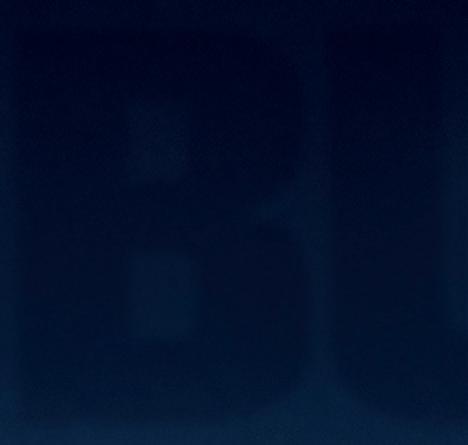


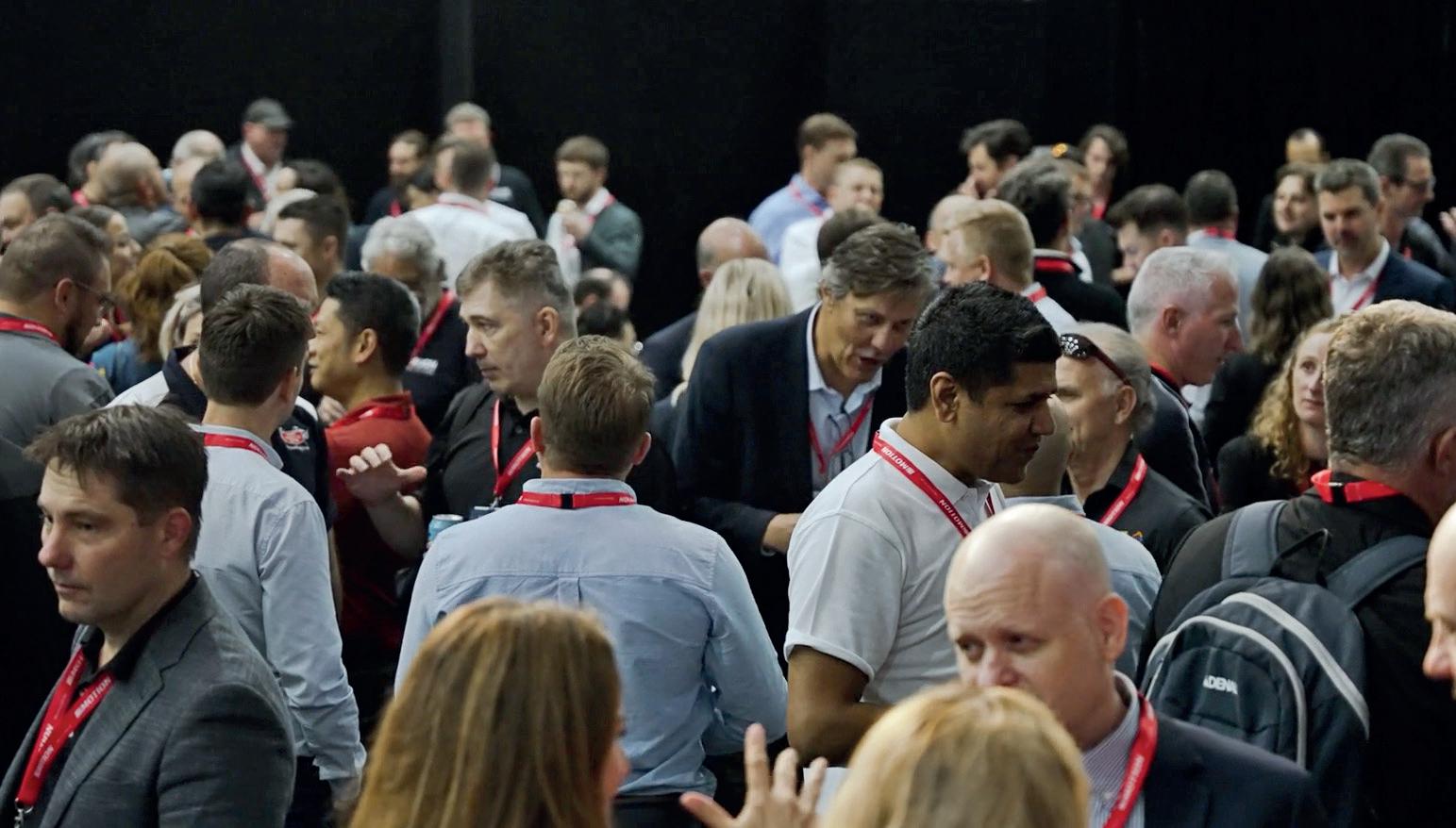
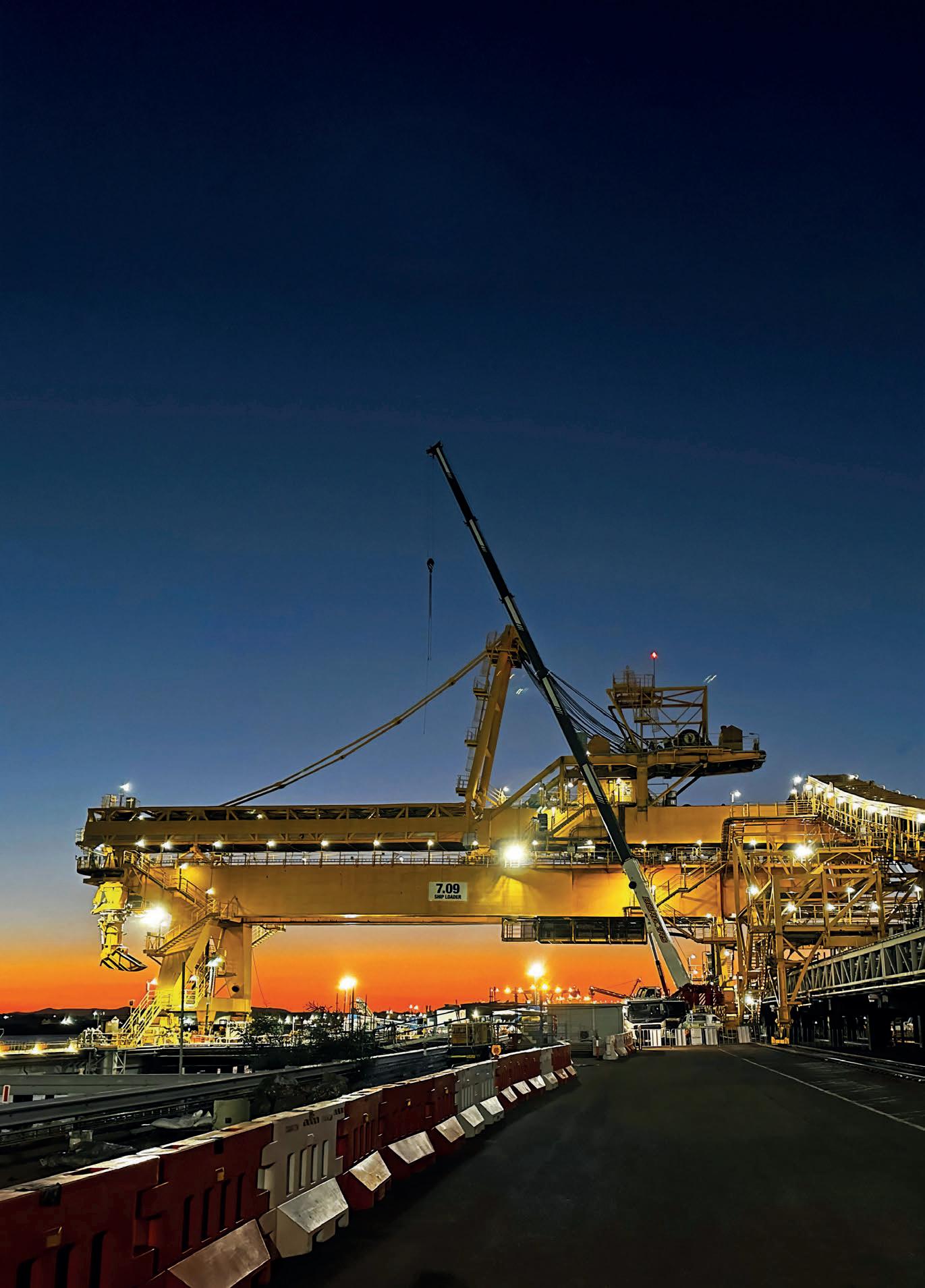
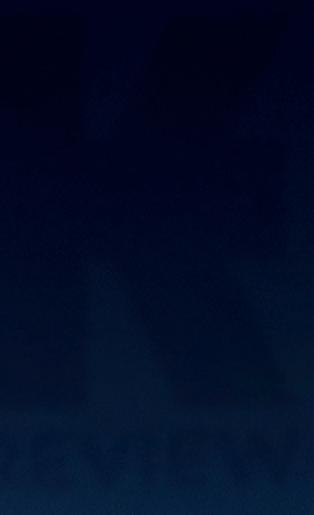
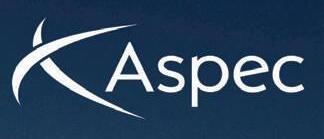
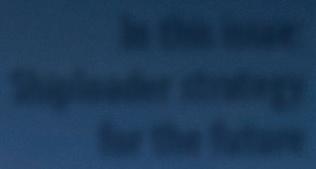
Driven by Innovation, Backed by Experience.
Since 1985, Kinder Australia has been at the forefront of conveyor solutions, delivering trusted, innovative products that improve e ciency, safety and productivity in bulk materials handling.
We support our customers with:
• High-performance products that evolve with industry needs
• Expert advice and genuine customer care every step of the way
• Reliable outcomes that support long-term site success
As we mark 40 years of progress, we continue to engineer smarter, safer and more sustainable solutions for every site we serve.
Discover what Kinder can do for your operation.
6 Industry news
8 Fit for the long term
10 Boral cements its Australian status
12 Finding the needle in a haystack
14 Supporting farmers through rain and shine
16 Showcasing solutions at WA Mining
18 The centrifugal force behind dewatering
20 A single solution for dry-mix plant designand construction
22 Boosting batch accuracy
24 Nice mill for Nice Rice
26 Australian-made precision
28 Sights set on Australia
48 X-Stand’s X-cellence
50 Complete support
52 Sandvik powering sustainable innovation at AIMEX
54 Critical minerals: addressing bulk solids handling challenges
58 ASBSH Member Profile: Jason Hogue
30 Outdated belt scales suppress productivity
32 So ening the impact
34 Value up close and personal
36 Polyethylene protection
38 BULKtalk: Ship shape shiploaders
42 Sensor on the pulse
44 Made to measure for marine operations
46 Shaping the future of shiploaders
COVER STORY: FIT FOR THE LONG TERM
When Port Waratah set out to extend the life of its three ageing shiploaders – each at a di erent stage of their lifecycle – it engaged Aspec Engineering for practical, innovative solutions grounded in decades of site knowledge. Aspec Director Adam Mayers and NSW Manager Robert Gibson reflect on a close collaboration that’s delivering long-term outcomes for one of Australia’s most critical coal export terminals.
For the full story, see page 8
Published by:
379 Docklands Drive
Docklands VIC 3008
T: 03 9690 8766
www.primecreativemedia.com.au
COO
Christine Clancy
E: christine.clancy@primecreative.com.au
Editor William Arnott
E: william.arnott@primecreative.com.au
Assistant Editor
Adam Daunt
E: adam.daunt@primecreative.com.au
Business Development Manager
Rob O’Bryan
E: rob.obryan@primecreative.com.au
Client Success Manager
Janine Clements
E: janine.clements@primecreative.com.au
Head of Design
Blake Storey
Design
Laura Drinkwater
Subscriptions
T: 03 9690 8766
E: subscriptions@primecreative.com.au
www.bulkhandlingreview.com
The Publisher reserves the right to alter or omit any article or advertisement submitted and requires indemnity from the advertisers and contributors against damages or liabilities that may arise from material published.
© Copyright – No part of this publication may be reproduced, stored in a retrieval system or transmitted in any means electronic, mechanical, photocopying, recording or otherwise without the permission of the publisher.
One quirk of being an island nation is that exports need to travel across the ocean to get to their destination. Planes, unfortunately, do not have the capacity to move the millions of tonnes required to get bulk cargo to its destination, which means shipping plays a vital role in the supply chain. round the country shiploaders are used to fill these ships full of Australian bulk material, whether it’s grain, iron ore, or coal. It’s an important task, as the faster tonnes are loaded onto the ship, the more profitable the endea our
A lot of engineering knowhow has gone into making sure these massive machines are up to the task. The ships themselves come in all shapes and si es and the ship s captain has the final say on how their ship is loaded
They also need to withstand a brutal environment for machinery. Strong sea winds, corrosive salt water, and tidal forces can wear downthemachinery.
Often shiploaders need to be operating around the clock, so downtime needs to be carefully managed. If something goes wrong, it can lead to millions of dollars in lost productivity.
That’s why this edition of the Australian Bulk Handling Review (ABHR) includes special coverage on shiploaders. In this edition, we speak to some of the leading engineering firms from around the country who are working alongside ports and mines to find the right solution for their assets
Bulk handling expert Steve Davis also takes a deep dive into some of the key design considerations when it comes to the equipment.
This edition also features coverage of conveyor systems, the backbone of bulk handling. ABHR speaks to key manufacturers about the latest innovations and equipment in the sector, whether it’s stopping spillage, mindful measurement, or prudent protection.
Next edition, we will continue to highlight major machinery with a spotlight on balanced machinery such as stackers and reclaimers. If you would like to get involved, please get in touch.
INTRODUCING AN EASY WAY TO PROTECT YOUR WORKERS AS WELL AS PROTECT YOUR INVESTMENT INTO YOUR EQUIPMENT. THE CONVEYOR SAFETY SYSTEM™ IS AN EASY, COST EFFICIENT WAY TO GET PEACE OF MIND AND PROTECTION FOR CONVEYOR EQUIPMENT. BY BUNDLING OUR MODEL RS SAFETY STOP SWITCH WITH OUR MODEL TA BELT ALIGNMENT SWITCH, MODEL DB DAMAGED BELT DETECTOR WE HAVE YOUR WORKERS AND EQUIPMENT COVERED. COUPLE THAT WITH ADDING ONE OF OUR MOTION SWITCHES (MAG-NEAT-O™ OR MODEL CMS), YOU CAN FEEL CONFIDENT KNOWING THAT YOUR SYSTEM AND WORKERS ARE PROTECTED FOR A FRACTION OF THE COST OF DOWNTIME, REPAIRS AND REPLACEMENT EQUIPMENT.
THE INTERNATIONAL CONFERENCE
on Bulk Materials Storage, Handling and Transportation ICBMH 2026 has secured four of Australia’s top conveyor belt and manufacturing companies as industry sponsors of the 3-day event running from 7-9 July 2026 in Fremantle, Western Australia.
