Natalie Foeng
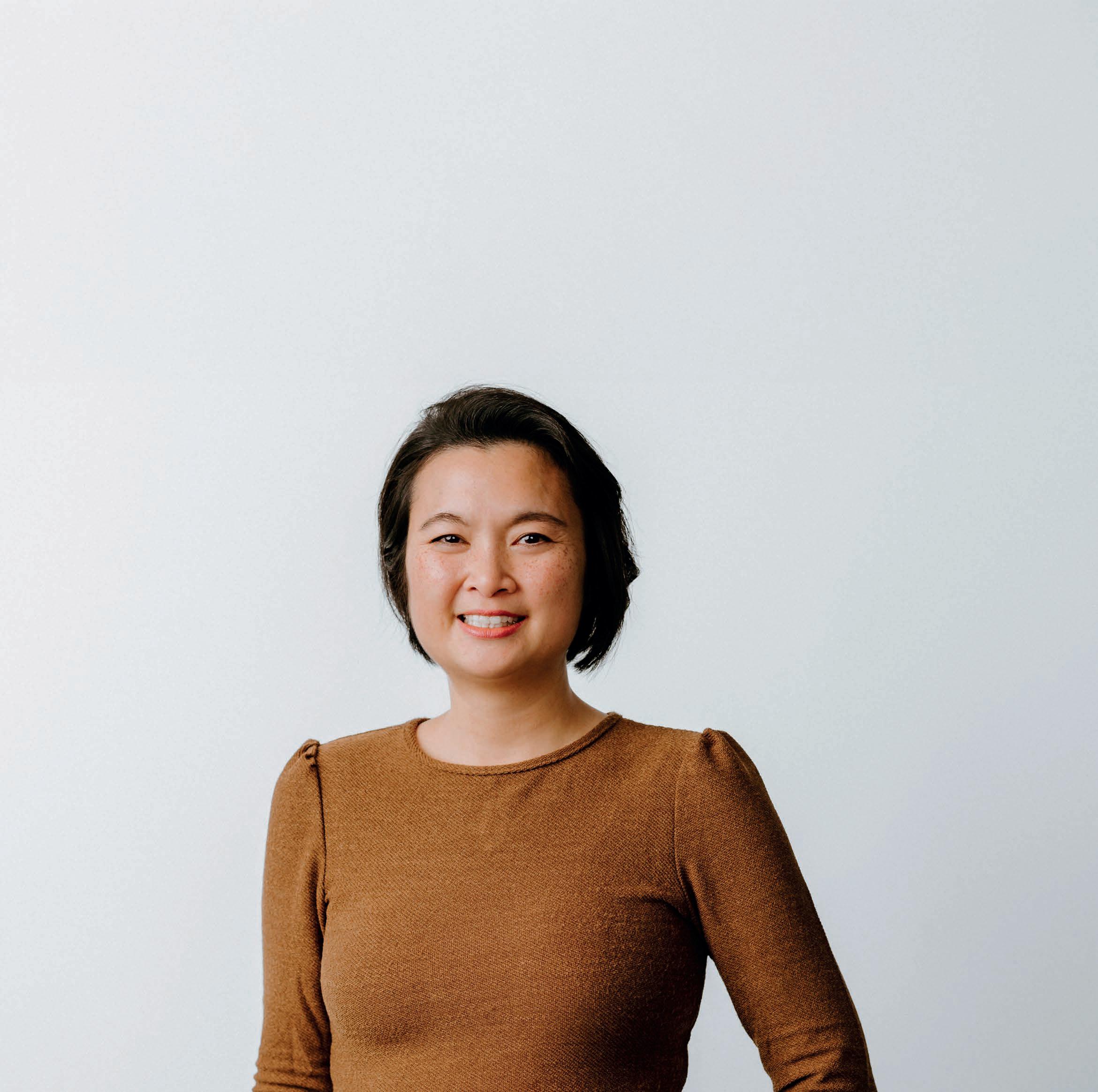
Charging up
Maximising Essential Energy’s network to boost EV uptake
YVW’s new MD is championing for a bright future Water secured
Another milestone for Fitzroy to Gladstone Pipeline
Charging up
Maximising Essential Energy’s network to boost EV uptake
YVW’s new MD is championing for a bright future Water secured
Another milestone for Fitzroy to Gladstone Pipeline
As a global leader in IoT and connected transportation, Geotab processes and analyses data from over 4 million connected vehicles, generating over 75 billion data points per day. It’s a huge amount of data, and it is most powerful when we have the right tools to securely and efficiently manage it. That’s why we have partnered with Google to leverage Google Cloud’s data analytics and machine learning solutions.
Geotab has been awarded two Google Cloud Customer Awards for its achievements in the transportation sector. Recognition in both the Cross Industry and Sustainability categories underscore Geotab’s successful use of Google Cloud’s analytics to innovate and drive sustainable practices in fleet management.
Kirsten Kliphouse, the President of Google Cloud Americas says that the Awards are an opportunity to recognise the most innovative, technically advanced, and transformative cloud deployments across industries globally built on their platform.
In her congratulatory message to Geotab, she acknowledged Geotab’s role in “serving as an innovator for the industry”, which also highlights Geotab’s innovative integration of data to revolutionise the transportation sector, leading to transformative impacts across organisations and customers around the world.
As the world’s premier EV telematics provider, Geotab has demonstrated its commitment to reducing emissions through its Electric Vehicle Self-Assessment (EVSA) tool, which won Google Cloud’s Award for Sustainability.
The tool provides tailored EV recommendations to support businesses and governments in transitioning to electrified fleets. For two consecutive years, Geotab was also identified as a Cross-Industry winner impactful transformation facilitated by Google Cloud. The award also acknowledges the launch of the Intelligent Transportation Systems (ITS) and its flagship transportation analytics platform Altitude.
Altitude has been pivotal in supporting government agencies by offering actionable, privacyconscious data insights for city planning and transportation network enhancements.
Strong synergy of Geotab and Google Cloud show great potential
As a valued partner in the Google Cloud Ready - Sustainability validation program, Geotab plays a crucial role in accelerating sustainability programs and informing strategic decisions for future developments.
Geotab’s collaboration with Google Cloud delivers significant benefits, including real-time improvements in driver safety and behavior, advancement of sustainability goals, enhanced productivity and significant cost savings.
This partnership not only redefines fleet management standards but also illustrates the impactful role of technology in fostering a more sustainable and efficient transportation industry.
An industry-leading solution
Geotab’s partnership with Google demonstrates the company is at the forefront of leveraging data analytics and machine learning to enhance fleet management, drive sustainability and create safer transportation systems worldwide.
By integrating Google Cloud’s advanced analytics with its telematics expertise, Geotab is confident of continuing its lead in the development of sustainable transportation solutions, demonstrating the profound impact that innovative technology can have on the transportation system today.
While the sector was still reeling from a jampacked quarter, the start of the 2025–26 financial year snuck in quietly and just like that we’re halfway through 2025.
In the last three months, we’ve seen energy placed at the centre of an unprecedented federal election – and now with heightened certainty that the energy transition is powering ahead, the federal and state/territory budgets have outlined major investments in critical infrastructure.
While Australia powers towards 82 per cent renewables, the AEMC is rolling out new rule changes to ensure that tomorrow’s energy system is one that works for everyone. Over in the water sector, significant updates to the Australian Drinking Water Guidelines have now come into effect, as have the amendments to the Security of Critical Infrastructure Act 2024, which uplifted security obligations for telecommunications providers.
Australia’s water, energy and communications sectors are on a path towards a brighter future, but moving forward means navigating increasingly complex challenges and complete unknowns. In our July 2025 edition Utility, we’re celebrating some of the leaders, innovators and workers who are the champions of this change, and in these pages you’ll find expert advice and thought-leading content from some of the brightest minds in the sector.
The utility industry is fortunate enough to be guided by some incredible leaders, and Yarra Valley Water’s new Managing Director, Natalie Foeng, is certainly no exception. Ms Foeng’s drive and passion is reflected in her vision for both the utility and the communities it serves. And when we caught up with her for in this issue, it’s safe to say we were impressed.
Over in the energy sector, distribution networks are balancing the need to encourage electrification and keep prices low while ensuring that the grid remains secure in the face of new demand. We joined Essential Energy, Race for 2030 and UNSW for a deep dive into an incredible research project that is exploring potential ways to incorporate more EV fast chargers on this grid, without having to upgrade existing transformers.
This edition covers two fantastic industry events, Ozwater’25 and Australian Energy Week. And we also spoke with Coliban Water, about the utility’s biggest capital investment to date, and got the latest update from the Gladstone Area Water Board about the Fitzroy to Gladstone Pipeline.
While the world is throwing many hurdles at our essential service providers, it is truly encouraging to see them rise to the challenge, and deliver a reliable, affordable and sustainable future.
Australia as we know it would not be the same without the important work you do – and it’s a privilege to be able to share your knowledge so that utilities from all sectors can learn and grow together.
Katie Livingston, Editor
Drop Katie a line at katherine. livingston@primecreative.com.au or feel free to call on 03 9690 8766 to let us know what you think.
Don’t forget to follow Utility on social media – find us on LinkedIn, X and YouTube.
EDITOR
Katie Livingston
ASSISTANT EDITOR
Sarah MacNamara
MANAGING EDITOR
Paul Hayes
CEO Christine Clancy CHAIRMAN
John Murphy
ART DIRECTOR/DESIGN
Daz Woolley
Alejandro Molano
NATIONAL MEDIA EXECUTIVE
Rima Munafo rima.munafo@primecreative.com.au 0413 475 078
CLIENT SUCCESS OFFICER
Louisa Stocks
PUBLISHER
Sarah Baker
Cover: Yarra Valley Water’s new Managing Director, Natalie Foeng. Image: Yarra Valley Water
Scan to subscribe to Utility’s weekly newsletter –delivered to your inbox every Thursday morning.
32 The right environment
The power of water 36 Springing into action
38 Moving forward with a brighter water future 40 Reliable automation 42 Engineering the next generation
Keeping water networks fit for service
46 Driving the future
A transformative solution
Powering progress 54 Leaving no one behind 56 A look back on Australian Energy
the
We go beyond installation to ensure your investment in digital metering translates into measurable outcomes.
Solving real operational challenges, from leak detection to billing accuracy, with right-sized, scalable solutions.
The complexity, so you stay focused on your community. Most importantly, we work with you to define success upfront and ensure benefits are realised, not just assumed. From day one to long after rollout, we’re your partner in outcome-driven digital metering.
As we step into the next financial year, Energy Networks Australia continues to unite the sector on the path towards net zero.
Energy Networks Australia (ENA) is the national industry body representing electricity transmission and distribution and gas distribution networks, and its goal is to unite create a reliable, sustainable energy future for everyone.
As part of its advocacy work, association conducts key industry research and hosts a diverse range of events from in-depth discussions on energy regulation to exclusive gatherings with government representatives, and major industry conferences – and there’s a look to look forward to from ENA in 2025–26.
EN2026
EN2026 is ENA’s flagship biennial conference and exhibition, and is the definitive event for energy leaders, innovators, and professionals. With the theme ‘Powered by Connection’, the event will bring together Australia’s energy networks, policymakers, advocates and innovators to build a sustainable energy future.
On Tuesday 17 March – Thursday 19 March 2026, the industry will come together at the Adelaide Convention Centre to tackle its biggest challenges – from grid transformation to decarbonisation – through real solutions.
This premier platform showcases cutting-edge technologies, fosters invaluable networking opportunities, and inspires action through thought-provoking discussions with influential voices.
Registrations are now open, and ENA is inviting the networks industry, researchers, and innovators to submit an abstract for consideration in the 2026 program – but submissions close 11 August 2025, so get in quick. For more information, visit energynetworksconference.com.au
The 2025 Energy Networks Australia Regulation Seminar –Hard Reset? Disruption, Transition and the Customer is just around the corner on 6 August 2025.
Join 200 energy innovators – from network businesses, market bodies, and key industry partners – at State Library of Queensland to tackle the toughest regulatory challenges facing the sector today.
ENA invites attendees to spend the afternoon with thought leaders as they explore whether the current regulatory framework needs a hard reset to address today’s disruption and accelerate the transition to renewables – with customers at the heart of the journey.
For more information, visit www.energynetworks.com.au
Energy Networks Australia’s annual Awards celebrate excellence, innovation and leadership across Australia’s energy networks sector. Designed to recognise the individuals and organisations driving impactful change, the program highlights achievements in consumer engagement, industry innovation, women in networks and individual contribution.
These awards showcase the sector’s brightest ideas and boldest leaders – those who are improving customer outcomes, advancing the energy transition, and fostering a more inclusive, futureready industry.
With rigorous criteria and a focus on real-world impact, the ENA Awards are a prestigious platform for recognising outstanding contributions across all levels of the energy network landscape.
Finalists will be notified in early August, ahead of the gala dinner and ceremony on 11 September 2025, which will be held in Melbourne. The 2025 award categories:
• Individual Contribution – recognising exceptional dedication to the energy sector
• Industry Innovation – celebrating groundbreaking projects and initiatives
• Consumer engagement – highlighting efforts that prioritise customer outcomes
• Women in Networks – acknowledging leadership and accomplishment of a female in the sector.
The awards are open to regulated electricity and gas networks that are full financial members of Energy Networks Australia.
Applications open for NEPKI Board
Lead by ENA and Synergy, the National Energy Public Key Infrastructure (NEPKI) is a critical new initiative that aims to helping to secure Australia’s clean energy future.
As NEPKI takes shape, applications are now open for its inaugural Independent Chair and Board Directors.
These positions offer a unique opportunity to guide the governance and long-term direction of NEPKI, shaping the digital backbone of Australia’s energy transition.
The NEPKI Board will play a foundational role in:
• Guiding the establishment and growth of the organisation
• Supporting trusted, secure digital engagement with consumer energy resources
• Ensuring NEPKI operates in the public interest, aligned with its not-for-profit mission
Appointments will be made by the Interoperability Steering Committee, established under the Australian Renewable Energy Agency (ARENA). Board positions are expected to have a three- to four-year term. U
Creating an inclusive work environment and fostering a diverse workforce are essential to meeting the water sector’s challenges.
At Ozwater’25 in Adelaide, the Water Services Association of Australia (WSAA) launched its new report, BELONGING: Diversity, Equity and Inclusion in the Australian water sector
The comprehensive BELONGING report forms part of its commitment to lead efforts in diversity, equity and inclusion (DEI) across the sector. It highlights the collective work across the sector to promote DEI, showcasing the progress made and the initiatives being implemented to ensure all employees, regardless of background, feel they belong.
WSAA understands that creating a diverse, inclusive and equitable environment where all individuals can succeed is essential for the continued growth and success of the sector. DEI drives greater innovation, enhances decision-making and improves overall performance in the water sector.
While many water organisations are making progress in integrating DEI into their operations, it’s important
The NHP Services and Solutions team of highly skilled and qualified service technicians across Australia and New Zealand can help your organisation with:
Preventative maintenance
Commissioning and start-up
Modernisation: retrofits and upgrades
Site assessments and reliability evaluations
A host of training options
Repairs in accordance with the manufacturers’ recommendations
For more information, please go to nhp.com.au/services
Australia nhp.com.au
1300 647 647 nhpservice@nhp.com.au
The
water sector is on the cusp of a new era, and Yarra Valley Water’s new Managing Director says moving forward means bringing everyone together.
With more than two million people relying on its services, Yarra Valley Water is the largest of Melbourne’s three metropolitan water corporations.
To be at the helm of an organisation that is responsible for ensuring that a third of Victoria’s population has access to vital water services is a monumental task –but after speaking with the company’s new Managing Director, Utility is confident that Yarra Valley Water is in good hands.
For Natalie Foeng, it was a sense of purpose that drew her to the water industry.
“There’s a lot of great people who work in this water industry, and when you’re in it, you really feel that vibe; they’re passionate and very aligned on why we exist, and the importance of what we do,” she said.
“Water is such an essential thing, it’s a human right, and it’s a precious resource that I’m a custodian of. You don’t just get to do whatever you want with it.
“You’ve got to make choices very consciously with the voice of the community, and the voice of future generations and our Traditional Owners as well.”
Ms Foeng grew up in Adelaide, and as a second generation Australian coming from a vulnerable community with lots of hardship, she never took her education and career for granted.
“Multiculturalism was quite a foreign concept back then in the northern suburbs of Adelaide, and I also grew up in a period of recession, so when it came to job opportunities, finishing school and landing a job, nothing was taken for granted,” she said.
“Business and commerce was the pathway I chose back in those days, and it opened up the doors in a magnificent way for me.
“I was able to take on a variety of corporate roles, starting off in a big-four accounting firm known as PricewaterhouseCoopers back then (now PwC). I relocated
“It also enabled me to step out into industry in the private sector as well, by giving me exposure to corporate organisations that were ASX-listed.”
Ms Foeng said that journey took her to many places and exposed her to a variety of work, starting with financial reporting roles and then growing into enterprise risk management.
“I really loved my time in industry. I travelled the world a fair bit and spent some time in the supply chain as well.
“That was my first taste of really getting a handle on what sustainability and sustainable business was about, with ethical sourcing and human rights, as well as a chance to learn the ropes in operations and manufacturing.”
Not long after that, Ms Foeng had another change of scenery.
“I hopped back into a big multi-faceted telecommunications organisation, and there I ran a very large global shared services team – which had lots of interesting challenges, but that really taught me to be wellgrounded and disciplined in terms of doing good business,” she said.
“It also taught me the things that worked and the things that didn’t in my journey as an executive.”
In 2017, Ms Foeng made her foray into the water sector as Yarra Valley Water’s Chief Financial Officer.
“It was a deliberate move to wrap my arms around something a bit different. And what I really love about the career I’ve had here in the water industry is the purpose orientation and that real strong connection to customer and community,” she said.
“When you come into the water sector, you’ve got to be able to grasp onto lots of things. You’ve got to view yourself as a custodian of resources and really be able to prioritise and make difficult trade-off decisions.
“You’re doing this on behalf of the voice of the customer and the community, so you need to manage risks and opportunities really well to get great outcomes for them.
“It’s not just about being focused on the financials – to be sustainable as a business, you’ve got to be strategic and think about sustainability in a much broader lens.”
While this purpose-orientation is what drew Ms Foeng to the industry, it was the sector’s focus on partnering with the community, the environment and our Traditional Owners that kept her there.
“As the owners of the land and the waterways in which we operate, First Nations peoples were our first scientists. There’s so much wisdom to embrace, which will be a greater focus for us as we mature more in that space and bring forward the voice of the environment and our guiding principle of caring for Country.
“Something that’s kept me here in the water sector, is just the collaborative spirit of us all as a sector. I don’t think I’ve been in any other industry where the collaboration is so strong.”
There’s something undeniably sincere about Ms Foeng’s passion and her commitment to the industry, and Yarra Valley Water saw that too. So, when the utility’s Managing Director, Pat McCafferty, stepped down after 11 years in the role, the Board chose Ms Foeng to take Yarra Valley Water forward as its first female Managing Director.
A positive, sustainable future
Ms Foeng is an exceptional leader; she has strong financial, commercial and risk management expertise, and proven track record in driving sustainable business performance across corporate and utility environments –but what stood out to Yarra Valley Water’s Board was her vision for the future.
“I think the next era of water calls for an evolved approach – a new approach,” Ms Foeng said.
“It means that we’re going to have to really plan our investments across multiple horizons, not with a shortterm focus.
“We’ve got to think about the longer term as well, and start to put the voice of the future generations in our minds. We need to be thinking about partnerships in a dedicated and intentional way – because a siloed, competitive approach is not going to help get us there.”
Looking ahead to the next decade, Ms Foeng said that the water sector is facing several complex headwinds.
“At the moment, we are in a very high inflationary environment – and the economic conditions call for us to be resourceful with our decision making and prioritise where we put our investments – because it is all community funded,” Ms Foeng said.
“We also have to bear intergenerational equity in mind, because we know that there’s a growing gap – particularly with the cost-of-living challenges, higher levels of vulnerability and the socioeconomics that we are seeing play out in the community.
“And we need to think about future generations. They’re not here today when we’re making decisions, so, we have to look after the planet and the waterways to make sure that water is always there for the future, and that we’re not making life harder for them when it’s their turn.”
Ms Foeng said that a growing population, climate change and ageing assets mean that Yarra Valley Water has high levels of capital expenditure on the agenda.
“We’ve obviously got a need for more housing, and we’ve also got infrastructure coming to the end of its life – we need to make sure we’re being responsible, and we’re not leaving the future generations with broken infrastructure that will cost a lot of money all at once to repair,” she said.
“There’s also the evolution of digitisation and AI, and we’re looking at new technologies as opportunities, not risks.
“And it’s about how we can be really intentional and deliberate in using new technologies, and invest in the ones that we think are going to make a big difference – not just when it comes to the business, but for our customers and community, and in helping us work together with our supply chain and our partners.”
For Ms Foeng, solving all these challenges requires a whole-systems approach.
“We need to be a collective force,” she said.
“We need to be thinking around how each of us plays a role, understand the challenges we’re trying to solve and solve them together.
“All of us can contribute to that ecosystem – whether it’s resources, our IP, our technology and our innovation, or whether it’s funding to help get things up and running.”
Ms Foeng said that it’s incredibly powerful when public organisations, communities and the private sector come together and really listen to each other.
“When you bring all those forces and stakeholders together, imagine what you can achieve for problems like climate change and water security,” she said.
For Ms Foeng, tackling all these challenges, and particularly those that directly impact customers, means approaching issues with open communication and a learning mindset.
“In terms of customers in particular, the most obvious way that we can help out as a water corporation is with hardship support – and we know that many of our customers are facing cost of living challenges,” she said.
Like many water authorities, Yarra Valley Water already has a service, Watercare, that supports vulnerable customers with their bills and connects them with other government assistance. However, Ms Foeng said that more awareness is needed.
“Affordability is a real issue for many customers, but a lot don’t actually know that the support programs are available,” she said.
“So, we’re putting a greater focus on trying to build awareness of these programs. We know that sometimes it’s really difficult for people to feel comfortable reaching out, but the more we talk about it and the more we reach out to them, the more we can support customers through financial challenges.
“Our goal is always to try and get out there, really support customers and make them feel comfortable.”
Family and domestic violence is another issue that Ms Foeng said the utility needs to continuously be mindful of.
“It’s a really important thing that probably isn’t talked about enough, and for us, it’s about having a learning mindset. Because it’s only in recent times that we’re learning more about how utility organisations come into it,” she said.
“We can be weaponised by perpetrators and not even know when we’re talking to our customers that they are in a vulnerable position. So we’re looking at how we can start to change our systems, our processes, training and awareness, and build up the skill sets of our workforce to be able to help support and deal with these customers.”
According to Ms Foeng, Yarra Valley Water is working to ensure it is playing its part and leading the way to genuine improvement.
In 2024, the Yarra Valley Water joined forces with Flequity Ventures, the Thriving Communities Partnership – of which Yarra Valley Water is a founding member –Safe and Equal, and the Centre for Women’s Economic Safety to form the Safety by Design partnership. The goal of the initiative is to identify risks in utilities’ systems, and proactively prevent these products and services from being weaponised against consumers experiencing family violence.
The utility is also a founding corporate member of the One Generation national business alliance, and was among the first Victorian water corporations to join the Respect and Protect initiative.
“We are one of the few to have done that in the water industry, but we still have lots to learn,” Ms Foeng said
“And one of the sectors that has led the way and is a little bit more down the track from us in terms of maturity is the financial services area.”
Ms Foeng said that Flequity Ventures founder, Catherine Fitzpatrick, comes from that financial sector, and has a lot of those valuable insights to share with the water and energy industry
“It all comes back to collaboration,” she said.
“For example, in Melbourne’s water sector we have an accord forum where all the managing directors come together regularly. And the more we talk about these things, and share the great work we’re doing in the space, the more we create a ripple effect.”
This accord between Melbourne’s metropolitan water authorities goes beyond tackling customer’s challenges, and Ms Foeng said that by working together, they are progressing issues such as water security, financial resilience and traditional owner engagement.
“It’s that unified and consistent approach that really helps to shift the dial,” she said.
“For example, bringing a collective force together of government, private and public sector, and Traditional Owners groups is a great way to tackle the challenge we have around housing affordability and growth.
“There’s so much there that we can learn from our Traditional Owners, and when you combine Western and Aboriginal philosophies, I think we can move forwards in a very positive way.
“Collaboration can really make a difference. Because you’re often disrupting the way things are done at the moment to be able to make a change for the future.”
All 18 of Victoria’s water corporations have pledged to power their operations with 100 per cent renewable electricity by the end of 2025 and reduce their emissions to net zero by 2035 – and Yarra Valley Water is among those who’ve already reached that goal. Ms Foeng said that while the utility’s current focus on community, customers, the environment, and honouring and healing Country will remain absolutely relevant, strategies should never really stay static all the time.
“When I’m thinking about that longer term horizon, we need to adapt, and dial up the focus areas we want to be more intentional about,” she said.
“Creating a positive, equitable and sustainable future really comes down to choices that we make.”
Looking back at her career across many different organisations, Ms Foeng said that she sees herself as a very different leader now at Yarra Valley Water.
“That’s come with growth. Those organisations have a taught me all different forms of leadership. Some of them were corporate environments where I felt like I needed to carry a different persona to be able to fit into them. But here in the water industry, what’s really shifted for me is that thriving environment to be my best self,” she said.
Ms Foeng said that being okay with not knowing everything, having a curiosity to learn from others, and surrounding yourself with good people and working as a collective can be seen as signs of weakness in some competitive corporate environments.
“The water sector has taught me something very special, and that is when we’re leaning into a different future, you’ve actually got to have a very different type of leadership,” she said.
For Ms Foeng, a good leader means leading with your heart, head and hands.
“What that translates into is leading with purpose. For me, that’s about how we can influence others to align to a purpose as a collective, and how they can see their contribution towards that common goal and feel rewarded,” she said.
“It’s about listening generously, being curious and embracing the diverse voices around the table. It’s the ability to remain calm, not sweat the small stuff and have fun along the way.
“Great leadership is also about humility. It’s about being able to make hard decisions when the time calls for it. But when something hasn’t gone the way you expect it to, it’s also about having the humility to say you don’t necessarily know it all and that you’re here to learn, and then looking at what can you do differently.”
Ms Foeng said that encouraging more diverse voices into STEM requires strong sponsorship and mentoring.
“When you’re thinking about gender diversity and attracting more females into leadership roles, the importance of allies to champion the change can’t be underestimated,” she said.
“I’ve been very privileged to have many different leaders teach me in my career, but it would be remiss of me not to recognise my most recent inspiring mentor, Pat McCafferty.
“I feel humbled and energised to demonstrate what’s really possible for women in the water industry. Many leaders have really inspired me on this journey, but what Pat’s done is be a great sponsor for me and a champion of change.
Ms Foeng said that through leadership rotations, Mr McCafferty helped her grow her experience in other parts of the business
“Opening up the doors within Yarra Valley Water has helped shape me to take on a gig like the Managing Director position – and that’s certainly something that I will truly cherish for many years to come.”
