ENOUGH IS ENOUGH
The Road Safety Revolution has begun, with a new resource targeting road trauma reduction
SUSTAINABILITY FIRST
Multiple players in the infrastructure sector are playing their part in the sustainability space
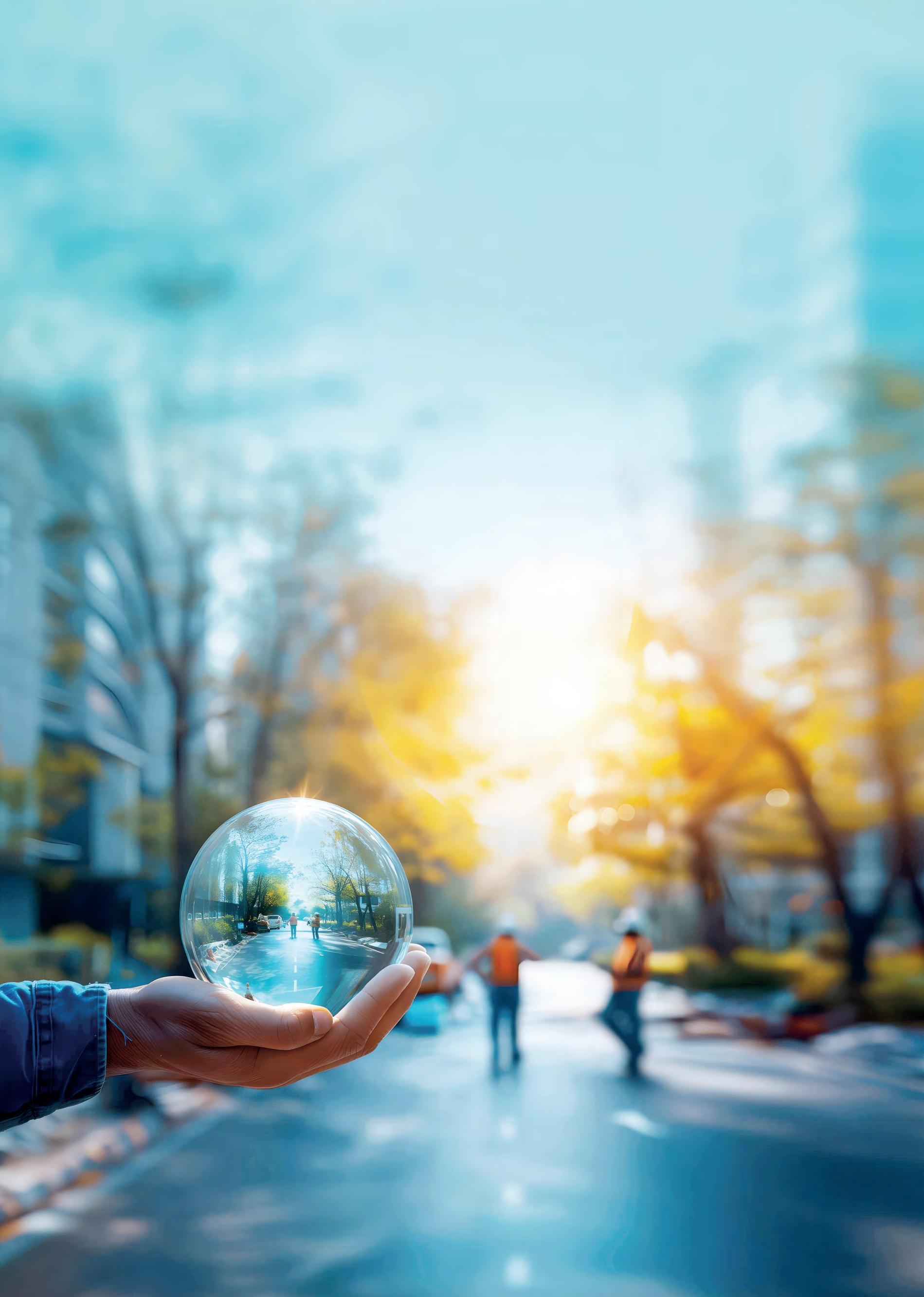
The Road Safety Revolution has begun, with a new resource targeting road trauma reduction
Multiple players in the infrastructure sector are playing their part in the sustainability space
A highly anticipated event will provide a peak behind the curtain into the future of the municipal and construction sectors
VÖGELE SUPER 1700-3(i) / SUPER 1703-3(i)
VÖGELE SUPER 2000-3(i) / SUPER 2003-3(i)
The number one paver manufacturer on the global market presents innovative “Dash 3” pavers and screeds for Australia. Equipped with state-of-the-art Cummins engines available in either Tier 3 or Tier 4 Final / Euro Stage V emission standards, are the perfect choice for any application in the Universal (2.5m) and Highway (3.0m) paver classes. Thanks to the easy-tounderstand ErgoPlus 3 operating system which is common across all VÖGELE products both paver and screed operators can handle all VÖGELE pavers simply and safely. These machines are also available with vibrating screeds or high compaction tamping & vibrating screeds for those critical jobs. In combination with advanced optional features, such as VÖGELE EcoPlus, AutoSet Plus and Navitronic Plus 3D, these models are the stars of any road construction site.
www.wirtgen-group.com/australia
6 Showcasing the solutions of tomorrow Municipal Works Australia’s National Municipal Works and Engineering Conference is back once again.
11 CCF Victoria partners with Converge 2025 Australia’s premier event for municipal works, civil and commercial construction has announced an exciting association partner.
12 Leading the road safety revolution
The National Transport Research Organisation is hoping to inspire a change through the development of its ‘Road Safety Revolution’ resource.
16 Declaring environmental efficiency ResourceCo has embarked on a journey to develop Environmental Product Declarations.
19 Built for green Matthews Brothers Engineering is optimising its designs and customer options, allowing operators of its spraying equipment to unlock their full potential.
22 Leading a global change
Sripath has continued its rich history of developing environmentally friendly mix additives, this time learning from best practice across several sectors.
25 Efficiency at your fingertips Komatsu’s myFleet platform is handing data and unique insights back to the customer.
28 Comprehensive Solutions for Civil Construction
Geoquest Australia is meeting industry challenges head-on by expanding and diversifying its capabilities.
31 Playing the long game
An innovative Trackout Control Mat design is helping to provide a much safer, sustainable and cheaper option than conventional site access methods.
34 All in
R&S Grating’s rich 50-year history reflects its s tability, expertise and drive to stay at the forefront of the grating industry.
37 Smooth, steady and simple: CAT’s AP400
D espite the growing success of its asphalt pave range, Caterpillar is still determined to showcase the benefits of its patented units.
40 Putting words into action
Responsiveness and shorter lead times have b ecome staples of Specialised Roading Equipment’s service.
4 3 Unleash the power with Kobelco
A brand new Kobelco model from renowned distributors TRT is set to shake up the Australian market, offering greater reliability, versatility and performance.
46 Teaching the tools of the trade
The Wirtgen Group takes pride in providing a customer support offering that’s opening new doors for operators.
49 State-of-the-art safety
1300TempFence has introduced a brand-new product offering highly suitable for major infrastructure and civil works.
52 Small but significant Tutt Bryant compactors come in many sizes and have many design advantages that work across a range of job sites.
55 Gaining cost efficiencies with Road-Ant
The Road Ant has become a preferred forward spreader for spray seal works.
59 All for sustainability
AfPA is dedicated to reducing its carbon footprint, embedding circular economy practices, and driving sustainable operations to help the industry meet its ambitious targets for 2030 and 2050.
63 Innovative walling solutions
Precast elements have been used on the Sydney Gateway project in New South Wales.
66 Roads & Infrastructure provides an update on some of the contracts and tenders recently awarded or put to market across the Australian infrastructure sector.
Below: This edition of Roads & Infrastructure will showcase the latest events, products and resources that are contributing to the overall growth of the sector.
NOW THAT WE’RE THREE MONTHS IN, most of us have been able to shake off any rust and dust from the Christmas holidays to start ramping up in 2025. Optimism is in the air, so is hope that this year will be a bounce back for a sector that’s done it tough for the past year or so.
We’re very excited to bring you the March 2025 edition of Roads & Infrastructure magazine, which features a variety of upbeat and hopeful insights into the industry’s achievements so far this year, as well as important topics that require addressing. Roads & Infrastructure magazine is also extremely proud to be partnering with Municipal Works Australia for the Association’s 2025 National Municipal Works and Engineering Conference, taking place from Thursday 20th to Friday 21st of March in Bendigo.
Now in its 31st year, the 2025 National Municipal Works and Engineering Conference will combine practical equipment showcases with conference presentations, with a focus on “sharing solutions”. The event program will provide opportunities for corporate members and local governments to share knowledge and learn from each other. We look forward to seeing plenty of our readers at the show, so please feel free to swing by and say hello!
Also in this edition, we speak to the National Transport Research Organisation about its Road Safety Revolution resource, an approach that aims to move away from traditional and siloed approaches to road safety, instead seeking to engage in a more collaborative and community-driven process. The development of the Road Safety Revolution resource aims to challenge existing paradigms and engage a broader crosssection of society to address the issue. David McTiernan, National Leader, Transport Safety – NTRO says that while there’s a long journey ahead, it’s steps like this that will set up the sector, and the nation, for more successful outcomes.
There’s also been a massive announcement for Converge, another event that Roads & Infrastructure magazine is proudly partnering with. Converge 2025 will unite professionals across the construction and infrastructure sectors, including subcontractors, project engineers, council fleet managers and large-scale contractors.
The event promises to showcase cutting-edge innovations, foster valuable connections, and explore the future of major projects.
Also partnering with the event will be the Civil Contractors Federation (CCF) Victoria. A leading advocate for the civil construction sector, CCF Victoria provides essential support, training and resources to its members. The partnership with Converge offers an opportunity to connect its members with new innovations, resources and networking opportunities to address the challenges of modern construction.
This and so much more in this edition of Roads & Infrastructure magazine.
Happy reading!
Tom O’Keane
COO
Christine Clancy
christine.clancy@primecreative.com.au
PUBLISHER
Sarah Baker sarah.baker@primecreative.com.au
MANAGING EDITOR
Lisa Korycki lisa.korycki@primecreative.com.au
EDITOR
Tom O’Keane tom.okeane@primecreative.com.au
JOURNALIST
Jennifer Pittorino jennifer.pittorino@primecreative.com.au
HEAD OF DESIGN
Blake Storey
ART DIRECTOR
Bea Barthelson
BUSINESS DEVELOPMENT MANAGER
Brad Marshall brad.marshall@primecreative.com.au
CLIENT SUCCESS MANAGER
Isabella Fulford isabella.fulford@primecreative.com.au
HEAD OFFICE
Prime Creative Pty Ltd
379 Docklands Drive, Docklands VIC 3008 Australia p: +61 3 9690 8766 enquiries@primecreative.com.au www.roadsonline.com.au
SUBSCRIPTIONS
+61 3 9690 8766 subscriptions@primecreative.com.au
Roads & Infrastructure Australia is available by subscription from the publisher. The rights of refusal are reserved by the publisher.
ARTICLES
All articles submitted for publication become the property of the publisher. The Editor reserves the right to adjust any article to conform with the magazine format.
COVER IMAGE
Municipal Works Australia
COPYRIGHT
Roads & Infrastructure Australia is owned and published by Prime Creative Media. All material in Roads & Infrastructure Australia is copyright and no part may be reproduced or copied in any form or by any means (graphic, electronic or mechanical including information and retrieval systems) without the written permission of the publisher. The Editor welcomes contributions but reserves the right to accept or reject any material. While every effort has been made to ensure the accuracy of information, Prime Creative Media will not accept responsibility for errors or omissions or for any consequences arising from reliance on information published. The opinions expressed in Roads & Infrastructure Australia are not necessarily the opinions of, or endorsed by the publisher unless otherwise stated.
MUNICIPAL WORKS AUSTRALIA’S NATIONAL MUNICIPAL WORKS AND ENGINEERING CONFERENCE IS BACK ONCE AGAIN, WITH ITS 31ST ITERATION SET TO FOCUS ON PROVIDING THE TOOLS AND IDEAS FOR IMPROVED SOLUTIONS SECTOR-WIDE. ROADS & INFRASTRUCTURE SPEAKS WITH CEO PETER ALI TO LEARN MORE.
works sector.
Its origins can be traced back to 1936, when the non-for-profit, memberbased organisation first laid its roots in fostering excellence. In recent times, the Association’s community-based events have also shined a spotlight and inspired further development for companies providing products and services for local government.
Now in its 31st year, the National Municipal Works and Engineering Conference has made Bendigo, in Western Victoria, its home. As Peter Ali, Chief Executive Officer – Municipal Works Australia explains, the show, and the Association, has undergone big changes, especially in the past few years.
“We’ve had eight shows now in Bendigo, before that the show moved around. The conference has a really rich modern history at Bendigo,” he says. “Off the back of the success of the event last year, we’ve almost doubled the number of exhibitors,
25 of which are brand new members of the Association as well.”
Ali attributes this growth to local governments understanding and identifying the value and benefits that these types of events provide, especially when it comes to training and development.
“Local government has matured a lot,” Ali says. “The conference is one of the few chances we get as a sector to come together in this region, to learn specifically about the day-in, day-out and how to improve it.
“Those improvements are now being demonstrated through this conference, while also connecting and helping individuals to network in a supportive environment.”
The main theme of the 2025 National Municipal Works and Engineering Conference is “sharing solutions” –
that there’s so many ways to tackle industry challenges.”
This focus on sharing solutions will be delivered in a variety of ways, with the show designed as both a conference and a field day.
Introduced in 2024, the National Municipal Works and Engineering Conference’s field day component provides an opportunity for attendees to see the latest equipment and innovations from some of Australia’s leading industry providers.
Ali says the growth of this area represents a strategic shift by organisers to better engage local government staff and provide them with a more immersive and hands-on experience.
“We’ve done a lot of work around engaging local government attendees.