Major Sponsor: Continental Conveying Solutions
Continental Conveying Solutions are experts in conveyor belt solutions o ering customers worldwide an advanced portfolio of products, technologies and services for industry and mining applications. They support customers, partners, and distributors with a growing range of value-added services along the entire lifetime of a conveyor belt operation, from planning and commissioning, to technical advice, training, digital monitoring, and onsite maintenance heir cost e ecti e sustainable, safe and innovative conveying solutions reduce downtimes through state-of-the-art monitoring and predictive maintenance, supporting mining, construction and plant
engineering projects around the world as a development partner.
Fenner Conveyors are an original equipment manufacturer and service provider specialising in conveyor solutions for various industries and commodity groups. They design and manufacture a wide range of durable and high-performance conveyor belts, systems, components, and accessories that ensure efficient materials mo ement With a focus on safety, innovation and sustainability, Fenner Conveyors emphasises quality and reliability of their conveyor products and services, providing tailored solutions to meet the unique needs of their clients. Their commitment to advancing smart conveyor technologies and delivering enhanced customer service positions them as a trusted partner within the conveyor solutions market.
inder ustralia o ers inno ati e global conveyor components for conveyor
systems in Australia and overseas, including solutions for a stronger Bulk Materials Handling operation. Kinder o ers comprehensi e engineered conveyor solutions designed to tackle common problems and maximize efficiency producti ity and safety Kinder is one of the leading suppliers and manufacturers of practical solutions for conveyors and bulk materials handling equipment used in heavy process industries.
Flexco specialises in designing and manufacturing high-performance products that enhance belt conveyor productivity, including belt cleaners, ploughs, trackers, impact beds, conveyorrollers, skirting systems, pulley lagging, mechanical belts fasteners and safety tools. Flexcohelpscustomers be more productive byproviding solutions that increase beltconveyor uptime and facility output.In addition, Belt Wise, WagnerVulcanizers, andAgilitusaregeneral sponsors of theconference.
have converted low-grade clay into a high-performance cement supplement, opening a potential new market in sustainable construction materials.
Replacing some cement with clay reduces the environmental impact, but the high-grade kaolin clay best suited for cement replacement is in increasingly high demand for ceramics, paints, cosmetics and paper.
Researchers at RMIT have demonstrated illite clay can be mixed with low-grade kaolinite clay, to make stronger concrete.
The study published in Construction and Building Materials introduces a new process, where low-grade illite and kaolin clays are mixed at an equal ratio then heated at 600 Celsius. Processing the two ingredients together, rather than separately, led to several improvements in the material’s performance.
Project lead Dr Chamila Gunasekara, said low-grade illite clay does not normally bind well with cement and water, but that the joint heating, or co-calcination, process greatly enhances illite clay’s binding ability, known as pozzolanic reactivity.
“Based on this approach, we are able to replace 20 per cent of cement usage using low-grade illite and kaolin combinations, while achieving even better performance of the yield product,” Gunasekara said.
ust and spillage from insufficient transfer sealing can jeopardize worker health, impair equipment performance, and negatively impact your bottom line. Martin Engineering delivers comprehensive solutions to control emissions and maintain a clean and efficient operation.
Martin's easy-to-install Modular Transfer Point Kits — with several loading, settling, and stilling zone configurations — combined with our ApronSeal™ dual-seal skirting, wear liners, and impact cradles, effectively arrest fugitive material while maximizing material flow. When transfer locations are properly designed and maintained, operations run cleaner, safer, and more efficiently.
When Port Waratah set out to extend the life of its three ageing shiploaders – each at a di erent stage of their lifecycle –it engaged Aspec Engineering for practical, innovative solutions grounded in decades of site knowledge.
of the Hunter Valley coal export supply chain, has provided its customers with reliable access to contracted terminal capacity for more than 45 years.
Aspec Engineering NSW manager Robert Gibson said Port Waratah is looking to ensure that the terminal facilities are positioned to meet customer expectations and Hunter Valley coal chain demand beyond 2030. One of the Aspec Engineering’s specialties is life extensions of ageing assets such as shiploaders.
“Key to the Port Waratah loading process are the shiploading facilities – the shiploaders and the wharves,” he told ABHR. “A pre-feasibility study was carriedout on thecondition and remaining life of three shiploaders.”
“Aspec Engineering was heavily involved in the structural fatigue assessment, which is a key issue in lifeextension.”
The shiploaders at the site have a large bridge structure that spans50metres.
Because there are heavy masses moving regularly on the bridge structure, with variations in load, metal fatigue is an issue that needs tobeaddressed.
“The outcome of those studies was that the oldest shiploader is being replaced, and the two newer machines are having major overhauls,” Gibsonsaid.
To support Port Waratah in executing this strategy, Aspec Engineering has been appointed as the design engineer for the two shiploader
refurbishment projects, and design auditor for the replacement machine.
The company’s relationship with Port Waratah can be traced back to when Aspec Engineering was founded in2003.
For more than 20 years, Aspec Engineering’s team has been a trusted engineering partner of Port Waratah, providing local engineering support for terminal operations and asset management – especially when it comes to shiploaders, stackers, andreclaimers.
“A big emphasis for Aspec is that we work very closely with our clients to provide pragmatic technical advice, targeted at their specific business needs - that’s the way we like to operate,” Gibson said.
Aspec Engineering has been an engineering partner of Port Waratah for more than 20 years.
“These life extension projects are not just maintenance –they are strategic investments in Port Waratah’s future.”
“We can move quickly thanks to our detailed knowledge of the site. Port Waratah is our biggest New South Wales client and a key part of the state’s economy. We are very proud of our association with Port Waratah.”
Aspec Engineering’s director, Adam Mayers, said the top priority in the two shiploader refurbishment projects was ensuring adequate fatigue life of thebridge.
“It’s a fundamental issue that a ects the life of the asset he said “We completed detailed calculations to estimate the life of the machine which suggested there was potentially a fatigueissue.”
This analysis was successfully used to target inspection locations and identifydefects.
Of the two shiploaders receiving major overhauls, the project involved not only solutions to repair the defects but extending the life of the machines and reducing the likelihood of similar defects in the future.
“In standard practice, replacing fatigued steel components entirely is often the first consideration ayers explained. “However, in this case, other more feasible, less intrusive repairs needed to be considered – taking into account access, constructability, and other constraints.”
Faced with this, the Aspec Engineering team dived deep into the problem and leveraged its experience to find techni ues that ha e pre iously worked in other industries – primarily the bridge maintenance sector.
“The team developed a blended refurbishment strategy which combines fatigue repairs, weld improvements and a pragmatic inspection regime, to successfully chart a course to address the defects and implement improvements to achieve the required life extension,” Mayers said.
“We used fracture mechanics to quantify how existing defects might grow over time and under what conditions they could become critical,” Mayers said. “This allowed us to prioritise repairs and implement life extension techniques withconfidence
This approach balanced safety, cost, and operational continuity – extending the life of two of the shiploaders without requiring full-scale replacements.
Aspec Engineering has a lot of experience when it comes to asset management of dynamic structures. The company has carried out similar work on dozens of other machines, across the full equipment lifecycle –from newmachines to those that are operating beyond their design life and require life extension.
It has an established process, which has evolved over time and places a large emphasis on knowledge management and sharing project experiences within the business. This was important for the Port Waratah project, which had a compressed engineering phase, and required an efficient engineering approach
“It was quite an aggressive schedule to complete all of the engineering – especially with the refurbishment projects,” Mayers said.
One of the reasons the company was able to move so quickly was thanks to its history working with PortWaratah and its emphasis on good project records.
“A lot of time can be spent trying to reinvent the wheel or searching for past knowledge,” he said. “That’s part of the reason we were able to do the work in a compressed timeframe. We’re not coming up to speed - we’re already at speed when we start the job and we make sure past project knowledge is easily accessed and leveraged to achieve the desired outcome for our clients.
“We’re extremely proud of our team for delivering on time, on budget, and providing everything that was asked of us. All of the complex engineering work was done in under six months.”
Aspec Engineering will continue to work closely with Port Waratah over the coming years to deliver the remaining stages of this critical project.
Mayers highlighted the collaborative nature of the partnership.
“Port Waratah has a lean and highly capable team that brings a cooperative and forward-thinking approach to the table.
“These life extension projects are not just maintenance – they are strategic investments in Port Waratah’s future,” he said. “We are humbled to be working alongside them and appreciate being selected as their partner for this work.”
“We are proud to have contributed to this phase of Port Waratah’s journey,” Gibson said. “Their commitment to proactive asset management and collaborative delivery continues to set the standard in the industry.”
Boral supplied cement to help construct Australian icons like the Sydney Opera House and Parliament House inCanberra. Now it’s investing more in its mobile assets and solutions to continue to build Australia.
BORAL HAS LAUNCHED ONE of its most significant asset renewal programs in recent history focusing on hea y mobile e uipment to impro e on operator safety reliability and optimisation of assets ince ecember we e commenced the deli ery of our new assets across the business o date more than ha e been deployed with the rest scheduled o er the coming months head of assets and capital pro ects at oral aul oung told he in estment spans a wide array of machinery from loaders and e ca ators to load and haul trucks and touches e ery part of oral s operation including asphalt concrete cement recycling and uarrying
It s a one in one out approach e re not ust adding more gear we re upgrading with purpose It s about
deli ering more for our people and ourcustomers oung said he new eet incorporates ad ancedtechnologies that boost safety enhance producti ity and deli er superior fuel efficiency he new generation of o ers impro ed reliability and ease of use and that translates into a better e perience for our people on the ground and better performance across the board oung said
ltimately it s part of our mission to put safe compliant reliable and optimised assets into the field
Fixed and mobile assets
entral to oral s supply chain strategy is achie ing the right balance between fi edand mobile assets ensuring materials are close to market while managing costs e ecti ely
ne of our key ad antages is the scale of our ertically integrated network oung said e operate roughly sites across ustralia and ha e more than hea y ehicles on the road e ery day
he network is structured around upstream assets like uarries and cement manufacturing plants and downstream assets like batch plants and mobile e uipment
It s critical that those downstream assets are as close as possible to our customers hat pro imity helps reduce downtime and ensures timely deli ery which is particularly important in concrete gi en it s a perishable product oung said
he importance of location is underscored by recent data from the ement oncrete ggregates ustralia which shows that
increasingtransport distances can significantly in ate deli ery costs he ement oncrete ggregates ustralia report highlighted that increasing the haulage distance of aggregates by to kilometres can increase concrete costs by anywhere from to per cent oung said onsidering that aggregates make upabout per cent of concrete costs ha ing our plants close to market is essential
oral s mobile capabilities are a ma or enabler for infrastructure deli ery particularly in remote or logistically challenging en ironments
ot all construction sites are con eniently located oung said ur mobile concrete batch plants and crushing operations gi e us the e ibility to support pro ects in regional or hard to reach areas
oral s recent deployments illustrate this capability well obile batch plants were set up to ser ice the olden lains ind arm and the orth ast ink in ictoria arious tunnel pro ects and for the pro ect in ew outh ales e also had a mobile asphalt plant running at estern ydney irport to support runway construction and another in o s arbour for the local bypass pro ect oung said hese operations are only possible with strong coordination across the supply chain
ith population growth dri ing infrastructure demand across both metro and regional areas oral s supply chain is calibrated to reduce friction and impro e deli ery timelines
ur ertically integrated network is one of our most important competiti e ad antages oung said e e got a combination of hard to replicate pri ed manufacturing and uarrying assets and well located batch plants all of which work together to bring product to marketefficiently hat integration doesn t ust benefit oral it s designed with the customer inmind y reducing transport distancesand building in redundancy
and e ibility the company ensures fewer delays and cost o erruns on critical pro ects
ach year we mo e about million tonnes of construction materials and supply around kilometres of road pa ing oung said fter nearly years in business oral remains the country s largest ertically integrated construction materials pro ider Its footprint is deeplyembedded in ustralia s landscape from e eryday streets andfootpaths to
ou d be hard pressed to go through a day without encountering something we e helped build whether it s a bridge tunnel road or building oung said ement from oral s errima plant was used in the construction of the ydney pera ouse the nowy ydro cheme and the ydney arbour unnel ince alone we e produced about million tonnes of cement at errima hat s enough to manufacture around million cubic metres of concrete the e ui alent of
Discovering new mineral deposits can be a di icult and demanding process, which is why recognising and celebrating
AI, robotics, and geophysics to make smarter, cleaner discoveries.”
hile additional drilling didn t increase the size of the Dogleg deposit, Fitzpatrick believes the discovery has already sparked wider interest in the est imberley
as part of the sia acific s International
is often likened to searching for a needle in a haystack – and rarely is this truer than in the pursuit of high-grade nickelcopper sulphide deposits in the remote imberley region reenfields e ploration in this area is rugged and difficult to navigate. So when Fitzpatrick and his team achieved precisely that, it marked a rare and transformative moment, not just for them but for the broader resources sector.
Fitzpatrick, a geophysicist, was at the helm of the team behind the Dogleg disco ery a polymetallic mafic associated nickel-cobalt sulphide deposit.
“It was a tremendous honour and a alidation of our team s e ort and capability,” Fitzpatrick said. “It really highlights what can be achieved when cutting-edge exploration technologies and techniques are applied with discipline and insight.”
For Fitzpatrick and his team, the Prospect Awards provided more than a trophy it was an opportunity to re ect on years of dedication.
“Sometimes you’re so caught up in your own little bubble that you don’t realise how significant your work is. This kind of external recognition reinforces that what you’re doing matters,” he said. “Everyone in the company started taking notice. Itsends a ripple e ect through theorganisation.”
Fitzpatrick also believes the Prospect Awards serve a broader purpose for the mining industry.
“They showcase the best of what we’re doing – whether that’s technological innovation, sustainability, or working with heritage groups,” he said. “People think mining is just about digging holes, but we’re using
“It has proven the fertility of the region and will likely encourage more exploration, whether by IGO or others,” he said. “Even if Dogleg ends up being a smaller deposit, it could still play a critical role in a hub-and-spoke modelwith other finds like erlin hat gets me out of bed these days is watching people grow – giving them the same opportunities I’ve had and hopefully helping them lead the next great discovery.”
The recognition was not just a professional milestone for Fitzpatrick –it was a high point in a career that had already spanned research, public service, and industry.
Beginning in academia, Fitzpatrick completed a PhD focusing on the geophysical responses of economic sulphide systems before working for Geoscience Australia in Canberra then the CSIRO. He re-entered mineral exploration14 years ago, joining IGO seven years prior to the ogleg disco ery his was the first exploration award I’d ever won,” he said. “It had been about 15 years since I’d received any external recognition, so to win this felt incredibly rewarding. Awards like these are rarer than the discoveries themselves.”
The award night was particularly memorable e had a full table there not ust the geologists but the field sta the contractors the broader team Everyone who made the discovery possible,” Fitzpatrick said. “There were a few drinks afterwards. It was a real careerhighlight.”
Australian manufacturer Agridry is helping farmers stay profitable through periods of floods and drought.
