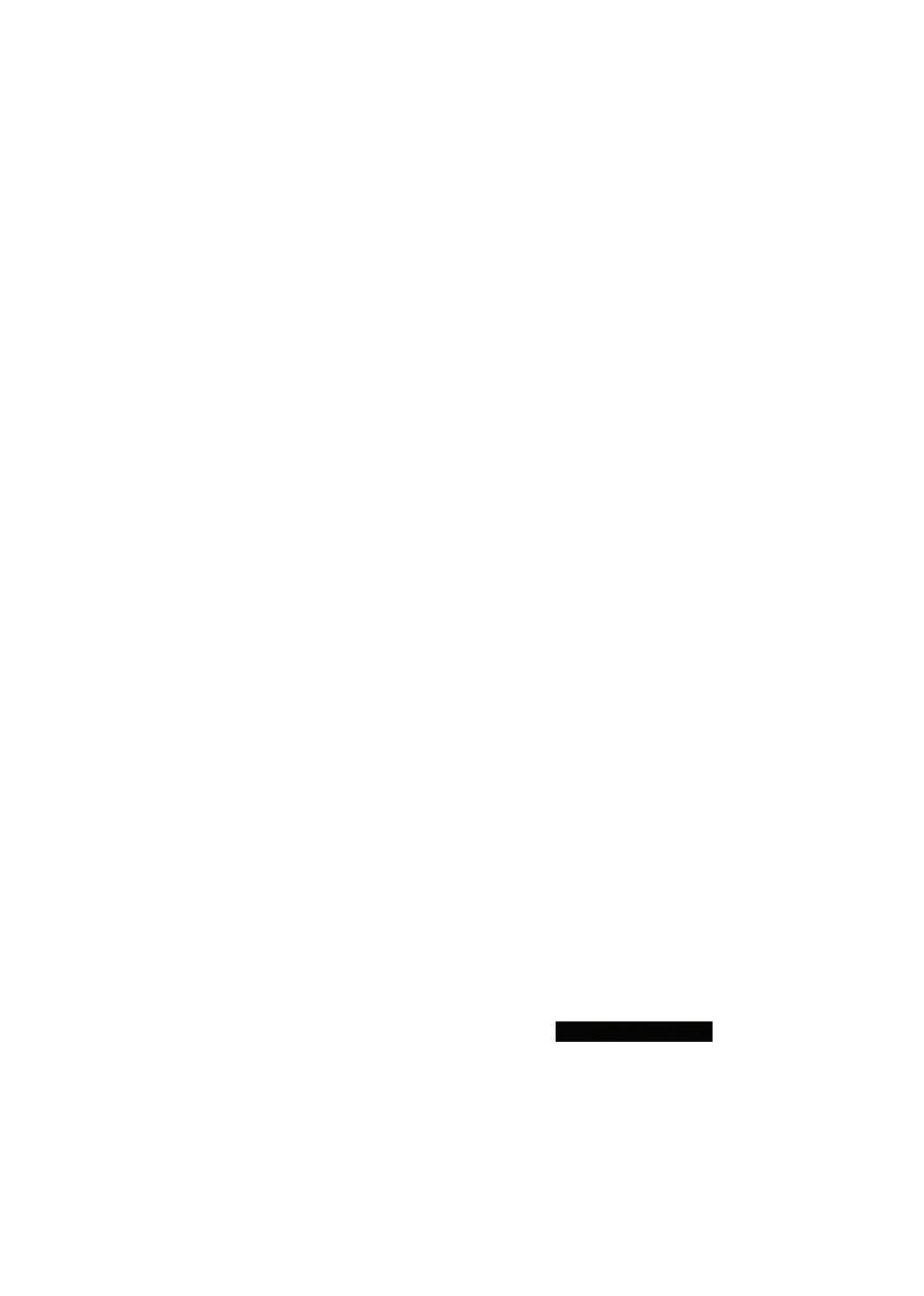
An era of evolution
Autumn is in full swing and it’s hard to believe we’re almost halfway through 2025. This year’s February issue claimed the title of our largest ever, however, that fame was short-lived because this May 2025 edition of Utility has broken just about every record.
We crammed as many insights into this issue as we possibly could, and in these pages you’ll hear from some of the incredible leaders who are shaping not just the future of Australia’s essential services, but the country as a whole.
We also sought out a plethora of subject matter experts, and collated their expert advice on some of the industry’s biggest challenges.
But most importantly, this May edition is celebrating the dedication and hard work that our utilities put in to keep the country running – and every industry in Australia wouldn’t get very far without the important work you do.
While we knew extreme weather events were becoming a more frequent occurrence, nothing could have prepared Queensland for back-to-back disaster. Just as Ergon Energy’s crews had recovered from major flooding, Cyclone Alfred reared its disastrous head. But the utility rose to the challenge, and in this issue, we follow along its incredible journey of recovery.
Over in Victoria, AusNet is gearing up to future-proof its network and safeguard against extreme weather events with a proposed $3.5 billion investment. But what really makes this proposal so groundbreaking is that it’s actively being shaped by customers.
We sat down with AusNet General Manager Strategy and Regulation (Distribution), Charlotte Eddy, who took us on a deep dive into the utility’s extensive engagement program.
The energy sector isn’t the only one preparing for the future, and in this edition we caught up with SA Water’s Chief Executive, David Ryan, who took as through the incredible work the utility is doing to support growth and housing, as well as deliver a secure water future for South Australia – we also got a sneak peek at some of the exciting things SA Water will be sharing at OzWater25.
‘An era of unprecedented growth’ has become a bit of a catch phrase, but it really is a time of change for the sector – and as the industry grows, Utility needs to evolve alongside it. Our new logo offers a more modern look to reflect the sector’s ongoing focus on innovation, while paying homage to our roots. As always, it’s such a privilege to share the incredible work that utilities from all sectors are doing to build a secure and sustainable future and we’re excited to see what this next chapter holds.
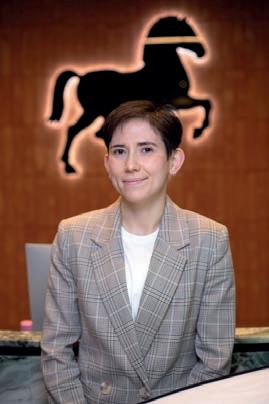
EDITOR
Katie Livingston
ASSISTANT EDITOR
Sarah MacNamara
MANAGING EDITOR
Molly Hancock
PUBLISHER
Sarah Baker
COO
Christine Clancy
CEO
John Murphy
KATIE LIVINGSTON, EDITOR
Drop Katie a line at katherine.livingston@primecreative.com.au or feel free to call on 03 9690 8766 to let us know what you think.
Don’t forget to follow Utility on social media – find us on LinkedIn, X and YouTube.
ART DIRECTOR/DESIGN Daz Woolley Alejandro Molano
NATIONAL MEDIA EXECUTIVE Rima Munafo rima.munafo@primecreative.com.au 0413 475 078
MARKETING MANAGER Radhika Sud
MARKETING ASSOCIATE Bella Predika
DIGITAL MARKETING ASSISTANT Louisa Stocks
Scan to subscribe to Utility’s weekly newsletter –delivered to your inbox every Thursday morning.
ISSN: 2203-2797
So much more than quality electrical and automation products
The NHP Services and Solutions team of highly skilled and qualified service technicians across Australia and New Zealand can help your organisation with:
Preventative maintenance
Commissioning and start-up
Modernisation: retrofits and upgrades
Site assessments and reliability evaluations
A host of training options
Repairs in accordance with the manufacturers’ recommendations
For more information, please go to nhp.com.au/services
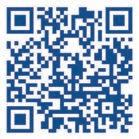
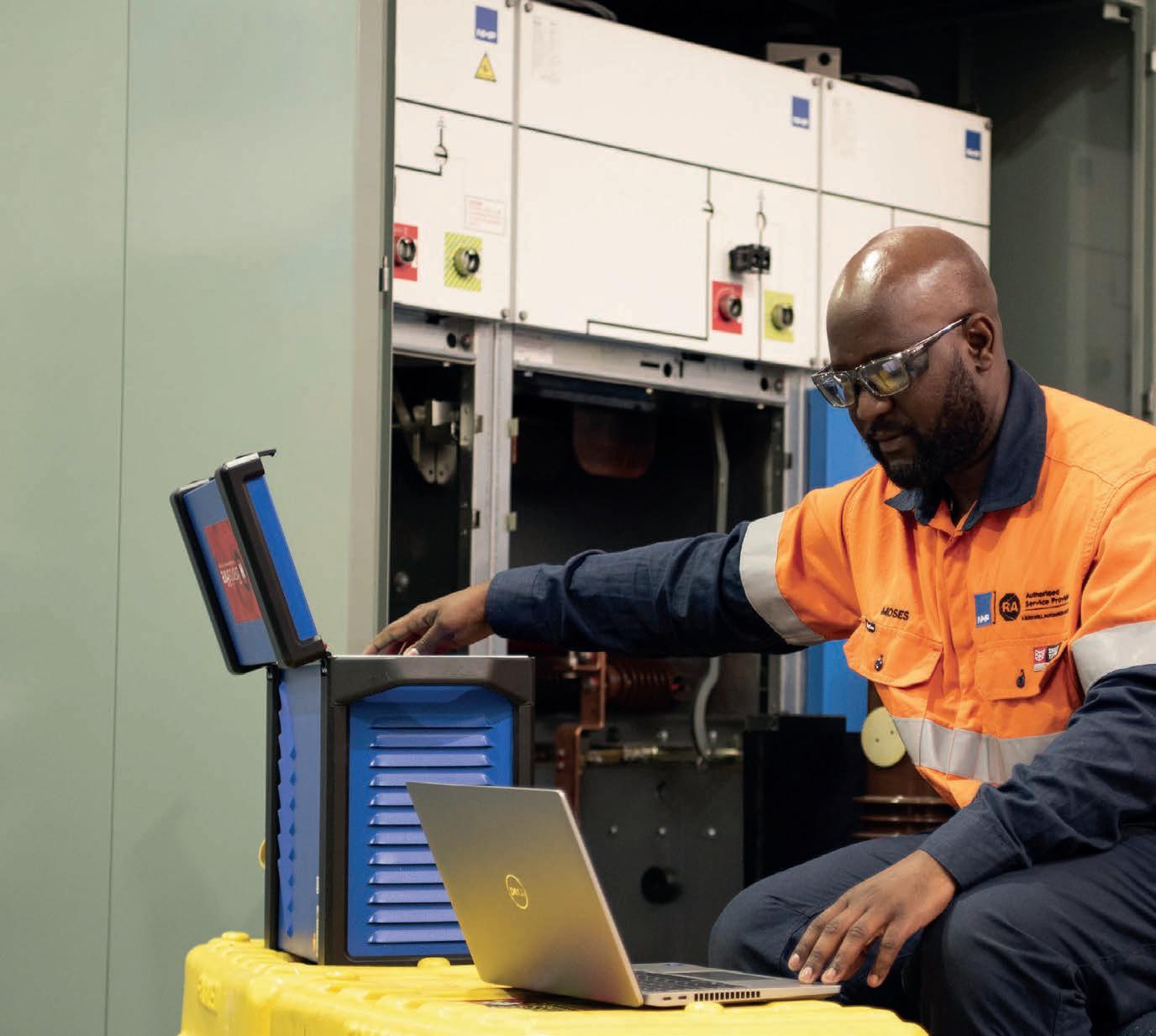
Australia nhp.com.au
1300 647 647 nhpservice@nhp.com.au
Services Enquiry
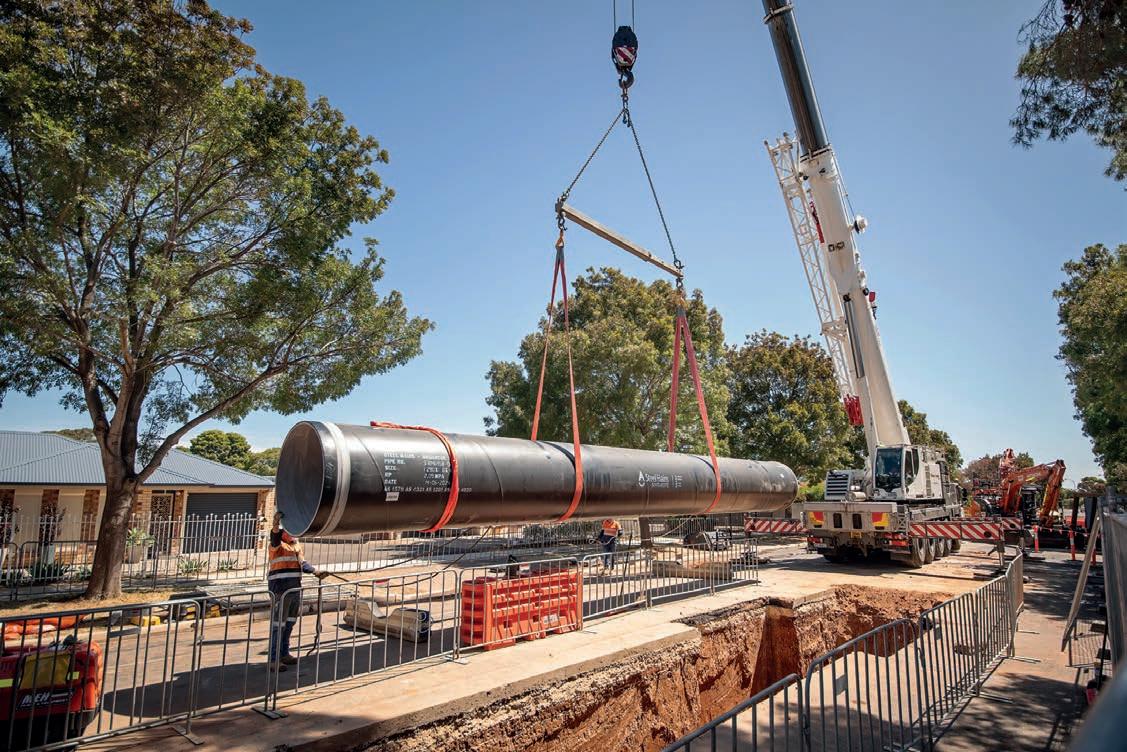
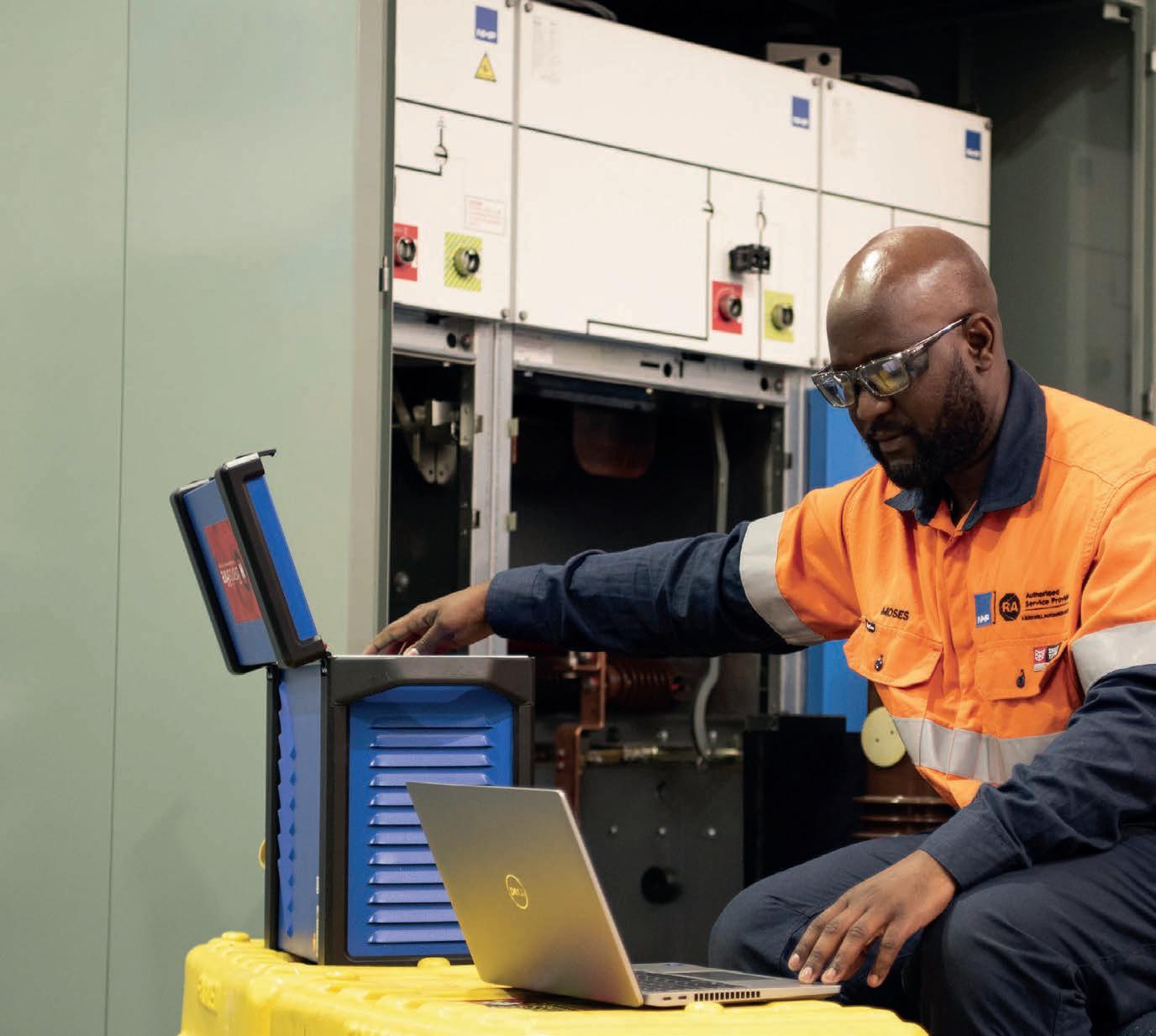
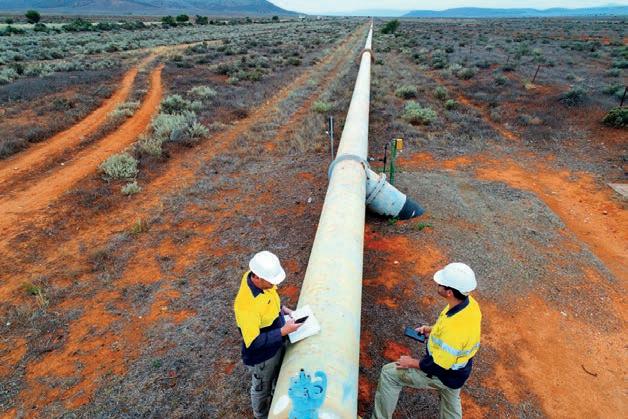
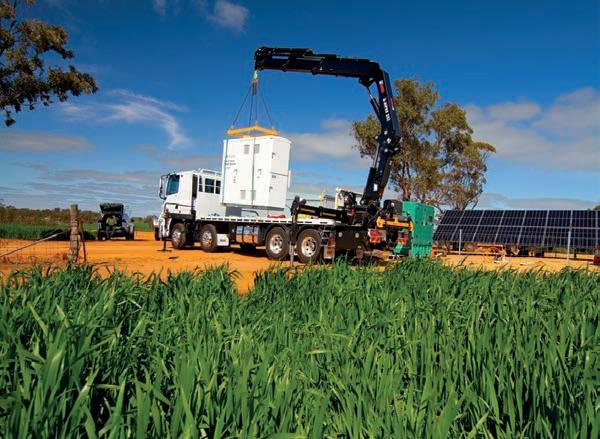
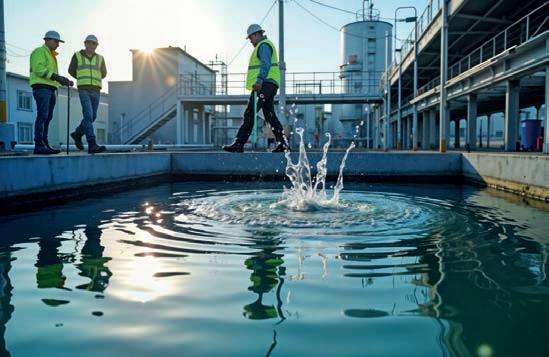
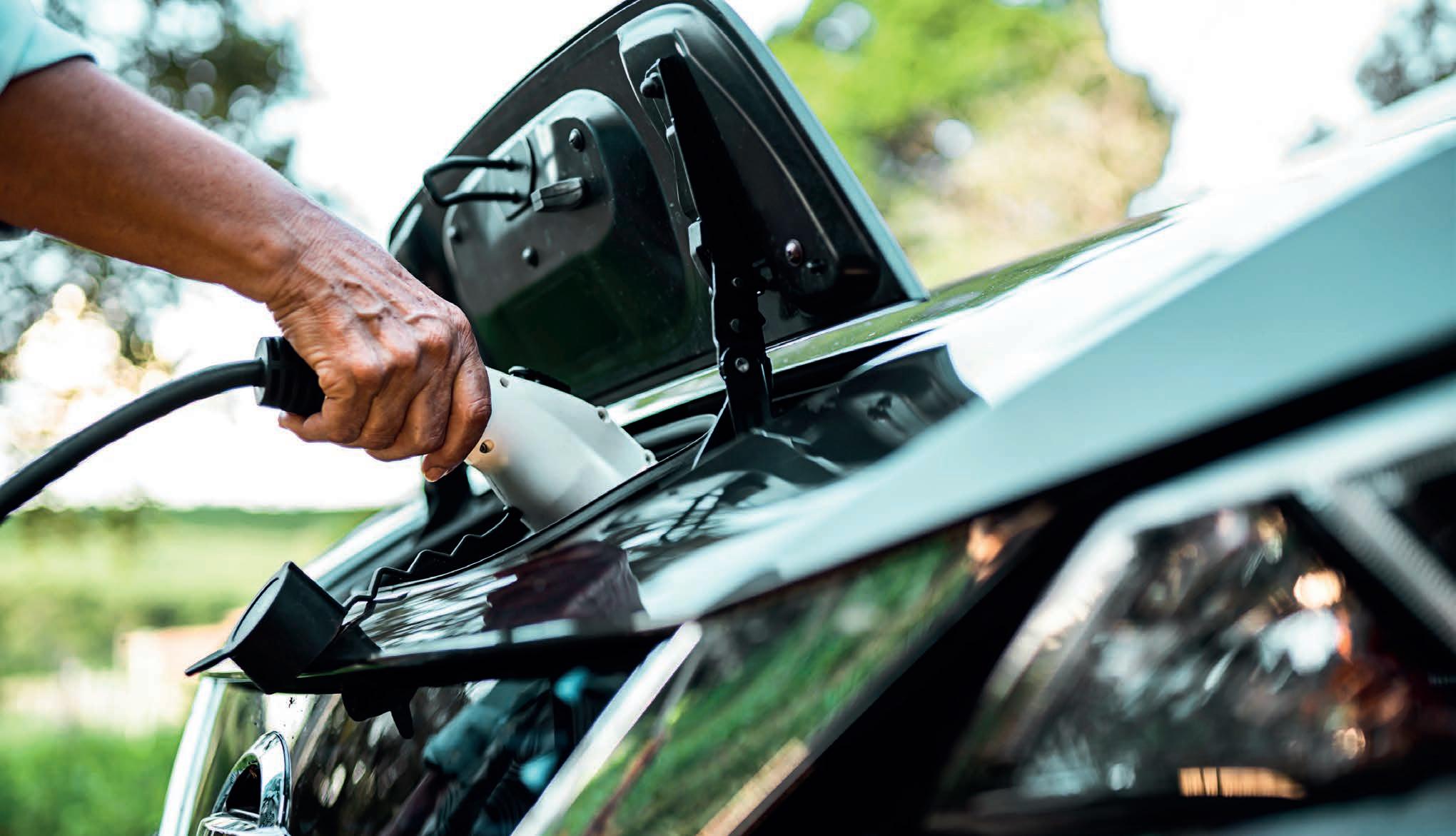
Powering the EV transition
Insufficient public charging infrastructure is hindering Australia’s uptake of electric vehicles, but an answer lies with the humble powerpole.
By Dom van den Berg Energy Networks Australia CEO
The global shift to electric vehicles (EV) is undeniable. Yet, Australia’s progress is hampered by inadequate public charging infrastructure.
However, an elegant solution exists; using our existing powerpoles as a means to rapidly deploy charging stations. This move not only boosts convenience and grid stability but also accelerates our journey towards a lower emissions future. We have modelled it; it’s doable, it can happen now, and it doesn’t take competition out of the market.
Electric car sales jumped 35 per cent globally in 2023, with almost 14 million new EVs registered. They now account for nearly one-in-five cars sold – a quantum leap in the past five years. Car makers are retooling production lines in response to consumer demands. As technology and markets mature, the price of buying and driving an EV is coming down, and consumer interest rising.
But Australia has been immune to the trend, with a slower take-up and reports that drivers are reverting to hybrid vehicles, with inadequate public charging a key barrier. Research also suggests the lack of charging infrastructure means that almost half of current Australian EV drivers are considering switching back to internal combustion engine vehicles. Given that range anxiety is a legitimate issue for drivers, policymakers must turn their minds to smart solutions that give drivers confidence to purchase and make it easier for them to use EVs, with the benefit of saving them real money.
Facing the facts
Let’s start with the environmental imperative. Passenger and light commercial vehicles account for more than half of the transport sector’s emissions. They add 55Mt of carbon dioxide equivalent – more than ten per cent of the emissions reduction task we face to hit net zero. Put simply, unless we turbocharge the nation’s embrace of EV, Australia will struggle to meet its emission reduction targets.
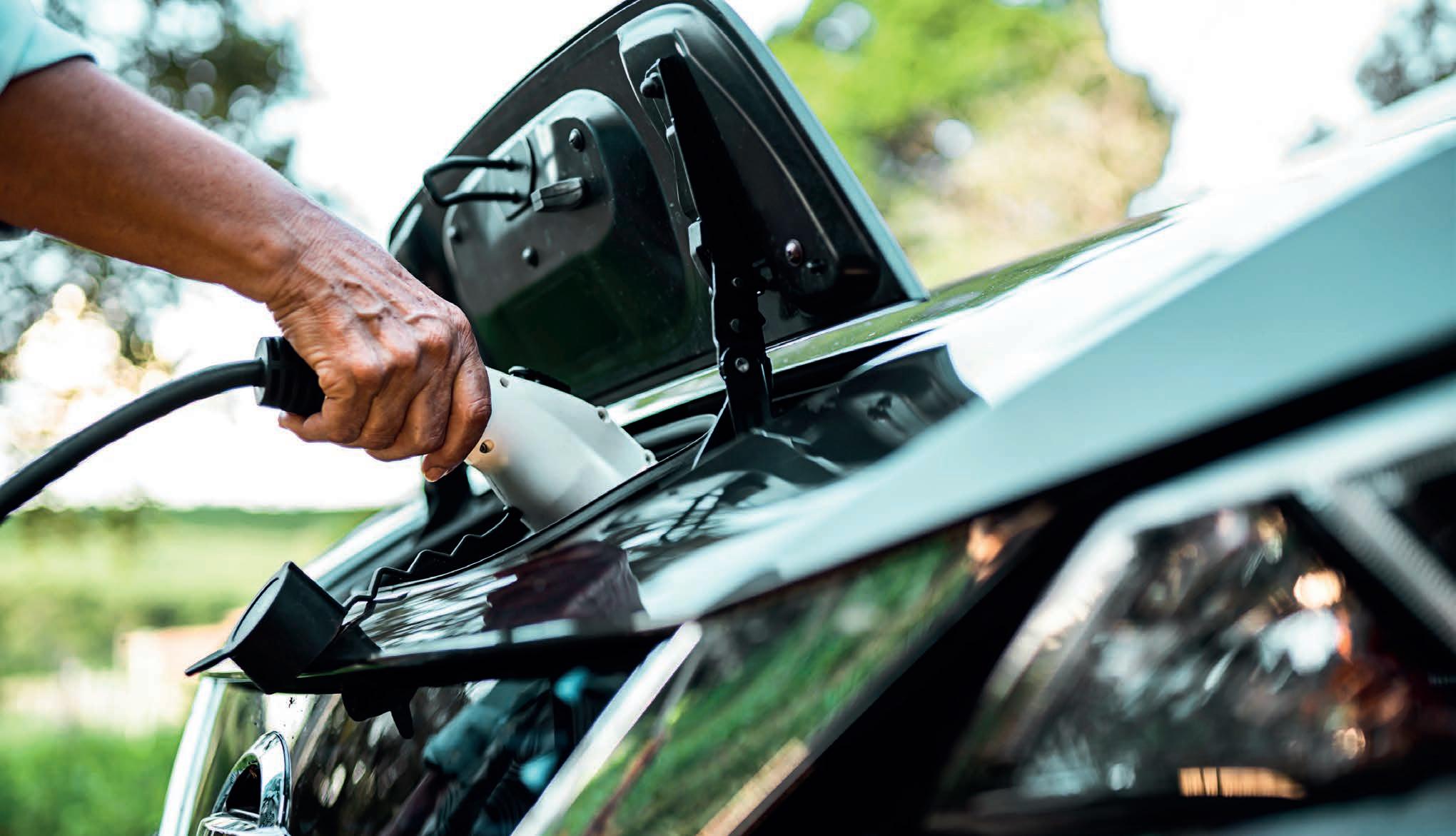
We need to be frank that the lack of availability and the reliability of charging infrastructure is a major impediment to car buyers turning to EVs.
Our network is immature by global standards. We currently have 68 EVs per public charge point, compared to the global average of 11, and this is only getting worse over time.
A piece of the puzzle lies in the infrastructure available on nearly every street in Australia – the existing poles and wires that already carry electricity to homes and businesses.
By mounting small EV chargers on existing powerpoles, we can avoid the need for extensive (and often expensive) work that can disrupt the community.
In doing so, we get chargers installed kerbside at a faster rate and lower cost.
It’s a plug-and-play solution that benefits consumers and the environment – and all it requires is a regulatory change to make it happen.
Driving change
Existing arrangements block distribution networks from offering kerbside charging services to retail service providers.
Electric car sales jumped 35 per cent globally in 2023, with almost 14 million new EVs registered. They now account for nearly one in five cars sold – a quantum leap in the past five years.
Classifying kerbside EV charging infrastructure as a ‘distribution service’ in the regulatory framework would be a game-changer for customers. It would allow distribution companies to install and maintain kerbside EV chargers and then provide open access to commercial charging operators who ‘sell’ the charging services to customers.
The Climate Change Authority’s Annual Statement, released in 2024, said, “Government can also look for other ways to more suitably classify charging as a service under electricity regulation to better utilise Australia’s existing grid infrastructure”.
Trials are already underway, and the statement suggests potential for government to catalyse a faster roll-out of this infrastructure.
It’s also a case of better using what we already have – a grid that can do more for customers than just lights and power points.
The change would boost the charging network’s dependability and reliability, given that the skilled workforce already employed by distribution networks would mean they are properly maintained, and always available.
Alongside other initiatives that gets the local grid doing more for customers, recent modelling commissioned by Energy Networks Australia estimated that the regulatory change would allow a faster rollout of chargers across our cities and regions, likely encouraging a further one million EVs onto the road by 2030.
Market momentum would become self-fulfilling as drivers seize the opportunity to save up to $2500 per year in fuel costs.
These are simple steps, well within our reach. They will combine to lower costs for drivers, cut our emissions and help take advantage of the infrastructure we already have. We should seize the opportunity to join the global revolution well underway.
The time to act is now. U
Energy Networks Australia released Street Smart: Scaling-Up Kerbside EV Charging in Australia in January 2025 as a follow-up to its report The Time is Now: Getting Smarter with the Grid, released in August 2024.
Research suggests the lack of charging infrastructure means that almost half of Australian EV drivers are considering switching back to engine vehicles.
The future of recycled water
World-first research has shown purified recycled drinking water use is set to double by 2050.
An Australian-led research project has mapped out the future of purified recycled water across the world, with predictions it will be consumed by more than 55 million people over the next 25 years.
The first of its kind project was led by the Water Services Association of Australia (WSAA) following more than two years of research and consultation with the water sector across the world. It shows that more than 100 cities could be using purified recycled water as part of drinking water supplies by 2050, with the number of people consuming it also expected to double.
The findings come as a number of states and cities across Australia are now exploring future water sources in the face of growing populations, variable rainfall brought on by a changing climate, and the comparative cost of new water sources.
A series of interactive online maps have been developed to chart the global growth of purified recycled water systems. Despite the fact that the technology has been proven for decades, purified recycled water schemes are only now starting to be rolled out at scale.
There were a handful of operating systems in use worldwide before the 2000s and that number has steadily increased over the past two decades. More than 35 cities or locations have schemes that are operating and providing clean and safe water to more than 30 million people.
The technology that is used to make purified recycled water clean and safe to drink is overseen by numerous health regulators and water authorities around the world. It uses multiple barrier treatment systems and advanced purification technology so the water can be added to drinking water supplies. Places like California, Texas, and Virginia in the US are already using purified recycled water to augment their drinking water supplies. While other major cities and regions such as Singapore, Essex in the UK, Barcelona in Spain and Oland in Sweden are also using purified recycled water sources.
California and South Africa emerge as two major regions where purified recycled water systems are set to substantially increase over the coming decades. But, other major cities and regions are also set to embrace the technology at scale such as Florida and Arizona, Bangalore in India, Leon in Mexico and Hampshire in the UK.
Closer to home, Perth has an operating purified recycled water scheme supplying groundwater sources, while a scheme in south-east Queensland is available as part of the region’s drought plan.
Sydney has built a demonstration plant as part of a major community education campaign, along with Auckland following a citizen’s assembly which backed purified recycled water as its preferred new future water source. The interactive maps chart the use of purified recycled water from the early 1960s to 2050, based on the number, location and types of systems being built and planned. U

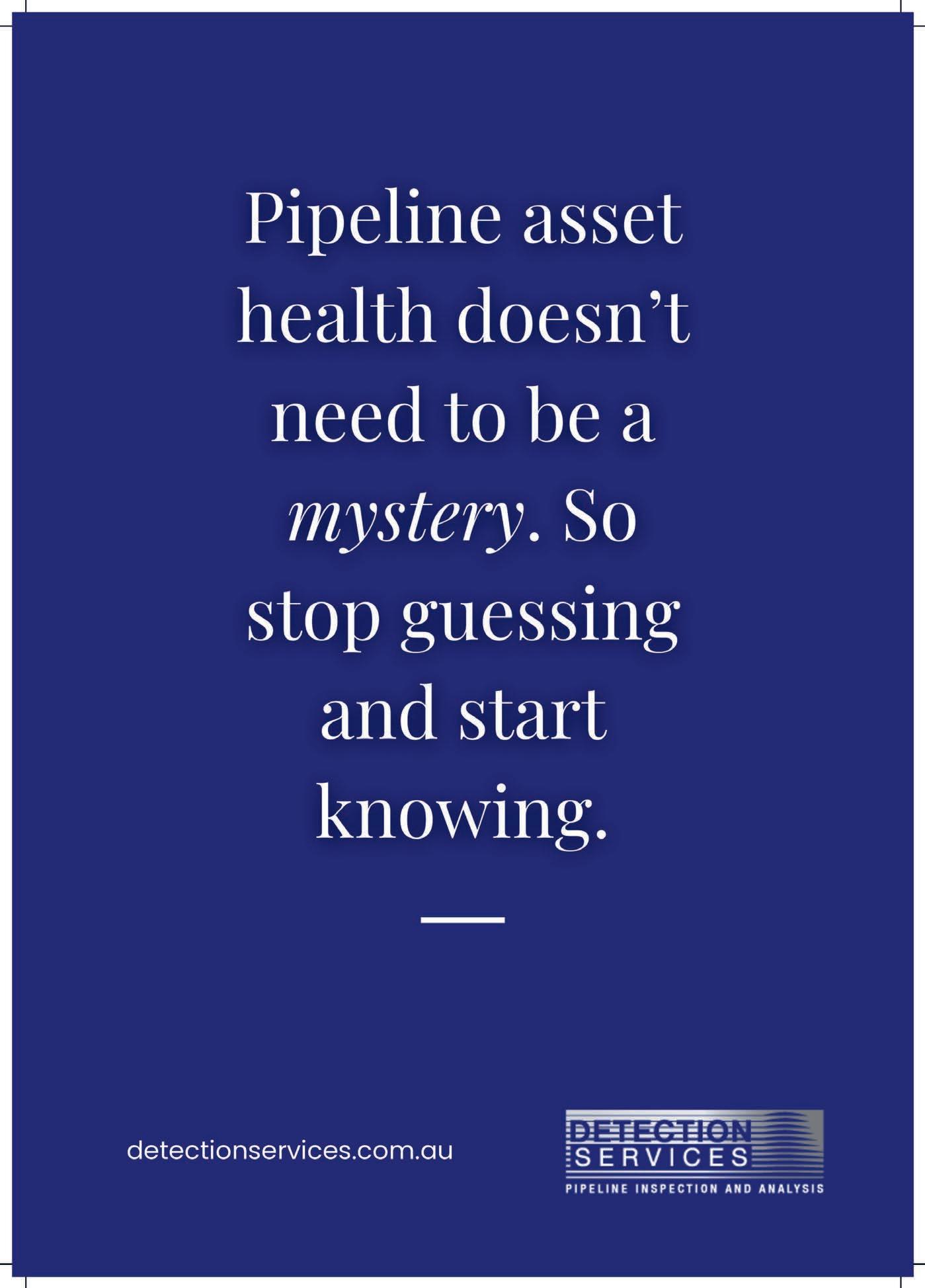
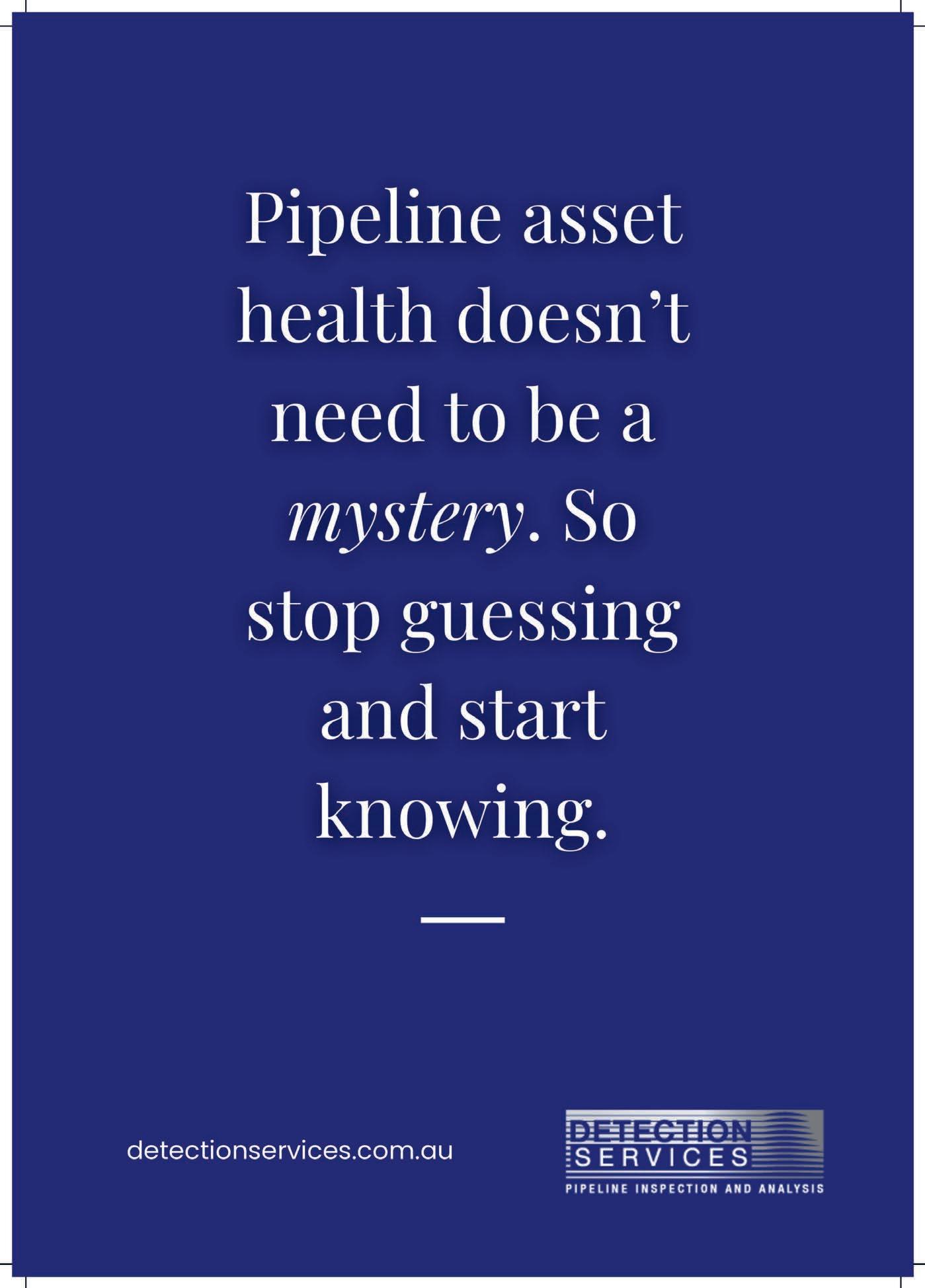
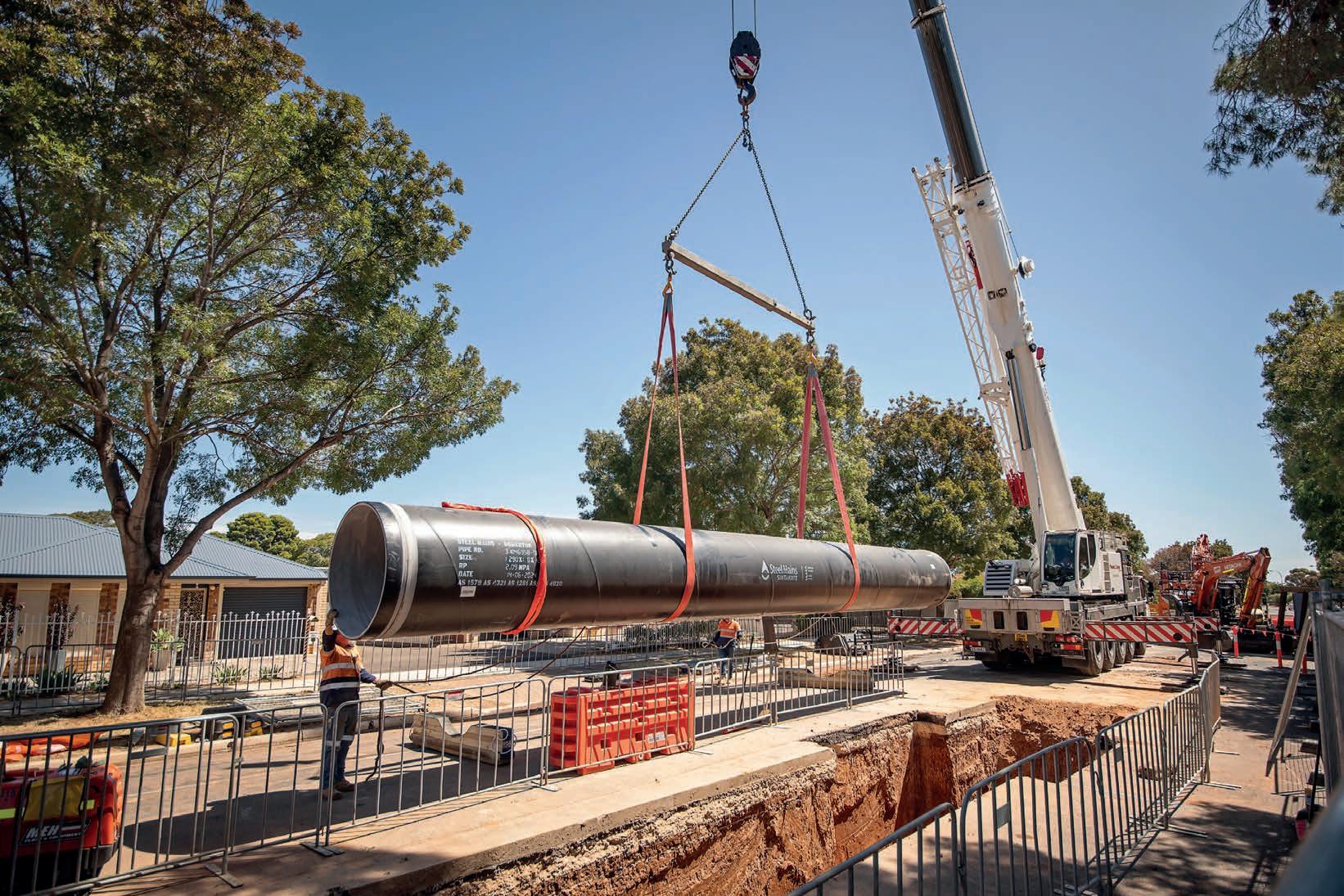
Moving forward
With growth presenting both exciting opportunities and new challenges in South Australia, SA Water Chief Executive, David Ryan, offers a glimpse into the incredible work the utility is doing to deliver a secure water future.
Since 2022–23, South Australia became home to around 60,0001 more people, and by 2051, the population of Greater Adelaide is forecast to increase by a whopping 46 per cent2.
To support this significant growth, the South Australian Government has created the Housing Roadmap, which outlines a plan to tackle housing challenges and help the next generation of homeowners break into the market.
It forges a path towards a very bright future for the state, but the backbone of a thriving community is our most precious resource – water.
Water security and housing demand are inseparably linked; and despite climate change and cost-of-living pressures throwing additional hurdles into the mix, SA Water is rising to the challenge to deliver an unprecedented network investment that will underpin South Australia’s growth.
Investing in the next generation
SA Water Chief Executive, David Ryan, explained that the utility has several key hurdles to overcome the next five years – but equally there’s a lot of excitement and opportunity in the road ahead.
“I think a lot of our challenges are very similar to not only most water businesses, but most infrastructure businesses across the country, and certainly water security in a drying climate is something we’re all working through,” he said.
“But we’re in a very dry period here in South Australia –and many of our customers are feeling the pinch.
“We’re acutely aware of that – we were temporarily running the Adelaide Desalination Plant at higher production rates, and relying upon the River Murray and our dams.”
Another key priority for SA Water is ensuring its network can meet demand – not just today but for the next generation too.
“Like many water businesses, our infrastructure has been in the ground for a long time. It’s served us really well, but much of it is coming up to be renewed,” Mr Ryan said.
“So, there’s both a big spend and a challenge to deliver all of that into the future. We’ve also got great opportunities around growth and how we service growth, and there’s a real sense of optimism in the state.
“With lots of big infrastructure projects, we also require housing for people – not just existing residents, but also new people coming into the state to work on those projects.
SA Water's capital program includes $1.5 billion in funding to enable growth across its networks and support new housing.
Images: SA Water
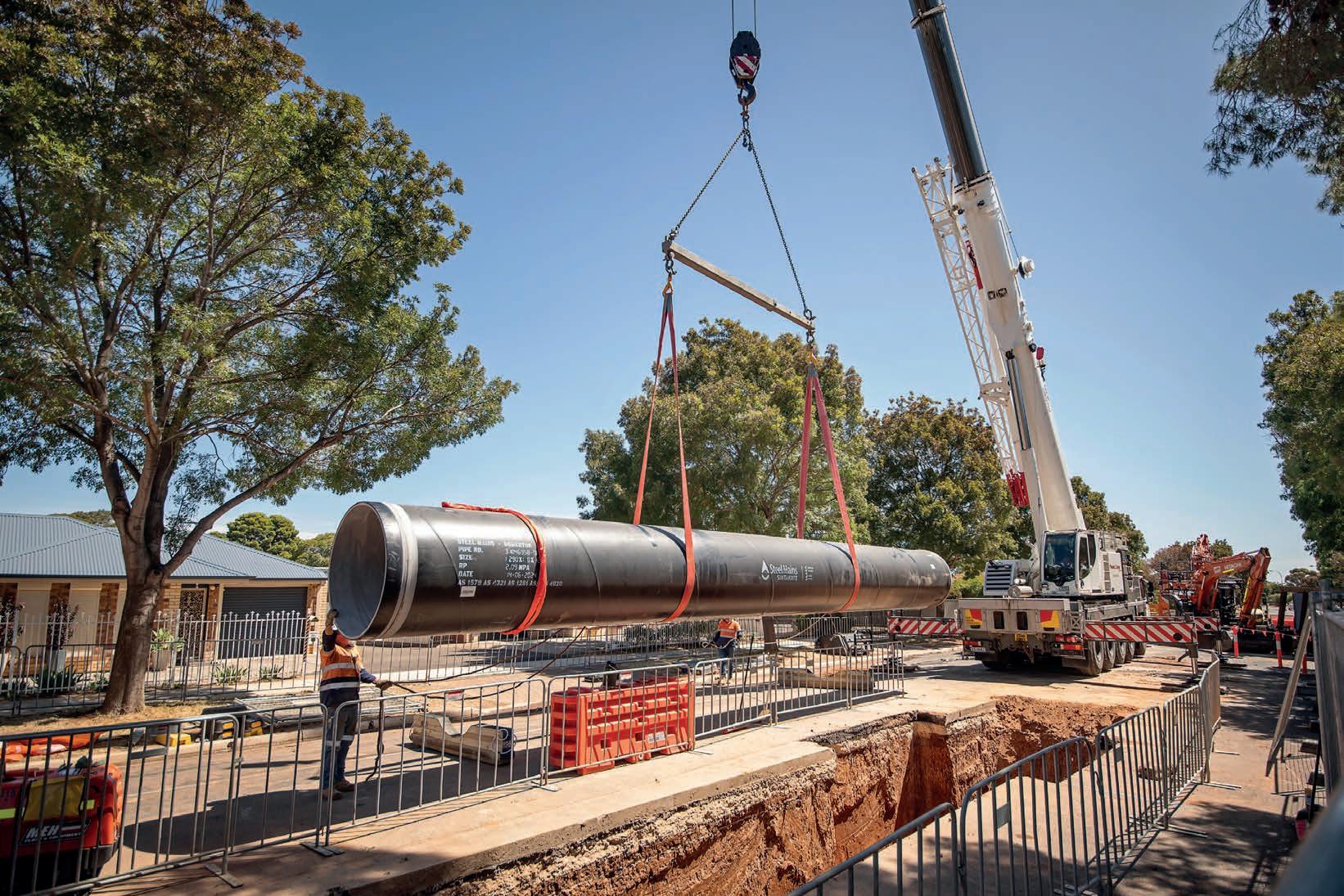
“And all of this is happening in a real cost-of-living challenge, not only for South Australians, but right across the country. So, we’re working really hard to be able to support growth and water security challenges, which all require a lot of investment, and at the same time we’re trying to keep bills as low as reasonably possible.”
To meet these challenges head on, SA Water has unveiled a landmark $3.3 billion capital program over the next four years, with a significant portion dedicated to increasing the capacity of South Australia’s water and sewer networks.
“Thankfully, we’ve seen some really significant investment over the last 12 months – which will carry on over the next three to four years – where our capital program has basically doubled,” Mr Ryan said.
“Through the [South Australian] Government’s Housing Roadmap, we’ve had around $1.5 billion of investment to be able to service growth, as well as a lot of investment to be able to maintain and upgrade ageing infrastructure.
“The time for this investment is now, and we’re seeing a real commitment in the state for that to happen. But at the same time, we’re also talking about what happens beyond these four years.”
Mr Ryan explained that with this commitment from the South Australian Government, SA Water can deliver key network upgrades to support the water demands of a growing population and unlock a potential 40,000 new allotments across the state.
“Many of the improvements we’re making and the new infrastructure we’re putting in the ground now is not only for existing customers – it’s for future generations,” he said.
“The decisions that we make now will have impacts on our customers’ grandchildren, their grandchildren, and beyond.”
What’s in the pipeline?
While a hotter, drier climate and increased demand is reducing available water supplies in many different regions across the state, Mr Ryan highlighted the Eyre Peninsula as a key focus area for water security.
“The community across the whole peninsula relies predominantly upon an aquifer system, which is under a lot of pressure,” he said.
“So [as part of our capital program] we’re looking to supplement that system with a desalination plant – the Eyre Peninsula Desalination Project – and that will help us tackle a really acute water threat over there on the Peninsula.”
Early works for this project are well underway, with the plant expected to deliver first water in mid-2026.
Mr Ryan said that over the next four years SA Water has a significant pipeline of key projects to accommodate growth and ensure it can continue to support existing customers.
The decisions that we make now will have impacts on our customers’ grandchildren, their grandchildren, and beyond.
“We’re doing some major upgrades to our largest wastewater treatment plant, located at Bolivar. This will increase its capacity and performance, and it’s the first of a multi-staged upgrade to that really important asset,” he said.
“We’ve also got ongoing renewal projects across our network for both water and wastewater services, and one of the major ones is the replacement of significant portions of the Morgan to Whyalla Pipeline.”
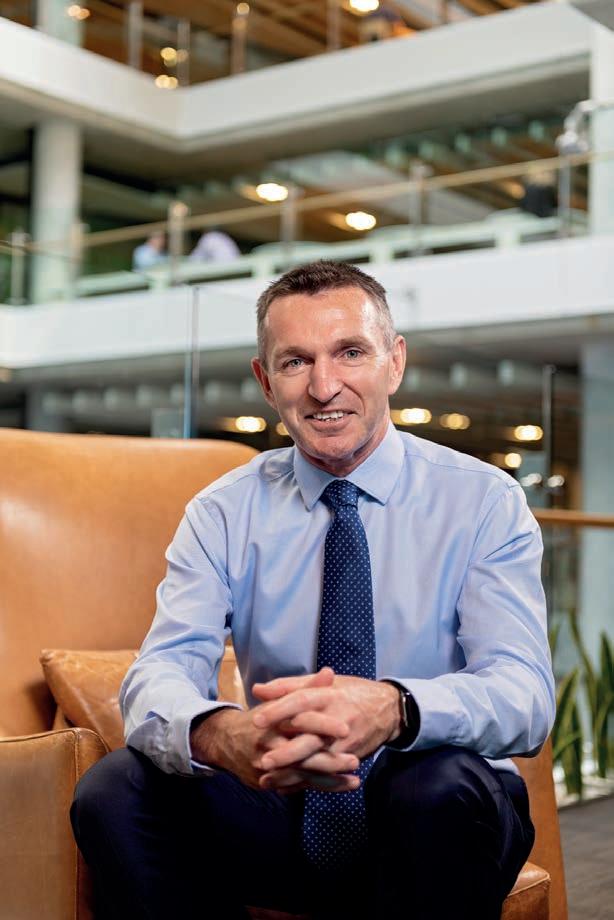
SA Water Chief Executive, David Ryan.
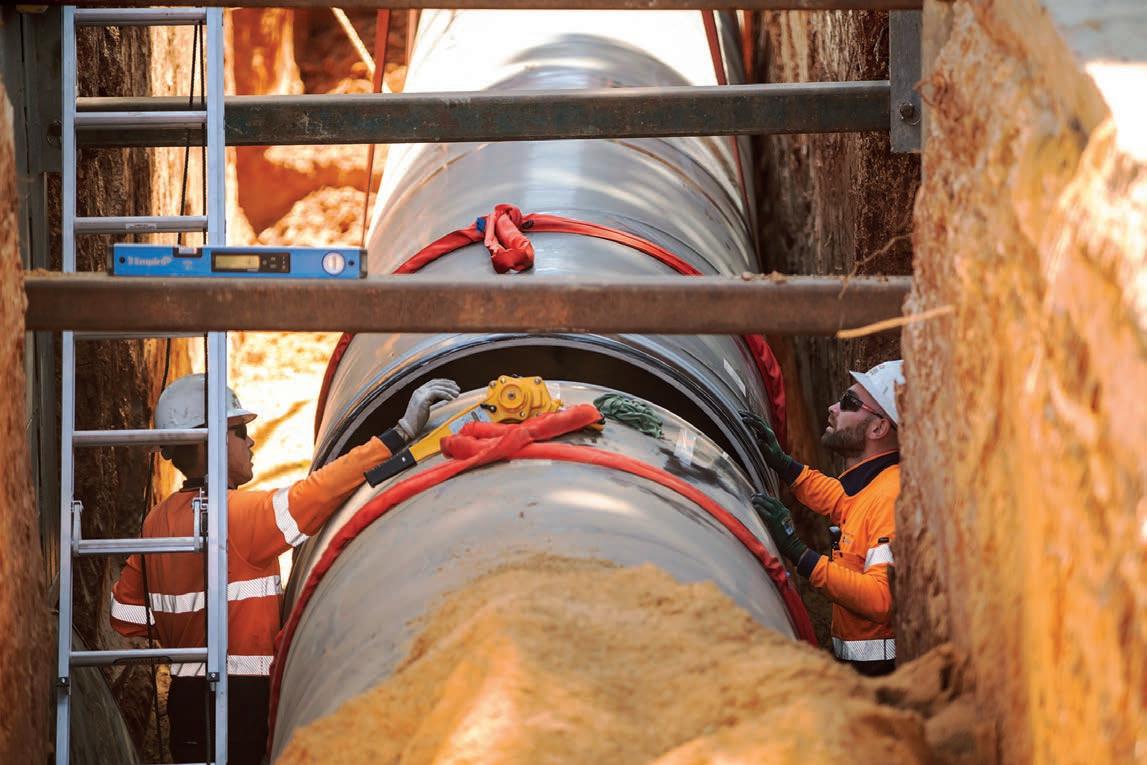
SA Water is also playing a key role in enabling many of the state’s big infrastructure projects.
“South Australia is building a new women’s and children’s hospital, which will require changes to our water and wastewater network,” Mr Ryan said.
SA Water is also helping to deliver another important piece of critical infrastructure for the state – the River Torrens to Darlington (T2D) Project.
Construction of this $15.4 billion upgrade is set to begin in 2025, and it will complete 78km of non-stop, traffic light-free motorway between Gawler and Old Noarlunga in South Australia. The T2D project encompasses two separate tunnels that will be connected by an open motorway – and Mr Ryan explained that these major works are being supported by SA Water.
“It’s a major tunnel project that we’re doing over here as a state, and we’re heavily involved, particularly around the relocation of existing assets,” he said.
Working together
This $3.3 billion capital program is a once-in-a-generation investment, and delivering these major projects would be impossible without a strong, skilled and dedicated team behind it.
Mr Ryan said that SA Water is constantly doing the work to be an organisation that people not only enjoy being a part of but see a future with.
“We’re really working very hard to ensure we have a really supportive, high-performing culture within the organisation,” he said.
“I think that it’s critically important to be a place where people want to come to work, they’re engaged, and they believe in where the organisation is going.
“We’re seeing continued uplift in our culture and engagement scores, which has been great to see. And we’ve entered into some long-term partnerships where we’ve been able to demonstrate to them that we’re a good partner to work with.”
With such a long pipeline of work ahead, Mr Ryan said it’s worth investing in those organisations and ensuring that SA Water’s partners also have the skills and capability they need to deliver this program.
“We also work really closely with our industry bodies to ensure we’re clearly spelling out what the pipeline of work looks like, and where the opportunities are to engage and work with us. We’re seeing lots of organisations who are really excited about the program of work that we’re doing and want to be a part of it,” he said.
“I actually think one of the things that really inspires and excites people who work in this industry is that we’re building long-lived assets that will provide benefits for our customers’ grandchildren, their grandchildren, and beyond.
“And that’s no more evident than [when you look at our existing assets] – we replace pipes that have been in the ground for well over 100 years, and you marvel at the engineering and the construction techniques that they used way back then that allow an asset to still be delivering value for customers here in modern times.”
With such an exciting, and challenging, road ahead for South Australia’s water sector, it’s fitting that the state is set to host the country’s biggest water conference and exhibition in 2025.
Ozwater kicks off from 20–22 May 2025, and Mr Ryan shared highlights from the huge schedule of presentations SA Water has lined up over the three-day event.
SA Water is ensuring its network can meet demand today and for future generations.
“[Attendees] will certainly hear more about the size of the program of work that we’re delivering, and I do want them to hear about many of these projects that have multiple benefits,” he said.
“It’s more than just improving water supply or providing improved wastewater services, [we’re also looking at] what we’re doing from an environmental perspective and from a carbon reduction perspective.
“I think [attendees who] see a few presentations from us will get an idea of just the huge diversity of this business –both in the services that we provide, but also the areas that we provide services in.”
SA Water has some incredible stories to share at the event, and attendees will have insight into the key services the utility is providing across the state – from the remote Anangu Pitjantjatjara Yankunytjatjara (APY) lands in the far north-west, to Mount Gambier in the south-east and over on the Eyre Peninsula.
We’re seeing lots of organisations who are really excited about the program of work that we’re doing and want to be a part of it.
“It’s just an enormously diverse and exciting business to work in and be a part of. And whenever you hear our people present about it, they do so with enormous pride.
“We’re fond of saying we’re at a pivotal time for the industry, and in many ways, we are, but equally, we’ve also got an incredible history of delivering great value services for customers for many generations,” Mr Ryan said.
“I think we should be proud of that and use that for a sense of inspiration as we work through some big challenges in the sector.” U
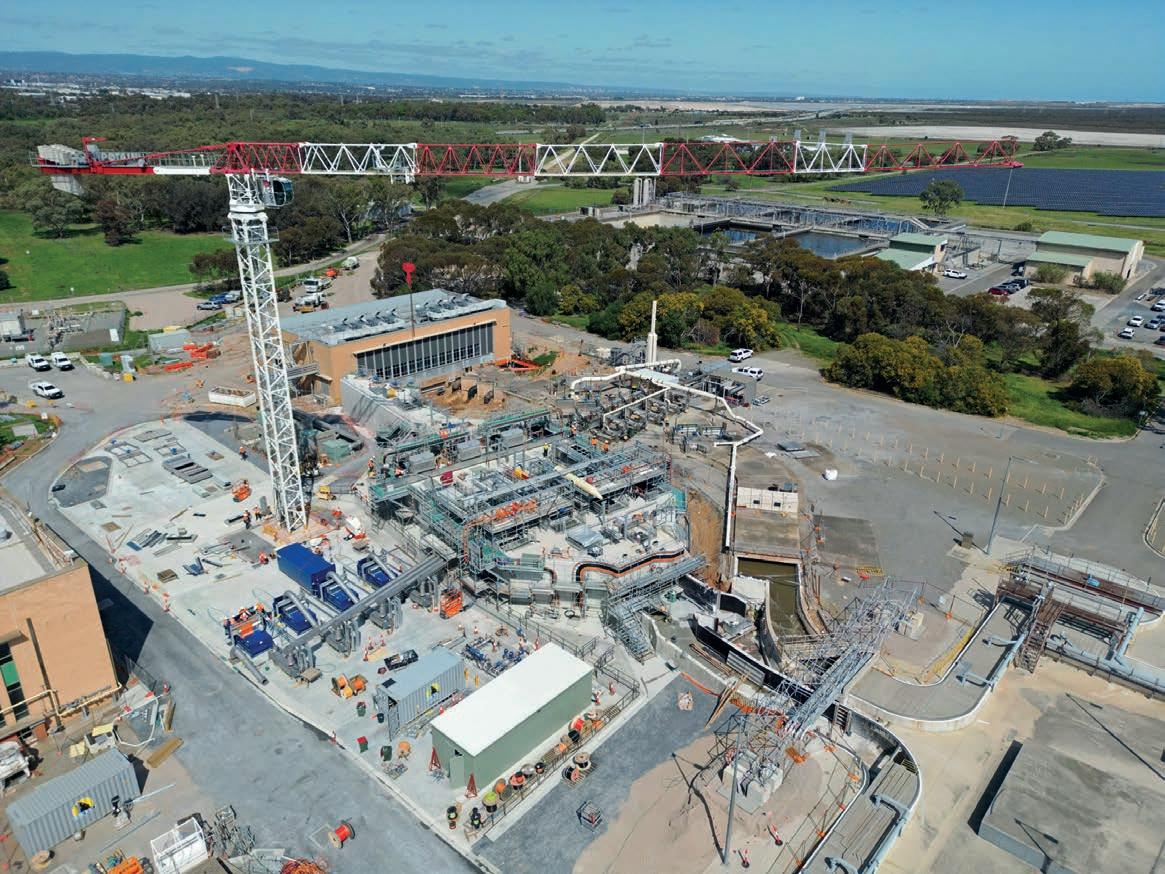
Ongoing construction works for the new inlet at SA Water’s Bolivar Wastewater Treatment Plant.

Looking back, moving forward at Ozwater’25
The Australian water sectors’ premier event is just around the corner, and in line with this year’s theme, Utility looks back at some of our highlights from Ozwater’24 and shares some of the events we’re most excited about in 2025.
From 20–22 May 2025, some of the most brilliant minds in the water industry will gather at the Adelaide Convention Centre to connect, share their knowledge and work together to build a vibrant water future for everyone.
This year’s theme is ‘Looking back, moving forward’, which the host, the Australian Water Association (AWA), said is an invitation to reflect on the past while embracing a future where water is central to sustainable growth.
AWA Chief Executive, Corinne Cheeseman, said, “Ozwater’25 is a celebration of our shared journey, connecting people, ideas and solutions.
“By planning for the future and drawing lessons from our history, we equip ourselves to embrace the challenges of tomorrow, together.”
and innovation to shape sustainable, resilient services that help our communities grow and thrive.
Looking back
Since 1962, the AWA has been connecting the people and organisations tasked with managing Australia’s most precious resource, and helping them to navigate the water industry’s most complex challenges.
Today, the association is Australia’s largest water network with more than 5000 individual and business members – and Ozwater is a key part of the AWA’s long and inspiring history.
The first ever event – known back then as the Federal Convention – was held in 1964 in Canberra, with 64 delegates in attendance. Since then, Ozwater has grown to be Australia’s biggest water conference and exhibition – with more than 225 exhibitors and upwards of 4000
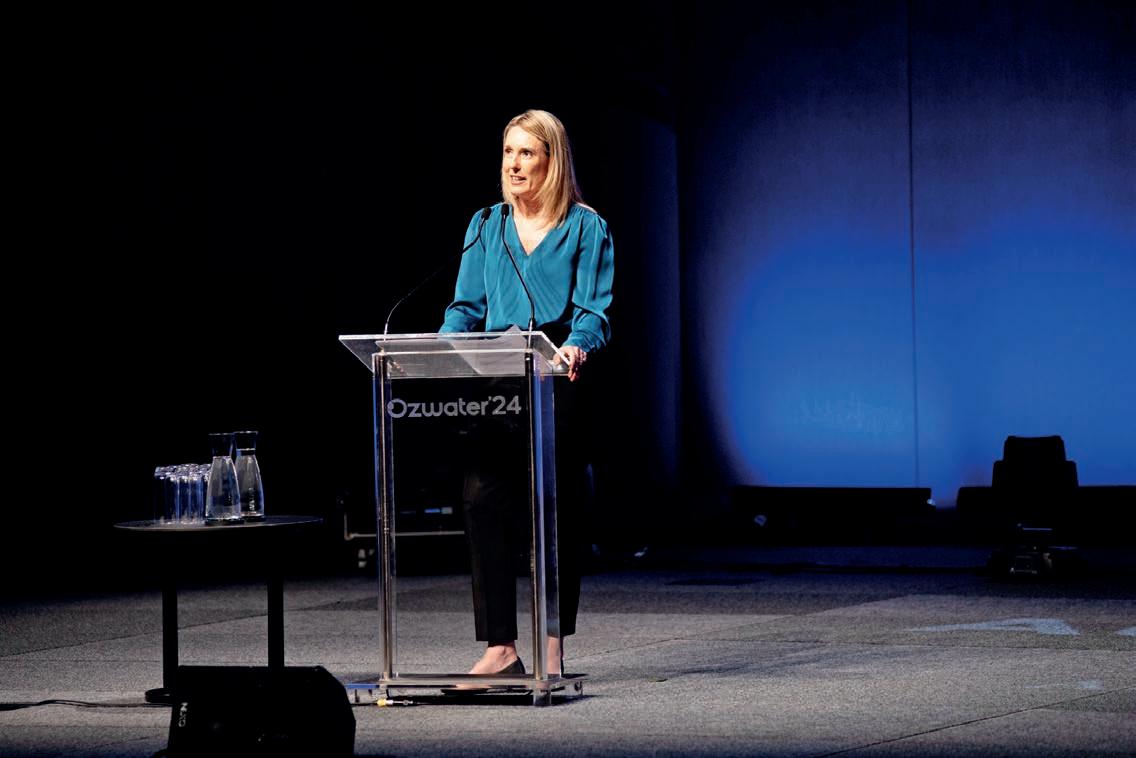
’s experience in 2024 is anything to go by, Ozwater’25 is shaping up to be an industry event you don’t
There was an incredible program of workshops, panels and papers at Ozwater’24 – and with a huge spread of topics covered across 12 themes, the Utility team’s only regret was that we couldn’t attend them all.
We heard from some truly inspiring thought leaders and thoroughly enjoyed Gina Chick’s keynote at the 2024 opening ceremony, who shared how she survived on her own within the Tasmanian wilderness for 67 days.
Last year’s event also treated us to insights from Minister for the Environment and Water, Tanya Plibersek, and a really informative social license forum lead by Seqwater.
Ozwater is the largest water conference and exhibition in the Southern Hemisphere.
Images: AWA
AWA Chief Executive, Corinne Cheeseman.
South East Water’s, Ninad Dharmadhikari, also presented on Hydrotrak technology at the event – which inspired an article in the February 2025 edition of Utility.
As always, the Australian Water Awards were a major highlight of the three-day event, and the Utility team were certainly very impressed by the innovation, dedication and leadership the winners displayed.
As soon as the event was over, we couldn’t wait to do it all again in 2025.
Moving forward
In an era of competing priorities and unprecedented growth, the AWA said water must rise to the top as a catalyst for economic development and innovation.
Ozwater’25 aims to create this space for water to lead with a curated program of powerful keynote speakers and interactive workshops across ten sub-themes.
“We’re thrilled to bring Ozwater to Adelaide in 2025 and deliver such a high calibre program of speakers, insights and ideas,” Ms Cheeseman said.
“Ozwater’25 is more than a conference, it’s a launchpad for the knowledge sharing and collaboration that will shape the future of our sector.”
Day one
The first day dives into the critical issues shaping the water sector, with discussions on wastewater optimisation, asset management and rural water challenges.
Highlighting opportunities for bold action and innovative solutions, streams on day one will cover emerging contaminants, customer and community engagement, the circular economy and climate resilience.
In the morning, attendees will hear from SA Water on resource and recovery and how it is helping to drive a
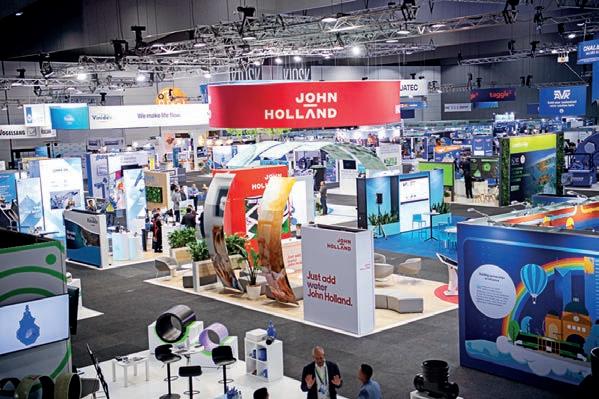
visionary thinking. Delegates can hear from Yarra Valley Water on how the sector can better understand financial hardship; and attend a range of key events, including the Student Water Prize, and the improving Aboriginal Representation in Water panel.
Day two
The second day wastes no time, delving straight in to the transformative power of technology, culture and collaboration in the water sector.
Sessions will spotlight digital innovation, AI and machine learning, as well as themes of diversity, accessibility, and First Nations knowledge – with Taswater set to share insights into attracting how diversity and inclusion lead to high employee engagement, while GWM Water will take us on its renewable energy journey.
The second day will also highlight global perspectives and offer actionable insights from WSAA.
Workshops and panels throughout the day will encourage peer collaboration and thought leadership, balancing technical depth with broader discussions on resilience, conservation and community connection.
The evening will culminate with the much-anticipated Australian Water Awards to be celebrated with a spectacular gala dinner.
Day three
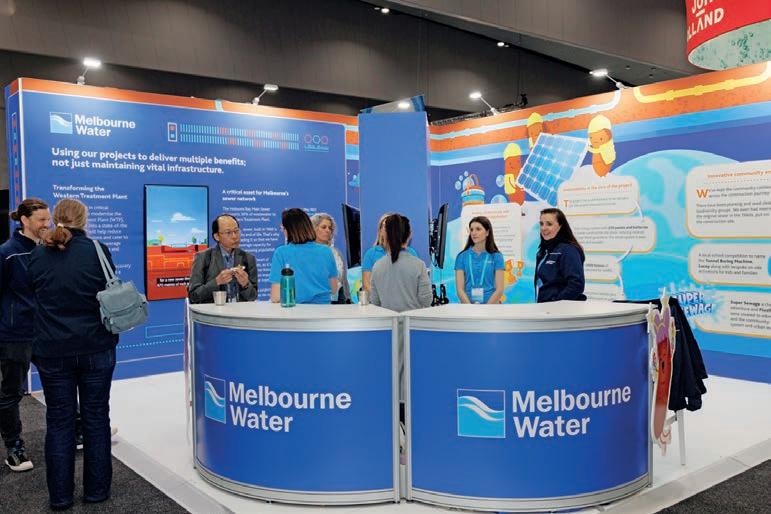
Ozwater’25 has saved some of the best for last, with the third day set to bring a powerful close to the conference.
This day is rich in thought leadership and innovation, spotlighting practical solutions, innovative technologies and collaborative strategies for the water sector’s biggest challenges – including South East Water’s investigation into the removal of PFAS using water treatment sludge and biochar.
Key themes include achieving a circular economy, enhancing customer experiences, and developing resilient strategies for extreme events. Streams and panels offer actionable insights and opportunities for collaboration, making it a day rich in thought leadership and innovation.
As the water sector enters a time of unprecedented change, this three-day event aims to unite the thought leaders that are shaping a sustainable water future for the next generation of Australians and beyond.
A limited number of conference tickets are still available, and for those unable to commit to the full program there is an option for free trade delegate registration – but get in quick, this Ozwater is one not to be missed.
Will we see you there? U
For more information, visit ozwater.org
Melbourne Water’s stand at Ozwater’24.
Ozwater’25 is expecting more than 225 exhibitors and 4000 attendees.
p-CAT was developed at the University of Adelaide and is an entirely Aussie invention. Image: Darren/stock.adobe.com
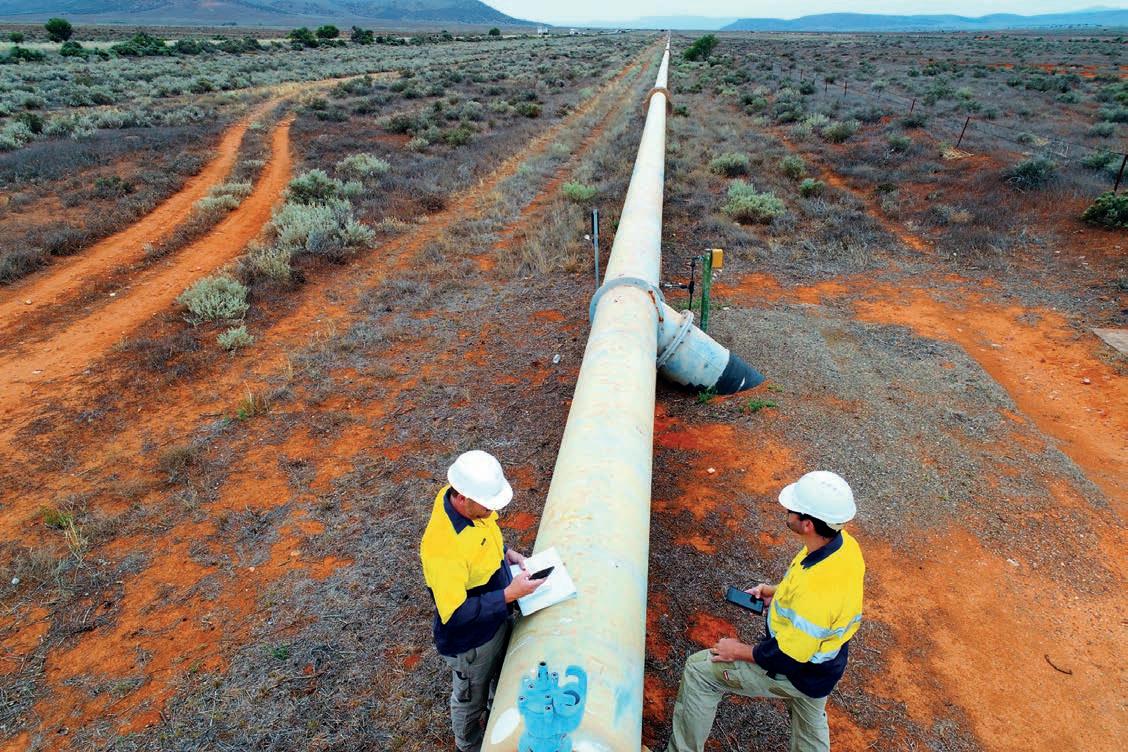
A future made in South Australia
As the Federal Government pushes to sell more Aussie products to the world, a condition assessment technology from the University of Adelaide is already leading the charge.
Since 2017, many Australian water authorities have been using a unique pipeline assessment tool, p-CAT, to detect leaks and deterioration in their networks, and tackle them before they become bursts.
This clever technology is a bit different from other forms of condition assessment; it’s completely non-invasive, can cover large distances in short periods of time as well as pinpoint damage within a 10m section – and it’s an entirely Aussie invention.
p-CAT was developed by a team of researchers at the University of Adelaide and commercialised by a local specialised water management company, Detection Services, who then puts a cut of every analysis fee back into the university to fund more research and development.
And now this technology is taking the world by storm.
Making waves
The core technology that p-CAT is based on has been studied at the University of Adelaide for almost three decades.
Dr Young-il Kim was a member of that original research group, who were the first to apply a new transient-based analysis technique to pipe wall condition assessment. He began working on the technology as part of his PhD and then continued this work even after he became a research fellow at the university.
After some time, Dr Kim began a push to turn this technology from a research project into a solution that can actually be used by the industry – and in 2013 he joined forces with Detection Services Director, Stephen Simmons, to commercialise p-CAT.
Dr Kim then moved over to Detection Services to perform condition assessments for clients with p-CAT as a viable commercial technology.
Detection Services Senior Analyst, Penny Wrightson, was one of the first employees to join the Condition Assessment Team after Dr Kim, and she said that p-CAT has come a long way since she started.
“They’re always looking at ways to improve it or simplify it, but the core basis of the technology has largely remained the same,” Ms Wrightson said.
“Where we’ve really come a long way is in providing what clients are really looking for – not just what the university thinks is interesting.”
p-CAT works by analysing hydraulic waves as they travel through the pipeline – which means that the asset doesn’t need to be taken offline while the assessment takes place.
A number of temporary sensors are installed in existing pipe fittings at a maximum of 1km intervals along the length of the pipeline; and one of these fittings is also used as a generator station, which creates a controllable mild pressure wave in the pipeline.
As the wave travels through the pipeline, some of its energy is partially reflected when it encounters change in the pipeline structure – such as corrosion or a section of the pipe where the wall thickness is reduced. Deterioration can also change the fundamental hydraulic characteristics of a pipe network, which is also able to be determined.
All this information is then picked up by the sensors and Detection Services analyses that data to create a highly accurate report about the condition of the pipeline.
“When we first started, the reports were providing information in a way that makes sense only if you are a hydraulic pipe engineer with a lot of background information,” Ms Wrightson said.
“But now we’ve changed the way we present the results so that we can give it to asset managers who might not [have much technical knowledge] about pipes or who come from a non-civil background, and they can actually use the information.”
Detection Services CEO, Chris Evans, explained that Detection Services has since expanded p-CAT into a system of solutions that leverage this core technology to address a range of different challenges, including valve integrity and air and gas pockets.
“[When we first came on board], it was quite a raw package, and we’ve taken the time to refine the solution so it can be used operationally and then take it to [utilities] and confirm that it’s the right tool for their operational needs,” he said.
A fair assessment
According to Mr Evans, p-CAT has been embraced in Australia by utilities and pipeline asset owners and is now used almost daily in operations across Victoria and Queensland.
“I think the benefit of developing it in Australia is the willingness and acceptance of the water industry to give it a fair go,” he said.
“It’s become the go-to tool now for critical large diameter pipeline condition assessment and rising sewer mains.”
With more than two million people and 62,000 businesses relying on its water and sewerage services, Yarra Valley Water is one of the largest water utilities in Australia. As the utility manages a network that spans across a vast 4000km2 area, Yarra Valley Water takes a proactive approach to asset management and employs a condition assessment program to help it understand the condition of its assets.
Yarra Valley Water Planning Engineer, Tristan Rennick, explained that the utility has been using p-CAT as part of this condition assessment program for four-to-five years.
“For the past two years [of that] we have had a longerterm contract in place to focus on our critical trunk mains, which has allowed us to be less reactive and more strategic in our maintenance and management of our network,” he said.
It was quite a raw package, and we’ve taken the time to refine the solution so it can be used operationally and then take it to [utilities] and confirm that it’s the right tool for their operational needs.
“p-CAT enables Yarra Valley Water to understand the condition of entire pipelines. Since we first took up this technology, we have approximately 160km of p-CAT completed or currently in progress.”
p-CAT is able to scan long distances in a very short amount of time, without taking the pipe offline. This speed, however, doesn’t compromise the quality of the assessment, and p-CAT can identify everything from the thickness of the pipe wall to blockages and illegal connections, as well as air and gas pockets.
These results are highly detailed, and Detection Services can get the resolution down to 5–10m sections, which means utilities like Yarra Valley Water can pinpoint specific areas for intervention rather than replace the entire length of the pipeline.
Mr Rennick said that the utility also employs SmartCAT as part of this condition assessment program – a magnetic flux leakage technology provided by Detection Services that is particularly helpful for pipelines that don’t meet the requirements for p-CAT.
The p-CAT suite, as it’s now referred to, is quite versatile, and Ms Wrightson said that it can be adapted to suit the individual system – with new variants of the technologies being added to bring more confidence to clients who are looking to survey more of their assets without spending large sums of money on refurbishment.
“We can work with water, bore water, sewer rising mains, sludge mains – but there is no pipe that is exactly the same as the last and every one of them has their own challenges,” she said.
“Some might not have enough fittings while others might not have enough pressure – they’ve all got their little quirks and the technology suite is really flexible.”
But to solve these problems, Ms Wrightson said she and the Detection Services team also need to be flexible.
“The way that we conduct our testing is we first determine as a team what we can safely do on [the pipeline] – and we talk to the client about what pressures and test conditions they are okay with,” she said.
As part of this tailored approach, Detection Services also offers a range of other condition assessment solutions to accommodate almost any pipeline.

What’s in the pipeline?
This Aussie innovation is now being used by water utilities, municipalities and government agencies around the world, and Mr Evans announced that Detection Services is now launching an international arm – with Dr Kim as the Project Director.
“PIA, which stands for Pipeline Inspection and Assessment, is the business we’ve created to meet the international market’s demand for condition assessment technology,” Mr Evans said.
“PIA has a bit of a unique business model, where we work with local distribution partners in these countries and enable them to offer the full p-CAT suite to their market.”
Previously, Detection Services would have to send teams
“They act as the front end; they meet the clients, do the tests in the field and send the information back to us – then we then we do the analysis back in Adelaide and can provide support from behind the scenes [as needed],” Mr Evans said.
“The benefit here is that every time we [analyse] a kilometre of pipeline, the University of Adelaide gets a royalty to fund further research and develop more innovative solutions. And even without that investment back in the university, when we charge international clients for the analysis, the money comes back into PIA, and PIA pays its tax back into the Australian economy.”
With 21 international partners already on board, PIA officially launched on 28 April 2025 – but Mr Evans said that there’s even more exciting things in the pipeline.
“[Detection Services] is constantly looking for new innovation, in fact, we’re looking at some other interesting non-invasive solutions right now that are about to go to trial,” he said.
“We want to act as an advocate for the industry. We’re not just bringing in something that’s bright and shiny for the sake of it being new – we’re acting in the industry’s best interest, even before our own.
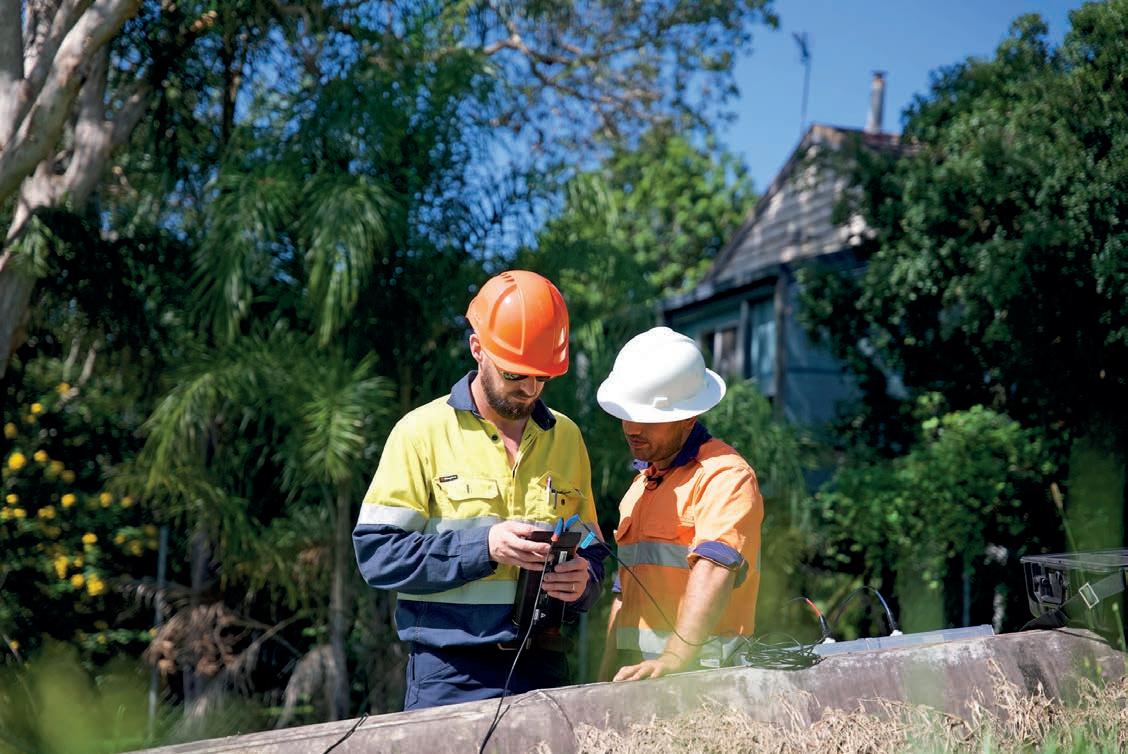

p-CAT is a completely nondestructive, non-invasive pipeline condition assessment solution. Image: Detection Services.