For the next generation of women who aspire to take on a leadership role, Ms Foeng encourages them to embrace all the new opportunities.
“Whatever it might be, the experiences that you gain from going a little bit left of centre will really enrich and shape your leadership journey, and often help break down those glass ceilings,” she said.
“I think for women aspiring to a long career in STEM, it’s important to acknowledge that leadership comes in all shapes and sizes.
“It’s not necessarily always about going up the corporate ladder – it can be about growth across the business as well, and the water industry has that for you.”
Encouraging everyone to be their best selves is the most important thing Ms Foeng said an organisation can do, and she encourages mentors in the sector to step up for women in STEM.
“You need those champions of change and allies to band together and support each other,” she said.
“It’s a different way of working, a different form of leadership, but it’s one that we very much appreciate –because diversity is important.” U
Interflow’s new Sustainability Framework is about leaving a better legacy for future generations, and that’s everyone’s business.
When Interflow Sustainability and Environment Manager, Pam Johnson, joined the company she recognised that some good foundations had already been established to drive meaningful and positive sustainability outcomes. What the organisation now required was structure, clarity and momentum.
“That’s what the Sustainability Framework delivers,” she said.
Sometimes, sustainability is mistakenly reduced to just environmental management, particularly in operational or project-based industries. Instead, Interflow’s latest Sustainability Framework deliberately connects environmental protection, social considerations, governance, ethical practices and economic sustainability together and brings Interflow’s purpose to life, that is ‘to improve the lives of the people we work with, the communities we serve and the environments we work in, for generations to come.’
While the broad focus of the framework is on the United Nations Sustainable Development Goals that will help improve global outcomes, such as Responsible Consumption and Production, Climate Action and Clean Water and Sanitation, Ms Johnson and her team are working to translate its pieces into personal, relatable outcomes for all members of the Interflow family.
Interflow’s key areas of sustainability focus
The new Sustainability Framework identifies three pillars, environmental stewardship, social responsibility and governance. From the environmental angle, this means a commitment to net-zero emissions by 2040.
Less than 20 per cent of the company’s emissions come from operations, with over 80 per cent coming from Interflow’s supply chain. And so, the framework will also help to guide action and influence within that supply chain and with business partners.
“There is going to be an increased focus on supplier prequalification and engagement,” Ms Johnson said.
“We want to be working with suppliers that share our sustainability values. It’s not necessarily going to be onesize-fits-all, but for us to achieve our goals, we’re going to need to bring our suppliers along with us.”
In terms of social responsibility, there is a strong focus on health and wellbeing amongst Interflow’s people and communities, as well as diversity and inclusion.
From the governance side, the framework describes a robust structure that underpins everything, ensuring every agreed idea is translated into actions and outcomes.
The framework is driven by the Interflow leadership team, who are responsible for oversight and integration into the business’s strategy and decision-making processes. Pam then leads execution, working with regional managers, team leaders and business partners to ensure implementation at all levels.
Ms Johnson said that transparent reporting is a key focus.
“We need to measure and document what we’re doing and what we’re achieving, so we can continually improve,” she said.
“Sustainability isn’t the responsibility of one person or one team, it needs to be woven into the work of so many within the business, from site crews to executives and outside the business, including our suppliers and customers,” Ms Johnson said.
“That’s why Interflow’s message is clear, that this is a journey we take together.
“And as the framework says, as a business and as partners, we can drive meaningful change, create shared value and improve lives for generations to come.” U
We’re Creating the Future of Water for climate, communities and our kids
Coliban Water is delivering a new solids handling facility, and this “once-in-ageneration” investment will set Bendigo up for a sustainable water future.
By December 2028, a new solids handling facility at the Bendigo Water Reclamation Plant in Epsom is set to be completed. For Coliban Water, this is a landmark capital investment and an important step in an upgrade project that will “benefit every bum in Bendigo”.
This new facility will replace the current solids handling treatment process, and is designed to increase the plant’s treatment capacity, reduce odour emissions and increase the reuse of biosolids. Coliban Water Managing Director, Damian Wells, said it will benefit Bendigo’s future generations, with the population expected to approach 200,000 by 2050.
“When you think about it, it may be the only piece of community infrastructure that connects and benefits everyone, or every ‘bum’, in Bendigo,” he said.
“We don’t consciously think about it but every time you flush your toilet, use the sink or wash something down the drain, our plant in Epsom is where it ends up. So much of what happens at our plant and across our network is out of sight and out of mind for people.
“This truly is a once-in-a-generation upgrade of essential public health infrastructure for our community. It will benefit not only those living in Bendigo now, but those who move to our region in the future.
“As a customer-funded company, we are always keen to ensure our customers know we spend the money from their water bills wisely to meet their needs today and support our community tomorrow.”
The Bendigo Water Reclamation Plant currently receives and treats more than 22ML of sewage from 110,000 people across Bendigo each day – the equivalent of around nine Olympic swimming pools. When complete, the planned Solids Handling Upgrade will ensure the Bendigo plant – a critical community asset – can provide an essential service to the growing city for the next 25 years.
“We need to act now and address the challenges of our changing and drying climate, ageing infrastructure and our increasing population,” Mr Wells said.
“As always, we are working hard to make sure our customers, communities, Traditional Owners, partners and other stakeholders are right there with us and up to date with our progress against our Big Water Build plans.”
Coliban Water is also planning to upgrade the liquids treatment stream at the Bendigo Water Reclamation Plant to complement the new solids handling facility.
The central Victorian water company is on-track to deliver its biggest ever program of capital investment, supporting the current 180,000 customers around the region, supporting business, industry and future growth.
Coliban Water will deliver around $500 million worth of capital investment during its current 2023–28 pricing period.
Other major projects on the agenda for include a major upgrade of the Castlemaine Water Reclamation Plant, upgrades at a number of drinking water treatment plants, and the first phase of the Water and Sewer Network Program, the latter of which will help to grow and futureproof the region’s enormous network of water and sewer pipelines and pump stations.
The new solids handling facility will be a complete replacement of the existing part of the treatment process that takes the solid sludge from the wastewater and turns it into biosolids that are able to be used in farming.
“With Bendigo’s expected growth in the coming decades, this solids handling facility will process the increased volumes of sewage coming from the community, turning it into high quality biosolids that can be used sustainably as fertiliser by local farmers,” Mr Wells said.
“We are choosing to invest for the long-term to ensure the next generation inherit a plant that is safer, more sustainable, more energy efficient and more resilient to the impacts of our changing and drying climate.”
To help complete the works, Coliban Water has awarded a contract to LC Envico – a joint venture between Laurie Curran Water and CCB Envico.
Awarding the contract is the first major milestone for the project, with a focus on detailed design over the coming months ahead of electric infrastructure upgrades to be completed through the remainder of 2025 and early 2026, before construction on the new aerobic digestor, thickening and dewatering equipment begins in mid-2026.
“The procurement process has been extremely thorough, with first-class due diligence carried out by our project team,” Mr Wells said.
“Our partner, LC Envico, is highly regarded and experienced across the water sector when it comes to delivering water infrastructure upgrades of this scale.”
Works on the new solids handling facility is expected to be completed in the next three-and-a-half years.
“When complete, the aerobic digestor will be one of the largest in Australia, with four cells measuring 36m on each side with the whole facility to have a capacity of 24ML,” Mr Wells said.
“All of this work will be carried out on-site, near the existing facility, to minimise disruption to the usual treatment process.”
Bendigo’s wastewater treatment has always been at the Epsom site, which opened in 1923 and has been modernised regularly through the decades – with the last major upgrade in the early 1990s.
“This wastewater facility has been serving our community for more than 100 years, and it’s nearing the end of its asset life,” Mr Wells said.
“Like our predecessors, we know effectively managing the city’s sewage is vital for people’s health. We also know our region will continue to prosper and our population grow. That is why these upgrades are so important.
“We started the planning for these upgrades back in 2016, so it is close to ten years in the making. But we know there is still much more to do.
“We recognise this facility has reached a critical point and that we must continue to invest in our capability and capacity to support more people, in more homes, in new suburbs, with more industry and with increasing opportunity.” U
For more information, visit connect.coliban.com.au/bendigo-wrp-upgrade-project
When a pump fails, utilities have two choices: replace or repair.
But what if there is a third option – reviving old assets to perform better than ever?
Embracing circular economy and waste-reduction principles means making the most out of existing assets. But, while a ‘repair over replace’ mindset helps reduce unnecessary waste and delays the need for a major investment in new equipment – it’s not necessarily always the most cost-effective solution.
The costs of repeated repairs on ageing assets add up, and, over time, these interventions often become more frequent. Older pumping solutions are also usually less efficient, and consume more energy to do the same job.
It seems like a lose-lose situation, but what if the solution isn’t a replacement? What if the right coating system could rewind the wear, rebuild the performance and reset the clock?
The legacy mindset for degraded pumps or fan housings was simple: replace worn metal. However, this incurs costs, delays and repetitive problems.
Rotating equipment rebuilds offer a smarter way forward. A simple polymer-ceramic coating can restore an assets structural integrity, reclaim hydraulic efficiency, and offer greater resistance than the original design. It’s not just about running old assets – it’s about improving them.
These coatings give rotating equipment a second life, and at the forefront is Chesterton’s ARC coating technology, designed to rescue, reinforce, and future-proof pumps and fans in harsh conditions.
Let’s start with ARC 858. This coating isn’t just tough –it’s smart tough. Formulated to smooth internal surfaces of pumps and flow equipment, it reduces turbulence, enhances flow and resists erosive wear from suspended solids or cavitation.
Maintenance teams use ARC 858 to resurface volutes, impellers and casings, where micro-erosion affects performance. Chesterton said that operators can see immediate improvements in efficiency, reporting up to seven per cent energy savings and significant extensions
in mean time between failure (MTBF) – a crucial metric in environments where community reliability depends on asset performance.
The ARC BX series offers heavy-duty rebuild composites to replace lost metal quickly and permanently. Whether volutes are corroded or fan blades eroded, BX coatings fill, reinforce and restore the geometry for safe operation. Rather than new parts, teams adopt a new mindset: restore and reinforce with a material that firmly bonds and lasts longer than welded overlays or epoxy fillers.
Pumps handling abrasive slurries or aggressive chemicals often require coatings with high wear resistance. In one mining application, a tailings pump lost more than 12mm of material in six months. A repair using ARC MX1, BX2, and a topcoat of ARC 855 extended the pump’s service life by more than 12 months. Repairs were minimal, the pumps returned to service within 72 hours and the company say annual savings of approximately $13,700 per unit.
ARC coatings replace reactive patchwork with engineered resilience. This isn’t just a repair: it’s a redesign, with reliability in mind. U
For more information, connect with an expert at enquiries_apac@chesterton.com
Predict. Prevent. Perform. Stop unplanned downtime before it starts! The Chesterton Connect™ System empowers you with real-time predictive maintenance, optimising equipment performance and keeping your operations running smoothly.
Anytime, Anywhere Monitoring – Access critical pump health data straight from your smartphone, tablet, or computer with our cutting-edge IIoT technology.
Easy Setup. Instant Insights. Maximum Efficiency. Choose from preconfigured solutions tailored to your needs and take control of your equipment’s future today.
Get Started Now!
chesterton.com
chestertoncustomseal.com.au
What
As water scarcity becomes a growing concern, recycled water and circular economy principles can help us get the most out of our most precious resource.
The circular economy offers many opportunities for the water sector. Adopting these approaches can boost the climate resilience of water supplies by reducing reliance on freshwater sources and minimise environmental impact by promoting resource efficiency and regeneration.
In its Circular economy framing document, the Water Services Association of Australia (WSAA) outlines three principles upon which the circular economy is based: designing out waste and pollution; keeping products and materials in use for as long as possible; and regenerating natural systems.
When it comes to opportunities to embody these principles through in water, WSAA identified the urban water cycle, secondary resource management, energy and carbon, and environmental outcomes as key focus areas. Recycled water and resource and recovery facilities maximise the lifecycle of water and allow useful resources to be recovered and returned to the economy, and James Cumming and Sons Managing Director, John Cumming, highlighted that sustainable water treatment doesn’t have to come at the expense of performance or cost-effectiveness. Recycled water has the potential for widespread use, including industrial, agricultural and residential applications; but, it’s vital that this water is treated to the highest quality to preserve the environment.
When it comes to water quality, Mr Cumming said your choice of filter medium can make a significant difference in the quality and sustainability of the treatment process.
“[When selecting a filter medium, it’s important to] know the types of contaminants or targets you’re removing to and the regulatory limits you need to meet,” he said.
“Compared to alternatives like sand alone, filter coal enables higher filtration rates, longer filter runs and lower backwash frequencies – meaning less water and energy usage over time through a conventional water treatment plant, or desalination plant pre-treatment process.”
As electricity is responsible for the majority of water and wastewater facilities’ Scope 2 emissions, minimising energy consumption can both reduce the environmental impact and help asset owners cut costs.
“Australian Filter coal offers a low embodied energy product with a long service life – typically lasting 15–20 years in a filter bed if operated correctly,” Mr Cumming said.
“It’s cost-effective over its lifespan because it reduces operational costs in water treatment plants.”
James Cumming and Sons is the sole manufacturer of Australian Filter Coal, and sustainability is deeply embedded in its entire operations.
“We are continually investing in plant and equipment that is more energy efficient. We operate our plants almost exclusively at off peak and shoulder times to reduce the load on the grid,” Mr Cumming said.
“As a fourth-generation Australian family-owned and -operated business in Western Sydney, we approach sustainability with a long-term vision and strategy to minimise any negative environmental impact and maximise customer value.
“We manufacture our filter coal through careful selection of raw materials, consistent supply relationships and optimising a drying, crushing, screening and packaging plant in Western Sydney.
“We use is Australian black Coal that is sustainably sourced and mined, and our manufacturing process and inherent coal properties are unique in that there are no by-products created that aren’t used for environmentally friendly applications.”
Mr Cumming explained that in order to meet customers’ specific sizing needs, processing the coal inevitably creates undersized coal, which doesn’t fit within their specification, and “fines” that aren’t suitable for the water industry.
“Typically [that undersize coal] is burned for energy production in power plants because – whereas our coal has many inherent properties suitable for a wide
range of industries, and isn’t used in any thermal power generation applications.
“Instead it’s used for glass colourisation and in iron foundries as a casting additive.”Circular economies are most successful when the loops are small and Mr Cumming encouraged utilities to source products locally.
“[Choosing] an Australian-made product minimises supply chain emissions associated with importing filter media from overseas,” he said.
“Customers can trace the origin and processing of the product, ensuring responsible sourcing and compliance with Australian environmental standards – and supporting local manufacturing strengthens regional economies and secures jobs,
“It also secures our water infrastructure that relies on our product. Local suppliers can offer technical advice and shorter lead times in an emergency.”
Mr Cumming said that by choosing Australian Filter Coal, industries can contribute to a more sustainable future.
“Australian-made filter coal offers a proven, highquality solution that supports environmental goals while delivering reliable results,” he said
“We’re proud to continue our legacy as a local manufacturer contributing to sustainable water infrastructure in Australia and beyond.” U
Once
Regional Queensland is one step closer to long-term water security, with the first water flowing into the Fitzroy to Gladstone Pipeline as testing continues.
The Fitzroy to Gladstone Pipeline (FGP) is more than just a pipeline – it’s a carefully engineered system designed to deliver water efficiently and reliably to the Gladstone region.
A key part of this system is a network of valves installed along the 117km alignment. These valves manage water flow, maintain pressure and support safe operations across the entire pipeline.
A variety of valves have been installed to ensure the FGP operates smoothly when it comes online in 2026:
• Butterfly valves – used to control water flow through the pipeline with minimal resistance.
• 8 00mm control valve – located at the Gladstone Area Water Board (GAWB) network connection at Mount Miller, serving as the master control point.
• DN750 isolation valves – spaced approximately every 10km, allowing sections to be isolated for maintenance or emergencies.
• Scour valves – placed every three kilometres at low points to help remove trapped air and assist with efficient water filling.
• Air valves – located at high points every kilometre to release air and support system filling during commissioning.
Each valve plays a specific role, but together, they form a critical part of the FGP’s operation.
With installation nearing completion, Principal Contractor McConnell Dowell BMD Joint Venture has begun testing sections of the pipeline.
Water has now been pumped into a section of the new pipeline as part of testing prior to completion in 2026.
GAWB CEO, Darren Barlow, said the milestone marks significant progress for the $983 million project.
“This is the first time water has flowed through a section of the new pipeline, and it’s an exciting sign of what’s to come,” Mr Barlow said.
The FGP comprises a 117km pipeline (now almost completely constructed), reservoirs and a water treatment plant, all of which are progressing well.
As each component is built, it undergoes rigorous testing to ensure safe and reliable operation during commissioning in 2026. Around 3km of pipeline has now completed hydrostatic testing – a key process that involves filling the pipeline with water and pressurising it to check for leaks or weaknesses.
“Hydrostatic testing is a vital step in confirming the safety and reliability of the infrastructure before it is brought into full service,” Mr Barlow said.
“Reaching this stage is a testament to the skill and commitment of our project team and partners. It brings us one step closer to delivering a secure water future for Gladstone.”
Construction is advancing across all major components:
Laurel Bank Intake
Key structural elements are now in place, with backfilling completed around the pump station and preparations underway for mechanical installations. The earthing grid for the control building is being installed to support the next stage of electrical works.
Clarifier wall pours are nearing completion. Mechanical and electrical crews are preparing for the next stage of fit-outs, while roofing is progressing on the control and administration building. At the silt dewatering facility, wall cladding continues, and preparations are being made for final concrete pours and equipment installation.
Aldoga Reservoirs
Each of the two reservoirs will hold up to 50ML, enough water in each to fill around 20 Olympic-sized swimming pools. All 120 precast concrete wall panels have been installed and stitched together for a watertight structure, and internal support columns for the roofs are complete.
Construction of the pipeline remains on track for completion in 2026, weather and conditions permitting. The FGP will provide a second source of water to Gladstone, reducing long-term supply risks from Awoonga Dam and supporting the region’s industrial growth.
GAWB, as a Queensland Government Bulk Water Supply Authority, delivers safe and reliable water services that promote economic development and enhance the lifestyle of regional Queensland. GAWB owns and operates Awoonga Dam, along with a network of pipelines, water treatment plants and other distribution infrastructure. GAWB also owns and operates Aquaculture Gladstone, a fish hatchery and interpretive display at Lookout One at Lake Awoonga.
To ensure long-term water security for customers, the 117km FGP is under development. When delivered, the FGP will become part of the GAWB network and provide enhanced water security and reliability for the region.
For more information about GAWB and the FGP, please visit
To specific customer requirements, suitable for a range of water and wastewater applications Certified quality – Australian Made for Australian conditions by
Reduced rainfall and a growing population are stretching Perth’s water supply to its limits. The Alkimos desalination plant is set to provide a long-term solution, and every aspect of this project needs to be delivered with the future in mind.
Water Corporation is powering ahead a new major water source for Western Australia.
With a declining rainfall and a growing population, it’s projected that the state will need and extra 75–125GL of water per year by 2035. To meet this demand, Water Corporation has joined forces with Acciona and Jacobs Group to deliver a new climate-independent, sustainable drinking water source – the Alkimos seawater desalination plant.
Once complete, the first stage of the project will deliver an additional 50GL of clean, reliable drinking water to customers every year, with a second stage planned to increase the plant’s capacity to 100GL per year.
With enabling earthworks complete as of January 2025, this critical water project is now in full swing and expected to be completed in 2028.
To support the development of the new desalination plant, Water Corporation is also building a 33.5km pipeline to connect the plant to Wanneroo Reservoir, which feeds into the Integrated Water Supply Scheme (IWSS).
Delivered in alliance with Georgiou, with DM Drainage and Construction, this project will be the largest water pipeline that Water Corporation has constructed, with a diameter of up to 1600mm. It has been designed to accommodate this significant amount of water and also allow for future desalination expansions.
While the project is slated for completion in 2027, around 6km of the pipeline are being constructed early as part of major transport infrastructure projects in Alkimos.
The final pipeline will be entirely below ground except for a small section crossing the rail line near Alkimos Station and some discreet access valves installed at intervals along the pipeline.
To facilitate this challenging project, one of Kwik-ZIP’s customers deployed HDXT-103 spacers with load inserts to facilitate the slip-lining of a 914mm Sintakote® mild steel cement lined (MSCL) carrier pipe into a 1399mm reinforced concrete jacking pipe casing (RCJP), as well as a 1422mm Sintakote MSCL carrier pipe into a 1708mm casing at a rail crossing in Yanchep.
This installation was fully grouted, however, as longevity is key in this critical project, the HDXT spacers and load inserts would adequately support the pipes and water for the life of the installation.
Kwik-ZIP said that the HDXT’s unique load sharing design maximises the load bearing capacity of each runner and reduces point loading.
HDXT load inserts are designed to be used with the Kwik-ZIP HDXT casing spacers to provide additional load capacity for very heavy applications or where high
Kwik-ZIP’s HDXT spacers have a unique load-sharing design that allows them to carry heavy loads at elevated temperatures. Image: kwik-ZIP
point loadings on one runner are experienced. They also allow HDXT spacers to continue to carry heavy loads at elevated temperatures.
These spacers have no metal parts and are made from Kwik-ZIP’s engineered thermoplastic blend that is flexible, extremely tough and has a low co-efficient of friction.
Projects like the Alkimos to Wanneroo desalination pipeline are the foundation of Australia’s water security, so it’s vital that they’re prepped to stand the test of time.
The fusion-bonded coating on Sintakote® pipes is crucial for corrosion prevention and must stay undamaged to work effectively. Kwik-ZIP spacers not only provide protection but also feature integrated rubber grip pads, preventing slippage and preserving the coating’s integrity and safeguarding this essential asset. U
For more information, visit kwikzip.com
29 & 2 2 |
Get ready for the ultimate gathering of water industry operations professionals in Newcastle! oin us for a day filled with insightful discussions, networking opportunities, e citing e hi itions, Women of Water Breakfast, IXOM Best Tasting Tap Water Competition, eece Civil + iadu Main
Tapping Competition, and acknowledging e cellence at our wards
Ceremonies Whether you're a seasoned pro or just starting out in the Water industry, this event is perfect for e panding your knowledge and connecting with like-minded individuals. Get involved
Apply to participate in the competitions
Become a WIOA Member View more details & register today Award bmissionsNominate today
To help meet growing water demand in Australia’s second largest city, Yokogawa is supplying integrated SCADA for Melbourne Water.
Yokogawa Electric Corporation has announced that its subsidiary, Yokogawa Australia, has received an order from Melbourne Water to implement Yokogawa’s flagship supervisory control and data acquisition (SCADA) system – OpreXTM Collaborative Information Server – to help modernise the city’s water supply network that serves more than five million people.
Yokogawa Australia was selected to deliver OpreX Collaborative Information Server and engineering services for Melbourne Water’s SCADA for our Future project, which will take up to three years to complete.
Key considerations in the selection process included the company’s strong local capabilities combined with a globally proven SCADA software platform, meeting Melbourne Water’s scale, business and operating requirements. The new SCADA system will serve as a modern platform that can scale as Melbourne Water expands its network and capacity to meet the demands of the growing city. OpreX Collaborative Information Server will deliver advanced integration capabilities with more flexible access, and support increased resilience to both cyber security and business continuity threats.
The platform will provide Melbourne Water with a centralised source of truth for all operational data and will make this available to all business users and applications to support operational efficiency, advanced analytics, and future technologies. The project is a key element of Melbourne Water’s digital strategy and it’s goal to create a an intelligent network, leveraging automation and analytics to enable effective planning, efficient operations and responsive decision making.
Melbourne Water Senior Manager of Asset Knowledge and Technology and project sponsor, Aidan Hollier, said, “We are very excited to have Yokogawa working with us to support our continuous growth requirements. We provide water for over five million Melbourne residents, with a 24/7 operation, and this requires technology solutions that are reliable and can be continuously maintained for the foreseeable future.”
Reflecting on the two-year selection process, Yokogawa Australia Managing Director, Russell Palmer, said, “The thorough and intensive selection process conducted by Melbourne Water left no stone unturned and really challenged our engineering team. We are excited to partner with Melbourne Water to implement OpreX Collaborative Information Server and support their modernisation and growth objectives.
“A significant project like this allows us to strengthen our local engineering capabilities and continue to expand support for our customers as we commemorate the Yokogawa Group’s 110th anniversary this year.”
Yokogawa provides advanced measurement, control and information solutions to customers across a broad range of industries, and addresses customer issues regarding the optimisation of production, assets and the supply chain with the effective application of digital technologies, enabling the transition to autonomous operations.
Founded in Tokyo in 1915, Yokogawa continues to work toward a sustainable society through its team of more than 17,000 employees across a global network of 126 companies spanning 60 countries. U
Asset management means navigating many competing priorities and success hinges on making strategic decisions – not just for operations but for your equipment, too.
When a water authority invests in its assets, that money ultimately comes from the communities and customers that rely on it.
Water is a non-negotiable, so it’s vital that all customers not only have access to a secure, clean supply – but they can also afford this service.
At the same time, utilities need to be mindful of the land on which they operate and ensure their ageing infrastructure is kept up to scratch to prevent harmful sewer spills and to ensure precious water is not being lost through leaks and bursts.
Customer expectations and government regulations are also constantly evolving, and water authorities are having to meet increasingly stringent environmental regulations, water quality standards and net-zero targets.
Utilities have to make clever, strategic decisions about which assets they prioritise and what products they purchase. This is especially important when it comes key pipeline maintenance solutions like water jetting and trade fleet equipment, according to the team at Enviroline.
Every service area comes with its own unique maintenance challenges that the local utilities need to
And according to the team, if there’s one thing that they’ve learned in that time it’s that utilities need more than just the right equipment – they need expertise, insight and a partner they can trust.
Enjoy Plumbing Director, Robert Shipway, has known some of Enviroline’s team members for more than ten years, so he knew who to turn to when he launched his new business in January 2025.
“I started a very large company down in Sydney called Hello Plumbing, which had 12 trucks on the road at our highest point, that company won multiple local business awards, and I even won the Young Entrepreneur of the Year when I was 30,” he said.
“Then my long-term apprentice bought the business from me, and I moved up to the mid-north coast of New South Wales and I started Enjoy Plumbing.
“There was a major gap in the market up here for a professional plumbing company, but because our service area is about a 200km radius from Port Macquarie, we have to have all the tools on-board. Making sure we have the correct equipment to be able to do our job correctly is a major challenge.”
Mr Shipway said building up the number of vehicles the company needs for its trade fleet was a full-time job.
“We used to employ someone full-time on staff to do that. And now, with Enviroline’s, new water jetting utes, I can just click a button and get a new car on the road ready to rumble,” he said.
Because Mr Shipway and his team service such a large area, they need to be equipped to tackle a range of different landscapes and environments.