IT CAN BE TOUGH TO BE
in a land of drought and ooding rains
In May, the Bureau of Meteorology o found record breaking amounts of rainfall in northern ew outh ales eanwhile the opposite was happening throughout southern ustralia he o reported that it was the se enth driest ay on record for ictoria with rainfall below a erage in most of outh ustralia southern estern ustralia and western ither end of the spectrum is painful for farmers who are looking to ma imise the alue of their grain
gridry general manager oshua orrison said this weather olatility is one of the biggest challenges facing the company s customers
armers are facing rising costs of inputs ta es labour shortages and the pressure of maintaining the high ustralian grain uality he said any farmers are dealing with an older infrastructure that isn t keeping up with the demands of modern farming e o er a practical and durable
gridry established in manufactures drying and aeratione uipment
It focuses on product de elopment for markets including grains almonds pulses nuts wood chips and other commodity products
Its e uipment pro ides growers and processors with a way of controlling the moisture le els in their grain
ithout a dryer in periods of high rainfall a farmer may need to wait weeks for the crop to naturally dry uring this time the crop will degrade losing some of its protein and shape
ryers can help pre ent this and e en allow farmers to begin the har est process earlier letting them reap the benefits of greater e ibility and higher profits orrison said gridry s dryers are self sufficient easy to operate systems that help minimise the e ects of inclement weather
hey allow farmers to be more e ecti e in the field and so they can har est at any time of the day It doesn t matter if there s high moisture or
he company s range of aeration control systems ha e also pro ed popular in areas facing a potential drought gridry s range of silo aeration units are designed to ensure that silo stored grain remains low in temperature low in moisture and low in insect and mould acti ity and maintain a germination rate if stored at or below gridry s silo aeration controllers do all the hard work toring grain for longer periods of time allows farmers to sell grain at the best possible price impro ing the profitability of their crop
Moving on up
gridry s customers aren t the only ones futureproofing operations he company has recently relocated to a newfacility orrison said that the business s site had ser ed its purpose but had been holding the team back in terms of efficiency and growth
elocating ga e us an opportunity to design a facility around the modern manufacturing ow and to gi e us space and infrastructure to scale our production and inno ation he said
“There will be more room to build bulk items in a cost e ecti e way and we e been looking at using laser welders to increase efficiencies and decrease manufacturing costs
lean manufacturing process means we can reduce waste and deli er our e uipment faster
he facility is also located along the Inland ail corridor which orrison said was a big strategic win for the company e can mo e our finished goods faster and more cost e ecti ely he said uring har est time this is e erything e ha e been listening to farmers throughout this e pansion and we re collaborating with key partners to o er them with machines that deli er real world results
Rice Lake Weighing Systems’ 1280 Enterprise™ Series indicator revolutionizes weighing operations with the ultimate combination of power and programmability. Increase e ciency with the 1280’s highly customizable graphical user interface, built-in web server, systems integration and data tracking. Monitor processing operations, including vehicle and in-motion weighing.
Compatible with the 1280, the SCT-4XD is a high-speed digitizer, capable of reading two speed encoders and managing two totalizers. Manage up to four load cells of a belt scale with complete diagnostics, calibration and remote configuration.
Visit www.ricelake.com/fullcontrol or scan the QR code for more information.
www.ricelake.com
With WA Mining Conference and Exhibition taking place in October this year, companies in the industry can showcase solutions and expand their presence in Australia’s largest mining state.
invaluable opportunities for companies to connect directly with the market and industry.
WA Mining Conference and Exhibition (WA Mining) is a premier trade show for those who want to connect, network and display their solutions and o erings Strategically located in Perth and spread across two –days, a major theme for the 2025 event is looking to the future of theindustry.
This is why Kinder Australia will be showcasing its solutions at the event.
Kinder Australia supplies specialised products tailored to real-world conditions. To do this, the company relies on feedback from the field to direct its research and de elopment e orts
Kinder sales and marketing manager Sam Veal said this approach ensures that Kinder’s solutions not only meet current industry standards but help push them forward.
“We have a strong engineering department that works closely with our field teams he said hey re constantly identifying issues at site level and feedingthose insights back into the innovation pipeline. That’s how we continue to e ol e our product o erings and stay rele ant
Whether it’s improving belt hygiene, managing spillage, or enhancing material ow inder s products are designed with productivity, safety, and sustainability inmind.
That’s why Veal said the decisionto exhibit at WA Mining was a no brainer
“What we’ll be showcasing at WA Mining are solutions that directly address operational pain points – dust control spillage management and ow optimisation. These are the kinds of impro ements that boost both efficiency and sustainability on site
As Western Australia continues to be a powerhouse of Australia’s mining
sector, Kinder Australia is seizing the opportunity to deepen its engagement with the region.
“The Western Australian market is a very important growth prospect for inder eal said e re doing a number of trade exhibitions this year, but WA Mining made particular sense given our priority to meet the growing demand in WA. It allows us to be front and centre with our customers in the region
“The broader focus of WA Mining is a good match for us. It gives us the chance to engage with a wide range of mining operations – iron ore, gold, nickel, bauxite, lithium – you name it. That range aligns perfectly with the breadth of our materials handling e pertise
Beyond product promotion, exhibitions like WA Mining provide an invaluable opportunity for site-based personnel – those who work daily on mining operations – to interact directly with Kinder’s solutions.
It s often difficult for our field application specialists and engineers to physically demonstrate our products on site eal said ining enables those working on the ground to see and understand these solutions in real life, rather than through a brochure or online ideo
This hands-on exposure is critical inan industry where practical application and real-world performance often determine whether a product delivers value.
While WA Mining has a strong focus on the WA market, the impact of Kinder’s participation extends across the broader Australia and New Zealand regions. Vealsaid events like this are instrumental in building recognition and driving expansion.
“Kinder’s presence in WA is growing, and events like WA Mining help reinforce that. But more broadly, they give us the opportunity to showcase our capabilities to operators across Australia and ew ealand
Setting the global
For conveyor belts that deliver the lowest cost per tonne of material conveyed, you need more than just durability—you need synergy between the cover compound and the carcass, tailored to your specific needs.
Using the highest quality materials and state-of-the-art manufacturing processes, we consistently produce the toughest and longest lasting conveyor belts in the industry.
Bulk material handling and heavy mining operations that fit their conveyors with Fenner Dunlop Conveyor Belting benefit from maximum uptime, less belt maintenance, higher productivity, and lower total costof-ownership.
Lincom Group is helping bulk operations dewater slurries and concentrates with ease.
THOMAS BROADBENT AND SONS
is a British engineering stalwart that, for more than 160 years, has been at the forefront of centrifuge technology. ounded in uddersfield est Yorkshire, in 1864, Broadbent began manufacturing industrial textile machinery, pioneering development into centrifugal separators.
At the time, using centrifugal force to separate solids from liquids or classify di erent densities was re olutionary o ering speed and efficiency previouslyunattainable.
Each Australian industry deals with enormous volumes of materials that need to be processed separated classified or dewatered. This is where the centrifuge steps in as an indispensable tool. et products are difficult to transport with conventional bulk handling equipment, Lincom Group product manager Alan Dunbar told ABHR
“Centrifuges produce a solid cake
The unsung heroes of bulk handling
Precise separation can be critical in the production process, from pharmaceuticals to plastics, paints, kaolin, coal, and potash.
Broadbent centrifuges isolate active ingredients, remove impurities, and dewater slurries, ensuring product purity and efficient downstream bulk handling The extraction and processing of minerals often involve slurries and suspensions that re uire efficient dewatering Broadbent centrifuges separate valuable minerals from waste, reduce transportation costs by lowering moisture content, and facilitate environmental compliance by better managing tailings.
Dunbar said the importance of efficient bulk handling in comple manufacturing and resource management cannot be overstated.
“It directly impacts production costs, product quality, environmental footprint, and industry competiti eness he said
slurries usually carry valuable materials, they are hea y difficult to handle and costly to transport.
“Traditionally, dewatering might involve large settling ponds, which are land-intensive, environmentally challenging (due to potential dam breaches and inefficient ther methods like filter presses are batch oriented and less suitable for continuous, higholumeoperations
Broadbent’s decanter and basket centrifuges, engineered for continuous operation and high forces o er a dramatically more e ecti e solution hey rapidly separate fine solid particles from the liquid phase, delivering a ‘cake’ of dewatered solids with reduced moisture content.
The impact of this dewatering prowess e tends directly to the efficiency of bulk material transport, particularly via conveyor belts – the arterial network of any large-scale facility. et products are substantially heavier than their dry counterparts. By dewatering, the overall mass being transported is reduced. This translates to less demand on conveyor belts, motors, and structural components, extending their lifespan and reducing maintenance costs perators can also transport more material per tonne, boosting throughput without investingin larger, more expensive conveyor systems.
High moisture content can also lead to material sticking, blockages, carryback, and messy spillage. This results in material loss and necessitates frequent cleaning and maintenance, leading to costly downtime.
Product consistency, in both dryness and volume, improves conveyorperformance.
Dunbar said low moisture content in the feed benefits many processing steps downstream of the centrifuge.
roadbent s continuous design o ers products like the Divergent Decanter Centrifuge, which provides the highest throughput and moisture recovery of any comparati e machine he said
“A drier product from the centrifuge reduces energy consumption in subsequent drying stages, lowering operational costs and improving the o erall efficiency of the entire processingchain
Compliance and sustainability
Adhering to transportable moisture limits is a critical safety and regulatory requirement for products shipped globally. Excess moisture can cause bulk cargoes to liquefy during transit, leading to dangerous cargo shifts and potential vessel instability. The receiver will also check moisture content, and penalties may apply if out-of-spec products
Long term support
Lincom Group are the Australian distributors of Broadbent equipment. The two companies work together to
World leaders with 50 years’ experience in Bulk Materials Handling Research and Consulting
“These machines are an important part of the bulk handling process, so we have invested a lot into a fast turnaround for customers
TUNRA Bulk Solids develops custom solutions to suit the individual needs of our clients.
Services:
Flow Properties and Materials Testing
Dust (environmental) Testing
Wear Testing (Impact, Abrasion and Erosion)
Conveyor Belt, Idler Roll and Pulley Testing
Discrete Element Method (DEM) Modelling
DEM Calibration Testing
Materials Handling Consultancy and Contracted Research
Bin and Stockpile Design
Pneumatic and Hydraulic Conveying
Computational and Scale Modelling
Site Visits
Professional Development Courses
2 4033 9055
2025 Professional Development Opportunities:
Storage, Feeding, Transfer and Belt Conveying Course: 11-13 November (Perth)
Belt and Idler Showcase and Site Tour: 6th August (Newcastle)
Belt Conveyor Design, Optimisation and Research Course: 27-30 October (Newcastle)
Enquiries to Danielle.Harris@newcastle.edu.au
HAVER & BOECKER is providing a one-stop-shop for dry-mix plants to the local Australian market via its combined specialist plant engineering and construction divisions.
the town of Hahnstätten, Germany, lies one of the purest limestone deposits on Earth. The lime mined from the quarry is used to synthetically process the fundamental raw material precipitated calcium carbonate (PCC), which is used in industries ranging from construction, iron, steel, paint and plastics to paper, food and pharmaceuticals.
On the edge of the quarry is the PCC processing and packing plant, operated by the quarry owner, SCHAEFER KALK. The plant is currently undergoing a major expansion to include a new dry mix packing operation, comprising a silo, packing line, storage, and logistics.
Five years in the making, this important construction project will set a new benchmark in efficient clean and resource-saving packing, strengthening SCHAEFER KALK’s market advantage.
With its packaging product quality assured, SCHAEFER KALK will be able to maintain its role as a quality-leading supplier of special PCC while enhancing support for its customers worldwide in the ongoing development of their ownproducts.
Behind this engineering feat is the dry-mix process and packing specialist, HAVER & BOECKER.
Over a two-year period, HAVER & BOECKER planned, calculated, analysed and carried out feasibility studies with experienced civil engineers and 3D scans on site, while other company e perts selected the best fit machines and systems.
Then came the active phase, which included construction drawings ow charts, and estimates for external services. In 2023, construction began.
Here in Australia, HAVER & BOECKER’s Australian operation is providing this ‘one-stop shop’ for drymix plants to the local market. This is achieved through its combined capability with its specialist plant engineering and construction divisions IBAU Hamburg andAML.
IBAU Hamburg is a provider of state-ofthe-art bulk material handling solutions and has been synonymous with the Australian cement industry for more than40years.
Its range of services includes multicompartment, central cone silos, plant design, engineering, supply of individual components such as ow control and cut o gates rotary bottom and rotary side dischargers, pneumatic conveying systems, bulk loading technology, mechanical mixers and mixing plants.
“IBAU Hamburg played a leading role in the engineering of the world s first large-volume, drive-through dome silo at Hallett Group’s Port Adelaide green cement distribution hub,” HAVER & BOECKER Australia sales engineer Les Szalai said.
“The scale of that project really showcased IBAU’s capabilities and advanced silo technology to the market.”
In officially oined the HAVER & BOECKER group, bringing its expertise in plant design, engineering and construction for the building materials industry. Prior to that AML had been a partner of HAVER & BOECKER for over 20 years, working together on more than 30 joint projects.
o ers comprehensi e engineering services and support globally, from design through to the commissioning of new plants retrofits and expansions.
It focuses on distinct target applications to create unique solutions, including cement-based building materials plants, chemical manufacturing facilities, gypsumbased building materials plants, dust removal technology, sand preparation, handling, and storage, as well as paste productionplants.
“AML can and will adopt a standard mixing tower style solution where it is feasible and warranted,” Szalai said.
“But its specialty is developing mixing plant solutions where height limitations are an issue or where a plant must be shoe-horned into an existing facility where space and available footprint are highly constrained.
“This custom approach aligns perfectly with IBAU and HAVER & in that we all firmly belie e that each and every application is di erent e steer clear of the typical cookie-cutter-style solutions.”
In addition to plant construction, another AML core competency is in the field of dedusting technology where it leads in the production of filters and filtration systems for dust remo al in bulk material plants.
A recent example of AML’s custom approach was the turn-key delivery of a sand preparation and dry mortar mixing plant for a client in Jakarta, Indonesia.
The target production capacity was 50 tonnes per hour. The raw materials storage and handling process involved
16 main component silos along with an additional 16 additive silos.
Dosing of the ingredients was accomplished using several weighing scales, after which the ingredients were thoroughly mixed. The end products were then directed to two packing lines for paper valve bags or four bulk loadingsilos.
AML prides itself on being extremely versatile and is comfortable in extending its range of design functions from static,
standalone facilities at any scale through to mobile plants.
“They have a wealth of knowledge and experience to provide an unparalleled level of service in the areas of assembly, supervision, commissioning and aftersales support,” Szalai said.
“With the combined capability of IBAU Hamburg and AML there is no dry-mix plant that is beyond the scope of HAVER & BOECKER Australia’s ability to design, engineer and supply.”
Manufacturer of conveyer belt scales (weightometers), weigh belt feeders and volumetric and gravimetric auger feeders all manufactured in Australia
Conveyer Belt Scales and Weigh Belt Feeders to measure instantaneous and total throughput or control Blending, Dosing or Feeding.
