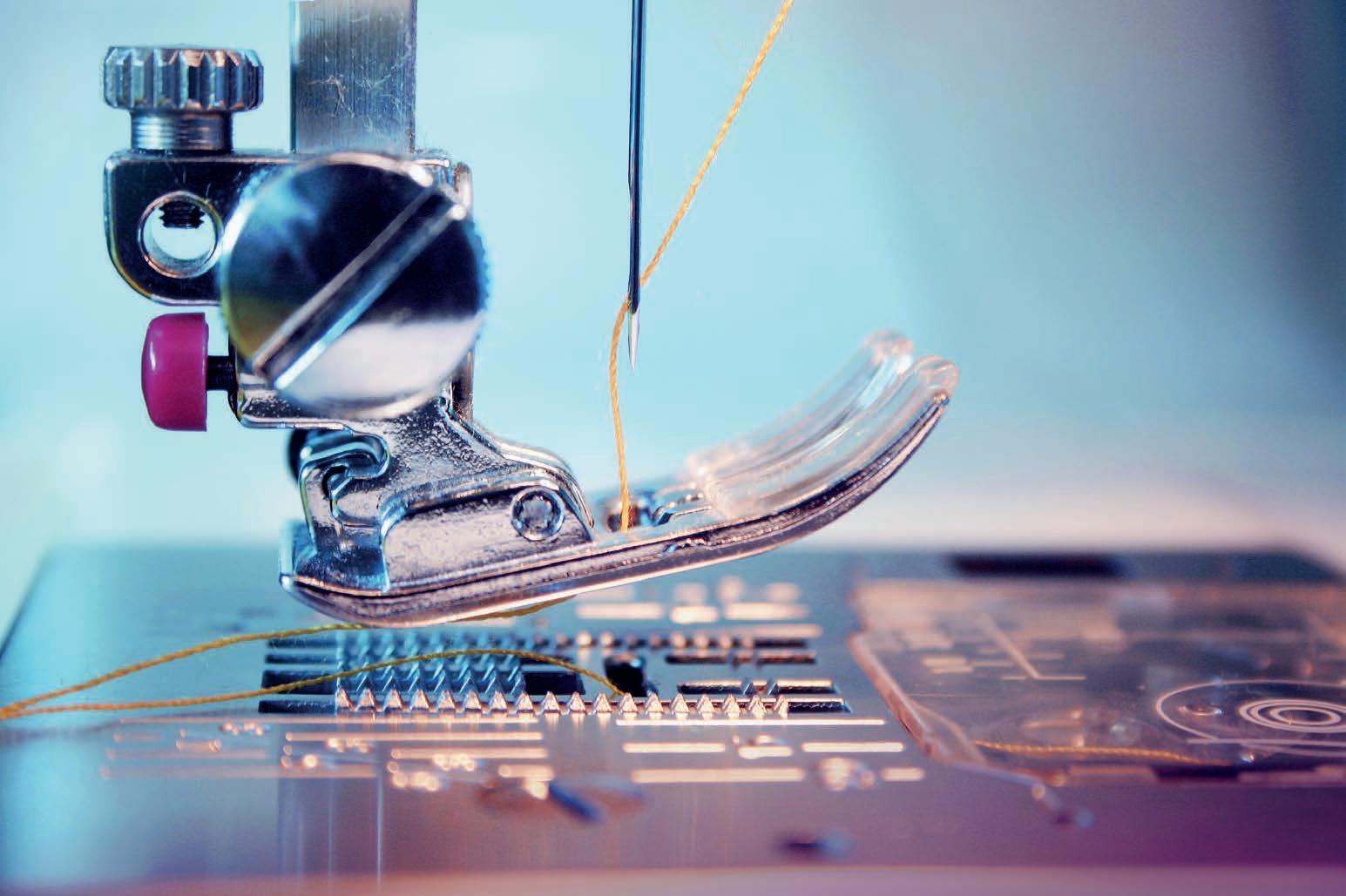

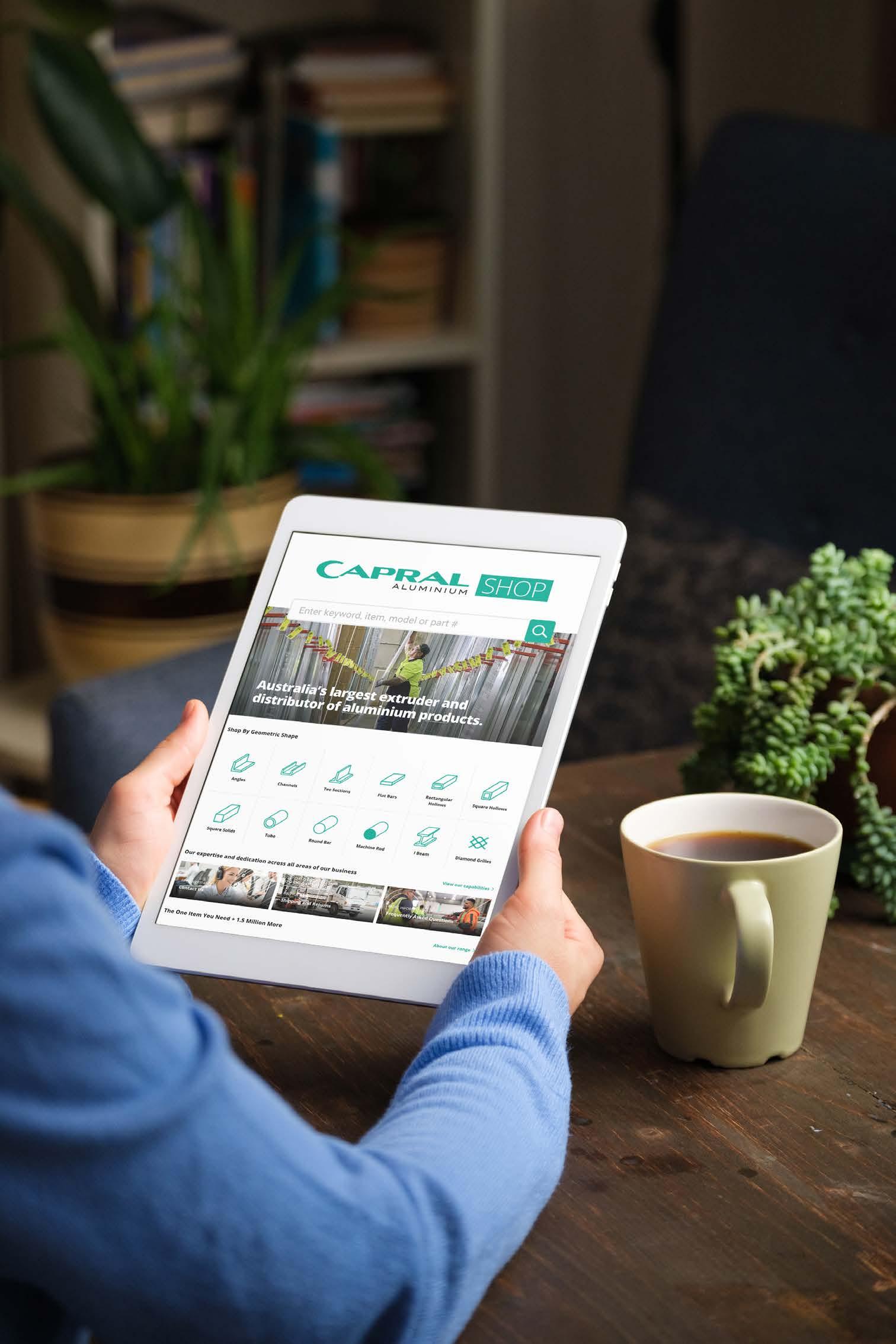

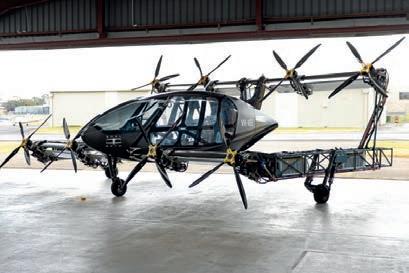

CEO: John Murphy
Chief Operating Officer: Christine Clancy
Managing Editor: Mike Wheeler
Assistant Editor: Jack Lloyd jack.lloyd@primecreative.com.au
Journalist: Mannat Chawla mannat.chawla@primecreative.com.au
Head of Design: Blake Storey
Design: Alejandro Molano
Sales/Advertising: Emily Gorgievska
Ph: 0432 083 392 emily.gorgievska@primecreative.com.au
Subscriptions
Published 11 times a year
Subscriptions $140.00 per annum (inc GST)
Overseas prices apply
Ph: (03) 9690 8766
Copyright
Manufacturers’ Monthly is owned by Prime Creative Media and published by John Murphy.
All material in Manufacturers’ Monthly is copyright and no part may be reproduced or copied in any form or by any means (graphic, electronic or mechanical including information and retrieval systems) without written permission of the publisher. The Editor welcomes contributions but reserves the right to accept or reject any material. While every effort has been made to ensure the accuracy of information, Prime Creative Media will not accept responsibility for errors or omissions or for any consequences arising from reliance on information published.
The opinions expressed in Manufacturers’ Monthly are not necessarily the opinions of, or endorsed by the publisher unless otherwise stated.
© Copyright Prime Creative Media, 2025
Articles
All articles submitted for publication become the property of the publisher. The Editor reserves the right to adjust any article to conform with the magazine format.
Head Office
379 Docklands Drive
Docklands VIC 3008
P: +61 3 9690 8766 enquiries@primecreative.com.au www.primecreative.com.au
Sydney Office Suite 11.01, 201 Miller St, North Sydney, NSW 2060
Printed by: The Precision Group
83-89 Freight Drive.
Welcome to the March edition of Manufacturers’ Monthly.
For this edition’s Cover Story, Capral Aluminium offers insight into its online store that provides Australian manufacturers with reliable and convenient access to high-quality aluminium. Showcased in March’s Manufacturer Focus is Space Machines Company, the manufacturer of ‘Optimus Viper’ – a rapid response system that delivers orbital intelligence and protection. Also, this edition’s Engineering Focus article follows AMSL Aero’s innovative VTOL aircraft ‘Vertiia,’ set to take flight commercially in 2027. Rounding out the issue is Decision Makers comment from Boeing Aerostructure’s managing director, Adnan Raghdo, who discusses trends in Australian aerospace manufacturing
With firm momentum heading into the second quarter of the year, Australian manufacturing has seen many positive developments surrounding defence, pharmaceuticals, automotive manufacturing, renewables and critical minerals. In our second edition of the year, we explore recent developments in these sectors that are driving manufacturing forward.
Primarily, however, we delve into different advancements, stories and insights into one of Australia’s most burgeoning industries – aerospace.
A representation of aerospace’s renewed momentum is AMSL Aero, a company led by Andrew Moore, which manufactures long-range, hydrogenpowered VTOL aircraft designed for emergency response and medical transport applications.
Spotlighted in this month’s Engineering Focus, the company’s co-founder runs us through the journey of the ‘Vertiia’ aircraft, which is set for commercial launch in 2027.
For March’s Manufacturer Focus, we shift to
another exciting arena within the sector as we focus on Space Machines Company (SMC), a manufacturer of technology that ensures the longevity of space infrastructure.
Through projects like Optimus Viper – a ‘roadside assistance’ vehicle for satellites – SMC is enhancing sustainability in orbit while showcasing expertise in advanced space manufacturing.
Aside from industry’s advancements, we also hear from one of Australia’s largest voices in aerospace manufacturing – Boeing Aerostructures Australia. The company’s managing director Adnan Raghdo speaks of the current innovation, collaboration, and digital tools in use within Australia’s aerospace manufacturing industry.
On the topic of innovation, representatives from CSIRO and DMTC joined Manufacturers’ Monthly to discuss the development of a nanofibrebased prototype uniform that effectively filters harmful particles – in defence and first responder applications – while remaining lightweight and breathable.
Aside from these innovations, the March edition also delves into the aluminium industry. Specifically, this month’s cover story details Capral Aluminium’s online store, Shop.Capral. Offering 24/7 ordering, next-day delivery, and account-based pricing, the platform provides manufacturers with an efficient and transparent user experience.
Finally, we also cover what could be the start of a new manufacturing industry in the country – Australia’s first Vanadium Flow Battery (VFB) project – a $150 million initiative in Kalgoorlie.
After this development and a symposium celebration at UNSW late last year, it’s evident that Australia is beginning to experiment with VFB technologies to enhance energy security, support the global energy transition and boost local jobs.
As we progress deeper into the year, it is clear Australian manufacturing is gaining momentum with advancements in these sectors that represent a commitment to new ideas and sustainability.
GEOFF CRITTENDEN, CEO, WELD AUSTRALIA
Australia’s welding industry continues to grapple with a severe skills shortage, with a projected shortfall of more than 70,000 welders by 2030.
The importance of quality standards in manufacturing cannot be overstated.
Adherence to stringent standards plays a critical role in ensuring public safety, maintaining product integrity, and fostering a competitive edge in the global marketplace.
However, the landscape of standards compliance in Australia presents a complex picture that demands our attention and action.
Australian Standards are renowned for their rigour and comprehensiveness, often matching or surpassing international benchmarks. Our standards development process involves consultation with industry experts, ensuring that they reflect best practices and knowledge. However, a challenge lies in their implementation and enforcement.
Unlike many of our international counterparts,
the majority of Australian standards are not underpinned by legislation or regulation. This results in a voluntary compliance framework that, while flexible, can lead to inconsistent application across industries. The absence of mandatory compliance creates a scenario where cost considerations may overshadow quality and safety imperatives, particularly when faced with competition from overseas manufacturers operating under different regulatory environments. If applied properly, standards ensure that fabricated structures meet all design criteria, are fit for purpose, and remain structurally sound for the lifecycle of the asset. The application of standards to a process such as welding is particularly important as it is impossible to undertake complete verification of a welded joint without destroying it. Unfortunately, inspection after completion does not guarantee weld serviceability. As such, quality must be built into the welding process, right from the very beginning.