“OFF THE BACK OF THE SUCCESS OF THE EVENT LAST YEAR, WE’VE ALMOST DOUBLED THE NUMBER OF EXHIBITORS, 25 OF WHICH ARE BRAND NEW MEMBERS OF THE ASSOCIATION AS WELL.”
providing opportunities for corporate members and local governments to share knowledge and learn from each other.
“We believe that’s exactly what our Association strives to do,” Ali says. “There’s a whole range of maintenance approaches and techniques to solve any problem. We’re hoping that attendees will come with their day-to-day problems in mind and ask, ‘how do I solve this?’, and then leave with three to four different approaches that they can take back to their roles.
“Some solutions might work better for others than it does for you, but it’s about opening your eyes and seeing
Speakers will focus on showcasing solutions and engaging in discussions to improve processes across the entire municipality sector.
In the past it was more of a formal conference format, now we also treat it as a field day, that way anyone can attend and go through the trade floor,” Ali says. “It’s one of the biggest reasons we’ve seen increased foot traffic over the past few years.”
This section continues to expand, as Ali explains.
“An innovation this year is the introduction of an operators challenge,
to represent Australia at the PWX competition in the US in 2026, which is the American version of our event.
“We’ll be looking to expand that portion of the event even more in the near future.”
The National Municipal Works and Engineering Conference will also include a live demonstration, showing road pavement reconstruction equipment in action, thanks to Hiway.
The National Municipal Works and Engineering Conference will also provide thought-provoking content that goes beyond just technical presentations, with a mix of keynote speakers alongside more traditional local government case studies and showcases.
These keynote speakers include Nicole Livingstone. A sports administrator and commentator, Livingstone is a former Olympic swimmer who represented Australia at three Olympics, winning a silver medal and two bronze medals.
Livingstone has also been the General Manager of Women’s Football and was appointed as the CEO of the Victorian Institute of Sport last year.
She’s joined by another former professional athlete, AFL great Shane Crawford, a Brownlow Medal-winner and four-time All-Australian player.
Other keynote speakers include Mell Greenall, CEO of Before You Dig Australia, who will be promoting safe excavation practices, Justin Herald, Managing Director – Major Motivation will touch on reshaping people’s perception of success and his experience as a self-made, global business owner, as well as entertainer and former Australian Cricketer Rodney Hogg. These keynote speakers will be joined by
sector experts and leaders, touching on a wide range of industry topics.
Just one of these is a “next gen” session, focused on career and intergenerational discussions to explore the gap between older and younger workers in local government.
It’s a growing area of focus that’s needed in the municipal works sector, as Ali explains, to bridge the gap between experienced workers in the industry and the next generation coming in.
“We started this panel because we
transitioned out. Then there was a whole group of new people coming in, which left a massive gap in the centre.
“Sometimes you see these ‘next gen’ sessions and they’re all geared towards ‘let’s get young, emerging people in the room and make a session just for them’. That’s not what this is about. It’s about exploring concepts, facilitated by our younger members, that’s relevant to everyone. We want to bring everyone together for that knowledge exchange.”
Following the success of the Bendigo
the only Australian-owned major event showcasing the latest tools and technology in the municipal works, civil and commercial construction space. The show will bring together leading decision makers from these sectors to see the latest developments helping them to build Australia’s future infrastructure.
“Converge and similar events are really important to us,” Ali says. “It’s great to have something that can provide for our urban-based government members. Partnering with Converge allows us to
“We’re also examining how we can expand our own events, particularly in states such as Queensland. It might not be the size of Bendigo initially, but we’ve got to start somewhere and build ourselves up. That’s a big goal for us.”
Ali says 2025 is the year of growth and solidifying the Association’s impact and reach throughout the market.
“We’re really excited about the level of traction that we’re getting, as well as the companies and local government members that are signing up right across the country,” he says. “We really believe in the people that work in this industry, and how we can have a positive impact in terms of support and recognition.”
And for those who might be sitting on the fence when it comes to the National Municipal Works and Engineering Conference…
“Come have a look. I’m certain you won’t be disappointed,” Ali says.
The Cat® AP400 is the perfect machine for those asphalt paving jobs where space is at a premium.
It’s got the compact size, flexibility and versatility you need, especially in built-up urban areas.
Plus, when you purchase a new Cat AP400, you’ll also have the option of:
• access to locally supported parts via the national dealer network
• a comprehensive warranty package
• a Cat Customer Value Agreement (CVA).
To find out more contact your local Cat dealer or visit cat.com/AP400-au
IN EXCITING NEWS FOR CONVERGE 2025, AUSTRALIA’S PREMIER EVENT FOR MUNICIPAL WORKS, CIVIL AND COMMERCIAL CONSTRUCTION, THE CIVIL CONTRACTORS FEDERATION (CCF) VICTORIA HAS JOINED AS AN ASSOCIATION PARTNER.
Converge 2025 will unite professionals across the construction and infrastructure sectors, including subcontractors, project engineers, council fleet managers and large-scale contractors. The event promises to showcase cutting-edge innovations, foster valuable connections, and explore the future of major projects.
The partnership with CCF Victoria further solidifies Converge 2025 as a vital industry platform. CCF Victoria, a leading advocate for the civil construction sector, provides essential support, training and resources to its members.
These members are the driving force behind Australia’s critical infrastructure, from roads and bridges to pipelines, ports and utilities. They also play a key role in land development, ensuring access to essential services like power, water, gas and communications.
“This partnership reflects the shared vision of Converge and CCF Victoria to advance the construction and infrastructure sectors,” Siobhan Rocks, director of Converge says. “CCF Victoria is a cornerstone of civil construction in Victoria, and their expertise and involvement add immense value to the event.”
“CONVERGE 2025 IS A GREAT OPPORTUNITY TO MEET AND MIX WITH KEY STAKEHOLDERS AND HAVE CRITICAL CONVERSATIONS AROUND CURRENT CHALLENGES AND THE FUTURE OF VICTORIA’S CIVIL CONSTRUCTION INDUSTRY.”
For CCF Victoria, this partnership offers an opportunity to connect its members with new innovations, resources and networking opportunities to address the challenges of modern construction.
“Converge 2025 is a great opportunity to meet and mix with key stakeholders and have critical conversations around current challenges and the future of Victoria’s civil construction industry,” CCF Victoria CEO Lisa Kinross says.
“Civil infrastructure is the very foundation of our cities, towns and suburbs – you can’t spend a dollar on housing until you’ve invested in
the underpinning infrastructure that enables more communities and housing developments to come to fruition, and the same goes for the renewable energy transition.
“We are well-positioned to build a sustainable future for our industry through the delivery of highly-skilled training and workforce development, with industry partners and stakeholders, to ultimately deliver on the future vision for the Victorian community.”
Converge 2025 will take place
on 17 to 18 September 2025 at the Melbourne Convention and Exhibition Centre. Attendees can expect a comprehensive showcase of the latest equipment, technologies and solutions, alongside a dynamic program of expert panels, keynote speakers and networking opportunities.
Join CCF Victoria and other industry leaders in shaping a sustainable and innovative future for municipal works, civil and commercial construction. For more details, visit convergeexpo.com.au
WITH AUSTRALIA’S NATIONAL ROAD DEATH TOLL RISING, THE NATIONAL TRANSPORT RESEARCH ORGANISATION IS HOPING TO INSPIRE A CHANGE THROUGH THE DEVELOPMENT OF ITS ‘ROAD SAFETY REVOLUTION’ RESOURCE. DAVID MCTIERNAN, NATIONAL LEADER – TRANSPORT SAFETY EXPLAINS.
Over the past four years, Australia has had a concerning rise when it comes to road safety statistics.
For the first time since the 1960s, the number of road fatalities has seen a continued and steady increase, with 2024 figures showing a significant jump to more than 1300 people killed on Australian roads, despite substantial investment from government and road authorities.
With the 2030 National Road Safety targets now looming, the National Transport Research Organisation (NTRO) has identified that conventional thinking
in a more collaborative and communitydriven approach.
As David McTiernan, National Leader, Transport Safety – NTRO explains, development of the Road Safety Revolution resource aims to challenge existing paradigms and engage a broader crosssection of society to address the issue.
“We can’t keep doing the same thing over and over and expect a different outcome,” he says. “That’s what this ‘revolution’ is all about, looking outside the box and reassessing how we can better tackle this issue.”
“It’s such a multi-faceted issue,” McTiernan says. “If you look at the Safe System approach and the basic five pillars, which are Safer Vehicles, Roads, People, Speed and Post-crash Care, all of those need to be working in concert.
“All of those need to be kicking goals if we’re really going to achieve what we’re trying to achieve, which is a vision of zero road deaths by 2050. If even one of those factors is falling short, it can make a massive difference in our delivering on this vision (or targets if you want to limit it to 2030.”
David McTiernan, National Leader, Transport Safety –NTRO.
focus on inspiring change at a grassroots level, as well as designing and delivering more adequate transport infrastructure where applicable.
The first key focus of the Road Safety Revolution is challenging the mindset that road safety is someone else’s problem to fix. Instead, the NTRO wants to make it clear that all road users have a personal responsibility to drive safely, be considerate of others, and make choices that prioritise their safety and the safety of other road users.
McTiernan believes framing the challenge of road safety as a shared community issue will help to build a sense of collective responsibility. He adds that this focus has always been a priority but may have been underrated in terms of its potential impact.
“In some cases, we forgot to bring the community along with us on that journey,” he says. “We focused inwardly, which we needed to do technically, but we forgot that the community needs to be on board with the change required to reduce road trauma, that’s why there needs to be a renewed focus.
“It’s about the community understanding that road safety impacts every aspect of their life. It’s not someone else’s responsibility to make our roads safer. As a driver, I have my own responsibilities, to not speed, to not drink and drive or make other choices that have the potential of causing harm.
“Once we’ve got the community on board, they can start to lobby for more
The Road Safety Revolution aims to turn the tide and ongoing pattern when it comes to road safety and road trauma.
The second pillar of the Road Safety Revolution resource places a focus on ‘changing the system’. The NTRO wants to ensure road safety is considered from the start to the end of every journey. This applies to all road users, including pedestrians, cyclists, and public transport passengers.
“The moment you step out the front door, you’re a road user,” McTiernan says. “We as road managers, road designers and government should also be thinking about that journey.”
In the past, funding and investment in
and speed. He says this doesn’t just mean lowering speeds across the board, rather it’s about ensuring that the speed limit matches the function and design of the road.
“We can’t just say, ‘let’s lower speeds everywhere’. It’s about having the right speed for the right road,” McTiernan says.
This is particularly important on rural and regional roads, where travel demands and crash types can differ from metropolitan areas.
“The key is finding the right balance between mobility needs and safety,
“SOME ROADS ARE PRIMARILY FOR MOVEMENT AND EFFICIENCY OF TRAVEL, WHILE OTHERS ARE MORE FOCUSED ON A PLACE FUNCTION, WHERE PEOPLE LIVE AND WORK.”
road safety has targeted vehicle-centric infrastructure. One example is the Black Spot Program, which targets dangerous road locations where fatal and serious crashes are occurring, or are at a high risk of occurring.
While acknowledging these projects and funding are important to saving lives, the NTRO believes approaches such as this neglect the needs of other vulnerable road users.
“We need to think more broadly. We’ve targeted and delivered on the low hanging fruit, but the road crash data indicates that we need to shift focus on other areas,” McTiernan says.
He adds that the third pillar of the Road Safety Revolution is about delivering
which is where the ‘Movement and Place’ framework has been effective,”
McTiernan says. “Some roads are primarily for movement and efficiency of travel, while others are more focused on a place function, where people live and work.
“The speed limits and infrastructure need to match each of these different road functions. In regional Australia, the most frequent types of crashes are single vehicle run-off road or head-on collisions in highspeed environments. Most times that can be put down to a function of the quality of the road, as well as the speed limit. In some areas, the speed might be the simplest trigger that you can pull to improve safety. But that’s not always palatable with the community and elected officials.”
The fourth and final pillar of the Road Safety Revolution framework, similar to the first, addresses the importance of change at a grassroots level and the important role the community can play.
It outlines the need for clear messaging to help the community to understand why road safety is important and why their influence is imperative.
“If we’re going to see change, leaders need to see that the community is calling for it,” McTiernan says. “If this was a workplace health and safety issue, there’s clear legislation that sets out clear lines of responsibilities of employers, management and staff. But with road safety, there isn’t clarity. We need to try and make it clear that it’s everyone’s responsibility.
“It’s about saving the lives of those in our communities.”
McTiernan says the Road Safety Revolution represents the first phase in what will be a long, but important journey.
“The first thing we need to do is understand different perspectives,” he says. “How do people in non-traditional
“IF THIS WAS A WORKPLACE HEALTH AND SAFETY ISSUE, THERE’S CLEAR LEGISLATION THAT SETS OUT CLEAR LINES OF RESPONSIBILITIES OF EMPLOYERS, MANAGEMENT AND STAFF. BUT WITH ROAD SAFETY, THERE ISN’T CLARITY. WE NEED TO TRY AND MAKE IT CLEAR THAT IT’S EVERYONE’S RESPONSIBILITY.”
road safety areas, our community and business leaders, perceive road safety?
Then it’s about taking that information, using NTRO’s experience and expertise, to understand these views and looking at it from our perspective.
“We’re now in the exploratory phase. We want to ask the question to those without a road safety background to learn what they see as being both the problem and potential solutions .”
It’s worth noting that a rising road toll isn’t a trend that’s exclusive to Australia. Developed countries around the world are seeing either a slowing in the reduction of road trauma or gradual increases in road fatalities, even in nations traditionally viewed as road safety leaders, such as the UK, Sweden, and the Netherlands.
With that in mind, McTiernan says the NTRO’s 2025 International Technical Conference in May (7-9) will play an important role in adopting concepts that are working in other countries.
The Technical Conference will be attended by international delegates, as well as industry leaders in Australia, to discuss important topics such as sustainable assets, smart mobility, material innovation, decarbonisation in transport and more.
“Australia still has a lot to learn from our international counterparts,” McTiernan says. “In saying that, other countries are also really keen to hear what we have to say, as we’ve had some great success in the past.
“It’s important to see what’s being done differently. We can’t just be isolated in that respect.”
