Transport’s crystal ball
Artificial Intelligence is granting unprecedented access to project data and forecasts
From research to roads
The latest university research is leading to improved outcomes for the sector
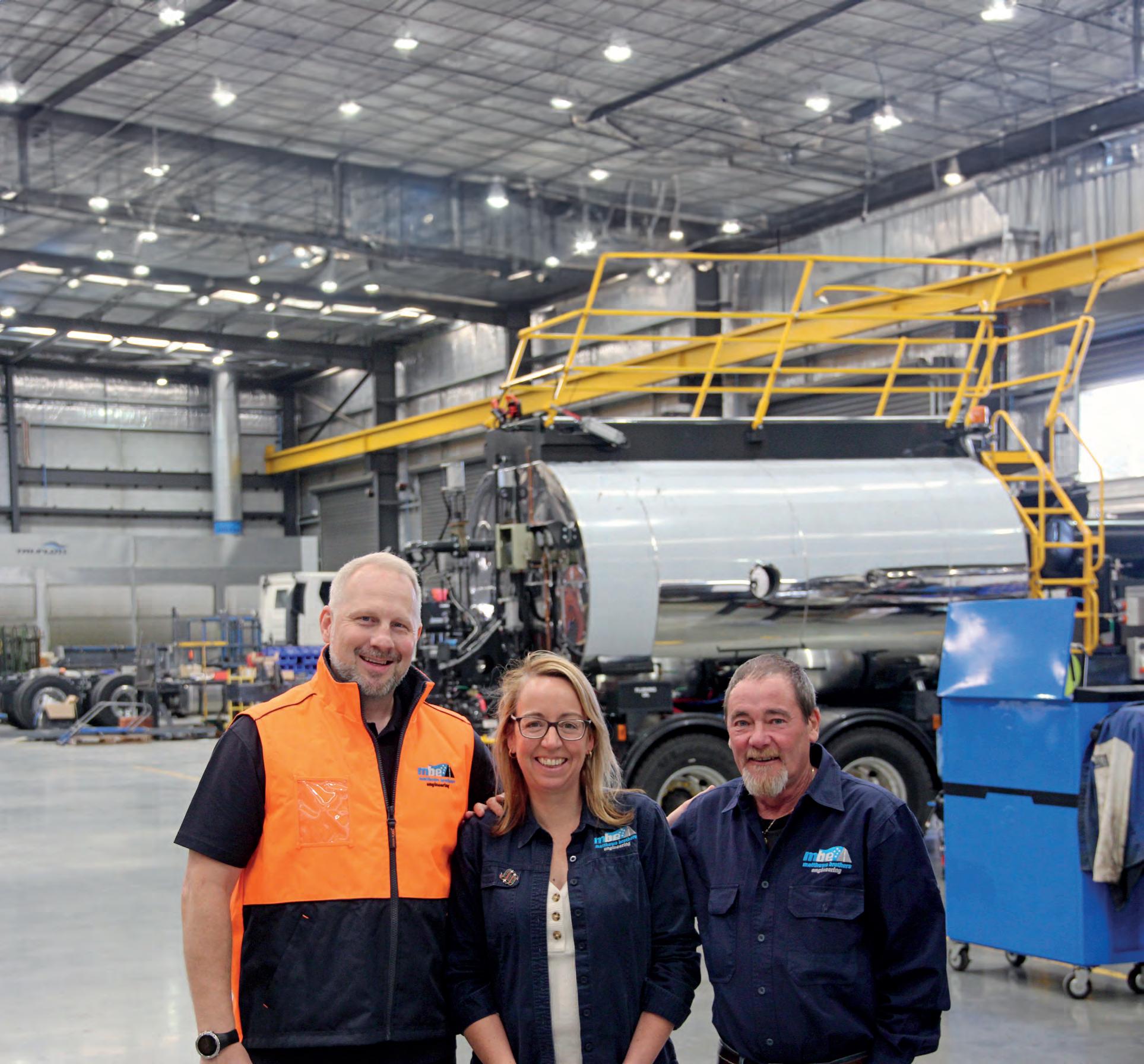
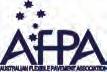
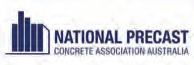
Artificial Intelligence is granting unprecedented access to project data and forecasts
From research to roads
The latest university research is leading to improved outcomes for the sector
A proud local business is making the big leap interstate
VÖGELE SUPER 1700-3(i) / SUPER 1703-3(i)
VÖGELE SUPER 2000-3(i) / SUPER 2003-3(i)
The number one paver manufacturer on the global market presents innovative “Dash 3” pavers and screeds for Australia. Equipped with state-of-the-art Cummins engines available in either Tier 3 or Tier 4 Final / Euro Stage V emission standards, are the perfect choice for any application in the Universal (2.5m) and Highway (3.0m) paver classes. Thanks to the easy-tounderstand ErgoPlus 3 operating system which is common across all VÖGELE products both paver and screed operators can handle all VÖGELE pavers simply and safely. These machines are also available with vibrating screeds or high compaction tamping & vibrating screeds for those critical jobs. In combination with advanced optional features, such as VÖGELE EcoPlus, AutoSet Plus and Navitronic Plus 3D, these models are the stars of any road construction site.
www.wirtgen-group.com/australia
14 Bridging the gap
The customer always comes first for Matthews Brothers Engineering, one of the biggest reasons why the company is expanding its business from the east coast to the west.
17 This month, we asked the industry’s decision-makers, ‘what’s next when it comes to decarbonising the infrastructure and transport sectors?’
18 Transport’s crystal ball
The National Transport Research Organisation (NTRO) is launching its brandnew NTRO Project AI platform, an innovative tool that will give unprecedented access and insight into potential project challenges.
22 A dedication to Darwin
One of the biggest councils in Australia recently started using the services of one of the largest national civil engineering providers in the nation, Civiltech Solutions.
26 Sustainability on show Geotab has released its 2024 sustainability report analysing its current position on its ambitious goals, all while helping the infrastructure industry with its own.
29 Roads & Infrastructure helps you keep up with the latest movements across the roads and infrastructure sectors.
30 The rejuvenator of choice Sripath’s ReLIXER asphalt rejuvenator is among the leading global rejuvenation technologies, with more than a decade of application to show for it.
32 Every step of the way Geoquest Australia has again showcased its ability to deliver major infrastructure project components, this time on the Wilman Wadandi Highway project.
34 No limits with the B-Air Atlas Copco’s B-Air compressor is the newest eco-friendly piece of machinery set to revolutionise the roads and infrastructure industry.
37 Precision blending Crusher Screen Sales & Hire’s IMS PM1200-20TB pugmill is a gamechanger for increasing accuracy in road base production.
40 Lifting the curtain Komatsu has returned to bauma 2025, one of the world’s largest trade fairs for construction machinery, showcasing its electric and innovative machinery solutions of tomorrow.
42 Out with the old New equipment is providing a muchneeded boost to research infrastructure in the transport and construction space.
45 Paving the way forward
The Australian Pavement Recycling and Stabilisation Association looks ahead to the next wave of change.
Above: Learn more about the projects, research and developments that are helping to push the sector forward, in this edition of Roads & Infrastructure magazine.
49 Future ready roads
The Australian Flexible Pavement Association has announced its 20th International Conference, set to take place from October 28-30, 2025, at the Adelaide Convention Centre.
52 Bridging the gap
Artificial Intelligence and automation are reshaping the future of construction. As National Precast writes, keeping things simple is essential.
54 Industry’s platform for collaboration Victoria University Associate Professor Malindu Sandanayake outlines the importance and opportunities to come from the highly anticipated Converge Expo.
56 Solutions shaping future cities
A look ahead to the highly anticipated NoDig Down Under Conference.
58 Roads & Infrastructure provides an update on some of the contracts and tenders recently awarded or put to market.
Every Cat® soil compactor is engineered with durability and reliability at its core. And with built-in real-time compaction measurement technology, Cat soil compactors allow you to track compaction so you reach target density quickly, without guesswork.
Plus, when you purchase a new Cat soil compactor you’ll enjoy access to locally supported parts via the national dealer network as well as a comprehensive warranty package. Better still, there’s the option of a Cat Customer Value Agreement (CVA), designed to help you lower the cost of owning your Cat machine and maximise your investment.
To find out more contact your local Cat dealer or visit cat.com
WE’VE OFFICIALLY HIT THE HALFWAY MARK IN 2025, and what a year it’s been already!
Now’s a good time as ever for the industry to catch its breath. But not for too long! With many major infrastructure projects on track to open, or hit major milestones as we enter the third quarter of 2025.
One aspect that really stood out to me in this edition has been the sector’s willingness and ability to adapt and adopt.
Methods, technology and materials are all transforming – and quickly – with hopes that the construction and transport industries can turn a new page and continue delivering what is the backbone of the nation.
For the cover story in this edition, we speak with Matthews Brothers Engineering, a company at the forefront of exciting expansion. For the first time ever, Matthews Brothers Engineering has established a representative and presence in Western Australia, supported by the company’s main headquarters in Victoria. The move is set to provide a major boost to Matthews Brothers Engineering’s loyal interstate customer base, giving operators and fleet managers local access to parts and expertise.
Two universities are also helping to bring about more sustainable and efficient outcomes for the sector, with ground-breaking research introducing new methods and materials for use in major infrastructure works. We speak with representatives from Victoria University, as well as the University of South Australia, to learn how this research is benefitting the sector.
Exciting research and development in Artificial Intelligence (AI) is also set to make a big difference. The National Transport Research Organisation, in partnership with Octant AI, has developed Project AI. This platform uses AI to predict and prevent cost overruns in transport infrastructure projects. The platform reviews project data monthly and uses advanced learning algorithms to forecast potential cost escalations three to six months in advance. There’s hope that such a platform will be commercialised in the near-future, allowing more contractors in the transport space to deliver more projects on time and under budget.
This and much more, in the latest edition of Roads & Infrastructure magazine.
Happy reading!
Tom O’Keane
COO
Christine Clancy
christine.clancy@primecreative.com.au
PUBLISHER
Sarah Baker sarah.baker@primecreative.com.au
MANAGING EDITOR
Lisa Korycki lisa.korycki@primecreative.com.au
EDITOR
Tom O’Keane tom.okeane@primecreative.com.au
JOURNALIST
Jennifer Pittorino jennifer.pittorino@primecreative.com.au
HEAD OF DESIGN
Blake Storey
ART DIRECTOR Bea Barthelson
BUSINESS DEVELOPMENT MANAGER
Courtney Burton courtney.burton@primecreative.com.au
CLIENT SUCCESS MANAGER
Sabrina Zor sabrina.zor@primecreative.com.au
HEAD OFFICE
Prime Creative Pty Ltd
379 Docklands Drive, Docklands VIC 3008 Australia p: +61 3 9690 8766 enquiries@primecreative.com.au www.roadsonline.com.au
SUBSCRIPTIONS
+61 3 9690 8766 subscriptions@primecreative.com.au
Roads & Infrastructure Australia is available by subscription from the publisher. The rights of refusal are reserved by the publisher.
ARTICLES
All articles submitted for publication become the property of the publisher. The Editor reserves the right to adjust any article to conform with the magazine format.
COVER IMAGE
Matthews Brothers Engineering
COPYRIGHT
Roads & Infrastructure Australia is owned and published by Prime Creative Media. All material in Roads & Infrastructure Australia is copyright and no part may be reproduced or copied in any form or by any means (graphic, electronic or mechanical including information and retrieval systems) without the written permission of the publisher. The Editor welcomes contributions but reserves the right to accept or reject any material. While every effort has been made to ensure the accuracy of information, Prime Creative Media will not accept responsibility for errors or omissions or for any consequences arising from reliance on information published. The opinions expressed in Roads & Infrastructure Australia are not necessarily the opinions of, or endorsed by the publisher unless otherwise stated.
Work has started on a new $52 million materials handling facility at Geraldton Port – the first major works as part of the $350 million Geraldton Port Maximisation Project in Western Australia.
The new facility will improve safety, increase efficiencies and reduce dust emissions. It will allow vessels to be loaded at increased speeds, delivering
Funding to the value of $85 million has been committed to upgrading the intersection which forms the meeting of two major commuter, freight and public transport routes as part of the journey to Adelaide Airport.
The intersection is currently over capacity, creating significant congestion, particularly during peak periods.
The upgrade is jointly funded by the Federal and South Australian governments and will include new dedicated turning and through lanes, an extended left turn lane from Marion Road onto Sir Donald Bradman Drive towards the airport, and new bike
significant cost savings to the region’s exporters, as well as improve the port’s overall efficiency.
It marks the first major activity on site as part of the State Government’s $350 million Port Maximisation Project (PMaxP), which will significantly expand capacity of Geraldton Port and facilitate the export of new commodities from the region.
The next project in the PMaxP pipeline is the proposed Surge Protection Breakwater, which will address wave action restrictions that prevent ships entering and exiting the port which currently cost the port 30 lost productive days per year.
The project is currently under assessment by the Western Australia Environmental Protection Authority.
lanes on all approaches. The improvements for travel through the intersection will reduce rat-running on adjoining streets and create safer roads.