Welding must be done correctly the first time. A weld cannot be adjusted once it is complete. The only course of action is to scrap the weld entirely and start again. As such, the welding processes set out in Australian and international standards are crucial – they must be followed exactly.
If Australian and international standards are not followed exactly, then there is a high chance that a structure will fail.
Just such a failure occurred late last year in China. Typhoon Yagi made landfall on 6 September, causing widespread destruction. The typhoon’s 300 km per hour winds resulted in severe damage to at least five or six massive turbines at a coastal wind farm in Hainan. The destruction witnessed in China should be a wake-up call for Australia’s governments. The incident in China highlights the importance of stringent quality control measures in manufacturing – particularly the manufacturing of public assets.
To appreciate the Australian context, it’s instructive to look at how other nations approach standards compliance. In the European Union, for instance, adherence to relevant international standards is mandatory for companies involved in welding, with certification required from independent, accredited third-party authorities. This approach ensures a baseline of quality and safety across the continent.
Similarly, Japan’s industrial landscape is characterised by the ubiquitous JIS (Japanese Industrial Standards) mark, a symbol of compliance that is ingrained in their manufacturing ethos. Canada, recognising the critical nature of welded structures, implemented a mandatory compliance system for publicly funded welded structural steel projects as far back as 1947. Closer to home, the situation in many Asian countries presents a contrast.
Nations such as China, Thailand, Indonesia, Malaysia, and Vietnam often lack welding compliance regulations. Instead, production is frequently tailored to individual customer specifications, which can result in inconsistent quality standards and potential safety risks when these products enter the Australian market.
The disparity between our world-class standards and their voluntary application creates a precarious situation. When non-compliant products are identified, we often encounter resistance from manufacturers to rectify issues, with some opting to pass liability down the supply chain or simply accept the risk. This approach not only jeopardises public safety but also undermines the integrity of Australian manufacturing.
The influx of imported fabricated steel that does not meet Australian Standards is particularly concerning. As projects increasingly turn to offshore manufacturing to reduce costs, we must be vigilant about the quality and safety implications. The potential consequences of substandard welding in structural applications are severe, ranging from costly failures to catastrophic accidents that could result in loss of life.
At Weld Australia, we firmly believe that the time has come for a paradigm shift in how Australia approaches Standards compliance. We have long advocated for federally recognised legislation and regulations that mandate adherence to Australian Standards, particularly in critical areas such as welding and fabrication of public assets.
If we take the example of renewables manufacturing again, the main competition for Australian wind tower manufacturers are overseas suppliers from Vietnam, China and Indonesia. The issue is that the quality of imported wind towers is low. They do not adhere to Australian standards. In contrast, local fabricators comply with internationally recognised Australian standards like AS/NZS ISO 3834 Quality requirements for fusion welding of metallic materials, and are certified by the relevant Australian authority. In this way, Government and private clients can ensure the quality and safety of projects.
These quality and safety issues will only be exacerbated by increased global demand. The whole world is looking to transition to renewable energy. Not only will increased global demand likely reduce the quality of wind towers manufactured overseas, but it will also increase scarcity of supply.
Weld Australia urges Australia’s governments to mandate that all steelwork for our renewable
energy transition and all public assets – both local and imported – is manufactured and erected according to Australian Standards. The Federal Government and State Governments must act now to foster a sovereign manufacturing industry, create jobs in regional areas and ensure public safety.
This approach aims to create a level playing field for Australian manufacturers while ensuring that all products, whether domestically produced or imported, meet the high Standards necessary for public safety.
In line with our commitment to elevating industry standards, Weld Australia is proud to announce the launch of our new certification service. This innovative offering combines certification for AS/NZS ISO 3834 with AS/NZS 5131 Structural steelwork fabrication, providing a streamlined, cost-effective solution for companies seeking to demonstrate their commitment to quality and compliance.
Our new certification service addresses the growing need for a unified approach to welding quality and structural steel fabrication certification in Australia. By integrating these two critical Standards, we offer a single, comprehensive audit process that reduces time and resource investment for clients while ensuring adherence to the highest industry standards.
This service is particularly timely given the current landscape of voluntary compliance. It provides companies with a tangible way to differentiate themselves in the market, demonstrating their commitment to quality and safety beyond the minimum requirements. For clients and end-users, certification through this program offers assurance that their suppliers are operating at the forefront of industry best practices.
The challenges facing Australian manufacturing in terms of Standards compliance are significant, but not insurmountable. By advocating for mandatory compliance, we can create an environment that prioritises safety, quality, and fair competition. This approach not only protects the public but also strengthens the position of Australian manufacturers in the global marketplace.
As we move forward, it’s crucial that industry, government, and regulatory bodies work together to create a framework that supports the consistent application of our world-class Standards.
This collaborative effort will be essential in ensuring that Australian manufacturing remains synonymous with quality and innovation.
TAFE NSW’s managing director, Stephen Brady, is leaving the role after leading the organisation in overseeing reforms in the vocational education and training sector for the past three years.
Brady led TAFE NSW through the NSW VET Review, a State Government commitment to restoring TAFE to the heart of the VET sector.
TAFE NSW now enters a phase of implementing the VET Review, including the finalisation of a new operating model, while new leadership is set to guide it through this next stage.
The process to appoint a new managing director will commence in due course with the interim position going to deputy secretary, Education and Skills Reform, NSW Department of Education, Chloe Read.
Read has served in several senior public service roles and has more than ten years’ experience at NSW Department of Education
The Federal Government is set to invest $262 million to boost the local defence industry and develop the AUKUS nuclear-powered submarines supply chain.
This move is set to support jobs that are at the forefront of the build and sustainment of Australia’s conventionally armed, nuclearpowered submarines. It is also set to strengthen supply chains between Australia, the United Kingdom and the United States.
“The Australian Government continues to work in a targeted way with our AUKUS partners and Australian industry to get Australian products into UK and US supply chains,” said minister for Defence Industry and Capability Delivery, the Hon Pat Conroy MP.
“Our commitments highlight the pivotal role of Australian industry in driving progress not just for our own conventionally armed, nuclear-powered submarines, but for the fleets of our AUKUS partners as well.”
The funding will be spread across a range of initiatives designed to uplift the nation’s local defence industry, supporting around 125 businesses in the next two years. This includes new and existing programs.
minister, the Hon Richard Marles
The first tranche of funding will support the industry through:
“We are continuing to build and invest in an Australian submarine industrial base capable of supporting our future nuclear-powered submarine fleet and underpinning a strong local economy over the coming decades,” said deputy prime
• T he defence industry development grants program.
• T he global supply chain program.
• T he defence industry vendor qualification program.
reading for IT security pros tackling industrial cybersecurity.
This guide, designed for experienced IT security professionals, skips basic cybersecurity concepts and focuses on operational technology (OT) security.
Vaxxas has secured Coalition for Epidemic Preparedness Innovations (CEPI) approval for a $7.2 million program to develop heat-stable, needle-free mRNA vaccines that are administered by its HD-MAP technology.
The approval follows promising results from Vaxxas’ preclinical work, including expression of a seasonal influenza antigen that demonstrated dose-dependent immunogenicity of mRNA in lipid nanoparticles (LNPs) when delivered by Vaxxas’ HD-MAP technology.
The studies also showed that, once loaded onto the HD-MAP, the mRNA-LNPs have the potential to maintain stability at 2–8°C and 25°C for at least 12 months, and 40°C for at least one month.
“Our HD-MAP technology offers a potential solution to the growing need to significantly expand global access to innovative mRNA vaccines by eliminating the current ultra-cold storage requirements for these vaccines,” said Vaxxas CEO, David Hoey.
Vaxxas will partner with global vaccine developer SK bioscience in this next phase to advance the company’s mRNA vaccine for Japanese Encephalitis Virus (JEV) on Vaxxas’ HDMAP towards a Phase I clinical study. The work will focus on further optimising mRNA vaccine formulations for assessment by in vitro and in vivo preclinical studies.
“With compelling proof-of-concept results in
advance to the next stage of development. We’re equally excited to be working with SK bioscience and its JEV mRNA vaccine on this program to realise the potential of our HD-MAP technology and move the world closer to a commercially available, thermostable patch-based mRNA vaccine,” said Hoey.
Vaxxas expects the development work performed with the JEV vaccine candidate to be transferable across all mRNA vaccine antigens delivered by LNPs, providing a platform approach that can be advanced to human trials.
Currently, mRNA vaccines require expensive
distribution and storage requirements, presenting a barrier to vaccine accessibility.
Vaxxas’ HD-MAP technology has demonstrated the potential to achieve improved thermostability with several vaccines and reduce the cost and complexities of current cold-chain requirements. Previous studies in hundreds of trial participants have also shown the potential of the technology to be easy to use and require less training to administer.
The continued success of this program could enable increased global access to innovative, lifesaving mRNA vaccines.
Australian owned bus manufacturer, Foton Mobility Distribution, is set to build a 6,000 square metre electric bus manufacturing facility in South Nowra in late 2025, subject to council approval.
This follows the NSW Government awarding a contract to Foton to deliver 126 battery electric buses that will be built in Nowra and service bus routes across Greater Sydney.
The facility will also produce battery electric trucks, as well as hydrogen fuel cell engines, creating around 100 ongoing manufacturing jobs for local workers.
Foton’s bus contract was one of the first bus orders made through the NSW Government’s Zero Emission Buses (ZEB) program.
This program also involved the conversion of 11 existing bus depots in Greater Sydney to battery electric technology, the build of a new battery electric
depot at Macquarie Park and the procurement of around 1,200 new electric buses by
Victorian acting premier Ben Carroll and minister for the State Electricity Commission, Lily D’Ambrosio, have welcomed the installation of two 335-tonne transformers at the 600-megawatt Melbourne Renewable Energy Hub (MREH) in Plumpton.
This is a milestone for one of the world’s biggest renewable energy storage batteries, with all 444 Tesla Megapack ‘big battery’ components now in place at the MREH. The giant transformers are the final pieces that will connect the battery’s power to the grid and allow it to be pumped at higher voltage.
“This is one of the world’s biggest batteries that can store enough energy to power 200,000 homes,” said D’Ambrosio.
“Soon, we’ll plug a publicly owned energy asset into the electricity grid for the first time in more than 25 years.”
A third transformer will arrive next month, with the big battery coming online later this year.
The system works by soaking up excess solar and surplus energy from the grid during the day and releasing it back into the grid during the evening peak to boost supply and put downward
pressure on bills. It will also allow 1.8 gigawatts of new renewable energy generation to be added to the grid.
More than 790 people have worked across all aspects of the project, including 30 apprentices, trainees and cadets.
The SEC will build 4.5 gigawatts of new renewable energy and storage projects – enough to power more than 1.5 million homes – with all profits set
to be reinvested back into Victorian projects that deliver cheaper renewable energy.
Construction is also underway on the first 100 percent government-owned renewable energy project in Australia – the SEC Renewable Energy Park in Horsham. This $370 million investment includes a 100-megawatt two-hour battery and 119-megawatt solar farm that will power 51,000 homes and create 246 jobs.
A roadside assist service, but for space? Space Machines Company (SMC) is pioneering on-orbit satellite servicing with technology to monitor, maintain, and safeguard orbiting infrastructure.
Space exploration has grown sizeably in recent years through increasing investments and a race to expand humanity’s presence beyond Earth.
Satellites, once a tool of governments and research institutions, are now pivotal to an array of sectors, from communications to weather forecasting, navigation, and even global financial systems. However, as the number of satellites in orbit increases, so does the need for their protection and maintenance. Space Machines Company (SMC) is at the forefront of addressing these concerns, offering solutions to monitor, maintain, and safeguard satellites, ensuring their continuous functionality for the modern world.
Space Machines Company is an Australian-based company specialising in building advanced systems for space, both hardware and software.
Established in 2019, the company focuses on leading the transformation of space operations through its Orbitside Assist capability. This is crucial for services that billions of people depend on, such as GPS, communication, and banking apps.
“How do we protect the satellites we have? How do we understand what might have gone wrong with them? How do we make sure there’s not a lot of debris being created in space? We build space systems that focus on making sure that the satellites we have that service are safeguarded,”
said Space Machines Company CEO and cofounder, Rajat Kulshrestha.
The goal of SMC’s primary products is to ensure the safety and longevity of satellites in orbit, which can be crucial to maintaining global infrastructure.
SMC operates from Sydney, where its manufacturing takes place; Adelaide for Mission Control and government operations; and Bangalore, India, for component manufacturing.
At the heart of SMC’s product offerings is the “OrbitSide Assist” system.
With space infrastructure investment soaring – $53 billion in the past year alone –understanding satellite
risks, whether due to internal issues, damage, or security concerns, is crucial.
As satellites become increasingly integral to services such as GPS, telecommunications, and financial transactions, any malfunction or disruption of these systems can have catastrophic consequences.
“OrbitSide Assist was created to fill the gap that exists in satellite maintenance today”, said Kulshrestha.
“It is our solution that helps customers gain a better understanding of what’s happening around their satellites. It’s essentially like roadside assistance, but for space.”
Traditionally, satellite repair and maintenance are long-term, time-consuming and expensive processes. If something goes wrong with a satellite, the only option has been to either send a team to investigate (which could take months or even years) or launch a new satellite, which comes at a tremendous cost.
SMC’s OrbitSide Assist provides insights into satellite conditions, helping customers quickly assess and act on potential problems. It enables fast, effective support for satellites, even when they’re hundreds of kilometres away.
In the evolution of this technology, SMC developed the Optimus spacecraft. Optimus was designed to reach satellites in orbit, carry out inspections, and potentially conduct repairs.
