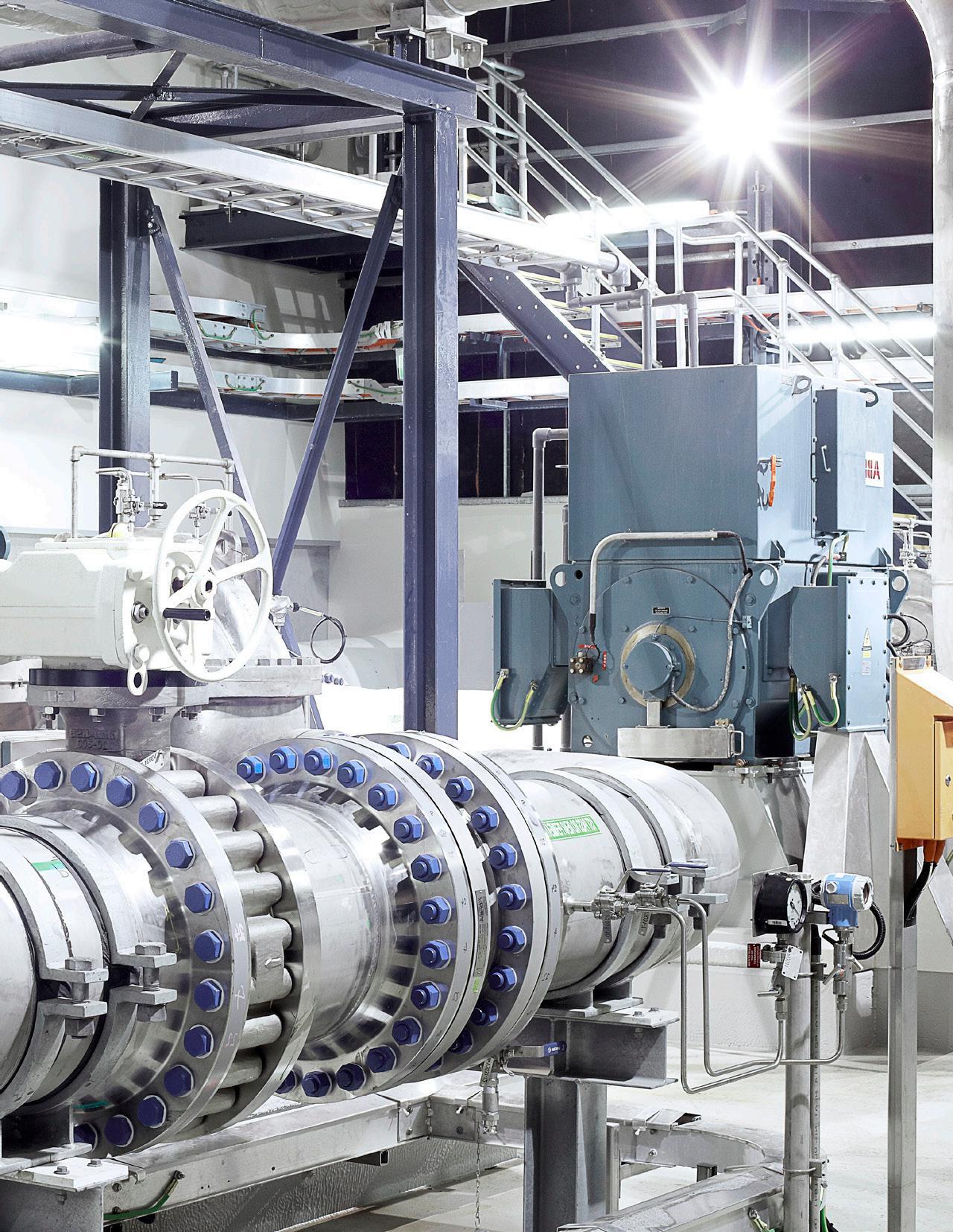
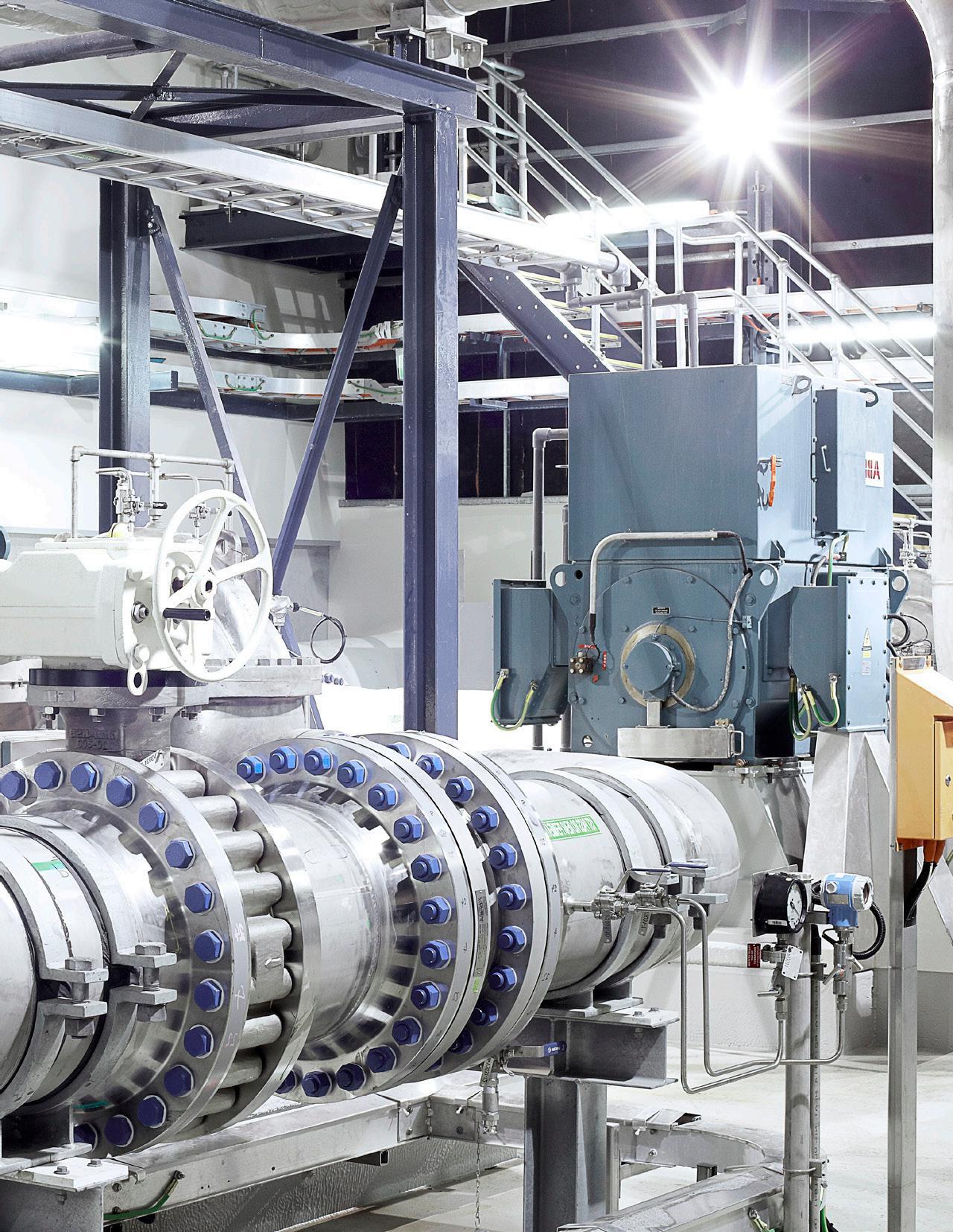
Energy Efficiency pumpindustry
FEATURES:
• Import & export update
• Fire pump standards
• Water industry advocate
• History: Bob Moore interview
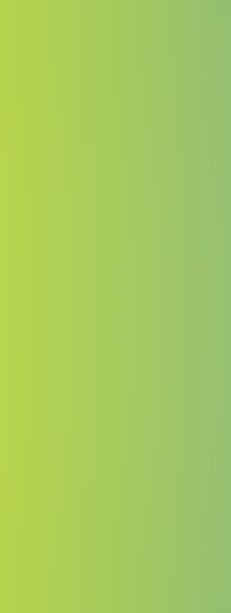




Meet the pump people
PIA Exhibition & Seminar 9-10 October 2012
Visit the exhibition for free, or register today for the seminar Register at www.pumps.asn.au
When?
Tuesday 9 October






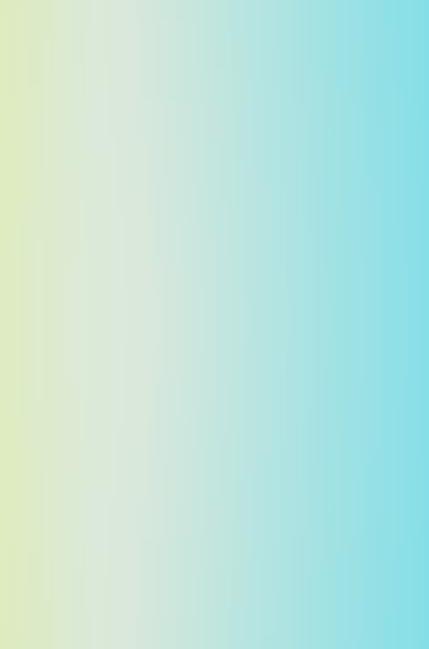

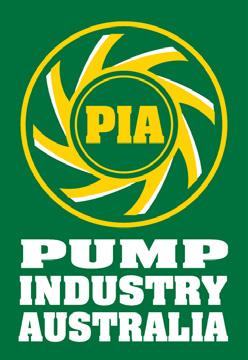
Exhibition trade day and seminar (advance registration required) 9:30am - 5pm
Wednesday 10 October
Exhibition open to trade and public, 9:30am - 4pm
Where?
The Whitehorse Centre
397 Maroondah Highway Nunawading, VIC (At rear of Civic Centre)




The venue is within easy reach of the Eastern & Eastlink Freeways and there is ample free parking available.




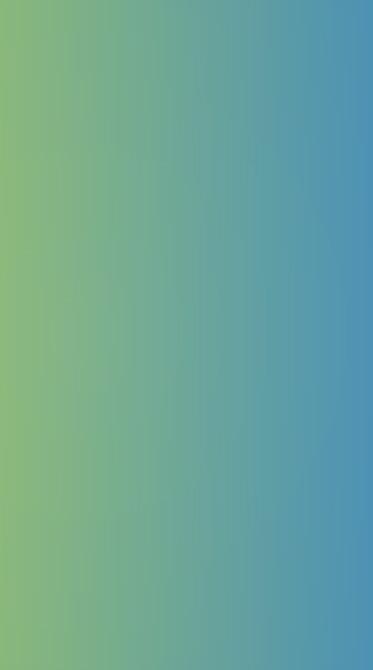












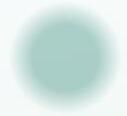





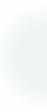




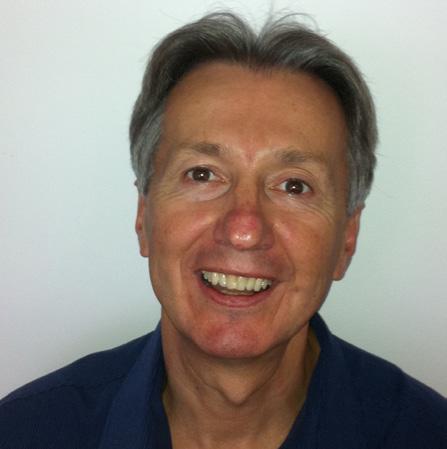
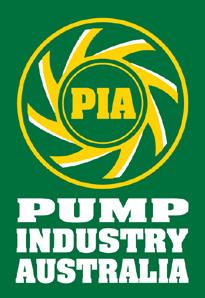
Pump Industry Australia Incorporated
Kevin Wilson – Secretary PO Box 55, Stuarts Point NSW 2441 Australia
Ph/Fax: (02) 6569 0160 pumpsaustralia@bigpond.com
Harry Katunar – President KSB Australia
Ron Astall – Vice President Astech Consulting Services & United Pumps Australia
Brad Antrim – Councillor Grundfos Pty Ltd
Michael Bauer – Councillor Dynapumps
Geoff Harvey - Councillor Davey Products Pty Ltd
John Inkster – Councillor Brown Brothers
John Link – Councillor Link Pumps
Alan Rowan – Councillor Life Member
Keith Sanders – Councillor Australian Industrial Marketing & Life Member
President’s welcome
Iwould like to welcome all readers to the first edition of the pump industry magazine. It’s great to see that our industry has attracted enough interest to have its own dedicated magazine.
We need to remind ourselves that the Australian pump industry is a significant contributor to the Australian economy, with an annual market for pumping equipment estimated at $1,000 million annually, and over 2,500 people employed in manufacturing and distribution. We make an impact in many areas across the community from delivering drinking water, irrigating our crops, fire protection for our property, airconditioning for our buildings, enabling our power stations to deliver electricity, and helping our miners and oil and gas producers to process their export orders or ensuring your backyard swimming pool or domestic water supply runs smoothly.
Our proud history in Australian manufacturing goes back to the gold rush era in the 1870s. Although there has been major change over past decades with the introduction of new technology, removal of trade protection and globalisation, we still make a wide range of pumps here in Australia that are exported worldwide. Many of our local companies have been acquired by international operators; this has provided new opportunities for employees in the industry to develop their technical and professional skills, as well as ensuring we keep pace with latest manufacturing technology and design.
Our association now represents not only manufacturers but distributors, resellers, agents and other businesses supplying products and services to our market. Many of our smaller members are value adding by packaging pumps with ancillary equipment to supply innovative total package solutions to
their customers. There is a growing trend for pump users to seek out end to end total package solutions, with single point responsibility for delivering a fluid at the required capacity and pressure for an application. This presents opportunities and challenges for our industry, as does the focus on energy efficient pumping systems and fast tracking of projects and increasing demand for faster deliveries and a fiercely competitive market place.
Our vision is for PIA to play a leadership role in the growth of the Australian pump industry. The PIA offers our members, big and small, a voice to the market place, a way of showing our capability to general industry and consulting with government, providing education to industry and student, and a great way to network and learn from peers.
Our PIA executive officers are currently working in 3 main areas:
1. Publications; Alan Rowan is working on an update of our popular Pump Handbook and Friction Loss Book.
2. Standards; Ken Kugler is working with Standards Australia to amend the Fire Pump Standard AS 2941 We are also working with Sustainability Victoria and the E3 Committee in developing a minimum efficiency standard for pumps.
3. Marketing & Media; Keith Sanders produces our regular PIA newsletter, and our market research & statistics.
Upcoming PIA events include our pump exhibition in Melbourne on 9th & 10th of October and the AGM on November 22.
For more information on our activities and upcoming events, please turn to pages 10-11 or visit our website www.pumps.asn.au
Harry Katunar President, Pump Industry AssociationEnergy Efficiency pumpindustry
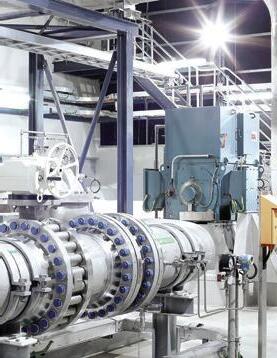
Cover shows pump, pipework and motor on the WA Water Corporation’s new Southern Seawater Desalination Plant
This magazine is published by Monkey Media in co-operation with the Pump Industry Association (PIA). The views contained herein are not necessarily the views of either the publisher or the PIA. Neither the publisher nor the PIA takes responsibility for any claims made by advertisers. All communication should be directed to the publisher.
The publisher welcomes contributions to the magazine. All contributions must comply with the publisher’s editorial policy which follows. By providing content to the publisher, you authorise the publisher to reproduce that content either in its original form, or edited, or combined with other content in any of its publications and in any format at the publishers discretion.
Published by Monkey Media Enterprises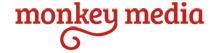
ABN: 36 426 734 954
GPO Box 93, Melbourne VIC 3001
P: (03) 9440 5721
F: (03) 8456 6720
monkeymedia.net.au
info@monkeymedia.net.au pumpindustry.com.au magazine@pumpindustry.com.au
Design by Linda Tucker Happy Places Design www.happyplaces.com.au
ISSN: 2201-0270
Editor’s welcome
Welcome to the first edition of pump industry magazine. This is a magazine by the pump industry and for the pump industry and I thank the PIA for the opportunity.
As I’ve worked on this magazine, the one statistic I’ve heard again and again is that pumps are the second most common type of machinery in the world, so it is only right that they have their own magazine in Australia.
Of course, it’s a changing industry, as industry stalwart Bob Moore points out later in this issue. The industry has shifted from manufacturing to a larger number of importers. On the positive side this has resulted in many small-medium enterprises specialising in various areas and providing a high standard of technical expertise and service. As such, the Australian pump industry is in good health.
The users of pumps are as diverse a group as any, and this magazine is aimed at reaching a wide range of these end-users, communicating useful information about pump applications and being seen as a one-stop shop and trusted source for all pump informationwhatever industry you are in.
Pumps do not operate in isolation, and pump systems include a range of other equipment, such as motors and drives, valves and monitoring equipment. This magazine will seek to cover the full range of products and equipment used in pump applications. The editorial schedule on the second-to last page should give you some indication of the planned scope of future editions.
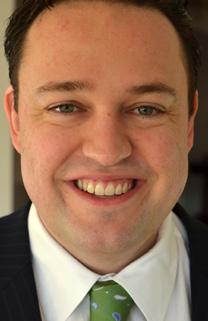
Many of the people I have spoken with have wondered why I would choose to publish a pumps magazine. For those who don’t know me, I have spent the last decade in trade publishing and have launched many successful industry titles. I have seen how an industry magazine can draw businesses together and grow the industry and the association, creating new opportunities by improving communication in and about the industry
The pump industry deserves a high quality magazine to showcase its capabilities, and this is what I hope to deliver. Any modern magazine must of course have a strong online component as well, and pump industry will be simultaneously published as a digital edition, as well as being supported by a website and newsletter containing exclusive online-only content.
I would like to thank all the members of PIA for their co-operation. I have spoken with virtually all members and I appreciate your time and ideas and have taken action on your input. I would particularly like to thank those who stepped up and backed this first issue with advertising and editorial.
The response has been overwhelmingly positive, and I’m very pleased to say the magazine is going ahead and we are here for the long haul, with your ongoing support and feedback.
Chris Bland Publisher and Editor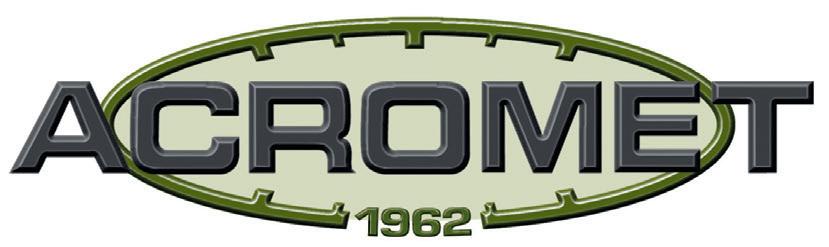
Acromet (Aust) Pty Ltd design and manufacture innovative solutions for a wide range of system applications.
• Customised Design
• Detailed Manufacturing
• Comprehensive Factory Testing
• Professional Installation
• Reliable Service
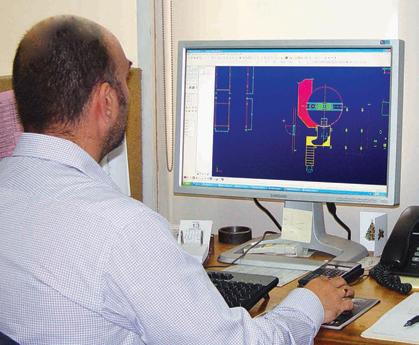
Acromet’s extensive experience and proven track record, delivers a cost e ective solution to meet the client’s operational demands.
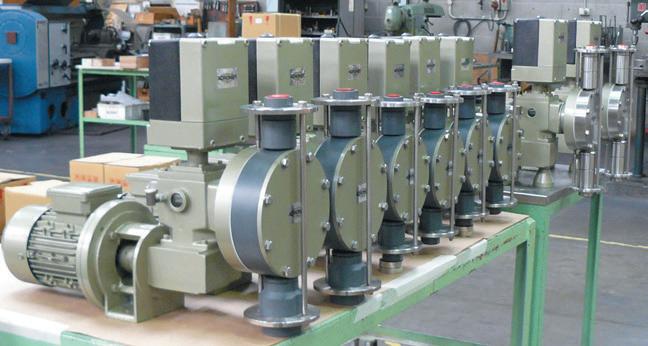
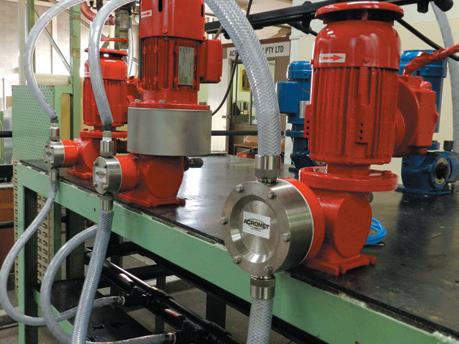

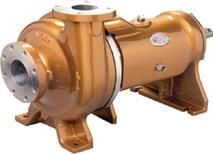

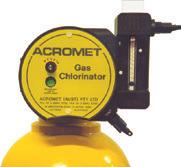
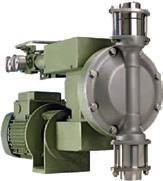
pumpindustry 6
All the latest news
The Hydraulic Institute (HI) has recently updated two pump standards, covering allowable operating region for centrifugal and vertical pumps and submersible pump tests.
Plus a look at the latest projects and industry developments, both locally and internationally.
14
Energy efficiency
An update from Sustainability Victoria on the progress towards MEPs for pumps, as well as a look at optimising overhauls to save energy from Ray Beebe and a project update from KSB.
Import and export update
PIA has been routinely conducted an analysis of the import and export activity of commonly used pumps in the Australian market. This has been achieved by monitoring ABS Import and Export Statistics over the period 2003 – 2011.
32
Advocating for industry
The Australian Government’s Water Supplier Advocate, Bob Herbert AM, is leading a strategy to develop, improve and promote the Australian water industry and champion the firms in this vital sector.
34
Fire pump standards
A look at the requirements for fire pumpsets in new buildings in accordance with the Building Code of Australia and maintenance of existing fire pumpset installations. Fire pumpsets are critical infrastructure installations in many buildings and facilities throughout the world. The efficiency of water as a fire suppression agent is well recognised however water’s suppression qualities are often measured by the quantity and speed by which it can be applied to a fire.
PUMP PIONEERS
40
MAIN FEATURES 24 43
Robert J “Bob” Moore
Robert J “Bob” Moore is a Life Member of PIA and one of the true elder statesmen of the industry, having started working in pumps in 1955, and regarding himself as a lifelong pump-man. Chris Bland recently had the chance to ask Bob, now 85 and still going strong, to reflect on his life and career.
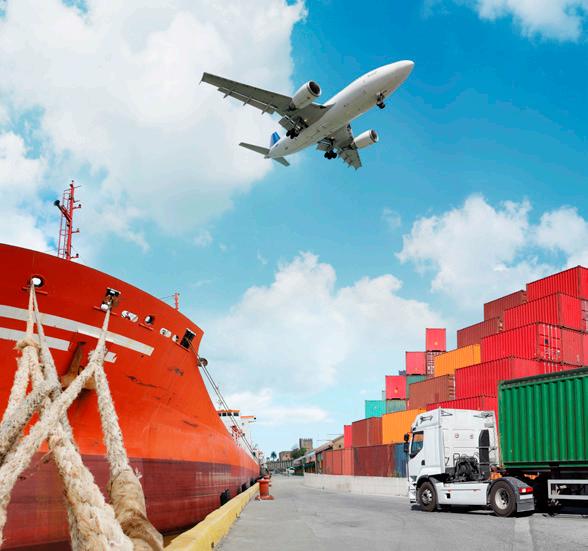
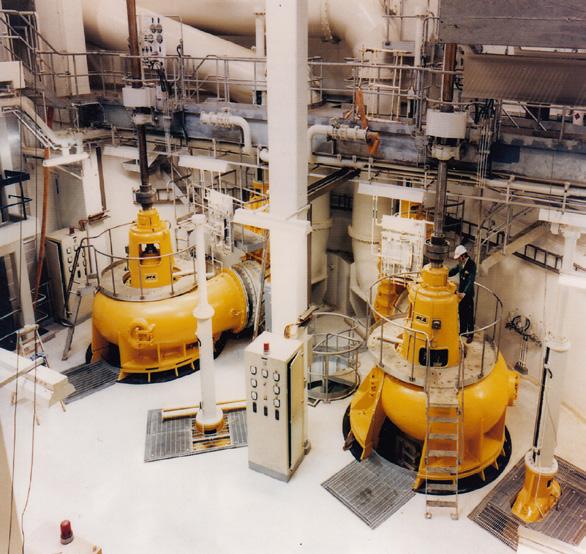
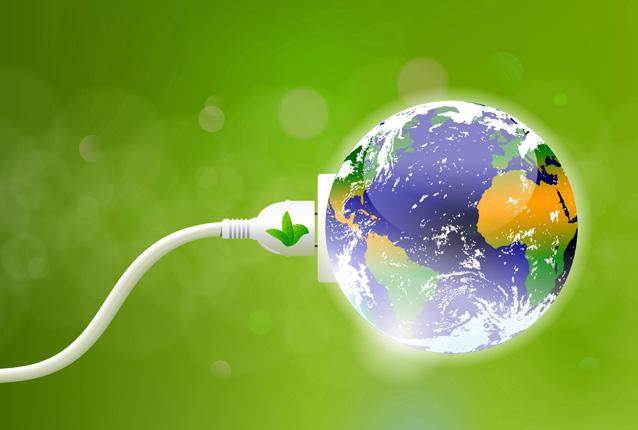

