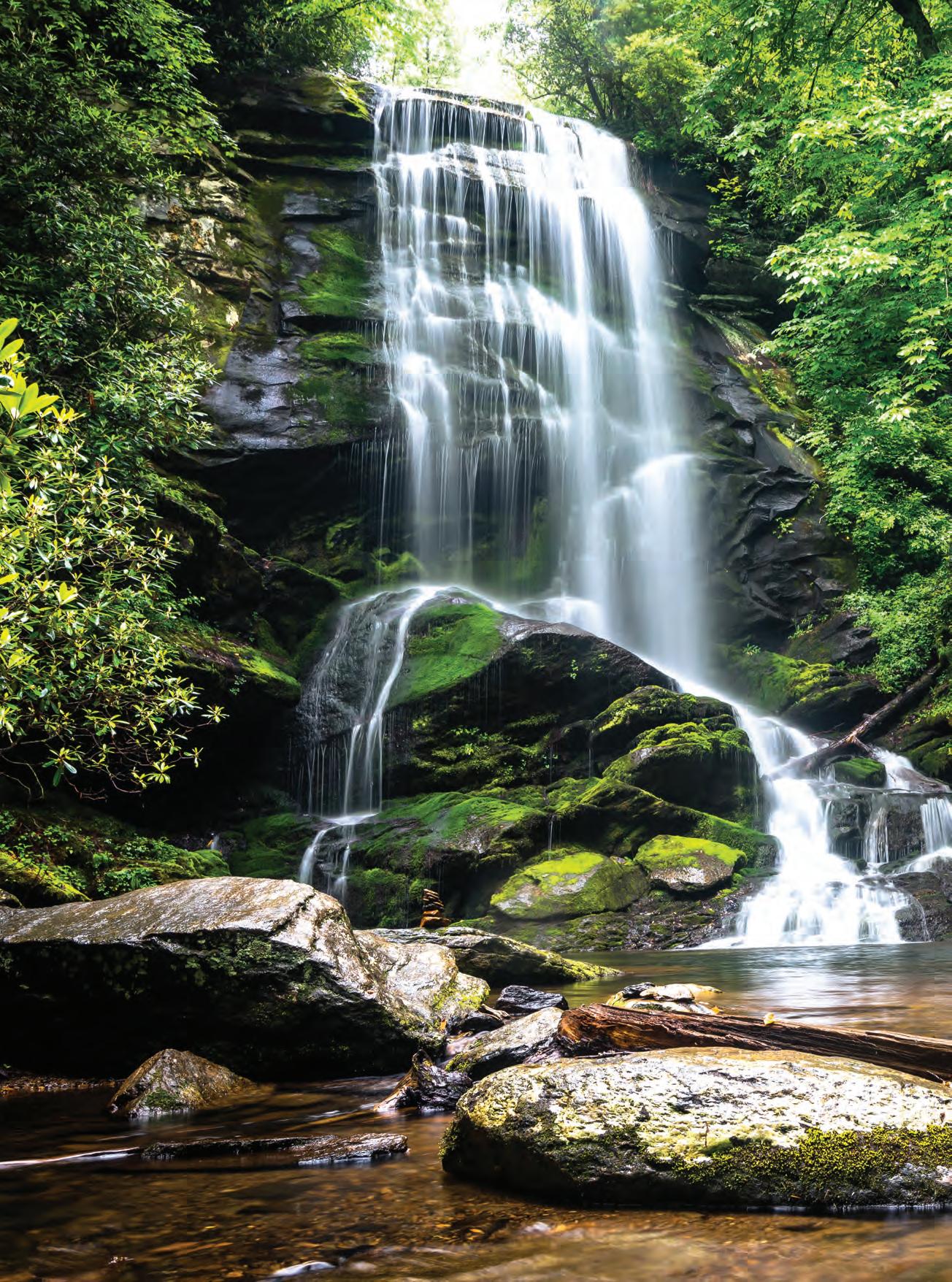
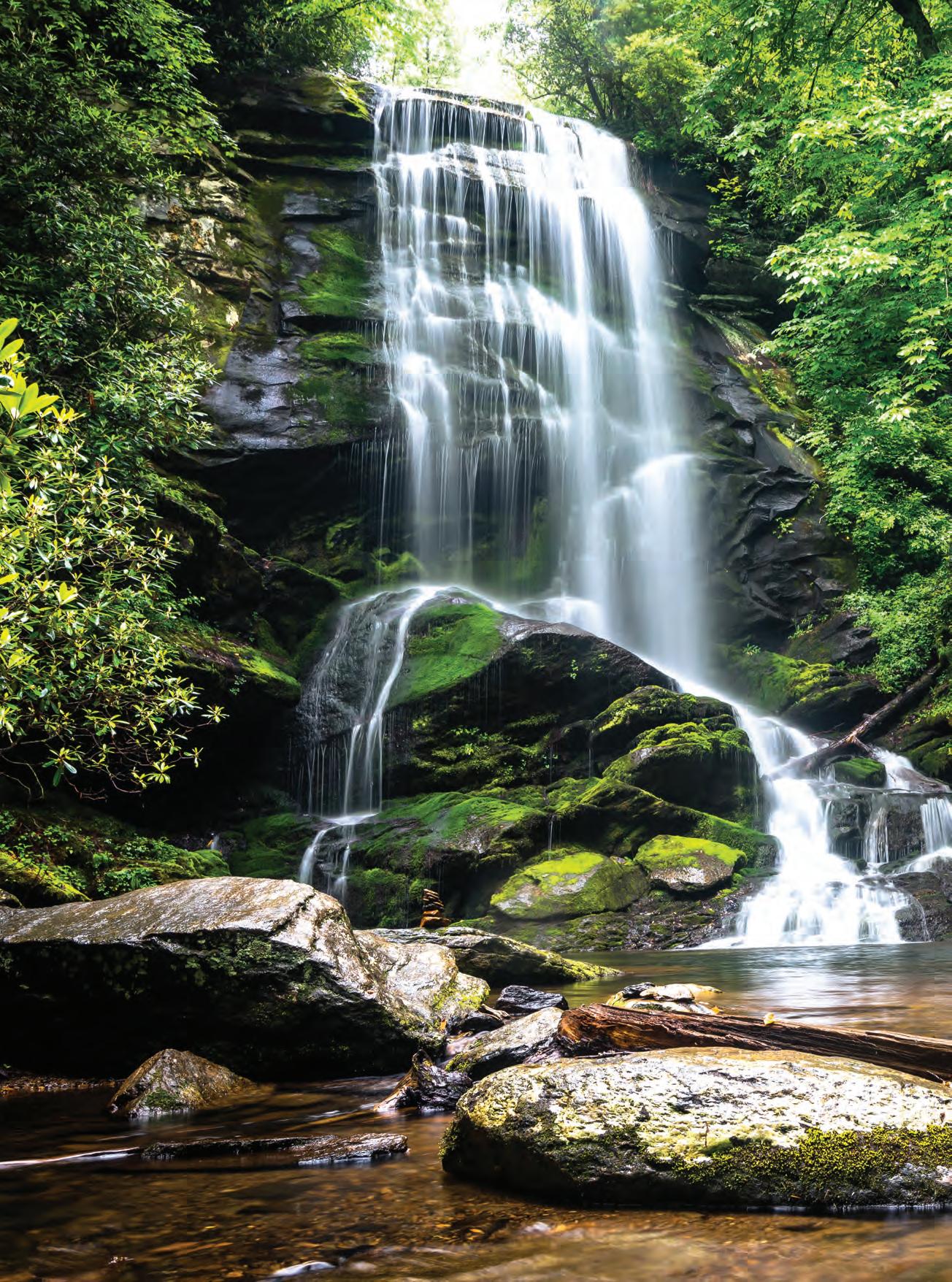
RELIABILITY A reputation built on
New partnerships have been the culmination of hard work for this local road construction business
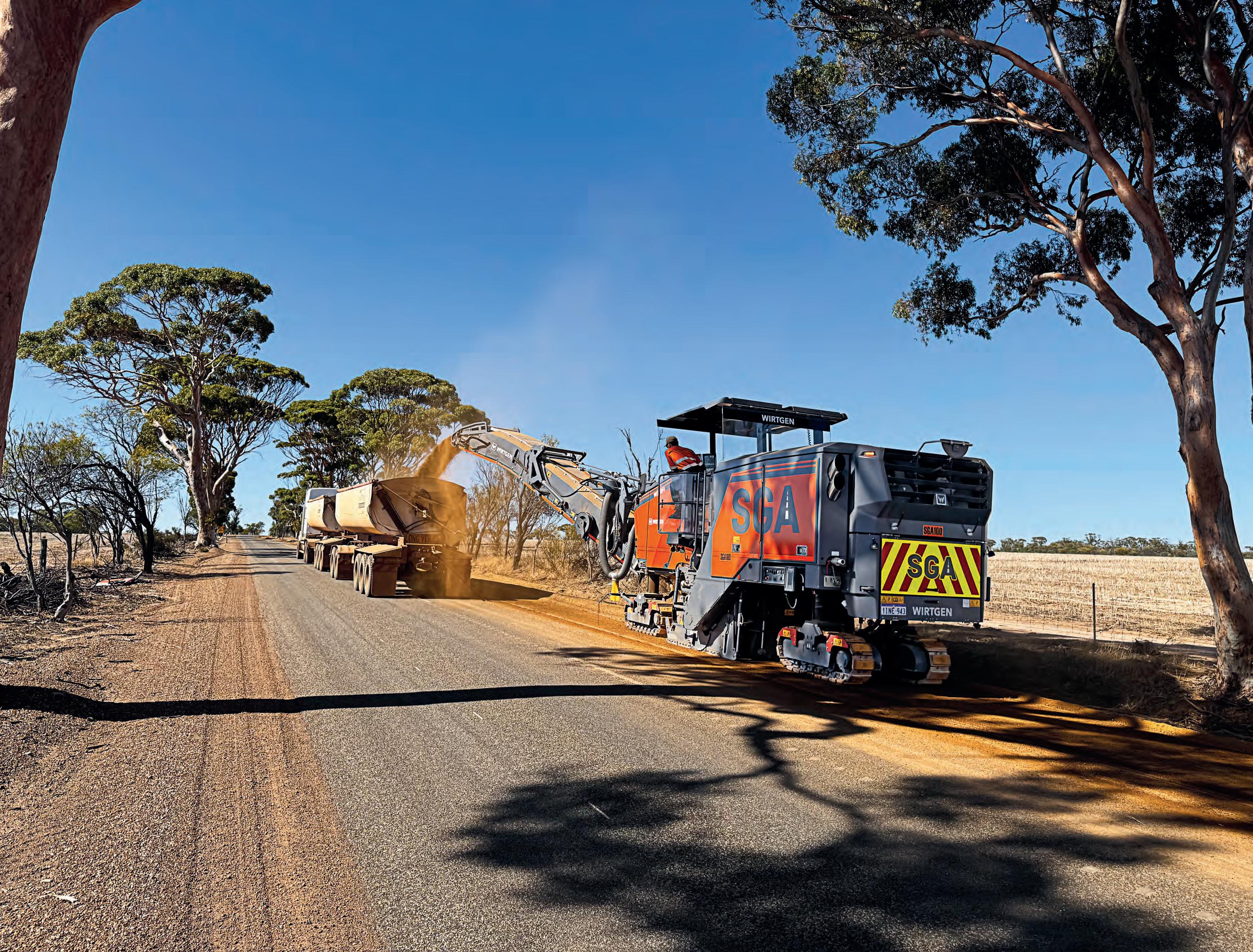
Empowering the next generation
‘A Day in Her Boots’ is giving young female and non-binary students hands on experience in construction
3D for safety
Latest trials have evaluated the use of unprecedented three-dimensional road markings
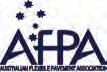
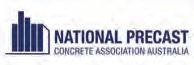
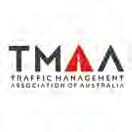
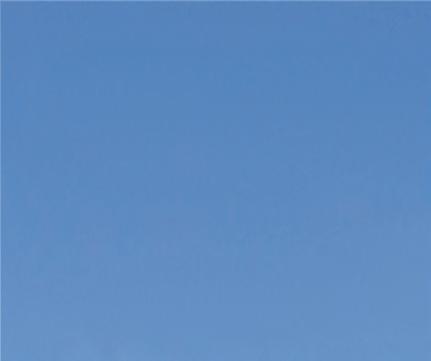
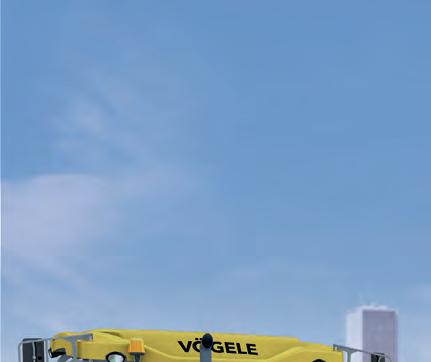
The Most Innovative Paver Technology!
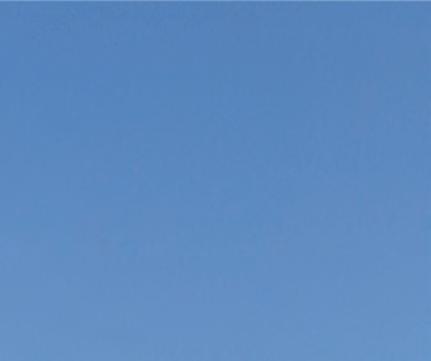
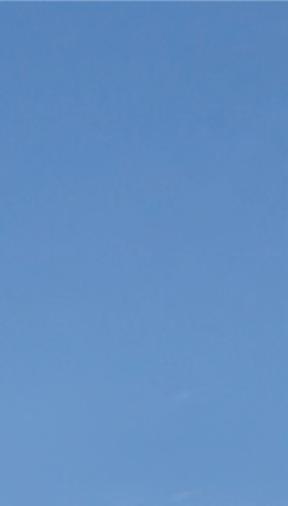
VÖGELE SUPER 1700-3(i) / SUPER 1703-3(i)
VÖGELE SUPER 2000-3(i) / SUPER 2003-3(i)

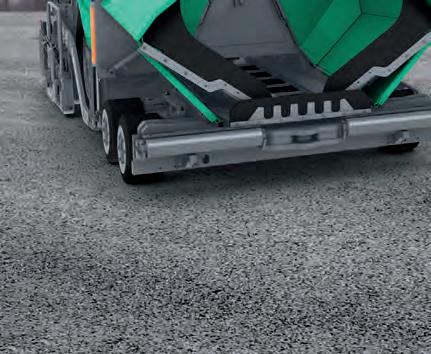



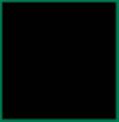



The number one paver manufacturer on the global market
Equipped with state-of-the-art Cummins engines available in either Tier 3 or Tier 4 Final / Euro Stage V emission standards, are the perfect choice for any application in the Universal (2.5m) and Highway (3.0m) paver classes. Thanks to the easy-tounderstand ErgoPlus 3 operating system which is common across all VÖGELE products both paver and screed operators can handle all VÖGELE pavers simply and safely. These machines are also available with vibrating screeds or high compaction tamping & vibrating screeds for those critical jobs. In combination with advanced optional features, such as VÖGELE EcoPlus, AutoSet Plus and Navitronic Plus 3D, these models are the stars of any road construction site.
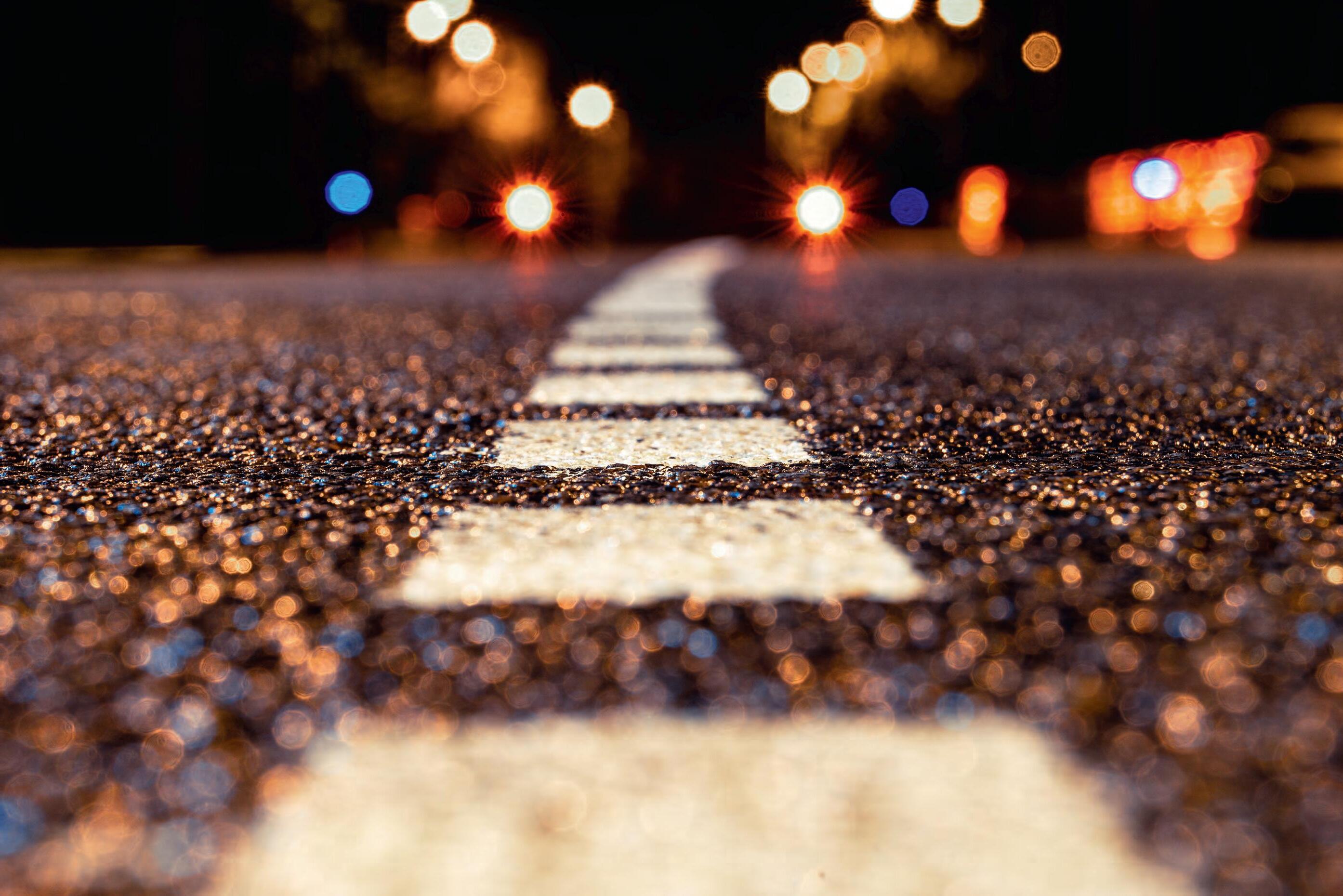
Diversity and community is a primary focus for the sector, as well as this edition of Roads & Infrastructure magazine
COVER STORY
14 A reputation built on reliability SGA Roads’ fleet of Wirtgen machinery continues to grow, a testament to the ingenuity of the manufacturer’s machinery, as well as the long-standing and ever-growing partnership between the two companies.
ROADS REVIEW
17 This month, we asked the industry’s decision-makers, ‘What can we do better to improve both road and onsite safety?’
DIVERSITY
18 Empowering the next generation Delivering on its commitment to increase opportunities for female and non-binary individuals in the construction sector, Fulton Hogan has again held its ‘A Day in Her Boots’ event.
PEOPLE ON THE MOVE
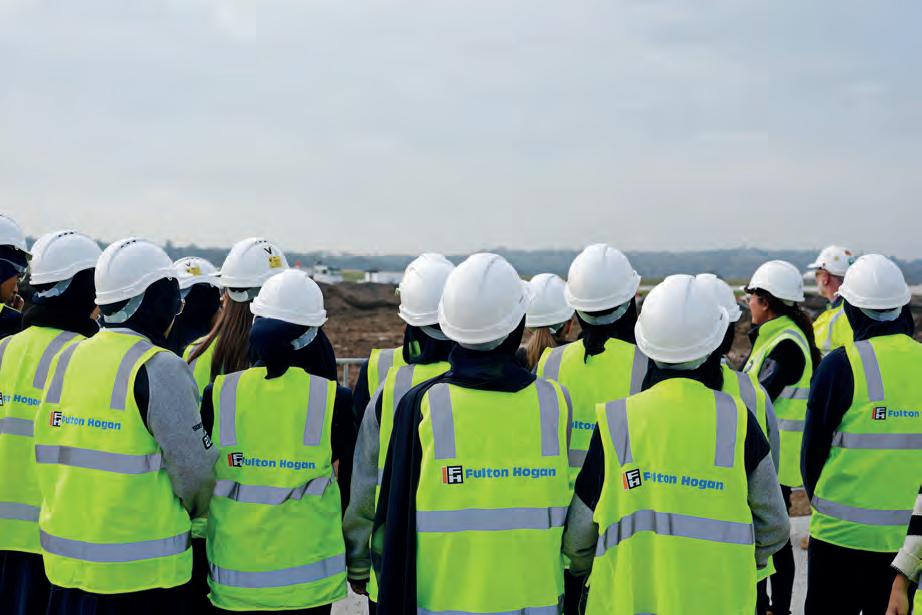
33 Machinery for a new age Komatsu’s ‘Boots On’ event has peeled back the curtain on the equipment manufacturer’s upcoming slate of innovative equipment releases.
36 Equipped for defence
21 Roads & Infrastructure helps you keep up with the latest movements across the roads and infrastructure sectors.
PROJECT REPORT
22 Answering the call Kennards Hire’s works on the West Gate Tunnel Project in Melbourne have exemplified its capability and capacity to cater for major infrastructure projects.
MACHINERY AND EQUIPMENT
24 Joining the Astec family
HT Road Surfacing, a proud family and local company, has purchased its first Astec unit.
27 One-stop-shop Caterpillar’s entire paving range has been designed and curated for Australian applications, offering a variety of solutions to fit every project type, scale and environment.
30 The first step
A handover event has cemented a first in what’s expected to be a long stretch of milestones for both ANA Asphalt and sprayer manufacturer Specialised Roading Equipment.
145 machines and 850 parts later, JCB CEA has completed a contract for the Australian Defence Force (ADF).
39 Grading done right Bell Equipment, in partnership with Hitachi Construction Machinery, will soon introduce the Bell G140 antler controlled motor grader.
42 Recognising remarkability
John Deere is set to sponsor the Awesome Women in Construction (AWIC) Awards, celebrating the achievements of women working across all sectors of the construction industry.
INDUSTRY INSIGHT
44 Road safety goes 3D
A brand-new method for road safety is being trialled in South Australia. Adelaide University’s Dr Mario Mongiardini explains how three-dimensional line markings could help curb the road toll.
ASSOCIATION SECTION
46 Ellenbrook Wildlife bridge: Engineering with nature in mind
The Ellenbrook Wildlife Bridge in Western Australia represents a milestone in ecologically conscious infrastructure.
48 More action
The Australian Flexible Pavement Association writes on the importance of tackling road maintenance challenges throughout regional Australia.
51 Is sustainability in pavement recycling still just a buzzword?
The stabilisation industry asks tough questions as it looks toward a more actiondriven future.
53 Mental health message central to Municipal Works Australia Forum Municipal workers and contractors from across southern Tasmania gathered at Kingston Twin Ovals for a powerful Mental Health Awareness Forum.
EVENTS
54 Converge Expo: Solution specialists front and centre
Survey Management Solutions will be showcasing its service offerings and technologybased innovations at Converge 2025.
56 Underground infrastructure solutions shaping future cities
Underground infrastructure solutions are reducing disruption and delivering better outcomes for communities and councils alike.
CONTRACTS AND TENDERS
58 Roads & Infrastructure provides an update on some of the contracts and tenders recently awarded or put to market across the Australian infrastructure sector.
Images: Fulton Hogan
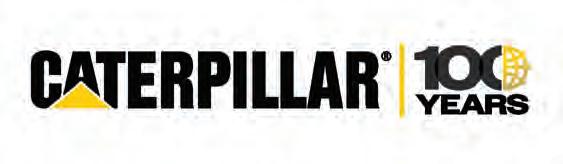
QUALITY COMPACTION TRUSTED RESULTS
CAT® SOIL COMPACTORS
Every Cat® soil compactor is engineered with durability and reliability at its core. And with built-in real-time compaction measurement technology, Cat soil compactors allow you to track compaction so you reach target density quickly, without guesswork.
Plus, when you purchase a new Cat soil compactor you’ll enjoy access to locally supported parts via the national dealer network as well as a comprehensive warranty package. Better still, there’s the option of a Cat Customer Value Agreement (CVA), designed to help you lower the cost of owning your Cat machine and maximise your investment.
To find out more contact your local Cat dealer or visit cat.com
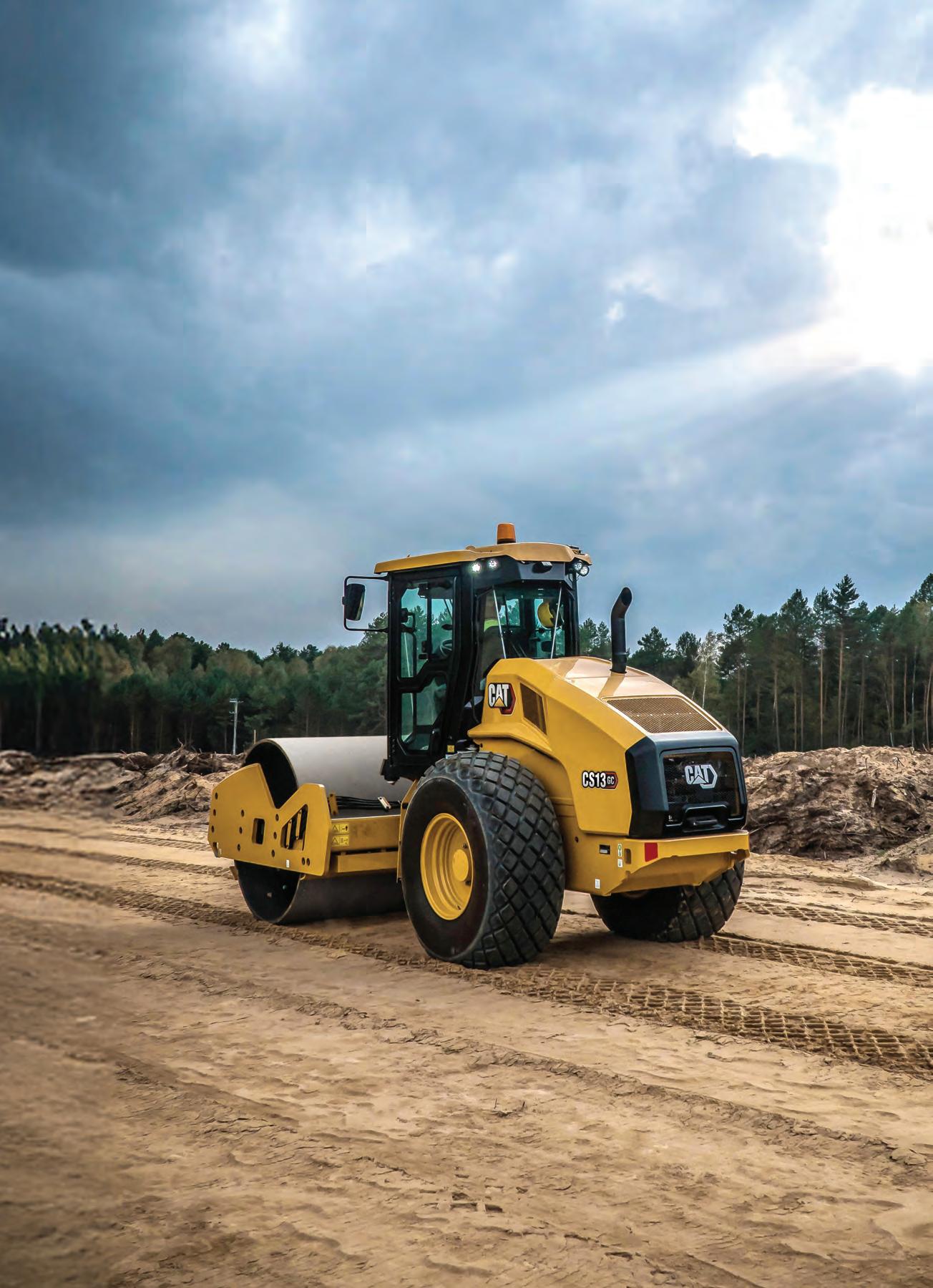
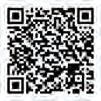
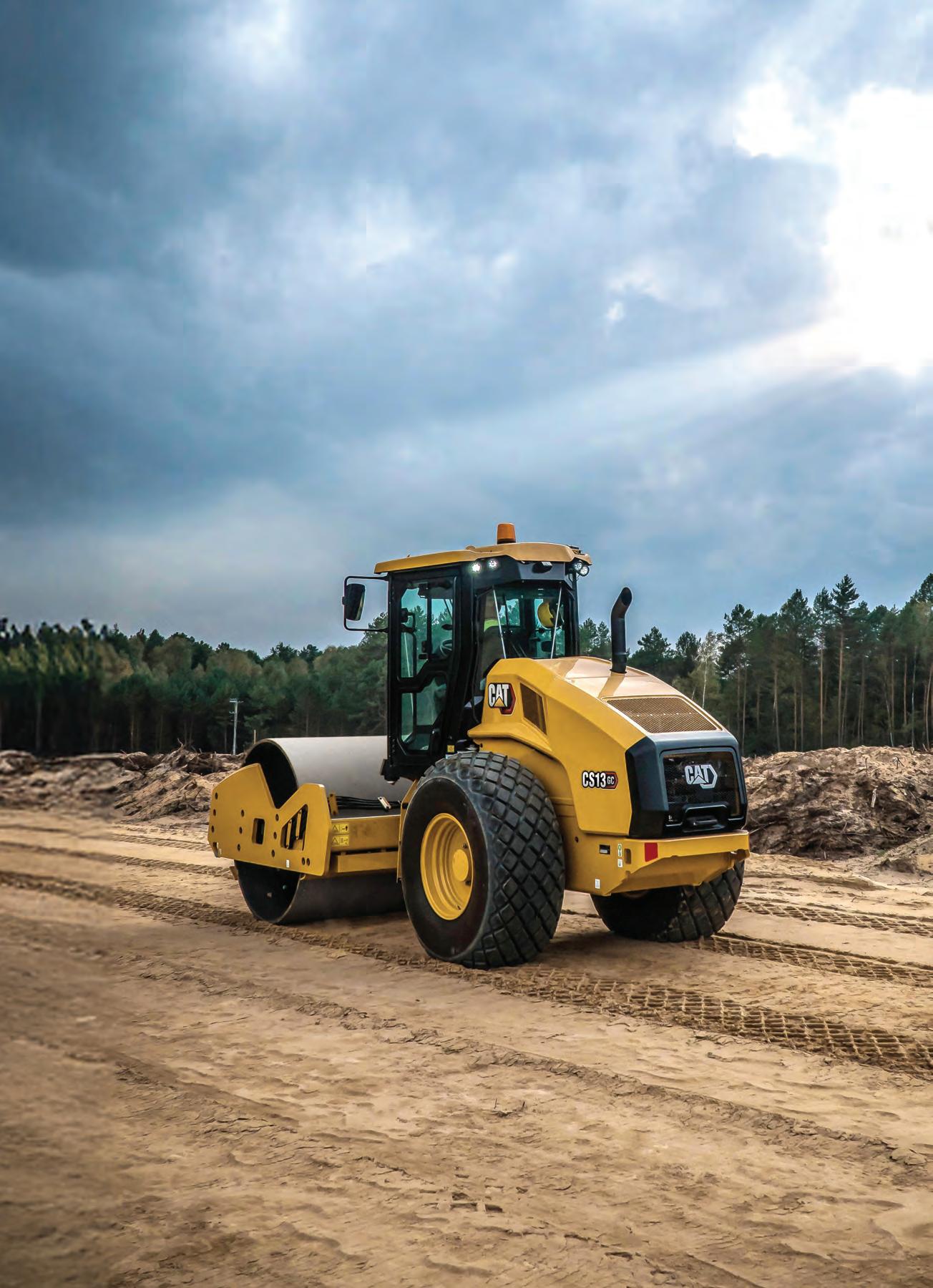
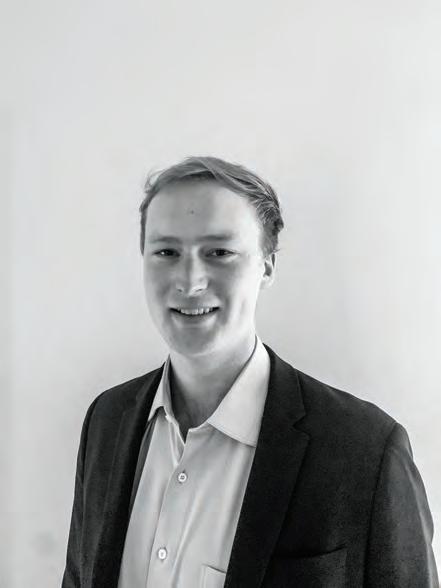
SUPPORT LOCAL, SUPPORT INDUSTRY
WITH ALL 2025-26 STATE AND TERRITORY BUDGETS now handed down, the infrastructure sector has a firm view on future opportunities and the health of the sector overall. It’s great to see additional spending allocated to essential works, in particular local projects.
Incidentally, community and local business emerged as hot topics during the drafting of this edition, which I believe firmly reflects the industry’s heightened recognition and acknowledgement of the local operators and businesses that form the bedrock of the sector.
It’s organisations like this that benefit the most when local projects reward local contractors and suppliers, a notion that must endure for the sustained success of Australia’s transport and infrastructure sectors.
For the cover story in this edition, we spotlight SGA Roads, a new customer of the Wirtgen Group. Through hard work, word of mouth and high-quality project outcomes, SGA Roads has grown exponentially over the past few years to become a preferred provider for medium-to-large-sized projects in Western Australia. Jason Hind, Owner and Operations Manager, touches on why the company went with Wirtgen machinery, as well as how the partnership between the two companies is providing benefits across both organisations.
Another local contractor that’s taken a big leap is HT Road Surfacing, a company that since its foundation three years ago has grown by leaps and bounds. In what is a major milestone, HT Road Surfacing has acquired its first Roadtec paver from Astec. The professional relationship between Astec and HT Road Surfacing has flourished, with a real family feel holding the long-term prosperity of such a partnership in great stead.
Also in this edition, we sit down with Fulton Hogan to learn more about the organisation’s ‘A Day in Her Boots’ event, which aims to provide clearer pathways for younger female and non-binary students, by giving them hands-on experience and education. Through this program, Fulton Hogan is hoping to inspire the next generation of diverse leaders to consider a future career in construction, therefore, helping to break down barriers and challenge the status-quo of what is still unfortunately a male dominated industry. One of the founders and developers of the program takes us behind the scenes of this year’s success.
With road safety an ever-present issue, we also ask key decision makers in the industry what more can be done to increase road and construction site safety.
Keep an eye out for this and so much more, in this edition of Roads & Infrastructure magazine. Happy reading!
Tom O’Keane
COO
Christine Clancy christine.clancy@primecreative.com.au
PUBLISHER
Sarah Baker sarah.baker@primecreative.com.au
MANAGING EDITOR
Lisa Korycki lisa.korycki@primecreative.com.au
EDITOR
Tom O’Keane tom.okeane@primecreative.com.au
JOURNALIST
Jennifer Pittorino jennifer.pittorino@primecreative.com.au
HEAD OF DESIGN
Blake Storey
ART DIRECTOR Bea Barthelson
BUSINESS DEVELOPMENT MANAGER
Courtney Burton courtney.burton@primecreative.com.au
CLIENT SUCCESS MANAGER
Sabrina Zor sabrina.zor@primecreative.com.au
HEAD OFFICE
Prime Creative Pty Ltd
379 Docklands Drive, Docklands VIC 3008 Australia p: +61 3 9690 8766 enquiries@primecreative.com.au www.roadsonline.com.au
SUBSCRIPTIONS
+61 3 9690 8766 subscriptions@primecreative.com.au
Roads & Infrastructure Australia is available by subscription from the publisher. The rights of refusal are reserved by the publisher.
ARTICLES
All articles submitted for publication become the property of the publisher. The Editor reserves the right to adjust any article to conform with the magazine format.
COVER IMAGE SGA Roads
COPYRIGHT
Roads & Infrastructure Australia is owned and published by Prime Creative Media. All material in Roads & Infrastructure Australia is copyright and no part may be reproduced or copied in any form or by any means (graphic, electronic or mechanical including information and retrieval systems) without the written permission of the publisher. The Editor welcomes contributions but reserves the right to accept or reject any material. While every effort has been made to ensure the accuracy of information, Prime Creative Media will not accept responsibility for errors or omissions or for any consequences arising from reliance on information published. The opinions expressed in Roads & Infrastructure Australia are not necessarily the opinions of, or endorsed by the publisher unless otherwise stated.
TOM O’KEANE – EDITOR
Billions of Australian dollars have been allocated to hundreds of roads and infrastructure projects across three state budgets. Image: stock.adobe.com/torjrtrx
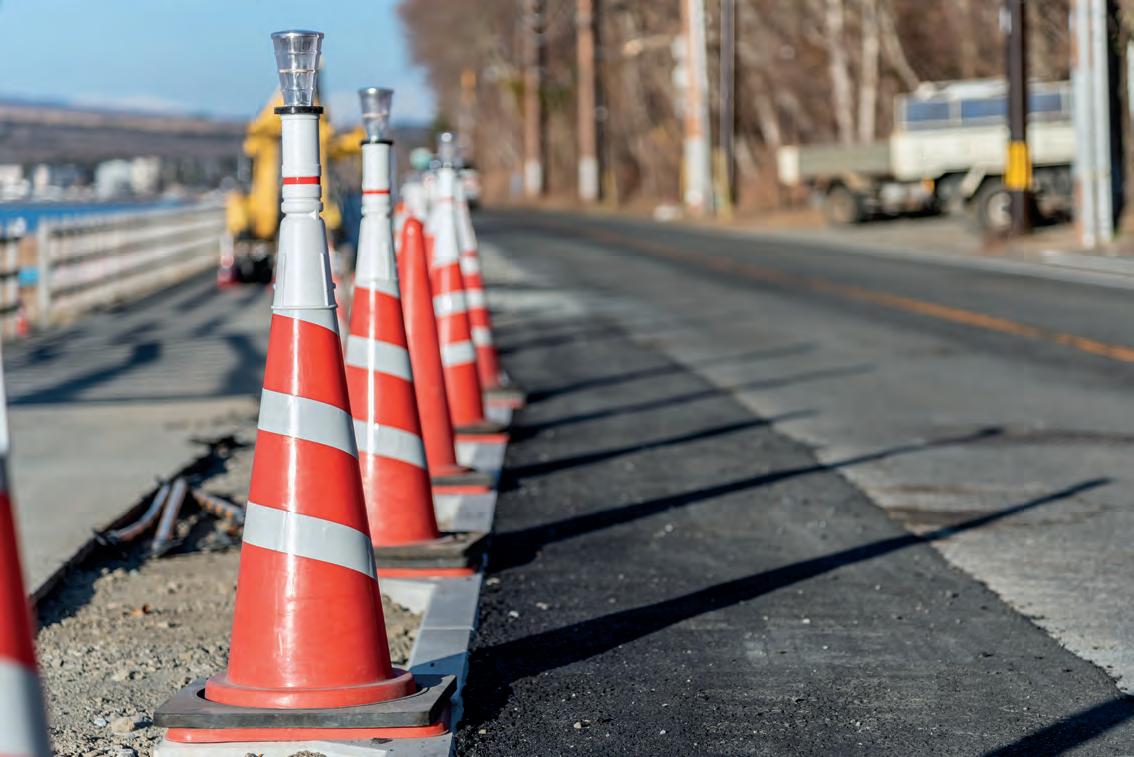
STATE BUDGET BREAKDOWN
Three state budgets have been handed down in the past month. Roads and Infrastructure magazine discusses what these mean for the Roads and Infrastructure sectors.
VICTORIA
The Victorian Budget outlined $15.9 billion in infrastructure funding by 2027-28.
Regional drivers will benefit from $976 million in total investment in 2025-26, which will support the delivery of the State Government’s ‘Better Roads Blitz’ program to fix potholes and resurface roads across Victoria.
The Metro Tunnel project has received $727 million to switch on and run services, with an additional $46 million helping to deliver additional services on the Sandringham, Craigieburn, Upfield and Werribee lines, while another $52 million will go to supporting regional train services.
Just over $4 billion has been committed
to rebuilding Sunshine Station into a ‘transport superhub’, one of the first milestones required for the delivery of the Melbourne Airport Rail.
TASMANIA
The Tasmanian Government allocated $399.7 million in funding for roads and bridges for the financial year.
Road safety projects will make up $30.5 million, $14.3 million of which has been allocated for the Federal Government’s ‘Safer Local Roads Program’ to address current and emerging priorities in road infrastructure needs.
The new Bridgewater Bridge has been allocated $76.2 million, while $75 million has been allocated for the construction of the Northern Access Road.
The Tasmanian Government has allocated $51 million for roads and rail funding as well as $14.6 million for road corridors, $23 million for roads of strategic importance, and $114.8 million for infrastructure maintenance.
SOUTH AUSTRALIA
The South Australian Government allocated $27.3 billion in funding over four years for priority infrastructure projects, with a number to be delivered in partnership with the Federal Government.
The Budget provides a boost for the $15.4 billion North-South Corridor as well as the $3.2 billion new Women’s and Children’s Hospital.
The South Australian Government will contribute $125 million to the High Productivity Vehicle Network Stage One as well as $125 million to the Curtis Road Level Crossing Removal.
The Main South Road upgrade between Myponga and Yankalilla will benefit from $40 million from the South Australian Government as well as $350 million for the South Eastern Freeway Upgrade, $330 million for the Eyre Peninsula Desalination Plant, $185.9 million for the New Technical Colleges and $133.8 million for the new Ambulance Headquarters.


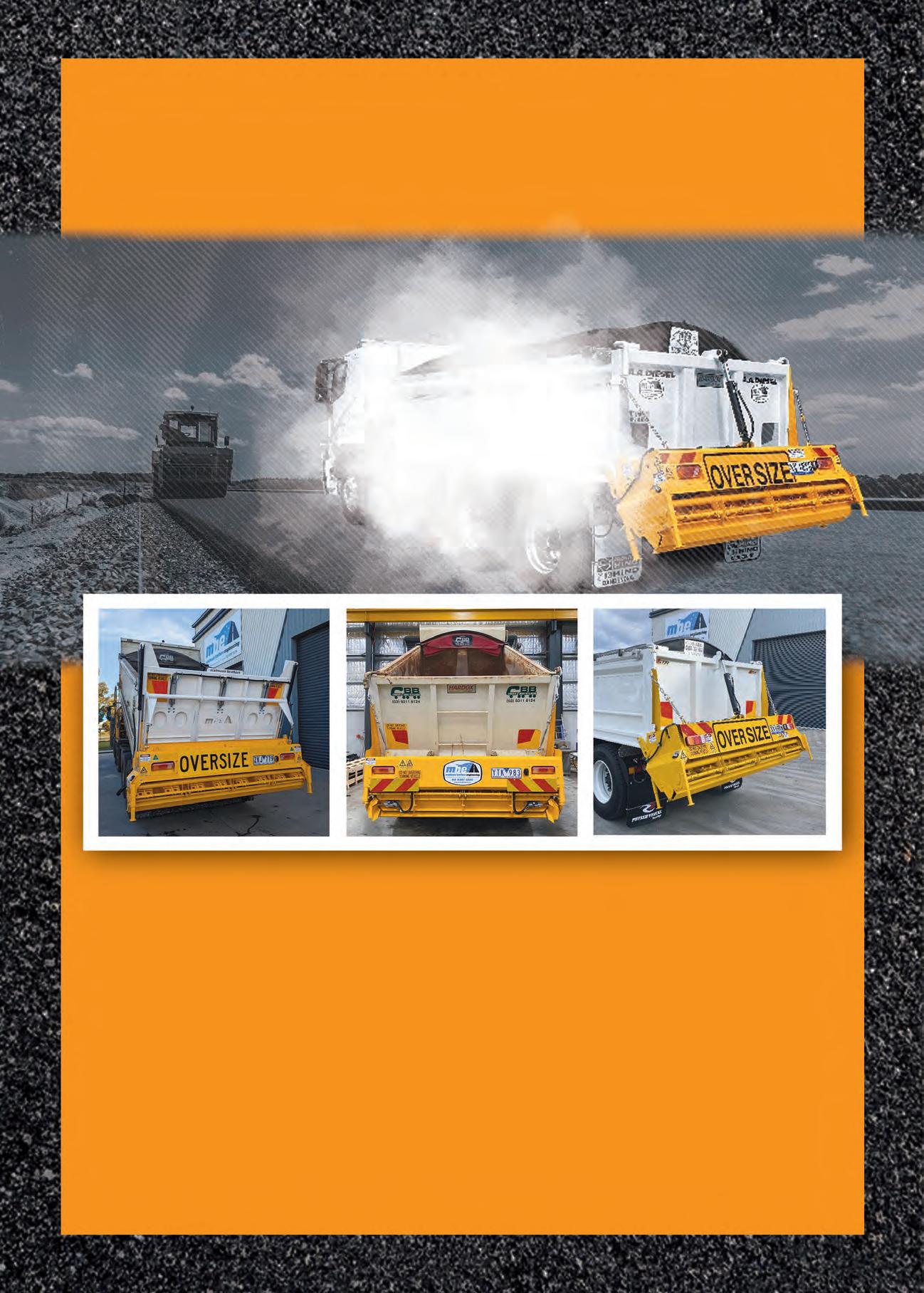
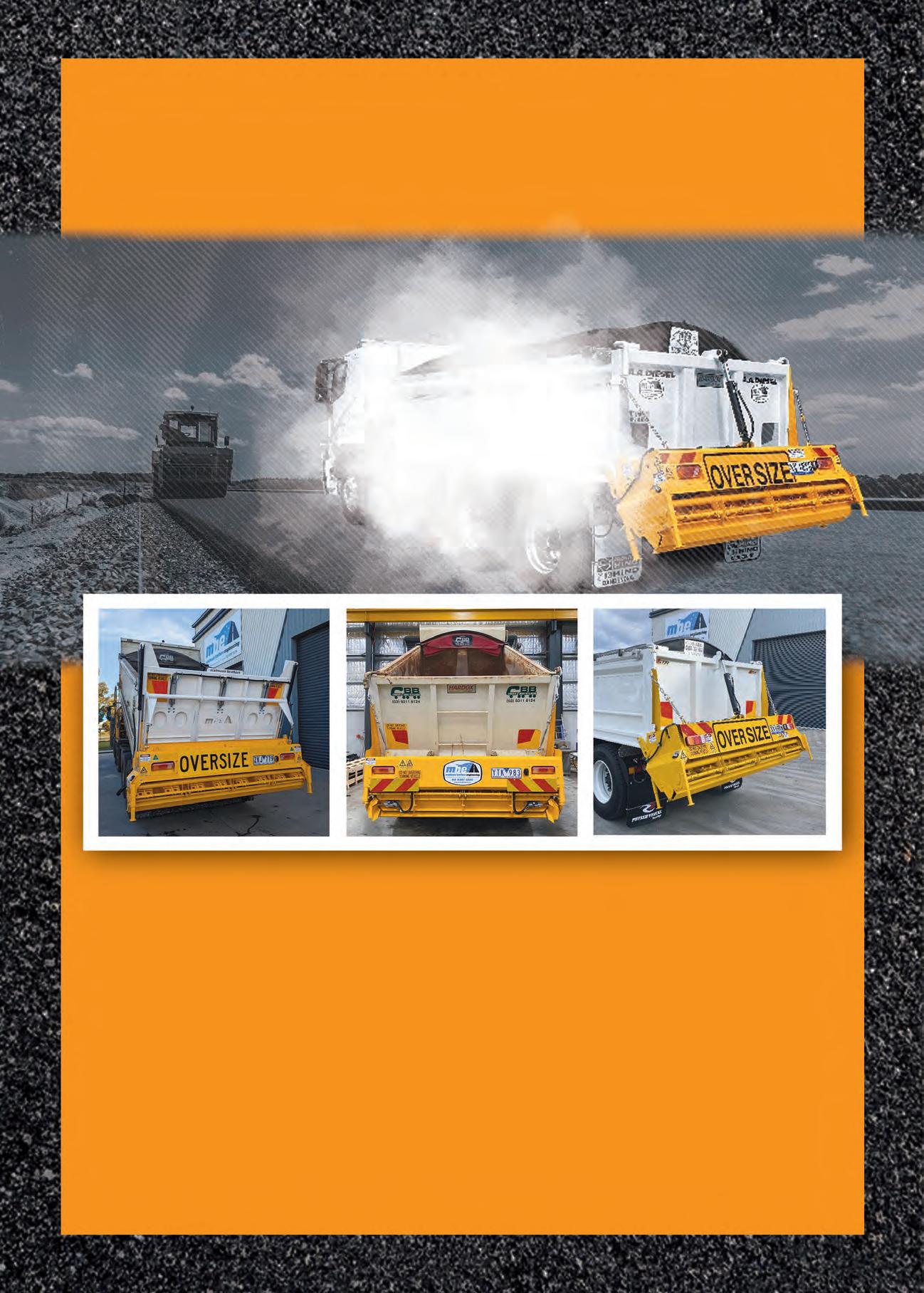
ADDITIONAL INVESTMENT ANNOUNCED FOR $250M CURTIS ROAD PROJECT
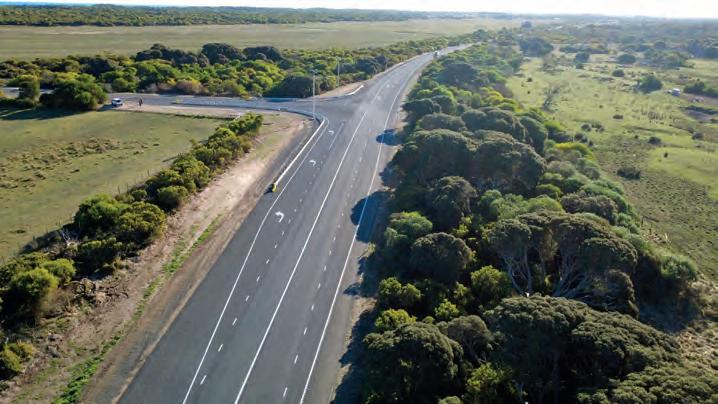
The South Australian Government will match the Federal Government’s $125 million investment to remove the Curtis Road level crossing in Munno Para, a key connection in Adelaide’s growing northern suburbs.
The northern suburbs of Adelaide –which includes areas such as Munno Para, Angle Vale, Riverlea, Kudla, Concordia, and Roseworthy – are predicted to see significant population and economic growth over the next 30 years and beyond. It’s the fastest growing region in the state.
The State Government recently undertook the Northern Adelaide Transport Study, which identified Curtis Road as an important east west link and access route to the North South Corridor.
Currently, the Gawler Railway line crosses Curtis Road, 500 metres west of Main North Road. Approximately 21,000 vehicles pass through this level crossing each day, and during peak periods the boom gates can be down for up to 15 minutes every hour.
The removal of the rail level crossing and
SUNSHINE STATION PROGRESSING AS PART OF MELBOURNE AIRPORT RAIL
Work to turn Sunshine Station into a superhub and transform Melbourne’s western rail network is moving ahead, with procurement now progressing on the project.
The complex program of works spanning six kilometres from West Footscray to Albion will be divided into five works packages, enabling works, freight line works, metropolitan line works, regional line works and the Albion Station redevelopment, each delivering a specific aspect of the works.
Initial packages will be delivered using the Level Crossing Removal Project’s program alliance model. The enabling works package will be the first to be
awarded in early 2026 and will include the diversion, relocation and protection of utilities and underground services needed for major construction to progress on the rest of the project.
The remaining works packages will follow progressively.
The regional line works package will be open to market, with a new alliance formed to deliver these works, while the other works packages will be delivered by existing program alliance teams.
This program of works will ensure Sunshine Station can support more than 40 train services per hour, creating capacity for additional services for the growing west and to the airport.
grade separation will improve safety and travel time reliability by reducing road and rail network conflicts.
A planning study for the works will soon commence, with a concept design to be released in 2026. Major works will commence by 2027, with an expected completion in 2030.
The 2025/26 State Budget for South Australia will also include $80 million in joint funding from the State and Federal governments (50:50) over five years for safety improvements on a section of Main South Road between Myponga and Yankalilla.
Upgrades will include the construction of two new overtaking lanes, targeted curve easing and road widening, as well as widening narrow bridges and culverts.
These improvements will increase overtaking opportunities and create a safer environment for all road users travelling to and from the Fleurieu Peninsula.
Together, this now brings a total investment of $111.8 million to deliver five overtaking lanes and other safety upgrades on Main South Road between Myponga and Cape Jervis.
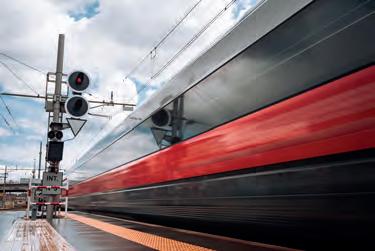
Major changes to the rail network around Sunshine Station will enable a rail line to the airport and pave the way for electrification to Melton. Image: stock.adobe.com/ Daniele Mastrangelo
Upgrades to Sunshine Station are required to be completed before tracks can go to the airport.
Design and planning work is well underway, with works expected to start in early 2026 and be complete in 2030.
The Australian and South Australian governments have jointly (50:50) funded $250 million to remove the level crossing at Curtis Road. Image: South Australian Government
NEW ROAD SAFETY CAMERAS DEPLOYED IN VIC
The last of 35 new road safety cameras has been switched on in Melbourne, aiming to reduce road trauma as part of a $49.4 million investment by the Victorian Government.
Research by the Monash University Accident Research Centre shows a 47 per cent reduction in crashes where speed and red-light road safety cameras are installed.
Speed contributes to approximately one third of all road trauma in Victoria, or around 100 deaths and 2000 serious injuries every year.
Even small increases in vehicle speed can significantly raise the risk of a driver having a crash. Exceeding the speed limit by just three kilometres an hour can increase a driver’s risk of being involved in a crash by 25 per cent, and drivers travelling at 65 kilometres per hour in a 60 kilometres per hour zone double their risk.
Every dollar received from road safety camera enforcement goes to the Better Roads Victoria Trust, where it is spent on road restoration, surface replacement, bridge strengthening and other improvements.
In the 2023-24 financial year, fines issued
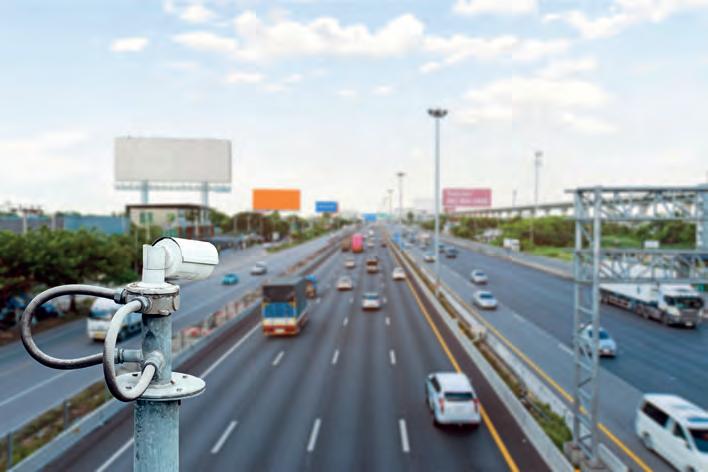
from road safety cameras amounted to $473 million.
Road trauma costs Victoria between $4 and $6 billion per year, this amount includes serious injuries and fatalities.
The Victorian Government’s second Road Safety Action Plan will invest more than $1.1 billion over the next four years to deliver
NEW LION CREEK BRIDGE COMPLETE
Works on the Lion Creek Bridge are now complete, the first of 18 old timber bridge replacements to improve flood resiliency and accessibility in Queensland as part of the $1.98 billion Rockhampton Ring Road project.
The original crossing of the Lion Creek bridge was built in the late 1800s. The completion of the new bridge coincided with the re-opening of Canoona Road, as work on the West Rockhampton local road connections to the Ring Road are finalised.
The Rockhampton Ring Road project will deliver 17.4 kilometres of new roadway including a 14.7 kilometre western link of the Bruce Highway, extending from the Capricorn Highway (at Nelson Street) in the south through to the intersection of the Bruce Highway and Rockhampton–Yeppoon Road in the north.
The project will transform the way commuters, freight and travellers access Rockhampton, with improved flood resilience, travel times and road safety.
The ring road will improve connectivity to
These cameras, located across the state, target speeding and red-light running, which are major contributors to intersection crashes. Image: stock.adobe.com/ETAP
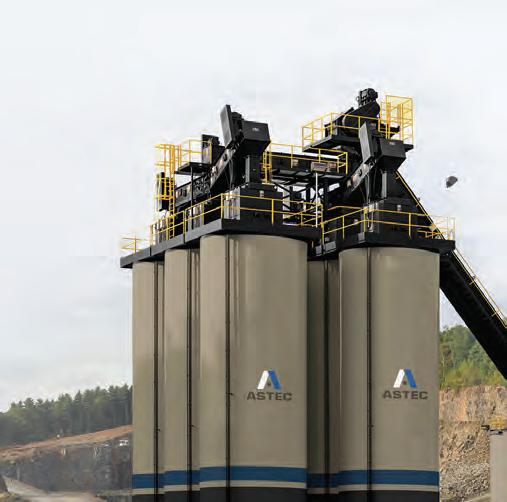
key destinations including the Rockhampton Airport, the Rockhampton Hospital, and defence, education and leisure precincts in Wandal and Rockhampton City, and industrial precincts in North Rockhampton.
The project will also deliver an additional eight road overpasses and seven water
life-saving road safety infrastructure and strengthen enforcement efforts to reduce road trauma.
The first Road Safety Action Plan for Victoria, released in 2021, aimed to halve road deaths and significantly reduce serious injuries by 2030, and set the state on a path towards zero road deaths by 2050.
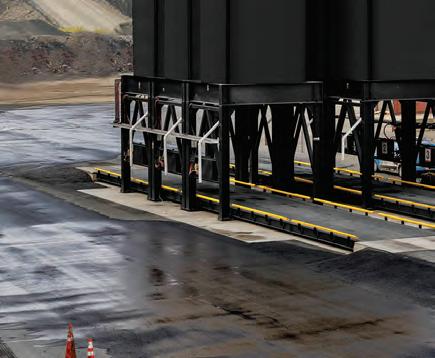
crossings on top of the 18 bridge replacements.
The $1.98 billion Rockhampton Ring Road project is funded by both governments, with the Federal Government providing $1.4 billion and the Queensland Government providing $580 million.

