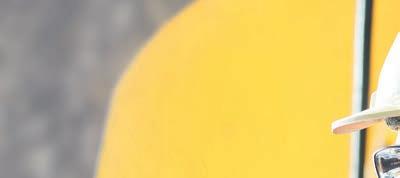
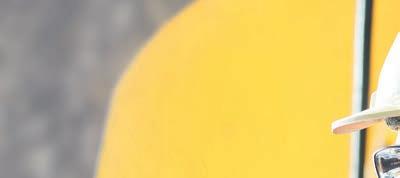
IN SIGHT Sustainability
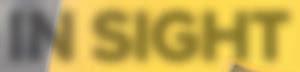
A new era of safety technology
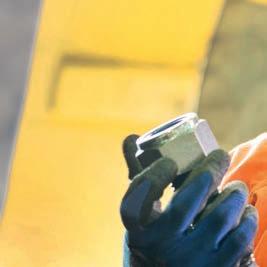

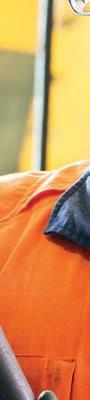
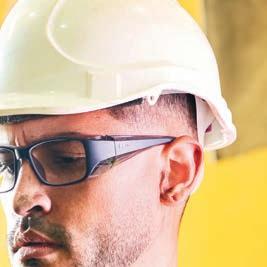
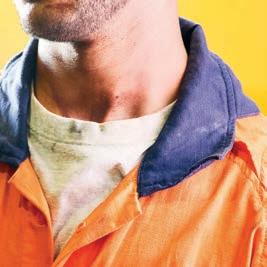

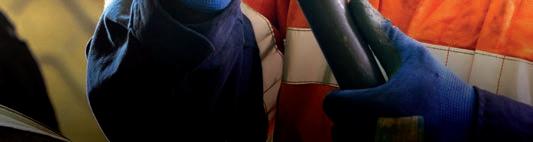
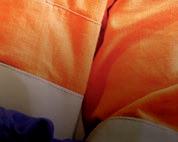
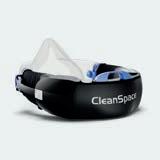
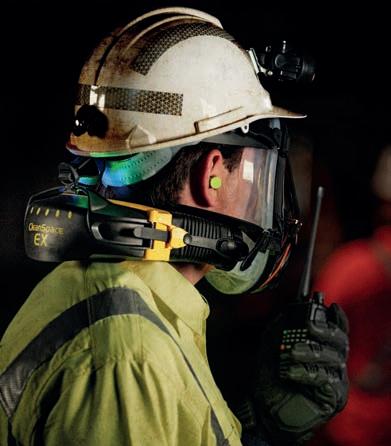
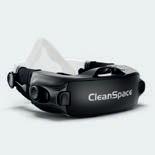
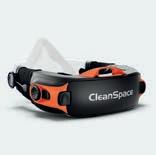
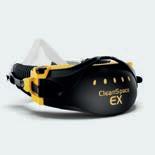
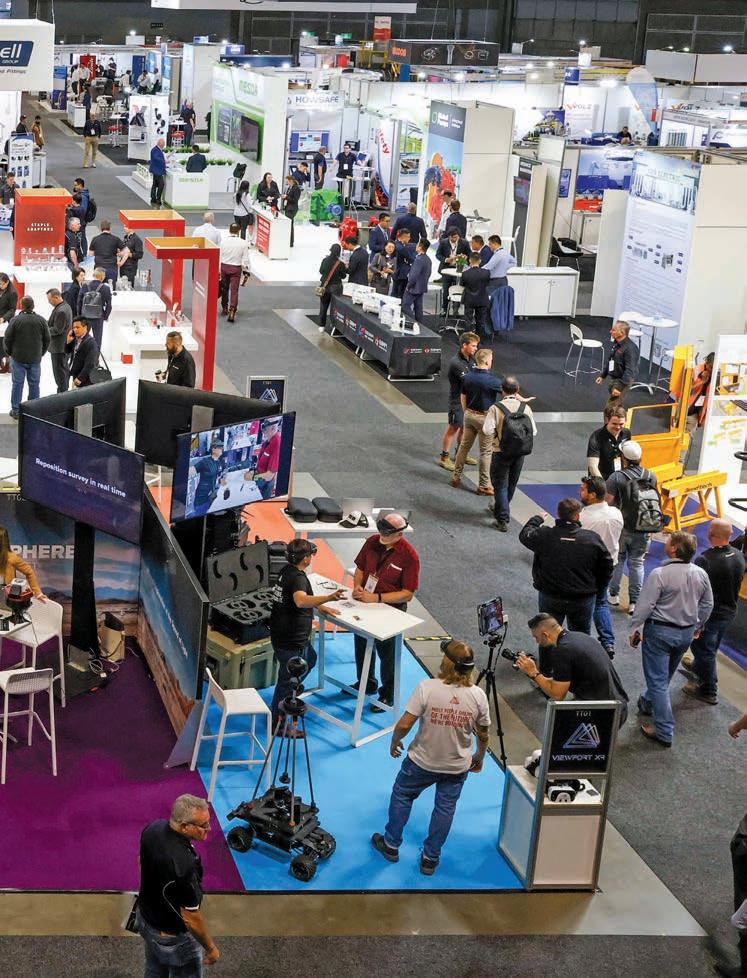
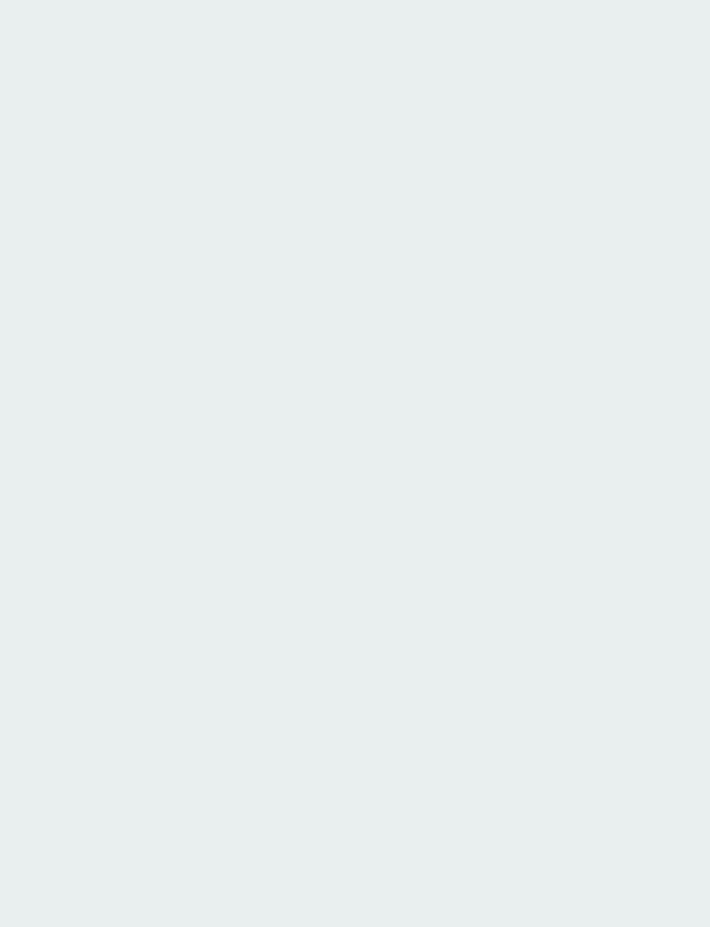
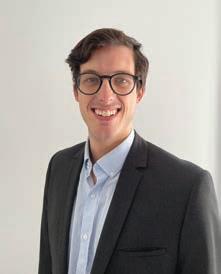
TOM PARKER
IA new era of safety
THE EMERGENCE OF ADVANCED TECHNOLOGY IS ELEVATING MINE SAFETY STANDARDS TO NEW HEIGHTS.
n mining, progress is defined not only by what we extract from the ground, but how we protect those who make extraction possible. While the industry continues to evolve in scale and capability, the integration of safety technology is becoming the true marker of forward-thinking operations.
From smart sensors that track fatigue in real-time to predictive analytics that prevent failures before they occur, innovation in safety technology is transforming how mining companies approach risk. These advancements are no longer optional – they are essential tools for creating safer, smarter and more resilient workplaces.
Embracing technology extends far beyond the adoption of new tools or software. It demands a shift in culture, where innovation is not an add-on but a core principle embedded within every layer of a company’s safety strategy.
It means empowering workforces with data, predictive insights and intelligent systems that inform decision-making and drive proactive risk management.
As the digital transformation of mining accelerates, the challenge is not simply to adapt but to lead with clarity, conviction and purpose.
JOURNALISTS
OLIVIA THOMSON Tel: (03) 9690 8766
CEO CHRISTINE CLANCY
MANAGING
Tel: (03) 9690 8766
Email: tom.parker@primecreative.com.au
ASSISTANT EDITOR
PREALENE KHERA
Tel: (03) 9690 8766
Email: prealene.kherA@primecreative.com.au
In this edition of Safe to Work, we explore the cutting-edge technologies reshaping safety across Australian mining and influencing best practices around the world.
Through case studies, expert insights and real-world applications, we examine how the sector is leveraging innovation to safeguard its people and future-proof its operations.
We also shine a spotlight on the Queensland Mining Industry Health and Safety Conference, a landmark event where industry leaders, regulators and innovators gather to share critical learnings and advance safety standards.
This year’s conference promises to elevate the conversation around technology, collaboration and the next chapter of mine safety.
Safe to Work is proud to support the exchange of knowledge and ideas that keep our industry strong, sustainable and safe.
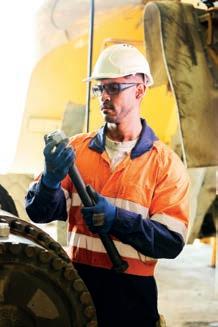
and innovations to create comfortable, high-quality and sustainable products that people love to wear.
Tom Parker Managing Editor
Email: olivia.thomson@primecreative.com.au
DYLAN BROWN Tel: (03) 9690 8766
Email: dylan.brown@primecreative.com.au
CLIENT SUCCESS MANAGER
JANINE CLEMENTS
Tel: (02) 9439 7227
Email: janine.clements@primecreative.com.au
ART DIRECTOR
MICHELLE WESTON
RESOURCES GROUP LEAD
JONATHAN DUCKETT
Mob: 0498 091 027
Email: jonathan.duckett@primecreative.com.au
BUSINESS DEVELOPMENT MANAGER
JAKE NIEHUS
Mob: 0466 929 675
Email: jacob.niehus@primecreative.com.au SUBSCRIPTION RATES
Having gained a strong reputation for its mining eyewear solutions, Bollé is also becoming a green leader, with the company successfully integrating sustainable practices into its product design, manufacturing and packaging stages to cater to the increasing need for environmentally conscious safety equipment.
Image:
Bollé Safety
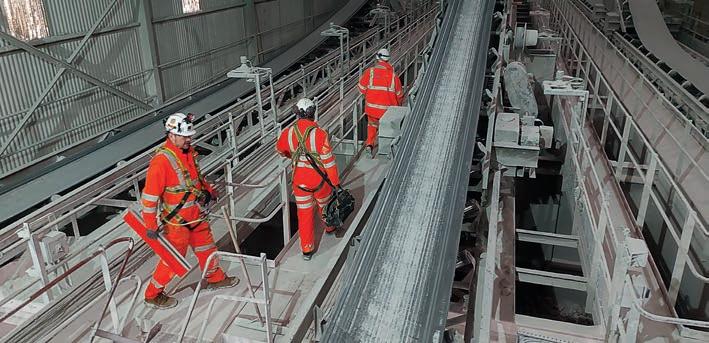
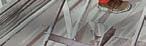
6 Eyeing eco excellence
What if your safety eyewear could protect both you and the environment? Bollé Safety puts that question to the test.
8 Safety snapshot
Safe to Work recaps the recent developments driving improved processes in the Australian mining industry. 16 Nowhere to hide Emesent’s autonomous mapping system has been a game-changer for underground stope mapping.
24 A fire-proof future
MusterFire is helping the mining industry adapt to emerging fire risks and evolving safety demands.
32 QMIHSC showguide
Safety is going back to basics at this year’s QMIHSC, with the conference re-enforcing the core principles that have always been essential for mine workers.
42 The emergence of AI
The International Labour Organization finds AI and digital technologies are improving
44 The perfect pour
Body Armour is redefining hydration on mine sites with its additive-free formulas and solutions.
50 Chamber of safety
When crisis hits on a mine site, refuge chambers can be a vital lifeline, providing essential protection and shelter.
68 What’s on the mining calendar?
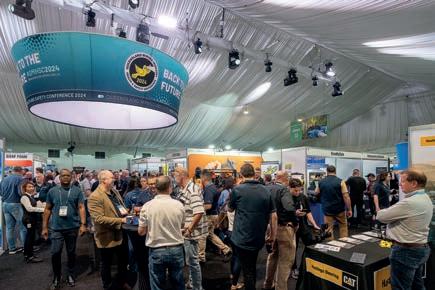
A series of major events are spotlighting innovation,
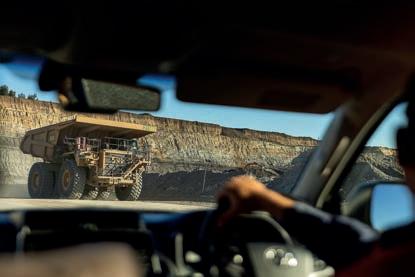
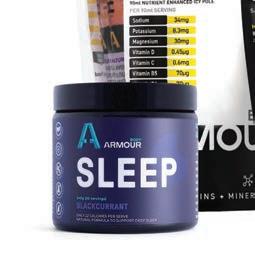
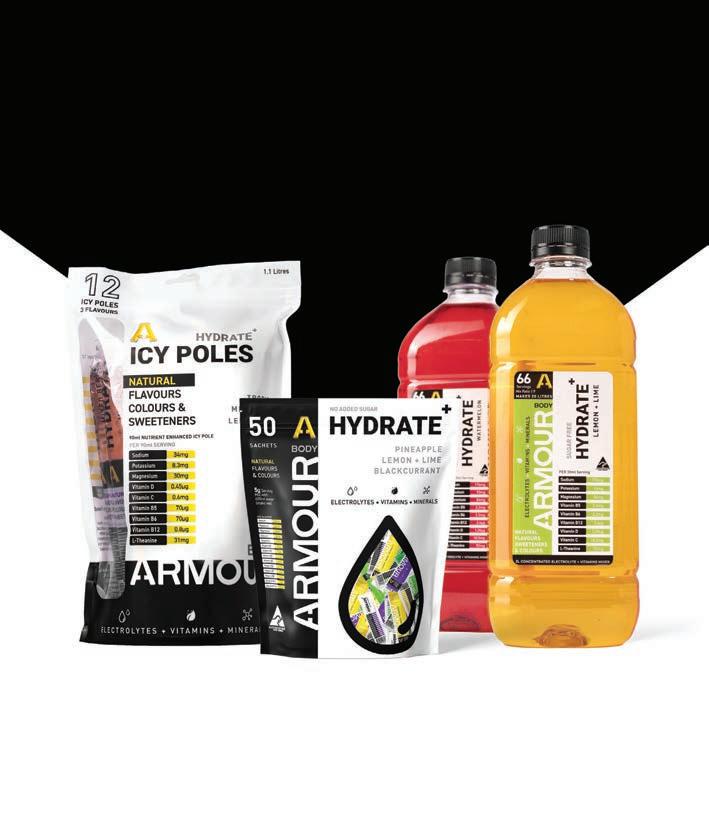
PREMIUM RECOVERY AND PERFORMANCE SOLUTIONS SPECIFICALLY DESIGNED FOR HEAVY INDUSTRY
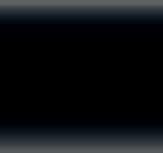
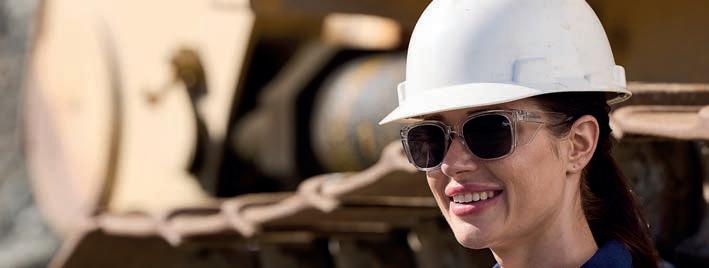
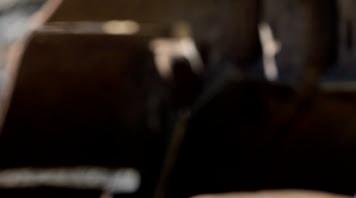
Eyeing eco excellence
WHAT
IF SAFETY EYEWEAR COULD PROTECT BOTH WORKERS AND THE ENVIRONMENT? BOLLÉ SAFETY PUTS THAT QUESTION TO THE TEST.
When working on a mine site, the likelihood of locking eyes with a dangerous hazard is high. From dust particles and loose metal fragments to chemical projectiles and debris, the risks are many and varied.
Miners rely on appropriate personal protective equipment (PPE) and durable eyewear to safeguard themselves against some of those harmful elements.
However, as environmental responsibility rapidly gains momentum in the industry, PPE is tasked with more than just evading foreign bodies.
Beyond shielding workers from visual impairment, safety glasses must now also protect the mine’s green interests.
And Bollé Safety is seeing to this growing demand in the market.
As PPE eyewear specialists, Bollé Safety believes eyes can be the window to a safer and eco-friendly future. Without compromising on safety, the company has successfully
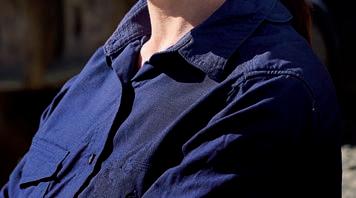
integrated sustainable practices straight into its product design, manufacturing and packaging stages to cater to the increased need for environmentally conscious safety equipment.
At a time when pressure is building on miners to ensure worker wellbeing while meeting their environmental, social and governance (ESG) goals, Bollé Safety is stepping up to the plate.
SUSTAINABLE SWITCH
Bollé Safety’s sustainability vision is thrust forward with a simple desire: wanting to live in a better world.
And as most people know, all global change first starts at home.
Driven by that very idea, the company has opted for an “up-front” approach in developing its products.
“Even if a product is fully recyclable, we don’t know if the user is going to do the right thing and recycle it,” Bollé Safety APAC trade marketing manager Tamara Mika told Safe to Work
“We have zero control over that, and if they throw it in the wrong bin all that good work has gone to waste.”
So in addition to developing products and packaging which can be recycled, Bollé Safety decided to enact change where possible. It now produces several fit-for-purpose safety glasses from ethically-sourced recycled materials, effectively reducing emissions at the front-end.
“When we have full control, which we do during product manufacturing, we’re trying to do everything we can to make our offerings environmentally friendly,” Mika said. “We ensure our glasses are sustainable before they even reach the customer.”
GOING GREEN
What started with humble beginnings in 2000 has rapidly accelerated in recent years. Supported by Bollé Safety’s golden triage – optical clarity, safety standards and sustainability –the Go Green initiative has driven the company to radicalise its approach towards product development.
The STKS Crystal’s modern frame design delivers a sharp, athletic look while protecting vision.
Images:
Bollé Safety
Putting its best foot forward from the get-go, Bollé Safety has integrated eco-design at its core and has set high standards for itself.
Products bearing its ‘GOGREEN’ label are required to satisfy clearly defined prerequisites while adhering to at least one sustainable criterion.
For products to be assigned the eco tag, their recyclable or biomaterial make-up must come with certifications or proof indicating their benefits.
Products also need to satisfy various sustainability criteria. They must be made up of at least 20 per cent recycled or bio-based material, possess over 50 per cent increased durability, ensure CO2 reduction is 20 per cent higher than a standard product, or be almost entirely recyclable at the end of their life.
Bollé Safety’s environmental push doesn’t hamper product calibre; with premium quality retention at the centre of its sustainability research.
“Bollé Safety is known for quality and our optics are second to none,” Bollé Safety Queensland and New South Wales sales manager Craig Yuile told Safe to Work when you have a recycled product like toilet paper, for example, it’s not as white and the paper is different. With things like toilet paper, we’re willing to accept that lower quality. We would never accept that with safety glasses; they still need to be perfect. That perfection is what we’re creating.
“Our products are based on extensive research. We spend a significant amount of time sourcing ethical and recycled materials, before we then do a lot of testing with prototypes to ensure they are of a durable quality.”
TRIPLE VISION
Released in 2021, the frames currently available under Bollé’s Go Green series are a combination of style, safety and sustainability.
Klassee – Industrial is a Bollé Safety prescription eco-frame compliant with international standards. Made in Grilamid BTR 600 LS, a bio-sourced polyamide based on 58 per cent
renewable resources, nearly half of its weight comes from castor oil.
Possessing a durable mould, Bollé Safety reduces waste by 49 per cent during the manufacturing process of Komet – Industrial. This range also serves as an entry-level polarised product to increase accessibility to premium lens technology.
In developing these glasses, Bollé Safety used a new injection process, allowing it to reduce its footprint during manufacturing, one of the top sources of carbon emissions in a product’s lifecycle.
SEAMLESSLY SAFE
Bollé Safety’s research and development team is firing on all cylinders, beyond improvements to its sustainable practices.
Alongside addressing PPErelated environmental concerns, the company is responding to another issue commonly faced by remote mine operators: access to services.
Through its new online prescription system, the Seamless Program, Bollé Safety is making it easier for miners to secure the right fit. The program’s augmented reality allows customers to virtually try on glasses, extracting measurements through a precise pupillary distance calculator. They can tailor eyewear to their liking, upload it to the system, and place the order.
“It’s an amazing platform because, for people working in the middle of nowhere, it can be really challenging to get to an optometrist,” Mika said. “Since its launch in November ... we’ve completed thousands of Seamless jobs.”
The Seamless Program isn’t the only product to be embraced by industry, with the company’s entire suite of offerings attracting demand.
“We only do high quality, and we only do safety eyewear,” Yuile said. “You get two eyes and you can’t replace them – ensuring their safety is our specialty.”
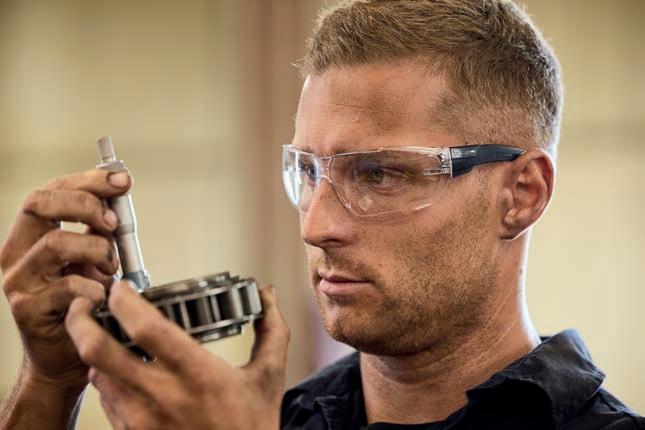
Bollé Safety’s environmental push hasn’t hampered product calibre.
Safety snapshot
SAFE TO
WORK
RECAPS THE RECENT ANNOUNCEMENTS AND EVENTS DRIVING IMPROVED PROCESSES ACROSS THE AUSTRALIAN MINING INDUSTRY.
The Australian resources sector has seen a number of safety-related developments in recent months. From new appointments, safety recommendations and serious incidents to conferences and broader industry trends, there’s been no shortage of news-worthy stories.
Safe to Work has compiled a snapshot of events that made headlines in May and June.
SAFETY INSIGHTS
The launch of an industry-first database in Victoria kicked things off in May.
The ‘Former Mines and Quarries Framework Consolidated Database’ report, released by Resources Victoria, contains information on 111,000 historic mine sites located on Crown land within Victoria. It will improve emergency responses in
some of the most remote parts of the state.
SafeWork SA and ReturnToWorkSA launched a free training course for South Australian businesses to help them understand how to protect workers from mental health risks. The two agencies produced the ‘Managing Psychosocial Hazards and Risks in the Workplace’ course, delivered by specialist training provider GPEx.
The Queensland Government appointed barrister Wayne Pennell as its new mining and resources coroner to help investigate fatalities and make recommendations to enhance safety for all workers.
The Workplace Health and Safety Show in Victoria was a major success, with over 5500 safety professionals packing the Melbourne Convention and Exhibition Centre from May 21–22. Exhibitors and visitors from across the
country took part in Australia’s largest showcase of technology, products and services to keep workforces and work environments safe.
An overview of the NSW mining industry’s health and safety performance throughout the 2023–24 financial year was also released with zero fatal injuries, 105 serious injuries, 256 lost time injuries, and 834 total recordable injuries reported in that period.
May concluded on a high note, with the announcement that employment in Western Australia’s mining industry reached a record high in 2024. With 135,693 on-site full-time equivalent positions filled last year, WA mining sector jobs have shown steady growth for eight consecutive years. Iron ore, gold, lithium, nickel, and alumina/bauxite remained major contributors to on-site mining employment.
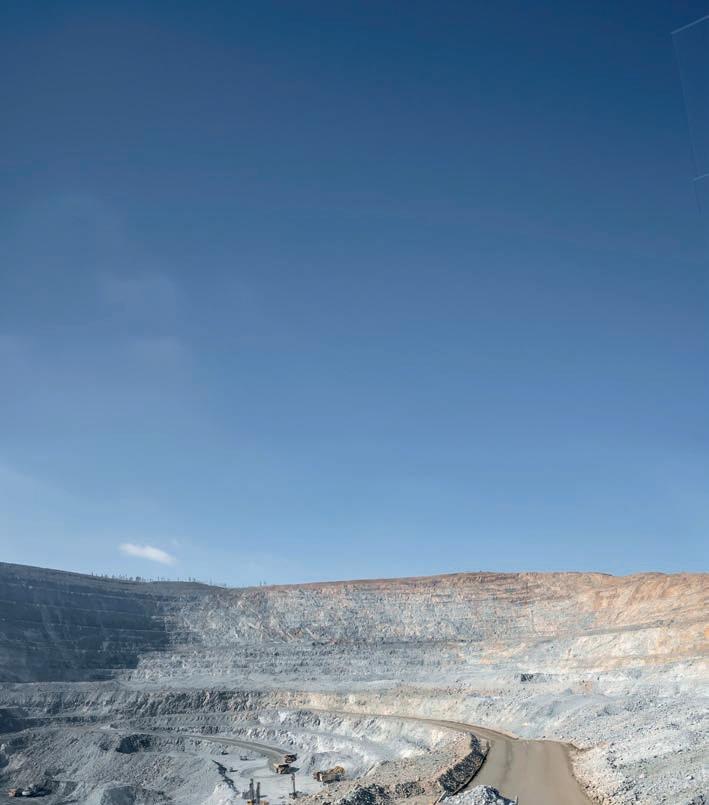
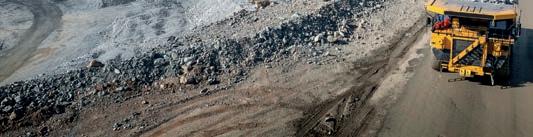
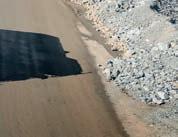
The June release of updated technical standards for elevated work platform manufacturers and operators was welcomed by the industry’s peak representative body, Elevating Work Platform Association. The organisation called the move a significant step forward in improving safety across the industry.
Chris Shaw was appointed as the director general for Western Australia’s new Department of Mines, Petroleum and Exploration.
SafeWork SA also launched a series of industry-specific compliance campaigns to eliminate potential hazards after noting a rise in workplace incidents. Under the initiative, employers were asked to keep on top of appropriate equipment maintenance, follow safety procedures, not take shortcuts, and ensure workers take regular breaks to maintain concentration and reduce fatigue.
Resources Victoria’s Earth Resources Regulator visited mines and quarries across the state as part of an initiative focusing on operational risk.
June ended with the Queensland Government releasing Terms of Reference for a review of the state’s resources safety framework. The review will scrutinise the regulatory model of Resources Safety and Health Queensland to ensure it delivers best outcomes in the mining, petroleum, gas and explosives industries.
SAFETY ALERTS
Several incidents were recorded at mine sites across the country within the two months, with some prompting the release of important recommendations to the industry.
In early May, a conveyor caught fire at a coal mine in New South Wales, with the state safety watchdog deeming it preventable. The incident occurred when a worker detected smoke and discovered glowing embers below a conveyor near the drive head area. The incident was a reminder for operators to have systems in place to monitor, assess and prevent issues to avoid the risk of conveyor fires.
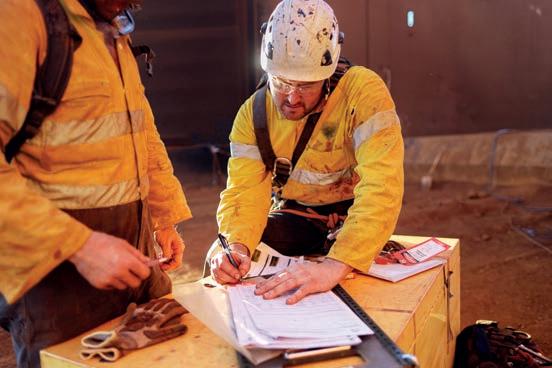
Soon after, a safety alert highlighting the hazards of operator distraction was issued following a near-miss between a light vehicle and front-end loader at an open-cut coal mine. The alert emphasised the need for unhindered situational awareness while operating mobile equipment.
Recommendations were also made following investigations into a 2023 incident at Mt Magometon Quarry where a worker’s arm was surgically amputated after being entangled in the idler drum of a moving conveyor belt. Mine and quarry operators have been urged to manage entanglement risks by implementing correct introduction-tosite procedures.
The NSW Resources Regulator also raised concerns regarding the growing number of electric shock incidents in the mining industry. The body reminded operators that they must ensure equipment is fit-for-purpose and maintained in a state without risk to workers, with regular maintenance and inspection systems in place.
June started with another safety advisory issued by the NSW regulator to curb the growing trend of heavy vehicle rollovers in the mining industry. The regulator noticed, with some “considerable concern”, an escalation in truck rollovers in the past 12 months, advising mine operators to have a structured, risk-assessed approach to address adverse vehicle interactions.
Mine workers were once again reminded to exercise situational awareness when operating mobile equipment following a two-vehicle collision at an open-cut coal mine, while a serious incident at a metalliferous mine prompted renewed attention on ground support safety measures.
A worker narrowly avoided serious injury after a large rock dislodged from an unsupported underground face, hitting the worker’s head and shoulders before landing next to him. In response, the NSW regulator said it will consider adopting a clearer and more definitive position on the management of unsupported ground at working faces
Employment in Western Australia’s mining industry reached a record high in 2024.
Image: Gorodenko shutterstock.com
Smarter safety underground
AS UNDERGROUND OPERATIONS GROW MORE COMPLEX, MINE OPERATORS MUST FIND NEW WAYS TO MONITOR AND REDUCE SAFETY RISKS.
Underground mining remains one of the more extreme working environments, where visibility is low, spaces are tight, and margin for error is razor thin. Even small inefficiencies can trigger major safety risks.
“People and large equipment don’t mix, especially underground, with confined environment and poor visibility amplifying the risk,” Mine Site Technologies (MST) sales executive Leo Crespin told Safe to Work
Air quality is a prime concern underground. Traffic congestion and idle time generate localised emissions that endanger workers and impact environmental compliance.
Collision ‘interactions’ between vehicles and people have also grown in recent years. To mitigate such hazards, Crespin said the industry has traditionally followed the hierarchy of control, aiming to engineer people out of risk.
“When this isn’t feasible, reliance falls on training and PPE (personal protective equipment),” he said. “But these are the two weakest components of the hierarchy of control.”
As balancing safety, compliance and efficiency becomes increasingly difficult, Crespin said the industry must
re-evaluate traditional approaches to hazard management.
MST is helping the sector do just that with HELIX, a powerful, integrated digital platform designed to enhance situational awareness, reduce risk and support safer, more efficient underground operations.
“HELIX brings together multiple safety and efficiency solutions into one platform,” MST product manager Ramodh Rangasamy told Safe to Work. “It enhances visibility across your entire operation, from emergency response to ventilation control.”
At its core, HELIX enables centralised automation and monitoring of infrastructure – fans, lights, alerts, and ventilation systems – while overlaying critical technologies that target key underground hazards.
Take vehicle interactions and air quality, for example. HELIX Dispatch enables live fleet tracking, reducing traffic congestion and smoothing vehicle flow. HELIX Telemetry monitors run-time, idle-time and fuel burn, helping teams cut diesel consumption and reduce emissions.
“This isn’t just about operational efficiency; it’s about protecting lives,” Crespin said.
Some of the other solutions the HELIX platform offers include:
Proximity detection
Low-frequency transmitters can detect personnel from up to 20m away and alert drivers and pedestrians when someone enters a high-risk zone.
Situational awareness
Using Wi-Fi radio-frequency identification (RFID) tags, vehicles and personnel are monitored in real-time, with the option to set up zone-based escalations for smaller alert zones with high-risk proximity.
Personal emergency devices
PEDs can be used for evacuation alerts, messaging and emergency response, allowing direct communication between personnel and the control room, even when other systems are down.
Tracking systems
With a live, 3D view of personnel, vehicles and fixed assets, applications range from pre- and post-blast management to monitoring traffic flow to supporting ventilation on-demand.
MST can deliver a complete, endto-end system, or integrate HELIX with existing infrastructure.
“MST can deliver the entire ecosystem,” Crespin said. “But we’re agnostic and can incorporate pieces of the puzzle to find the right solution.”
Rangasamy agreed.
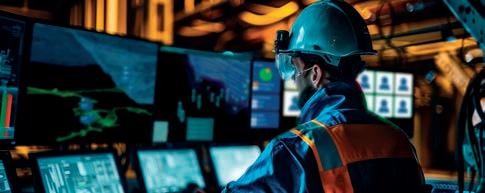
“HELIX ... integrates seamlessly with fixed assets already in place. You’re not locked into proprietary systems or disconnected platforms,” he said.
Everything feeds into a single interface – no third-party log-ins, no siloed data – giving operators a full picture of their underground operations.
And in an environment where seconds count and visibility is everything, that unified view could be the difference between a close call and
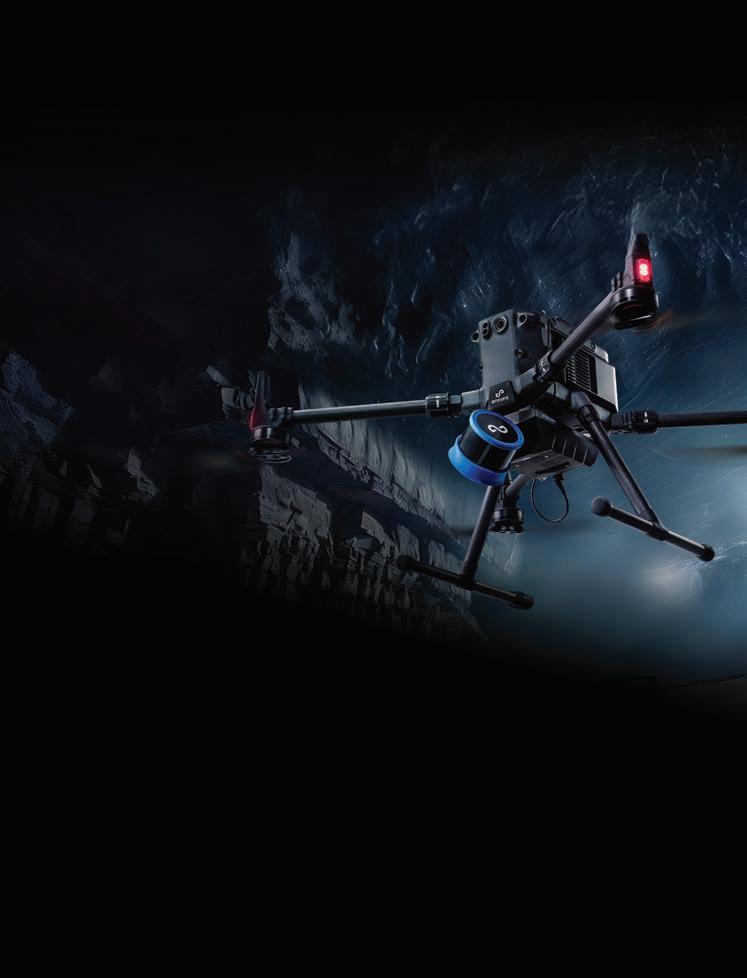
MST Global’s integrated software platform, HELIX, is solving many problems in the mining industry.
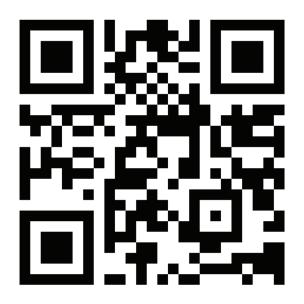
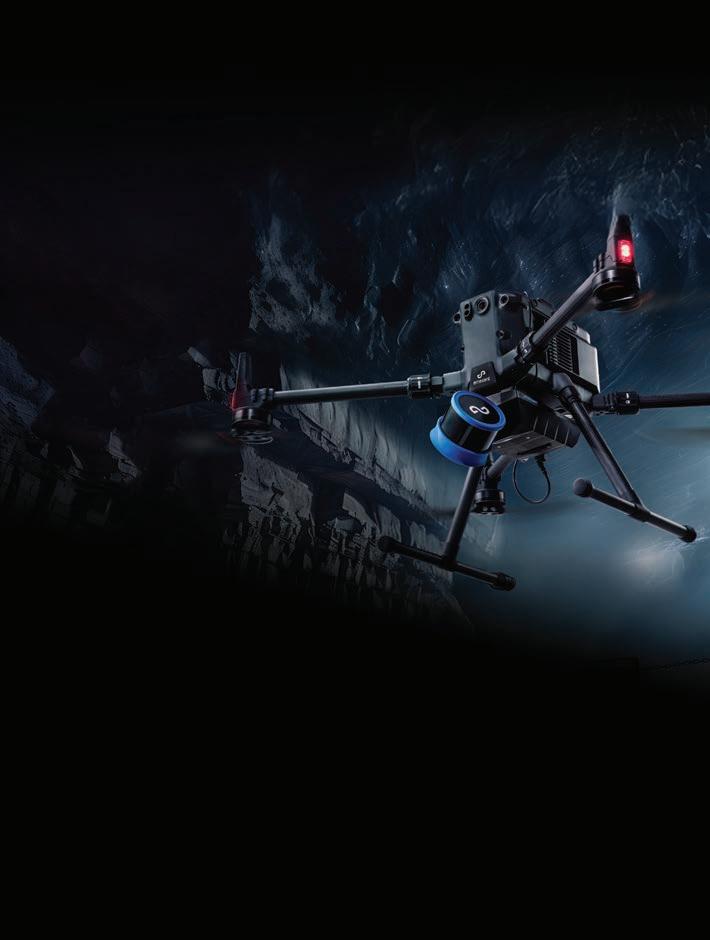
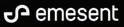
Safety technology
Simplifying strata safety
NOME’S ROCK MONITOR XR SYSTEM IS SETTING A NEW STANDARD IN REALTIME STRATA MONITORING.
For Nome managing director
Nathan Owen, the drive to develop safer underground mining solutions comes from personal experience. Descending from three generations of coal miners, Owen is acutely aware of the risks associated with underground work.
“I’ve seen my father’s co-workers injured and killed in coal mines,” Owen told Safe to Work. “When the opportunity came along to make a difference and help prevent those injuries and fatalities, it was important for me to pursue it.”
Underground mine managers, geotechnical engineers and geologists have long relied on a combination of experience, manual observation and mechanical monitoring to manage strata stability. But as mines extend deeper and ground conditions become more dynamic, the need for real-time scalable solutions has become increasingly important.
Nome has developed the Rock Monitor XR system to meet that demand. Installed into mine roofs or sidewalls, each telltale (a displacement monitoring sensor) includes either two or four anchor points to accurately capture strata movement at different strata height levels.
These instruments connect to an underground controller that transmits continuous data to a central server, viewable in real-time, eliminating manual inspections and providing instant data. The system also integrates with client smart centres to view all mine data simultaneously from a single control room.
“By implementing real-time strata monitoring, mines eliminate the need for personnel to inspect instruments
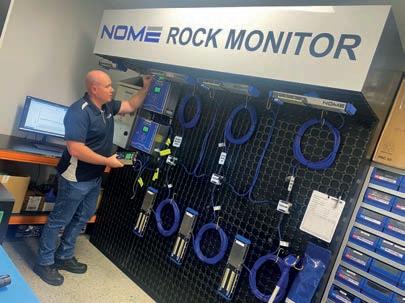
incidents before they escalate.
It also boosts efficiency. One site previously halted operations three times a day for manual readings. With Rock Monitor XR, inspections dropped to once daily, recovering up to $400,000 per day in lost production.
At under $250,000, the system typically pays for itself in less than one uninterrupted shift, Nome said.
Engineering efficiency is another key benefit. Without live data, ground support is often over-engineered. With real-time insights, however, engineers can optimise designs and reduce material use, labour, and manual handling risks.
“The data allows you to make decisions based on real conditions rather than assumptions,” Owen said.
Simplicity and scalability are built into the design. Any worker can install instruments in under five minutes, with no specialist training needed.
A single controller supports up to 150 instruments along a 10km daisychained cable, with extra controllers expanding coverage as needed. Many other systems require individual cables for each sensor – up to 150km of cabling for the same scale – making them costly and less practical.
Unlike wireless systems that face
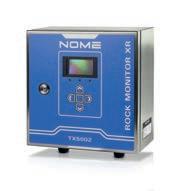
reliability and safety issues in gassy environments, Rock Monitor XR is Intrinsically Safe Certified (IECEx/ATEX). It is tested to ensure no ignition risk, even in methane-rich atmospheres or instrument damage scenarios.
Originally developed for the coal sector, Rock Monitor XR is now used in hard rock and civil tunnelling. According to Nome, other systems may be more complex and expensive to install, requiring larger boreholes, in-situ grouting and specialist teams.
From managing high-stress ground conditions in hard rock mining to monitoring tunnels for convergence, RockMonitor XR adapts to each application with minimal site disruption and no need for specialist crews.
“We’ve created something that’s not only easy to use but is also creating better outcomes,” Owen said.
With Rock Monitor XR, Nome is redefining underground strata monitoring, delivering scalable, intrinsically safe, user-friendly, and cost-effective solutions that empower operations to protect lives, increase efficiency, and drive innovation across the mining and tunnelling industries.
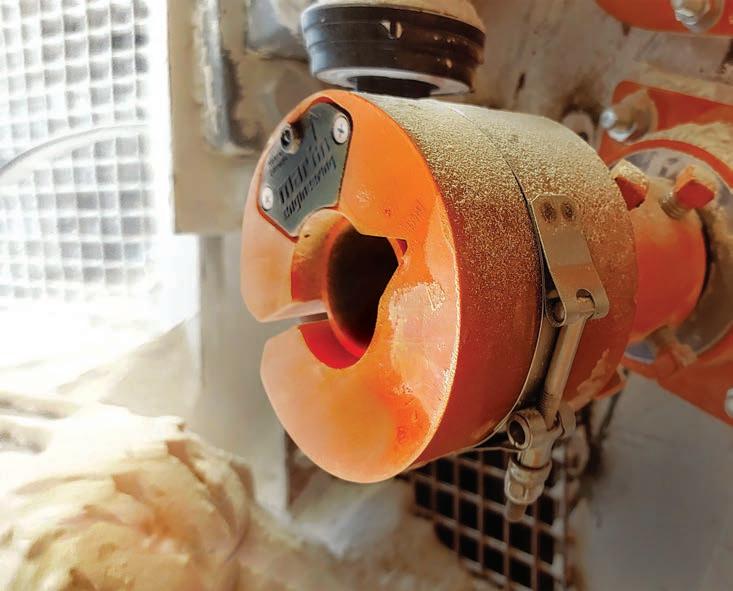
Nome managing director Nathan Owen developed the rock monitoring solution to make a di erence in the industry.
Images: Nome.
A single Nome Rock Monitor XR controller can support up to 150 instruments.
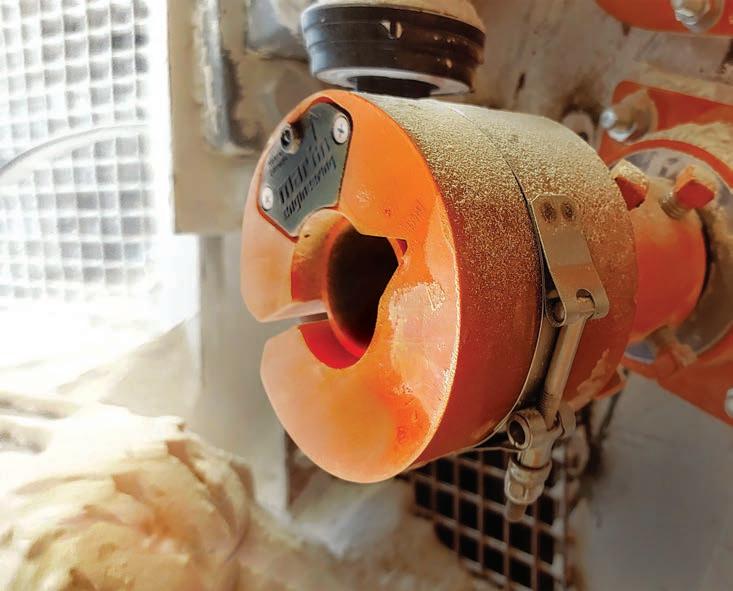

