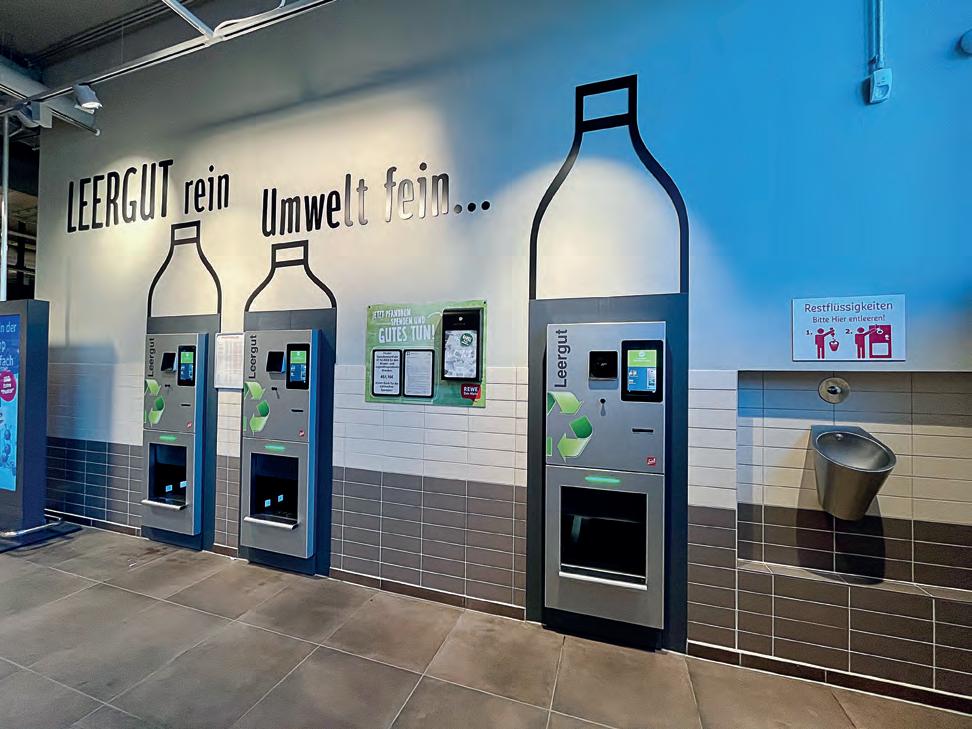
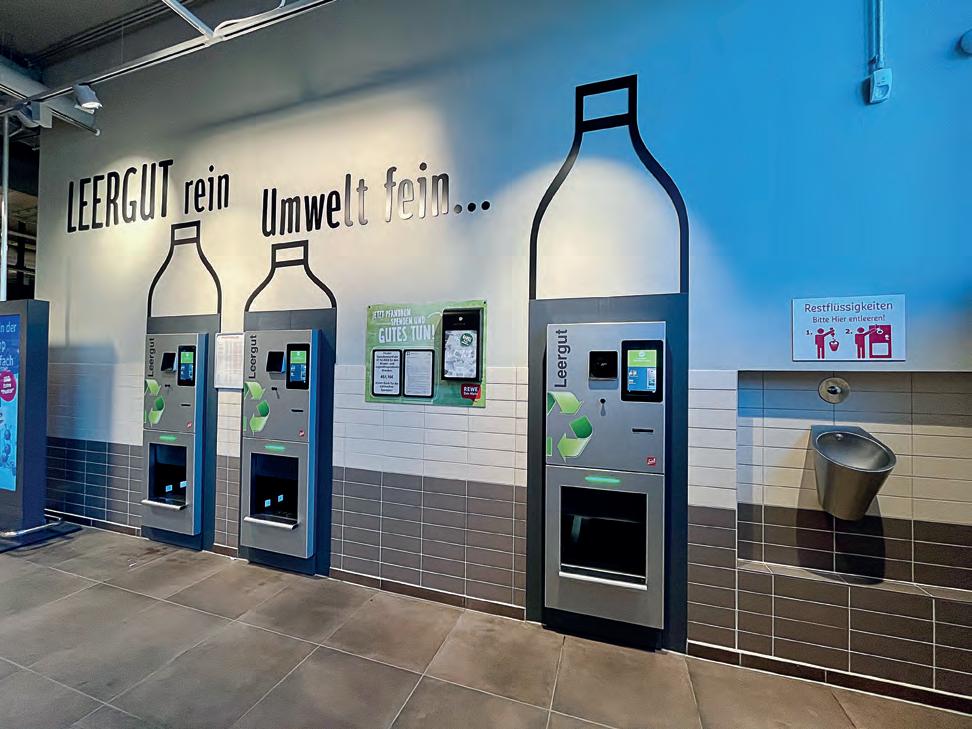
The case for higher refund values in CDS’s
By Samantha Millette and Robert Kelman
Australia faces a mounting waste crisis. According to the Australian Packaging Covenant Organisation (APCO), Australia uses nearly 7 million tonnes of packaging every year, with almost half (44 per cent) ending up in landfill. Of the post-consumer packaging that ended up in landfills in 2021-22, 33 per cent was plastic packaging, 14 per cent was glass packaging, and 5 per cent was metalbased packaging.
The Australian Government has set ambitious national targets to address this. Established in 2018, the 2025 National Packaging Targets aim for 100 per cent of packaging produced in Australia to be reusable, recyclable, or compostable by 2025. They also
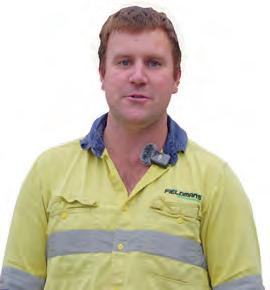
include a goal for 70 per cent of plastic packaging to be recycled or composted and a mandate requiring an average of 50 per cent recycled content in packaging by the same deadline. Despite some progress, recent data indicates that achieving these targets is unlikely.1 While 84 per cent of packaging (plastic, cardboard, metal) is recyclable, less than 20 percent of plastic packaging is actually recycled. 2
Australia needs a regulated packaging scheme that covers the net costs of recycling and pushes used packaging through from collection to end markets. Reloop looks forward to working through 2025 with our federal colleagues to realise this potential. Meanwhile, we have state-based CRS-EPR schemes on beverage containers that are
among the least effective in the world.
In 2022, Australia’s State Heads of EPA’s (HEPA) released consumer studies 3 that demonstrated a combination of collection point inconvenience and the low $0.10 refund value were the key obstacles to consumer participation in Australia’s schemes and the resultant low and stagnating return rates.
This article looks at why consumers did not engage in a CRS, and outlines key data sets for this conclusion.
In November 2023, HEPA also committed to ‘assessing the regulatory impacts of increasing the refund value’4, as part of a suite of measures to rebuild consumer participation, though like the CRS return rates, this policy process seems to have stagnated.
(Continued on page 8)
“ Jake Mansfield, Fieldmans Waste Management With a new bespoke plant from FOCUS enviro,
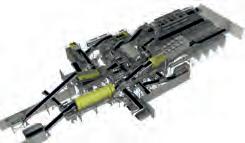
By Inside Waste
During the Waste Expo held in Melbourne at the end of 2024, one of the key seminars was titled Advancing Product Stewardship Schemes and Extended Producer Responsibility in Australia
It was an apt title. Product Stewardship can be a triggering word in some parts of the industry. Should it be compulsory and legislated? Should it be voluntary? How much responsibility is in the hands of the manufacturers? The buying public? Councils? Government? Advancing the ideals of product stewardship leads to healthy and robust debate. The panel who discussed the theme consisted of various people who had a horse in the race.
On board were Sophi MacMillan, CEO of flooring product stewardship initiative ResiLoop; Danielle Kent, general manager of Industry Transformation at clothing product stewardship scheme Seamless; Suzanne Toumbourou, CEO, Australian Council of Recycling (ACOR); and Matt Genever, CEO, Sustainability Victoria. Moderating the debate was Nick Harford, managing director, Harford Consulting.
Macmillan said Resiloop was launched with 15 brand owners, suppliers, and product suppliers on board, as well as some major retail groups such as Carpet Court.
“It’s very much a collaborative effort across the value chain,” she said. “Our focus is not just singular. As a product stewardship scheme, it’s not just about waste recovery and diversion from landfill – it’s about trying to drive that circular mentality.”
(Continued on page 18)
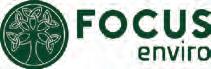
Image: DAN_SHMIT/shutterstock.com
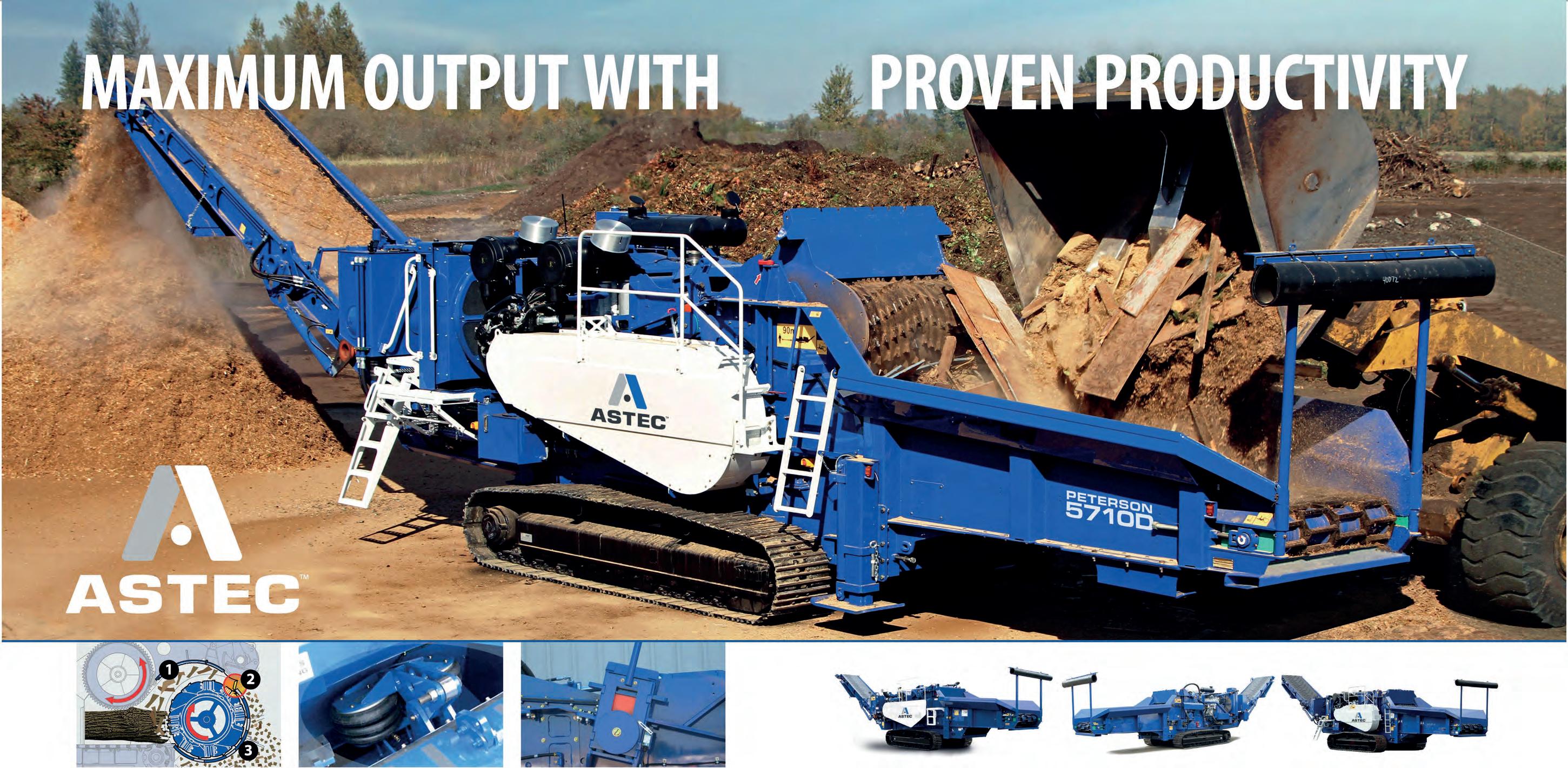
3-Stage Grinding Process
Provides Faster Reduction
Astec - Peterson's powerful up-turn 3-stage grinding process provides better fracturing of material and a more consistent product, giving you just the product your buyers are looking for.
The Impact Release System
Protects Your Investment
Astec - Peterson's patented Impact Release System's air bags provides uniform grinding and protection from contaminated feedstock, a feature unique to Astec - Peterson grinders.
Land clearing, mulch, compost, asphalt shingle tiles, scrap wood, biomass, green waste-we can handle it am
www.komatsuforest.com.au
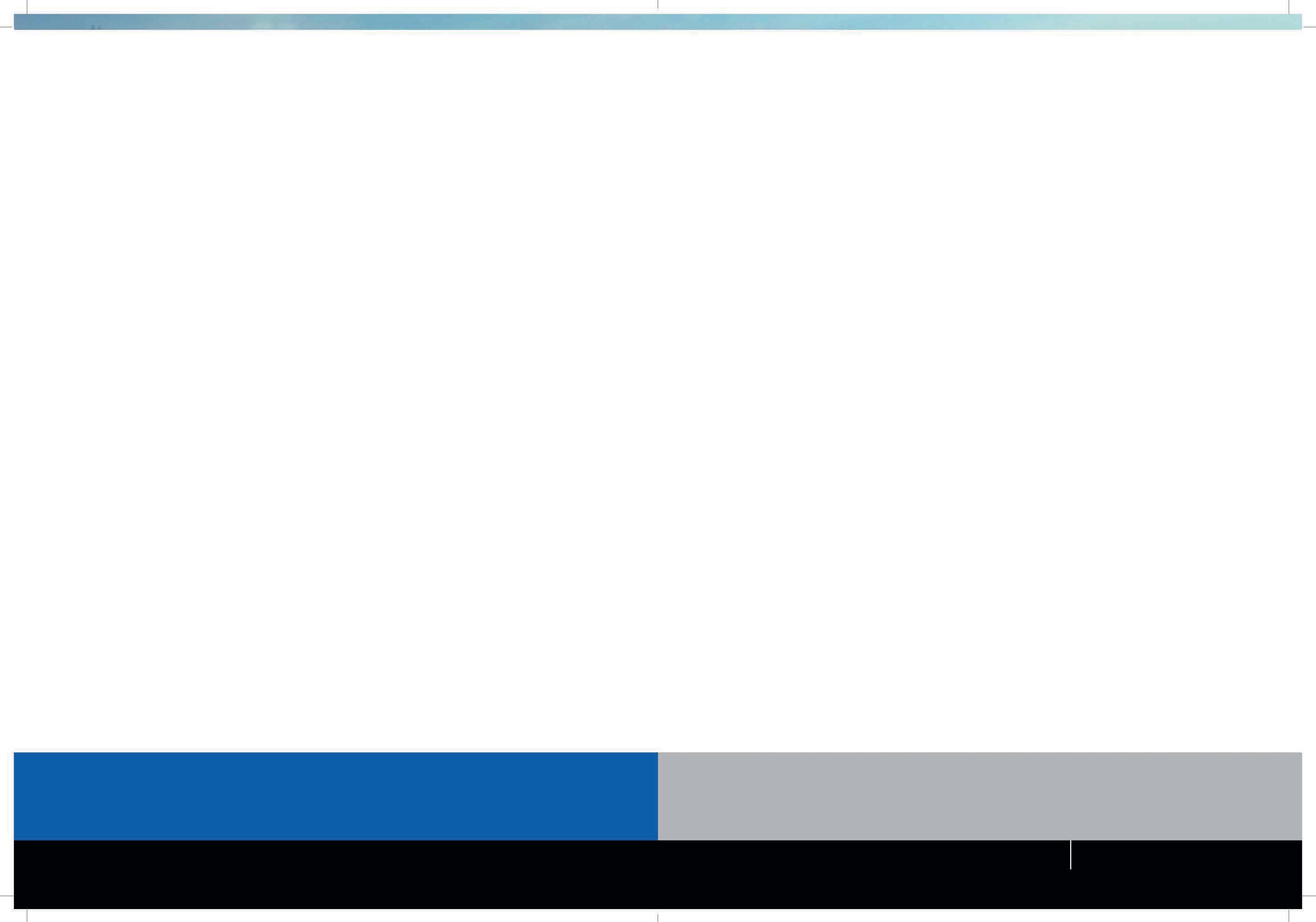
The Impact Cushion System
The Second Line of Defence
Urethane cushions and shear pins help protect the mill from catastrophic damage in the event of a severe impact from contaminants in the feedstock.
Astec - Peterson offers horizontal grinders from 433-839 kW, offering grinding solutions with output at the lowest cost per ton. Visit us at www.astecindustries.com and see why we have been leading the industry for over 35 years!
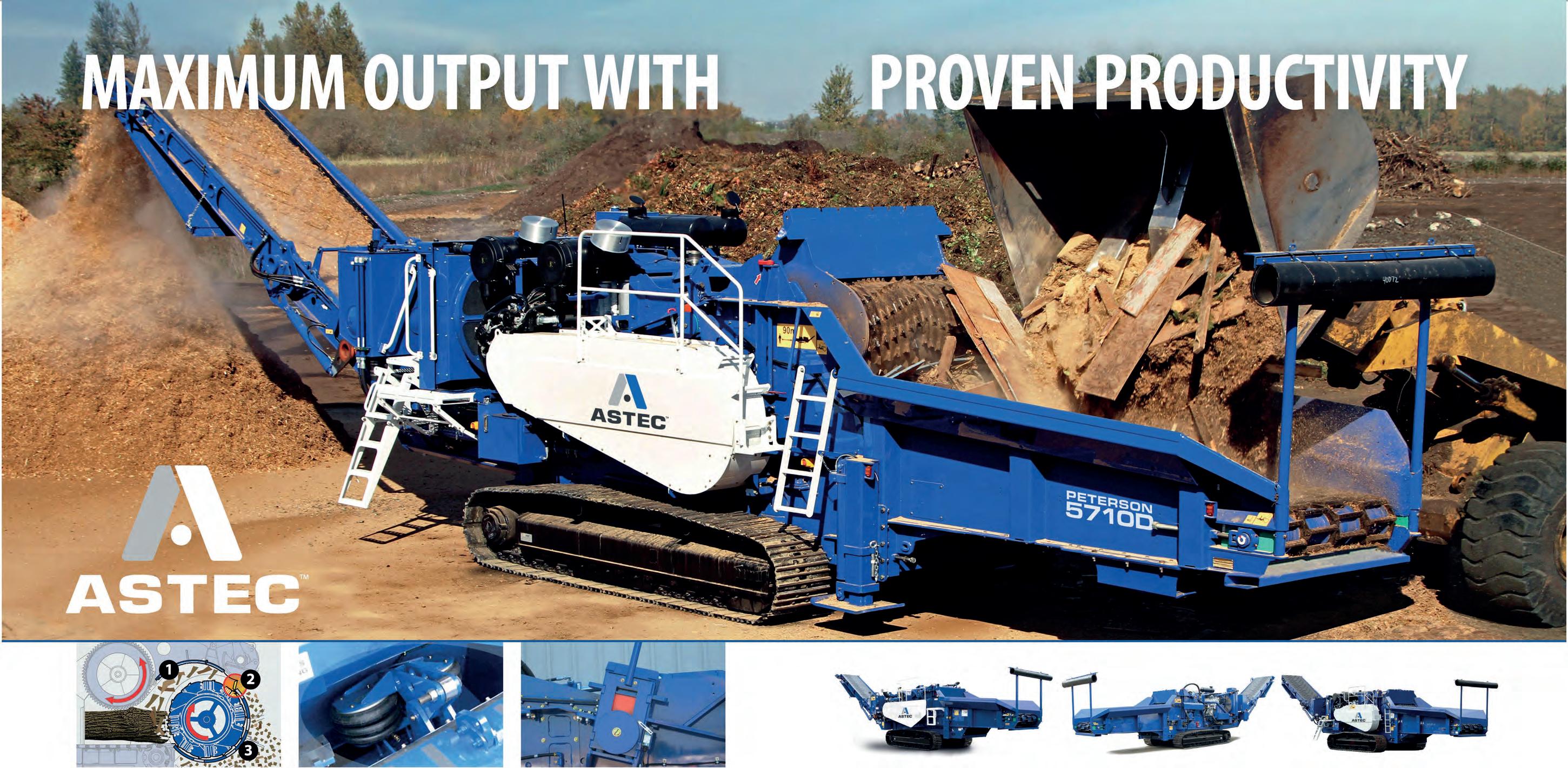
2710D Horizontal Grinder
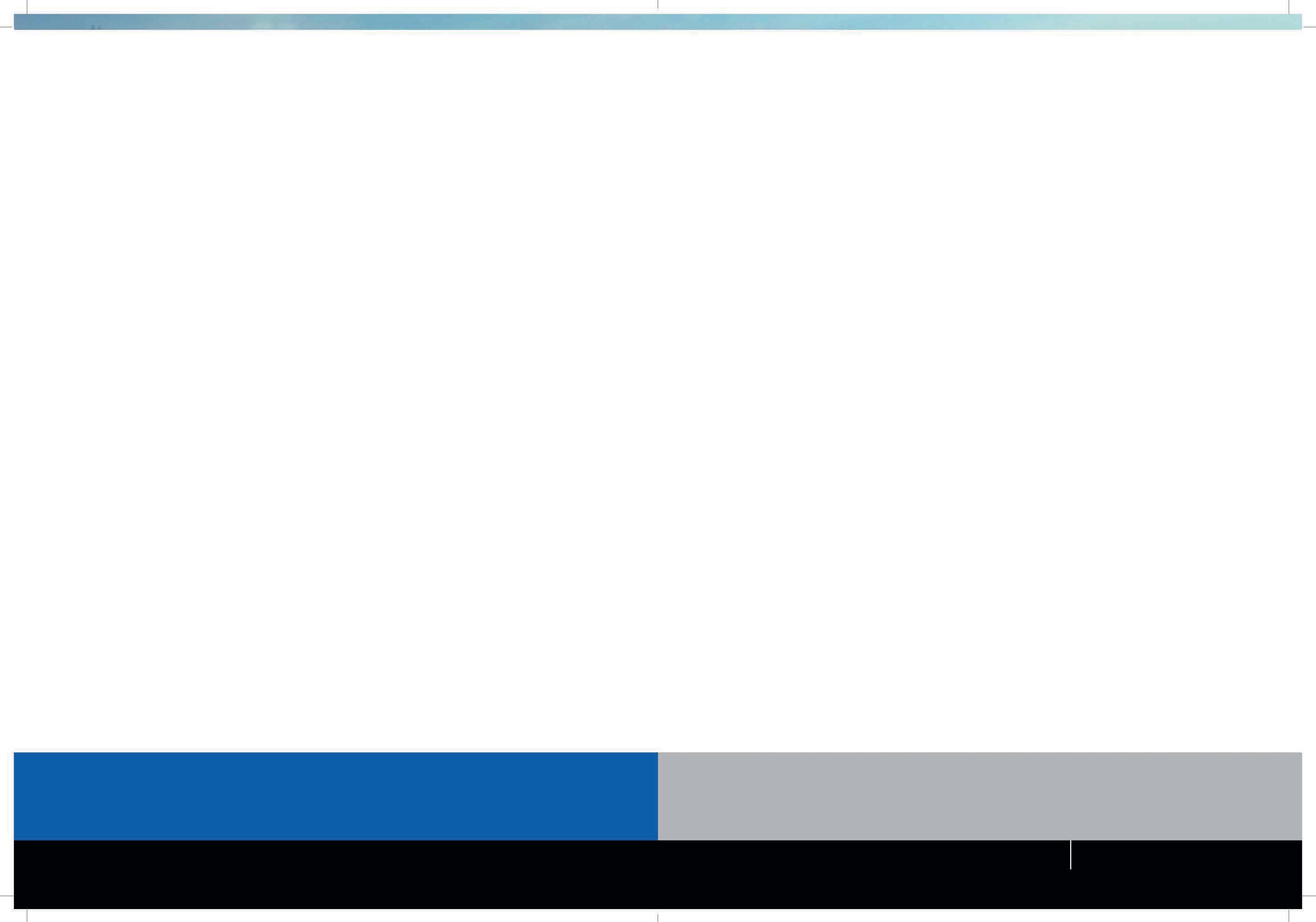
5710D Horizontal Grinder
6710D Horizontal Grinder
Largest
Chief Operating Officer
Christine Clancy
christine.clancy@primecreative.com.au
Managing Editor
Mike Wheeler
mike.wheeler@primecreative.com.au
Brand Manager
Chelsea Daniel chelsea.daniel@primecreative.com.au
Ar t Director
Bea Barthelson
Client Success Manager
Louisa Stocks louisa.stocks@primecreative.com.au
Head Office
Prime Creative Pty Ltd
379 Docklands Drive
Docklands VIC 3008 Australia
p: +61 3 9690 8766 enquiries@primecreative.com.au www.insidewaste.com.au
Subscriptions
+61 3 9690 8766 subscriptions@primecreative.com.au
Inside Waste is available by subscription from the publisher. The rights of refusal are reserved by the publisher
Articles
All articles submitted for publication become the property of the publisher. The Editor reserves the right to adjust any article to conform with the magazine format.
Copyright
Inside Waste is owned by Prime Creative Media and published by John Murphy.
All material in Inside Waste is copyright and no part may be reproduced or copied in any form or by any means (graphic, electronic or mechanical including information and retrieval systems) without written permission of the publisher. The Editor welcomes contributions but reserves the right to accept or reject any material. While every effort has been made to ensure the accuracy of information, Prime Creative Media will not accept responsibility for errors or omissions or for any consequences arising from reliance on information published. The opinions expressed in Inside Waste are not necessarily the opinions of, or endorsed by the publisher unless otherwise stated.
AI is on its way
Artificial Intelligence (AI) news and gossip has been ramping up over the past 18 months. Gone are the days where movies like Minority Report and I, Robot, were stuck in the realms of science fiction –they are turning into science fact. While AI is not quite at the technological level those movies portray, it is starting to get there. What does this mean for the waste industry? Some see it as a game changer that is here to take jobs, much like the Luddites did in the early 19th century. While the chances of those working at the coal face going around destroying machinery – like the fate of many cotton and woollen mills in the early 19th century – is remote, the advancement of AI does hold concerns to some. This is not only over jobs concerns, but because nobody really knows its full capacity and how it will affect our day-to-day lives. Others see it is an opportunity to upskill. Many papers and reports on the subject say that while some jobs will disappear, a more educated and technologically sound workforce will arise.
Take Naser Soueid, for example. He’s started up a company that utilises AI to assist when auditing bins. Cameras gather information as the waste is collected. It’s image capture system
A BOLD NEW ERA IN WASTE MANAGEMENT
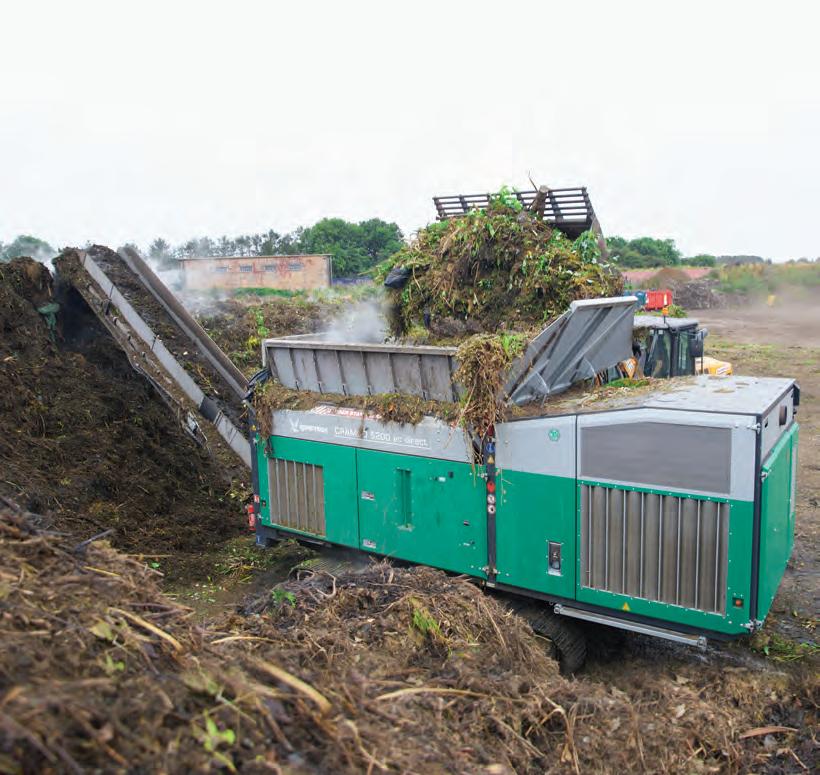

catalogues the different streams, which
the main benefit of the system, as it helps create data points that can be referenced, which in turn gives councils information as to whether households are using the correct bins.
Another benefit of AI is safety. This is especially so in materials recycling and processing facilities. Those companies investing in new infrastructure are starting to utilise cobots and robots during the sorting process. As well as doing what some consider to be mundane jobs, automated AI-enhanced machinery offers a level of safety that isn’t there when it comes to manual sorting.
While there is some uncertainty about where AI sits on the resource recovery landscape, it is here to stay. Only the next couple of years will give a true insight as to how it will be fully utilised.
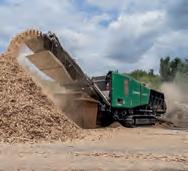
Komptech offers a comprehensive range of equipment, each designed to master every critical step of modern waste managementfrom shredding and separation to recycling and organic waste.
Built to the highest standards of precision and durability, the equipment is engineered to excel under the most challenging conditions, providing the reliability and results you can rely on.
We are proud to be Komptech’s new home in Australia, and together, we’re ready to lead the way.
AUSTRALIA’S WASTE & RECYCLING POWERHOUSE.
Onetrak is thrilled to announce the acquisition of CSS Recycling, a leading provider of waste & recycling solutions. This partnership marks a significant milestone for Onetrak, further solidifying our position as the specialists in material processing equipment.
This partnership reflects our shared commitment to innovation, quality, and excellence, enabling us to deliver a broader range of solutions, greater value, and exceptional specialised service to our customers.
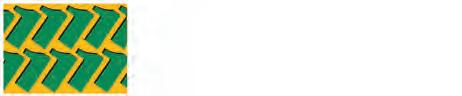



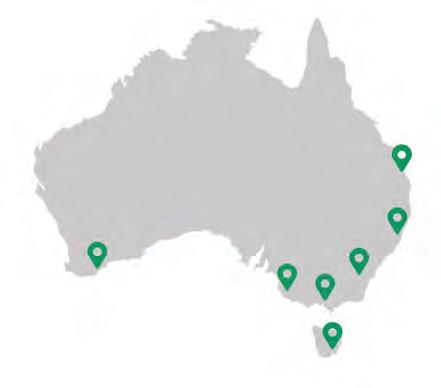
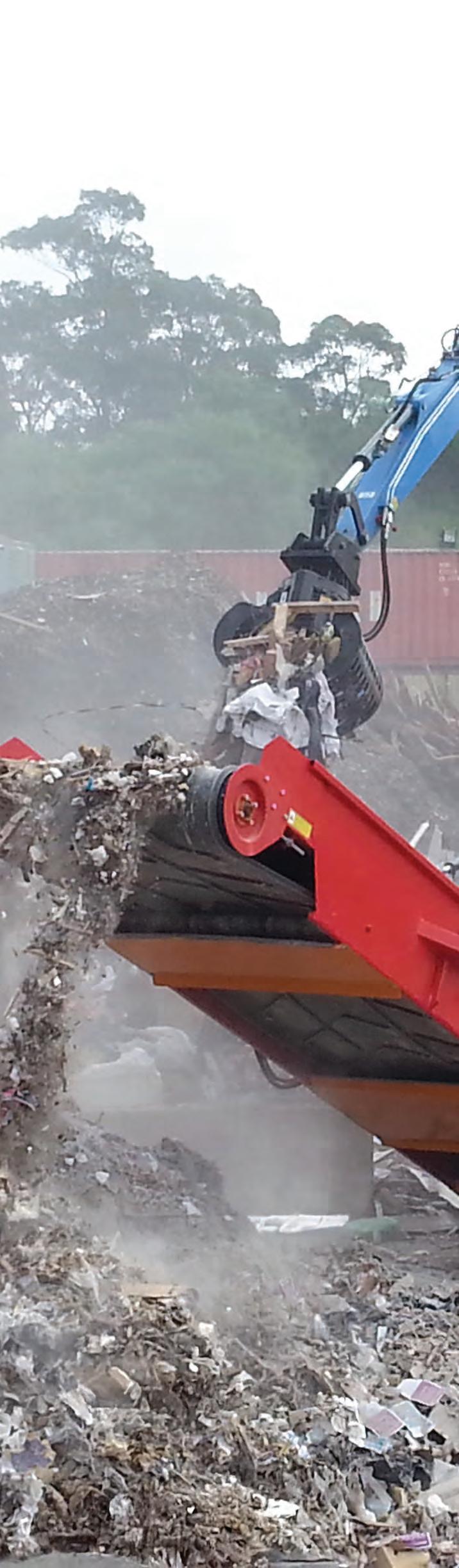


























































































Isuzu’s FVY Dual Control
We’re about to make a big splash in trash, because we’ve just launched a new range of dual control trucks. With lower tare weights than similar models from our competitors, these new trucks can carry bigger payloads. Up to 300kgs per trip! Apply that across a fleet and you’ll see huge boosts in e ciency and reduced operating costs. Visit isuzu.com.au/waste





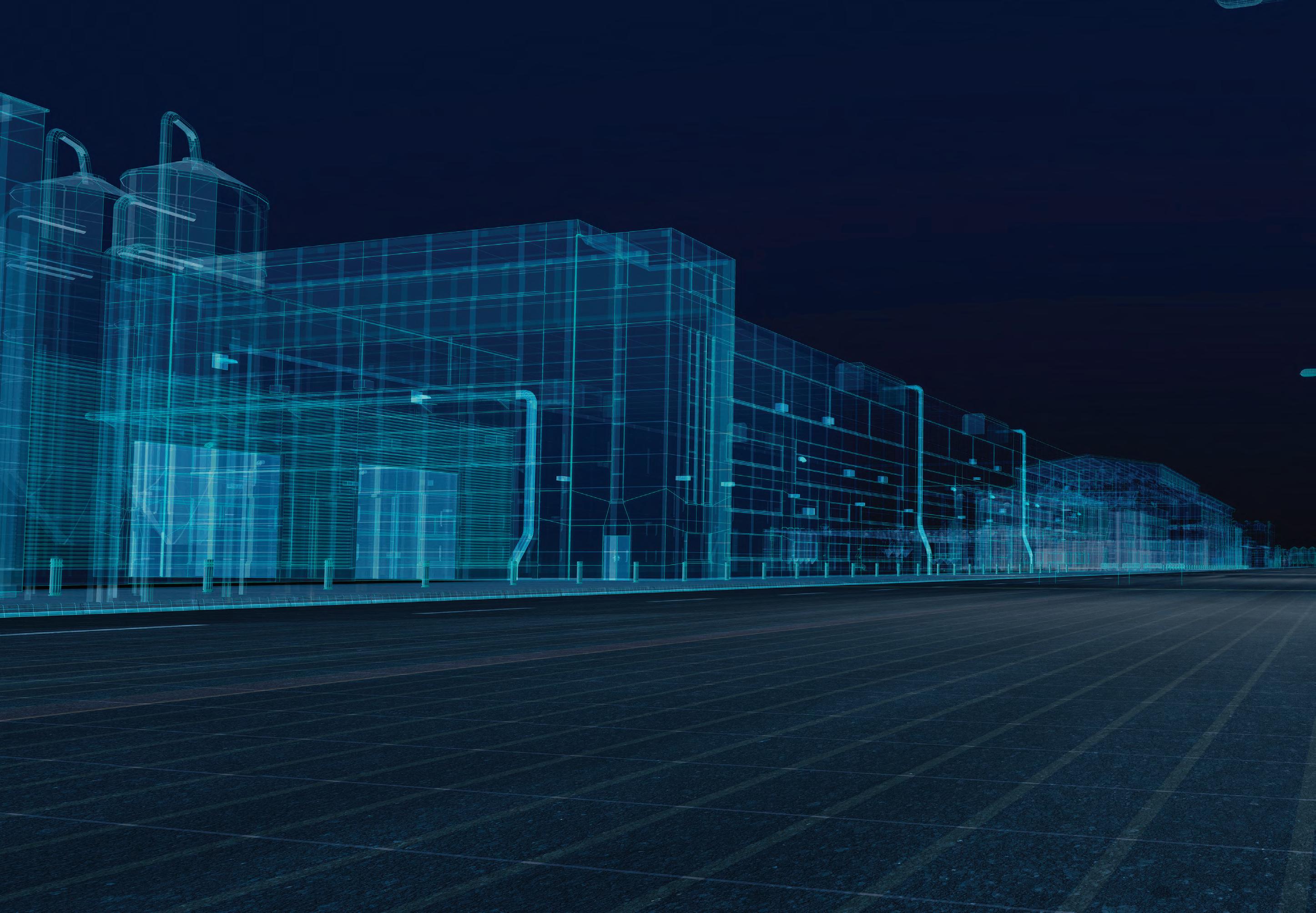

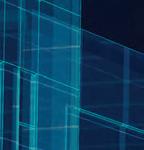
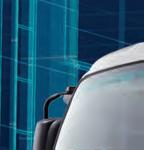

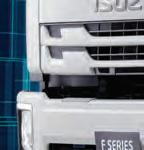
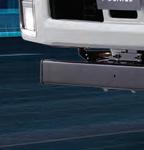
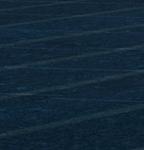
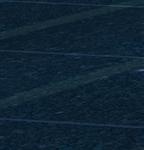
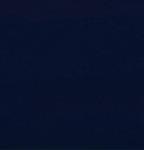
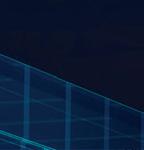
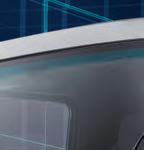
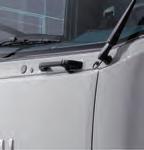
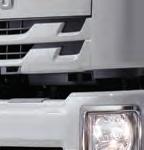
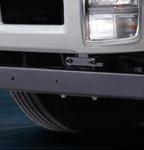
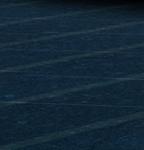
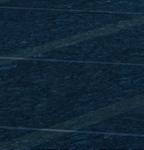
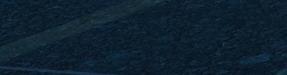

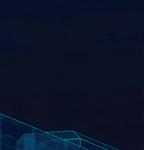
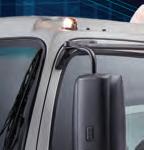

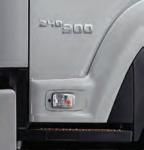
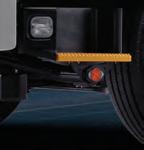
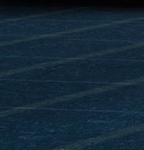
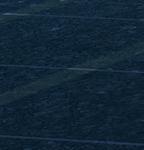
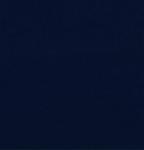

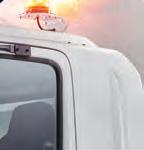

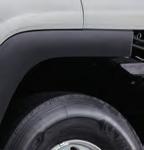
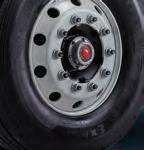
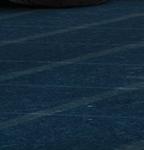
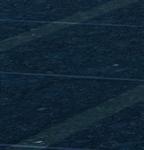
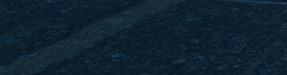

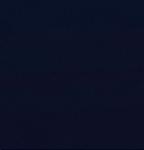
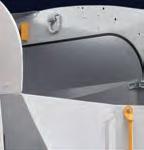
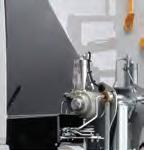

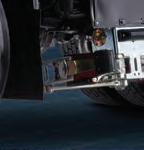
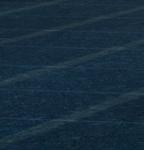
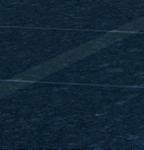
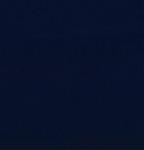
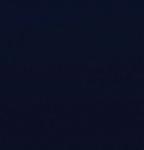
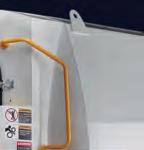
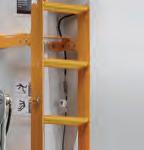
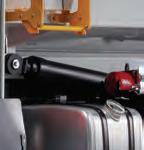

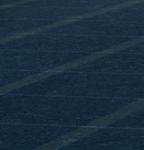
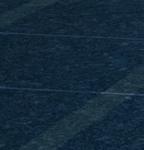
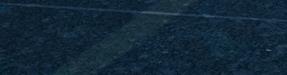
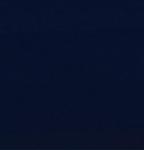
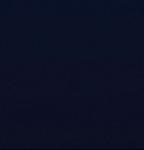
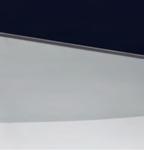
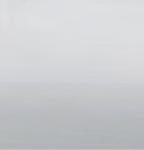

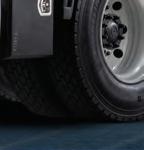
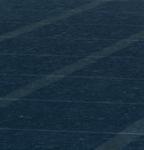

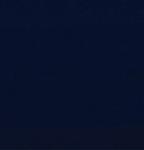



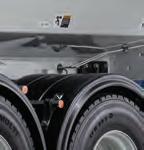
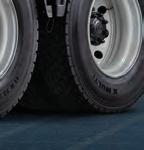
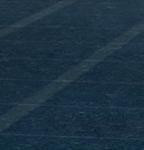
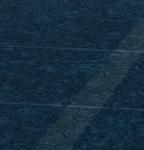
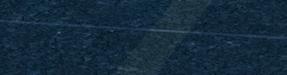
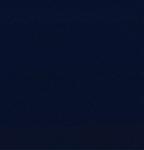
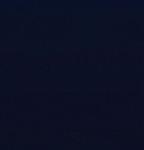
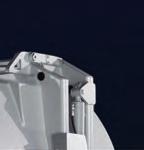
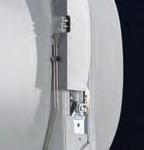
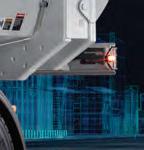
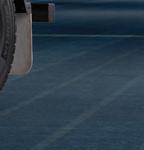

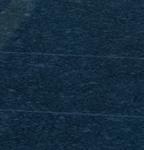
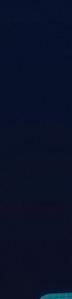
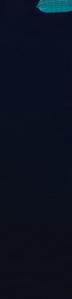
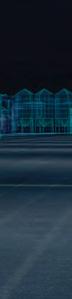