The PL1500 is a gamechanger for pipeline construction. The unique, quick-hitch, vacuum lifter attaches to your existing excavator, reducing your machine hire cost and getting things moving fast. Capable of safely lifting 15,000kg, the heavy-duty, self-contained unit can handle all types and lengths of pipe. It integrates seamlessly with the host excavator, using the main controls and hydraulics to operate the vacuum lifter. Plus, built-in smart tech ensures it’ll only pick up or put down a pipe on a solid surface. That’s safer than many other vacuum lifters on the market. To find out more, speak to the Pipeline Plant Hire team today.
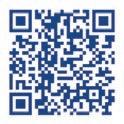
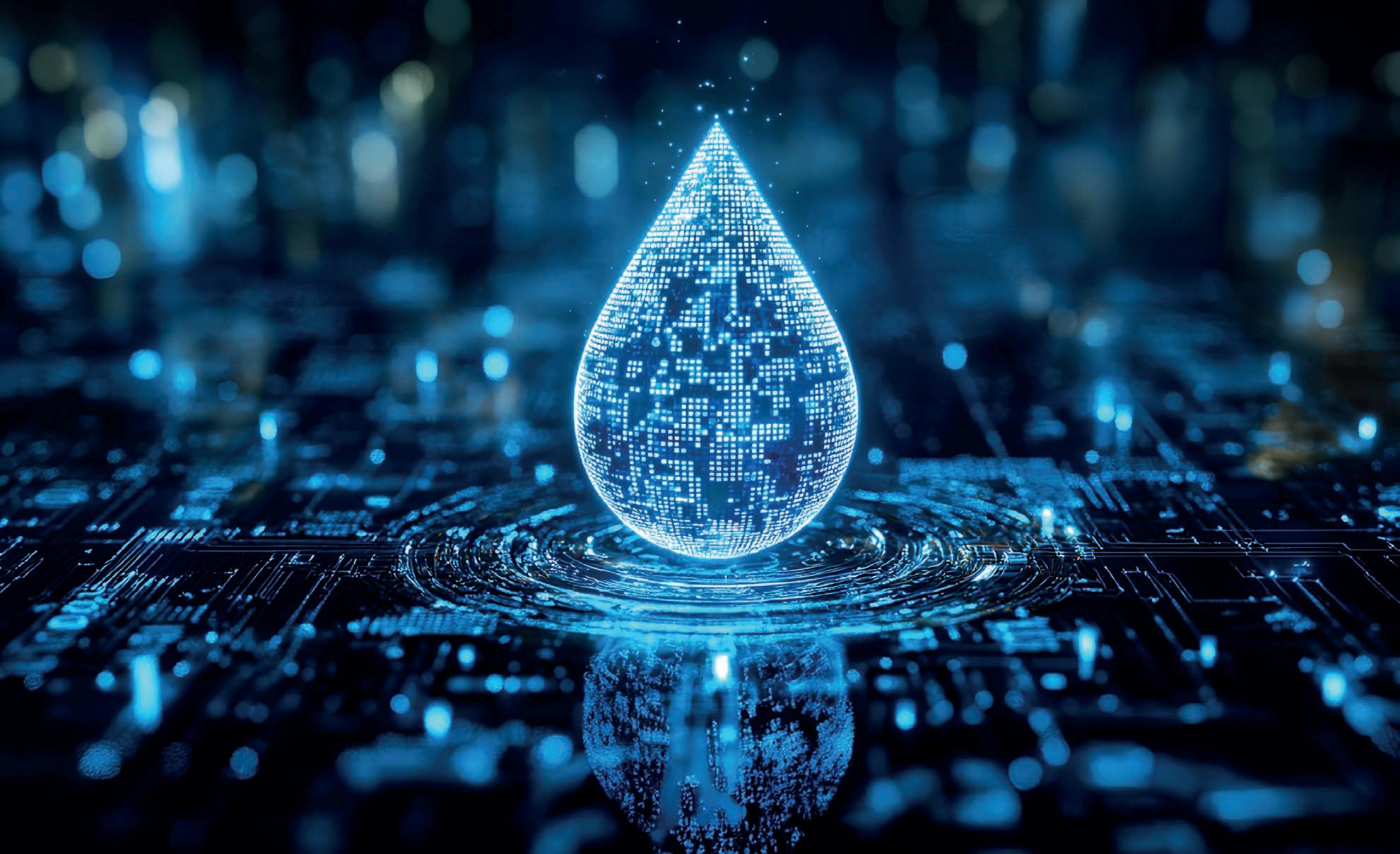
Good company
The road to digitisation is filled with both challenges and opportunities, but it’s the people you have on your team that will ultimately determine your success.
Over the past two decades, Mario Tieppo has held six Chief Information Officer or equivalent roles, most recently at major Australian utilities such as AusNet, Australian Energy Market Operator (AEMO), and SA Power Networks.
Now retired from executive life, Mr Tieppo focuses on helping essential service providers navigate the digital transformation, and sits on audit and risk committees across government, water, agriculture and technology.
He’s also joined the new Advisory Board at Nucleus 3 – an Australian consultancy and systems integrator that takes a bit a novel approach to digitisation.
“I started my own advisory business four years ago, and now I’m part of this recently established Advisory Board [too]. And what I do is impart my knowledge
around [not just] technology strategy, but also delivery –which is where a lot of organisations actually fall over,” Mr Tieppo said.
“We always talk about the why, the what and the how, and I think most organisations have a reasonable handle on why they want to [digitise] and what they need to do – the [challenge] is the how. They often struggle in terms of delivery, and that’s where costly mistakes can be made.”
According to Mr Tieppo, this ‘how’ comes down to three things: the people, the innovation and the outcomes.
“[Many companies] don’t know where to start, and I’ve encountered large organisations where either the objectives aren’t clear, or lot of different executives have different ideas about what those objectives are,” he said.
Nucleus 3 works closely with customers to understand what they actually need, and then puts together industry-specific solutions.
“And one of the first things I try and do is get people aligned and on the same page about what those objectives are.”
A digital transformation is by no means easy, utilities have to grapple with escalating costs, cyber security risks, implementation challenges – all while trying to decipher the best solution for them in a market flooded with hundreds of different technologies.
However, Mr Tieppo said that perhaps one of the biggest challenges is finding people with the experience and talent to navigate this transformation.
“[For example], for a lot of councils and water authorities, besides the big tier ones, water is only one part of their responsibility as an organisation, and they have [to stretch] their budget across [these different responsibilities] – which [makes it difficult] to source the right person with talent and the knowledge [they need],” he said.
“It’s about investing in people, systems and innovation – and that’s why I think Nucleus 3 always focuses on those things.”
Three heads are better than one
When Nucleus 3 CEO, Louis Limnios, founded the company more than a decade ago he realised that in order to help utilities with their digital transformation, he needed to be able to walk in his customers shoes and see things from their perspective.
And the only way to do this is by investing in the right people.
The establishment of this new Advisory Board might be the latest chapter of that journey, but Mr Tieppo said that energy Nucleus 3 puts into its own team are what drew him to the business.
“I’m really excited to have the opportunity part of Louis advisory panel, because I think it’s a great business, I just love the energy of it,” Mr Tieppo said.
“Louis has a lot of energy, and he’s very passionate about his people and his clients and his technology – probably in that order.”
Ted Turner also sits on the Advisory Board, but he brings a vastly different wealth of expertise.
“I stepped out of university and went into public practice, specialising in business services and then into more strategic and advisory work, which I’ve been doing now for around ten years,” Mr Turner said.
“During that journey, I met Louis more than 30 years ago, when he was a simple tax return, and over time, built up a relationship of trust as accountant and advisor.
“Then in June 2024, I sold out my accounting practice and took on a number of board positions with the mantra that I wanted to choose the people I wanted to work with.”
Just like Mr Tieppo, Mr Turner found Mr Limnios’ energy infectious.
“I have a lot of trust in that energy and drive. And one
of the things that always attracted me to what Louis was doing is how he talks about his team, his customers, and his outcomes – and I always like that idea of team coming first. If you’ve got a [bad] team, you can’t put the customer first,” Mr Turner said.
“I’m really excited to be on this advisory board in part because of Louis energy, but also just recently being introduced to Mario as well – knowing he comes from a different background to me allows me to keep learning and as well as contributing within my area of expertise.”
The right kind of people
Nucleus 3 has a team of more than 125 consultants and engineers, who each contribute their own extensive industry experience across the entire spectrum of the delivery model. By empowering this team to innovate and working closely with customers to understand what they actually need, Nucleus 3 is able to put together industryspecific solutions.
“We shouldn’t be looking at technology as the fixer and you shouldn’t change your organisation to suit the technology – technology is only an enabler to give you the outcome you want,” Mr Limnios said.
Nucleus 3 works with a huge network of technology partners (the N360) so it can offer an agonistic service to its customers.
“We picked leading providers who have been in the industry for a long time who are already invested in future-proofing their own technology,” Mr Limnios said.
In response to feedback from small and medium water authorities and local councils, Nucleus 3 developed Water Bureau – a IoT service specifically tailored to utilities with limited in-house resources or immediate access to the capital required to undertake large-scale projects.
By eliminating the complexity and upfront capital expenditure, Water Bureau helps makes IoT and smart meter projects accessible for all water authorities. Powered by Itron Temetra AMI, this integrated platform enhances
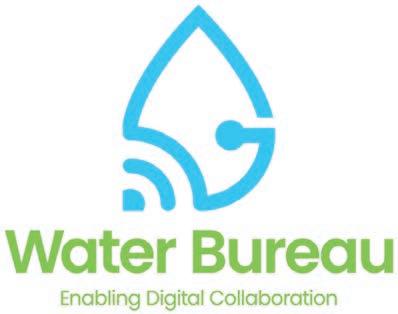
The water Bureau is designed to help empower smaller water authorities in their digital transformation. Image: Nucleus 3.

they need, and took those requirements back to N360 and asked for the top two or three leading capabilities that the customers are asking for.
“From that feedback, we went and chose a handful of products, and we spent a fair bit of time and investment in integrating those systems together to give the customers that interoperability and that flexibility that they were asking for in the one solution.”
“And we built a lab has an evidence-based capability, because we wanted to be able to show the strength of our interoperability, our networks and our platform beyond a PowerPoint presentation – we wanted to show the customers real evidence of it working.”
way to having a good team.
“You can always teach skill, but the right motivating factors and the right attitude towards what you’re trying to achieve is a hell of a lot more important than how good you are as an IoT engineer or how good you are as an executive.
“The team is what actually makes the business. Being able to put ourselves in our customer’s shoes and create Water Bureau is truly derived from our own team’s experience and capability to actually identify and draw those requirements out of the customer – if it wasn’t for our team, we would have never been able to build the capability we’ve built.” U
Nucleus 3 CEO, Louis Limnios, at the Nucleus 3 lab.
Image:
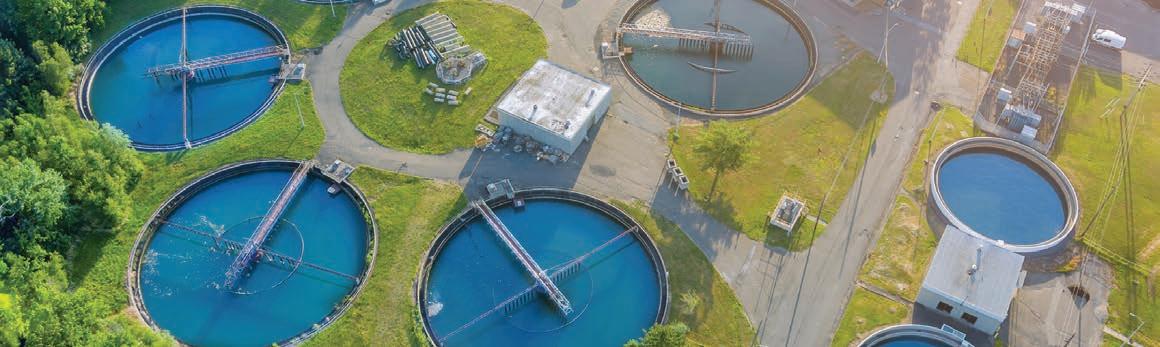
COLORIMETRIC & ISE MULTI-PARAMETER ANALYZER TECHNOLOGY
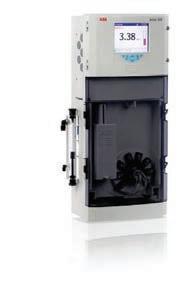
UV/VIS MULTI-PARAMETER ANALYZER TECHNOLOGY
SENSORS TARGETING SPECIFIC APPLICATIONS
UviTec™ Modular digitally enabled platforms
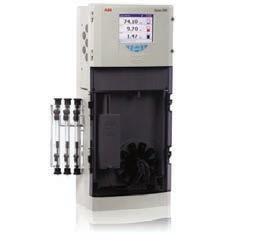
• Aluminium
• Ammonia
• Water colour
• Fluoride
• Hydrazine
• Iron
• Manganese
• Phosphate
• Silica
• Sodium Aztec
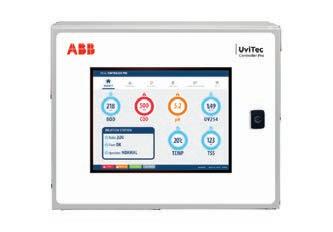
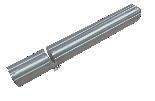

• BOD/COD
• TOC/DOC
• UV254/UVT
• Surfactants
• TSS
• Ozone
• Benzene
• Chromium
• Nitrate/Nitrite
• Permanganate

Contact us
Bella Garg
National Sales Specialist Continuous
Water Analyzers
Tel.: +61-473240521
Email: bella.garg@au.abb.com
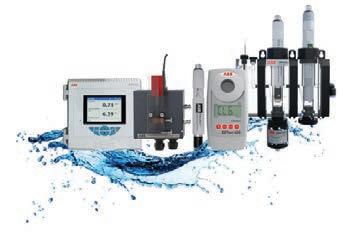

• pH • ORP
• Conductivity
• Chlorine
• Chlorine Dioxide
• Dissolved Oxygen
• Turbidity/TSS
• Liquid AI/ EZlink
• Transmitters
• Recorders and Controllers
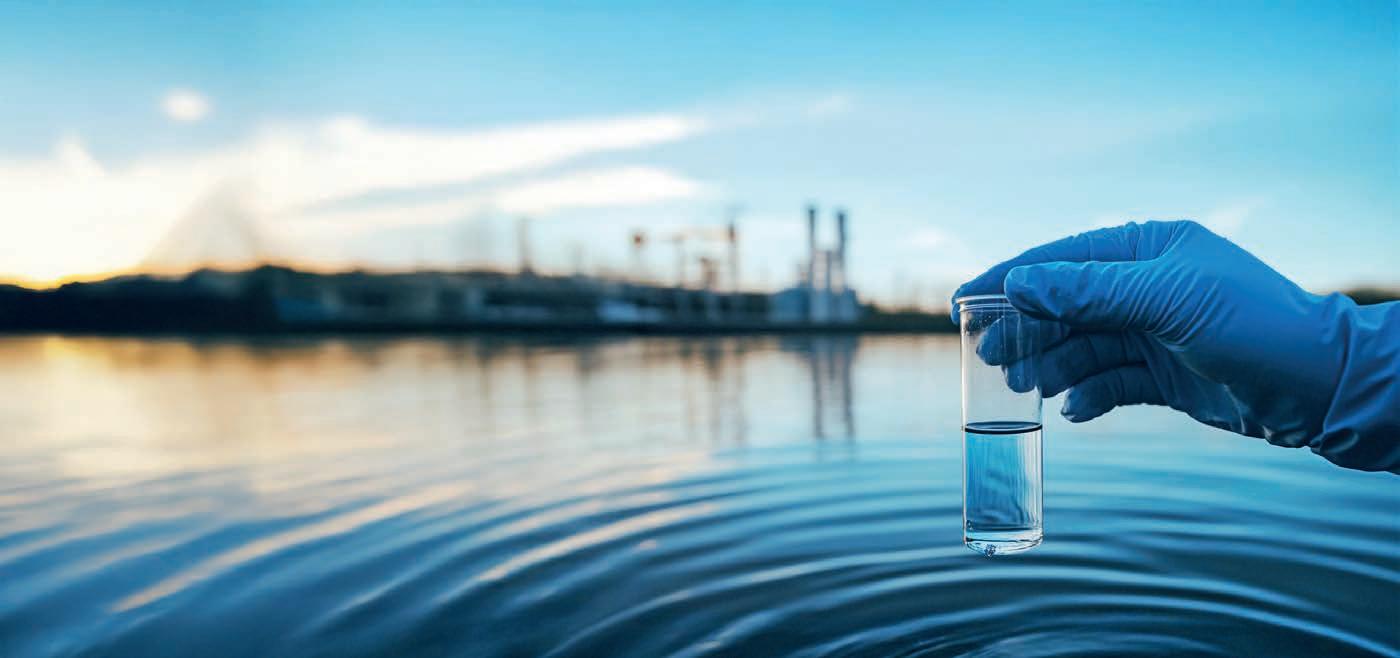
Quality control
Climate change isn’t just reducing the amount of water available – it’s also impacting the quality of source water and putting a strain on Australia’s treatment facilities.
As hotter and drier weather becomes the new norm, climate change is opening the doors to severe bushfires, and unpredictable storms and floods.
While the risk of water scarcity looms large due to less rainfall over time and extended droughts, these long dry periods followed by heavy rains can also impact the health of our waterways and disrupt the quality of our source water.
At the same time, Australia’s population is booming, which not only increases the demand for water, but increased urbanisation also means more surfaces that are impervious to water, like roads and buildings, which prevent rainwater from soaking into the ground and being naturally filtered. Instead, more pollutants such as oil, metals and sewage are carried into our water supply, particularly during heavy rainfall events.
These issues aren’t isolated, however; climate change increases the risk of bushfires, the ash then hinders the soil’s ability to absorb water and makes it prone to erosion1 – then if an extreme flooding event comes along afterwards, that soil is washed into the waterways. This soil is often full of chemicals used in fire suppression activities, while the ash and charcoal release numerous nutrients, metals and toxins into the waterways that otherwise wouldn’t be there.
At best, this disrupts the balance of metals and chemicals – such as ammonia, fluoride, aluminium, iron, manganese and phosphate – found in source water, and at worst it introduces dangerous toxins that prevent the use of that catchment entirely, exacerbating water scarcity.
Customer expectations around the quality of drinking water are also higher than ever, and as cost-of-living increases water treatment facilities are also feeling the pressure to tackle these challenges while ensuring prices remain as affordable as possible.
Good measure
The climate, population and geographical conditions of source water greatly determines the amount of chemicals that need to be used during the treatment process.
The Australian Drinking Water Guidelines (ADWG) sets out a strict limit for the amount of certain chemicals that can be in our drinking water – but if the quality of the source water varies considerably then it must be closely monitored to ensure optimal treatment.
To navigate these challenges and take immediate action when an issue arises, utilities need to be able to analyse the current process conditions in real-time. Manual testing methods are not only time consuming, but they
take up operators’ precious time. Continuous water quality analysers like the ABB Aztec 600 series arms water treatment facilities with the information they need to adapt to any changes in water quality – but as every treatment facility has its own unique challenges water authorities need to choose a solution that can work the way they work.
Starting from the source
Depending on the nature of your facility, automatic water quality analysers can typically assist with all the key stages of the water treatment process – and in ABB’s case, the Aztec 600 series is designed to work both as a single system or part of a multi-stream configuration, and can even be integrated with existing analysers2.
As raw water enters a treatment facility, the initial levels of ammonia, iron, manganese, phosphate and aluminium can be measured before the application of treatment processes including aeration and chemical dosing.
As the levels of these substances fluctuate depending on conditions like climate, ground erosion, thermal changes and disturbances of water sources, closely monitoring these initial levels helps streamline the treatment process, optimise resource and avoid wasted chemicals.
Ammonia can be found naturally as a result of biological degradation and can enter both ground and surface water through runoff of waste products, such as fertiliser. It is also used as part of the treatment process – carefully measured doses of chlorine and ammonia are added to water to monochloramine, which works as a disinfectant. However, it’s essential to have just the right balance of the two chemicals – too much ammonia can encourage the growth of nitrifying bacteria, whereas too little can reduce the efficacy of the disinfection process and create harmful byproducts.
Similarly, water scarcity has led to a rise in the levels of naturally occurring minerals like manganese, aluminium and iron in raw water sources – however a range of factors causes variation in these quantities, not just between different service areas, but on a day-to-day basis.
Elevated concentrations iron and manganese can impact the taste and colour of drinking water, as well as stain of pipes and fittings. Iron can also be introduced via corrosion of cast iron water mains, and damage to these assets exacerbates this issue.
Aluminium is also used as a flocculant to remove impurities during water treatment processes, and helps reduce the turbidity and bacterial content of water prior to the final stages of treatment and disinfection.
1: https://www.waterquality.gov.au/sites/default/files/documents/impact-bushfires.pdf. 2: Whitepaper: ABB Aztec 600 colorimetric analyzer: Pure continuity, clear compliance
3: https://guidelines.nhmrc.gov.au/australian-drinking-water-guidelines/part-5/physical-chemical-characteristics/aluminium. 4: https://guidelines.nhmrc.gov.au/australian-drinking-water-guidelines/ part-5/treatment-chemicals/sodium-hexametaphosphate. 5: https://guidelines.nhmrc.gov.au/australian-drinking-water-guidelines/part-5/physical-chemical-characteristics/fluoride
Climate change has an impact on the quality of source water, making the treatment process more challenging. Image: Nuchylee/stock.adobe.com
The ADWG strongly encourages authorities to keep acid-soluble aluminium concentrations as low as possible, preferably below 0.1mg/L, but levels must not exceed 0.2mg/L3. While the there is no health-based guideline set for aluminium at this time, according to the National Water Quality Management Strategy there is considerable evidence that aluminium is neurotoxic.
While a key component in fertiliser, polyphosphates, such as sodium hexametaphosphate, are also sometimes used to prevent corrosion in water treatment facilities.
Under the ADWG, sodium hexametaphosphate should be used in such a way that any contaminant or by-product formed by the use of the chemical does not exceed guideline values for that particular chemical4.
By arming themselves with real-time information about the quality of the water going into the facility, operators can ensure a high level of accuracy in the dosing stages and reduce the additional costs associated with overdosing. If an issue does occur, then crews are empowered to immediate action to prevent failure.
ABB’s Aztec analysers uses advanced optics to ensure that measurements remain precise, even in challenging conditions. Each Aztec 600 analyser incorporates automatic LED intensity adjustments during calibration, compensating for drift and fouling to provide stable readings even in environments with high suspended solids, a problem common in water sources following bushfire events or heavy rainfall.
VIP treatment
Close control of treatment processes can help reduce energy consumption, optimise chemical usage and minimise wastage from incorrectly treated water.
After any pre-treatment processes have been completed, analysers can once again be used to monitor things like iron or manganese concentrations. Where a clarification process is used, water may also be monitored to assess whether coagulants used in the treatment process are being under or overdosed.
Online monitoring provides plant operators with an early warning of any changes to the treatment process, enabling operational decisions to be made in near realtime. This level of process control is not possible with manual testing alone, where potentially important events that occur between less frequent manual sampling can be missed.
Colourmetric analysers like the Aztec 600 that include automatic two-point calibration enable operators to verify analyser’s performance against standards of known concentration.
Self-cleaning abilities can also improve accuracy by ensuring the optical cell and analyser tubing used for sample measurements remain free of residual particles between each analysis. The Aztec 600, for example, includes patented mechanical cleaning function uses
the piston movement to wipe the optical cell with every measurement – which is particularly important when measuring raw waters where optical contamination can be a real issue.
The Aztec 600’s piston and optical sensor use air to mix the sample and reagents, eliminating the cost and maintenance associated with mechanical or electrical stirring systems. The inherent product design and autocalibrating features means that maintenance is only required annually.
The finishing touch
After the filtration process is complete, continuous analysers can then take a final sample to ensure that the treated water meets the required standards and can also assist with the fluoridation process.
The ADWG say that fluoride has been shown to improve dental health, however high concentrations can result in a range of health issues5 – so accurate dosing is vital.
However, underlying levels of natural fluoride in certain areas as can complicate this – and aspects like climate, water consumption and groundwater quality need to be taken into account to determine the optimal approach.
Situating a sampling point for any online monitoring instrument in a location where the sample is likely to have been sufficiently mixed but before the water is drawn off to the distribution network can help maximise accuracy.
Again, solutions like the Aztec 600 Fluoride offer built-in alarms prevent incorrect dosing of fluoride, and can detect process failures before they affect the quality of the water leaving the plant. This process optimisation also increases plant efficiency; reducing capital and operating costs, as well as chemical and energy usage – cost savings than can then be passed on to customers
To aid in a smooth integration into existing infrastructure without causing significant downtime or operational challenges, the Aztec 600 analysers are designed easy installation and minimal maintenance.
The system’s advanced communication protocols – such as Ethernet connectivity, Profibus DP v1.0 and SD memory cards for data storage – allow for easy integration into existing control systems, offering real-time monitoring and enabling remote data access.
Online instrumentation takes the guesswork out of water quality management, and continuous analysers like the Aztec 600 are the key to overcoming treatment challenges and ensure a secure water supply for all Australians. But with a host of variables to consider, utilities need a solution that can work the way they need it to. U
For more information scan the QRcode or contact bella.garg@au.abb.com for expert advice
Streamlining the digital transformation
As utilities embrace digital innovation, effective field services are the driving force behind widespread integration.
Smart meters are revolutionising the utility sector, providing a mechanism for utilities to accurately monitor energy and water consumption and share real-time data on usage with customers.
As demand for this infrastructure continues to rise, utilities need to step up the pace on the rollout – but this is easier said than done.
Field crews play a crucial role in the rollout of intelligent devices, tasked with everything from installation to troubleshooting, upgrades and repairs.
However, their jobs are often complicated by the restraints of conventional logistics methods that struggle to keep up with the demands of real-time inventory management, last-mile delivery and tight schedules.
Overcoming these challenges and optimising field services holds the key to success to the sector’s digital transformation.
Intellihub has been at the forefront of the smart meter rollout taking the industry by storm.
With an extensive rollout schedule and specific customer order requirements to meet, the company engaged field service providers (FSPs) across the country to get the job done, distributing inventory into the FSP supply chains.
However, this approach presented various issues, ranging from FSPs with overlapping warehouses and distribution networks, to reduced visibility and control of assets leading to ‘lost stock’, over-ordering and a lack of robust scanning systems and processes.
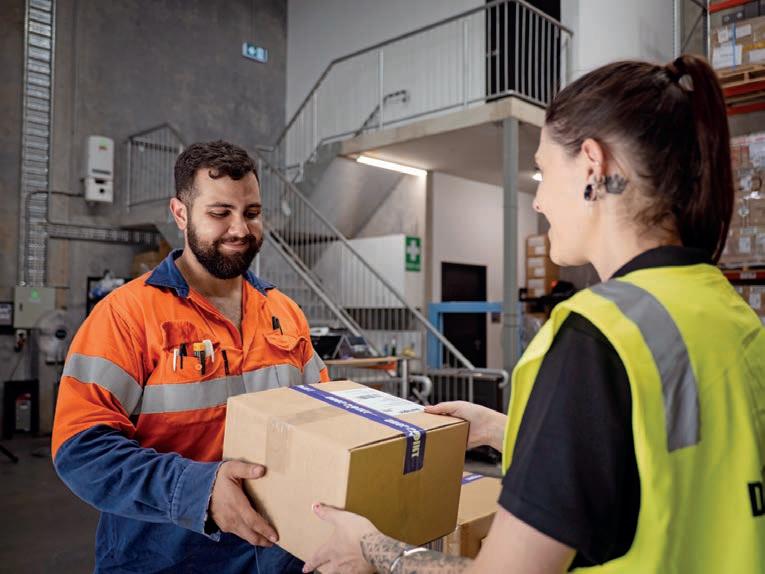
supply chain, from dispatch to installation. This gives Intellihub real-time insights into inventory consumption and lifecycles, enabling data-driven decisions for continuous improvement.
These challenges highlighted the need for Intellihub to find a reliable partner who could improve inventory management and last mile logistics, leading the company to Droppoint.
Collaborating closely with key stakeholders, Droppoint developed a comprehensive inventory management solution, perfectly tailored to the unique needs of each FSP.
This included:
• Strategic inventory hubs: using historical and predictive analysis, Droppoint used pinpointed optimal locations for inventory collection, ensuring easy access for technicians whilst minimising retrieval time.
• Reliable replenishment: Droppoint leveraged transport time data to guarantee technicians always had the necessary stock, preventing delays and maximising productivity.
• Customised configurations: each inventory location was configured to FSP specifications, including dedicated areas for returns, refurbishment and disposal. Security was prioritised with two-factor authentication, ensuring only authorised personnel could access materials.
• End-to-end visibility: Droppoint’s layered platform provides complete transparency across the entire
The custom solution had immediate impacts on the project, with Intellihub seeing an additional two–three jobs completed per technician each week, a 30 per cent reduction in depot inventory holding and a ten per cent increase in scanning compliance.
As the utility sector charges towards a digital future, optimising field services will be essential to the smooth and timely rollout of intelligent devices – and Droppoint makes this transformation easy.
As the leading field service inventory management software provider in Australia and New Zealand, Droppoint partners with utilities to create bespoke logistics solutions that take the stress out of field operations. From forward stocking to parts management and logistics, in-night deliveries, real-time tracking and a flexible network of more than 500 pick-up and drop-off locations, Droppoint ensures the right part gets to the right place at the right time.
“The Droppoint solution allows technician inventory collection near their home location or job site, increasing their jobs per week and greater ease of processing,”
Intellihub GM Supply Chain and Procurement, Stuart Sproull said.
This innovative approach offers a glimpse into the future of efficient field services in the utility sector. U
With Droppoint, utilities no longer need to suffer through ineffective logistics.
Image: Droppoint
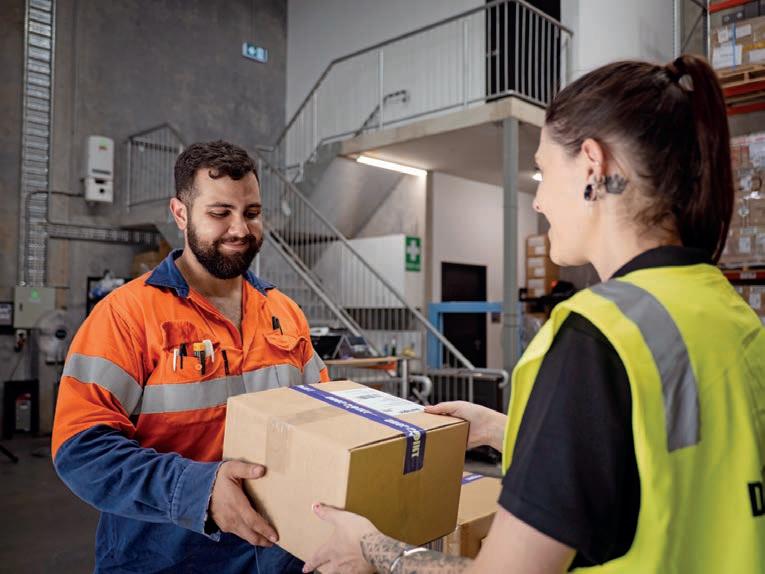
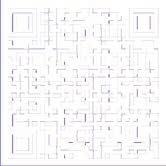
Save your energy
Energy efficiency is the first step on the road to decarbonisation, but how can older wastewater treatment plants cut down power usage without impacting performance?
According to Atlas Copco Low Pressure Specialist, Greg Williams, blowers are responsible for around 70 per cent of all energy used on a wastewater treatment site. However, optimising power consumption is not just about choosing a more efficient device.
“In older plants, blowers are primarily used for aeration in large tanks. These tanks require more air during peak times and less during off-peak periods,” he said.
“The diffused air introduced into the tanks sustains the microorganisms that decompose waste in the bioreactors. Precise aeration is critical, as over- or under-aeration can disrupt the delicate balance required for optimal biological activity.
“This process, combined with the changing demands, results in variable air requirements from the blowers, rather than a fixed flow rate.”
Mr Williams explained that the ability to adapt to this variability is critical to optimising a blower’s energy consumption.
“Atlas Copco’s range of ZS oil-free rotary screw blowers can incorporate a variable speed drive that allows them to adjust the flow range. This ensures that only the required flow is delivered to the tanks during low-demand times, saving energy and costs.”
Silent treatment
Mr Williams said that the Atlas Copco team recently assisted a wastewater treatment plant in New South Wales to overcome similar challenges. He explained that the plant’s existing turbo blowers, which were around 25 years old, no longer met the facility’s diverse flow rate demands.
“The old machines were very noisy and had significant issues with turndown. At night, they had to vent the extra air to the atmosphere because they couldn’t adjust the blowers, leading to noise pollution and wasted energy,” he said.
After a detailed assessment where the company examined the system and simulated new installations to identify the best solution, Mr Williams said that Atlas Copco recommended ZS5VSD Screw Blowers as an ideal replacement.
“[Compared to older machines], the ZS5VSD is about 35 per cent more efficient, and they couldn’t believe how quiet our machines were,” he said.
“Due to the efficiency of our rotary screw technology, we were able to reduce the installed power total significantly. They previously had five 132kW blowers on site and the new package included five 75kW ZS5VSD blowers to do the same job.
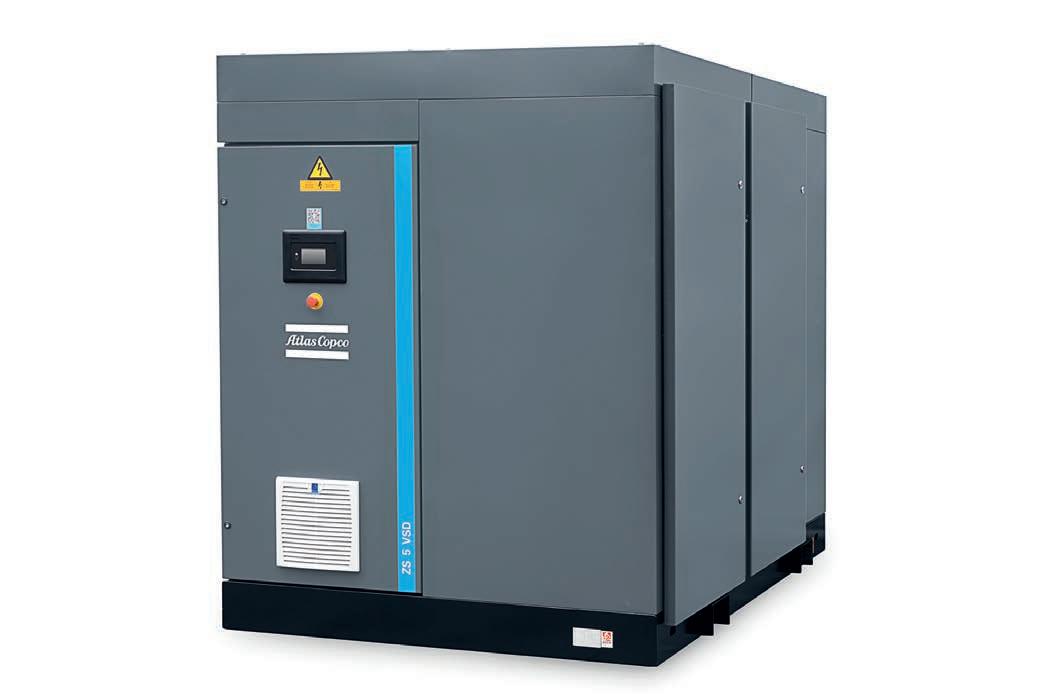
“Atlas Copco also undertook all the design and engineering work and collaborated with local contractors to complete the installation. The site team was extremely satisfied with the overall outcome.”
Efficient operator
For Mr Williams, taking a customised approach is non-negotiable.
“For existing wastewater plants looking to reduce energy, we typically place data loggers on the installed blowers for a full week. The collected data is then input into dedicated Atlas Copco software to simulate our machines within the system,” he said.
“This allows us to demonstrate energy savings and assess the plant’s performance, enabling the customer to see their air usage clearly.”
While Atlas Copco’s line of ZS screw blowers were the correct solution for this site, Mr Williams said that the company offers a range of low-pressure technology to meet every site’s requirements.
“You don’t have to replace your existing machines with the same blower technology. We’ll collaborate with you to understand your specific process and recommend the most efficient and reliable technology for your site,” he said.
“We always listen and work with each of our customers to find the best solution for them.
We’re not just offering the customer one type of technology – we’re providing them with the right technology.” U
For more information, visit www.atlascopco.com/en-au/compressors
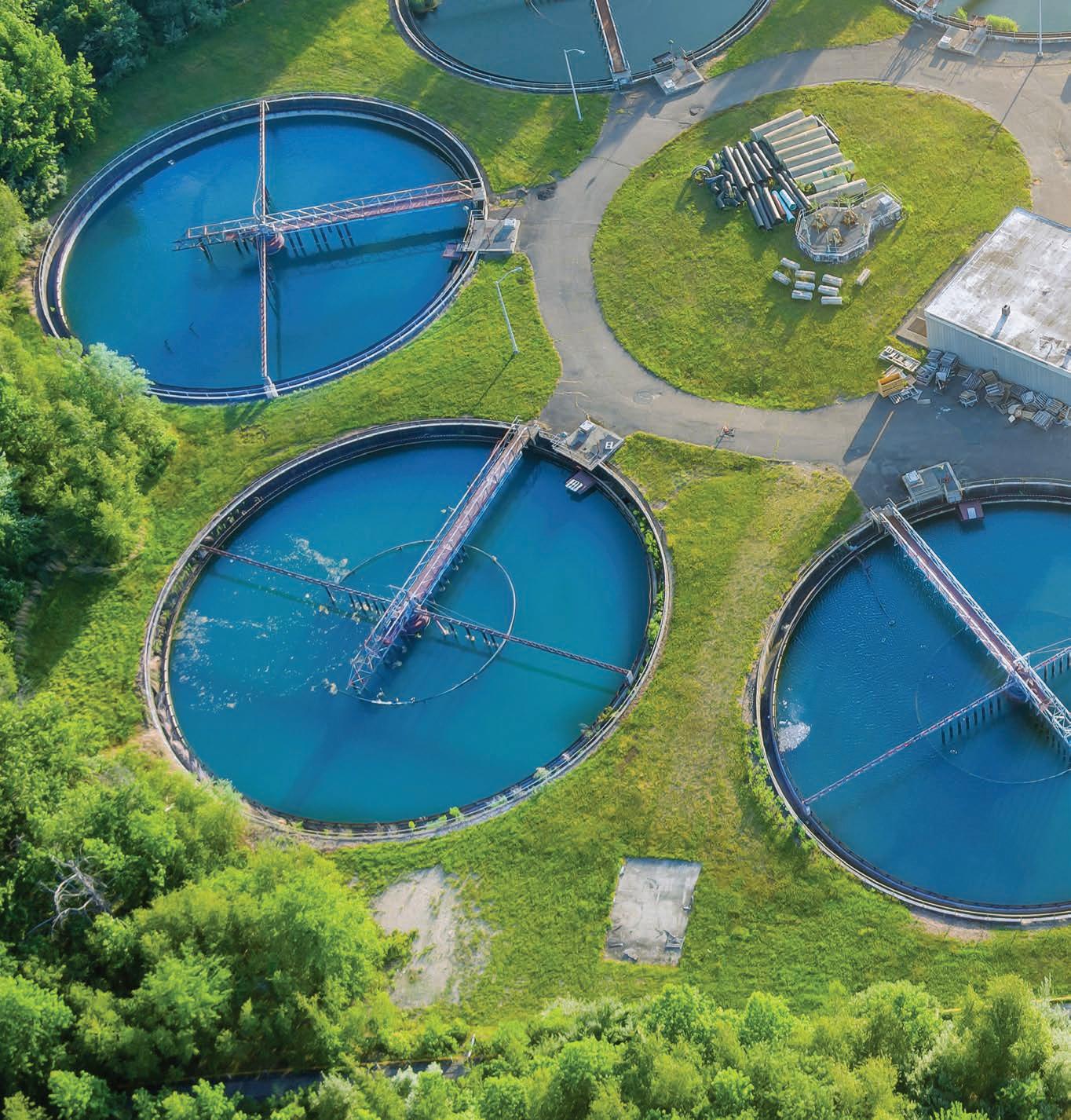
Image: Atlas Copco
Innovative Solutions for Your Efficient and

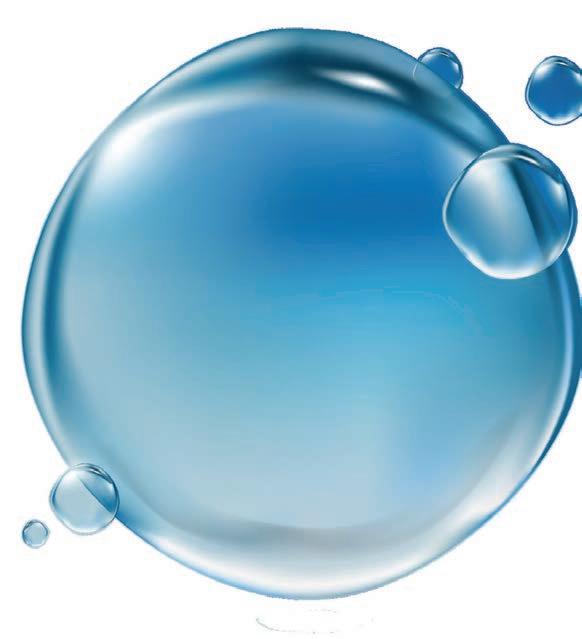

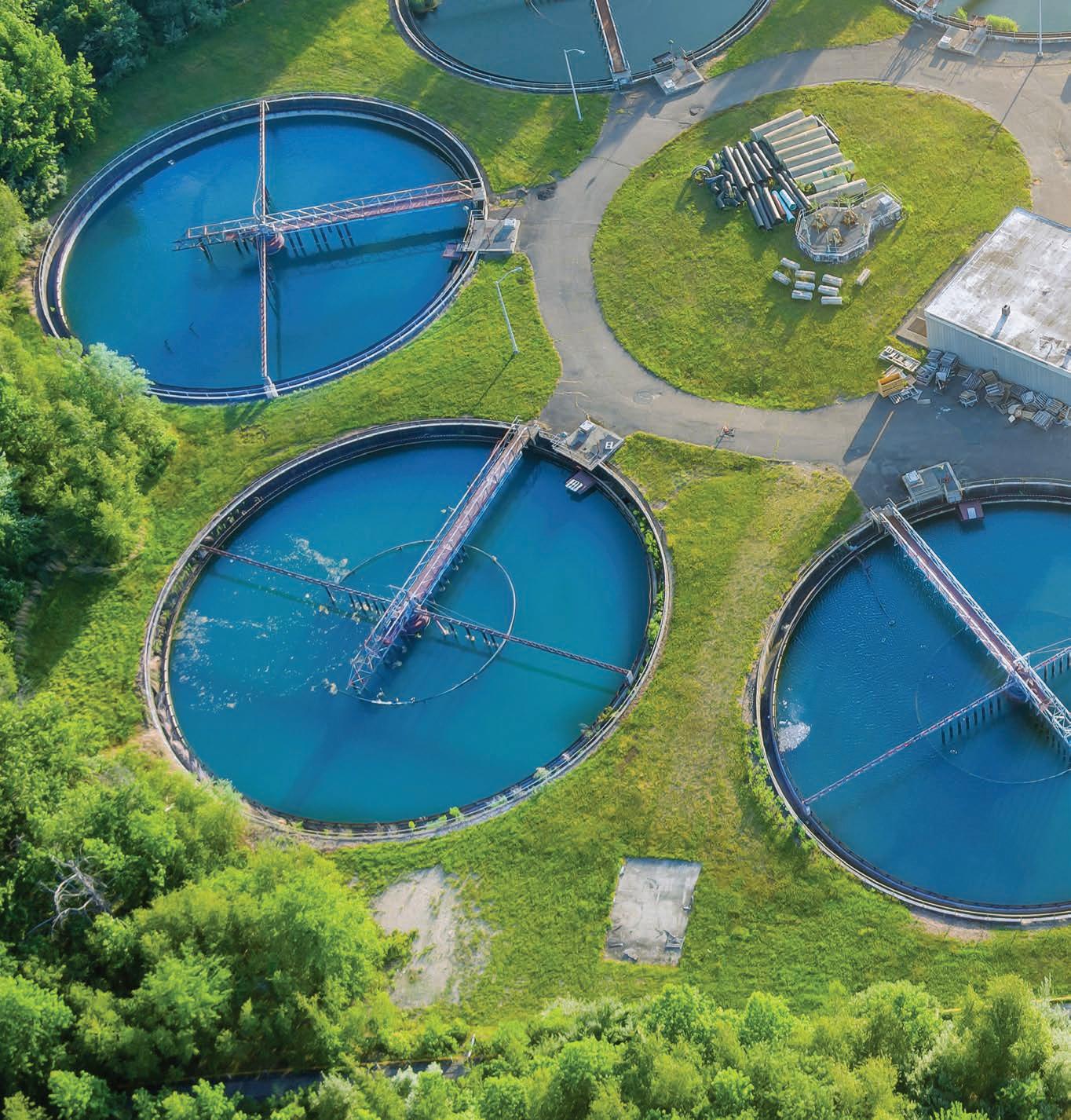
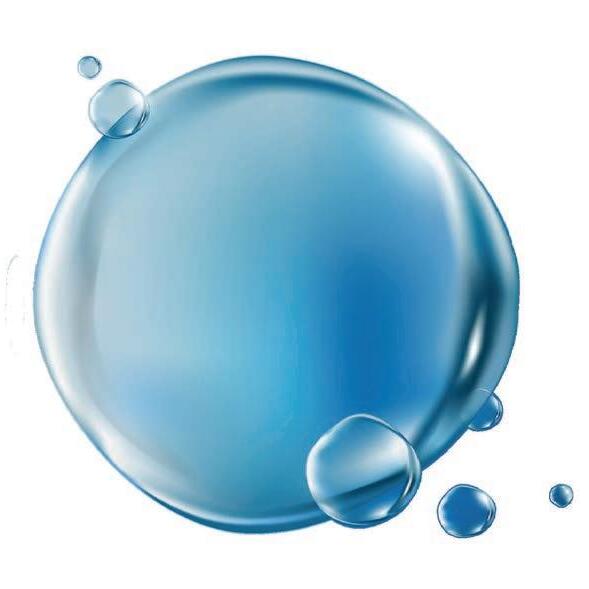
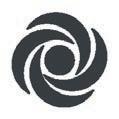
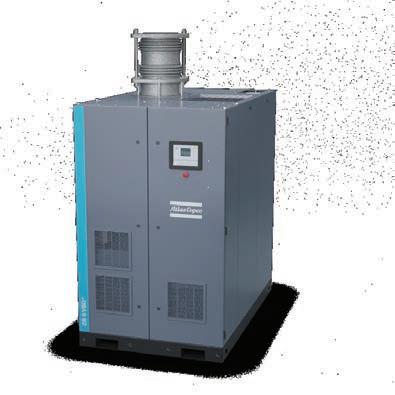




Low pressure blowers and compressors
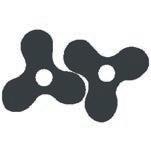
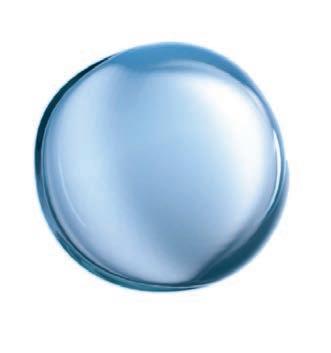
Air blowers can use up to 70% of the energy in water or wastewater treatment plants. To help reduce this, Atlas Copco offers a wide range of energy-efficient blowers. Let Atlas Copco help you choose the right technology to optimise performance and lower your overall costs.
Lobe | Rotary Screw | Turbo | Multi-stage
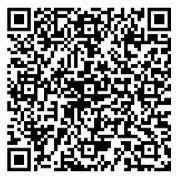
Making every drop count
As Australia faces a future affected by climate change, the reliability of its water systems become more important than ever. But when water security covers such broad ground, where do water authorities focus?
Interflow Contracts Manager, John Weaver, said at the centre of most water security success is a well‑maintained asset base.
“In the late 1970s and early 1980s there was a flurry of new sewer and water construction throughout Australia,” he said.
“In the late 80s and early 90s, the sector moved away from new construction and towards asset management.”
Legislation was introduced locking councils and water authorities in to coming up with long‑term plans to maintain the value of their assets.
“That led to a lot of the relining work that Interflow did from the early 1990s, which is how we became deeply involved in water security,” Mr Weaver said.
While maintenance will always be a core focus, the attention of water managers is also shifting towards ensuring water supply will not be affected by climate change.
“In other words, how do we take the stuff that falls from the sky, hold on to it and reuse it over and over again,” Mr Weaver said.
“That’s the next phase of water security.”
Recycling will play a major role in the water security solution in Australia, he believes. This has to do with reusing wastewater in the potable supply, as well as considering where wastewater is being sent.
How do managers prevent water loss?
Non revenue water loss is a very big issue globally. In Australia, according to the Bureau of Meteorology, non‑revenue water loss stands at around ten per cent of water utilities’ system input.
Mr Weaver said, however, that the more networks reduce water loss, the less water required in the long run.
The combination of the reuse of water and the prevention of water loss could dramatically reduce the amount of water required in our systems.
“And so, a large part of the solution lies in the network,” Mr Weaver said.
“How can the water network be optimised and operated with a program that identifies potential leaks before they actually occur?”
That solution involves a mix of data d riven technology and proactive renewals programs.
How can Interflow help with water security?

Interflow’s role in water security right now is in collaborating with water authorities on their water and sewer renewals targets.
The organisation’s goal is to continue to improving asset reliability and service life, so utilities see less bursts and
leaks, and instead conduct more proactive maintenance.
“A big part of the solution comes from innovating better ways of doing things, which is what Interflow does best,”
Mr Weaver said.
“When we’re part of the conversation from the start we can often help release funds and resources into other areas, so water authorities can continue to improve.” U
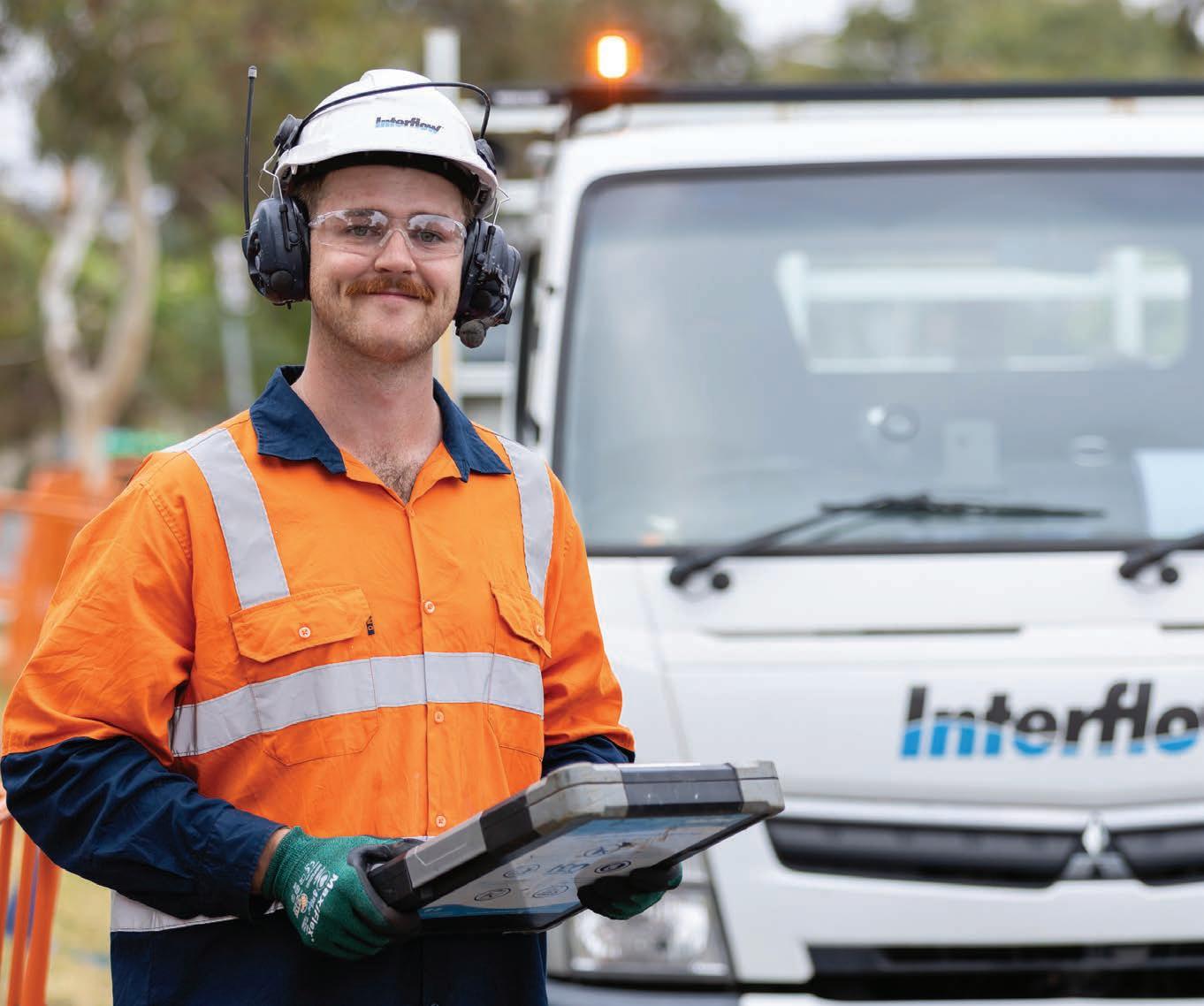
Image: Interflow.
The centre of most water security success is a wellmaintained asset base.

We’re Creating the Future of Water for our people and communities, for generations to come
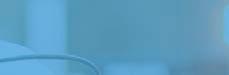
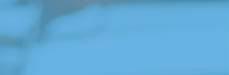
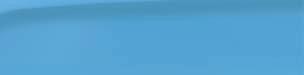
“When we’re part of the conversation from the beginning, we can often help release funds and resources into other areas, so water authorities can continue to improve.”

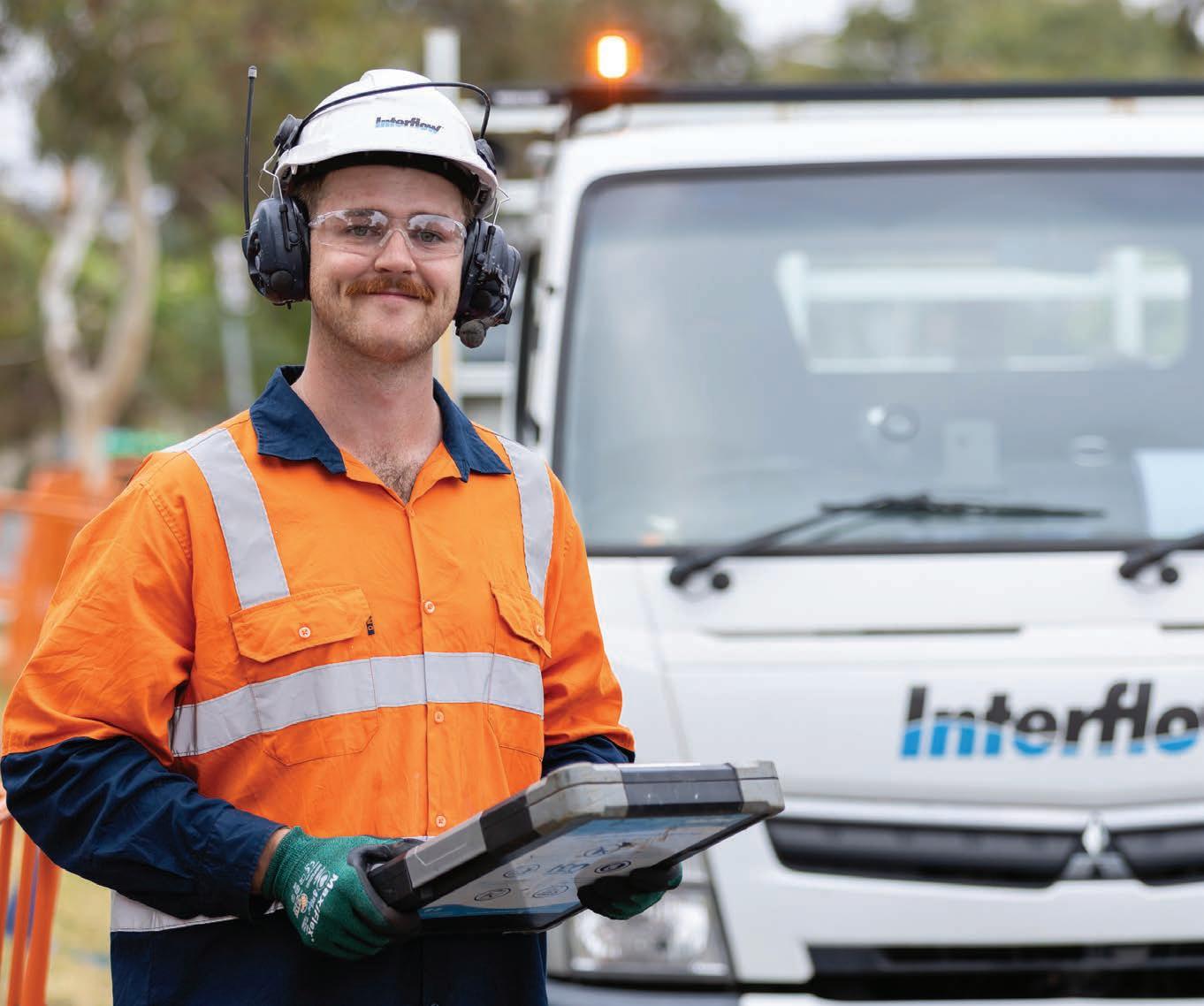
Operation sustainability
Advanced sealing solutions can help both reduce the energy consumption and optimise the performance of water and wastewater pumps.

With everyone depending on vital water and wastewater services, the pressure is on to keep assets running while meeting new standards for sustainability and efficiency.
As water and wastewater treatment facilities age, keeping these assets up to scratch requires utilities to carefully balance a need for environmental compliance and a growing demand for sustainable practices, while also maximising operational efficiency.
Not only is it essential that costs are managed carefully to keep prices affordable for customers, it’s also critical that the water continues to flow while maintenance and innovative works are carried out.
When water and wastewater facilities that operate with equipment that has surpassed its intended lifespan –including corroded tanks, leaking pipelines and ageing pumps – this all too often leads to inefficiencies, frequent breakdowns and escalating repair costs.
But modernising this infrastructure is no small feat; it involves planning to minimise disruptions while addressing the core issues.
Chesterton has developed solutions that allow facilities to extend the life of critical assets without the need for expensive replacements. By restoring worn components and protecting them from future damage, facilities can maintain operational reliability while managing costs and staying compliant with international standards.
Breaking the cycle
An ongoing cycle of reactive maintenance presents its own set of challenges. For many facilities, maintenance is an emergency response triggered by equipment failures, which leads to costly downtime and strained budgets.
This approach is unsustainable for operations requiring continuous reliability. However, a shift to predictive maintenance allows asset owners to leverage advanced monitoring technologies to track equipment performance in real-time.
These data-driven insights enable utilities to identify potential problems before they escalate, allowing for timely interventions that reduce downtime and improve resource allocation, bringing a sense of reassurance and confidence to your operations.
As pumps and motors are required to run continuously, energy efficiency is another key concern for water and wastewater facilities.
Improving efficiency without compromising performance is essential to reducing costs and meeting environmental regulations. Advanced sealing and lubrication solutions can minimise friction, prevent leaks and optimise performance – thereby lowering energy use and reducing environmental impact.
Safety comes first
Safety is of paramount in water and wastewater facilities, where hazardous chemicals, high-pressure systems, and heavy machinery pose significant risks.
Creating a safer environment for operators requires robust training and technologies that minimise manual intervention.
Protective coatings, durable sealing solutions, and remote monitoring tools can both enhance safety while improving operational efficiency. By proactively addressing risks, facilities can create safer environments for their teams and ensure continuity in operations.
As water scarcity becomes an increasingly urgent global issue, water and wastewater facilities are under pressure to adopt sustainable practices. These include conserving water, reducing resource waste and aligning with environmental regulations.
Facilities can advance sustainability by reducing water loss, extending equipment life and optimising efficiency –an approach that both protects resources while ensuring long-term operational viability.
The success of water and wastewater facilities can often lie in their ability to adapt to these multifaceted challenges while delivering reliable, efficient and sustainable operations.
Partnering with an experienced solutions provider like Chesterton ensures access to expertise, innovative tools and tailored strategies to address the industry’s unique demands. U


Advanced monitoring technologies enable utilities to identify potential problems before they escalate.
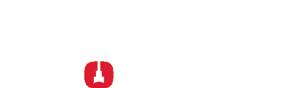

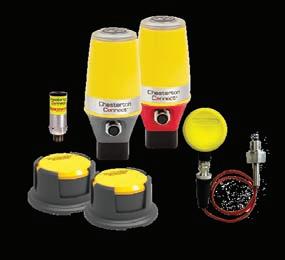
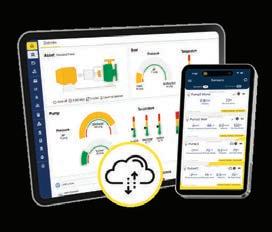
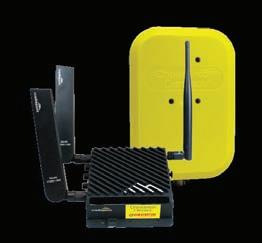
Stay Ahead of the Curve
Predict. Prevent. Perform. Stop unplanned downtime before it starts! The Chesterton Connect™ System empowers you with real-time predictive maintenance, optimising equipment performance and keeping your operations running smoothly.
Anytime, Anywhere Monitoring – Access critical pump health data straight from your smartphone, tablet, or computer with our cutting-edge IIoT technology.
Easy Setup. Instant Insights. Maximum Efficiency. Choose from preconfigured solutions tailored to your needs and take control of your equipment’s future today.
Get Started Now!
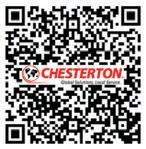
chesterton.com
chestertoncustomseal.com.au
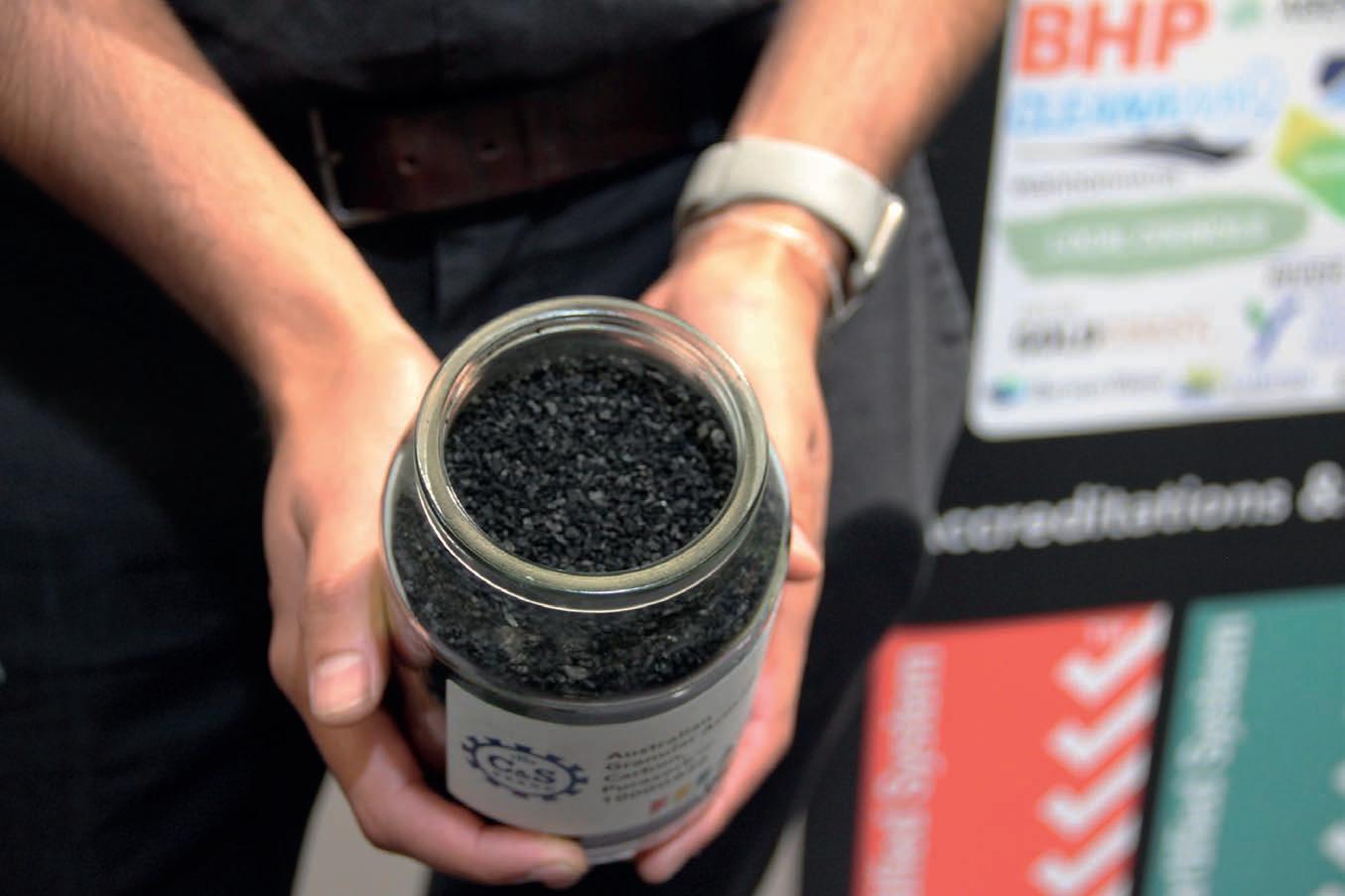
What’s the big deal about PFAS?
Recent attention from mass media outlets has sparked concerns about forever chemicals in Australia’s water supply – but there’s a few myths that need to be busted.
PFAS, or per- and polyfluoroalkyl substances are a group of man-made chemicals that are commonly used in products that are resistant to heat, grease or water – such as non-stick pans, waterproofing and firefighting foams.
Often dubbed ‘forever chemicals’, PFAS don’t break down in the environment, they are highly mobile and they’re very difficult to remove once they enter a waterway.
So, are they in our drinking water?
For those not in the know, when these reports are talking about PFAS traces being detected, they’re talking about source water, such as dams or reservoirs, which undergoes extensive treatment before it enters the potable water network.
However, not all treatment methods can effectively remove PFAS from water, and with new drinking water guidelines on the horizon we turned to an industry expert to get some practical advice on just how utilities can tackle these chemicals.
Forever is a long time
As the fourth generation to lead this family business, James Cumming and Sons Managing Director, John Cumming, grew up in the water industry. With multiple diplomas and certifications in water treatment under his belt, Mr Cumming has spent more than a decade helping water authorities solve filtration challenges.
For Mr Cumming, it’s important that the community sees and understands the constant work that water authorities are putting in to keep PFAS out of our drinking water.
“They’re very conscious of [the risks] and a lot of water authorities are regularly engaging with people like us to [constantly improve] the way they tackle that issue. They’re going through options for [both] assessments, and [for the best way to treat] different levels of PFAS,” he said.
Water authorities regularly test both treated and untreated water supplies, and many utilities not only share these results publicly but also commit to a very high standard for testing procedures.
To further tackle this issue, the National Health and Medical Research Council (NHMRC) released draft update to Australian Drinking Water Guidelines on PFAS in late 2024, which proposes an even wider safety margin for the acceptable levels of four different PFAS.
Although at this stage these guidelines are a draft only, Mr Cumming said it’s important that water authorities are equipped with the right knowledge to make the best decisions they can about how they treat their water.
“PFAS is a group of compounds with a molecular structure that is characterised by either a long- or shortchain carbon-fluorine bond,” he said.
“The most prevalent source of PFAS in Australia comes from AFFF foams, particularly around defence sites and because these compounds are highly mobile, they infiltrate soil and groundwater, and then pass into our waterways. Their use through non-stick cookware, Tupperware and clothing also means that they circulate within our wastewater network.
“Because they are ‘forever’ chemicals, there is no natural biodegradation process and circulate until they either find a stable home or are removed from the network [via the treatment process].
“The challenge is that conventional treatment processes and infrastructure aren’t necessarily geared toward treatment of PFAS.”
Mr Cumming explained that the unique molecular structure of a carbon-fluorine bond – as opposed to a carbon-hydrogen bond – makes these compounds thermally and chemically stable.
PFAS are hydrophobic, but the heads of these compounds are also water soluble, which makes them very transferable through water and soil, and therefore they’re difficult to treat and highly mobile, In other words, they are amphiphilic.
“The biggest challenge with PFAS compounds is that they can’t be removed through, coagulation, flocculation, clarification, filtration, disinfection and pH adjustment – which make up the typical treatment train of a water treatment plant,”
Mr Cumming said.
Granular activated carbon is often the most cost-effective way to remove PFAS compounds from water.
According to Mr Cumming, the most economical way to actually destroy PFAS is to break down the carbonfluorine bond, which usually requires it to be heated to more than 1100°C. There are other destruction methods but nothing yet presents a economically viable method.
“There’s not that many places that can perform thermal destruction of compounds in the first place, and you obviously can’t just boil water at 1100°C to destroy PFAS,” he said.
“So, what you’re doing with treatment technologies is just containing the compounds themselves and moving them somewhere where they don’t end up in our environment, activated carbon does that.”
Treat them right
To meet the proposed new Drinking Water Guidelines, PFAS must be barely present in treated water, and according to Mr Cumming, the first step to hitting these targets is to establish a baseline and closely monitor water pre- and post-treatment.
“Then, [they’d need to] upgrade or retrofit plants with the advanced treatment techniques to meet the guidelines,” he said.
“The most common technologies used to remove PFAS from water are ion exchange resins, reverse osmosis (RO) and activated carbon, and [utilities should conduct] a cost–benefit analysis to find [the one that’s best for them].”
Granular activated carbon (GAC) and powdered activated carbon (PAC) are often the most cost-effective way to remove most, if not all, PFAS compounds depending on their chain length and molecular weight.
Mr Cumming explained that RO systems and ion exchange resins are effective, particularly as polishing steps for industrial wastewater treatment, but require a bigger investment and come with additional challenges in terms of maintenance and regeneration.
“GAC also needs to be replaced when it’s determined that breakthrough levels have exceeded guidelines, but RO and ion exchange resins require often burdensome additional infrastructure, whereas if the current filter beds are deep enough, and allow enough contact time, GAC will remove PFAS,” he said.
Chemical attraction
As there are thousands of PFAS variants, with different chain lengths and chemical structures, Mr Cumming said the right solution must be selected for effective treatment.
“[First of all] not all filters remove PFAS, and there can be some confusion between our filter coal and activated carbon. With filter coal, particles get trapped between the granules themselves, and it is very good at removing turbidity and particulates [but not PFAS].
“Whereas activated carbon both filters out turbidity and adsorbs compounds through Van der Waals forces, where these compounds adsorb to the pores within the granules.”
make activated carbon, and Mr Cumming said that coal, wood and coconut shell are the most common.
because a lot of PFAS, especially the ones in firefighting foams, tend to be larger molecules with longer chains you want more of a macro and meso porous structure –so coal-based carbons are typically more effective than coconut or wood-based carbons,” he said.
variation on raw material source, manufacturing and activation technique and particle size grading.
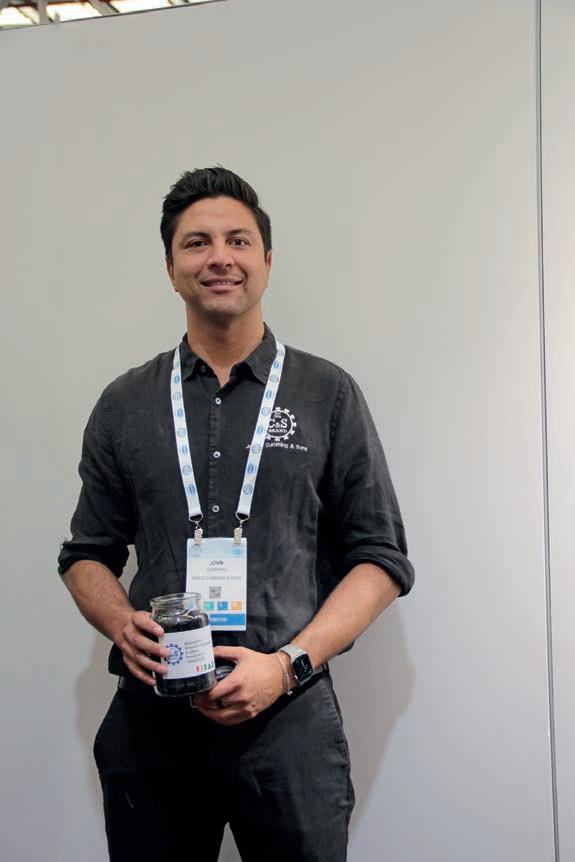
“We focus on premium Australian coal, which gives us some advantages in terms of how the pore structure is formed within the carbon. The activation process [plays a big role] and the residence time that our coal spends in the activation kilns is longer compared to traditional activated carbon manufactured overseas, which gives it a uniquely Australian pore structure.”
Even with the best product at your disposal, Mr Cumming said that this method is only effective if the water is in contact with the activated carbon for the right amount of time.
“The longer the contact time, the better or more likely, the PFAS is to be removed,” he explained.
“A lot of conventional treatment plants already have a filtration system, and if they have sufficient bed depth, they can just retrofit GAC in a similar profile to what they’re currently using to be able to treat PFAS.”
If a facility does not have the sufficient bed depth for GAC, then they can use PAC to tackle PFAS, but it can be more difficult to ensure enough contact time with this approach.
“Essentially, if you’re wanting a cost-effective method of removing PFAS in water, typically GAC will be the first line of defence,” Mr Cumming said.
“PAC can also be used, but as it’s a dosed product, and PFAS levels tend to vary in the water, GAC is often going to be more effective because it can be saturated over time. Whereas PAC will be filtered out with other turbidity and not sustained within the treatment train.
“But [before we recommend any product] we’ll usually work with a water authority and supply samples for them to perform jar testing or pilot plant work to help them substantiate the effectiveness and value of our product for their specific plant or application. U
James Cumming and Sons Managing Director, John Cumming.
Images: Prime Creative Media
Setting the digital stage
A wide-scale smart meter rollout is a mammoth undertaking, but how can utilities successfully set up a staged digital journey?
The transition to digital metering is a transformative journey for water utilities, offering significant benefits in efficiency, customer engagement and water conservation.
However, rolling out a digital metering program across an entire network can be daunting and complex. The experts at Taggle recommend a staged approach as a structured and scalable way to implement digital metering while ensuring clear, measurable outcomes at every step.
By breaking down the deployment into manageable stages, utilities can mitigate risks, optimise resources and continuously improve their strategies – but it’s important to define clear objectives at each step.
Seeing the future
The first stage, which is often a validation or pilot stage, has proven most successful at achieving outcomes when it is based around a district metered area (DMA). Creating a microcosm with one or two DMAs provides a clear snapshot to understand, visualise and experience what the future state looks like when you scale up.
Conversely, Taggle has found that pilots where the meters are scattered across the network, for example the top 100 water users, can provide some good savings from large leaks but do not represent a microcosm and prepare the utility for scaling in the same way that a DMA approach does.
The DMA structure is also the most efficient deployment program, as it focuses on a concentrated area for customer communications and installation. This also helps maximise the benefits by not just capturing water wastage (leaks behind the meter), but also network non-revenue water within that DMA. Data on how water usage behaves within a DMA provides insights into time of day and peak demands which can provide valuable information for pumping operations.

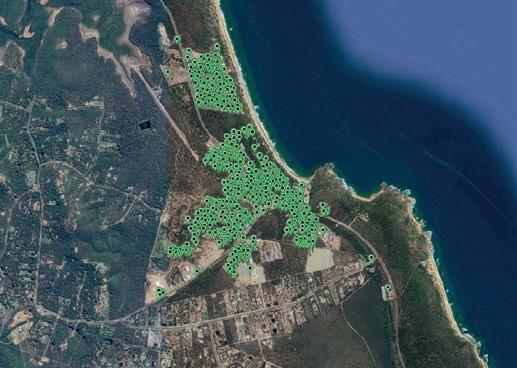
Taggle said it’s important that the first stage represents a complete but small portion of the full network – as this is used to assess the work needed to manage the organisational change process as digital meters are rolled out.
The DMA approach gives a snapshot of all the benefits that can then be used to validate assumptions in the business case, critical when funding a large-scale rollout.
As stage one wraps up, it is crucial to evaluate if the outcomes were achieved, if there were challenges or processes to polish prior to the next stage before planning the next stage.
Going all out
With the insights gained from stage one, utilities can refine their strategy for full-scale deployment. Expanding beyond the initial DMA requires careful planning to ensure that installation teams, customer engagement strategies and data integration processes are optimised.
Lessons learned from the pilot should inform broader staff training, process improvements and system adjustments to handle increased data volumes. By progressively increasing coverage, utilities can scale up digital metering in a way that ensures efficiency, stakeholder confidence and a maximised return on investment.
Defining clear outcomes helps ensure the success of a staged digital metering journey and prove the business case. Utilities must set clear key performance indicators (KPIs) at each phase, such as:
• Reduction in non-revenue water losses and network leaks
• L eak management on residential and commercial lots
• Improved customer engagement and satisfaction
• Cost savings from operational efficiencies
• Billing efficiency and accuracy with system integration By regularly assessing progress against these metrics, utilities can make data-driven decisions and refine their approach for optimal outcomes.
This methodical approach ensures that the benefits of digital metering – enhanced efficiency, water conservation and improved customer engagement – are fully realised across the entire network. U

Taggle employee Khoi Ninh gives a thumbs up after a successful meter installation.
The first stage of a digital meter rollout should represent a complete but small section of a water network.
Images: Taggle

Saving Water... by detecting leaks
Revolutionising
The utility sector is powering ahead, with a huge pipeline of critical infrastructure projects set to be rolled out over the next decade – and it’s vital that they’re delivered on time.
AEssential services are the backbone of just about everything we do, and our water, energy, transport and telecommunica tions networks need to be able to support Australia through t
to build the critical infrastructure we need – and Service Stream saw how important it was to have a partner that was equipped to navigate the fast-paced world of service delivery.
A new era of standardisation
Service Stream’s Project Execution Framework (PEx) is a comprehensive tool designed to enhance the company’s project management and service delivery capabilities.
changer for standardising service delivery, streamlining governance process and fostering continuous improvement and sustainable best practices.
should be planned, executed, monitored, and controlled. Through this standardisation, the PEx Framework ensures that all projects, regardless of their complexity, adhere to the same high standards of quality, safety and sustainability.
management, quality management, and health, safety, and environmental management.
Streamlining governance
The PEx Framework includes a streamlined governance process, which outlines a series of mandatory gates, known as PEx Gates, that serve as internal hold points and must be passed before progressing to the next phase of a project.
all reviews, approvals, and quality checks are completed, reducing the overall risk to delivery.
standards; it’s about continuous improvement, turning best practice into common practice.
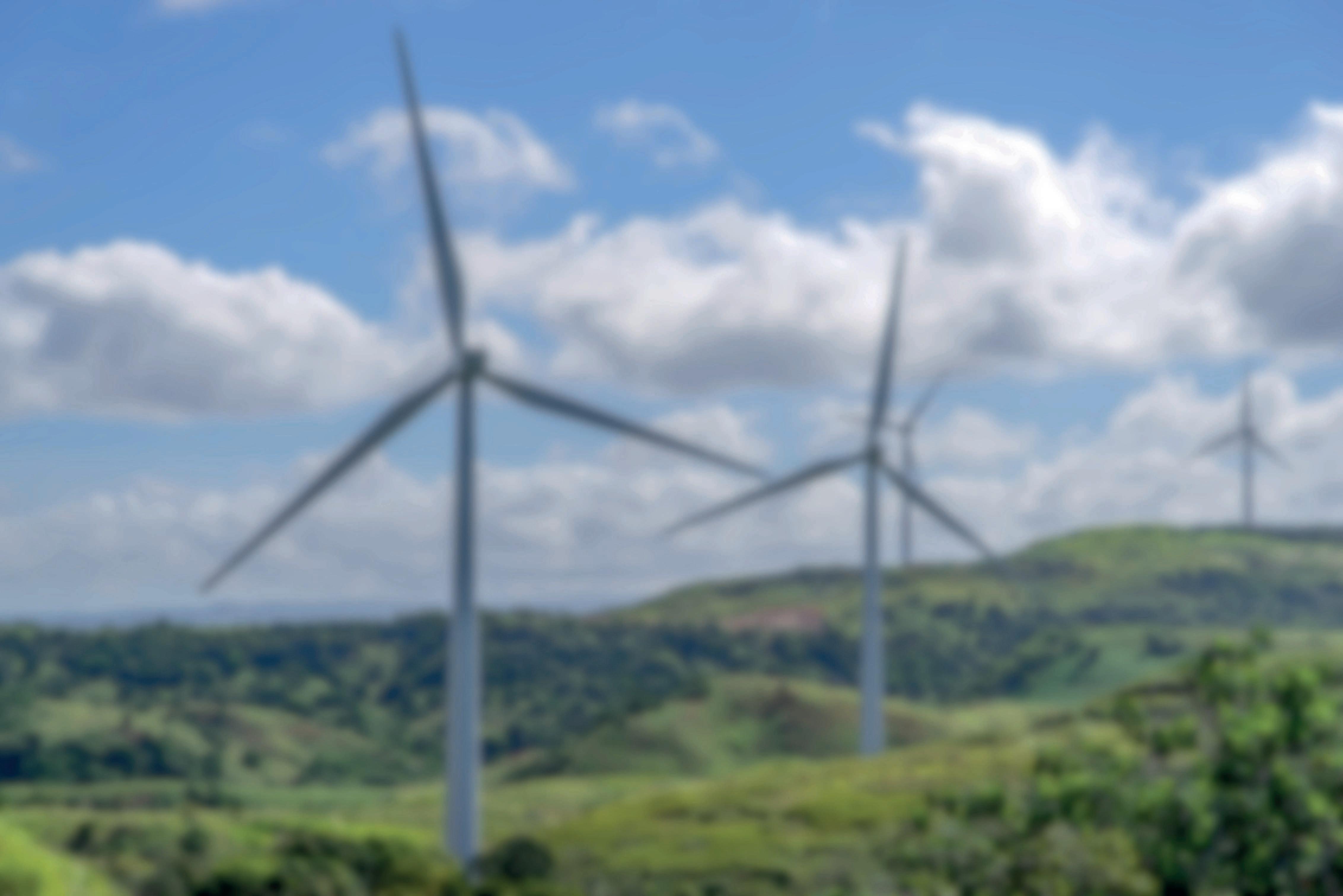
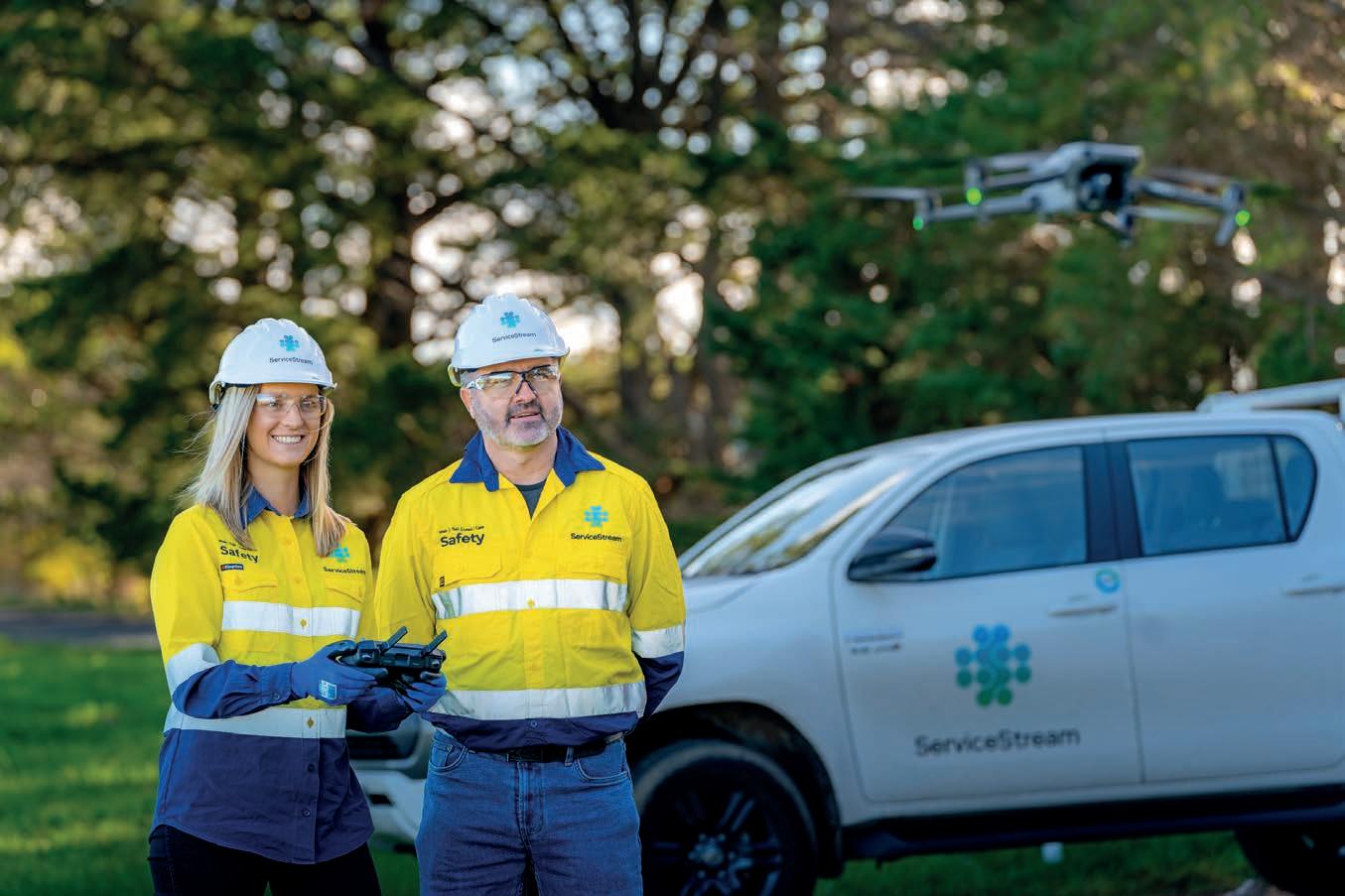