“We encounter a lot of very hard-to-access properties and that’s why we run our jetter on our vehicles, instead of trailer jetters, because we need it to be compact and to be able to get up the mountains,” he said.
Mr Shipway said that Enviroline really made an effort to understand his needs as a business. A water jetting vehicle or a trade fleet fit-out are big investments, so the Enviroline team understands just how important it is to have comprehensive support at every stage of the project.
The team were more than happy to share their knowledge and work alongside Mr Shipway to ensure that Enjoy Plumbing could meet its own customer’s needs.
“Enviroline was very easy to deal with. We ran with what they recommended for their utes, and we found that to be the best way – they’ve been absolutely awesome,” he said.
When it comes to choosing a supplier, Mr Shipway said it’s important to consider not all services are equivalent, and to look at all the offerings each company brings, not just the price of a particular product.
“Go for someone that backs your warranties, which Enviroline does, and just make sure you’re comparing apples to apples,” he said. U
Fleet Solutions: Jetting Trucks, Vans, Trailers.
Whether you need a trailer fitted out for serious stormwater work, or a whole fleet of customised trucks for a state-wide Water Authority, Enviroline Group has the range, knowledge and services to deliver a solution tailored just for you.
From SA Water to Singleton Council to the Shire of Kojonup, we work with local, state and federal government authorities, water authorities and major civil contractors across Australia to provide expert advice, tailored commercial equipment, servicing, repairs, parts and accessories.
When rainwater or groundwater enters a sewer network uninvited, a small leak can quickly waterfall into an environmental disaster and, according to this expert, prevention is always the best solution.
Water is a powerful force. It will find its way into the smallest crack and seep into the finest fissure, inevitably growing the size of the crack through physical and chemical actions.
As the gap grows, the flow of water will continue to increase, accelerating this deterioration. When the crack is large enough, the water flow will start carrying increasingly larger particles through the gap, not only increasing the erosion but removing the critical embedment material that supports pipes, culverts, maintenance holes and pump stations.
As this embedment material is lost, ISC Services Owner, Dennis Bentink, explained that pipes and other structures can move and settle, which further increases the size of the defect and the risk of directly damaging these valuable assets due to loss of support for loads and excessive pressure and forces on joints and connections.
Mr Bentink said that the continued loss of soil and material supporting pipes can cause surface assets including footpaths, roads and railway structures to become undermined with the potential for serious damage to the both the surface assets and the underground structures.
“The issue with water getting into the network is that when the water moves it generally takes soil with it, which will disrupt the support around pipes and maintenance holes and pump stations – and you can even get roads collapsing.”
Not only do these leaks and soil movement risk damage to the surface structures and the pipes themselves, the soil that is transported through the cracks is often deposited inside the pipes and culverts, reducing their designed capacity and resulting in flow restrictions and contributing to blockages.
It is not uncommon for tree roots to find their way in at these points and compound the damage and potential for blockages.
Mr Bentink explained that additional water takes up capacity in the network, but the big problem is the soil getting into the network
“Now the pump stations aren’t just pumping too much water – they’re also pumping soil and sand and grit. This increases both wear and tear and power consumption,” he said.
Over time, if nothing is done to stop water, soil and root ingress at these points, assets will eventually completely fail.
According to Mr Bentink, while the initial phase of the leak formation may be subtle, the progress only accelerates over time and once formed, leaks only get worse.
“The cost of unresolved leaks grows exponentially the more you have, and the longer you wait before addressing them,” he said.
“Leaks can increase costs either directly through asset damage and equipment wear, or indirectly through increased operation and maintenance costs all the way downstream including pump stations and treatment plants.”
Mr Bentink said that prevention is always the best approach, and ISC Services has sourced a range of solutions to prevent the formation of leaks and to stop leaks of different sizes, types and locations in pipes, culverts, pits, shafts and pump stations.
“HydraTite Internal Joint Seals are a perfect example of a solution to arrest surface damage caused by failing pipes and culverts,” he said.
“HydraTite is a heavy duty, trenchlessly installed, mechanical seal, which can address failing joints in pipes and culverts as well as extensive cracks and leaks in large diameter pipes, box sections and shafts for stormwater, irrigation, sewer and potable water applications.”
Mr Bentink said that it’s absolutely vital that asset owners use a solution that is meets the unique needs of their network, so HydraTite Internal Joint Seals are custom made to size and shape to extend the working life of pipes, culverts and tunnels of any size or shape with the largest ever installed in a 7300mm diameter tunnel.
ISC Services works closely with asset owners and designers to develop the most suitable combination of seals and retaining bands to suit a wide range of industries.
“I start off by looking at what the problem is and work back from there,” Mr Bentink said.
“I look at ISC Services as being a giant toolbox with a range of different tools to help councils, water authorities and contractors select the right tool for the job of stopping inflow and infiltration.” U
• Lighter and Safer
•
• Better value for money
• Half the CO2 emissions of concrete to manufacture
• Leak tight
• Trafficable Class - D
• Proven solution
• Recyclable
Innovative products to improve the return on your valuable sewer, stormwater and potable assets
• Raise MHs to surface safely, quickly and cost-effectively
• Permanently seal leaking pipes and MH joints
• Prevent leaks forming
Automated water metering has identified a major network leak in the Tamworth Region.
Tamworth Regional Council’s digital metering program has proven its worth, uncovering a non-revenue water leak in the network equivalent to a small town’s daily water use, disguised as a natural spring.
This recent finding in Tamworth Regional Council’s water network has not only showcased the transformative power of digital water metering but also underlined the urgency of investing in data-driven solutions.
With Tamworth’s population growing and its water resources remaining limited, the Tamworth Water Management Strategy has become a cornerstone of the Council’s operational priorities.
Remarkably, the city uses a similar volume of water today as it did in the 1990s despite the population having significantly increased. This achievement underscores the impact of targeted conservation efforts and infrastructure improvements, including the recent deployment of more than 23,000 automatic digital water meters by Taggle across the Council’s local government area (LGA).
Tamworth Regional Council General Manager, Paul Bennett, explained that digital water metering is a water security project within Council’s broader Water Management Strategy.
“Having access to the community’s water consumption data is a big part of informed decision making to better manage our water resources,” he said.
The small township of Nundle, with 250 properties, became the stage for a stunning discovery. Analysis of the towns digital meter data revealed a significant amount of non-revenue water, while residents were consuming 100,000L of water daily, the water treatment plant was producing 200,000L daily.
“[We were thinking] where has the other 100,000L gone?” Mr Bennett said.
“So, we sent the teams out to investigate, and what they found was that water was leaking out at a break at the end of the network, flowing directly into the creek. It was difficult to find and looked like a natural spring.”
The early awareness of an issue like this can only be achieved by data provided by automated water meters, and the reporting of the data in platforms such as the Aqualus Water dashboard.
“We knew the area had a significant network leak,” Mr Bennett said.
“However, with the data provided by the dashboard, it was evident that it was being lost in the network, and we took immediate action.”
Through the data recorded in the Aqualus Water Property Dashboard, Council staff can monitor input versus actual usage on an hourly basis.
In this particular case the difference was staggering and raised some important questions: how long had this been happening? How much water had been lost? What was the cost of treating and delivering that water that was ultimately lost?
“We won’t know the full impact because in the past we didn’t have the data,” Mr Bennett said.
“But now, we can clearly see what’s happening in the network. The digital water meters were well and truly worth the financial investment for solving this particular leak and so many others, and encouraging all water users to be aware and mindful of their usage.”
Tamworth Regional Council’s commitment to full automatic water meter coverage means every property, from the urban centre to the rural towns and villages, have access to automated water metering.
Serving communities across six water sources, the network provides real-time insights that are crucial for reducing non-revenue water, planning infrastructure upgrades, and enhancing resilience against future shortages.
In a landscape where every drop counts, Tamworth’s leap into automated water metering stands as a compelling case for other utilities. The integration of technology not only saves water and money, it changes the way we understand and manage it. U
The Australian Water Association’s flagship event, Ozwater’25, brought utilities, researchers, industry and government together to reflect on their collective knowledge and move the sector forward.
From 20–22 May 2025, water professionals from across Australia gathered at the Adelaide Convention Centre for Ozwater’25. Hosted by the Australian Water Association (AWA), this premier event was a nexus for the voices, technology and initiatives reshaping the water sector.
Ozwater’25 spotlighted future-facing and First Nations leadership, groundbreaking research and innovation, and some of the key work being undertaking to build an inclusive, equitable sector for everyone; but the key clear takeaway that emerged from the event was importance of valuing water – not just as a resource, but as the foundation for healthy, resilient communities. Through its 2025 theme, ‘Looking back, moving forward’, the AWA invited attendees to reflect on the lessons of the past while embracing a future where water is central to sustainable growth.
Over three days, delegates enjoyed some incredible keynote addresses, and insightful technical presentations and workshops. But perhaps most importantly, the event provided a platform for these bright minds to connect and share meaningful conversations on how the water sector can leverage both historical and contemporary knowledge to deliver lasting impact.
At the opening of Ozwater’25, AWA CEO, Corinne Cheeseman, urged attendees to lead with purpose.
“Our sector is facing some of its most complex challenges yet, but we also have more tools and talent than ever before,” she said.
“Ozwater’25 is about bringing that collective energy together to move our sector forward.”
The 2025 Australian Water awards acknowledged excellence, innovation and leadership across 11 categories, and celebrated the incredible individuals and initiatives shaping the future of water.
At the Ozwater’25 Gala Dinner, AWA Chief Executive, Corinne Cheeseman, commended the finalists and winners for their achievements.
“These awards recognise not only excellence, but the commitment our sector has to continually improving how we manage, protect and value water,” she said.
“Their work reminds us that with the right partnerships and purpose, we can rise to any challenge.”
The AWA thanked the evening’s sponsor, ANZ, as well as the individual category sponsors: Hydroflux, Water Research Australia, Laing O’Rourke, Water Services Association of Australia, Guidera O’Connor, Xylem and KSB Australia for their support for the sector and it’s achievements.
From industry leading research, excellence in leadership and community engagement to groundbreaking infrastructure developments, the 2025 winners were spotlighted for their exceptional contribution to the sector:
• Organisational Excellence Award – Water Corporation, Department of Water and Environmental Regulation, Department of Primary Industry and Regional Development, Murdoch University and Curtin University for the WaterSmart Farms Water Security and Resilience in a Drying Climate project.
• R&D Excellence Award – Icon Water, Yass Earth Movers and ACT NoWaste Transport Canberra and City Services, for the Spoil to Topsoil: Local Circular Economy Outcomes with Global Implications project.
• Infrastructure Project Innovation Award (metro) – John Holland Group and Melbourne Water for the Hobsons Bay Main Sewer Duplication Project .
• Infrastructure Project Innovation Award (regional) –Grampians Wimmera Mallee Water (GWMWater) for its first fully off-grid facility, The Elmhurst Water Treatment Plant.
• Water Industry Safety Excellence Award – Interflow, for rehabilitating eight sewer lines using Midline Expansion technology.
• Customer experience award – Urban Utilities for it Developer Services Transformation Project
• Best Water e-journal Paper – David M. Kempisty, Charlie Gordon, Jessica Haxen, Omid Mowla, Michael G. Nickelsen, and Steve Woodard for The Treatment of PFAS-Impacted Groundwater Using Novel Regenerable Ion Exchange Resin: A Five-Year Case Study.
• Australian Stockholm Junior Water Prize – Matthew Young, Barker College for Robotic Sub-surface Venturi Aerator for the Prevention of Algal Blooms project.
• St udent Water Prize – Weiwei Duan, University of South Australia for the Utilising Alum-Based Water Treatment Residue in Producing Highly Durable Alkaline-Activated Material research project.
• Young water professional of the year award – Dr Jessica Bohorquez, Aurecon.
• Water Professional of the Year Award – Celeste Morgan –Arup, Australasia Integrated Water Management Lead.
Connecting with Country
The conference kicked off with a deeply moving Smoking Ceremony and Welcome to Country led by proud Kaurna, Narungga and Wirangu man, Jack Buckskin. Mr Buckskin is the only fluent speaker of the Kaurna language, which he shared in a Welcome to Country that highlighted the enduring connection between water, language and Country.
“It is an honour to share our language and Country – as long as we understand the significance of where it comes from,” Mr Buckskin said.
“The influence and the impact we’re going to be leaving for the next generation – you might not see it now, but it will have a lasting effect.”
Later at the event, Office of Water Security, Executive Director, Nerida Horner, and Principal Policy Officer, Dr Susannah Clement, shared a compelling demonstration of inclusive water planning from the Northern Territory, and highlighted what the Territory Water Plan is doing to embed Aboriginal interests at every stage of water governance.
We also heard from Unitywater Environmental Planning and Cultural Heritage Specialist, Emma Newton, and Kabi Kabi Peoples Aboriginal Corporation Director, Kerry Jones, about the work Unitywater is doing to drive meaningful reconciliation, honouring Aboriginal and Torres Strait Islander peoples through partnerships, integrating First Nations knowledge, protecting cultural heritage and enhancing cultural capability.
Unitywater isn’t the only water authority taking a novel approach to infrastructure delivery, and South East Water General Manager, Liveable Water Solutions, Charlie Littlefair, joined up with KBR Integrated Planning Lead,
Jane Espie, and Fulton Hogan Utilities Program Director, Martin Sutherland, to share an overview of South East Water’s new Integrated Planning and Delivery (IPD) model.
The trio highlighted how the IPD successfully created truly integrated partnerships by bringing partners into South East Water’s world to work together and think beyond individual projects to help deliver joint program objectives and empower employees to learn.
On the customer side, Yarra Valley Water Head of Customer Insight & Strategic Research, Catherine Nicolas, walked us through some of the ethnographic research that the utility undertook as part of its ongoing efforts to support customers experiencing financial hardship.
The goal was to understand why customers are not seeking financial support and find ways to encourage contact.
Ms Nicolas explained that while Yarra Valley Water had expected to hear customers say that they were too ashamed to get help or tell anyone they’re struggling, they found that many expressed pride in finding new way to pay their bills and save money. Customers reported that this shift came from knowing that their financial struggles are widespread, and that everyone is in this together – and Mr Nicolas said this new context calls for clearer, direct communication and proactive outreach from organisations.
With a drying climate reshaping the way our water networks operate, Water Corporation Principal – Asset Risk, Matthew Stenhouse, shared how the utility preparing for the future in the face of climate change .
“What’s changed is not just the science; it’s the expectation that we must act. Beyond drying climate, we’re now seeing risks from sea level rise, extreme weather, and bushfire across our infrastructure,”he said.
Mr Stenhouse said that risk is no longer theoretical.
“We’re building resilience into every system, starting with how we assess and prioritise action.”
Ozwater’25 left the water sector with a renewed sense of purpose, and the event not only empowered the sector to tackle key challenges and build a secure water future, it also equipped leaders with the knowledge to take action.
With Ozwater’25 now under wraps, the AWA is looking ahead to the Water Efficiency Conference 2025.
The global gathering is hosted by the AWA in partnership with the International Water Association (IWA), and is a unique chance to connect with international peers and learn from some of the world’s leading water experts.
From 16–18 September 2025, the best minds in water efficiency will come together in Melbourne to explore how everyone can build more sustainable and climate-resilient water systems. This event is a chance to hear what’s really working, beyond reports and theory, and connect and collaborate with a global network of water professionals dedicated to practical solutions.
We can’t wait to see you there! U For
As demands on water infrastructure grow, so does the need for smart, resilient and autonomous systems.
Reliable automation in water and wastewater treatment isn’t just a convenience – it’s a critical necessity for safeguarding public health, maintaining compliance, ensuring operational continuity and protecting natural ecosystems.
In recent years, process automation technology has evolved from analogue hard-wired systems that were complex and costly to implement and maintain, to digitally networked systems that are easier to implement and provide far more information to help manage the process.
Due to this digitalisation, modern automation systems can now also be integrated with AI to offer predictive insights, such as impending equipment failure, or seasonal demand changes.
Modern digital technologies are making it easier than ever to implement smart automation with lower infrastructure costs.
This is where Bürkert’s modular range of process valves, valve islands and process controllers for valves offer a distinct advantage.
For example, the Type 8802 continuous ELEMENT valves enable the easy integration of digital automation modules, and they can be used with an integrated fieldbus interface to a digital process controller.
The fully integrated system with control valve and automation unit has a compact and smooth design, integrated pneumatic lines, IP65/67/NEMA 4X degree of protection and superior chemical resistance – as well as compliance with Australian water quality standards and regulations.
Compatibility with modern digital SCADA systems is also important for minimising operating and implementation costs.
The close cooperation between Siemens and Bürkert has resulted in the Type 8647 and 8652 valve islands, producing an innovative electropneumatic automation system that can be integrated into the Siemens SIMATIC ET 200SP and SIMATIC ET 200SP HA I/O systems. They are also compatible with the PCS 7 process control system, allowing all pneumatic process and device data to be represented at the highest plant level.
Digitalised technology also allows for more space-saving automation designs. The AirLINE SP Type 8647 and valve island can control up to 64 valve functions on a valve block, with up to 48 valve functions for the Type 8652.
The valves are directly connected to the Siemens I/O system, enabling fast and seamless integration during commissioning and operation monitoring. This allows the valve islands together with all Siemens modules to be placed together in the control cabinet, saving space.
The AirLINE SP valve islands also offer continuous air pressure sensor monitoring and can provide alerts when the available air pressure drops below a defined threshold – helping mitigate a common issue in pneumatic valve implementations.
The AirLINE Quick baseplate allows the valve island to be mounted directly on the control cabinet floor, eliminating the need for bulkhead fittings. Commissioning with PCS7 is also possible.
AirLINE valve islands also support hot swapping of valve modules, without disconnecting air supply, and fast diagnostic feedback is provided direct to the central controller, speeding up diagnostics and maintenance. Automating with digital process control valves –directly integrated with digital controllers – in water and wastewater processing facilities can improve plant efficiency in a way that is both cost-effective and spacesaving, while providing future-proof digital capabilities to support the process control systems of the future. U
For more information, visit burkert.com.au
The way we deliver our essential services is changing forever. To meet shifting customer needs, and rising environmental and regulatory pressures, utilities are rethinking operational efficiency.
As utilities across the nation face a new era of rising expectations from customers, the pressure is on to deliver services that are faster, safer and more sustainable.
Water may be our most precious resource, but in a connected world, time is coming in at a close second. Customers now expect fast responses to service interruptions – if they occur at all – better communication during outages and evidence that public works are being done safely, efficiently, sustainably – all without seeing an impact on their bills.
This presents a dual challenge for utilities that are already grappling with ageing assets, rising demand and labour shortages. On the one hand, utilities must modernise utility networks and service delivery. On the other, they must improve the experience of frontline teams whose work underpins every customer experience.
Meeting rising expectations isn’t just about improving customer communication; it’s about lifting performance across every aspect of service delivery.
For example, vacuum tankers play a vital – if often invisible – role in day-to-day utility operations. Responsible for critical tasks like sewer cleaning, stormwater maintenance, unblocking drains and non-destructive digging, these machines may not
be associated with the delivery of essential services, but their performance has a direct impact on service quality and reliability – particularly during unexpected service disruptions.
In an era of digital transformation, smart equipment design and integrated systems offer a chance to reimagine the operator experience and improve service delivery in the process. Well-designed equipment that is intuitive, safe and able to integrate with digital systems can support utilities to deliver the essential services their customers expect.
As the water sector adapts to new challenges, Bucher Municipal knew it needed to evolve alongside it. But in a time of change, simply upgrading existing machines isn’t going to meet the needs of tomorrow’s industry – so the team approached the new Gen 2 C140 Combination Vacuum Tanker by looking at the industry’s future needs.
efficiency
To support the industry under these growing regulatory, environmental, and workforce pressures, Bucher Municipal has officially launched the first of its nextgeneration vacuum jetting solution – the Gen 2 C140 Combination Unit.
The Gen 2 delivers a purpose-built response. It’s crafted with direct input from operators and industry stakeholders across Australia, and looks to raise the standards for equipment design, with a focus on safety, operator usability, performance, and compliance.
Rather than simply updating an existing design, Bucher approached the Gen 2 as a complete rethink.
The development program placed equal emphasis on engineering excellence and real-world application –resulting in a unit that is easier to use, faster to learn, and more efficient to operate.
Operational efficiency has long been a key benchmark for vacuum tankers, but Gen 2 introduces a new definition. Every element – from component layout to system integration – has been optimised to reduce downtime, streamline processes, and get more done with fewer inputs.
Whether deployed in metropolitan maintenance operations or regional network clearing, the Gen 2 is designed to maximise productivity per shift. With less idle time, reduced manual intervention, and intelligent control logic, operators can complete more work using fewer resources – directly improving fleet ROI.
By embedding operator experience into the design, equipment can help reduce fatigue, shorten training time and enable teams to perform reliably from day one.
Features such as the Gen 2’s visual indicators, intuitive controls and reduced manual inputs are examples of how design can simplify complex tasks and support safer, more efficient operations. Adopting a user-first philosophy also reduces operator fatigue, lowers training time, and enhances engagement – contributing to better overall fleet utilisation and safer daily operations.
Digital connectivity also plays a critical role in meeting rising expectations. The Gen 2 incorporates remote alerts, data tracking and remote monitoring tools. For forwardthinking utilities, the ability to monitor equipment remotely and proactively schedule maintenance is key, reducing downtime and enabling better planning –outcomes that feed directly into customer satisfaction.
And as customer expectations continue to evolve, it’s essential that utilities remain ready to meet them. The Gen 2’s future-ready design supports future upgrade without requiring a full unit replacement, enabling utilities to extend the value of their investments.
As utilities work to modernise from the ground up, modern, adaptable solutions such as Bucher Municipal’s Gen2 C140 Combination Vacuum Tanker are reshaping how utilities approach the customer experience, supporting them to become more responsive, more efficient and more in tune with the expectations of a modern customer. U
UltraAnalytix is a non-intrusive and non-destructive evaluation method that provides objective data.
As water authorities face the critical task of delivering our most precious resource, they need a reliable way to determine the remaining service life of ageing infrastructure.
Australia’s fluctuating climate pushes critical water systems to their limits. Hot, dry conditions exacerbate water scarcity, and the accompanying harsh UV degrades water transport and storage assets, causing them to crack and leak.
On the other hand, intense floods and storms risk physical damage to treatment plants and pipelines, and lead to significant fluctuations in water quality, including increased turbidity and algal blooms.
In turn, these stressors team up with varied soil and water conditions to exacerbate corrosion and promote premature degradation of vital water infrastructure – and as those asset age, the risk of failure only increases.
Fibre Reinforced Polymer (FRP) composites offer an alternative to traditional materials like steel, ductile iron and concrete that can better withstand extreme temperatures and harsh conditions. These composites are immune corrosion, and their non-porous surface prevents biofilm and sediment buildup, FRP composite tanks and above-ground pipes can also be manufactured with UV-resistant coatings that protect them from the intense Australian sun.
Despite their durability, FRP composites are also inherently lightweight and can be easily transported and installed in remote or disaster affected areas.
Designed for a longer lifespan at lower cost than stainless steel, FRP composites are already widely used in potable water and wastewater systems for pipes, storage tanks, scrubbers, ducting, covers and other equipment.
While FRP has a long design life, maintaining these assets poses unique challenges as internal defects like
delamination or fibre breakage are often hard to detect, and although there are established objective methods for determining remaining service life of steel asset, there are no standards for determining ongoing fitness-forservice of FRP
Navigating hidden challenges requires proactive solutions, however, traditional assessment techniques rely on visual inspection – and not only are these methods time-consuming, the provide limited insight and require the asset to taken offline.
RPC Technologies is one of the most experienced manufacturers of FRP assets in Australia and it also has the exclusive licence to a world-leading condition assessment technology, UltraAnalytix®.
UltraAnalytix leverages sophisticated ultrasonic technology to perform in-service condition assessments of FRP pipes and tanks, and this proven non-intrusive and non-destructive evaluation method provides objective data to evaluate the current condition and remaining service life of FRP equipment without the need for costly shutdowns.
This detailed data helps asset owners to shift to a more proactive maintenance strategy, and regular condition assessment and inspection using the UltraAnalytix® system can help the water sector significantly reduce losses of valuable assets through leaks and other failures, improve safety and reliability, and increase operational uptime and lower capital replacement costs.
UltraAnalytix® non-destructive testing is a fast, accurate, safe and cost-effective way for asset owners to assess the remaining service life of their FRP assets while avoiding unnecessary downtime and replacements. U
With more EVs hitting the road, installation of fast charging infrastructure needs to keep pace. Essential Energy, Race for 2030, and the University of New South Wales may have found a transformative solution.
The uptake of electric vehicles (EVs) and fast charging facilities across Australia poses both challenges and benefits to the distribution network. More EVs means more fast chargers, which in turn requires significant investments in upgrading or installing transformers to meet the load of these EV chargers.
According to data from the International Energy Agency’s (IEA) ‘Trends in charging infrastructure’ reports, Australia’s ratio of public chargers to EVs is worsening. In 2023, the data showed that for every EV fast charging facility there were 35 EVs1 on the road – but in 2024 the ratio had declined to one for every 68 EVs2
EVs are set to play a vital role in reaching Australia’s decarbonisation goals, but a lack of adequate public charging infrastructure not only creates a barrier to their uptake but, according to the Energy Networks
Australia’s (ENA) ‘Street Smart: Scaling Up Kerbside EV Charging in Australia’ report, many existing EV owners are considering switching back to an internal combustion engine vehicle due to difficulties charging3
RACE for 2030 CRC Program Leader – Electric Vehicles, Oliver Hill, said passenger vehicles account for just over ten per cent of Australia’s total emissions.
“We’re seeking net zero by 2050, that’s the ultimate goal, and because electric vehicles have such a large role to play in that, it’s really important that we get the transition to electrified mobility right,” he said.
According to Mr Hill, technology hesitancy and the availability of charging stations are among the key barriers that customers cite as deterring them from switching to an EV.
“There’s a couple of different [elements] to this: there’s the number of actual charging stations out there, and then there’s people’s perception of whether that charging is available or not,” he said.
“And fast charging in particular gives the perception to people that it is more available – especially in regional areas where people are travelling long distances.”
To overcome these challenges, Australia needs to deploy a huge number of EV fast chargers in a relatively short period of time. However, Essential Energy Manager of Innovation, Bradley Trethewey, said EV chargers themselves consume a significant amount of energy, and this could result in grid congestion issues as more come online.
To support the extra load, these chargers will place on the distribution network, utilities like Essential Energy will need to increase the capacity, which typically requires a significant investment, and a lot of time.
It’s vital that distribution network operators understand the impact of this extra load on the grid and make changes where needed. So, Mr Trethewey and the team at Essential Energy joined forces with Race for 2030 and the University of New South Wales (UNSW) to investigate whether they can increase the capacity of existing transformers to speed up the deployment of EV chargers.