“We started building Optimus five years ago with the goal of creating a spacecraft that was highly capable, cost-effective, and offered rapid access to satellite,” added Kulshrestha.
“Our first mission taught us a lot about building large satellites. The original Optimus was the largest satellite ever designed and built in Australia. Based on that experience, we’re now developing a new variant, the Optimus Viper, which is leaner, more optimised, and set to fly next year on an Indian SSL rocket.”
These spacecraft are designed to help governments and commercial satellite operators monitor satellite health, inspect potential threats such as space debris, and respond swiftly to issues that might otherwise disrupt services for long periods.
SMC’s commitment to sustainability in space is not limited to satellite maintenance and debris management; it extends to collaborative projects that enhance global space cooperation.
One such initiative is “Space Maitri,” a project that SMC proposed and is supported by the Australian Government. In April 2024, $8.5 million through the Australian Space Agency’s International Space Investment India Projects program.
It is a collaboration between India and Australia, which focuses on ensuring the sustainability of space through debris management and collaboration
underscored by data-sharing and supply chain development.
“SMC won the largest part of that grant,” said Kulshrestha.
“Space Maitri is a project where we will be flying one of our Optimus Viper satellites aboard a dedicated Indian rocket, the Small Satellite Launch Vehicle (SSLV).
“This initiative aims to promote sustainability in space by sharing data on space debris behaviour and exploring ways to manage and remove it in the future.
It also focuses on improving data-sharing between India and Australia and fostering collaboration within the supply chains and manufacturing ecosystems of both countries.”
Maitri is crucial in this perspective, allowing Australian companies to learn how to work alongside Indian partners and the Indian government, especially given India’s space heritage and sector growth.
“Space Maitri involves a 200-kilogram spacecraft that will be launched atop the SSLV rocket,” explained Kulshrestha.
“Once in orbit, it will release an object and then capture it back, demonstrating the potential to retrieve space debris and reduce the creation of additional debris. The spacecraft will also inspect other pieces of debris to better understand their behaviour, and through this, explore techniques that could be applied to remove them.”
Safe and sustainable manufacturing SMC’s manufacturing operations are largely based in Sydney, where the company produces its spacecraft and components. However, it has expanded its supply chain to various parts of Australia, including Adelaide and Queensland, where specific manufacturing processes like propulsion systems are handled.
Additionally, SMC works closely with international partners, such as suppliers in India and Europe, to bolster its manufacturing capabilities.
With a team of 45 employees, SMC is currently focused on producing three spacecraft for launch in the coming years, with plans to scale up production to 20 units annually by 2027.
By focusing on efficient manufacturing techniques,
such as the use of 3D printing and CNC machinery, SMC aims to reduce costs while maintaining high standards of reliability and quality.
The company’s focus on sustainability permeates its production processes. Through careful sourcing of materials, minimising waste, and reusing test equipment, SMC is working toward making its manufacturing operations as environmentally
responsible as possible.
“We focus on streamlining multiple tests and production processes into a single shift, reducing the need for repetition,” said Kulshrestha.
“These small efficiencies improve sustainability and resource use, and we collaborate with vendors to ensure they apply these principles practically when purchasing equipment.”
pressure and temperature.
“We follow strict safety guidelines to maintain sustainability and, operationally, ensure the spacecraft can safely deorbit without contributing to space debris.”
Looking forward, SMC’s immediate focus is on completing the upcoming missions for the Space Maitri project, as well as the deployment of additional Optimus spacecraft.
SMC’s ability to provide “on-demand” satellite servicing will reshape the way the aerospace industry operates. It promises a future where satellite operators will not have to wait months or even years for satellite repairs, potentially saving billions of dollars and preventing critical infrastructure failures.
“Our key focus is building sovereign capability in Australia by emphasising what we excel at,” concluded Kulshrestha.
“While we may not compete on labour costs, we can lead in developing innovative, high-value technology. Our goal is to combine international supply chains with Australia’s manufacturing expertise and innovation, creating circular supply chains.
However, according to SMC, the most important factor is safety.
“We ensure that anything we send into space won’t create dangerous situations, either during re-entry or if something goes wrong,” added Kulshrestha.
“We invest significant effort in modelling to account for factors like spacecraft strength, stress, and the limits of components, such as tanks’ exposure to
“Beyond building spacecraft and serving customers, our team is driven by showcasing the capabilities of Australian manufacturers to the world.”
SMC is not just solving current problems in satellite servicing but also laying the groundwork for the next generation of space exploration and satellite maintenance.
Capral’s national market manager for Industrial Solutions, Mark Murray, speaks to the role of the company’s online store as a reliable source of sustainable and trustworthy aluminium.
As Australia’s largest extruder and distributor of aluminium products, Capral Aluminium manufactures and distributes a wide range of aluminium products to Australian manufacturers across a variety of industries. This range includes extrusion, plate, sheet, mesh, treadplate and low-carbon aluminium
“We extrude around about 55,000 tonnes of aluminium annually and distribute around 10,000 tons of rolled aluminium product a year,” said national market manager for Industrial Solutions, Capral Aluminium, Mark
Mark explained that Capral’s diverse range of products – including custom designs – are kept readily available and widely
“These products are kept in stock at our Regional Distribution Centres and usually available for next day collection or delivery. We also provide custom, proprietary extrusions which are designed to meet the needs of an individual customer,” he
“Often customers in industries like transport, construction, marine or renewable energy will have their own bespoke extrusion designs that we supply on demand.”
The company’s national footprint enables it to work with customers across various industries, including manufacturing. This footprint includes six manufacturing sites as well as regional distribution centres in all states supporting Capral’s
retail Aluminium Trade Centres and network of experienced account managers.
“Our business services all types of customers, from large multinationals to micro businesses, we take pride in being able to meet the needs of our customers regardless of their size or unique industry requirements” added Mark.
With such a firm hold on the national distribution of its aluminium, around half a decade ago, Capral established a flexible way to service customers on their own terms, providing customers with better visibility and access to the Capral’s Industrial Solutions aluminium offering. This innovation came by way of Shop.Capral, an online store that is available to all the company’s industrial customers along with general consumers and trade customers.
“In the store, we offer everything from all our standard extruded aluminium products as well as sheet and plate products. Currently, we don’t include our range of window systems or hardware but otherwise you will find most Capral Aluminium products available there,” said Mark.
“The online store reflects Capral’s commitment to innovating and evolving to meet customer needs in the aluminium industry.”
Mark said the store was launched to not only enhance the experience for Capral’s regular customers, but to enhance the product access of the customers that may not be as frequent buyers.
“There could be 10,000 customers that might buy once a year, often these businesses won’t have an established relationship with an account manager or
our customer service team. This service is well suited to these customers,” he said.
“Rather than having to ring or work out where to go and pick up a product, they can just jump online on order.”
Running across the country, the online store offers pick-up options for its products from any of Capral’s RDCs or Aluminium Trade Centres – 28 locations nationally – or a next day delivery option.
“It’s all part of our enhancement for customer
experience to give our products better availability to customers,” said Mark.
He said that the online store has numerous advantages, including its easy-to-use interface, timely processing and accessibility.
“You can jump on, place an order and be checked out and ready to move on to your next step within 30 seconds. You can do it on a computer, or a mobile,” he said.
As a part of this accessibility, Mark said that a fan
favourite among customers is its 24/7, around-theclock access.
“Being able to order 24/7 wasn’t possible five years ago. We’re moving with the IT world to make the customer experience better,” he said.
“People can say, ‘I need that tomorrow, I better get that now and put the order in’, and have it delivered the next day.”
Mark recalled scenarios that occur quite often where people will be working all day at welding and fabrication workshops and will not be able to order aluminium until nine or ten o’clock at night. The online store is also open for weekends, catering for people who don’t want to waste an hour or two on a Monday morning working out what products they need.
“Quite often I see orders come through at seven to 10 o’clock on a Sunday night. People are sitting down and working out what they need for the week. They could jump on an order on Sunday night and have it delivered the next day, ready for the week’s work,” he said.
Aside from accessibility and timeliness benefits, the store also caters to account customers, who receive access to their negotiated pricing, past orders and invoices. Account customers can also benefit from the recent reordering, shopping list and favourites features. It also adds to accountability
and user experience through the ability for customers to track their orders and deliveries.
“Account customers can see their agreed pricing offers for the business so they can jump online and look at all their exclusive products, and then order and track their next day delivery,” said Mark.
Mark describes the customer response Capral has received since the store’s launch as excellent, and something that the company values – shown through the regular updates the system received based on feedback.
“Early last year we did a survey around the online store, and the feedback provided was excellent. Our customers have found the online store very user friendly,” he said.
“We also continue to develop the platform and have put a lot more features and enhancements into the system since we originally launched the site almost 10 years ago.”
A manufacturer of pontoons, gangways, jetties and decks for marine access – Aqua Pontoons – has been a customer of Capral for 15 years. Coowner of the company, Mel Dyer, said Capral has been instrumental in the company’s operations by supplying a range of components used in its products.
“We use a broad range of products from Capral’s extensive range, including its flat bar, angle, sheet, treadplate right up to our personalised whaler and handrail,” she said.
Dyer said to add to the already strong relationship between each company, Capral representatives at the Burleigh Heads branch alerted Aqua Pontoons of the online store. Now, the company has used the store for several years, with Dyer saying that she would recommend the service to any manufacturer who needs easy and reliable access to aluminium.
“It makes ordering easier and efficient, and you are able to know your pricing without any surprises. The online experience is a time saver, and any queries can be sorted out quickly by a quick call to the wonderful staff at our branch,” she said.
“We’ve been a client of Capral’s for so long. It is testimony to their services.”
Another beneficiary of Capral’s services in a similar industry is MDS Marine, an Australian-owned and operated manufacturer of pontoons, jetties, marinas, bridges and associated components.
“MDS Marine has been using Capral for approximately 18 years. MDS Marine predominantly uses extruded structural profiles
Identify potential risks and vulnerabilities
Protect against cyber attacks and production stoppages
Enhance employee safety, cyber security, and machine availability
Verify correct implementation of risk-reducing measures
Ensure machinery protection per Industrial Security requirements
Essential for the EC Declaration of Conformity
including mill run exclusive sections,” said MDS Marine’s administration manager Janelle Brewin.
Brewin said that after a timely relationship with Capral, they were approached by their account manager who notified them of the new online store. She said that because the system allowed any staff member to place an order, it was very convenient.
“It is more efficient as we do not have to wait for quotes, and we can see stock availability and estimated date if not in stock,” she said.
“We purchase multiple sections, so it is easier to order looking at section numbers. Having less human interaction and the ability to track history and view open purchase orders and estimated delivery dates means less chance errors.
“MDS Marine would recommend it as we have found the system easy to use and accessible to all staff members. It greatly assists in quoting projects and ordering materials.”
Going forward, Mark emphasised that Capral would continue to prioritise customer satisfaction. He said the company currently has several enhancements listed that they are set to target within the foreseeable future.
“We are starting to look at what the next level of enhancements are to make the user experience even more friendly,” he said.
Experts from RSM Australia share insights on the key trends and growth opportunities Australian manufacturers should capitalise on in 2025.
As we enter the first quarter of the new year, Australian manufacturers – both large and small – are evaluating industry trends to identify opportunities for growth and success. After a 2024 that saw the industry’s landscape continue to evolve, businesses are striving to find ways to enhance supply chain efficiency and product quality.
As a cornerstone of the nation’s economy, the manufacturing industry relies on informed decision-making. Audit, Tax and Consulting firm RSM Australia remains committed to analysing trends and providing strategic insights to support manufacturers nationwide.
National Manufacturing leader at RSM, Louis Quintal, believes that sustainability initiatives, technological advancements, workforce development, supply chain resilience, and energy cost management will ultimately shape the sector’s 2025.
“These trends are driving the industry towards greater sustainability, efficiency, and resilience,” said Quintal.
National Manufacturing Sector, business advisory director at RSM, Ross Dixon, echoed Quintal’s sentiments, adding that financially, he believes we will see a more buoyant landscape than in 2024.
“Hopefully, this will encompass some interest rate reductions and election promises that could provide SME manufacturers with a more optimistic perspective,” said Dixon.
Aside from a broad 2025 outlook, Quintal identified sub sectors within the industry that are expected to experience growth due to broader shifts towards sustainability, technological
innovation, and changing consumer preferences. He said the first and obvious beneficiary of the shift to a sustainable industry is renewable energy manufacturing.
“The production of solar panels, wind turbines, and hydrogen fuel cells is expected to grow.
Australian manufacturers are making strides towards decarbonisation,” he said.
Additionally, Quintal believes that advanced manufacturing – including aerospace, and medical technology – are also slated to continue their positive momentum. Finally, he emphasised that food and beverage processing will gain popularity as Australia’s reputation for highquality produce continues to spread in a world that has an increasing demand for processed foods. Dixon agrees with this sentiment, adding that food and beverage associated sectors, like ag tech, are also set to benefit.
“Ag tech and food and beverage processing is where we will see a lot of value. You look at certain regions like WA and the Riverina, the exports are strong,” he said.
Quintal predicts that Industry 4.0, AI, robotics, and automation will also continue to have a large impact on shaping manufacturing strategies in 2025.
“AI and predictive analytics will enable manufacturers to optimise operations, reduce downtime, and improve quality control,” he said.
“Robotics and automation will handle repetitive and hazardous tasks, allowing human workers to focus on more complex and creative activities.
“Additionally, digital twins and IoT will provide real-time insights into production processes, enabling better decision-making and proactive maintenance.”
Quintal and Dixon both agree that while large manufacturers look poised to invest into these technologies at a time where cost of labour and electricity are increasing, challenges will arise with what they refer to as a “two speed economy.”
“Smaller businesses are maintaining their position and waiting to see how the future unfolds,” said Dixon.
Because of this, Dixon recommends SMEs to wait and assess whether consumer and business sentiments are strong enough for investment.
