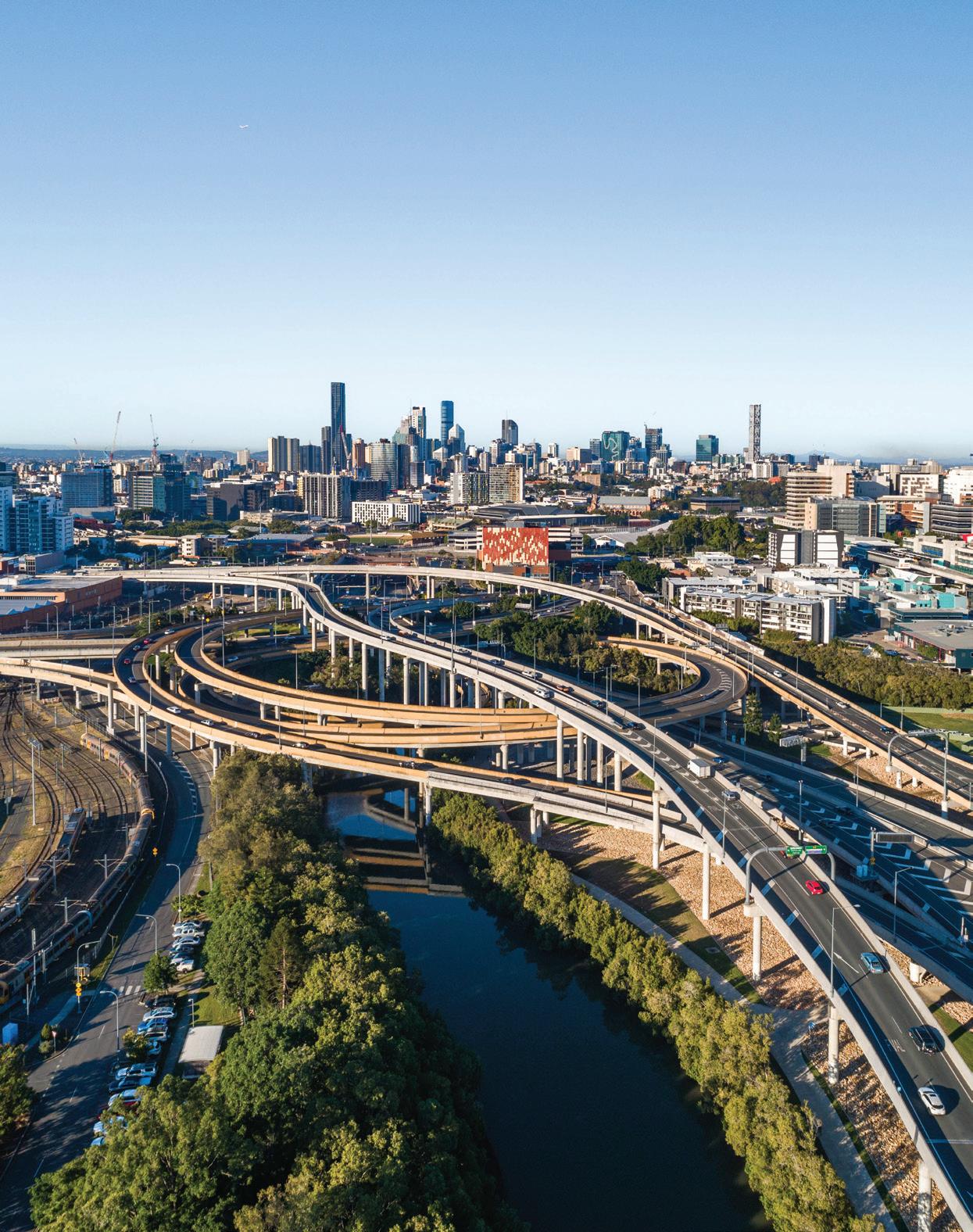
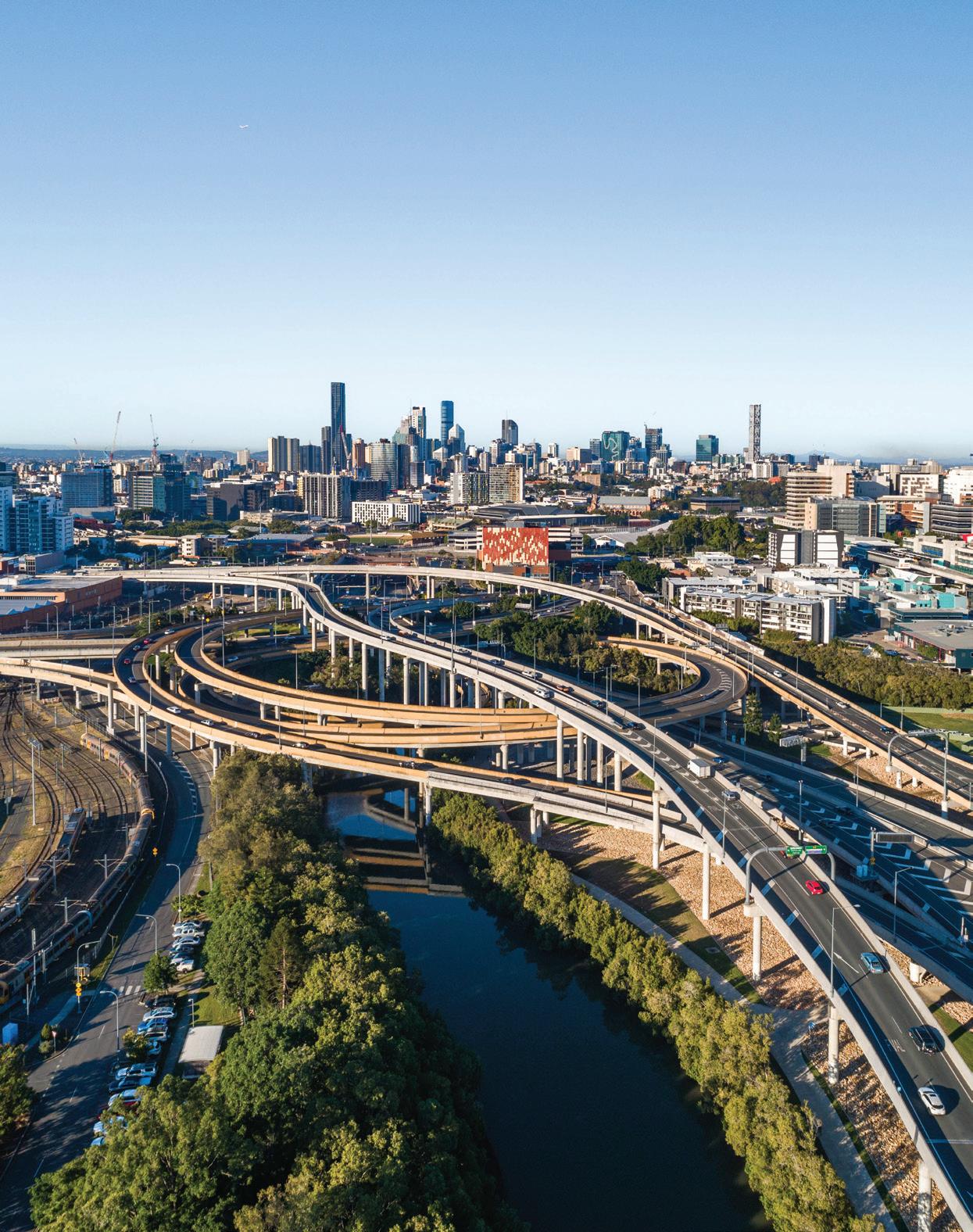
FOR
ECONOMY INFRASTRUCTURE THE
From
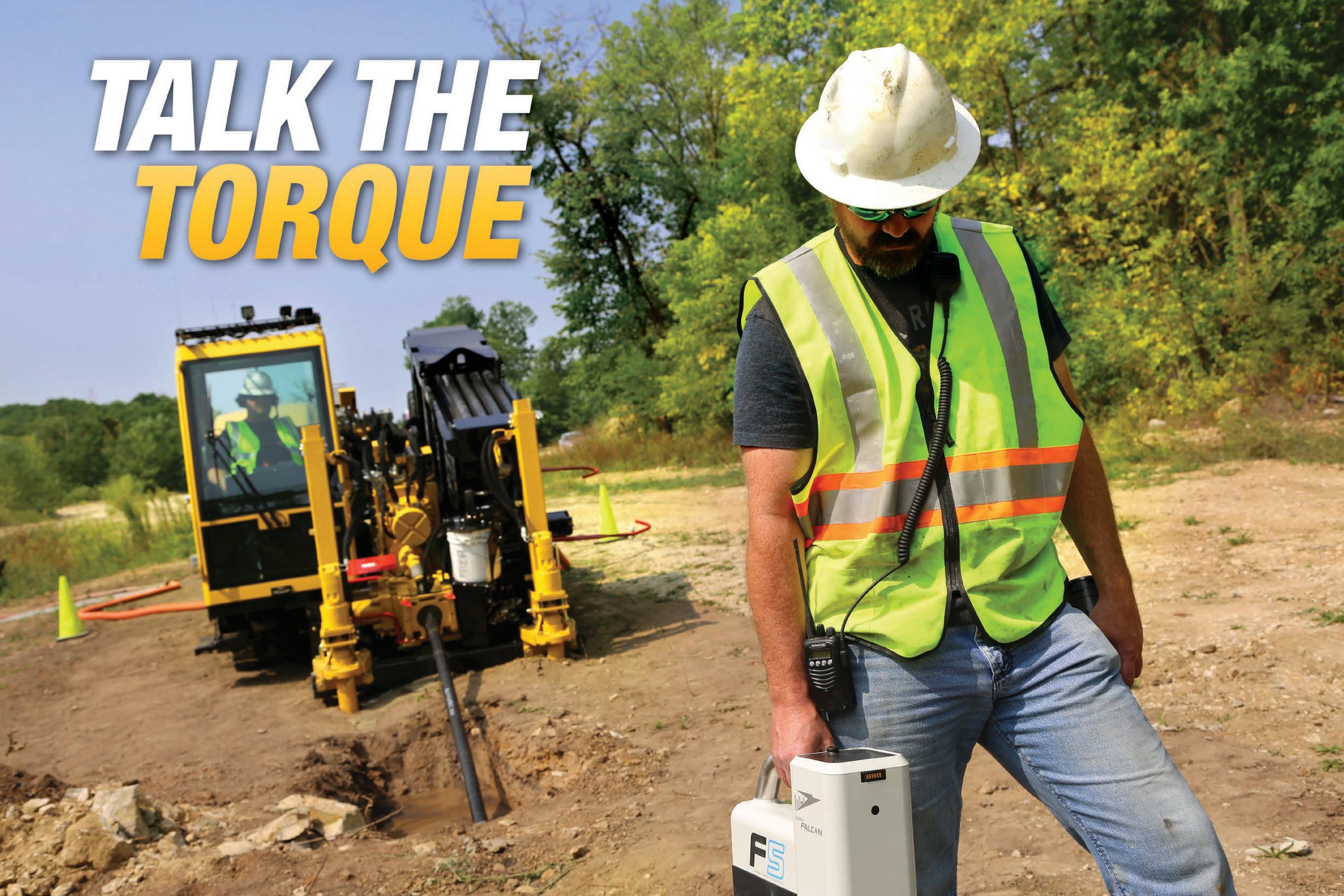
NEW RANGE OF ROCK DRILLS TO CONQUER ALL TERRAIN
When drilling in rock, you need a rig that can take on the tough ground conditions. Vermeer’s latest additions to the HDD market are two new intuitive compact rock drills; the D23x30DR S3 and the D40x55DR S3.
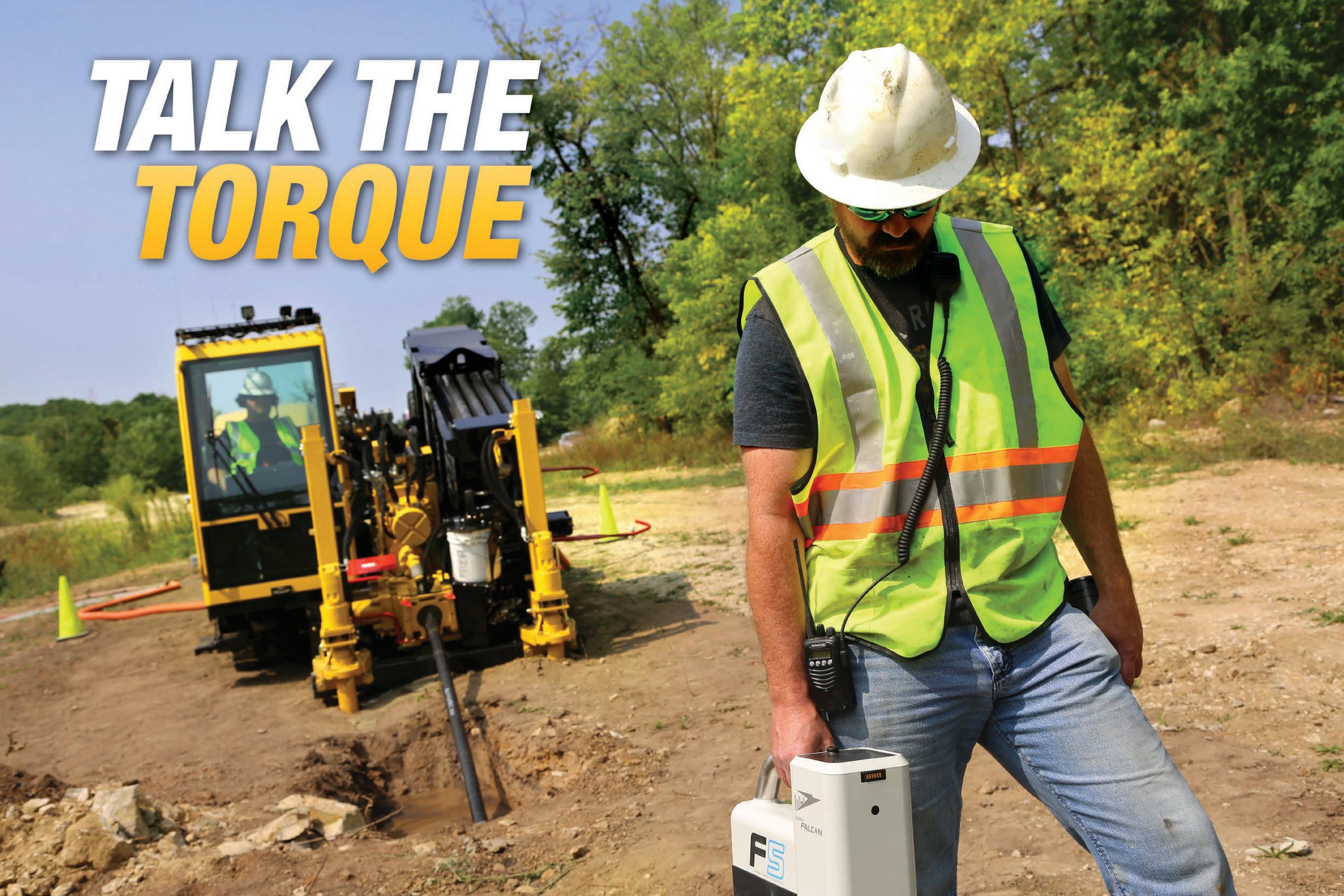
The new DR HDD range has the bene t of superior steering in extreme conditions. They are easy to use, versatile for both rock and clay drilling, and have a quieter noise level at the operator's ear, making them the perfect machines when minimal disruption in urban areas is required. Call Vermeer Australia today for further information.
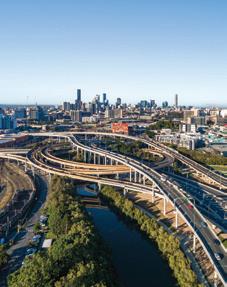

EDITOR’S WELCOME
Each edition of the magazine so far in 2020 has been put together in widely different circumstances than the last, and this issue is no exception. While our previous edition saw us move quickly to adapt to changes due to this new thing called COVID-19, the country is now arguably more settled into this new way of living during a crisis.
While the infrastructure industry has been great at keeping essential services going, the sector is also critically looking ahead at what these changes mean long term.
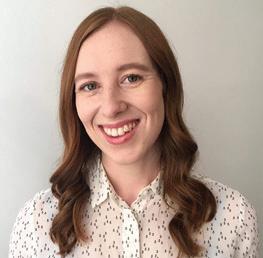
for you to hear, and be a part of, the conversations that come from this. You can find out more about the event on page 22.
Innovations come with challenges though as NSW’s Chief Data Scientist, Dr Ian Oppermann, notes in his article, with issues around data privacy and security also needing to be addressed, especially given Australia’s recent cyber security breach.
ABN: 36 426 734 954
204/23–25 Gipps St Collingwood VIC 3066
P: (03) 9988 4950
F: (03) 8456 6720
monkeymedia.com.au
info@monkeymedia.com.au infrastructuremagazine.com.au news@infrastructuremagazine.com.au
Editor Jessica Dickers
Assistant Editor
Kim Ho
Journalists
Lauren Butler
Imogen Hartmann
Eliza Booth
National Media and Events Executives
Rima Munafo
Brett Thompson
Design Manager
Alejandro Molano
Designer Jacqueline Buckmaster
Publisher Chris Bland
Managing Editor
Laura Harvey
The potential for innovation following economic turmoil has been well documented, and the post-COVID economy could provide these conditions once more. Throughout this issue, our expert contributors explore what the new infrastructure for a new economy could look like, from renewable energy to electro-mobility, smart cities, digital twins, and the circular economy. These could very well be part of the next wave of infrastructure innovation.
Looking at where new opportunities lie, and what can be done now in order to start planning and preparing our assets for the future, was a key focus of Infrastructure's recent Virtual Conference The Future of Infrastructure.
Similar to the magazine, we gathered some of the industry's brightest minds to explore what the industry will look like post-COVID, looking at everything from digital infrastructure to mobility, sustainability and asset resilience.
If you missed the event, we’ll be running it again in September as one part of the Critical Infrastructure Summit 2020. The summit involves five freeto-attend Virtual Conferences, running 2pm every Wednesday in September, covering the whole infrastructure lifecycle – construction, asset management and disaster resilience.
This mega conference has been in the works for a while now and I can’t wait
The last few months have seen a slowdown in many industries, with restrictions causing decreases in passenger numbers at airports, on trains and on our roads.