Spanning more than 61 metres and using locally manufactured concrete decks, the Rockhampton Ring Road project’s new Lion Creek Bridge is complete and ready to use. Image: stock.adobe. com/MiguelAngel
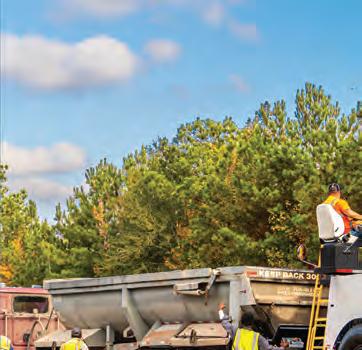
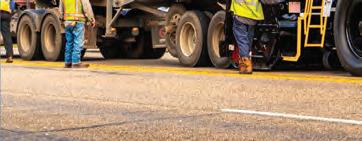
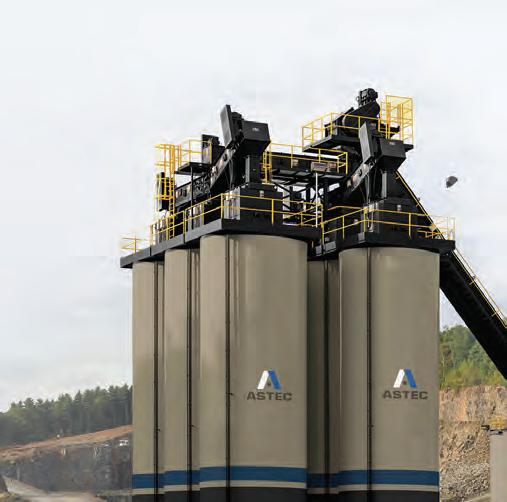
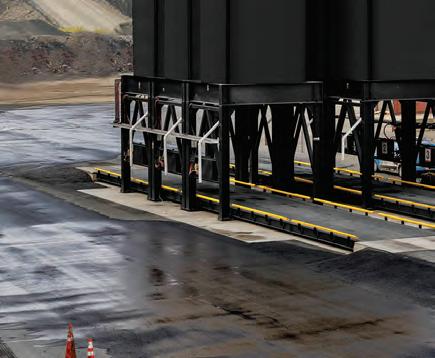
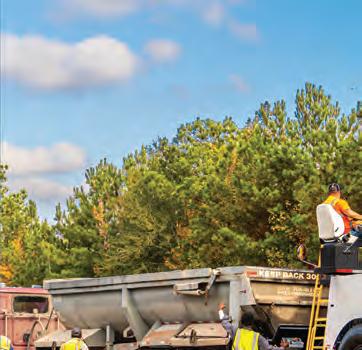
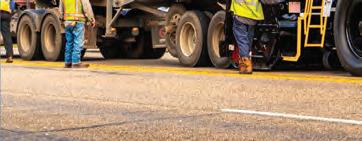
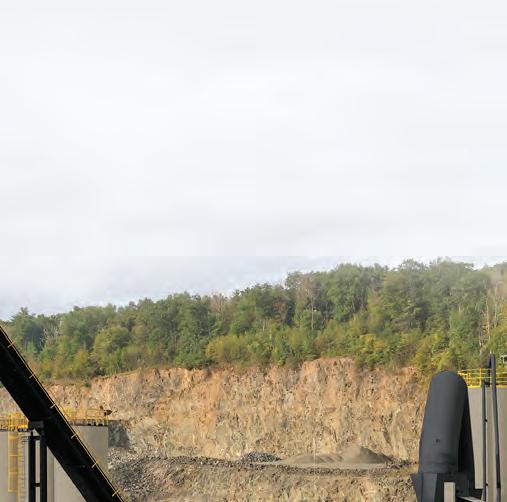
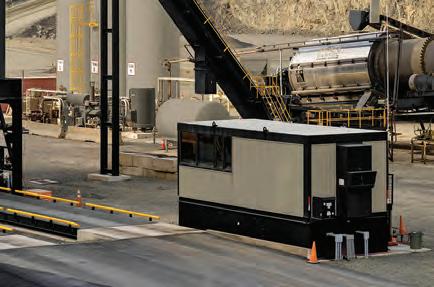
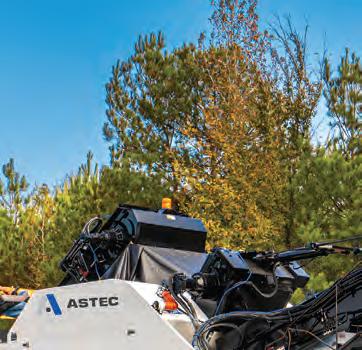
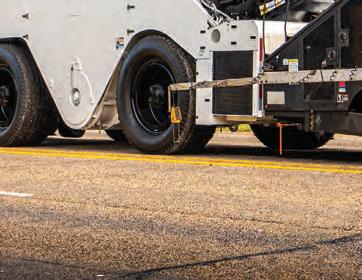
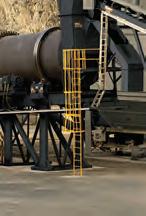
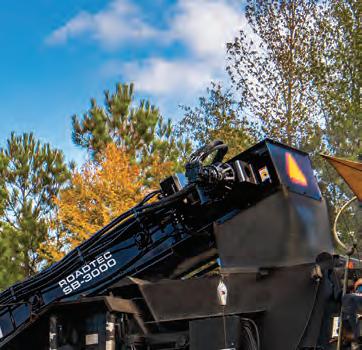
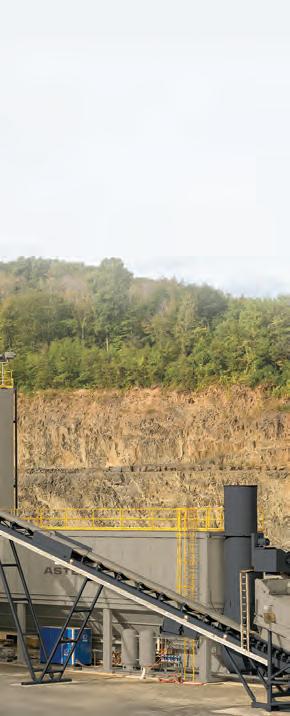
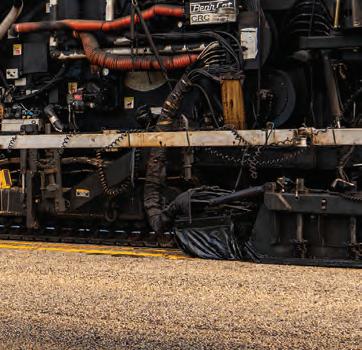


Creating, connecting, and caring for communities
Fulton Hogan delivers high-quality infrastructure to improve the lives of people in Australia and New Zealand, every day.
We’re a growing, forward-looking and family-oriented business that’s investing in the talent of tomorrow.
Come and join our team.
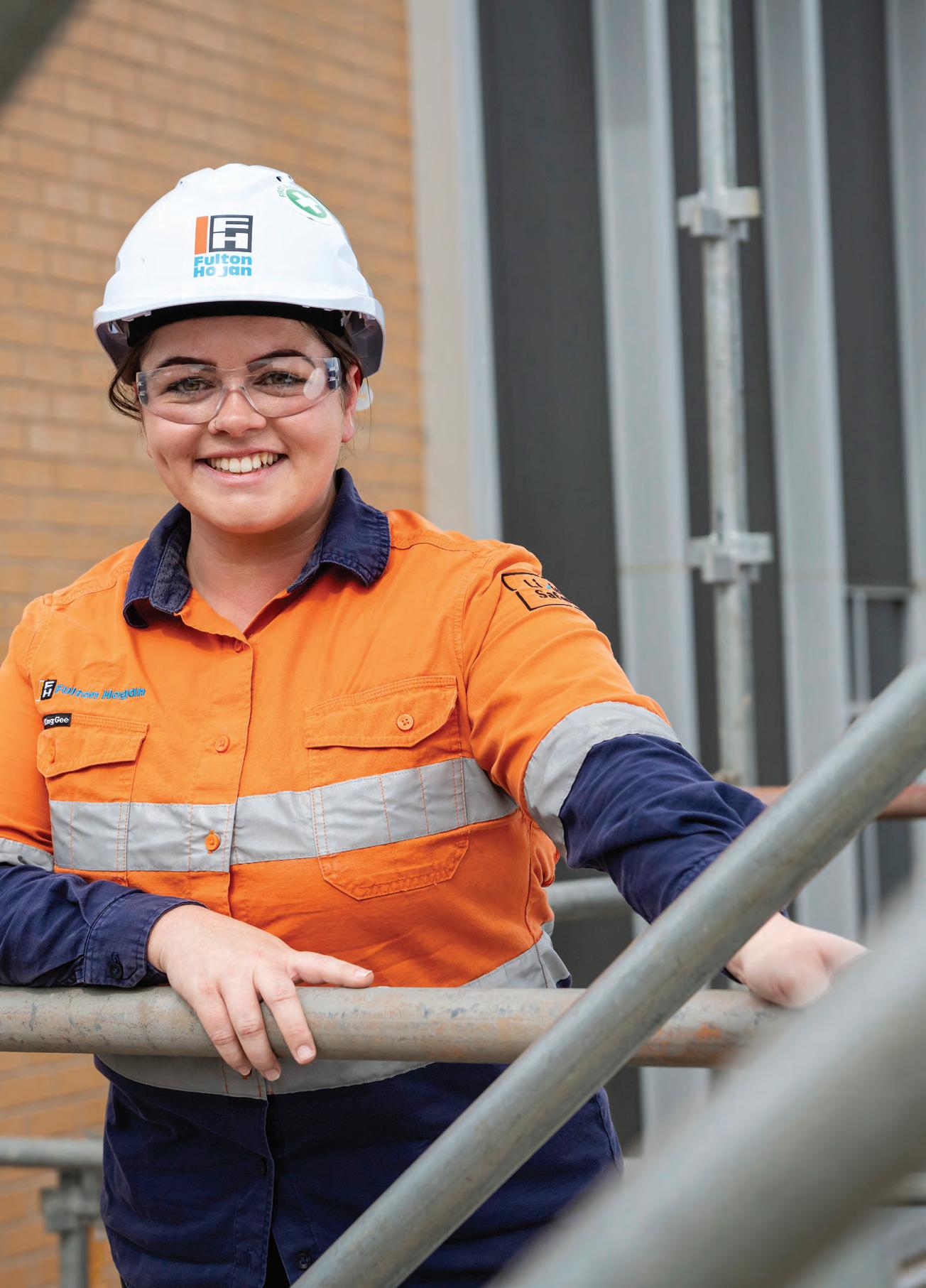
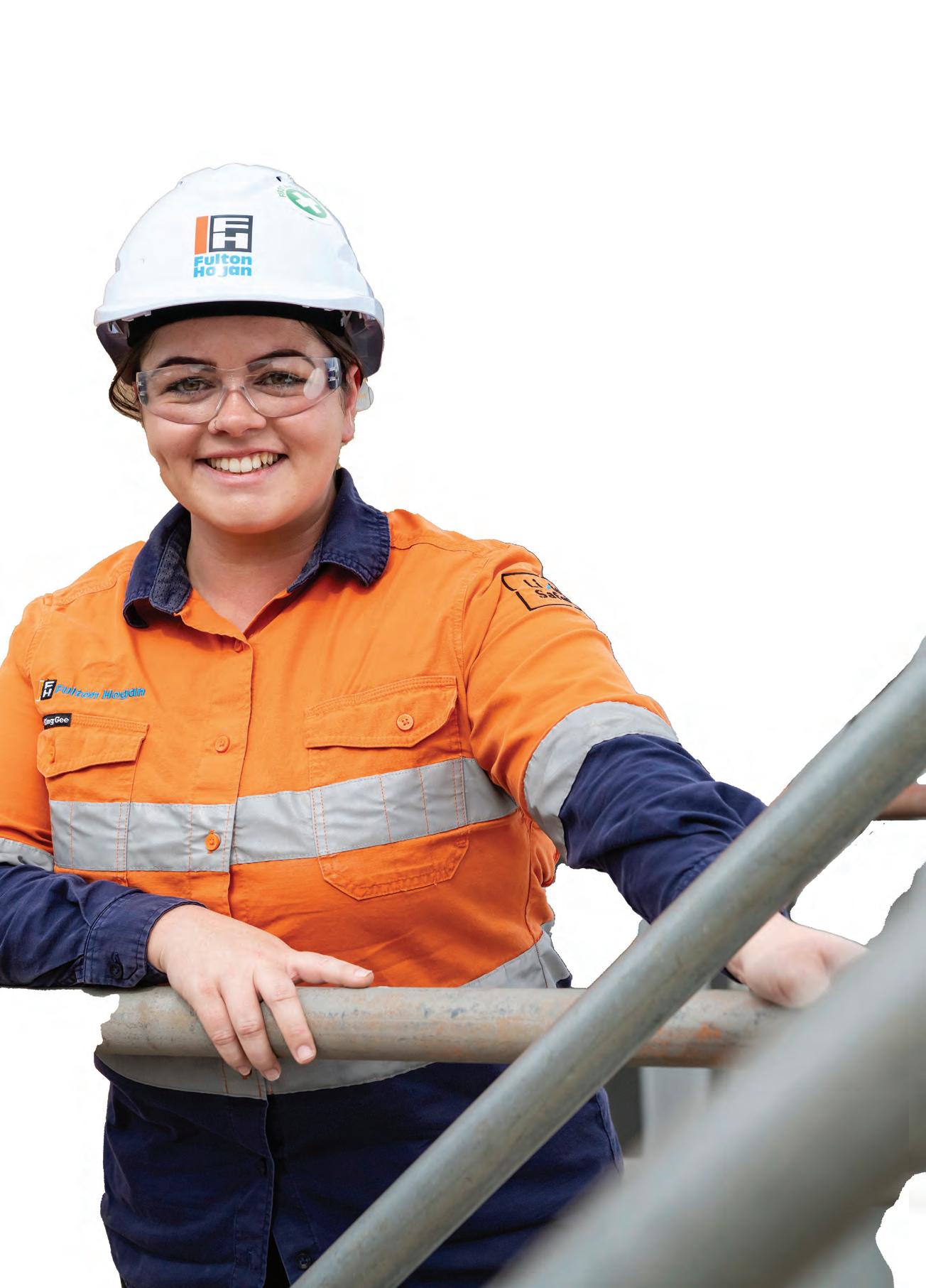
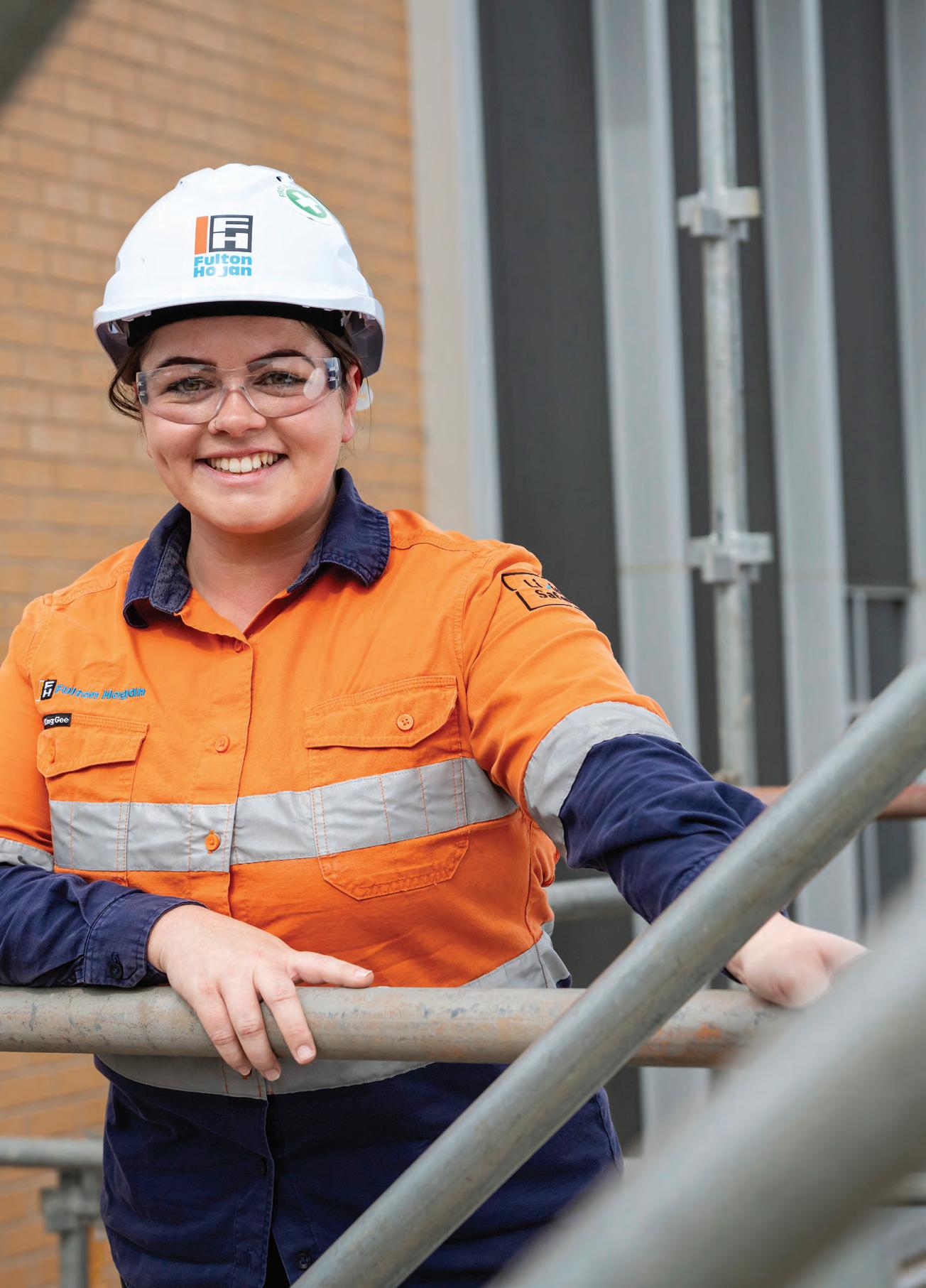
SECTION NOW OPEN ON $2B WARRINGAH FREEWAY UPGRADE
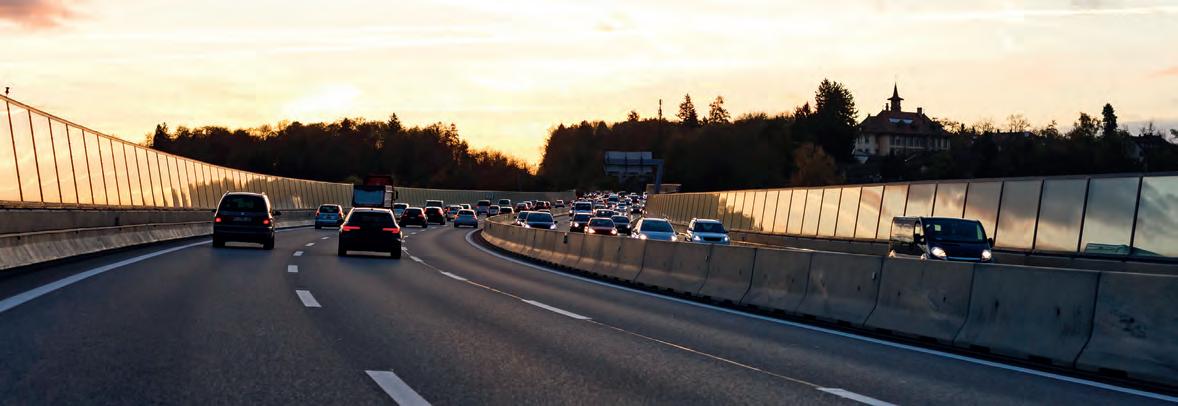
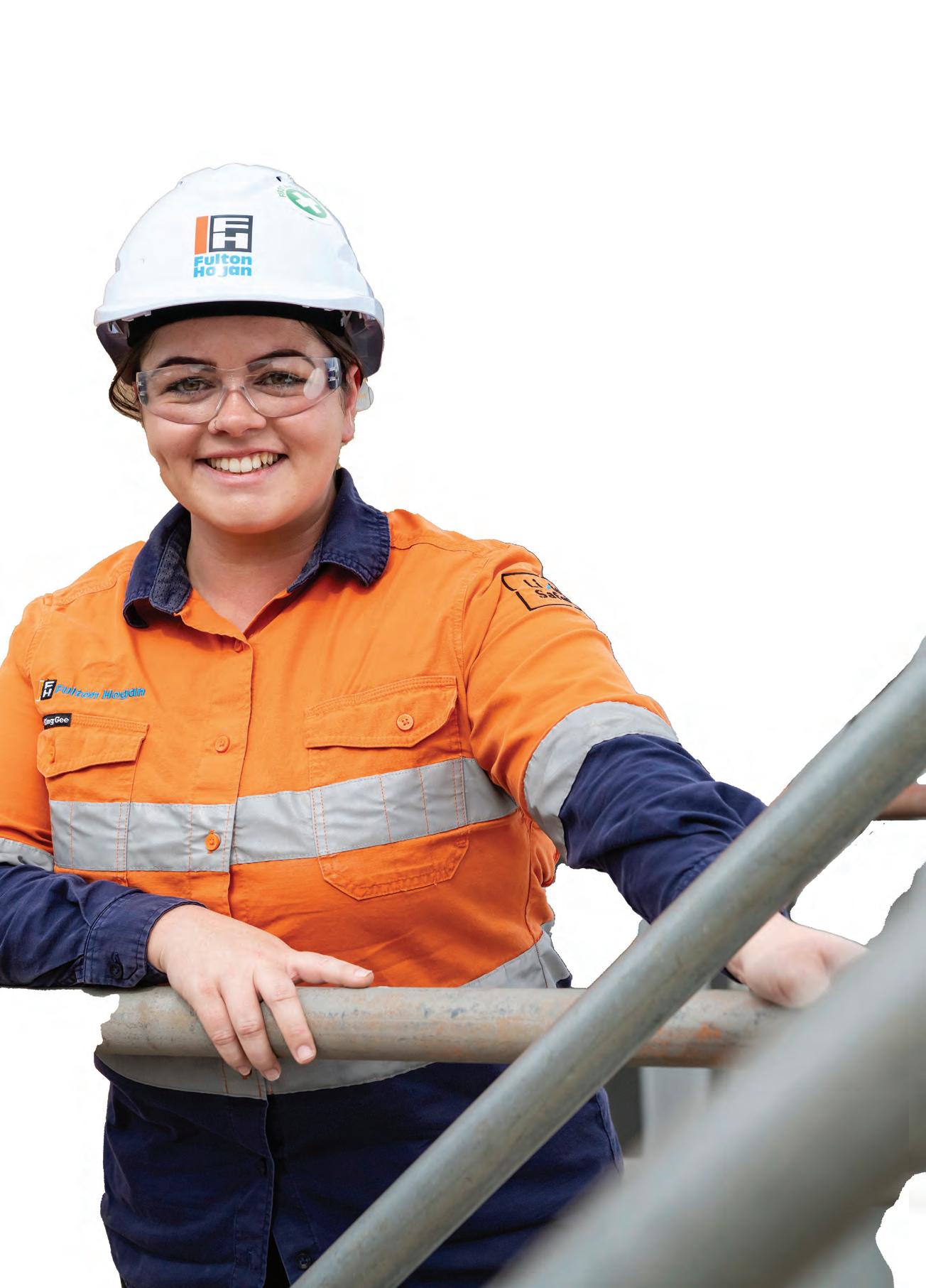
A new southbound on-ramp has opened to traffic on the $2 billion Warringah Freeway Upgrade in New South Wales.
The Miller Street southbound on-ramp opening is the first key piece in a series of structures that will open progressively over the next 12 months as the project motors towards the finish line.
The Warringah Freeway is one of Australia’s
busiest and most complicated roads, providing the northern gateway to the Sydney CBD via the Sydney Harbour Bridge and Sydney Harbour Tunnel for 250,000 vehicles daily.
This new on-ramp at Cammeray separates general traffic from buses, taking motorists from Miller Street over the freeway’s future dedicated citybound bus lane. This means
Left: The Warringah Freeway Upgrade is a major transport infrastructure project that will make it easier, faster and safer to get around Sydney. Image: stock.adobe.com/Angelov
the 3000 vehicles using the on-ramp each day will avoid merging and weaving with the thousands of buses that will use the bus lane.
Later this year the new Brook Street onramp will also connect into the new Miller Street on-ramp as a single viaduct structure, further untangling the freeway and improving traffic flow.
The new on-ramp is 200 metres long and 10 metres wide and has been built using 40 precast Super-T girders (the concrete structures which support the ramp), each weighing around 48 tonnes.
The Warringah Freeway is an enabling project for the Western Harbour Tunnel. Together they will create a more efficient link between Sydney’s north, west and airport precincts when the Tunnel opens in 2028.
MAJOR WORKS UNDERWAY ON LARGEST EVER SA INFRASTRUCTURE PROJECT
Construction activity is ramping up on the first major works for the $15.4 billion River Torrens to Darlington (T2D) Project in South Australia.
The T2D Project is the final 10.5-kilometre section of the North-South Corridor, and will complete 78 kilometres of non-stop traffic, light-free motorway between Gawler and Old Noarlunga. Drivers will be able to bypass 21 sets of traffic lights between the River Torrens and Darlington as they travel through two separate tunnels, connected by an open motorway.
Heavy machinery is onsite and construction activity has ramped up at the Southern Precinct in Clovelly Park. The Southern Precinct – located between Tonsley Boulevard and Norrie Avenue on the western side of South Road – will become the purpose-built site from where Tunnel Boring Machines (TBMs) will launch to construct the southern tunnels.
These two TBMs will launch from the Southern Precinct to construct the twin 4.5-kilometre Southern Tunnels, while the
twin 2.2-kilometre Northern Tunnels will utilise a third TBM. TBM works for the Southern Tunnels are planned to begin in the second half of 2026.
The three TBMs were purchased in September 2024 from manufacturer Herrenknecht based in Schwanau, Germany. The TBM components are being manufactured in Germany and China, before being assembled and factory assurance tested in China, and then delivered to Adelaide by ship. The first of three TBMs is expected to arrive in late 2025.
Two additional, smaller TBMs will also be used to carry out excavation work for cross passages between the main tunnels.
The past few weeks have seen a significant increase in works on site, including the start of construction of the diaphragm walls for the TBM launch box – the first piece of permanent works on the project. The diaphragm walls will be up to 35 metre deep and form the outside of the TBM launch box – a large open trench where the TBMs will be assembled and then begin excavating
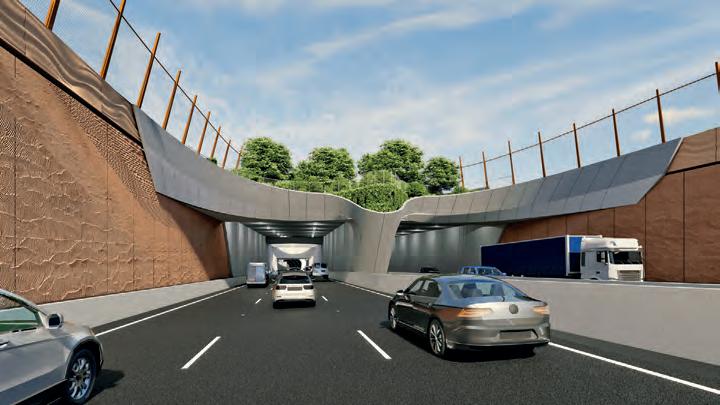
Right: The Australian and South Australian governments are jointly delivering the $15.4 billion T2D Project. Image: South Australian Government

A REPUTATION BUILT
ON RELIABILITY
SGA ROADS’ FLEET OF WIRTGEN MACHINERY CONTINUES TO GROW, A TESTAMENT TO THE INGENUITY OF THE MANUFACTURER’S MACHINERY, AS WELL AS THE LONGSTANDING AND EVER-GROWING PARTNERSHIP BETWEEN THE TWO COMPANIES.
Afew pieces of equipment and a vision. That’s all that the SGA Roads’ team had at its disposal, and all it’s taken, to grow what was a modest runway grooving business into a mainstay of the road construction industry.
With reliable equipment and an entrepreneurial spirit in tow, SGA Roads has carved a niche within the Western Australian market, offering services to projects and clients of all sizes.
As Owner and Operations Manager, Jason Hind explains, the company is also the culmination of resilience and hard work.
“I’ve been in the job and worked my way from the ground up. I started on the rake and shovel and worked my way up to the screed,” he says. “My business partner, Stephen (Hamill), he’s done exactly the same, but from the profiling side.
“We know what we’re talking about, because in most cases, we’ve done it first hand.”
They expanded into asphalt contracting, hiring their own crew out and subcontracting to a local Perth contractor, these works signified real traction in the market for SGA Roads. To complete this project and to increase the overall
capabilities of the business, Hind and Hamill sought two rollers, as well as a fulltime contracting crew, marking a major milestone for the company.
Shortly after acquiring additional units, as well as personnel, SGA Roads caught the attention of several major players in the sector. This led to contracts on major infrastructure projects, such as the Tonkin Highway Gap project, Albany Ring Road stage two, as well as works relating to the delivery of new railway stations, such as the Allure train station.
“We introduced the rollers and the crew that contractors could hire, we then bought some tippers and things really kicked off from there,” Hind says. “That’s when we decided that we needed a paver. 10 months later, we bought another.
“After subcontracting for a further two years, we saw an opening in the market and an opportunity to go straight to the customer. And off we went.”
When discussing internally, only one option stood out, as Hind explains.
“I used to work for a tier one contractor and towards the end of my career there, they started to bring in more and more Wirtgen machinery,” he says.
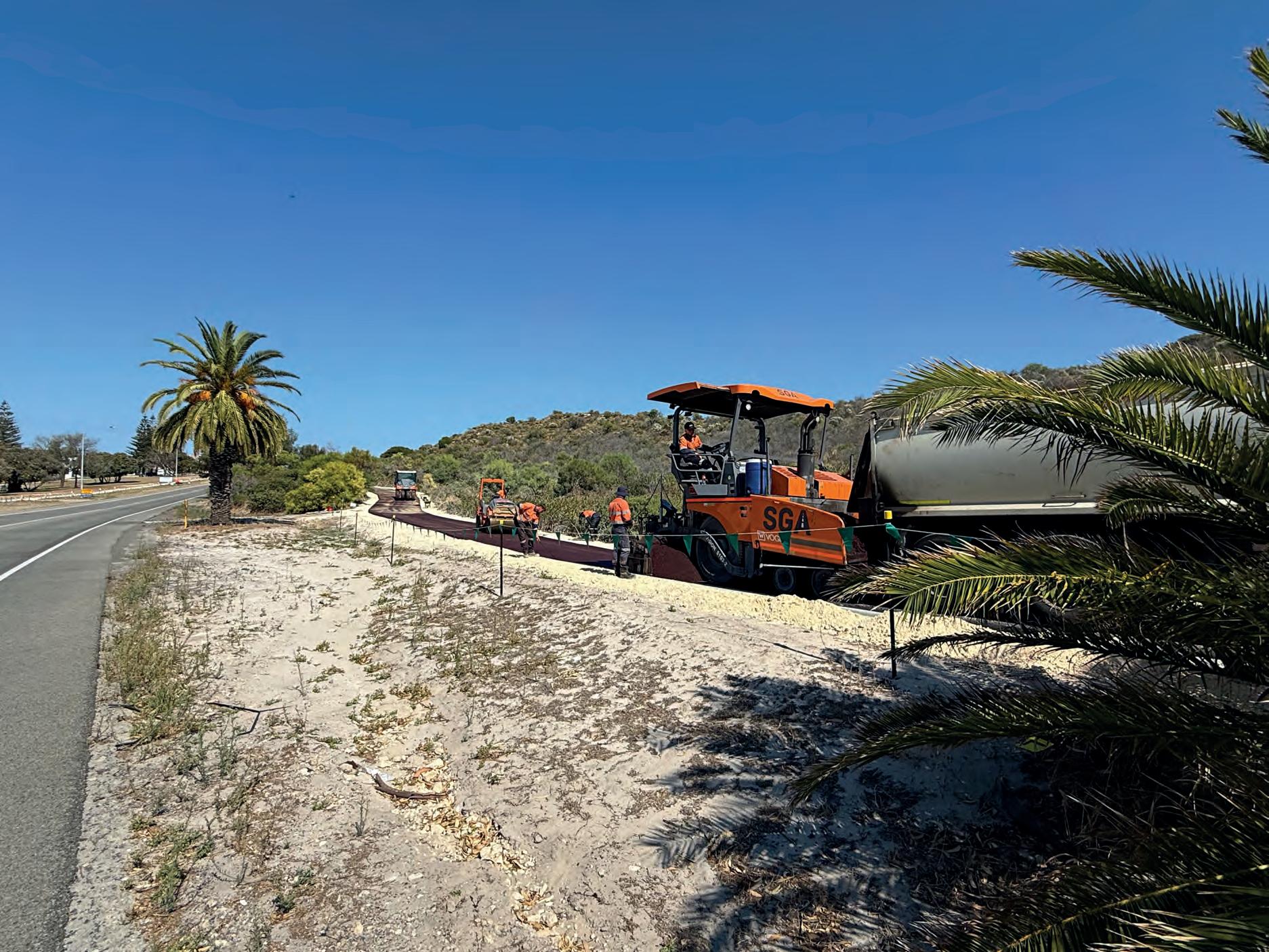
Just one of SGA Roads’ units is the Super 1803-3, the most powerful eight-foot class wheeled paver in VÖGELE’s range.
SGA Roads has an ever-expanding fleet of Wirtgen machinery.

With Wirtgen machinery and support behind it, SGA Roads successfully delivered the Olympic Dam works before further opportunities were identified.
WIRTGEN KEY TO GROWTH
The expansion of the company’s project portfolio demanded additional equipment. Hind says the critical factors that he and the company were looking for were reliability, durability and availability.
This is on top of versatility, which Hind says is essential in such a dynamic and fastpaced sector.
“We’re a one-stop shop. When a client comes to us, they expect that we can tackle multiple aspects of a project. That’s what we pride ourselves on, taking on a project from start to finish,” he says. “That includes profiling, sealing and laying the finished product.”
Once again, SGA Roads turned to
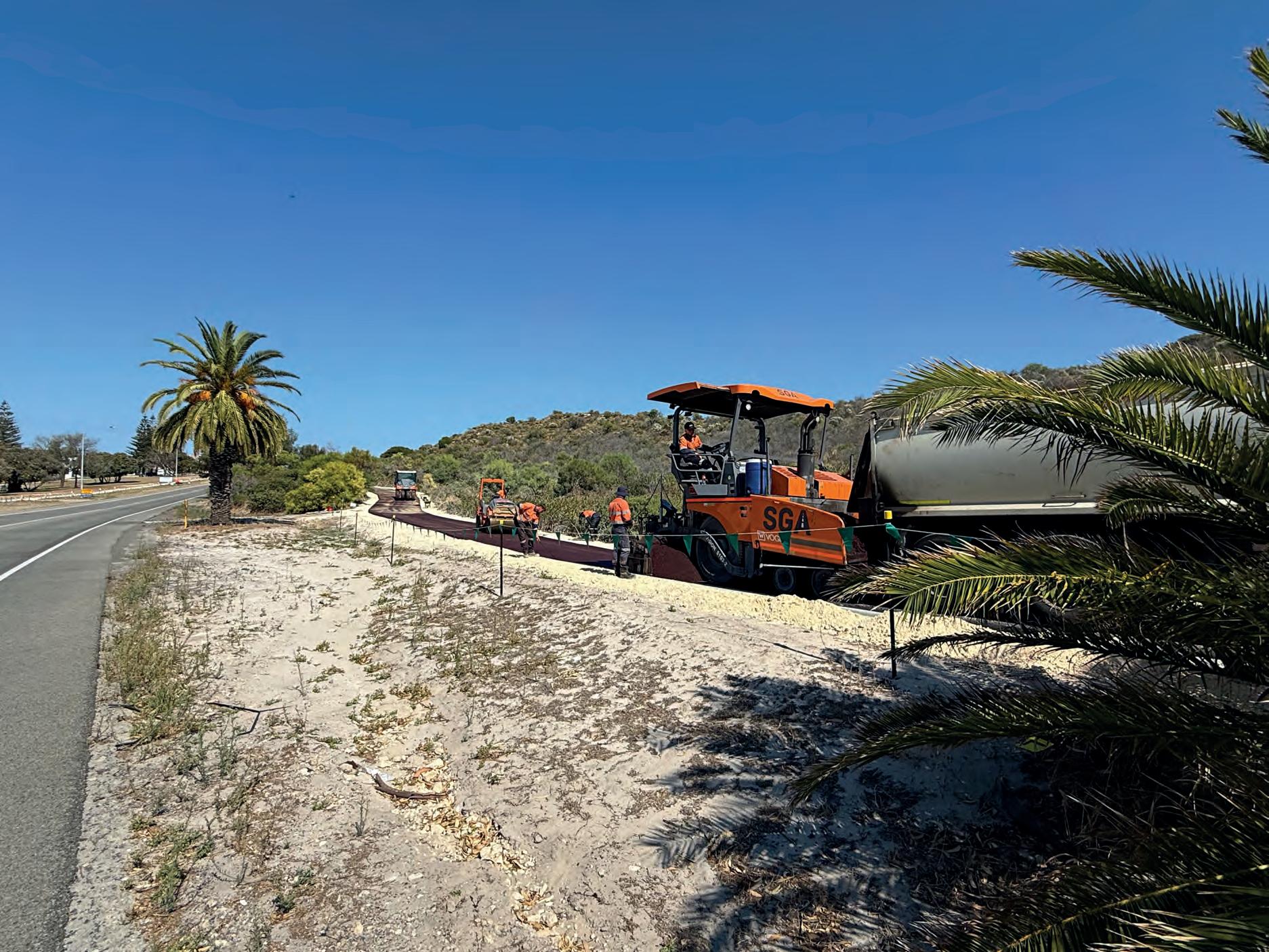
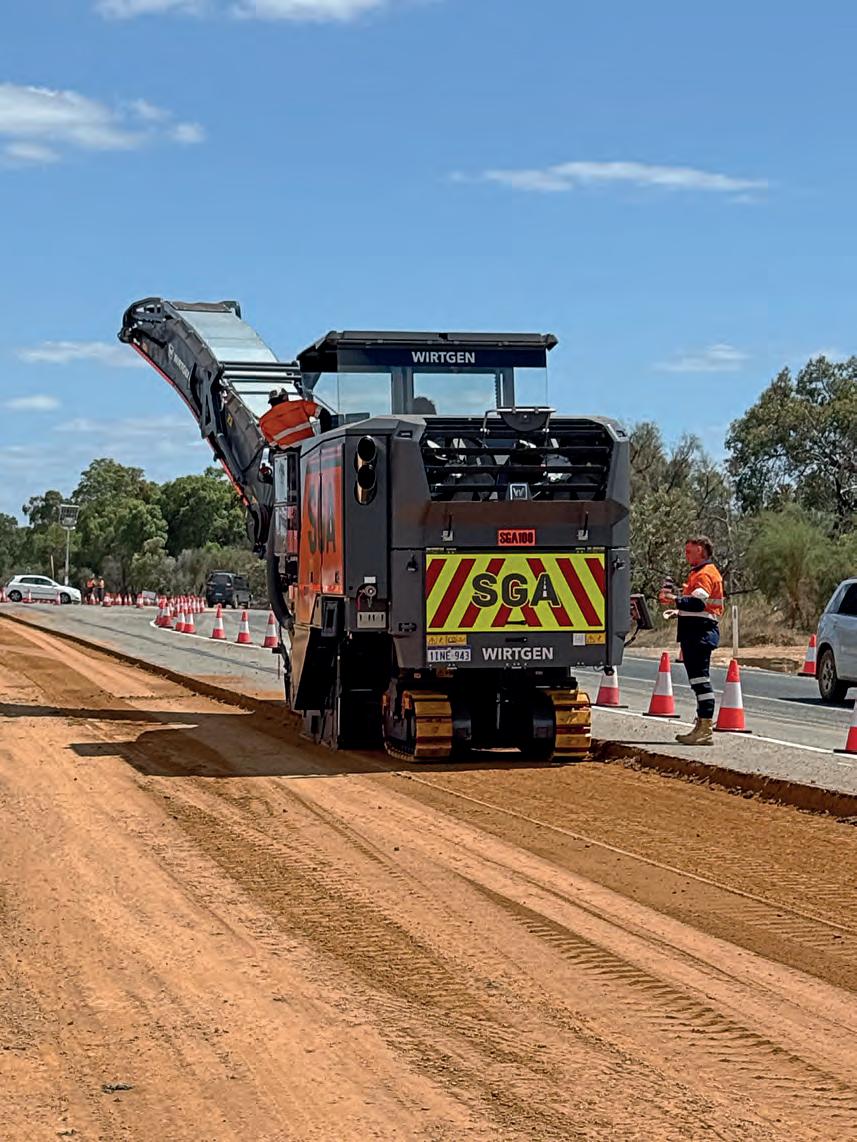
The purchase of a new units signifies just the beginning of what could be a long-lasting partnership.
In just a few years,
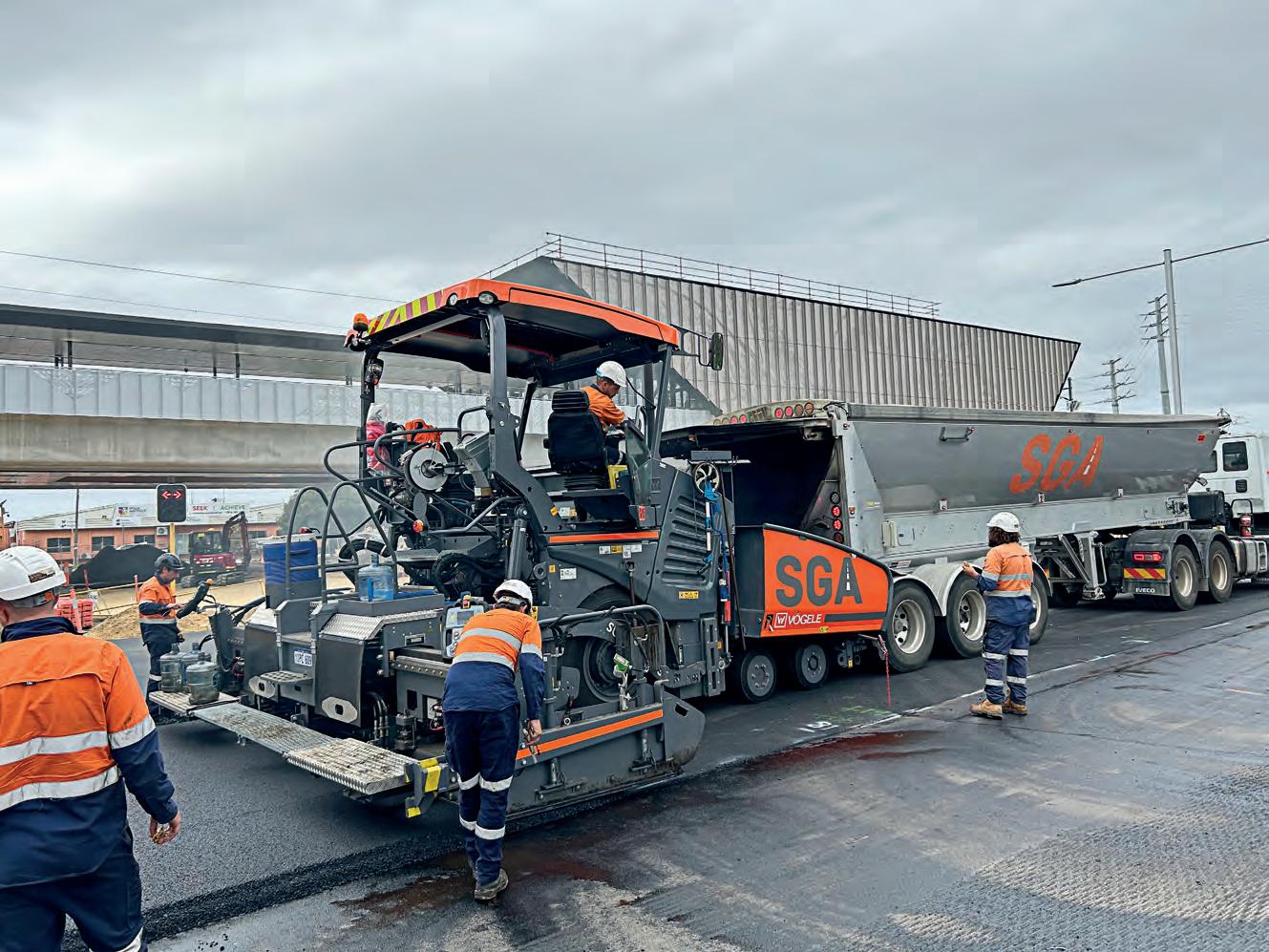
largest purchase to date. Wirtgen’s (and now SGA Roads’) Super 1803-3 unit is the most powerful eight foot class wheeled paver in VÖGELE’s range, capable of delivering high-quality outcomes for a large range of applications and paving widths, up to eight metres.
Boasting high traction and manoeuvrability, the Super 1803-3 is powered by a 127-kilowatt diesel engine, while also sporting a variety of automated features, each aimed at decreasing time required for setup while improving the quality of the final mat.
“I rang [Marc Fernandes] and mentioned that we were interested in a Super 1803-3. He had one on the forecourt and within two weeks, it was coloured in our
company livery and ready for handover,” Hind says.
Hind adds that the Super 1803-3 has already been used on a smaller roundabout project. He says the high quality finish was clear for all to see.
“The client said that he’d never seen a finish as good as that from a paver,” he says, “and that was the first day of commissioning.
“It’s state of the art, it’s got all of the technology we wanted and needed, and it looks great in company colours.”
GOOD STEAD
With the company soon to launch its third crew, SGA Roads’ aggressive growth shows no signs of slowing down, with additional
exploration underway on further opportunities in niche markets.
It’s Hind’s belief that this strategy, combined with the latest Wirtgen machinery, will see SGA Roads become a preferred provider of “comprehensive infrastructure services”.
“We didn’t expect a year and a half ago that we’d be in the position that we are, that we would explode as big as we have,” he says. “That desire to be a one-stop shop, that’s now a reality. We’re breaking into new markets and competing with the larger companies out there.
“Few can take on a project from start to finish. With the expertise and equipment that we’ve got, it’s an exciting time for SGA Roads.”
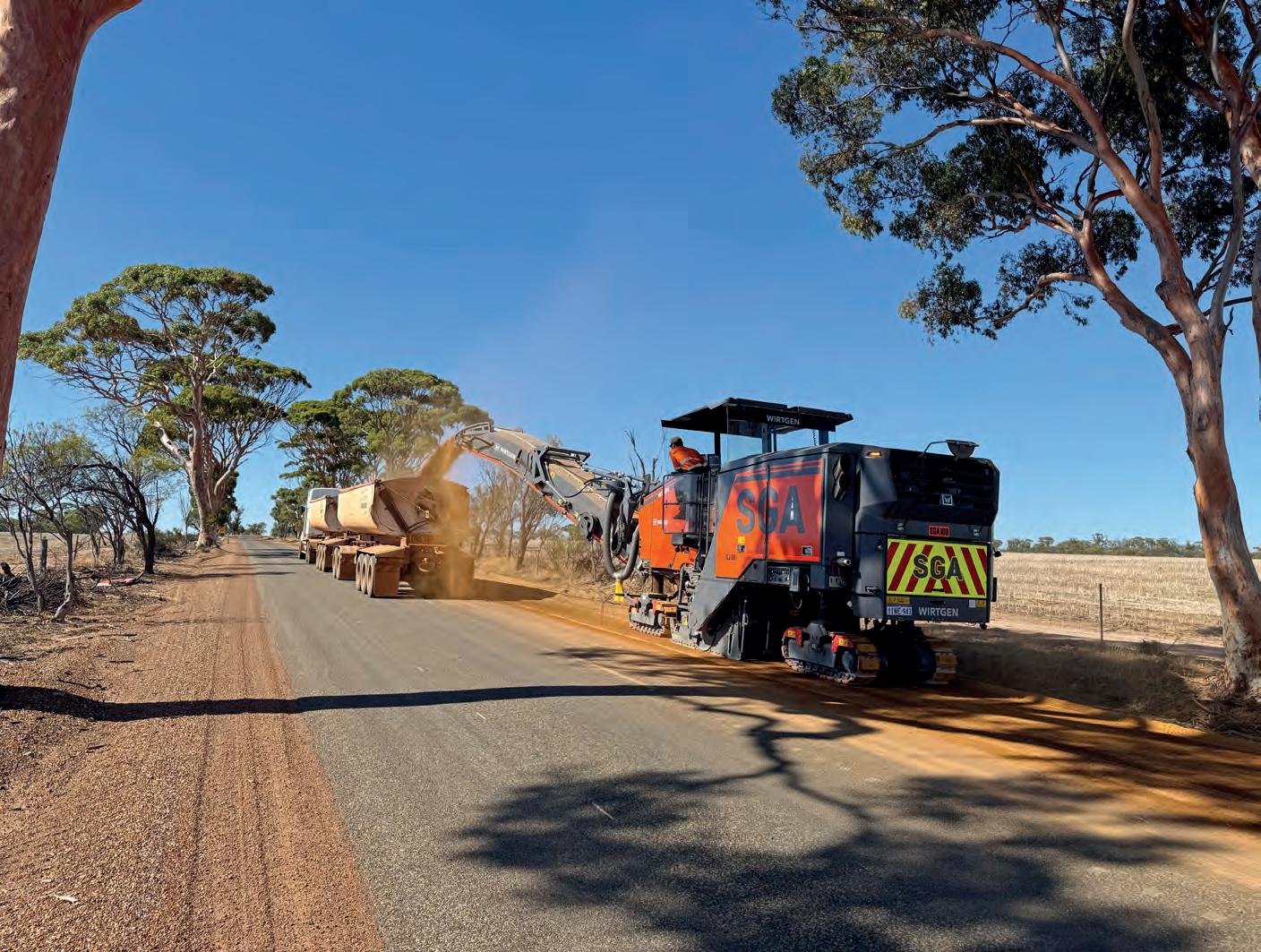
SGA Roads has grown into a major player in the Western Australian market.
Wirtgen machinery is tasked with working in rain, hail and shine as part of SGA Roads’ works.
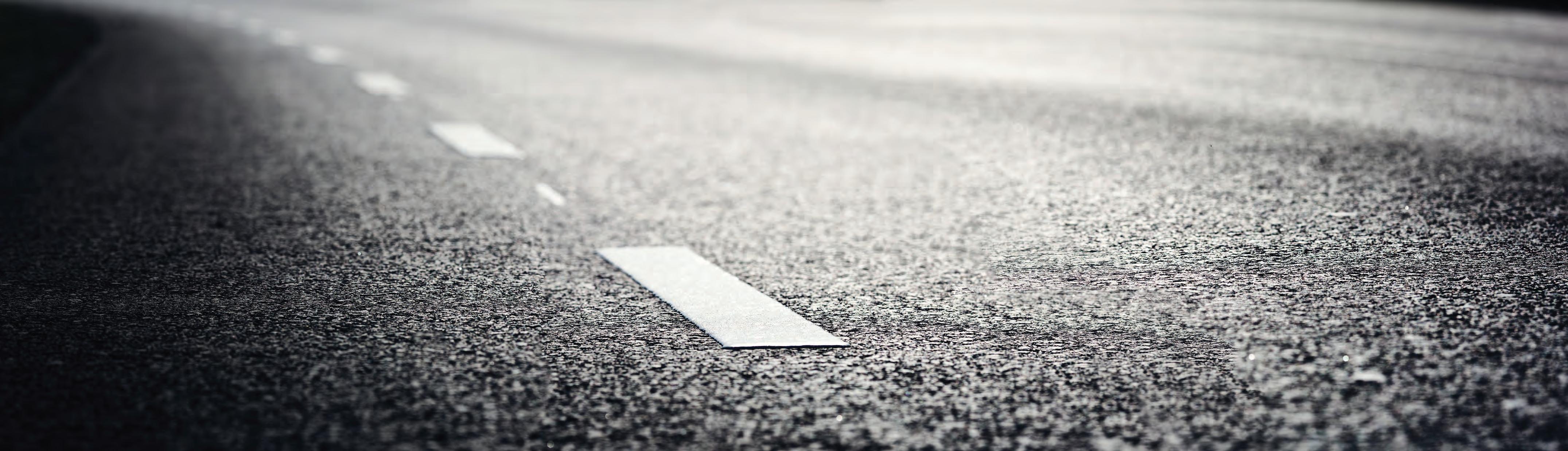
ROADS REVIEW
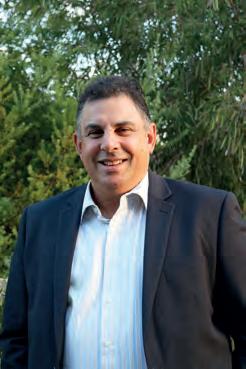
THIS MONTH, WE ASKED THE INDUSTRY’S DECISION-MAKERS, WHAT CAN WE DO BETTER TO IMPROVE BOTH ROAD AND ON-SITE SAFETY?
PETER ALI, CHIEF EXECUTIVE OFFICER – MUNICIPAL WORKS AUSTRALIA
Improving road and on-site safety remains a top priority for local government maintenance teams. As municipal operations expand and traffic volumes increase, the risks to both workers and the public also rise. Addressing safety in these circumstances requires a multi-layered approach that goes beyond compliance to create a culture of care, vigilance, and continuous improvement. Regular and targeted training offers the primary line of defence. Training should not only focus on mandatory safety instruction but should also include regular updates on emerging risks, new technologies, and evolving protocols. Some innovative councils have implemented simulated scenario training, including live roadwork drills. Training of this type can help prepare teams for real-world hazards, enhancing both confidence and competence.
Image: Municipal Works Australia
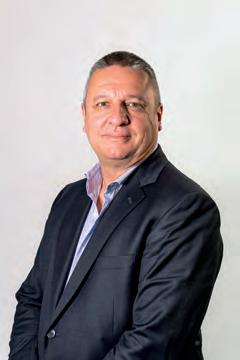
JIM WALLER, EXECUTIVE PROGRAM DIRECTOR
– NORTH EAST LINK
Road safety is one of the many benefits that North East Link will bring to Melbourne’s north east. The project will take 15,000 trucks off local roads every day, and the business case found there would be 100 fewer crashes per year on local roads in Melbourne’s north east. Upgrades to the Eastern Freeway and M80 Ring Road will also include smart technology to help monitor and manage traffic incidents, and a seamless connection to the North East Link tunnels for drivers. The upgrades to walking and cycling paths will include safer connections for the local community including schools and sports clubs.
Image: Major Road Projects Victoria
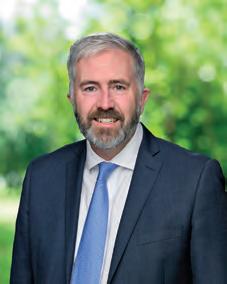
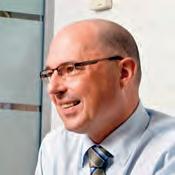
ANTHONY CHISHOLM, ASSISTANT MINISTER FOR REGIONAL DEVELOPMENT – QUEENSLAND GOVERNMENT
Keeping people safe on our roads is a critical priority of our government, which is why we’re rolling out much-needed funding to support projects that will make a real difference in changing the way we think about road safety. We’re also supporting new research to fill gaps in our understanding of how to drive safely, including how to prevent risky driver behaviour and how much sleep you need in order to drive safely. Everyone has a role to play when it comes to road safety, and by working together to deliver projects like these, we can support better road safety outcomes for Australia.
Image: Queensland Labor
MARK PIORKOWSKI, EXECUTIVE DIRECTOR QLD/NT – AUSTRALIAN FLEXIBLE
PAVEMENT ASSOCIATION
As the industry peak body, AfPA believes safety improvement begins with comprehensive team training – where we must focus energy to make real difference. Safe Work Australia data reveals seven workers die annually from vehicle and mobile plant incidents – preventable tragedies that proper education can address. Our courses, including ‘National Worker on Foot Awareness’ and ‘Be Bitumen Safe Online Training’, are critical for all operators – particularly those developing safety resources.
As a peak body, AfPA facilitates cascading learnings from established organisations to members building capacity. There’s no IP in safety and sharing knowledge creates industry-wide improvement. A rising tide lifts all ships. Well-trained teams become active safety participants, regardless of company size.
Image: AfPA
If you or someone at your organisation is an industry leader and would like to be a part of this monthly column in 2025, please get in touch with Editor, Tom O’Keane: tom.okeane@primecreative.com.au