The innovative N2® Position Indicator enables continuous remote monitoring of belt cleaner performance anytime, anywhere, even from hard-to-reach locations. Actionable information is delivered directly to your mobile device via Martin's proprietary OnSite app.
N2® Position Indicator’s comprehensive predictive service technology tracks tension, blade wear, and mainframe integrity —minimizing inspections and downtime while improving safety and efficiency.
Martin Engineering.
We make the connection. N2® delivers the message.
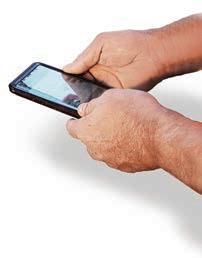
N2® Position Indicator HD mounted on a QC1+™ Cleaner HD
All eyes on safety
HEXAGON HAS HELPED A TASMANIAN BASE METAL MINE COMBAT FATIGUE THROUGH ITS OPERATOR ALERTNESS SYSTEM.
Deep in the belly of Tasmania’s Rosebery underground mine, truck operators have access to a high-tech solution guarding worker safety and wellbeing.
Hexagon’s Operator Alertness System (OAS) kicks into action before fatigue sets in, averting potentially dangerous accidents caused by unmanaged or neglected fatigue.
As an internationally recognised digital solutions provider, Hexagon stepped up to the challenge of meeting the unique and complex requirements of mine owner MMG. Both parties, guided by the same tenets, have worked towards a singular goal.
“We want everybody to get home safe every day,” Hexagon principal safety advisor Josh Savit told Safe to Work. “Those are the absolute necessities, and there is no discussion beyond that. The cost of a human life is the ultimate cost, and fatigue and distractions are a critical aspect of that.”
Savit said it’s essential to eliminate any traces of guesswork from the safety process.
“Human beings have the luxury of knowing that they’re tired and that they need rest, but by the time they know they’re tired they’re well into the high-risk zone,” he said.
“But we’ve got a lot of triggers, both physical and emotional, that Hexagon systems can pick up and detect if something is happening. This is when operators can take action.”
Hexagon’s OAS unit detects fatigue-led events, from spotting a driver chewing on their cheeks or frequently turning their head side-to-side to the rate and duration of blinking.
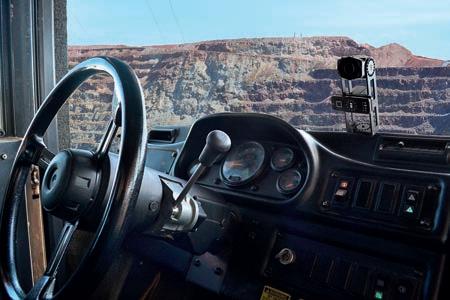
In response to drowsiness or micro-sleeps, the system’s software provides real-time alerts to operators, empowering them to act well before they enter the high-risk zone.
It sends data to a remote monitoring centre, providing an independent assessment of each notification before informing the mine through email or text of any critical events that require immediate attention.
OAS is also easy to install and configure. Ultimately, it’s built to look out for operators.
“OAS is focused on two key factors,” Savit said. “First is the understanding of what’s happening in the moment. The alarm and vibrator might go off, notifying the operator they’ve just had a micro-sleep or they weren’t paying attention to where they were going. This helps them become immediately aware and realise that they were distracted.
“At the same time, all the data is collected for continuous-improvement purposes, which helps to understand operators’ longer-term health risks.”
CHANGING OUTCOMES AT ROSEBERY
Working with MMG, Hexagon deployed OAS on Rosebery’s underground haulage fleet.
But technology is just one layer of mine safety; change management and data insights are also important layers. Even when solutions are integrated, operators must still be engaged and re-engaged in a cycle of improvement.
To configure the solution to the mine’s challenging underground environment, Savit and his team had to first take a more hands-on approach.
“We got fully inducted into the mine and went on several different routes with the operators, across different shifts,” he said. “This helped us build a solid understanding of the mine and its unique requirements.”
Severe fatigue events have reduced 81 per cent at Rosebery since the implementation of OAS.
“Any worker that comes to work should go home safely every day,” Rosebery general manager Steve Scott said. “Hexagon has a system that allows us to deliver on that promise to our employees.”
While a shared philosophy has been the catalyst for a successful partnership between Hexagon and MMG, there’s another ingredient ensuring safer outcomes: passion.
“We have a drive for safety; it’s something shared across all of Hexagon,” Savit said. “It’s not just a mantra, it’s a core belief.”
Image: Hexagon
Hexagon OAS is designed to combat operator fatigue and distraction in mining operations.
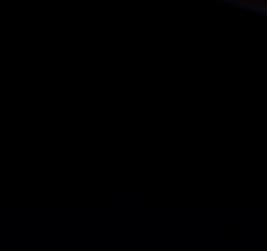
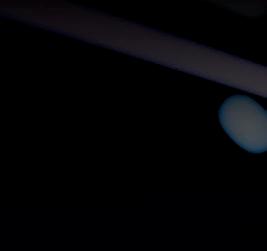
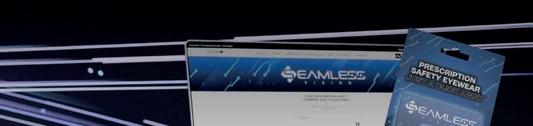
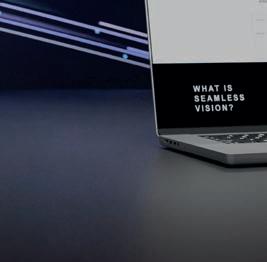
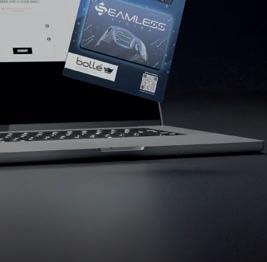
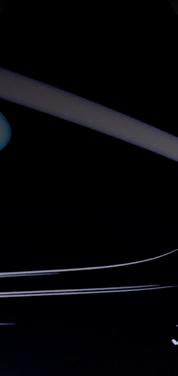
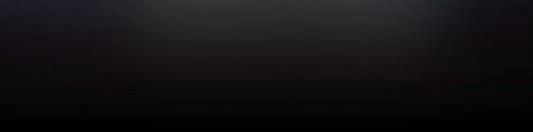
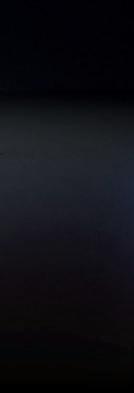

Safety technology
Nowhere to hide
EMESENT’S AUTONOMOUS MAPPING SYSTEM HAS BEEN A GAME-CHANGER
FOR UNDERGROUND STOPE MAPPING,
MAKING A DIFFERENCE AT SOME OF THE WORLD’S
BIGGEST MINES.
“One key instrument for us is the Hovermap; it’s an essential part of the team’s toolkit.”
Those are the words of James Comeau, an operations manager at one of the world’s deepest base-metal mines, where Emesent’s autonomous mapping system has swapped guesswork for speed and precision.
From mapping stopes and surface infrastructure to monitoring deformation, Hovermap does it all, and does it accurately.
“Hovermap is outstanding … it makes our time underground more efficient,” Comeau said.
Precise stope mapping is critical in underground mining, providing the data needed to monitor structural integrity, assess ore quality, and maintain production efficiency. But mining teams have long relied on tools and processes that can fall short.
Traditional cavity-monitoring systems (CMS) are slower to deploy, capture incomplete data, and can put personnel at risk. Manually operated drone-based systems come with their own hurdles, relying on constant communication signals and highly skilled operators. These limitations make uninterrupted and comprehensive mapping difficult.
Enter Emesent’s Hovermap.
Hovermap has delivered a faster, safer and more precise approach to stope mapping. It is powered by SLAM-based LiDAR (light detection and ranging), enabling operation in GPS-denied environments where other systems can struggle.
The system reduces data-capture time by producing high-resolution 3D models in minutes. It adapts easily to complex voids or spaces and operates with minimal human input, making
it ideal for hazardous or previously unreachable areas. Even in dark, wet and dusty underground conditions, Hovermap is built to perform.
Its advanced autonomy and obstacle avoidance allow smooth navigation in challenging environments. Increased efficiency and accuracy are a given, with its automated georeferencing eliminating manual steps. The result is rich, consistent data that enables confident planning and decision-making.
Hovermap can be mounted on drones, vehicles and poles, or operated by hand. This flexibility means teams can tackle a range of tasks using the same device. It also allows for remote operation, ensuring personnel stay safe while capturing detailed, actionable data.
Hovermap offers several methods for stope mapping to suit different site conditions. The drone-mounted system enables fully autonomous flights beyond visual line of sight, navigating through complex and dusty environments without GPS or communications.
Emesent’s autonomous exploration and mapping o ers set-and-forget operation.
For hard-to-reach voids where drones can’t fly, Hovermap can be attached to a CMS boom or pole to collect 3D point clouds in minutes.
Vehicle-mounted capture provides another option, with Hovermap connected to the machine and operated from the surface. This offers near real-time scans and 360° coverage, supporting faster decisions and keeping workers from harm’s way.
The high-resolution data captured through all three methods allows for accurate calculations when required.
Operators can identify overbreak and underbreak, material dilution, and plan backfill paste scheduling with greater confidence, helping to reduce delays, cut costs, and support better reconciliation. More detailed imagery also helps verify compliance with bund height and placement regulations.
Hovermap is effective above ground, where it can scan stockpiles, inspect infrastructure, and build digital twins for rehabilitation or condition monitoring. Whether underground or on the surface, the system puts the inaccessible within reach.
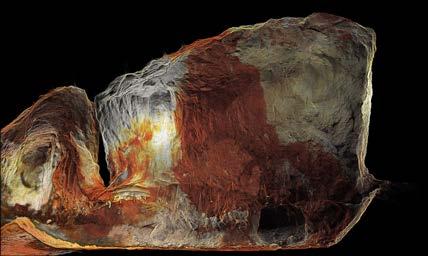
EMBEDDING CYBERSECURITY BY DESIGN, NOT
AFTERTHOUGHT.
Remote monitoring: Principles versus practice
WITH REMOTE MONITORING SYSTEMS KNOWN TO PRODUCE A RANGE OF BENEFITS, MARTIN ENGINEERING EXAMINES WHETHER THERE ARE ANY PITFALLS IN ADOPTING ADVANCED TECHNOLOGIES.
The potential for remote monitoring systems to virtually eliminate the need for physical inspections and improve safety in the mining industry is enticing. And that’s before considering the time savings and productivity improvements.
However, while technologies such as remote monitoring systems on conveyor belt cleaners can help to overcome significant maintenance challenges, their implementation can also create new unforeseen problems for operators.
Over the past decade, Martin Engineering’s team has developed remote monitoring solutions that use sensors to provide data on the condition and performance of conveyor belt cleaners without maintenance teams having to physically attend to the equipment to perform a manual inspection.
Traditional inspection regimes can not only introduce unnecessary operating costs but also create
needless exposure to maintenancerelated hazards that are responsible for many serious incidents in mining.
That’s why remote monitoring is especially effective.
VIABLE REMOTE MONITORING
Martin Engineering’s Center for Innovation, located at its headquarters in the US state of Illinois, designed and developed the first N2 Position Indicator (PI) for monitoring polyurethane conveyor belt cleaners.
The conveyor belt cleaners’ performance and condition information is transmitted via a central ‘gateway’ to the cloud. Data is then presented and accessed via a dedicated mobile app or desktop platform.
Martin’s N2 PI is the ideal solution for drastically cutting down on inspection time, and the more difficult the belt cleaners are to inspect the greater the potential for time saving.
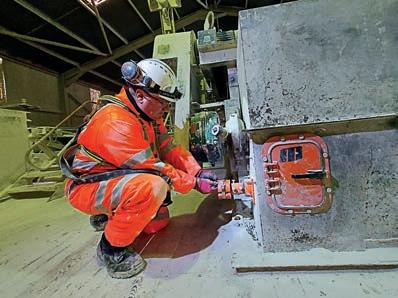
much as 90 per cent. In addition, remote monitoring helps to remove the guesswork around belt cleaner servicing; the condition of the blade is based on data-driven facts rather than human observation.
That unleashes the prospect of true preventive and, over time, predictive maintenance.
Since its introduction, there are now thousands of N2 PI devices installed at more than 40 mineral processing operations worldwide.
While operators monitored the performance of their equipment during extensive trials, Martin monitored the performance of the PIs, discovering that it might not be the right fit for some operators.
Working closely with customers, Martin engineers identified four key areas to consider with the implementation of a remote monitoring system:
DOES IT ADDRESS YOUR PAIN POINTS?
Martin Engineering research found that many technological solutions falter because they only address the symptoms, rather than the real pain points. In other cases, developers do not clearly explain to operators how their innovative solution addresses their problems, leading to misunderstanding and misuse.
And, perhaps worst of all according to Martin Engineering research, are those examples where technology introduces new pain points overlooked during development and testing.
It was therefore critical for Martin’s designers to ensure the N2 PI supported the identification
Installation of the N2 PI system.
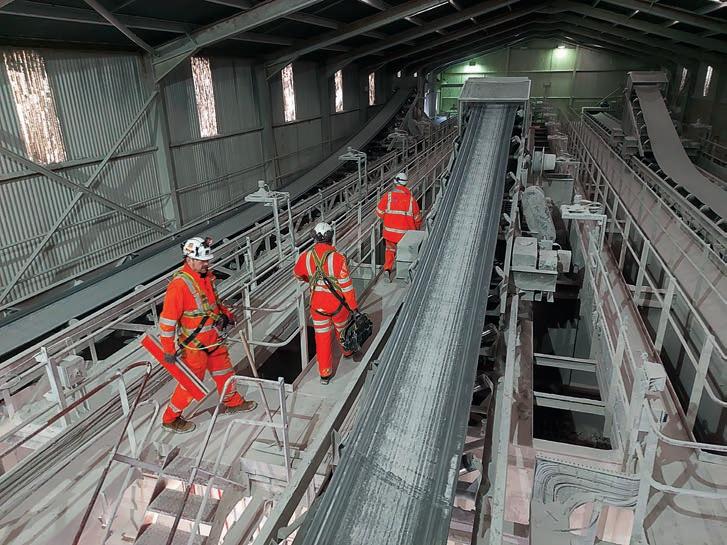
operational discrepancies between individual belt conveyors.
DOES IT DELIVER USEFUL, ACTIONABLE DATA?
No matter how impressive technology is, or how interesting remote monitoring metrics may be, data collection alone doesn’t achieve better productivity. The information needs to be helpful, accurate and presented in a way that helps decision-making.
The Martin OnSite mobile app and OnSite dashboard provides a series of clear charts with actionable information that’s automatically analysed, interpreted and presented in a way that makes decisions straightforward.
ARE YOU WILLING AND ABLE TO CHANGE?
Introducing any technology requires proper change management. The installation and integration of the system must ensure the benefits of the change are well-anticipated and understood by stakeholders, and the new workflows are less onerous than the current regime.
In some cases, conveyor belt maintenance teams who aren’t told that sensors are fitted, or aren’t trained on how they function, have
trained in the right way, including explaining the rationale for installing remote monitoring systems, as well as reassurance about motives to limit the resistance to change.
DOES IT INTEGRATE WITH EXISTING SYSTEMS?
The N2 PI is designed to be retrofitted to belt cleaners without other upgrades to the system. It’s also scalable across operations of all sizes, types and ages without incurring additional cost. However, there may be numerous physical obstacles ranging from accessibility and available space to legacy steelwork that needs refabricating.
Once the central ‘gateway’ is installed and powered, each N2 PI can be fitted and paired in just a few minutes. A single gateway can handle thousands of PI sensors, so expanding the N2 network doesn’t require further investment in the communication infrastructure.
If an operation has centralised its remote monitoring for other components, systems like N2 data can integrate with existing systems, although it may require additional work to ensure compatibility. To avoid data overload, it’s recommended to
begin with simple core actionable KPIs, such as status and wear times, before expanding as required.
“LISTENING TO UNDERSTAND” IS THE KEY TO SUCCESS
After spending around five years developing its N2 PI for conveyor belt cleaners, Martin Engineering formally launched the technology in 2020. Working hand-in-glove with customers’ production and maintenance teams, Martin service technicians listened, resolved teething challenges and worked to address reported issues.
As a result, Martin has gone on to develop two further N2 conveyor products sensors that work with the same gateway and is expected to launch a “game-changing” new flow aid sensor in 2025.
Martin is dedicated to helping customers accomplish their safety and efficiency goals, so the inspection of operations for viability followed by a proper introduction and phased integration of the OnSite system is recommended.
To achieve the desired productivity improvement, it is critical to understand the potential pitfalls that accompany change. Having the right conversations, understanding the true pain points, embracing the challenge and working together are critical to transforming this opportunity into action and delivering tangible results.
Images: Martin Engineering
Martin technicians installing the new N2 PI smart monitoring system at a lime works.
Building TRUST
TRUST ITM SENSORS ARE RISING TO MEET A GROWING DEMAND FOR REAL-TIME UNDERCARRIAGE COMPONENT MONITORING FOR MINING EQUIPMENT.
Mine site conditions can change on a dime, and that means quick thinking is needed to keep operations running smoothly.
But without access to all relevant information, workers risk making uninformed decisions that could have long-term safety consequences.
Through the power of data, ITM Group is aiming to shine a light on a largely unseen side of mining: equipment undercarriages.
Well known in the industry for its undercarriage components, ITM Group has spent years researching, developing and collaborating with its global network of original equipment manufacturers (OEMs) to deliver the latest product developments to the mining, construction, utility, forestry, roadbuilding and agriculture industries.
The ITM Group product range covers all crawler machine types, such as dozers, excavators, shovels and drills, across multiple manufacturers and applications. The company’s Australian division, ITM Mining, specialises in undercarriage systems
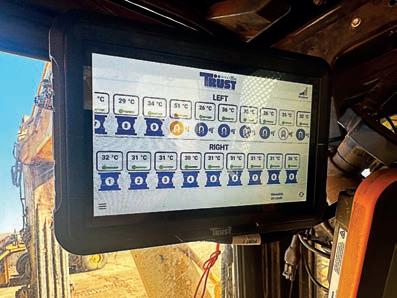
for resources-specific heavy fixed and mobile equipment.
“Apart from supplying high-quality ITM-manufactured undercarriage systems and components, we also service our customers through our track shop services and track frame refurbishments programs,” ITM Mining product support manager Shane Skipper told Safe to Work
“We provide on-site undercarriage inspections to our customers on the mine sites, and we provide custom or special projects to assist our customers with their unique requirements.
“Our customers here in Australia are also seeing the benefits of remote monitoring with our TRUST ITM technology.”
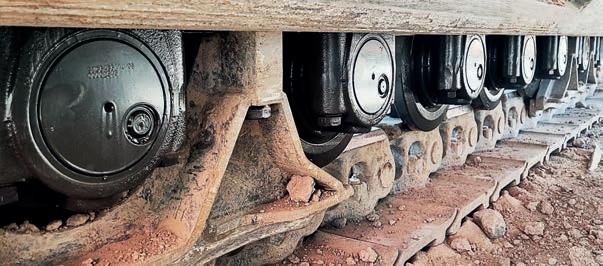
The TRUST ITM in-cab dashboard displays critical data to operators.
TRUST ITM sensors embedded into undercarriage componentry.
TRUST ITM sensors were developed to meet the growing demand for the real-time monitoring of undercarriage components in the mining industry. The sensors continuously collect data during machine operation, which is displayed in the cabin for the operator and transmitted to a cloud platform via a gateway, enabling centralised monitoring and data analysis.
ITM Mining provides customers with on-site product installation, training and ongoing support for TRUST ITM.
“The sensors are embedded within ITM-manufactured parts, such as rollers and track chains, to measure critical parameters like temperature and wear,” ITM Group smart technology solutions business unit manager Mattia Ruggeri told Safe to Work
“The goal was to enable predictive maintenance, reduce unplanned downtime, and enhance safety and operational efficiency.”
Key applications for the technology include monitoring temperature to prevent overheating and supporting data-driven maintenance strategies.
In addition, using magnetic sensors provided in the company’s Trust Mobile Kit can expand TRUST ITM’s range of applications to other machine components beyond the undercarriage, providing a versatile solution for monitoring a variety of critical parts.
ITM is also undertaking wear measurement functionality testing, with the aim of further enhancing the system’s capabilities in the near future.
To help the system integrate smoothly and continue providing value to customers, ITM personnel are also notified immediately of any TRUST ITM alerts on the machines, allowing product managers and technical experts to notify the customer and rectify issues.
Skipper personally visits customers to demonstrate the system in action, supervise the installation of TRUST ITM gateways, provide training and troubleshooting, and assist customers with further requirements.
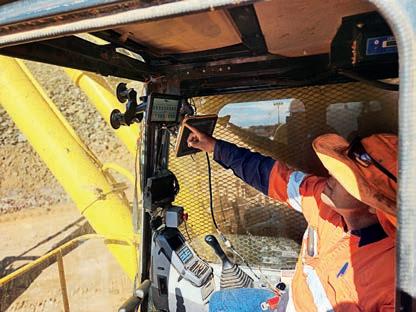
“TRUST ITM sensors significantly improve safety by removing the need for manual temperature checks onsite,” Skipper said.
“In mining environments, this eliminates the need for personnel to approach heavy machinery to monitor components, reducing exposure to potentially hazardous situations.”
ITM Mining is a firm believer that efficiency is enhanced through predictive maintenance.
By monitoring wear and operating conditions in real-time, ITM Group smart technology solutions digital innovation manager Nicolas Moretti told Safe to Work that operators can avoid unexpected failures, schedule maintenance only when necessary, and extend the lifespan of undercarriage components.
“Data-driven solutions are the foundation of modern mining safety and efficiency,” Moretti said. “TRUST ITM helps reduce machine idling time by providing precise data that enables operators to optimise machine usage and maintenance intervals, improving overall operational efficiency.”
TRUST ITM sensors are designed to be highly adaptable, offering flexibility to suit various customer needs.
Data collected by the sensors can be accessed remotely via ITM’s TrackAdvice software or through a mobile app for field operations.
ITM offers customisation options for customers who wish to integrate TRUST ITM data into their own maintenance software.
“As the proprietary owner of the TrackAdvice software, ITM can provide application programming interface-based integration or use other tools that have been successfully implemented for different clients,” Skipper said.
“This ensures seamless compatibility with existing systems while maintaining robust data management and analysis capabilities.”
One of the key differentiators of TRUST ITM technology is its patented components, which can measure the internal temperature of undercarriage parts.
Skipper emphasised that this unique capability allows malfunctions to be detected much earlier than external temperature measurements, providing operators critical time to address issues before they escalate.
“TRUST ITM technology represents the culmination of seven years of rigorous testing and development, positioning ITM as a pioneer in this field,” he said.
“Our extensive experience ensures a reliable, proven solution that meets the demands of even the harshest mining environments.”
Mining equipment operators can directly access real-time data from TRUST ITM sensors.
Clearing the air
EXPOSURE
TO AIRBORNE
DUST
REMAINS A KEY CONCERN IN THE MINING INDUSTRY. CLEANSPACE’S BREAKTHROUGH TECHNOLOGY IS LOOKING TO CHANGE THAT.
Underground miners are surrounded by a cluster of hazards, but certain dangers aren’t always visible.
While fine dust particles might not be easy to spot, their long-term impact on worker health can leave a trail of illnesses that’s impossible to ignore.
Miners exposed to poor air quality face serious conditions such as silicosis, black lung, and even lung cancer, which can occur after years of breathing in harmful particulates on the job.
These risks aren’t new. They’re also preventable when using appropriate equipment.
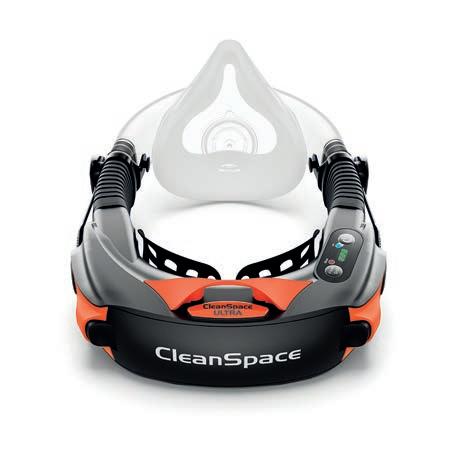
Although technology has permeated many areas of mining, respiratory protection has seen relatively little innovation in more than 20 years.
Many workers are still issued powered air purifying respirators (PAPRs) that are heavy, bulky, awkward and slow to put on or clean. They are often fitted with external belts and rigid hoses, all of which contribute to added discomfort and physical strain. As a result, even when the safety gear is readily available, compliance or usage rates can be low.
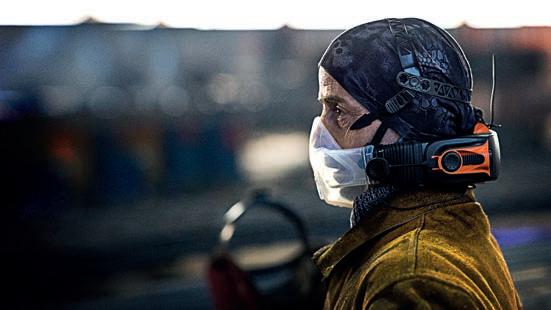
To boost its understanding of the issue, CleanSpace – a provider of cutting-edge respiratory protection –conducted a series of interviews with 12 occupational hygienists, most of whom shared similar responses.
Across the board, there was a clear demand for lightweight, intuitive, and high-protection solutions.
A TECHNOLOGICAL BREAKTHROUGH
CleanSpace has developed a new generation of respiratory solutions that prioritise ease, comfort and protection.
At the core of its offering is AirSensit, a patented, breathresponsive system that adapts airflow to the wearer’s natural breathing pattern. This means the device only delivers clean air when the wearer inhales, ensuring efficiency and safety.
Weighing in at less than 450 grams, these respirators are quiet, compact, and built for unrestricted movement. With a filtration efficiency of 99.97 per cent, they also meet the highest powered air purifying respirators (PAPR) standard.
CleanSpace respirators are becoming increasingly popular on mine
Images:
CleanSpace’s new generation of respiratory solutions prioritises ease, comfort and protection in harsh environments.
The CleanSpace ULTRA model is designed for tough working conditions.
sites across the globe, freeing the way miners breathe.
Not only is CleanSpace equipment easy to don, it’s also designed to withstand demanding working environments; the company’s product suite has been specifically engineered to meet the real-world pressures of the mining sector.
The CleanSpace ULTRA model is built for environments with high dust concentrations and tough working conditions. It’s water-tolerant, simple to operate, and compatible with fullface masks and helmets, making it especially effective for underground and tunnelling sites.
For environments where there’s a risk of explosion or combustion, the CleanSpace EX offers intrinsic safety, and has been tailored to suit the needs of the mining and energy sectors.
There’s also a digital tool propelling the company forward, with the CleanSpace SMART App providing clear usage metrics.
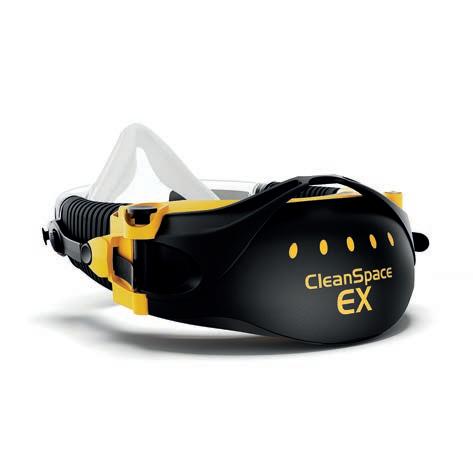
It’s free to download and designed with ease-of-use in mind for workers and supervisors alike.
The mining industry has embraced innovation in automation, data and operational safety – it’s now time to breathe fresh life into personal protective equipment.
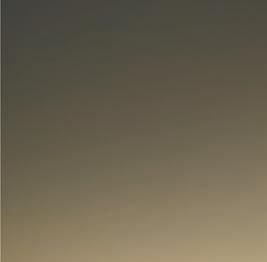
legal, operational, and ethical pressures to protect its workforce, reliable and well-designed respiratory gear is no longer optional.
It’s now about making sure that every breath taken underground is a safe one.
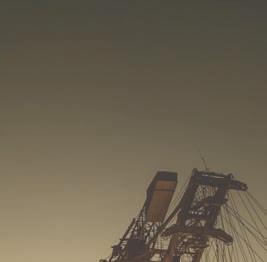
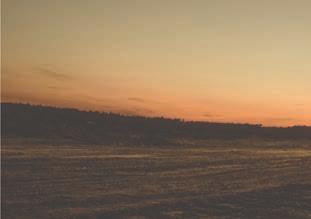
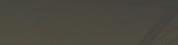