According to Mr Trethewey, most utilities use the nameplate rating of distribution transformers to determine the available load on the asset and whether there is a need to upgrade, but this research project aims to investigate whether transformers can be momentarily loaded higher than their initial nameplate rating –which would allow for greater EV charging without substantially increasing transformer temperature.
“We are seeking to understand the impacts on the temperature range that transformer windings will need to tolerate,” Mr Trethewey said.
“This will, in turn, improve our understanding of a transformer’s thermal behaviour during EV fast charging sessions, with the goal of reducing the need to invest.”
Mr Trethewey said that there are two phases to this research project: a desktop feasibility model and a longitudinal study.
“Part one is doing a classic research-orientated project, basically building some theoretical thermal models that have got some relationship to the real world,” Mr Trethewey said.
“We’ve then used those theoretical models to put in the EV fast charging characteristics and some simulation outcomes.”
When a high enough load is placed on a transformer, its hotspot temperature – the temperature at the hottest part of the winding – will exceed what the thermal management system can handle. This damages the asset and ultimately decreases its operational lifespan.
However, in contrast to conventional load profiles used to develop overload guides, EV fast charge loads are peaky short duration loads, which means they have a high load requirement but only for a very short period of time before dropping rapidly as the vehicle battery is charged.
UNSW Researcher Dr Omair Khan was one of the lead investigators on the project, and he explained these chargers are not continuously drawing power from the grid.
“For example, a 300kW charger would only withdraw all that power for maybe five to six minutes of the 30-minute charging session. So they peak only for a very small time, and then they gradually decrease and that is where transformers thermal inertia comes into play,” he said.
“It will take some time for the corresponding power to heat the transformer up corresponding to that power. So if you load it to 1MW and then bring it back down to 750kW, the transformer wouldn’t have time to heat up.”
Mr Trethewey said these transformers are cooled using dielectric fluid and that traditionally, thermal management is performed with mineral oil. However, improvements in ester-based oil (vegetable oils) over the last decade have shown that they can provide equivalent and in some cases better thermal transfer in sealed transformers and are biodegradable.
“If you flick your kettle on and then you turn it off after a just minute, you probably can touch the element, because the thermal capability of the water that’s in the kettle has taken the heat away. That’s kind of how oil in a transformer works in that it takes the heat away from the windings,” Mr Trethewey said.
“So if you’ve got something that’s got a better thermal transfer capability, you can take that heat away a lot faster, and that’s one of the benefits of improved esterstyle oil; so they can help with that thermal transfer of heat away from the windings.”
For more than two decades, Essential Energy has been gathering data that shows how this natural ester enhances the insulation of electricity transformers.
The utility began researching the insulative properties of natural esters in power transformers in 2004, and installed the first electrical zone substation transformers filled with vegetable oil adjacent to National Parks in New South Wales in 2005. These power transformers were among the first in the world to use natural esters as an alternative to mineral oil. The utility now has 22 power transformers up to 132kV, each containing about 10,000L of vegetable oil along the borders of the National Parks, with more at other sites in its network.
Data on the condition of the transformers has been collected during the past 20 years, with oxidation the primary concern when using vegetable oil. All of the data has so far remained well within standards, even during faults and extreme temperatures, and strongly indicates that vegetable oil is effective as insulation over the longterm if the tank is sealed. According to Essential Energy, the testing has not indicated a long-term degradation of the oil, nor has there been a reduction in the cyclic rating or operation of the transformer. This gives the utility confidence that the transformers will last another 20–30 years depending on the quality of manufacturing, operating conditions and maintenance, as well as ambient temperature, load levels, and environmental conditions.
Dr Khan said that in order to get the most accurate results, the desktop feasibility model had to cover a lot of different variables and scenarios, such as the charging requirements of different EV models.
“We first created 23 charging session profiles of different models of EVs, and we stacked them sequentially,” he said.
“We also integrated the switchover time between the two EVs in our study, because that impacts how many EV charges you could install.
“Let’s say you have a changeover time up to three minutes. That would be vastly different to in a setting where the changeover time is five to ten minutes, and you could have even more EV chargers on the same transformer in a rural place where the EVs wouldn’t show up as often as in the city.”
The study looked at how low-congestion (15-minute intervals), medium-congestion (ten-minute intervals) and high-congestion (five-minute intervals) affected the capacity of the transformer. Dr Khan said that where the transformer was located was also important, as the weather conditions and ambient temperature could affect the hotspot temperature.
“We also considered the ambient conditions and [whether] you could have more EV chargers on the existing transformers in a cooler climate compared to a hotter place,” Dr Khan said.
“To look at that we got the data from the BoM [Bureau of Meteorology] in Australia, but they don’t give you data per minute. For the EV chargers, we depend on the power changes within minutes.
“So, we created a synthetic data by recording the minimum maximum temperatures for the day, and then generated synthetic data for the temperature at every minute of the day and we used that in our analysis.”
To determine how many EV chargers they could connect, for how long, and in which different charging scenarios, Dr Kahn said the team developed a model to calculate the year-on-year ageing factor of the transformers under different conditions.
This equivalent ageing factor represented the rate at which the transformer’s insulating paper degrades, and a higher ageing factor indicated faster degradation and a shorter remaining lifespan. When the hotspot temperature of the transformer rises, the insulating paper starts to deteriorate, and the ageing factor goes up.
According to Dr Khan, this model leveraged the thermal parameters of distribution transformers as provided by the IEC60076–7 loading guide, and takes the initial load and the ambient temperature as inputs and runs them against the different charging profiles to calculate initial values for the available capacity and hotspot temperature, as well as the ageing factor and loss of life for the transformer.
These variables could then be modified to account for specific scenarios, allowing the team to analyse the effects of EV charging in a range of different conditions, such as the level of non-EV load on the transformer, ambient temperature, and the interval between charging sessions.
This model demonstrated that a higher ambient temperature, and an increased steady-state (or non EV) load raised the hotspot temperature of the transformer –and therefore its equivalent ageing factor.
It also indicated that longer intervals between charges allowed the transformer to dissipate heat more effectively and thus slow the ageing process.
These transformers typically have a 40-year-plus lifespan, and Dr Khan said nameplate rating outlines the per-unit (pu) value of a transformer’s load capacity in order to maintain that lifespan.
The study then modelled the number of 250kW EV fast chargers that could connect to a 1MVA distribution transformer without adversely affecting its lifespan under three different utilisation levels, and three congestion scenarios.
“What surprised me more most was that the existing transformers are massively oversized, they are underutilised, and for a lot of the transformers it lower 50 per cent,” Dr Khan said.
The results showed that significant untapped transformer capacity is available, particularly in cooler climates or during seasons where temperatures are lower.
As the intermittent nature of EV chargers prevent prolonged overloading, and by relying on the thermal inertia of the oil in the transformer to slow the rise of the winding temperature Essential Energy could exceed the nameplate capacity without impacting the longevity of the asset.
“We found you could have up to four 250kW EV chargers – which would give you the equivalent of 1pu of peak loading on the transformer – but you would still have year-on-year less than 1pu so you wouldn’t be contributing to any accelerated ageing,” Dr Khan said.
The exact amount of extra capacity available was impacted by several factors, including the location, use of the local network and predicted charging profile.
The percentage of non-EV utilisation on the transformer was a major contributing factor, and for all three congestion scenarios the study found that at 25–50 per cent utilisation the transformer could support up to four additional 250kW chargers without going above the temperature threshold – however, it could only support up to two at 75 per cent utilisation.
However, it’s likely the amount extra capacity shown by the desktop model is a more conservative estimate, and Dr Khan explained that there are a variety of real-world factors that will impact the results.
“The desktop model [was based on the use of] mineral oil but with the ester oil, you have a better heat dissipation, higher heat capacity, so it’s more suitable for short peaky loads,” he said.
“In the [next phase] Essential Energy has set up two equivalent transformers – one filled with mineral oil and the other with ester oil – to compare the behaviour of transformers and EV chargers with the two oils.”
With the next phase of the project underway, Mr Trethewey said he’s optimistic about the results.
“I’m really excited because we’re 100 per cent confident we have extra capacity, so we’re putting that into practice in a real-world scenario,” he said.
“We’ve had Tyree Transformers make two special transformers with fibre optic couplings inside the windings that give us the exact temperature during loading cycles. We’ll take that data and run that through our theoretical model, and I suspect we’ll find that we’ve even got more available to us than what we originally anticipated.
“We’ve already got a model that says you can release capacity more right now, and we hope the longer study will provide even better value in terms of the available capacity that then translates into better charge rates for customers.”
As Australia moves toward an electrified system, Mr Hill said it’s important to get the most productivity out of every single asset to deliver the transition at the lowest possible cost to consumers.
“The [first stage] of this project showed that there is extra capacity that you can squeeze out of the transformers – and that’s so important because that allows the distribution networks to get more out of the grid.
“Research in Australia, compared to internationally, is critically underfunded – but it’s so important.
“For example, with this project, in just a few months of works we’re already shown the substantial differences that can be made from something like this.
Fortunately, Essential Energy are really innovative –they really do want to make a difference, and Brad’s a great advocate for that.
“But, it’s challenging because this can’t just be supported by the distribution network – these things need to be shared across the wider industry and if we had greater avenues to seek funding support we could move forward a bit faster.”
Mr Trethewey encourages other distribution network providers to try new ideas in the energy transition.
“We have to think a bit more differently than how we normally have as infrastructure providers,” he said.
“The diversification of energy on our network means that we have to apply new ideas to how we manage the assets from the generator through to the household.
“We’re now having to turn conventional single direction energy flows asset management practices on its head to accommodate bidirectional energy flows and figure out how we can change the way we manage our assets to drive more value out of them for customers. That’s probably the biggest learning for me.” U
Scan the QR code to view the full report from stage one of the study or visit racefor2030.com.au
Natural esthers not only improve the safety of distribution transformers, they can increase their lifespan too. Image: anulak/stock.adobe.com
Australia’s energy grid needs to be greener, more resilient and more reliable than ever – and transformers need to be able to keep up.
Liquid-filled transformers have been the trusted workhorse powering Australia’s energy grid for decades. These transformers, which can be found in almost every transmission and distribution network, derive their name from the use of a dialectic fluid to cool and insulate the core and windings.
Inside an Australian transformer, you’ll find one of three types of dialectic fluid – mineral oil, natural and synthetic esters, and silicone oil – each of which has different physical, chemical and electrical properties.
Distribution network providers have historically relied on mineral oil as the dialectic fluid of choice, and it’s still the most commonly used solution. However, while this fluid is known for its reliability, it has one major weakness – high fire hazard.
According to Cargill Bioindustrial Southeast Asia and Pacific Regional Application Engineering Leader, Kin Yu Lam, the incorporation of an increased number of renewable energy sources means that energy grids are often subjected to greater stress due to higher and more fluctuating loads as well as the effect of harmonics.
Due to its limited thermal stability, mineral oil is less capable of withstanding the added stress a high variable load places on transformers.
This increases the likelihood of dielectric failure of the transformer insulation. And when that happens, mineral oil can pose a major fire risk.
“Increasing the number of renewable energy sources in the power grid could potentially increase the failure rate and maintenance cost due to higher, more fluctuating loading, and the influence of harmonics,” Dr Lam said.
“When there is a dielectric failure, mineral oil could pose a major fire risk because of the high energy released from the electric arc.”
In addition to the fire hazard, having a transformer filled with mineral oil exposed to excessive thermal stress over time can also negatively impact its lifespan.
With that said, Dr Lam explained that due to their cost and track record in Australia’s energy sector, mineral oil transformers are still the preferred option for many utilities who may be uncertain about adopting new technology.
“While [mineral oil] has certainly been a reliable dielectric fluid for over a century, its lack of thermal stability and moisture-handling capability has become an increasingly limiting factor that hinders the industry from taking full advantage of technological advancement in achieving longer equipment life, higher loading capacity and efficiency,” Dr Lam said.
Because mineral oil is also of very low biodegradability, Dr Lam also warns that in the event of a transformer leak or fluid spill, the environmental risk is very high.
“As it is also essentially a non-renewable fluid with a potentially high carbon footprint due to the energy intensive oil exploration and refining processes, it is in many ways a liability to the power industry from an environmental sustainability perspective,” he said.
However, as mineral oil has been the industry norm for generations, most of the engineering design specification and standards are developed based on its properties of this fluid.
“Reliability is clearly of the highest priority in the power industry, so it is understandable that adopting new technologies is going to take time because of the need for thorough evaluation and testing,” Dr Lam said.
“Having said that, we are clearly seeing a sharp increase in interest level of adopting the solution of alternative fluid in the industry.”
According to Dr Lam, natural esters offer a smart alternative solution going forward.
“They’re by far the best in class in terms of safety and sustainability due to their high fire point and biodegradability, as well as its non-hazardous traits and possible negative lifecycle carbon footprint (-0.74kg CO2eq/kg)from cradle to gate,” he said.1
However, implementing change is a big step and with so many customers relying on utilities to keep the lights on, they need robust technical proof to make informed decisions. There are a lot of natural esters out there, but Dr Lam said choosing the right dielectric fluid ultimately comes down to the availability of relevant test data and end user experience. To prove this point, he offered the example of a transformer ageing test.
Through this rigorous ageing tests in actual transformers, conducted in accordance with the IEEE standard over ~12,000 hours, the lifespan of transformers filled with FR3 fluid was found to be about four times that of those filled with conventional mineral oil. No other natural ester fluid on the market is known to have been subjected to such extensive, long-term testing.2
“Also, as the original natural ester fluid first introduced almost three decades ago, FR3 fluid has been used in operating transformers beyond the IEEE nominal transformer life, and the fluid in the very first FR3 fluid transformer is still like new without the need for maintenance intervention,” he said.
Dr Lam explained that FR3 has a unique property that allows it to absorb moisture and remove it through hydrolysis reaction, which means it can continuously dry the paper insulation while the transformer is operating.
“Apart from prolonging the paper insulation and transformer life, keeping the insulation system dry would also help to minimise the risk of dielectric failure, and therefore reduce maintenance and downtime costs as it would not be necessary to dry the insulating liquid and paper frequently,” he said.
“This also means that FR3 transformers can be operated at a significantly higher temperature without the risk of premature failure. In other words, the use of FR3 fluid would allow transformers to have extra reserve capacity in coping with increased loading demand, hence reducing the need to invest in new transformers of higher rating.”
Dr Lam said that with significantly higher reserve capacity, it is often possible to deploy more compact FR3 transformers of lower rated capacity in place of conventional mineral oil transformer.
“Apart from the saving on transformer cost, this approach is particularly well-suited for public distribution network and renewable energy installations where the peak loading demands are often much higher than the average daily loading,” he said.
“With reduced no-load loss, the smaller sized FR3 transformers are therefore more energy-efficient to run and would also deliver substantial conservation on nonrenewable resources like steel, copper and aluminium in the building of the transformers.”
By mitigating the risk of dielectric failure, FR3 fluid addresses the root cause of devastating transformer fire and costly outages. And even if transformer failure does occur, the consequence can be effectively mitigated with minimal risk of pool fire outbreak and a much lower environmental concern over fluid spill than mineral oil – because the fluid is readily biodegradable in accordance with EPA OPPTS835.21000 and non-hazardous in accordance with the Globally Harmonized System of Classification and Labelling of Chemicals.
“As renewable energy sources are increasingly located in remote and environmentally vulnerable areas, the consequences of a transformer failure are becoming more severe – potentially causing devastating bushfires and environmental contamination,” Dr Lam said.
Derived from vegetable oil, FR3 fluid is not only a more sustainably produced option, but it also significantly reduces environmental risk in the event of a spill.
“With the highest biodegradability, above 90 per cent within just 20 days in standard laboratory tests, the pollution hazard of FR3 fluid in the event of a spill is much lower than any other dielectric fluid,” Dr Lam said.
He also emphasised that because of its non-hazardous nature, it is acceptable to carry out bioremediation on soiled contaminated with FR3 fluid using harmless microbes like natural yeast to facilitate biodegradation, according to the environmental regulations in many countries, including the US.
Given FR3 fluid is derived from a renewable resource, its production is also much kinder on our ecosystem.
“Even after discounting the fossil fuel being used in the manufacturing process and the land use in growing the plant crops, the cradle-to-gate lifecycle carbon footprint of FR3 fluid could still be negative1, whereas other petroleum and synthetic fluids will contribute significant amount of greenhouse gas emission,” Dr Lam said.
As Australia’s energy grid evolves, so too must the technologies that support it.
With its proven performance, environmental advantages and ability to meet the demands of a renewable-powered future, FR3 fluid represents a transformative step toward a safer, more sustainable grid. U
1 Calculated according to ISO14025:2006 and ISO21930:2017 verified by a third party accredited LCA that is only representative of FR3 fluid and not natural ester as a category.
2. Based on accelerated ageing tests with Kraft and thermally upgraded Kraft (TUK) paper, per IEEEC57.100.
more information, visit www.cargill.com
From storing 2D and 3D models in a secure environment to managing design data from concept to completion, Autodesk Vault is
the
heart of SA Power Networks’ Digital Engineering Assets team.
As the sole electricity distributor in South Australia, SA Power Networks’ infrastructure spans the entire state, and managing these assets and the associated workflows is a mammoth task.
The utility does this with Autodesk Vault, managing and storing all engineering and associated data within the software – whether it’s a new asset, a modification or a whole new substation.
The adoption of Autodesk Vault lifecycles enabled SA Power Networks to digitise paper-based workflows, significantly improving manual processes such as printouts and approvals, reducing errors and enabling more seamless sharing.
These lifecycles allow teams to move designs from ‘work in progress’ to ‘check’, and finally to ‘authorisation’, while automatically handling sign-off, watermarking, PDF files and distribution.
The automation involved virtual machines called job processors, which would access jobs posted to queues and schedule various tasks in an automated way.
Before this project commenced, there were 12 different document lifecycles running in PowerShell on six job processors. As jobs increased, the utility was met with significant processing bottlenecks.
SA Power Networks Application Specialist, Leigh Menzel, said individual jobs would typically take three to four minutes per file to go from ‘work in progress’ to ‘check’.
“It wasn’t uncommon for the job processor to be busy for more than half the day,” he said.
Adopting Autodesk Vault Professional enabled SA Power Networks to:
• Securely store engineering designs and associated data
• Keep automatic history of changes
• Ensure the latest revision of files is accessible to all users
• Digitise workflows and abandon paper-based processes
• Promote seamless collaboration
Once using the software, the team identified an opportunity to speed up the third-party job processor, as Autodesk Vault Professional’s open API allows for further automations.
The task involved team and intra-team collaboration, and the utility reports that this has resulted in a range of benefits.
For example, job processing times have become six times faster, plummeting from an average of more than three minutes per job to about 35 seconds.
On top of this, three times more jobs are being processed, with teams now posting more than 7500 per fortnight.
The utility has also seen significant cost savings since adopting Autodesk Vault. By removing the third-party tool, SA Power Networks said it is saving $16,500 per year in licensing costs, and the additional automations have resulted in an 1800 per cent increase in throughout.
Other benefits include centralised storage of LOG and CONFIG files, and more options to tweak processors in Azure to generate future savings.
SA Power Networks Digital Engineering Asset Manager, Gary Maguire, said cutting transaction time from three minutes to just 35 seconds is no small feat.
“This translates to a saving of $2.30 per transaction, which adds up to an impressive $414,000 per year in productivity,” he said.
Across the board, users report that jobs process faster and better, with the reduction in bottlenecks meaning wait times are no longer an issue.
SA Power Networks exemplifies how partnering with Autodesk and embracing digital engineering can transform operational efficiency and drive cost savings. By standardising with Autodesk tools, the utility has not only streamlined its workflows, but also enhanced collaboration and information sharing across departments. The Digital Engineering Assets team’s initiative in redeveloping Autodesk Vault’s backend environment stands as a testament to its commitment to innovation and continuous improvement.
SA Power Networks continues to leverage Autodesk’s cutting-edge solutions to maintain its leadership in the energy sector and deliver reliable electricity services to South Australia. U
For more information, visit autodesk.com/au
Optimise the water systems of today while building the sustainable infrastructure of tomorrow. Autodesk serves every stage of water management.
Optimise water quality and efficiency, minimise leaks, conserve resources, and enhance customer satisfaction through intelligent design, accurate modeling, and real-time analytics.
Enhance flood resilience through advanced hydraulic simulations and predictive management, enabling better forecasting, capacity planning, and emergency preparedness.
Access real-time insights to manage wastewater system pressures, mitigate environmental impacts, and justify capital investments in capacity improvements.
Enhance wastewater and water treatment plant management with digital twin technology and cloud-based collaboration solutions. Optimise performance, reduce risk, and improve service quality.
Leverage real-time data and predictive analytics to enhance water asset management, reduce costs, extend asset lifespans, and improve efficiency and compliance.
Learn more
Consumer energy resources are fundamental to reaching 82 per cent renewables. But as the grid changes, how can utilities build trust with communities as partners in the energy transition?
EXL believes the transition is a chance to create a reliable energy system that customers can easily participate in. Image: TC/ stock.adobe.com
Ators are leading the charge towards net zero, but they’re tasked with delivering more than just renewable energy; they’re building an equitable, resilient and lower-cost energy system that is designed to leave no one behind.
None of this can happen without community support but, according to EXL Global Head, Energy, Utilities & Infrastructure, Mitch Donnelly, consumer trust has eroded over time.
When the power is on, no one sees all the hard work that the generators, distributors and retailers put in to keep the grid running – but when the power is out, everyone is paying attention.
“I think consumer trust is largely eroded because of consistent bad news stories,” Mr Donnelly said
Mr Donnelly said that it’s important for consumers to see that utilities are there ultimately to serve them, and to trust that the energy sector has their best interests at heart.
“We need to start having a more honest conversation as retailers and network operators with consumers about the role that we play, about what we do, why we do it, and bring them into the community,” he said.
“And, most importantly, we cannot leave communities behind – whether they’re rural communities, whether they’re First Nations communities, or any communities who traditionally have been excluded from the energy dream.
“We’ve made great investments into the future and into reinforcing the network, and it’s incredibly important to look at how we manage the grid going forward and move towards net zero.
“What we’re not doing is showing consumers what they get in this.”
According to Mr Donnelly, this transition is a chance to create an energy system that is more reliable, fairer and more affordable – and one in which customers can easily participate.
“Australia has the resources to be an energyindependent nation to manage its own pricing for the benefit of its citizens. That relies on this transition,” he said. “That means in 2030 customers have access
to low-cost solar and battery storage, but they are also empowered to navigate a complicated energy market in a way that meets their needs.
“But we’re not asking them to do this as a part-time job. That shouldn’t be a challenge that customers have to face, it should be something that can be done for them – and it can actually be done through AI and data that energy retailers provide.”
Australia’s uptake of rooftop solar is among the highest in the world, and Mr Donnelly said that embracing consumer energy resources (CER) gives customers agency and control over their power bills.
“There are some really active ‘prosumers’ in Australia. They’re tech savvy and they want to make choices and be engaged in energy. But the vast majority of customers want energy to be a silent service, they don’t want it to make their lives more difficult,” he said.
“And this is where we run the risk – the more complexity we add into the market, we need to look at how we simplify things for consumers that have invested into CER. It shouldn’t become a burden for them.”
According to Mr Donnelly, Australia’s energy markets are some of the most complicated in the word. Not only does the country have three entirely disconnected energy markets, but Australians also have to navigate complicated tariff arrangements, as well as pricing offers, rebates and structures that differ depending on where you live.
“We have all of this level of complexity that needs to be simplified. We need to start meeting customers where they are, personalise their journeys, help them understand what they are getting, what are they paying, and how they can manage it,” Mr Donnelly said.
EXL Vice President – Australia and New Zealand, Samit Gayen, explained that around 90 per cent of Australians live in Victoria, New South Wales, Queensland, South Australia and Tasmania and buy their electricity through the National Electricity Market (NEM).
Of the remaining ten per cent, the majority live in Western Australia and their electricity comes from the Wholesale Electricity Market (WEM), which is largest standalone electricity grid in the world. The last one per cent Australians are hooked up to the Northern Territory Electricity Market (NTEM), which again has its own set of regulations and rules.
“What people across the world don’t really know is we have three markets in the same country – I don’t even think many Australians know that as well,” he said.
“But ten per cent of consumers in this country have a separate way of selling electricity, the way measure outcomes and service customers is different across these markets. Since the discovery of AC and DC alternating current more than 100 years ago, the grid has operated largely the same way.
“But as we transition towards a sustainable, renewable future, we’re taking a leap of faith into new technology that doesn’t have a century of historical data to leverage.
“We have to transition, but the transition needs to be in a considered manner, and to understand how we take that journey it’s important to have data and analytics, because that’s how you’re going to be able to predict the future.”
Mr Donnelly said it’s vital that we take a purposeful approach and focus on what’s important.
“Customers don’t all want masses of data. They want simple things that work, simple service that’s effective, simple solutions that meet their need,” he said.
For Mr Donnelly, it’s about understanding how data is used and who it serves.
“In the energy market, we have more data than we’ve ever had in the past. We have sensors, we have smart meters, we have AMI we have all of these insights into what customers are doing, but we’re drowning in that data,” he said.
“Finding meaningful insight from that data becomes a real challenge, so we need to focus on the things that are important to us as a market and things that are important to consumers.”
According to Mr Gayen, there are three key actions retailers can take help build customer trust.
“The first part is transparency around usage data, but the second part is then proactively sharing that data with the customer,” he said.
“If they’re using too much energy washing dishes in the day and that there’s a better time of the day they could do it, we can share that information proactively. [For example], in the email with their bill, you can [give the customer] three points on how they can save energy.
“The third area where [retailers] can build trust boils down to transparency around the pricing mechanisms and supporting customers struggling to pay bills.”
Mr Donelly said some international markets are already using consumer data to personalise messages.
“We can use consumers’ data to put them on the best deal because they’re experiencing [serious hardship],” he said.
Mr Gayen said the first step is identifying vulnerable customers.
“One thing we need to be conscious of is that people don’t open up on the first instance. We try our best to hold on for as long as we can before we put the plug and say we’re really struggling to pay,” he said
“That’s where the power of data and AI comes in, and today there are intelligent solutions that can be deployed to identify a vulnerable customer at a very early stage.
“At EXL, we use an algorithm that can pick up the customer’s tone and their choice of words to identify that they might be going through a challenging time.
“You can even use customer behaviour for this – if someone has a payment plan put in and then that person breaks that promise and doesn’t pay on [the agreed] date, then that is a trigger event [that shows] the customer is going through a difficult time.”
The next stage is working with that customer to help them navigate that hardship.
“Once we’ve established that they’re [experiencing hardship], we can then reach out to the customer proactively, before they reach out to us,” Mr Gayen said.
“Again, it’s about building trust. Instead of [the customer] calling me and then I assess them, let’s do it the other way.
“If [tell them] I’ve already assessed them, [offer to] put them into a hardship program and then work with them to come up with a plan that works for them, then we can drive a much better outcome for the customer.”
Mr Donnelly said it’s important not to leave rural and remote communities out of the conversation.