Major construction works have progressed, including kerbing, drainage works, road lighting, electrical infrastructure and pavement works.
(north of Jenkins Street), is being upgraded to become a Pedestrian Actuated Crossing (push-button), improving safety for pedestrians visiting local shops, schools and public transport.
Included with every eligible PC138US-11:
• 2,000 hours Komplimentary servicing
• 4-year / 8,000-hour standard warranty
• Tilting quick hitch and tilt piping - Free
Add 3D Machine Guidance, Payload and UHF radio for just $30K more.
Major construction has kicked off on the Suburban Rail Loop in Victoria, ahead of tunnelling commencing at the start of 2026.
Suburban Rail Loop is a 90-kilometre orbital rail line that will help transform the way
The SRL is set to deliver more homes and transport options once complete. Image: Victorian Government
Cheltenham and Glen Waverley in the south east, while Terra Verde is building the tunnels north of Glen Waverley to Box Hill.
From 2026, Tunnel Boring Machines (TBMs) will be launched from Clarinda – two digging towards Glen Waverley, and two towards Cheltenham.
The TBM launch site in Clarinda will use ‘flying launches’ which allows tunnelling to begin while the TBM continues to be built
from behind, from a smaller launching area. In total, each TBM will take about three months to assemble and will travel up to 90 metres a week.
In Burwood, excavation of the second SRL East TBM launch site has passed the half-way mark and is on track to be finished by midyear – with tunnelling from Burwood to Glen Waverley also set to begin in 2026.
Trains are expected to start running on the project in 2035.
Inland Rail has released designs and visualisations for upcoming works on two areas of the Hume Freeway, as well as a bridge replacement at Marchbanks Road, in Victoria.
Inland Rail is lowering the tracks under the Hume Freeway at Tallarook and Seymour and replacing the Marchbanks Road bridge to provide sufficient height and width clearances to allow the safe passage of double-stacked freight trains through these sections.
At the Hume Freeway sites, tracks will be lowered by 1.5 metres to 2.1 metres under the bridges and work will be undertaken up to 500 metres to one kilometre
The route will be about 1700 kilometres and include more than 1000 kilometres of major upgrades. Image: NSW Government
either side of the bridge to create the safe gradient and clearance for doublestacked trains.
In Seymour, works will extend up to one kilometre south and 700 metres north of the bridge.
The new Marchbanks Road bridge will be higher and wider and will replace
the existing structure on the same alignment. The new bridge will also feature four-metre-wide traffic lanes and safety screens.
Inland Rail and construction partner John Holland will present the new visualisations and provide more information at several community engagement sessions.
The designs for each Sydney Metro –Western Sydney Airport station have now been finalised.
Each station will complement the qualities of the Cumberland Plain landscape and aim to establish a sense of connection.
First Nations design professionals Djinjama, with lead architect Hassell, were engaged to lead the design process, and collaborated and engaged with key Knowledge Holders of Country throughout.
The final designs feature colours, textures and materials derived from Country and these will be experienced by passengers throughout stations, including communal areas like plazas, walkways and buildings.
Feedback from stakeholders and community members was incorporated into the final station designs after initial plans were exhibited during a consultation period.
Sydney Metro is a jointly funded public transport project by the Federal and New South Wales governments.
The project’s scope involves building, operating and maintaining a network of four metro lines, 46 stations and 113 kilometres of new metro rail, expected to open in 2032.
The project will connect Sydney’s northwest, west, southwest and greater west with new metro services and fully accessible stations. The metro program includes the operational M1 Line and
three projects under construction: the Southwest, West and Western Sydney Airport projects.
Once completed, Sydney’s new metro railway will have a target capacity of about 40,000 customers per hour, compared to Sydney’s current suburban system which can reliably carry 24,000 people an hour per line.
The first tracks have been laid at Luddenham for the Sydney Metro – Western Sydney Airport line as the 23-kilometre new metro railway takes shape.
The first portion of track was installed at Luddenham, just north of a new rail bridge that will take metro services over the future M12 motorway.
Synergy’s Collie Battery Energy Storage System is set to become one of the biggest batteries in Australia. When completed, the 500-megawatt battery with 2000 megawatt hours of energy storage will be able to power around 785,000 homes.
The Collie battery, situated about 200 kilometres south-east of Perth, will help to replace coal-fired power generation with renewable energy generation infrastructure and energy storage solutions.
The battery is Synergy’s third gridconnected battery, with two existing battery energy storage systems in Kwinana (KBESS1 and KBESS2) supporting the reliability of Western Australia’s energy system.
The battery is on track for completion later this year. Construction and installation begun in May 2024, with commissioning works now commencing.
Brand new upgrades will help to modernise and increase accessibility for the heritage-listed Moss Vale Station in New South Wales.
Two new lifts will be in operation for the first time, each located at the ends of the existing Argyle Street footbridge.
In addition to the lifts, a second stage of work has delivered a new pedestrian ramp and stairs from Argyle Street, resurfacing to Platform Two, installation of Audio Frequency Induction Loop Systems (AFILS)
– also known as hearing loops – on both platforms, and enhanced the accessible pedestrian pathway in the station forecourt.
Delivered through Transport for NSW’s Safe Accessible Transport (SAT) program, these upgrades acknowledge the station’s important role in the Moss Vale community.
The work will ensure Moss Vale Station meets Disability Standards for Accessible Transport 2002 (DSAPT) and complies with the Disability Discrimination Act 1992 (DDA). The next stage of work will deliver
improvements to the Lackey Road entrance, forecourt and Daly’s Way and is expected to be completed in June.
The NSW Government is also upgrading the stabling yard to improve functionality and accessibility for current train storage and operations, and to accommodate the new Regional Rail fleet.
Parliamentary Secretary for Regional Transport and Roads Anna Watson said the opening of new lifts brings the historic station into the 21st century.
The South Australian Government will launch a new pilot program in 2026 that aims to support up to 1000 new apprenticeships in the construction sector, as part of efforts to address shortages in the state’s civil construction workforce.
The Industry Accelerated Apprenticeship Pilot (IAAP) is an Australian first program, which will focus on several high-demand trades: carpentry, civil construction, plant operations, mechanical engineering, and fabrication engineering.
Planning by South Australia’s Department of State Development estimates that the state will need 78,000 additional vocational qualifications over the next five years to meet forecast demand.
South Australia already offers a flexible apprenticeship framework,
which allows early completion in some trades. The South Australian Skills Commission will be tasked with undertaking stakeholder engagement
across industry, unions, employers, and
THE CUSTOMER ALWAYS COMES FIRST FOR MATTHEWS BROTHERS ENGINEERING, ONE OF THE BIGGEST REASONS WHY THE COMPANY IS EXPANDING ITS BUSINESS FROM THE EAST COAST TO THE WEST. GENERAL MANAGER RICHARD BAILEY EXPLAINS.
From agriculture, to mining, transport and even World War II, Matthews Brothers Engineering’s (MBE) expertise has contributed to, and intersected with, a wide variety of industries and historical events.
No matter the decade, industry or task at hand, MBE has taken great pride in delivering the best possible outcomes – a philosophy that’s sustained to this day.
Richard Bailey, General Manager –MBE says the manufacturer of Bitumen Sprayers, Bitumen Road Tankers, Tack Coaters, Bitumen Melting Tanks and Aggregate Spreaders has successfully delivered on this vision for its strong customer base on the east coast of Australia.
But what about its customers around the rest of Australia?
Acknowledging the challenges presented by interstate communication with operators, MBE’s leadership began discussions around how the company could better cater for its Western Australian customer base.
“We’ve got a great presence on the east coast, and we support our customers really well,” Bailey says.
“But there will be times when a Western Australian customer might ring up on a Friday afternoon to ask for a part. Due to the time difference, our production staff might be unavailable or closing for the day, but for the WA customer it’s still the morning.”
Bailey’s well-rounded skill set and broad understanding of business operations across several roles at MBE, under the tutelage of company Director Paul Matthews, made him an ideal candidate to become the company’s first permanent representative for the Western Australian market.
Paul Matthews, MBE Owner and Director, says Matthews Brothers is a proud Australian company that sees Western Australia as a key part of its future.
“Sending Richard across is a strategic move, not just to support our growth, but to deepen our relationships with valued customers in the region,” he says.
“WA is known for its laid-back lifestyle, but when it comes to equipment support, we know our customers want things done right and done quickly. The good news is, our gear rarely misses a beat, but when support is needed, we’ll have someone local to make sure downtime is kept to an absolute minimum.
“Richard brings a wealth of experience and the right attitude to represent Matthews Brothers. He’s there to support our current clients, form new partnerships, and ensure WA operators get the best of what we offer – Aussie-built trucks made tough for Australian conditions, backed by full parts availability and on-theground service.”
Bailey, who joined the company seven years ago, says the Western Australian move reflects not only the “exciting progression” of the company, but also his own growth in the business.
“Sally (Rolfe – Operations Manager) and I have worked really hard to drive efficiency across the business, we’ve brought in new equipment and new staff for key roles. That has allowed me to step back from the project management aspect of the role,” he says.
“The nature of my role has evolved a lot. I was originally brought in to run the design engineering department, but it just kept on expanding.”
The move marks MBE’s first major geographical expansion beyond the east coast, indicating the company’s ambition
to become a larger equipment provider.
Bailey says the shift also demonstrates MBE’s progression and growth, from a small family business to a more sophisticated operation.
“Seven years ago, would I have imagined that we’d be in Western Australia? No, probably not,” he says.
“It’s about getting amongst the customers and understanding how we can support them better. The need for a contact and representation in the west was a common theme in customer feedback.
“Without our customers, we’d be nothing, and our great Western Australian customers deserve the same level of
sprayer maintenance season. Bailey says a local presence will help to provide the technical support team with eye and ears on the ground, allowing them to diagnose equipment issues quickly, while also ensuring the correct replacement parts are ordered first time.
“The feedback that we’re getting around our support and maintenance is really positive, but that hasn’t stopped us from refining our process, as well as machinery upkeep, to make sure operators are keeping their vehicle within optimum running conditions,” he says.
“Our aim for the future is to effectively forecast and plan what stock levels we need to hold over here, so that we
“OUR GOAL IS TO ENSURE WE CAN CONSISTENTLY MEET CUSTOMER DEMAND FOR PARTS, IN TERMS OF BOTH AVAILABILITY AND LEAD TIME.”
support that we offer on the east coast. We want our customers to have the opportunity to take advantage of local spare parts and maybe in time, service and maintenance support or even local manufacturing. This move puts MBE one step closer to achieving that.”
Another key aspect of MBE’s expansion to the Western Australian market is the opportunity to provide local expertise and parts during the busy bitumen
can respond to client requests much more efficiently.
“We want to move away from ‘we’ll get that to you in a few days’, to being able to provide requested parts to our customers as early as the next day, maybe even same day, by getting ahead of the demand. Our goal is to ensure we can consistently meet customer demand for parts, in terms of both availability and lead time.”
Bailey adds that this approach will be gradual and customer-led, saying MBE will evolve support capabilities
based on what customers actually want and need.
“We want to deliver the same level of service, that’s comparable to our east coast operations, with the flexibility to adapt to local market requirements,” he says. “In terms of delivering on what the customer wants, MBE has set the benchmark in this area. MBE sprayers are the number one sought-after unit, so we want to be able to deliver this and more to operators and fleet managers.”
The quality of this service is not only a priority for MBE, but also a matter of personal pride. As Bailey explains.
“I’m very proud of the product that we can offer, it’s one that we’ve been able to stand behind, time and time again,” he says.
While it is an exciting shift, Bailey explains that MBE’s WA presence is still very much in its infancy, with what has been
achieved so far being a building block for future success.
“The sky’s the limit, but at the core of every decision is servicing our customers and exploring how we can provide a better service for them,” Bailey says. “That’s a journey that’s ongoing and one that we’re looking forward to taking with our clients into the future.
“I’m excited to work with our partners and clients to say, ‘let’s build something together’. That’s what it’s all about.”
THIS MONTH, WE ASKED THE INDUSTRY’S DECISION-MAKERS, WHAT’S NEXT WHEN IT COMES TO DECARBONISING THE INFRASTRUCTURE AND TRANSPORT SECTORS?
DUNCAN ELLIOTT, CHIEF EXECUTIVE OFFICER – MAJOR ROAD PROJECTS VICTORIA
North East Link has become the first infrastructure project in Australia to receive the internationally recognised PAS2080 certification – a global standard that focuses on the management of carbon emissions in infrastructure projects. This standard has assisted us in making tangible reductions in the emissions associated with the design development and ultimately operation of the North East Link. Some of the measures that have been implemented across the project include ensuring 100 per cent renewable electricity is used during construction, supplementing concrete with low carbon recycled materials, and committing to net zero emissions in the operation and maintenance of North East Link.