Acromet - Celebrating 50 year s of service
October 2012 marks 50 years since Acromet was founded, we take this opportunity to speak to General Manager Keith Gardner.
Balance matters
Imbalance of rotating components is one of the most common sources of machine faults in rotating assemblies, pumps and fans, and is a major cause of complete equipment failure.
COVER STORY
Converting the Indian ocean into drinking water
26
Most states in Australia have recognised the importance of purifying seawater using reverse osmosis technology and have desalination plants either operating or under construction in an effort to drought-proof our nation.
PROJECTS
Sewer bypass success
28
In August, Pump Affinity performed a key role in the 450mm rising main valve replacements from Wyong Shire Council’s Sewer Pumping Station (SPS) T22. SPS T22 receives sewage flows from 8 other sewage pumping stations, two private pumping stations and has over 4400 Equivalent Tenements in its catchment. The Peak Wet Weather Flow is up to 190L/sec.
Sweet upgrade
30
Recent negotiations between Sugar Australia and Stevco Seals & Pumps Victoria has resulted in Stevco Vic being awarded a tender to supply and commission a second replacement pumpset to upgrade the 100 year old water injection system.
TECHNICAL
36
ARC valves - best practice
Centrifugal pumps are one of the most common pieces of process equipment. In modern process systems there is a requirement for multiple flow conditions to meet process requirements. In times of start-up, shutdown or abnormal process conditions system flow can be greatly reduced and flows through centrifugal pumps may fall below the pump’s minimum flow value.
Understanding pump curves
38
This edition, we look at Net Positive Suction Head Required (NPSHR) versus suction lift and self priming capability.
PUMP SCHOOL
Net Positive Suction Head (NPSH)
Many people are of the belief that a pump “sucks”. While not entirely incorrect, it’s easy to see why so many operators still struggle with pump problems.
Hydraulic Institute updates standards
The Hydraulic Institute (HI) has recently updated two pump standards, covering allowable operating region for centrifugal and vertical pumps and submersible pump tests.
HI updated the 1997 edition of the ANSI/HI standard on allowable operating region for centrifugal and vertical pumps and published ANSI/HI 9.6.3 – 2012 Rotodynamic (Centrifugal and Vertical) Pumps –Guideline for Allowable Operating Region.
The updated guideline discusses the effects of operating a rotodynamic pump at rates of flow greater than or less than the rate of flow at the pump’s best efficiency point (BEP). These effects influence the power consumption and life of pump components and, therefore, considering the operating rate of flow is essential to reliable, efficient pump operation.
The preferred operating region (POR) and the allowable operating region (AOR) are defined for rotodynamic pump types and related to specific speed. Factors that affect AOR are discussed and NPSH margin versus rate of flow is presented.
The guideline also indicates when stable or unstable operation may be expected based on typical system head curves, for pumps exhibiting a drooping head curve or a head curve with a dip. Considerations such as the robustness of a pump are also discussed.
HI has also updated the 2001 edition of

the ANSI/HI standard on submersible pump tests and published ANSI/HI 11.6 – 2012 Rotodynamic Submersible Pumps for Hydraulic Performance, Hydrostatic Pressure, Mechanical, and Electrical Acceptance Tests. The updated standard applies to customer acceptance testing of submersible pumps driven by induction motors, unless otherwise agreed or specified.
ANSI/HI 11.6 – 2012 provides uniform procedures for performance, hydrostatic, net positive suction head required (NPSHR), submersible motor integrity, and vibration testing of submersible pumps; and data recording and reporting of the test results. It is intended to define test procedures that may be invoked by contractual agreement between a buyer and manufacturer. It is not intended to define a manufacturer’s standard practice.
A submersible pump is defined as a close-coupled pump/motor unit designed to operate submerged in the pumped liquid. This definition includes submersible pumps operating in either a wet-pit or dry-pit environment. A standard test measures pump
performance from suction flange to discharge flange and electrical input power. It does not include accessory items, such as discharge elbows, suction fittings, or valves, unless specified by a contractual agreement.
The following submersible pump designs are covered in the 2012 edition of the standard:
• Semi-permanent/pull-up/wet-pit types
• Dry-pit/dry-installed types
• Portable/flexible discharge types
• Chopper/cutter/grinder types
• Close-coupled types
• Integral electric motor types
Information in the standard may be applied to pumps of any size and to any pumped liquids behaving as clean cold water. This standard does not deal with the structural details of the pump or with the mechanical properties of their components.
ISO 9001 CERTIFIED
AS2417 ISO9906 API 610 Hydraulic Institute
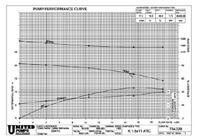
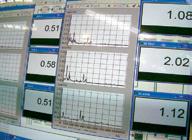

Coliban Water pumps water out of tourist attraction
Coliban Water is installing pumps to remove water from the Central Deborah Gold Mine, while they look into longer term solutions to Bendigo’s rising water table.
The water authority is in communications with two other local agencies for a solution, which may involve releasing water into the sewerage system.
In the meantime, the popular tourist attraction will have the water pumped out to ensure the site remains operational.
New pumping stations in Tasmania
Tasmania’s Southern Water is replacing a 108-year old pump station in Salamanca Place in Hobart, as well as pumping stations in Glenorchy and Clarence.
The upgrades form part of a $180 million, three year project to overhaul the city’s waste and wastewater systems.
“The existing pump station was never designed to cope with the amount of wastewater which comes from all the venues in the area,” Southern Water executive manager Russell Fox said.
Geelong Water Plant starts pumping
Commissioning has begun on Barwon Water’s Northern Water Plant in Geelong.
The $94 million project is located adjacent to the Shell Geelong Refinery and will produce around 2 billion litres of high quality class A recycled water.
Construction began on the plant in March 2011 and the plant will be fully operational in early 2013. John Holland is the principal contractor.
This major water-saving initiative will produce Class A recycled water suitable for industrial and community use in Geelong’s northern suburbs.The plant will use cutting-edge treatment technologies including biological treatment, ultrafiltration, and reverse osmosis.
Queensland Resources Council calls on government to help pump water from Queensland’s flooded mines
QRC Chief Executive Michael Roche used the recent Coaltrans conference in Brisbane to call for government help in solving the problem.
Roche said that while the industry was “on track to export more than 200 million
tonnes of coal in 2010-11...extensive flooding across our main coal-producing regions – the Bowen and Surat Basins –cost some 40 million tonnes in scheduled production and exports” which translated in $7 billion dollars in lost sales.
He cited the “cumbersome environmental processes under the previous state government” as having prevented the opportunity to pump out the pits while local rivers and streams flowed strongly, resulting in mines still holding around 250 to 300 gigalitres of water. some 19 months later.
The QRC is seeking a transition program from the state government to start shifting water this wet season and over subsequent wet seasons. According to Roche, “this is not about compromising environmental standards, but taking advantage of the heavy rainfall that nature traditionally throws at central and north Queensland over summer. In this case, dilution is the solution.”
Coal companies are reportedly investing strongly in preparation for the wet season including the construction of additional on-site water storages, pipelines, pumps and water treatment plant.
Reliable, long-term supply of drinking water.
As one of the world’s largest artificial islands, “Palm Jumeirah” in Dubai must rely on high performance pumps to meet its enormous demand for drinking water. The developers of this highly ambitious project put their trust in KSB to provide solutions which are extremely energy-efficient and easy to maintain. HGM – RO high pressure and Omega water transport pumps from KSB help to reliably produce 32,000 m3 of pure water every day and keep life cycle costs as low as possible. KSB is one of the world’s leading manufactures of pumps, valves and systems.
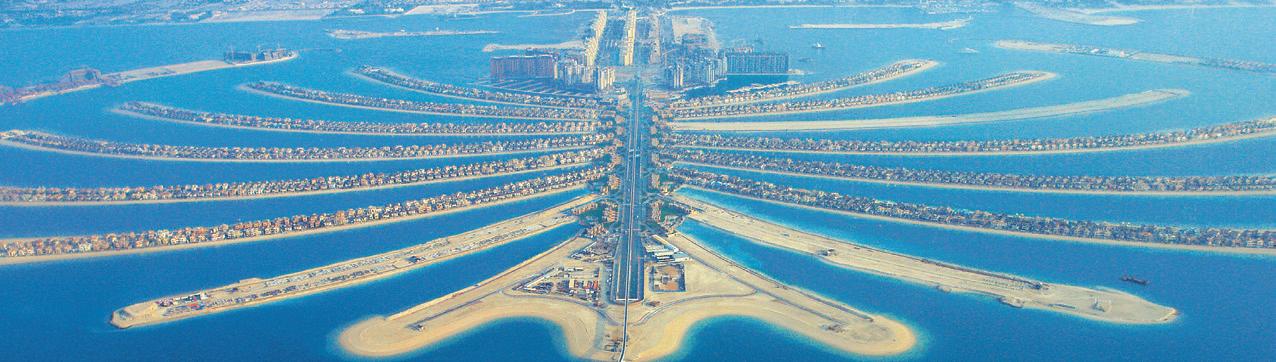

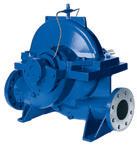
Franklin Electric acquires Cerus Industrial
Franklin Electric Co has acquired Cerus Industrial Inc. Based in Oregon, USA, Cerus designs, manufactures, and distributes motor controls, motor starters, contactors, protection devices, and variable frequency drives to a wide range of distributor and original equipment manufacturers in North America who serve three primary markets: HVAC, industrial motor sales and service, and pumping systems. Founded in 2003, Cerus has 65 employees and totalled $US14 million in sales last year.
Scott Trumbull, Franklin Chairman and Chief Executive Officer, said, “Cerus has deep technical and manufacturing strengths in several areas that are of strategic interest to Franklin Electric including variable frequency drives, starters, and control panels.
“The demand for electronic drives and controls for pumping applications is growing rapidly because these devices allow our customers to reduce energy cost, increase system life, and manage system parameters such as pressure and flow. While Franklin has been a leader in applying drive and control technologies to groundwater pumping systems, we believe that the Cerus acquisition will enable us to further accelerate our growth by increasing our technical and product development capacity, broadening our
product line, reducing our manufacturing costs and moving us into adjacent market areas.”
World’s largest lumping station planned for Abu Dhabi
Abu Dhabi Sewerage Services Company (ADSSC) is constructing what is expected to be the world’s largest pumping station. Located in the Emirate of Abu Dhabi, United Arab Emirates, the pumping station will be over 100m deep and approximately 40m in diameter and will have an ultimate peak pumping capacity of approximately 3.3 million cubic metres per day.
ADSSC is the service provider for sewerage services and currently owns and operates the sewerage network and treatment plants throughout the Emirate of Abu Dhabi. To address projected growth within the Emirate, ADSSC has developed a comprehensive plan to increase system capacity. The cornerstone of this plan is the Strategic Tunnel Enhancement Programme (STEP).
Mott MacDonald has been appointed by ADSSC to provide contract administration and site overview services for the development of one of the world’s largest underground pumping stations.
The focus of STEP is a deep 41km long tunnel sewer and several systems of link sewers which will collect and transport wastewater to a main pumping station for onward treatment at the Al Wathba
Independent Sewage Treatment Plants (ISPTs). The link sewers will intercept the flows from existing gravity sewers upstream of the existing pumping stations, both on Abu Dhabi Island and the mainland. These flows will be channelled by gravity into the deep tunnel. At the downstream end of the deep tunnel, in the AI Wathba area, an underground pumping station will be built to lift the sewage to the surface, and into newly constructed ISTPs.
The pumping station will be housed in a large deep structure at one end of the tunnel. The facility will also accommodate electrical and power generation facilities, operations and maintenance facilities, standby power fuel storage and pumping and a flow distribution facility.
Mott MacDonald will undertake the role of engineer for the contract administration and construction oversight. This will involve project, design, cost, contract and health, safety and environment management.
Peter Hall, Mott MacDonald’s project director said,“the UAE is the third largest consumer of water in the world after Canada and the USA. There is a daily water consumption rate of nearly 550 litres per person in a region that receives less than 1cm of rain per year. Therefore, management and reuse of wastewater is a critical component to Abu Dhabi’s longterm sustainability.”
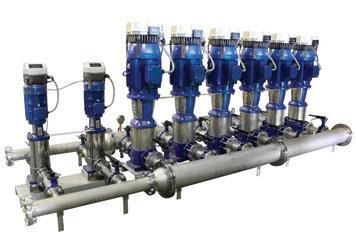
• Motor or wall mountable
• Fully programmable on site
• Software specifically designed for pump operation, control and protection
• High level hardware design
• More flexibility and cost savings
• Energy savings up to 70%
• Simple mounting “clip and work”
• Multi-pump capability up to 8 pumps

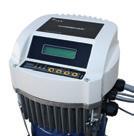
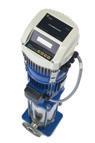
Monitoring of Yallourn Mine water continues
The EPA continues to monitor the flood waters being pumped from the Yallourn Mine, with early results indicating there have been no harmful levels of contaminants such as heavy metals or hydrocarbon.
TRUenergy’s Yallourn Mine in the Latrobe Valley was flooded on June 6 this year after the collapse of an artificial river bank constructed to carry the Morwell River across the middle of the mine. The flooding limited the operation of Yallourn power station that generates 22 per cent of Victoria’s electricity. TRUenergy applied to EPA for emergency approval to pump flood water from the mine.
In an emergency, a company can apply to EPA for approval to discharge waste to the environment. EPA may grant its approval if the company can demonstrate that the discharge will not cause any long-term negative impacts on the environment. An emergency discharge approval can only be issued for 120 days, after this time, the company must reapply for approval to discharge.
The discharge approval granted to TRUenergy requires the company to monitor the impact of the discharge on the river using an independent laboratory with a

NATA accreditation (National Association of Testing Authorities) to take and test the samples.
The results do indicate the discharge of water from the mine has increased turbidity levels (cloudiness due to silt) in the Latrobe River and there have been traces of some naturally occurring compounds, such as iron.




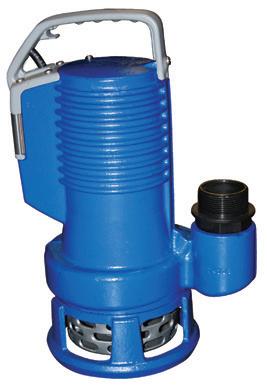

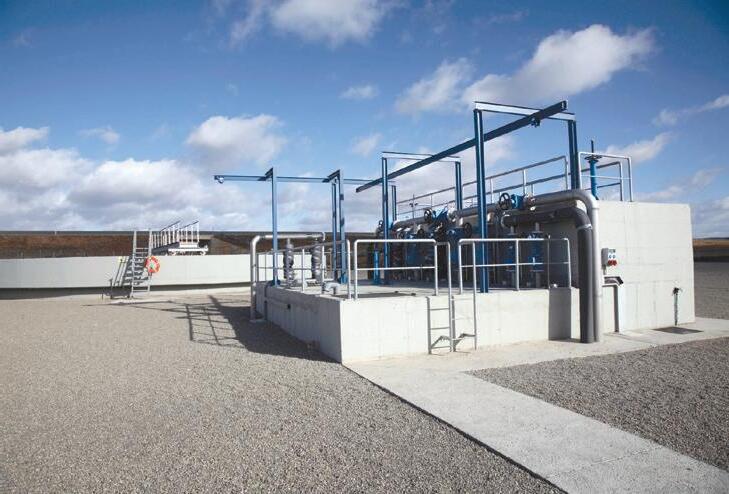


Zenit ECO pumps have been approved for Class 1 Zone 2 hazardous areas since 1998.






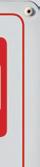

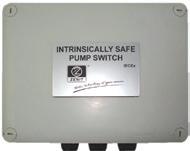
Due to regulatory changes in 2008 regarding certification standards, both White International and ZENIT have obtained the higher international standard IECEx, rather than only the ANZEx certification applied for in the past.

PIA Events
Event Calendar Opportunities in the resource sector
PIA held a successful seminar in Brisbane on August 29 which focused on pumping equipment for the resource sector.
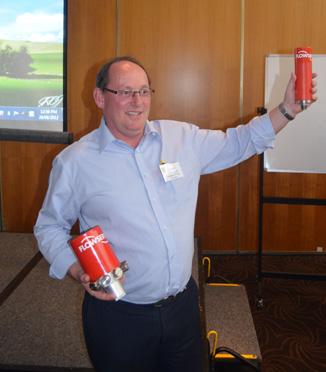
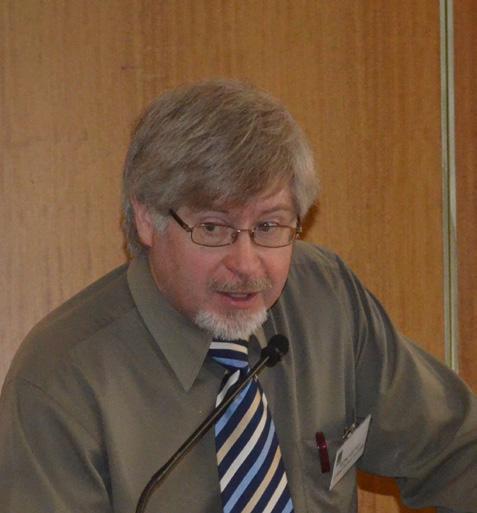

The program was chaired by PIA Vice President Ron Astall, and included a range of pump companies and endusers presenting papers on the latest applications in pump technology in the resources sector.
The day opened with a presentations from Frank Passmore from Fire by Design discussing maintenance of fire pumps in remote locations. Gareth Munro of Weir Minerals demonstrated how operational costs of slurry pumping could be reduced and Jeremy Tuerlings of Flowseve demonstrated the latest monitoring equipment for pumps.
The afternoon included an interesting look at permanent magnet motors from
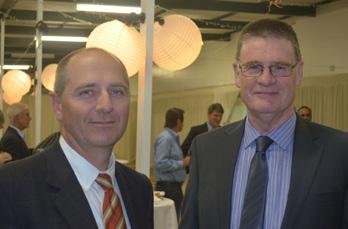
Rajan Tulasi at ABB, as well as a look at using model motor analysis to monitor driven machine condition from Mike Davis of Machine Monitor, a division of GE Energy. The day was rounded out with Marty Williams of BP Kwinana discussing pump reliability improvements and Andrew Nicolin from John Crane looking at diamond faces for mechanical seals.
The seminar followed the PIA General Meeting on the previous day, also held in Brisbane. The General Meeting included an address from Dugald Anthony from Austrade and export opportunities and support and a presentation from Ivan Hernandez from Frost & Sullivan about pump industry statistics. The general meeting was followed by casual drinks.
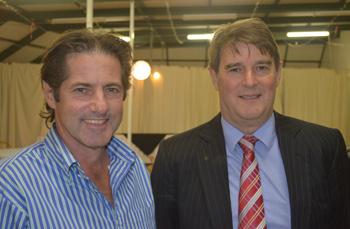
PIA Seminar and Exhibition
Whitehorse Centre, Whitehorse Rd, Nunawading,VIC
Tuesday & Wednesday, 9- 10 October, 2012
PIA Annual General Meeting & Dinner
Graduate House, University of Melbourne, Parkville, VIC Thursday, November 22, 2012
For more information or to register for PIA events, visit pumps.asn.au or email pumpsaustralia@bigpond.com
Other Events
All Energy
Melbourne 10-11 October, 2012 www.all-energy.com.au
Australian Pipeline Industry Assoc. (APIA)
Brisbane 13-16 October, www.apia.net.au/events
Fire Australia
Melbourne 14-16 November, 2012 www.fpaa.com.au/events/
2013
Australasian Oil & Gas (AOG)
Perth 20-22 February, 2013 www.aogexpo.com.au
OzWater
Perth 7-9 May 2013 www.ozwater.org
National Manufacturing Week
Melbourne 7-10 May 2013
www.nationalmanufacturingweek.com.au
APPEA
Brisbane 26-29 May, 2013 www.appea.com.au
Auspack Plus
Sydney 7 - 10 May 2013 www.auspackplus.com.au
Meet the pump people
Pump Industry Australia is pleased to invite pump users, consulting engineers, university and TAFE students to attend our exhibition & seminar program to be held at the Whitehorse Centre, Nunawading, Victoria on 9 & 10 October 2012.
The Exhibition will feature some of Australia leading Pump Suppliers and will focus on SME’s with particular expertise in applications and technologies that are leading edge. Many of us need to use our time wisely these days and this is an opportunity
When, where and how?
Tuesday 9 October - Exhibition trade day and seminar (advance registration required) 9:30am - 5pm
Wednesday 10 October - Exhibition open to trade and public, 9:30am4pm
The Whitehorse Centre, 397 Maroondah Highway Nunawading, VIC (At rear of Civic Centre)
The venue is within easy reach of the Eastern Freeway and there is ample free parking available
Register at www.pumps.asn.au
to“meet and learn” from some of Australia’s most experienced Pump People.
The Exhibition will be conducted in a relaxed atmosphere and will lead in to 6 stimulating seminars that will help to explain the black art of Pump Technology. Attend one that is of particular interest to
you or register for all, if you wish.
The general theme will be “environmental protection and energy efficiency”, but with pumps as the main focus of attention.
Seating will be provided for up to 60 participants and there will be time for Q&A. Register now to ensure you have a seat!
Seminar program - Tuesday October 9
Time Topic Presenter
10.00 – 10.30 Are you running your pumps too slowly?
11.00 – 11.30 ErP directive on MEPS for pumps in Europe
12.00 – 12.30 MEPS for Pumps in Australia
1.00 – 1.30 Developments in small pumping systems
2.00 – 2.30 Innovative vacuum pumping systems
3.00 –3.30 VSD’s in pumping systems
Ron Astall, Astech
David Kerridge, Wilo Australia
Ian McNicol, Sustainability Victoria
Ashley White, Davey Water Products
David Hobson, Emtivac Engineering
Bou Spithoven, CAP Industries
Join Pump Industry Australia
There are many worthwhile benefits you’ll receive from becoming a member of Pump Industry Australia Incorporated. Membership of the Association is available to the following types of persons or organisations:-
Member Qualifications
• Pump manufacturers.
• Pump importers
• Pump wholesalers
• Pump retailers
• Pump repairs & maintenance
• Pump consultants
• Pump training or education
• Suppliers to the pump industry
Membership Benefits
• Regular general meetings held at a members’ facilities provide the