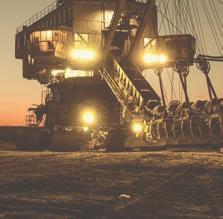
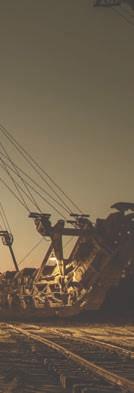
The CleanSpace EX is a preferred choice in situations where there’s risk of explosions.
Safety technology
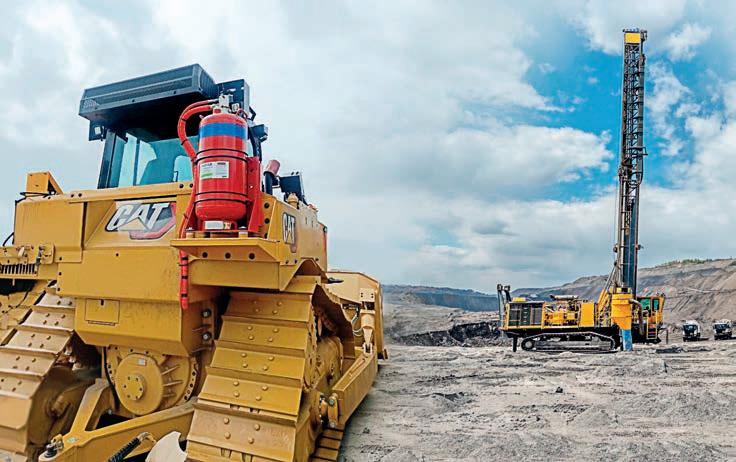
A fire-proof future
MUSTERFIRE IS HELPING THE MINING INDUSTRY ADAPT TO EMERGING FIRE RISKS AND EVOLVING SAFETY DEMANDS.
As industries evolve, so too do the risks they face. New technologies are reshaping operations, creating fresh challenges that demand new approaches to safety. Safe to Work sat down with MusterFire regional manager Dale Sharpe to discuss how the company is staying at the forefront of these changes.
How is MusterFire driving innovation in fire suppression?
We work closely with both original equipment manufacturers (OEMs) and major mining companies to understand where they’re heading over the next five to 10 years, and develop solutions tailored to the technologies they plan to adopt.
What are some key fire safety trends you’re seeing?
We’re seeing an increased adoption of battery-powered machinery, which is bringing new opportunities as well as challenges.
Lithium-ion batteries, while powerful, do present safety concerns. At the same time, there has been some progress towards alternative battery technologies.
Hydrogen-powered machinery is gaining attention right now, electric vehicles are picking up momentum, and underground miners are also gradually introducing electric equipment, testing new technology piece by piece.
These developments require us to reconsider fire suppression approaches, which is an exciting challenge for us.
What separates MusterFire systems?
Traditional fire suppression foam systems like fluorine-free foam work well for internal combustion engines and Class B fires, but battery fires require a different approach.
MusterFire uses solid aerosol generators to suppress flames long enough for operators to evacuate
safely. However, battery fires can continue burning internally due to thermal runaway, sometimes causing vapour cloud explosions. This is why we focus on prevention, conducting detailed fire risk assessments to reduce the chance of ignition.
Does mining pose additional fire suppression challenges?
Yes, especially the high salt content in underground mine sites, which can cause corrosion. This is why all our key components are made from stainless steel and are built to withstand harsh conditions. We take a full 360° approach.
Before releasing any product, we run extensive testing against Australian standards, including vibration, salt spray, high heat, and extreme cold.
Once the system is installed, we continue gathering customer feedback to ensure it performs as expected in real-world conditions. This ongoing process helps us
MusterFire solutions have proven their capabilities in the field. Images:
fine-tune our systems for maximum reliability on-site.
How are customer fire-protection needs changing?
Customers are definitely looking for more automation, integration, and control.
A large portion of the machinery we work with is now autonomous, so there’s no physical operator on board to monitor the fire system directly. That makes automatic detection and real-time communication essential.
The fire system needs to integrate with the equipment and report its status continuously, so operators know exactly what’s happening even from a distance. As automation increases, customers want fire protection systems that can provide reliable data, full visibility, and rapid response – even when no one is physically present.
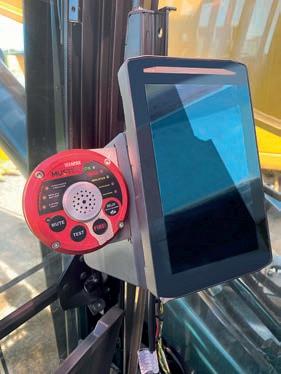
What’s the next leap in fire suppression technology?
With the rapid growth of small lithium-ion batteries and disposables products that rely on them, there has been an increase in the number of waste disposal truck fires – especially if these batteries are damaged, which can then cause thermal runaway.
There is, therefore, a growing need for a smart early detection system using AI and Internet of Things to rapidly report the onset of fire and reduce collateral damage.
Due to some toxic by-products, there is also a growing demand for sustainable firefighting products to effectively control these toxic fires while reducing the runoff of excessive toxic water.
These innovations will ensure a more intelligent, responsive and sustainable fire suppression, while enhancing safety.
No compromise on safety
Enhance site operations, security and resident experience in a single solution.
With Salto access control, every access point across an entire accommodation camp plays a role in keeping residents safe.

Contact our expert Adrian Taber for a comprehensive demo:
saltosystems.com.au > +61 417 777 414


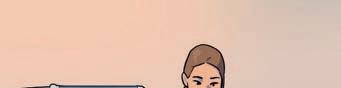
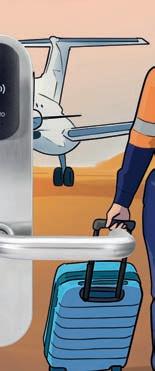
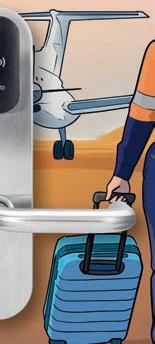
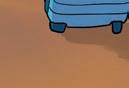
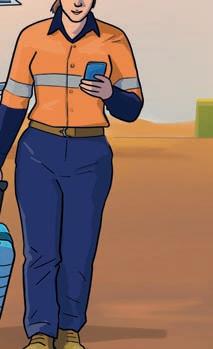
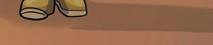
MusterFire provides state-of-theart systems for mining excavators.
Safety technology
ViPR Agentic AI redefines high-risk work
VIPR IS SET TO TRANSFORM WORKPLACE SAFETY WITH AGENTIC AI, SOFTWARE ARCHITECTURE THAT HELPS PREDICT INCIDENTS BEFORE THEY OCCUR.
ViPR’s Agentic AI platform introduces a new model of safety intelligence for mining and other highrisk industries. At its core, ViPR Agentic functions as a hidden layer of autonomous intelligence, continuously scanning the environment to detect patterns and flag emerging hazards.
Rather than relying on human oversight, ViPR Agentic independently operates in real-time, drawing from diverse data streams to anticipate and prevent risks before they escalate into harm. This allows supervisors and management to stay focused on people and operations, while ViPR handles the complex data analysis.
“Instead of a supervisor, manager or safety professional sitting in the office absorbed in historical incident reports to anticipate what might go wrong next, ViPR Agentic AI is doing that work for you in the background” ViPR founder Michael Jones told Safe to Work. “It’s looking forward, not backward, identifying patterns and risks that typically go unnoticed until after an incident occurs – which we call over-the-horizon safety”.
The ViPR system analyses company-specific safety protocols, considers environmental-specific conditions, and runs ‘what-if’ simulations in real-time – building a dynamic understanding outcome pattern detection based on the work environment, task demands, and workforce behaviour.
Jones said the goal is simple: prevent incidents by recognising the warning signs early. That means interpreting signals across the diversity of sites – such as vehicle
acceleration, temperature changes, or shifts in worker behaviour – and flagging when conditions begin drifting toward danger – to identify early signs of unwanted events.
“We have exclusion zones, but Agentic AI doesn’t just trigger an alert once you’ve crossed a line,” Jones said. “It applies reasoning to the context, predicting the likelihood of entry based on behaviour, site conditions, and task risk.
“ViPR stops you before you step into danger.”
The system integrates a range of operational factors – fatigue levels, prior shift history, time of day, regulatory requirements, and previous incidents – to build a dynamic and situational risk profile.
“We’re building more than a monitoring tool,” Jones said. “Agentic AI brings together everything from fatigue indicators to humidity, past performance and environmental data to form a live view of behavioural trends and risk intersections.
ViPR Agentic is designed to blend into the background, giving supervisors and safety professionals confidence that real-time risks are being monitored continuously, not just after something goes wrong.
Jones acknowledged that some may worry about over-surveillance, but clarified that the platform doesn’t introduce new tracking. Rather, it interprets data that is already being collected, just more intelligently.
“Most sites already have the sensors, the logs and the systems,” he said. “We’re not adding complexity. We’re using what’s already there and giving it purpose.”
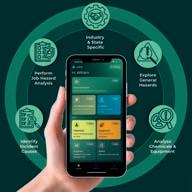
ViPR’s Agentic AI transforms high-risk sites into intelligent safety ecosystems.
Many organisations still rely on disconnected systems for safety, which can create communication silos. ViPR Agentic helps bridge those silos, consolidating data and translating it into actionable, predictive awareness.
One of the core enablers of this system is Bluetooth Low Energy (BLE), a widely available but often underutilised technology. BLE allows ViPR to track movement, monitor entry into restricted zones, and conduct emergency headcounts, using minimal power and infrastructure.
“The BLE layer is incredibly powerful when you connect it with suitable AI technology,” Jones said. “It becomes more than a tracker; it becomes a sitewide sensing network.”
Integrated with ViPR Agentic, BLE enables seamless, real-time situational awareness. Combined with advanced AI reasoning, the system creates a smarter and more responsive network that supports proactive decisionmaking in high-risk environments.
ViPR is aiming to meaningfully reduce incidents in high-risk industries by changing how safety information is gathered, interpreted and actioned. With the Agentic prototypes already outperforming expectations, that mission is entering its next phase.
Image:
A safe mine is a profitable mine
Mine safety is about more than technology. Change management and data insights are important, too. Hexagonintegrates systems for collision avoidance, operatoralertnessand vehicle intervention into your mining workflows. On topof that, we partner with customersto engage and re-engage operators in a cycleof continuous improvement.
Our solutionsare OEM-agnostic and smart enough to adapt to mixed fleets and diverse sites while helping you to exceed safety and productivity standards.
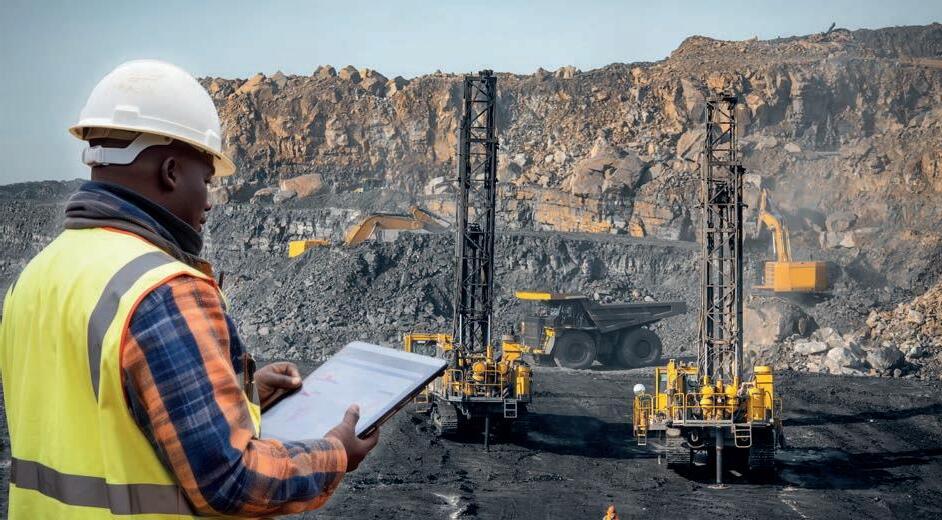
Locking in peace of mind
ACCESS CONTROL SOLUTIONS COULD PROVIDE THE SECURITY AND PATHWAY TOWARDS ATTRACTING A MORE DIVERSE WORKFORCE.
The mining sector recognises the value of a diverse workforce — attracting a wider range of workers helps to address labour shortages, provides varied skills and innovative thinking, and helps performance and profits.
As part of that drive, women in particular are in demand in the mining sector, and companies are setting themselves challenging targets to achieve a better gender balance right across their workforces.
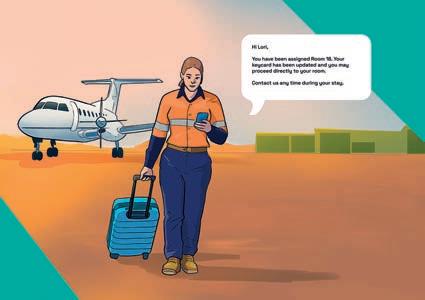
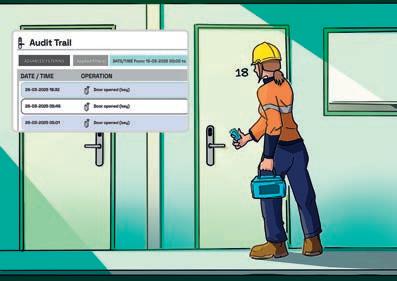
But the culture of the sector has room to evolve if it is to attract and retain the more balanced workforce it needs. The Western Australian Government’s ‘Enough is Enough’ report on sexual harassment and assault, for example, noted “a failure of the industry to protect its workers”.
That change is happening, however, with initiatives such as Rio Tinto’s ‘Everyday Respect’ program starting to show positive results, gender pay gaps being reduced, and a focus on creating safe and welcoming workspaces.
A Harvard Business Review case study of one mine’s success in attracting women identified “investment in fostering a welcoming and safe mining camp” as one of the five key factors for success.
One such investment is in technology, which can play an important part in providing a safe environment, especially through access control systems.
Access control systems consist of electronic locks, opened with a programmable access ‘credential’ — a keycard, fob or the user’s mobile phone. The system is managed from a central console to provide tightly controlled access, high security and a fully visible audit trail.
Here’s an example of how access control can provide a safer workplace:
Lori is a fixed plant operator in a site in WA. She’s on a two-weeks-on, two-weeks-off fly-in, fly-out (FIFO) schedule, with an allocated room on a two-week roster. The room has an electronic lock, which Lori accesses via a keycard.
When she leaves the site, her card is re-programmed so that it no longer gives access to the room and her roommate’s key is given the access. Lori can leave her belongings in her
Images: Salto
Salto’s system programs a keycard based on the allocated room.
Audit trails provide vital room entry and exit information.
locker in the room, only accessible via her keycard.
When Lori returns, the access control system is notified that her flight has landed by the transport booking system, and access is automatically reinstated to her card. She can go straight to her room without having to check in.
Once in her room, Lori can use the privacy button on the inside, meaning that not even the cards held by the maintenance or cleaning staff can open her room.
After work, Lori decides to exercise and then do her washing.
Her room keycard also gives her access to the gym and the laundry. These areas have been programmed so access is only granted to female employees at designated times.
A few days later, Lori can’t find her keycard and reports it missing. It’s immediately deactivated, so that even if someone finds it, they cannot use it
to enter her room. She is immediately issued a new key.
If someone does try to use the card, the attempt will show up on the audit trail within the access control system and linked to CCTV for details that will help a further investigation.
The audit trail can also help with monitoring Lori’s health and wellbeing; for example, flagging if her room door has not been opened for a period of time, or if she has accessed her room but her card not been presented elsewhere, such as the restaurant, in a 24-hour period.
The access control system is designed to help Lori feel safe and strike the right balance between security and convenience:
•Lori knows that she is the only person who can access her room
•A lost key does not mean risk of a security breach
•Access can be blocked when Lori is inside her room
•Lori can use communal spaces at female only times
•The room is ready and available as soon as Lori arrives at the site
•Any attempt to access the room will be audited
•Management will be alerted in the event Lori is unable to leave her room
This system is designed so Lori not only has an increased feeling of being physically safe, but also a far greater sense of psychological wellbeing.
She can feel that she has a balance between freedom and safety, and that her on-site accommodation is more akin to a home away from home.
Salto will be demonstrating this functionality and explaining how its access control solutions drive worker safety at the Asia-Pacific’s International Mining Exhibition (AIMEX) in Adelaide in September and WA Mining Conference and Exhibition in Perth in October.
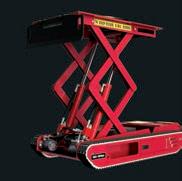
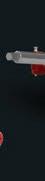

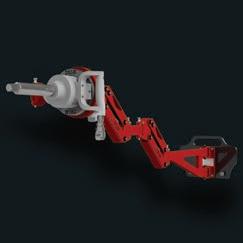
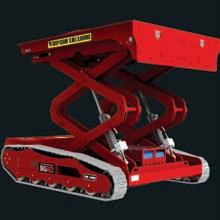
Safety technology
Simplifying safety technology
SAPHI ENGINEERING’S SHELLSHOCK AI SOLUTION IS TAKING THE GLOBAL MINING INDUSTRY BY STORM.
SAPHI Engineering has been on quite the journey since forming in 2017, evolving from a bootson-the-ground engineering consultancy into a technology company supporting Tier 1 miners around the world.
“We started as a small team of engineers who’d spent enough time on-site to know what actually works and what just looks good on paper,” SAPHI chief commercial officer Liam Manning told Safe to Work
“From the beginning, we weren’t in it for flashy tech or buzzwords. We were driven by a simple, powerful belief: no one should die at work.”
Designed, developed and manufactured in Australia, SAPHI’s offerings aim to deliver both safety and operational efficiency.
The company’s flagship solution is Shellshock AI, a suite of rugged, edgepowered systems that seamlessly capture and integrate critical insights into existing vehicles, cameras, sensors and databases to inform improved decision-making.
The suite includes:
• Shellshock VIS, an AI-powered vehicle intelligence system that monitors in-cab operator behaviour while detecting external risks
• Shellshock Connect, which enhances existing infrastructure by layering AI onto video and sensor systems to detect site-wide risks
• Shellshock Thermal, which combines industrial-grade thermal imaging with site-specific AI models to distinguish between expected heat sources and true fire risks.
“At the core of Shellshock AI are custom AI models that analyse video and sensor data in real time – not just to detect hazards, but to act on them,” Manning said. “Shellshock automates compliance and process optimisation
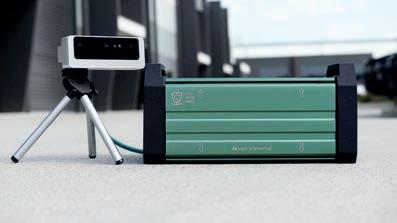
workload, freeing up staff while lifting both safety and performance.
“It’s not just recording; it’s taking action. And when new risks emerge, we push updates remotely – no downtime, no hardware swaps.
“From in-vehicle safety above and below ground, to facility-wide coverage, Shellshock keeps your people safe and your operation sharp, without adding complexity.”
SAPHI trains Shellshock AI by using customer data rather than generic datasets, making detections more accurate and relevant to workflows.
“At SAPHI, we believe AI means nothing if it isn’t tailored to you,” Manning said.
“Every site is different – different risks, different layouts, different workflows. That’s why we don’t roll out generic models and hope for the best.
“Instead, we work closely with each client to understand their unique operating environment, mapping out site conditions, safety priorities, and any technical constraints. Our team then customises Shellshock specifically for those conditions, ensuring it performs where it matters most: on the ground.”
Shellshock AI is being rolled out across operations in eight countries, supporting surface and underground mining operations.
to address safety concerns around fatigue, distraction, and proximity risks in high-hazard zones.
“We began by deploying Shellshock across vehicles and fixed infrastructure to detect and alert, in real-time, when operators entered danger zones or displayed signs of unsafe behaviour,” Manning said.
“Because Shellshock is designed to adapt, we worked with the client to train custom AI models on their own footage and workflows, ensuring detection accuracy aligned with their specific vehicles, layouts and lighting conditions underground.
“The system continues to adapt as the site evolves, supporting both short-term wins and long-term transformation. What this means for our customers is a system that adapts as fast as their priorities shift – delivering new capabilities instantly, with no downtime or hardware changes.”
Shellshock AI is designed to be more than a safety system; it’s a practical tool for the mining industry to take control of risk and performance.
“It helps teams reduce incidents, stay compliant, and keep operations moving, without needing more infrastructure, more people, or more cost,” Manning said.
Image: SAPHI Engineering
Shellshock AI is helping to improve decision-making on mine sites.
Save Lives… Revolutionise Industries
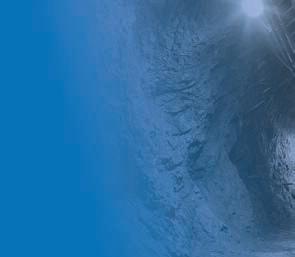

Nome’s RockMonitor systems alert and prevent undeground collapses through real-time strata monitoring, enhancing worker safety and transforming mining hazard managementworldwide.
Nome Services is an Australian-based company focused on delivering innovative safety solutions to the global underground mining industry. Our flagship technology, RockMonitor, is a real-time strata monitoring system designed to detect ground movement and provide early warning ofpotential collapses. This data-driven approach helps mining operations enhance safety, protect personnel, and reduce the risk of unplanned downtime.
■ Real-Time Strata Monitoring – Continuously tracks underground ground movement to provide early warning of potential collapses andhazards.
■ Enhanced Safety & Compliance – Helps protect workers and meet strict regulatory requirements with automated, accurate data reporting.
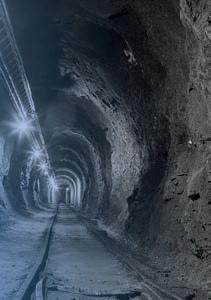
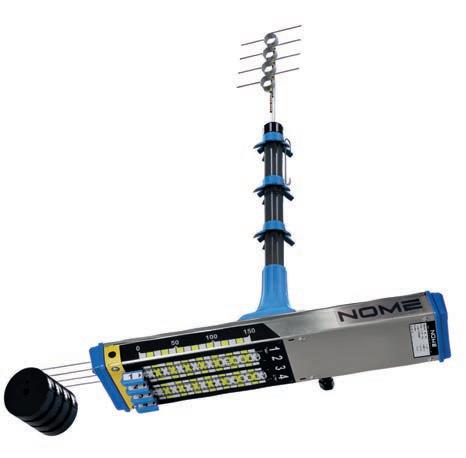
READY TO TAKE YOUR MINE SAFETY AND PRODUCTIVITY TO THE NEXT LEVEL?
■ Increased Productivity & Uptime – Reduces the need for manual inspections, minimises unplanned downtime, and supports proactive operational decision-making.
Partner with Nome Services and experience the future of real-time strata monitoring. Whether you’re looking to trial the RockMonitor system, become a regional distributor, or explore our full suite of underground safety solutions — we’re hereto help.
Let’s talk about how Nome can help your operation work smarter, safer, and more profitably. +61 (0) 756 481 315 admin@nomeservices.com.au nomeservices.com.au
Rock solid safety
SAFETY IS GOING BACK TO BASICS AT THIS YEAR’S QMIHSC, WITH THE CONFERENCE RE-ENFORCING THE CORE PRINCIPLES THAT HAVE ALWAYS BEEN ESSENTIAL FOR PROTECTING MINE WORKERS.
The Queensland Mining Industry Health and Safety Conference (QMIHSC) returns in 2025 for its 36th year, bringing together industry leaders, professionals, and innovators at The Star Gold Coast from August 17–20.
Under this year’s theme, ‘Rock Solid: The Foundations of Safety Excellence’, the conference invites attendees to revisit the core principles that have long supported the mining industry’s safety culture.
While technological advancements continue to reshape operations, the fundamental pillars of clear communication, proactive hazard identification, and strict adherence to protocols remain the industry’s true bedrock.
According to QMIHSC 2025 chair Gavin Lawrence, the mining sector thrives on solid geological foundations, and so too must its safety systems be built on unwavering commitment.
He said the event will explore how reinforcing these timetested basics not only prevents incidents but fortifies the sector’s ability to adapt in an increasingly complex landscape.
QMIHSC 2025 promises another year of networking and collaboration.
“Safety is a collective effort, and together we can ensure that the Queensland mining industry remains rock solid on safety,” Lawrence said.
Following the momentum of last year’s groundbreaking discussions, this year’s conference promises a robust and dynamic program.
It will tackle pressing topics such as the power of simplicity in safety, critical lessons from past incidents, and effective strategies to cultivate an enduring culture of safety awareness.
THOUGHT-LEADING KEYNOTES
Attendees will hear from a range of experts, with the QMIHSC 2025 line-up bringing together some of the most respected voices in mine safety and risk management, each offering unique insights into the evolving landscape of workplace safety.
Forensic engineer Sean Brady will draw on his extensive experience investigating failures and incidents to unpack the underlying causes hidden beneath the surface of major events. In 2020, he completed the Brady Review, which investigated fatality causes in the Queensland mining industry. Tabled in Parliament, the
review made 11 recommendations to the state regulator and mining companies on how to improve safety.
Safety advocate Helen Fitzroy will offer a deeply personal and powerful perspective on the human cost of workplace incidents. Having turned personal tragedy into a lifelong mission to improve safety standards, Fitzroy’s advocacy serves as a sobering reminder of why safety excellence must remain the industry’s highest priority.
Fatigue management will also take centre stage as specialist consultant Naomi Rogers addresses one of mining’s most persistent and complex safety challenges.
Human factors and safety expert Sidney Dekker will challenge conventional thinking with his forward-thinking approach to safety management. Known for his ‘Safety Differently’ movement, Dekker advocates for empowering frontline workers, simplifying safety systems, and creating environments where people can succeed rather than merely avoid failure.
Naomi Rogers and John Tate will also take to the stage as keynote co-
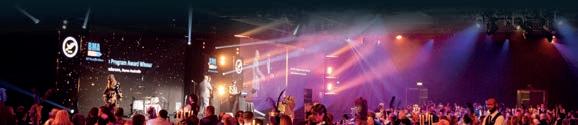
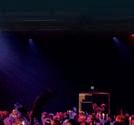