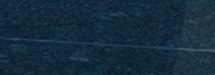
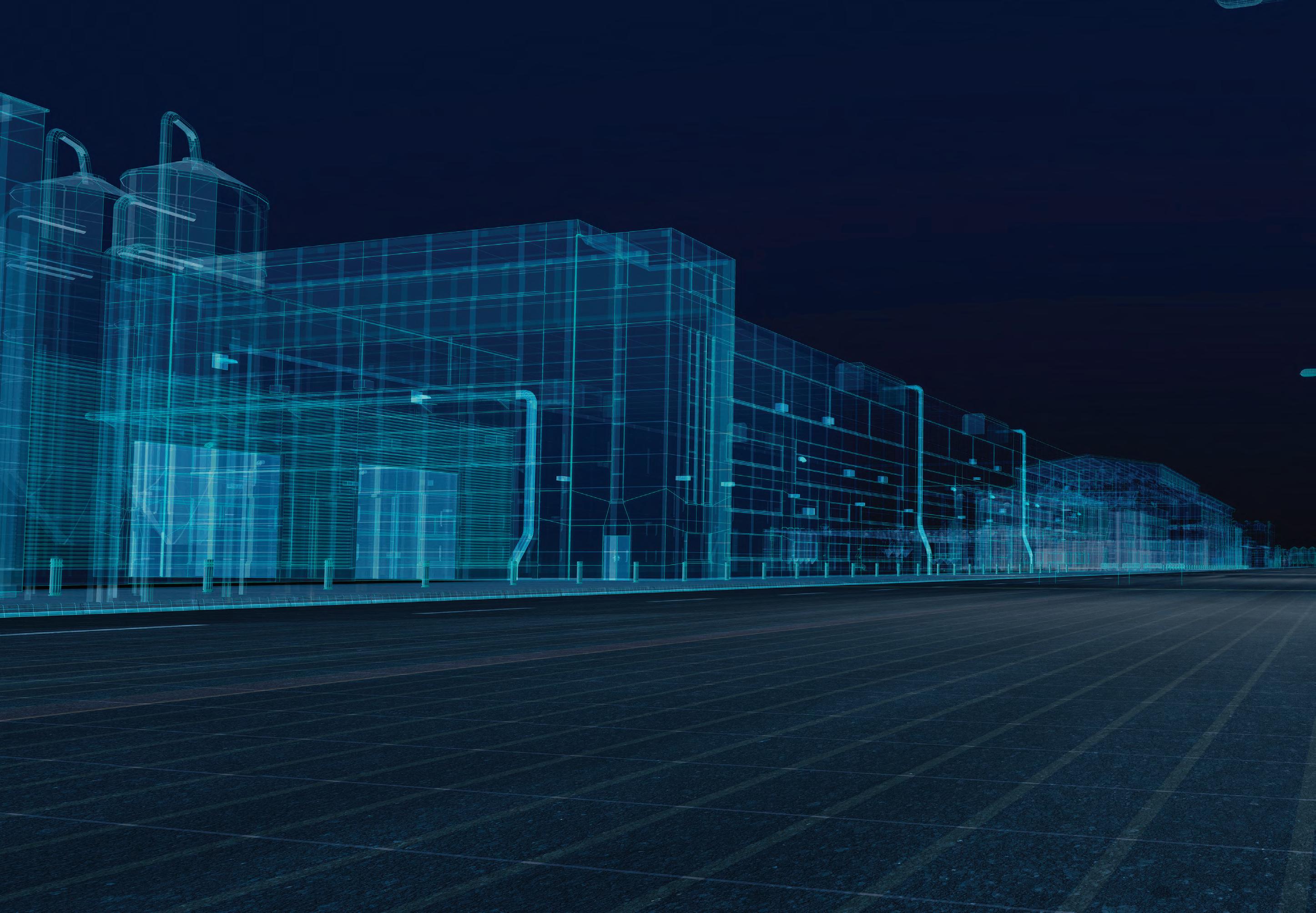
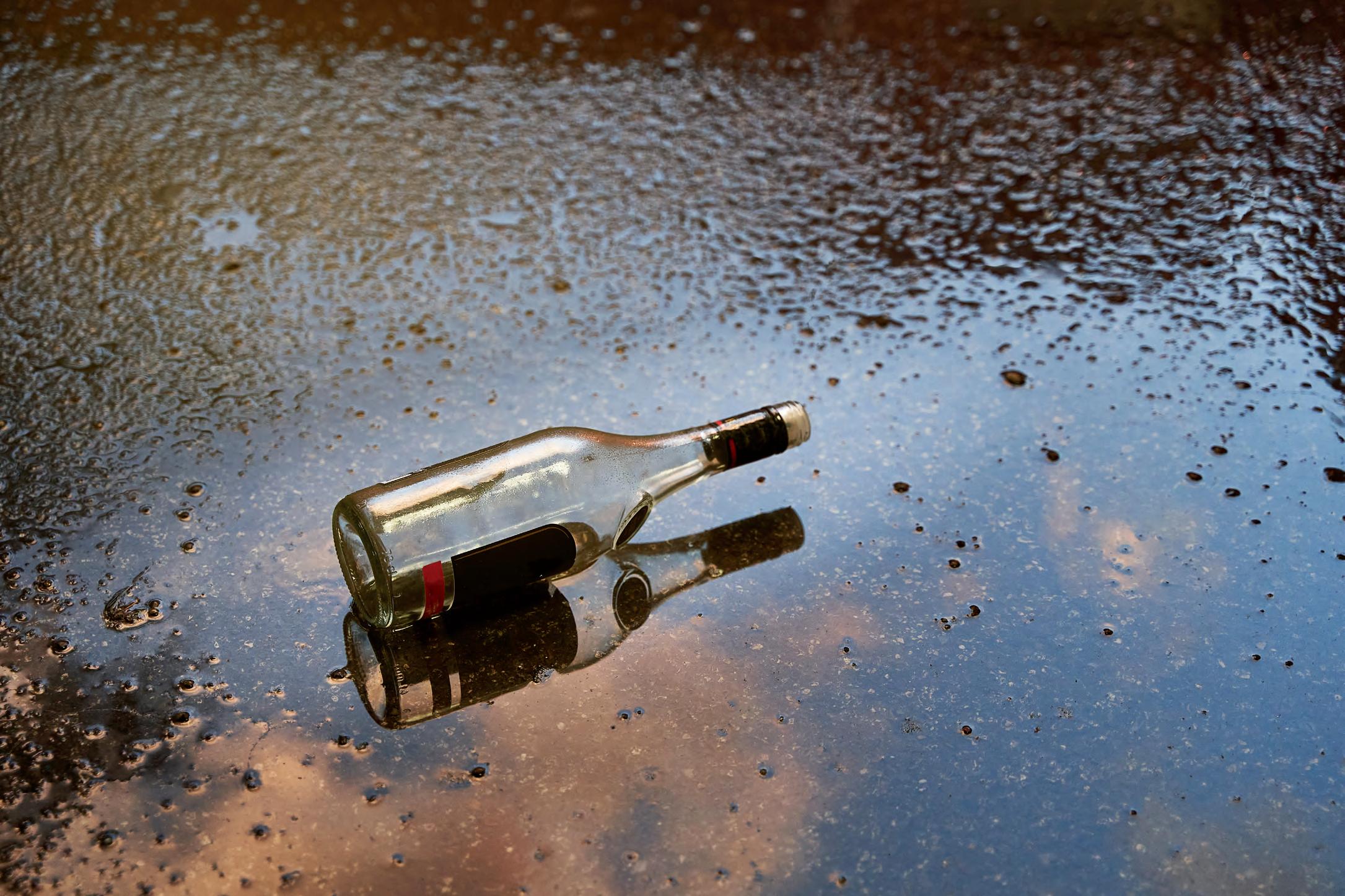
The case for higher refund values in CDS’s
By Samantha Millette and Robert Kelman
(Continued from the front cover)
Beverage containers — aluminium cans, plastic bottles and glass — are among the most recyclable materials in Australia, yet billions still end up as waste each year. According to Reloop’s What We Waste Dashboard, Australia wasted an estimated 3.9 billion recyclable beverage containers in 2024 – enough to fill the Sydney Opera House twice. On a per capita basis, this equates to 146 wasted containers per Australian, including 58 glass bottles, 46 metal cans and 42 PET bottles. Over the past decade (2015-2024), the total waste amounts to an estimated 54.3 billion containers, including 15.2 billion PET bottles, 17.3 billion metal cans and 21.7 billion glass bottles – equivalent to 8.7 million tonnes of material lost to disposal or the environment. This waste represents a market value of $657.7 million.
If current collection for recycling rates remain unchanged, Reloop projects
that Australia will see another 20.2 billion glass, metal, and PET beverage containers between 2025 and 2029 littered or landfilled. Deposit return systems (DRS), referred to as “container deposit’ or “container refund schemes” (CRS) in Australia, offer a solution.
Currently operating in 57 jurisdictions worldwide, these systems incentivise recycling by attaching refundable deposits to beverage containers, which are returned to consumers when the empty container is brought back to designated collection points.
Since South Australia pioneered CRS in 1977, nearly every state and territory has followed suit. Victoria’s long-awaited CRS kicked off in November 2023, making it the last state on mainland Australia to introduce such a system, and Tasmania’s CRS is set to launch in May this year following several delays. This milestone will make Australia the first continent to achieve full CRS implementation. Despite this progress, untapped potential remains. By expanding and modernising these schemes, Australia
could increase recycling rates, reduce waste, and recover millions of dollars in valuable materials for the circular economy.
Reloop estimates that if a national best-in-class CRS – designed to achieve a 90 per cent return rate – were introduced in states across Australia today, an additional 11.4 billion units of beverage containers could be recovered from 2025 to 2029 instead of being lost to landfill and the environment. This would equate to an additional 1.5 million tonnes of glass, metal, and PET containers recycled over the five-year period, which, at 2024 prices, would hold a market value of approximately $178 million. Beyond its economic benefits, it’s projected that a best-in-class system could prevent more than 887,000 tonnes of CO2e (carbon dioxide equivalent) emissions — equivalent to avoiding the burning of 447,064 tonnes of coal or saving nearly 378 million litres of petrol. Furthermore, it would provide brand owners with a more reliable supply of recycled materials, enabling them to meet both voluntary and legislated recycled content targets.
What can be done to improve their performance?
Reloop’s Global Deposit Book 2024 released in December, highlights room for improvement in Australia’s container refund schemes. In 2023, the median
The Loss of a Valuable Commodity: Every beverage container is a valuable commodity, and each container not returned through the DRS signifies an economic loss, as producers must import foodgrade resin from other sources to manufacture new bottles. These unreturned containers also burden costly municipal waste management systems and contribute to the growing problem of plastic pollution.
return rate for CRS-eligible beverage containers across Australia – including those collected via kerbside recycling and material recovery facilities (MRFs) – stood at 68 per cent (see Figure 1). When MRF collections are excluded, aligning with the reporting standards of most container refund schemes worldwide, the median return rate drops further to 55 per cent. These figures fall short of global benchmarks. The European median return rate, which reflects only containers returned through CRS collection points, is 89 per cent, while Canada’s median stands at 76 per cent Boosting beverage container recovery in Australia’s CRS programs is within reach. Several international deposit systems have already achieved return rates exceeding 90 per cent, including Germany (98
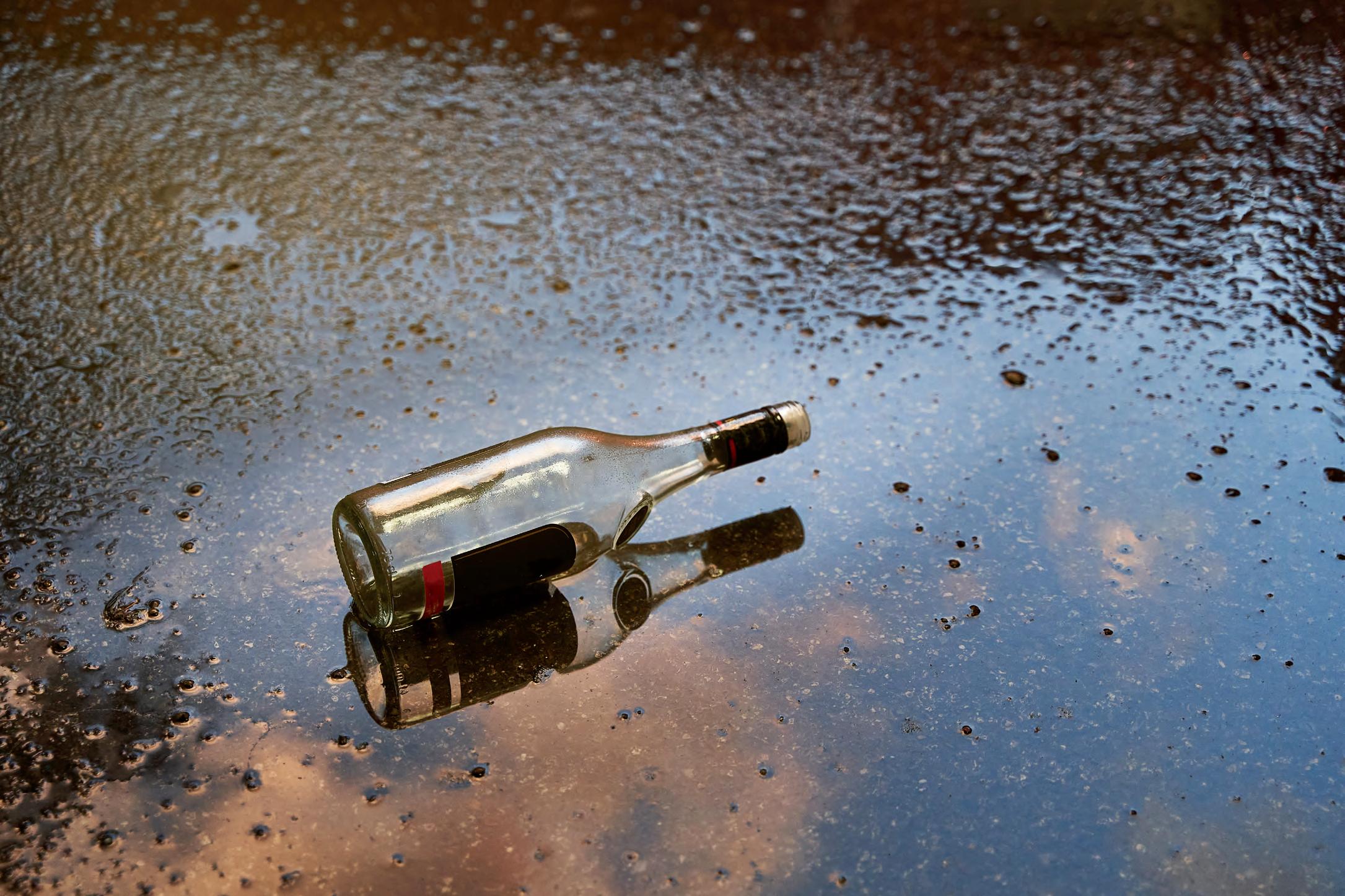
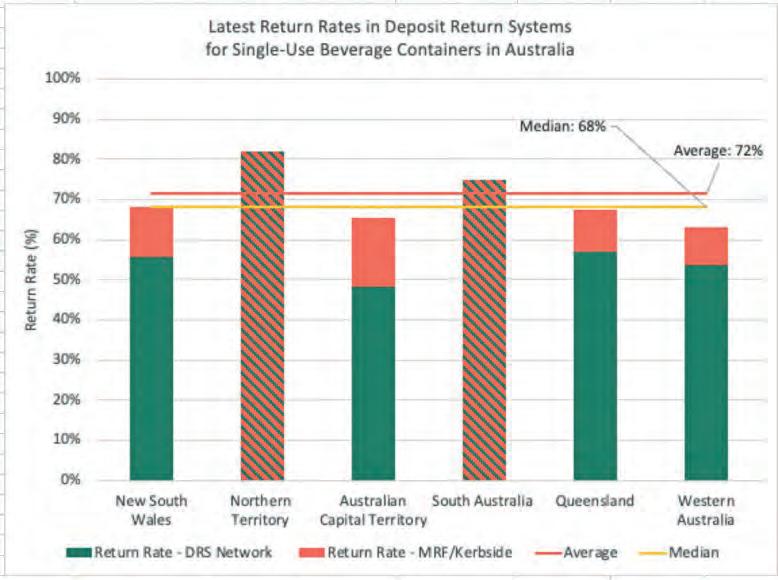
1.
in
for
per cent), Finland (96 per cent), and Denmark (93 per cent). With the right improvements, there is no reason Australian states and territories cannot reach similar levels of success in container recovery. Reloop’s analysis of more than 50 deposit schemes worldwide highlights three critical factors that impact return rates and can help explain Australia’s lagging performance.
Deposit/refund values: Research across multiple jurisdictions
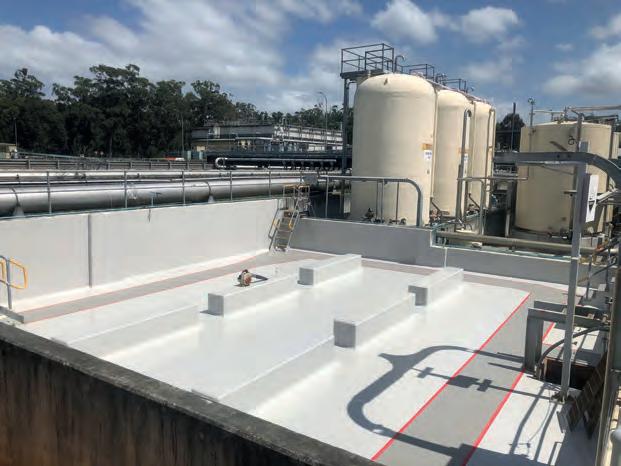
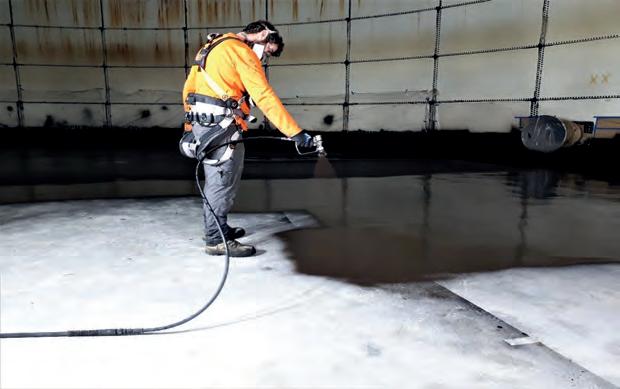



highlights a clear and consistent link between higher deposit/refund rates and increased return rates. Figure 2 illustrates this strong positive correlation. The data shows that systems with a minimum refund value of $0.20 achieve the highest return rates, underscoring the importance of adequate financial incentives in driving consumer participation.
Currently, all Australian deposit schemes offer a $0.10 refund per eligible container. This is much lower
Figure
Latest return rates
container refund schemes (CRS)
single-use beverage containers in Australia.
than deposit rates in most leading international CRS programs where return rates exceed 90 per cent, such as Germany ($0.42), Norway ($0.28-$0.42), Finland ($0.17-$0.66) and Denmark ($0.22-$0.67) (see Figure 3). This disparity is particularly notable given Australia’s economic standing relative to these countries (see Figure 4). When adjusted
for purchasing power parity (PPP), which accounts for differences in relative purchasing power across jurisdictions, Australia’s GDP per capita is higher than three of the leading international container refund schemes. In 2023, Australia’s GDP per capita (PPP) was 55 per cent higher than Slovakia’s, 30 per cent higher than Lithuania’s, and 8 per
PROVEN RELIABLE AND PRODUCTIVE
cent higher than Finland’s⁵ Aside from being well below comparable European deposit rates, there’s also the fact that refund amounts in Australian CRS programs have not been adjusted for inflation, eroding their value over time. This reduces the incentive for consumers to participate and contributes to return fatigue,
where the effort of returning containers outweighs the perceived reward. Consumers broadly are highly supportive of a refund increase. As a 2024 survey outlined, across all political persuasions 83 per cent of the electorate supports a refund increase and just 7 per cent opposed⁶
Convenient return processes: Next to

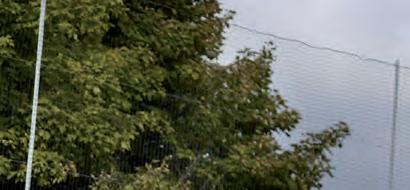
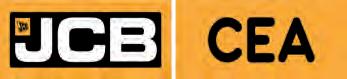
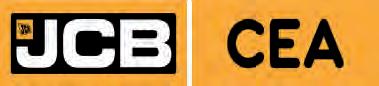


Figure 2. International CRS Return Rates Compared to Minimum Refund Values, in Australian dollars (includes material collected from kerbside recycling programs/ MRFs in Northern Territory and South Australia).
Figure 3. Refund Values vs. Overall Return Rates in Leading International CRS vs. Australian Schemes.
YOU SPOKE, WE LISTENED.
THE LS3600TX SOLVES THE ISSUES THAT MATTER TO OPERATORS!
The LS3600TX stands apart from other shredders, tackling long-time frustrations and maintenance challenges head-on. With unrivalled access to the rotor, comb, and engine, it’s one of the most maintenance-friendly shredders on the market. Adjustable comb pressure, spacing, and tooth configurations provide flexibility for achieving optimal product sizing. Powered by a CAT C13B Tier 4 Final/Stage 5 diesel engine delivering 456 horsepower, the LS3600TX doesn’t compromise on performance. Reach out to your local product specialists at Vermeer Australia today!
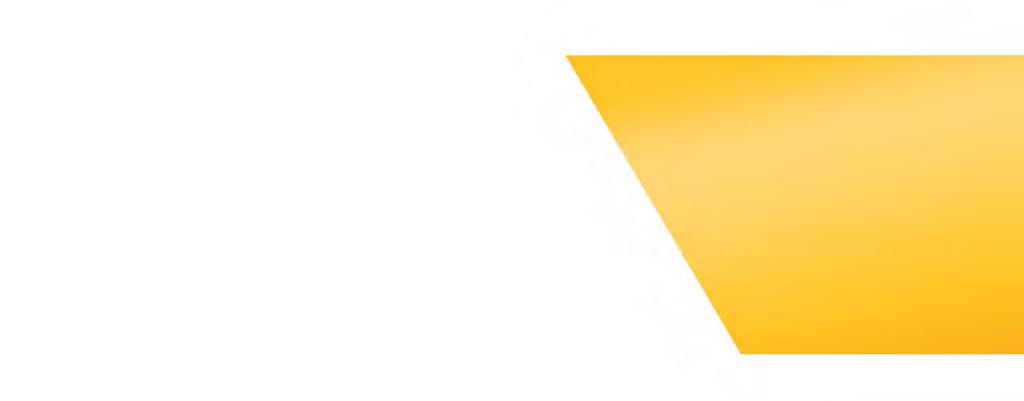

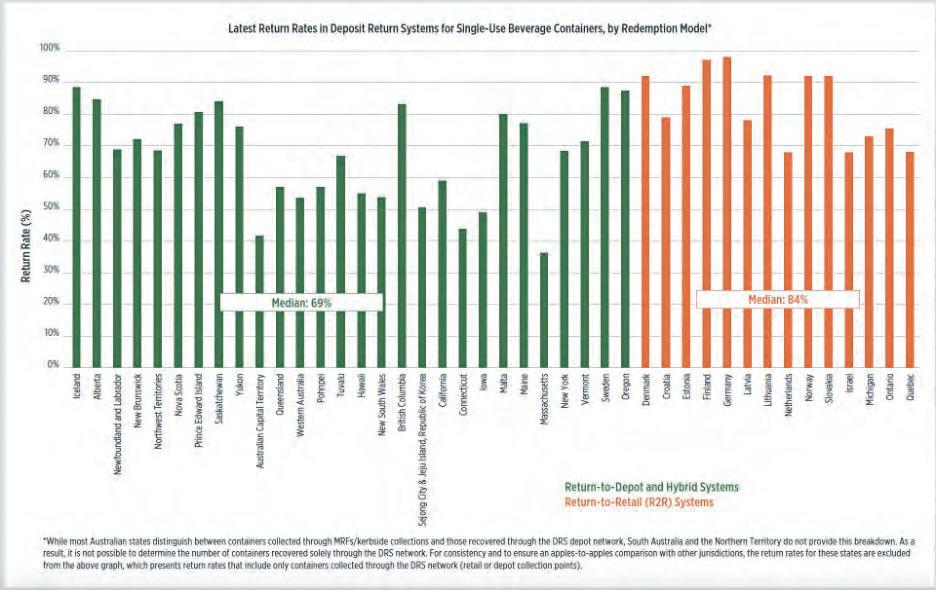
refund values, the accessibility of return options also plays a critical role in system performance. Jurisdictions that utilise a return-to-retail (R2R) model — where retailers are legally required to accept container returns and provide refunds — achieve a median return rate of 84 per cent (Figure 5). This is higher than the 69 per cent median return rate in jurisdictions that rely on depots or hybrid models.
In Australia, some CRS programs (primarily Queensland, South Australia, and Western Australia) follow a largely return-to-depot model, requiring consumers to return containers to stand-alone depots (often located in industrial precincts rather than convenient locations for consumers) to receive their deposit refunds. New South Wales (NSW), Victoria, and soon Tasmania, operate a hybrid model that includes depots alongside voluntary retail return points. However, unlike leading international CRSs, where return-to-retail (R2R) is mandated by law, Australia’s retail collection points are voluntary. This means retailers are not legally required to accept container returns, and where retail-based reverse vending machines (RVMs) do exist, they are limited in number, often located
Norway
outside rather than in-store, and not universally available. As a result, hybrid and return-to-depot models in Australia are generally less convenient than legislated R2R systems, which provide consumers with a guaranteed option to return containers at the same locations where they shop.
Compounding this issue, the number of return points per capita in Australia is low compared to leading international schemes (see Table 1). This limited accessibility reduces convenience and hampers the overall effectiveness of Australia’s CRS programs.
Comprehensive scope: Schemes with broad scopes that include a variety of beverages and container types achieve higher return rates. For example, New York’s experience demonstrates the impact of expanding program coverage. When water bottles were added to its system in 2009, the number of PET plastic containers returned for recycling doubled, according to a 2021 report⁷ Similarly, Denmark offers a compelling case. Despite already achieving a worldleading beverage packaging recycling rate of 90 per cent in 2018, the Danish government expanded its scheme in 2020 to include single-use juice and concentrate bottles. This expansion was
Redemption Model Number of Collection Points Population per Collection Point
Lithuania Return-to-retail2,6001,110
Finland
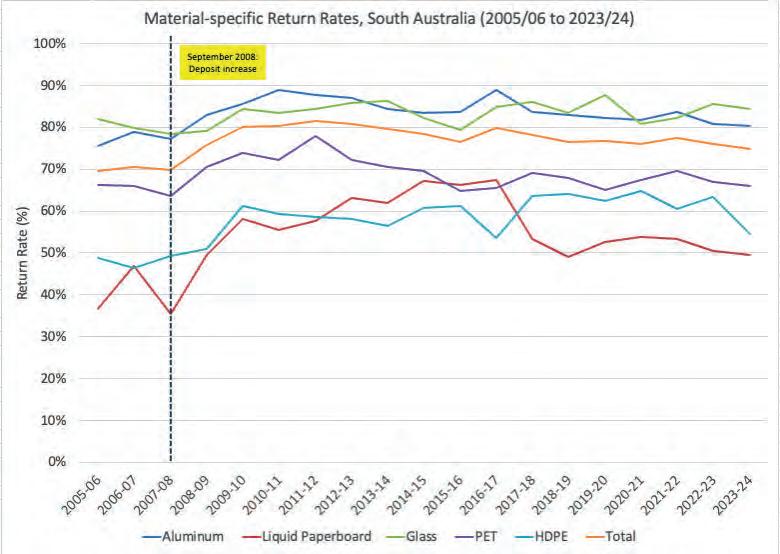
projected to result in an additional 52 million bottles being recycled annually, increasing the schemes’ recyclable packaging volume by 4-5 per cent⁸
In contrast, many of Australia’s CRS programs exclude key categories such as wine and spirit bottles, as well as non-carbonated beverages like milk and juice. These exclusions not only limit the volume of recyclable materials captured but also contribute to consumer confusion over which containers are eligible for a refund, potentially discouraging participation. Expanding the scope to include these containers would reduce uncertainty, encourage greater engagement, and unlock untapped potential –boosting recovery rates and ensuring more packaging waste is diverted from disposal.
Consumers are generally also more likely to participate in CDS schemes if they cover a more complete range of beverage products. The following paper from WA’s Curtin University outlined this consumer preference in 2022⁹.
Greater container eligibility was a recurring theme throughout the survey and a key barrier to CDS uptake, with many participants taking the opportunity to express their frustration at the lack of eligible containers. Overall, 87 per cent of survey participants would participate more in the $0.10 refund scheme if wine bottles, milk cartons, cordial/syrup containers and alcoholic spirits were eligible for a $0.10 refund (Figure 9). This response was split evenly across the respondents, regardless of their past, current, or non-existent use of the CDS. This reflects the demand and the need for including more items to motivate individuals to participate in CDS.
Why increasing refund values boosts recovery rates
To unlock Australia’s potential for higher recovery rates, and in the absence of a revised legislative mechanism to require retail take-back, raising refund values stands out as the most effective strategy. Evidence from schemes worldwide
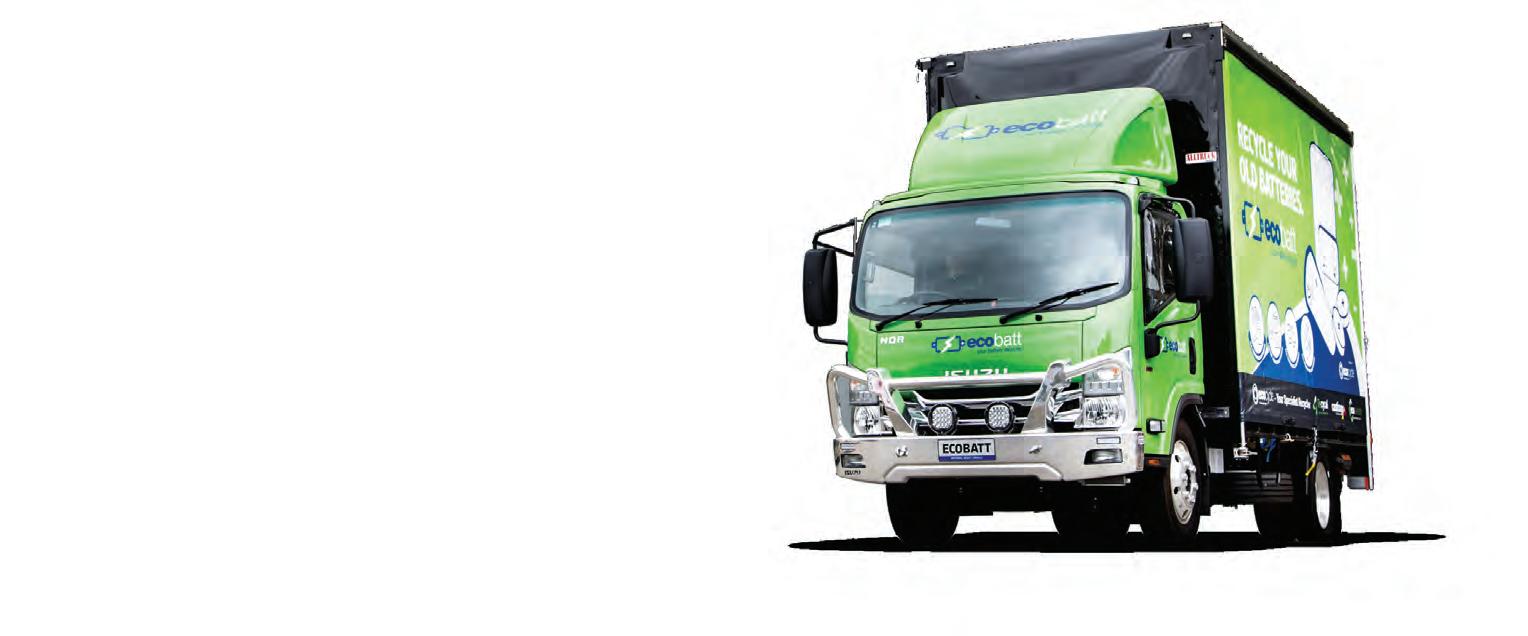

Figure 4. GDP per Capita (PPP) (Current International $), Australia vs. Leading International CRS Countries, 2023.
Gross Domestic Product (GDP) per Capita (PPP), Australia vs. Leading International CRS Countries, 2023
by Redemption Model (excludes material collected from kerbside recycling programs or material recovery facilities [MRFs]).
Table 1. Accessibility Metrics in Australian CRS vs. Leading International Schemes, 2023.
Figure 6. Impact of Refund Increase on South Australia’s Return Rates.

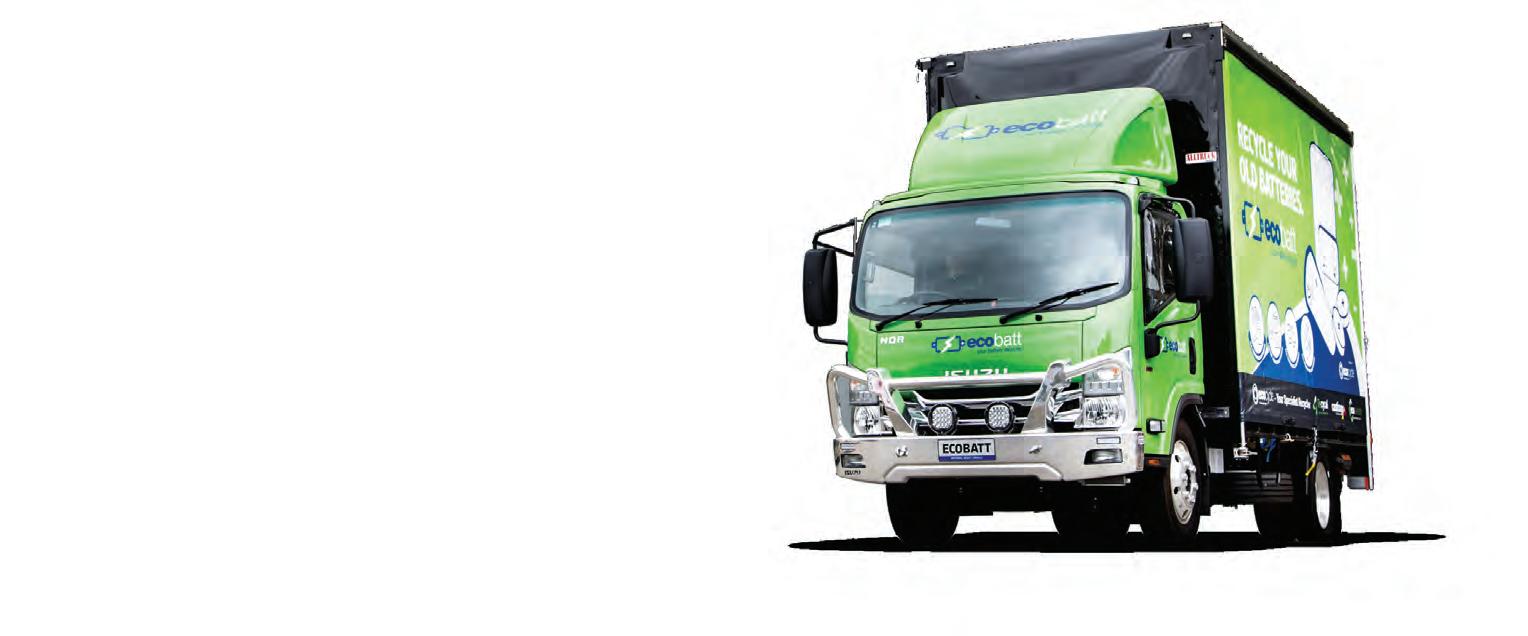
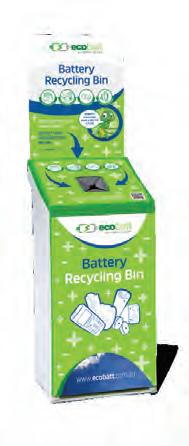
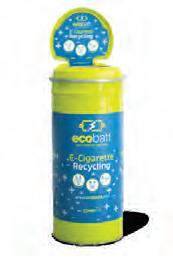
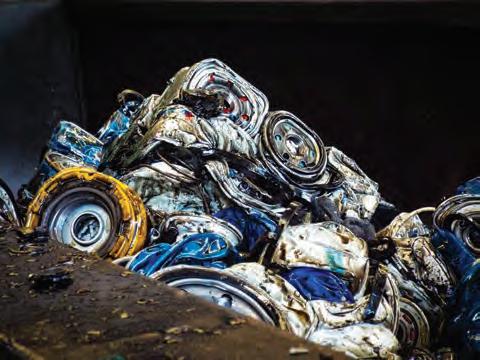
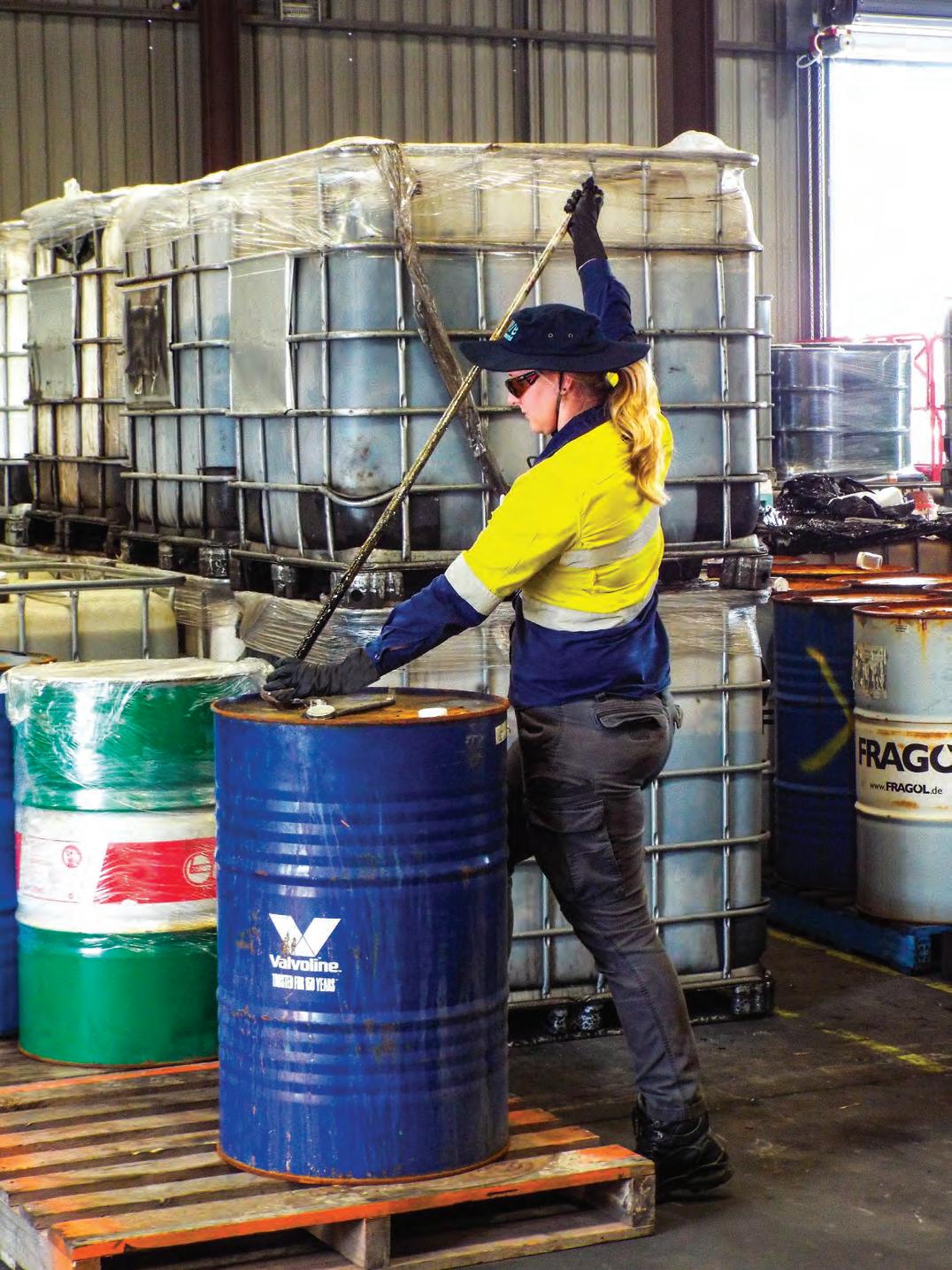
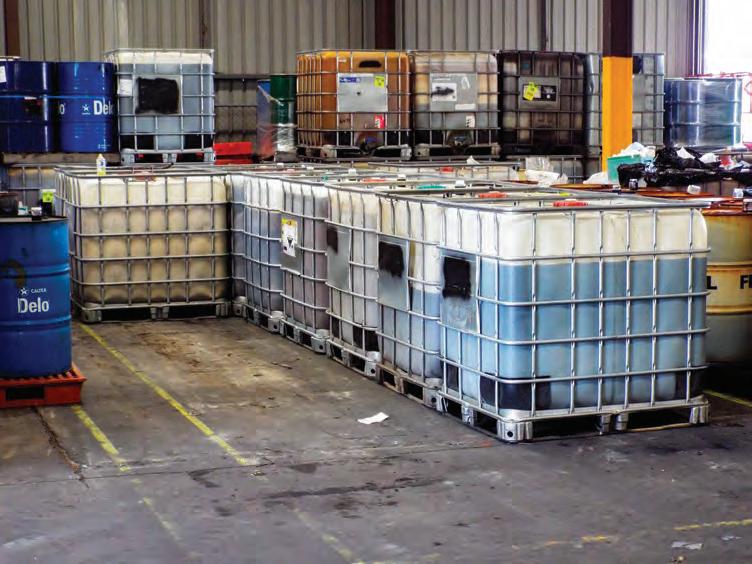
Innovative, Sustainable Waste Management Solutions
Pure Environmental is a wholly Australian-owned company founded with the mission to transform the circular economy through advanced resource recovery. We believe in pushing boundaries and challenging norms in waste management, providing exceptional, innovative, and sustainable solutions.

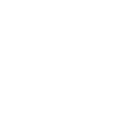

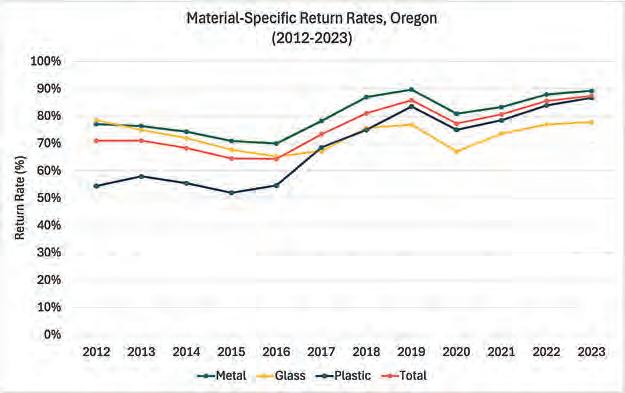

demonstrates that higher refunds directly correlate with increased return rates, offering a proven solution to address current gaps in performance.
South Australia provides a compelling case study. In September 2008, the state government doubled the refund on beverage containers from $0.05 to $0.10, leading to a sharp rise in return rates. Within a year, the return rate climbed from 69.9 per cent to 76 per cent, reaching 80 per cent by 2009-10 and eventually peaking at 81.4 per cent (Figure 6) – a total increase of 16 per cent following the refund hike. This data highlights the effectiveness of financial incentives – when the value of the refund increases, consumer participation rises accordingly.
Both Oregon (United States) and Alberta (Canada) provide additional compelling evidence of how increasing refund values can drive improvements in beverage container recovery. In Oregon, return rates had stagnated at around 60 per cent between 2014 and 2016. However, in 2017, the state doubled its deposit from $0.08 to $0.16, resulting in a turnaround. By the end of that year, the return rate had surged to 73 per cent, eventually reaching 86 per cent by
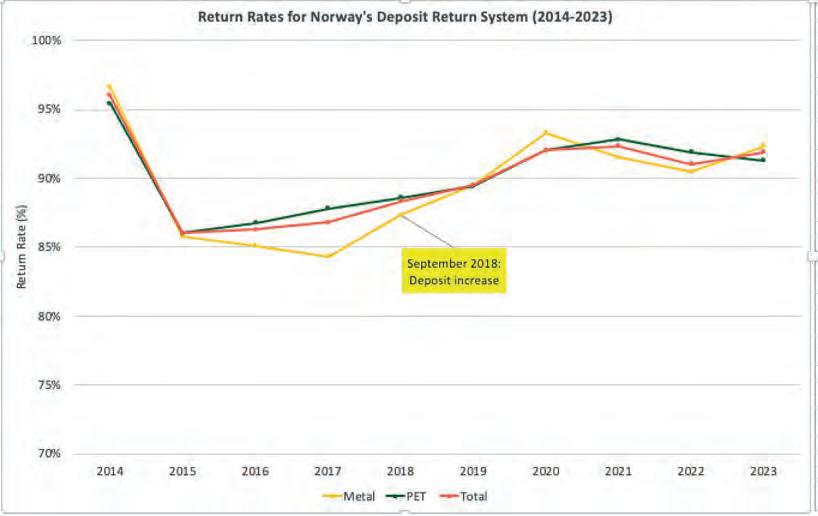
goal of not just meeting but exceeding the 90 per cent threshold, as Sweden’s 2023 return rate stood at 88.5 per cent and 2024 figures are expected to be even higher. This is not Sweden’s first deposit increase; since the system’s establishment in 1984, the deposit on metal cans has been raised twice – once in 1987 and again in 2010. Additionally, Sweden has expanded its program’s scope over time. Initially limited to metal cans, the system began covering plastic PET bottles in 1994 and, as of January 2023, includes all fruit syrup and juice containers.¹²
Why aren’t Australia’s refund values high enough?
value due to inflation.
These figures are based on calculations using the Reserve Bank of Australia’s inflation calculator, which adjusts historical amounts to current values using the Consumer Price Index (CPI). The CPI measures average price changes over time for a basket of goods and services. Without inflation adjustments, refund values steadily lose their impact, diminishing the financial incentive to return containers and contributing to “return fatigue.” Consumers may begin to question whether the effort of returning containers is worth a reward that feels increasingly insignificant.
2019 (Figure 7). Similarly, the province of Alberta increased its deposit at the end of 2008 which led to a 10 percentagepoint increase in the overall return rate by the end of 2009 (Figure 7) 10
Turning to Europe, in September 2018, Norway implemented a doubling of its deposit rates, raising the fee for containers under 500ml from $0.14 to $0.28 and for containers over 500ml from $0.28 to $0.42. This adjustment had an immediate impact: within two years, return rates surged across all material types. The return rate for cans increased from 84 per cent in 2017 to 93 per cent by 2020, while plastic bottles rose from 88 per cent to 92 per cent. Overall, the system’s return rate climbed to 92 per cent in 2020, up from 87 per cent in 2017 (Figure 8) ¹¹
Despite achieving a high return rate of 88.5 per cent, the Swedish DRS operator announced in January this year that it will be increasing deposit values to ensure compliance with its mandated 90 per cent return rate target. As of September 2025, deposits on aluminium cans and small PET bottles will be increased from $0.14 to $0.29, and for large PET bottles, from $0.29 to $0.43. This decision was driven by the
At $0.10, Australia’s refunds values were already too low, and inflation has further eroded their real value, weakening their effectiveness as a financial incentive.
Figure 9 shows how South Australia’s $0.10 refund value, set in 2008, would compare today if adjusted for inflation. To maintain its original purchasing power, the refund would need to be raised to $0.15 in 2024.
In other words, the $0.10 refund now holds the equivalent purchasing power of just $0.05 – a 46.5 per cent reduction in
Restoring the deposit value to at least $0.15 would help revive its financial appeal and reinstate the effectiveness seen when South Australia increased its refund to $0.10 in 2008. At that time, the higher refund helped boost return rates from 70 per cent to 80 per cent within just two years (2009-10). Without such adjustments, the incentive to participate in container refund schemes will likely continue to wane, further challenging efforts to improve recovery rates.
But if we want to get to global best practice of 90 per cent-plus we have to
Figure 7 Impact of Deposit Increase on Beverage Container Return Rates in Oregon’s CRS,
Figure 7 Impact of Deposit Increase on Beverage Container Return Rates in Alberta’s CRS, 2004-2023
Figure 8 Impact of Deposit Increase on Material Return Rates in Norway’s CRS, 2015-2023
Figure
Innovative Environmental Experts
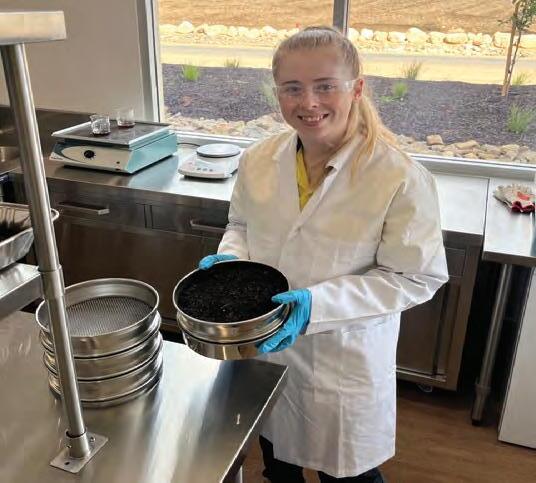

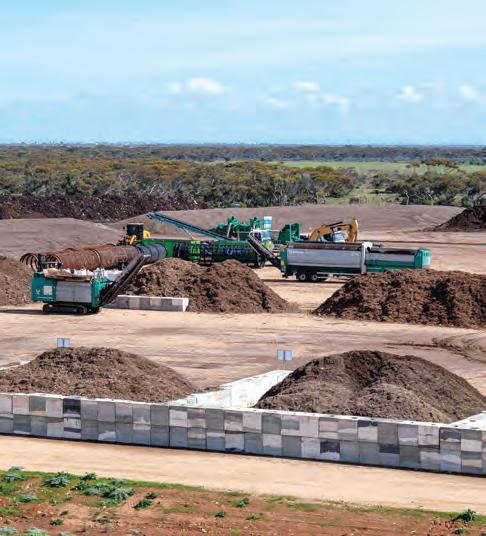
Ennovo provides comprehensive solutions for the management of recycled organics based on extensive experience with designing, constructing and operating recycled organics facilities.
Specialist Services
FOGO management and processing
Site assessment and approvals
Market assessment and development
Composting – open windrow and in-vessel
Process and product development
Third party compliance support
Carbon credit development and management
Ennovo’s Carbon Air system automates forced aeration for efficient composting in windrow and in-vessel applications. With telemetryenabled automation, it reduces costs, optimises operations, and ensures high-quality output, making it ideal for FOGO composting. Ennovo provides end-to-end solutions from design to market development.
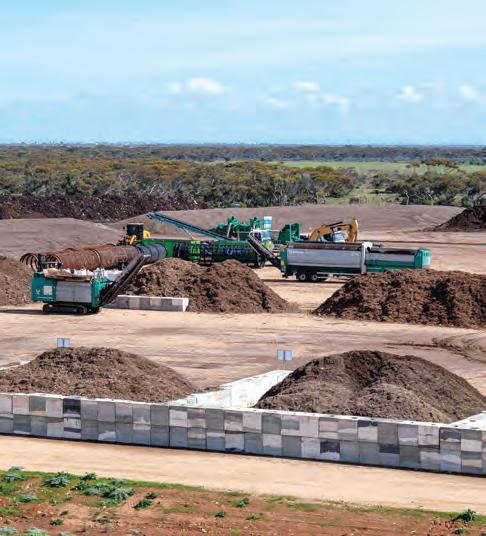
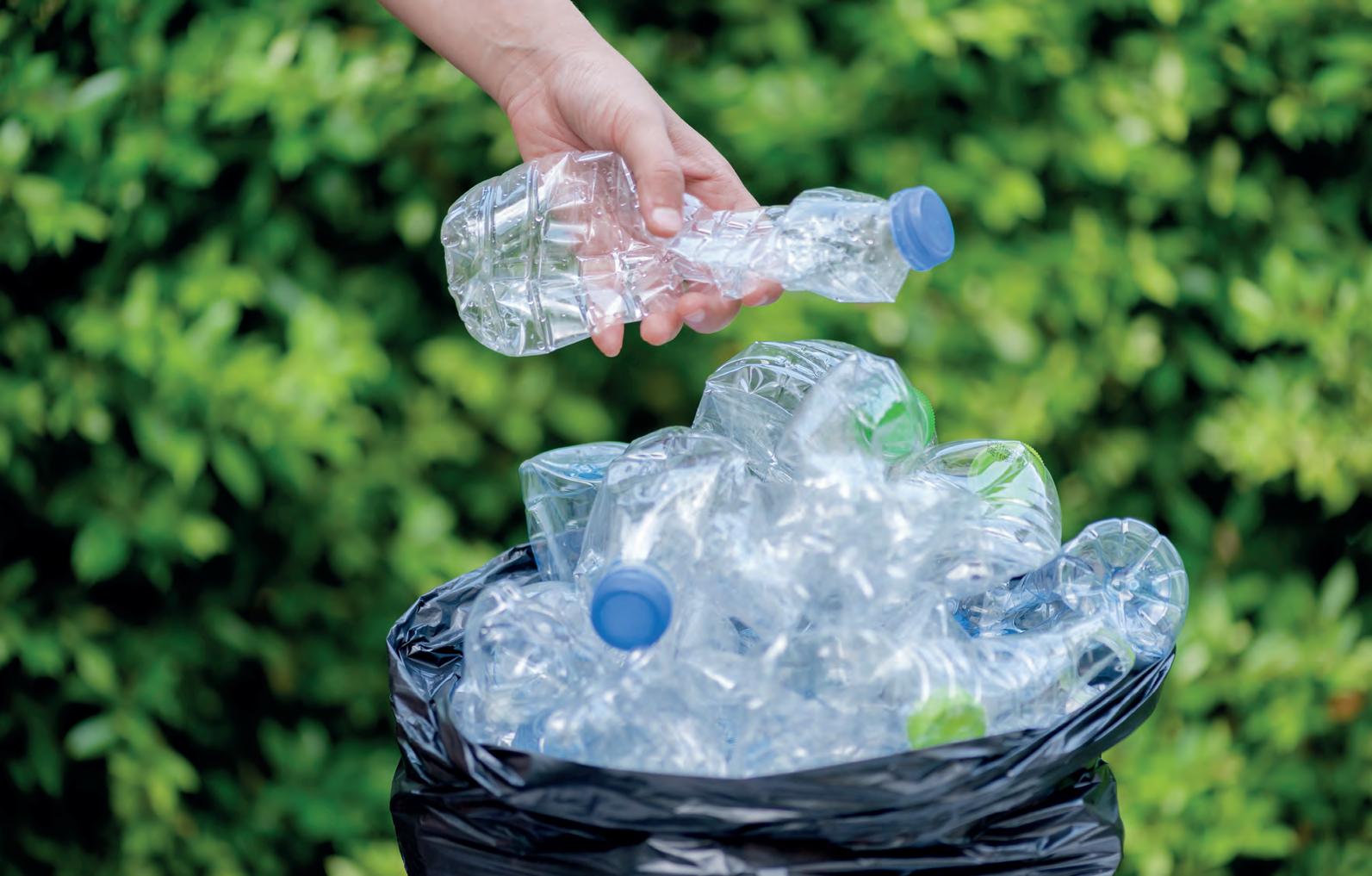
start looking to a refund value of $0.20 to $0.30 and ensure a mechanism is in place to maintain parity with CPI over the coming decades.
The path to higher recovery rates
Australia’s recycling system stands at a pivotal moment. With stagnating recovery rates and the loss of valuable materials to the circular economy, the need for systemic change has never been more urgent.
Among the most effective solutions are container refund schemes that align with global best-in-class principles, offering a proven path to addressing these challenges.
By modernising its CRS programs through higher refund values, broader coverage of beverage containers, and improved accessibility for consumers, Australia can unlock the full potential of these schemes. These enhancements would not only drive higher recycling rates but also recover $178 million dollars in material value (from 20252029) currently lost to landfills and the environment, transforming the nation’s recycling landscape.
Encouragingly, progress is already underway. In April 2021, Australia’s environment ministers committed to harmonising CRS programs across all states and territories by the end of 2025 and HEPA has previously suggested starting a regulatory impact process to assess increasing the refund.
These initiatives also include expanding the scope of eligible containers, increasing public participation, and aligning schemes to maximise recovery and recycling rates. While the specifics are still being finalised, increasing refund values as part of this harmonisation effort would boost the perceived value of recycling and incentivise greater participation.
While an increased refund across the country would be ideal, there should be nothing to prevent individual jurisdictions acting unilaterally. Such an approach was evident throughout the years of South Australia being the only state with a CRS and is now also apparent as wine and spirit glass containers are incorporated into new state schemes as those policy decisions are taken.
To remain competitive in a world transitioning toward a circular economy,
Australia must align its CRS programs with international best practices.
Achieving a 90 per cent return rate – a milestone already reached by numerous European countries – will require bold action. Increasing refund values and expanding program scope to include more beverage and container types are essential steps to ensuring Australia’s
recycling system meets its full
Samantha Millette is the research and analysis manager for Reloop Platform, an international nonprofit organisation focused on advancing circular economy initiatives.
Robert Kelman is the director of Reloop Pacific.
1. APCO. “Australia’s 2025 National Packaging Targets.” Accessed 22 January 2025 from https://apco.org.au/ national-packaging-targets
2. Arreza, J. 8 October 2024. “Boomerang Alliance: ‘Don’t go soft on packaging.’” Accessed 21 January 2025 from https://www.packagingnews.com.au/sustainability/boomerang-alliance-don-t-go-soft-on-packaging
3. EPA October 2022
4. https://www.epa.sa.gov.au/files/15790_hepa_cds_national_research_report_nov2023.pdf
5. World Bank Group. “GDP per capita, PPP (current international $). Accessed 7 February 2025 from https:// data.worldbank.org/indicator/NY.GDP.PCAP.PP.CD
6. Redbridge Group report for Boomerang Alliance, August 2024 (available on request)
7. TOMRA. 2021. “Rewarding Recycling: Learnings from the World’s Highest Performing Deposit Return Systems.” Accessed 7 February 2025 from https://8151194.fs1.hubspotusercontent-na1.net/hubfs/8151194/ TOMRA_Rewarding_Recycling%20-%20English.pdf?utm_campaign=DRS%20-%202023&utm_ medium=email&_hsenc=p2ANqtz--s99aMaKRFGo1kpltNuDzXK8rYge0SqLCMbFaKG-H1xDvF9pCrpuUO bPdl9JwWQbLuywrMg1gM_Q3wI901eDvlyAiJ66a0d8uMnxF3JPkFPkPWayk&_hsmi=326414365&utm_ content=326414365&utm_source=hs_automation
8. State of Green. 10 July 2018. “Denmark expands its deposit and return system to increase recycling.” Accessed 7 February 2025 from https://stateofgreen.com/en/news/denmark-expands-its-deposit-and-returnsystem-to-increase-recycling/#:~:text=The%20expansion%20is%20expected%20to,collected%20by%20 the%20deposit%20system.
9. Https://www.mdpi.com/2071-1050/14/19/11863/htm
10. Reloop. May 2024. “Fact sheet: Deposit return systems – How they perform.” Accessed 4 November 2024 from https://www.reloopplatform.org/resources/deposit-return-systems-how-they-perform/
11. Reloop. May 2024. “Fact sheet: Deposit return systems – How they perform.” Accessed 4 November 2024 from https://www.reloopplatform.org/resources/deposit-return-systems-how-they-perform/
12. “Increased deposit on beverage packaging in Sweden 2025.” Recycling Magazine. Accessed 21 January 2025 from https://www.recycling-magazine.com/2025/01/15/increased-deposit-on-beverage-packaging-insweden-2025/
Australia could will see another 20.2 billion containers littered or landfilled if the refund rates stays the same. Image: Pinglabel/shutterstock.com
potential.
Getting onboard with product stewardship schemes
(Continued from the front cover)
SHE said that ResiLoop encourages suppliers that are part of the scheme to think about the upfront design of their products so they can be better prepared to offer products that have a longer life and can be recycled properly.
“A major part of our funding goes into investment for R&D work to try and build that capacity and capability of recycling here in Australia,” she said.
One of the key challenges for the flooring industry is that a lot of the product is imported, so it is hard to have a producer responsibility if the manufacturer is not based in the country.
Meanwhile, Kent said Seamless has spent a lot of time in consultations,
workshops, and meetings with all of the stakeholders including talking to recyclers, reuse operators and brands to understand the challenges and opportunities across the supply chain when it comes to solving for the problem of textile waste. Utilising a grant from the federal government, Seamless was able to do a deep dive into global best practices around the world for the disposal of textiles and build a scheme that would fit what was needed in Australia. It allowed them to see how the flow of material goes from the reuse sector through to the recycling sector.
Seamless has also created a funding model where brands pay $0.04 per garment, which will help fund programs to “incentivise clothing design that is
more durable and recyclable, foster new circular business models, close the material loop and expand clothing collection, sorting and recycling”, according to the Australian Fashion Council’s website.
“On July 1, 2024, we commenced our operations, and we had 69 brands standing proudly with us,” said Kent. “We’ve welcomed many more since then. We’re really pleased with the uptake, and we’ve had strong encouragement from the minister, Tanya Plibersek, which has helped the momentum of the membership.”
There are four priority areas where the funding will be going, one being circular design. Kent said that means keeping clothing at its highest use for
Upfront
as long as possible. She also pointed out that, currently, there’s no national system for the collection and sorting of unwearable clothes.
“We all know that when we do our spring clean, we have the bag that goes to St Vinnies or the Salvos, but we also have the pile of stuff we don’t know what to do with,” she said.
Another priority is citizen behaviour. Kent said it’s not just about the point of consumption; it’s about the decisions that are being made before a piece of clothing has been purchased.
“Do I need it? Have I already got it? Could I get this another way without buying it into my wardrobe?” said Kent. “Then, once you’ve purchased it, how long do you have it for? And then, at the
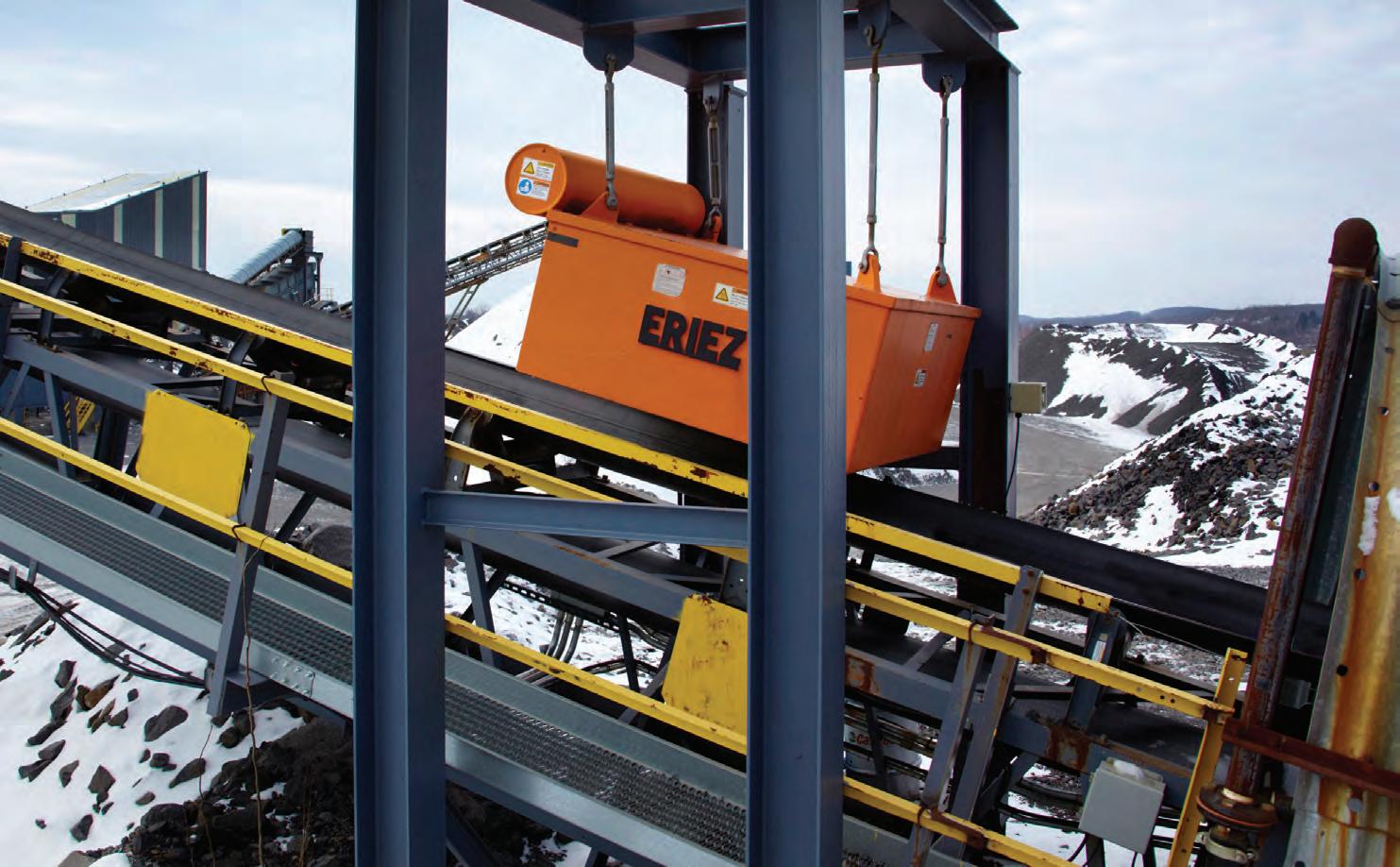