for Australia, Papua New Guinea and South East Asia
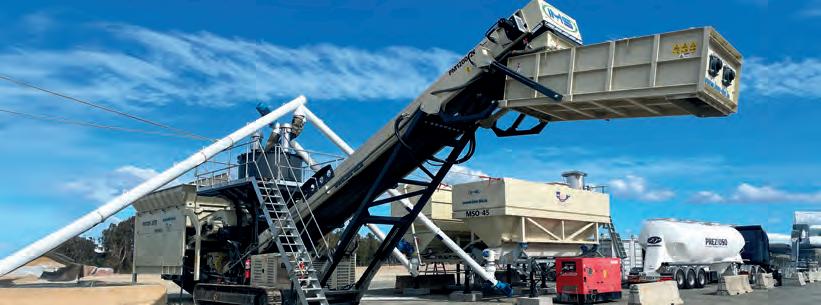
PM1200-20TB PUGMILL
• Two 10m3 each feed hoppers for blending road base
• Can add two powders at once up to 60 TPH of powder
• The option of adding two liquids
• Production up to 500 TPH
•
EMPOWERING THE NEXT
GENERATION
DELIVERING ON ITS COMMITMENT TO INCREASE OPPORTUNITIES FOR FEMALE AND NON-BINARY INDIVIDUALS IN THE CONSTRUCTION SECTOR, FULTON HOGAN ONCE AGAIN HELD ITS ‘A DAY IN HER BOOTS’ EVENT, OFFERING HANDS-ON EXPERIENCE AND EDUCATION AROUND INDUSTRY OPPORTUNITIES.
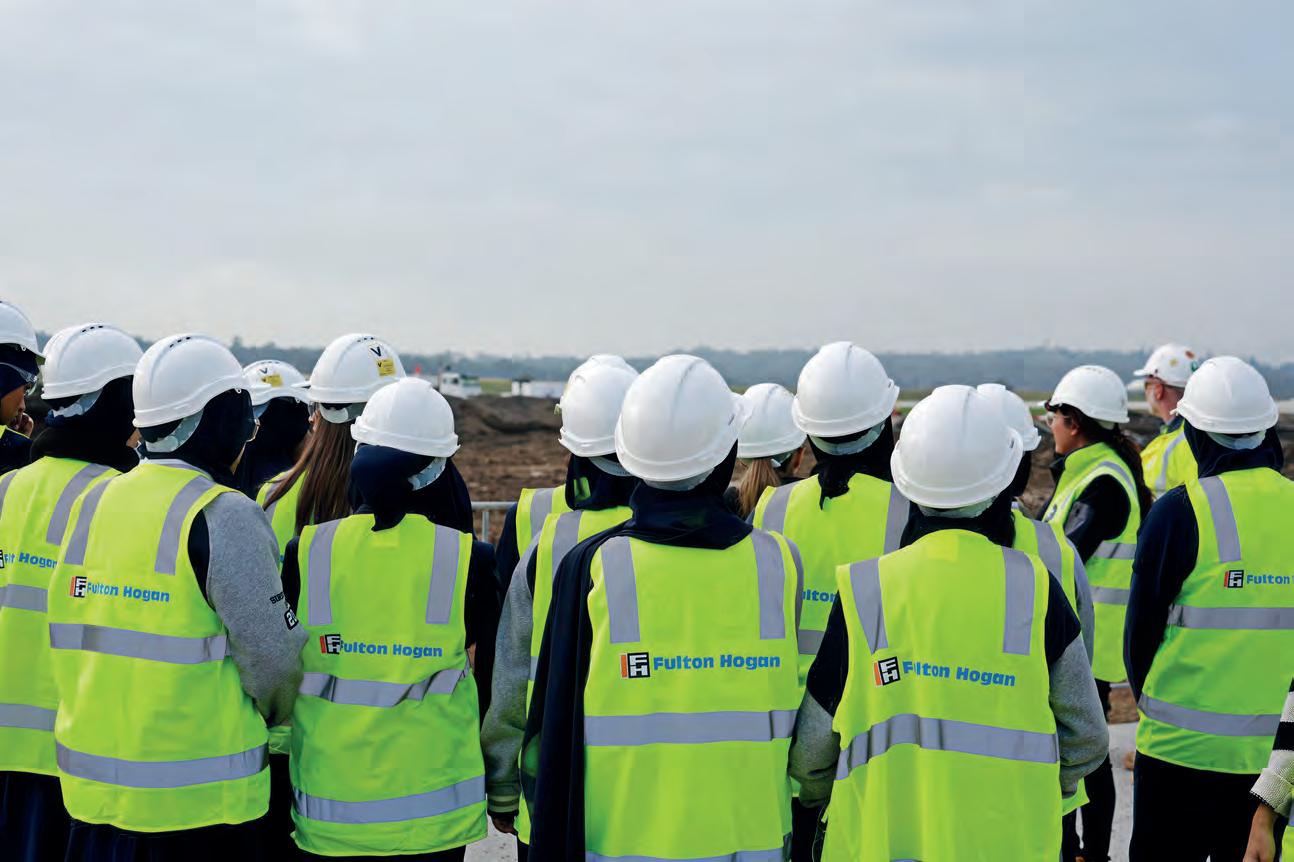
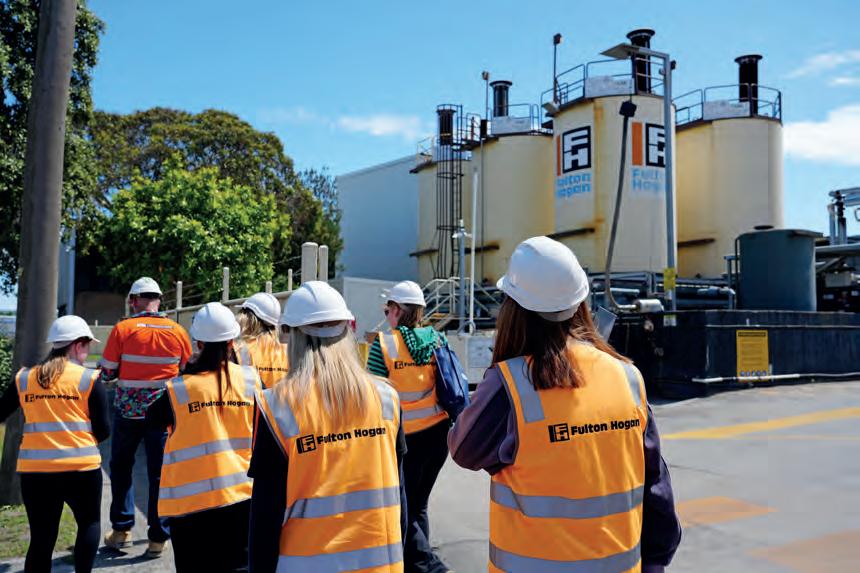
Less than 14 per cent of total construction employment consists of female individuals (per Master Builders Australia), a statistic and issue that’s well known throughout the sector.
Diversity and inclusion have long been a core focus for Fulton Hogan, a company that prides itself on not only supporting the community, but also those who may not receive the same opportunities or encouragement to succeed within the construction sector.
Christine Hogan, Communications and Marketing Manager, Southern Construction – Fulton Hogan says the ‘A Day in Her Boots’ program was conceived to showcase the wide variety of opportunities and pathways that people can take within the industry, while breaking down barriers and challenging perceptions about the sector.
“We know that inspiring and encouraging more females into the
Fulton Hogan’s ‘A Day in Her Boots’ program helped to show the multitude opportunities available for female and non-binary students considering a job in construction.
Visits to an asphalt plant is just one example of the onsite experience provided through the ‘A Day in Her Boots’ program.
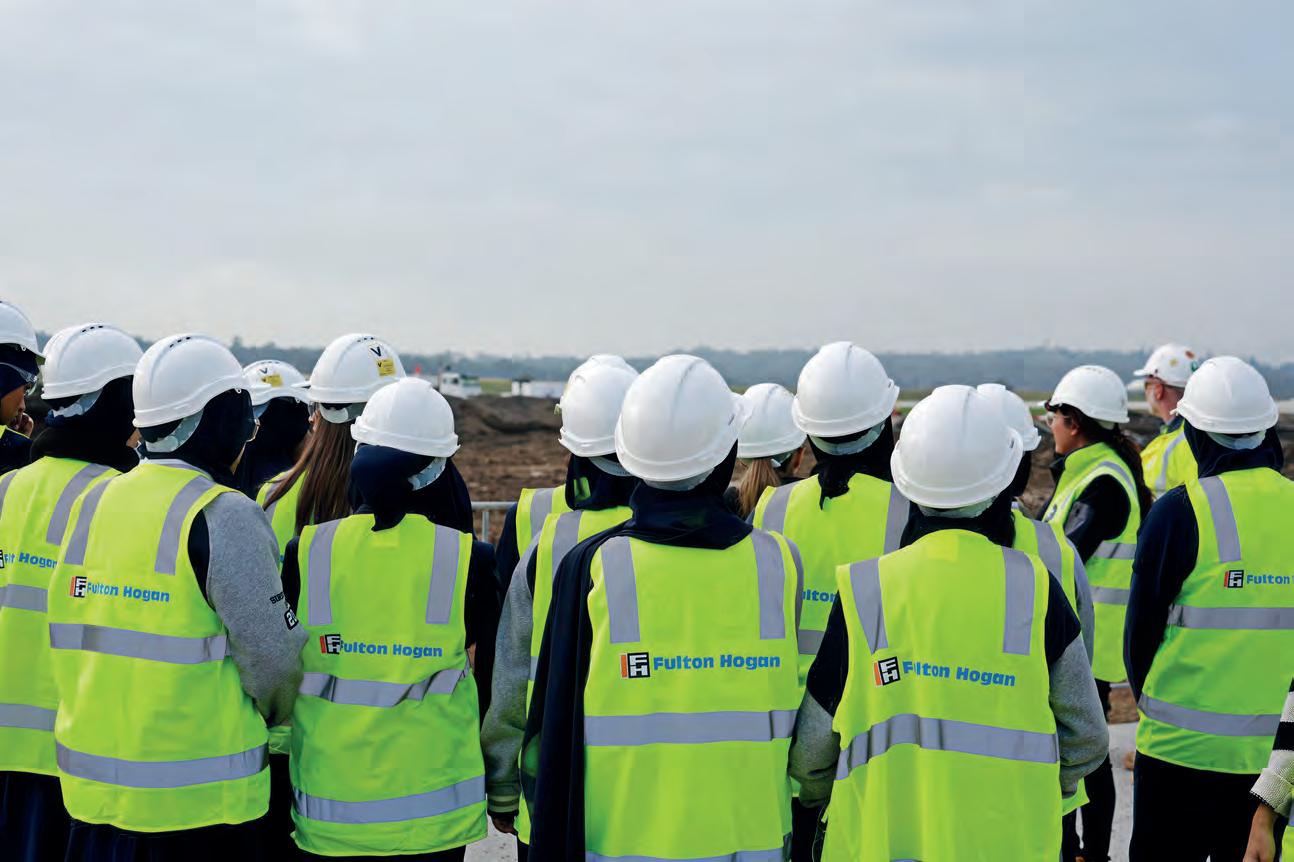

industry starts with awareness,” Hogan says.
First held in 2023 in Melbourne’s east, the event combines Fulton Hogan’s three divisions – Construction, Infrastructure Services and Utilities – providing participants with direct exposure to construction careers.
Aimed at high school female and nonbinary students, the ‘A Day in Her Boots’ program has been designed to create awareness around opportunities within the infrastructure industry, showcasing the variety of career pathways available across the sector at all levels.
Key to the day is demonstrating that there are so many roles and opportunities available in the industry – ensuring students are informed, so that when they start selecting subjects or thinking about what they want to do when they finish school, they know about the diverse opportunities in the sector.
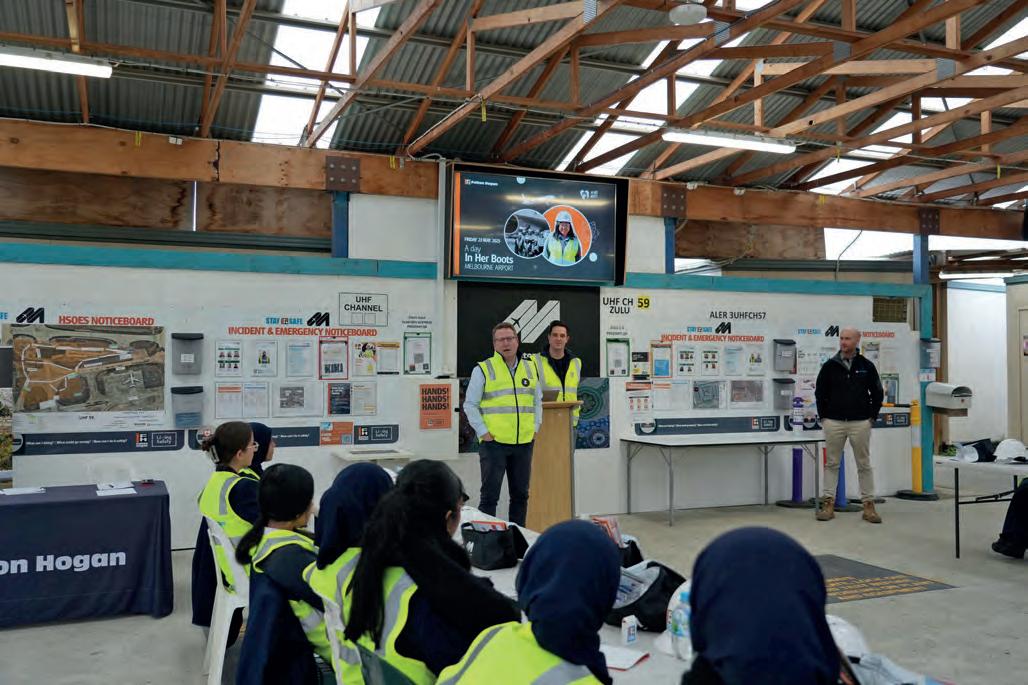
The program includes plant demonstrations, activities focused on different disciplines, panel discussions, and opportunities to speak with various people from within the industry.
This year students from Sirius College in Melbourne were in attendance, a school that prides itself on its establishment and support of STEM (Science, Technology, Engineering, and Mathematics) topics and curricular.
These students attended a panel discussion, site visit, and activity rotations
as part of the program. The panel involved Fulton Hogan personnel and industry experts across various disciplines sharing their experience and journey into the construction industry. This included younger female engineers to ensure they were relatable to the students.
“It was important to showcase the diverse roles within the industry, and the various pathways taken into these positions – demonstrating that there are many pathways and career journeys that can be taken, and non-traditional career routes can be just as effective,” Hogan says.
The site visits are a critical component of the program, offering students direct
exposure to the unique opportunities and challenges in construction environments. This hands-on experience, showing real-world working environments helps to connect the practical aspects of construction work with the career steps required to contribute to such projects.
Program activities have a different focus each year, with plant demonstrations and discipline-specific activities covering essential aspects such as stakeholder management, safety, environment, engineering and project management.
ADAPTING AND GROWTH
Based on the success, Fulton Hogan is looking to grow and expand the ‘A Day in
Students heard from young engineers and other specialists on their career pathways through the sector.
The ‘A Day in Her Boots’ program has successfully run for several years now, with another iteration on the cards for next year.
Images: Fulton Hogan
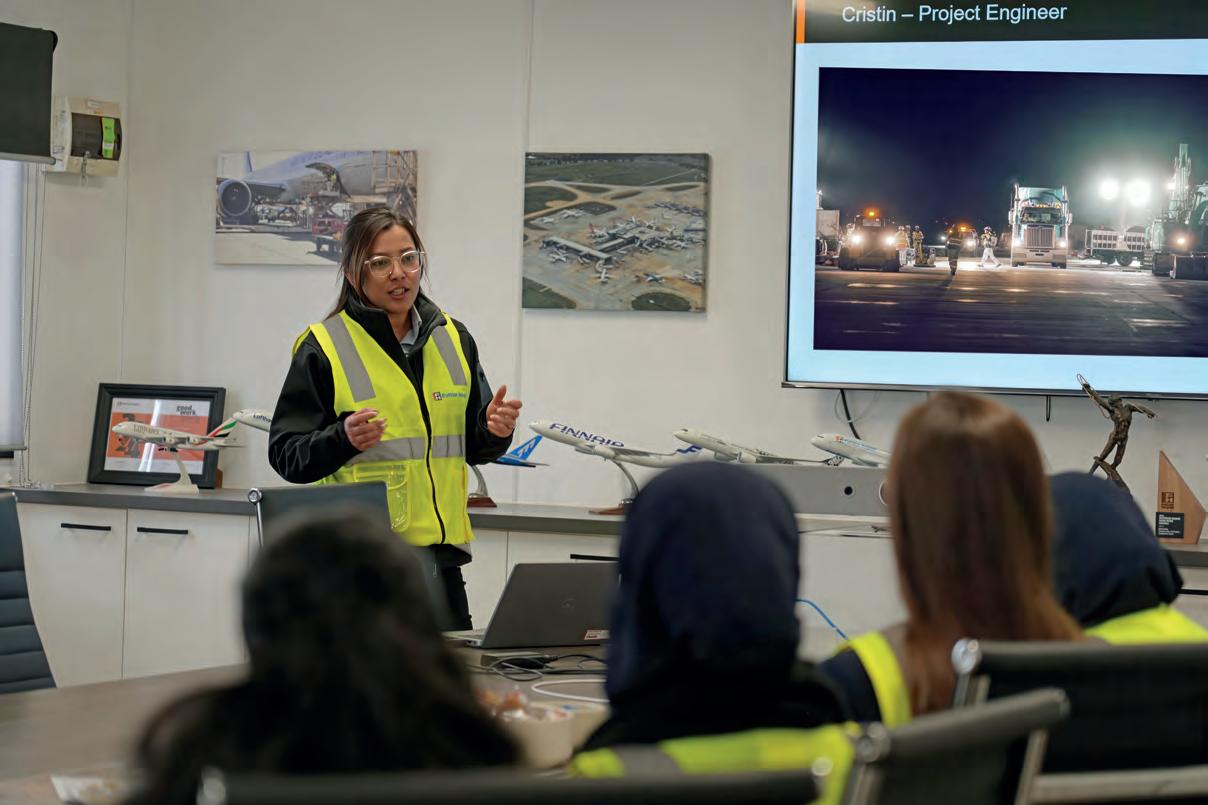
Her Boots’ program, with feedback from the students, teachers and parents being overwhelmingly positive, highlighting the importance of such a day in providing valuable insights on career opportunities for young women.
“It’s exciting to see a genuine interest and participation from the students,” Hogan says. “We know that we’ve been able to provide something that the students can go home and talk to their friends and family about.”
The success of the program is also helping to inspire the creation of
additional initiatives, joining Fulton Hogan’s vast list of activities aimed at supporting the community, such as ongoing partnerships with the Clontarf Foundation, Invictus games, as well as the Black Dog Institute.
Setting an example is the biggest benefit, with Hogan adding that even she might’ve considered a career in construction earlier had such a program been available during her upbringing.
“It goes back to the adage of ‘you can’t be what you can’t see’ – unless students get exposure to
the diverse and rewarding careers in the construction industry, it can be incredibly hard for them to see this industry as somewhere to start a career,” she says.
By exposing students to a day in the shoes of a female civil engineer working on a major project – or a plant operator, or someone in a safety or community and stakeholder role –Fulton Hogan hopes to demonstrate that the opportunities in the sector are endless, and that there’s a career for everyone interested.
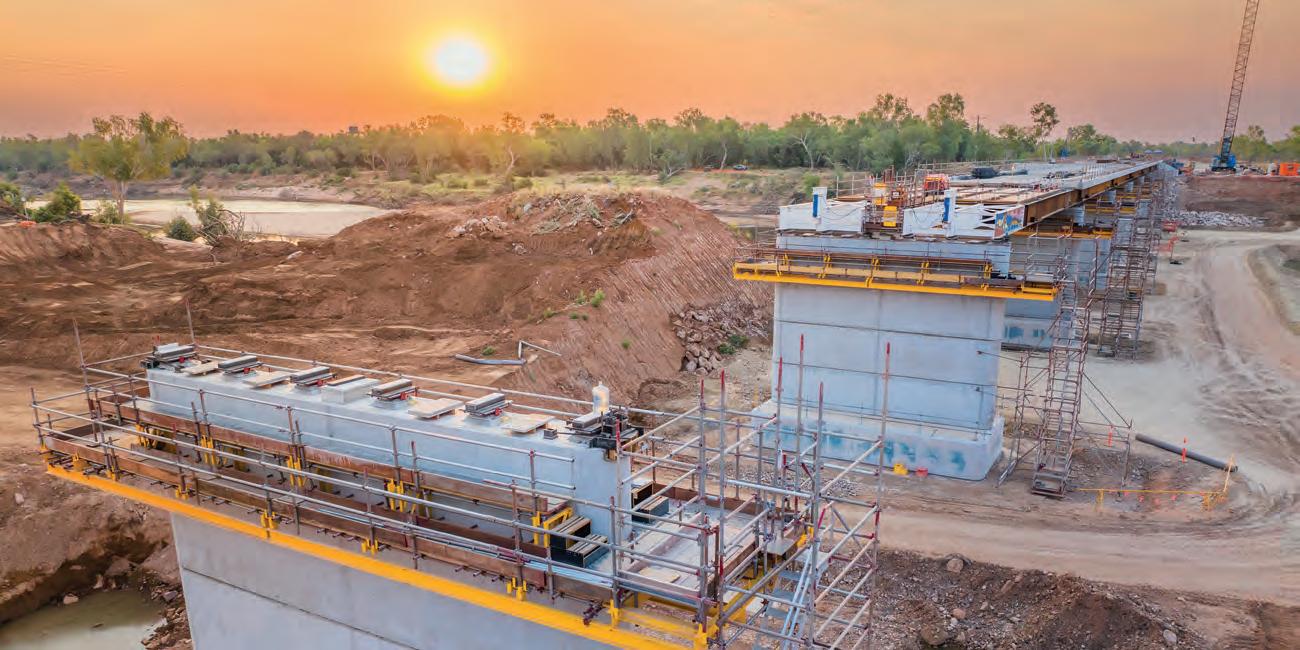
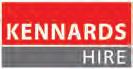
A mixture of classroom and hands-on sessions aimed to educate students on conventional and non-conventional pathways to a career in construction.
People on the move
ROADS & INFRASTRUCTURE HELPS YOU KEEP
UP
WITH THE LATEST MOVEMENTS ACROSS THE ROADS AND INFRASTRUCTURE SECTORS.
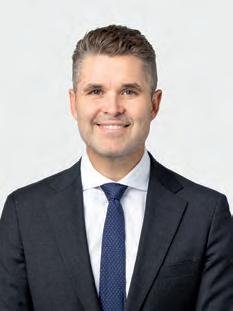
MAINMARK APPOINTS NEW CEO
Mainmark has announced the appointment of Peter Bierton as the company’s new Chief Executive Officer. Bierton has previously served as Downer’s General Manager for Transport and Infrastructure Maintenance division based in Sydney since 2022. Prior to this, he held senior leadership roles at UGL Engineering and Zinfra, working on major projects such as Sydney Metro, Light Rail, and expanding telecommunications networks across New Zealand. A spokesperson from Mainmark’s board said his expertise in commercial and infrastructure projects will complement the company’s continued growth in these sectors. They added that his knowledge will reinforce the company’s core technologies, support global expansion, and enable the delivery of innovative solutions while expanding its range of services. Bierton said he was drawn to Mainmark for its unique mix of innovation, practical application, and global potential. Bierton’s tenure commenced Monday, June 2.
Image courtesy of Mainmark
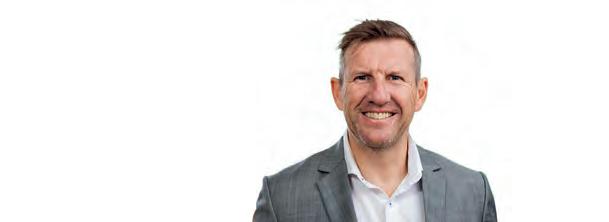
NEW GROUP TECHNICAL MANAGER FOR MCCONNELL DOWELL
McConnell Dowell has announced David Middleton as the company’s new Group Technical Director – Water. Middleton brings with him 33 years of executive leadership across international engineering consulting and delivery in the water and power sectors. With a proven track record in strategic growth, governance, innovation, and digital transformation, Middleton is a respected leader whose experience spans Australia, New Zealand, and Southeast Asia. Most recently, he has served on the Board of a number of water organisations. The Middleton appointment is expected to strengthen the company’s commitment to growing its water business. His deep experience across the water sector – from both the client and service delivery sides – gives him a unique ability to shape solutions that are technically sound, sustainable, and commercially astute. As Technical Director – Water, Middleton will focus on expanding the company’s presence and partnerships in the water sector, drawing on his extensive industry relationships and passion for building highperforming, inclusive teams.
Image courtesy of McConnell Dowell
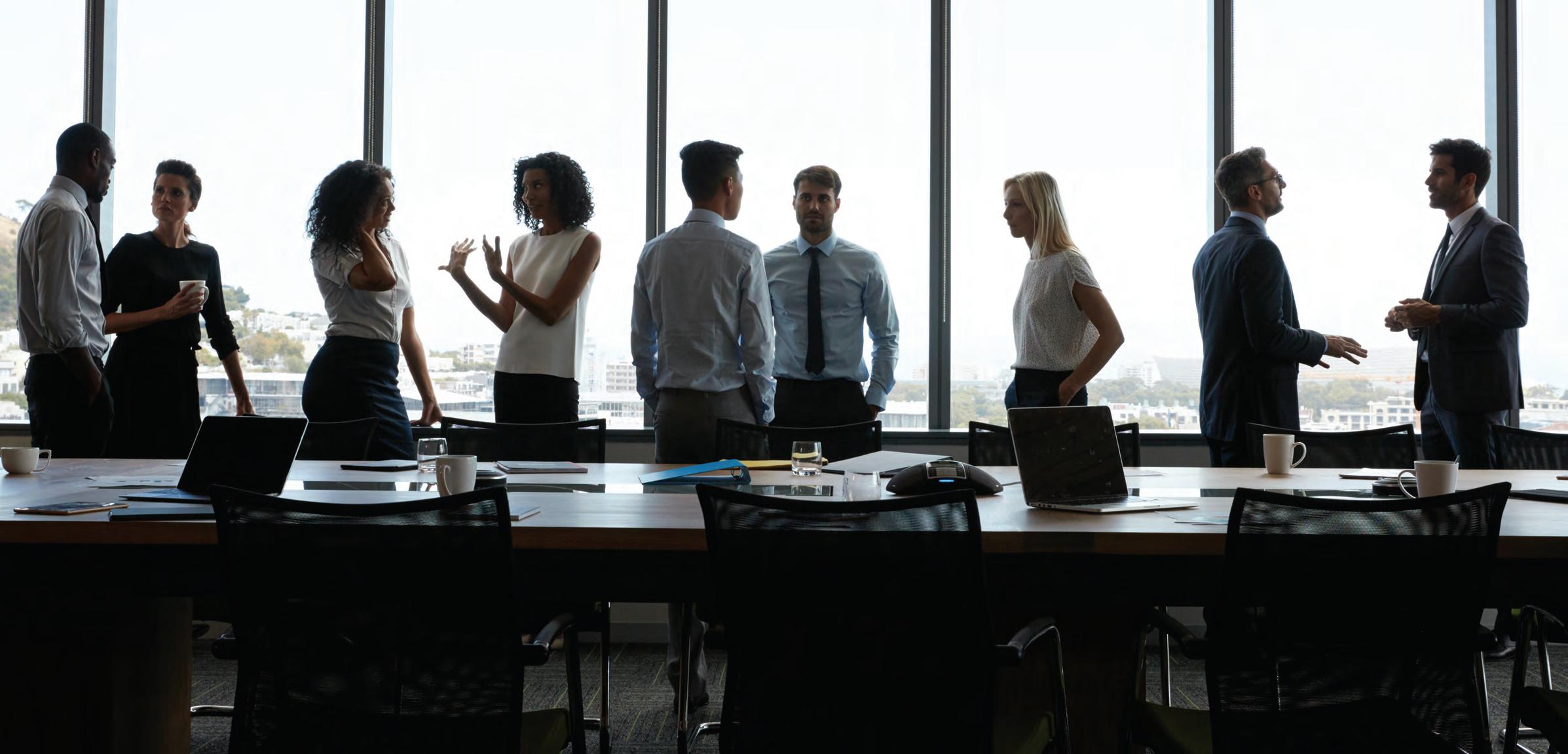
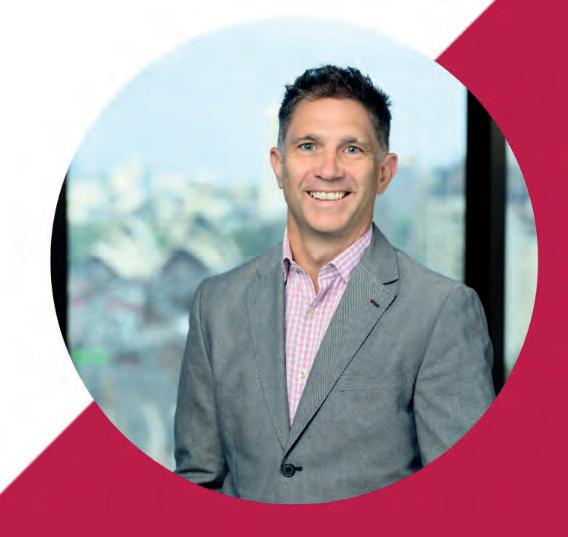
GEORGIOU WELCOMES NEW GENERAL MANAGER FOR NEW SOUTH WALES
Georgiou has announced the appointment of Nick Fryday as the new General Manager of the company’s New South Wales Business Unit. Fryday will step into a key leadership role that will shape the future of Georgiou’s operations across New South Wales. Fryday brings experience in infrastructure delivery, as well as a leadership style and set of values that strongly align with Georgiou’s culture. With a career that has taken him from Ireland and New Zealand to regional New South Wales, Fryday brings more than two decades of hands-on industry knowledge. He holds a Bachelor’s degree in Civil Engineering and Mathematics, a Master’s in Project Management, and is a Chartered Professional Engineer (CPEng). Fryday’s impressive portfolio includes senior leadership on complex infrastructure projects such as the Georgiou CPB Joint Venture M12 Motorway West Project, Dubbo Regional Rail Maintenance Facility, and Northern Road Stages Five and Six. Fryday’s breadth of experience spans multiple delivery models – PPP (Public Private Partnership), D&C (Design and Construct), ECI (Early Contractor Involvement), Construct Only and Alliances.
Image courtesy of Georgiou
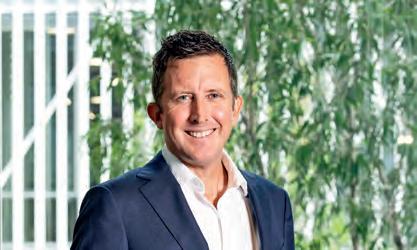
FRESH APPOINTMENT FOR AURECON
Aurecon has appointed Todd Battley as its new Chief Executive for Australia. Battley will work closely with incoming Group Chief Executive Officer Louise Adams and other members of Aurecon’s Group Executive Leadership Team to drive strategic growth across Australia and shape Aurecon’s global response to the future of engineering, design and advisory services. Battley joins from AECOM where he held roles including Chief Strategy Officer and Chief Executive for Australia and New Zealand. Throughout his 29-year professional career he has developed a purpose-driven and collaborative leadership style focused on inspiring innovation and achieving business growth.
Image courtesy of Aurecon
NEW APPOINTMENTS ANNOUNCED FOR KEY RAIL BOARDS
The Federal Government has announced seven new appointments to the Australian Rail Track Corporation (ARTC) and the National Intermodal Corporation (National Intermodal) boards. Ingilby Dickson, Janet Finlay, Michael Carter and Jill Rossouw have been appointed for three-year terms, and Marlene Kanga for a two-year term, as Non-Executive Directors of the ARTC Board. Other announcements include Michael Carter’s appointment as Deputy Chair, Janice van Reyk as Non-Executive Director and the reappointment of Michael Byrne as Non-Executive Director of the National Intermodal Board, each for a three-year term. Dickson is expected to provide the ARTC Board with expertise in freight, supply chain, rail and safety following his roles with Sadleirs Transport Group, Ron Finemore Transport and the Australian Logistics Council. Finlay has held roles across multiple sectors as well as government, including as the Deputy Chancellor of Adelaide University, Director of the SA Water Corporation and Deputy Chair of the State Planning Commission of South Australia. Carter has a strong construction background and rail experience, principally in rail operations, including at Queensland Rail and Aurizon Holdings. Rossouw is an experienced director, having held Non-Executive Director positions with the Port of Brisbane and the Brisbane Airport Corporation. She is the current Chair of the High Speed Rail Authority. Kanga has extensive board director experience, having been a board member of Endeavour Energy, the Sydney Water Corporation, Innovation Australia and Airservices Australia. van Reyk has held roles at NSW Ports, Port of Melbourne/Ports Victoria and the Australian Naval Infrastructure, with Byrne being an existing director of National Intermodal with experience in the ports, logistics and supply chain sectors, as well as board roles with the CBH Group and Peel Ports UK.
ANSWERING THE CALL
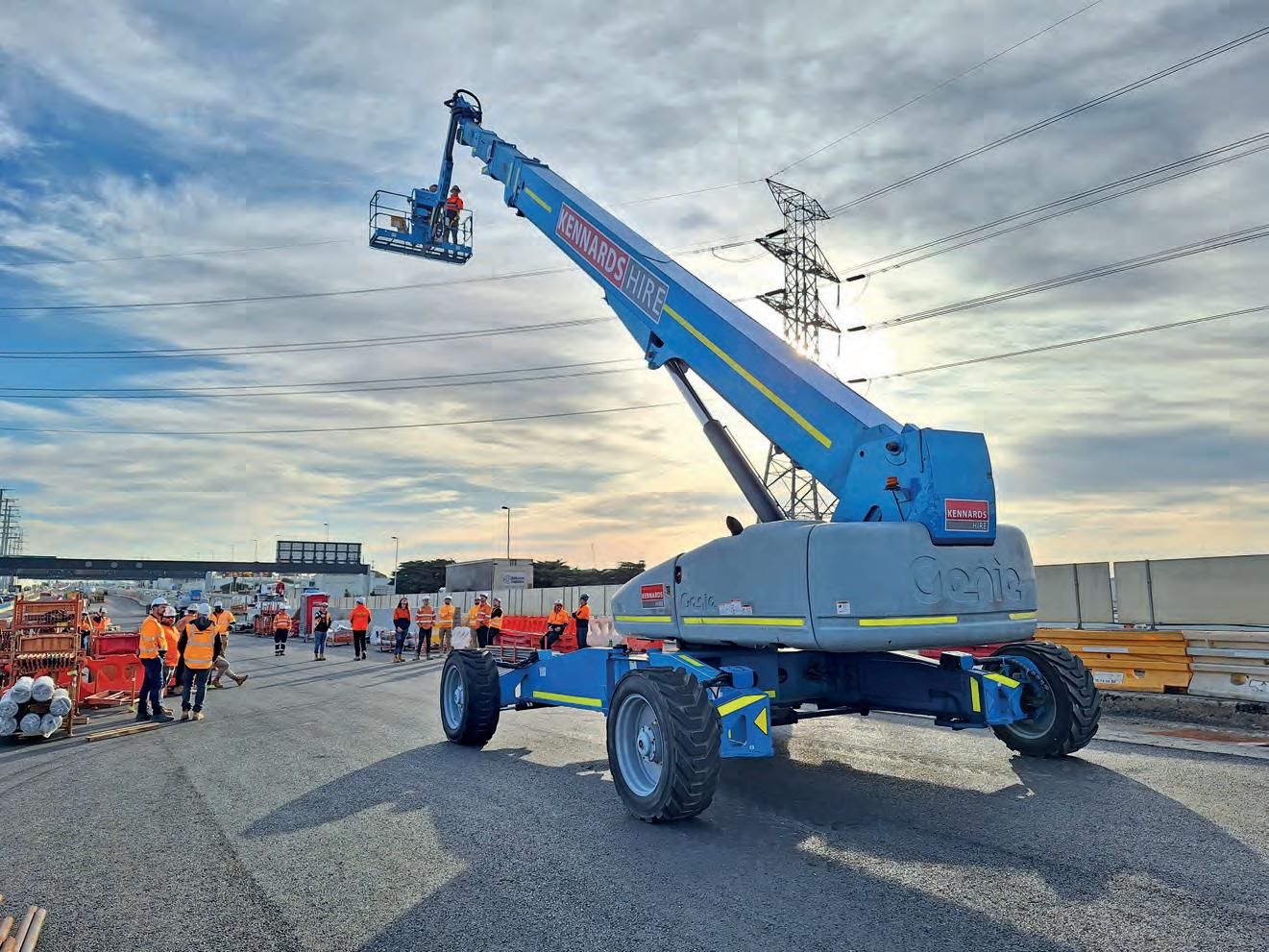
KENNARDS HIRE’S WORK ON THE WEST GATE TUNNEL PROJECT IN MELBOURNE HAS EXEMPLIFIED ITS CAPABILITY AND CAPACITY TO CATER FOR MAJOR INFRASTRUCTURE PROJECTS, OR IN THIS CASE, ONE OF THE BIGGEST TRANSPORT PROJECTS IN AUSTRALIA’S HISTORY.
Melbourne is the fastest-growing city in Australia, with the city’s population expected to increase from 4.6 million to almost eight million by 2051, according to the Victorian Government.
In order to future-proof and ensure the continued efficiency of the city’s surrounding transport infrastructure, there has been ongoing investment and development to upgrade and improve existing routes.
Major works are also creating brand new transport options and connections for future generations. Melbourne’s West Gate Tunnel Project (WGTP) is one such project.
The WGTP is one of the largest and most significant infrastructure developments ever undertaken in Australia, delivering a brand-new underground tunnel to provide an alternative transport route to the West Gate Bridge, which is approaching its serviceable capacity.
Once completed, twin tunnels under the suburb of Yarraville (between the West
Gate Freeway and the Maribyrnong River) will deliver a vital alternative route that will remove thousands of trucks off residential streets and provide quicker and safer journeys for commuters.
Vehicle entry and exit points situated at both the southern and northern ends of the tunnels – otherwise known as portals –form a key part of the aesthetic and desired efficiency that will be provided as part of the overall project, delivered as part of Victoria’s ‘Big Build’ program.
Few local providers could cater for the size and volume required to deliver this essential and complicated project stage. Kennards Hire is one of them.
With a dedicated division and vast experience in project management, Kennards Hire can provide a dedicated team that works together with project stakeholders to deliver optimal outcomes. For major projects, such as this one, Kennards Hire also appoints a KMP manager (Kennards Major Projects), meaning
assistance is only one call or a tap on the shoulder away.
Having already been engaged to deliver service and equipment to aid site entry on the project, as well as crib sheds, power tools and other smaller equipment – Kennards Hire was given the opportunity to tender.
Its pitch included extra EWPs (Elevated Work Platforms), 10 180-foot boom lifts –that would facilitate the mid-air transfer of structures – and two 135-foot boom lifts. Two 215-foot boom lifts were also required to fix the structures over the ventilation building, which form part of the southern and northern tunnel portals.
Kennards Major Projects Victorian Manager, Cody Rowan, says the project was a great opportunity to showcase Kennards Hire’s access capabilities on one of the biggest and most visible civil construction projects in Melbourne.
“We were very transparent with our quote – there were no hidden costs or any hidden agendas,” Rowan says.
“We knew we could supply the equipment and provide training but what gave us a point of difference was offering a dedicated project manager to the project.
“That was really important, that we were honest and upfront about costs and delivery, that we had the backing of our national
Kennards Hire has delivered several access enhancements to the West Gate Tunnel Project in Melbourne.
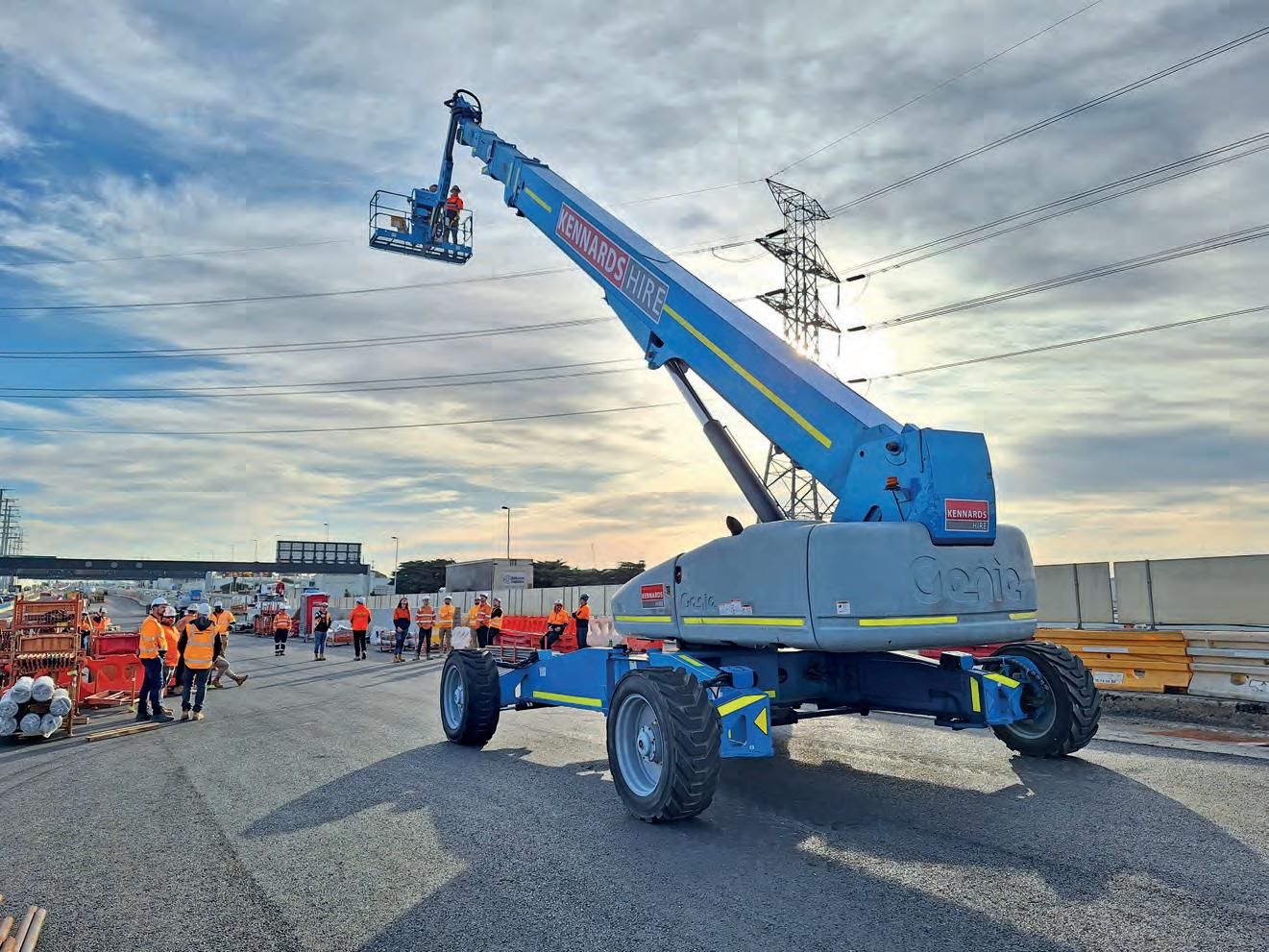
Kennards Hire network, a demonstrated reputation for quality equipment, while also being able to provide expert project management support onsite.”
Richard Impey, Project Manager – Kennards Hire was appointed to oversee this delivery, drawing on his vast industry experience and existing relationships with the West Gate Tunnel Project delivery team.
“Richard gave them a single point of contact and the confidence that we had the ability to deliver on what we said we were going to deliver, especially with regard to this specialised access equipment,” Rowan says.
RIGHT MAN FOR THE JOB
The equipment offered, as well as expertise, was seen as comprehensive, leading to Kennards Hire being handpicked for the job by CPB John Holland Site Superintendent, Unakea Taiki.
Taiki says that the timeliness and assistance offered play a key role in keeping a major project like this moving.
“Whenever I need equipment, Kennards Hire has delivered it then and there, no questions asked,” he says.
“With the great service we’ve already received, asking them to quote for this job was a ‘no-brainer’.”
He adds that a key standout has been the direct rapport with Impey, an individual who he says has added great value to the project delivery team.
“Richard is onsite every week to check on the equipment and the project. I’ll give him
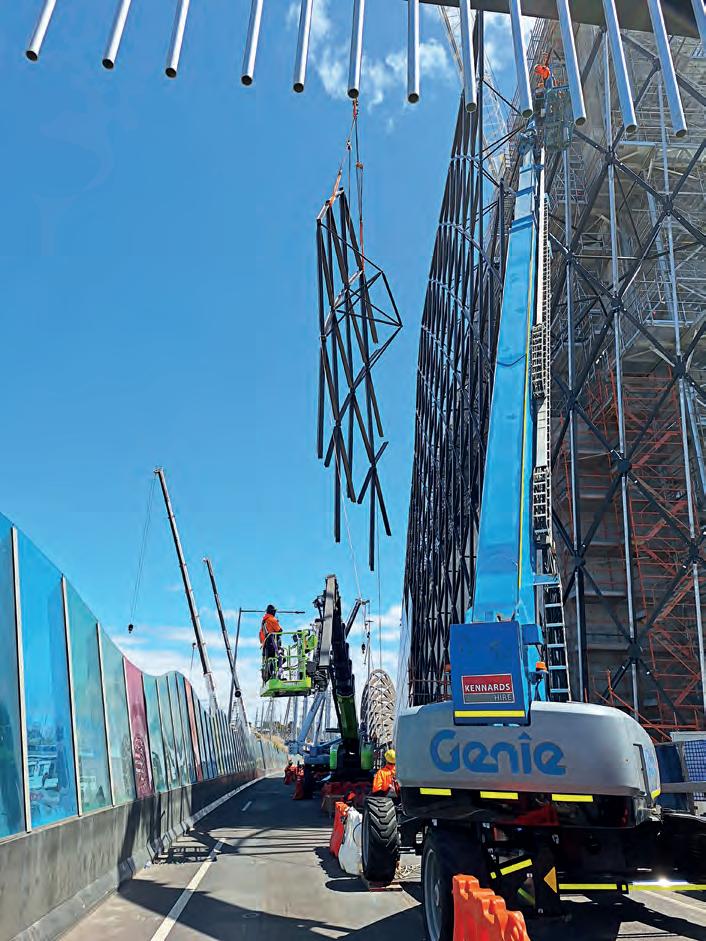
unrealistic deadlines, where I need a piece of equipment in the next hour or two and it’s always been supplied,” Taiki adds.
“If there’s an issue with anything, I know
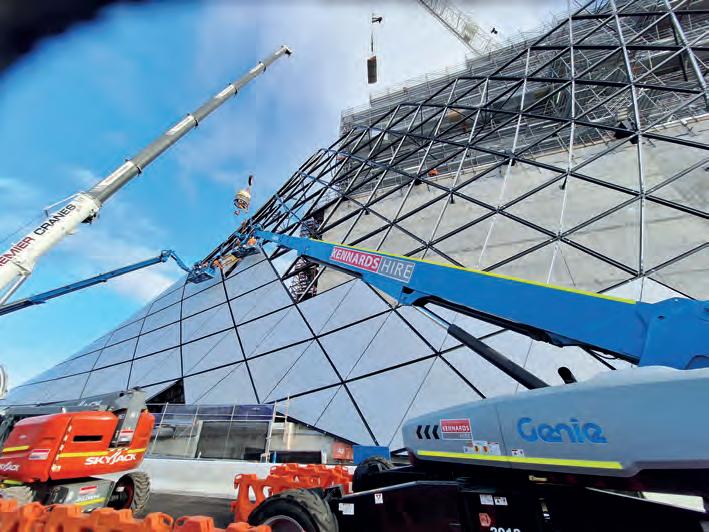
I can call him, and someone will be there within the next half an hour.”
Kennards Hire knows that time equals money, and for a project of this magnitude, every second counts. Which is why the company’s around-the-clock on-call service has become so important, Taiki says.
“We’re on multi-million-dollar projects, and when we want something, we want and need it now,” he says. “At the moment, Kennards Hire is the only one providing that level of service.
“With the project operating 24/7, downtime is simply not an option. It’s critical to know there’s someone from Kennards Hire available at all times to solve our problems, should anything arise.”
The service and project capability has surpassed expectations, with Taiki saying Kennards Hire has set the standard for hire equipment services on major infrastructure projects.
“What I’d say to other hire equipment suppliers is if you want to be on the same page as Kennards Hire, your service needs to be top notch,” he says.
Images: Kennards Hire
Kennards Hire appointed a dedicated project manager to oversee the works, as part of its regular project management service.
Kennards Hire has been used as part of several lifts at the northern and southern portals of the project.
JOINING THE ASTEC FAMILY
HT ROAD SURFACING, A PROUD FAMILY-OWNED AND LOCAL COMPANY, HAS PURCHASED ITS FIRST ASTEC UNIT. REPRESENTATIVES FROM HT ROAD SURFACING AND ASTEC REFLECT ON THE MILESTONE, AS WELL
Led by an ambition to become the most trusted subcontract crew in south-east Queensland, HT Road Surfacing has achieved monumental growth for a family business, since its foundation three years ago.
Established by Jason Liley, along with his business partner Craig Jennings, HT Road Surfacing conducts a variety of road construction services for sites of all scales in Brisbane and the surrounding area. With 70 years of experience between them, Liley and Jennings have intentionally
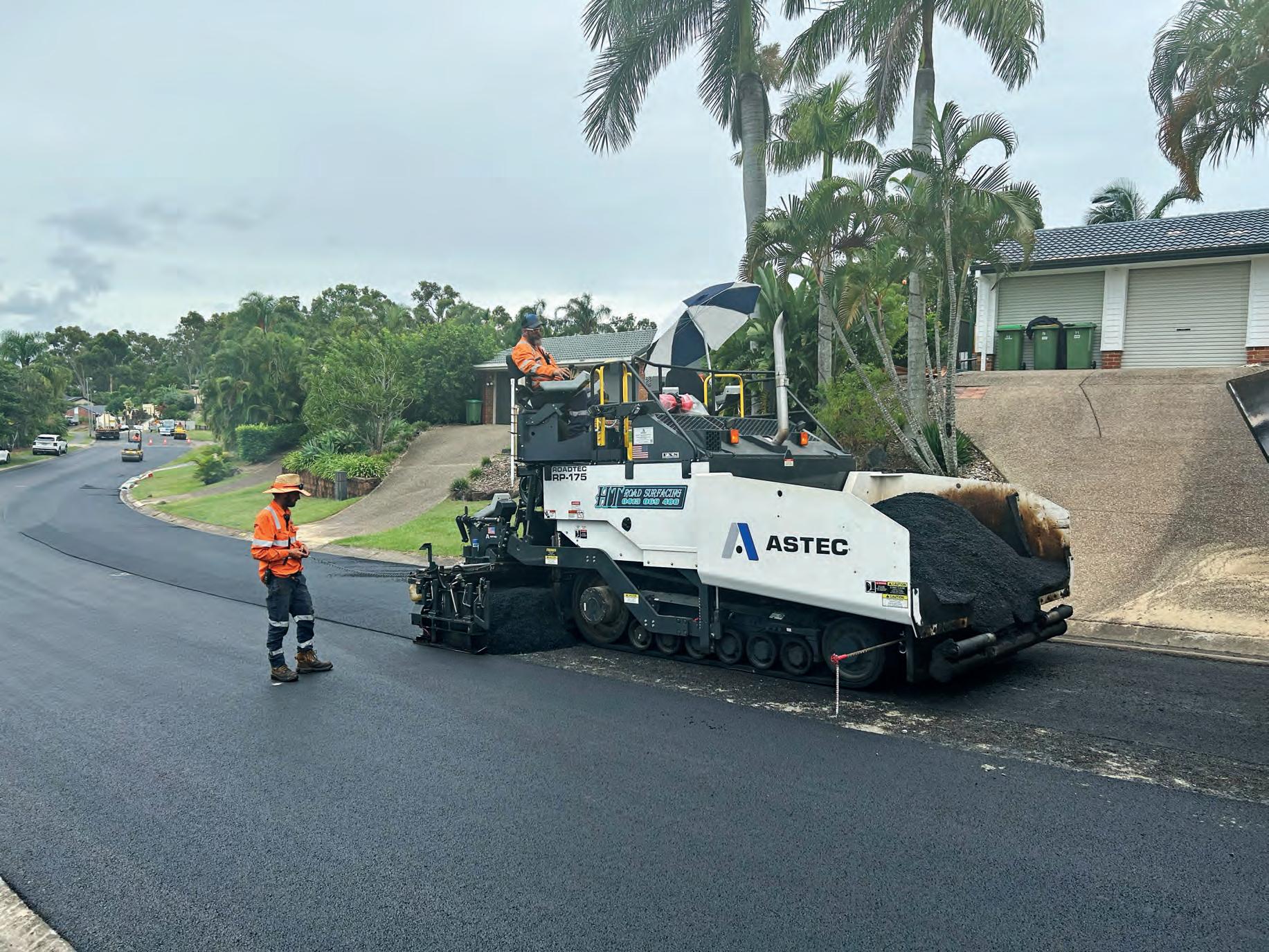
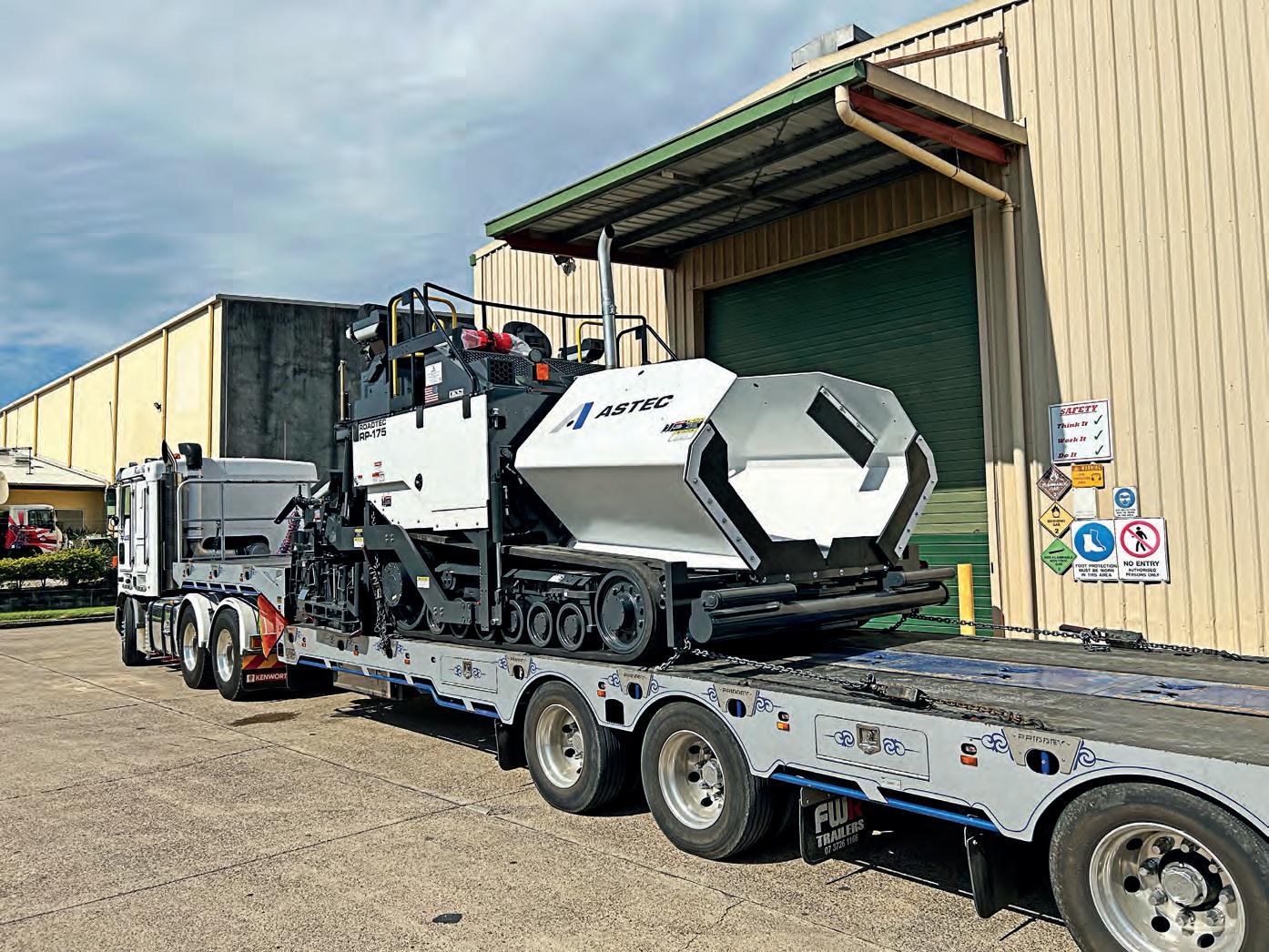
HT Road Surfacing’s RP175ex on site.
HT Road Surfacing loading up the RP175ex as part of the handover.
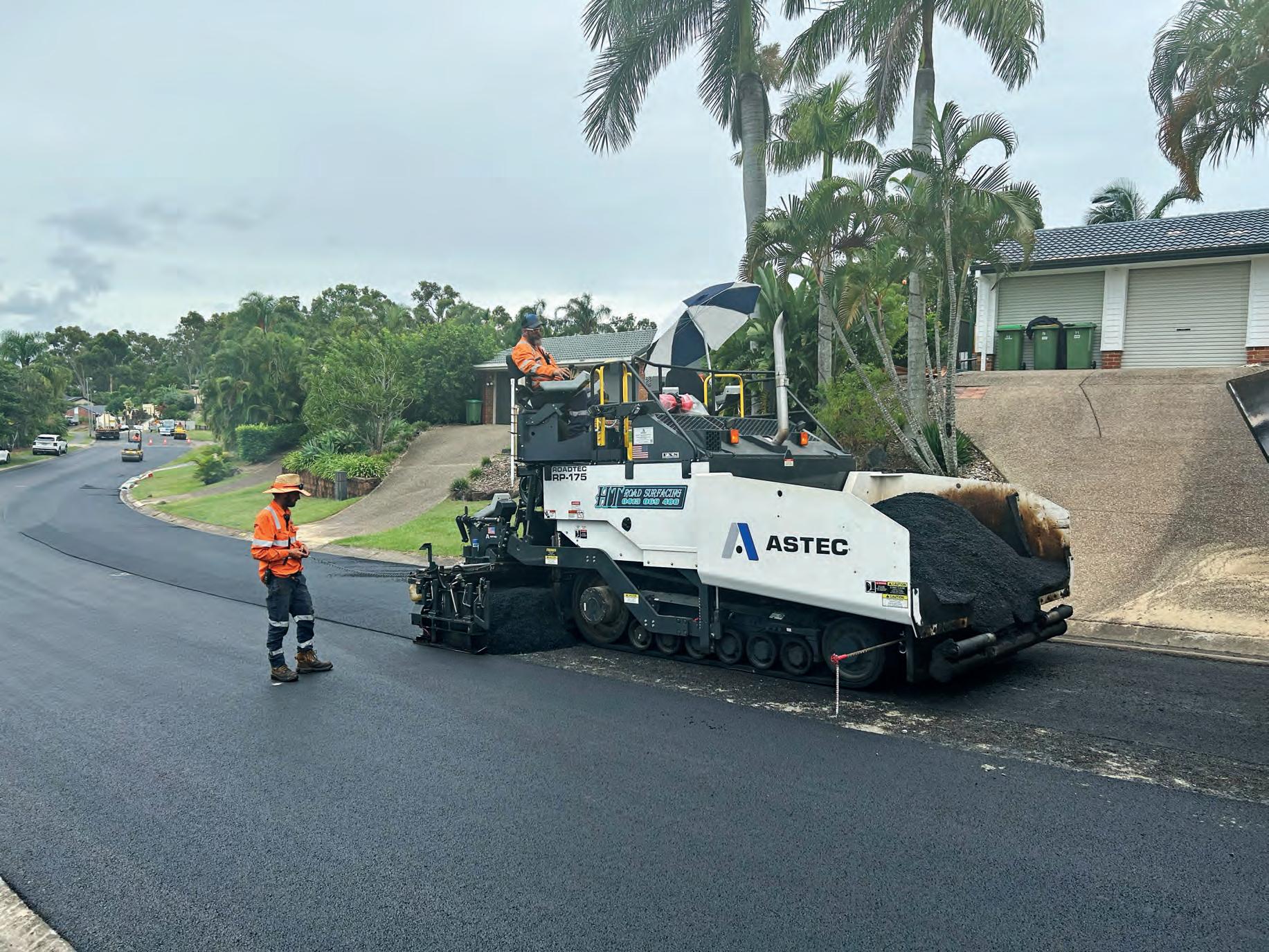
deliver high quality outcomes for projects.
“We pride ourselves on the reliability and affordability of our service. Having the best machinery is a big part of that,” he says.
To further its growth trajectory, the HT Road Surfacing team last year began discussions around adding to its machinery fleet.
At the time, the company was borrowing a lot of equipment, with the hope that purchasing its own unit could benefit the businesses’ bottom line.
“The whole team sat down to work out exactly what we needed,” Liley says. “We wanted something that was going to be reliable, have a good warranty period and good after-sales service. Those were the three big things that we came up with as requirements.”
Liley had been aware of Astec machinery’s Roadtec paving line for some time. On top of he receiving positive feedback from others in the market, he himself was impressed from the outset.
Wanting to learn more, Liley and the team visited Astec’s site to enquire.
“We were welcomed straight away,” he says. “We actually felt like we were already part of the Astec family. They gave us a big tour around the shop floor and the machines they had there. It was a service that we hadn’t really received when going to other locations.”
After being shown the different options, one stood out from the rest.
BIG STEPS
The RP175ex Roadtec highway class asphalt paver represents HT Road Surfacing’s first venture into the Astec machinery range.
The machine’s manoeuvrability and power were identified as major benefits that could support the company’s ambitions to compete for larger works. Sporting a standard paving width of eight to 15 feet, along with a six-cylinder, 173 horsepower, 2200 revolutions per minute Cummins QBS 6.7, the tracked RP175ex can work across all types of sub-grades and paving applications.
“Everyone has commented on the exceptional quality of the mat it can lay,” Liley says. “We’ve found that the RP175ex is just as good at doing both the smaller and larger projects.”
Another benefit, Liley says, is Astec’s commitment to tracked paving units, offering greater control and versatility, particularly in potentially challenging terrain.
“In some ways it’s better than having a wheeled machine, because you can access, and get into, what are sometimes funky places,” he says. “If you’re coming up to a project where there’s going to be soft
ground or related issues, the track machine can be a big help.”
HT Road Surfacing has also had its wish for strong after-sales support granted, with Astec staff regularly checking in on both the machine and the relationship.
“A typical salesperson would sell you the machine and leave,” Liley says. “Astec keeps in touch and asks to come out to site, to have a look at what we’re doing and to examine how the mat’s been laid.
“We really look forward to growing and building that relationship.”
HT Road Surfacing has been so impressed that it’s considering purchasing a larger 195 model in the future.
“I can’t see us buying anything else but an Astec paver from now on,” Liley says. “Their machine and service have been incredible.”
Kevin Vercoe, CMS Territory Manager –Astec says the company has stayed true to its word, providing service and advice wherever possible.
“HT Road Surfacing is a well-respected business that’s letting its work do the talking,” he says. “As a family business trying to grow in the market and produce quality work, this is an enormous first step on that journey. Their future is really bright; the relationship is fantastic and it’s just a testament to how much they value this partnership with us.”
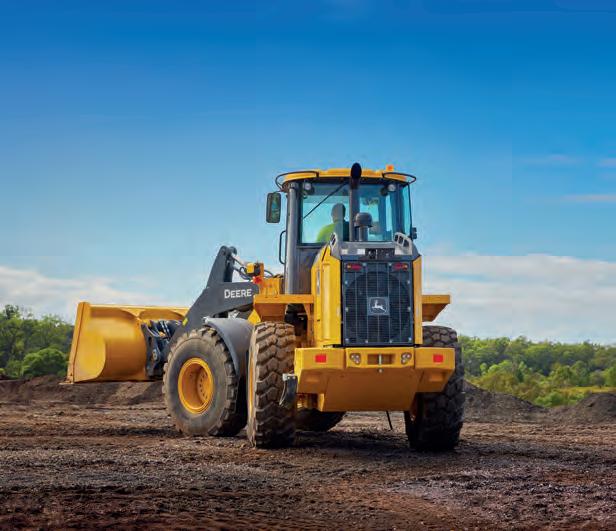
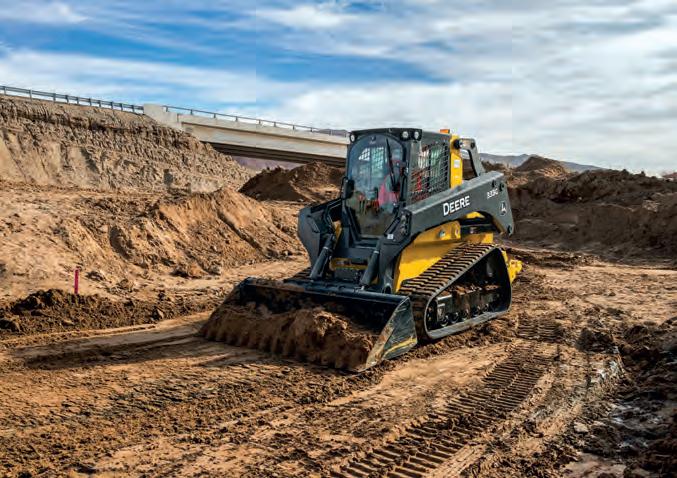
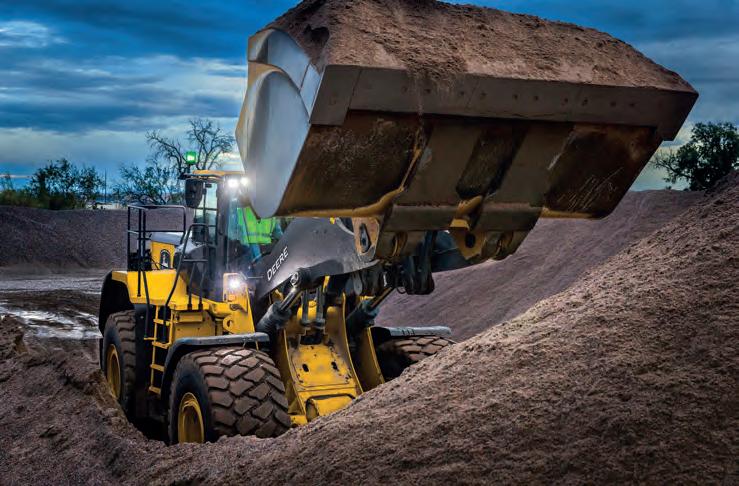
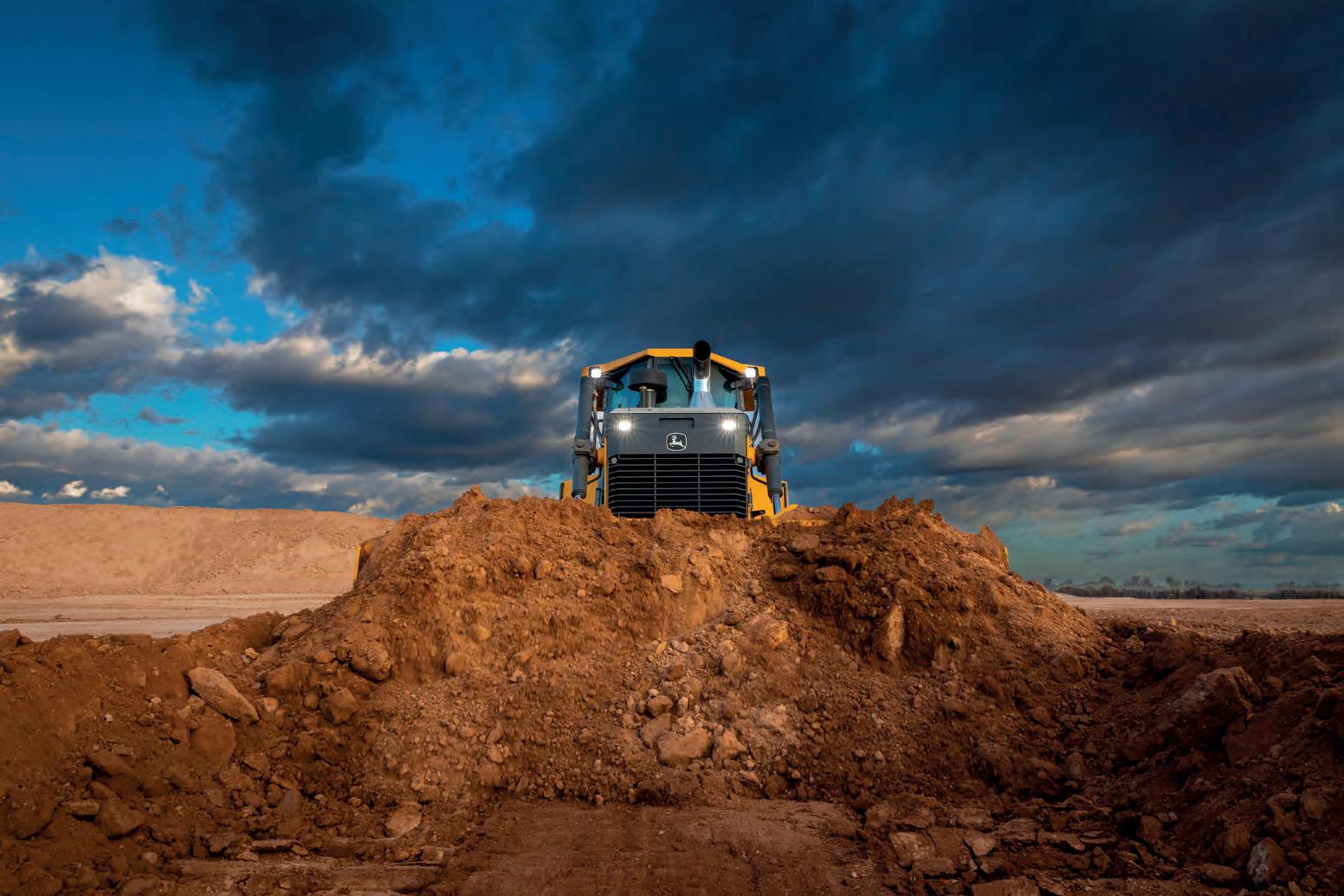
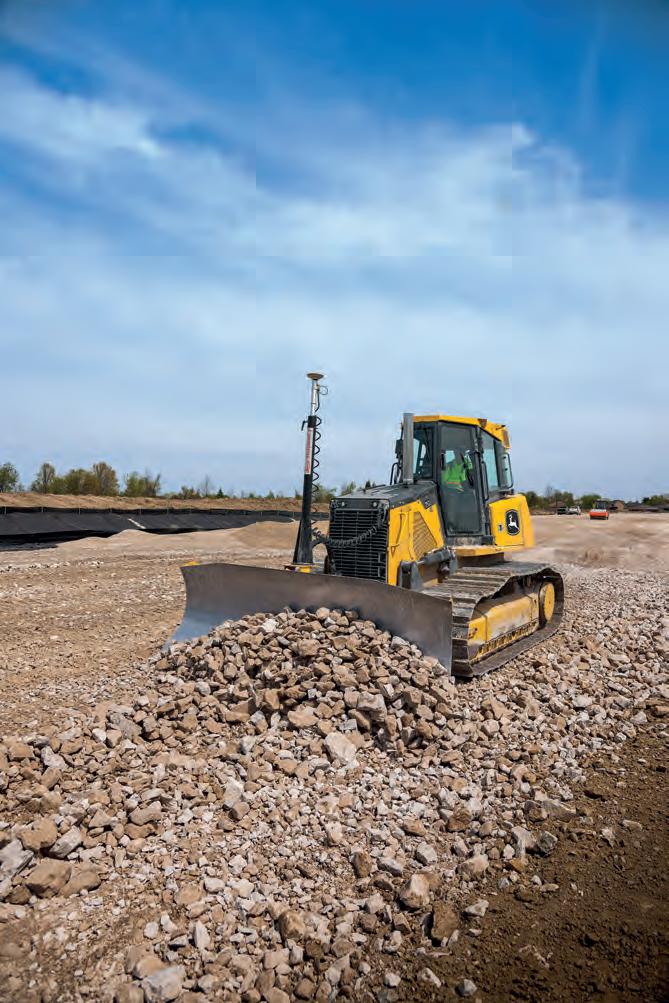