WITH A LONGSTANDING COMMITMENT TO CIRCULARITY AND CREATING THE BEST RECYCLED PRODUCTS FOR ITS CUSTOMERS, RESOURCECO IS WALKING THE TALK BY DEVELOPING ENVIRONMENTAL PRODUCT DECLARATIONS (EPDS) FOR ITS RECYCLED AGGREGATE PRODUCTS.
As a leader in the recovery and re-manufacturing of primary resources, ResourceCo is always looking to find ways to best support its customers.
Its new initiative, developing Environmental Product Declarations (EPDs), is focused on supporting customers towards quantifying and improving their sustainability performance.
Since the 1990s, ResourceCo has worked with governments, communities and multinational companies to progress the circular economy and preserve natural resources for a sustainable future.
As an industry leader, ResourceCo is a multi-faceted resource recovery company in Australia.
In addition to recycling soils, tyres, as well as commercial and industrial waste, ResourceCo also receives and transforms construction and demolition waste materials, including asphalt, concrete, bricks and rubble, along with glass, into a range of recycled products for construction and infrastructure developments.
ResourceCo recognises the need for its customers to be equipped with the information that can provide evidence of environmental performance. Especially with environmental credentials and emissions reporting emerging as key requirements in federal, state and local government procurement policies and tenders.
The EPDs provide independently verified, quantified data on the environmental results associated with a given product at each stage of its lifecycle.
ResourceCo provided its site-specific data to undergo a Life Cycle Assessment (LCA), which tracks the processes, inputs, and outputs involved in each step of the development of a product and calculates the environmental impact at each stage.
The LCA practitioner assessed the life cycle impacts of the products before they were taken to an international accredited verifier who signed off the EPDs for the Australasian register.
In March 2023, ResourceCo began its journey to acquire its first set of EPDs for its recycled glass sand products.
Brad Lemmon, ResourceCo’s Chief Executive Officer, Recycling and Waste, says the process took over 12 months to be finalised, but it has been well worth it, given the benefits for customers.
“It can be a lengthy process because the LCA practitioner has to set up the site, model each part of the process and then monitor 12 months of data,” says Lemmon.
“Looking at the recycling and waste pillar of the business, we have EPDs for all facilities within this part of the business complete, besides Hampton Park in Victoria which is under development.”
With the modelling already complete from previous EPDs, Lemmon says the Hampton Park EPDs are on track to be done by mid-2025, completing all ResourceCo
management handling facilities across the country.
CUSTOMER PRIORITISATION
Although recycled construction materials have been in use for some time, Lemmon says the industry still displays scepticism around how sustainable the materials really are.
“We find customers frequently asking questions about the makeup of the product, how well the product will work, if it will work better or worse than a nonrecycled product, and more,” says Lemmon.
“Although our products are certified to be used on Australian projects nationwide, our customers still ask if the products achieve the sustainability benefits we claim.”
Lemmon says the only way to answer these questions is to present independently quantified data displayed in the new EPDs.
“The reality is not all recyclers are the same as us. There are a number of recyclers
that can’t validate the sustainability benefits of their products” he says.
“But we can, and that is really what underpinned our desires to get these EPDs done.”
With customers requesting more data on recycled products, Lemmon says the new EPDs have allowed ResourceCo to provide all the necessary information.
“Customers want to be able to validate that the materials they’re using do provide sustainability benefits for their projects,” he says. “One of ResourceCo’s main objectives is to actively listen to our customers about what we can do for them, to benefit their business in the long run.
“Internally these declarations give us a new and effective way of zoning in on areas where we can make further operational improvements and changes to our supply chains. We are constantly looking for ways to improve across all our sites across the business, no matter how big or small.
“We are committed to the ongoing review process for the EPDs to benefit the future of the industry and its sustainability journey.”
Having EPDs for these products has already
proven a success, according to Mitchell Bacon, ResourceCo’s Environmental Development Manager.
“We have started to pick up feedback around the EPDs, which has been measured by organising meetings with customers who have historically been hard to reach,” says Bacon.
“Councils have an increasing focus on understanding and reducing their embodied carbon emissions. As soon as we started highlighting our EPDs, we noticed councils’ desire to talk to us about the things we are doing, solely on having already undergone the process.”
Bacon says the EPDs last for five years unless there is a material change in operations.
Despite the long time frame, Bacon says the business will continue to monitor the frequency at which the EPDs should be reviewed.
“Once the EPD is on the register, we receive a full life cycle assessment report which we can use to assess making changes to business operations,” says Bacon.
“For example, if we were to switch to an alternate source of energy on one of our facilities, we would get the EPD for that facility reassessed, in order to reflect the new change.”
An independent practioner assesses the Environmental Product Declarations (EPDs) in line with Australian standards.
With the EPD process well underway for most aspects of the business, Bacon says ResourceCo is now looking at what else can be done to further accredit other pillars of the company.
“ResourceCo is actively looking at what else we can be doing to support our customers. We’re not stopping here, the EPDs are just one of a range of things we’re working on to support the developing needs of our customers as we grow,” says Bacon.
Astec revolutionised the paving industry with the introduction of the Shuttle Buggy, and now the SB-3000 sets a new standard in material transfer vehicles. Effortless maintenance, unmatched performance, and four steering modes for ultimate agility to keep paving seamless. Experience groundbreaking innovation with the patented Ground Crew Control Station for the ultimate user experience and protection. The SB-3000 isn’t a machine, it’s a revolution in material transfer, built on Astec’s legacy of industry firsts.
MATTHEWS BROTHERS ENGINEERING IS OPTIMISING ITS DESIGNS AND CUSTOMER OPTIONS, ALLOWING OPERATORS OF ITS SPRAYING EQUIPMENT TO UNLOCK THE FULL POTENTIAL OF SUSTAINABLE PROJECT DELIVERY.
Crumb rubber, a refined rubber product derived from recycled tyres, has long been a sustainable option for asphalt in road construction.
The industry has widely adopted crumb rubber since its first use in 1975, with 50 years of innovation leading to 24,911 tonnes of crumb rubber being used annually, the equivalent of 4,151,875 passenger car tyres (Tyre Stewardship Australia).
Machinery and equipment manufacturers are playing their role to greater support the use of crumb rubber and other sustainable products. Few more than Matthews Brothers Engineering (MBE).
The bitumen sprayer, bitumen road tanker, tack coater, bitumen melting tank and aggregate spreader manufacturer has long identified this industry shift, developing specialised solutions to meet
the changing needs of the roads and infrastructure sectors. As Richard Bailey, General Manager – MBE explains.
“It’s definitely something that’s coming up more in conversation,” he says. “The internal changes and additional options we’ve added over the years reflects our commitment to crumb rubber use.
“Now we’re able to be proactive when speaking to our customers, around ‘will they be using crumb rubber? Is that something they need to consider?’ We’ve got a full stock of options to better support our customers in this space.”
MBE has made a number of changes and additions to its spraying units, allowing its customers to use sustainable and alternative materials with ease.
One example is the introduction of larger filter pots with bigger basket filters to
accommodate the thicker, more viscous crumb rubber, aiding output and helping to reduce maintenance over time.
Inline strainers, manifold strainers, and suction filter pots with larger orifice sizes have also been introduced to handle the thicker crumb rubber, as well as an additional circulate line that allows the product to be circulated into the tank at two points, helping to emulsify the crumb rubber and prevent separation.
Upgraded hoses have also been designed for the higher temperatures associated with crumb rubber applications.
Some of these features, such as an extended bar return, were specifically developed for crumb rubber, while others were general improvements requested by clients, which also happen to benefit crumb rubber usage.
MBE has also improved its production process, making it easier for customers to understand and select options that would best suit crumb rubber applications.
“We’ve completely revised our quoting structure to create packages focused on crumb rubber,” Bailey says. “There are so many customisable options that we can offer, and now we can provide a preselected package that we’d recommend, whether that’s for crumb rubber, or an operational health and safety package, among others.”
Bailey adds that MBE sees crumb rubber as an important and growing part of the industry, with the company prepared to continue innovating and adapting its products and services to meet the evolving needs of customers.
“We’re very much a customer-driven business, so we can deliver and further improve our options as feedback and orders are received,” he says.
To further aid customers in their bid for sustainable projects and works, MBE has developed some key features for its dog trailers, to better accommodate the use of crumb rubber.
The dog trailers have their own onboard
bitumen pump, which allows the product to be circulated and kept homogenised while the trailer is left on site. This helps to prevent separation of the crumb rubber in the tank when the trailer is not actively being used.
These units are also equipped with
The
has been doing a lot of work on improving internal systems and processes over the past two to three years.
agitators that run down the length of the tank. These agitators help keep the crumb rubber mixture well-blended and prevent settling or separation while the trailer is stationary.
Other standout features include a standalone engine and hydraulic system, independent of the towing vehicle, allowing the circulation and agitation systems to continue operating even when the trailer is left on site, without needing to keep the towing vehicle running.
Bailey believes 2025 will be a good year for MBE, as the company starts to see the benefits of internal process improvements. This includes a key focus around reliably meeting and even exceeding delivery targets, providing customers with more certainty around lead times.
The company has been doing a lot of work on improving internal systems and processes over the past two to three years, bringing in a new purchasing officer and production planner to better monitor progress and address any potential supply chain issues.
For Bailey and the team, it’s business as per usual.
“We’re really starting to see the fruits of our labour from our hard work these past few years,” he says. “We’re in a great position to pass these benefits on to our customers.”
SRIPATH HAS CONTINUED ITS RICH HISTORY OF DEVELOPING ENVIRONMENTALLY FRIENDLY MIX ADDITIVES, THIS TIME LEARNING FROM BEST PRACTICE ACROSS SEVERAL SECTORS TO DEVELOP THE PHALANX WARM MIX ADDITIVE, AN INNOVATIVE DESIGN FOR HOT ASPHALT AND POLYMER MODIFIED BITUMEN (PMB) MIXES.
Sripath has long excelled in innovative product development, technical expertise, customer-centricity, and global adaptability.
The company continues to seek opportunities to expand its product portfolio, exploring innovative concepts and incorporating exciting technologies to design, develop and launch new products.
Sripath’s newest innovation, PHALANX “a superior warm mix additive”, represents yet another revolution in sustainable roadway delivery.
PHALANX is an environmentally friendly warm mix additive, designed to improve compactability of both hot asphalt mixes (HMA) and polymer modified bitumen (PMB) mixes.
In developing PHALANX, Sripath’s team focused on better understanding how warm mix additives work.
The team developed a unique, highly dosage efficient molecule that helps to significantly reduce both the mix production and paving temperatures. These reduced temperatures help lower energy consumption and reduce greenhouse emissions, making the process more environmentally friendly and cost effective.
Sripath realised that increased lubricity and reduced friction were key for efficient and optimal aggregate packing in the asphalt mix. To gain further insights, Sripath tapped into a network of experts from various industries, whose specialised skillsets were geared towards reducing friction and improving packing efficiency.
Vince Aurilio, Senior Technical Director – Sripath says this unique approach to product development opened the door to an exciting approach for product development.
“It all boils down to lubricity and friction. When we looked around, there are other
Just like Sripath’s
products, the
industries that have a strong history of better understanding lubricity, friction, and particle packing,” he says.
“For asphalt mixes, you want the stone aggregates to slip and slide past each other and pack very efficiently, with the least amount of energy. That’s why we thought it best to borrow insights from other industries that knows how to best achieve this. This was the foundation of some pioneering work done at the University of Wisconsin.”
Using such best practice, as well as research conducted at the University of Wisconsin in America and RMIT University in Australia, and by its renowned internal research and development team, Sripath
was able to create a brand-new molecule that outperforms other warm mix additives.
“We started with the basics and asked the fundamental question, which was ‘what was needed for warm mix?’. We simply didn’t accept the status-quo. This allowed us to develop a new molecule that’s far more effective and user friendly, delivers performance, is easy to incorporate in a plant environment, is safe to use, and makes the mix easy to pave,” Aurilio says.
“It’s a chain of events and thought processes that’s led us to where we are with the product and the way in which we developed it.”
Borrowing methodologies and techniques on how to test for this lubricity, Sripath
PHALANX performs well in a number of different temperatures, environments and applications.
developed a new molecule for PHALANX that’s more effective and user-friendly compared to traditional warm mix additives.
PHALANX’s ability to improve HMA and PMB compactability, while reducing production and compaction temperatures, can be attributed to a number of factors.
As Ravi Rajagopalan, General Manager, Sripath Asia-Pac explains, PHALANX represents Sripath’s ambition to create products that not only improve sustainability, but also deliver desired roadway performance and durability.
“The addition of PHALANX to our product portfolio underscores our commitment to offering products that enhance performance and are safe to use, while also supporting industry-wide sustainability efforts,” he says.
“With sustainability continuing to gain importance in the Australian paving market, we are pleased to offer a specially designed warm mix additive that exceeds the performance of other WMAs, while helping customers meet their environmental goals.
The PHALANX EPD (Environmental Product Declaration) can be downloaded from our website.”
With a suggested dosage of 0.25 to 0.50 per cent, PHALANX works effectively in most situations.
On top of offering superior compactability at lower compaction temperatures, PHALANX also improves wettability, enables greater aggregate coating and offers wider paving windows and longer haul distances.
These performance characteristics have already been showcased successfully in
Australian conditions, with a PHALANX trial conducted in June 2024.
The two-day trial aimed to evaluate the implementation of PHALANX on a roadway in Queensland.
A control mix without PHALANX and trial mixes with 0.25 and 0.45 percent PHALANX were paved on a roadway 490 metres in length, 12 metres wide and 60 millimetres in depth.
The trial showed that with the addition of PHALANX, it was possible to reduce the production and paving temperatures by more than 25 degrees Celsius, even at 0.25 per cent PHALANX addition.
“The data from this trial demonstrated the performance of PHALANX and its dosage efficiency. The fact that there were no issues producing and applying at those lower temperatures means a lot,” Rajagopalan says. “The data is very impressive.
“The field trials confirmed the results from the laboratory evaluation. PHALANX is a superior warm mix additive that helps to reduce both the mix production and road paving temperatures.”