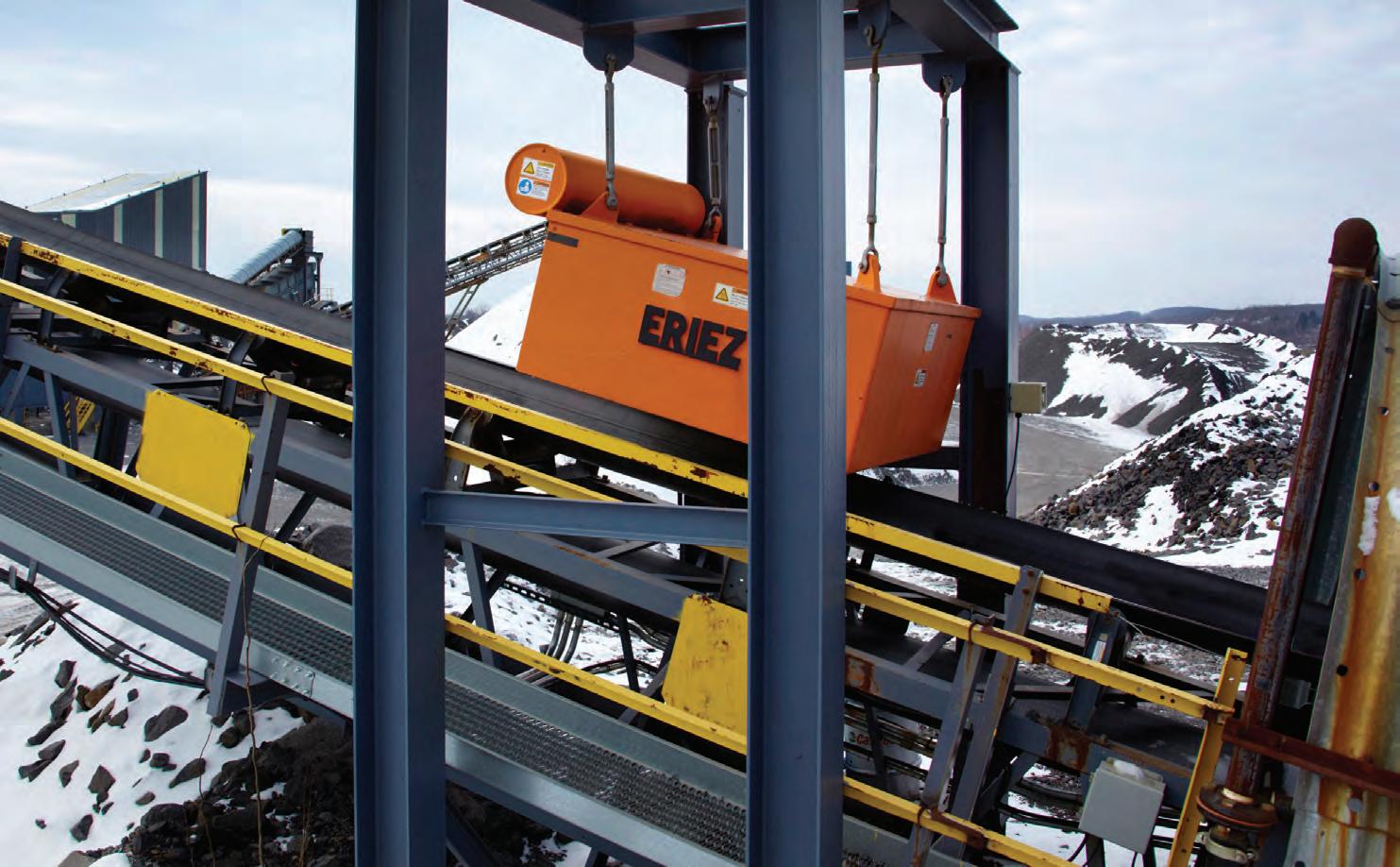

in the Best Tramp Metal Protection
With more than 80 years of magnetic expertise behind them, Eriez Suspended Electromagnets offer peace of mind, knowing your processes are protected against tramp metal. Eriez. Always the Right Choice.

end of its life, how do you dispose of that thoughtfully and purposefully.”
Toumbourou reminded the audience that one of the priorities of her organisation was to educate the public and industry that recycling should come at the end of other circular priorities such as avoidance, repair and reuse.
She said ACOR has a keen eye on trying to make sure that product stewardship schemes ensure the products they are attached to reach their end of use and deliver real recycling outcomes. And it hasn’t always been smooth sailing, she said.
“Collecting is not recycling,” she said. “In order to recycle, you need three key elements. You need a collection system that is scaled and accessible and is able to collect material that might have an inherent value. You need processing capability that can make that material into a product that can reach a market. Then you must have a market for it.”
She said it is a priority for stewardship schemes to work hand-in-hand with the recycling sector to make sure these elements are met. Toumbourou said there have been significant grants via the Australian Government with several millions of dollars dedicated to industry-
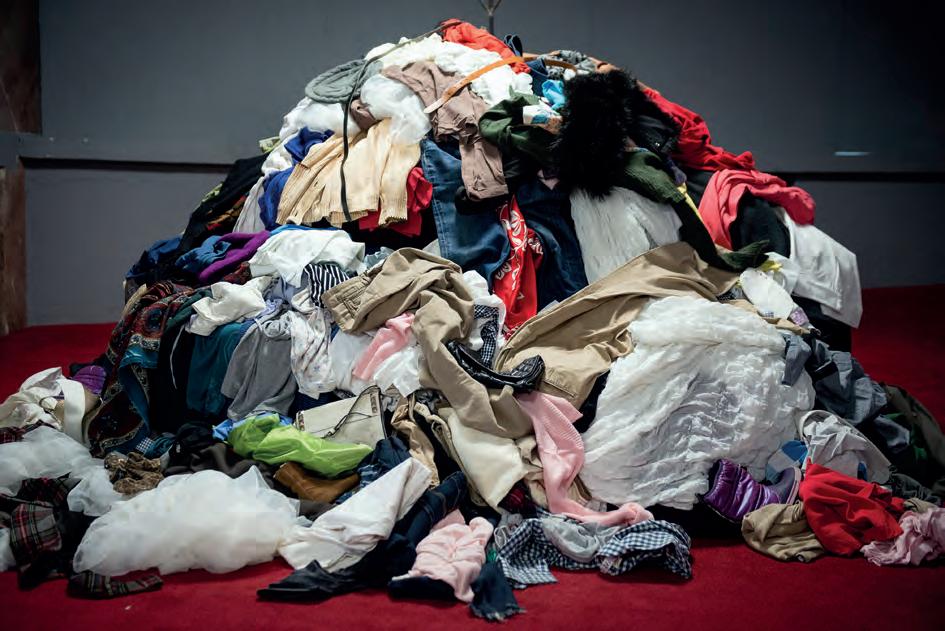
“Collecting is not recycling. In order to recycle, you need three key elements. You need a collection system that is scaled and accessible and is able to collect material that might have an inherent value. You need processing capability that can make that material into a product that can reach a market. Then you must have a market for it.”
Struggling to recycle your plastics?
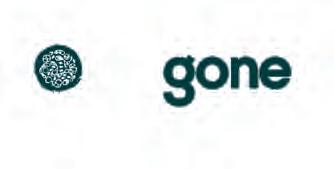
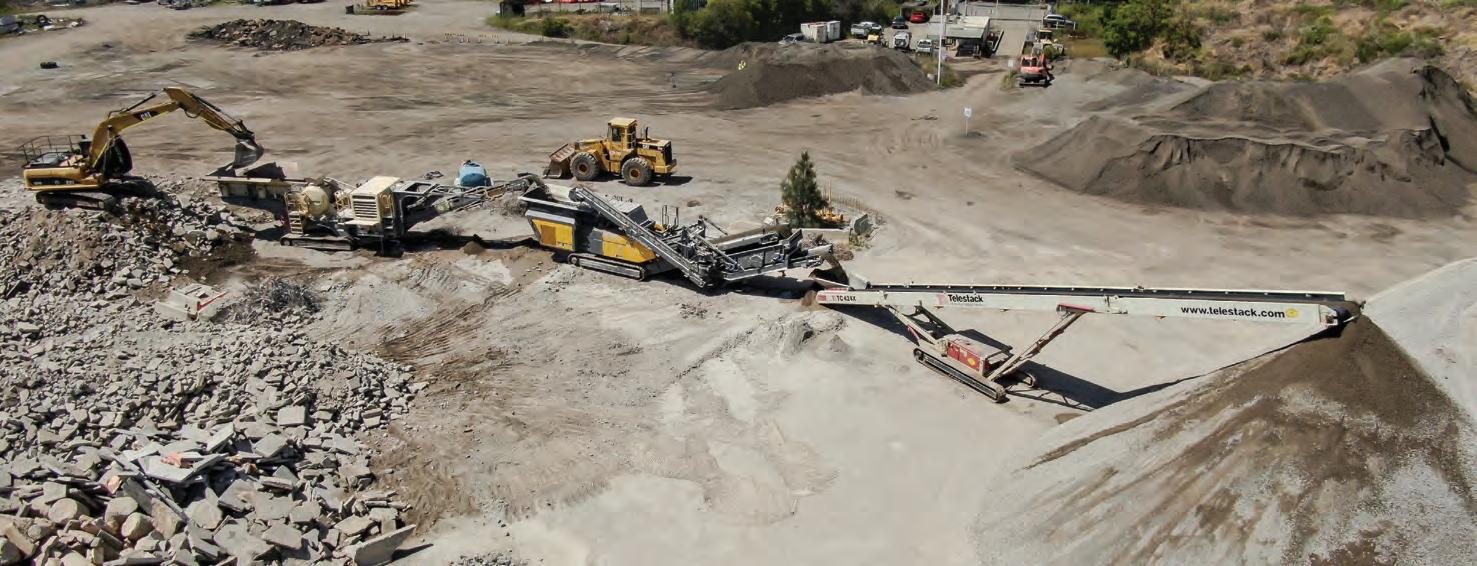
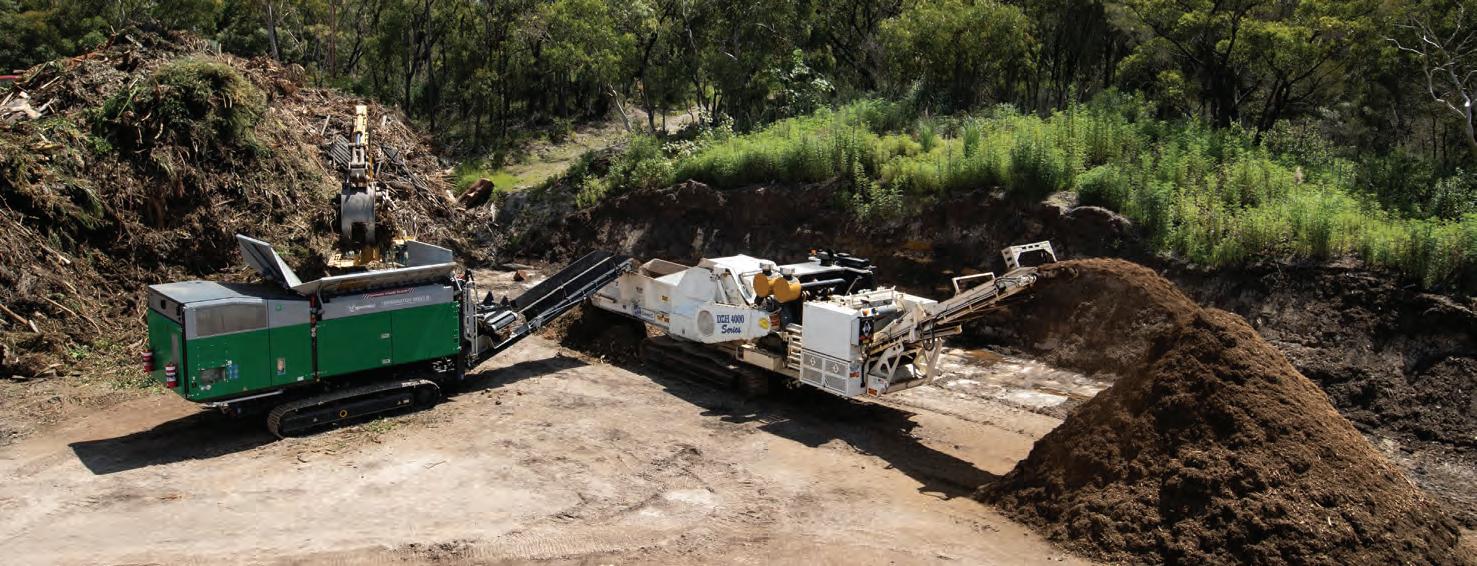
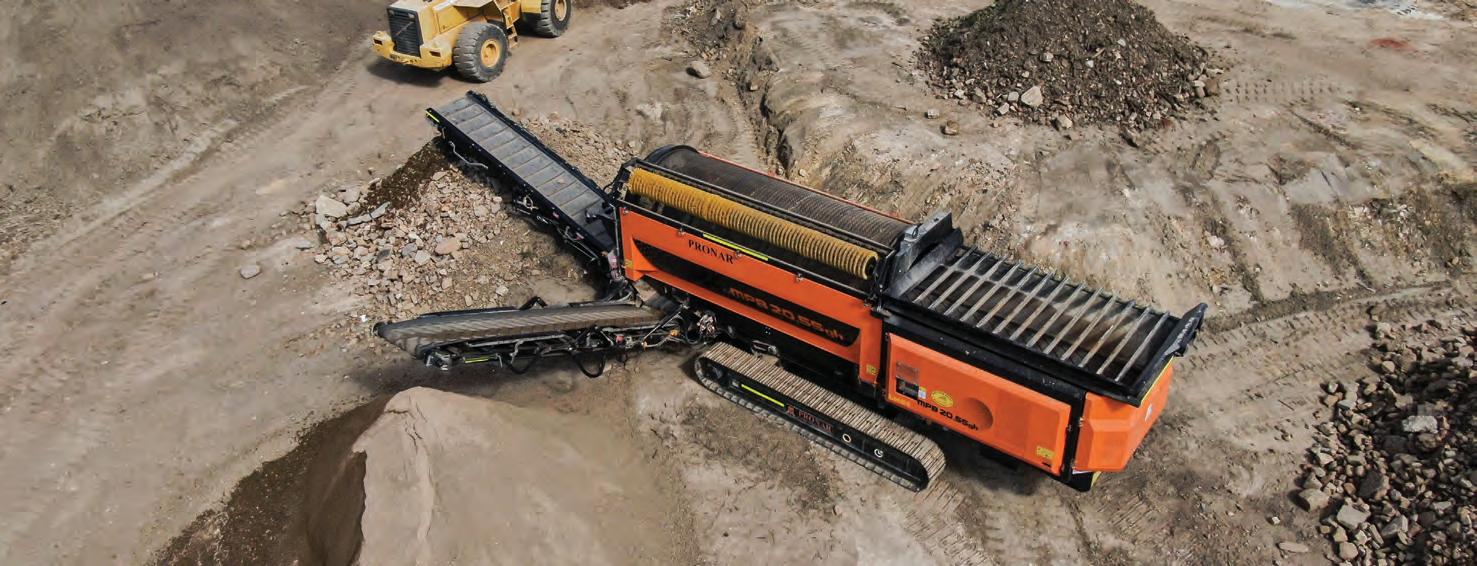

Seamless has some major fashion brands onboard as they look for ESG kudos. Image: ventura/shutterstock.com
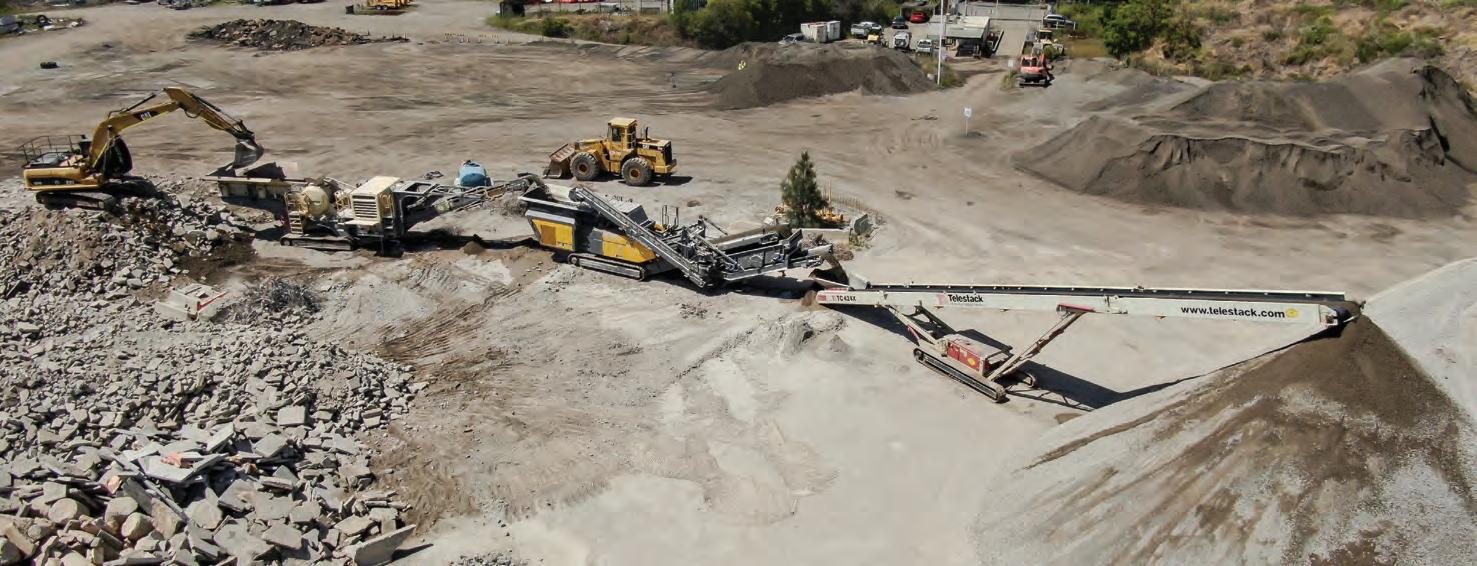
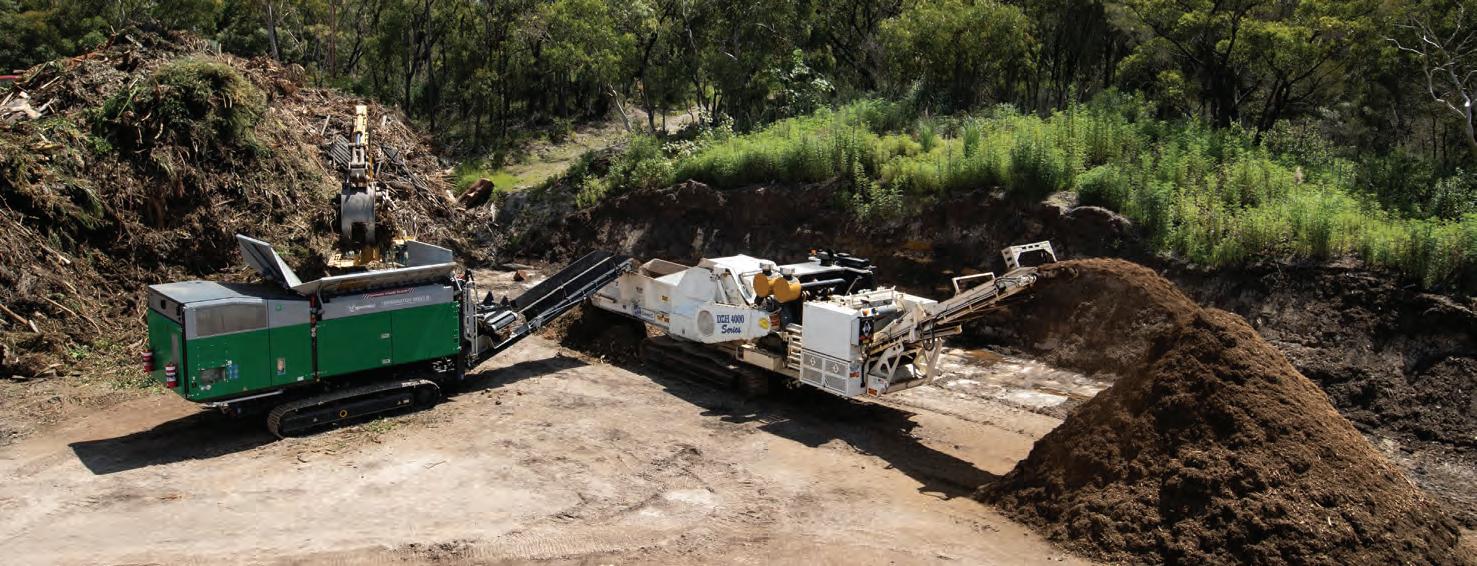
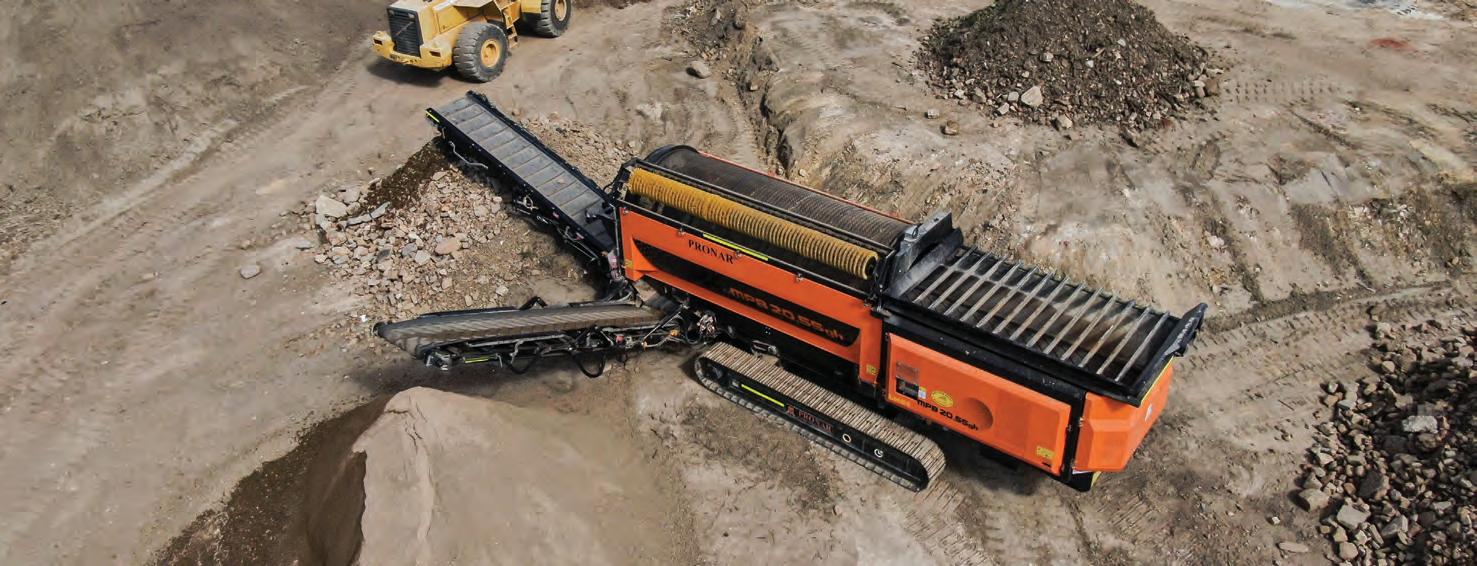
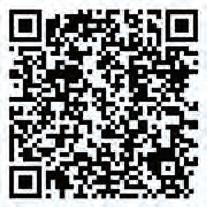
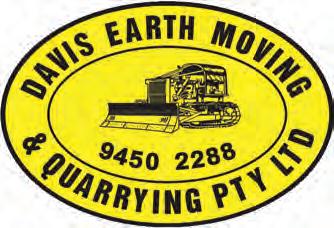
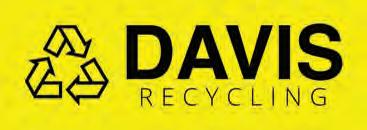

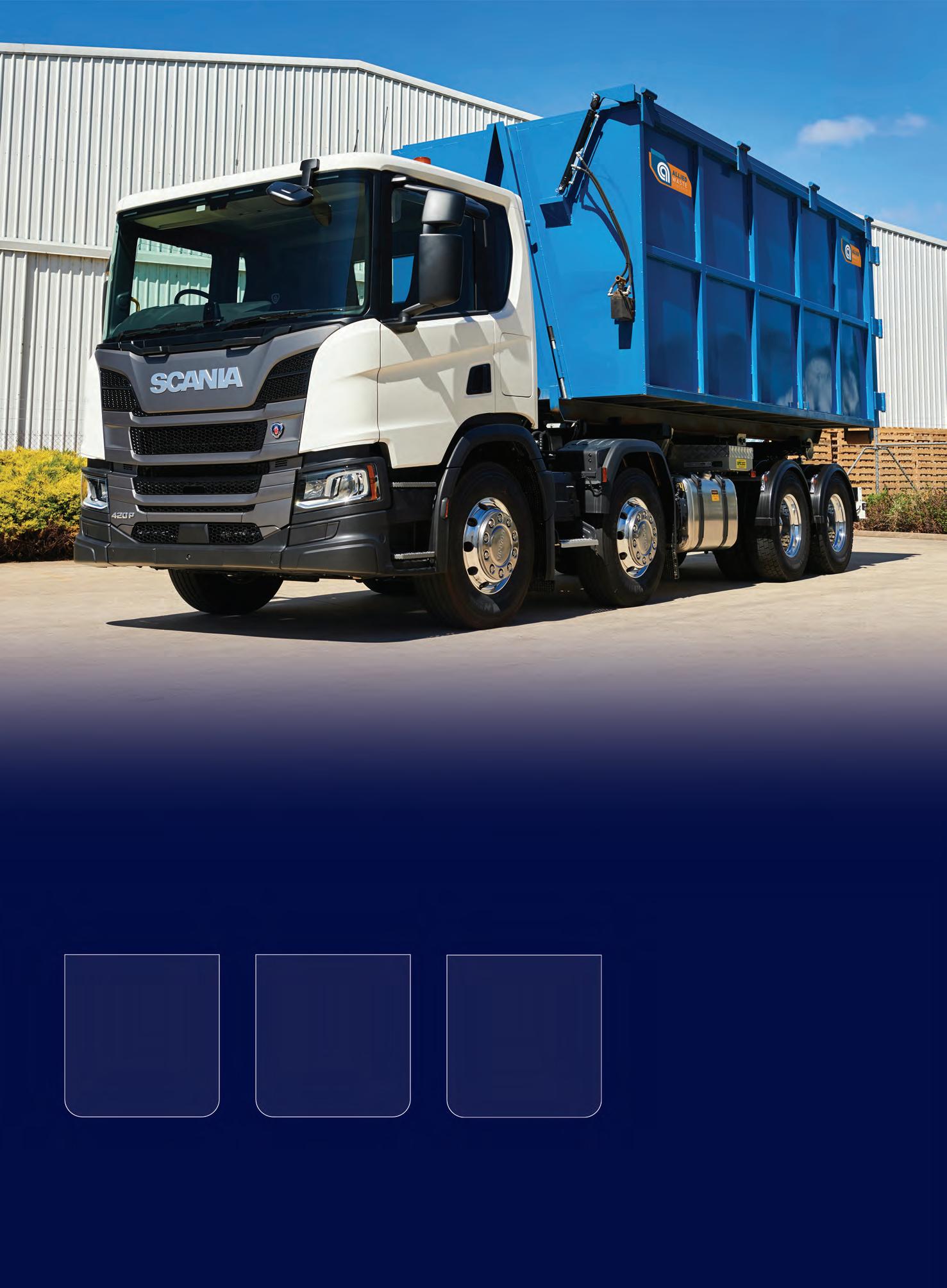
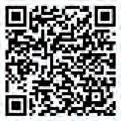
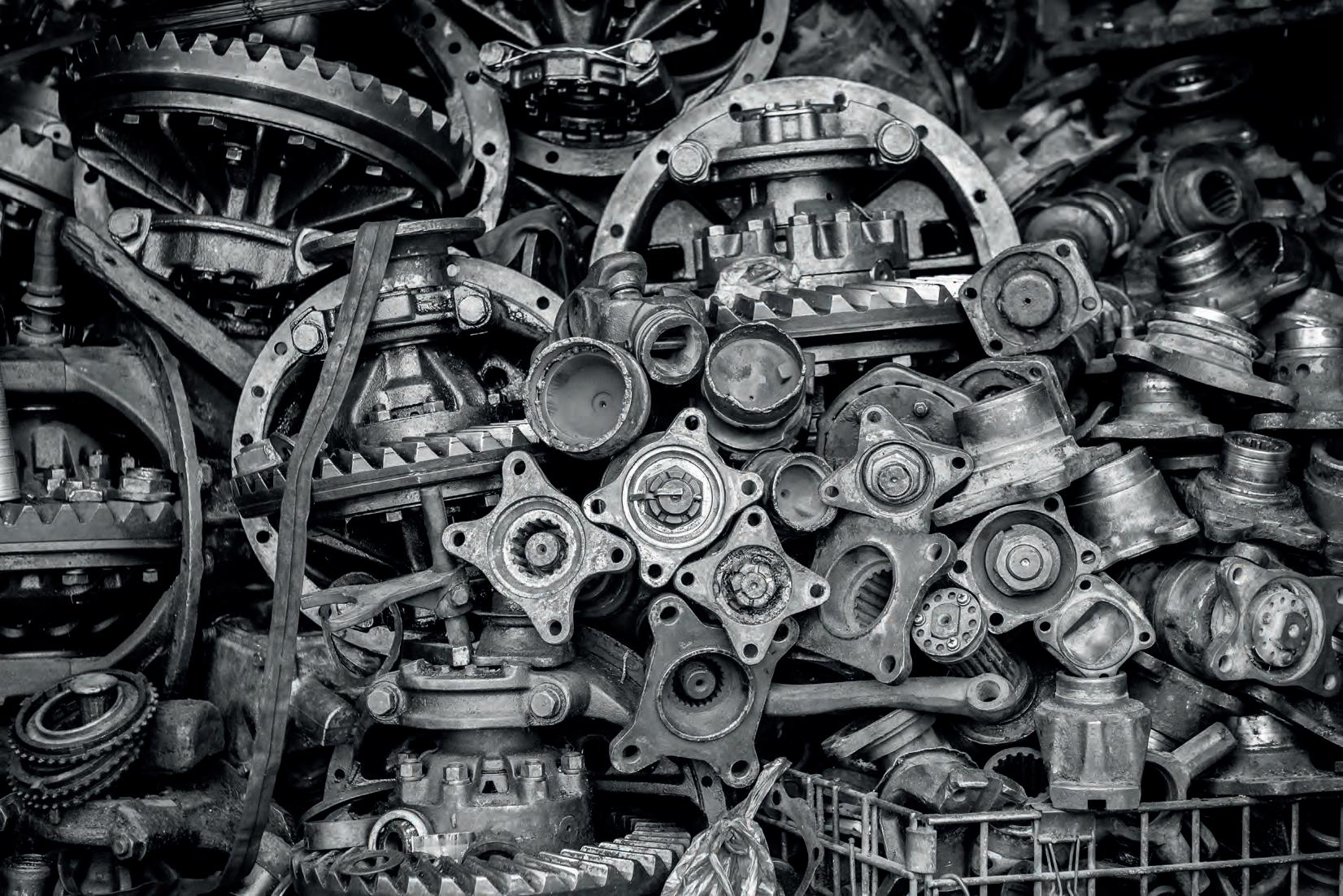
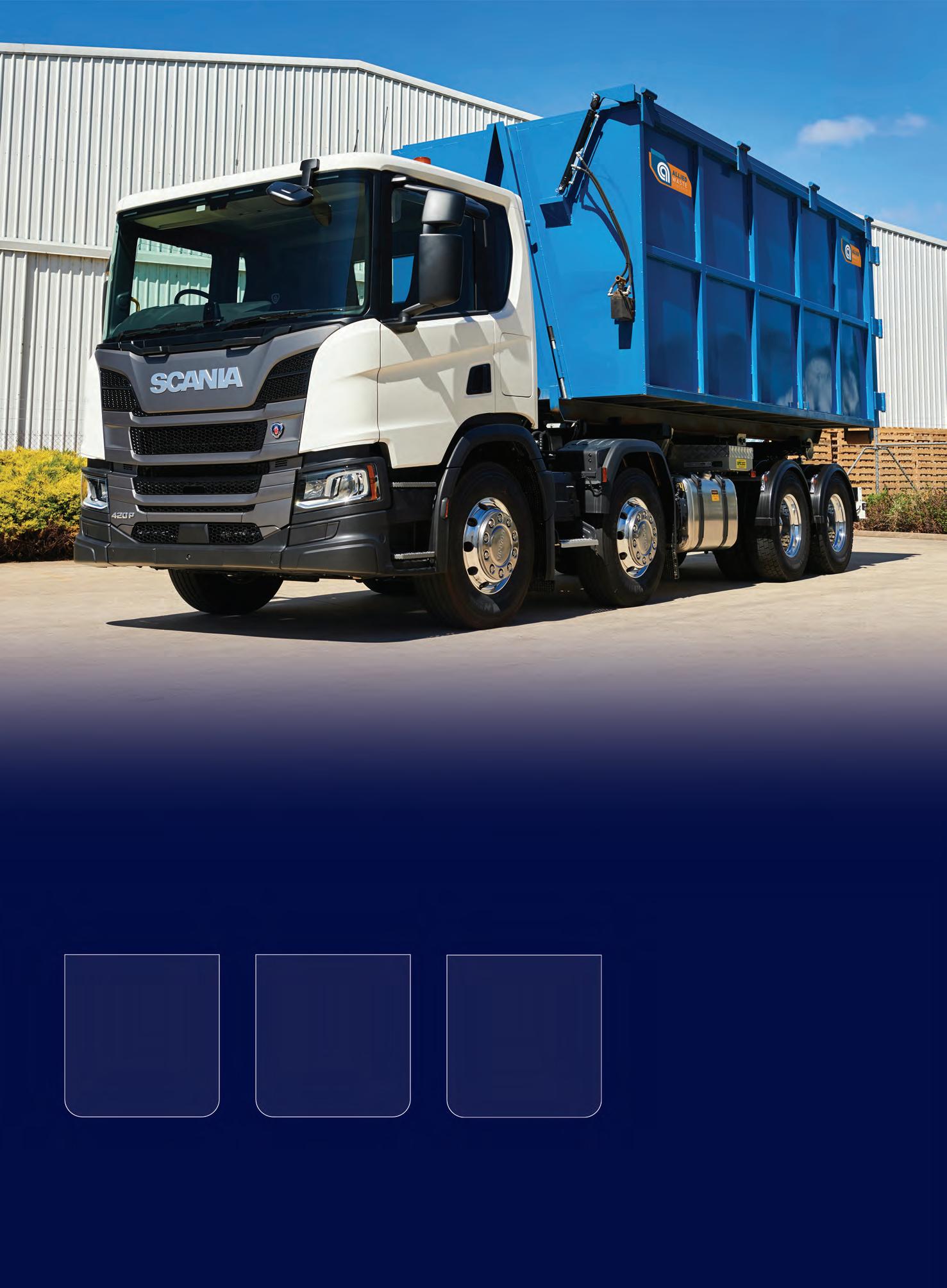
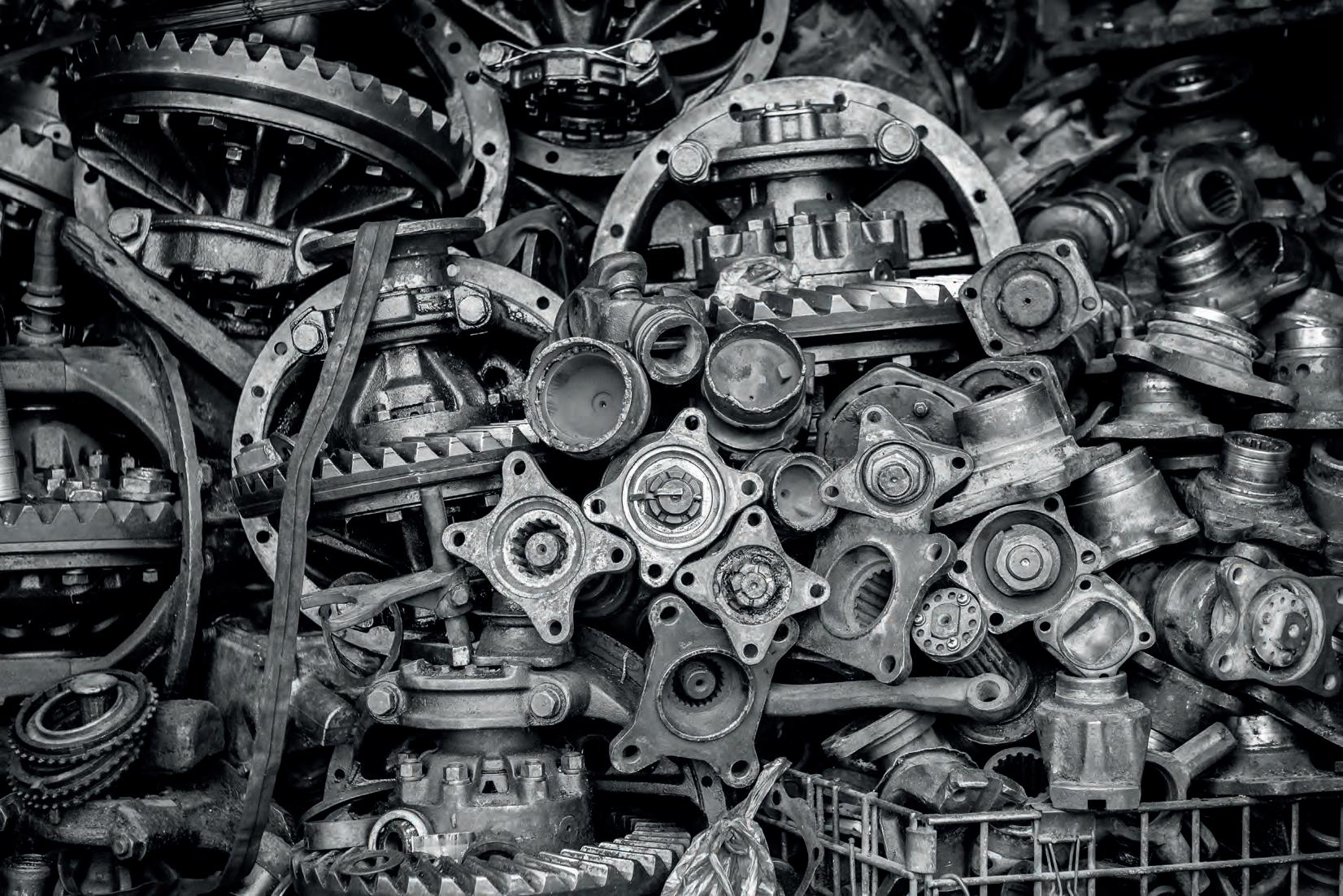
led schemes. However, she feels that currently, they might not be sufficiently meeting community expectations as they relate to the outcomes.
“It’s a priority to make sure that those schemes are taking a genuine supply chain focus, and they’re working genuinely in partnership with the whole supply chain, and that includes the part of the supply chain that sits – not just at the end of use – but at the beginning of the next supply chain, which is the recycling sector,” she said.
Local investment
All panelists agreed that there needed to be more investment in Australian infrastructure to process the various product stewardship’s waste streams. Macmillan said one of the reasons ResiLoop came into being was because the leftover flooring products could no longer be sent back to their (mostly) European manufacturers for more reprocessing.
“That door shut, and that was what brought the players around the table to decide that we were going to have to have some solutions locally to deal with our waste stream,” she said. “We quickly realised that the only way we would get scale was if we collaborated to make this work. Doing it individually wasn’t going to cut it. We do need local solutions.
“We haven’t taken off the table that we might end up having to – if we’re really successful in collecting and processing – export some of that
material back to those plants in Europe, the US and Asia as a valuable resource.”
A question asked of the panel by an audience member inquired as to whether harmonisation was key to making sure product stewardship schemes could be run smoothly, especially when there could be multiple stewardship schemes involving one stream. Cars were given as an example.
“As we see more stewardship approaches start to emerge, it makes more sense to look for the opportunities for efficiency and leverage,” said Genever.
“If we end up with a scheme for tyres and a scheme for car seats and a scheme for seat belts, you do start to think, ‘Okay, well, maybe it’s now time for the automated industry to package this up,’ and therefore have something that’s consolidated.”
Being truly circular
Kent was keen to point out that while a lot of industries, including textiles, have come a long way, there is still a way to go. She stated that when it comes to clothing, some of the recycled content could be higher.
“It’s about paying attention to what the purpose of that product is and then making the best decisions that will lend itself to being durable and washable and wearable 100 times over,” she said.
“Recycled content is not putting fibre into a T-shirt, it’s putting plastic bottles into a T-shirt. When you see a T-shirt
William LeMessurier is convicted of and penalised for the commission of a hazardous waste offence at Warwick Farm William LeMessurier was prosecuted by the Environment Protection Authority (“EPA”) for one offence relating to his actions as the former directors of MRI (Aust) Pty Ltd for the unlawful storage of hazardous waste at a premises at Warwick Farm. Approximately 712 tonnes of waste material was stored at the site, including crushed cathode ray tube glass and waste batteries of various types including lead-acid, nickel-cadmium, lithiumion, lithium-polymer, alkaline and nickel-metal hydride batteries. Jackson did not hold an environment protection licence permitting the storing of hazardous waste at the site. The storage of such hazardous waste carries an increased risk of fire due to the nature of the materials. Were a fire to break out, it could result in risk to human safety, risk to neighbouring properties, and risk to the environment.
On 13 December 2024 the Land and Environment Court of NSW (“the LEC”) convicted LeMessurier for an offence for use of a place as a waste facility without lawful authority and ordered him to pay a monetary penalty in the sum of $40,000, with 50% being paid to the EPA as a moiety, to pay the EPA’s investigation costs in the amount of $14,399 and its professional costs as agreed or assessed, and to publish this notice. The LEC’s judgment may be accessed at https://www.caselaw.nsw.gov.au/ decision/193b94b7069146c933e47a98.
This notice was placed by order of the LEC.”
Bruce Jackson is convicted of and penalised for the commission of a hazardous waste offence at Warwick Farm
Bruce Jackson was prosecuted by the Environment Protection Authority (“EPA”) for one offence relating to his actions as the former directors of MRI (Aust) Pty Ltd for the unlawful storage of hazardous waste at a premises at Warwick Farm. Approximately 712 tonnes of waste material was stored at the site, including crushed cathode ray tube glass and waste batteries of various types including lead-acid, nickel-cadmium, lithiumion, lithium-polymer, alkaline and nickel-metal hydride batteries. Jackson did not hold an environment protection licence permitting the storing of hazardous waste at the site. The storage of such hazardous waste carries an increased risk of fire due to the nature of the materials. Were a fire to break out, it could result in risk to human safety, risk to neighbouring properties, and risk to the environment.
On 13 December 2024 the Land and Environment Court of NSW (“the LEC”) convicted Jackson for an offence for use of a place as a waste facility without lawful authority and ordered him to pay a monetary penalty in the sum of $40,000, with 50% being paid to the EPA as a moiety, to pay the EPA’s investigation costs in the amount of $14,399 and its professional costs as agreed or assessed, and to publish this notice. The LEC’s judgment may be accessed at https://www.caselaw.nsw.gov.au/ decision/193b94b7069146c933e47a98.
This notice was placed by order of the LEC.
Should old car parts become one product stewardship scheme instead of being splintered into different waste streams?
Image: Nixx photography/shutterstock.com
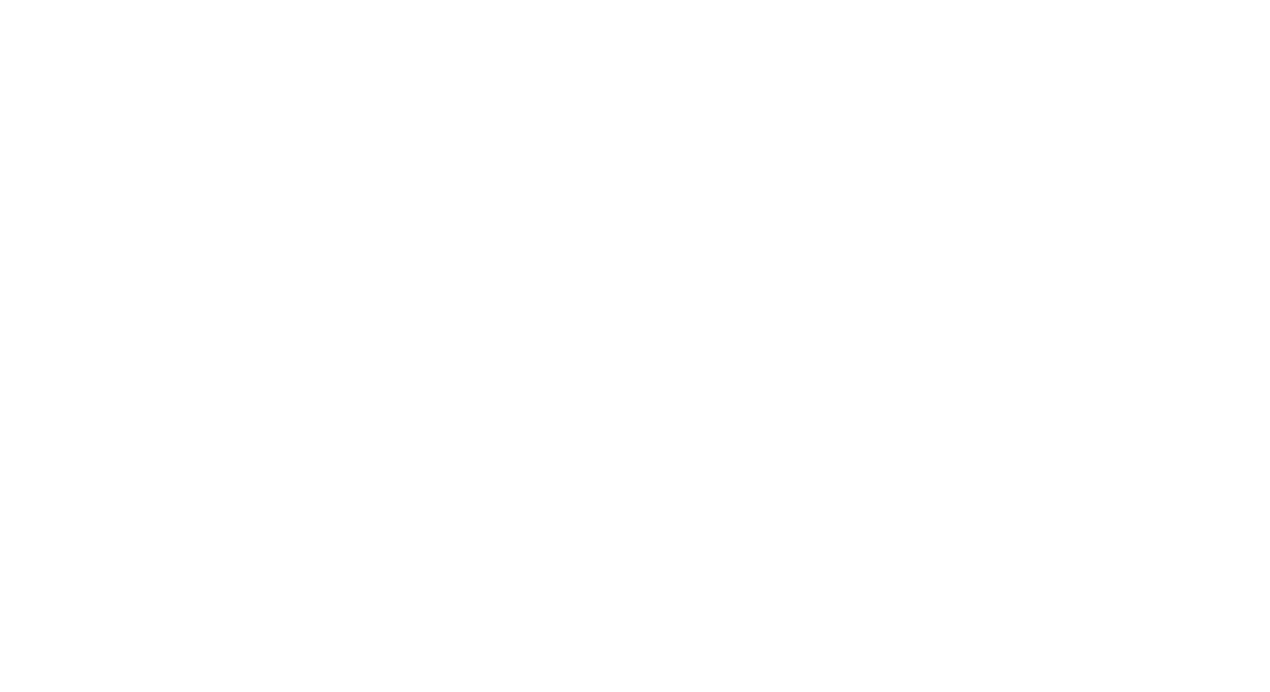
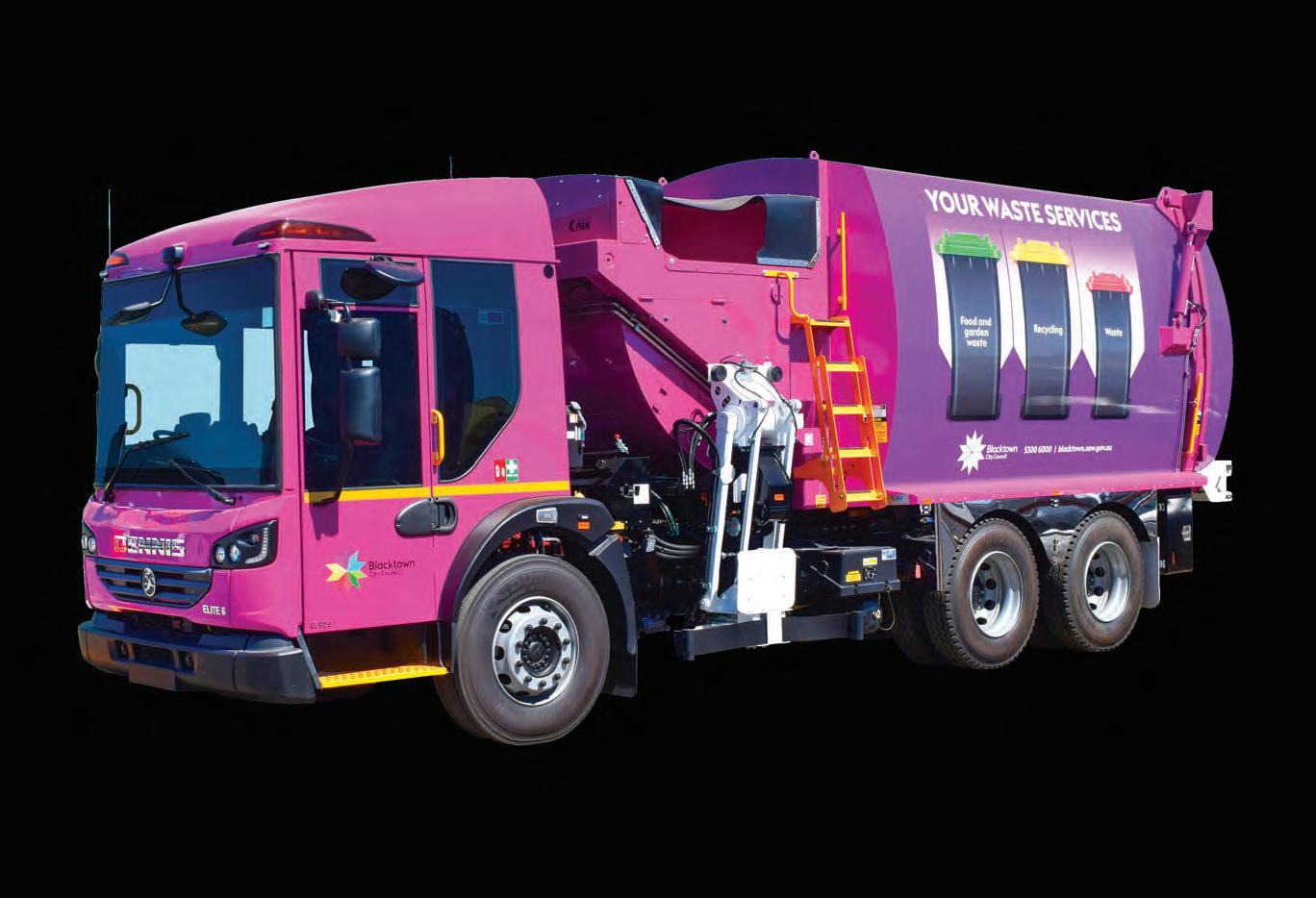
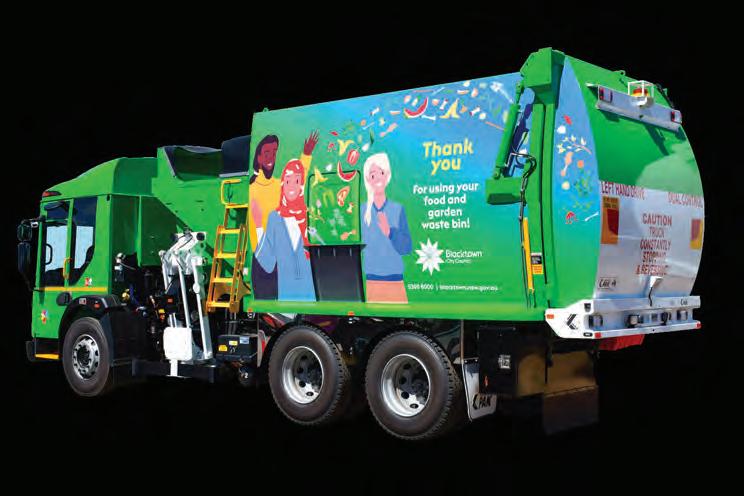
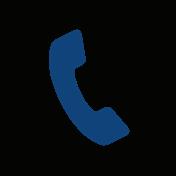