Image: Major Road Projects Victoria
SARAH BACHMANN, CHIEF EXECUTIVE OFFICER – NATIONAL PRECAST CONCRETE ASSOCIATION AUSTRALIA
Precast concrete structures offer long-term environmental benefits that extend well beyond construction. Over their lifespan, precast structures naturally reabsorb carbon dioxide through a process known as carbonation, helping offset a portion of the emissions from production. Their high thermal mass also contributes to energy efficiency by regulating indoor temperatures, reducing reliance on heating and cooling systems. The industry is further advancing sustainability through the increased use of supplementary cementitious materials such as recycled slag and flyash, which lower embodied carbon. Together, these features make precast concrete a smart, sustainable choice for resilient, energy-efficient buildings and infrastructure across Australia.
Image: National Precast
TANJA CONNER, CHIEF EXECUTIVE OFFICER – AUSTSTAB
The next frontier in decarbonising the infrastructure and transport sectors lies in scaling up circular practices, low-carbon materials, and smarter asset management. For the pavement recycling and stabilisation industry, this means increasing the use of reclaimed materials, adopting alternative binders with lower embodied carbon, and embedding lifecycle carbon assessments into every project. In-situ stabilisation offers a proven, immediate pathway to cut emissions by reducing haulage, material use, and construction time. Coupled with data-driven design and performance monitoring, these innovations can deliver resilient, low-emission road networks – helping the sector meet sustainability targets without compromising on safety
If you or someone at your organisation is an industry leader and would like to be a part of this monthly column in 2025, please get in
THE NATIONAL TRANSPORT RESEARCH ORGANISATION (NTRO) IS LAUNCHING ITS BRAND-NEW NTRO PROJECT AI PLATFORM, AN INNOVATIVE TOOL THAT WILL GIVE TRANSPORT AGENCIES UNPRECEDENTED ACCESS AND INSIGHT INTO POTENTIAL PROJECT CHALLENGES. NTRO CEO MICHAEL CALTABIANO EXPLAINS.
Cost and scheduling overruns continue to be a significant impact on infrastructure delivery.
According to a report filed in 2020 by the Grattan Institute, costs exceeded budgets in 21 per cent of projects (valued at $20 million or more) completed
over the past two decades. It’s why the National Transport Research Organisation (NTRO) has been working on a brand-new platform, aimed at directly addressing this industry issue.
NTRO Project AI is an innovative tool developed in conjunction with Octant AI, that uses artificial intelligence to predict and prevent cost overruns in transport infrastructure projects.
The platform reviews project data monthly and uses advanced learning algorithms to forecast potential cost escalations three to six months in advance.
major problems.
NTRO Chief Executive Officer Michael Caltabiano says the NTRO holds a unique
responsibility in the sector, with the ability to advise both public and private industry on solutions that can improve the entire transport sector.
“The NTRO is in a really interesting position,” he says. “Our job is to provide insight, guidance and technical support on the challenges that transport agencies face into the future, to help them overcome these challenges through the application of technology, skills, standards and specifications.
“Over the past four to five years, it’s been clear that cost escalation on road, rail, port and airport projects is really costing the community, as less is being built with the same amount of money and a lot of it has been the consequence of cost overruns.”
A fortuitous run-in during an overseas trip provided a ‘light bulb moment’
for Caltabiano and the NTRO team, as he explains.
“Project management and the skills around project delivery are a field of endeavour in its own right. I was talking with some colleagues that I had met in my international travels from Oxford, who had developed an AI model to look into how projects change and whether some of the related challenges were predictable,” he says.
“We expressed interest in partnering to develop such a tool, that supports both the public and private sector with having a line of sight over project items, as well as a chance to prevent potential cost blow outs.
“If you know the problem you’re trying to solve, you can solve it before it becomes a massive problem.”
Project AI is the brainchild of Octant AI and its Co-Founders, David Porter and Cuong Quang. Both colleagues of Oxford University, Porter and Quang’s combined knowledge of the construction industry and Artificial Intelligence technology helped to pave the way for the innovative tool. As Porter explains.
“Every project and portfolio has only three outcomes: benefits outcome, completion time outcome, and completion cost outcome. When things don’t turn out as expected, it hurts all stakeholders,” he says.
“Now people are listening and the value of accurately predicting cost and time outcomes is increasingly understood in a world that’s increasingly uncertain. If you can increase [project] certainty, then the whole world is a better place, and we’ve developed some technology which is quite unique in its ability to do that.”
Quang says that before the NTRO came onboard, it was imperative for the company and the platform that benchmark performance and value were demonstrated on real projects. Not only to deliver on Project AI’s promised features, but also to justify its use in both the public and private sectors.
“These were rail projects, road projects and more. These projects not only helped us to develop the technology, but became very important proof points for the NTRO,” he says.
“What came out of that was independent validation that what we said
that become increasingly accurate as more data sets are added to the platform.
NTRO Project AI can also learn more and provide increasingly accurate assessments on a given project as works progress, providing comprehensive insight across the entire project lifecycle. The tool has so far been validated through several case studies, particularly with Queensland’s Department of Transport and Main Roads.
Caltabiano says these trials have reflected the platform’s ability to provide greater certainty, improve project management, and deliver better value for money in infrastructure development.
“It’s been a great project and partnership in understanding the geography of Australia, how projects are delivered and running these models over projects that have been completed, and seeing where projects went wrong,” he says.
“We have seen over the last two years, through our work with industry and government, Project AI’s ability to predict what can go wrong and then observe lessons from those mistakes.
Equipped with a range of data collection systems, iPAVE can assess both the structural and functional
we with them. They had the vision to realise that sooner or later, AI would be addressing everything, and they
“WE ARE WORLD LEADING IN OUR ABILITY TO PROVIDE INSIGHT INTO AIRPORT, PORT AND ROAD STRUCTURE PERFORMANCE, SO THAT WHEN CONTRACTORS GO OUT TO DO MAINTENANCE, THEY’VE GOT THE MOST ACCURATE DATA SETS TO ALLOW THEM TO DELIVER WORKS ON TIME AND ON BUDGET.”
condition of the road, using laser technology to look at characteristics including roughness, surface texture, and rutting. The iPAVE can also collect sub-surface data at the same time, giving experts a better understanding of what’s happening underneath the road surface.
“It’s the NTRO’s goal that we can be a partner and set up the sector for success throughout the whole life cycle of design, data capture, setting up the project for success, building the project, using Project AI to deliver turn costs and then monitoring the performance of the road, port or airport using iPAVE for
understood the value of the technology,” Porter says.
“If you can increase that certainty, then the whole world is a better place, and that’s a really worthwhile thing to strive for.”
Quang agrees, saying that the sky’s the limit when it comes to Project AI, as well as the on-going partnership with the NTRO.
“Seeing that technology being transformed into actual value, something that improves the way these projects perform. That’s what really excites me,” he says.
Contact our Sripath Asia-Pac team at ravi@sripathapc.com or 1800 191 799
AS DARWIN CONTINUES TO GROW, SO TOO DOES THE PRESSURE ON ITS ROAD, PATH, AND DRAINAGE NETWORKS. TO STAY AHEAD OF AGEING ASSETS AND RISING EXPECTATIONS, THE CITY OF DARWIN HAS PARTNERED WITH CIVILTECH SOLUTIONS.
With a road network shaped by tropical rains, high temperatures, and heavy vehicle use, the City of Darwin faces unique challenges in maintaining its civil infrastructure.
To meet these demands the City of Darwin engaged Civiltech Solutions to deliver a comprehensive asset data capture program across its road, footpath, driveway and drainage networks.
Civiltech Solutions, a Darwin-based civil engineering firm with national reach, won the contract in 2024 to provide
city’s transport assets.
The goal – better insights, clearer investment decisions, and safer infrastructure outcomes for the community.
The platform – developed by infrastructure intelligence platform Cyvl and deployed by Civiltech – combines light detection and ranging (LiDAR), highresolution imagery, and Global Navigation Satellite System (GNSS) positioning to capture asset location and condition at scale.
Within weeks, the system had mapped
assets – giving the council one of its most complete asset datasets to date.
Nik Kleine, Executive Manager of Infrastructure for the City of Darwin, says the council is required to undertake a renewal of its assets every four years as part of the Local Government Act.
“We saw this as an opportunity to not only uphold our requirements as stated in the Act, but also to access a richer data source than we’ve ever been able to have before,” says Kleine.
“We have found the information provided by Civiltech to be invaluable,
Civiltech Solutions data can be used for a number of things, including checking line marking and damage on roads operated by local governments.
“THE AUTOMATION OF THE PROCESS AND THE FACT THAT IT TAKES HUMAN INTERPRETATION OUT OF THINGS WAS ATTRACTIVE TO US.”
Beginning the sweep of the municipality in October 2024, Kleine says the City of Darwin was excited to begin the journey and access a new range of information.
Among the most impactful insights, were more than 12,000 road signs being located and assessed for presence, condition, and visibility, while 22,570 pavement markings were recorded and evaluated for clarity, wear and compliance.
High-resolution condition data was also captured for kerbs, footpaths, pram ramps, and pavement surfaces, using LiDAR and imagery to detect cracking, rutting, displacement, and other structural issues.
“This data is something the council has been after for some time,” says
Kleine. “We learnt in 470 kilometres there are 28,749 trees. This is relevant information for the council to have, both from an operational but also a strategic perspective.
“The next steps are identifying which types of trees they are. This means we can start to view our street trees as assets, which is something many councils are moving towards.”
Delivered in Geographic Information System (GIS)-ready formats, the dataset has empowered Darwin’s infrastructure team to develop forward-looking works programs and clearly communicate priorities to decision-makers.
With the data on roads, Kleine says he and the asset management team have been able to construct in-depth asset management plans to present to the councillors.
“We now have information on pavement conditions right across the whole municipality,” he says.
“The maintenance team can now easily get a snapshot of the network and pull together a maintenance program for the next two to three years.
“This plan can then be shown to elected members or other forms of government, displaying what needs to be repaired and the amount of money that would be required to do that.”
One of the most attractive aspects of the partnership for the council has been the ease of accessibility to data.
Kleine says previous data collection involved looking at videos of roadways and then interpreting the data into the database.
“Prior to Civiltech, collecting that type of information was done manually by us,” he says.
“The automation of the process and the fact that it takes human interpretation out of things was attractive to us.
“Whilst there are nuances that you have to work with to apply the data, it replaces the boring aspect of manual data collection.”
As soon as the council started using the program, Kleine says the council knew it would be a huge time saver.
“Having the data filtered straight into our asset management system means there is little room for error,” he says.
“Being able to repeat that same
assessment the same way every single time also takes out any sort of bias.”
Leigh Carnall, Founder and Chief Executive Officer, Civiltech Solutions says there is no limit to how the data can be accessed.
“The data can be exported into any format from Excel to web maps, depending on how each council prefers to integrate it,” he says.
“We want the City of Darwin to have full access to all transport asset data in a digital format.”
EVOLVING WITH COUNCIL NEEDS
Working with the City of Darwin has enabled Civiltech Solutions to refine and expand how its platform supports local government workflows.
“There’s growing interest in treating footpaths as managed assets,”
“WE HAVE ALSO BEEN TRIALLING ASSESSMENTS FOR PRAM AND DISABILITY RAMPS WHICH IS SOMETHING WE ARE STILL WORKING THROUGH.”
Carnall says. “Just like roads or kerbs, they deserve regular assessment and that starts with better data.”
“Our role is to give councils the tools to measure, monitor and plan with confidence.”
In response, Civiltech has enhanced its platform’s ability to identify surface cracking, displacement, and accessibility issues such as non-compliant kerb ramps and trip hazards.
These updates help councils move beyond basic inventory to understand the true condition of their pedestrian networks.
“There’s growing interest in this technology to understand footpaths as
managed assets, just like roads or kerbs,” Carnall says.
“Our role is to provide councils with the tools to measure, monitor and plan with confidence.”
By listening to council needs and building in flexibility, Civiltech is helping local governments take the next step in infrastructure intelligence – combining innovation with practical, on-theground outcomes.
These new features are already in use and available to councils across Australia.
Especially those looking to make smarter, more confident infrastructure decisions without increasing inspection effort.
SRE’s telescopic bitumen sprayers or our newly developed 8m fixed wing bitumen sprayers are available for early 2026 delivery.
Fully compliant with all Australian regulations our sprayers meet all Austroads performance requirements for bitumen sprayers and are ready to go straight to work.
GEOTAB HAS RELEASED ITS 2024 SUSTAINABILITY REPORT ANALYSING ITS CURRENT POSITION ON ITS AMBITIOUS GOALS, ALL WHILE HELPING THE INFRASTRUCTURE INDUSTRY WITH ITS OWN.
As one of the global leaders in connected transport, Geotab recognises its responsibility to lead by example in reducing emissions and promoting sustainable practices.
The telematics company has committed to achieving net zero emissions by 2040 and a 50 per cent reduction of greenhouse gas emissions by 2030.
These ambitious goals and its progress have been highlighted in Geotab’s 2024 Sustainability and Impact Report.
Will Batty, Associate Vice President, Business Development at Geotab says the report is Geotab’s way of being transparent on a key pillar of the business.
“We want to be at the forefront of the industry when it comes to sustainability, and this report is Geotab’s way of displaying the commitments we have in place,” he says.
