ELEPHANTINE TASK FOR LOOKING AFTER SHARKS
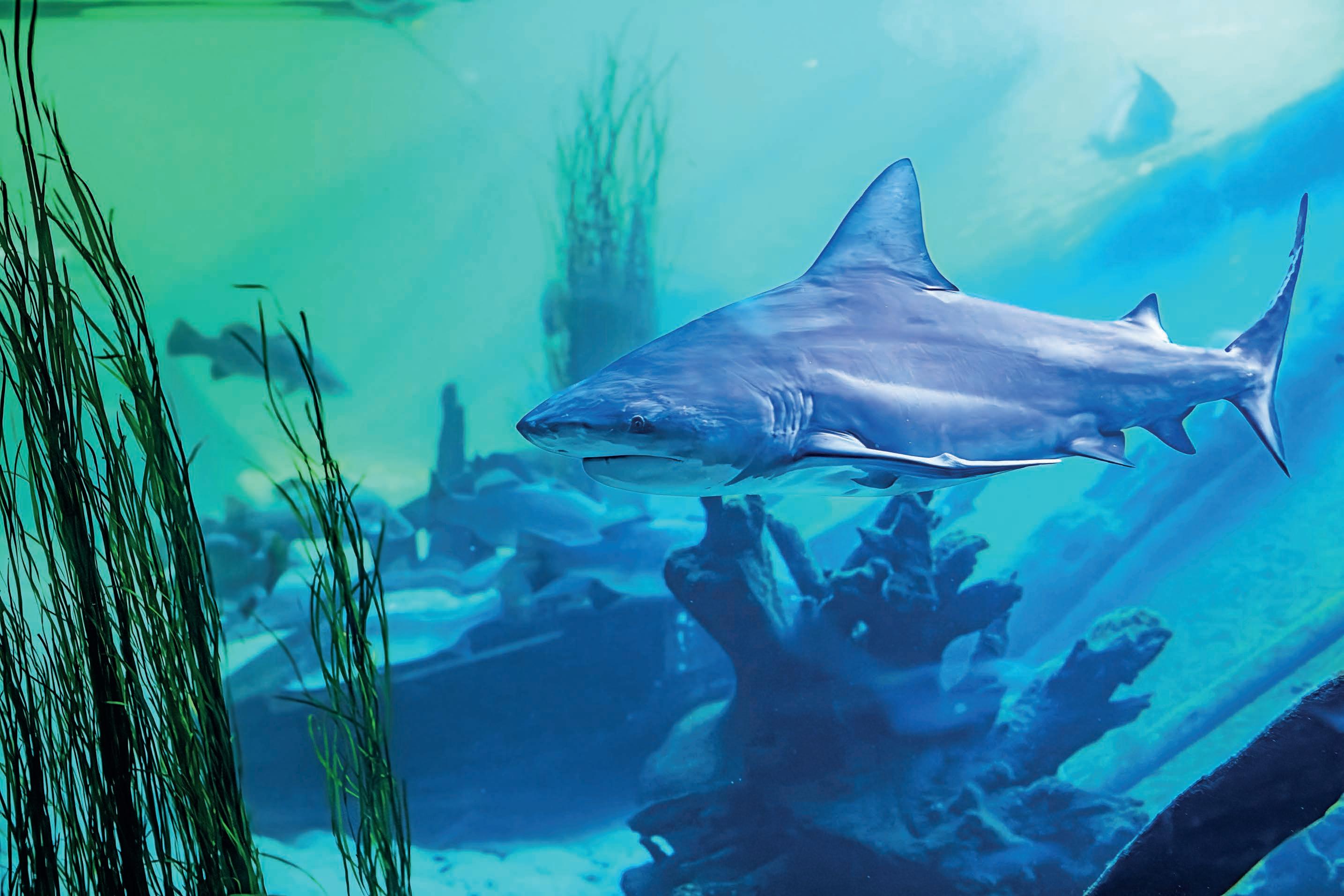
Company acquisitions shake up industry
Smart pump technology for greater efficiency
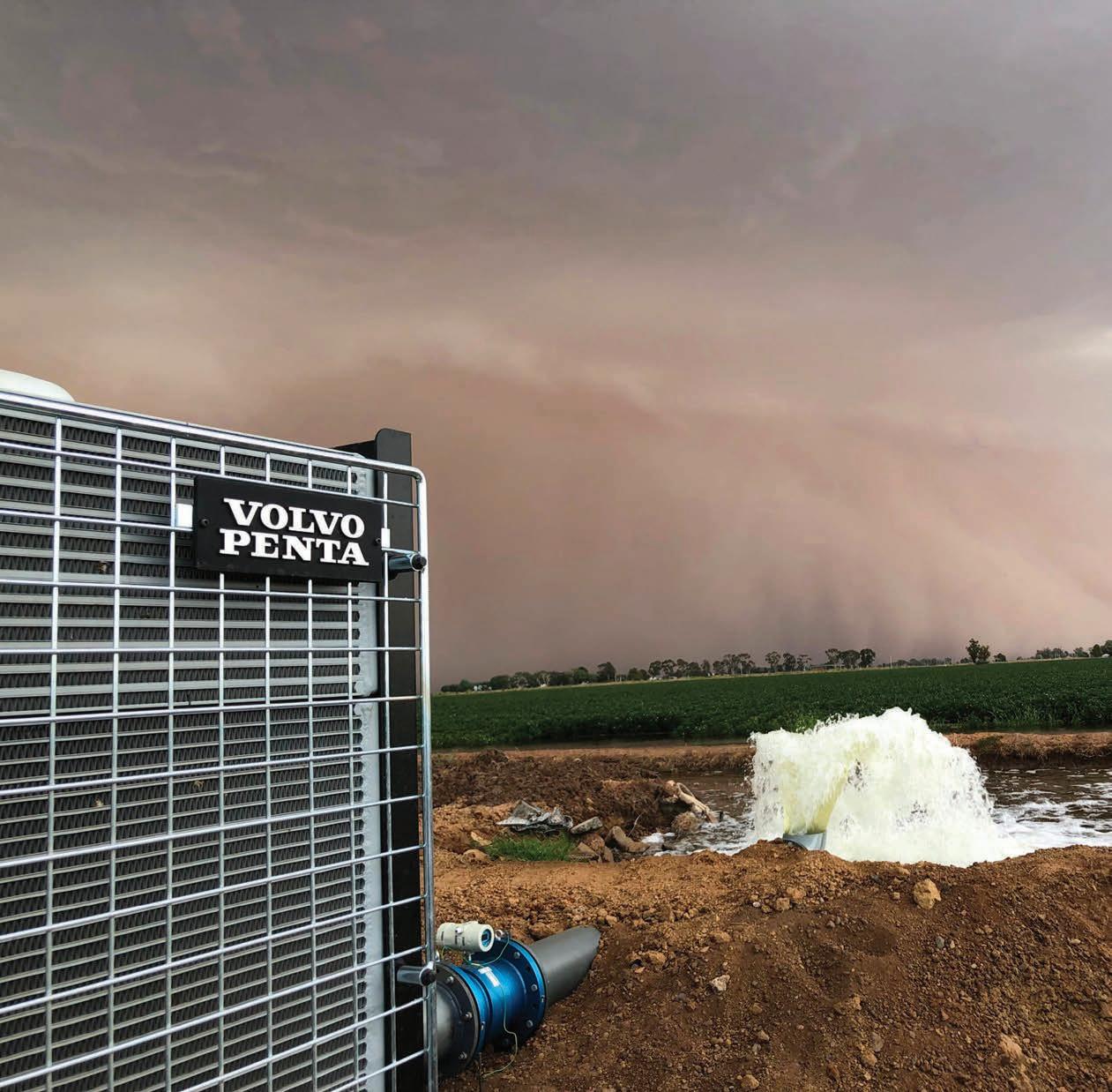
Powerful Partnership
ELEPHANTINE TASK FOR LOOKING AFTER SHARKS
Company acquisitions shake up industry
Smart pump technology for greater efficiency
Powerful Partnership
Engines that keep running even in the toughest conditions. Easy to install, operate and maintain. A powerful partnership you can trust all the way from the drawing board throughout the operational life of your engine. Competitively priced complete power-pack units ready for delivery Australia wide with a local support team on hand 24/7.
To find your nearest dealer visit volvopenta.com/industrial
Pump Industry Australia Incorporated
PO Box 527
YARRAWONGA VIC 3730
Phone: +61 493 975 931 secretary@pumps.org.au www.pumps.org.au
PIA Executive Council 2025
Kylie Kinsella - President Regent Pumps
Joel Neideck – Vice President TDA Pumps
Tracey Guida – Treasurer/Secretary
Alan Rowan – Councillor Executive Officer – Publications and Training, Life Member
Ken Kugler Executive Officer – Standards, Life Member
Steve Bosnar – Councillor Franklin Electric/Pioneer Pumps
Michael Woolley – Councillor Tsurumi Pumps
Luke Biermann – Councillor Mechanical Seal Engineering
Tim Yakup – Councillor Regent Pumps
Alex Calodoukas – Councillor Pump Strategy
Keith Bowen – Councillor Xtron Pumps Australia
Welcome to the autumn edition of the Pump Industry magazine. As Australia transitions into autumn, many people will be relieved to finally see some cooler weather, indicative of the new season. The vibrant tapestry of leaves and the gentle warmth of the sun make it an ideal time for individuals to go outside and embrace the cooler conditions.
Many people will embrace major events held in each Australian city over autumn, including the Melbourne Grand Prix, Adelaide Festival, Tasmanian Autumn Festival, Vivid in Sydney, and the return of the AFL season.
The committee’s priority over the summer has been to critically examine the future of our association and listen to our members and industry colleagues so that we will thrive, continue to grow, and welcome new members into the future.
As part of this critical review the Pump Industry Committee has been focused on renewing our value proposition and providing clarity for our members.
We have agreed to strive for the following values as we plan for 2025.
• We’re dedicated to promoting, expanding and improving the pumping industry through progressive leadership, education, communication and advocacy.
• We advocate on legislative and regulatory issues that greatly affect the pumping industry to create safe practices.
• We offer tailored educational events to help those engaged in the industry become more successful in their business.
For our members and industry colleagues considering joining our association, your membership will provide the following benefits for your business:
• Company Listing on the PIA website’s Member Directory
• Company listing in the printed PIA Magazine annual Pump Capability Guide
• FREE subscription PIA Magazine
• D iscounts for advertising in PIA Magazine
• N etworking opportunities with industry professionals
• D iscounted industry handbooks
• Certified training events
• Lifetime membership opportunity rewarded for contribution to the PIA ARCH
• D iscounts on PIA handbooks.
• Access to pump professionals.
• Tools for commissioning pumps.
• M embers rate for events and AGMs.
• M eetings and discussions around market trends.
• M entoring of new pump professionals.
• M embership pack
We hope that formalising the association’s benefits and values will encourage current members to renew and other businesses in our industry to join us this year.
The Pump Industry Committee announces the following events for 2025.
Technical Training – Installation and Commissioning
Social Event (in association with fundraising for the Cancer Council).
Dates and venues announced soon.
Annual AGM/Dinner – 13 November (Crown Plaza, Melbourne)
The PIA would also like to thank WEG, Caterpillar and Mechanical Seal Engineering for their commitment to sponsorship for 2025.
The committee is looking forward to seeing you at the planned events for 2025.
I wish you all a lovely Easter break. Stay safe.
Kylie Kinsella PIA, President
Scan to subscribe to Pump Industry’s weekly newsletter –delivered to your inbox every Thursday afternoon.
Cover image: Sydney Water, Sydney Zoo
COVER STORY
Published by
Chief Executive Officer
John Murphy
Chief Operating Officer
Christine Clancy
Editor Chris Edwards
Journalists
Kody Cook
Design
Jacqueline Buckmaster
Head of Design
Blake Storey
Business Development Manager
Rima Munafo rima.munafo@primecreative.com.au +61 413 475 078
Client Success Manager
Louisa Stocks
Head Office
Prime Creative Media
379 Docklands Drive
Docklands Victoria 3008
P: +61 3 9690 8766 enquiries@primecreative.com.au pumpindustry.com.au
Subscriptions
P: +61 3 9690 8766
subscriptions@primecreative.com.au
Pump Industry is available by subscription from the publisher. The rights of refusal are reserved by the publisher.