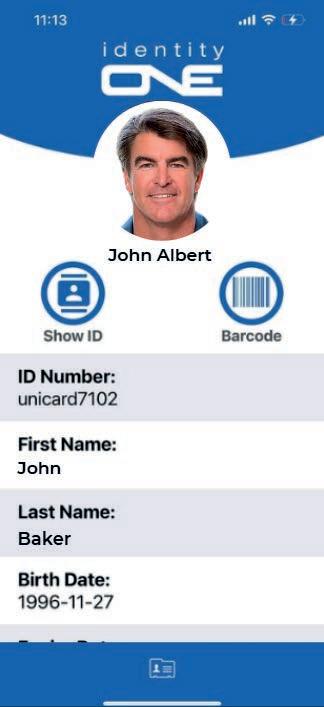
Hey team, I hope you’re all doing well! I wanted to share some exciting news about our onboarding process. We can now send digital IDs to new staff instantly, even when they can’t make it to the office. This means we can onboard new remote workers in real time, providing them with their digital IDs before their first day. It’s a great way to enhance both efficiency and security with our streamlined process.
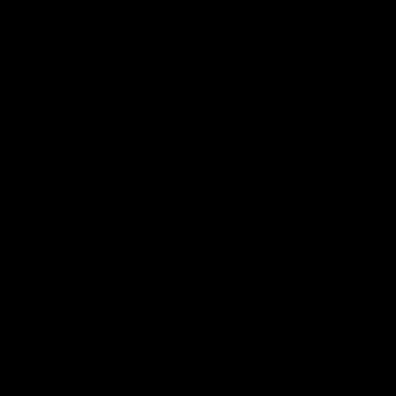
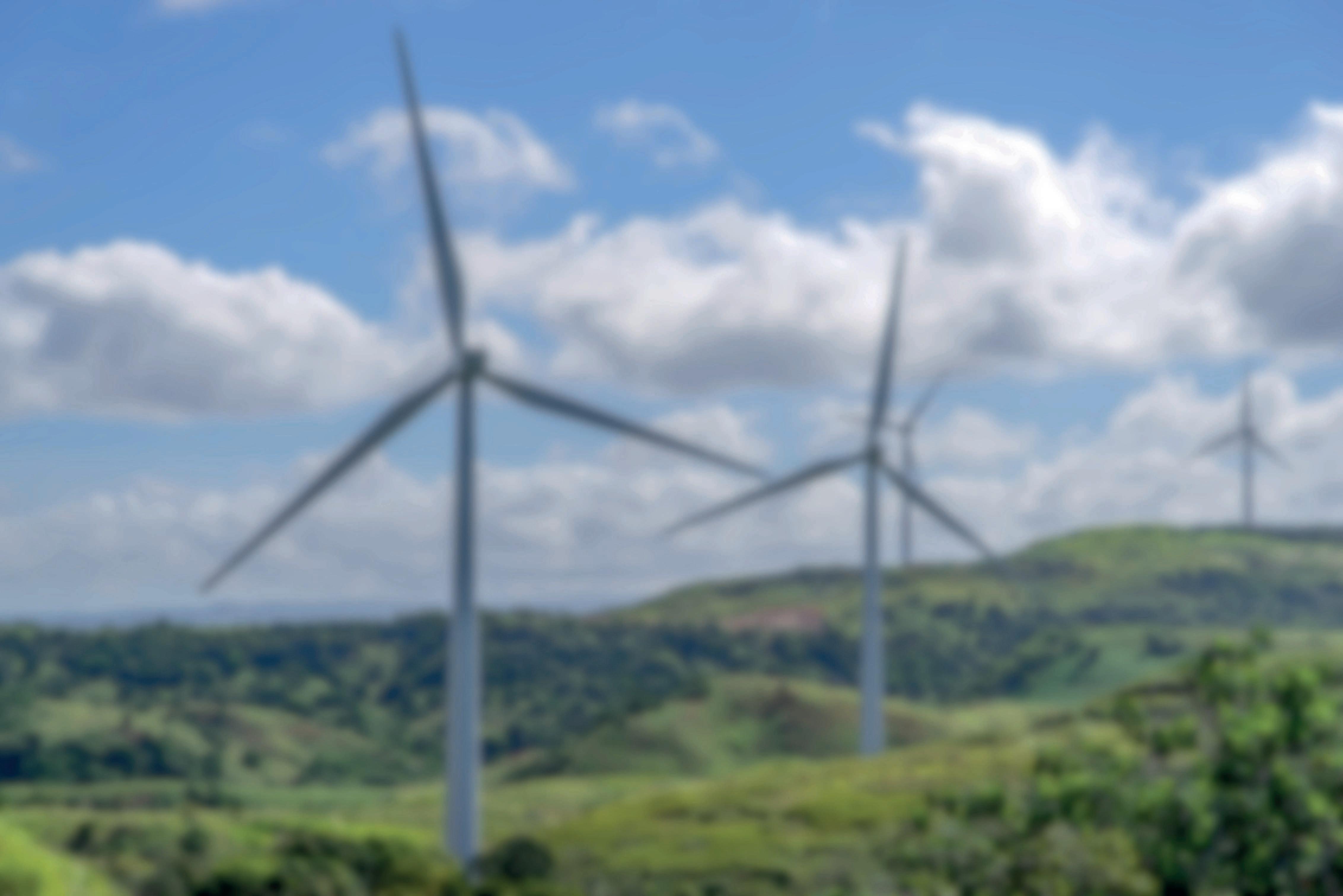
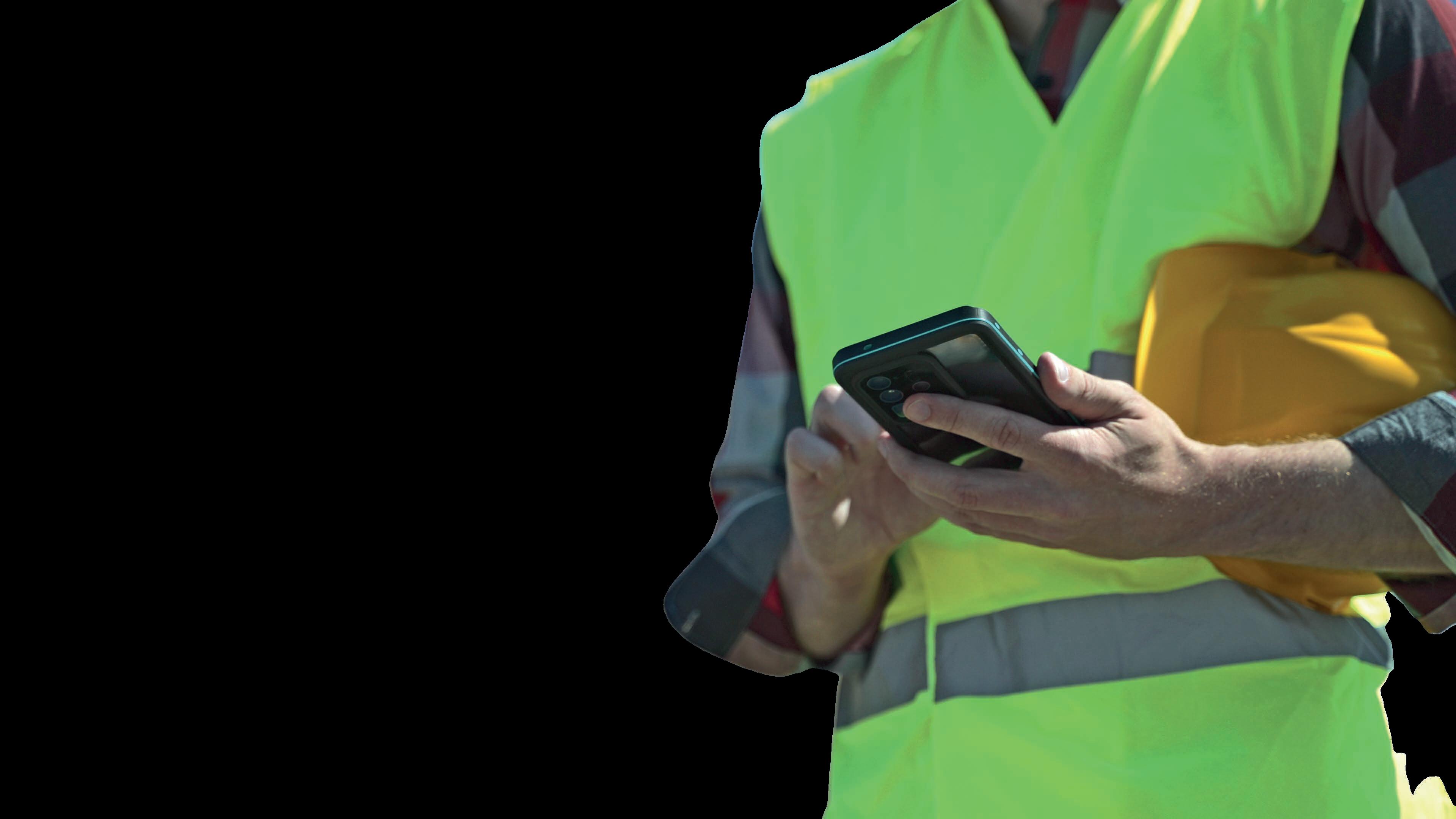
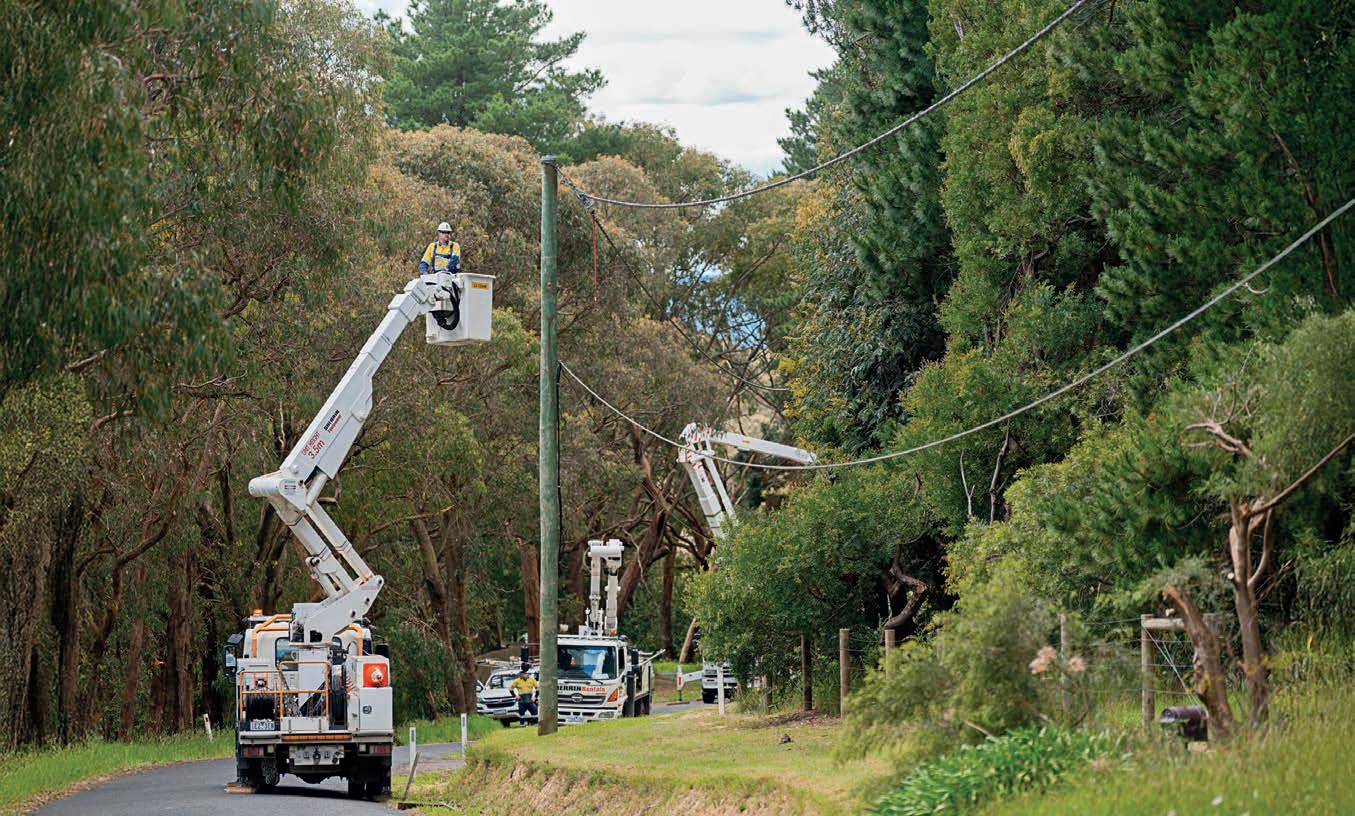
From engagement to action
AusNet’s $3.5 billion investment proposal aims to ensure its network meets customers’ needs now and into the future – but this plan is not just for customers, it’s actively shaped by them.
On 31 January 2025, AusNet submitted its five-year regulatory proposal for the electricity distribution network to the Australian Energy Regulator (AER) as part of the electricity distribution price review (EDPR) process.
The EDPR proposal outlines the future plans and costs for AusNet’s electricity distribution network for 2026–31 and, if approved by the AER, will see a $3.5 billion capital investment to support the reliability and safety of the network and drive the transition to renewable energy.
But for AusNet, this proposal is really about its customers.
Having an honest conversation
The energy sector is entering the greatest era of change since the grid powered up for the first time, and AusNet knew the way it navigated this change needed to keep pace with its customers’ needs as they evolve.
To do that, this regulatory proposal needed to be built around an in-depth understanding of what challenges customers are facing, the level of service they want and how they use the network.
AusNet General Manager Strategy and Regulation (Distribution), Charlotte Eddy, explained that this process kicked off in late 2022 with an extensive engagement program to inform the draft plan.
“We recruited a number of customers and advocates through advertising in a newspaper and online. We wanted to attract a really diverse group to make sure that they could speak for all customers across our network – and we particularly wanted representation from regional areas,” Ms Eddy said.
“Those customers filled six panels that focused on different topics, and we also took a member from each of those groups to form an overarching Coordination Group, which was tasked with helping us bring the whole proposal together.
“We have had regular discussion and engagement with those reps over the past two and a half years. During that time, we also held three off sites at various locations across our network, where we all came together and spent two days as a group to discuss the proposal as a whole.”
The six panels that informed the 2026–31 proposal were:
Tariffs and pricing
This panel focused on fair revenue allocation, the role of tariffs in the transition to renewable energy, and principles for good tariff design and pricing objectives. It also looked at the relationship between tariffs and customer outcomes and how to build customer agency.
Future networks
This panel looked at demand forecasts and the potential implications of network investment plans. This group also discussed key topics around the transition to renewable energy, including how AusNet enables the connection of new generation, how it can support community energy projects, and how the transition can unlock value for customers – including through solar and
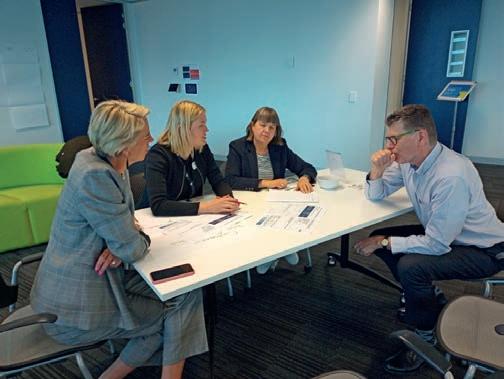
A big priority area for AusNet’s customers was improving network reliability and disaster resilience.
To really understand its customers’ needs, AusNet committed to open, honest and genuine engagement.
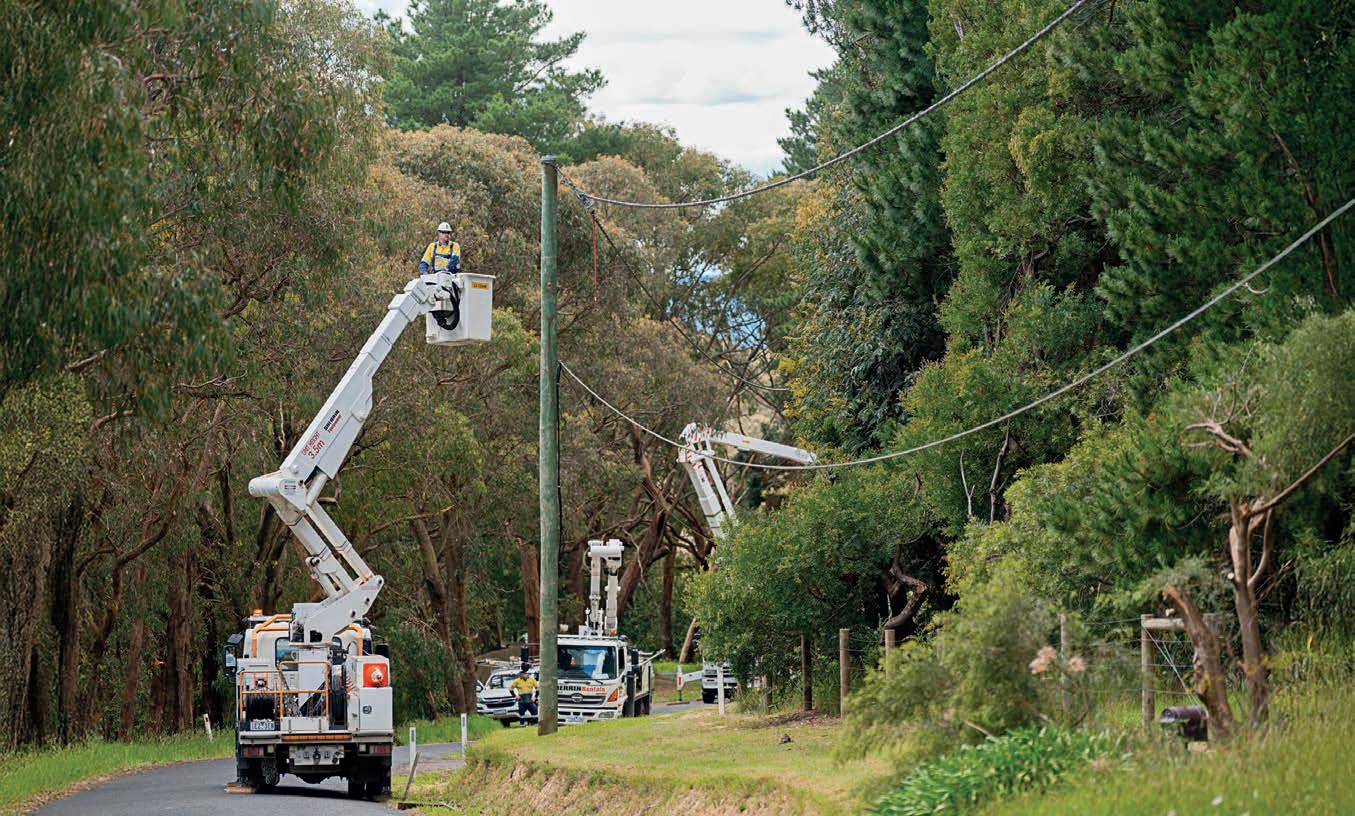
Electricity availability
Customers in this panel discussed ways in which AusNet could improve the reliability of its network, particularly for its worst-served customers, as well as general reliability standards, planned outages and power quality. They also looked at resilience to climate change and extreme weather events.
Customer’s experience
This panel delved into how AusNet can provide a fitfor-purpose service for all its customers, discussing the connection process, communications and customer service channels, and a Customer Service Incentive Scheme. It also addressed how AusNet could minimise the impact of planned and unplanned outages on customers.
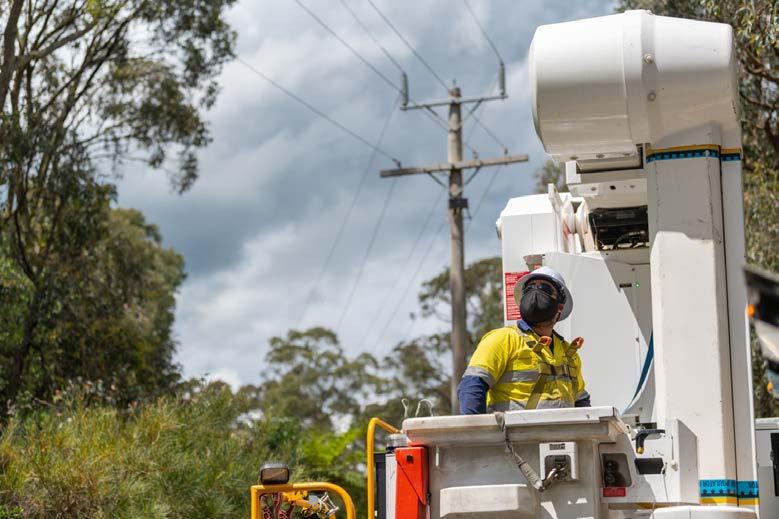
AusNet’s proposed $3.5 billion capital investment will support the reliability and safety of the
Quantifying Customer Values study
Benchmarking and operational expenditure
The goal for this panel was to look at AusNet’s approach to operational expenditure, step changes and trend parameters. It also discussed benchmarking methodologies and performance.
Customer research and engagement
This process-focussed panel was established to support the design of AusNet’s customer engagement activities, such as its Quantifying Customer Values research project. This group collaborated on the key design elements of 20 customer workshops and on AusNet’s new Customer Satisfaction (C-Sat) tracker design. They also interviewed 26 business customers to gather their own independent insights to help fill gaps and identify blind spots in AusNet’s engagement.
Ms Eddy said that several major customer research projects also underpinned AusNet’s proposal.
“We did several big pieces of customer research during that time to help inform our discussions and make sure that they were representative of the whole of our customer base,” she said.
“One of those things we did was a very large quantitative study asking customers about their willingness to pay for different levels of service, including reliability, network, resilience and exporting their solar. And we got some really strong quantitative data that we then fed into our proposal and tested the outcomes in various ways with customers.
“We also held customer workshops with residential and small business customers. They were face to face in Epping, Wangaratta and Morwell, and we also did two groups online.
“We held four rounds of those workshops with each of those groups.”
More than 17 unique research and engagement activities involving over 15,800 customers have informed AusNet’s draft plan, including:
This study quantified the value customers place on benefits that are not currently in investment evaluations. AusNet considered not only how much customers value certain benefits, but also what service changes they’d be willing to accept.
Energy Sentiments research
This bi-annual survey tracks how customers feel about AusNet, a range of energy-related matters, appliance use and purchasing trends. The questions in this study are high-level and are designed to monitor general sentiment for changes over time.
Customer Satisfaction (C-Sat) research
Building on AusNet’s business-as-usual research program, these monthly surveys track customer satisfaction with planned and unplanned outages, new connections, and complaints, helping AusNet identify areas where it is and is not meeting expectations and prioritise improvements.
Customer segmentation study
This innovative study combined residential customer attitude surveys with smart meter data to analyse how customers are using electricity today and forecast how that could change over time. The findings were used in the demand forecasting approach for its 2026–31 EDPR.
Digital Energy Futures study
In partnership with Monash University, Energy Consumers Australia, the Australian Research Council and Ausgrid, AusNet also took part in the most extensive study of energy demand and consumers’ energy futures in Australia. The Digital Energy Futures project involved 200 residential AusNet and Ausgrid customers and covered future lives and the implications for energy forecasting. This research informed conversations about the needs and expectations of AusNet’s future customer base, and what can be done to meet them.
In order to really understand its customers’ needs, it was important to AusNet that it committed to open, honest and genuine engagement, and that it did not shy away from challenging conversations.
network and drive the transition to renewable energy.
By engaging on complex and divisive topics, Ms Eddy explained that the goal for the proposal was not to achieve 100 per cent customer consensus but address these topics in collaboration with customers and develop a solution that balanced the needs of everyone and was supported by a majority.
“There’s an increasingly large diversity of views and needs across our customer base,” she said.
“We’ve got to keep an eye on affordability, because we know that a lot of customers are struggling with cost of living, but there’s also customers that are early adopters with a big interest in EVs and batteries who have slightly different perspectives than others.
“There’s also a big diversity in the level of service they’re currently getting – some of our regional customers have quite poor reliability, whereas our urban customers tend to have fantastic reliability.
“Because we’re a network with a uniform price, our job is to balance the interests across our whole customer base and come up with a proposal that is acceptable to all of our customer panels.”
Taking action
A clear set of customer priorities emerged from AusNet’s engagement program, and Ms Eddy explained that balancing reliability with energy affordability was a key objective in the development of its 2026–31 EDPR proposal.
“Because we know that customers are concerned about cost of living, we really need to make sure that we’re balancing affordability with the investment that we’re proposing,” she said.
“A big priority area for [customers] is needing to us to improve our network reliability and resilience to large weather events.
“We have experienced four major storms over the last four years and a very significant bushfire events five years ago as well. Customers really want us to do more to try to avoid the prolonged outages that can be caused by those events.
“They also want us to respond quicker and be more visible in the communities to provide support should the power be off for a long period of time. It was actually one of the things that they were willing to pay the most for us to invest in, and they also want us to uplift reliability outside of those events.”
The energy transition was also a prominent area of interest for customers.
“They’re interested in how we’re adapting for the future – our need to innovate, and [how we] accommodate electrification of gas, electric vehicles and unlock more renewable energy,” Ms Eddy said.
Once it had identified the key areas of interest for its customers, AusNet turned these expectations into key tangible outcomes in its 2026–31 proposal:
• Prioritising energy affordability and value for money
• Delivering reliable and safe electricity
• Continuously improving customer service
• Innovating to find better, more efficient ways to do things
• Preparing the network for net zero
• Delivering a fair and equitable transition for all
• Building customers’ agency
• Staying accountable
A range of initiatives and actions that AusNet will take are then identified within the proposal to deliver on these outcomes.
Reliable, safe, affordable
According to Ms Eddy, AusNet’s EDPR proposal includes several investments to boost reliability.
“We’ve got a $21 million program to uplift the reliability of our ten worst-served feeders, and we’ve also got a dedicated project in Euroa – which is a $22 million investment to deal with some acute reliability issues that we’ve seen up there in the last couple of years,” she said.
“We’re also proposing a $77 million regional reliability allowance, which will be overseen by a group of our customers and will be targeted at problem areas in the worst served parts of our network. But importantly, our customers have a say in how that money is spent, and we will report back on the outcome from that investment.
AusNet is also proposing a $264 million investment to make the network more resilient to extreme weather and a further $16 million to reduce the impact of outages on communities.
“Extreme weather events are expected to become more frequent and larger scale, so we’re reducing the risk that they will result in long power outages. But if they do [cause an outage], we’ll have more support on the ground of customers that are off supply, and more support to work with local councils and other critical utilities to prepare for those events,” Ms Eddy said.
AusNet’s 2026–31 proposal also includes a $1.35 billion investment to replace ageing network assets, maintain safety and reliability, and meet compliance obligations. While these upgrades are strongly supported by customers, AusNet knew it was also critical to keep its network charges as low as possible and strike that perfect balance between affordability and reliability.
To achieve this, the proposal outlines flat rates for residential customers that incorporates quantitative measurement of the value customers place on service improvements. It also includes an in-depth top-down assessment to identify potential areas to save and removes or defers investments areas that won’t significantly impact customers’ experience.
A greener future for all
Ms Eddy said that one of the key challenges AusNet found was that it needed really test the limits of the current regulatory framework.
“It was really designed for a different time and the energy transition is throwing some new challenges,” she said.
“As [customers] electrify, they’re more dependent on electricity and we need to make sure that they’re getting a level of service that’s commensurate with that.
“Another issue with the framework is that there’s more uncertainty over forecasts than there has been before. The regulator needs to make a decision on our expenditure out to 2031 but there’s quite a bit of uncertainty about what’s needed between now and then. So, we need to find ways of flexing the funding provided if things happen faster or slower than we expect today.”
To ensure that all its customers were positioned to benefit from the transition to renewable energy, AusNet needed to close the reliability gap between metropolitan and regional customers and ensure that everyone had access to the right information.
“Customers want more information about the transition, because there’s a lot of confusion out there, and our panels said that AusNet had more of a role to play in putting out trusted information,” Ms Eddy said.
“Whether it’s about how and when to use energy to lower costs, or [how they can invest in] consumer energy resources, that [information] will really help them build their agency to make their own decisions for the transition.”
AusNet’s proposal also looks at rolling out flexible solar export limits for all new systems, which Ms Eddy said will enable solar customers to export more most of the time, but means that AusNet can limit that export in times where it would be problematic for network security.
“As an extension of that, we’re also starting to look at flexible load and we want to offer large customers, and large grid scale batteries, flexible load connections in exchange for lower costs. We’re also intending to do a trial looking at flexible load for residential customers with electric vehicles,” she said.
“[The proposal also includes] a $15 million innovation fund, which will again be overseen by a customer governance panel called our Innovation Advisory Committee. It will be targeted at areas of innovation, where us and the wider industry need to learn more to support customers through the transition.”
While AusNet is seeing an increase in household electrification and greater uptake of electric vehicles, it’s also seeing large population growth, particularly in the south-east and north-east of Melbourne.
“We have a substantial $770 million proposal to increase
AusNet’s goal was to create a plan that responds directly to what its customers have said they want.
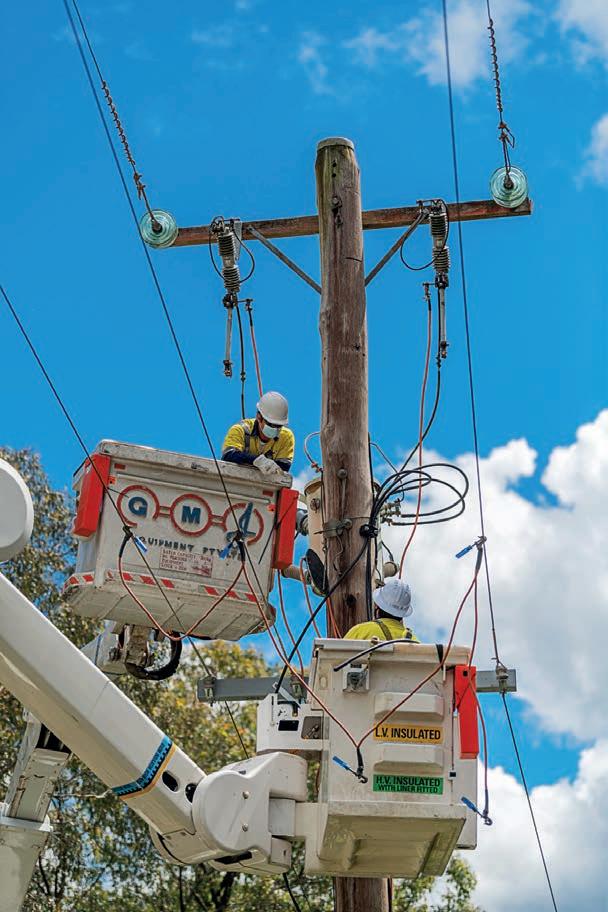
of the network, which includes investing in two new zone substations – one in Wollert and one in Pakenham – as well as increasing the capacity of other growth areas,” Ms Eddy said.
To address constraints on the low-voltage network, Ms Eddy said that AusNet’s proposal also includes an upgrade program to ensure that the street level network can deal with the expected electrification over the next five years.
“If the proposal gets approved, we will also unlock new renewable generation to keep lower pressure on wholesale market prices,” she said.
“We proposed a proactive investment in large scale generation around the Morwell and Wodonga areas of our network so that we can utilise the existing capacity on the distribution network to unlock those connections at a lower cost than would otherwise be able to be achieved.”
Continuously improving
Once the draft proposal was released, AusNet’s customers were again called upon to provide feedback and refine the EDPR before it was submitted to the AER.
“We did a round of customer workshops to really test whether we have got the balance right,” Ms Eddy said.
“The most material change we made after that is deferring $70 million of expenditure on improving the resilience of our network to extreme events beyond 2031 to keep costs slightly lower.”
But, even with the proposal now in the hands of the AER, AusNet’s customers will still have a key role to play if it’s approved.
As the initiative under the proposal take shape, the Customer Consultative Committee will hold AusNet to account on things that matter to customers and there would be channels established for AusNet executives to hear directly from customers.
From the very beginning, AusNet put its customers at the heart of its 2026–31 EDPR proposal. Its goal was to create a plan that responds directly to what its customers have said they want and delivers those needs in a way that balances investment and affordability. U
For the full 2026–31 EDPR, visit communityhub.ausnetservices.com.au/engage
the capacity
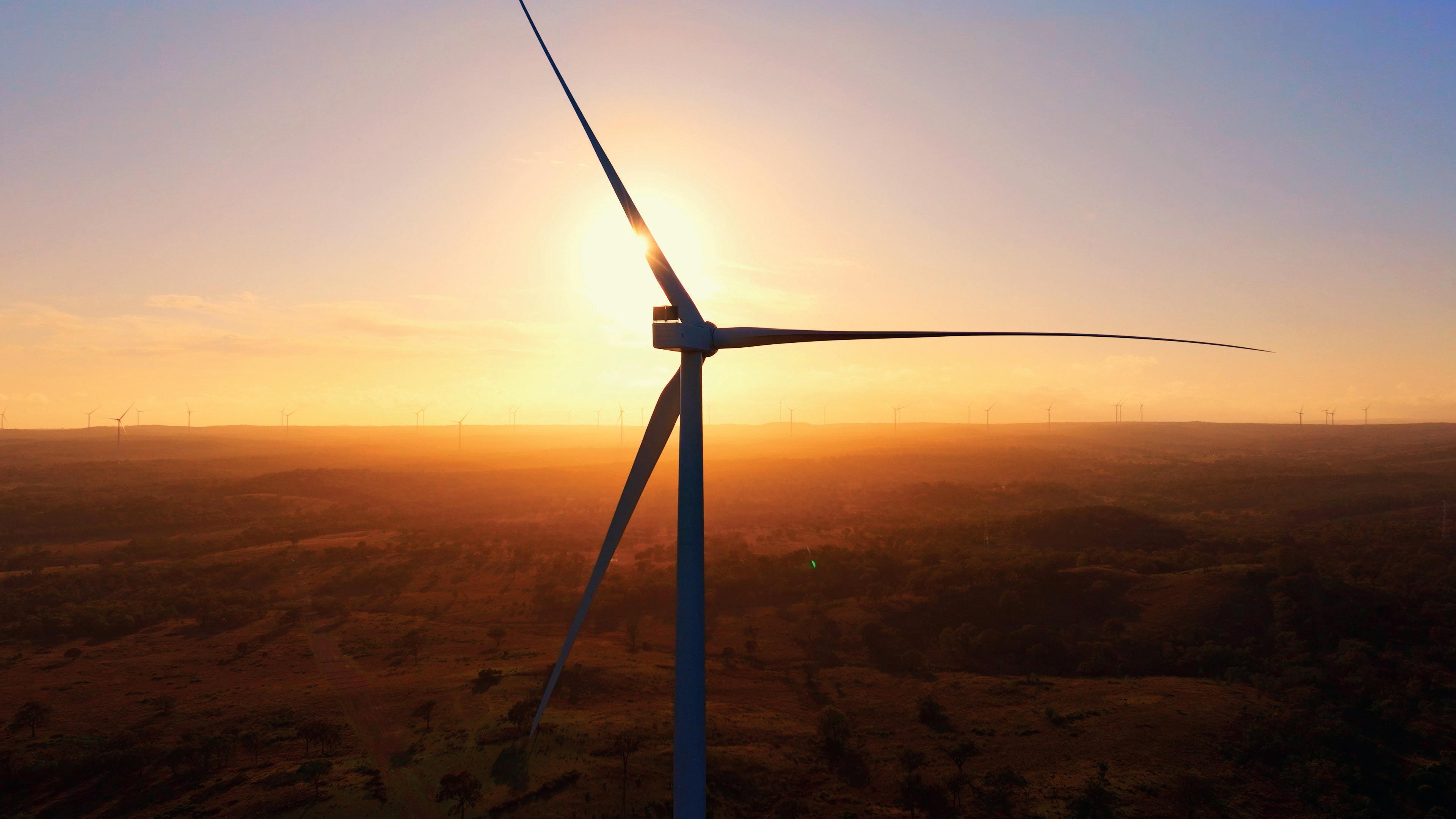
Building a better tomorrow
Over the next decade, utilities are faced with the huge task of delivering the critical infrastructure that will support Australia’s future – and connectivity is their partner on the road to success.
Australia is powering towards a renewable future, with the entire energy sector rallying to deliver the vital generation, transmission, storage and firming projects that we urgently need to hit net zero and safeguard the grid.
At the same time, there’s an urgent need for new water infrastructure to secure our most precious resource as populations grow and the climate changes.
ACCIONA is a sustainable infrastructure company that has been charged with delivering and maintaining some of the largest and most critical utility projects in Australia – including the Central-West Orana Renewable Energy Zone (REZ) transmission project, the Alkimos Seawater Desalination Plant in Perth and the Maclntyre Wind Farm.
In the modern world, connectivity is essential to not only operate these assets but to build them too.
ACCIONA Group Head of ICT – Australia and New Zealand, Mark Opitz, explained just how much major utility assets rely on connectivity.
“It’s impossible to efficiently run a wind turbine on its own in the middle of nowhere, you need someone controlling it,” Mr Opitz said.
“We continually have to send these facilities instructions on how it needs to operate, and that facility needs to be connected to the market regulators and operational team.
“And for those facilities to be remotely controlled, we rely on comms to do that.”
Mr Opitz said that many of these projects are also in remote locations and spread across long distances.
“Our Maclntyre facility, which is being energised now, is currently Australia’s biggest wind farm with 180 turbines in a massive 32,000ha paddock, and each of those turbines is seeking instruction on what to do, how much power to export and whether it needs to turn faster or slower,” he said
“We also monitor the maintenance and health of the entire turbine, which has hundreds of sensors on it, and all this information is fed through a continuous stream of comms – and without reliability there we’d be in some trouble.”
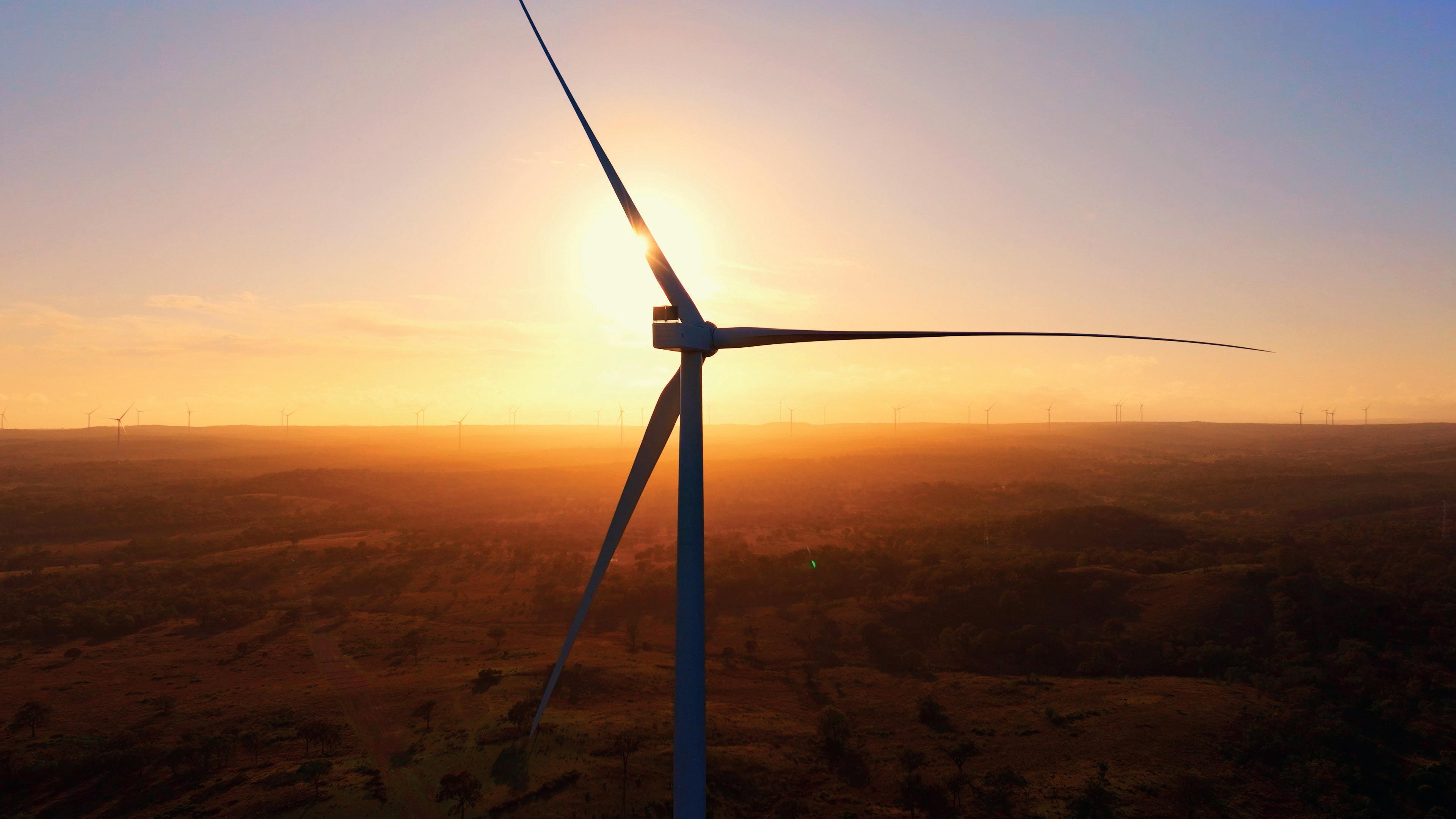
Hit the ground running
There’s absolutely no time to waste during construction; not only do delays directly impact costs but the urgent need for these vital water and energy projects means there’s no room for setbacks.
As a global company, ACCIONA has access to some of the best design teams in the world, but leveraging this international expertise means transferring a lot of large files and data daily. A stable network connection on-site means faster communication between teams, streamlined project management and a greater ability to swiftly respond to challenges as they arise.
According to Mr Opitz, standing up construction sites requires an immense amount of flexibility and agility.
“We’ve had requirements from project teams to mobilise a site with 48 hours’ notice, which is a bit extreme, but a lot of the time we’re only given a week.”
“Previously, we would never get a service level agreement for comms anywhere within one week, but Starlink and Vocus’ service have been an absolute game changer for us,” he said
Vocus provides ACCIONA with Starlink and fibre network solutions, which Mr Opitz said has been an enormous help in cases where ACCIONA needed to mobilise a site as quickly as possible.
“With Vocus, we’ve been able mobilise sites in short timeframes multiple times over. I’m talking one or two weeks, whereas it used to take 12 to 13 weeks to get fibre communications up and running,” he said.
Vocus was the first company to bring Starlink satellite broadband to the Australian market, and ACCIONA was one of the very first to adopt their technology.
“Vocus put Starlink in our hands and now we’re quite efficiently getting sites connected that were untouchable by all forms of comms,” Mr Opitz said.
“We used to have to use satellite services that were time consuming and expensive to establish in these remote locations, whereas with the Starlink service you can mobilise and commission it within a of couple of hours.”
Acciona is delivering some of the most critical energy projects in Australia, including the Maclntyre Wind Farm.
Images: Acciona
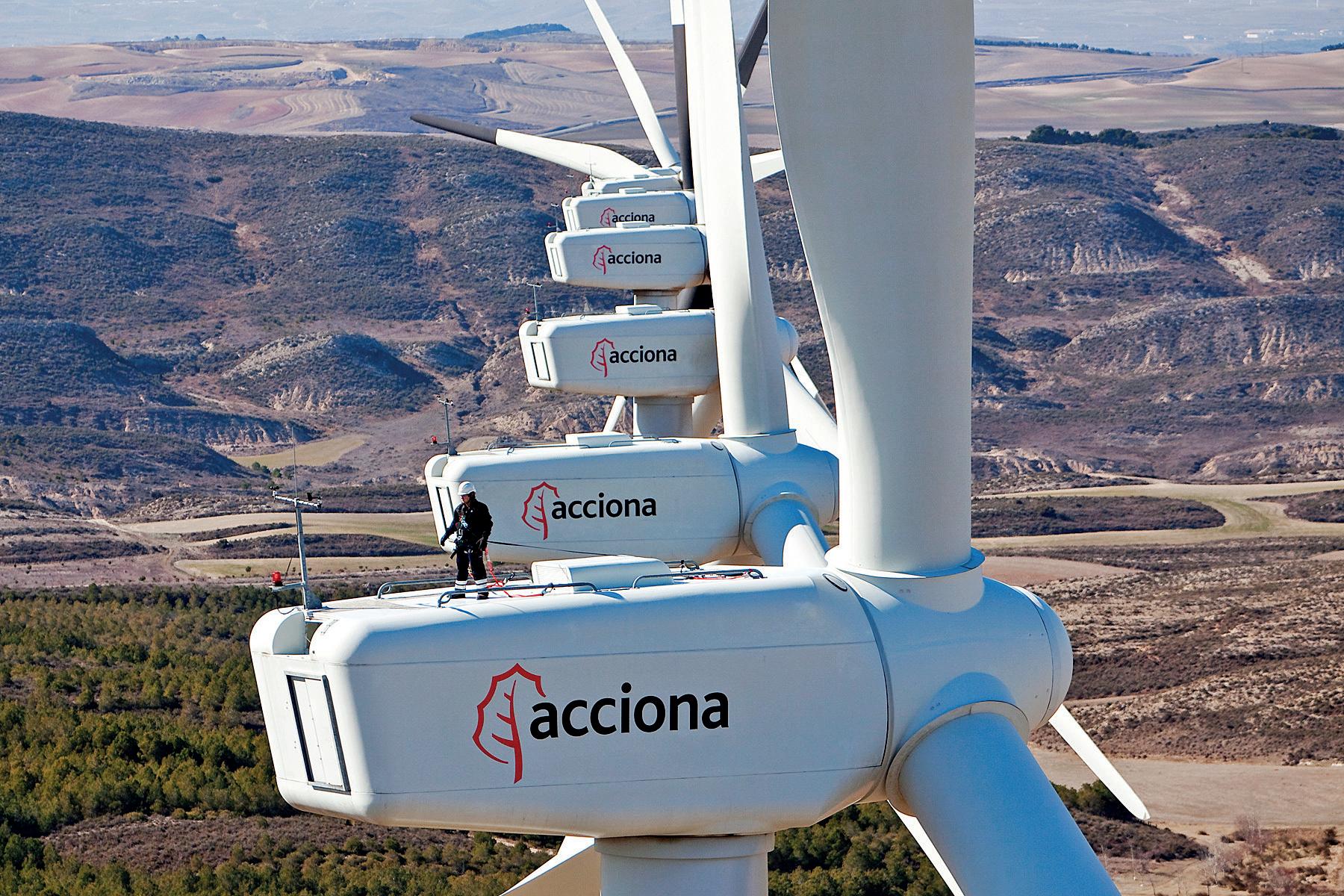
of a vehicle to keep crews connected at all times.
This solution provides WI-FI for a range of up 100m from the vehicle and was custom-built with a Vocus partner. The system is encapsulated in a protective pod that keeps it cool and safe in harsh conditions, and they can also easily be swapped between vehicles without causing damage.
Rather than offer out-of-the-box satellite connectivity, Vocus works alongside its partners to tailor and develop new solutions – and this philosophy around innovation is one that ACCIONA also embodies.
“Vocus is a certainly a massive enabler of that. And our vendors enable us to ramp up and mobilise our sites to use this new technology, because almost everything we deliver tech-wise has to go through a connection somewhere.
“Their reliability allows us to build and create more solutions that rely on comms and connectivity so our business can keep embracing innovation.
“Sometimes we work a bit too hard trying to change and make the world a better place, I must be honest, but it’s worth it at the end of the day.” U
For more information, visit vocus.com.au
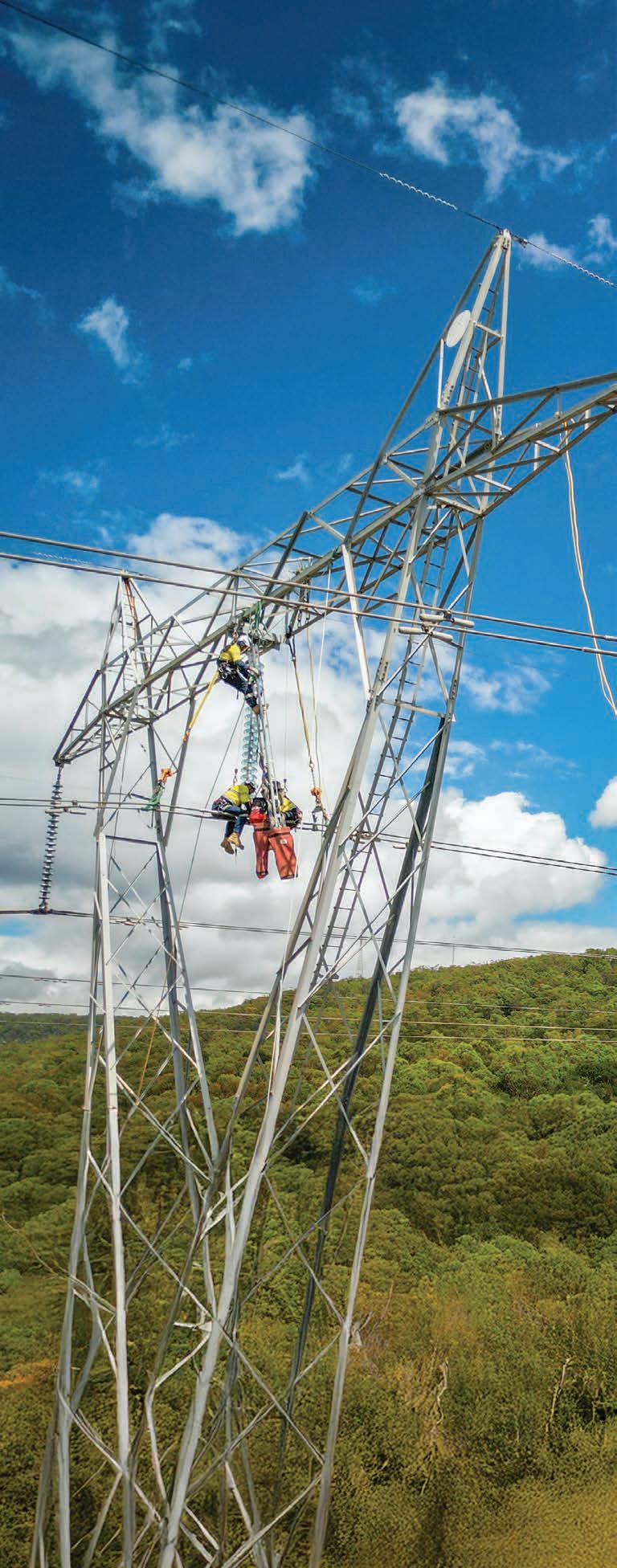
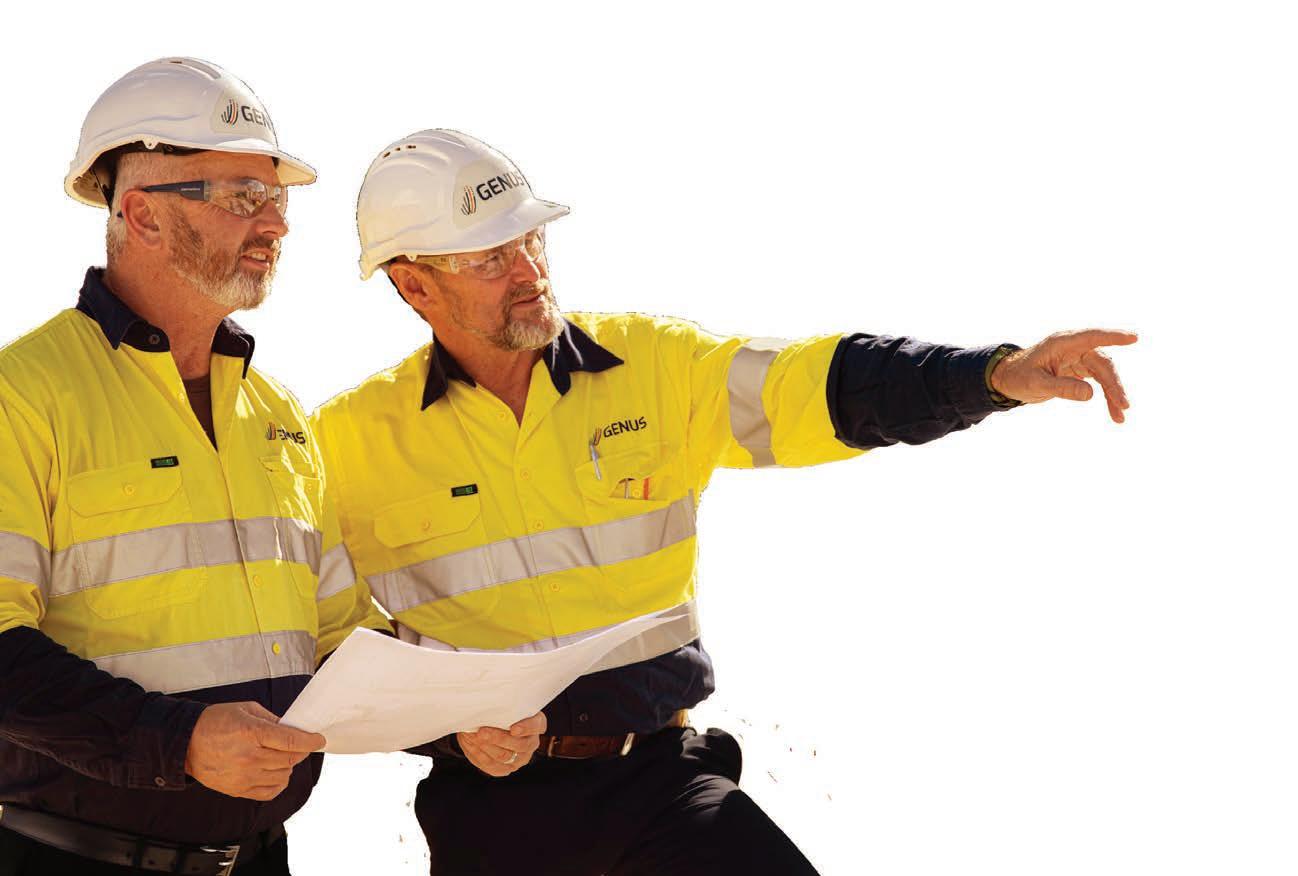
Connectivity is essential to not only operate utility assets but to build them too.
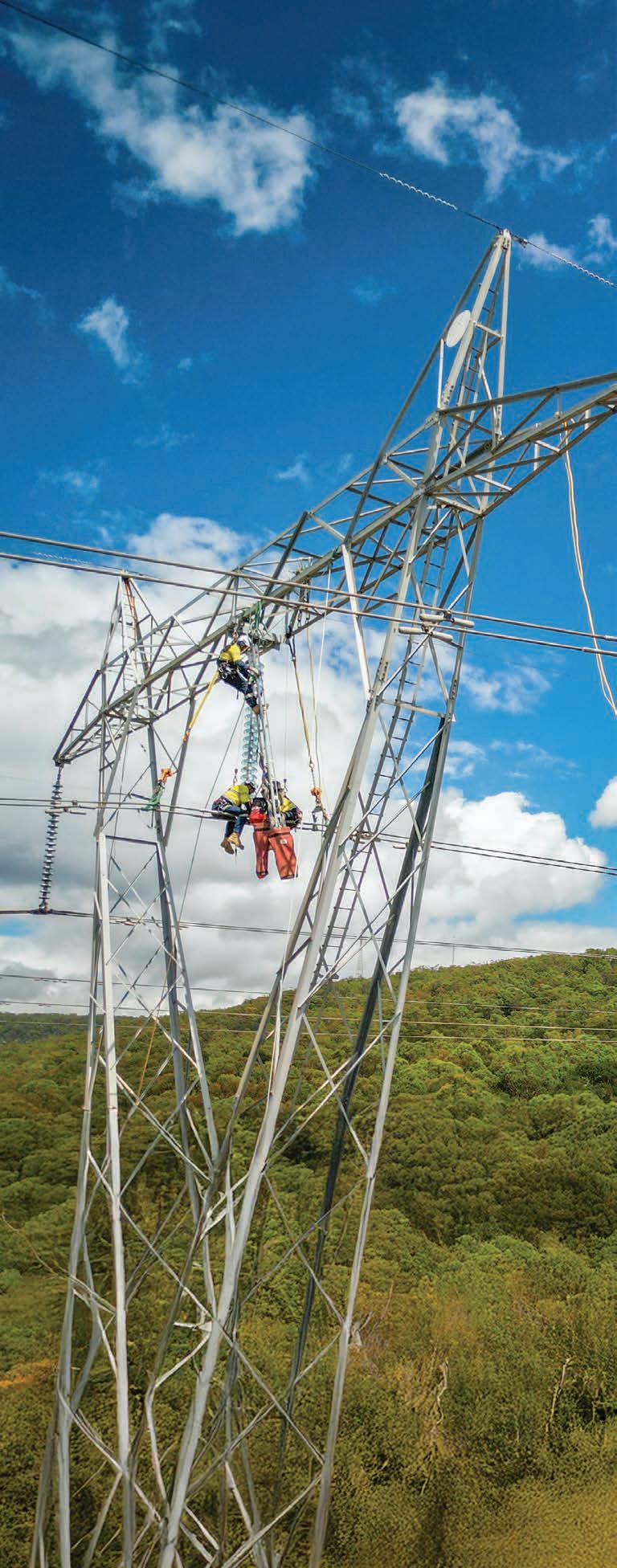
PROUDLY POWERING WHAT MATTERS
At Genus, we’re not just building power and communications infrastructure; we’re shaping Australia’s future. From transmission lines and substations to communications solutions and renewable energy, we design, construct, and maintain the systems that keep the country moving forward.
We’ve become one of Australia’s fastest-growing infrastructure companies, winning landmark projects and setting new industry standards.
Our difference? A challenger mindset, hands-on approach, and commitment to our people.
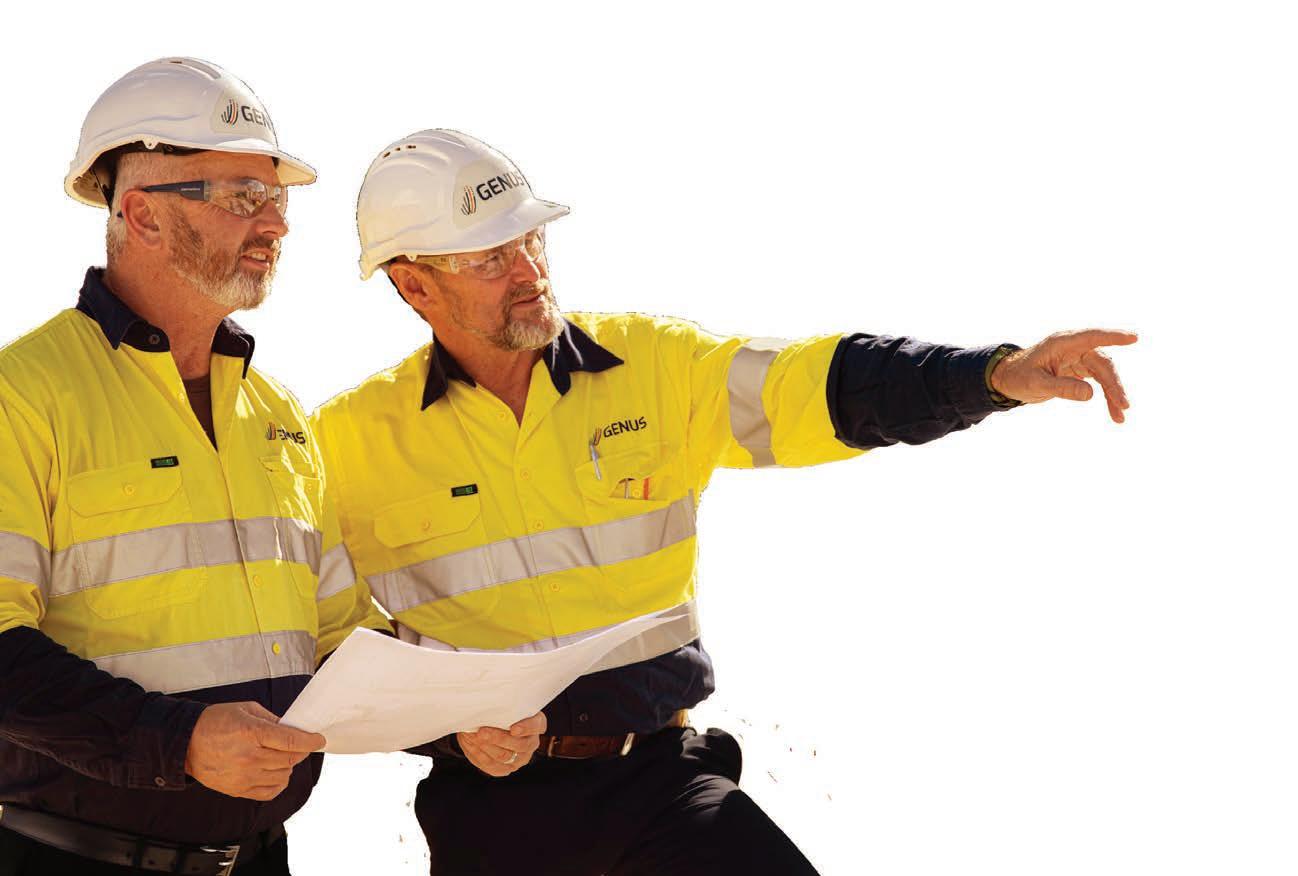
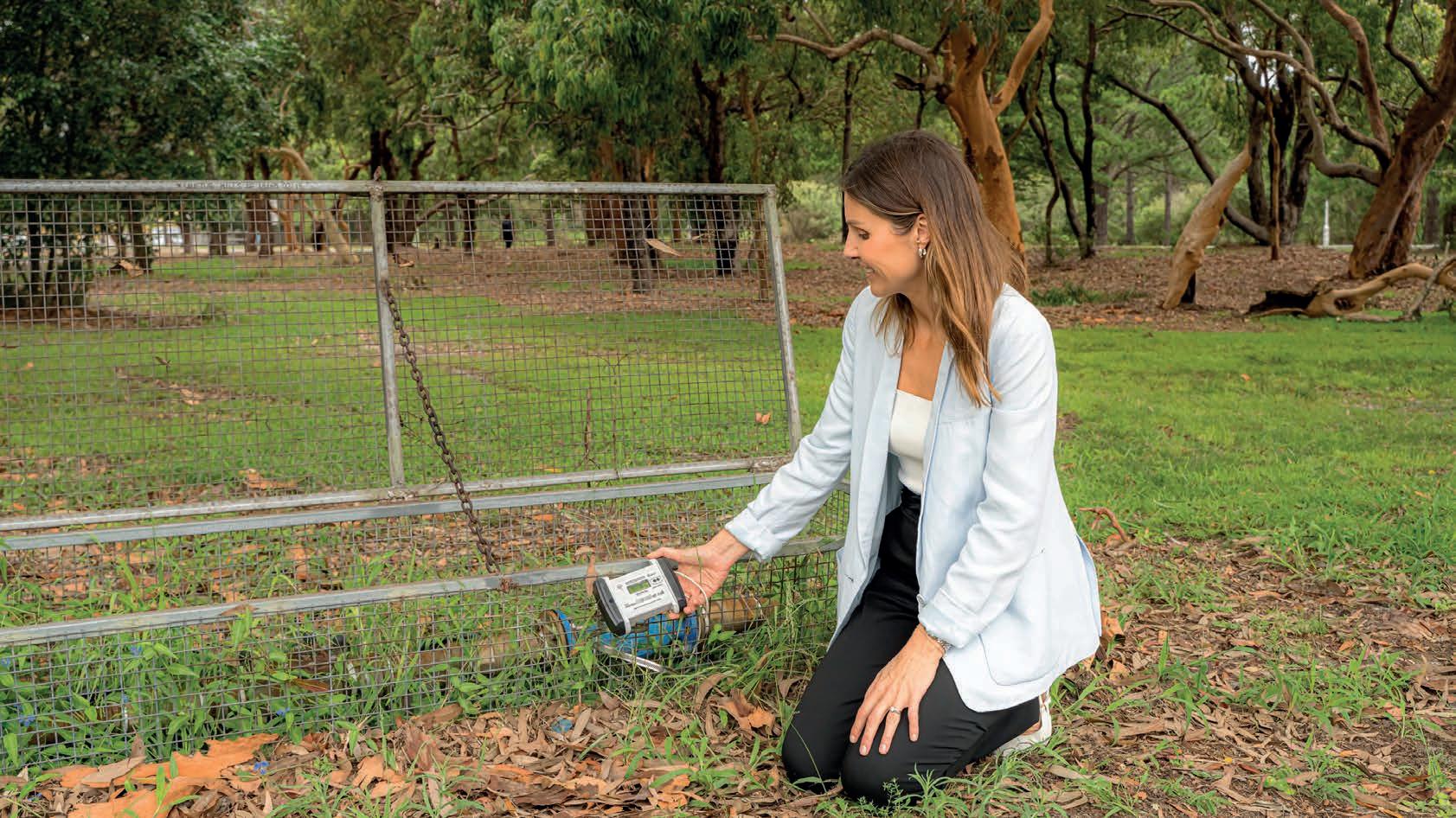
Smart metering goes abroad
Australia’s utilities sector is undergoing wholesale change, as the ongoing shift to renewable energy sources accelerates.
By 2030, the Australian Energy Market Operator (AEMO) predicts solar and wind capacity in the national grid will triple, rooftop solar capacity will double, and storage capacity will increase six-fold. This significant expansion is occurring amidst a growing population, urban densification and continued climate change – all while customers face increasing cost-of-living and have higher expectations of their services and providers.
Smarter data
Smart meters are digital devices that measure and record electricity usage in real-time. They enable the automatic distribution of data to retailers or distributors, where older meters previously required manual readings – and are becoming a crucial part of the energy transition taking place around the world.
Australians are set to install more than ten million energy consumer devices in their homes by 2030, namely solar and battery energy systems, more electric hot water units, EV chargers, pool pumps and more – with smart
meters at the heart of unlocking accessibility. Currently, the UK is the global leader in offshore wind energy. It has more capacity installed than any other country and powering more than 7.5 million homes. With a plan to increase this four-fold by 2030, the nation is well on the way to decarbonising its power system by 2035, and like Australia, smart meters are playing a key role in its energy transformation. And it’s not just smart electricity meters – the technology is also driving efficiencies across other utilities, such as water.
Delivering change
United Utilities, which serves more than seven million customers in north-west England, plans to install more than one million smart water meters by 2030, to increase household coverage from 52 per cent to 70 per cent. This smart metering program is a key component of its Water Resources Management Plan 2024 (WRMP24), which outlines strategies to ensure a sustainable water supply for future generations.
Image:
Intellihub
Smart meters are becoming a crucial part of the energy transition.
The plan includes a 50 per cent reduction in leakage (from a 2017–18 baseline) and reductions in water use to 110L per person per day by 2050.
To fulfill this portfolio of work, United Utilities selected Arqiva under a prime contract structure (a model in which it assumes full responsibility for the management of the project).
In its research, United Utilities found this structure would provide it with the best value-for-money, when compared to a utility-led deployment.
It worked together with the Water Services Regulation Authority, or Ofwat, the body responsible for economic regulation of the privatised water and sewerage industry in England and Wales.
Through the increased deployment of smart meters, United Utilities projects it will be able to improve water resource management, reduce consumption, and minimise leakage across its network.
This will help it support environmental sustainability and provide enhanced service delivery for its customers.
Through the increased deployment of smart meters, United Utilities projects it will be able to improve water resource management, reduce consumption, and minimise leakage across its network.
Future outlook
Like in the UK, Australian digital water meters re having a significant impact – and have already helped to save millions of litres of water, significantly reduce costs for customers and streamline operations.
Targets of 82 per cent renewable electricity by 2030 and net zero emissions by 2050 loom – and there may be valuable insights to be taken from how other nations are using smart meters to help drive their electrification and decarbonisation journeys. U
For more information, visit intellihub.com.au
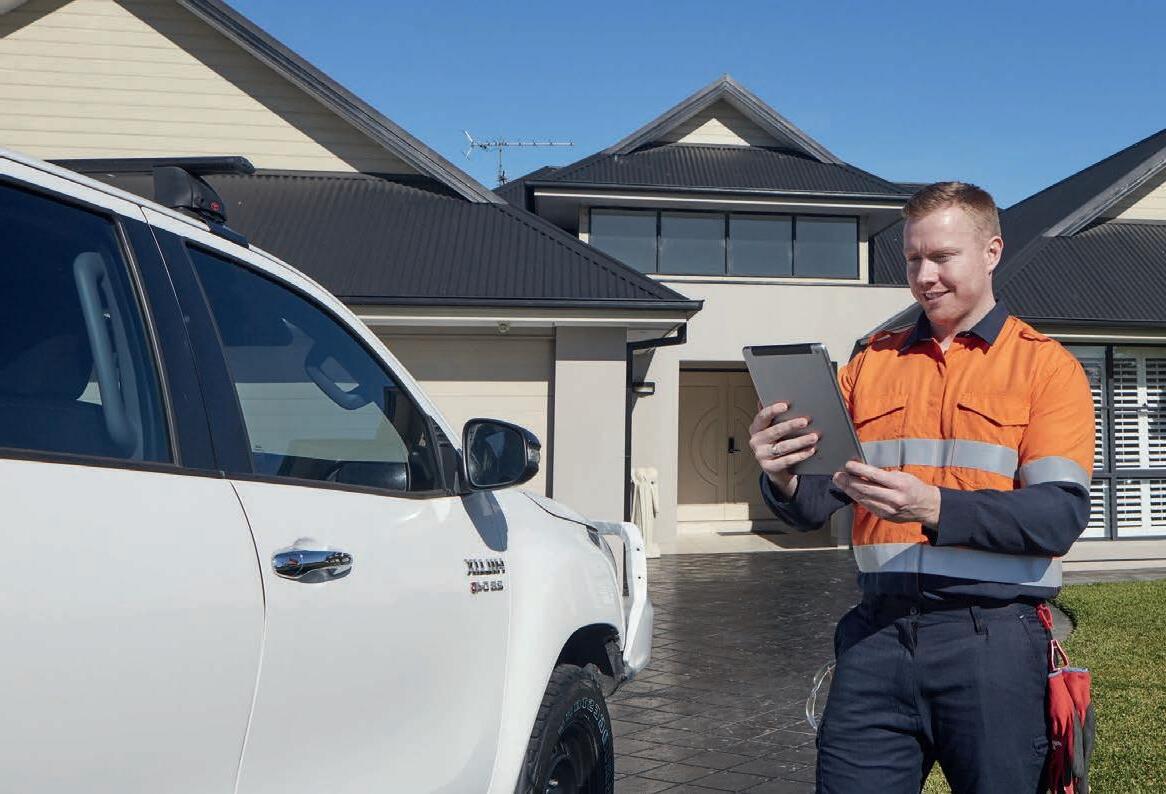
Scalable digital water metering
Refocus your investments with an end-to-end solution without the upfront cost.
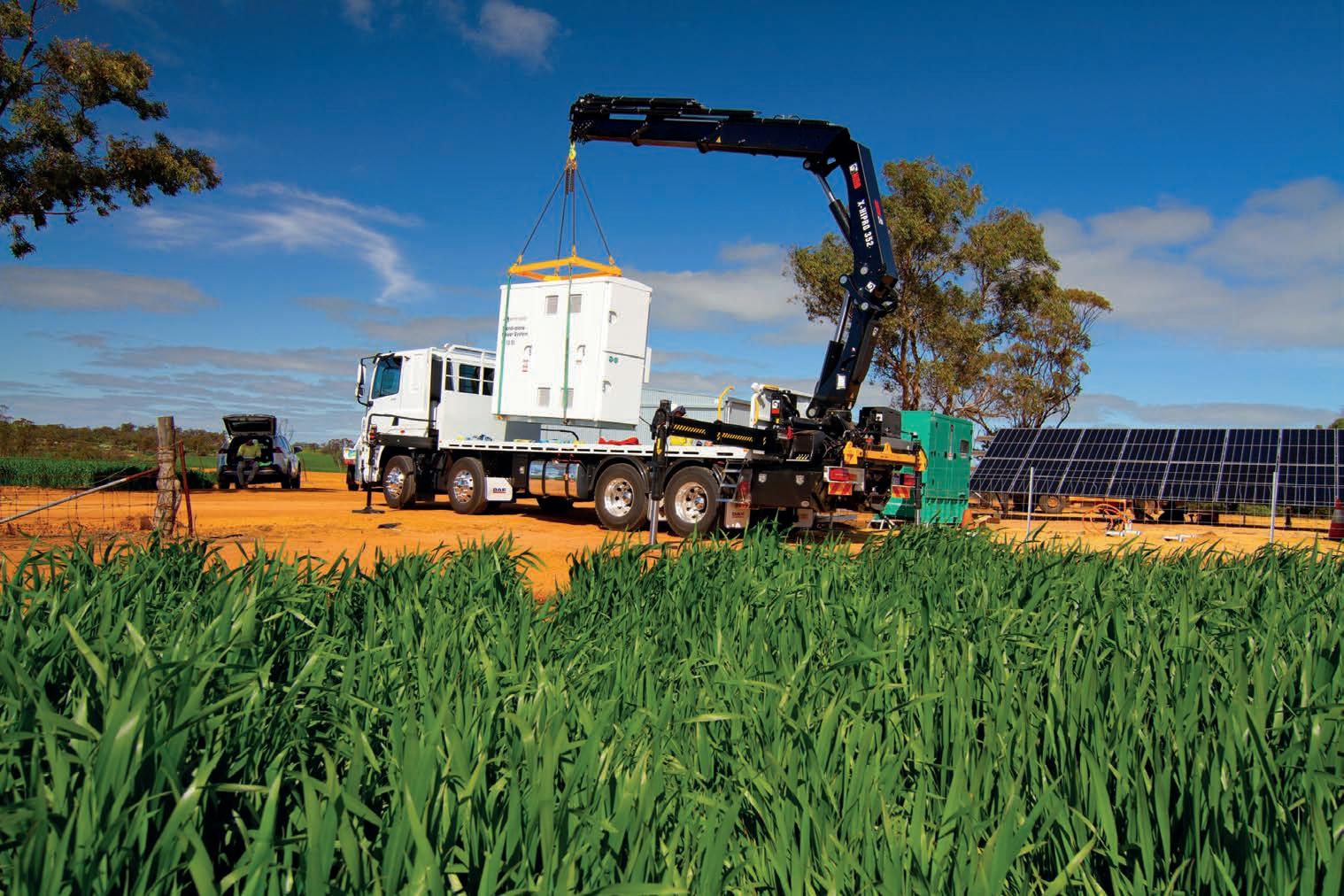
Supercharging grid reliability
A secure, reliable National Energy Market is the key to unlocking Australia’s renewable energy future – but what can the sector do to take us there?
The National Electricity Market (NEM) is at a critical juncture, grappling with challenges that threaten its stability and efficiency. As Australia transitions towards renewable energy, it’s largest network faces issues such as grid reliability, integration of distributed energy resources, and maintaining a balance between supply and demand.
Pacific Energy Managing Director Connected, Mark Sinclair, is heading up the energy solutions provider’s new east coast division and said that the company is poised to address these challenges through its expertise in stand-alone power systems (SAPS), battery energy storage systems (BESS), and more.
“Pacific Energy has been working with network
Stand-alone power systems
SAPS are increasingly being deployed to customers on the NEM, particularly in fringe-of-grid areas where they experience higher-frequency outages and where traditional grid extension is not economically viable.
“As their name suggests, SAPS are not connected to the grid. Instead, the systems combine solar panels, battery storage and backup diesel generators that together supply reliable power to end users, 24/7. For the right application, we can also provide hydrogen solutions as a substitute for diesel,” Mr Sinclair said.
SAPS are primarily used in regional areas to supply farmers, remote communities and customers on single wire earth return (SWER) lines with safer, cheaper and more reliable power.

The units, which are typically owned and maintained by network providers (DNSPs), can replace significant corridors of the poles-and-wires network, thereby reducing installation and maintenance costs and power outages due to farming hazards, bushfire risks and natural disasters.
Pacific Energy has been pioneering SAPS technology since 2019, supporting early adopters like west coast power utility, Western Power, to improve power safety and reliability, and to make renewables more accessible to its regional customers.
“We’ve already rolled out more than 160 SAPS to Western Power’s fringe-of-grid customers as a part of its world-leading SAPS program, and we’ve signed up to deliver nearly 200 more as a part of the program’s second and third rounds,” Mr Sinclair said.
SAPS are primarily used in regional areas and can safeguard these communities during power outages.
Images: Pacific Energy
SAPS combine solar panels, battery storage and backup diesel generators to supply reliable power to end users, 24/7.
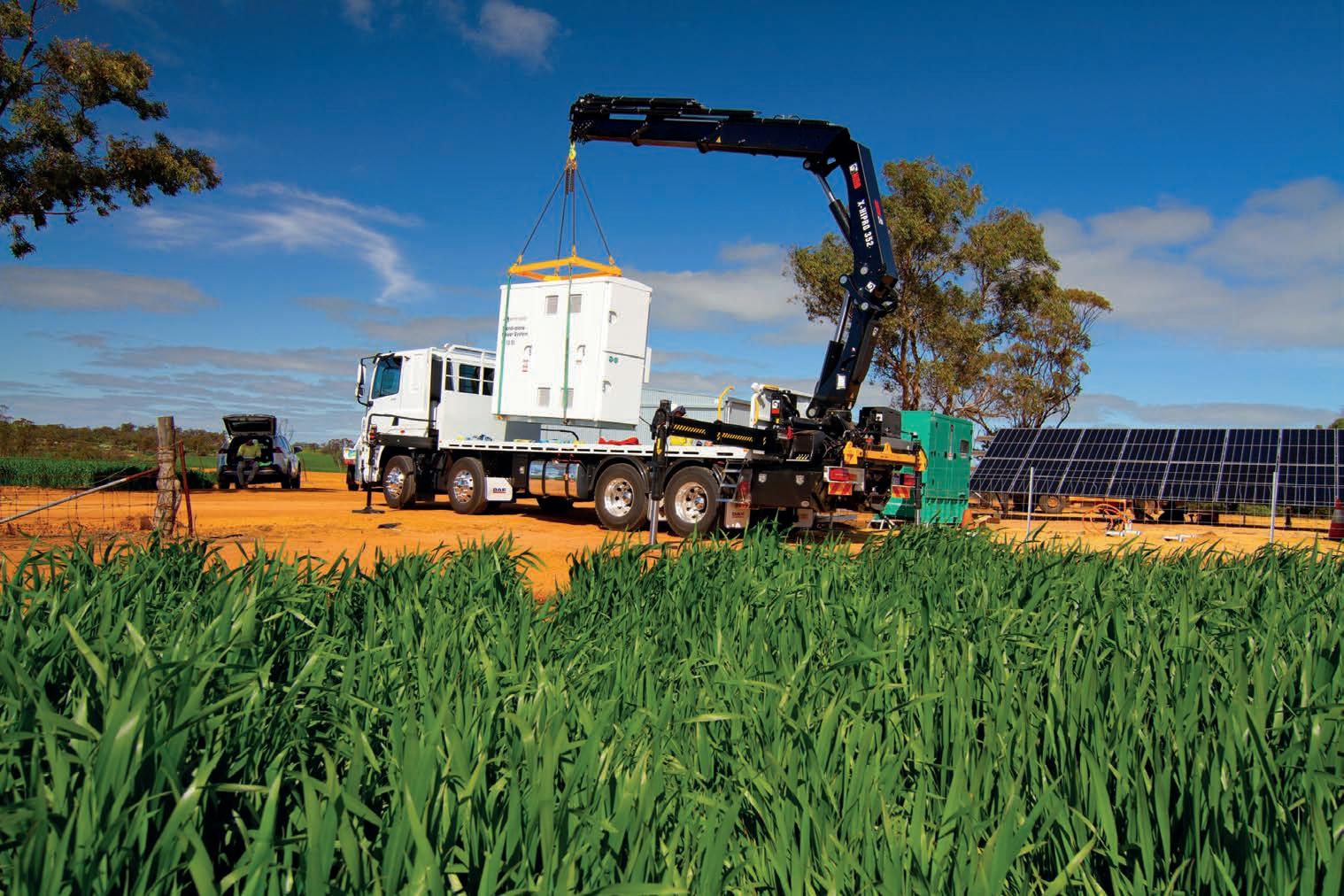
“Every unit is designed by our electrical engineers to meet the unique load profiles of each customer, and then it’s manufactured to specifications in our WA-based, purpose-built workshop so it can withstand the harsh environmental conditions it will need to operate in.”
Western Power’s program aims to replace around 15,000km of overhead lines across regional parts of the South West Interconnected System (SWIS) with up to 4,000 SAPS, and Pacific Energy is playing a pivotal role in the rollout.
“Our involvement in Western Power’s SAPS program represents the largest deployment of utility-spec SAPS worldwide. We know the challenges utilities can face, and we know we can bring NEM customers the solutions and assurances they are looking for to accelerate their own large-scale SAPS deployments,” Mr Sinclair said.
Battery energy storage systems
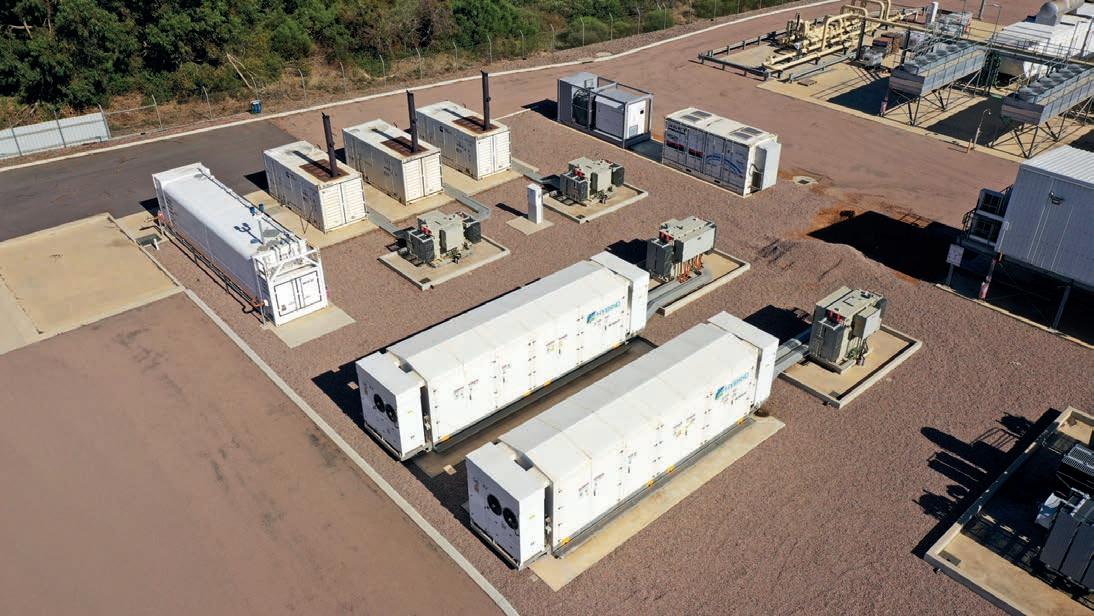
Pacific Energy’s dual-purpose BESS in Esperance, which was delivered for Horizon Power.
The Esperance system’s BESS incorporates both grid forming and energy storage units, which support the power system’s wind and solar farms, and enable the town’s residents to install rooftop solar.
SAPS are not the only technology stepping up to meet the NEM’s grid reliability challenges. Small and large-scale battery systems, or BESS, are playing a critical role in managing utility-scale renewables and distributed energy resources, like rooftop solar.
“NEM network providers are looking for material BESS capacity at the distribution level, with solutions commonly around 5MW that can help manage localised generation through both grid stabilising and energy storage functionality, but we’re seeing strong interest for greater sizes as well,” Mr Sinclair said.
Pacific Energy has been engineering battery solutions since 2016. The company is now at the point where it’s using some of the most sophisticated technologies on the market, which are ultra-responsive to faults and fluctuations, and provide excellent support to an increasingly complex grid.
“We’ve deployed our unique battery solutions at various scales and for varying purposes, including to support town power supplies, like the dual-purpose BESS in our Esperance power system, which we delivered for WA’s regional power utility, Horizon Power.”
The Esperance system’s BESS incorporates both grid forming and energy storage units, which support the power system’s wind and solar farms, and enable the town’s residents to install rooftop solar.
In 2024, Pacific Energy announced that it is again partnering with Horizon Power, this time to deliver a 49.6MWh BESS for its Exmouth power system. This BESS, which includes a significant storage component, will supplement the adjoining solar farm to supply the town with up to 80 per cent of its annual energy needs.
“Like our SAPS, we design, manufacture and test all of our BESS in our local workshops. This means we are not limited to standard sizes, and that we can control the quality of the builds and maximise the technical capabilities of OEM components,” Mr Sinclair explained.
“We’re now working with east coast DNSPs to supply batteries around 5MW under design-and-install and build-own-operate (BOO) arrangements, so they can be delivered quickly and alleviate pressures on the network. Plus, because we manage the assets, we can monitor them from our own Perth-based 24/7 Remote Ops Centre and respond to any operational issues immediately.”
On the horizon
Mr Sinclair said that Pacific Energy will continue to evolve its offering on the east coast as demand picks up steam.
“We’ve been looking at the role we can play in balancing supply and demand on the NEM. Distributed energy resources are becoming more viable for businesses, and when included in a virtual power plant (VPPs), they provide a key tool in supporting the NEM’s planning and operations,” he said.
Pacific Energy has already delivered four VPPs for Synergy’s Schools VPP Pilot Project in WA, which is testing how VPPs can manage local electricity consumption and support local grid stability, reliability and sustainability.
As the NEM navigates the complexities of integrating renewable energy and maintaining grid stability, Mr Sinclair is confident Pacific Energy’s innovations will be able to alleviate some of the pressures network providers are feeling.
“Our vertically integrated delivery model and local manufacturing capabilities offer our clients some unique benefits,” he said.
“We are not as impeded by international supply chains as some of our competitors, we are able to meet very specific requirements, and, with a strong focus on local manufacturing, we’re also contributing to the upskilling of our industry’s workforce.
“And these are just a few of the benefits that position us as an important partner in the National Electricity Market’s transformation.” U
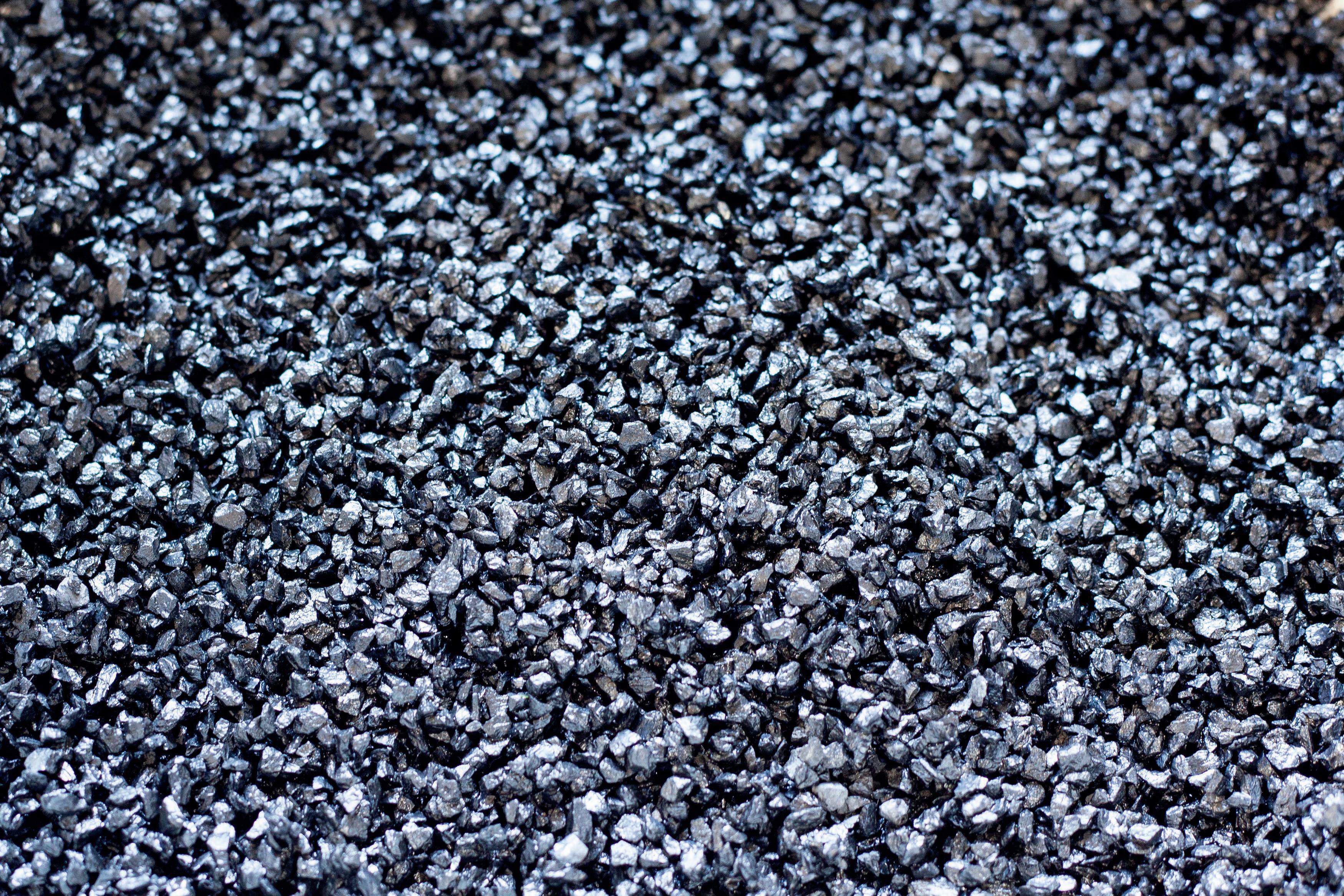
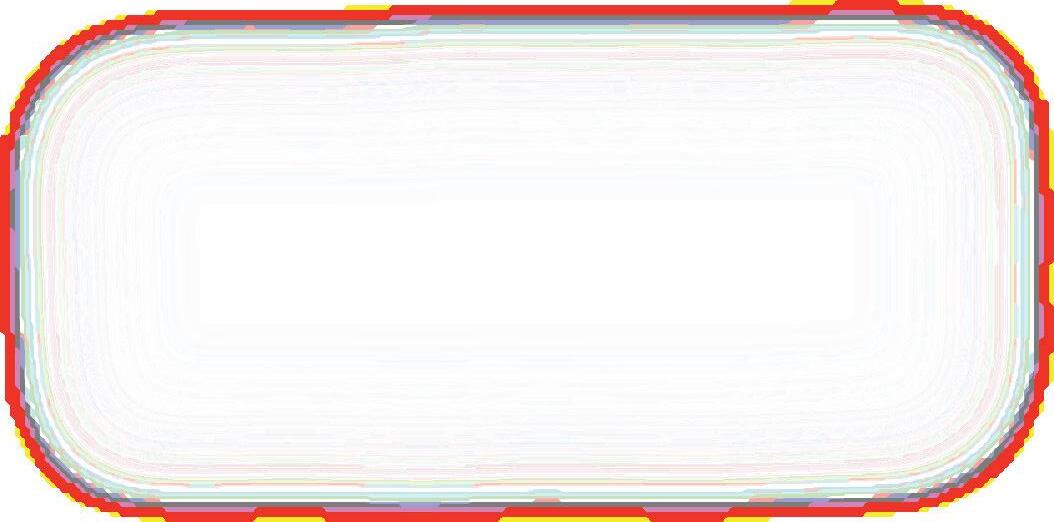
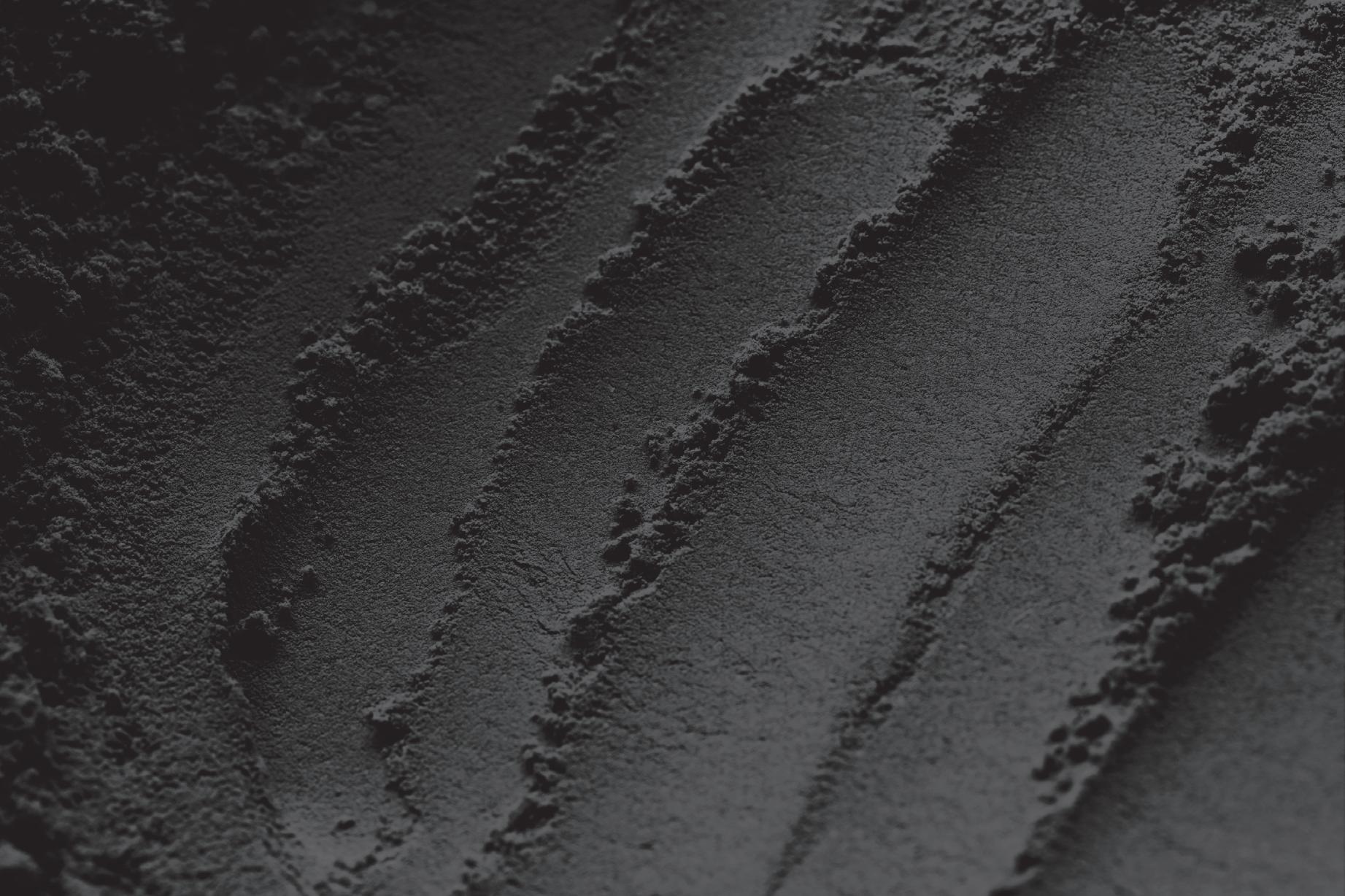
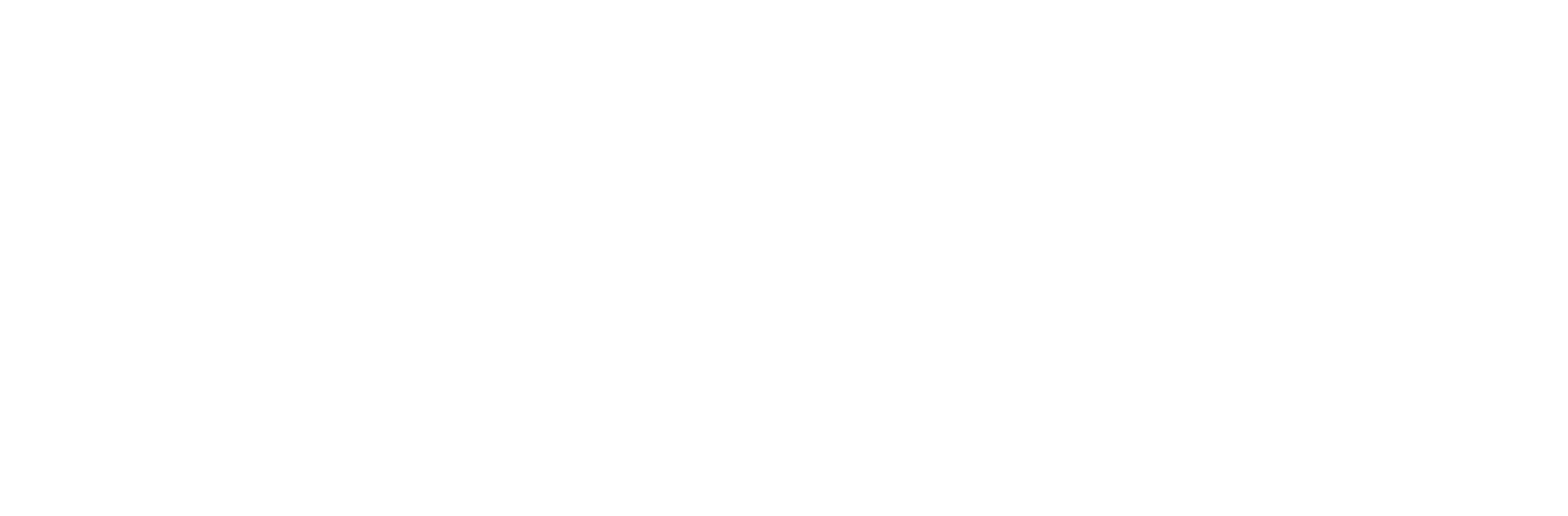
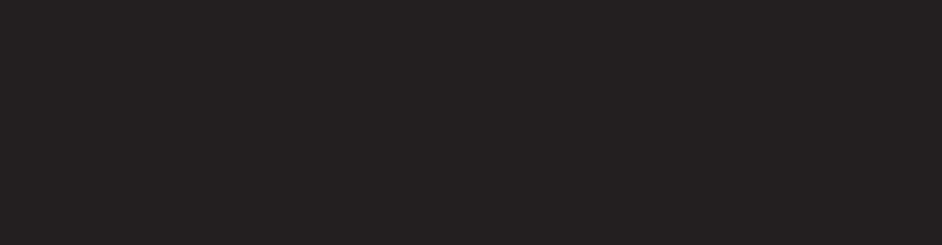
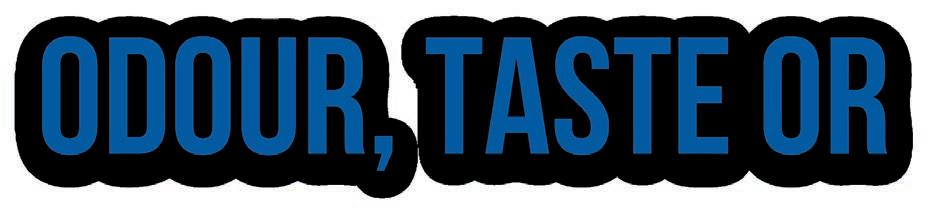
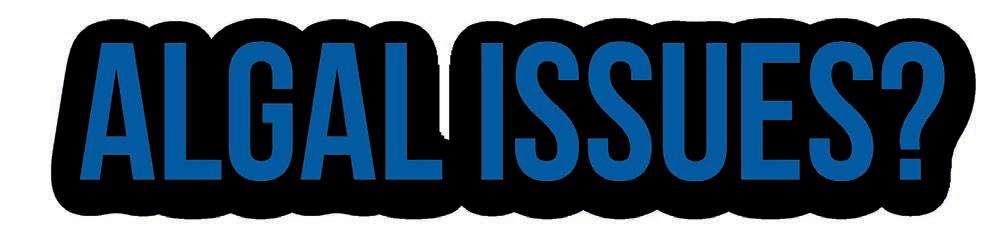
Purazorb™ by James Cumming & Sons
Coal-based Activated Carbon
To specific customer requirements, suitable for a range of proven applications Certified quality – made by Australia for Australian conditions
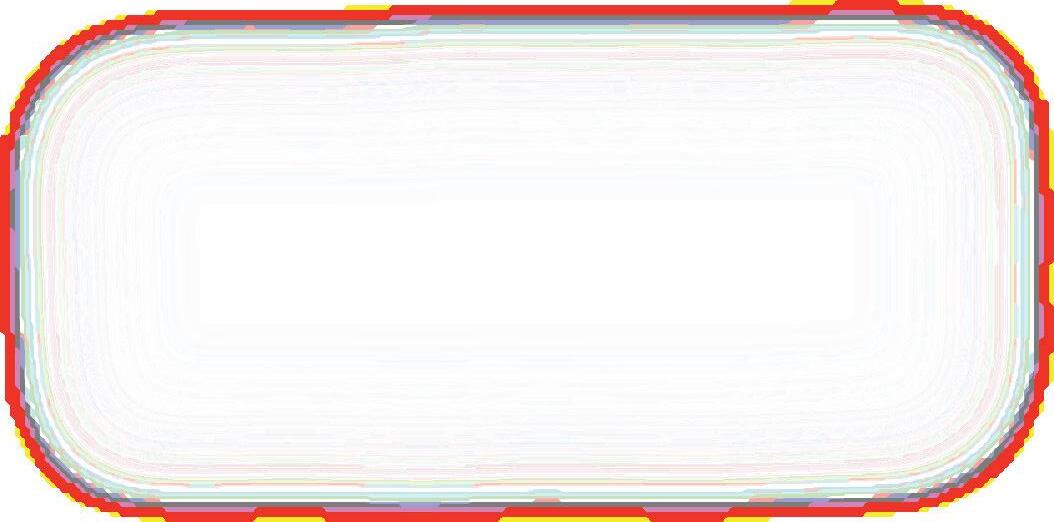
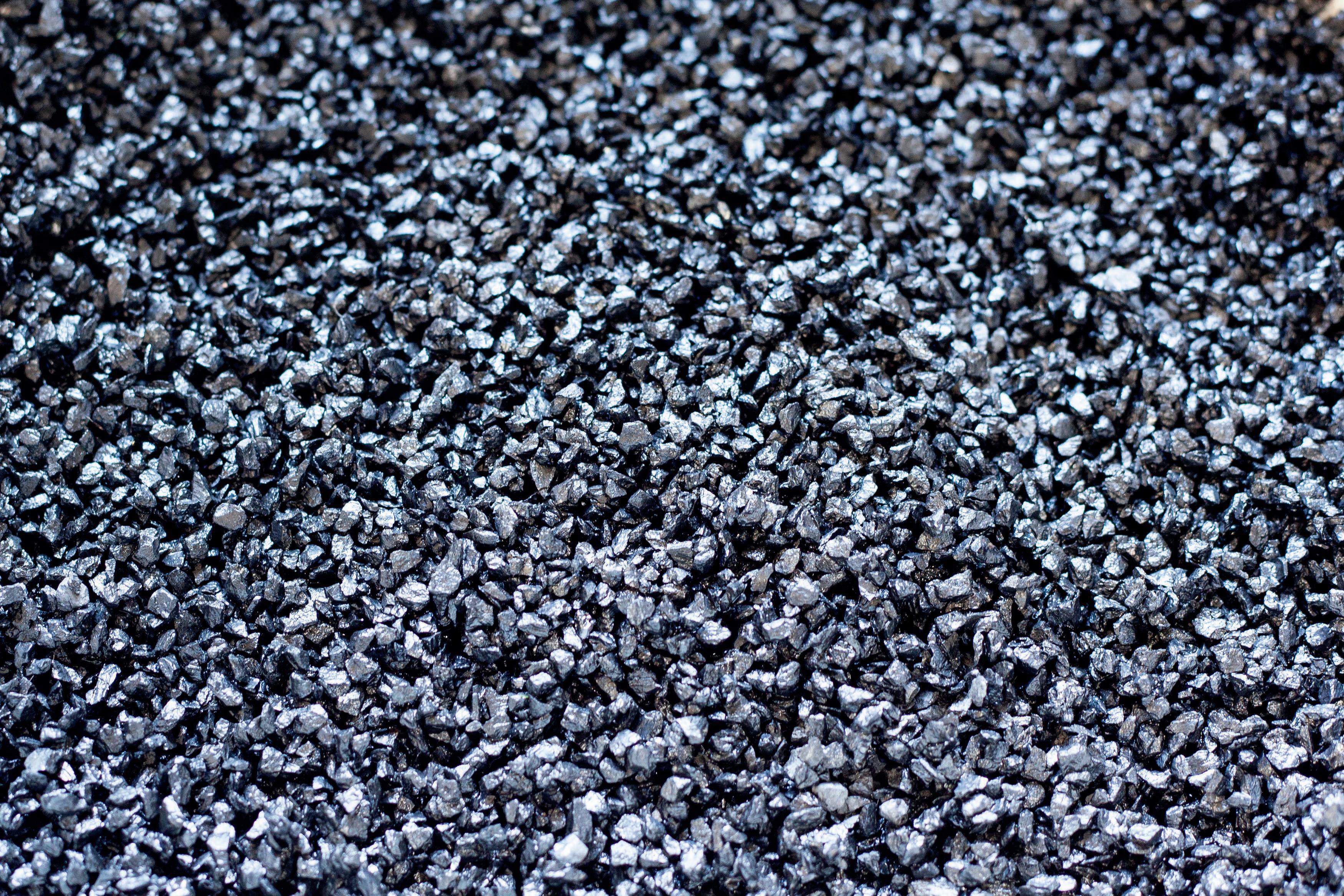
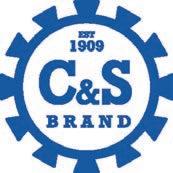
JAMES CUMMING & SONS