Quintal agreed with this suggestion, saying that government intervention is the only way to overcome this issue.
“These processes come with a cost that can only be achieved through reduced interest rates,” said Quintal.
“ We have the National Reconstruction Fund and other initiatives in place. Let’s wait and see if these will truly support businesses through tax reform,” said Dixon.
Quintal emphasised that this government intervention is also a large talking point heading into 2025, with initiatives set to have a large impact on the sector’s prosperity.
“Grants and incentives for energy-efficient systems and advanced manufacturing, along with favourable taxation policies, are expected to influence manufacturing growth and investment decisions,” he said.
Quintal also believes that tax incentives for investing in energy-efficient equipment and renewable energy projects can help in lowering the overall tax burden for manufacturers.
“Programs such as Industrial Energy Transformation Funds (IETF) and various green technology grants will assist in adopting new techniques and making Australia procedures more attractive,” he said.
A major, yet still uncertain part, of Australian manufacturing’s 2025 outlook is the impact it will feel from the current global economic environment. Quintal predicts that it will have a mixed impact on exports and commodities, with several challenges posed.
“Global trade risks and rising export prices could pose challenges and volatility in commodity prices, such as coal and iron ore. It may also affect export revenues,” he said.
Describing this as the “million-dollar question,” Dixon said it is hard to tell whether rhetoric will evolve into tariffs.
Aside from trends and outlooks, to stay ahead Quintal recommended that Australian manufacturers should strengthen supply chain resilience, prioritise workforce development and embrace technological innovation and sustainability. Dixon said to embrace these elements, businesses should plan finances to ensure targeted investment.
“The focus will be on ensuring that individuals prepare for the next six to nine months, so when opportunities present themselves, they are wellpositioned to take advantage” said Dixon.
Quintal also noted several common financial and operational mistakes to avoid for manufacturers in 2025. These included poor inventory management, inadequate production tracking, overuse of machinery, neglecting workforce development and ignoring sustainability practices. Additionally, Dixon pointed out that meeting your statutory obligations to the ATO as a company is vital to avoiding any financial trouble.
“Cash flow management is so important to try and stay compliant in terms of meeting those obligations,” he said.
More than its industry knowledge, RSM Australia supports manufacturing businesses by providing a range of advisory services designed to help them navigate these challenges and capitalise on opportunities.
“RSM provides services ranging from regional Australia to international clients. We offer competitively priced support to SMEs while also catering to world-class industries ” said Dixon.
RSM offers audit and strategic advisory services to help manufacturers innovate, boost efficiency, and expand. Its financial and tax expertise includes securing grants for energy-efficient systems and managing financial risks. RSM also advises on sustainability, regulatory compliance, and supply chain resilience while addressing skills shortages through workforce development.
“By utilising these services, Australian manufacturers can enhance their competitiveness, drive innovation, and achieve growth,” said Quintal.
RSM’s services were applied to Omega Manufacturing Group, an advanced manufacturer in Wodonga. Here, the company helped Omega leverage automation and vertical integration to enhance manufacturing capabilities.
“Automation is something that we have been transitioning to over the past three to five years to enhance operational efficiency,” said Finance and Commercial Support manager at Omega Manufacturing Group, Emma Forbes.
With support from RSM, Omega continues to accelerate growth through R&D incentives, grant programs, and a planned US expansion, positioning itself as a global competitor in automotive manufacturing.
“Part of it is finding a niche and setting yourself up to be able to manufacture as efficiently as you can in that niche,” she said.
RSM continues to aid Australian manufacturing companies – like Omega – in adapting to a forever evolving industry.
The newly launched IndustrialPI by Pilz is an Industrial PC designed to support a range of applications in industrial automation. Its versatile uses include as an industrial PC, industrial controller (Soft-PLC), or a IIoT gateway for data management.
Its modular design, open Linux-based operating system, and integrated interfaces make it a suitable solution for realising IIoT, automation, and motion control projects in industrial environments. Engineered for industrial automation, it is based on the familiar Raspberry Pi and housed in an industrialgrade enclosure with an expansion board for robust interfaces and connections. It can also be expanded with digital and analogue I/O modules as needed.
IndustrialPI as an IIoT Gateway
As a gateway for the Industrial Internet of Things (IIoT), the IndustrialPI collects data in the
immediate vicinity of machines and systems and connects the IIoT with cloud services. For example, when used as an IIoT gateway, the IndustrialPI sends data from the configurable small controllers PNOZmulti to the cloud. This gives users worldwide access to their data, no matter where they are. It is possible to use and analyse data across different systems to optimise processes. It is also possible to set up interfaces to a user’s own IT systems as well as to cloud solutions.
Automation control with IndustrialPI
It can be used as a modular Soft-PLC for a variety of automation projects whether this is for pure control applications such as reading inputs and switching outputs, or for synchronous axis movements and in the drivetrain of a machine. With the help of IndustrialPI, the most diverse and complex tasks can be implemented easily and quickly.
Features:
• A solution for many industrial applications, such as within the packaging industry or intralogistics.
• Flexibly usable as an automation controller or IIoT gateway, tailored to an application.
• Robust housing and 24V connection allow for industrial use.
• Integrable into all common system architectures.
• Easy programming is possible.
Pilz’s IndustrialPI is a versatile solution for automation and IIoT applications, offering flexibility, robust design, and seamless integration into industrial systems. The system helps optimise processes and enhance connectivity for modern industry by being used as either a controller or a gateway.
For more information contact Pilz at sales@pilz.com.au or 1300 723 334
With NetSuite dynamically adjust production scheduling, quickly manage work orders, get better insights over costs, streamline operations, and more.
At Fusion5, we’ve helped countless businesses navigate their ERP journeys. We know what works, what people get stuck on, and how to create a successful transition to a superior ERP solution.
Talk to a Fusion5 NetSuite expert today by calling 1300 156 640 or scan the QR code for more
Dragos highlights common pitfalls IT cyber professionals should avoid when working with OT staff and showcases how its OT cybersecurity program can eliminate these challenges.
In the complex world of Cybersecurity, industry veterans should be aware of the common stumbling blocks that frequently impede progress in establishing a workable OT cybersecurity program.
The first is a lack of understanding of safety focus, as OT cyber incidents can cause safety problems but so can patching systems. This means risk calculations will be different.
The lack of understanding of uptime requirements compared to IT systems, similarly to above, sees uptime trumps confidentiality and even integrity concerns.
Culture disconnects between OT engineers and IT staff are also vital to avoid. OT engineers are cut from a different cloth and are running on different priorities than IT staff. Cybersecurity experts must be willing to understand the lingo and the culture in order to bridge the divide.
Failing to use OT-native capabilities is also a common stumbling block. IT tools that have been retrofitted to ‘work’ in OT environments are often unable to offer full visibility into OT systems and processes. More detrimentally, many of them introduce an unacceptable amount of downtime or disruption risk to critical industrial control systems.
A robust OT cybersecurity program focuses on protecting the most vital assets. Although frameworks like NIST and ISA/IEC 62443 exist to guide the development of a thorough plan, their complexity can sometimes hinder prompt action.
A Dragos recommendation is to start with the implementation of the SANS 5 Critical Controls for ICS Cybersecurity, which includes:
An OT-specific and operations-informed incident response plan with a focus on system integrity and recovery capabilities during an attack.
D efensible design architecture that supports visibility, log collection, asset identification, segmentation, industrial DMZs, and processcommunication enforcement.
ICS network visibility and monitoring enables continuous network security monitoring of the ICS environment using protocol-aware toolsets and a system of systems, interaction analysis capabilities.
S ecure remote access identifies all remote access points and allowed destination environments and implements on-demand access and multi-factor authentication (MFA) where possible.
Risk-based vulnerability management helps understand the cyber digital controls in place and device operating conditions to make riskbased vulnerability management decisions regarding your OT environment.
Working with an operations team and OT security experts to start implementing these controls ensures they are operational and can efficiently handle key scenarios. As a program evolves, a user will establish a risk management framework. This will allow the user to fine-tune their investments and enhance risk mitigation efforts.
It is crucial to recognise that implementing the right cyber controls can lead to improvements in operational efficiency and uptime. In production
environments, the question of “What happened and why?” is frequently posed. While some answers may be straightforward, identifying the root cause of emergent problems often proves challenging. Controls that enable the identification of new devices, monitor third-party remote access, and log OT system commands offer a valuable data set. This data can be analysed to understand events leading up to and following issues, enhancing OT network visibility and monitoring.
The question arises: Can we prevent a production shutdown, or if necessary, how can we execute an orderly shutdown? Implementing risk-based vulnerability management offers alternatives to IT-driven device patches that could halt production lines. In the event of an incident, a robust OTspecific incident response plan, which considers critical processes and safety systems, is essential.
Protecting critical processes and assets from IoT devices, transient network traffic, or thirdparty remote access is paramount. This involves creating defensible architectures that segments
Working with an operations team and OT security experts to start implementing SANS 5 controls ensures they are operational and can efficiently handle key scenarios.
equipment types and networks. Such strategies lead to more resilient operating environments and minimise disruptions.
Staying vigilant and continuously searching for problems is essential for maintaining operational integrity and safety. This proactive approach helps in early detection and resolution of issues, ensuring the smooth functioning of operations.
Reframing common cyber terms and concepts for ICS/OT
Just like in IT environments, cyber attackers target ICS/OT environments with ransomware attacks. However, the risk from ransomware against OT organisations and OT assets is higher stakes all the way around, with greater risk to physical safety and continuity of critical processes at play. The 2021 ransomware attack that temporarily halted OT operations at Colonial Pipeline was a high-profile example of just such an attack.
Just as with IT security, network segmentation is a key best practice for limiting the blast radius of attacks against IT or OT assets in industrial organisations. However, the consequences of poor segmentation are much more severe, as an attacker that moves laterally from a foothold made in an IT system to a critical OT system could threaten human safety or the sustainability of the business itself.
Attacks using fileless malware and leveraging
existing system utilities and remote admin capabilities to execute commands are favoured not just by advanced IT attackers but also those that target ICS/OT systems. In addition to using tools that cross OT/IT boundaries like Powershell, Windows Management Instrumentation, and Server Message Block, OT-threat groups also can use ICS protocols for living off the land (LOTL) attacks in ICS environments.
The Computer Emergency Response Coordination Centre’s (CERT/CC) now, next, never methodology, used within the Dragos Platform, is a method of prioritising patching and vulnerability remediation. It is especially important for OT assets, as patching can sometimes be riskier than leaving a flaw in place and mitigating it in some other way.
As US Security and Exchange Commission cybersecurity risk management rules tighten reporting timeframes for cyber incidents –whether in IT or OT networks – and other regulatory directives increase OT cyber response preparedness, organisations are increasingly seeing a need to practice their OT incident response procedures through OT cyber tabletop exercises.
Managing vulnerabilities in OT environments can be a different affair than in IT because the tools, the methods for mitigation, and the risks –especially in the physical realm – are all unique
to OT. For example, the highest risk OT flaws are those that can cause loss of view or loss of control in ICS systems. On top of that, OT systems often run continuously, with months or years before a maintenance window allows for patches. This means creative mitigations are crucial.
As zero trust and micro-segmentation grow in importance for IT network security, many cybersecurity pros wonder if they can transfer the same principles to OT networks. Because of the unique demands and operational realities of ICS networks, organisations can’t take a cookie-cutter approach to OT zero trust. MFA is crucial, but measures like active monitoring and how zones or segments are designed will be different.
IT-style active scanning for asset discovery and vulnerability management is frequently problematic for OT systems and can have operational and compliance ramifications for industrial processes. This is why OT-native cybersecurity tooling places a heavy emphasis on well-designed passive scanning.
Just like IT environments, Internet of Things (IoT) devices are pervasive in OT settings. Industrial Internet of Things (IIoT) devices are commonly used for sensors that can help measure and optimise operational processes. The Dragos Platform extends its coverage to IoT and IIoT devices when they are used in OT processes and systems.
NetSuite has features that increase efficiency in production planning, scheduling and waste minimisation.
Manufacturers’ Monthly explores Fusion5’s capabilities in project management and expertise with NetSuite ERP solutions.
Founded on the belief that no single technology solution suits every business, Fusion5 specialises in project management and systems integration, delivering tailored solutions to diverse organisations.
“We start by tailoring our strategies to align perfectly with the needs and goals of each business,” said general manager of NetSuite Australia at Fusion5, Deborah Reidy.
“Our team of experts ensures that every project is meticulously planned and executed, keeping our clients’ best interests at the forefront.”
Fusion5 supports manufacturing businesses with applications, consulting, development, and managed services, as well as offering a range of digital solutions and support services. One of the company’s digital solution offerings is NetSuite, a cloud-based ERP platform that streamlines operations and decision making whilst also bringing all business functions together.
“Fusion5 has been assisting manufacturers with operations for over 20 years and has introduced NetSuite as a solution for over 10 years,” said senior sales manager for NetSuite Australia at Fusion5, Joel Mikkelsen.
The company has been an implementer of NetSuite solutions to businesses across diverse industries, evidenced by its seven consecutive years as the NetSuite Solutions Provider Partner of the Year.
“We’ve partnered with NetSuite since 2009 and have built the largest practice in JAPAC and third largest globally, assisting over 400 customers with
• Fusion5 has the highest accreditation tier for NetSuite Partners.
• Fusion5 is NetSuite’s largest Australasian implementation partner.
• Fusion5 is NetSuite’s third most significant global partner.
• Fusion5 has more than 400 NetSuite customers.
• Fusion5 has a NetSuite team of more than 100 people across ANZ who have deep knowledge and experience.
• NetSuite ANZ Solution Provider Partner of the Year from 2021 to 2024.
their NetSuite solutions today,” said Mikkelsen.