“For rural customers, there’s a perception that investments into the network aren’t going to benefit them – [they see] the whole market as designed to benefit the metropolitan [areas],” Mr Donnelly said.
“Government regulating the market is good for government perception with the public, but it builds trust in government, not in suppliers and network operators,
“I think there needs to be a bottom-up approach from grid providers and from network operators to engage with communities. This means getting out and talking to people to encourage participation and engagement. And a lot of that is about face-to-face engagement and enabling rural communities to get together collectively into community energy projects.
“This is something we see in the US quite a lot. I talk to consumers who are out in the Midwest [states] and they feel completely detached from the metropolitans sitting on the two coasts. What some parts of the US do very well is community energy projects that give ownership back to those rural communities.”
“We can [also] use data to give them a genuine journey that makes them feel valued as a customer,” he said.
Mr Donnelly said not only do retailers, networks operators and government need to work together to deliver Australia’s energy future; they also need to collaborate with other sectors and look to learn from the challenges that other nations have already faced.
“It’s so important to bring in those external, different perspectives, because this is a transition and we need to start looking externally at what happens here, what happens in different market,” he said.
“This is not a reshaping of what we have. This is this is a revolution, not an evolution.” U
For more information, visit www.exlservice.com
Is the energy transition an evolution or a revolution? This was a recurring theme at Australian Energy Week 2025, where the sector’s leaders came together and shared their take.
Australian Energy Week 2025 saw some of the best and brightest from the entire energy supply chain come together to tackle the challenges of the energy transition.
The event didn’t shy away from tough questions, and more than 100 industry leaders shared their incredible insights, and engaged in open conversations to find new solutions. It truly was an unmissable event, but if you are one of the unlucky few who couldn’t make it then Utility has you covered.
The core event kicked off on Wednesday 18 June 2025, and we jumped straight in with a plenary on Australia’s energy market outlook – where EnergyAustralia Managing Director, Mark Collette, outlined an optimistic vision for the energy transition.
Mr Collette shared a practical pathway towards netzero that looked at more than just how we can expand renewable energy and storage to meet 2030 climate targets, but how this era of transformation can make energy cheaper and, in turn, build a stronger, fairer future for all Australians.
Then, NEM Wholesale Market Settings Review Chair, Tim Nelson, invited us to re-imagine the future of the National Electricity Market (NEM) and discussed how we can reform the market alongside the evolving energy grid.
We also heard Federal Minister for Climate Change and Energy, Chris Bowen, drop the news that reforms are on the horizon for the Capacity Investment Scheme – with the tender process to be streamlined.
Minister Bowen said there was a lot of catching up to do over the last decade, and that it’s now time to knuckle down and get on with the job of delivering a better, fairer, more reliable, more affordable, lower emissions energy system for Australia.
With some food for thought to chew on, Transgrid CEO, Brett Redman, and Endeavour Energy CEO, Guy Chalkley, put their heads together with executives from Woodside Energy and Solstice Energy to discuss how the sector can ensure reliable renewable energy integration.
In this panel – led by McKinsey & Company Partner, Victor Finkel – the group explored the key changes required within the sector to facilitate the energy transition and how leaders can steer the sector through this transformative period.
For AGL Managing Director and CEO, Damien Nicks, managing the energy transition means putting customers at the centre and making it easy for them to actively participate.
In his speech, Mr Nicks said that consumer energy resources are not only the key to enabling customers to participate in the energy transition, but they present an opportunity to bring the cost of energy bills down.
According to Mr Nicks, the energy transition is an evolution, not a revolution, and we need to get regulation right to keep customers at the heart and create an energy system for generations to come.
Picking up where Mr Nicks left off, ElectraNet CEO, Simon Emms; Energy Networks Australia Chief Executive, Dominique van den Berg; Hydro Tasmania CEO, Rachel Watson; and Ausgrid CEO, Marc England, discussed how we can balance the urgent need for new energy investment with rising cost-of-living pressures.
The panel explored the competing need for government to subsidise energy prices to ease cost-of-living pressures, and this risk of this delaying investment in the energy transition.
The topic of customers was further addressed by Australian Energy Market Commission Chair, Anna Collyer, who emphasised the need for decisive action to navigate complex energy transition challenges.
“Amidst all of the things we know we cannot yet know, sometimes you just have to be brave and to get on with it,” she said.
The conference resumed on Thursday 19 June 2025 with the Women in Energy Breakfast, before delegates broke off into one of four streams.
With Ms Collyer’s sentiment still fresh in everyone’s minds, SA Power Networks CEO, Andrew Bills, didn’t waste any time in kicking off the Re-engineering the grid stream with his case for urgent change as a distribution system operator in a rapidly evolving energy landscape.
“Waiting for perfection simply isn’t an option because every delay adds complexity, cost and missed opportunity for consumers, businesses and the economy,” Mr Bills said.
“And we need the right rules to keep progress moving, now – without getting stuck in endless debates.
“In South Australia, we’re not just managing poles and wires anymore, we’re managing a system. We’re actively taking part in the orchestration of how energy flows – not just from large generators to homes, but from homes, from businesses and back again – all in real-time, and all to ensure the system stays reliable and delivers value.
“Some see it as a future model. Some as a set of technical functions. To us in South Australia, it’s not a concept – it’s the job we’re doing right now, and we’ll continue to do more of.
“But more importantly – for customers – it means we are doing more with what we’ve got.”
Mr Bills said that SA Power Networks is working the system harder and smarter, to unlock the full value of the infrastructure and technology that customers have already paid for. And in doing so, making their lives simpler, more sustainable and more affordable.
“This shift wasn’t optional. It was born of necessity –because South Australian customers led the way,” he said.
“They installed rooftop solar at world-leading rates. They invested in batteries and began to adopt new technologies.
“And while much of the energy sector has been asking, ‘What does the future look like?’ In South Australia, we’ve been living it – and adapting in real time.
“We as an industry have spent years talking about this shift – consulting on it, reviewing it, modelling it.
“Meanwhile, the cost of living has risen. Customer expectations aren’t being met. And the need for action has only grown.”
According to Mr Bills, the time for pondering how we shift is gone, and to realise the full potential of a smart, flexible, customer-led energy system, there are four big shifts we still need to make.
“We’re not tearing down the system and starting over. It’s an evolution, not a revolution.
“We’re making smart, practical tweaks – doable changes that unlock huge value for customers and the system,” he said.
“In South Australia, we’ve been testing our powers under pressure. We’ve proven that it’s possible to build a smarter, more flexible grid – even within today’s market and regulatory settings.
“We can do a lot with the system we already have – but not everything.
“You’ve got a head start. You can use what we’ve learned to plan ahead, build smarter – and leap over some of the hurdles we had to crash through. But only if we’re all willing to accelerate and stay the course of a couple of critical changes underway.”
Mr Bills said that there are four essential reforms that needed to progress quickly to help unlock value for customers in the next phase of Australia’s energy transition:
• Interoperability standards so devices and systems work together
• Retail pricing reform – paired with government support – to reward flexibility and improve access to enabling technology
• Balanced investment signals across supply and demand
• Regulatory models that empower smarter investment choices by networks
“Affordable, reliable, sustainable energy is possible. And distribution system operators will be the quiet heroes who make it happen,” Mr Bills said.
“It isn’t about one part of the system over the other, but rather a whole of market collaboration. Let’s get on with it. Together.”
After lunch, ElectraNet CEO, Simon Emms, gave us further insight into the South Australian experience and how households can be encouraged to adapt energy consumption based on electricity prices and grid demand, improving grid stability and efficiency.
Then, Western Power Executive Manager Energy Transition and Sustainability, Matt Cheney, shared insights from project Jupiter and how Western Power is Coordinating DER to improve network efficiency and lower energy costs for consumers.
Mr Cheney shared several of the key lessons learned throughout the project, but one of the key points for him was the opportunity for both the WEM and the NEM to learn from each other.
“The challenge of delivering everything we need to deliver, for the energy transition of the transmission, build, the upgrades for distribution, as that load grows, all of those sorts of things – we’re not going to be able to do it all without extra tools in our toolkit. And what you’re doing here is you are changing people’s paradigm,” he said.
“To reflect on the wise words of Yoda, this is a do or do not moment, not a try moment. And we’ve learned as an industry to do it in a particular way. But now, this is changing how we do things in a dramatic way – so we need to unlearn what we’ve learned for this to be successful.”
Over in Generation 2.0, EnergyCo Director, Strategy and Relationships, Jim Chesterfield, shared an update on what New South Wales is doing to keep the lights on and unlock that affordable, reliable, clean energy new generation.
Mr Chesterfield also highlighted the power of collaboration as a key takeaway from the state’s renewable journey.
“We really need to work together as a whole sector to bring everyone on the transition,” he said.
“We need to coordinate as a whole industry, because none of us can do this on our own, but also because the real people we will deal with on the ground often don’t differentiate between someone with an EnergyCo logo on their upper vest, or Transgrid, or a developer. They often see us as a group.
“We all need to be joined up in how we approach them and how we bring people on the renewable energy zone journey, because if we build support, even in piecemeal ways, project by project, it’s going to be really helpful.
That’s also why we should all be thinking about how this generation of investment from this energy transition and not just decarbonising our power supply, but leaving a positive legacy for those communities hosting the infrastructure for all of us.”
Then in the afternoon we analysed the role gas will play in the future generation mix with EnergyAustralia Operations and Projects Executive, Sue Elliott, and closed things off with a panel discussion on the future of gas.
As this blockbuster event came to a close, Australian Energy Week, left us with a positive outlook for the future. There’s much to be done to reach our 82 per cent renewable energy target, but with the whole sector bringing their heads together, Utility believes they can make it happen. U
The energy sector is getting on with the transition to renewables, but a skilled workforce is the key to the successful delivery of new critical infrastructure.
The energy sector is in the middle of a massive, complex transition. New infrastructure must be delivered urgently to meet climate targets, accommodate rapidly growing demand and replace ageing coal-fired assets – and delays cannot be afforded.
To support this critical network expansion, the sector requires not just advanced equipment but highly trained personnel. However, skilled labour shortages are putting pressure on project timelines, and the race is on to replace experienced personnel approaching retirement.
Vadym/stock.adobe.com
On top of an ageing workforce, the skills required to delivered essential electricity projects have evolved over the last few decades, and without adequate training infrastructure, building a workforce with the expertise required is a slow-moving project.
These skill gaps also pose a risk to site safety and operational efficiency, particularly in high-risk environments involving live assets – resulting in further delays.
Quinlan Cranes Director, Sacha Sikka, explained that operating near high-voltage infrastructure demands precision, strict adherence to protocols and deep operational knowledge – and the growing complexity of safety regulations further intensifies these demands.
“
To support this critical network expansion, the sector requires not just advanced equipment but highly trained personnel.
For Mr Sikka, if personnel aren’t trained correctly or their common sense doesn’t prevail, then that’s where an accident starts and finishes.
This shortage of skilled workers creates a ripple effect throughout the sector, and the pressure to meet tight deadlines can often force the industry to bring less experienced or insufficiently trained personnel on site.
Mr Sikka said that the physical nature of construction work as poses unique health risks, particularly in lifting and rigging operations. Workers face repetitive stress injuries musculoskeletal issues and fatiguerelated risks – and an environment that fails to properly manage these risks may experience higher high turnover and accident rates, compounding the labour shortage issue.
The solution to these challenges lies in a dependable workforce that not only fills the skilled labour gap but does so with a safety-first mindset.
Quinlan Cranes specialises in navigating highrisk projects, and its personnel are certified to work around live electrical assets. According to Mr Sikka, the company’s strength lied in its safety-first approach, which is underpinned by continuous training and ISO-accredited management.
Mr Sikka said that in the utilities industry, where projects are often high risk, it’s important to work with a provider that is reputable and committed to excellence.
“In the utility space, people understand the importance of doing things properly. We’re in the industry of doing things right the first time and not coming back,” he said,
As the energy transition powers ahead, the need for reliable, skilled labour will only increase. With a team of highly skilled, safety-trained personnel, Quinlan Cranes is uniquely positioned to support this growth, offering specialist services and a certified workforce tailored to the sector’s complex needs.
Ultimately, the success of the energy transition hinges on a whole-of-sector approach, and the right industry-specific expertise and skilled workforce are the key to not just making a reliable energy future possible, but sustainable and safe. U
For more information, visit quinlancranes.com.au
There’s
In an industry where performance and safety are non-negotiable, AS4044:2024 marks a pivotal step forward for critical infrastructure. The new Australian Standard for DC power systems in fixed installations sets a clear framework for compliance – elevating expectations across testing, safety, and continuity.
For power, utility and transport providers operating in high-risk environments, this clarity is vital. Intelepower’s integrated DC solutions, built around Yuasa’s proven battery and charger technology, are engineered to align with AS4044:2024 from the ground up.
The standard formalises critical system design and performance criteria across six key compliance areas:
Battery testing and maintenance
The updated standard requires systems to be proactively tested and monitored throughout their lifecycle, preventing failure at point of load.
Charger reliability
AS4044:2024 mandates proven performance under load and fault conditions – placing increased scrutiny on equipment selection and installation quality.
Electrical Safety
By introducing measures to protect personnel and equipment from DC hazards, this standard helps align systems with evolving OHS requirements.
Insulation and overvoltage protection
To safeguard systems from breakdowns in harsh conditions, AS4044:2024 reinforces creepage, clearance, and insulation standards.
Control logic and redundancy
This new standard also validates all changeover and redundancy mechanisms through tested logic sequences.
Installation and commissioning
AS4044:2024 makes proof-of-testing and detailed documentation a compliance requirement, not a best practice.
Intelepower treats compliance not as a minimum threshold, but as a benchmark for performance. The company partners with clients across Australia and New Zealand to deliver DC power systems designed to exceed regulatory expectations and ensure uninterrupted operation in mission-critical settings.
With integration of Yuasa battery and charger technologies – including the industry-trusted UXL range – Intelepower systems deliver:
• Proven charger performance in high-load conditions
• L ong-life VRLA batteries for zero-maintenance and reliability
• End-to-end installation, commissioning and lifecycle support
• ISO-certified engineering (9001, 14001, 45001)
• Coverage across Australia and New Zealand for service continuity
The Power Systems team at Century Yuasa understand the environments that critical systems like substations, emergency response centres and utilities operate in –and the stakes if they fail. Their role is to ensure that doesn’t happen.
As compliance requirements evolve, Century Yuasa is setting out to blaze the trail with integrated, standards-aligned solutions that bring together bestin-class components, expert engineering and deep market understanding. U
To
Our integrated approach keeps legacy assets efficient and compliant, so you can focus on the future.
As custodians of Australia’s most critical infrastructure, utilities cannot compromise on security. But how can they ensure these measures don’t impact operational reliability?
In the ever-evolving landscape of critical infrastructure, utilities face a unique challenge: protecting a sprawling array of physical assets, often in remote or high-risk areas, without compromising reliability.
As cyber threats rise and regulations tighten, the need for integrated, intelligent, and resilient physical security has never been more urgent. However, Utility caught wind of a transformative solution – and it’s designed to bridge
the gap between traditional locking systems and the digital era of access control.
EKA CyberLock is a strategic platform engineered to unify hardwired and key-centric systems under one software ecosystem, and it promises to be a game-changer for managing substations, cabinets, enclosures, remote field assets and more.
This unified solution eliminates siloed control systems and streamlines audit, control and access, all while working seamlessly with existing infrastructure.
EKA CyberLock can secure anything that can be locked, from gates to cash boxes and containers, even switch rooms. If it can be fitted with a CyberLock cylinder, it can be managed, secured, and tracked using CyberLock’s advanced platform.
Many traditional access control systems are known to falter during power outages, but EKA new this was an unacceptable flaw for critical infrastructure in sectors where reliability and uptime are non-negotiable.
This system is designed to offer sophisticated security, in the simplest way possible. Because it allows one key to access multiple assets, which is secured by permissions set in the cloud, it eliminates the need for bulky key rings or lost master keys
All CyberLock keys are powered independently, ensuring access remains available even if central systems go down. For security professionals, installation and integration can often be the biggest hurdle, particularly for legacy infrastructure. So EKA designed its CyberLock solution in a way that requires no new cabling.
The CyberLock cylinder retrofits directly into existing door hardware and padlocks, eliminating the need for costly rewiring or invasive installations, and also allows access with CyberLock padlocks in areas where you cannot provide network and power cables such as hatches and pits. The system can also be integrated with almost any other security system, including traditional hardwired systems, network systems like HVAC, and HR systems to ensure access is provided to rostered employees.
From an economic perspective, CyberLock delivers a highly cost-effective alternative to traditional access control solutions. It provides the full functionality of an electronic access control system at a per-lock price point comparable to – and often more scalable than – a master key system, without sacrificing control or visibility.
Speaking of visibility, security teams gain granular audit trails even for mobile and remote locations, with data on every access attempt and denial. In terms of deployment, time is money, EKA said that CyberLock installs at super speed compared to conventional access control technologies. For utilities managing thousands of dispersed assets, this rapid rollout translates into faster protection and compliance, and reduced project timelines.
This system is designed to offer sophisticated security, in the simplest way possible. Because it allows one key to access multiple assets, which is secured by permissions set in the cloud, it eliminates the need for bulky key rings or lost master keys. It’s just smart, programmable access that’s easily updated and instantly revocable.
EKA CyberLock’s goal is to bring control, visibility, and adaptability to the physical security of utilities and critical assets. It’s a solution designed for the real-world demands of modern infrastructure – resilient, intelligent, and ready for the field.
As ENGIE ANZ’s former COO looks back on his 40 years in energy, he said a career isn’t judged by what you did, but rather the opportunities you gave to others.
After more than four decades in the energy sector, ENGIE ANZ Chief Operating Officer (COO) for Generation, Graeme York, has bid both ENGIE and the industry farewell.
Mr York began his career 1983 with the original State Electricity Commission of Victoria (SEC), and has since worked overseas in Europe, the US and south-east Asia.
With the support of ENGIE, he returned to Australia to work in his current role in January 2023. His last day with ENGIE will be Friday 16 May 2025.
When Mr York first stepped into the industry as a junior engineer at one of the SEC’s La Trobe Valley power station, his goal wasn’t to race to the top of the corporate ladder.
“It wasn’t really my objective to get into management,” he said.
“I found myself a manager of 120 people within about nine years. But I think from day one, I enjoyed just a variety of different things that you can do in power stations.”
When the Victorian energy sector began to shift towards privatisation, Mr York moved to the newly commissioned Loy Yang B power station. This role with international company, Edison Mission Energy, kickstarted Mr York’s first venture overseas, where he worked in the UK and the US, before returning to Australia and Loy Yang B in 2003 as its Plant Manager. He then joined International Power as the CEO of Hazelwood Power Station in 2005
“I’ve worked across all the power stations in the La Trobe Valley at some stage,” he said.
“I was the CEO of Hazelwood, and that was a very difficult job because it was an old asset, but that actually really developed me and set me up for international roles again.
“So, when ENGIE bought International Power, I moved to London, [and took up the role as] Head of Operations, [where I] drove the operating standards of our plants all around the world.”
Mr York spent four years in the UK, before gradually working his way back to Australia – moving to Bangkok in 2015 and subsequently Singapore in 2019 as the COO for ENGIE’s Asia-Pacific Business Unit.
“When we moved our office to Singapore, I got the opportunity to run one of our assets again at was a plant called Senoko – so I’ve been an asset manager four times in my career,” Mr York said.
In his time overseas, Mr York worked across some vastly different energy systems.
“The European network is just so interconnected, compared to the Australian network,
“Our network is quite unique – the National Electricity Market (NEM) is largely a very thin transmission line running around the eastern seaboard, from South Australia,
For more information, visit website
to Victoria, New South Wales, Queensland, and then down to Tasmania.
“But what that means is that [for us], is that what’s happening in other states is very important – we can’t just buy electricity from France or Germany or Belgium. Whereas in Europe [you can] so what’s happening in a local area is less important.”
After a combined total of 18 years overseas, Mr York and his family felt it was time to return to Australia – a move that he is grateful of ENGIE’s support for.
“I was lucky that ENGIE found a position for me here in Australia to support the business. And I must say, it was nice to start my career in Australia and finish my career in Australia,” he said.
While the transition to renewables is certainly reshaping the energy sector, Mr York said digitisation has been the biggest change in his lifetime.
“At my first job, there was one computer for the engineering department out in the back room. Everything was done with hard copies, and there was no internet, so no computers on your desk.
“And when the company needs to communicate something, there’s a memo in an envelope that’s passed around the desks.
“If you’re doing a project and you want to look up some regulatory standards, you have to talk to someone and order the standard – and then you might get it a week or two later only to look and realise it’s not really the one you want.
“When you compare that with how we work today, and it’s just chalk and cheese.”
Another major game changer for Mr York was the launch of the NEM in 1998.
“Previously, the model around the world was that a government utility would run the power stations and source the fuel, they owned the transmission lines and the distribution network, and they sold energy to the customer – and there was no choice.
“But the NEM changed how things were run. Because once you divide the business up like that, and the electricity
market is now providing the signals for new generation, there’s not a central provider deciding when to build a new power station, everyone stands on their own merits.
“And this changed how things are run – in the power stations that I worked in, the production of those power plants under privatisation typically increased by about 25–30 per cent because with about a third of the people, because now there’s a strong business focus.”
As new technologies emerged over the past 40 years, Mr York said they reshaped the conversation around energy, as well as the way we use it.
“Customers now can generate electricity and the IT systems allow them to be a prosumer. They’re in a lot more control,” he said.
“And then we’re now merging the transport sector with the energy sector, but the energy sector itself is changing.
“We used to talk about efficiency one of the ways we were going to reduce emissions is by using less electricity. But now you’re seeing massive growth in data centres, particularly with AI, and we can do that because we’re reducing emissions in power plants and in the industry. So now reducing energy [usage] isn’t so important – you can use more of it.”
During his time with ENGIE, Mr York has spearheaded a number of key projects in Australia.
He led ENGIE’s Yuri Renewable Hydrogen Project, which is currently being built in the Pilbara, Western Australia, to produce renewable hydrogen as a zero-carbon feedstock for Yara Pilbara Fertiliser’s ammonia production facility in Karratha.
Mr York has also overseen ENGIE’s gas power stations in South Australia, including the flagship 489MW Pelican Point Power Station, which has recently been upgraded to allow it to run more efficiently and at lower levels, to better firm the huge amount of renewable energy in the state.
“This power plant couldn’t operate during the day because electricity prices go negative and would come online with too many megawatts and completely collapse the market, because the market doesn’t want its energy.
“We had 180 people look at what can we do differently in this asset to adapt to new markets and one of the key things we did was we introduced some new technology from the OEM that allowed the unit to run down to 40MW, instead of 130MW.
“And that meant it could afford to stay on in negative prices during the day and then only bring the load up if the market needs it to provide grid stability. It’s really been a reinvention of the asset.”
Mr York said when he first joined ENGIE there was a big push to reduce the cost of air inlet filters in company’s gas turbines.
“We had about 150 or 200 gas turbines around our portfolio around the world, and to reduce the cost of the of these gas turbine air inlet filters most people decided to go to another manufacturer get a lower price – but I had a really clever person in my team that looked at it a different way,” he said.
“If it takes a lot of energy to suck the air through these filters, then you use more fuel. And a lot of the time, people try to save money by not replacing the air filter, and they think they’ve saved money but actually they’ve actually used more fuel for the year because of the reduced efficiency that came with running a dirty filter.
“So this guy, he created these models where we could look at different filtration systems for different gas turbines, and the fuel savings ended up saving more than 100 per cent of the cost of air filters.
While a lot has changed in the sector since 1983, Mr York said that new and different technologies come with exciting opportunities and he feels very blessed to have had so many of these opportunities over the course of his career.
“What I like about the energy sector is that it’s dynamic – we’re seeing the technological change and it’s just so exciting,” he said.
“I’ve had so many opportunities, having worked overseas for 18 years in multiple different countries, and working with all corners of the globe, and in different electricity markets.
“But even if you come back to Australia, you can spend your life in a power station and not get bored because there’s change and there’s new challenges.”
There have been many people who’ve inspired Mr York over the decades, but he said that early on in his career, one his bosses said some words that have stuck with him ever since
“You don’t judge your career by what you did. You judge your career by the opportunities that you gave to others.
“And I really like that, but it’s actually self-serving as well, because I want a good team so I want to empower that them. Good leadership involves listening to your team, making decisions amongst your team and allowing people to get the recognition for those decisions,” Mr York said
“You can grow the people that work under you all the time – even if they grow and they leave, it’s better than you not giving them the opportunity to grow. That message really stuck with me for life.”
Mr York said he looks at organisations upside down.
“My role as a leader is to support my team – their objective should be aligned with my objectives and my job is to support them,” he said.
“I challenge them, but I’m not trying to outsmart them. If you’re a manager you must accept that the people that work for you know more about their subjects than you do.
“You want to extract their ideas and work together to understand what the problem is and find solutions.
“You’re helping them get to the decision, but you’re not making the decision for them. When everyone owns the decision, they embrace it and they work towards it.”
“I’m not the boss telling you what to do – I’m here to help you do a better job.
As Mr York bids the industry farewell, he imparted some advice for the next generation of energy leaders.
“The first thing you need to do is do a good job – if you do a good job, people notice and that is that opens the doors for further opportunities.
“And my other piece of advice is that up is not the only way forward.”
Mr York said he’s had more lateral moves in his career, and he’s learned a lot by moving sideways into new roles.
“I would rather see a good employee able to grow and leave my business then try to hold a person down and keep them there, because that is just the wrong thing to do” he said.
“And sometimes when person leaves your business, if they’ve had a good experience with you then they grow and they come back later on.
But, he said it’s up to the individual as well to put themselves in positions where they can grow and experience different parts of the business.
“Get involved in things – you need to stick your head outside of your existing job and take those opportunities so that you can grow yourself,” Mr York said. “And in my opinion, that is growing upwards.” U
Utility companies including power, gas, and water have vast opportunities to improve operational efficiency and customer service by upgrading infrastructure with smart devices and automated systems — and by implementing broadband connectivity solutions that maximize data and improve communications. Ericsson's enterprise wireless solutions unlock the power of 5G and LTE to securely connect power grids, smart meters, personnel, stations, and beyond
Connecting the facilities and components of a utility with a private cellular network can provide significant benefits. Complete control of the network enables layers of security that aren’t possible over Wi-Fi or public networks, eliminates traffic competition, and boosts performance and quality of service.
Ensuring persistent oversight and security is just as critical for physical facilities as it is for the network. With surveillance cameras and sensors providing on-demand feeds — available in real time though LTE- and 5G-enabled wireless edge routers — teams can quickly conduct video, thermal, and LiDAR-based inspections across widely distributed sites
For systems and installations located in remote or difficult to reach areas, reliable wired connectivity isn’t always readily available. Sites
(R s) can be monitored and managed centrally, but also process analytics, run applications, and more in the field
Installation and maintenance of power, water, and gas lines involves a wide range of specialized services. Vehicles equipped with mobile routers have the wireless connectivity necessary to enable the continuous transmission of important data between field workers and headquarters.