“We want to be an innovative driver in the industry as we continue to push innovative solutions for all industries, including the roads and infrastructure sectors.”
For more than 20 years, Geotab has invested in ground-breaking data research and innovation to enable partners and customers to transform their fleets and operations.
This is on top of providing telematics, vehicle and asset tracking solutions to over 55,000 customers in 130 countries, including Australia.
Connecting to over 4.7 million vehicles and processing more than 80 billion data points a day, Geotab aids its customers in increasing productivity and achieving their sustainability goals.
As a global leader in telematics, with millions of subscriptions around the world, one of the biggest impacts Geotab can have is assisting the transportation industry’s transition to a clean future.
Two years ago, Geotab launched its Impact Agenda to focus its efforts on three core areas where it can make the biggest difference.
These include accelerating decarbonisation in vehicle fleets, powering driver and road safety and advancing progress to net zero through data, research and partnerships.
“We know the transportation industry is rapidly evolving and having access to data that empowers the roads and infrastructure industry to plan, manage and transparently report on progress is essential,” says Batty.
With this model, Geotab hopes its customers can build a foundation for working through their own sustainability goals.
“Many of Geotab’s customers are now looking for ways to drive more sustainable practices right across the roads and infrastructure industries,” says Batty.
“Whether its transitioning to electric vehicle fleets or looking at ways to reduce fuel wastage or reduce carbon emissions, they are actively working on their sustainability.”
“One of our motivating factors from the report is to help our customers understand how to move their data into actionable insights.”
Geotab’s newly launched Sustainability Centre can provide actionable insights to address decarbonisation, cost management
“THE SAFETY CENTRE USES SMART TECHNOLOGY TO PREDICT AND PREVENT RISK. WE WANT OUR CUSTOMERS TO MOVE FROM A REACTIVE STANDPOINT TO A PROACTIVE POSITION WHERE WE CAN PREVENT
ACCIDENTS FROM HAPPENING.”
Batty says those in the sector can use Geotab’s tools to focus on key metrics such as excessive idling or driver behaviour to reduce costs, while also delivering a reduction in carbon dioxide emissions.
“There are a number of tools in the platform that are relevant to the roads and infrastructure industries and can help drive sustainable practices,” he says.
“In 2024 particularly, Geotab launched a number of new tools and resources that can help support organisations with their efficiency and electrification goals.
and opportunities to improve performance.
“This centre helps customers balance the dual challenge of enhancing operational efficiency while minimising their environmental impact,” says Batty.
“The Sustainability Centre is a fleet’s environmental dashboard and a central platform where businesses can easily see the environmental impact on aspects like fuel consumption and carbon dioxide emissions.”
Batty says the Sustainability Centre can also help guide customers transition from a traditional vehicle fleet into an electric vehicle fleet.
“This assists fleets in determining which vehicles are suited for electrification, because not every vehicle today is suitable to be an electric vehicle replacement,” he says.
“It looks at historical patterns like distance travelled, maintenance and fuel cost while also looking at the overall environmental impact and the cost to acquire an electric vehicle. All used to analyse the potential transition to an electric vehicle.”
In addition to the establishment of the Sustainability Centre, Geotab has also introduced its Safety Centre.
Described by Batty as a central hub for fleet safety, the Safety Centre unites all data in one place to aid businesses when making decisions about safety.
Two of Geotab’s focusses include driving sustainability in the industry and promoting the safety of drivers and their vehicles.
“The Safety Centre uses smart technology to predict and prevent risk,” Batty says.
“We want our customers to move from a reactive standpoint to a proactive position where we can prevent accidents from happening.”
For example, Batty says fleet managers can look at patterns in risky driving to potentially avoid accidents from occurring.
“This is done so we can get ahead of the game and help drivers stay safe on the road,
reduce accidents and lower expenses that are associated to them.”
With over 700 partners and 55,000 companies using Geotab worldwide, Batty says Geotab hopes the report can help pave the way when it comes to everyone’s own sustainability goals.
“A change in thinking is required when it comes to sustainability where we start to think of it more as a competitive advantage, and at Geotab we have a number of different tools that the roads and infrastructure industries can utilise to further their sustainability goals,” says Batty.
“Geotab can support their transition to electric vehicles, and we can also look at improving safety and reducing risks, as we know safer operations means fewer accidents and less downtime.”
“We can also provide the data to help businesses report on their sustainability performance,” he says.
In the past year, Batty says Geotab has noticed a growth in its sustainable solution adoption across the company.
“Sustainability is driven by practical benefits such as cost savings, and not just about things we can do to help lower emissions,” he says. “There has been a 39 per cent increase in
the use of Geotab’s sustainability platforms, which means the tools are being used by our customers.”
Batty says Geotab understands the urgency of climate action and the need to accelerate decarbonisation and the circular economy.
Geotab employs the Greenhouse Gas Protocol Corporate Accounting and Reporting Standards for emissions disclosure. It analyses three scopes across the board compared to a 2019 baseline.
Scope One looks at direct emissions sourced, owned and controlled by Geotab. Scope Two is comprised of indirect emissions from electricity, steam, heat and cooling.
Scope Three is comprised of indirect emissions from the supply chain through the procurement of goods.
In 2024, Geotab achieved a 40 per cent reduction in Scope One and 78 per cent in Scope Two. Batty says the decrease is primarily due to changes in facility operations and signifies a shift in the right direction.
“In 2024, Geotab continued to make progress in decreasing direct operational emissions,” he says. “We are actively exploring opportunities to increase renewable energy procurement and are evaluating the feasibility of on-site renewable energy generation to support our sustainability goals.”
“In an industry where project overruns are commonplace and practices have remained largely unchanged since the middle of last century, Octant AI’s predictive capability is revolutionary.”
—Bent Flyvbjerg, Saïd Business School, Oxford University
& INFRASTRUCTURE HELPS YOU KEEP UP WITH THE LATEST MOVEMENTS ACROSS THE ROADS AND INFRASTRUCTURE
Glen Billington has been appointed General Manager – Defence after a distinguished career with the Australian Army before transitioning to the Army Reserve. During this time, Billington completed a range of appointments relating to the planning and delivery of Defence facilities, including a secondment to the Department of Prime Minister and Cabinet. Billington’s experience in the policy, planning and delivery of capital works projects spans the United Kingdom, Middle East, Pacific Region, and Australia. Rod Aves has also joined Laing O’Rourke from Babcock International Group in the United Kingdom in the role of Programme Director – AUKUS. Aves has an extensive global nuclear new build background, having worked on nuclear project delivery across many technologies and continents. He has also held nuclear licensee appointments in both Civil and Defence sectors. Most recently, Aves led infrastructure delivery at Devonport Royal Dockyard to enable full lifecycle Maintenance of the United Kingdom Astute class submarines.
Glen Billington (left) with Rod Aves. Image courtesy of Laing O’Rourke.
Georgiou has announced the appointment of Nick Fryday as the new General Manager of the company’s New South Wales Business Unit. Fryday will step into a key leadership role that will shape the future of Georgiou’s operations across New South Wales. Fryday brings experience in infrastructure delivery, as well as a leadership style and set of values that strongly align with Georgiou’s culture. With a career that has taken him from Ireland and New Zealand to regional New South Wales, Fryday brings more than two decades of hands-on industry knowledge. He holds a Bachelor’s degree in Civil Engineering and Mathematics, a Master’s in Project Management, and is a Chartered Professional Engineer (CPEng). Fryday’s impressive portfolio includes senior leadership on complex infrastructure projects such as the Georgiou CPB Joint Venture M12 Motorway West Project, Dubbo Regional Rail Maintenance Facility, and Northern Road Stages Five and Six. Fryday’s breadth of experience spans multiple delivery models – PPP (Public Private Partnership), D&C (Design and Construct), ECI (Early Contractor Involvement), Construct Only and Alliances.
Image courtesy of Georgiou.
Aurecon has appointed Todd Battley as its new Chief Executive for Australia. Battley will work closely with incoming Group Chief Executive Officer Louise Adams and other members of Aurecon’s Group Executive Leadership Team to drive strategic growth across Australia and shape Aurecon’s global response to the future of engineering, design and advisory services. Battley joins from AECOM where he held roles including Chief Strategy Officer and Chief Executive for Australia and New Zealand. Throughout his 29-year professional career he has developed a purpose-driven and collaborative leadership style focused on inspiring innovation and achieving business growth.
Image courtesy of Aurecon.
The Australian Institute of Architects has announced the appointment of Adam Haddow as National President of the Institute and David Wagner to the position of National President Elect. Haddow’s tenure will begin at the conclusion of the 2025 Annual General Meeting, with Jane Cassidy’s tenure ending as National President, instead moving to the position of Immediate Past President. Haddow is a strong advocate for the value architecture brings to communities throughout Australia and the world. He is a firm believer that Australia’s future will be better where architecture and design thinking are prioritised, and that good design can deliver both economic benefits and improved health and wellbeing outcomes. With over 30 years’ experience across diverse scales and typologies, Haddow’s contributions to architecture are recognised both nationally and internationally. Wagner is an experienced architect, a dedicated advocate for the profession, and the newly appointed National President Elect of the Australian Institute of Architects. With over 30 years of practice in Melbourne, Canberra, and London, Wagner is a partner at Atelier Wagner, a studio he co-founded in 1998. Wagner is especially focused on how innovation and design led policy can enable more sustainable, liveable, and equitable built environments. He brings a broad perspective on practice, advocacy, and education to his leadership role.
Image courtesy of the Australian Institute of Architects.
The Federal Government has announced seven new appointments to the Australian Rail Track Corporation (ARTC) and the National Intermodal Corporation (National Intermodal) boards. Ingilby Dickson, Janet Finlay, Michael Carter and Jill Rossouw have been appointed for three-year terms, and Marlene Kanga for a two-year term, as Non-Executive Directors of the ARTC Board. Other announcements include Michael Carter’s appointment as Deputy Chair, Janice van Reyk as Non-Executive Director and the reappointment of Michael Byrne as Non-Executive Director of the National Intermodal Board, each for a three-year term. Dickson is expected to provide the ARTC Board with expertise in freight, supply chain, rail and safety following his roles with Sadleirs Transport Group, Ron Finemore Transport and the Australian Logistics Council. Finlay has held roles across multiple sectors as well as government, including as the Deputy Chancellor of Adelaide University, Director of the SA Water Corporation and Deputy Chair of the State Planning Commission of South Australia. Carter has a strong construction background and rail experience, principally in rail operations, including at Queensland Rail and Aurizon Holdings. Rossouw is an experienced director, having held Non-Executive Director positions with the Port of Brisbane and the Brisbane Airport Corporation. She is the current Chair of the High Speed Rail Authority. Kanga has extensive board director experience, having been a board member of Endeavour Energy, the Sydney Water Corporation, Innovation Australia and Airservices Australia. van Reyk has held roles at NSW Ports, Port of Melbourne/Ports Victoria and the Australian Naval Infrastructure, with Byrne being an existing director of National Intermodal with experience in the ports, logistics and supply chain sectors, as well as board roles with the CBH Group and Peel Ports UK.
SRIPATH ASIA-PAC’S RELIXER® ASPHALT REJUVENATOR IS AMONG THE LEADING GLOBAL REJUVENATION TECHNOLOGIES, WITH MORE THAN A DECADE OF APPLICATION TO SHOW FOR IT. THE PIONEERS BEHIND RELIXER SIT DOWN WITH ROADS & INFRASTRUCTURE TO EXPLAIN MORE.
While it may seem like a blanket statement, the use of RAP (Recycled Asphalt Pavement) is increasing globally day by day.
Australia in particular has seen an influx of RAP applications over the past decade, becoming the largest source of recycled material used to replace conventional materials nationally, according to a report by Infrastructure Australia.
While asphalt can be fully recycled, asphalt mixes exceeding 25 per cent RAP are typically dosed with an asphalt rejuvenator to help restore the functionality of the aged RAP binder.
It’s here that Sripath has shone, providing guidance and products that have led to more sustainable outcomes nationally while also helping to support greater sustainability in North America, Asia, Europe, and South America.
John Riccardi, Customer Service Manager at Sripath Asia-Pac, says the company’s philosophy is as simple, as it is critical.
“Sripath has close to 20 years of experience in being a customer-centric organisation,” Riccardi says. “We are proud of our ability to handle complex logistical situations and provide top-notch customer service and technical support to our Australian customers.”
ReLIXER, the company’s asphalt rejuvenator, has helped contractors worldwide reduce their costs and carbon footprint for more than a decade without sacrificing roadway performance and durability.
Comprising a blend of green bio-based oils, ReLIXER helps to restore functional balance of aged bitumen in RAP, reducing the need for virgin bitumen and aggregates.
Jill McConaghie, Marketing Specialist at Sripath, says the difference in outcomes can be night and day when ReLIXER is or isn’t used.
“Every region of the world does it differently, but the end result is the same,” she says. “You can utilise higher levels of RAP when you have an effective rejuvenator like ReLIXER in your pocket.
“When you utilise a high RAP mix, and you add a rejuvenator like ReLIXER, you get a roadway with a performance similar to or better than a roadway without RAP.”