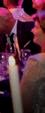
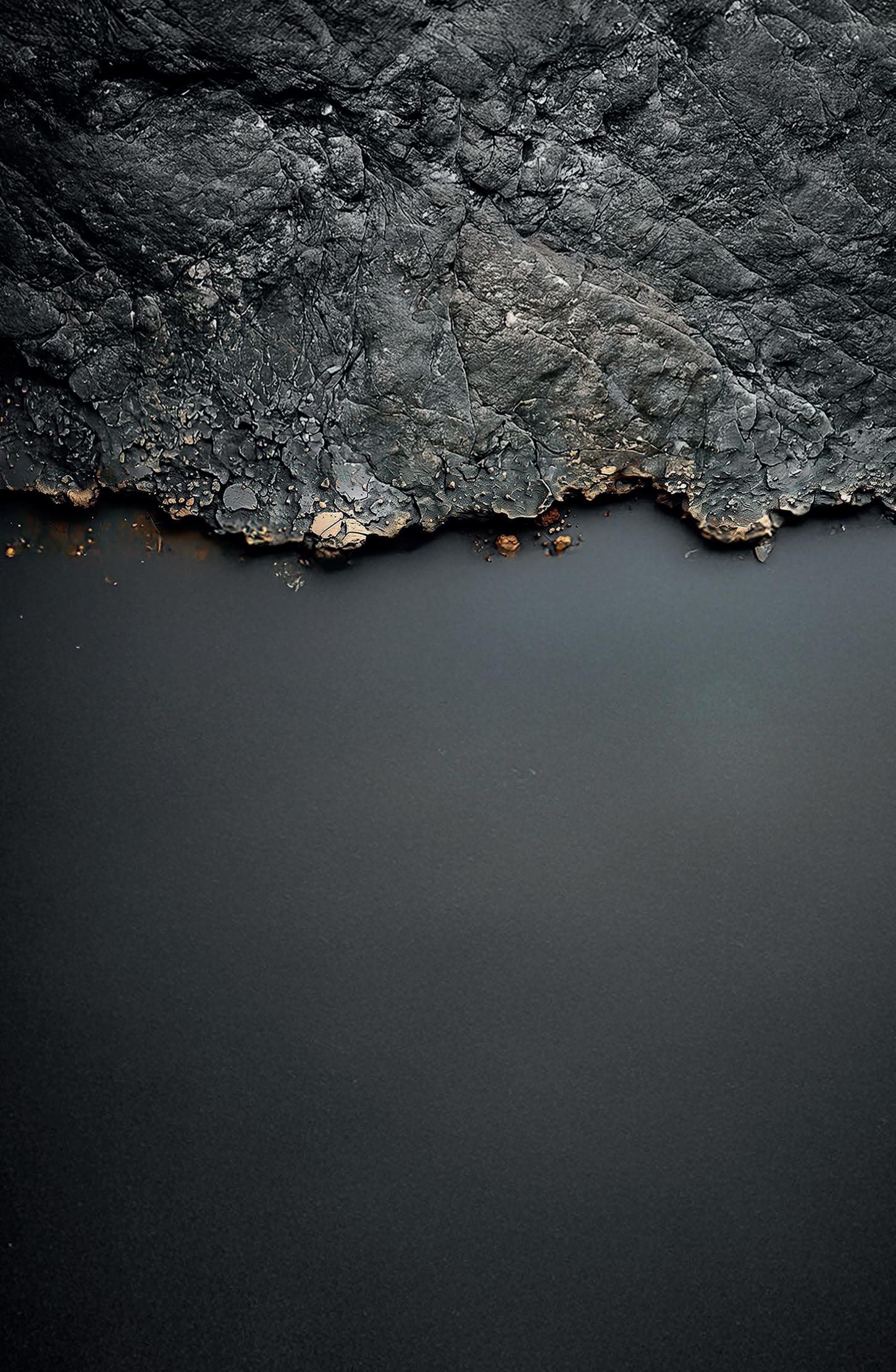
Images: Alister Randell
presenters. Together, they will bring a powerful combination of academic insight and real-world experience to the event.
Rogers is an internationally recognised expert in circadian disruption, sleep loss and fatigue. She’s worked as a specialist fatigue consultant across multiple sectors, including coal mining, transport, maritime, defense, aeronautics and healthcare.
As a barrister with extensive experience, Tate has had a longstanding focus on safety and health management systems, accident investigation, training and compliance, and is a regular speaker at industry forums and conferences.
Those interested in unlocking the power of sleep should not miss Nicholas Mabbott’s presentation. As a fatigue risk management specialist with more than 28 years of experience in sleep science across industries
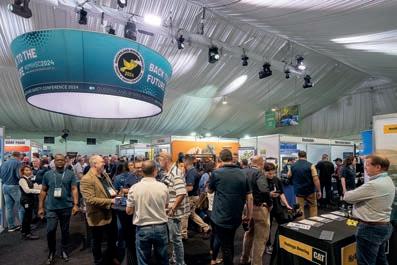
such as mining, transport and law enforcement, Mabbott has trained more than 34,000 people, helping them improve sleep quality, safety and wellbeing. His insights have helped not only reduce risk but also enhance productivity and personal health outcomes across workforces.
Audiences will also get the opportunity to hear about a

champion’s journey from tragedy to triumph, with adaptive rower Ben Houlison sharing his story.
Houlison was working as a coal miner when he became paraplegic after a workplace accident in 2004.
He took up rowing a short time later and by 2006 became the New South Wales state champion, shortly followed by Australian champion
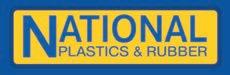
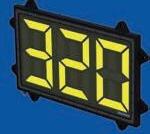
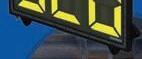



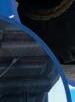
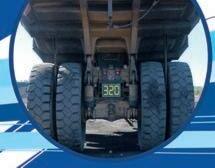
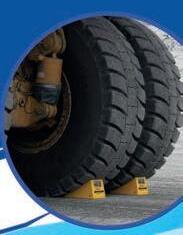
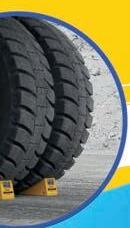
Don’t Compromise on Safety Reduce Risk, Increase Uptime
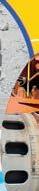
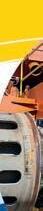
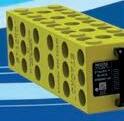
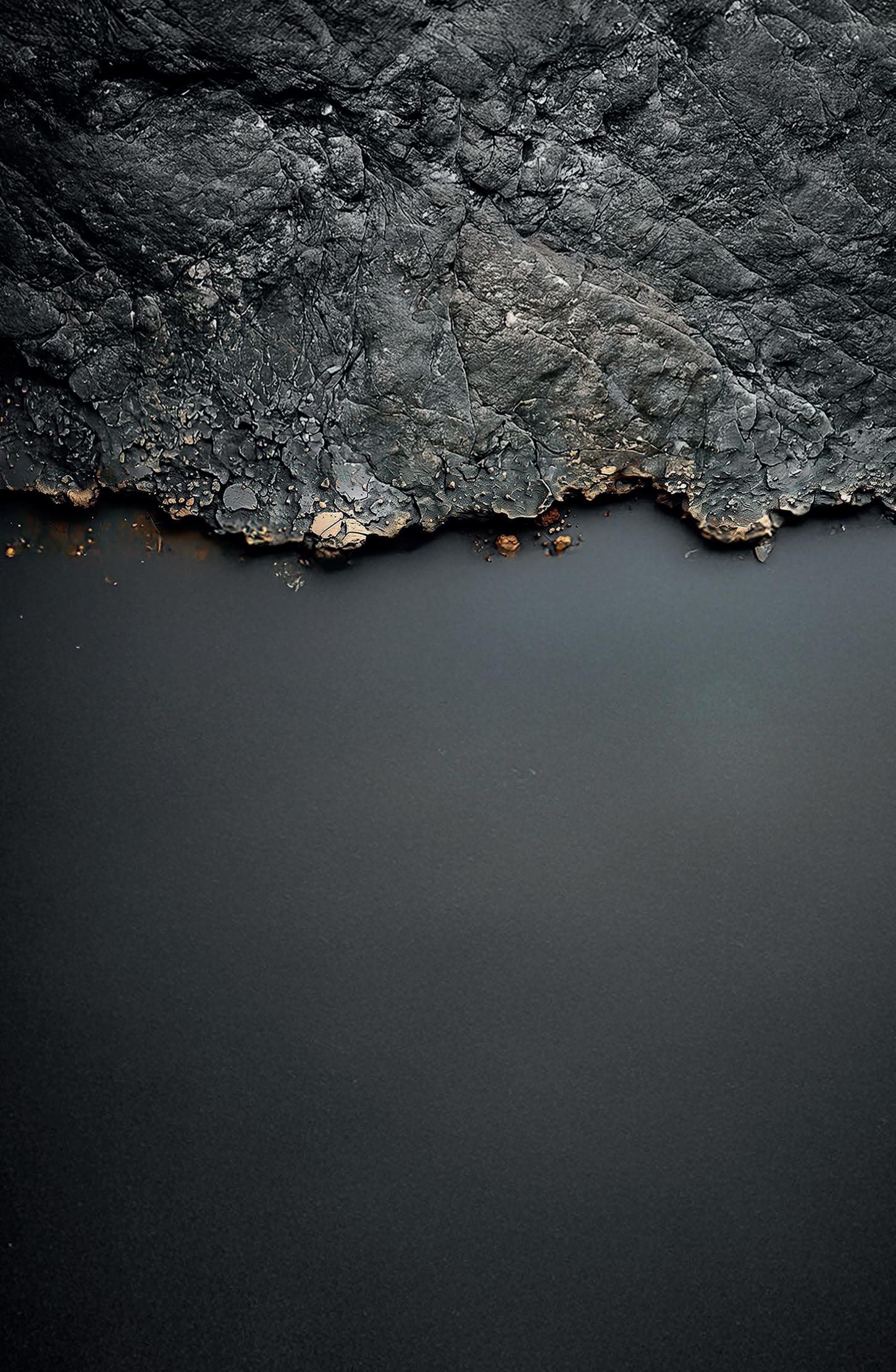
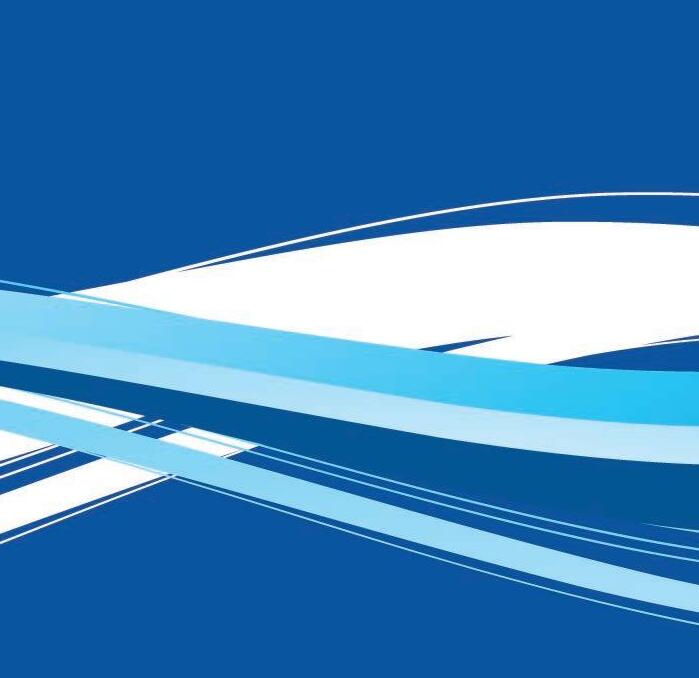
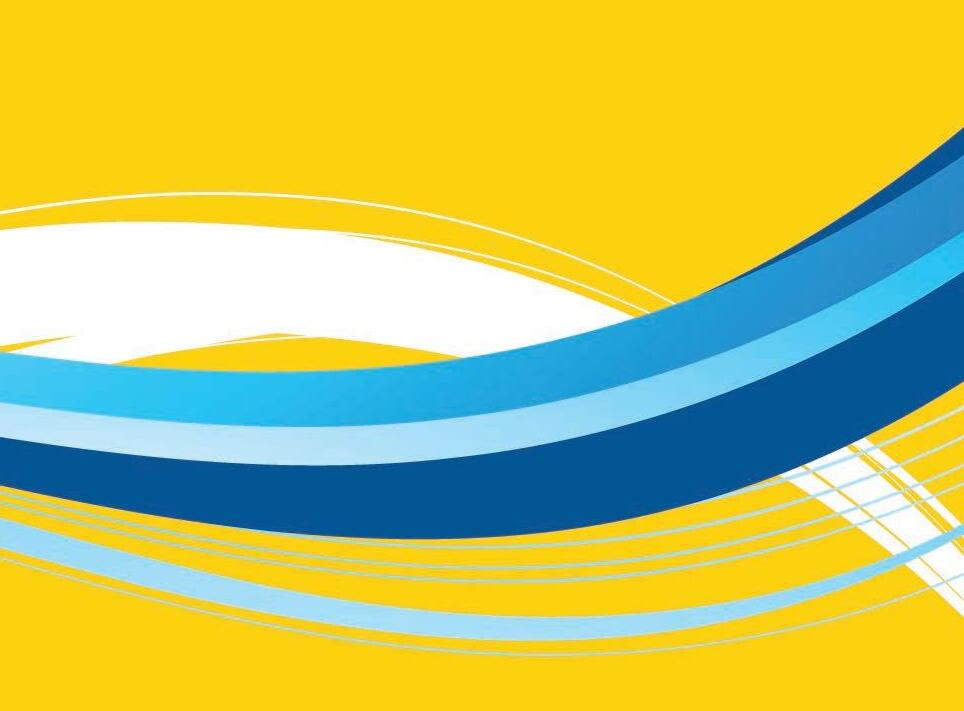
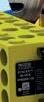





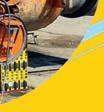
The exhibition floor will celebrate safety across the mining industry.
Championships in Poland.
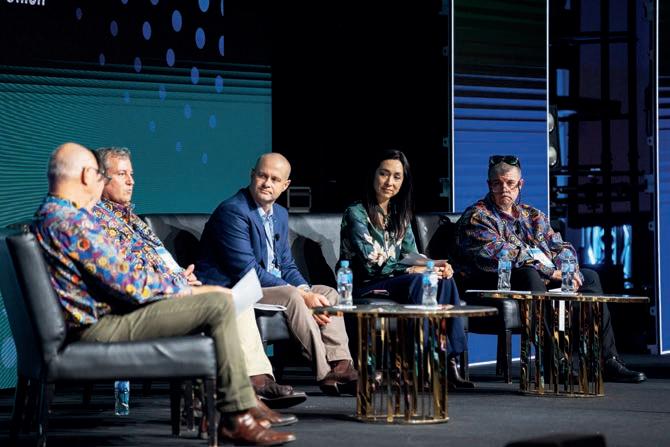
Together, these keynote speakers promise to spark critical conversations and equip attendees with actionable insights to enhance safety culture across the mining industry.
INNOVATIVE SESSIONS
Interactive workshops will also provide delegates with hands-on, practical tools designed for immediate workplace application. These sessions aim to turn theory into action, equipping attendees to make meaningful changes as soon as they return to site.
The ‘Emergency Management and Response’ session will see experts from Queensland Mines Rescue Service lead participants through incident management team structures, emergency response fundamentals, and a live mock exercise tailored for coal, mineral and quarrying operations.
The ‘Introduction of Critical Controls in the Queensland Resources Sector’ workshop will break down new legislative requirements under the Resources Safety and Health Legislation Amendment Act 2024. As critical controls become mandatory from 2025, participants will gain a clear understanding of compliance expectations and hear
In ‘When Quiet Gets Loud: Cracking the Code of the Unspoken’, delegates will examine the unspoken dynamics that shape safety-critical environments. Using behavioural science and human factors principles, the session will provide tools to navigate difficult conversations, interpret non-verbal cues, and foster open, learning-focused safety cultures across all levels of the workforce.
Throughout the event, the conference’s exhibition marquee will serve as a bustling hub of innovation.
Delegates can directly engage with more than 60 exhibitors showcasing cutting-edge technologies, emerging solutions, and the latest industry trends. Extended Q&A sessions will offer rare opportunities for direct conversations with keynote speakers and exhibitors, fostering deeper discussions on the challenges and opportunities shaping mining safety.
Networking remains at the heart of QMIHSC 2025. The carefully curated social program offers multiple chances for delegates to build relationships and share insights in relaxed settings.
The conference kicks off with a welcome reception and trade display, where attendees can
reconnect and forge new connections over food and drinks before the formal sessions begin.
The informal dinner and appeal auction on the evening of August 18 promises an electrifying night under a ‘Legends of Rock’ banner. Live music, good company and a lively charity auction will set the stage for an unforgettable evening. Proceeds from the auction will support CapRescue, the 2025 recipient of the conference’s fundraising efforts.
An exhibition happy hour offers yet another casual networking opportunity within the exhibition space, encouraging conversations and collaborations after a productive day of learning.
The Gala Dinner, themed ‘Happily Ever After: The Fairytale Ball’, will close the conference with an evening of elegance, live entertainment and a touch of magic, providing the perfect setting to celebrate the collective commitment to safety excellence.
As delegates gather to share knowledge, exchange ideas, and celebrate achievements, QMIHSC 2025 reinforces a simple-yetpowerful truth: – by returning to and strengthening safety foundations, the mining industry can continue to protect its workforce and lead the way into a safer, brighter future.
QMIHSC 2025 invites attendees to revisit the mining industry’s core principles.
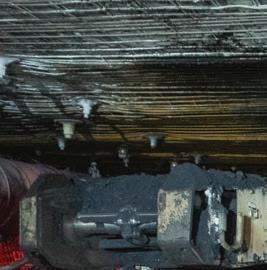
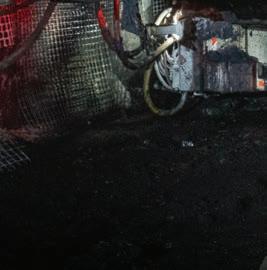
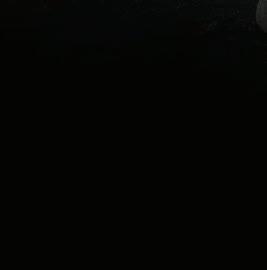
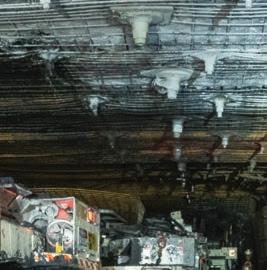
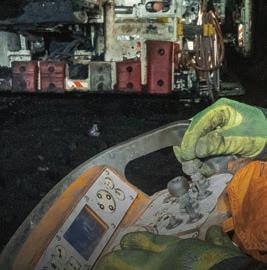
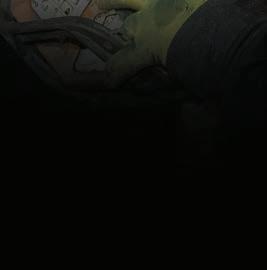
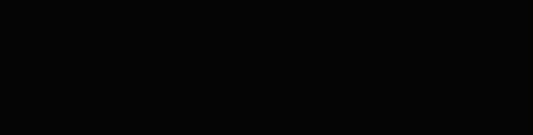
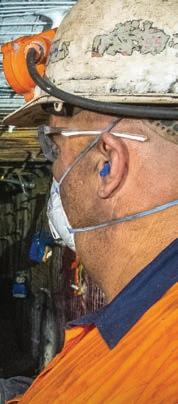
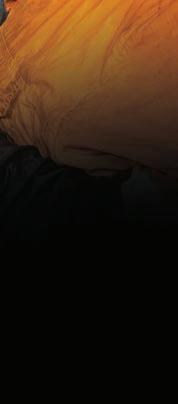
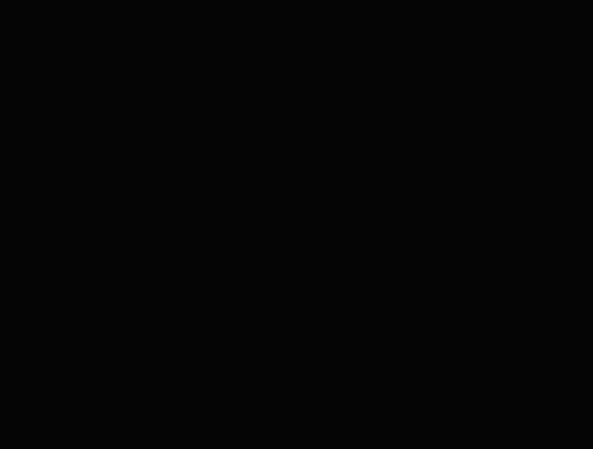
QMIHSC 2025
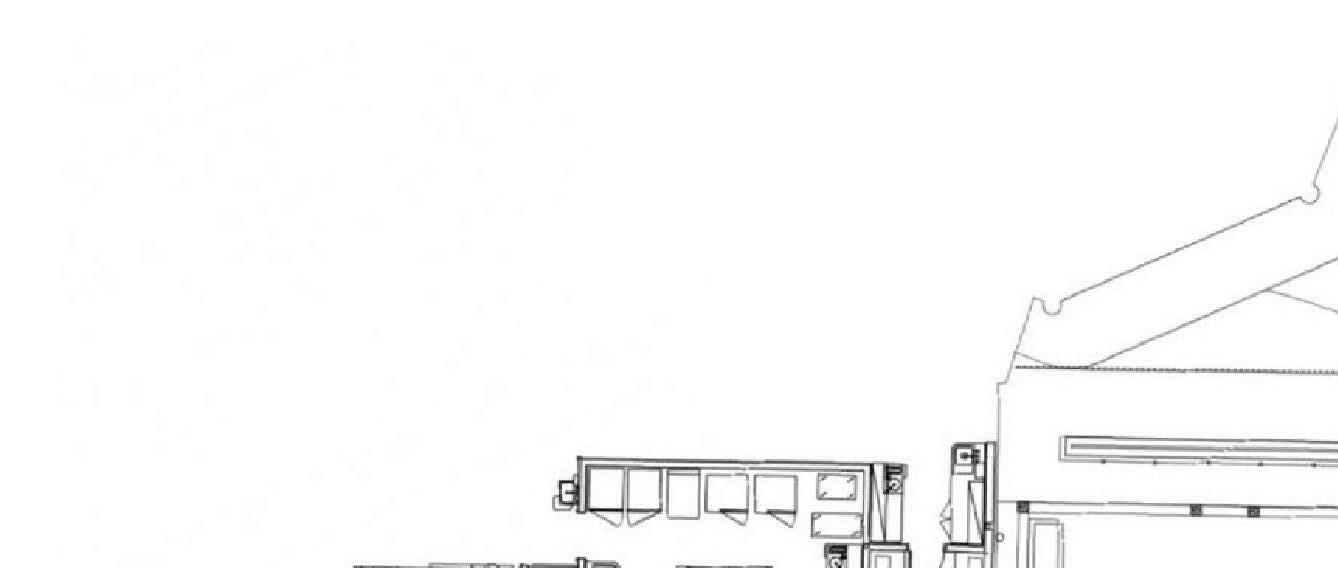
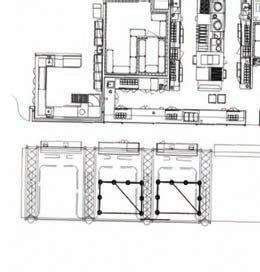
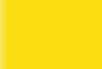
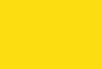
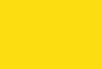
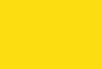
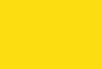
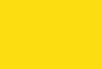
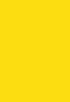
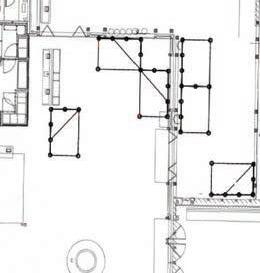
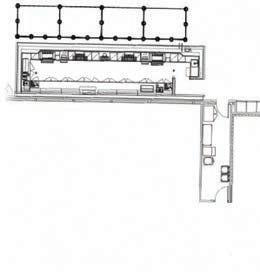
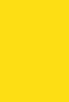
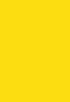
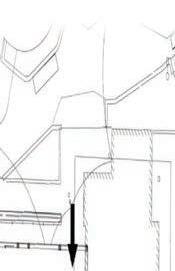
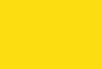
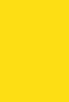
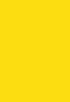
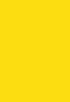
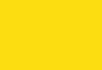
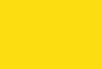
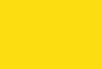



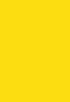
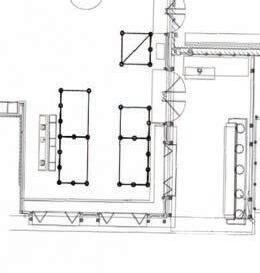
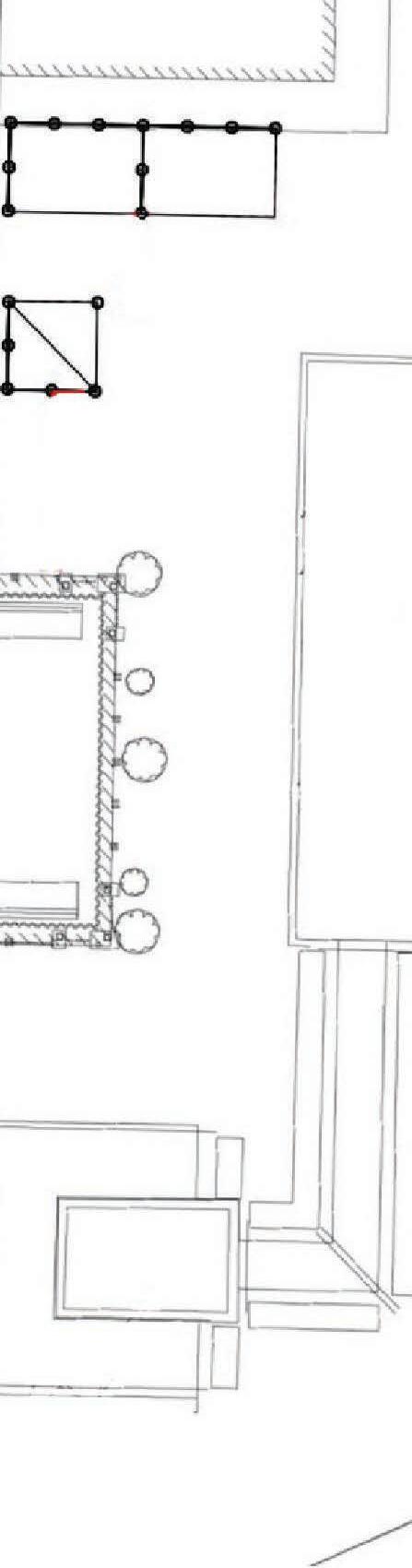
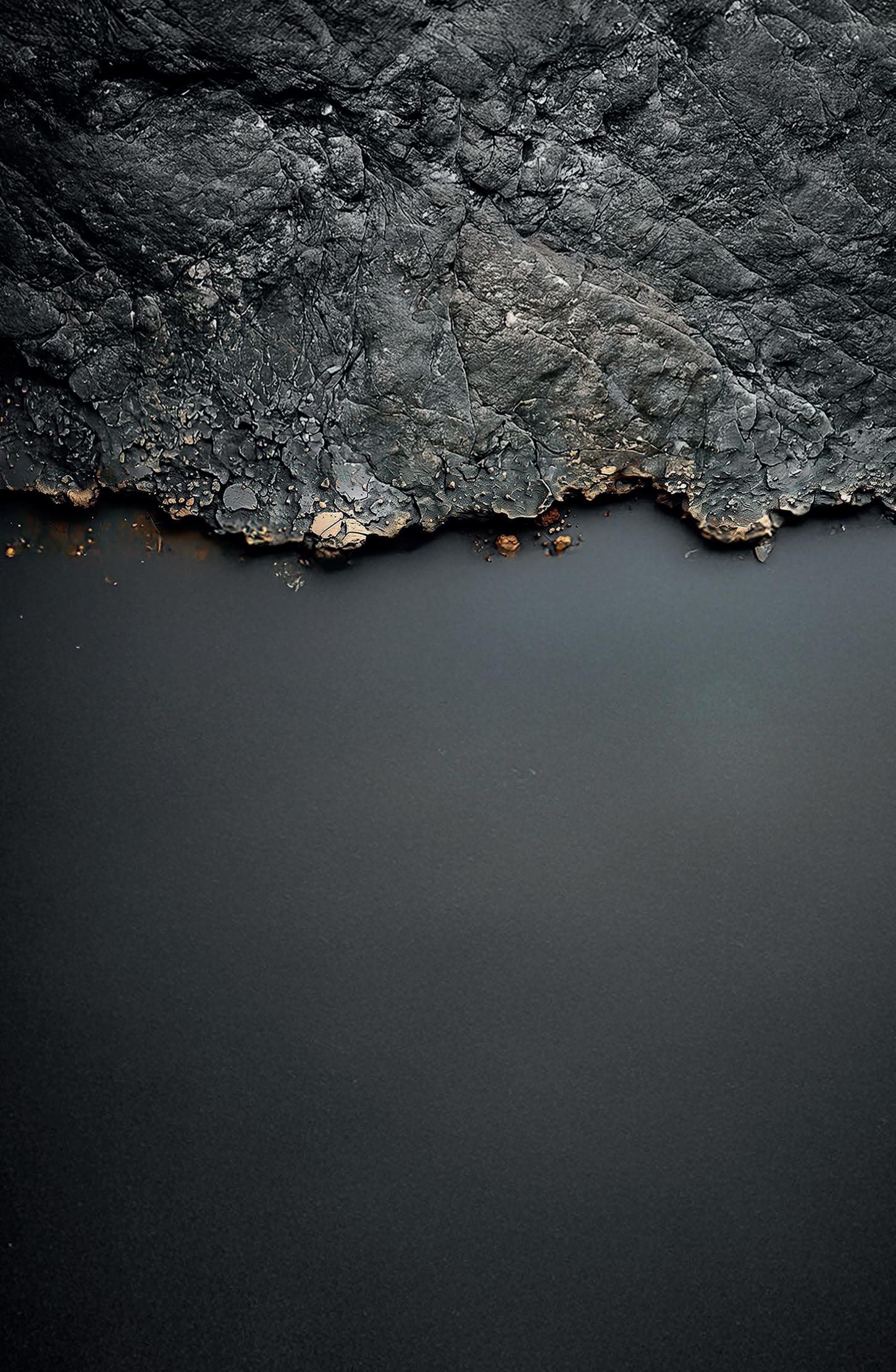
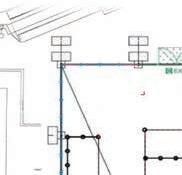
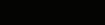

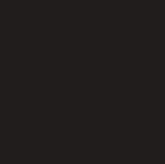

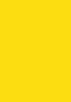
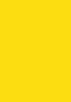
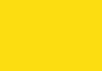
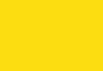
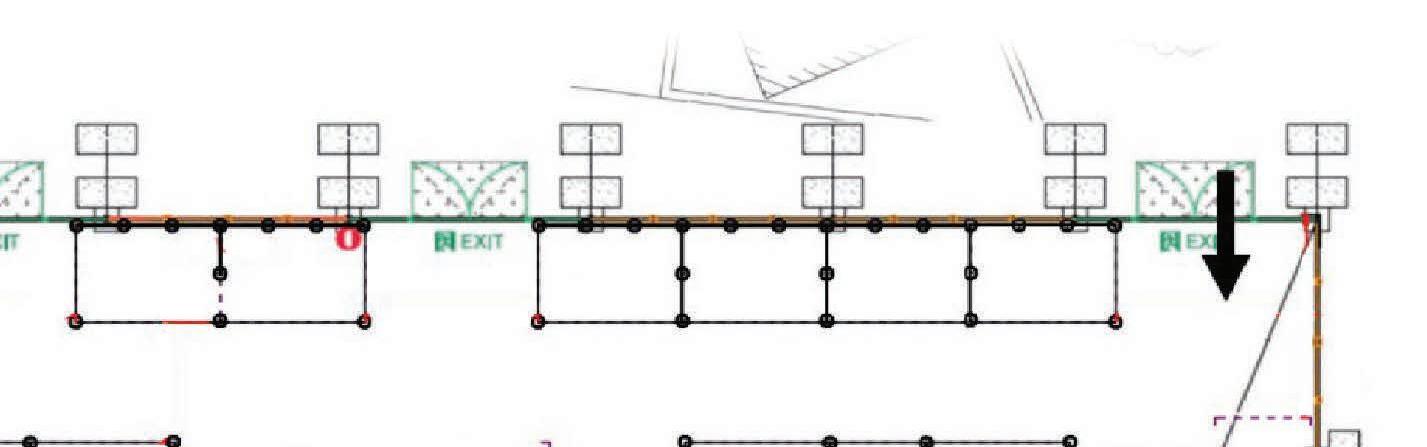
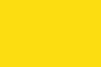
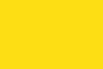
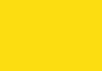
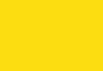
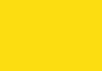
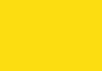
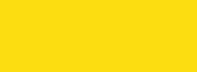

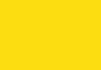
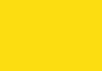
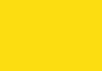
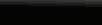