MAINTENANCE
6Saving water at Sydney Zoo
PIA MEMBER NEWS
10 Pumping up performance with latest innovations
12 Enhancing safety in pumping operations
14 Optimising water flow with Franklin Electric pumps
17 The powerhouse behind industrial pumping
18 Pump testing: The heart of making pumps
20Cutting pumping costs with smarter controls
22 Powering pump efficiency with new technology
FLUIDS
25 First Australian implementation of Smart Air Injection
28 Smart dosing made simpler and safer
31 Pioneering positive displacement pump technology
3 President’s welcome PUMP CURVES
48 Seals under pressure: Part 3
32 A smarter, process-first approach to condition monitoring
MINING
34 Achieving world-class results under the pump
SUSTAINABILITY
36 Powering progress together for a sustainable future
ACQUISITIONS
38 Industry shake-up: Major pump players make bold moves
INDUSTRY ADVOCATES
42 Safeguarding the future of energyefficient heating
44 The need to lead
EVENTS
46 Global influence of pump progress at AIMEX
PUMP HANDBOOK
51 Pump installation
PUMP SCHOOL
54 How do you maintain an air-operated diaphragm pump?
This magazine is published by Prime Creative Media in cooperation with the Pump Industry Australia Inc. (PIA). The views contained herein are not necessarily the views of either the publisher or the PIA. Neither the publisher nor the PIA takes responsibility for any claims made by advertisers. All communication should be directed to the publisher.
The publisher welcomes contributions to the magazine. All contributions must comply with the publisher’s editorial policy which follows. By providing content to the publisher, you authorise the publisher to reproduce that content either in its original form, or edited, or combined with other content in any of its publications and in any format at the publisher's discretion.
Pumps Industry acknowledges Aboriginal Traditional Owners of Country throughout Australia and pays respect to their cultures and Elders past, present and emerging.
Precision-engineered for the most demanding applications, FELUWA’s MULTISAFE® technology ensures safe and efficient handling of abrasive, aggressive and toxic media – even under extreme operating conditions.
Our pumps are designed for high-pressure and high-performance requirements, delivering:
Flow rates up to 1,000 m³/h
Pressures up to 350 bar
YOUR SOLUTION FOR:
Reactor, autoclave and gasifier feeding
Concentrate and tailings transfer
Fly and bottom ash disposal
Wet oxidation
Mine dewatering
A splash of innovation: How Sydney Zoo and Sydney Water are working together to reduce water waste – with pumps playing a crucial role.
Sydney Zoo has implemented a comprehensive stormwater capture and recycling system to reduce its reliance on potable water. It involves collecting stormwater runoff and repurposing it for use in moats and garden areas, significantly decreasing drinkable water consumption. By capturing stormwater, the zoo conserves valuable drinking water and mitigates the environmental impact of stormwater runoff.
“We most certainly do have a sustainability focus on water management,” a Sydney Zoo spokesperson said. “All rainwater is captured in the bottom dam, which feeds all the moats throughout the Zoo. With this, we don’t use potable water to top up these moats.”
Suhanti Thirunavukarasu, Sydney Water’s Water Conservation Programs Manager, highlighted the importance of water conservation beyond Sydney Water’s direct influence.
“The interesting thing about the zoo is that they have really taken on board the messages we are sharing with businesses about water conservation and efficiency,” Thirunavukarasu said. “There’s a whole side to water conservation that falls to businesses to step up and use the stormwater they have at their sites. Thanks to this partnership with Sydney Water, we are now able to guide Sydney Zoo through the next steps in their water efficiency programs and complement their stormwater strategy work.”
The zoo’s approach to stormwater management supports its sustainability goals and sets an example for other facilities seeking to optimise their water use. As urban areas continue to grow, finding alternative water sources and improving water conservation efforts become essential in ensuring long-term resource availability.
The role of pumps in stormwater management
The zoo’s stormwater management strategy aligns with broader environmental conservation goals. Effective stormwater harvesting and reuse can alleviate pressure on municipal water supplies, especially during drought or water restrictions. Implementing such a system requires careful planning and collaboration.
Sydney Zoo’s partnership with Sydney Water exemplifies how organisations can work together to achieve environmental objectives.
One of the fundamental aspects of stormwater conservation at Sydney Zoo is ensuring the infrastructure effectively manages fluctuating water levels while maintaining efficiency. Pumps are critical in ensuring stormwater is efficiently captured, stored, and redistributed where needed.
“Even with the Hydraloops that are being trialled across Australia, you need to have a pump to recirculate the water,” Thirunavukarasu said. “It’s a fundamental part of anything where you’re recirculating water because you need to be able to have the pressure to send it back. It’s a key component of these systems.”
Optimising pump efficiency for sustainable operations
Selecting the right pumps is essential to maintaining system efficiency. Pumps must be designed to handle fluctuating demand while operating within an optimal efficiency range.
“When we specify pumps that are used in our system, we look at the system head curves and the different conditions the pumps would have to operate in and come up with a bit of a plan to ensure they’re running efficiently,” Thirunavukarasu said. “We also need to consider energy consumption and heat generation, as these factors directly impact system longevity and operational costs.”
By integrating efficient pumping systems into stormwater management, Sydney Zoo ensures that its water conservation efforts are
both practical and sustainable in the long term.
“The main filtration for the shark tank uses a combination of mechanical, biological, and chemical filtration,” a Sydney Zoo spokesperson said. “The life support system combines glass media filters, carbon filters, foam fractionators, and an ozone generator with a contactor unit.
“These filtration processes work together to tackle different aspects of cleaning and clarifying within the large body of water. With the addition of physical cleaning via dive vacuuming, this process can take up to five to six hours at one time to vacuum the gravel, scrub the walls and furniture, and clean the acrylic viewing area so the public can see the sharks and fish.”
Efficient filtration: maintaining water quality
Ensuring high-quality water is essential in environments housing diverse species. Bull sharks require stable salinity, pH levels, and pathogen control to support their health. Their water must be continuously filtered to remove organic matter, maintain oxygenation, and prevent bacterial growth, mimicking their natural estuarine habitats.
Sydney Zoo’s 1.1 million-litre bull shark tank relies on an advanced recycled water system incorporating ultraviolet (UV), ozone, and chemical treatments.
“Sharks require special considerations,” a Sydney Zoo spokesperson said. “Maintaining an
entire ecosystem balance is essential for their health and welfare. Bull sharks are Euryhaline, which can adapt to varying salinity levels – fresh, brackish, and marine. We keep the tank at five parts per trillion (ppt), whereas marine is 35 ppt. Salt levels also have therapeutic benefits. Temperature is between 22 and 24 degrees, with pH levels between 6.5 and eight.”
This system ensures the water remains free of harmful bacteria while retaining necessary minerals and salinity. Since 2022, it has saved over 30,000 kilolitres of drinking water, demonstrating how advanced water recycling supports marine conservation and sustainability.
Maintaining water quality through advanced filtration
Thirunavukarasu highlighted the similarities between Sydney Water’s drinking water management and Sydney Zoo’s water quality efforts.
“The way the zoo manages water – monitoring daily, checking chemical levels, disinfecting, and removing pathogens – is quite similar to how we ensure Sydney’s drinking water is safe,” said Thirunavukarasu.
Filtration is key to maintaining a healthy aquatic environment. By
implementing advanced technology, Sydney Zoo ensures water quality while reinforcing its commitment to sustainability. To minimise water waste, the zoo captures and recycles 40,000L of vacuum water from the shark tank per dive.
“This water undergoes chlorine treatment and filtration before being safely reintroduced to the system,” a Sydney Zoo spokesperson said. “We still use fresh water to top up what is lost through evaporation and normal system management such as backwashing.”
Energy efficiency: powering sustainable operations
Energy consumption is a critical factor in water management. Sydney Zoo integrates water efficiency with broader sustainability initiatives to minimise its environmental footprint. The zoo spokesperson emphasised how its landscaping supports water conservation across the whole property.
“With all the planting done throughout the zoo, we prevent erosion to ensure we don’t silt up the bottom dam,” they said. “Additionally, with planting through the swale system (a shallow, vegetated channel designed to manage stormwater runoff by slowing, spreading, and infiltrating water), lots of
nutrients and impurities are taken out of the water, ensuring the water in the moat system stays healthy.”
Thirunavukarasu focused on Sydney Zoo’s water side and its work to ensure it makes the most of its precious water resources.
“Sydney Zoo is making the most of every drop they’ve got – that’s recirculating, using alternative water, and improving efficiency in how they manage on-site,” she said. “Even the bathrooms have efficient fixtures and fittings.”
Energy-efficient technologies like variable frequency drives and energy-efficient motors help reduce excess energy use. Smart pump control systems and regular maintenance further optimise energy consumption. By integrating these technologies, Sydney Zoo balances conservation with operational efficiency, demonstrating how targeted infrastructure investments create long-term sustainability benefits.
Collaborative efforts: a blueprint for success
The partnership between Sydney Zoo and Sydney Water is a model for crossindustry collaboration in environmental conservation. Both organisations have
achieved significant water savings and operational efficiencies by combining resources and expertise, demonstrating how private enterprises and public utilities can work together towards shared sustainability goals.
“We are excited by this fantastic opportunity to work together,” said Thirunavukarasu. “They’ve got one big tank that they’re already recirculating the water in, and it’s saved something like 30,000 kilolitres over the past couple of years, which is huge.”
This kind of collaboration enables both parties to leverage their strengths – Sydney Water provides expertise in water conservation and efficiency, while Sydney Zoo offers a real-world application where these strategies can be tested and refined. As industries become more conscious of their environmental impact, partnerships like this highlight the benefits of proactive water management.
Engaging with external partners can also provide access to additional resources, such as funding opportunities and technical expertise.
“It’s about more than just water savings; it’s about knowledge-sharing and innovation,” Thirunavukarasu noted. “By working together, we can identify new opportunities to reduce consumption, improve efficiencies,
and apply these lessons across different industries.”
This collaboration ensures that sustainability projects can be implemented efficiently and costeffectively while paving the way for broader adoption of advanced water conservation technologies in commercial and industrial settings.
Looking ahead: Opportunities for broader application
Sydney Zoo’s strategies offer valuable lessons for other industries and institutions. Implementing stormwater capture systems, investing in advanced filtration technologies, and embracing energy-efficient practices can be adapted across various sectors.
These strategies demonstrate the importance of a multi-faceted approach to water conservation, where efficiency, innovation, and collaboration combine to create meaningful and lasting impacts.
Thirunavukarasu pointed out the significance of Sydney Zoo’s efforts as a case study for other organisations.
“The Sydney Zoo example will help create this visibility of what other businesses could be doing,” she said. “They’ve got that unique combination of having the aquarium and the land animals, so looking at that as a case
study and seeing how other zoos or other businesses can apply similar strategies is a real opportunity.”
Moreover, these initiatives can lead to cost savings, regulatory compliance, and enhanced community relations. They demonstrate a proactive approach to environmental challenges, positioning organisations as leaders in sustainability.
Beyond the direct financial and operational benefits, these strategies reinforce corporate responsibility, demonstrating a commitment to resource management and ecological preservation.
Thirunavukarasu said Sydney Water and Sydney Zoo’s work will likely influence broader industry trends, encouraging more businesses to re-evaluate their water use.
“Every day, we look at innovative ways we can save water while providing world-class animal care,” said a Sydney Zoo spokesperson. “Sustainability is at the heart of our operations, and we are committed to continuously improving and reducing our water footprint.”
“Water is a finite resource, and every drop counts,” said Thirunavukarasu. “By taking proactive steps today, we can create a more resilient future – not just for businesses, but for the communities and environments that rely on sustainable water management.”
Energy efficiency, compliance, and reliability are not pipe dreams –new pump technology is setting new standards across key industries.
Pumps do more than move water –they power essential systems in commercial buildings, industrial operations, and fire protection networks. The heating, ventilation and air-conditioning (HVAC) industry is conscious of pumps’ important role in devices dotted across the country and worldwide.
With rising energy costs and stricter regulations, businesses need smarter, more efficient solutions to stay ahead. The latest innovations optimise performance, reduce downtime, and ensure compliance.
Leading the charge is EBARA PUMPS AUSTRALIA. With more than 100 years’ experience supplying high-quality pumping solutions nationwide, it has built a reputation for reliability and innovation.
Since establishing a local presence in 2000, it has expanded its range and developed a nationwide dealer network to provide expert support and service. With a new lineup of cutting-edge pumps, industries can access smarter, more efficient solutions than ever before.
Smarter HVAC pumping with the 3E series
The 3E series is the latest in-line centrifugal pump for HVAC and industrial applications. It comes in two configurations: the 3E model, featuring an extended shaft with the impeller mounted directly on the motor shaft, and the 3ES model, which uses a stub shaft to connect separate motor and pump shafts, allowing compatibility with
commercial standard motors. Built with a durable cast-iron casing, the 3E series supports 2-pole and 4-pole motors for long-lasting performance.
A back pull-out design speeds up servicing, reducing downtime, while standardisation with EN733 end suction pumps shortens lead times and lowers manufacturing costs.
Designed for circulation, heating, and air conditioning systems, the 3E series combines efficiency, reliability, and easy maintenance, making it a smart choice for demanding applications.
Efficiency in motion with E-SPD+
Energy efficiency is no longer optional – it’s a necessity. The E-SPD+ motor-mounted variable speed drive delivers savings by adjusting pump speed to match system demand. Designed for circulation, pressure boosting, and HVAC systems, it optimises performance while reducing energy waste.
The system adapts to different applications with multiple operating modes, including constant pressure, differential pressure, and temperature control. Intuitive programming simplifies setup, while seamless integration with 0-10V analogue input and Modbus communication enables external control and monitoring.
