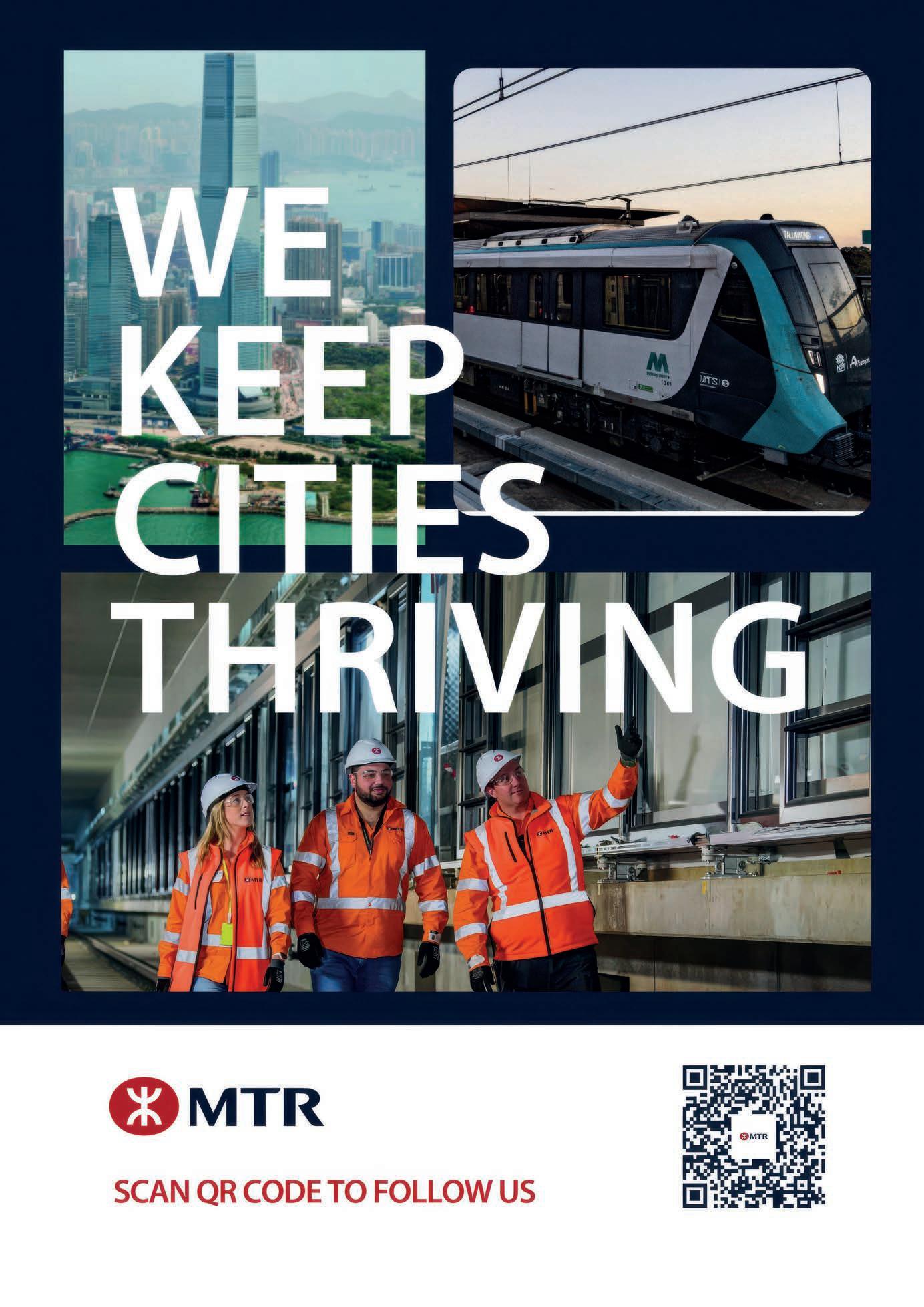
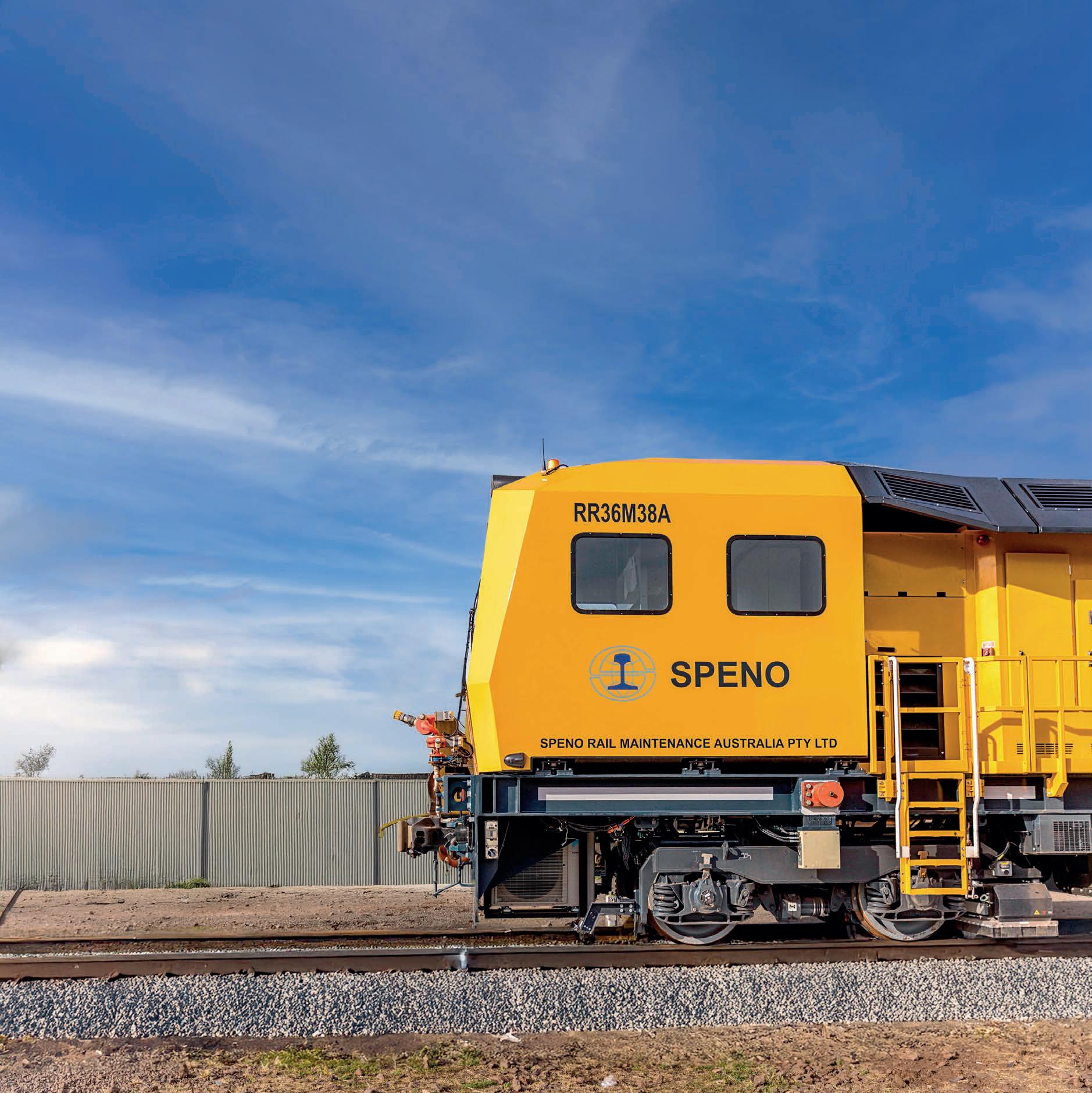
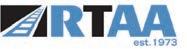

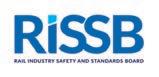

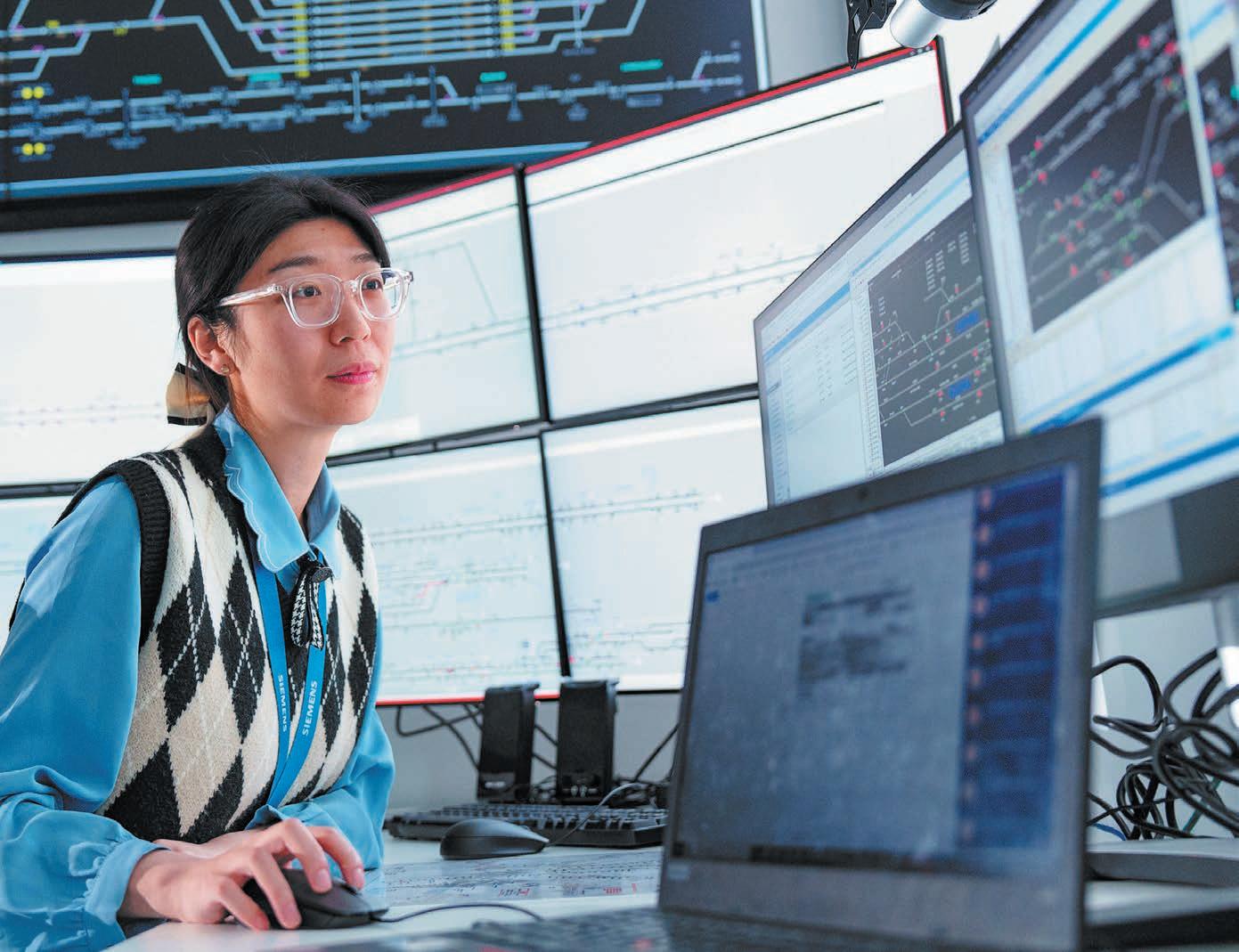
MAXIMISED NETWORK CAPACITY
MAXIMISED NETWORK CAPACITY
At Siemens Mobility, we are pursuing technologies and solutions for more sustainable, comfortable, and cost-effective rail transport to shape the future of mobility and #transformtheeveryday for a better tomorrow.
Published by:
379 Docklands Drive
Dockalnds, VIC 3008
T: 03 9690 8766
www.primecreativemedia.com.au
Publisher John Murphy
E: john.murphy@primecreative.com.au
Chief Operating Officer
Christine Clancy
E: christine.clancy@primecreative.com.au
Managing Editor Lisa Korycki
E: lisa.korycki@primecreative.com.au
Editor Kayla Walsh
E: kayla.walsh@primecreative.com.au
Business Development Manager
Arron Reed
M: 0466 923 194
E: arron.reed@primecreative.com.au
Client Success Manager
Karyssa Arendt
E: karyssa.arendt@primecreative.com.au
Head of Design
Blake Storey
E: blake.storey@primecreative.com.au
Designer Apostolos Topatsis
Subscriptions subscriptions@primecreative.com.au
www.RailExpress.com.au
The Publisher reserves the right to alter or omit any article or advertisement submitted and requires indemnity from the advertisers and contributors against damages or liabilities that may arise from material published.