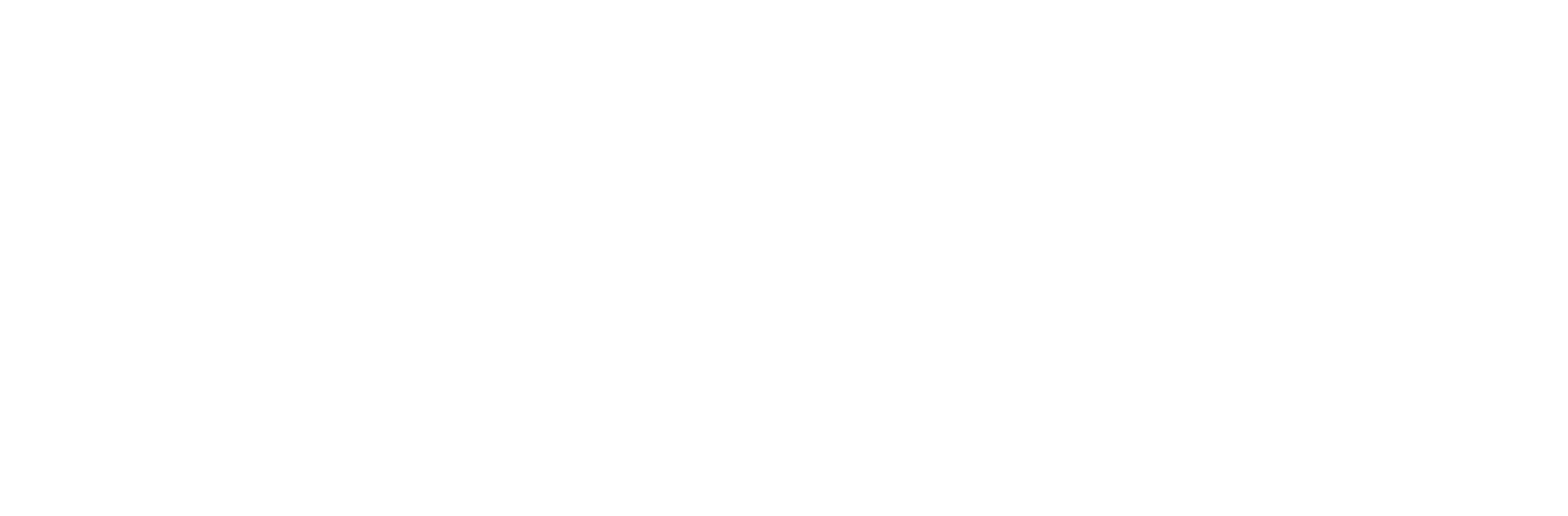
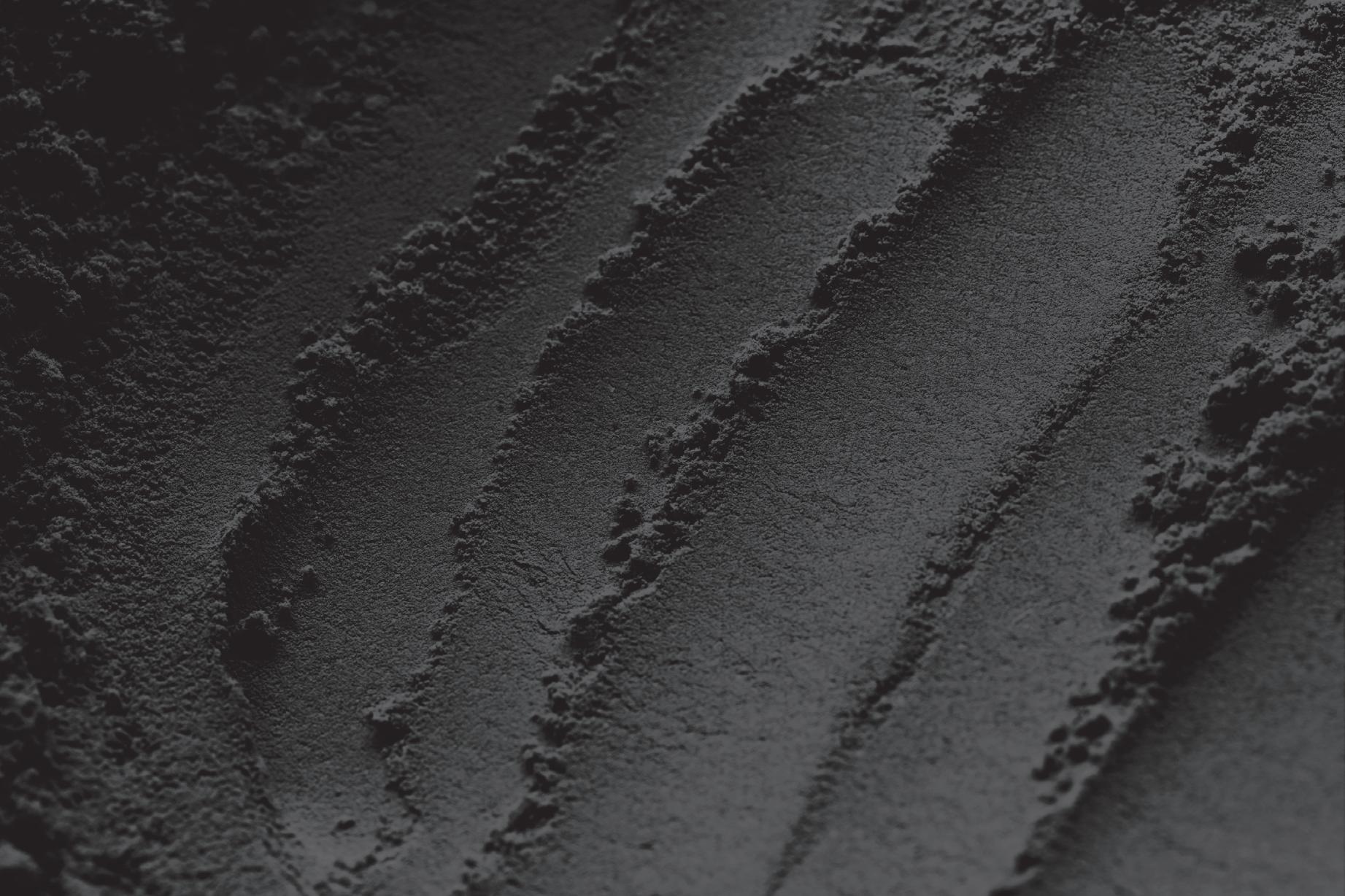
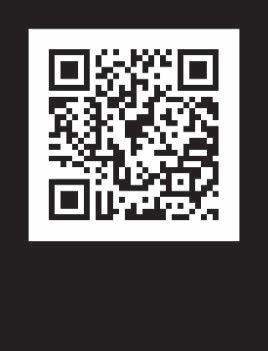
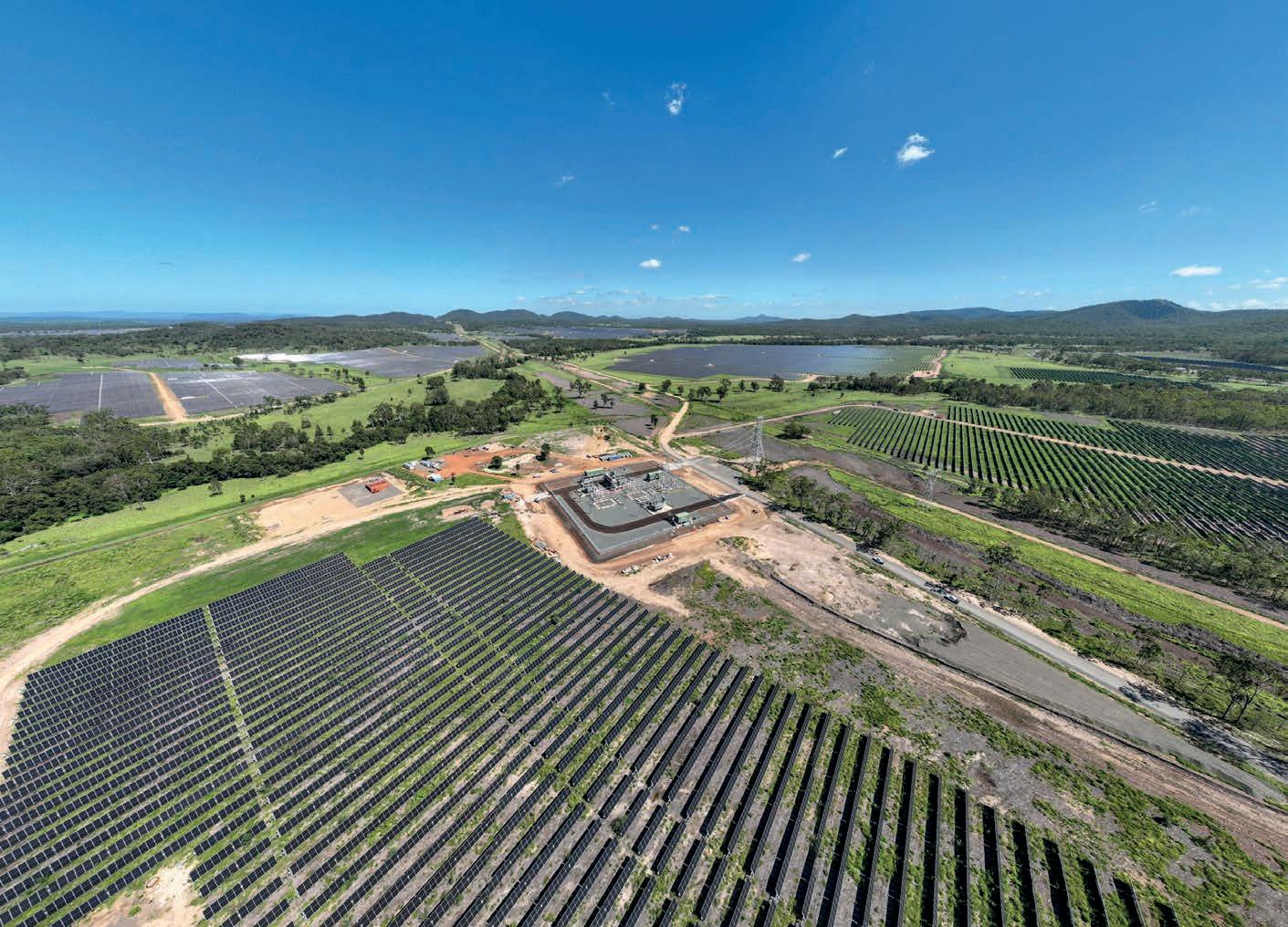
Transforming energy infrastructure delivery
Australia’s energy system is undergoing a period of major transformation. How can utilities live up to mounting pressure to deliver more projects within tighter deadlines?
Australia’s energy transition is well underway but delivering the infrastructure that underpins it is becoming harder, not easier.
Utilities face rising pressure to build faster, integrate new technologies, and manage increasing complex projects, and traditional infrastructure delivery models are struggling to keep up.
Projects are more technically demanding, timelines are tighter, and the risks are higher.
Genus, however, is doing things differently.
By integrating engineering, construction, commissioning, and maintenance into one connected model, the company is helping utilities deliver the full spectrum of modern energy infrastructure –from transmission lines and substations, to battery energy storage systems (BESS), wind, solar and communications systems.
Genus’ end-to-end capability reduces friction between project phases, enables real-time decision-making and gives clients a clearer, more controlled path from concept to completion across even the most complex builds.
Utility sat down with Genus Executive General Manager Industrial Services, Kevin Arnold, to learn how this model is enabling faster, smarter delivery, and why it all starts with deep collaboration and tailored client solutions.
What are the core challenges utilities face in delivering today’s energy infrastructure?
There’s no shortage of pressure – utilities are being asked to do more, faster. But the biggest risk we see is how those pressures affect planning and sequencing.
Without a clear understanding of technical requirements early on, and how those feed into the supply chain, you build risk into the project from day one.
At Genus, we work hard upfront to deeply understand our clients’ needs from a technical aspect and feed that into the supply chain to ensure we manage the risks around it in terms of cost and time blowouts.
Ultimately, it’s this understanding that our clients trust, and it drives our success.
How does Genus overcome these risks without impacting speed or cost?
It comes down to integration, alignment and flexibility.
We’re not just bundling services together – we’ve built a model where design, engineering, construction and asset management sit under one roof, which means we can act quickly, make changes without delays, and reduce dependencies that would otherwise slow a project down.
But it’s not one-size-fits-all. We collaborate deeply with clients at the front end.
We ask: what are your commercial drivers? What timelines are critical? What risk tolerances do you have? And we design the solution around those answers, not the other way around. That’s how we’re able to move quickly without compromising on scope or blowing the budget.
What are the challenges with the multicontractor model?
With multiple contractors working on a job, you obviously have multiple interfaces, and multiple teams each with their own process and timelines and they all have a direct impact on each other.
As Australia forges ahead with its energy transition, traditional delivery methods are struggling to keep up.
Images: Genus
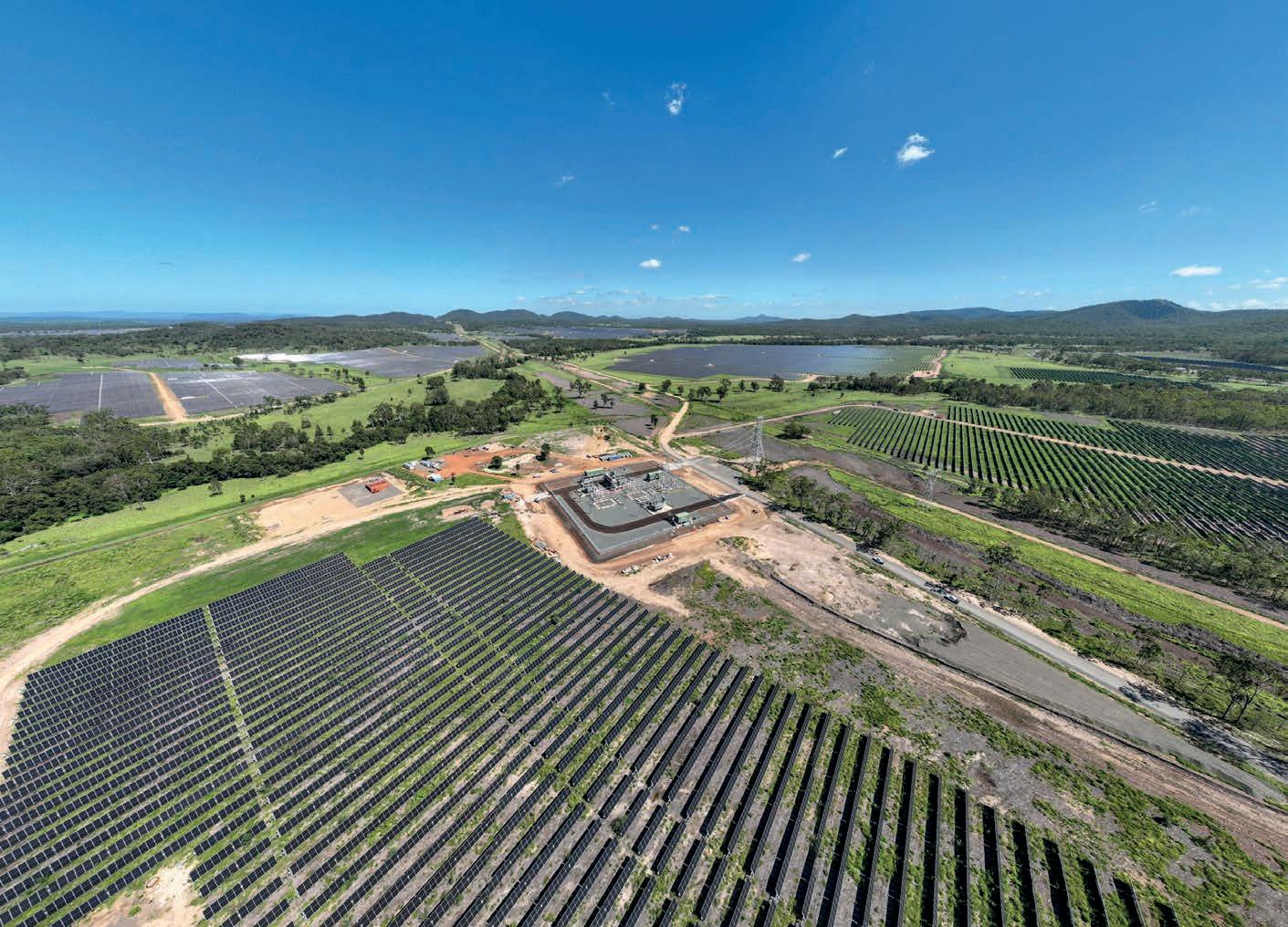
If one element slips, let’s say a delay in engineering, that pushes out civil works, which cascades through the entire project. With a fully connected, fully integrated solution like Genus, we’re in control of the whole journey to get to our destination.
So, if we want to move our workforce around or resequence the project, we can do it quickly and efficiently, making decisions earlier and finding workarounds to roadblocks to ensure we mitigate time overruns or cost blowouts. That responsiveness is what sets us apart.
What gives you that ability to be agile without losing control?
We understand our clients’ needs from a technical aspect and feed that into the supply chain to ensure we manage the risks around it in terms of cost and time blowouts.
It’s this understanding that makes us successful in our projects and earns trust from our clients.
Experience and process are key. We make sure to put the right process in place from the beginning and then use our experience to properly implement the process and ensure there are no deviations.
It can involve having tough conversations with clients around timings and costs, but once we sit down and talk them through our reasoning, they fully understand that what we are doing is reducing risk.
For example, on a recent job, we challenged a client spec that was pushing the project $3 million over budget. We asked the client to consider if they really needed that element and they decided that they didn’t. The client changed the spec, and we brought the job back within cost.
That’s the value of early engagement and collaboration.
Genus Executive General Manager Industrial Services, Kevin Arnold.
Experience and process are key. We make sure to put the right process in place from the beginning and then use our experience to properly implement the process and ensure there are no deviations.
Can you give a real-world example of how this plays out on site?
A great example is the Aldoga Solar Plant Substation project we completed with ACCIONA Energia.
We had an issue with the transformer being overweight when it landed at port, which caused problems for ACCIONA Energia when trying to get it cleared.
However, we were able to work with the team to resequence part of the project and accelerate a few things here and there, which helped us mitigate the delay and keep the project on track.
We also had full control of the delivery schedule from ECI through to commissioning, which meant we could adapt quickly without escalating delays or disputes.
The client didn’t have to chase us. That kind of consistency is only possible when you control the whole journey.
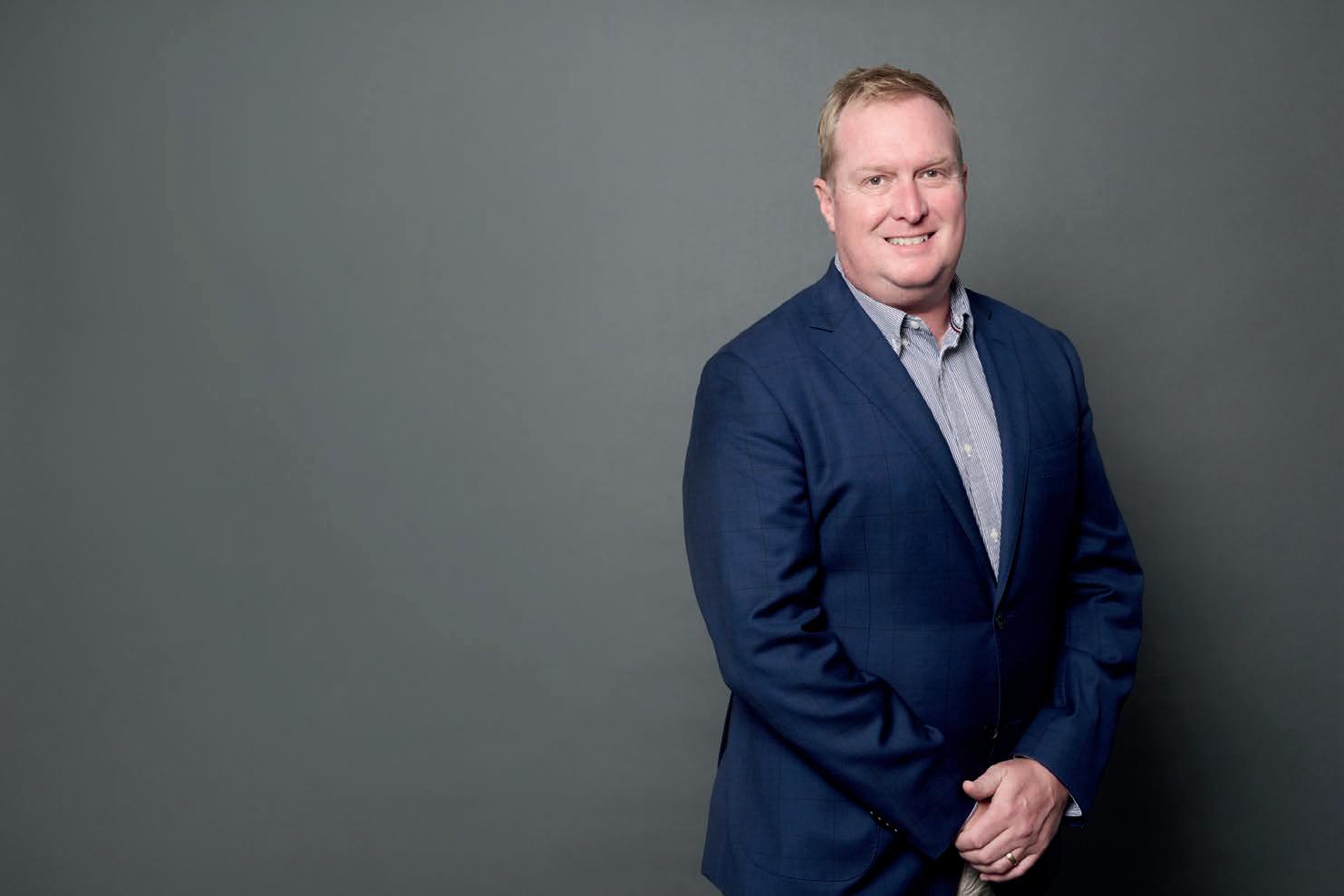
Genus has grown quickly – how do you keep your culture as you scale?
We’ve grown into a Tier 1 infrastructure provider, but we still act like a challenger.
Our leadership team is hands-on. We still walk the floor, get on site and engage directly with clients.
We’re big enough to deliver, but not too big to not care. That’s why our clients keep coming back – they know they’re getting a partner, not just a provider.
What’s ahead for Genus in this evolving market?
We’re already delivering some of Australia’s most important energy infrastructure, including: Stage one of TasNetworks’ North West Transmission Project, Clean Energy Link North, sub-transmission works for Ausgrid’s Hunter-Central Coast Renewable Energy Zone and Humelink East in joint venture with ACCIONA.
But what excites me is that we’re doing it differently: smarter, faster and in a way that genuinely supports our clients’ outcomes.
The grid is changing, and we’re proud to be helping deliver the infrastructure that will power it. U
For more information, visit genus.com.au

Powering back up
Following a monumental recovery effort, Energy Queensland shares the pain, the power and the glory of back-to-back disasters.
Even for Energy Queensland’s emergency response veterans with plenty of notches in their belts, 2025 is a disaster season that will go down in history.
Energex and Ergon Energy Network joined forces to support flood-ravaged communities across the state and restored power to more than 500,000 customers after Cyclone Alfred left a trail of destruction in south-east Queensland.
Energy Queensland Emergency Manager, Max Hogan, said the cyclone response teams had put in more than 300,000 hours of work to inspect 9000km of network, restring more than 175km of powerlines and manage the operations, logistics, and other support services that underpinned a record power restoration effort.
“It was by far the biggest emergency response that we or our predecessor network businesses have ever undertaken, with 2400 crew members on the frontline and working around the clock,” he said.
“The thing that made me most proud was our people, who collectively and safely responded and successfully delivered on our mission for the impacted communities.”
While there are common threads in emergency response, every disaster is different and Alfred was the first cyclone in more than 50 years to cross the south-east Queensland coast near the state’s most densely populated areas, including Brisbane and the Gold Coast.
Mr Hogan said that from his perspective, the biggest challenges were the uncertainty and inevitable delays associated with a cyclone crossing. These included the volume of crews, equipment and vehicles that would be required; sourcing safe accommodation and suitable staging areas; the significant network damage caused by vegetation from outside network clearance corridors; and the site access issues created by fallen trees and flooding.
“We took advantage of Alfred’s slow track to dispatch large-scale generators to communities that would be hardest to reach, like the Moreton Bay islands, and muster as many additional troops as possible from outside the cyclone zone,” he said.
“On the flipside, it was a race against time during flooding at Nudgee, where we built a temporary levee around the zone substation and used sandbags to successfully safeguard electrical equipment from inundation.
“In the face of widespread impacts and some of the most challenging conditions you can imagine, to have power safely restored to more than 500,000 homes and businesses within 11 days is a phenomenal effort.”
The human touch is harder to quantify. Energex and Ergon have left a powerful legacy that goes well beyond the newly installed poles and wires.
Images: Ergon Energy
The cyclone response teams put in more than 300,000 hours of work that underpinned a record power restoration effort.
The crews have inspired community spirit, gratitude, respect and even a new generation of power workers if the cheers in the street, tears of joy, gifts of baked goodies, and thank you cards are anything to go by.
In a sweet token of appreciation, Energex crews and their bucket trucks starred in a book created by Ollie’s Playhouse family day care:
“The children have put a lot of thought and care into making it and we hope it brings a smile to your faces, just as your work has brought relief to so many.
“We want to express our heartfelt gratitude for all your hard work and dedication in restoring power and keeping our communities safe during Cyclone Alfred.”
We’re not out of the water yet
There wasn’t much time to celebrate setting south-east Queensland on the road to recovery before western communities were swamped by catastrophic floods, which looked impressive from space and terrifying on the ground.
The small number of customers impacted by power outages belies the incredible scale of the floods and the complexity of Ergon’s response.
A few hundred properties equals entire extended communities in this part of the world, where townships became islands as roads became rivers. With an area twice the size of Victoria underwater, the only way in was by air.
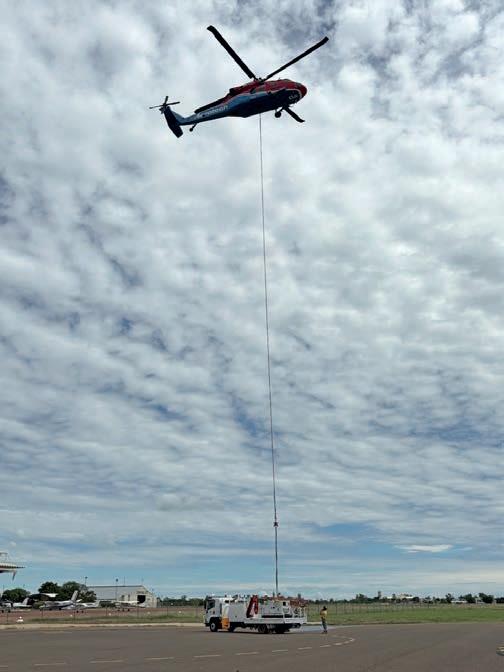
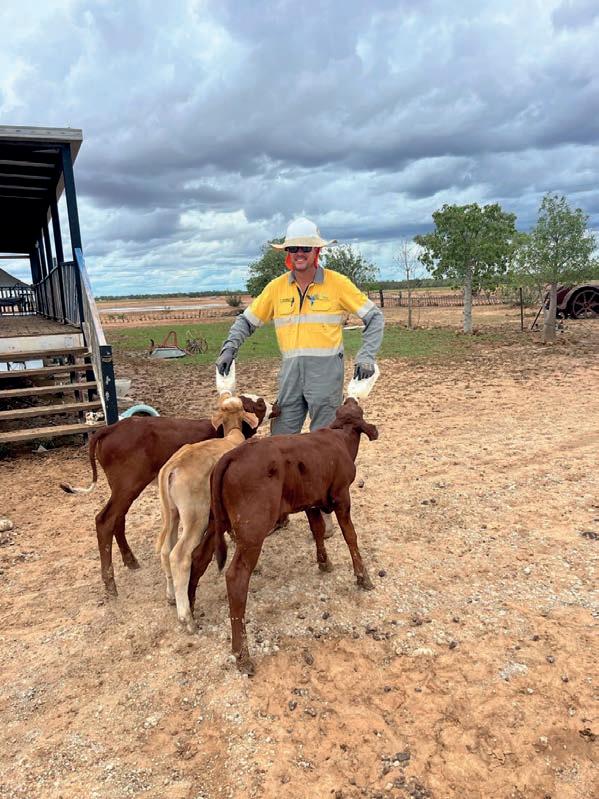
lift Blackhawk and two fixed-wing planes supporting our response, but that meant we were at the mercy of weather and flying conditions,”
Mr Hogan said.
“We had to airlift generators, fuel, tools, communications equipment, food and water in, along with crews. Even when it was safe to land, with limited transport options on the ground, crews had to walk to worksites and carry their gear – which makes their job that much harder.
“We had a much smaller team responding to this event, but they punched above their weight in some atrocious conditions.”
Crews went the extra mile to relieve the burden on flood victims, including people who had been evacuated from their homes.
At Thargomindah, Ben from Ergon’s Hervey Bay depot installed a big screen TV at the evacuation centre to provide a welcome distraction from the disaster.
At Adavale, Damien from Ergon’s Charleville depot fed poddy calves under instructions from their grateful but absent owner in a moo-ving display of compassion and multi-skilling. Crews also kept watch for the pets of evacuated owners – reporting back with sightings and putting out food for the survivors.
Small acts of kindness from people going above and beyond their day jobs have generated an enormous amount of goodwill in back-to-back disasters.
In deep water
In early February 2025, north Queensland bore the brunt of a tropical low that caused record rainfall, major floods, landslides, highway closures and power outages for 33,000 customers from Mossman to Mackay, including Townsville, Ingham and Palm Island.
With major flooding putting an area twice the size of Victoria underwater, the only way crews could get in was by air.
A team member from Ergon Energy’s Charleville depot, Damien, feeding calves at Adavale.
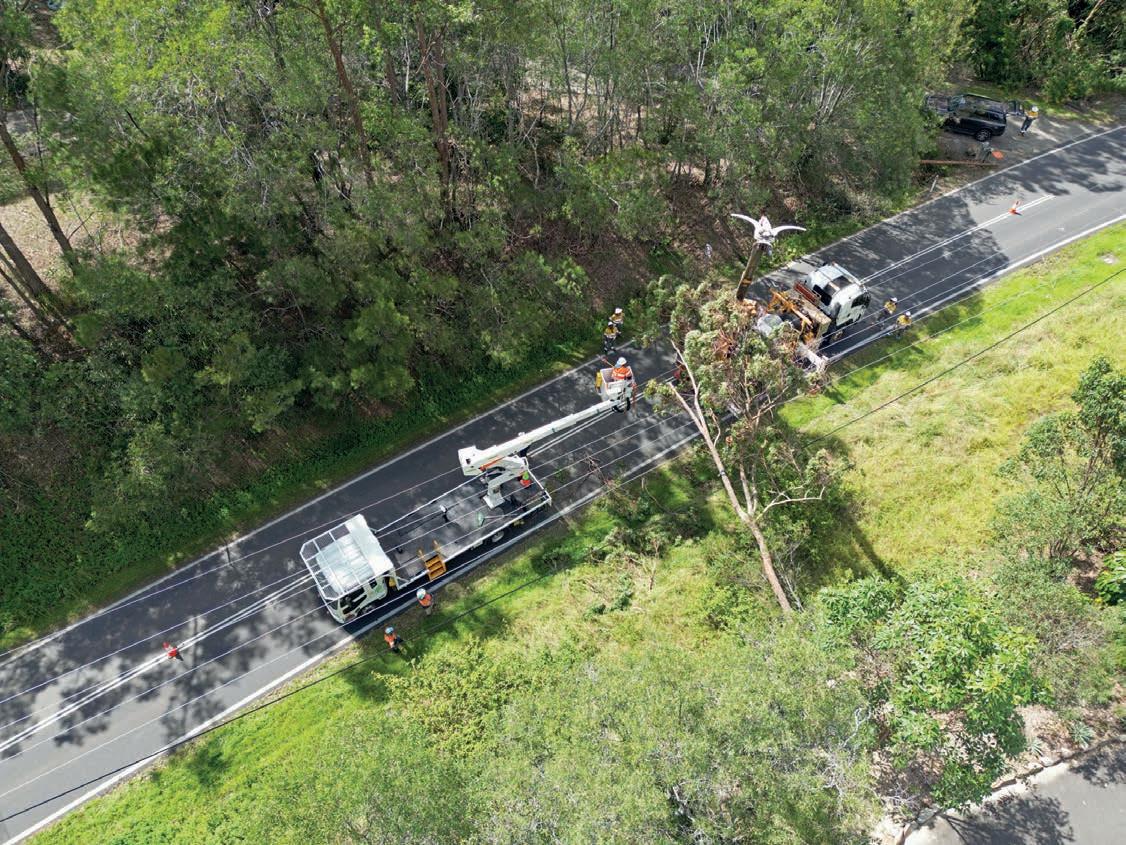
restoration effort in the air, on the ground and on the water.
“We pulled out all the stops; from our specialist substation crews who flew into Ingham to get the town’s substation back online in record time, to the team in the 24/7 Network Control Centre, and our lineys and electrical fitter mechanics slogging it out in the torrential rain and mud,” he said.
“I even got back on the tools myself when we needed all hands on deck in isolated Ingham, and the reaction from customers when the lights came back on was a
It was here that Ergon Energy crews rebuilt the backbone of the high-voltage network after poles and wires were washed away in the flood. At the same site, Australian Defence Force (ADF) personnel installed a temporary bridge across the national highway before RoadTek crews rebuilt the bridge, also damaged by raging floodwaters.
While the bridge works were underway, Queensland Rail carted first responders, Ergon crews and local residents across the highway on the rail line.
“We never walk alone in disaster response, and we are always grateful to everyone involved for their help and support with logistics, including the ADF who used
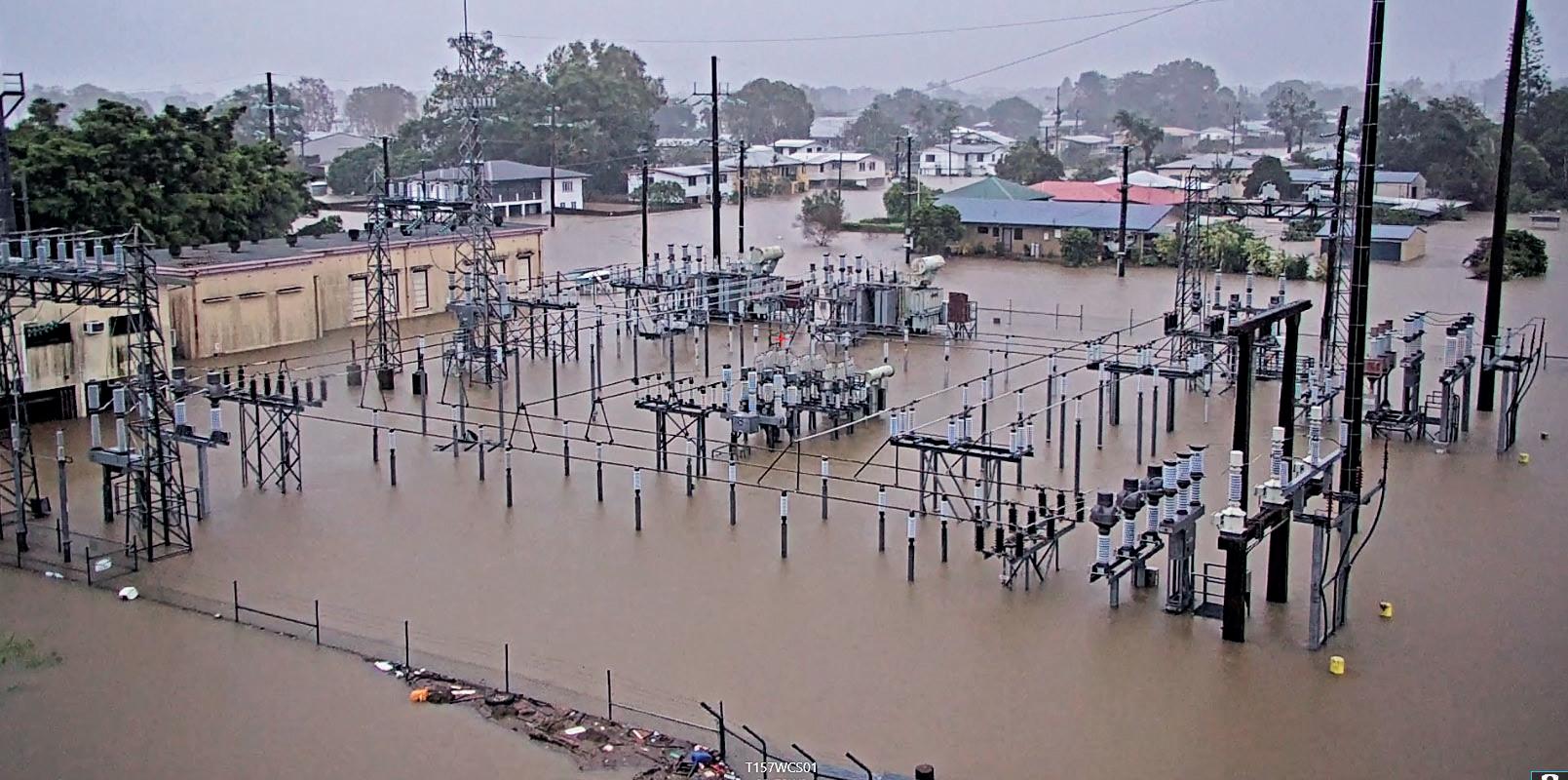
Queensland’s energy utilities joined forces to restored power to more than 500,000 customers after Cyclone Alfred left a trail of destruction.
The completely flooded Ingham substation during a February 2025 extreme weather event.
“We could not get the job done without emergency services, disaster management groups, local councils, community groups, licensed electrical contractors, and everyone who provided timely information, transport, equipment, accommodation and meals.”
At every link in the chain, communication is critical, especially for electrical safety messages and helping people make decisions for their households and businesses based on power restoration targets.
Energex and Ergon kept the community informed at every stage using every available channel – traditional media, social media, an Outage Finder and live news feeds on their websites, 24/7 Network Contact Centres, outbound text messages to life support customers, and face-to-face community outreach in the disaster zones.
During the Cyclone Alfred response, potential media audience reach was more than 170 million, there were upwards of 1.3 million engagements on the networks’ social media platforms, more than 30 million hits on Outage Finder, and in excess of 120,000 views of the live news feed. Community sentiment is arguably the most important metric and the hardest to measure, but the positive feedback and support from every corner of Queensland has been overwhelming.
Key management
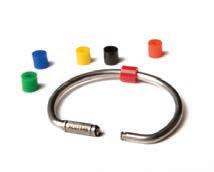
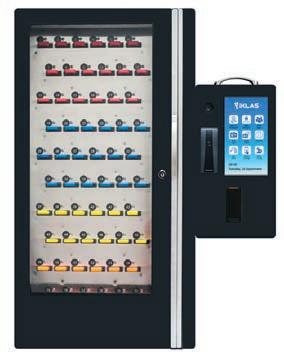
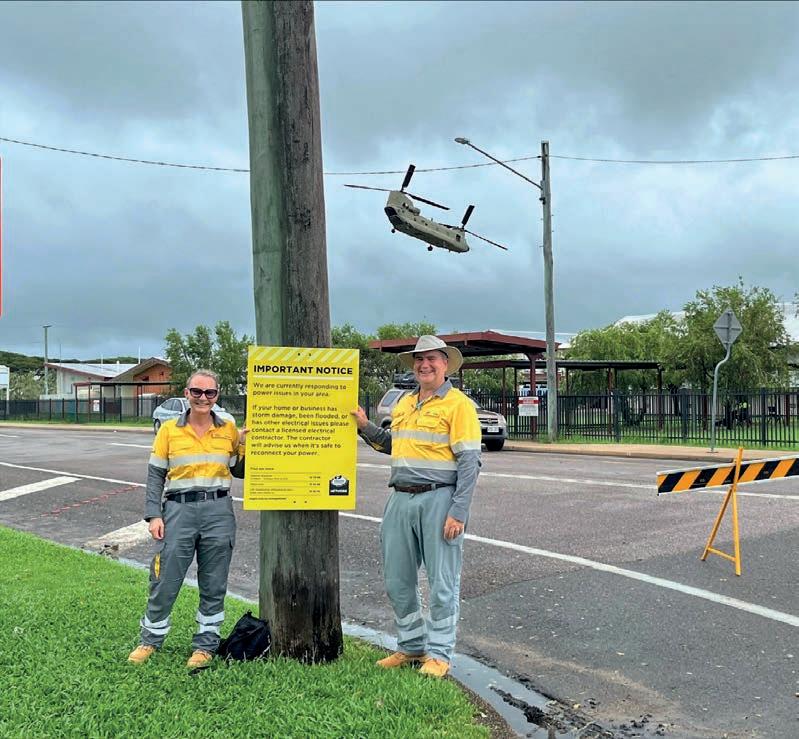
“In all my career across various sectors, I have never been prouder than of our efforts in Queensland during the three big events this year,” Mr Scott said.
“It’s been exhausting, but so meaningful for our Queensland families, friends, mates and strangers.”
Meter security seals

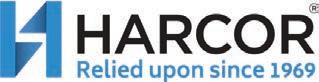
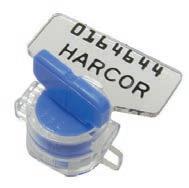
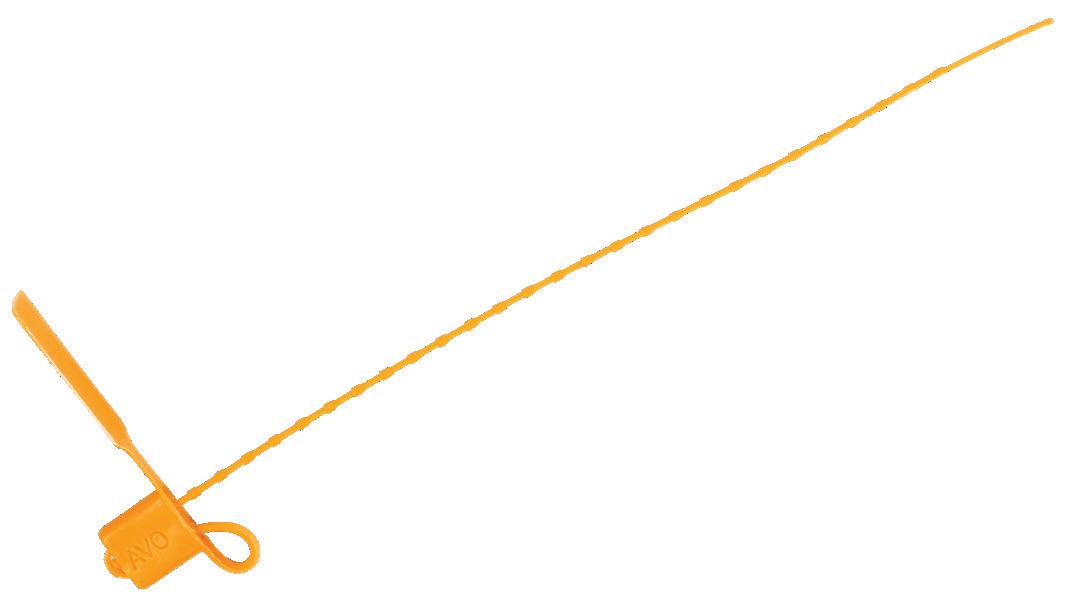
A personal note to the disaster response teams from Energy Queensland CEO, Peter Scott, summed it up beautifully.
The Ergon Energy community outreach team in Ingham.
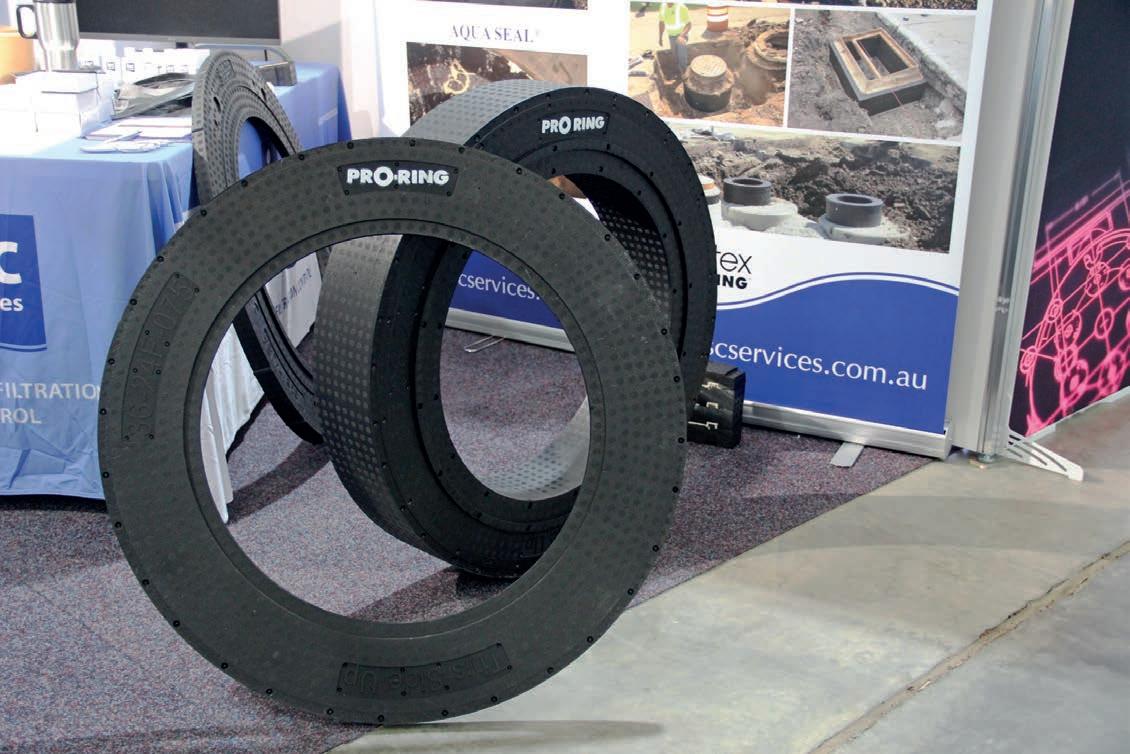
The flow-on effect
Wastewater networks are home to a plethora of assets, often of varying ages and materials, so tackling inflow and infiltration can seem like an insurmountable task – but this industry expert says every little bit counts.
When rainwater (inflow) or groundwater (infiltration) make their way into a sewer network through pipeline damage or joint defects they’re starting a countdown to asset failure, increased operating costs and worst case – overflows.
ISC Services Owner, Dennis Bentink, explained that while it’s virtually impossible to completely eliminate inflow and infiltration, there’s a lot that can be done to control and mitigate it.
“It’s a difficult problem to tackle, and a lot of people don’t know where to start because it’s such a big animal,” he said.
“There’s a misconception that you can’t make a difference but starting to control inflow and infiltration reduces the ongoing cost and problems – every little bit helps.”
It all adds up
Mr Bentink explained that the most vulnerable part of a sewer network is anywhere there’s a connection or joint.
“Basically, a sewerage network can leak from anywhere, it could be an illegal downpipe connected to the sewer, a mistake during construction or, commonly, failed joints,” he said.
“But a big cause of rainwater getting in the sewer is joints, and particularly maintenance holes.

“The top 300mm of the access chamber is disproportionally high risk because you’ve got a lot of joints very close to the surface. And even in new estates, a new maintenance hole might be vacuum tested and pass, but then a machine or vehicle comes along during building works and disrupts the surface, so your brand-new asset starts leaking.”
Ageing infrastructure is not only prone to inflow and infiltration, but Mr Bentink said the two challenges can exacerbate each other.
“[When] Groundwater [raises and lowers] soils expand and contract, and this movement causes joints to separate and leak and old infrastructure to crack and fail,” he said.
“A major issue is that when water moves it generally takes soil with it. So, this will disrupt the support around pipes, maintenance holes and pump stations – and you can even get roads collapsing.”
ISC Service Owner, Dennis Bentink, holding the Pro-Ring. Image: Prime Creative Media
The Pro-Ring has a maximum weight of less than 7kg and can easily be held in one hand. Image: Prime Creative Media
But, if sewer systems are designed to handle water, then why is it a problem if water gets in?
Mr Bentink explained that additional water takes up capacity in the network, but another big problem is the soil that inflow and infiltration brings along for the ride.
“The soil also takes up capacity and also causes excessive wear and tear on pumps and equipment,” he said.
“Now the pump stations aren’t just pumping too much water – they’re also pumping soil and sand and grit. This increases both wear and tear and power consumption, but also [utilities are now stuck with the cost of] treating water they didn’t want in the first place.
“Worst case, it ends up overflowing and now you’ve got environmental concerns too.”
Staying afloat
As these networks have a lot of assets in the ground, digging around each one to find out if its compromised is just not practical.
According to Mr Bentink, prevention is always the best solution. Advanced monitoring solutions can be very helpful in providing the data to tackle this challenge, however, this can be costly and time consuming – but Mr Bentink said that there are a lot of ways utilities can use the information they already have to identify inflow and infiltration and mitigate it with simple solutions.
“They’re already going to have a lot of information through pump operations. If they get a rain event and a pump station increases its operation three or four times, then there’s obviously water getting in somewhere. So, they can focus their efforts on that particular catchment [for repairs],” he said.
“Another simple and effective way to identify problems is smoke testing – [which can find] everything from illegal downpipes, leaking maintenance holes and cracked pipes.
“There’s also a lot of valuable knowledge held by the operators. They will have observed issues over the years, so they [will often] know that if there’s a rain event, there’s going to be a problem in a certain area.”
Once the source of trouble has been identified, there are a range of simple yet cost-effective ways to both repair damages and prevent inflow and infiltration.
“Every new asset should start with prevention. Gator wrap is an external joint wrap, which can be placed around the joints of brand-new pre-cast assets to stop water, soil and roots from getting in and stop premature failure of the joints,” Mr Bentink said.
“For assets that are already in the ground, let’s say you’ve got a very fast water leak, you can use something like Aqua Seal – which is an expanding polyurethane foam that you inject in. It will push into the soil around the back of the leak and form a mushroom shaped plug, so the pressure doesn’t allow it to pop out, but it fills that void to reduce any surface damage and stop the active water flow and soil coming in.”
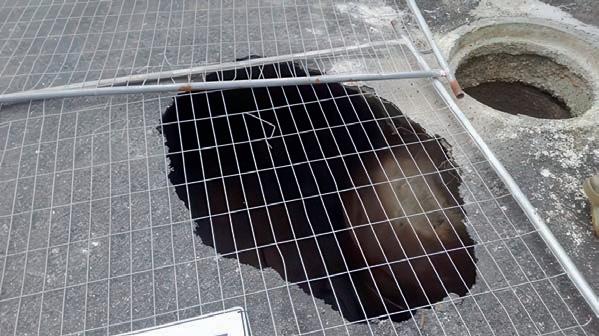
Bentink said that he works closely with water authorities to identify appropriate solutions.
to have a bunch of different options so [we can help customers] choose the right tool for the job,” he said.
customer trying to achieve [and work back from there].
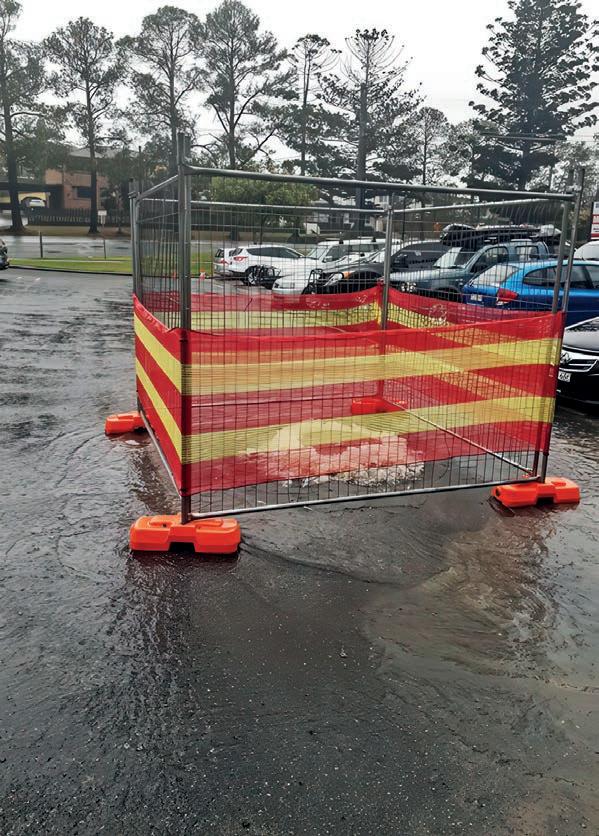
that there are a lot of low maintenance holes – which let rainwater in and, being low, become covered and create access issues – there was a lot of damage to infrastructure and there was a lot of manual handling injuries associated with moving concrete risers.
“I had quite a few people talk to me about wanting to improve safety and stop the leaks in the maintenance hole chimney, so I looked around for a solution to raise maintenance holes, and the Pro-Ring was already proven overseas and had a well-established track record, with its light weight and high strength. There are other materials out there, but I chose this one because of the strength, durability and its ability to properly seal.”
ISC Services has a range of simple, yet clever solutions to tackle inflow and infiltration, but for Mr Bentink, the best thing you can do is start sooner rather than later.
“A lot of people don’t know where to start because it’s such a big problem. But not starting doesn’t help – leaks don’t fix themselves and they just cause more and more damage to the assets over time and downstream,” he said.
“Inflow and infiltration are very difficult to eliminate, but by reducing it, we can reduce the burden on the assets and prevent avoidable overflows.” U
For more information, visit iscservices.com.au
Inflow and infiltration can be difficult to tackle, but every little bit helps. Image: ISC Services
Soil and road collapse next to leaking maintenance hole. Image: Regional New South Wales Council
No spills
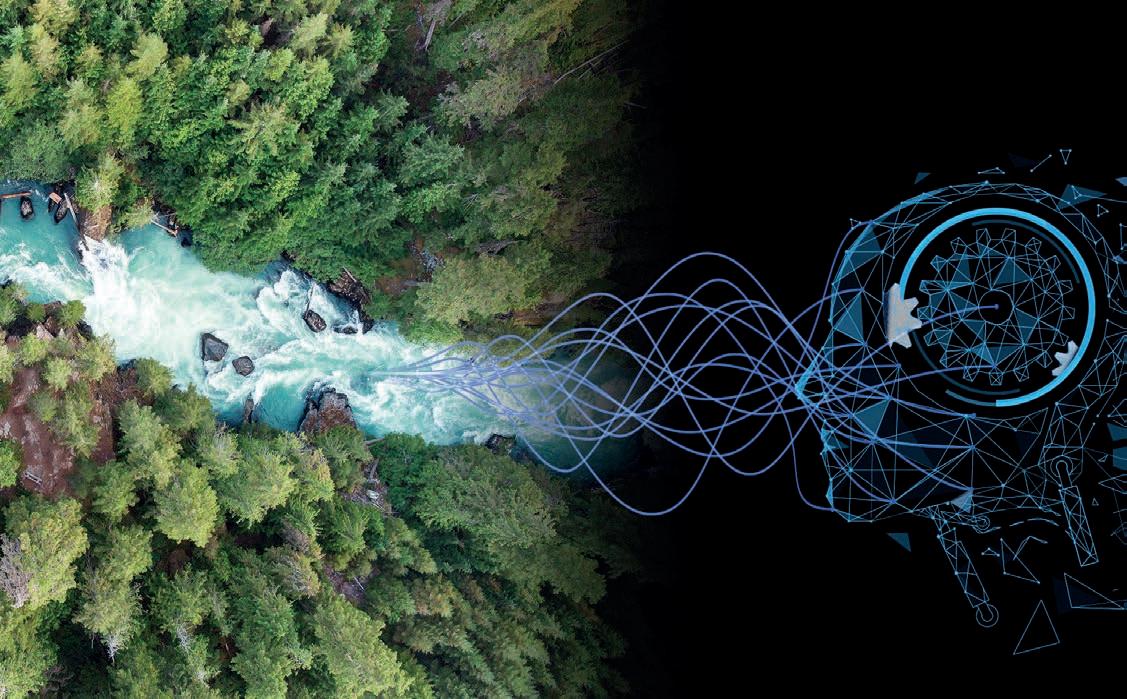
By leveraging AI tools, utilities can enhance efficiency, optimise resource allocation, and adopt proactive maintenance strategies.
AI and machine learning (ML) is invaluable in demand forecasting, accurately predicting operational needs based on historical data, weather conditions, population growth, and other relevant factors.
This enables utilities to optimise production, distribution, and capacity management, even in the face of increasing droughts, population growth, and ageing infrastructure.
For clean water, ensuring ample water is available at the right time and place, is a clear goal, considering increasing droughts, population growth and ageing assets.
For wastewater, it covers some gaps from long-term underinvestment and focus. The drivers are similar, in that climate change and increasing populations impact networks not designed to withstand these challenges.
Predict and prevent has been Metasphere’s focus for years.
A specialist in wastewater management, Metasphere provides smart network management solutions to the global utility industry.
Its intelligent solutions offer full visibility and forecasting for remote assets and systems, reducing telemetry ownership costs.
Highly accurate hyperlocal weather forecasts are changing how councils control localised flooding, utilities manage remote raw water sources and how pollution events are reduced.
Metasphere’s mantra is ‘no spills’. The company believes shifting from a reactive monitor and alarm to proactive predict and prevent operational mentality, is the answer to achieving no spills, with technology playing a critical role.
AI/ML technology has already proven its worth in energy consumption optimisation for water utilities.
Metasphere say that by analysing energy consumption and system performance data, utilities can identify opportunities for improvement.
ML algorithms can optimise pumping schedules, adjust treatment processes based on real-time conditions, and predict energy demand. This allows utilities to operate at optimal efficiency, reducing costs and minimising environmental impact.
A significant challenge for utilities is transitioning from the management of isolated assets to automated and integrated networks. Taking a holistic approach by considering catchment areas, weather data, and utility network information allows for better prediction of impacts on natural watercourses and coastlines.
Predicting water quality, including soil moisture data and information on agricultural use, such as fertiliser by crop type and proximity to watercourses, is an obvious and valuable albeit not simple addition to catchmentbased management.
Integrating data from various sources, such as traditional methods like IoT and citizen science data, is essential but presents challenges.
Overcoming these challenges is critical for utilities to fully leverage the potential of AI/ML.
Metasphere believe integrating data sources and tapping into the expertise of subject matter experts, utilities can continue improving their assets and networks.
In conclusion, AI/ML plays a critical role in water utility operations. By harnessing AI technologies, utilities can enhance efficiency, reduce costs, optimise networks, and protect the environment while delivering sustainable water services to the communities they serve. U
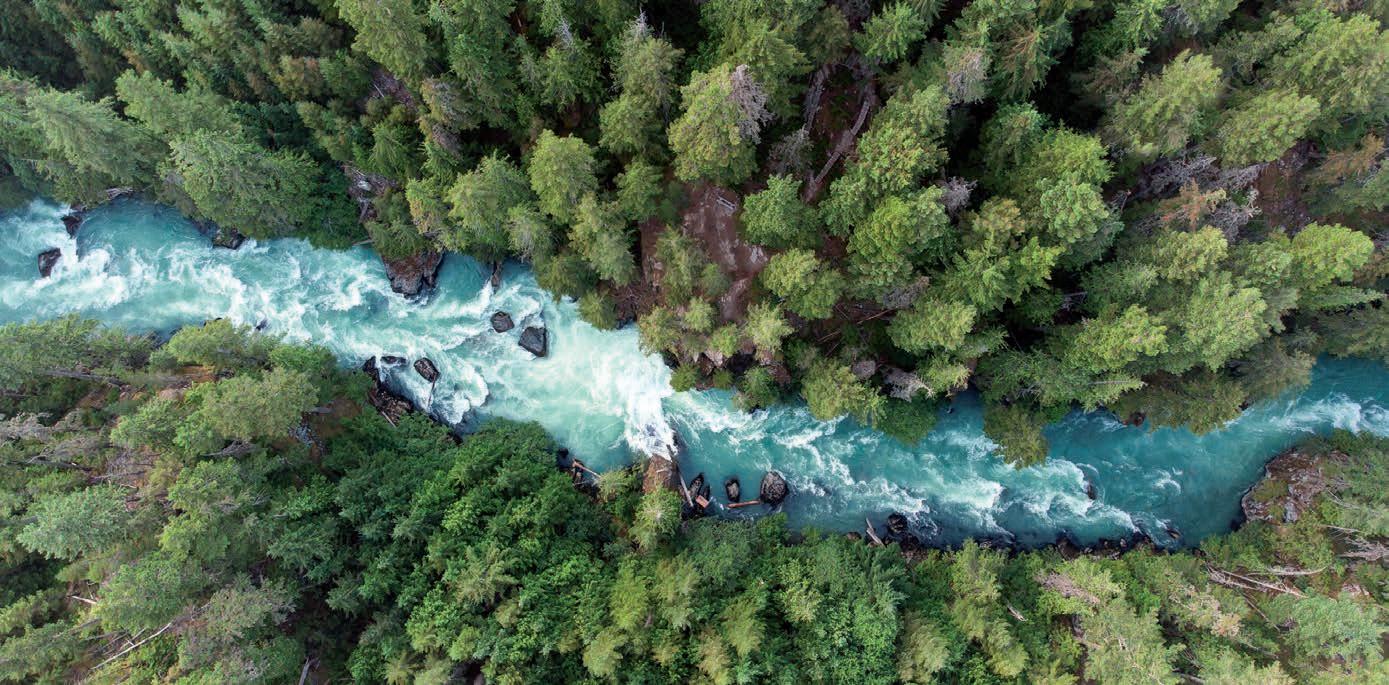
Metasphere believes shifting from a reactive to proactive operational mentality is the key to preventing sewer spills.
Metasphere helps customers prevent leaks and spills for a cleaner, greener world
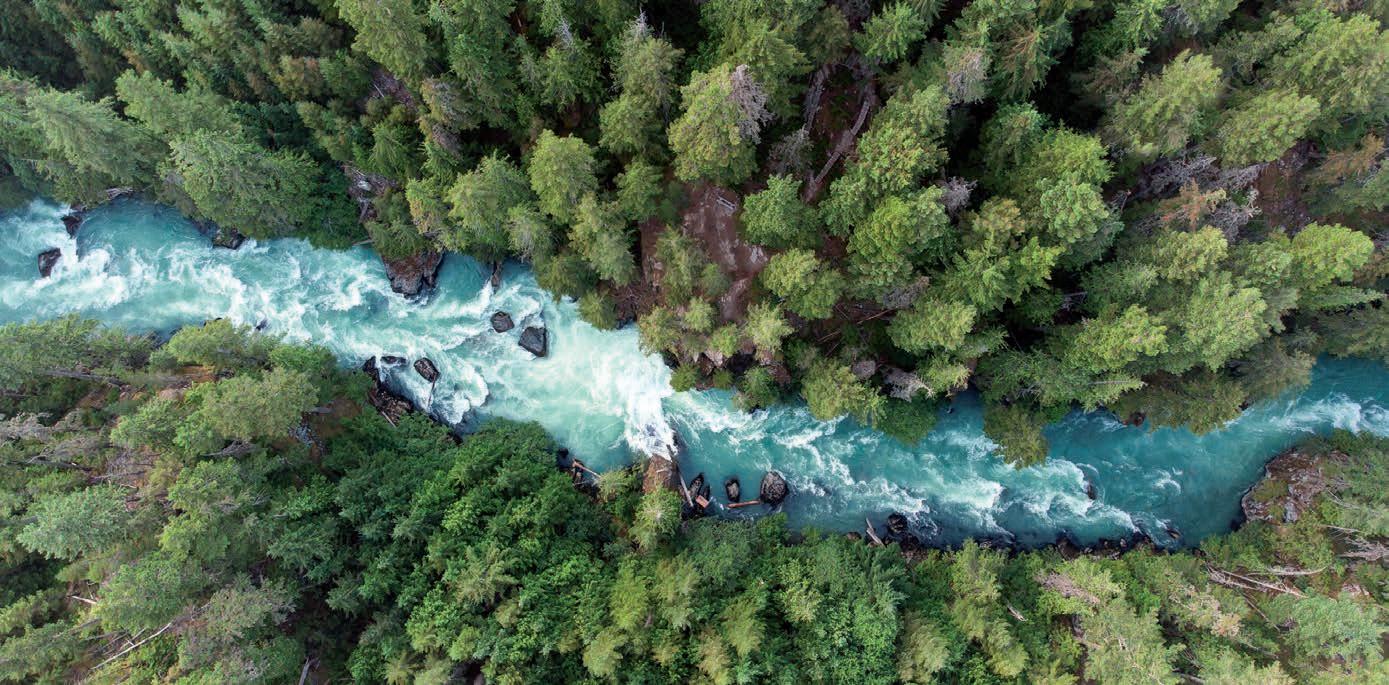
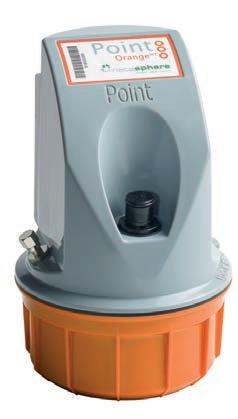
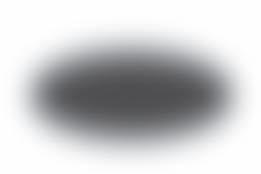
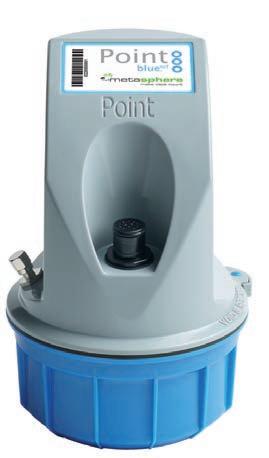
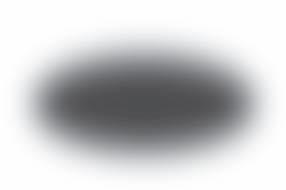

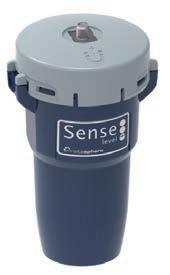
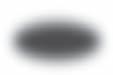
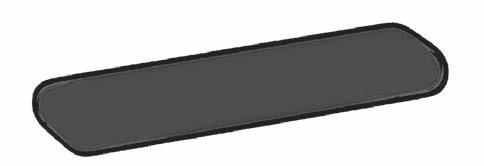
Our intelligent, innovative all-in-one telemetry solutions provide full network visibility, performance and forecasting.
Reducing telemetry ownership cost for customers to manage time-critical remote assets and systems.