With utility systems going digital and wirelessly connected sensors and smart meters streaming real-time data, information about leakage, diversion, downed wires, faults, and grid imbalances can be collected and analyzed quickly and automatically. Machine-learning and AI subsequently enable predictive maintenance to decrease outages and identify where investment is needed
The shutdown of Australia’s coal-fired power plants is on the horizon – but it’s not here just yet. Until then, the way we manage these assets will lay the foundation for the future of the energy sector and underpin the stability of the transition.
By 2038, the AEMO forecasts that all the country’s remaining coal-fired power stations will be shut down. But while this era of energy is drawing to a close, the National Electricity Market will still depend on these assets for the next few years while new renewable generation is developed.
In the interim, managing these assets requires a considered and purposeful approach –we need to ensure that they can continue to meet our energy needs, but investment in retiring assets is strategic and has to be future-focused to support and firm renewable generation.
To achieve this equilibrium, power generators need support from partners that not only share their goals, but who will be there alongside them throughout the journey with a mutual desire for long-term success.
It all depends on trust, and for EnergyAustralia and Service Stream that meant transcending traditional contract models and adopting a more collaborative approach to manage an ash repository at the Mt Piper power station in New South Wales.
Mt Piper Power Station was the very last coal-fired plant built by the now abolished Electricity Commission of New South Wales, and Service Stream has been a part of the fabric of the business since the first unit came online in 1993.
The asset consists of two coal-fired steam turbine generators that generate up to 1430MW of electricity by heating steam using a coal-fired boiler – which creates ash as a byproduct.
As long as electricity is being produced, ash is being created – and, as the operations, maintenance and construction contracting partner, it’s Service Stream’s role to take this ash from the hoppers and place it into the repository or send it offsite for other use.
When EnergyAustralia acquired the Mt Piper Power Station in 2013 from Delta Electricity it saw a need to ensure that this ash was managed in a sustainable manner, and a new ash placement area in Lamberts North was created.
Every day since, Service Stream’s trucks have carried significant volumes of ash to be stored at the Lamberts North Ash Repository. The consistent ash production means there is an ongoing need to manage storage capacity – and while fly ash can be repurposed in many ways, including, road bases, agricultural applications and other construction activities, a large amount of this byproduct still needs to be stored until such time as the power station is no longer operational.
EnergyAustralia and Service Stream came together and found that the key to navigating this project was to break away from traditional contract structures.
The teams needed to ensure the repository was constructed and filled in a way that was not only geotechnically stable but ensured that significant weather events and extreme rainfall were strategically managed to continue protecting the environment. Ensuring on-time delivery was just as critical to their joint success, and given the complexities of the project it was necessary that Service Stream, as both
the construction and the operations and maintenance partner, proactively collaborated with EnergyAustralia as well as the project’s designer.
Service Stream shared its extensive site experience to ensure the project was designed and constructed in a way that addressed the logistical requirements of the site – including the placement and management of the ash, and how bulk material handling machines would operate around the new cells.
To embrace circular economy principles, EnergyAustralia sought to use operational ash in the project’s construction materials wherever possible – and the ash was incorporated as part of construction base instead of using an external fill.
Simply aligning construction activities with operational outputs posed challenges to the construction, as any time station generation was low, less material would be generated, impacting the construction program.
So, the teams came together and found an innovative solution: reclaiming material from the existing repositories. Not only did this reinforce the construction process, but it also created additional capacity in the existing operating repository.
Additionally, to meet the operational needs of the station, the construction sequence of cell release was adjusted periodically to achieve the capacity requirements of the site. Navigating these complexities requires a foundation of trust between partners. In more traditional construction contracts, risk is typically managed on either side of the agreement.
However, in this case EnergyAustralia and Service Stream adopted a contract model that was grounded in performance-based outcome management.
This incentivised the parties to share challenges early and align the solutions of both organisations.
This kind of collaborative framework leads to something very special – unlocking, true best-forproject decision making and encouraging the partner organisations to actively manage the risk and the asset outcomes as effectively as they can on behalf of the asset owner.
In Service Stream’s case, the company had more than three decades to build trust and familiarity and to understand its partner’s needs. Business objectives evolve and people come and go, so it’s no small feat to maintain an on-site relationship for that length of time.
But for Service Stream, the secret to unlocking collaborative frameworks is not that complex.
Service Stream General Manager (Energy), Benjamin Chapman, said that Service Stream places immense value in its position as a trusted partner to EnergyAustralia and the Mt Piper operation.
“It is crucial to us to bring a full lifecycle view to the table when we interact in critical projects such as the Lamberts North Ash Repository,” he said.
“We ensure that we engage in a transparent manner with our partners so that we can make informed decisions to ensure successful outcomes for everyone.”
For all parties involved, the Lamberts North cell construction project met its time, quality, cost, safety and operability goals, and this integrity, accountability and alignment between partners was the key to its success. U
The future is digital, but connected critical infrastructure is a prime target for cyberattacks. So how can utilities secure remote assets without compromising performance?
When a bushfire cuts power to a remote water pumping station, back up systems need to work flawlessly to ensure the local community has access to vital drinking water. But what happens when that same station relies on public internet to report its status back to operators? Suddenly, the very connectivity that enables remote monitoring becomes a potential gateway for cyberattacks.
Image: kraskoff/stock.adobe.com
Utilities know all too well that this kind of scenario is a very real threat across Australia. Critical infrastructure operators face a difficult choice: deploy digital tools to manage remote assets more effectively or maintain security by keeping systems ‘air-gapped’ and isolated. The problem is that isolation no longer works in a world where extreme weather events are increasing and skilled technicians are in short supply.
For example, regional water authorities managing dozens of pump stations across hundreds of kilometres, traditionally had to send technicians out to check each site manually. This not only consumes valuable time, but increases the chance of problems going undetected until they become failures. Digital monitoring promised to solve this challenge, but it created new vulnerabilities that operators have struggled to address.
Australia’s infrastructure transformation is happening at breakneck speed. Coal plants are shutting down while renewable energy projects race to fill the gap. New water infrastructure must service growing populations while ageing assets require constant monitoring. Climate change brings more extreme weather events that test every system’s resilience.
Australia needs to install more than 40GW of renewable energy capacity by 2030 as ageing
coal of this infrastructure will be in remote areas where connectivity options are limited. Wind farms in South Australia’s mid-north, solar installations across Queensland’s outback, and pumped hydro projects in Tasmania’s highlands all require reliable communications to operate safely.
Digital tools offer solutions to these challenges. Remote monitoring can detect problems before they become failures. Automated systems can respond to emergencies when human intervention isn’t possible. Real-time data helps operators make better decisions about resource allocation and maintenance scheduling.
But digitalisation creates a fundamental security problem.
Traditional approaches to securing remote infrastructure relied on physical isolation – if a pump station was 200km from the nearest town, it had inherent protection from attackers – physical distance. Modern connectivity requirements eliminate this protection.
Vocus Satellite Development Manager, Ash Grove, explained that digitisation means having centralised control of assets, which eliminates the need to have systems and people stationed at all remote sites.
“However, if control data has to go over the internet, that opens up the possibility that attackers could access systems too,” he said
This creates a particular problem for Australia’s geography. Critical infrastructure in metropolitan areas can use secure private networks over existing terrestrial connections like fibre, NBN and wireless. However, assets in very remote locations without land-based networks don’t have this option.
Remote locations could invest in multi-hop wireless solutions or have fibre installed, but both are costly and have long lead times. A single fibre connection to a remote wind farm might cost hundreds of thousands of dollars and take months to complete. More importantly, depending on a single connection type creates a single point of failure that could bring down entire systems.
communications, they face delays that affect their ability to participate in energy markets effectively. Without real-time monitoring and control capabilities, operators can’t optimise performance or respond quickly to grid stability requirements.
Satellite’s tantalising promise
LEO satellites now offer high-speed, low-latency connectivity to any location in Australia, and unlike traditional geostationary satellites, they provide performance closer to fibre levels while covering areas that fibre and wireless can’t reach economically.
But until recently, they only offered connectivity over the public internet – exactly what critical infrastructure operators needed to avoid. The fundamental architecture of satellite internet services required traffic to flow through the public internet, leaving the possibility open that critical infrastructure control data could be intercepted or modified.
“Critical infrastructure providers know internet access doesn’t provide the level of security they need,” Mr Grove said. “If you use internet access to monitor, protect, view or control critical infrastructure systems, it means there’s a chance it could be accessed from the public domain.”
This security concern isn’t theoretical. Critical infrastructure faces constant cyber threats from both criminal organisations and state-sponsored actors. Water treatment facilities, power generators and telecommunications networks have all been targeted by sophisticated attacks designed to disrupt essential services or steal sensitive operational data.
The consequences of successful attacks can be severe. When cybercriminals compromised a water treatment facility in Florida in 2021, they attempted to increase sodium hydroxide levels to dangerous concentrations. Luckily, a plant operator happened to be looking at a computer screen as a hacker was adjusting the values and their quick action prevented potential harm to thousands of residents. But what if they weren’t there to save the day?
Critical infrastructure in metropolitan areas can use secure private networks over existing terrestrial connections but assets in very remote locations don’t have this option. Image: LisaGageler/stock.adobe.com
isolated systems that couldn’t benefit from digital tools.
The industry needed a third option: satellite connectivity that didn’t traverse the public internet.
In 2022, Vocus became the first major telco in Australia to sign an agreement with SpaceX to deliver Starlink Business satellite connectivity to enterprise and government customers.
But signing the agreement was just the beginning of a complex engineering challenge.
According to Mr Grove, the real breakthrough came when Vocus worked with SpaceX to develop a private layer 2 solution over the Starlink satellite service that removes internet access from the network.
This creates a secure pathway combining the speed and coverage benefits of LEO satellites with the security requirements of critical infrastructure.
Think of this as building a private highway system that uses satellite links instead of terrestrial cables. Traditional satellite internet services function like public roads – traffic from multiple users shares the same internet protocol pathways.
Vocus’ solution creates dedicated lanes that bypass public networks entirely, ensuring that critical infrastructure data never remains on an infrastructure provider’s private WAN network and never touches the public internet.
“We are the first carrier globally to privately peer with Starlink for secure customer services,” Mr Grove said.
As Vocus is a critical infrastructure provider itself, Mr Grove said the team know just how important security is when it comes to these assets.
“Our customers have been asking for this from the moment we launched Starlink Business services in Australia. That’s why we developed the service, called Vocus IP-WAN over Starlink Ethernet Access,” he said
The technical complexity of this achievement can’t be understated. Creating private connectivity over satellite networks requires sophisticated integration with Starlink’s network at the core level.
systems that ensure security policies are maintained across satellite links.
For Mr Grove, the technical achievement is significant, but the human impact is more important.
Infrastructure operators can now deploy secure, highperformance connectivity to remote locations without compromising their security posture.
Water utilities can monitor pump stations in real-time while maintaining the same security standards they apply to metropolitan facilities.
In fact, the satellite connections can become part of their standard private network architecture just like a landbased fibre or NBN connection.
Australia’s infrastructure expansion requires skilled workers to build new facilities in remote locations. However, if connectivity takes too long to establish, then these vital projects can stall, creating delays that cascade through entire project timelines.
“Wind and solar farms are often in very remote locations where there isn’t a nearby fibre route or a reasonable mobile network, to connect and establish camps or enable employees to build out there,” Mr Grove said.
Construction teams need reliable communications for safety coordination, technical support and basic quality of life. Without connectivity, the workers entrusted to deliver Australia’s future can’t access technical documentation, coordinate with suppliers or maintain contact with families during extended deployments.
Traditional approaches meant waiting six to 12 months for communications access in remote locations, or spending large chunks of valuable project capital on dedicated connections. Either option could cripple a project’s business case.
Vocus’ Starlink services can be deployed in approximately 14 days from contract to activation, and where a asset owner already has private networking through Vocus, the team can then activate the Vocus IP Wan over Starlink Ethernet Access service in just a few days.
This dramatic reduction in deployment time supports project economics and enables infrastructure development in locations that may have previously been unviable.
“This greatly reduces the cost to deploy, which removes those roadblocks that infrastructure developers face in remote locations,” Mr Grove said.
The speed advantage also becomes critical during emergencies. When extreme weather events damage infrastructure, communities need backup communication quickly to access critical information about safety procedures and evacuation routes.
The community then needs to be able to apply for government assistance to rebuild their region –something that relies on digital connectivity that can be securely provided through Vocus IP WAN over Starlink Ethernet Access.
It’s not just communities that rely on essential services, utilities also depend on each other to keep the country running. But this interconnection can create cascading failures during emergencies. When storms knock out power, telecommunications and water infrastructure need backup energy or they fail as well – and as the industry embraces digitalisation, telecommunications become vital to operating these assets.
The 2019–20 bushfire season was a tragic demonstration of these interdependencies. As the energy sector raced to get the lights back on, power outages led to telecommunications failures, which then impacted emergency services’ ability to coordinate evacuations.
“A lot of mobile towers rely on grid power,” Mr Grove said.
“Many have battery backup, but they only last a relatively short time because these towers require a lot of power.”
Vocus Satellite – Starlink solutions operate differently, they’re not connected to local network infrastructure and don’t rely on local or grid power connectivity. The equipment can operate longer on battery or solar systems, making it easier to maintain during power outages.
“You can be entirely off grid from a communications perspective,” Mr Grove said.
This resilience proves value beyond emergency situations. Remote infrastructure monitoring helps prevent problems before they affect communities. Early warning systems can alert operators to equipment failures, weather-related stress or intruders on-site.
Before launching Vocus IP-WAN over Starlink Ethernet Access in June 2025, Vocus trialled the technology with several customers, including a water utility, government agencies and a mining operation.
“We were able to talk to customers about the product, how it would work for them, and make sure we solved their challenges,” Mr Grove said.
The trials revealed applications beyond basic connectivity. Critical infrastructure providers found they could deploy secure communications for temporary construction sites, provide backup connectivity for critical facilities, and establish monitoring systems for remote assets that previously operated without oversight.
Water utilities discovered they could implement realtime monitoring systems that improved their ability to detect problems in real time and respond to them.
Performance exceeded the industry’s – and Vocus’ – expectations.
“We knew that a private access solution over Starlink satellite was going to be successful, but what we found was that it outperformed our estimations,” Mr Grove said.
This success opened new possibilities.
“We thought we were developing one unique solution for connecting to major physical assets, but then customers told us they could also use it to connect remote devices like remote pumps, switches, gates and CCTV,” Mr Grove said. Government agencies found the technology particularly valuable for monitoring border security infrastructure and coordinating emergency response activities.
Vocus’ approach combines Starlink’s technical capabilities with established network engineering practices. The company established private peering points with Starlink’s network in Sydney and Perth.
This integration allows organisations to apply the same security policies to remote facilities that they use at core locations.
Network administrators can manage satelliteconnected sites using the same tools and procedures they use for their land-based connections.
Vocus is continuing to develop additional services around the Starlink platform.
“It’s a constantly evolving sector, and Vocus aims to be Australia’s satellite system integrator of choice,” Mr Grove said.
But, Mr Grove said solving real problems for Australian customers remains the core focus.
“We know what it takes to operate critical infrastructure, to maintain critical networks and provide services to our customers,” he said.
“We know that if communications assets go down then it can just waterfall into more problems.”
For infrastructure operators, the choice is no longer between security and connectivity. They can have both – and the communities that depend on their services benefit from more resilient, more responsive infrastructure that’s better prepared for Australia’s challenging environment. U
For more information, visit vocus.com.au/starlink
When the lights go out, remote communities are relying on SA Power Networks to come to the rescue – and field crews need to stay connected in order to respond quickly.
As the sole electricity distributor for South Australia, more than 1.7 million customers rely on SA Power Networks’ field crews to keep the lights on. The utility’s service area spans an enormous 178,000km 2 and encompasses numerous remote and regional communities.
To support these small towns and communities, the regulated service provider operates a 24-hour faults and emergencies hotline. However, these locations are often highly remote, have limited services and infrastructure, and require long drives to access cellular coverage, creating challenges for utility response and repair teams.
SA Power Networks Head of Power, Paul Salter, explained that a lack cellular coverage risked delaying repairs.
“Our field crews are working in regional and remote parts of the state, some of which have next to no cellular coverage. Without reliable service, crews could arrive at site to carry out works, but then need to travel to the nearest location with a cellular tower to communicate or access critical information related to the job,” he said.
SA Power Networks crews were often forced to drive more than 20 minutes from the service sites to reach the coverage areas needed to receive approvals, look up information or provide status updates. These delays slowed restoration efforts in regional and remote areas, putting SA Power Networks at risk of not meeting restoration SLAs.
To keep its fleet connected, SA Power Networks deployed ruggedised Ericsson Cradlepoint routers across more than 170 vehicles to facilitate active Starlink satellite connectivity with cellular failover. Network performance is managed and monitored via Cradlepoint’s NetCloud Manager for single-pane-of-glass visibility from anywhere. Due to the remote locations where maintenance work occurs, SA Power Networks uses Starlink satellite connectivity as the primary WAN connection. If the router detects degraded satellite performance or a clear line of sight is unavailable, service vehicle networks can fail over to a cellular connection, ensuring uninterrupted connectivity.
“The connectivity solutions we now have with 5G routers and Starlink LEO satellites are saving our field workers significant time on travel and administration effort,” Mr Salter said.
With network connectivity no longer a constraint, Mr Salter explained that SA Power Network’s crews could accomplish more digital tasks and make on-site decisions, which significantly reduced travel time and administrative effort. This enabled faster responses, fewer repeat trips and improved customer restoration times.
“Regional crews can now access consistent high-speed internet from anywhere at any time, making it faster and safer to carry out restoration and maintenance tasks and to keep head office and customers informed of their progress,” he said.
Through this guaranteed connectivity, SA Power Networks has estimated a per-year savings of 1845 hours as a result of enabling and improving digital technologies in the field. It also saved another 1844 hours per year by making it easier for crews to close out and approve jobs, and a further 1230 hours were saved by eliminating the time previously spent traveling to find a connection.
The combination of satellite and cellular to provide constant connectivity allows uninterrupted lines
With
the combination of 5G and LEO
satellite, crews have full connectivity in their trucks, which makes their jobs safer. “
of contact with crews as they traverse remote areas throughout the state, giving field workers and their families peace of mind about their safety.
“With the combination of 5G and LEO satellite, crews have full connectivity in their trucks, which makes their jobs safer while outage times for our customers can be significantly reduced,” Mr Salter said.
Another essential resource for SA Power Networks was Ericsson’s NetCloud Manager, which offers centralised visibility and management of the organisation’s entire fleet of routers, along with clear insights into uptime and data usage across cellular and Starlink WAN interfaces.
The platform’s robust security and ability to export information such as SIM numbers for asset management have effectively met critical utility data handling requirements.
By leveraging innovative solutions to streamlining processes and decreasing dependence on offline capabilities, SA Power Networks was able to boost operational efficiencies and liberate valuable time and resources. This time saved operationally paves the way for SA Power Networks to drive future innovations, ensuring it continue to lead in service quality and technological advancement. U
network connectivity no longer a
For
Utilities and councils are leading the charge towards a reliable, sustainable future. Digitisation offers the path to take us there, but shared knowledge and genuine collaboration are what will propel us forward.
The digital transformation is happening now. Whether it’s electricity, water, gas or telecommunications, the way Australians interact with essential services is changing forever.
There’s promise of a bright future ahead, but utilities must first navigate a sea of challenges, from water scarcity to population growth and the ever-evolving question of grid security.
Smart meters, IoT, AI, data and operational technology (OT) are the tools that are going to empower utilities to solve these challenges. But without a guide, struggling through a digital transformation is a challenge of its own.
For Nucleus 3 General Manager – Digital Enablement, Alana Chong, it’s not about purchasing the latest technology, it’s about finding a solution that empowers outcomes now but also has the ability to scale.
“There isn’t necessarily bad devices and good devices or bad software and good software – it’s just about [matching them to] the problem they’re trying to solve,” she said.
“At the end of the day, you want to get outcomes. You shouldn’t go out to market to decide on a device or decide on a system. You need to decide on what outcome you’re looking for, what problem you need to solve, and then that’s how it comes together.”
Nucleus 3 is one of the best-kept secrets in digital utility space. This team manages clients with around 400,000 devices, but they won’t tell you that they’re part of the second-largest digital metering company in Australia –instead they’ll tell you how much they love what they do.
On 26 June 2025, Nucleus 3 brought its people and partners together for a gala event to celebrate a year of growth and the people that made that journey possible. After hearing the news that the company had recently appointed a new leadership team, Utility tagged along to get the scoop.
More than 120 team members, partners and clients attended the event, but even for such a diverse group of professionals there was very real sense that everyone was aligned on the same goal. That shared vision can be traced back to Nucleus3 Founder and CEO, Louis Limnios, who’s values and genuine passion for the industry have shaped every part of the business. And those values are simple: Nucleus3 is about the people, it’s about loving what they do, and it’s about winning the right way.
“I thought it just was really important to bring everybody together and say thank you – it means a lot,”
Mr Limnios said at the event.
“To our partners, thank you for trusting us and representing your brand, your offerings, and that means a lot to us – our business is better because of you.
“And to all our customers in the room – we wouldn’t be here without you. Your trust in us to deliver real outcomes is what drives our success.”
For Ms Chong, who had joined the team a few months earlier, the event was a meaningful affirmation of what had already drawn her to the company: a genuine focus on purpose, customers and people. The alignment of values on display was a reminder of why the work matters.
Before Ms Chong came on board, Mr Limnios led a strategic restructure to realign the business around clearly
defined service areas. With that came the opportunity to shape a new leadership model, and he invited her to join the business as the GM of Digital Enablement.
“I’ve always been someone who’s deeply customerfocused, and in the water sector especially, that mindset is shared across the industry,” Ms Chong said.
“What really stands out to me about Nucleus3 is their genuine commitment to not just our clients, but to the communities those clients serve. We understand that delivering value to our customers means delivering outcomes for their end users too.
“We don’t compete with our partners, we complement them. We sit within the ecosystem, helping to connect the dots and make things work better for everyone. That’s what I love about being part of this team.”
Nucleus 3 has a team of more than 100 consultants across three business units, with a wealth of knowledge they can’t help but share.
“At first, I found myself pushing back a little, Louis has this incredibly generous nature, he’ll give away every insight he’s ever learned because he genuinely wants to help everyone,” Ms Chong said.
“But over time, I came to really appreciate that mindset. Digital transformation, especially in utilities, is incredibly complex, and that can be overwhelming for customers. What I’ve learned is that it’s not about holding onto knowledge, it’s about making things feel simple. I want our customers to feel confident and say, ‘don’t worry about the complexity, we’ve got it handled’.”
Across its four business units – N3Z, N3Evolve, N3Edge and InteliEON – Nucleus3 empowers utilities in all aspects of the digital journey, including ICT and engineering strategy and operations, consulting and advisory services, business analysis, service improvement, data centre and cloud software, as well as operation technology consultancy, managed services, security, IOT/analytics and software delivery.
market-leading technology, but what they’ve learned is that customers aren’t just looking for impressive tech. “They’re looking for clear use cases and real outcomes. So that’s what we focus on delivering,” she said.
And when these different parts of the business work together, there’s little the team can’t do.
“N3Z is led by Jinene Clark, she’s bringing all of what we do here to New Zealand,” she said.
N3Evolve is a dedicated provider of business strategy and execution solutions, which Ms Chong described as a team of skilled, like-minded professionals that operates with the depth and capability of a large consulting firm, but with the agility and focus of a close-knit team.
“N3Evolve is run by Neil Dickson, and he’s got some amazing leadership sidekicks in there, Melainie Reddy and Geoff Tranah. And then there’s 125-plus consultants that all get deployed out to all over the country,” she said.
Ms Chong heads up N3Edge and InteliEON, and her team take care of the research and development (R&D).
“The business units I take care of are highly complementary. N3Edge is focused on deep R&D, developing industry-specific IoT solutions and working
“When we meet with a council, for example, they might say, ‘We want to detect leaks.’ They’re not necessarily interested in what sits under the device cover, even though we can show them, what matters is that the solution addresses their need. It’s all about the use case.
“To make that happen, we fill gaps between different systems with our own IP [the Water Bureau], bringing everything together into a cohesive, orchestrated solution. It becomes about enabling the ecosystem, stitching together partners, platforms and technologies to deliver real value in the market.”
“What I really love is that the reason our solutions are market-leading and genuinely solve problems is because our team truly cares, about people, about outcomes and about making a difference. They listen, they ask the right questions, and they build with empathy and purpose.”
For Nucleus 3, people are the key enablers of change, growth and innovation.” U
For more information, visit nucleus3.com.au
control systems are key to efficient water operations.
Future-ready water operations start with unified, intelligent control infrastructure.
Water treatment plants are never still – valves open and close, pumps pulse and water constantly moves through filters.
Each component plays an important role in keeping water clean and flowing. But what happens when they don’t speak the same language?
For many water utilities, control systems have evolved organically, with new features and technologies added over time, often as quick fixes to specific challenges, rather than a deliberate choice as part of a long-term strategy.
While these fragmented systems might function day-today, they rarely operate in harmony – limiting visibility, making data more difficult to interpret and limiting the ability to act swiftly when issues arise.
As population growth heightens the demand for treated water, and with ongoing challenges like ageing infrastructure, sustainability targets and stringent compliance regulations, the need for connected, unified systems is clearer than ever.
That’s why many utilities are turning to modern distributed control systems – not just as a technology upgrade, but as a foundation for sustainable, future-ready operations.
Recognising the value of seamless integration, NHP works with utilities across the country to modernise and streamline their operations using advanced distributed control systems. The company is the exclusive Australian distributor of PlantPAx by Rockwell Automation, a modern, scalable distributed control system that helps utilities make faster, better-informed decisions and respond quickly to changing conditions, regulatory demands and community needs.
PlantPAx acts as a central nervous system for the entire facility, eliminating many of the inefficiencies and blind spots that come with patchwork systems.
Built on a common automation platform, PlantPAx integrates every part of the process, from intake and treatment to pumping and discharge. Operators gain full visibility across the entire water treatment plant, rather than just individual assets.
For water treatment plants, the benefits of this kind of integration are immediate.
Operators can monitor chemical dosing, filtration performance, energy use and system diagnostics from a single interface, improving situational awareness and response time. Instead of reacting to issues, teams can start anticipating them.
The system is designed to be scalable across sites. From small, rural facilities to large metropolitan networks, PlantPAx can support the evolving needs of regional and urban utilities alike.
As cyber threats become of greater concern for critical infrastructure, PlantPAx also offers built-in protection. Its TÜV-certified architecture aligns with international standards such as ISA-99/IEC 62443-3-3, helping utilities safeguard their networks from cyber attacks.
But for NHP, technology is only part of the solution. With more than 50 years of experience in industrial automation, the company’s on-the-ground team provides local support through every stage.