© Copyright – No part of this publication may be reproduced, stored in a retrieval system or transmitted in any means electronic, mechanical, photocopying, recording or otherwise without the permission of the Publisher.
Kayla Walsh Editor - Rail Express
It’s hard to believe we’re halfway through the year already, and the world of rail has been as busy as ever!
I’m just back from a trip to Japan, where I witnessed the wonders of its train networks – from one of the busiest stations in the world to the remarkable Shinkansen bullet train that took me from Tokyo to Kyoto in just two hours and 15 minutes.
I share some of my experiences as a passenger and how Japan compares to Australia when it comes to public transport, while my colleague Chris Edwards chimes in with his own thoughts on the Chinese rail network.
Our cover stars, Speno Rail Maintenance Australia, are setting a new standard in rail grinding with an impressive machine that has just arrived in Sydney. We find out more from Managing Director Mark Green.
Also in this issue, Siemens Mobility takes a look at European Train Control Systems (ETCS) Level 2, while Salix explores how it delivers slab track solutions for rail and the integral part it has played in Auckland’s City Rail Link.
MGC Solutions looks back at the Victoria Park-Canning Level Crossing Removal Project and shares some of its innovative track monitoring systems.
Meanwhile PRM Engineering explains the advantages of its impressive Sentinel Height and Slew Limiting machines and Sigtech opens up about its extensive capabilities in ETCS.
After METRONET's Morley-Ellenbrook Line Project recently swept the boards at the Western Australian Architecture Awards, I got some insight into the inspiration for the design and how the team ensured sustainability and durability remained at the heart of it.
I also spoke to a passionate not-forprofit that is battling to restore services to a railway line in the Northern Rivers which has been without trains for over two decades.
In addition, this issue takes a look at the Endeavour Awards, which celebrate excellence in manufacturing. Nominations are open now!
Plus we have our regular columns from the Australasian Railway Association, the Rail Industry Safety and Standards Board, and the Permanent Way Institution.
Happy reading!
kayla.walsh@primecreative.com.au
Nearly half of New Zealand motorists do not always stop at level crossing Stop or Give Way signs, a new study has found.
KiwiRail has shared research in the hope that motorists will take the New Zealand Road Code more seriously.
The operator commissioned the research through engineering and personal services firm WSP, to monitor motorist behaviour at railway level crossings.
The study was aimed at identifying low-cost improvements that could be
made to signage at crossings with Stop or Give Way signs, particularly those where there was a short distance between the tracks and a state highway.
After observing more than 3600 drivers, the data showed 47 per cent failed to stop at crossings with Stop or Give Way signs.
Earlier research had found more than half of the deaths in serious level crossing collisions over a ten-year period occurred at crossings with Stop or Give Way signs.
Under current guidelines, not all level crossings need to have additional ‘Look for
Trains’ signs. However, the research found the percentage of motorists who stopped to be significantly higher (93.4 per cent) when they were in place.
Stopping compliance was almost twice as high for truck and trailer vehicles compared with cars.
The research also showed motorists were less likely to exhibit safe behaviours if there were only Give Way signs. It recommended Stop signs be used instead of Give Way signs to improve safe driving behaviour.
The New South Wales Government has launched industry engagement for the Future Fleet Program, which is seeking to revive domestic train manufacturing.
The government has committed to begin procuring replacement trains for the ageing Tangara fleet by early 2027.
Replacement of the suburban passenger trains will require about 450 new train carriages to be manufactured. The government has a 50 per cent local content target for designing, building and maintaining the new fleet.
Transport for NSW commenced a market
analysis and engagement campaign with manufacturers and suppliers to gather insights, identify key considerations, and help it shape the direction of further engagement for the Future Fleet Program.
The NSW Government will return to industry in August 2025 with suggestions on how it will implement the survey findings.
The replacement Tangara fleet will be the first in a long-term pipeline of locally built trains that extends out to the 2050s.
The Millenium and Oscar fleets will need replacing by the 2040s and the Waratahs in the 2050s.
The replacement fleet will be the first in a long-term pipeline of locally built trains that extends out
Hundreds of artefacts, some dating back to the early 19th century, have been uncovered during a recent dig at the future site of the Hunter Street metro station in Sydney.
Excavation has been ongoing at the site for the past 20 months, to create a giant cavern – measuring 180 metres long, 28 metres wide and 20 metres high – for the station.
Artefacts discovered by the crew included sandstock brick footings believed to be part of a property once owned by prominent Sydney merchant, Prosper de Mestre.
The footings, dating from the 1820s to 1840s, were found near the former De Mestre Place, a laneway off George Street, that is now part of the station’s footprint.
Archaeologists also unearthed a well, which is likely tied to De Mestre’s redevelopment of the site in the 1840s.
Descendants of the De Mestre family recently joined Sydney Metro and the site’s Excavation Director, Ronan McEleney, to view some of the artefacts recovered.
Relics of interest also included gun flint and bullet shells believed to be from George Street Barrack, Sydney’s first military barrack, that once stood opposite.
Among the smaller items discovered were glass beads, a coin dating back to circa 1834, slate pencils, glass bottles, bone and metal buttons.
While archaeological excavation at the site has concluded, work by heritage experts continues to preserve the heritage-listed Skinners Family Hotel, built in 1845, which will be incorporated into the future over station development.
When completed, Hunter Street Station will be the final stop on the 24-kilometre Sydney Metro West line that will double rail capacity between Greater Parramatta and the Sydney CBD.
Crews are making progress at Ferris Road in Melton, Victoria as part of the Level Crossing Removal Project.
The level crossing is being taken out and a new road bridge is being built over the rail line, which the Victorian Government said will “make journeys safer and provide more reliable travel times for the thousands of vehicles that travel through the crossing every day”.
Piling is now complete and 130,000 litres
of concrete have been poured to create the foundations of the new road bridge.
The road bridge embankments are also under construction, with 12,500 tonnes of earth moved so far.
Over the coming months, retaining walls will be built from reinforced soil, and more than 600 reinforced concrete panels will be installed to support the weight of the new bridge.
The Ferris Road level crossing will be
gone for good and the new bridge open to traffic in 2026.
The Government said this will ease the issue of motorists experiencing delays of up to 28 minutes each morning, when 16 trains travel through the crossing.
Another three “dangerous and congested” level crossings will be removed next year at Coburns and Exford roads in Melton, and at Hopkins Road in Truganina, and a new Melton Station will open in 2026.
With major works now completed on the Stockinbingal to Parkes section of Inland Rail and just a few weeks of minor works remaining at the time of going to print, the latest employment figures have shown how many people it takes to deliver one section of the 1600 kilometre rail project.
Figures show it took 596 people to complete major works on the section – the total number of people directly employed by contractor Martinus working in the rail corridor to deliver the project.
Some 55 of those people are First Nations, while 184 are local residents and 60 are women.
The figures also stated $12.2 million was spent with local businesses and $427,400 spent with First Nations businesses Australia-wide.
Major works at the Daroobalgie Loop, Lachlan River Bridge, Forbes Station and Wyndham Avenue have now been completed and the number of people needed on site has reduced, reflecting the progress made.
Construction will begin in the Albury to Illabo and Illabo to Stockinbingal sections of the Inland Rail project later this year.
Stephen Jones, Inland Rail Executive Director Program Health, Safety, Environment & Sustainability said: “We have been able to complete major works on the Stockinbingal
Inland Rail south of Parkes by 2027 so it is important to be able to finish major works on this section, and we can only be as successful as the teams on the ground putting in the hard yards.
“It is demanding work to upgrade rail infrastructure – it requires accuracy, safety and physical effort, often in testing conditions and sometimes while wearing hot and heavy protective equipment.”
Jones expressed his gratitude to the locals who have worked on the Stockinbingal to Parkes section, some of
their original glory.
The Sunbury Line Biosite Connectivity Project has been researching the best way to
and on time will also be of enormous benefit on other parts of Inland Rail when they go into the construction phase later this year.
“Inland Rail is not just about helping the Australian economy, it is also about delivering ongoing opportunities and benefits at a local level.”
Inland Rail is a freight rail backbone that will connect Melbourne and Brisbane via regional Victoria, New South Wales and Queensland.
It is intended to better link producers, manufacturers, and businesses to national and global markets.
restore native grasslands along rail lines.
It is re-using soil excavated from rail construction sites, and reintroducing plant species that existed there 40 years ago.
This work is being done as part of the Sunbury Line Upgrade Project, and aims to enhance and connect more than three hectares of land on the Sunbury Line.
Metro Trains Biodiversity Manager Ben Roberts said: “The Sunbury Line Biosite Connectivity Project adds tremendous value to Metro’s existing biodiversity program. It will enhance some of our most significant native grasslands and improve biodiversity connectivity.
“By working with the University of Melbourne on this project, we have been able to incorporate industry leading techniques to restore native grasslands and reintroduce both threatened and otherwise common species that have been lost from the rail corridor in recent history.”
Regional councils in New South Wales will share in $1.17 million in grants to improve safety at level crossings.
The funding, delivered through the Level Crossing Improvement Program – Regional Council Minor Works, will support 21 projects, benefiting 81 level crossings on council-managed local and regional roads.
This is a sub-program of the New South
Wales Government’s broader Level Crossing Improvement Program – a $7.3 million annual investment to upgrade public level crossings and increase awareness through safety education and enforcement campaigns.
Successful projects were determined through a merit-based application process which considered key safety data including the Australian Level Crossing Assessment
$1.17 million in grants will be shared amongst 21 level crossing removal projects in New South Wales.
Model (ALCAM) rating and New South Wales safety incident data.
As part of the package, Forbes Shire Council will receive $20,000 to fund critical minor engineering works and essential safety upgrades at seven level crossings.
Warrumbungle Shire Council and Central Darling Shire Council will collectively receive more than $200,000, while Armidale Regional Council and Uralla Shire Council will collectively receive more than $211,000.
Shellharbour City Council will receive $186,000 to fund critical minor engineering works and essential safety upgrades at level crossings, including road approaches at Creamery Road and Albion Park Rail.
Lockhart Shire Council will receive more than $52,000 for engineering works and essential safety upgrades at 16 level crossings, while Hilltops Council receives $60,000.
Another $196,000 will fund engineering and safety upgrades at three level crossings at Sandy Hollow across Muswellbrook Shire Council.
The freight sector will employ an additional 235,000 workers and add $131.5 billion to the New South Wales economy by 2061, according to a new report.
The report, Delivering Freight Policy Reform in NSW, led by Dr Kerry Schott and a three-member panel, was requested by the state government in January 2024.
It sets out a clear roadmap of short, medium and long-term actions to ready the state to better integrate freight into transport networks into the future.
The New South Wales Government has accepted the report’s recommendations and requested that Schott carry out further work investigating the barriers and opportunities for moving more freight at night to take advantage of off-peak capacity in the transport system.
This would include roads, motorways, rail network, terminals and distribution facilities.
The value of freight to the New South
Wales economy is now $74 billion, and the sector employs 330,000 people, according to Transport for NSW data.
The sector’s Gross Value Add (GVA) is expected to grow by an average of $1.6 billion a year to 2061, by which it will provide 565,000 jobs.
The roadmap provides short-to-long-term actions to boost productivity, including developing a freight master plan to ensure an integrated and long-term approach through enhanced strategic planning for freight, as well as a package of initiatives to increase rail modal shift by improving the competitiveness and efficiency of rail freight.
It also recommends adopting a new port policy regarding container terminals, in which the government should not determine the timing or location of any future container terminals but recognise that Port Botany remains the key container port for the state.
The report also recommends delivering
the Industrial Lands Action Plan, in partnership with Department of Planning, Housing and Infrastructure, focused on strategic land planning for freight purposes and addressing the shortage of industrial land availability.
It recommends that the government support a program, in partnership with industry, to promote recruitment to address skills and workforce shortages which are consistently identified as a major risk facing the sector.
The report acknowledges the New South Wales Government’s current review into the future use of the Glebe Island Port and the entire Bays precinct ahead of the metro station linking the area to Parramatta, the CBD and the inner west.
It also notes the role of Glebe Island and freight more generally but highlights that the co-location of homes and freight activity is typically not sustainable.
Any impacts on freight are being closely considered as part of that review.
Arc Infrastructure has executed an agreement with the Western Australian Government to deliver upgrades to the Midland Railway (MR) track between Mingenew and Carnamah.
The agreement is part of the State Government’s Agricultural Supply Chain Improvements program, which aids in upgrading various rail networks across the state.
It finalises a $45 million commitment by the state and federal governments, alongside a $22 million contribution from Arc Infrastructure.