Taking environmental responsibility
Following on from Steel Main’s SINTAKOTE® steel pipe system receiving an Environmental Product Declaration at end of 2022, the company is continuing to ramp up its end goal of reducing emissions.
Steel Mains Environment and Sustainability Lead, Ben Twigg, voiced the company’s goal going for‑ ward – drive significant carbon reduction across its operations.
“The company’s climate strategy focuses on reducing emissions and improving waste management to minimise our environmental impact,” he said.
Emphasising the rigorous verification process that goes into acquiring an environmental product declaration (EPD), Mr Twigg said it is more difficult for a product associated with a hard to offset industry like steel manufacturing.
“We performed a full lifecycle assessment of our SINTAKOTE pipe. Every step of the way, from raw materials, manufacturing supplies, waste outputs, to the decommissioning stage,” he said.
“We want to take accountability for any emissions and waste involved in our products. Ultimately, this process clearly indicates the impact of current operations and shows us what we need to do to reduce emissions, to remain competitive.
“The direction industry is moving towards emissions reductions – is obvious. It’s about getting ahead and making sure that we’re not only serving customer’s needs now but continue to do so over the next ten, 15 or 50 years.”
In 2025, Steel Mains has a goal to align with science‑based targets and support global efforts to limit warming to 1.5°C.
As a result, the company has set clear near term (2030) and long term (2050) emissions reduction goals. Mr Twigg said an important part of reducing the environmental impact of SINTAKOTE steel pipe systems is recyclability of materials.
“Recycling steel consumes 75 per cent less energy than production of steel from raw materials. SINTAKOTE steel pipes are made from 17.4 per cent recycled material, which, combined with long service life, results in a sustainable and robust product,” he said.
In order to achieve its goal, Steel Mains has achieved Level 3 certification with the Steel Sustainability Australia (SSA) program.
This marks a significant step towards an improved sustainable and environmentally friendly manufacturing process for a local Australian manufacturer.
With Level 3 being the highest level of certification under the program, it requires Steel Mains to display:
• A reduction of two per cent or more in operational carbon emissions per tonne of production over the last five years
• Minimum 80 per cent of waste redirected from landfill
• Commitment to pursue decarbonisation within our supply chain
• A robust health and safety system which covers the entire life cycle of our product
The SSA Certification Program is participated in by steel suppliers and fabricators around Australia, including Bluescope, and aims to support responsible manufacturing of steel and steel products in Australia.
“Both our Manufacturing facilities in Victoria and Western Australia have achieved Level 3 certification,” Mr Twigg said.
As one of Australia’s major suppliers of SINTAKOTE mild steel (MSCL) pipes for water, wastewater and sewer, Steel Mains’ proven interest in reducing emissions and supporting a circular economy in the industry has the potential to impact other elements of industry, from manufacturing to transport. U
For more information, visit www.steelmains.com.
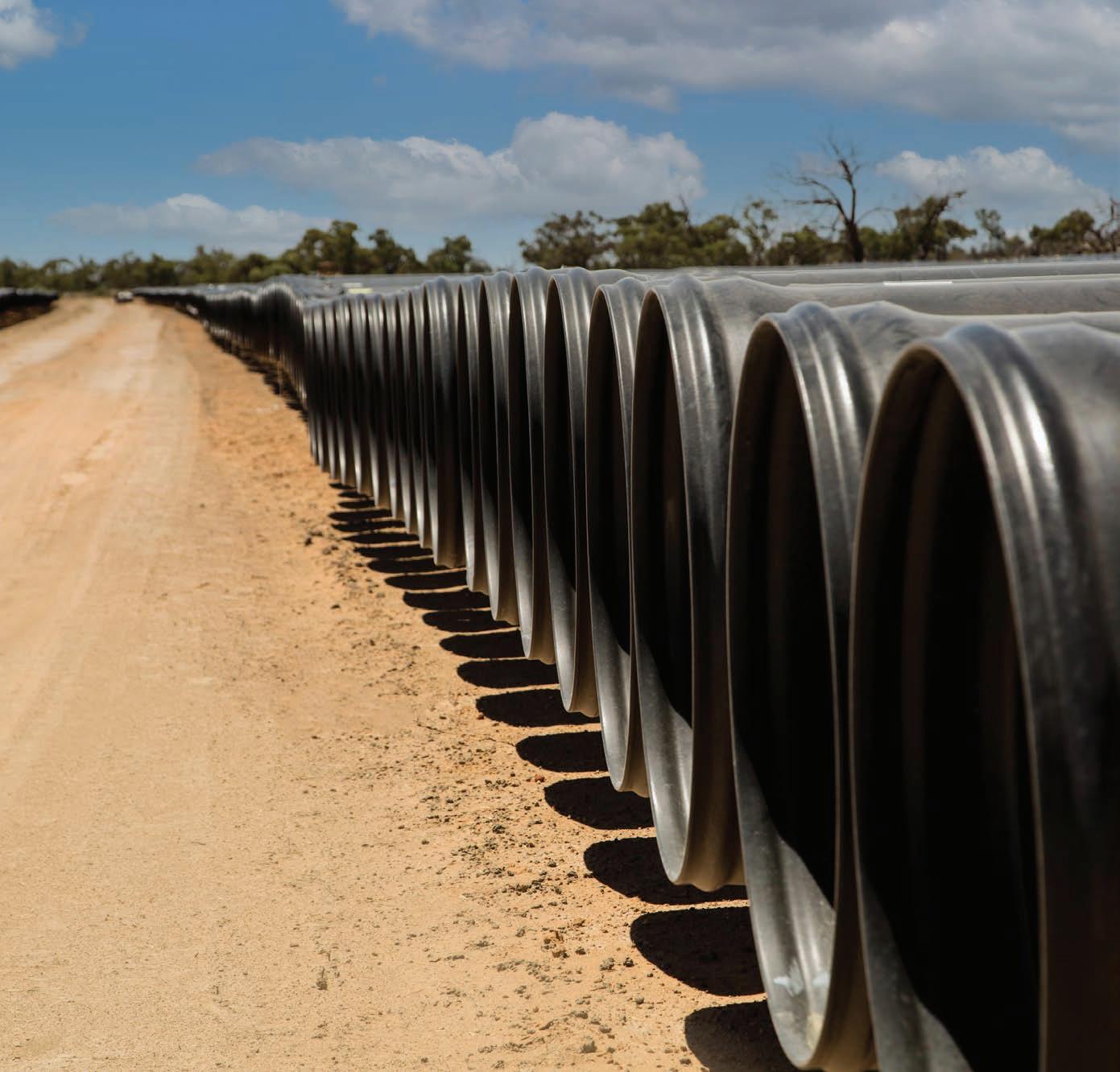
SINTAKOTE steel pipes are made from 17.4 per cent recycled steel, which consumes 75 per cent less energy than production from raw materials.
Image: Steel Mains
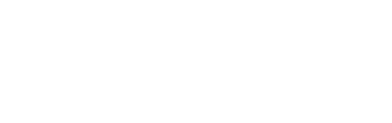
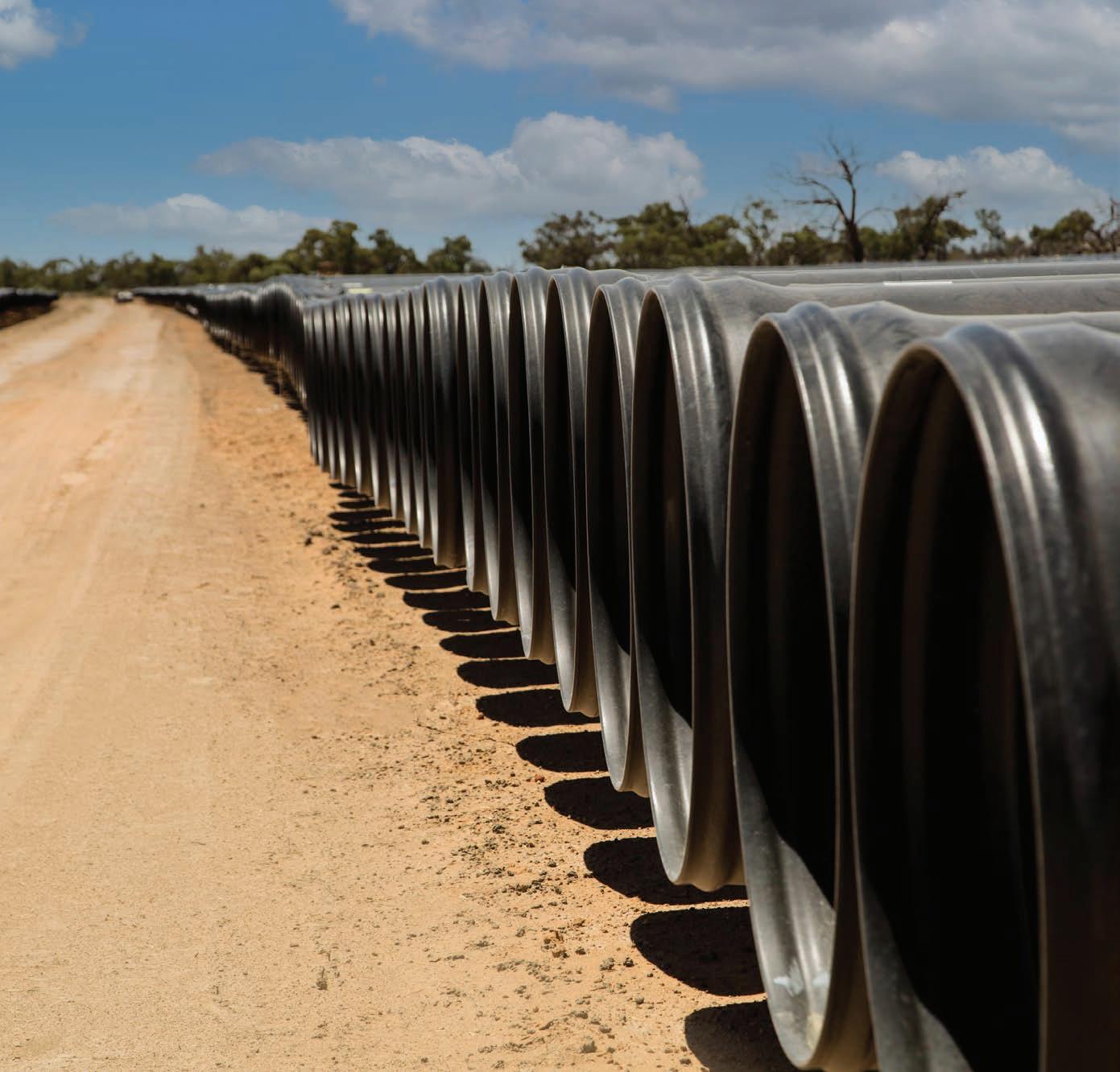
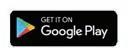
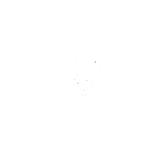


A sustainable water future
Australia’s water sector is facing unprecedented challenges and innovation holds the key to building a resilient and sustainable industry.
Climate change, population growth and increasing industrial demands are placing immense pressure on the nation’s water resources. Meeting these challenges requires a fundamental shift towards smarter, more sustainable water management practices. This includes improved monitoring and maintenance, efficient demand management, and a greater focus on the circular economy and future energy solutions.
A recent initiative from Veolia Water Technologies Ireland offers a great example of how advanced monitoring technology can significantly improve water treatment efficiency and reduce waste.
Smart thinking
Although the project was based in Ireland, the principles are directly applicable to the Australian context.
In both countries alike, traditional chlorine detection methods often rely on reagents, leading to inaccuracies and increased maintenance. To overcome these limitations, Veolia implemented Burkert’s online water analysis system, specifically for chlorine detection.
With precise, real-time monitoring, the Burkert system offers a reagent-free alternative that result in more accurate, reliable data and reduced operational costs.
This improved monitoring not only enhances the quality of treated water but also enables proactive maintenance, a critical component of a sustainable water management strategy.
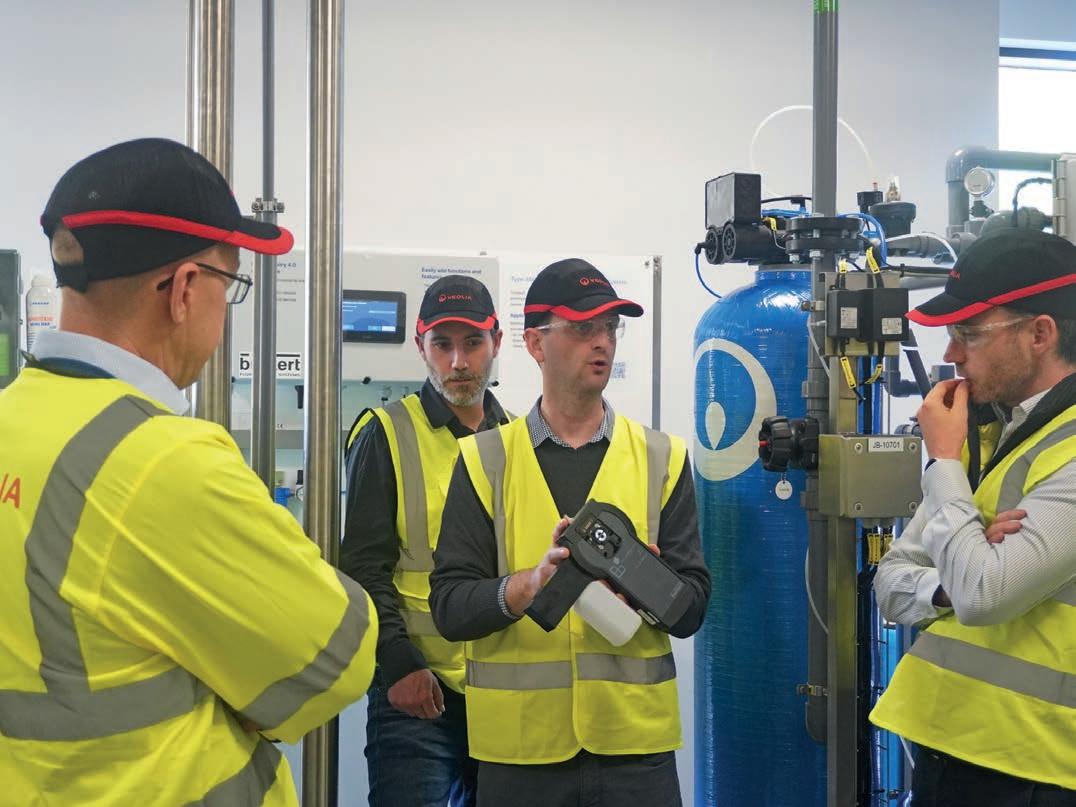
Early detection of anomalies like chlorine breakthrough allows for timely intervention, preventing damage to downstream processes like reverse osmosis (RO) membranes and ensuring the uninterrupted supply of purified water.
The real-time alerts and remote monitoring capabilities provided by the system further enhance operational efficiency – which is particularly relevant in for Australia’s own essential service providers, many of which operate extensive networks across the nation’s vast distances.
A well-rounded approach
Beyond precise monitoring, a circular economy approach to water management is crucial.
This involves minimising water loss, maximising reuse and recycling opportunities, and reducing the environmental footprint of water treatment processes.
While Veolia’s project primarily focused on chlorine detection, the company was indirectly supporting this approach by optimising the performance of the granular activated carbon (GAC) filtration system.
Efficient GAC filtration not only improves water quality but also extends the lifespan of the filters, minimising waste and reducing the need for frequent replacements.
Demand management also plays a vital role in sustainable water practices. By implementing smart metering systems and employing data-driven strategies, utilities can effectively manage water consumption, reducing overall demand and minimising wastage.
Data from the Burkert system could be integrated into a broader demand management program, providing valuable insights to inform water allocation decisions and optimise network operations.
Looking ahead, future energy considerations are increasingly important, and the energy intensity of water treatment processes presents a significant environmental challenge.
Exploring renewable energy sources to power these processes and integrating energy-efficient technologies can substantially reduce carbon emissions and improve the overall sustainability of the water sector. This might include solar-powered water treatment plants or using energy recovery systems to harness waste heat.
Veolia’s case study highlights how smart monitoring solutions like the Burkert system offers a path towards a more efficient, reliable and sustainable future for Australia’s water utilities.
The principles of proactive monitoring, optimised filtration, demand management and responsible energy use are all key to creating a resilient and environmentally conscious water sector. By embracing innovation and adopting a holistic approach, Australian water utilities can navigate the challenges of the future and ensure the long-term security of our precious water resources. U

Burkert’s water analysis system provides Veolia with precise and reliable data to help it reduce waste at its Ireland treatment facility.
Image: Burkert


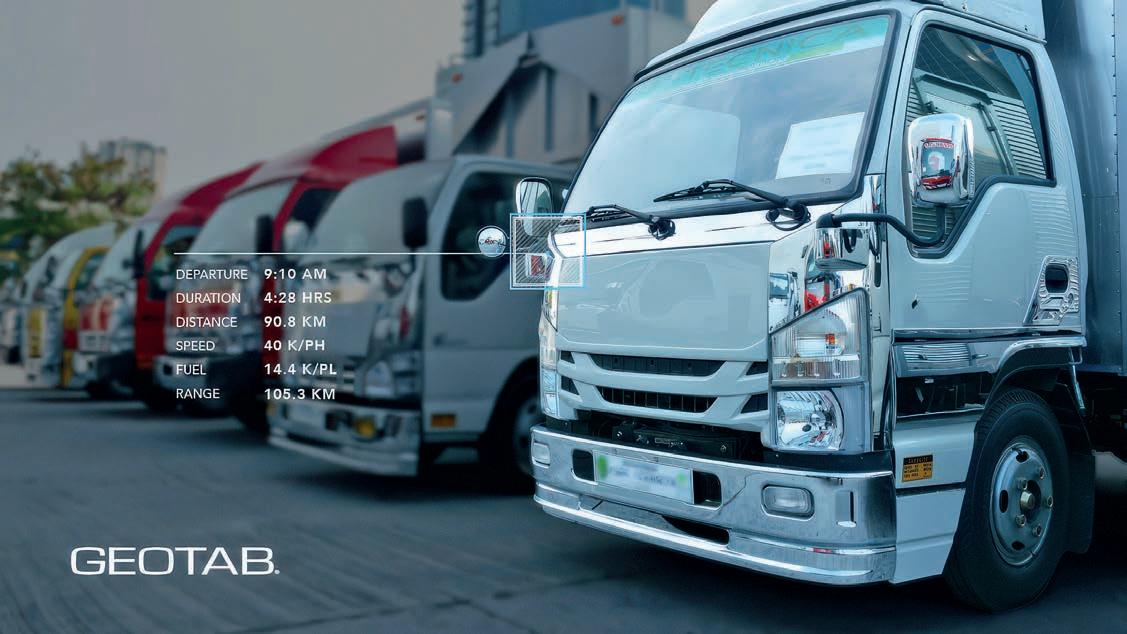
The road to sustainability
Telematics has the potential to revolutionise the utility sector, and Dubbo Regional Council leveraged this enhanced visibility to boost sustainability outcomes and cost savings.
Fleet management is a critical element of utility operations, with vehicles playing a key role in delivering the essential services we rely on every single day.
The transport sector, however, is one of the largest contributors to Australia’s greenhouse emissions.
As we approach the 2050 net zero target and sustainability takes centre stage, tackling emissions is a key priority. But how can industry reduce emissions when vehicles are so vital to the provision of essential services?
If you ask the team at Dubbo Regional Council, they’d point to telematics.
With a large fleet of vehicles and equipment ranging from street sweepers to whipper snippers, the council felt it needed better visibility into the fleet’s operations to pinpoint where it could make improvements on sustainability and cost-effectiveness.
Dubbo Regional Council teamed up with Geotab to achieve these goals, trialling telematic devices across 40 of its vehicles, and the insights were immediate.
Dubbo Regional Council Manager Fleet and Depot Services, Daniel Peterson, said a lack of visibility into how the equipment was being used caused a lot of the challenges.
“During the trial, we found that we had a very high idle time. We ended up doing a calculation, and we found that we were spending around $180,000 a year on diesel in idle time alone,” he said.
Armed with this knowledge, the council promptly got to work on improving this, and the inexpensive installation was quickly offset by the savings made with the new ability to monitor fuel consumption.
This, of course, also has the benefit of reducing the emissions produced by the council’s vehicles and equipment.
However, that’s not all Geotab’s telematic solutions were able to do for Dubbo Regional Council.
The council also leveraged the technology to improve its road and waste management, using the devices to map out road maintenance and monitor contamination in rubbish and green waste collections.
Using telematics in these innovative new ways not only helped Dubbo Regional Council improve its services, but it also paved the way for innovation in other sectors, with Council winning the inaugural IPWEA Fleet Innovation Award in 2024.
Mr Peterson said since introducing the system, Council has been able to significantly increase its efficiencies.
“That has meant we’re able to offer a better service at a lower price for the community,” he said.
With the success of the trial under its belt, Dubbo Regional Council plans to roll out the devices to 280 vehicles in total to further boost its sustainability and cost-effectiveness.
Sustainable made easy
For essential service providers like Dubbo Regional Council, utilising telematics can have a profound impact on sustainability outcomes.
As one of the world’s leading providers of commercial telematics solutions, Geotab has been helping businesses slash costs and carbon emissions for more than 20 years with its connected transportation and fleet management solutions.
By providing detailed insights into fleet operations, Geotab empowers users to make informed decisions to drive the transition to sustainability. U

• Lighter and Safer
•
• Better value for money
• Half the CO2 emissions of concrete to manufacture
• Leak tight
• Trafficable Class - D
• Proven solution
• Recyclable

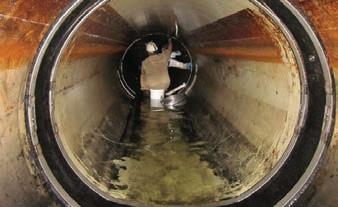
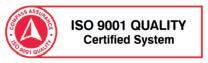
Specialists in control of Inflow and Infiltration
Innovative products to improve the return on your valuable sewer, stormwater and potable assets
• Raise MHs to surface safely, quickly and cost-effectively
• Permanently seal leaking pipes and MH joints
• Prevent leaks forming
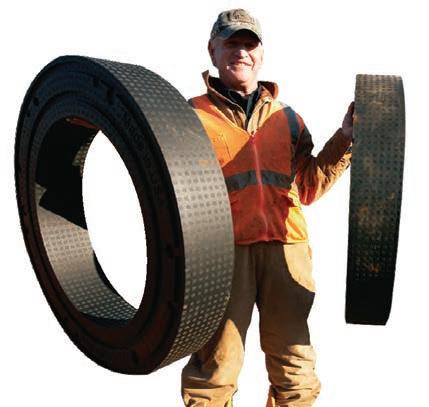
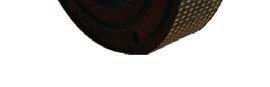

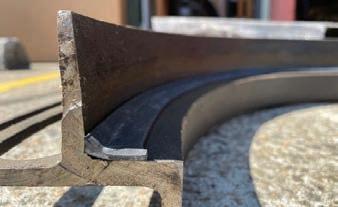
Gator Wrap
HydraTite
Manhole Lid Gasket
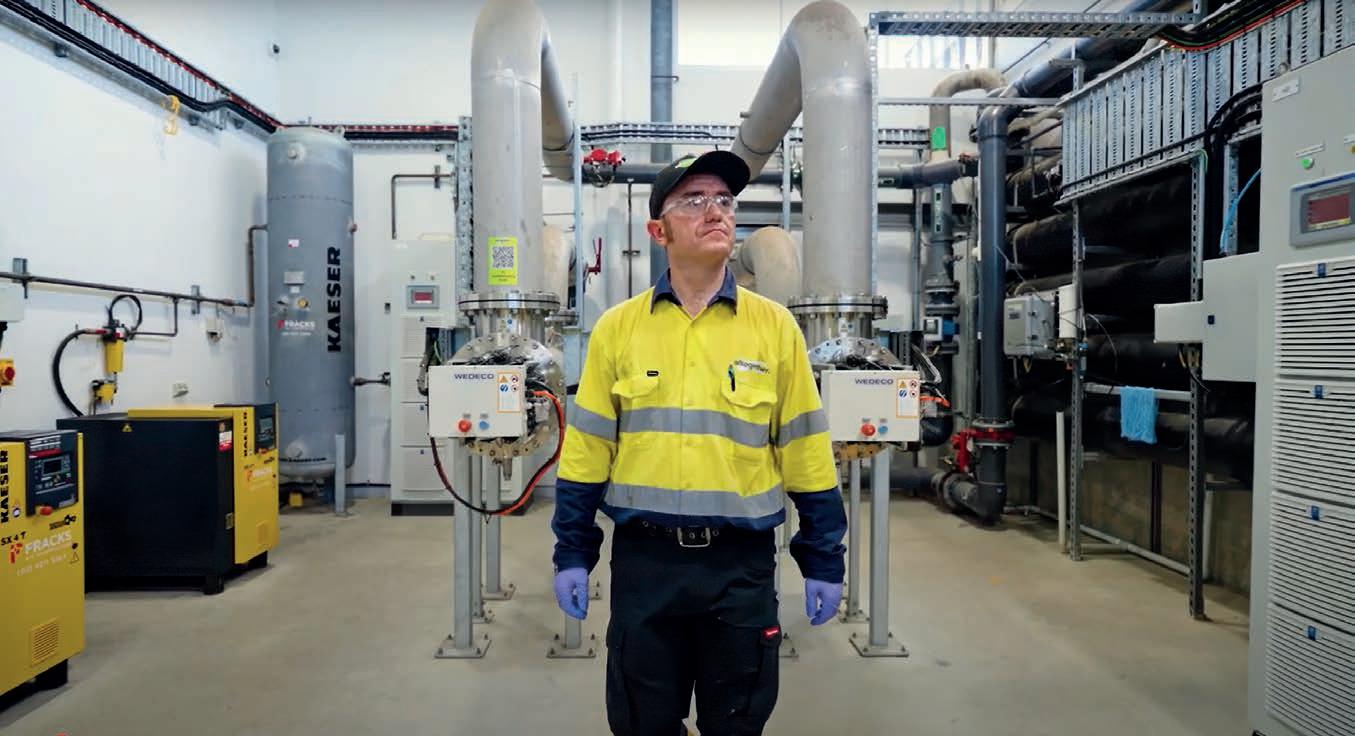
Thinking outside the box
As storm events grow more severe, so does the risk of inflow and infiltration –highlighting the need for smarter, more resilient sewer system management.
Climate change is intensifying the water cycle, driving more extreme weather events across Australia. As a result, the risk of inflow and infiltration in sewer systems increases, placing greater pressure on downstream network assets and raising the likelihood of disastrous spills.
The issue is amplified in areas where traditional gravity fed systems are deemed cost prohibitive and alternative systems like low pressure sewer systems are used, such as in areas of hilly and rocky terrains or where old and complex septic tanks need to be replaced.
Many of the brilliant minds at South East Water and its commercial arm, Iota, have first-hand experience with these challenges, and saw that the water industry had a need for a solution that could manage difficult terrains and that didn’t just monitor, control and optimise an individual sewer system – but managed the overall network too. Enter OneBox.
Ticking all the boxes
South East Water originally developed OneBox – a low pressure sewer system - to monitor its wastewater assets and identify issues without the need for customer intervention. However, the technology quickly evolved into a smart system that could digitally manage an entire low pressure sewer network in near real-time.
To tackle challenges like inflow, infiltration, spills and network overloading, sewer asset owners needed a solution that could help them take a proactive approach. To do this, it was identified that OneBox needed to combine clear network visualisation with real-time data and control functionality to turn an essentially dark system into a smart one.
OneBox was put to the real test when South East Water, supported by Iota, began a project to replace around 16,500 septic systems with a low-pressure sewer system controlled by OneBox.
Implementing the devices on such a large scale meant that Iota had the perfect platform to continuously enhance and refine OneBox by incorporating operator feedback throughout the project.
Fighting spills, OneBox at a time
OneBox allows operators to remotely monitor their sewer system in near real-time through a user-friendly portal.
Operators can turn pumps on and off via the portal; they have clear visibility of the entire network including tank levels, pump operation, power usage and alarm status; and can run diagnostic reports to identify potential issues.
But what makes this technology so clever is the way it leverages data to pre-empt issues before they become serious problems and removes the need for the customer to report an issue.
OneBox tracks the number of times the pump is discharged throughout the day and notes how this typically fluctuates on weekends or public holidays.
It then pulls rainfall data from the Bureau of Meteorology and overlays this with the pump data to create a complete profile of how the sewer discharge system should work, regardless of weather. This means that a pump operating outside that profile, particularly during a rainfall event, is an indication that there is infiltration in the system.
When this happens, operators can use the OneBox portal to see which tanks are affected, if the pump is running and whether the water level is dropping.
OneBox allows operators to remotely monitor their sewer system in near real-time through a user-friendly portal.
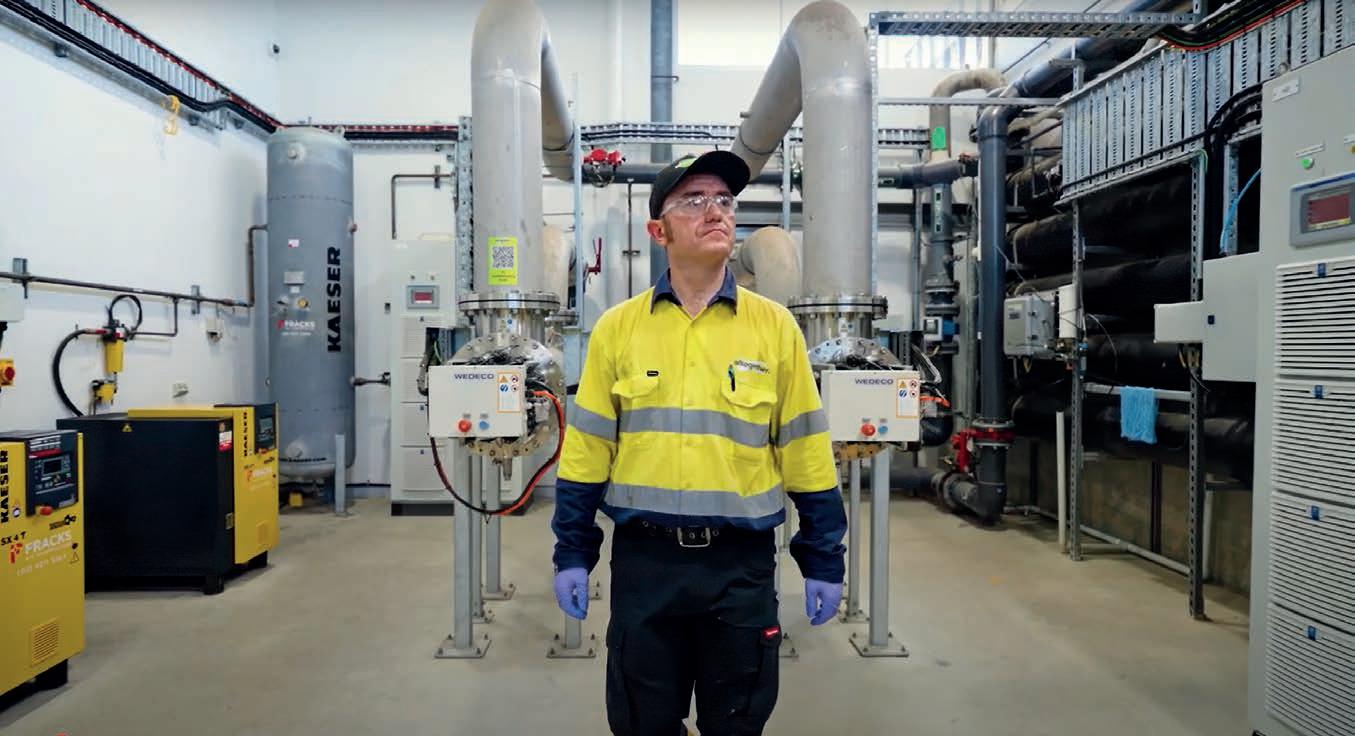
The portal also uses historical operating data to assess surrounding pumps and tanks to see if the issue is isolated to just one tank outlet or if it is a potential network blockage.
This helps crews to pinpoint the severity of the issue and make an informed decision about whether it can be addressed remotely – thereby avoiding unnecessary site visits.
Today, OneBox is being used in sewer networks both across Australia and overseas – and each case provides Iota with an opportunity to collaborate directly with users to further mature the product and develop new features to meet specific customer needs.
In Altogether Group’s case, a low pressure sewer system was chosen to help minimise stormwater infiltration into its network at the Gables new development area in Western Sydney.
By identifying and eliminating infiltration, Altogether Group can meet the community’s needs with a much smaller treatment plant. However, while pressure sewer systems are resistant to infiltration in the network itself, the on-lot pipe connections and plumbing are still vulnerable, particularly in areas like Gables where there is a high groundwater level.
Because these low-pressure systems rely on pumps and other mechanical components, they also require a lot more work to maintain. Although pumps in these systems are typically fitted with sensors, unlike OneBox they often only monitor wastewater levels and trigger a simple alarm when they detect an issue, which the operator must then go out and respond to.
These basic alarms don’t provide crews with any visibility or control of the network, meaning they could potentially be making unnecessary trips or in some cases they might even be alerted too late.
Boosting community resilience
Altogether Group is a multi-utility service provider that delivers sustainable water, power and data services to more than 500 communities in both greenfield and brownfield environments.
Altogether Group Executive General Manager – Water, Doug Fagerstrom, explained that the company works together with developers and communities to deliver reliable, localised essential services.
“We help those communities become more resilient and self-sufficient by integrating local resources,” he said.
“For example, at Gables in Box Hill, we have a recycled water plant within the community. So, when the wastewater comes to our plant, we treat it and send it back out [to the community] as recycled water, which can be used for things like irrigation and car washing.
“This reduces drinking water consumption, cuts down [the need] to pump large volumes of water across Sydney for treatment, and allows [the water] to be used locally.”
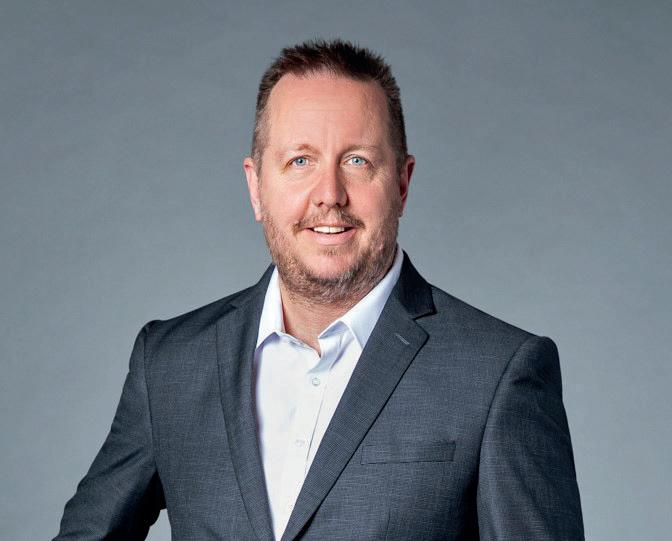
Mr Fagerstrom said that this recycled water plant is supplied by a pressure sewer network, but the original system didn’t offer much in the way of visibility of the network.
“Initially we had a standard pump controller and pump system. There’s a small tank in everybody’s front yard, and inside that tank is a small pump that pressurises the sewage and pushes it to our treatment plant,” he said.
“The system we had was analogue. It had a red light [that would come on] if there was a problem and the customer then had to call us if [they saw] that red light on the box.
“That worked fine, except we didn’t have good visibility of the kind of problems that we were having, or what was happening during a rainstorm.”
These tanks are the most susceptible part of the network to inflow and infiltration, and with Gables also navigating a seasonal high-water table and a recent increase of significant wet weather events, Altogether Group knew it needed to take a proactive approach.
After investigating its options, Altogether Group decided that OneBox, and especially its web portal, was just the solution the team needed. Iota then collaborated with the company to understand its specific needs and, where necessary, tailor the product to its specific requirements.
“OneBox, with its data connectivity and web portal, now allows us to monitor the individual status of each customer that’s connected,” Mr Fagerstrom said.
“[Because] we have real-time, alarming and monitoring, we’re able to go out and perform some type of maintenance before the customer was even aware there’s an issue. [Whereas] the old system was very dependent on the customer to take action.”
When an alarm is activated in the OneBox portal, Mr Fagerstrom explained that the first thing operators do is check the level of the tank to determine how urgently they need to respond.
“If the tank has pumped itself down already and there was a failure during that process, then we’ve got a bit of time because it takes a day or two to fill up a tank from a house, depending on the number of occupants in the house,” he said.
“We also have the trend data from the customer, so we can go back and see how many times the pumps operated in the last few days to help us estimate when we need to have that situation resolved. It also helps us identify when customers might have a leak they’re not aware of that’s draining into the sewer.
Altogether Group Executive General Manager – Water, Doug Fagerstrom.
Image: Altogether Group
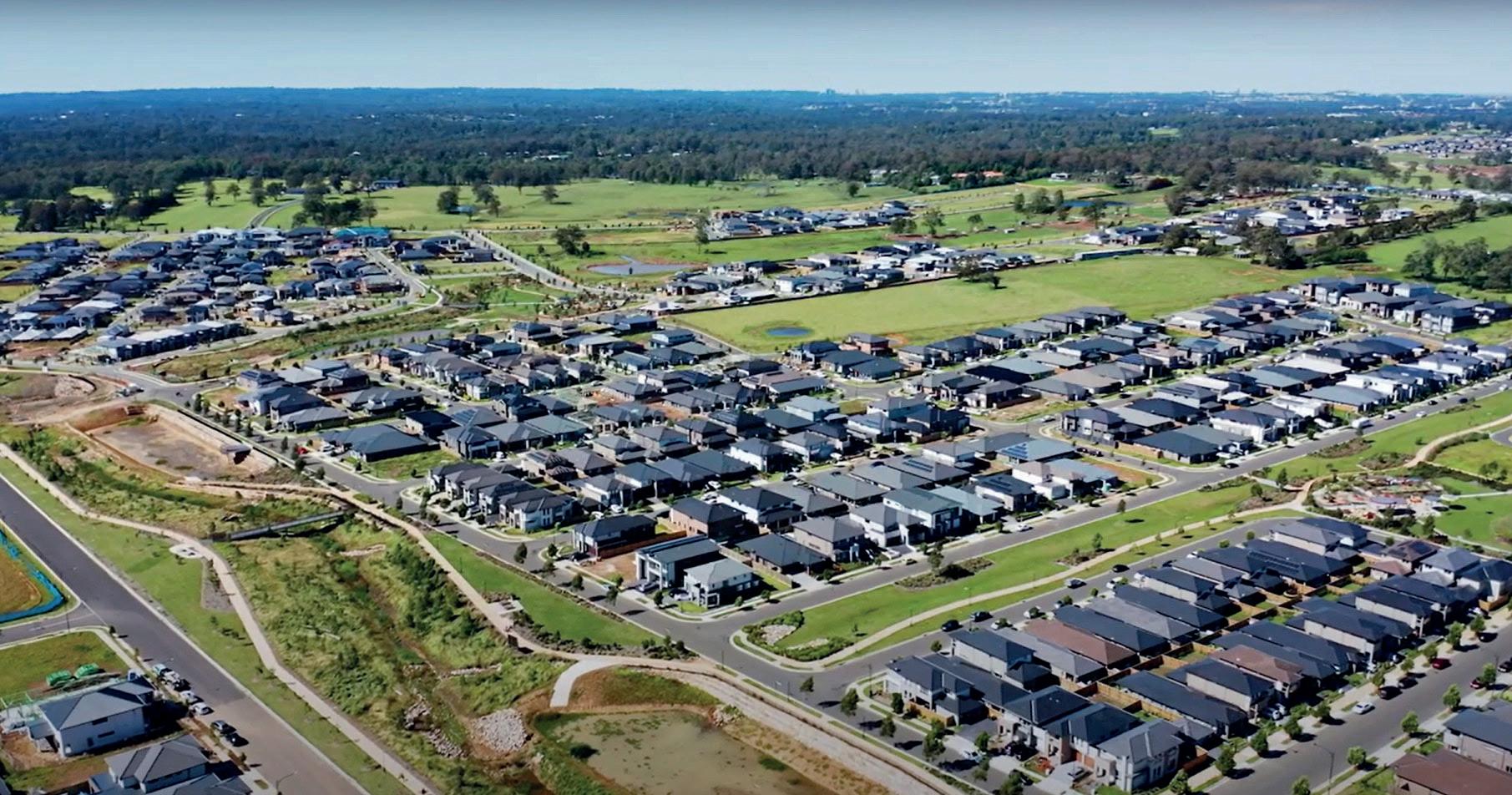
“For instance, during the construction of one customer’s property, the builder cracked one of the sewer lines by driving over it with some equipment.
“We noticed an unusually high amount of flow coming from that property, so we went out and we inspected our equipment to make sure it was okay. Then we got a plumber out to camera the sewer lines and they found a cracked pipe. The customer was able to then go back to the to the builder and get them to fix it under the defect liability period.”
Proactive monitoring and control
To meet Altogether Group’s needs, Iota incorporated custom reports into the portal that are sent out every day. These reports provided more granular hourly pump runtime data on wet weather days and highlighted pumps that ran more than a certain number of times per day.
This information enables operators to more effectively diagnose issues and differentiate between inflow of stormwater from illegal connections and infiltration caused by water table ingress.
Mr Fagerstrom explained that OneBox also allows operators to monitor and adjust flows based on network capacity.
“We can use the tanks as temporary storage during rain events to manage inflows into the treatment plant,” he said.
By holding flows in tanks reaching capacity while pumping from others nearing capacity, Altogether Group can help downstream assets manage increased loads. And in limiting the number of pumps operating concurrently, the company can carefully manage and smooth flow to the treatment plant – reducing the risk of it being overloaded and overflowing.
“By maximising the system to store sewage so [it doesn’t overload] our plants, we can minimise our footprint within the community,” Mr Fagerstrom said.
For Altogether Group, the benefits of OneBox are multilayered. Not only does it empower the team to keep spills at bay and help safeguard the company’s assets from damage, but it also allows the company to provide the best possible service to its customers.
OneBox transforms low pressure sewer systems into intelligent, responsive networks that deliver efficiency, reduce costs and help protect the environment. With its combined control functionality and portal visibility OneBox currently provides a smart solution that no other low pressure sewer system can offer. U
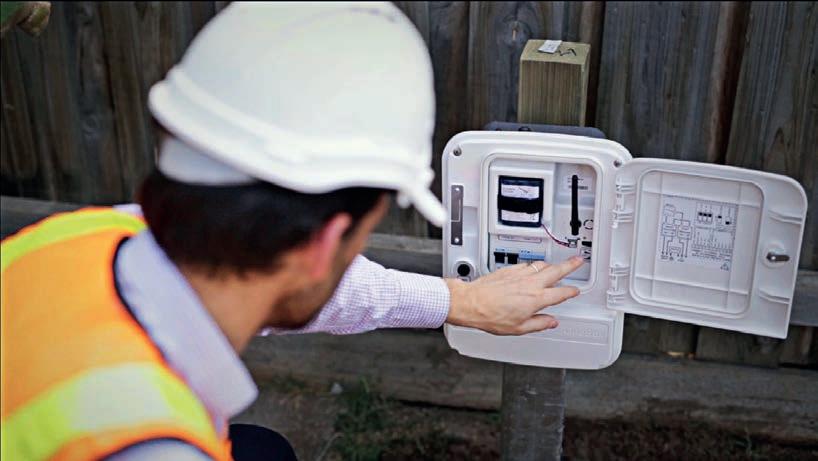
The Gables Greenfield development in Box Hill, Western Sydney. Iota’s OneBox solution helps utilities crack down on sewer spills.
Image:
Altogether Group
Image: Iota
Monitor and control low pressure sewer networks remotely, in near real-time to minimise inflow, infiltration and spill risk, reducing pressure on network assets.
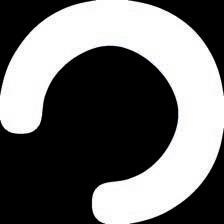






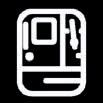
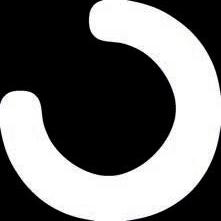

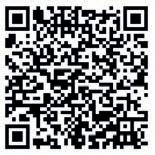


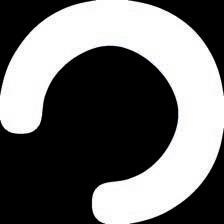
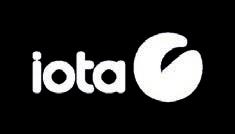
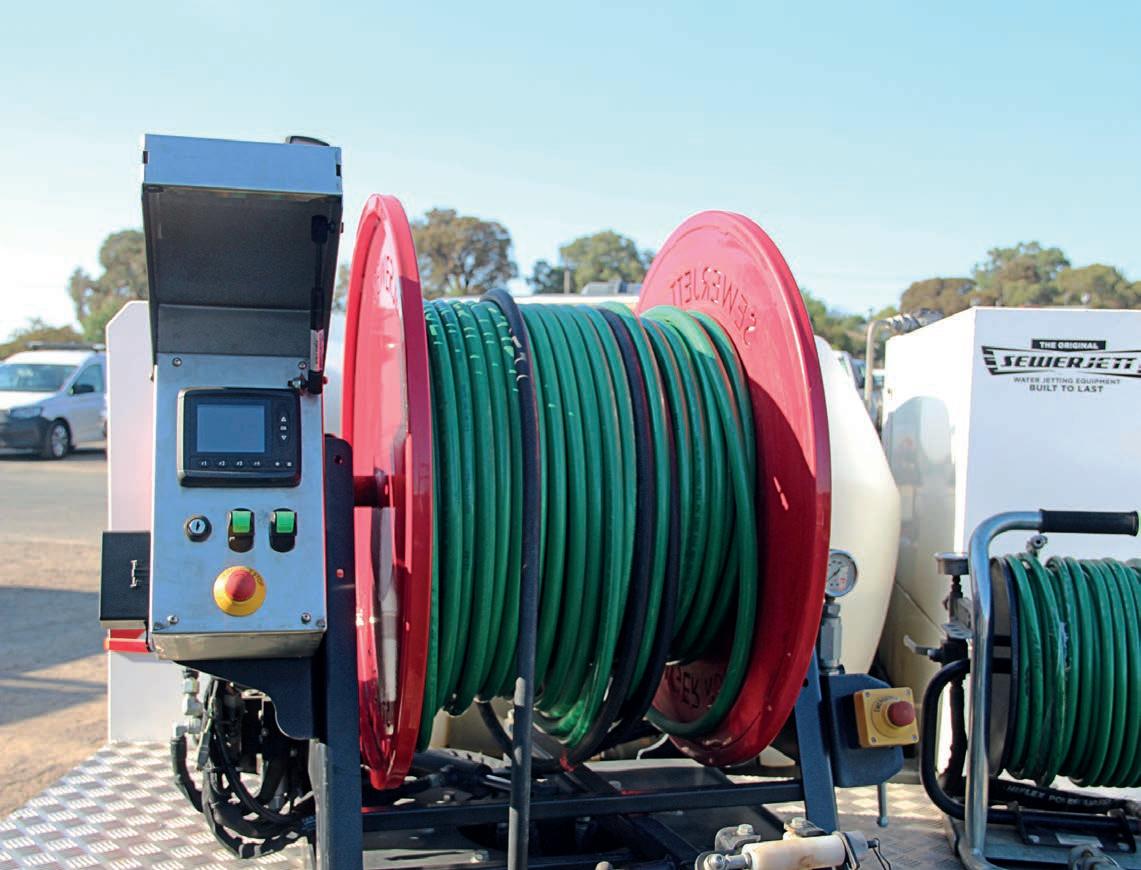
Jetting round the block
When it comes to operations and maintenance, there are some things you just can’t learn from a textbook.
With frequent storms putting more pressure on our wastewater networks, utilities have no time for sewer blockages, but the key to tacking these challenges is using the right equipment for your environment. Utility turned to long-standing industry professional and Enviroline Sales Representative, Peter Sinclair, for advice.
“I started in this business in 1991, and in those days, we were selling steel rods and hand tools to water boards,” Mr Sinclair said.
“At that time, we had to learn on the job, and it doesn’t take much embarrassment to learn how to do it quickly. Older plumbers talked about using cane rods [to clear blockages] in the 60s.
“They used to screw them together and shove them down the pipe and poke a hole through the blockage.
“But the tools for an operator nowadays are much better than what we had in the 90s when I was going out and cleaning drains – there were too many busted shoulders and injuries to the operators with those older mechanical systems.”
For more than five decades, Enviroline has been providing water authorities and municipalities with specialised pipeline maintenance equipment, and Mr Sinclair said that the company’s approach has not only aligned with new technology as it comes to market, but it’s tailored to the needs of Australian utilities.
“Over time, it progressed into the type of machines we have today, and water jetting machines are a lot safer, and [operators] aren’t going to be exhausted as much,” he said.
“Water jetting was just coming out in the early 90s. In the old days, the jet machines for the councils were much smaller and close circuit TV (CCTV) equipment was in its infancy, and gradually it’s [grown] more sophisticated, and the machines respond better to customers’ needs.
“And over time Enviroline has also taken on board customer feedback and made their products better.”
Mr Sinclair explained that the blockages utilities encounter here in Australia are typically quite different challenges compared to those faced internationally. So, when he found a company that was making products in Australia, for Australia, he really wanted to be a part of it.

Enviroline has very strict quality standards for the hoses it uses on it jetting trucks and trailers.
Images:
Prime Creative Media
“When I came on board, I got walked around the factory, and I saw what they were doing, and I just thought to myself ‘I’ve got to be a part of this – this exactly what I want’. So, here I am, a long while later, still working in the industry,” he said.
“We get a lot of dry weather in Australia, and during droughts tree roots go into the joins of the pipe seeking water. And a lot of [coastal areas] get sand in the sewers.
“But it’s quite different [overseas]. A lot of the carrier sizes are different in Europe and America, and European sewage systems are often dual systems [and have] larger pipes because the population tends to be a lot bigger, and they often have better access to these large sewer systems.
“So, their [jetting machines] tend to be lower pressures, but higher volume because they don’t get a lot of tree roots – more often it’s fat and grease blockages.”
For water jetting, it’s vital to use the right machine for the job – and Mr Sinclair said that very much depends on your location and the type of blockages you have.
“You can go high pressure, lower volume or you can go higher volume, lower pressure – and it’s always a scale because not matter what size [a water jet is] you have to feed it, which means balancing road regulations with the carrying capacity of the trucks and the distance you travel, so you’re restricted to a certain amount of water,” he said.

We produce everything in house... and assemble all the parts and components in our factory.
“On the coast, where there’s sand in the system, you want higher volume. Whereas out to the west or towards the mountains you want higher pressure to cut tree roots.”
Mr Sinclair said that Enviroline’s jetting trucks and trailers are about as Australian built as anything could be.
“We produce everything in house – we laser cut all the aluminium for all the parts, we weld up all the hose reels and assemble all the parts and components in our factory.
“The hose is important, ours meets international requirements but we have our own standards on it, and we have a good quality that we use with a 2.5:1 standard for minimum burst pressure – so if it’s 5000psi rated, the minimum burst is 12,500psi.”
Enviroline sources all its components from local suppliers, and preferences Australian products where practical. However, Mr Sinclair explained that providing a quality solution that can tackle Australian conditions is always the first priority.
An Enviroline Jetting Truck, made and designed in Australia.
“If we buy from overseas, it’s always to our specifications, and we maintain a supply spare parts in our factory – we’re not just bringing something in from overseas and then years later when [it needs repairs] making you wait three months to get [the parts] to fix it,” he said.
“If something goes wrong, you can ring up and you can get a part. And the good thing about a local product is we can take on more feedback and make it better.”
Another important part of the job for Mr Sinclair is providing clients with proper advice about which products are best for them.
“When people submit an enquiry about a product, the first thing we do as a sales team is we ring them,
“Then we’ll suggest the correct product that will do that job – and quite frankly if someone [is dead set] on buying the most expensive machine we’ve got then I’ll sell it to them, but first, I’ll really try to sell someone something that will do what they want to achieve.”
His advice to utilities considering a new jetting system is to always get a demonstration of the product.
“First thing to do is ring the manufacturer, have a conversation and get some feedback – then have a look at the product and get a demonstration,” Mr Sinclair said.
“A lot of the time, you’ll also find your neighbours have
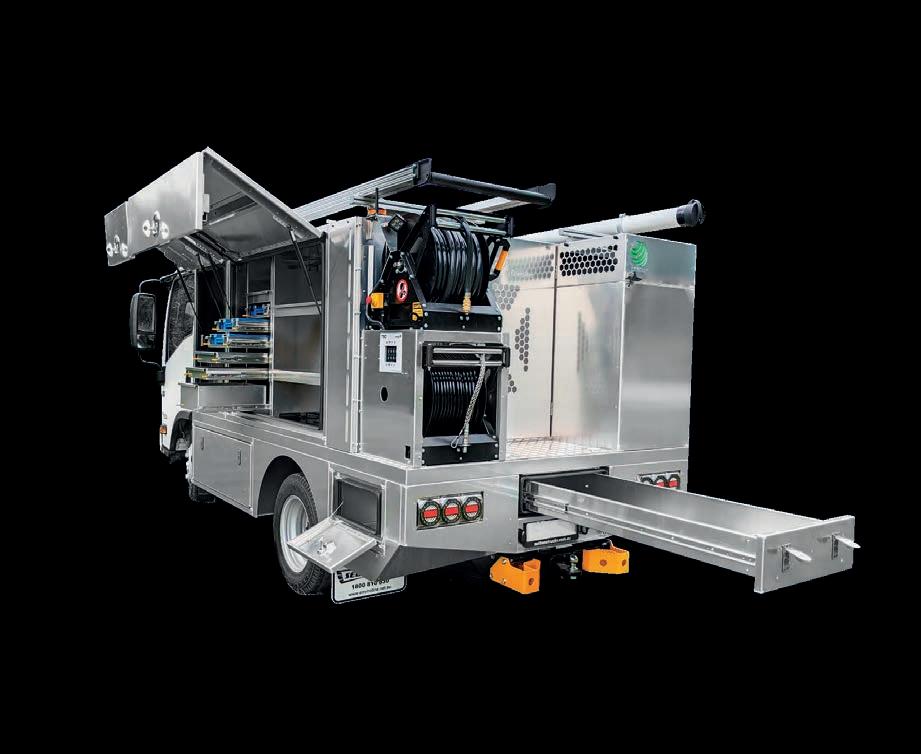
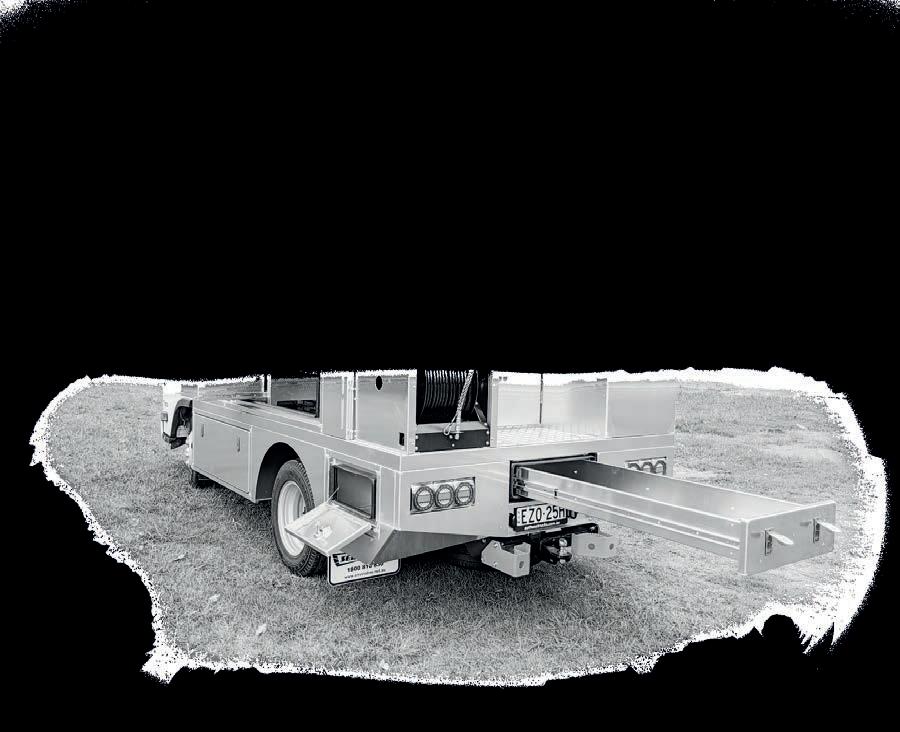
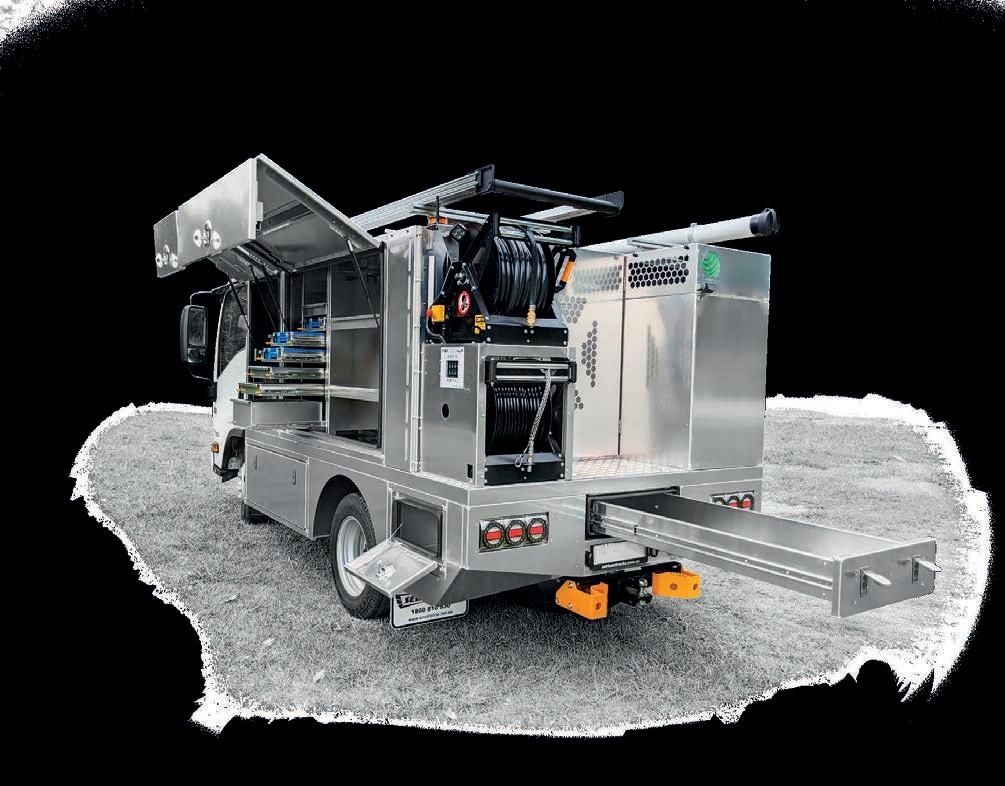
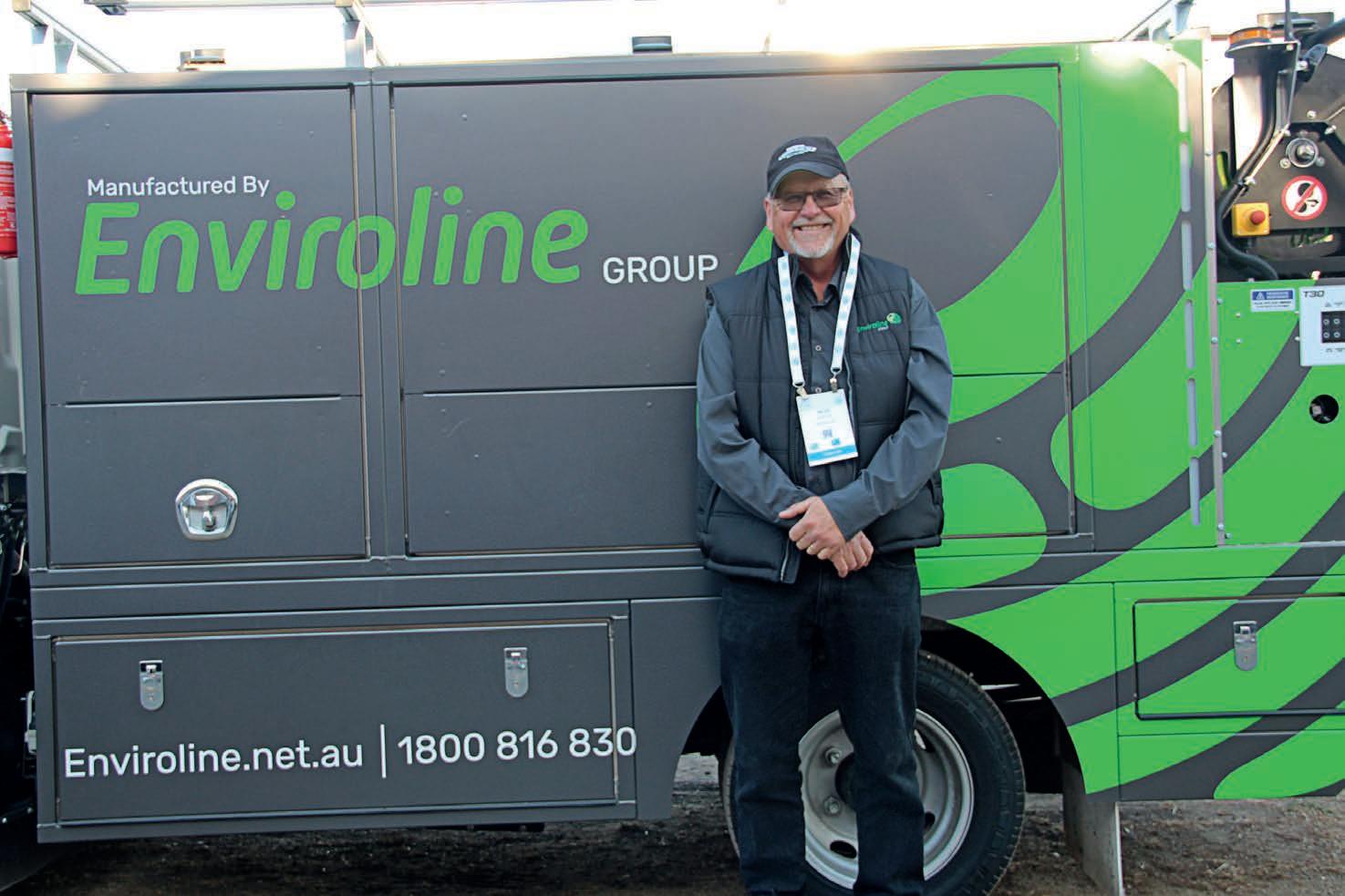
Enviroline Sales Representative, Peter Sinclair.
The Water Jetting and Pipe Maintenance Specialists
Fleet Solutions: Jetting Trucks, Vans, Trailers.

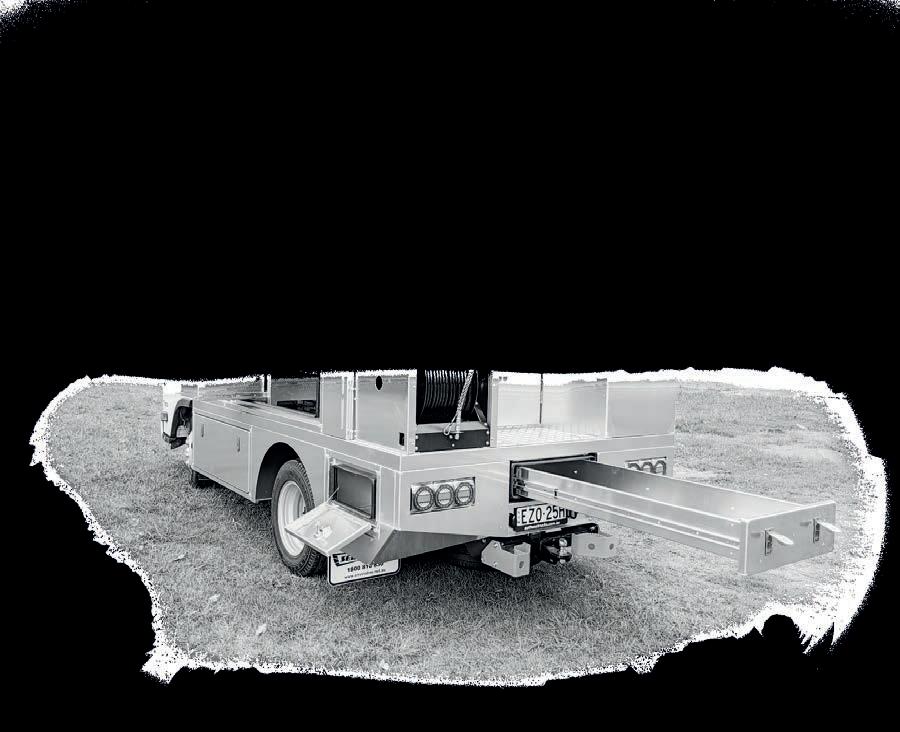
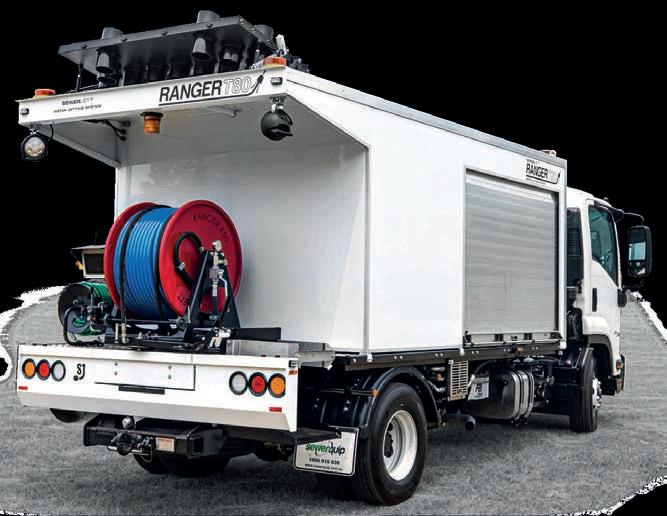
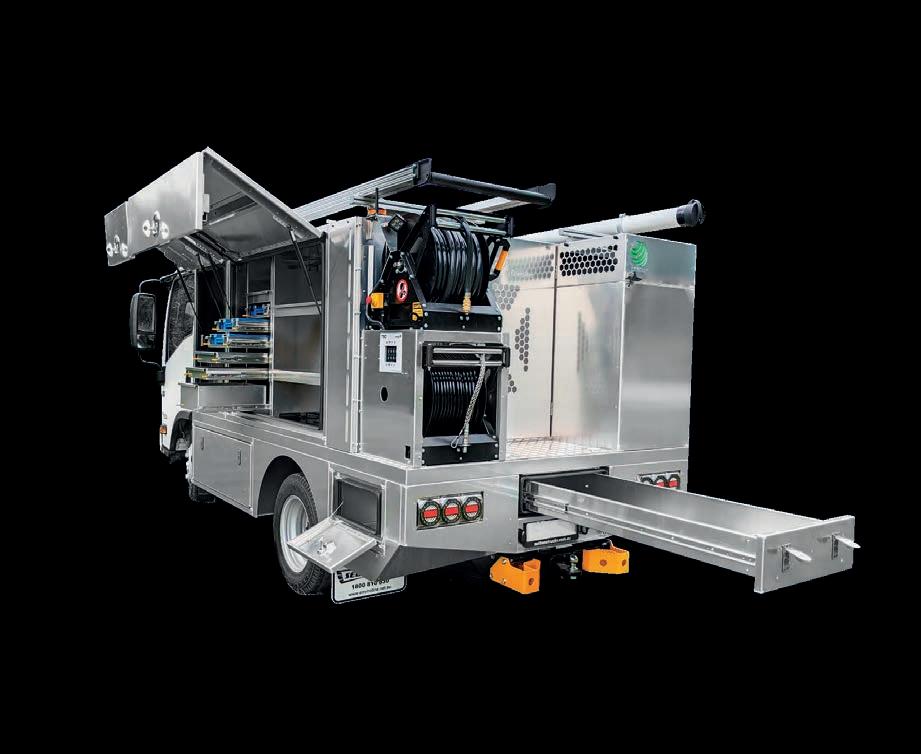
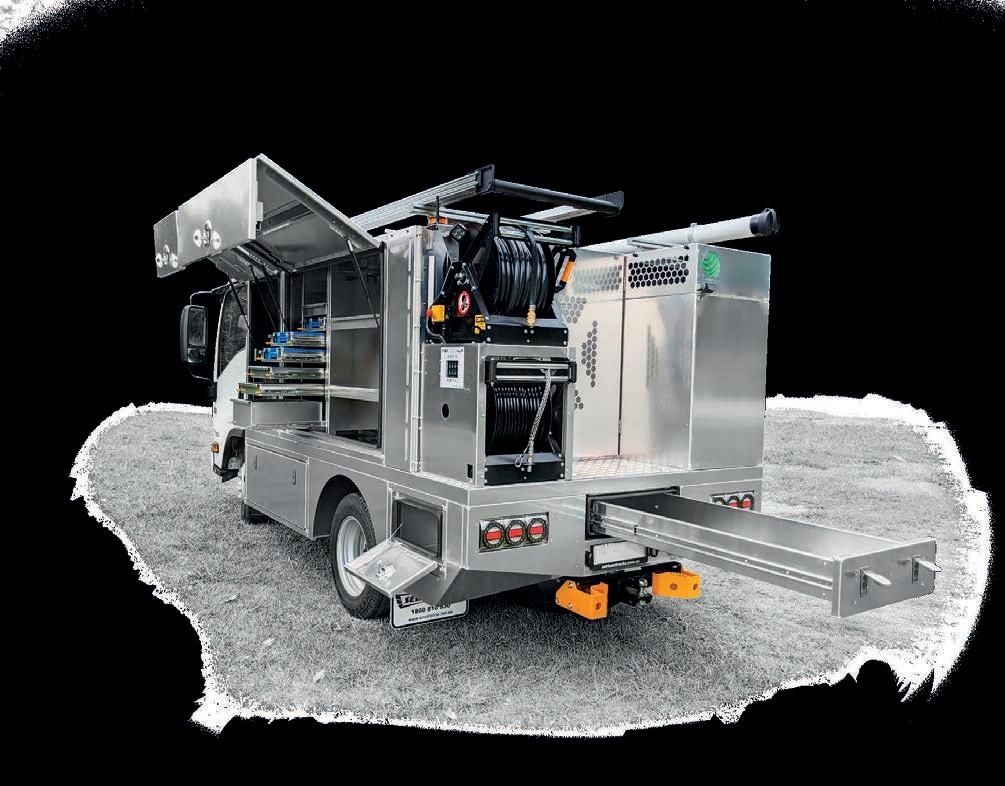
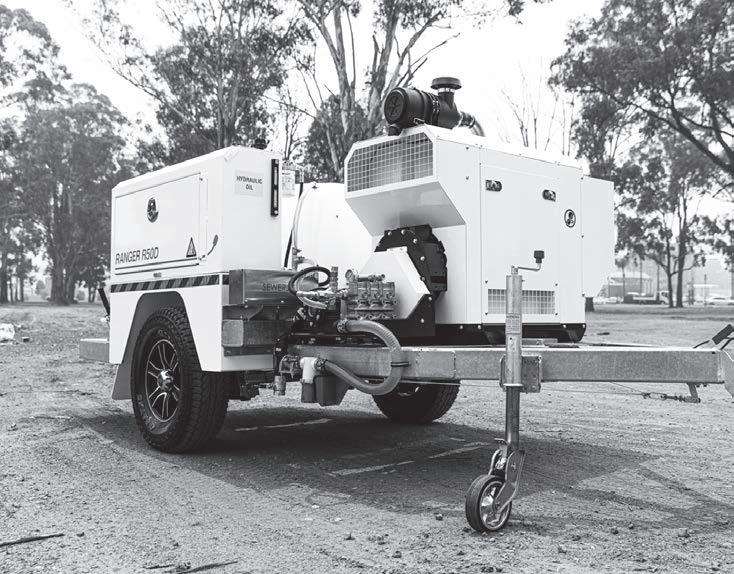
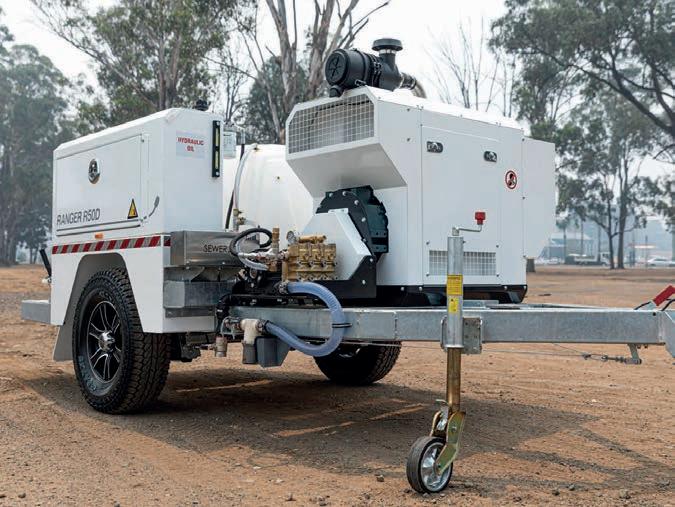

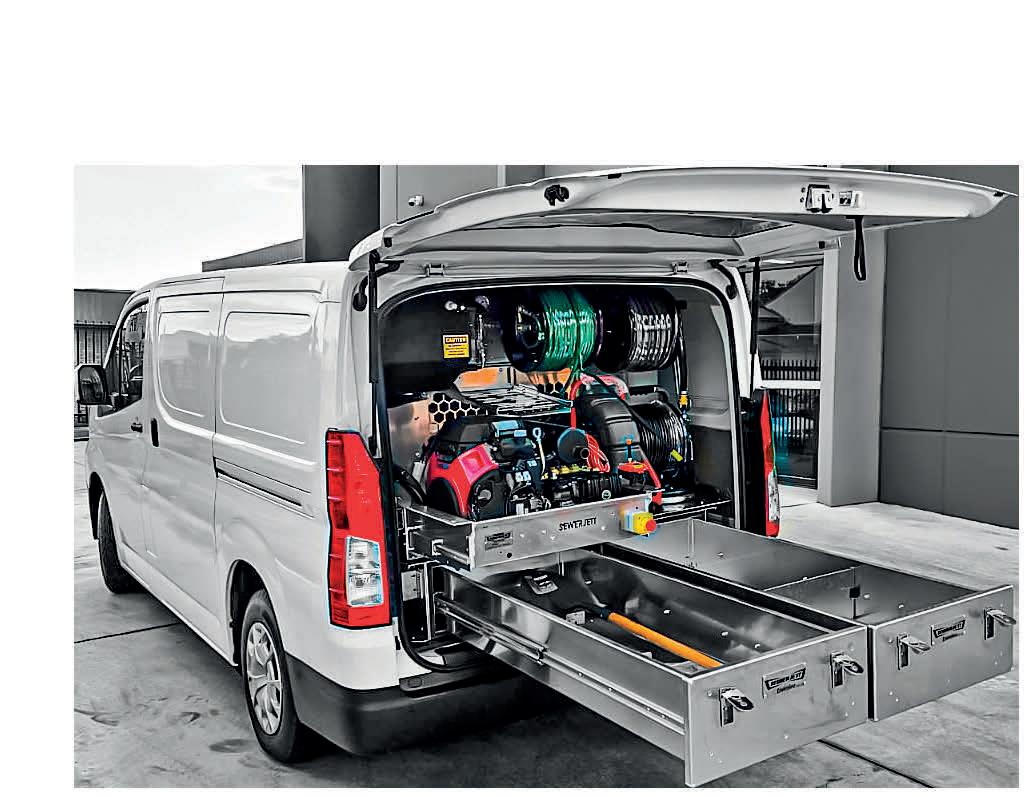
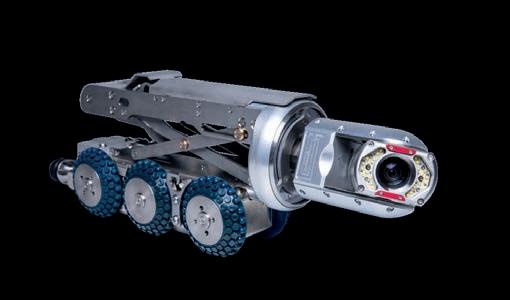
Whether you need a trailer fitted out for serious stormwater work, or a whole fleet of customised trucks for a state-wide Water Authority, Enviroline Group has the range, knowledge and services to deliver a solution tailored just for you.
From SA Water to Singleton Council to the Shire of Kojonup, we work with local, state and federal government authorities, water authorities and major civil contractors across Australia to provide expert advice, tailored commercial equipment, servicing, repairs, parts and accessories.
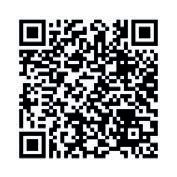
T80 PTO Jetting Truck
Ranger R50-D Jetter Trailer
V20 Van Jetting Kit
IBOS Camera Crawler
EST 1972
T30 PTO Jetting Truck
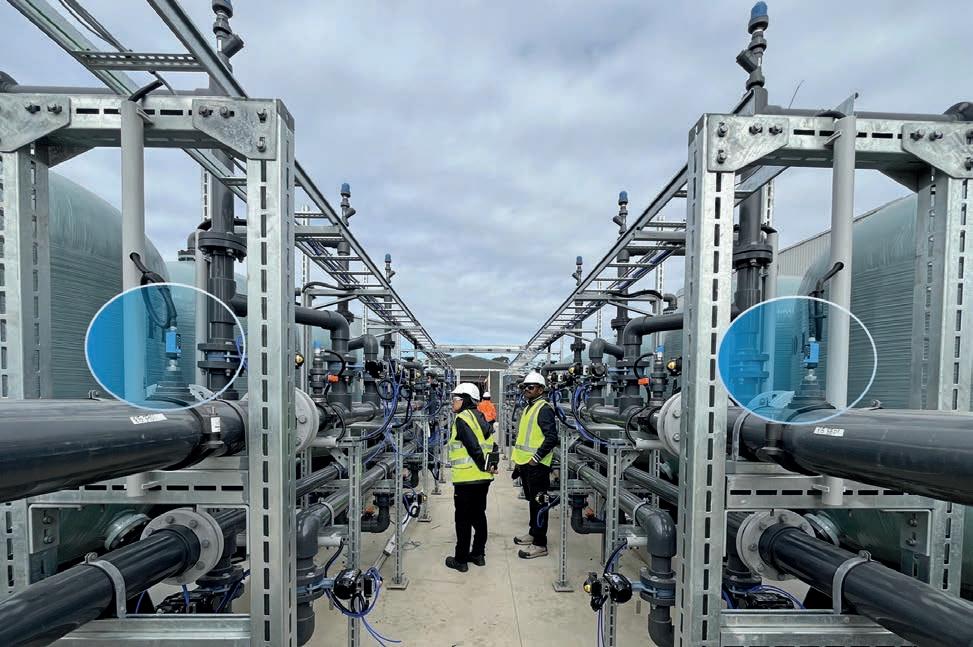
From data to action
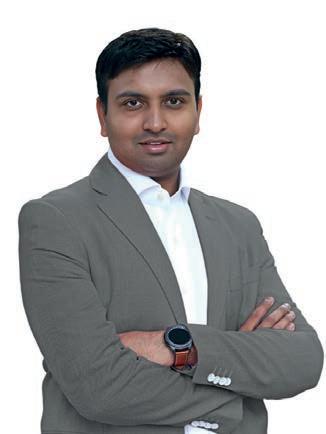
Digitisation offers a shining solution for the water industry’s challenges – but how can we ensure a highly usable system that also protects customer data?
Water management is smarter than ever before.
Innovative sensor and automation technology allows utilities to monitor and safeguard their assets against failure, improve customer experiences, streamline operations, improve energy efficiency and more.
But, with access to withheld customer, network, and system operational and behavioural data comes the great responsibility to keep it strictly private and secure.
SICK Market Product Manager, Kashyap Patel, explained that more data means you can make more informed decisions, but the way you manage that data is the key to both maximising the benefits and defending against cyber attack.
“When it comes to cybersecurity in any industry, a critical factor is the security of the platform managing your data,” he said.
Mr Patel said that with the right software, data from sensors and instrumentation can be leveraged to enhance asset monitoring, automate maintenance and inspections, track customer usage patterns, detect leaks early and optimise workforce efficiency and resource allocation.
“With all this data, you can build a comprehensive model of your operations, return on investment, and spending –but ensuring it stays secure is critical, as you don’t want a hacker gaining control over it,” he said
“Building a fully secure system requires multiple layers of connectivity, but each added layer increases complexity, making it crucial to balance security with system efficiency.”
Simplicity meets protection
According to Mr Patel, the ideal solution strikes a balance between security and usability.
“[It needs to be] robust and complex enough to deter hackers while remaining intuitive for users,” he said.
For SICK, this means adopting an agile product development approach and collaborating closely with customers to meet their specific needs.
“We focus on tailoring a complete solution, starting with purpose-built sensors for the utility industry, integrating hardware connectivity, and ensuring secure data management,” Mr Patel said.
“SICK plays a key role in advancing IO-Link technology and standards to drive innovation in automation. Our latest product, the Sensor Integration Gateway 300 (SIG300), functions as an IO-Link master, facilitating seamless communication between sensors, control systems and analytics platforms.”
Mr Patel said that the SIG300 is designed to feed sensor data into AI prediction models, such as SICK Field Analytics digital solution, enabling real-time asset condition monitoring.
“By integrating with modern cloud interfaces, you can get notifications on your phone from anywhere in the world. However, if you’re concerned about cloud-based data potentially exposing your system to hackers, we offer a local solution. It’s still digital, but your data remains stored on-premises,” he said.
The SIG300 undergoes rigorous vulnerability testing and features a hardened operating system to safeguard against malicious attacks. Mr Patel said that this high standard of security is matched by an exceptional user experience.
“We have a very intuitive web interface and a logic editor that allows the SIG 300 to function as an affordable standalone PLC. No other product in the industry offers this level of functionality,” he said.
With technology advancing at a record pace, Mr Patel said that the key to robust cybersecurity lies in staying ahead of threats and selecting the right solution for your specific application.
“At SICK, we are consistently innovating. We’ve revamped our customer engagement model to deliver more tailored solutions,” Mr Patel said.
“It is essential to thoroughly understand your application’s nature and requirements. Start small and scale up as you gain confidence and insights.” U
SICK smart sensors ensure precise control and real-time monitoring in a cutting-edge water treatment plant.
SICK Market Product Manager – Motion Control and Industrial Instrumentation, Kashyap Patel.
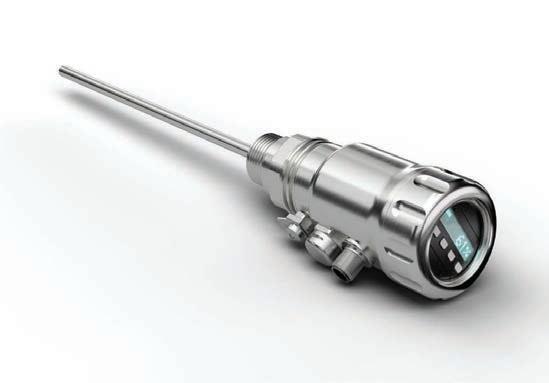
Connect. Control. Conquer.

Smarter process automation starts here.
Smarter automation starts here. The SIG300 IO-Link Master makes it easy to collect sensor data and communicate with your control system—programmable, compact, and quick to configure. Paired with the rugged LFP Inox sensor for precise level measurement in challenging environments, this duo brings reliable performance and intelligent connectivity to your process.
Keeping corrosion at bay
Australia’s harsh, varied climate often creates the perfect conditions for corrosion in critical pipeline assets – but what can utilities do to protect their vital infrastructure?
When corrosion strikes, essential infrastructure is at risk of life-threatening failure at worst and expensive repairs at best.
Corrosion occurs naturally resulting from continuous environmental attack on an asset’s surface. While it can impact a wide range of critical utility assets – including both metal and non-metal pipelines, valves, cables and fittings – pipelines that are constantly exposed to extreme environments are very high risk.
This was the challenge that one port authority faced with some of the key pipelines at its tank farm in Queensland.
This authority plays a vital role in supporting Australia’s import and export trade with the tank farm serving as a critical hub for fuel, bulk commodities and freight transportation. The infrastructure within the tank farm includes firewater, diesel and jet fuel pipelines that are all essential to ensuring the port’s smooth operation.
Given the harsh coastal environment and continuous exposure to corrosive elements, protecting these assets is crucial for maintaining long-term serviceability and minimising the risk of failures.
To tackle these challenges, the port authority enlisted the help of Denso Australia, an industry leader in corrosion prevention, who provided the company with several made-to-measure systems to extend the lifespan of these pipelines and maintain their structural integrity.
Got it covered
For the firewater and diesel pipelines, Denso recommended the VISCOTAQ™ Field Joint Coating System, which is fully compliant with AS 4822:2024 (external field joint coatings for steel pipelines).
This system also offers superior adhesion and can conform seamlessly to irregular surfaces.
The firewater pipeline is a mission-critical safety asset and as such, maintaining its optimal condition is essential. The parent coating, FusionKote, on this pipeline required a field joint system compatible with its characteristics to ensure full continuity of corrosion protection.
Because VISCOTAQ ViscoWrap ST can adhere to polyethelene coatings, conform tightly to irregular surfaces and provide a self-healing corrosion barrier, it was an ideal choice for this application.
Before work could begin, Denso provided training to all applicators to ensure proper system installation across all 60 field joints.
Following this, VISCOTAQ ViscoMastic was applied to the sharp edges around the collar of the field joints to prevent water ingress.
VISCOTAQ ViscoWrap ST was then wrapped around the joint to form a corrosion-resistant, self-sealing barrier, before the VISCOTAQ PVC Outerwrap was installed for mechanical protection.
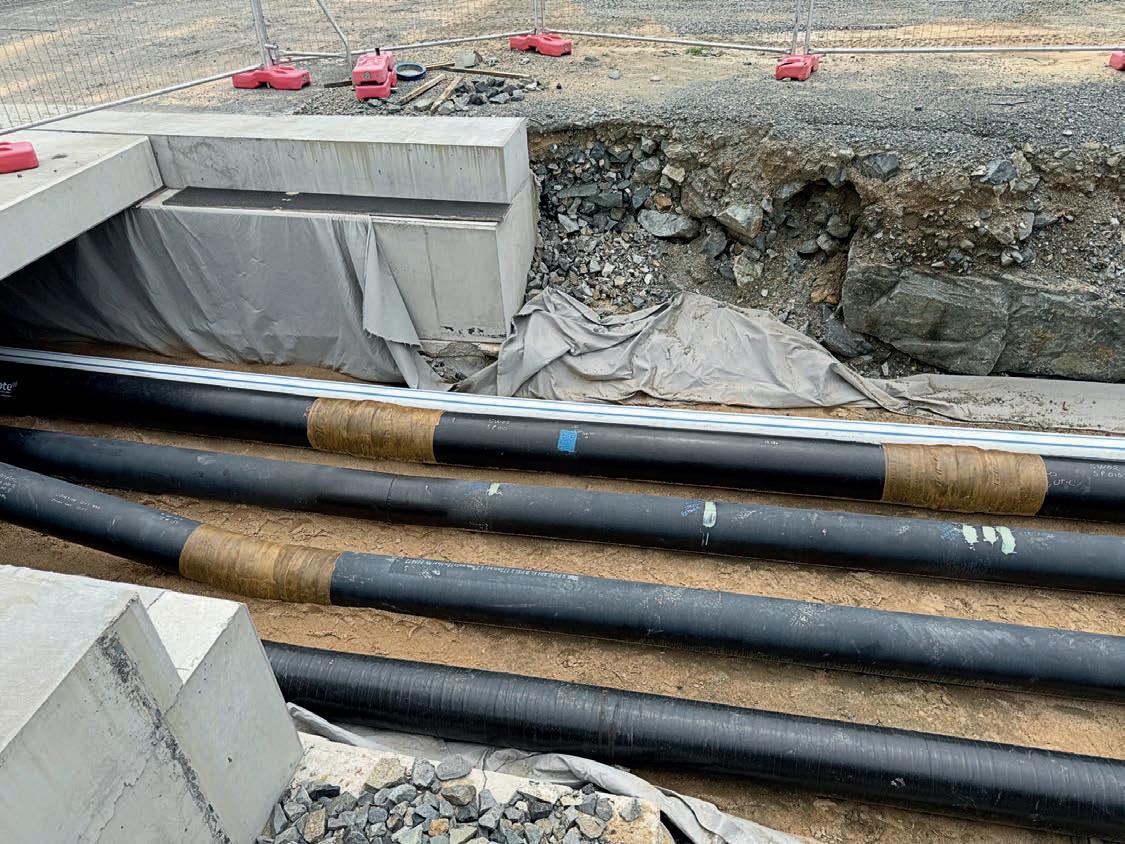
Key pipelines at Queensland tank farm protected with Denso and VISCOTAQ systems.