However, Australia’s freight and port sector saw the opposite, with a significant increase in demand. There’s a lot of exciting developments in the works for this sector, with the National Freight and Supply Chain Strategy and projects such as the $125 million Port Rail Transformation Project at the Port of Melbourne and Port Botany’s on-dock rail, among others. To quote Ports Australia CEO, Mike Gallacher, “Resilience is the first thing that comes to mind when reflecting on the ports’ role through COVID-19.”
Over the last few months, it has also been great to see the amount of funding that has gone towards fast-tracking shovel-ready infrastructure projects, to not only help the economy, but keep our workers employed. With recent spikes in COVID-19 cases again (especially here in Victoria which saw a large portion of Melbourne go back into lockdown), the pandemic is not an issue that is going away anytime soon, but it’s hopeful to see the continued resilience and adaptiveness of the industry, as well as the confidence that funding and accelerated projects are providing.
Let’s hope this continues as infrastructure has a big role to play in the country’s recovery.
Jessica Dickers Editor
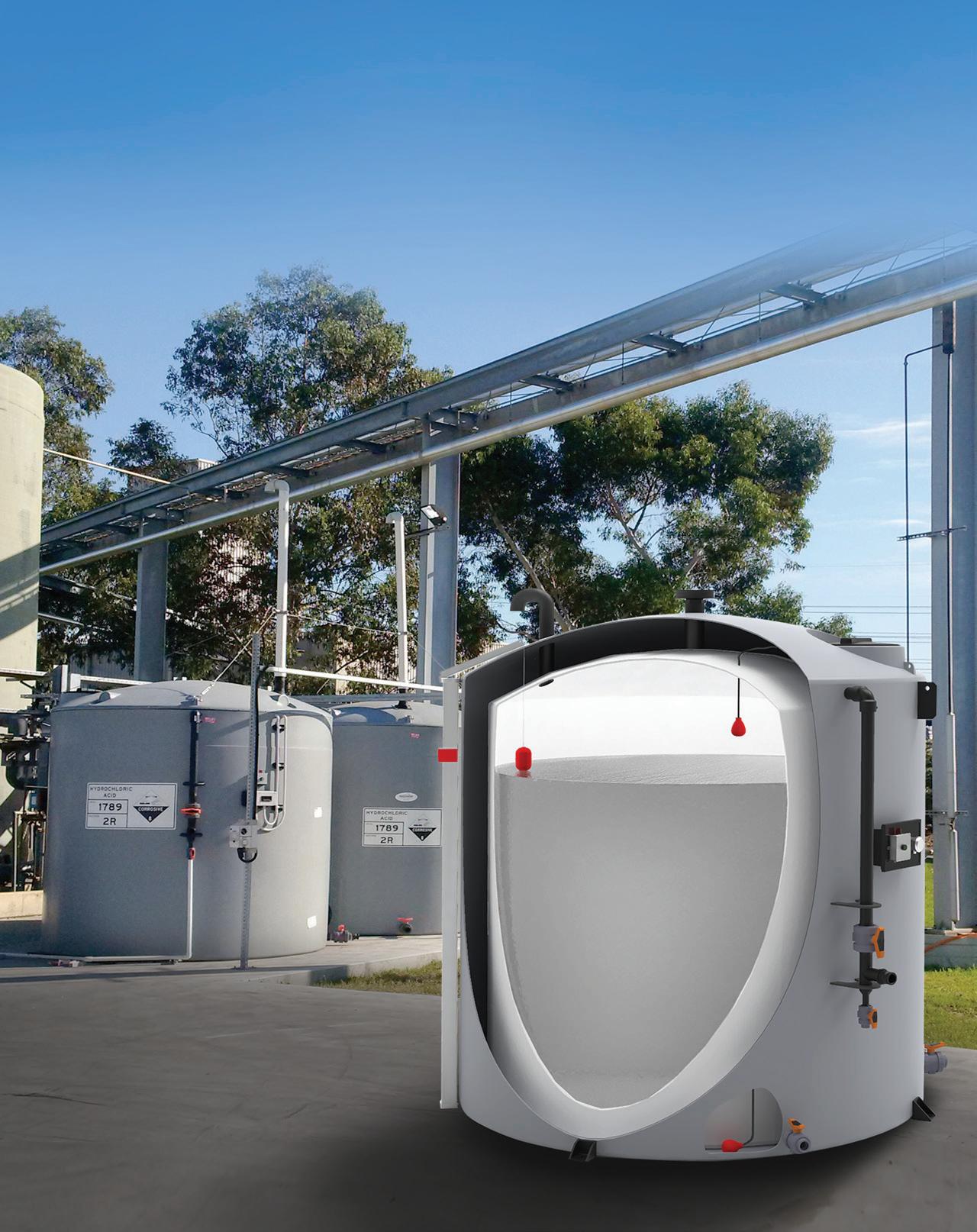
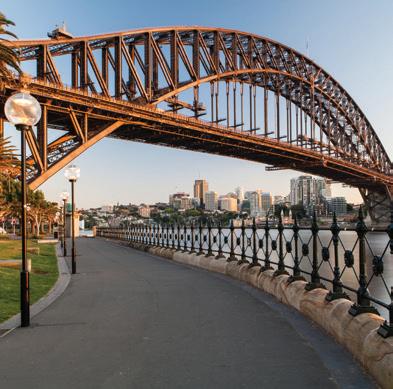
HEADING
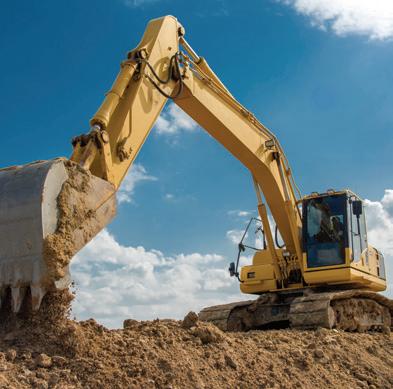
A WORD FROM INFRASTRUCTURE AUSTRALIA
REMAKING A RESILIENT ECONOMY
The year 2020 has produced a roll call of calamities that have tested the resilience of all Australians: bushfires, drought, floods and an ongoing pandemic. Now, after 28 years, Australia is in a recession, with the unemployment rate up to 7.4 per cent and expected to climb.
INDUSTRY INSIGHTS
THE NEW INFRASTRUCTURE FOR A NEW ECONOMY
The next economy is emerging rapidly based on new infrastructure that has been ready, but not yet mainstreamed.
CIVIL INFRASTRUCTURE SECTOR READY TO BOOST THE ECONOMY
SEVEN TRENDS SHAPING THE FUTURE AUSTRALIAN CONSTRUCTION MARKET
JOIN THE CRITICAL INFRASTRUCTURE COMMUNITY
MACHINERY THAT MAKES A BOOM
DIGITAL INFRASTRUCTURE
HOW INFRASTRUCTURE PROJECTS CAN EFFICIENTLY USE VIRTUAL EXPERIENCE TWINS
DIGITAL
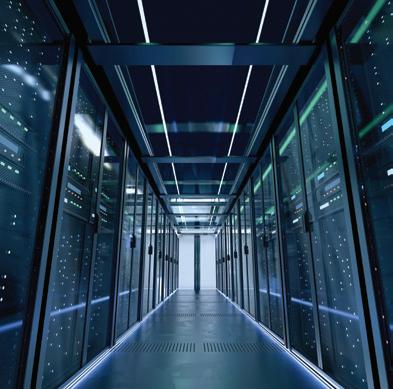
ROAD AND
TRAFFIC
WHY CHANGING HOW WE PAY FOR TRANSPORT IS A GOOD MOVE
OPTIMISING TRAFFIC FLOW THROUGH DETECTION AND DATA
FREIGHT AND LOGISTICS
THE PLANS ARE IN PLACE, SO LET’S GET TO WORK
TIPS
USING RECYCLED MATERIALS IN MAJOR CONSTRUCTION PROJECTS
NEW VIRIBAR® 750 FITMENT IS SUSTAINABLE AND EASY TO SUBSTITUTE
REBUILDING SUSTAINABLY AFTER THE BUSHFIRES
ADAPTING ASSET MANAGEMENT TO NEW WAYS OF LIFE
SOUND PROTECTION MEASURES AGAINST RAILWAY NOISE
LEADING AN ASSET MANAGEMENT TEAM REMOTELY
With many companies and asset management teams now having to work from home, here are three areas of focus that can help teams transition to new ways of working and create more opportunities.
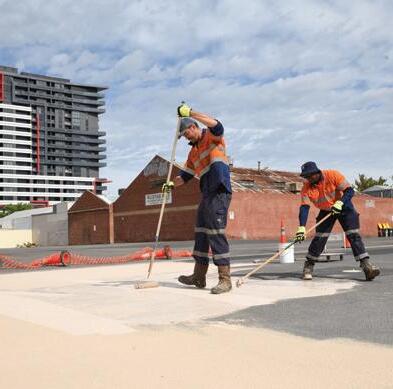
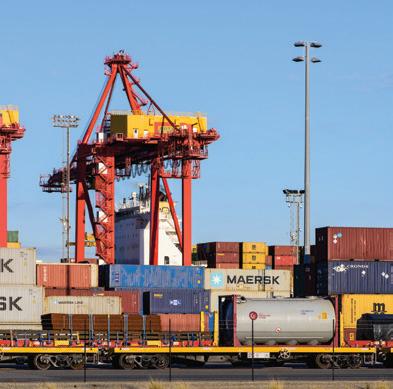

IMPLEMENT RADIO FREQUENCY IDENTIFICATION ON RAILROADS?
OPTIC SENSORS MONITORING BRIDGES AND CRITICAL STRUCTURES
PORTS
BUILDING RESILIENCE IN THE PORTS SECTOR
PORT BOTANY ON TRACK TO SUPPORT NSW
In the next 40 years, NSW’s population is forecast to grow to 12.5 million, which includes an extra 3.8 million people living in Greater Sydney alone. Ensuring our port supply chains are able to efficiently cater for the growing trade needs to support this population growth is crucial to the economic vitality of the state.
INCIDENT DATA PAVES WAY FOR CHANGE IN THE CRANE INDUSTRY
HOW TO CREATE SAFER, MORE EFFICIENT STORAGE FACILITIES
& HEAVY LIFTING SAFETY AND RISK MANAGEMENT
MANAGING WORKSITE COVID-19 SAFETY RISKS
Under Australia’s model Work Health and Safety (WHS) laws, employers are required to protect the health and safety of workers and others at the workplace by eliminating or minimising risks arising from work.
HEADING
Tammy Falconer Director Engineering & Asset Management, KPMGPreamble
Tammy has carved out a successful career working for and driving change in state-owned corporations and public sector organisations. She is currently the Director of Engineering & Asset Management at KPMG and was previously the Head of Asset Knowledge at Sydney Water.
Tammy leverages her expertise in asset management, data and analytics to place trusted information into the hands of decision makers to deliver customer-centric asset management solutions. Her achievements span unique and diverse work experiences including increasing fare compliance and customer satisfaction across all modes of public transport in Sydney; leading the implementation of GIS and asset management information systems, and improving asset management practices to deliver power, water and wastewater services to 72 remote Indigenous communities across the Northern Territory.
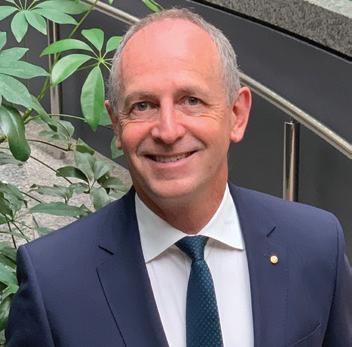
FPeter
Newman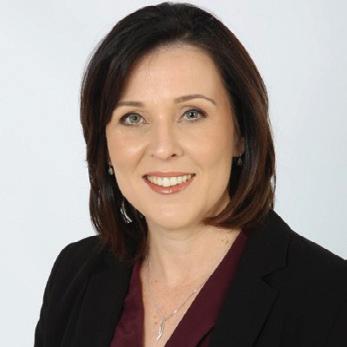
Kirk has been the CEO of the Australian Logistics Council since January 2019. Prior to this, Kirk was the National Executive Director of the Urban Development Institute of Australia (until December 2018), and headed the Master Builders Association of the ACT as Chief Executive.
Kirk has also occupied senior positions with Leighton Holdings, the Australian Medical Association and the Murray Darling Basin Commission; served as a diplomat; been a Captain in the Australian Army; held senior media roles within government; and worked as a journalist. Kirk received his Medal of the Order of Australia for his work with the crisis taskforce following the bombings that occurred in Bali on 12 October 2002.
Professor of Sustainability, Curtin UniversityPeter is an academic who has written 20 books and over 350 papers on sustainable cities with a global reputation and has worked to deliver his ideas in all levels of government. Peter has worked in local government as an elected councillor in Fremantle; in Western Australia's State Government as an advisor to three premiers; and in the Federal Government on the Board of Infrastructure Australia and the Prime Minister’s Cities Reference Group. He is the Coordinating Lead Author for the UN’s IPCC on Transport In 2014, Peter was awarded an Order of Australia for his contributions to urban design and sustainable transport, particularly for his work in saving and rebuilding Perth’s rail system. In 2018/19 he was the WA Scientist of the Year.
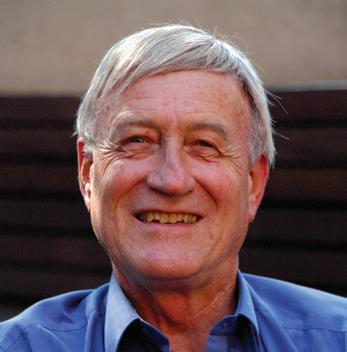
Contributors
Dr Ian Oppermann
NSW Government’s Chief Data Scientist
Ian is the NSW Government’s Chief Data Scientist and an Industry Professor at the University of Technology Sydney (UTS). From 2015 to 2019, Ian was also the CEO of the NSW Data Analytics Centre (DAC). Ian has nearly 30 years’ experience in the ICT sector and has led organisations with more than 300 people, delivering products and outcomes that have impacted hundreds of millions of people globally.
Ian has held senior management roles in Europe and Australia as Director for Radio Access Performance at Nokia, Global Head of Sales Partnering (network software) at Nokia Siemens Networks, and then Divisional Chief and Flagship Director at CSIRO. He is considered a thought leader in the area of the digital economy and is a regular speaker on Big Data, broadband enabled services and the impact of technology on society.
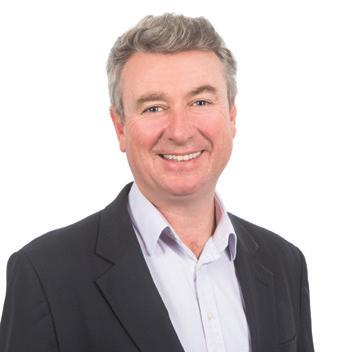

Marika Calfas
Chief Executive Officer, NSW Ports
Marika has operated in the port sector for 18 years across a broad range of portfolio areas including strategy, planning, environment and infrastructure. Marika was appointed by the Federal Minister for Infrastructure and Transport to the Expert Panel advising the Government Inquiry into the National Freight and Supply Chain Strategy Priorities in 2017. Marika is a board member of Infrastructure NSW and Ports Australia, Deputy Chair of the Australian Logistics Council, member of Infrastructure Partnerships Australia’s National Advisory Board and Wollongong University’s SMART Advisory Council, as well as Australia’s representative to PIANC International Environmental Commission.
Michel Masson
Chief Executive Officer, Infrastructure Victoria
Michel started his career at Deloitte before joining the Bollore Group where he held various senior finance positions in the transport and logistics division in the UK, Australia and New Zealand. In 2005 he joined Keolis as head of Finance and Operations for the International Division where he was responsible for leading public transport operations in seven countries and held various non-executive director positions in UK and German rail franchises.
Michel was appointed CEO of Yarra Trams in 2009 and helped lead the development of Keolis Downer throughout Australia, before joining the Calibre group in 2014 to create and lead its Transport Infrastructure business.
Michel is a graduate from the EDHEC Business School in France, and the Australian Institute of Company Directors. He also completed the Advanced Management Program from the Harvard Business School.

PM COMMITS $1.5 BILLION TO INFRASTRUCTURE
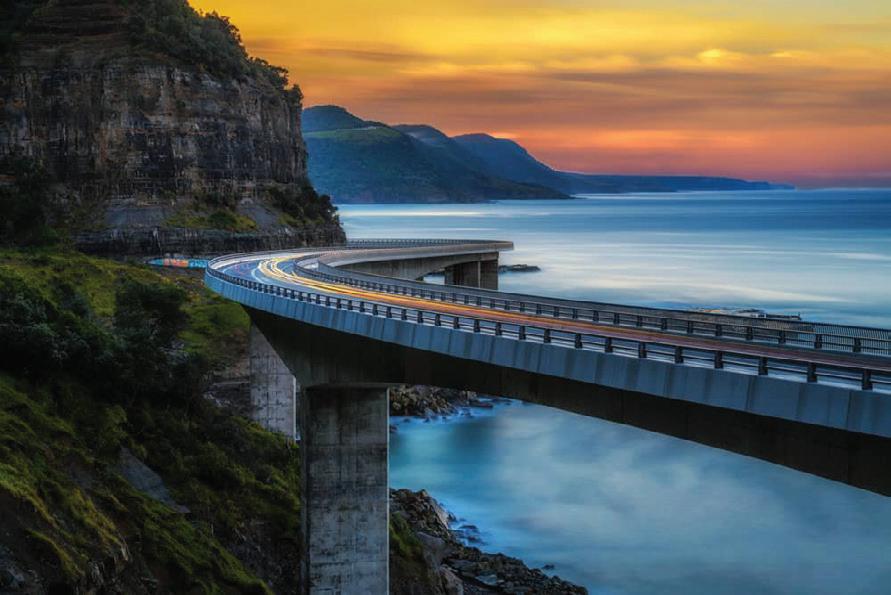
The Federal Government will fast-track investment in critical infrastructure projects including Inland Rail; the Marinus Link; the Olympic Dam extension; NSW emergency town water projects; and road, rail and iron ore projects in Western Australia, as part of its new JobMaker plan.
In a speech at CEDA’s State of the Nation Conference, Prime Minister Scott Morrison, announced that infrastructure investment and deregulation would play a “critical” role in the five-year JobMaker plan, as well as skills, industrial relations, housing and construction, and major reform of funding approval processes.
The Prime Minister announced the Federal Government would commit a further $1.5 billion to immediately commence work on priority projects identified by states and territories as part of new bilateral partnerships designed to expedite approvals.