made up of up to 30 per cent recycled content, it’s most likely plastic bottles that are going into that T-shirt, which is okay, but I think we can do better.”
She also stated that, in recent times, Seamless has been building up
an understanding of its membership base from an aggregate view. She said members are interested in circular design and circular business models because those are the areas they can control, enabling them to make decisions that
can affect and impact those at the coalface of the industry.
Bringing everyone onboard
Finally, Macmillan talked about how various schemes are trying to bring
more companies on board. Currently, the flooring scheme has a lot of major players as part of the scheme, but it is voluntary.
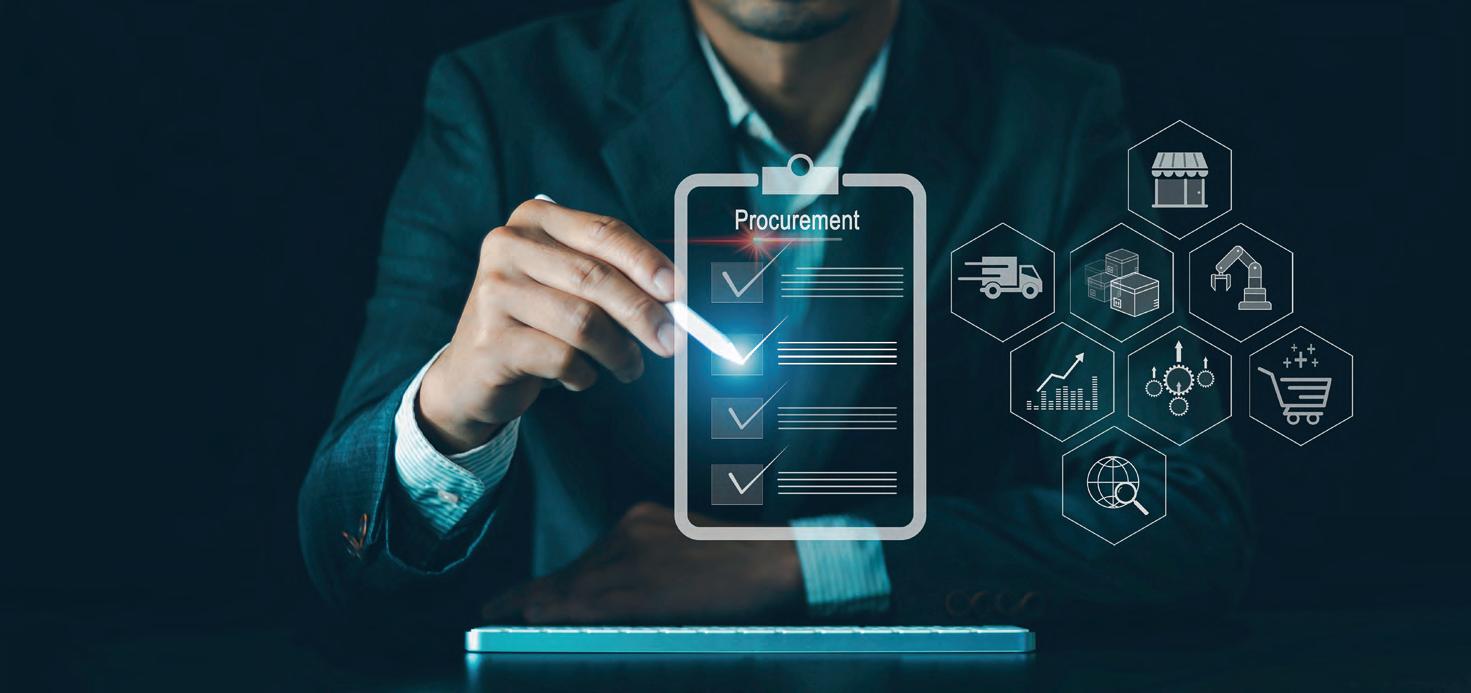
“We’re not mandated, and it’s been a voluntary initiative of a core group of major players,” she said. “They are global brand names that do tend to have very strong ESG focus, particularly the European companies. They’ve come into it with the right mindset and the commitment to then make it happen.”
She said a grant from the federal government helped lay the foundation for the scheme, which allowed the instigators to connect with the whole value chain and get people around the table in order to bring other stakeholders on board.
“We were quite surprised at how much interest there was from those parts of the value chain to engage in the process,” she said. “Our members are probably about 30 per cent of the market, so we’ve still got quite a long way to go. We have found that some of the bigger players are resistant to that collaborative approach. For us now, it’s about trying to build that compelling business case by trying to advocate with other stakeholders for incentives.”
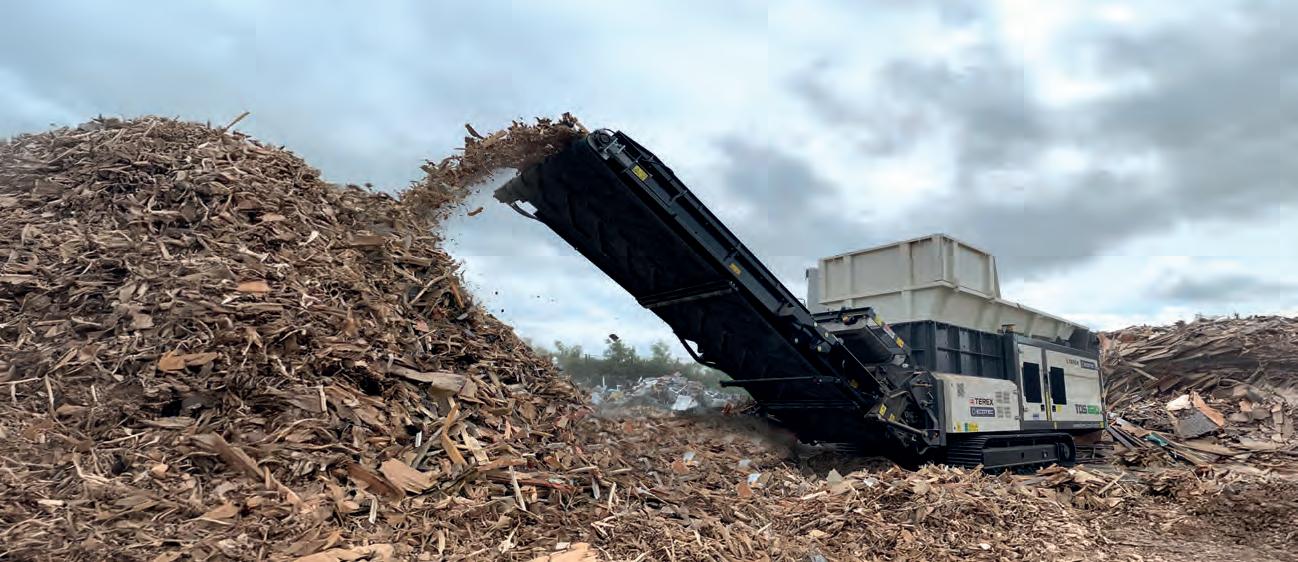
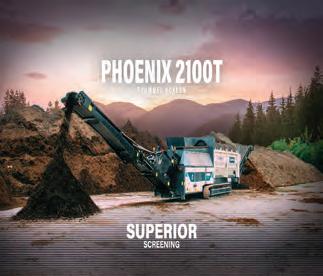
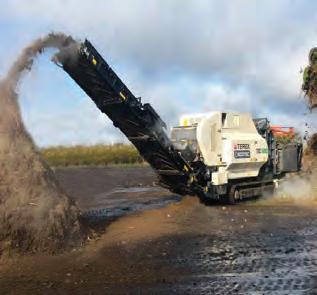
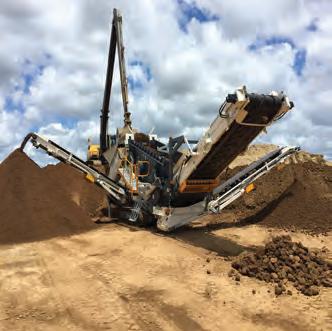
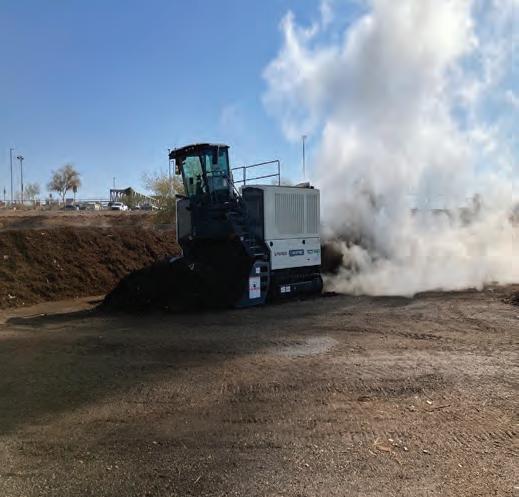
SLOW SPEED SHREDDER
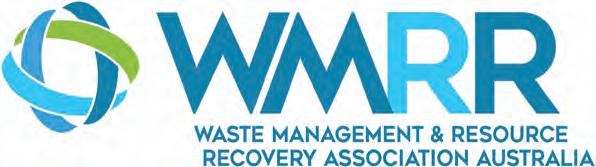
From the CEO’s desk

Finally some good news, but still plenty to do
After what seems like months of false starts and a general lack of action to move towards our often-cited Net Zero and Resource Recovery targets, it was pleasing to end 2024 with a little bit of good news; the increase in the national recovery rate of 3 per cent (about 2 million tonnes) in National Waste and Resource
Environment Ministers will meet for the second time this year on 7 December, following the first 2018 Meeting of Environment Ministers (MEM) in April, which was in part a response to the import restrictions driven by China’s National Sword Policy and the effects this policy has had across the Australian waste and resource recovery (WARR) industry. Key decisions derived from the April MEM include:
In December 2024 we watched the Environment Minister’s Meeting pass us by without even a whimper. If not for the NSW Environment Minister’s commitment to act on batteries, we would wonder what the meeting discussed. While I appreciate that an updated National Waste Action Plan (note the word ‘action’ but the lack of actions within) and a Circular Economy Framework were adopted (Framework but no action in this one either), their lack of enforceable actions (let alone penalties) to achieve the 2030 targets or apparent desire to achieve these was bitterly disappointing.
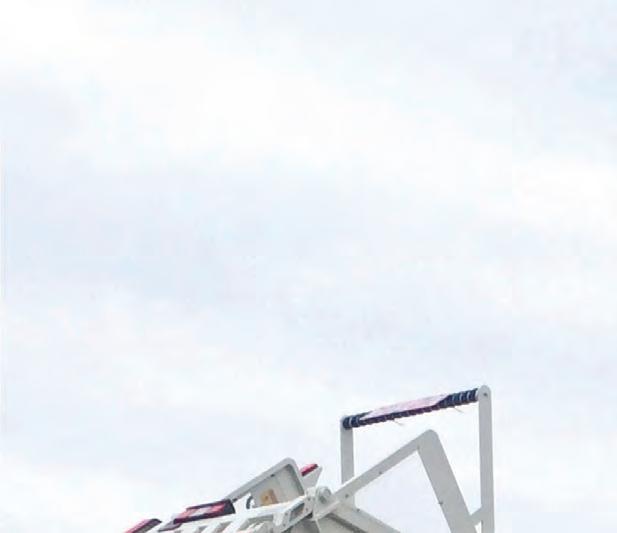
•Reducing waste generation, endorsing a target of 100% of Australian packaging being recyclable, compostable or reusable by 2025, and developing targets for recycled content in packaging.
• Increasing Australia’s domestic recycling capacity.
• Increasing the demand for recycled products.
• Exploring opportunities to advance waste-to-energy and waste-to-biofuels.
It acknowledged that the hard work of so many in our industry is paying off, with target areas such as organics increasing by 1.4 per cent. This demonstrates that with policy, markets and targeted funding, there can be change. And while the total amount of waste generated increased by about 1 million tonnes, there was a slight decrease per capita – another (small) positive.
•Updating the 2009 Waste Strategy by year end, which will include circular economy principles.
However, I think we all know that despite this good news, it is nowhere near enough of a shift to put Australia on the necessary sustainable path required to hit the national 2030 targets.
It is time to take stock and examine what has been achieved since these decisions were announced. Now, seven (7) months may not seem like a long time, however in that time we have seen further markets close (Malaysia, Indonesia, Vietnam) and if you are an operator under continued financial stress, seven (7) months could make or break you.
As we kick off 2025, you might be forgiven for wondering how we got here. Since China’s National Sword thrust us into the national spotlight (and we saw for the first time since Peter Garrett was Environment Minister real discourse about our essential industry at the Federal level), we appeared to be on a strong trajectory for continued action to create both the economic and environmental settings required for the planet
I think we would all agree that the current Federal government started with a positive energy – a clear stated commitment to legislative action to reduce Green House Gas (GhG) Emissions to 43 per cent below 2005 levels by 2030 and action on the Safeguard Mechanism to assist. Coupled with this we saw commitments to protect 30 per cent of Australia’s land and seas by 2030, create a nature repair market and establish an independent EPA.
Following the April MEM, we have had three (3) states step in with varying degrees of financial assistance for industry (councils and operators). This should be expected considering almost all states (except Queensland and Tasmania) have access to significant waste levy income each year. On the eastern seaboard, Victoria has approximately $600 million in waste levy reserves in the Sustainability Fund and NSW raises more than $700 million per annum from the waste levy. There is certainly no lack of funds that can be reinvested into our essential industry.
We even had a new Environment Minister saying all the right things – that she was “prepared to regulate” and understood the importance of focusing on the system. For a moment there we had a commitment to create mandatory packaging design standards by 2025 and regulate packaging as well as solar panels and electrical equipment – all of which create problematic waste streams for our industry and the community at large.
Funding helps but as we know, the money goes a much longer way with Government support and leadership, as well as appropriate policy levers.
VICTORIA
The stage was literally set for our industry to succeed: reduce emissions, reduce reliance on virgin materials and finally, it appeared the need for regulation was understood. And this wasn’t for the sake of it, but to create the necessary level playing field and rules of engagement that all in the supply chain require to thrive.
Victoria has arguably been the most active and earnest in supporting the industry post-China, with two (2) relief packages announced to support the recycling industry, valued at a total of $37 million. The Victorian Government has also gone above and beyond all others states by announcing it would take a leadership role in creating market demand for recycled products.
SOUTH AUSTRALIA
I vividly remember attending a speech by Minister Chris Bowen when he was appointed Minister for Energy and Climate Change, where he lamented the lack of action of the previous government and reminded us that there were only 90 months until 2030. Well, here we are with only 60 remaining and what do we have and what’s happened? Not much I am afraid.
Government announced a $12.4 million support package comprising $2 million of additional expenditure, $5 million additional funding for a loan scheme, together with targeted funding from the Green Industries SA budget. The Government has also offered grants for recycling infrastructure.
NEW SOUTH WALES
At first glance, New South Wales’ eye-watering $47 million recycling support package was heralded as the spark of hope industry needed. However, on closer inspection, the bulk of this package that was funded via the Waste Less, Recycle More initiative and therefore the waste levy, was not new, making it very difficult for stakeholders, including local government, to utilise the funds as they were already committed to other activities. Some of the criteria proposed by the NSW EPA also made it challenging for industry to apply to these grants. On the plus side, efforts are being made by the NSW Government to stimulate demand for recycled content through the intergovernmental agency working groups that have been established, though no tangible increase in demand or facilities have developed… Yet.
QUEENSLAND
industry however the Queensland Government has embarked on the development of a waste management strategy underpinned by a waste disposal levy to increase recycling and recovery and create new jobs. The State will re-introduce a $70/ tonne landfill levy in March 2019. There are also strong attempts to use policy levers (levy discounts and exemptions) to incentivise the use of recycled material and make it cost competitive with virgin material. However, little has been done to establish new markets and Government has not taken the lead in the procurement of recycled material. There are grants available for resource recovery operations in Queensland although no monies have been allocated to assist in 2018. This is troubling as Queensland rolled out its Container Refund Scheme on 1 November, which will likely impact the cost and revenue models of the State’s MRFs – as we have seen most recently in NSW.
These documents did however quietly move some of these targets. For example, we lost the target date for eliminating problematic plastics and moved out the target for ‘creating a circular economy’. When you look at the data in the National Waste and Resource Recovery Report and see that the recovery rate of plastics is now at 12.5 per cent (a decrease of 0.4 per cent) yet the amount of plastic waste generated has increased by 14.5 per cent (11.6 per cent per capita) – you can possibly understand politically why these changes occurred. But given the desire for a high ambition for plastics globally, why can’t we have the same ambition at home?
WESTERN AUSTRALIA
The Western Australian Government set up a Waste Taskforce in direct response to the China National Sword. As part of this announcement, the State Government urged all local councils to begin the utilisation of a three (3)-bin system - red for general waste, yellow for recyclables and green for organic waste - over the coming years to reduce contamination. While this taskforce is a step in the right direction, we are yet to see any tangible results from it or any funding for industry. In October, the WA Waste Authority released its draft Waste Strategy to 2030, which comprises a comprehensive and detailed roadmap towards the State’s shared vision of becoming a sustainable, low-waste, circular economy.
COMMONWEALTH
In 30 months, what have we seen at a Federal level? In essence, not a lot. We have seen a continuation of the previous government’s agenda, with the continued application of the export restrictions, and the rollout of the Recycling Modernisation Fund (RMF). Yes, we are grateful that this funding was not halted. However, the promise of creating local Australian demand and onshore markets to date has been avoided. And while we would much rather remanufacture in Australia, the lack of sufficient market demand for recycled products and the lack of both policy and regulatory action in this space means that we do need to continue to tap into the global market and export materials (in particular plastics) that can be recycled. The systems thinking does not appear to have arrived in practice as yet, I’m afraid.
It was one area that desperately required attention, given it is at the forefront of every household’s thinking and behaviour, and the material most impacted by the export restrictions is packaging. This is one area wholly (in theory) in the Federal government’s area of responsibility with the Used Packaging NEPM, and the independent review of the scheme in 2021 makes it clear that it requires reform. However, we enter 2025 with APCO publicly stating that yet again it will be missing its targets (no problems as no consequences for that). There is no proposed reformed scheme, or even worse, no adopted mandatory design guidelines that will stimulate demand for local recycled materials on shore. Albeit it remains a ‘priority’ (but unlikely to be addressed before the Federal election I suspect).

Following the MEM in April, Australia now has a new Federal Environment Minister, Melissa Price, who in October reiterated to media MEM’s commitment to explore waste to energy as part of the solution to the impacts of China’s National Sword, which is troubling (EfW is not a solution to recycling). The Commonwealth has also backed the Australian Recycling Label and endorsed the National Packaging Targets developed by the Australian Packaging Covenant Organisation (APCO), which has to date, failed to incorporate industry feedback in the development of these targets. To the Commonwealth’s credit, there has been significant coordination in reviewing the National Waste Policy, with the Department of Environment bringing together industry players and States during the review process.
After all the talk of being ‘prepared to regulate’, we are heading towards the end of this term of government with none in sight, and very unlikely to have any prepared by the time a federal election is called. The one bright spot to possibly bookend the year with is the proposed review of the Recycling and Waste Reduction Act 2020, which is slated to occur in early 2025. This, if used well, must assist Australia in transitioning to a legislated future circular economy regulating the environmental performance of materials and products including imports, implementing clear design rules and labelling. It was also great to see the report of the Circular Economy Ministerial Advisory Group recommend this legislative approach and lay out what that could look like in their ‘Circular Advantage’ report released in December 2024, highlighting that we can have the tools to do this – we just need the political will.
The updated Policy will now go before Environment Ministers on 7 December. The Commonwealth can play a key role – one that goes beyond the development of the National Waste Policy. WMAA is supportive of the Federal Government maximising the levers it has, including taxation and importation powers, to maintain a strong, sustainable waste and resource recovery industry.
AHEAD OF MEM
2
Let’s hope 2025 is finally then the year of action that we all know we need.
There may be movement across Australia, with some states doing better than others, but the consensus is, progress is still taking way too long. It is evident that there are funds available in almost all States to assist with developing secondary manufacturing infrastructure, however the only way that this will really happen is if there is government leadership around mandating recycled content in Australia now, not later.
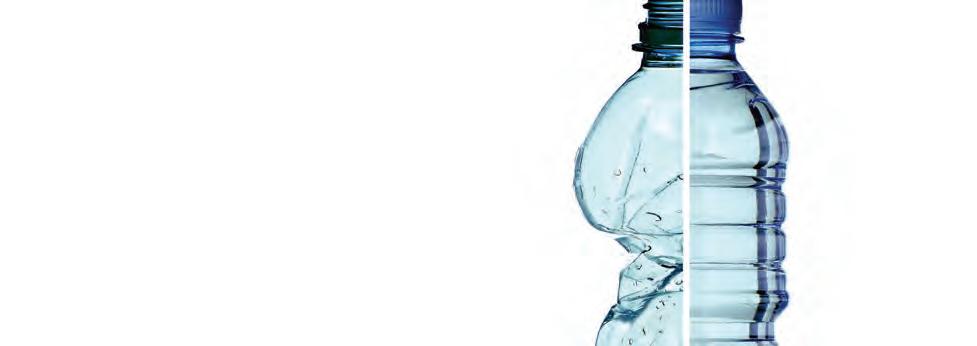
Unlike its neighbours, Queensland did not provide any financial
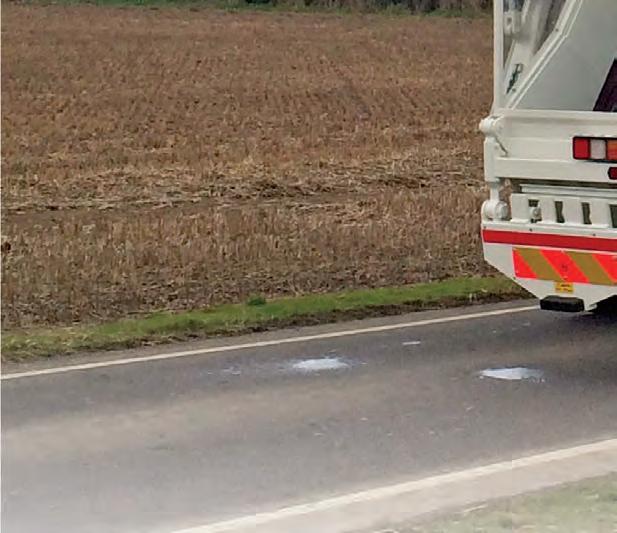
Voluntary schemes like the Used Packaging NEPM, under which APCO is auspiced, are not working. We have 1.6million tonnes of packaging waste in Australia, which needs to be used as an input back into packaging. Barriers to using recycled content in civil infrastructure must be identified and removed, and Government must lead in this field and prefer and purchase recycled material. A tax on virgin material should also be imposed as it is overseas. MEM must show strong leadership on this issue. Ministers have, since April, dealt directly with operators and councils that are under stress and we have a chance to create jobs and investment in Australia at a time when manufacturing is declining. Ministers have the opportunity to be leaders of today, not procrastinators – leaders of tomorrow and we are urging them to act and not just talk in December.
Gayle Sloan Chief Executive Officer
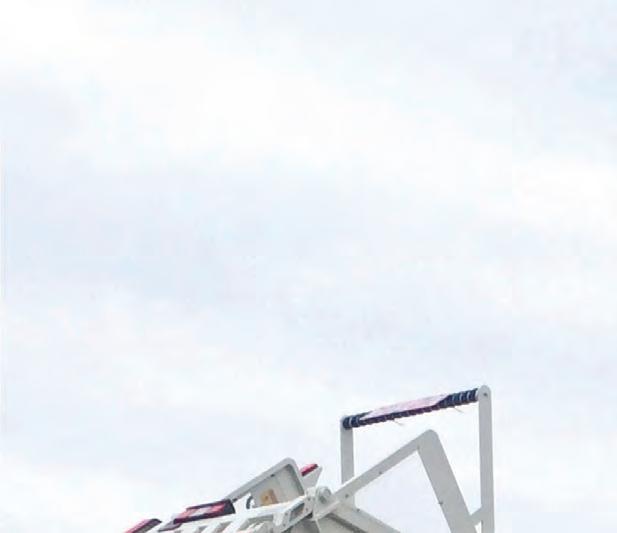

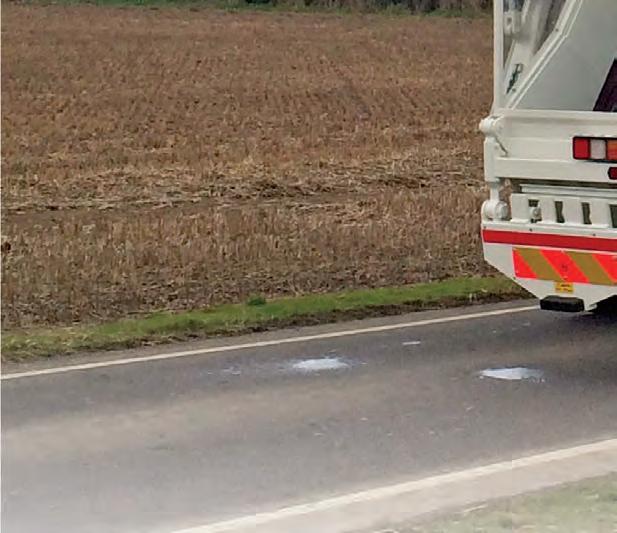


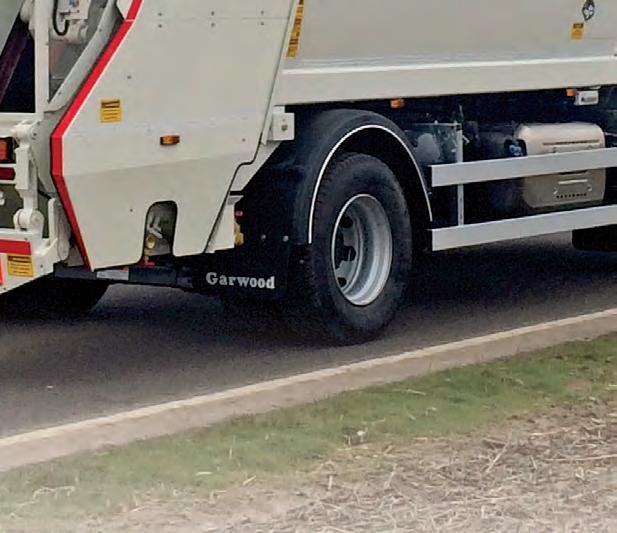
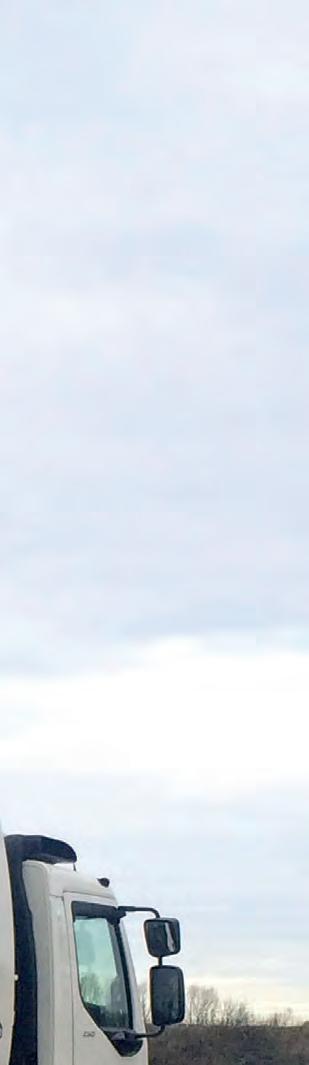
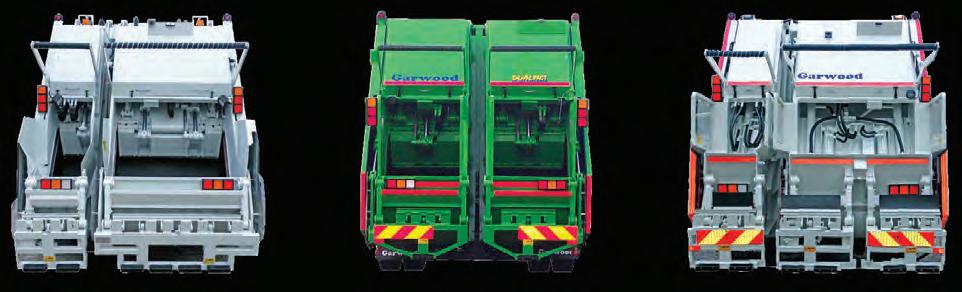
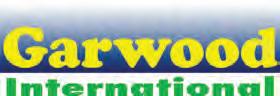
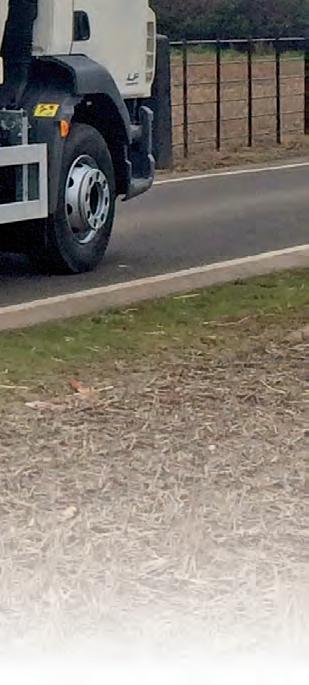
Compostable plastics and the 2025 targets
By Dr Ross Headifen
IN 2018, the federal government set out the 2025 plastic packaging targets for industry to try and meet. Its top two targets were:
1 00 per cent reusable, recyclable or compostable packaging.
7 0 per cent plastic packaging being recycled or composted.
Both targets mention compostable materials. However, there are issues with this terminology.
When they listed the targets, the government did not mention there are two different types – commercial compostable and home compostable. They did not specify which type they were referring to when it came to the targets. Their simple mention of compostable is not a proper
description of the requirements and is causing confusion.
The government is also causing confusion when it later stipulates compostable and biodegradable. Those are not separate terms. Compostable is biodegradable, (where it biodegrades is a different story). However, just saying biodegradable doesn’t mean compostable.
As mentioned, when discussing compostable plastics, it is important to distinguish between commercial or home compostable materials. One important aspect they have in common is, they are not recyclable. Therefore, their continued use is still promoting the single-use economy and detracting from a circular economy and the 2025 targets. This is counter to the push to promote recycling and the circular economy.
Commercial compostable is made from plants, which is attractive to some users from a source point of view. However, for a commercial compostable product to biodegrade it must go to a commercial compost facility of which there are few. The public has little to no education on how to dispose of a commercial compostable product like a cup for example.
The common perception is it is compostable so it will biodegrade when disposed. Those trying to dispose of such streams have no access to a commercial compost facility – i.e. there is no infrastructure to separately collect commercial compostable plastic, so the consumer has little option but to really dispose to a rubbish bin. It is labelled with the recycling symbol number 7 on it, which is a ‘send to landfill’
instruction. In a landfill, it is too cold, has too little oxygen or moisture for the required aerobic microbes to live. Hence the commercial compostable item will not biodegrade there. Should a commercial compostable plastic actually be sent to the correct special facility and it does get to biodegrade, it is aerobic biodegradation with CO2 as the byproduct and any chance to have the plastic’s embodied energy capture is lost.
Home compostable plastic material is not clear but cloudy-opaque, which impacts its suitability to be used as display packaging. The material is not as strong as a PP or PE type plastic, so it requires a thicker wall thickness to get the same strength.
Home compostable material is approximately three times the cost of normal PP or PE type materials. However,
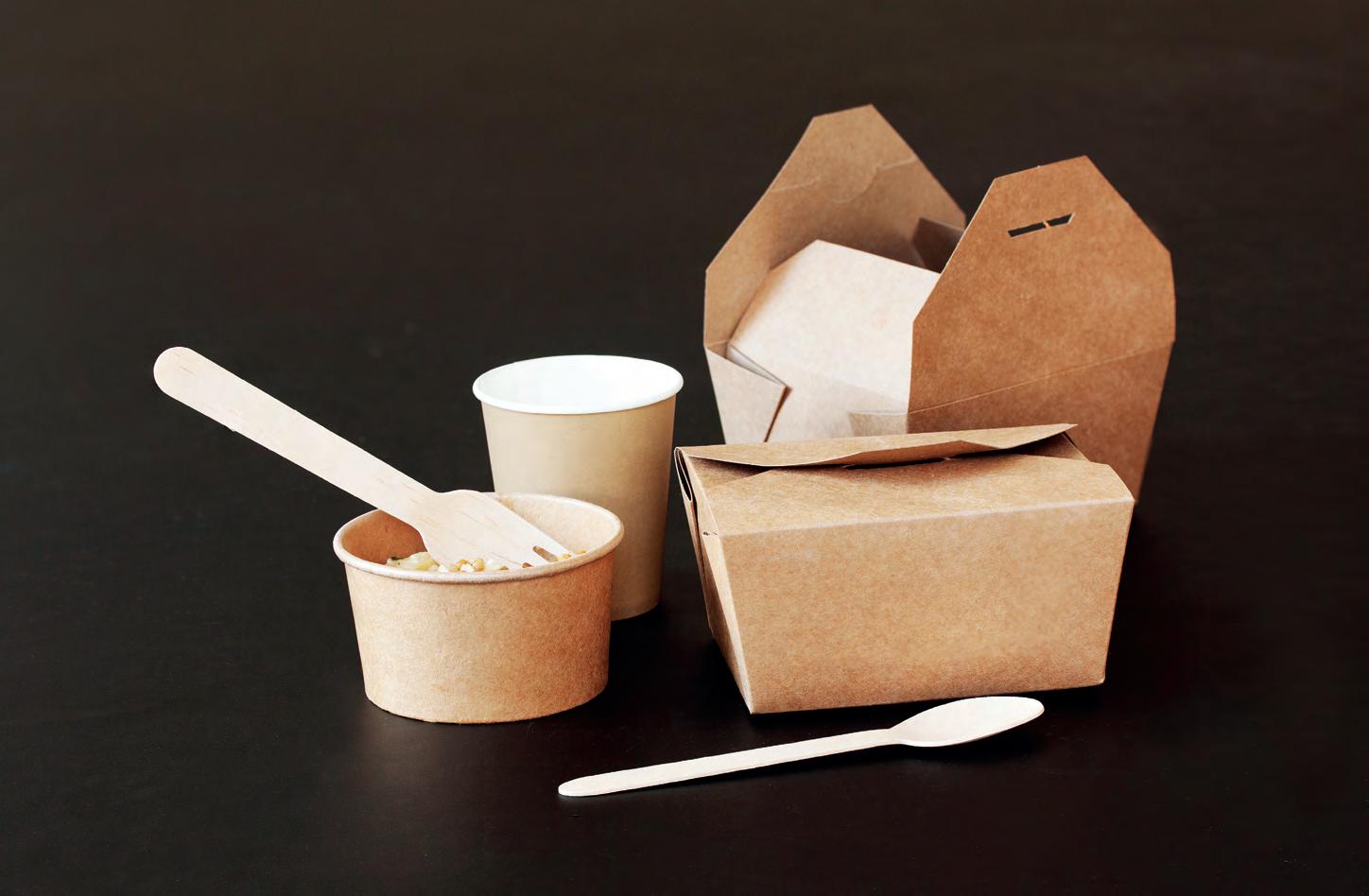
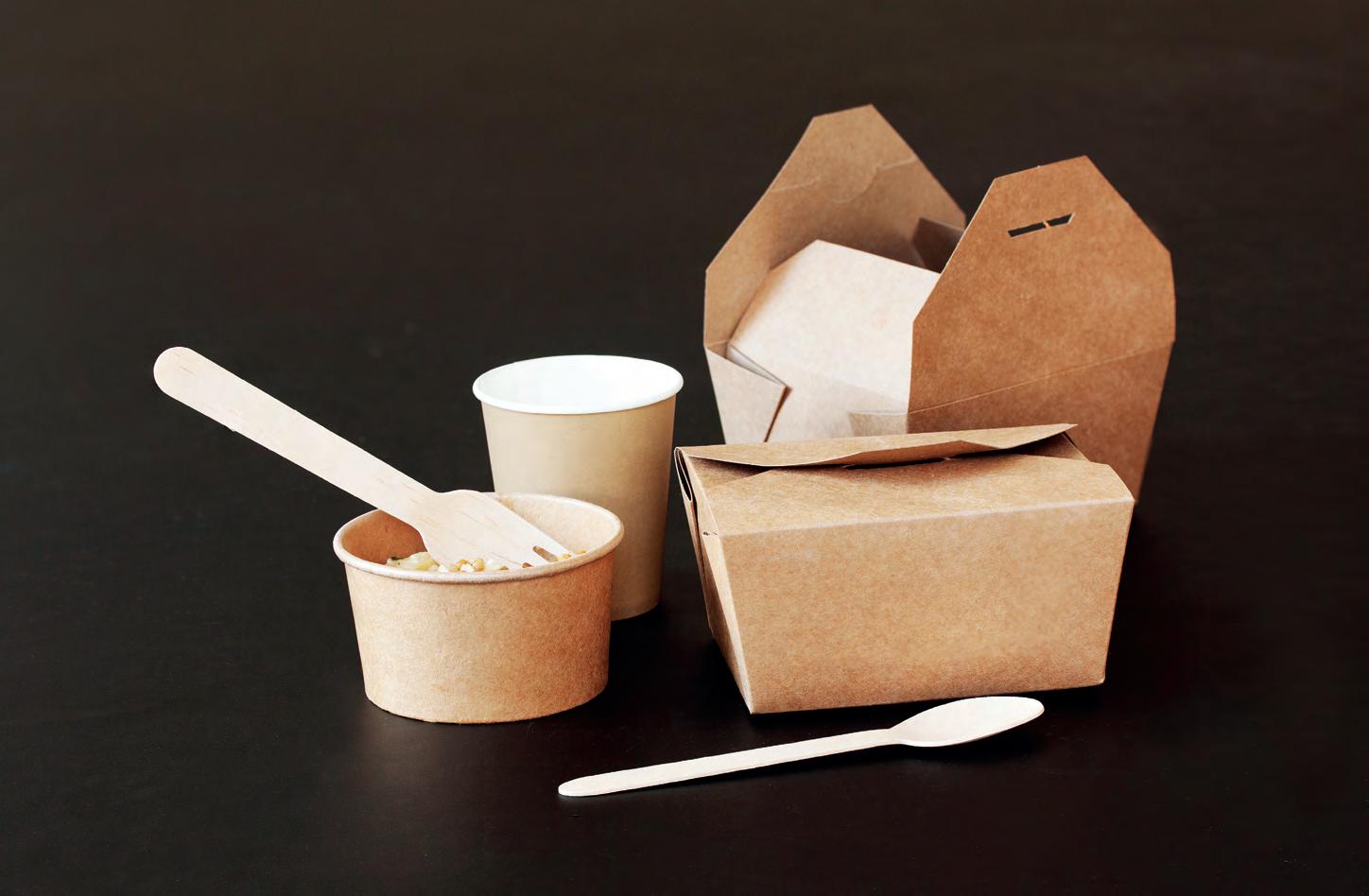
it will readily biodegrade at ambient temperatures in home composts or commercial composts or in landfills.
To make a home compostable plastic able to biodegrade at ambient temperatures, it has a significant amount (60-plus per cent) of a material called PBAT added to it. This is a fossil fuel derived highly biodegradable component. The PBAT means that home compostable plastic is only 30-40 per cent plant based, and 60-plus per cent oil based. This detracts from the ‘Green’’ perception of home compostable plastics.
Home compostable plastics have a limited life of about 12 months after which they start to fall apart. Practically all home compostable products are made overseas, which means by the time they arrive in Australia and at a point of sale, their working life is reduced to 6-7 months. Customers are going to expect three to four months or more of life from the products. For example, a roll of bin liners may contain 20 bags. That could be five months supply for them, which means the last few bags may no longer be of useful service or their rubbish will end up on the floor, which is a common complaint.
Use of home compostable products has also resulted in importers and
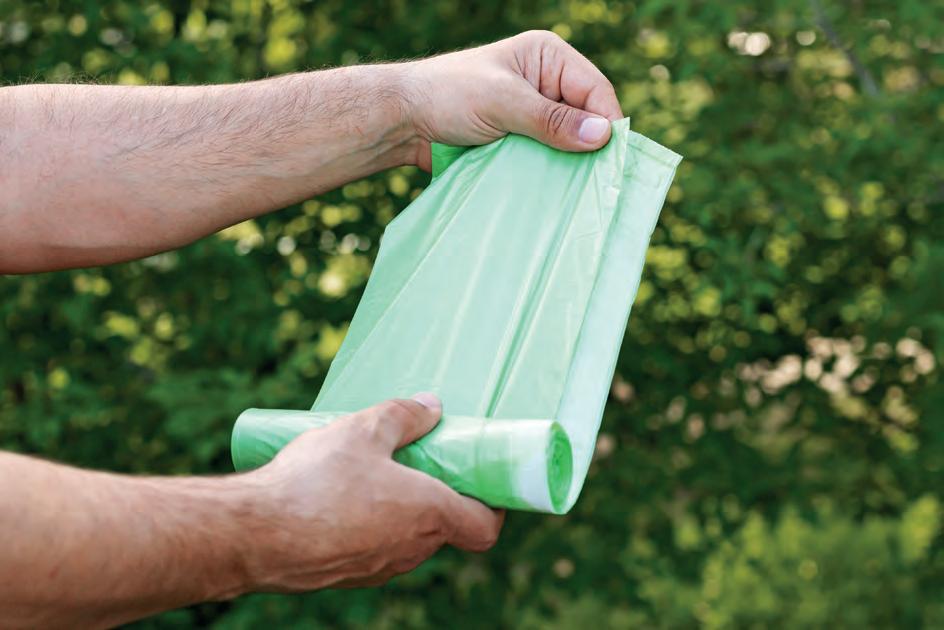
as it has passed its saleable life. The sustainability aspects of having a product made overseas, shipping here to Australia and then having to send it to landfill is low. Getting everyday plastics to be recyclable and recycled is difficult and will take many years for industry and consumers alike to adapt.
Commercial compostable products
venue where the waste is collected by waste managers who can then sort and transport it to the appropriate compost disposal facility.
Home compostable products can have an application in high turnover applications where they are used within a few months, like bin liners, but sold in rolls of fewer number of bags. If we
do so, then moving to a circular economy is incompatible to specifying plastic should be made compostable. The plastic packaging targets need to be reviewed in light of the practicality of using ‘compostable’ materials.
Dr Ross Headifen is co-owner of Biogone.
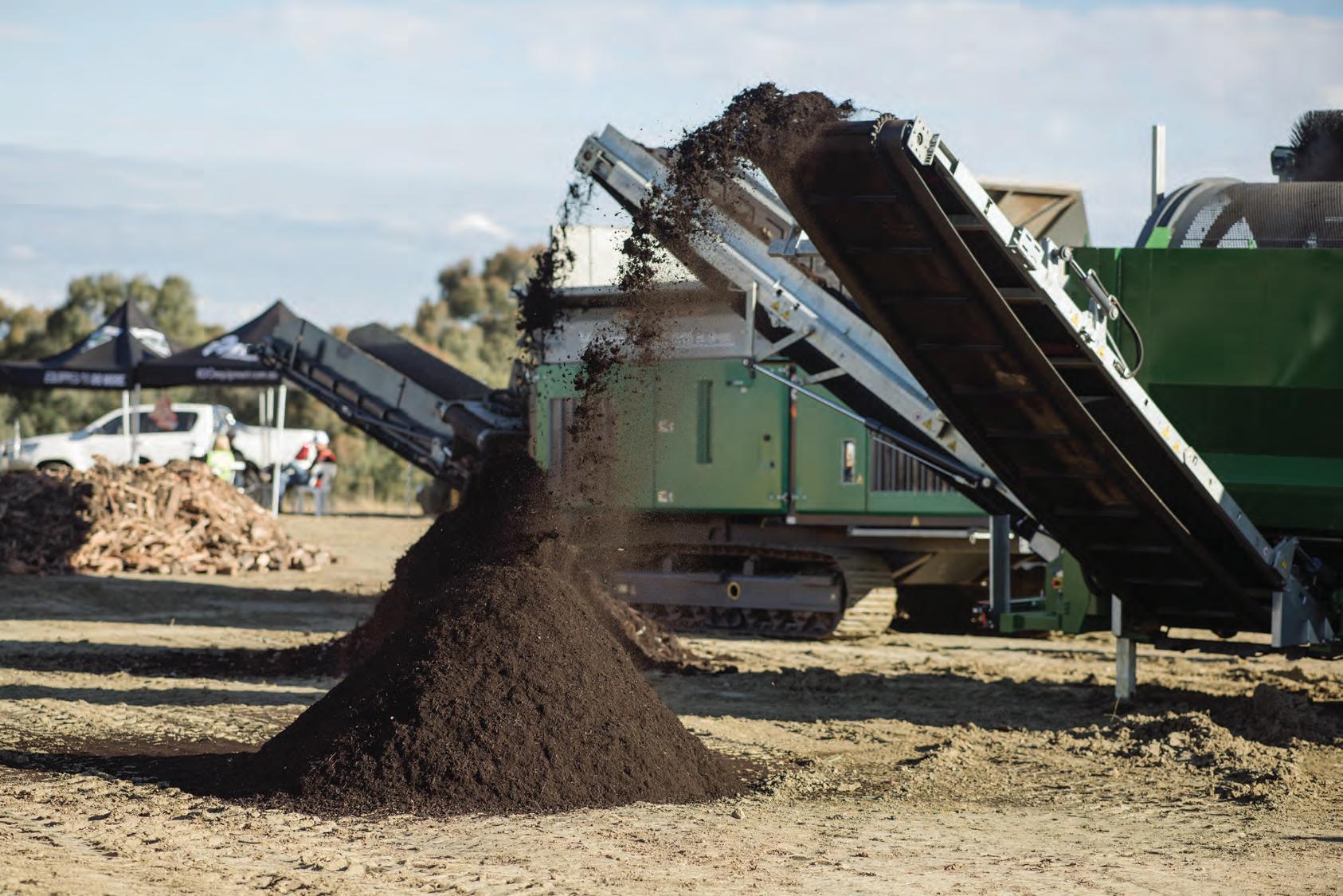
People sometimes get confused between something that is compostable and biodegradable. Image: kristini/shutterstock.com
Anaerobic digestion and composting collaboration – a success story
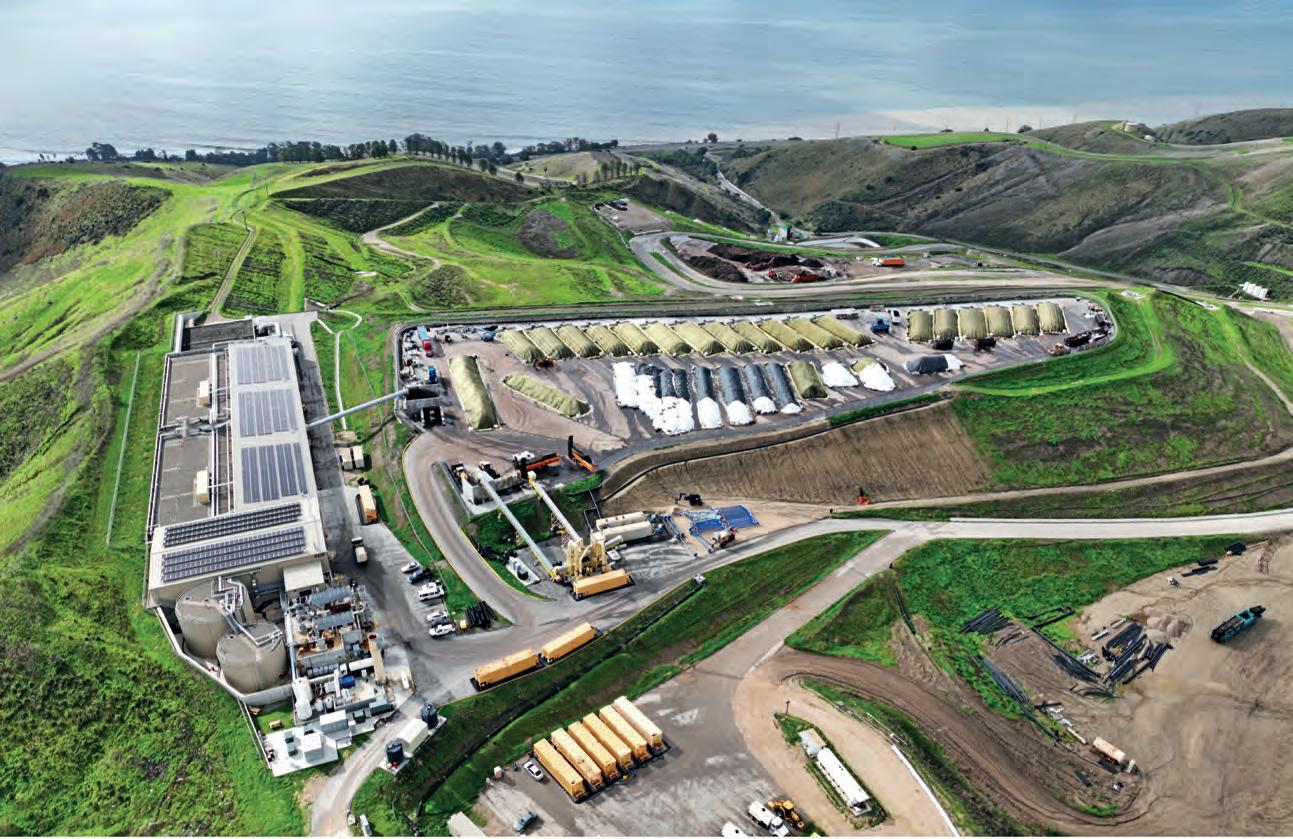
DRIVEN by legislation in California (SB1383) in 2022, Santa Barbara County’s Anaerobic Digester Facility (ADF) began operating to generate renewable energy from the organic portion of Municipal Solid Waste (MSW). This waste was processed and recovered at the County’s Materials Recovery Facility (MRF) located at the Tijiguas Landfill.
At the ADF, the organic material underwent a 28-day digestion process. During this time, 50 per cent of the material was recycled back to the beginning of the process, while the remaining 50 per cent was sent for further composting using an open windrow method. The goal was to convert the residual digestate into high-quality, sellable compost.
Management recognised the need to retrofit the operation due to site constraints related to odour control, stormwater management, and litter management associated with open
windrow composting methods. The retrofit aimed to eliminate odours and enhance process control. Since odour reduction was the most critical issue, management selected Sustainable Generation, which features the SG MOBILE System with GORE Cover, for a pilot study.
“GORE Cover has over 20 years of experience composting digestate as an additive to existing composters for FOGO, as well as acting as the after-treatment post-AD treatment for finishing digestate to control odour, moisture, re-hygienise, and produce high-quality compost,” says Brian Fuchs from W.L. Gore & Associates.
Santa Barbara County conducted an evaluation comparing the SG MOBILE System with GORE Cover against existing open windrow technology and a competing Aerated Static Pile (ASP) system. The competitor failed to meet performance expectations and could not provide any performance data.
The study focused on five key objectives:
1. Odour mitigation;
2. stormwater control;
3. litter control;
4. recipe optimisation; and
5. compost quality.
In February 2023, Sustainable Generation delivered a demonstration unit, and composting operations began within days. Over a 90-day period, multiple batch tests were conducted to validate the system’s effectiveness. Third-party independent testing confirmed results, including:
• A 9 7.5 per cent odour reduction.
A 9 8 per cent reduction in VOC emissions.
C lear separation of stormwater from leachate during adverse weather events, including atmospheric rivers from the Pacific Ocean.
M aintained PRFP temperatures.
P roduction of stable, high-quality compost.
These results demonstrated the system’s ability to transform organic waste into premium compost while mitigating environmental impacts.
Full-scale implementation
Following the success of the pilot project, Santa Barbara County moved towards full-scale implementation. Within ten months, the site transitioned to a fully operational 20-heap SG MOBILE System processing 100,000 tonnes per year. The upgraded system improved site conditions, addressed odour concerns, minimised litter accumulation, and enhanced stormwater management.
As of July 2024, county officials reported that odour issues associated with the composting process had been effectively eliminated. Additionally, the project has reduced ecological impacts on the surrounding coastal area while increasing operational efficiency, setting a new standard for sustainable waste processing.
The odour has all but dissipated due to the SG MOBILE System with CORE Cover.
Images: Sustainable Generation
A model for future sustainability
“In the fast-evolving landscape of technology and business, swift decisionmaking is paramount,” said Scott Woods, founder and CEO of Sustainable Generation. “The SG MOBILE System addresses this necessity by providing a robust solution designed for rapid deployment and expedited data collection.
“This system aids in proof-ofconcept processes and accelerates economic buyer decision-making. Coupled with our professional services staff, and remote serviceability platform, the SG MOBILE System ensures efficient speed-to-market decision-making anywhere in the world.”
The rapid shift from a pilot project to full-scale implementation in Santa Barbara County highlights the effectiveness of Sustainable Generation’s technology and the benefits of proactive collaboration. This project sets a benchmark for municipalities seeking innovative and environmentally responsible waste management solutions while efficiently tackling regulatory and operational challenges.
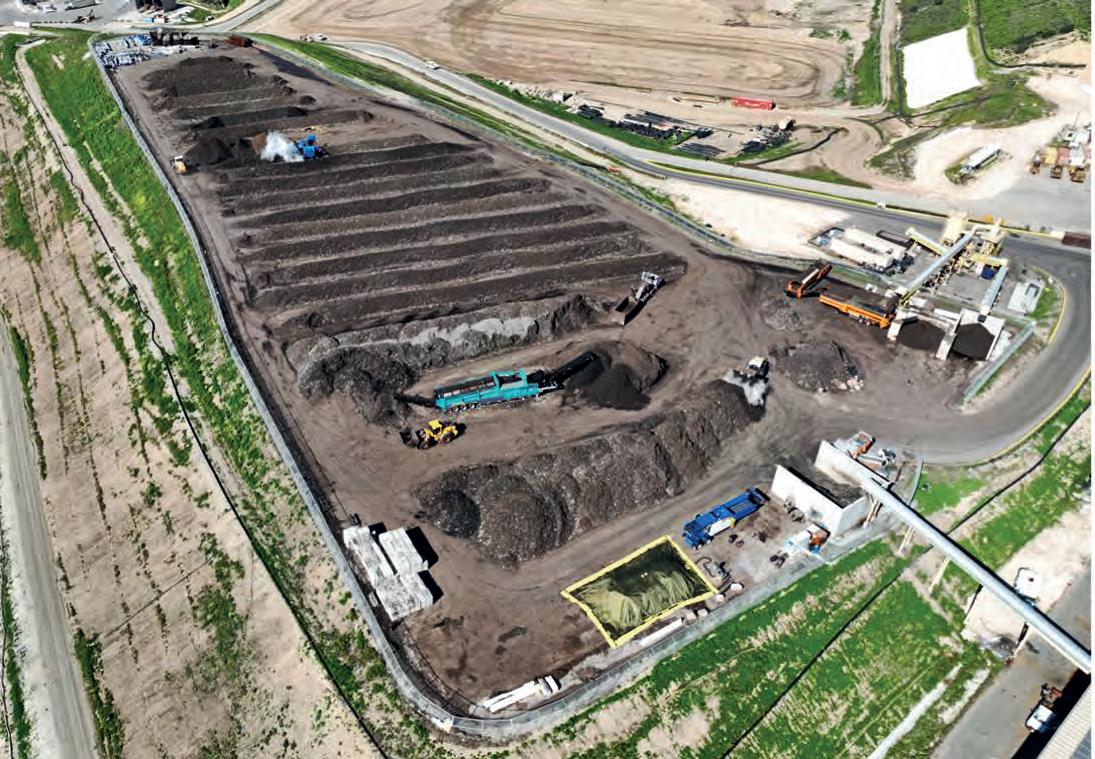
Improving speed and efficiency FORCE Front Loader
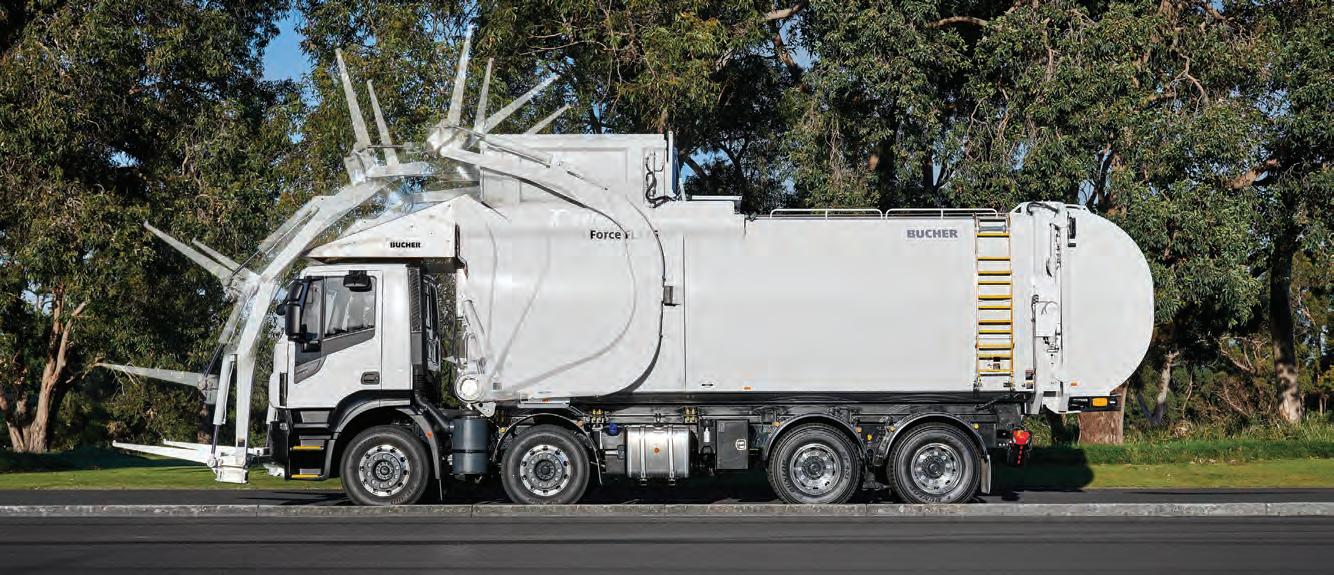
Scissor type compaction
Composting our way to sustainability
By Virginia Brunton and Mike Ritchie, MRA Consulting Group
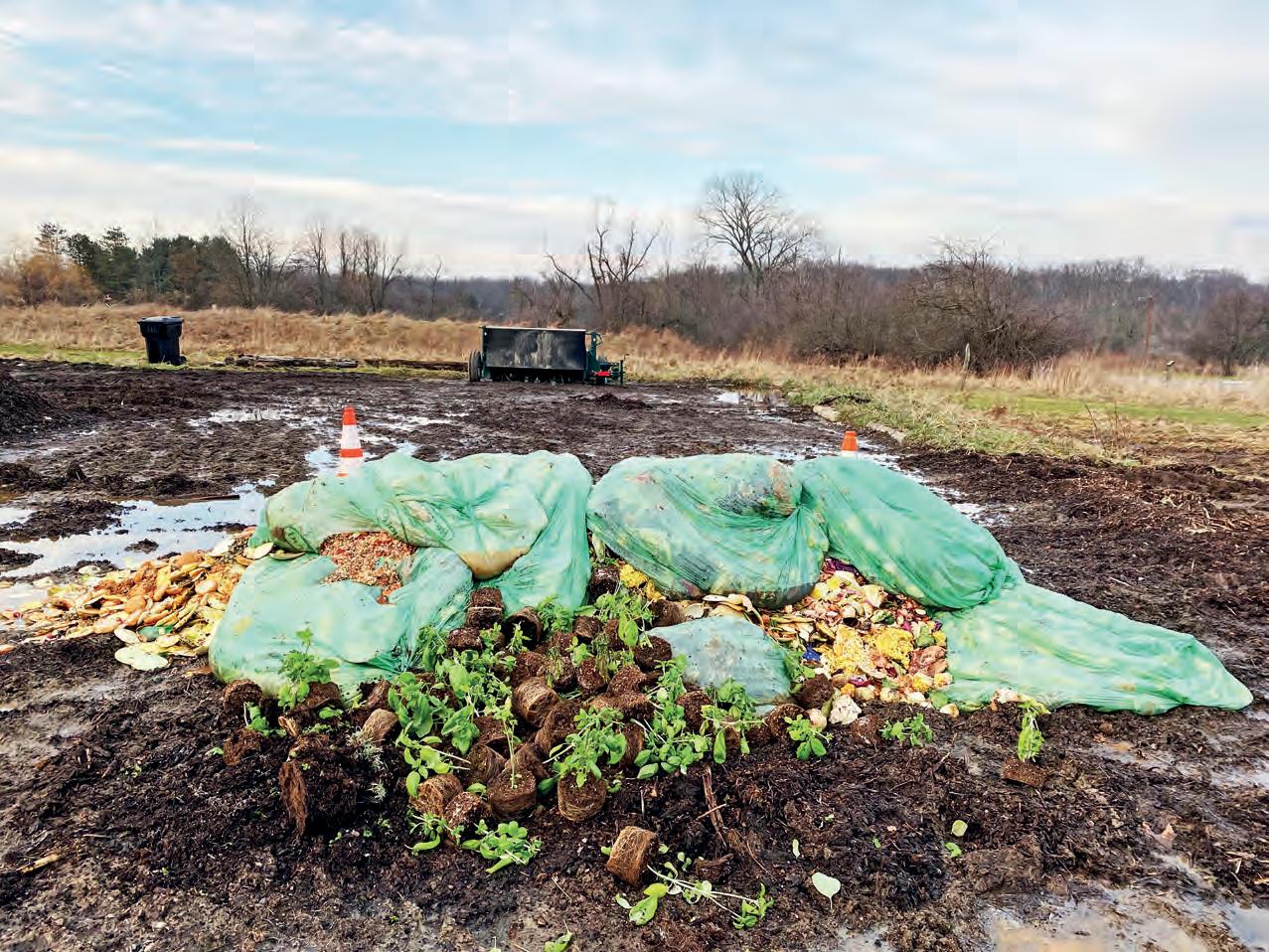
FOGO is taking off across Australia. That is a good thing. It will reduce waste to landfill, divert up to 3 MT of organics from landfill, reduce greenhouse gas emissions by millions of tonnes and create thousands of new jobs. Win, win, win.
But some readers will know that we have been harping on about compost standards for a while now and not a lot is changing.
The only real problem with FOGO as a model is that contamination rates from households are higher for FOGO than for separated GO by about two per cent. Doesn’t sound like much but if that contamination finds its way into compost and onto farmland or parks and gardens, we will hear the roars of protest from users followed by the silent crash of the market as buyers desert. This is a prognosis we need to avoid.
The key is to reduce the contamination of FOGO by households in the first place followed by better contamination removal
But that costs money. Someone needs to pay to maintain high standards of compost. Particularly when there are low cost/low standard providers in the market who can use contaminated compost for mine site rehabilitation or landfill cover material.
The answers are:
1. Better contamination education of households.
2. Pricing structures that incentivise Councils to invest in lower contamination rates, collection contractors to selectively manage contaminated bins and processors to remove contamination.
3. Investment in cleaning equipment at the front and back of compost facilities.
4. Establishing and enforcing a national minimum compost standard specification before the product goes to market.
In MRA’s view, the best way to achieve all of those at the same time is
Government contracts for processing of FOGO.
Those schedules have the effect of rewarding low contamination with cost reductions and penalising high contamination with cost increases. That provides the revenue for processors to clean up contaminated FOGO.
It provides councils with a direct financial incentive to invest in education to reduce contamination at source (i.e. at the household) before it enters the supply chain. The minimum quality standard (also set in the Local Government contract) stops freeriders undercutting the quality market players and producing rubbish compost for low-grade uses. We have written previously about the Local Government Best Practice Standards, a product specification that Virginia Brunton of MRA has developed for voluntary use by councils (but it needs to be mandatory).
There are other ways to skin this cat, but MRA believes you can do all
contamination penalties, collection performance criteria, minimum standards). Local Government just needs an incentive to do it, which is where the State Government and grants need to come into play.
We noticed that the Commonwealth Government commenced a review of the AS4454 – Compost Standard in 2021 and four reports have been completed (two on the public record and two still held behind closed doors). The first two are about policy options and the last two, apparently, have to do with costs and the role of Government. All should be released for public information. None have been actioned.
One key finding is that Europe and North American States have set physical contamination levels (plastic, glass and metal contamination) at levels 50 per cent lower than those allowed in the Australian Standard AS4454 (0.25 per cent vs 0.5 per cent). This is a bit of a nobrainer first action.
Improvement in compost contamination removal is just one issue that needs to be improved upon.
Image: Anna B. Locci/shutterstock.com