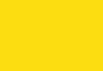
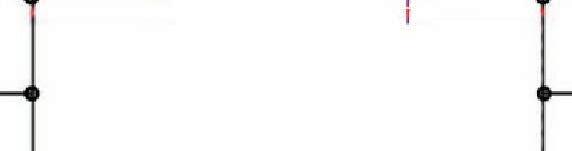
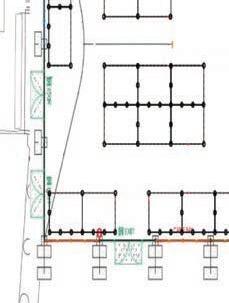
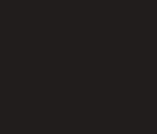
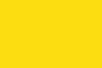
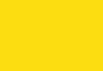
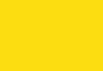
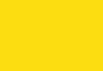
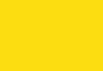
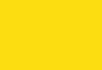
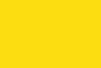
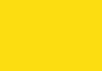
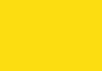
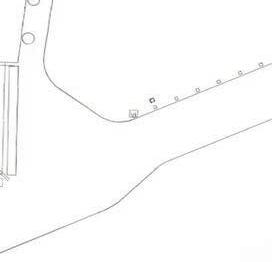
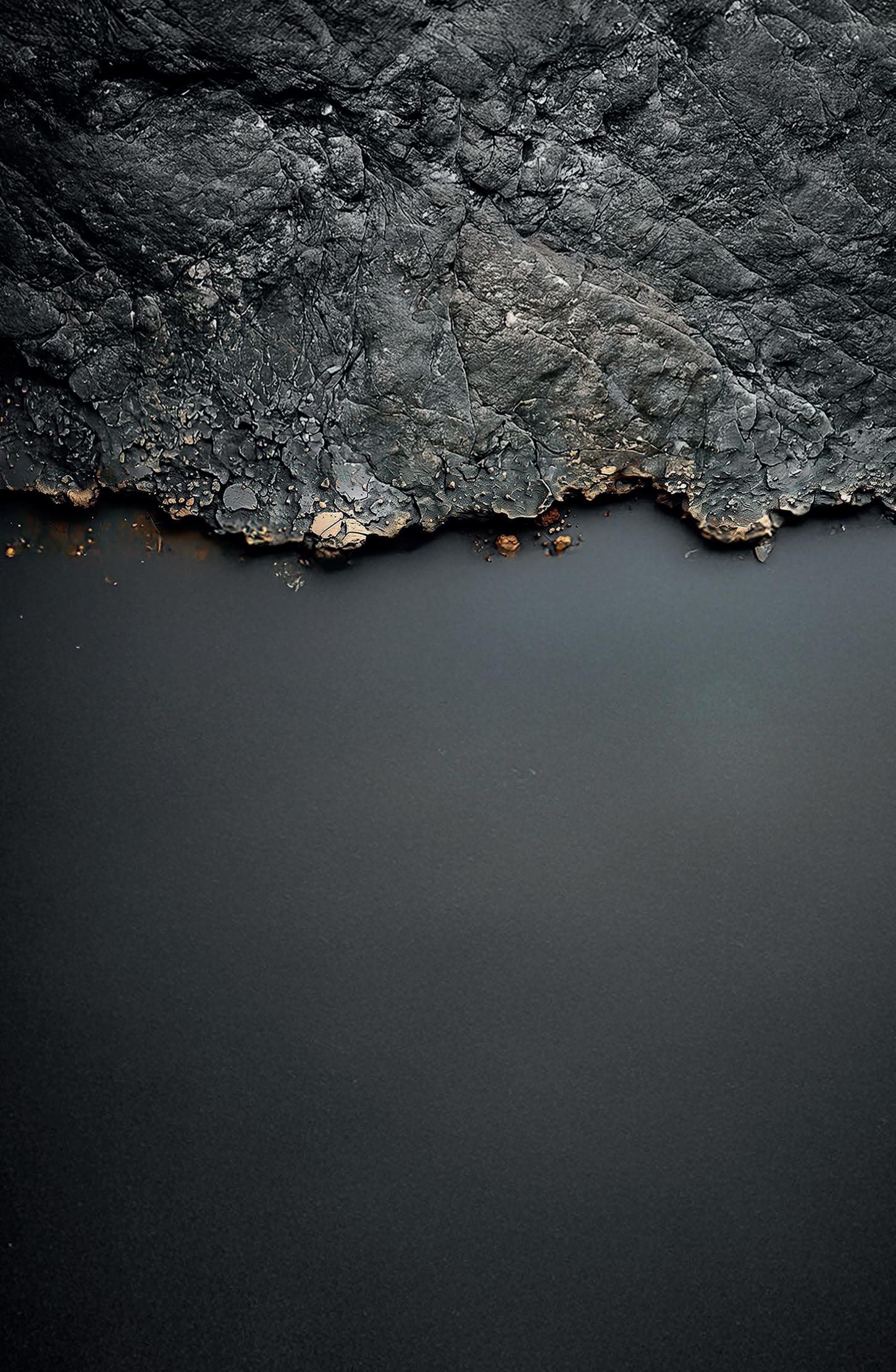

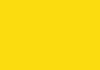

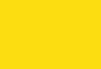
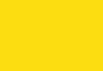

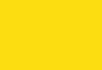
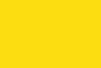
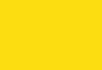
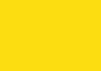
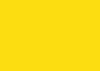
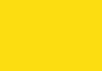
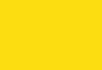
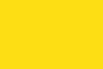
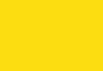
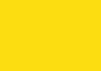
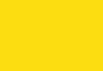
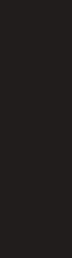
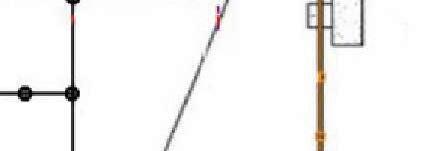

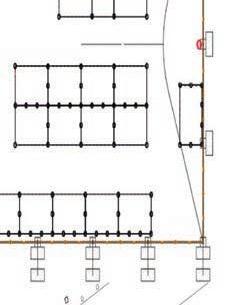
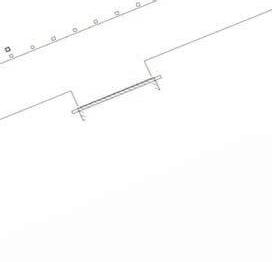
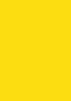
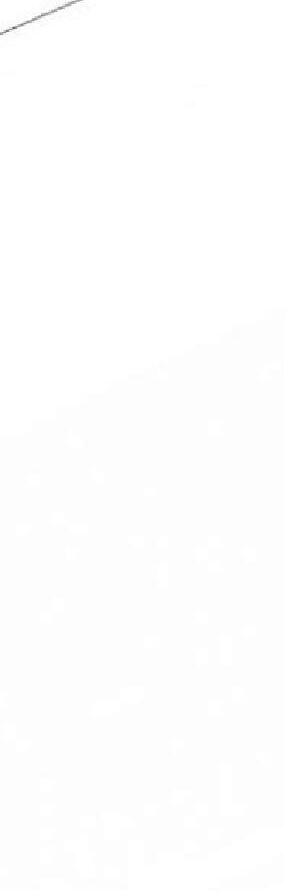
Strata
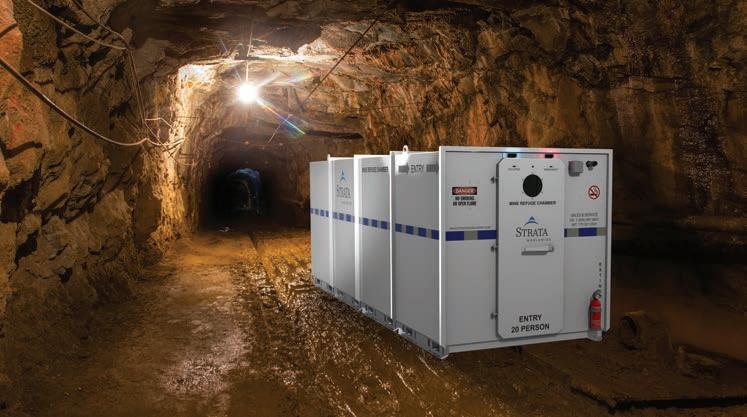
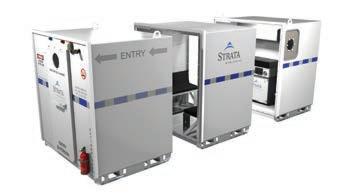
The Strata ERCM is a modular chamber design that offers greater flexibility in sizing options, faster delivery times, and improved handling capabilities.
Strata refuge chambers are designed for individualised configurations and include advanced communication and monitoring technologies that ensure emergency readiness and safety.
Strata is committed to safety, let us be your partner in emergency preparedness and ensure your peace of mind.
Tel: +61 1300 054 469 • info.au@strataworldwide.com
www.strataworldwide.com
BOLLÉ SAFETY
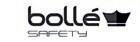
As a leader in the global PPE eyewear market, Bollé Safety’s commitment is to protect eyes and nothing else. Protecting the vision of more than 20 million wearers every day, Bollé Safety uses the most advanced technologies and innovations to create comfortable, high-quality and sustainable products that people love to wear.
bolle-safety.com
UVEX SAFETY AUSTRALIA
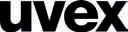
uvex safety Australia provides PPE designed to keep workers safe in a range of environments. As part of the global uvex group, the company utilises German manufacturing expertise to deliver innovative, sustainable safety solutions in eyewear, footwear, gloves, hearing, and respiratory protection across diverse industries.
uvex-safety.com.au

Body Armour delivers clean, science-backed hydration and recovery solutions, free from artificial additives, and backs it with on-site training that helps crews manage common site stressors that impact their safety and performance. Trusted by industry leaders, Body Armour lifts productivity, and helps protect your most valuable asset: your people.
bodyarmour.com.au
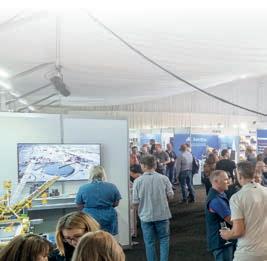
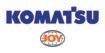
Komatsu develops and supplies technologies, equipment and services for construction, mining, forklift, industrial and forestry markets. For more than a century, the company has been creating value for customers through manufacturing and technology innovation, partnering with others to empower a sustainable future where people, business and the planet thrive together.
komatsu.com/en-au
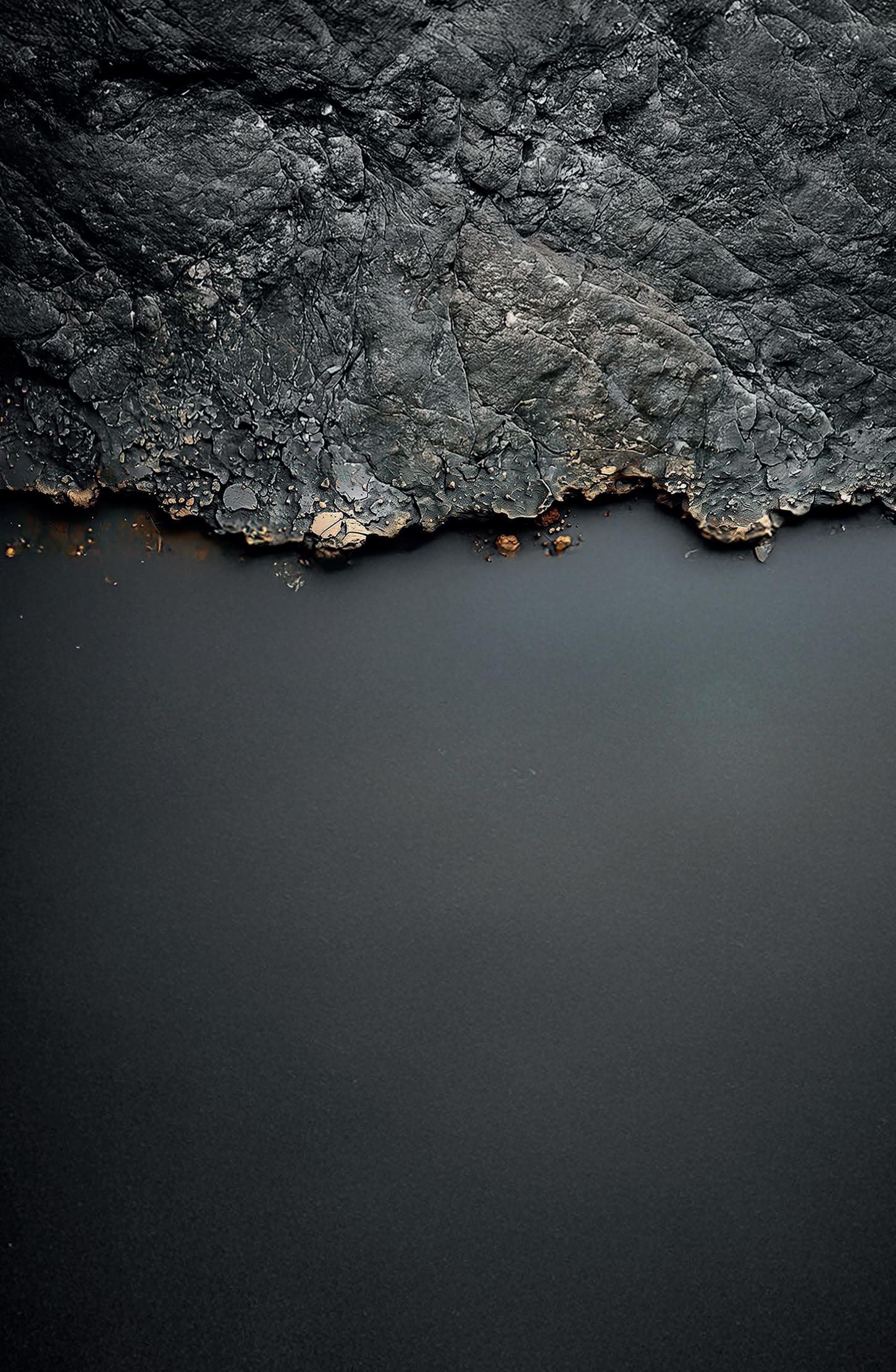
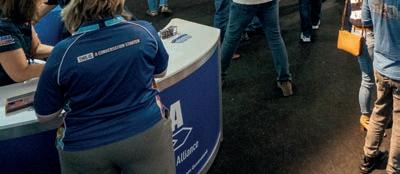
Booth 58
Booth 36
BODY ARMOUR
Booth 47/48
JOY GLOBAL AUSTRALIA
Booth 15 & 45

Strata Worldwide delivers advanced safety and networking technologies to mines globally, focusing on enhancing safety and promoting efficiency. The company offers solutions like proximity detection, collision avoidance systems and emergency refuge chambers, and specialises in underground support and industrial networking for communications and operational technology.
strataworldwide.com
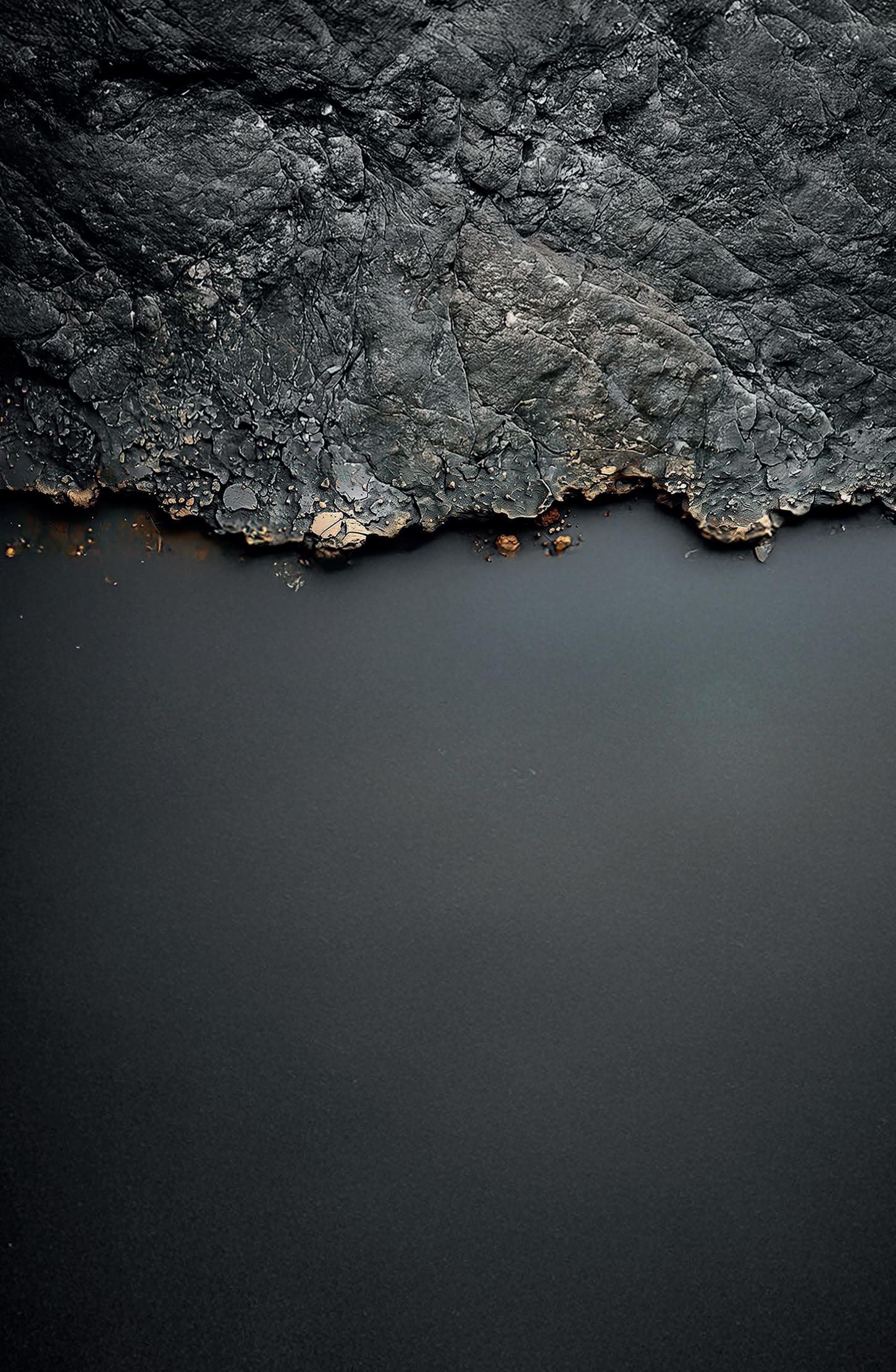
Emesent Hovermap offers a gold-standard in LiDAR-based mobile mapping. Enabling safer, faster and more detailed identification of underground hazards, Emesent specialises in autonomous mapping solutions – on a drone, robot, backpack, vehicle or handheld – leveraging advanced SLAM technology to ensures accurate data capture in inaccessible environments.
emesent.com
INDUSTREE GROUP
Industree Group, which delivers best-in-class PPE, is a market leader in sustainability, innovation, designing and producing premium brands
TRIDENT, EPIC, PITBULL, and eniQ. Its safety specialists collaborate with distributors and clients to understand challenges, provide expert guidance, and deliver protective solutions that help to ensure the safety of workers worldwide.
industree.com.au
NATIONAL PLASTICS AND RUBBER
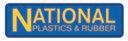
Operating since 1997, National Plastics and Rubber (NPR) has partnered with mining, quarry, and drilling teams to deliver high-quality, reliable polymer solutions that enhance safety and productivity. Trusted in Australia and around the world, NPR is known for innovation, sustainability and service excellence. nationalplastics.net.au
Booth 31
WORLDWIDE
Booth 32
Booth 3
Lounge 3
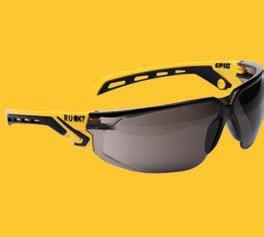
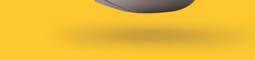
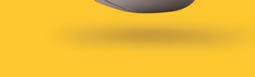
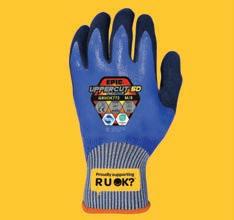
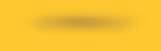
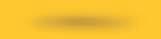
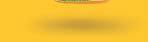
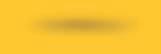
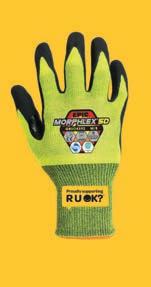
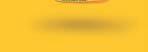
Reach out to your work mates. Look out for your work mates.
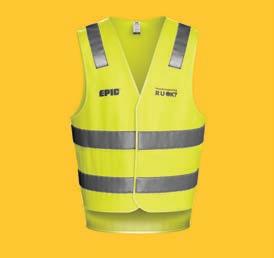
Make sure your work mates are seen and heard. Give your work mates a hand.
The emergence of AI
THE INTERNATIONAL LABOUR ORGANIZATION FOUND DIGITAL TECHNOLOGIES ARE IMPROVING WORKPLACE SAFETY, BUT ALSO HIGHLIGHTED OF NEW RISKS.
Digital technologies have fundamentally transformed workplace safety and health practices across global industries, with artificial intelligence (AI) and automation replacing workers in hazardous environments while simultaneously creating new categories of occupational risks.
The transformation has proved most pronounced in removing workers from dangerous tasks previously considered unavoidable hazards, according to analysis from the International Labour Organization (ILO). The report, ‘Revolutionising Health and Safety: The Role of AI and Digitalization at Work’, highlights how emerging technologies are improving worker health and wellbeing while underscoring the need for proactive policies to address new risks.
“Digitalisation offers immense opportunities to enhance workplace safety,” ILO team lead – OSH policy Manal Azzi said. “Robots can replace workers in hazardous ‘3D jobs’, which can be dirty, dangerous, and demeaning, while automation can reduce repetitive tasks, such as in-factory production lines or in administrative work. But for us to fully benefit from these technologies, we must ensure they are implemented without incurring new risks.”
The report outlined how advanced robotics handle operations in extreme temperatures, toxic environments, and high-risk scenarios, with mining operations utilising unmanned systems for material extraction.
Smart monitoring systems emerged as game-changers for predictive safety management, according to the report, which said wearable devices and AI-powered sensors now provide real-time hazard detection and risk assessment capabilities.
These systems track everything from air quality and noise levels to worker fatigue and ergonomic risks.
The research involved analysis across automation and advanced robotics, smart monitoring systems, extended reality applications, algorithmic management, and changing work arrangements.
The digital revolution, however, has introduced new risk categories that safety frameworks struggle to address. Extended reality technologies, while revolutionising training through immersive simulations, can cause balance issues, visual strain, and cognitive overload for workers.
The shift towards remote and platform work arrangements has presented safety challenges. Without direct oversight, ergonomic risks, environmental hazards, and inadequate safety measures often go undetected. Platform workers face heightened safety risks due to irregular schedules and limited employer-provided protections.
Gender disparities have also emerged as a significant concern. Women showed higher susceptibility to cybersickness from virtual reality systems, while robotic systems and exoskeletons often lacked gendersensitive design. The ILO noted that women are disproportionately affected by generative AI, with their exposure to automation being more than double that of men in most regions.
Successful digital transformations require proactive risk management. To maximise benefits while mitigating risks, the ILO said a proactive, evidence-informed and participatory approach is essential. Workers should be actively involved at all stages of digital implementation. It also noted that organisations must conduct regular risk assessments that account for impacts of new technologies.
Digital tools should complement rather than replace human judgment in safety practices, maintaining the human element that remains essential for effective workplace protection.
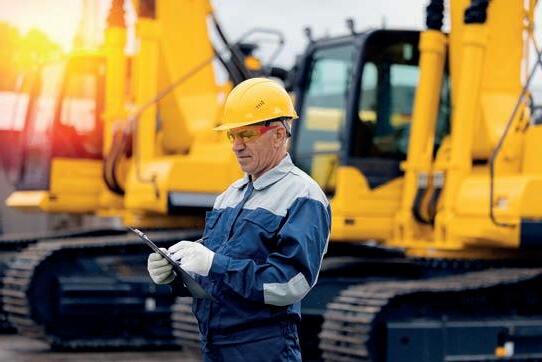
Digital technologies are redefining the safety landscape.
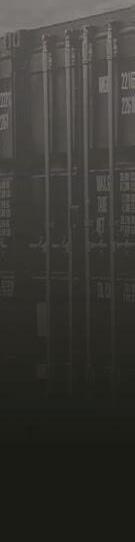
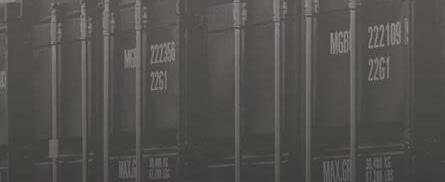
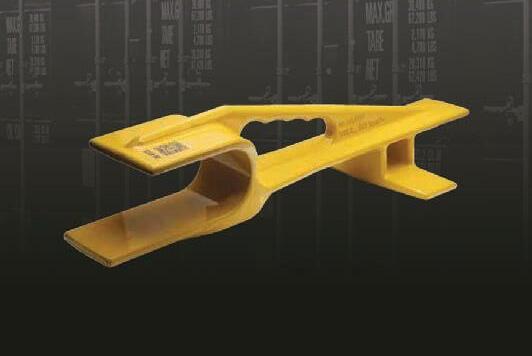
No tools. No welding. No downtime.
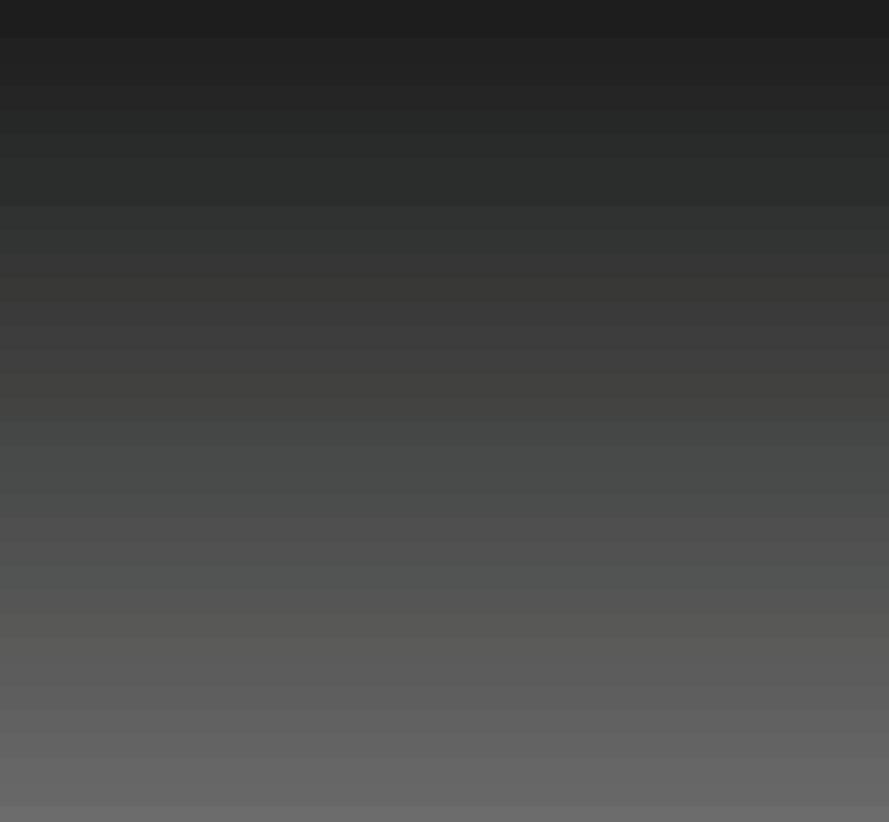
Lock your container doors open instantly and eliminate the risk of sudden swings and potential entrapment.
While your team works, BenStop stands guard — preventing injuries, reducing liability, and keeping safety front and centre.
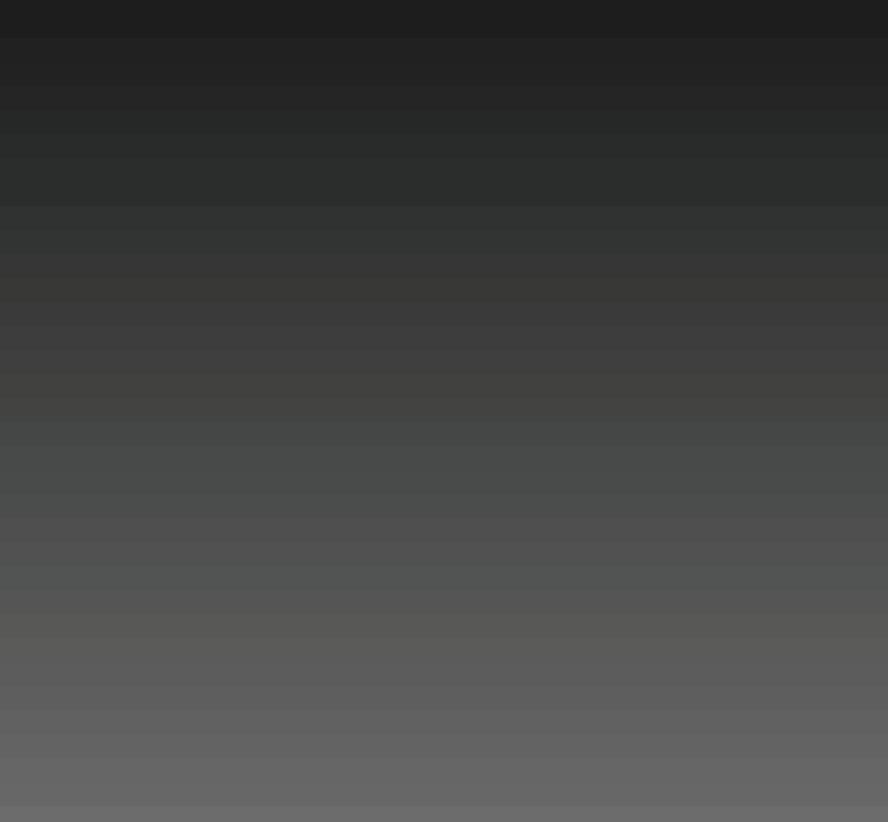
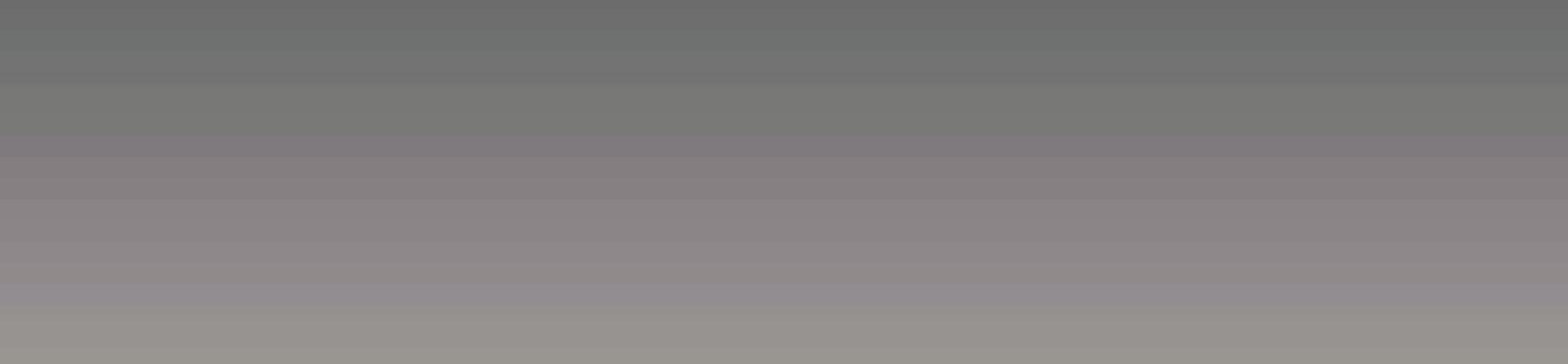
Protect your people.
Secure your site. Choose BenStop.