The agreement enables the upgrade of the MR track to move forward to the delivery phase and has allowed order placements for long lead materials.
Arc Infrastructure manages and operates 5500 kilometres of rail freight network in Western Australia, including the Midland Railway track.
the replacement of 96 kilometres of rail. Upgrades will increase the line from 16
Tonne Axle Load (TAL) to 19 TAL and deliver a more productive and resilient freight rail
KiwiRail and Matamata-Piako District Council are removing some trees and trimming the remaining ones along the rail line adjacent to SH27 in Matamata
who was struck by a train outside her school in March.
There are more than 70 trees in the area which currently obstruct visibility for train
line, which is used throughout the year to transport grain to Geraldton Port.
Construction is expected to commence in mid-2026.
along the embankment next to Swap Park will also be removed.
After Morton’s death, there had been calls for KiwiRail to slow down trains or not
Speno is taking rail grinding to new heights with a groundbreaking new machine.
In the heart of Australia's railway industry, stretching along the backbone of the nation’s economy, a technological revolution is transforming how networks are maintained.
One of the companies spearheading this exciting rail grinding innovation is Speno Rail Maintenance Australia (SRMA).
In recent years, SRMA has been developing a new rail grinding machine that redefines precision and productivity – and now, it’s ready to lead the way – in real time!
“This machine is an absolute game changer for the rail industry,” said Mark Green, the company’s Managing Director.
“In terms of rail grinding precision, Speno is very proud of what this machine can achieve."
THE MACHINE
In the rail industry, time is always of the essence. SRMA’s next-generation machine aims to ensure a minute, or even a second, is never wasted.
“Any network delays obviously have a snowball effect for our clients, whether that be on passenger, freight or heavy haul networks,” Green said.
“Every minute you’re on the track, you must be productively grinding. This machine is designed around
creating the most accurate and most efficient grind within the track maintenance window.
“The machine comes with multiple levels of redundancy, including gensets [a combination of an engine and electrical generator] to ensure power supply and motive traction, as well as multiple lines of redundancy throughout the machine, to optimise uptime.”
Green said what makes this machine revolutionary is its ability to measure and manage rail conditions in real time.
Unlike traditional approaches, the machine processes rail data instantly, allowing highly skilled operators to make immediate, precise, and accurate adjustments.
“We manage the rail grinding profile live,” said Green. “The system measures the rail's
condition as it enters the machine, and our expert operators manage the grind onboard the machine, so that the rail emerges fully compliant with our client’s specifications.
“We have measuring systems on the front and rear of the machine that measure the rail in real time, so there are no delays between measuring and grinding, and data is constantly being fed to the operator to allow them to make appropriate decisions.
“We’ve always ground rail this way, treating the rail grind live, but the latest technology we have on the new machine is absolutely going to change the game in terms of productivity and efficiency.”
Green said that measuring the grind in real time ensures accurate grinding data, thus grinding the rail efficiently, and effecitvely extending the life of the rail.
“If you’re applying a level of grind that isn’t appropriate, then you’re likely to be doing more harm than good,” he explained.
“As an example, if you remove too much, or not enough, metal relative to the cycle compliance, then you're likely to be exposing defects, rather than treating them.That is going to create a more significant level of defect across the network over time.
“By managing the grind live, we can ensure that we have the appropriate speed, load control, and motor angle, so we’re not removing too much or too little metal from the head of the rail.”
SRMA has been operating the first generation of this style of grinding machine in the Pilbara for the past five years, with great success.
“We’ve been using the learnings from this machine, and from the significant investment in our research and development, to continually enhance the features of the machine, to create this next generation,” said Green.
“Because we own and operate the machine, and we have our engineering team here in Perth, we’re only an arm’s length away from each of our operations and our partners.
“Any opportunity for improvement in the machine is identified, understood, recorded and diagnosed, and that learning is reflected either in the maintenance or the future design of the machine.”
SRMA incorporates multiple levels of expertise within the business, even having a highly valued and industry respected PhDlevel expert in the wheel/rail interface in the Australian business.
“We invest heavily in understanding how the rail responds to the wheel/rail interface. By understanding that completely, you can provide a unique strategy appropriate for each network, as every network within Australia is uniquely different in operation and maintenance," Green said.
“Each typical rail defect has its own version of a signature, and it’s highly dependent on the environment in which it is operating – whether it be tonnage-based, on a curve, on a grade, on a driver changeout station, whatever it may be.
the network.”
Green said that if these factors aren't understood the results can be catastrophic to the rail condition, including increased formation of rail surface defects, and subsequently sub-surface defects.
“The knock-on effects can be huge,” he said. “If you’re not managing the grind appropriately and thinking about the flowon effect to rail maintenance, you’re actually creating more maintenance on your network – increased surface deterioration and potential rail breaks.
“That is going to create a phenomenal amount of extra costs and wasted track maintenance time for your business.”
Green describes SRMA’s new machine as an “ecosystem”, with SRMA putting vast amounts of thought and local expertise into every single component.
“SRMA has the stones supplied through ASI,” he said. “Having direct input into the manufacturing of the stones ensures that we can design and manufacture a stone that gets the appropriate surface condition, life extension of the stone and metal removal on that network.
“And it doesn’t stop there. We design the trolleys, the dust extraction, how to manage the heat within the trolley, and the appropriate loads on the trolley and on
works in harmony to get the best result.”
Other aspects of the machine that SRMA has improved include the ergonomics: several years ago, the company worked with researchers at a leading university in Perth to develop the most comfortable solution for operators.
“We looked at human factors like the placement of the operator and the control panel,” Green said.
“Now, whether you are a left-handed operator or a right-handed operator, you can use the machine in absolute comfort.
“It’s just a small ergonomic change, but it has a massive impact for the operator, which has an equally impressive impact on the rail grind quality.”
Green said that the teams that manufacture SRMA’s machines are often operators as well, so they know how each machine works and the best way to assemble, operate and maintain them.
“Feedback on the new machine’s design has come from the ground up as well as the top down,” he said.
“You’ve got the world’s leading technology, and our industry-leading operational skills combining perfectly in this game-changing machine.”
The first machine in the two-machine consist is already in Sydney and will soon be
put to work in Australia’s largest city, set to deliver massive grinding productivity gains for the network.
“Sydney has got such tight timetabling between trains, so we’ve worked intensively to provide a solution which gets the best efficiency in the maintenance window,” said Green. “That comes down to a balance between productivity, cost and service provision.”
The new machine is precisely sized and configured to meet the requirements of the customer’s network – a level of customisation that Green said sets SRMA apart.
“This isn’t a situation where the biggest machine is going to solve the problem,” he said. “As an example, if you put a machine that’s too long into the Sydney network, you won’t have long enough sidings to park it in. Due to the modular design, we can size our machines appropriately for each customer’s network.
“It’s a really simple example of how being locally based and understanding your client and the network means that we can provide the optimum solution.”
For more than five decades, SRMA has been at the forefront of ensuring rail networks remain safe, efficient and reliable.
SRMA kicked off with the first “grinding train” commencing operation in the Pilbara in 1969.
Since then, SRMA has established itself as one of the country’s leading providers of rail maintenance, technology, diagnostics and rectification. It has successfully
delivered projects for major mining, resource and rail infrastructure companies, with long-standing partnerships that reflect how it delivers on its promises.
With the SRMA head office in Perth and about 240 employees spread across Australia and New Zealand, SRMA’s new machines are Australian designed and Australian made, specifically for Australian conditions.
“We design, manufacture and operate our new machines completely out of Australia,” Green said. “Our machines are purposebuilt to withstand all types of Australian conditions, including environments ranging from incredibly high temperatures and harsh conditions in the Pilbara, through to high suburban traffic and tight timetabling such as Sydney.
“We are also very efficient at managing and environmentally treating dust. We run our own dust extraction system on each grinding wagon which shifts a significant volume of air per hour from each grinding trolley.
Green is perhaps most proud of the fact that the company supports Australian jobs, not only directly through employment but through purchasing locally sourced components for its machines.
“When you both manufacture and source parts locally, the positive benefits stretch a lot further than just your own employees – you’re supporting many other local businesses and growing the wider industry,” he said.
Upskilling and training its staff is a major priority for SMRA, and this also flows onto its local service providers that can also continue to upskill and build their own local business.
“We employ highly skilled people as a starting point, and we build up their rail grinding operational skills from there,” Green continued.
“You can’t just employ an operator off the street, it takes about 12 to 18 months to train them – from how to professionally and appropriately grind rail, how to operate and maintain our unique machines, to how to work to specific client requirements.
“We have great staff retention and several multi-generational families in the business.”
Being Australia-based has other advantages too, with limited wait times for imported manufactured parts.
“All of our spare parts are either stored in Perth or on the appropriate sites for our client partners. Having locally sourced manufactured componentry limits the wait times for international delivery times or border control,” Green said.
“We are happy to be able to provide a much faster response time and superior service to our clients.”
If a customer ever needs support, SRMA’s team is always ready to help.
“All of our management and operational team are based in Australia and New Zealand – we understand the local culture and our clients’ needs in terms of service delivery,” Green said.
“Our solutions are always expertly tailored to the client.”
Although SRMA is proud of its deep Australian roots, the company also has the advantage of drawing on its vast international expertise and resources.
Green said Speno International operates around the world and is delivering significant volumes of rail grinding for
high-speed and high quality networks in Europe and Japan.
“We’re a local company with local knowledge, backed by significant international experience. We’ve got this nice blend of modern technology and local practices,” he said.
As Australia's rail infrastructure continues to evolve, SRMA stands ready to meet the challenge.
Its commitment to local design and manufacturing and its unrivalled expertise positions it uniquely in a competitive market.
“We are about integrity and delivering on our promise,” Green said.
"We're thriving in the current environment, expanding sustainably, delivering multiple machines to Australia and New Zealand in 2025, and we’re excited for the future.”
For SRMA, rail maintenance isn't just a job – it's a calling.
Its new machine is more than a piece of equipment. It's a symbol of Australian innovation, precision engineering, and a deep commitment to keeping the nation's rail networks moving safely and efficiently.
In the world of rail maintenance, Speno isn't just keeping pace – it’s setting the standard.
Australia and New Zealand’s rail networks are on the brink of a major step change. Rail Express discovers why ETCS technology is the key to efficiency now and for years to come.
European Train Control System (ETCS) technology, which has already proven itself across Europe as well as in Australia, is steadily transforming local signalling standards. The implementation of ETCS Level 1 in New Zealand has improved safety and the drivers’ experiences, but should New Zealand prepare to evolve from ETCS Level 1 to Level 2 and move to a solution with increased frequency, flexibility and long-term digital readiness?
After rolling out ETCS Level 1 across the entire Auckland metropolitan network, New Zealand is exploring how both Auckland and Wellington’s metropolitan rail infrastructure can progress to the next stage and transition to ETCS Level 2. The aim is to enable higher-capacity train movements on a growing passenger network without the need for expensive new track.
Rail Express spoke with Siemens Mobility New Zealand Sales and Branch Manager Fred Grace and Head of Systems, Projects and Specialty Engineering Mark Kilby, as well as KiwiRail Engineering Design Signals Lead, Leroy Koen and Senior Signals Engineer, Martin Tompkins, about the impacts and benefits of ETCS technology in New Zealand, and what the future could look like with a transition to ETCS Level 2.
ETCS technology was originally developed to harmonise train signalling across Europe’s borders, but its impact is increasingly global.
Kilby explained that ETCS was developed “to move trains safely from A to B” by standardising multiple and often incompatible systems to enable rail travel across countries, allowing greater control and a vast improvement in safety compared to traditional signalling systems.
The technology delivers automated train protection by continuously monitoring a train’s position, speed and movement authority. This allows operators to maintain shorter, safer headways between services. ETCS exists in several levels, each delivering increased functionality.
ETCS Level 1, now standard in Auckland, overlays digital control on top of existing signals using eurobalises – track-mounted devices that transmit information to trains. Level 2 goes further, removing the reliance on trackside signals and replacing them with continuous data communication via GSM-R or other radio systems.
Auckland’s adoption of ETCS Level 1 marked a national first and, according to
Grace, may have been the first full Level 1 deployment in a metropolitan city in the southern hemisphere.
“It really was a step change in safety,” Grace said. "New Zealand had a significant number of SPADs (signals passed at danger). If the country wanted to modernise the railway and bring in rolling stock, it was clear that the signalling system was just not acceptable."
The decision to adopt ETCS was made during a broader modernisation of Auckland’s metropolitan network. The project, Grace noted, delivered measurable improvements in operational safety, with a dramatic drop in safety risk metrics following rollout.