As part of this package, $1 billion will be allocated to priority projects that are shovel-ready, with $500 million reserved for road safety works targeting areas across the country, not only in rural and regional areas.
Investment will be directed to transport infrastructure, but also to water infrastructure to secure supply and underpin agricultural expansion; telecommunications services; the electrical infrastructure
required to remove bottlenecks in Australia’s electricity grid; and advance manufacturing, especially in regional areas.
Joint assessment teams will work on accelerating these projects, which are worth more than $72 billion in public and private investment and are expected to support over 66,000 direct and indirect jobs.
The Prime Minister’s priority list of fast-tracked projects includes:
♦ Inland Rail from Melbourne to Brisbane
♦ Marinus Link between Tasmania and Victoria
♦ Olympic Dam extension in South Australia
♦ Emergency town water projects in New South Wales
♦ Road, rail and iron ore projects in Western Australia
MAJOR DEREGULATION TO STREAMLINE APPROVALS
The Prime Minister said that the key to build the pipeline of future projects was for government to “get out of the way” and speed up progress by improving approvals processes.
“Ultimately, our objective is the streamlining of Commonwealth and state processes to a point of ‘single touch approvals’,” he said.
In an effort to drive a whole-ofgovernment approach to how regulatory policy is prosecuted, he announced he
would bring the Deregulation Taskforce into his own department, the Department of Prime Minister and Cabinet.
The Prime Minister established the Federal Deregulation Taskforce in 2019 with his Assistant Minister, Ben Morton. This included simplifying business registers, streamlining export documentation and making it easier for a sole trader and micro-businesses to employ people.
The next phase of the taskforce work will focus on areas to assist COVID-19 economic recovery.
The Prime Minister cited occupational licensing and registration requirements as a key example, often varying across states and territories, which increases costs on businesses and workers who operate or move across Australia.
A NEW BILATERAL MODEL BETWEEN FEDERAL AND STATE LEVELS
In addition to streamlining Commonwealth approvals, the Prime Minister said a new bilateral model would be implemented to speed up communication and decision-making between the federal, state and territory governments.
Under this new model, jobs will be brought to market earlier by targeting a 50 per cent reduction in federal assessment and approval times for major projects, from an average of 3.5 years to 21 months.
CONSTRUCTION ON WESTERN SYDNEY AIRPORT RAIL LINE TO BEGIN IN 2020
Construction is set to commence in 2020 on the $11 billion Sydney Metro – Western Sydney Airport rail line, providing an economic boost as NSW plans its recovery from COVID-19.
The rail line will service the greater Western Sydney region as well as the Western Sydney International (Nancy-Bird Walton) Airport, which is currently under construction.
The project includes six proposed metro railway stations:
♦ Two stations within the airport site, at the airport terminal and at the airport business park
♦ A station serving the commercial heart of the Western Sydney Aerotropolis
♦ A station at St Marys, interchanging with the existing suburban railway station and connecting customers with the rest of Sydney’s rail system
♦ A station at Orchard Hills to service a future commercial and mixed-use precinct
♦ A station at Luddenham to service a future education, innovation and commercial precinct
Construction on the project is expected to support about 14,000 jobs, including 250 new apprentices.
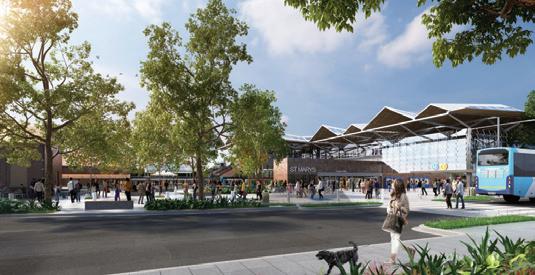
Sydney Metro – Western Sydney Airport is a key part of the Western Sydney City Deal, a 20-year agreement signed in March 2018 by the Federal Government, NSW Government and eight Western Sydney councils.
The new metro railway line will become the transport spine for the region, connecting travellers from the new airport to the rest of Sydney’s public transport system.
Under a new agreement between the Federal and NSW Governments, a further $3.5 billion will be injected into the project in time for the opening of the airport in 2026.
NSW GOV AWARDS TWO RAIL CONSTRUCTION CONTRACTS WORTH $600 MILLION
The NSW Government has awarded two contracts for modernisation and upgrade works on the state’s rail network, worth a combined $600 million.
The infrastructure upgrades, which form part of the NSW Government’s $4.3 billion More Trains, More Services program, will be delivered as two separate packages of work, each worth around $300 million.
The Next Rail partnership, comprising John Holland and Jacobs, will deliver all projects from Central to Hurstville, while the Transport for Tomorrow partnership, comprising Laing O’Rourke and KBR, will deliver all projects between Mortdale and Kiama.
The essential upgrades to rail infrastructure include the stabling yards, signalling, track, station platforms and power supply at key locations between
Central, the T8 Airport Line tunnel and the South Coast.
These lines are being prioritised because they are among the busiest on the network, catering for 440,000 trips in a typical day – approximately one third of daily rail customers.
Construction for the rail upgrades will begin in the middle of 2020 and be completed in advance of the service improvements, which are planned for late 2022.
Further improvements will be delivered under the More Trains, More Services program in 2024, including on the T4, T8 and South Coast Lines, to effectively integrate Sydney Metro City and Southwest.
NSW Transport Minister, Andrew Constance, said the two most recent contracts will support around 550 jobs.
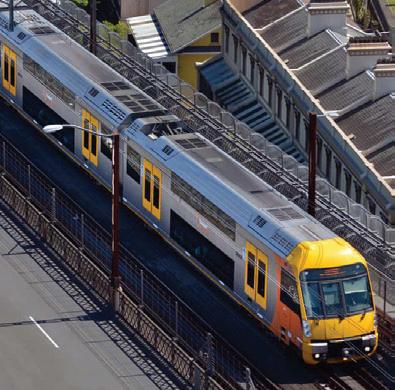
The jobs will cover a range of disciplines including engineers, rail construction workers, security guards, truck drivers, electricians, plumbers, labourers, concrete workers and apprentices.
CUSTOMISING AND INTEGRATING PUBLIC INFORMATION DISPLAY SYSTEMS
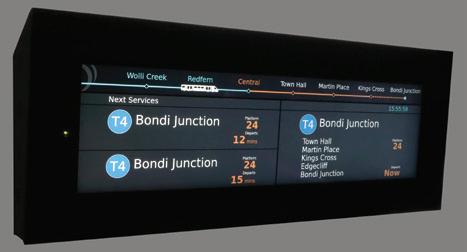
The Smart pi EYE range now includes:
♦ PID – Passenger Information Displays module
♦ EYE-HD – 1080P Embedded HDMI Output for screens
At AusRail 2019 tm stagetec systems launched the new Smart pi EYE Public Information Display System. The Smart pi product range has evolved into high-quality hardware and software technology solutions for public information audio, display and distribution.
The flexible topology allows the system to be installed in smaller environments and expanded as needed to support more displays or integrate into other services. From a single web interface, content management administrators are able to select the display type/template, which automatically renders the information for the PID Client in the correct format and style.
The system is based on templates, allowing for easy customisation of all screen types, sizes and orientations. tm stagetec systems has partnered with Manuco Electronics
to provide Hyundai IT industrial outdoor screens, built to withstand harsh environments with IP65 and higher ratings.
Energy saving has also been a major consideration for the whole system. The embedded EYE-HD runs off a 5V USB input and has very low power consumption. Additionally the Hunyadi IT Screens automatically adjust brightness and fans depending on environmental requirements, saving significant power.
Smart pi EYE can be integrated with the entire Smart pi range including the Smart pi DSP and Smart pi DVA Audio Systems (and other AES70 devices). All server infrastructure can be virtualised to help reduce the hardware count across the entire network.
For more information, contact tm stagetec systems at www.tm-systems.com.au, or look for their stand at AusRail 2020
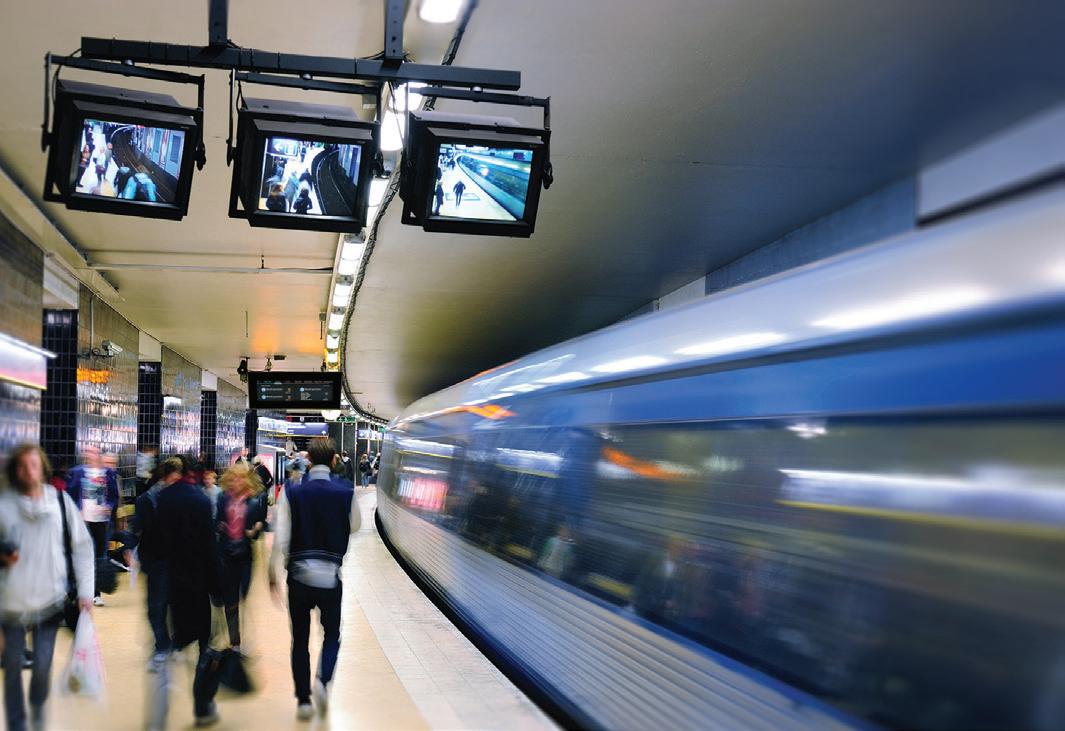

THE CHANGING FACE OF
INFRASTRUCTURE
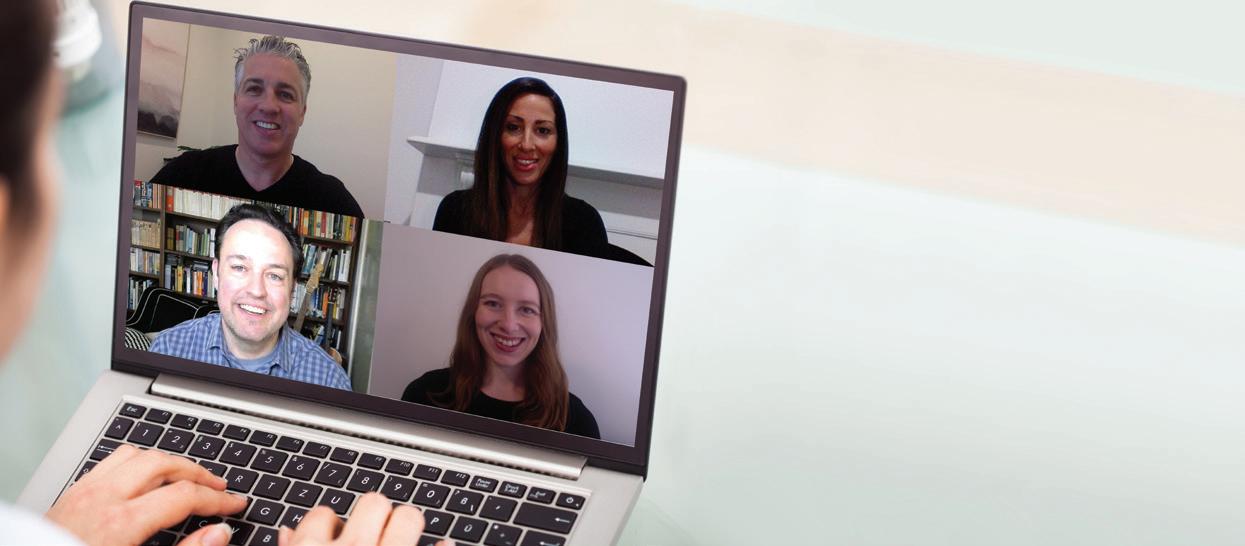
The pandemic has seen a significant number of our subscriber base shift to working from home, while many others are involved on the frontline of essential projects. The demand for timely information has increased, and with the mainstream press providing constant updates on the broader situation, we have dedicated our resources to more analysis and reflection on the impacts on the infrastructure sector.
This has included an increased focus on digital newsletters, social content, videos, webinars and Virtual Conferences, all of which have received unprecedented levels of engagement since March.
According to Infrastructure Editor, Jessica Dickers, the sector has been particularly interested in stories about new infrastructure funding, and the fast-tracking of projects.
“The infrastructure industry has huge potential to help with Australia’s economic recovery, so people are craving updates on projects and funding, to see where these opportunities lie,” Jessica said.
“Content around digital technologies and innovations such as digital twins, for example, is also proving popular with our readers, as is any news on significant megaprojects such as the construction of Inland Rail and the Western Sydney Airport.
“This shows that the sector wants to know more about where the future of the industry is headed and what can be done now to prepare for challenges surrounding population growth, climate change, and the changes to how people live and move around the country after the current pandemic threat is reduced.”
And while change is a constant when it comes to the infrastructure industry and publishing alike, according to Infrastructure Publisher and Monkey Media Managing Director, Chris Bland, some things do stay the same.
Monkey Media, the publisher behind Infrastructure, has been adapting to the changed world brought about by COVID-19.
Top L-R: National Media and Events Executives, Brett Thompson and Rima Munafo.
Bottom L-R: Infrastructure Publisher, Chris Bland, and Infrastructure Editor, Jessica Dickers.
"While we will keep updating the platforms and methods of delivery, we have always focused on understanding the industry, and delivering the best content we can to the key players in that industry,” said Chris.
“That part of our approach hasn’t changed, we’re just reaching our audience in more ways now than ever before.”
This adaptation has led to a broader range of marketing services and options for companies looking to get their message to the industry, with custom EDMs, content marketing, lead generation, and Virtual Conferences and webinars among the most popular options.
The changing situation has also seen some changes to the team, with Brett Thompson recently joining as National Media and Events Executive. Brett brings years of experience in similar roles, and joins long-standing National Media and Events Executive, Rima Munafo. The two of them will work closely with Infrastructure's commercial partners to help them develop new content and strategies to communicate with our audience.
Chris said, "I've worked with Brett for many years previously, and it's great to be back on the same team with him again. There are so many exciting new ways that we're able to help companies to get their message out there and play a leading role in this sector.
“Brett and Rima both have a great passion for getting results for our partners, and I’m excited about what they’ll be able to achieve in the future.”
REMAKING A RESILIENT ECONOMY
by Romilly Madew AO, CEO, Infrastructure AustraliaThe year 2020 has produced a roll call of calamities that have tested the resilience of all Australians: bushfires, drought, floods and an ongoing pandemic. Now, after 28 years, Australia is in a recession, with the unemployment rate up to 7.4 per cent and expected to climb. In these challenging times, infrastructure is uniquely placed to support jobs and drive productivity.
One of our nation’s greatest infrastructure feats, the Sydney Harbour Bridge, was a product of the Great Depression, nicknamed the ‘Iron Lung’ as it sustained the lives of thousands of workers and their families.
While history might be on our side, we must still recognise that the acceleration of infrastructure investment and reform is not without risk. In order to ensure sustained growth and true economic resilience for future generations, spending should be productivity-enhancing to enable a stronger growth trajectory than prior to the crisis.
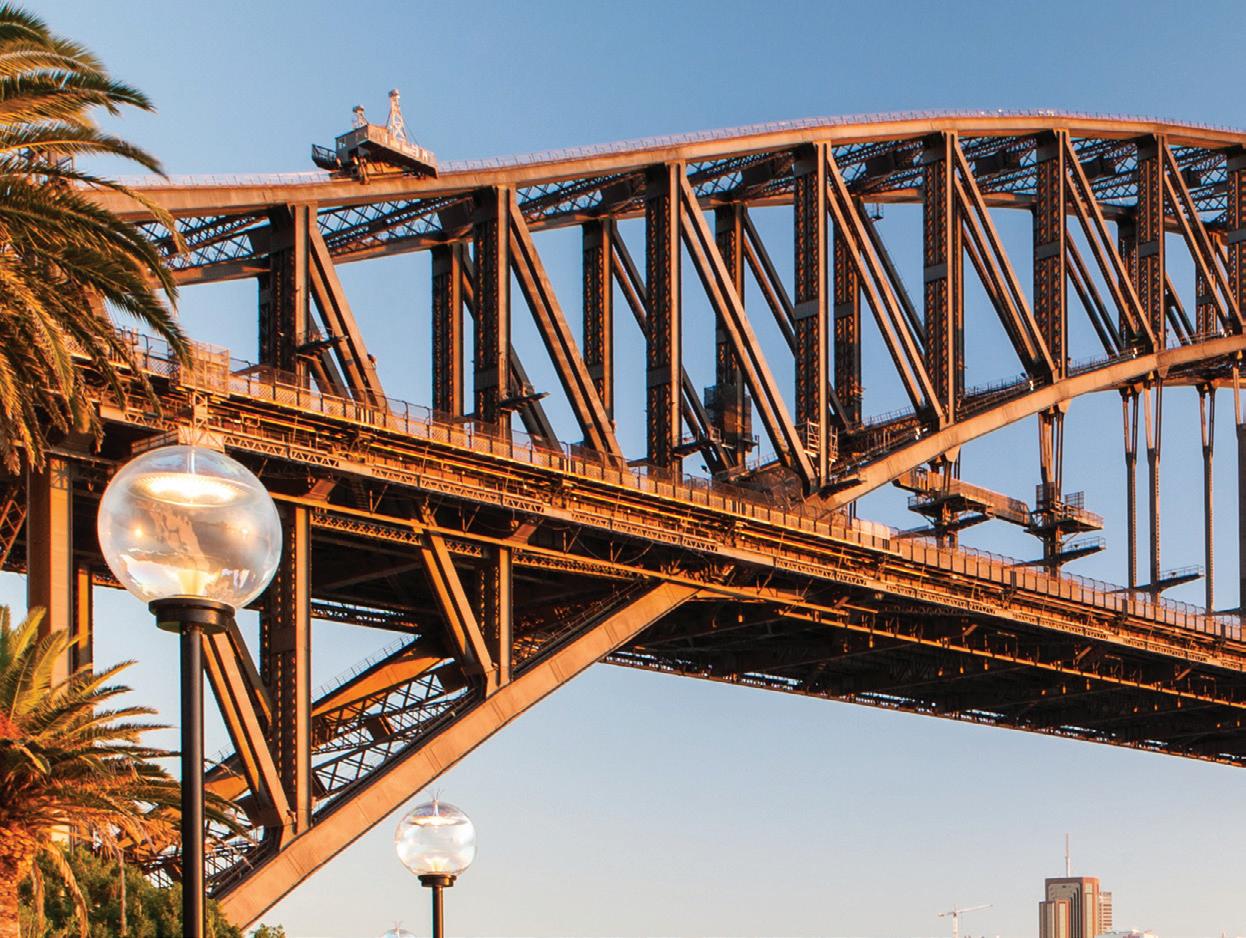
SMALL-SCALE PROJECTS ARE OF HIGH VALUE
Since the competing health and economic issues have impacted the economy, Infrastructure Australia’s advice has been to focus on a staged infrastructure recovery response; first by protecting and maintaining the existing pipeline of projects, then moving to the mobilisation of new projects, small and large. As important as large major projects are on the road to recovery, we must not forget the value of smaller projects.