Withstands winds up to 60 km/hr
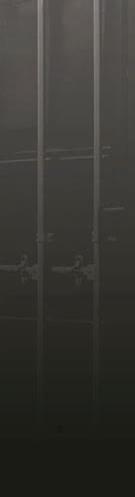
Fits ISO 20’ & 40’ Containers
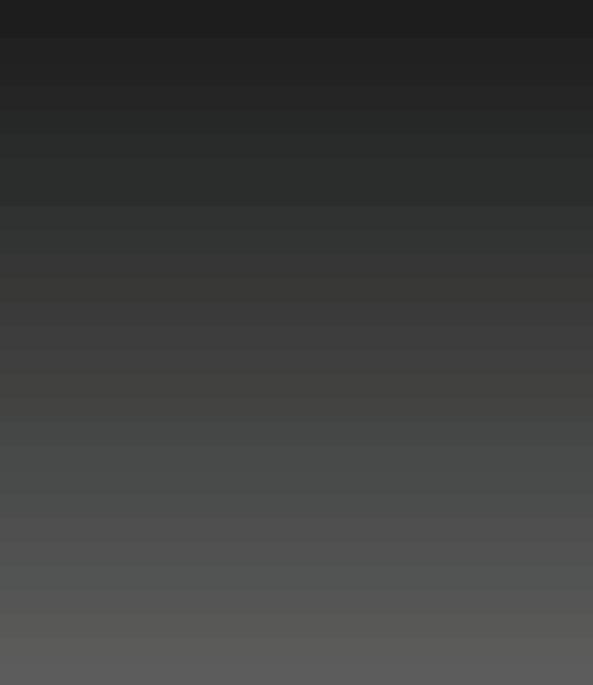
Use on left and right sided doors
Corrosion resistant

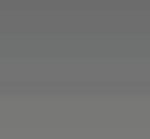
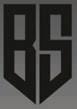
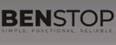
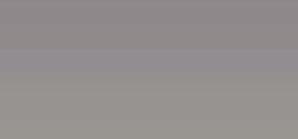
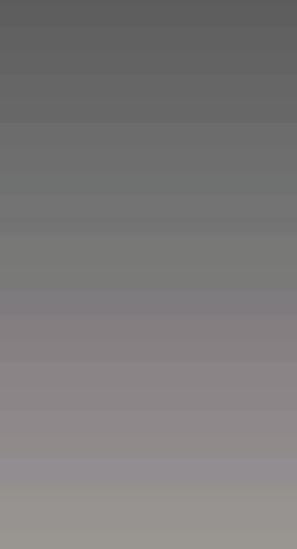
The perfect pour
BODY ARMOUR IS LEADING A SHIFT IN MINE SITE HYDRATION WITH CLEAN, SCIENCE-LED FORMULAS AND SOLUTIONS.
It only takes mild dehydration to put a worker’s mind and body under the same strain as being above the drink-driving limit. On mine sites – where concentration and precision are non-negotiable – that level of impairment can carry serious safety consequences.
Analysis conducted by the Georgia Institute of Technology involving more than 400 healthy adults found that with just three per cent hydration loss, attention dropped by 52 per cent, motor coordination by 40 per cent, and executive function by 24 per cent.
Body Armour founder Toni McQuinn said these findings reflect what can happen to mine workers under heat stress in a single shift.
“While these aren’t extreme cases of dehydration, the impairment is still comparable to a blood alcohol level of 0.05 per cent,” McQuinn told Safe to Work.
However, when it comes to hydration, not all solutions are created equal.
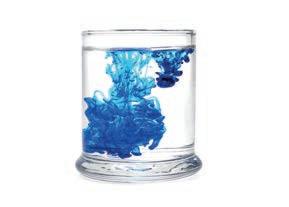
While Body Armour is an industrial hydration and recovery company, McQuinn and his team are driven by a broader mission: to challenge outdated norms and bring attention to what goes into the products workers consume every day.
Many hydration products still contain synthetic colours, and artificial sweeteners and flavours. McQuinn said these ingredients are increasingly linked to health concerns.
“For workers performing in challenging environments, the nutrition and recovery solutions they consume should support their health, not compromise it,” he said.
CHANGING THE GAME
Having spent 15 years working across various mine sites, McQuinn has
“Over the years, my colleagues joked around saying I should do something about it,” McQuinn said. And so, he did.
When McQuinn and his team examined the market, they discovered a troubling reality.
Most hydration products contain synthetic dyes, artificial sweeteners, and chemical additives with no performance or health benefits. Miners consuming these solutions multiple times daily, year after year, face a cumulative toxicological risk.
“The danger isn’t in one drink, it’s the compounding effect of repeated exposure over time,” McQuinn said.
Globally, countries like the US and several European nations are responding to growing scientific
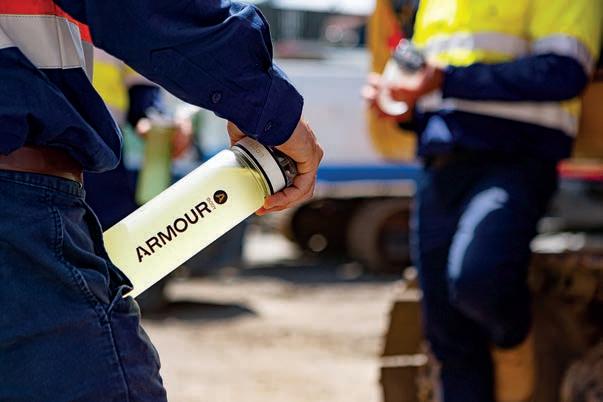
Armour’s hydration products are free of synthetic dyes and artificial sweeteners..
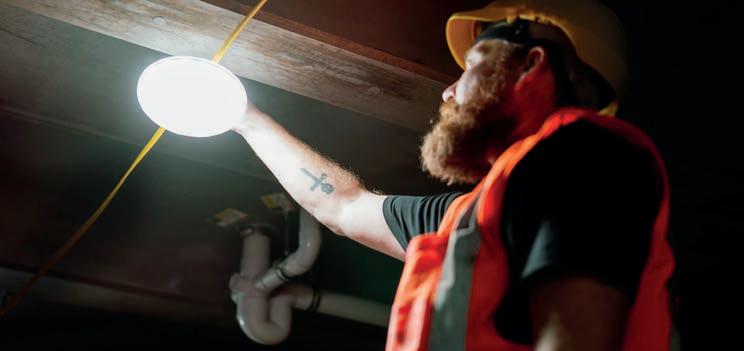
Images:
The Brilliant Blue 1 dye in plain water.
Body
HIDDEN RISKS
The concern extends beyond general health.
In mining environments where dehydration, heat and fatigue are common, additives like Red Dye 40, Yellow 5, Yellow 6, and Brilliant Blue 1 pose a heightened threat. Several studies have linked these petroleumbased dyes to serious health issues including gut microbiome disruption and behavioural effects.
“These dyes offer zero nutritional, functional or performance benefit, so why are we taking the risk?” McQuinn said. “Many people don’t realise they’re still consuming artificial colours that are being phased out globally, and they don’t have to; healthier, more effective alternatives are already available.
“Our goal at Body Armour is to shine a light on this issue and encourage individuals, from safety leaders to frontline workers, to critically examine what they’re putting into their bodies.”
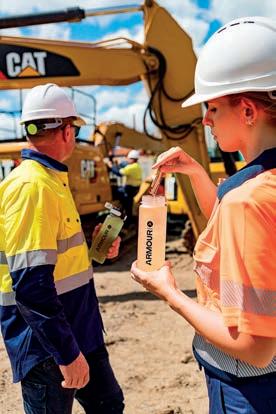
While sites have banned asbestos, limited silica dust, and imposed controls on alcohol and drugs on-site, McQuinn said a hidden risks remain present in the industry.
“Artificial dyes may not be as acutely toxic, but we’re seeing the early warning signs,” he said. “We can choose better now, especially given that we already have the data and
other countries have taken the lead in change.”
That kind of change, however, requires wider commitment.
“Real transformation doesn’t happen overnight,” McQuinn said.
“It takes a collective effort across the sector.”
CHARGING AHEAD
Body Armour is helping reshape the conversation by investing heavily in on-site training and safety toolbox
talks, which translate insights from sports science into practical tools for heavy industry.
The response has been overwhelmingly positive.
“We’ve been really encouraged by the feedback,” McQuinn said. “Hearing that our hydration solutions help people feel better, stay sharp longer, and recover faster reminds us why we started.
Since its inception, Body Armour’s natural formulations have been providing hydration that not only replenish fluids but restores critical electrolytes and minerals necessary for brain function, muscle coordination, and energy – all without artificial colours, flavours or sweeteners.
“Effective hydration isn’t just about quenching thirst,” McQuinn said. “It’s about protecting performance.
“In high-risk environments, the right formulation can not only significantly impact how we feel, it can increase performance and productivity”
For the mining sector, which prides itself on being a safety and innovation leader, the shift to clean hydration represents not just a health initiative but a broader opportunity to elevate performance and wellbeing.
“This isn’t about following trends,” McQuinn said. “It’s about being proactive, accountable and genuinely committed to the long-term health of our people.”
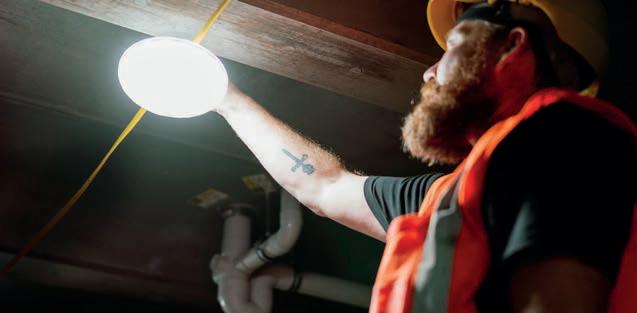

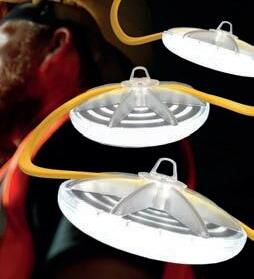


Body Armour is helping mine workers stay hydrated by pivoting to natural formulas free of harmful additives.
Hazard avoidance
Raising the bar
NIVEK IS AT THE FOREFRONT OF PROVIDING SOLUTIONS THAT EASE THE PHYSICAL DEMANDS OF LABORIOUS AND DANGEROUS MAINTENANCE WORK.
Founded with a sole focus on protecting workers at the coalface, Nivek launched a groundbreaking innovation in 2011 – the Tracked Elevating Device, also known as TED.
It was a world-first solution born from of Nivek founder Kevin Cant’s near-death experience in 2008.
As a mechanic and fitter working in the Hunter Valley in New South Wales, Kevin narrowly escaped being crushed by a half-tonne belly plate during a routine bulldozer maintenance task.
The weight of these plates, which can be hundreds of kilograms depending on debris accumulation, posing a significant safety risk.
Motivated by this life-threatening close call, Kevin spent three years
With its low-profile scissor lift design, remote-control operation and all-terrain capabilities, TED became the ideal tool for navigating tight spaces and lifting heavy components without putting workers at risk.
The system quickly gained traction across Australia’s mining sector and was soon adopted internationally.
A growing range of attachments, from fork tynes and front jibs to extension blocks and custom trailers, further extended TED’s versatility, making it a crucial asset for workers aiming to complete their shifts safely.
But Nivek didn’t stop there.
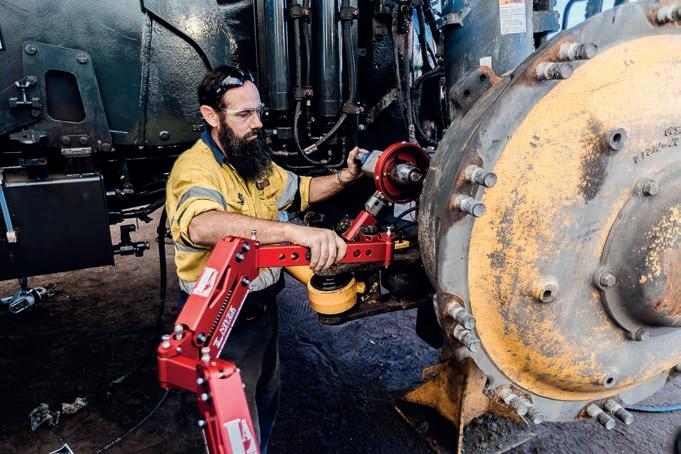
More than a decade later, the company continued to expand its offerings, developing another set of equipment solutions that would
manage bulkier components and more complex tasks.
It can lift up to 3000kg while operating continuously for up to two hours on battery power.
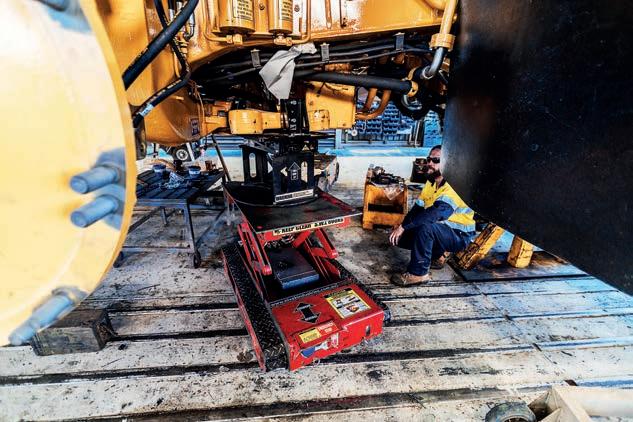
Despite Big TED’s increased capacity, it retains the low-clearance design and manoeuvrability that made the first TED so popular and effective. It also integrates smoothly with Nivek’s suite of attachments and features joystick control for exact precision.
Another one of Nivek’s key innovations is the Lift Assist (LA40), a compact arm that gives workers a safer, strain-free way to handle heavy tools such as rattle guns and impact drivers weighing up to 40kg.
Easily mounted on a mobile stand or attached to TED, the LA40 is designed to reduce fatigue and musculoskeletal injuries on the job.
Nivek Industries general manager Derrick Cant said cutting down exhaustion has been a game-changer.
“There are some well-documented links between fatigue and serious accidents, particularly in high-risk industries,’’ he said. “We’re hearing from fitters and safety workers that the
Images: Nivek Industries
Nivek Industries is at the forefront of safer, more productive machinery maintenance.
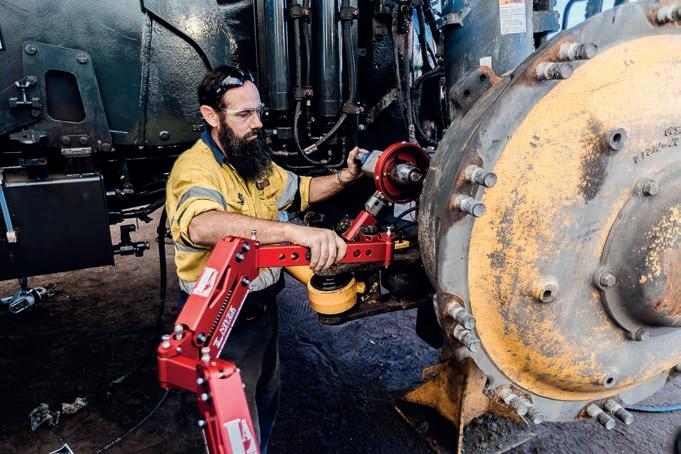
fatigue reduction they’re experiencing using the system is huge.”
That kind of input also plays a vital role in how Nivek approaches design.
“Feedback from engineers, fitters and safety personnel is incredibly valuable to us, given they are the people who will ultimately be using the system,” Cant said.
“This gives us the parameters to work within and get the design right straight up, meeting some pretty tough criteria.”
Looking ahead, Nivek’s focus is on expanding the capabilities of its current suite of products, especially the attachments, in order to boost flexibility and on-site efficiency.
“Essentially, our products are tracked power units, with unique attachments that deliver true value,” Cant said.
Since Nivek handles design and manufacturing in-house, the company also develops custom-certified
attachments tailored to specific customer requirements, without raising concerns around intellectual property or warranty limitations.
Beyond improving safety, Nivek’s technology is having a wider impact across the mining industry.
By removing the need for brute strength to manage tools and components, the company’s products are helping make the sector more inclusive and accessible to workers of all physical builds.
“When you consider the tools themselves weigh 30kg to 40kg just to do up a nut or a bolt, our equipment has taken the weight out of the job –that physical requirement has been eliminated.” Cant said.
“It opens up the mining industry to a broader range of people.”
Guided by the principles of safety, accessibility and innovation, Nivek is continuing to redefine what’s possible in the industry.
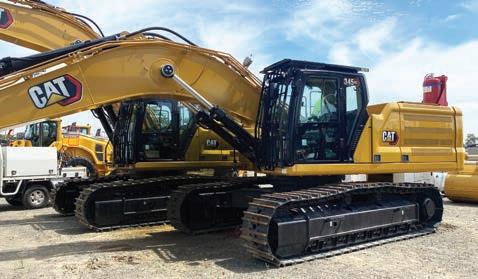
PROTECT YOUR ASSETS WITH MUSTER
24/7 Fully Monitored Solutions
Muster brings unmatched fire protection to your world. With cutting-edge systems and advanced technology, we stand as your steadfast defense against the unexpected. From engine bays to critical spaces, the Muster range offers multiple agents to provide the best solution to your specific risk.
Our detection options allow for rapid detection in the risk areas identified during the fir e risk assessment, thereby protecting your machinery and your all-important personnel.
Designed by fitters who have worked in the field, Nivek’s products take the pressure o personnel.
Hazard avoidance
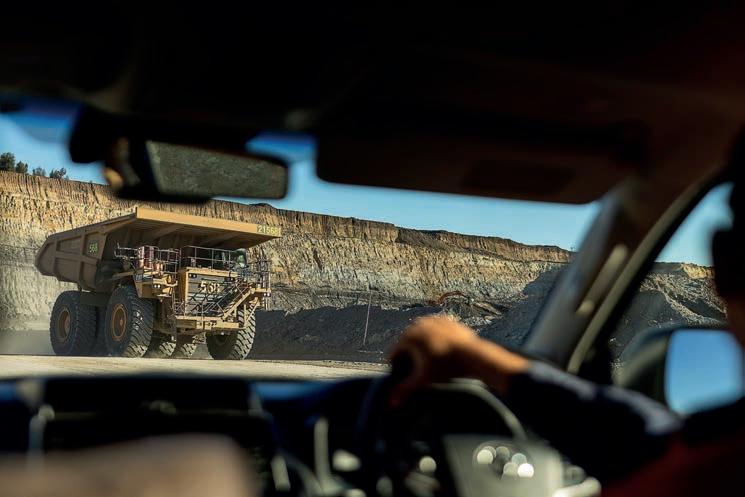
Smart safety solutions
MINING COLLISIONS OFTEN STEM FROM BLIND SPOTS, FATIGUE AND MISSED SIGNALS – BUT SMART TECHNOLOGY IS STEPPING IN.
Arecent collision in a New South Wales open-cut coal mine involving a bulldozer prompted an alert from the NSW Resources Regulator, underscoring that positive communication and visual contact alone aren’t always enough to prevent life-threatening incidents.
No one was injured, but the message is clear: if existing controls aren’t adequately effective, the consequences can be serious.
The incident has added urgency to a growing conversation across the mining and civil sectors about the limitations of traditional workplace safety methods, particularly when they rely on human input under high-risk, high-fatigue conditions.
“We know operators are doing their best,” Aptella executive manager mining Andrew Granger told Safe to
Work. “But it’s well documented that fatalities and incidents have occurred in mine sites.
“While at times it can be accepted that it is a dangerous environment, it cannot be accepted that we’re not doing anything about it.”
TURNING REACTIVE INTO PROACTIVE
Solutions like Torsa’s Collision Avoidance System (CAS) use real-time data and automated responses to help prevent accidents before they happen.
While most safety systems are designed to respond to problems after they occur or once they’re already in motion, CAS is designed to shift that paradigm.
Its platform doesn’t just alert operators; it actively interprets and prioritises risk using a multisensor approach.
The system fuses real time data from AI-camera, LiDAR (light detection and ranging), GNSS (global navigation satellite system), and V2V (vehicle to vehicle) communications to build an accurate 360° awareness of moving and static hazards.
Torsa relies on an intelligent risk-based approach, alerting the operator only when a verified risk is imminent. And, critically, it’s capable of escalating from warnings to automated intervention. This functionality is also available with Torsa’s integrated antifatigue solution in cab.
Aptella, a provider of intelligent positioning and automation solutions, is a distributor of Torsa’s technology in the Asia-Pacific.
Aptella product manager Denzil Khan told Safe to Work the true beauty of the Torsa technology lies in its multisensor approach.
Torsa alerts the operator only when a verified risk is imminent.
Images: Aptella
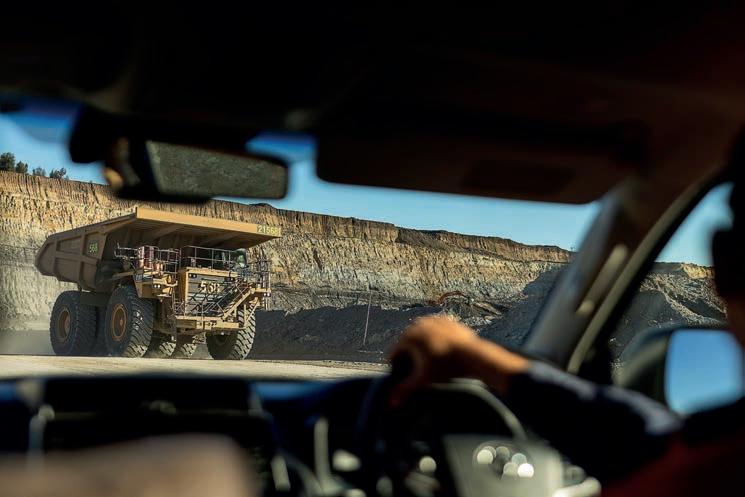
“Being able to harmonise such a rich set of data and not tire or frustrate the operator with false alarms is key,” he said.
“When procedures fail, technology should not, and Torsa’s intervention level systems ensure that.”
Khan believes collision avoidance is ultimately about buying extra time.
“Particularly when handling fatigue,” he said. “If something is going wrong, you don’t just want to be warned; you want a system that’s already working to protect you.”
TECHNOLOGY THAT FILLS THE GAPS
The advisory from the NSW Regulator reinforces some key site safety messages: maintain visual contact, confirm intent to move, and communicate clearly.
While these remain critical, they rely entirely on people. And when people are operating huge machines in lowvisibility zones, dealing with pressure, fatigue or distraction, that system often isn’t enough.
have to choose between focus and vigilance – our technology does both, continuously.”
Torsa’s intelligent prioritisation system is vital in environments where multiple machines are operating simultaneously. The technology distinguishes between real and perceived threats, filtering unnecessary alerts while acting decisively on high-risk interactions. This helps to ensure critical warnings are not missed, while also avoiding alarm fatigue.
In relation to the aforementioned bulldozer incident, the NSW Regulator highlighted three typical failure points: human error or skipped checks under fatigue; poor communication or silence between operators; and over-reliance on procedural controls instead of engineering fixes. Torsa’s CAS is engineered to activate in these exact situations, replacing assumptions with real-time, automated awareness while only alerting the operator to verified risks and hazards.
Lack of communication is addressed by real -time V2V communications of position and trajectory, reducing dependency on two-way radios, and 3D sensing covers blind spots and detects
all objects, eliminating situational awareness issues.
The CAS also has a built-in engineering control that is always active, not just when procedures are followed.
Khan is very clear about the technology’s purpose.
“We’re not trying to replace people, we’re backing them up,” he said. “In the moments where things break down, you want a system already working to hold the line.”
Torsa’s CAS has been developed in partnership with industry and aligned with the Earth Moving Equipment Safety Round Table (EMESRT) Level 9 safety framework. It is designed to intervene when human systems fall short, without compromising operator trust or adding cognitive load.
“Torsa has been developed with miners for miners,” Khan said. “It reflects the real conditions and challenges operators face and, most importantly, gives them a system they can trust to step in when needed.”
Granger said Aptella and Torsa’s united mission is a simple one.
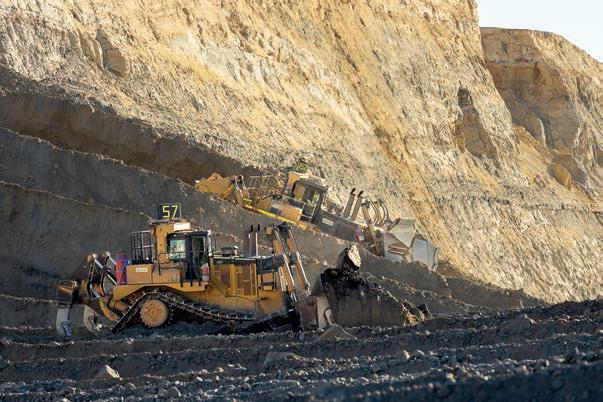
“This isn’t just about ticking boxes on compliance,” he said. “It’s about engineering real, proactive protection into daily operations.”
Torsa’s intelligent prioritisation system is vital in dynamic environments.
Emergency refuge
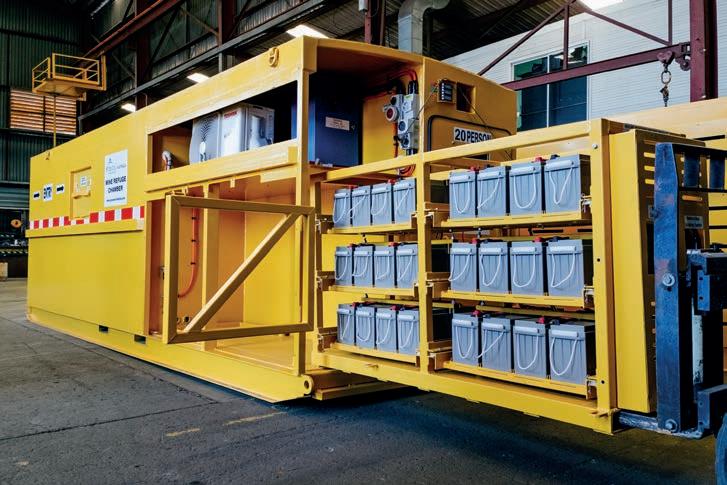
Chamber of safety
REFUGE CHAMBERS CAN BE A VITAL LIFELINE WHEN CRISIS HITS ON A MINE SITE, PROVIDING ESSENTIAL PROTECTION AND SHELTER.
When emergencies strike or air quality deteriorates underground, workers on mine sites rely on sophisticated safety systems for protection.
Powered by a commitment to better understand the challenges of operating beneath the surface, Strata Worldwide is setting a new standard for underground mine safety with its advanced emergency refuge chamber systems.
“Our solutions are designed to provide immediate refuge and breathable air to workers in the event of an emergency or when underground air quality becomes compromised,” Strata Worldwide chief operating officer Tony Napier told Safe to Work.
“We invest considerable time and resources into fully understanding the underground working environment, and work closely with customers to
develop effective solutions to manage problems and limitations.”
ALL SHAPES AND SIZES
Offering a diverse range of refuge chambers, Strata has developed a range of solutions that are suited to specific mining scenarios or operational requirements.
The large-capacity chambers, capable of holding 8–30 people, are designed primarily for static use in hard rock, coal and tunnelling environments where workers may need to shelter for longer periods.
For operations that require flexibility and mobility, compact chambers accommodating 4–6 people are available. These smaller units are built for quick and easy deployment near work areas and can be equipped with wheels, hitch packages, or integrated transport attachments to assist in movement.
Where shaft access or handling restrictions pose challenges, Strata’s segmented chambers are delivered in parts and assembled underground, overcoming countless logistical barriers.
Tunnelling environments benefit from narrower chamber designs that can be mounted directly onto tunnel boring machines and rails, or positioned within active tunnels without hindering operations.
Maintaining a continuous supply of breathable air is key in refuge situations, and Strata’s chambers incorporate advanced systems to guarantee uninterrupted and safe air quality. According to Napier, they connect directly to a mine’s main air lines, allowing an unlimited supply of fresh air filtered through specialised filtration units.
To control carbon dioxide levels, the chambers are equipped with
Images: Strata Worldwide
The battery system is located at the front of the chamber for ease of access.
active scrubbers that help remove CO2. Oxygen bottles provide supplemental oxygen regulated to maintain safe concentrations.
For the management of carbon monoxide, small amounts of which are produced by human exhalation, a catalyst converts carbon monoxide into CO2, which is then scrubbed out using soda lime chemicals.
In addition, monitoring systems such as Strata’s HMI and Trolex units enable real-time tracking of air quality, helping to ensure all occupants remain safe and informed.
POWERING ON
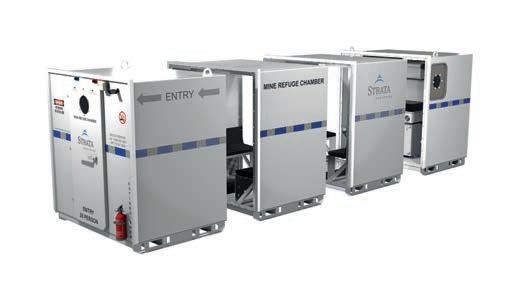
minimise the need for manual handling of individual batteries.”
Ensuring comfort and livability is also essential in the events miners face an extended stay in emergency chambers.
Keeping the power on is another crucial aspect of chamber safety, especially during emergencies that disrupt electrical supply.
Strata chambers are designed to operate indefinitely when connected to the mine’s main power source.
In the event of a power failure, a fully automatic battery back-up system activates seamlessly, providing at least 36 hours of power.
Built from lead acid, fibre mat and crush-proof materials, the battery
High temperatures in the mine, combined with body heat in confined spaces, can create dangerous conditions over time.
Strata tackles this by installing air conditioning units with dehumidifying capabilities to maintain a safe and tolerable climate inside the chambers.
Thermal insulation applied to walls and ceilings provides further protection for occupants from external radiant heat sources.
To enhance overall comfort
This is designed to ensure chambers can be installed and configured to maximise safety without interfering with mining activities.
PROVEN IN EMERGENCIES
Napier said Strata’s refuge chambers have proven their worth in several real-life situations, including a recent incident where an underground main power cable overheated and caught fire.
All personnel immediately evacuated to the refuge chambers. As the mine’s power had failed, all 30 units were running on back-up batteries throughout the emergency.
“Strata’s refuge chambers performed to the client’s
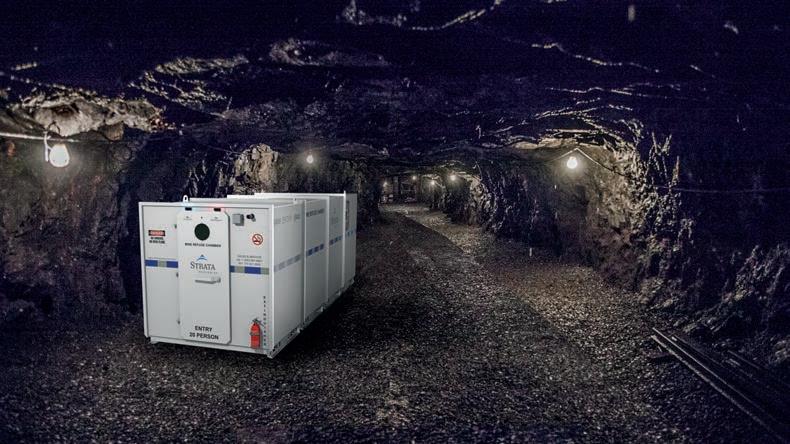
The economical modular chamber helps overcome potential handling concerns.
Strata ERCM features two seating modules.
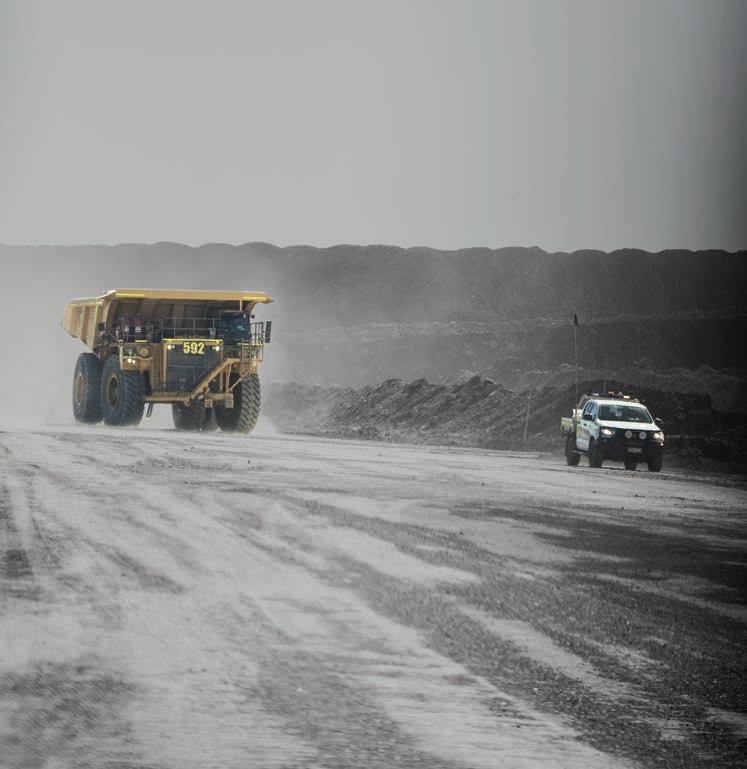
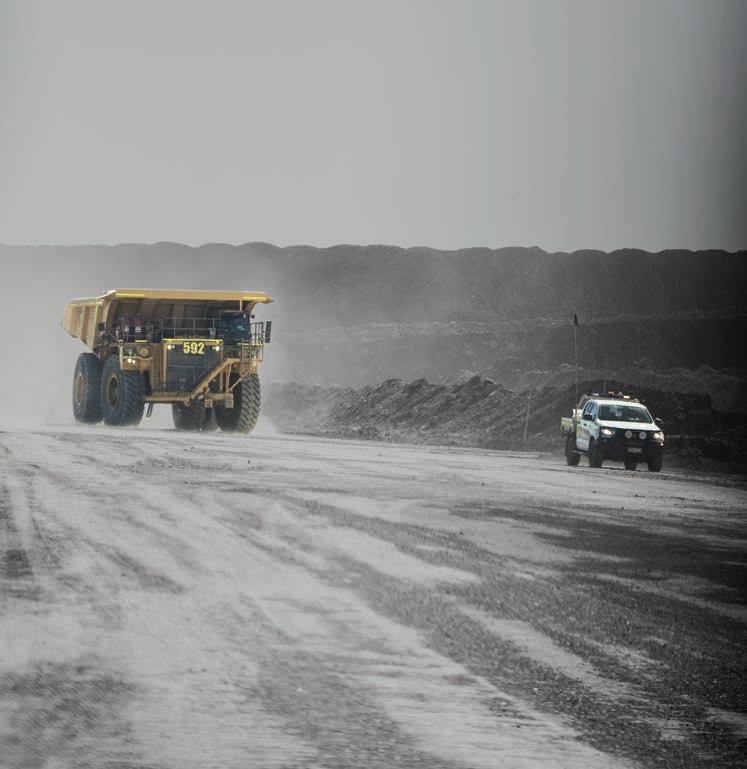
Leading with safety
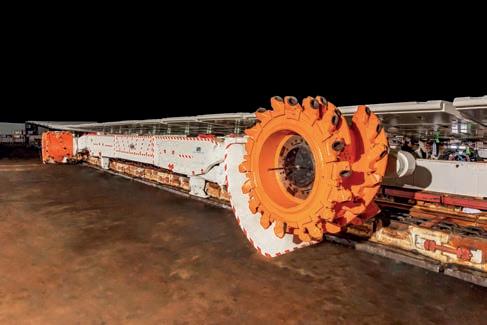
IN THE HIGH-PRESSURE WORLD OF UNDERGROUND COAL MINING, FEW CHALLENGES LOOM LARGER THAN SAFETY AND PRODUCTIVITY,
estimated eight per cent productivity increase through consistent cutting and fewer stoppages.
According to site management, the automation enabled a shift in workforce deployment, moving personnel out of the highest-risk areas without compromising coal recovery.
Acontinue to push deeper into complex geological seams, the industry’s appetite for safer, smarter technology has never been greater.
Enter Komatsu’s next-generation longwall system – a fully integrated, automation-ready solution that’s transforming safety outcomes across Australia’s underground coal sector.
Australia’s underground coal mines, particularly in New South Wales and Queensland, operate under some of the world’s strictest safety frameworks. From the WHS (Mines) Regulations to compliance with Longwall Automation Steering Committee (LASC) standards, operators are expected to not only maintain productivity but drive toward zero harm in the process.
For Komatsu, this is not a constraint; it’s a design principle.
“We’ve engineered every component of our longwall technology to reduce manual interaction, enhance operational visibility, and anticipate failures before they happen,” Komatsu engineering manager control and automation Shane Cooling told Safe to Work. “In Australia, that’s non-negotiable.”
safety-first approach is the Longwall Automation Package (LAP), a suite of tools that removes the need for constant human presence at the longwall face. Whether its advancing powered roof supports or managing horizon control on the shearer, LAP automates some of the most hazardous tasks in the section.
Paired with Faceboss RS20s and Faceboss 2.0 controls and the Joy Smart Solutions analytics, this system doesn’t just respond to conditions, it predicts them.
Personnel can monitor operations remotely, well away from the face, with real-time alerts for hydraulic loads, convergence data, and equipment performance.
FIELD-PROVEN IN THE HUNTER VALLEY
A standout case study comes from Mandalong Mine (Centennial Coal), where Komatsu’s RS20s PRS and full automation suite were deployed in a low-seam panel (<1.6m). The results were hard to ignore, with an average of more than 95 per cent across all shifts using surface remote automation, and an
In addition to automation, Komatsu has a Personal Proximity Detection System (PPD), a proven technology in NSW and Queensland coal mines. These systems create safety zones around the moving machinery and can automatically halt powered roof supports and the shearer when people breach defined boundaries.
Combined with predictive maintenance tools and remote diagnostics, the full longwall package supports a “control-first approach”, engineered safeguards that reduce reliance on procedural workarounds or reactive interventions.
While safety is the priority, operators aren’t ignoring the commercial upside. Komatsu reports that mines implementing full LAP and JoySmart systems are seeing reduced unplanned downtime, lower injury-related insurance costs, and faster panel development with fewer stoppages.
With payback periods often under two years, Komatsu said the value proposition is hard to dispute.
As automation moves from “nice to have” to “critical path,” the company believes its integrated longwall system will become the default for mines aiming to meet safety and production benchmarks.
“Our vision is simple,” Cooling said. “Keep miners out of harm’s way, give engineers better data, and let the system do the heavy lifting. In Australia, that’s the future of longwall mining.”
Image: Komatsu
Komatsu’s longwall technology embodies the company’s safety-first approach.