DIFFERENT
Trials such as this have not only allowed Sripath to evaluate PHALANX’s effectiveness, but they’ve also allowed the company to adopt a more robust product launch process. As Deepak Madan, Chief Operating Officer – Sripath explains.
“For this product, we conducted laboratory evaluations and trials simultaneously in select markets around the globe,” he says. “In other words, field trials and laboratory testing were conducted simultaneously in Australia, USA, and Europe.
In Australia, Professor Filippo’s (Giustozzi) labs at RMIT helped to validate the product.
“This parallel approach in the US and Australia gave technical experts in both countries the chance to rigorously test PHALANX and gain deeper insights. Our thanks to Professor Filippo Giustozzi, of RMIT University and Professor Hussain Bahia, of the University of Wisconsin for their help in advancing our understanding of PHALANX.”
Professor Filippo Giustozzi – RMIT University, says both organisations have a close relationship and rich history of collaboration.
“RMIT and Sripath Technologies have a long-standing research partnership, working together on joint research and testing to introduce innovations to the Australian market,” he says.
“The novel molecule behind PHALANX was developed by Sripath scientists; RMIT’s contribution focussed on determining the optimal dosage and understanding its interactions with commonly used Australian road materials, such as polymermodified binders and various bitumen grades.
“One of the advantages of working with Sripath is their willingness to share global research data, which essentially allows for conducting worldwide research.”
PHALANX is slated for further trials as Sripath gears up to rollout the product across Australia and rest of the world. Sripath is also eagerly eyeing more growth across the Australian market.
“We’re really enjoying working with authorities and customers in Australia. There’s a healthy exchange of ideas, people are very receptive, and the industry has been very welcoming,” Rajagopalan says.
“Australia is certainly a high priority for us.”
KOMATSU’S MYFLEET PLATFORM IS HANDING DATA AND UNIQUE INSIGHTS BACK TO THE CUSTOMER, ALLOWING THEM TO MAKE MORE INFORMED DECISIONS AND UNLOCK EVEN GREATER EFFICIENCIES FOR THEIR BUSINESSES.
Quality products, services and commitment. That’s the Komatsu promise.
For more than 100 years, the company has been putting the power back into the hands of its customers, listening to and implementing product feedback to evolve the company in its current form.
One big part of this approach has been opening the door for customers to learn more about the machinery they operate, providing much more than just a peek behind the curtain of what makes Komatsu machinery tick.
The platform was initially developed in 2015 as an internal solution to streamline data from multiple systems, giving service technicians rapid access to machine information to better prepare for customer visits, ensuring a more efficient and informed service.
This development led to the creation of a platform that could generate a service
report in 10 seconds, rather than the average of 45 minutes.
Following seven years of internal use, as well as growing demand from customers for such as platform, Komatsu launched myFleet in June 2023, available to customers through myKomatsu.
Steve Williams, National Manager, ICT and Fleet Management – Komatsu says myFleet centralises data from about 30 Komatsu systems, allowing customers to access machine information in one place, without having to log into multiple platforms.
“While we were running our machinery diagnosis’, the first thing customers would say was ‘when can I get it?’ They wanted to be able to do the same things that we could, to help with their business operations,” he says.
“Now – within seconds – users can start to build a more accurate picture in their minds around what’s been going on with their machinery.”
myFleet aims to provide an improved management experience for fleets of all sizes, by utilising data from Komatsu’s own machinery.
It does this in a number of ways. Firstly, by tracking metrics, such as engine hours, idling time and fuel consumption, providing more insight into machine use.
Data from metrics such as this is then gathered to provide a health score for each machine, helping to highlight any potential issues that need attention. The system can also detect error codes and abnormality alerts.
All this information is simplified so the customer can understand the issue at hand, as well as how to resolve it.
myFleet also enables Komatsu to further educate customers on habits and operational mistakes that may be damaging equipment over time.
“When a machine is operated incorrectly or has maybe completed an action that
it shouldn’t have, we can process that abnormality code and advise the operator,” Williams says.
“For example, our newer products comply with tier four emission regulations, which may include Ad Blue systems to clean up emissions. During the shutdown, as the machine is removing the Ad Blue from the lines, operators can sometimes disconnect the battery to adhere to site requirements. If that happens, that process stops, which means the ad blue can settle and crystalise, which has the potential of being harmful to the machine.
“You could end up having to replace hoses or worse. We can see that in the data, then go to the operator and explain ‘here’s what it means, here’s the issue and the impact and here’s how you can resolve
it or change that behaviour’. That’s an example where we can use data to change those habits to lengthen the lifespan and output of their machinery.”
On top of reducing potential costs for repairs, myFleet can also play a big role in increasing the sustainability of fleet over time, with data able to paint a better picture on the environmental impact of a project, thanks to metrics such as CO 2 emissions.
“It’s something that’s very front of mind for our customers, with many having to report on their environmental impact as part of their projects and tenders,” Williams says. “There’s now an added incentive to upgrading to fuel-efficient, lower-emission equipment, as customers can now better measure these aspects accurately.”
It’s metrics like this that can help operators to discover new ways to optimise their operations.
“I was visiting a customer late last year. We got them online with myFleet quickly and easily and we started looking through their machines when we noticed that one unit was burning about 30 to 40 per cent more fuel than the average machine in Australia,” Williams says.
“It was contributing a lot more in terms of emissions and financially through unnecessary fuel use. One of their leaders said, ‘it doesn’t matter what the solution is here, the fact that we’re having the conversation is important’. Now they’re hypothesizing on ways to reduce costs and maintain productivity, which is so important in today’s market.”
Williams adds, myFleet is a free add-on for eligible Komatsu customers.
“For our customers who are already online though our customer portal – which is a free sign up – and have already got a trading account with us, myFleet is just another free add-on, on top of that,” he says.
Komatsu is constantly updating its myFleet platform to satisfy the evolving needs of the market, as well as its customers.
Williams says that within 18 months since its launch, myFleet has been updated 19 times. And there’s more on the way.
“One of the things we’re working on now, based on feedback from our customers, is to provide more information on the components that are used to meet emission regulations, specifically the DPF, or diesel particulate filter, to better help our customers to track and plan maintenance of these components,” Williams says.
Customer feedback is also pointing towards more features to track and manage for rental companies. Williams says the platform is becoming more popular with rental companies due to its ability to aid invoicing and customer transparency when it comes to machinery use, as well as any potential machine performance issues.
“It makes end of month invoicing much quicker. We want to get the platform to a stage where rental companies can reduce the time required by 10, 20 or even 50 per cent. Being able to provide that evidence and also remove any guesswork, that’s a real benefit that we’re working to unlock,” Williams says.
first
HEAD-ON BY EXPANDING AND DIVERSIFYING ITS CAPABILITIES, OFFERING AUSTRALIAN CLIENTS AN UNPARALLELED ONE-STOP SHOP FOR CUTTINGEDGE CIVIL ENGINEERING SOLUTIONS.
precast concrete solutions, Geoquest Australia brings decades of expertise to civil construction. For more than 50 years, the company has been a trusted partner in Australia and New Zealand, providing solutions that form the foundation of essential road, rail and mining infrastructure, among other sectors.
The company’s recent rebranding and international expansion marks a new chapter; the diversification into geosynthetics and geohazard protection to offer more holistic geotechnical solutions.
Geosynthetics are uniquely designed to deliver varying functions such as soil and slope stabilisation, reinforcement,
In terms of Australia’s growing environmental challenges, Geoquest Australia deploys robust protection systems to mitigate damage from geohazards and natural disasters, including rockfall protection, debris flow mitigation and erosion control. The team also design and supply structures to resist industrial risks.
As Riccardo Musella, Managing Director – Geoquest Australia explains, expansion opens new doors not only internally, but also for the wider industry as a whole.
“These systems seamlessly integrate with, and add value to, our existing solutions, allowing us to provide more
holistic support for projects, from structural retaining walls, reinforcements, erosion control and hazard protection, ensuring long-term durability,” he says.
One standout expansion to Geoquest Australia’s geosynthetics portfolio is additional erosion control systems, gained following the acquisition of US-based designer and manufacturer, Synthetex.
These innovative fabric-formed concrete solutions protect infrastructure on land, in water and even subsea, helping clients safeguard assets against environmental water damage.
“It’s an extension of what we offer, in the sense that we can provide a turnkey solution, whether it’s erosion, flooding or landfall issues. By acquiring Synthetex, we’ve got greater manufacturing capability for these geo-synthetic products,” Musella says.
Geoquest Australia also now supplies DRAINTUBE to Australian clients, a highperformance geo-composite solution used in mining and construction to ensure optimal drainage and safety across projects.
Used for mechanical protection, filtration, drainage and leak detection, DRAINTUBE geosynthetics handle high loads to offer a higher capacity drainage than many current products supplied in Australia at present.
Sustainability is also at the core of Geoquest Australia’s growth and expansion.
By expanding its own geosynthetics manufacturing to develop new products, such as EcoStrap HA, the company now enables clients to reduce carbon footprint on projects by using sitewon recycled materials as backfill for mechanically stabilised earth walls.
EcoStrap HA reinforcements, are made of polyvinyl alcohol (PVA) tendons contained in a polyethylene sheath, are ideally suited to high pH (basic environment) as it is the case when recycled concrete or lime (or cement) stabilised soils are used as the select backfill.
EcoStrap polymeric strips also provide additional benefits in terms of stiffness and capacity to sustain higher temperatures.
“As designers and manufacturers, having
Geoquest Australia’s acquisition only adds to its existing civil construction solution portfolio, including its patented rockfall and landslide protection systems.
control over the full product lifecycle means we can optimise sustainability outcomes for our customers,” says Musella.
“From sourcing materials to manufacturing, we ensure every step works towards environmental best practices.”
Geoquest Australia’s transformation from a design-focused company to designer-manufacturer empowers clients with end-to-end project support. With design, manufacturing and project management under one roof, the company ensures quality, safety and cost-efficiency.
“We’re a partner in innovation, helping clients tackle complex infrastructure challenges while achieving their sustainability goals,” says Musella.
“We’re now much more than just a design office. We’ve always had the design know-how, but now we’ve also got the capability to have more input in terms of quality control, responsible sourcing and safety.
“We have visibility, control and knowledge across the entire supply chain. To process, design, project manage, procure and manufacture are all
things that we can now achieve in-house, which gives us a massive advantage.”
As part of the global Vinci Construction, Geoquest Australia is able to invest heavily in research and development to deliver new solutions for the infrastructure sector. There’s ambitious plans for 2025 and beyond when it comes to environmental considerations, as well as further diversification of solutions.
“Geoquest Australia is a civil engineering business that has a long history of new innovations worldwide,” Musella says.
“There’s lots more to come, and sustainability and the environment is a big focus for us; developing and supplying new solutions to address growing environmental hazards and also helping reduce carbon footprint across the lifecycle of projects.”
• Reinforced backfill applications
• Soil-structure interaction
• Precast concrete solutions
• Geosynthetics
• Environmental hazard protection
www.geoquest-group.com.au
AN INNOVATIVE TRACKOUT CONTROL MAT IS HELPING TO PROVIDE A MUCH SAFER, SUSTAINABLE AND CHEAPER OPTION THAN CONVENTIONAL STABILISED SITE ACCESS METHODS. THE TEAM BEHIND FODS’ FLAGSHIP PRODUCT SHARE WHY THE SYSTEM IS MAKING A SPLASH IN THE AUSTRALIAN MARKET.
For commercial and civil infrastructure projects in particular, industry guidelines generally dictate the need for a stabilised entry and exit point to site, which helps to minimise the exposure and spreading of sediment onto the public transport network.
Many construction sites are also required to have a mechanism in place to clean vehicle tyres in order to prevent sediment from going into the stormwater system.
In many areas, sediment control is mandated by local government, as such it’s become a primary concern and focus of project delivery.
Traditional rock entrances which are built by laying a bed of aggregate over a geotextile are a common solution, but they have limitations in terms of effectiveness and environmental impact.
So, what else is out there?
It’s the question that the folks over at FODS have been answering for years.
Based and founded in the US, FODS has been developing, designing and delivering improvements to its patented Trackout Control Mats system, and helping project managers get their worksites up and running faster and cheaper.
As Nathan Barker, Director – FODS explains, the system is just as simple as it is “genius”.
“The conventional solution is to put in a 200-300 millimetre thick rock or gravel driveway, but that requires regular maintenance, the installation of additional rock, then removal and disposal at the end of the project, and in all it can end up being quite expensive and labour intensive over the length of a project,” he says.
“What this system provides is a one-time purchase solution that lasts about 10 years.
The person accessing or exiting the site drives over the mat, which has engineered pyramids that are around three inches (about 75 millimetres) tall and designed to deform the tyres. All the mud and dust falls to the bottom of the mat.”
Trackout Control Mats consist of several HDPE (high-density polyethylene) mats, with vehicles only contacting the top quarter to half inch of the pyramid.
The product can be installed by two people in 30 to 40 minutes, without the need for heavy equipment.
Maintenance typically involves sweeping or shovelling off any accumulated mud or dust, which can be done as part of the regular site cleaning routine.
Following the completion of a project, the mats can be easily transported and reused, and even recycled once the end of their serviceable life span has been reached.
With a domestic distribution network in Australia, construction companies across the nation can now get their hands on the Trackout Control Mats.
Kevin Montgomery, Technology and Innovation Manager – FODS, says the successful implementation of the system on major infrastructure projects domestically and abroad can be attributed to a variety of factors.
The first being, that FODS Trackout Control Mats are equally as effective in all working environments, regardless of rain, hail or shine, and can be installation on
nearly any substrate.
“It’s just as effective removing mud, as it is dust,” Montgomery says. “It’s been on tonnes of sites in dry areas where contractors are driving along dusty roads, as soon as they hit the mats, the dust stops because they’re no longer kicking it up.”
He adds that the reusable nature of the mats allows them to be easily deployed and redeployed across multiple dry, dusty project sites, unlike rock and gravel entrances.
Another reason for the product’s success is its influence on safety.