opportunity to see different aspects of the industry, and to formally discuss current market conditions and other issues.
• Occasional Technical Seminars with presentations by specialists on the latest technology in pumping equipment and systems.
• Informal networking within the association with customers, suppliers and competitors.
• Discounts off retail prices when purchasing PIA publications.
• Annual Dinner with partners and guests.
• Opportunity to lobby government on issues important to the Industry.
• Discussion groups on marketing, statistics and training.
Annual Membership Fees
• Private Member $80 + GST
• Company Member less than 10 employees $150 + GST
• Associate Member (for large companies who are not participating directly in the pump industry however do have a strong interest in the industry eg. a motor supplier $250 + GST
• Company member (10 to 25 employees) $300 + GST
• Company member (25 to 100 employees) $600 + GST
• Company member (over 100 employees) $1,200 + GST
Celebrating 50 years of service to the industry
October 2012 marks 50 years since Acromet was founded, we take this opportunity to speak to General Manager Keith Gardner.
Congratulations on reaching 50 years - how did Acromet get started?
Acromet (Aust) Pty Ltd commenced operations in October of 1962 as a wholly Australian-owned company with Australian distribution agreements for American and Canadian equipment for the water supply and treatment industries. The initial product range specialised in gaseous Chlorination and Metering Pump Chemical feeding equipment.
How innovative were Acromet’s products at the time?
At this time, Acromet was the first company to introduce the then unique All Vacuum Chlorination system into the Australian market – a system now adopted by all major manufacturers.
Our beginnings were based on innovative equipment for its time, designed by our founder who has a passion for providing robust and reliable products with the highest accuracy possible.
What have been some of the key turning points in the company’s history?
In 1969 Acromet increased its expansion in the industrial market with the introduction of an All Australian designed and manufactured range of Diaphragm and Plunger Metering Pumps and accessories. This range of pumps, known as the 900 Series, became the chemical metering work-horse for many industries throughout the late 1960’s, 1970’s and early 1980’s where some are still in operation today.
During this early period, the company also established a technically strong engineering division, responsible for the introduction of newly developed process pump technology into the general and Petro-Chemical industries.
The product range was further extended with the addition of Electro-magnetic Metering Pumps, Gear Pumps and Motor Driven Sealless and Specialized Centrifugal Pumps.
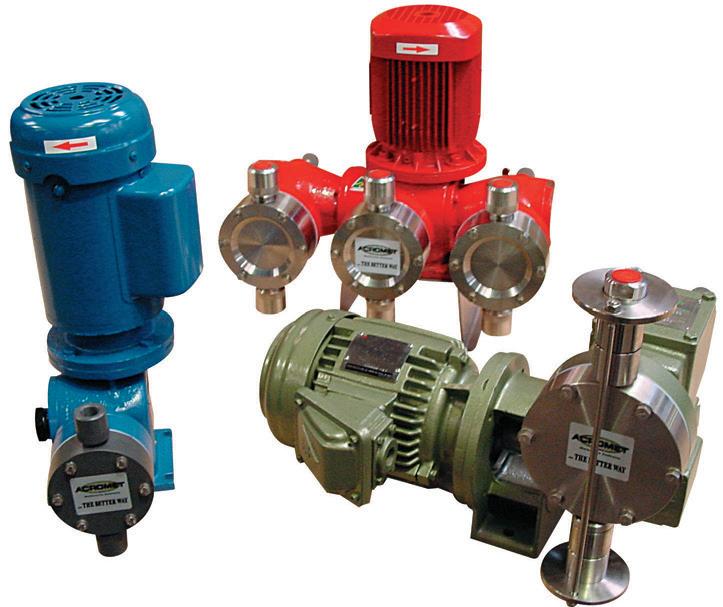
In 1982, after considerable investment in design and development, the company released a range of Dry Material Feeders that now cater for an extensive market in the Bulk Materials Handling industries.
During this period the 900 Series metering pumps were redesigned to incorporate a wider range in the performance envelope that increased the number of liquid heads that could be fitted to a single unit. The new pump was released in 1983 as the Acromet 3000 Series that has become a dominant player in the market and remains in production today at our Clayton, Victoria manufacturing facility.
What happened once the 900 series was discontinued?
Although 900 Series metering pumps were discontinued from production, our spare parts, factory service and repair support were maintained for 17 years. This philosophy is rarely seen in the industry today, yet still continues with all our manufactured products. This level of commitment is one of the reasons that Acromet is the only Australian manufacturer of metering pumps. This has
assisted us with the expansion of our extensive and satisfied customers around the world who use our Australian-made products.
What hasn’t changed over the years?
Throughout the years, product design and development has always been a priority on Acromet’s agenda with further development culminating in the release of the Acromet robust 2000 and 2500 Series metering pump along with the Acroflex flexible dry powder screw conveyor and our expansion into the Bulk Materials Handling systems. This principle continues our founder’s philosophy of a robust, reliable and accurate range of metering equipment.
In 2012 Acromet remains a fully Australian-owned and operated business proudly celebrating its fiftieth year of operation. The momentum of growth has been maintained in the past decade with a continuing emphasis on new product design and development positioning Acromet as a leading Australian manufacturer of Metering Pumps and Dry Material Feeders.
Balance matters
Imbalance of rotating components is one of the most common sources of machine faults in rotating assemblies, pumps and fans and is a major cause of complete equipment failure. Most people’s awareness of balancing is limited to knowing a car’s wheels and tyres that must be balanced, to avoid steering-wheel shudder and uneven tyre wear.
Equipment failures can have dramatic impact on a plant’s production and manufacturing commitments. If there is a grumble or a groan, a banging or shaking, or if things just don’t seem right it may be time to get it checked out. This can be critical especially as up to half of electric motor breakdowns are caused by damaged bearings, due mostly to the vibration occurred by the rotor’s imbalance.
Industrial balancing and vibration analysis on rotating machinery enables the early detection of faults before breakdown, and assists commercial and industrial facilities reduce their maintenance costs and unscheduled downtime. Dynamic Balancing of this rotating equipment offers many benefits, including:
• Increasing equipment’s performance and longevity, ensures optimum performance of machinery
• Improves running conditions to reduce ongoing maintenance costs and maximise return on investment, improving equipment operating costs and economy
• Lengthens service life. Bearings, suspensions, housings and foundations can be subjected to very high stresses caused by vibration resulting from unbalance and these result in greater wear.
• Products with unbalanced parts often have a shorter service life.
• Decreasing breakdowns and unscheduled downtime. Vibrations can reduce the frictional grip of screwed and clamped connections. Electric switches can be destroyed by vibration, pipes and cables can fracture at the connections.
• Reduces chances of equipment failure, vibration and imbalance can lead to catastrophic failure.
Note in these photographs the damage imbalance can cause.
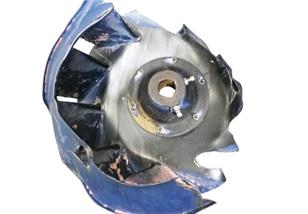

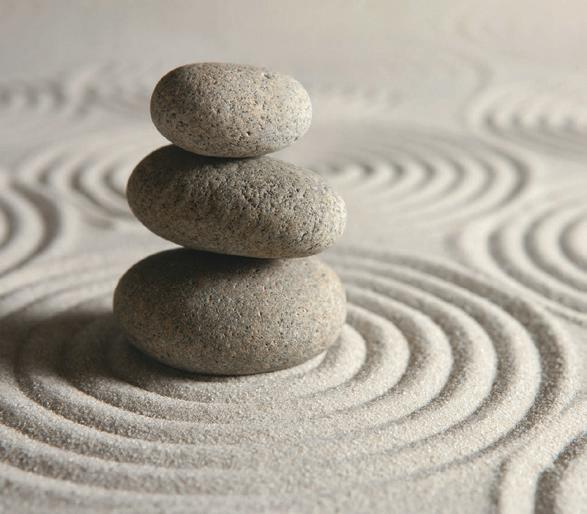
Industrial balancing is the procedure where the mass distribution of a product, be it a pump, roller, impeller or the like, is accurately measured and suitably adjusted. This will ensure that the forces on the bearings, at a frequency corresponding to the devices operational speed, are within limits as specified in International Standards, such as ISO 1940-1:2003 Mechanical vibration (Balance quality requirements for rotors in a constant rigid state).
Precision Balancing has been offering in house and on site dynamic balancing and vibration analysis services since 1989 and have the equipment, skills and experience to satisfy your industrial balancing requirements. Owned and operated by qualified mechanical engineers, members of the Australian Institution of Engineers, with years of experience in mechanical engineering and industrial balancing. Precision Balancing has been offering a range of specialised balancing services for pump impellers since the company began, and has worked on a huge range of models and sizes. Precision Balancing offer personalised service including on site balancing, and quick turnaround or emergency after hours breakdown services. For more information on how industrial balancing can help you in achieving machine harmony visit www.precisionbalancing.com.au.
An efficient future for pumps and fans
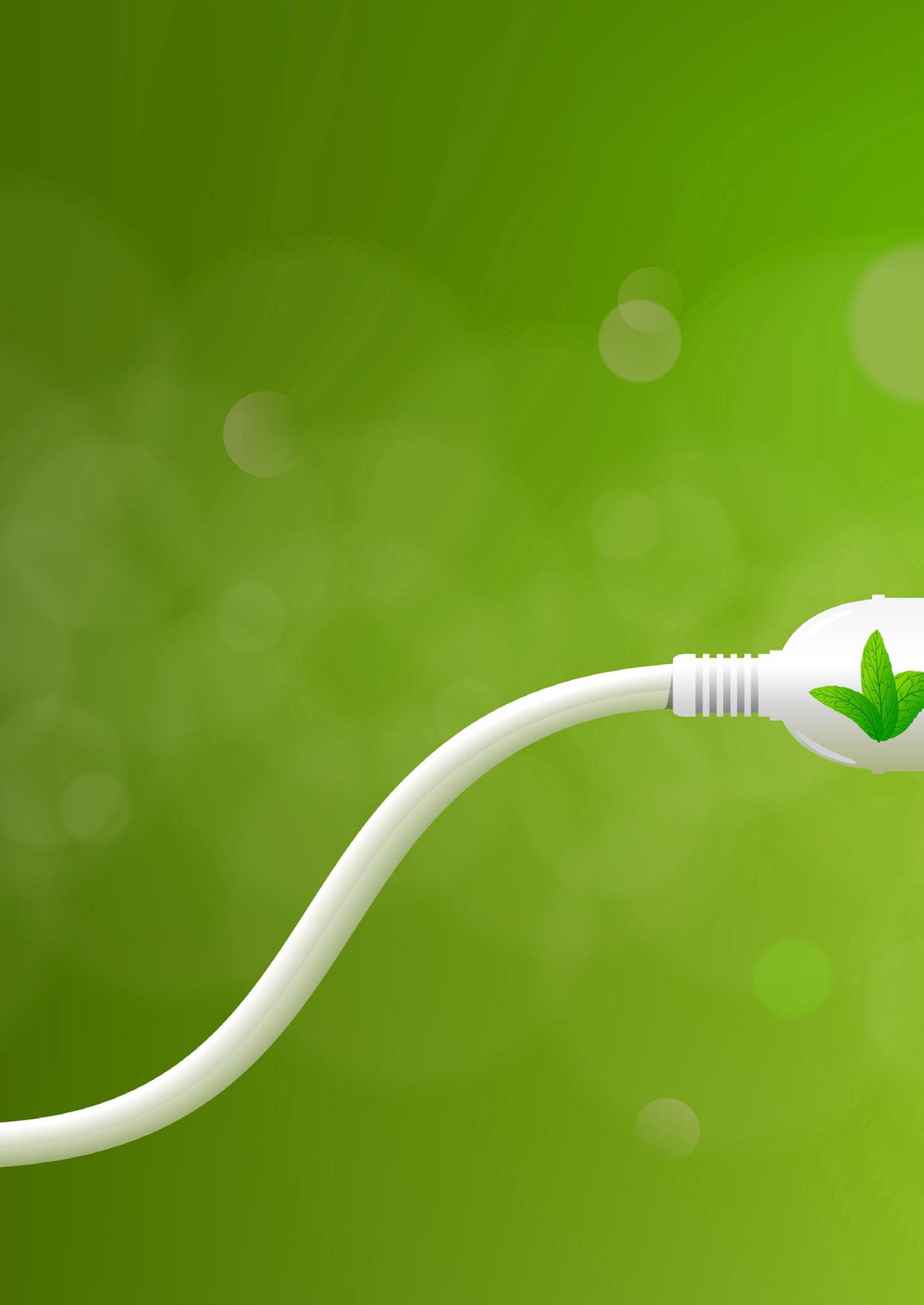
Fans and pumps used in the commercial, manufacturing and mining sectors are a very significant source of energy use and greenhouse emissions. The Pump Industry Association and the Fan Manufacturers Association of Australia and New Zealand have been working with Sustainability Victoria to improve standards.
The energy used by pumps and fans is a significant part of total energy consumption as the below figures demonstrate, and this consumption is expected to increase.
The International Energy Agency (IEA) estimates that there is the potential to achieve across the board savings of 20 to 25% from ‘motor systems. This translates to around $1 billion in energy bill savings for pump and fan systems.
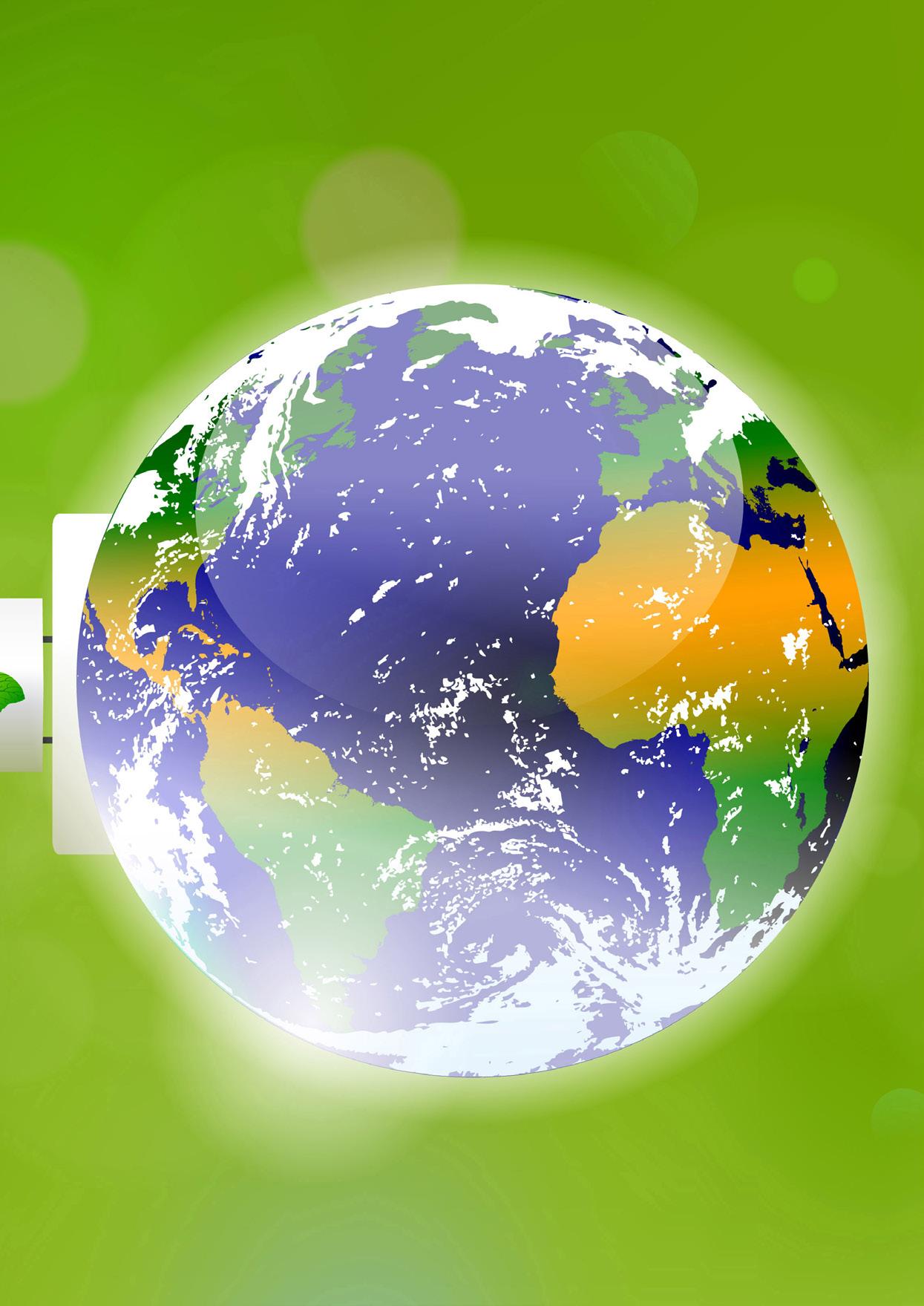
A number of key approaches can be taken, including the correct sizing of motors to match load requirements, use of variable speed drives where the load is variable, use of high efficiency components such as motors, couplings and end-use equipment. Optimisation of downstream distribution system, and elimination of losses and leaks as well as proper maintenance and repair all can contribute as well.
Barriers to saving energy
Of course, there are many barriers to achieving this. Firstly there are split incentives, such as the party which specifies the equipment is not directly responsible for paying the energy bills. Additionally, risk minimisation in the supply chain can mean like is replaced with like, or standard equipment is specified. A lack of information may also exist where equipment is not ‘energy rated’.
Further, the availability of information is not always enough. Energy costs are small percentage of total business costs and energy is not a ‘core business’, the focus is often on keeping the production line going, and on upfront cost and not lifecycle cost.
Energy costs can be a significant proportion of lifetime operating costs; up to 85 per cent for pump systems and 67 per cent for fan systems. Paying more upfront for a more efficient system can be a classic “win – win” situation for both the end use customer and the supplier
Energy efficiency regulations
In Australia, the Equipment Energy Efficiency (E3) Program coordinates the regulation of appliance and equipment energy efficiency. The main policy tools are Minimum Energy Performance Standards (MEPS) and Energy Labelling. They currently regulate around 20 types of equipment for MEPS and seven appliances for labelling

Industrial equipment
Regulation is expanding into industrial equipment. 3-Phase electric motors (0.75 to 185 kW) have been subject to MEPS since 2001. In July 2009, COAG agreed to implement the National Strategy for Energy Efficiency (NSEE). Measure 2.2.1 called for the expansion of MEPS significantly into the industrial sector to cover off-the-shelf products. A discussion paper on Industrial Equipment was released in September 2010 which identified pumps, fans and boilers as a key priority.
Key international developments
The EU’s Framework Directive on EcoDesign of Energy Using Products (2005) has been progressing work in four areas relevant to motor systems; electric motors, water pumps, circulator pumps in buildings and ventilation fans.
Forthcoming EU Regulations will commence for pumps in 2012 and be made more stringent in 2014. It covers
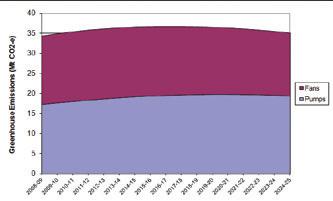
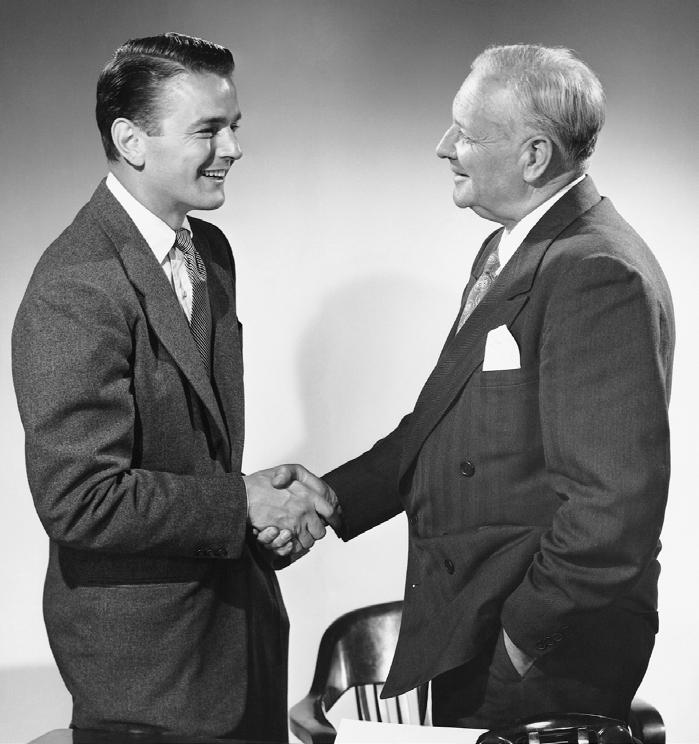
clean cold water pumps (0.75 kW to 150 kW) and building circulator pumps. ISO9906 sets the test standard. Similar regulations for fans are also being implemented in the EU.
Australian developments
Since the PIA workshop on pumps in 2011, work on both non-domestic fans and non-domestic pumps has proceeded, although the work on fans has been given a higher priority. A Product Profile Discussion Paper on Non-Domestic Fans was publicly released by the E3 Committee in May 2012, and consultation workshops held for industry stakeholders in both Melbourne and Auckland. Comments on this Product Profile have now closed, and the E3 Committee will consider the responses before deciding on a way forward.
A Product Profile on Non-Domestic Pumps is in the final stages of preparation and is expected to be released for public consultation by October 2012. The Profile will look at the markets for pumps in both Australia and New Zealand, will look at what is happening internationally to improve the efficiency of new pumps sold, and will consider a range of options which could be implemented in Australia and New Zealand to drive improvements into the efficiency of new pumps. As with
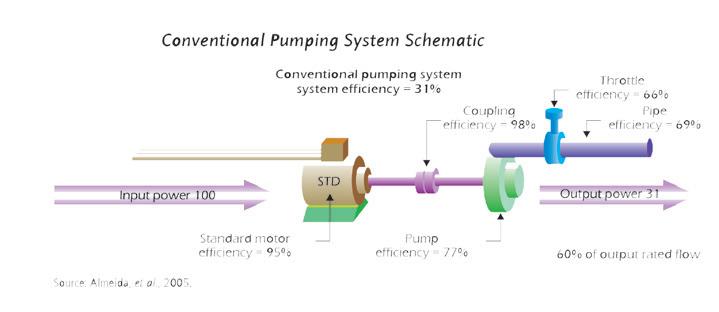
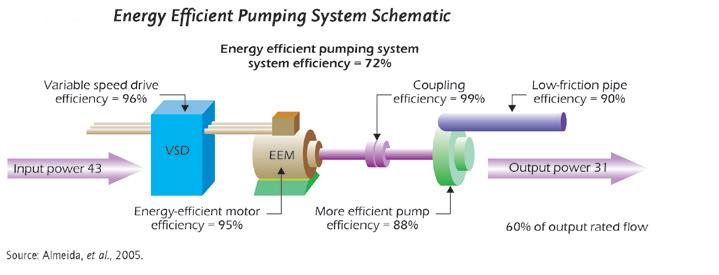
The above figures show how pump systems efficiency can be increased from 31 per cent to 72 per cent.
the fan profile, it is likely that consultation workshops will be held in both Australia and New Zealand to discuss the Profile with interested stakeholders and written submission on the Profile will also be considered.
An efficient future?
Electricity prices will continue to increase in real terms; generation and distribution costs are the key driver and the implementation of the carbon tax will add to this. Energy costs account for the majority of lifetime operating costs. Any future MEPS regulations will drive some improvements to the new pumps and fans installed, but much bigger savings are possible. Upgrading the efficiency of pump and fan systems is a “win-win” situation for end users and suppliers.
More information
If any pump industry stakeholders have questions concerning the E3 Committee’s work on non-domestic pumps, they should contact Ian McNicol at Sustainability Victoria on (03) 8626 8772. Ian is leading the non-domestic pump work on behalf of the E3 Committee.