ReLIXER not only supports sustainability by allowing the use of higher levels of RAP in an asphalt mix; it is also sustainably produced. It’s highly dosage efficient, with production also leaving no burden on food sources.
It was essential to Sripath that the company take a transparent and accountable approach to the sustainable production of environmentally conscious products like ReLIXER.
That’s why ReLIXER, among several other Sripath products, has an independently verified Environmental Product Declaration available to view anytime on its website.
In addition to production considerations, Sripath Technologies also sought to deliver a product that was as user-friendly as it was versatile, as Ravi Rajagopalan, General Manager of Sripath Asia-Pac, explains.
“ReLIXER is highly efficient at low dosing levels, easy to incorporate in a mix plant, non-hazardous, and safe to handle,” he says. “Our customers are routinely utilising ReLIXER with a range of conventional and PMB (polymer modified) binders to pave high-RAP mixes on roadways in Australia.”
ReLIXER’s qualities have been tested with several field projects aiming to demonstrate the product’s effectiveness.
Just one of these was a project led by the Australian Flexible Pavement Association (AfPA), which organised a national pavement rehabilitation project in Queensland to evaluate the use of high-RAP mixes dosed with a rejuvenator.
The trial was conducted on Hymix Road, a quarry road in Gaven, Queensland and involved several major stakeholders, including Austroads, the City of Gold Coast, Fulton Hogan, and RMIT University.
The selected road featured pavement ranging from good to poor condition, with the surface having to cater for large machinery, and with heavy vehicles making up 60 per cent of vehicle traffic on the connection.
“The whole idea of the project was to demonstrate that ReLIXER works with local materials, gives you the benefit you’re looking for, using local standards and local materials, on top of being tested by local labs,” McConaghie says.
The project used a mix of 40 per cent RAP, an A15E PMB binder, and a rejuvenator to pave a wearing course on the road.
ReLIXER performed strongly, exemplifying the rejuvenator’s ability to adjust to different regional testing standards, meet viscosity requirements, and enable more environmentally friendly road construction methods in the future.
that we not only wanted to do a project to lay down some of the product onto a roadway, but we also wanted to look at the durability and do some follow-up studies,” McConaghie says.
Professor Filippo Giustozzi, Royal Melbourne Institute of Technology, says that projects in Australia and across the globe continue to validate Sripath’s claims, and that the product is among the leading rejuvenator technologies available.
“Sripath has tremendous amount of technical data evaluating the impact of
is being routinely used in Australia, the Americas, Asia, and Europe.
mixes and roadways around the globe,” he says.
“High-RAP mixes dosed with ReLIXER, consistently show superior fracture toughness and demonstrate long-term ageing performance.
“Asphalt mixes properly dosed with ReLIXER meet or exceed established specifications.
“It is gratifying to now have customers in Australia who are regularly using high-RAP mixes dosed with ReLIXER,” says Rajagopalan.
THROUGH CLOSE COLLABORATION AND CAREFUL DESIGN, GEOQUEST AUSTRALIA HAS AGAIN SHOWCASED ITS ABILITY TO DELIVER MAJOR INFRASTRUCTURE PROJECT COMPONENTS, THIS TIME ON THE LARGESCALE WILMAN WADANDI HIGHWAY PROJECT IN WESTERN AUSTRALIA.
Despite the name change – from Reinforced Earth to Geoquest Australia – one thing that’s remained consistent is the company’s ability to cater for major infrastructure projects.
Geoquest Australia has five decades experience of providing Reinforced Earth solutions to projects in Australia and New Zealand, combining three elements; controlled backfill, precast concrete facing panels and soil reinforcements to form a durable retaining structure.
These techniques for Reinforced Earth walls, also called mechanically stabilised earth (MSE) walls, were invented by Geoquest 60 years ago, and are now widely adopted in infrastructure projects worldwide.
Recent works on the Wilman Wadandi Highway in Western Australia have highlighted this capability.
The Wilman Wadandi Highway project is a 27-kilometre, four-lane road linking Forrest Highway to Bussell Highway, aiming to ease congestion and increase safety for motorists.
The use of Reinforced Earth walls and other precast elements were essential components of the project, with these structures designed to provide additional stability, protection and sound minimisation for road infrastructure.
But when it comes to tackling major transport projects, where do you start?
Rhys Senior, Regional Manager, Western Australia – Geoquest Australia says the company begins with early and proactive engagement.
“Geoquest has strong relationships with clients and client designers, so conversations begin six to 12 months before we have even started the design and supply for the project,” he says.
“It is a collaborative approach – to share advice and expertise that helps clients in the process.”
Geoquest Australia specialises in civil, structural and geotechnical engineering services, offering a wide range of tailor-
made solutions for a variety of applications. These are presented in five business lines –Retain (RE walls, TechWall, T-Wall, Steepened Slope), Cross (TechSpan arches and precast elements), Protect (Rockfall Protection –nets and barriers, and TechRevetment), Strengthen (Geogrids, Basal Reinforcement) and Precast, offering bespoke solutions to a wide array of market segments.
The company’s expertise has secured contracts for works on several nationally significant infrastructure projects, such as the West Gate Tunnel project, Brisbane’s Cross River Rail as well as a number of rail projects that form part of Victoria’s Big Build.
Senior believes the vast experience of Geoquest Australia’s team, as well as the company’s extensive technical capabilities, are just some of the key reasons for the organisation becoming a favourable provider nationally.
“We’ve been producing reinforced earth walls and precast solutions in Western Australia for many years,” he says. “For the past 13 years, we’ve also operated our own precast yards, which has provided us in-depth knowledge, and hands-on control over quality, consistency, and delivery. That in-house design and manufacturing expertise is a key strength.
“Geoquest has been manufacturing bespoke items in-house for many
years, and over that time, our team has developed a wealth of unique expertise. Several members of our design team have been with us for over 30 years – their accumulated knowledge is invaluable and truly irreplaceable.”
Senior says early collaboration with clients also helps to reduce potential design and technical challenges before they become costly problems during manufacturing, a crucial aspect of the Bunbury Ring Road works.
“Down the track, when we started to engage in manufacture and production, we’d already ironed out all the kinks,” he says.
One of the challenges highlighted was the discrepancy in foundation conditions between the northern and southern sections of the project.
The northern section, which connects Forrest Highway to Boyanup Picton Road, was situated on top of a flood plain, consisting of an interconnected network of smaller creeks.
This also created large differential sediments in some sections, an outlier for a state and city (Perth) that typically sees full height walls erected due to predominantly solid ground conditions.
These full-height walls, known as Geoquest Australia’s TerraTilt product offering, are precast concrete solutions that combine
selected granular, engineered backfill with steel tensile reinforcements and a modular precast facing system.
To offset the presented challenge, Geoquest Australia worked with the client to produce accurate readings on soil properties, loading requirements, geometric requirements, and architectural considerations.
This critical information helped Geoquest Australia to recommend the most viable walling solution. Which, in this case, was its TerraPlus designs.
TerraPlus is Geoquest Australia’s range of segmental walls that offer greater flexibility, thanks to the combination of smaller and more modular panels, providing a solution suitable for
challenging ground conditions.
As Senior explains, Geoquest Australia’s approach to project delivery allows the company to evaluate each individual project on its own merits, understanding that no single solution is capable of catering for every project.
“The client generally determines the geometry of the walls. From there, we take those measurements away to do a detailed design of individual panels and the soil reinforcement required to hold the walls up,” he says.
All up, Geoquest Australia supplied the TerraPlus and TerraTilt Reinforced Earth walls, used as both bridge abutments and retaining walls, approximately 1000 barriers and parapets, about 1200
panels and post retaining walls, as well as column formers.
Senior says the company is pushing to expand what is already a holistic range, with Geoquest Australia now a one-stop shop when it comes to integrated solutions such as MSE walls, precast concrete elements, rockfall protection and geosynthetics.
“We’ve diversified significantly the past few years. That was part of the reason why we’ve renamed our company from Reinforced Earth to Geoquest Australia, because our offering is now extremely diverse and far more than Reinforced Earth walls,” he says.
“On top of our proprietary precast arch system, TechSpan, and our other precast items, we also design, manufacture and supply a wide range of geo-synthetics, geo-grids, concrete revetment mattresses and rockfall protection systems. For geosynthetics, we operate manufacturing hubs in India and USA for all our products.
“Geoquest has a heritage of research, innovation and inventions, and we continue that path today. There are a lot of new products that we’re bringing into the market here in Australia, with both reducing carbon footprint in mind, as well as helping to robustly respond to fast-changing environmental conditions.
“I’m really excited to see what we can achieve in the next few years, with more projects getting underway and adding further to our capabilities.”
ATLAS COPCO’S B-AIR COMPRESSOR IS THE NEWEST ECO-FRIENDLY PIECE OF MACHINERY SET TO REVOLUTIONISE THE ROADS AND INFRASTRUCTURE INDUSTRY WITH POWERFUL, PORTABLE AIR.
There is a new electric air compressor on the market, which hopes to transform how the roads and infrastructure industry uses air compressors on site.
The Atlas Copco B-Air has been tipped as the world’s first mobile screw compressor powered by a battery.
David Buttigieg, Brand Leader for Atlas CEA, says this means operators will be able to use the B-Air in sensitive environments and urban areas, where strict noise and pollution regulations need to be adhered to.
“With a low noise level of 61 decibels at seven metres, it can deliver a full working shift of operation under typical conditions on a single charge, so it doesn’t hamper the ability to complete tasks,” he says. “It also removes the challenge of having to adhere
to strict timeframes or environmental conditions when completing larger jobs.”
The B-Air has been crafted with autonomy at the forefront, ensuring the machine can run for long periods of time without requiring a recharge.
KEY FEATURES
Buttigieg says the B-Air presents a suitable solution for the roads and infrastructure sector, given the industry’s increased focus on sustainability and operational efficiency.
“Making the switch from an internal combustion engine to an electric motor brings with it several benefits, including no local emissions being produced,” says Buttigieg.
The B Air saves 140 tonnes of carbon dioxide emissions, which is equivalent to the yearly use of about 30 passenger cars.
“With zero local emissions and significantly reduced noise levels, it directly addresses stringent environmental and occupational health and safety (OHS) requirements, particularly in enclosed or sensitive areas,” says Buttigieg.
“It is not only the way of the future, but more and more becoming a requirement to offer sustainable solutions, which is in turn driving industry behaviour.”
The B-Air is equipped with a 57-kilowattper-hour (KW/H) lithium-ion battery for emission-free operation.
Buttigieg says lithium-ion batteries are recognised in the industry for their versatility and high efficiency.
“This makes them suitable for a diverse range of applications due to their high energy density, relatively low selfdischarge rate and lack of memory effect,
making them suitable for electronics,” he says.
“One of the most notable advantages of lithium-ion batteries is their ability to withstand numerous charge and discharge cycles without significant degradation in capacity.”
Other batteries can experience a rapid decline in performance after a limited number of cycles.
However, Buttigieg says lithium-ion batteries can withstand hundreds of cycles while maintaining optimum performance, making them a clear choice for the B-Air.
Buttigieg says efficient design and reduced number of parts guarantees extra durability and peace of mind for operators, while extended intervals between regular maintenance grant savings on operating costs.
“The triple-enclosed, liquid-cooled battery pack and the overall rugged construction are critical for ensuring durability in the face of dust, moisture, and temperatures changes found on site,” he says.
“It also drastically reduces downtime and maintenance because the B-Air electric motor has far fewer moving –
“WHILE A REGULAR COMPRESSOR IS LIMITED TO A CERTAIN PRESSURE AND FLOW RATE, THE B-AIR CAN BE USED FOR A VARIETY OF APPLICATIONS, INCLUDING RUNNING AS A HANDHELD TOOL, FOR SANDBLASTING, OR FOR CABLE BLOWING,”
and therefore wearing – parts compared to a diesel engine compressor.
“It only needs service every 2000 hours, as opposed to 500 hours for a diesel engine unit.”
The B-Air has a range of safety features including PACE (Pressure Adjusted through Cognitive Electronics) technology.
This technology allows the compressor to have an adjustable working pressure from five to 12 bar (72-175 pounds per square inch).
Buttigieg says the PACE feature optimises the output specific to the task, reducing unnecessary strain on the compressor.
“While a regular compressor is limited to a certain pressure and flow rate, the B-Air can be used for a variety of applications, including running as a handheld tool, for sandblasting, or for cable blowing,” he says.
At the core of the air compressor is a Variable Speed Drive (VSD), a permanent magnet motor which helps achieve the exceptional efficiency Atlas Copco air compressors are known for.
The B-Air is equipped with a 57-kilowatt an hour lithium-ion battery, promising emission-free operation no matter the job.
Buttigieg says the VSD enables operators to match the motor speed to the air demand, ensuring it is not working overtime, all while remaining stable during operation.
“A triple enclosure for the battery not only protects critical components but eliminates the risk of potential hazards in and around the compressor,” he says.
“The motor is also sealed from water and dust to further deliver consistent and dependable performance and ensure uninterrupted operations.”