Volumetric or Gravimetric Auger Feeders with TT20 Weight Controller.
The TT20 is a single unit gravimetric processor that o ers four modes of operation: Loss-in-Weight, Loss-of-Weight,
Gain-in-Weight, and controlled-rate-batching for bag filling The controller accurately and consistently feeds material into a process at desired rates and batches.
The TT20 has a user friendly HMII allowing the operator to monitor critical process operations. In addition, PLC communication protocols enable the controllers to seamlessly interface with a plant’s control system with access to the Scales Parameters in Real Time.
ABHR speaks with Tecweigh’s Barry Gamble about how the company’s TT20 gravimetric processor is helping customers achieve better accuracy, lower waste, and improved e iciency.
THE FOOD
it’s not uncommon for producers to spend months or years working to perfect the right mixture ofingredients.
Whether its chilli or salt, too much of a good thing can spoil a snack, which is why Techweigh’s TT20 gravimetric processor is designed with accuracyinmind.
“With the TT20, you’re using weight feedback from either a scale base or load cells to enhance accuracy throughout the entire process,” Tecweigh’s business development manager Barry Gamble said.
This weight-based feedback loop ensures that even as material properties or ow rates ary the dosing remains spot on – bridging the gap between traditional volumetric systems and the precise standards required in modern production. By continuously measuring weight in real time, the TT20 eliminates the guesswork of variable ow ensuring the correct amount of product is delivered with each cycle.
From construction to snacks and agriculture, the TT20 is proving its value across multiple sectors.
“In cement, for instance, we’re filling and kilo bags like the ones you see in hardware stores,” Gamblesaid.
In food manufacturing, the TT20 deli ers accurate a ouring for snacks ecweigh e en o ers a purpose built auger specifically for dosing salt which has a unique combination of low throughput and high bulk density.
“It can apply additives directly to the middle of a moving conveyor, achieving even distribution across the product,” Gamble said.
One of the TT20’s key advantages is its e ible operating modes
“In continuous loss-in-weight mode, it delivers product at a constant rate until told to stop –ideal for feeding tumblers or dryers in food processing,” Gamble said.
For batching, the gain-in-weight mode o ers pinpoint precision
“It dispenses rapidly until it nears the target, then slows to account for inight material he result is an accurate repeatable fill e ery time he said
The TT20 is ready for Industry 4.0 environments, with Ethernet TCP/ IP connectivity allowing seamless integration into plant-wide controlsystems.
“While it can run standalone, the TT20 also connects easily to central control systems,” Gamble said.
This allows real-time visibility into load cell readings, screw speeds, and paddle movements – enabling process optimisation and reducing the risk of error.
Ease of use is baked into the design. The TT20 features a bright, intuitive interface and integrates easily with programmable logic controllers.
“The interface makes setup simple and reduces user error. Once programmed, it’s just a matter of hitting the start button,” Gamble said.
It also features automatic tare functionality, resetting the scale before each cycle to maintain accuracy.
ecweigh s o ers tangible return on investment. By minimising the need for operator input, the TT20 streamlines processes. Supervisors can lock in parameters, while operators just press start and stop.
Proudly Australian-made, the TT20 is constructed from food-grade stainless steel for long service life.
“With over 20 years of experience making feeders, Tecweigh systems are used around the world,” Gamble said. he unit includes a month warranty, and spare parts are readily available from Melbourne. “The system is so robust that 99.9 per cent of our customers handle maintenance themselves,” he said.
In a time when reducing waste ismore important than ever, the TT20 helps businesses meet their sustainabilitygoals.
Its high-accuracy dosing prevents overuse of materials, supporting leaner operations and reduced environmentalimpact.
With proven performance across cement, agriculture, andfood manufacturing, the TT20 is helping businesses improve product quality, reduce waste, and increaseefficiency y combining reliability e ibility and advanced integration capabilities, ecweigh s is redefining what gravimetric processing can achieve.
DYNA Engineering has developed a “chamfered mesh pattern”, designed to reduce washdown splash back and increase visibility through the guard panels.
This design feature is a major “point of difference” compared to standard HDPE mesh and will improve inspection and cleaning operations.
Washdown Mesh
• Up to 50% additional spray-through for washdown.
Increased Visibility
• Up to 25% additional viewing angle and see-through visability.
Satake has harnessed its international expertise to deliver a major rice mill with intake storage system for a local Australian cooperative.
IT ALL BEGAN AT THE LOCAL football oval, early in the morning, when 10 local growers convened to discuss the future of rice growing in the Riverina and surrounding New South Wales region.
The Riverina region has ideal conditions for growing rice. The temperate climate, clean environment, and nutrient rich soils means it is home to about 98 per cent of all the rice grown in the country.
Around 18 months after that fateful meeting, the community’s vision came to life through the incorporation of Nice Rice, a cooperative dedicated to
Nice Rice project manager Russel Ford said the company has grown rapidly since being formed two years ago, with around 30 growers invested in the business.
The time had come to build the company s first rice mill ur first atake mill was small and specialised,” he told ABHR. “It could handle one tonne per hour and gave Nice Rice a change to get product out.”
“It meant we could get product on the shelf and start learning about customer demands and the logistics involved.
“It was a good introduction and allowed the business to train a few sta
Soon it came time to expand. The business decided a second mill was needed to handle the increased production capacity and began exploring the market
atake was a clear contender atake Corporation has more than 125 years of experience in delivering rice mills around the world dating back to its foundingin1896.
Ford said Nice Rice wanted to stand out in the competiti e rice market
“At the end of the day, we had to make sure our products were right up there with the best,” he said.
I got introduced to atake around
– there’s not many who are better at milling in the world.”
As the two companies began workingwith each other uality was the top priority.
o make sure the business was buying from the right supplier, Nice Rice sent a team to Thailand to inspect some of atake s manufacturing processes
What they saw was impressive.
atake had incorporated artificial intelligence (AI) into the milling process, which was a ma or benefit for the growing business.
atake senior pro ect engineer a anIllanko an said the ice ice team were blown away by the optical sorting system.
ptical sorting is the final step before packing he said he milling process includes Intake system pre cleaning, cleaned paddy storage with aeration, post-cleaning, dehulling, whitening, separating grain sizes and sorting by colour to packing
“The optical sorting system automatically detects chalkiness glass impurities black spots lumps brambles or sticks
The automated system means less people are re uired to operate the mill vital for an industry that is in the middle of a labour shortage.
Flexibility was also crucial. Nice Rice has a variety of products, all of which would need to be milled through the same infrastructure.
Illanko an said atake s mill went against the grain, which is exactly what ice ice was looking for
Nice Rice didn’t want a conventional mill, which are usually designed with a large footprint and se eral oors
“The method we used was a modular rice mill system. It was one storey with several mezzanines in it,” Illanko ansaid
his had less of a footprint re uired less energy and o ered high uality milling at a competitive price.”
When it came to delivering the pro ect atake took a turnkey approach It pro ided all the intake systems Denny’s silos, aeration systems andmore.
Its engineers also provided advice on what would and wouldn t work for
the mill, drawing upon the company’s extensive history within the industry.
ord said atake s approach made life much easier.
It is much easier to stick with one manufacturer when putting something like this together
atake s engineers also helped ice Rice plan for the future. Currently, the site can store around 500 tonnes, but there is space set aside to expand this to a 6000-tonne silo complex. The shed has also been designed so that a new rice mill system can be incorporated next to it, when the time comes to continuegrowing.
Illanko an said this forward thinkingstrategy is part of atake s design process.
hen we do the initial design works we sit down with the client and ask them what their plan is now, and what they
hope to achieve in the next 10 years,” hesaid.
“We design based on what the building should look like in a decade which saves on costs in the long run.”
ice ice officially cut the ribbon at a grand opening ceremony on 30 May. Withthe site now up and running, Ford said the company foresees a lot of milling in the future.
“We’ve had a good harvest and there s uite a few options as far as rice varieties go,” he said.
“We’re excited to start sending out uality products and to continue learning processing and looking for new opportunities to improve.”
atake looks forward to commencing this partnership with Nice Rice and is committed to supporting their success well into thefuture.
FlowForce Technologies is proud to be building its solutions from the ground up in Australia.
THE RARE
purity is everything. Producers are paid significantly more for higher purity, but overprocessing can reduce yield without increasing alue
o help strike the optimal balance manufacturers ha e turned to low orce echnologies solutions
ased in delaide s egency ark the company manufactures impact weighers and cross cut samplers used across industries including cement
grain and increasingly rare earth minerals Including this technology at the discharge point of the separation processes allows producers to measuretonnage and sample uality in real time
low orce managing director lenn obling said locally assembled products are playing a role in enabling customers to boost efficiency reduce waste and ensure compliance all while na igating supply olatility
Precision engineering
low orce s impact weighers ow measurement de ices that calculate theweight of bulk solids in motion andits cross cut samplers which e tract representati e samples for ualityassessment are some of its o erings hese units are built from the ground up in low orce s delaidefactory
ur impact weighers are made in outh ustralia in delaide obling said ur suppliers laser cut the steel to e act specifications and fabricate all ma or components hese are then returned to our facility at egency ark where our technicians assemble the sub assemblies into complete systems he instrumentation includes load cells for force measurement and robust electronics modules for data indication and control hile some components are sourced globally final integration and uality control are kept firmly in ustralian hands
ur controllers are manufactured from circuit boards made in ri anka and assembled into modules by a partner in ueensland he load cells were pre iously sourced from India but we re now transitioning to a ew ealand supplier obling said e belie e the ustralia ew ealand supply chain is more reliable and better aligned with ourstandards
low orce s solutions are designed for di erse applications but their alue shines particularly in high stakes en ironments like cementmanufacturing
ement plants generate a lot of fine dust during processing obling said eighing systems are used to bleed fines back into the product stream to maintain strength specifications If too much is added the whole batch can be re ected ur impact weighers help blend correctly and a oid costly errors
eyond process control low orce s e uipment also plays a ital role in safe transport logistics or applications like grain or bulk minerals being loaded into trucks or rail wagons our impact weighers ensure operators don t o erload hat protects infrastructure complies with road limits and impro es safety obling said
Resilient supply chain strategy
low orce s decision to keep core design and assembly operations local has paid o especially in recent years as global supply chains faced unprecedented disruption obling said the company took early action to protect its customers from such risks
hen we began sourcing controllers from ri anka we built up a large warehouse bu er here in ustralia hat ga e us breathing room during any disruption he said en when political unrest occurred in ri anka last year our supplier s factory was
outside the a ected capital hat meant we could continue operations largelyuninterrupted
Innovation through necessity ne of low orce s most strategic product de elopments has been the release of the eries i e impact weigher a direct replacement for the now obsolete and models once supplied by hermo isher amsey
bout two years ago hermo isher announced they would no longer supportthe and models here s a large installed base across the industry and we recei ed a ood of in uiries oblingsaid
o we designed the eries i e as a bolt in replacement It takes around two hours to swap out and that s been a huge success for us
ecognising industry shifts toward high temperature processing particularly in rare earths low orce also de eloped a ersion of its weighers
DHHI the leader in designing and manufacturing reclaimers, stackers, shiploaders, shipunloaders and car dumpers globally with over 100 machines delivered last year.
with e ternal load cells enabling accurate measurements at ele ated temperatures any rare earth producers are now heating product to or degrees elsius to impro e mineral separation obling said ut that heat used to damage our electronics o we redesigned the impact weigher so the electronics are no longer in the ow path ow e en high temperature products can be measured reliably
his new design is also retrofittable to e isting systems gi ing customers an upgrade path that avoids fullreplacement espite importing select high tech components low orce s approach remains deeply rooted in ustralianmanufacturing ur sales actually increased during I obling said hat s because most of the system is built here in delaide and the parts we do source o erseas are managed through robust supply agreements and localpartnerships
Reclaimers, Stackers, Shiploaders, Shipunloaders Car Dumpers
Conveyors
Processing plants and tailings
Local After Sales
The Conveyor Components Company is looking to partner with an Australian distributor to assist its expansion plans.
THE CONVEYOR COMPONENTS
Company (CCC) has spent the past 60 years manufacturing a wide range of equipment designed to help its customers keep employees safe, and to reduce unwanted downtime.
While the Michigan-based business has built up a strong following in the United States, Canada, Mexico, and South America, it wants to continue growing the business in Australia.
CCC sales manager John Carlson told ABHR that finding the right business partner was the next step.
“Right now, we’re in the recon phase he said he first thing we want to do is get a better understanding of the Australian market.”
hat means finding out about what things Australian businesses need, what type of industries need our equipment, what the safety requirements are.
“We know that the mining industry is huge, but what are some of the other con eyor operations that could benefit from our technology?”
CCC prides itself on manufacturing rugged, durable equipment for monitoring and protecting conveyorsystems.
Its four most popular products are its emergency stop switches, belt misalignment controls, belt damage controls, and belt motion controls. Combining these products helps ensure that any conveying system is working as it should be.
Carlson said the main challenge facing the company is reach.
“We’re on the other side of the planet. We don’t want to just dive into a market with no understanding,”hesaid.
“The challenge for us is ensuring that we have done our due diligence to understand what the industry requires and that we can meet those needs.
“That way when customers reach out to us for a product, we know that it will be the right fit
Finding the right distributor is key is interested in finding a reliable partner that understands the
local industry, with the capacity to promote its products.
Carlson said it is important that any distributor also has the same approach to customer service as CCC.
“We want a distributor that’s going to learn about our products so they can promote the right ones for the application,” he said.
“It’s our missions to create very long-lasting, durable products that the industry needs – and it’s important that any business partner shares this vision.”
CCC is no stranger to international trade. It has been shipping its equipment around the world for more than 50 years. This experience has led to the creation of robust supply chains to make sure product gets exactly where it is needed, when it is needed.
y the end of the financial year plans have a better understanding of what the Australian market needs, and how it can support it. Armed with this knowledge, the company can go forth and start contacting distributors to find the right fit
Trusted by Industry. Delivered by Satake
With decades of proven experience, Satake Oceania designs and delivers tailored grain silo and storage systems—built to perform, built to last.
We provide end-to-end solutions for every scale and need:
• Small seed storage to large-scale silo complexes
• Grain handling, bulk storage, and full milling systems
• Feedlots, our, rice, and seed processing solutions
Every project is backed by:
• Local manufacturing in Australia
• Complete design, build, and installation services
• On-the-ground project management and long-term support
Our hands-on approach ensures each solution aligns with your operation—today and into the future.
Rice Lake Weighing Systems® and Minprovise are collaborating to implement sophisticated systems in the mining and quarrying industries.
IN AUSTRALIA’S RUGGED MINING and quarrying environments, accuracy, durability, and integration matter more than ever. As operations grow in complexity and scale, old systems struggle to keep up, often missing tonnes, costing the site owners money and slowing down processes. Modern, reliable belt weighing systems are essential for e ecti e material tracking and process control.