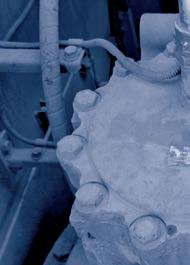


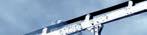

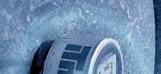
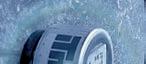
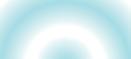
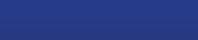


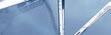







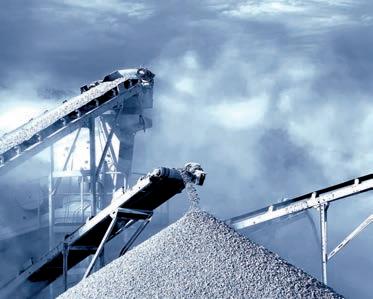


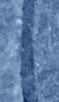
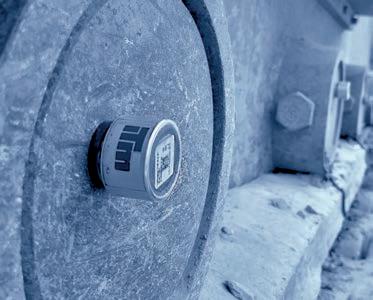

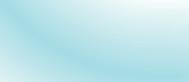
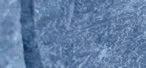







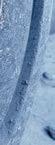

















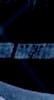
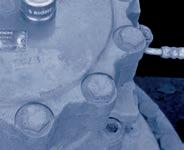
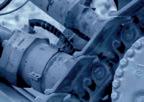
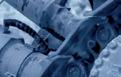
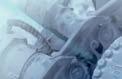


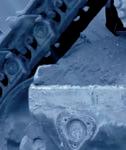
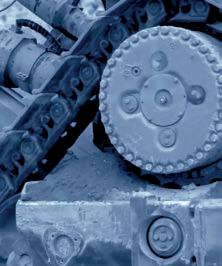
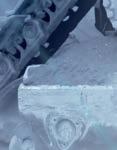

ONE SOLUTION, ENDLESS APPLICATIONS
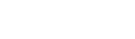

TRUST ITM® MOBILE KIT: ALL-IN-ONE FOR ADVANCED MACHINE TEMPERATURE MONITORING
ITM, pioneers in undercarriage sensor technology, introduces the advanced TRUST ITM® Mobile Kit (TMK). This ready-to-use diagnostic toolkit, equipped with smart magnetic sensors, a display, and an external receiver, monitors the temperature of critical machine parts in real-time. The magnetic sensors can be easily attached to any metallic surface, and the TMK can be reused on multiple machines, enhancing safety and efficiency for any crew in the field.
TRUST ITM®. Track your future.






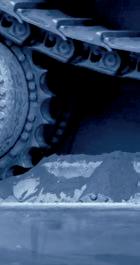
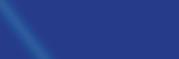

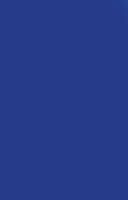
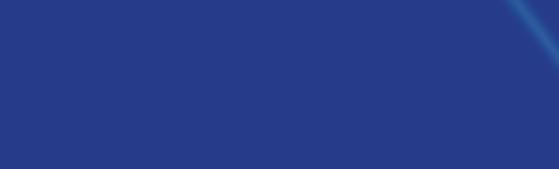
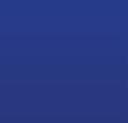


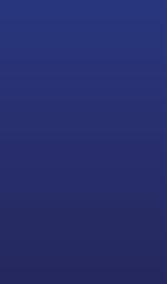







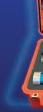






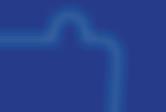










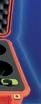
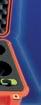
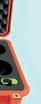
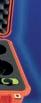

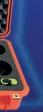
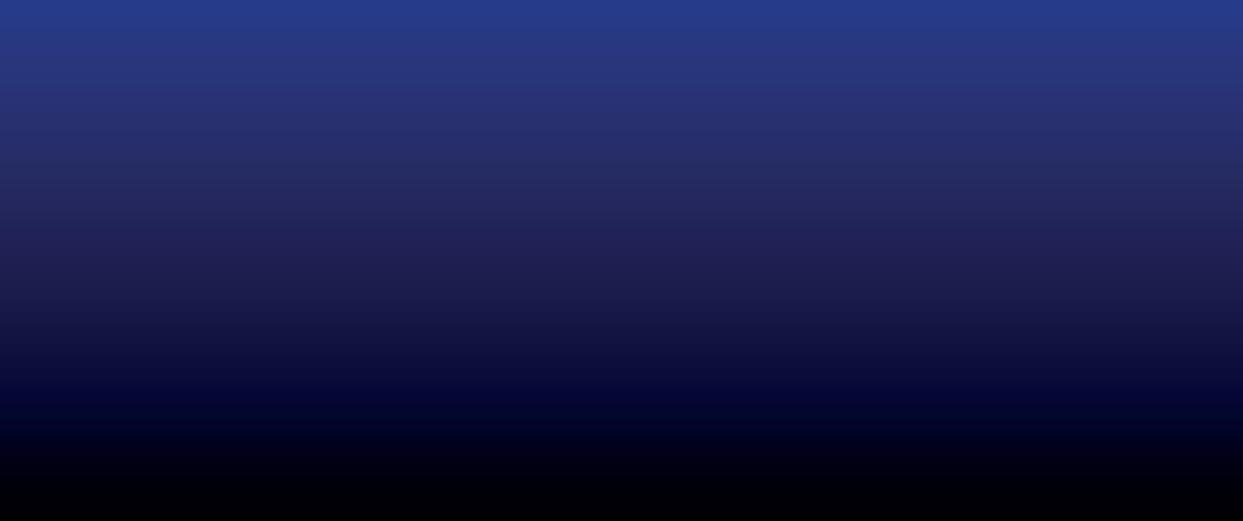
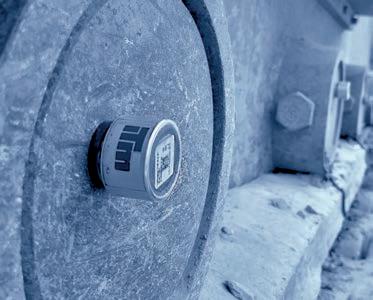
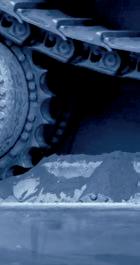
Polymer pioneers
SINCE 1997, NPR HAS WORKED WITH THE MINING INDUSTRY TO DESIGN AND MANUFACTURE LIGHTER, TOUGHER, MORE DURABLE SOLUTIONS.
National Plastics and Rubber (NPR) has come a long way since it first opened its doors in 1997.
From its humble beginnings as a specialty plastic and rubber products supplier, the company has grown into Australia’s leading provider of polyurethane and rubber products for mining and heavy industry.
“We’re not just a rubber or plastics company anymore,” NPR managing director Peter Georgiou told Safe to Work. “We’ve evolved from only doing specialty work to now having a real focus on equipment that actually improves safety and operational efficiency. This includes providing polymer solutions.”
From custom-formulated compounds to on-site training, NPR’s approach is rooted in safety and performance. In-house engineers design every product, which are then manufactured on-site in the company’s 2000m² Brisbane facility, with rigorous testing conducted throughout. The result is stronger, lighter and more durable solutions tailored to real-world mining and industrial risks.
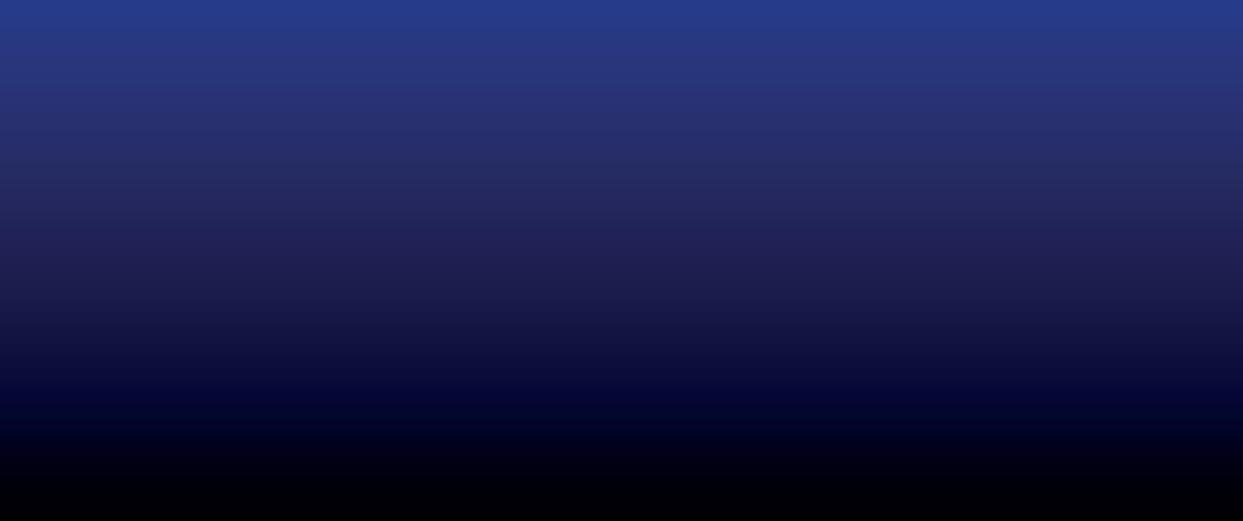
One of NPR’s signature innovations is its Stacko blocks, lightweight, loadrated blocks used to safely elevate heavy equipment.
Georgiou said that unlike traditional timber blocks, Stacko blocks are load rated and engineered for strength and ease of handling.
“If you’re walking under a 60-tonne machine, you want to know the block underneath can handle the weight,” he said.
Another flagship is NevaFail, NPR’s LED machine-identification panels. Built to provide visibility in even the most arduous environments, NevaFail panels remain legible up to 150m away and are designed to last.
Then there’s HoseMate, a specialised hose support system that prevents rubbing, rupture and fluid leaks. This “small-but-mighty” product helps to prevent spills, premature wear and tear, and complete hose failures, protecting equipment and personnel.
All three of these solutions will be on display at the Queensland Mining Industry Health and Safety Conference (QMIHSC) to be held in Brisbane from August 17–20.
NPR is set to showcase how its solutions address the safety and operational efficiency demands of modern mining environments.
“We know the challenge of balancing safety with productivity,” Georgiou said. “Our products are designed to help sites achieve both.”
NPR values collaboration during product development.
“We’re a solutions provider. We don’t assume we know the answer,” Georgiou said.
“Our customers know the problem better than anyone – they bring it
to us and then, together, we find a solution.”
This flexibility is backed by the company’s deep expertise in materials. All of NPR’s polymers are formulated in-house to suit the specific performance needs of each project.
“We’ve invested in the machinery and processes to mix our own formulations to spec,” Georgiou said.
The ability to tailor each product’s composition ensures the right balance between strength, weight and safety.
“That’s our specialty; matching the product to the solution that’s needed,” Georgiou said.
For NPR, safety isn’t just a priority – it’s a core value. Having spent more than a decade on mine sites, Georgiou speaks from experience.
“I’ve worked on sites where people didn’t make it home,” he said.
“This drives NPR’s mission: we produce products that ensure that at the end of the day our customers go home safely.”
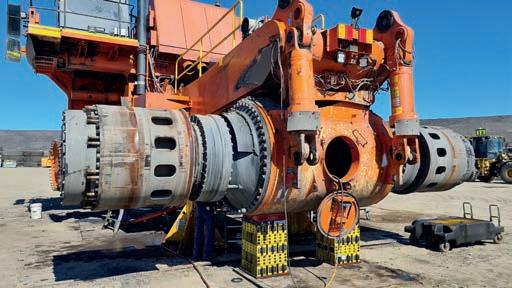
Image: National Plastics and Rubber
Stacko blocks are engineered for strength and ease of handling.
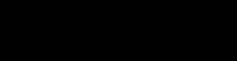

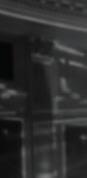




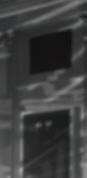
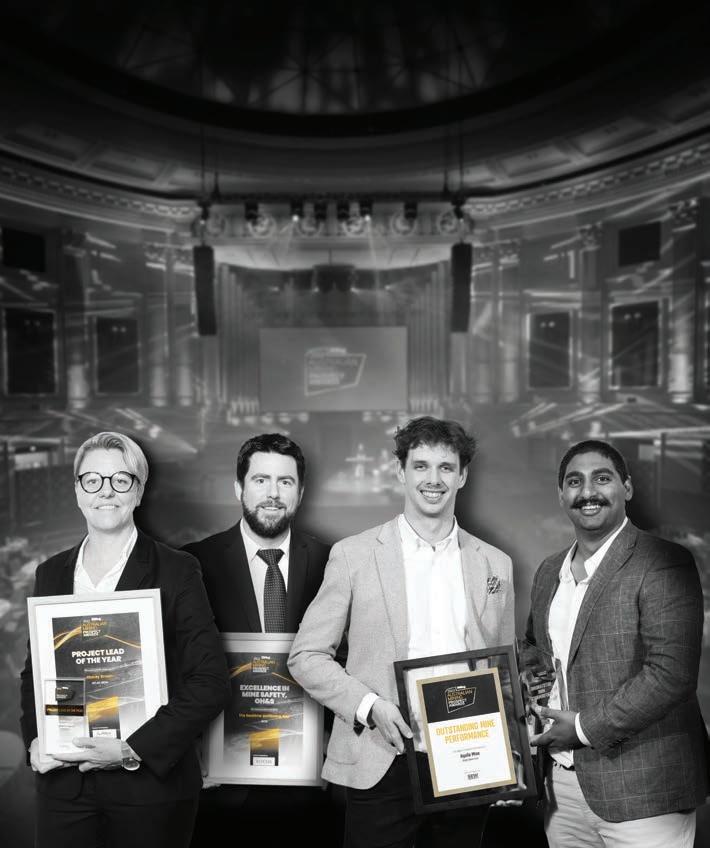
WEDNESDAY, 24 SEPTEMBER
Dissecting safety and operations
ICAM AUSTRALIA DOESN’T JUST FIND OUT HOW ACCIDENTS OCCUR –IT DIGS DEEPER TO FIND OUT WHY THEY HAPPENED IN THE FIRST PLACE.
Mining remains a complex and high-risk industry where the consequences of even small oversights can be severe. To create safer and more resilient operations, many companies are turning to ICAM Australia for a structured approach to uncovering the deeper, systemic factors that lead to incidents.
ICAM Australia client relationship manager Robert Gillespie told Safe to Work the company’s methodology is designed to identify the drivers behind events.
“ICAM doesn’t just look at what happened – it looks at why it happened,” Gillespie said. “That includes organisational issues, environmental conditions, individual actions, team dynamics, and failures in existing defences.”
By focusing on the full context of incidents, ICAM empowers miners to implement long-term solutions that strengthen safety and operational reliability.
One of the most powerful shifts ICAM brings to operations is cultural. Its systems-focused, blame-free approach helps reduce finger-pointing and encourages constructive dialogue.
“After an incident, there’s often a lot of pressure to find someone to blame,” Gillespie said. “ICAM challenges that by showing how systems and structures influence people’s actions. It fosters cross-functional learning instead of siloed responses.”
By guiding teams through structured reviews and collaborative discussions, ICAM has improved communication between operations, safety and management. Its emphasis on shared learning helps mitigate
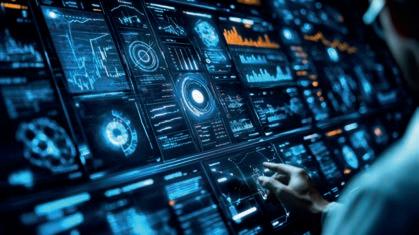
similar incidents and promotes more targeted, accountable safety actions.
As mining becomes increasingly digitised, ICAM has adapted to meet the needs of a new kind of incident: cybersecurity breaches.
The ICAM framework now supports investigations into digital disruptions that impact data security and operational continuity.
“In a mine, a security breach isn’t just an IT issue, it’s an operational risk,” Gillespie said. “ICAM allows teams to examine the same categories – organisational, task-related, human factors and failed defences – through a cybersecurity lens.”
This flexibility helps to ensure mining operations can apply consistent investigative principles, regardless of whether the threat is on the ground or in the cloud.
ICAM’s strength also lies in driving ongoing improvement through the analysis of near misses and lowseverity hazards.
By treating these events with the same seriousness as major incidents,
companies can spot warning signs earlier. This proactive approach helps embed safety into day-to-day operations, ensuring lessons are captured and acted on, even when nothing goes dramatically wrong.
Artificial intelligence (AI), which is beginning to shape the way safety professionals analyse data, represents a new frontier in that digital approach.
With the ability to identify patterns across massive data sets, AI presents exciting opportunities for predictive safety. However, Gillespie said this power must be used responsibly.
“AI can spot trends faster, but it can also introduce new risks, like bias or over-reliance on automated systems,” he said. “ICAM provides a disciplined framework to interpret those insights.”
Rather than replacing human judgment, ICAM encourages safety leaders to use AI as a support tool –enhancing but not undermining the human thinking.
ICAM Australia continues to refine its programs and delivery to meet the evolving needs of the mining sector.
The ICAM framework now supports investigations into digital disruptions.
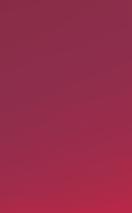

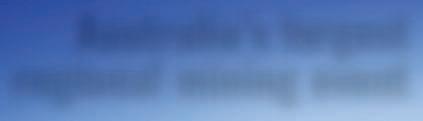


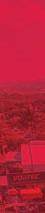
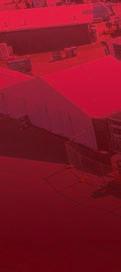
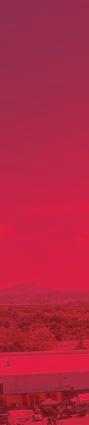

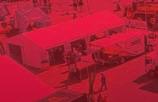


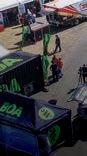
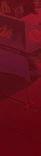

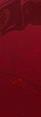

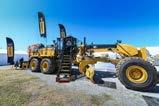
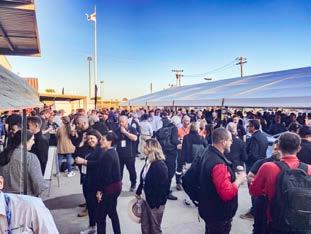
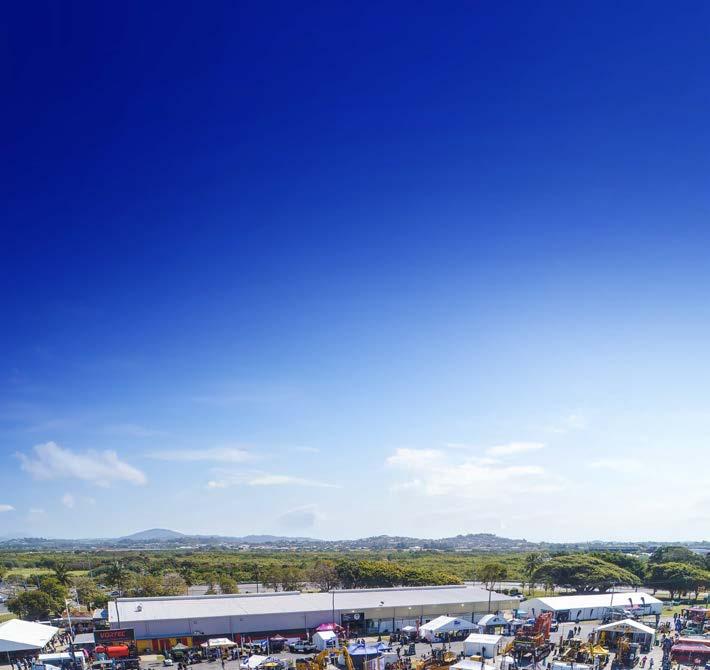
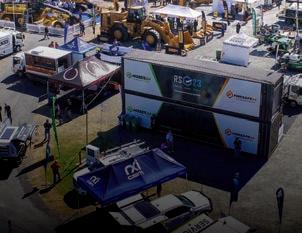


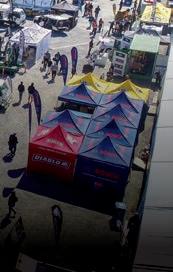
Protecting mind and body
MENTAL HEALTH IS BECOMING PART OF THE DAILY SAFETY ROUTINE ACROSS AUSTRALIAN MINE SITES, WITH A UNIQUE PARTNERSHIP LEADING THE CHARGE.
What began as a shared commitment to protect the bodies and minds of mine operators has, in just 12 months, blossomed into a stronger culture of connection across the industry. One year into its partnership with R U OK?, Industree Group is celebrating its contribution in redefining workplace safety in the mining sector.
The anniversary highlights one of the personal protective equipment (PPE) manufacturer’s key beliefs –mental wellbeing is just as vital as physical safety for miners. In industries where long hours, remote locations and extreme conditions are the norm, fostering a supportive environment has proven essential.
charity – has been at the centre of its efforts to integrate mental health awareness into everyday practices.
One of the main initiatives launched during this partnership was the introduction of co-branded PPE, including gloves, safety glasses, respirators, and hi-vis vests displaying R U OK? messaging.
These items not only protect workers physically but serve as daily reminders to check in with colleagues, making mental wellbeing a part of every shift.
The widespread adoption of this form of PPE has elevated mental health culture on-site, according to Industree marketing director Chris Foster.
“(We know) the importance of mental health in the workplace and want to
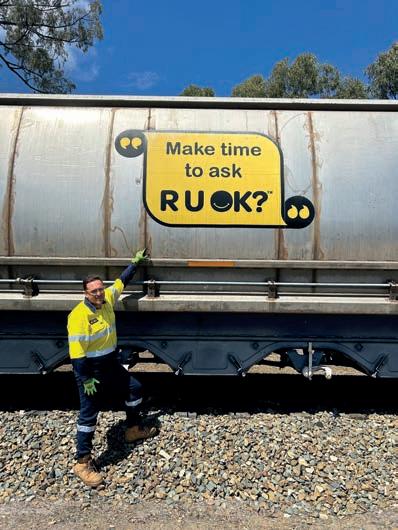
Beyond PPE, Industree has fully embedded R U OK? workplace resources into its operations. These free practical tools empower employees to start conversations about mental health and seek support when needed, making discussions about wellbeing a natural part of workplace culture.
The Industree–R U OK? partnership also includes a fundraising element.
A portion of every sale of R U OK?branded PPE is donated directly to the charity, turning everyday purchases into support for mental health programs.
Throughout 2025, Industree has also organised events and training sessions to keep mental health front of mind, building stronger connections among employees and partners well beyond R U OK? Day. This ongoing commitment directly supports the ‘social’ pillar of environmental, social and governance (ESG) standards, for Industree and the operators that purchase its products.
By integrating mental wellbeing into PPE and everyday practices, Foster believes Industree is breaking down barriers and setting a positive example.
“Industree is leading change by blurring the line between physical safety and emotional safety, and encouraging other industry players to follow suit,” he said.
As the partnership enters its second year, Industree remains dedicated to expanding its collaboration with R U OK?, ensuring mental health remains a central focus in the resources sector.
“The partnership has moved beyond symbolism to form a practical, sustained approach to mental health in mining and heavy industries through product, process, fundraising and training,” Foster said.
Industree
“It’s not just about asking “R U OK?” once a year – it’s about creating a culture where that question is part of daily life on mine sites.”
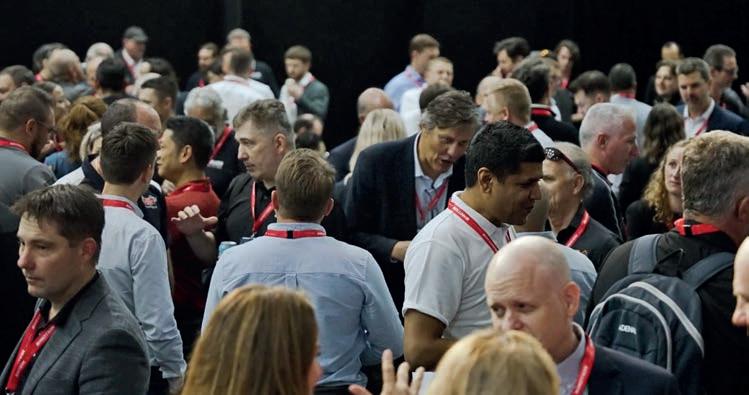
8-9
Keeping cool under pressure
KEEPING SAFE IN HOT AND HUMID AUSTRALIAN WORK ENVIRONMENTS INVOLVES MORE THAN WATER AND THE RIGHT CLOTHING.
The Australian climate can present challenges for industrial workers, with heat management an increasingly important health and safety priority.
While much of the focus has traditionally been on hydration, rest breaks and clothing, new research is drawing attention to safety footwear.
Footwear is essential for protecting workers from traumatic injuries, but it can also contribute to physiological workload. Dr Caleb Wegener, uvex director of product management with a PhD in footwear biomechanics, said the weight, rigidity and lack of breathability in many safety boots can worsen the risk of heat stress.
“Safety footwear is often overlooked in heat-stress management plans,” Wegener told Safe to Work. “But when designed to reduce muscle work with breathability in mind, it can decrease physiological demand, which can keep workers cool through lower heat generation. Around 80 per cent of energy used in muscle contraction is converted to heat, highlighting the importance of reducing muscular work in hot environments.”
Wegener led a recent study that compared the uvex 3 x-flow zip, a boot specifically designed for enhanced breathability, against a comparable 150mm zip-side boot. Both styles were tested in a controlled climate chamber using a sweating foot mannequin.
The aim was to measure the heat index (a combination of temperature and humidity) and absolute humidity to gauge breathability.
At 23°C and 50 per cent relative humidity, the uvex 3 x-flow outperformed the competitor, with a 15 per cent improvement in the climate index and an 11 per cent improvement in absolute humidity.
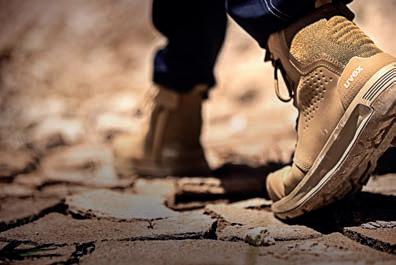
four-week wear trial was conducted in Queensland with 10 participants working in conditions where daily maximum temperatures reached 28.1–31.9°C. Workers were asked to rate breathability, comfort, fatigue, and perceived weight using a validated 10-point scale.
Feedback supported lab findings, with eight workers rating the uvex 3 x-flow boots as more breathable than their existing safety footwear, with an average improvement of 38 per cent.
“Laboratory measurements are one thing, but the real test is whether workers can feel the difference in the field,” Wegener said.
“And they did – consistently.”
Workers rated the x-flow boots 12 per cent more comfortable, 13 per cent less fatiguing, and 23 per cent lighter than their existing footwear.
In a broader follow-up involving over 100 Australian workers, the results were even more significant. The x-flow boots were rated 14 per cent more comfortable, 37 per cent less fatiguing, and 44 per cent lighter than existing footwear .
The success of the uvex 3 x-flow zip boot lies in its holistic design. Unlike products that rely on breathable panels or mesh inserts alone, the boot has been engineered from the foot down with breathability in mind.
Material selection, reduced layering and advanced manufacturing techniques work together to create a boot that allows heat and moisture to escape more efficiently.
“It’s not just about adding a vent or using mesh,” he said. “Every aspect of the footwear’s design needs to work in harmony to minimise heat build-up and improve comfort.”
With the likelihood of extreme heat events increasing, workplaces need to review all potential contributors to heat stress – including footwear.
Wegener said safety managers should treat footwear design and breathability as a controllable variable when developing heat-stress management plans.
“Choosing lightweight, biomechanically optimised footwear and extremely breathable footwear is a practical and measurable way to reduce heat-related stress and fatigue in the workplace,” he said.
uvex’s boots have been engineered from the foot down with breathability in mind.
Image:
uvex
Safety solutions
An unheralded safety measure
BENSTOP PROVIDES A CONTAINER DOORS SOLUTION TO MAKE MINE SITES SAFER.
Shipping containers are a ubiquitous feature on Australian mine sites. Used as tool stores, workshops, and storage units, their rugged, weatherproof design makes them ideal for the harsh outdoor mining environments.
But this very design, combined with environmental factors such as gusty winds, uneven ground, and incidental contact from equipment, introduces a serious and often overlooked hazard: uncontrolled door movement.
“When a container door swings unexpectedly, the consequences can be severe,” BenStop inventor and director Ben Portman told Safe to Work.
“We’re talking about crush injuries, entrapment and near-miss incidents that don’t always get reported but occur far too often. Workers enter and exit these containers constantly as part of their daily jobs.”
To address this long-standing safety issue, BenStop developed the GP20/40 door brace – an engineered solution designed to secure container doors in an open position, eliminating the need for improvised fixes such as ropes, tyres, blocks or toolboxes.
“Makeshift solutions often fail and can introduce new hazards,” BenStop director Lauren Portman told Safe to Work. “The BenStop brace provides a purpose-built, rugged safety tool that actually works.”
PROVEN IN THE FIELD
Since its introduction, the BenStop GP20/40 door brace has been met with overwhelming approval from the mining industry. From frontline workers to safety officers and procurement teams, the feedback has consistently highlighted the product’s practicality, reliability and ease of use.
One standout example came from a coastal site in Western Australia that is regularly exposed to strong winds.
“Store access had always been dangerous due to the wind,” Ben said. “After integrating BenStop braces into their daily routines, workers can now open container doors at the start of their shift and leave them safely braced throughout the day. This has improved peace of mind and worker safety significantly.”
Another site in the remote northwest of WA had a close call when a worker was trapped inside a container
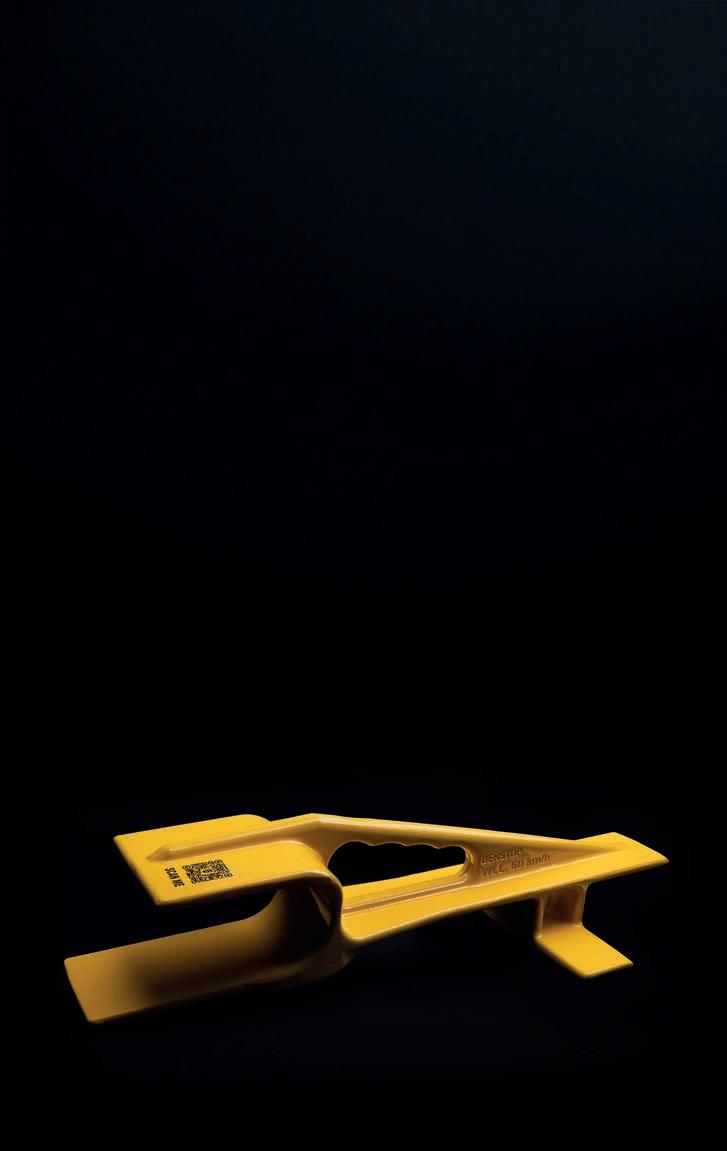
after a wind gust slammed the door shut, engaging the camlocks.
“It was a 40°C day, and the worker was alone. Thankfully, they had a two-way radio and were eventually freed,” Lauren said. “Before BenStop, their only option was a costly standby person procedure. Now, the brace eliminates that need and reduces manhour costs while improving safety.”
The brace also made a strong impression at the recent Perth Tradie Expo, where interest spanned all levels of mine site personnel.
“Attendees were surprised something so simple and effective hadn’t been available sooner,” Lauren said. “Several committed to recommending it within their organisations.”
Despite the clear risks, improvised methods of securing container doors remain common across the sector. According to Ben, the slow uptake of engineered solutions is largely due to habit and the historical lack of alternatives.
“For years, there simply wasn’t an off-the-shelf product that addressed the issue,” he said. “Now that BenStop is available and we’re expanding our
The BenStop door brace is an innovative solution.
outreach, more sites are recognising that there’s finally a simple, effective fix.”
Lauren agreed, adding that the industry has been slow to recognise the movement of container doors as a legitimate hazard.
“Near misses go unreported, and the true risks are often underestimated – especially when makeshift fixes have become routine,” she said. “Once sites acknowledge the hazard, the value of a proper solution becomes undeniable.”
Mine sites are known for their unforgiving conditions, particularly in remote regions where access to medical help can be delayed. The BenStop brace has been engineered specifically with these realities in mind.
“It’s strong, has no moving parts, and is easy to use,” Lauren said. “It integrates into workflows without disruption and is suitable for both temporary and permanent container set-ups. In remote areas, where lone workers may be at risk, it provides a low-touch, high-impact safety solution.”