Compatible with inline and vertical multistage centrifugal pumps, the E-SPD+ provides flexibility without compromising efficiency. With power options up to 11kW, it can help businesses cut costs while improving performance.
Fire protection that meets Australian standards
Fire protection systems demand reliability, especially in critical moments. The GS series end suction pump meets AS2941:2013, ensuring compliance with Australian fire safety regulations and delivering dependable operation when it matters most. This is why the GS series is sought after across the Australian and New Zealand markets.
To meet this standard, the pump must handle 130 per cent of its duty flow while maintaining at least 80 per cent of its duty head. At shut-off, its pressure must stay below 140 per cent of duty head.
Designed for continuous operation during emergencies, the GS series ensures durability and performance under high-stakes conditions.
Built for fire protection applications such as sprinklers, hydrants, water spray, and hose reel systems, this pump withstands the demands of emergency use with reliable pressure and performance.
A legacy of performance
For more than 40 years, EBARA pumps have powered Australian businesses with quality, reliability, and efficiency. Since establishing a local presence in 2000, EBARA PUMPS AUSTRALIA has expanded its range to meet growing industry demands. Backed by a nationwide network of dealers, EBARA ensures expert support and service every step of the way.
For more information, visit ebara.com.au
As a Japanese pump manufacture with a 100-plus year history, EBARA PUMPS AUSTRALIA offers a range of energy effecient, reliable products with cutting-edge technology. Our solutions are designed to exceed your expectations and exceptional performances.
3E series For HVAC E-SPD+(plus) For energy saving
Q max: 216 m3/h H max: 70 m
Q max: 1,300 m3/h H max: 150 m
Engineered solutions meet stringent safety standards, ensuring reliable performance in hazardous and safe environments.
In today’s manufacturing and processing environments, it is vital that electro-mechanical equipment used in OEM machines such as pumps are not only designed to high standards, but are also compliant where hazardous environments are present, such oil and gas, chemical plants, marine and mining. Hazardous environments are created where dust is generated, gases may escape, or solvents could evaporate. These scenarios can cause serious issues or harm if the correct mechanical/ electrical products are not selected, so it is vital to align with a supplier who understands the risks and has a product range to suit.
WEG is a well-known global manufacturer of electromechanical equipment, that now offers the range of WG20 helical gearboxes to complement its industryleading range of safe and hazardous electric motors and automation products.
From this expanded portfolio of rotating machines, WEG can provide both standard and hazardous area geared motor packages that are designed for specific industrial pumping applications where operational performance and safety are priorities.
The WG20 gearbox range consists of inline, parallel shaft, helical bevel, and helical worm, with the C series inline the most common reducer used in pumping applications. With its male shaft, foot/ flange mounting options, IEC input, and industry standard mounting dimensions, the C series can easily be integrated into most common pump configurations.
The hazardous area helical geared motor from WEG helps provide the correct speed for pump applications Image: WEG
of ratios covering the higher speeds predominantly seen in progressive cavity pumps. With ratios from as low as 2.52, and additional ratios to allow a more gradual increase in speeds, it is now easier for the customer to achieve a precise and coordinated flow rate.
With a modern design focusing on efficiency and reliable operation, the C series is available in both hygienic smooth die cast housing up to 600 Newton-metres (Nm), and a robust MONOBLOC cast iron housing for the 800Nm to 18,000Nm range.
With the pumping sector in mind, WEG’s Austrian-based R&D department recently increased the range and spread
There are many pumping applications where safety is just as important as flow rates, and this is where WEG can accommodate, courtesy of its extensive range of hazardous area motors, to provide a complete geared motor package.
The WEG Hazardous range of motors consists of; Flameproof (ExdB) and Increased Safety (ExeC, Extc, Extb,
Exeb), all of which are designed to be used in environments where there are risks of explosive gases, dust, or vapours.
WEG motors are certified for ATEX (Europe), IECEx (International), UL (USA), or CSA (Canada) standards, and are also certified to run on any PWM Variable Speed Drive. This provides peace of mind, knowing they are suitable for use in hazardous environments, and applications requiring a range of speeds.
For more information on WEG’s range of hazardous and safe area geared motors, visit www.weg.net/au
This advanced water pumping system offers superior efficiency, silent operation, and reliable pressure control, meeting the demands of modern applications.
Since 1962, Franklin Electric Australia has been a reliable source of water solutions for the Australian water industry as a subsidiary of Franklin Electric, established in 1944 in Bluffton, Indiana, USA.
Originally a small motor manufacturer, Franklin Electric has evolved into a global leader in comprehensive water and fuelling systems. Renowned for its technical excellence, the company’s products
are applicable across various sectors, including residential, industrial, agricultural, mining, municipal, commercial, and fuelling sectors.
VNQP 5” Series constant pressure submersible pump
The powerful VNQP 5” Series Constant Pressure Submersible Pump from Franklin Electric is designed for versatility and is suitable for household water supply, water transfer, sprinkler
systems, industrial applications, rainwater harvesting, washdown units and commercial water supply.
What is a constant pressure system?
A constant-pressure pump system brings several benefits that cater to the needs of modern consumers and enhance system efficiency.
Firstly, it ensures consistent water delivery, providing users with reliable and steady water pressure regardless
of fluctuations in demand. Secondly, unlike traditional systems that can suffer from pressure drops when multiple outlets are active, a constant-pressure system eliminates such fluctuations. This enables various taps and appliances to operate simultaneously without any degradation in performance, making it suitable for households with high water usage.
These systems often incorporate advanced technology, such as variablespeed drives and innovative controls, optimising energy consumption. This reduces homeowners’ operational costs and lessens the environmental impact.
Constant-pressure systems require less maintenance due to their stable operation, ultimately increasing longevity and reliability.
Finally, the increased comfort and convenience associated with constant pressure can enhance the overall user experience, making it an attractive option for residential and commercial applications.
VNQP 5” Series highlights
The VNQP 5” Series is engineered for efficiency, durability, and ease of use.
This advanced system’s variablespeed operation optimises water pressure and energy consumption, achieving maximum efficiency for users while effectively adapting to varying demands.
Its durable stainless-steel construction features top-of-theline corrosion-resistant hydraulic components for long-lasting performance in challenging environments such as coastal areas or industrial settings. Moreover, integrating the innovative DrivE-Tech
MINI VFD controller allows for precise speed and pressure control, further enhancing overall efficiency and ensuring optimal functionality.
This compact, design provides a strong and reliable water flow while occupying minimal space. One noteworthy characteristic is its silent operation, which minimises noise disturbances, thus contributing to a more comfortable user environment and reducing distractions in any space.
Additionally, the system offers versatile installation options, supporting both vertical and horizontal configurations to meet diverse application needs, both residential and industrial.
Easy maintenance has been prioritised, as the design allows for convenient servicing and repairs, ultimately saving time and effort for users. The streamlined service process enhances overall efficiency, further improving user satisfaction.
Supported by Franklin Electric’s long-standing reputation for quality, the VNQP 5” Series offers outstanding performance, dependability, and efficiency.
This style of pump is advantageous when pumping high temperature liquids that have a tendency to vaporise. As the pump is submerged in the liquid the risk of cavitation is greatly reduced.
These pumps are useful when pumping dangerous chemicals as they eliminate the chance of leakage. They are also used as an alternative to surface mounted self-priming pumps. Regent Sump Pumps are available in a variety of construction materials giving them the ability to handle aggressive liquids.
When it comes to moving massive amounts of liquid, size does matter. Regent Pumps’ 300/400 pump is making waves across industries that can’t afford to slow down.
Having the right size makes a difference in the pump industry, particularly in a flood situation or any time when there’s a lot of liquid to move somewhere else. Enter the 300/400 pump from Regent Pumps, a heavyweight champion in fluid dynamics. This behemoth can shift 300 litres per second at a 50-metre head, tipping the scales at a hefty 720 kilograms and stretching over 1155 millimetres. To put that into perspective, it’s akin to having a compact car dedicated solely to pumping duties.
“The 300/400 pump is engineered for high-demand applications where reliability and performance are nonnegotiable,” said Tim Yakup, National Sales Manager for Regent Pumps. “Its robust construction ensures it can handle the rigorous demands of various industries.”
One of the primary sectors benefiting from this powerhouse is mining, particularly for dewatering operations. In mining, efficient water removal is crucial to maintain operational continuity and safety. The 300/400 pump’s capacity ensures
water accumulation doesn’t hinder mining activities, even in the most challenging environments.
Wastewater treatment plants also find the 300/400 pump indispensable. These facilities require reliable equipment to manage large volumes of effluent, ensuring that treatment processes run smoothly and environmental standards are met. The pump’s ability to handle substantial flow rates makes it a trusted component in these critical infrastructures.
The 300/400 pump plays a pivotal role in agriculture, particularly in large-scale irrigation systems. Efficient water distribution is essential for crop health and yield. With its high flow rate, this pump ensures that vast agricultural lands receive an adequate water supply, supporting farmers in their quest for productivity.
Fire protection systems for expansive buildings and industrial complexes rely on the 300/400 pump. In emergencies, the ability to deliver large volumes of water rapidly can be the difference between containment and catastrophe. The pump’s design meets stringent safety standards, providing peace of mind to facility managers and occupants alike.
“Our pumps are designed with versatility in mind,” Mr Yakup said. “Whether it’s a mining operation needing rapid dewatering or a wastewater plant requiring consistent flow, the 300/400 pump rises to the occasion.”
Beyond its impressive specifications, the 300/400 pump is a testament to Regent Pumps’ commitment to quality and innovation. The company’s extensive experience, with over 300 years of combined knowledge, ensures that each pump is built to withstand the test of time and demanding conditions.
Metrology, the science of measurement, plays a crucial role in developing and manufacturing pumps like the 300/400. By ensuring precise
measurements and adherence to standards, metrology guarantees that each pump performs optimally and meets the specific needs of its application. This meticulous attention to detail underscores the importance of accuracy in engineering and manufacturing processes.
“Precision is at the heart of what we do,” Mr Yakup said. “Our adherence to stringent measurement standards ensures that our pumps deliver consistent performance across all industrial applications.”
As industries evolve and demands increase, the need for reliable and efficient pumping solutions becomes even more critical. The 300/400 pump stands ready to meet these challenges, embodying the blend of power, precision, and reliability that modern applications require.
Looking ahead, integrating advanced technologies and smart systems in pumps like the 300/400 could revolutionise fluid management across industries. As the landscape shifts towards greater efficiency and sustainability, staying informed about these advancements will be key for professionals seeking to optimise their operations.
The testing at Sterling Pumps and United Pumps is comprehensive, ensuring that only Images: Sterling Pumps, United Pumps
With pump performance under growing scrutiny, comprehensive testing has become essential – not only to verify design integrity but also to ensure efficiency, reliability, and compliance across a wide range of operating conditions.
Hydraulic design, 3D modelling, intellectual property (IP), and manufacturing expertise are all vital components in the development of efficient, high-performing pumps. With increasing emphasis on energy efficiency and the ongoing demand for reliability, manufacturers must continually assess and refine design and production methods.
Theoretical design lays the groundwork for pump development. However, casting and machining processes significantly affect how well a design performs in practice. Variations in these processes can lead to discrepancies in final pump performance, making real-world testing an essential step in the manufacturing cycle.
Pump testing verifies whether the intended design translates into operational success. It allows for identifying and implementing improvements, helping to optimise efficiency, durability, and performance.
Testing is equally critical for reconditioned pumps that have been
re-rated or modified to meet new hydraulic conditions.
Melbourne-based manufacturers United Pumps and Sterling Pumps operate two dedicated test facilities that support this process. One is a one megawatt (MW) facility in Pakenham, focused on deep well submersible and vertical turbine pumps, featuring a 15-metre-deep test pit. The other is a 2.5MW facility in Sunshine dedicated to horizontal pumps.
This site includes two independent sealed test loops and a 400,000-litre underground tank. Together, these facilities accommodate flow rates of up to 3000 cubic metres per hour (m³/h) and heads of up to 1800 metres.
These testing environments enable comprehensive performance validation, including flow, head, power, efficiency, vibration, sound, and net positive suction head required (NPSHr). The ability to assess performance across the full operating range – including mechanical run and endurance testing – assures that each pump will operate reliably under real-world conditions.
United Pumps provides end-to-end pump engineering and manufacturing services, covering the full lifecycle from concept and design through to fabrication and testing. The company produces API (American Petroleum Institute) 610-compliant, high-quality centrifugal pumps for the oil, gas and process industries, and for high end industrial and municipal applications. Engineering teams conduct detailed analysis using finite element analysis (FEA) and torsional analysis to ensure mechanical integrity and low-noise, low-vibration operation. Design principles such as double volute casings, balanced impellers, and double suction impellers are used to minimise stress on shafts and thrust bearings, improving long-term reliability.
Many clients require legacy pumps – including those from other manufacturers – to be overhauled and re-rated for new duty parameters. This work is supported by full-scale factory testing to ensure both pump and motor meet the updated performance and operational requirements.