“Our system prevents rocks from being kicked up onto the road, reducing the
risk of accidents and damage to vehicles,” Barker says. “The cost of the system is nothing compared to the potential liability costs if you harm someone. It’s a very real risk.”
The Trackout Control Mats can also handle heavy equipment and vehicles of all sizes, with no practical limitations on weight or vehicle type.
It’s hard to miss the mat’s bright yellow colouring, a familiar sight across a number of major projects already in Australia, and are in use on the majority of major infrastructure projects in United States and Canada. This includes works at both NASA and SpaceX sites.
and Metro Tunnel projects in Victoria, where they were deployed for a month across five different sites.
Barker says the successful trial on the West Gate Tunnel project helped to validate the product’s performance and effectiveness in the Australian market.
“It was definitely a keystone moment for us in the Australian market, as it is one of the biggest, high-profile projects in the country and one of the largest to date we’ve been a part of in Australia,” he says.
“The project team found that the mats reduced sweeping by 40 per cent. The mats also withstood the weight of heavy construction equipment, such as an 80-tonne piling rig. And this was all on a site that had over 800 truckloads of soil in total.”
As well as being easy to handle and adjust, the effectiveness of the Trackout Control Mats at a shorter distance of travel (35 feet) compared to the typical 70-foot rock entrance specification, was also noted.
Off the back of the successful trial, FODS is looking to grow in the Australian market. And if last year’s growth is any indication, both the company and the product have an exciting future ‘Down Under’.
“Last year we more than tripled our sales in Australia,” Barker says. “The amount of leads we’ve had from Australia has grown significantly. We’re really excited about our future prospects and we believe 2025 is going to be a huge year for us.”
SRE’s new fixed wing sprayer is available for delivery for the 2025/26 spray season. Fully compliant with all Australian regulations the sprayer meets all Austroads performance requirements for bitumen sprayers and is ready to go from November 2025.
R&S Grating has been supplying products to the Australian market for more than 50 years.
R&S GRATING’S RICH 50-YEAR HISTORY REFLECTS ITS STABILITY, EXPERTISE AND DRIVE TO STAY AT THE FOREFRONT OF THE GRATING
R&S Grating’s history is rooted in family and humble beginnings.
From a small stable in Mentone, Victoria, the company has grown to become a well-known entity in the grate space, as well as one of the few grate vendors that still designs and manufactures in Australia.
As a second-generation employee, Tim Hockham, Product Development – R&S Grating says the company stands out from others due to its family business feel, matched with the capability and innovation you’d typically find in a larger corporation.
He says one example of the company’s innovative approach to grates and covers has been R&S Grating’s SMC composite lids, a plastic alternative to conventional concrete covers.
“It’s a moulded, plastic lid that’s supplied with a steel frame around the edge. They were originally designed to replace heavy concrete lids, which have long been an OH&S maintenance nightmare for local authorities,” he says.
“The composite lids are ideal for driveways or in the nature strip, they only
weigh 20-25 kilograms but at the same time, they’re up to 10 times stronger than the concrete lids they were designed to replace. There’s a big push in Victoria to replace concrete lids with these, so all councils are on board because they can send out just one person to open it, instead of sending out someone with a mini crane.”
Since its launch, the SMC composite lid range has continued to expand, becoming R&S Grating’s single largest growth product over close to two decades.
“We introduced our SMC composite lids around 15 years ago. We’re now the market leader in Victoria. Other companies have started to make their own, but we’ve become the dominant force by continuing to push the bounds of innovation, striving for our lids to be the lightest, strongest and safest,” Hockham says.
These products are just a relative splash in the pond when it comes to R&S Grating’s total product offering, which has been evolving since day one in 1974.
Hockham says celebrating the company’s 50-year milestone gave
him an opportunity to reflect on R&S Grating’s history and origins, as well as the values that have guided the company for generations.
The passing of his father Stephen (R&S Grating’s Founder), a major driver in establishing these values and the company culture, presented a significant challenge in 2024. Hockham says the legacy of his late father is embedded in R&S Grating’s identity.
“It really just showed the type of company that we are,” he says. “The whole business came together as one big family to console each other and to celebrate his life.”
The strong family ethic and feel of the business is also partly due to R&S Grating’s refusal to move from its strong roots manufacturing in Melbourne, remaining a local business that supports local suppliers and projects.
Hockham says the company’s local manufacturing and distribution capabilities can provide a variety of benefits for customers in Victoria and interstate.
“We do a lot of the design work here.
We’ll go out to site, have a look at the ground conditions, then make a prototype solution to see if that would work,” Hockham says. “If the council or whoever we’re supplying is happy with that solution, we can mass produce it.
“If we were solely an import company, we wouldn’t have that capability.”
This has also provided a competitive advantage, especially for products such as R&S Grating’s trench gates, as Steve Skinner, National Sales and Business Development Manager – R&S Grating, explains.
“We looked across the market to see what was out there and it was all onemetre sections. The innovation was to develop a product that was available in one metre, 1.5, 2.5 and all the way up to three metres,” he says
“It caught on and before you know it, we had a steady sweep of people coming into the driveway and picking up trench grating, almost supermarket style. The big benefit of us being a local manufacturer for the trench gate is that it’s a difficult product to import as a finished product because it’s got bulky elements.
R&S Grating’s products are manufactured locally and designed specifically for the Australian market.
“As a result, no one’s really got a product offering to compete. It just shows the strength of local manufacturing.”
To make sure every product is “up to scratch”, R&S Grating has a design and testing team, responsible for
“We have a dedicated team that does batch testing on all our products. Simultaneously, they’ll develop prototypes that are then tested to see how they perform against expectations,” Hockham says.
Through its strong ties to local industry, as well as its growing base of council customers, R&S Grating has direct access and understanding of
Further innovation and development is already underway for R&S Grating.
why the company has quickly climbed the grate offering ladder. So has R&S Grating’s ability to stay up to date with – and sometimes ahead – of the latest regulatory changes.
Just one example is the company’s aforementioned SMC composite lid offering, where R&S Grating was already ahead of the regulatory curve, having developed a full-depth composite cover before changes to the standard necessitated such a design.
“Once the requirements changed, we were suddenly in a leading position,” Skinner says. “We’d already done the legwork.”
He says keeping ahead of the rest is what drives the team, with the company aware of the need to innovate and improve to remain a pioneer in the grating space.
“We have to constantly try and improve the product; you can’t just rest on your laurels. It’s a more competitive market now, and gets harder every year,” he says.
“It’s quite easy these days to import a container of grates in a paddock somewhere and sell from there, that’s the type of setups that we have to compete with. But if you go to one of those places, you don’t get the overall service, you don’t get quality. You get an inferior and cheaper product.
“That’s what drives us, to keep innovating and optimising, while providing the best possible service.”
At Tyrecycle, we are committed to recycling end-of-life tyres otherwise destined for landfill. We are paving the way to produce more Crumbed Rubber Asphalt to cater to growing domestic demand with over $40 million invested in setting up new and upgrading plants, creating long term value for all stakeholders.
DESPITE THE GROWING SUCCESS OF ITS ASPHALT PAVE RANGE, CATERPILLAR IS STILL DETERMINED TO SHOWCASE THE BENEFITS OF ITS PATENTED UNITS. A RECENT TRIAL DAY OF ITS AP400 PAVER, WITH WELLKNOWN CONTRACTOR ASPHALTECH, HAS AGAIN SHOWED THE PROMISE OF CATERPILLAR EQUIPMENT.
According to GlobalData, Caterpillar is the largest construction equipment manufacturer in the world (by revenue). Despite its placement at the top, the company is always looking for ways to give back to its customers and apply customer feedback.
As part of this push, Caterpillar recently sought to display the capabilities of one of its latest paving machinery models in a reallife setting, enabling operators to get their hands on what the future has in store.
The demonstration day, in Thomastown, Victoria, gave Caterpillar and the wider William Adams (Caterpillar’s dealer in Melbourne) team the opportunity to showcase their latest machinery offerings to Asphaltech, a company that traditionally uses alternative equipment.
Dean Alley, Territory Manager, Paving Products – Caterpillar, says the day was a “perfect” opportunity to showcase all that the company’s asphalt compaction machinery has to offer.
“It’s a chance for us to showcase the AP400, as well as our wider asphalt compaction machinery portfolio,” he says. “William Adams has put on a great show. There’s also been great levels of engagement from the team at Asphaltech, who’ve generously allowed us to demo some of our equipment on one of their sites.”
Caterpillar’s AP400 wheel-type asphalt paver provides greater flexibility, visibility and mobility over its competitors in this weight class, with front wheel assist and more making the 13.6 tonne option highly suitable to the Australian market.
The machine is also equipped with the very popular front mount screed SE47 FM, allowing our customers to lay highquality mats up to 2.5 to 4.7 metres wide with Caterpillar’s consistent and reliable paving performance.
Zayne Watson, Metro Melbourne Sales Manager for William Adams says the demo day was the first of its kind for the company, and was highly successful.
“It’s the first time that we’ve put a brandnew machine into live, hot asphalt and enabled our customers to experience and operate the machine and see what kind of mat it lays in the asphalt,” he says.
“The AP400 is a new machine that was built from the ground up to fit a specific niche in the marketplace, between certain machinery sizes and classes that a lot of our customers have been asking for worldwide. It provides the customer with versatility, having the ability to do everything from driveways, commercial parking lots, residential roads and even up to the larger national road works. It’s a very flexible machine,” he says.
The AP400 is ideal for small to mid-sized applications, such as city streets, country roads and car parks.
John Anderson, Global Sales Consultant
– Caterpillar says the compact size, simple operation and increased flexibility of the AP400 means the machine is suitable for contractors of all sizes.
“It’s a really nice fit because of the mobility and the manoeuvrability,” he says. “It’s a little bit smaller than the machines we’ve built in the past, making it easier to transport. It’s also got better ground clearance, if you’re coming up to kerbs you can get in tighter when you’re doing commercial work.
required. It’s a straightforward setup,” he says.
“The automatic levels are easy to use with the automatic screeds, along with the digital screens and controls on top, making it nice and easy to work and use,” he says
Vasily Leota, Paver Operator – Asphaltech says thanks to the unit’s simplistic design, all that was required was a brief rundown before he could take the machine “for a spin”.
“The controls are a lot easier to operate and overall, it’s pretty straightforward, especially when we’re getting help with training,” he says. “It’s only taken about five minutes, but after that you can pretty much pick it up straight away. It’s very easy to learn.
“It’s also a lot quieter and very comfortable. If we get a chance, hopefully in the future, which I believe is the plan, we’ll be going back to Caterpillar.”
Alley says the positive feedback received from the crews who participated in the demonstration day provides even greater confidence that the AP400 is firmly placed as a “best in class” option.
“Most of what we’ve been hearing is that they love the machine,” Alley says. “They love how simple it is, and they’ve been able to pick it up really fast. We’ve also heard how intuitive the controls are, they’ve been able to start laying down the material relatively quickly, which they’ve all been really impressed with.”
“THAT ABILITY TO GET INTO TIGHTER SPOTS, WHILE STILL BEING ABLE TO CARRY OUT THAT 2.5 TO 4.7 METRE WORK, MEANS THE AP400 FITS A REALLY NICE SPOT IN OUR LINE-UP. IT’S A NICE SIZE CLASS THAT HAS BEEN MISSING IN THE INDUSTRY FOR A WHILE.”
“That ability to get into tighter spots, while still being able to carry out that 2.5 to 4.7 metre work, means the AP400 fits a really nice spot in our line-up. It’s a nice size class that has been missing in the industry for a while.”
Darren Clark, Supervisor – Asphaltech was impressed with the machine and its capabilities.
He says a few features stood out above the rest, but overall, the machine is an impressive package.
“The other operators have loved it too. We’ve found it quick and easy to learn. There’s been barely any adjustment
The quietness of the machine is as apparent as the high level of visibility provided by the AP400’s operator platform, thanks to features such as eco-mode and Automatic Engine Speed Control.
“They’ve also been impressed with the noise level of the machine. It’s extremely quiet, so the crew can talk to each other while laying down the material,” Alley says.
“The operators also pointed out how good the visibility is, allowing them to have sight lines around the entire machine.
“We’re really happy with how the demo has gone. We just really want to thank Williams Adams, as well as Asphaltech for giving us the time to do a demo with the AP400.”
RESPONSIVENESS AND SHORTER LEAD TIMES HAVE BECOME STAPLES OF SPECIALISED ROADING EQUIPMENT’S SERVICE, AND AS MANAGING DIRECTOR MARK WANSBROUGH EXPLAINS, THE COMPANY IS COMMITTED TO ONLY GETTING BETTER IN THIS AREA.
Responsiveness is a core part of Specialised Roading Equipment’s (SRE) philosophy. From its experienced and highly trained staff to its innovative facilities and equipment, everything within the business is geared towards optimising manufacturing time – and more importantly – surpassing customer expectations.
Or at least that’s how Mark Wansbrough puts it. As the Managing Director of SRE, Wansbrough has led a mission to enhance the company’s responsiveness and production timelines, while ensuring that quality is maintained.
He says it begins with having the right company attitude. One that puts customers first.
“We’ll do whatever it takes to get a sprayer out on time,” Wansbrough says. “We believe it’s our point of difference. We recognise that sprayers are gold mines, that there’s often massive crews that rely on these machines every day.
“If there’s any issues or delays with the delivery, it can have a real impact on the profitability of the job. Whether it’s a new build, or a customer needs a unit delivered by a certain time, we’re there for them when they need us.”
SRE designs and manufactures a range of high quality, road construction machinery, including (but not limited to) bitumen sprayers, emulsion sprayers and tack coaters. Despite being separated by the Tasman Sea, the New Zealand-based SRE takes great pride in offering lead times that are often shorter than even some Australianbased manufacturers.
Wansbrough says SRE customers know that distance is no object when it comes to product deliveries.
“We’ve always held the view that customers shouldn’t have to wait for any piece of gear for longer than 12 months,” he says.
“To make sure we can keep delivering on this, we’ve worked to increase the capacity of the business to be able to meet those expectations.”