According to Minprovise product specialist Robert Arezio and Rice Lake Weighing Systems regional sales director for Oceania Phil Maillols, pairing the SCT-4XD smart transmitter with the 1280 touchscreen controller delivers a powerful, future-ready solution designed to handle real-world challenges without compromise.
At the heart of this pairing lies a synergy between hardware toughness and smart software design. The SCT-4XD is engineered as the ‘signal expert’ capable of cleaning up noisy load cell signals even under punishing site conditions. “The gi es us e ibility with calibrations re io said e re able to fine tune algorithms to improve accuracy, and early results have shown excellent performance straight o the first calibration
Meanwhile, the 1280 touchscreen controller acts as the system’s brain, providing high-end logic power in a user-friendly interface.
It s basically its own system Arezio said. “For some applications – like remote or mobile batching plants – it can even eliminate the need for an external logic or batching system entirely. We can do it all from the
The combination of the SCT-4XD and 1280 is more than just an upgrade
in capability, it is a smart investment in system simplicity.
“The 1280 includes full onboard logic to automate batching, alarms, and scheduled tasks aillols said “That reduces hardware complexity and cuts costs, particularly on remote or ruggedised sites where every failure pointmatters
Belt scale frames such as the MasterTM BS221DB and BS14X from Rice Lake are designed specifically to handle the harsh conditions of a materials handling industry ice ake puts a lot of e ort into the uality of their product re io said. “They’re extremely robust. I’ve seen them hold up better than others in similar en ironments
Maillols reinforced this, pointing to the frames’ heavy-duty steel construction and field pro en performance in mining and quarrying sites across the country. “They’re built to resist shock, dirt, moisture, and the daily abuse of high load operations he said hese
frames can be bolted into most existing con eyors with minimal modification which is a big plus when retrofitting
Additionally, Rice Lake’s frames are equipped with engineered mounting points that isolate load cells from belt noise and vibration. Combined with SCT4XD’s fast sampling rates and advanced signal filtering the result is highly secure and accurate data, even when dealing with belt bounce or uneven loads. “It’s the integration of the speed sensor signal, load cell signal and algorithmic filtering that gi es us such consistent results Arezio said.
In today’s connected industrial environment, seamless communication between weighing systems, PLCs, and SCADA networks is critical. The SCT-4XD supports major industrial protocols such as ProfNet, Modbus TCP, and Ethernet/ IP, without the need for converters. This capability streamlines installation and ensures reliable data ow throughout theplant.
“The ability to log in remotely is one of the big ad antages re io said “Whether it’s through a tablet onsite or a computer in the control room, we don’t need to be physically in front of the integrator to adjust or diagnose thesystem
Maillols said the 1280 comes with a built-in web server, allowing for browser-based access. “That means you can set up, calibrate, and run diagnostics from irtually anywhere he said he 1280 can even mirror its screen over WiFi or Ethernet and send email alerts or export data via FTP. It’s real-time control at your fingertips
The SCT-4XD and 1280 system are standard Rice Lake products, not custom belt specific de ices hey re made per cent in house Maillols said. “That means we’re not relying on third parties which simplifies support and logistics – especially when managing systems across multiple sites
“Spare parts are available from any Rice Lake or Dini Argeo dealer worldwide, and we provide lifetime support on both hardware and software updates
In Arezio’s experience, this level of standardisation and support delivers long-term reliability. “They’re solid systems, and you can tell there’s been a lot of thought put into things like calibration and maintenance he said In fact we re e en able to o er calibration weights that can be activated remotely, meaning the belt doesn’t have to stop during the process. That’s a big safety and producti ity win
Accurate belt weighing is critical for cost management, inventory control, blending operations, and regulatory reporting. That accuracy becomes even more challenging when dealing with ibration uctuating loads, and harsh operating environments.
“Rice Lake’s approach is all about integrating reliable signals, isolating mechanical noise, and using advanced
algorithms to clean the data aillols said. “The SCT-4XD features one of the world’s fastest industrial digital A/D converters and uses four independent channels –so each load cell is monitored separately. If one cell drifts or fails, the system detects it instantly. For example, at one client’s site in a major fertiliser plant, the system detected load cell failure before shift even started. No downtime, no drama
That level of monitoring and data integrity ensures throughput data is consistent, even under load surges or belt misalignment. “It helps keep stockpile data precise and supports reliable blending processes. “This is not just an upgrade. This is the new standard. If you are still using old gear, you’re already behind aillols said
With their powerful combination of robustness, accuracy, integration, and smart control, Rice Lake’s SCT-4XD and 1280 system is proving itself as a reliable weighing solution for materials handlingindustries.
Telescopic Cable Mast Conveyor
• Versatile, affordable conveyor solution
• Quick and cost-effective installation
• It can be lowered to the ground to provide easy access for maintenance
• No head or tail undercarriage provides greater clearance under the conveyor
• Complies with all relevant Australian Standards, AS1170, AS4324.1 and RPEQ requirements
ESS Engineering is providing specially designed conveyor support systems to safeguard conveyor infrastructure.
CONVEYOR
critical to bulk material handling industries like mining, logistics and manufacturing. Damage to the conveyor belt shortens its life and cuts into profits hile all con eyor belts will wear out over time, damage should be avoided where possible to ensure a reasonable return on investment. Bulk solids impacting the conveyor at transfer points and load zones can cause accelerated damage to the idlers, structure and belt.
hat s where ngineering o ers expertly designed conveyor support systems that maintain stability, ensure correct elevation and extend the life of expensive belts.
ESS Engineering’s impact beds and cradle systems are purpose-built to protect and prevent belt sag and absorb the impact of falling material at load zones and transfer points.
“Stability and alignment are critical when you’re dealing with large lumps of material dropping onto a belt,” ESS Engineering business developer Aden Prisk said. “Our impact beds help eliminate belt sag and provide essential protection. The systems are robust and designed for ease of maintenance –individual components can be swapped out easily and economically.”
ngineering s impact beds o er continuous contact with the underside of
the belt, reducing sag between idler sets – a common source of belt damage and sealing issues.
“Impact rollers only contact a small part of the belt, leaving gaps where sag can occur hen sagging happens in the skirt zone, we lose the tight seal required to contain material and dust. Our impact beds stabilise the belt across its full width, reducing the chance of punctures and preser ing sealing efficiency Engineering accounts development manager Tom Stahura said.
“Conveyor belts can cost hundreds of thousands of dollars – even up to a million – so protecting that asset is a major priority.”
At high-impact transfer points, uncontrolled spillage and dust emissions can degrade equipment and threaten worker safety. ESS Engineering’s impact beds, including its GAB Impact Cradle and Modular Impact Bed, help mitigate this.
“The impact bed supports the belt longitudinally, preventing it from being pierced by falling material between idler sets,” Stahura said.
It also keeps the belt at and
The GAB Impact Cradle and Modular Impact Bed are selected based on the size and type of material being conveyed, loading rates and site constraints. or estern ustralia we typically use heavy-duty or extra heavy-duty impact beds,” Prisk said.
“But for smaller operations in places like ictoria or ew outh ales the modular beds are a great o the shelf solution – more economical and easiertoinstall.”
ESS Engineering doesn’t believe in onesi e fits all solutions
“Every impact bed we supply is custom designed risk said e take into account belt width, material size, drop height, throughput rates and the speed of the receiving belt.”
In some cases, modular units may be used back-to-back to match the impact one length e sometimes supply 600mm long beds instead of the standard 1200mm units if space is limited or easier handling is required. But we’re always mindful of sag between supports – if needed, we’ll insert idler sets between modular beds to maintain stability,” Stahura said.
ngineering also o ers a range of cradle options – including combi cradles and roller cradles to suit di erent applications here you re not dealing with large lump drop, a roller cradle or combi cradle with a central roller set and support bars can be ideal,” he said.
At the end of the day, ESS Engineering’s conveyor support systems are about more than just mechanical components – they’re about protecting vital assets, reducing downtime and keeping people safe.
“From impact zones to sealing systems we re o ering tailored solutions that work in harmony,” Prisk said. “And if you maintain them properly, they’ll keep your plant running smoothly foryears.”
Fenner Conveyors is o ering its customers the opportunity to visit its manufacturing facilities and see how its products are made.
CONVEYORS ARE A VITAL PART of day-to-day operations that keep mines moving. To keep these operations going, it is important that workers understand all facets of the conveyor system.
Fenner Conveyors recognised the value in demonstrating how their equipment is manufactured and how customers can ma imise its benefits
This is why the company welcomes mining partners to visit its manufacturing facilities and see how the equipmentismade.
Visitors from BHP, Roy Hill and Rio Tinto have toured Fenner Conveyors’ Kwinana factory in Western Australia.
“We take clients on a tour of the facility to put our manufacturing process into perspective,” Finlen told ABHR. “It highlights the commitment to detail we
Fenner Conveyors operates a dedicated registered training organisation complete with a training conveyor system and classroom facilities at its Kwinana location alongside the conveyor belt factory, which makes the perfect location to deliver these training sessions.
Participants receive an in-depth explanation of conveyor belts and system engineering from the company’s embedded engineers.
“This is then usually followed up by some theory in a classroom setting. We explain in detail why we manufacture things the way we do and open up the oor for uestions
“This practical approach to customer support allowed participants to learn more about how Fenner Conveyors engineers belting unique to system and application requirements,” Finlen said.
“Once customers attend this type of training opportunity, it’s clear the lengths we go to for ensuring highly engineered and quality conveyor solutions.
“Providing customers with a holistic understanding of our equipment, especially when they are in the early stages of their career, means we start to build trust with future leaders of theindustry.”
One key aspect of both client and graduate tours is to highlight the company’s strict quality assurance processes at its on-site laboratory.
Fenner Conveyors’ Kwinana factory operates the latest generation Siempelkamp Steel Cord press lines, designed to deliver the industryleading conveyor belt quality and productionefficiency
“Our customers appreciate seeing
productivity standards. It achieves this through advanced instrumentation that collects production data, which can then be presented to operators, leaders, and quality assurance teams.
It is not just the Kwinana factory that hosts these in-person, informative visits. Most of the company’s manufacturing facilities have an open-door policy allowing customers to visit and learn how the equipment is made.
Conveyor Products and Solutions (CPS), one of Fenner Conveyors’ brands, has also welcomed graduate engineers and other key sta working with conveyors from major mining companies.
CPS head of engineering Peter Copley said these visits have been an excellent opportunity to showcase CPS’ innovative manufacturing processes.
“People knew we were local, but they didn’t understand the scale of the facilities or know that this type of mass manufacturing was still happening in Australia,” he said.
“CPS uses robotics, automation and digital job tracking, all supported by our internal systems team, to stay at the forefront of manufacturing excellence. These systems allow us to produce faster and better, as well as allowing us to track job status and quality dataelectronically.”
Both types of facility tour also allow customers to provide important insights
challenges customers face on site helps Fenner Conveyors and its portfolio of conveyor solutions brands to develop solutions that can then be used to advance the industry as a whole.
“A great example of this is our polyurethane range of rollers,” he said. “Within about three months we developed a solution in response to impact roller failures and issues on belts carrying acidic process materials.
“Everyone can contribute to the improvement of the products and operations, for instance, last year there were approximately 520 safety and quality improvement actions proposed and implemented from our production crews.”
Feedback on the factory tours themselves has also been glowing. Attendees were impressed by the
fromtheexperience.
“By allowing visitors to interact with actual examples of the conveyor belting and products, and understand how they interact on a conveyor system, we are supporting them to have an enhanced educational experience, whilst strengthening our relationship as a trusted supplier for their miningoperations.”
Finlen said more and more Fenner Conveyor customers are seeing the value it brings and are getting in touch to take up the opportunity.
“We build up a partnership with our customers, we don’t just supply them something and then leave them on their own,” he said.
“These facility visits show that we’re invested in our customers’ success, for the long-term.”
(UCG), often called drop objection protection, protect personnel, wildlife and the environment from falling debris.
spillage and other ob ects from falling o the conveyor belt and down through the conveyor structure when in operation.
Dyna Engineering’s (DE) general manager, Thomas Greaves, said until recently, UCG panels were always made of steel mesh.
“This had several disadvantages for maintenance and operations teams in terms of safety and high maintenance costs,” he said.
“The main problems being heavy to lift and fit easily damaged and deformed ulnerable to corrosion and rust needing regular repainting not sustainable nor environmentally friendly.”
The company began manufacturing conveyor guards made from 100 per cent recycled and recyclable HDPE plastic rather than steel in 2019.
Since then, the company has launched several other conveyor components made from HDPE rather than steel, saving conveyor owners mainly in the bulk handling, mining and construction industries huge savings and providing greater efficiency
In addition to being kinder to the environment through the use of the 100 per cent recyclable and sustainable HDPE plastic, these new UCGs overcome several difficulties encountered with steel
The panel is designed to capture objects greater than the slot size and prevent them falling to the ground. The mesh allows fine small material to fall through as it generally doesn’t pose a risk of injury and can be easily washed down during maintenance.
DE designs each UCG HDPE panel to suit the application. The company’s team considers the customer’s expectedimpact forces and deadloads which will be applied to the system.
“The need for a hinged panel arose because the available space at the customer’s site was unsuitable for our e isting panel solution specifically there was no side access to the panels.
“To address this, we collaborated closely with the customer to develop a hinged panel design. This solution allows the panel to be released at one end and safely lowered using mechanical aids, providing easier access for maintenance and inspection” he said.
The HDPE panel is engineered so it can be removed from the support system which allows access to the guarded area without removing the support bar from the structure. This ensures easy access for cleaning and equipment change-outs.
The panels are 10mm thick HDPE with an estimated service life of 1015 years. They can be made in any colour although black is recommended as it’s the most resistant colour to ultravioletradiation.
The steel support bar is designed to be retrofitted around the con eyor truss or other structures with little or no
modification to the e isting structure
The panel simply slides into two support bars and is lightly clamped between the panel retaining frame and panel mounting channel.
The mounting assembly is designed to suit many di erent con eyor trusses and stringer structures. Other standard steel variations are available. The support bar is hot dip galvanised and has a service life of 15 years.
Support for sustainability Greaves said customers have responded positively to DE’s HDPE developments and have been impressed with their sustainability benefits
“Our customers want to use a product made out of plastic that can be recycled, that isn t going to end up in landfill Greaves said.
“And our HDPE products are fundamentally sustainable, assisting the mining industry establish sound environmental outcomes.”
Steve Davis discusses Australia’s bulk handling sector, highlighting the advancements the industry has made and the organisations that are providing local innovations and expertise.
Steve has worked in bulk handling for 30 years, for both resource companies and professional engineering firms, in Australia, South Africa, the Middle East and Canada. His experience encompasses such commodities as iron ore, coal, potash, phosphates, petcoke, sulphur, sands andgrain.