For utilities tasked with providing the critical water services on which people rely, systems that simply monitor aren’t enough – they need to optimise.
Modern distributed control systems like PlantPAx are enabling that shift, turning disconnected equipment into unified infrastructure that’s ready for the future.
And with NHP’s support, utilities can adapt these systems with confidence and get back to the bigger picture: delivering safe, reliable and sustainable water for their communities. U
For more information, visit nhp.com.au/Solutions/Modernisation/PlantPAx
A decade into IoT-enabled water-quality monitoring, utilities are preparing for the next generation of intelligent devices.
The water industry has undergone quite the digital transformation over the past decade.
From the early rollout of 2G-connected devices to today’s cloud-integrated, artificial intelligence (AI)-supported platforms, Internet of Things (IoT) technologies have become a core part of the way utilities manage quality, compliance and efficiency.
With such rapid technological advances, the past ten years have been a steep learning curve for the industry. Utility sat down with Metasphere National Water Quality – Environmental Sales and Product Management Specialist, Adam Simpson, to reflect on the sector’s growth during this time, and to find out where it might be heading next.
“It’s hard to believe how far we’ve come in the last decade of IoT water-quality monitoring,” he said.
According to Mr Simpson, the early years of IoT in the water sector were defined by infrastructure uncertainty. Cellular networks evolved quickly, which meant the industry had to learn how to future-proof products and deployments in a fast-changing landscape.
Technology wasn’t the only early challenge. Mr Simpson said when IoT first started to take off, the biggest barrier to deploying water quality sensors at scale was the high hardware cost.
“This was also true for smart metering,” he said. “And for some utilities, it still is.”
While prices have gradually fallen over the years, Mr Simpson said there has also been a shift in conversation from cost to value.
“The greater value of smart sensors lies in enabling utilities to do more with less,” he said.
Perhaps nowhere is that need more pressing than in regional Australia, where an ageing workforce is generating serious resourcing challenges. “As experienced water industry workers are retiring, backfilling these roles is proving increasingly difficult,” Mr Simpson said.
This creates a critical opportunity.
“Smart sensors can automate routine tasks like meter reads and water-quality checks, reducing the need for
long-distance field travel and freeing up skilled staff for higher-priority operational roles,” Mr Simpson said.
At the same time, the technical capabilities of these devices are still evolving. While cloud-based data visualisation was previously perceived as a nice-to-have, it’s now considered a minimum requirement.
Mr Simpson said the sector is also seeing the convergence of cloud and on-premise control systems into hybrid platforms, which offers a unified “singlepane-of-glass” view of critical and non-critical data.
“These systems are also increasingly integrating with machine-learning models to support proactive network management and improve compliance with the Australian Drinking Water Guidelines,” he said.
So what’s next?
If you asked Mr Simpson, he’d say the sector is close to seeing truly scalable, cost-effective smart water sensors.
“With AI-enhanced data visualisation, Australian utilities will be better equipped than ever to manage their networks efficiently, intelligently and sustainably.”
Indeed, from automated alerts to predictive analytics, smart sensors and IoT technologies are no longer just futuristic tools; they are shaping how utilities deliver critical water services to their communities. U
Metasphere helps customers prevent leaks and spills for a cleaner, greener world
Our intelligent, innovative all-in-one telemetry solutions provide full network visibility, performance and forecasting.
Reducing telemetry ownership cost for customers to manage time-critical remote assets and systems.
Telematics is transforming the way utility fleets are monitored and managed.
As utilities face growing pressure to reduce costs, lower emissions and strengthen operational safety, fleet management is under the spotlight.
From supporting asset maintenance to enabling emergency response, fleet operations are integral to the delivery of essential services – but how can utilities optimise their fleet management?
The answer lies in telematics.
Providing access to real-time vehicle data, telematics presents a unique opportunity for utilities to unlock savings across fuel usage and maintenance and boost safety and sustainability.
Fuel use remains one of the most significant fleet expenses, particularly given the vast distance of essential service networks. Monitoring vehicle idling, route optimisation and driver behaviour through telematics can deliver powerful results in fuel consumption.
Fuel tax credits are another opportunity to reduce costs. For eligible vehicles and equipment, utilities can claim fuel tax credits to offset fuel expenses – but accurate, compliant records are essential. Telematics can track fuel consumption with geospatial precision, simplifying the documentation process and ensuring maximum returns.
Telematics also enables a more proactive approach to fleet maintenance.
Real-time detection of engine fault codes means maintenance schedules can be aligned with actual vehicle condition, rather than spaced out at fixed intervals. This reduces the risk of breakdowns, shortens downtime and helps extend vehicle life, all while improving service reliability and worker safety in the field.
The transition to electric vehicles (EVs) is gaining traction across the sector as utilities look to reduce their carbon footprint while also reducing operating costs. Telematics can support this shift by providing insights into factors such as vehicle performance, charging requirements and battery efficiency.
With access to this data, fleet managers can evaluate the total cost of ownership and infrastructure needs of EVs and create targeted deployment strategies based on actual fleet usage rather than assumptions.
Insights about fuel consumption can also support broader emissions reduction goals and environmental reporting requirements, while proactive maintenance supports the longevity of utility fleets, contributing to a more sustainable future.
Safety also remains a top priority for fleet operations in any sector – and utilities are no exception.
In-vehicle alerts can help address harsh braking or speeding and ensure drivers are wearing seatbelts. Furthermore, predictive analytics means telematic platforms can flag risk-prone drivers or routes – even before incidents occur.
The technology also supports compliance with chainof-responsibility obligations and provides valuable data for incident investigation and insurance claims with the assistance of tools such as video footage and collision reconstruction.
With more than 25 years of experience and solutions trusted by more than 55,000 customers around the world, Geotab is a leader in the evolution of connected fleet technology. The company’s platform brings together realtime insights, seamless integrations and accurate data to help utilities manage fleets more intelligently.
April 2025 saw Geotab receive certification as an Application Service Provider for the Telematics Monitoring Application (TMA) and Road Infrastructure Management (RIM) programs under Australia’s National Telematics Framework.
The new certification enables the company to help transport operators enrol in government schemes and initiatives that use TMA and RIM, allowing utilities to participate with confidence.
From lowering costs and emissions to improving driver safety, telematics is shaping the future of utility fleet management. And Geotab is driving the transformation. U
Through our expertise, brilliant network, and unique customer focus, we make brilliant digital solutions simple.
Boosting economy and communities with critical remote connectivity across the Pilbara region.
Community Enterprise Queensland (CEQ): uninterrupted access to metro-grade high speed, low latency connectivity.
WA Police: Anywhere communications project, connecting remote police stations and vehicles across Western Australia.
Backed by a team of leading network experts, solution architects, dedicated account teams and strategic partners, our reliable and secure network provides connectivity across Australia and into Asia Pacific. Visit vocus.com.au
Providing mining industry with safety and productivity via above and below ground LTE network connectivity.
Whitsunday Regional Council: enhanced communication for work crews and critical support for emergency services.
Providing mobile in vehicle Starlink for large scale construction e.g. transmission line builds
SA Power Networks: Connecting 200 Starlink units across the state via a scalable, resilient network environment.
When disaster strikes, we’re all relying on front line utility workers to keep the lights on and the water running – and it’s vital that they’re equipped with the tools to succeed.
The utility sector stands at a juncture, constantly balancing the demands of critical infrastructure management with the imperative to innovate. While discussions often centre on grid modernisation and renewable integration, there’s a quieter transformation underway: the evolving nature of our workforce.
A significant portion of this workforce operates remotely, in the field, at isolated substations or across vast service territories. For these essential employees, the traditional onboarding and identity management processes can often feel like an unnecessary hurdle, rather than an essential tool.
Picture a new field technician, hired to cover a wide rural area. Historically, their onboarding might involve multiple trips to a central office for document verification, followed by a wait for a physical access card to be mailed or picked up. This isn’t just inconvenient – it delays their ability to contribute meaningfully.
Now, envision an alternative – a streamlined digital onboarding process, completed securely from their home or a local office, using a solution that allows for the easy upload and verification of all necessary identity documents. This doesn’t just expedite the administrative side, it returns the new employee’s time and reduces logistical burdens.
The IdentityONE cloud solution is not a replacement for human interaction – it’s an enabler of it.
Remote workers are often the first on-site during an outage or tasked with routine maintenance in a remote location. For them, the ability to quickly and securely prove their identity and gain necessary access isn’t just about efficiency – it’s about safety, compliance and, ultimately, service continuity.
With a secure Digital ID issued directly to their smartphone, not only do these professionals have piece of mind that their credentials are safely stored away from unauthorised access, but with less physical paperwork to carry, the risk of losing critical identification is significantly lower.
This isn’t just a digital photocopy of their driver’s license. It’s a dynamic, verifiable credential that contains all the necessary, securely uploaded and validated information.
These digital IDs can also be integrated with physical access control systems, meaning that a field technician arriving at a remote substation, for instance, can use their secure digital ID on their phone to gain instant, validated access.
This eliminates delays associated with lost physical cards, expired credentials or manual gate checks. It means they can get to work faster, whether it’s responding to an emergency or performing routine maintenance. This fluidity of access, driven by a secure digital identity, directly translates to improved response times, increased productivity and a smoother operational flow for dispersed teams.
This shift isn’t about adopting technology for technology’s sake, but about strategically empowering employees with the tools they need to perform their vital roles more effectively, securely, and with greater autonomy. It’s a move that strengthens not just individual productivity, but the overall resilience and responsiveness of the entire utility operation.
Many forward-thinking energy and utility companies are already recognising these significant benefits and have rolled out IdentityONE. By embracing solutions like Unicard’s IdentityONE, CaptureME and IDmobile, they are joining a growing cohort of industry leaders who are actively investing in the capabilities of their remote workforce.
They are providing tools that enhance convenience, bolster security, and enable quicker, more efficient access to the critical assets and locations that define their roles. It’s about recognising the unique needs of those on the front lines and equipping them with the digital keys to succeed, allowing them to focus on what they do best, no matter where they are. U
For more information, visit identityone.com/utilities-energy
Utilities, councils and road authorities don’t just service communities, they’re a part of them. And for everyone to thrive, they need to collaborate.
Communities are the building blocks of society, but being part of a community isn’t passive, it’s something you actively do – it’s about working together.
According to the Streets Opening Coordination Council (SOCC), communities that help each other solve problems, provide support, and educate each other are stronger and more likely to thrive.
That’s why SOCC is on a mission to build a culture of collaboration between utilities, traffic authorities and councils across Australia.
Uncoordinated street works present several critical challenges, including financial waste, public inconvenience and reduced asset integrity due to repeated excavation and repairs.
Working together means councils, road authorities and water, energy and telecommunications asset owners can coordinate their capital works programs to minimise community disruptions, reduce costs and deliver better outcomes for customers.
Burwood Council Mayor, John Faker, has seen firsthand the power of collaboration in tackling complex urban challenges.
“As Burwood’s longest-serving Mayor, having proudly served for almost 20 years, I’ve had the privilege of leading our community through significant growth, renewal, and transformation,” he said.
“Burwood [is] a vibrant and diverse community in the heart of Central Sydney. While we’re one of the smallest councils geographically, we’re a highdensity centre that plays a big role in the metropolitan landscape, with significant infrastructure, transport, and planning responsibilities. I currently serve as President of the Southern Sydney Regional Organisation of Councils (SSROC), which recently joined SOCC.”
Mayor Faker said that Burwood is also proud to be chairing the SOCC board.
“I encourage all councils across Greater Sydney to come on board. It’s not just about improving coordination, it’s about strengthening our collective voice and influence across government and industry,” he said.
“When councils work together, we amplify our impact. By collaborating with neighbouring councils, we’re able to share resources, align planning, and solve shared challenges, particularly those that cross borders, like infrastructure coordination and asset management.”
Mayor Faker said the strength of SSROC lies in its ability to think regionally while delivering locally. It also allows these councils to present a more unified voice to state agencies and utility providers, which helps accelerate progress for their communities.
“Collaboration is not just a nice-to-have, it’s essential. The challenges facing local government today don’t recognise LGA boundaries. Whether it’s utilities, roads, public transport or population growth, we achieve more when we work together,” he said.
According to Mayor Faker, Burwood along with a number of town centres in the SSROC region are undergoing significant re-development and transformation, which has led to a significant increase in both utility works and Council’s own capital works.
“This has made the coordination between Council and the utility authorities more critical than ever as we try to deliver the best outcome for the community,” he said.
“Uncoordinated street works have long been a frustration, not just for councils, but for residents and businesses.
“From unexpected road closures to duplicated digging and incomplete information, the lack of real-time coordination between utilities and councils can lead to inefficiencies and avoidable disruption. In a place like Burwood, where foot and vehicle traffic is constant, even a small oversight can have big consequences.”
Driven by a desire to improve efficiency through smarter collaboration, SSROC saw a partnership with SOCC as an opportunity to move from reactive coordination to proactive planning.
Through SOCC, SSROC now has access to the association’s web-based, GIS-enabled platform, iWORCS (infrastructure WORks Coordination System), which acts as a platform for councils, road authorities and utilities to share their planned work programs.
“SOCC provides the governance and shared leadership model that brings councils and utilities together, and iWORCS delivers the digital platform to enable that collaboration,” Mayor Faker said.
“For us, it means better visibility, fewer conflicts, and more transparency around who is doing what, where, and when.
Mayor Faker explained that his community is navigating a complex urban environment and they want better communication, fewer surprises and certainty that council remains on top of things.
“Through iWORCS, we’re gaining tools to not only coordinate better internally and with utilities, but to also keep residents informed about upcoming works. This transparency builds trust and helps residents plan their day-to-day lives with less disruption,” he said.
“Our residents expect smooth, safe, and reliable streets. With iWORCS, we’re aiming to minimise disruptions, improve communication, and reduce the frequency of repeated works.
“That means less inconvenience for commuters, safer environments for pedestrians, and greater confidence in council’s ability to plan and deliver. It’s also about better stewardship of public funds, if we can coordinate works more efficiently, we stretch every dollar further.”
Off the back of the development and national rollout of iWORCS, SOCC CEO, Nabil Issa said the organisation saw a need to share its knowledge and collaborative culture with the rest of Australia.
The future we’re trying to build is smarter, more resilient and more liveable “
“The issues that our members have day to day are the same issues that will be happening in every other state in Australia,”Mr Issa said.
“We saw a great opportunity to open chapters in other states so they can share the same level of collaboration that we enjoy in New South Wales.”
Another key goal for SOCC’s national expansion is to provide a platform for knowledge sharing not just between states, but between different sectors too.
According to Mr Issa, many of the challenges a water authority in one state might be facing are applicable to utilities in other sectors, and he wants those learnings and solutions to be available across the country.
SOCC runs regular ongoing community practice sessions to share knowledge, innovation and success stories that other organisations can utilise in their own operations.
“Within the community practice events, we’ve also showcased a number of safety innovations that have then been shared across all industry service providers,” Mr Issa said.
“There’s great value in learning from someone else that’s done it all before. SOCC is not for profit; we’re here to help everyone create a positive change in their state.
“Wouldn’t that be great if everyone had a story to share that helps to prevent damage and safety issues and provide cost savings right across the industry?
“We’ve embedded a collaborative culture within SOCC where we can grow together across all industries. It’s important to protect your organisation, but we can be better together.”
Mayor Faker said that local government is often closest to the community, but Councils can’t do it all alone.
“Platforms like iWORCS help turn good intentions into real improvements. I’d encourage other councils and other asset owners such as electricity, gas, water and telecommunication network operators to get involved. iWORCS is not just a tool, it’s a shift in mindset toward greater accountability, better planning, and shared outcomes for the people we serve,” he said.
“The future we’re trying to build is smarter, more resilient and more liveable, [and that] relies on genuine partnerships across sectors. iWORCS and SOCC are great examples of that in action.
“I’d like to sincerely thank SOCC CEO, Nabil Issa, and the SOCC Board for driving this important initiative, and acknowledge the strong support of all SSROC councils who have come together behind it.
“This kind of collaboration is exactly what we need to deliver smarter, more seamless outcomes for the people we serve.” U
For more information, visit www.streetsopening.com.au
Australia’s utility networks are built on infrastructure that has largely stood the test of time, but with inefficient logistics that time might soon be up.
With much of Australia’s critical infrastructure operating well beyond its original design life, utilities are under mounting pressure to extend asset lifespan without compromising service quality, safety or reliability.
While maintenance is the frontline defence, behindthe-scenes logistics play a significant role in the success of these maintenance efforts – and with our essential service networks evolving faster than ever before, Droppoint identified a real need for smarter and more efficient approaches to inventory and logistics.
From ageing transformers and substations to decadesold water and gas pipelines, legacy assets still form the backbone of essential service delivery across the country. Replacing them outright is expensive, time-consuming and disruptive, so many utilities are focused on extending the life of legacy assets.
But as these assets age, they also become harder to support, making strong proactive maintenance and rapid reactive maintenance especially important; however, both rely on fast, reliable access to the right inventory and materials.
This equation calls for visibility over spare parts, timely resolutions and a logistics model designed to increase uptime, otherwise field service teams are left scrambling – chasing inventory, waiting on deliveries from vendors, improvising workarounds, or losing time on return visits.
Ineffective logistics models place added pressure on field technicians who are already stretched by labour shortages, complex maintenance schedules and increasing service level agreement (SLA) expectations.
Maximising the time these technicians can spend on their specific roles is key to ensuring critical infrastructure continues to power ahead. So, rather than continuing to rely on static warehouse models, utilities are increasingly turning to smarter, more proactive approaches to inventory and logistics – and that’s where Droppoint comes in.
As one of Australia’s leading providers of field service inventory management software and logistics solutions for field workforces, Droppoint ensures utilities always get the right part to the right place at the right time.
As one of Australia’s leading providers of field service inventory and logistics solutions for field workforces, Droppoint leverages its Material Orchestration System (MOS) in combination with its partners to ensure utilities always get the right part to the right place at the right time.
Droppoint’s expansive inventory logistics network includes more than 500 secure pick-up and drop-off (PUDO) locations across Australia and New Zealand. These 24/7 access points reduce time from vendor to delivery, bringing parts closer to technicians and reducing the time, cost and delays associated with transporting or retrieving spare parts, even in remote locations.
The company’s MOS ties it all together behind the scenes.
Purpose-built for field environments, MOS gives utilities real-time visibility over spare parts across vans, depots, bespoke locations and PUDOs, integrating seamlessly with existing systems to support smoother workflows and proactive decision-making.
By aligning logistics with preventive maintenance schedules, MOS helps reduce emergency repairs, improve SLA compliance and extend the working life of ageing infrastructure. And when the unexpected does happen, MOS enables a faster response by ensuring field technicians have the right parts available exactly where they need them.
As infrastructure continues to age, utilities around the country are facing a growing disconnect between what their assets require and the logistical support available to their field teams. Bridging that gap is critical to the continued success of Australia’s essential service delivery.
Droppoint empowers utilities to take control of their spare parts and logistics, and for utilities that have made the switch, the benefits are almost immediate. According to Droppoint, clients report up to three extra technician jobs per week, a more than ten per cent increase in scanning compliance, and a 30 per cent reduction in inventory holding.
The smarter field logistics and improved inventory visibility provided by Droppoint, utilities can boost their uptime, increase technician productivity and keep legacy infrastructure running stronger for longer. U
Australia’s water networks are feeling the pinch from all sides, and utilities need support from experienced engineering partners to navigate the road ahead.
Urban water infrastructure is one of Australia’s most critical networks, having quietly supported communities for decades. From dams and desalination plants to pipelines and pump stations, these systems underpin every aspect of modern life.
However, this infrastructure is under more pressure than ever. Population growth, climate change and shifting demand are all placing increasing strain on legacy water systems, many of which were designed for a very different level of demand.
Infrastructure that once served communities through periods of major growth must once again be adapted to suit an increasing complex environment.
The specific challenges also vary by location.
Across large cities with booming populations, density is increasing, including through large apartment buildings.
While this can increase efficiencies for services such as water supply and sewerage, it also places existing infrastructure under strain, heightening flooding and fire risks by concentrating patterns of demand within smaller geographic areas and during peak periods.
New sources of demand, like large-scale data centres, are also adding to the pressure. These facilities require substantial water and energy input, creating new design considerations for utilities when planning upgrades or expansions to ageing assets.
In rural areas, where populations may not be growing as rapidly, existing assets may have sufficient capacity to meet local needs for the foreseeable future but are likely to require upgrades over time to meet rising standards and community expectations.
However, for utilities in metropolitan and regional areas, the overarching goal is the same: ensuring these projects come at the lowest cost to consumers while at the same time ensuring the service quality is not compromised as assets are renewed or upgraded.
Many of these challenges can be mitigated through effective urban design and engineering solutions, which is why it is essential to partner with an experienced provider –particularly when it comes to new challenges.
With more than 25 years of experience in the design, management and delivery of infrastructure projects in the water sector, Lanco Group has built a strong reputation across Victoria’s utility sector.
Lanco Group works closely with water authorities, local councils and private developers, offering a full suite of services including civil infrastructure design, hydraulic and drainage services, project management, contract administration, construction auditing and technical drafting.
As an accredited consultant with Melbourne Retail Water Agencies and the state’s regional water authorities, the company brings deep familiarity with urban and regional utility environments.
Lanco Group’s engineers are experienced in navigating the complex regulatory, environmental and practical considerations that shape today’s infrastructure projects – including the increasing complexities that come when considering the impact of demand-heavy infrastructure such as data centres. One of the company’s key strengths is its ability to deliver practical, specialised engineering solutions to legacy water assets.
Lanco Group provides tailored, technically sound solutions trusted by utilities to make the most of their investments, without compromising on quality or reliability. The team’s customer-focused approach means every project is shaped by collaboration, problemsolving and technical excellence, all backed by decades of hands-on knowledge.
Australia’s water utilities are entering a critical period of renewal. To keep pace with a growing and changing population, networks must evolve, and utilities need partners they can trust to help make this happen.
Lanco Group is a trusted partner to utilities, councils and developers across Victoria, and the company is continuing to expand across the country.
With its decades of experience, Lanco Group is helping utilities upgrade, renew and future-proof their water infrastructure to meet the demands of tomorrow. U
State and federal budgets have allocated billions to the utility sector in 2025–26. Image: robynmac/stock.adobe.com
From initiatives to accelerate the energy transition and boost water security to telecommunications and cost-of-living relief, Australia’s state and federal governments are committing billions to modernise critical services and lay the foundations for future growth.
The Federal Government set the tone with the 2025–26 Federal Budget in March 2025, featuring major investments in clean energy and telecommunications. Each state and territory – except for Tasmania, which will deliver its Budget following an upcoming election – has since followed suit, delivering funding for a range of local projects.
Utility highlights the major funding in energy, water and telecommunications in each of the budgets, highlighting how the utility sector is set to benefit.
Billed as ‘Building Australia’s Future’, the 2025–26 Federal Budget aims to help people plan for the future, with the energy sector a core focus.
Key energy investments include $2 billion for the Clean Energy Finance Corporation (CEFC); $36.9 million to optimise existing grid infrastructure; and a $10 million Accelerated Connections Fund to address grid bottlenecks.
The Budget also includes $13.7 billion in tax incentives for hydrogen and critical minerals production tax incentives, and $1.5 billion through the Future Made in Australia Innovation Fund. This includes $750 million for green metals, $500 million for clean energy technology manufacturing, and $250 million for low-carbon liquid fuels. Affordability is also a priority, with $1.8 billion to extend energy-bill relief to the end of 2025.
nbn
The Federal Government committed to completing the nbn rollout, committing $3 billion in equity to provide access to faster and more reliable broadband services to a further 622,000 premises by 2030.
The New South Wales Government’s 2025–26 Budget allocated funding across the utility sector, with major investments in energy, water and disaster recovery.
The Budget includes a $2.1 billion investment over four years in the Transmission Acceleration Facility, which will primarily support the state’s five renewable energy zones (REZ). An additional $115.5 million investment supports a new logistics precinct at the Port of Newcastle to provide storage for equipment used in renewable projects.
The Budget also allocates $128 million to the Community and Employment Benefit program for the Central-West Orana REZ, with future funding expected for other REZ hot communities.
The Budget has earmarked $319.1 million for the Sustainable Diversion Limit Adjustment Mechanism Program to improve environmental outcomes for rivers, wetlands and wildlife using less water. It also outlines a further $75.1 million to protect river health; $2.7 million to provide critical local water reforms; and $5.2 million to finalise the state’s first Aboriginal Water Strategy.
The Federal and New South Wales governments are investing in disaster recovery and relief in the state, with a further $4.2 billion allocated in the 2025–26 State Budget. This includes $33.9 million for telecommunications to strengthen the Public Safety Network and $27 million for repair and restoration of water and sewer infrastructure damaged by severe weather and flooding in the central west in 2022.
The South Australian Government said its 2025–26 Budget is focused on securing the state’s future, supporting communities through immediate challenges while laying the foundations for longterm prosperity.
The Powering Business Grants provide a $20 million boost to support small and medium businesses to invest in energy efficiency equipment or improvements.
The South Australian Government is also committing $650 million to support the Whyalla steelworks and local community, which it said is set to play a critical role in the state’s hydrogen future.
The 2025–26 State Budget also allocates $12.5 million over five years to transition the current Mount Barker On-Demand (Keoride) trial service into a permanent Adelaide Metro service, including the purchase of six new electric buses and associated infrastructure upgrades to support electric vehicle charging.
The Budget allocates $300 over four years for the Eyre Peninsula Desalination Plant, which is set to be completed in June 2027.
In partnership with the Federal Government, the South Australian Government is investing $109.7 million over three years to support the River Murray. This includes $71.1 million to remove barriers to the delivery of environmental water to floodplains and wetlands and $20.9 million for councils to invest in alternative water resources and infrastructure.
The Digital Investment Fund will be expanded by $103 million, including $75 million over four years to provide increased and ongoing capacity for digital modernisation and cybersecurity initiatives across the public sector.
The 2025–26 Budget allocates $8.3 million for early works for COP31, including significant planning for security, transport and infrastructure, with Adelaide named the preferred city to host the event should Australia’s national bid for the conference succeed.
Energy affordability is a key theme in the Victorian 2025–26 Budget, with $50 million to deliver a $100 Power Saving Bonus to vulnerable families and an additional $600,000 towards the Energy Assistance Program.
The Budget also allocates $29.7 million for Solar Victoria to install electric heat pumps and solar hot water systems in 27,000 homes, and a further $12 million to support discounts on ceiling insulation through the Victorian Energy Upgrades Program.
It also includes $13.2 million towards delivering the first 2GW of offshore wind capacity in the state, and a $2.3 million investment to develop the Industrial Renewable Gas Guarantee to secure gas supply into the future.
The 2025–26 Northern Territory Budget aims to deliver action, certainty and security for Territorians, allocating funding to the energy and water sectors.
The Northern Territory Government said it stands firmly behind its gas industry and the Beetaloo sub-basin, which it said will secure energy for the Northern Territory and the nation.