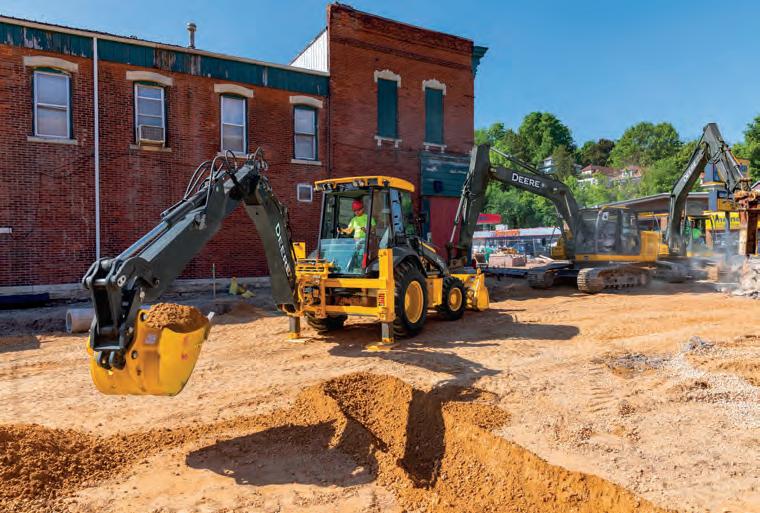
NOW’S THE TIME TO… DIG IN WITH A DEERE
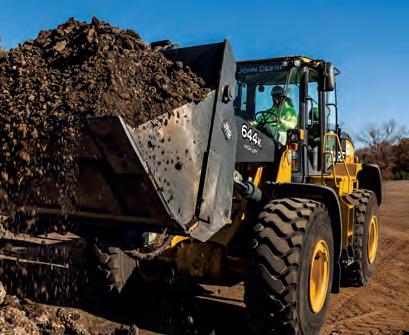
NEVER IDLE
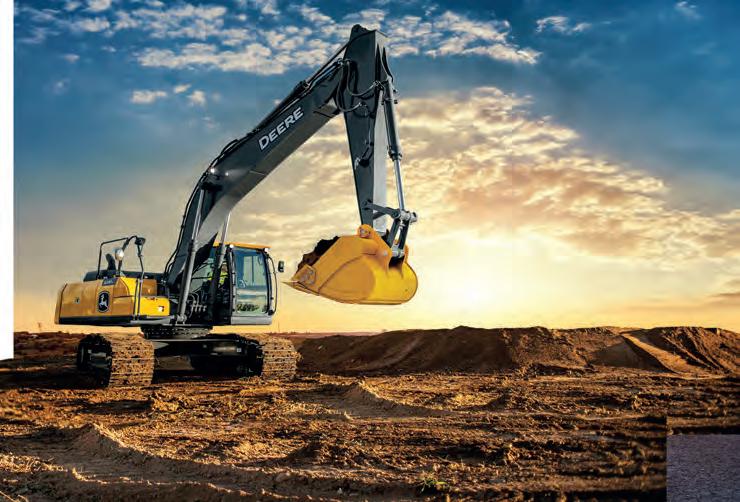
Ready to dig in and get more done? Invest in a Deere today and see how the perfect mix of power, precision and reliability can make your work easier and more efficient.
With Motor Graders, Dozers, Wheel Loaders, ADTs, Backhoes, Excavators, Skid Steer and Compact Track Loaders in stock and ready to go, now's a great time to dig in with a Deere. Be quick! Contact your dealer today.
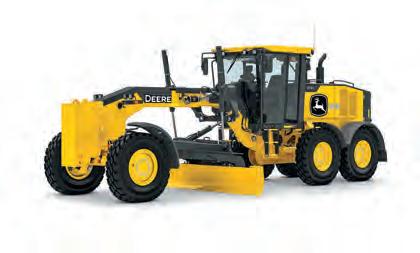
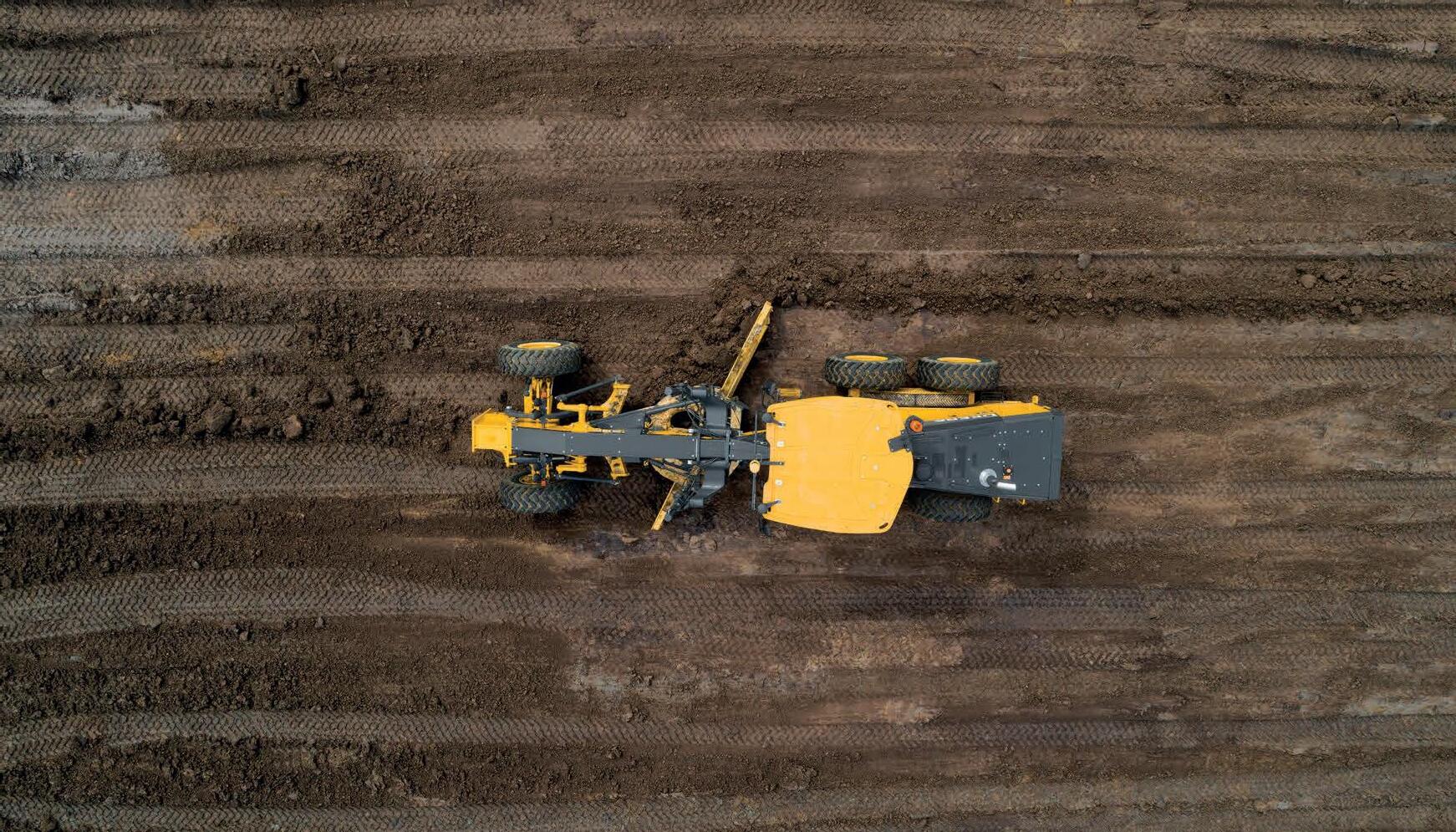
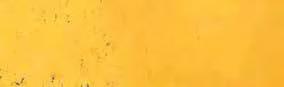
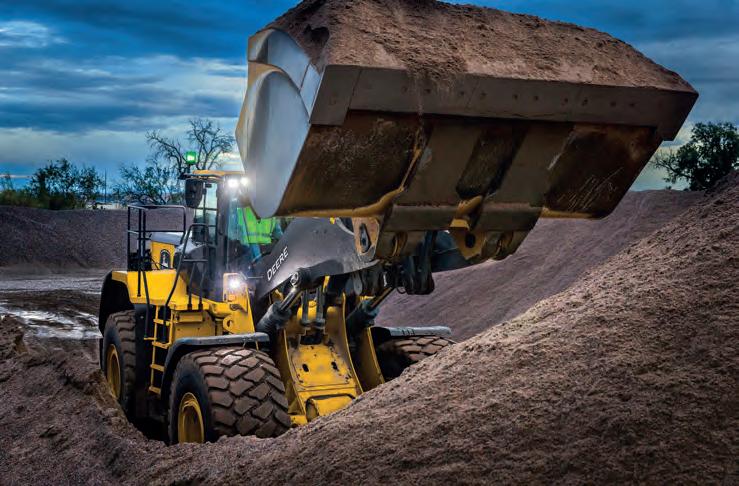
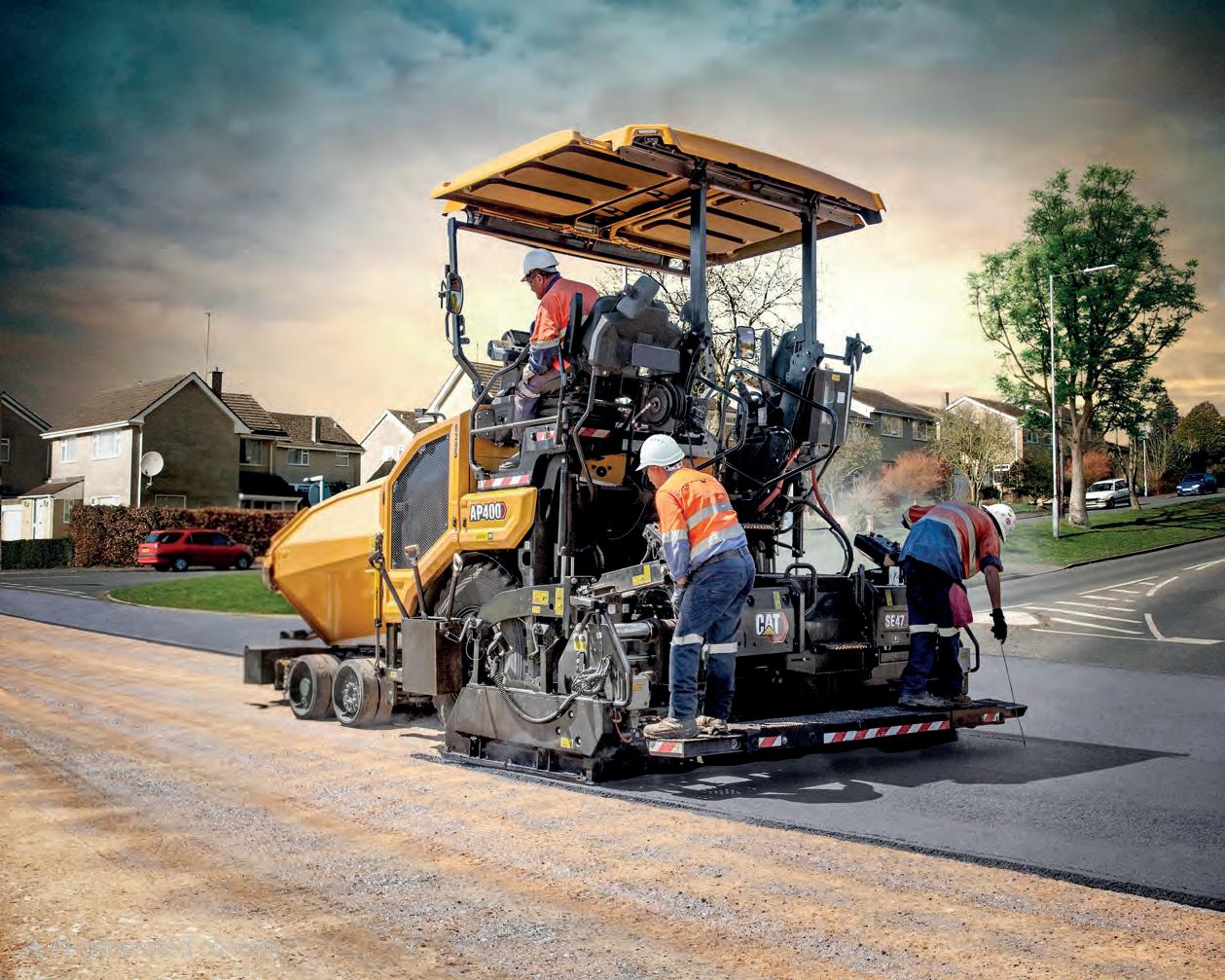
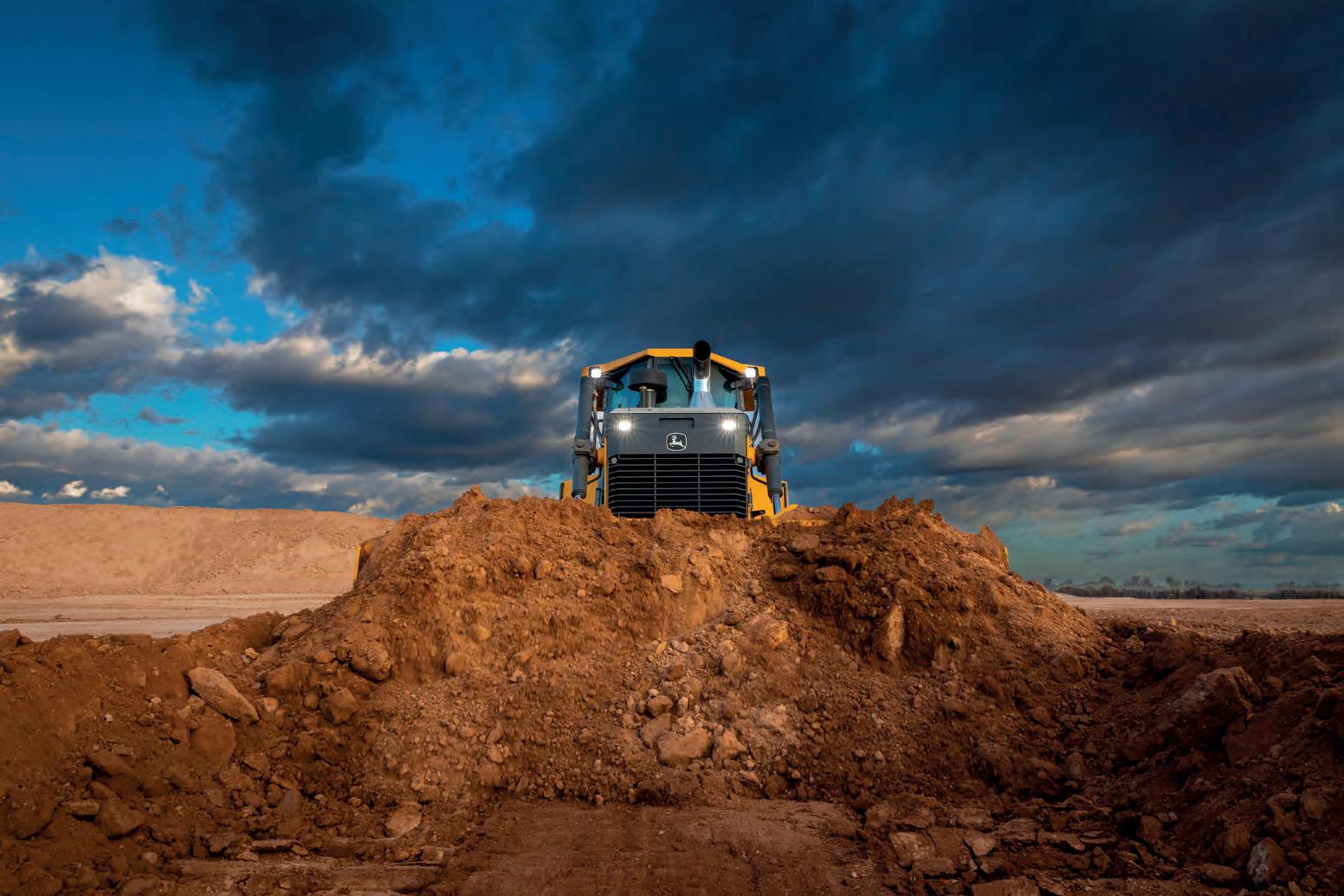
Caterpillar’s AP400 paver is just one of many innovative and specially designed pavers, fully supported by the company’s after-sales services nationwide.
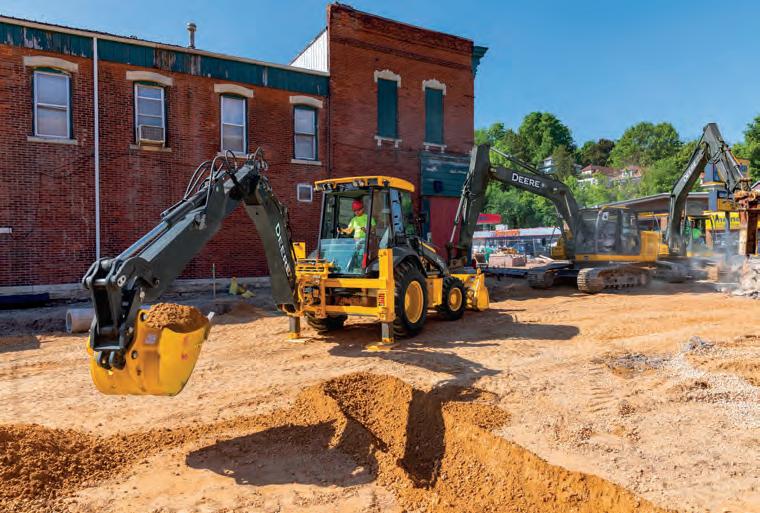
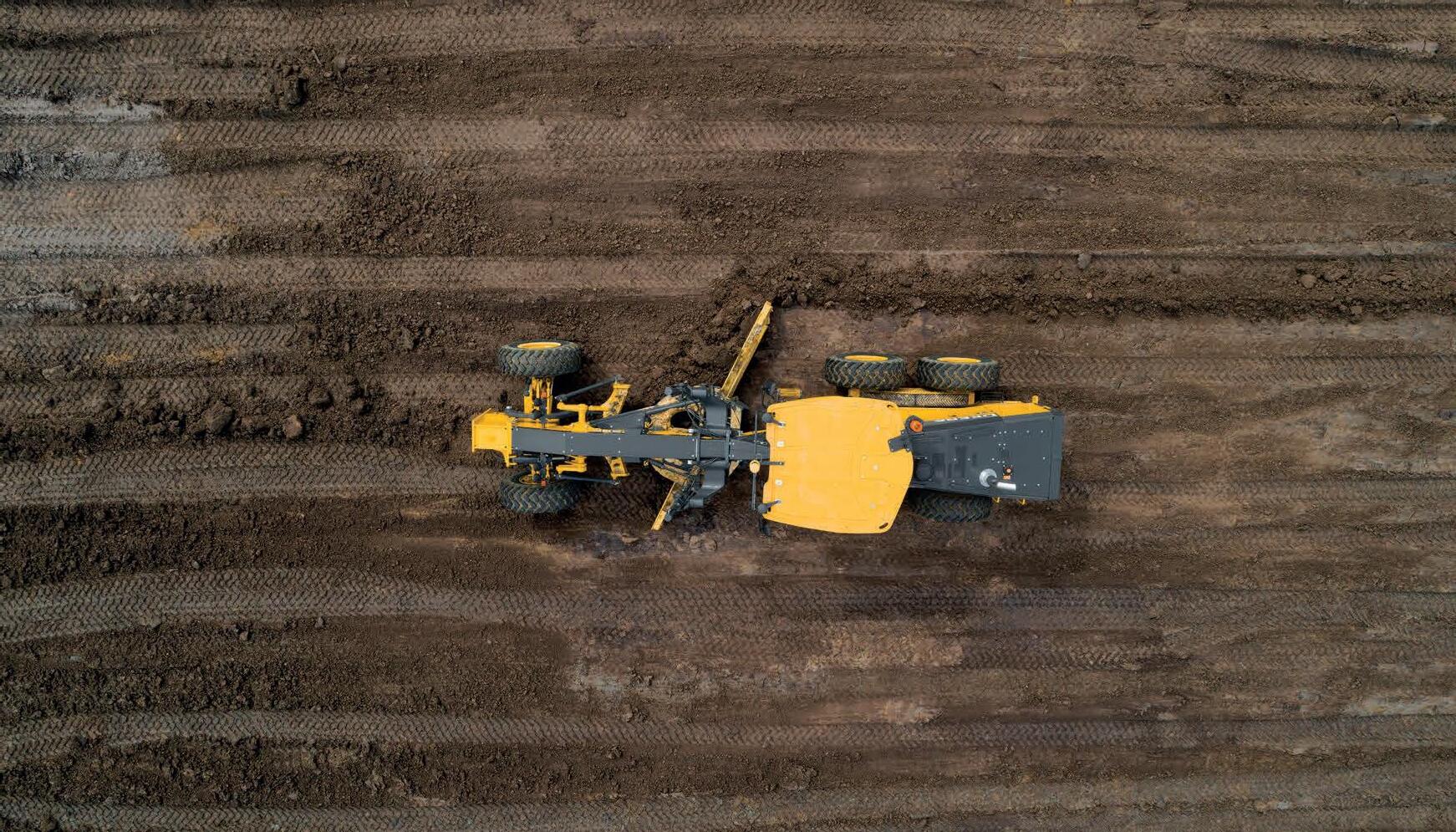
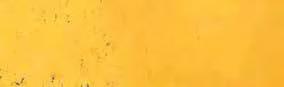
ONE-STOP-SHOP
CATERPILLAR’S ENTIRE PAVING RANGE HAS BEEN DESIGNED AND CURATED FOR AUSTRALIAN APPLICATIONS, OFFERING A VARIETY OF SOLUTIONS TO FIT EVERY PROJECT TYPE, SCALE AND ENVIRONMENT.
hether it’s asphalt pavers, tandem vibratory rollers, cold planers, road reclaimers, or vibratory soil compactors, Caterpillar has become a trusted, and one of the preferred options, for contractors of all sizes nationally who are aiming to use the best machinery
Luca Mancin, Product and Training Consultant, Paving Products – Caterpillar says that between the company’s rubber tyre, steel track, rubber belt and screed options, there’s something for everyone.
“In urban environments, where asphalt surfaces need to remain intact and machine repositioning is frequent, wheeled machines offer increased flexibility,” he says. “Wheeled machines are easy to move between job sites without needing extra transport. For many job sites they strike a balance between efficiency and cost-effectiveness.
“On the other hand, tracked pavers perform exceptionally well on softer surfaces.”
One option, which supports all the aforementioned parameters, is Caterpillar’s AP400.
A wheel-type asphalt paver that provides easy transport, versatility, and a wide paving range, the AP400 has been designed to tackle urban streets, parking lots, rural roads, and many other small-to intermediatetype applications.
The AP400s flexibility has made it a customer favourite, with the quietness and comfort provided further elevating the machine into consideration for asphalt contractors tiered infrastructure providers. Chris Harkness, Sales Manager, Paving Products ANZP and Japan –Caterpillar explains.
“The AP400 is designed for easy transport, with an optional configuration that allows it to have a width of less than 2.5 metres while maintaining a weight of 13.6 tonnes,” he says.
“The market is still starting to understand that you don’t necessarily need the big expensive pavers to do driveways and car parks. A model like the AP400 can handle these jobs very effectively.”
Mancin says that between the vast options on offer, Caterpillar’s entire paving range is expected to grow over the coming years,
reflecting greater demand for innovative technologies and machinery to tackle major infrastructure projects nationally.
“First, infrastructure projects are expanding, with governments and private entities investing in roads, urban development, and resurfacing. Compact paving models like the AP400 offer versatility and efficiency, making them ideal for tighter job sites and urban settings where manoeuvrability is crucial,” he says.
He adds that Queensland continues to be an area of growth, again reflecting the company’s ability to design and deliver machinery capable of working on challenging environments.
“The state’s diverse landscape, which includes urban centres and vast regional areas, requires paving equipment that is both durable and adaptable,” he says. “Caterpillar machines are well suited for these conditions, offering reliability and efficiency across various applications.”
TECHNOLOGY FIRST
As well as offering versatility and flexibility,
Images: Caterpillar
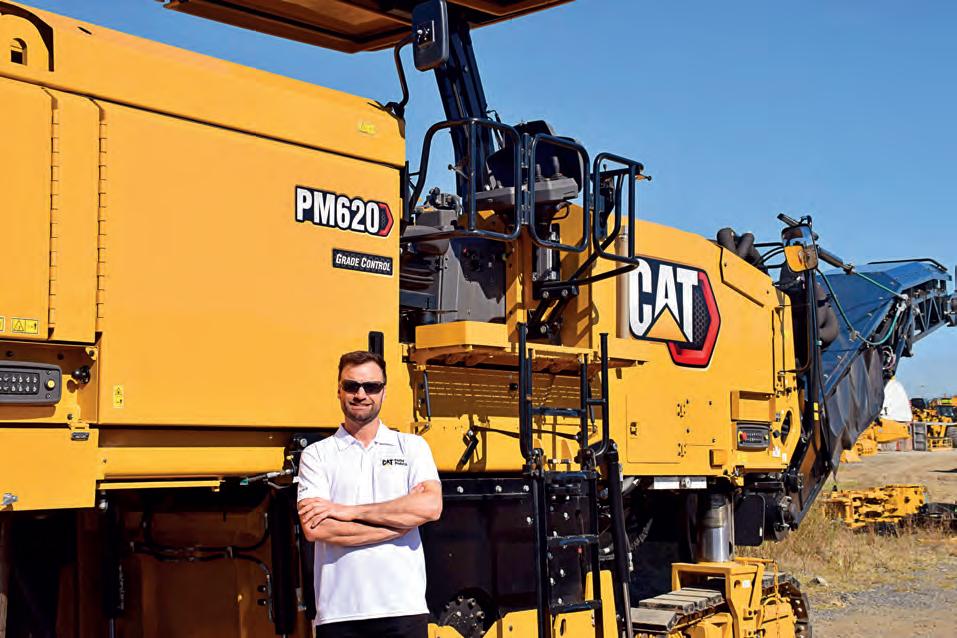
Caterpillar’s paving range supports a variety of technologies, ensuring that operators can reach the full potential and optimise output with their machinery.
Just one of these technologies is eco-mode. This feature optimises fuel consumption by adjusting engine power based on operational needs. This results in lower fuel costs and reduced emissions, making it a more environmentally friendly option.
Machines equipped with eco-mode also operate more quietly, improving communication on the job site and enhancing overall working conditions.
Another is CAT Grade Control technology, which enhances paving accuracy and efficiency by helping operators maintain consistent surface levels and reduce material waste. This minimises the need for adjustments and rework, allowing contractors to complete projects more effectively while saving time and money.
“Advancements in paving technology, improved fuel efficiency, and operatorfriendly features are making these models more appealing to contractors looking for cost-effective and reliable solutions,” Mancin says.
Another added benefit is that these technologies are scalable, helping operators – with the assistance of Caterpillar specialists if needed – to use a machine that’s highly tailored to their exact needs. As Harkness explains.
“You can have a machine that’s just entry
level, or you could go the whole other side of the spectrum and have a whole suite of technologies,” he says.
“If your machine needs more power for example, the AP400 and other units have a feature that senses if more power is needed. As a result, it’ll raise the RPM (revolutions per minute) up to 2200 and then if it’s beneath the minimum threshold it’ll actually drop it back to 1650 RPM.”
CAT SUPPORT
Caterpillar’s paving range hosts a variety of technologies, all scalable to cater for both experienced and newer operators.
of locations featured across the country, customers can rest assured that they’ll be supported by a local expert if required after each purchase.
It’s an area where Mancin particularly excels, with a big part of his role focusing on supporting customers to become the best operators that they can be.
“Caterpillar’s extensive dealer network provides reliable support, ensuring contractors have access to expert guidance, parts, servicing, and operator and service training whenever needed,” he says.
“Comprehensive training programs help crews maximise productivity and get the most out of their equipment, making Caterpillar pavers a perfect choice for a variety of paving projects.”
Due to the vastness of Caterpillar’s sites and network across the country, customers can benefit from consistent technical support, regardless of the location of their machinery or project.
Harkness says this is thanks to the standardisation of systems and process between each Caterpillar location, with sites in Western Australia, New South Wales, Queensland, the Northern Territory, as well as the Australian Capital Territory.
“If you take your machine out of the territory, the next dealer will have the same trained technicians and servicing tools, making the experience seamless for operators and fleet managers,” he says.
“We’ve arguably got the best parts network of any construction machinery manufacturer
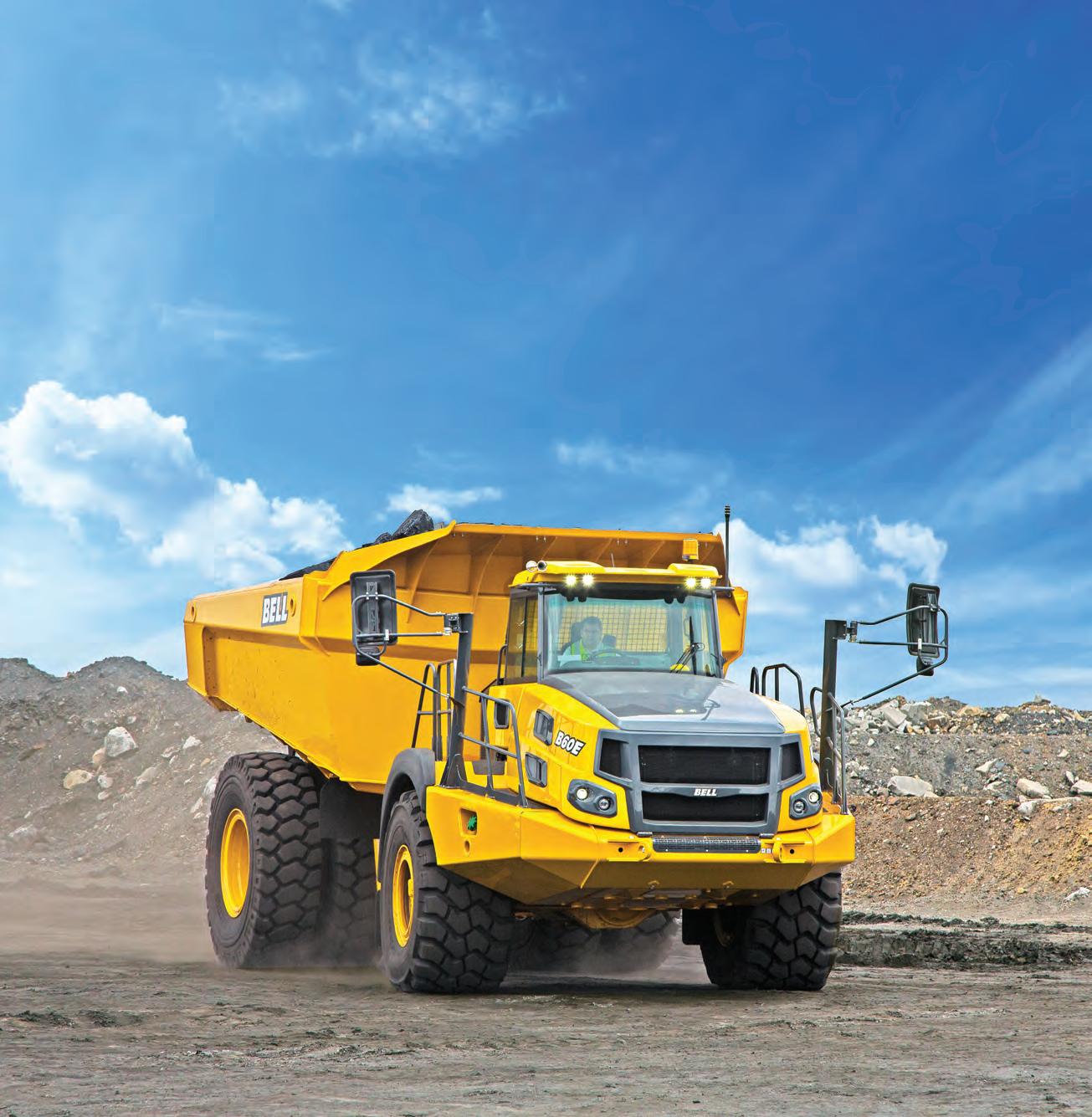
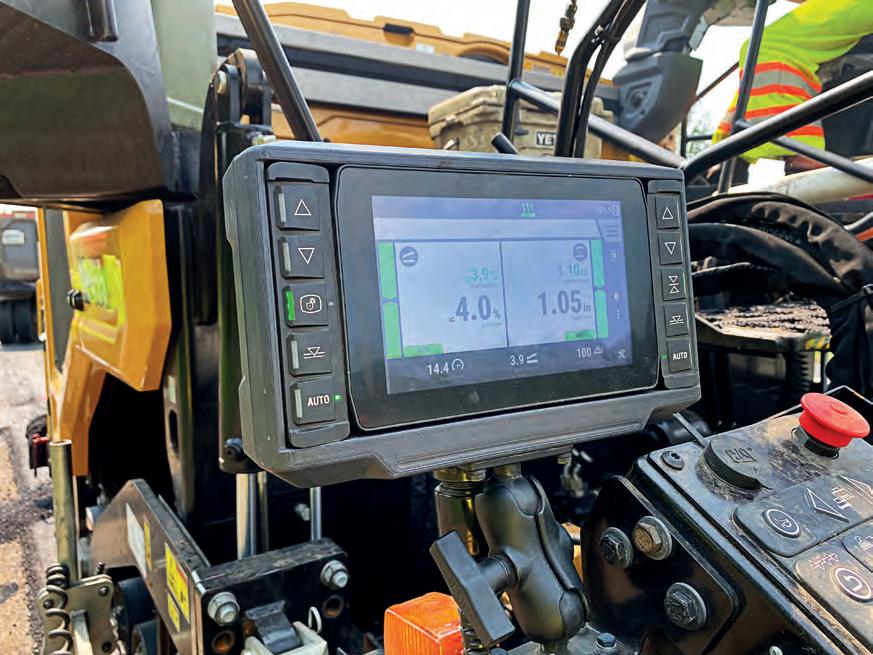
Luca Mancin, Product and Training Consultant, Paving Products Caterpillar.
EVOLUTIONARY IN DESIGN NEXT GENERATION IN SAFETY
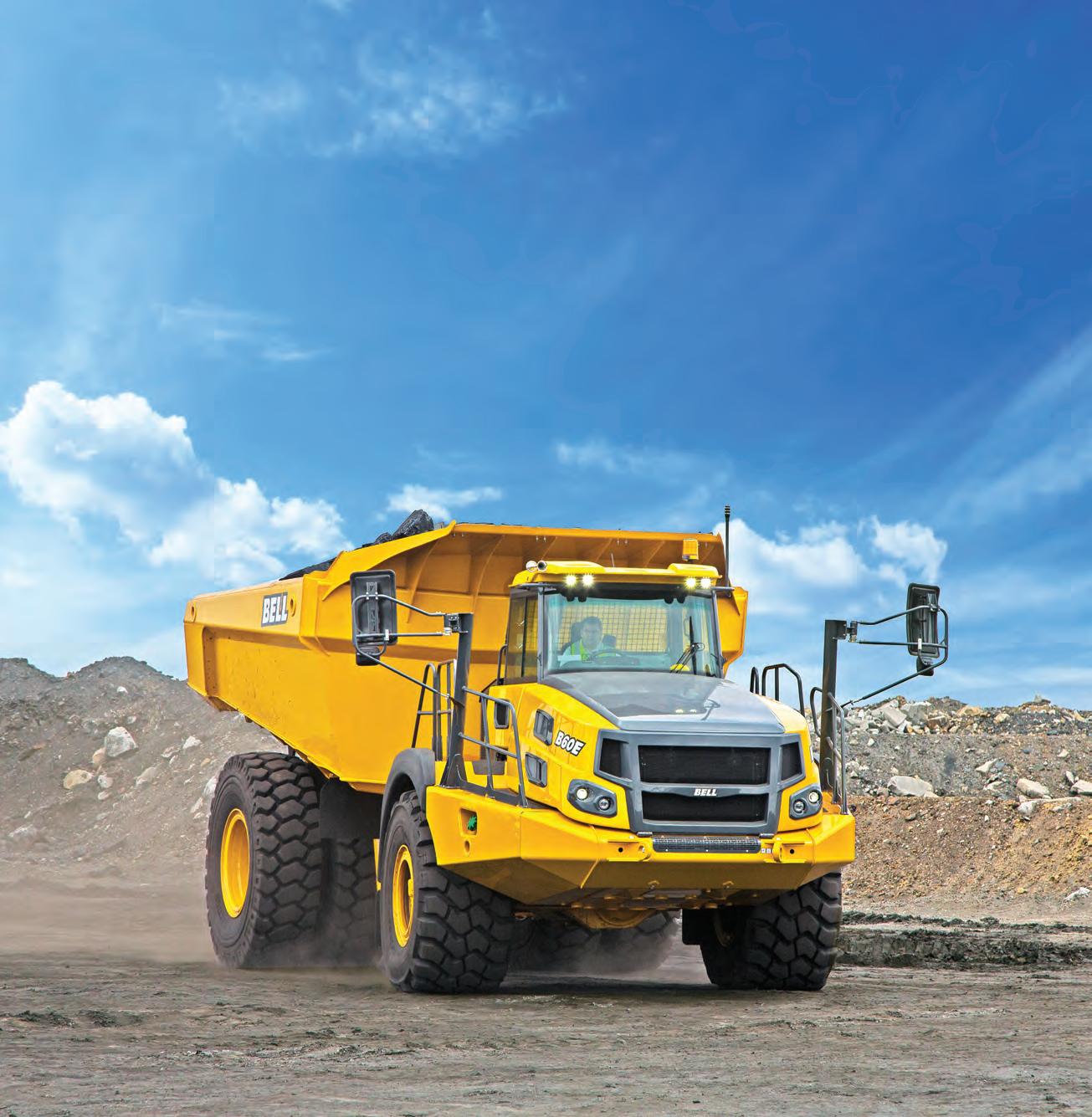
Articulated Dump Trucks
Engineered and factory-built tough for Australian conditions, BELL’s evolutionary design delivers exceptional safety, control, performance, and uncompromised reliability.
Hitachi
Construction
ANA Asphalts’ new asphalt and spraying division has been given a big boost with its new SRE telescopic sprayer.
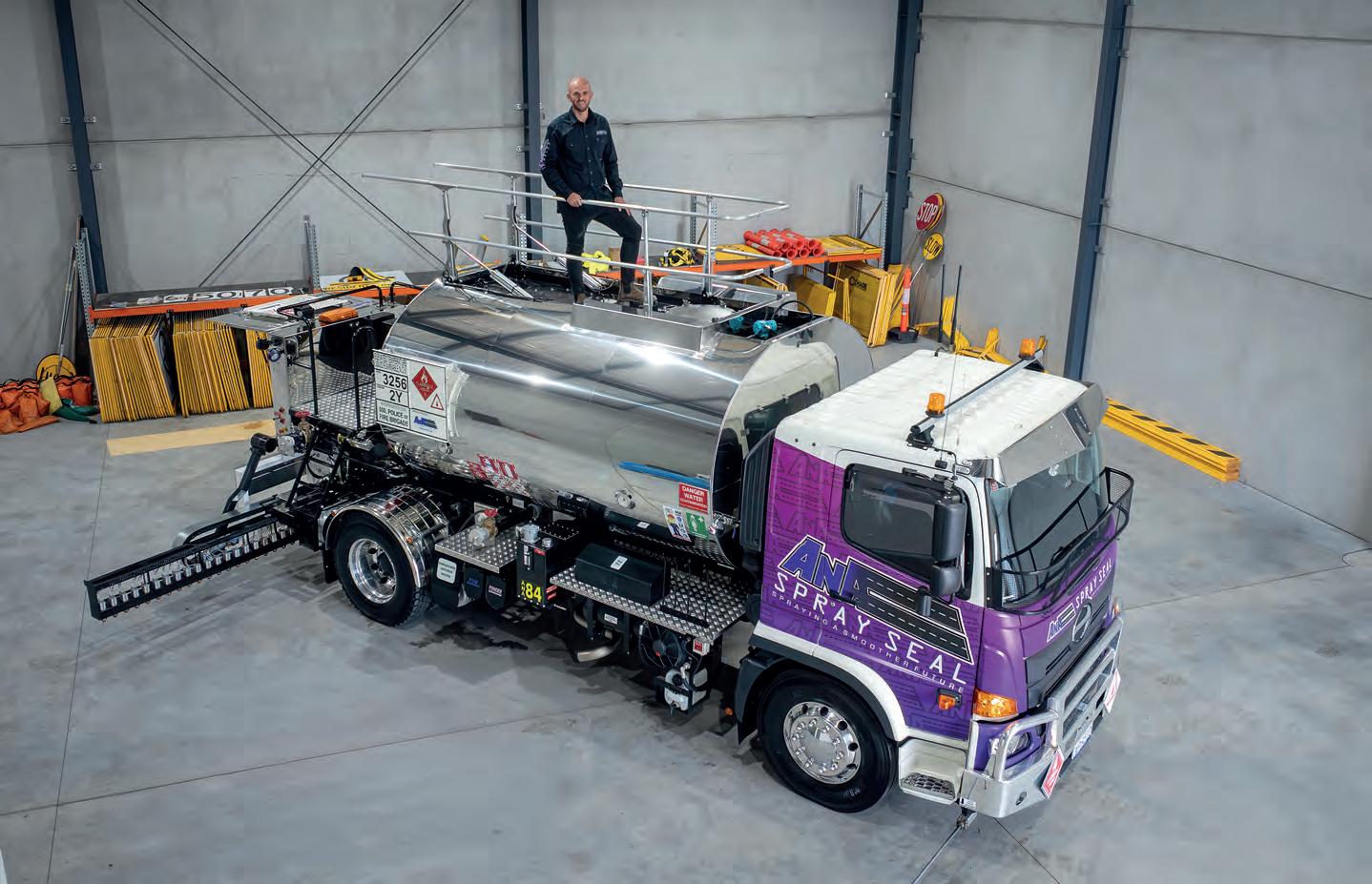
THE FIRST STEP
A
HANDOVER EVENT
HAS CEMENTED A FIRST IN WHAT’S EXPECTED TO BE A LONG STRETCH OF
MILESTONES
FOR BOTH ANA ASPHALT AND SPRAYER MANUFACTURER SPECIALISED ROADING EQUIPMENT. WE SIT DOWN WITH BOTH COMPANIES TO HEAR HOW THE EVENT WENT, AND WHAT’S PLANNED FOR THE FUTURE.
New partnership. New impact.
That’s the words of ANA Asphalts, which recently acquired a brand new (and first ever) telescopic spraying unit from Specialised Roading Equipment (SRE) – an emerging manufacturer whose representation in the Australian market continues to grow daily.
“We like to think that we’re a pretty innovative business, that’s always looking outside of the box to steer away from traditional methods,” says Brad Greaves, Operations Manager – ANA Asphalts.
“The idea of potentially adopting new and innovative technology is
something that very much aligns with our business strategy.”
ANA Asphalts – part of the wider ANA Group – recently welcomed a brandnew spraying arm to the business, aiming to grow on the evident success of the asphalt division over the past few years.
Greaves says it’s a division that’s now run for more than a year and a half with a clear focus on innovation, client service and technological advancement in the spray seal sector. The new SRE unit, he says, is yet another step forward for the business.
“One of the biggest challenges that we have in the Australian market, when it
comes to obtaining bitumen sprayers, is the extended lead times,” Greaves says. “SRE was not only extremely responsive, but they were also able to have a new unit built and turned around, ready for spraying in eight months.
“This instantly helped us as a business, particularly from an efficiency point of view.”
MEETING DEMANDS
ANA Asphalts began its journey to acquire a new sprayer in 2024, having already owned a fixed wing sprayer, along with other units in its fleet.
After hearing and reading about SRE in Roads & Infrastructure magazine, Greaves and the wider ANA team began early discussions. A step in the process that he says played a big part in the decision to buy the 4.5 metre telescopic unit.
“They took the initiative to come over from their base in New Zealand to sit down with us, talk us through the process and show what it would look like, all without any formal commitment from our end,” Greaves says.
After the build commenced, SRE invited Greaves and the team to fly out and
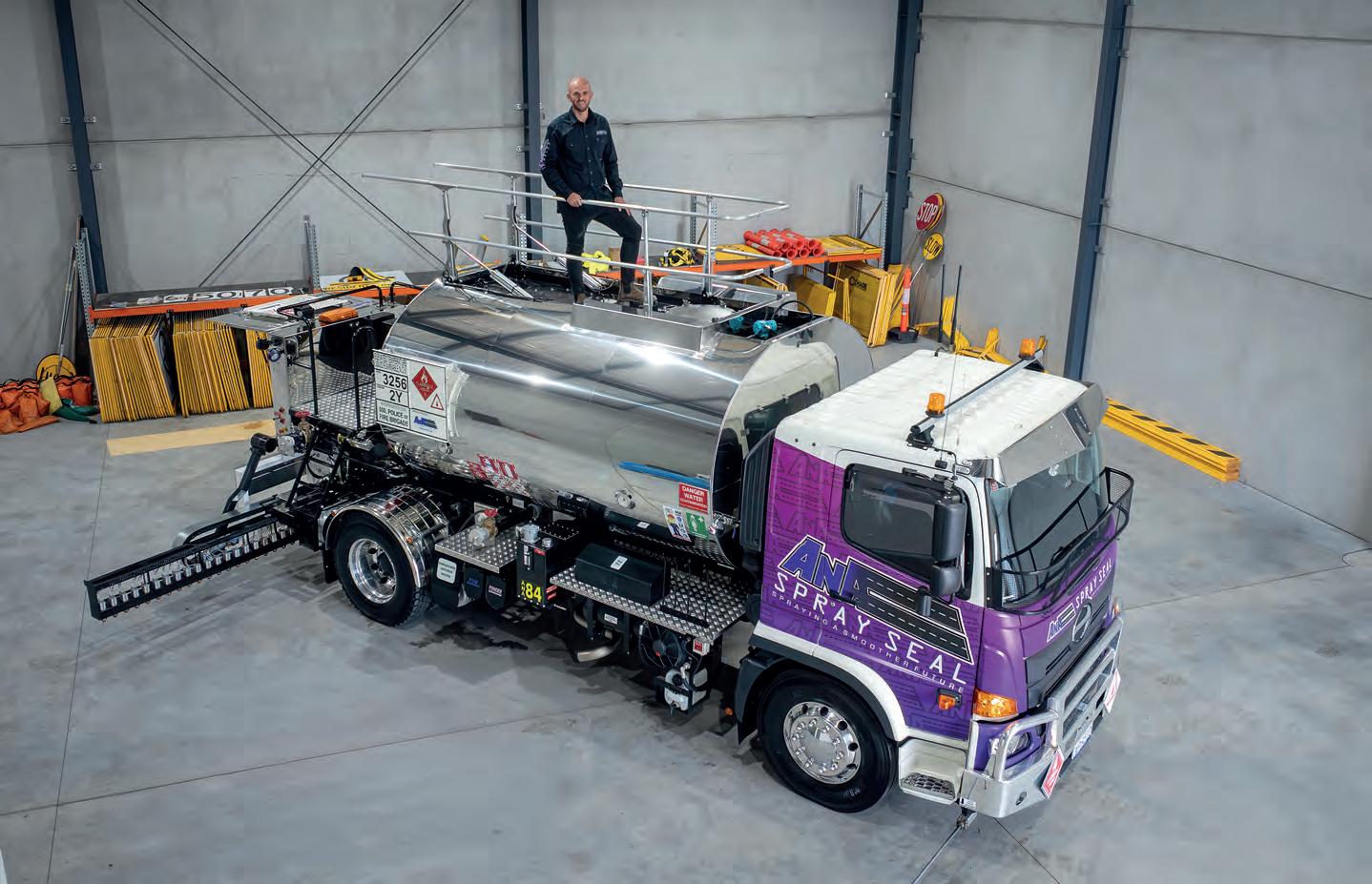
inspect the unit, during which it held a detailed session on the functionality and wider capability of the sprayer.
During this time, ANA Asphalts was given the opportunity to provide feedback and insight into its requirements, helping to influence the ultimate build, which was handled inhouse by SRE.
“The support that SRE has given us has been second to none,” Greaves says.
After delivering on the promised eightmonth turnaround, SRE conducted a formal handover, spending a week with ANA Asphalts’ operators and wider team, leading hands-on and on-site training.
“The handover has been extremely streamlined,” Greaves says. “The information and time that SRE has provided has been extremely valuable to our business. It’s something that’s going to play a key role in the future growth of our company.”
INDUSTRY BENEFITS
On top of the formal handover, ANA Asphalts recognised an opportunity to showcase the new sprayer, not only to its team, but also the wider industry and community.
As Greaves explains, this ‘handover event’ aimed to bring the industry together.
“We’re very passionate about driving continuous improvements, not only within our own business, but also trying to encourage and act as a leading innovator to improve the industry overall,” he says.
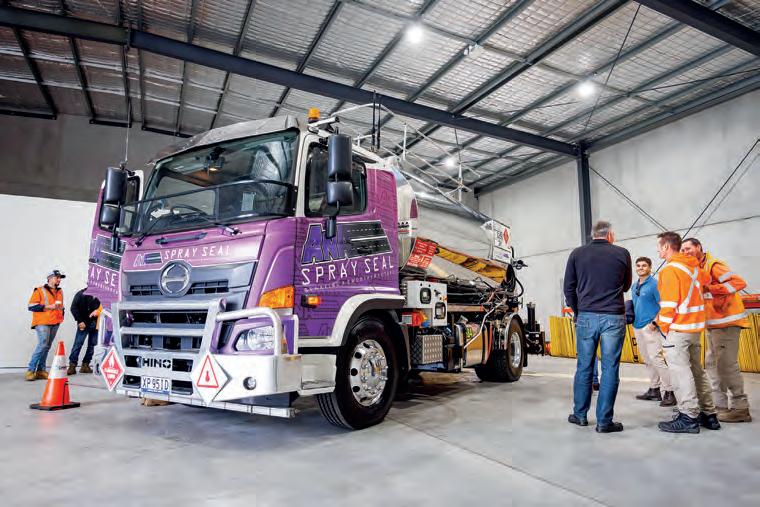
“It’s not very often that you get an opportunity to see a brand-new sprayer from overseas on our doorstop and see it in person. There’s only a handful of these sprayers in the country, and we’re extremely proud to be one of the few.”
Mark Wansbrough, Managing Director –SRE says it’s this focus and ambition that sets ANA Asphalts apart from the rest.
“Their point of difference is that they put a big emphasis on having leading machinery,” he says. “They’re seen as innovators, so the new sprayer fits the bill perfectly.”
Wansbrough adds that the event involved a cross section of local government, sub-contractors, as well as tiered infrastructure providers, showing the unity that exists between organisations aiming for higher quality
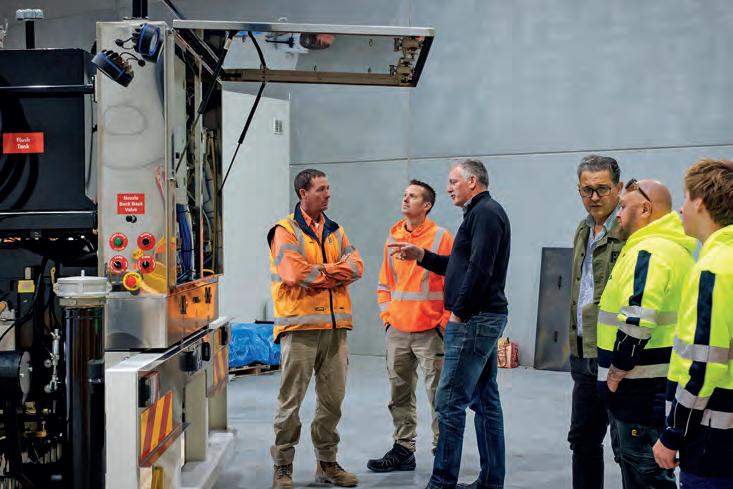
outcomes for the sector overall.
“The event really summed up how closely linked and interconnected the industry is in Australia,” he says. “That’s the power of word of mouth. Everyone wants to get better and be better at what they do. With a unit like this, they can.
“We had people from Sydney, right up to Townsville. There was another guy from Tasmania, and they all came just to see the sprayer.”
Greaves says the ultimate goal is to set a new standard for service, safety and project delivery. Seeking equipment with unique capabilities and being willing to adopt new machinery is just a slice of this objective.
“Introducing SRE to more people in the market is going to provide big benefits for the industry,” he says. “We’re really looking forward to continuing to push the barriers in the sector.
“Together we can do some really great things in the market and further contribute to innovation in industry, to allow the sector to keep up with the demand we’re currently seeing across the country.”
With the 4.5 metre telescopic unit now in its arsenal, ANA Asphalts is set on servicing its clients at full capability and capacity, Greaves adds.
“As we grow, the bottom line for us is providing maximum benefit and value for money to our clients,” he says. “Investing in businesses and partnering with companies like SRE is essentially going to act as a tool and a driver to provide the highest level of service that we can.”
This marks the first purchase of an SRE unit for ANA Asphalts.
Mark Wansbrough, Managing Director – SRE (third from left) instructs interested parties on the features and capabilities of the unit at the sprayer launch event.
Images: ANA Asphalts
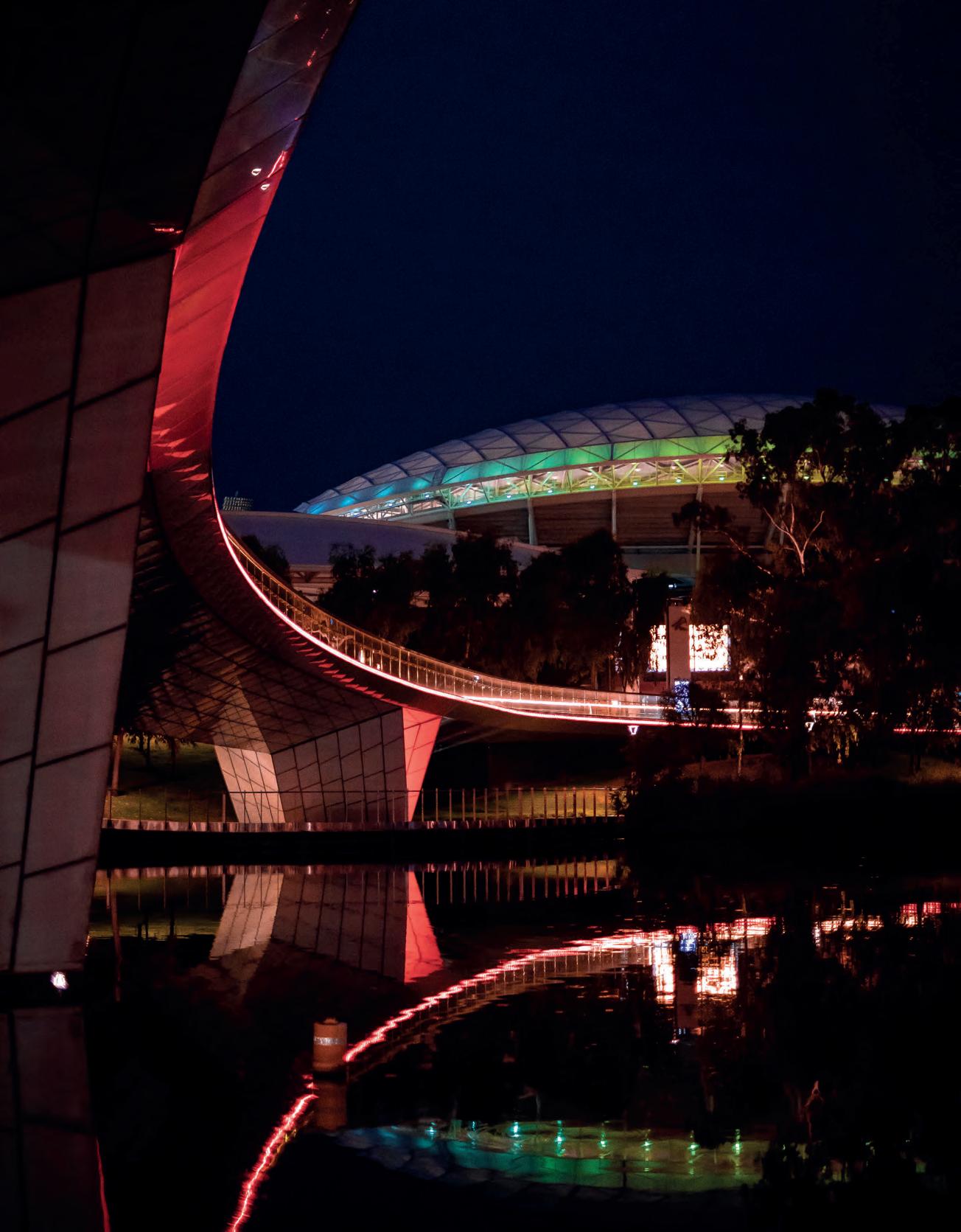
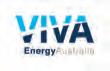