Bulk carriers come in all shapes and sizes, so expert Steve Davis explores some of the key design considerations for shiploaders.
have many similarities to stackers, generally being conveyor fed and discharging from a boom, which may shuttle lu or slew
Although many shiploader run on parallel rails along a land backed or similar wharf structure there are other designs (quadrant loaders) that use a radial rail system and a telescopic boom to simplify the conveyor feed and the need for a solid wharf or etty Both types are selected such that
a ship can be fully loaded without being mo ed
Ship loaders must be designed to consider all ships that might be loaded ulk carrier ships do not adhere to any standards when it comes to dimensions in length, beam, and draft, but are generally classed into various groups of similar si e
Handimax is a small ship, from around 30,000DWT Panamax, Post Panamax and Cape size increase in stages to about here are
two sizes of Panama Canal locks and therefore Panamax and new anama classes here are smaller ships and special class ships for some ports e g amsarma for amsar port
There are larger Super Cape ships also up to
The number of hatches and their size also vary on similar si e ships anama for e ample often have seven hatches, however there are variations from fi e to ele en hatches on ships that are designated as Panamax in
one listing atch dimensions and co er opening are not consistent either
Some ships have on board cranes (gearing) that interfere with hatch access hese cranes are used to load and unload where there are no wharf machines he crane can be centrally mounted or o set to one side and the shiploader must be able to move along the wharf without colliding with them
Adding to this, we must consider variations in relative loading height due to tidal e ects and to changes in ballast while loading he term air draft is used to define the machine clearance required over the highest part of the de ballasted ship at the highest tide In most operations the shiploader must be able to start loading in this condition
The shiploader may have to start loading a fully ballasted ship at low tide too e certain that the design en elope includes all possibilities and even allows for some growth as ship blend can change in the life of the machine
There are many older installations where available ships have superseded the original parameters, and loading re uires special processes
Although operators may try to obtain similar ships every time, most do not own their own eet and are constrained by a ailability on the day ne further common issue relates to the ship’s captain who generally ha e the final say in how their ship is loaded his cana ect the loading se uence and ratesignificantly
The captain of a ship with seven hatches will normally require at least two part fills in each hatch and a distribution that ensures that the ship does not e ceed sag and hogg limits Final trimming will usually take place giving at least 14 shiploader movements between the loads draft sur ey may be taken before the final trim
Some captains limit load rate for arious reasons he result is that a shiploader designed for continuous
loading at perhaps 5000 tonnes per hour, may only be able to load at an aggregate rate of less than 2500 tonnes per hour here are many other ship operations and upstream feed conditions that can also reduce the efficiency of loading
Shiploaders are more constrained environmentally than stackers, as spillage into water is difficult to reco er and may have an immediate impact on sea life
Shiploader booms are often fully enclosed and have a telescopic or cascade chute at the head of the boom to limit dust emission ome shiploaders may need to add a jet slinger to throw material into the hold, or a dust e traction system his gi es a significant additional mass at the end of the boom which impacts all aspects of the structural design
Shiploaders may need to have complete spillage protection and catch trays that then require to be discharged
to an acceptable location hese dust management components cannot just be added late in the design as the extra weight and forces on the rails can lead to a complete redesign of the machine and or the wharf
Replacement of older shiploaders by machines that meet current design practice, for example AS4324, and environmental expectations, and increased throughput will usually result in a significantly hea ier machine that may require wharf and rail upgrades to support it
It is good practice to build a wharf that allows the shiploader to be maintained in a discrete bay with access platforms under the complete machine, including the boom If this facility is not available some aspects of maintenance may need to be completed from a barge, which is inherently more difficult and unsafe his maintenance bay can also become a safe tie down area for use in storm e ents
It is recommended that all wharf machines have automatic rail clamps that will hold the machine against wind Include substantial stop blocks at the end of tra el
Many yard machines are autonomous, and stack and reclaim withlittle manual inter ention Shiploaders are almost all manually controlled within the limits of the various safety systems that prevent collision and e uipment damage
Some trials have been conducted to assess automated shiploading in recent
An issue related to ship loading is that reclaim operation from storage is mostly continuous, whereas the shiploading operation is batched due to hatch change his is one of the issues that a ect the aggregate load rate
The ship’s master has absolute say on the sequence of loading a ship, and a series of hatch changes that interrupt loading It cannot be assumed that the loading sequence can be controlled to suit the materials handling system Neither should it be assumed that similar ships will have similar loading patterns e may prefer not to interrupt reclaim so it is practical to include a bu er bin in the loading stream as near as possible to the shiploader in the loadstream
When a hatch change occurs, the reclaim stream is di erted to filling the bu er bin hen loading resumes the reclaim stream feeds direct to the ship; at the same time a ‘bleed’ from the bu er bin is added such the bin empties before the ne t hatch change i ing these bins, which can be 2000t to 5000t capacity, and the bleed rate, should be done using simulation modelling to keep the bin as small as possible for costreasons, but not so small that loading is compromised
If a surge bin is used there is often an issue with what to do with any remnants left in the bin, or how to empty the bin if needed ome stockyards have a recycle conveyor system that allows material to
restacked thers ha e a simpler truck discharge system he decision should be taken based on criticality of cross contamination or likelihood of the material consolidating if left in the bin
The action of warping ships along the wharf to give access for the shiploader is time consuming and presents a significant safety ha ard
A single point ship loader or shiploader on a fi e hold ship will require at least 12 warp movements, each of which risks losing control of the ship, may require a tug present, and may extend ship operations by about six to eight hours
A decision to use this method of dealing with ships, which is generally only done to save capital cost, or for very low shiploading rates, should not be taken lightly, and is notrecommended
If this option is taken there should be safety cages on the wharf for ste edores and a defined procedure for operation ther facilities might bere uired
If a wharf shiploading facility is built that is on the limit for ships of an intermediate size, perhaps 190m-long anama the first time an o ersi e ship, perhaps a 225m-long Panamax, is chartered warping could be required to be included in the loading sequence, and this is usually a ‘surprise’ activity on a wharf that has no facilities or procedures sk if the wharf be designed with some additional space
ASIA-PACIFIC’S INTERNATIONAL MINING EXHIBITION
23-25 SEPTEMBER 2025
Adelaide Showground, South Australia
Register to attend AIMEX’s inaugural event in South Australia
Rockfield Technologies is using data-driven technologies to keep bulk handling equipment in good shape.
ockfield echnologies has grown into a multidisciplinary team of around 50 professionals that helps asset owners across Australia monitor, manage, and meaningfully e tend the lifespan of critical infrastructure.
he company is helping asset owners mo e away from reacti e maintenance and towards predicti e data backed asset strategies through ad anced sensor technology with real time analytics.
ou can t argue with data ockfield echnologies technical director of mechanical engineering Scott Anderson said. “A lot of fatigue issues in machines are in isible to the naked eye ut with strain gauges and other sensors we can monitor critical connections see trends and gi e owners the information they need to act before failure occurs
ockfield s work with balanced machines pro ides a te tbook e ample of the firm s uni ue approach hen a large rocker boom pin – a one-tonne component bearing approximately 600 tonnes of load – began causing concern,
confirmed rising friction in the bearing and impending failure.
ecause we had the data we could gi e the client si months to plan the replacement nderson said hat s critical when components that si e take months to source from o erseas e also used the sensor data to refine the replacement bearing design It was a clear case of how sensors turn unknowns into action
e re not ust collecting data we re using it to inform predicti e engineering models ockfield echnologies e ecuti e director and general manager homas Bainbridgesaid.
hat sets us apart is the blend of hands on field diagnostics and deep in house design and analysis hat means we can not only detect emerging issues but also trace their root causes and pro ide cost e ecti e solutions
uch of this is made possible through ockfield s custom designed tool ercuto which enables clients to isualisestructural health data and fatigue life through a dashboard interface
pro ides asset owners with alerts isualisations and engineering insights in real-time, facilitating faster and more accurate decision-making.
eal time operational data allows us to close the plausibility gap where engineering assumptions can now be replaced by measured reality ainbridge said. “You can model all you like, but until the asset is in ser ice you ust don t know how it s really going to beha e
ockfield s ability to fuse data ac uisition with computational simulation has helped asset owners undertake option studies to weigh capital e penditure considerations of remediation ersus full replacement In one e ample the team conducted a comprehensi e re iew of ageing assets at a silica sand mine including a shiploader and stacker reclaimer.
e worked with contractors to cost remediation options against replacement ainbridge said ltimately one machine was replaced while the other was gi en a remedial upgrade to e tend its life by another eight to years e designed the replacement o ersaw fabrication and ser ed as the
owner s engineer throughout the pro ect It s that full life cycle support that reallymatters
his full spectrum approach from inspection and monitoring through to end of life planning is helping asset owners reduce unplanned outages a oidcatastrophic failures and defer capital expenditure.
sset owners want to know can we get another fi e years out of this machine before a ma or o erhaul nderson said ith sensor data and finite element analysis we can pro ide clear answers ometimes it s as simple as saying a oid that particular process it s doing per cent of the damage e en if it s only used fi e per cent of the time
ockfield s approach helps redefine end-of-life not as an arbitrary design milestone, but as a dynamic and measurable point determined by realworld operating conditions y combining
structural and mechanical engineering insights with ad anced instrumentation the company helps clients understand the true condition of their machines
It s a bit like human health nderson said ou can t ust look at someone and know their blood pressure or cholesterol achines are the same ensors are how we get the information and engineering is how we interpret it ounded as an o shoot from ames ook ni ersity ockfield echnologies was born out of a desire to apply academic rigour to realworld engineering challenges he company continues to contribute to uni ersity programs to support the ne t generation of engineers.
mentoring student internships it s part of our any of our sta were recruited directly from James Cook and other uni ersities
oday ockfield operates across erth risbane owns ille and Melbourne, and remains deeply focused on helping clients achie e operational e cellence with a sustainable mindset
“Our purpose is to maximise asset performance for a sustainable future ainbridge said hat means helping clients get more out of e ery dollar theyspend on infrastructure while reducing consumption and en ironmentalimpact
Engineering and performance plastics specialists, E-Plas, with the assistance of Mitsubishi Chemicals Advanced Materials, collaborated on a marine retrofit project.
FROM THE BELLY OF A BULK carrier to the oor of a elbourne manufacturing facility las is pro ing how homegrown inno ation local machining capabilities and hands on problem sol ing can deli er e ceptional results for comple large scale ship loading applications hen las team was approached to assist with a ma or marine materials handling pro ect the scope was far from simple he task re uired replacing wear liners aboard an older ship not a straightforward retrofit but a highly technical made to measure installation performed in a confined and unpredictable en ironment
It wasn t a brand new ship with clean surfaces ready for liners e had to remo e the e isting liners prep the old surfaces measure the chutes oursel es and determine hole positions and sheet si es on the y here was no room for error las national operations manager upin oshi said
Precision materials
he installation called for high precision wear lining using materials sourced from itsubishi hemicals d anced aterials specifically I and I
It simply wouldn t ha e been possible without s e pertise oshi said hey pro ided the support and the know how that helped us impro ise in real time measure e erything on site and machine and install the components with accuracy he first few days were the hardest but once our teams got into a rhythm we were able to e ecute the pro ectsmoothly nlike land based con eying systems where gapping between liner sheets is often acceptable shipboard applications
demand a much more robust and tailored approach he ow of bulk materials inside a ship is immense and sub ect to far more intense wear and tear
In ship applications if material gets behind the liner it can pull it out completely which defeats the purpose of installing it in the first place oshi said hat s why we used an o erlapping installation method and connecting hedge bars designed by his approach eliminated the need for welding and significantly impro ed performance
Leveraging local manufacturing
las didn t ust apply imported solutions its local manufacturing facility in a enhall ictoria played a critical role in the pro ect s success hough the ship lining task was distinct from the con eyor and machine components the company typically machines the e ibility of las in house setup pro ed indispensable e ha e engineers e pert in plastics manufacturing our machines include outers athe illing achine and pindle oulder so when customers come to us with drawings our
engineering team can immediately begin planning and machining oshi said nlike o erseas suppliers who will only produce tens of thousands of standard parts we o er e ibility If you can draw it and it fits within material boundaries we can machine it
his e ibility is especially ital in applications like marine loading where conditions are rarely ideal oshi e plained that almost e ery section of the ship re uired its own measurements and a bespoke lining solution ery single sheet had to be cut to a di erent si e ou couldn t take a measurement from one spot and reuse it elsewhere he said e had four teams out there each with a super isor who could measure and cut accurately bout per cent of the ob was impro ised on site only per cent was knownbeforehand
Smart material selection
nother uni ue challenge in ol ed material selection ecause the lining is e posed not only to wear but also
to en ironmental conditions such as ultra iolet radiation the selected material needed to be stabilised while o ering superior ow characteristics to ensure rapid material discharge
eople assume wear resistance is the main factor but owability is ust as important his is where I e cels It is also a weldable liner pro iding additional ad antages he faster the product can be unloaded the sooner the ship can be refilled oshi said ur collaboration with our material supplier helped us select a product that balanced wear and ow and that made a big di erence
e ecting on the broader importance of las ustralian manufacturing capability oshi was uick to highlight both customer satisfaction and national economic benefit
eing ustralian made is a huge part of what we do he said here s a big di erence between waiting to weeks for parts from o erseas
and being able to produce something locallywithin a week or a few depending on comple ity
Speed and responsiveness
ocal production also allows las to bemore responsi e and adaptable to client needs
e e had clients using the same design for years suddenly re uest a small tweak maybe a new radius on a wear strip and we can turn that around uickly oshi said ry asking an o erseas factory for that kind of change and it s not going to happen oshi who has been with las for o er a decade has witnessed first hand the growth of the company s localcapabilities
here s been a big e olution in how much we can do locally he said It s not ust about machining more parts it s about o ering smarter faster more e ible solutions that are made right here in ustralia
Aurecon is working closely with its port clients to get the most out of their shiploader assets.
SHIPLOADERS IN THE MINING industry are responsible for moving millions of dollars of material everyhour.
As a result, their reliability is key. If something goes wrong, the lost productivity quickly stacks up.
Unfortunately, the conditions at a port are ruthless to machinery. Shiploaders sit out over the water and are subjected to salt water, strong winds and driving rains, not to mention the commodities they handle can also accelerate corrosion.
Aurecon resources industry director Michael Argent said that many of these critical machines are also reaching their end of life.
“Australia’s resources sector is getting to the point where a lot of the assets and equipment it uses to operate are reaching an age where they need to be replaced,” he told ABHR
“Shiploaders are critical machines, because they need to be utilised almost 90 per cent of the time, 24/7, 365 days per year.
here are a lot of trade o s that need to be made when deciding to replace a machine: not only access to capital but also the impact of the ageing machine on both the productivity and risk of the operation. And this includes the shortterm production impacts associated with alternatives such as refurbishment.”
During the resources boom around 20 years ago, there was a huge demand for iron ore and coal – cornerstones of Australia’s economy.
Argent said that at the time, it was all about how fast a mining company could get tonnes into the market. Cost was a lesser concern, because the returns were so high due to the global demand.
Decades later, the dynamic has shifted. The voracious hunger for steel
has softened and new competition for iron ore has begun to emerge. Major mining companies like BHP and Rio Tinto are also starting to prioritise investment in critical minerals of the future, like copper, lithium and potash.
rgent said there is a finite amount of capital that can be spent, which has led the industry to find ways of impro ing the productivity of existing assets to remain globally competitive.