Government transparency is needed when it comes to reporting on compost standards. Image: create jobs 51/shutterstock.com
So, where to from here:
1. Get the State Governments to mandate FOGO contamination schedules and minimum quality standards into all new LG FOGO contracts (so we don’t end up with a patchwork of arrangements by progressive and laggard councils).
2. Get the Commonwealth Government to finish the AS4454 review and adopt
the European physical contamination





councils to do it voluntarily via grants and other mechanisms.
Virginia Brunton and Mike Ritchie work at MRA Consulting Group.
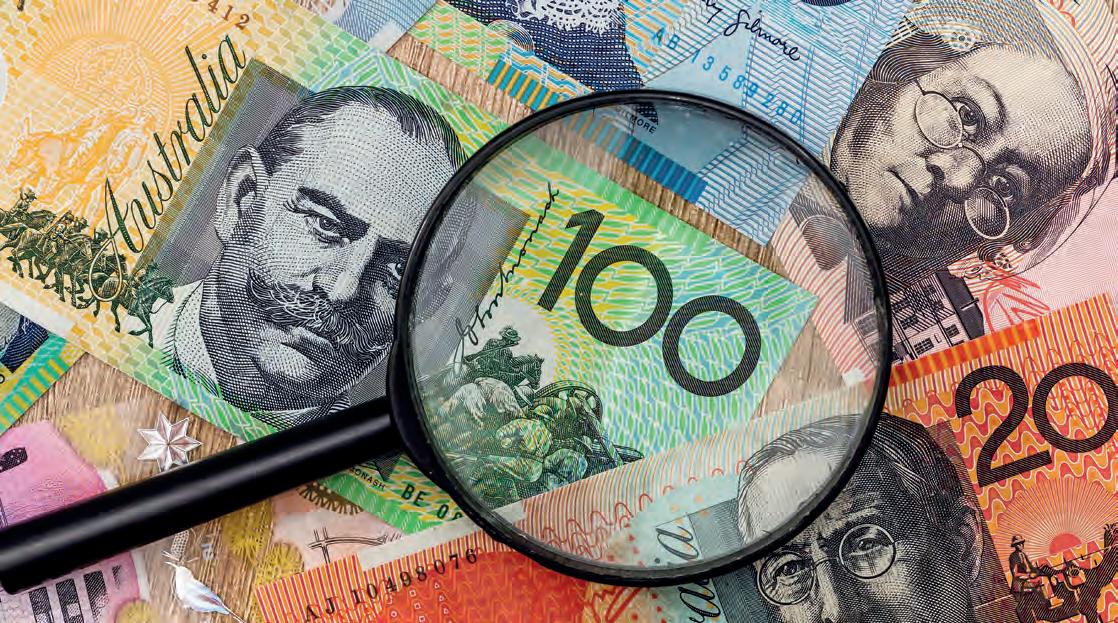
Local action • Global impact





Get ready for the premier event in waste management!
The industry’s top conference is almost here, and now’s your chance to register.
13-15 May 2025 OPAL COVE RESORT Coffs Harbour
Bringing together industry leaders, government officials, and passionate waste management advocates, you’ll be inspired by an engaging program that highlights the latest innovations and challenges in the field.
• 3 immersive days
• 17 diverse conference streams
• 4 insightful panel discussions
• 6 hands-on workshops
Can’t make it in person?
• 3 exciting social events
• Over 700 delegates
• Over 100 council representatives
• More than 80 exhibitors
No worries! Enjoy live broadcasts in real-time or at your convenience. There’s truly something for everyone at this event—you won’t want to miss it. Register today!
coffswasteconference.com.au | 0474 629 908
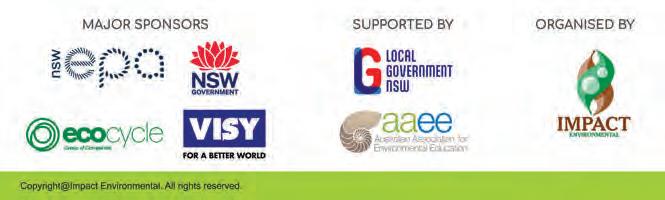
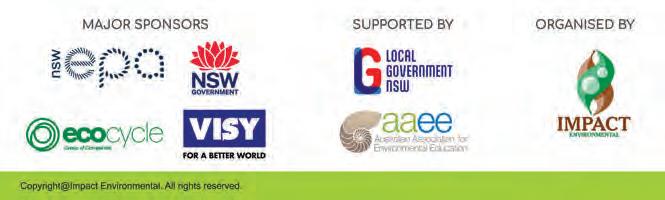
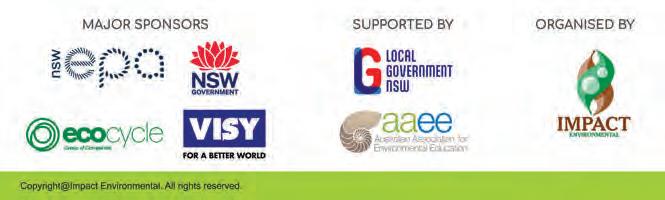
Why the forced-aeration system is a game changer in organics
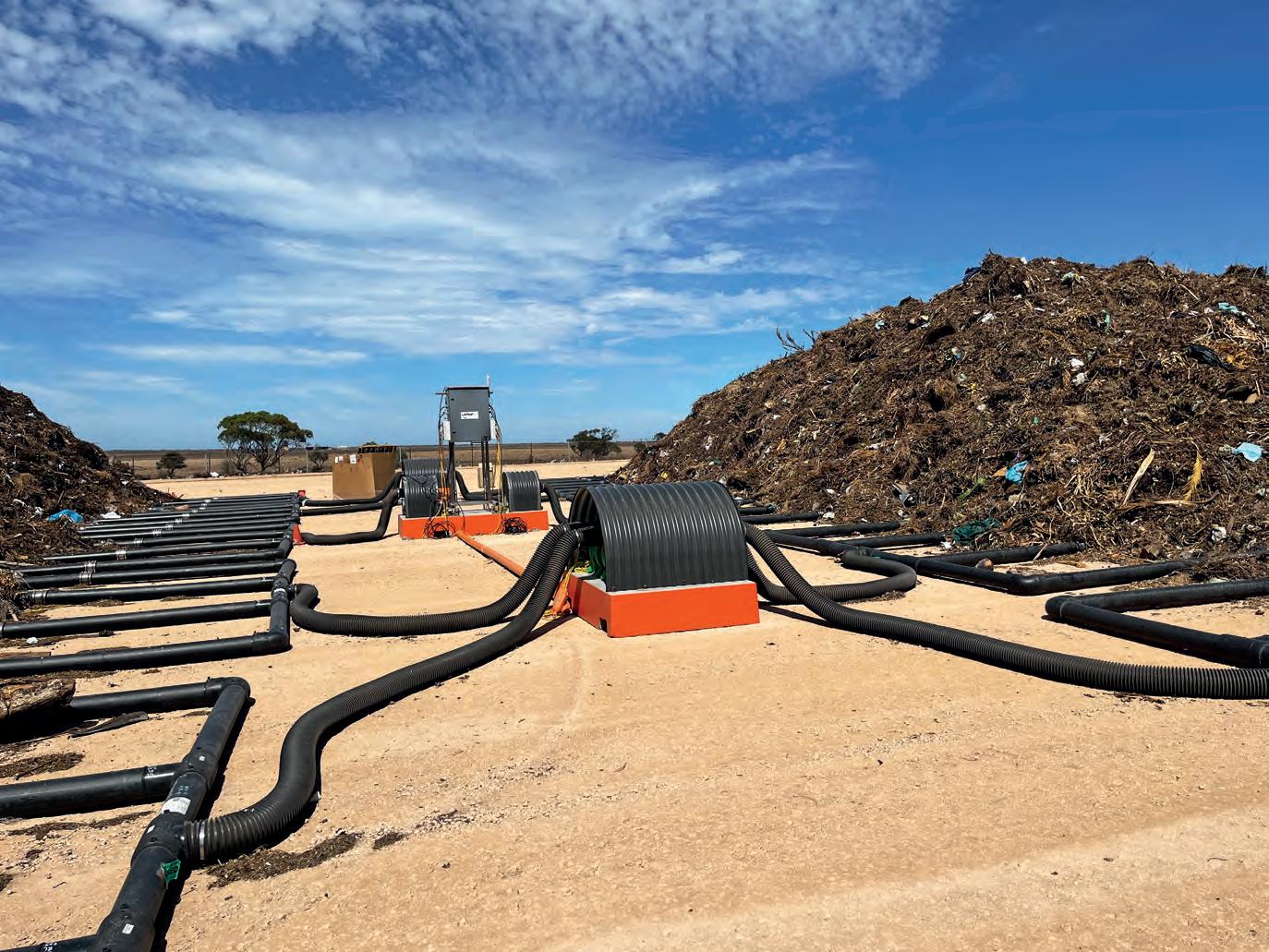
FINDING the right markets for recycled organic products has always been an issue and is something that the resource recovery industry needs to pay more attention to, according to Dr Ben Dearman from Ennovo.
Dearman, who has a PhD in Environmental Biotechnology, is the managing director of the Adelaide-based Ennovo, a company that specialises in finding solutions within the resource recovery industry, including organics.
What are the issues surrounding finding such markets? There have been a few traditional ones, according to Dearman. Trying to explain to farmers the benefits of using organic fertilisers,
and the lack of machinery that can apply organics in an agricultural setting are two. Things have changed though.
“There are a few drivers around that change,” said Dearman. “One is that there has been a greater acceptance from the farming industry for using organic fertilisers. Another is the increasing cost of inorganic fertilisers. Also, recycling the nutrient value within organic waste can only be realised through the use of recycled organic products and good-quality compost products.”
He said that the development of machinery used for the application of compost products has also come a long
way, especially around broadacre and horticulture. The use of pelletisation has been an important focus because it has helped with the material handling and application aspect. And what about the lack of education about the role of carbon rich organics in fertilisation? Has that been an issue?
“Absolutely”, said Dearman. “Farmers, want to know that any changes they are making are for long term benefits”, he said.
Recycling Organics
While there can be some residual benefit to landfilling organics – gas capture being one – it is not the ideal
endgame for the substance. There are many reasons why composting is preferred, and not just because it doesn’t create as much greenhouse gas as landfilling. There is a more intrinsic benefit being missed.
“You’re not capturing the fertiliser benefits,” said Dearman. “By recycling–either through composting or dedicated anaerobic digestion – you are able to unlock the full benefits of this waste material.”
Paul Bowden is the Director Environmental Services at Integrated Waste Services (IWS), a company that is a client of Ennovo. He acknowledges that the cost of organic fertiliser is not
The telemetry-enabled, automated forced-aeration system is designed for composting and saves on labour. Images: Ennovo
as cheap as its inorganic counterpart on a chemical weight basis, but there is an important reason for that.
“Inorganic fertiliser is only a nutrient, so it’s only providing a nutrient value to the soil,” he said. “Whereas an organic fertiliser, like a compost, not only has the nutrient value, but is also carbon rich and it also has microbes. It’s doing much more than just the chemical addition to the soil. It’s looking at the chemical, physical and microbial aspect of the soil.”
Bowden said that if there is no carbon in your soil, then there are no microbes. They are an important ingredient because the most efficient pathway for nutrients from the soil to the plant is through microbial activity. He added that if you’re always taking carbon out of the soil, it becomes depleted, which means you have to saturate it with chemicals to get the plants to absorb it.
“Whereas if you have a soil that has got carbon and microbes and its got life in it, you don’t need as many chemicals, because the microbes will assist with that nutrient exchange for you,” he said. “Most of the farms in Australia are just taking the carbon out of the soil, and they’re not putting any back.”
But will there be enough organic compost feedstock to go around? In a nutshell, no, said Dearman.
“One of the critical issues is that there is a gap between the manufacturing of good-quality compost and mulches and the application to farmland,” he said. “If you look at trying to do it on a large scale, it’s going to be more difficult to do with organic feedstocks – whether they be manures or other food/green organic materials. It’s really about what you can get out of the city centres, and then you’ve got issues with logistics as well. Also, another barrier to that market is contamination of the material.”
Dearman points out that the knowhow to create organic soils is not a new science – it’s been around for thousands of years.
“If you go back 10,000 years ago in the Amazon Forest, the soil was very low in nutrients,” he said. “What the people of the rainforest did was basically make biochar and organic compost and bury it and called it Terra preta soil. And that was the base from which they grew their crops. What we’re doing is not new, it’s been done for thousands of years.”
To help move things along, Ennovo has developed a telemetry-enabled, automated forced-aeration system for composting, which has been implemented at the IWS compost facility. This means instead of using a windrow turner to turn the windrows, they are using this system.
“It reduces the amount of equipment and labour needed to process the organics and provides a very high level of process control,” said Bowden. “Because it is telemetry-enabled, it allows you to identify issues and get a data set to manage the process. When you’re looking at certification and trying to meet a particular standard, such as AS4454, it gives you a much greater chance of being able to do that.”
Bowden said the company’s workforce used to have to exclusively mechanically turn the compost to produce the end product. The forced aeration beds now ensure the materials are oxygenated continuously. The system is on an automatic control that is paired with a sensor, which turns air pumps on and off, so the material is optimally composting all the time. He said that records are kept through the different probes and sensors in the pile. This allows the company to show its quality assurance to independent auditors for the certification.
“And as a result of that, not only have we had process efficiency, as well as product quality improvement, we’ve had that double whammy of getting an easier, cost-effective process, while at the same time improving our quality,” said Bowden. “It’s been a good experience going through that process –specifically with the application of that technology.”
Both Dearman and Bowden know that there is still some education needed for everybody to get onboard around organic composting. They feel that the general public will get onboard, as will farmers.
“The corporate farming model will take a bit longer,” said Dearman. “Changing behaviours, changing practices and changing business models will take more time. With them, you have to be able to show that it’s got a return on the investment and a lot of corporate models and structures are based around chemical fertilisers.”
Why collaboration works
Ennovo has been working closely with IWS to get the composting part of its business up and running to a large commercial scale. Their collaboration has been important in building the business.
“I engaged Ennovo to not only expand our processing but to expand our end markets, too,” said Bowden.
“As mentioned, this included going through the process of attaining our Australian Standard certification to AS4454. They have also supported us technically throughout that process. We’ve attained that certification, and we’ve also produced a broader range of Living Earth compost products available to broader markets.”
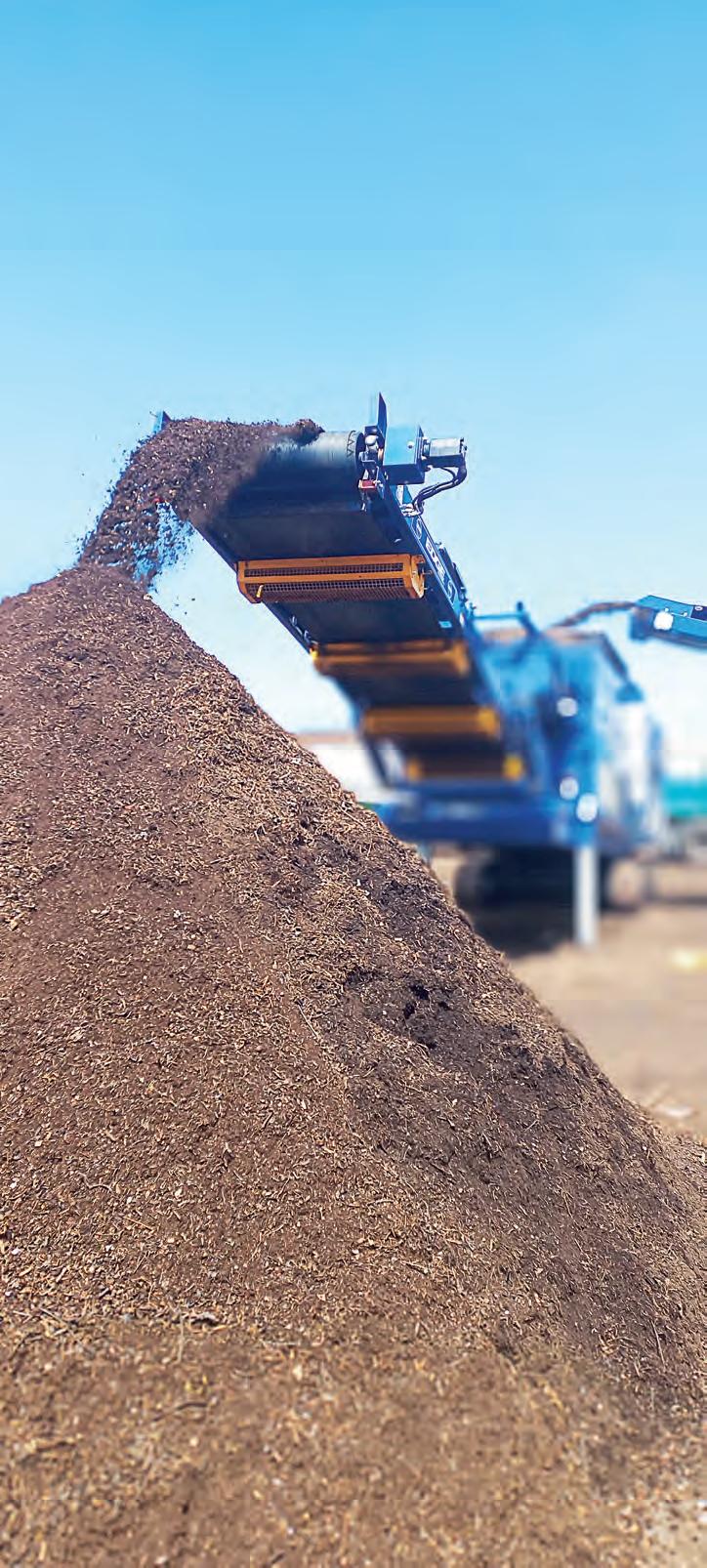
Financial Management
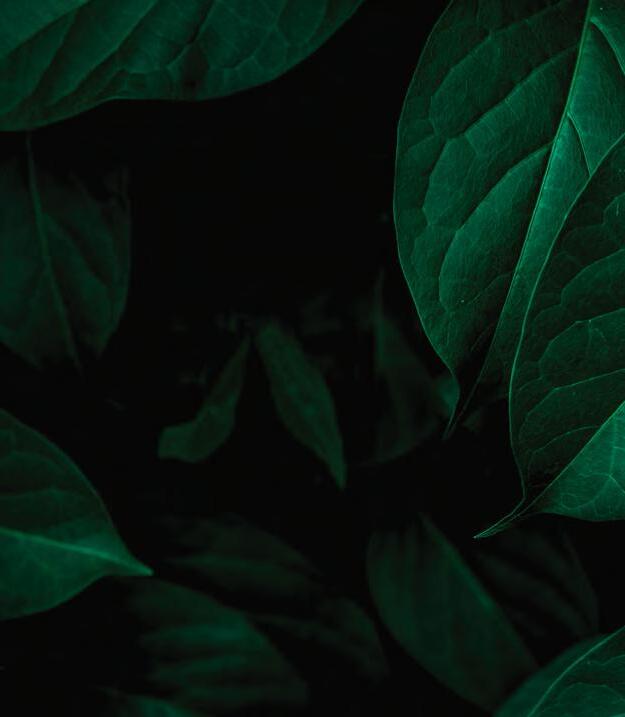
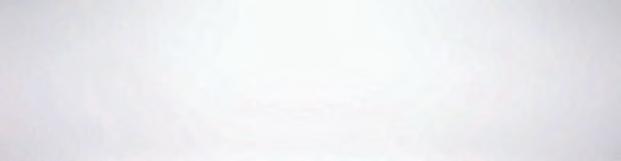
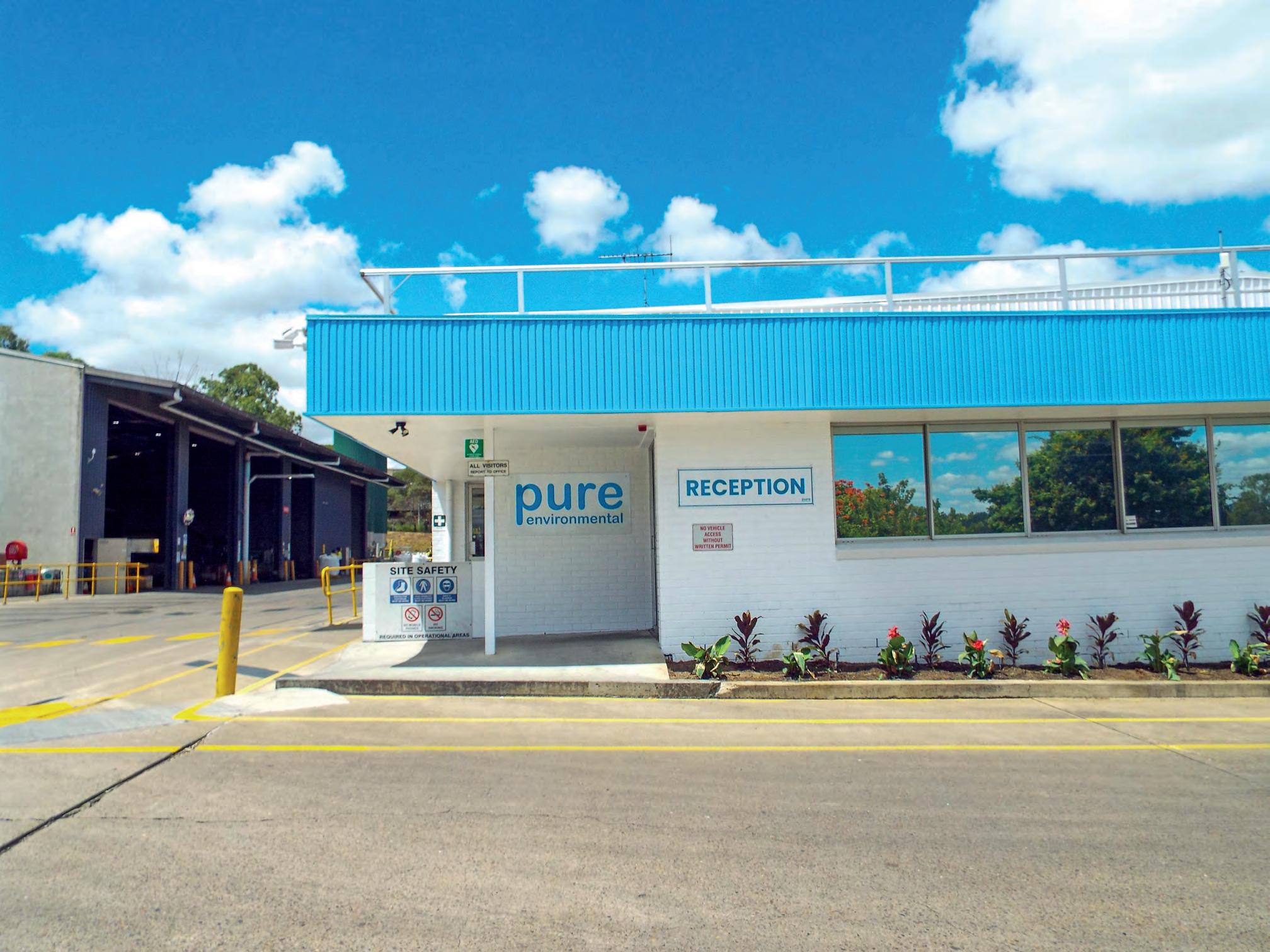
companies shy away from due to the nature of these waste streams.
While Pure is still in the business of processing/disposing of hazardous and regulated wastes, there is more it can do to help the sector.
Dr Karl Baltpurvins is the company’s CEO. He realised that the company could take that extra step further and help customers delve a little deeper into what can be done with regulated and hazardous wastes.
“Historically, a lot of how this stuff would work – like wastewater treatment, for instance – was that somebody would inquire about a commoditised quantity of waste (eg 1,000 litres of oily water, a drum of acid, or can of paint) and you simply gave them a quote to bring it in
to do, he said, is find solutions to its customers’ problems, instead of just doing the basics. It might involve a lot more project management, such as going out to a customer’s site and identifying material or packaging and doing a risk assessment.
It might involve complex logistics, such as loading or cleaning material. It is also focussed on its customers’ ESG objectives that typically favour recycling over landfill disposal
“What we’re trying to present is more of an integrated solutions-based business,” he said. “To that end, we’ve been employing and developing a broad range of people to try and meet that change in the market. We’ve got a lot of resources in terms of people, plant,
skill sets to find working solutions for customers.
“In the past, I’ve found very heavily technically focused people often don’t think commercially and don’t communicate necessarily that well,” he said. “We’ve really focused on getting a team together that can come up with not only technically competent solutions, but ones that are also commercially viable, proven and provide good outcomes to our customers. Around 15 per cent of our workforce is technical skilled – scientists and engineers – and we also employ other skilled people such as health, safety and environmental experts, accountants, technical sales and communications experts – the whole range of specialised operational people – who are trying
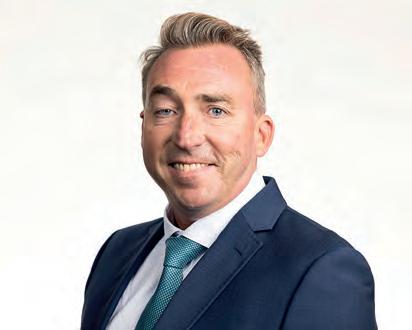
to bring those technical skills into the business and applying them to a business framework.”
He said one of the key features Pure is able to offer is communicating what can be complex ideas in an easy-tounderstand manner for the client. This especially applies to other stakeholders, such as the various regulators around the country who are often working in conjunction with Pure’s clients.
“That client could be a multinational,
Pure CEO Dr Karl Baltpurvins.
Pure Environmental is a think tank with technical expertise that can review any complex queries when it comes to hazardous waste.
Images: Pure Environmental
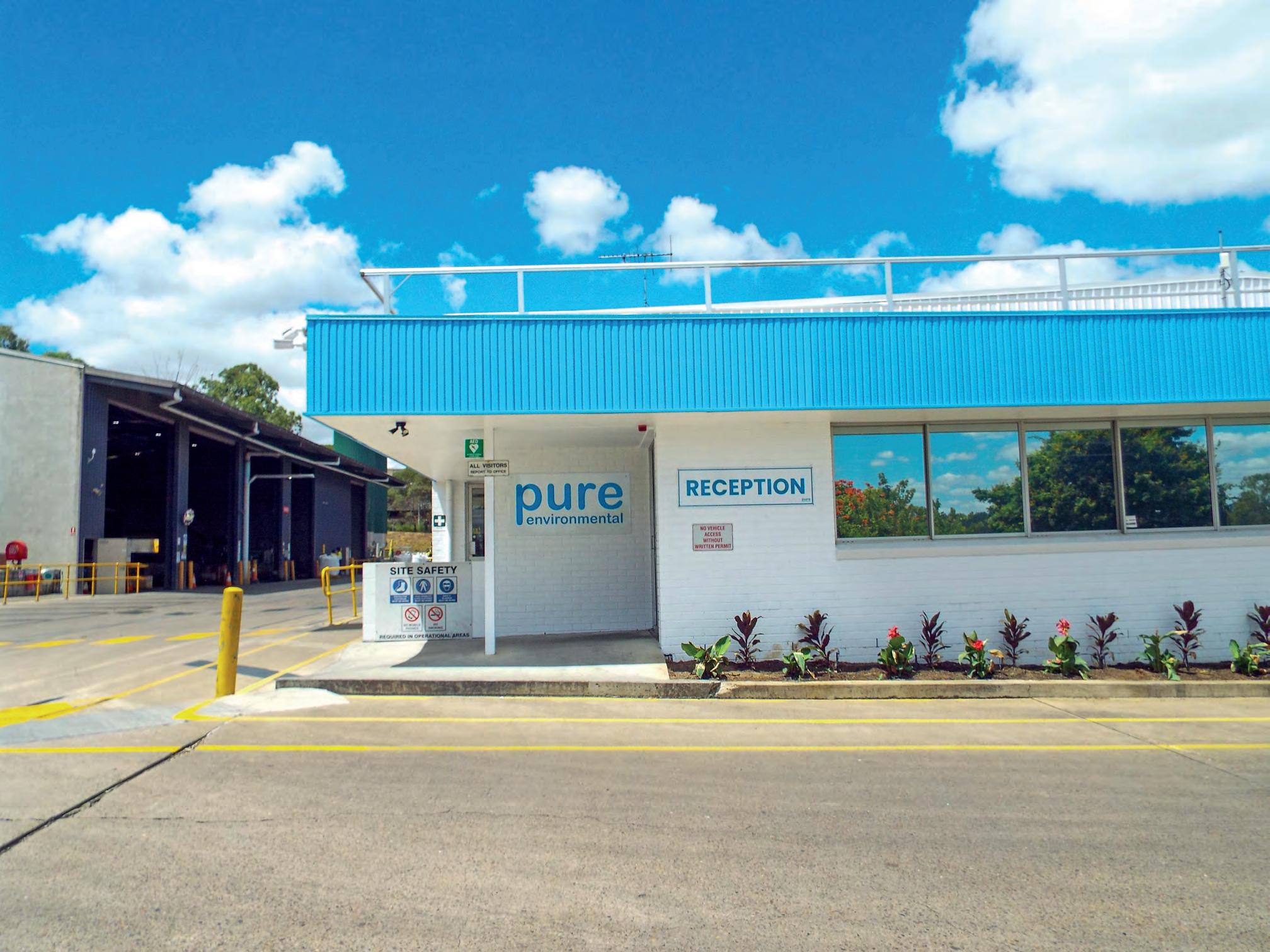
or it could be a small business and could be working in remediation or demolition,” said Baltpurvins. “It’s being able to configure the answer to suit the client and to suit the stakeholders, which I think is really important. We’re also finding a lot of our stakeholders and clients are looking for ESG-focused solutions.
“We’re particularly focused on reduction of environmental impacts to human health and the environment –that’s the core of our service. If we can convey that well, we’re able to align with those ESG practices and get a better outcome for everyone.”
Having been in the role for more than two years, Baltpurvins has seen a change in how clients view the company. He sees Pure as a think tank with a technical committee that can review any complex queries when it comes to hazardous waste. The company is also expanding its footprint. With Australia crying out for processing facilities, Pure is developing its portfolio of assets to complement its existing operations in Queensland
“What we’re trying to present is more of an integrated solutions-based business. To that end, we’ve been employing and developing a broad range of people to try and meet that change in the market.”
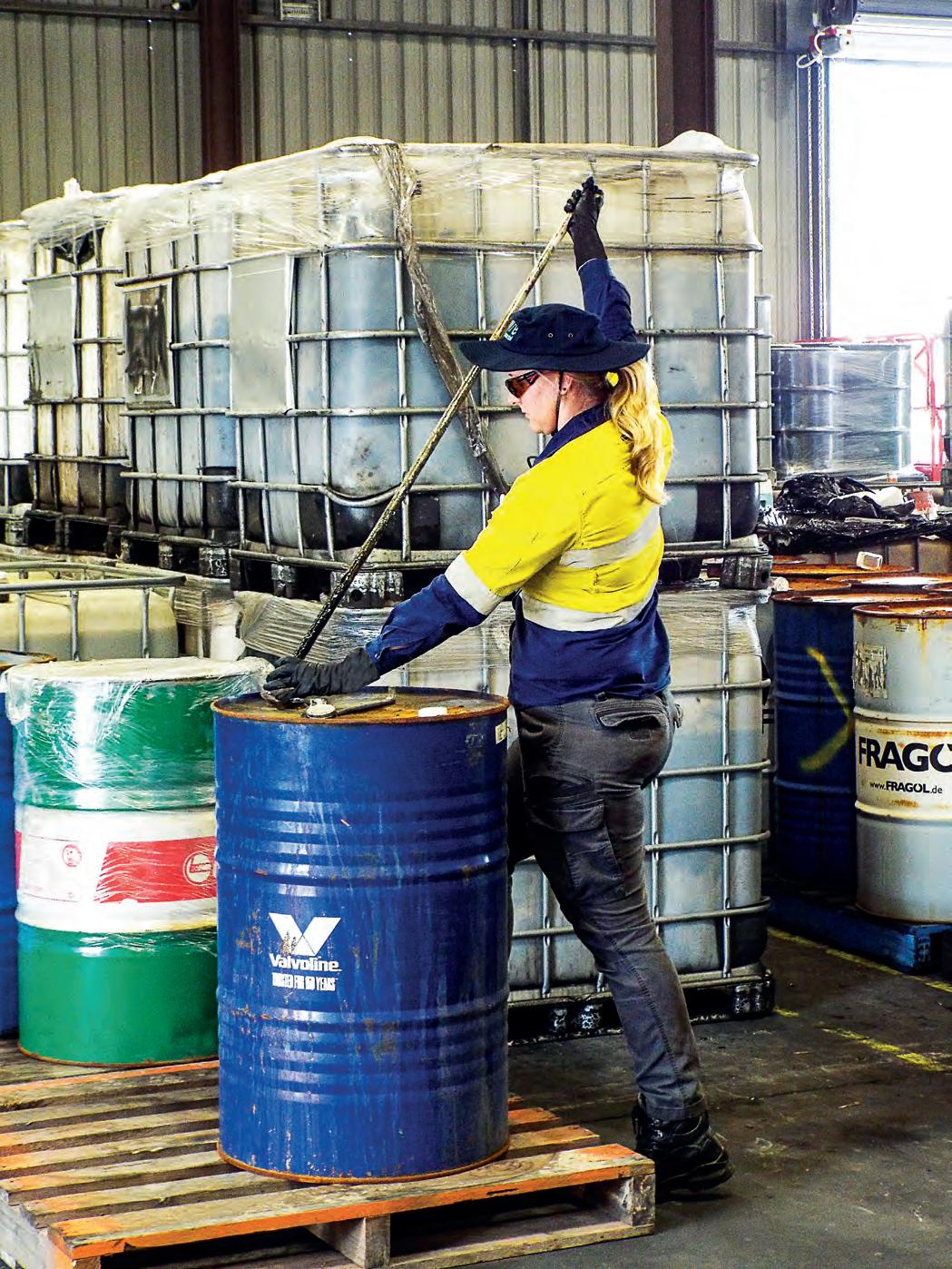
and Western Australia. He’s hoping for a national footprint in the near future.
Pure did start out as a series of small businesses, but Baltpurvins and his team have brought them under one brand “Pure”. And for good reason, too.
“There were a few reasons we did that, including embedding them with our common systems and platform so we’re operating on the same quality management system, right across the entire framework,” he said. “We’ve found it’s really hard to grow if you don’t have an integrated business – you’ve got to have the spine of the business straight before you can grow – and that’s where we are now.”
The importance of culture
Like any successful business, culture
is at the core of what Pure does on a day-to-day basis. Finding a person with the right skill set is not that hard, but finding someone aligned to your values and being great at their job can be more difficult.
But Baltpurvins is adamant that buying into what the company is trying to achieve is just as important as the skill set they bring to the job.
“In the beginning, it was really hard to attract high-quality talent,” he said. “What we’ve found is that as the business has gained in scale and reputation, it’s been easier to recruit good people.
“We’ve also developed a very valuesdriven culture, which we have embedded, which means we’ve provided a lot of ownership to our employees, so they’ve
had an impact on the operation and success of the company. People are now coming to us looking for roles, and we’ve been able to get a lot of the key people within the industry to come and work for us. If you can keep that culture, you’ve got half a chance of success – it’s been a very valuable feature for the business.
“There’s nothing worse than working for someone who is completely misaligned with the way that you work.”
It’s been a good period of growth for Pure Environmental, but every step has been purposeful.
Baltpurvins and his team know that building something worthwhile takes a bit of time, and not rushing is something that they take into consideration when making decisions.
“We’ve been very careful to not over scale – you’ve got to finish something before you start five new things,” he said. “We’ve just been really careful with our strategy, which is really about team development. We’ve worked really hard at that for two years, and we’re now starting to see the fruits of our labour.”
Site chemists assess characteristics of all incoming waste streams.
Bright future for Lincom in resource recovery stakes
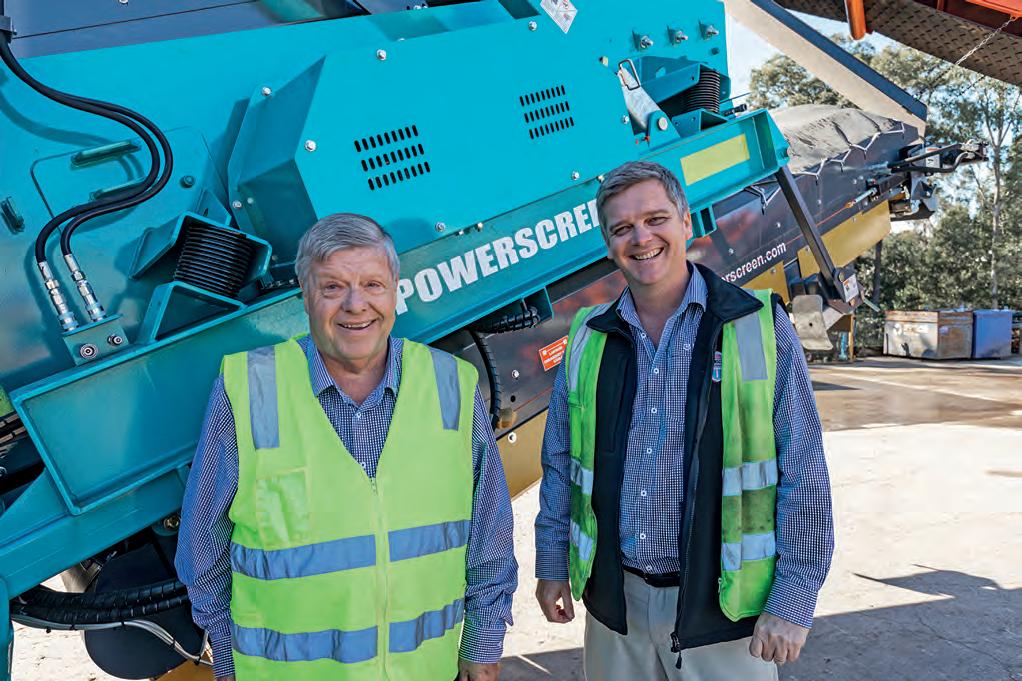
has paid his dues with the company, travelling all over Queensland and the Northern Territory in the early years. It was a good foundation and set up a lot of relationships with his clients that still hold to this day.
“It was the best apprenticeship ever,” he said. “It was an apprenticeship in life. You were learning a lot of things about people up there and business in general. I was a guy in my early 20s trying to sell a million-dollar tractors – it was a big challenge. My father was in the industry from 1982, and he had a big presence up there, so for me the easy part was being able to get in front of customers. It was a good inroad to help me get in there and have a chat with the customers and build those relationships.”
By Inside Waste
OVER the past three decades, Lincom has forged a name as a reliable supplier of an array of plant and machinery in the resource recovery space. This year the company is celebrating its 30th anniversary, and while dealing with clients in China and the mining industry was its main source of income in the first couple of years, it didn’t take long for it to diversify.
“Dad started the business in 1995, but by 1998 he started in the crushing and screening space,” said CEO Stephen Watterson.
Watterson himself joined in 1998, having left school and worked in a storage manufacturing facility.
“They were doing roll forming for sheet steel and doors and panels,” he said. “I was a roll former at that business. I never sold anything in my life before I started with dad.”
When his dad, Roy, asked Stephen to join the business, they both agreed it was a good idea and that began the Australian side of the business. What started out as a two-man band has now grown to an enterprise that employs more than 90 people throughout Australia. Initially they were a sub-dealer of the brands they worked with, as Sydney was already covered by the main dealer. Lincom looked after Queensland, Northern Territory, Coffs Harbour North, and Papua New Guinea. Now the company is nationwide. What changes
has Watterson seen over the past 30 years? For one, the sheer volume of the competition has increased.
“It’s a big ocean out there,” he said. “But like everything, the good part is competition is good and healthy for
every business. You have to educate clients about the unique selling features of the brands that separate themselves from each other.”
Although Watterson is based at Lincom’s head office in Brisbane, he
He admits that at the beginning it was not a dynamic sector. Back then, Queensland wasn’t known for its forward thinking in terms of landfill levies, while other aspects of the industry – such as infrastructure – were still in its infancy. However, it didn’t stop Lincom from becoming a solid business.
“It was a long, slow burn initially,” said Watterson. “To be honest, it’s been
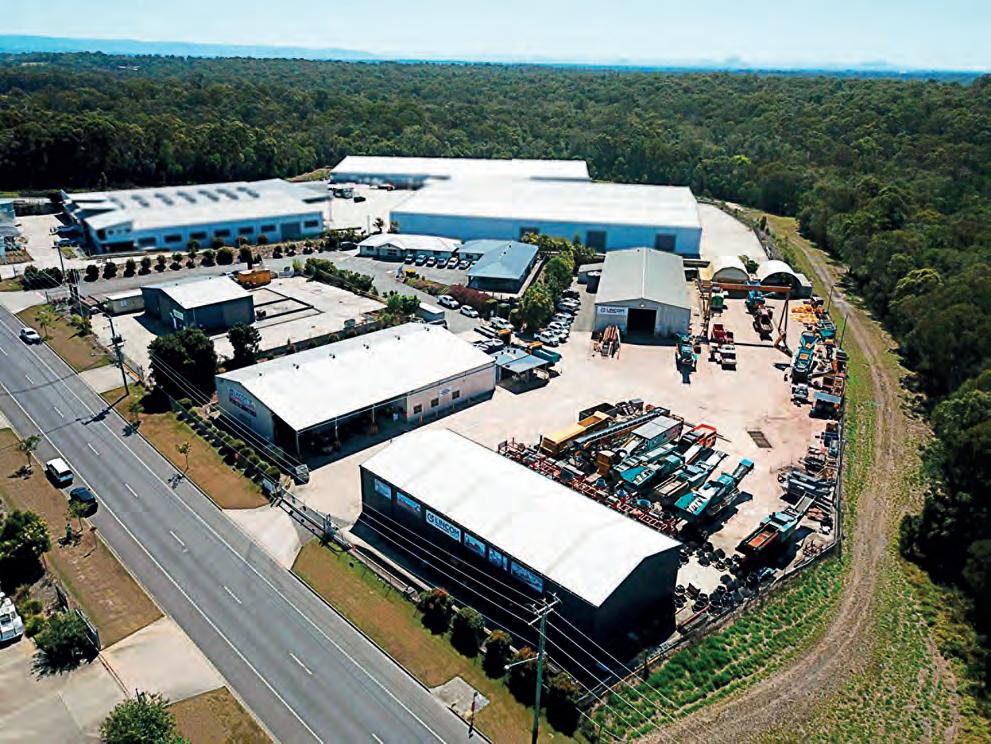
An aerial view of Lincom’s Narangbah facility.
Roy Watterson (left) and Stephen Watterson in front of one of Lincom’s screeners.
Images: Lincom
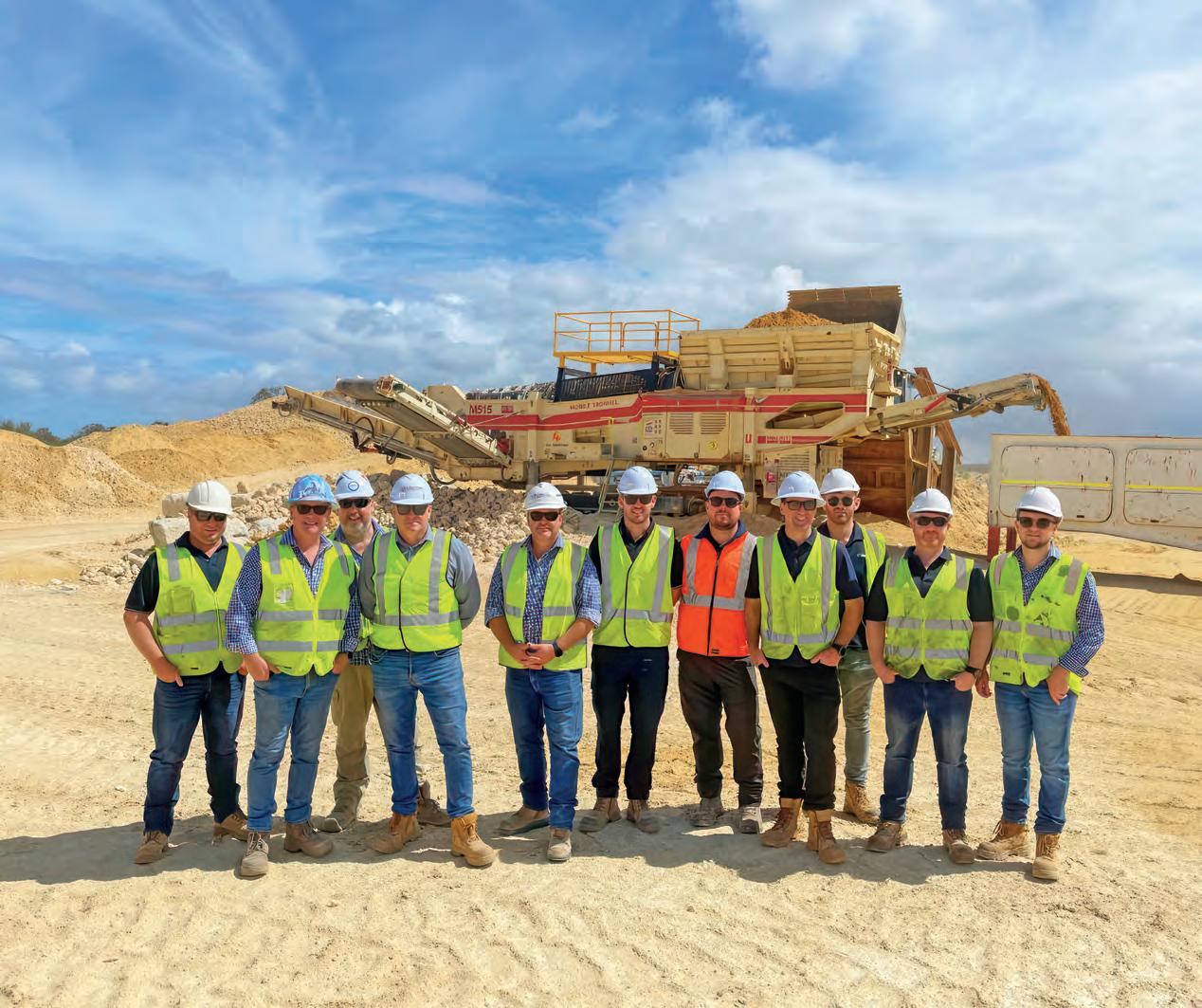
“The most technology advances have been definitely in the crushing range, as far as things like safety features and operational features. With the screening side of the business, Lincom has been a big part in driving forward to make sure these machines comply with local Australian standards and safety expectations.”
a good one, because we have put in a fair few plants around the place, and the sector is absolutely heating up.”
He said this uptick is mainly due to pressure from the public to turn waste into value and minimise what is going to landfill. He said an exciting part of Lincom’s business is a few projects that it’s finalising/commissioning, and there are more on their way in.
Materials handling is its main business, and the crushers and screeners from Powerscreen are one of the key product groups in its portfolio. In terms of technology, what have been the biggest improvements since he started?
“The most technology advances have been definitely in the crushing range, as far as things like safety features and operational features,” he said. “With the screening side of the business, Lincom has been a big part in driving forward to make sure these machines comply with local Australian standards and safety expectations.”
He said it is an exciting time to be
in the industry. A lot of Lincom’s clients use its crushing and screening machines, with many of them being used in recently constructed resource recovery infrastructure. The company’s collective knowledge means that whether it’s dealing with coal mines, iron ore mines, mum and dad quarries, multi-national quarries, or council quarries, it knows what machine is best suited for what operation. With eight depots around the country, Lincom has a wealth of experience if clients need a helping hand.
“We’ve got 25 dedicated field service engineers, admin staff, parts staff, internal workshop fitters, sales guys, and a health and safety officer, too,” Watterson said. “It’s important to have all that infrastructure behind you, because we pride ourselves on our aftersales and support – I know it’s a cliché –but you’ve got to be able to back it up.”
Watterson still likes to be “on the tools,” so to speak. Even though he is now a director and CEO of the company, he still has relationships with customers.
“I’m not just behind a desk. I believe that real impact comes from direct involvement, and I make it a priority to stay connected, ensuring that our work drives meaningful results,” he said. “I’ve got a great rapport with our customers, and a lot of them are good mates of mine now.”
As for the future, while he is confident that Lincom will do well, the industry could do with a little more love from the various forms of government. This is especially so around new pieces of infrastructure and the compliance issues around getting these projects off the ground and up and running.
“What worries me is how harsh some of these compliances are, yet at the same time the government’s trying to push ahead to really get into this sector and do things,” he said. “On the one hand, you’re getting pushed, but on the other hand, you’re getting pulled. I think there’s definitely going to be a lot of noise around the recycling space.
“This country, being as small and
as young as it is, could learn a lot from Europe and the UK and not make the same dramas, issues, and mistakes over again. Let’s go to those guys and look at what they’ve done, what mistakes they made, and where they are now. I think that would be a fantastic outcome to help us in our journey – to get it done right and to get it done quicker.”
Finally, Watterson also believes that two areas the industry can improve on immediately are harmonisation between the states and educating the public. The former is something the industry has to rely on the governments to come to an agreement over. However, the latter is in the hands of the industry itself.
“It’s an education process from people like myself and others in the industry who are putting rubbish in our wheelie bins every day,” he said. “We have to educate people to understand that waste isn’t a dirty word, recycling is not a dirty word, and that there is a resource that we can get out of those products. This will help Australia move forward.”
The Lincom sales team has an array of quality screens and crushers designed for working in the waste/resource recovery industry.
Rebrand looks to the future
By Inside Waste
ONE of the must-see events of the 2025 waste/resource recovery sector is ReGen 2025. Formally known as AWRE, the event will be held at Sydney’s International Convention Centre (ICC) from July 23-24, 2025.
Organised by Diversified Australia, this showcase of the resource recovery industry has been rebranded to be inclusive as it now encompasses aspects of the circular economy and the industry – and Australia’s – move towards a resource recovery-orientated sector instead of waste alone.
“At ReGen – Australia’s Circular Resource Expo – sustainability is at the core of everything we do,” said event director Ali Lawes. “We recognise that as an industry, we have a responsibility to reduce our environmental impact and drive meaningful change. That’s why we are taking action through a range of initiatives that promote resource efficiency, waste reduction, and responsible business practices.”
The event will showcase cuttingedge technical displays, offer industry insights, and feature keynote addresses, panel discussions, and networking opportunities. The seminar program aims to help attendees navigate their roles in creating a circular economy, which keeps resources in use, minimises waste, and regenerates natural systems.
“Our commitment extends beyond the show floor through partnerships