When searching for an ERP solution, manufacturing businesses will pay attention to how it helps in enhancing production efficiency. Mikkelsen said NetSuite has many benefits to assist efficiency with production planning, scheduling and waste minimisation.
“NetSuite planning tools optimise resource allocation and scheduling to prevent bottlenecks. NetSuite also facilitates lean manufacturing support
to manage processes that minimise waste and improve operational flow,” he said.
Beyond efficiency, NetSuite streamlines processing with end-to-end integration and automated compliance reporting, with procurement to production combined into one unified system.
“Real-time data from the production floor also helps identify inefficiencies and improve throughput, whilst also ensuring seamless coordination,” said Mikkelsen.
“The solution also utilises automated compliance reporting to simplify adherence to regulatory and industry standards.
“These aspects result in faster order fulfillment, with automation reducing processing times and ensuring timely delivery.”
NetSuite also leverages cloud accessibility for real-time insights, enhancing decision-making, productivity, and responsiveness.
Alongside ensuring a time, material and resource efficient production floor, NetSuite aids manufacturing businesses in managing their inventory to avoid time-consuming manual methods. As a part of this offering, Mikkelsen said that NetSuite provides real-time inventory, lot and serial number tracking, alongside materials resource planning forecasting.
“Advanced tracking tools monitor stock levels, locations, and movements in real-time. NetSuite also offers lot and serial number tracking to ensure
traceability for compliance and quality control purposes. This also assists with cost tracking,” he said.
“Predictive analytics also helps manufacturers maintain optimal inventory levels based on demand trends.”
Mikkelsen said as a part of inventory management, NetSuite also offers a multiwarehouse management solutions across multiple locations to ensure better resource utilisation.
“It connects with RF enabled warehouses to help mobile operators in stock movements,” he said.
On top of benefits within production and processing, NetSuite has a positive effect on revenue and gross margin performance. At the front of this positive effect is the company’s pricing strategies based upon sales and procurement information.
“Comprehensive data analysis supports dynamic pricing strategies to maximise revenue,” said Mikkelsen.
NetSuite also helps manufacturers optimise revenue opportunities by reducing operational costs, increasing customisation capabilities, and ensuring scalability.
“Reduced costs come from streamlined processes and reduction of waste. NetSuite can also adapt product offerings to market trends or customer-specific needs to increase sales and profitability,” said Mikkelsen.
“Moreover, as businesses grow, NetSuite scales to enable expansion without revenue bottlenecks.”
NetSuite’s impact on a business’s sales results is another appealing aspect of the system which practices sales forecasting, faster quote-to-cash process, upselling and cross-selling opportunities and easier customer relationship management.
“Real-time data improves demand planning and
forecasting accuracy, whereas Integrated CRM and ERP systems speed up the sales cycle, from quotes to payments,” he said.
“Insights from customer data enables the sales teams to offer complementary products and enhance customer insights through NetSuite CRM.”
As well as revenue, production and process benefits, NetSuite prioritises the customer experience by offering an array of services such as enhanced order accuracy and real time communication portals.
“Automated order processing minimises errors, ensuring timely and accurate deliveries, while selfservice portals keep customers informed about orders,” said Mikkelsen.
Moreover, NetSuite CRM enhances communication and quality management, resolving issues swiftly or preventing them altogether.
“Real time communications between inventory, manufacturing and sales processes, allow staff to provide real-time and accurate updates on stock visibility and order status,” said Mikkelsen.
The benefits of NetSuite were seen in action when the solution was applied to Chain and Rigging Supplies, an equipment supplier across the Asia Pacific. Accounts manager, Jackie Edwards, was at the time frustrated with an outdated software.
“The previous solution wasn’t cloud-based... so it really impacted business productivity. There were lots more benefits to using NetSuite,” said Edwards.
Edwards praised NetSuite as a powerful yet cost-effective solution as it brought to the business real-time reporting, increased accountability, userfriendly dashboards, and mobile accessibility to improve the businesses’ efficiency.
“NetSuite is very clean and user-friendly, and there aren’t many restrictions. Everyone in the business finds it easy to use,” she said.
To accommodate NetSuite and avoid disruptions, a smooth implementation process is required, bringing Fusion5’s project management team into play at it helps its clients start off on the right foot in the pre-sales process.
“Fusion5 removes risks from the solution and implementation projects via our alignment process where we align the customer’s processes and requirements to NetSuite’s leading practices, identifying and solution gaps,” said Reidy.
This continues through to the project’s launch, when Fusion5 enters a two-week initiation phase with the primary objective being that the customer and project managers are aligned on scope, responsibilities, timeline and budget.
“We utilise project management tools and
methodologies to keep track of progress, identify potential risks, and implement mitigation strategies proactively,” said Reidy.
Fusion5’s governance framework helps further ensure everyone is on the same page, with status updates, committee meetings, and comprehensive reporting.
“Our governance structure also allows for timely decision-making and issue resolution,” said Reidy. After implementation, Fusion5’s ‘change management’ takes over, as it identifies a strategy including training and support to ensure that the customer is well-equipped to leverage NetSuite’s capabilities.
“Our commitment to post-implementation support ensures that clients continue to receive assistance and guidance long after the project is completed,” she said.
Fusion5’s services also extend after to its customer success team that – after implementation – offer ongoing support and guidance to help clients navigate any challenges they may encounter.
“We proactively monitor their systems, providing timely updates and recommendations to keep their technology running smoothly and efficiently,” said Reidy.
In finishing, Reidy said that Fusion5 distinguishes itself by fostering lifelong client partnerships. With expertise in project management and ERP solutions, the company continues to empower manufacturers to streamline operations and drive growth.
Elexon Electronics is driving innovation in Australia’s electronics manufacturing, focusing on quality, continuous improvement, and advancements in Industry 4.0.
Founded in 2006 in Brendale, Elexon Electronics is an Australian company renowned for its expertise in designing and manufacturing advanced electronics.
The company has built a reputation for turning ideas into products, offering custom electronic solutions across various industries.
Elexon serves markets ranging from acoustic and ultrasonic monitoring to water quality management and mining. Its expertise spans from developing smart sensors for underground mining to producing commercial products like display controllers for ovens.
Amongst others, Elexon is an important player in livestock management through the design and manufacturing of RFID systems used for animal identification in Australia.
Over the years, Elexon has expanded its reach and capabilities, particularly by setting a strategic direction toward Industry 4.0. This shift led to the establishment of an advanced manufacturing facility to cater to sectors such as medical devices, defence, and aerospace.
Manufacturing capabilities
Elexon Electronics drives its manufacturing capabilities through the principles of Industry 4.0, focusing on controlling product quality by optimising process quality.
“By carefully monitoring and controlling critical process parameters, we consistently achieve high-quality products,” said CEO, Elexon Electronics, Frank Faller.
Elexon has invested in advanced technologies, including integrated inventory management, advanced soldering processes, and nextgeneration automated optical inspection systems. These systems enable precise inspection to detect component misalignment, missing parts, solder joint defects, polarity issues, solder paste inconsistencies, voids, and internal PCB structural flaws.
“Whenever we find a defect, we automatically go back and fine-tune our processes. Our philosophy is simple: avoid defects rather than detect them and fix them. This is our key motto,” said Faller.
Elexon2Zero (E20) is the company’s continuous improvement program, born out of necessity and driven by a relentless pursuit of quality. The program’s roots can be traced back to a fire in August 2023, which destroyed Elexon’s factory and manufacturing equipment.
“After our manufacturing equipment was destroyed, we moved to a new facility, replaced our equipment, and used the opportunity to improve,” said Faller.
“We upgraded from 2D to 3D X-ray, introduced the best optical inspection system, and enhanced machine speed, capacity, and testing capabilities.”
As Elexon returned to production, it became clear that each product run was like a New Product Introduction (NPI) due to the loss of tools and test checks in the fire. This challenge sparked a new vision: to leverage the momentum from the rebuild and establish Elexon as a leader in quality. Drawing inspiration from previous experiences in the automotive industry, where a target of 10 PPM (parts per million) returns was set, Elexon sought to create a similar benchmark.
customer returns. If the initial product quality is high, the risk of defects slipping through is minimised, ensuring that no returns are necessary.
“Elexon2Zero represents a commitment to striving for zero defects, zero delays, and zero returns from customers,” added Faller.
“While some may view this goal as ambitious, it reflects the company’s dedication to continuous improvement.”
Achieving zero defects at Elexon goes beyond production – it involves aligning every part of the business towards a common goal. The process starts with a review of the entire business, from creating the right work environment to ensuring that engineering processes are robust and accurate.
This includes enforcing stringent practices like proper use of ESD clothing and gloves and eliminating distractions like phones at workstations. Product design and supply chain management are also key, ensuring components are available on time to prevent production delays.
A critical factor in achieving zero defects is
The company emphasises specific production processes like SMD and final assembly, with tailored solutions for unique product challenges. After each production batch, Elexon conducts reviews to identify quality issues and define corrective actions. By capturing and reviewing these actions, the company continuously improves key metrics such as first-time test pass rates, delivery, and warranty returns.
“Everything starts with quality,” added Faller.
“For business efficiency and profitability, it’s crucial. However, without quality, efficiency becomes rushed and creates more problems. We focused on quality first, and efficiency followed naturally.”
For manufacturers considering the implementation of E20, focusing on collaboration is essential. Building strong networks with suppliers, customers, and industry partners can help exchange valuable insights.
“It is very important to foster a cultural shift within the organisation – empowering staff to take responsibility for quality, prioritise root cause analysis, and eliminate workarounds,” said Faller.
“We’re even looking into integrating other forms of automation.
“Everyone’s talking about AI, which is challenging in our field, but it’s something we’re exploring. It all comes back to networking – being surrounded by
experts who are the best in their fields.”
Manufacturers should also take a holistic approach centred on continuous improvement. This includes investing in team upskilling, strengthening quality management systems, and enhancing manufacturing capabilities.
By integrating connected equipment, manufacturers can analyse real-time data, identify optimisation opportunities, and leverage AI and smart software to boost productivity and streamline the conversion of design data into machine programs.
Elexon Electronics is making progress toward its ambitious goals, with a target to achieve quality improvements by the end of the year.
“The next thing to tackle will be our delivery performance, as short lead times and on-time delivery are our customers’ top priorities,” concluded Faller.
“Once we have our quality and processes right, this will enable us to drastically shorten our lead times, which will be a natural continuation of our program and greatly benefit our customers.”
Elexon is a strong advocate for the region’s sustainable growth, the development of our sovereign capabilities, and the independence of
Australia from overseas suppliers. Recently, Elexon has played an important role as the industry partner of an initiative called PCB Connect 2025, started by the Regional Development Australia Moreton Bay and Sunshine Coast (RDAMBSC). PCB Connect is an initiative aimed at revitalising Australia’s electronics manufacturing, focusing on establishing the local production of printed circuit boards (PCBs) in Australia.
The event, held in Modern Bay on the Sunshine Coast on 26 February, brought together key stakeholders – PCB manufacturers, defence industry experts, government representatives, and industry associations – to discuss the potential for setting up a local PCB manufacturing facility.
Frank Faller, as the RDAMBSC board member, is involved in the initiative, advocating for the importance of this capability to strengthen national security, reduce reliance on overseas suppliers and facilitate vital conversations around supply chain resilience and innovation.
The event culminated in a formal communiqué outlining the industry’s needs and next steps, which is now with the federal government.
To know more about Elexon Electronics, meet Frank Faller and the Team at Avalon, Stand POD 31, from 24-28 March 2025, to discuss Industry 4.0 and aerospace/defence manufacturing.
Minitab brings more than 50 years’ worth of expertise in helping manufacturers boost production yields and reduce errors with its software solutions.
More than 50 years ago, chairwomen and co-founder of Minitab, Barbara Ryan, would found the company at Penn State University to revolutionise the way statistics and analytics were taught and applied. The company’s Minitab Statistical Software was the first solution to take off, intended to help students perform calculations easier.
The software’s applications would continue to grow, where at present, Minitab has become a leader in analytics across diverse industries.
“The software was first adopted by universities, high schools and then across industries, becoming the market leader for analytics used in quality and continuous improvement fields,” said Minitab’s new Analytics Solutions design manager, Bass Masri.
Its data driven solutions offerings have grown since the company’s beginnings to now include:
• Model deployment.
• Predictive analytics and machine learning.
• Statistical analysis and business intelligence.
• Data access, automation, statistical process control and real-time monitoring.
• Idea generation and management.
• Project planning and management.
• Problem solving methods.
• Tracking and measurement.
• Education and training.
Despite Minitab’s headquarters remaining in Pennsylvania, the company has its sights set on breaking into the Asian-Pacific market, specifically within Australia and New Zealand.
A large use case for Minitab’s services is the continuous improvement of production processes within the manufacturing industry. Sectors that have the potential to benefit from these services the most, include food and beverage, automotive, pharmaceuticals, medical technology and semiconductors.
Minitab’s software solutions help businesses in these sectors by addressing challenges to ensure machine efficiency, optimal inventory levels and smooth manufacturing processes.
“You can improve quality, increase production yields, and bring products to market faster. Our new tailored solutions and process improvement platforms can predict changes to your process or variation in demand and to eliminate problems before they occur. That means you can prevent downtime, reduce defects and improve productivity,” said Masri.
Minitab’s solutions provide an ecosystem for manufacturers to collect data, detect defects, analyse findings, prevent issues before they occur and get to market faster.
A current solution at the forefront of Minitab’s offerings is its Real-Time SPC, which increases organisational value and efficiency for manufacturers by delivering quality assurance and process monitoring capabilities.
Real-Time SPC increases organisational value and efficiency by delivering quality and process monitoring.
“Real-Time SPC makes quality analysis and improvement easy, in one convenient and comprehensive solution. While our monitoring and alerts in real-time allow for immediate action when quality varies, saving both time and money,” said Masri.
“We all strive for quality and perfection in our production processes.”