Additional capabilities at the test facilities include in-house mechanical seal systems, which allow for the evaluation of pumps fitted with pressurised dual seals, and in-house variable speed drives for testing across a broad range of speeds.
Testing is conducted in accordance with the recognised industry standards:
• A PI 610
• A S ISO 9906
• A NSI/HI 14.6
Through robust design validation and rigorous testing, manufacturers can ensure that each pump delivers the efficiency, reliability, and performance demanded by modern applications.
Oil & Gas, Industrial, Defence, Power, Municipal, Irrigation & Mining. Engineered and Manufactured in Melbourne
Submersible Pumps and Motors, Ballast pumps, Vertical Turbine Pumps API610 Pumps – Extensive Reference Lists Repairs, Design Upgrades, OEM spare parts and 2.5mw test facility
United Pumps support our heritage product Harland Pumps, Indeng, Johnston Pumps
Outdated pump systems waste energy and money – the latest Variable Speed Drive (VSD) technology slashes costs, improves system efficiency, and enhances reliability.
With energy costs increasing, it is now more important than ever to keep track of energy usage and to implement efficiency solutions in all areas of power consumption. Electric motors account for approximately 85 per cent of the world’s power consumption and is expected to double by 2040. The US Department of Energy has conducted research that suggests pumping systems alone account for nearly 20 per cent of the world’s electrical energy demand.
In some industrial applications, pumping consumes 25 to 50 per cent of the available electricity. Over 80 per cent of this energy is wasted by oversized pumps and lack of control or non-efficient control, such as valve control.
Techtop has partnered with Invertek Drives in the UK and developed a dedicated pump control technology algorithm that pays for itself. A Techtop spokesperson said companies sometimes recoup their costs in less than six months.
The Techtop TTA-3 Eco Variable Speed Drive (VSD) can reduce energy consumption and total system cost, simplify systems by eliminating complex control panels, and improve process control and system reliability.
The system provides energy-efficient, consistent, matched, and pressurised water flow on demand, thanks to built-in motor and pump protection, including dry run protection, pump prime, burst pipe detection and protection, load monitoring, blockage detection, and pump alternation on multipump systems.
The Techtop TTA-3 Eco VSD offers solutions for a wide range of pumping applications and is ideal for standalone multi-pump booster systems that can be adapted to different requirements.
The Techtop TTA-3 Eco VSD has a built-in Optiflow controller that is energy efficient, provides low harmonics, and is suitable for self-redundant or multi-pump cascade controllers. This
provides an ideal solution for water pressure booster systems widely used in all pumping applications.
Designed for easy installation, with a user-friendly interface and simple to commission, The Techtop TTA-3 Eco VSD exists in three different enclosure types: cabinet-mounted IP20, wall-mounted IP55 and outdoor-rated IP66 enclosures. The IP66 version can be supplied with or without a front-mounted mains input isolator, Start/Stop switch and speed control potentiometer. This makes installation simple, with less time installing ancillary contactors and switches.
Proven results
There have been several examples of the
The Techtop P2 IP55 VSD has been built with high performance, excellent usability and flexibility in mind.
Techtop technology generating savings for its clients. In one case, a customer experienced a 36 per cent reduction in energy and reduced downtime on a high-powered water pump at a large water treatment plant. One major shopping centre found it was saving an additional 30 per cent on its energy bills. An 18-hole golf course found a reduction in water and energy usage through the control of an irrigation system. A major hospital in the Middle East secured a constant and reliable water supply with energy and cost savings. Finally, a 10-storey apartment block developed a continuous and reliable water supply for controlling 4kW pumps.
The Techtop TTA-3 Eco VSD is rated to operate in ambient conditions from -100C to +500C and has optional Bluetooth connectivity. Using a smartphone or PC, users can wirelessly commission or check parameter settings in the drive.
The Techtop TTA-3 Eco VSD has a motor preheat function that helps ensure moisture does not build up in the motor during periods of inactivity and before motor start-up.
The Techtop story so far Techtop was founded by directors Rohan Pollard and Jeff Aird. In 2013, they entered a joint venture partnership with Shanghai Top Motor Company, China’s largest aluminium motor manufacturer. The combination of a leading global motor manufacturer and Australia’s most experienced sales and engineering teams has seen the business grow to have warehouses and workshops in all states of Australia and several locations in New Zealand via the recent acquisition of John Brooks Ltd.
Techtop also provides an extended VSD warranty when purchased in combination with a suitable Techtop motor. Techtop Australia stock VSDs up to 160kW across all locations.
For more information, visit techtop.com.au
Motors drive a significant portion of industrial energy consumption, so even a small improvement in efficiency can result in substantial cost savings and extended equipment lifespan.
While many solutions focus on complex digital systems and proprietary ecosystems, the TECO MAXe3 IE3 High-Efficiency Motor provides a practical, immediate upgrade – delivering efficiency gains without requiring new infrastructure, costly monitoring systems or extensive retrofits.
Designed for seamless integration with IP66 protection, Class F & H insulation systems, and a robust cast-iron frame, the TECO MAXe3 IE3 is a suitable drop-in replacement for existing pump motors. It ensures instant energy savings, reduced maintenance, and long-term reliability.
For pump operators looking to cut operating costs and enhance system performance, TECO MAXe3 is a practical, high-efficiency choice – ready to perform from day one.
Balancing performance, efficiency and costs
Pumps are the backbone of many industrial systems, from water treatment plants to heating, ventilation and air condition (HVAC) systems and oil and gas operations. The challenge, however, is balancing energy efficiency, equipment reliability, and operational costs.
Many efficiency solutions today require businesses to invest in smart monitoring platforms, integrated digital controls, and/or brand-specific drive systems. While these technologies offer long-term benefits, they often come with significant upfront costs, training requirements, and compatibility issues.
TECO Australia and New Zealand take a different approach, focusing on plugand-play efficiency. The TECO MAXe3 IE3 High-Efficiency Electric Motor is designed for immediate performance improvement in pump applications, with no need for additional infrastructure or proprietary software. The result? Lower energy costs, improved reliability, and a seamless transition to a more efficient system.
Why select TECO MAXe3 IE3 HighEfficiency Motor?
The TECO MAXe3 IE3 motor delivers outstanding efficiency, reducing power consumption from day one. This motor directly replaces standard motors, minimising downtime and installation costs. It is designed to operate in demanding environments, including industrial, mining, water treatment plants, food and beverage, HVAC, and oil and gas applications.
The motor features IP66-rated
TECO is offering the MAXe3 High-Efficiency Electric Motor. Images: TECO
protection for enhanced resistance to dust and water ingress. It also has Class F and H insulation, ensuring a low-temperature rise of 75°C or less, prolonging the motor’s lifespan.
TECO’s advanced grease pressure relief system extends bearing life and reduces maintenance needs. Notably, the TECO MAXe3 IE3 provides full flexibility. It functions seamlessly with existing set-ups without being locked into a specific ecosystem.
The motor is compatible with all major pump drive systems, eliminating the need for exclusive variable speed drives (VSDs). Additionally, it works with industry-standard mounting and connections, facilitating easy replacements and future efficiency improvements.
What are the industry applications?
The MAXe3 IE3 High-Efficiency Motor is built for critical pump applications across industries, offering instant benefits without complex retrofitting. For example, TECO can reduce energy costs for municipal water treatment, desalination, and wastewater management. Heating, ventilation, and air conditioning (HVAC) systems can optimise pumps and fans in commercial and industrial climate control. High reliability in fluid transfer and processing applications is vital in the oil and gas industry. The mining industry can benefit from this technology for its dewatering, process pump and slurry pump applications.
TECO Australia and New Zealand provide a straightforward, effective solution that enhances pump efficiency. The TECO MAXe3 IE3 High-Efficiency Motor offers a path to lower energy costs, reduced maintenance, and long-term reliability – with no additional investment in software, monitoring, or proprietary systems.
For more information, visit electricmotors.teco.com.au
PLUG & PLAY EFFICIENCY
• IE3 high efficiency lowers power use from day one.
• Direct drop-in replacement for standard motors – minimal downtime, no costly upgrades.
• Fully compatible with existing Variable Speed Drives (VSDs) – no custom setups needed.
ENGINEERED FOR HARSH ENVIRONMENTS
• IP66-rated for dust & water protection, built for mining, water treatment, oil & gas, HVAC & more.
• Class F & H insulation with low temperature rise (≤75°C) extends motor lifespan.
• TECO’s grease pressure relief system minimises maintenance and maximises durability.
TOTAL SYSTEM FLEXIBILITY – NO LOCK-INS
• Works with any pump drive system – no need for exclusive VSDs.
• Industry-standard mounting & connections for hassle-free replacement.
• Future-proof design – upgrade efficiency as needed, without restrictions.
Efficiency should be simple. Upgrade to TECO MAXe3 IE3 today! Scan the QR code for further information.
Increased safety
Reduced costs
Longer service-life
Efficiently transport semi-solid and highly viscous food waste with lower energy consumption, minimal maintenance and enhanced safety. SEEPEX Smart Air Injection (SAI) transports by-products over long distances through a closed piping system, eliminating spillages, odors and safety risks.
YOUR BENEFITS WITH SAI FOOD WASTE
Saves energy and reduces operating costs
Easy maintenance features minimize downtime
Enclosed pipework prevents spillages and eliminates unpleasant odors
Easily transports food waste over long distances and elevation changes
Low-pressure operation ensures longer component service life
Sydney Water’s successful trial of innovative air injection technology at West Camden WRRF highlights efficient biosolids handling and sets new standards for sustainable wastewater management.
Sydney Water, Australia’s largest water utility, plays a crucial role in delivering essential water services to over 5.2 million people across Greater Sydney, the Illawarra, and the Blue Mountains. As part of its commitment to sustainable wastewater treatment, the organisation continually seeks innovative solutions to improve efficiency and meet growing demand.
One of its key facilities, the West Camden Water Resource Recovery Facility (WRRF), has been undergoing significant upgrades to expand its capacity and accommodate up to 72,000 new dwellings by 2046. SEEPEX’s Smart Air Injection (SAI) system was introduced as a temporary but highly effective solution to enhance biosolids handling during these developments.
A strategic opportunity for SAI implementation SEEPEX has been a long-standing partner of Sydney Water, providing pumps for various wastewater applications, including digested sludge, waste-activated sludge (WAS), and
thickened waste-activated sludge (TWAS). While SEEPEX’s SAI technology had not yet been permanently established in Australia, the ongoing upgrades at West Camden created an ideal opportunity to trial its capabilities.
During renovations to the dewatering building, a mobile dewatering system was required to maintain uninterrupted operations. Recognising the potential of SAI, Mark Ziogas, Principal Engineer at Sydney Water, collaborated with Downer’s Robert Elson and their teams to implement the technology in a temporary capacity.
Traditional biosolids handling vs SAI Before implementing SAI, biosolids transport at West Camden relied on traditional shaftless screw conveyors. This method involved several steps, including the use of vertical screw conveyors and silos, which required extensive structural support. The complexity and footprint of these conventional systems posed various challenges regarding efficiency, cost, and operational flexibility.
A Smart Air Injection system features an open hopper pump, boundary layer injection, and a control unit for optmised biosolids transport. Images: SEEPEX
SAI benefits:
• Cost savings: Reduced capital and operational costs compared to conventional belt and screw conveyors.
• Operational efficiency: Streamlined biosolids transport with a low-pressure pumping system, minimising maintenance needs.
• Environmental and safety enhancements: The sealed pipeline system reduced odour emissions and eliminated open-air biosolids exposure, enhancing workplace safety.
• Flexibility and scalability: SAI’s modular design allows for easy adaptation to temporary and permanent applications, and it can transport pipelines up to 1000 metres long.
SEEPEX’s SAI technology provides a groundbreaking solution. By integrating progressive cavity pumping and dense-phase pneumatic conveying, SAI facilitates the efficient movement of highly dewatered sludge in short plugs. This approach greatly minimises friction losses, enabling biosolids to be transported over long distances with low energy expenditure. Additionally, the system’s enclosed pipeline removes the necessity for elaborate odour extraction and emission controls, enhancing workplace safety and environmental results.
Proving performance: Testing and future applications
The successful trial of SAI at West Camden included rigorous performance evaluations, including odour and stickiness tests conducted at the NATA-accredited West Ryde laboratory. These tests confirmed that the system did not increase odour potential and maintained stable biosolids consistency throughout the process.
Given SAI’s effectiveness in this temporary application, Sydney Water is now exploring opportunities to integrate the technology into permanent facility designs. SAI can also be deployed for
Setting a new standard in biosolids handling
The introduction of SEEPEX’s Smart Air Injection at West Camden WRRF represents a key advancement in Sydney Water’s commitment to innovative and sustainable wastewater management. By demonstrating the efficiency, cost-effectiveness, and environmental advantages of SAI, this project paves
As Sydney Water continues to improve its wastewater treatment infrastructure, collaborations with industry leaders such as SEEPEX will be crucial in providing smarter, more sustainable solutions for the future.