“That balance between capital and productivity is really delicate,” he said. “Overlaid on top of this is the fact that capital is needed to replace ageing equipment without the promise of new returns on that capital.”
“The industry is looking for the most capitally efficient way to replace or refurbish these assets, whilst still meeting production targets.
urecon s point of di erence in this space is that we don’t want to sell our
clients a new machine. We want to show up and really understand in a deep way the problems and challenges our clients are facing to find the right solution
Aurecon, as a design, engineering, and advisory company, helps clients with integrated solutions across the entire asset lifecycle.
The company has almost a century of history in this space, designing highly complex and integrated machine, wharf and port systems for industries across theglobe.
As part of its process, it helps clients “shape” their investment decisions by looking at an asset’s performance, understanding the intricacies of the operations, and how the extraneous elements of the value chain integrate into the process.
The company has heavily invested in industrial mathematics including simulation, machine learning and artificial intelligence to help optimise its solutions to align with the strategic objectives of its clients.
Argent said the Aurecon team thrives in situations where they can work out how to sol e a problem with a finite amount of capital.
“Where we love to operate is at the very beginning, where a client is just starting to consider the right project to pursue,” he said.
“Our experience and ‘design to innovate’ methodology helps us home in on the client’s problem and keep that front and centre.”
Aurecon aims to take a holistic view of the challenges facing its clients. In many cases, several problems they may be facing could be caused by one issue, or could all be addressed at the same time.
Argent said that often a collection of problems will collide, especially when it comes to a port.
“With the majority of Australia’s bulk export facilities located in tropical environments, long-term resilience to extreme conditions such as tropical cyclones is vital for business continuity. With many of these facilities being close to 50 years old, the challenges are not isolated to the condition and resilience of the supporting wharf infrastructure to these extreme events, but also the lessening availability and
reliability of the shiploaders as they age,” he said.
“It’s our role to bring these problems together in an integrated way, so that we can arrive at a solution that is better optimised than addressing each problem individually. Wharves and shiploaders operate as integrated systems. Innovations in the design of a replacement machine (with even marginally higher cost for the machine itself) can enable an order of magnitude reduction in costs to preserve the underlying wharf.”
Replacing an ageing shiploader is a significant undertaking where e ery hour counts. Availability is critical, because every hour a shiploader isn’t running is costing the business dearly. Planning is imperative. The decision to take a shiploader down for a period is not taken lightly. It requires mitigation tactics that o set the impact of the shutdown and these can be difficult to alter at short notice. So, the certainty of delivery outcome – both quality and timeliness are critical.
The design requirements have shifted as a result. Argent said ports are looking for “plug and play” equipment that is completely constructed and tested o site integrated into the asset quickly and start working reliably as soon as possible.
To deliver on this, Aurecon has changed how it designs these machines. Its engineers work with the client and constructor to ensure that everything is designed for fast, highly sequenced and precise fabrication – to the extent that the designs leverage automation to produce unprecedented levels of definition where e ery aspect of the machine is defined down to the ery smallest services pipelines.
Argent said the other factor for shiploaders is that they often operate as a eet across se eral berths herefore the best decisions are made when the system is managed as a whole, rather than a singular approach that considers each machine individually.
“When you’re getting to the point where your business may su er because of lessening machine performance, the first step can be to replace one of the machines to be the backbone of the operation” he said.
“Technology has moved forward a lot over the past 50 years, so that machine can perform much better than the original. This can enable a staged approach to capital allocation to the remaining machines without impacting overall production.”
“Aurecon helps our clients strike the right balance between cost, productivity, and risk, giving them the tools to make
Martin Engineering has introduced a heavy-duty air cannon mounting system to improve safety, lower operational costs and keep walkways clear.
AIR CANNONS ARE ONE OF THE most e ecti e ways to clear clogs and material that has adhered to silowalls
Instead of beating essel walls with hammers e posing workers to e treme heat or entering dangerous confined spaces air cannons do the ob safely andremotely
air system deli ers a powerful shot triggered from a solenoid bo ointed in the direction the material ows the high elocity air passes through a no le
across essel surfaces to dislodge adhered material and clogs promoting efficient throughput with minimal downtime artin ngineering product manager id e said air cannons can be precariously placed around preheaters hoppers and drop chutes making them hard to get around or reach by
ir cannons are commonly secured to a no le assembly ne t to the essel wire tether ensures the tank doesn t fall should it suddenly detach from the assembly his positioning can make access a challenge particularly when the units are set close to a hot wall like a preheater or kiln
formulate a more practical and long term
he positioning also becomes an issue when air cannons ut into narrow walkways or workers must step o er tubing to access maintenance areas incetrips and falls commonly top the list of workplace in uries proper headspace and unobstructed walkways help sta mo e through the area easily particularly important when carrying large or unwieldy e uipment or replacement parts he artin tand is an organisation system that safely keeps air cannons away from super heated or potentially ha ardous areas while o ering easy ser ice access he tand is a rugged steel cube frame that comes in three si es to fit l l and l air cannon tanks ach cube has a sturdy crossbar frame designed to distribute weight and absorb ibration from the cannon s firing he central top hole allows easy access to the al e and attachments while the bottom hole accommodates a standard cm kg bolt ange to hold the cannon securely in place he open sides allow easy access to the ange hose connection and tank remo al olenoid bo es that enable manual firingand control the firing se uence can be con eniently mounted on the side oftherack
he tand is specially designed to fit di erent spaces and stack in se eral configurations for optimum space sa ing safer access and ease ofmaintenance he air cannons are stillsecured with a tether for added safety tands are deli ered in assembled blocks with all the bolts and nuts re uired to secure them using standard tools
Installing an tand system allows air cannons to be placed in the optimum position and pro ides the opportunity to rearrange tubing leading to no les It also allows e uipment to be mo ed away from areas of e treme heat hrough testing we e found that there is negligible air blast power loss by e tending the distance a few feet and only about per cent power is lost with each elbow in the pipe e said ith strategic placement the tand will deli er safety results that ustify any increase in the number of shots per se uence
ome air cannon installations re uire mesh tubing to properly accommodate the tank s position and handle ibration from firing lthough commonly made with metal strands the mesh tubing is considered a wear part that needs changing after long term e posure to the punishing production en ironment heated walls and constant ibration he tand promotes the use of hard pipes with a longer e uipment life and less maintenance for added safety and a lower cost of operation
X-amples from the fieldCement
cement plant operator sought to mo e cannons farther away from the super heated kiln wall he tand construction mo ed the pipes o erhead attached to pipe assemblies with hermo afety hields he increased distance from the wall allowed for regular maintenance in a comfortable en ironment
lthough no le replacement re uired workers to wear heat suits the ob could be done without downtime he process was made faster and safer by merely closing the shield guard to pre ent blowback remo ing the ange in the ipe and uickly replacing the no le a fi e to minute operation depending onpositioning
Molten ash
o mitigate molten ash buildup that limited production along a superheated wall in a steel mill four air cannons were placed to dislodge material and a oid downtime o precisely place the air cannon shot the tanks obstructed the
inspection doors pre enting them from opening fully
o ing the tanks to stacked tands a few feet away from the hot wall reduced the heat e posure for maintenance crews and reduced the time and e ecti eness ofinspections
ne bulk material operation had a hopper silo raised o the ground to load transport ehicles passing beneath easonal changes would raise moisture le els that cause clogging in the downspout grated walkway around the essel was partially obstructed by uttingair cannons ather than the standard configuration with the cannons on their sides and al es facing outward installers set up the tand with the al es facing upward oles were cut in
the oor grating and the pipes were run under the walkway toward the no le assemblies his ensured the tanks were organised and the walkway was clear while optimising production
fter testing participating operators said they liked the more organised approach in helping to keep congested operational areas as clear as possible hey were impressed with the cleaner look and the inno ati e solutions to pipe placement articipants in field tests recognised no substantial change in performance from the original configuration artin is always listening to customers for ideas to impro e safety and efficiency e said he tandis a result of that and is the ne t step to a clean safe and efficient bulk handlingoperation
Kinder is helping eliminate dust and spillage across Australia with a combination of its conveyor solutions.
CONVEYORS CAN BE USED TO handle a staggering number of materials, from sand to sulphur, and sugar. But even with such a broad range of materials, environments, and e uipment similarissuesa ect them all.
Kinder Australia business development manager Bart Fox said the company’s engineers have decades of experience working with bulk handling sites and have seen the same problems crop up.
“Most sites have the same problems, but not all sites have the samesolutions. For example, a hard rock quarry and a grain silo might both have spillage issues but solving thatisgoingtore uire a di erent approachentirely.
“The main issues are always going to be dust control, spillage control, belt hygiene, and belt life,” he said.
“There’s rarely a cookie-cutter approach. Our teams look to deal with the sitetofindtherootcauseoftheproblems andfindoutwhatthebestdesignisto prevent the problem from happening.”
Fugitive dust poses serious risks. It can harm nearby workers and the environment, and it can create unnecessary risks – especially if the dust is explosive. Spillage also creates plenty of headaches. Material can get caught in machinery, leading to more maintenance woes, or it can pile up and create tripping hazards around heavy machinery.
Cleaning up these messes is a Sisyphean task, with workers needing to spend their valuable labour on cleaning.
“There’s never enough time to do something properly, but there’s always time to do it twice,” Fox said, referencing a common saying in the industry.
“That’s being challenged – more sites wanttogetthingsrightthefirsttimeso they can focus on further productivity.”
“We’re also seeing more sites seeing the value in Kinder’s solutions, which provide value by eliminating these problems entirely.”
One solution that has proven to be e ecti eateliminatingdustandspillage is Kinder’s Essential AIR Seal Dust Containment Combination.
Suited for some of the harshest mining industries, the system combines several key components that work in tandem to contain dust and spillage.
Key to the system is the AirScrape, a highlye ecti econtact freecon eyor skirting and sealing system. Designed with a unique diagonal arrangement of hardened lamellae, air is led from the outside into the middle of the belt, creating powerful air suction.
The material movement together with the moving belt increases the suction e ectenablingfinedustparticlesto remain in the conveyor section.
Because the skirting and sealing system hovers freely above the conveyor belt, skirt friction and belt damage can be eliminated, and the service life of other conveyor components can also beextended.
Additionally, the AirScrape fully integrates with the TailScrape, which provides sealing at the rear area.
The TailScrape blade structure on theunderside ensures a negative pressure environment within the conveying area. The negative pressure created prevents dust and other material spillage from escaping through the millimetre-thick gap.
The K-Containment Seal enhances the success of the outer seal by reducing the
high internal pressure experienced inside the chute and protects the vulnerable chute edges from damage.
It is also an engineered polyurethane system whicho erse ceptional resistance to wear. The slotted arrangement allows for installation adjustment to ensure that material and finescannotbetrappedandsoreducing the risk of premature belt damage.
Fox said it’s not enough to just have a good skirting system – a conveyor needstherightbeltsupportande ecti e primary containment so that the skirting system can do its job properly.
“If the belt isn’t supported properly, it can sag between rollers and create fugitive dust,” he said.
“If the load zone lacks adequate primary containment, it doesn’t matter how good the soft skirt is. It will wear prematurelyandceasetobee ecti e
“Both are needed to ensure minimal wear and to protect a site from dust and fines
That’s where the K-Shield Dynamax Combi Impact Bed comes in. It features a tapered skirt support zone and independent dynamic suspension, which allows each twin centre impact roller to move independently of the other impact rollers. The static slider rails also provide optimal belt support at critical transfer points.
The Combi Impact bed also incorporates a roller bush. The polyurethane bushes help to absorb impact and prevent damage to the steel roller support frame and roller shafts themselves, increasing the life of these parts or components.
To make sure the system will work for the application, Kinder supplies comprehensive drawings. Its engineering department can also assist with the endto-end design and supply process.
Fox said the system has proven to be a hit with bulk handling sites across the country, as clients are able to improve the availability of machinery and manpower.
“Kinder is going through a growth periodatthemoment e resignificantly expanding and have plenty of proven technologies with good data behind them,” he said.
ursalessta areoncallasneeded too, which is one thing that keeps our customers coming back. They get a much more personalised approach and ongoing technical support.”
Organisations throughout the industry are gearing up for Asia-Pacific’s International Mining Exhibition in Adelaide this September.
Mining Exhibition’s (AIMEX) new home in Adelaide is attracting key exhibitors who are eager to engage with mining professionals from across the region.
For global, high-tech engineering group Sandvik, AIMEX presents a great opportunity to showcase its latest o erings in sustainability digital transformation and energy efficiency for the mining and mineral processingsector.
Sandvik’s global head of marketing for the company’s screening solutions di ision eter ewfield said I s relocation to South Australia makes the event far more relevant to his division’s business, particularly as the region is becoming a central hub for critical minerals such as copper.
“South Australia is very important to the Australian mining industry and is rapidly emerging as a key source for the world’s growing need for copper,” ewfield said ith its mo e to rime Creative Media and Adelaide, AIMEX has come back onto our radar after manyyears.”
ewfield said and ik has been encouraged by the momentum behind the reimagined event, noting key industry players such as BHP and Magnetite Mines have signed on as exhibitors, and peak industry bodies Austmine and AMEC have showntheirsupport.
“The fact that this year’s Australian Mining’s Prospect Awards will take place on day two of AIMEX is the cherry on top ewfield said e are proud to be sponsoring the Indigenous and Community Engagement award once again, a category which we have supported for several years.”
The mining industry remains one of the most energy-intensive sectors globally, consuming an estimated six to seven per cent of the world’s total energy.
ewfield told ABHR that almost half of this energy is consumed in the comminution process – crushing, screening, feeding and milling. About 40 per cent of the mining industry’s total energy consumption can be attributed to the grinding process.
“Crushing is up to 10 times more energy efficient than con entional grinding. By crushing more and pro iding a finer feed to the milling circuit significant efficiency gains can be made in the overall comminution process,”hesaid.
The Sandvik 800i cone crusher series integrated with the new ACS-c 5 automation system, combine robust mechanical design with powerful, user-friendly automation, supporting diverse operational needs. These machines can be tuned to output a very fine product which can significantly reduce the load on the downstream grinding process.
ewfield said that leading gold producer Gold Fields was able to take advantage of this in its new crushing and screening plant at the Agnew gold mine in estern ustralia
“According to Gold Fields senior management the finer feed from their new crushing and screening circuit has improved downstream mill performance, increasing the maximum throughput rate from 155 to 170 tph,” he said.
The company conducted a comminution crushing and grinding survey, which indicates that the new circuit is around 18 per cent more energy efficient than the pre ious one
AIMEX will also provide Sandvik with the opportunity to spotlight its latest digital o erings eading the showcaseis eck app ear pp a cloud-based software platform designed to revolutionise screen deck maintenance.“This highly innovative solution is set to transform how maintenance is planned and executed,dramatically improving
the efficiency and operational performance of mineralprocessing plants.”