Koen agreed: “The initial benefit of the ETCS Level 1 was its ATP (automatic train protection) safety benefit.”
However, implementation wasn’t without challenges. Introducing cutting-edge signalling to a legacy rail network required an entirely new knowledge base.
As Kilby put it: “You’re building a virtual map where data is very calculated and carefully designed.”
“The system expects to see precise inputs – balises, points, track geometry – exactly as designed. If a renewal team shifts something like a set of points greater
than one metre, and the change isn’t communicated, that can affect the data.”
This highlighted the need for closer coordination for KiwiRail and its suppliers, as well as a mindset shift in how rail data and infrastructure are managed.
But the ETCS Level 1 journey isn’t over just yet. Koen shared that KiwiRail is currently working on fitting the DL class Freight locomotives with ETCS Level 1 to improve the safety of the Auckland Metro area, which would involve upgrading the trackside ETCS infrastructure.
“The trackside ETCS infrastructure is currently optimised for the passenger EMUs, which means we need to take into consideration the different requirements of heavy freight trains. The addition of ETCS Level 1 to the freight locomotives will enhance operations of both the freight and passenger operations.”
Upon reflection of KiwiRail’s experience with the ETCS 1 implementation, Tompkins said: “The key lesson learned has been that ETCS Level 1 can’t just be a signal engineering solution imposed on the railway. It needs all the stakeholders in both the safety and operational efficiency of the railway onboard and involved from the beginning so that the maximum benefits of the system can be realised.”
WHY MAKE THE MOVE TO ETCS LEVEL 2?
ETCS Level 2 removes fixed signals and operates using ‘virtual blocks’ – dynamic
zones calculated in real-time based on braking distance and train speed. This enables trains to operate closer together, boosting frequency and throughput, especially in bottlenecked hubs such as Wellington and Auckland.
“It’s a big step forward,” said Kilby. “You move away from line-side signalling; everything is now very much within the data. You don’t have all that cost of the installation, the maintenance and the power.”
While Auckland has had its Level 1 system in place for nearly a decade, Wellington is now exploring what is needed for a Level 2 upgrade.
Grace noted that although no major funding has been allocated specifically for new signalling projects in New Zealand’s latest rail budget, conversations about Level 2 and detailed business cases are already underway.
“Wellington needs a solution like ETCS L2 to bring about a step change in improved driver and passenger safety, increase the capacity and frequency of passenger EMU services and greatly improve the operational reliability.”
The introduction of new, innovative technology brings with it the ability to support the creation of stronger connections for the rail network, which aligns with KiwiRail’s vision for a more networked and digital railway environment, Koen explained.
“The introduction of ETCS Level 2 will provide much more real time information
on the state of the railway and its assets. This will benefit both KiwiRail and its customers in terms of improved reliability, rapid information sharing and a more predictable service.”
As the New Zealand rail network continues to grow and passenger demands increase, Koen said the number of trains in metro areas will need to increase.
“The number of trains also increases the ETCS train protection that we will need to migrate from the current Level 1 system in the Auckland Metro to a Level 2 system on both the Auckland and Wellington Metro networks to maximise the network capacity.”
For passengers, Level 2 offers the potential for more frequent trains, better reliability, and timetable-free travel, which is promising news.
“Turn up and Go is a concept where you won't actually have to look at the timetable, because you know there's going to be a train coming soon,” Grace said.
“That would be a transformative change from a psychological perspective – a big step up, which this enables.”
Removing visual signalling reduces breakdown risks, meaning fewer delays due to failed signal aspects.
The radio-based data exchange provides drivers with real-time authority via an incab interface, giving them a clearer picture
Kilby added: “When we upgrade our systems, we get some great benefits. The new technology means we need fewer trackside components to maintain, which makes everything safer and more efficient. It's really a win-win – we're making operations smoother while saving money in several different ways.”
Upgrading to Level 2 requires more than new software. Rail operators need to prepare their fleets, infrastructure and teams.
“You can't just suddenly turn off the signals on one day and hope that you're in Level 2,” Kilby said.
“Every train has to be fitted. Anything that rides on the railway has to be prepared for that jump forward.”
Operationally, it’s a significant change. Drivers used to waiting for red and green aspects must instead rely on digital instructions displayed in-cab. Kilby pointed out that this shift requires psychological adaptation as much as technical training.
“There’s going to be a big psychology change,” he said.
“Previously, you would have gone past a green signal; here, you don’t have that visual. You’re putting your faith in the technology.”
Initially, Koen said that the ETCS Level 1 implementation meant that drivers had to adapt.
“As time has gone on the drivers have learned to use all the additional information that the DMI display gives them allowing then to drive more confidently”.
upskill the drivers, engineers, and operators.
“I think it moves them into more high skill level jobs – skilled up to look at the digital aspects of the railway.”
BRINGING SIEMENS MOBILITY’S GLOBAL EXPERTISE TO NEW ZEALAND
Grace highlights that Siemens Mobility’s global experience and ongoing product development makes it a future-proof choice for customers looking to upgrade their signalling systems to improve safety, productivity, and passenger experience.
"You are investing in a product that has a future road map and will be future proofed going forward."
Kilby added: “You're part of this international data standard. You're not getting left behind.
“Customers can follow upgrades like Baseline 3 and remain aligned with international best practice.”
implementations including the United Kingdom’s East Coast Main Line, Norway, and the Sydney Digital Systems Program.
Kilby said these projects set a strong precedent for how to work internationally.
“It’s proven that it can be done – and done well – even across different hemispheres.”
In New Zealand, Siemens already holds a strong position with more than 100 commissionings in the past six years.
“Our capability speaks for itself – and the trust we’ve built with the customer does too.”
Looking ahead, both Grace and Kilby see ETCS Level 2 as an enabler, not just for more trains, but for a smarter, greener rail system.
“It sets you up in the world of digitalisation and virtualisation,” Grace said.
“You’ve got safety, new jobs, a greener environment, less congestion on the road; it’s an enabler for all of these things to happen.”
For local railways, the real signal change is just beginning.
Salix is an integral part of major rail infrastructure projects across Australia, New Zealand and further afield.
Salix is known for delivering comprehensive rail product solutions, having supported major tunnel projects on networks across Australia and internationally. Notable projects include METRONET in Perth, Cross River Rail in Brisbane, and the City Rail Link in New Zealand.
Salix’s evolution has been defined not just by the quality of its products, but by its role as an engineering partner capable of guiding complex solutions from design through to delivery.
Widely regarded as New Zealand's most technically demanding underground rail build, the 3.45-kilometre twin-tunnel City Rail Link (CRL) project runs beneath central Auckland, reaching depths of up to 42 metres.
As the exclusive partner of Sonneville for Australia and New Zealand, Salix manufactured the Low Vibration Track (LVT) systems in Australia which were used throughout the CRL, including approximately 65,000 LVT mainline block system across Mt Eden, Newmarket
and Britomart stations. At Britomart station alone, 10,280 LVT blocks were used to ensure a smooth ride for future passengers.
Known as one of the first slab track systems in the world, the LVT system consists of a concrete block, a resilient pad and a rubber boot, all encased in surrounding concrete.
“We were looking for globally proven products, and the versatility of the Sonneville LVT system aligned with our quality standards," said Engineering Manager Dinesh Nagarajan.
The partnership between Salix and Sonneville has grown into a deeply collaborative arrangement. Salix’s relationship with Sonneville started during Brisbane’s Cross River Rail project, where the LVT system was used on 5.9 kilometres of twin tunnels under the Brisbane River and Brisbane CBD.
This marked the first time the LVT technology was used in Australia. The blocks play a crucial role in mitigating noise and vibration – particularly in urban environments, near hospitals or heritage structures, or wherever community impact
is a concern – helping to protect structural integrity while supporting a quieter, more liveable environment.
In tunnels, the LVT blocks act as part of a mass-spring system that absorbs and disperses train-generated vibration, reducing impacts on nearby buildings and improving ride comfort.
“Because the rubber boots dampen vibration and the resilient pads distribute loads evenly, the system reduces structural stress and noise,” Nagarajan explained. “It’s durable and long-lasting.”
Sales Manager Silvana Kinninmont added: “Our team understands the types of complex approvals required, and all the procurement hurdles our clients face. We combine our local engineering and manufacturing with Sonneville’s worldwide expertise.”
Apart from the reduction in structureborne noise and vibration, the advantage of the system is the versatility of the fastening process.
“As long as a rail pad is incorporated, any fastening combination can be used, depending on the project or client preference," Kinninmont continued. “This is where our clients can really save money
and factor in future maintenance costs for their projects.”
For turnout applications, the LVT system uses elastically-mounted blocks designed for flexibility and adaptability.
various turnout and crossing geometries using a modular combination of five standard block types. It can also be customised with longer or Monoblock units, especially for areas requiring lateral axis
block length. The LVT system is suitable for bridges and viaducts, heavy haul, metro and high speed lines. Thanks to its versatile design, the system is an ideal solution for mainline operations as well as special trackwork.
Manufacturing the blocks in Australia means more cost savings for clients, certainty in delivery and surety of quality versus alternative imported systems.
Salix has flexibility in manufacturing location, which allows it to set up facilities near project sites.
This means cost savings in transport which can be passed on to the client.
“Manufacturing and assembling the blocks locally makes sense economically and environmentally," said Kinninmont.
“Practically, it shortens reaction times and contributes to hassle-free project logistics.”
The rail industry faces growing pressures when it comes to cost, speed and quality.
“You need to be competitive without compromising quality. That’s why our partnerships and collaborations matter. They let us do things faster without cutting corners.”
Sonneville’s LVT system has a solid track record across metro, freight, light rail and high-speed projects around the world.
LVT Rail Support systems are proven to be maintenance-free, providing excellent life cycle cost benefits.
“When you factor in the overall costs (i.e. cost per track kilometre, the high industrial prefabrication of the LVT Rail Support, the fact that the system comes ready for use), it is the perfect choice,” said Kinninmont.
According to Sonneville, another benefit is that the preferred 'top-down’ installation method allows for a consistently high quality of manufacturing of the system, as well as fast installation rates (approximately 200 metres of track per 10 hour shifts) resulting in precise track geometry. The track geometry is paramount and guarantees maintenance-free operation for decades.
With a growing project portfolio, exclusive access to proven global technology, and a locally-embedded, highly collaborative delivery model, Salix is setting a new standard for track infrastructure supply in Australia and New Zealand.
While the CRL and Cross River Rail projects were a major milestone, for Salix, they were just one step in a broader journey – track by track, tunnel by tunnel.
MGC Solutions is a dab hand at delivering complex projects on time and under budget –and it’s got some more tricks up its sleeve too.
MGC Solutions is a company without an ego. Run by two business partners who prefer to stay out of the limelight, the quiet achiever has successfully delivered a wide range of high-profile projects – from power upgrades to ARC Infrastructure’s signalling network in the Avon Valley, to critical works as part of the Bayswater Turnback Project.
More recently, the company played an integral role in the bid, planning and delivery of Metronet’s Perth Level Crossing Removal Project.
The project involved removing six level crossings along the Armadale Line by raising the rail over the road at Mint/Archer Street, Oats Street, Welshpool Road, Hamilton Street, Wharf Street and William Street.
Modern elevated stations have been built at Carlisle, Oats Street, Queens Park, Cannington and Beckenham stations, with Welshpool Station closed permanently.
“The level crossings had to be removed because of massive congestion and traffic safety issues,” said Mark Byrne, General Manager of Operations at MGC Solutions.
“The project has also improved the station precincts, and freed up six hectares of public space to introduce parks and landscaping.”
MGC Solutions carried out all of the signalling and fibre works for the project, installing overhead line equipment, wayside signalling and more.
“It was a very interesting project that used all the internal skill sets of the business, from prewire of all of the signalling equipment rooms and location cases to building the major cable route,” said Byrne.
“We hauled over 40 kilometres of signalling and fibre cables, installed all the wayside signalling equipment like breakback signals and axle counters, and put in the automatic train projection systems, from the civil installation of foundations to the termination and testing of the equipment.
“This was all done on time and under budget, and we got great feedback from the client.”
With the largest full-time signalling workforce in Western Australia, Byrne said
MGC Solutions is the right choice for largescale projects like this.
“We have 140 staff that are fully trained and experienced in signalling,” he added.
“We were also heavily involved in the project management side – one of the client project managers was a young lady called Julie Labeyrie, who was seconded to the client.
“She did a fantastic job. We’re proud of all the women who are part of our business.”
With numerous subsidiaries involved and station building going on at the same time as the level crossing removal, Byrne noted that integration was probably the biggest challenge MGC Solutions faced while undertaking the project.
“Communication and organisation were key,” he said. “Thankfully we’re used to working to a strict schedule.