The successful integration of SAI at West Camden demonstrates the potential of cutting-edge engineering in transforming biosolids management for years to come.
“Implementing SEEPEX Smart Air Injection at West Camden WRRF has been a transformative step in biosolids management. This innovative technology enhances efficiency, reduces costs, and significantly improves safety and environmental outcomes. It represents the future of sustainable waste handling.”
—
Mark Ziogas, Principal Engineer, Sydney Water
The enhanced capabilities offered by the DDA SMART digital dosing pump could be vital for your business. Images:
Grundfos’ new DDA SMART Digital pump delivers precision and safety, proving that chemical dosing doesn’t have to be a headache.
Chemical dosing can be a tricky business. Get it wrong, and you’re looking at wasted chemicals, costly rework, or worse – unsafe conditions for operators. However, the new Digital Dosing Advanced (or DDA) SMART Digital dosing pump from Grundfos could change the game. With enhanced safety, streamlined setup, and top-tier accuracy, the company is confident it has developed the most usable and sustainable dosing solution on the market.
Tom Sels is Grundfos’ Global Product Manager for Dosing. Having worked with the company for over 14 years, he understands how it is working to make dosing smarter and simpler for every user.
“Grundfos is committed to making dosing easier and chemical management safer for the operator, and with help from our users, we redesigned the way operators interact with our dosing pumps,” he said.
Precision at its core Grundfos argues that precision is nonnegotiable in dosing applications. The DDA SMART Digital boasts a variablespeed stepper motor with a turn-down ratio of up to 1:3000, allowing for continuous, smooth dosing with minimal waste. The patented Digital Dosing technology ensures that whatever the user’s setting is, they get it on the other end. The pump automatically adapts to maintain its setpoint, even in changing conditions. As a result, end-users can enjoy reliable performance and increased efficiency through reduced chemical waste. That means cost savings and improved sustainability outcomes.
The integrated Flow Control Management (FCM) sensor further enhances process reliability, monitoring flow and pressure in real time. According
process safer and more predictable.
Remote control, effortless setup
Commissioning a dosing pump can be time-consuming and error-prone. However, Sels is certain its solution simplifies the process. The DDA SMART Digital connects to the Grundfos GO app, allowing users to set up and monitor the pump remotely via a smartphone or tablet.
“The guided setup menu walks operators through commissioning step by step,” Sels said. “You can even copy and paste settings from one pump to another, reducing setup time significantly – especially useful for large installations.”
The pump also features Condition Check, an automated fault diagnosis system that verifies the installation at startup. Grundfos believes this feature eliminates the need for return visits to troubleshoot setup errors, saving time and reducing operational risks.
Enhanced operator safety
Chemical handling presents risks, but Grundfos has incorporated several features to make the DDA SMART Digital safer. The high-resolution display and a guided user interface make it simple to
configure the pump without accessing chemical areas. The new control cube can be positioned in multiple ways and adds flexibility while preventing unauthorised adjustments.
Additionally, the integrated safety functions, such as AutoFlowAdapt, continuously monitor performance and make real-time adjustments to maintain dosing accuracy. Alarm logs and remote monitoring capabilities ensure any issues are quickly identified and addressed, minimising risks to operators and processes.
Sustainability is more than just a buzzword; it’s a necessity. Grundfos has designed the DDA SMART Digital with longevity in mind, offering replaceable spare parts to extend the pump’s lifespan.
“In addition to traditional spare parts like diaphragms and valves, we’ve made the pump’s electronic control unit replaceable,” Sels said.
“This means you don’t have to discard the entire pump if an electronic component fails, reducing waste and lowering the total cost of ownership.”
The unit’s modular design allows for flexible installation. The control cube can be positioned left, front, or right to suit different set-ups.
Looking ahead
Innovative, adaptable solutions are needed as industries strive for greater efficiency and sustainability. Grundfos is showing that the DDA SMART Digital is not just another dosing pump – it’s a step toward a more connected, sustainable, and user-friendly future.
For more details, visit grundfos.to/food-and-beverage
As Australia’s longest running mining show, Asia-Pacific’s International Mining Exhibition (AIMEX) has a long, established history of showcasing and supporting the latest trends and developments in the industry.
SEPTEMBER 2025 23-25
AIMEX is relocating and will call South Australia home for the next 10 years, following market feedback and strong support from the local government and key mining players.
The move marks an exciting new chapter for the event and the region’s resource sector, with the state leading the way in future-focused mining.
AIMEX offers unparalleled opportunities to connect with Australia’s largest community of mining suppliers and professionals in an environment that stimulates innovation and collaboration.
Combining the resources of our respected editorial team with the knowledge and insights of some of the best and brightest minds in the sector, Pump Industry is Australia’s only dedicated pump magazine and provides the latest information about pumps and associated equipment across all industries.
Advanced engineering meets industrial resilience – discover how innovative pump technology is solving critical challenges in the mining, power, and chemical industries.
The pump technology behind FELUWA’s growth is rooted in traditional diaphragm and diaphragm piston pumps. The company launched the hose-diaphragm piston pump – a hermetically sealed, leakfree, oscillating positive displacement pump – 50 years ago. This innovation has established benchmarks across diverse industries globally.
In 2002, FELUWA introduced the patented MULTISAFE® double hosediaphragm pump, combining the efficiency of a piston diaphragm pump with technological advancements.
Functionality of the MULTISAFE double hose-diaphragm pump
The crank drive converts the drive motor’s rotary motion into a reciprocating piston movement. This movement is transferred to the double hose-diaphragm via a noncompressible fluid, creating the pumping effect in the pump head.
The hose diaphragm moves in a controlled manner with each pump stroke, ensuring a linear flow without turbulence. This has several benefits, including reducing the risk of sedimentation and mechanical stress while extending hose-diaphragms’ service life.
Due to their design principle, FELUWA MULTISAFE pumps are perfect for demanding pressure levels and large flow capacities. They operate at discharge pressures of up to 350 bar and handle flow rates of up to 1000 cubic metres per hour.
Providing better diaphragm pumps
The MULTISAFE double hose diaphragms inside each pump head create a redundant hermetic seal, effectively isolating the processed media from both the external
environment and the hydraulic drive. This design enhances operational safety while safeguarding internal components. With fewer wetted parts than conventional pumps, the medium remains separate from the pump head and hydraulic section. Depending on application requirements and media properties, carefully chosen materials minimise chemical erosion and wear.
performance with abrasive and aggressive media
The MULTISAFE pump operates without dynamic seals, protecting moving components from abrasive and aggressive media. This design increases durability and operational reliability. Additionally, material configurations can be adapted to changing process requirements.
In Australia, FELUWA pumps are widely used in the mining and minerals sector for demanding applications such as tailings disposal, ore concentrate transport, autoclave and leaching processes, filter press feeding and mine dewatering. Their robust design ensures long-term reliability, even in the harshest operating conditions.
FELUWA pumps are also suited to other industries and challenging applications that include reactor feeding, spray dryer feeding, fly and bottom ash disposal from coal-fired power plants, bauxite and red mud transfer, coal gasification feeding, the chemical industry – many, varied applications.
All MULTISAFE pumps are equipped with advanced monitoring and diagnostic systems that continuously track
The MULTISAFE double hose-diaphragm pump represents new standards in technology. Image: FELUWA
the condition of hose diaphragms and check valves. These systems provide timely information on wear and maintenance needs. If one hose diaphragm fails, the second ensures continued safe operation. A precision leakage compensation valve maintains hydraulic fluid balance, providing reliable performance. These features facilitate planned maintenance and integration into existing operational schedules.
Local support and reliable spare parts
FELUWA is committed to providing reliable and efficient support for its customers in Australia. With a dedicated representative based in Perth, it offers direct local expertise and assistance, ensuring that its customers receive prompt technical support and service. Additionally, its warehouse in Perth is stocked with essential spare parts to facilitate quick delivery and minimise downtime. This local presence allows FELUWA to respond swiftly to customer needs, ensuring smooth operations and uninterrupted performance of its pumps in demanding industrial applications.
For more information, visit feluwa.com
It’s critical to understand the state of your pumps and condition monitoring is key to that.
Image: A.W. Chesterton
2025 is a year of bold advancements, and Chesterton is here to ensure operations thrive through better condition monitoring.
In today’s fast-changing industrial landscape, pump reliability is more critical than ever. Traditional methods, such as vibration monitoring, have been instrumental in detecting mechanical issues.
However, while vibration sensors detect when something goes wrong, they fail to alert users before it happens.
Recognising this challenge, A.W. Chesterton developed Chesterton Connect™, an IIoT Twin-based condition monitoring solution designed to take a proactive, process-first approach to pump system health.
The system enables automatic and scalable 24/7 monitoring to improve pump reliability, extend equipment life, and maintain a safer work environment.
The limitations of traditional vibration monitoring
While vibration monitoring has been a cornerstone in identifying mechanical anomalies in pumps and rotating equipment, it primarily signals that an issue has already manifested. A 2011 ImechE study that looked at 11,000 seal failures across 143 process plants, indicated that more than 70 per cent of pump problems originate from process-related factors, with nearly half stemming from operational conditions.
Relying solely on vibration data can lead maintenance teams to reactive measures, addressing failures after they
occur without insight into underlying process deviations.
Introducing Chesterton Connect IIot Twin-based Condition Monitoring Chesterton Connect goes beyond traditional monitoring by integrating Bluetooth-enabled wireless sensors with a Cloud-based platform to continuously track critical process parameters.
This system monitors essential metrics such as (for example) suction, discharge, and sealing pressures, providing real-time data to ensure pumps operate within their Best Efficiency Point (BEP). Monitoring these parameters enables proactive adjustments to prevent mechanical failures before they occur.
This pump-focused IIoT Twin solution collects and organises sensor data into intuitive visualisations, providing anomaly notifications through visual alerts, automated emails, and push notifications. Flashing lights and colour-coded graphics indicate system anomalies, allowing action to be taken quickly and effectively.
The Chesterton Connect System operates independently of plant networks by using global cellular communications, helping to ensure ISO 27001-certified security and reliability without interference with the controlled process.
features and benefits
The system offers comprehensive monitoring that goes beyond mere vibration detection. By tracking vital process conditions, it captures a holistic view of pump health.
With a user-friendly interface that employs visual indicators and colourcoded warnings, Chesterton Connect enables personnel at all levels to quickly assess and respond to potential issues.
Furthermore, it boasts seamless integration and is designed for backward compatibility, which allows existing users to easily upgrade with minimal additional sensors, ensuring a transition that is both cost-effective and efficient.
This innovative system enhances reliability by reducing unplanned downtime and extending the equipment’s lifespan, helping to maintain operations near the Best Efficiency Point (BEP).
A paradigm shift in pump maintenance
Embracing a process-first monitoring strategy with Chesterton Connect marks a transformative shift from reactive maintenance to proactive reliability management.
By addressing both immediate symptoms and underlying causes of pump inefficiencies, this advanced, data-driven solution enhances operational performance, improves efficiency, and ensures longterm pump reliability.
Predict. Prevent. Perform. Stop unplanned downtime before it starts! The Chesterton Connect™ System empowers you with real-time predictive maintenance, optimising equipment performance and keeping your operations running smoothly.
Anytime, Anywhere Monitoring – Access critical pump health data straight from your smartphone, tablet, or computer with our cutting-edge IIoT technology.
Easy Setup. Instant Insights. Maximum Efficiency. Choose from preconfigured solutions tailored to your needs and take control of your equipment’s future today.
Get Started Now!
chesterton.com
chestertoncustomseal.com.au
ROTO Pumps recently assisted a mining client overcome a challenging and sticky situation with effective solutions and expert advice.
Since 1968, ROTO Pumps has been a leading name in providing innovative solutions for the mining industry. With decades of experience and a wealth of expertise, the company has established itself as a reliable partner for miners facing complex pumping challenges.
When one miner was in dire need of a dependable pumping solution, ROTO Pumps stood out, recognised not only for its long-standing history but also for its commitment to quality and customer satisfaction.
ROTO Pumps Queensland and Northern Territory manager Brett Layt said the miner’s decision to reach out to ROTO Pumps was a testament to the trust and confidence that the industry has in its products and services, ensuring that operations run smoothly and efficiently in the demanding environment of mining.
The mine’s entire processing and dewatering network was struggling to keep up with the site’s demands, which had significant implications for overall operations. The project deals with harsh conditions and aggressive media that require high head pressure, calling for pumps capable of heavy lifting beyond the norm.
Mr Layt said the ROTO Pumps team deployed to the site immediately and met the challenge head-on.
“ROTO Pumps has the capability to supply any PCP [progressing cavity pump] package worldwide, meeting any site or national standards and requirements,” he said.
“For this client, we created a bespoke dual-positive displacement helical rotor pump package with in-built dewatering fish tank to meet and exceed the sitespecific application.”
The ROTO Pumps team was wellversed in the mine system’s intricacies and executed the necessary adjustments efficiently, minimising downtime and maintaining operational effectiveness.