This commitment to improvement and customer fulfilment has led to constant expansion for SRE, in order to cater for a growing number of orders in Australia and New Zealand.
“We’ve nearly tripled the size of our workforce and soon we’ll be moving to a brand-new facility that’s roughly three times larger than our current one,” Wansbrough says. “We’ve got to keep tweaking the business to make sure that we can deliver
This year is set to be a big one for the Specialised Roading Equipment team, with exciting announcements in the pipeline.
on those time frames.”
This is also true when it comes to after sales support. SRE goes to great lengths to ensure that customers are supported long after the initial delivery, with its team members even flying across to Australia to provide parts personally.
“We’ve had team members race to the airport in Auckland, an hour and a half drive away, to get a special component onto a plane, to make sure our Australian customer could have that part and an expert ready to go the next morning,” Wansbrough says.
customers in Australia. In the past, that’s been making sure we’re holding stock and had great freighting arrangements to send parts overnight,” Wansbrough says.
“That was the starting point, but now we’re taking it a step further. We’re developing a parts store in Australia, so that all key parts will be on hand in the local market. We’ve also got a 24-hour, technical support line through a dedicated team member.”
When it comes to the responsiveness of its support and servicing, SRE doesn’t stop there.
“OUR TOP-OF-THE-LINE SPRAYERS HAVE A FULL DIAGNOSTIC SYSTEM, ALLOWING US TO HOOK INTO THE SPRAYER REMOTELY IF THERE’S EVER ANY ISSUES.
“The customer didn’t ask for that, but that’s the level of responsiveness that we thought was appropriate. Some companies might think ‘oh well, we can send it to the courier, and they’ll get it in a few days’. But no matter what it takes, we’re there for our customers.
“When something happens, we pride ourselves on having the willingness to jump straight on it. The fact that the ‘Tasman’ is there is irrelevant, because we can back up what we say with actions for our customers.”
SRE is also launching its first permanent Australian parts site, offering a local touchpoint for customers.
“The biggest thing has been making sure that we’ve got the parts available to our
“Our top-of-the-line sprayers have a full diagnostic system, allowing us to hook into the sprayer remotely if there’s ever any issues. We’re always there when we need to be,” Wansbrough says.
At the end of the day, it’s about making the process as simple as possible, Wansbrough adds.
“I’m a big believer, particularly with these high capital value items, that you’ve got to be easy to deal with,” he says. “It starts with the very first interaction with us, even with our quotes, we’re turning these around in a day, while we’re hearing that others are waiting months.
“That attitude permeates across the
Above: Specialised Roading Equipment is able to provide equipment in a timely fashion, without compromising on quality.
business and that’s how we conduct our business, across the whole life cycle of the sprayer.”
And more’s on the way.
“Seeing the first fixed wing sprayer being delivered into Australia and building the momentum overall is really what excites us,” Wansbrough says. “Australia’s our major focus for 2025.”
BOMAG delivers unmatched performance with innovative machines for every challenge. The compact BF300 is ideal for confined sites, featuring a 55 kW engine with Ecomode management, Magmalife heating elements, and a sideview system for up to 5-meter laying widths. The BM1000/35 in the 300 HP class boasts a unique centre-rotor design with four steerable track chains and working widths from 1.0 to 1.3 meters, ensuring precise, costeffective planning. Together, these models set a new standard in efficiency, durability, and versatility.
A BRAND NEW KOBELCO MODEL FROM RENOWNED DISTRIBUTORS TIDD ROSS TODD (TRT) IS SET TO SHAKE UP THE AUSTRALIAN MARKET, OFFERING GREATER RELIABILITY, VERSATILITY AND PERFORMANCE.
For seven years, Kobelco’s CKE3000G has dominated international markets when it comes to the 300-tonne crane range. The unit’s success, namely in the United States, has led to a wider push and introduction to more markets.
Australia has only recently had the opportunity to get its hands on the CKE3000G, thanks in part to growing demand nationally for larger crawler cranes over 300 tonnes.
Troy Hand, Crane Sales and Pacific Islands Manager – TRT says customer expectations and feedback has pointed towards a greater need for larger and heavy-duty solutions.
“It really comes down to the strength of the crane,” he says. “The first thing that our customers look for are the load charts. Those in the industry already know the Kobelco brand, they understand the reliability, the smoothness of operation and the quality of the build.”
The CKE3000G standard specification has a maximum lifting capacity of 300 tonnes, combined with a maximum boom length of 90 metres with options for fixed jib, heavy fixed jib or luffing jib. The CKE3000G Heavy Lift/Super Heavy Lift Specification has a lifting capacity of 350 tonnes, combined with a maximum boom length of 102 metres with options for luffing jib.
Operators of the CKE3000G benefit from being able to operate the unit in standard
crane, heavy lift and super heavy lift configurations, with options for luffing jib, heavy fixed jib and fixed jib.
The luffing jib itself can be used as a fixed, heavy-duty jib, with a single boom tip that can be used for both fixed and luffing configurations, increasing the crane’s versatility and working load limits. Maximum lifting capacity for luffing 120 tonnes, with a maximum luffing boom length of 84 metres and a maximum luffing jib length of 90 metres respectively.
Like the rest of TRT’s products, Kobelco’s CKE3000G has evolved over time, but quality, reliability and ease of use has remained consistent. This is thanks to the company’s systematic approach to improving its products without drastically changing the core design.
A big focus during the design of the CKE3000G and wider CKE-G series was transportability. The entire crane series has been designed for easier transport, while ensuring safety during assembly and disassembly.
The design also helps to reduce associated
A big focus during the design of the CKE3000G and wider CKE-G series has been transportability.
costs for transport and storage. This is thanks to Kobelco’s upper frame design, with reduced body width. The CKE-G series also has a ‘self-removal device’, allowing components to be assembled and dissembled without the assistance of another crane. Other design tweaks, such as easy to remove side steps, easily transportable ‘nested boom’, and insertable boom handling lugs, further contribute to efficient transport and assembly.
“Like the rest of the TRT and Kobelco ranges, this unit is much easier to transport, thanks to it coming in under three metres. Disassembly and assembly are always a focus,” Hand says.
The environment was also a major consideration during development.
“A major focus has been placed around fuel and emission savings,” Hand says. “This model has the capability of running HVO (Hydrotreated Vegetable Oil) diesel fuel, giving you reduced CO2 emissions compared to standard diesel, while keeping the service intervals the same. G Modes still run throughout the Kobelco range as well.”
G-Winch and G-Engine are two separate modes that aim to maximise the sustainable operation on every job site. The former allows the line to be raised or lowered at maximum line speed without raising engine speed, applying to lifts without or with a light load.
G-Engine helps to improve fuel consumption by at least 10 per cent thanks to the unit keeping the engine running within fuelefficient parameters, by limiting maximum engine speed. Pump capacity is still controlled to maintain maximum winch speed for running or lifting. Another feature is Auto Idle Stop (AIS), which stops the engine automatically if the operator is waiting for another load to arrive, reducing energy consumption over the length of a day’s work. A new manual stop function can also help to reduce unnecessary fuel burn.
“Kobelco has put a big focus on reducing carbon emissions across the board,” Hand says. “It’s a space that Kobelco is committed to continue pushing into the future.”
Hand says that on top of transportability and efficiency, significant investment and development has led to improvements in safe operation, both for the operator, and surrounding ground crews.
The field of view from the operator platform has been increased by about 28 per cent, compared to conventional cabin designs. The left window has also been lowered to increase left foot visibility. External alarms and visual cues while moving, or swinging notify
those surrounding the area, while a function lock lever also prevents accidental operation. Hand says it’s safeguards and changes like this – some of which may not be obvious to the naked eye – that add up to a supreme crane unit package.
“If it’s worked, they’ve kept it. They’ve kept progressing on what’s worked and kept it simple,” Hand says.
He adds that this helps to create familiarity for operators who may be switching between different Kobelco models.
“When you sit in the cabin, the Kobelco’s layout are all the same. That’s the beauty of Kobelco, that operator familiarisation. [It] Doesn’t matter if it’s an 80 tonner or a 600 tonner, the layout is very similar,” he says.
Kobelco’s history and experience providing interchangeable components also aids maintenance and servicing, making it safer and easier to conduct servicing on site if required.
“It’s a very streamlined type of machine. A lot of the parts and sensors have remained as the machinery has evolved. So, if you have a fleet of Kobelco’s, it’s much easier to maintain,” Hand says. “They rarely break as it is.”
Counterweight detection, over-swing prevention and machine inclination sensor devices help to accurately diagnose main unit and attachment conditions. Hand says the secret to Kobelco’s quick and easy maintenance requirements are simplicity, standardisation and accessibility.
“There isn’t any computers or systems to log into to see error codes. It’s a very maintenance-friendly machine,” he says.
To assist further, each crane delivery comes with a Kobelco trained service technician to help with training, covering each phase of assembly, disassembly and maintenance, as well as general familiarisation to increase operator confidence. This is also tailored to each customer’s needs.
The CKE3000G is just one of many Kobelco models within TRT’s range, reflecting a partnership that’s prospered for years. Hand says the relationship adds to the product quality, customer trust and growth.
“It really feels like we’re part of a family,” he says. “Together we’ve gone from strength to strength, there’s great transparency and support from both sides. The relationship has opened a lot of doors. It strengthens our integrity as well with the products that we sell.”
Kobelco’s CKE3000G is now available for order in Australia.
THE WIRTGEN GROUP TAKES PRIDE IN PROVIDING A CUSTOMER SUPPORT OFFERING THAT MATCHES – AND IN SOME CIRCUMSTANCES SURPASSES – THE RENOWNED QUALITY OF ITS ROAD CONSTRUCTION EQUIPMENT.
“The right program for everyone”. That’s the Wirtgen Group’s philosophy when it comes to customer training and servicing.
For what is one of the world’s largest manufacturers and distributors of road construction equipment, customer training holds a higher ranking on the pecking order than you might think.
Despite having a network that reaches Europe, Asia, South America, Africa, New Zealand and Australia, customer desires are always put first, regardless of the region or native language. And this is a consistent aspect across all its Wirtgen, Vögele, Hamm, Kleemann, Benninghoven and Ciber brands.
Chris Adams, Service Manager Australia and New Zealand – Wirtgen, says the Wirtgen Group’s devotion to training and servicing is about keeping customers up to speed with the rapidly evolving industry.
“It really comes down to the technology that we have within our equipment. We’re constantly evolving and developing new technology to keep up with the market’s demands and requirements,” he says.
“A profiler might do the same job that it did 20 years ago, but there’s now so many more options and advanced features that allow our customers to do the job safer and more economically. When we release
a new model, it’s important that we’re able to offer training to let them understand how they can get the best out of each of our units.”
Wirtgen has a national product support management team with dedicated managers for different product groups and regions. It’s through these product managers that the Wirtgen Group provides application training and technical support to customers.
One of these managers is Brett Ferris, Product Support Manager – Wirtgen.
As part of his role, Ferris looks after the Streumaster portfolio, the Wirtgen Group’s new binding agent spreading units.
He says that customer support and training is much more than just an added benefit. It’s now an essential key to long-term success.
“Gone are the days where we can put a machine out the front door and let the customer take care of the rest,” he says. “The technology is evolving and understanding the technology that the machines are equipped with is vital to the success of our customers’ businesses.
“Without customer support we don’t have customers. It’s a team effort and a relationship, if a customer calls for help and we can’t assist in a short time frame, that customer is losing money and faith in our brand. It’s my opinion that
and teaching them about X when they wanted to learn Y,” he says.
“This can be anywhere from a specialist onsite giving tips and tricks, to machine walk arounds, to classroom-based in-depth training with a room full of people. It’s fully catered and much more than just how to run the machine, instead it’s all the features of the machine, how to get the most from them, good and bad practices and much more.”
Adams adds that training is also focused on the application and machine at hand, rather than painting broad strokes over one model range.
“For certain product lines, like paving and rollers, the training is more focused on the application at hand and proper usage of the equipment, rather than just the technical features,” he says.
“That’s the main focus, application consulting and really ensuring that our customers understand how to use the equipment to their biggest advantage.”
The Wirtgen Group’s flexibility and options for classroom or on-site training is designed to offer a more hands-on and
“ALL OF THE TRAININGS I CONDUCT START WITH ME ASKING ‘WHAT DO YOU WANT TO GET OUT OF THIS?’ THERE’S NO USE GOING TO A CUSTOMER AND TEACHING THEM ABOUT X WHEN THEY WANTED TO LEARN Y.”
Wirtgen has succeeded because we offer and encourage these close customer support relationships.”
Ferris says a big part of building this relationship is tailoring the training programs to the specific needs of each customer, rather than offering generic sessions.
“All of the trainings I conduct start with me asking ‘what do you want to get out of this?’ There’s no use going to a customer
directly applicable approach, depending on the customer’s equipment and work environment.
“Even if they don’t have the time, we have a training program dedicated to our customers that’s always available, and that’s our website,” Adams says.
This constant support is also available from a repairs and servicing perspective, as Ferris explains.
“We offer all the required maintenance
for the entirety of the machine life. We have factory trained technicians across all our locations across the country, who all have a local network of Product Support Managers for each of our brands for support on issues that may arise,” he says.
“It’s often a misconception that servicing is just ‘change the oil and spin the filters’. It’s so much more than that, and we can offer immediate service, not just a ticket and wait system.”
This is also reflected internally, with team members within Wirtgen always willing to learn about new machinery and processes to ensure they can deliver the best possible service to their customers.
This includes bringing in specialists from the factory in Germany, to provide advanced training on new product introductions and features while Wirtgen’s learning management system, helps to track and address any gaps in technical expertise.
“A technician can’t efficiently repair a machine if they don’t know how to drive one or what the machine is supposed to do when a function is operated,” Ferris says. “We are now adopting learning paths to include a full curriculum that a technician can follow to become qualified on particular products.
“It’ll give our technicians a better understanding of the whole machine and product, and makes repairs faster and more effective, keeping costs down for Wirtgen and in turn, our customers.”
Both customer and internal training is set to receive a big boost, with two facilities in Melbourne and Queensland respectively set to be relocated and expanded.