“It also helped that we are locally-based and accustomed to working with Metronet, so we understand their networks and their needs. We’re currently working with them on the new Midland Station project and the Bayswater Turnback project, continuing our successful partnership.”
Its engineering teams have created two innovative track monitoring systems that boost productivity, minimise train delays and ensure the integrity of infrastructure.
“Our track monitoring systems enable fast response from both train controllers and maintenance staff, reducing the risk of derailments,” explained Byrne.
“This avoids reactive maintenance that puts employees at risk by requiring them to work in live rail environments.”
MGC Solutions’ rail Embedded Longitudinal Stress Management System (eLMS) stands out from other stress monitoring systems as it looks at ambient temperature while tracking the actual stress caused by the temperature and the effect that a moving train has when passing over the area, all in real time.
It uses strain gauges that are physically attached via a pole mount or a signalling or communications cabinet next to the track.
“It is a great tool for de-stressing the rail, as you can monitor the growth of tension in the track due to the history built up by the system,” said Byrne.
“When you are approaching an unsafe threshold, alerts will be sent to your team. There may be a kickout or break in the rail expected in the area due to the stress measured at the time. This system is a great move away from general Rail
Ambient Temperature Systems (RATS) as it is designed to monitor high impact areas in networks.
“The system was initially designed for freight networks with heavy axle loads, but has proven to provide invaluable knowledge of infrastructure more widely, with accumulated data for metro railways with a lot of movement on the network.”
The Metropolitan Rail Network in Western Australia recently carried out trials of two of MGC Solutions’ eLMS systems, with great results.
“The trial allowed us to validate in real time what benefits the system can provide to our network partners, ensuring realtime understanding of this critical asset," Byrne said.
“We got great feedback from the Metropolitan Rail Network after the trial and they are looking to install more of our systems.”
BROKEN
Another innovative product MGC Solutions has created is its broken rail detection (BRD) system.
It’s currently the only patented system on the market that offers real-time monitoring of a track and looks at the voltage that is sent back to the system after finding an anomaly in infrastructure.
“The system can look at three to five kilometres of track in real-time, scanning it for clean breaks that have occurred in the
rail between train movements over the network,” said Byrne. “It’s an extremely useful device in sidings that have no constant monitoring, as well as mainline track where mainly axle counters are used to control the signalling in freight or metro networks.”
The product can be rapidly deployed, not requiring any extended shutdowns for installation – saving operators time and money and keeping crews out of harm’s way.
“Depending on the network owners’ requirements, it can be a simple sleeper mount or pole mount or location case to keep it outside of the danger zone,” Byrne added.
The solar-powered equipment is an Internet of Things (IOT) device that can use multiple connection technologies, including WiFi and GSM (Global System for Mobile Communications).
It is also self-learning, so it can build an image of the rail it is monitoring.
“With time, it can detect small anomalies within the track – for example ballast condition degradation, rail welds cracking etc,” said Byrne. “Nothing else works the way this thing works.”
MGC Solutions will install five of its Broken Rail Detection Systems along one of the Metro Trains lines on the East Coast as part of a new trial this winter – so watch this space.
The Australasian Rail Directory is a comprehensive, all encompassing rail services directory, available both online and as a traditional hardcopy publication.
The Rail Directory is an industry driven project to provide a complete listing of all businesses involved in the Australasian, Oceanic and Asian rail industries.
This year’s rail directory will be revamped to become even simpler to use. Listings will be sorted into categories allowing users to easily find businesses working in each area of the rail industry.
With over 1000 listings from areas as manufacturing, signalling and maintenance, make your listing standout with a frame advertisement.
To ensure you are in prime position in this year’s rail directory contact Arron Reed today.
To ensure that the Australasian Rail Directory is comprehensive, we offer all businesses who operate or trade in the region one free listing in the directory.
From $600 (+gst)
Double page, full page, half page and quarter page advertisement space also available.
To discuss the advertising opportunities available, please contact: Arron Reed on 0466 923 194 or email: arron.reed@primecreative.com.au
A grassroots not-for-profit is fighting to bring trains back to a line in the Northern Rivers which has been without rail services for over two decades.
In the lush landscape of the Northern Rivers region in New South Wales, a passionate group of community advocates is battling to restore a dormant railway line.
Northern Rivers Rail Limited (Ltd), a not-for-profit company, is spearheading an ambitious campaign to secure the licence to restore the 72-kilometre railway corridor between Lismore and Yelgun at the top of Byron Shire.
Led by company co-founder and Director Lydia Kindred, the group is challenging perceptions around the feasibility and value of reviving local train services.
“We're standing up for the rights of all the people in this region, and the visitors who would love to be able to get around and visit all these local towns more easily,” Kindred said.
“We have over 315,000 people who live in our region and we welcome millions of visitors each year.
“Byron Bay is known all around the world and to have a viable local train service would change everything. It’s a no-brainer, as far as we’re concerned.”
Kindred said trains would also make transport more accessible for young people, disabled people and the elderly.
“There are buses here, but they don’t run very frequently,” she said. “We’re losing our
youth from the region, partly because we haven’t got much public transport – they are moving to Brisbane and Sydney.
“I know one lovely older lady who can’t visit her sister in Mullumbimby because she doesn’t have a car and she can’t really get the bus. It’s quite isolating.”
The Murwillumbah railway line, which ran from Casino to Lismore, Byron Bay,
Mullumbimby and Murwillumbah, first opened in 1894, but Kindred said the heyday of trains on these services was the 1970s and 80s. From 1973, the Gold Coast Motorail transported passengers and cars between Sydney and Murwillumbah, and in 1978 the North Coast Overnight Express was introduced to meet increasing demand.
“You could put your car on the train at Murwillumbah, have a meal and a couple of drinks, and wake up in the morning and your car’s there in Sydney,” said Kindred.
“There was also a freight service to Sydney and back, and a morning and an afternoon passenger service.
“Families would get the train in the morning, spend the day at the beach in Byron, have a great time and get home safely on the train in the afternoon.”
In 1990, the Gold Coast Motorail and North Coast Overnight Express were replaced by a CountryLink XPT that ran as a night service, with reduced seating capacity leading to a drop in patronage.
“It would come into our region at about 9pm and do the rounds, and go out again at 11pm,” Kindred said.
“It was to fit in with Sydney times but no-one was really going to use it at that time of night.”
When the last train left Lismore Railway station in 2004, a crowd of about 200 dejected locals turned out in mourning, carrying candles, a mock coffin and protest signs.
“We only had one service, but it was something at least, and we had lost it.
“I was on that last train journey, and it was very emotional.”
Kindred said that as its first priority, Northern Rivers Rail Ltd is hoping to extend a similar service to what is currently being provided by the Byron Solar Train, with the first stage extending from Byron Bay to Mullumbimby, and the second stage between Byron Bay and Bangalow.
“We’re calling it the Country to Surf Train – people could just hop on the train with their surfboards and get to the surf like they used to in the old days.
“The views there are to die for, it would be such a tourist attraction as well as locals being able to use it. The potential is huge.”
The topic of restoring the Northern Rivers Railway is a controversial one in the region, with parts of the railway already converted into a rail trail for cyclists and walkers.
According to data released by the Tweed Shire Council, the 24 kilometre trail between Murwillumbah and Crabbes Creek attracted more than 70,000 users in four months when it opened in March 2023.
Kindred said that Northern Rivers Rail Ltd supports in principle the idea of a bike trail running alongside the restored railway, but the company's focus is to reintroduce a train service.
“Having both will be a win-win for the whole region, as each element will
complement the other,” she said. “Bike riders and walkers can use the train to ride back, on a comfortable, all-weather service, running throughout the day and into the night. This type of public transport is much needed in our region.”
“The rail trails in our railway corridor have pulled up the tracks on each end, so we’re working to not let that happen to the rest of the 72 kilometres of our remaining railway line.”
A government study from 2013 found that fixing the tracks and bringing railway services back to the Northern Rivers region would cost over $900 million.
However, a 2019 degradation study carried out by a leading engineering company found that the track “appeared to be in reasonable condition” in the areas inspected. "It was much better than they expected,” Kindred added.
Northern Rivers Rail Ltd has prepared a business case for the restoration of the
railway. This has been presented, along with other required reports, to relevant transport authorities.
At the time of going to print, the company was working on raising the $29 million needed for the first stage of the project.
“We are looking for major transport infrastructure partners to get on board and invest in the Country to Surf Train, which will be powered by renewable energy technology.”
Although the odds might be against Kindred and the rest of the rail supporters in the area, she’s determined to keep fighting.
"This is an exciting infrastructure project for regional New South Wales that aligns with government targets to lower transport emissions," she said.
“I’m able to stay positive because I really believe I’m doing the right thing for the region, which deserves a better non-road public transport future.
“I’m not giving up.”
Lydia Kindred was part of the team that helped to clear the tracks ahead of a degradation study in 2023.
With the most comprehensive expertise among independent contractors across Australia’s rail networks, Sigtech is your trusted partner for all aspects of Signalling projects.
Sigtech Solutions Australia is a 100% Australian owned company. We specialise in delivering turnkey rail systems and multidiscipline solutions, including design, construction, maintenance, testing & commissioning, system integration, safety assurance and advisory services.
CERTAINTY, CAPACITY, COMPETENCE
Contact us for reliable and expert solutions to all your signalling needs. Visit our websit: sigtechsolutions.com.au
Enquiries: admin@sigtechsolutions.com.au
A new version of PRM Engineering Services’ Sentinel Height and Slew Limiting Systems has been released, with a host of updated features to keep crews safe.
around bridges and inside tunnels, safety is paramount.
That’s where PRM Engineering Services’ Sentinel Height and Slew Limiting Systems come in.
The systems can be used on both new and existing vehicles, from excavators to loaders to skid steers and backhoes, protecting against operator error and maximising safe use of equipment in all conditions.
An updated version of the product has recently been released, with new and improved safety features. We spoke to the design engineer at PRM Engineering Services to find out more.
Sentinel Height and Slew Limiters can be used on any machine that has an
sensors that attach to the boom, which measure the height reached by the machine. The system integrates with on-screen and audible alerts to warn operators when they are approaching unsafe operating limits, and there are several different types of stops that can then be activated.
A new slow-stop option decelerates fastmoving machine booms before the height limit is reached, to prevent a sudden jolt.
“If the boom is moving at speed and it stops suddenly, the machine will rock back and forth,” PRM's engineer explained.
“With a slow stop, you’re minimising bucket spillage and reducing that unpredictability of movement for the operator. If the boom is moving slowly or is far from the limit, the full machine strength is maintained.”
overshooting at any speed by taking into account the speed of the machine.
“If you try to stop a machine when the boom reaches the limit, and it is going fast, it will overshoot. PRM’s Sentinel systems will begin to stop the machine earlier, so by the time it stops fully it is right at the limit, where we want it to be," he said.
Site supervisors have the ability to set height limits, via a key switch and password.
“As an example, Queensland Rail and Aurizon both use the Sentinel system, and they have specific height limits that they work to – often 3 to 3.4 metres, depending on the site.
"Our system allows their supervisors to input those limits without the operators being able to change them
themselves, which is an added layer of safety protection."
Each arm on a machine can be limited individually, to maximise the available operating room.
Different machine attachments can also be set and selected from the user interface, which can automatically adjust the height settings for the current attachment, saving a lot of time for operators with a wide range of attachments.
PRM’s Sentinel Height and Slew Limits also come with a safety lock level input, to reduce current draw when the machine is not in use and improve battery life.
Meanwhile a black box functionality records all events when the system is running.
“Internal logging records every time the system starts, every time it hits the limit, and every time the operator changes something."
PRM’s Sentinel Height and Slew Limiters are designed and made in Australia, with local support, national installers and local engineering.
The product has already been tried and tested by operators across the country, with excellent results and feedback.
PRM's engineer said the system is robust, can withstand harsh weather conditions and is suitable for use on construction sites and around railways.
“It has industry standard screens and protection for the sensors as well. In some cases, the sensors have five millimetres thick steel plates protecting them.”
Sentinel’s SIL 2/ PLd (safety integrity level 2/ performance level 2) system option
is suitable for high-risk use cases such as working under rail power lines.
It is currently the only system designed in Australia that meets the requirements set out in SIL 2, with improved redundancies in the latest version of the system.
“When you’re working with rail power lines, there is inherently a greater risk, with high voltage which can jump, leading to injuries and even loss of life, so you need to achieve SIL 2," the engineer continued.
“That means the system needs to have redundancies and components
that we know won’t fail. Even if they do fail, the system detects failure and has failsafe.
" We use two angle sensors in redundancy to measure the angle of the boom. If one of them is giving us the wrong angle, we can stop the machine, get it out of harm’s way and repair it before we end up in a dangerous situation.