Mr Layt said their expertise not only facilitated a rapid resolution but also bolstered confidence in the reliability of the pumping systems going forward.
How did they deliver so quickly?
“We hold stock of all required mining pump service parts ready to go,” Mr Layt said. “Our knowledgeable team is always on hand to troubleshoot any enquiries. Our optioned package for this client is designed to increase the pump’s service life, with multiple baffles and flushing points to mitigate the harshness of the
media collected in the fish tank.”
ROTO Pumps also offers on-site aftersales training on its pumps and systems to ensure its clients get the most out of their solutions. For Mr Layt, keeping the mining industry’s pumping systems running smoothly is more than just a job well done.
“Our adaptability and attention to detail for the requirements of every application set us apart,” he said. “We strive to be a cost-effective option and smash lead time while providing a more personable experience.”
Over more than 57 years, ROTO Pumps has gained deep insights into the mining industry’s major pumping challenges. ROTO Pumps has developed a comprehensive range of progressive cavity pumps and systems to effectively handle all mining and explosive applications.
Central to the company’s practices is a deep commitment to, and passion for, supporting clients in setting and achieving larger goals. Mr Layt believes this is the only way to drive the industry forward into a successful future.
“ROTO Pumps’ range and capabilities are forever growing and evolving,” he said. “We will continue to be a valued ally with our customers to provide stressfree pumping solutions.”
ROTO Pumps has worked tirelessly to provide solutions to a broad range of industries, including the mining industry.
E mpowering your mine operations with Roto’s high pressure flexible shaft series pumps. Unleash the solution that challenges excess water, ensuring safe and efficient operations ; the Underground Maintena n ce Engineers’ Choice for ground water control.
Features:
•Robust construction for prolonged life and reliable performance
• Adaptable for challenging underground environments, available in fixed station configurations for single lift or staging along with portable packaged solutions
• Forge a direct connection with the manufacturer, ensuring personalised support, reliable service, and unparalleled product knowledge
Greener, cleaner, and more efficient – powering sustainability in Australia’s pump industry with eco-friendly industrial pumping solutions.
In the ever-evolving landscape of Australia’s pump industry, staying ahead requires more than innovation – it demands strategic alliances that drive progress.
Volvo Penta and its Australian distribution network combine local expertise with global engineering excellence to deliver cuttingedge solutions for marine and industrial applications. Together, they are reshaping how pumping systems operate, focusing on sustainability without sacrificing performance or reliability.
Volvo Penta: A cornerstone in Australian pumping
Volvo Penta Networks’ commitment extends beyond sales and distribution,
providing specialist servicing, system integration, and technical support, ensuring that customers receive the latest technology and expertise to maximise efficiency and longevity.
Volvo Penta’s portfolio caters to diverse industries that rely on dependable pumping solutions, from diesel engines to propulsion systems. However, as industries move toward reducing emissions and minimising environmental impact, Volvo Penta is increasingly focused on delivering solutions that align with long-term sustainability goals.
“Our distribution network is not just a channel for our products; it is a vital partnership built on trust, innovation, and shared success,” Nic Hansford, Volvo Penta Sales Manager,
said. “Together, we drive forward the future of industrial solutions, ensuring reliability and excellence at every turn.”
Volvo Penta’s innovative strides in sustainability
Volvo Penta has long been at the forefront of engineering, consistently pushing the boundaries of what’s possible. As industries worldwide seek cleaner, more efficient power solutions, the company is taking major steps toward a more sustainable future.
A prime example is Volvo Penta’s advancements in Battery Energy Storage Subsystems (BESS), designed to improve energy efficiency and reduce reliance on fossil fuels in high-demand applications. These fast-charging, compact storage solutions stabilise
investing in alternative fuels, exploring biofuels and hydrogen-based solutions as potential pathways toward reducing emissions in heavy-duty applications.
The synergy of partnership: Driving sustainable change
The Volvo Penta TAD842VE is a diesel engine built on the Volvo Group in-line size concept, offering power, reliability and economical use.
power grids in industries such as construction, mining, and large-scale pumping. With an increasing push for hybrid and fully electric powertrains in industrial settings, BESS technology offers a glimpse into the future of low-emission operations.
“The work we do through our distribution network is a cornerstone in our journey towards sustainable innovation,” Mr Hansford said.
“By working hand-in-hand with the Australian distributors, we are pioneering eco-friendly solutions that propel the pumping industry forward. Together, we are committed to creating a greener future where efficiency and environmental responsibility go hand in hand.”
Beyond battery storage, Volvo Penta continues to refine its internal combustion engine technology to reduce fuel consumption and emissions. The development of the new D16 engine exemplifies this commitment, delivering greater power with improved fuel efficiency. By lowering overall fuel burn while maintaining high output, the engine aligns with global efforts to curb carbon footprints in industrial operations. The company is also
The partnership between Volvo Penta and its Australian distributors is more than a strategic business move. It represents a commitment to improving sustainability outcomes in the pump industry. With pumping operations often running for extended periods in industrial and marine environments, any increase in efficiency translates to environmental and financial benefits.
Mr Hansford said the ability to integrate Volvo Penta’s latest innovations into real-world applications ensures that Australian industries are equipped with cutting-edge, energyefficient solutions.
“Through our valued partnership, Volvo Penta and its distribution network are transforming the dewatering industry, delivering cutting-edge solutions that enhance efficiency and reliability,” he said. “Together, we are setting new standards, ensuring that every drop is managed with precision and care. Partnership is the new leadership.”
Looking ahead: A greener future for pumping technology
As global regulations around emissions and energy efficiency become increasingly stringent, the demand for sustainable industrial power solutions will only grow. The pump industry must evolve in
response, adopting technologies that minimise environmental impact without compromising operational effectiveness.
Emerging technologies, including hybrid powertrains, fuel cell systems, and AI-driven efficiency monitoring, are expected to play an increasing role in industrial pumping applications.
Mr Hansford said that by staying ahead of these developments and ensuring that local industries have access to the best available technology, Volvo Penta is positioning itself as a key enabler of a cleaner, more sustainable future.
“Looking ahead, the future is bright for Volvo Penta and its distribution network, as innovation remains one of our key pillars for success,” he said. “Together, we are poised to seize new opportunities, driving advancements that redefine industry standards and power the possibilities of tomorrow.”
Pumping up the volume: Recent acquisitions reshape the global pump landscape, driving innovation, market expansion, and strategic growth for industry leaders.
The global pump industry is undergoing a transformation as major companies engage in a series of strategic acquisitions. These developments are reshaping the competitive landscape, with multinational corporations and specialised manufacturers expanding their market presence and technological capabilities.
As businesses position themselves for future growth, these acquisitions reflect broader industry trends in consolidation, innovation, and global expansion.
Honeywell’s strategic acquisition of Sundyne Honeywell International has announced a definitive agreement to acquire Sundyne, a leading manufacturer of pumps and compressors, from private equity firm Warburg Pincus for approximately US$2.16 billion.
This acquisition aims to strengthen Honeywell’s presence in the energy and petrochemical sectors, aligning with its strategy to expand in high-growth industrial markets. Sundyne’s portfolio includes high-speed centrifugal pumps and compressors used in refining, chemical processing, and power generation, making it a valuable addition to Honeywell’s operations.
Honeywell expects the acquisition to immediately contribute to sales growth and adjusted earnings per share in the first full year of ownership. The company anticipates integrating Sundyne’s advanced technologies, enhancing its industrial solutions portfolio and enabling Honeywell to meet the growing demand for energy-efficient pumping solutions.
Sundyne, based in Arvada, Colorado, has approximately 1000 employees and serves customers in industries such as petrochemicals and oil and gas transportation and processing. The company’s products, including leakage-free pumps, are used in plants worldwide, underscoring Sundyne’s global reach and reputation for reliability.
This acquisition is part of Honeywell’s broader strategy to transform its portfolio and focus on high-growth sectors. The company has been actively engaged in mergers and acquisitions, announcing approximately $10 billion in deals since 2023, excluding the Sundyne transaction.
Honeywell also plans to spin off its aerospace-technologies unit and its advanced-materials business into three publicly traded companies, reflecting a strategic shift to concentrate on core industrial offerings.
Midea Group’s strategic acquisition of Arbonia’s climate division
Midea Group finalised its acquisition of Arbonia’s climate division for an enterprise value of €760 million. This strategic move strengthens Midea’s presence in the European Heating, Ventilation, and Air Conditioning (HVAC) market and aligns with its global expansion strategy.
Arbonia’s climate division, previously part of the Swiss-listed Arbonia AG, specialises in developing and manufacturing sustainable heating and cooling systems, energy storage solutions, ventilation, and air treatment products. The division encompasses renowned system brands such as
Kermi, Prolux, Sabiana, and Vasco, along with focused brands including Arbonia, Britec, Brugman, Cicsa, PZP, Solius, Superia, Tecna, and Termovent. Employing over 3000 individuals across multiple European production sites and development centres, Arbonia’s climate division has established a robust market presence in the region.
In 2016, Midea acquired Clivet S.p.A., an Italian company specialising in HVAC systems. Building on this, Midea has now incorporated Clivet into Arbonia’s climate division to form MBT Climate, a new entity poised to become Europe’s leading HVAC solutions provider. This merger leverages both companies’ complementary product offerings and market strengths to deliver comprehensive and efficient climate control solutions tailored to diverse customer needs.
Establishing MBT Climate signifies Midea’s strategic focus on enhancing its global footprint and delivering localised solutions. By amalgamating Arbonia’s climate division’s deep market presence and diverse European product offerings with Midea’s technological expertise and continuous R&D investment, MBT Climate is well-positioned to respond swiftly to market demands and contribute to a smarter, more sustainable future.
Franklin Electric acquires PumpEng Franklin Electric Co., Inc. also made a big move in late February, acquiring PumpEng Pty Ltd., an Australian-based original equipment manufacturer (OEM) specialising in submersible pumps for the mining sector.
This strategic move aims to bolster Franklin Electric’s commitment to the mining industry and enhance its operations in Australia, complementing existing brands such as Pioneer Pump® and Minetuff™.
“This strategic partnership combines PumpEng’s innovative dewatering approach and strong Australian presence with Franklin Electric’s global resources and technical leadership in water systems,” Greg Levine, President of Global Water Systems at Franklin Electric, said.
He noted that Australia’s mining regions are among the most challenging globally. PumpEng has established a solid reputation for addressing these challenges with pumps that excel in demanding environments.
The acquisition, valued at AUD $24 million, will support the inclusion of
PumpEng’s 50 professionals into the Franklin Electric family. This reflects the company’s commitment to leveraging local expertise and maintaining highquality service standards.
PumpEng’s operational model, known as “The PumpEng Way,” focuses on selecting the right pump for each application and providing comprehensive training and support. This approach aligns with Franklin Electric’s legacy of support and dedication to ensuring high-quality mining products and services.
DXP Enterprises acquires Arroyo Process Equipment
DXP Enterprises, Inc. purchased Arroyo Process Equipment, a distributor of pumps, process equipment, and related services. This strategic acquisition enhances DXP’s presence in the southeastern United States and aligns with its vision to become a leading North American rotating equipment company.
“We are pleased to announce the acquisition of Arroyo Process Equipment,” Chairman and Chief Executive Officer of DXP, David Little, said. “We have always respected and followed Arroyo’s success over the years. Arroyo adds another great company to our rotating equipment platform and furthers our vision of being the leading North American rotating equipment company.
“Arroyo provides DXP with exceptional sales expertise to enhance our efforts and ability to collaborate, serve our customers, and grow DXP further. Arroyo provides us with a clear leader in Florida.”
DXP has highlighted the acquisition as part of a broader growth strategy focused on industrial solutions and geographic expansion. The company believes Arroyo’s expertise in pump solutions and process equipment will complement its existing portfolio and provide better service to its expanding customer base.
This acquisition underscores DXP’s commitment to expanding its rotating equipment platform and enhancing its service capabilities across diverse industrial sectors.
To enhance its presence in the Australian HVAC market, Sojitz Corporation has acquired a 70 per cent stake in Climatech Group Holdings Pty Ltd. This acquisition was executed through Sojitz’s subsidiary,
Ellis Air Group Pty Ltd, positioning the conglomerate as a leading HVAC contractor in Australia.
Climatech, established in 1989 and headquartered in New South Wales, specialises in designing, constructing, and maintaining HVAC and refrigeration systems. The company has approximately 250 employees and has been involved in significant projects, including iconic buildings such as Wynyard Place and Quay Quarter Tower in Sydney.
The combined annual sales of Climatech and Ellis Air are projected to reach approximately AUD 450 million, solidifying Sojitz’s position in the Australian HVAC sector. This acquisition aligns with Sojitz’s strategic objective to expand its energy solutions business and contribute to the realisation of a net-zero society by providing energy-efficient HVAC systems that reduce CO₂ emissions.
Australia’s HVAC market is anticipated to grow at an annual rate of six per cent, reaching an estimated AUD 74 billion by 2033. This growth is driven by increasing demand for residential and infrastructure development, particularly in preparation for the Brisbane Summer Olympics and Paralympics in 2032. Additionally, stringent environmental performance standards, as mandated by the National Australian Built Environment Rating System (NABERS), foster a heightened demand for energy-efficient HVAC solutions.