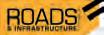

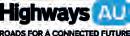

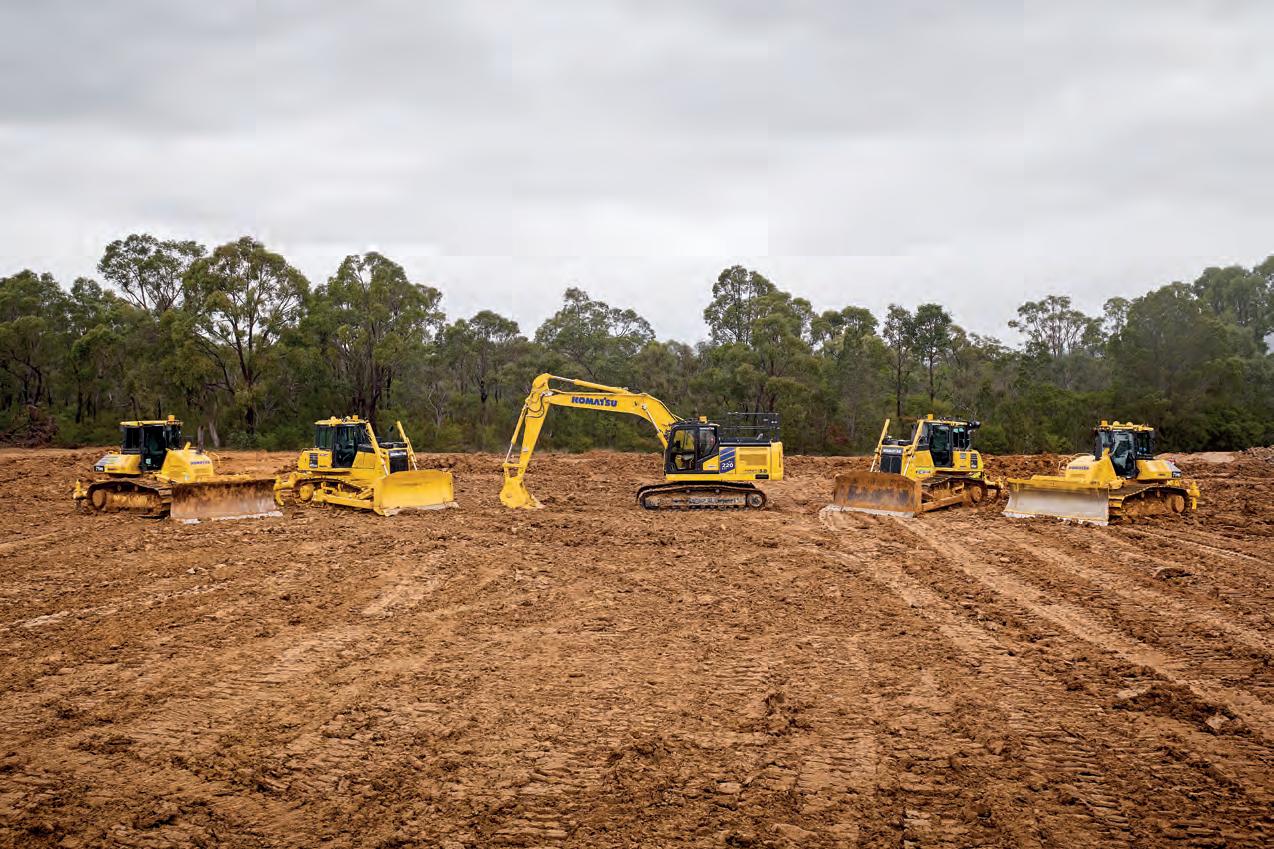
Image: Adelaide Oval by Tom Stuart
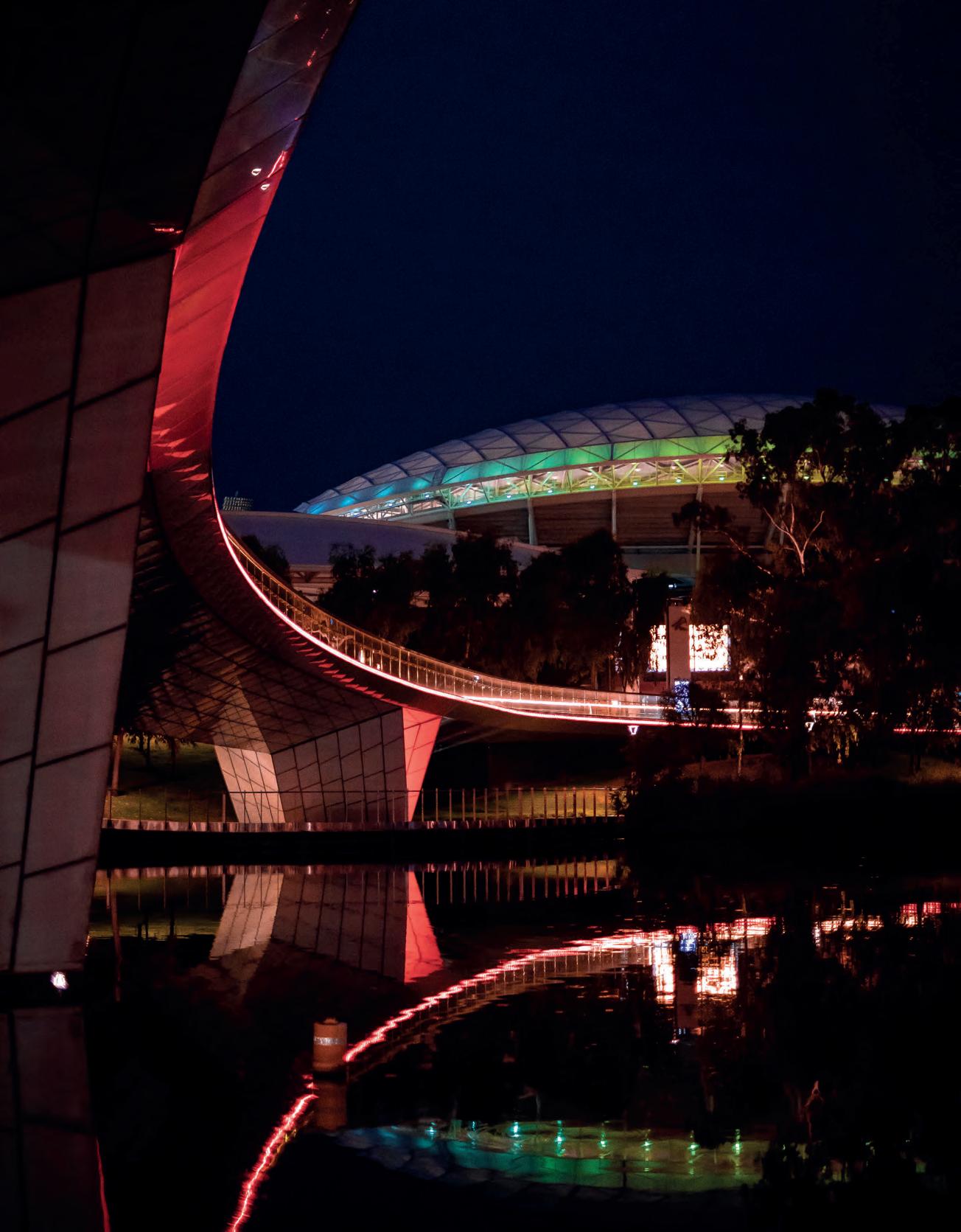
A NEW AGE MACHINERY FOR
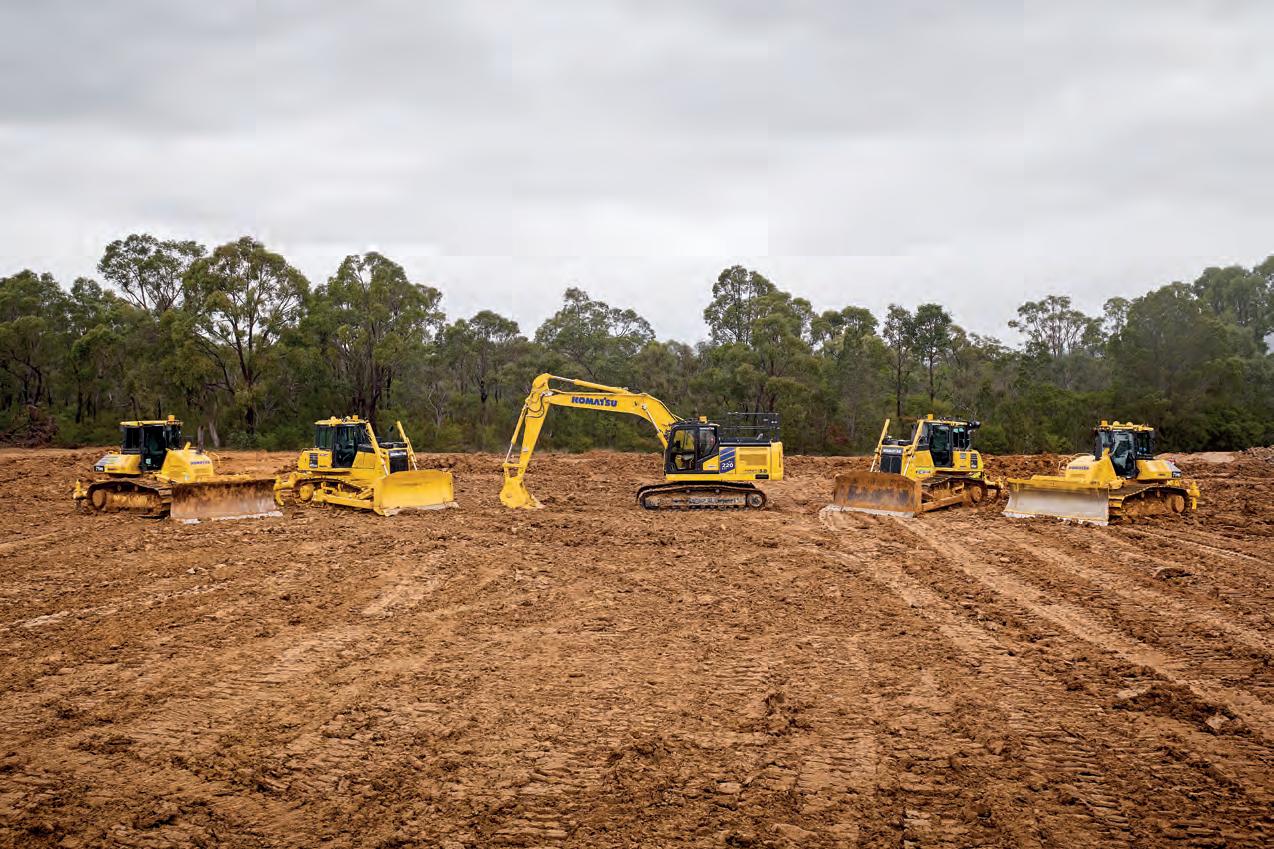
KOMATSU’S ‘BOOTS ON’ EVENT HAS PEELED BACK THE CURTAIN ON THE EQUIPMENT MANUFACTURER’S UPCOMING SLATE OF INNOVATIVE EQUIPMENT
Rarely do operators and stakeholders get a true glimpse behind the scenes of major machinery manufacturers in the construction sector, with big reveals in the highly competitive space usually reserved for major expos and industry shows.
Major benefits can be discovered on the shop floor, but true insights into the future of machinery are often out of a customer’s reach. That is, until now.
Komatsu Australia’s ‘Boots On’ event provides an opportunity for staff, media and customers to learn more about new and upcoming machinery announcements, shining a light on the future of the company’s construction machinery range.
Through live demonstrations, sessions and interactions, the latest innovations from the machinery manufacturer are on show, also allowing attendees to connect and learn from each other.
Mark Boyes, National Business Manager – Construction Excavators and Mobile Crushers at Komatsu says just one highlight of the show was the HB215LC-3.
The Komatsu HB215LC-3 hybrid excavator combines an electric capacitor with motor generators to deliver a highly efficient machine in the 20-tonne class.
“What the hybrid system enables is for
the pump to be stroked while the engine runs at low idle – meaning it can maintain productivity while significantly reducing fuel consumption,” Boyes says.
For projects where fuel efficiency, emissions reduction and reliable performance in the 20-tonne class are priorities, the HB215LC-3 is a strong option. It brings together hybrid technology and trusted Komatsu reliability into one very capable package.
In the right application, this machine can be up to 25 to 35 per cent more fuel efficient than comparable conventional
RELEASES.
models, Boyes adds. When paired with Komatsu’s 3D Machine Guidance, operators can see additional gains in overall efficiency. The system not only provides payload information but also precise guidance to bucket tip position, helping deliver better results in less time.
The HB215LC-3 is a long carriage machine and comes equipped with a suite of Komatsu standard features including flashing beacon, operator protective guard (OPG) top guard, colour touchscreen display and proportional hydraulic controls.
Hybrid technology, as well as Intelligent Machine Control were some of the key highlights from
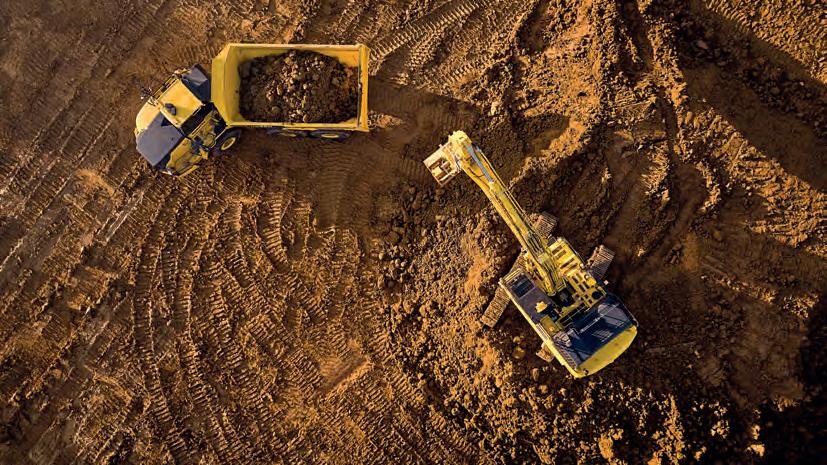
Komatsu has put its new machinery on show as part of its ‘Boots On’ show.
Images:
Komatsu
the event.
The potential for fully automated construction sites was just one of the topics discussed as part of the
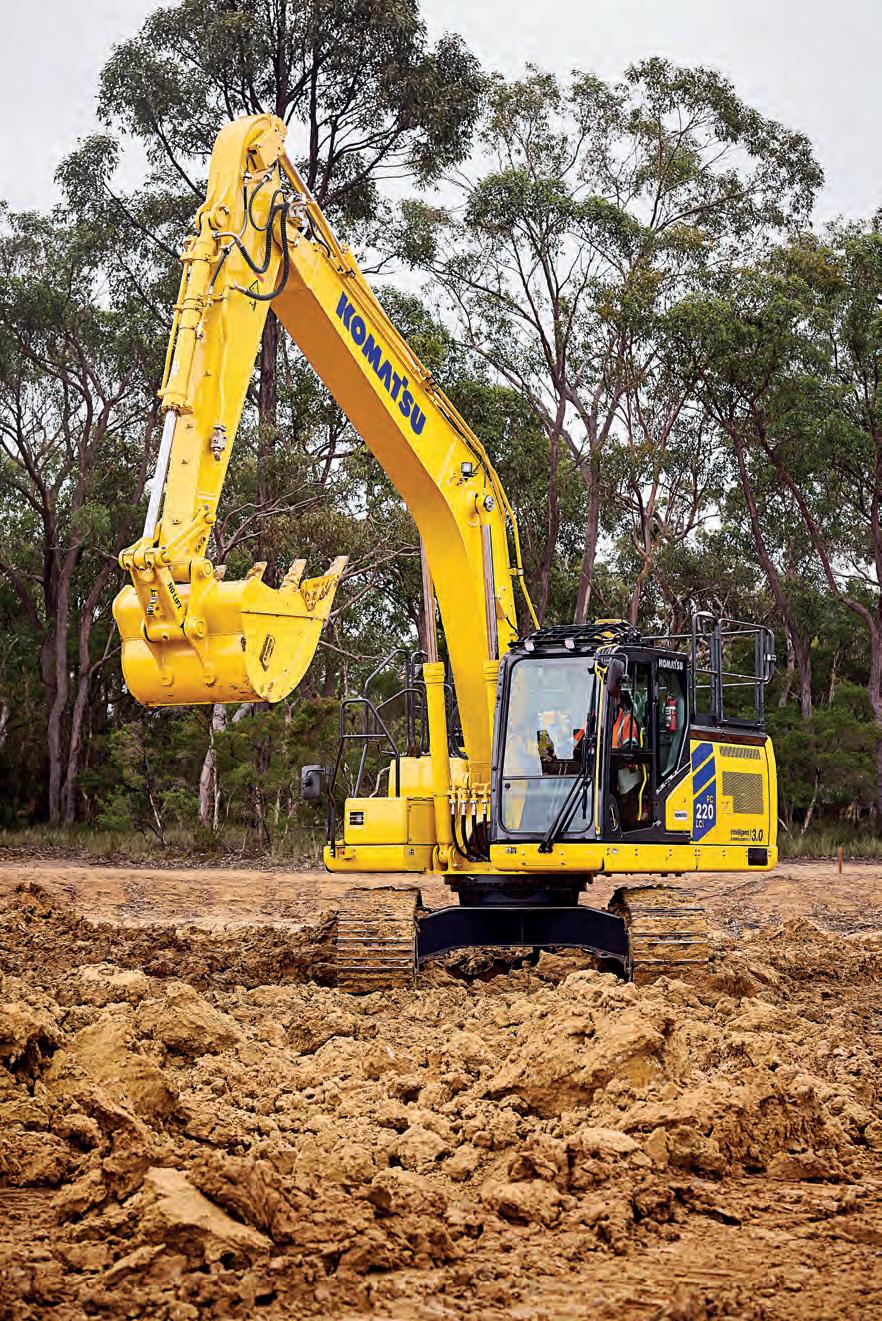
“Safety is another key focus,” Boyes says. “The HB215LC-3 is fitted with KomVision, our 360-degree camera system, which provides operators with full visibility around the machine.
“That is a major advantage when working on busy or constrained sites – you can see anyone or anything that moves into the slew radius, improving site awareness and reducing the risk of incidents.”
Speaking to these ‘Smart Construction’ features, as well as the upcoming release of Komatsu’s iMC 3.0 (Intelligent Machine Control) James Muir, General Manager for Smart Construction at Komatsu, says these technologies are much more than just complimentary tools.
can train people faster. It allows new operators to become highly efficient in a much shorter period.”
Muir says it’s not just about ease of use; it’s also about accuracy.
“These machines are accurate to within three centimetres. That means the job gets done right the first time. There’s no double handling of material or reworking cuts,” he says.
“That accuracy translates into major efficiency gains on site. It saves time, reduces fuel use, cuts machine operating costs and lowers emissions, because we’re not burning extra fuel to redo work.”
KEY UPGRADES
Another highlight of the ‘Boots On’ event was a showcase of Komatsu’s new PC220LCi-12 hydraulic excavator, which debuted at bauma 2025.
The PC220LCi-12 is the result of a comprehensive design process shaped by a decade of customer feedback, with operators asking for greater comfort, better safety and improved efficiency.
The PC220LCi-12 represents the first major re-design of the line in 20 years, as Boyes explains.
“We’ve overhauled the engine, hydraulics and, most notably, the cab. The new cab offers increased space, an intuitive user interface and a fully updated control system. It’s all been developed with a clear focus on operator experience, performance and ease of use,” he says.
Ideal for civil construction, particularly on detailed or mid-sized jobs, the PC220LCi-12 can also be used in quarrying or agricultural work. With the latest
“THAT ACCURACY TRANSLATES INTO MAJOR EFFICIENCY GAINS ON SITE. IT SAVES TIME, REDUCES FUEL USE, CUTS MACHINE OPERATING COSTS AND LOWERS EMISSIONS, BECAUSE WE’RE NOT BURNING EXTRA FUEL TO REDO WORK.”
“What we’re achieving with this is greater efficiency on site. One of the biggest challenges we face, not just here in Australia but globally, is the shortage of construction operators. It’s becoming harder to attract new talent into the industry, and many of the more experienced operators are retiring,” he says.
“One of the benefits of semiautonomous technology is that we
safety technologies built in, it’s a versatile machine that can operate confidently across multiple sectors.
The PC220LCi-12 is one of many new Komatsu models that’s equipped with iMC 3.0.
“iMC 3.0 builds on the strengths of 2.0 by introducing features that give operators more control, more safety and more flexibility on site,” Boyes says. “One of the major upgrades is 3D boundary
‘Boots On’ event.
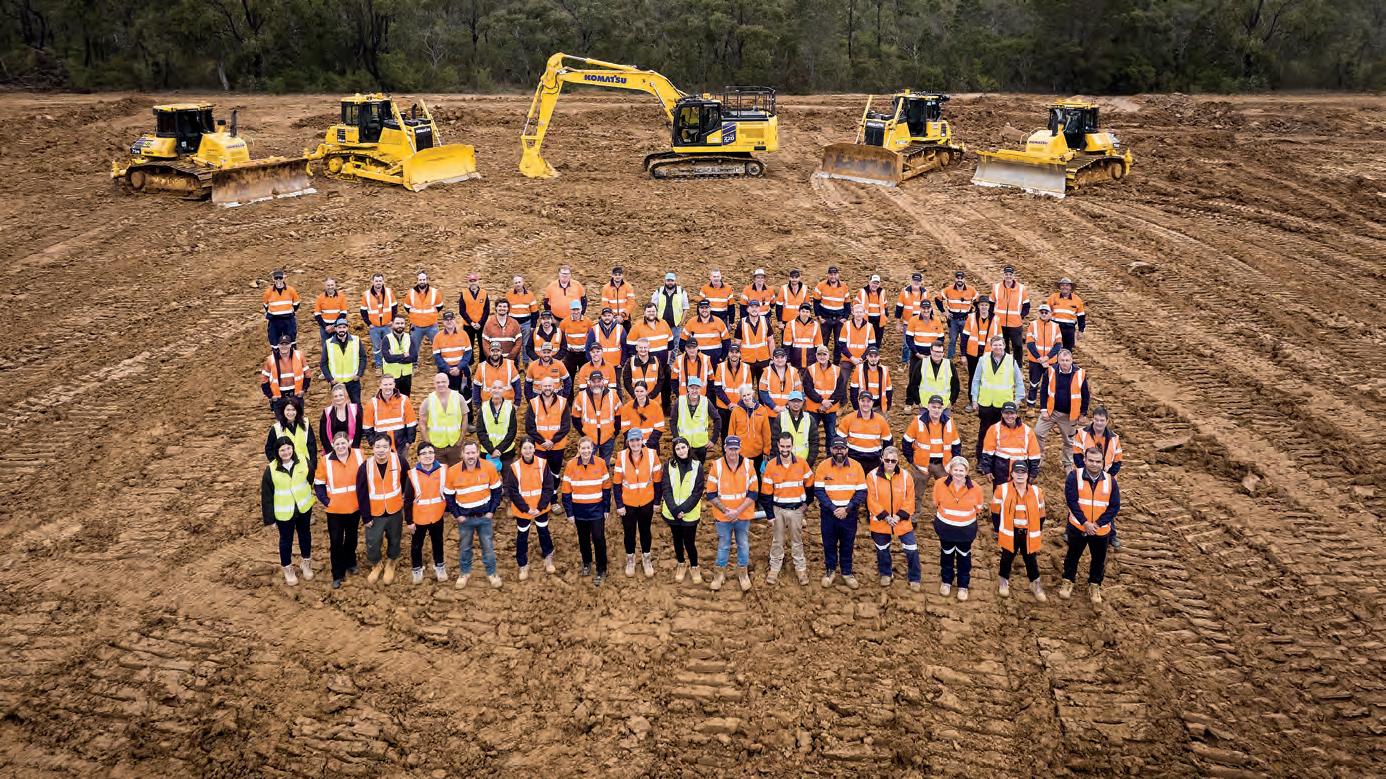
control – a significant safety enhancement that helps prevent the machine from breaching defined work limits.
“We’ve also introduced in-field design capabilities, so operators can make quick adjustments without needing to return to the office. It’s about smarter, safer and more autonomous operation, which ultimately means more productivity and less downtime.”
across multiple machinery classes and types, reflecting the adaptability and versatility of Komatsu’s smart construction offerings.
“This can be applied to an excavator, dozer or even a wheel loader,” he says. “It gives the operator guidance aligned to the construction plan. They load the design onto a screen in the cab, and the system helps guide their excavation in line
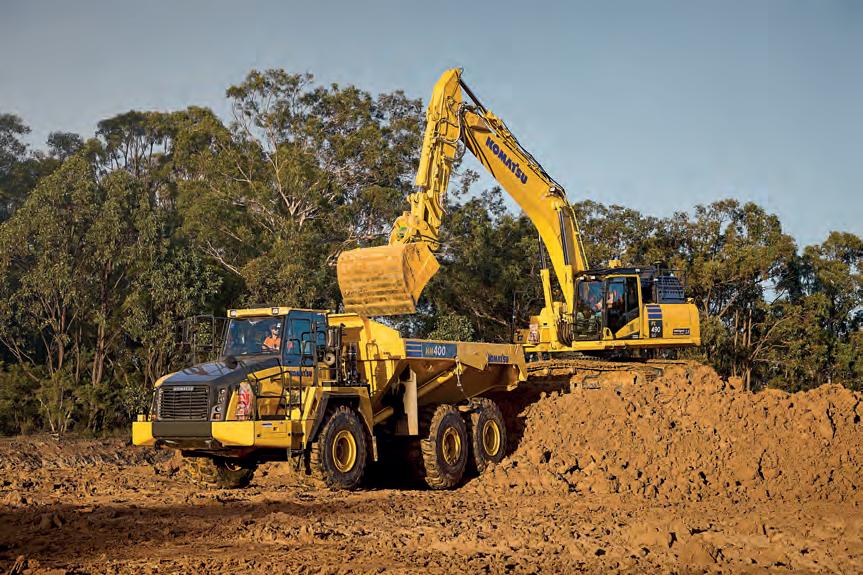
“iMC, or intelligent Machine Control, is a step above 3DMG. While 3DMG provides guidance only, iMC takes things further. It actually controls parts of the machine’s operation. For example, on a bulldozer, it can control the blade to optimise the cut according to the design. So, you start to get semi-autonomous features built into the machine. With 3DMG, there’s no machine control at all; it’s entirely up to the operator to follow the guidance.”
And when it comes to autonomy, could we see a fully automated site in the near future? Muir says it’s possible and while it may be a while away, technology is inching closer and closer.
“As you’d appreciate, safety is paramount on any construction site. For fully autonomous machines to operate, we have to make sure that nothing –people, animals, anything – can enter the site and be put at risk,” he says.
“There’s still a lot of work to do. The machines themselves are ready. We can already make excavators and dozers fully autonomous, and we’ve demonstrated that it’s possible. But we need the right regulatory frameworks and safety systems in place, not just to comply with legislation but to ensure the whole site can function safely in a fully autonomous way.”
Customers and industry can expect these brand-new models and technologies to be rolled out later this year.
A number of Komatsu representatives, as well as leaders from industry, got a chance to get a first glimpse at new technology.
EQUIPPED FOR DEFENCE
145 MACHINES AND 750 ATTACHMENTS LATER, JCB CEA HAS COMPLETED A CONTRACT FOR THE AUSTRALIAN DEFENCE FORCE (ADF).
Earthworks, route development, combat site readiness, maintenance, airfield construction and repair are all efforts undertaken by the Australian Defence Force (ADF).
They are also jobs which require earthmoving equipment and heavy construction machinery.
JCB CEA recently completed the delivery of 145 machines for a Department of Defence, Capability Acquisition and Sustainment Group (CASG) contract.
JCB CEA supported infrastructure services provider and Prime Contractor Ventia in the contract.
Phil Withell, Project Lead, JCB CEA, says the project’s successful and on-time completion is a testament to the collaborative effort between JCB, CEA, Ventia, Capability Acquisition and Sustainment Group (CASG) and the Australian Defence Force.
“We are here today because when Ventia won the tender, they selected JCB CEA as one of the suppliers,” says Withell.
For this project, Ventia also partnered with QinetiQ, engineering specialists in the Defence sector.
COLLABORATION
In 2019, the tender was made available to Ventia and in turn JCB CEA. Early in the process, the contract outlined several key dates to be achieved.
These “milestone dates” as outlined by Withell, were critical in ensuring the six-year project was completed on time.
One of these milestone moments came in mid-2023. It was at this point JCB CEA started to deliver the first of the machinery. As agreed, the final handover was completed in April 2025.
Withell says the two-year duration for the fleet delivery was expected and necessary to ensure the manufacturing, production and attachment procurement from Australian suppliers.
He says CEA’s build and preparation processes were done to a high standard and effectively.
“The cooperation on the project demonstrated a shared understanding of the operational needs and the importance of delivering on time,” he says.
“Under the adept leadership of Richard Cave, Land 8120 Project Director from
Ventia, the collaboration across all participating teams was truly exceptional.”
Like any project of this scale there were hurdles and challenges. Yet they were never of concern for Withell and the team because of the dedication and teamwork displayed by all daily.
“We always found a way to ensure that we could deliver on time and to a high standard. Without strong collaboration that couldn’t have happened,” he says.
THE ORDER
The project focused on the delivery of a comprehensive suite of machinery which will provide essential earthmoving and material handling equipment.
Withell says the diverse range of JCB machinery highlights the varied and demanding tasks the ADF will be undertaking with the equipment.
Machinery varied across seven platforms including large excavators, skid steers, backhoe loaders, mini excavators, wheel loaders, and compaction rollers.
The 20-tonne JCB wheeled excavators, known for their strength and efficiency, will play a pivotal role in larger earthmoving and construction tasks.
The inclusion of 39 Teleskids will provide the ADF with increased capability over conventional skid steers. Unique to the industry and JCB CEA, the Teleskid has an extending telescoping boom, allowing it to lift higher, reach further and dig deeper.
Eighteen mini excavators were included in the order and will provide the agility and precision necessary for working in confined spaces or on more intricate projects.
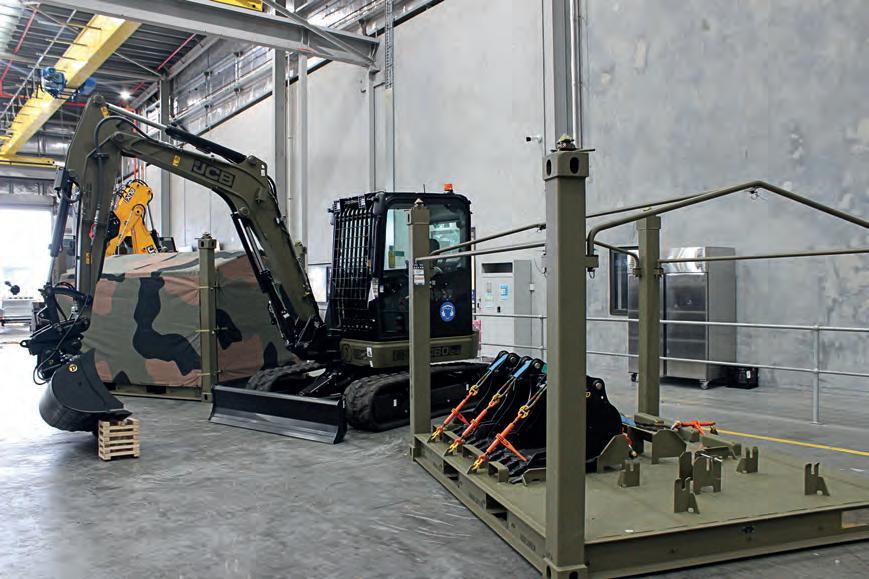
According to Withell, the 22 15-tonne wheel loaders are essential for efficient material movement.
The 15 Compaction Rollers will play a critical role in preparing and maintaining infrastructure, such as roads and airstrips, while the 32 4CX backhoe loaders have been built with the capability to wade in deep fresh and ocean water.
The order also included 15, 220X heavy line tracked excavators which feature a spacious cab, latest generation Japanese hydraulics, and a proven X-frame undercarriage.
“The provision of this modern equipment will undoubtedly enhance the ADF’s engineering and support capabilities, allowing for more efficient and effective deployment in various scenarios, from disaster relief to infrastructure