“The system eliminates the risk of human error, keeping rail industry and construction workers safe with consistent, real-time protection.”
Australia’s rail networks are undergoing a once-in-a-generation transformation, and at the centre of it is the European Train Control System (ETCS).
Promising safer, more reliable, and interoperable train operations, the European Train Control System (ETCS) is fast becoming the signalling standard of the future.
But for a complex, fragmented network like Australia’s, delivering this level of change takes more than technology. It's about delivering and integrating it in the real world – and successfully – before advising others on how to follow suit.
That’s where Sigtech comes in.
With an immensely experienced team and a strong footprint across Australian rail networks, Sigtech is a leading independent specialist in ETCS design, testing and commissioning, and systems integration.
As General Manager of Signalling Design Adam Bird put it: “Sigtech has an extremely strong Australian ETCS delivery team with years of hands-on experience.
“We've been in the field, solving the real challenges of integration. You can’t advise with confidence on ETCS unless you’ve delivered it end to end.”
Sigtech’s journey into ETCS is built on 15 years of hands-on experience commissioning traditional signalling systems.
Founded in 2010 and currently one of Australia’s largest providers of independent signalling solutions, the company recognised early on that the industry was shifting – and proactively evolved to lead in the digital signalling and ETCS integration space.
“ETCS integration is complex,” said Abel Hurtado Tato, Sigtech’s ETCS Technical Lead. “But we’ve covered the whole life cycle, not just the design or the testing.
“We start from helping the operator define how they want to operate, and we stay through to system integration.”
The European Train Control System originated in Europe to overcome a major barrier: incompatibility between national signalling systems.
In the past, trains travelling across borders often had to switch locomotives, signalling systems, or rolling stock entirely. ETCS provided a harmonised standard that eliminated these inefficiencies. In Australia,
the signalling situation between states is surprisingly similar.
“We’ve had different rail gauges, different power distribution systems, different signalling systems,” said Sigtech’s Commissioning Manager Jesse Crick.
“ETCS gives you the ability to harmonise it. It’s not yet a problem, but it’s about to become a very big one if we don’t get it right.”
Put simply, ETCS is an advanced Automatic Train Protection (ATP) system that improves safety, enhances network capacity, and lays the foundation for digital, interoperable train control across diverse networks. It provides continuous speed and distance monitoring, real-time data exchange, and in later stages, automated train operation (ATO).
Hurtado Tato put it plainly: “It’s about interoperability and what it means in the Australian context. That’s something big in Australia right now.”
The transition is already underway. New South Wales, Queensland and South Australia have begun adopting ETCS across selected corridors.
Victoria is expected to make a call soon, and the National Transport Commission has signalled a nationwide push through its interoperability framework.
According to Bird: “It really comes down to national strategy, state and federal funding, and collaboration. The rules are there – it’s
about adopting and implementing them across the country.”
The European Train Control System is far from a turnkey solution. While standards are defined, every implementation must be adapted to local infrastructure, legacy systems, operational practices, and safety requirements.
“People think ETCS is like a USB,” said Hurtado Tato. “You just plug it in, and it works. It doesn’t. You need the umbrella of system integration to make sure everything works together.”
That means more than upgrading hardware. It means replacing trackside signals with in-cab displays, integrating trainborne equipment, digitising communications, and sometimes retraining drivers to shift from visual to digital signal interpretation.
“It’s a top-to-bottom transition,” said Bird. “From removing lineside assets, to ensuring cyber-secure communications, to introducing new driver practices –it’s holistic.”
In practice, Sigtech supports clients with both new-build integration and retrofit implementations. And while retrofitting to legacy systems poses challenges, it also
“You can keep your existing system live, then deliver ETCS over the top as a shadow system to facilitate integration and deployment strategies,” said Crick.
“You’re not duplicating work or changing things twice. You get the benefit all at once.”
Sigtech’s track record in ETCS now spans several states and multiple levels of integration.
In Sydney, the team has worked on the Digital Systems Program, integrating ETCS Level 2 trackside and into onboard equipment. It’s also played a key role in Sydney Trains’ Level 1 limited supervision (LS) rollout – an entry-level ETCS implementation that allows onboard speed supervision without major disruption to operations.
“That project delivered the entire network rollout with almost no operational impact,” said Crick. “It’s a good entry point to ETCS and proved the system could be integrated with minimal disruption.”
In Queensland, Sigtech is engaged in both Cross River Rail and the North Coast Line ETCS deployments, supporting everything from system integration to operational readiness.
The remit extends beyond infrastructure. Sigtech has integrated multiple ETCS onboard systems across different rolling stock fleets with the trackside equipment of multiple suppliers. In addition, the company is currently undertaking ETCS design activities to support the entry into service for the New Intercity Fleet and the New Regional Fleet for Transport for NSW. These enabling works also include the ETCS design for Automatic Selective Door Operation (ASDO), which uses ETCS data to safely control passenger doors within platform boundaries. After these
enabling works, Sigtech personnel will have contributed to the successful integration of four discreet onboard subsystems with the trackside subsystem of multiple suppliers, which demonstrates the depth of knowledge and experience that Sigtech has.
“We’re doing the signalling design to support rollout, integration, and safety assurance – all the way through to station-level enabling works,” said ETCS Engineering Manager Bryce Gallen.
While safety is a key selling point of ETCS, its value lies in measurable improvements to how trains operate.
“You don’t want trains passing signals at stop. You don’t want overspeeding,” said Crick.
“ETCS continuously supervises speed and distance, providing a constant layer of protection that supports drivers and enhances overall system safety.”
That includes monitoring of odometry accuracy, automatic braking profiles, and in some cases, fully automated train operation (ATO) – which not only increases safety but improves headway, energy efficiency, and service frequency.
“By removing lineside signals and going digital, you can bring trains closer together without compromising safety,” said Crick.
“The driver has information in the cab, not out the window.”
In turn, that reduces the need for on-track infrastructure, cutting maintenance costs and failure points. With fewer trackside assets, systems become more reliable and downtime is reduced.
“And when you bring in digital,” said Hurtado Tato, “you can start enabling real-time monitoring and predictive maintenance. That’s a big step forward.”
Sigtech’s approach to verification and validation (V&V) is key to ensuring these systems work.
“It’s about identifying hazards early,” said Crick. “We start from the operator’s specific risks – things like SPADs [signal passed at danger], low adhesion, braking – and make sure we’re addressing those all the way through the system life cycle.”
What’s next for ETCS in Australia? Sigtech sees a tipping point approaching.
“We’re just at the beginning,” said Hurtado Tato. “But already, Australia ranks as one of the top countries worldwide for ETCS activity.”
Still, full interoperability remains a challenge unless national bodies, rail infrastructure managers, and operators move in sync.
“There is a real risk that networks working in silo to develop and deploy ETCS to their own needs will result in creating a new form of network segregation and incompatibility,” said Gallen.
To prevent history from repeating, he said, Australia needs a top-down approach.
“We need a national level approach. Otherwise, the fragmentation will persist.”
Bird agreed: “There’s going to be a real explosion in ETCS projects over the next five years. It’s coming from state and federal levels. But to make it work, we need collaboration.”
That’s the message Sigtech wants decision-makers to hear loud and clear: act now, and act together.
“ETCS isn’t just a project,” said Crick. “It’s the foundation of the future rail network. The benefits will only be realised if we get harmonisation right.”
If there could be one statement made to the Australian rail industry on the transition to ETCS, Gallen said it is that collaboration between all stakeholders is key.
“Whether they are rail infrastructure managers (RIMs), government entities, equipment suppliers or private delivery firms, only through early and consistent collaboration, particularly between networks, will a truly interoperable national network become a reality.
“With the considerable experience that Sigtech has, it is well placed to support these early engagements and assist RIMs and networks on the journey.”
As the rail industry looks to a digital, efficient, and unified future, Sigtech is helping keep that future firmly on track.
The METRONET Morley-Ellenbrook Line Project picked up four gongs at the recent Western Australian Architecture Awards. We catch up with one of the architects who made it all happen.
The METRONET Morley-Ellenbrook Line Project, Perth’s largest public transport project since the Mandurah Line, has halved travel time for commuters from Perth CBD to Ellenbrook – and its impact hasn’t stopped there.
The project recently swept the board at the Australian Institute of Architects Western Australian Architecture Awards, picking up four accolades including Western Australia’s highest architectural honour, the George Temple Poole Award.
The team that made it happen also took out the Wallace Greenham Award for Sustainable Architecture, the Colorbond Award for Steel Architecture, and the Public Architecture Award.
Designed by Woods Bagot in collaboration with Taylor Robinson Chaney Broderick (TRCB), TCL and UDLA, the MorleyEllenbrook Line Project delivered 21 kilometres of track and five new stations and precincts at Morley, Noranda, Ballajura, Whiteman Park and Ellenbrook.
The awards jury said the stations make an outstanding contribution to the social and
public infrastructure of a rapidly growing area of Perth.
The judges praised the project for setting “an impressive new sustainability benchmark for government infrastructure in Australia, and for being an exemplar of public transport and community facilities, with the end-user experience at the forefront of the design.”
Kukame McPierzie, Project Director for Architecture and Landscape for the METRONET Morley-Ellenbrook Line Project and Woods Bagot's Principal in Charge, is thrilled by the success of the project.
Speaking to Rail Express after the win, he said: “Projects like this take years and years to pull together, through planning, design and construction.
“Winning the awards, particularly the George Temple Poole Award, was a really nice acknowledgement at the end of the process for the team, for our clients and for the public.”
The MELconnx Alliance between Laing O’Rourke and the Public Transport Authority delivered the $1.65 billion contract to design and construct the METRONET
Morley-Ellenbrook Line.
Laing O’Rourke won the project in 2020, which is when McPierzie and the Woods Bagot team also started design work.
“The project was delivered as a multidisciplinary alliance, with the contractor, engineers, architects, landscapers and more involved,” he explained.
“We spent about two years working intensively on the design before construction began.”
McPierzie said delivering the project during the pandemic was one of the biggest challenges the team faced.
“At the start of the job, we were in and out of lockdown and collaborating virtually,” he said. “There was a lot of pressure on the delivery of projects broadly during Covid, from skilled labour to costs.
“Credit to the government, they backed the project and said ‘This is a piece of infrastructure that’s going to be there for 100 years, we’re going to commit to it.’
“The fact that the government pushed through and did that has been really transformational for the city.”
According to McPierzie, Woods Bagot seized the opportunity to create a holistic identity for the Morley-Ellenbrook Line.
“We were delivering the 21-kilometre train line and five train stations as one project, so we wanted the train stations to be almost like a family.
“They are familiar. They have the same materials, similar roof forms, similar geometries – but then they're all slightly different depending on their context and the suburbs that are around them.”
McPierzie said the team took inspiration from the “aspirational” qualities of the suburbs that are home to each station.
“They’re all about light and landscape and that sort of aspirational Australian suburban living, combined with future development.
“So we use brick, we use verandas, we have lots of natural light, the stations are simple and easy to get around. They are fundamentals that are familiar to people who live in these communities. We started with those ideas and took it from there.”
The alliance also engaged with local Indigenous communities, with 14 local and Noongar artists creating 20 public art pieces across the stations.
“We’ve got the same skylight, with an artwork embedded within it, that runs across all five stations,” McPierzie said.
“It projects shadows down as you walk through each station, and that was inspired by the local context and created by an artistic team involving Indigenous artists.”
Another important factor for the architects to consider was the durability of the materials being used.
“We had very stringent design criteria to meet, as some of these stations and structures need to still be here in 120 years.
“We used products like Colorbond steel that we know is tried and tested in a Western Australian context and will go the distance. It doesn’t need much maintenance and it looks good.”
McPierzie added that the team worked hard to create a “kit of parts” with modules and repeatable units that could be used in all of the stations.
“We had the same structural steel for the lifts, the same roof profile, the same roofing material, or the same canopies.
“What this meant was, we were able to specify products that we could then apply across all five stations, and we could get great efficiencies in the use of that.”
Sustainability was also at the heart of the stations’ design, and Ellenbrook Station was one of the first railway stations in Western Australia to achieve the Green Star Design Review rating.
“This was a project where sustainability featured on every level,” said McPierzie. “From solar panels on the station roofs, to water-sensitive gardens that preserve water, to materials that minimise the use of carbon, electric generators being used on the sites and recycled aggregate and concrete being used in the car parks.
“The landscape pioneered the first use of FOGO (Food Organics and Garden Organics) in Western Australia, which is mixed through the soil. There was layer upon layer of sustainability baked into every aspect of the project. We’re very proud of winning the Wallace Greenham
Although McPierzie is delighted by the awards, he said the biggest reward is seeing the difference the project has made in the community.