Sojitz’s acquisition of Climatech is expected to support better internal collaborative outcomes by leveraging the technological expertise and customer networks of both Climatech and Ellis Air.
Sulzer’s Middle East expansion
In January 2025, Sulzer, a global leader in fluid engineering, acquired Davies and Mills, a prominent electromechanical services (EMS) provider based in Bahrain. This strategic acquisition expands Sulzer’s footprint in the Middle East to six service locations, enhancing its capacity to serve industrial customers in the region.
Davies and Mills bring a wealth of experience to Sulzer, specialising in maintaining and repairing rotating equipment like generators, alternators, motors, and pumps. By welcoming 53 employees from Davies and Mills into Sulzer’s Bahrain operations, Sulzer will be able to enhance its technical capabilities and elevate its service offerings.
“This acquisition supports Sulzer’s long-term strategy to strongly position our service capabilities in growth markets such as the Middle East,” President of Sulzer’s Services Division, Ravin Pillay Ramsamy, said.
“Davies and Mills bring exceptional expertise to our portfolio. With Sulzer’s regional footprint and global network, we create a powerful partner for our customers’ benefit.”
The addition of Davies and Mills aligns with Sulzer’s commitment to providing comprehensive, in-region support tailored to the needs of industrial clients. The new facility in Bahrain will deliver maintenance and repair services for rotating equipment, including generators, alternators, motors, and pumps, while enhancing its presence in Bahrain and Saudi Arabia.
“Joining Sulzer represents an exciting new chapter for our team and our customers,” General Manager of Davies and Mills, Martin Stratford, said.
Mergers and acquisitions across the heating, ventilation and air conditioning HVAC) scene provide opportunities for all companies. Image: EKH-Pictures/stock.adobe.com
“With Sulzer’s extensive resources and global network, we are confident that this partnership will unlock new opportunities and elevate the quality and reach of our services across the region.”
This acquisition reflects Sulzer’s ongoing commitment to expanding its presence in the Middle East, adding a sixth service centre in as many years. By combining Davies and Mills’ technical expertise with its global network, Sulzer aims to strengthen its ability to meet the growing needs of industrial customers in the Middle East.
Dover’s acquisition of Cryogenic Machinery Corp.
In January 2025, Dover Corporation expanded its presence in the cryogenic equipment market by acquiring Cryogenic Machinery Corp. (Cryo-Mach), a specialised designer and manufacturer of cryogenic centrifugal pumps, mechanical seals, and accessories. Founded in 1964 and headquartered in North Hollywood, California, Cryo-Mach has established itself as a notable player in the cryogenics industry, serving customers
in the industrial gas market and applications involving liquefied oxygen, argon, and nitrogen.
This acquisition adds Cryo-Mach into Dover’s PSG (Pumps & Process Solutions) business segment, enhancing Dover’s participation in cryogenic applications and expanding its industrial gas and transportation market offerings. Adding Cryo-Mach’s cryogenic centrifugal pump technology diversifies PSG’s core portfolio within the cryogenic end market.
“We are thrilled to add Cryo-Mach to our best-in-class portfolio of pump businesses,” President of PSG, Karl Buscher, said. “This acquisition strengthens PSG’s position within cryogenics and is consistent with our strategic approach of expanding our core and securing access to adjacent markets that enable sustainable, profitable growth.”
The pump industry is undergoing rapid transformation, driven by strategic acquisitions, market consolidation, and an increasing focus on innovation. Companies are no longer content with
maintaining their current positions – they are actively seeking growth, diversification, and new technological capabilities to stay ahead in an evolving global landscape.
These recent acquisitions reflect a broader industry shift, where businesses are aligning themselves with emerging trends in sustainability, digitalisation, and efficiency. The push for energy-efficient solutions, greater automation, and enhanced service capabilities is shaping the sector’s direction as companies strive to meet the demands of modern infrastructure, resource management, and environmental responsibility.
Mergers and acquisitions are not just about expanding product lines but about securing long-term competitiveness. By acquiring specialists in niche markets, larger companies gain access to new customer bases, advanced technologies, and operational efficiencies that would take years to develop organically. For smaller players, these deals provide opportunities for scaling up, leveraging global networks, and accessing greater investment in research and development.
With thousands of people across Australia working on pump-related technology and products, we invited Glenn Evans, CEO of the Australian Refrigeration Council (ARC) to contribute to Pump Industry. The ARC is central to the training and licensing of refrigeration technicians across Australia. Image: nikomsolftwaer/stock.adobe.com
Hot water heat pumps are becoming increasingly popular across Australia as an energy-efficient solution for heating water and pools. These systems, which extract heat from the outside air, use about one-third of the energy of traditional electric storage hot water systems. While heat pumps are an excellent choice for reducing energy consumption, proper installation and servicing are essential to meet environmental and safety standards. Heat pumps operate similarly to refrigerators but in reverse, transferring heat from the air into water. They often rely on refrigerants regulated by the Australian Government. While these refrigerants are necessary for the heat exchange process, many are potent greenhouse gases that can contribute to global warming if mishandled. Additionally, some refrigerants, such as hydrocarbons or CO 2, present safety risks due to their flammability or highpressure characteristics.
To support the growing demand for hot water heat pumps and ensure installers are properly trained, the Australian Refrigeration Council (ARC) has recently released a new fact sheet outlining the licensing requirements for installing these systems.
There are three primary configurations of hot water heat pumps commonly used in Australia:
1. I ntegrated Systems: These selfcontained units include a refrigeration system, a combined water tank, and a heat exchanger. Installation requires essential electrical and water connections.
2. I ntegrated Pool Heater Systems: Like integrated systems, these units integrate refrigeration and heat exchange components but do not have a water tank. Instead, they supply heated water directly to a pool.
3. Split Systems: These systems have an outdoor unit with refrigeration components and a separate water tank. Refrigerant pipes connect
the two. Installation requires more expertise due to the need for refrigerant handling. The first two types are sealed systems that do not require refrigerant handling during installation. However, split systems require a licensed refrigeration technician due to the specialist nature associated with high-pressure refrigerant pipes and components.
Installing, servicing, and decommissioning these systems necessitate a technician with the appropriate refrigerant handling licence from the ARC, reflecting the specialist nature of the works.
Technicians with this licence are trained to manage refrigerants safely and minimise emissions, ensuring compliance with environmental regulations.
As the adoption of energy-efficient technologies like heat pumps continues to rise, it’s crucial that we equip professionals with the right skills to ensure these systems are installed and serviced correctly. The ARC is committed to providing the necessary licensing and training to safeguard the environment and the safety of the Australian public.
As Australians increasingly adopt energy-efficient technologies like heat pumps, it is vital to ensure that licensed professionals carry out installation and servicing. At ARC, we remain committed to providing the right skills and qualifications to support this transition to a more sustainable future.
Heat pumps are changing the way Australians heat water and warm their homes.
Image: Australian Refrigeration Council
Sami Zheng, Chief Executive Officer of the Australian Institute of Refrigeration, Air Conditioning and Heating (AIRAH), reflects on a tumultuous few months in global politics and what they could mean for Australia’s sustainability goals.
For those of you who are not familiar with AIRAH, we’re a member organisation and the peak representative body for the Australian heating, ventilation, air-conditioning and refrigeration (HVAC&R) building services industry. Our members range from refrigeration and air conditioning technicians (affectionately known as “fridgies”) to mechanical engineers and experts in fields like indoor air quality, infection control, electrification, building physics, big data, and system commissioning.
We’re aware that our industry is essential for the functioning of modern life as we know it, but we also know that it has a significant impact on the health of the planet. According to the World Green Building Council, the built environment is responsible for 39 per cent of the world’s greenhouse gas emissions, with heating
and cooling responsible for the bulk of that energy use.
That’s why, since the turn of this century, one of AIRAH’s primary focuses has been improving sustainability in the Australian HVAC&R industry. We promote the use of refrigerants with low environmental impact, as well as smart design and technologies such as heat pumps that reduce the energy required for heating and cooling.
We’re lucky to have great support from within the Australian HVAC&R industry. But with the global political order experiencing upheaval, can we count on similar support from the political sphere in the future?
Deregulation frenzy
While Donald Trump’s recent imposition of widespread tariffs has stolen global headlines, a much
more serious development has gone largely unnoticed. A few days before I wrote this article, the USA’s Environmental Protection Agency (EPA) announced plans to repeal several key environmental regulations.
These include caps on CO 2 emissions from power plants, classifications of greenhouse gases as harmful to public health, and regulations encouraging the uptake of electric vehicles.
The success of these repeals remains uncertain, but the concern is that the EPA’s stance appears to be shifting away from its core mission of protecting the environment. While there is no immediate indication of similar rollbacks in Australia, history has shown that policy shifts in the United States can influence Australian discourse – we have already heard rumblings, for example, about freezing energy
efficiency provisions in the National Construction Code. The potential rise of climate scepticism could hinder progress on sustainability initiatives, making it crucial for industries to lead by example rather than wait for government directives.
The lesson I take from this is that leadership from organisations such as AIRAH and Pump Industry Australia is more important than ever. We can’t rely on governments to set the tone; we need to promote best practices to our own members.
After all, they’re in the best position to understand the issues affecting sustainability in our industries, how to address them, and why doing so is vital. We must push harder than ever to promote sustainable practices within our industries, regardless of what’s happening around us. Our planet is counting on us.
For more information about AIRAH, go to airah.org.au
Sami Zheng is the CEO of the Australian Institute of Refrigeration, Air Conditioning and Heating (AIRAH)
AusProof has been dedicated to providing industries around Australia with safe, innovative, and high-quality cable coupler solutions since 1994.
AusProof has been dedicated to providing industries around Australia with safe, innovative, and high-quality cable coupler solutions since 1994.
The Aluminium Restrained Range, released in 2022, was designed specifically for use in Non-Ex environments, such as pumping, tunnelling, and open-cut mining.
Products in this range are a light-weight and cost-effective alternative to stainless steel for Non-Ex sites, all while retaining key features such as single piece contacts, easy termination, and full phase to phase segregation with earth.
Curious? Get in touch with AusProof to learn more!
There will be many fantastic exhibitors showcasing their technological innovations in Adelaide later this year.
Image: Prime Creative Media
Smarter, longer-lasting pumping solutions keep mining operations efficient, reliable, and sustainable as the demand for resources grows.
The Asia-Pacific’s International Mining Exhibition (AIMEX) is Australia’s longest running mining event, bringing together suppliers, manufacturers, and decision-makers from across the sector.
It provides a stage where innovations can shine, allowing industry leaders, engineers, and executives to explore cutting-edge technologies that push mining operations towards a more sustainable and efficient future.
With advancements in materials, energy-saving designs, and predictive maintenance, the sector is redefining what it means to keep the industry in flow.
For an industry built on moving mountains, avoiding equipment downtime is essential. Every minute a pump is out of action, mining companies haemorrhage money, efficiency, and, increasingly, sustainability credentials.
Equipment failures lead to costly delays, safety risks, and lost productivity, making reliable pumping solutions more critical than ever. The search for efficiency extends beyond
just maintaining operations. Mining companies are looking at ways to optimise existing systems, enhance durability, and reduce environmental impact. Innovations in pump technology, wear-resistant materials, and energyefficient designs are making a tangible difference in how resources are extracted and processed. Reducing downtime isn’t just about improving operations but creating a more resilient and responsible industry. Because in a sector where every second counts, the right equipment can mean the difference between profit and loss.
With a legacy spanning nearly half a century, Global Pumps has built its reputation on keeping the mining industry moving – literally and figuratively.
Its expertise lies not just in supplying pumps but in delivering tailored solutions that address the unique challenges of mining operations. From tackling extreme wear conditions to improving energy efficiency,
Global Pumps offers a range of products designed to perform in the harshest environments.
Beyond reliability, longevity is key. Global Pumps’ solutions extend the lifespan of critical equipment and contribute to a more sustainable, cost-effective approach to resource extraction.
From gold mines in Victoria to major nickel operations in Western Australia and across the world, Global Pumps has built a reputation for delivering longlasting solutions.
Darren Seeley, Sales Director at Global Pumps, believes that the company’s edge lies in helping mining operations extend the life of their pumps beyond conventional expectations.
“Our biggest point of difference is focusing on longer-lasting products,” Mr Seeley said. “For example, we worked with a nickel client in Western Australia that operates a number of mine sites across the state. We introduced our
Verderflex hose inside their existing hose pumps. The trial period alone saw pump life triple. Over time, they achieved ten to 12 times the lifespan they were getting before.”
He said it’s a story that’s played out across the industry. When a gold mine in Victoria trialled impellers from Global Pumps’ SlurryPro range, it reported twice the wear life compared to their previous slurry pump impellers.
Mr Seeley said that these case studies are not just technical wins but also proof of how better pumping technology directly benefits those working on the ground.