Both the motor and NEOS Xtreme inverter are unique Atlas Copco designs that have been specifically developed to thrive in the most challenging environments.
The NEOS Xtreme is part of Atlas Copco’s series of oil-injected screw compressors, typically designed for harsh mining conditions.
Buttigieg says the NEOS Xtreme is a game changer due to its design for operators to get the most out of the battery.
“These designs allow the B-Air compressor to operate reliably in a wide range of temperatures, ranging from -25 degrees Celsius to 45 degrees Celsius, as well as dusty or wet environments,” he says.
“This makes the B-Air a highly versatile solution for various industries and applications, regardless of the environmental rigors.”
As a global leader in IoT and connected transportation, Geotab processes and analyses data from over 4 million connected vehicles, generating over 75 billion data points per day. It’s a huge amount of data, and it is most powerful when we have the right tools to securely and efficiently manage it. That’s why we have partnered with Google to leverage Google Cloud’s data analytics and machine learning solutions.
Innovation and Sustainability
Geotab has been awarded two Google Cloud Customer Awards for its achievements in the transportation sector. Recognition in both the Cross Industry and Sustainability categories underscore Geotab’s successful use of Google Cloud’s analytics to innovate and drive sustainable practices in fleet management.
Kirsten Kliphouse, the President of Google Cloud Americas says that the Awards are an opportunity to recognise the most innovative, technically advanced, and transformative cloud deployments across industries globally built on their platform.
In her congratulatory message to Geotab, she acknowledged Geotab’s role in “serving as an innovator for the industry”, which also highlights Geotab’s innovative integration of data to revolutionise the transportation sector, leading to transformative impacts across organisations and customers around the world.
Empowering sustainable transportation
As the world’s premier EV telematics provider, Geotab has demonstrated its commitment to reducing emissions through its Electric Vehicle Self-Assessment (EVSA) tool, which won Google Cloud’s Award for Sustainability.
The tool provides tailored EV recommendations to support businesses and governments in transitioning to electrified fleets. For two consecutive years, Geotab was also identified as a Cross-Industry winner impactful transformation facilitated by Google Cloud. The award also acknowledges the launch of the Intelligent Transportation Systems (ITS) and its flagship transportation analytics platform Altitude.
Altitude has been pivotal in supporting government agencies by offering actionable, privacyconscious data insights for city planning and transportation network enhancements.
Strong synergy of Geotab and Google Cloud show great potential
As a valued partner in the Google Cloud Ready - Sustainability validation program, Geotab plays a crucial role in accelerating sustainability programs and informing strategic decisions for future developments.
Geotab’s collaboration with Google Cloud delivers significant benefits, including real-time improvements in driver safety and behavior, advancement of sustainability goals, enhanced productivity and significant cost savings.
This partnership not only redefines fleet management standards but also illustrates the impactful role of technology in fostering a more sustainable and efficient transportation industry.
An industry-leading solution
Geotab’s partnership with Google demonstrates the company is at the forefront of leveraging data analytics and machine learning to enhance fleet management, drive sustainability and create safer transportation systems worldwide.
By integrating Google Cloud’s advanced analytics with its telematics expertise, Geotab is confident of continuing its lead in the development of sustainable transportation solutions, demonstrating the profound impact that innovative technology can have on the transportation system today.
CRUSHER SCREEN SALES & HIRE’S IMS PM1200-20TB PUGMILL HAS BECOME A GAME-CHANGER FOR INCREASING ACCURACY IN ROAD BASE PRODUCTION.
Despite only being introduced by Crusher Screen Sales & Hire (CSSH) earlier this year, the IMS PM120020TB pugmill has already left its mark, bringing high precision material processing to quarries across the country.
CSSH Manager John Andersen says the PM1200-20TB pugmill has been a hit with industry due to its accuracy and reliability.
“Crusher Screen Sales & Hire is the Australian distributor for IMS from Ireland and both companies have worked together to create pugmills and blenders suitable for Australian conditions, as well as the changing requirements for blended material in the quarry, construction and mining industry,” he says.
“Some quarries have difficulty meeting road base standards without blending fines into the product. There is also increased use in the industry of blending recycled products into virgin quarry products in order to reduce the amount of raw material being used, reduce the amount of waste being taken to landfill and reduce the amount of transport movements on the road.”
This, he explains, is where the PM120020TB pugmill provides significant benefits to quarrying customers, due to its largescale throughput and ability to handle several additives at once.
“The new IMS PM1200-20TB track pugmill has two five-metre-long feed hoppers
holding 10 cubic metres each, with separate hopper conveyors fitted with belt scales enabling the blending of two products with accuracy,” he says.
“The pugmill has the option of one or two powder hoppers and the ability to add two liquids. This is fully automated with a PLC (Programmable Logic Controller) and recording system that can be operated with an iPad in a loader or site office.”
The PM1200-20TB has a longer three metre pugbox to ensure a quality mix when blending high percentages of powder – like roller-compacted concrete. A four-sided access platform with stairs gives complete access around the cement hoppers for maintenance and visibility.
A series of IMS-PM1200-20TB pug-mills, along with the single-hopper IMS PM105016TB tracked pugmill, are working in quarries across Australia, blending road base for major new infrastructure projects.
Andersen says the ability of the IMSPM1200-20TB pugmills to blend two raw
powders and liquids has been a major draw for his customers.
“These machines also offer great serviceability, and the improved PLC control and recording system that can be monitored from an office and our service department increases both safety and ease of maintenance,” he says.
“The PM1200-20TB pugmill stands out, as it is the only pugmill blender on the market that has two separate conveyors on both feed hoppers. Others have a dividing wall, but only one conveyor belt, so you can only adjust the percentage of product from both sides with a front of hopper flow gate.
“The PM1200-20TB has a front of hopper adjustable flow gate, plus a variable speed conveyor belt fitted with belt scales and PLC control system, making it more accurate.”
It also has an improved Australian designed PLC with a full reporting program showing the percentages of each product used, along with a supporting graph for each batch and will auto stop if the blend is not making the programmed percentages.
It will also give daily totals of all the different products used for the day, which helps with the management of stock materials and ordering.
Alongside the IMS PM1200-20TB pugmill, IMS has also released the new BP120048TB track blender.
This has four five-metre-long feed hoppers, each holding 12 cubic metres, and is powered by a Cat C7 generator that can be connected to mains power.
The BP1200-48TB blender can work in conjunction with the IMS modular electric pugmill.
“THESE MACHINES ALSO OFFER GREAT SERVICEABILITY, AND THE IMPROVED PLC CONTROL AND RECORDING SYSTEM THAT CAN BE MONITORED FROM AN OFFICE AND OUR SERVICE DEPARTMENT INCREASES BOTH SAFETY AND EASE OF MAINTENANCE.”
KOMATSU HAS RETURNED ONCE AGAIN TO BAUMA 2025, ONE OF THE WORLD’S LARGEST TRADE FAIRS FOR CONSTRUCTION MACHINERY, SHOWCASING ITS ELECTRIC AND INNOVATIVE MACHINERY SOLUTIONS OF TOMORROW.
Acentury of innovation. That’s Komatsu’s commitment to the market and the world.
With 211 sales, service and distributor companies across 151 countries, Komatsu has a firm grasp on the global market, with each location and representative able to deliver optimal outcomes for local markets. This is especially important in a market like Australia, where conditions, applications, and geographies each present unique challenges on a daily basis.
Despite its well-established global presence, Komatsu continues to look for opportunities to grow. After all, it’s this ambition that has transformed the company, from its Japanese roots and
foundation in 1917, to becoming one of the largest manufacturers on Earth. Few trade shows and conferences enable companies to showcase their solutions to a truly global audience, all at once. Enter, bauma 2025.
Komatsu has long been an exhibitor and partner of bauma, one of – if not the world’s largest trade fairs for construction, building material and mining machines, construction vehicles and construction equipment.
Komatsu returned with a bang this year, showcasing 34 machines across a dedicated exhibition area of more than 7500 square metres. Of the 34 on show, 13 were brand new
machines, with each debuting to the global market.
Charles Wheeldon, General Manager, Construction and Utility says the trade show lifted the curtain on what’s next for Komatsu, while also celebrating the company’s progress in the electric machinery market, as well as its advances in intelligent machine control (iMC).
“bauma 2025 highlighted Komatsu’s latest advancements in construction equipment, showcasing intelligent machine control and electric solutions designed to elevate project efficiency and sustainability,” he says.
The all-new Komatsu PC220LC-12 and PC220LCi-12 excavators made their highly
anticipated international debut at bauma 2025.
Visitors witnessed the machines’ capabilities first-hand through dynamic, live outdoor demonstrations and a static indoor exhibit, which enabled attendees to jump in the operator cab and check out the machine’s most innovative features.
Both machines are powered by a 129-kilowatt, high torque Komatsu next generation engine, paired with the new high efficiency electronically controlled hydraulic system, which translates to an 18 per cent reduction in average fuel consumption.
Advanced technologies provided as standard include an integrated payload meter, integrated 2D machine control designed for simple depth and slope grading, and a 2D virtual safety wall.
Wheeldon says it’s features and capabilities such as these that will make the PC220LC-12 and PC220LCi-12 excavator models highly sought-after across Europe and Australasia.
“The new PC220LCi-12 excavator featuring iMC 3.0 technology is set to deliver enhanced precision and operational control, aligning with our commitment to providing cutting-edge solutions for Australian construction and utility projects,” he says.
iMC 3.0 represents the continual growth and success of Komatsu’s intelligent machine control platform, a major differentiator for Komatsu’s patented machinery and technology.
iMC 3.0 offers advanced features, such as 3D boundary control and automated steer-to-line. Advancing towards autonomous operation, iMC 3.0 introduces auto swing, enabling semiautomatic truck loading.
Features such as swing-to-line and travel-along-line functionalities further simplify trenching operations for operators of any skill level. All of this and more can be viewed on a new, 10-inch iMC 3.0 monitor.
bauma provided just a small taste of iMC 3.0, with more information to come on the newest iteration in Komatsu’s well-established iMC software line.
Komatsu also presented three new electric mini excavators – the PC20E,
PC26E, and PC33E – as part of an additional live demonstration.
All three models offer a range of benefits to operators, including zero-emission operation, powerful performance, extended runtime, reduced maintenance, and versatility.
With no exhaust fumes, high torque and instant power, on top of highcapacity batteries, the PC20E, PC26E, and PC33E are capable of working on a wide range of applications, including indoor or built-up areas where conventionally fuelled machinery may not be suitable.
Another key aspect of Komatsu’s bauma presentation was recognising and celebrating its principal partnerships, including the ongoing affiliation with the Williams Racing Formula 1 team.
With both organisations sharing a rich history of pioneering mechanical and machinery excellence, Komatsu sought to honour its partnership with a specially liveried HB365LC Hybrid excavator, adorned in the Williams Racing colour scheme.
Wheeldon says that bauma 2025 was a great success, providing plenty of opportunity to learn and engage with industry to further grow Komatsu’s product range, while also giving the company time to reflect on its achievements and partnerships thus far.
“With a focus on reducing rework and maximising productivity, these innovations reflect our ongoing dedication to helping customers complete projects faster, safer, and more efficiently,” he says.
NEW EQUIPMENT IS PROVIDING A MUCH-NEEDED BOOST TO RESEARCH INFRASTRUCTURE IN THE TRANSPORT AND CONSTRUCTION SPACE. UNIVERSITY OF SOUTH AUSTRALIA PROFESSOR YAN ZHUGE EXPLAINS.
Research is a fundamental aspect of the transport and construction sector.
The sector has universities to thank for seemingly everyday materials and methods, such as Recycled Asphalt Pavement, prefabrication and modular construction, digital twins, sustainable timber and more.
The University of South Australia’s newest addition, the Hopkinson bar, will help to greatly accelerate and validate such research. So, what is a ‘Hopkinson bar’ and what does it help to do?
The Hopkinson bar is a specialised scientific piece of equipment used to simulate and study dynamic loading conditions, particularly impact loading.
Primarily used in civil engineering to test how materials perform under sudden, high-speed forces, the Hopkinson bar
has previously been used to simulate impacts from earthquakes, car crashes, bombings and other impactrelated events.
The mechanical device was invented in 1914 by British electrical engineer Bertram Hopkinson, originally used to measure the pressures created by small explosions and projectile impacts.
In 1949, Herbert Kolsky improved the technique by using two bars to measure the stress and strain that materials can withstand.
In the intervening years, the Hopkinson bar has been modified to allow for tensile, compression and torsion testing.
The existing bar is not advanced enough to test new materials that have different impact energies, hence the need for improvements.
The current generation of Hopkinson bars in Australian universities also have accuracy issues and are time-consuming to use. That’s why the University of South Australia is developing a new version with improved technology to overcome these limitations.
This technology comprises a $720,000 new-generation biaxial Hopkinson bar that uses electromagnetics to apply pressure in two directions, investigating how well the materials stand up to a high-impact force.