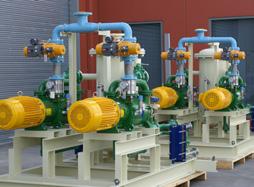
Optimise overhauls of pumps to save energy
Ray Beebe, DipMechE, MEngSc, FIEAust, CPEng(ret)Pumps are arguably the most common machine in power and process industry, and major consumers of energy, yet relatively little information is available on the application of predictive maintenance/condition monitoring to them. When deterioration in performance of a centrifugal pump causes a drop in plant production, overhaul is readily justified, as its cost is usually small in proportion. When the effect of deterioration is only to increase power consumption, the time to overhaul for minimum cost can be calculated from test results. This article describes some basic condition monitoring tests for pumps, and how to use these condition monitoring methods to estimate the increased power consumption caused by pump wear.
The extent and effects of internal wear in centrifugal pumps vary with the nature of the liquid pumped, the pump type and its operating duty. Some pumps last for years, others for only months.
Overhauling of pumps on a fixed time or breakdown basis is rarely the most costeffective policy. Use of condition monitoring ensures that pump overhauls to restore performance are performed when they are really necessary. There may of course be other factors to consider, such as field or OEM experience. However, despite the many excellent pump textbooks until recently there was little information available on how to apply conditionbased maintenance to pumps (ANSI/HI, 2000 and Beebe, 2004).
Monitoring methods should be chosen where justified that will detect each of the degradation modes which are experienced or expected:
• Vibration monitoring and analysis (probably the most widely applied method of condition monitoring for rotating machines in general, and suited to detect such faults as unbalance, misalignment, looseness),
• Sampling and analysis of lubricants for deterioration and wear debris (relevant for bearings/lubrication system faults),
• Electrical plant tests (relevant for motor condition),
• Visual inspection and Non-Destructive Testing (particularly relevant for casing wear),
• Performance monitoring and analysis (relevant for pump internal condition).
For critical machines, more than one method of condition monitoring may be justified. This Note will demonstrate use of performance analysis with some examples of condition monitoring in practice.
An understanding of basic pump performance characteristics is assumed, as is how to measure test data repeatably, as for condition monitoring, repeatability is more important than absolute accuracy.
The Head-Flow method shows pump wear
The most useful condition monitoring method is by Head-Flow measurement, because as well as pump deterioration, it detects any changes in system resistance. The method can be used for all pumps where flow, or a repeatable indicator of it, can be measured
Throttling the pump to obtain points over the full flow range is not necessary for monitoring. Some points near the normal operating duty point are sufficient to reveal the effects of wear, usually shown by the head-flow curve moving towards the zero flow axis by an amount equal to the internal leakage flow. (See “Test points-worn pump” on Figure 3).
A series of test readings at steady conditions at about 15 second intervals is sufficient, taking the average values to plot. Speed must also be measured for variable speed pumps, and the head-flow data corrected to a standard speed using the affinity laws.
Field tests sometimes give results slightly different from the manufacturer’s works tests because site conditions for flow and pressure measurement are rarely available as required by the various Standards for pump testing. However, note again that for monitoring it is relative changes we are seeking rather than absolute accuracy.
Non-intrusive ultrasonic flowmeters are applicable in many cases. A permanent flowmeter installed as part of a pump’s minimum flow protection or for process measurement can be used, provided its long-term condition is considered to be constant, or it can be inspected regularly.
Figure 1 shows the trend in degradation of two pumps over some years. Wear amplitude is expressed at duty point flow as the percentage reduction in Total Head compared with the new datum condition. This is usually derived from Head-Flow tests near duty point, but can also be obtained using the shut-off head test where this is allowable.
Where a plant has a DCS, then regular interrogation of the plant historian can be used, as shown for the multistage boiler feed pump in Figure 1. Data points are extracted each six months from a run of ten days at steady load. (Constant speed pump, 4 stage, 5853 r/min, 5744kW, 171kg/s @20.4MPa)
Such performance information can show the extent to which a pump has deteriorated, and pumps can be prioritised for
overhaul on the basis of their relative wear. But, is the overhaul of the worst pump justified economically? A method for helping this decision is given later.

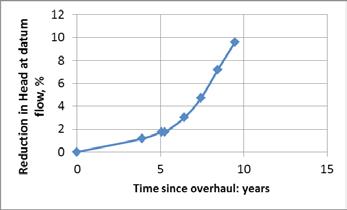
Figure 1: Degradation of pumps shown by Head-Flow testing (top) 230kW, (bottom) 5744kW
The shut-off head method for PdM of pumps
Measuring the Head at zero flow is a simple test. It is only possible where it can be tolerated, which is not so for high energy pumps nor for pumps of high specific speed where the power at shutoff is greater than that at duty point. Some pumps have exploded from built-up pressure when left running at zero flow!
With the discharge valve closed fully for no longer than 30 seconds or so, suction and discharge pressures are read when steady. The liquid temperature is also needed to find the density, which is used to convert the pressure readings into head values.
Wear of vane outer diameters will show readily, as the head-flow curve of a worn pump moves towards the zero flow axis. To show sealing ring wear, the pump head/flow curve needs to be relatively steep. (Note that if the pump has a rising curve, internal leakage will initially give an increase in shutoff head).
The thermodynamic method for PdM of pumps
Another method of pump monitoring is to measure the temperature rise of the liquid through the pump. This reflects the inefficiency of the pump. As the differential temperature is very small,
great care is required to measure it. Any effects of recirculation at pump inlet and outlet must be eliminated, and tests are not possible at very low flows or zero flow. The efficiency can be calculated from the measured data of inlet temperature, differential temperature and head. Comparisons if it changes with time can be made on plots of Efficiency vs Head. For high head pumps, an allowance must be made for the isentropic temperature rise which occurs as a result of pressure increase (Beebe, 2004).
Commercially available devices are widely used, especially in the water industry (Robertson, 2007). Tappings at suction and discharge are required to be two diameters away from pump flanges, for the installation of pressure/ temperature probes. Tong-type detectors are placed to measure motor power.
Pump efficiency is then found from the precise measurement of the head and temperature rise through the pump. From assessment of motor losses, the power absorbed by the pump is computed. From all this data, the pump flow can be found.
For condition monitoring, tests at around normal operating point are usually sufficient. The thermodynamic method would be more attractive economically if no special tapping points were required. Research at Monash University on high head pumps using special semi-conductor temperature probes on the outside surface of the piping, covered with insulation, gave usable results, provided the pump is allowed to run at steady operation conditions for 30 minutes in order for the piping temperature to stabilise (Beebe, 2002).
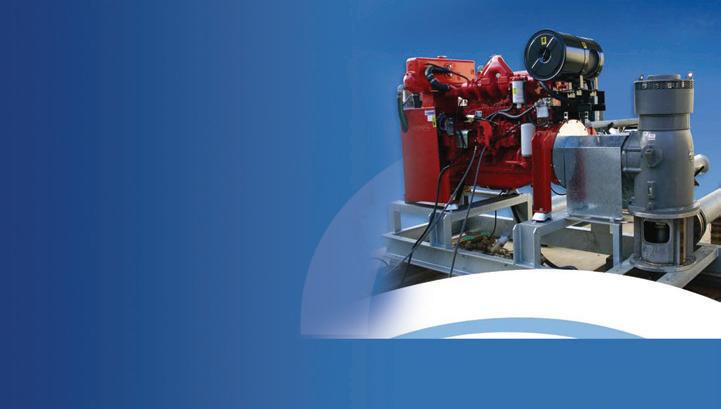
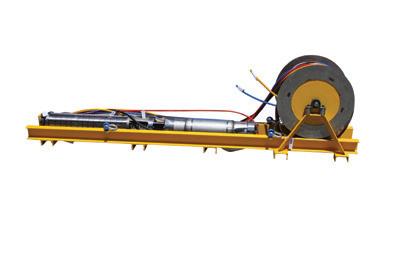

Percentage efficiency for pumps on water at up to 54°C is given by this empirical formula, which includes a correction for the isentropic temperature rise (Total Head is in kPa, temperatures in °C) (Whillier, 1972)
Measurement of balance flow for PdM of pumps
Multi-stage pumps with the impellers facing in the one direction usually have a balance disc or drum arranged such that final stage discharge pressure counteracts the axial thrust on the shaft line. Another method for condition monitoring is to measure the leakoff from the balance device (Karassik, 2001). The basis is that if there is increased wear in the annular space to the balance device which is evident from increased leakoff flow, then the interstage clearances are also worn. As the leakoff line is quite small compared to the pump main flow piping, a permanent flowmeter is relatively inexpensive.
At one power station, for some years overhauls have been scheduled on this basis on some boiler feed pumps. Flows are read manually, and trends plotted using a database program (Figure 2). Note that here the balance flow of 15 L/s corresponds to about 10 per cent of the duty flow, and consumes about 250kW of extra power. When added to the likely internal recirculation, this would mean an even larger proportion of the power absorbed being wasted. These pumps are variable speed and other tests show that the measured flows must be corrected in direct proportion to the speed.
On a set of pumps of another design elsewhere, both head-flow and balance flow were measured for some years, but no correlation was found between the two.
On yet another pump type, of 11 stages, the head-flow performance was tested as well below the datum curve. As the pump was dismantled, measurements showed that the interstage clearances were not worn. A condition monitoring credibility crisis was averted when the balance seat area was reached and found to be severely eroded from water leaking past the valve seat. Balance flow had obviously been very high. For the best monitoring, it is therefore considered that both head-flow and balance flow should be measured, particularly if the balance area can be separately dismantled in the field.

Figure 2: Condition monitoring of a high energy multi-stage pump by measurement of balance device leakoff flow. (Note: flows are corrected to a standard pump speed)
How to calculate the optimum time for overhaul
The most economic time to restore lost performance by overhaul will vary with the circumstances.
If the deterioration is constant over time, then a cash flow analysis can be done to ensure that the investment in overhaul will give the required rate of return. This is the same process as used in deciding on any investment in plant improvement.
If the deterioration rate is increasing with time, then the optimum time for overhaul will be when the accumulated cost of the increased electricity consumption equals the cost of the overhaul.
The method is now described for some of the situations which occur.
Pump deterioration results in a reduction in plant production
Where the cost of overhaul is insignificant in proportion to the cost of lost production, prompt overhaul is usually simply justified at a convenient “window”.
Pump which runs intermittently to meet a demand
In a pumping installation such as topping up a water supply tank or pumping out, deterioration will result in the pump taking more time to do its duty. The extra service time required therefore results in increased power consumption which can be related to the cost of overhaul.
Pump deterioration does not affect plant production, at least initially: constant speed, throttle valve controlled pump
The internal wear does not cause any loss in production from the plant, as the control valve opens more fully to ensure that pump output is maintained. Eventually, as wear progresses, pump output may be insufficient to avoid loss of production, or the power taken will exceed the motor rating.
Figure 3 shows the Head-Power-Flow site test characteristics of such a pump. Its output is controlled using a throttle control valve. The duty flow is 800 m³/h, and the duty point in the new condition is A. The power absorbed by the pump is read off the Power-Flow curve as 2150kW: B. The power-flow curve should ideally be found on site, but the works tests information may have to suffice.
After some service, the “Test points -worn pump” plotted indicate that internal wear has occurred. When worn to this extent, the operating point moves to C, as the system resistance curve lowers when the throttle valve is opened further.
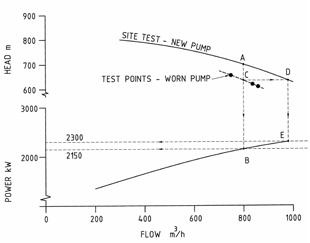
Figure 3: Head-flow-power characteristics of new pump, and head-flow points from worn pump.
The increased power required in the worn condition can be estimated by extending from the Head-Flow curve at constant head from the operating point to D, and then dropping to intersect the Power-Flow curve for new condition at constant flow: E. Follow the arrowed line in Figure 3. This assumes that the original curve still represents the flow through the impellers, of which less is leaving the pump to the system due to internal wear. (If the pump was motor-driven, the actual power may be able to be measured on test at extra expense).
In our example, the power required for this duty in the worn condition is shown in Figure 3 by the projection from the duty flow of 8003/h to the test curve to find 640m head, then across to the “Site test - new pump” curve, then down to the power curve, to find 2300 kW.
The extra electricity consumption is therefore 2300 - 2150 = 150kW ÷ motor efficiency (here it is 90%), to obtain 167kW.
If the sealing clearances are known, by previous experience of correlation with measured performance, or if the pump is opened up already, the extra power consumed likely to be saved by overhaul can be estimated (Stepanoff, 1957, and HI).
Finding the optimum time for overhaul from Head-Flow data
For this example, the test points were obtained following 24 months of service since the pump was known to be in new condition; an overhaul would cost $50,000; electricity costs 10c/kWh; and the pump is in service for 27 per cent of the time on average. The increased power consumption is estimated at 167kW (motor efficiency included).
Our test shows that the rate of increasing cost/month has reached 167 × 0.10 × 0.27 × 720 = $3240/month (taking an average month as 720h).
As the time now is 24 months, $3240 ÷ 24 gives the average cost rate of deterioration as $135/month/month.
The optimum time for overhaul can be calculated (Haynes and Fitzgerald, 1986) from
which is at 27.2 months. If plotted as cost/month against time, the resulting curves will show the cost per month of overhaul dropping with time, with the cost of lost energy increasing with time.
(The time value of money could also be taken into account if required). Usually the total cost curve is fairly flat for ± 20% or so. The calculations can be easily set up using a spreadsheet).
If the overhaul was delayed until, say, 30 months, then the accumulated cost of lost energy would have reached $135 × ½ × 30² = $60 750. At 27.2 months, the cost is $135 × ½ × 27.2² = $49939. The cost of delaying overhaul is thus the difference, $10811.
wear state than for a constant speed pump.
To estimate the power required in the worn state, the Head-Flow curve must be drawn for the current higher speed in the new condition. Select a Head-Flow point on the original new condition curve, and correct it to the higher speed: multiply the Flow by the speed ratio, multiply the Head by the (speed ratio)². Repeat this for some other points at flows above duty flow to draw the new condition HeadFlow curve.
where: O = cost of overhaul
C = cost rate of deterioration
giving here T = 27.2 months, but it is better to calculate and plot the average total cost/month values for a range of times. Seen clearly will be the cost impact of doing the repairs at some other time, such as at a scheduled plant shutdown.
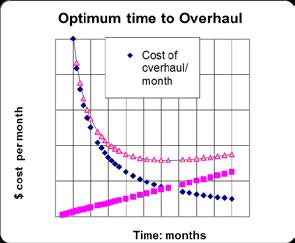
Figure 4: Spreadsheet used to show the optimisation point graphically
How to calculate the total average cost per month, month by month
For example, take the time as 22 months:
The average cost of overhaul is now $50 000 ÷ 22 = $2273/month
The average cost of extra energy is now $135 × ½ × 22 = $1485/month
The total average cost/month is now the sum of these two figures = $3578/ month.
Repeat this calculation for several months, perhaps using a spreadsheet, and look for the minimum total cost,
Note that this calculation is only correct if the wear progresses at a uniformly increasing rate with time, but as Figure 1 shows, this is not unusual. Information may not be available to make any other assumption, but decision makers have to start somewhere! Other formulae apply for rates of change which are not linear (Haynes & Fitzgerald, 1986).
Note:
• Some relatively small pumps may never justify overhaul on savings in energy use alone, but may be justified on reduced plant production rate.
• The method does not apply to pumps of high specific speed that show little change, or even a reduction, in power with increased flow.
• If a pump varies in its duty, then the energy usage would be corrected in proportion.
• The cost of electricity to be used here may vary with the power supplier’s tariff structure. The cost may be less in stepped blocks with higher consumption levels for the plant, or a peak demand charge may apply
Pump deterioration does not affect production, at least initially: variable speed controlled pump
For a pump where the speed is varied to meet its desired duty, the effect of wear on power required is much more dramatic than for the case of a constant speed throttle controlled pump. This is because the power usage increases in proportion to the speed ratio cubed.
Unless the pump output is limited by the pump reaching its maximum speed, or by its driver reaching its highest allowable power output, then no production will be lost. However, power consumed will increase more dramatically for a given
Follow the same method and calculations as before to find the time for overhaul for minimum total cost. The operating point is projected from the worn curve to the new curve at the same speed as the worn curve. Figure 4 shows the performance of a variable speed pump. When new, operation at 1490 r/min meets the desired duty flow, at operating point A, requiring 325 kW power: point B.
After some time in service, internal leakage has increased such that the pump must run at 1660 r/min to meet the required duty - still point A.
To estimate the power required now, the Head-Flow curve must be drawn for the higher speed in the new condition. Several Head-Flow points are selected and corrected to the higher speed: multiply each Flow by the speed ratio, and multiply each matching Head by the speed ratio squared. This will result in the Head-Flow curve @ 1660 r/min in the new condition.
Project across from the Head at the duty flow - point A –to meet the head-flow curve @ 1660 r/min (new condition). (Line C in Figure 5). Projection downwards at constant flow leads to the increased power required at 425 kW. The extra power is 31 per cent more! (This pump is driven by a steam turbine, so power consumption cannot be measured).
The same calculations as before are followed to find the time for overhaul for minimum total cost.
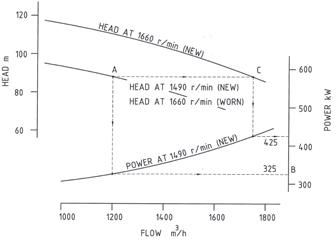
Figure 5: Head-flow-power characteristics of new variable-speed pump, and headflow points from worn pump.
Optimisation using shut-off head test results
The shut-off head test information can also be used to estimate power used in the worn state and do the optimisation calculations as explained in the above section
Head-Power-Flow characteristics in the “new” state are needed as before, and the operating point must be known. Note the power required at operating point as before.
Make an overlay trace of the Head-Flow curve in the new condition. Place it over the “new” curve and move to the left horizontally until the curve cuts the Head axis at the value of shut-off head obtained on the test. The trace is now in the position of the “worn” HeadFlow curve which is being experienced. Exactly the same process can be followed as explained above.
Conclusion
A method of determining the optimum time for overhaul of a pump based on energy savings has been given. It is hoped that this valuable tool will help asset managers and engineers in their role of managing assets to provide capacity for production, and to improve energy efficiency and minimise greenhouse impact. This optimisation approach can also be applied to any item of plant where deterioration results in loss of efficiency and energy consumption can be measured or estimated.
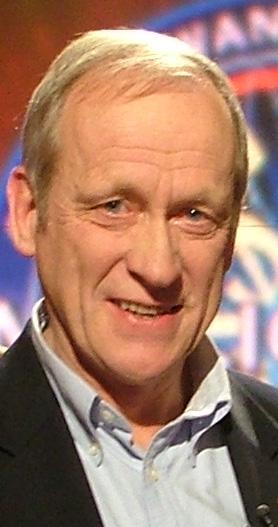
About Ray Beebe
References
ANSI/HI 9.6.5-2000 American National Standard for Centrifugal and Vertical Pumps for Condition Monitoring
Beebe, R S (2004) Predictive maintenance of pumps using condition monitoring Elsevier, London
Beebe, R S (2002): Thermometric testing of high energy pumps using pipe surface measurements 3rd ACSIM (Asia-Pacific Conference on Systems Integrity and Maintenance), Cairns, Australia (2002)
Haynes, C J and Fitzgerald, M A (1986): Scheduling Power Plant Maintenance Using Performance Data ASME Paper 86-JPGC-Pwr-63
Karassik, I J et al (Eds) (2001) Pump Handbook McGraw-Hill
Robertson, M et al (2007) Continuous Pump Performance Monitoring and Scheduling IMechE Symposium - Energy Savings in Pumps and Pumping, London
Stepanoff, A J: Centrifugal And Axial Flow Pumps Wiley (1957), and Figure 1-77A of the PDF figures on www.pumps.org
Whillier, A (1972): Site testing of high-lift pumps in the South African mining industry IMechE paper C155/72 Conference on Site testing of Pumps London (1972) pp209-217 (I attended this while working in the UK 1971-73)
Ray Beebe, DipMechE, MEngSc, FIEAust, CPEng(ret) followed 28 years in power generation with 20 years at Monash University, based in Australia. He led the postgraduate programs in maintenance and reliability engineering for 15 years, with students all around the world studying by off-campus learning. His commitment to sharing knowledge and experience has led to writing and presenting at many conferences and conducting training courses in condition monitoring around the world. His second book gained the George Julius Medal of Engineers Australia for the best publication in mechanical engineering in 2004. His third book, on condition monitoring of steam turbines, will be published later this year. He is an active volunteer in Rotary and Scouting.