“Rail services had been promised to Ellenbrook for 30 years, so to see it finally being delivered is amazing,” he said.
“The opening day was incredible, but what I loved most was when we went out two or three weeks after that, when the hubbub had died down. Seeing so many people using the line in their daily commute, whether they were going to work or TAFE or university or home, is pretty exciting as architects.
RAIL EXPRESS is compulsory reading and a vital tool for all people working in and around the rail sector.
Rail Express is Australia’s authoritative business to business rail publication.
Combining the resources of our respected journalism team and our unparalleled industry contacts and affiliations, Rail Express provides extensive, comprehensive and balanced coverage of breaking news and trends in key areas like infrastructure, investment, government policy, regulatory issues and technical innovation.
Published both in print and digitally every month, Rail Express is the only publication to have both the official endorsement and active participation of the main railway associations in Australia and the broad support of the rail industry.
The only way to ensure you get every copy of Rail Express is to subscribe today. Visit railexpress.com.au/subscribe.
Japan and China are both recognised around the world for their fast, reliable and technologically advanced rail networks. Journalists Kayla Walsh and Chris Edwards give a first-hand account of riding the rails.
WORDS BY KAYLA WALSH
As someone who grew up in a small town in Ireland and went to university in Dublin – a capital city with a population of over a million people but only two tram lines – I was instantly impressed by Melbourne’s public transport network when I moved here.
With the largest tram network in the world now on my doorstep, a reliable metro train system with frequent services easily
But as dazzled as I was by Melbourne’s transport system, I was about to experience awe on another level when I visited Japan.
When I arrived at Haneda Airport in Tokyo after my red-eye flight, I was feeling pretty overwhelmed and exhausted, but I had no choice but to power through and make my way to my accommodation.
The Narita Sky Access train line, the Keisei line and the JR line all connect directly to
confused by these directions so I went to the information desk at the train station to ask for help. They kindly explained that the directions I had been given were completely wrong and would have taken me to a station a 10-hour walk from my hotel!
Once armed with the correct directions, I managed to safely get to my destination and collapse in a heap on the bed.
I purchased a rechargeable green Suica card for 500 yen (about $5.37 AUD) and topped it up by a few thousand yen to get me started. Unlike in Australia where Sydney has its Opal cards and Melbourne has Mykis, and neer the twain shall meet, you can actually use your Suica card in different cities around Japan. You can even use it to buy snacks and drinks at vending machines!
This card can be returned at the end of your trip at designated JR stations or ticket counters, and your deposit will be refunded as well as the remaining balance on your card –you just have to pay a 220 yen handling fee.
Alternatively, you can buy a red “Welcome” Suica card, which is especially for visitors to Japan. It lasts 28 days and you won’t have to pay a deposit.
I’m not going to lie – getting around Tokyo by train can be intimidating. During my trip, I visited the second busiest train station in the world, Shibuya Station, which transports about three million passengers every single day. It’s the main connecting hub for rail traffic between central/eastern Tokyo and Western Tokyo on inter-city, commuter and subway rail lines, and it’s a sight to behold. Pop above ground and you’ll find the biggest pedestrian crossing in the world – Shibuya Crossing, which can have up to 3000 people crossing at once.
As the train stations in Tokyo are so crowded, organisation is key. You need to know where you’re going and have your Suica card topped up and ready to go, or you’ll be leaving a long line of frustrated commuters waiting behind you. Etiquette is also important – everyone lines up neatly on the left side of escalators, following directional arrows through the stations and queuing in an orderly fashion at points on the platforms that indicate where the doors of each carriage on the train will open. Inside the trains, the passengers tend to be silent – loud conversations and phone calls are frowned upon. Thankfully, you’re also not very likely to be forced to breathe in the aromas of your fellow commuter’s tuna sandwich, as eating on public transport is pretty taboo.
When it comes to rush hour, though, all hell breaks loose! While an Australian might look at a train that’s completely full to the brim with people and admit defeat, the commuters of Japan don’t seem to have the
same thought process. I saw one woman tenaciously fighting her way inside a carriage that was so packed that her arm didn’t fit through the doors. Said arm dangled outside the train while the doors attempted to close on it and she screamed. Eventually, with the help of staff on the platform, her arm joined her on the train. With another train coming in three minutes’ time, I wasn't sure it was worth the drama. . .
Scenes like this are apparently a common occurrence in Tokyo, with “pushers” hired to physically push people onto trains and make sure they are full to capacity. I recommend avoiding the trains during rush hour unless you want to get up close and personal with someone’s armpit.
Although many of the train stations have multiple levels and can get very confusing, after a couple of days I was able to navigate the network quite easily with the help of Google Maps. As a bonus, if you miss your train or go the wrong way, there’s usually another train in a few minutes to get you where you need to go.
The trains are remarkably punctual, and if there is even the smallest delay, the train operator will usually apologise over the intercom. When a train is more than five minutes late, the staff at each station along the way will issue “lateness slips” to passengers, proving that their tardiness for work was through no fault of their own. In 2018, A Shinkansen bullet train accidentally departed 25 seconds early. Japan Railways said in a statement that the “great inconvenience” placed upon customers was “truly inexcusable”.
I was lucky enough to get the famous Shinkansen bullet train from Tokyo to Kyoto, which was one of the highlights of my trip. The Shinkansen was the world’s first highspeed rail network and the trains travel at up to 320 kilometres an hour.
It took me to Kyoto in just two hours and 15 minutes, and the ride was so smooth it was hard to believe how fast we were travelling. The train was clean and quiet, with great views of the Japanese countryside. If you’re lucky you can even catch a glimpse of Mt Fuji – make sure you get a window seat on the right-hand side!
The only downside of the bullet train that I could see was if you have large baggage, you have to pre-book a storage area for it. Otherwise you’re going to have to be able to lift it into the overhead racks, and you risk putting your back out – like my poor friend who kindly (but foolishly) offered to help me with my bags!
With the train a major tourist attraction in itself, making it extremely easy to travel between major cities around Japan, it’s clear that the country’s investment in high-speed rail has paid off. I, like many Rail Express readers, am dreaming of the day Australia follows suit.
WORDS BY CHRIS EDWARDS
When I arrived in Shenzhen in 2013, I had no idea what high-speed rail in China looked like. As a fresh-faced man in his early 30s, I was unsure what to expect from what is now one of the leading proponents
of Chinese infrastructure. Now, I am a massive supporter. Having travelled tens of thousands of kilometres across the Chinese rail system, I have a solid understanding of not just the system, but routes and timings.
My first ever trip on high-speed rail in China was on one of the most trafficked routes in the country between Shenzhen and Guangzhou, not dissimilar to travelling between Sydney and Melbourne by air. On the main high-speed route, trains depart every five to ten minutes, with express trains completing the 118-kilometre journey in just 29 minutes. A trip to Beijing took about 10 hours (11 hours if taken on an overnight high-speed sleeper train), and travelling to Shanghai took anywhere from 8 to 11 hours, depending on the number of transfers and the use of express trains.
Buying a train ticket when I first arrived in China was a daunting experience. Practically every transaction was conducted in Mandarin, and as a foreigner, I had to visit ticket booths and arrange for the tickets myself. This has since changed, with apps like Trip.com offering an easy English language booking service. It’s not as fast as the official platform, but I found its fees to be reasonable. As long as you weren’t trying to book things immediately, you generally got into the class of seating and the time you wanted.
Buying a ticket is now akin to purchasing an airline ticket. Pick your departure and arrival cities, select
the relevant day, and then scroll through the (sometimes) long list of timetabled services. However, the significant difference lies in when the tickets go on sale. For most of the year, tickets are only available 15 days before departure. This is, in part, to minimise the impact of scalpers trying to take up spots and then on-sell the tickets at a higher price. It can make planning far more challenging, as you may not be able to purchase the exact tickets you need or want.
Buying tickets during Chinese New Year or any of the Golden Weeks presents a unique challenge. These are times of the year when people travel for holidays, or, in the case of Chinese New Year, return to their home towns to spend time with their families. In this case, tickets are released about four weeks prior to the travel date. These tickets sell out quickly – really quickly. Some routes sell out faster than Taylor Swift tickets. I remember having to make note of the exact time and date tickets went on sale – it was the only way to secure a spot in the first wave of purchasers and ensure we got the tickets we wanted.
My local colleagues also felt this stress. Some of them could only access one specific set of routes to get home each year, which would run once a day, and it
regularly sold out early. Unofficial reminders would be sent through group chats to ensure we all had the best chance to obtain the tickets. The additional trains put on during this period would help, but over 14,000 train journeys would not be enough to help everyone.
The high-speed rail stations can be a considerable distance from the city, but some of them have been integrated into city centres. The station I used to go to regularly was Shenzhen North Railway Station. Built just north of the core of Shenzhen, Shenzhen North now has three different metro lines running through it, with a fourth line due to run under its western concourse. This is in addition to the 20 platforms dedicated to high-speed trains, with trains running almost non-stop from 6am until midnight.
It was an imposing building at 40 metres tall. Much of its height is buried in a local mountain, with the range of tracks heading north and south. One metro line ran through the basement of the station, while the other two lines ran through the roof of the station. It makes for one of the longest subway transfers I have experienced, and I would actively seek a better way to commute to and from
work to avoid that transfer.
The two forecourts at the station are significant open spaces, providing space for the hundreds of thousands of people who pass through the station every day.
Getting into the station itself is reminiscent of entering an airport. Large scanners for luggage are set up at every entrance, with multiple queues ensuring that people move through the space as quickly as possible. There is also a metal detector for people to walk through. Some reports indicated that by 2020, Shenzhen North Railway Station would serve about 44.5 million people per year, and I have no doubt that this figure has been surpassed.
Once you enter the station, the space is enormous. The waiting area of the station is situated above the platforms, which can be accessed from either side of the line (A and B). A and B are used to split the people getting on the train, directing them to each end, minimising crushes at specific doors. The waiting area is also an enormous shopping centre, featuring fast food outlets, snack stores, clothing and luggage outlets, VIP lounges, and more.
People tend to gather near their gate from about 45 minutes before departure. Queues will develop quickly, but rarely before each individual train. It’s essential to remember that, like an airport, multiple trains will use each platform throughout the day.
Once it’s time to join the queue, get in early. The gates will open 10-15 minutes before the train departs and close three minutes prior to departure. That closure is adhered to with brutal efficiency. I have seen
above the waiting area, and in even smaller cities, there might be just two platforms. In these smaller cities, the commercial opportunities are significantly smaller.
There are three classes on the vast majority of high-speed trains. Second class is a 2-3 split and tends to be the most affordable option. The seats still fold back, and there’s a tray table for every passenger as well.
Business class is the most expensive class. There are usually only five seats in this single carriage, which is typically located at the nose or tail of the train. The seats could be lifted from an aircraft with their wrap-around shell design. They can go completely flat if you prefer, and the multiple points of articulation allow for anyone to find a comfortable position. You also receive complimentary snacks, slippers, and a blanket when necessary.
The train itself is incredibly quiet and steady. I experimented with balancing a coin on its edge, and once I got it there, it was as steady as any table that might get an occasional bump in passing.
The most noise from outside commonly occurs when trains are passing each other at 300 kilometres an hour or faster, with the whoosh of sound making people jump. A similar phenomenon occurs when entering or exiting a tunnel at high speed.
The café on these high-speed trains is quite good, but the option to order takeaway from outlets at upcoming stations and have it delivered to your seat is a nextlevel development.
If you have the chance to travel in China, consider taking a high-speed train. It’s going to be cheaper than flying, the service will be better, you will be more comfortable, and you’re far more likely to be on time.
The Endeavour Awards are a chance for the Australian manufacturing industry to celebrate its many successes throughout the year.
Nominations are now open for the 2025 Endeavour Awards.
Presented annually by Manufacturers’ Monthly magazine, the awards amplify and celebrate the outstanding achievements made across the Australian manufacturing industry.
Award categories include Technology Application (sponsored by Weld Australia), Innovation in Aerospace, Innovation in Health Technology, Innovation in Transport, Outstanding Start-Up, Leader of the Year (sponsored by BDO Australia) and Manufacturer of the Year. In 2025 a new category has been introduced – Innovation in Food & Beverage Manufacturing.
To be held on November 13 in Melbourne, the 2025 Endeavour Awards will be a celebration of innovation, resilience, and excellence across a range of sectors, including rail.
More than 900 companies support Australia's rail manufacturing and supply industry with a wide range of equipment, including locomotives, passenger cars, freight wagons, trams, and light rail vehicles.
This also includes the production of related components and systems such as traction motors, bogies, doors, brakes, and track materials.