CEA JCB made a number of tweaks and design changes to suit.

development in remote locations, to site preparedness with the combat enabler teams,” says Withell.
CUSTOMISATIONS
Although most of the machines were required to be built commercially off the shelf (COTS), all the platforms required special customisations and refinements to suit the ADF’s needs.
Five of the seven platforms were equipped with attachment points that provide air transport capability, adding to the equipment’s versatility and rapid deployment.
The 20 tonne excavators required attachments such as digging buckets, grabs, pneumatic hammers, augers and auger drives.
All three digger models required similar attachments and each of the machine’s attachments are in covered cradles. The early collaboration with Australian suppliers Digga Australia, Doherty Couplers and Attachments, EI Engineering and Groundtec ensured that CEA was able to safely cover off on all attachment requirements.
“The heavy line excavators and wheel loaders required scales to be added to each machine so payloads can be accurately measured and ensuring load weights are contained within their truck’s capabilities. SmartTec supplied the perfect solution with Loadrite products,” says Withell.
Every machine was required to have a range of bespoke decals and mounting provisions for Defence specified equipment. Collaboration with Army HQ was critical to the delivery of this requirement.
A bespoke solution was required for each product configuration and CEA engaged EFC Industries, a local manufacturer to design, manufacture and powder coat all 145 packages. There was a highvolume requirement for custom decals and identification plates over and above standard JCB supply and Government Furnished Equipment.
CEA turned to Bright Print Group for 4100 specialist decals and data plates required to correctly complete the machines to the DEF (AUST) Specifications.
HANDOVER AND CARE
Before the final handover, the ADF thoroughly checked all machines based off a strict checklist. This helped to ensure all specifications and attachments were up to scratch, as well as the quantity and quality of the machinery.
The machines were then prepared and made ready for transport by the Commonwealth.
The final handover took place at JCB CEA’s Darra, Queensland facility, although machines have been dispatched all over the country.
“Distribution of the machines was spread country-wide,” says Withell.
Hylton Taylor, Chief Executive Officer, JCB CEA says the completion of the handover signified more than just the delivery of machinery.
“It represents the successful fulfilment of a critical agreement to equip the ADF with modern, reliable, and high-performing equipment,” he says.
“The project has been a long-term undertaking, and we are proud to have been involved.”
As the final pieces of equipment are now in the hands of the ADF, JCB CEA’s focus now shifts to the ongoing support, maintenance, and training associated with the machines.
“The true long-term success of the project will be measured by the reliability and performance of the JCB fleet in the field,” says Withell.
“Ensuring we have the right after market support in place to meet the ongoing requirements of the ADF is now critical.”
After-care support will include training the operators, supporting the equipment and providing parts in a timely manner.
“The completion of this project reinforces the brand’s position as a key partner in supplying essential equipment for national needs while significantly bolstering the operational readiness of the Australian Defence Force,” Withell says.
CEA has completed a contract for the Australian Defence Force (ADF).
Images:
CEA
Challenges with noise and dust?
For us it’s no problem.
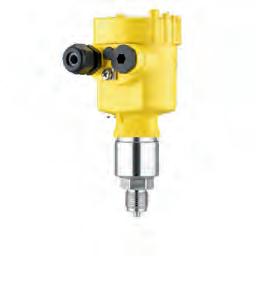
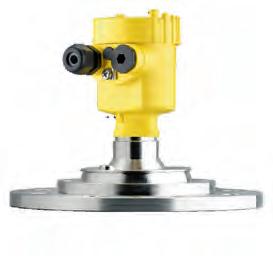
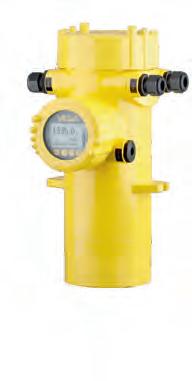
From large stones to the smallest grains: Bulk solids come in all types, shapes and sizes, but choosing the right measurement technology is surprisingly easy. With our level and pressure sensors, you can effortlessly keep an eye on all your important process values – and still have time to crack the really hard rocks.
Everything is possible. With VEGA.
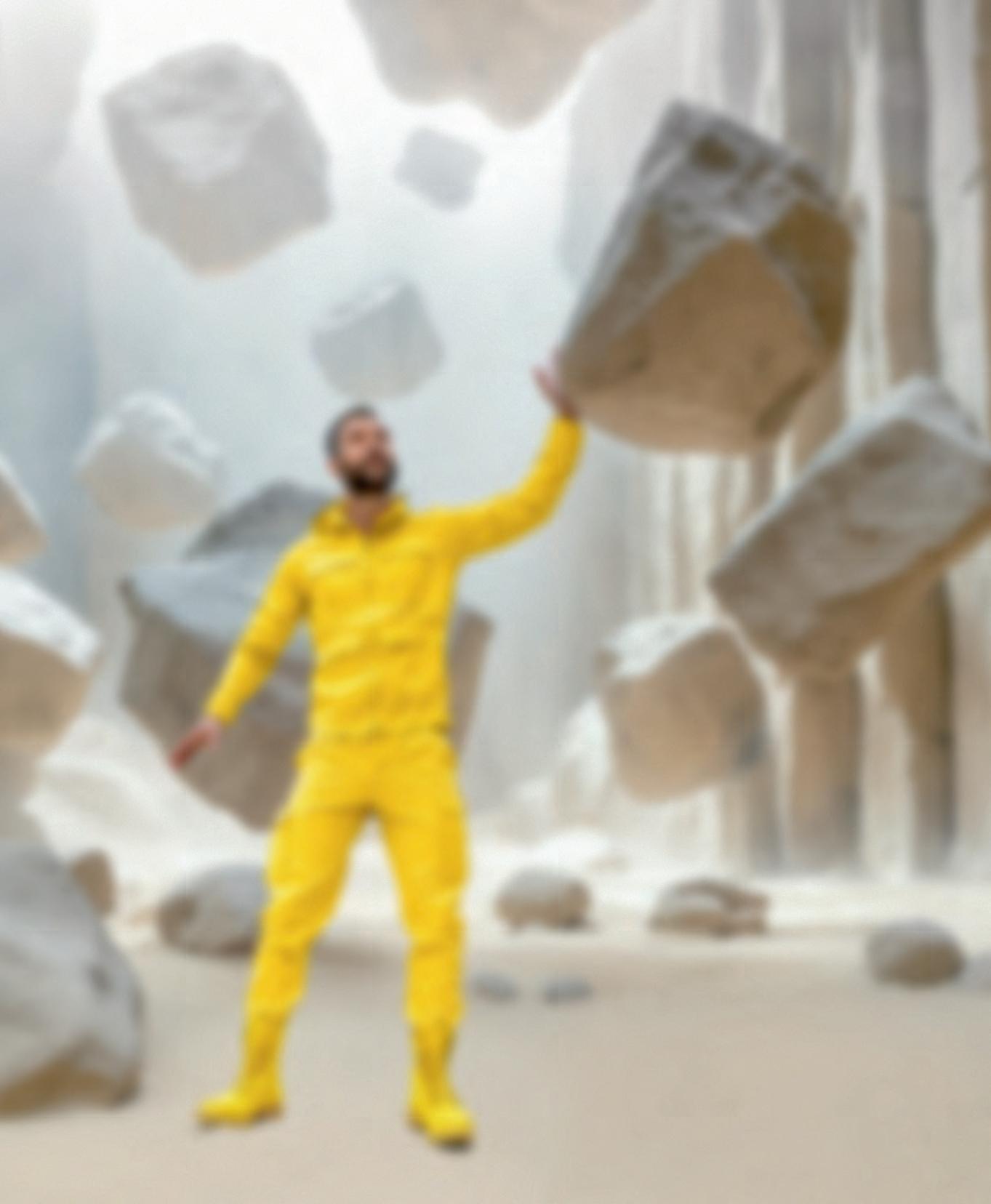
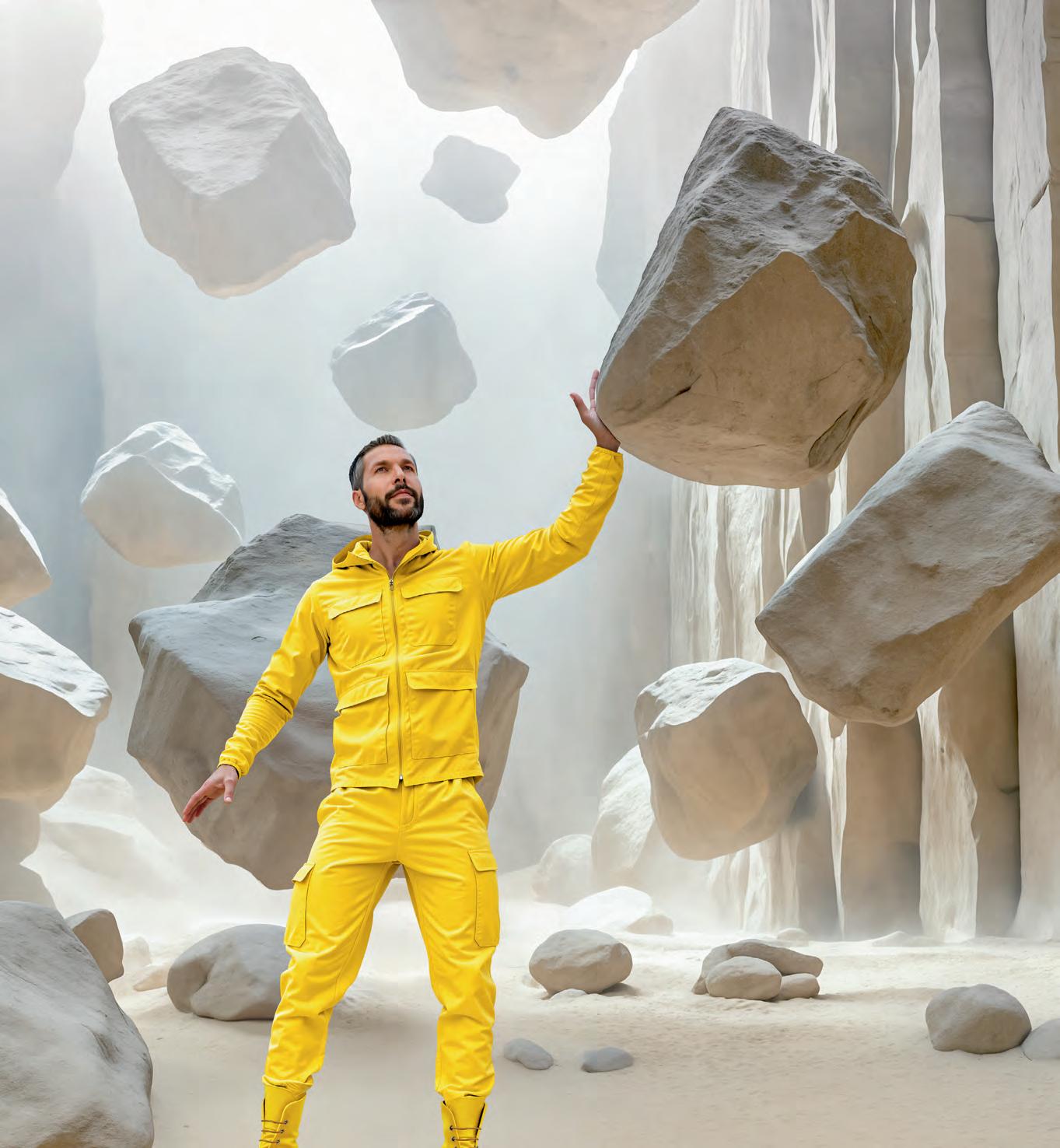
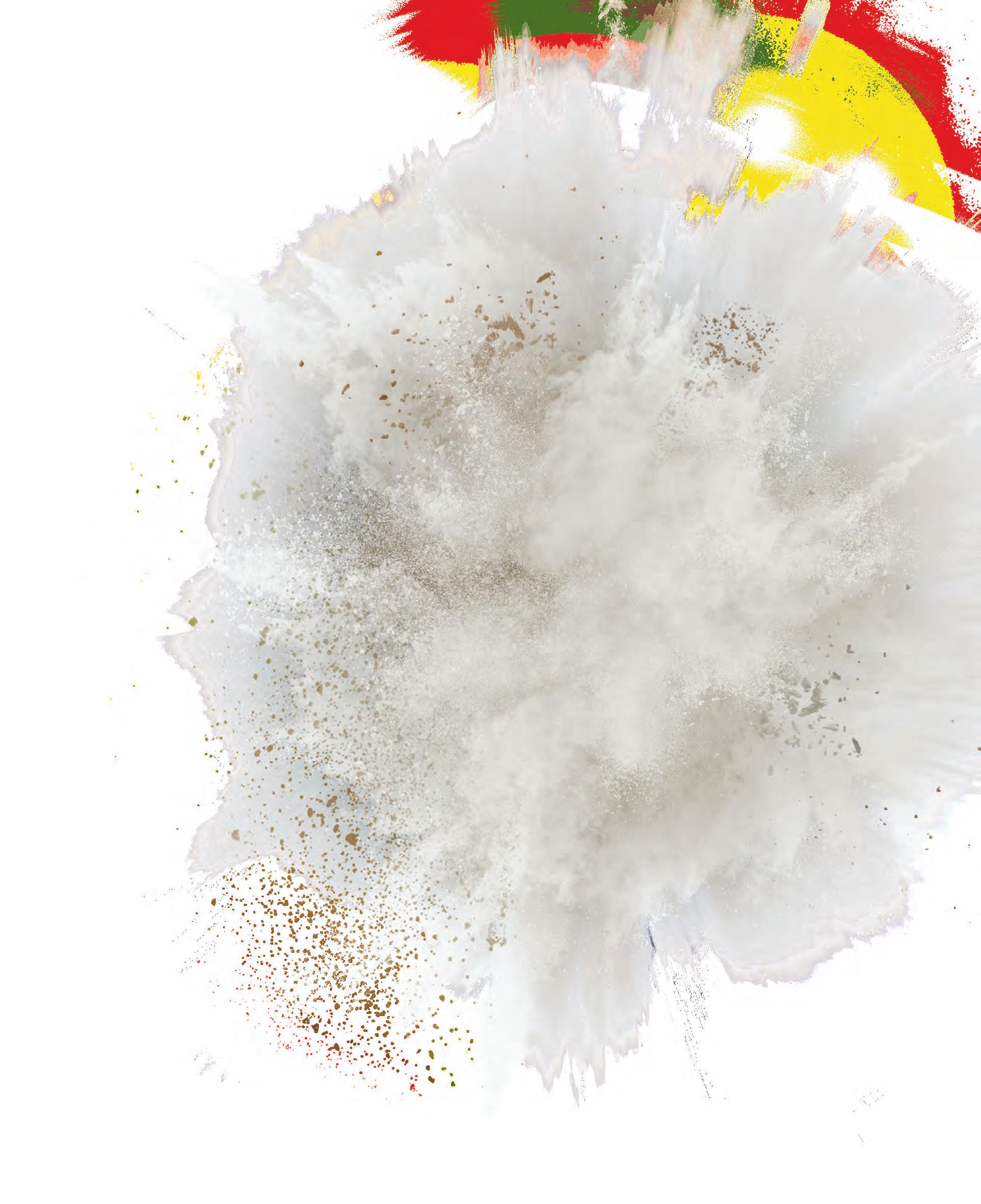
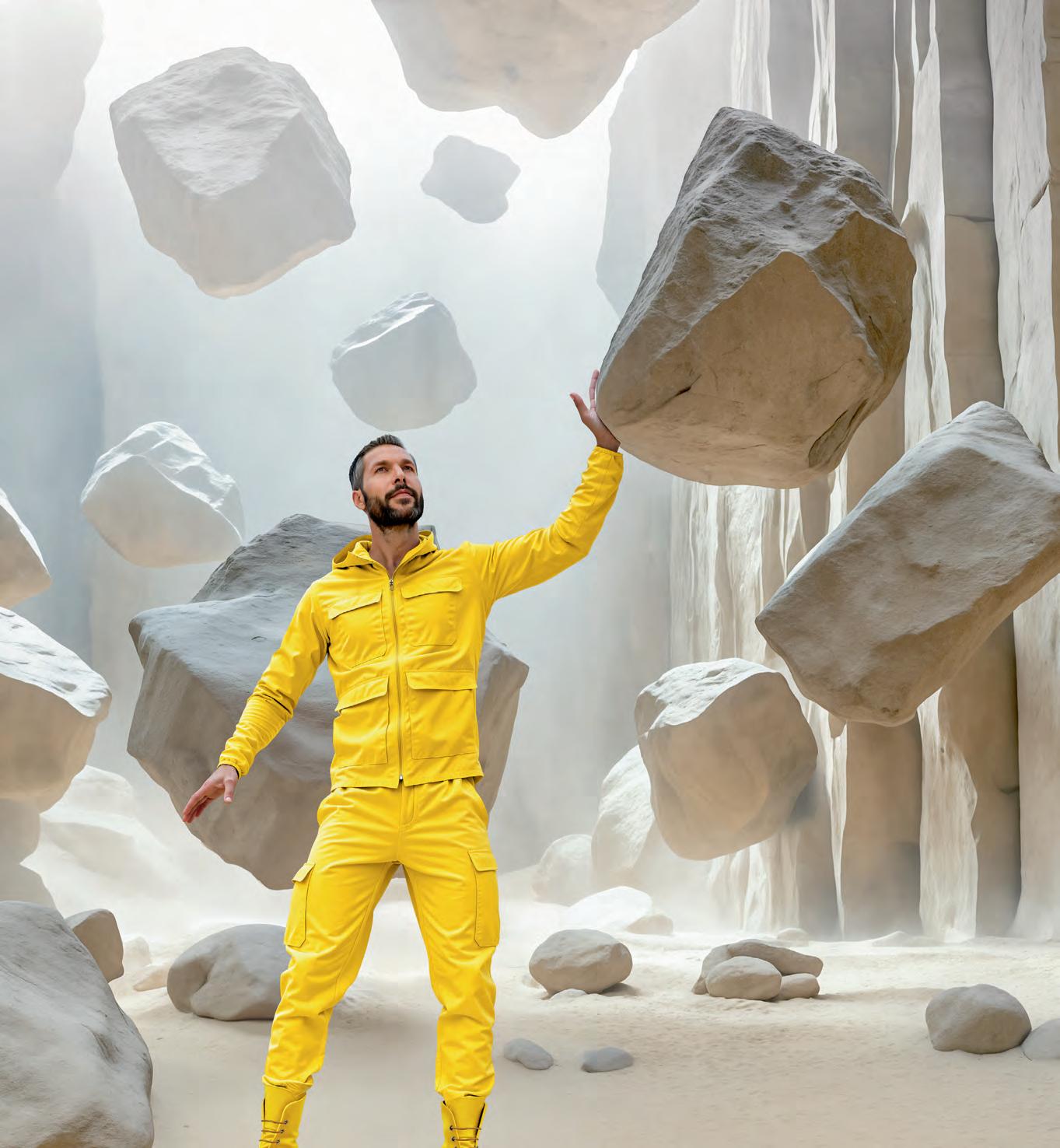
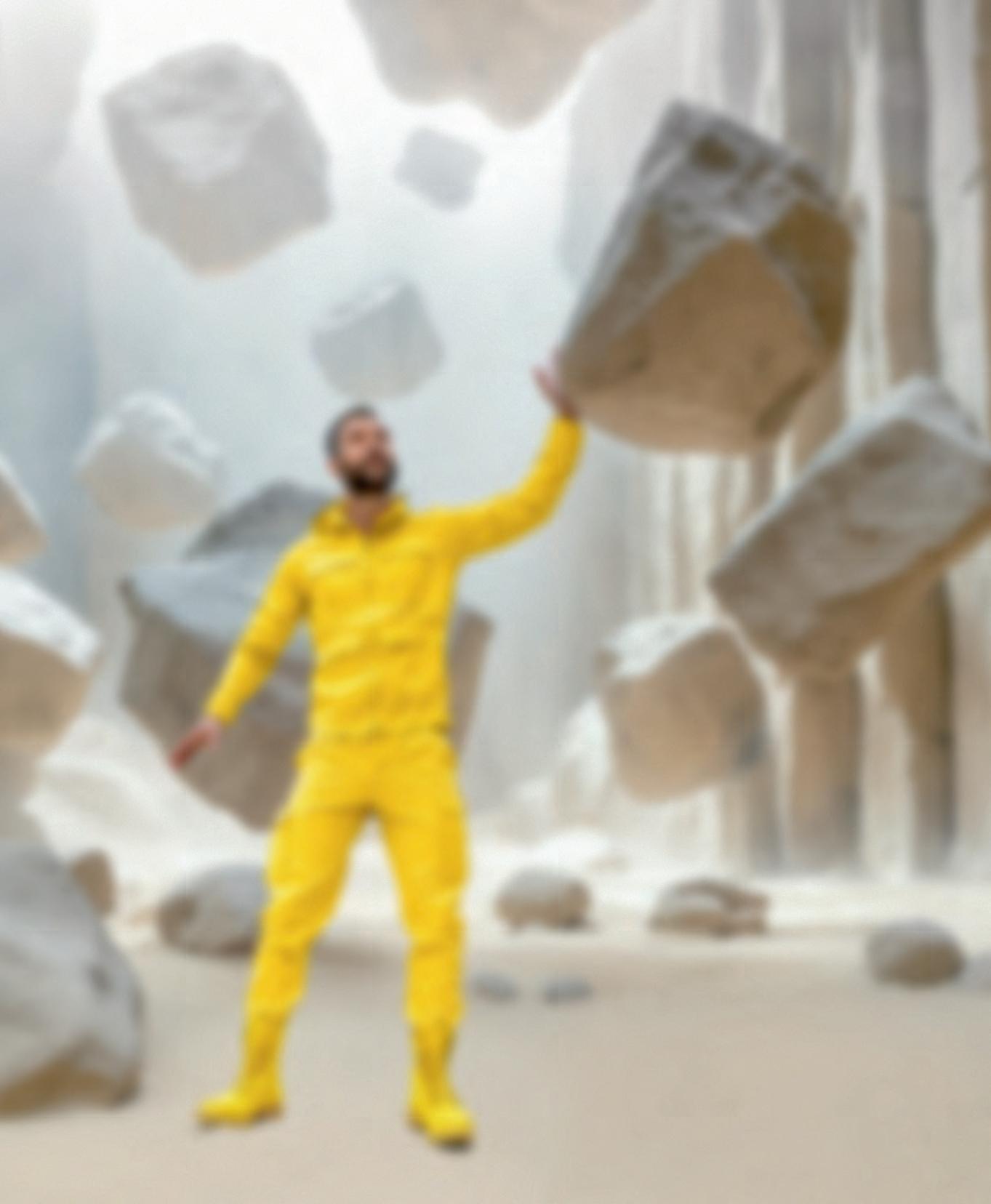
DONE RIGHT GRADING
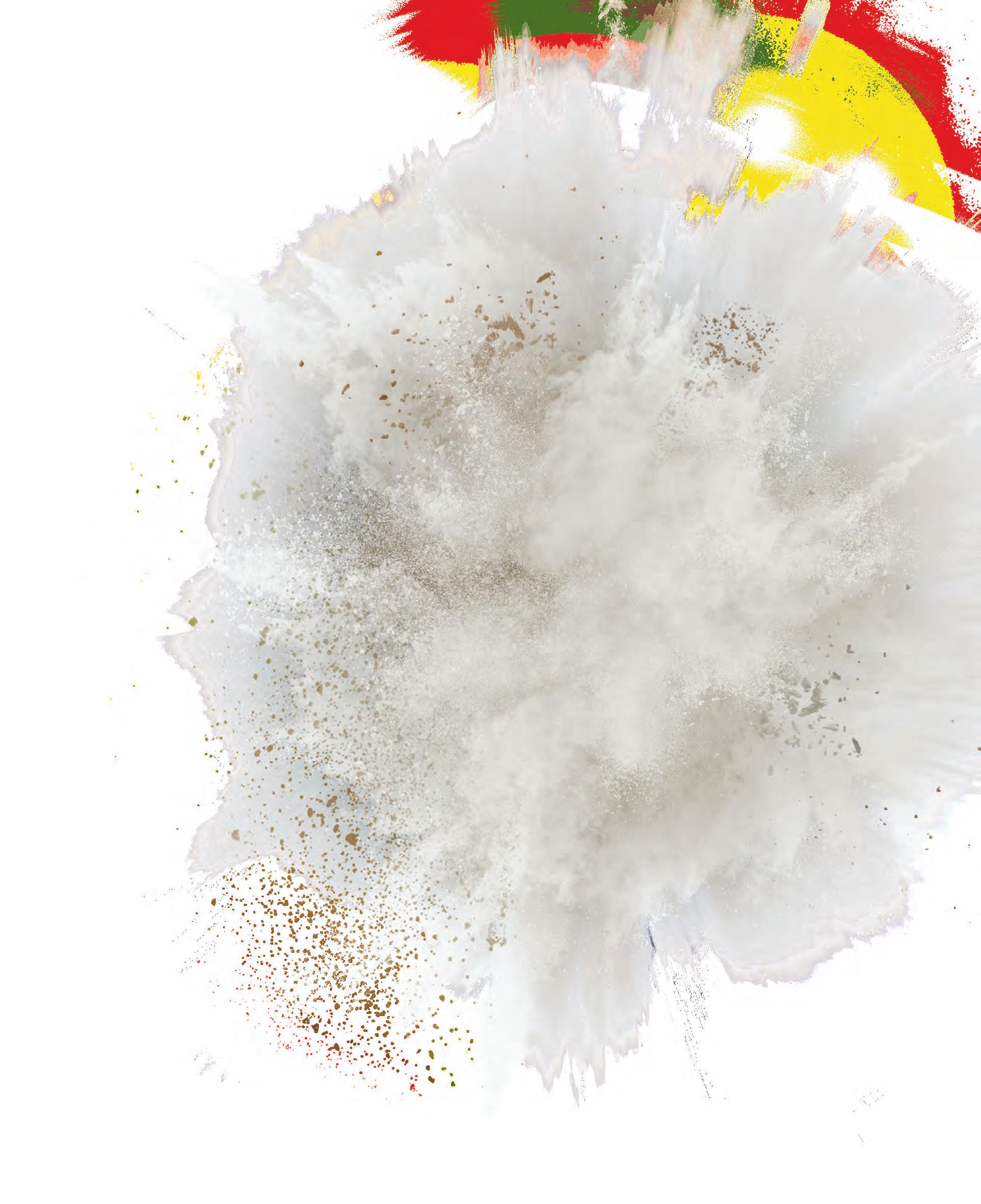
BELL EQUIPMENT, IN PARTNERSHIP WITH HITACHI CONSTRUCTION MACHINERY, WILL SOON INTRODUCE THE BELL G140 MOTOR GRADER, DESIGNED SPECIFICALLY FOR LOCAL GOVERNMENT AND LIGHT-TO-MEDIUM CONSTRUCTION APPLICATIONS.
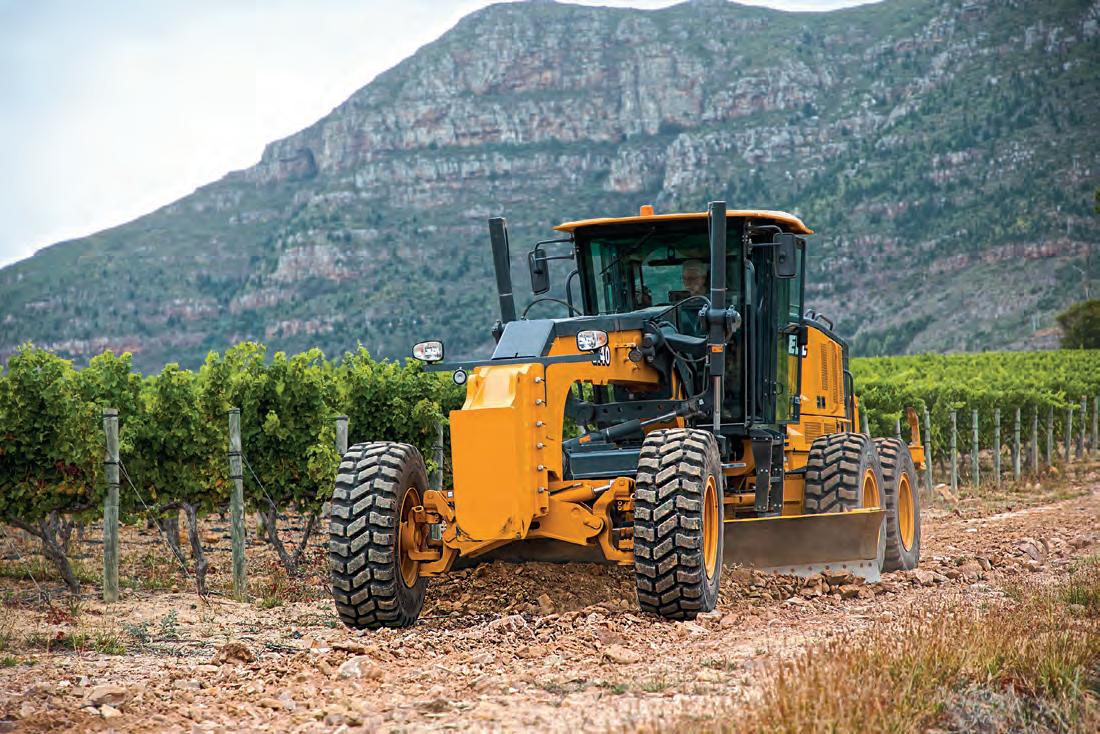
on the horizon for Australia, with with the company’s full range of joystickexpansion of Bell Equipment’s offerings in the country, specifically targeting the
supporting motor graders tailored to the unique demands of the Australian landscape.
The Bell Motor Grader range consists of three base models, the G140, G160 and G200 – each available in either a 4WD or 6WD configuration.
The G140 is well suited to all maintenance and light-to-medium construction tasks such as road maintenance grading, site preparation, and finishing work. The G160, with increased power and performance, can handle heavy construction applications; the G200 is designed for bulk earthworks and the mining industry.
Powered by a Cummins QSB6.7 Stage 3A engine – with the option for Stage five – and paired with a ZF ERGOPOWER transmission, the G140 is designed for reliability and performance.
It typically features a 4267 millimetre (14 feet) high-strength moldboard and has a typical operating weight of approximately 21,289 kilograms for the 6x4 configuration. Bell also offers a 6x6 configuration for this model.
The use of globally recognised components such as Cummins engines and ZF transmissions is a strategic decision aimed at enhancing customer
Bell Equipment’s new G140 Grader is suited to all maintenance and light-tomedium construction tasks.
Images: Bell Equipment
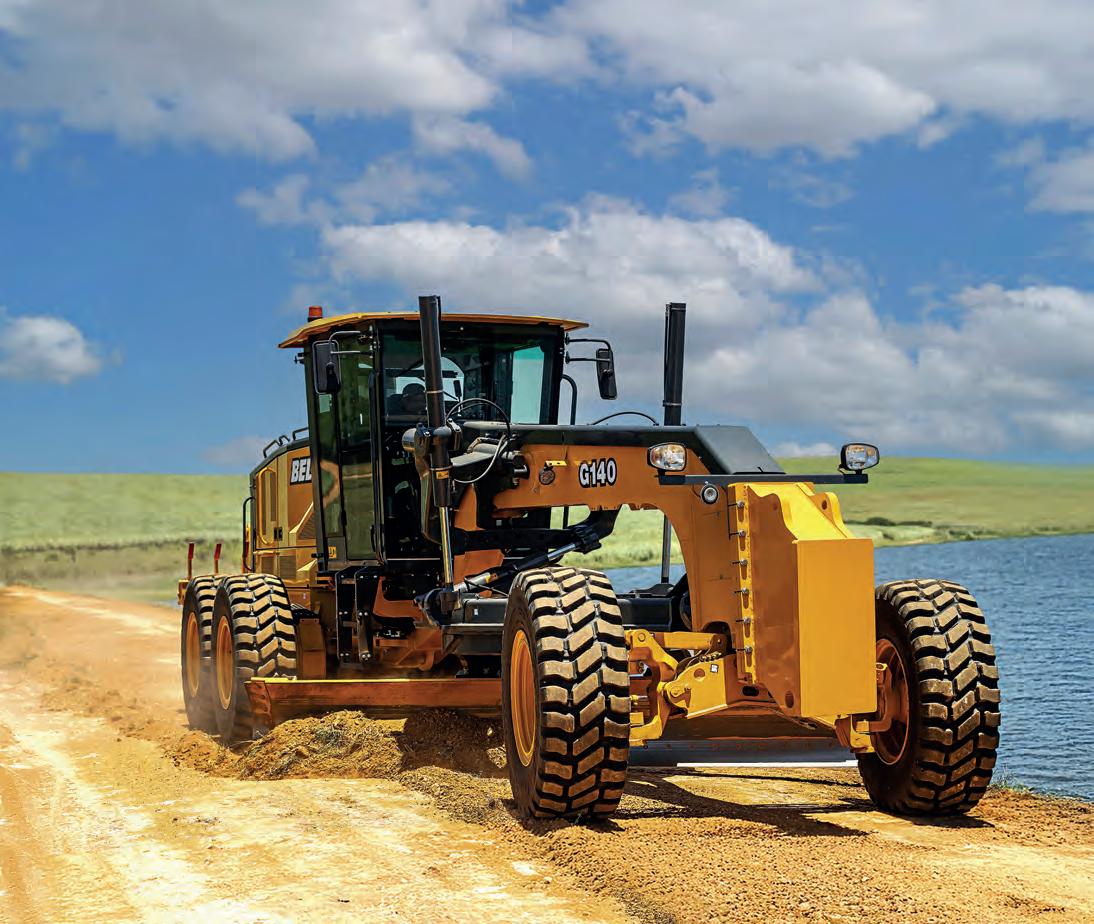
confidence in the machine’s reliability while simplifying maintenance and parts availability across Australia.
Automation was a key focus during the design process, allowing the operator to focus on precision grading.
While retaining familiar controls and layouts, the G140 incorporates a range of advanced components and features that will help operators improve productivity and accuracy, maintain costs, and deliver work efficiently.
It offers key benefits, such as saving on fuel and operating costs, as well as enhanced serviceability.
Fully sealed circle bearings extend service intervals, ensuring consistent performance and eliminating the need for costly wear inserts and regular adjustments.
To further simplify operations, advanced diagnostics are incorporated into the machine to reduce the complexity of daily checks and servicing, on top of being supported by HCA’s national network.
Ideal for tasks requiring accurate grade control, the G140 guarantees precision on all sites.
Modern engine technology contributes to lower operating costs, while a certified steel cab frame guarantees safety and comfort.
The G140’s gooseneck main frame is engineered as a single piece, eliminating fatigue on fabricated joints and providing maximum confidence in hard applications.
David Gallina, Product Manager of Hitachi Construction Machinery says the G140 is a right-sized solution for Australian conditions.
“The G140 is backed by decades of proven grader expertise and reflects our ongoing commitment to delivering reliable, practical equipment that meets local needs.”
WELL ROUNDED PARTNERSHIP
The introduction of the Bell graders is more than just a new product launch. Hitachi says it signifies a continuation of Bell and HCA’s long-term commitment to the Australian grader sector.
Bell Equipment, a globally recognised original equipment manufacturer (OEM) with more than 70 years of experience, is renowned for its Articulated Dump Trucks and a diverse range of equipment for various industries.
HCA contributes decades of specific experience in distributing and supporting motor graders across Australia, with an unparalleled understanding of local customer needs and operating conditions.
engineering and manufacturing expertise with HCA’s deep market knowledge, established customer relationships, and proven support capabilities.
WESTERN
LAUNCH
The Local Government Works Association Local Government Conference in Western Australia scheduled for August 5–7, 2025, at Joondalup Resort, will serve as the primary launch platform for the Bell G140.
The conference is ideally positioned to offer direct access to key decisionmakers within the local government sector, a primary target market for the G140.
The G140 will be on full display, demonstrating its suitability for light construction tasks and maintenance, all while highlighting its precision, reliability, efficiency, and operator comfort. These strengths are underpinned by decades of proven capability and the unmatched local support and expertise of HCA.
The event will position the G140 not as a new venture, but as the next evolution in a long-standing commitment to the Australian grader market.
Powered by a Cummins QSB6.7 Stage 3A engine, the G140 Grader is designed for reliability and performance.
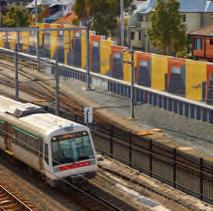
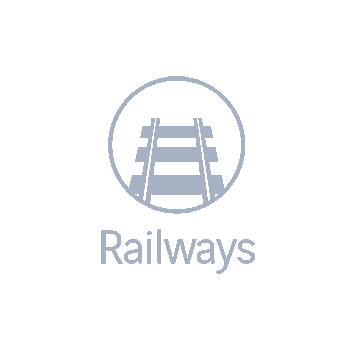
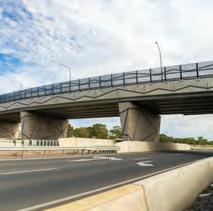
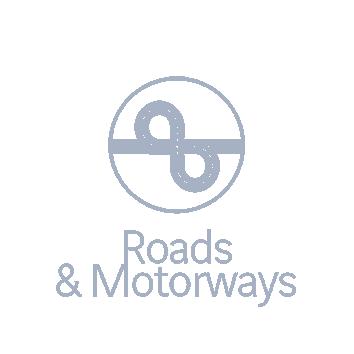
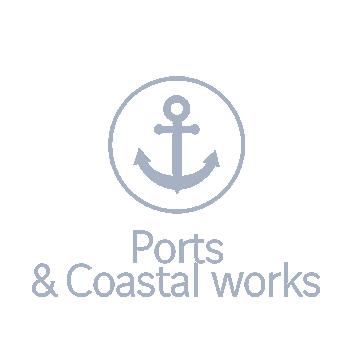
• Reinforced backfill applications
• Soil-structure interaction
• Precast concrete solutions
• Geosynthetics
• Environmental hazard protection
www.geoquest-group.com.au
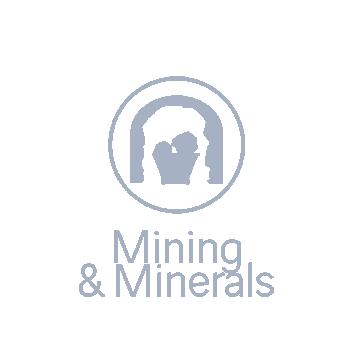
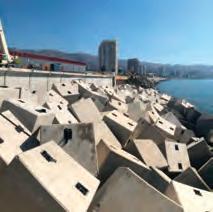
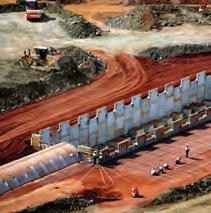
RECOGNISING REMARKABILITY
JOHN DEERE IS SET TO SPONSOR THE AWESOME WOMEN IN CONSTRUCTION (AWIC) AWARDS, WHICH CELEBRATES THE ACHIEVEMENTS OF WOMEN WORKING ACROSS ALL SEGMENTS OF THE CONSTRUCTION INDUSTRY.
“Ihope that one day we can talk about the construction industry without mentioning that it’s a male dominated industry.”
Amanda Bulow, the Chief Executive Officer and Founder of Awesome Women in Construction (AWIC) has more than 25 years’ experience in the construction industry and has spent the past nine empowering women in the industry.
AWIC – a Queensland-based notfor-profit organisation with a national footprint – connects thousands of women in Australia’s construction sector annually.
Since 2022, the organisation has hosted the AWIC Awards annually, to further amplify and celebrate the achievements of women in the construction industry. The event returns this year on October 10 at Brisbane’s Pullman Hotel.
The idea for the organisation originated over breakfast. Bulow invited 14 women to connect and support each other over breakfast, unaware it would turn into a thriving organisation.
“It turned out everyone loved the catchup and wanted to do it again,” she says. “Two months later we had up to 48 ladies in attendance, who were there for no other reason than to connect and support each other.”
By the end of August, Bulow had more than a not-for-profit, she had a community.
“We use International Women’s Day as our birthday and this year we had 511 people attend our International Women’s Day lunch,” says Bulow.
“That is some significant growth, and it signifies that the industry was missing that connection.”
The premise of the AWIC Awards was to not only highlight the contribution that women in construction are making, but also to recognise all contributors, no matter the gender.
“I wanted it to be a little different in that we also highlight the employers and male advocates, those people that support us throughout our careers,” says Bulow.
Many industry stakeholders have supported the event, including John

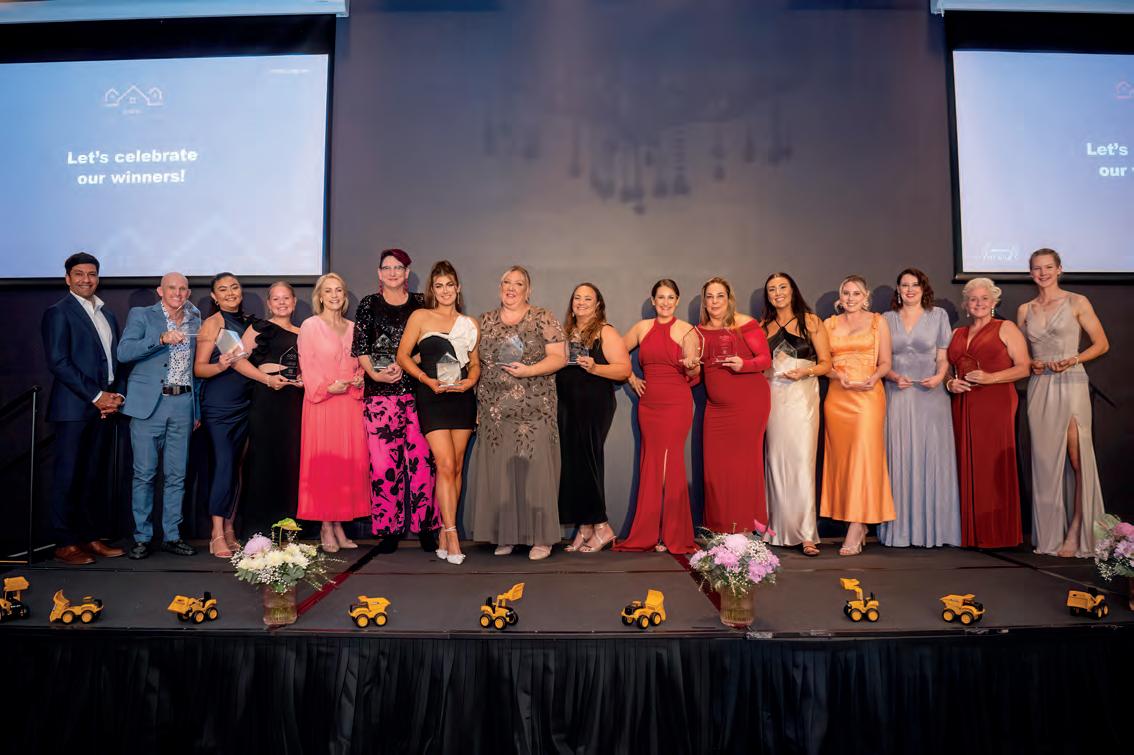
John Deere is a long-standing partner of the Awesome Women in Construction Awards, supporting the future of women in the sector.