Also on display will be ACS-s, Sandvik’s nextgeneration condition monitoring system, designed tooperate 24/7, the platform provides early detection of anomalies before they resultin major failures, giving site personnel the chance to act early and minimise costly unplanned downtime.
“Errors in maintenance and operations can lead to component damage. ACS-s is designed to alert plantpersonnel to small problems before they can become big ones ewfield said his is critical to ma imising plant uptime safety andefficiency hese technologies re ect and ik s broader ambition to support decarbonisation e orts within the industry. By combining mechanical reliability with digital intelligence, Sandvik’s solutions help mining operations transition towards moresustainable and efficient mineral processingmethods.
“At Sandvik, we leverage digitalisation as a cornerstone of ourinno ation ewfield said “Notonly is our latest equipment easyto operate, manage and service, but it alsocontributes to our industry’sneedtoreduce its environmentalimpact.”
ith I now committed to outh ustralia for the next decade, Sandvik is optimistic about forging deeper relationships within the region and e panding its presence in the sia acificmarket
“Having AIMEX in South Australia allows the mining industry to e perienceour leading o erings right onits doorstep ewfield said
This year’s Sandvik stand at AIMEXpromises to be a highlight, featuring notonly live demonstrationsof its digitalplatforms, but also a full-sized mining screen to give visitors an up-closelook at the engineering behindits highthroughput equipment.
e re e cited to showcase our e tensi e range of crushers alongside our mining screens and feeders, capable of handling up to 8000 tonnes per hour ewfield said ur e perts will be on handto discuss how our solutions can help drive process efficiency plant uptime and safety fter a period away from the I show oor Sandvik’s return to the event signals the company’s confidence in rime reati e to deli er a high quality forum for customer engagement, industry collaboration, and the pursuit of technology-driven sustainability outcomes.
“AIMEX is shaping up to be a great event,” ewfield said e look forward to meeting with ourfriends in the miningindustry and congratulating the finalists and winners of this year’s Prospect Awards.”
Many conveyor belt load zones experience impact damage from large lump sizes and long drop heights at velocity. This results in punctures, damage to idlers and structure, and decreased material containment.
ESS GAB Impact Cradles are custom designed and manufactured to suit your specific conveyor application and plant operation requirements to prevent damage to conveyor components and reduce fugitive material escaping the conveyor system.
•Polyethylene Surface: Minimises friction to improve belt performance.
•Rubber Body: Absorbs impact to protect belts and structure.
•Stable Bases: Ensure effective sealing to prevent spillage.
•Trac-Mounted Components: Slide in and out for easy inspection and servicing.
•Material Options: Available in Mild Steel or Stainless Steel.
INSTALLATION & OPERATIONAL BENEFITS
•Reduces manual handling during installation and maintenance.
•Eliminates conveyor belt sag between idlers.
•Minimises material spillage and leakage.
•Reduces downtime for servicing and inspections.
•Prevents material rebound and associated cleanup.
•Protects the conveyor belt, structure, and idlers from impact damage.
•Reduces belt drag, improving energy efficiency.
Scan the
Dr Priscilla Freire, mechanical engineer, and Dr Bin Chen, technical director at TUNRA Bulk Solids, discuss the importance of materials testing in critical minerals projects.
WITH THEIR IMPORTANCE FOR the global energy transition, critical minerals have seen a growing gain in popularity over the past couple of years ith significant in estment from local and federal governments, Australia is leading the way not only in the exploration and production of critical minerals but also in providing consultancy for overseas miners.
As with every other type of bulk material, understanding the handleability of critical minerals is of utmost importance to ensure reliable operations.
TUNRA Bulk Solids has seen an increase in projects involving not only critical minerals but also the so-called ‘strategic materials’ such as aluminium, copper, phosphorous and zinc.
Critical minerals and strategicmaterials
According to the Department of Industry, Science and Resources, critical minerals are the minerals essential to modern technologies, economies and national security for which Australia has a geological potential for resources, in demand from strategic international partners and vulnerable to supply
chain disruptions. On the other hand, strategic materials are important for the global transition to net zero and broader specific applications for which Australia has geological potential for resources and in demand from strategic international partners, but their supply chain are not currently vulnerable enough to meet the criteria for the critical minerals list. Thisnaturally means the list is somewhat uid and is bound to change according to supply and demand.
Knowledge transfer from ‘traditional’ commodities to criticalminerals
In a recent article published by AusIMM, specialists from Sedgman discussed the question “Can existing expertise be leveraged to support critical minerals processing in Australia?”. Discussion points include the fact that Australia has historically placed significant focus on the ‘direct shipping ore’ (DSO) model for bulk exports, with in-country processing predominantly focussed on primary concentration (coal, base metals, bauxite) and gold. With the increase in demand for critical minerals combined with the fact that ustralia holds significant reserves of critical minerals and strategic materials, incentives have recently been put in place to encourage downstream processing opportunities aimed at adding value to these resources, especially those related to electronics, renewable energy and electric vehicles.
According to the authors, the Australian mining and minerals processing industry possesses several of the skills and technical expertise and is well-placed to succeed in this space when it comes to mineral processing.
Similarly, Australia is a worldwide reference in the discipline of bulk materials handling in comparison to
other prominent mining countries, and now it is time to leverage this extensive experience in more ‘traditional’ commodities to also grow capability in the critical minerals and strategic materials sector. Understanding the challenges posed by these commodities plays a key role in maintaining Australia’s technical leadership.
Recent projects have involved, in some cases, rather comprehensive scopes with ow properties testing at their core others were focused on specific challenges anticipated by the clients including dust issues or excessive moisture, potentially leading to concerns in transportation. Outside the testing space, TUNRA has also assisted clients with engineering and design aspects, including design review of existing handling equipment to ensure their adequacy when applied to ‘new’ materials. The experience gained in these projects has contributed to the development of TUNRA’s team in gaining a deeper understanding of the challenges posed by these materials.
TUNRA’s lab experts recently tested a sample of vanadium oxide, a material that plays a critical role in industrial applications and is growing in popularity in the energy transition due to its application in anadium ow batteries for energy storage. The material was tested at dry condition at the request of the client, and measurements taken with a direct shear tester resulted in low bulk strength and moderate friction against the liners tested. However, when looking at all the ow property results in conjunction, the conclusion
was that in order to promote mass ow in bins designed for this material under the tested conditions, very steep wall angles would be required, which would potentially make the design impractical to achieve the storage capacity. One potential solution is to adopt an expanded ow mode though this approach would need to account for structural constraints – particularly the limited head height of the building housing the silo lternati ely a planar ow hopper would require a less steep hopper angle. TUNRA’s client, an Australian design house, is now investigating the use of bin inserts that would transform the conical ow profile into pseudo planar ow and hence reducing the space requirements.
Materials requiring testing are not only being produced in Australia but also in other major mining countries.
A recent overseas project involved the testing of rare earths from a development that has been regarded in the industry as having a uniquely high reward from a metallurgical perspective given its high-quality material and relatively simple owsheet to e tract alue nce the materials handling testwork started, however, TUNRA’s experts soon noticed that the materials handling part of the process was proving to be much
more complex and has the potential to introduce bottlenecks to the production.
Testing at the moisture of content of interest resulted in very steep ow functions with e tremely high strength for low consolidation under instantaneous conditions, yielding critical opening dimensions larger than eight metres, which are naturally not practical for design.
he ow function is a measure of the material’s internal strength as a function of the consolidation pressure applied to it, and interpretation of the material strength coupled with wall friction measurements against the liner of interest result in the determination of the critical opening dimension for bins to prevent cohesive arching for given wall inclination angles and to promote mass ow It is noteworthy that for the design of storage systems the ow functions under time consolidation should be used instead of the instantaneous condition, and, for highly adhesive materials such as this one, the material under consolidation is likely to exhibit even higher strength. lso important to note is that the ow functions are specific to the e act sample tested, under the conditions tested (i.e. moisture content, consolidation pressures, particle size distribution) and may vary greatly for materials of the
same type In other words a di erent Rare Earth Elements ROM Ore might beha e ery di erently from the e ample described herein.
Another recent project involved testing of Lithium Carbonate originated in South America. Flow properties testing resulted in some challenging handling conditions due to the ery fine nature of the filter cake coupled with high moisture content. Moderate to large critical arching dimensions were calculated to overcome cohesi e arching during mass ow discharge. With respect to hopper half angle, for this material, only a limited design window exists in which true mass ow may be de eloped which is hea ily dependent upon the type of finish of the liners tested.
nother challenge with fine concentrates being produced for export is the potential risk for liquefaction. Concentrates such as copper and nickel are known to have caused serious accidents in seaborne transport over the years, leading to the development of standards and testing methods to determine the transportable moisture limit (TML) of bulk cargoes. The TML is the moisture considered the limit for safe shipping, and the International Maritime Solid Bulk Cargoes
I clearly identifies which bulk materials are susceptible to liquefaction and must therefore be shipped with a certificate
According to the Bulk Carrier Casualty Report 2013-2022, while safety has overall improved in comparison to the pre ious decade significant loss of li es was still experienced associated with cargo liquefaction. The report also lists the most recent major loss of life incident associated with liquefaction: in 2019, the Nur Allya ship (Indonesia) sank near Buru Island, causing the death of all 27 crew onboard. The vessel was carrying a cargo of nickel ore. In addition to this accident, another three ships also carrying nickel ore were also a ected as well as a bauxite ship.
TUNRA regularly contributes to the testing of several materials for shipping purposes including bauxite/alumina, concentrates (copper, zinc, magnetite) and coal. However, some new operations involving critical minerals are also using TML testing as an indication of material stability and behaviour with changes in moisture for purposes other than shipping. Recent projects have involved lithium tailings from a few di erent producers to aid in the investigation of dry stacking operations or to investigate potential for liquefaction in truck transport. Although not the intended use of the standardised TML testing methods, modified ersions or customised test rigs are sometimes applied to these projects with the aim of replicating, as
close as feasible, the vibration conditions experienced during truck or train transport which provide some insight into the possibility of transporting such materials via the intended means.
On the opposite side of the moisture spectrum, materials being handled at very low moistures are sometimes at risk of dust issues. Conducting a Dust Extinction Moisture (DEM) test is often the starting point in understanding the material’s propensity to dustiness, and, depending on the application, the dust lift o potential can also be assessed using a wind tunnel. A recent project involved a series of wind tunnel tests to evaluate the dustiness potential of a sand material composed of Delithiated Beta Spodumene (DBS), a by-product of the lithium production chain, mixed with sand for use in road construction. The aim was to investigate the dustiness potential of this material when stockpiled under di erent compaction conditions moistures and how e ecti e would the use of an inorganic surface spray could be to reduce the dust potential.
Projects involving critical minerals have expanded beyond materials testing. Working with renowned engineering houses in Australia and overseas, TUNRA has also contributed to the design of materials handling facilities for these materials. One of such projects involved testing and Discrete Element Method (DEM) calibration and simulations for a
client who was re-purposing a transfer chute originally designed to handle iron ore which was now being assessed to handle spodumene. TUNRA had done a third party design erification for the transfer when handling iron ore and then was approached by the engineering company working on this project to also test the spodumene and conduct a designcheck to assess whether the existing geometry would be appropriate for a material with ery di erent handling characteristics. The analysis involved verifying the geometry for blockages, material build-up and residual material after ow impact and abrasi e wear on ceramic liner and central loading onto the belt.
Other engineering projects in the lithium chain comprised a design review of an existing acid roast feed bin to assess its suitability to handle two types of spodumene fter conducting ow properties testing on both bulk materials, TUNRA’s experts analysed the geometry of the existing bin, as provided by the client, and concluded that the bin’s opening was larger than the determined critical opening dimension, such that cohesive arching was not expected to form. However, testing on the existing wall liner material produced steeper angles than those of the bin’s current hopper suggesting that mass ow was unlikely in the gi en configuration Evaluating alternative liners revealed potential solutions to reduce wall frictionand achie e mass ow without modifying the hopper geometry. Considerations were also made with regard to using a uidiser to enhance ow inside the bin
Working with our clients in the critical minerals space has allowed TUNRA experts to gain insight into some of the handling challenges that might be present in the production chain. As with traditional bulk commodities, a deep understanding of the material ow properties and the complex interactions between the bulk material, moisture and the surfaces it interacts with is key for the design of efficient storage and handling facilities as well as to define transportation and disposal options.
The most prestigious awards for the Australian mining and
THE ICONIC ADELAIDE OVAL WEDNESDAY, 24 SEPTEMBER
ABHR speaks to Jason Hogue, principal engineer at HMA Group and member of the ASBSH.
I have been a member of ASBSH for… around 17 years.
I am a member of ASBSH because… I am interested in learning about new developments within the bulk materials handling industry. In my role, I am always looking for new products or designs that can complement my designs.
I got into bulk handling because... It was just an opportunity that came up at a time when I was not happy in my current role. The previous companies that I worked for had nothing to do with bulk handling but I was once asked in an interview “Given your prior experience has nothing to do with our products, how do you think you will go?” to which I replied “My skill is problem solving, once I know the first principles I can apply engineering knowledge to find and develop appropriate solutions. That is what engineering is, solving problems”. This is something that has stuck with me for many years and something I see in a lot of new engineers today. So long as you have the drive, willingness to learn and the ability to break down a problem into manageable pieces, a solution will present itself.
customers and suppliers and getting hands on with our equipment. A design on the computer is great but the real knowledge comes from getting out into the industry. Implementing the design, talking to operators about how the equipment works and what could be done better, discussing with fabricators about how to improve the design to suit fabrication and keeping up to date with current product trends really
In my role it’s important to...
Never assume that what has been done before is correct or the best option. Constantly monitor the quality of our products and ensure the most efficient designs are being undertaken from an operation, cost and project timeline perspective. Always keep up to date with current standards and legislation. Always read and understand the projects requirements. If something is unclear, clarify anddocument.
My career highlight is...
Reaching the level of knowledge of our industry and its products, although this is constantly growing as I continue to research and develop new products and new techniques
The ASBSH’s mission is to enhance the discipline of bulk solids handling through research, education and sound engineering practice. It aims to promote cooperation between universities, research establishments, consultants, equipment manufacturers and suppliers, and industrial users.
The Society also aims to encourage research and development, technology transfer and training. It holds national and international conferences at regular intervals.
I am currently researching… Safety in design and developing engineering document management processes to complement our business.
I love my current work because... every project is a challenge. Customer requirements are never the same and we are also constantly searching for ways to improve our designs in all aspects, safety, operation, fabrication, and installation.
My current work encompasses all facets of the project, management, sales, design, commissioning and troubleshooting. So, while I am managing our day-to-day activities, I am also designing, liaising with
The most valuable lesson I have learned is…
To communicate. Ask questions, don’t assume you know everything. Talk to people who can support you.
My plans for the future are… to continue in my current role for the foreseeable future. There is still so much I want to implement and achieve. Long term, consult and offload all the information and lessons learnt that are in my head to those who are coming behind me in the industry.
When I am not working you will probably find me...
In my shed working on my many sideprojects.