The solution allows for immediate action – saving both time and money – and reducing waste and rework originating from under-performing processes, machinery or equipment.
“Improving quality can be achieved using a variety of tools which can be found in Minitab Statistical Software, Minitab Workspace, and across Minitab’s solutions,” said Masri.
These solutions are applicable within the medical device manufacturing industry, particularly where manufacturers are tasked with documenting the process to ensure quality standards are met. Process validation is defined as establishing by objective evidence that a process consistently produces a result or a product that meets its predetermined requirements. Minitab’s capability analysis program functions by estimating whether a process, product or service will meet the customer’s specifications and determines through capability indices whether these levels are acceptable.
“Process validation results in a process that consistently produces a high-quality product for your customers. Think about this in terms of your customer’s satisfaction, customer experience and your brand’s reputation,” said Masri.
“Validation not only complies with regulatory requirements but also improves product quality by adhering to the customer specifications. Failure to do so is not an option for manufacturers in the highly competitive Asia Pacific market.”
Moreover, Minitab’s solutions can help manufacturers in developing new and sustainable manufacturing methods. This was on full display when it helped a global lighting manufacturer, Signify, to develop new manufacturing methods that utilised reliability engineering analysis. The process involved demonstrating the reliability of recycled materials and 3D printing, conducting validation tests and aging treatments, and using accelerated life testing to model failure times under stress.
“Minitab harnessed the power of life data to demonstrate that recycled materials and 3D printing will make reliable products, by measuring time to failure,” said Masri.
Minitab’s implication on streamlining manufacturing production and processes is heavily reliant on the use of predictive and preventive maintenance, which spotlights reasons for production shortcomings.
“Minitab solutions provide insights into production failures with a click of a few buttons and by identifying trends, patterns and unusual observations” said Masri.
The company’s predictive tools detect deficiencies using graphical analysis and integrate operational data with advanced data analytics, machine learning, and pattern recognition to provide insights for predictive maintenance.
Minitab’s services took global home appliance manufacturers’ error identification from a reliance on delayed and costly product warranty returns to a predictive analytics solution that enabled warranty prediction, faster quality improvement and prevention of defects.
“The dilemma was obvious – they needed to solve the problems faster,” said Masri.
Minitab’s Statistical Software – originally intended to help students perform calculations – was the first solution to gain popularity.
Minitab’s solutions to increase production yields were again in play as the company helped compact equipment manufacturers, Bobcat Company, in increasing performance, quality and production. It did so by 20 per cent. The partnership came about as Bobcat wished to improve its laser-cutting process at one of its North Dakota plants.
Despite having seven lasers, the company still outsourced some laser work due to capacity constraints.
Minitab aimed to find a way to enhance cutting speed while maintaining or improving part quality, leading to the use of its Minitab Statistical Software. After conducting designed experiments and analysis, the company identified the key factors affecting performance, such as power, feed rates, gas pressure, nozzle width, and focus distance. This allowed Bobcat to increase efficiency and reduce costs. This eliminated the need to purchase additional manufacturing equipment, resulting in nearly a $1 million savings in new equipment installation.
Minitab showcased its services’ applicability within the semiconductor manufacturing industry where production yield losses occur because of defects, rework, or scrap in a machine or process. In one instance, to gain insights, Minitab applied a wafer map to identify the root causes of problems
“Due to the costly nature of semiconductor manufacturing, any additional insights that can improve yield can drive real cost savings. By using a wafer map, an engineer can visualise whether defective chips display a systematic pattern or cluster,” said Masri.
Not only do Minitab offer solutions that can improve production yields and reduce process errors, the company also provides training to help businesses build a skilled workforce.
One of these offerings is its public and opento-all education training program that focuses on improving manufacturing processes. This involves giving participants exposure to its graphical and statistical tools.
“Statistics provide objective, graphical and descriptive information about data. We use examples with measures such as diameter, pressure, and hardness. Analytical and Statistical techniques are presented through real-world examples and exercises,” said Masri.
Minitab also offers the same service, as an on-site training offering that takes place at the manufacturer’s offices.
Going forward, Minitab will continue to grow as a broad solutions provider for manufacturers.
A part of this growth is represented through the company’s most recent acquisition of simulation software Simul8. This new solution helps simulate the operations of a system – such as a day-to-day manufacturing production line.
“By using a virtual simulation to test the impact of process changes and test ‘what-if’ scenarios, you can find an approach that delivers the best results,” said Masri.
Minitab continues to expand its offerings, bringing data-driven solutions, predictive analytics and process improvement software to manufacturers worldwide, helping them improve quality, streamline production and
Co-founder of AMSL Aero, Andrew Moore, joined Manufacturers’ Monthly to discuss the company’s innovative VTOL aircraft ‘Vertiia,’ which is set to take flight commercially in 2027.
Founded in 2017, AMSL Aero specialises in the design and manufacture of the ‘Vertiia,’ a long-range Vertical Take-off and Landing (VTOL) aircraft.
“We founded the company to change the way we transport around Australia,” said co-founder of AMSL Aero and original inventor of the aircraft, Andrew Moore.
Vertiia transitions from vertical take-off – like a helicopter – to efficient wing-borne flight – like an airplane. The hybrid design harnesses the best of both aviation forms to achieve the right balance of performance, speed, and manoeuvrability.
Due to these capabilities, the aircraft can reach speeds of 300 km/h and travel up to 1,000 km while still landing within an area half the size of a
tennis court. These advantages make it suited for emergency evacuations, transport, and firefighting.
“Vertiia can fly faster than helicopters whilst still being energy efficient,” said Moore.
Additionally, the aircraft is powered by electrified hydrogen fuel cells, eliminating the need for a gas turbine, cutting operating costs, and ensuring emissions-free transport.
“The electric propulsion means that you don’t have the high maintenance and fuel costs of a gas helicopter turbine,” said Moore.
Discovering an application for such an innovation
The story behind this innovative piece of Australian aerospace starts with Moore, who had an interest
in the technology. Prior to the creation of Vertiia, he completed an Aeronautical Engineering degree and had experience within the Australian Navy. Moore’s journey toward the innovative aircraft would only begin when he started focusing on aircraft modifications.
“I started to design medical fit-outs for the Royal Flying Doctor Service and came up with a radical new take that became standard across that industry,” he said.
After this and further experience with Raytheon and Yamaha Motor Company, Moore would pursue a PhD in Electric Aviation, during which time he met an individual who expressed the need for new ways to evacuate soldiers from the battlefield. This demand pushed Moore to innovate.
transport over long distances.
“One of the most common potential applications for the aircraft is moving patients from hospital to hospital,” said Moore.
This application is among the most immediate for Vertiia, as the aircraft represents a more cost-effective and efficient method of patient transportation compared to traditional methods.
“In Australia, all hospitals have a helipad for Vertiia, which allows for more efficient use of medical staff. It’s also lower cost than transporting patients on a turboprop aircraft and is a better experience for the patient,” said Moore.
“It can carry four or five passengers and has a 500 kg payload capacity. We also have the capability to sell Vertiia as a remotely piloted application to move cargo and to firefight. You could fight fires at nighttime.”
assembly, integration, and final flight tests,” said Moore.
While AMSL Aero does the assembly and integration of systems itself, the company outsources the manufacture of many components.
“We use various subcontractors, in New South Wales, Victoria, Queensland and South Australia. Most of those components are to our own designs,” said Moore.
Despite a portion of outsourcing, Moore ensures that anything in development from his manufacturing team meets strict requirements.
“We incrementally validate and verify that those requirements are met. You test the component, the system, the assembly, and the whole aircraft,” he said.
“We then run through a ground test regime and then undergo the flight test to prove that it meets our requirements.”
“I stopped all the work I was doing on conventional aircraft and came up with a concept that I believed would be a world-leading, lighter ambulance for a casualty evacuation,” he said.
“This is where the concept of Vertiia was born.”
Shortly after this, Moore started AMSL Aero with co-founder Siobhan Lyndon. Today, seven years on, the company sits at the leading edge of VTOL development in Australia with signed civil and military orders for the aircraft and a roadmap to deliveries in 2027.
Vertiia has attracted local and international interest from operators that address both critical applications, including casualty evacuation, air ambulance services, emergency response operations, and regional freight and passenger
At present, AMSL Aero’s manufacturing capacity is at the highest of the company’s history, meaning that its presence has grown into multiple hangars and even states.
“Most of our main assembly and manufacturing work happens here in Bankstown, Sydney. We also have testing facilities in NSW and VIC,” said Moore.
In what Moore described as a seamless and diverse supply chain, the company employs just under 70 workers who work across design, integration, and assembly.
“We have both an engineering workforce and a technician workforce. We also have support functions that sit around to ensure the team is highly streamlined from design through to manufacturing,
Late last year, Vertiia made Australian aviation history and passed a critical milestone as AMSL Aero successfully completed its first fully autonomous free flight – demonstrating the craft’s ability to fly without a pilot on board.
“Watching Vertiia take to the sky in free flight was a breathtaking experience for our incredible team,” said Moore.
“This landmark is proof that the design we pioneered seven years ago works, moving us closer to our goal of improving the lives of remote, rural and regional communities in Australia.”
The groundbreaking test flight has been followed by more than 100 more successful flights, marking a step toward deliveries that – after numerous landmark contracts were signed last year – are expected by 2027.
The company’s civil contracts included deposits for a total of 26 Vertiia aircraft, including up to 20 from general aviation and regional airline group, Aviation Logistics, which signed a deal to support passenger, freight, and aeromedical services across Australia.
Moore said because of these orders, a key focus for the company going forward is to scale up production capacity.
“We are in the early stages but we’re working closely together to really build it out, and to take advantage of this great long-range hydrogen VTOL aircraft,” said Moore.
A part of AMSL Aero’s success stemmed from earlier developmental contracts with international partners.
One of these international partners is NZ’s Life Flight, which last year signed a partnership agreement with AMSL Aero to help develop Vertiia for future aeromedical operations in Australasia.
“It’s very exciting to have an international partner who is a keen operator and has great experience within the New Zealand aeromedical market,” said Moore.
AMSL Aero has also ventured into the defence market where it signed an agreement with Hanwha to establish a strategic partnership to develop and scale up production of Vertiia aircraft.
“Hanwha is a global giant when it comes to
manufacturing and aerospace. It’s an exciting arrangement where they certainly have the capability to enable us to scale our manufacturing,” said Moore.
Another noteworthy partnership that AMSL Aero established in 2024 was with The Bases Conversion and Development Authority (BCDA) in the Philippines. Moore said this partnership is grounded by the fact that the technology has potential in areas like the Philippines and Indonesia to “change the way their economy functions.”
“Long range VTOL aircraft have the tremendous potential to change fortune within archipelagic nations. Anywhere that is mountainous and has lots of small islands have traditionally been challenged with transport infrastructure,” he said.
“We believe the market opportunity is for the 1000s of aircraft per year, and we are exploring local partners that could help us bring that to fruition.”
Going forward, while Moore expressed his excitement for upcoming events within the walls of AMSL Aero – such as developments within the company’s hydrogen system development and certification program – he also made a plea for Australia to start prioritising a sovereign aerospace industry.
“We have an incredibly talented workforce, and we produce great graduates and technicians. Our capability as a nation is incredible. I just don’t think
there are as many opportunities as there should be to take advantage of that,” he said.
The company points out that manufacturing in the aviation sector has compound growth benefits that flow into other high-tech sectors and therefore generate wider economic benefits.
Moore said that Australia needs to adopt Sweden’s sovereign approach to its manufacturing industry.
“Australia is heavily reliant on aviation and aerospace for the way that our nation functions.
Sometimes I wish we could be a little bit more like Sweden, who can build their own submarines, fighter jets, tanks, and cars,” he said.
“We need to go from importing 40 to 50-year-old aircraft designs from other nations to knuckling down and making our own.”
Despite emphasising potential areas of improvement for the country, Moore finished by identifying trends such as the National Reconstruction Fund that seem to be pushing Australia toward the right direction.
“Manufacturing is a key piece of society and a critical capability, so we need to aspire to be selfreliant. We have all the right starting points, markets,
and talent. We just need a little bit more of a risk appetite from a few decision-makers,” said Moore.
“I think as a nation, we are becoming better at recognising how much we can do and how costeffective we can be in broader aerospace.”
Moore hopes to one day witness a future where Australia embraces its aerospace potential, driving innovation and self-reliance in the industry.
With the recent announcement of Australia’s first Vanadium Flow Battery project, discussions from last year’s 40th Anniversary Flow Battery Innovation Symposium at UNSW may soon become a reality.
Arecent $150 million investment from Western Australia’s State Government is set to have implications for the future of energy storage in Australia. This announcement surrounds an Australian-first project focused on manufacturing a 50-megawatt vanadium flow battery (VFB) in Kalgoorlie to reinforce the Goldfields’ energy grid.
“In addition to the 150 local jobs created during construction, I want to work with industry to develop a local vanadium battery manufacturing industry here in Kalgoorlie,” said Western Australian premier, Roger Cook.
These plans come after a recent push for a sovereign VFB manufacturing industry as UNSW Sydney hosted the 40th Anniversary Flow Battery Innovation Symposium last year. The event celebrated four decades since the development of the first 1kW VFB by emeritus professor Maria Skyllas-Kazacos and her team.
“The vanadium flow battery offers a unique solution to the energy storage needs of renewable sources like solar and wind,” said Skyllas-Kazacos.
The symposium brought together industry leaders and researchers who discussed how the nation can leverage its vanadium reserves to improve long-duration storage solutions and thus lead the global energy transition. Other key messages of the Symposium surrounded VFBs being:
• Unlimited and flexible in deployment.
• Ideal to use when temperatures are too high for lithium.
• Ideal for microgrid environment to replace lithium batteries and diesel generators.
• Supply chain constraints are the only limitations in Australia.