Deere, which is returning for the third time as the official 2025 AWIC Awards diamond sponsor.
The manufacturer is also sponsoring the Outstanding Women in Machinery award, which celebrates women’s achievements in any machinery-related field. This could include training, operation, or sales of machinery, leadership, innovation, or high achievement in their fields.
John Deere is one of AWIC’s longest standing corporate partners, supporting its vision to increase female representation in the sector.
“Over the next five years, the construction industry needs an additional 250,000 people to be able to meet demand for infrastructure projects,” says Karen Poulton, Marketing Manager of John Deere.
“Less than two per cent of on-site roles are being occupied by women, these roles include operators of construction machinery.”
Bulow says John Deere’s global reach has proven to be invaluable for the annual awards.
“It has been incredible for us because John Deere is not just national, they are international, which helps us share our message around the globe,” says Bulow.
“Having a business like John Deere onboard helps promote women in the industry. It is great to have the support of John Deere, they’re genuinely good people, and they enable us to help support the next generation of women in construction.”
AWIC hosts roadshows for school students in regional areas of Queensland to demonstrate potential roles in the construction industry, always a highlight for Bulow.
an electrician, and we need to have additional roles more visible.”
Bulow says AWIC has many contacts within the community, and when they see people wanting to enter the industry, they can help connect them.
“That network is, as they say, your net worth, and it also allows you to know what else is out there in your industry,” she says.
“The awards have become a great event, not only for the award winners
“LESS THAN TWO PER CENT OF ON-SITE ROLES ARE BEING OCCUPIED BY WOMEN, THESE ROLES INCLUDE OPERATORS OF CONSTRUCTION MACHINERY.”
It also hosts industry-led site visits, factory tours, and other opportunities to help end the under-representation of women in the construction industry.
Upon reflection, Bulow says it has been inspiring to watch her community grow and witness the former winners support the next generation of female leaders.
“We want to let the next generation know that there are many careers available in the construction industry,” she says. “There are more options than being a plumber, a carpenter or
but also for those nominating their colleagues. They see a strength which deserves recognition.
“For the award winners, in many cases, it has accelerated and amplified their careers and has given them a confidence boost.”
The AWIC Awards 2025 currently have nominations open across all award categories available through AWIC’s website.
Nominations close August 1. For more information, awic.org.au
Brisbane’s Pullman Hotel is set to host an awards night recognising the inspiring achievements of women in construction.
Images: AWIC
ROAD SAFETY GOES 3D
A
BRAND-NEW METHOD FOR ROAD SAFETY IS BEING TRIALLED IN SOUTH AUSTRALIA. ADELAIDE UNIVERSITY’S DR MARIO MONGIARDINI EXPLAINS
HOW THREE-DIMENSIONAL LINE MARKINGS COULD HELP CURB THE ROAD TOLL.
New technology is constantly being adopted and adapted by the transport sector to tackle what is one of the most prevalent issues – the large number of fatal and serious road trauma incidents on Australia’s roads.
Recent research in South Australia is shining a light on alternative line marking methods that could be used to curb concerning trends nationally.
These three-dimensional markings are a variation of so-called ‘dragon teeth’, which are white triangular markings placed on both sides of a road to create a sense of lateral friction. Dragon teeth are designed to alert drivers and induce them to slow down. The added 3D effect in the trialled variation of these markings is aiming to enhance their effectiveness.
The trial is being spearheaded by Adelaide University’s Centre for Automotive Safety Research, a multidisciplinary group of experts who specialise in specific research areas such as vehicle design, road infrastructure safety, intelligent transport systems, as well as driver behaviour and psychology, and more.
Dr Mario Mongiardini says the centre represents a diverse group of professionals, each specialising in niche areas and collectively offering unique expertise into transport design.
“We are a very heterogeneous group of engineers and psychologists working on different aspects of road safety,” he says. “We deal with most of the aspects related to road safety.
“We are probably one of the oldest road safety centres in Australia, having started back in the late ’60s. Road safety is a very multi-disciplinary field and something that was considered more like
a by-product of transport in the past. Now we understand that it’s much more front and centre when it comes to the transport industry.”
The trial was inspired by similar markings used in Singapore and is being tested in Adelaide to help drivers reduce speed when entering areas with lower speed limits, particularly near businesses or pedestrian-heavy zones. The goal is to use these markings as a visual cue for drivers to be more cautious and reduce their speed in specific urban environments.
Mongiardini says the Centre for Automotive Safety Research adopted Singapore’s design to examine its potential in an Australian setting.
“We took their design and modified that to adapt it to what we think would be more suitable for the Australian scenario, in an urban application,” he says.

“In Singapore, they initially installed these in the CBD ‘silver zones’ (areas with many elderly pedestrians). Singapore’s markings were designed to reduce speeds to 30 kilometres per hour in specific zones, which proved to be very effective. As part of our trial, we’re evaluating a 40 kilometres per hour speed limit.”
This trial, similar to other programs and initiatives being investigated by the centre, focuses on the ‘Safe System approach’. This recognises that humans make mistakes, and that transport infrastructure needs to be designed to minimise the impacts of these mistakes – an essential aspect of research for the centre now and into the future, Mongiardini says.
“What we always have to consider is
The Centre for Automotive Safety Research’s trial aims to evaluate the performance of 3D line markings in increasing road safety.
that humans are not perfect, we all make mistakes, and we can’t pretend to be perfect when we are behind the wheel,” he says. “That’s why we need to have systems in place that can account for these mistakes. Travelling at a speed that is safe relative to both traffic conditions and the surrounding road environment is a crucial component of the Safe System approach.
“The ambitious goal that we have in road safety in Australia – as well as the world – is to reduce fatal or serious injuries from crashes to zero by 2050. That’s coming up very quickly, and it’s research and systems like this that will help us to inch closer to achieving this.”
The Centre for Automotive Safety Research received funding for the trial as part of the Federal Government’s National Road Safety Action Grants Program. The grants program was designed to provide funding for noninfrastructure road safety projects and programs across Australia and encourage the development of innovative, potentially low-cost solutions. Such

solutions would be particularly helpful for local governments, which typically operate under a fairly limited budget.
With funding for the 3D ‘dragon teeth’ road markings secured, the next step was to identify potential areas for implementation in the surrounding Adelaide area. Locations were considered based on a range of criteria, including areas where the road environment may not naturally encourage drivers to slow down.
The Centre for Automotive Safety Research focused on areas with speed limit changes, particularly near businesses or pedestrian-heavy zones. In collaboration with the South Australia road authority, the Department for Infrastructure and Transport (DIT), and local councils, the team selected four sites, with installation of the 3D ‘dragon teeth’ occurring across two separate phases.
Mongiardini emphasises that the goal was not to implement these markings everywhere, but to use them strategically in specific urban environments.
“If you install a perceptual treatment like this everywhere, people will start to get oblivious to them, because they will see them everywhere,” he says. “You would dilute the effectiveness, and people will quickly lose interest and trust in the treatment.
“That’s why it’s been a very targeted focus. We want to use these markings as a heads up, ‘hey look I’m here, I’m unmissable, be careful there’s a change in the road environment ahead’. By giving that channelling and gating effect, we want drivers to be more careful in these areas.”
While the trials are still underway, Mongiardini says initial feedback and results have been very positive. Local government has also expressed its support and interest in applying such a treatment.
“People and motorists in the community are curious about the markings, and drivers seem to adapt without dramatic braking or lane changes,” he says. “While we still don’t have the full results and context yet,
I’ve been pleasantly surprised with the reaction of drivers and members of the community so far.
“Ideally, if it is successful, we would like to have these 3D markings considered for specific areas similar to where we’re trailing them now. Which are areas where the speed limit changes from 60-50 kilometres into 40.”
Mongiardini says results will be evaluated over the coming months, but overall he’s optimistic for the impact that technology is – and will have – on increasing road safety. This includes technologies such as automation, which could potential overcome human limitations when it comes to reactions and perception.
“What really excites me is that we have a lot of technological advancements coming through,” he says. “We already see safety technology in our cars, like automatic emergency braking or lane assist.
“We’ve shown that technology can have a real impact. Now we’ve got to maximise what that impact could be.”
Image: Adelaide University
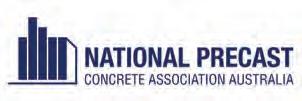
ELLENBROOK WILDLIFE BRIDGE: ENGINEERING WITH NATURE IN MIND
THE ELLENBROOK WILDLIFE BRIDGE IN WESTERN AUSTRALIA REPRESENTS A MILESTONE IN ECOLOGICALLY CONSCIOUS INFRASTRUCTURE, DEMONSTRATING HOW
ENGINEERED SOLUTIONS CAN HARMONISE WITH THE NATURAL ENVIRONMENT.
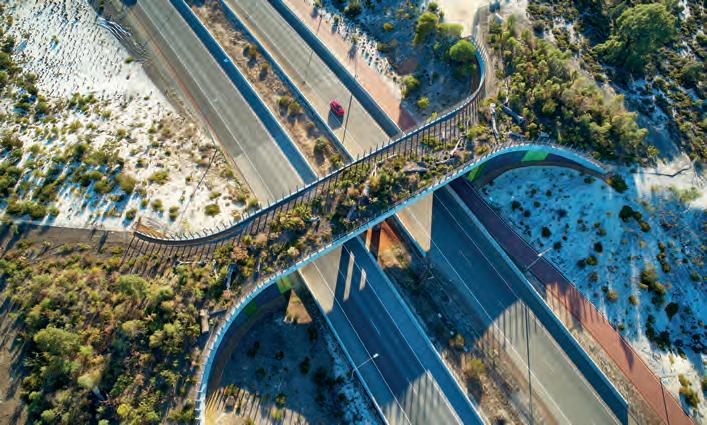
PROJECT: Ellenbrook Wildlife bridge
LOCATION: Tonkin Highway, WA
PRECASTER : Geoquest
CONTRACTOR: Great Northern Connect
Designed to provide safe passage for native fauna across Tonkin Highway, the 12-metrewide bridge stands as a testament to sustainable design and thoughtful construction practices.
As part of the NorthLink WA Central Section, the bridge was constructed by contractor Great Northern Connect – a joint venture between BGC Contracting and Laing O’Rourke – under the direction of Main Roads Western Australia.
ENGINEERED FOR THE ENVIRONMENT
National Precast Master Precaster Geoquest Australia played a critical role in the project, supplying more than 32,600 square metres of Reinforced Earth® walls and precast concrete elements. These components were essential not only to the structural performance of the bridge but also to its environmental credentials.
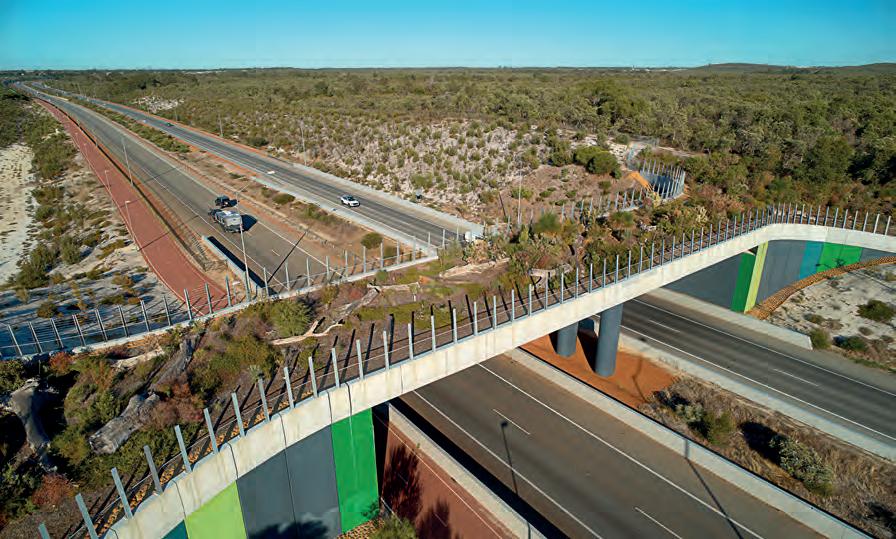
“We were proud to contribute to such a forward-thinking and environmentally significant project,” said Riccardo Musella, Managing Director of Geoquest Australia.
“The Ellenbrook Wildlife Bridge shows what’s possible when infrastructure is designed with wildlife in mind. It’s a great example of how engineering can support biodiversity and create positive, lasting outcomes for communities and the environment.”
Manufactured following factorycontrolled processes, the precast elements ensured consistency, precision and timely delivery.
Combined with Geoquest’s expertise of the engineered fill and soil-structure interaction, the result was a durable, structurally sound solution capable
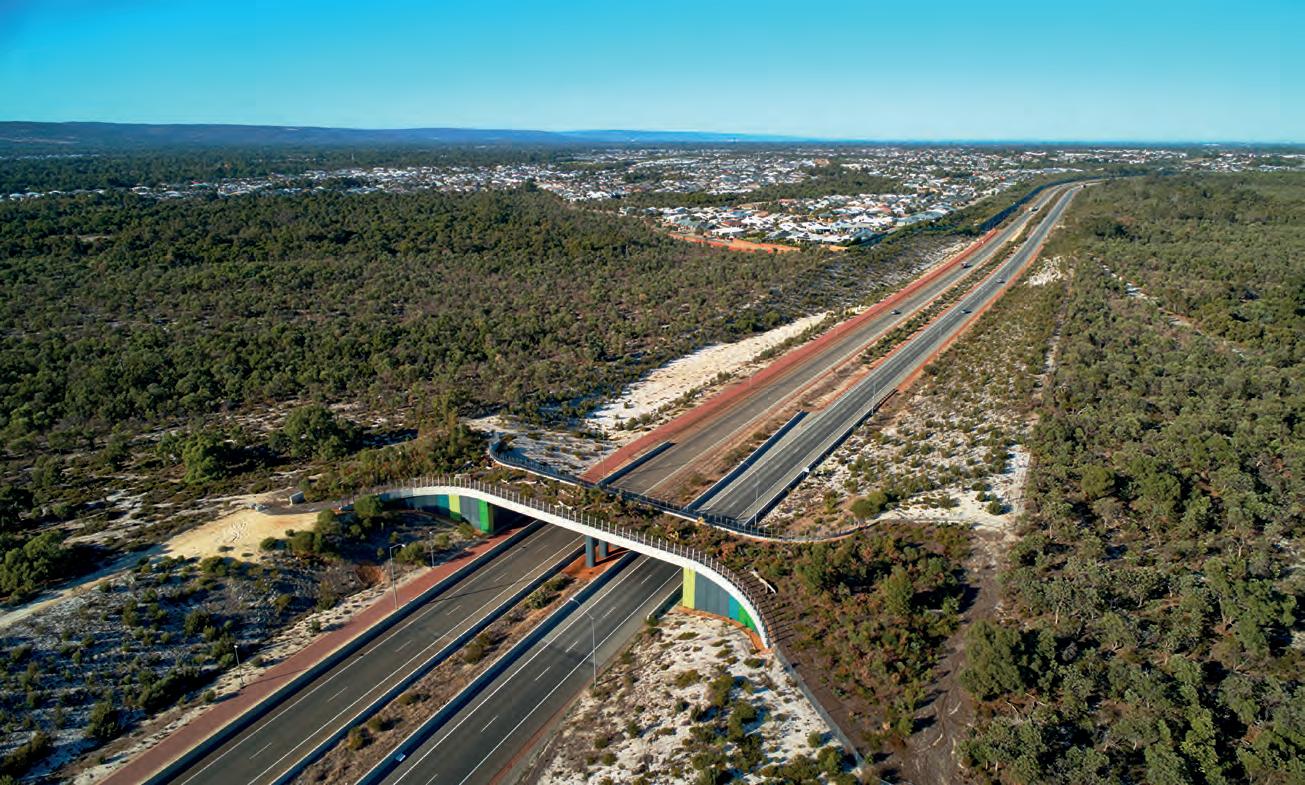
Success on the project has already influenced other works nationally.
The connection provides a vital link to help local wildlife pass the highway safely.
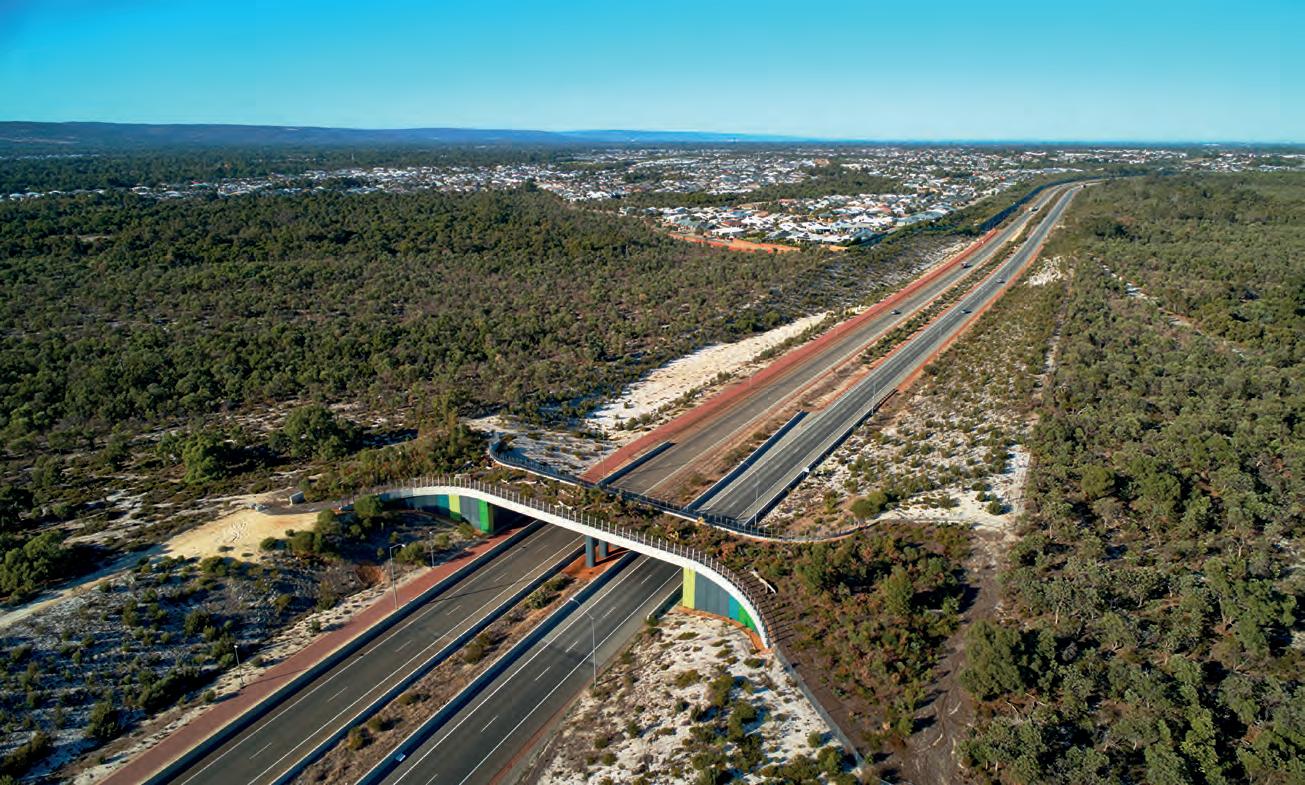
of supporting both ecological and civil objectives.
ENHANCING BIODIVERSITY THROUGH DESIGN
The bridge’s form and function were carefully considered to support wildlife movement and encourage species use.
Precast elements were designed for seamless integration into the landscape, providing a foundation for natural features such as rockeries, logs and mounding. The bridge was then fully vegetated using native trees, shrubs and ground covers that reflect the surrounding bushland, creating a familiar and inviting habitat for fauna.
Today, several years after its completion, the bridge has evolved into a densely planted corridor that functions as a thriving ecosystem. Monitoring efforts have confirmed that the structure is regularly used by local wildlife – including larger species such as emus – highlighting its effectiveness in restoring habitat connectivity.
A LEGACY OF SUSTAINABLE DESIGN
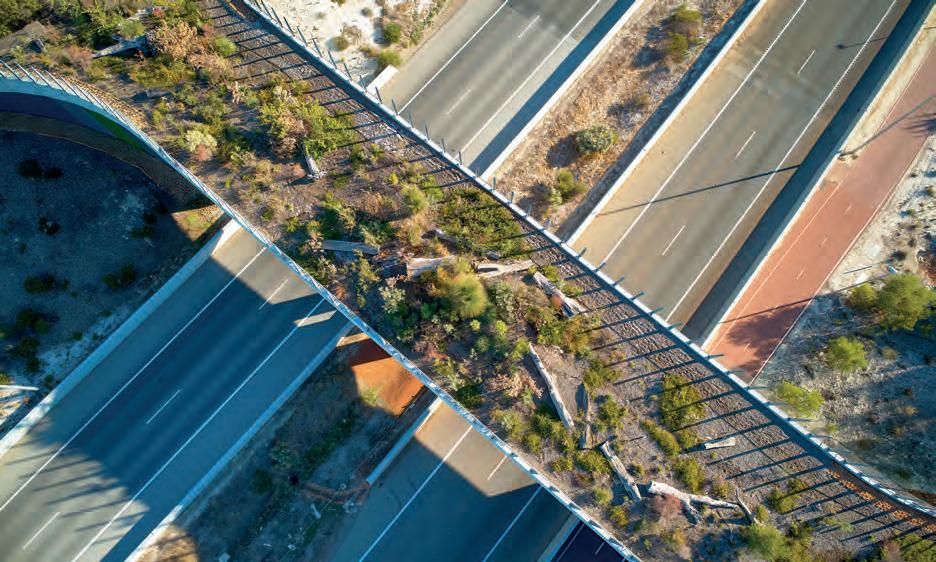
The project has exemplified how precast can be implemented to achieve environmentally conscious project outcomes.
environmental outcomes. It has proven that it is possible to reduce ecological impact while maintaining structural integrity and performance.
Its success has already inspired the adoption of similar wildlife infrastructure across the state, including on the Wilman Wadandi Highway (formerly the Bunbury
BUILDING FOR THE LONG TERM
The Ellenbrook Wildlife Bridge exemplifies how modern construction methods, such as precast concrete, can deliver sustainable, resilient infrastructure without compromising on
Outer Ring Road), where Geoquest once again supplied critical components.
“Projects like this redefine what infrastructure can be,” said Mr Musella.
“When we prioritise sustainability, habitat protection and innovative design, we’re not just building roads and bridges – we’re building a better future.”
The Ellenbrook Wildlife Bridge spans 12 metres and is designed solely for fauna, featuring native vegetation, logs, mounding and natural rockeries that discourage human use while supporting species movement. Years on, it continues to function as a thriving habitat corridor – a model for future infrastructure that respects and preserves Australia’s unique ecosystems.
Environment has come first for the Ellenbrook Wildlife Bridge.
A LITTLE LESS CONVERSATION, A LITTLE MORE ACTION
THE AUSTRALIAN FLEXIBLE PAVEMENT ASSOCIATION (AFPA) WRITES ON THE IMPORTANCE OF TACKLING ROAD MAINTENANCE CHALLENGES THROUGHOUT REGIONAL AUSTRALIA.
At the recent Regional Road Maintenance and Rehabilitation Forums hosted across Bendigo, Port Augusta, Murray Bridge, Lismore, and Dubbo, a clear and urgent message echoed across every workshop, panel, and coffee break: “We need a little less conversation, a little more action, please.” The iconic Elvis lyric couldn’t be more appropriate in summarising the collective frustration of road maintenance professionals grappling with the widening chasm between community needs and funding realities.
These pivotal two-day events, co-hosted by the Australian Flexible Pavement Association (AfPA) and the Pavement Recycling and Stabilisation Association (AustStab), provided a crucial platform for state and local government professionals, contractors, and consultants to address the compounding challenges facing Australia’s rural and regional road networks. Despite the wealth of knowledge shared at these events, one concern dominated the agenda:
insufficient and inconsistent funding availability to achieve the required outcomes.
THE FUNDING GAP
The forums laid bare a difficult truth: while Australia’s regional road assets are critical to national connectivity, they are persistently underfunded. Discussions revealed that the current level of funding is not only delaying repairs but also accelerating the deterioration of infrastructure, leaving local councils and State Road Authorities caught in a vicious cycle of reactive maintenance.
The data collated during workshop sessions reflects this stark reality. Attendees repeatedly cited “lack of funding” and “inadequate budget” as root causes of systemic issues like workforce shortages, loss of skilled workers, and sub-optimal asset management processes. The results? A network increasingly vulnerable to extreme weather events, reduced road safety, and communities left disconnected.
PEOPLE POWER
Human capital remains one of the sector’s greatest assets, but also one of its most strained. Workforce shortages, high staff turnover, and the exodus of experienced personnel were prevalent concerns.
Compounding the issue is the rise in lowerskilled staff and the challenge of attracting talent into local government roles.
Participants from all five regions emphasised that without investment in workforce development, even the most innovative engineering solutions will struggle to scale. Additionally, community expectations are increasing, while asset managers are faced with ageing infrastructure and several external factors beyond their control. This situation leaves them without the autonomy and resources needed to achieve effective results.
RESILIENCE
An important topic of discussion was the challenges posed by bureaucratic processes and complex procurement systems. Asset managers noted that some of the existing procedures could be seen as inflexible and somewhat outdated, which can slow down innovation and delay maintenance schedules. While these processes serve essential functions, there was a recognition that they may not always align with the practical realities faced on the ground.
Many delegates highlighted how the issue of resilience amidst climate change is often tied to limited funding for preventative maintenance. They discussed how recent natural disasters have highlighted the importance of adopting more sustainable and forward-thinking asset management strategies. Unfortunately, these approaches are frequently not implemented as much as they could be, often due to the focus on short-term priorities and reactive budgeting.
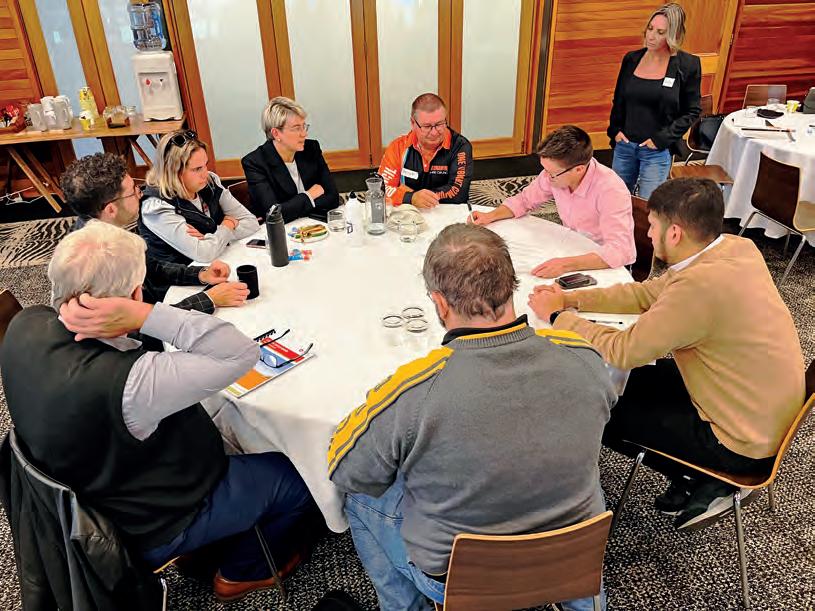
TURNING THE TIDE
Despite these challenges, the forums showcased innovative thinking that could chart a more sustainable path forward. Sessions on AI in maintenance, microsurfacing techniques, bitumen emulsions, and crumb rubber asphalt offered concrete (and sometimes literally asphaltic) strategies for better outcomes.
The circular economy also took centre stage. The case for rehabilitation and
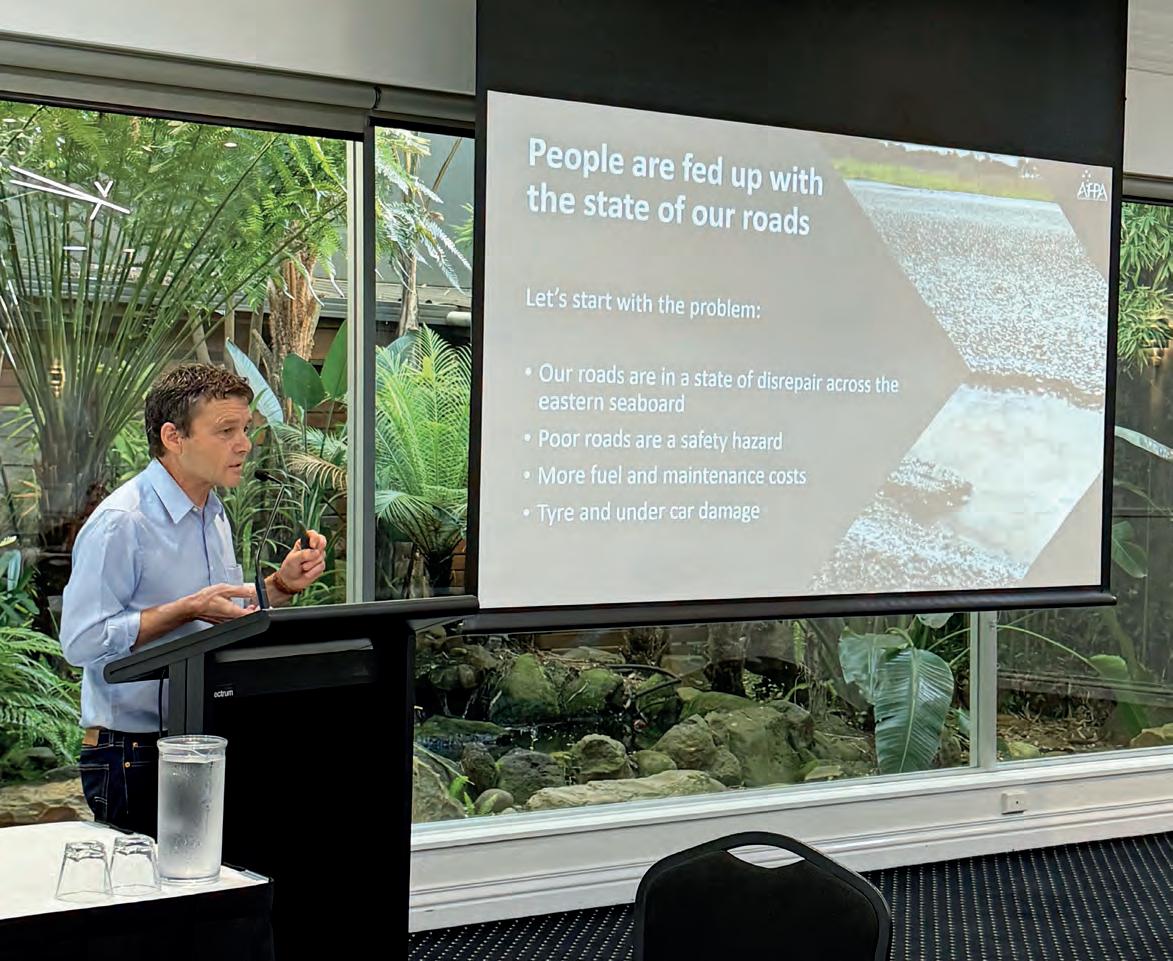
A
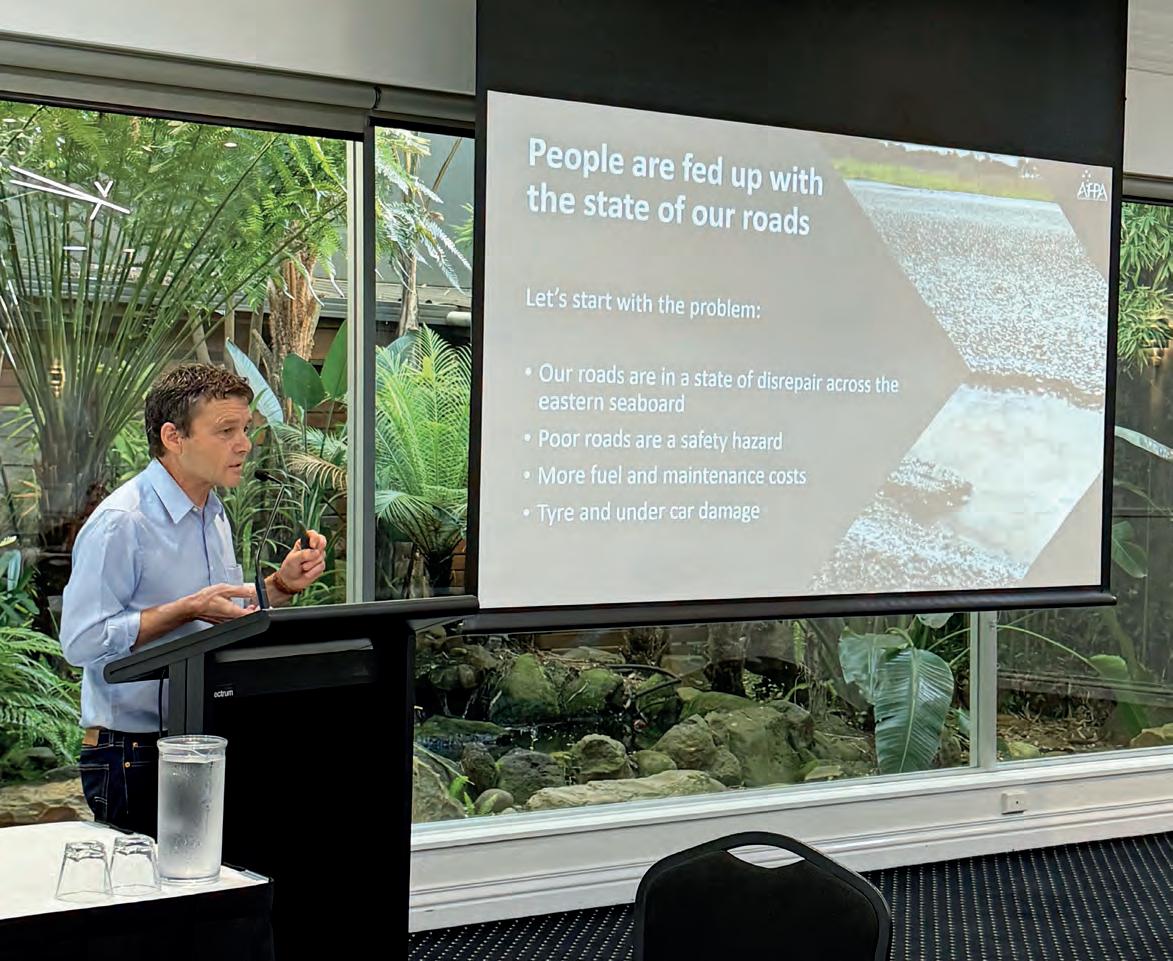
recycling, particularly through in-situ material testing and stabilisation, was made with passion and evidence. Not only are these methods environmentally sound, but they also promise long-term cost savings and improved pavement performance.
Furthermore, collaborative planning emerged as a key solution. Multiple speakers emphasised the importance of a shared vision between state departments, local councils, and industry players. As one delegate succinctly put it, “We don’t just need money; we need shared goals, flexible policies, and trust in local expertise.”
FORUM LEGACY
AfPA and AustStab have positioned these forums as a catalyst for change, creating a space for open dialogue and practical problem-solving. This movement has the potential to redefine rural and regional road maintenance, but for it to succeed, key industry stakeholders must move beyond a narrative and implement actionable solutions. Insights gained from the forums must translate into streamlined procurement processes, reliable funding models, and workforce development programs that reflect real-world challenges.
These forums have quickly established themselves as premier gatherings for infrastructure professionals in regional contexts, offering more than just lectures. They provide an interactive and collaborative environment for attendees to gain insights, share knowledge, and forge meaningful
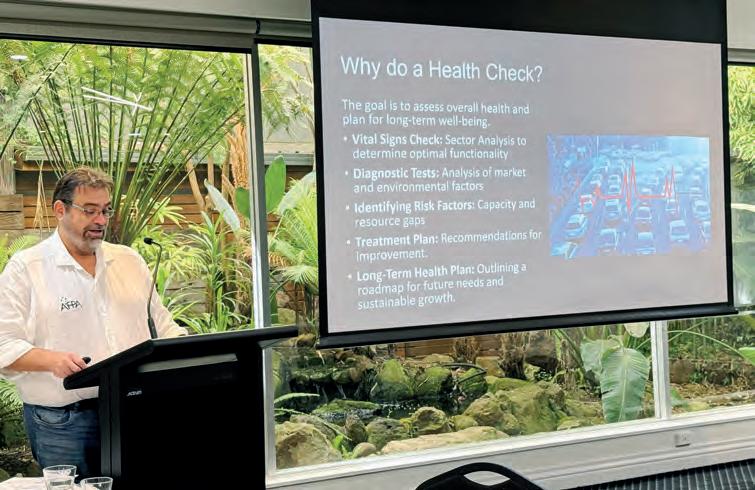
presentations that explore sustainable maintenance strategies, new technologies, and practical innovations to improve road network performance.
Moreover, the forums serve as a platform for professionals to connect, build crossregional relationships, and gain a clearer understanding of how similar challenges are being addressed elsewhere.
The events create an opportunity to step back from day-to-day pressures and examine strategic approaches that can be adapted or scaled locally.
From community-focused engineers to government asset managers, the sense of shared purpose is strong and energising. It’s time for “a little more bite and a little less bark.”
call to arms. The ingenuity, experience, and commitment across the sector are unquestionable. What they need now is meaningful collaboration from all parties.
Without a shift from conversation to action, Australia’s regional roads and the communities that rely on them will continue to fall through the cracks.
AfPA and AustStab would like to thank the Sponsors for these Forums: BildGroup, Fulton Hogan, and Stabilised Pavements of Australia. Without their generous assistance, these events would not be possible.
We look forward to seeing continued engagement, sustained investment, and systemic reform, ensuring that the road forward is not only paved but resilient, smart, and shared.
A number of AfPA specialists contributed to what was a beneficial program for the whole sector.
Tony Aloisio, AfPA CEO, speaking at the forum.
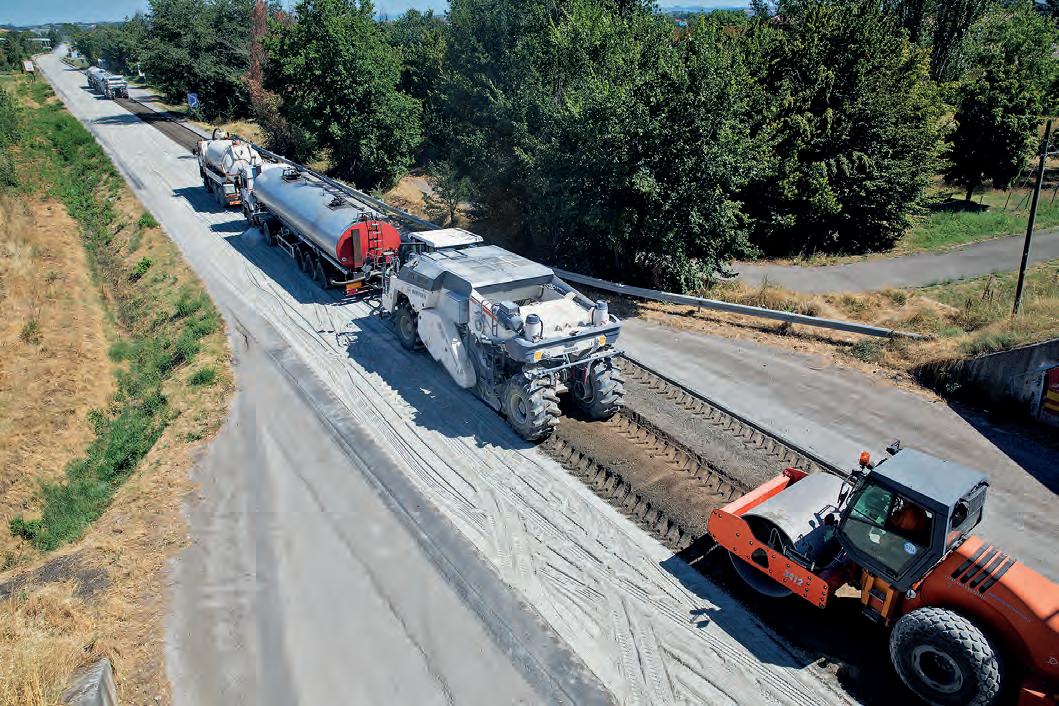
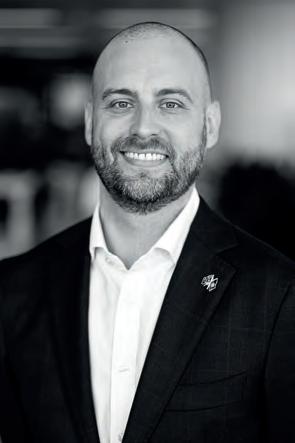
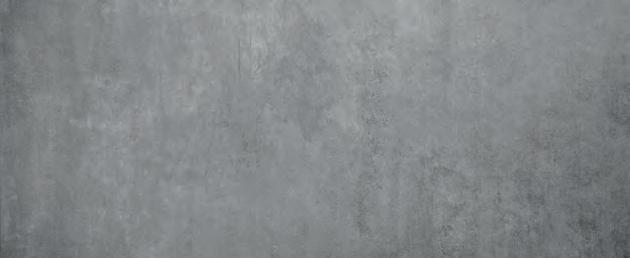
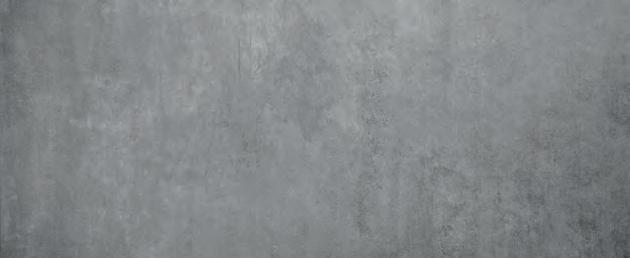
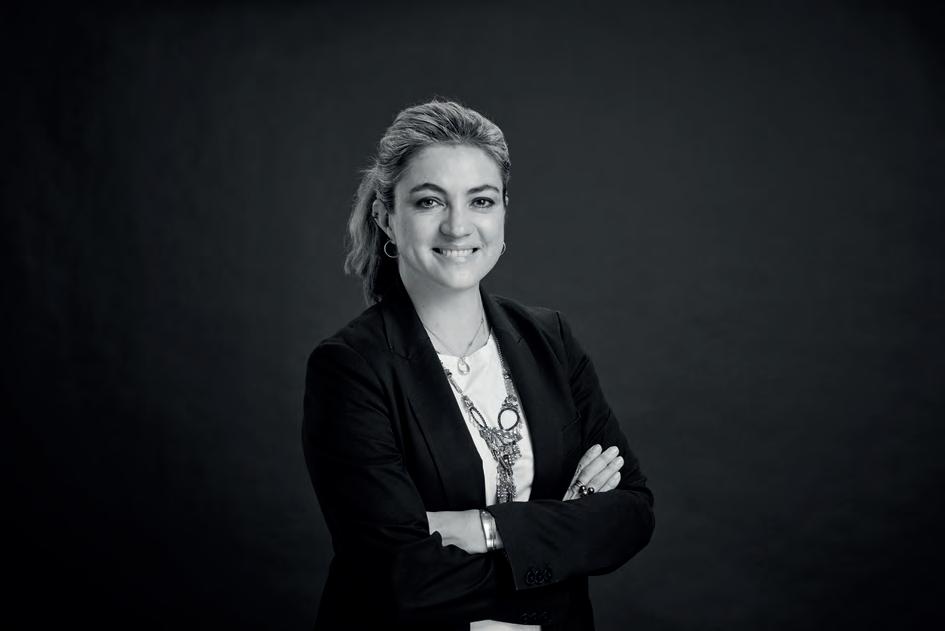
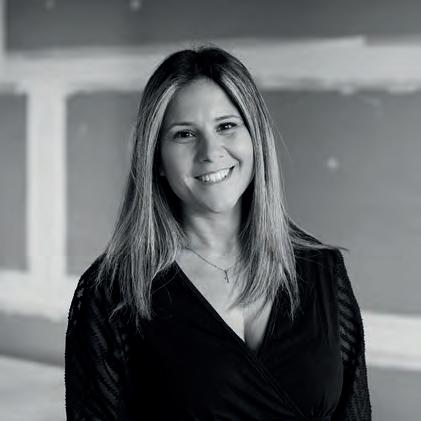
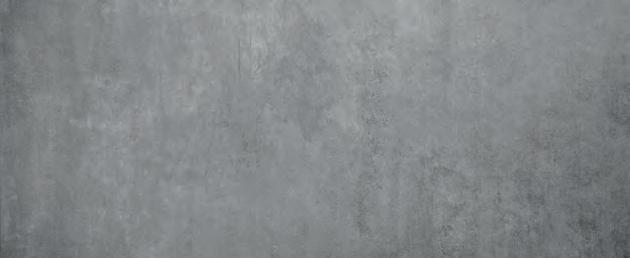
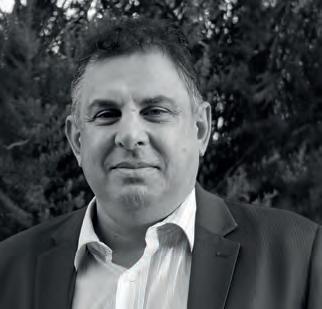
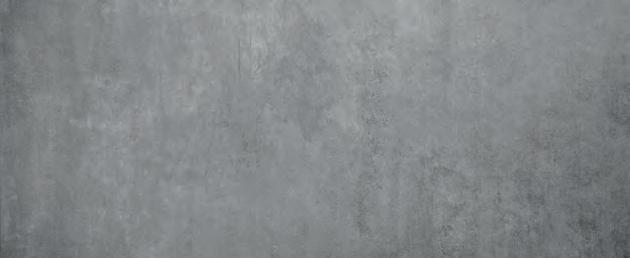
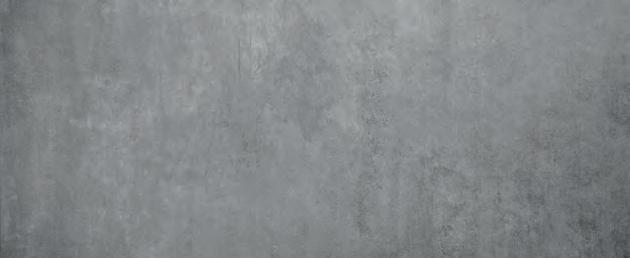
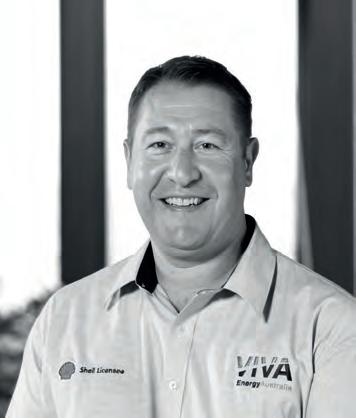
Left:
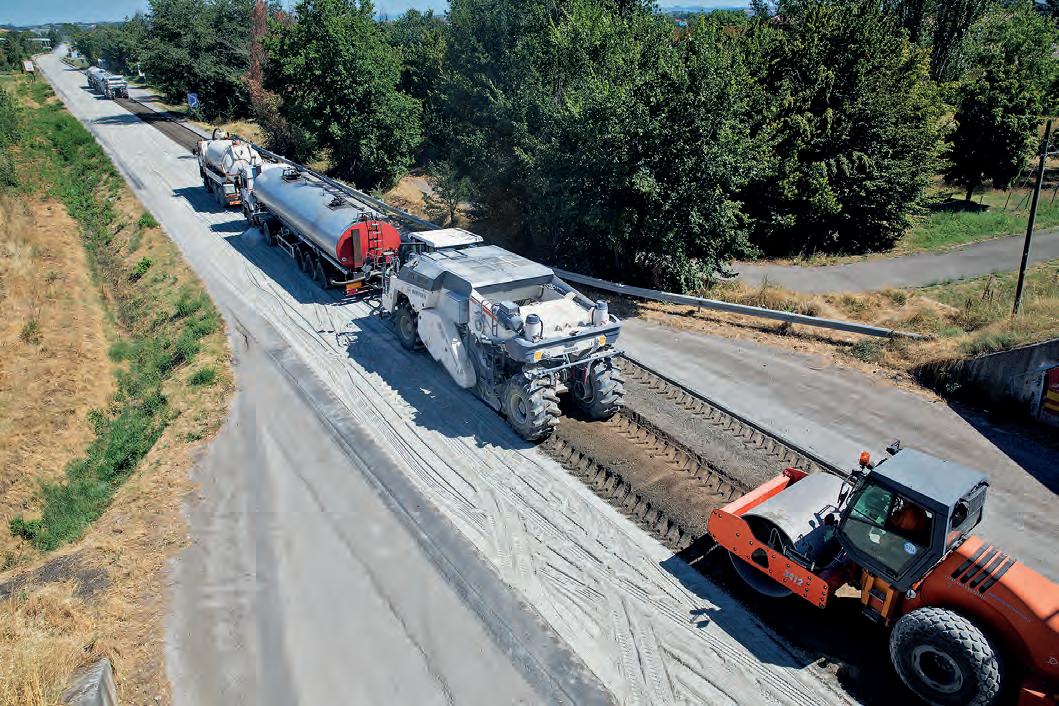
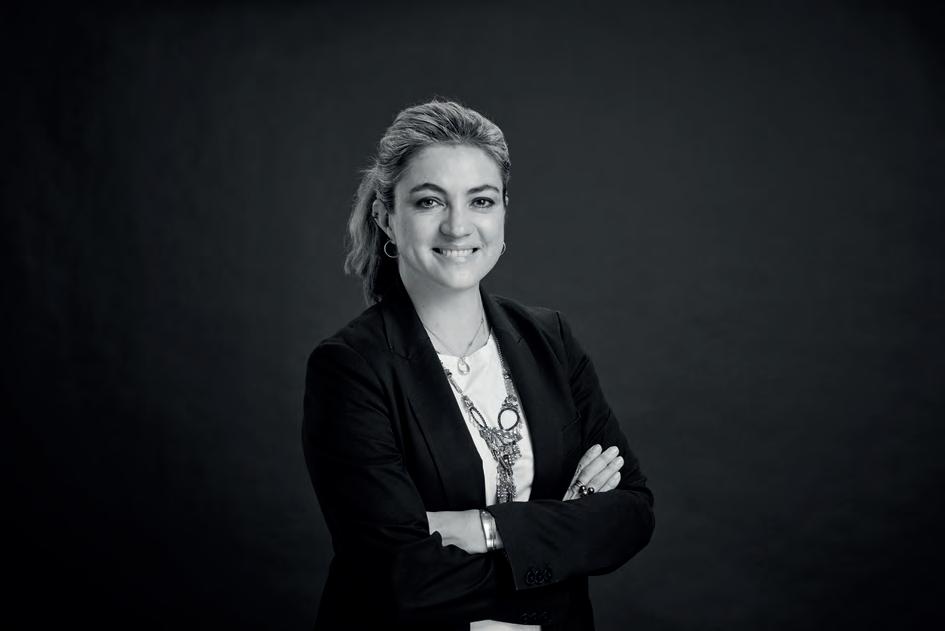
IS SUSTAINABILITY IN PAVEMENT RECYCLING STILL JUST A BUZZWORD?
THE STABILISATION INDUSTRY ASKS TOUGH QUESTIONS AS IT LOOKS TOWARD A MORE ACTION-DRIVEN FUTURE.
By Tanja Conners, Chief Executive Officer, AustStab – Australian Pavement Recycling & Stabilisation Association
Sustainability. It’s the word on everyone’s lips. From funding announcements to conference stages and corporate strategies, there’s barely a presentation or policy that doesn’t reference it.
But in the world of pavement recycling and stabilisation, the critical question is no longer what could be done, but what is actually being done?
As we approach AustStab’s 2025 National Conference – marking 30 years of industry leadership – our theme cuts straight to the point: are we seeing meaningful action, or are we still stuck in conversations?
Despite a clear pathway forward, including proven techniques, established specifications and real-world examples of cost and carbon savings, there’s a growing sense that sustainability, for all its hype, is not yet embedded where it counts: in procurement
strategies, project scopes, or long-term funding models.
SO, WHAT’S HOLDING US BACK?
Let’s be frank. The technology is here. Insitu stabilisation, foamed bitumen, lime and cement treatments all offer measurable environmental and economic benefits. Yet adoption remains inconsistent.
Too often, stabilisation is considered too late in the planning cycle, if at all. And worse still, many road projects are scoped with no serious conversation about betterment, let alone sustainability.
Betterment should be the lens through which all pavement construction is viewed. Instead, decision-makers are frequently cornered by short-term thinking, siloed responsibilities and rigid funding models that reward replacement over reuse.
The barriers are systemic, not technical. There’s a lack of confidence, a lack of capability in some corners and a persistent belief that innovation introduces risk, when in reality, the risk lies in not adapting.
THE COLLABORATION CHALLENGE
At the 2025 AustStab Conference, we’ll be asking tough questions – not just of ourselves, but of our stakeholder partners.
How can we shift the culture of collaboration between government, contractors, and consultants to drive long-term value rather than lowestcost outcomes?
What mechanisms can we create to ensure betterment is not seen as scope creep, but as future-proofing?
And how do we advocate more effectively – not just within our industry – but to the decision-makers shaping transport policy and funding frameworks?
One key focus will be strengthening the alignment between technical specification and practical delivery.
Our industry is too often excluded from early discussions, despite being ready and willing to contribute solutions that extend pavement life, reduce emissions and minimise waste.
We need early contractor involvement to become the norm, not the exception.
TURNING DIALOGUE INTO DIRECTION
The upcoming conference isn’t about handshakes and high-level optimism, it’s about facing the reality that sustainability requires more than strategy statements. It requires courage to challenge outdated processes. It requires leadership to back betterment from the outset.
And it requires a united industry voice to push for reform that supports sustainable outcomes, not just sustainable headlines.
AustStab has never been more committed to advocacy, education and action.
Through our national forums, working groups, and technical partnerships, we’re not just raising awareness, we’re building capability. But we can’t do it alone.
If sustainability is to move beyond the buzzword, we need a shift in mindset at every level of the infrastructure life cycle.
We need procurement policies that value whole-of-life outcomes.
We need funding structures that reward re-use over rebuild. And most importantly, we need accountability, so the next time we talk about sustainability, we’re talking about what is being delivered, not what might be.
Join the discussion at the 2025 AustStab National Conference in Adelaide, 11–13 August. Together, let’s move the conversation from potential to progress.
NO-DIG DOWN UNDER