The new bar will help researchers better understand how materials like concrete and infrastructure components respond to dynamic loading conditions, ultimately leading to more resilient and safer design of roads, bridges, tunnels, and other critical infrastructure.
and construction industries to adopt new technology. That’s our aim, to develop and investigate new technology and methods, in the hope of developing new, resilient and green infrastructure. After all, resilient structures are greener structures.”
On top of trialling the new Hopkinson bar, Zhuge and the rest of the University of South Australia team are looking into alternative materials and manufacturing processes that the market could adopt.
Just one of these is research into low-carbon materials, with the end goal being the development of concrete materials with reduced carbon emissions, by using waste materials to partially replace cement.
Zhuge says the key objectives of such research, in addition to reducing the carbon footprint of these materials, are maintaining high stress performance while preserving durability.
University of South Australia will also benefit from a $402,221 ARC Discovery Project grant, which has been awarded to Professor Zhuge. This funding will help investigate the viability of three-dimensional (3D) printing reinforced concrete.
“AUSTRALIA URGENTLY NEEDS MORE EFFECTIVE DESIGN METHODS TO ENSURE ITS AGEING BUILDINGS, BRIDGES, AND ROADS CAN WITHSTAND A PROJECTED INCREASE IN NATURAL DISASTERS BY 2050 DUE TO CLIMATE CHANGE.”
The equipment is partly funded by a $420,000 ARC Linkage Infrastructure Equipment Facilities (LIEF) grant and supplemented with $300,000 cash from eight Australian universities. As University of South Australia Professor Yan Zhuge explains.
“Australia urgently needs more effective design methods to ensure its ageing buildings, bridges, and roads can withstand a projected increase in natural disasters by 2050 due to climate change,” she says. “It is essential that we create sturdy structures and systems to protect against a whole range of events, including human-made disasters. The existing testing methods for construction materials are not only time-consuming but often inaccurate.”
More resilient infrastructure not only provides benefits in terms of durability
and performance, but it also helps to aid the overall sustainability of infrastructure development.
“If you have a resilient structure, that’s also sustainable, the structure can last 100 or 200 years, instead of designing it for 50 years,” she says. “That’s truly sustainable in its own way.”
Similar to sustainable practices, the adoption of new technology has traditionally been a challenge in the sector, Zhuge explains. She hopes that once universities can validate their claims with research, stakeholders will show greater buy-in.
“I want to talk to all these civil and construction companies to encourage them to try to adopt new technology, because I think the people in this field are pretty traditional,” she says. “It’s very difficult for the Australian infrastructure
3D printing is now common in digital construction, but it is currently restricted to printing concrete, not the reinforced material, so cannot be applied in a real-world setting. The project will also investigate a sustainable 3D printing alternative to Portland cement – an alkali-activated slag binder that hardens quickly and has significantly lower CO 2 emissions.
“This is the first research project in the world to see if it’s possible to simultaneously print fibre-reinforced polymer along with concrete,” Zhuge says.
“We’re excited for the future in the transport space, especially with Artificial Intelligence and automation technology coming in. It’s research like that of UNISA’s doing that will lead to these significant changes.”
AUSTRALIA’S ROAD NETWORK IS ONE OF THE NATION’S MOST VALUABLE PUBLIC ASSETS. AS OUR CITIES EXPAND AND REGIONAL COMMUNITIES RECOVER FROM CLIMATE SHOCKS, THE DEMAND FOR SMART, SUSTAINABLE AND COST-EFFECTIVE INFRASTRUCTURE SOLUTIONS HAS NEVER BEEN GREATER.
By AustStab – the Australian Pavement Recycling and Stabilisation Association.
That’s where innovation in pavement recycling and stabilisation is making its mark –and reshaping the way we think about road construction and maintenance.
At AustStab, the Australian Pavement Recycling and Stabilisation Association, we’ve seen first-hand how cutting-edge thinking and collaborative effort are unlocking new levels of performance, resilience and sustainability across Australia’s roads.
As we celebrate the progress made, we’re also looking ahead to the next
wave of change. Over the past two decades, pavement recycling and stabilisation have evolved from niche techniques to essential tools in the road maintenance and construction toolbox. Several key innovations have been central to this transformation:
FOAMED BITUMEN STABILISATION
This method revolutionised how we treat existing pavement materials. By injecting bitumen with a small amount of water and air, it creates a flexible, highly workable binder that enhances the durability of road bases – particularly under hightraffic conditions.
The injection of water causes the bitumen to rapidly expand into a foam. As it contracts, the bitumen coats the fine particles within the pavement material, effectively filling voids and creating a moisture-resistant, flexible matrix.
This not only enhances water resilience but also contributes to longer pavement life, especially in areas subject to wet and variable climates.
Foamed bitumen pavements can also be constructed in thinner layers than conventional cementitious stabilised pavements, offering significant advantages in reducing material use, haulage, and construction timelines.
The result? Faster construction, improved rideability, and a significant reduction in resource use and emissions.
QUALITY CONTROL WITH INTELLIGENT COMPACTION
By integrating GPS and sensor technologies, modern compaction equipment now provides live feedback on compaction efforts.
This not only improves construction outcomes but also offers traceability and assurance that performance standards are being met consistently.
Lifecycle carbon calculators and performance models have demonstrated the significant environmental benefits of in-situ stabilisation – reducing the need for haulage, virgin materials and greenhouse gas emissions. These tools help road owners make informed, futurefocused investment decisions.
What’s next? The future of stabilisation is smarter, greener and more connected. Innovation doesn’t stop.
Across the country, industry leaders, researchers and road authorities are investigating a new wave of technologies and practices that could reshape the future of pavement delivery.
The industry is exploring alternative binders such as geopolymer mixes,
AustStab is encouraging greater use of pavement recycling methods and processes, which provides a multitude of benefits to motorists, as well as project stakeholders.
waste-derived materials and hybrid additives. These offer the potential to further reduce the embodied carbon of stabilised pavements, without compromising strength or durability.
Emerging artificial intelligence (AI) tools are helping councils and asset managers assess pavement condition, predict maintenance needs, and optimise treatment selection.
Combined with historical performance data, this technology promises smarter, more strategic planning.
Digital twin models are providing virtual replicas of roads, allowing engineers to simulate stress loads, environmental conditions and traffic impacts before any work begins.
This leads to better design decisions and reduced whole-of-life costs.
Au stStab is working alongside education partners to roll out new modular training programs, virtual reality simulations, and mobile learning units. These resources will support operators, engineers and contractors across urban and regional areas to access high-quality, consistent training.
The stabilisation sector is at the forefront of reusing reclaimed materials – such as crushed concrete,
recycled asphalt (RAP), and industrial by-products. By further embedding circular economy thinking, we can extend material life cycles and reduce the environmental burden of road construction.
I nnovation in our industry is not driven by technology alone – it’s powered by collaboration.
From pilot projects to policy reform, AustStab continues to work closely with state road agencies, local governments, contractors, and research institutions to turn ideas into action.
One such partnership is with the National Transport Research Organisation (NTRO), where we are co-developing educational resources and standards to help future-proof stabilisation practices in line with national infrastructure goals.
Through AustStab’s leadership, we are closely collaborating with state road agencies for the development of national specifications and guidelines, which will bring muchneeded consistency to the sector. This harmonisation enables contractors to deliver quality outcomes efficiently across state borders.
T he future of our roads depends on decisions we make today.
As we face rising construction costs, more frequent weather extremes, and tighter budgets, the case for innovative, evidence-based approaches has never been stronger.
Through ongoing research, knowledge-sharing and investment in capability, the pavement recycling and stabilisation sector is ready to meet these challenges head-on – building roads that are not only fit for purpose but fit for the future.
To learn more about AustStab, access technical resources, or get involved in shaping the future of sustainable pavement delivery, visit www.auststab.com.au
THE AUSTRALIAN FLEXIBLE PAVEMENT ASSOCIATION (AFPA) HAS ANNOUNCED ITS 20TH INTERNATIONAL CONFERENCE, SET TO TAKE PLACE FROM OCTOBER 28-30, 2025, AT THE ADELAIDE CONVENTION CENTRE.
This prestigious event will bring together industry leaders, policymakers, innovators, and stakeholders to explore leading research, innovation, and global best practices in policy and procurement, construction and maintenance.
Read on to learn more about why you should attend the AfPA 2025 International Conference.
WHO SHOULD ATTEND THE CONFERENCE?
The conference is open to anyone involved or interested in the flexible pavements industry, including suppliers and contractors, innovators, policy makers and procurement managers, asset owners, consultants, researchers and academics, students, as well as government (federal, state and local).
Early bird rates are available now, along with special rates for large groups, students and local government representatives.
WHAT ARE THE MAJOR THEMES BEING DISCUSSED AT THE CONFERENCE?
“Future Ready Roads” underscores the critical need to proactively ensure that the pavements of today can withstand future challenges through advanced materials, innovative design, and strategic construction and maintenance. There are three overarching themes for the conference.
The first is ‘Towards Zero Carbon and Circular Economy’, discussing the flexible pavement industry’s role in shaping Australia’s low-carbon road policies and sustainable procurement and construction practices.
The second is ‘Innovative Pavement Materials Selection, Design, and Construction’, exploring breakthroughs in materials and technologies that reduce carbon footprints and enhance pavement durability.
The third is ‘Resilient Roads for a Sustainable Future’, highlighting the importance of sustainable road systems that are resilient to climate impacts and minimise life cycle costs.
WHAT CAN YOU EXPECT FROM THE CONFERENCE PROGRAM?
Through a carefully crafted program the conference will feature a mix of dynamic keynotes, technical sessions, interactive panel discussions and workshops, designed to inspire action and facilitate collaboration between local and international experts.
The entire conference program will
“ALL OF THESE DISCUSSIONS WILL HIGHLIGHT THE IMPORTANCE AND IMPACT OF COLLABORATION ON ADVANCING SUSTAINABLE AND FUTURE-READY ROADS.”
be released in August, but in the meantime, keep an eye on AfPA’s social media for speaker announcements.
In addition, our exhibition hall will feature an Education Stage where attendees will be able to hear about the latest products and innovations from suppliers as well as see demonstrations of the latest plant and equipment.
Attendees can look forward to various networking events, including a welcome reception, networking drinks, a gala dinner, workshops, forums, and dedicated spaces within the exhibition and conference venue for informal gatherings. These events are designed to foster connections among attendees.
The National Gala Dinner, taking place on the final day of the conference at the iconic Adelaide Oval, will celebrate outstanding achievements across the industry. Awards will be presented for projects valued under $10 million, over $10 million, safety innovation,
and to recognise our emerging leaders. Nominations can be made via www.afpa. asn.au
AfPA offers a range of customisable sponsorship and partnership opportunities, designed to align with attendees’ strategic goals and deliver measurable value. Exhibitors and sponsors will have the chance to showcase their innovations and solutions to a targeted audience of national and international delegates.
Attendees will also be able to strengthen brand visibility across AfPA’s comprehensive marketing and communications campaign, as well as connect with government officials, industry experts, researchers, and clients from across the transport infrastructure ecosystem.
All of these discussions will highlight the importance and impact of
collaboration on advancing sustainable and future-ready roads.
For more information on how to get involved, AfPA is calling on potential attendees to refer to the conference prospectus or contact them directly, with them encouraging the market to not miss on this opportunity to be part of a transformative event in the flexible pavements industry.
CAN I BRING MY PARTNER?
Delegates are encouraged to bring their partners, who can enjoy a variety of partner programs during the conference. Additionally, post-conference activities and accommodation packages can be arranged for those wishing to extend their stay and explore more of what South Australia has to offer.
Make the most of your visit to Australia’s food and wine capital and discover what all the excitement is about! Contact AfPA via the conference website to learn more: www.afpa2025conference.com
Below: Potential attendees can learn more about the upcoming conference by visiting AfPA’s website.
For the precast sector in particular, the message is clear: keep it simple, make it practical, and let automation work for the people doing the job.
Precast manufacturing has long embraced innovation, often ahead of other construction methods. But even in this forward-looking sector, a digital disconnect sometimes persists between the planning that happens in the office, the activity on the factory floor, and the reporting delivered at project handover. That gap can mean lost efficiency, reduced traceability and unnecessary rework.
One of the most effective ways to bridge that gap is through the digitisation of Quality Assurance and Control (QA/QC). As compliance demands grow, particularly in government and infrastructure projects, digitised QA offers a straightforward path to improvement. It creates a live, traceable record during production, streamlining both internal processes and client reporting.
“We’re not digitising for the sake of it. In precast, every tool must help people on the ground, making work safer, faster, or more consistent. If it doesn’t achieve that, it’s not worth the investment,” says Sarah Bachmann, Chief Executive Officer of National Precast.
“Digital tools like CONQA are already making this a reality for many of our members.”
Used by a growing number of Australian precasters, the software helps capture and manage quality data throughout production. This reduces paperwork, simplifies compliance, and produces accurate Manufacturers’ Certificates of Compliance – otherwise referred to as birth certificates – for each element. This is a particularly valuable asset in large
infrastructure projects where detailed traceability is now expected.
Bachmann says that what sets it apart is its development model. The platform has evolved through a long-standing partnership with National Precast and its members, ensuring it remains grounded and delivers on what’s required by industry.