Since the first VFB was built at UNSW, the technology has grown internationally with its capacity evolving into a gigawatt hour scale. The scaling up of its capabilities internationally has seen it become a fitting solution to stabilise an energy grid in a future that is renewable energy driven.
VFBs first gained traction internationally due to their ability to provide safe, reliable, and longduration energy storage in comparison to traditional lithium-based batteries, which are flammable, explosive, and limited in scalability.
“Unlike traditional batteries, flow batteries store energy in electrolyte solutions, allowing for flexible and scalable energy storage at lower costs for longduration applications,” said Skyllas-Kazacos.
For Australia, this presents an economic opportunity to develop and manufacture these batteries on a global stage, due to its large vanadium reserves and sovereign renewable technology expertise.
“Australia is ideally placed to become a major manufacturer of flow batteries, both for domestic use and for the international market,” said SkyllasKazacos.
Resource extraction and the production of electrolytes and flow batteries is set to be a good opportunity for the Australian economy, as the nation holds a quarter of the world’s vanadium reserves. This potentially burgeoning industry has already gained attention from global players, such as Rio Tinto, a company that has plans to use VFBs for decarbonising operations in regions such as Iceland, South Africa, and Oman. Other global players such as Sumitomo Electric in Japan and Invinity Energy Systems’ deployment in South Australia have also showcased plans for VFB projects.
With last year’s symposium highlighting the worth of a sovereign VFB supply chain, early February saw a nation-leading announcement from WA’s State Government, when Cook unveiled a $150 million, Australian-made, 50-megawatt vanadium battery project.
“Strengthening and reinforcing the electricity system is my number one priority for the Goldfields,” he said.
Kalgoorlie MLA, Ali Kent, said the development is
just another part of the State Government’s $130 million investment in measures to improve energy reliability in the area from 2021.
“Today’s commitment will add another layer of protection to the system, making sure there is another back up in place when the region experiences serious weather events or other disruptions to the system,” he said.
“I’m incredibly proud that Kalgoorlie-Boulder has been selected for this Australian-first project.”
Cook said the VFB – once operational – is set to provide back-up power for 10 hours when needed while potential disruptions or weather events hit the region.
The project originates from the WA Government’s recognition that Vanadium is expected to play an increasing role in batteries around the world. With the USA, Europe, South Korea and Japan all being potential markets for WA vanadium, the state has a unique opportunity to break into the industry. This opportunity originates as WA’s vanadium deposit being developed south of Meekatharra is one of the largest in the world.
Cook said that he wants this project to drive the emerging industry in WA so that the potential of new mining and local processing jobs, as well as export income, is realised.
“I want this project to be a catalyst to drive a new vanadium mining, processing and export industry for WA - to make more things here, diversify the economy and create the jobs of the future,” he
This system reinforcement is set to add to the WA Government’s work to replace West Kalgoorlie Power Station by 2026. The 50MW, 10-hour VFB is planned to be operational in 2029 and will be located near transmission infrastructure.
Kalgoorlie project, alongside increasingly present industry commercialisation efforts, could see the industry develop into one that supports energy security, economic diversification and Australia’s position as a global leader in long-duration renewables storage.
global picture remains to be seen – the momentum
Icontinue to have the privilege of witnessing firsthand the incredible transformation of Australia’s manufacturing ecosystem whilst at the helm of the Advanced Manufacturing Growth Centre (AMGC).
Now entering our ninth year of operations, I am pleased to see many of our early co-invested manufacturing companies evolve. These businesses have grown from small to medium and some even from medium to large entities, consistently delivering high-quality products to both local and global customers, and in many cases, they have done so through collaboration.
At AMGC, collaboration isn’t a buzzword - it’s a strategic cornerstone of how we drive innovation, growth, and global competitiveness for Australian manufacturers. In fact, we mandate collaboration as a non-negotiable element of every initiative. Manufacturers work with at least one other industry participant and a research institution – where research is a means to an end, which
ultimately is a paying customer. Collaboration isn’t a checkbox requirement; it is a deliberate strategy to amplify impact.
While I hear the term collaboration used widely, I still believe there is a lack of understanding about what true collaboration entails and the competitive advantages it can unlock. It doesn’t have to be hard or onerous. Sometimes, it is as simple as joining a network like AMGC, attending a meeting, or sharing a challenge with peers. You never know where such conversation might lead.
The synergies formed between businesses and research institutions, as a result of AMGC’s programs, have solved complex problems and improved commercial viability, while collaborative relationships between manufacturers have unlocked new commercial opportunities far beyond what they could achieve alone.
One recent example of this power is the partnership between two AMGC members and project alumni, one in Victoria and the other
in New South Wales: ActionLaser (NSW) and OptoTech (Vic). Together, they tackled a seemingly insurmountable challenge and emerged with a solution that illustrates what can be achieved when manufacturers join forces – and there are some lessons for all manufacturers, including those making vaccines.
ActionLaser specialises in precision laser drilling technology, succinctly describing its expertise modestly as, “We make small holes in thin metal.” These tiny holes are critical to its MeltFilter screens, which are used in industries like plastic recycling, water filtration, and food and beverage processing.
ActionLaser faced a significant hurdle: qualifying the performance parameters of its MeltFilters. Until recently, this process relied on manual inspections using microscopes, which was labour-intensive and literally eyewatering, hence inadequate for ensuring the required precision. Through a chance comment at an AMGC
Manufacturing Council meeting, ActionLaser and OptoTech were introduced to each other by AMGC which kicked off a three-month collaborative project that would revolutionise ActionLaser’s capabilities. Together, they developed a bespoke system that can inspect and map every one of the approximately 500,000 holes on a single MeltFilter disc – which is no bigger than a dinner plate.
This system provides precision, delivering detailed analysis of hole size distribution, residual material, and quality of the discs. As a result, ActionLaser is now the first manufacturer anywhere in the world to be able to calculate filter ‘flow through’ – a critical performance metric –with unmatched accuracy.
This collaboration wasn’t without its challenges. For OptoTech’s director, Mircea Petre, it required innovation, expertise, and a deep understanding of ActionLaser’s unique needs.
“Measuring half a million tiny holes on a disc is not something you can solve with an off-the-shelf solution,” said Petre.
“It required a bespoke system developed through close collaboration.”
ActionLaser’s production manager, David Pask, was very pragmatic in his views.
“That chat with OptoTech might’ve gone nowhere, but it was the right place, right time to
do something. As a result of this collaboration… we can then calculate what we and our customers call ‘flow through’, a critical measure of performance and something up until now nobody on the planet could do,” he said.
The results speak for themselves. For ActionLaser, this breakthrough is transformative. Its new inspection system enhances product performance and positions it as a global leader in their field. With this capability, ActionLaser projects a 1,500 per cent increase in sales with further growth on the horizon.
This story highlights an essential truth: collaboration is a powerful tool that every manufacturer should consider in their growth strategy. By finding the right partners and leveraging their expertise, or speaking with the right industry bodies, manufacturers can achieve solutions far beyond their in-house capabilities. The first step requires intention and a willingness to share.
ActionLaser and OptoTech embody AMGC’s approach, which has been deployed across all of our Federal, State and Territory initiatives. AMGC’s programs have unlocked $137 million in combined industry and government funding, leading to an estimated $1.62 billion in additional national revenue and 4,300 new jobs. More importantly, it’s created a network effect that
underscores the value of collaboration.
More broadly, the Australian Government’s Industry Growth Program (IGP) provides fresh opportunities to enhance manufacturing capabilities through collaboration. AMGC’s recent appointment as an Industry Partner Organisation (IPO) underscores our commitment to supporting Australian manufacturers. Through this initiative, we’ll offer expert advice, access to technology, and tailored support to help SMEs qualify for funding and build industry connections spanning the national priority areas of transport, defence and value-add to resources.
Challenges that manufacturers face are too complex for a small company to tackle alone. Yet, through collaboration, we can overcome these challenges and create new opportunities. The story of ActionLaser and OptoTech is just one example of what’s possible when manufacturers work together. By fostering a culture of true collaboration, we can further nurture a globally competitive manufacturing industry in Australia.
As we enter 2025, my advice to every manufacturer is don’t go it alone. The expertise and resources you need might be out there, waiting to be unlocked through collaboration. Organisations like AMGC can help you find the right partners and connections to succeed.
From collaborating with OptoTech,
Manufacturers’ Monthly were joined by CSIRO and DMTC representatives to discuss how nanofibres form the basis of a prototype uniform capable of filtering out harmful particles in broad applications.
CSIRO researchers have developed a prototype uniform using nanofibres that is poised to deliver improved protection for Australian troops and other first responders from chemical and biological threats. With initial tests complete, the lightweight fabric material has successfully filtered out harmful particles while retaining a lightweight and breathable nature to help users in extreme temperatures.
“Our nanofibre technology has the potential to improve the level of protection soldiers’ uniforms provide and can also be used for non-military applications, including protecting emergency responders and hazmat crews,” said CSIRO Manufacturing director, Dr Marcus Zipper.
Zipper leads a larger CSIRO research and development unit that focuses on materials science to improve how a particular material functions.
“We work across a broad range of advanced materials including metals, composites, polymers, adsorbents and nanofibres,” he said.
However, the textile innovation is the result of a greater collaboration with industry and research partners, including the Department of Defence, Bruck Textiles, Defence Science and Technology Group (DSTG), RMIT University and DMTC (formerly, the Defence Materials Technology Centre), who coordinated the successful prototype development.
“CSIRO’s scientific excellence in nanofibre research has been matched with the expertise of our partners in textiles, defence science, and manufacturing,” said DMTC’s head of program management, Deepak Ganga.
Founding a potentially life-saving innovation
Prior to discovery of what Ganga now views as a “groundbreaking solution,” he recounted the moment when DMTC were approached by DSTG to help roadmap an innovation targeted at filling the universal gap in protection from aerosolised particles.
“DSTG had done early work on this technology at a
lab scale, and realised that while there was potential, they needed other partners to take it from the lab.
That was when we got involved,” he said.
“We effectively put together the roadmap for this technology, and assembled the collaborators who would need to be involved.”
After this roadmap, the project received Defence funding to further develop the technology.
“It was a lot of lab work and intellectual horsepower to prove that this technology could work at some sort of intermediate scale and would have the ability to be produced at small quantities,” Ganga said.
After this consolidation period was successful, the idea made it beyond the lab, but just short of the manufacturing stage. This would entail the exploration of available material options to ensure the best protection, safety and manufacturability outcomes.
“The success of that phase led to a submission into what was then the Defence Innovation Hub in 2021. We were successful in applying for further funding to move to the technology demonstration phase,” said Ganga.
This Hub funding, Ganga said, allowed the team to bring in specialist input from RMIT and Bruck Textiles to scale up the technology to design and produce a representative garment, and to understand what manufacturability at scale would look like.
While Ganga’s roadmap of the innovation may appear simple, CSIRO project lead Dr Yen Truong’s work with its innovative nanofibre technology –the key to the prototype’s success – was far from elementary. Truong, alongside a team of CSIRO scientists, harnessed the unique properties of these nanofibres to create the prototype’s lightweight fabric to filter out harmful particles while remaining breathable.
“CSIRO has been working with nanofibres since 2009. They have a diameter of less than one micron.
Your hair is about 100 microns in diameter,” she said.
“Because they’re very fine, they have a high surface to weight ratio, so you don’t need very much to get a lot of surface area. When they form a membrane or a non-woven textile or a material, they have very high porosity.
“Because of this, they can close all the gaps and produce a material that doesn’t let things go through. This therefore prevents any harmful aerosol from coming through.”
Truong described producing nanofibres as a challenging process, as you are required to start off with raw material that is to be made into an optimum formula.
“A lot of work was spent in the early stages doing a lot of developmental work here at CSIRO to perfect the formulation and operating conditions and make the nanofibre the right size,” she said.
After scientific consolidation, Truong said the prototype undertook rigorous testing, of which it reached all performance targets for air filtration, air permeability, thermal comfort, and chemical protection.
“This means it effectively filters pollutants from the air, allows for breathability, maintains comfortable temperatures even in extreme conditions, and offers superior protection from hazardous chemicals,” she said.
Ganga described the fabric testing process as one that follows a lot of standard methods and takes place within different environments.
“We used air permeability as the primary screen, and if it looks good, then particular formulations can be taken forward to other parameters like thermal resistance and the thermal burden,” said Ganga.
“Then we hand them over to Defence to do the actual chemical testing because they have the facilities to do that.”
Aside from fabric testing, Ganga said the testing utilised DSTG’s specialist facilities in Melbourne. This helped the research group better understand suitable joining techniques for the garment.
“You put the garment on the mannequin, and you
The unique properties of nanofibres help create the prototype’s lightweight fabric that filters out harmful particles while remaining highly breathable.
can make the mannequin sweat and challenge it with chemicals and aerosols,” he said.
“The suit has joints, so we test the border of the joint to make sure that it performs. We carried out thorough testing of all the parts, like sections and pockets.
“The benefit of this testing was it also meant we had to investigate what garment joining techniques would be suitable for these types of garments.”
Beyond the level of testing that has already been conducted, DMTC Limited, Truong and the project team are seeking funding to progress to the next stage of development that is to involve field testing with the Australian Defence Force.
“That will be massive in terms of realising this as an Australian sovereign capability. We need input from the users at this stage to be able to develop the design further,” said Ganga.
Truong said that once the whole suit can be tested
on Defence personnel, the garment will be open to explore and be tested within other applications.
“Next would be our first responders and even for environmental uses. A farmer emailed and said, ‘Do you have one of these for me to spray with?’ I think it can go to your everyday use for people who come across hazardous chemicals and aerosols,” she said.
Ganga agreed, stating that while the project’s funding came from Defence, it also represents the most stringent use case.
“The next use cases could even be more general use cases in factories, agriculture and any environment where there’s aerosol contamination or potential for aerosol contamination,” he said.