with industry leaders in sustainability,” said Lawes. “We are proud to work with ICC Sydney as our Sustainable Venue Partner, ensuring environmentally responsible event operations. Harry the Hirer, our Sustainable Contractor Partner, provides hire solutions that prioritise reuse and circularity. The CN Agency supports us in measuring and reducing our environmental impact, while Huskee Cups is our Reusable Cup
Partner, helping us reduce singleuse waste. We also collaborate with Global GreenTag and GECA to highlight exhibitors whose products meet high sustainability standards.”
ReGen will incorporate Circularity, Australia’s original circular economy conference, into its 2025 education program. Circularity will reach a broader audience, offering free sessions on topics such as circular product design
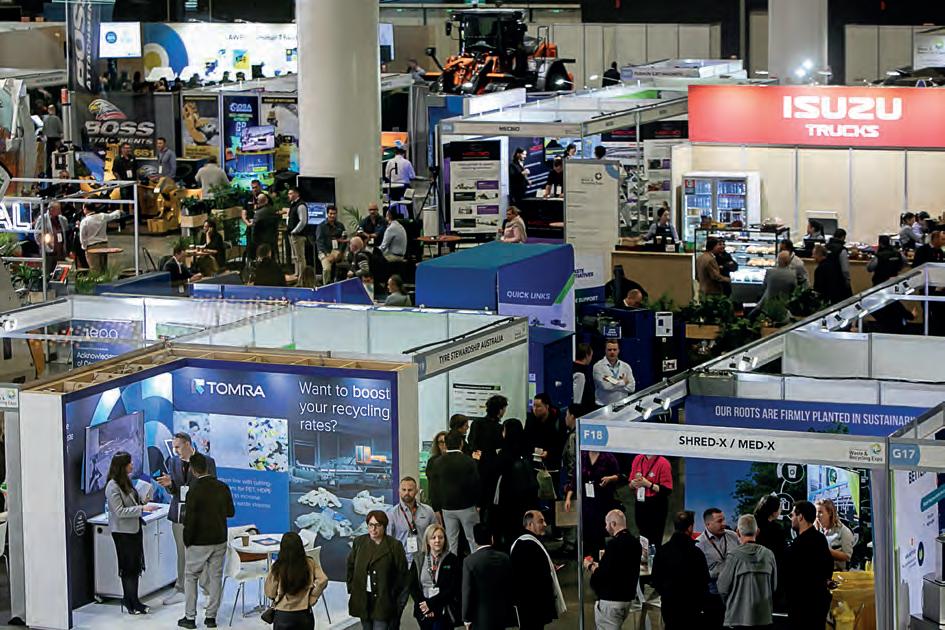
and sustainable waste management –ensuring these critical insights remain accessible to all attendees.
The expo’s name, ReGen, represents both the regenerative practices it champions, and the generational transformation required to meet sustainability goals. ReGen invites participants to “Rethink, Redesign, Repurpose, and Renew” as they contribute to a circular and sustainable future for Australia.
Diversified is also championing a new awards program, specifically for the event.
“Our Sustainable Exhibitor Awards will celebrate exhibitors who are leading the way in reducing their environmental footprint, from using recycled materials and energy-efficient lighting to minimising waste and adopting carbon-conscious practices,” said Lawes. “Through these awards, we aim to inspire and recognise those making a tangible impact. This includes encouraging digital signage and reusable materials to composting food waste and investing in green energy – every decision we make is guided by our goal of creating a more sustainable future. By working together – exhibitors, visitors, and partners – we are not only shaping the future of events but also contributing to a broader movement towards a circular economy. At ReGen, sustainability isn’t just an ambition; it’s a commitment in action.”
There will be cutting-edge displays and keynote addresses at ReGen 2025. Images: Divcom
Organisers are expecting big crowds at the rebranded event.
Shredders and grinders make short work of organic waste

By Inside Waste
ORGANICS and green waste recycling is at the forefront of Australia’s circular economy transition, offering business savings and environmental benefits. But how are organics and green waste processed, and how is mulch produced?
Timber mulches are processed by shredding and grinding to different particle sizes and shapes to meet different specifications. That’s where mobile recycling specialists DAVIS EARTHMOVING come to the helm. A privately owned company, DAVIS specialises in green waste processing, mulching and recycling of timber and vegetation. The company is responsible for the provision of all necessary personnel and equipment for processing of materials in accordance with its own high standards. Its machinery can assist with processing for landfills, recovery facilities, road widening or land clearing operations around NSW.
It’s the job of a 20-plus tonne
“The key is having reliable equipment available, capable operators, stringent WHS procedures and running an efficient operation that allow us to achieve the work in the requested time frames.”
excavator to use hydraulic shears to shear up any larger logs, stumps and trees. Next, is the 1050 horse-power horizontal grinder’s time to shine. Horizontal grinders are suitable to process large green waste, garden organics, trees and limbs, logs, stumps, root balls, crates and pallets. Material may be derived from domestic, commercial, industrial and demolition sources; scrap wood recyclers, logging, the pallet industry, sawmills and lumber remanufacturing, land clearing and mulch producers.
DAVIS has a comprehensive fleet of horizontal grinders and shredders for hire or contract within NSW, with six grinder shredders available and 20 excavators plus shear attachments. It also has a
range of track-mounted trommel screens to produce high-quality mulch sizes and soil conditioners.
DAVIS is celebrating 50 years in business this year with the most recent addition to its mulching fleet being a Diamond Z DZH5500TKT horizontal grinder.
“We have a Diamond Z 6000 and 4000 and are so impressed with their production and running capacity, we were compelled to purchase the 5500 model as well,” said CEO Eric Davis explained. “It’s the newest addition to the Diamond Z Grinder line and is the perfect combination of size, power and performance.”
With a CAT C-27 Tier IV Final power, 3,800 square inches of screen area, the
DZH5500TKT does the work of bigger machines, yet is easily transportable.
“We have worked hard over decades to refine our skills and earn many of the big timber and green waste processing jobs around NSW,” said Davis. “The key is having reliable equipment available, capable operators, stringent WHS procedures and running an efficient operation that allow us to achieve the work in the requested time frames.”
Davis notes the importance of being capable to undertake the work sometimes within days of being notified.
“If a waste facility’s site is overflowing with green waste stockpiles at capacity, they will need us to come in a hurry to process with our equipment,” said Davis.
“Our tracked machines are mobile, meaning that we can travel anywhere, and operate in tough terrain. Moving machinery to each stockpile for grinding.”
Green waste and organics processing is economical and environmentally friendly. Diverting organic green waste from landfill, effectively closes the loop.
DAVIS EARTHMOVING’s fleet of horizontal grinders and shredders can process most FOGO waste streams. Image: DAVIS EARTHMOVING
Onetrak acquires CSS Recycling Equipment Solutions
By Inside Waste
ONETRAK has acquired CSS Recycling Equipment Solutions, a provider of specialised waste and recycling machinery.
This merger unites two familyowned Australian businesses with a shared commitment to delivering innovative solutions to the resource recovery and waste industry. Founded by David and Jaime Hazell in 2006, Onetrak has grown over 18 years into a trusted heavy equipment distributor, serving industries such as forestry, construction, quarrying, and material handling. It represents international brands like Tigercat, Terex Fuchs, Anaconda, and Hidromek. It provides sales, hire, service and parts across its seven branches nationwide.
“Our aim has always been to go beyond selling machines,” said Onetrak managing director David Hazell. “We offer solutions that add value to our
customers’ operations. The integration of CSS Recycling allows us to expand into the waste and recycling sector, a rapidly growing industry with exciting opportunities for innovation and sustainability.”
For CSS customers, this merger enhances the level of support and resources available, such as:
A n expanded support network –access to more tan 50 4×4 field service vehicles and factory-trained technicians across Australia.
P arts availability – a network of parts ensures timely delivery for machine maintenance and repair.
B roader expertise – continued service and personalised attention from Neil Coyle, CSS director, and his team, supported by Onetrak’s 100-strong workforce.
Multiple locations – seven strategically located facilities equipped with state-of-the-art tools and multi-bay workshops.
“This is an exciting opportunity to grow CSS Recycling’s footprint and offer our customers access to an even broader range of equipment and expertise.”
“This is an exciting opportunity to grow CSS Recycling’s footprint and offer our customers access to an even broader range of equipment and expertise,” Coyle said. “By joining forces with Onetrak, we’re building a stronger, more capable organisation ready to t ackle the challenges of the waste and recycling sector.”
Why the waste and recycling sector matters
Onetrak’s decision to expand into the waste and recycling sector is both strategic and timely. The industry aligns with Onetrak’s commitment to industries that process and add value to materials. Several factors make this sector an ideal focus:
Existing synergies – many of Onetrak’s OEM partners, including Tigercat, Terex Fuchs, and Anaconda, already supply equipment that serves the periphery of the waste and recycling industry. Expanding further into this space is a natural progression.
Industry growth potential – the waste and recycling sector is
Australia, driven by a surge in new projects and initiatives focused on sustainability and resource recovery.
Value-adding opportunities – recycling processes involve significant downstream processing, creating opportunities to maximise the value extracted from materials. This aligns with Onetrak’s expertise in delivering solutions that optimise efficiency and output.
S olution-driven approach – Onetrak prides itself on being more than just a heavy equipment retailer. The company specialises in offering professional advice and tailored solutions to help customers achieve the best outcomes from their capital investments. Whether it’s timber, organics, sand, or scrap metal, Onetrak provides the expertise needed to navigate the complexities of material processing.
By partnering with CSS, Onetrak combines its infrastructure and solutionoriented philosophy with CSS’s expertise in recycling technologies. This integration positions the company to lead in offering solutions for Australia’s evolving waste and recycling industry.
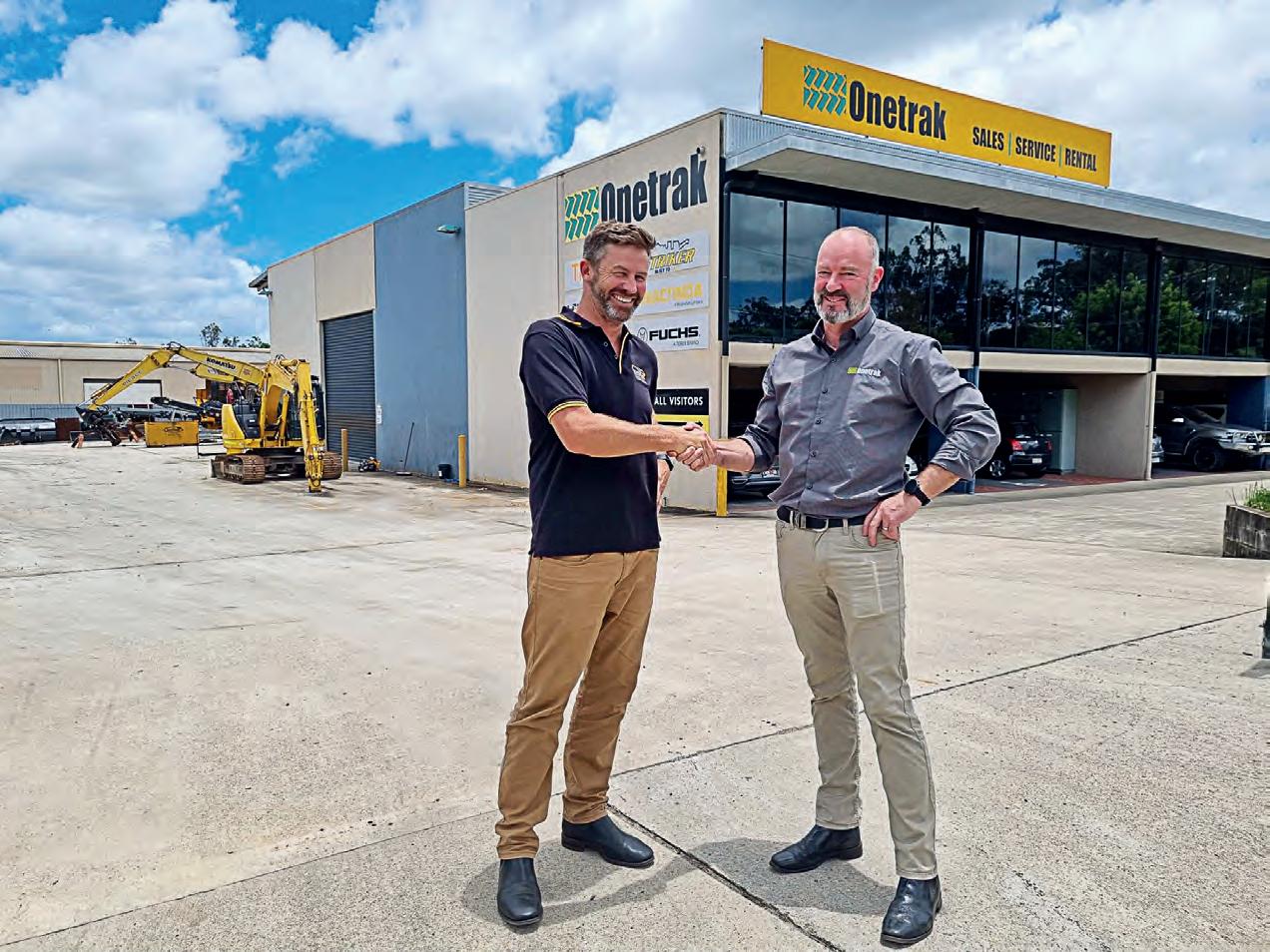
CSS’s Neil Coyle (left) and Onetrak’s David Hazell seal the deal. Image:Onetrak
Low-speed shredder for rugged environments
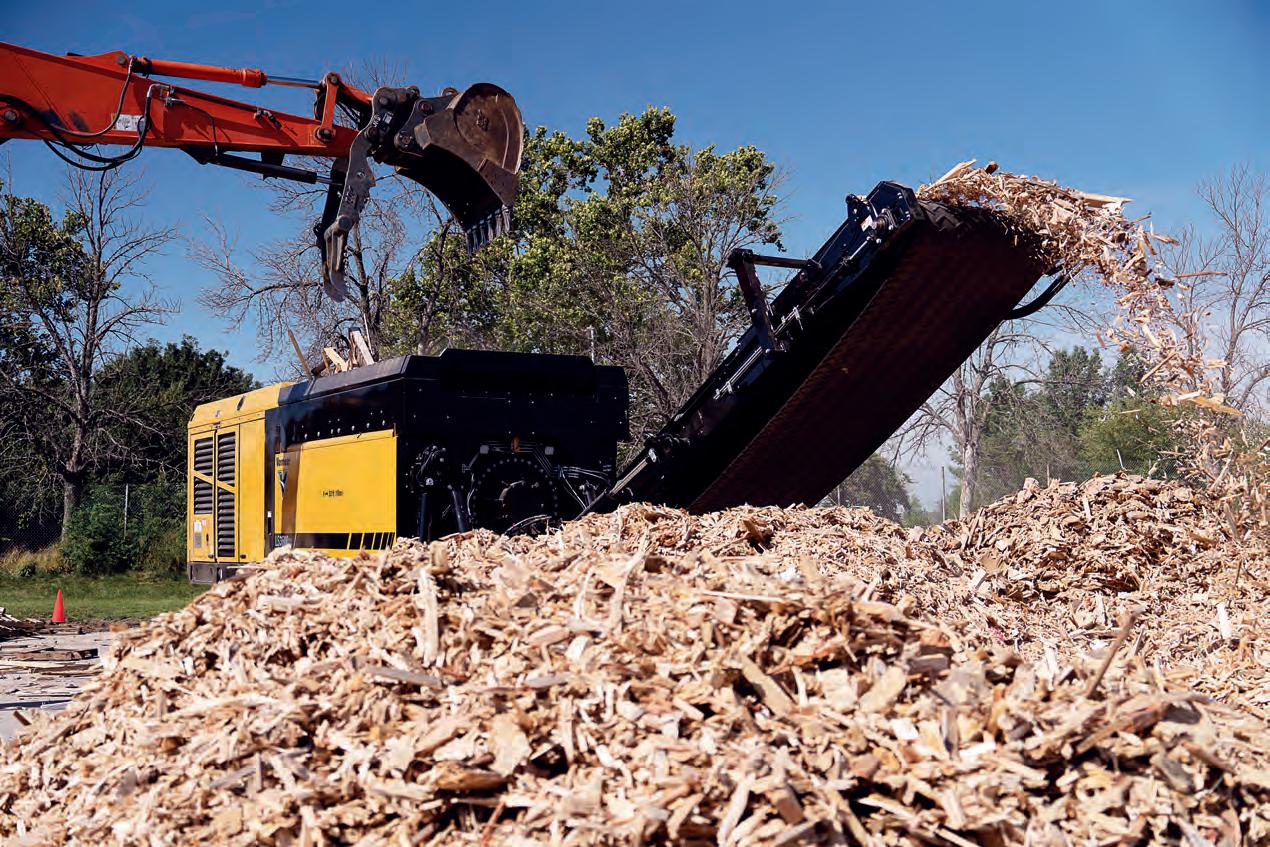
SINCE 1994, Vermeer has been at the forefront of transforming the wood processing industry, delivering solutions designed to meet the unique needs of its customers. One of its key offerings is the LS3600TX low-speed shredder.
This unit is powered by a 456-horsepower CAT C13B Tier 4 Final diesel engine, offering 2082 foot-pounds of maximum torque with a 552-litre fuel tank capacity.
It provides maximum productivity over long periods time. The Vermeerengineered mechanical drive system allows for maximum horsepower transfer to the rotor compared to hydraulically driven systems, resulting in maximised torque while running at low horsepower. This design provides longevity and engine life without impacting productivity.
Engine service and maintenance are redefined with easy access to the machine’s internal mechanisms. The maintenance-friendly and readily accessible engine bay design includes large accordion-style access doors,
larger maintenance projects, the entire engine enclosure can be removed.
At the heart of the machine, users will find a multi-application durable design that maximises productivity while minimising maintenance. Aggressive rotor teeth positioned along the drum face are engineered to maximise performance while minimising contact points to process material more efficiently. This 10-foot-long welded rotor comes in a 21-tooth configuration consisting of both tall and short teeth. Reliability and maintenance are a focus, as evidenced by the dual bolt quick-change teeth.
Its individual bolt-in comb teeth that have two usable edges, help to extend the life of the teeth while minimising maintenance costs. With a hydraulically movable comb structure, comb teeth maintenance can be performed from ground level, providing ease of maintenance when required. Its design gives the operation versatility with the ability to control the size of the material by adjusting the spacing between the comb and rotor.
Like any piece of heavy equipment, operator safety is a key element in the LS3600TX’s build. It offers three stages of protection to help minimise the likelihood of damage due to contaminants.
1. The Comb – constantly monitors cylinder pressure and will open when a set pressure is reached, providing protection to the rotor, transmission, and driveline.
2. The Transmission – equipped with a twin-disc reversible mechanical transmission for efficient power transfer that maximises productivity. The software design includes a lockout feature to help protect the clutches from locking up.
3. The Drive Line – includes a ball detent torque limiter that automatically disengages the driveline when maximum torque is experienced. Resetting the torque limiter is as easy as reversing the rotor until you no longer hear clicking from the mechanism.
Transition is key with the utilisation
and longevity. The belly belt cartridge does not require the rear discharge conveyor to be removed when changing the belt, which allows for efficient maintenance.
The self-supporting discharge conveyor includes a proportional valve for speed customisation, and the height of the conveyor is adjustable from the remote. For ease of transportation, the conveyor folds up and over the machine.
All controls are located at the front of the machine on the control panel outfitted with touchscreens. Most operational functions can be achieved at this station, but the few that can’t are initiated with the wireless remote, giving the operator the freedom to control the unit from the seat of a loader. The remote provides live data and feedback, allowing the operator to make adjustments as material changes. The tracked unit is controlled from our remote transceiver with proportional joysticks, giving the operator ultimate control.
The LS3600TX is powered by a 456-horsepower CAT C13B Tier 4 Final diesel engine. Image: Vermeer
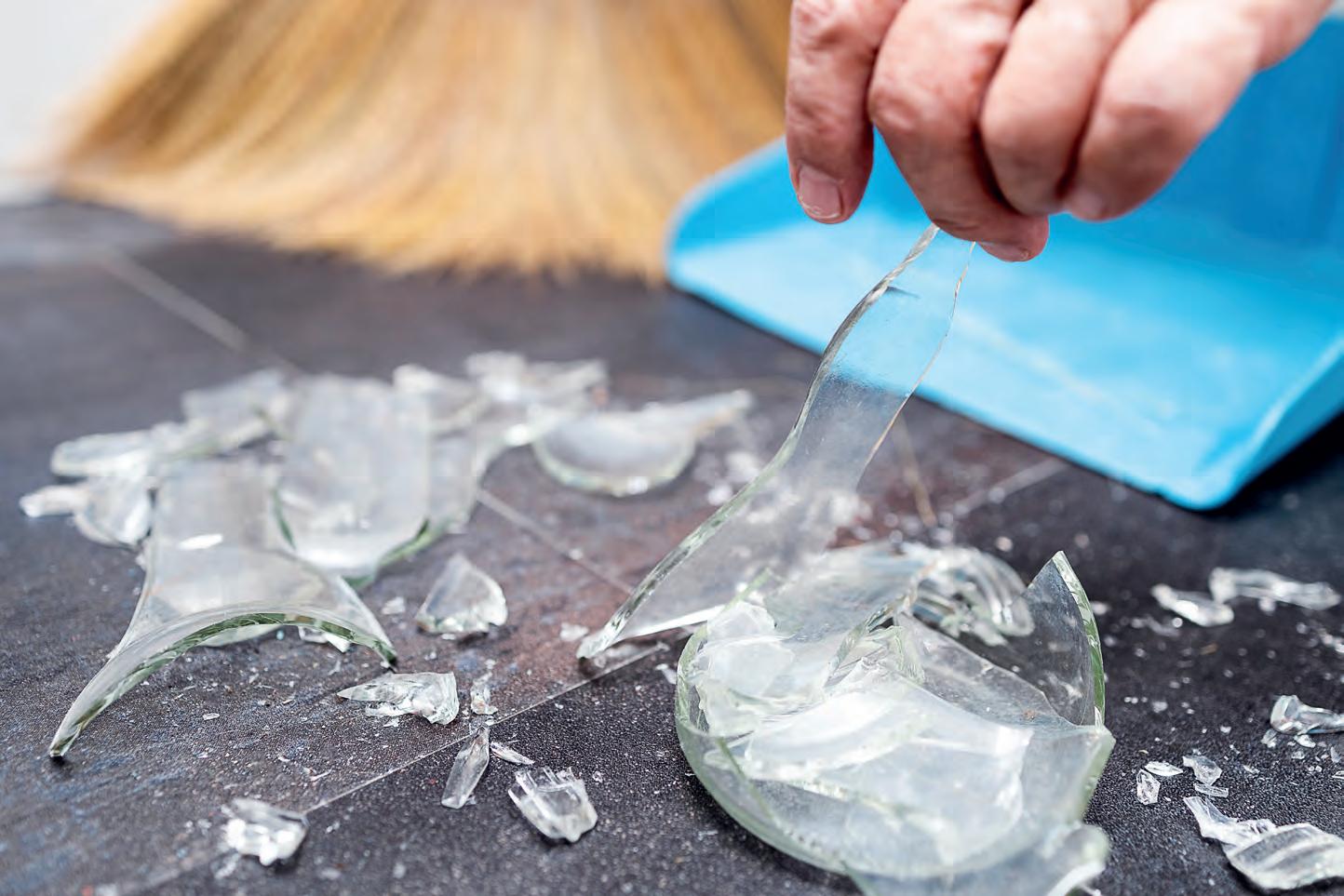
Taking on contaminants one bite at a time
By John McKew
THERE’S AN old adage that the way to eat an elephant is one bite at a time. I cannot help but think that this has correlation to organics recycling and contamination – is it time to solve contamination, one contaminant at a time? Do we need to start focusing attention and action on specific contamination problem areas, providing focus and attention to specific items instead of broadly speaking of contamination as a wide-ranging issue and hoping that will help solve the myriads of issues?
Recently, I visited an organics’ recycling facility in Melbourne. A facility that is well regarded for best practice and leading-edge operations in processing and material handling. Yet, despite all of this, contamination is easily visible and pervasive. The biggest visible problem – plastic. Despite continuing significant investment by most organics recycling processors into managing contamination, the problem is not getting resolved. Perhaps we need to start consuming the contamination elephant one bite at a time. At AORA, we have started advocating on the contamination issue in just that way.
Batteries – not a week goes by without another disastrous fire in a recycling facility or truck that has been caused by the inappropriate disposal of batteries. AORA joined with ACOR and eight other peak industry bodies in October 2024 with an urgent call on Australian, State and Territory Governments to implement a range of measures to reduce the battery fire risk including, but not limited to, prohibiting the disposal of batteries in household and commercial waste. There should be penalties for non-compliance and the establishment of easily accessible collection points for safe disposal of loose and embedded batteries across Australia.
Glass – AORA released its glass position paper in February 2025. Glass is a problem within organic processing facilities. It can break easily when not handled with care and once that happens, segregating it up becomes difficult and dangerous. Unfortunately, when it does find its way into an organics stream, it is either broken on tipping into the truck or it will often be broken (shattered) when the truck delivering the organics unloads its contents onto a concrete floor.
Once this occurs, removal becomes almost impossible. Shards of glass are hard to see and impossible to remove completely from the organics. It becomes a health and safety issues risk for those operators dealing with it. Glass is a serious contamination problem within an organics processing facility for all of the aforementioned reasons. Furthermore, no one wants to see shards of glass in their compost when they come to use it on their garden, lawns, fruit trees or vegetable patch.
AORA’s Better Compost with Smart Bans position paper was released in October 2024. It calls for bans on (1) Plastic fruit and vegetable food labels, (2) Plastic bread seals and (3) Styrofoam food packaging. It also wants better disposal options on a range of other contamination including disposable wipes and all plastic packaging.
Understanding how best to dispose of a ‘waste’ item is not too difficult. Local councils can provide information and assistance to their households with what can go into what kerbside collection bin, and they are a great place to start for any household. The various State governments also have
a range of information and guides available, which something as simple as a Google search can help lead the way.
The Recycle Mate app is another great option. By using a smartphone camera to take a photo of an item, the app can aid in finding the right disposal option in the local area.
Of course, the contamination issue is not just an organics recycling industry issue. We need everyone on board to help resolve this – the Federal government, State governments, regulators like the EPAs, Local government, and the community/ general public. If we do not collectively take responsibility and work in the best interests of all recycling industries, including organics, the problem will not go away. Yes, we need broad-based, recurring education programs that encourage and reward best behaviour in recycling. The rewards are there for all if we succeed – socially, economically and environmentally. But perhaps the starting point is to focus on one contamination issue (bite) at a time.
John McKew is the national executive officer for the Australian Organics Recycling Association
Broken glass is a malevolent contaminant that is hard to get rid of once it is in the organics waste stream. Image: CGN089/Shutterstock.com
Mobile screener saves time and increases efficiency
By Inside Waste
SCREENS
play a big part in recycling by separating materials. Once such piece of gear is the Terex Ecotec TRS550 Spaleck screen – a piece of equipment that is designed to efficiently separate and screen a wide range of materials. This makes it suitable for waste management and composting operations with its patented flip-flow technology. This specialised machine does the tough jobs in the harshest of conditions.
The Ecotec TRS550 Spaleck Screen minimises down time and maintenance costs while increasing productivity and overall efficiency.
Its compact design and low energy consumption makes it cost effective and environmentally friendly choice for any recycling facility.
Western Composting Technology, based in Shepparton North, Victoria, is one company that has invested in the machine.
And they’re glad they did, according to the company’s operations manager John Wilson.
“We like the screen a lot,” he said. “In the past we were using a fixed trommel, while this is a mobile screen. We’re finding it to be more efficient and we can feed material in a lot quicker than the fixed trommel.”
As well as being an efficient and versatile mobile screening machine, it comes with a specialist screen box from
• M agnetic head drums on fines and mid fraction conveyors.
S uitable for feeding heavy of bulk material.
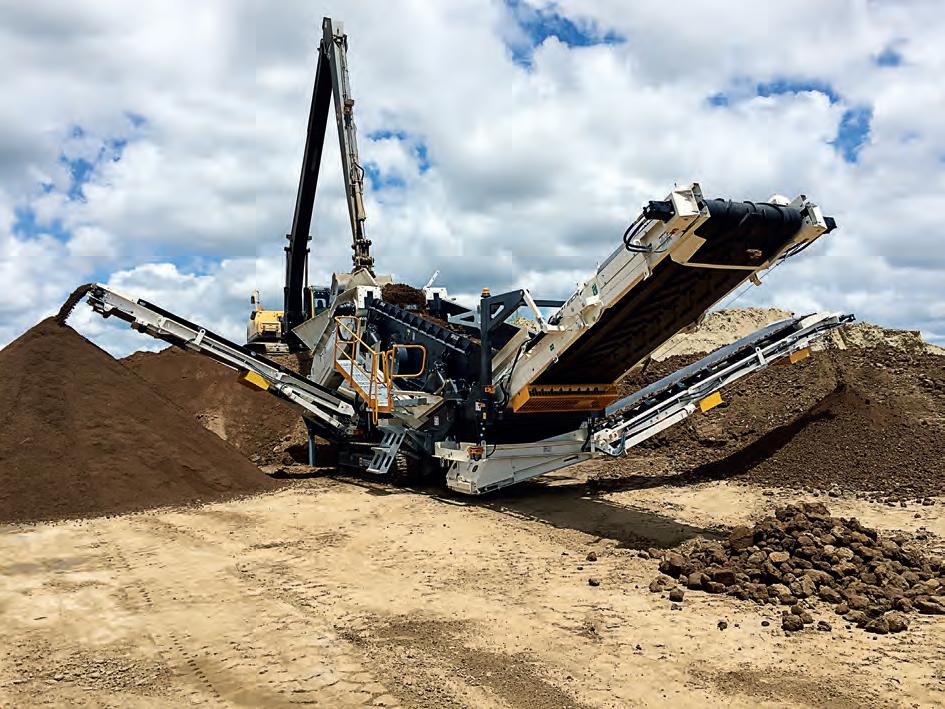
deck screening panels and an aggressive flip-flow bottom deck, allow the machine to perform difficult applications. Then there is the time savings from continuous operation.
The flexible top deck option virtually
steel waste are just a few of the many applications this machine excels.
Features of the machine are:
Self-cleaning screen media using intelligent design.
H eavy-duty, abrasion-resistant,
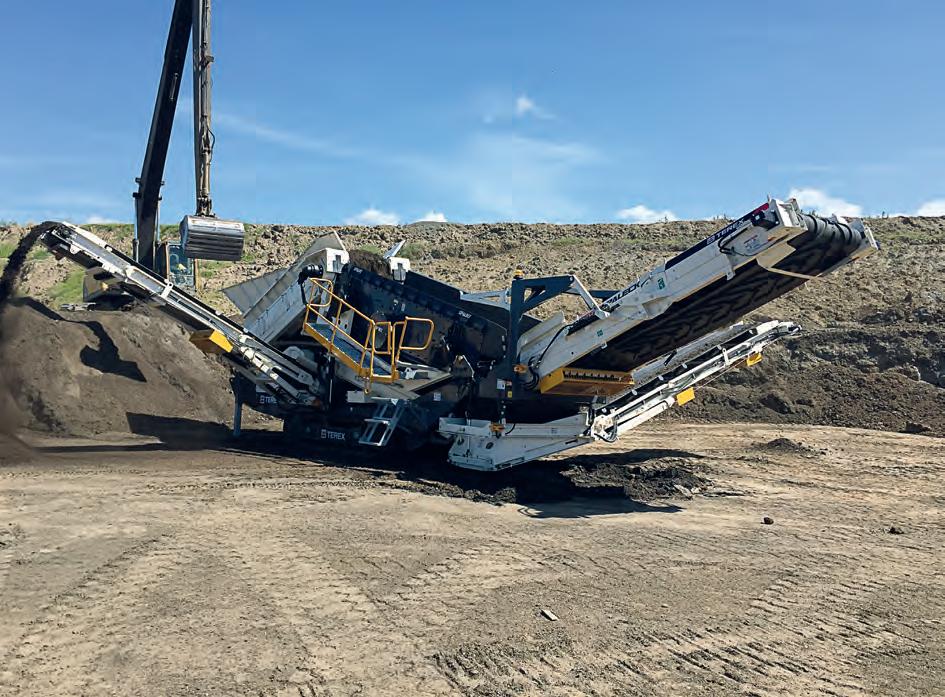
O n tracks making it easy for moving the machines in operational areas.
Additional specifications are:
Tier 3/Stage IIIA: Caterpillar C4.4 engine power: 83kW (111.3hp) engine speed: 2200 rpm.
O p deck: 4.8 m x 1.53 m; Bottom deck: 4.8 m x 1.53 m.
Weight: 30,500kg.
L en gth: 14.8 m; Width: 3 m; Height: 3.4 m.
Overall, Wilson said that they notice a big difference in their operations since bringing the machine onboard.
“Being mobile is probably the one highlights, because you can save a lot of travel time in your loader,” he said.
“Driving from our wind rows to the fixed trommel can take a lot of time.
“And certainly, once you get to the get to the furthest corner of the yard, to where the trouble is, you’re saving a lot of time, because you can just keep on moving that screen based on where you’re working.
“When it comes to maintenance and safety, it’s pretty good. We haven’t had any issues. We’re just really happy with it – it’s doing a fantastic job. We couldn’t be more happy with the choice we’ve made.”
The Terex Ecotec TRS550 Recycling Screen is available only through Finlay Waste & Recycling.
The machine has many features that allow it to perform difficult applications.
The TRS550 Spaleck Screen minimises down time and maintenance costs. Images: Finlay
Cleaner waste streams via Eriez eddy separators
By Inside Waste
IN the late 1960s, Eriez patented both permanent magnetic and electromagnetic eddy current separators. These machines were designed to improve permanent magnetic circuits with rare earth magnetic material for stronger eddy currents and improved separation of nonferrous materials.
Its non-ferrous separators utilise permanent rare earth magnets to induce eddy currents into metallic particles. This produces repelling forces that separate the metallics from non-metallics. The result is a cleaner waste stream that can be further processed. Removal of the metallics is selective, and product loss is minimised, according to Eriez.
The nonferrous metallic separator has an external drum, an internal permanent magnetic rotor, a drive, and a belt conveyor. The external drum shell of non-metallic composite material rotates at normal belt conveyor speed. The internal rare earth alternating polarity rotor turns at much higher RPM than the external shell. Through the induction of eddy currents and the resulting repelling forces, the alternating magnetic field selectively repels the non-ferrous metals and physically separates them from other materials.
RevX-E Eddy current separators
The company’s RevX-E Eddy current separators feature an eccentrically mounted magnetic rotor within a nonconductive shell for the separation of nonferrous metals. The rare earth rotor produces a powerful, focused field at the end of the belt.
Features include:
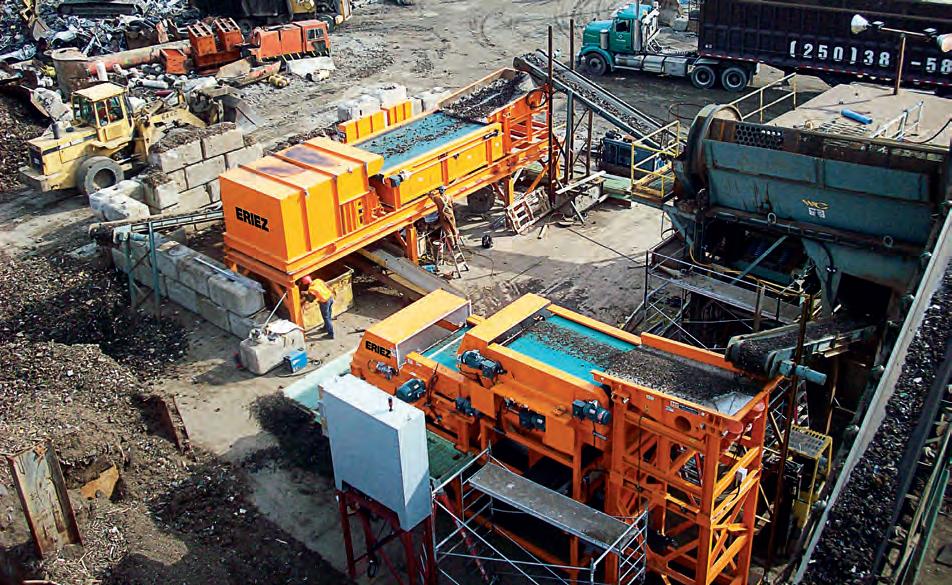
Cantilevered frame design for quick conveyor belt changes (10 minutes).
R ack-and-pinion splitter adjustment for precise splitter placement for optimum separation.
L arge access panels that allow for easy maintenance access.
Compact design requires less space.
Direct drive rotor and direct drive conveyor.
Other feature:
S izes offered – 1m wide, 1.2m wide, and 1.5m wide.
R otors o ffered – LT2 rotor assembly: eight pole rare earth eccentric rotors for coarse (+1”) size fractions. ST22 rotor assembly: 22 pole rare Earth eccentric rotor for +1/4-inch to -1-inch size fractions.