Now’s your chance to recognise the industry’s manufacturing and assembly
“Sometimes it can be easy to overlook the importance of taking a moment to reflect on and celebrate the small improvements and changes being made to the industry.
“We think recognising the valuable contributions made across all industries is important to highlight the role they have in the economy.”
Amiga Industries, which specialises in 3D printing, gearboxes and CNC machining, is a two-time winner of the Manufacturer of the Year award, claiming the title in 2023 and 2024. Accepting the award last year, Managing Director Michael Bourchier said the recognition was amazing.
“This achievement is truly a result of the incredible efforts of our team, who consistently bring creativity and innovative thinking to our business,” he said. “They continue to come up with remarkable ideas that drive us forward.”
Hancock said recognising industry achievements can foster more innovation and investment across industries, which will ultimately benefit everyone.
“Regardless of the size or the duration of the project, everybody should be proud of their work across the sector.
"Just knowing that the industry has somehow benefitted from the work is special,” she said.
“It is also worth noting that others can gain insights from previous work and apply similar strategies in their own workplaces, in turn inspiring them to pursue greater and impressive achievement themselves.”
Nominations are now open across all categories. Nominate an exceptional Australian manufacturer, or a business that supplies to the sector, and give them the recognition they deserve. Nominations close 11.59pm, Thursday, 2 October.
For more information, visit: endeavourawards.com.au
The ARA will undertake several new research projects this year to support its advocacy efforts and provide the evidence needed for governments to continue to invest in rail.
Several new research projects will get underway this year to support the rail industry’s ongoing efforts to improve the operating environment of rail, increase mode share and ensure continued investment in rail infrastructure projects.
The research covers the economic, environmental and social benefits of rail, the impact of road and rail freight access charges, sustainability initiatives, passenger trends and the procurement pipeline outlook.
The projects include updating the Value of Rail 2020 report, an accompanying Future of Rail report, research into passenger trends, rail freight access and a rail procurement pipeline rail market outlook.
The ARA’s comprehensive Value of Rail 2020 research report will be updated to ensure industry has the latest data in relation to the economic, environmental, and societal benefits that rail provides Australia, as well as a breakdown for each jurisdiction.
The updated report is by Deloitte, however, Scyne has been engaged to deliver the Future of Rail report, looking
at the impact of key trends on the rail industry over the next 15 years. This will include a comprehensive breakdown of rail’s contribution to the economy, the value of passenger rail and freight rail to society (including analysis of the national freight task, with historical and forecast trends, and changes since 2019). The report will also include an overview of the local rail supply chain, including rollingstock manufacturing and maintenance, rail infrastructure construction, and other suppliers.
The ARA has commissioned Scyne to deliver a new report on the Future of Rail , looking at the impact of key trends on the rail industry over the next 15 years.
The report will explore a wide range of issues including population growth and demographic changes, technology and automation, transport funding, housing development, the energy transition and more, to determine how these megatrends will impact the industry, and how rail can lead solutions to drive positive economic and community outcomes.
The first phase of the research is now underway, with the project to be completed later this year.
The ARA has been conducting preliminary research into access user charging for both rail and road to understand both current and historic models. The Road/Rail Competitive Neutrality Project has now been scoped and the project will analyse the true extent and impact of differences in access and regulatory imposts for non-bulk road and rail freight. This project will assist with the development of an evidence base to underpin compelling industry advocacy at Commonwealth and state levels.
The ARA has engaged Oxford Economics Australia to provide a consolidated update to the rail procurement pipeline market outlook. The purpose is to have a more transparent and accessible understanding for the rail pipeline for suppliers and contractors. This report will provide 10 years of historical data
and a 10-year outlook for rail construction and maintenance activity by Australian state and territory and at the national level. This updates the 2022 Rail Market Outlook and expands the analysis to include a Major Projects and Programs table which lists cost, status, ‘confidence to proceed’ and timing details of significant construction projects, contracts for rollingstock, and funding for maintenance programs.
The ARA has commissioned new consumer research to assess passenger perceptions of rail transport and identify opportunities to support greater use of rail. The survey builds on similar research completed in 2022, identifying the key issues that promote greater public transport use in our capital cities.
The research has assessed people’s likelihood to use public transport more often as a result of the delivery of new, mega-projects across the country. The ARA will launch the research in the near future.
The ARA has engaged Social Traders to complete the First Nations engagement project, in partnership with its delivery partners Akina and Humanize Media. The project has been informed via desktop research, member-wide surveys, interviews with First Nations people and organisations, and impact modelling workshops with key stakeholders.
The second stage of data collection for the project has been completed, and the final draft is under review. The second stage involved additional interviews with First Nations employees, as well as a survey completed by First Nations businesses who have engaged with projects or contracts in the rail sector.
Preparation is underway for the formal launch and publication of the report, in consultation with project sponsors and the ARA’s First Nations Consultation Group.
The ARA has commissioned a Ngunawal artist to create a cover artwork for the project, highlighting the role of rail in
connection people, places, and opportunity. In anticipation of the launch, the ARA has commenced development of its first Reflect RAP.
Research to assess the skills requirements to support the infrastructure sector’s transition to net zero is nearing completion. The project maps where infrastructure sector workers need to upskill to support net zero decision making, identifying the roles that can have the greatest impact in supporting decarbonisation.
The project has been led by Infrastructure Australia (IA). The ARA is a sponsor for this project, together with Engineers Australia, IA and a number of state bodies.
Infrastructure Net Zero will identify priority areas of focus to 2030 at its next meeting, with an emphasis on initiatives that can accelerate emissions reductions across the rail sector.
The Permanent Way Institution Executive Breakfast series continues to strengthen links between policy, planning, and the rail community.
It was a full house at the inaugural Permanent Way Institution (PWI) Executive Breakfast at the Fullerton Hotel Sydney as we welcomed Tim Parker, Chief Executive Officer of the High-Speed Rail Authority Australia (HSRA), as our guest speaker.
Parker delivered an engaging overview of the progress made by the authority to date and shared insight into the strategic direction ahead. Of particular interest was the authority’s proposed approach to Early Contractor Involvement (ECI), signalling a collaborative path forward for industry engagement.
Parker emphasised that more than just a rail line, high-speed rail is about delivering better outcomes for communities, unlocking new economic and housing opportunities, enhancing access, and transforming regional centres for the opportunities of the next century and beyond.
It was a timely and thought-provoking discussion that reminds us of the broader impacts of infrastructure investment.
PWI extends its sincere thanks to Parker and the HSRA team for his time, insights, and commitment to future opportunities for industry.
The PWI Executive Breakfast series has become a valued annual fixture on the industry calendar, offering a unique opportunity to engage with senior leaders from across the transport and infrastructure sectors. Designed to provide keynote speakers on relevant, timely topics, these breakfasts foster meaningful dialogue and promote strategic thinking in an informal, collegial setting.
With a curated format and senior audience, the series continues to strengthen links between policy, planning, and the rail delivery community. As rail evolves in scale, complexity, and national significance, bringing together public and private stakeholders has never been more important.
From a PWI perspective, this series is also an important opportunity to regularly engage with senior leaders across the transport sector, offering keynote presentations on topics that shape the direction of the industry.
It’s a chance to pause, reflect, and connect, ensuring our members stay ahead of emerging trends, policy changes, and collaborative possibilities across the broader rail landscape.
Following this, we reflect on the success of our recent Western Australia launch. With more than 100 people in attendance, the energy in the room was palpable.
The recognition of PWI as a valuable forum for learning, collaboration and professional growth is spreading fast across Western Australia. We are thrilled to see this appetite and look forward to nurturing a growing and connected community.
To our friends in Western Australia, we welcome you to the fold and encourage you to get involved.
As we move into the second half of 2025, there are plenty of exciting opportunities for our members to get involved, stay connected, and contribute to the rail industry community through PWI events and initiatives.
Next on the agenda is our July Lunch ‘n’ Learn, which will take place on Wednesday 9 July. This session is proudly hosted by Vossloh and will focus on Dual Gauge
Turnouts – a highly relevant topic as we continue to navigate the complexities of Australia’s diverse and often incompatible rail network infrastructure.
This will be an invaluable technical session for members looking to deepen their understanding of the integration challenges across national and state-based networks.
First up in the second half of the year is the Railway Team Soccer Cup, a new initiative built around camaraderie, fun, and a shared purpose.
The R U, OK? Foundation continues to do extraordinary work in our sector and beyond, encouraging individuals to check in with each other, have meaningful conversations, and reduce the stigma around mental health challenges.
The significance of this initiative within the rail industry cannot be overstated. Long hours, shift work, isolation, and pressurefilled environments are commonplace in our field, and the value of a conversation, a connection, or even a game of soccer cannot be underestimated.
at the Newcastle Convention and Exhibition Centre on October 30 and 31, 2025.
This two-day event is a cornerstone of the PWI calendar and offers unparalleled opportunities for networking, knowledgesharing, and celebrating innovation in the rail industry.
Our conference planning team is currently finalising the finer details, and we promise a memorable event with engaging speakers, practical sessions, and recognition of industry excellence.
In partnership with the Rail Track Association Australia (RTAA), this event promises to be a highlight on the calendar, with all proceeds directed towards the R U OK? Foundation. Scheduled for 10 October 2025 at 5sports in Caringbah, this is more
Corporate members are invited to support the event through sponsorship, and we encourage teams from all parts of the sector to register, play, and show their support. Let’s bring our teams together in a celebration of teamwork and resilience.
We encourage all members to save the date and keep an eye out for registration information coming soon.
PWI FELLOWSHIP: RECOGNISING EXCELLENCE
In addition, we are proud to see our
For further information about these events or to get involved, visit www.pwinsw.org.au or follow us on LinkedIn.
The new Monitoring Fatigue Risk Management Programs Guideline helps operators identify and monitor key fatigue-related metrics.
– it’s a well-documented safety hazard that continues to affect the rail industry worldwide. For workers in critical roles such as train driving, signalling, and maintenance, the consequences of fatigue can be serious, and in some cases, tragic.
A recent report from Great Britain’s Rail Safety and Standards Board found that fatigue was a contributing factor in 20 per cent of rail incidents.
Australia is not immune.
Investigations by the Australian Transport Safety Bureau (ATSB) into incidents such as those at Jumperkine (December 2019) and Port Hedland (March 2024), both of which involved fatigue – with the former resulting in a fatality – highlight the urgent need to improve how the industry identifies and manages fatigue risk.
“We use outcomes of such major incident investigations, as well as key safety risks from RISSB’s Australian Rail Risks Model (ARRM), national interests and regulatory priorities, to identify products that are critical for industry,” said Cris Fitzhardinge, Senior Standards Development Manager, Rail Industry Safety and Standards Board (RISSB).
Working closely with a development group comprising members from rail transport operators across Australia and New Zealand, RISSB has developed a new Monitoring Fatigue Risk Management Programs Guideline.
transport operators (RTOs) in meeting their obligations under the Rail Safety National Law, which requires the implementation of effective Fatigue Risk Management Programs (FRMPs).
“The passion and drive of the development group for this guideline was evident from the first day,” said Fitzhardinge.
“Everyone was keen to see this product developed so rail transport operators could better manage fatigue risk to reduce the chances of fatigue being a factor in serious incidents.”
While many operators already collect valuable data through their FRMPs, the new RISSB guideline addresses a key gap – how this information is interpreted and used to inform decisions. In some cases, fatigue risks are identified in the data but are not fully recognised or acted upon by the RTO.
RISSB’s Guideline seeks to change that. By focusing on work scheduling and rostering, it helps operators identify and monitor key fatigue-related metrics, use this data to make better decisions, and ultimately redesign rosters and processes to reduce risk.
Importantly, the guideline cautions against over-reliance on biomathematical modelling tools. While such tools are useful in identifying potential fatigue windows, they should not be the sole source of
fatigue, shift length data, and incident reports, are just as vital in painting a complete picture.
The guideline goes beyond theory, offering real-world case studies that illustrate how fatigue data has been used to make practical changes in rail operations. It also covers best practices in monitoring, continuous improvement, and training – empowering rail organisations to build a culture of safety around fatigue risk management.
“I greatly appreciate the support that RISSB has provided in developing this guideline, and I am sure there are a lot of rail industry members who will benefit from this,” said Development Group member Nathan Hines, Human Factors Specialist, Transport for NSW.
By improving the way rail transport operators use the data they already collect, this guideline offers a powerful opportunity to take fatigue risk management to the next level.
It represents a practical roadmap to safer operations, healthier workers, and fewer fatigue-related incidents on rail networks.
For an industry committed to continuous improvement, this is a timely and vital resource – and a strong step toward a safer future.