While it may not draw the same fanfare and attention as new train lines and motorways, road maintenance is a great example of the need to prioritise a smaller program of work. A road maintenance program can generate high involvement of labour, trade and skills; deliver significant benefits to safety; and reduce transport costs for the growing freight industry and individual road users.
The Federal Government’s decision to bring forward $1.5 billion for local infrastructure projects, with $500 million of that targeted for road safety, is well placed. This decision aligns with existing priorities on the Infrastructure Australia Priority List, such as a National Road Maintenance strategy and a priority initiative for regional and rural WA road network safety improvements.
We expect our Infrastructure Priority List to continue to play an important role in supporting the national conversation around Australia’s spending priorities. Four of the fast-tracked projects already announced by the Prime Minister have come from the Infrastructure Australia Priority List, including Inland Rail, Marinus Link, and regional town and water security investment.
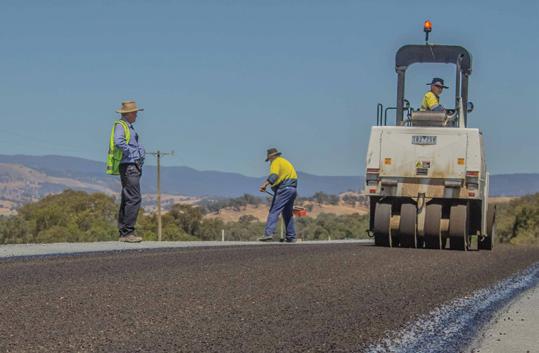
As we move past mobilisation and beyond shovel-ready projects, we will need to continue to develop a high-quality pipeline of infrastructure, ensuring it is constantly refreshed with high-quality projects. Investment in planning and design is critical to ensure the pipeline of projects continues. This pipeline gives confidence to industry, certainty to government, helps employ Australians, and supports the national economy. Maintaining this pipeline is especially true if we are going to attract private capital investment in infrastructure.
However, investment in building infrastructure will not be sufficient alone. We must also turn to the tougher path of reform.
REFORMS OF CURRENT SYSTEMS
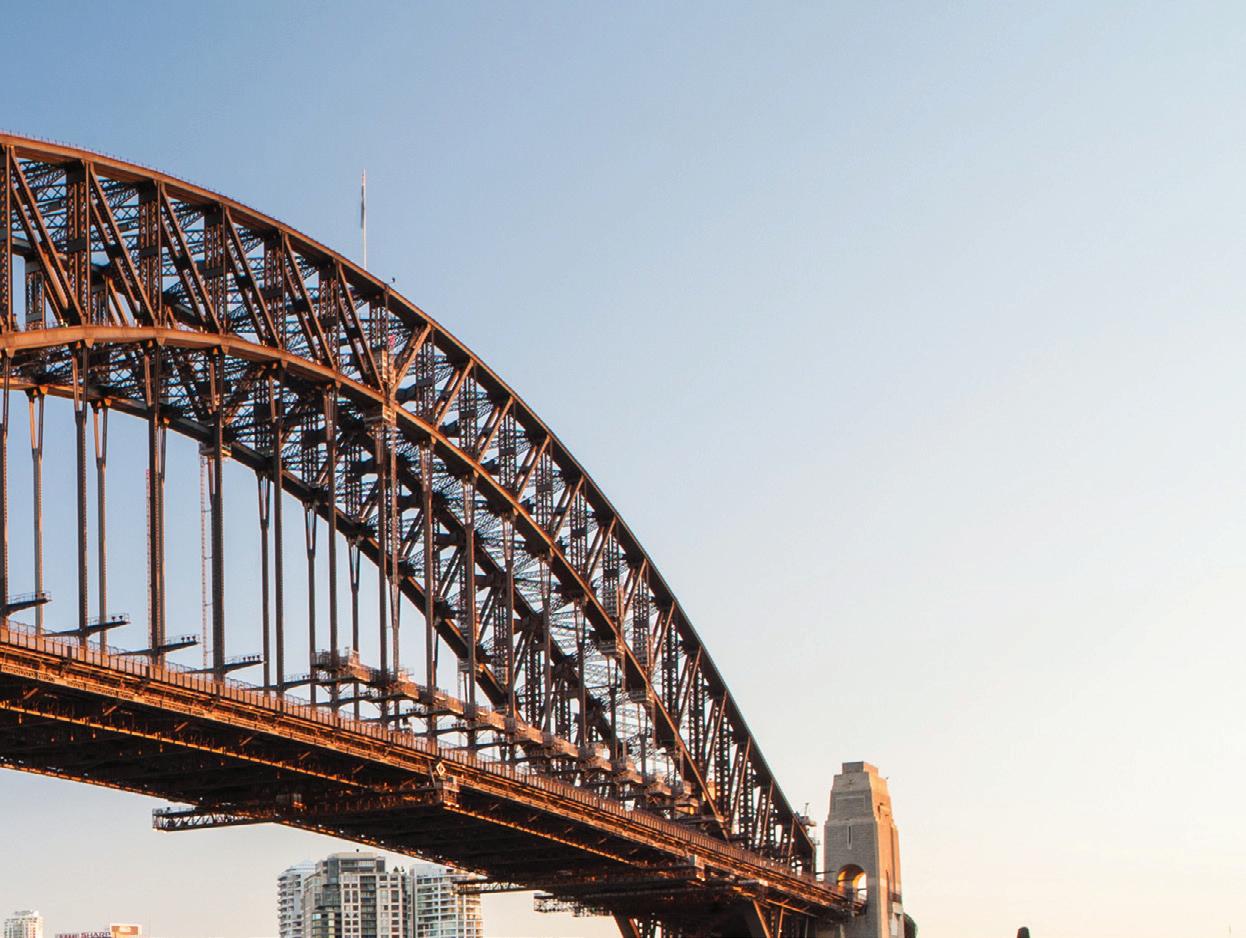
We need to reform our planning systems and policy interventions to accelerate and boost productivity. We also cannot ignore that the acceleration of major infrastructure could reduce the opportunity to provide scrutiny of proposals prior to investment. Less scrutiny leaves the door open for the possibility of over-scoping and cost escalation.
While it could result in potential job creation, it could also leave communities with white elephant projects and our economy in a worse debt position than we started.
So, how do we avoid this? By ensuring business cases for large infrastructure projects continue to include rigorous planning, evidenced-based problem definition, options analysis and independent assessment.
The recovery from COVID-19 will likely be the most significant challenge for our generation. If we expect to build our way out of this crisis and breath life back into our economy, it will come down to industry, government and the community working in concert to take the right measured steps, in turn making our economy more resilient, not less.
Romilly Madew.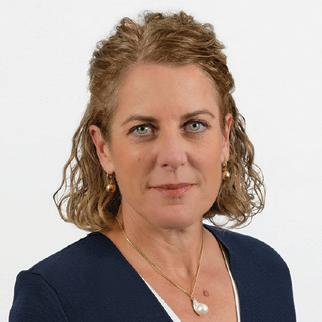
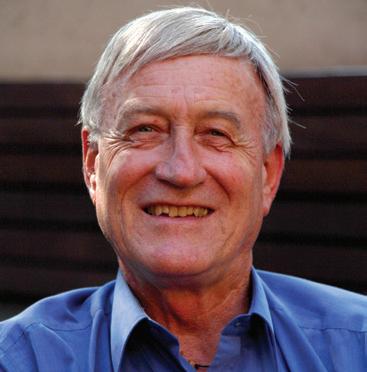
THE NEW INFRASTRUCTURE
The next economy is emerging rapidly based on new infrastructure that has been ready, but not yet mainstreamed.
Since the 1920s long wave theory economists have analysed the waves of innovation following economic collapse in the past 250 years. Figure 1 shows the past five waves and the potential for innovation in the postCOVID economy.
The innovations in infrastructure outlined in Table 1, along with the suggested emerging innovations that replace the stranded old assets, attract new investment as they cost-effectively solve multiple problems. These include:
♦ Renewable energy, especially solar PV with batteries
♦ Electro-mobility, especially with non-automobile systems
♦ Smart cities, especially sensors, Apps and ICT focused on efficient demand management
♦ Hydrogen, especially replacing fossil fuels in heavy industry
♦ Circular economy waste and recycling technologies
♦ Biophilic urbanism bringing nature into buildings and infrastructure

1. Waves of innovation over the past 250 years that emerge after economic collapse and create the next economy.
The new wave of infrastructure is an integrated ‘cluster of innovations’ –especially the first three (solar, batteries and electro-mobility) which are rapidly being adopted. These three will be the focus of change over the next decade.
POWER: RENEWABLE ENERGY, PV AND BATTERIES
Solar and wind are now the cheapest form of power and are easy to mass produce and implement in most cities and economic systems. Cities will become much more distributed into
INFRASTRUCTURE
FOR A NEW ECONOMY
local areas of infrastructure management, but they will still fit into a grid for equity and balance.
Shared solar, using batteries and blockchain or other community-based methods, has now been demonstrated for medium and high-density areas, industrial estates, and rural and remote villages.
Electro-mobility will also be a part of grid stabilisation. Gas turbines (and diesel backup in small grids) have been seen as necessary for grid stabilisation but Li-ion batteries are now cost-effective at over 150MW, making them cheaper than gas turbines and more effective at providing a rapid peaking function.
100 per cent renewable power systems will rapidly take over with Australia being a leader. The 2020 AEMO report on the Australian grid shows that it can be 75 per cent renewable by 2025, which will be pushed mostly by rooftop solar.
The COVID downturn is accelerating this transition as shown in Figure 2, as new solar and wind systems have marginal costs near to zero, thus the reductions in demand must be made by fossil fuel-based power.
Accelerated adoption of renewables has been seen across all 41 nations in the OECD where IEA data showed that in March 2020, compared to the previous year, electricity fell by 3.6 per cent but coal fell by 21.6 per cent, as solar grew 15.6 per cent, wind by four per cent and gas by a mere 2.7 per cent (and that was almost all in North America).
This is a classic example of how exponential growth in renewables and batteries can be expected to take over power grids in the near post-COVID infrastructure future.
TRANSPORT: ELECTRO-MOBILITY, MICRO-MOBILITY, TRANSIT, WALKABILITY AND ACTIVE TRANSPORT
Electro-mobility has had a growth rate of over 40 per cent per year in the past decade, with predictions for how quickly the internal combustion engine will be phased out of new vehicles now coming down into the 2020s.
Electric vehicles are rapidly reducing in cost, with battery packs reduced from $1000/kWh in 2010 to less than $200/ kWh in 2020. EVs are also preferred for other social and environmental reasons such as cleaning up local air pollution, particularly since it was discovered that COVID is carried on diesel particulates.
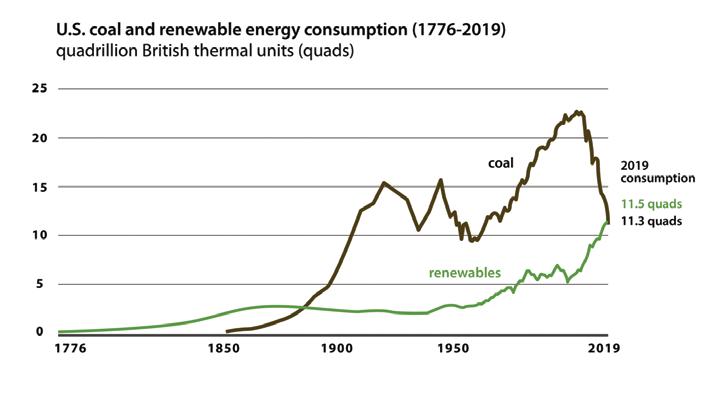
Micro-mobility – electric tuk tuks, electric bikes, electric scooters and electric skateboards – is becoming a major part of the EV revolution. Electric micro-mobility will be a growing focus for the new economy, so cities will need to make space for them on shared paths.
The co-benefits of active transport are very high and include local economic development. Enabling local centres to work without cars and to enable transit systems to work without the need for car-dependent corridors has been
emerging over the past decades. Transit was seriously damaged during COVID, but so was car traffic, thus the growth of local walkability and active transport has been a global phenomenon, with many cities building this into permanent change.
A significant innovation in electromobility in terms of common-good outcomes is the electrification of public transport. The electrification of heavy train and tram systems is a mature technology but new Li-ion batteries have revolutionised the electrification
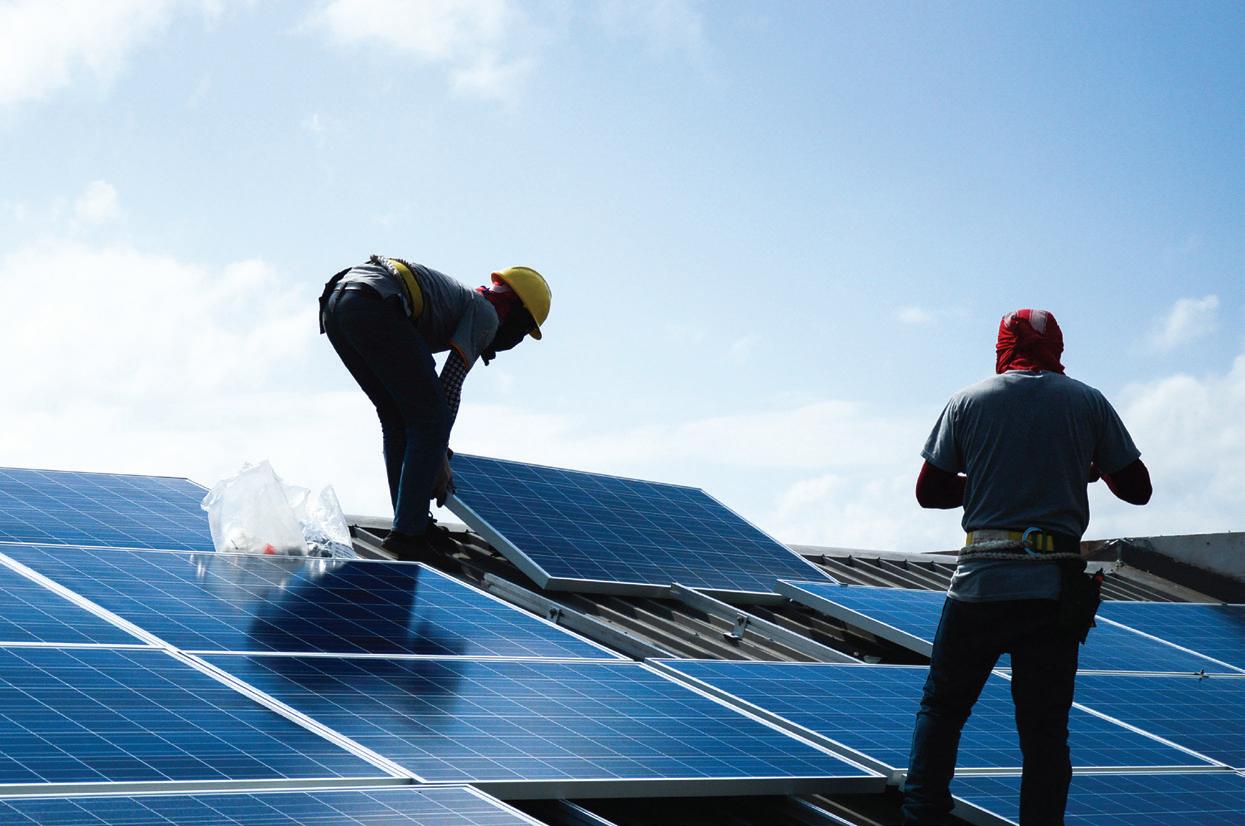
of buses into electric BRTs or Trackless Trams. These are now able to fit into cities by enabling whole main road corridors to be developed with dense precincts around stations due to their quiet, pollution-free accessibility. Such systems can replace the equivalent of six lanes of traffic.
All forms of electro-mobility need recharging, and in cities these can become part of Recharge Hubs to support grid balance. Power utilities will pay for these grid services as cities move to electrify their bus fleets (e.g. Shenzen and Canberra). Depots and stations covered in PV and with batteries inside can become important mini power/substations.
SMART CITIES-BASED DEMAND MANAGEMENT
Smart cities infrastructure works best in facilitating re-localised centres with reduced resource consumption. Localised infrastructure using machine learning can use sensors to manage local energy, water, waste and transport infrastructure, like a set of neural networks that are
constantly improving the ecosystem in which they operate. The local precincts set up with such simple technology will be highly efficient and can be optimised to share equitably and enable job creation through enterprise facilitation in local communities.
The hydrogen story is best left in Ross Garnaut’s hands. He suggests that Australia can become a superpower by applying solar-based hydrogen in northern regions to refine minerals. Hydrogen, the new circular economy and biophilic innovations are not going to go mainstream as quickly as solar, batteries and smart city infrastructure. These three are likely to at least continue to grow in niche demonstrations as part of the cluster of innovations for infrastructure in the next economy.
But solar, batteries and EVs will dominate the infrastructure of the next economy.