Less hot air in Canberra
Australia’s Parliament House on Capital Hill is one of the main attractions in the nation’s capital, Canberra. Opened in 1988, the building is now 24 years old and has recently undergone some modernisation to ensure high standards of energy efficiency. During the city’s hot summers, KSB pump sets equipped with PumpMeters ensure temperatures stay comfortable.
Modernisation work in Parliament House sought to employ energyefficient and environmentally friendly technology, especially when it comes to the air-conditioning system. In keeping with this aim, KSB supplied pumps from the Etanorm series equipped with PumpMeter monitoring units. These ensure that the Etanorm pumps always run at the correct operating point, guaranteeing efficient operation.
Energy Efficiency
The system operation is demand driven and only operates at the required actual performance level to ensure the required optimum comfort level. The mode of operation is realised via the use of highly efficient and reliable Etanorm pumps, coupled with high efficiency electric motors and performance regulated via frequency controller.
Water Savings
As the system automatically adjusts to the required demand levels, it only ever pumps just the right amount of water required to meeting the cooling requirements.
Innovation
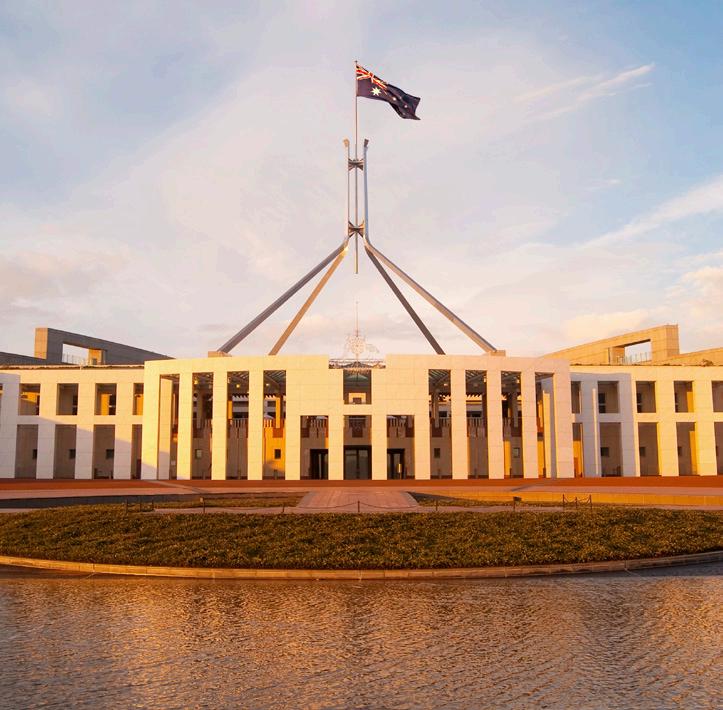
The automatic performance regulation from Etanorm, was only one aspect of the innovative solution. The incorporation of PumpMeter took innovation to a whole new level.
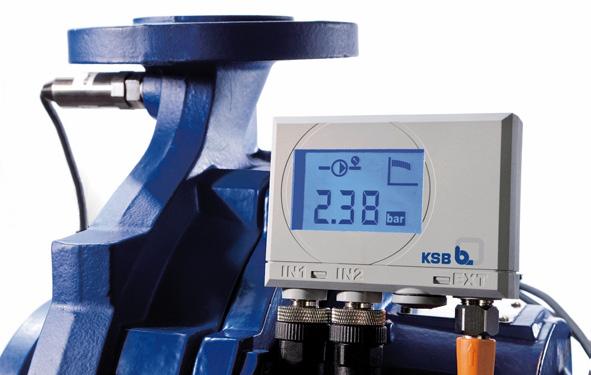
Parliament House facts
The building was designed by Mitchell/ Giurgola Architects and opened on 9 May 1988 by Elizabeth II.
At the time of the construction, it was the most expensive building in the world at more than A$1.1 billion.
The building itself is 300 m in length and width and contains 250,000 m2 of floor space and contains 4,700 rooms
Construction required 300,000 cubic metres of concrete, enough to build 25 Sydney Opera Houses and has a design life of at least 200 years.
About PumpMeter
PumpMeter continuously analyses the pump operating data and allows operators to see at a glance if they are operating economically. It won the prize for environmental contribution of the year at the Pump Industry Awards UK in 2011.
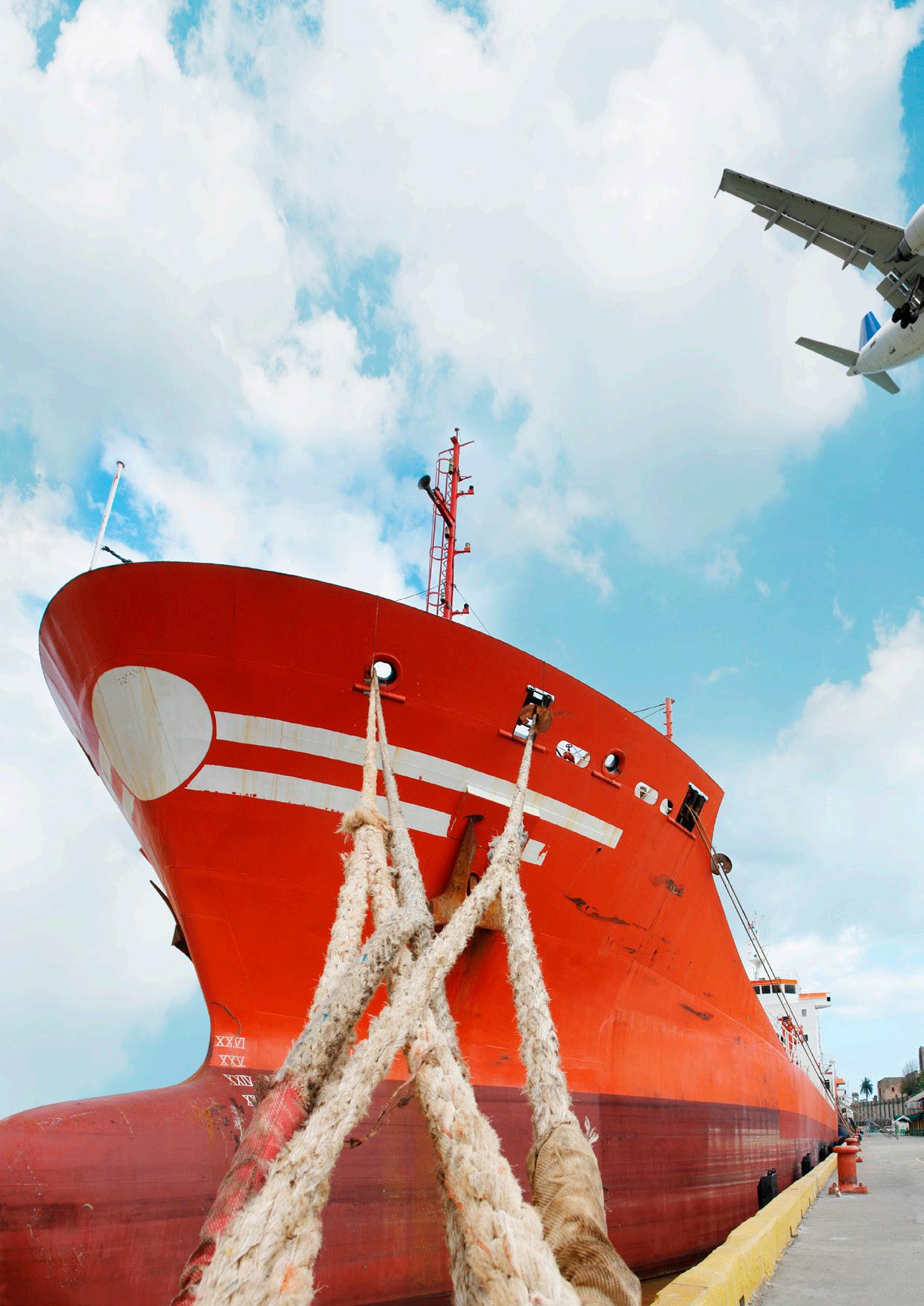
The state of the import and export market
PIA has routinely conducted an analysis of the import and export activity of commonly used pumps in the Australian market. This has been achieved by monitoring ABS Import and Export Statistics over the period 2003 – 2011. This provides some useful insights into the state of the industry and the level of manufacturing currently conducted in Australia.
Imports
Pump imports into Australia increased marginally in 2011 from 2010. Anecdotal evidence suggests bare pump production is decreasing in favour of imports. However the ability of the local industry to build pumping equipment for specific applications has increased and become more sophisticated to meet market demand.
The statistics show that growth in centrifugal pumps has been strongest, while the trend for rotary pumps has been flatter. The general growth trend of the past decade showed some drop off in 2010 but appears to be increasing again.
USA remains the main port of origin with 24 per cent of all pump imports to Australia originating in the US. China is in second place with 14 per cent, just ahead of Germany with 13 per cent. Other notable ports of origin are Japan, the UK, Sweden and Italy.
Exports
Pumps exports from Australia have shown a strong growth trend over the past decade and increased substantially in 2011, with pump parts showing the greatest improvement. Southeast Asia remains the main destination, with exports to Indonesia at 26 per cent in 2011. New Zealand is in second place with 9% and other notable destinations include PNG, China and the USA.
Considering the impact of the global financial crisis, the Australian pump market seems to have performed well and demand for pumping equipment is trending upwards
Pump types included:
The statistics are available by analysing the tariff codes applied to the goods. The following codes have been included in this analysis.
8413.50 – Other reciprocating positive displacement pumps. (diaphragm, “oil-cushion”, electro-magnetic pumps and machines using the suction or forcing action of two pistons)
8413.60 – Other rotary positive displacement pumps. (gear, vane, rotary piston, lobe type, helicoidal and peristaltic pumps)
8413.70 – Other centrifugal pumps
8413.81 – Other pumps (electro-magnetic, ejectors, emulsion, gas combustion, steam pulsators, compressed air chamber elevators and hydraulic ram pumps)
8413.91 – Pump parts
Pump types not included
Pumps for dispensing fuel or lubricants – used in filling stations, hand pumps, fuel lube or cooling medium pumps for internal combustion engines, concrete pumps, liquid elevators.
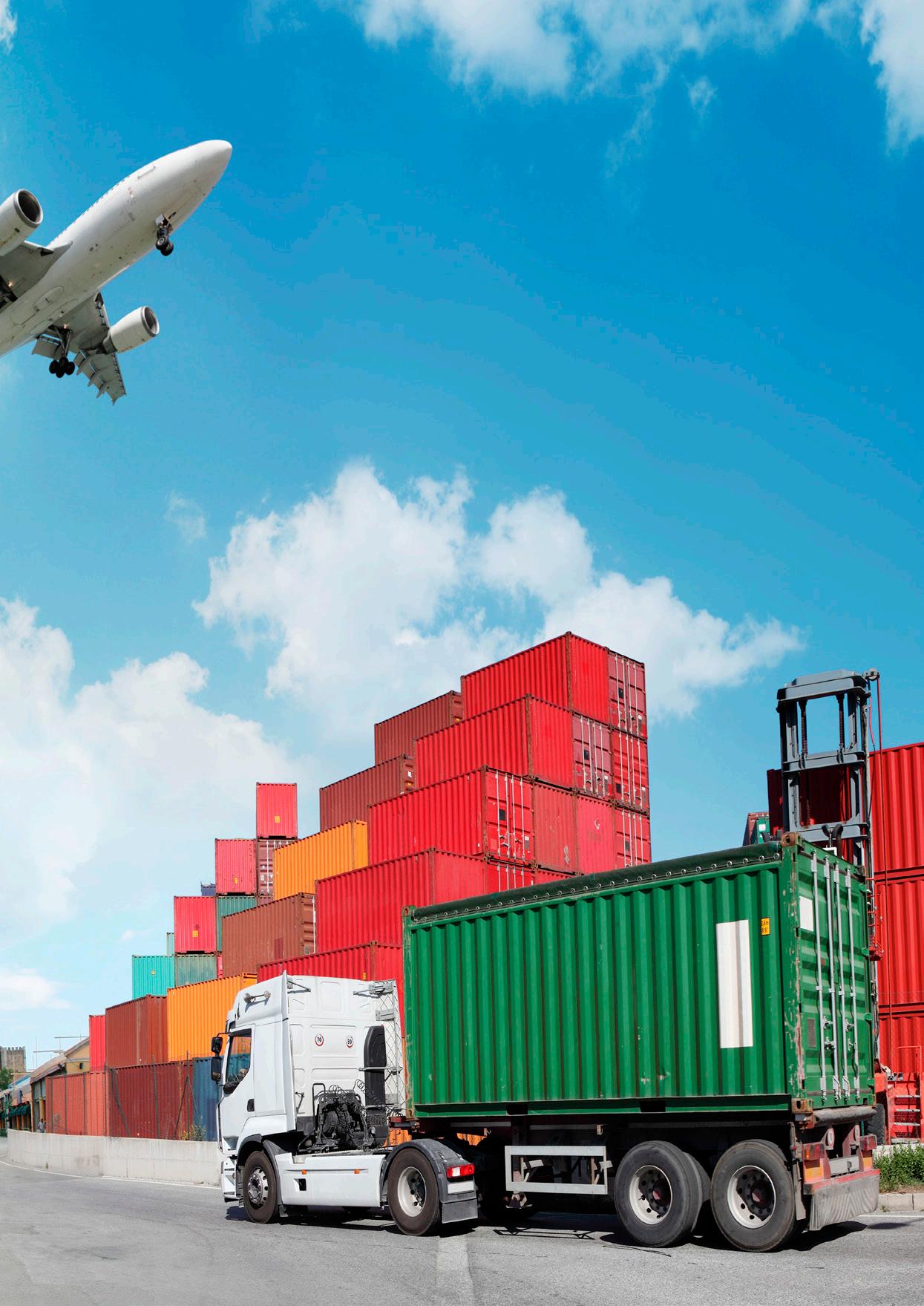
Full statistics are available to PIA members, see page 11 for more information on joining. Or for more details on the pump market, please contact pumpsaustralia@ bigpond.com
Exports by product
Pump parts
Other Pump Types
Centrifugal Pumps
Rotary PD
Reciprocating PD
Exports by country
All others, 24.99%
Russia 2.17%
UAE, 2.54%
Phillipines, 2.54%
New Caledonia 2.94%
UK, 3.46%
Singapore, 4.20%
China, 4.63%
Indonesia, 26.46%
New Zealand, 9.34%
USA, 8.55%
PNG, 8.19%
Converting the Indian Ocean into drinking water
We need fresh water to survive but two-thirds of our planet is covered with salt water so an obvious solution seems to be to remove the salt from the water that is readily available to make drinking water. Most states in Australia have recognised the importance of purifying seawater using reverse osmosis technology and have desalination plants either operating or under construction in an effort to drought-proof our nation.
ABB’s drives and motors surpass the energy efficiency requirements of Western Australia’s new Southern Seawater Desalination Plant whilst it pumps seawater which is converted into 50 billion litres of fresh drinking water for Perth residents annually. This, combined with the existing desalination plant based in Kwinana, ensures that more than 30 per cent of Western Australia’s water supply will come from climate independent sources.
The first stage of WA’s latest desalination plant was officially opened in September 2011, three months ahead of schedule and within the $955 million budget, ensuring an ongoing climate independent water source for West Australians. This new plant, the second for the west coast, is located between Binningup
and Myalup, south of Perth and the desalinated water will be fed into the existing Integrated Water Supply Scheme (IWSS). The IWSS pumps fresh water into Perth’s metropolitan dams which supply residents with high quality drinking water.
To achieve the optimum operating efficiencies, the Southern Seawater Alliance (SSWA) awarded ABB the contract to supply nine identical 800 kW 3.3 kV drives to power and control the main reverse osmosis (RO) and seawater intake pumps for the desalination plant following a competitive tender process.
SSWA are mindful of the ongoing environmental impact of a desalination plant on the local area and hence, all aspects of engineering design on the project required the highest possible
energy efficiency performance. This exacting standard also ensures the site will continue to have the lowest possible environmental impact into the future.
In order to prove the high levels of energy efficiency offered by ABB, the motors and ACS 1000i variable speed drives were thoroughly tested and achieved results which not only met, but exceeded the customer’s rigorous energy efficiency expectations.
John Kutniewski, medium voltage drives specialist for ABB in Australia said, “in our initial tender, we quoted an efficiency of 96.1 percent at maximum operating speed and the results of the testing carried out at our drives factory in Turgi, Switzerland revealed the efficiency was 96.4 percent.
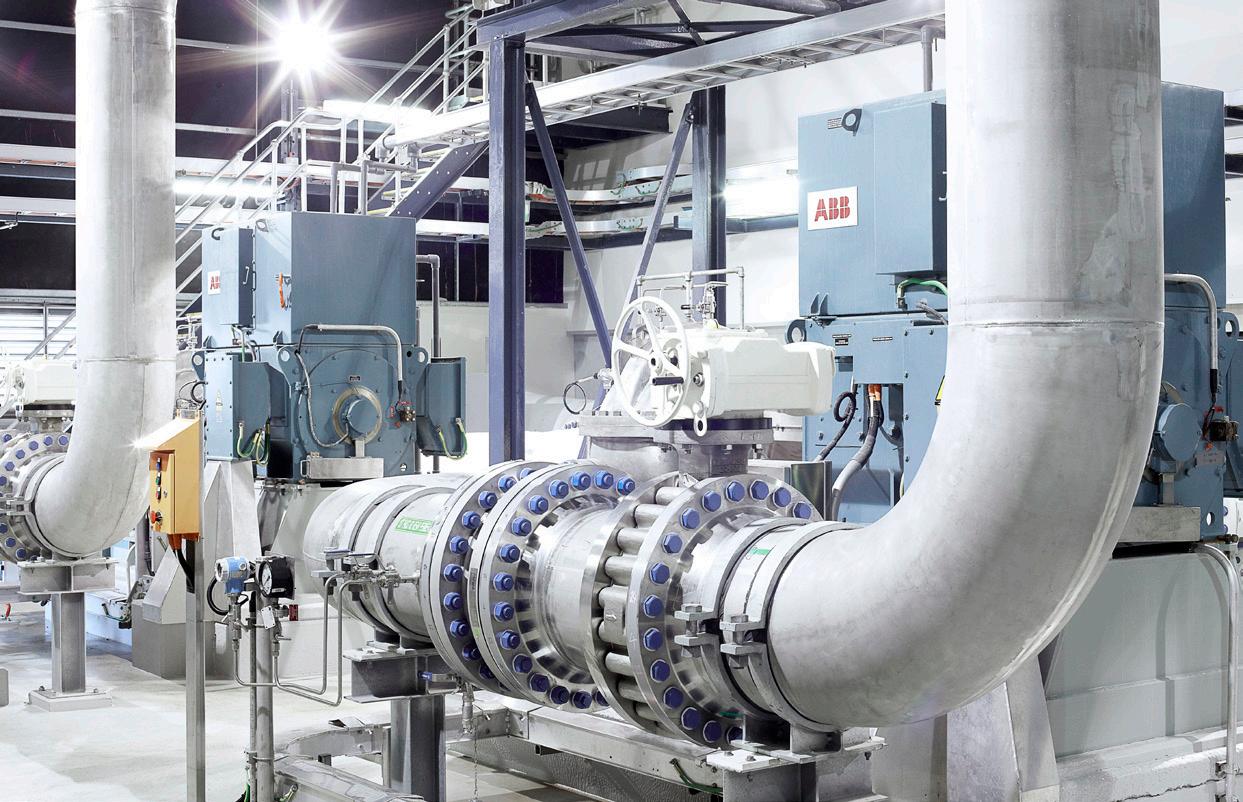
ABB's motors and drives were thoroughly tested and achieved results which not only met, but exceeded the customer's rigorous energy efficiency expectations

“The ACS 1000i model is a fully integrated standard drive which includes an 11,000 volt input transformer. This combination is an unbeatable solution for pumping stations in the water industry. By employing our drives on the pumps instead of throttling, SSWA’s energy bill can be reduced by as much as 60 percent for the RO and seawater intake pumping applications.”
“In addition to being efficient, the drives include key interlocking to prevent
opening of the inverter power sections while the drive is energised. ARCGuard and output isolators were also included to address site operation and maintenance requirements without increasing floor space.”
The desalination plant has also ordered five ABB 750 kW motors to operate in conjunction with the ACS 1000i Drives and the pumps manufactured by FlowServe which will be operating on site. ABB has been working with FlowServe
Optimize process performance without compromising energy efficiency.
to test their drives and motors to ensure they will achieve maximum efficiency with the customers chosen pump supplier.
Additional to the drives systems provided on this project, ABB has also supplied low voltage switchboards, motor control centres, power factor correction equipment and transformers. All products have been designed with the aim of delivering reliability, lower operating costs and minimising life-cycle costs.
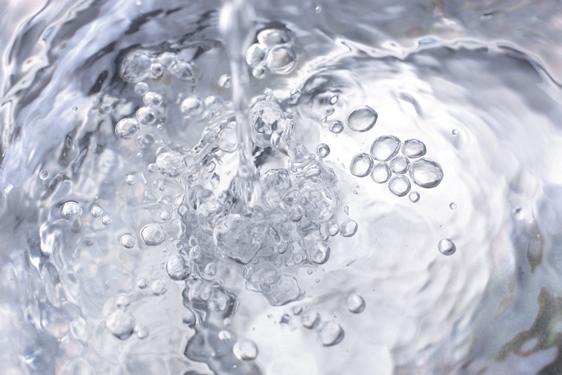
Water and wastewater utilities are facing many challenges from managing leakage and pressure, optimizing pump performance, improving potable water quality, reducing energy consumption and CO 2 emissions to lowering maintenance costs. ABB’s drives, motors and PLCs are designed to help motor-driven applications such as pumps, fans, compressors and conveyors, tackle these, and other, challenges.
To discover how to improve your utility’s energy efficiency and productivity, visit www.abb.com/water
Sewer bypass success
In August, Pump Affinity performed a key role in the 450mm rising main valve replacements from Wyong Shire Council’s Sewer Pumping Station (SPS) T22. SPS T22 receives sewage flows from 8 other sewage pumping stations, two private pumping stations and has over 4400 Equivalent Tenements in its catchment. The Peak Wet Weather Flow is up to 190L/sec.
Pump Affinity provide quality flow management and ground water solutions, including horizontal, wellpoint and well dewatering, pH dosing, pump project management, flow gauging, and pump hire.
Eire Contractors engaged Pump Affinity’s services in the tendering process as well as during the bypass and rising main works. Successful liaison on past projects has meant that Pump Affinity is Eire Contractors preferred company to provide dewatering, bypass management, including flow management plans, onsite monitoring and pump hire. Operating as an exclusive hire agent for Vortex Hire, Pump Affinity supplied, serviced and maintained four QSCP150i for the works.
The night of the rising main commenced at 9pm on 14 August 2012 and continued until 9.30pm on 15 August, involving the transport of almost 3 mega litres of sewage, via 322 truckloads to Toukley Treatment Works. Pump Affinity staff provided onsite monitoring of the pump station wet well throughout this tankering process, to ensure operating levels were maintained.
The works are part of a $3.5 million sewer rehabilitation program and pump station upgrade being undertaken by Wyong Shire Council as part of its commitment to providing a safe and efficient sewer network. The two main components of the program are the sewer rehabilitation program which includes the inspection, cleaning and relining of approximately 10 kilometres of sewer mains and will improve the performance and reliability of the sewer system in the area and the Budgewoi
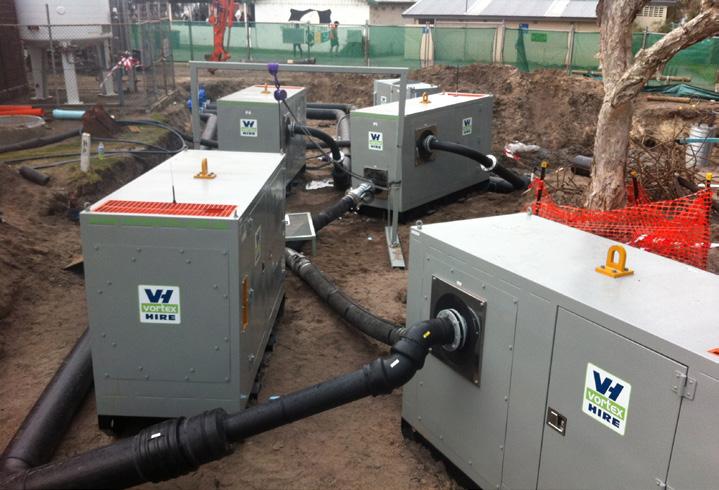
sewer pumping station upgrade to provide reliable and efficient sewerage infrastructure to the local community. Both projects are expected to be completed by December 2012.
Wyong’s sewer network is around 50 years old, and Council’s commitment is to review and maintain the system every year to ensure minimal impact of overflows and odours to the community and environment. Council’s Director of Infrastructure Management Greg McDonald said the works are a significant investment to boost the operation of the region’s 1,252 kilometres of sewer pipelines.
“This program will make sure we can continue to protect local residents and businesses against mains breaks and sewerage leaks, and have efficient and
safe pump stations,” Mr McDonald said. “This investment in the sewer system will ensure a safer environment for the shortterm and that the sewer system remains functioning into the future.”
Wyong Shire Council’s Project Manager for the SPS T22 upgrade works, Martin Drake noted that the commitment of the bypass team, including Eire Contractors staff and their subcontractor, Pump Affinity, ensured an efficient and effective result was achieved maintaining the integrity of their asset for many years in the future. The rising main valve replacement and its flow management provided council with confidence for the second stage of augmentation works in September requiring full isolation of pump station and eight weeks of bypass all designed and supplied by Pump Affinity.
Wyong Shire Council Sewer Operations
Like the local water supply infrastructure, the Wyong Shire sewerage system is modern and was mainly built since 1970.
All new urban development must be connected to the system which consists of sewage gravity collection pipes, pumping stations and pressure mains to convey the mainly liquid waste (sewage is more than 99.9% water) to sewage treatment facilities.
At the treatment facilities, mechanical and biological processes are used to separate the solids (sludge) from the water (effluent). The sludge is removed and subsequently used for beneficial uses by external companies. Effluent, which has been treated to a high standard typically contains less than 0.002% solids and is discharged to the ocean via outfalls at Bateau Bay (Wonga Point) and Norah Head.
The Wyong Shire sewerage system services more than 60,000 properties through a network of 1240 km gravity and pressure mains and 142 pumping stations. There are six treatment plants located at Toukley, Bateau Bay, Charmhaven, Wyong South, Mannering Park and Gwandalan.
Effluent from Toukley, Charmhaven, Wyong South, Mannering Park and Gwandalan sewage treatment plants is discharged to the ocean at the Norah Head outfall.
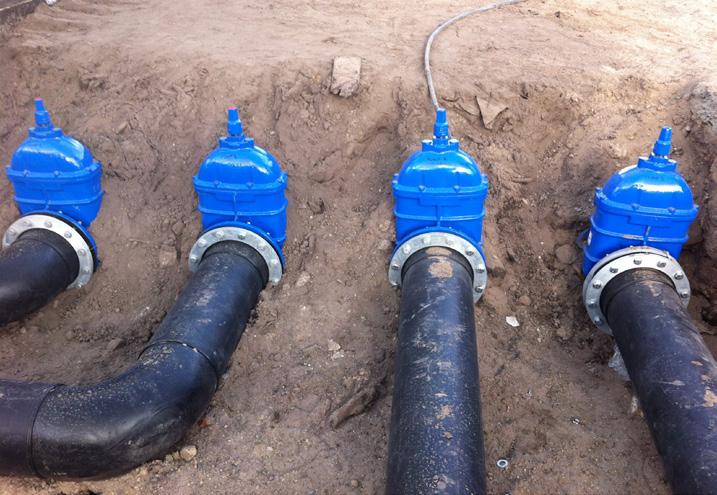
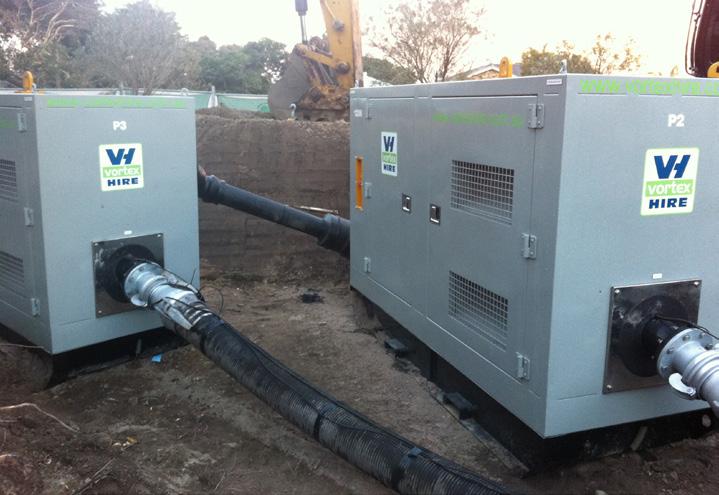
Sweet upgrade
Sugar Australia’s Yarraville Refinery in Melbourne is Australia’s longestestablished sugar refinery. Sugar refining has been conducted on the site since 1873. Many modifications have been made to the site and process over the years to provide efficient and highly-automated production and packaging of a broad range of refined sugar products. Recent negotiations between Sugar Australia and Stevco Seals & Pumps Victoria has resulted in Stevco being awarded a tender to supply and commission a second replacement pump-set to upgrade the 100-year-old water injection system.