opposed to PE or HDPE) was dictated by the fact that this was a buried or below-ground application that did not require a UV-stable solution. The system was further bolstered with the application of Denso™ Glass Outerwrap for additional reinforcement and long-term durability.
Another 60 field joints on the diesel pipeline underwent a similar treatment, which ensured consistency across the project and streamlined training for applicators.
The diesel pipeline was coated with a two-layer fusion-bonded epoxy (FBE), which meant that the field joint solution needed to bond effectively to the parent coating while providing superior corrosion resistance at the welds.
As strong as steel
The unique characteristics of the port authority’s jet fuel pipeline, however, called for a different solution. In general, stainless steel is highly resistant to corrosion, but when it’s used in ethanol pipeline carrying jet fuel, additional protection is required to prevent pitting and external environmental degradation.
system, applicators were trained on correct system application. The Denso MP Primer was applied first to enhance adhesion and provide an initial corrosion barrier. The pipeline was then wrapped with Densyl Tape to create a self-sealing, water-resistant protective layer. Finally, the PVC Outerwrap was applied to give mechanical protection against external environmental factors. By implementing a combination of Denso and VISCOTAQ solutions, this project successfully mitigated corrosion risks on critical port infrastructure. The selected systems were chosen based on compatibility with the parent coatings, pipeline function and site conditions, ensuring seamless integration and maximum service life extension. Denso Australia’s expertise in corrosion prevention ensures that this Queensland tank farm’s assets will remain protected for years to come, reducing maintenance costs and safeguarding essential fuel and firewater pipelines in this vital port facility. U
For more information, visit densoaustralia.com.au
Crew members applying VISCOTAQ™ ViscoWrap Field Joint Coating to a pipe
Images: Denso
NBN Co’s FTTP rollout provides an opportunity for utilities to digitise their operations and boost sustainability outcomes.
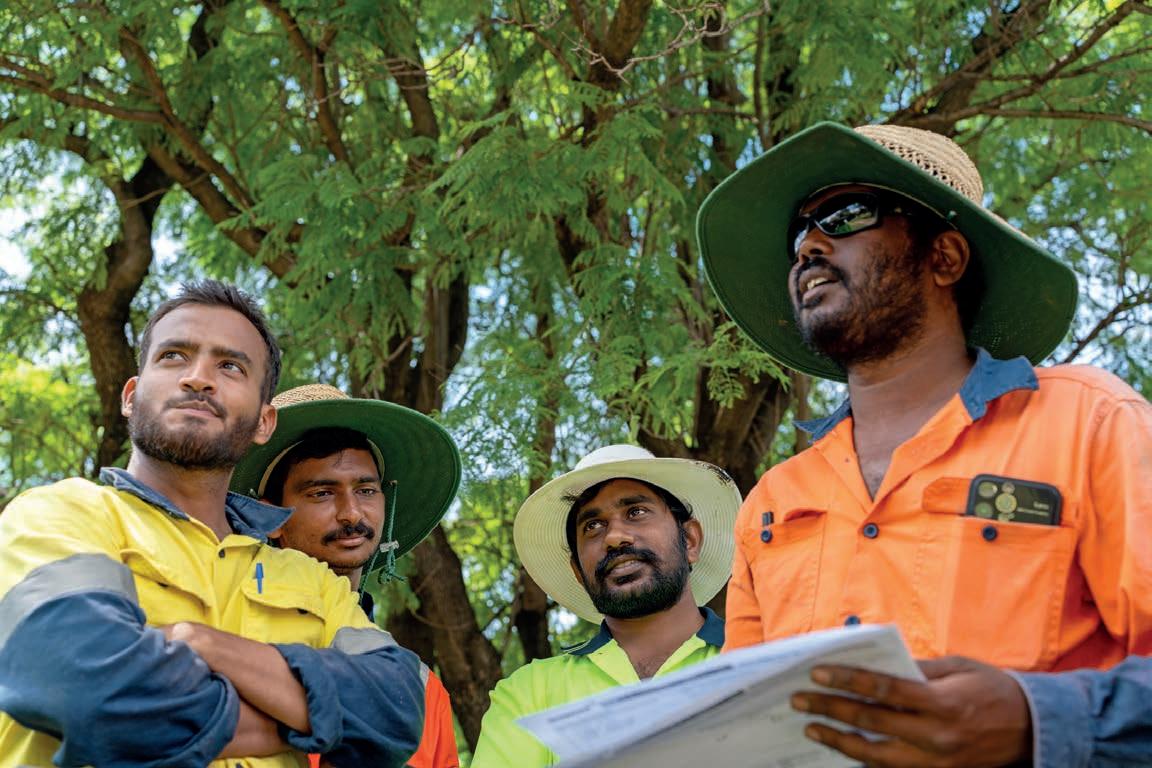
Australia’s full fibre revolution
The rollout of NBN Co’s full fibre network is about more than just connectivity –it’s unlocking smarter, greener operations for utilities across Australia.
Australia is in the midst of a digital transformation, and at its heart lies the National Broadband Network (nbn).
Initially launched in 2009, the nbn network aims to provide fast and reliable internet access to every Australian home and business via the delivery of a modern, fibre-optic telecommunications network.
It was designed to replace the legacy copper network that dated back to the 1960s and was unable to keep up with the digital demands of the 21st century.
In 2009, the Commonwealth of Australia established NBN Co as a Government Business Enterprise (GBE) to design, build and operate the nbn – one of the most significant infrastructure projects in Australia’s history.
Rollout challenges
The initial plan for the nbn rollout aimed to deliver full fibre – or fibre to the premises (FTTP) – to 93 per cent of premises by June 2021. However, the strategic direction of the rollout was altered several times due to changes in government.
In 2014, it was announced that the nbn would be delivered using a mix of old and new technology, in which fibre would run part of the way, while the existing copper and cable network would be used for the rest.
This change led to a mix of outcomes, with some areas experiencing slower speeds and less reliable service, and by 2020, the original FTTP plan was reinstated.
In October 2022, NBN Co announced a plan to upgrade almost 1.5 million homes and businesses that were still on fibre to the node (FTTN) to a full fibre network.
More recently, in January 2025, NBN Co announced that it would upgrade the remaining FTTN network across the country, backed by a $3 billion investment from the Federal Government.
The company is on track to deliver the 2022 upgrade plan by the end of 2025 and expects to complete the remaining FTTP upgrades by the end of 2030.
The upgrades will be beneficial to households and businesses alike, with the Australian Competition and Consumer Commission (ACCC) finding in 2024 that full fibre delivers the most reliable broadband connection.
nbn digitising utilities
The rollout of the full fibre nbn marks a significant step forward for the Australian utility sector.
From digital metering to smart grids, technology has revolutionised the way utilities deliver essential services. Digital connectivity now underpins every facet of the sector.
As smart devices and solutions become more popular, the Internet of Things (IoT) leverages real-time data and machine learning to optimise utilities’ operations and improve service delivery.
For example, digital meters provide unrivalled insights into network usage, benefitting both utilities and their customers.
Images: NBN Co
IoT data can also enable the creation of digital twins, or virtual replicas of real-world infrastructure such as a pump station or electrical transformer.
These sophisticated models use real-time and historical data to represent the past and present, as well as simulate predicted future events.
Digital twins have powerful applications for utilities, ranging from predicting equipment failures, testing system modifications, to training workers on complex or hazardous systems.
In the energy sector, IoT can even play a role in the energy transition.
Distributed energy resources (DER), such as rooftop solar, offer an opportunity introduce clean energy into the grid at scale and are expected to be an integral part of Australia’s move away from coal-fired power.
However, for DERs to help Australia reach net zero, it is essential to understand, monitor and manage the supply and demand for energy on a system-wide scale, which requires connection to a fast and secure wireless network such as the nbn.
Connecting DERs to form a network of smart devices can bolster the impact of DERs, allowing energy operators to optimise energy resources and maximise performance
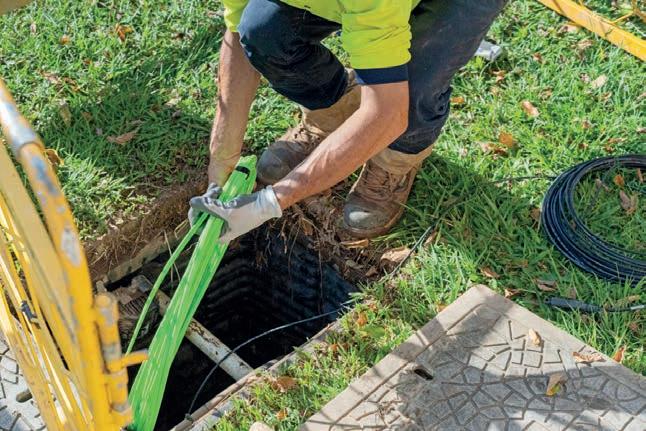
The sensors enable utilities to act before a potential overflow, preventing contamination to customer properties and the environment and the associated health risks, clean-up costs and reputation damage. However, none of these digitisations can succeed without a fast, reliable internet connection. The nbn opens the door to an unprecedented opportunity for utilities to digitise, innovate and improve their operations.
Accelerating decarbonisation
NBN Co’s FTTP rollout also has a role to play in Australia’s decarbonisation efforts.
The company’s network investment plan is taking energy-efficient fibre deeper into communities to meet the growing digital demands of Australian homes, businesses and utilities. Connecting more customers to fibre enables
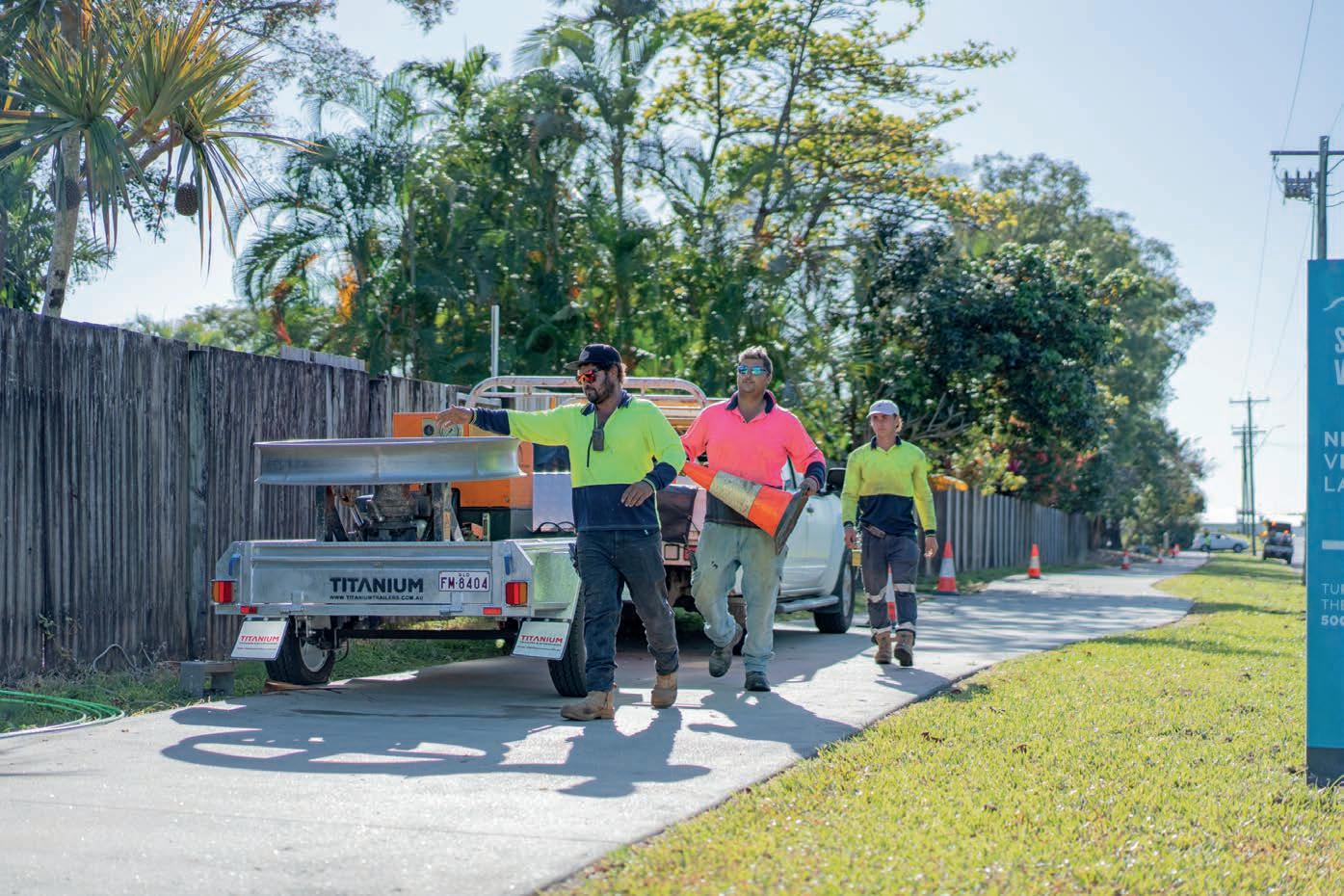
NBN Co is upgrading the remaining FTTN network across the Australia, backed by a $3 billion investment from the Federal Government.
The nbn network aims to provide fast and reliable internet to every Australian home and business.
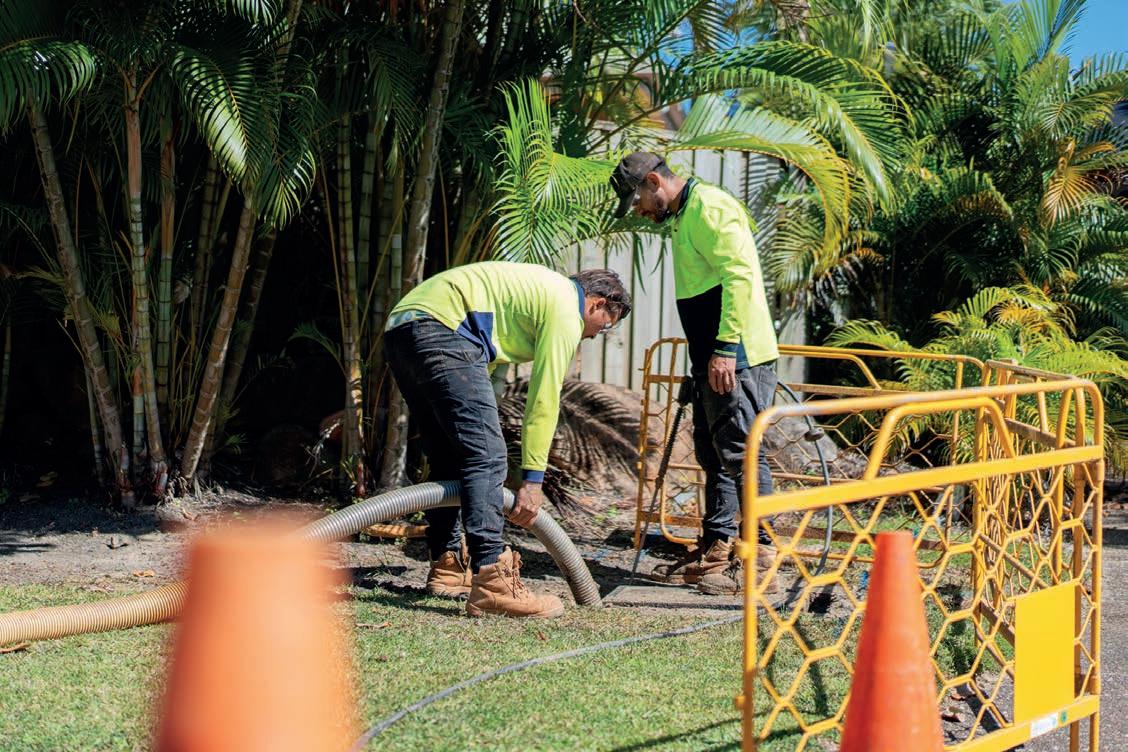
emissions avoidance. It found that the network has already contributed to emissions reductions – and will continue to do so – and faster adoption of digital technologies could help Australia reach its net zero targets.
This is also true for utilities.
The construction and operation of physical infrastructure assets for industries such as energy, water, waste and communications are estimated to directly contribute to 15 per cent of Australia’s annual emissions and influence an additional 55 per cent through the activities they enable.
The nbn provides utilities with an opportunity to turn this around through digitisation, reducing emissions across the entire project lifecycle from design through to construction, handover and maintenance.
Network powered by renewables
NBN Co also promotes sustainability within its own operations and has committed to achieving net zero by 2050 or sooner through long-term emissions reduction targets and sustainability initiatives.
In 2021, NBN Co became the first Australian telecommunications company and first GBE to join RE100, committing to 100 per cent renewable electricity purchases from December 2025.
To achieve this, the company has signed several power purchasing agreements (PPA) to receive clean energy from renewable projects across the country.
For example, in late 2023 NBN Co began purchasing the equivalent of 90Gwh of renewable energy per year from the Wyalong solar farm in New South Wales under a tenyear agreement with Mytilineos.
As of 1 January 2025, the company sources an additional 90Gwh per year from the Macarthur Wind Farm in Victoria, under a six-year PPA with AGL.
NBN Co is also set to purchase approximately 59GWh of clean energy per year from the Munna Creek solar farm in Queensland upon its completion in mid-2025, through a second PPA with Mytilineos signed in November 2023.
the company is striding towards its target of sourcing 100 per cent of its purchased power from renewable sources from December 2025.
Other initiatives the company has taken to power its operations with renewables include a commitment to use electric or hybrid vehicles where suitably available by 2030, installing on-site renewables such as solar panels, and piloting wind turbines on its facilities.
Widespread impact
It’s not just utilities that are digitising – from agriculture to healthcare, virtually every industry across Australia is turning to digital solutions to improve efficiency, reduce costs and meet sustainability targets.
Across the board, Australians are consuming more data than ever before – both businesses and individuals.
NBN Co CEO, Ellie Sweeney, said that a decade ago, the average Australian home had around seven connected devices and consumed about 40GB of data every month.
“Today, the average household consumes more than ten times that amount, and we have something like 22 connected devices on average,” Ms Sweeney said.
In the next decade, that number is expected to rise to 40 internet connected devices and more than 1100GB of data consumed per month in the average Australian home.
“With more than 20 million Australians using nbn’s network every day, having a robust and reliable futureready internet connection is more important than ever,” Ms Sweeney said.
By providing the foundation for the widespread adoption of digital solutions, NBN Co’s full fibre rollout is crucial to Australia’s digital transformation and net zero journey, supporting everything from household streaming and remote work to the digitisation of utility operations and beyond.
As Australia’s digital backbone, the nbn is not just about faster internet – it’s providing the infrastructure that will carry Australia into a sustainable digital future. U
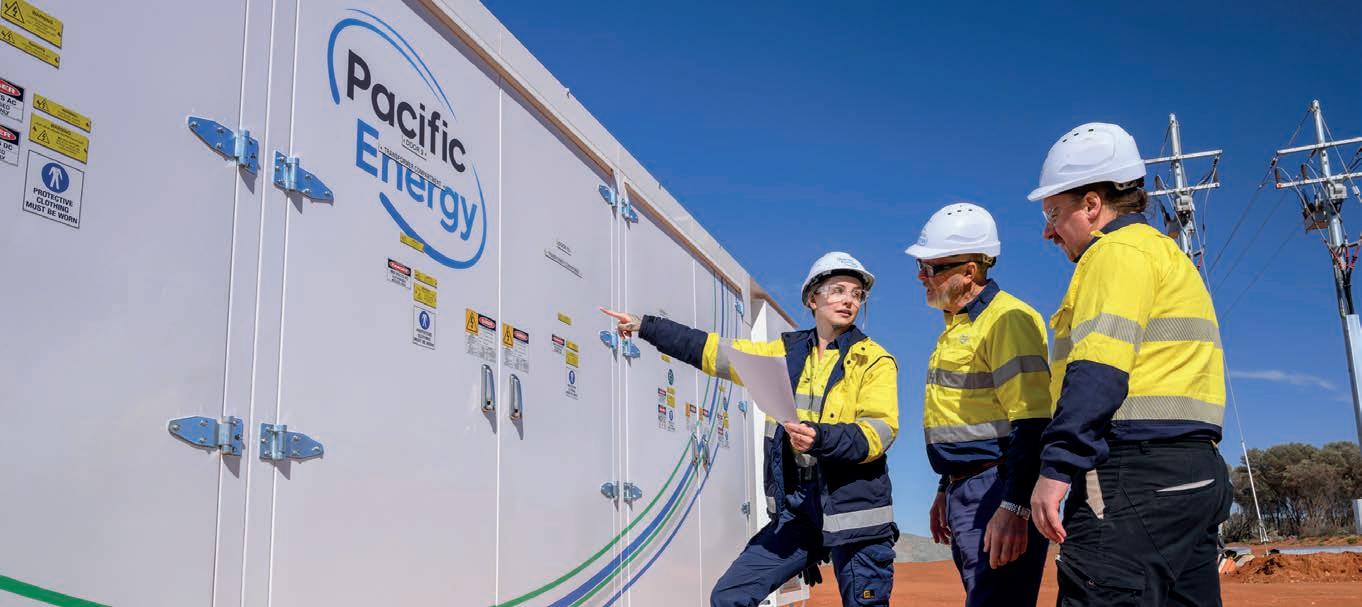
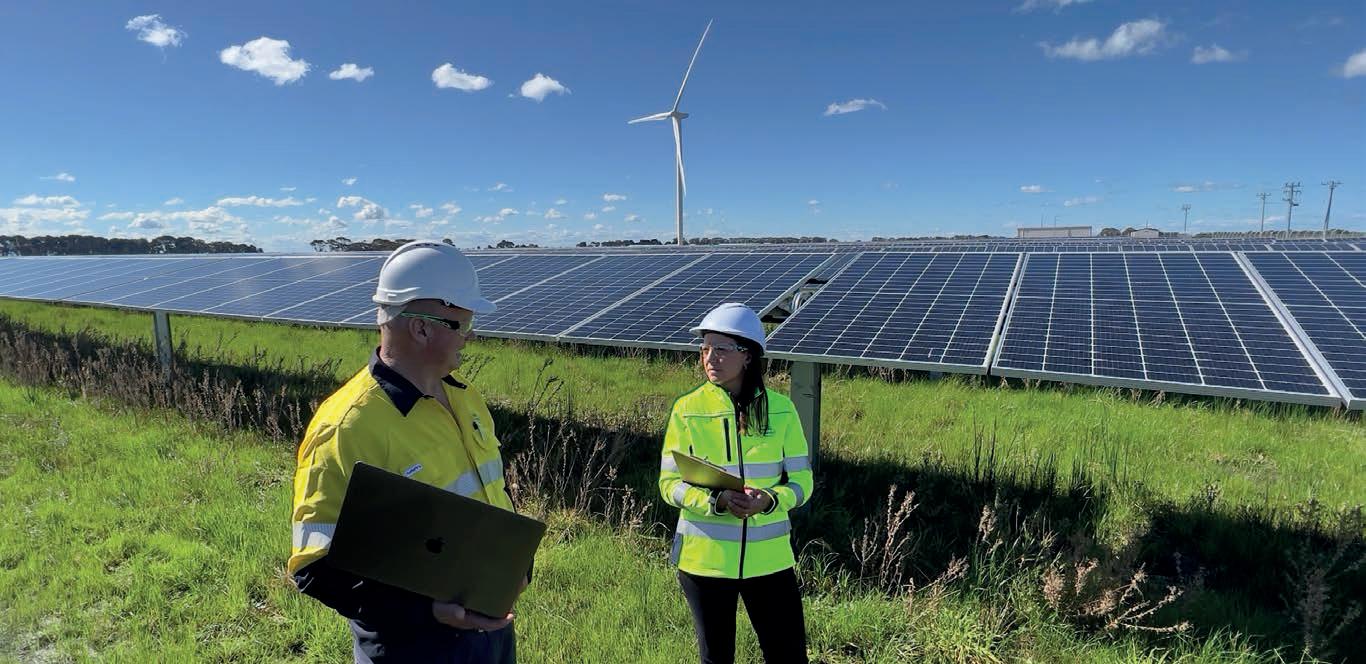
NBN Co also promotes sustainability within its own operations and has committed to achieving net zero by 2050.
Transitioning Australia to a clean energy future
As leaders in sustainable distributed energy, we provide end-to-end solutions to our diverse clients Australia-wide. We manage design, construction, and operation of scalable energy assets ensuring optimal outcomes for our clients’ energy and decarbonisation goals.
Our in-house capability and experience
Hybrid systems | Wind | Solar | Gas | Stand alone power systems | Integrated battery storage | LNG storage | Green hydrogen | Hydrogen refuelling stations | Diesel | Hydroelectric
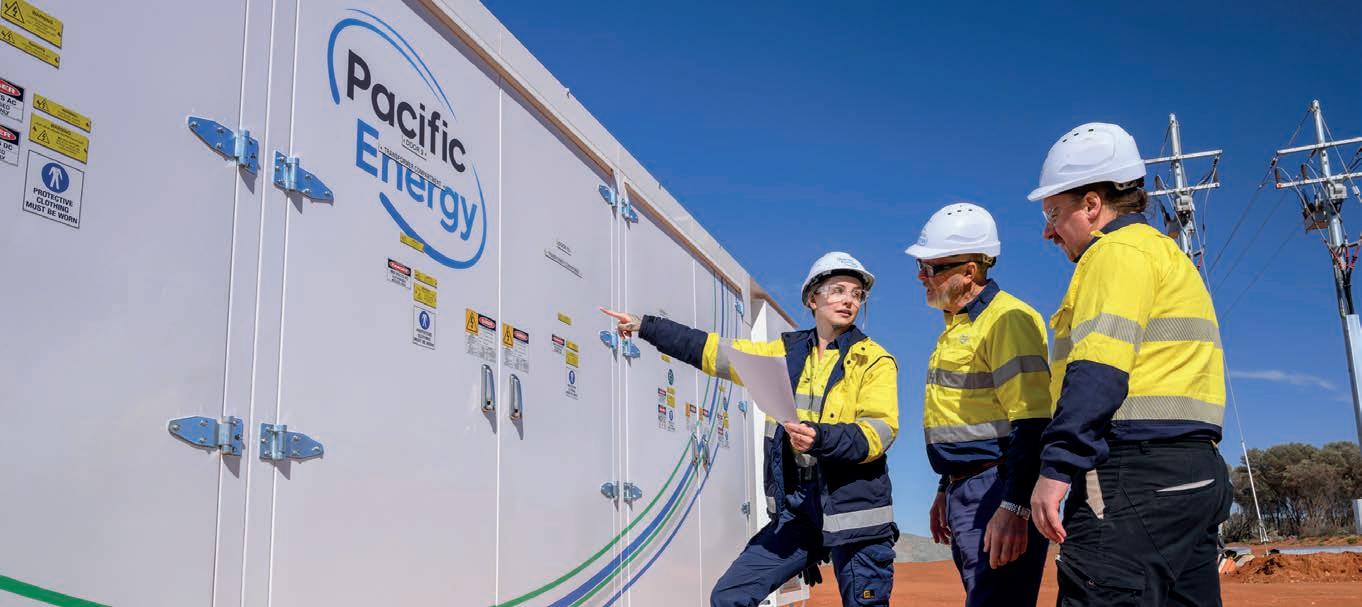
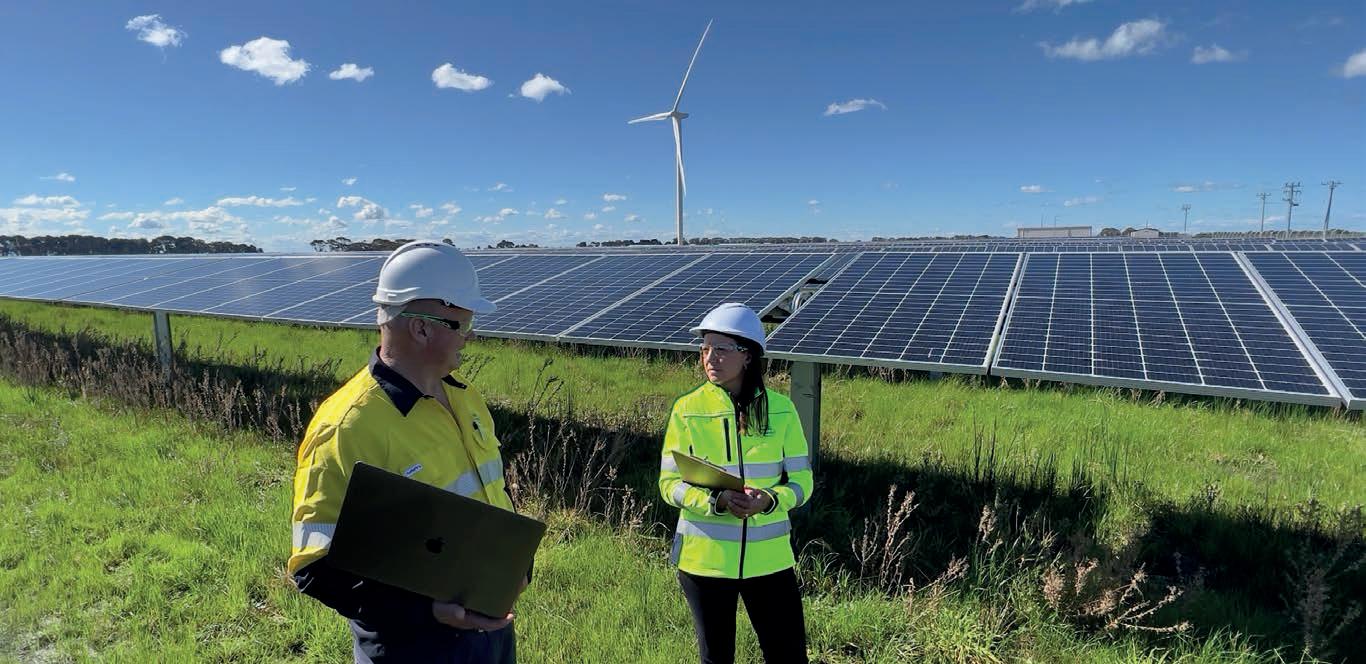
Pacific Energy is Australia’s only independent power provider with in-country manufacturing.
Compliance for critical power
As the demand for resilient power solutions grows, ensuring battery charger safety, compliance and reliability for stationary applications is critical.
To address evolving industry needs, Australian Standard AS4044:2024 has established new benchmarks that protect critical infrastructure while improving operational efficiency.
For essential service providers, adherence to this standard is key to maintaining uninterrupted power and long-term asset performance.
Addressing industry needs
Stationary VRLA (valve regulated lead acid) battery chargers play a critical role in maintaining backup power for essential infrastructure, including telecommunications networks, utilities and industrial applications.
These systems support uninterrupted operations during grid failures, emergencies and planned maintenance – thereby ensuring resilience in the face of increasing energy demands.
The AS4044:2024 standard enhances the safety and performance of these systems by ensuring compatibility with Australian conditions, reducing equipment failure risks, enhancing the operational lifespan of critical infrastructure, and meeting stringent compliance standards
The key features of AS4044:2024 are:
Modern technology compatibility
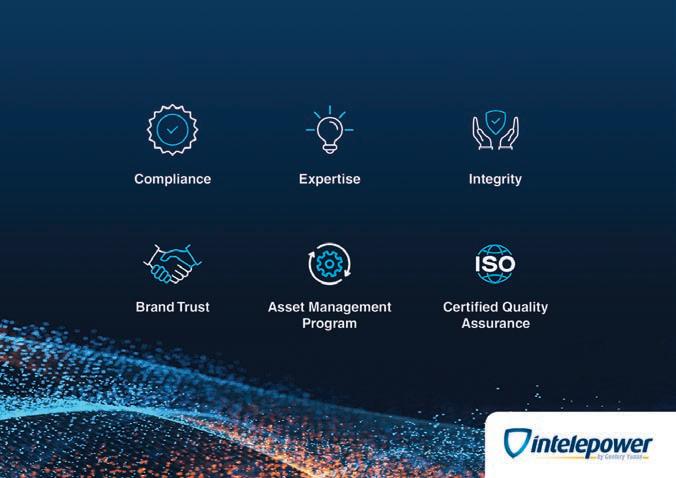
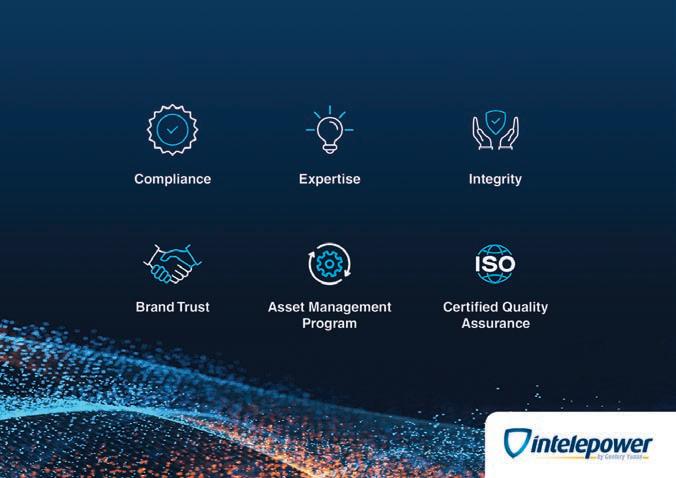
Long-term safety
AS4044:2024 ensures efficient operation of switch mode rectifiers and phase-controlled chargers, reducing energy loss and enabling flexible three-phase design.
Neutral current limitation
This prevents overheating, system imbalances and power inefficiencies.
Built-in charge control
In-built charge control features help optimise battery life, prevent overcharging and reduce maintenance costs.
Updated cable colour standards
Standardised colours simplify installation and enhance safety.
Advanced monitoring and diagnostics
This enables real-time tracking and predictive maintenance.
EMC compliance
Complying with electromagnetic compatibility (EMC) requirement helps minimise electrical interference for seamless industrial operation.
In adopting AS4044:2024, asset owners and utility providers can meet Australian industry standards, reducing risks of penalties and disruptions. By enhancing reliability, this standard also provides safety assurance and helps mitigate risks associated with battery failure. Recognising the clear benefits this standard has for the industry; Century Yuasa remains committed to full compliance with AS4044:2024 and guarantees that this compliance is reflected in all its Intelepower systems to ensure it can provide safe and efficient solutions for critical infrastructure.
All Century Yuasa’s Intelepower systems are:
• Built to Australian standards to ensure reliability and longevity
• Have optimised battery performance and advanced charge control to extend its lifespan
• Come with nationwide support, reliable maintenance and compliance assistance
The AS4044:2024 standard represents a significant leap forward in the safety, performance and compliance of stationary battery chargers. Ensuring compliance not only protects critical infrastructure but also enhances long-term efficiency and reliability. As a trusted leader in energy solutions, Century Yuasa Power Systems ensures full compliance with AS4044:2024 – delivering safe, efficient and innovative power solutions for utility providers and asset owners across Australia. U
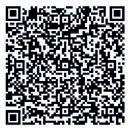
For more information, scan the QR code or visit intelepower.com.au
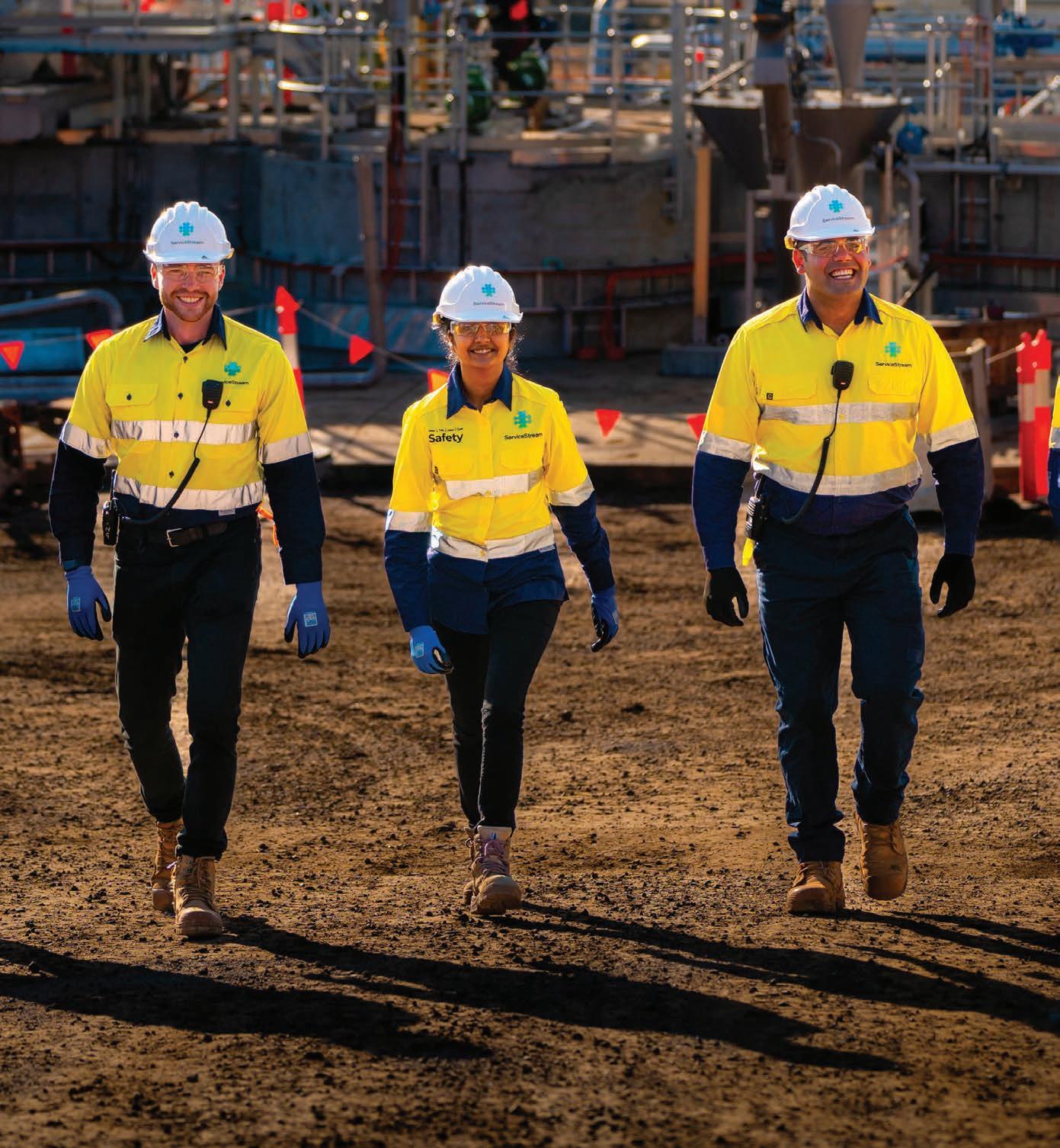
AS4044:2024 sets the benchmark for critical power systems.
Image: Century Yuasa
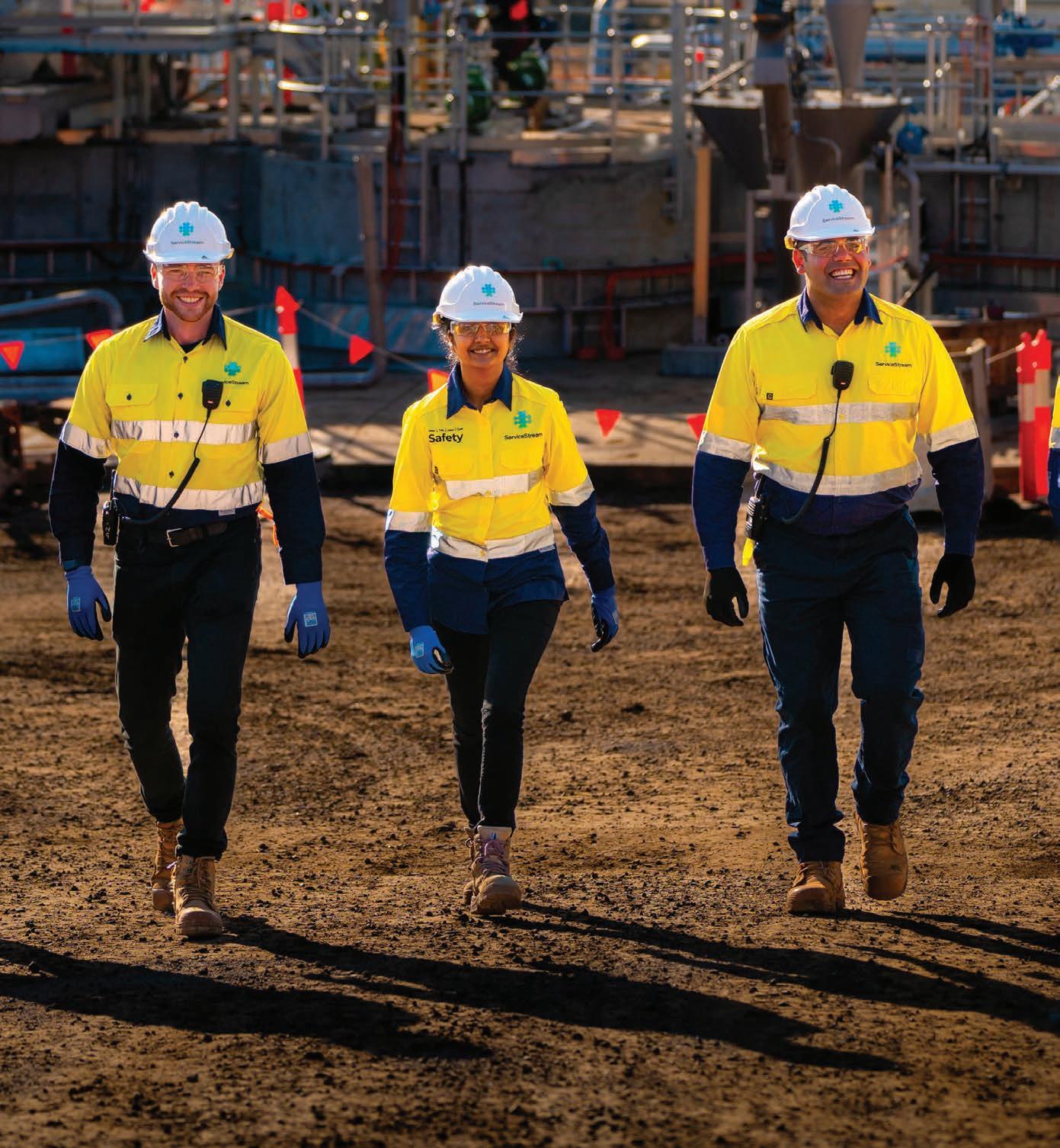
Harnessing the power of data to deliver exceptional project management for Australia’s most critical utilities networks
We deploy our Project Execution Framework (PEx) across our projects to ensure service delivery excellence, streamlined governance and integrated sustainable and innovative solutions.
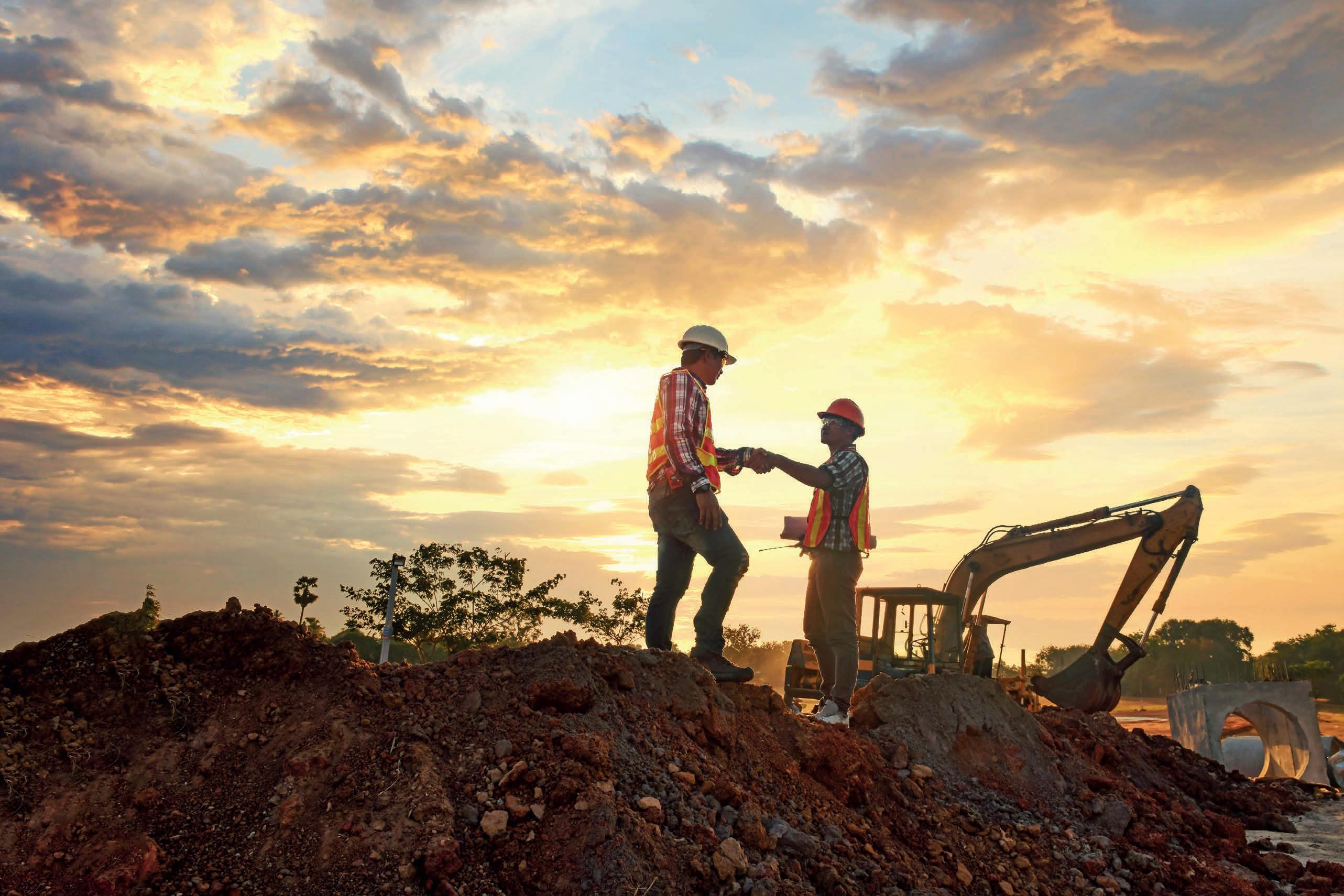
Building the future together
The utility industry is in the middle of an infrastructure boom and as every sector powers ahead with their own major projects, there’s never been a better time to collaborate.
Between water authorities launching major capital programs to service growth, the National Energy Market getting a renewable overhaul, nbn’s nation-wide rollout and not to mention the upcoming Olympics – Australia’s essential services are expanding faster than ever before.
While each of these developments have customer’s needs at their heart, the work required to deliver this new infrastructure comes with unavoidable disruptions to the community. And with each sector embarking on their own critical projects, these communities sometimes barely have time to breathe before another round of construction works begin.
But what if there was a way for all utilities, road authorities and councils to work together?
This was the future the Streets Opening Coordination Council (SOCC) envisioned when it made the decision to become a national organisation.
Sharing across state lines
SOCC CEO, Nabil Issa, explained that Queensland is the first stop on the organisation’s national rollout journey.
“I’m currently planning the rollout of SOCC in Queensland, which is going to be our test bed, and June 2025 is our target date for bedding that in,” he said.
“We’ve had authorities in Queensland approach us requesting SOCC’s operation be extended to the south-east. They acknowledged the success of SOCC in New South Wales and wanted to promote a similar culture between Queensland water, gas, electricity, telecommunications, councils, transport authorities and railway operators – a culture that brings all stakeholders together and promotes a unified approach to working in public road reserves. So, whenever there’s work happening on a road reserve, SOCC’s simple, yet powerful iWORCS platform provides registered stakeholders visibility of each other’s work schedules and indentifies opportunities to
What if there was a way for all road asset owners to work together?
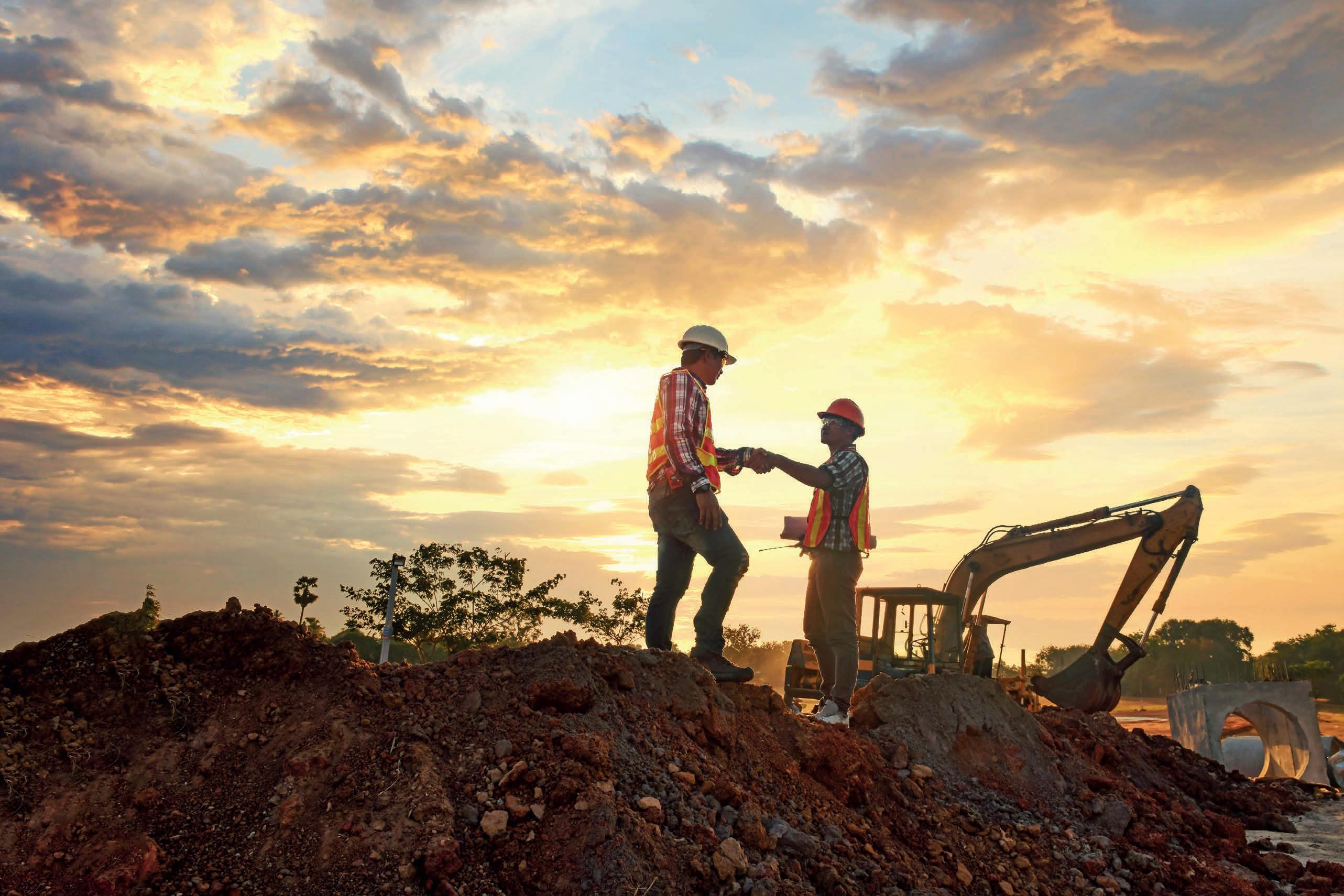
align them. An essential target of iWORCS is to ensure that if work schedules cannot be combined, they are at least implemented in the correct sequence.”
saravut/stock.adobe.com
Mr Issa said the goal is to get everyone working together as if all projects were one, rather than having multiple projects at different times in the same area.
“From the community perspective, they would see one government working for them. They shouldn’t see the local council one week, a power company the second week and then a telecommunications carrier the week after – they’ll see everybody working together to deliver value to the community,” he said.
Mr Issa said this will greatly reduce interruptions of public services and help avoid extended roadworks and disruptions to the community.
“That also brings the opportunity to share resources and reduce costs – not just the cost to the organisations, but also the cost of disruptions to the community,” he said.
When we approach your state, we’ll be kicking off with a workshop to explain how it’s going to work, and then it’s going to be led by [the local utilities] – not me or the national board.
“When we look at cases where there’s been lack of coordination – and what it has cost individual entities – many say they would do things differently if they had visibility of each other’s works and the opportunity to do it again, and we can actually quantify what costs can be saved by working together.”
Another key goal for SOCC’s national expansion is to provide a platform for knowledge sharing not just between states, but between different sectors too.
Mr Issa explained that many of the challenges a water authority in one state might be facing are applicable to utilities in other sectors – and he wants their learnings and solutions to be available across the country.
“The structure of SOCC will be a board that governs the national framework, and then under that board will be state-based chapter committees – and each committee will have a representative on the national board to make sure there is consistency and alignment nationally,” he said.
“[That means there’ll be] consistency in the governance, but also a mechanism to share information across states. We want to be learning from each other, rather than each state reinventing the wheel and keeping everything to themselves – we want that experience to be shared nationally.”
A history of collaboration
“Another of our key learnings from more than 100 years in operation is that members need to be able to measure the value of their involvement with SOCC, we ensure that Image:
SOCC was originally founded in 1909, but it was focussed on the Sydney Metro area until 1995, when it expanded to encompass the whole of New South Wales. Now the organisation is bringing more than a century of experience to authorities nation-wide, and Mr Issa said that the way it embodies collaboration has been key to its success.
“When it comes to decision making, SOCC very much operates on the principle of consensus. We don’t try to force outcomes if we don’t have the support of every member. We want all members to be behind every strategic decision to ensure its success and longevity.
SOCC helps the water, gas, electricity, telecommunications, council, transport and railway sectors collaborate on their projects.
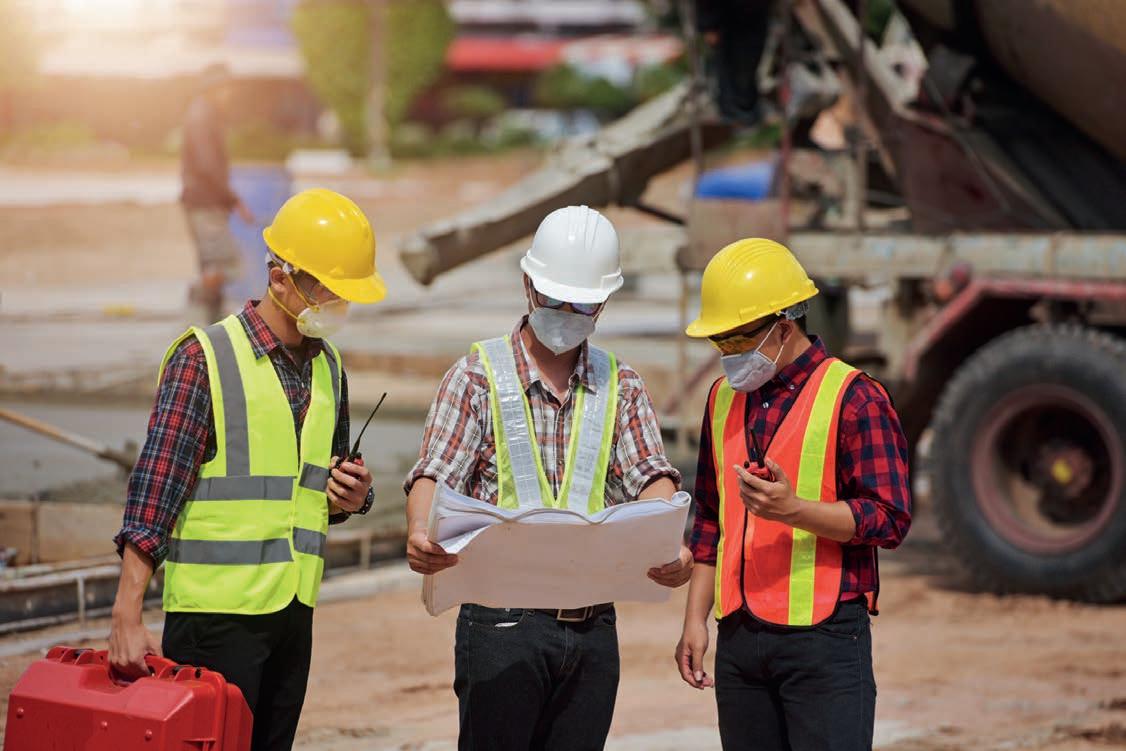
With this renewed national focus also comes new logo, which was developed in collaboration with the marketing specialists at SOCC’s commercial partner, PelicanCorp.
“The old logo had the New South Wales map at its core and a few circles representing different utility services. The new logo is made up of colour-coded utility services that are shaped to mimic the map of Australia to signify SOCC’s expanded area of operations,” he said.
“These colours are detailed in the Australian Standard AS5488, so yellow represents gas, orange represents power, white represents telecommunications, and so on. We also wanted to link the logo back to the history of SOCC, so we refer to 1909 as the year it was established.”
An even better tomorrow
Both SOCC and Mr Issa’s vision for the future is a national framework that supports essential service providers to plan, build and learn together.
“What I’d like to see right across the nation is all industries having an integrated platform that drives their capital works. But it’s not just about doing the work, it’s also about planning for the work – and up until now, there hasn’t been that visibility,” he said.
“If utilities and road authorities don’t have visibility of other stakeholders’ proposed works when they plan and design new infrastructure, they could face challenges in implementing their designs, which may force them to rethink their designs. By that stage, they will have committed a lot of resources that might be wasted depending on the amount of rework required.”
Mr Issa said he’d love to see some of the country’s biggest builds delivered with a collaborative approach between all stakeholders concerned.
“Queensland will be hosting the 2032 Olympic games, which require a lot of new infrastructure. Using a collaborative framework to deliver this infrastructure
national sustainability and waste reduction targets. SOCC can play a critical facilitating role in this space.”
While street works are critical to SOCC’s vision, it is also focusing on standards and best practices.
“[For example] we’re seeing a lot of electric vehicle (EV) charging stations being built on footpaths and car parks, but there isn’t a nationally accepted standard for locating them,” Mr Issa said.
“It is important to ensure that surface enclosures do not create maintenance nightmares for other utilities due to being incorrectly located. SOCC is now developing guidelines for the location of EV charging stations as a part of the review of its best practice guide to codes and practices for streets opening. The aim is to place chargers away from existing or dedicated spaces for utilities.
“We’re also developing a best practice road restoration standard for local roads. It is not only important to ensure that a disturbed road surface is restored to an acceptable standard, but also that the restoration of subsurface layers is undertaken to an acceptable industry standard. This is important to reduce the risk of failure of utility services and minimise the community cost of maintaining essential assets.”
For those looking to be a part of SOCC, Mr Issa said the best way to get involved is to contact him directly.
“We will be progressively setting up chapter committees to represent all states in Australia. We envisage the process will involve an initial workshop to explain governance structure and operational responsibilities, and be followed by the election of committee members – [we want] all key stakeholder groups to be represented,” he said.
“Those who want to put their hands up first, all they need to do is call or email me and I’ll get to the ball rolling for them – or I’ll update them on the timeframe and what’s happening in their state.” U
For more information, visit streetsopening.com.au/contact
Building Australia’s future of digital connectivity
Through our expertise, brilliant network, and unique customer focus, we make brilliant digital solutions simple.
Boosting economy and communities with critical remote connectivity across the Pilbara region.
Community Enterprise Queensland (CEQ): uninterrupted access to metro-grade high speed, low latency connectivity.
WA Police: Anywhere communications project, connecting remote police stations and vehicles across Western Australia.
Backed by a team of leading network experts, solution architects, dedicated account teams and strategic partners, our reliable and secure network provides connectivity across Australia and into Asia Pacific. Visit vocus.com.au
Providing mining industry with safety and productivity via above and below ground LTE network connectivity.
Whitsunday Regional Council: enhanced communication for work crews and critical support for emergency services.
Providing mobile in vehicle Starlink for large scale construction e.g. transmission line builds
SA Power Networks: Connecting 200 Starlink units across the state via a scalable, resilient network environment.
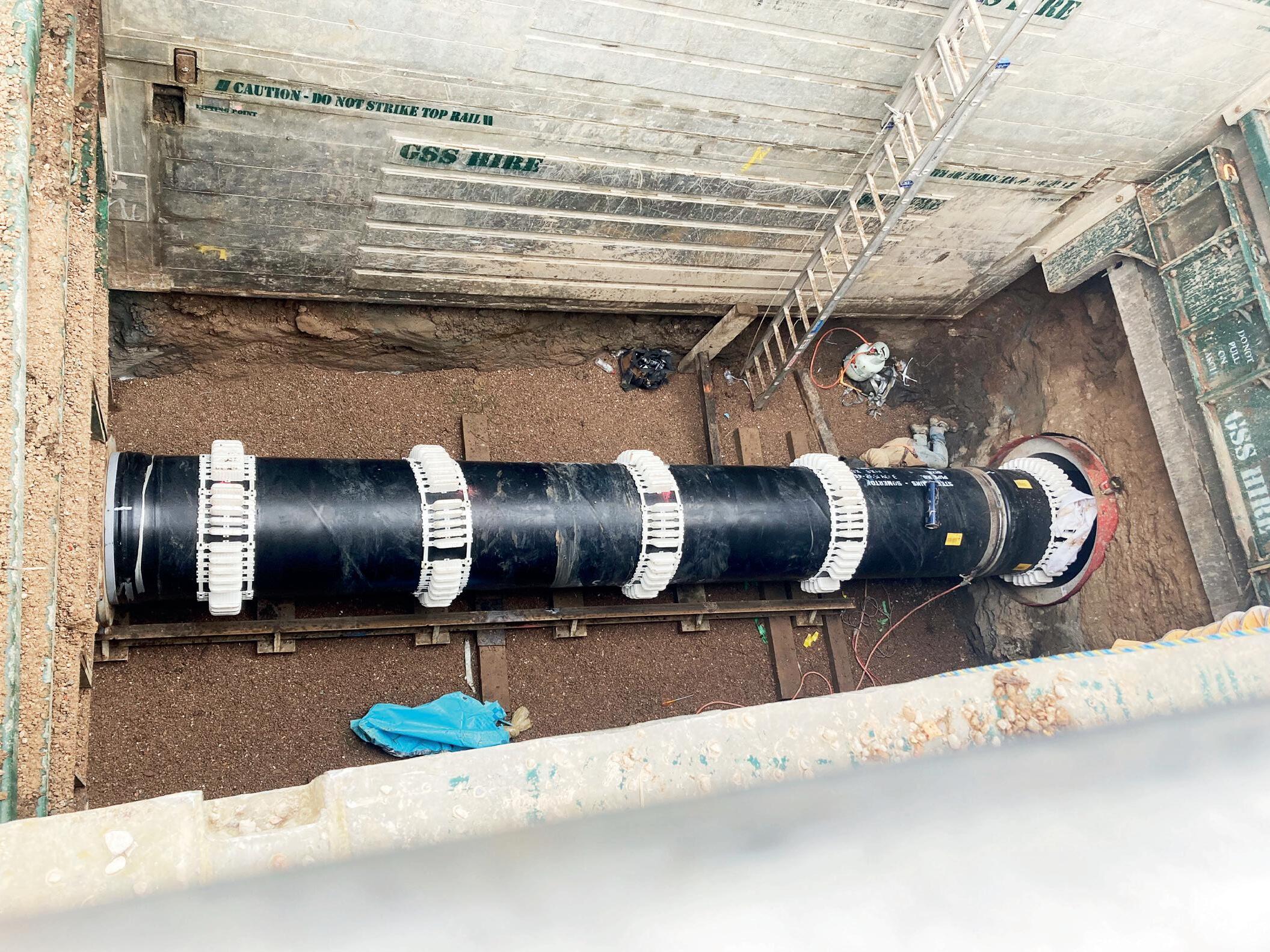
Race for space
A new water main is ensuring that residents in western Sydney will have a reliable water supply for generations to come – with the help of clever installation techniques.
In the rapidly growing Western Sydney Aerotropolis, Sydney Water and its construction partner, John Holland, are delivering vital water infrastructure support population and economic growth in the region – including one of the most advanced wastewater recycling facilities in the southern hemisphere.
This world-class facility is supported by the larger Upper South Creek (USC) project, which was implemented to improve environmental flows by transferring treated water from the new advanced water recycling centre (AWRC) to local waterways.
To deliver a treated water main for this USC project, contracting company Jonishan utilised kwik-ZIP HDXT103 spacers to facilitate the slip-lining of a 914mm Sintakote® mild steel cement lined carrier pipe into a 1200mm reinforced concrete jacking pipe casing.
While this installation was fully grouted, the HDXT spacers adequately supported the pipe and water for the life of the installation.
As the pipe weights 292kg/m when empty, and a whopping 880kg/m when full – this was no small feat. The HDXT’s unique load-sharing design maximises the load bearing capacity of each runner and reduces point loading, which enabled it to support the weight of the pipe.
Kwik-ZIP’s spacer solutions do not require any special tools to install, making the process as simple and as efficient as possible.
These spacers are also designed to help increase the lifespan of pipelines.
Kwik-ZIP’s
spacer
solutions do not require any special tools to install, making the process as simple and as efficient as possible.
They contain no metal parts that would promote corrosion and feature a load-sharing suspension system designed to support heavy loads, which is especially crucial when the pipe is filled with water. The engineered thermoplastic blend used in kwik-ZIP’s spacers is flexible, extremely tough and has a low co-efficient of friction. These spacers are specifically designed to allow for good grout flow and to minimise voids during the grouting process. They firmly grip the pipe surface on anti-slip rubber pads that prevent spacer dislodgement during the installation process and thus maintaining the correct spacer intervals.
kwik-ZIP maintains a focus on cost-effectiveness, simplicity, and rapid on-site assembly, to ensure that its spacer solutions deliver significant cost, time and operational advantages to customers. U
For more information, visit kwikzip.com or email sales@kwikzip.com
A portion of the Upper South Creek Treated Water Main with Kwik-ZIP HDXT- spacers installed.
Image:
Kwik-ZIP
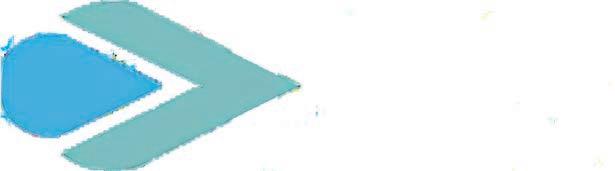

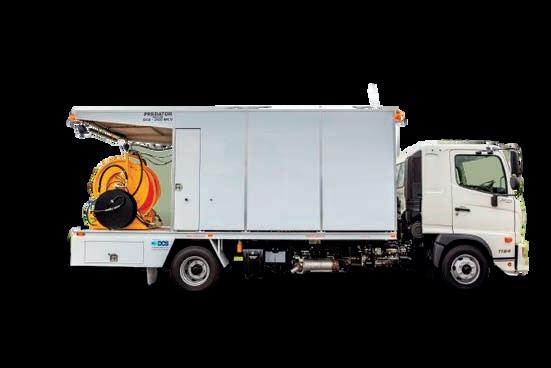
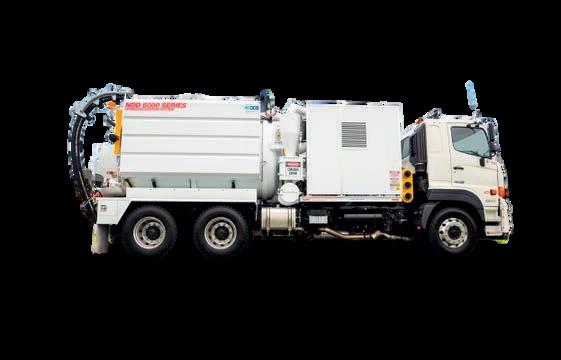
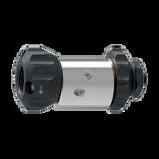

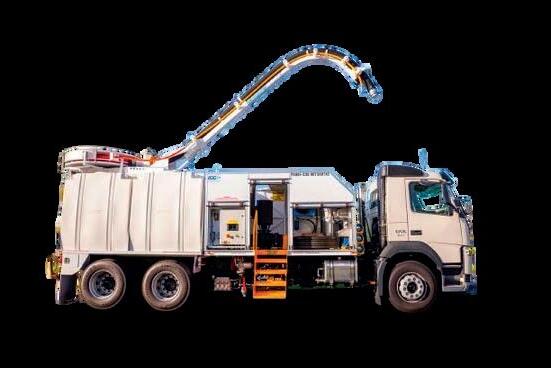
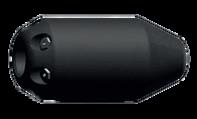

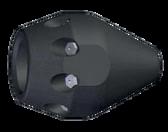
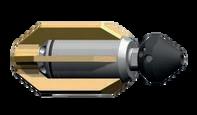
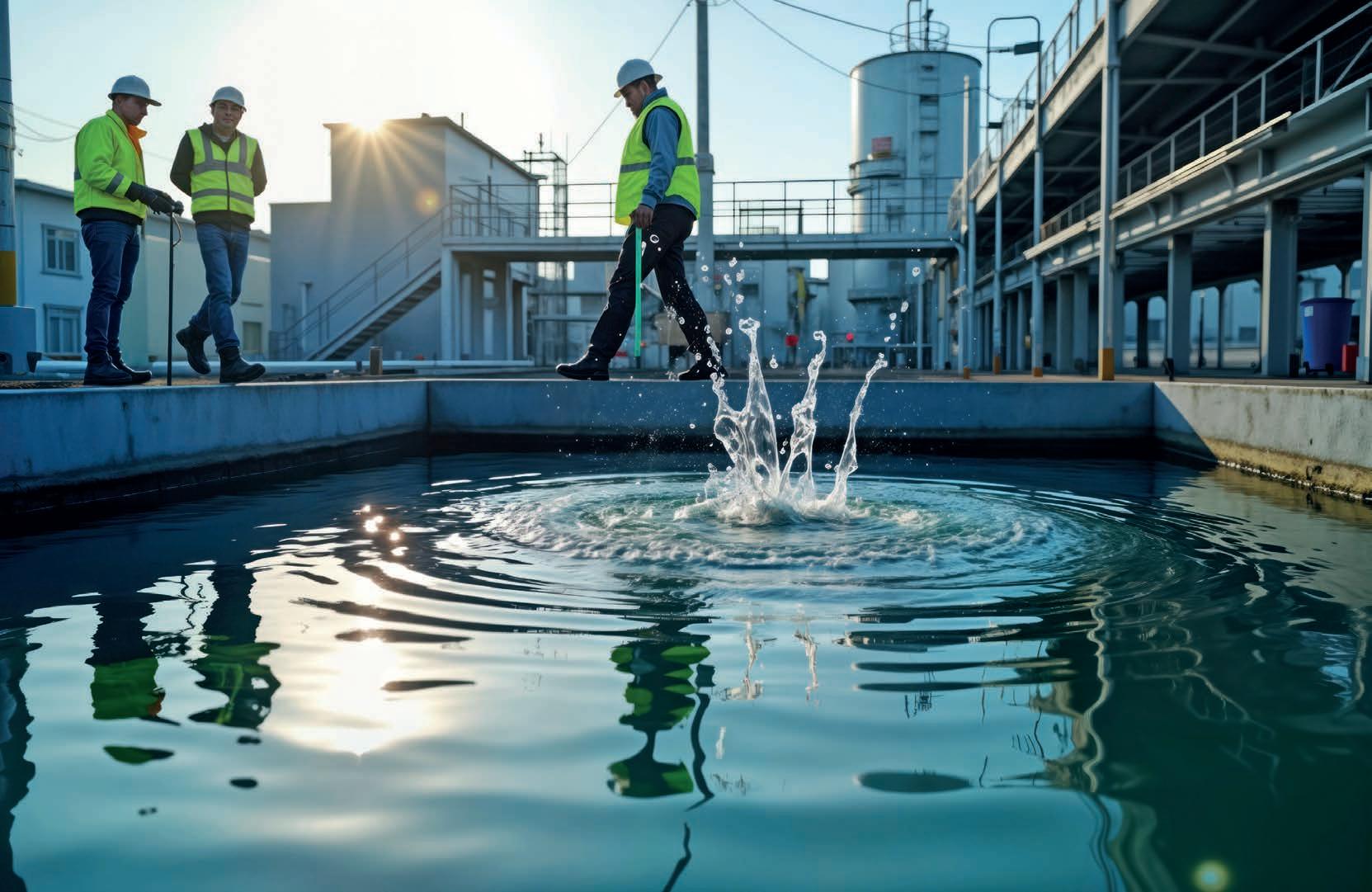
Securing skills for a thriving future
Behind all of Australia’s critical water infrastructure lies a team of expert engineers, but how can utilities secure this talent during a skills shortage?
Engineers are integral to the planning, design and construction of the water and wastewater infrastructure that all Australians rely on every day.
As the population continues to grow, water utilities must service more people than ever before, adding pressure to infrastructure that, in many cases, is already at capacity.
Building new infrastructure and replacing or upgrading existing assets requires the specialised skills of engineers – however, utilities are facing unprecedented challenges in hiring them.
This is largely due to the broader skills shortage, which has hit Australia’s construction and engineering sectors particularly hard in recent years – an estimated 50,000 engineers will be needed in coming years to meet demand across various sectors.
With engineers in high demand across all industries, it’s no surprise that utilities are struggling to secure the skilled workers they need to complete these critical projects.
Fortunately, there is a solution.
By partnering with the right engineering group, utilities can gain access to the expertise needed to ensure their systems operate efficiently and are evolving with the changing needs of their customers.
This is where Lanco Group, a Melbourne-based civil engineering consultancy, can help.
Established in 1998, the company has developed a strong reputation for providing quality engineering services, project management, contract administration and drafting to Victoria’s water sector.
With engineers in high demand across all industries, partnering with a trusted engineering group is the key to overcoming skills shortages for water utilities.
As an accredited consultant with Melbourne Water and trusted partner of the state’s retail water companies and regional authorities such as Goulburn Valley Water and Gippsland Water, the engineering firm has considerable experience in the design and supervision of a wide range of projects in the utility sector. However, what really sets Lanco Group apart is its commitment to innovation and embracing new operational technologies.
With such a long history serving the water sector, Lanco Group has witnessed the industry transform firsthand, and as such, has a deep understanding of the engineering solutions needed to address current and future demands.
Lanco Group’s record of success in the water sector can be attributed to its dedicated team of highly skilled engineers, who are committed to delivering engineering excellence and nothing less.
All staff at the company receive ongoing training – both internally and externally – to ensure they have a strong and up-to-date understanding of design and construction principles. The company encourages its team members to adopt innovative design techniques and cutting-edge
The company encourages its team members to adopt innovative design techniques and cutting-edge technologies during both the design and construction phases.
technologies during both the design and construction phases. By staying at the forefront of technological advances, Lanco Group helps utilities remain agile and prepared to meet the needs of their communities.
As communities continue to grow and change, utilities must evolve with them. Engineers that can navigate the evolving demands of the industry and keep up with the latest innovations are critical to this.
The skills gap in Australia won’t be solved overnight, but with Lanco Group, utilities can continue to build and maintain water infrastructure that serves the community now and into the future. U
For more information, visit lancogroup.com.au

Unlocking reliability
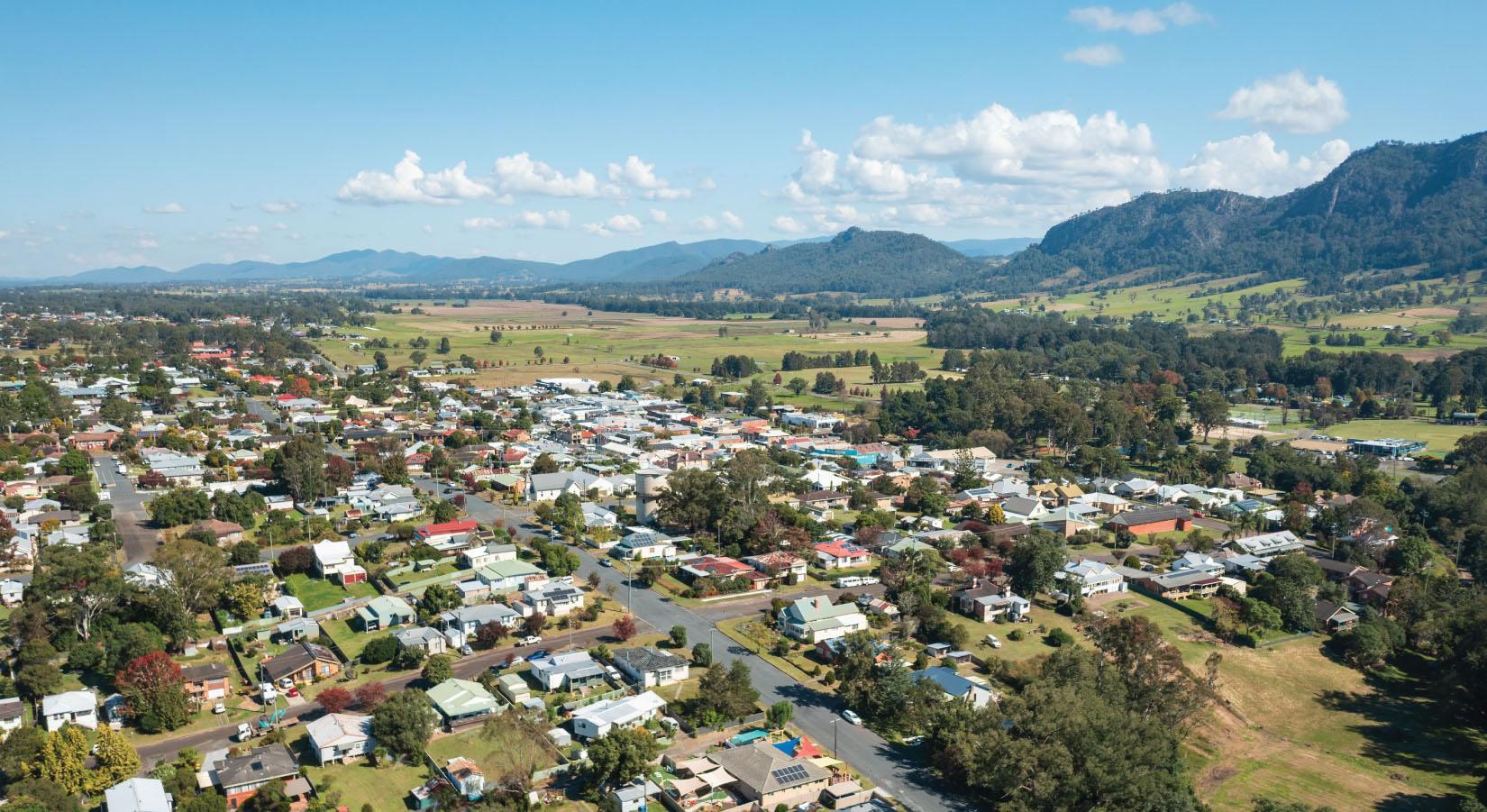
When a regional council’s existing access system began to hinder its asset management program it set out to find a more reliable security solution.
Like many other council water authorities, one Australian regional council was responsible for a wide variety of assets, including: eight wastewater treatment plants, an entertainment and convention centre, an art gallery and museum, a communities and families precinct, local botanic gardens, as well as several libraries and leisure centres.
This regional council’s service area was just as diverse as its facilities, spanning more than 10,000km2 that includes national parks, state forests, pristine coastlines, beaches, islands and major industries, and is home to a population of more than 66,000 residents.
Keeping all these assets safe and secure was a constant concern, and the council faced significant security challenges with its existing access control setup.
The key challenges
The setup used a combination of mechanical keys –primarily from an older mechanical master key system – and a hardwired electronic access system, which frequently failed and proved unreliable for managing critical infrastructure.
“Our previous system was unreliable – mechanical keys were difficult to manage, and the electronic access often failed. It was clear we needed a more dependable solution for our diverse facilities,” a council spokesperson said.
The previous system also presented licensing difficulties, with a complex structure that required additional licenses or extended maintenance for each new door or fob added to the network. This complication hindered flexibility and added extra expenses to council’s access management efforts.
A top priority for the council was the need for comprehensive audit trails, particularly across its remote locations, to enhance oversight and security. The council also experienced typical issues those face with a mechanical master key system: lost or misplaced keys. This then led to high costs for rekeying across facilities, further driving the need for a more reliable solution.
“Lost keys were a constant headache, and each incident meant rekeying multiple sites. We needed a system that could reduce these costs and improve control over our access points,” the spokesperson said.
“Without audit trails, especially in remote areas, we had limited insight into who was accessing our facilities.”
Locking in a solution
In 2011, the council began addressing its access management challenges by implementing the EKA CyberLock system with a short-term trial on a single council building.
EKA
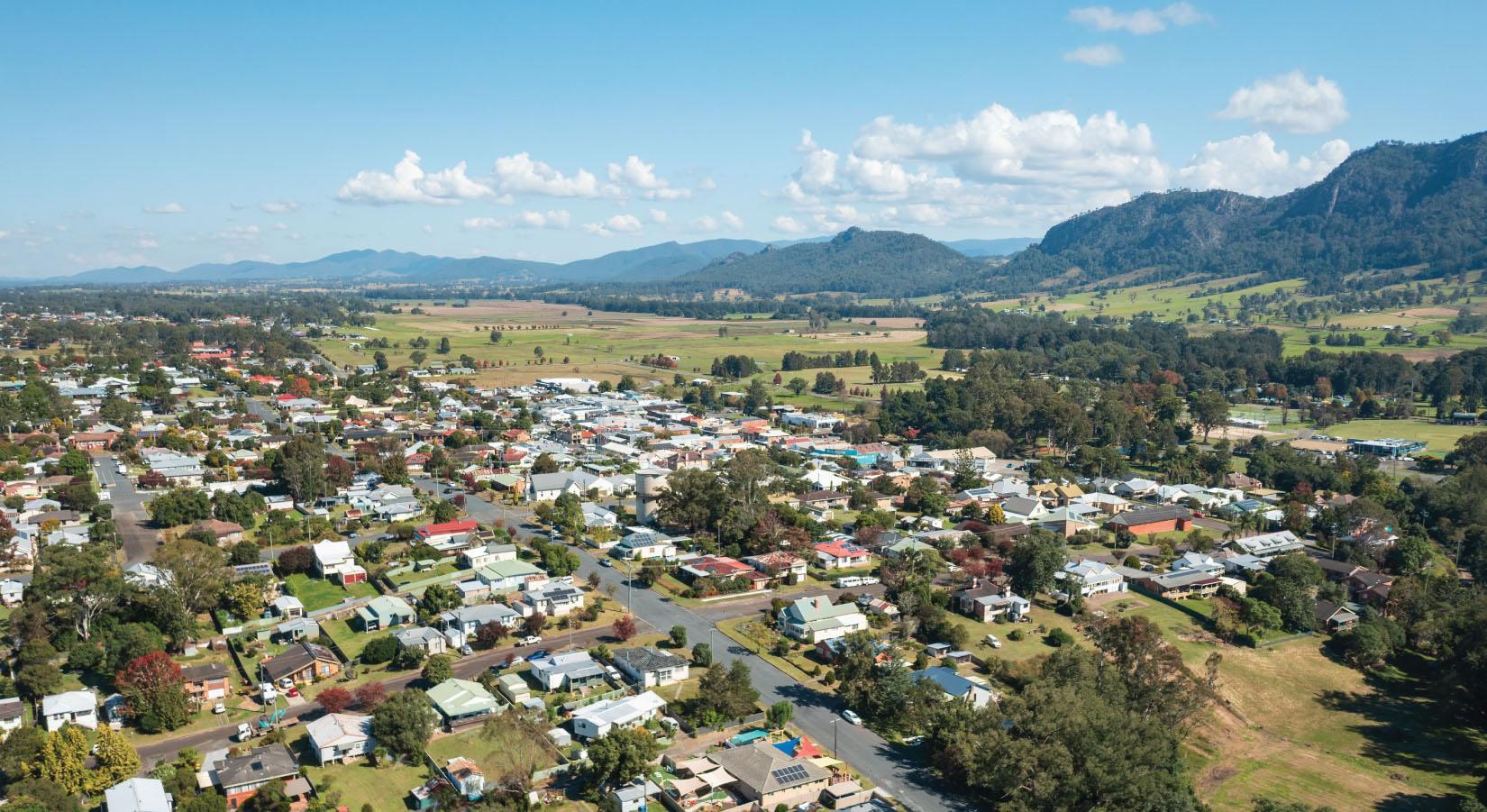
Impressed by the system’s capabilities, particularly its reliability, ease of use and alignment with their requirements, council committed to a phased implementation across its facilities.
The initial solution involved installing Flex‑controlled doors and CyberLock cylinders, along with wall authorisers and USB stations for easy authentication. Contractors were issued CyberKeys, while staff primarily used fobs to access Flex. Key personnel, senior executives and maintenance staff, received CyberKeys, enhancing secure access and tailored permissions across its assets.
“We started small, and as the system proved itself, we expanded it across nearly all of our facilities. EKA CyberLock has been easy to scale up and adapt to our growing needs,” the spokesperson said.
A key factor in the decision to continue with EKA CyberLock was the battery design – located in the key rather than the cylinder. This feature eliminated the need for remote battery maintenance, a vital consideration for the council’s geographically dispersed facilities. The ability to charge CyberKeys on the go made them an efficient choice both in terms of user convenience, and from an environmental standpoint as well.
Additionally, CyberLock’s weatherised 20 key vault and two key vaults were implemented to streamline access for contractors in remote areas.
EKA CyberLock has been a game changer for our council facilities. It’s reliable, easy to use and flexible enough to meet the unique needs of our team.
For instance, truck drivers could authenticate via fob at the depot, retrieve a pre authorised, rechargeable CyberKey from the vault and carry out tasks at multiple locations with ease.
Each CyberKey is programmed with permissions based on the individual user’s access permissions or profile ensuring secure, efficient access tailored to specific missions.
“Our operations and facilities span multiple locations with varying levels of access needs, from senior execs to maintenance staff and contractors. Finding a solution that could support different permissions seamlessly was essential,” the spokesperson said.
The council also leveraged EKA CyberLock’s audit trail capabilities by securing mechanical key cabinets, providing a record of key removals – which was ideal for areas where EKA CyberLocks were not installed, particularly across shared lands and services where multiple asset owners were involved.
Across the council’s service area, EKA CyberLock became the preferred access method, with fobs and CyberKeys enhancing both security and traceability. The rollout encompassed various sites, including depots and offices, with the civic centre being the first in 2011 and other buildings and facilities following suit over the years.
In an effort to stay up to date with the latest technology, the council has also upgraded all its systems and CyberKeys in 2023 to Generation2 technology. Most recently, significant upgrades have been made at a community centre, as well as an esplanade by the water.
Today, almost all the council’s facilities operate on EKA CyberLock. Although it predominantly uses the Flex system, the council also implements EKA cylinders for overrides and padlocks, while authorisers are strategically placed across the region for ease of access.
The council’s access infrastructure includes 20‑key vaults, two key vaults at a local depot, 1450 EKA cylinders and 193 EKA Flex doors. In terms of keys and fobs, 1535 cards/fobs have been issued for the Flex system, and 1076 CyberKeys and a handful of CyberKey Blue3 units have been deployed for specialised access – all of which demonstrates a comprehensive adaptable and future proof security solution.
“EKA CyberLock has been a game changer for our council facilities. It’s reliable, easy to use and flexible enough to meet the unique needs of our team and contractors across various locations,” the spokesperson said. U
For more information, visit www.ekacyberlock.com.au
Image: Davcor
CyberLock can easy be scaled up and adapt to growing business needs.
Growing
To help the utility sector deliver its huge pipeline of work over the next decade, Edge Underground has expanded its national footprint.
Edge Underground, a leader in trenchless technology and microtunnelling, is expanding its footprint across Australia with the opening of a new base in Adelaide.
With existing bases in Melbourne, Sydney, Gold Coast and Townsville, Edge Underground –alongside its parent company, OptionX Group – has built a reputation for delivering innovative, reliable and cost-effective trenchless solutions. The new South Australian base marks another milestone in the company’s growth, helping it better serve clients across the country.
OptionX Group CEO, Stuart Harrison, said this move reflects Edge Underground’s overall growth strategy and strengthens its ability to provide industry-leading solutions to more clients nationwide, ensuring faster response times and greater project efficiency.
“Expanding to South Australia just made sense –it’s a natural progression that allows us to grow Edge Underground while staying close to the needs of our clients,” Mr Harrison said.
“At the same time, our commitment to supporting the growth of microtunnelling across Australia reflects our belief in smarter, less disruptive infrastructure delivery. We know our technologies have the potential to help shift markets away from traditional open trenching and toward more advanced trenchless solutions.”
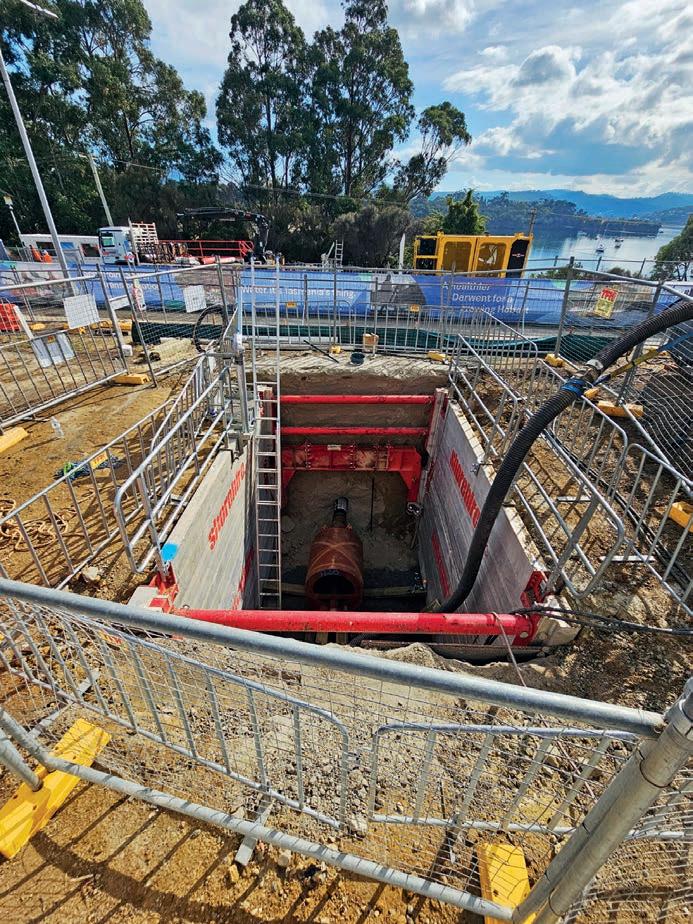
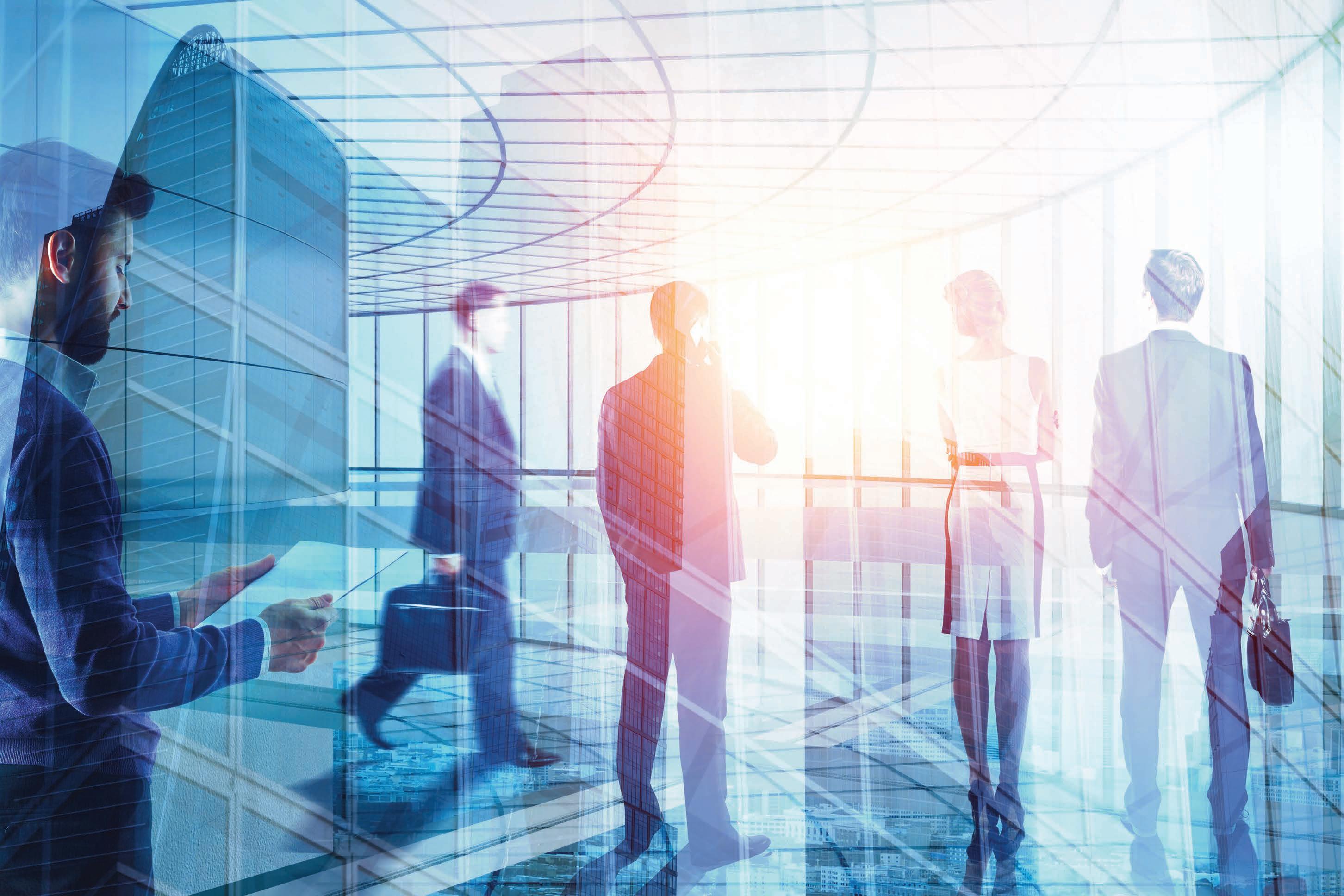