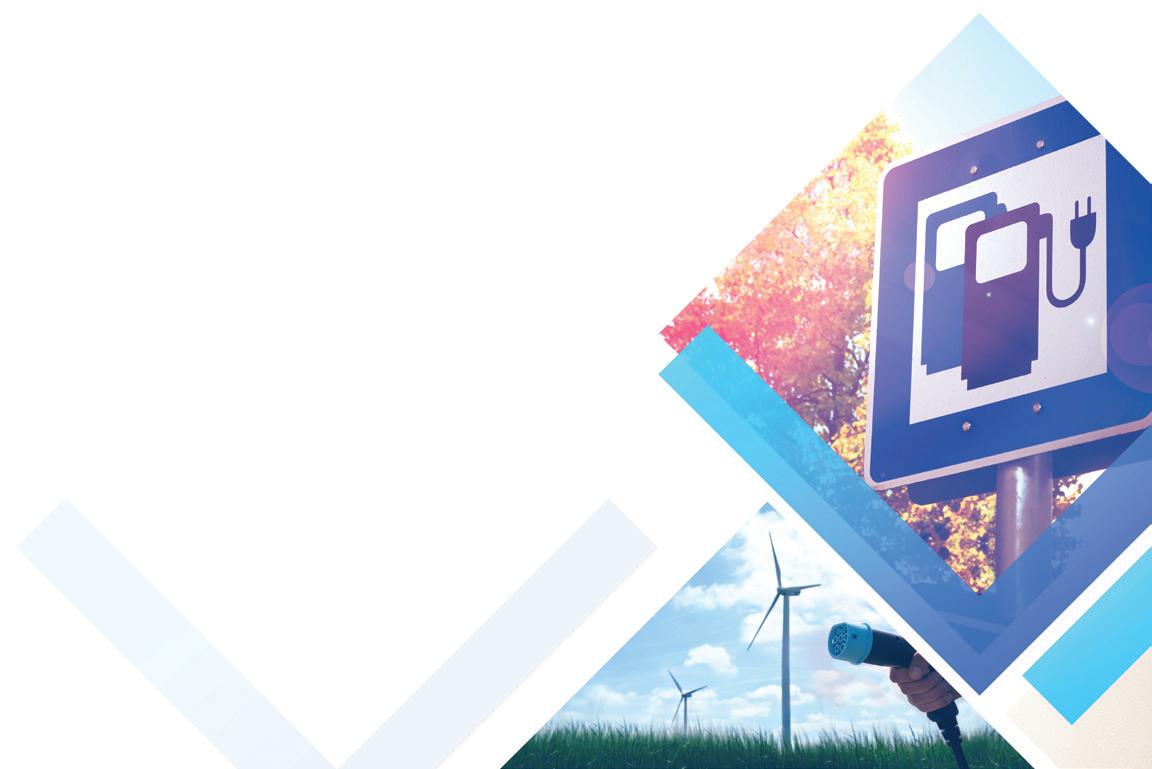

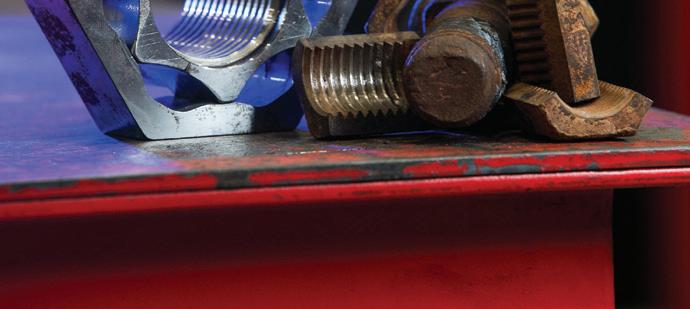
Segnut
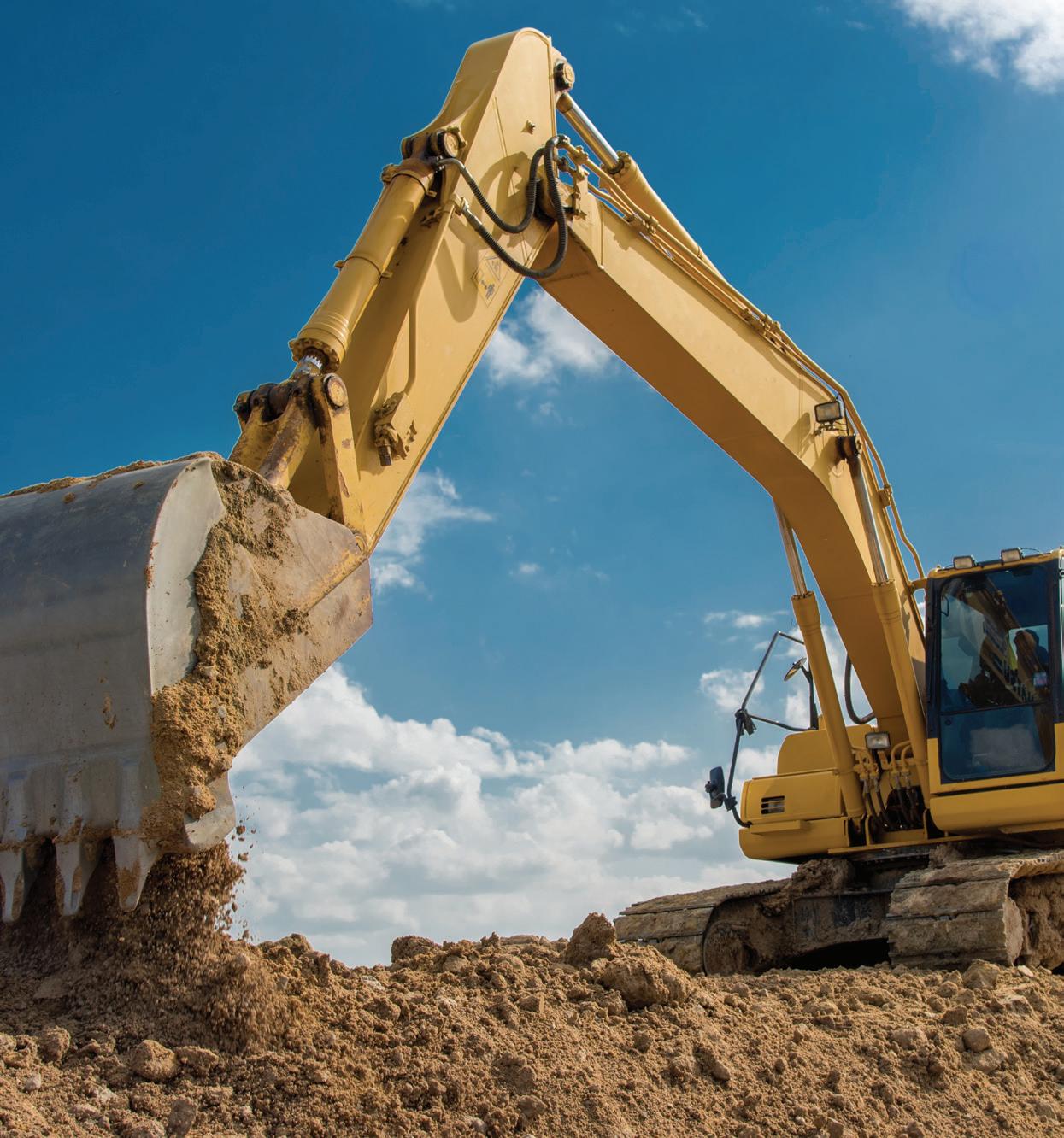
CIVIL INFRASTRUCTURE SECTOR READY TO BOOST THE ECONOMY
by Chris Melham, CEO, Civil Contractors Federation (National)The civil construction industry has demonstrated its strength and resilience in its response to the challenges thrown at it from COVID-19. Companies continue to deliver much needed civil construction projects right across the country, helping to reinforce to governments the importance of the industry to the national economy.
The industry has been adaptable and flexible, with companies implementing new measures at worksites to manage the health and safety of their workers.

And in every state and territory, the Civil Contractors Federation is working tirelessly with governments to support and facilitate greater investment in civil construction projects.
COVID-19 is presenting a two-speed economy regarding its business impact on different industry sectors and its health impact and recurrence across the country. It continues to pose challenges for the industry in the weeks and months ahead.
COVID-19 does, however, present the industry with opportunities that it can take advantage of to ensure it emerges from this crisis stronger and more resilient.
To take advantage of these opportunities, Civil Contractors Federation National (CCF National) has been playing an active role on behalf of the civil construction industry by providing the Federal Government with a clear, consistent and unified voice.
CCF National is bringing to the government’s attention the steps that need to be taken to minimise the impact of the crisis on the civil construction industry and the Australian economy which is now in recession, and what needs to be done to come out stronger on the other side.
INDUSTRY PROVIDES FEEDBACK
CCF National is advocating directly to the Prime Minister, Deputy Prime Minister and Department of Infrastructure on some specific measures that need to be implemented as a matter of urgency to deal with short and long-term challenges.
It has put forward five separate submissions on the measures needed to bolster Australia’s response to COVID-19.
Central to these submissions has been its recommendation to bring forward capital investment from the already committed ten-year $100 billion infrastructure program, to disaggregate large projects, and to spread the allocation across as many Tier 2, Tier 3 and below companies as possible.
To strengthen its advocacy campaign, CCF National recently carried out a survey of its members to gauge the impact of COVID-19 on their businesses and in turn the civil construction sector to ensure it has strong evidence to support its submissions and recommendations.
The survey sought to obtain feedback and data on three key areas:
♦ The business impact of COVID-19 on civil construction companies
♦ The capacity for companies to tender for more civil construction projects in the short term
♦ The likelihood of companies employing more workers should they be successful in a tender
The survey was completed by companies who operate across the broad spectrum of civil construction, including: roads, bridges, drainage, ports, water, power, utilities, telecommunications, etc. and responses were received from Tier 1, Tier 2, Tier 3 and smaller companies.
The overriding conclusion of the survey strongly reaffirms the need for swift and targeted action by governments of all levels to manage the impacts of COVID-19, and importantly, it confirms that the civil construction sector has the capacity to boost the economy during these difficult economic times.
CCF members confirmed they can take on more civil infrastructure projects and employ thousands more workers to stimulate the Australian economy if additional project monies were invested into the sector.
♦ 92 per cent of respondents indicated they would be in a position to tender for projects in the value of $0-$50 million if the government increased funding for civil construction projects
♦ 64 per cent of respondents indicated they would need to employ additional people if they were successful in tendering for a new infrastructure project/s
These results send a strong message to governments that the civil construction sector is ready, willing and able to boost the economy during and after COVID-19.
CCF’S RECOMMENDATIONS
The survey report provides five key recommendations to government based on the results. These recommendations are designed to assist the government and CCF National’s policy making process, both during and post COVID-19, to ensure both government and industry challenges are addressed.
CCF National has provided the survey results to the Prime Minister and relevant ministers with a request that the government tables the report to members of the National Cabinet.
These investments and reforms include:
♦ Immediately increasing Federal Government spending for civil infrastructure projects by bringing forward monies from the ten-year $100 billion rolling infrastructure investment program
♦ Allocating more projects to civil construction companies operating at Tier 2, Tier 3 and below
♦ Disaggregating larger projects
♦ Ensuring there is a fairer spread of projects across all Australian jurisdictions
♦ Developing and releasing a public agency supplier payment policy as a matter of urgency as a form of injecting cash into the civil construction supply chain by ensuring the immediate payment of all outstanding claims and prompt payment of all future claims
♦ Urgently reforming contracts and the procurement policy/process aimed at achieving a more balanced approach to risk allocation and the development of collaborative contracts
♦ Increasing the level of training, education and up-skilling funding
CCF National will continue to advocate to the Federal Government on the industry’s behalf, both during and beyond COVID-19, including the need to increase the longer-term civil construction investment pipeline by using debt funding in this era of historically low interest rates.
In particular, it will build upon the results of its member survey to strengthen its ongoing advocacy agenda on behalf of the civil construction industry, which contributes $134.2 billion to the national economy and employs 1.1 million people.
Full results of the survey can be found at www. civilcontractors.com/communication/national-policies. For further information, visit www.civilcontractors.com or contact the CCF National Office on (02) 6273 8312.
About Civil Contractors Federation (CCF)
Civil Contractors Federation (CCF) is the peak industry body representing Australia’s civil construction industry, with more than 2,000 contractor and associate members nationally.
CCF Members are responsible for the construction and maintenance of Australia’s infrastructure, including roads, bridges, pipelines, drainage, ports and utilities. Our members also play a vital role in the residential and commercial building industry by providing earthmoving and land development services including the provision of power, water, communications and gas.
SEVEN TRENDS SHAPING THE FUTURE
AUSTRALIAN CONSTRUCTION
MARKET
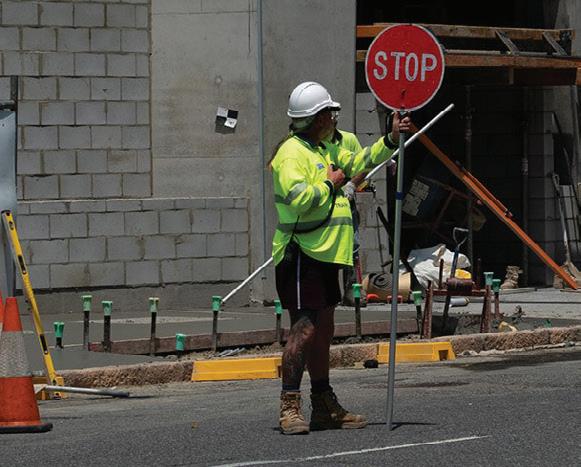
Total construction activity in Australia has struggled since 2017. Forecasters predict that most of the market will remain flat or post small gains in the years ahead. Still, there are bright spots on the horizon as highlighted in an August 2019 report from Master Builders Australia.
CIVIL PROJECTS WILL LEAD THE WAY
The civil construction sector is expected to be ‘the biggest winner’ over the next several years, thanks largely to the ramping up of government-led transport infrastructure projects. Forecasters predict the best bets coming in civil are in oil and gas, rail construction and roads, while electric, recreation and telecommunications appear “to have peaked and are beginning to contract”, the report said.
RESIDENTIAL GROWTH IS STILL STRUGGLING
Due to a raft of circumstances such as lower birth rates, declining migration and an overbuilding of housing before 2017, residential growth has flattened in Australia and is expected to decline in the coming years, the report said. Expert estimates put residential projects at about 168,000 for 2020, which is 28 per cent lower than the peak in 2017.
COMMERCIAL GROWTH WILL STRUGGLE, BUT NOT IN EVERY SECTOR
Commercial growth has been a ‘star performer’ over the last couple of years, however, such above-average growth is expected to fall back to normal levels in the years ahead. Office buildings, education and accommodation will contract significantly, and although transportation, health and retail have more favourable projections, they aren’t enough to overcome the general slowdown. Expect that the drop in commercial growth will also lead to more spaces originally designed for offices to transition to other uses as people continue to switch to off-site or shared workspaces.
FEWER NEW HOMES, BUT MORE RENOVATIONS
If you’re in the Australian home renovation business, there’s good news – the ultra-low interest rates for loans are expected to help many Australians open up their floorplans or redo their kitchens. This is particularly true for houses built in the late 1980s.
MAJOR CONSTRUCTION FIRMS ARE INCREASINGLY ‘GREEN’
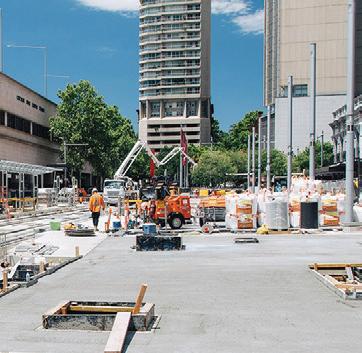
The largest construction firms in Australia – those handling the country’s big projects – are ‘greening’ their practices. For example, CPB Contractors has made environmental and sustainable solutions part of its approach to every project. Lendlease, the multinational Australian builder and property manager, has been recognised five years in a row by the Global Real Estate Sustainability Benchmark (GRESB) as the world’s most sustainable property fund.
MODULAR AND PREFAB WILL INCREASE MARKET SHARE
Most Western countries like Australia consider modular or prefabricated construction cheap or tasteless. Asian and Nordic countries, however, have long made prefabricated elements and even entire homes a significant part of their market. In recent years, prefabricated and modular homes have grown more popular for their cost savings and diminished environmental impact. And while the market for prefabs is only about 3.5 per cent in Australia, that is expected to double in the coming years as quality and design improves.
TECHNOLOGY IS SPEEDING UP THE BUSINESS
It might feel like construction sites are increasingly out of science fiction, with GPS-enabled equipment, wearable technologies, drones and digital documents such as blueprints and checklists. The result of this is that work happens faster, with better organisation, and with much tighter supply lines and schedules. Contractors will be well served to implement new technologies to keep their competitive edge – or at least understand and have a flexible attitude towards technology as the larger firms lead the way.
Read the full article at https://go.bluebeam.com/construction-trends.