“Having our members involved in shaping tools like this ensures the solutions are practical. They’re built by the industry, for the industry, and aligned with real factory workflows and project pressures,” Bachmann says.
“As an example, this collaborative approach led to the development of ‘Progress Tracking’, a feature designed to simplify project setup and final reporting. It improves communication between the office and the yard and closes the loop between preconstruction planning and delivery. It’s the kind of feature that sounds simple but helps to solve a host
Digitising quality management assists in the process of delivering high quality precast outcomes, maximising strength, durability and aesthetic results.
“WE’RE NOT DIGITISING FOR THE SAKE OF IT. IN PRECAST, EVERY TOOL MUST HELP PEOPLE ON THE GROUND, MAKING WORK SAFER, FASTER, OR MORE CONSISTENT. IF IT DOESN’T ACHIEVE THAT, IT’S NOT WORTH THE INVESTMENT.”
of day-to-day challenges for busy precast manufacturers.”
This type of digitisation has benefits that go beyond quality for everyone in the supply chain. They include better time management, stronger risk controls, and greater consistency across teams. For management, it provides real-time visibility across operations. For clients, it means more accurate, timely handovers.
“It’s a practical way to deliver on quality while lifting efficiency. For many
precasters, this kind of digitisation is a quick win,” Bachmann says.
As ESG (environmental, social, and governance) and compliance reporting become more complex, digital systems will only grow in importance. But they don’t need to be complicated.
The right technology respects the realities of factory life, supports workers, and delivers measurable value across the business.
For precast manufacturers, keeping it simple may be the smartest strategy.
Few in the construction sustainability space can say that they’ve had the same impact, in the same short space of time, as Malindu Sandanayake.
As the Associate Professor, Built Environment and Engineering, College of Sports, Health and Engineering at Victoria University, Sandanayake is part of a dedicated team looking to inspire fundamental change in the delivery of sustainable infrastructure.
Sandanayake has been working in infrastructure research for about five years, with a background in sustainability, digital transformation, and material innovation.
His key areas of focus include using waste materials in construction, developing sustainable concrete mixtures, and exploring digital technologies, among others. But most
of all, Sandanayake’s passion lies in establishing and delivering research that will help to turn the tide on infrastructure sustainability.
“Roads and infrastructure are areas that I’ve been fascinated by ever since I was studying and doing work in civil engineering,” he says. “It’s a resourceintensive sector and very dynamic. It’s a space that’s continually changing and continually moving.”
Sandanayake says being part of the research segment of the sector has provided unique insights into what should be – and is – happening when it comes to increasing the use of sustainable products in construction.
“We would like to see more focus from the industry on a holistic approach to how recycling is being implemented, right from the bottom of the supply
chain,” he says. “There are plenty of aspects that we as researchers, and industry as consumers, can consider and try when it comes to reuse and reducing waste overall.”
To further promote the importance of proactive and considered sustainability implementation on major projects, Sandanayake will discuss the challenges and opportunities as part of a sustainability-focused panel at the upcoming Converge expo.
Converge 2025 will unite professionals across the construction and infrastructure sectors, including subcontractors, project engineers, council fleet managers and large-scale contractors. The event promises to showcase cutting-edge innovations, foster valuable connections, and explore the future of major projects.
Converge 2025 will take place on 17 to 18 September 2025 at the Melbourne Convention and Exhibition Centre. Attendees can expect a comprehensive showcase of the latest equipment, technologies and solutions, alongside a dynamic program of expert panels, keynote speakers and networking opportunities.
Sandanayake will take his place, alongside three other industry leaders, as part of the Green Revolution: Redefining Sustainability in the Built Environment panel.
This panel will focus on the latest trends and innovations that are shaping sustainable construction practices.
This also includes how to close the loop with recycling material in the construction industry, integrating recycled material in the industry, the
Sandanayake is investigating the use of shredded high-vis vests as concrete fibre reinforcement. His team has so far achieved 10-15 per cent cement replacement and is currently conducting 90-day durability testing.
He says the ultimate goal is to demonstrate the social and environmental benefits of innovative materials, with the next step being commercialisation.
“Often, this research doesn’t go past the R&D stage and doesn’t end up being implemented,” he says. “Some still see sustainability as ticking a box, rather than fully seeing the social benefits.
durability of the recycling material and overall, how to make the industry more sustainable.
Sandanayake says trade shows such as Converge help to connect researchers directly with the end market, leading to more desirable outcomes for all parties.
“It gives us a platform to network with the industry to focus on research aspects,” he says.
“We get to know what their problems are, while also allowing us to showcase our expertise and our ideas, with opportunities to set up potential collaborations in the future.”
Just one example of such collaboration is Sandanayake’s ongoing project to transform high-vis work vests and recycle them into a substitute for cementitious components.
As his primary research project,
“The whole idea is for us to not just use waste material as a value-add. Instead, to work holistically, to tackle the cost-effectiveness of a product, as well as how we can source these materials locally.”
Sandanayake’s comprehensive, socially conscious, and practical approach to sustainability research has earned him several Sustainability Victoria grants, both as the Lead Investigator and as a partner investigator.
It’s this expertise that he hopes to share at Converge, to enlighten attendees on what’s possible.
“What excites me is the chance to see new technology,” he says. “There’s always a chance to learn, and I hope to see a lot from that aspect.”
For more information on exhibiting and attending, visit convergeexpo.com.au to download the prospectus, or contact our team directly on +61 3 9690 8766 or converge@primecreative.com.au
UNDERGROUND INFRASTRUCTURE SOLUTIONS ARE REDUCING DISRUPTION AND DELIVERING BETTER OUTCOMES FOR COMMUNITIES AND COUNCILS ALIKE. JUST ONE OF
both financially and socially. But new techniques have proven that upgrades don’t have to come with detours and delays.
“Councils often use legacy systems under roads that are now high-traffic zones,” Edmunds says. “Digging those up isn’t feasible. That’s where trenchless makes sense. It allows work to proceed where access is tight and disruption is unacceptable.”
While capital works programs traditionally focused on visible outcomes, today’s focus is shifting underground. That’s where KRE comes in as a manufacturer and supplier of trenchless equipment, with its clients using such equipment to perform trenchless pipe rehabilitation and related services.
“Projects that once required weeks of digging can now be completed in a fraction of the time,” Edmunds says. “And we’re getting better results with less impact on the community.”
This is particularly relevant in dense urban areas, where utility corridors are congested, and surface space is congested.
Trenchless technology removes many of the logistical headaches that once plagued civil works projects. It also minimises conflict with other infrastructure, helping to avoid costly rework or service clashes.
“We’ve seen enormous gains in coordination between councils, utilities, and contractors,” Edmunds says. “Trenchless methods naturally encourage early planning and collaboration.”
The rise of trenchless technology hasn’t happened in a vacuum. It has been underpinned by strong industry collaboration, knowledge sharing, and dedicated platforms for learning.
No-Dig Down Under, organised in partnership with the Australasian Society for Trenchless Technology, has become a flagship event for professionals working with subsurface infrastructure. Bringing together local government, contractors,
utilities, and engineering specialists, the conference blends technical presentations, training, and exhibitions. It’s where ideas move from theory into practice.
“Staying ahead means continuous learning and adaptation,” Edmunds says. “Conferences and workshops are vital for sharing insights and driving the industry forward.”
Training programs delivered through No-Dig Down Under also play a key role in upskilling the industry. From horizontal directional drilling (HDD) techniques to risk management and safety best practices, the focus is squarely on capability development. For engineers looking to future-proof their careers, or their council’s asset strategies, these sessions provide direct access to global knowledge.
“OUR FOCUS IS ON DELIVERING SOLUTIONS THAT ARE NOT ONLY EFFECTIVE BUT ALSO CONSIDERATE OF THE COMMUNITIES WE SERVE.”
Equally important is the chance to see new tools and systems in action. From robotics to real-time mapping and vacuum systems, trenchless innovation is being matched by technological progress.
“It’s not just about digging smarter,” Edmunds says. “It’s about how we plan, how we train, and how we invest in the right tools to get the job done right.”
With climate pressures rising and infrastructure demand accelerating, trenchless technology is positioned to be more than a niche offering. It’s becoming central to how Australian cities approach underground asset management.
Asset condition, carbon emissions, and life cycle costs are increasingly front-ofmind for local governments. That makes low-impact solutions essential.
As more councils embed sustainability targets into procurement and project delivery frameworks, trenchless solutions offer a practical way to meet those goals without compromising on performance or safety.
“Our focus is on delivering solutions that are not only effective but also considerate of the communities we serve,” Edmunds reflects. “Trenchless technology embodies that balance.”
ROADS & INFRASTRUCTURE PROVIDES AN UPDATE ON SOME OF THE CONTRACTS AND TENDERS RECENTLY
Contract awarded for Transgrid works
A three-year delivery services panel contract has been awarded, which will see the delivery of projects across Transgrid’s transmission network, including lines, substations, commissioning and testing. Ventia has been awarded the contract and will work with Transgrid to support the delivery of upgrades to the transmission grid. These projects also aim to support Australia’s energy transition to net zero. Transgrid’s network extends throughout New South Wales, Queensland, Victoria and the ACT. Ventia has extensive experience and a positive track record delivering works on power systems in Australia and New Zealand.
Contract awarded for Port to REZ project
The contract for the first stage of the Port to REZ (renewable energy zones) project, from the Port of Newcastle to Elong Elong in New South Wales, has been awarded. Delivery of projects in REZs requires the transportation of large and heavy renewable energy components from ports such as the Port of Newcastle. These can include wind turbine components and transformers for generation and transmission infrastructure. BMD has been awarded the contract to deliver these works for EnergyCo and Transport for NSW. The first stage of Port to REZ upgrades includes 19 intersection upgrades between the Port of Newcastle and Elong Elong in the Central-West Orana REZ, with these upgrades to be funded by the NSW and Federal governments. This will see upgrades and modifications being delivered over more than 300 kilometres of the New England, Golden, and Castlereagh highways, including new turning lanes and safety measures. These enhancements aim to ensure the smooth passage of OSOM components as well as reduced delay times and easier travel through intersections for all road users. Works are scheduled to begin in late April.
Alliance awarded contract for $5.75B Logan to Gold Coast Faster Rail project
The ActivUs Alliance has been awarded the design and pre-construction contract for the main works package on the $5.75 billion Logan and Gold Coast Faster Rail project. The alliance consists of CPB Contractors, UGL, ACCIONA, SMEC and WSP. These companies will work in partnership with the Queensland Department of Transport and Main Roads, as well as Queensland Rail to progress design and project planning activities. The Logan and Gold Coast Faster Rail project will double the capacity of the Gold Coast rail line and reduce waiting times at stations between Brisbane, Logan and the Gold Coast. The project will also upgrade stations to improve accessibility, remove five level crossings, improve park ‘n’ ride facilities, and provide a new continuous active travel path connecting to stations along the 20-kilometre project corridor. The Alliance will now commence the design process and project planning activities and undertake further site investigations to ensure the project is completed ahead of the Brisbane 2032 Olympic and Paralympic Games. The project is being jointly funded by the Federal and Queensland governments.
Exact Contracting awarded contract for Carpentaria Highway u pgrade project
The Federal and Northern Territory governments have awarded the contract for the next stage of the $254 million Carpentaria Highway upgrade project in the Northern Territory. Each year, about 30,000 head of cattle are transported along the Carpentaria Highway to East Arm Port, with 15 pastoral stations relying on the route for market access. The Carpentaria Highway is a key access road to the Beetaloo Sub-basin, Borroloola and an important service route for the pastoral, tourism, agricultural and mining sectors.
The upgrades will improve safety and travel times, reduce vehicle operating cost and improve flood immunity to increase yearround access. Exact Contracting will design and construct the next stage of works from the Tanumbirini Propacc Track to five kilometres past the October Creek Bridge. Jointly funded by the Federal and Northern Territory governments, the works form part of a five-stage upgrade to the Carpentaria Highway. Stage Three will include the construction of a dual-lane sealed road, a new, two-lane sealed October Creek Bridge and upgraded flood immunity through widened and elevated road infrastructure. Construction on Stage Three is expected to begin in May 2025 and be completed by December 2025.
UGL awarded $150M in new and extended contracts in WA CIMIC Group company UGL has been awarded several new contracts and contract extensions with existing clients in Western Australia. In total, the contracts will provide approximately $150 million in revenue for UGL across multiple years. The contracts include an 11-month contract extension for the supply of services to Alcoa’s mining and refining operations in Western Australia for the continued management and execution of mechanical, electrical, and access services for maintenance work. Another contract with Chevron Australia will be for construction services, supporting the installation of modules, equipment, structure, piping, and electrical and instrumentation works. An additional two-year contract extension on the supply of maintenance, tank turn around and construction services has also been announced with BP at the Kwinana Energy Hub. This is on top of a one-year extension of a non-binding Framework Agreement with Woodside Energy Global through UGL company, IAS Group, to provide, surface preparation and coating, cladding and insulation, and technical services.