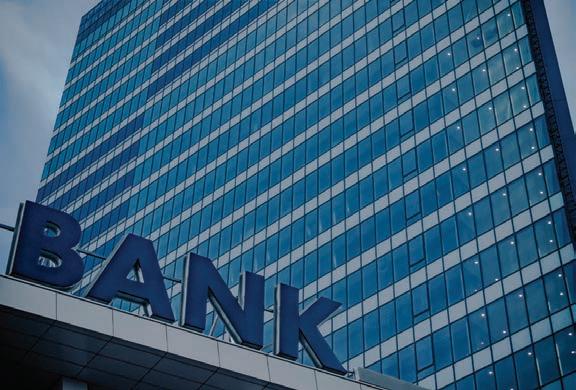
FUTURE OF SECURITY SURVEY

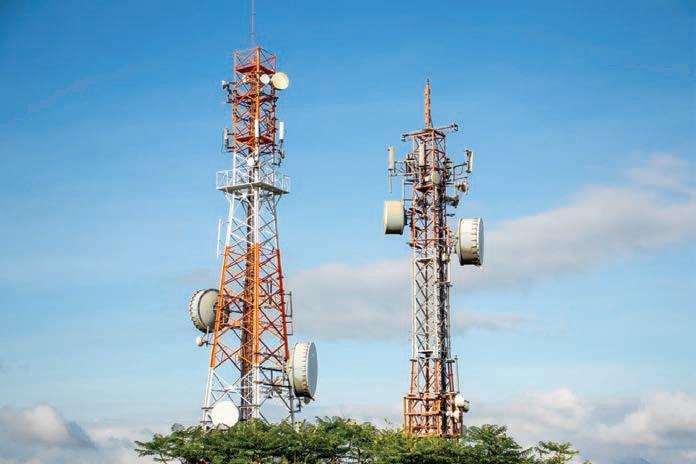
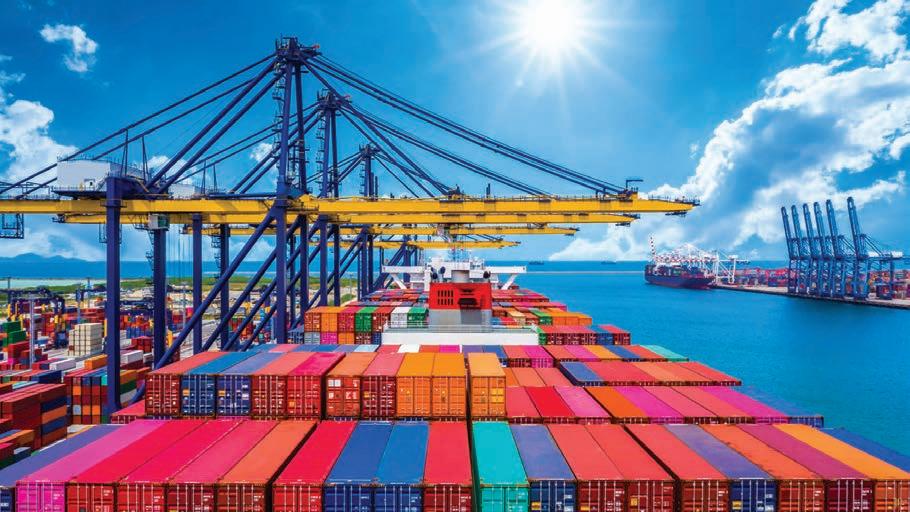
Your input will help drive meaningful change.
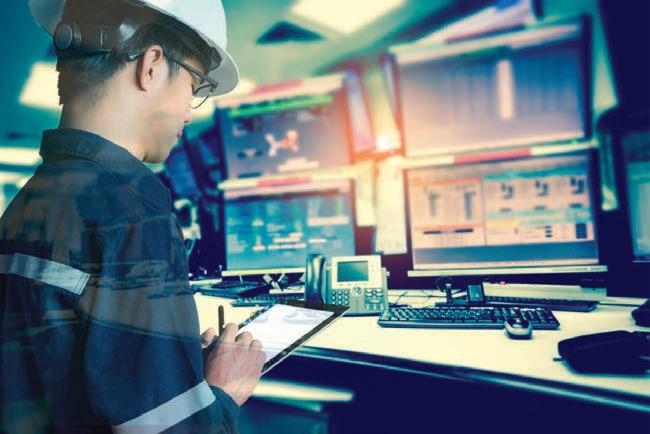
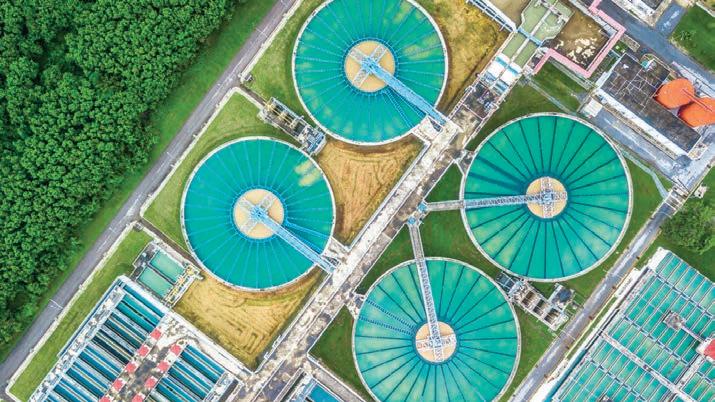
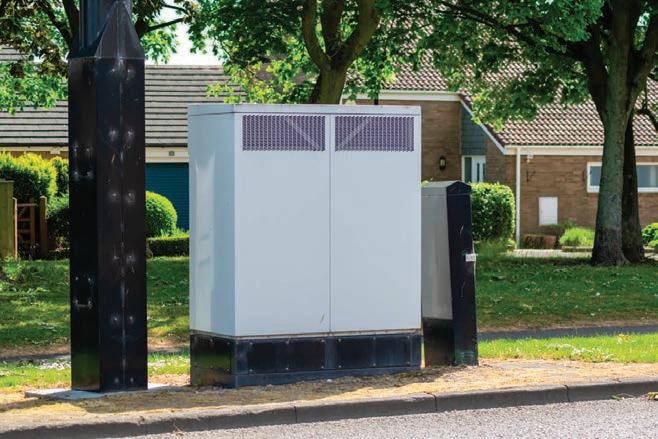
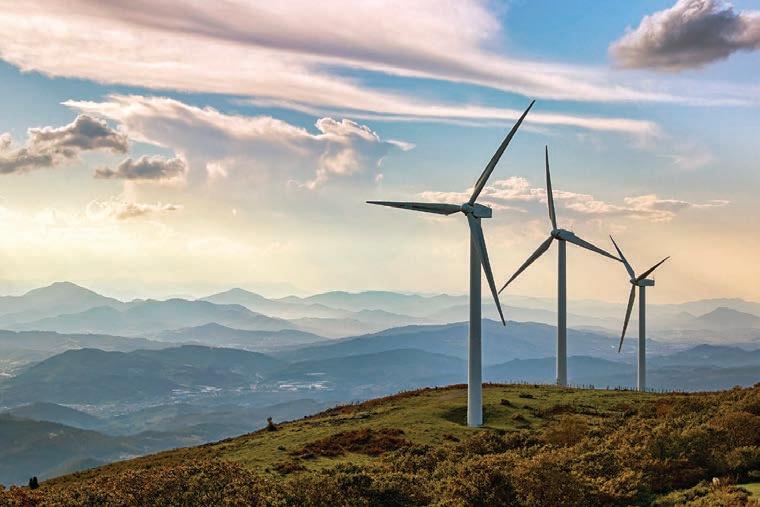
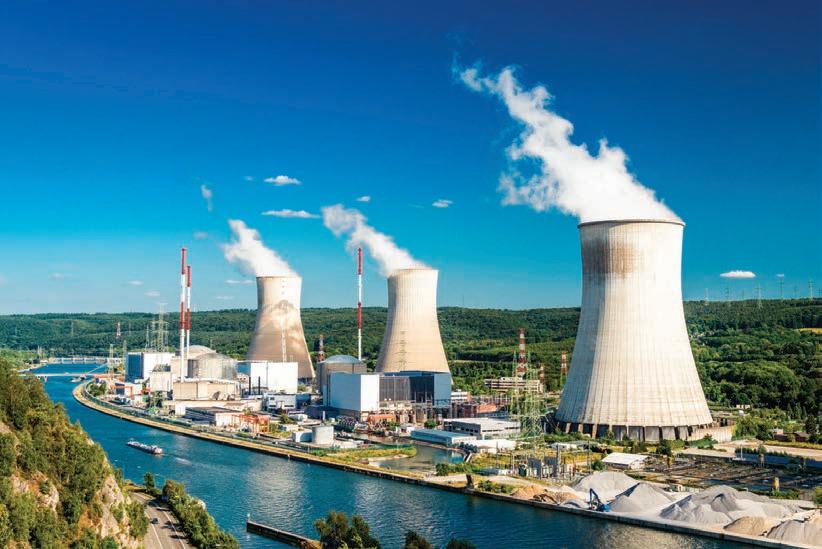
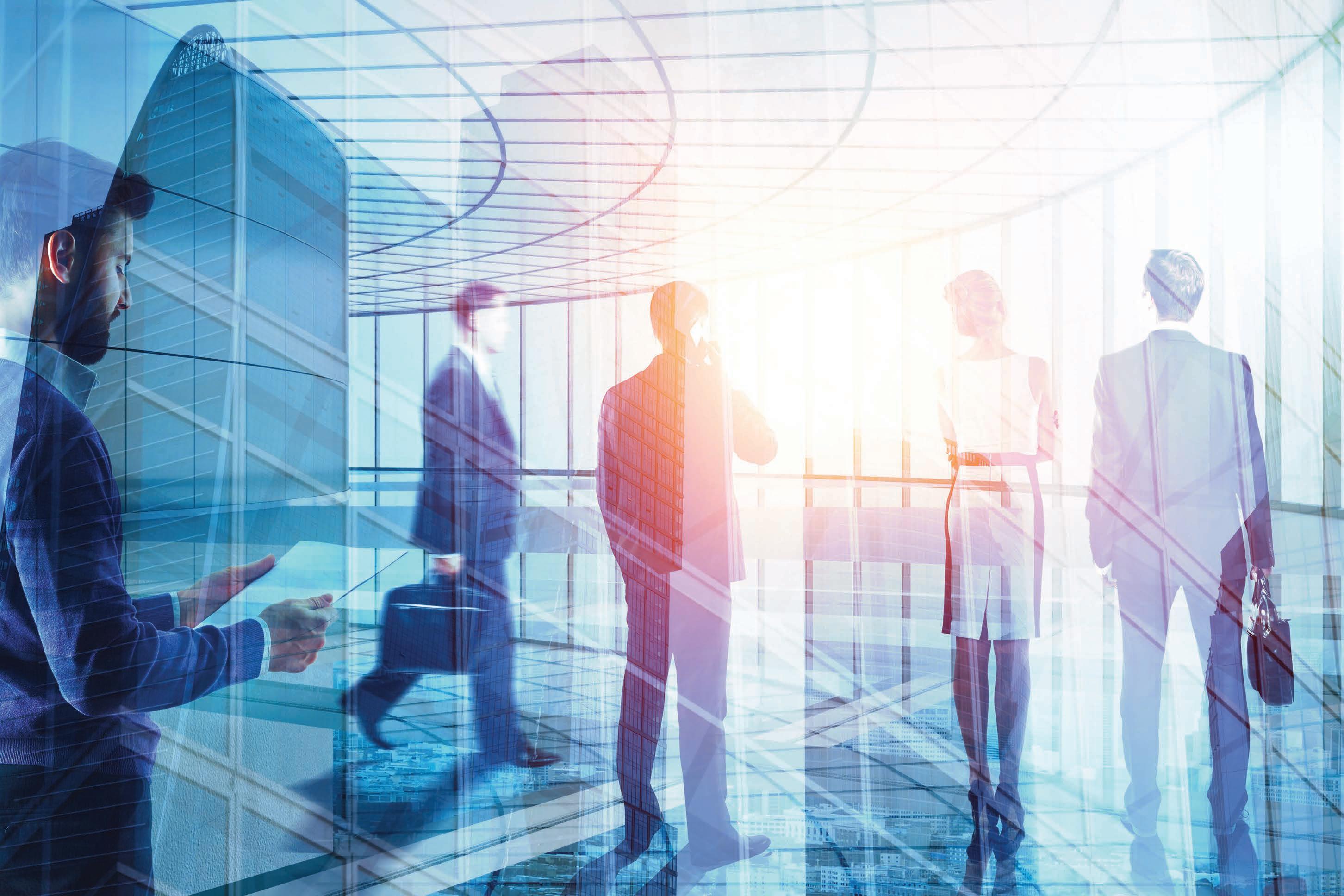
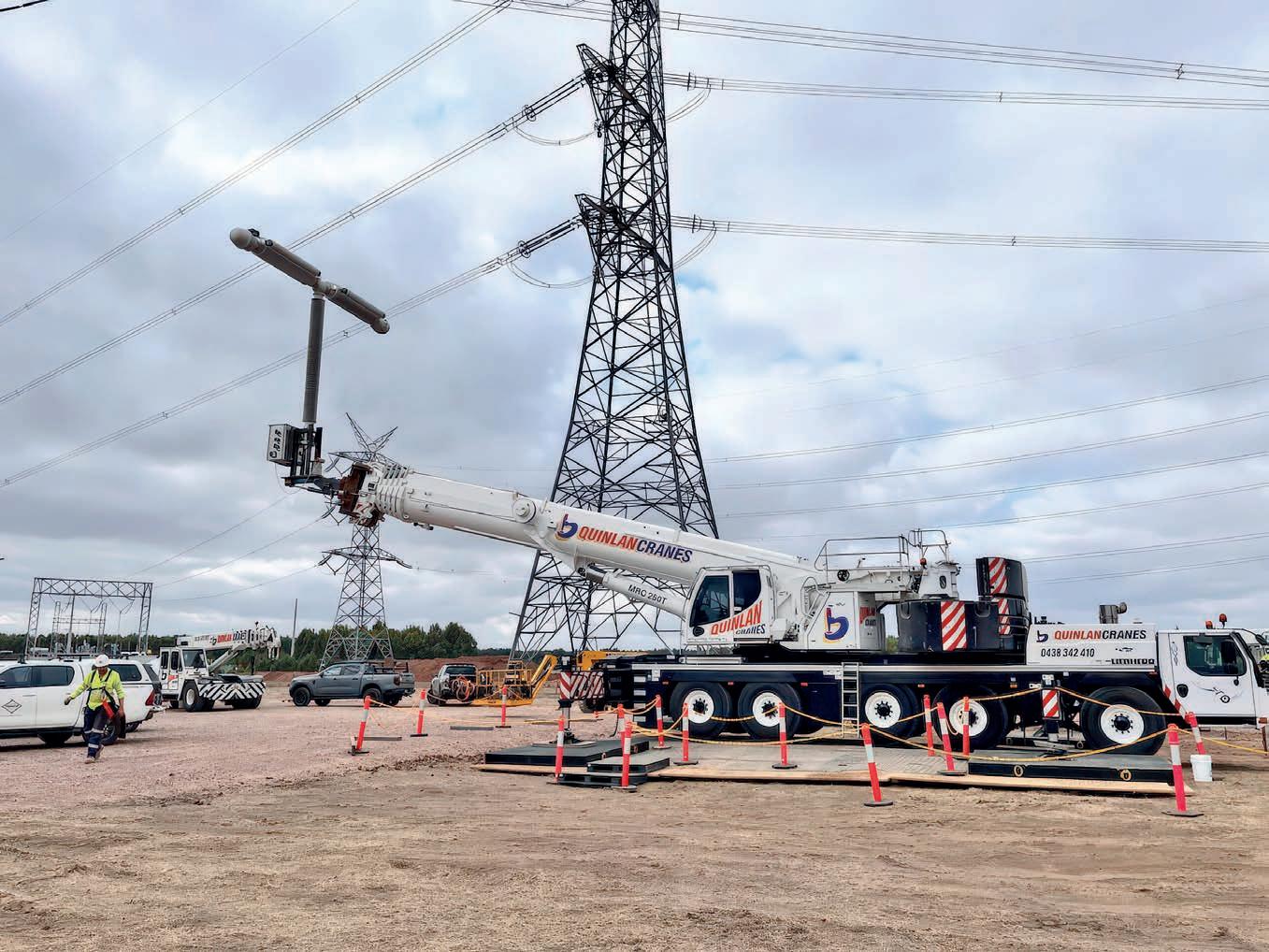
Rising to the challenge
When disaster strikes and vital network infrastructure goes down, it’s all hands on deck – but utilities and communities need people they can depend on to get the grid back up as soon as possible.
Australia’s network operators are the unsung heroes that keep the entire country running. It’s business as usual when power is on – but when it goes out, we realise how much we depend on them for just about everything.
To ensure the grid keeps running smoothly, these utilities are working around the clock to future-proof their networks and adapt to customers’ needs. But just as the grid enters the biggest era of change in its history, extreme weather events keep coming back to cause more trouble.
Not only do vital transmission projects require a strong attention to detail, working around any live asset comes with a lot of risks – it’s not a job just anyone can do.
Utilities, and their customers, need skilled professionals they can trust on-site; experts who can solve problems on the fly and who will be there when they need it most.
That’s great in theory, but when it comes to finding this ideal contractor, what should you actually look for in a business? To find the answer, Utility tracked down one of the Victorian sector’s go-to teams on the ground, who shared the joys and challenges of working on some of the state’s most critical projects.
Let’s get technical
In his own words, Quinlan Cranes Director, Sacha Sikka, is not a businessman – he’s a crane operator.
“I’ve always been in cranes, it’s all I’ve ever known,” he said.
“I started in cranes as a mechanic at 16–17 years old, and then from there I went into crane use – and I travelled Australia with some of the biggest cranes that we had in the country at the time. [After that] I worked for a big steel manufacturer in Australia, but we did projects all over the world.”
Quinlan Cranes started up in 2001, when the company’s Founder and Director, Tom Quinlan, saw a need for a more tailored service and struck out on his own.
“I’ve known Tommy for 25 years, and about six or seven years ago, I bought half the business off him,” Mr Sikka said.
Quinlan Cranes has supported the construction of some of the key transmission lines enabling not just Victoria’s transition to renewable energy, but also major infrastructure projects like the North East Link.
But regardless of the scale of the project, the two directors still take a hands-on approach.
“That’s something we take pride in. We’re crane people, that’s what we do,” Mr Sikka said.
For almost a decade, Consolidated Power Projects (CPP) Construction Manager – Transmission Lines, Walter Fiedler, has worked alongside the Quinlan Cranes crew on various major projects – and recently on AusNet’s Mortlake Turn-In project.
“The Quinlan boys work well with our crew and give us confidence in their abilities as crane operators – [they] always help out in providing a lifting solutions especially
Quinlan Cranes on-site during the Mortlake Turn-In project.
in complex lifts and among live circuits,” Mr Fiedler said.
While he’s now at CPP, Mr Fielder also worked with the Quinlan team at his previous role at Zinfra, and said that over the years they’ve helped him overcome key project challenges.
“The team has been great to work with, very competent operators – [they really helped us solve on-site problems] during some of our conductor transfers – especially when we were working over the M80 freeway,” he said.
Quinlan Cranes specialises in utility projects, and the team have decades of combined experience working safely around high-voltage transmission lines – with the company holding an ISO accreditation for Quality, Safety and Environment.
But for Mr Sikka, this focus and attention to detail stems from a genuine love for his job.
“I really enjoy the power space – we’ve done a lot of good projects, like on the M80 and we’ve relocated towers and worked in between live-line.
“Walter [and I], we’ve done a lot of technical jobs together that took a lot of planning and time but for me, they’re the rewarding jobs. I suppose they’re jobs other people don’t want to do, but I take a bit of pride in them.
“At a recent live-line job we did, we worked with engineering teams to manufacture these robots and these adapters that would bolt to the end of the cranes to go and do this line work, and that’s something that interests us, our crews enjoy [doing] something that you don’t see every day.”
Under pressure
Mr Sikka and the Quinlan team have helped the sector not just deliver vital projects but respond quickly to emergencies and get customers connected as soon as possible.
“About 18 months ago, we had a call in the middle of the night that six high-voltage towers are blown over, the power station was tripped, and thousands of people were without power in Victoria,” Mr Sikka said.
“We had to mobilise half our fleet to site the next day and still supply our other utility customers. It was a massive job, and they just needed everyone on hand. We were working around lines that had gone over, there was a big push to get the power back and to get them all back up into temporary towers.
“They’re the hard jobs, when you get that call in the middle of the night – but they’re also rewarding and that’s the service we offer.”
When disaster strikes, the Quinlan team need to be able to solve problems quickly – and with thousands of customers depending on them to play their part in restoration works, there’s no room for error.
“I think a key difference with utilities is the pre-planning [we do]. We work closely with designers in the early stages of switchyard builds and transmission line projects to look
at constructability, and for us, that makes a big difference,” Mr Sikka said.
“In our general construction, you still find a solution to their problem, but you’ve got very little input up until [you’re actually on-site], whereas in utilities, especially power, we find they’re working with us and thinking about [the best way to position] the crane – I think that just creates a successful project at the end, when everyone’s on the same page from an early point.”
Meeting high standards
Mr Sikka can’t stress enough the how important is it for crane operators to have the right experience to tackle these challenges and keep everyone safe on-site.
“Our guys are trained and they know the machines [back-to-front]. Especially when you’re on these critical projects or you’re working under an outage, you don’t want to be the reason that you failed,” he said
“That’s sort of something we pride ourselves on, what we do, we do well. And, problems happen, don’t get me wrong, things happen – but we’ll find a way, we don’t give up easily.”
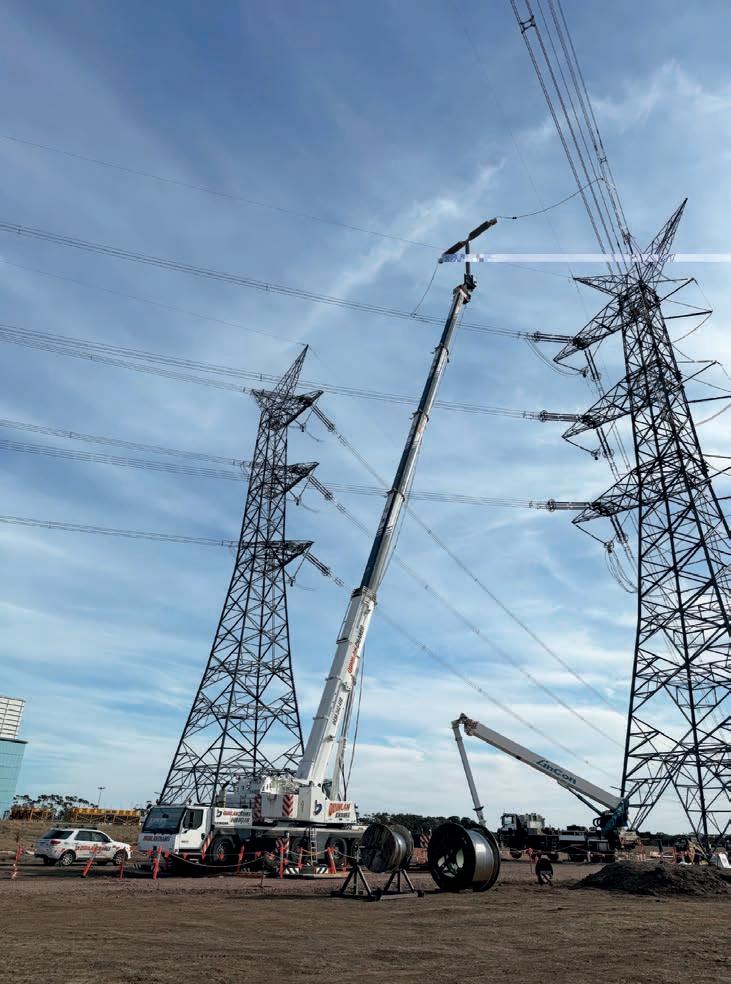
Images: Quinlan Cranes
Quinlan Cranes takes pride in ensuring they have the right machine for the job.
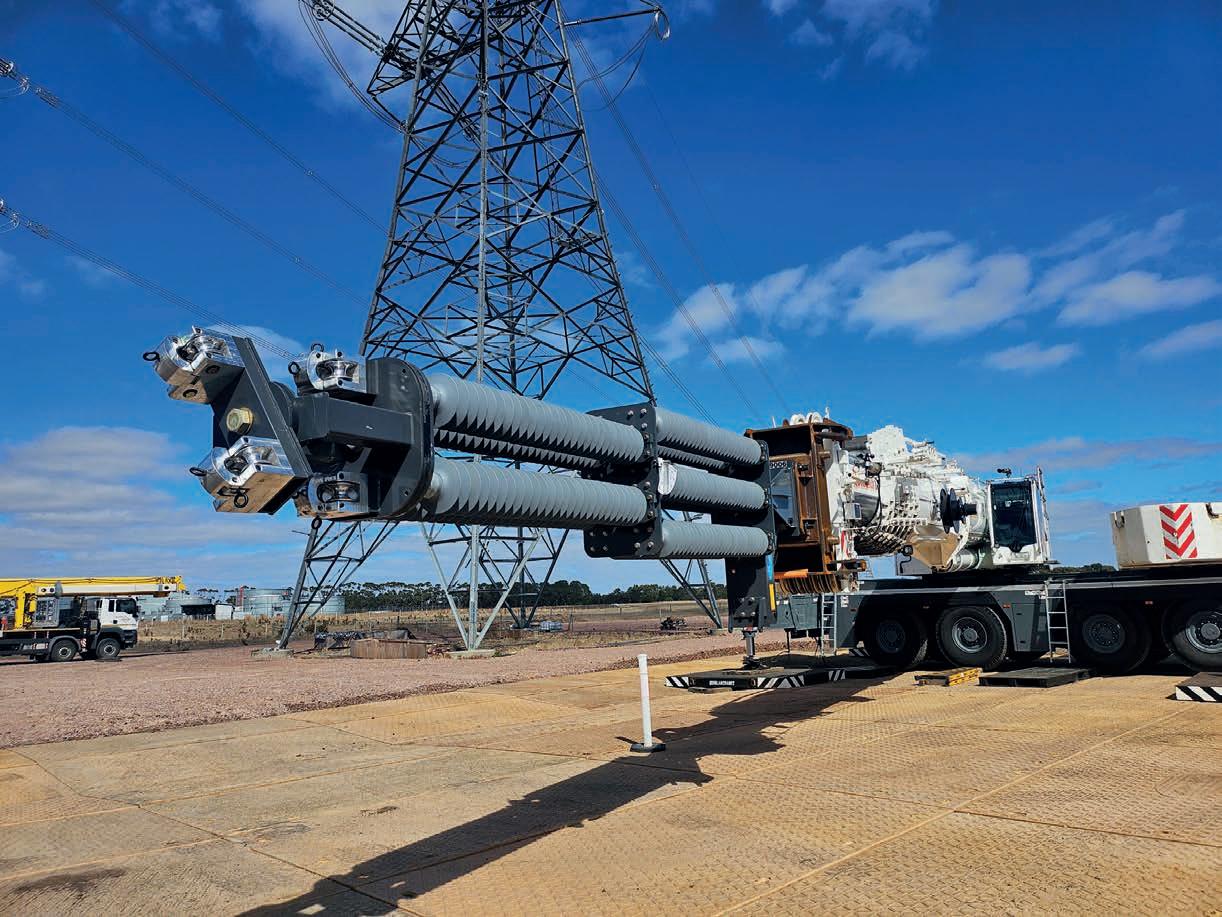
textbook – and Mr Sikka said that the most valuable way to learn is on the job, from those who actually have years of hands-on experience.
“When I was starting out and I made the move to bigger cranes, it’s different once you start lifting things that weigh hundreds of tons,” Mr Sikka said.
“When you lift a piece that weighs 220t before, you learn to go with it a little bit. Our industry is a dangerous industry – it doesn’t matter if it’s 1t or 100t, if it hits you, you’re in a bit of trouble.
“It’s about keeping calm and learning and in those big jobs, you learn to stay calm and collected and in control, which is the key to it all.”
Mr Sikka explained that while the job has a physically demanding aspect – the ability to think quickly and find a solution under pressure is what defines a good crane operator.
“It’s more about your brains. A good operator, or even a good rigger, isn’t the strongest guy – often, it’s a good problem solver.
“Something I noticed early on is that if you can solve a problem, you can go wherever you want in the industry – and it’s a rewarding industry for the guys working in it, but on the same token, they also put in and learn a lot.”
Next level machines
While the crew are well-versed in solving challenges and decades of experience working critical utility projects has given Quinlan Cranes a huge knowledge base to leverage on-site – it’s just as crucial that they’re armed with machines that are tailored to the industry’s needs.
Mr Sikka explained that Quinlan Cranes invested in a brand-new, modern fleet to meet these needs.
“We [specifically] bought cranes to suit the utility
art cranes and our average fleet age would be five years or less,” he said.
“Last year, we bought a new model 110t crane, and we were the first ones to get one in Australia. But we bought it because it was specifically able to carry a lot of counterweight and it had a long boom, which suited highvoltage tower work.
“We also, about three or four years ago, bought the first 230t crane into Australia, [again] it was a new model with a 75m boom – whereas before you needed 300–400t cranes to do that work. Reliability is a big thing, so we try and buy from just one or two the leading manufacturers.”
According to Mr Sikka, flexibility and variety are key.
“We don’t just have one crane to suit the job, we’ll have multiple options with different solutions, depending on the constraints on-site. We’re not just finding a solution we have, we’re finding the best solution – even if we have to go and buy a machine for it,” he said.
“[For example], most of our most cranes run around at 12t per axle, but we’ve got machines that you can strip back to 10t and still run around and we’ve also got machines that have high counterweight carrying capacity.
“Some of the sites we go to, you’re going down fire tracks and things like that, and you can’t get a semi trailer in there. So, these cranes are suited for that sort of work.
“We’ve really thought about the work we do and the cranes we buy.”
Mr Sikka said that his favourite part of the job is seeing people happy at the end,
“At the end of the day, we’re providing a service and a solution to someone’s problem. I know we’re a crane hire company, but for us, it’s about giving people a safe solution to their problem, realistically, and that’s probably what fills my cup.” U
For more information, visit quinlancranes.com.au
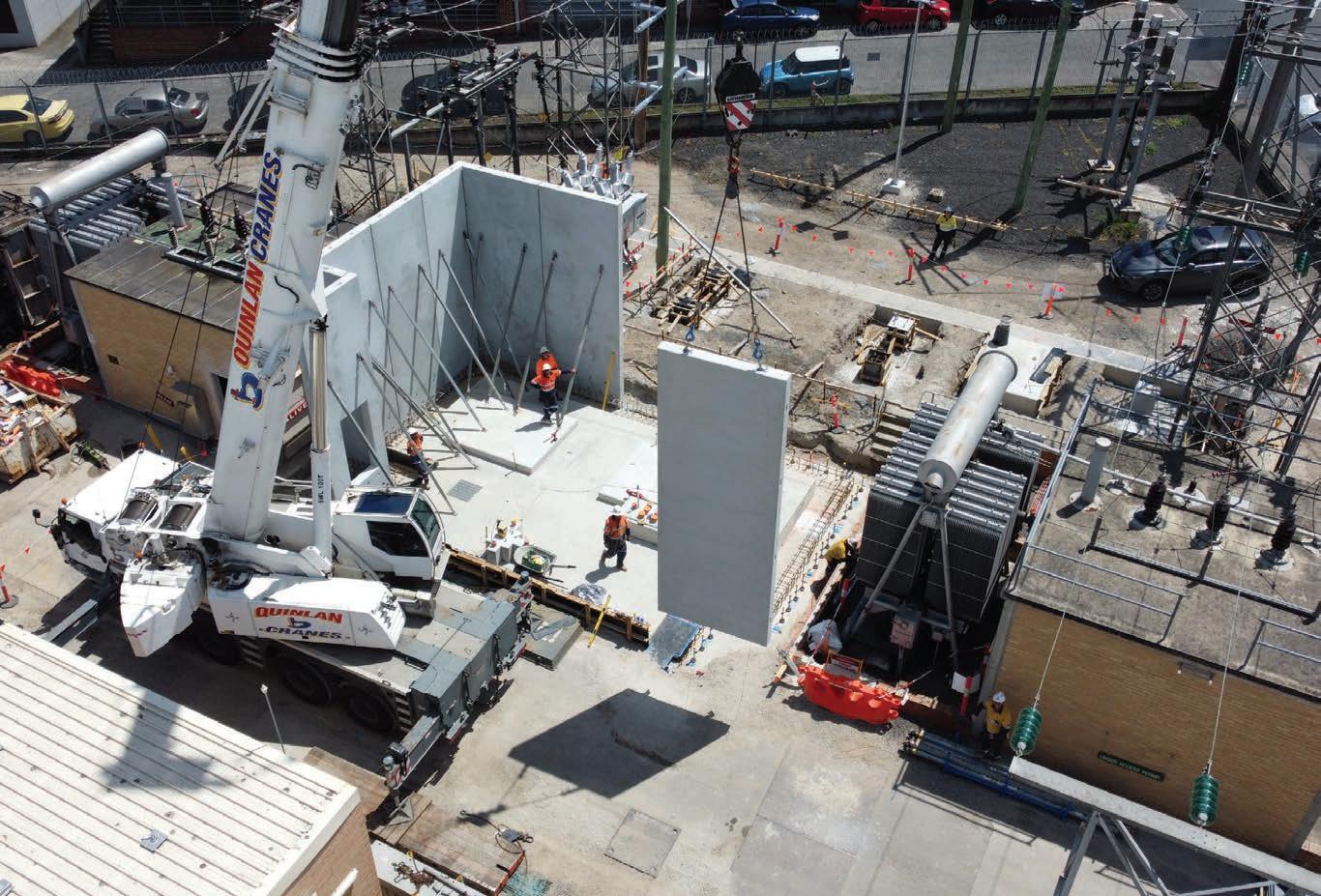

On a recent job, Quinlan Cranes worked with engineering teams to manufacture robot-arm adapters that can bolt to the end of the cranes to do line work.
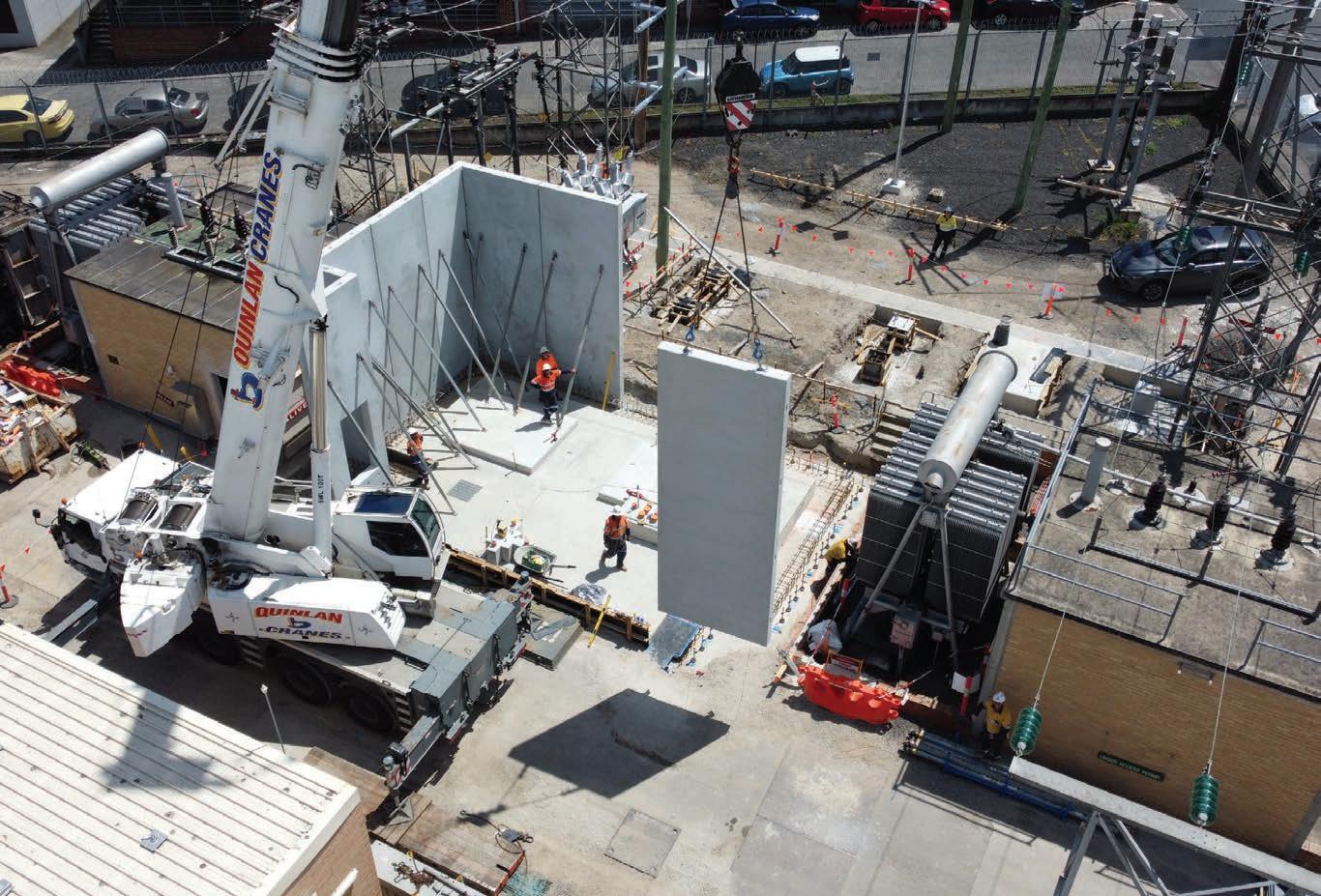

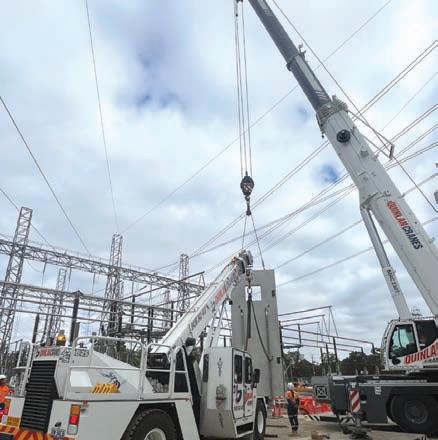
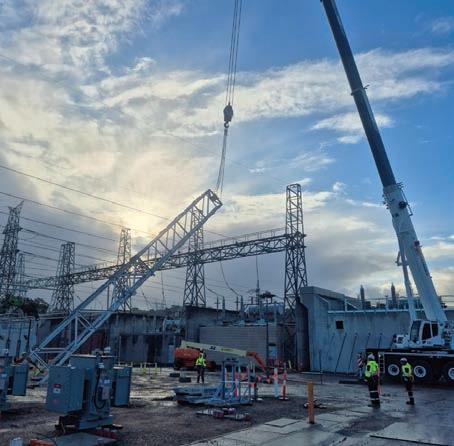
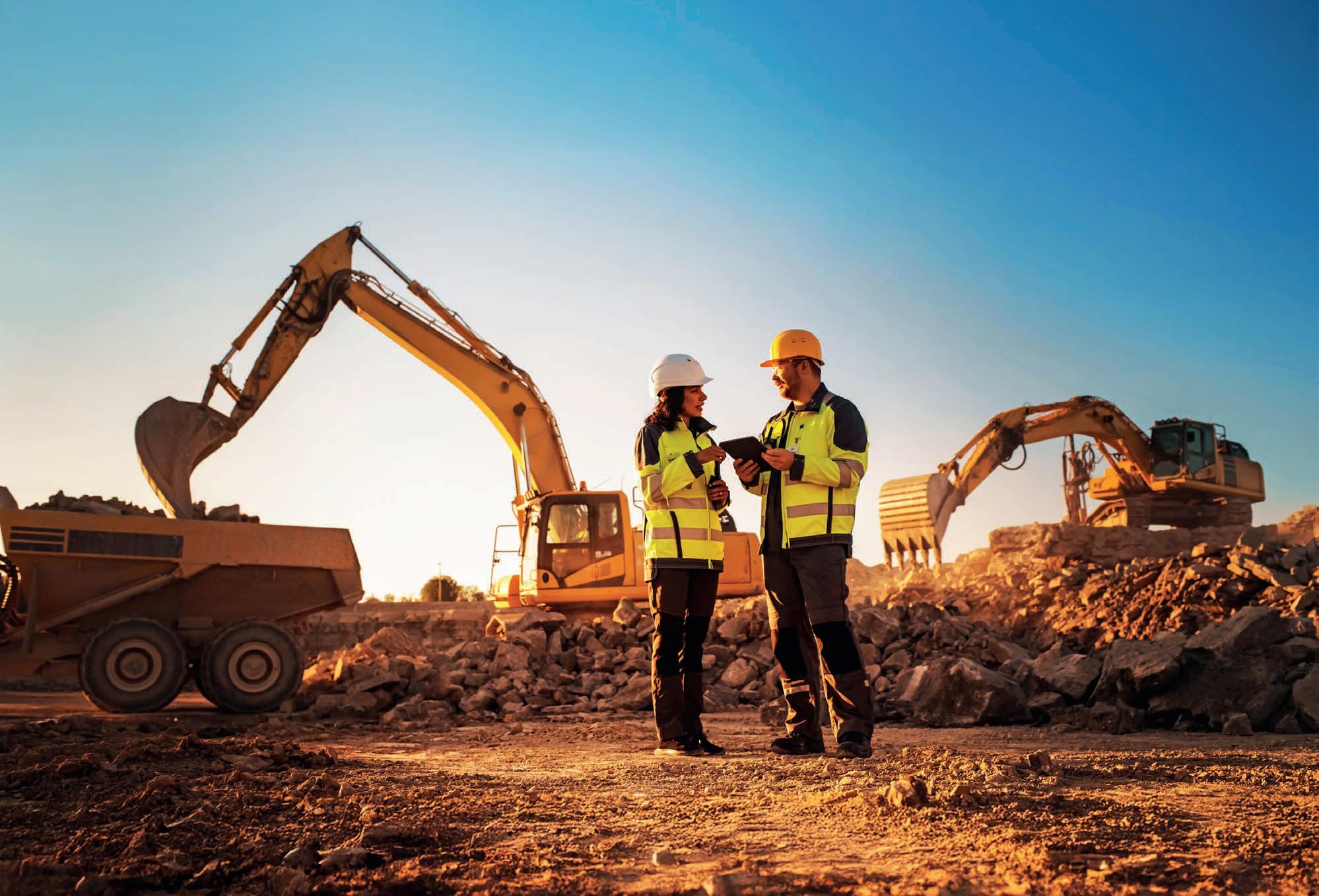
Civil innovation
The race to modernise Australia’s essential services hinges on innovation and collaboration – and Converge is making it happen.
Australia’s municipal works, civil and commercial construction and utility sectors are gearing up for Converge, a landmark event set to unite industry leaders at the Melbourne Convention and Exhibition Centre on 17–18 September 2025.
The inaugural event promises to bring leading decision-makers from these sectors to showcase the latest technology and innovations transforming Australia’s utility industry.
As the only Australian-owned major event in the civil, construction and utility space, Converge will be a one-stop-shop for utility managers and subcontractors.
As an Association Partner for the event, Municipal Works Australia is proud to support Converge in its very first year.
The not-for-profit, member-based association upholds and assists local government employees and companies supplying products and services within the municipal works sector – which is exactly why it is backing Converge.
Municipal Works Australia CEO, Peter Ali, said the event will be a fantastic opportunity for its members to network, discover new tools and technologies and learn from other areas of the infrastructure industry.
Converge is more than just an exhibition – it’s a dynamic space for utility professionals to explore the innovative solutions the industry has to offer, from live demonstrations to equipment showcases, to insightful conferences.
The event will bring the best of all industries together
Converge is the only Australianowned major event in the civil, construction and utility space.
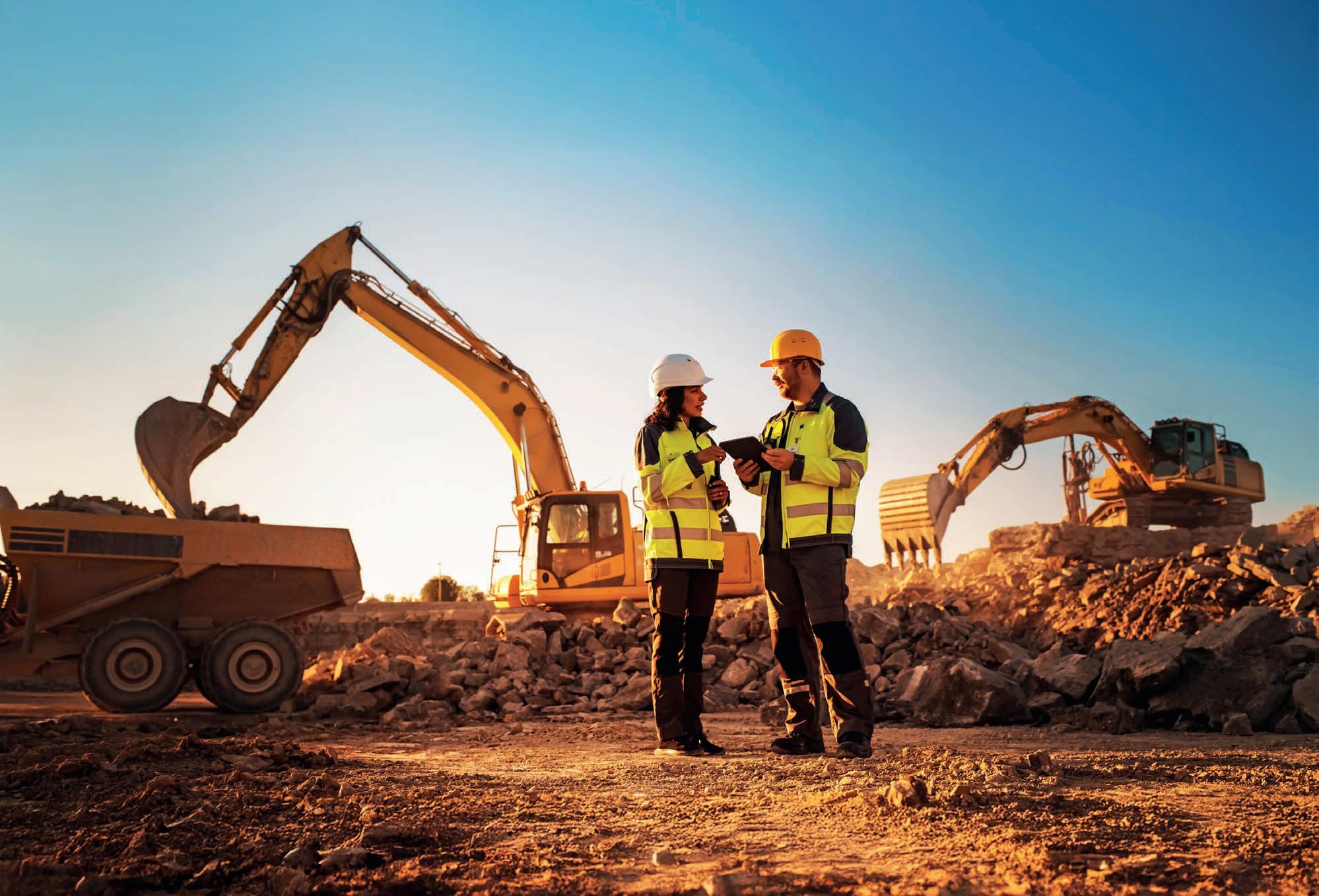
to learn from each other while providing visitors with the solutions they need to build and maintain the essential services of tomorrow.
Mr Ali said a key pain point in the municipal works sector is adopting innovation to achieve community outcomes in an efficient manner and Converge is an exciting opportunity to overcome this hurdle.
“The exhibitors at the event are subject area experts,” he said.
“There will be such a wide variety of innovative solutions on display – I can see our members gaining a lot, interacting with the exhibitors, sharing the issues they’re struggling with and asking questions to find the best solutions.”
This focus on innovation will be a key draw for decision makers sector-wide looking to stay ahead in a continuously evolving industry.
As Mr Ali put it, “Attendees and exhibitors at Converge are at the cutting edge”.
Bringing the municipal, civil and commercial
There
display – I can see our members gaining a lot, interacting with the exhibitors, sharing the issues they’re struggling with and asking questions to find the best solutions.
infrastructure and utility sectors together in one major event like Converge is crucial to sharing innovative technology and solutions across different parts of the utility landscape.
With more than one million decision makers in its orbit, Converge is set to become the go-to event for professionals looking to drive the sector forward. U
For more information, visit convergeexpo.com.au to download the prospectus, or contact the team directly on +61 3 9690 8766 or converge@primecreative.com.au
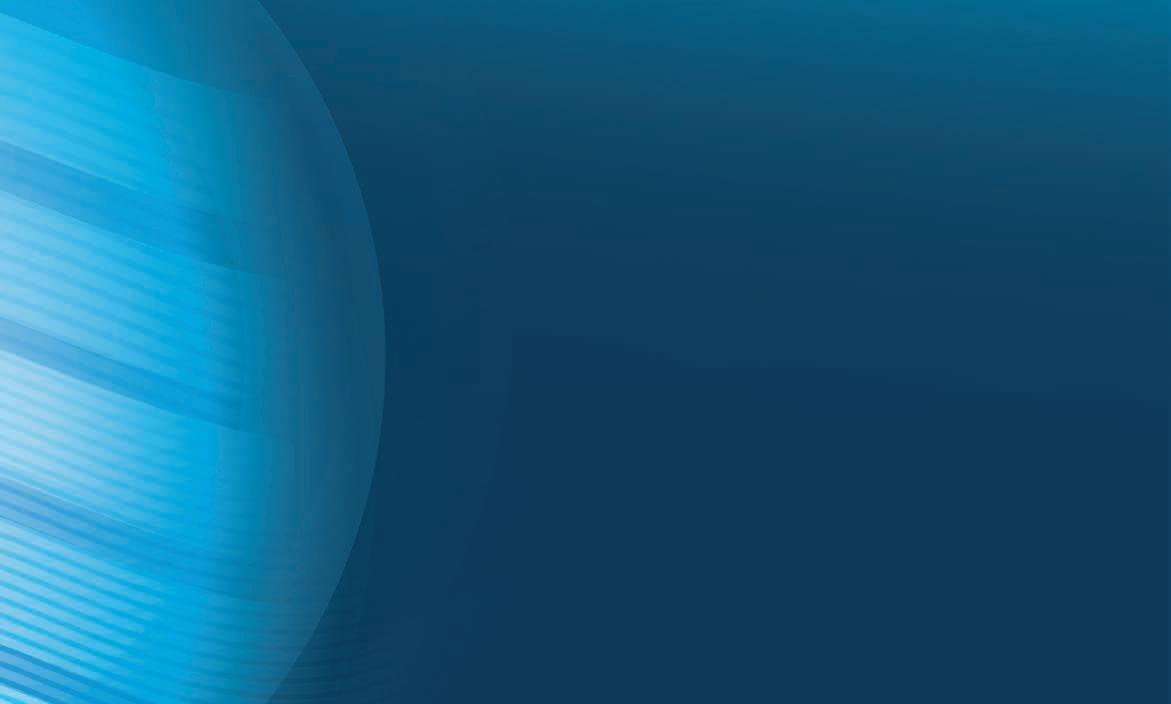

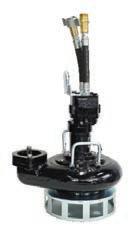
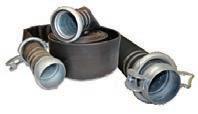
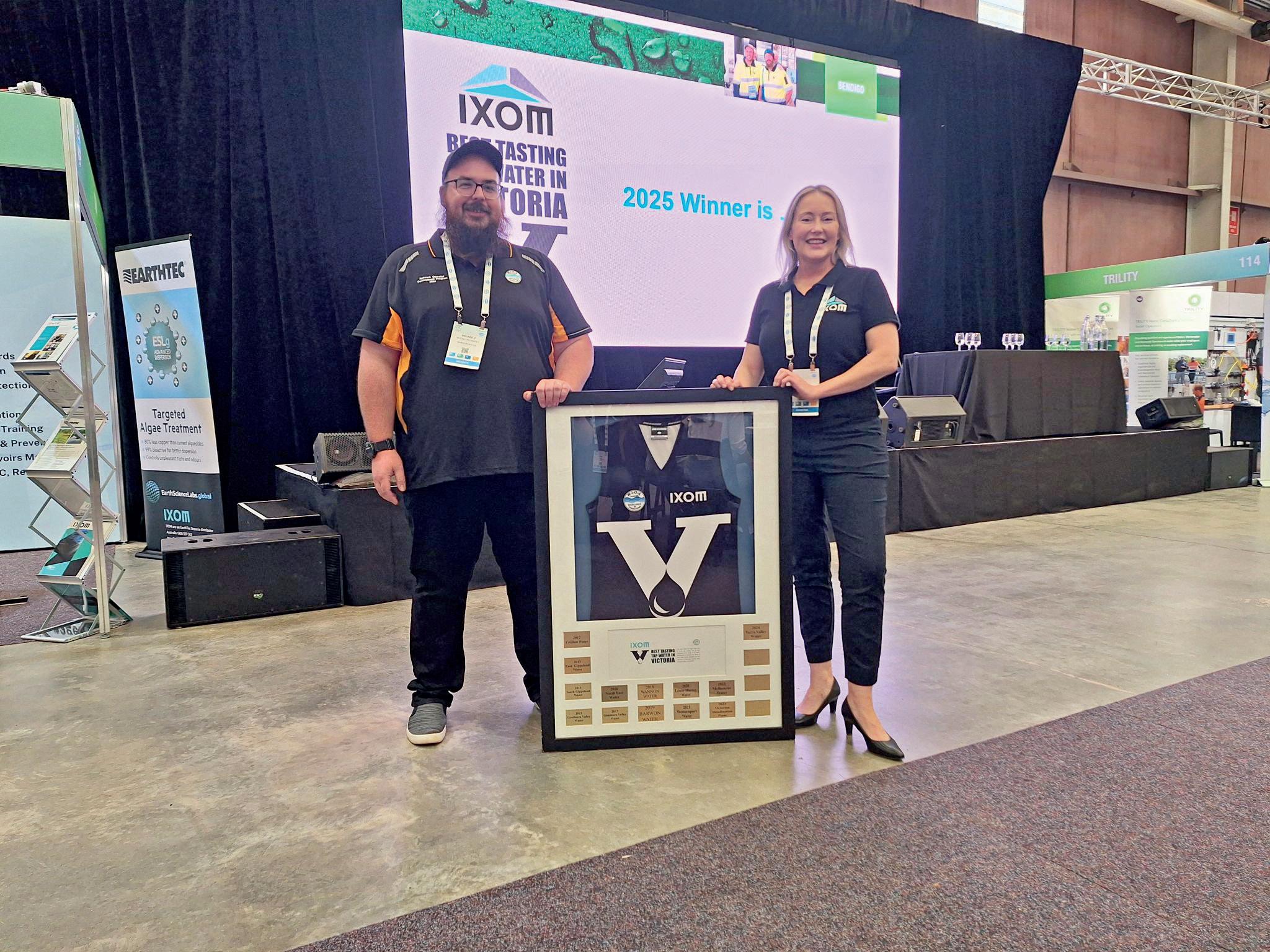
Smooth operator
With a record number of attendees, 2025 Victorian Water Industry Operations conference and exhibition was a roaring success – here’s a few of our highlights from the event.
Every year, the Water Industry Operations Association of Australia (WIOA) holds a series of key industry events – and while excellence is the bar we’ve come to expect, the 2025 Victorian conference just raised the standards a little higher.
From 2–3 April 2025, water industry professionals from all over Australia gathered at the Bendigo Exhibition Centre for the 86th Victorian Water Industry Operations Conference and exhibition. Delegate passes had sold out well ahead of time, and the event recorded the highest number of attendees since 2018.
The two-day event was jam-packed with insightful discussions, outstanding presentations and fierce competitions – and was host to the largest expo in WIOA’s history, with 210 exhibitors.
A ceremony on the final night saw water industry professionals, both old and new, recognised for their outstanding achievements – while Coliban Water, Barwon Water and Central Highlands Water went head-to-head for the coveted title of Victoria’s best tasting tap water.
For those who couldn’t make it, here’s what you missed.
Speak now
With more than 20 operations-focused presentations and posters, as well as an inspiring keynote from the Centre for Optimism, picking just one favourite is a tough call.
Each speaker offered valuable insights into industry trends and challenges, covering everything from emergency management and enhanced treatment processes to odour management, diversity and inclusion – as well as some industry-leading discussions around supporting the next generation of operators.
But, when it came to the crunch there were two standout presentations that earned themselves an award for their efforts.
A duo from Albury City Council, Zhofi Boglari and Adam Carty, won the Best Operator Paper award for their presentation, Leading with fresh eyes, while E M Fluid’s Dr Kruti Shulka and Thermofisher’s Richard Durand teamed up to deliver the ‘Best Paper Overall’ – A SolarPowered EMF Aeration Technology to Enhance Sludge Digestion and Improve Effluent Quality for Water and Wastewater Management.
Barwon Water Operator, Dalkeith Hanley, being presented with the award for the IXOM Best-Tasting Tap Water in Victoria competition.
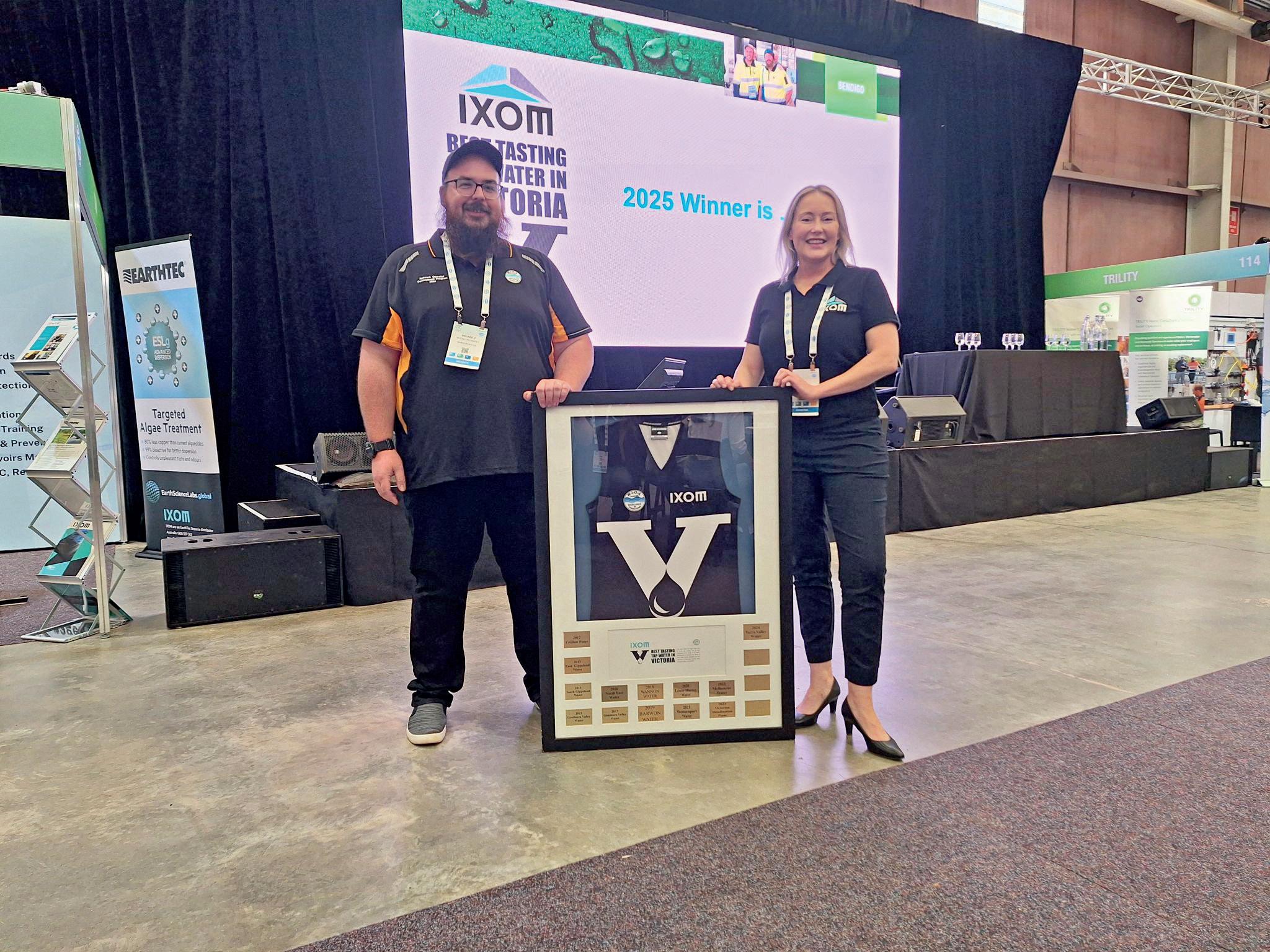
While they may not be taking home a shiny new award, some of the other highlights the Utility team enjoyed were:
• Improving operational response to water quality emergencies – Yarra Valley Water
• Working as One – Adaptive Management of Sydney Taste & Odour Event – Sydney Water
• L anders Shute WTP Raw water main drain, repair and refill –Seqwater
• Improving oxygen delivery in aerobic wastewater treatment and promoting the growth of nitrifiers using nanobubbles –Greater Western Water
• Investing in the Next Generation of Water Industry Experts – Coliban Water
The best of the best
The IXOM Best Tasting Tap Water competition is arguably one of the most exciting parts of any WIOA event, and this year didn’t disappoint.
After an intense round of eliminations, the only three left standing were Coliban Water Trentham Water Treatment Plant (WTP), Barwon Water’s Lorne WTP, and Central Highlands Water’s Lal Lal WTP.
These three were then put to the real test, and a panel of expert judges cast their vote on which one would be crowned Victoria’s best tasting tap water.
It was a close call, but ultimately Barwon Water clinched the win, claiming the 2025 title and earning bragging rights for the next 12 months.
Barwon Water will now go on to battle it out against other states for the national best-tasting tap water title later in 2025.
However, this was only the beginning of a string of accolades for Barwon Water, and the utility not only bested all other teams at the Water Main Tapping competition, but one of its team members, Dalkeith Hanley, went home with the 2025 Young Operator of the Year Award.
The awards dinner was a fantastic conclusion to the event, which celebrated some exceptional people and the important work they do in the water industry.
Joining Mr Hanley up on stage, Melbourne Water’s Kirsty Fudge was named Network Operator of the Year, while South East Water’s Ben Evans claimed the coveted Victorian Operator of the Year title – an award well-deserved for his decades of outstanding service.
Empowering the next generation
The event also celebrated the graduates from the 2024 Network Operator Development Program and honoured the dedication of some of WIOA’s longstanding members.
The Network Operator Development Program was established in 2017 to identify, mentor and nurture future industry leaders.
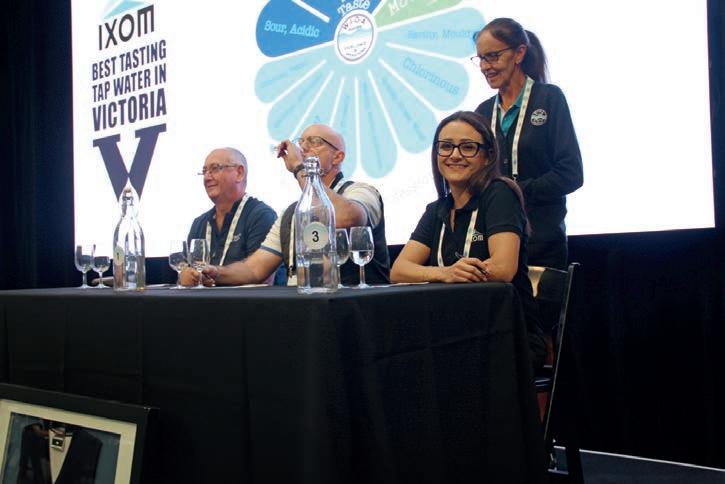
This Victorian- and New South Wales-only program aims to expand the knowledge, skills and practical experience of network operators; it also helps them grow their network and encourages strategic thinking and best practice initiatives in technology, business management, and leadership. Over eight months, participants undertake one training session per month, which include workshops, field days, technical sessions, conference and projects. As part of the program, the Advisory Committee selects one participant to win the WIOA Network Operator of the Year award – and as the 2025 recipient Ms Fudge will receive sponsorship from Water Training Australia and is invited to participate in a technical paper or poster presentation at the next annual conference.
The Advisory Committee plays an instrumental role in mentoring and empowering this next generation of leaders, and the 2024 members were:
• Mick Mahoney – Wannon Water
• Mike Rankin – Water Training Australia
• Neville Whittaker – Gouburn Valley Water
• Grant Powell – Greater Western Water
• Michael Wink – Gippsland Water
• Adam Carty – Albury City Council
• Mathew Leehane – Central Highlands Water
• Glenn Alford – WIOA
At the event’s opening reception, WIOA Board Chair, Mat Greskie acknowledged both the incredible efforts of the Advisory Committee, as well as the outstanding achievements of the participants themselves.
“This is an enourmous investment in your future and your career, and thank you for your commitment to development,” Mr Greskie said.
“And to everyone in the water industry, thank you for what you do. I know we tend to very modest, but now’s not the time to be modest – put that aside and be proud of what you do.”
WIOA CEO, Dean Barnett also highlighted the value the program has for both its participants and the industry.
“The most rewarding part for me, watching this timid group on day one, [who by the end] are confident and really shining in their roles,” Mr Barnett said.
The judges cast their votes on Victoria’s best-tasting tap water.
Images: Prime Creative Media
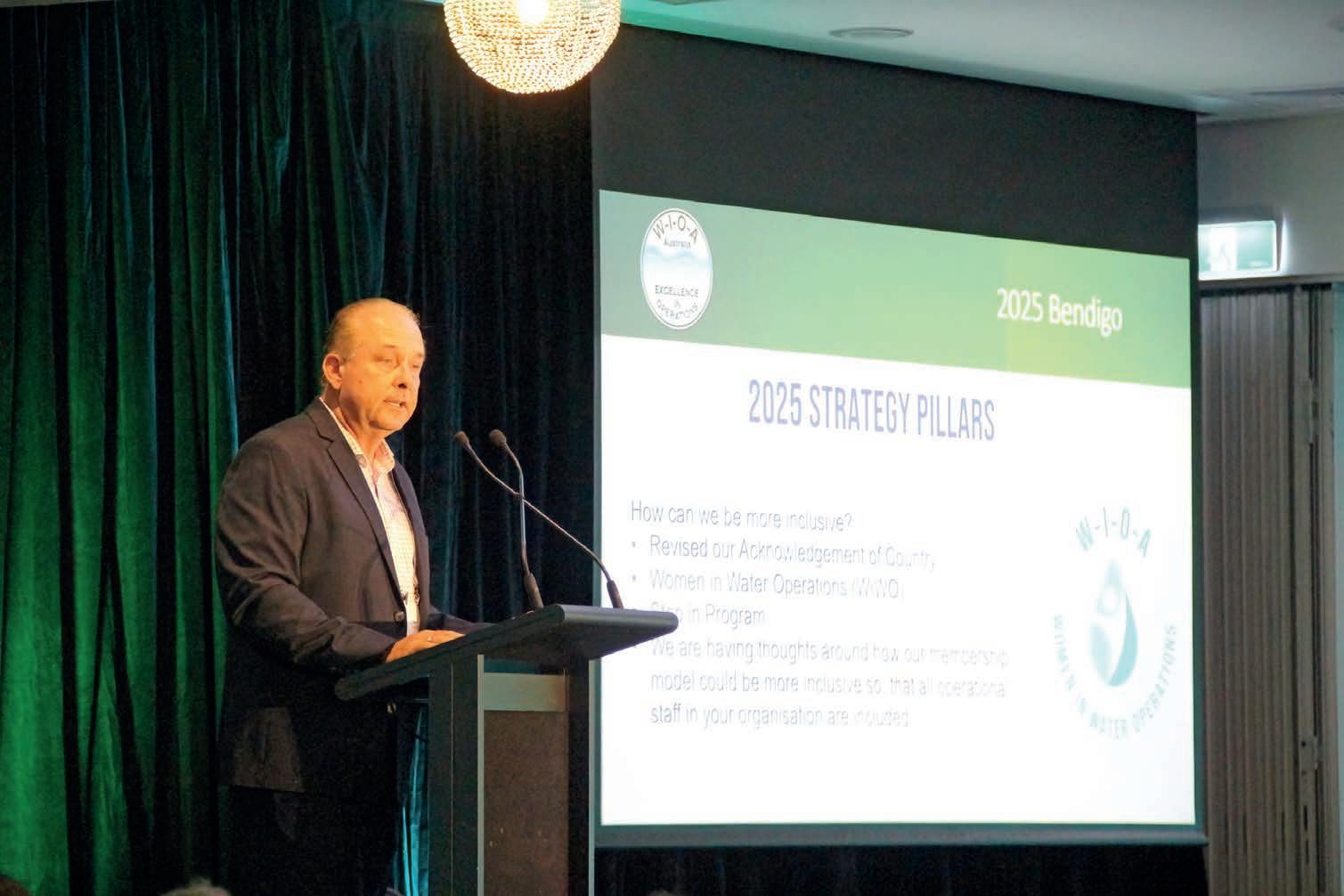
“You only get what you put in, and what you got out of the 2024 program is a testament to your [hard work].”
The event also celebrated the legacy of two longstanding directors, who are now retiring from the WIOA Board.
WIOA Life Member, John Harris, is a past Chair of the WIOA Board has been a part of the association for 31 years.
Mr Greskie acknowledged Mr Harris’ outstanding 45
“Being a Director on the WIOA Board in incredibly rewarding, but also a huge investment. As we say farewell to two long-standing solid directors, I would like to thank John for his 30 years of service, during which he really helped me to transition into the Chair role,” he said.
Ron Bergmeier has also stepped down from the Board, and his incredible 40 years of service did not go unnoticed.
“Ron is a dear friend and mentor as well as a brilliant and successful [Director] and I don’t think you’ll find a more intelligent or more eloquent Director in the country,”
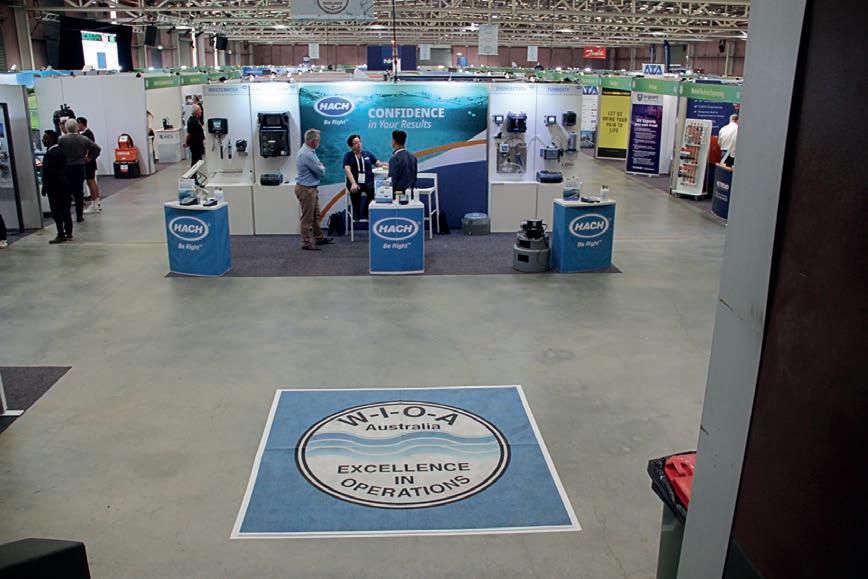
While a position on the WIOA Board might be a huge investment, for Mr Bergmeier it was a pleasure.
“I’ve been here a long while, but it hasn’t really been a job, I did what I wanted to do, and what had to be done. It’s been a huge journey, and the benefit for me has been to see the personal improvement of our operators,” he said,
“The development I’ve seen in people has been a huge catalyst for what they’ve achieved. I’ve had a ball and it’s been an absolute pleasure, thank you.” U
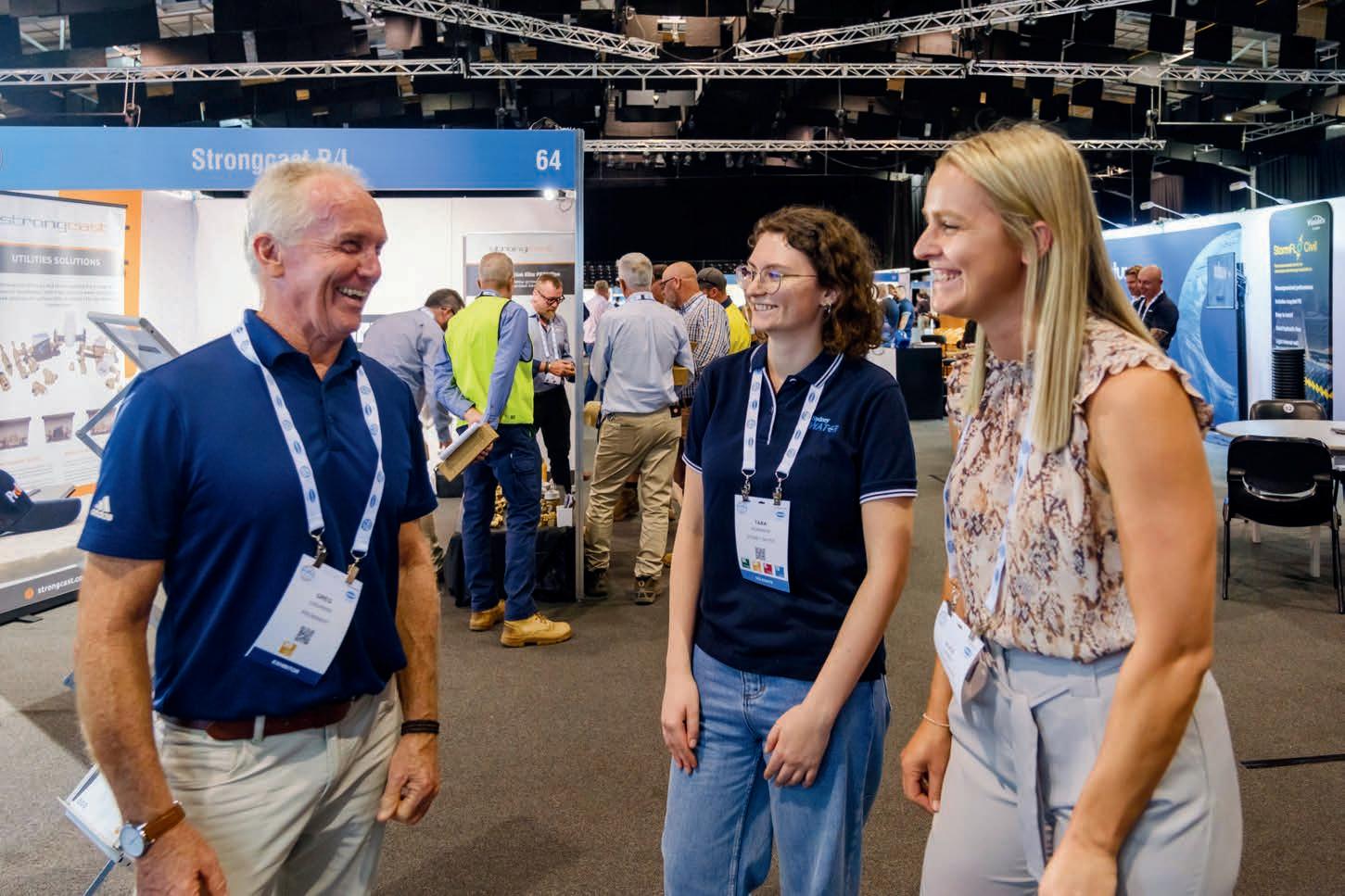
Although the Victorian event may have come to a close, there’s no rest for WIOA as the association gears up to do it all again in New South Wales.
This Newcastle event kicks off from 23–24 July 2025, with new additions to the program, updated menus and a new location – it’s shaping up to be bigger and better than ever. Will we see you there?
WIOA CEO, Dean Barnett, acknowledges the industry’s best and brightest at the awards gala.
The 2025 Victoria Water Industry Operations conference had a record number of exhibitors on the floor.
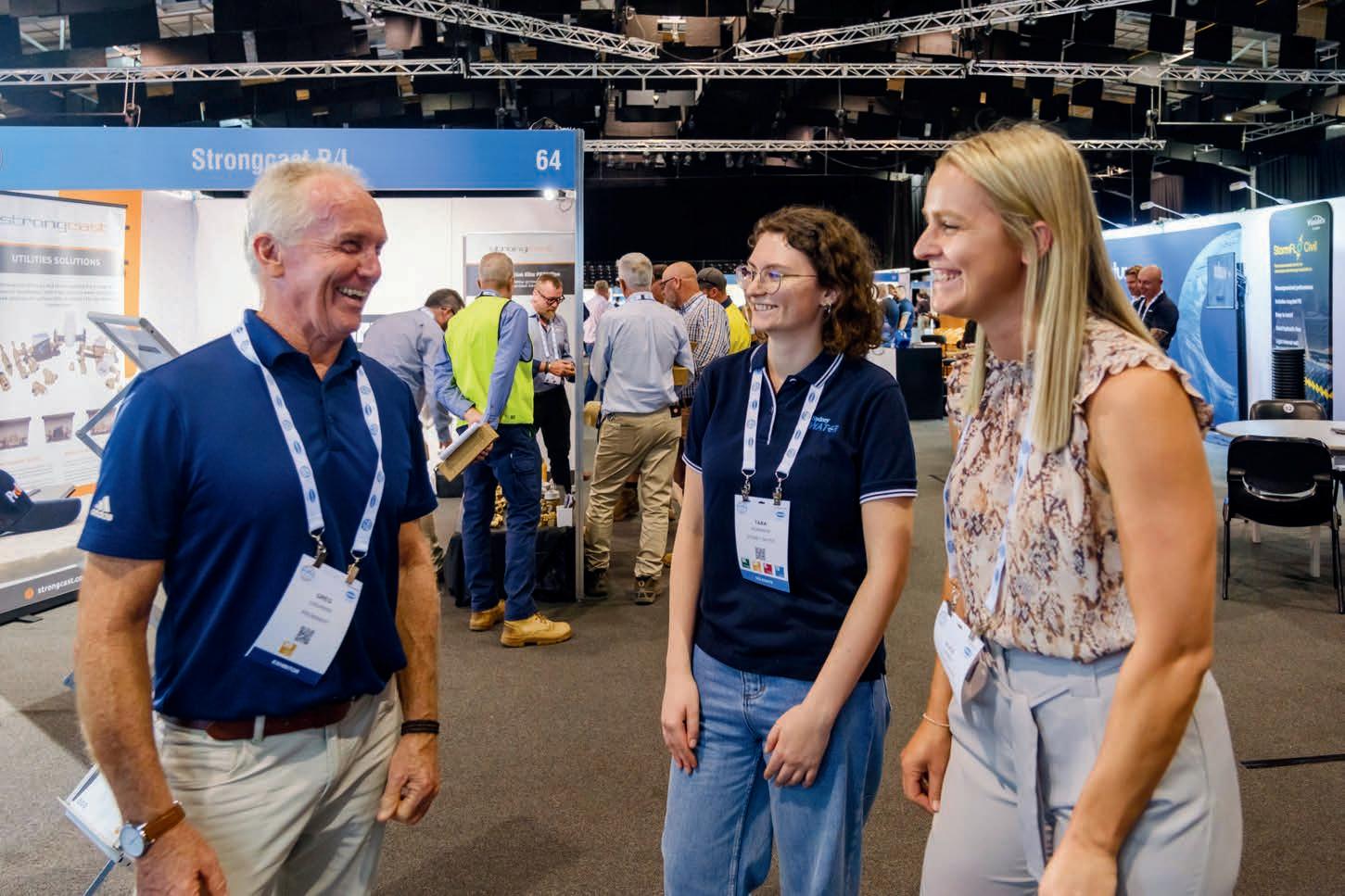
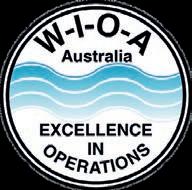
2025 New South Wales Water Industry Operations Conference & ExhibitioN
23 & 24 July 2025 | Newcastle NSW
Get ready for the ultimate gathering of water industry operations professionals in Newcastle! Join us for a day filled with insightful discussions, networking opportunities, exciting exhibitions, Women of Water Breakfast, IXOM Best Tasting Tap Water Competition, Reece Civil + Viadux Main Tapping Competition and more. Whether you're a seasoned pro or just starting out in the Water industry, this event is perfect for expanding your knowledge and connecting with like-minded individuals.
Get involved
Become a WIOA Member
Call for Papers & Posters - Now open
Exhibitor BookingEnquire within Award SubmissionsNominate today

An operator you can count on
A success story three-decades in the making, South East Water’s
Ben Evans has been named winner of the 46th annual Water Industry Operations Association Victorian Operator of the Year award.
Driving down the highway in his Ford Ranger, heading back to Port Fairy for the weekend, Water Recycling Plant Lead Operator Ben Evans is a stickler for the blues.
The Rolling Stones and Tom Petty provide the soundtrack for his commute, a time of reflection after another week ensuring our water recycling plants run safely and smoothly.
“How did the week go? What could be done differently?”
These are some of the thoughts that swirl in Mr Evans’ mind as he rides the rhythm home. Despite racking up a laundry list of achievements over the past three-and-a-half decades, he remains focused on improvement.
It’s a long trip – one that would test the mettle of even a seasoned truckie — but Mr Evans is unphased by it, he said the drive is “all good fun”.
This easy-going demeanour is just one of the many qualities that earned Mr Evans the prestigious accolade of Water Industry Operations Association’s Victorian Operator of the Year for 2025, rising above a field of exceptional candidates from water corporations across the state.
“I was very humbled and surprised on the win and eel very honoured,” Mr Evans said.
Ben Evans at the WIOA Victorian awards with South East Water Managing Director, Lara Olsen.
Images: South East Water

“I would like to thank my Westernport Team and the Peninsula Team but also the great support we receive from Carolyn Madden, our Tech Support and Works and Services Team.
“It’s really a combined effort by all to keep these plants running smoothly with minimal issues.”
South East Water Managing Director, Lara Olsen said Mr Evan’s recognition is a proud moment for the organisation.
“Ben embodies everything that’s great about our organisation and our industry – reliability, teamwork and a deep sense of responsibility in delivering for our customers and community,” Ms Olsen said.
“He’s a mentor to many, a steady hand in a difficult situation, and a highly respected leader at South EastWater. This award is a fitting recognition of his dedication and contribution over nearly
I was very humbled and surprised on the win and feel very honoured. I would like
to thank my Westernport Team and the Peninsula Team but also the great support we receive from Carolyn Madden, our Tech Support and Works and Services Team.
Leading by example
Although Mr Evans has spent his entire career with South East Water, his service predates the organisation itself. He started his traineeship in 1988 under the Pakenham Water Board, which amalgamated into South East Water in 1995.
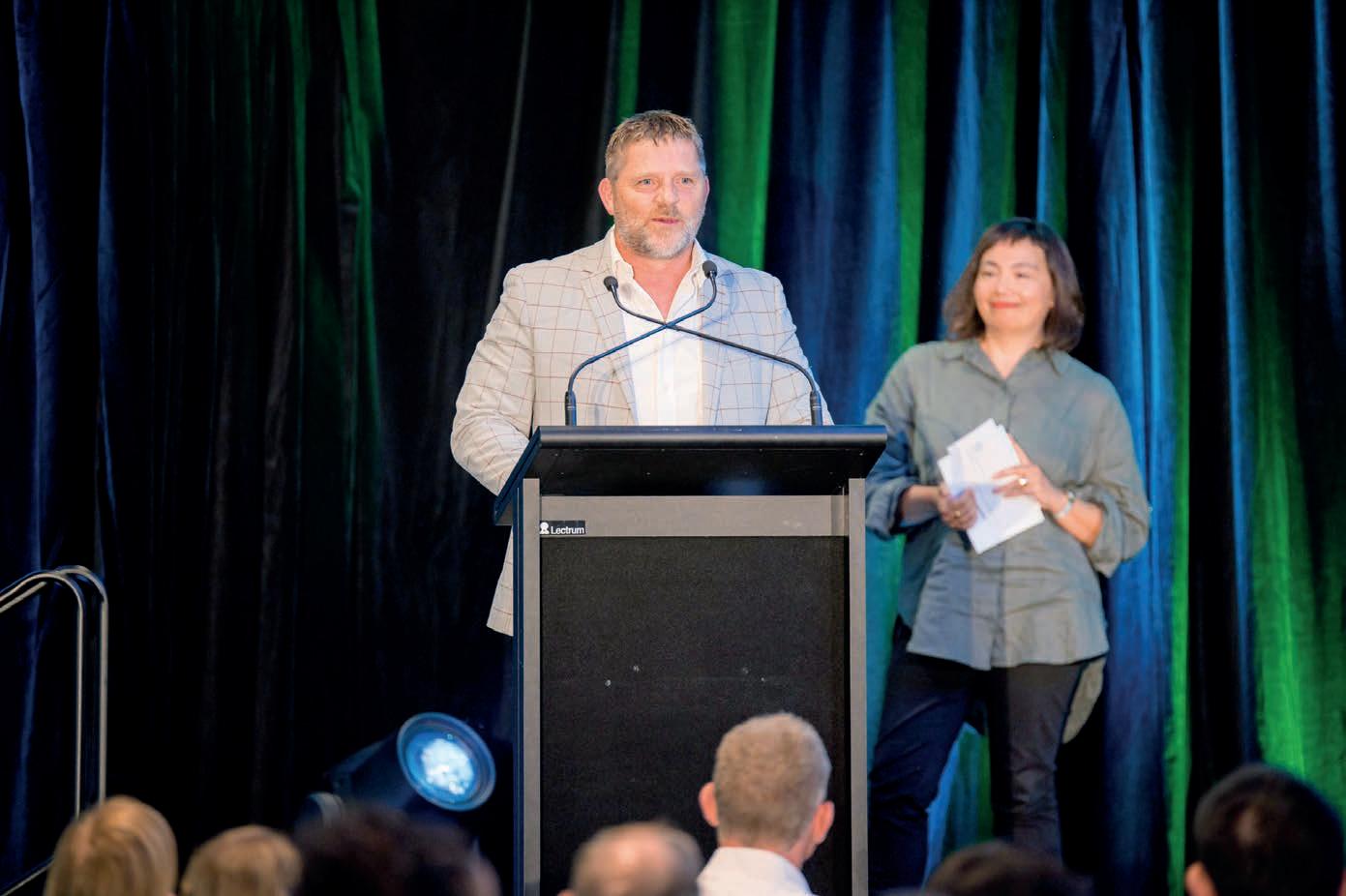
Mr Evan’s tenure with South East Water predates the utility itself.
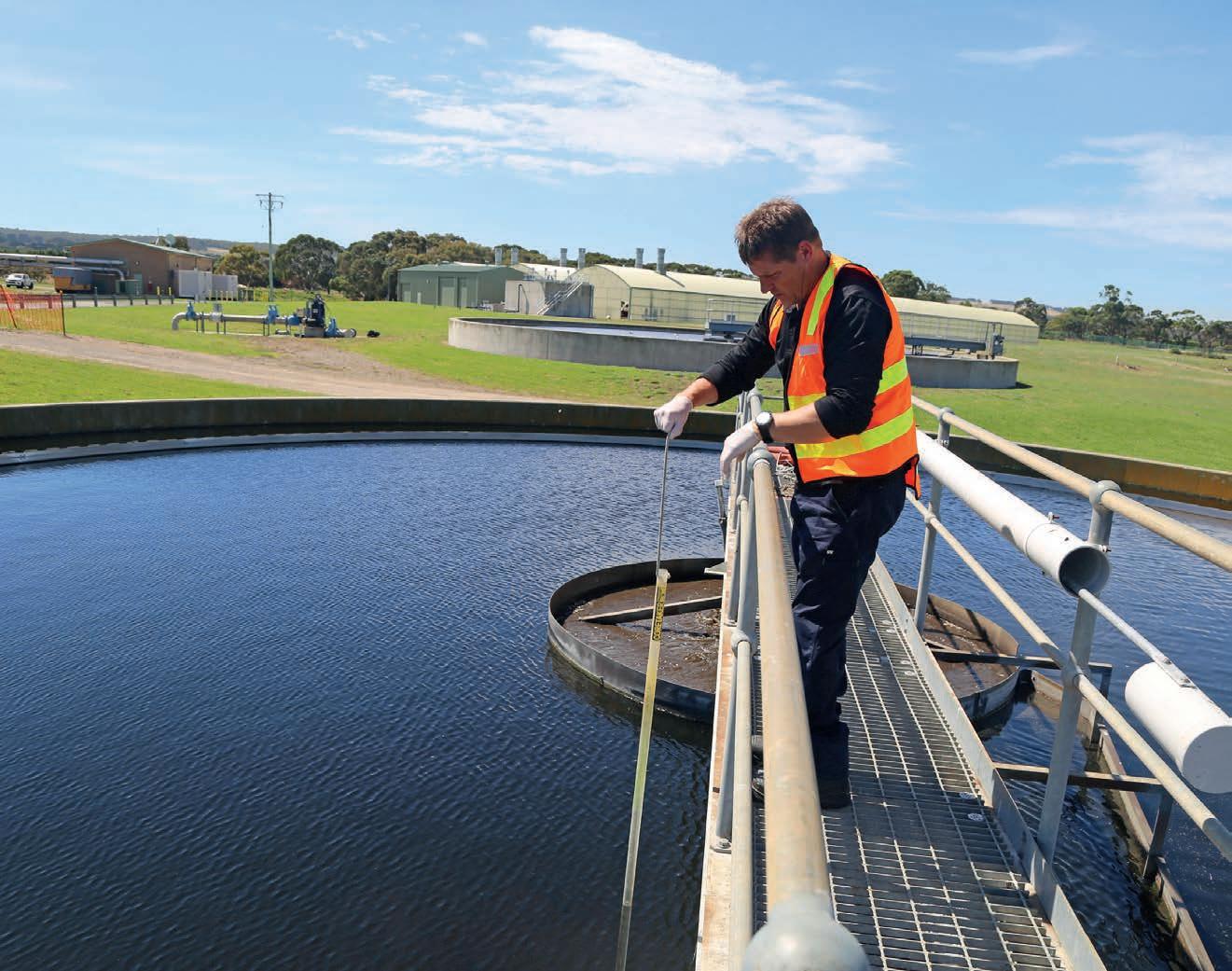
His career trajectory, from trainee to Western Port Lead Operator overseeing six water recycling plants today, highlights his extensive industry knowledge, leadership prowess and unwavering commitment. That commitment is reflected not just in his many accomplishments and 37 years of service, but even in the way he structures his life – renting in Officer during the week to be close to his Pakenham plant base, before making that four-hour drive home to his family on a Friday night.
A walking encyclopaedia of South East Water’s history and operations, Mr Evans keeps optimising the utility’s operations by diarising incidents, processes, and procedures spanning decades – resources often turned to in times of need. If there’s a challenge on site, chances are Ben has seen something similar before – and he’s got the records to prove it.
Mr Evans takes a practical approach to innovation – and thanks to his impressive track record of improving plant processes, the scope of his current role was expanded to help plan for and provide feedback on South East Water’s future recycling plant projects.
Over his career, Mr Evan has been the driving force behind several key innovations to, including bypassing the blind bight effluent holding basin to allow for liner replacement and cleaning operations, ensuring the system remains functional while undergoing essential maintenance.
sludge pans, issuing an alarm once the target is met to prevent overfilling.
Another of his successful initiatives involved automating lagoon diversions by integrating automated valves, ensuring seamless transitions between sources without manual intervention.
Additionally, his plant optimisation strategies for nitrate and ammonia control have significantly improved performance while maintaining compliance with environmental standards.
His leadership isn’t about titles or qualifications –though he’s certainly racked up his fair share, undertaking between 40 and 50 courses throughout his career, from a Certificate III in Water Industry Operations and a Certificate IV in Frontline Management to specialist fields such as algae control, laboratory training, biological nutrient removal.
For Mr Evans, his focus is people. He says a strong team fit outweighs a list of degrees. He fosters a culture of camaraderie, often bringing the team together over a bonding barbecue.
But perhaps his greatest quality is his presence in a crisis. The cool, calm and collected leader is the first to step up when things go wrong – even when it’s not his responsibility. His mantra? “Stop, breathe, don’t panic”.
It’s an approach that has guided many through challenging situations.
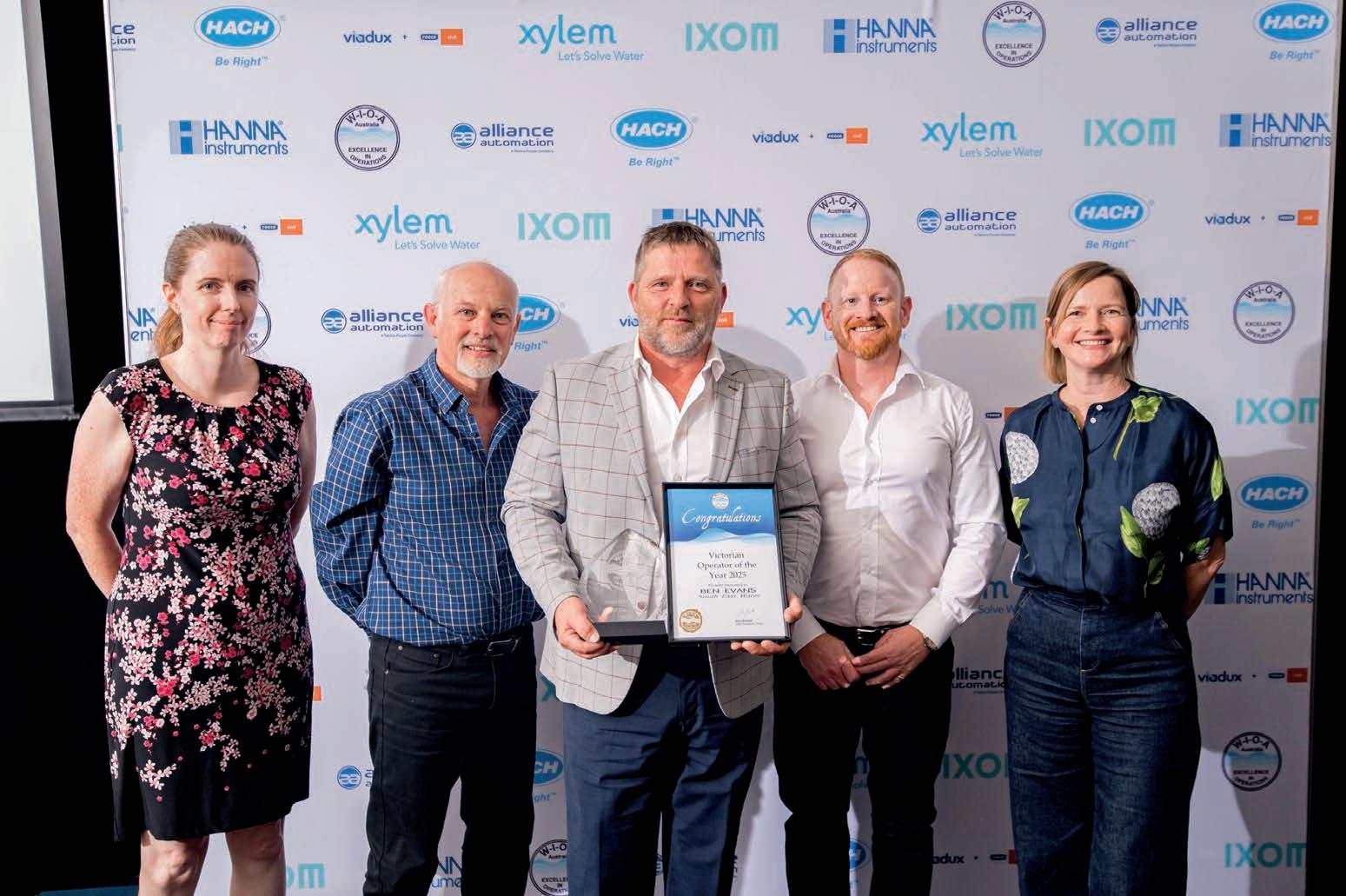
Mr Evans began his traineeship with South East Water in 1988 and has been a steady hand through decades of change.
Nothing is ever too much trouble for Mr Evans. He’s the first to roll up his sleeves, the go-to person for isolating assets safely before work can be done, and the calm presence when things don’t go as planned.
When a pump fails, it’s Mr Evans who ensures it’s taken offline safely and efficiently, minimising disruption while keeping his team and contractors safe. It’s this steady approach that has seen him through some of the toughest moments in his career. One night, at 2am, a plant was spilling, and then the generator failed. Mr Evans went to check the creek levels, only to find himself stuck as floodwaters closed in on the switch room. He managed to navigate the situation safely, a testament to his experience
could be pulling poo out of a hopper,” he said.
It’s this diversity – and the people he works with – that keeps him coming back every day, still as passionate as ever. As he makes that trek home on a Friday, the music playing and an open road ahead, Mr Evans reflects on another week well spent. He wouldn’t have it any other way.
Whether guiding new recruits, optimising treatment processes, or stepping in to manage unforeseen challenges, Mr Evans has proven time and again that he is a pillar of the industry. His unwavering commitment to excellence makes him a deserving winner of the WIOA Operator of the Year Award, which was announced at the WIOA Awards Dinner in Bendigo on Thursday 3 April 2025. In addition to the prestige and recognition of being named the award winner, he will also receive a professional development prize of an all-expenses paid trip to an overseas water conference. U
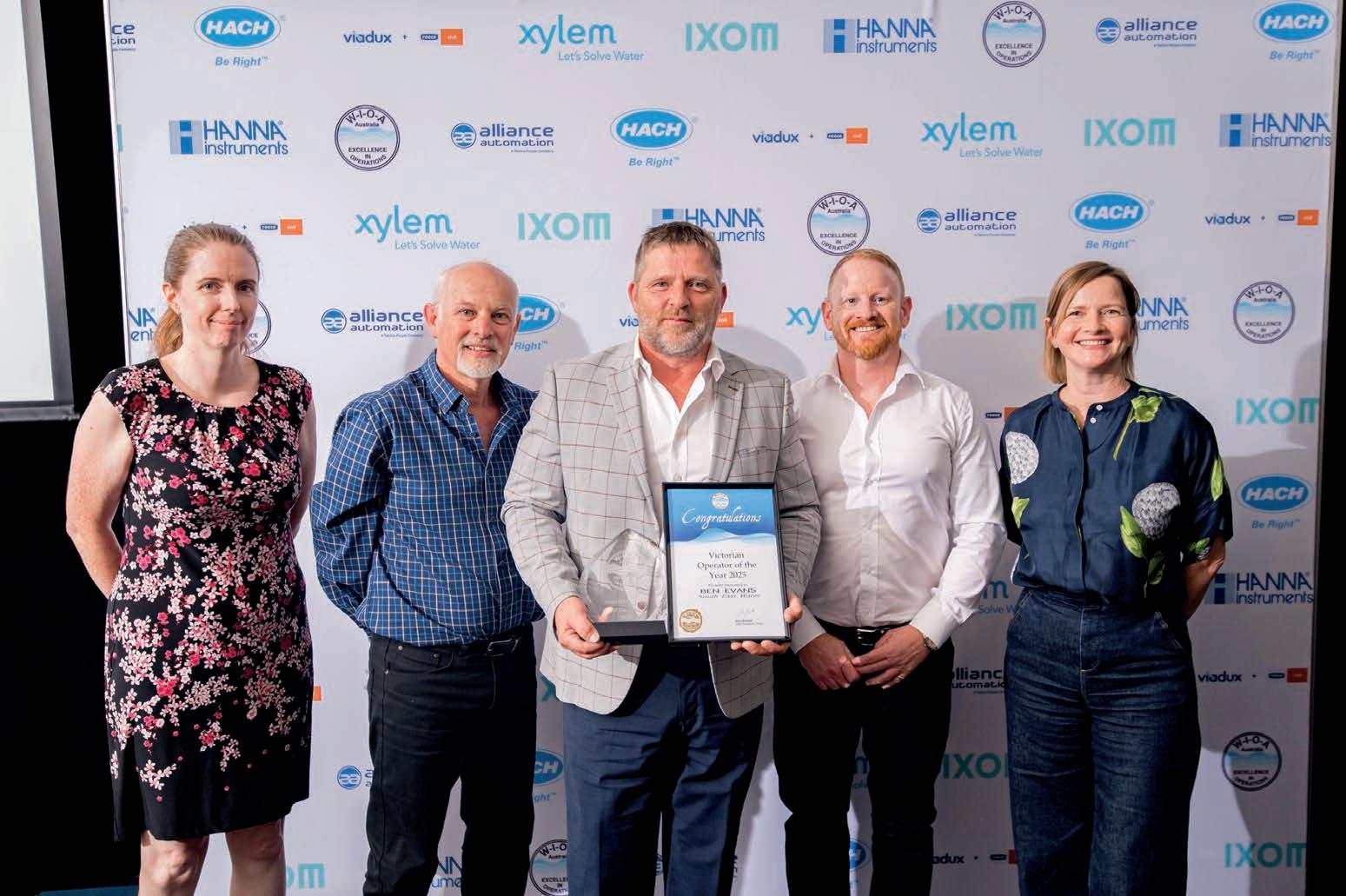
Mr Evans and team at the 2025 WIOA Bendigo Conference and Exhibition.
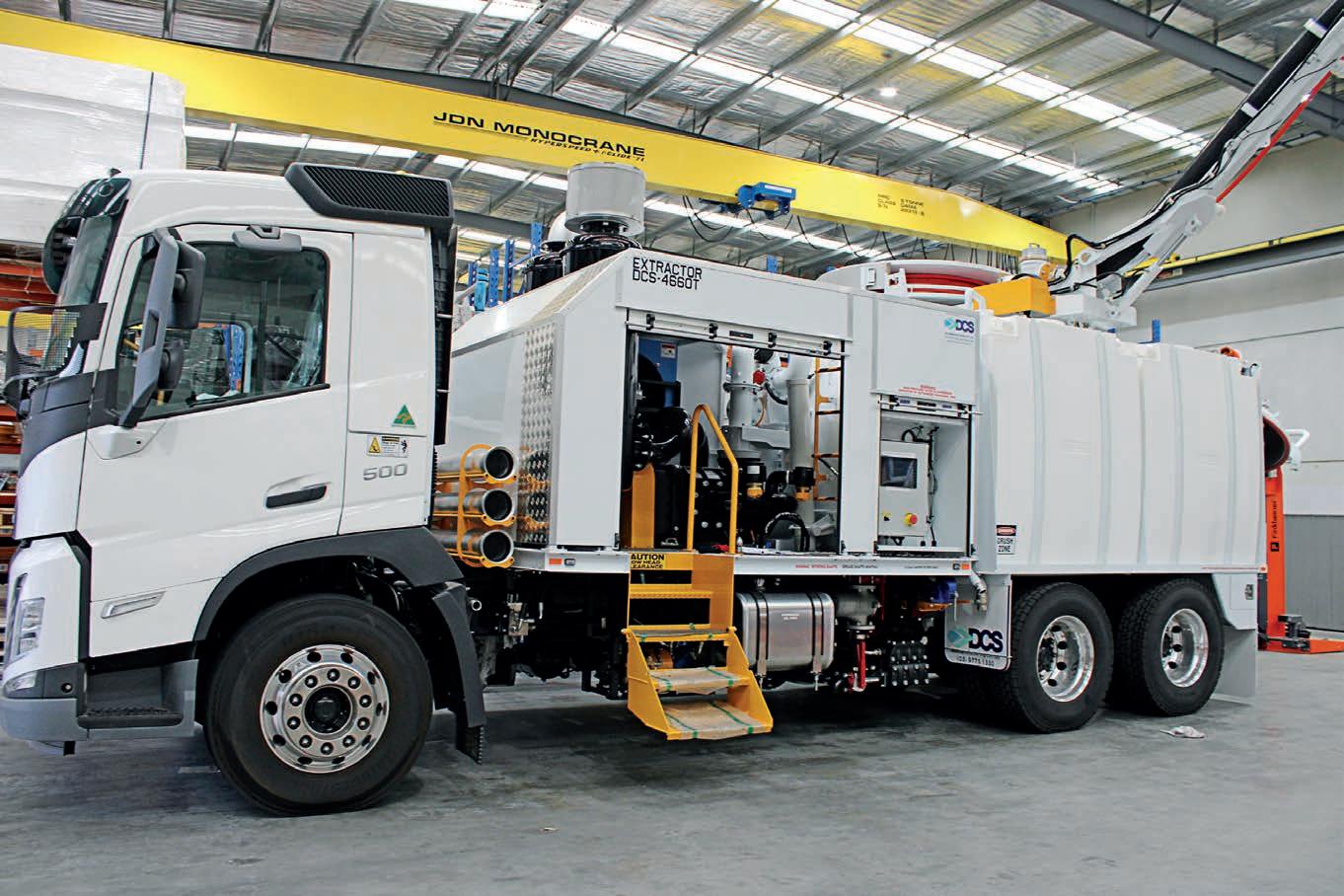
Taking care of maintenance
Stormwater and sewer asset owners often have to maintain many different types of networks, but the optimal equipment for one material might not meet the unique requirements of another.
Without regular maintenance, stormwater pipelines and sewer networks are prime locations for disaster.
Unchecked tree roots, fatbergs, waste and debris can quickly take hold, causing dangerous blockages, network disruptions as well as health and environmental hazards.
To keep communities safe, utilities work around the clock to clean and maintain these assets, but not only do they often need to cover a huge area, they also have to contend with a variety of different asset types.
DCS Regional Sales Manager, Michael Donaldson, explained that one of the key challenges is working with a plethora of different pipeline materials.
“Way back in the in the heyday we used clay pipes for absolutely everything, but now you’ve got polyethylene pipes right through to concrete and metal – and each of those comes with its own unique challenges,” Mr Donaldson said.
“[For example] clay pipes will shatter based on movements in the earth, heat and other environmental factors, but you’ll often find, for instance, there’s 200m of clay and then you start with concrete.
“So, you have to account for both of those [materials].”
Mr Donaldson said that while a lot of ‘off-the-shelf’ maintenance equipment like jetters or cutters can be used for all applications, you’re not always going to get the best or the fastest results – and in some cases you can risk seriously damaging your assets.
“Once you start moving towards more delicate pipes, such as metal, polyethylene or even clay, you do have to adjust your approach,” he said.
“For instance, if you’re looking to remove some tree roots in a polyethylene, concrete or metal pipe, then you can just use a standard tree root cutter. But for a clay pipe, you can’t just use a straight edge – you need a concave or a curved blade, so you’re not destroying or weakening the clay pipe.”
Mr Donaldson said it’s his responsibility as a supplier to ensure that his clients are provided with equipment that meets the requirements of all their assets.
“There are a lot of considerations that have to be taken into account and it’s our responsibility to ask those quantifying questions so we can ascertain the best options for the client,” he said.
DCS builds all its vehicles in-house at its facility in Dandenong, Victoria.
Image: Prime Creative Media
Going the extra mile
The end-user experience is one that Mr Donaldson is all too familiar with. Before joining the team at DCS, he worked as a compliance and government contract manager for various companies supplying to water boards and later as a liquids and hazardous waste contracts and compliance manager for a national waste company.
“I have jumped the fence, so to speak, and now I deliver the products that help facilitate those jobs, with efficiency, safety, and compliance at the core of what we deliver,” he said.
For Mr Donaldson, what he appreciates most about DCS is that the company really goes above and beyond to ensure it delivers right service for each customer.
“As someone who’s come from an end-user perspective, [a good supplier] is someone who’s there to support you and walk you through the journey,” he said.
“It’s very important for a vendor to understand that as a customer you’re not just investing in a $10 ‘Tomy Tipper’ – you’re investing in hundred-thousand- to million-dollar
We’ve over engineered the cooling and exhaust system in a lot of our vehicles. So, unless that truck is running in 100-degree heat, it should never overheat.
DCS is a specialist in sewer jetting and cleaning vehicles, combination extractors, and non-destructive digging vehicles, but the company does a lot more than just supply these solutions.
“We are very proud to say that we are 100 per cent Australian manufactured, and we design and build everything from the chassis up in-house,” Mr Donaldson said.
This not only gives the company the flexibility