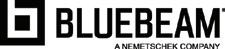
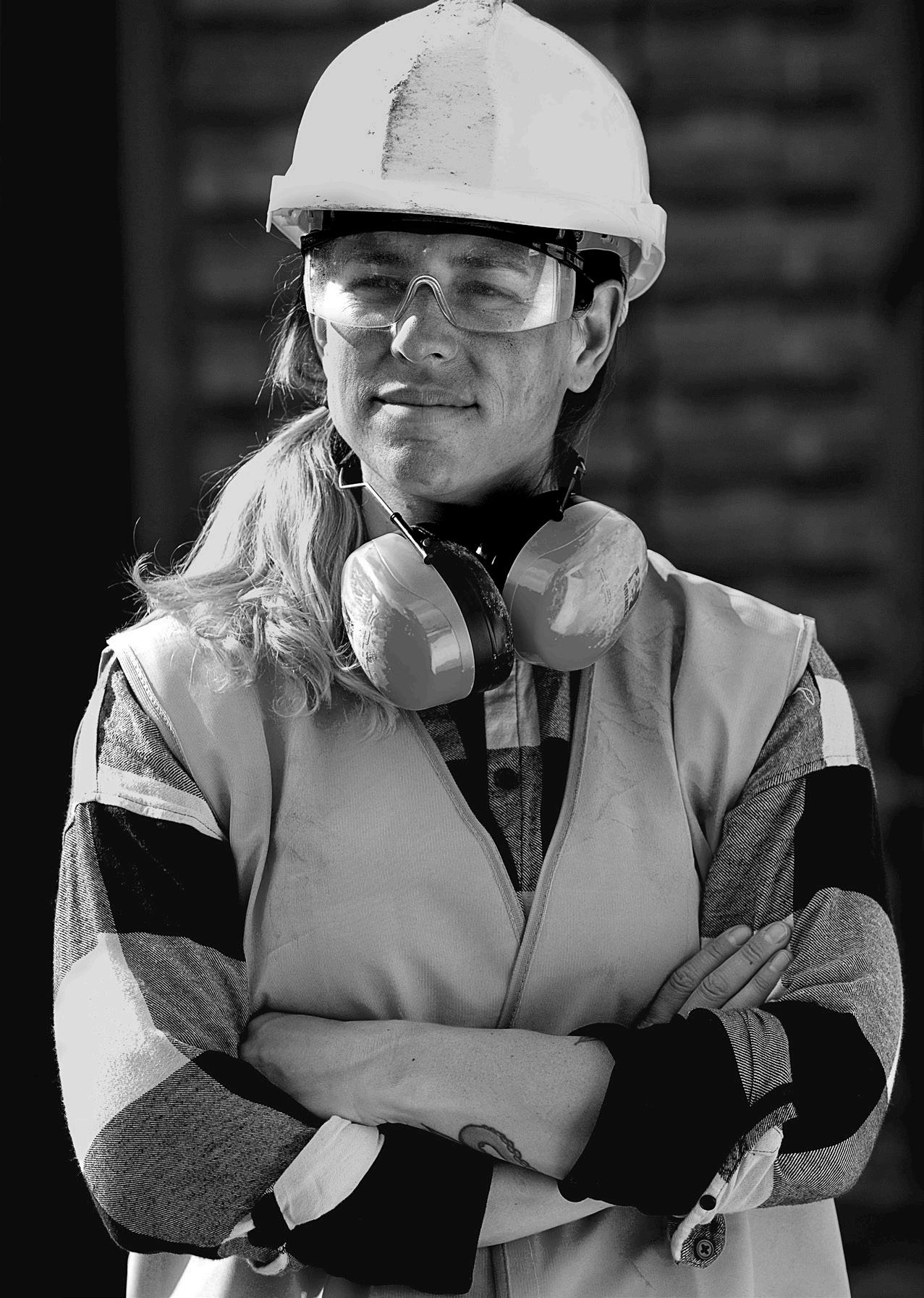
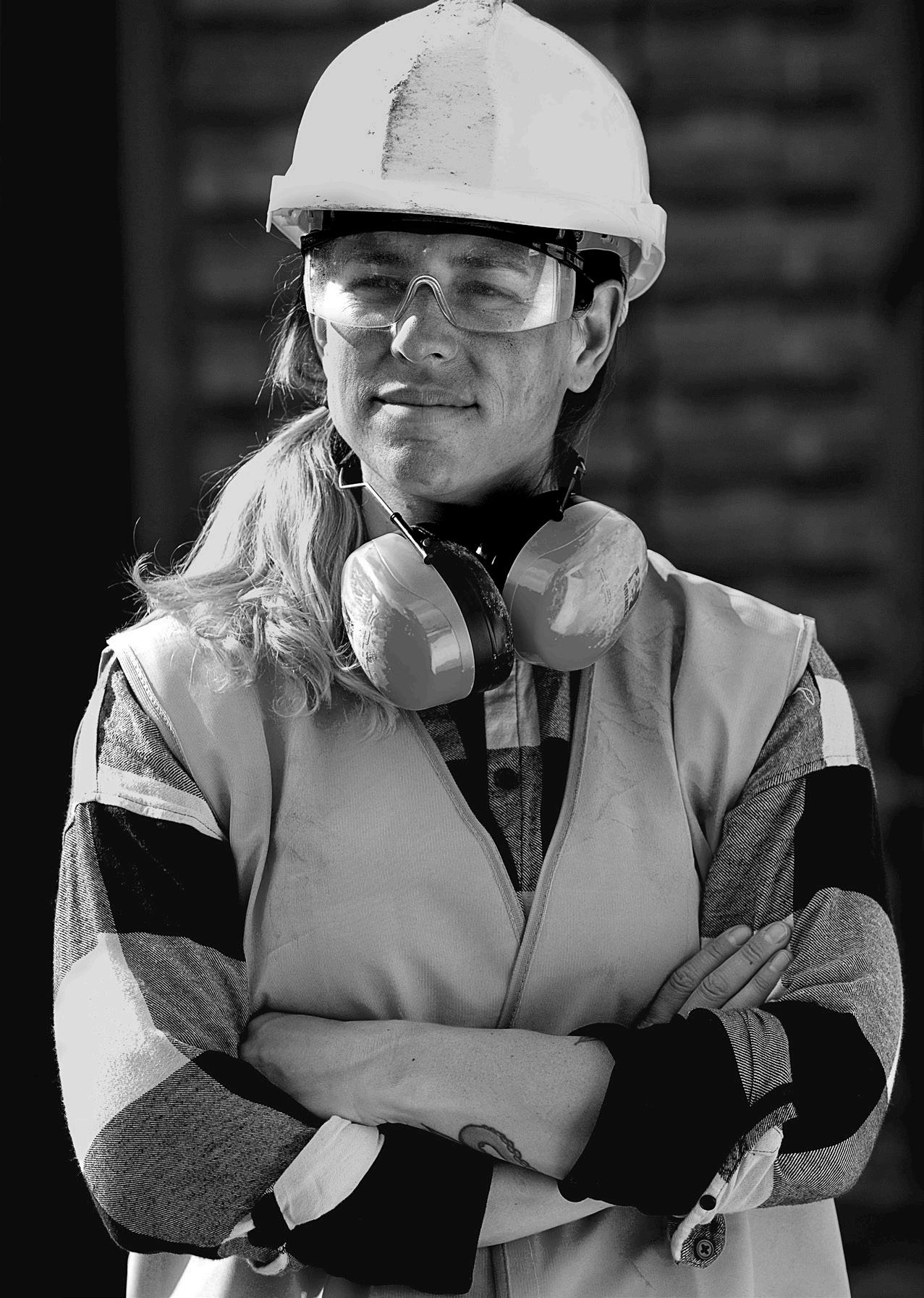
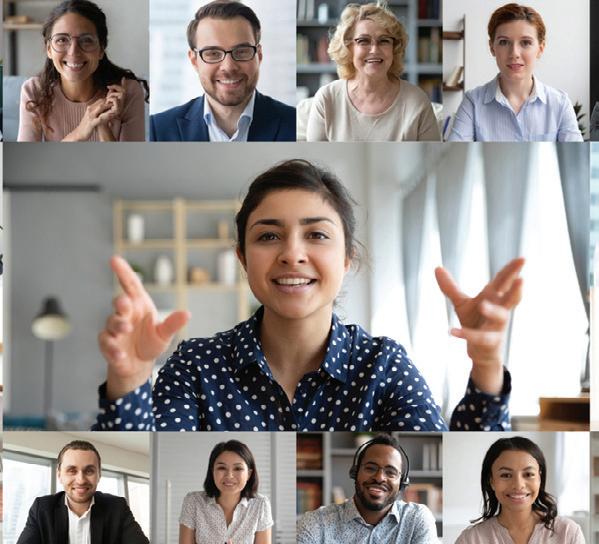
The Critical Infrastructure Summit 2020 will be the premier event for the whole infrastructure lifecycle – construction, asset management and disaster resilience – and create an online community that can meet again in person once COVID restrictions ease. The Summit’s five Virtual Conferences will explore how we build, manage and protect our infrastructure, as well as the biggest issues the sector faces and future predictions. These issues will be the keystone of infrastructure in the post-COVID world.
FIVE INDUSTRY-LEADING VIRTUAL EVENTS
Each Virtual Conference will explore a certain part of the infrastructure industry, and combined, the Summit will be the place to go for industry updates, predictions and networking. The conferences include:
Critical Infrastructure: State of play – 2 September
This is the opening session of the Summit and will set the scene, exploring the state of infrastructure in Australia including current challenges and opportunities. This conference will feature presentations from keynote speakers, an industry panel, and a virtual networking session to allow you to make new connections, despite not being able to meet in person.
Construct 2020 – 9 September
Construct explores some of the biggest infrastructure projects underway in Australia across road, rail, airport, port, urban construction and utilities. The Virtual Conference will look at current projects, providing delegates with milestone updates, insights into new technologies and smart processes being employed, and a look at potential opportunities. Delegates will hear first-hand from the people leading some of Australia’s biggest infrastructure projects.
Asset Management for Critical Infrastructure – 16 September
Running for the sixth time, Asset Management for Critical Infrastructure is the place to be for updates on technologies, projects and processes that help to better manage critical assets in Australia, from water pipes and energy networks, to transport infrastructure.
JOIN THE CRITICAL INFRASTRUCTURE COMMUNITY
Infrastructure is hosting the Critical Infrastructure Summit – a landmark virtual event for the Australian infrastructure industry involving five free-to-attend Virtual Conferences, running every Wednesday in September.
It will explore topics such as developing strategic asset management plans in an uncertain future, resilient asset management, and the role of machine learning, artificial intelligence and digital twins. The event provides practical solutions to improve the way critical assets are managed, with a speaker lineup featuring senior leaders from utilities, infrastructure asset owners, industry associations, consultancies and government.
There will also be a separate Asset Management training workshop held the same week as this conference – limited spots available.
Disaster Management – 23 September
Disaster Management looks at the impacts a range of disaster events can have on the owners of critical assets; and provides tools to help essential service providers minimise the impact of a disaster, and emerge stronger than ever before. There’s never been a more pressing time for this kind of expertise with Australia dealing with bushfires, drought, cyber attacks and the COVID-19 pandemic. The Virtual Conference expert speaker lineup will help critical infrastructure organisations prepare for, survive and then thrive in the face of disaster.
The Future of Infrastructure – 30 September
The way people live, work and move around Australia’s cities has changed dramatically due to COVID-19, and while some things will soon go back to normal, there is likely to be a significant transformation of transport, utilities and social infrastructure in the future. Now is the time to take stock and look at what the future of the sector could look like, so critical infrastructure owners can start planning and preparing their assets. The Future of Infrastructure gathers the industry’s leading experts to explore their predictions for future trends and what these can mean for the sector and individual organisations.
To register for free to any or all of the conferences, or to find out more, visit critical-infrastructure.com.au.
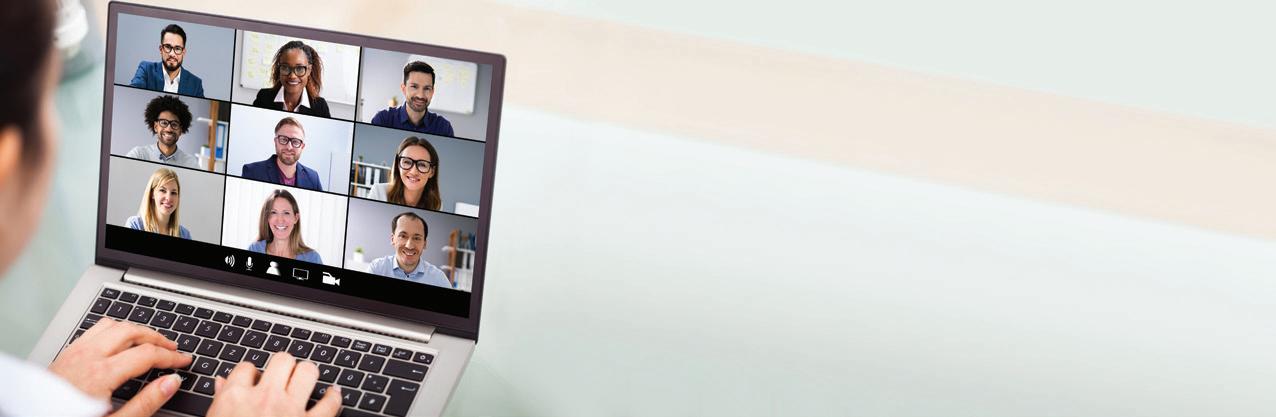
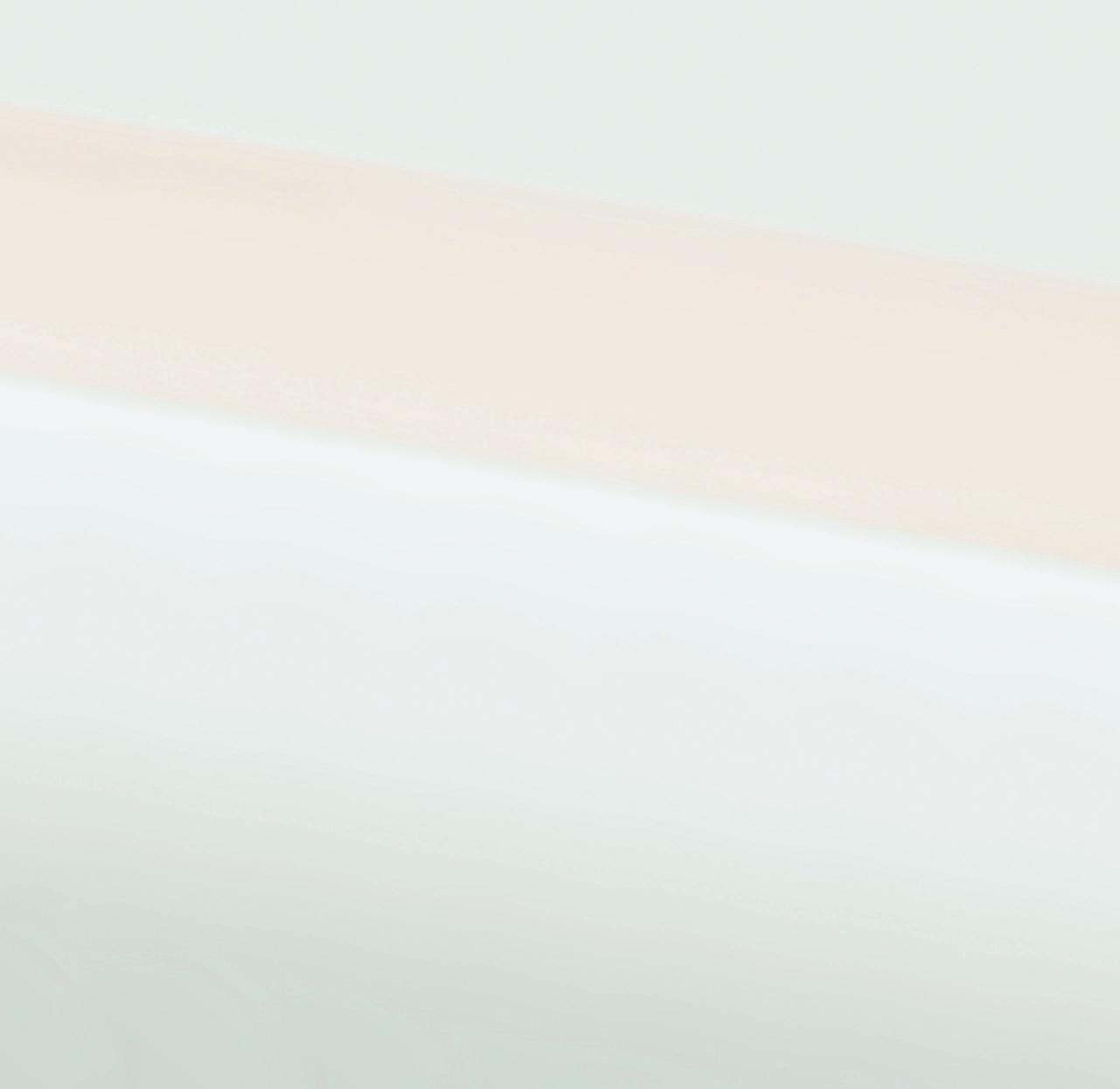
Critical Infrastructure: State of play
BOOM MACHINERY THAT MAKES A
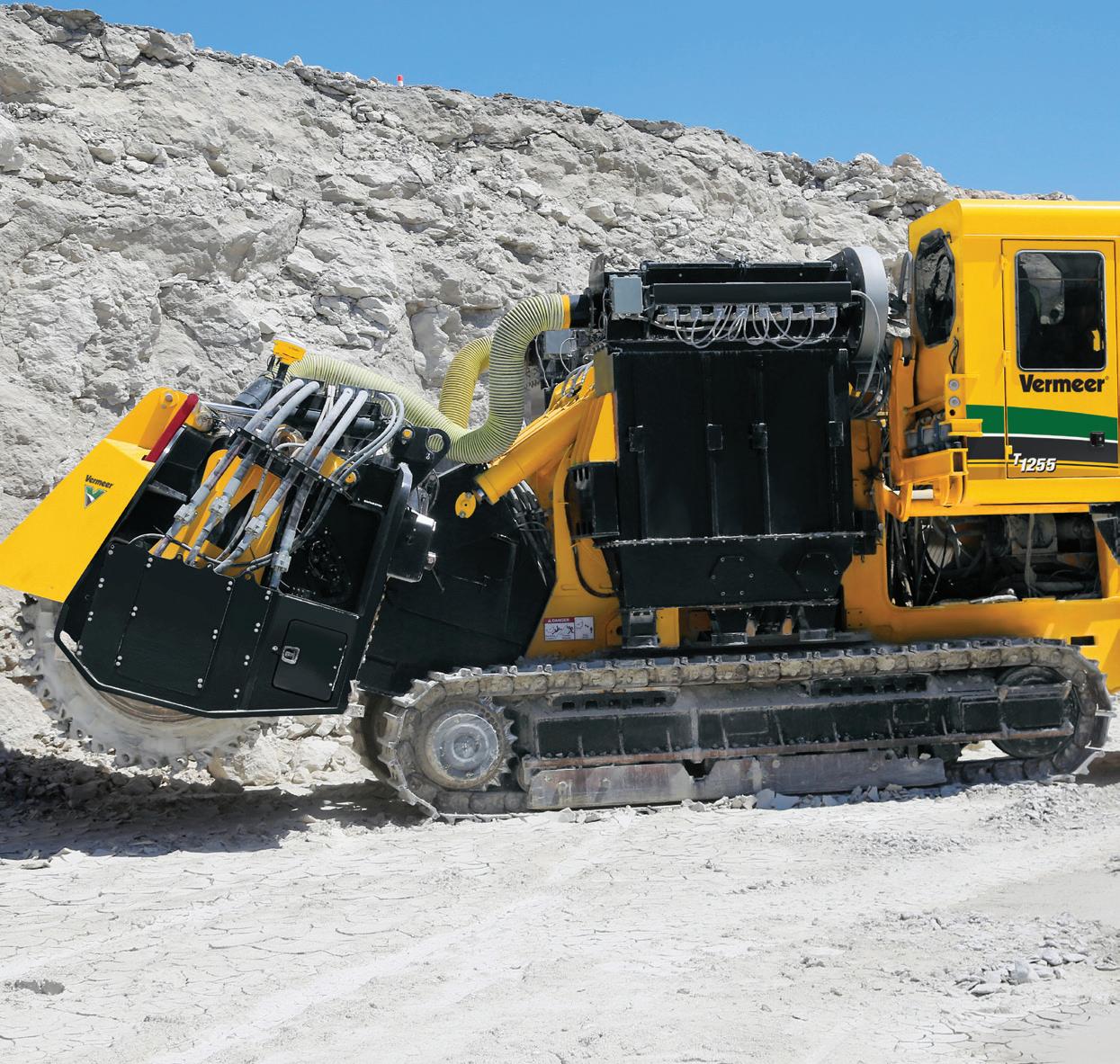
With Australia’s population expected to increase by 24 per cent by 2034, the infrastructure sector is seeing huge, ongoing growth – a boom that is expected to last for at least the next 15 years. With so many infrastructure projects currently underway, a competitive edge is more important than ever, making it critical for developers to invest in high-quality machinery and equipment that is fit for the job.