“That’s going to increase our complete after sales presence in Melbourne and Queensland. It’s going to be a big improvement to give us more space and training facilities in those regions,” Adams says.
“It reflects our constant investment, to be able to better support our customers and product, from an after sales perspective, repairs and maintenance, while also offering training facilities for customers in-house.
“Our customers are always looking to seek information like this, especially in a challenging environment with labour shortages. They’re looking to us to be there for them and with expansion and investment like this, we can continue to do that, on a larger scale.”
1300TEMPFENCE HAS INTRODUCED A BRAND-NEW PRODUCT OFFERING THAT IS HIGHLY SUITABLE FOR MAJOR INFRASTRUCTURE AND CIVIL WORKS. BRUCE FOURACRE, MANAGING DIRECTOR –1300TEMPFENCE EXPLAINS WHAT MAKES THE SMARTWALL SO UNIQUE.
To the naked eye, it’s a component of little influence and often disregarded. For those in the infrastructure space, it’s an essential tool in maintaining the safety and wellbeing of those within the project’s vicinity.
The component in question is that of the temporary fence, which plays a crucial role in the delivery of projects of all sizes.
As a preferred specialist in temporary fence hire and sales, 1300TempFence provides what is an essential physical barrier component, helping to ensure not only the safety of the public and construction workers, but also applying an additional level of security and privacy.
1300TempFence has a rich and famed history providing solutions to projects right across Australia. Now the company has developed a new unit, inspired by the success of an international concept.
Development of 1300TempFence’s SmartWall focused primarily on improving handling, safety, transport economics, and customisation when compared to conventional temporary fencing solutions.
The SmartWall is a single, integrated unit, unlike other products that are two-piece. This reduces the risk of breakage when moving and handling the filled units. Built-in handles also make it much easier to lift and move the empty walls around, addressing the difficulty of handling bulky and often slippery products. The one-piece design
relocation when needed.
“The biggest benefits of the SmartWall design are preventing tripping hazards, a great aesthetic, and having removable ballast (water) so manual handling risks are reduced,” Fouracre says. “The beauty of our one-piece system is that we can stack the SmartWall far more effectively for transport than conventional designs. We can pack up to 30 units on a truck within just four pallet spaces, making them far cheaper to get to and from site”
Coming in at 2385 millimetres (L) x 464 millimetres (H) x 388 millimetres (W), a capacity of 273 litres and unfilled weight of 31 kilograms, the SmartWall is suitable for projects of all sizes, including high profile projects. The SmartWall’s brightly coloured bases providing maximum visibility, alongside a sleek and visually appealing aesthetic.
1300TempFence can also tailor the SmartWall design to meet specific project requirements, such as adding
can also include options to cater for different wind speeds, with extensive engineering work being completed to ensure the SmartWall meets AS 4687:2022, the current Australian Standard for Temporary Fencing and Hoardings.
“We’ll get our engineers to come up with a design that suits the customer’s requirements, to withstand whatever the conditions are on their specific site,” Fouracre says.
For higher wind speed applications requiring more ballast, 1300TempFence has worked hard to create engineer certified designs incorporating additional SmartWall units, or utilising conventional temporary fencing braces and weights.
The features and versatility of the SmartWall has them in high demand on major projects across the country, including more than 100 units deployed to the Melbourne Airport, the Suburban Rail Loop, as well as additional units
“WE’RE RAMPING UP OUR TOOLING AND PRODUCTION CAPACITY TO BE ABLE TO MAKE MORE SMARTWALL UNITS, AS WELL AS OUR OTHER DESIGNS.”
at the Perth Airport and University of Sydney.
“We’re also looking to produce the product out of recycled plastic down the track,” Fouracre says. “Once we’ve got the supply and a proven concept, we’ll look to make that a big part of the SmartWall’s production going forward.”
Recycling for production is an aspect that’s far from alien for the temporary fence manufacturer and distributor.
“We’ve been recycling our ‘dead’ water barrier units for years, as well as the unrepairable steel temp fence panels and concrete feet. This is just another arm and expansion on that,” Fouracre says.
For 1300TempFence, 2025 is an opportunity to consolidate and strengthen its national reach. The company is focused on ramping up its presence beyond its Melbourne stronghold, including New South Wales, Queensland, Western Australia, and South Australia.
Fouracre says the goal is to grow 1300TempFence’s locations and gain more market share in these other regions.
To do so, 1300TempFence is introducing more water barrier products to its line, including the X-Site and the X-Stream, which are coming into full production.
The company is also taking steps to ensure adequate supply to meet growing customer demand.
“We’re ramping up our tooling and production capacity to be able to make more SmartWall units, as well as our other designs,” Fouracre says. “We’re going from just a couple of SmartWall tools (rotomoulding moulds) to four to six, which will allow us to double and then triple our production.
“I’m really excited about where the SmartWall will go. The inquiries that are coming through have been really positive and we’re getting really good feedback on a number of our other products. There’s a lot of interest being generated across the board.”
Melbourne contractor reduces trackout street sweeping by 40%.
Read case study on page 31
REPLACE ROCK WITH REUSABLE CONSTRUCTION ENTRANCE SOLUTION
FODS mats enables contractors to keep dirt where it belongs: on the job site. With it’s patented design, FODS pyramids flex vehicle tyres to dislodge mud, dirt and debris. Unlike rock, the system does not require additional materials on each application, and is easy to maintain and clean with a sweeper or shovel, reducing costs on every project.
DEPLOY ON ANY SUBSTRATE
EASY TO TRANSPORT & INSTALL
SUPPORTS 1,000,000+ KG
REDUCE LABOR AND COSTS
EXPECTED 10+ YEAR LIFESPAN
TUTT BRYANT COMPACTORS COME IN MANY SIZES AND HAVE MANY DESIGN ADVANTAGES THAT WORK ACROSS A RANGE OF JOB SITES, WITH ITS FIVE TONNE AND BELOW TANDEM ROLLERS HAVING BEEN DESIGNED FOR EVERY PURPOSE.
With most jobsites requiring machines like landfill compactors, Tutt Bryant Equipment’s range of smaller-sized BOMAG compactors stand out.
A leader in compaction technology, BOMAG provides a range of rollers under five tonnes for the compaction of refuse, soil and asphalt.
John Glossat National Business Development Manager – Tutt Bryant, says the BW100ADM-5, BW120AD/AC-5, BW138AD/AC-5 compactors offer the best machines for small to medium projects.
With operating weights of 1700, 2700 and 4400 kilograms respectively, the BOMAG light double drum rollers are essential when working on smaller projects.
“Just because operators are using a compact machine doesn’t mean they should miss out on productivity, operator comfort, performance and innovation,” says Glossat. “To ensure Tutt Bryant customers receive the best out of a
BOMAG machine, BOMAG engineers do all they can to make each new generation even more economical and more productive.”
“That is why every BOMAG aids our customers in efficiency, comfortability and professionalism.”
Ranging from 1.5 tonne to five tonne operating weight, the smaller tandem rollers are ideal for footpaths and repair work, as well as finishing work in road construction. Glossat says the compact BOMAG tandem rollers have also acquired an excellent reputation in landscaping around the world.
“In order to increase flexibility in tight spaces, BOMAG offers rollers with clearsided drums, which are only suspended on one side and off-centre,” says Glossat.
“As a result, the rollers can compact cleanly right up to high walls of buildings and other boundaries.”
Asphalt surface quality can also be improved when using a BOMAG light combination rollers.
“The rolling and kneading effect of the rubber wheels pulls bitumen to the surface and achieves maximum sealing of the asphalt layer,” says Glossat.
“Several other features have been added to the light tandem roller range available to our Australian clients.”
Australian clients also have the benefit of the quick to service aspect of the BOMAG range, which saves on time and simplifies daily maintenance.
“Our BOMAG range was designed with practical usage at the forefront of our engineers’ minds, which is why we introduced BOMAG’s EasyService concept,” says Glossat.
He says BOMAG EasyService also means access to all maintenance points, which can be comfortably reached from the ground.
“The single-unit hood, made of composite materials with strong gas springs, swings up readily and reveals the entire engine compartment, meaning all fluids can be drained through external drains,” he says.
“The articulated joint is also maintenance free, while the motor, central electrics and water pumps are easily accessible, saving time and simplifying maintenance.”
Glossat says BOMAG tandem rollers are efficient to service because the easiest and most cost-effective service is one that is not necessary.
All machines are also equipped with the crabwalk function, special hermetically sealed bearings and permanent highquality grease filling, which Glossat says guarantees reliable lifetime lubrication.
In case of an emergency, Glossat says the articulation joint has not been welded to the frame and is easily accessible if need be.
Operator comfort was also a key priority when designing the range, as
“THE ROLLING AND KNEADING EFFECT OF THE RUBBER WHEELS PULLS BITUMEN TO THE SURFACE AND ACHIEVES MAXIMUM SEALING OF THE ASPHALT LAYER.”
machines are equipped with a spacious operator’s platform, compact steering wheel and a robust dashboard with large switches.
Glossat says other key features include a soft responsive control lever, dual travel
levers to safely and easily operate from each side of seating position and a clear view of the drum edges.
Special features of the BW120AD/AC-5 and BW138AD/AC-5 include a temperature sensor and the ‘economizer’, a tool used to display the increase of compaction to operators.
No set up or calibration is required on the ‘economizer’, designed for easy use by all operators.
Glossat says the tool always reads compaction results and automatically determines the compaction progress as the day progresses.
“A light strip indicates the end of compaction to the driver to avoid over compaction, while a warning lamp also lets you know when there is a risk of over compaction,” says Glossat.
“The ‘economizer’ saves time, money and fuel. It helps avoid unnecessary passes, reduces wear and tear and ensures stressfree and flexible on-site work.”
For more information, visit: https://tuttbryant.com.au/
When your measurement is crucial, VEGA is the right choice. Our level and pressure measurement technology is not just state of the art – it sets the industry standard. With clear vision, technical expertise and strong innovation, we always have the right answer. No matter what the question is.
Everything is possible. With VEGA.
WITH THE ROAD ANT BECOMING THE VICTORIAN INDUSTRY’S PREFERRED FORWARD SPREADER FOR SPRAY SEAL WORKS, SAVING ON LABOUR COSTS WHILST DE-RISKING WORK SITES, IT IS NOW GETTING ATTENTION INTERSTATE AND OVERSEAS.
In a move to increase safety on VicRoads’ construction projects, the road authority announced that aggregate spreaders would be required to be forward moving. In July 2017, VicRoads implemented a five year transition period to phase in Forward Moving Spreading and on 1 July 2022 this was mandated.
In a direct response, Quality Fabrication & Engineering created the Road Ant, a dual controlled forward moving aggregate spreader, to increase safety on spray sealing projects across the road network.
Twenty-five units have been sold to date to companies such as Fulton Hogan, Primal Surfacing, InRoads, Cranes Civil & Surfacing, Rich River Asphalt, Szabolics Construction and Moyne Shire. Glenn Hardiman, General Manager, Quality Fabrication & Engineering, says it’s no surprise that the Road Ant is now operating interstate.
“We have carried out trials and demonstrations interstate at the request of road authorities in New South Wales,” says Hardiman. “It’s encouraging to see an interest Australia-wide in improving safety in the spray seal industry.”
Hardiman says current funding from the Department of Transport Victoria for preventative Spray Seal maintenance contracts on the Victorian regional road network are very scarce.
“This means major companies are using Road Ants on Shire work where forward spreading is not necessarily mandated, further cementing their acknowledgement for safer methods of spreading aggregate.”
He says that the Road Ant has been well adopted by the industry in its first three years of operations.
“The spray sealing industry adopted the Road Ant well because they were already familiar with its operation,” he says.
“Although it is very precise in its stone distribution, it is a very simple machine to use and to operate, which the drivers find comforting. We found even though there are other methods of forward spreading, our solution seems to be popular because it fits in with the same way spray sealing has been done for 70 years.”
RICH RIVER ASPHALT
Since acquiring two Road Ant forward moving aggregate spreaders, Rich River
QF&E says the Road Ant largely removes the risk of reversing over a pedestrian, worker, object or vehicle.
Asphalt, located in Echuca, Victoria, has noticed previously closed doors and opportunities opening.
Like other spray seal and asphalt
Fabrication & Engineering. They were fantastic throughout the whole process.”
Prior to receiving the forward moving aggregate spreader units, Rich River
to employ less crew members. You save money in the long run and the impacts on risk and safety outweigh the cost.”
With expanding interstate interest and fresh enquiries from the United Kingdom and with QFE holding global rights to the IP, Hardiman says the future looks bright
“The Australian Patent #2020307144 and United States Patent #17622639 all have a 20-year priority date from 24 June 2020; its unique design and practical uses is a rewarding outcome for an Australian owned company. Further patent applications are pending in Asia and Europe” says Hardiman.
In an effort to continue advancing the Road Ant, Hardiman says Q-FE has improved the simplicity and operation of the control system and its fault-
“If there is a fault somewhere within the hydraulic or electrical system, the fault-finding screen on the dash will tell the driver exactly where the issue is so it can be quickly and easily remedied,”
In addition to fault finding, Hardiman says Q-FE are also working on further driver aids which can be expected to
“There are some tweaks that we’re working on, which will further enhance the driving experience for operators,”
For more information, visit: https://qualityfab.com.au
Heavy-duty performance. Lightweight handling.
Strong and ductile
Designed to withstand multiple heavy impact strikes.
Lightweight
Easier to install & handle than traditional straight wall HD conduits.
Material efficient
Uses less material than traditional HD straight-walled conduits.
Compliant
Meets Australian standards and exceeds impact testing requirements.
Lower embodied energy*
Requires less embodied energy to manufacture.
Flexible
Suitable for long radial bends.