As its name suggests, the ultrahigh-frequency eddy current separator recovers ultra-fine aluminium, copper, and other non-ferrous fines materials typically missed on traditional eddy current separators from ASR.
This separator’s combination of a rotor designed to produce high Gauss at the belt’s surface, with many magnetic poles operating at higher rpms. This creates ultra-high-frequency changes resulting in the separation of fine non-ferrous and bare copper wire. This machine provides a cost-effective solution to improve zorba recovery without the need for additional expensive sensor-based or optical sorting equipment.
Each 1m-wide unit ships with an Eriez Brute Force feeder to provide even distribution of material across the width of the conveyor.
It is also capable of recovering bare copper wire and other valuable nonferrous metals as small as 2-3 mm.
Other features include:
A carbon fibre shell.
P recise rack-and-pinion splitter adjustments.
Eriez’s design includes a cantilever frame to expedite conveyor belt maintenance. A belt can be replaced in under ten minutes.
FinesSort system
Eriez’ FinesSort Metals Recovery System uses magnetic components to recover
valuable ferrous and nonferrous metals from the fines waste stream in scrap yards. This system not only reduces the amount of waste destined for landfill, but also reclaims thousands of valuable pounds of metals per day.
Features include:
Recover metals less than one inch.
M ulti-stage separation process.
P owerful magnetic circuits.
6 0-inch machine width.
Pa y back in as little as six months.
RCS – Rougher, Cleaner, Scavenger
Positioned downstream of ferrous separation and screening equipment.
Eriez’s Rougher, Cleaner, Scavenger (RCS) non-ferrous processing system employs three ECS units in a specific sequence to produce a high-grade zorba while maximising recovery. This type of processing circuit has been used in highvalue mineral processing and mining operations for decades.
Through months of full-scale testing, Eriez’ research revealed these averages:
A single ECS at the “rougher”setting yields 81 per cent recovery when producing a 90 grade zorba product.
An RCS system with multi-stage “rougher,” “cleaner,” “scavenger” processing averaged 98 per cent recovery while meeting the (Green Fence) 98 per cent metals quality standard.
An Eriez eddy current separator recovers copper and other nonferrous metals. Images: Eriez
These eddy current separators can recover metals less than one inch in size.
Collective vision – shaping the future of waste management
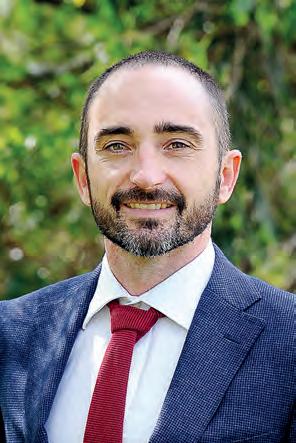
By Inside Waste
AUSTRALIA’S waste industry is evolving rapidly, navigating shifts in policy, technology, infrastructure and consumer expectations in its pursuit of a thriving circular economy. According to Thomas Freeman – managing director of Impact Environmental, the company responsible for the Coffs Harbour Waste Conference – there are many and varied challenges at play.
1996, much of the sector’s focus was on landfill and technical knowledgebuilding, and our programming
reflected that,” said Freeman.
“This remains an important part of the mix, but over the years the focus has grown beyond waste disposal to include the processing side of the industry, contracts, relationship management and much more. It is crucial for government, industry and community to work together to develop the strategies and solutions Australia needs now and into the future.”
The annual Coffs Waste Conference has long been the go-to for the Australian waste industry, uniting experts and practitioners across government and industry to explore critical challenges and innovations and spark collaborative solutions. This year’s conference, taking place at Opal Cove Resort from May 13-15, promises to be the most dynamic, interactive and relevant to date as Freeman and the Impact team build on the legacy his father—long-time industry leader Greg Freeman, now retired— nurtured across three decades.
“The program is very much determined by industry. We invite papers from a wide cross-section of professionals and organisations, revealing the challenges and innovations most relevant to the sector. We then build our key themes and agendas
Government’s new mandatory FOGO (food and garden organics) legislation to Energy from Waste, infrastructure needs, the circular economy, and education.”
Other key themes at Waste 2025 include recycling and resource recovery, collection, landfill, equipment and technology, strategy and planning, Indigenous waste management, and commercial, industrial, construction and demolition waste.
The intensive three-day schedule is divided into four streams to enable delegates to tailor learning to their specific needs. Participants will hear from more than 100 foremost experts from government, industry and advocacy bodies.
“We are excited to welcome NSW Environmental Protection Authority CEO Tony Chappel, who will deliver a keynote address’,” said Freeman. “We’ll also hear from the NSW Environment Minister Penny Sharpe.”
Other key speakers include Visy Industries executive general manager, recycling, Tierry Lauren on the future of recycling in Australia, Blue Environment director Joe Pickin on highlights of the National Waste and Resource Recovery Report 2024, and NSW EPA’s Bronwyn Isaac on the development of the NSW
their vibrant perspectives to rethinking communication for deeper community engagement. Further presenters will be announced in the lead-up to the event.
The three-day program includes four interactive expert panel discussions offering critical insights. Topics include accelerating progress towards 2030 resource recovery targets, leveraging textile waste, effective product stewardship, and mitigating the risk of battery-related fires.
“We’re also offering a diverse program of interactive workshops covering key issues such as local government waste procurement, optimising waste levy exemptions, illegal dumping investigation, composting and more.”
Freeman said that the social aspects of the conference are a central and much-loved part of the event, with ample networking opportunities and highly anticipated social events included in the program.
“Attendees look forward to this once-yearly opportunity to connect in person with their peers from across the full spectrum of the industry, at all levels, to share ideas and experiences and build community,” he said.
“Coming together as an industry
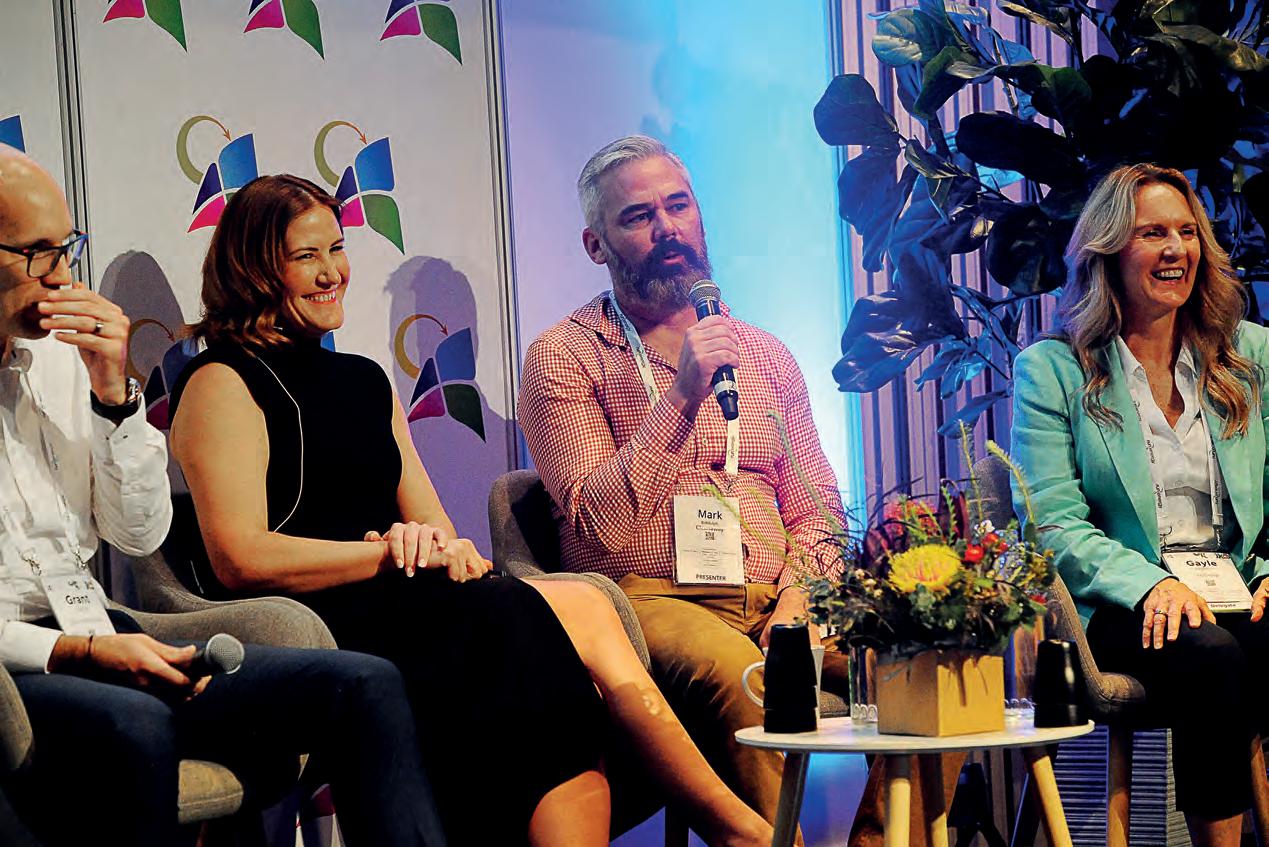
Impact Environmental’s Thomas Freeman said the Coffs Harbour Waste Conference has changed a lot over the past three decades. Image: Thomas Freeman
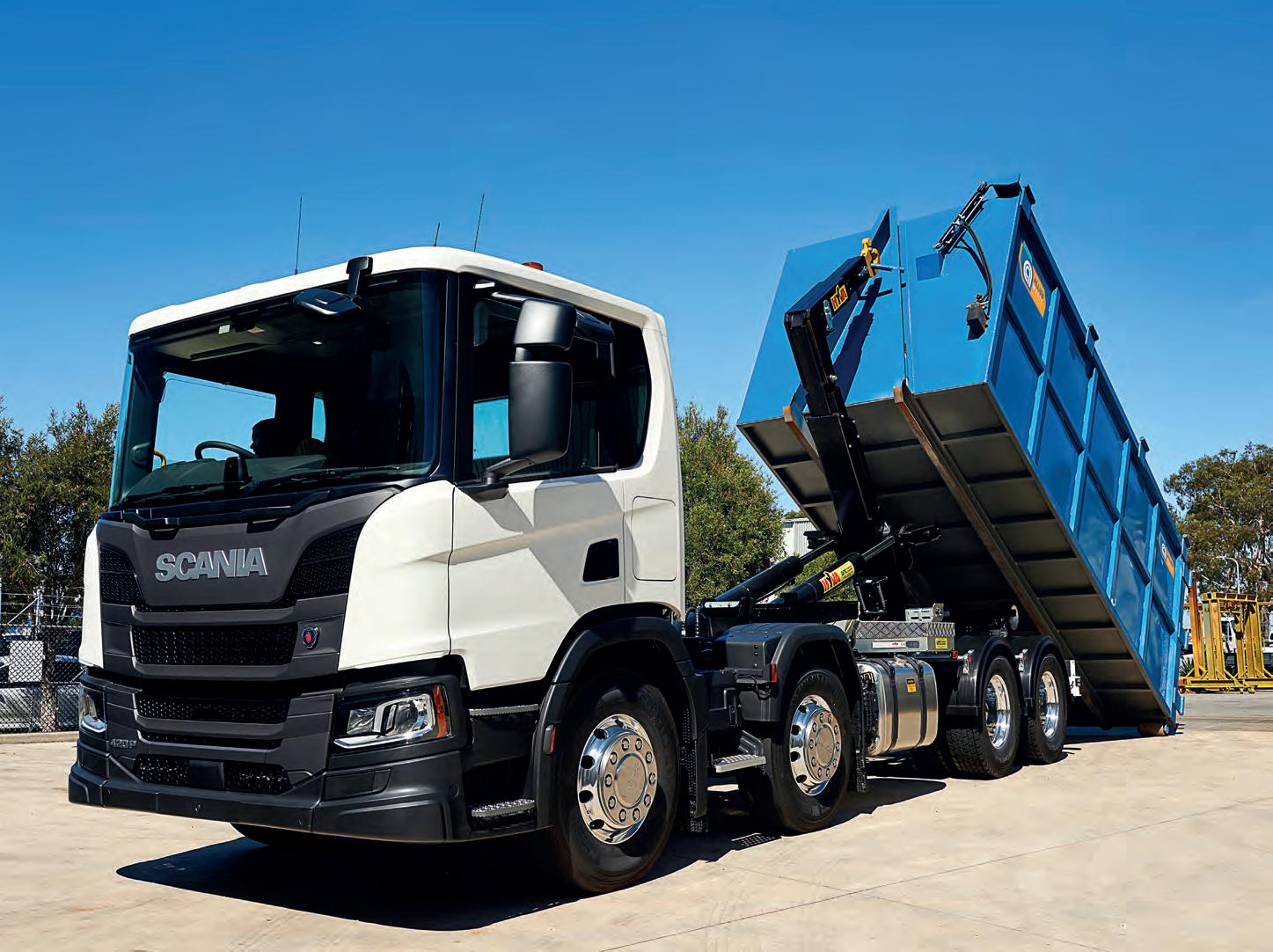
Scania trucks drive Allied Waste Concepts’ success
By Inside Waste
TRANSPORTING contaminated waste from civil construction projects around Melbourne keeps Allied Waste Concepts and their Scania 8x4s busy. This includes carting contaminated waste away from projects such as the North-East Link, the Westgate Tunnel, and the Metro Tunnel.
The family-run business, established in 2004, employs Doug Briggs and his three children, Jay, Matt and Dannielle, and is based in Brooklyn, in the outer western suburbs.
The company transports waste from building sites to reclamation or disposal locations, under the strict control of the EPA. Waste removal is highly regulated and managed through online processes so each load can be tracked and traced to ensure compliance with disposal regulations. As a result, cowboys are being run off the range and the industry is increasingly professionally run.
“We started off transporting asbestos waste,” says Jay, who worked as a driver for six years before moving
into a managerial role. “Via the closely associated Sunshine Groupe, we were operating landfill and plasterboard recycling, so much early work for Allied Waste Concepts was transporting plasterboard for recycling or waste, and we had one truck.
“We purchased our first Scania around five years ago and since then the business has been growing substantially.”
The first three Scania 8x4 rigids Allied Waste Concepts purchased were P 450 six-cylinder 13-litre powered trucks, while the latest new Scania is a 420 P SUPER, also an 8x4.
“The Scanias produce more fuelefficient running and driver comfort, which means we could push the boys a little bit longer in their days. They also give us the flexibility of moving different bins, flatbed trays, liquid bins and materials that we previously couldn’t do, prior to having the Scanias and Hyva multi-lift hooks. We’re now taking delivery of our fourth Scania, and it will be fitted with a Hyva hook as well,” Jay said.
We purchase trucks brand new. We came to Scania through pre-existing relationships with Jarrod Hegarty, Scania national sales manager and Tevfik Onguc, Scania Victorian sales manager, where we were customers, and we knew them before they came to Scania.
“When Tevfik joined Scania, we put a lot of time into understanding the Scania product and we had a lot of trust in him. We’d worked with him for many years, and in fact, Tevfik and I attended trade school together, so the relationship grew from there.
“Jarrod is an absolute gem and Tevfik is just taking it to the next level.”
A good product is important, but the service side is critical. The truck speaks for itself, with its fuel efficiency, reliability, safety, the comfort for the drivers, but it’s more the relationship with Tevfik and the service department at Scania Laverton that impresses Jay. The customer service advisor, Caitlin Talevski, is phenomenal, according to Jay.
“She’s an absolute star, always calling and asking how she can help us with
service scheduling,” he said. “She also reminds us of when services are due, and keeps us informed when something needs doing and how long it will take to get back on the road.
“Time is money. And if we ever have a breakdown or an issue, and there haven’t been many, they get the problem fixed and we’re back on the road straight away.
“We’ve had a couple of injectors fail within different trucks. And it’s just one of those things that happens. But it’s back on the road generally within a few hours. So, the service department’s very, very quick.”
With eight trucks on the fleet, each unit must pull its weight to keep the business on track and the drivers paid. Every vehicle plays a critical role in the business’s continued good health, said Jay.
“Uptime is critical, and we’ve had phenomenal uptime with Scania,” he said. “And it contributes to the viability of our business. It means we can service our customers to the best of our ability without having to let them down if you

The 420 P has a SUPER generation engine, which should see a 7-8 per cent fuel consumption improvement.
Images: Scania
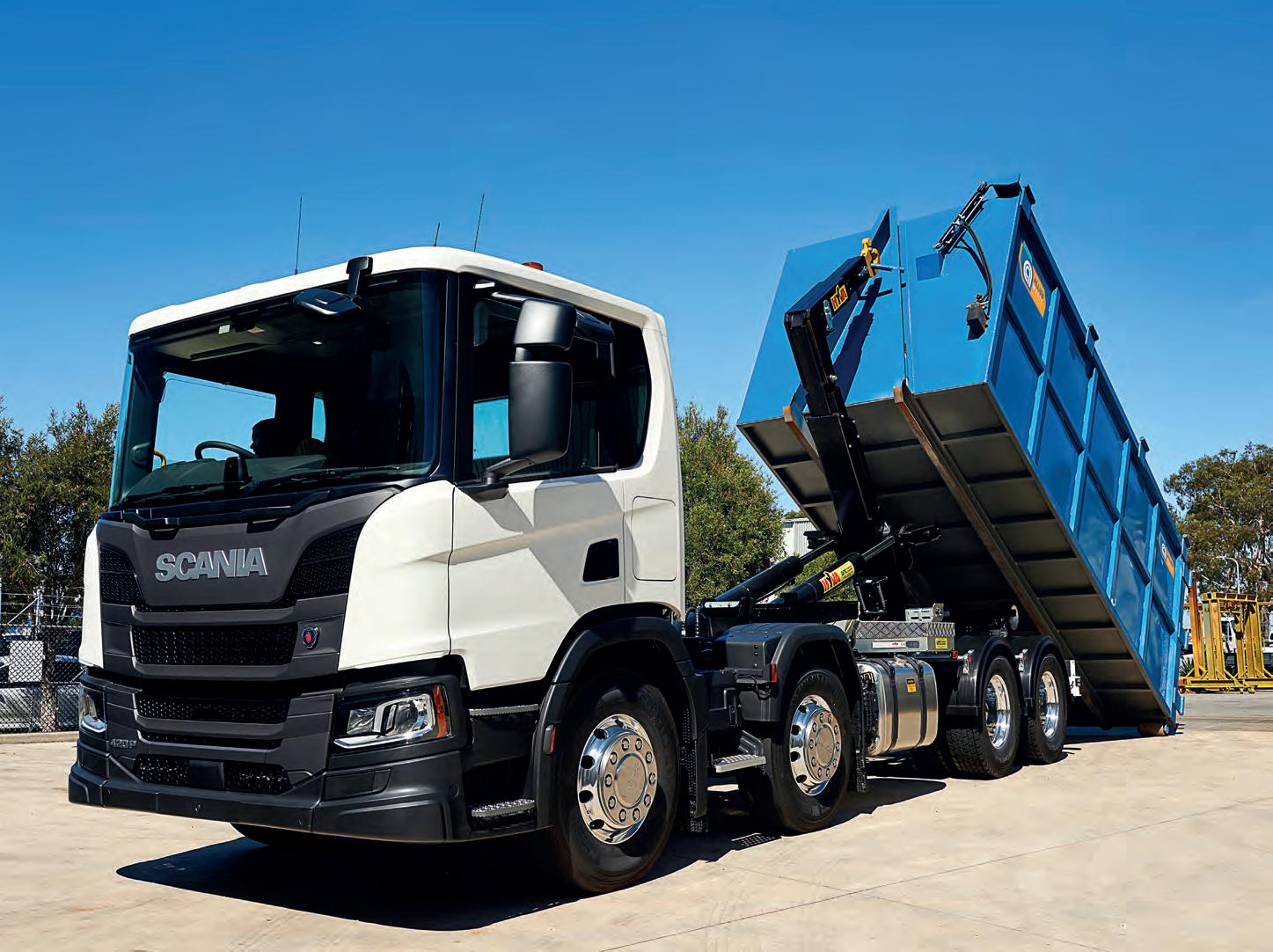

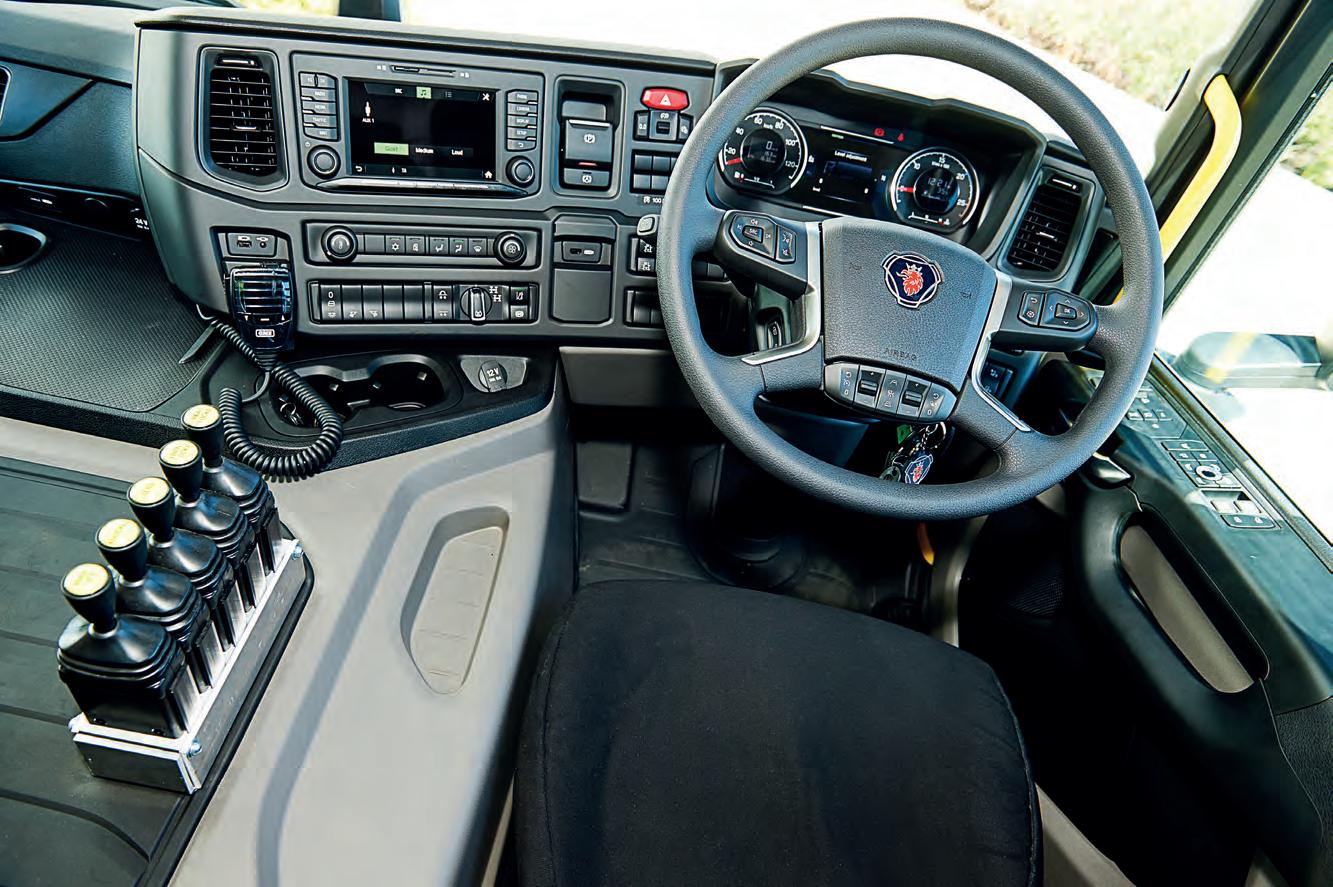
have an unplanned stop and a truck off the road. We do a lot of time-sensitive work. The contaminated waste or sludge can’t be sitting around. We don’t want to be responsible for bringing work to a halt on site because we can’t get the truck on the road.
“Eventually you get to a stage in a truck’s life where you have that reliability question versus the availability question, and the money you start spending on repairs can work out to be the same as actually paying finance on a brand-new truck, which is why we like to replace them at five years old.
One of Allied Waste Concepts’s business associates has had Scanias and swears by them, said Jay.
“He’s got a few of them, and one just tipped over to a million km, and they just rolled some bearings into it and sent it back out to work,” he said.
“If it wasn’t for Tevfik, the transition to Scania would have taken a lot longer than it did,” says Doug Briggs. “We’re creatures of habit in our family business, and we don’t just change for changes sake. There’s got to be a reason we change, and it’s got to be a benefit, and the benefit is not necessarily the cost of the item. If it was solely the cost, then probably Scania wouldn’t be in the picture.
“Scanias are not cheap, but when you look at the whole package, that’s a different story. You have to look at your
(uptime).”
Another benefit the family-run firm prizes is the constantly improving fuel efficiency of Scania’s engines. On its most recent purchase, the company is seeing between 3.6 to 3.8 km per litre, with a 22-tonne gross weight and a 12-13-tonne payload.
“Quite often that truck is also pulling a two-axle dog, so the gross goes up to 42.5-tonnes, and we’re still seeing fuel savings,” said Jay. “I think our first Scania is still returning 3.4 km/l. That’s amazing. The second one is similar, even though it is driven quite hard. With the new 420 P, which has the new SUPER generation engine, we should see at least a 7-8 per cent fuel consumption improvement, according to Tevfik. We’ll put the driver from the last new truck into the new one to see if he can feel a difference.”
“Fuel is a massive cost to the business. Switching to Scania from another European brand we calculated would save us around $70,000 over the fiveyear life of the truck. That’s a significant saving,” said Doug.
“Our drivers liked to compare their efficiency scores early on. But it is very hard when you are stuck in metro traffic all day, or just queuing on the freeway to get the scores up. You only need one set of lights to suddenly change to red, and
your score falls,” Matt Briggs said.
“I still have a photo from when I got 100 per cent, but I couldn’t get all three scoring functions to 100 per cent at the same time. It only takes one vehicle in front of you to pull it in front of you and it wipes it out. It’s very harsh.”
“When the drivers are trying to achieve a high score, you save on your servicing because they’re not driving it as hard, so brakes wear and tear is a lot less, and the drivers adapt to driving it properly, particularly the exhaust brake and retarder,” Jay says.
“The Scania product gives us the flexibility to chase all avenues of work that we can do with the hook lift. You can run regional to metro to interstate and know that the truck’s capable of doing all those runs fuel efficiently with driver safety. And the comfort is notable. Quite often we talk about it ourselves – that you can jump in a Scania and drive all day, and you don’t come out of it feeling fatigued. That leads to the drivers being more courteous to everybody, and it makes them a better employee.”
The vibe around the business is relaxed and happy and that’s not always the case with family-owned and run businesses.
“We all love what we do, working together as a family,” Jay says. “A lot of people say to work with families is hard, but we sit in the office to together every
day and my sister she does the accounts. She’s here a couple of days a week. She previously worked with Sunshine Groupe and then she came into this business about 14 years ago. Matt’s been in the business 15 years, and I have been here for 16 years.”
“Scania’s experience working with Allied Waste Concepts has been very successful,” said Onguc.
“Allied understand the benefits Scania brings to their business, and we are dedicated to maintaining their up time and keeping their Scanias in tip-top shape. Waste is a very demanding sector, with often hard-to-access sites and strict deadlines with thin margins for error. Our trucks are naturally at home here, being extremely manoeuvrable and powerful enough for any waste job. Because the drivers are largely working in built-up areas, good visibility and a tight turning circle are very important, as well as the latest Advanced Driver Assistance Systems, which protect the vehicle and vulnerable road uses.
“Allied Waste Concepts is playing an important role in the transportation of construction project waste, with a focus on recycling as much material as possible, while employing the latest Scania engine technology to reduce fuel consumption and emissions, while of course being Euro 6 compliant, another benefit for workers on site.”
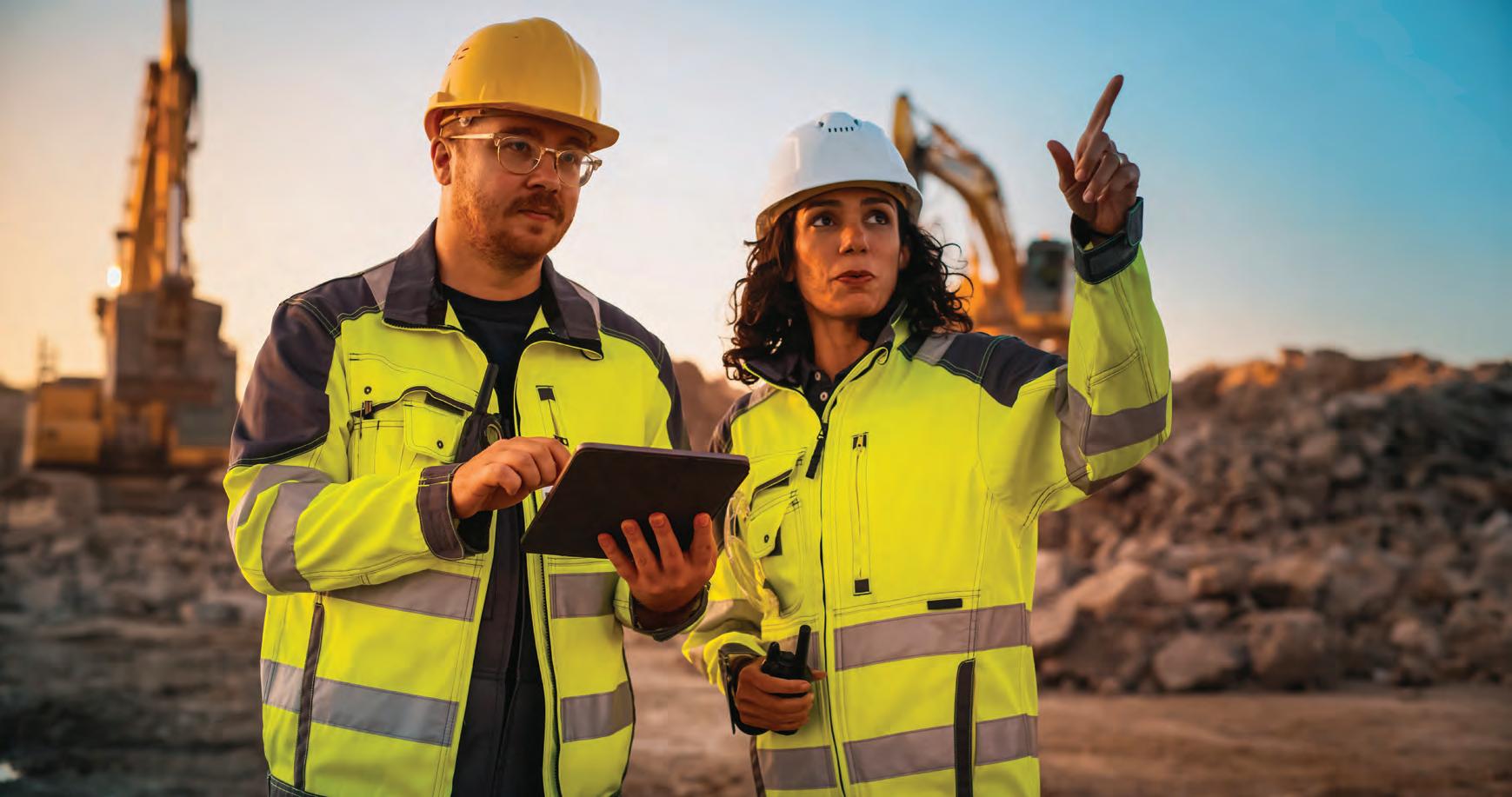
Scania sees driver comfort and safety as key features of its trucks used in the waste industry.
Building Australia’s Future – together.
Over the next 10 years, the Australian Government is investing more than $120 billion in infrastructure development. Will you be a part of it?
17–18 SEPTEMBER 2025
Melbourne Convention & Exhibition Centre
LEARN MORE
Find out how you can take part in Australia’s premiere event for the municipal works, commercial and civil construction industries. convergeexpo.com.au
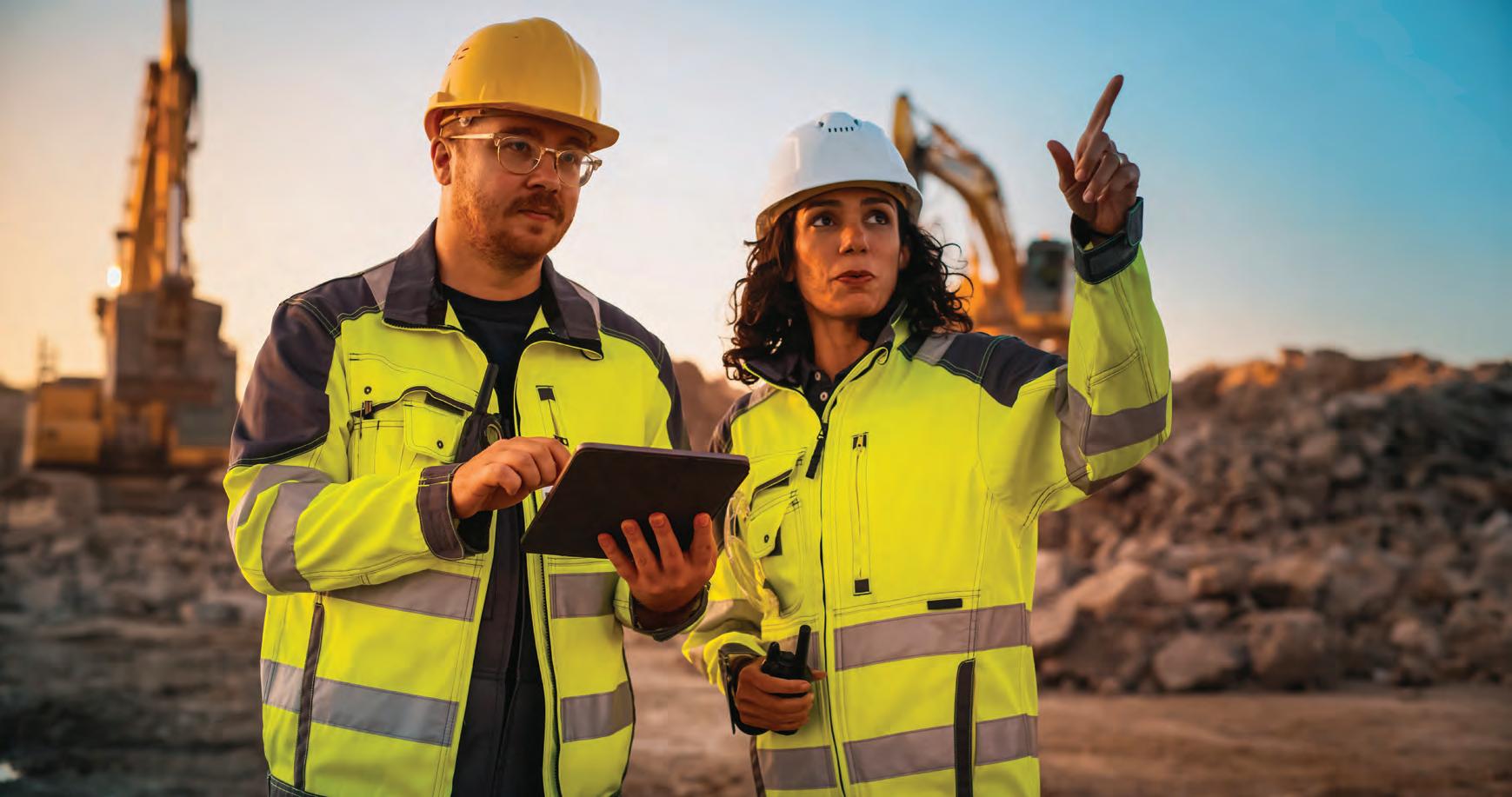



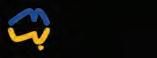

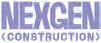
Isuzu FYJ tackles asbestos clean up
By Inside Waste
UNTIL the 1990s, asbestos was common in everything from concrete and walls to roofing, ceilings, and insulation.
Australia has one of the highest volumes of asbestos used in building materials globally; it’s estimated that one in three Australian homes still contains it.
Although the manufacture of asbestos products was banned in the 1980s, it was legally allowed to be used as a building material until 2003.
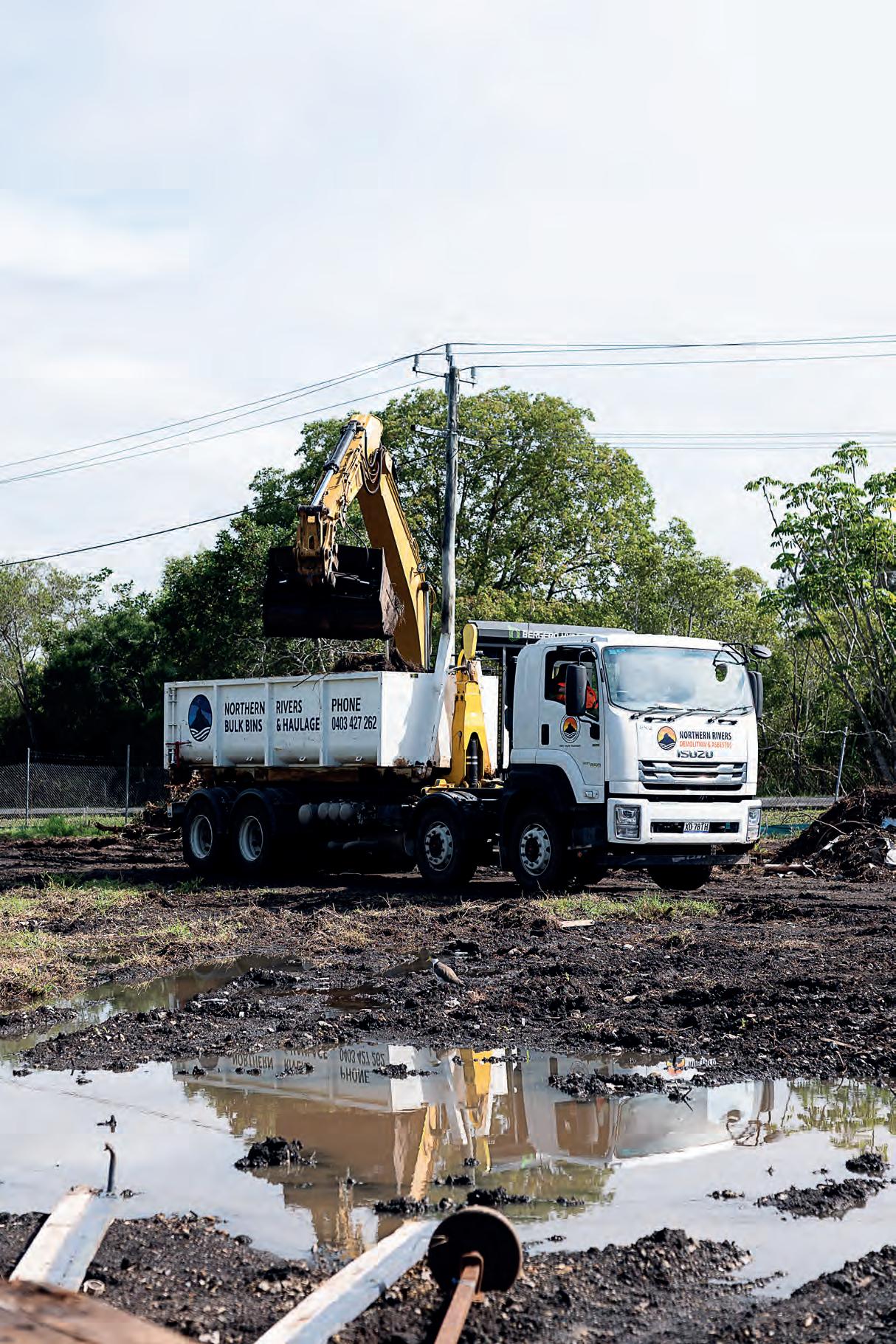
Asbestos can pose serious health risks when disturbed during renovations, demolition, or even due to weather events like storms or hail. Anyone handling asbestos needs specialised training and the proper Personal Protective Equipment (PPE) to ensure safety.
One company addressing this challenge is Northern Rivers Demolition & Asbestos in Ballina, New South Wales.
Launched in 2016, the business has provided a safe, high-quality service
removing asbestos and demolishing buildings, growing to encompass a waste and recycling facility in Lismore and a skip bin service designed for transporting asbestos safely to disposal sites.
“We specialise in asbestos removal, demolition, and recycling in both residential and commercial situations,” said managing director Samuel Northfield.
“Whether it’s an asbestos removal job or a large-scale demolition project, my role is to keep the cogs turning in all the
different aspects of the business.”
One of the biggest challenges in the asbestos removal industry is finding safe, licenced disposal facilities. In the Northern Rivers region, there are limited options for safe disposal and strict EPA guidelines on handling it.
To solve this problem, Samuel turned to Isuzu Trucks for a heavyweight transport solution, which could take sealed asbestos over the border to disposal facilities in Ipswich, Yatala, and Staplyton in Queensland.
This came in the form of an Isuzu FYJ 300-350 8x4 Auto featuring the manufacturer’s GVM of 30,000 kg and equipped with a Palfinger crane hook lift to manage the 30-cubic-square-metre skip bins.
With a high-torque 6UZ1-TCC engine – which offers a maximum power output of 257 kW @ 2,000 rpm and 1,422 Nm of torque @ 1,400 rpm – plus twin-steer axles and load-sharing front suspension, the FYJ is specified for these types of heavy, relentless duties.
“We can load up the skip bin over several days, sealing it each afternoon and continuing the next day. Once it’s full, we can head straight to Queensland for disposal,” explained Northfield. “Access to affordable, licenced disposal facilities is a major issue in our industry at the moment, so the Isuzu FYJ is our solution to this problem.”
Northfield’s 15-person team uses advanced safety equipment, including respirators and HEPA H-Class asbestos vacuums, all while following a strict code of practice.
Projects involving asbestos removal typically follow a multi-stage process, including assessment, removal, decontamination, and final clearance inspections.
For example, when a customer wants to renovate a home containing asbestos, Northfield’s strip-out team removes the asbestos and completes the decontamination.
The company also handles soil remediation and demolition projects.
Recent jobs include demolishing the Cedar Park caravan park in Ballina, Sedgers Reef Hotel in Iluka, and other commercial buildings in the Northern Rivers region.
What began as a small-scale asbestos removal service has expanded over the years. Northfield first started with a medium-duty truck and gradually grew his fleet, obtaining the necessary licences to meet increasing local demand. He noted that the call for safe asbestos removal is at an all-time high,
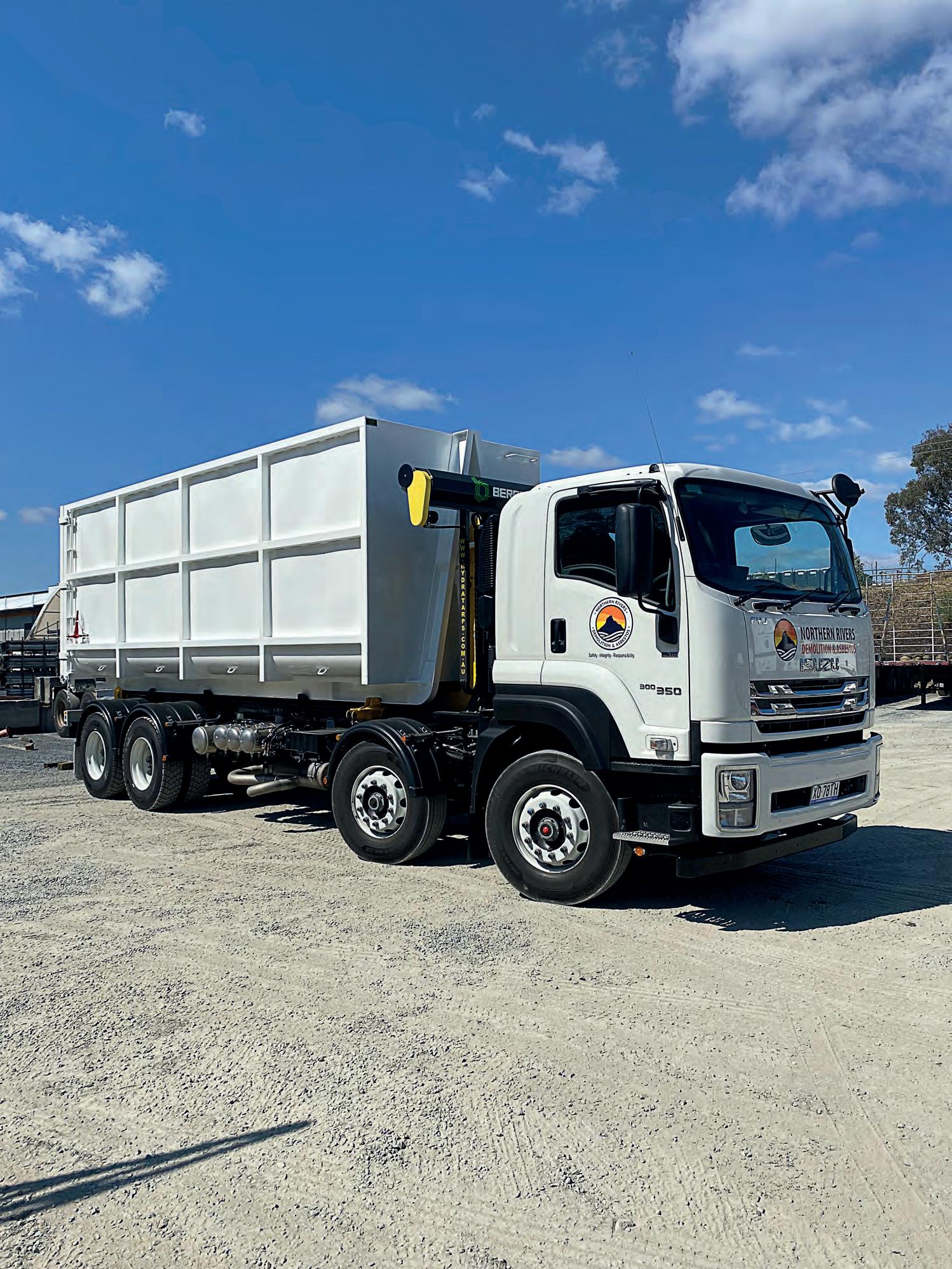
Northern Rivers Demolition & Asbestos fleet now includes four Isuzu trucks.
Image Credit: Miles Away Media
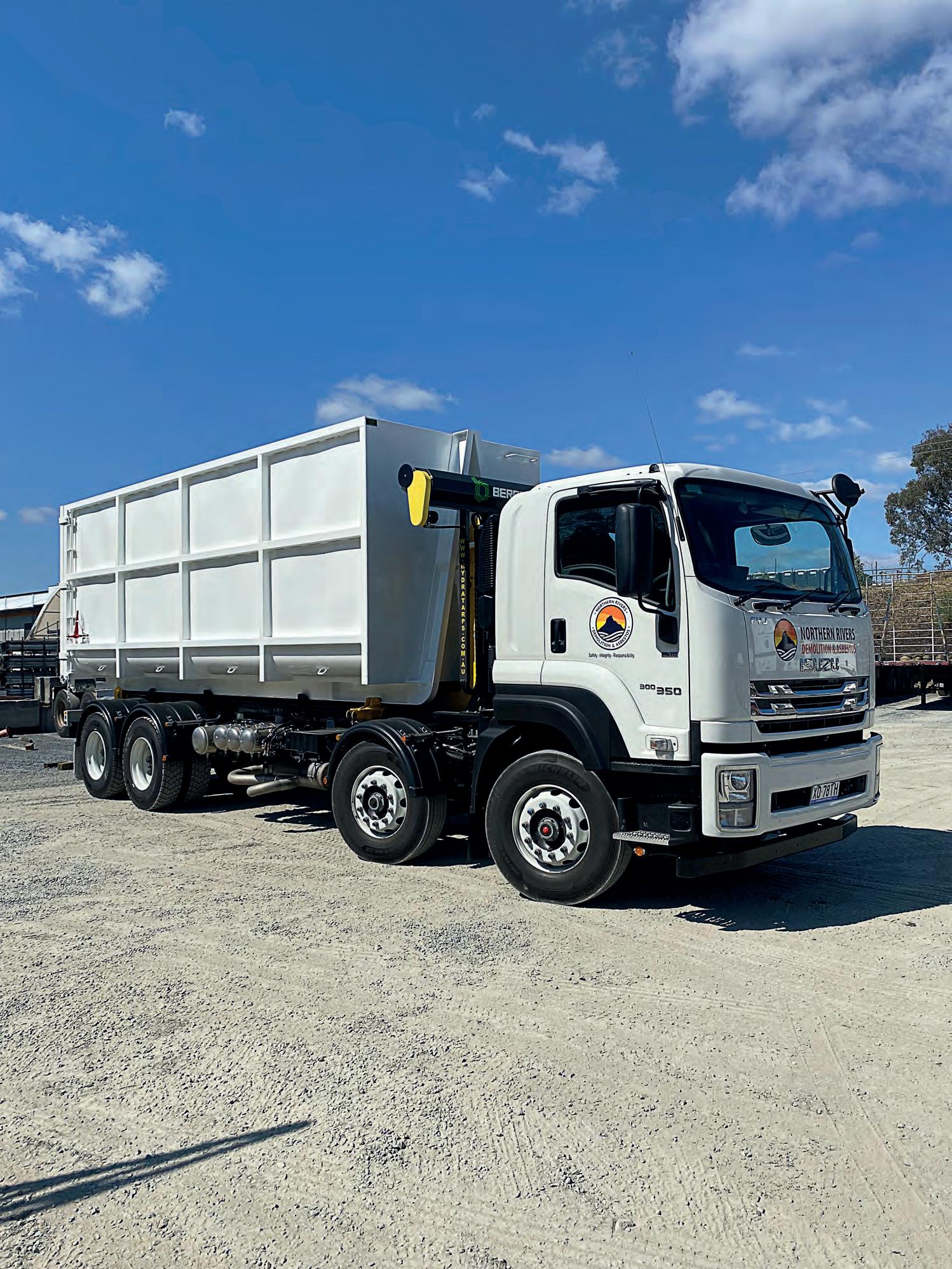
“Access
to affordable, licenced disposal facilities is a major issue in our industry at the moment, so the Isuzu FYJ is our solution to this problem.”
particularly due to the demolition of older buildings throughout New South Wales.
The company’s fleet now includes four Isuzu trucks: the FYJ 300-350 Auto, an NMR 60/45-150 tipper, an NPR 45/55155 tipper and an NLR 45-150 traypack.
Northfield even flew to South Australia to collect the FYJ 300-350 from Northeast Isuzu and drove it nearly 3,000 km back home to Ballina.
“The FYJ is comfortable and easy to drive, especially compared to other truck brands.
The cab’s standardisation makes it feel similar to driving one of our smaller Isuzu Tippers,” he added.
The FYJ’s heavy-duty Allison 4430 automatic transmission ensures smooth shifting, reducing driver fatigue during long journeys into Southeast Queensland, which can exceed 200 km one way.
Northfield chose the Allison transmission to help minimise distractions and make travel as effortless
as possible for his hardworking team.
Northern Rivers Isuzu provides excellent support, with Northfield praising the customer service from Isuzu sales manager Jake Everett, who ensures that any urgent repairs or parts replacements are handled promptly.
“Jake always makes sure to minimise downtime, which can really impact us,” he said. “If we need a part for our truck with short notice or a quick turnaround on service, he will get it done ASAP.”
Ongoing support from the dealership is appreciated as the business continues to evolve and diversify, such as their recently opened Northern Rivers Recycled Building Materials.
This arm of the operation salvages materials from demolition projects, like hardwood timber, which are then processed, sorted, and sold as a new product rather than sent to landfill.
Northfield is also expanding services with Northern Rivers Bulk Bins & Haulage, which offers safe asbestos
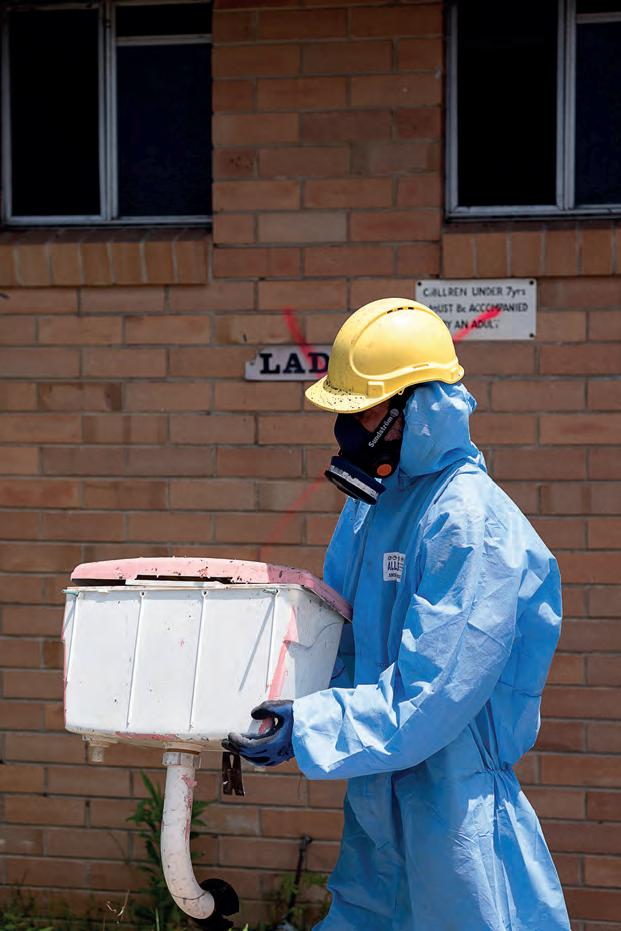
transportation services for other companies. To support this growth, he is considering adding another heavy-duty
“With Isuzu Trucks, you don’t have to worry about anything – if you take care of your truck, it will take care of you,” he said.
“Business owners have already got enough to juggle, so Isuzu’s reputation for reliability gives us peace of mind, letting us get on with the job at hand.”
Isuzu truck to the mix.
The Isuzu FYJ 300-350 is equipped with a Palfinger crane hook lift to manage the skip bins. Image Credit: Isuzu
The removal of asbestos means making sure workers have the correct PPE. Image: Miles Away Media

Using AI to address FOGO contamination
By Inside Waste
ARTIFICIAL intelligence could be harnessed to conduct bin audits and reduce FOGO (food organic, garden organic) contamination rates as councils around the country continue to roll out three- and four-bin collection services for residents. Australian government figures show 38 per cent of Australians have access to a FOGO service, and this number will grow in the coming years as states and territories seek to reduce landfill and greenhouse gas emissions by implementing ambitious recycling initiatives and targets.
However, contamination is one of the key problems to have emerged amid the FOGO transition. This includes the
creep of PFAS (per- and polyfluoroalkyl substances) “forever chemicals” and other harmful pollutants into FOGO waste collections.
The Australian Organics Recycling Association (AORA) has described the contamination of organic feedstock as the industry’s number one challenge, and it presents a huge issue for often cash-strapped local governments, given that monitoring contamination is an inherently time-consuming and expensive process.
Identifying contamination sources
At the Australasian Waste and Recycling Expo, Naser Soueid, co-founder of a company that is utilising AI during bin
audits, provided an overview of AI’s place in the waste and resource recovery landscape.
Soueid highlighted the importance of tracking the movements of PFAS chemicals, including their origins and why people are buying them, as one of the first and most important steps that can be taken across the waste management process, effectively addressing the problem as close to its source as possible.
The rationale is that by implementing actions to manage the problem early on, each subsequent step in the waste management process will be made easier. As it stands, conducting a bin audit consists of tipping rubbish on the ground and having people then sort through it to obtain a breakdown of waste make-up.
It is an intensive and time-consuming process.
“The result of this is that we don’t do it as often as we should because it’s so expensive,” Soueid said. “It makes it difficult to determine what actions we should take. If we don’t have good, timely insight into the problem, we don’t have fine-grained insight into the problem; figuring out what to do can be quite difficult.”
Not only that, but once data has been collated from audits, it needs to be harnessed to inform strategies about how to effectively identify and manage repeat instances of contamination.
“You can see why it’s laborious and expensive,” Soueid said. “We need to move from these methods that are laborious and expensive to ones that are automated and continuous. And this is where AI comes in.”
Data gathering provides for strategic insights
Soueid’s system involves the installation of cameras across recycling fleets, with the company’s image capture system cataloguing waste as it enters the
AI could possibly help track the movement of forever chemicals like PFAS.