Key investments include $2 million to the Petroleum Operations Unit to streamline approvals and maintain high regulatory standards for the onshore gas industry, and $2 million per year (ongoing) for the Beetaloo Regional Monitoring Program to track and manage the environmental impacts of gas development.
The Northern Territory Government also committed $206 million in community service obligation (CSO) funding to Power and Water Corporation and electricity retailers to subsidise utility costs.
The Budget includes $25.1 million over four years for the Remote Community Water Security and Water Quality program, which aims to improve drinking water infrastructure in remote Aboriginal communities. It also delivers $11 million for works at Kulaluk town camp in Coconut Grove for a new underground stormwater drainage system and upgrades to the dual-lane access road, water, power and street lighting.
The Western Australian Government made critical infrastructure a key priority in its 2025–26 Budget, with major investments in renewable energy and water security.
Energy
The Budget includes a $584 million investment in Western Power’s Clean Energy Link – North and Regans Ford terminal to unlock wind generation north of Perth. A $25 million investment aims to secure the poles and wires required for the state’s energy transition, including $10 million for an advanced manufacturing facility in Forrestfield to supply thousands of kilometres of transmission lines.
The 2025–26 State Budget also includes $337 million for the WA Residential Battery Scheme and $30 million for the Collie Industrial Transition Fund.
It also pledges $50 million to support local battery manufacturing; $83 million to produce electric buses and ferries in the state; and $30 million for the Investment Attraction Fund to support critical minerals, hydrogen and carbon capture and storage projects.
The Budget includes several major investments in key water infrastructure, headlined by a $543 million commitment to increase the capacity of the Goldfields pipeline by 7.2GL a day.
The State Government is also investing $10.3 billion in a pipeline of infrastructure works over the next four years to support growth and combat regional water scarcity in regional Western Australia. This includes:
• $20.6 million for the Onslow Seawater Desalination Plant
• $4.5 million for environmental regulation and water licensing assessment and approvals for the Pilbara region
• $4.2 million to accelerate water planning in the Pilbara region
• $2.5 million towards planning for a new water source in Exmouth
• $5 million for the Kalgoorlie–Boulder Water Bank Project
• $8.5 million to protect and improve the water quality of the Peel-Harvey estuary through the continued implementation of the Bindjareb Djilba (Peel-Harvey Estuary) Protection Plan
Telecommunications
The Budget also includes a $2 million investment, funded by the Federal Government, to establish a Western Australian Telecommunications Resilience Pilot Program in the Wheatbelt and Western Goldfields.
Queensland
One of the key priorities for the 2025–26 Queensland Budget is building generational infrastructure, including in the energy and water sectors.
The Budget allocates an additional $1.4 billion to CopperString 2032.
It also provides $42.9 to million to progress renewable projects across central Queensland; $50 million to progress the Mount Rawdon Pumped Hydro project; and $378.9 million for utility-scale batteries at the Stanwell, Tarong and Swanbank Power Station sites.
The Budget also includes $479 million for CS Energy to develop the 400MW Brigalow Gas Peaker Project at Kogan Creek to expand firming capacity in the state.
The Electricity Maintenance Guarantee has been allocated $1.6 billion over the next five years to maintain state-owned power plants and deliver affordable, reliable and sustainable energy supply.
The Budget supports the development of an Energy Roadmap, which the Queensland Government said will lay out a credible plan for the state’s energy system to 2030, providing certainty for investors, communities and consumers.
Major funding has been allocated to vital water infrastructure, including $4.4 billion to deliver a new Paradise Dam wall to ensure safe and secure water supply.
The Budget also includes almost $38 million to progress the business case for the Water for Warrill project, build new weirs at Barlil and Cooranga in the North and South Burnett regions, and five new or upgraded weirs on the Thompson Rover near Longreach.
Almost $51 million has been allocated over two years to deliver a 15 per cent discount for eligible irrigators to help make essential water resources more affordable for Queensland’s primary producers.
More than $41 million will be invested over five years to deliver vital upgrades to critical water and sewerage infrastructure in remote First Nations communities across the Torres Strait.
In addition, more than $34 million has been reallocated from Closing the Gap Priorities fund to deliver water supply improvements and infrastructure upgrades Aurukun, Kowanyama and Woorabinda communities.
The 2025–26 ACT Budget aims to continue making climate-conscious choices more affordable and accessible to all Canberrans as it transitions to lower-emission energy solutions.
The ACT Government said the Budget will guide the territory’s path to achieving net-zero emissions by 2045, building on the momentum of securing 100 per cent renewable electricity in 2020.
This includes $21.8 million over four years for the electrification of public housing and almost $15 million over four years for the Energy Efficiency Improvement Scheme.
Other key electrification initiatives to receive funding in the Budget include the Home Energy Efficiency Program; the Sustainable Business Program; the First Nations Home Energy Support program; and the commencement of the Commercial Building Electrification pilot program.
Under the new Budget, the ACT Government is also permanently increasing the Electricity, Gas and Water Rebate to $800 to eligible recipients in 2025–26. U
Asset failure is not an option. So when it comes to sewer and stormwater maintenance, utilities need a crew and equipment they can rely on.
Modern sewer and drainage systems are challenging operational environments at the best of times, but with frequent floods, prolonged droughts and extreme storms, Australian asset owners have a lot to contend with.
Communities depend on utilities to keep these assets in good working order, and the team at DCS Manufacturing know just how important it is that they are working with the most effective maintenance equipment that can meet their specific needs.
With this in mind, the Predator 3000 water jetting solution was purposefully designed to become the system of choice for government authorities, civil contractors and asset managers across the country.
When it comes to advanced stormwater and sewer line maintenance, the Predator 3000 leads the charge as one of Australia’s most reliable and intelligent highvelocity water jetting systems. Proudly designed and manufactured in Victoria, this robust and versatile solution has been engineered specifically for Australian’s harsh conditions.
What sets the Predator 3000 apart is its seamless blend of power, safety, and cutting-edge technology.
Engineered for both urban and regional applications, the Predator 3000 is compact in design yet extremely capable. It features a high-performance water pump delivering 269L per minute at 155bar (2250psi), providing the velocity needed to tackle the toughest blockages with ease. Operators have the flexibility of manual or remote controls, improving accessibility and user safety in confined or hazardous locations.
At the core of the system lies INTEL-JET – DCS Manufacturing’s proprietary smart control module –featuring photographed step-by-step guides to support correct operation. This intelligent, self-regulating unit gives operators full command of the jetting process, automatically adjusting settings to optimise performance while minimising risk.
Whether deployed in routine drain clearing or complex maintenance environments, the Predator 3000 offers an exceptionally high level of precision and control.
The system is equipped with 3000L of water and a rearmounted hose reel offering 180-degree rotation and 183m of 1” Piranha hose as standard – with optional threequarter-inch hose available to suit various job profiles. A secondary reel provides up to 100m of half-inch hose, supporting works from cleaning pits, to delicate or confined cleaning tasks.
The unit is housed within a thoughtfully designed body that prioritises efficiency and operator wellbeing. A large canopy-style storage compartment includes a walk-up staircase for safe and easy access to equipment and tools, as well as customisation options for CCTV rooms and more. Everything is built with Australian standards and compliance regulations in mind, ensuring the system operates safely, reliably and legally across all jurisdictions.
Support doesn’t stop at delivery. DCS Manufacturing offers extensive after-sales service, including spare parts availability and technical support. The Predator 3000 is built on an ISUZU chassis, which means utilities have ongoing asset support and reliability within their fleet that is backed by national support centres. These vehicles are chosen for their dependability in challenging Australian conditions and are supported by widespread service networks.
As water infrastructure and asset maintenance become increasingly critical to urban planning and environmental protection, the Predator 3000 stands out as the timeless and future-ready solution. With its intelligent system management, rugged engineering, and commitment to operator safety, it is redefining what professionals expect from water jetting technology.
For councils, utilities and contractors seeking a smarter, safer and more powerful solution, the Predator 3000 is more than just a machine – it’s a long-term investment in operational excellence. U
Marking utility services electronically doesn’t just ensure you always know where your assets are located; it’s also the foundation of an accurate digital twin.
Professional locators do a fantastic job of accurately marking services using the standard AS5488 paint colours throughout a worksite. This helps clients and supervisors make safe decisions before excavation works start. But if works are delayed or weather conditions have caused the paint to fade or wash away then the risk of damage to vital assets increases.
Access Detection Director, Anthony Johnstone, said that by marking services electronically, locators can provide a safer environment for excavation works.
“This technology allows the user to take accurate RTK based GNSS points while using their Electro Magnetic Field (EMF) locator and Ground Penetrating Radar (GPR). Dedicated locators, mapping software and the GNSS/GPS have become more affordable and easier to use for operators to effectively use these technologies,” he said.
Mr Johnstone said a great example is the Rycom Pathfinder Pro+ Map, an EMF locator that has made mapping affordable for operators including professional locate companies, councils, and utilities operators.
“The Pathfinder allows several popular GPS/GNSS manufactures for instance the Trimble DA2 and the EMLID RX to mount there antenna seamlessly onto the locator,” he said.
“This is a much more cost-effective as it allows you to disconnect the antenna and use it with your GPR or on a survey pole.”
To streamline locator tracing and marking services, the TerraFlow Mobile Mapping program integrates with the Rycom Pathfinder.
“TerraFlow have modified their mapping software to comply with our own Australia AS5488 colour and quality level standards,” Mr Johnstone said.
“Once connected you can select the service you are tracing and log points along the locate site. Quality level classifications can be selected based on your connection and locate accuracy. Photos can also be taken at the beginning and throughout the locate further enhancing safety.
“Then, once your service has been logged you can then continue with other utility assets. When you have completed the locate you can sync this with your PC/MAC and send the location out using different file versions for common GIS systems like ESRI, QGIS and AutoCAD programs this can be used to build an accurate digital twin for future reference.”
Mr Johnstone said a great benefit with this setup is a site operator or supervisor can also use the TerraFlow mapping program to navigate to any point on the locate site by simply walking to a selected point on the map.
“This of course relies on the operator or supervisor having a good understanding of the use and shortcomings of using this technology – for example you cannot rely on this technology to be used in congested high building areas or tree canopies when you cannot get an RTK fix – but this is a great way of confirming where services are even if the paint has faded or become unrecognisable,” he said.
“It also improves safety on the worksite and in some cases can eliminate the need to re hire the locator to again locate the site.” U
Pipeline projects often mean navigating challenging conditions and tight deadlines, and it’s vital to strike a balance between efficiency and safety.
Australia is one of the widest and driest countries in the world, which makes access to a safe and reliable water supply a constant challenge, especially for remote areas.
Pipelines are the backbone of water security, and a reliable water network begins with the safe and streamlined construction of these assets.
Given the critical nature of these works, utilities need to be able to trust that their contractors can provide the right equipment for the job.
Pipeline projects present a range of safety hazards, as construction often takes place in harsh conditions, involving heavy machinery and pipeline pieces that can weigh upwards of 10t.
Pipeline Plant Hire (PPH), in partnership with Global Equipment Services (GES), designs and manufactures a range of vacuum pipe lifting equipment, which have been optimised to increase the productivity, efficiency and safety of pipeline projects.
VacLift works by using a vacuum to suck pipe lengths into the grasp of an attachment fitted with rubber seals called a ‘shoe’ that raises lengths of poly or steel pipe weighing up to 15t, without causing damage during the lifting process.
Mr Dridan said that this results in enormous time and cost savings for customers, as the VacLift cycle time is under 40 seconds per pipe length, whereas conventional methods take between five and ten minutes.
The VacLift system is available for customers to hire as a fully integrated, ready-to-use system consisting of an excavator, fitted with a VacLift unit and mounted on the counterweight of the machine – to provide maximum safe lift capacity.
“We’ve also developed a VacLift attachment that can be fitted to the customer’s own machine using auxiliary hydraulics to power and control operations,” Mr Dridan said.
“Since the equipment has been designed to only lift or release the pipe lengths in a grounded position, it’s almost impossible to drop the pipe, and also safeguards any personnel involved, and protects the lifting equipment.”
Traditional methods of pipe handling put workers at risk when attaching and detaching slings and hooks, but VacLift significantly reduces the dangers involved.
GES Director, Matt Dridan, said that he is frequently surprised to find that project developers are not aware of the benefits of vacuum lifters.
“I’ll see some people using ladders and climbing up on trucks and I think, ‘Oh my goodness, I know for a fact that will result in an injury’,” Mr Dridan said.
“Failings in productivity can be made up for down the track. A failing in safety cannot. A contractor can complete a project over-budget or over-time, but if you injured anyone, there’s no point applying for the next project.”
PPH delivers training support for the use of its VacLifts, which can be provided either on the work site or at its factory.
“At our factory, in a more controlled environment, operators can get a better look at the development of the equipment and get an understanding of the process.”
Mr Dridan said that PPH isn’t just a manufacturing company that decided to take on vacuum lifts.
“We came from the pipeline industry, and from that experience we developed vacuum lifts that fit the sector and meet its unique requirements.
“The people at Pipeline Plant Hire have more than three decades of experience in the industry, so we understand the process, we understand the ramifications of not getting it right, and we understand the overlap of various equipment and conditions.
“We also have the largest hire fleet in the country, and this, combined with our round-the-clock local support, delivers the right outcome for any project.” U
The PL1500 is a gamechanger for pipeline construction. The unique, quick-hitch, vacuum lifter attaches to your existing excavator, reducing your machine hire cost and getting things moving fast. Capable of safely lifting 15,000kg, the heavy-duty, self-contained unit can handle all types and lengths of pipe. It integrates seamlessly with the host excavator, using the main controls and hydraulics to operate the vacuum lifter. Plus, built-in smart tech ensures it’ll only pick up or put down a pipe on a solid surface. That’s safer than many other vacuum lifters on the market. To find out more, speak to the Pipeline Plant Hire team today.
Keeping utility networks running requires portable, precise tools that can perform under pressure. Image: littlewolf1989/stock.adobe.com
Choosing the right specialist maintenance and machining equipment is integral to the efficient operation of essential infrastructure.
Portable, precision-engineered equipment is essential to the ongoing maintenance of Australia’s most critical assets – and whether it’s for pipes, valves or pressure systems, utilities need tools that they can rely on in the field.
However, every sector, region and asset have their own nuances, and what works for one asset may not be the optimal solution for another – so utilities need to be able to compare different options and make an informed decision about their maintenance equipment.
As Australia’s largest stockist of specialist on-site machining and portable maintenance equipment, Field Machine Tools (FMT) understands how important it is to match the solution to the challenge, and not the other way round.
The company offers one of the most comprehensive ranges of specialised fabrication and portable maintenance equipment suitable for a large range of applications, material and specifications.
With conveniently located branches in Queensland, Victoria and Western Australia, FMT helps utilities to keep their plant, pipe and valve infrastructure operating reliably across the country.
FMT’s range of portable equipment is available for rent or purchase and includes equipment for machining applications such as tube end prep machines, portable milling machines, portable lathes, clamshell pipe lathes, flange facers (OD and ID mount), line boring machines, vessel grinding machines and pneumatic-based drills.
Removing equipment from the job site to a repair facility can delay project completion, which not only impacts the delivery of essential services, but it also increases costs. FMT’s on-site repair and maintenance machines minimise downtime and keep utilities’ equipment working as they deliver some of the nation’s most critical services.
When it comes to valves, FMT also provides valve test equipment, valve repair equipment and portable valve actuators.
For the manufacture, repair and maintenance of heat exchangers, condensers and boilers, the company’s
offering includes tube pulling systems, tube cleaning systems, heat exchanger tools, torque-controlled rolling motors and Australia’s largest range of tube expanders and consumables.
For welding applications, customers can choose from orbital welding, bore welding and cladding machines, as well as induction heat treatment equipment.
FMT is also the Australian agent for leading international brands, including:
SFE offers one of the world’s most comprehensive orbital welding, fabrication, precision-engineered applications and cutting solutions.
This includes CLIMAX portable machining and welding systems, TAG Pipe Equipment, AXXAIR orbital cutting, bevelling and welding, Mathey Dearman, Magnatech, B&B Pipe & Industrial Tools and Sumner material lifting and welding solutions.
Modec
Modec Air Motors is a global expert in designing, developing and manufacturing high-performance air motors and OEM replacements.
Modec offers a versatile range of portable valve actuators for preventative maintenance of valves, including the H2O kit designed for the water industry. The company has recently launched its Connect module for smart valve monitoring, allowing for real-time data collection.
Krais Tube & Pipe Tools
Krais Tube & Pipe Tools has been delivering top quality tube tools for more than four decades.
The company offers a comprehensive range of condenser tube expanders, boiler tube expanders, tube rolling motors, tube installation tools, tube cutting and removal tools, tube pulling equipment and accessories.
Goodway Technologies is a US-based manufacturer of specialised industrial maintenance products for HVAC, energy, manufacturing, good and beverage production markets.
Established in 1995, FMT is a privately owned Australian company with a comprehensive range of equipment for precision-engineered tube applications, pipe fabrication, in-situ maintenance and on-site machining along with boiler and heat exchanger manufacture and maintenance solutions.
With its comprehensive range of tools and support, FMT supports utilities to keep their infrastructure operating safely, reliably and efficiently. U
For utilities looking to connect, collaborate and stay ahead, Converge 2025 is the place to be.
Australia’s utility sector is set to take a bold step forward with the launch of Converge 2025, a new event designed to bring together the country’s municipal works, civil and commercial construction and utility industries.
The only Australian-owned major event showcasing the latest tools and technology in the municipal works, civil and commercial construction sectors, Converge will be held in Melbourne from 17–18 September. The event will highlight the equipment, services and solutions that are shaping the future of Australia’s critical infrastructure.
It will also be co-located with No-Dig Down Under, the southern hemisphere’s only large-scale conference and exhibition dedicated to trenchless technology. Attendees will be able to visit both events, exploring innovations across all sectors of infrastructure construction and management.
This variety is a major drawcard for Cape Dunstans, one of Australia’s leading utility infrastructure contractors and trenchless delivery specialists.
“We deliver end-to-end utility and infrastructure solutions, from feasibility through to reinstatement, across power, water, gas and communications,” Cape Dunstans CEO, Greg Hutchinson, said.
“Converge and No-Dig bring together our key stakeholders across utilities, local government, and infrastructure, making it a natural fit for us.”
The company is exhibiting at Converge and will showcase its capabilities in high-performance trenchless projects with control, innovation, and technical excellence. Mr Hutchinson said attendees can expect to meet the team behind the company’s horizontal directional drilling (HDD) fleet.
“We’ll be sharing project insights, showcasing our capabilities in HDD and demonstrating why our clients trust us to get it right,” he said.
Beyond the exhibition, Converge will also feature live demonstrations and a robust conference program, offering insights into digital transformation, major projects, zero-emissions technologies, sustainability
Converge is Australia’s only one-stop-shop for professionals in the municipal works, civil and commercial construction and utility sectors.
and the growing role of artificial intelligence (AI) and automation. These themes reflect some of the most pressing challenges facing the sector – and the opportunities to do things differently.
“The sector faces ongoing challenges around integration, project coordination, and access to skilled trenchless professionals,” Mr Hutchinson said. “There’s also growing demand for innovation in design, sustainability and delivery methods.
“These events help close the gap by promoting dialogue, showcasing new technologies, and encouraging partnerships that break down silos across the project lifecycle.”
With a stand strategically positioned in the middle of Converge and No-Dig Down Under, Cape Dunstans is looking forward to engaging with attendees from all corners of the infrastructure sector.
More than the opportunities to network, Cape Dunstans sees Converge as a forum for progress.
“These events are vital for advancing the industry,” Mr Hutchinson said. “They connect the people who design, fund, build, and maintain the backbone of our communities.
“By sharing knowledge and innovation, they elevate delivery standards and drive smarter, more sustainable solutions – something Cape Dunstans is proud to be part of.”
Attendees can expect to see live demonstrations, equipment showcases and dynamic presentations, offering insights and solutions that will support the design, delivery and maintenance of construction projects in all industries.
By fostering collaboration across these interconnected sectors, Converge is set to drive innovation, collaboration and progress across the infrastructure landscape, helping the industry’s leaders to solve the challenges of today and built the networks of tomorrow. U
Converge 2025 will be held from September 17–18 at the Melbourne Convention and Exhibition Centre.
For more information, visit convergeexpo.com.au/attendee-enquiries/
Converge Expo brings together industry leaders across the municipal, civil and commercial construction sectors who are change makers shaping Australia’s future infrastructure.
17–18 SEPTEMBER 2025 Melbourne Convention & Exhibition Centre Australia’s hub for civil, commercial, and municipal solutions
The upcoming No-Dig Down Under celebrates trenchless technology as a smarter and less disruptive way to renew the assets beneath people’s feet.
For utilities, particularly those providing water, sewerage, gas or telecommunications services, the value of trenchless methods is undeniable.
As cities become more densely populated and demand rises, trenchless techniques offer a method for utilities to maintain and upgrade underground assets with minimal surface disruption.
The combination of ageing assets and the need to upgrade them without disturbing nearby communities means technologies are more essential than ever – and the sector is coming together to explore what might be next.
No-Dig Down Under is set to return to the Melbourne Convention and Exhibition Centre from 17–18 September 2025, bringing together industry leaders from around the country and across the globe.
Organised by the Australasian Society for Trenchless Technology (ASTT), the event is the southern hemisphere’s only large-scale conference and exhibition dedicated to trenchless technology.
No-Dig Down Under combines an engaging conference program, specialist training sessions and an expansive exhibition hall with the latest tools and techniques from innovators across the industry. It’s the perfect opportunity to explore new technologies, stay ahead of industry trends, and connect with fellow trenchless professionals.
The interactive conference sessions will feature worldclass experts and innovators who will share insights into new and emerging technologies, case studies of successful projects and strategies to overcome common industry challenges. Another standout feature is No-Dig Down Under’s training courses and technical program, led by international industry experts and innovators. These sessions will offer practical, interactive insights into the latest trenchless installation and rehabilitation for
underground infrastructure, from horizontal directional drilling to pipe relining, microtunnelling and beyond.
From utility contractors to civil engineers, project managers or consultants, the sessions provide an excellent way to build technical expertise and gain actionable insights that can be applied in the field.
With the constant evolution of utility infrastructure and assets, the sector is well-versed in the importance of continuing professional development (CPD). With an educational conference program that provide hands-on training and live equipment demonstrations, No-Dig Down Under allows trenchless professionals to stay at the top of their game. Attendees can also claim CPD hours for attending the conference through Engineers Australia.
In addition to education, the event is a key platform for engagement, helping those in the sector build professional relationships and celebrate collective achievements.
A full program of social and networking functions also offers even more chances to connect with the industry’s brightest minds. From the Welcome Reception and Young People in Trenchless Networking Event to the Pipe Core UV Relining Breakfast and Vermeer Australia Networking Evening, there will be endless opportunities to network.
The event’s flagship celebration – the prestigious ASTT Awards Dinner – will shine a spotlight on industry excellence and innovation, honouring the trailblazers moving the sector forward in an evening of glamour, fine dining and recognition.
As trenchless innovation continues to shape the future of Australia’s essential services, No-Dig Down Under is the key event driving the sector’s success. U
No-Dig Down Under will be held from September 17–18 at the Melbourne Convention and Exhibition Centre.
Utility rounds up the key appointments, resignations and other staff changes within the sector.
After almost eight years in the position, Victorian Department of Energy, Environment and Climate Action (DEECA) Secretary, John Bradley, has resigned from the role.
When making the announcement, Victorian Minister for Energy and Resources, Climate Action and the State Electricity Commission, Lily D’Ambrosio, thanked Mr Bradley for his service.
“Mr Bradley has been integral to delivering significant policy outcomes for the Victorian Government, including overseeing the transition of Victoria’s energy sector and taking nation-leading climate action,” she said.
“His leadership has helped transform the state, from recycling to water management and supporting selfdetermination for First Peoples.”
Mr Bradley will remain in the role until the end of September and will work with the Secretary of Department of Premier and Cabinet to help ensure an effective transition.
Horizon Power appointed a new Acting Chief Executive Officer (CEO) following the announcement that Stephanie Unwin would leave the organisation to pursue a new position. Krystal Skinner has stepped into the role, bringing with her more than 17 years of experience in the energy sector.
Ms Skinner has been a key member of Horizon Power’s executive leadership team since early 2020, most recently as the Executive General Manager, Remote Communities. The utility said her strong understanding of regional energy needs and customer-led innovation means she is ideally placed to lead the business.
NBN Co welcomed a new Chief Financial Officer (CFO) following the announcement that Phillip Knox would depart the corporation after more than six years in the role.
Mr Knox said that the time is right to move into the next chapter of his career, pursuing opportunities in nonexecutive roles.
Simon Atkinson stepped in as NBN Co’s new CFO on 16 June, working closely with Mr Knox during a transition period leading up to the company’s annual results.
Melbourne-based Mr Atkinson brings with him more than 30 years of experience in finance, strategy and executive leadership across highly regulated industries, including mining, rail freight and chemicals.
Kurt Baker has officially been appointed CEO of Synergy following a successful period as Acting CEO.
Mr Baker brings more than three decades of experience in the energy sector and has led Synergy through a period of significant transformation and delivery. The utility said his appointment reflects the board’s confidence in his leadership and the strategic direction already in motion.
“I look forward to continuing our work to deliver reliable, accessible and sustainable energy for Western Australians,” Mr Baker said.
Transgrid will farewell one of the energy industry’s most experienced executives, with the utility’s Executive General Manager of Network, Marie Jordan, set to retire at the end of the year.
The utility said Ms Jordan has played a pivotal role in accelerating Australia’s renewable energy transition and the nation’s journey to net-zero, capping off an extraordinary international career at the forefront of electricity reliability and innovation over the last 40 years.
“We will miss Marie’s leadership and presence, which have really helped shape our approach to the transition,” Transgrid CEO, Brett Redman, said. “Marie will always be part of the Transgrid family and we wish her all the very best for a fulfilling and well-deserved retirement.”
Western Australian Energy and Decarbonisation Minister, Amber-Jade Sanderson, announced a key appointment to Western Power’s board.
Former Western Australian Under Treasurer and distinguished public servant, Michael Barnes, will step up as the utility’s Deputy Chair as the state powers toward a renewable future.
The Western Australian Government said that Mr Barnes’ 11 years of experience as the state’s Under Treasurer makes him uniquely suited to drive Western Power through this critical period in the state’s energy transition. U
Intelepower delivers integrated DC power systems for essential industries across Australia and New Zealand — from utility infrastructure to defence, transport and emergency services.
Our capabilities include :
Engineered solutions for harsh and high-risk environments
Fully certified to ISO9001, ISO45001 and ISO14001
Ongoing system support, monitoring + compliance reporting
Designed to meet AS3011, AS2676 and AS5139 standards
Installation and service coverage across AU + NZ
Backed by the strength of Century Yuasa
From switchboard to battery room, we’re with you every step — ensuring continuity, compliance and performance every time.
Intelepower. Trusted Power. Unmatched Reliability.