Collaborating into the future
Ganga used this project as a call for greater collaboration within Australia. He said that the garment demonstrates the power of collaboration,
something that is critical for a small country.
“It’s been critical, predominantly because no single organisation in Australia has all the skills to be able to develop a solution like this. There’s so many long-term benefits from working in that way because all of the partners involved develop a deeper understanding of each other’s capabilities,” he said.
“We don’t have the scale or personnel, but what we do have is niche pockets of expertise, so if you can string the pockets of expertise together, and if we can work with government to overcome the challenge of stop-start research funding cycles, you can get a multiplier effect of all of the intellectual horsepower to be able to do developments like this.”
The development of this nanofibre uniform showcases Australian innovation and collaboration that has the potential to enhance protection across numerous sectors. To advance this innovation, securing further funding will be crucial.
HONI
SEMMA CEO Honi Walker maps out the year ahead for Australian manufacturing, with notable pressures and opportunities on the horizon.
There’s no doubt we are in turbulent times economically and politically. Both here in Australia and overseas, pressure on our economy is going to be influenced by US President Donald Trump’s tariffs and how China responds; the issues of the supply chain through the Panama Canal; the cost of raw materials; and; the geopolitical issues with war in Europe.
At home, we await the Reserve Bank’s next interest rate announcement if they will hold or increase the cash rate. Additionally, it seems the Federal Government is waiting for the most favourable economic environment to announce the election date. This is having an impact on business as we wait for that next lever to be pulled.
In the meantime, there are plenty of factors that are making manufacturers re-consider the viability of their business in Victoria, including an onslaught
and increase of taxes [land, payroll, Workcover], increased insurance premiums, increased wages, as well as red and green tape impacting Victorian manufacturers.
A lot of businesses have been doing it tough over the past few years, including in the manufacturing industry where more than a few companies have shut up shop.
Our State and Federal Governments need to remember that SME manufacturing currently employs almost 900,000 people* nationally, with 97 per cent of businesses employing 19 or less people. Governments must do more to encourage manufacturers’ productivity. Only through efficiency will productivity be increased – and that means AI and robotics – and upskilling the workforce will create higher skilled roles.
Access to a sustainable, secure energy supply in
Victoria has been the subject of a dozen meetings with the Government’s Environment minister Lily D’Ambrosio and her Gas Roadmap initiative. We think we are getting some relief for industry. However, be warned, as more domestic users leave the service, this means the operators will have to spread the cost of operating the service to the remaining users. This means service fees will increase.
Land tax bills have begun hitting our inboxes and the increases are high. Members are providing their statements, and some have had increases of up to 300 per cent in five years. No other state in Australia has such a regime and is burdened with such debt. While SEMMA advocates for reduced taxes, Victoria remains the highest taxed state in Australia. However, there are still noticeable bright spots for manufacturers. Defence remains a sector that can provide stability for manufacturing. Our advice,
get your DISP (Defence Industry Security Program) accreditation to lock in your manufacturing
The new renewables sector also offers some opportunity, although currently, several major elements (solar panels, wind turbines) are manufactured overseas – China to be
This brings me to the point of local jobs content. The Victorian Government, through its Local Jobs First Commissioner is supposed to ensure their contracts have a minimum of 60 per cent local content – the question must be asked how these huge solar farms and wind turbines can be manufactured overseas and assembled here? This is work our local manufacturers can do but due to a range of policies, more jobs and livelihoods are put at risk.
Other work through the development of the M1 corridor to Gippsland also offer pipelines of work for manufacturers, as do some supply opportunities for the Big Build and of course, the SRL (Suburban Rail Loop) – although it may also be shelved due to budget pressures.
These are all opportunities that SEMMA encourages our members to consider. We also encourage our members to look at upskilling their staff, consider where they can make efficiencies and look for collaborative opportunities within your networks.
SEMMA will be releasing our Manufacturing BLUEPRINT soon and we hope to start a real conversation about ensuring the longevity of manufacturing in Australia.
*GSEM data 2024
Australia’s aerospace industry is evolving through innovation, collaboration, and digital transformation.
The Australian manufacturing industry has seen significant changes over recent years, with aerospace continuing to represent an integral part of Australia’s economy, contributing through innovation, employment, and technological advancements.
Prior to the COVID-19 pandemic, the Australian aviation sector directly contributed around $20 billion to the economy and employed approximately 90,000 people. Established companies – including Boeing Australia, with its 98-year presence – now work alongside dynamic startups to grow and inspire the next generation of aerospace innovators. Our nation is collaborating and investing together within the aerospace ecosystem, through university partnerships and research organisations such as CSIRO, small to medium enterprises (SMEs) and support from all levels of government.
Apart from some assignments in the US, I have spent most of my 35-year career at Fishermans Bend in Melbourne, the heart of Australian aerospace manufacturing. During that time, I’ve witnessed Australian ingenuity at its finest, from my work as a design engineer on indigenous guided weapons, various program, R&D, and engineering leadership roles, and now as managing director of Boeing Aerostructures Australia. I lived the industry changes from design and build of complete airplanes at Boeing in the late 80s with the Nomad, to a focus as a centre of excellence producing advanced composite commercial airplane components including for global customers, and for Boeing 737 aileron, 777 rudder and elevator and 787 moveable trailing edge. And now, the Australian industry’s revival and return to aircraft design and manufacturing of complete aircraft, namely the military collaborative combat system, the MQ-28 Ghost Bat.
Aerospace, by its nature, is cyclical and susceptible to the world economy and countless variables that could impact travel. However, our 20-year forecast is bullish on global aviation growth: we project the global passenger and freighter fleet will nearly double by 2043, with airlines needing nearly 44,000 new commercial airplanes during that time frame. The Australian manufacturing industry continues to thrive through its ability to adapt and evolve, while
balancing Australia’s size and cost structure. This is in part thanks to key elements that speak to the Aussie spirit of collaboration, how we embrace an ecosystem, and our ability to adopt digital tools and autonomy with gusto.
Integrating R&D, engineering and manufacturing offers a distinct advantage in any manufacturing industry in Australia, not just aerospace. This ecosystem concept was the foundation of success for one of Australia’s largest aerospace manufacturing programs valued at $5 billion dollars over 20 years. The design and manufacture of wing components for the 787 Dreamliner at Boeing Aerostructures Australia harnessed this ecosystem. With an environment and a culture of working together, all the different skills and talents contributed to a common purpose. I firmly believe this ecosystem delivers the keys to success in
manufacturing by shaping the product design to enable the production system.
For the 787, it resulted in the selection of the best material system [developed in Australia], incorporated all the essential features for simplicity and first-pass quality during production into the product’s design, and enabled simple manufacturing processes that can accommodate automation in assembly and inspection. This ecosystem also delivered production efficiency and agility across the total cycle, an advantage when competing with other manufacturers around the world.
Automation in aerospace manufacturing, assembly and inspection continues to lag behind other industries – but we’re making progress in Australia. Our skilled manufacturing teams have welcomed automation as it provides improved workplace safety and ergonomics for them in otherwise
hazardous or repetitive jobs. Our engineers have used innovative approaches to off-the-shelf robots and cobots, adapting their use for drilling, cleaning and hard-to-access tasks, resulting in production quality and efficiency gains – while driving down repetitive stress injuries. Our Australian operations have some of the largest concentrations of robots and cobots within Boeing. Our concepts have been shared and implemented with Boeing operations around the world.
Whether it be a common Australian tradition or a necessity due to our nation’s size, collaboration has been crucial to the local aerospace industry’s endurance. The development of MQ-28, and the manufacture of the airframe on site at BAA, is a recent example of this success and of collaboration between the defence, commercial and R&D teams within Boeing Australia, together with the Royal Australian Air Force. The program also leveraged the skills and expertise of Australian industry including Defence Science Technology Group and more than 200 Australian suppliers, notably BAE Systems, many Australian SMEs, as well as universities. It’s gratifying at this point in my career to see the skills we used 50 years ago to produce Australian aircraft have resurfaced to such great results. It’s Australian know-how and ingenuity that has made the MQ-28 a reality for global customers.
Digital design and manufacturing tools continue to evolve, but their importance cannot be overstated. Australian industry, in general, has adopted and deployed these tools and quickly adapted to extracting their benefits for factory planning, design or flight testing.
This certainly was one of the main pillars for the MQ-28 from early concept development to detailed design and manufacturing and flight test, and the success stories will be implemented back into our factories for future products. These digital tools enable the creation of Digital Twins that enable
gets created by these digital tools. This truly enables simplicity and better quality of the production system and product, by forever having the continuous link and connection between the design, the manufacture and the in-service use of the product.
The key elements that have enabled the Australian aerospace manufacturing industry to survive and evolve are also the key to future growth and prosperity. The creativity, curiosity and courage of Australia’s manufacturing workforce, engineers and leaders, will drive innovation, competitiveness, and sustainable growth.
Backplane Systems Technology has released APLEX’s PhanTAM-916CP(H), a 15.6inch stainless-steel panel PC designed for demanding industrial environments. With its true flat design and IP66/IP69K rating, it offers durability against water, dust, and harsh cleaning processes, making it suitable for food processing, pharmaceuticals, and other hygiene-critical industries.
Housed in a 304 stainless-steel chassis (316 optional), it is both robust and easy to clean, with special hygienic bolts on the rear case. It supports versatile mounting options, including VESA, floor stands, and swing arms, ensuring flexible installation. Its slim frame design and waterproof wireless antenna covers add to its ergonomic appeal.
Powered by Intel’s 11th Gen Core i3 or i5
processors, it delivers strong performance with up to 64GB DDR4 memory and a 128GB TLC SSD. Expansion options include mPCIe, M.2, and a Nano-SIM slot, supporting modules like Wi-Fi, Bluetooth, and RFID.
The projected capacitive touchscreen features 90 per cent light transmission and is responsive to touch, enhancing usability. Operating temperatures range from 0°C to 50°C (or -20°C to 60°C optionally), and it runs on Windows 10 IoT or Windows 11. With M12 connectors and customizable I/O ports, the PhanTAM-916CP(H) is built to adapt to any industrial need.
Key features
• 15.6” new generation stainless steel panel PC.
• 11th Gen. Intel Core i3/i5 BGA type processor.
rue flat front bezel design and grade 304 stainless-steel enclosure (Grade 316 for option).
• IP66/IP69K rated with M12 connectors.
• Ultra-slim front frame design.
• Special hygienic bolts on rear case; and
• Waterproof wireless antenna covers to solve the bend damage and easy to clean support ergonomic versatile mounting: VESA Mount 100 x 100/floor stand/swing ARM.
The PhanTAM-916CP(H) combines durability, performance, and versatility to make it ideal for hygiene-sensitive and demanding industrial environments. With its robust stainless-steel design, powerful Intel processors, and flexible mounting options, it ensures reliability and efficiency in any operational setting.
Backplane Systems Technology has released Neousys’s NRU-52S+ rugged, fanless edge AI computer designed for demanding video analytics applications, offering robust performance with NVIDIA Jetson Orin NX/ Xavier NX systems on module (SoM).
The device leverages NVIDIA Ampere GPUs, CUDA cores, Tensor cores, and NVDLA for top-tier AI processing, delivering up to 100 TOPS for realtime inference.
With its power-efficient design, the NRU-52S+ can decode up to 18 streams of 1080p video at 30 FPS while consuming only 25W. This makes it suitable for applications with limited power sources, such as robots, vehicles, or rolling stock. Its industrial-grade thermal design ensures reliable performance in harsh environments, including roadside installations, construction sites, agricultural fields, and dusty factories. It features four IEEE 802.3bt PoE++ ports,
each capable of supplying up to 90W to IP or PTZ cameras, supporting AI-based detection, tracking, and recognition. Its flexible expansion options include two mPCIe sockets for NVMe storage, WiFi, GNSS, or V2X modules, one M.2 B key for 4G LTE or 5G NR modules, and five antenna holes for mobile broadband. Additionally, it includes one hardware-configurable RS232/ RS422/RS485 port, GPS PPS input, 3-CH isolated DI, and 4-CH isolated DO for external device communication.
Integrating PoE++ connectivity, 100 TOPS inference performance, and NVIDIA AI JetPack toolkits, the NRU-52S+ is suitable for real-time video analytics in autonomous machines, security, law enforcement, and V2X applications. Its -25°C to 70°C fanless operation, wide-range DC input, ignition control, and 4G/5G connectivity make it suitable for both indoor and harsh edge deployments.
Key features
• 1Powered by NVIDIA Jetson Orin NX or Xavier NX SOM bundled with JetPack 5.1.1.
• 1Rugged -25°C to 70°C fanless operation.
• 14x IEEE 802.3bt PoE++ GbE ports with screwlock.
• 12x mini-PCIe sockets for WIFI/GNSS/NVMe/ CAN modules.
• 11x 3042/3052 M.2 B key socket for 4G/5G mobile communication.
• 11x hardware configurable RS232/RS422/ RS485 port.
• 18V to 35V wide-range DC input with built-in ignition power control.
• 1MIL-STD-810H and EN 50155 certified.
The NRU-52S+ delivers AI processing, rugged durability, and flexible connectivity for real-time video analytics in demanding environments, ideal for autonomous systems, security, and V2X applications.
Many industries worldwide, including structural buildings, bridges, mining equipment, marine applications, and more, now require welding to comply with the AWS D1.1 code. Achieving this certification ensures fabrication and inspection meet stringent quality standards, helping companies reduce rework, minimise costs, and deliver projects on time.
Weld Australia is facilitating a two-day course, on 30 April and 1 May in Melbourne, that will give participants a working knowledge of AWS D1.1, including how to comply with its requirements. The course will be facilitated by Canadian expert and manager of Standards, Office of Public Safety, CWB Group, Cristian Zanfir.
This course explores the requirements for AWS D1.1 compliance, covering key topics such • C ertification for welding contractors, inspectors, and procedures.