Large-scale civil construction contracts across Australia are being planned more quickly than they can be completed, making the completion of projects on time and on budget a high priority. According to Vermeer, investment in reliable, purposebuilt machinery is a key first step to reaching this goal.
With decades of experience in providing equipment solutions to the construction industry, the team at Vermeer are experts when it comes to getting maximum production out of each hour, and know all too well the impact that investment in machinery has on quality and efficiency.
THE COST OF DOWNTIME
While using the most inexpensive machinery and equipment may make finances look favourable in the short term, Vermeer’s General Manager of Sales, Jeff Lawson, warns that this often comes at the expense of cost and time.
“When heavy construction equipment breaks down, it’s not only a waste of time, but also of human resources,” Mr Lawson said.
Large-scale construction projects rely heavily on their equipment, meaning that a worksite effectively comes to a standstill when that equipment is not operational. With many sites functioning as a result of several pieces of machinery working seamlessly together, a single faulty piece of machinery can have a huge impact.
Not only does downtime on-site mean that a project may take longer to deliver, it also has a flow-on effect to the overall cost of construction.
“While one piece of machinery may be down, other costs will continue to build, regardless of whether the project is any closer to completion,” Mr Lawson said.
MACHINERY THAT MAKES SENSE
According to Mr Lawson, the large-scale infrastructure projects currently underway in Australia call for some serious machinery.
“If infrastructure developers want a competitive edge, they will need to increase the quality of machinery and equipment to ensure it’s up to the job. That’s where we come in,” Mr Lawson said.
When it comes to earthmoving, civil projects require machinery that offers fast, precise and on-grade surface excavation.
Vermeer’s range of Terrain Leveler surface miners precisely excavate rock while also managing noise levels, vibration and air quality, and are backed up by Vermeer’s trusted after-sales support and service.
Where hard rock is involved, an effective solution for dealing with residual dust and debris will increase productivity and reduce overhead costs. Systems such as Vermeer’s onboard dust suppression system, which is compatible with its range of T1255 Terrain Levelers, will also eliminate the need for a separate trail-behind dust system unit.
“There are many benefits to this type of technology. The suppression system is hydraulically driven and reduces the need for an external power source or an operator. This also helps to reduce diesel consumption, as well as emissions and labour costs,” Mr Lawson said.
Sites will also get more productivity from a piece of machinery if there are options for optimisation. Vermeer’s T1255 Terrain Leveler SEM for example, is available with either a chain drive or direct drive drum attachment depending on the requirements of a job.
“The chain drive drum is ideal for the removal of ground surface or creating a smooth, level area for preparing a site, whereas with the drive motor mounted directly to the cutter drum, the direct drive drum maximises efficiency and reduces wear costs that can be associated with other types of transmissions,” Mr Lawson said.
With no end in sight for the infrastructure boom, machinery that eliminates exhaustive processes and can take on a diverse range of tasks is an investment that requires careful consideration.
To talk about maximising machinery efficiency to deliver projects on time and on budget, get in touch with the Vermeer Australia team at vermeer.com.au/contact-us.
HOW INFRASTRUCTURE PROJECTS CAN EFFICIENTLY USE
VIRTUAL TWIN EXPERIENCES
All construction projects are expected to be delivered on time and on budget, but real value comes when asset owners can save money and create efficiencies across the whole asset lifecycle. With the industry now managing construction in a digital world, Virtual Twin Experience technology is allowing companies to spot mistakes virtually before construction starts, and collaborate remotely with all stakeholders using one source of data that can be used throughout construction, operation and maintenance.
While ‘digital transformation’ might be a buzzword for many industries, the fact is that technologies such as BIM and 3D modelling have enormous potential to reduce costs and increase efficiency on large infrastructure projects.
Prashanth Mysore, Global Strategic Business Development and Industry Marketing Director at Dassault Systèmes – a global leader in 3D design and engineering software – said the infrastructure sector is conservative compared to other industries when it comes to digital technologies because of long project lifecycles, but there is huge potential for cost savings using processes like Virtual Twin Experiences.
“In infrastructure, we work with large projects and budgets which can be very complex, so if people make errors in the field, the cost of fixing them is huge,” Mr Mysore said.
“The benefit of Virtual Twin Experiences is that we can simulate everything first in a virtual environment. We virtually build the whole project with 3D software so we can forecast all the issues and risks you might face in the field. If an error is made in the digital environment, it's easier to fix and the cost will be very low. In this way, we can make sure that the real construction can be successful in one shot.”
It’s also common in infrastructure for design changes to occur even once construction has begun. If 2D drawings are used there is potential for mistakes
to occur and it takes time to update designs manually, as well as analyse what these changes could mean for the project. However, 3D models can be updated faster and simulations can be run to view all possible scenarios.
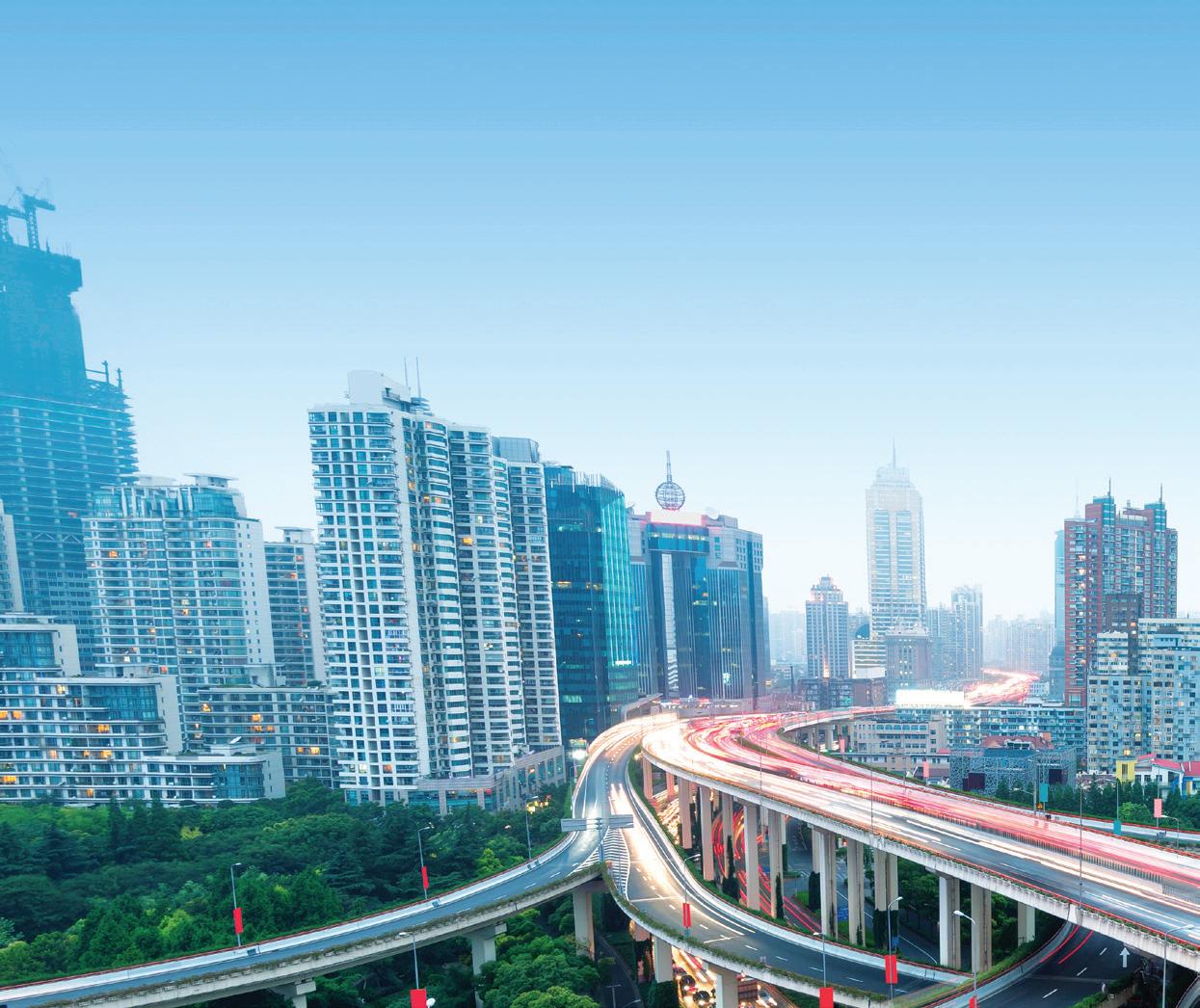
Mr Mysore said that when talking about Virtual Twin Experiences, it’s important to recognise that at Dassault Systèmes it doesn’t just mean a 3D simulation of the final asset, but also simulations of all the processes used to build it.
“Our 3DEXPERIENCE platform is a lifecycle management system. We not only include the 3D model, but also the project information, simulations, and all of the data in one single source, which can be put on the cloud,” Mr Mysore said.
COLLABORATION REGARDLESS OF LOCATION
While spotting errors and making changes early can avoid major delays and additional costs, having a Virtual Twin Experience as the management system also creates a collaboration platform for all stakeholders working on a project.
In Australia, there are a large number of joint ventures and consortiums where different companies are working on the same infrastructure project.
The advantage of having a Virtual Twin Experience is that these companies can collaborate and access the same single source of master data remotely.
With more companies working remotely and hosting virtual meetings as a result of the COVID-19 pandemic, communication has to be extremely clear for everyone involved. Mr Mysore said the 3DEXPERIENCE platform is a very supportive mechanism for current conditions as it connects everyone in different locations and different time zones so they can work together.
“Everyone with authorisation will be able to access the information no matter where they are. It allows everyone on the project to be on the same page and always have access to the latest information because they are all working on the same platform with a single data source,” Mr Mysore said.
Dassault Systèmes’ 3DEXPERIENCE platform is currently being used in a number of major projects including the Danjiang bridge in Taiwan, Beijing Daxing Airport, and the 370km Mu-Jia line railway project by the China Railway Design Corporation (CRDC), to name a
few. The technology is also now available in the Australian market.
The Mu-Jia line rail project involved a designer in one city and multiple construction companies responsible for different parts of the railway distributed in different locations along the 370km track.
Using the 3DEXPERIENCE platform meant that if the designer made any changes, it automatically synchronised with all the contractors in different locations, keeping everyone informed and up to date.
USING DIGITAL TWINS ACROSS THE ENTIRE LIFECYCLE
One of the benefits of a Virtual Twin Experience is that it is not only used in the design and construction phases, but also for the asset’s operation and maintenance. While the construction company’s job is to deliver the infrastructure, asset owners will also be thinking about future operations.
“One way to think about a Virtual Twin Experience is that it’s alive, and the information will grow with a project into the operation phase. If we imagine we operated projects for 50 or 100 years, there will be a lot of information and you’ll want to keep all this historical data with the 3D model so that you can optimise efficiency and save costs, so all of this information is part of our Virtual Twin Experience,” Mr Mysore said.
Now asset owners are often asking for two project outcomes – the real built asset and the virtual asset. Being able to deliver both will help construction companies build good relationships and get future work as they are delivering continuous value. By
optimising operational costs throughout the lifecycle, the benefits significantly outweigh the costs of adopting the new technology at the start.
Dassault Systèmes’ 3DEXPERIENCE platform also proved invaluable when COVID-19 hit as it produced a 3D simulation solution for Leishenshan Hospital in Wuhan that looked at HVAC systems and air flow to determine how infectious molecules might spread throughout the hospital in order to protect healthcare workers and patients. The project was highly praised by the hospital owner as well as the local government, and now Dassault has more hospitals asking to use the same technology in their projects.
While other systems may also use the cloud, Akio Moriwaki, Construction, Cities & Territories Industry Marketing Director at Dassault, said its 3DEXPERIENCE platform is different because it provides a single source of data that is always up to date.
“Some solutions just connect to the server, then you have to upload and download again, so the model is not really managing one single source of truth, but ours is integrated and the single master model is always up to date for everyone, which is a pretty important aspect for a Virtual Twin Experience solution,” Mr Moriwaki said.
For more information on how Virtual Twin Experiences can benefit your infrastructure project or Dassault’s 3DEXPERIENCE platform, please visit https://ifwe.3ds.com/ construction-cities-territories.
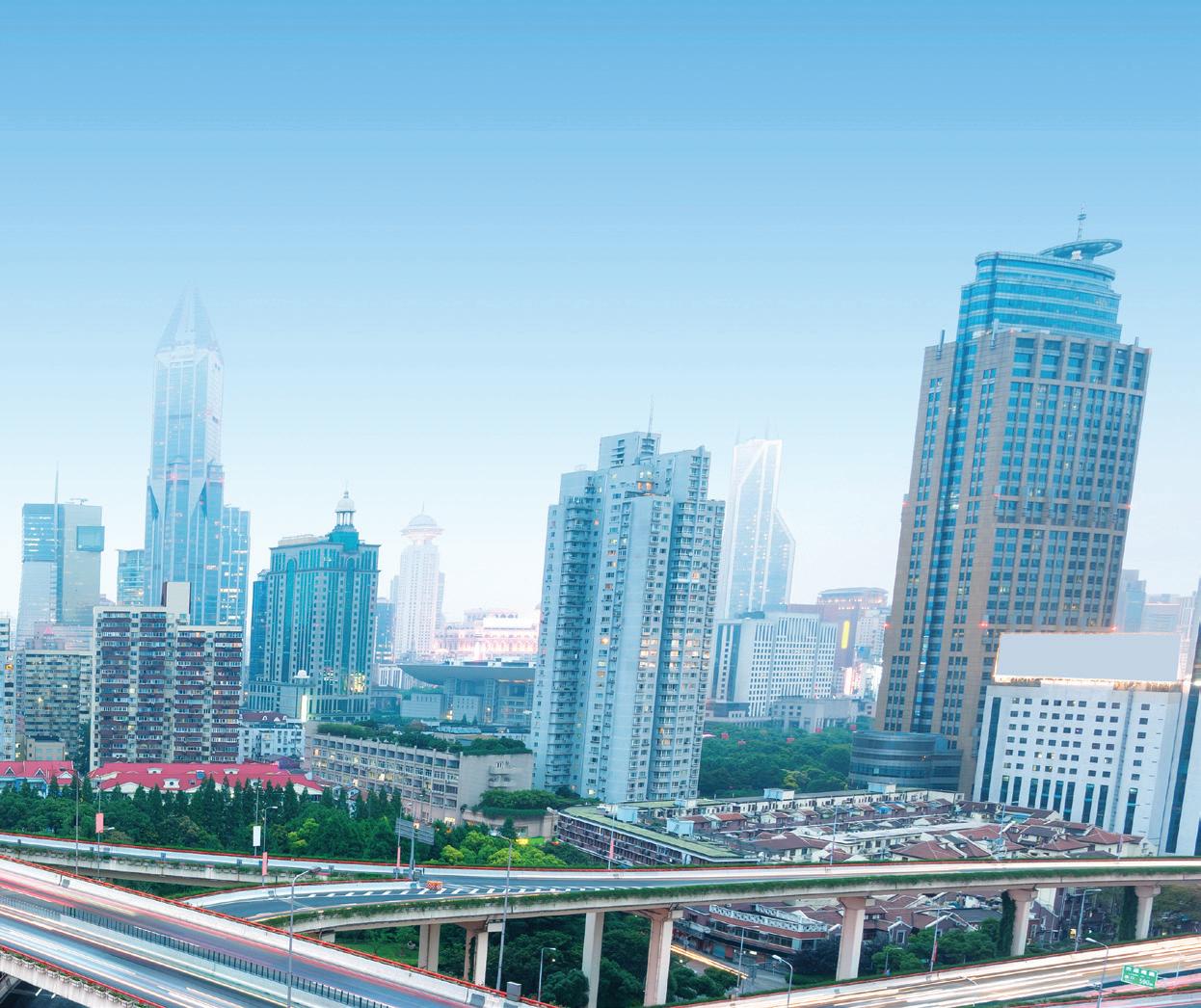
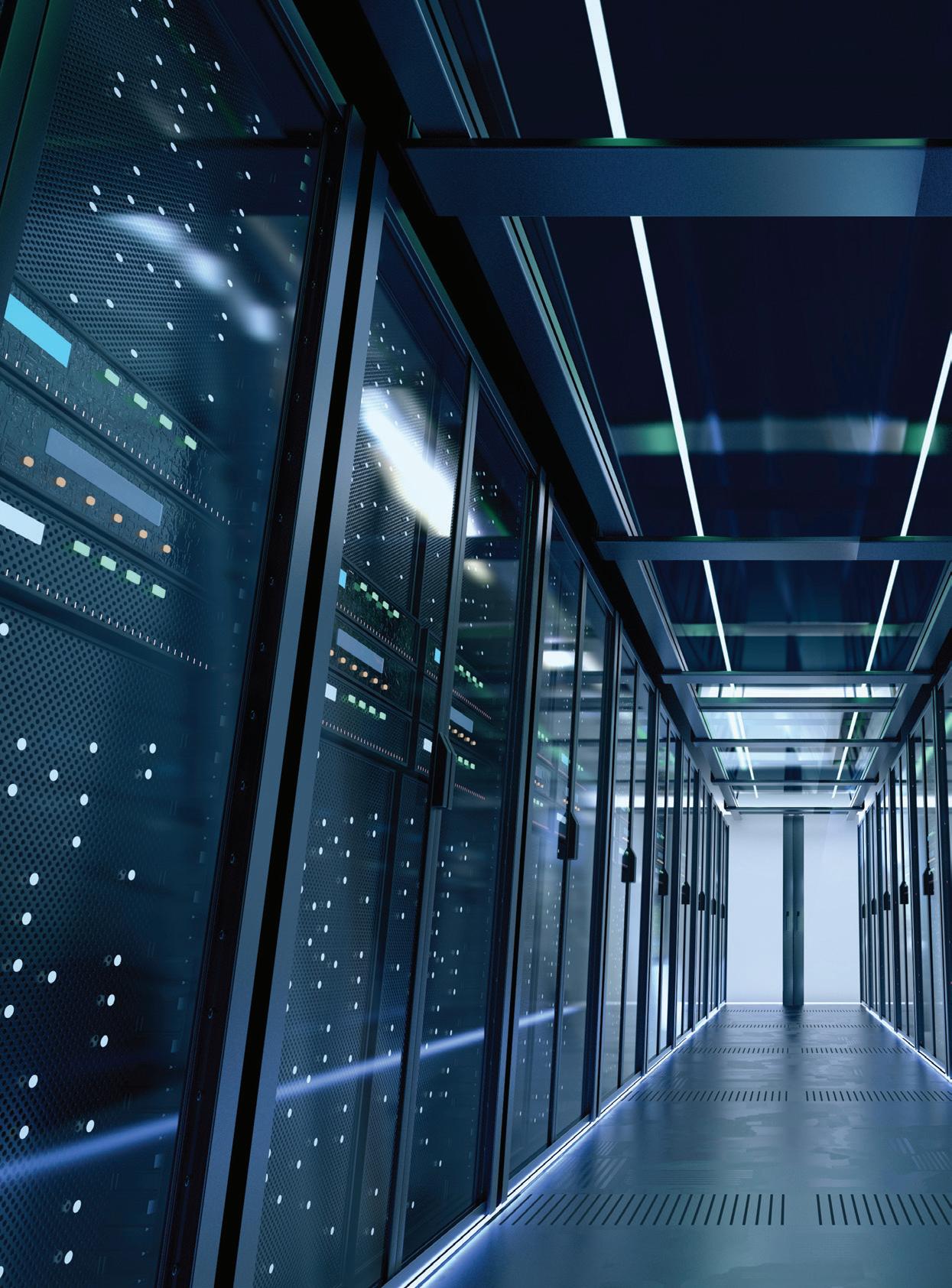
DIGITAL INFRASTRUCTURE: THE INFRASTRUCTURE OF THE FUTURE
by Dr Ian Oppermann, NSW Government Chief Data Scientist and Industry Professor at University of Technology SydneyWith recent changes to how people live and work due to the COVID-19 pandemic, the move away from physical assets and towards cloud-based infrastructure is more significant than ever. Here Dr Oppermann explores a future world that is more digital and connected, and the impact of smart infrastructure, digital twins, and data privacy and security.