By keeping everything in-house, DCS has the flexibility to fully tailor each vehicle to its intended purpose.
Image:
DCS
For
Under pressure
Because DCS designs every aspect of the vehicles itself, the company is able to keep all of these products in stock.
Mr Donaldson said that the challenge with vehicles that are imported is that replacement parts then also need to be shipped in from overseas.
“This means you’ve got a vehicle that isn’t working for four-plus weeks. But it just takes one delay and then your lead time goes from two weeks to three months – and you can’t have a vehicle that is unable to be used for three months,” he said.
“At DCS, because we carry all our products, we can have you up and running as quickly as possible. That’s typically one to two business days for our interstate customers, and if something’s really urgent then we express ship it, so they have it the next morning.”
Mr Donaldson explained that DCS has a dedicated service and spare parts division to ensure that all its customers are supported throughout the entire lifecycle of their product.
“It’s not just a ‘here’s the truck and have a great ten years’ – we go above and beyond to ensure that our customers are supported,” he said.
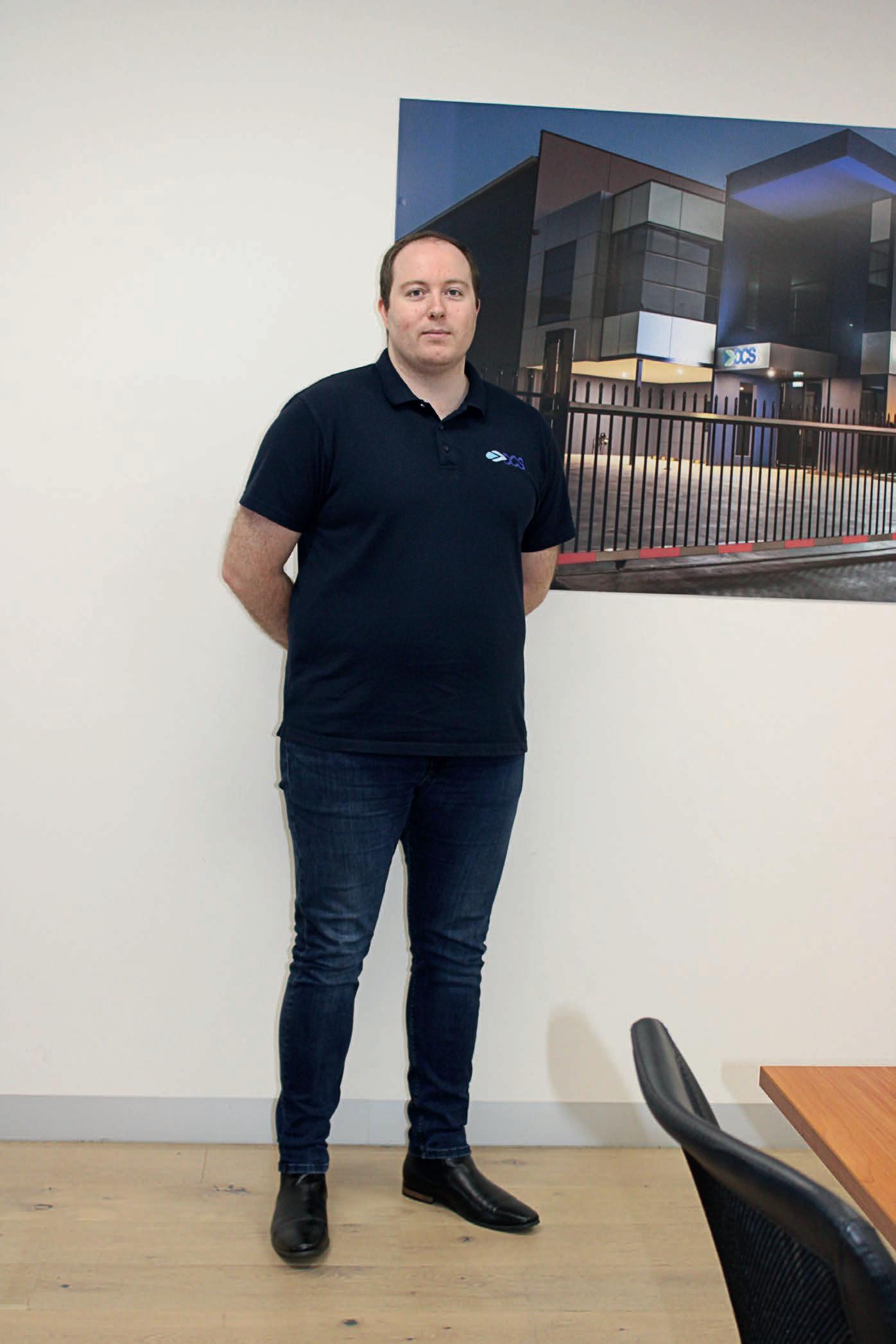
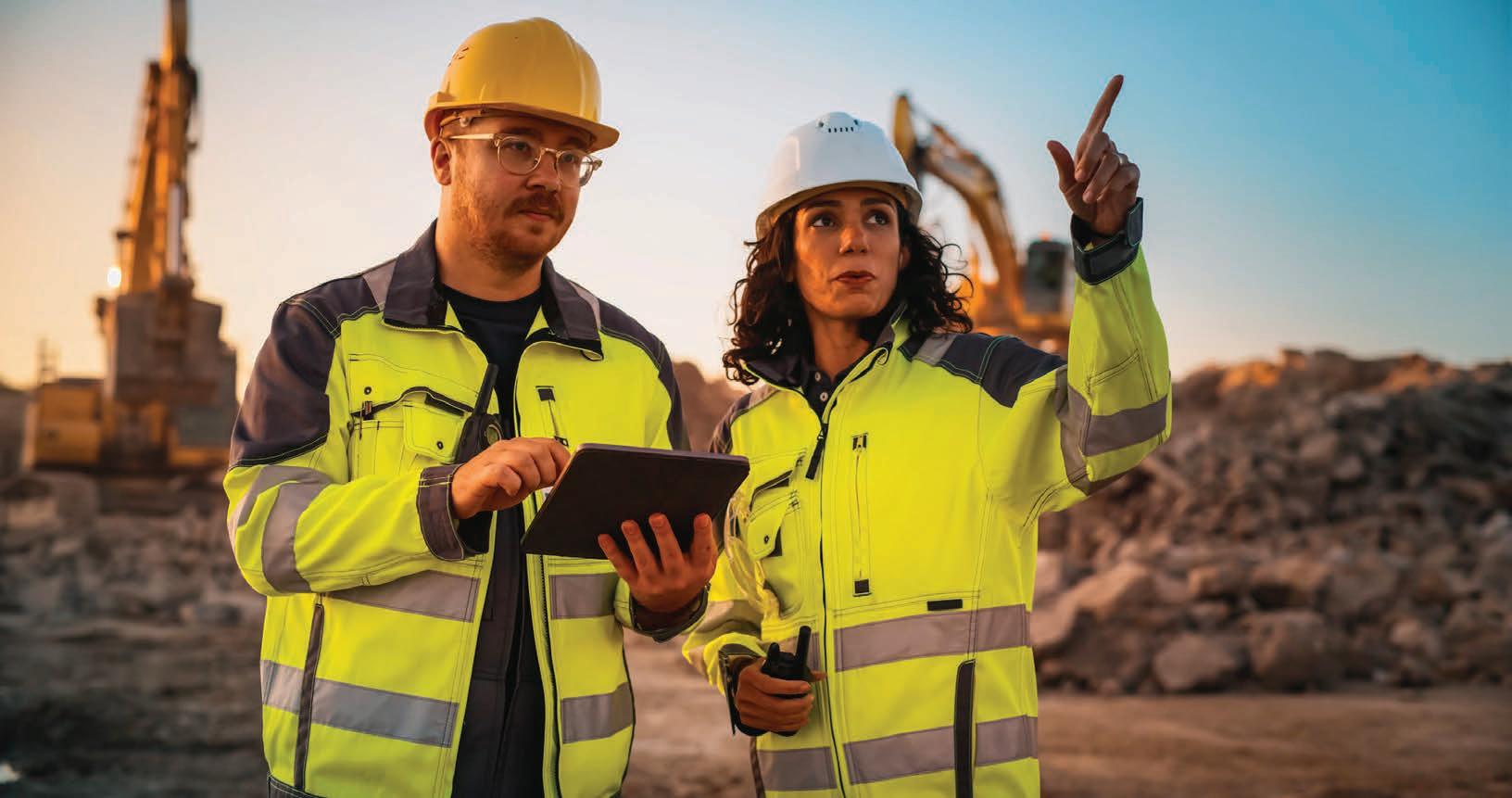
“That’s the importance of partnering with someone who actually understands not just your business but understands the urgency and has the same sense of response to ensure that this is resolved.” U
Sales Manager, Michael Donaldson.
Image: Prime Creative Media

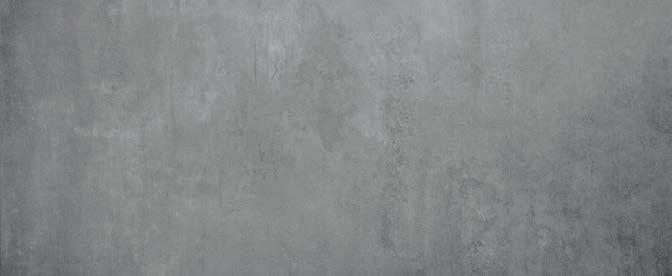
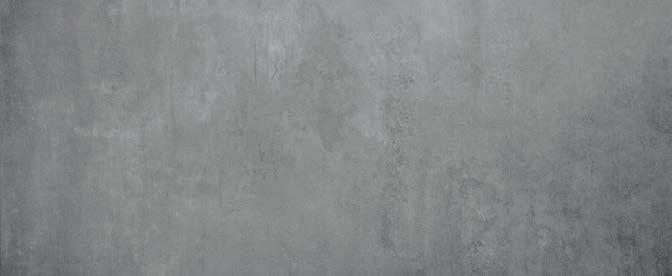


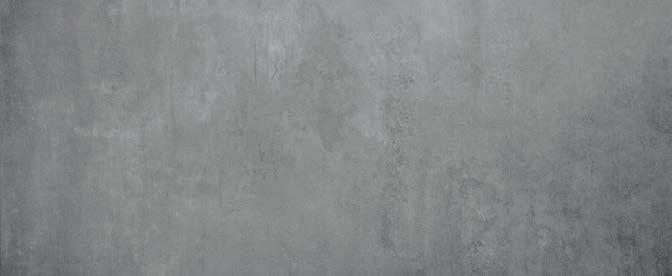
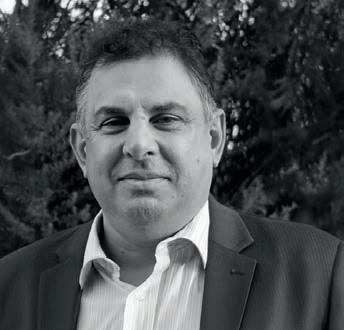
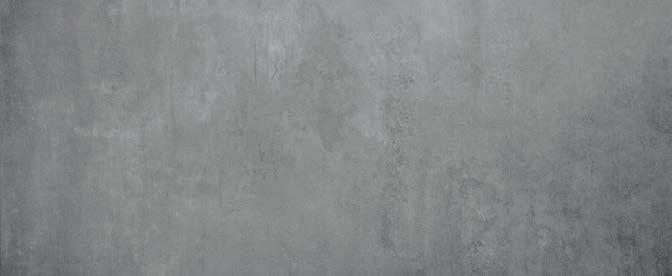
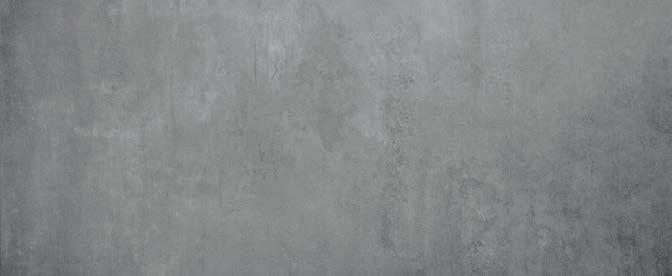
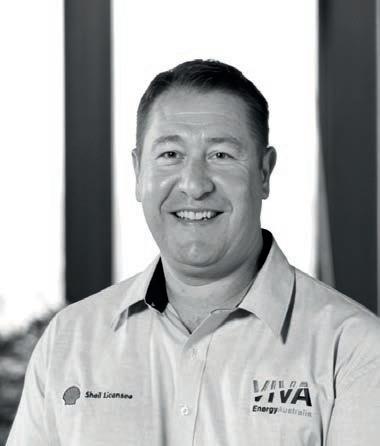
Shaping sustainability
As the impacts of climate change and population growth converge, utilities require adaptable, sustainable solutions to deliver the essential services we all rely on.
As Australia’s population continues to rise, utilities are facing increased demand for essential services such as water and energy.
On top of this, the increase in extreme weather events and natural disasters brought by climate change is causing significant strain on ageing infrastructure.
As the ramifications of these two issues collide, asset maintenance becomes more important than ever. To meet the needs of a growing population in a changing environment, utilities require reliable, fit-for-purpose equipment that not only addresses immediate needs but can adapt to future requirements.
However, equipment alone will not solve these issues –utilities must partner with organisations that are invested in the same goals to deliver truly sustainable solutions.
Measure of success
From leak detection in drought-prone communities to flow management at a hydroelectric power plant, sensors play an integral role in maintaining essential infrastructure.
In the water sector, precise measurement tools can enable utilities to monitor flow rates, detect leaks in realtime and ensure a consistent supply.
Level and pressure measurement technology also has a range of applications in the energy sector, ranging from monitoring oil levels in wind turbine gearboxes to monitoring hydrogen pipelines.
VEGA has been providing measurement solutions that make life easier and more secure for utilities for more than 65 years. The company offers measurement solutions in all areas of energy production – from hydrogen, wind, solar, hydropower, biogas and more.
When it comes to the water industry, VEGA’s sensors are perfectly adapted to all applications, from drinking water supply to wastewater treatment.
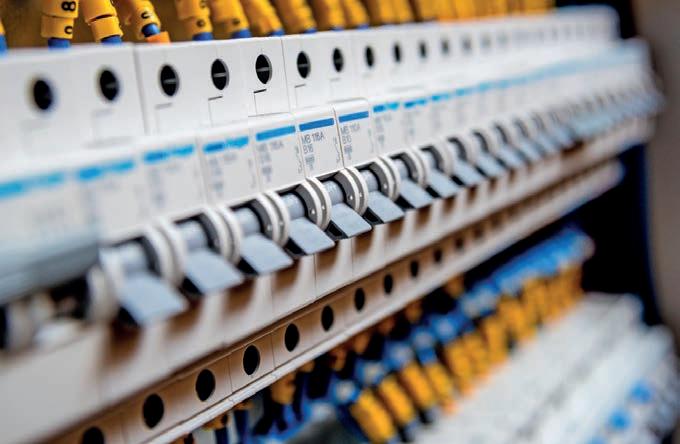
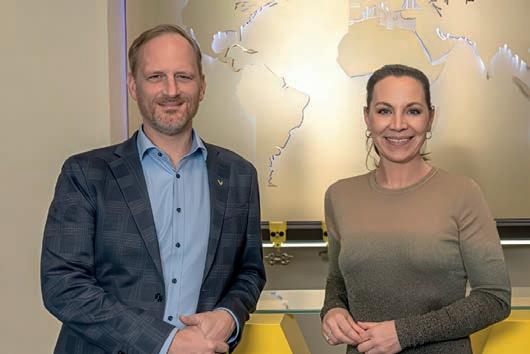
With a long history of pioneering innovative technologies, VEGA’s solutions offer instrumentation for maximum safety in every application.
Importantly, the company embodies its values in every single action:
Partnership: with trust, a deep understanding of partnership and exceptional service, VEGA creates added value for its customers and suppliers worldwide.
Innovation: VEGA has long been recognised for its innovative measurement solutions, bringing safety and efficiency to the water and energy sectors.
Sustainability: VEGA’s durable, resource-saving sensors and environmentally conscious actions set the sustainable measurement standard.
VEGA is united by its two CEOs, Isabel Grieshaber and Markus Kniesel, who share a clear vision of delivering the measurement technology of the future.
To achieve this, they combine their individual perspectives and expertise, foster the skills and talents of their employees, and drive the development of innovative business models.
Ms Grieshaber and Mr Kniesel share the same values and convictions: every idea has the potential to become a great new business opportunity.
“By responding to new situations with independence and courage, we can shape the future,” Ms Grieshaber said.
“Embracing new ways of thinking brings more advantages than any standard operating procedure, no matter how sophisticated.”
Ms Grieshaber said the focus of VEGA’s work is always on meeting the needs of its customers.
“Only when our sensors successfully meet the challenges of daily use, do we consider we that have done our job properly.”
Locally grounded and globally connected, VEGA gives values – both measurement and human – a home. U

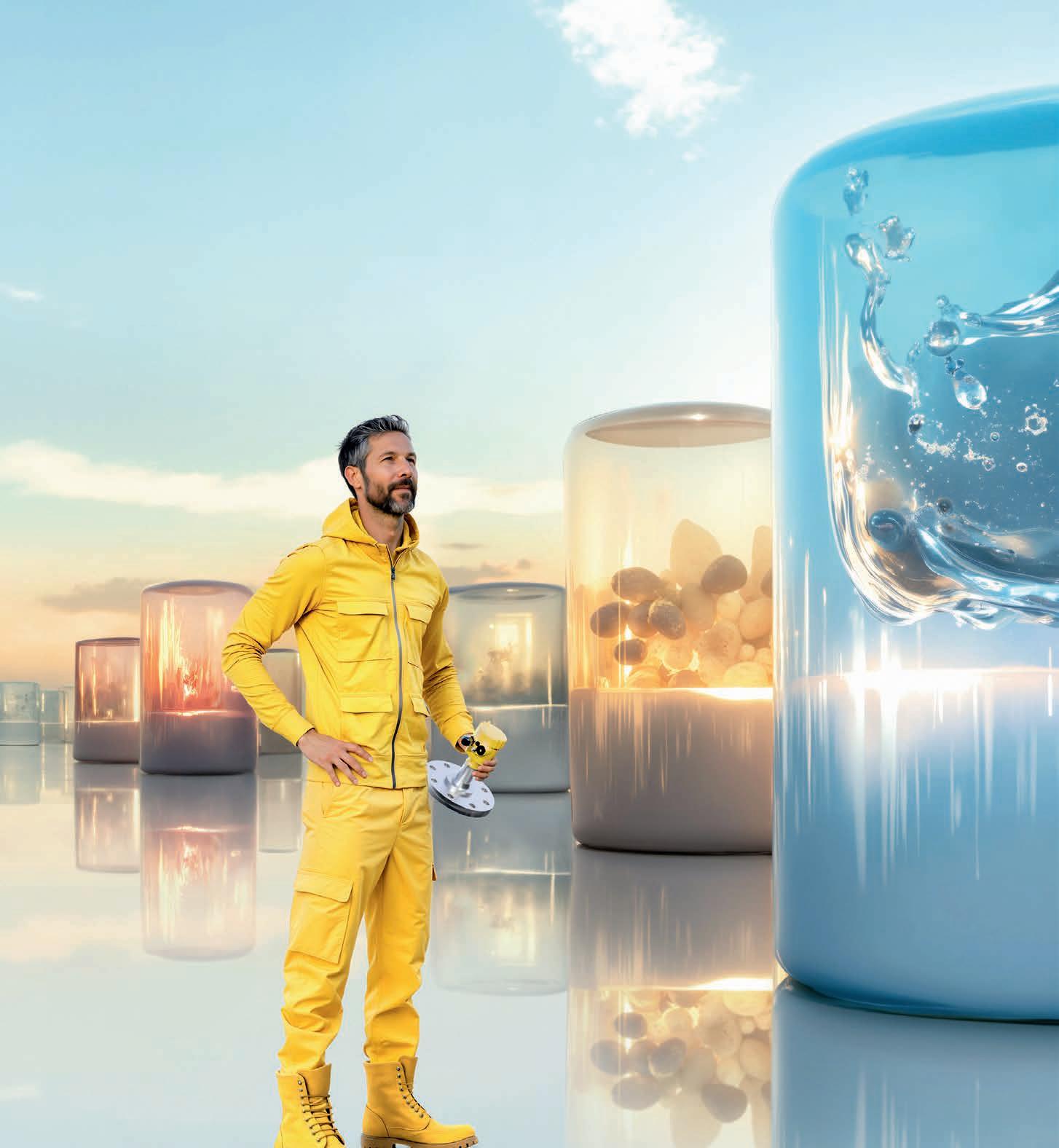
VEGA knows utilities gain more than just a measurement solution, they gain partnership and shared commitment to sustainability with a company they can trust.
Image:
VEGA
VEGA CEOs, Markus Kniesel and Isabel Grieshaber.
Our answer: Yes! What was the question?
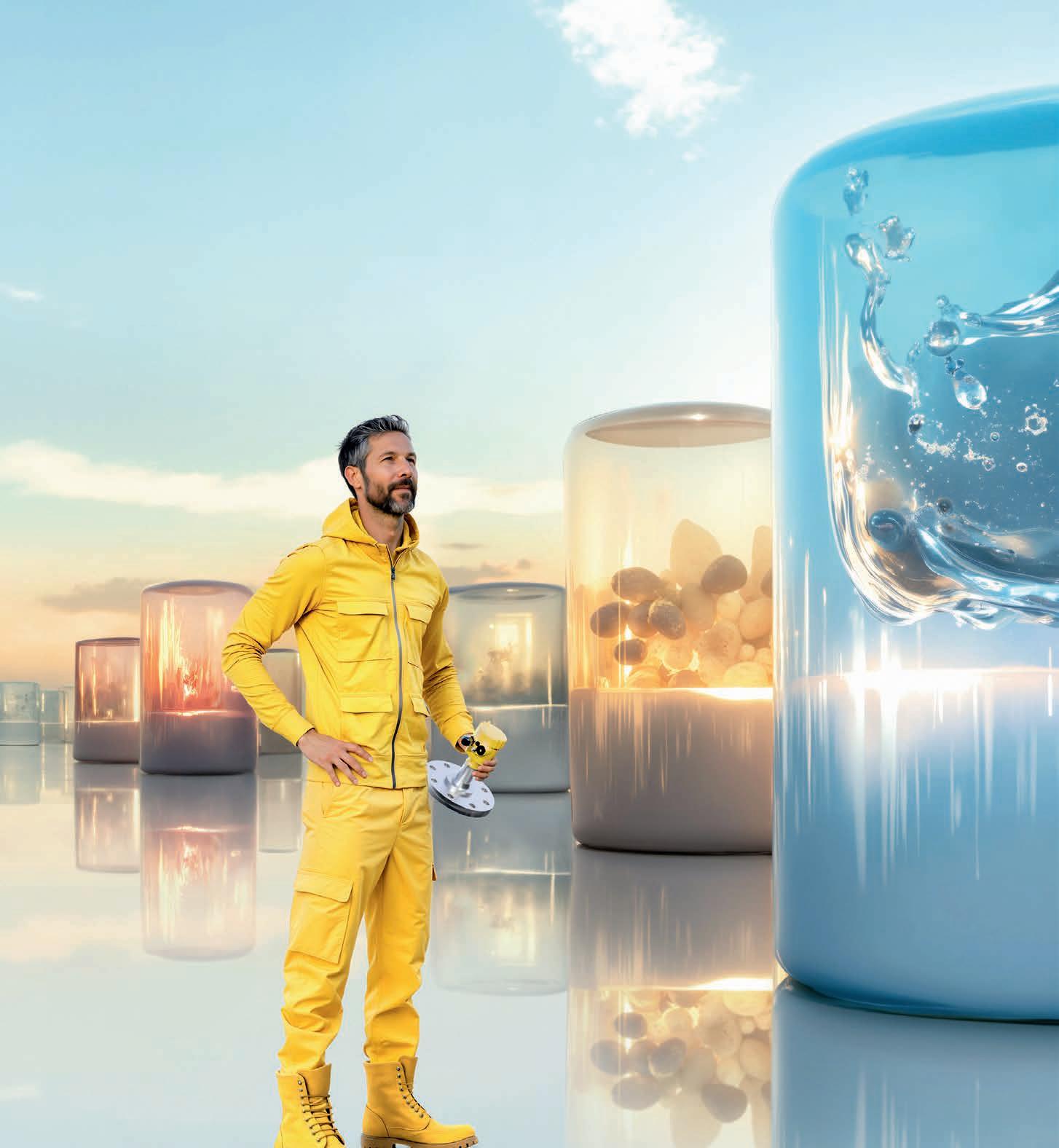
When your measurement is crucial, VEGA is the right choice. Our level and pressure measurement technology is not just state of the art – it sets the industry standard. With clear vision, technical expertise and strong innovation, we always have the right answer. No matter what the question is.
Everything is possible. With VEGA.

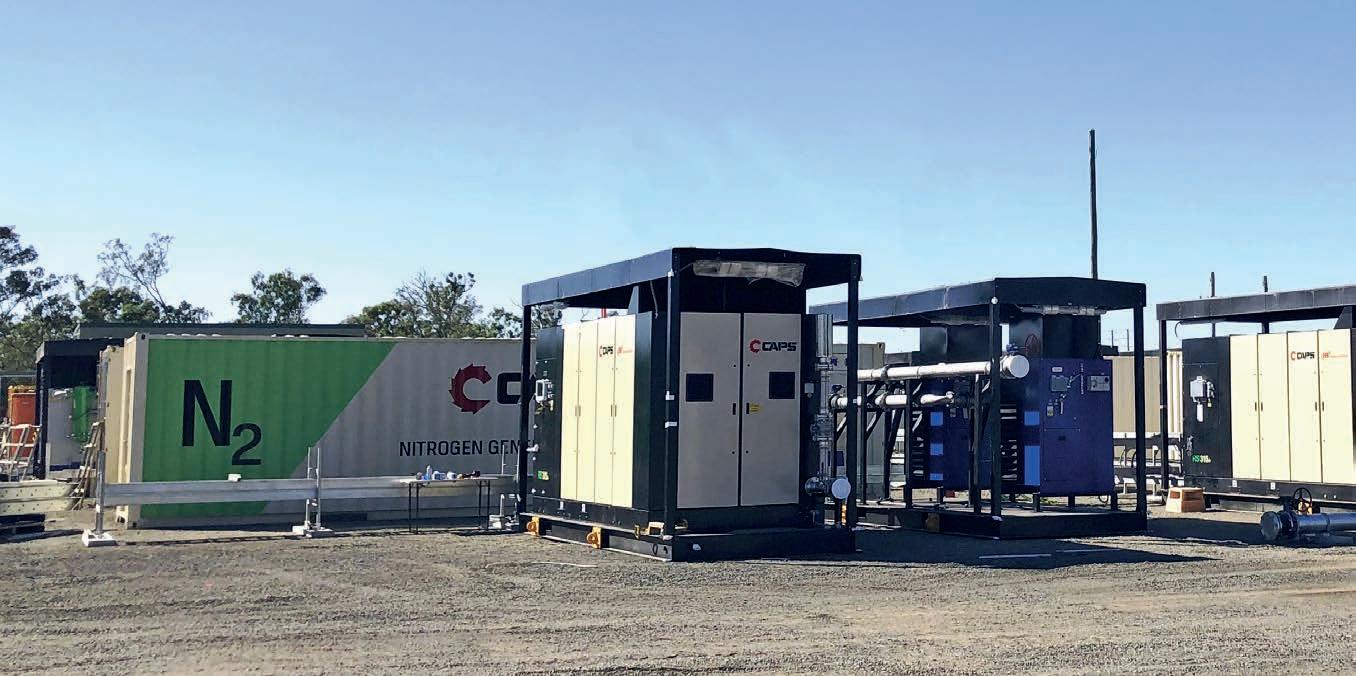
Maintaining pressure and flow
Choosing the right solution is not only about delivering the required performance but ensuring support is available to keep things running at their optimum.
Compressed air, filtration and power generation are vital elements in the successful operation of essential utility services, manufacturing facilities, industrial complexes and commercial environments. When it comes to sourcing these components, it goes without saying that it’s crucial to choose a solution that is optimised for your specific application. However, in order to get the most out of your equipment, it’s just as important to work with a supplier than can provide detailed advice and support long after the sale has concluded.
More than just hot air
Utilised in water and wastewater treatment, air blowers are vital in aeration processes, air scouring and filter backwashing activities. Providing compressed air to activated sludge basins in wastewater treatment is generally an energy hungry arrangement, requiring both blowers and generators to be optimally sized and selected for the application.
To ensure asset owners have access to the right product for their needs, CAPS Australia offers a wide range of positive displacement blowers, multi-stage centrifugal and single-stage centrifugal turbo blowers to ensure it can provide the ideal solution for a variety of industrial wastewater treatment applications.
When it comes to nitrogen or oxygen generation systems, generating just the right amount at-scale to support operational needs presents a key challenge. CAPS can configure its equipment as needed to support your on-site demands and produce dependable and economical supplies of nitrogen or oxygen. The systems are designed to generate the quantity and purity of nitrogen or oxygen necessary for any application. Whether you are looking for a reciprocating, rotary screw, oil free rotary screw, portable diesel or centrifugal air compressor, CAPS’ flexible solutions are engineered around you, with a commitment to delivering low-cost, best-in-class industrial air compressors that are built tough and engineered to last.
That’s a fine filter you’ve got there
As part of its commitment to providing specialised water solutions, CAPS has partnered with an industry leading filter manufacturer, Bollfilter, to deliver its range of automatic, manual, duplex and simplex filters, along with fine filter units and membranes. This allows CAPS to support water filtration applications and also chemicals and petroleum products.
Powering back up
Industrial, utility and commercial operations are reliant on uninterrupted power supplies. CAPS again takes an end-user-focused approach to the delivery of reliable and cost-effective backup power solutions, with the equipment sizes and power outputs able to be customised to meet specific needs and operating environments.
At the heart of every diesel-powered generator, the engine dictates the reliability and efficiency of the generator. This is the sole reason why CAPS only sources from manufacturers who use the best engines, such as Kubota, Perkins, Isuzu, Volvo, Mitsubishi and Yanmar, each paired with leading alternators and controllers to help ensure operational continuity.
Engineered to suit
CAPS delivers complete solution designs, developed by its in-house engineering team and supported through its Australian ISO9001 accredited manufacturing facility. The custom-built systems are perfectly matched to clients’ requirements, which also enables CAPS, where possible, to integrate new technology into existing installations, enhancing the operational performance and life of equipment and infrastructure.
With ten branches across Australia, CAPS’ dedicated team also delivers exceptional service, expert advice, 24/7 maintenance support and spare parts to ensure customers’ operations always run smoothly. U
CAPS systems are designed to generate the quantity and purity of nitrogen or oxygen necessary for any application.
AERATION & FILTRATION
SOLUTIONS & SERVICE
Optimise operations to improve your bottom line


Ingersoll Rand E Series oil-free rotary screw compressors
Bollfilter aquaBoll® automatic filter
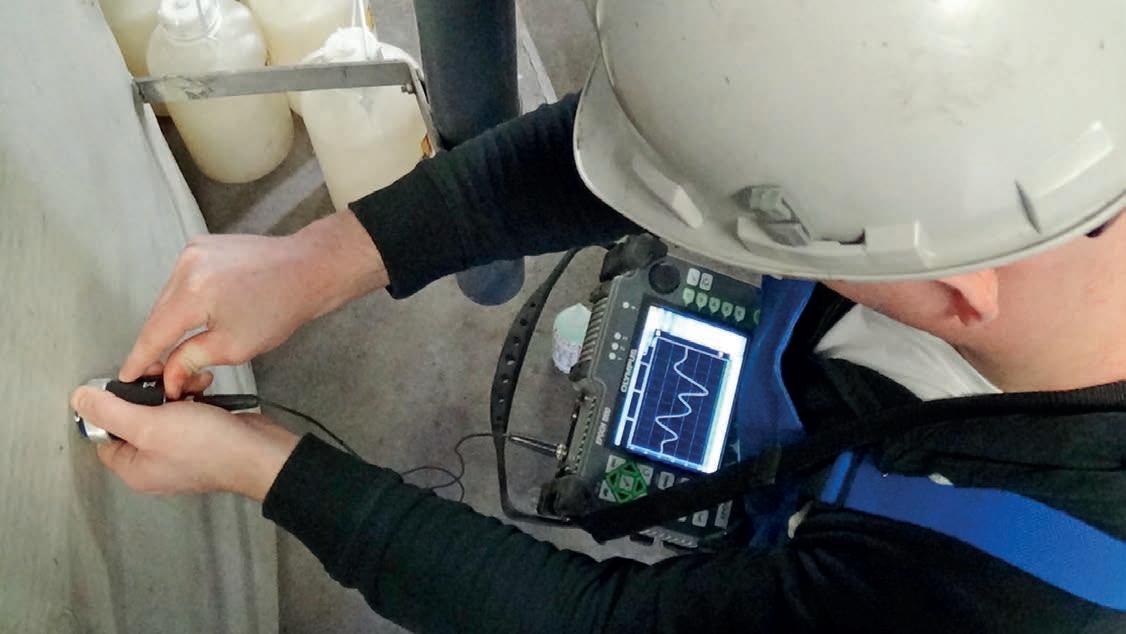
Inspect and protect
Many companies operating in the water and wastewater sectors are making a renewed commitment to predictive maintenance for FRP tanks, piping and pressure vessels as they understand that this approach to asset management will pay off significantly in the long run.
Predictive maintenance monitors the performance and condition of equipment under normal operations over time to determine its fitness-for-service and reduce the likelihood of failures.
Regular inspections are integral to predictive maintenance for three key reasons:
1. To track changes in FRP assets over time and keep owners informed of the condition and remaining service life of their assets.
2. To provide engineering data that can be used for ongoing fitness-for-service assessments, especially when any changes to processes or operating conditions are being considered.
3. To identify needed repairs or remediation at an early stage so the work can be planned and completed in a cost-effective and timely manner.
The three-year rule
As a leading FRP engineer and manufacturer, RPC Technologies has the exclusive licence to a unique technology called UltraAnalytix® NDT inspections – a world-first proven non-destructive, non-intrusive inspection system for FRP composite assets. Since deploying this technology, RPC gained extensive, first-hand experience working with FRP composites and the unique ways they deteriorate, so the team recommends that inspections of these assets take place every three years to ensure optimum safety and return on investment. The mechanical properties of FRP laminates change during normal service – in fact, fairly rapid changes happen to new equipment during the first three years of operations.
Assessing those changes early on provides baseline data and a good window for predicting what the future looks like in terms of repairs or replacement needs for that equipment.
Unlike damage to steel, which is relatively predictable and linear, damage to FRP is non-linear. The changes that occur in response to mechanical and chemical forces in FRP laminates are more complex and often invisible. Small changes in the polymer due to creep can have a major impact on reliability.
In addition, the three-year inspection interval represents about half the time that it takes for chemical damage to cause failures in the most common types of reinforcement used in FRP laminate, and polymer damage always occurs before reinforcement damage. The UltraAnalytix system detects and analyses polymer damage as a proxy for overall FRP condition.
Finally, a lot can happen in three years. Unexpected changes in service conditions due to over-pressurisation, accidental impacts, damaged or faulty supports, poor installation or repairs, can cause unseen degradation that weakens FRP and potentially leads to failure.
RPC Technologies has unmatched experience and unique knowledge of FRP that can help companies plan and budget for a predictive maintenance program that provides a clear, ongoing picture of the current condition and mechanical integrity of their FRP assets without shutting down operations, cleaning out processing equipment and risky confined space entry.
This RPC predictive maintenance plan will give asset owners and managers the accurate data they need to anticipate and schedule necessary repairs during planned shutdowns, while avoiding the expense and potential danger of an unexpected failure or replacing assets prematurely.
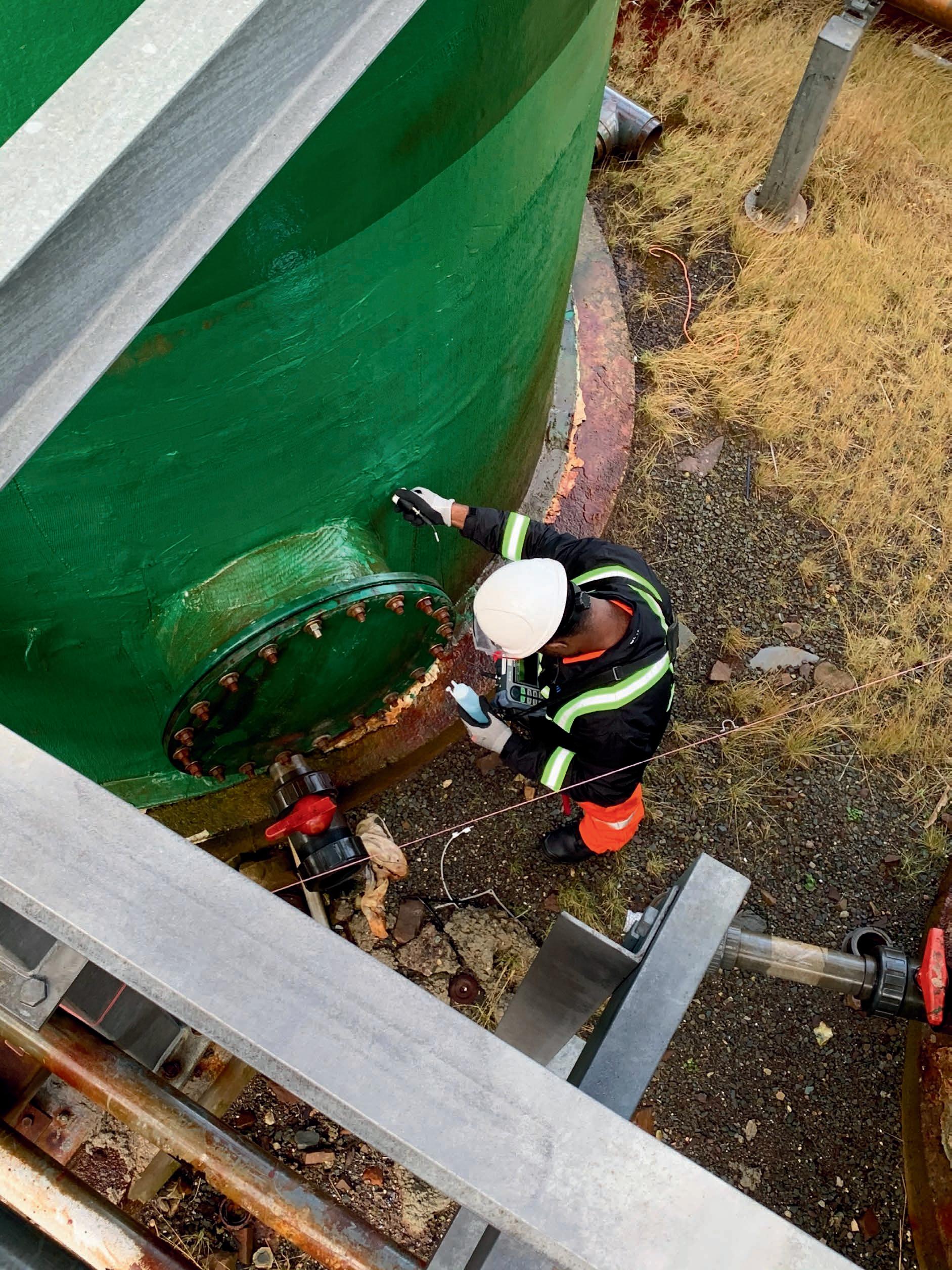
Regular condition assessments of FRP composite assets are vital in order to prevent failure in water and wastewater systems – here’s why.
Image:
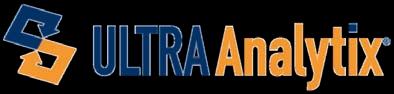
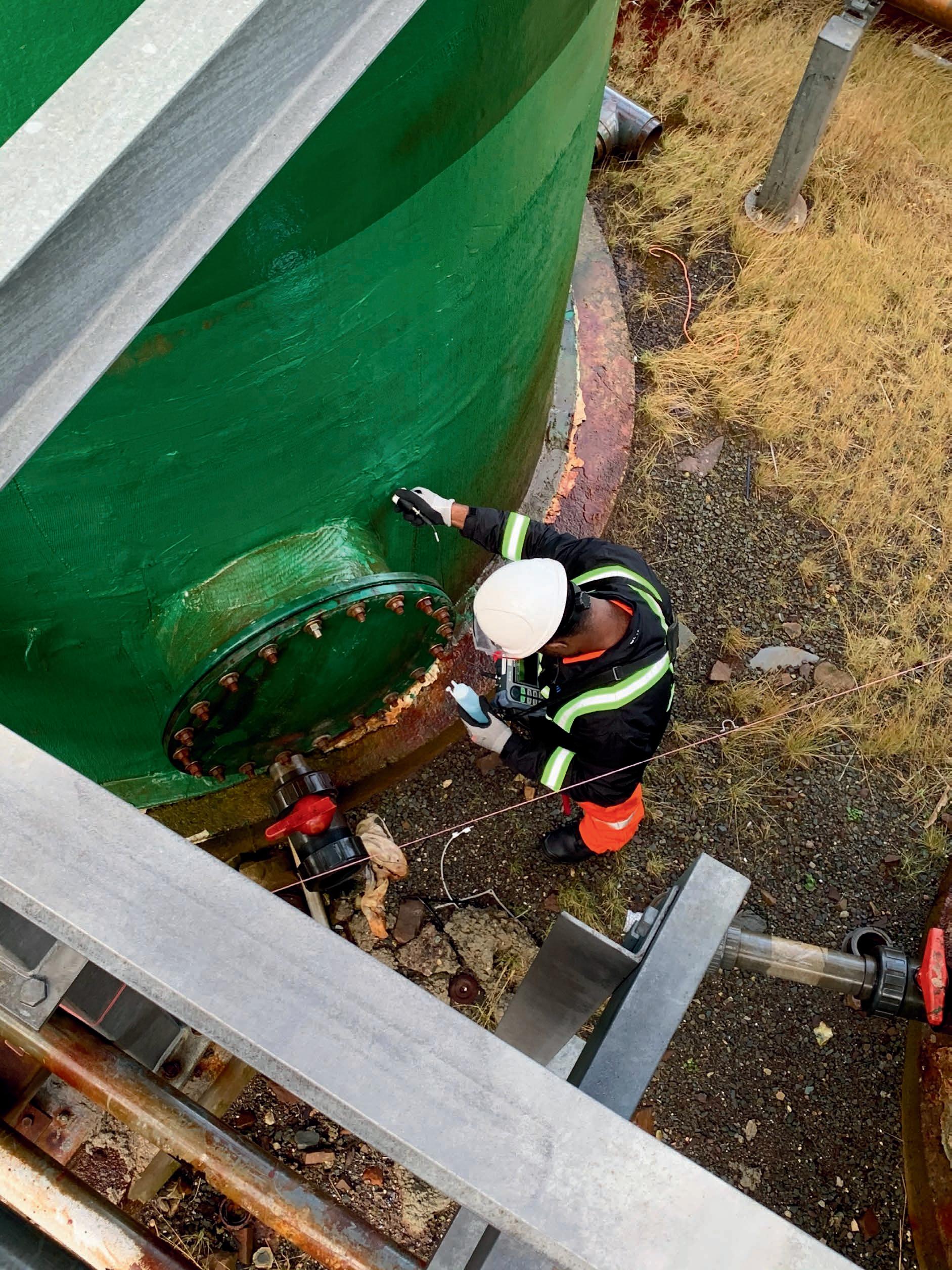

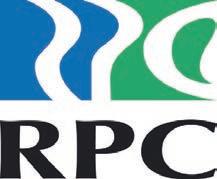
Supporting boots on the ground

Access Detection offers specialised training to empower regional councils and water authorities to play a more proactive role in leak detection.
Detecting small water leaks in challenging environments requires a highly skilled technician – and it’s vital that these operators are supported by the right training and technology.
By Anthony Johnstone Director, Access Detection
With recent advancements in water leak detection technology and large-scale smart meter rollouts, it would be easy to assume that utilities no longer need a water leak technician to go out to locate an actual water leak.
But the fact is, these new technologies now put more pressure on professional leak technicians to find even smaller leaks in very demanding environments. The challenge is that finding these smaller leaks often pushes current acoustic technology to its limits – so high-quality receivers with advanced microphones and well-trained leak technicians are essential.
While working with many councils and water authorities, one of the key challenges I’ve noticed for smaller councils is ensuring their staff are trained to be competent in using the equipment, this combined with irregular use makes it hard for these operators to continue to improve or retain these skills.
It’s important for councils to continue to invest in their operators, and Access Detection is leveraging its extensive industry experience to help water authorities tackle these challenges. In addition to supplying quality products, Access Detection offers specialised training and support for technicians, empowering regional authorities to play a proactive role in leak detection.
ABOUT THE AUTHOR
Anthony Johnstone has spent more than 20 years in the utility industry. He has worked with a range of experts, technologies and businesses to build a strong knowledge base, which he leverages to provide practical, detailed advice on the correct solution for each individual utility’ unique needs.
Technical advice
Using traditional noise loggers to monitor areas, followed by a correlator to confirm results and then applying standard acoustic leak detectors is still a very relevant approach today – and can even avoid costly dry holes. Using all or just one of these technologies offers smaller councils a more affordable approach when it comes to conserving water in their local areas.
The Sewerin AC200 is just one product that is proving popular with water authorities and regional councils throughout Australia. This combined correlator and advanced acoustic leak detection solution has improved several utilities’ ability to detect those harder to find leaks – including SA Water, Hunter Water and other smaller but important regional councils.
The Sewerin AC200’s leak-finding capabilities, combined with its friendly user interface and sensitive microphones, allows operators to locate leaks even in demanding pipe environments.
Another popular choice is the Sewerin Aquatest T10, which has a very sensitive microphone and simple interface for operators who may not use leak detection equipment every day.
This is great for smaller councils wanting leak detection for a variety of pipe types including AC, HDPE and other non-metallic mains.
A critical, yet sometimes overlooked, aspect of a good leak detection program is to know the vicinity of the pipe. A conventional EMF locator like the Rycom SnapTRACK is ideal for conductive or metallic mains, while the Sewerin Combiphon is ideal for nonmetallic services for instance AC or PVC mains.
For the right advice on leak detection and locating requirements talk to the team. Access Detection provide training for all its equipment, and this can be arranged on-site for staff too. U

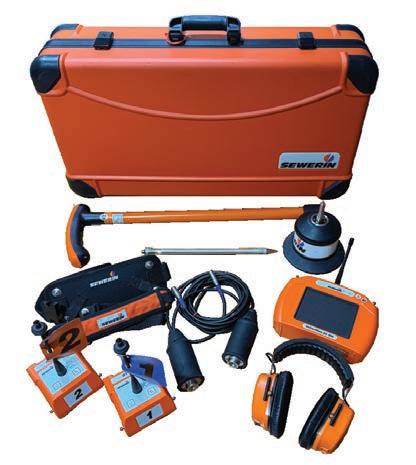
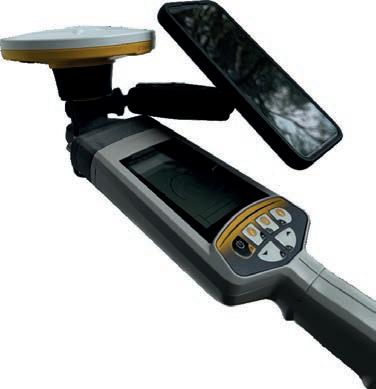
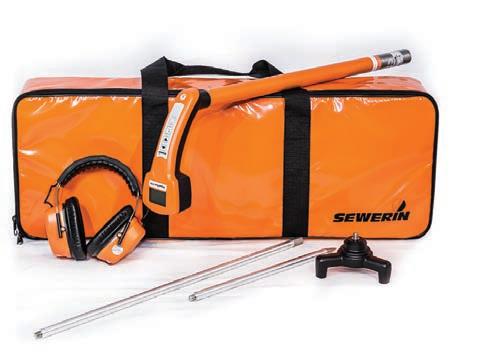
Smarter valve monitoring
For decades, Modec has collaborated across industries to offer versatile portable actuators.
By understanding market demands, Modec has pioneered a monitoring solution aligned with Industry 4.0 and IoT technologies. The key feature of this system includes seamless integration, allowing a smart sensor to connect to Modec actuators without requiring any modifications to the existing installation.
This ensures a hassle-free setup, providing an easy upgrade to the user’s system. Additionally, data management is simplified by transmitting critical information such as torque, speed, and rotation data through Bluetooth to a secure mobile and web application, enabling effortless analysis and real-time tracking.
Modec’s system also offers advanced team organisation capabilities, allowing users to assign different roles with varying access levels to optimise operational efficiency.
This feature ensures that only authorised personnel can access specific data and functions, streamlining workflow. Valve insights are also available on-the-go, enabling users to input and access important valve data anytime and anywhere, providing flexibility and ensuring informed decision-making in real time.
Modec Connect offers two distinct modes for measuring valve performance. In Free Mode, it provides real-time data on torque, speed, and revolutions, offering instant feedback on valve operation.
Guided Mode, on the other hand, helps users conduct a comparative analysis of valve conditions over time by providing step-by-step instructions for more detailed insights. This combination of modes ensures both immediate and long-term monitoring of valve performance.
For advanced reporting, Modec Connect enables the export of professional PDF reports, allowing users to share valuable insights and maintain thorough operation records. The system also simplifies performance analysis with visualised curves, making it easier to track and identify trends.
The LTN67 Sensor within Modec Connect measures torque and speed, sending real-time data directly to the mobile app via Bluetooth. Compatible with all Modec actuators, this lightweight sensor enhances the efficiency of monitoring manual valve networks, streamlining maintenance and operational decision-making.
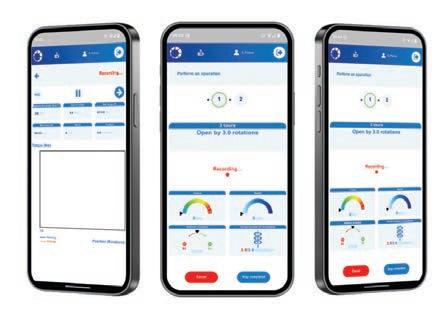
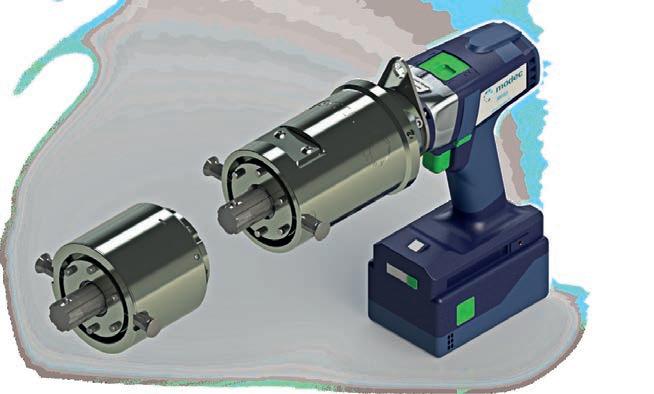
While industries continue to digitise their automatic valves and processes to streamline data collection, improve maintenance, and reduce costs, manual valves often remain unmonitored with little to no data.
Yet, despite their large numbers and involvement in critical processes, they are frequently overlooked. So why focus only on monitoring automatic valves and not manual ones?
Modac outlines four reasons why manual valves should also be monitored:
Reduction of unexpected shutdowns: by monitoring valve performance and condition, maintenance and repairs can be carried out and planned according to actual needs, rather than by assumption or routine schedules. This avoids unnecessary parts replacements and interventions, reduces costs, and improves overall process control, ensuring smooth and efficient equipment operation without unexpected disruptions.
Extended equipment lifespan: through non-intrusive installations, valves can be regularly monitored without disrupting operations, allowing early detection of the first signs of wear. By addressing issues before they worsen, equipment can be maintained more efficiently, extending its lifespan and avoiding costly breakdowns or premature replacements.
Track your work: by storing valve operation data, it becomes easier to share information with your team, facilitating performance verification and problem identification. This not only speeds up troubleshooting but also improves team collaboration and makes training new staff more effective.
Preparing for tomorrow’s innovations: by collecting data today, you lay the groundwork for future tools and technologies, such as AI, which is already entering the industrial sector. The more data you collect now, the more accurate and insightful future analyses will be, enabling smarter decision-making and predictive maintenance.
Field Machine Tools is the Australian distributor partner of Modec Pneumatic Motors and Portable Valve Actuators. U
For more information, contact sales@fmt.com.au
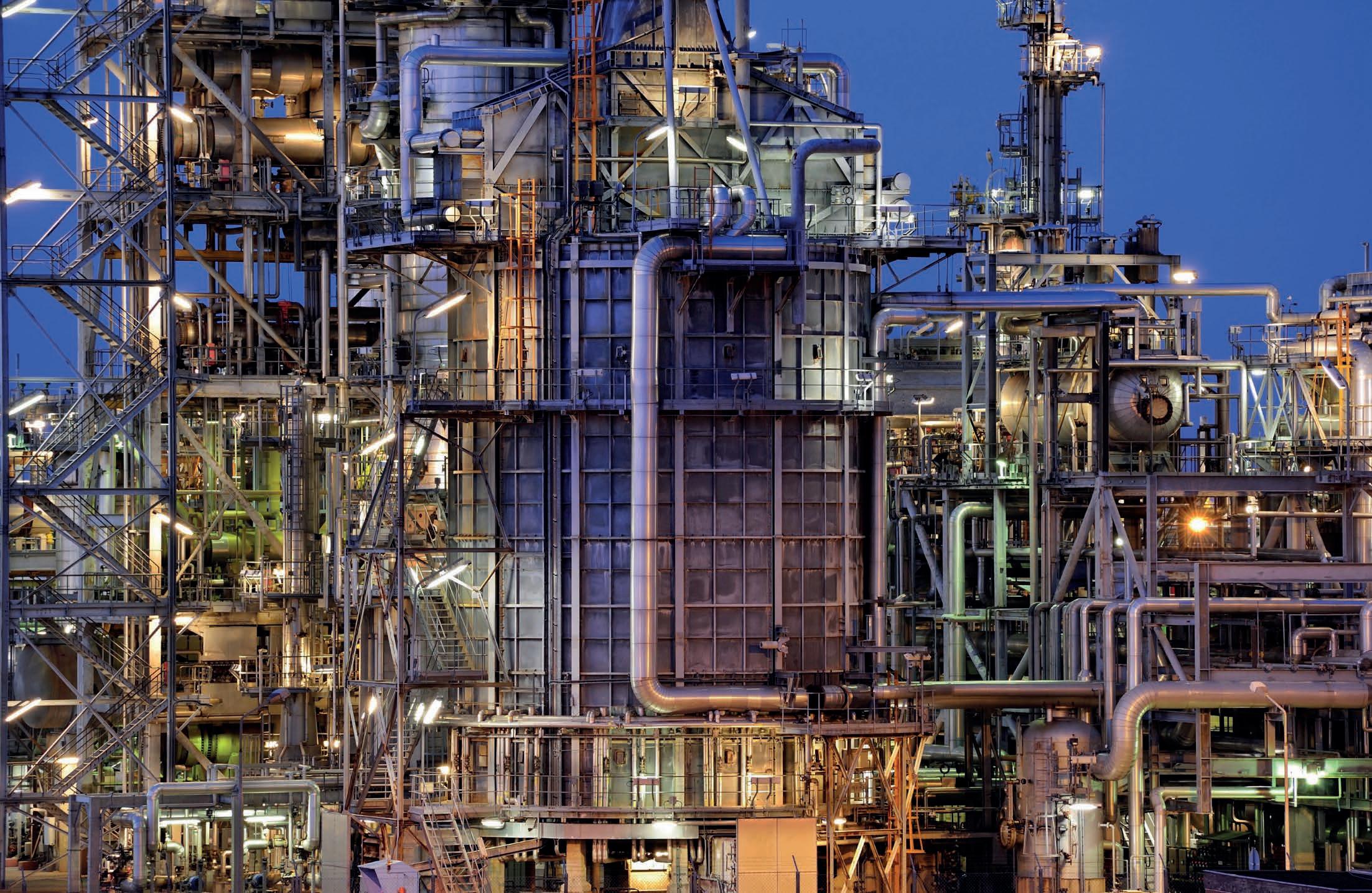
Modec’s system offers advanced team organisation capabilities.
Modec has unveiled a valve monitoring solution aligned with IoT technologies.
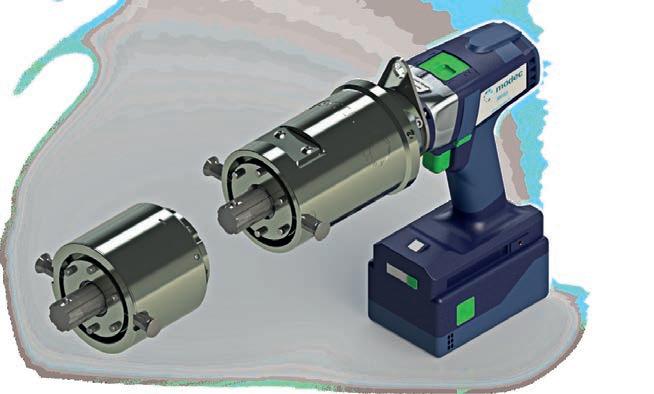
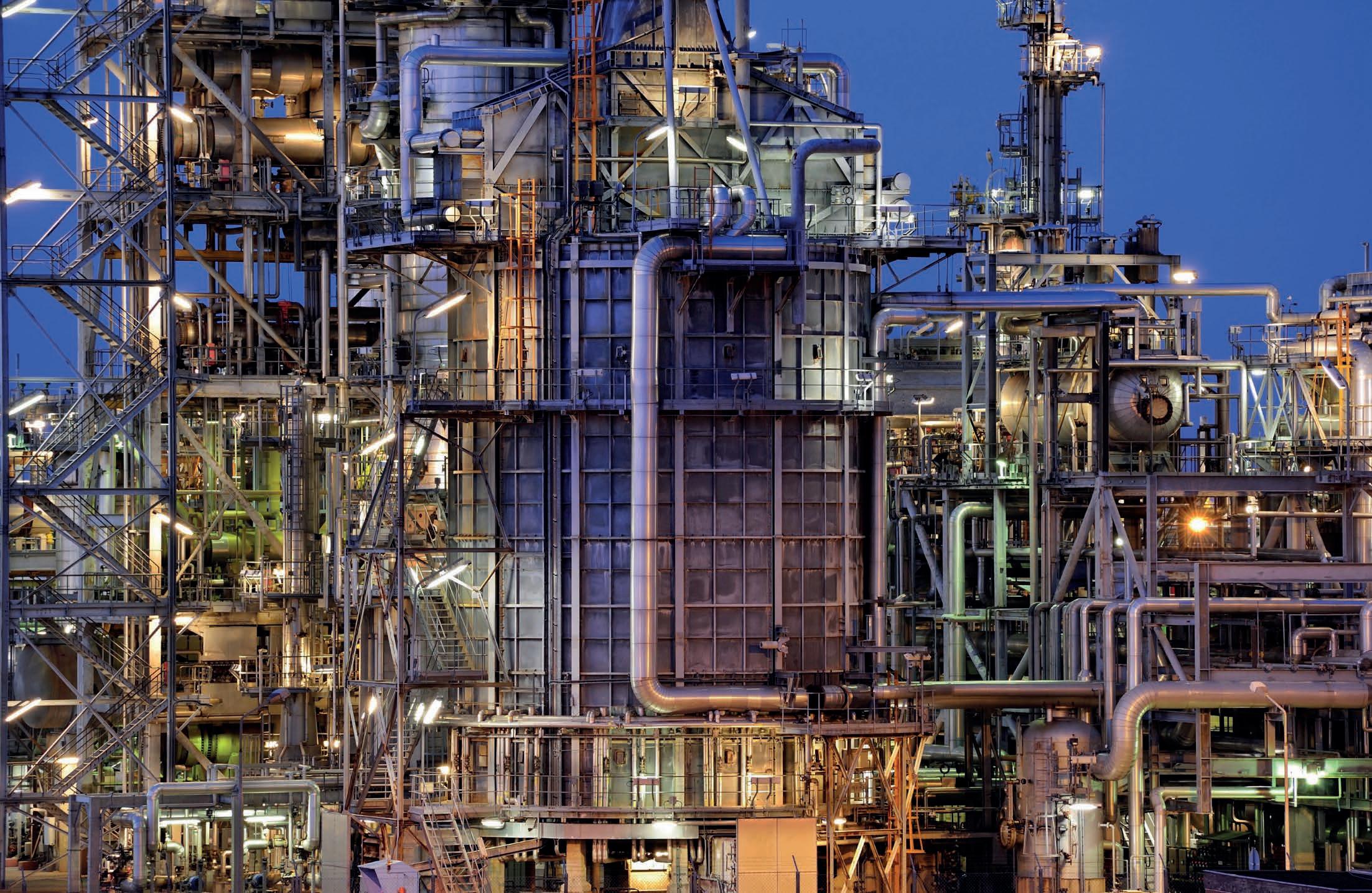

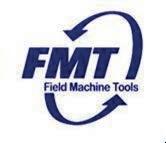
Industry movements
Important developments in the utility industry – we round up the key appointments, resignations and other staff changes within the sector.
AEMC
Ben Barr, Energy Market Commission (AEMC) Chief Executive, stepped down from his role in March 2025. Mr Barr said he loved being part of the AEMC. He joins Energy Queensland as its new Executive General Manager, Regulation, Strategy and Risk.
AEMO
The Australian Energy Market Operator (AEMO) has established a new Policy and Corporate Affairs division, which will be accountable for government and stakeholder relations, communications and media, along with strategic reform for both electricity and gas.
This division will be led by Violette Mouchaileh, who most recently held the role of AEMO Executive General Manager (EGM) Reform Delivery. Additionally, AEMO Services EGM, Nevenka Codevelle, has resigned and will finish up at the end of June 2025, allowing time for a smooth transition.
APA Group
APA Group has appointed Rob Evans as the company’s new Group Executive, Infrastructure Delivery. Mr Evans will take the reins from Kevin Lester, who will retire in June 2025 after almost four decades in the energy industry.
ARENA
The Federal Government has made appointments to the Australian Renewable Energy Agency (ARENA) Board. Marianna O’Gorman has been re-appointed to the board and will assume the newly created position of Deputy Chair. Stephen McIntosh has also been re-appointed as a board member, while Angela Karl joins the board for her first term.
ENGIE
Shannon Hyde has been appointed CEO of ENGIE Australia and New Zealand (ANZ). He takes over from Rik De Buyserie, who has taken up the role of Country Manager for ENGIE North Africa.
ENGIE ANZ COO Generation, Graeme York, will retire on 15 May 2025 after more than 30 years in the energy industry. The company will also farewell Chief Development Officer for Net Zero Energy Solutions, Anna Quillinan, after nearly six years and welcomed Frederik Baerts as the new Managing Director of Generation.
Gippsland Water
Gippsland Water has welcomed two independent Aboriginal delegates to its Board of Directors to incorporate fresh perspectives into its leadership.
Glenn Pellegrin has joined the Board as an Independent Aboriginal Delegate, and Laurie Marks has been appointed as Board Committee Independent Aboriginal delegate.
Gippsland Water Managing Director, Sarah Cumming, said Mr Pellegrin’s appointment would further strengthen the recognition and inclusion of First Nations perspectives as part of Gippsland Water’s decision-making processes.
Marinus Link
In February 2025, Marinus Link Pty Ltd (MLPL) announced the appointment of industry leader Stephanie McGregor to lead the project beyond the current critical design, development and approvals phase, and into project delivery. Ms McGregor joined the project on 31 March 2025 as CEO Designate and is set to assume the CEO position on 2 June 2025.
Current MLPL interim CEO, Dr Collette Burke, will remain in the role until 30 May 2025, guiding the project through a series of critical decision points and leading a comprehensive onboarding program before handing the reins to Ms McGregor. Dr Burke will then resume her role as a director on the Marinus Link Board.
Seqwater
Seqwater appointed Emma Thomas as its new CEO, who will steer the utility to ensure the continued delivery of safe, secure, and cost-effective drinking water to more than 3.8 million people.
Snowy Hydro
James Cain has been appointed Chair and Non-Executive Director of the Snowy Hydro Board, set to serve in the role for a three-year term.
The Federal Government thanked outgoing Chair, David Knox, for his service over the past five years including on the Snowy 2.0 reset.
Sydney Water
Sydney Water Managing Director, Roch Cheroux, will conclude his tenure after six years leading the organisation through key operational and planning phases.
As the utility moves into its next phase of delivery and strategic planning, the Board of Directors has appointed Sydney Water’s Executive General Manager, Paul Plowman, to the role of Acting Chief Executive.
Toowoomba Regional Council
Toowoomba Regional Council kicked off a nation-wide search for a new CEO, after longstanding CEO, Brian Pidgeon, announced his resignation in December 2024.
Toowoomba Region Mayor, Geoff McDonald, said Council was searching for an exceptional leader to guide the organisation during our next exciting chapter.
“The right person to lead our organisation will be a strategic, people-focused leader with a passion for driving sustainable financial performance and fostering a highperforming culture.” U
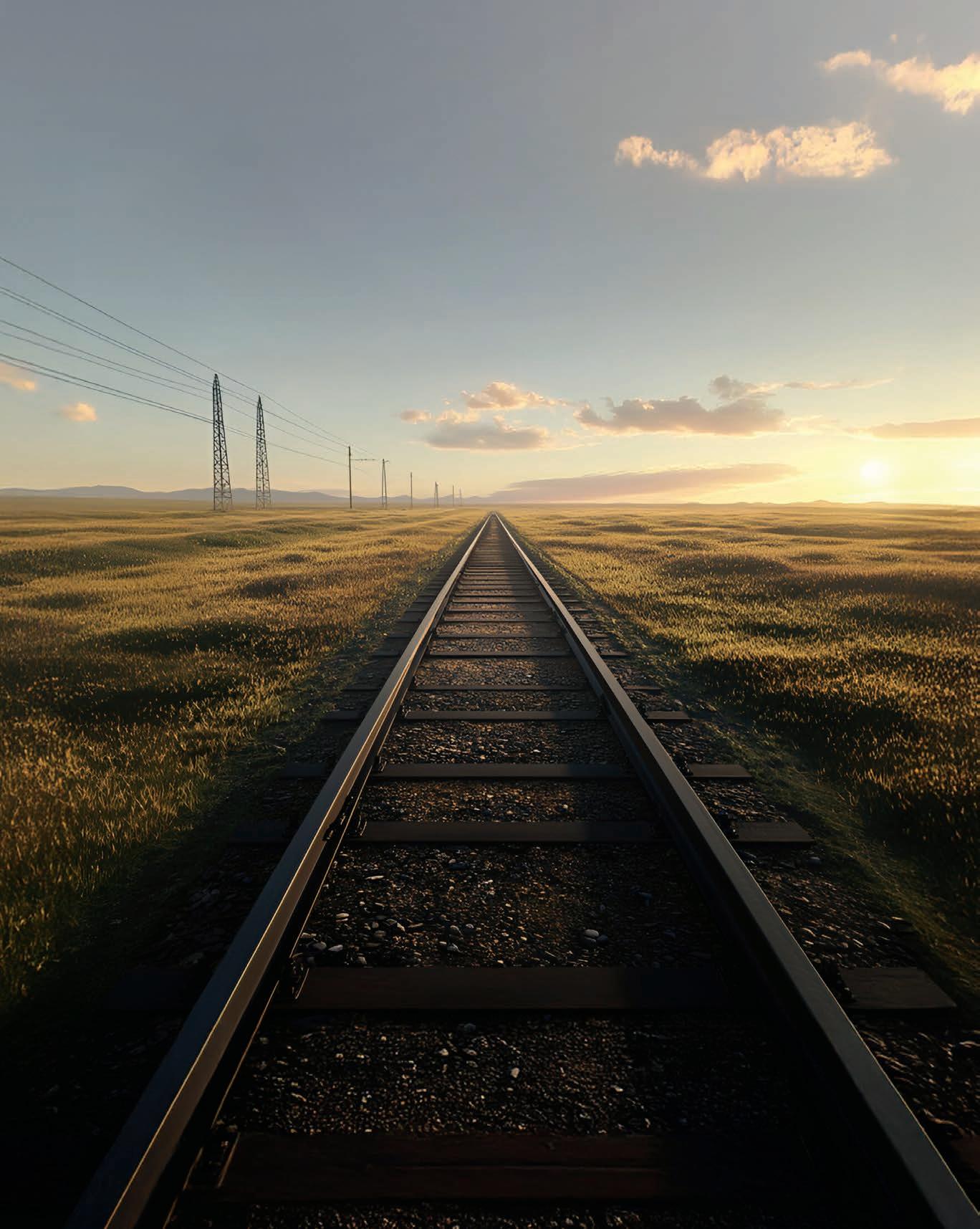
Trusted Power. Unmatched Reliability.
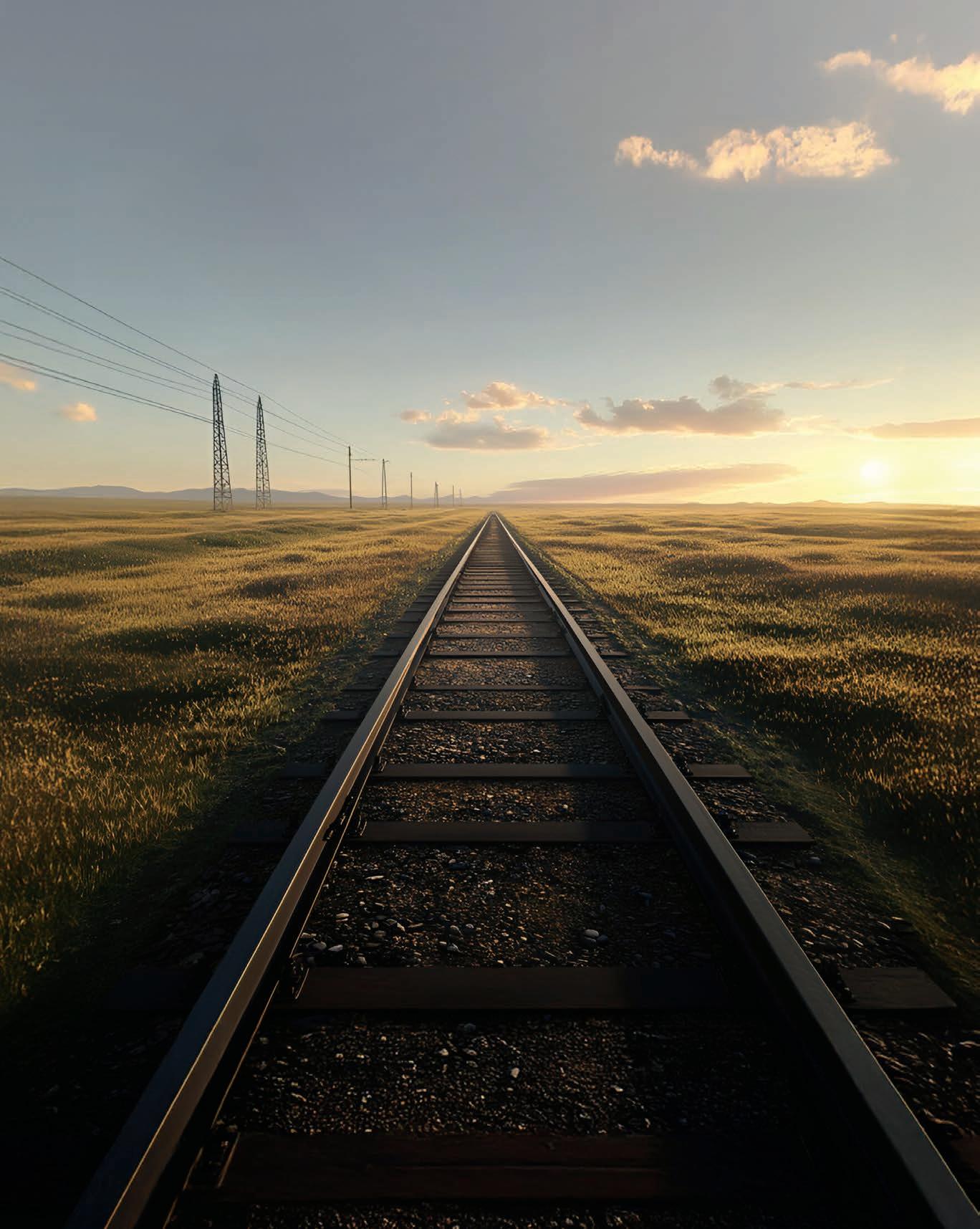
AS4044:2024 establishes a new benchmark for stationary battery chargers.
Intelepower by Century Yuasa delivers end-to-end systems that exceed AS4044:2024 compliance — enhancing asset performance — built on a legacy of trust.
For compliant, high-performance systems, trust us to deliver:
Lifecycle Replacement Programs - Prevent downtime with scheduled changeovers
Asset Management Plans - Structured testing and reporting for reliability
Certified Compliance - Fully aligned with AS4044:2024.
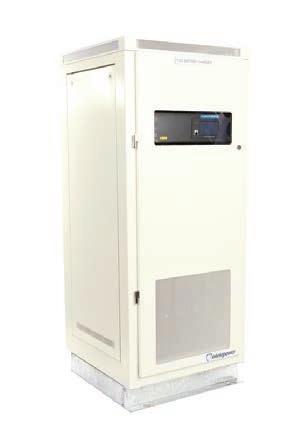
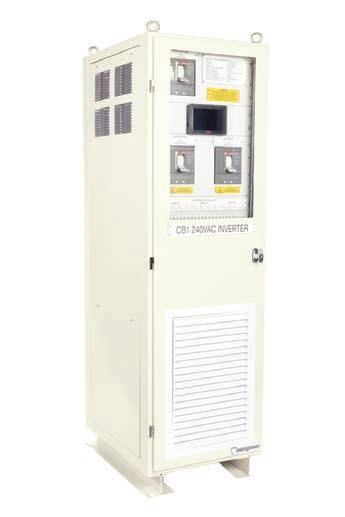
Backed by decades of experience and nationwide service support, we help you:
Extend asset life
Maintain compliance
Reduce operational disruption
Learn how we’re helping industries stay ahead of compliance and performance expectations.
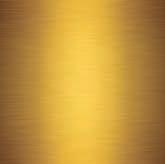



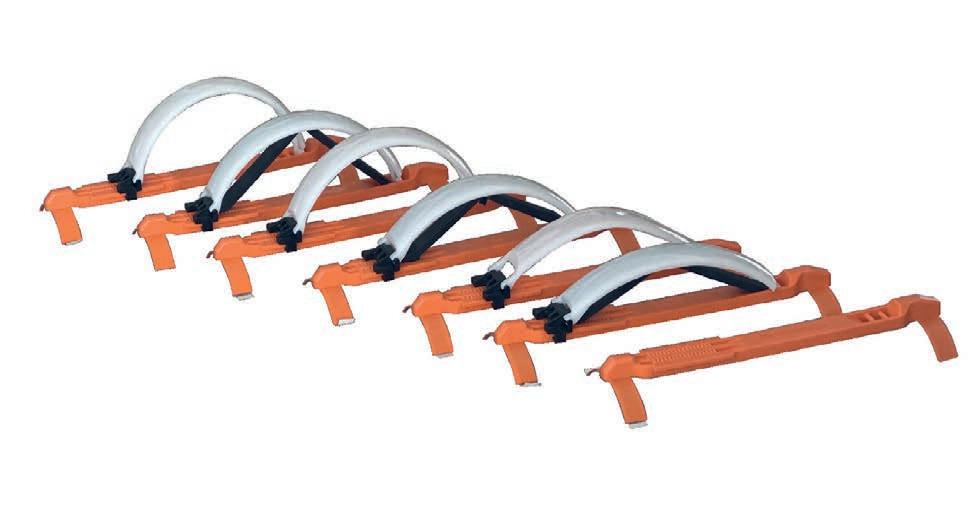
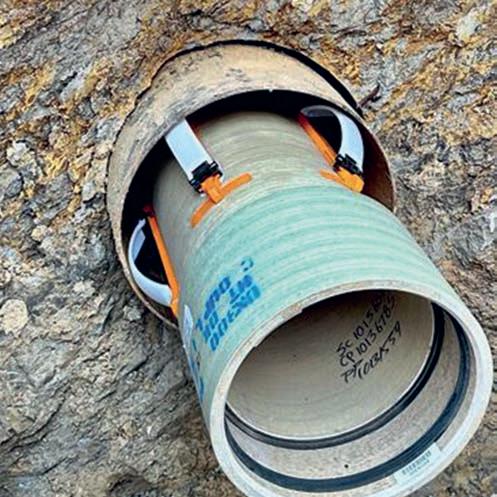
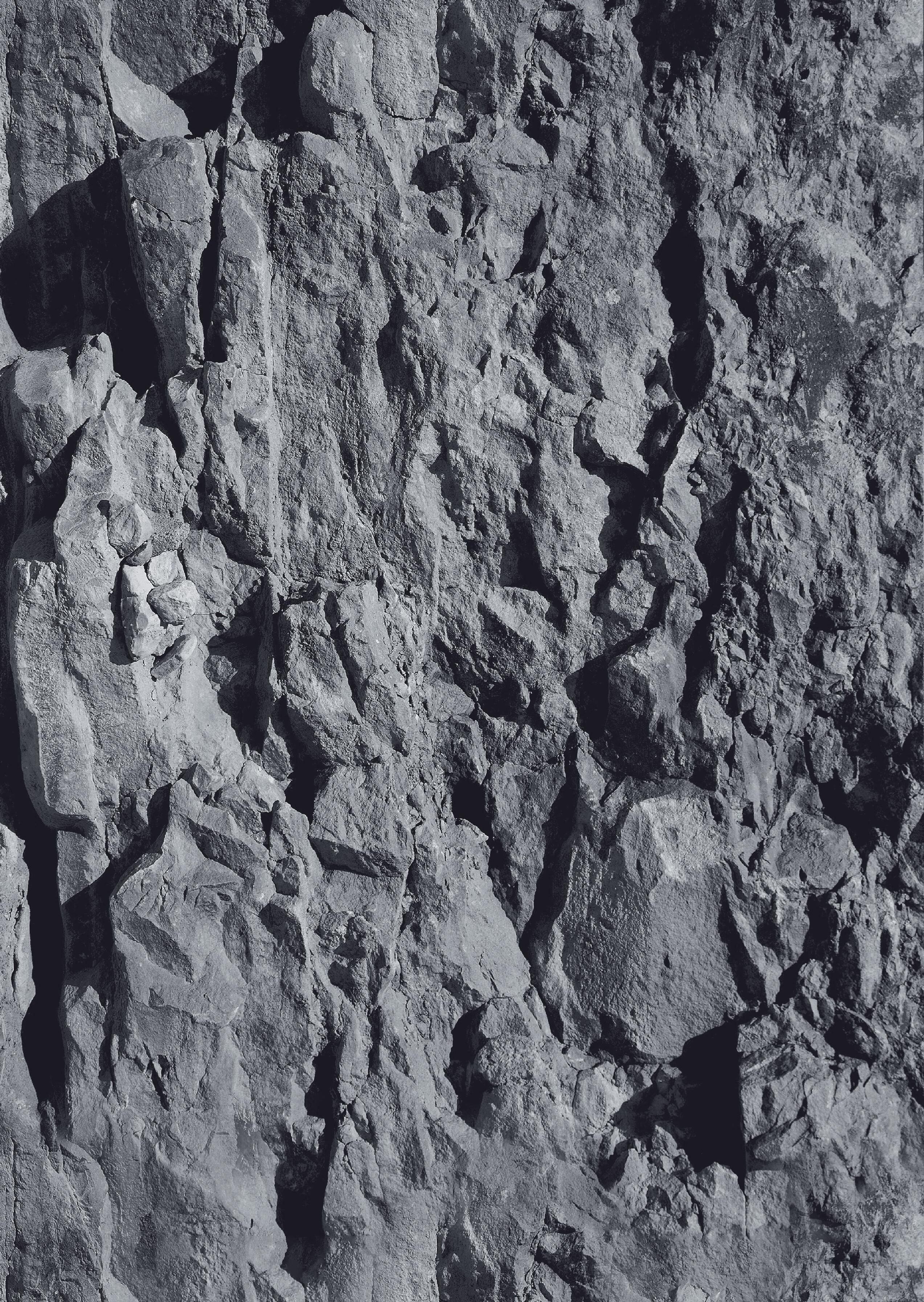