“We love hearing from end users who tell us that our pumps mean fewer breakdowns, fewer headaches, and more time at home with their families,” he said.
AIMEX: a showcase for mining’s future AIMEX is more than just a trade show. For Global Pumps, it’s an opportunity to connect with boots-on-the-ground operators and high-level executives looking to drive innovation.
“AIMEX brings together everyone from frontline workers to decisionmakers,” Mr Seeley said. “It is where new ideas get tested and where sustainability, efficiency, and uptime come into focus. These are the exact conversations we want to be having.”
With the mining industry under increasing pressure to improve sustainability and reduce downtime, Seeley said that the event is the perfect forum for discussing solutions.
“The industry is in a constant state of improvement. Sustainability isn’t just about reducing carbon footprints – it’s about making processes more efficient, reducing waste, and ensuring equipment lasts as long as possible,” he said.
AIMEX will take a significant step in 2025 by relocating from Sydney to Adelaide, where it will be centred for the next ten years. While Sydney has long been the event’s home, Seeley sees the shift as a strategic move that better aligns with Australia’s mining geography.
“The majority of mining activity happens on the west coast,” he said. “South Australia, with its major copper deposits and operations like Olympic Dam, Carrapateena, and Prominent Hill, plays a crucial role in the sector. Moving AIMEX closer to these operations makes sense.”
Mr Seeley said the new location removes perceived barriers for attendees from major mining hubs and allows for greater engagement across all levels of the industry.
Reliability is essential for maintaining mining operations for extended periods of time.
Image: Global Pumps
Seeley showing that such enormous pumps can move huge volumes of materials.
Image: Global Pumps
“This opens up the event to more mining companies, including those who may have found it difficult to justify the trip to Sydney,” he said. “It’s a bold decision, but one we applaud.”
What’s next for pumps in mining?
As the industry evolves, so does Global Pumps. The company is positioning itself as a supplier and solution provider of choice, ready to tackle the sector’s biggest challenges.
With the move to Adelaide, multiple conference stages and expansive exhibition floor, there is enormous potential for pump industry participants to highlight their contributions to this vital sector at AIMEX in September.
At AIMEX, Global Pumps will showcase these solutions and more, ensuring mining companies leave with practical ideas they can implement immediately. Looking ahead, Mr Seeley sees AIMEX as an opportunity to build relationships that go beyond selling products.
“Our goal is simple,” he said. “We want to change the lives of miners and mining companies from that day onwards.”
For more information, visit aimex. com.au/getinvolved
Ron Astall knows pump engineers want a stable liquid film at the seal faces. Venting, cooling and pressure control are ways of achieving this.
Previously, he outlined the role of primary seal flush plans as providing a better environment for our mechanical seals.
Why have a seal flush?
API 681 / ISO10349 standards define standardised piping plan layouts, which are helpful across all pump types and applications. A selection of common primary piping plans and their expected impact on seal chamber conditions are shown below.
In the last article, we looked at the simpler plans 01, 11, and 13. These plans provide flow through the seal area, which may limit heat build-up and, with appropriate pump construction, adjust liquid pressure at the seal faces. Pressure management in the seal chamber can be critical if we pump liquids close to their vapour pressure. That is, for liquids that are close to boiling (vaporising). For these situations, providing additional, positive cooling to lower the vapour pressure is a great advantage. Other difficulties that we may face include solids or just plain awkward and unpleasant liquid properties.
Following is a selection of additional, more sophisticated piping plans that can be very helpful.
This plan involves a recirculation loop through the seal chamber via an external cooler. A pumping ring in the seal is required to positively recirculate flow through the cooling loop. Typically, there will be a throat bush at the inboard end of the seal chamber to limit the mixing the hotter liquid in the pump with the cooled liquid in the seal chamber. This makes for an efficient arrangement because it reduces the ongoing heat load at the cooler. This simplified diagram does not show the high point vents (Fig 5), which ensures the cooling loop is fully primed with liquid. Vapor locking must be avoided. Ideally, piping runs will be sloped appropriately to encourage a thermosyphon flow when the pump is not operating. Inverted loops or high points must be avoided.
Plan 23 will not increase seal chamber pressure, but it is excellent at reducing the temperature. This improves the pressure margin above the liquid vapour pressure and
reduces heat transfer along the shaft to the bearings. It is the “go-to” plan for water above 80° C, particularly in Boiler Feed Pumps. Above 80° C, water loses its lubricity and may even flash (vaporise) at the seal faces.
For similar reasons, this plan is also standard in chemical and hydrocarbon services when there is a risk of flashing the pumped liquid at higher temperatures. The continuous recirculation aspect allows much smaller coolers than a once-through system. As mentioned earlier, the most critical design and installation tip is to achieve complete venting.
Similar in principle to Plan 11, Plan 31 provides a flush from the discharge to the mechanical seal, with the additional feature of a cyclone separator. The cyclone will separate out limited small solids, with the “clean” leg going to the seal and the “dirty” leg returning to the pump suction. See Fig 6.
As with Plan 11, this provides a flow through the seal, preventing heat build-up with the advantage of a degree of solids removal. A cyclone works best where the specific gravity of the solids is at least twice that of the pumped liquid, such as with sand or pipe slag. Unlike a filter, the cyclone does not require cleaning.
However, Plan 31 is not suitable for large solids or slurry applications. The differential pressure between the highpressure connection and the seal chamber & pump suction must be sufficient to drive the cyclonic action – typically 150 kPa as a minimum.
Install Plan 32, and the Mechanical Seal will be your best friend. Properly engineered with a compatible clean liquid, the seal will have ideal operating conditions. A throat bush at the inboard end of the seal chamber will often be installed to boost the chamber pressure and prevent dilution of the clean liquid (see Fig 7). So why not use Plan 32 all the time?
First, a suitable clean liquid must be economically available. Second, the liquid must be compatible with the pumped liquid and the process. Common concerns are whether the product’s dilution is acceptable and whether there will be removal and disposal costs associated with the introduced flush. If specialised, the flush liquid can be an expensive consumable.
One elegant approach I have seen is using a Plan 32 flush to metered inject a process additive via the pump seal chamber. One disaster I have seen is using Light Cycle Oil for a Plan 32 flush. The Pump was operating at 365° C. The Light Cycle Oil simply vaporized as it entered the seal chamber, making the seal’s life worse, not better. Nevertheless, where viable and convenient, Plan 32 is a great way to manage a Mechanical Seal’s environment.
What’s the importance of a seal flush?
The standards define standardised piping plan (flush) layouts, which are helpful across all pump types and applications. A seal flush plan is often indicated to provide a better environment for the mechanical seal. The aim is to provide a stable liquid film at the seal faces.
An appropriate seal flush plan can manage seal chamber venting, cooling flow, and pressure control. Our discussion has focused on the common “primary” seal piping plans, which directly affect the seal chamber conditions.
The next step is to determine the type of mechanical seal.
The “primary” seal flush plans above are probably all we need for single seals in nonhazardous service. Dual seals will usually come into play when sealing particularly nasty, dangerous, flammable or toxic liquids. We then need to consider the myriad of specialised “secondary” seal piping plans.
Secondary Seal plans manage the conditions inside the seals, which may be incredibly complex. A fancy dual seal management system may cost more than the pump itself.
Secondary seal systems are a topic for another day.
New Zealand International Convention Centre, Auckland 28 – 29 October 2026
International No-Dig provides an unparalleled opportunity to connect with the global trenchless technology industry. Hosted each year in a different country to showcase the global industry, International No-Dig will bring together the best of the innovations and advancements in trenchless technology.
This article continues the series on pump installation and covers how the suction and discharge pipework should be installed, including baseplate mounting and the different types of bases.
Suction Pipework:
It is good practice to have the suction piping as short and straight as possible. If practical, a straight length of 10 times the suction pipe diameter is recommended.
Inadequate sump design leads to entrained air bubbles and turbulence, which will damage the pump.
A submerged inflow pipe and tank baffles prevent turbulence and bubbles from entering the suction pipe. Keep the suction pipe short and
straight and eliminate all possibility of air pockets being trapped in the suction line, i.e., ensure the suction pipe rises continuously to the pump.
Air trapped in the suction system will reduce pump performance.
The diameter of the suction pipe is sized to suit the application and is often larger than the pump suction connection and provided with an eccentric taper which should be installed as shown in Figure 1.
The correct distance between the inlet
flange of the pump and the first elbow must be at least five pipe diameters.
Suction Strainers:
It is strongly recommended that suction strainers be installed in the suction line. For pumps drawing from rivers, dams, and open tanks, a suitable strainer should be installed at the start of the suction line to prevent debris that is too big from passing through easily.
In the case of a closed circuit system, which does not require a strainer because the fluid being pumped is clean, it is recommended that a temporary strainer be fitted in the suction line to prevent construction debris from clogging and damaging the pump.
This strainer can be removed once the pump has been run for a few hours. As a guide, all strainers should have a surface area at least three times the pipe diameter.
For temporary strainers, the screen should be made of No.12 mesh and reinforced with No. 2 mesh and 12.6 mm wire. For all other strainers, the screen should be sized to stop solids larger than the pump can easily handle.
Install the discharge pipework according to the provided drawings or, if no drawings are available, according to proper industry practice.
The common discharge arrangement consists of a pipe reducer, a non-return valve to prevent backflow when the pump is stationary, and an isolating valve for maintenance purposes.
All these valves and pipework must be separately supported so that the pump casing does not bear their weight.
N.B. It is quite common for pumps to be fitted with flexible pipe connections on the suction and discharge, in conjunction with anti-vibration mounts under the baseplate. In this case, it is imperative that the pipework is correctly supported even when no anti-vibration mounts are fitted.
Pipe Expansion Joints:
When installing pipe expansion joints, ensure the following:
1. T he expansion joint must have the correct pressure rating for the application.
2. W hen necessary, tie bolts will be needed to absorb the hydraulic loads in the discharge line from being transmitted to the pump set; if not, these loads can distort the baseplate.
Spring Mounts:
These are often used in conjunction with expansion joints.
Spring mounts are selected so that they deflect to half their deflection when the pump is mounted.
Seismic (restrained) anti-vibration mounts are required for earthquake zones, in accordance with the relevant standards). Some mining sites also specify them.
Baseplate types:
Skid-type baseplates are used for portable units, which are regularly moved around sites for ease of handling and are more robust than standard baseplates.
Pipework general:
1. A ll suction and discharge pipes and valves must be separately supported to prevent the pump from carrying their weight.
2. I f the pump is to be installed between fixed limits, it is recommended that it be temporarily connected to the pipes before it is grouted in.
3. W pump, the pipes should be taken to the pump, not the pump to the pipes.
4. Suction and discharge pipes should be firmly tightened after grouting is complete and before the final alignment check.
5. If the unit is installed outdoors, care should be taken to ensure that extremes of ambient temperatures do not adversely affect the alignment. The pump is installed on its foundation, grouted in and connected to the suction and discharge pipes and valves.
Summary
This article has continued the process of pump system installation such that the pump and its base and pipework are at a stage where they are almost ready for starting.
We will complete the process in the following articles on the alignment of the pump and driver, which is necessary before initial pump start-up.
Over
17–18 SEPTEMBER 2025
Melbourne Convention & Exhibition Centre
LEARN MORE
convergeexpo.com.au
Air-operated double-diaphragm pumps are known for their reliability, but even the best pumps can fail without routine maintenance. Here’s how to extend their lifespan and ensure optimal performance.
Like any piece of equipment, air-operated double-diaphragm (AODD) pumps need routine maintenance and repair to ensure longterm durability.
Correct maintenance is essential for ensuring the efficient and reliable working of a diaphragm pump.
Key factors to consider for preventative maintenance are:
• D iaphragm lifetime
• Compressed air quality
• Flushing of pumps after use.
How to maintain a diaphragm pump: Check the diaphragms regularly: Diaphragms are the most critical component of a diaphragm pump and can wear out over time. Check them regularly for signs of wear or damage and replace them as needed.
Inspect valves: Valves are also important components of a diaphragm pump. Inspect them regularly for signs of wear, corrosion, or other damage. Replace any faulty valves as soon as possible.
Check the fluid inlet and outlet: regularly for signs of clogs or other obstructions. Clean them out as needed.
Lubricate moving parts: Diaphragm pumps have several moving parts, such as the air motor and the valve mechanism. Lubricate these parts regularly to prevent friction and wear. Check air supply: Diaphragm pumps operate on compressed air. Check the air supply regularly to ensure the pump receives adequate air pressure and volume.
Inspect fittings and connections: Check the pump’s fittings and connections regularly for signs of leaks or damage. Tighten or replace any faulty fittings as needed.
Clean the pump: Clean the pump regularly to prevent the build-up of dirt, debris, or other contaminants that can interfere with the pump’s performance.
Maintaining your AODD pump often
starts with choosing the right pump for the right application. Consult a knowledgeable pump supplier such as Kelair Pumps to discuss your pumping requirements.
Article courtesy of Kelair Pumps Australia.
For more information, visit kelairpumps.com.au