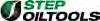


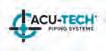
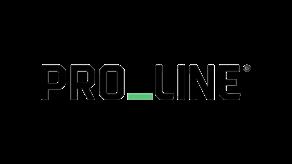
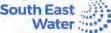
MENTAL HEALTH MESSAGE
CENTRAL TO MUNICIPAL WORKS AUSTRALIA FORUM
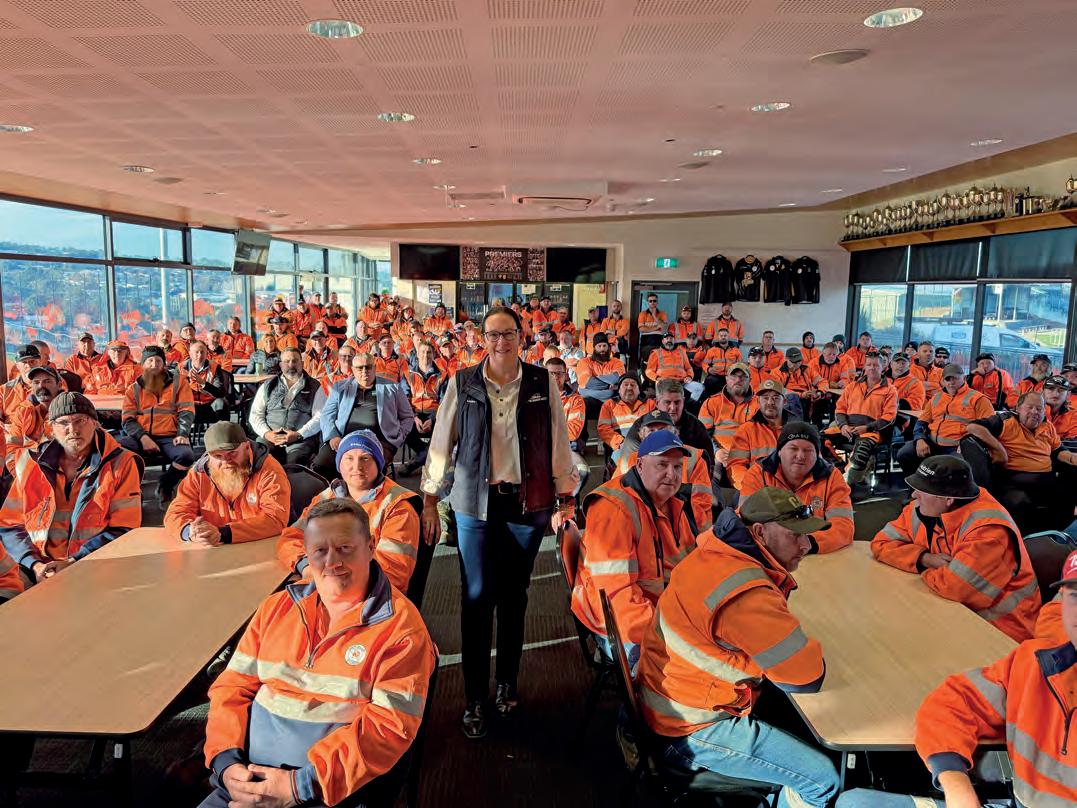
Municipal workers and contractors from across southern Tasmania gathered at Kingston Twin Ovals for a powerful Mental Health Awareness Forum hosted by the Kingborough, Clarence, and Huon Valley councils.
The keynote speaker was Mary O’Brien, founder of the nationally recognised initiative Are You Bogged Mate?, which focuses on rural men’s mental health.
O’Brien, a passionate advocate for agriculture who was raised on the land, shared her unique insights into the mental health challenges faced by men in rural and remote areas.
Drawing from her experiences working alongside country blokes, she emphasised the importance of recognising when someone is “bogged”– a metaphor she uses to describe being stuck in depression or mental distress. Her approach aims to break down the stigma associated with seeking help and to connect rural men with the professional services available.
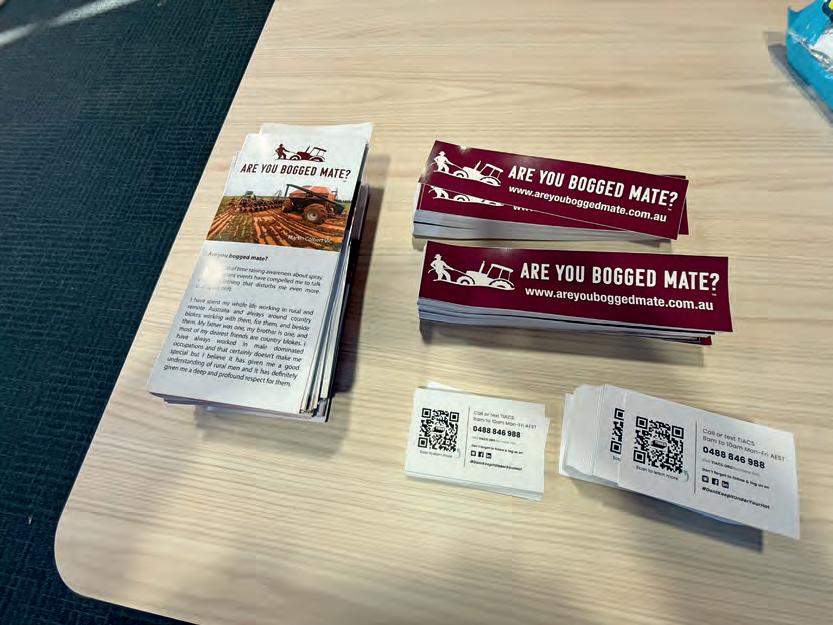
The forum provided a safe space for attendees to engage in open discussions about mental health, learn how to identify signs of struggle among peers, and explore practical ways to offer support. O’Brien’s relatable language and down-to-earth delivery
address the rising issue of depression and suicide rates among men in rural areas. By initiating conversations and providing resources, initiatives like Are You Bogged Mate? Aim to confront the challenges that municipal works staff and their families face daily and to light the path to support.
The success of the Hobart forum highlights the crucial need for ongoing
up when you need it can go a long way,” O’Brien said.
Municipal Works Australia is planning to hold similar forums in other rural and regional locations.
For more information on upcoming events, visit www.municipalworks.com. au. To access mental health resources, visit areyouboggedmate.com.au.
The discussion aimed to tackle the stigma and break down barriers for men to access mental health assistance.
Municipal Works Australia is aiming to conduct similar events in the future.
Images: MWA
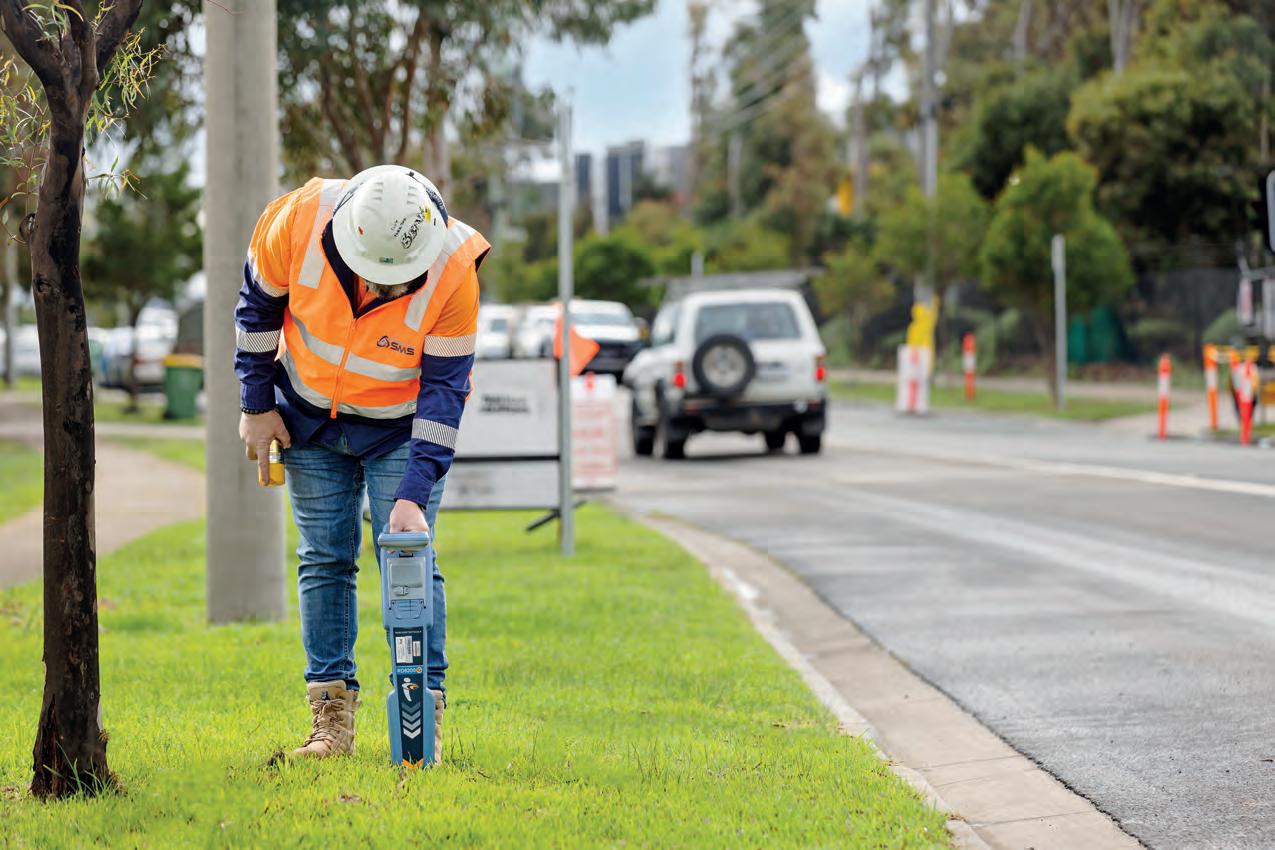
CONVERGE EXPO: SOLUTION SPECIALISTS FRONT AND CENTRE
SURVEY MANAGEMENT SOLUTIONS WILL BE SHOWCASING ITS SERVICE OFFERINGS AND TECHNOLOGYBASED INNOVATIONS AT CONVERGE 2025, OFFERING AN END-TO-END SOLUTION IN UNDERGROUND UTILITY INVESTIGATION AND ADVANCED DIGITAL MAPPING DELIVERABLES FOR THE CONSTRUCTION INDUSTRY.
Converge is the only Australianowned major event showcasing the latest tools and technology in the municipal works, civil and commercial construction space.
From September 17–18, 2025, leading decision makers from these sectors will come together at the Melbourne Convention and Exhibition Centre to see the latest developments that will help to build Australia’s future infrastructure.
Through a mixture of live demonstrations, equipment showcases and conference spaces, Converge will be a one-stop-shop for sub-contractors, project engineers, council fleet managers and large-scale construction contractors.
In addition to all this, it will be colocated with No-Dig Down Under, the southern hemisphere’s only large-scale conference and exhibition dedicated to trenchless technology.
It’s also a key reason why professional surveying company Survey Management Solutions (SMS) will be exhibiting at Converge.
SMS has over 15 years’ experience providing solutions for infrastructure and land development projects throughout Victoria, South Australia, northern New South Wales and Queensland.
Like Converge, SMS is also a one-stop shop for a variety of construction services, including construction set outs, feature surveying, utility investigation, drones and laser scanning, 3D/4D modelling, clash detection, non-destructive digging and a variety of mapping services.
“We’re just not a surveying company; we’re also a utility locating company, because we integrate utility locating and mapping into our services,” SMS Subsurface and Utility Mapping Manager Rajat Taneja says.
“Our team identifies underground utilities using industry leading instruments, Ground Penetrating Radar, and Non-Destructive Digging (NDD), ensuring compliance with Australian Standards.
“This data is then converted into 3D models to visualise complex utility networks, aiding in design and risk management. Additionally,
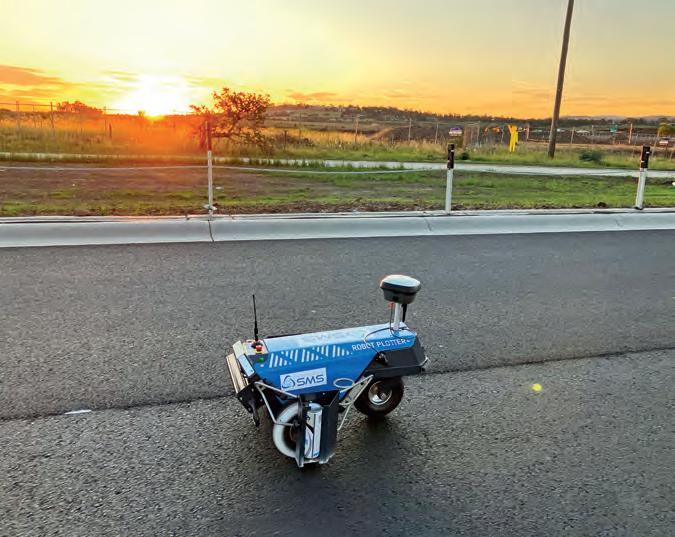
Survey Management Solutions (SMS) combines high quality technology and customer service.
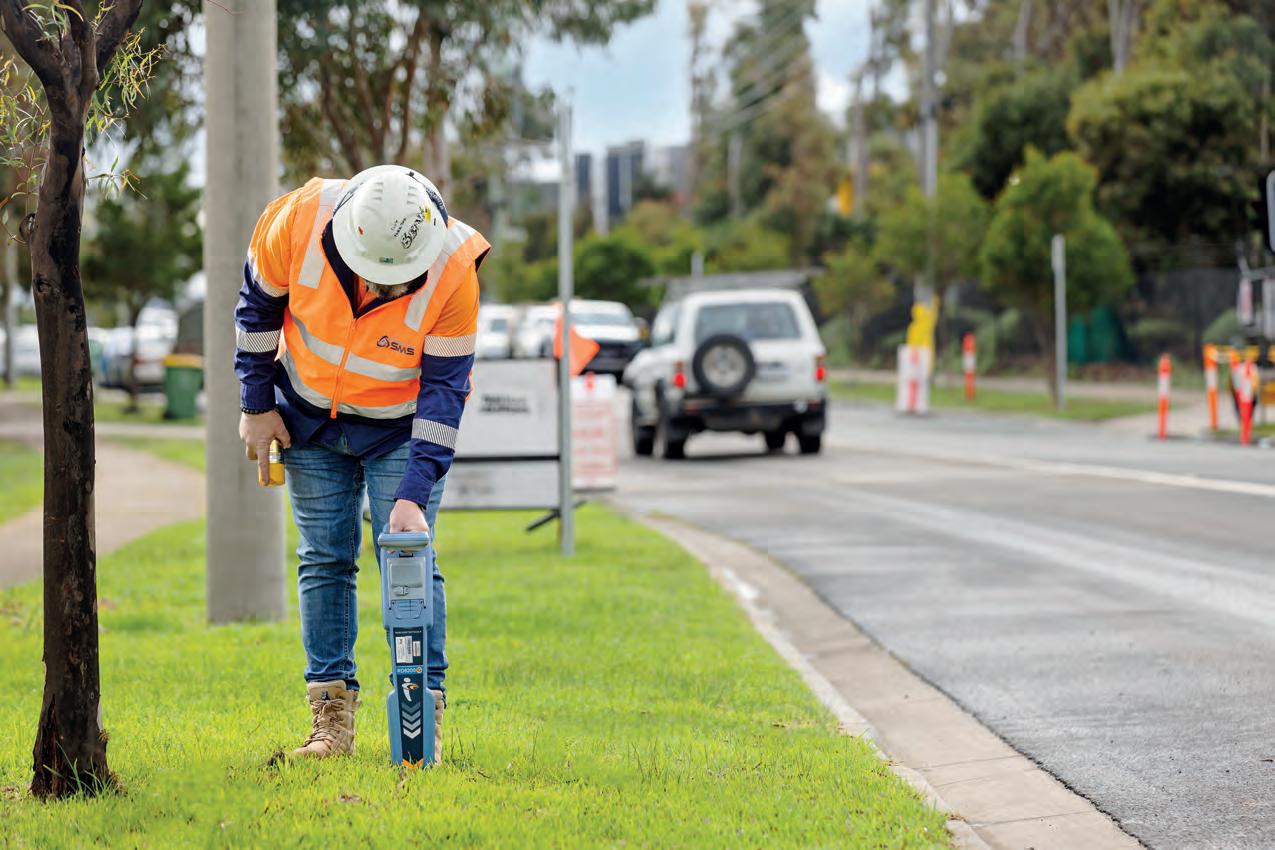
our Dial Before You Dig (DBYD) certified locators enable precise and safe utility investigations.”
This is a crucial aspect that sets SMS apart – it locates underground utilities to assist consultants and designers with their design for a new road, water, sewer, electrical or any other underground service.
These asset utility models are utilised by the construction companies who build according to the design.
Using cutting edge technology and equipment, SMS also works in collaboration with software developers to create custom-designed systems and programs for projects ranging from major road and bridge construction to rail infrastructure and subdivision work.
Taneja says exhibiting at Converge will enable SMS to demonstrate its technologybased solutions, while collaborating with key industry figures and other exhibitors.
“We’ll have the opportunity to speak with key players with varying perspectives, from councils and government to civil and other construction companies,” he says.
“There will also be other service providers, especially at the No-Dig Down Under Conference.”
Organised in partnership with the Australasian Society for Trenchless Technology (ASTT), No-Dig Down Under has grown over the years to become the second largest no-dig technology event in the world and is now considered a ‘mustattend’ for all industry professionals.
“That’s what appealed to us about
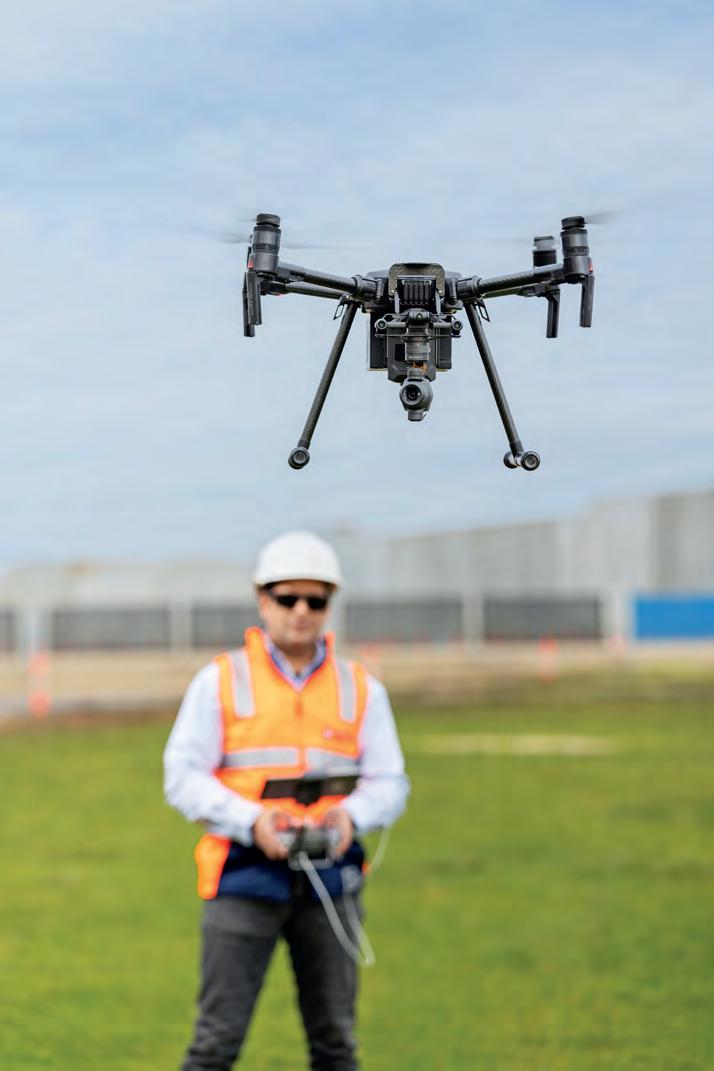
The company is proud to be partnering and exhibiting at Converge.
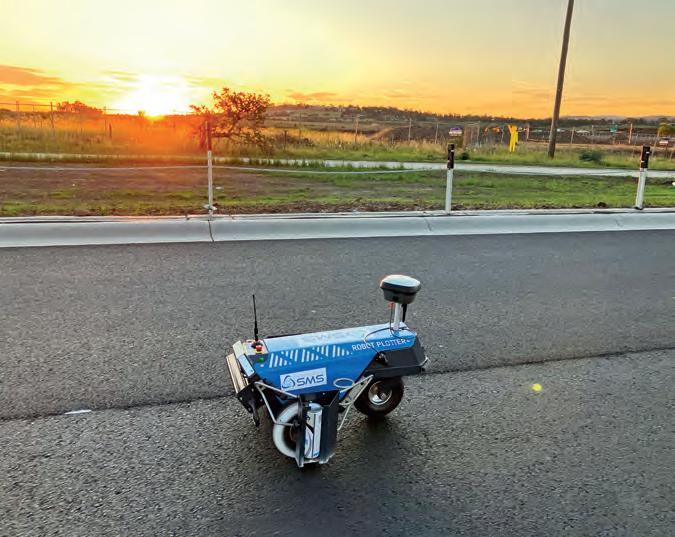
“WE’LL HAVE THE OPPORTUNITY TO SPEAK WITH KEY PLAYERS WITH VARYING PERSPECTIVES, FROM COUNCILS AND GOVERNMENT TO CIVIL AND OTHER CONSTRUCTION COMPANIES.”
Converge, it’s not just a construction exhibition, there are also many attendees who will be at No-Dig Down Under,”
“We were drawn by the prospect of shaping the industry’s future together with Converge, No-Dig Down Under, exhibition partners, and the various members of the construction sector you get to interact with.”
Eagerly awaiting Converge, Taneja says he’s looking forward to discussing the challenges facing the municipal works, civil and commercial construction sectors with leading industry figures.
“Converge is a great platform for everyone to come together and discuss ideas, because
we’re not just solution providers, we’re also problem solvers,” he says.
“Our priority is understanding the challenges engineers face to devise appropriate solutions. By doing so, we aim to effectively support them in overcoming their project complexities.
“The event will bring leaders that have years of experience in the construction sector, with a new generation of emerging leaders.”
For more information on exhibiting and attending, visit convergeexpo.com.au to download the prospectus, or contact our team directly on +61 3 9690 8766 or converge@primecreative.com.au
Images: SMS
SMS works in collaboration with software developers to create customdesigned systems and programs.
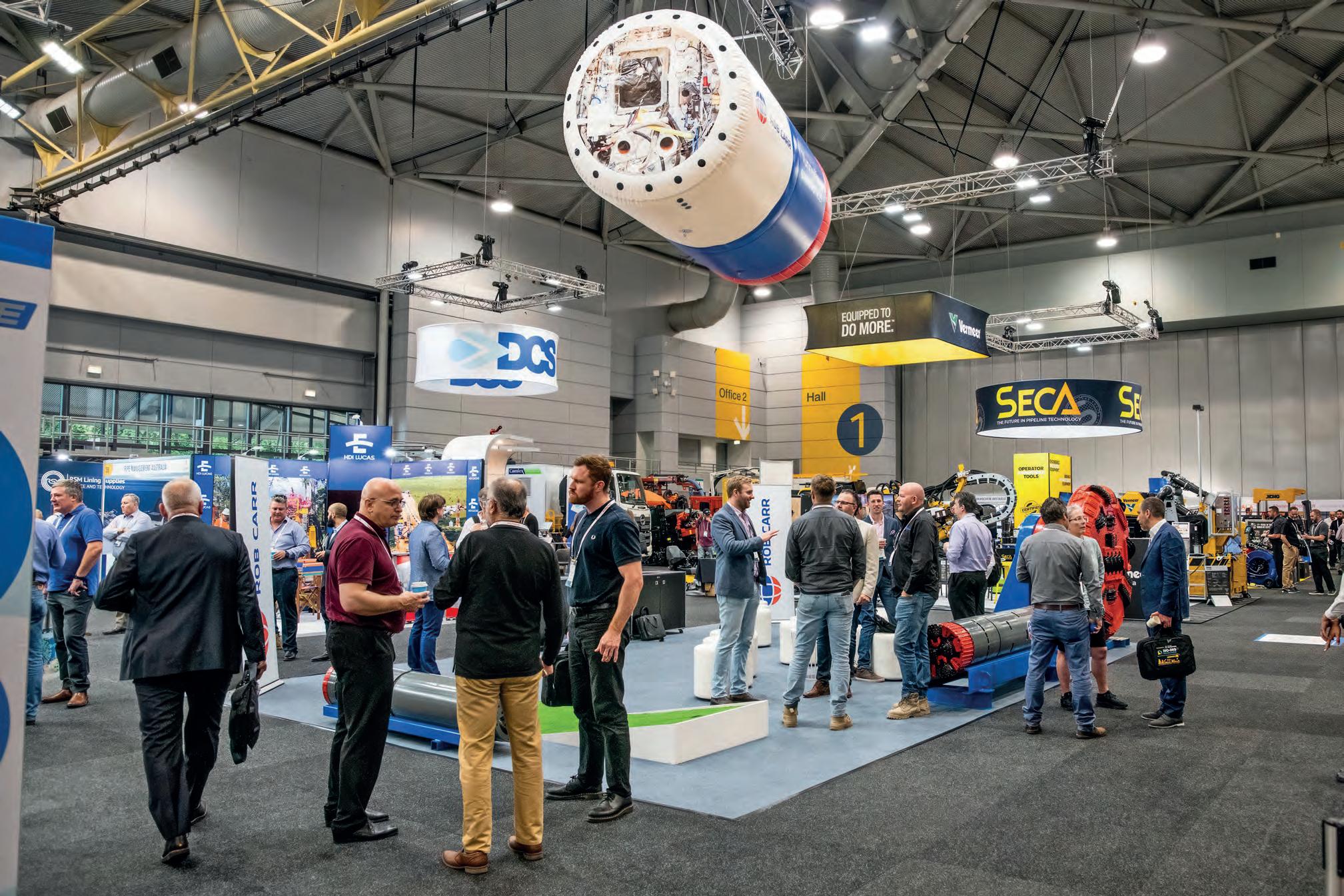
INFRASTRUCTURE SOLUTIONS SHAPING FUTURE CITIES
UNDERGROUND INFRASTRUCTURE SOLUTIONS ARE REDUCING DISRUPTION AND DELIVERING BETTER OUTCOMES FOR COMMUNITIES AND COUNCILS ALIKE. JUST ONE OF THE MANY FOCUSES OF THE UPCOMING NO-DIG DOWN UNDER CONFERENCE.
In the world of infrastructure, the most transformative work often happens out of sight. Beneath our roads, parks, and urban precincts, underground infrastructure solutions are reshaping how we manage critical services.
For engineers and planners, this shift is not just technical but strategic.
Trenchless methods have become a powerful alternative to traditional excavation. Whether replacing ageing pipes or laying new conduit, these no-dig techniques reduce surface disruption, cut emissions, and lower
project timelines. They also sidestep one of the biggest hurdles in public infrastructure: community resistance to visible construction.
Keith Edmunds, Director at KRE Engineering, has seen this shift firsthand.
“The beauty of trenchless methods lies in their efficiency and minimal footprint,” he says. “We’re able to upgrade infrastructure without the usual upheaval. That’s a win for councils, residents, and contractors.”
By reducing the need to tear up roads or shut down busy thoroughfares,
trenchless technologies are becoming the preferred approach for more and more municipalities.
From vacuum excavation and pipe bursting to cured-in-place pipe (CIPP) relining, the methods may vary, but the benefits are consistent: cleaner sites, quieter operations, and faster project turnaround.
A SHIFT TO SMARTER SOLUTIONS Historically, road and drainage upgrades have come at a steep price, both financially and socially. But new
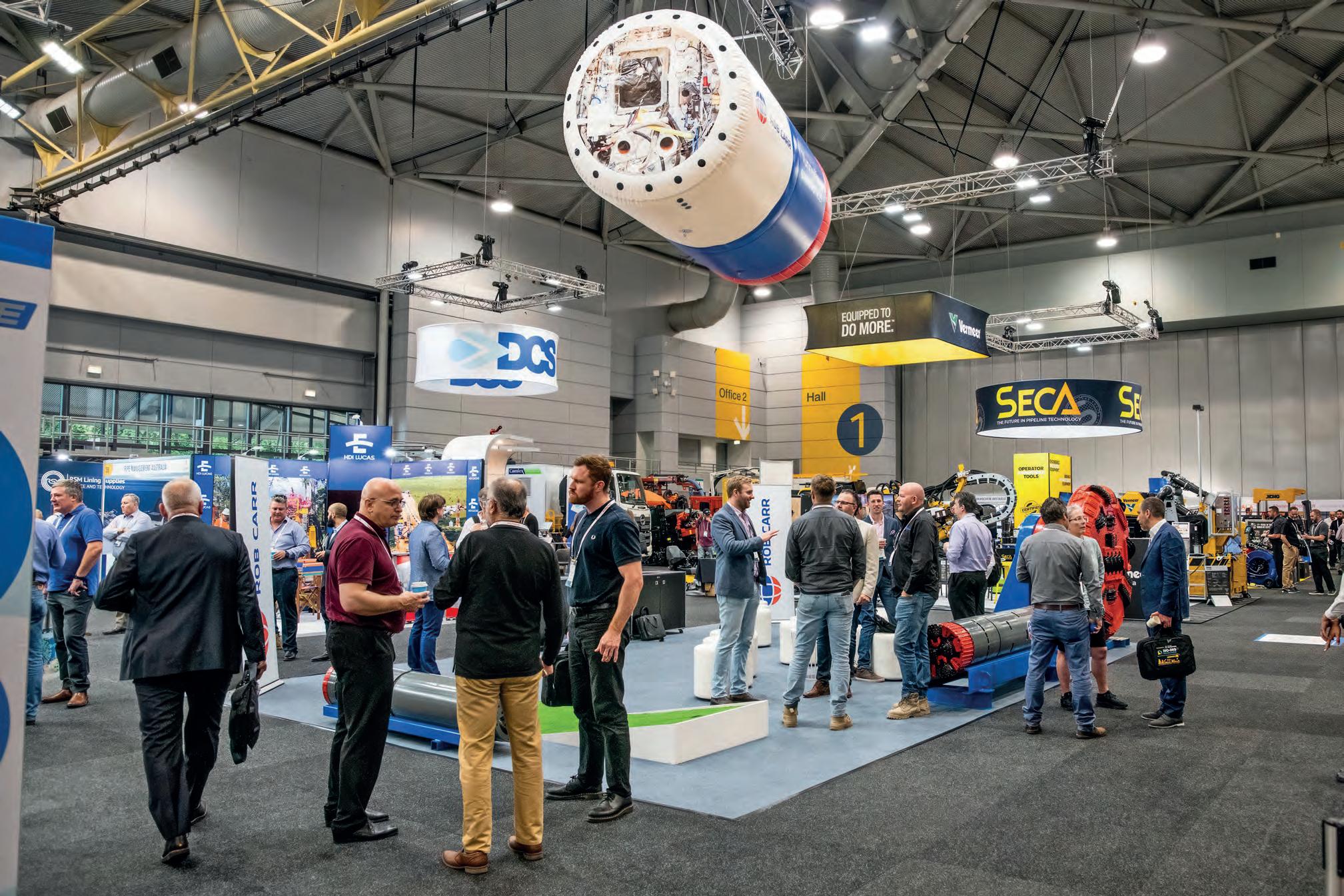
techniques have proven that upgrades don’t have to come with detours and delays.
“Some legacy systems under roads are now situated in high-traffic zones,” Edmunds says. “Digging those up isn’t feasible. That’s where trenchless makes sense. It allows work to proceed where access is tight and disruption is unacceptable.”
While capital works programs traditionally focused on visible outcomes, today’s focus is shifting underground. For asset managers and engineers responsible for long-term planning, trenchless solutions provide a more sustainable approach to managing aging infrastructure.
“Projects that once required weeks of digging can now be completed in a fraction of the time,” Edmunds says. “And we’re getting better results with less impact on the community.”
This is particularly relevant in dense urban areas, where utility corridors are congested, and surface space is contested. Trenchless technology removes many of the logistical headaches
that once plagued civil works projects. It also minimises conflict with other infrastructure, helping to avoid costly rework or service clashes.
“We’ve seen enormous gains in coordination between councils, utilities, and contractors,” Edmunds says. “Trenchless methods naturally encourage early planning and collaboration.”
EMBRACING INNOVATION AND COLLABORATION
The rise of trenchless technology hasn’t happened in a vacuum. It has been underpinned by strong industry collaboration, knowledge sharing, and dedicated platforms for learning.
No-Dig Down Under, organised in partnership with the Australasian Society for Trenchless Technology (ASTT), has become a flagship event for professionals working with subsurface infrastructure. Bringing together local government, contractors, utilities, and engineering specialists, the conference blends technical presentations, training, and exhibitions. It’s where ideas move from theory into practice.
“Staying ahead means continuous learning and adaptation,” Edmunds says. “Conferences and workshops are vital for sharing insights and driving the industry forward.”
Training programs delivered through No-Dig Down Under also play a key role in upskilling the industry. From horizontal directional drilling (HDD) techniques to risk management and safety best practices, the focus is squarely on capability development. For engineers looking to future-proof their careers, or their councils’ asset strategies, these sessions provide direct access to global knowledge.
Equally important is the chance to see new tools and systems in action. From robotics to real-time mapping and vacuum systems, trenchless innovation is being matched by technological progress.
“It’s not just about digging smarter,” Edmunds says. “It’s about how we plan,
“OUR FOCUS IS ON DELIVERING SOLUTIONS THAT ARE NOT ONLY EFFECTIVE BUT ALSO CONSIDERATE OF THE COMMUNITIES WE SERVE.”
how we train, and how we invest in the right tools to get the job done right.”
THE ROAD AHEAD FOR TRENCHLESS TECHNOLOGY
With climate pressures rising and infrastructure demand accelerating, trenchless technology is positioned to be more than a niche offering. It’s becoming central to how Australian cities approach underground asset management.
Asset condition, carbon emissions, and life cycle costs are increasingly front-ofmind for local governments. That makes low-impact solutions not just attractive, but essential.
As more councils embed sustainability targets into procurement and project delivery frameworks, trenchless solutions offer a practical way to meet those goals without compromising on performance or safety.
“Our focus is on delivering solutions that are not only effective but also considerate of the communities we serve,” Edmunds reflects.
“Trenchless technology embodies that balance.”
Image: Prime Creative Media
The No-Dig Down Under Conference will return in 2025.
CONTRACTS IN BRIEF
ROADS & INFRASTRUCTURE PROVIDES AN UPDATE ON SOME OF THE
CONTRACTS AND TENDERS RECENTLY AWARDED OR PUT TO MARKET ACROSS THE AUSTRALIAN INFRASTRUCTURE SECTOR.
MULTI-STATE
Ventia business awarded new fibre upgrade works with NBN Ventia has been awarded a new contract with NBN Co as part of a program to upgrade the remaining Fibre to the Node (FTTN) network across Australia. The contract, awarded to Ventia’s subsidiary, Visionstream Australia Pty Limited, is expected to deliver revenue of approximately $800 million to Ventia over the next 3.5 years. Under the new contract, Ventia will deploy additional fibre infrastructure to enable approximately 175,000 premises to transition from FTTN to Fibre to the Premises (FTTP) technology across Queensland, New South Wales, Victoria, Western Australia, and Tasmania. The agreement includes a two-year extension option, at the NBN’s discretion. These contracted works will commence midJune 2025.
TASMANIA
Tenders now open for TAS signalisation project
The Tasmanian Government has announced that tenders are now open for construction of the Olinda Grove roundabout signalisation project, which aims to improve safety by reducing traffic congestion. The project, which will be delivered in partnership with the City of Hobart, will focus on the installation of traffic signals on the approach from Mount Nelson to the Olinda Grove roundabout. This section normally sees vehicles queuing during the morning peak on the Southern Outlet offramp to Olinda Grove, which can extend to the northbound lane of the Southern Outlet. Traffic signals will meter this traffic, from Mount Nelson when there is queuing on to the Southern Outlet. The traffic signals will only operate when queuing occurs on the left northbound Southern Outlet offramp onto Olinda Grove.
SOUTH AUSTRALIA
Contract awarded, rollout continues for $150M road safety package
The rollout of the Federal and South Australian government’s $150 million
Adelaide Hills Productivity and Road Safety Package is continuing, with upgrades to be implemented throughout the Adelaide Hills, and a contract awarded for works on River Road. Works will also start soon to upgrade junctions along River Road as part of the Adelaide Hills Productivity and Road Safety Package, which includes a range of road improvements to support economic growth, improve road safety and increase fire resilience in the Adelaide Hills area, over five years. The package includes pavement works, road widening, easing of tight curves, shoulder sealing, audio tactile line marking, safety barrier installation, junction upgrades, and vegetation management on some of the region’s key strategic arterial roads. BMD has been awarded the construction contract for safety upgrades to junctions along River Road. The River Road Junction Improvements project includes widening the junction of River Road and Mount Barker Road to improve safety and allow trucks to turn left onto Mount Barker Road and right onto River Road, without encroaching on the opposing lanes. The project also includes targeted road resurfacing, upgrades to drainage and lighting and improved signage and line marking. The upgrade of the junction of Strathalbyn Road with River Road will have a new right turn lane from Strathalbyn Road into River Road, road widening and targeted resurfacing, drainage and lighting upgrades. It will also feature roadside protection and improved signage and line marking, as well as changes for pedestrian access to the Heysen Trail near the Strathalbyn Road and River Road junction. Minor improvements will be delivered at the junctions of River Road with Kangaroo Reef, Sawmill Gully and Fairview Roads including some road widening and improved signage and line marking. The River Road and Fairview Road junction will be realigned to improve sight lines. Main construction works are expected to commence in July and be completed in late 2025. The $150 million Adelaide Hills
Productivity and Road Safety Package is being jointly funded by the Australian and South Australian governments (80:20).
NEW SOUTH WALES
Contract awarded for Spring Farm Parkway Stage Two
The contract has been awarded and works are moving into the design phase for the second stage of the Spring Farm Parkway project in New South Wales. Jacobs Australia will design the three kilometre east-west connection along with the Review of Environmental Factors report. These critical elements will be used to develop a final business case from which construction funding will be determined. Transport for NSW said Spring Farm Parkway Stage Two is necessary to complete the key east-west link between the suburbs of Menangle Park and Spring Farm, realising a key corridor that was planned when the Spring Farm community was first established. It will connect Camden Bypass, Hume Motorway and Menangle Road, along with providing improved access to residential and employment precincts in the Greater Macarthur Growth Area such as Spring Farm, Elderslie, Menangle Park, Mount Annan and Glen Alpine. Providing an alternative to Narellan Road will also deliver direct access for freight trucks to the Southern Sydney Freight Line terminal and shared pathways for pedestrians and cyclists. The concept design and Review of Environmental Factors is expected to be released for public feedback in late 2026, with the final Business Case to be completed by early 2027. Detailed design and construction would follow, subject to final approvals and funding. Once operational, Spring Farm Parkway is expected to divert around 30,000 cars per day from Narellan Road.
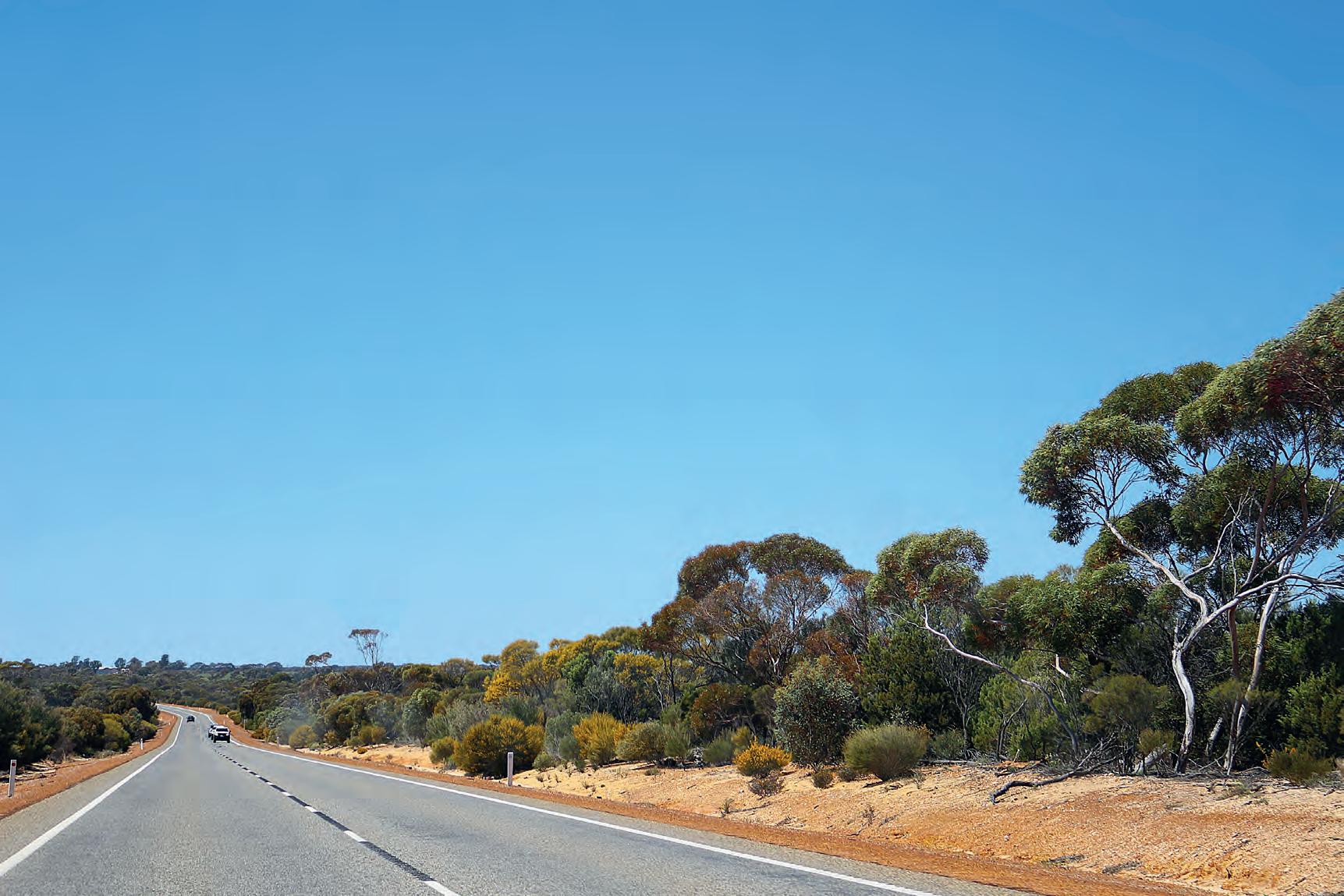
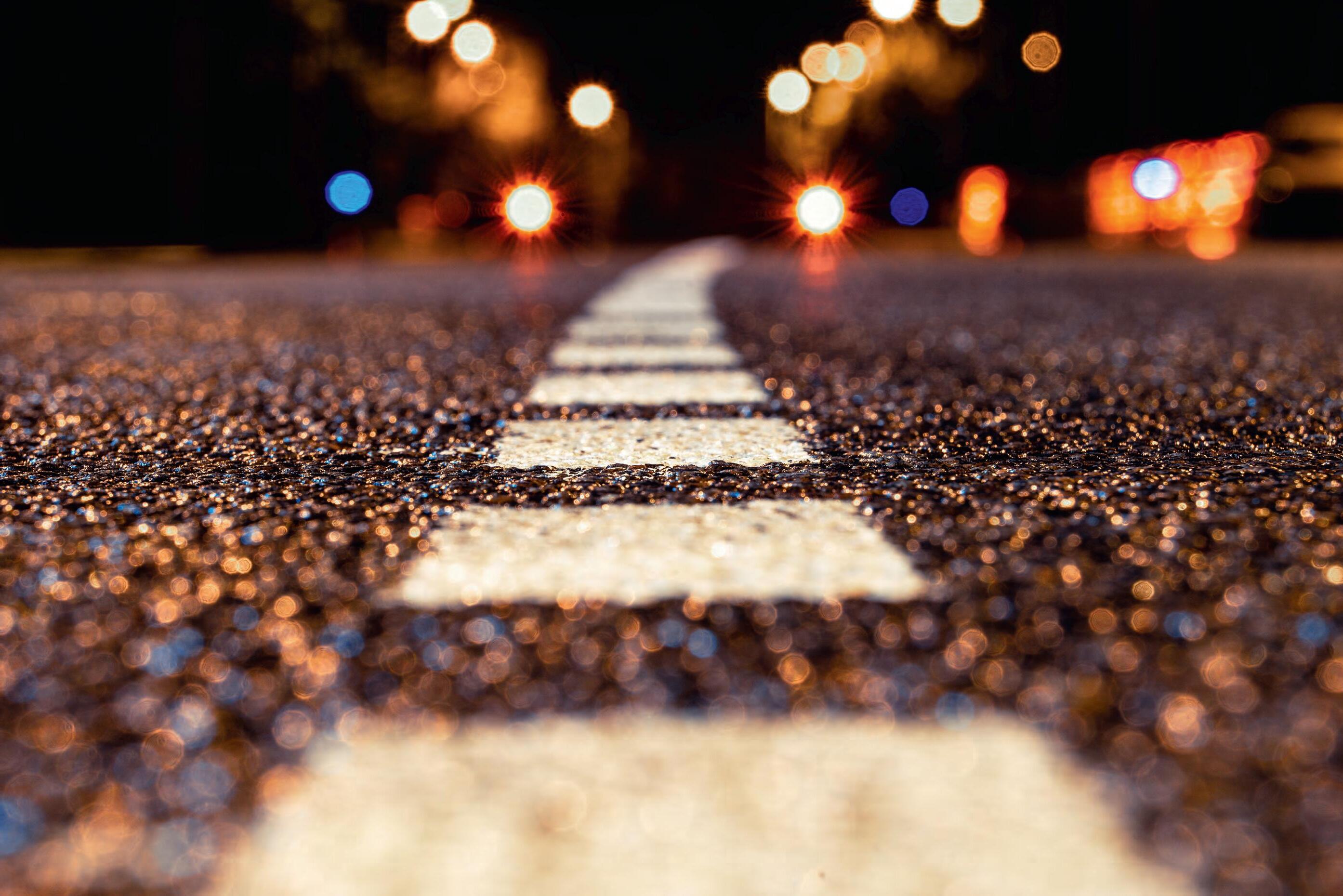
As pure as it gets
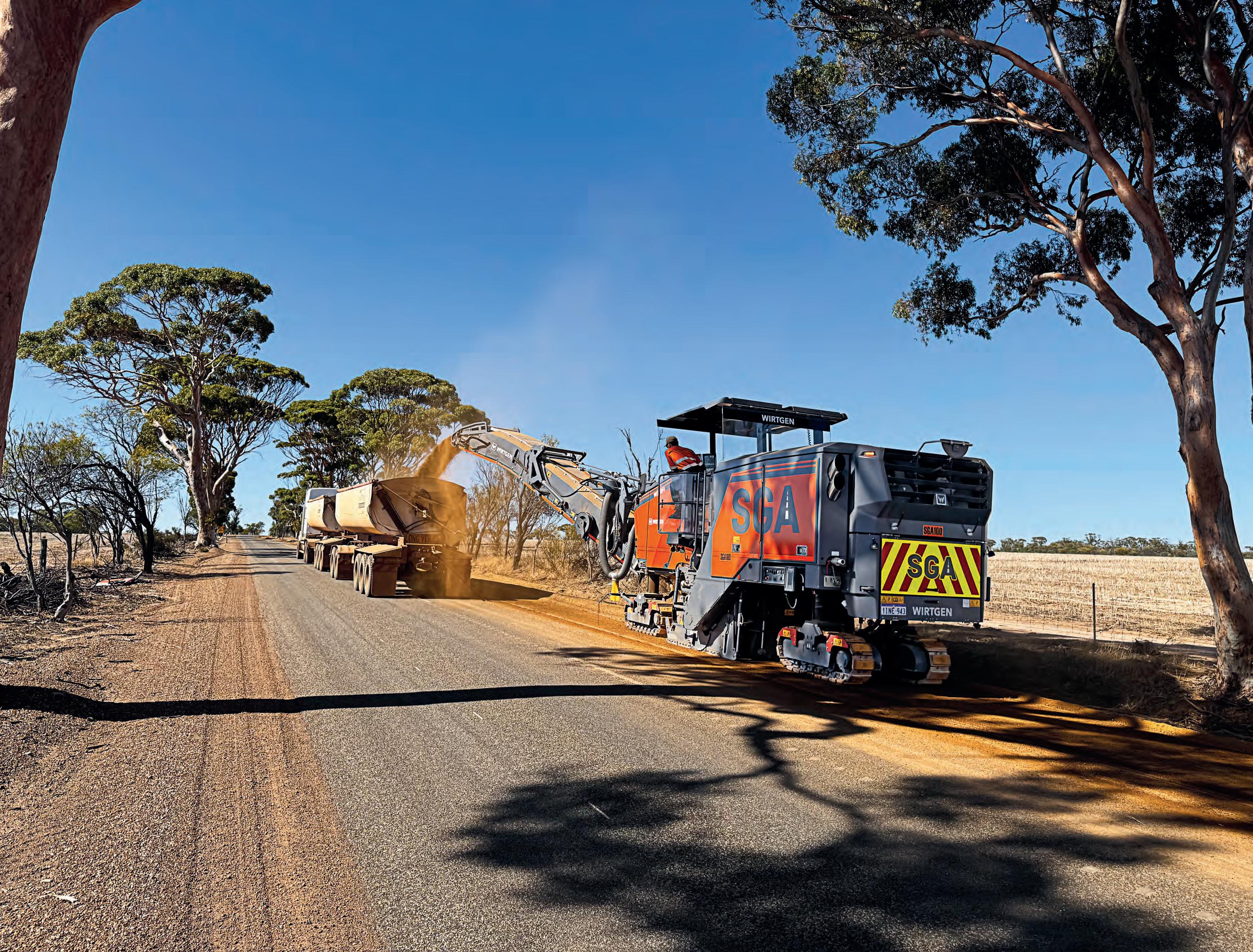
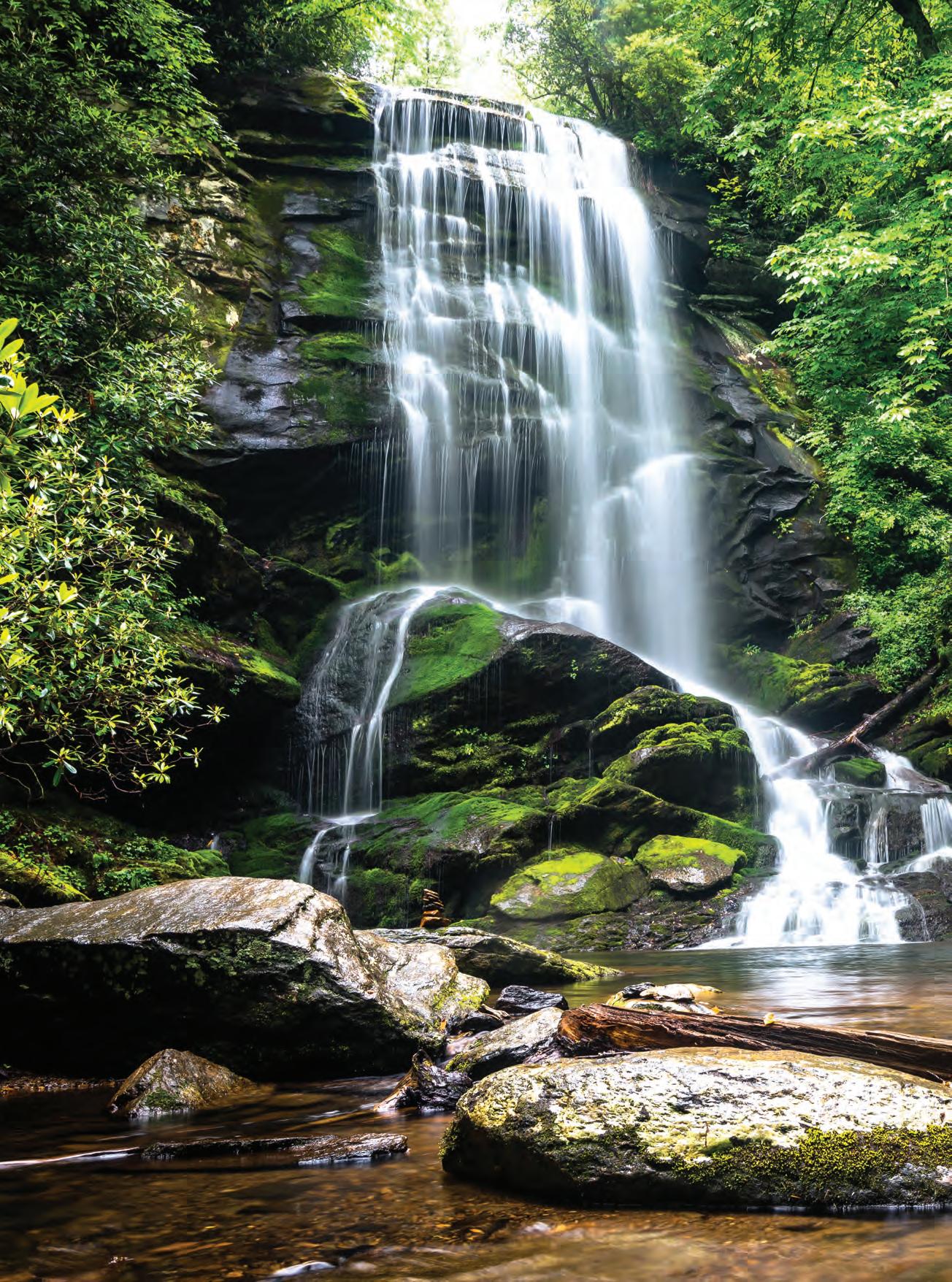