Stevco Seals & Pumps Victoria was established in 2004 with a clear mission to provide first class products, support & aftermarket service in pumps & mechanical seals.
We have selected products & aligned ourselves with leading manufacturers of high quality equipment to ensure we are able to offer our clients “best fit” solutions for all of their pumping & sealing needs.
We offer a comprehensive range of pumps and mechanical seals to suit almost every industrial pumping application.
Understanding our client’s process and commercial needs and building relationships through our dealings ensures we can deliver service and value above and
beyond the products we provide. Our workshop is well equipped to build new pump sets, overhaul your existing pumping equipment or perform improvements including mechanical seal upgrades and application of high efficiency abrasion resistant surface coatings.
We can also provide on-site servicing including pump installation, removal, routine servicing and repair with our suitably equipped vehicles and trained field personnel.
Supply of gland packing, gasketing, pump spare parts and mechanical seal servicing are also part of our all-inclusive range.
We are also distributors of the world famous Inpro-Seal compound labyrinth bearing isolators & “Air Mizer” dry running, air purged product seals.
Sugar uses sea water pumped straight from the mouth of the Maribyrnong River for injection in their vacuum system. The original pumps installed for this duty were bronze horizontal split casing units built at Worthington’s Bedford works in the UK in 1910.
Over the years spares availability had ceased and with changes in demand these units became extremely costly to maintain. Lack of parts availability necessitating re-engineering and fabricating of components such as impellers and shafts, along with deterioration of the housings and an antiquated pulley & belt drive system, finally coerced management at Sugar to replace the existing pumps with more modern technology.
Industries we currently service include:
• Water & waste water facilities
• Pulp & paper manufacturing
• Food Processing
• Beverage production & packaging
• Ink manufacturing & printing
• Pharmaceutical
• General process
• Specialist equipment manufacturers & pump OEMs (mechanical & Inpro seals) With support from our supply partners we provide ongoing product and technical training for all of our field and workshop staff and are active members of “Pump Industry Australia”. Visit
Capable of supplying sea water at a constant rate of 416L/s at 21 metre head, the Duplex Stainless steel Sulzer ScanPump BE4060-55 pump is driven by a 132kW, 8 pole high efficiency WEG electric motor controlled by VFD.
Stray current from the rotor is being diverted by an INPRO® CDR (current diverter ring). This assures that the current does not damage bearing races when passing down to earth.
Stevco built and installed the first of these new pump sets in mid 2007 and after 5 years of proven operation the decision was made to replace the remaining original pump with the same specification of ScanPump and motor.
The second new pump is being manufactured by Sulzer ScanPump in Sweden and fabrication of the new base and hardware is about to get underway at Stevco. Planned installation is set for December 2012.

About the Sugar Australia Yarraville Refinery
Raw sugar for the Yarraville refinery is sourced from Queensland where it has been milled from Australian -grown sugar cane. The main sugar refining processing steps at Yarraville are: dissolving and heating to 82oC, clarification by phosphatation, deep bed filtration, decolourisation over granular activated carbon, crystallisation, separation of crystals from syrup by centrifuging, drying, crystal size classification by sieving, and then packaging.
A substantial amount of refined sugar is delivered to customers in bulk road tankers in both crystal and liquid form.
The Yarraville Refinery can produce up to 300,000 tonnes per annum.
The benefit of the location of the Yarraville refinery in Melbourne is its proximity to some of the major food manufacturing industries in Australia which use refined sugar as an ingredient, and the site’s access to wharf facilities on the Maribyrnong River for receiving bulk raw sugar.
pumping news sealing news
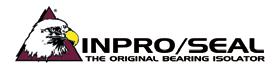
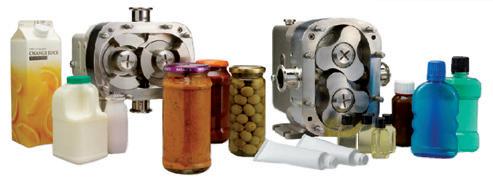
The USDA Approved Air Mizer®- PS is a permanent shaft sealing system that seals powders, liquids and bulk solids. It can be installed on mixers, blenders, agitators, fans, classifiers and other product applications.
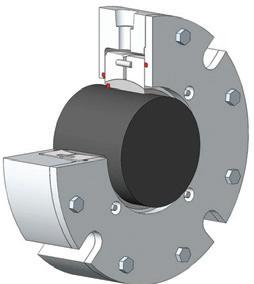
The Revolution™ is the latest innovation in Positive Displacement Pumps for the sanitary and Food markets, merging the benefits of competing technologies into one platform: Rotary Lobe (RLP) & Circumferential Piston (CPP).

Advocating for industry
The Australian Government’s Water Supplier Advocate, Bob Herbert AM, is leading a strategy to develop, improve and promote the Australian water industry and champion firms in this vital sector.
Bob has a life time career built around supporting Australian industry including eight years as Chief Executive of the Australian Industry Group. He has been admitted into the Victorian Manufacturing Hall of Fame and made a Member of the Order of Australia for exceptional services to industry.
Bob Herbert is proud to be assisting local water suppliers to increase their competitiveness and win more work. He spoke to Chris Bland about the Water Supplier Advocate initiative.
CB: What does the role of the Water Supplier Advocate encompass?
BH: I have been given a simple brief - to provide leadership to Australian water suppliers and assist them maximise their involvement in water projects in Australia and internationally.
I should mention that “water suppliers” has broad coverage, embracing manufacturers of products such as pipes, pumps, water tanks, etc. It also includes organisations that supply innovative services, technologies, practical solutions, management expertise, research, as well as those involved in policy settings and implementation.
To achieve practical benefits for this sector, I am implementing an industry development strategy to improve the competitiveness of water firms and increase their access to opportunities in the domestic and international water market. I work closely with businesses, industry associations and partner organisations such as waterAUSTRALIA, Enterprise Connect, Industry Capability Network (ICN), and Austrade to deliver this strategy and help firms develop and promote their capability.
What is one of the key activities currently underway helping to increase Australian firms’ access to opportunities?
Since being appointed as Water Supplier Advocate in May 2010, I am pleased to report that the important foundations have been laid to underpin the opportunities for capable suppliers.
One of the key activities I am leading, in
close partnership with peak industry body waterAUSTRALIA, is the establishment of “Water Industry Capability Teams”. With over 320 firms involved, this initiative is helping firms “hunt as a pack” and work together to market their offerings to customer groups and increase their access to opportunities. These firms are working in teams to pursue new supply chains, market their solutions, participate in workshops to better prepare them to meet customers and work collaboratively to establish networks and connections with other suppliers.
I am working closely with these teams to help facilitate their access to major customers. We are targeting resources companies and coal seam gas project proponents to understand their requirements, needs and drivers to see how we can link our capable local firms into these markets.
What progress has been made on some of the other initiatives you are leading?
I have been actively promoting the Australian water industry both domestically and internationally. The sector is world renowned for its water management expertise and ability to handle extremely variable weather conditions from drought to flood often occurring in different parts of Australia at the same time. We have a very strong standing amongst our international colleagues but we need to continue to get the message out there that Australia is the “go to” country for water technologies and solutions to suit a wide variety of needs.
I have been working closely with Austrade and waterAUSTRALIA to advocate Australia’s Dynamic Water Industry, a narrative that encapsulates Australia’s remarkable water story through its reporting on the level of local skills available in various areas of the industry as well as promoting the capabilities of local water industry suppliers.
I have also championed the need for an accurate and comprehensive understanding of our water industry and its capabilities. Last year we released the
Water Industry Capability Report, drawing on information of over 430 Australian water firms on the key capabilities, challenges and barriers Australian water firms are facing and the key markets they wish to pursue. This information is being used by ICN in their water directory to better promote the capabilities of Australian firms and assist in linking them with customers here and overseas.
One of the most significant customers of Australian water businesses are the urban water utilities. How are you working to increase the engagement of Australian water firms with this major customer?
With urban water utilities spending $10.3 billion on water projects and operations in 2010-11, the opportunities for Australian firms in this market are quite significant. I have engaged with the utilities, represented by the Water Services Association of Australia (WSAA) and water firms, through waterAUSTRALIA, to develop the “Water Supplier Compact”, launched by Minister Combet in April 2012.
The Compact represents an agreement between the water utilities and suppliers to work together to address barriers and increase suppliers’ access to opportunities. Through the Compact WSAA, waterAUSTRALIA and the ICN have identified and prioritised the forward agenda of the Compact. One of the first initiatives we are getting underway is to ensure Australia suppliers are well informed of upcoming opportunities being undertaken by the utilities. The Compact agreement also means that this is a two way exercise and that utilities will aim to increase their awareness of capable local suppliers for these projects.
It seems as though progress is being made in the domestic market. What work are you undertaking to market our capabilities internationally?
I have been working closely with waterAUSTRALIA and ICN in implementing a strategy to increase Australian firm’s ability to access opportunities in the
US market, building on the success of the G’Day USA water mission in January 2011 which identified $150 million in opportunities. A vital part of this strategy has been the appointment of Rubin Mallows under the Government’s Supplier Access to Major Project’s Program to work with Australian firms to increase their ability to win contracts in the United States.
To further pursue this strategy, I am leading a delegation of over 20 firms to the WEFTEC exhibition in New Orleans in late September and early October. Australian firms will be exhibiting under the unified banner of “waterAUSTRALIA” to present a team approach to promoting the Australian water industry.
In July 2012 I was also proud to work alongside waterAUSTRALIA to promote the Australian water industry and lead a delegation of 20 Australian organisations to Singapore International Water Week. This event identified over $50 million worth of opportunities for those firms involved - an incredible success for all of those involved.
These trade missions are proving the brand “waterAUSTRALIA” works and is quickly establishing credibility in international markets. Other international markets (including Asia and South America) are already approaching
Water Supplier Advocate, Bob
Herbert AM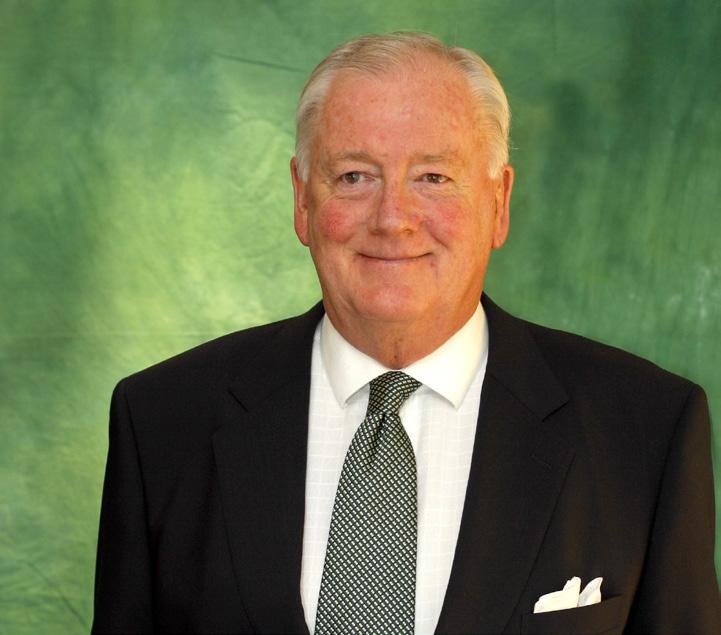
waterAUSTRALIA to learn more about our industry’s capabilities and how to best pursue these opportunities.
Australia is quickly becoming recognised as the country to go to for water technologies and expertise. Our variable climate has fostered a culture of
innovation in developing water related solutions in all market segments. We need to continue our support for Australia water companies to be at the leading edge of capability. As Water Supplier Advocate, this is where my focus will continue to be.
water problems...?
Comprehensive range of:
• Centrifugal Pumps
• Multistage Pumps
• Submersible Pumps
• Rotary Lobe Pumps
• Circumferential Piston Pumps
• Helical Rotor Pumps
• Mechanical Seals
• Inpro Labyrinth Seals
• Gland Packings
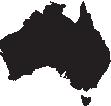
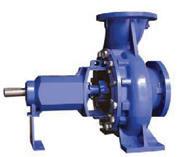

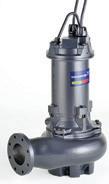
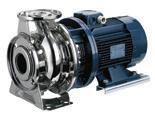

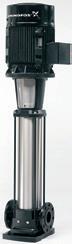
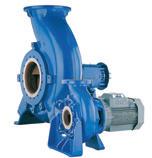
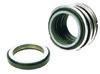
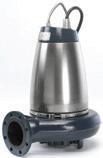
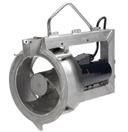
Fire pumpsets: critical infrastructure
By Matthew Wright – Chief Technical Officer / Deputy CEO, FPA AustraliaMatthew Wright from FPA Australia takes a look at the requirements for fire pumpsets in new buildings in accordance with the Building Code of Australia and maintenance of existing fire pumpset installations.
Fire pumpsets are critical infrastructure installations in many buildings and facilities throughout the world. The efficiency of water as a fire suppression agent is well recognised however water’s suppression qualities are often measured by the quantity and speed by which it can be applied to a fire.
The evolution of water based suppression systems includes such low tech endeavours of the “bucket brigades” of the 1800’s, installation of reticulated water supply and steam powered –horse drawn pumps right through to the comparatively advanced fire hydrant and sprinkler systems of the 21st century. Most conventional and contemporary water based fire suppression systems rely on the fire pumpset to deliver water on demand at an expected pressure and flow rate in order to achieve system performance.
New buildings
The Building Code of Australia, now part of the National Construction Code Series alongside the Plumbing Code of Australia contains performance requirements that require installation of suppression systems appropriate to fire hazard. The deemed-to-satisfy (DtS) provisions of the BCA may be used to meet these performance requirements and prescribe requirements for the installation of fire hydrant, fire hose reel, and sprinkler systems in buildings. Although alternative solutions may be legitimately developed to satisfy the performance requirements, this approach is dependent on building specific knowledge. Accordingly this article focusses on the prescribed requirements.
The DtS requirements reference Australian Standards to describe the minimum technical installation requirements regarding these systems. Where fire pumpsets are determined to be neces-
System
Fire Hydrants
Fire Hose Reels
Relevant
Primary installation standard referenced by BCA Secondary installation standard
2419.1 - 2005
2441 - 2005
2118.1 – 1999
2118.4 – 1995
2118.6 - 1995
sary to ensure water pressure and flow performance, these standards reference compliance with AS 2941 -2008.
The above table provides a basic outline of the DtS clauses and standards referenced by the BCA that lead to requirements to comply with AS 2941 –2008 – Fixed fire protection installations – Pumpset systems.
FPA Australia members are representatives of FP-009, the Standards Australia committee responsible for the development of AS 2941 – 2008. This standard is currently under review with the following aspects being considered:
• alignment between AS 2941 and AS/ NZS 3000 (Electrical) – clarifying all the electrical requirements. The most significant change being the need for a Circuit Breaker in the Electric Fire Pump Controller,
• providing a consistent fire pump design duty point for all applications – hydrants, sprinklers, combined hydrant and sprinklers, residential,
• clarifying and tightening of requirements for battery charges and batteries to address the spate of battery explosions that has been reported,
• tightening up wording and figures to ensure there are no inconsistencies and loopholes on a variety of issues – diesel driver heat exchanger cooling system,
2941 - 2008
circulation relief valve sizing, pressure relief valve applications and design, control systems for jockey and jacking pumps, etc.,
• all figures will be revised as needed,
• diesel Engine Power ratings clarified,
• significant change in requiring one ECM for Diesel engines instead of two.
Regardless of these revisions aimed at improving the pumpset standard, it is important to recognise that the current version referenced by the suppression standards included in the BCA remains the minimum installation requirement.
FPA Australia will provide further updates to the industry pending the publication of any revision(s) to the Standard and what this may mean for compliance.
In addition to prescribing installation requirements, the BCA also includes requirements to demonstrate evidence of suitability – that is – documentation that demonstrates products will achieve a level of performance necessary to comply.
Clause A2.2 of the BCA provides options regarding the type of documentation that may be presented as evidence of suitability. It should be noted that although there is essentially five different options, there is no hierarchy to the application of these and they are not equal in terms of rigour or application. The number of options assist in meeting Australia’s com-
mitment to the World Trade Organisation Agreement to reduce Technical Barriers to Trade and stimulate trade between member countries but retain minimum local requirements.
These evidence of suitability requirements have existed without much variation since the BCA was first published in 1990. However, FPA Australia is anecdotally aware that these evidence of suitability requirements are being applied to various degrees across the fire protection industry and is preparing to release comprehensive guidance on this matter to increase understanding and awareness of what is required. In the meantime fire pumpset manufacturers, suppliers, installers and certifiers would be well informed to ensure the evidence of suitability they provide, request or receive complies with the BCA options and does in fact confirm that the product in question complies.
Maintenance
Meeting the minimum installation requirements is insignificant if the pumpset is not maintained in order to perform as expected, when necessary. Maintenance of fire protection systems and equipment is regulated in each state and territory of Australia however an “ignorance is bliss” style complacency is still held by some property owners regarding the importance of maintenance. This seems to especially apply if the equipment is located in a dark room in the belly of their building –out of sight, out of mind.
Common issues reported to FPA Australia include simple and obvious issues such as;
• no fuel or power supply;
• battery failed; and
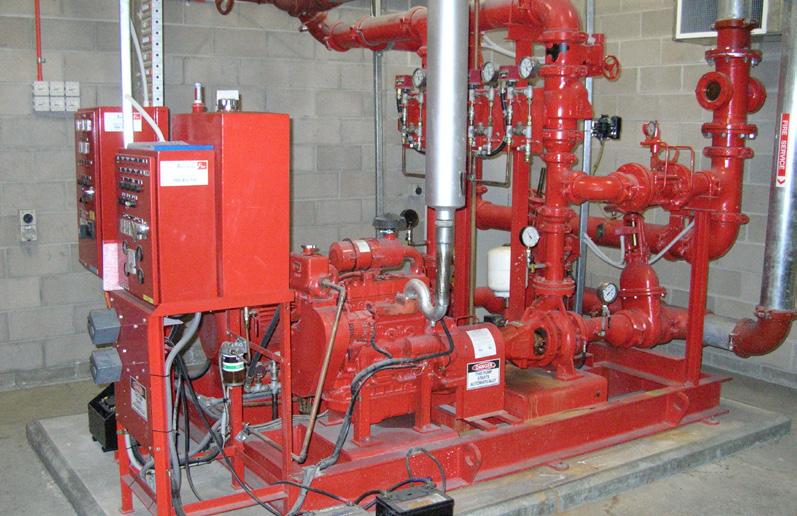
• pump not running right through to:
• inappropriate pressure limit settings;
• pump remaining isolated after repairs have been completed; and
• not running the pump in test mode. Fire pumpsets can often be one of the most neglected pieces of fire protection infrastructure despite being the “heart” of the systems they support. Consider the concessions provided to a building design on the basis of a sprinkler system installation. These can include, reduction of fire ratings, deletion of spandrels and even increasing of travel distances when alternative solutions are developed. Such concessions are of course predicated on the fact that the sprinkler system will perform. Where sprinkler systems include a fire pumpset, operation of the pumpset is fundamental to achieving such performance.
The Australian Standard for maintenance of fire protection systems and equipment is AS 1851 – 2005. This standard is referenced by regulation to varying degrees around Australia and is about to be superseded by a new version which has been the result of extensive development, public comment and review.
FPA Australia is preparing to offer a comprehensive national seminar series in relation to the new standard. The approach being considered is to provide information on the general parts of the standard that apply to all systems and equipment and then include individual streams dedicated to specific equipment. This will allow for focussed discussion.
Fire pumpsets are critical infrastructure and meeting the minimum requirements for installation and maintenance is important to achieving expected performance.
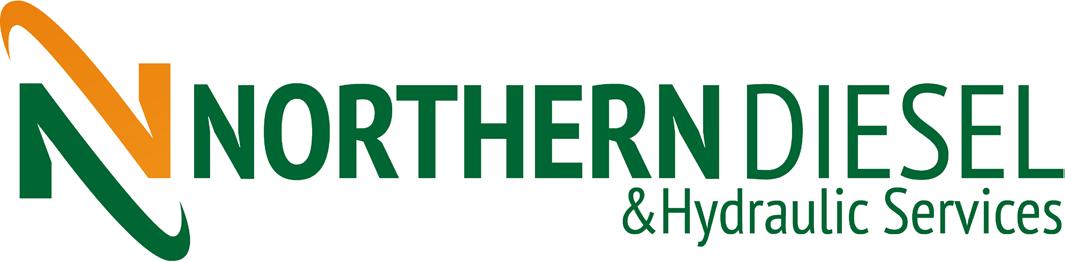

ARC Valves – best practice for pump protection
By Matthew Thompson – Technical Engineering Manager, Renroc Group (Pumps & Engineering)Centrifugal pumps are one of the most common pieces of process equipment. In modern process systems there is a requirement for multiple flow conditions to meet process requirements. In times of startup, shutdown or abnormal process conditions system flow can be greatly reduced and flows through centrifugal pumps may fall below the pump’s minimum flow value.
Pumps operating below minimum flow are unstable due to high thrust loads causing high vibrations, can overheat and cavitate due to the increase in NPSHR at lower flows. Typically 30 per cent of the flow at the pump’s Best Efficiency Point (BEP) must be circulated to avoid these operating conditions. The minimum flow value should be stated by the pump manufacturer. There are multiple ways that minimum flow can be maintained at all times and these are discussed below.
Continuous bypass system
This system installs an orifice plate or series of orifice plates in a bypass line. In this installation at all times the pump minimum flow is bypassed back to the suction tank.
By using this system;
• Pumps are oversized as they are required to pump duty flow and bypass flow, bigger pumps, bigger motors leading to higher capital costs
• There is a constant waste of power as flow runs through the bypass line unnecessarily. Even when only extra 2kW is required to give this constant bypass flow this equates to 17,520kW of power used per year which at 0.15c/kWh equals $2,628 per year and 19.3 tonnes of CO2 (based on coal power 1.1kg/kWh)
This system is no longer best engineering practice in a world concerned with efficiency and sustainability and the wastage can no longer be tolerated.
The orifice plates can also have high wear across them due to high fluid velocity and
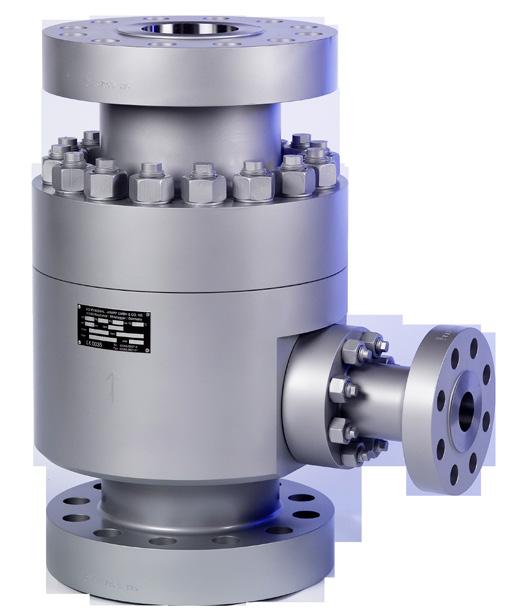
cavitation across the plate.
Controlled bypass systems
This system uses a control valve and instrumentation to divert flow to the bypass only when required. A flow sensor is used to determine low flow which will open the valve using an actuator to control flow back to the suction tank.
This system is quite complex and requires many parts to work together which is both difficult to commission and has a higher chance of failure. These systems are often high capital cost and higher maintenance cost as all individual components require periodic maintenance.
VSD Control
Pump systems may also be controlled by VSD allowing for different process
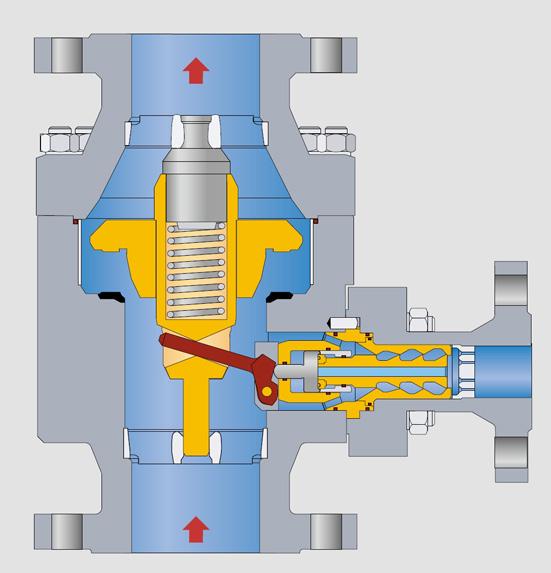

conditions. Maintaining minimum flow using VSD requires additional complex and costly electronics. These require cooling and control for the system to work effectively.
Schroedahl Automatic Recirculation Valve
The Schroedahl Valve is designed to keep the pump operating on its pump curve.
The Schroedahl ARC Valve provides the most economical and reliable form of pump protection. The valve combines the following 4 components in one;
• Flow sensing – The check valve is machined to in such a way that it senses process flow and opens accordingly. This check valve then operates the bypass line as it rises and falls.
• Check valve – The ARC is also a check valve eliminating the need for a separate valve
• Modulating function – The check valve will open or close based on process flow
• Pressure reduction without cavitation – Pump pressure is broken down over the bypass insert without cavitation.
The Schroedahl ARC valve is fully mechanical and activates by flow sensing reacting to the system flow controlled by a downstream process valve.
When no flow to the system is required the check valve will close opening the bypass, this is fully flow controlled based on shaping the check valve correctly. As the system opens and draws flow the check valve will unseat and move vertically sending flow to the system while closing the bypass line.
Schroedahl ARC valves are fail safe, in the unlikely event of a failure of the internals the valve will fail in a bypass open position insuring the pump is protected at all times.
Sizing the valve
When sizing the valve the following information is required;
• Fluid
• Temperature
• Specific Gravity / Density
• Pump duty flow and pump head at this condition
• Pump minimum flow and pump head at this condition
• The pump curve is always desirable
• The flange size and rating of the pump outlet (Ideally the valve should be installed direct on the pump discharge and will be matched to this flange)
• Material for body (Typically the body material is matched to the pump casing, valve internals are various stainless steels with a minimum
12% Chr)
• Installation (Vertical is the standard and preferred orientation for the valve, horizontal can be supplied upon request)
Conclusions
The Schroedahl ARC Valve is designed specifically for process conditions to give a reliable fully mechanical check valve/bypass valve. It is best engineering practice for maintaining pump minimum flow giving the most efficient system and best protection.
For further information or to view an animation of the valve in operation please visit;
renrocgroup.com/manufacturer/schroedahl/
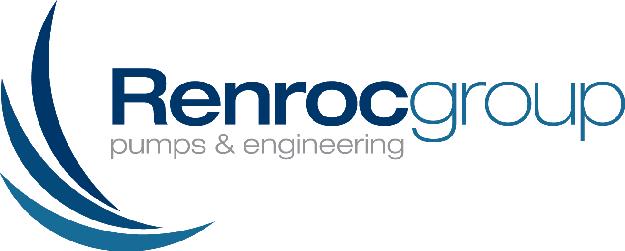
Renroc Advantage
48 years of pump experience in the petrochemical oil & gas industries relating to pumps. Specialists in the design & construction of fluid handling systems for many of the world’s leading EPCM contractors.
• We are specialists in the oil & gas industry for Australia, South & North East Asia
• Competitive pricing & shorter delivery times
• A professional approach to technical presentations and technical resources.
• We offer a diverse product range from global manufacturers
• A committed team with a mixture of youth and experience
Renroc Group (Pumps & Engineering) Australia represents outstanding global pump and valve manufacturers:
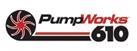
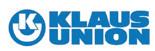
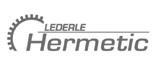
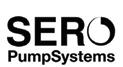