SIMPLICITY DRIVES EFFECTIVENESS
Safety gear must be intuitive and quick to use if it’s to be embraced in fast-paced mining environments. The BenStop brace fits that brief perfectly.
“The most effective solutions are the ones that don’t require a manual,” Ben said.
“It’s robust, quick to install, and instantly effective; crews can brace container doors in seconds and then get on with their jobs knowing they’re protected.”
The biggest challenge facing BenStop now isn’t product development – it’s awareness.
“Many sites still don’t realise that a purpose-built alternative exists,” Lauren said.
“Part of our mission is to give more visibility to containerrelated risks. Once people start recognising this as a serious hazard, the shift to using a product like BenStop becomes a no-brainer.”
Ben believes broader cultural change is needed in terms of recognising container safety.
“There’s still a tendency to see these incidents as isolated or freak accidents, rather than systemic hazards that can and should be prevented,” he said.
The development of the BenStop brace came from firsthand site experience and a clear gap in available safety solutions. For the Portmans, this is just the beginning.
“We know there are more opportunities to create practical, userdriven tools that reduce risk without complicating site operations,” Lauren said. “Our long-term goal is to build a suite of safety solutions grounded in the realities of mining work.”
Ben said BenStop is helping to shift people’s approach to safety.
“BenStop exists to make safety simpler,” he said. “Because, often, the most effective solutions are the ones that should have existed all along.”
The Future of AI-Powered Workforce Safety Starts Here
While most workplaces are constantly buried in outdated procedures and paperwork, we’re paving a new path. One where hazard awareness is instant, control measures are intelligently advanced, and your team never has to guess what’s next. Because in high-risk environments, reactive isn’t enough.



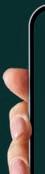
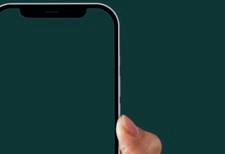
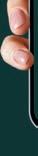
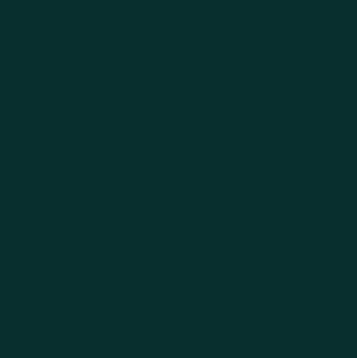

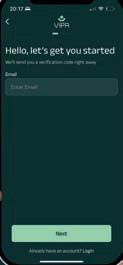
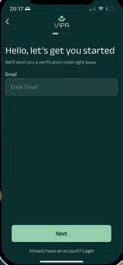
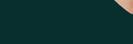
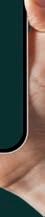

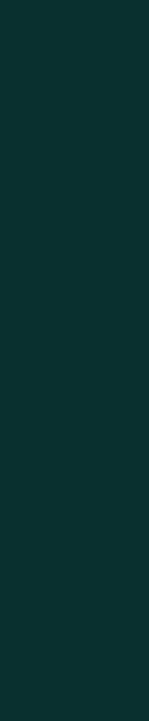

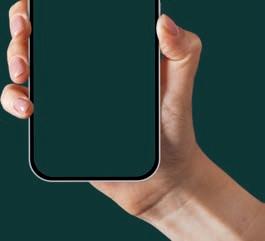
Conveyor solutions
Right on track
ESS ENGINEERING BELT TRACKERS
ENHANCE SAFETY ON MINE SITES ACROSS THE COUNTRY.
Conveyor belt tracking is a challenge across Australian mine sites. Several contributing factors may cause mistracking, including idler misalignment, belt condition and offcentre material loading.
While all modern conveyors are designed to allow for some belt wander, once the conveyor moves outside these parameters, issues like material spillage and damage to the conveyor structure, components and belt start to occur.
These issues each come with increased safety hazards. Material spillage can cause trip hazards as material accumulates on the ground and structure, and the size of the material spilling from a conveyor also potentially poses increased safety hazards from falling objects.
A misaligned conveyor belt may come into contact with the conveyor frame or other components. This friction causes premature wear on all components and can generate heat, leading to an increased risk of fire.
The downtime and costs of these issues can be significant, especially if belt misalignment results in an unexpected shutdown.
“There’s a lot involved in getting a belt back online when mistracking triggers a shutdown,” ESS sales and service technician Jerome Reid told Safe to Work
“At ESS, our aim is to keep belts aligned, operating smoothly and safely, reducing the need for shutdowns.”
ESS trackers utilise durable guide rollers that run along the belt’s edge to sense misalignment.
These rollers are linked to a mechanism that guides the belt back
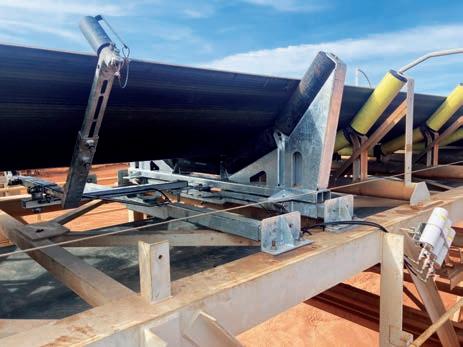
to its central position. The tracker does this continually, providing small corrections as it goes.
Through collaboration with a client, ESS has designed a retrofittable safety kit for the trackers.
“We worked extensively with the customer to create a solution which best suited their requirements,” ESS engineer Mitch Stone told Safe to Work. ESS’ kit improved existing features and added extra security by tethering major parts of the tracker assembly together, reducing the chance of falling objects in the unlikely event of component failure.
“It was important to make the solution easily retrofittable because of the large number of trackers already installed and the high cost associated with complete replacement,” Stone said.
Reid said the kit adds a layer of protection in heavy-duty applications where conditions cause accelerated wear to parts, but emphasised that not all sites are the same.
“ESS has the ability to tailor its solutions to the needs of any site,” he said. “It allows us to remain dynamic in our approach and help customers receive the best solution to suit their own requirements.”
sales.australia@regalrexnord.com
1300258726
ESS trackers can also be combined with the ESS retractable Quick Change Idler Frame, which allows for the idlers’ safe withdrawal from either side of the conveyor. Being able to slide the idlers out without having to lift the belt reduces manual handling risk during maintenance.
Whether it means making adjustments to an existing product or designing something entirely new, ESS leverages its design experience and manufacturing and service facilities around Australia to ensure the best outcomes for a client’s applications.
Reid said it’s all part of what drives ESS to reach new heights of success.
“Every client is different,” he said “We really thrive off meeting their challenges head-on and delivering solutions they can rely on.”
The ESS tracker with a retrofit kit adds extra security.
Image: ESS Engineering
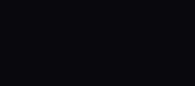





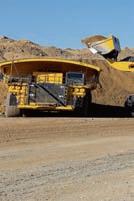


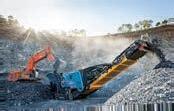



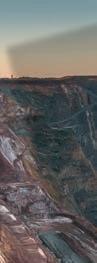

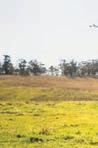







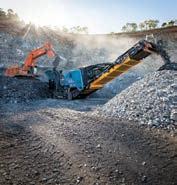

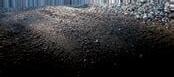


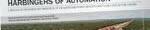

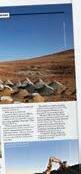
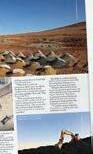
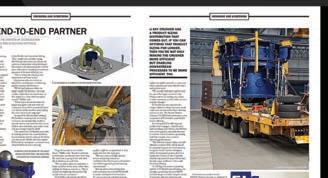


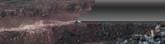
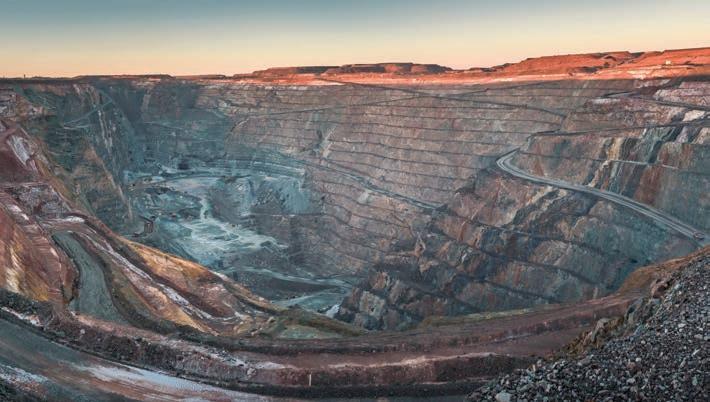
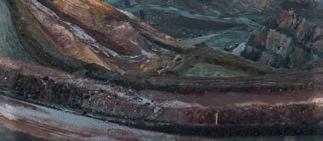
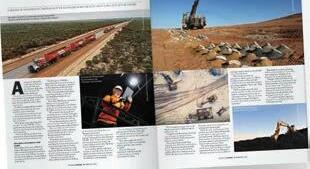
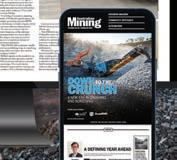
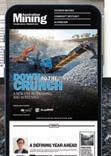

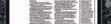
The right fit
WITHOUT PROPER FIT TESTING, A RESPIRATOR COULD LEAVE THE WEARER EXPOSED TO SERIOUS HEALTH RISKS.
In the often-high-risk working environment of mining, where airborne contaminants like silica dust, diesel particulate matter, and toxic gases are prevalent, respiratory protection is not just a precaution – it’s often
With this in mind, the effectiveness of even the best respirator hinges on one critical factor: fit.
Fit testing ensures that a respirator forms a proper seal on the wearer’s face, preventing hazardous particles from leaking in. In high-risk
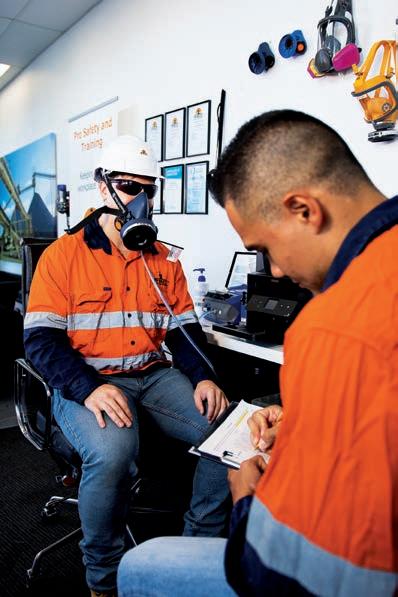
a small leak can mean prolonged exposure to harmful substances, leading to illnesses such as silicosis, COPD (chronic obstructive pulmonary disease), or even lung cancer. When fit testing is not conducted, the consequences can be severe. Workers may unknowingly wear illfitting respirators, leading to false confidence and increased exposure. This not only endangers health but also exposes companies to legal liabilities under Australia’s Work Health and Safety Regulations. According to AS/NZS 1715:2009, fit testing is a critical component of a compliant respiratory protection program.
COMMON MISTAKES
Some common critical errors when implementing respiratory protection programs include:
• Assuming one-size-fits-all: Facial structures vary widely, and a respirator that fits one worker may not fit another.
• Neglecting facial hair policies: Facial hair can compromise the seal of a tight-fitting respirator. RESP-FIT (respfit.org.au) recommends workers to be cleanshaven within 12 hours before fit testing.
• Skipping annual retesting: Fit can change over time due to weight fluctuations, facial injuries, or equipment wear.
• Inadequate training: Workers may not know how to properly don, check, or maintain their respirators. There are two main types of fit testing.
Qualitative fit testing (QLFT) involves a pass/fail test using a test agent like saccharin or Bitrex. It relies on the wearer’s sensory response and is suitable for disposable or half-face respirators.
Proper fit testing is crucial in ensuring a respirator forms a proper seal on the wearer’s face.
Quantitative fit testing (QNFT) uses specialised equipment to measure the concentration of particles inside and outside the respirator, providing a numerical fit factor. It’s more precise and more often utilised for respirators used in high-risk environments.
Fit testing must be conducted by a competent fit tester. RESP-FIT has developed a compliant accreditation process to support individuals to become a competent fit tester in Australia.
HOW OFTEN SHOULD FIT TESTING BE CONDUCTED?
According to AS/NZS ISO 16975.3:2023, fit testing should be conducted at initial assignment, annually thereafter, and whenever there is a change in the respirator model, facial structure, or health status that could affect fit.
More frequent testing may be warranted if workers report discomfort, experience weight changes, or if the respirator shows signs of wear.
Even the best respirator won’t protect a worker who doesn’t wear it correctly. Training is essential – not just on how to wear the respirator, but on why fit matters.
Workers should be taught to perform a fit check every time they don their respirator, ensuring a proper seal and also the importance of being clean shaven when wearing a tight-fitting respirator (facial hair can break the seal).
Compliance is also key. Supervisors play a key role in reinforcing these behaviours through regular toolbox talks, spot checks, and a culture that prioritises safety over convenience.
Recent innovations are making fit testing more accessible and accurate. These include:
• Accreditation for fit testers to demonstrate competence via RESP-FIT.
• Portable quantitative fit testing devices allowing for on-site testing with minimal disruption.
• Smart respirators with real-time seal monitoring, offering continuous feedback to the wearer.
• 3D facial scanning is being explored at the University of Wollongong to customise respirator fit, especially for workers with atypical facial structures.
These technologies could significantly enhance protection in mining environments, where conditions are dynamic and risks are high.
WHAT EVERY MANAGER SHOULD KNOW
If there’s one takeaway for site managers and supervisors, it’s this: fit testing is not optional – it’s a legal and ethical imperative.
A respirator that doesn’t fit is a respirator that doesn’t protect. Investing in proper fit testing saves lives, reduces liability, and fosters a culture of safety.
Conveyor belt mistracking leads to potentially expensive problems such as material spillage, reduced life for belting and structure, increased maintenance and increased safety hazards.
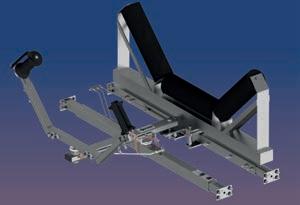
ESS BELT TRACKERS
Dynamic Belt Training Devices
Continuously correct the belt path for optimal alignment
Force Utilisation Design
Using the force of the wandering belt against the guide rollers to position the steering roller.
Versatile Application
Suitable for both the carry side and the return side of the belt
Standard and Heavy-Duty Options
Available in units for both standard and heavy applications.
OPTIONAL SAFETY FEATURES
Enhanced Safety Retrofit Kit
Tethers major parts of the tracker assembly together, reducing the risk of falling objects.
ESS QCTM
ESS belt trackers can be combined with the ESS QCTM Retractable Idler frame to allow the safe withdrawal of the idlers from either side of the conveyor.
FOR MORE INFORMATION ABOUT ESS BELT TRACKERS www.esseng.com.au



What’s on the mining calendar?
GET SET FOR A SERIES OF MAJOR MINING EVENTS SPOTLIGHTING INNOVATION, EXCELLENCE, AND COLLABORATION ACROSS THE SECTOR.
As the Australian mining industry continues to evolve, a new wave of landmark events is shaping the national conversation. These gatherings are more than just dates
on a calendar; they’re where the sector’s future is debated, celebrated, and propelled forward. From prestigious national awards to leading exhibitions, these events are attracting global
ASIA-PACIFIC’S INTERNATIONAL MINING EXHIBITION
For the first time in its history, Asia-Pacific’s International Mining Exhibition (AIMEX) – Australia’s longest running mining event – will be held in Adelaide. From September 23–25, the South Australian capital is set to welcome thousands of mining professionals from across Australia and around the world for three days of high-level business engagement and innovation.
One of the major features of the event is the AIMEX Mining Pavilion, a dedicated space for mining’s biggest players to showcase their latest initiatives and connect directly with delegates.
BHP, one of mining’s most influential companies, is the naming rights sponsor of the Mining Pavilion where it will showcase its operations and leadership in South Australia while also contributing expert insights to AIMEX’s comprehensive conference program. Other significant participants include Boss Energy and Magnetite Mines, both of which will join the Mining Pavilion and conference agenda.
The event is also being supported by the South Australian Chamber of Mines and Energy (SACOME), which has welcomed AIMEX’s 10-year commitment to the state.
Prime Creative Media general manager of events Siobhan Rocks said SACOME’s endorsement is a major milestone.
“AIMEX is about bringing together the entire mining value chain,” she said. “Having SACOME on board solidifies AIMEX’s position as a key gathering point for the industry.”
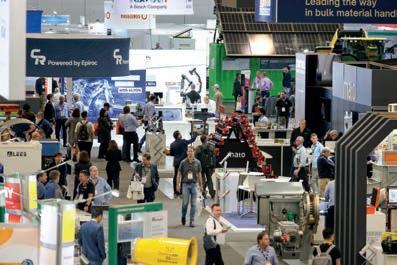
talent, major players, and industry decision-makers.
Here are four events that will bring the mining community together to innovate, recognise excellence, and build a shared vision for what’s next.
AUSTRALIAN MINING PROSPECT AWARDS
Taking place on the second night of AIMEX, the Australian Mining Prospect Awards will be hosted for the first time at the iconic Adelaide Oval.
Having long celebrated the individuals and companies driving progress in mining and mineral processing across Australia, the 2025 ceremony will recognise excellence in safety, sustainability, technology and leadership, shining a spotlight on initiatives that set industry benchmarks.
Among last year’s standout winners was Roy Hill, whose ‘Safer Summer’ campaign has led to a 36 per cent reduction in recordable injuries and fostered a new culture of proactive safety engagement.
“It showed that a proactive, people-led approach to health and safety can make a real impact,” Hancock Prospecting (Roy Hill’s parent company) health and safety head Paul Slocombe said. “Winning this award was incredibly rewarding for our team.”
Returning sponsors such as Sandvik, Bonfiglioli, ifm, and SEWEURODRIVE will support the 2025 awards, which promise to be a highlight of the AIMEX networking calendar and a powerful recognition of the industry’s best and brightest.
Date: September 24
Location: Adelaide Oval
AIMEX is set to welcome thousands of mining professionals from across Australia and around the world.
WA MINING CONFERENCE AND EXHIBITION
The WA Mining Conference and Exhibition (WA Mining) will return to Perth in October for two days of immersive industry engagement, innovation, and practical insights. The 2025 program will include a two-day conference and an expansive exhibition space. Conference sessions will explore topics such as artificial intelligence, automation, decarbonisation, and market resilience, with the goal of helping professionals lead through accelerated change.
This year’s event will also welcome new exhibitors, such as Tsurumi Pump Australia, which transitions from visitor to exhibitor in 2025. Known for its dewatering and water-handling solutions, Tsurumi sees WA Mining as a timely opportunity to showcase its miningspecific capabilities.
Returning sponsor Denver Technology, a long-standing player in mining and energy, will use the event to expand its brand visibility and build deeper connections.
QUEENSLAND MINING & ENGINEERING EXHIBITION
The Queensland Mining & Engineering Exhibition (QME) will return to Mackay in July 2026, cementing its place as one of Australia’s leading regional mining events. For more than 30 years, QME has brought together suppliers, operators, and innovators to highlight the strength of Queensland’s mining sector.
Returning as a major partner is the Bowen Basin Mining Club (BBMC), which will again play a key role in showcasing finalists of the Queensland Mining Awards.
According to BBMC director Jodie Currie, hosting the awards alongside QME elevates both events.
QME 2024 was a record-breaking instalment of the event, attracting more than 5000 visitors.
“Sponsoring WA Mining has helped us boost our branding and market awareness,” Denver Technology general manager – business development and customer success Matthew Clayton said.
Whether for product launches, partnership building or industry insight, WA Mining 2025 offers a valuable platform for companies keen to be part of mining’s next wave of innovation.
Dates: October 8–9
Location: Perth Convention and Exhibition Centre
“For us it’s all about really getting our finalists out there and showcasing them to every person that comes through the door,” she said.
The QME Mining Pavilion also returns, providing a dedicated space for companies and contractors to share initiatives, strengthen community connections, and display practical innovations in action.
With a strong sense of collaboration and excellence at its core, QME 2026 promises to continue its legacy as a regional events powerhouse.
Dates: July 21–23, 2026
Location: Mackay Showgrounds
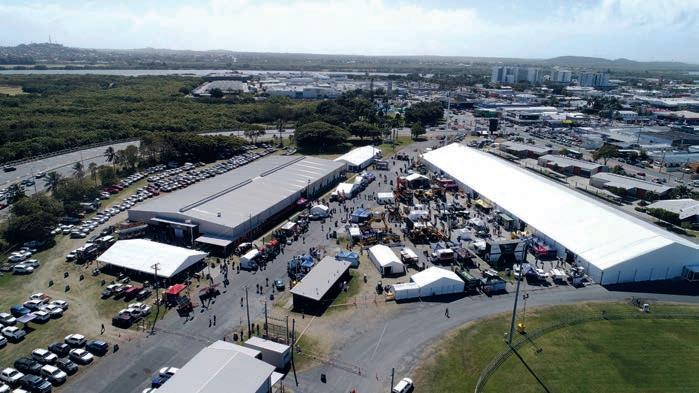
Industry events
The Workplace Health & Safety Show has been a key event driving safety in the industry.
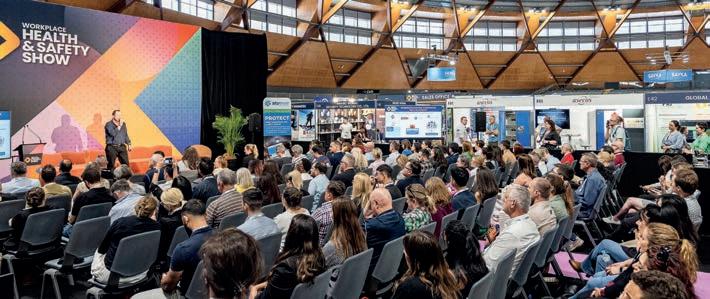
Showtime in Sydney

THE WORKPLACE HEALTH & SAFETY SHOW IS THE ONE EVENT THAT’S GOT INDUSTRY PROFESSIONALS MARKING THEIR CALENDARS IN ANTICIPATION.
Despite significant improvements in safety, injuries and fatalities continue to affect workplaces – it’s a challenge that the Workplace Health & Safety Show (WHSS) aims to address.
“WHSS answers the call for an event where professionals can discover the latest workplace safety solutions and innovations, stay up to date with evolving regulations and engage with industry experts on a wide range of issues. The date of the show is also significant with October being National Safe Work month,” the show’s portfolio director Stephen Blackie said.
The show is now returning to Sydney from October 22 to 23 at the Sydney Showground.
Preparations for the upcoming show are gathering momentum, especially on the heels of a very successful Melbourne event. A total of 5543 visitors attended the event in May – a 13 per cent increase from last year – and 80 per cent say this is the only event that matters for their health and safety needs.
“WHSS is so much more than a trade show; it’s quickly becoming the premier hub for professionals seeking to improve safety compliance and create safer, healthier and more productive work environments
– whether they’re the manager or foreman on a construction site, someone in charge of PPE procurement, or an executive in charge of building safety,” Blackie said.
WHAT’S NEW? WHAT’S NEXT?
The 2025 Sydney Show program includes over 200 exhibitors such as Safework NSW, Medibank, HSI Donesafe, ecoPortal, WeldClass, SafetyCulture, Maxisafe and AutogenAI – everything those responsible for safety and well-being would need.
This is where visitors can connect directly with suppliers of a wide range of products and services – from cutting-edge safety equipment and PPE to AI-driven solutions. At the adjacent Spotlight Stage, visitors will experience ground breaking product launches and live demos of the latest safety innovations.
“You’ll be able to explore solutions from vendors who understand your environment and your challenges, and present tailored solutions that reduce risks, simplify compliance and help you safeguard your people,” Blackie said.
The show also offers two full days of expert-led seminars – 40-plus hours of educational content, delivered by industry experts. Attendees can earn up to four free CPD hours daily,
helping them keep their professional accreditations up to date while they enjoy the seminars, networking and the expo.
WHO SHOULD ATTEND
The event is designed for anyone who’s responsible for safety strategy or culture in any way, including safety professionals, HR and wellbeing leads, operation managers and business owners.
“This is your best opportunity to stay ahead, whether you’re leading a high-risk workforce or just looking for smart tools to support safety compliance. The show offers everything you need, under one roof,” Blackie said.
He urges interested professionals to register soon at whsshow.com.au.
“Registration is free if you sign up in advance. If you wait and register at the door, it’ll cost you $75,” he said.
Only a limited number of stands remain for the Sydney Show.
Companies interested in securing a stand are advised to do so soon, as more than 80 per cent of the exhibition stands have been sold.
“We can’t wait to connect with the safety community again this October, and share the conversations, discoveries and resources that make workplace safety compliance easier and more effective,” Blackie said.

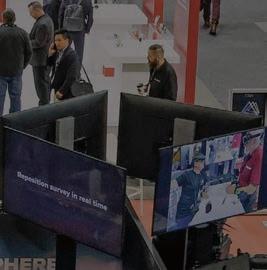
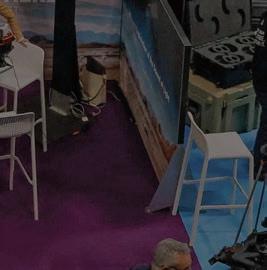
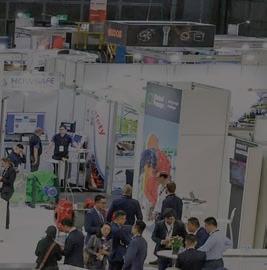
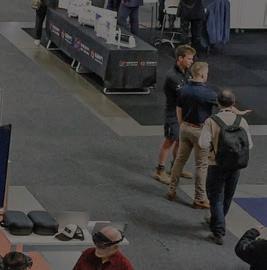
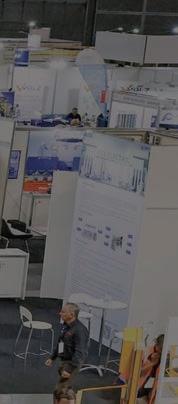
THE NEXT GENERATION OF MINING
ASIA-PACIFIC’S INTERNATIONAL MINING EXHIBITION
23-25 SEPTEMBER 2025
Adelaide Showground, South Australia
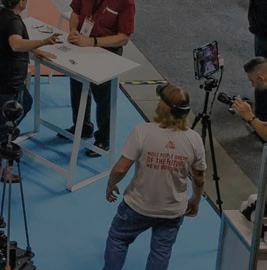
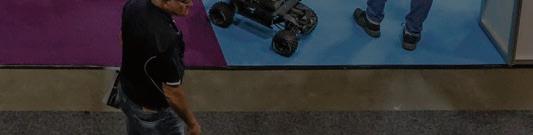
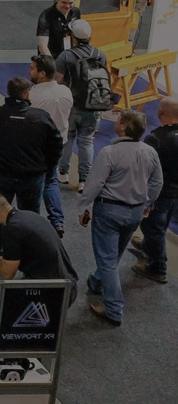
Register to attend AIMEX’s inaugural event in South Australia
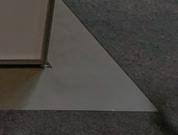

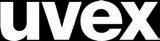
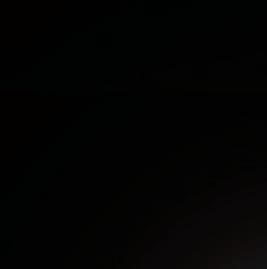
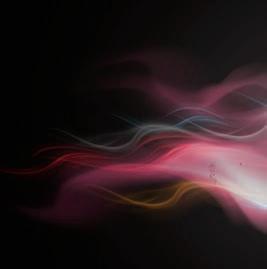
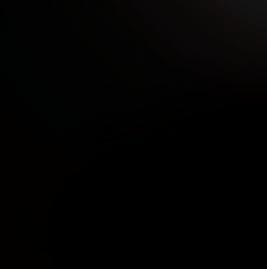
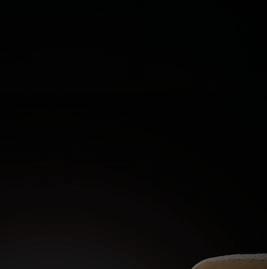
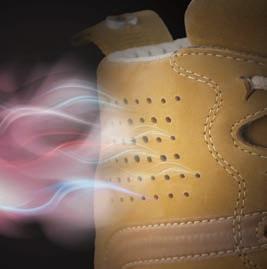
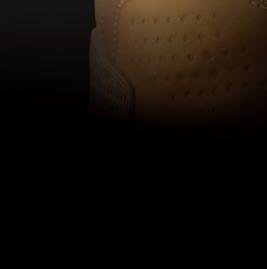
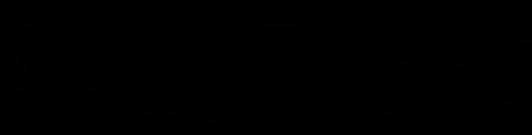
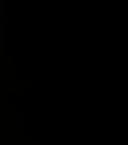