Scan the QR code to learn more about XGuard by Vinidex, or for more information visit us at vinidex.com.au
for Aust ralia, Papua N ew Guine a and South East Asia
IMS have added the new BP1200-48TB track electric twin power blender to its impressive collection of blenders and pugmills, the new BP1200-48TB has four separate feed hopper each five meters long holding 12m3 each. All feed hopper conveyors are fitted with belt scales and controlled by a PLC control and recording system that can be operated from an iPad or phone from its own Wi-Fi system from a loader or
THE AUSTRALIAN FLEXIBLE PAVEMENT ASSOCIATION (AFPA) DISCUSSES ITS APPROACH TO SUSTAINABILITY IN 2025 AND HOW IT AIMS TO SUPPORT ITS MEMBERS, AS WELL AS THE SECTOR AS A WHOLE. AS AFPA WRITES.
AfPA (the Australian Flexible Pavement Association), through its members, is dedicated to reducing its carbon footprint, embedding circular economy practices, and driving sustainable operations to help the industry meet its ambitious targets for 2030 and 2050.
To achieve this goal, AfPA has formed its National Sustainability Committee, made up of technical and operational experts from across the industry. The committee promotes the sustainable benefits of flexible bituminous pavements and supports both local and international best practices. Members, representing member companies, provide guidance, oversee projects, set standards, and help establish industry norms and benchmarks.
The objectives set for the National Sustainability Committee are to promote the sustainability of industry through best environmental management practices and to advance the industry’s reputation as leading, mature and trustworthy, partnering with key
stakeholders to drive best industry practice outcomes for Australia.
2025 represents a significant milestone as we fast approach the first hurdle in 2030. The priorities are therefore centred around:
AFPA LIFE CYCLE ASSESSMENT (LCA) TOOL The life cycle assessment (LCA) calculator
presents a simple solution for asphalt producers that want to calculate the cradleto-gate environmental footprint of their products, using specific data from any asphalt plant and for any mix-design. It provides users with the ability to optimise their mix designs and plant operations with the plant level carbon footprint.
In 2025 AfPA is undertaking a comprehensive update to the Calculator to simplify and improve user experience, and permit +A2 reporting to meet latest EPD requirements. The goal is to refine and update the tool to align with international standards, conduct third-party auditing, and secure its recognition as the industry standard. The tool will serve as a means to compare the carbon footprint of various materials, simplifying the process of evaluating road construction practices, which currently involves time-consuming and expensive individual assessments.
SUSTAINABILITY FRAMEWORK FOR PAVEMENTS (SF4P)
Finalising and implementing the Sustainability Framework for Pavements (SF4P), an audit tool designed to assess and monitor individual asphalt plants and their management practices to meet State Government requirements and drive industry improvement. The SF4P is a cornerstone of a broader sustainability strategy that helps road authorities and other stakeholders define best practices, measure sustainability achievements, integrate sustainability metrics into procurement processes, and recognise the industry for its continuous improvement efforts and investments.
SUSTAINABILITY FRAMEWORK FOR SEALING (SF4S)
The development of the Sustainability Framework for Sealing (SF4S), a sustainability audit tool designed specifically for spray sealing operations and management. This framework aims to enable stakeholders to establish measurable metrics and benchmarks for reducing the environmental impacts (e.g., greenhouse gases, energy use, waste and more) associated with sealing operations.
STATE FORUMS ON DECARBONISATION
In November 2024, AfPA hosted a forum in Newcastle focused on low-carbon innovations in road construction and maintenance. The event highlighted industry efforts to support road asset owners in achieving Net Zero targets while ensuring resilient infrastructure. Key themes included the circular economy, sustainable procurement, and advancements in asphalt technologies.
AfPA’s branch and committee members led thought-provoking discussions on the following topics:
AfPA has already identified multiple areas that could see growth in 2025.
Circular Economy in Road Materials: The forum emphasised the importance of the circular economy, which seeks to eliminate waste and pollution, keep materials in use for as long as possible, and regenerate natural systems.
Warm Mix Asphalt (WMA): Warm Mix Asphalt is a sustainable alternative to traditional hot mix asphalt, achieved by lowering production temperatures, which reduces energy consumption and emissions.
Low Carbon Asphalt (ECO5): ECO5 asphalt
more durable pavement layers due to its high binder content and low voids.
Sustainable Thin Asphalt Surfacing: Boral’s Durapave Plus, a high crumb rubber content asphalt, was highlighted for its ability to enhance crack resistance, reduce environmental aging, and extend durability. Challenges and Solutions: The forum identified several challenges to adopting sustainable practices, including inconsistent material classifications and regulatory variations across states. However,
“AS THE SECTOR EVOLVES AND NEW TECHNOLOGIES EMERGE, AFPA IS COMMITTED TO EMBRACING INNOVATIVE APPROACHES THAT PROMOTE SUSTAINABILITY.”
integrates low-carbon binders, RAP, recycled crushed glass, and warm mix technology to deliver a more sustainable product.
High RAP Asphalt: High RAP asphalt, which uses higher percentages of recycled materials, was highlighted as both an environmentally and economically beneficial solution.
Carbon Neutral Products: Viva Energy’s optin carbon-neutral bitumen was introduced as a practical step toward reducing emissions in the short term.
Innovative Additives and Repurposed Waste: The use of recycled rubber from old tyres was highlighted as a way to improve asphalt flexibility, rut resistance, and durability.
Advanced Asphalt Technologies (EME2): EME2, or high modulus asphalt, was showcased for its ability to create thinner yet
collaborative efforts, such as those between Transport for NSW and the NSW EPA, have resulted in clearer testing frameworks and streamlined approvals for trials.
AfPA, alongside its members and committees, will remain at the forefront of driving the flexible pavement industry towards achieving net zero carbon emissions. As the sector evolves and new technologies emerge, AfPA is committed to embracing innovative approaches that promote sustainability. By fostering collaboration, adopting cutting-edge solutions, and continually adapting to the shifting landscape, AfPA aims to lead the industry in reducing its carbon footprint while ensuring the long-term resilience and efficiency of road infrastructure.
network, addressing long-standing traffic congestion and significantly improving overall efficiency.
National Precast Master Precaster, The Geoquest Company Australia and New Zealand, a key partner in the Sydney Gateway project, played a crucial role in the project – designing, supplying and installing over 50 Geoquest Mechanically Stabilised Earth (MSE) walls.
These walls were constructed across five main work areas – Northern Lands,
St Peters Interchange, Tempe Tip, Airport Drive and Qantas Drive. They cover more than 15,000 square metres and include a range of structures, from abutment walls to approach ramps and retaining walls. Heights varied from 1.5 metres to over 8.5 metres.
The MSE wall technology incorporates the company’s TerraPlus® concrete panels, each three metres wide by 1.5 metres high.
According to the Geoquest’s Managing Director in Australia, Riccardo Musella, the walls provide not only structural
Precast elements have
in
The project replaced traditional cement with fly ash, further contributing to sustainability efforts.
the panels.
“This project marked a milestone for us as it was the first time we had provided both design and installation services, in partnership with a reputable installer,” Musella says.
Musella adds that the integration of design and installation streamlined the project, simplified processes and offered a cohesive solution, all under one contract.
Several innovative technologies were applied to optimise the project’s efficiency and sustainability. Among these were adjustable precast hanger bars for lifters and ferrules, the firstever three metre wide x 1.5 metre high concrete panels, and a panel block-out system using removable plates and z-bars. Additionally, multiple eight-in-arow table moulds were utilised, further enhancing production efficiency.
These technologies improved the speed and stability of the panel manufacture, while reducing waste and pour time,
Mechanically Stabilised Earth (MSE) walls are a type of retaining wall that are quick to install and adaptable to various site conditions. MSE walls rely on the interaction between soil and reinforcements to provide stability and support. They are usually integrated with precast concrete facing panels for enhanced performance and aesthetics. MSE walls are widely used in civil engineering and construction for their cost-effectiveness, flexibility, and ability to withstand various environmental conditions. Typically used in highway and rail embankments, on bridge abutments, at industrial sites and in urban construction, their immense value comes from their aesthetic appeal, durability, sustainability and cost efficiency.
ensuring both cost-effectiveness and environmental sustainability.
The Sydney Gateway project has had a profound impact on both the local community and the broader Sydney region. It is not only improving traffic flow but also returning local roads to communities, enhancing pedestrian and cycling links and creating better community spaces.
Environmentally, the project made significant strides with the use of a 25 per cent supplementary cementitious material (SCM) concrete mix, replacing
traditional cement with fly ash, further contributing to sustainability efforts.
The Sydney Gateway project exemplifies the transformative power of innovative engineering and infrastructure development. By connecting key parts of Sydney’s motorway network to the airport precinct, the project significantly enhances transport efficiency, safety and sustainability.
The successful integration of Geoquest’s MSE wall technology, coupled with the use of advanced construction methods and a focus on community and environmental benefits, sets a new benchmark for future urban infrastructure projects.
Over
Will you be a part of it?
17–18 SEPTEMBER 2025
Melbourne Convention & Exhibition Centre
LEARN MORE
Find
convergeexpo.com.au
Successful contractor announced for major VIC road project
A contract has been awarded for the construction of the 1.3-kilometre, four lane road between the Ison Road Overpass and the Geelong Road Princes freeway interchange in Victoria. Decmil has been awarded the contract to deliver the Ison Road Extension, to form the new link to the freeway between Melbourne and Geelong. Together, the Ison Road Extension and Overpass will form the new link between Ison Road and the Princes Freeway at Werribee, with the 29,000 motorists who use the connection daily able to use the new link by the end of next year. The link will include walking and cycling paths along the overpass and the extension to Geelong Road (Princes Highway). These upgrades will also allow the nearby dangerous and congested level crossing at Galvin Road in Werribee to be closed to traffic once the new connection opens. The $80 million project is jointly funded through the Victorian Government and Wyndham City Council. About $60 million of this has come from the Victorian Government’s Growth Area Infrastructure Contribution (GAIC) fund, which was established to help provide infrastructure in Melbourne’s expanding fringe suburbs. Crews have already clocked nearly 150,000 hours building the Ison Road Overpass and completed the road deck late last year. Workers will finish the bridge build and prepare the site for construction on the Ison Road Extension.
Major contract awarded for delivery of $1 billion Tonkin Highway
The contract to deliver the $1 billion Tonkin Highway Extension and Thomas Road Upgrade Project, in Western Australia, has been awarded to a consortium containing some of the largest infrastructure providers in the country. The contract to deliver the project has been awarded to the Tonkin Extension Alliance consortium which includes BMD, Civcon Civil and Project Management, Georgiou Group, BG&E, and GHD, bringing together a wealth of expertise and experience to deliver one of Western Australia’s most significant road infrastructure projects. The 14-kilometre extension of the Tonkin Highway will include a four-lane dual carriageway from Thomas Road all the way to South Western
Highway, including a number of gradeseparated interchanges, underpasses and roundabouts. Upgrades to Thomas Road will include duplication of 4.5-kilometres between Kargotich Road and South Western Highway, new principal shared path and upgrades to a number of local intersections including Kardan Boulevard, Masters Road and Plaistowe Boulevard. The project will deliver benefits to Western Australia’s freight and logistics network by creating a high-standard north-south transport link, improving road safety, freight efficiency, and connectivity for residents, businesses, and commuters. Construction of the project is scheduled to commence in mid-2025 with completion anticipated by late-2028. The project is expected to support around 4400 direct and indirect jobs.
A new contract has been awarded to deliver electrical works for Western Power, a Western Australian (WA) State Government-owned corporation responsible for building, maintaining and operating the South West Interconnecting System electricity network. UGL was awarded the contract and will design, supply, install and commission extensions to the existing Neerabup 132 kilovolt and 330 kilovolt substations, approximately 40 kilometres north of Perth, as part of the Western Australian Government-funded Clean Energy Link – North project. These substations form part of the South West Interconnecting System network and are responsible for connecting to transmission lines that supply electricity across the region. These works will aim to strengthen Western Australia’s largest electricity network to enable a greater supply of renewable energy from the Wheatbelt region and the Mid West region. The Wheatbelt and Mid West regions are ideal locations to harness renewable energy technologies such as wind and solar energy, with the State moving towards achieving net zero by 2050. This will be especially important, with current modelling predicting that ten times the current renewable generation will be required to meet future low emission electricity demand across the State (per Genus).
Contract awarded for Sheahan Bridge upgrade in NSW
A contract has been awarded for the $20 million jointly funded planning project for the Sheahan Bridge Upgrade project on the Hume Highway at Gundagai in New South Wales. WSP Australia Pty Ltd has been awarded the contract to progress with the next phase of the development to determine the design for the bridge’s upgrade or replacement. The Sheahan Bridge Upgrade project is investigating upgrade requirements and improvement options to allow Performance Based Standards (PBS) vehicles to use the Hume Highway Corridor without restriction. The concept designs will provide a development and environmental assessment of potential upgrade or replacement options for the northbound bridge over the Murrumbidgee River. The Hume Highway connects Melbourne and Sydney and is one of Australia’s busiest road freight corridors. The current northbound bridge was built in 1977, with duplication of the southbound lanes officially opened to traffic in 2009. While the load limit was increased from 68 to 85 tonnes in 2020 on the northbound bridge, for the safety of motorists Higher Productivity Vehicles still have to use a permit to travel on the New South Wales section of the Hume Highway due to the age of the bridge and structure limitations. These limitations on the northbound bridge also restrict opportunities for contraflow during emergency response or planned maintenance activities on the southbound bridge. The upgrade planning project will investigate potential solution options including building a replacement bridge on a new alignment upstream (east) or downstream (west) of the existing bridge, replacing the existing bridge on its current alignment and strengthening the existing bridge. It is expected that the preferred option will be identified by Transport for NSW for public display in mid-2026.
Experience a new era of compaction excellence with the groundbreaking Dynapac Rhino range. Engineered to deliver exceptional performance and efficiency, the newly updated Rhino series sets the benchmark in compaction technology.
Featuring:
• Powerful Cummins engines for exceptional performance and fuel efficiency.
• Advanced operator cabin with enhanced visibility and ergonomic controls.
• Uncompromising reliability for long-lasting durability and minimal downtime.
• Industry-leading compaction technology for superior results.
• Versatile to suit a wide range of compaction projects.
With its unparalleled power, precision, and reliability, the new Rhino range from Dynapac is the perfect choice for contractors who demand the best in compaction equipment.
Experience the new Dynapac Rhino difference today!