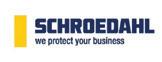


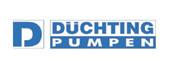

Industrial Pump Range
• API 610
• API 685 Seal less Centrifugal Pumps
• API 674
• Canned Motor Pumps including API 685
• ANSI B73.1, ISO 5199
• Non-metallic pumps
• Multi Function Side Channel Pumps for gaseous liquids in the process industry
• High Pressure Ring section pumps
Understanding pump curves
By Ron Astall, United Pumps AustraliaThis edition, we look at Net Positive Suction Head Required (NPSHR) versus suction lift and self priming capability.
NPSHR vs Suction lift
Showing Net Positive Suction Head Required (NPSHR) on a pump’s performance curve is the most accurate and universal method of showing the pump’s suction capability because NPSHR is valid for any liquid, provided the liquid vapour pressure and density are known.
For cold water applications it is often considered more convenient to show the pump “Suction Lift” curve, as this allows an evaluation of the pump’s suction performance in a more tangible form.
See figure 1.
It is important to realise that a Suction Lift curve is only correct for the particular liquid shown and will have been calculated on the basis of an atmospheric system at sea level (101.3 kPa abs). Normally cold water at 15oC is assumed.
For Water at 15oC, Suction Lift can be calculated from the NPSHR curve as follows :
Suction Lift (m) = 10.35 - NPSHR
It is also very important to understand that the Suction Lift values shown include all suction line losses which must be added to the difference in static liquid levels when assessing a pumping installation. Refer to figure 2.

Whilst the static lift (the difference between the liquid level and the pump centreline) is 2.0 metres, when the liquid is flowing there will be friction losses in the suction piping; in this example a 0.4 metre loss in the foot valve and a 0.3 metre loss in the rest of the suction piping. As the pump will also have to overcome these losses, they must be
added to the static lift to obtain the Total Suction Lift.
Self priming capability vs suction lift & NPSHR
Self Priming pumps will normally have their maximum Priming Lift capability detailed separately. As with the Suction Lift values, this will have been calculated on the basis of an atmospheric system at
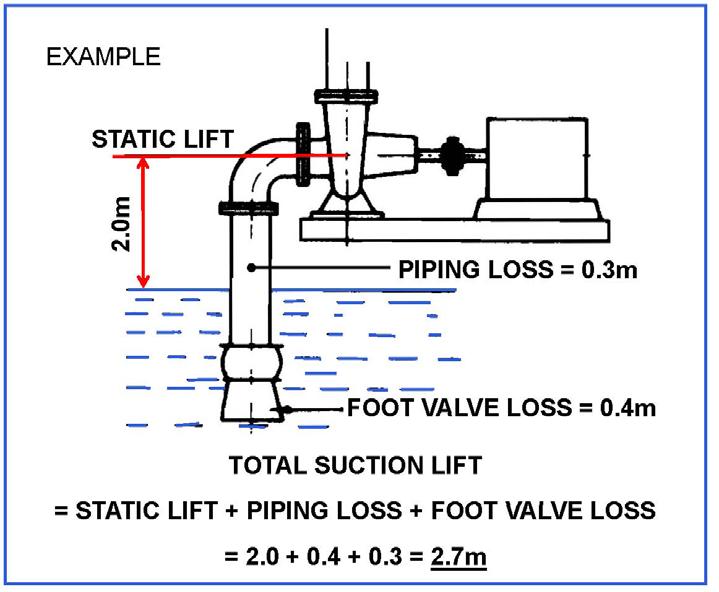
sea level (101.3 kPa abs). Normally cold water at 15oC is assumed.
The Priming Lift is normally significantly better than the pump’s suction lift capability in continuous operation. This is because the priming action is a short term function designed to draw liquid into the suction piping and pump casing during start up or after loss of prime.
Care must be taken not to confuse the Priming Lift capability with the Suction lift or NPSHR capability.
For continuous operation, the allowable Suction Lift (or NPSHR) remains the deciding factor for an acceptable pumping installation.
Reduction of suction lift with altitude and water temperature
At altitudes above sea level, the atmospheric pressure decreases, reducing the surface pressure on the liquid and hence reducing the Suction Lift possible.
Similarly, an increase in temperature will increase the liquid vapour pressure and hence reduce the Suction Lift possible.
See the following tables based on data in the PIA Australian Pipe Friction handbook.
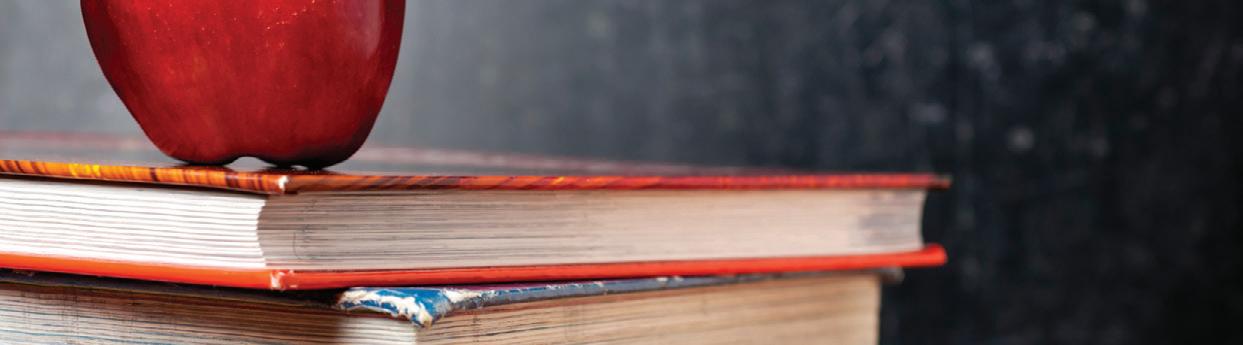
pump school
For a basic explanation of NPSH, turn to pump school on page 44.
Robert J “Bob” Moore
CB: What was your first job?
RJM: First job, 1945, Draftsman with the State Rivers and Water Supply Commission (SRWSC), no choice, sent there by the Manpower Dept late in World War II. I did five years in head office then two years in Heyfield designing irrigation block layouts for the Nambrok Denison Soldier Settlement Scheme. I was transferred to Tatura in 1952 to work on Goulburn Valley Irrigation District remodelling. Left the SRWSC in 1954 to join Victoria Public Works Department (PWD) as a District Engineer (Gippsland) operating out of head office.
How did you get into pumps?
During this time with PWD (1954-55), I worked weekends for F.N. Bethune P/L manufacturers of Pomona Deep Well Turbine pumps. This company also operated a fleet of drilling rigs searching for
quantities of underground water suitable for irrigation purposes. The deal was to visit properties, advise from geological studies the likelihood of a good quantity of underground water, select the drilling site and design a ten acre flood irrigation layout for the farmer. This was a most successful sales ploy. In 1956 Fred Bethune offered me a full time job which I accepted and this was my first involvement with pumps.
I eventually became the unofficial sales manager of FNB P/L (no one had titles!) and I was hooked on pumps and pump technology!
In late 1959 Bethune sold out to Clyde Industries, a NSW conglomerate and I immediately put myself on the market joining Kelly and Lewis Ltd, then a public company. I joined the staff as a Project Engineer to develop the range of Berkeley

borehole pumps, another US licensed product. K&L’s wide range of all classes of centrifugal pumps widened my experience in the pump industry.
In 1960 K & L was taken over by Brambles Industries (a NSW conglomerate) but they on-sold the company to a UK company, Manchester-based Mather and Platt Ltd in 1961. Some difficult times followed for K&L with one large structural steel bridge contract in Queensland showing a huge loss. Restructuring followed and local M & P man Harry Smith assumed command and I became Marketing Manager.
What do you like about the pump industry?
After my time at Bethunes I was a dedicated “pump man”. This was strengthened as I got to know the markets available for a company like K&L with such a wide product spread. I was also attracted to the fact that every project where a pump was required had different conditions and a spread of customers from farmers through to engineers on high value projects. There was always a challenge to land “that order”.
How did your career progress from there?
In 1964 after four years “learning the ropes” of the pump industry at K&L I was offered and accepted the job of General Manager of FN Bethune P/L (now owned by Clyde Industries). In the next three years turnover was doubled and profit trebled.
The next move was unexpected, Kelly and Lewis, now fully stabilised financially, had decided, with Mather and Platt’s approval, to form a local board of directors and start to ‘grow’ the business. Would I like the job of Sales Director as second in command to Harry Smith? After some thought and negotiation I accepted the job, later to become General Manager and then Managing Director after Harry
Robert J “Bob” Moore is a Life Member of PIA and one of the true elder statesmen of the industry, having started working in pumps in 1955, and regarding himself as a lifelong “pump man”. Chris Bland recently had the chance to ask Bob, now 85 and still going strong, to reflect on his life and career.
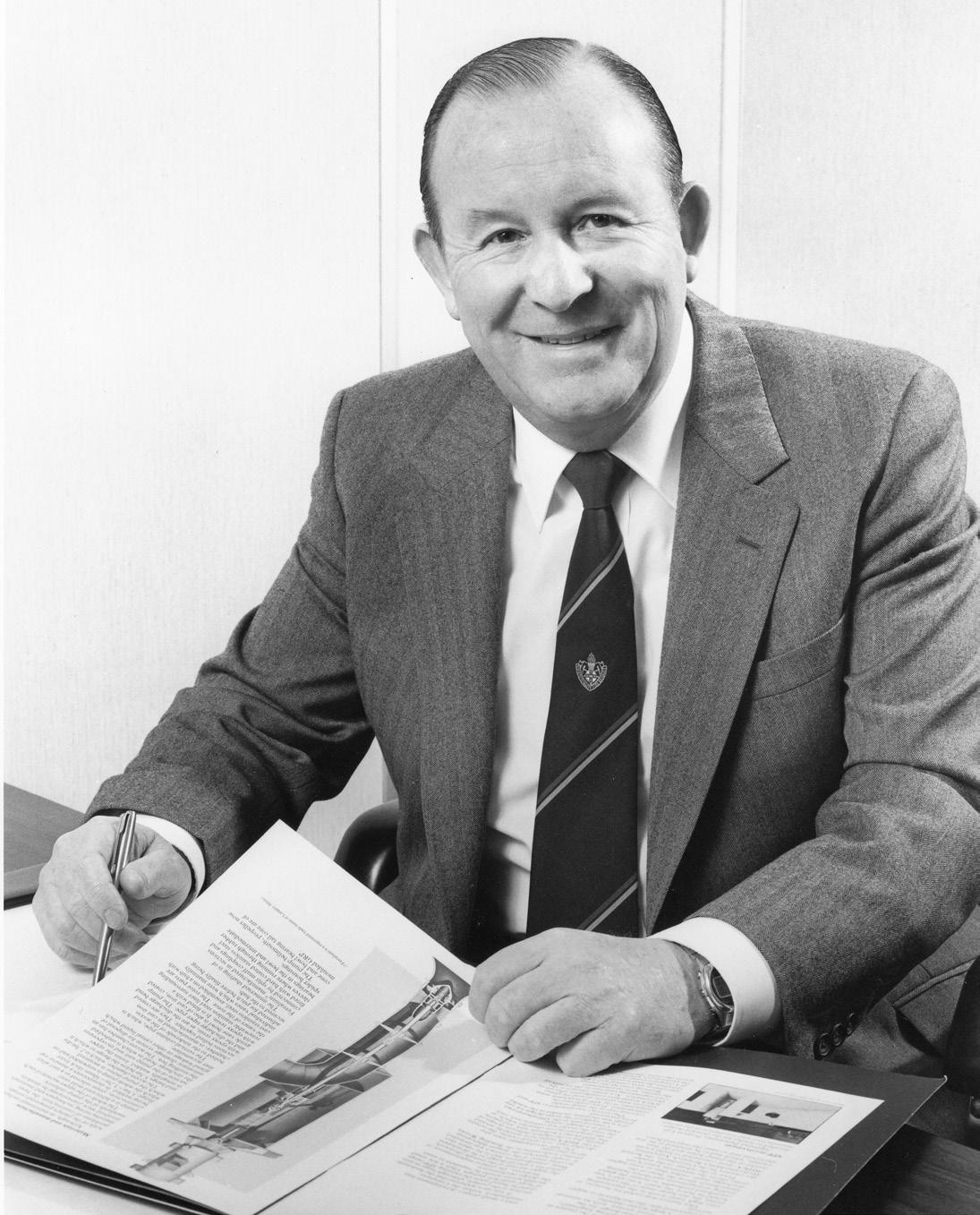
In 1976 Harry Smith was appointed MD of Mather and Platt Ltd and I moved to the UK to become MD of Mather and Platt’s Machinery Group. Also in 1976 Wormald International an Australian company made an audacious (and
successful bid) for M&P so once again I found myself working for an Australian company and later moved up to become once a Group MD of M&P. I resigned from Wormald and from M&P in 1981 to become MD of the SPP Group, Britain’s second largest pump company (after Weiss of Glasgow). SPP was owned by the Booker-McConnell plc group and in
1983 I led a successful management buyout. This was followed two years later by a flotation of SPP on the London Stock Exchange. At SPP, turnover in 1981 was £22 million and profit before tax £550,000. By 1988 this had increased to £58 million and PBT of £4.5 million. It was a good time to retire and I passed the baton to my colleagues at SPP.
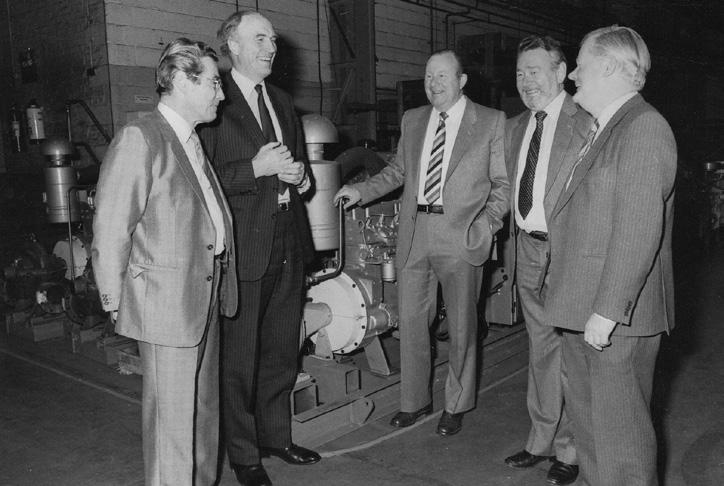
The industry must have changed a lot during your time in it. Looking first at the Australian pump industry, successive governments with their tariff policies and lack of support not just to the pump industry but to all metal manufacturing companies has condemned Australia to a second class manufacturing nation.
The Tariff Inquiries during the 1970s reduced the pump industries protection from 55 per cent to 27.5 per cent and there has been a further 2.5 per cent reduction per annum so that it now stands at zero.
This, of course, has had a marked effect of Australian capability to keep abreast of pump design. Overseas, operating challenges together with metallurgical developments have produced sophisticated products for power stations, for oil extraction, refineries and so on beyond the capability of Australian companies. Here the market has changed and importers have used their pump application knowledge to develop good business.
There is no doubt that the Kelly and Lewis’ pump design team in the 1970s was as good as, if not best, in the world. The team was led by a brilliant pump/ hydraulic design man Andy Gasuinas (who revitalised K&L’s methods and built up a group including Arthur Connor, Graeme Addie, Barry Pinder and others. Gasuinas was transferred to Manchester but sadly died suddenly aged 50. Within 12 months of his death, Arthur Connors went to Manchester for three years to carry on a world-wide design program commenced by Gasuinas.
Other Australian companies, notably Harland, Ajax and Thompsons of
Castlemaine all had solid design teams. Harland eventually failed and was closed down, Ajax now has a mixture of its own designs and imports, while Thompsons was ultimately acquired by USA group, Flowserve Inc. (see below)
During the period from the late 1950s to the late 1980s the two major all purpose pump companies in Australia were Kelly & Lewis and Thompsons of Castlemaine (excluding specialists Mono and Warman). Over this time each of these companies had a variety of owners. The takeover of Mather and Platt UK (K&L’s then current owner) in 1977 by Wormald International was primarily to get hold of M&P’s worldwide fire engineering companies and so to become the dominant force in the world fire protection market. However, by 1985 Wormald was under attack by corporate raiders and was in trouble financially, resulting in the disintegration of two great old companies, Mather & Platt and Wormald. In 1987 Kelly & Lewis was merged with Thompsons, to become Thompsons, Kelly & Lewis (TKL) and both were swept along with the wreckage. Ultimately, Flowserve Inc of the USA emerged as owner of the remains of TKL.
Over time, because of the factors mentioned above the Australian pump industry has changed from a primarily manufacturing industry to a mixture of a few manufacturers and many importers.
These importers generally are relatively small organisations. Previously Australia boasted 30 pump manufacturing companies and the organisation representing them was the Australian Pump Manufacturers Association (APMA). The status today is more like 10 manufacturers and 42 importers resulting in APMA changing
its name to the Pump Industry Australia Inc. (PIA). PIA is doing a great job promoting the industry with technical seminars, tradeshows and contacts with Government departments and industry.
Of course, as the manufacturers closed down apprentice training was downsized leading to the shortage of skilled tradesmen in Australia today. Also foundries, which supplied the necessary castings to the industry have been steadily closing down over the past fifteen years.
What are the highlights of your career?
I would list three. Firstly, Kelly and Lewis winning the orders in 1971 for the eight effluent and five outfall pumps for the large Carrum Southeast Sewage Treatment Plant which at that stage handled 50 percent of Melbourne’s sewage, valued at $3.5 million (in 1971 dollars) and probably the largest value pump order ever placed with an Australian company.
Secondly in 1983, organising the management buyout of the SPP Group.
Thirdly, in 1985 arranging the flotation of the SPP Group on the London Stock Exchange.
Career Timeline
• Civil Engineering Diploma from Swinburne Institute of Technology (now Swinburne University) .
• F.I.E (Aust), Chartered Professional Engineer
• 1955-1960 Sales Engineer FN Bethune P/L (Pomona Pumps)
• 1960-1965 Project Engineer, Marketing Manager Kelly & Lewis P/L (K&L acquired by Mather & Platt UK 1961)
• 1965-1968 General Manager F N Bethune P/L
• 1968-1976 General Manager, Managing Director; Kelly & Lewis
• 1976 – 1980 Managing Director Mather & Platt UK (acquired by Wormald 1977)
• 1981-1988 Managing Director SPP Group plc UK
Also served as President of the Australian Pump Manufacturers Association 1975/76 and Chairman of the British Pump Manufacturers Association 1986/87. Whilst with APMA major initiatives were in fighting the Tariff Board to keep a decent level of protection for the industry and trying to get government involved in rationalising the fragmented Pump Industry.
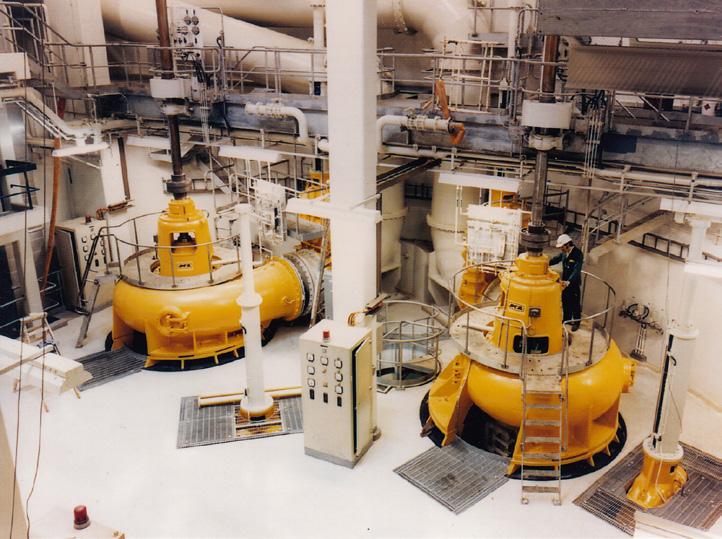

Tell me about some of the people you have worked with. Did you have a mentor?
In business if you wish to grow, you are constantly gaining experience and being educated by your superiors, your customers and indeed by your juniors. Having said that, I think I can say that generally I had a good relationship with, and training from, my bosses over the years, the exception being with the Wormald hierarchy. Harry Smith, M&Ps Australian MD and I had a unique relationship. I guess you could say we mentored each other knowing that we both had different ambitions.
At Kelly and Lewis there were a host of people who contributed. Andy Gasuinas and Arthur Connor in Engineering; Alan Jackson, Finance Director and later MD (Alan resigned after the Wormald takeover of M&P to become MD of BTR plc in the UK). Bill O’Hehir and Les Kilburn in manufacturing; Ken Willcock, SE Asian Manager for K&L and M&P and later Commercial Director of K&L; Kevin Wilson and Geoff Daniels who both went on to top jobs in other companies and many others. Earlier, in the 1960s, I had great respect for Ray Purves, who built up the Clyde Industries Conglomerate.
What does the future hold for pumps?
With the exception of electric motors, pumps are probably the most widely used items of rotary machinery in the world today. Even in depressed economic times there is always some industry or government department requiring pumping equipment.
Those companies still in manufacturing must look to continuous modernisation of machine tools and processes to reduce the labour element to a minimum. Both manufacturers and importers must continually train staff to be skilled in pump application and product knowledge.
All Pump Industry Association members should look beyond just the pump to the system requiring the pump. They should expand their effort to solve the customers’ problems by offering complete systems.
Finally, and often neglected, after-sales service and fast availability of spare parts are factors which promote future sales.
What advice would you give to young people in the industry?
Enjoy the diverse nature of the industry whatever the position you hold in the company. Watch the progress of orders through your factory, ask questions, seeks answers and finally, if the opportunity arises visit the final installations on site. Management and sales personnel should use their skills to solve customers’ problems thus ensuring good future relationships.”
In his spare time, Bob enjoys writing, reading and travelling, and remains involved in the pump industry only socially.
Copies of Bob Moore’s last two books, ‘Toss of a Coin’ and ‘Kelly and Lewis’ are available from the PIA at pumps.asn.au/publications/
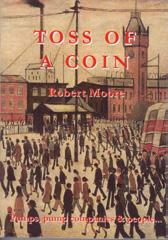
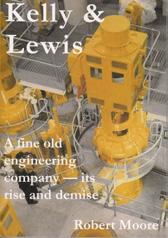
pump school