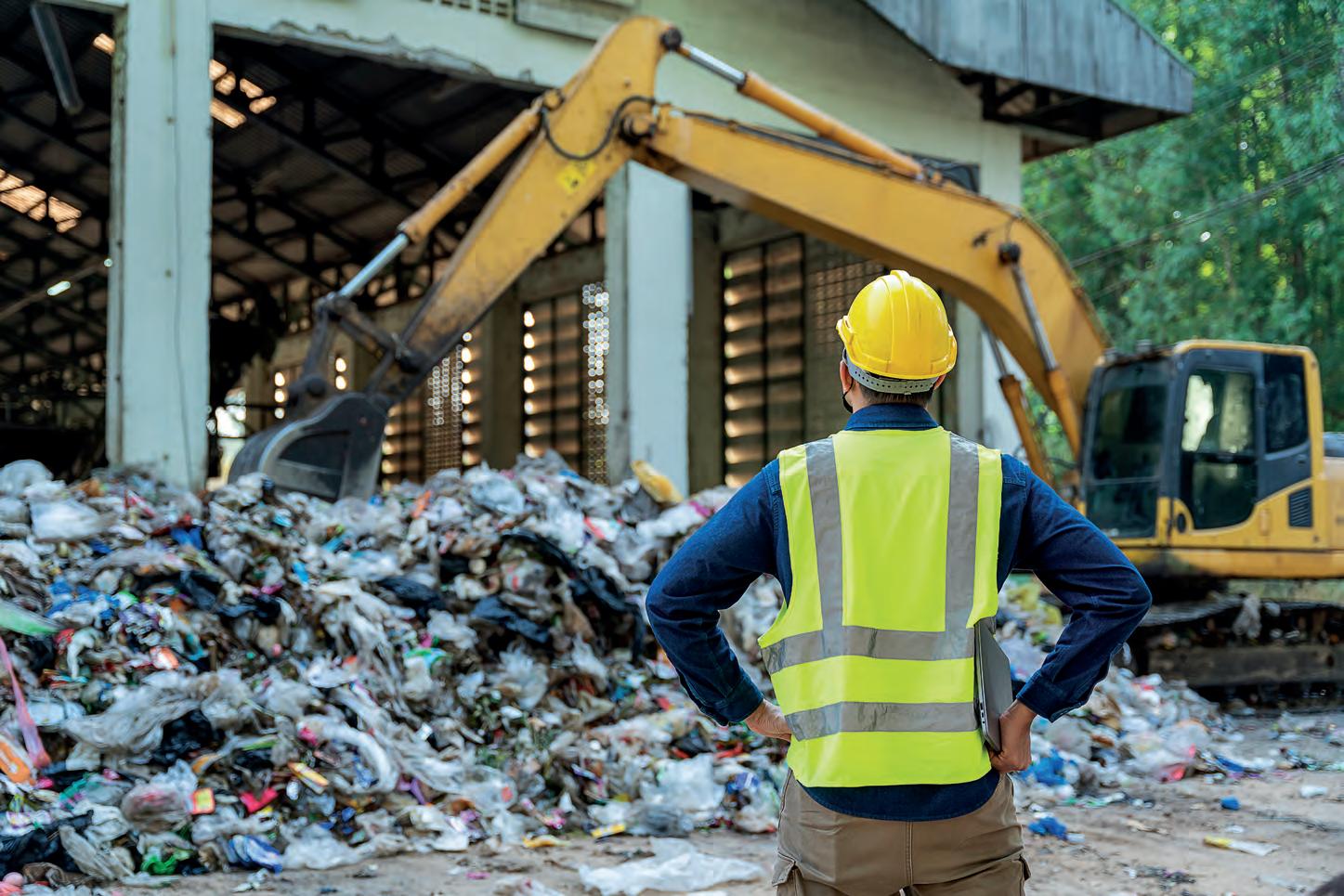
“We know what waste stream it belonged to. We know when it was picked up, where it came from, and we know exactly what was in that bin. We know the composition, and we know of the composition at that council area, what is considered contamination, and we have this data point for every collection in the entire council area over the entire period of observation.”
stream. When trucks return to the depot, data is uploaded to the company’s cloud platform for analysis.
Soueid said AI is used to “break the footage up into individual collections,” effectively creating data points for different households.
“We have a picture of the waste that was disposed of from that household,” he said. “We know what waste stream it belonged to. We know when it was picked up, where it came from, and we know exactly what was in that bin. We know the composition, and we know of the composition at that council area, what is considered contamination, and we have this data point for every collection in the entire council area over the entire period of observation.”
The system then creates reports and workflows, providing strategic insights such as building profiles that identify
high-impact contamination.
“This is particularly the households that are contributing to an outsized proportion of contamination and that are problematic or that are contributing repeat minor contamination,” Soueid said. “We can highlight both of these things, identify them, deal with them, and achieve better outcomes overall.”
Council areas can also be broken down into different geographic segments, providing insights into household, regional, or demographic differences.
“All of this information is tied, not only to time, but also to geography,”
Soueid said. “We can start to segment our council areas and start to make hypotheses about different demographics. If we’ve got a university area, the turnaround might be higher. People might be less incentivised. Their consumption patterns are different.”
Forward planning for better management
Ultimately, the system paves the way for the real-time management of waste streams and allows councils to carry out forward planning.
“We have a living, breathing insight into this metric,” Soueid said. “We know not just how much waste we’re collecting, but we know what proportion of that is contamination, and so we can adjust our collection figures.”
Analysis can be undertaken week-byweek, month-by-month, or quarter-byquarter, according to specific needs, and the impact of improvement initiatives can also be measured.
For instance, statistics can be applied to benchmark a council’s performance, or cost benefits can be determined for different tools.
Councils could also measure the
effectiveness of awareness campaigns and different types of educational materials.
“We can look at two areas with similar demographics, try out different strategies, see what works, and start to hone our tools over time and settle on those that are most effective,” Soueid said. “And we can do things like impact longevity analysis.
“For example, a university area might have a high turnover of students, and you might find that the gains that you make need to be reinforced much more frequently in that type of area than in somewhere where the residents are there for a much longer period of time.
“AI can help the situation. It helps us determine what actions we can take. It helps us take that action, and it helps us look back and assess how effective those actions were.”
Resource recovery a career choice from the beginning
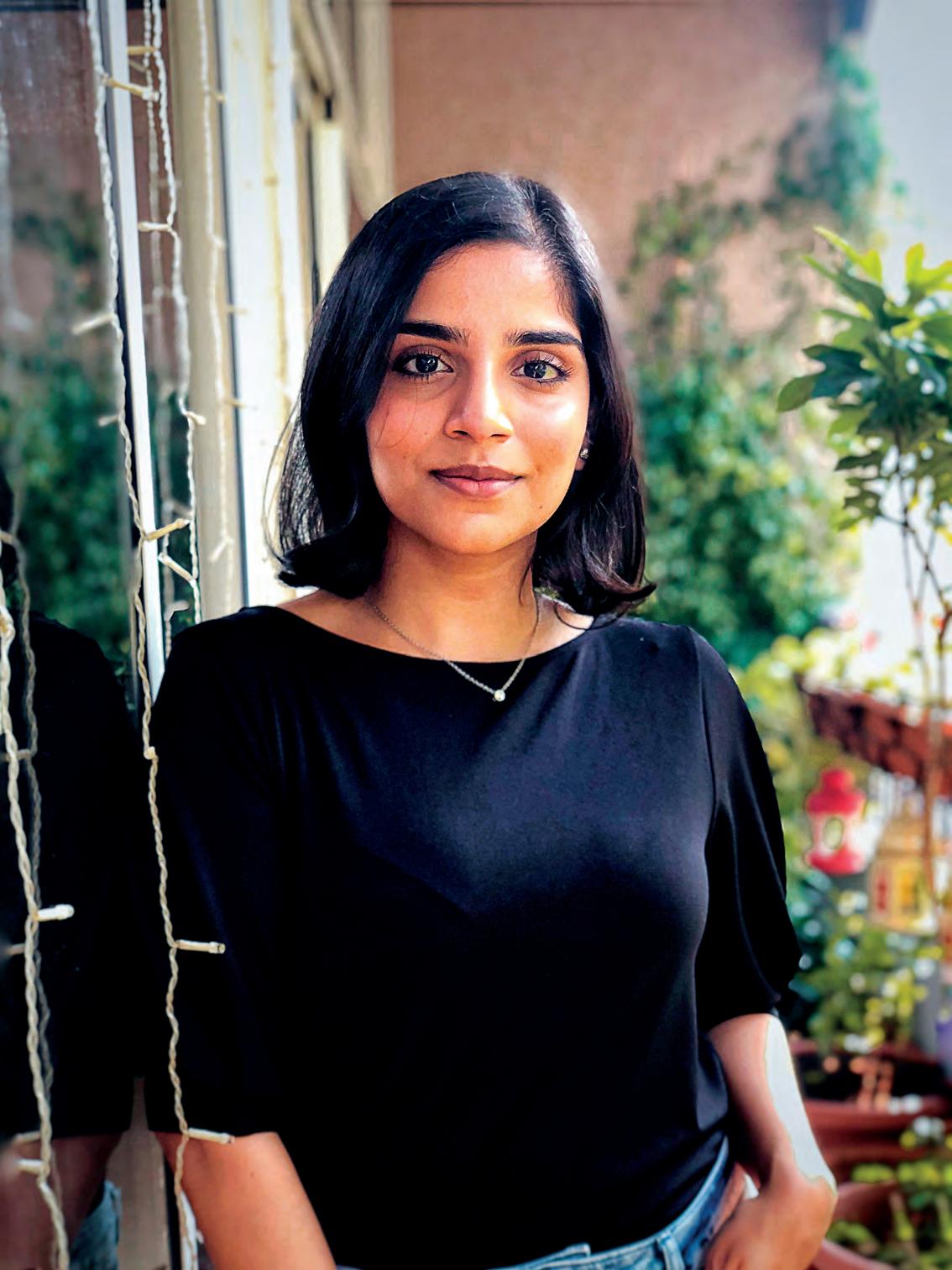
By Inside Waste
a lot of young professionals
featured in Inside Waste, Gopika Venugopal was interested in the waste industry from an early age. During her formative years, Gopika was raised by her grandmother who was a “strict, no-waste champion”, she said.
“There would be barely any food waste in the house,” said Venugopal. “She ensured that we only bought things that we needed. While shopping, she encouraged us to take our time and carefully consider whether something was necessary. When it came to clothing, she made sure we altered them to fit, and wore them for as long as possible. Once we no longer needed them, she ensured they were donated to charity.”
When at university studying (Bachelor of Science – Chemical Engineering, and Master of Engineering (Professional) – Environmental Engineering), her two favourite classes were Cleaner Production for a Circular Economy Solid Waste Management. Before taking those courses, Venugopal had not realised just how much opportunity existed in navigating the intricacy and complexity of the waste industry on a day-to-day level.
“I was very fortunate, because once I graduated, I knew I wanted to work in this space, but I didn’t know what it would look like,” she said. “One of the first jobs that came up was for a graduate waste engineer, which ended up being my first role.
“During that time, I gained extensive knowledge about landfill design and engineering, as well as operational and management planning for landfills. I also got the opportunity to spend a couple of weeks supervising the construction of a new cell at a landfill site. That’s an experience I’ll never forget.”
It’s not that Venugopal didn’t consider other careers; waste management simply captured her interest the most. She was determined to explore as many careers and industries as possible before deciding on her path. She gained experience in wastewater engineering, paint manufacturing, and health and safety within the oil and gas industry. Toward the end of her master’s degree, she also worked with a real estate developer, devising green infrastructure solutions for its latest development project.
Currently, Venugopal works at Arcadis
Venugopal studied chemical and environmental engineering at university. Images: Gopika Venugopal
as an environmental consultant. Like many roles in this field, her work is both varied and challenging, with her responsibilities depending on the specific project she is involved in.
As part of Arcadis’ Circular Economy and Waste Advisory Team, Venugopal contributes to a range of capabilities, including waste strategy and implementation, infrastructure technology assessments, material flow analytics, and risk management. She noted that some projects involve many moving parts, and she enjoys the dynamic nature and variety of tasks they bring.
“I enjoy data analytics and modelling,” she said. “There are two different approaches you can take on a data project. The first is like building a Lego tower, and the second is like assembling a jigsaw puzzle. In both cases, all you have to go on is have a vision of what you want the final product to look like.
“With the Lego tower analogy, you start with a strong foundation made up of reliable, direct, and accurate information from a primary data source. Then, you add the right blocks of secondary data to build your tower.”
She provided an example where, at the state level, she needed to determine how much of the state’s municipal solid
is available. She explained that data sources are first organised based on clear associations – similar to sorting the edge pieces and middle pieces of a puzzle – and the challenge lies in figuring out how to bring everything together. For example, in cases where information is not directly measured or reported, proxy or parallel data from other states, as well as national or international sources, might be used to extract insights. This approach ensures the final outcome is both reliable and useful for the client.
Venugopal admits it can be challenging, but it’s also a creative process, which she loves.
“One particularly interesting project involved developing a framework to assess risks in the waste service network for the Southern Sydney Regional Organisation of Councils,” she said. “We created a digital platform to evaluate risks in their system across multiple disaster scenarios, covering aspects like collection, transport, transfer, and final destination. The value of this platform was that it allowed them to analyse their current situation and identify potential risks stemming from these services.
It also helped them prepare for future disaster scenarios, including industry hazards, policy impacts, and natural disasters.”
As for the future of the industry, Venugopal says there are the obvious issues that need addressing including challenges around securing sufficient landfill airspace for future needs, contamination in various recycling streams, and emerging problematic waste issues, such as PFAS/PFOS. She emphasises that proactively collecting data is crucial to meeting the future needs of the resource recovery industry.
“The availability and accessibility of material data are critical for assessing our current situation and planning for the future,” she said. “I find this particularly interesting, especially as discussions around circular economy grows and we move toward building a system that supports it.”
She also said that with the release of the ISO 59004:2024 standard, there is a framework for what the performance of a circular economy should look like and how to measure it.
“The ISO standards not only define
“There are two different approaches you can take on a data project. The first is like building a Lego tower, and the second is like assembling a jigsaw puzzle. In both cases, all you have to go on is have a vision of what you want the final product to look like.”
a circular economy in a foundational manner, but, more importantly, how we can measure it,” said Venugopal. “This can be relevant for any system, process, or business. You can even execute these calculations at a state level if you really tried. You can have all this data, but that can only happen when we know what we’re trying to measure.”
She cites an example of another project she has worked on for a recycler. The Arcadis team audited the facility to learn what was coming in and going out. The company wanted to define what circularity meant for the business.
“We established a relevant Circular Economy outcome that they could achieve,” she said. “We then created a unique metric/measurement that they could employ to get a usable number. They ended up with a circularity rate, which then helped them communicate and influence their upstream and downstream stakeholders on how they operate.”
Venugopal doesn’t see any changes in her career path within waste and resource recovery.
“Through all these experiences, I found an area of work with a purpose that truly resonated with me,” she said. “While it wasn’t a straightforward path, I think I simply followed what felt right. I’m learning more about my strengths and areas for improvement, what I enjoy and what I don’t enjoy as much, and I continue to steer myself toward the right path.”
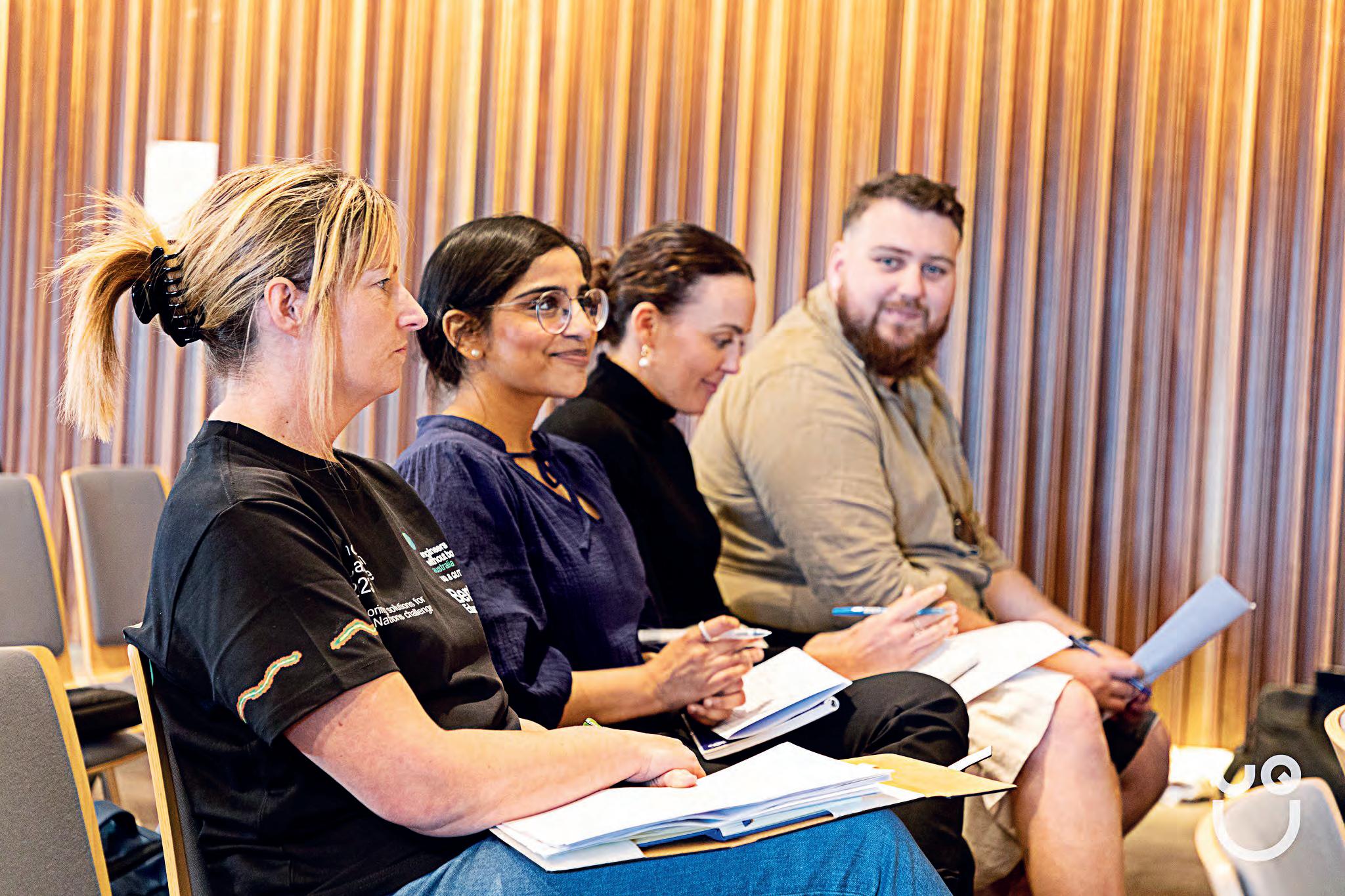
Venugopal on a judging panel for Engineers Without Borders Australia’s Innovation Challenge.
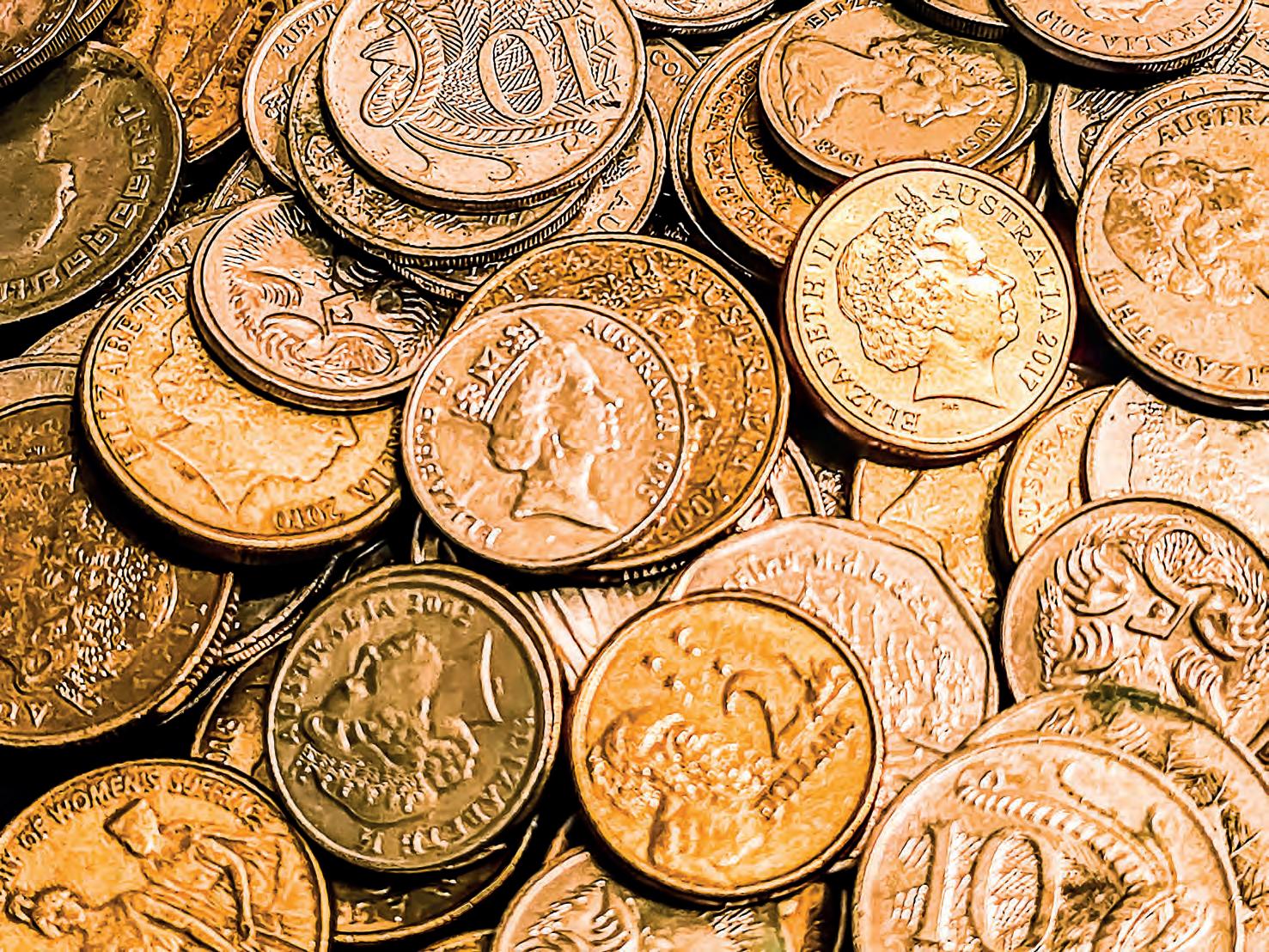
Money, money, money
Hello, Sir.
Money. We all love it, don’t we. To use a cliché, it is the root of all evil, but a necessary one. Which brings me to a rather interesting topic that has been doing the rounds for a couple of years. Refunds. Not talking about changing your mind about the poor tailoring of your latest Armani suit, or your Balvenie 30-year-old single malt being a little ‘off’ once opened. Talking about AUD$0.10 vs AUD$0.40. “Why are you worried about such piddly amounts?” I hear you ask. Good question, I reply.
It appears $0.40 is a lot if you are a multi-billion-dollar multinational, like, say, a very well-known soft drink/fizzy pop manufacturer, or any one of a dozen high-volume beer brewers. I won’t even start on spirits’ manufacturers or winemakers – they’re not even part of the conversation… yet.
Currently, in most Australian states, you get about AUD$0.10 for every soft drink/beer can/bottle/container you return to a variety of reverse vending machines or drop-off points. Most water
bottles and some drink cartons are also included. But not wines or spirits –although they are in the sights of many environmental groups.
“So, what’s the issue?” you might ask. Well, that’s a doozy, Sir. There are quite a few – Pandora’s box doesn’t even come close to trying to explain it. But I’ll try.
Most environmental advocates want the price of a return to go up by anywhere between AUD$0.20 and AUD$0.40 from the aforementioned AUD$0.10. Who pays for these returns? The drink manufacturers. Think CocaCola, Asahi, Lion Breweries, etc. You name it. Shouldn’t be too much of an issue you would think, as they’re loaded, right? But they also have shareholders, who generally want the highest return on investment they can get. In the past 10 years, in NSW alone, these companies have returned just over AUD$1.3 billion to community groups, charities, and individuals. Yes, that’s right, a billion. Not millions, not 10s of millions, but a billion. And that is NSW alone.
“Well, why don’t the manufacturers pass on the cost to consumers?” Well, they kinda do, but they don’t want people to think they do. And if you up a refund by a couple of cents, the corresponding increase on the original beverage might not be noticed. However, if you increase it by AUD$0.30, that will get noticed.
The average drink is about $2.50 to $3. You give it a 10 per cent increase when inflation is running less than six per cent and people are going to notice.
“So what?” you say, “That is the price of doing business.” True, but there’s this little two-word gimme called “social licence” and there’s nothing quite like a multi-billion-dollar multi-national crowing how environmentally friendly they are by backing a scheme that gives so much back to the community (even if the community is paying for it in the long run). These companies LOVE social licence.
However, something that gets lost in the ether of this debate – and trust me, this debate has been ongoing for at least the past five years – is why
environmentalists and others want the increase. Keeping litter to a minimum is one of the obvious outcomes. However, that is just part of the story. Let’s just say the current return rate overall in Australia is about 70 per cent.
In parts of Germany, it is close to 95-plus per cent. Do you know why?
Unsurprisingly, every time they increase the refund amount, more people come on board, and more containers get returned. And I won’t even go into the kerbside collection of beverage containers (but I will anyway). Local councils collect them, and they are separated at Material Recovery Facilities (MRFs), whereby the drink manufacturers don’t pay a cent. However, the MRF operators make a nice penny, especially out of the aluminium cans (that is a story for another day)
Anyway, that’s what has been ruminating through my head over the past month or two. Where this debate ends up is anybody’s guess.
‘Til next time
JB
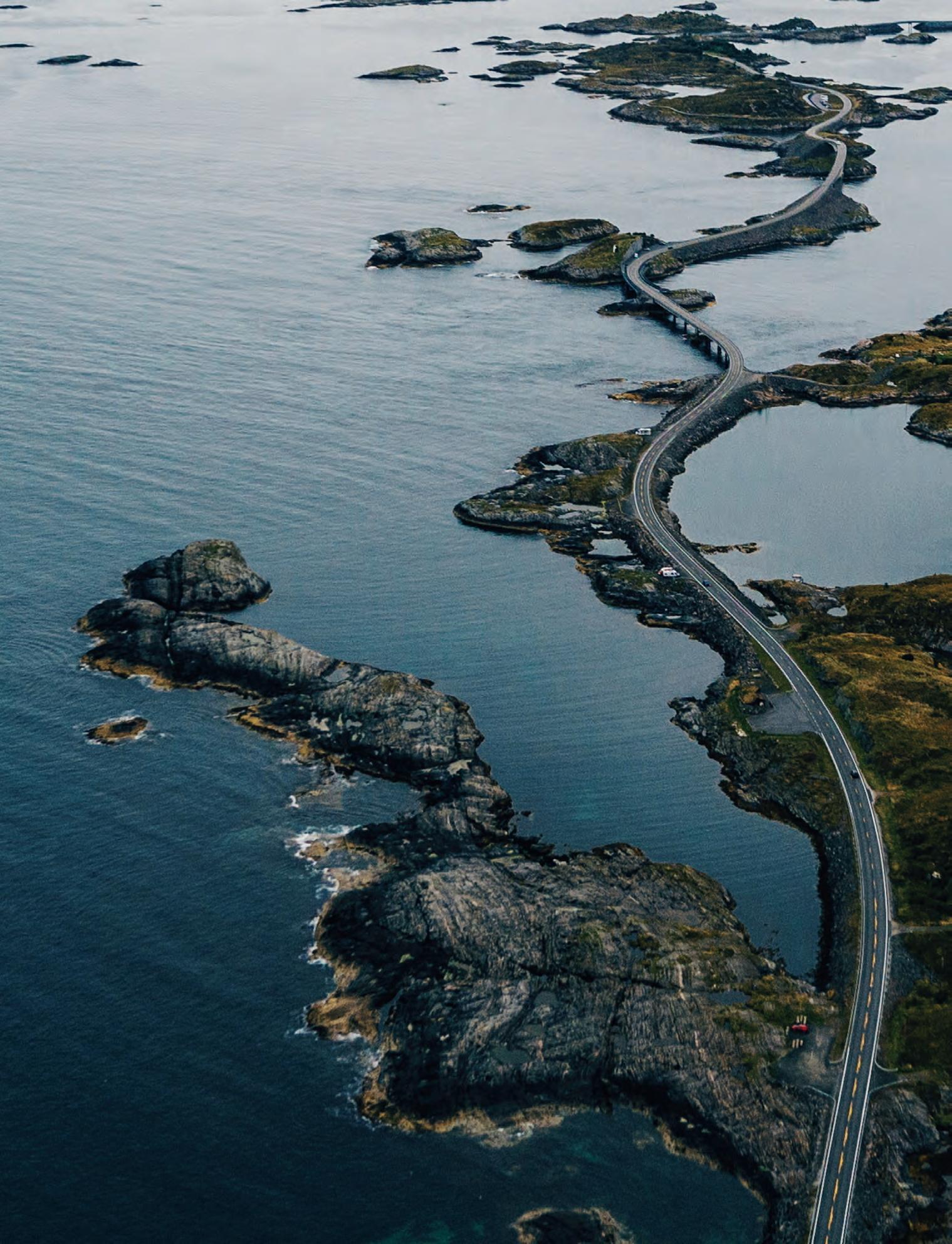
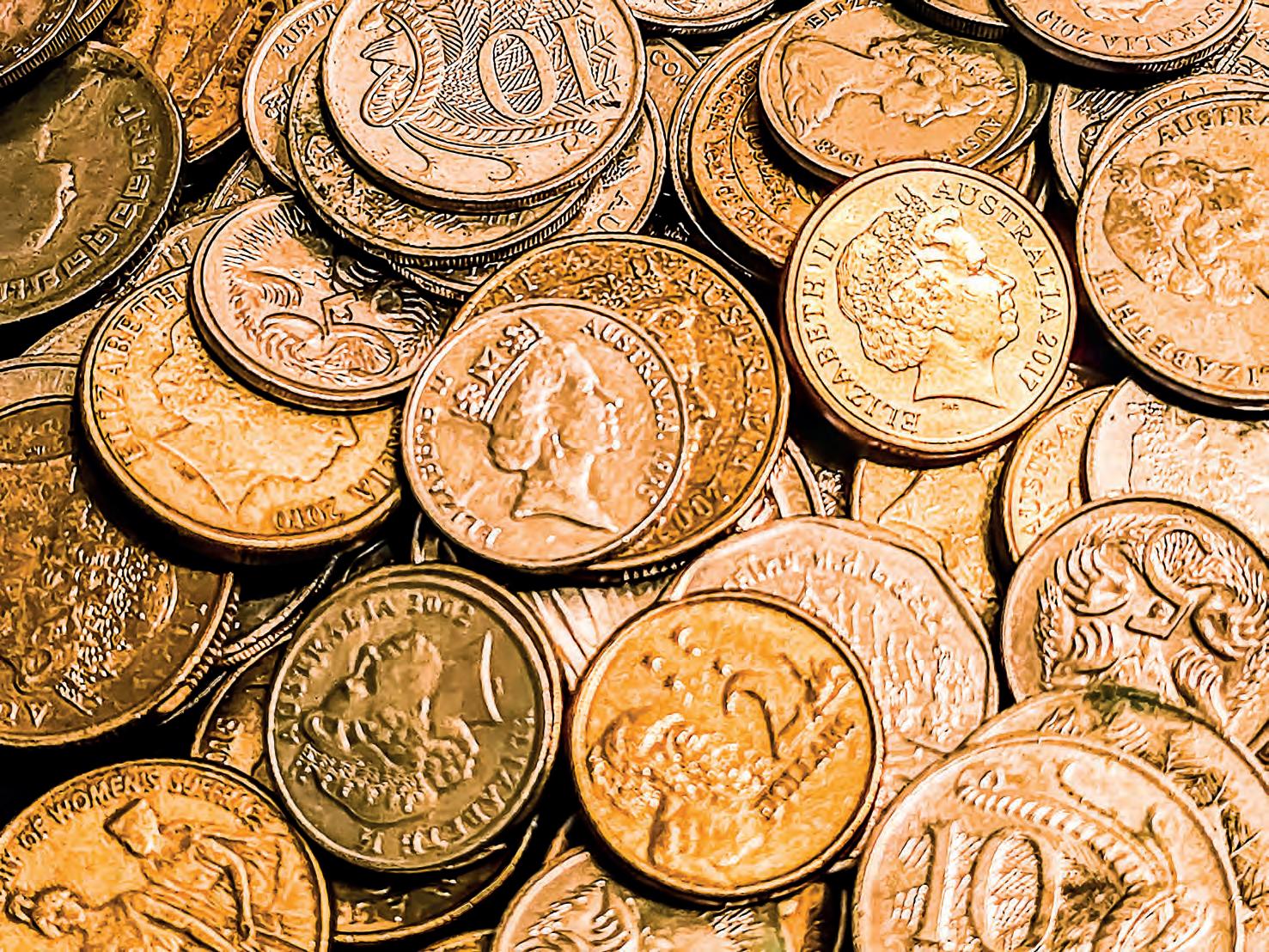
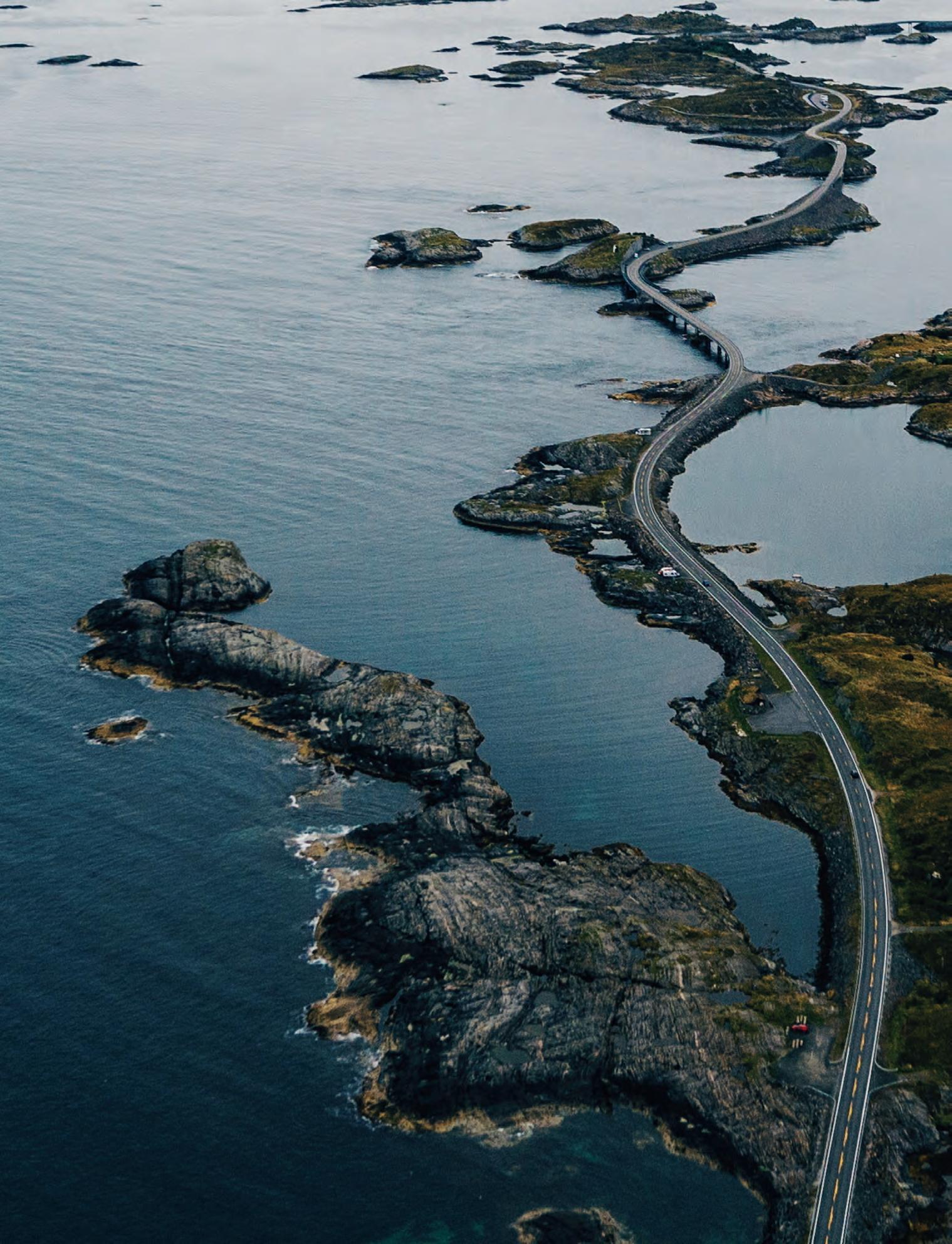
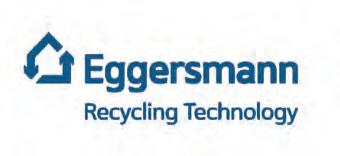
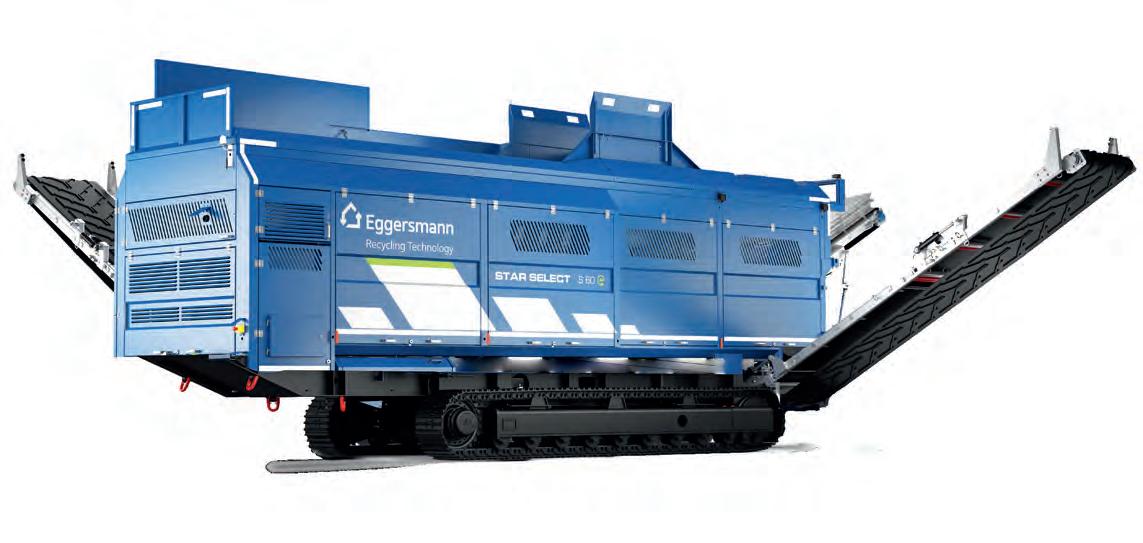
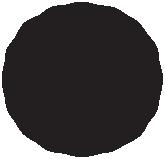

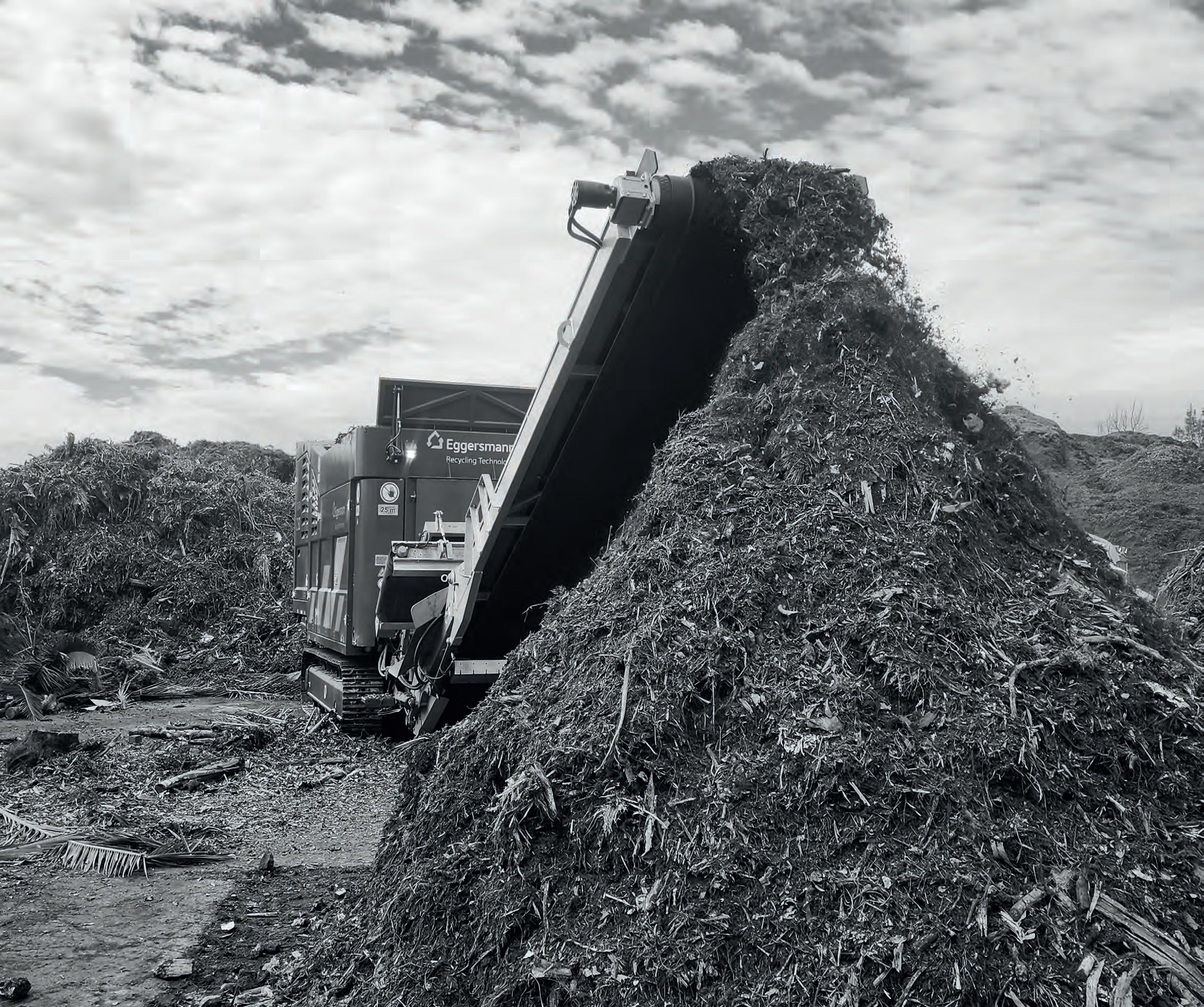
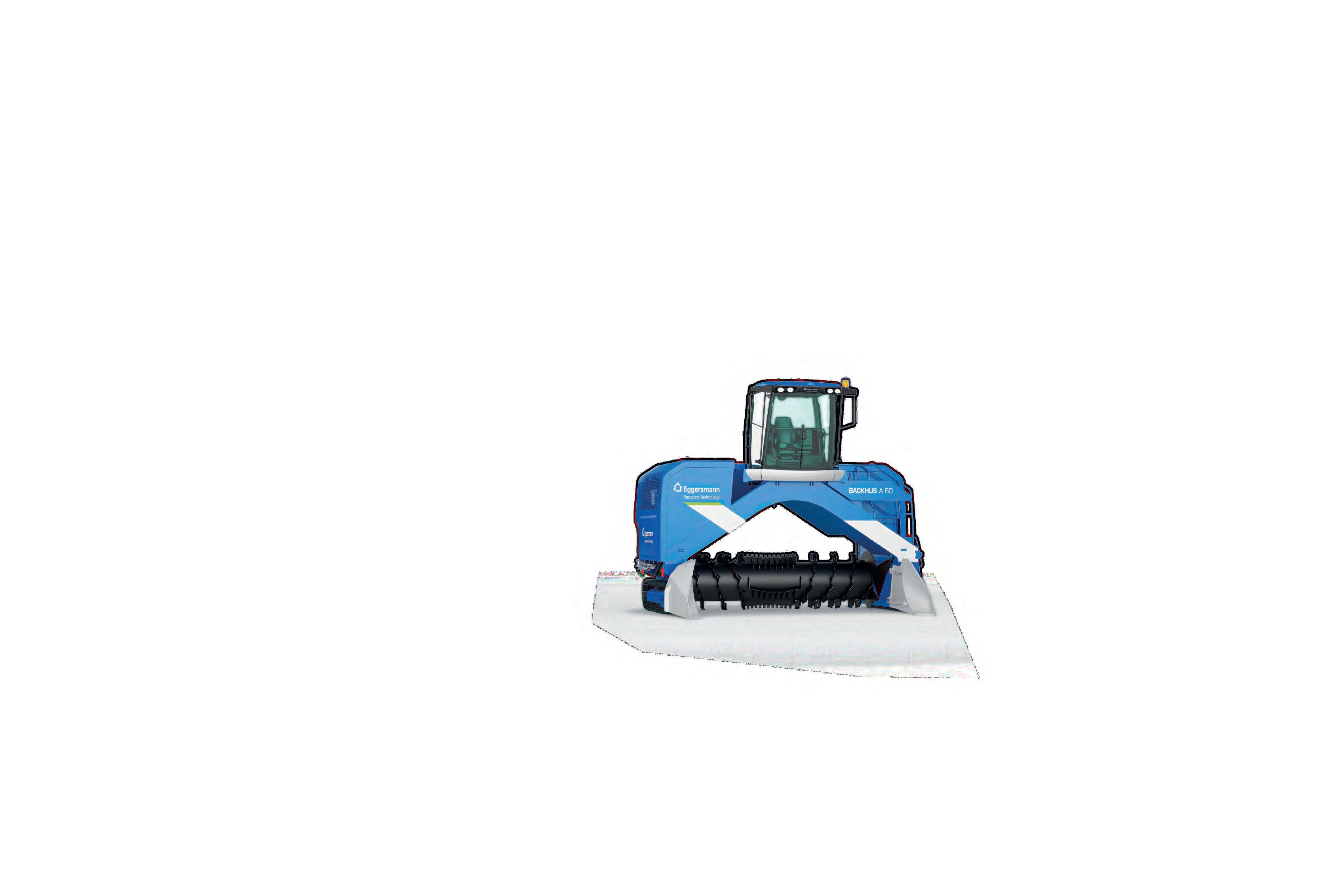