Net Positive Suction Head (NPSH)
Many people are of the belief that a pump “sucks”. While not entirely incorrect, it’s easy to see why so many operators still struggle with pump problems. Liquid flows from areas of high pressure to areas of low pressure. Pumps operate by creating low pressure at the inlet which allows the liquid to be pushed into the pump by atmospheric or head pressure (pressure due to the liquid’s surface being above the centre line of the pump). Even with a perfect vacuum at the pump inlet, atmospheric and external pressure limits how high a pump can lift the liquid. This limit is the key consideration for Net Positive Suction Head (NPSH).
It sounds complicated, but simplified
NPSH combines the effect of atmospheric pressure, water temperature, supply elevation and the dynamics of the suction piping.
NPSH is an important parameter to take into account when designing a pump system. If the pressure in the flowing liquid drops to the vapour pressure associated with the temperature of the liquid, vapour bubbles form inside the liquid. Vapour bubbles are carried by the flow and collapse suddenly if the static pressure increases above the vapour pressure at another location along the flow path. The zone of vapourization may reduce or stop the liquid flow and damage the system. This generation and sudden collapse of vapour-filled cavities (bubbles) is called cavitation. On the whole, it is very important to the successful operation of a pump.
There are two key elements to measuring Net Positive Suction Head:
1. NPSHR –Net Positive Suction Head Required
This is a function of the pump design and is the amount of liquid pressure required into the inlet of a pump. It is the lowest value of which NPSH that the pump can be guaranteed to operate without significant cavitation. NPSHR is determined at the manufacturer and can generally be found on the pump performance curve. There is no absolute criterion for determining what this minimum allowable NPSH should be, but pump manufacturers normally select a drop in total dynamic head (differential head) of 3% as the normal value for determining NPSHR.
2. NPSHA –Net Positive Suction Head Available
This is a function of the system in which the pump operates and is the amount
available to the pump intake after pipe friction losses and head pressures have been taken into account. NPSHA is determined by a calculation. NPSHA is equal to the absolute pressure head on the liquid surface (Ha) plus the static liquid level above the pump centreline (negative for suction lift) (Hs) minus the absolute liquid vapour pressure head at pumping temperature (Hvap) minus the suction friction head losses (Hf). Ie. NPSHA = Ha + Hs – Hvap - Hf
For the pump to perform properly, NPSHA must be greater than NPSHR for the pump system to operate without cavitating. Put another way, you must have more suction side pressure available than the pump requires.
It should also be noted that difference in altitude will change the absolute pressure head on the liquid surface when tanks are open to atmosphere.
Supporting the modern irrigator
The pump industry is no stranger to the complex and sometimes conflicting considerations faced by today’s irrigator. Dropping water pressures, ageing irrigation systems, changes in technology and ongoing budgetary constraints are just some of the realities that can intrude upon even the most dedicated efforts to achieve efficient irrigation. Combine this with the nation-wide focus on energy and water reform and it’s easy to see why choosing the right pump or pumping system is just one in a very long list of considerations for the modern irrigator.
It was with this mind that PIA member, CAP Industries joined together with irrigation products giant, TORO Australia and leading irrigation consultant, HydroPlan to present the “Achieving Irrigation Efficiency: How can it be done?” workshop in Geelong at the end of July.
The workshop was the first in what is expected to be a series of events conducted across Victoria over the coming months. The aim of the day-long event was to provide a productive and challenging environment where irrigators could access the information, skills and expertise needed to address a wide range of irrigation issues.
In order to achieve this admittedly ambitious goal, the three companies adhered to a very simple approach – less theory, more reality. This approach was upheld by all presenters, including the keynote speakers, who were required to include real-life examples, and perhaps more importantly, absolutely no branding or sales talk.
Keynote speakers for the day were Dr Dale Browne, Senior Engineer at E2 Design Lab, and Mr Richard Dilena, Irrigation Officer for the City of Greater Geelong.
Dr Browne began the day with a discussion on Water Sensitive Urban Design (WSUD) and opportunities for stormwater use in irrigation applications. His presentation highlighted how we can minimise the import and export of water resources across town and city boundaries by managing the use of stormwater, rainwater and wastewater resources available. Dr Browne illustrated how this approach is already being put to practice, drawing on examples at Elsternwick Park and the new Harcrest development in Melbourne’s outer eastern suburbs.
Mr Dilena from the City of Greater Gee-
long followed on with a frank presentation on variable water supply pressures and the implications for irrigation of sports grounds in and around Geelong. Irrigation and water management has had an increasing priority for Mr Dilena since 2000 and he now specializes in this area on a full time basis. In addition to his own presentation, Mr Dilena invited Toro, HydroPlan and CAP Industries to conduct an audit on the irrigation system at Geelong’s Drysdale Reserve. The findings of this audit were then presented to a panel for discussion, recommendations and audience participation.
Other presentations for the day were delivered by the hosts of the workshop. Topics ranged from sprinkler maintenance and central control options to the importance of irrigation design and, of course, a consideration of pumps and pump systems.
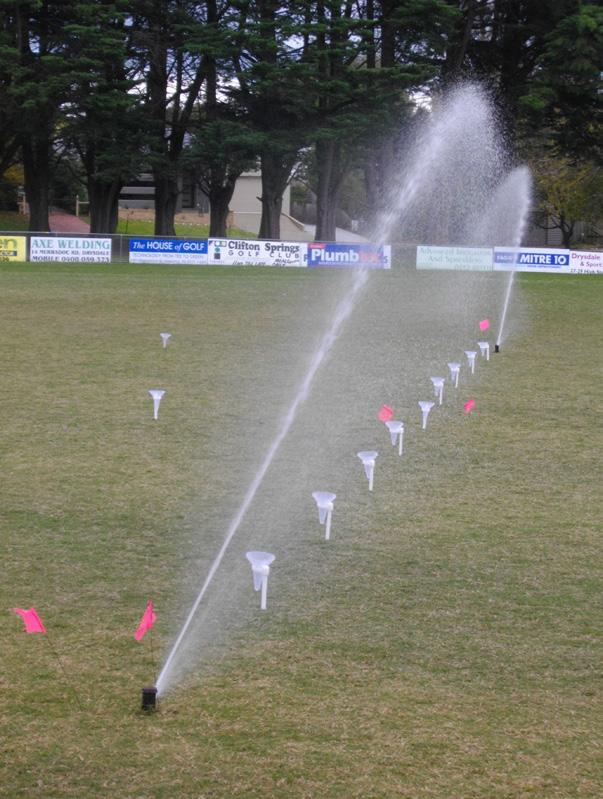
be able to gain some insights from the experiences of others while also acquiring some tools to help them tackle their own irrigation challenges.”
According to Bou Spithoven, Managing Director with CAP Industries, while the workshop touched on a wide range of issues, it was not intended to solve every irrigation challenge in an afternoon. “What we really hoped was that attendees would
Mr Spithoven highlights that the support of the City of Greater Geelong and in particular, Mr Dilena was invaluable to the event. “Efficient, effective irrigation is clearly a priority for Mr Dilena. I believe his willingness to get involved and share his experiences for the good of others is something we can all learn from.”
Wilfley Mining Slurry Pumps
SINCE 1962, pump equipment specialist Acromet has provided an extensive range of pumps, feeders and chlorinators to a diverse range of industries.
The only Australian company that manufactures its own range of metering pumps, Acromet produces state-of-theart equipment for use in applications including: processing; potable water and waste water treatment; food production; pharmaceuticals; cooling towers and boiler treatment; plastics; mineral processes; and pulp and paper.
Catering for gas, liquid, dry bulk materials and packaged systems, Acromet’s highly precise product range includes metering pumps, dry material feeders, chlorinators, sulfonators and process pumps.
Acromet’s new Wilfley’s Model Kpro solids-handling centrifugal pump, which the company recently introduced to the Australian market, is designed for abrasive solids applications such as those found in mining applications. The exclusive design features increased product versatility, improved pump reliability and lower energy consumption.
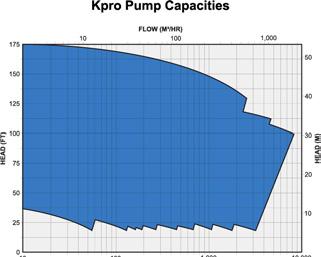
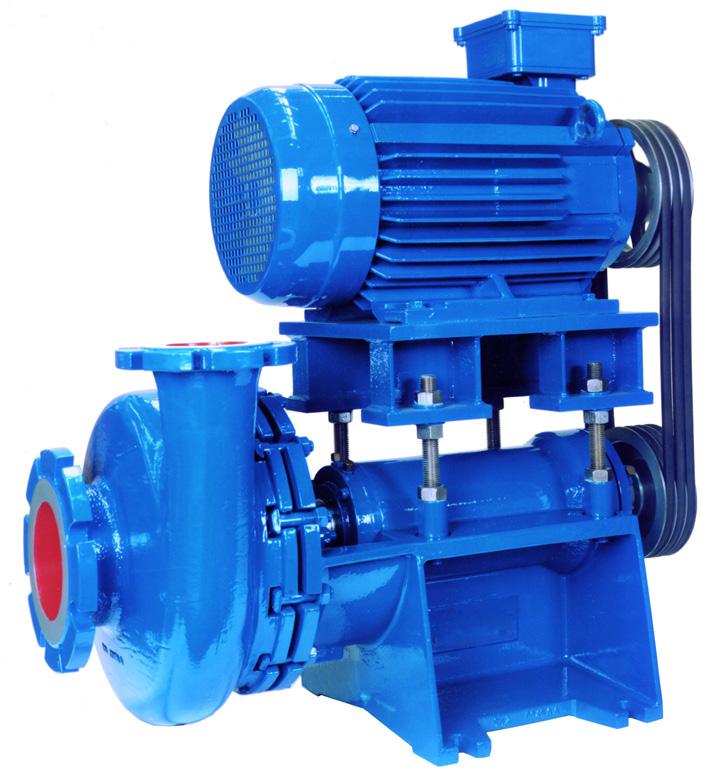
Wilfley is famous for pioneering the Hydro Dynamic Seal, eliminating the need for gland packing and typical mechanical seal designs. The Wilfley pump offers high reliability and ease of maintenance, with an inbuilt swing crane assembly that allows the pump casing to be opened to provide direct access to the impeller and expeller without disturbing the suction and discharge pipes.
It includes a closed impeller with extrathick shroud and vanes to maintain excellent performance characteristics, and a bearing assembly that provides an ample oil reservoir. The assembly is top filling, contains an oil sight glass to monitor proper oil level, and has a labyrinth endcover oil seal to prevent contamination and provide long bearing life.
Wright Flow Technologies Revolution TM, CIP (Clean in Place) Hybrid Circumferential Piston & Lobe Pump
The RevolutionTM, is the latest innovation of Positive Displacement Pumps for the Sanitary and Industrial Markets, merging the benefits of Lobe & Circumferential Piston technologies into one platform. This new platform delivers increased product yield, increased lifetime of components, reduced maintenance costs, with outstanding CIP clean ability and higher standards of hygiene.
The RevolutionTM was released this year throughout Australia and New Zealand and acceptance has be over whelming described Mathew Harris Idex Regional Manager for Australia.
“Wonderful, Fantastic, Uno spettacolo” explained an Italian Maintenance Manager currently using this pump on tomato pulp at 80/85°C. He comments: “Product damage has been 100% eliminated; linear pumping has resulted in 50% reduction of steam consumption through the heat exchanger and in the tank; and
this is the first pump that we are able to clean easily through CIP, eliminating the need to strip clean. Very good results!”
The RevolutionTM brings together the benefits of superb cleanability, improved volumetric efficiency and outstanding solid handling into one platform. It features capacities to 190 m3/hr, differential pressures to 31 bar, with all seals being front replaceable for minimum downtime, a pre-filled maintenance free gearbox, a self-draining pump head to minimise product loss, and the flexibility that allows the end user to choose the best rotor technology to fit the application.
ABOUT Wright Flow Technologies
Wright Flow Technologies, part of IDEX Corporation, offers technologies such as Rotary Lobe, Circumferential Piston, AODD, and Magnetic & Turbine Flow Meters. This portfolio provides solutions to applications in the Food, Dairy, Beverages, Personal Care, Pharmaceutical, Biotech, Chemical and other special
industries. For more information visit www.johnson pump.com.
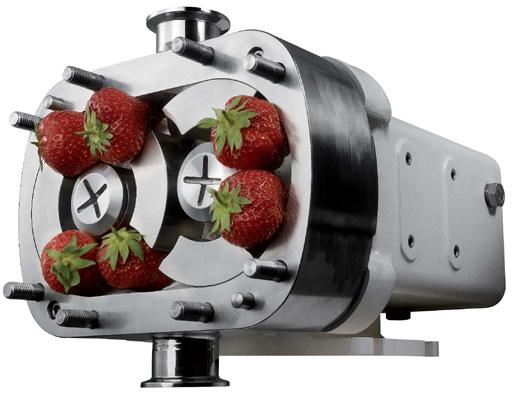
Pulsafeeder High Flow, High Pressure Pump PulsaPro 900
Pulsafeeder announces the PulsaPro 900, a hydraulic diaphragm process and metering pump specifically developed to target the robust needs of the oil and gas, chemical, and petrochemical markets. This pump was engineered with the strength to withstand a hurricane.
Designed to support higher flows and higher pressures, the PulsaPro 900 can
handle flows up to 62,000 lph (16,380 gph), standard pressures to 300 bar (4350 psi) and future design capabilities to 1000 bar (15,000 psi). This pump is precise and accurate up to +/-0.5%. It can handle process temperatures from -73°C (-100°F) to 260°C (500°F) with standard viscosities to 3000 cps. Engineered or custom configurations are also available.
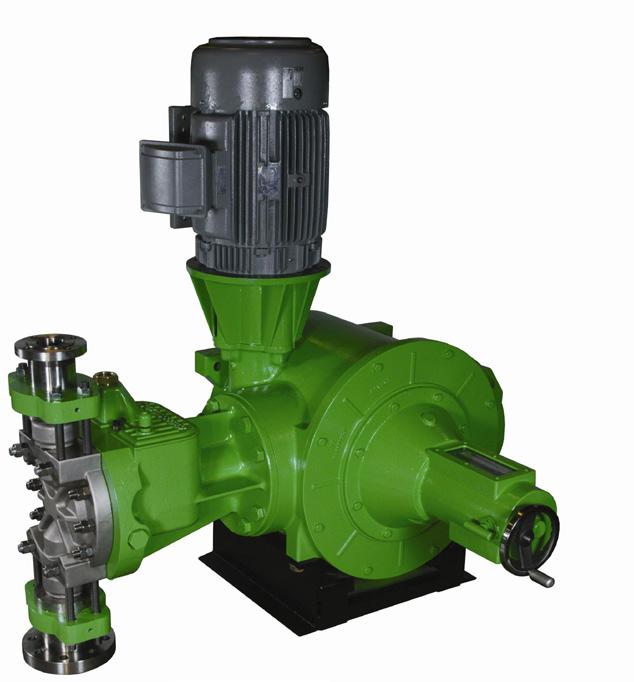
The PulsaPro 900 is a powerhouse of innovation. Modular in design, the PulsaPro 900 is adaptable to its environment. Motors can be mounted either vertically or horizontally on the unit and the gear box is available in five different configurations from a simplex configuration up to a quadruplex. The PulsaPro 900 comes equipped with the unparalleled patented Hydraulic Diagnostic Package which both protects the pump from damaging operation forces and presents a visual indication of
pump performance. The robust manual stroke adjustment is engineered to be simple to read and operate. A unique state-of-the-art option available on the PulsaPro 900 is the fluorocarbon lined reagent head which provides the highest corrosion resistance available at a cost much less than expensive high alloy metal constructions.
The PulsaPro 900 comes with a phenomenal five-year drive train warranty. Multiple packaged levels of “Keep On Pumping” or KOPkits are available for performing routine maintenance to assure optimal pump reliability and performance at the right price. The PulsaPro 900 is a versatile pump that is rugged, durable, and offers the lowest total cost of ownership in its class.
ABOUT Pulsafeeder
Pulsafeeder , part of IDEX Corporation, offers mechanically and hydraulically operated metering pumps and system solutions to applications in the Oil and Gas, Water Treatment , Chemical and other special industries.
For more information visit www.idexfmt-asia.com.
Editorial schedule
February 2013
Main feature
Training
Industry Focus
Oil & Gas
Manufacturing & Industrial use
Pump Products
Vacuum pumps
May 2013
Main feature
Imports & exports
Manufacturing
Industry Focus
Water
HVAC
Plastics, rubber, chemicals
August 2013
Main feature
Energy efficiency
Industry Focus
Mining
Food
Wastewater
Pump Products
Balancing
November 2013
Main feature
State of the industry
Industry Focus
Power generation
Fire protection
Irrigation
Pump Products
Repair & maintenance
Deadline: 30 November, 2012
Related Products
Valves Manifolds
Cylinders & actuators
Pipes and piping systems
Filtration systems
Lubricant & lubrication systems
Coatings
Custom casting
Deadline: 22 March, 2013
Related Products
Connectors
Couplings & seals
Bearings
Mechanical seals/support systems
Elastomeric seals/gaskets/packing
Wear rings
Deadline: 14 June, 2013
Related Products
Motors and drives
Gears
Cylinders & actuators
Compressors
Fans
Deadline: 6 September, 2013
Instrumentation, control & monitoring
Pressure, temperature and level gauges and sensors
Vibration instrumentation and analysis sensors
Flow meters, control panels
alignment tools
Condition monitoring sensors
Infrared thermography
Event distribution and more
IDEX Fluid & Metering
KSB Australia
Northern Diesel & Hydraulic Serv.
PIA Expo
Precision Balancing
Pump Affinity
Pump industry advertising
Pump industry subscriptions
Renroc Group (Pumps & Eng.)
Pumps
Stevco Seals & Pumps
Missed out this time?
Didn’t manage to get an ad into this issue and wish you had?
Don’t worry, as the next edition is just around the corner
Contact Chris Bland now to book in now for the next edition to ensure you don’t miss out again
magazine@pumpindustry.com.au
(03) 9440 5721
Many of the above features will tie in with major conferences and exhibitions to be held throughout 2013 and pump industry magazine will have a presence at many relevant events
Keep your eye on the website for the latest information www.pumpindustry.com.au




Hit all your targets


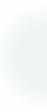


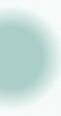





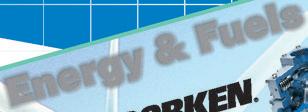
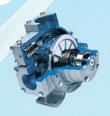

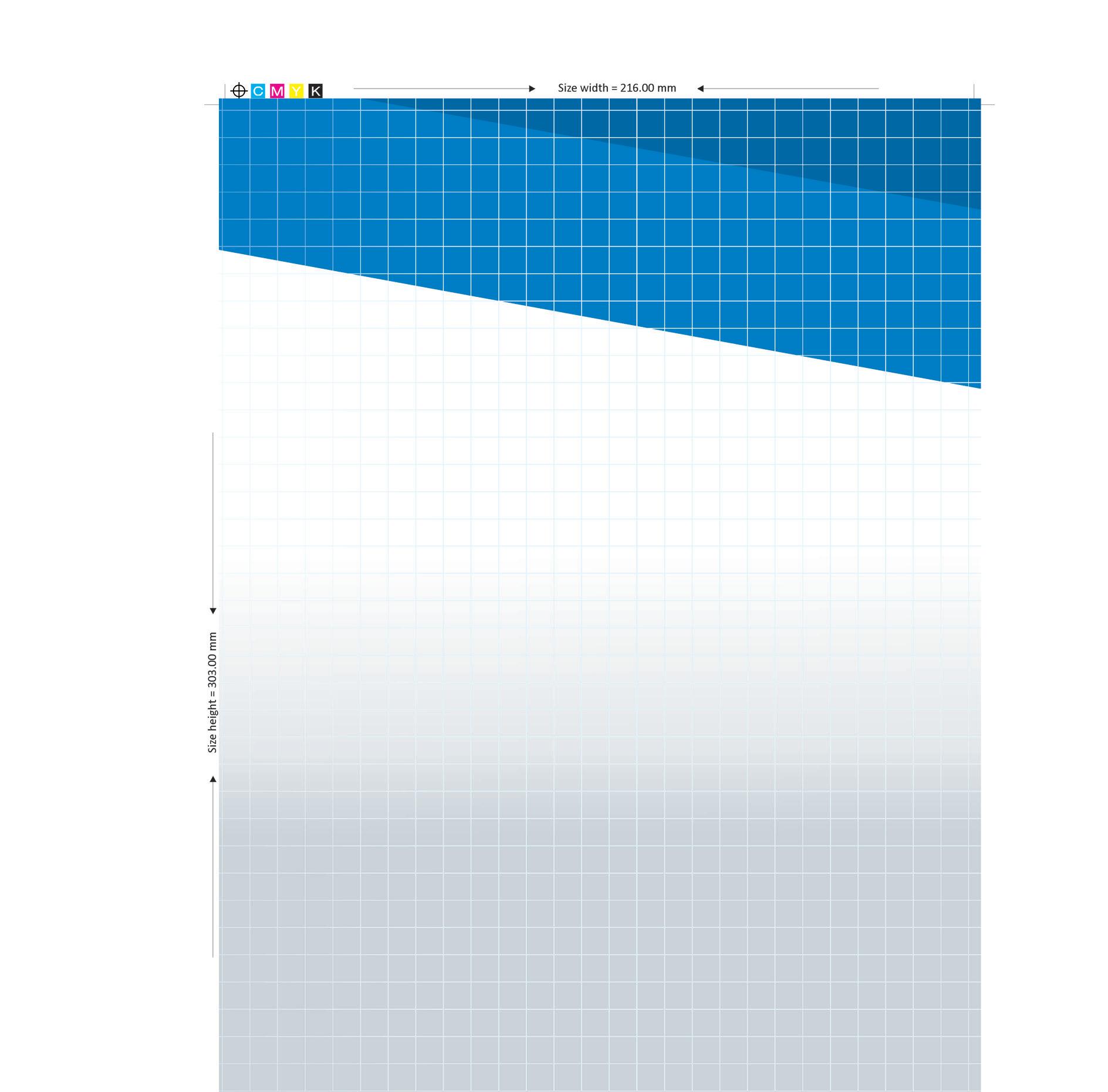
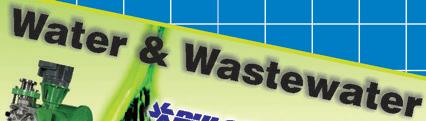
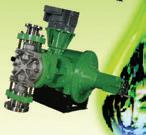
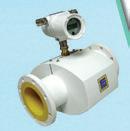
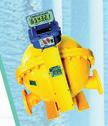
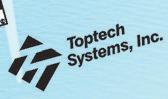
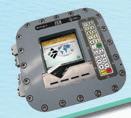
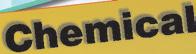
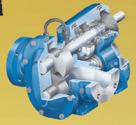
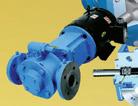


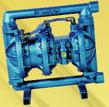
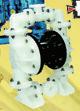

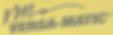
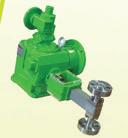
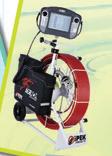
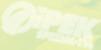
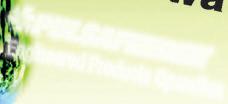
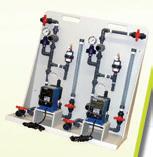
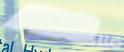
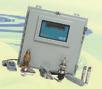



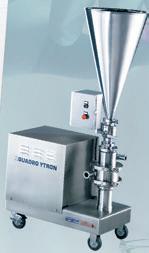
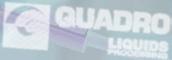




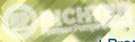
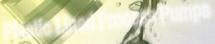
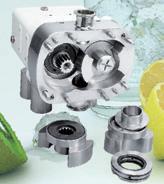
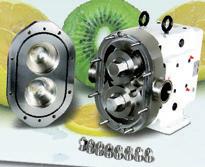