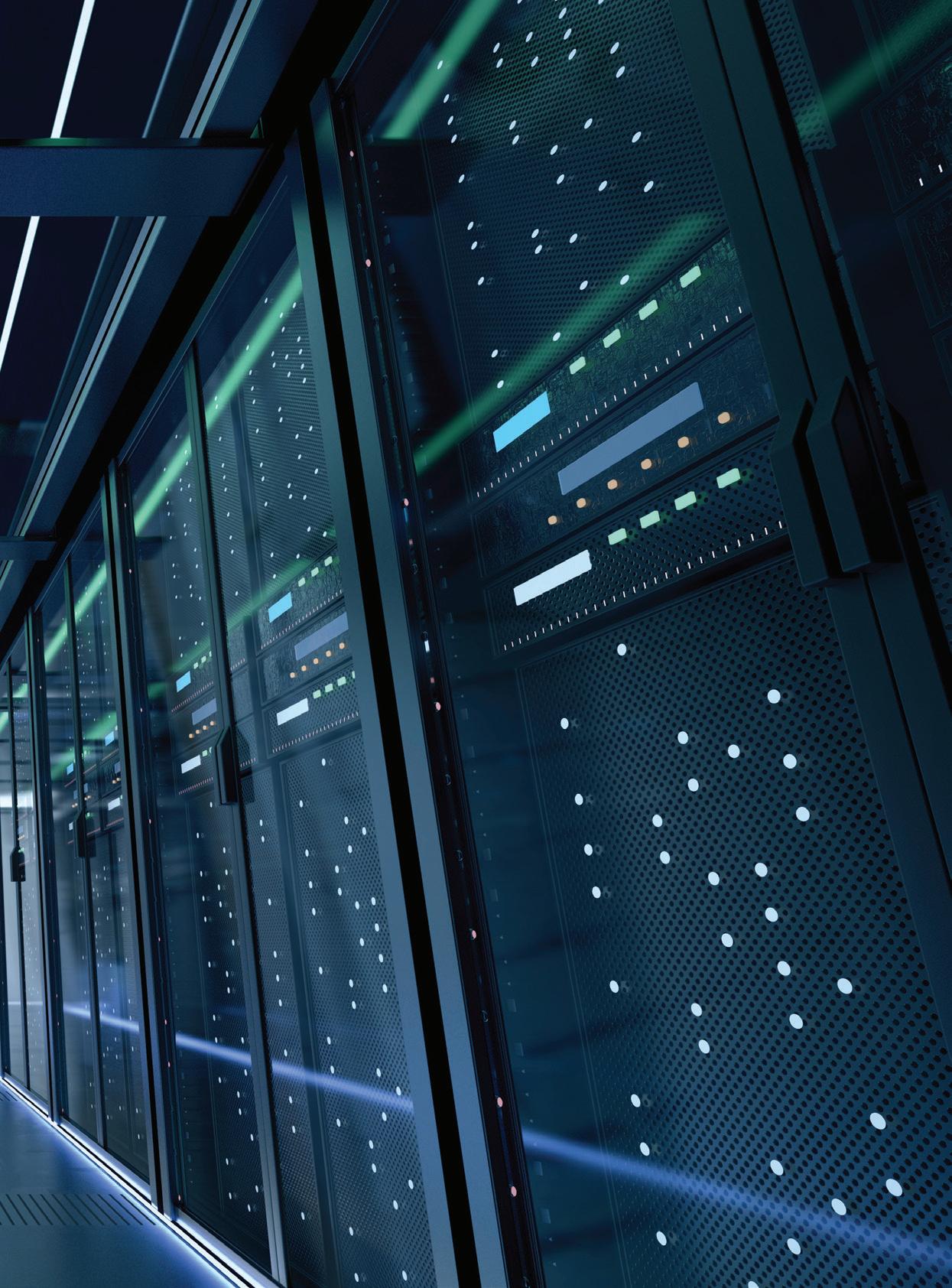
Many governments around the world have set smart city goals and funded pilot projects, but the reality is that little progress has been made in many countries. Challenges to these goals include the diversity of stakeholder interests, the complexity of coordinating planning/ construction/operation across stakeholders, and importantly, the lack of comprehensive digital twins of physical environments, and the lack of clear, data-driven outcomes frameworks.
Digital twins offer the potential to plan, model and optimise during all phases of smart infrastructure lifecycle and use. Outcomes frameworks allow the goals of smart cities to be described and measured. Smart cities are ultimately dependent on data-driven frameworks, indicators and models gathered from those who use the places and infrastructure of cities. Use of peoplecentric data needed to measure, model and analyse smart cities creates the final major hurdle in the form of privacy. All of these challenges must be addressed to make real progress in smart cities.
COVID ACCELERATING DIGITAL
Over dinner at an appropriately socially distanced hotel restaurant recently, I watched background footage of the foundations of Canberra being laid out and the growth of the city over the course of the 20th Century. It was stunningly old fashioned. Everything about the pomp and ceremony, the construction process, people learning to use these roundabout things was worthy of documentary. We are now much more digital, more connected and more online. We are living in the future.
The COVID-19 pandemic has taught us just how much of that last sentence is true. We rapidly jumped online rather than drive to work or drop the kids at school. We grappled with congested telecoms networks rather than congested roads. We switched between Teams, Zoom, Skype and Webex in seconds rather than fly between Sydney, Melbourne, Brisbane or Canberra for the day. We discovered some bottlenecks, but we largely went online and digital.
Productivity has arguably increased for “remoteable” professions. The network externalities of school start times, work start times, and the need to be seen to be “at work” changed. We survived, and we even started to understand some of the reasons why it has been so hard to be smart with our use of cities as we switched from moving atoms (us, our cars, our public transport) to moving bits (our voice, files, video feeds).
COVID was a major interruption to the steady progress of change towards the connected, online, digital future. The major drivers of this change are still coming from the intersection of a growing/ aging/urbanising population, a changing climate, the need to respond to an increasing number of global challenges (including pandemics), and our expectation of an ever-improving quality of life. These are challenging factors to reconcile and must be met with ever greater productivity and technological enhancements.
Our present, and future, are digital, hyper-connected and critically dependent on technology. For decades, most economies have been transforming towards a service dominated economy and our services economies are increasingly digital, online and driven by data. In all sectors, services are increasingly created, delivered and consumed via digital means, driven by the increasing adoption of online, mobile and digital technologies.
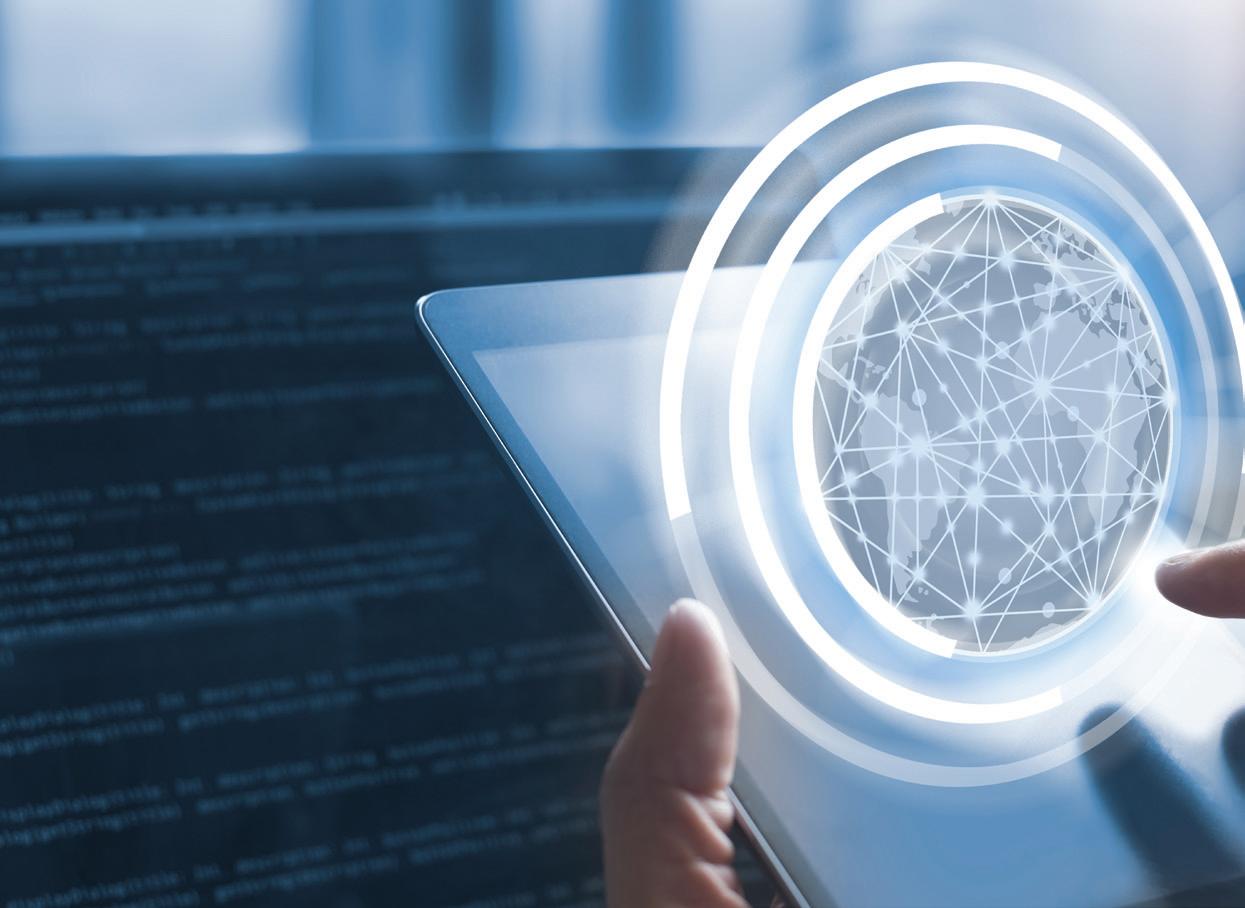
Recent years have witnessed dramatic changes in every aspect of our lives, from the way we consume music, watch movies, book holidays or choose hotels. Sometimes less obvious, there are dramatic changes underway in every industry, and in government, driven by changing consumer expectation, reduced barriers to new entrants and an increasingly borderless world of information flow.
The compounding factors of connected, digital and AI-driven “smart” means the rate of the change is actually accelerating. Hold on tight, these are now the “good old days”. We will never see the pace of change this slow again.
A DIGITAL TWIN
Digital twins of physical environments help us plan, model and optimise real world services. A smart light in your home, driven by a bit of AI, turns on and off as you move around the house, creates a simple digital model of your home and lighting use, and supports more efficient use of energy.
It will however also collect de-identified data about when you are home, which rooms you use and when, if there are other people in your home, and where in your home you spend your time. Within this de-identified data, there are insights about you and your relationships, habits and preferences.
In aggregate form, this data can be used by a service provider to optimise energy use and deliver more efficient lighting services to a suburb, by a smart grid to match energy demand to energy supply, or by a smart micro energy service provider to make best use of spot energy prices.
The benefit is the ability to locally optimise or individually personalise services based on personal preference, as well as to optimise the wider network for users and providers.
This idea of digital twin models of the home or office incorporate an ever-increasing range of “smart” devices (phone, TV, scales, toilet, refrigerator, watch) and “smart” environments (home, workplace, city). Increased efficiency, improved effectiveness and greater personalisation can present enormous benefits.
If these datasets are linked in a digital twin of the physical world, the resulting merged dataset may contain a great deal of personal information (PI), possibly enough to re-identify the individuals represented therein – making that data personally identifiable information (PII). How this data is used, by whom, and for what purposes determines risks and concerns. In many economies, it may force service providers and operators to rethink governance models to support regulatory requirements such as GDPR.
The challenge is quantifying the amount of PI in a dataset at any point in time and in any given context, and developing threshold tests for when an individual is reasonably identifiable, while considering personal attributes, temporal and spatial aspects of data, and rich contextual environments.
PI VERSUS PII
The terms personal information (PI) and personally identifiable information (PII) are often used interchangeably in legislative frameworks and in technical literature. The question becomes, how many features must be linked before
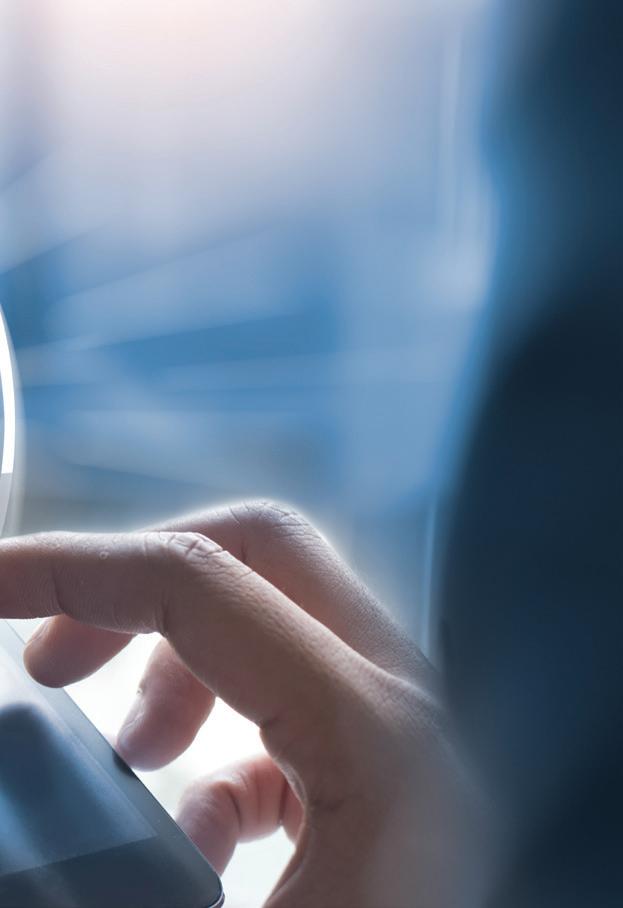
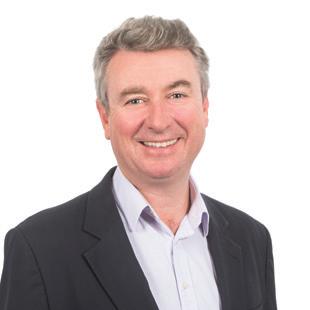
PI becomes PII for an individual known to be in a dataset? Context and rarity play important roles in the answer to this question.
Future smart or “mobile enabled” services will compound the complexity of these simple frameworks as greater fidelity and range of captured personal attributes, greater resolution in time and space, and richer contextual considerations are harnessed to deliver services or optimise network performance.
As feature-rich 4G mobile becomes 5G (and by 2030 becomes 6G), an understanding of the degree of PI in potentially highly time varying, context rich datasets, will challenge what we mean by de-identified data and the risk of re-identification. Understanding these challenges will provide a basis to anchor principles-based data sharing and governance frameworks to help ensure new smart or mobile enabled services operate within the regulatory frameworks designed to protect us all.
AUSTRALIA HELPING LEAD THE WAY
Through work with the NSW Government, the Australian Computer Society, Standards Australia and many other groups, ways to measure PI in data are being developed. The work is still at an early stage, but international standards are being explored to develop data sharing and use frameworks based on an understanding of context of data use, its inherent sensitivity, and the level of personal information in the data. It is early days, but the “Model T” tools developed so far show great promise for use in future smart services and smart cities. Stay tuned!
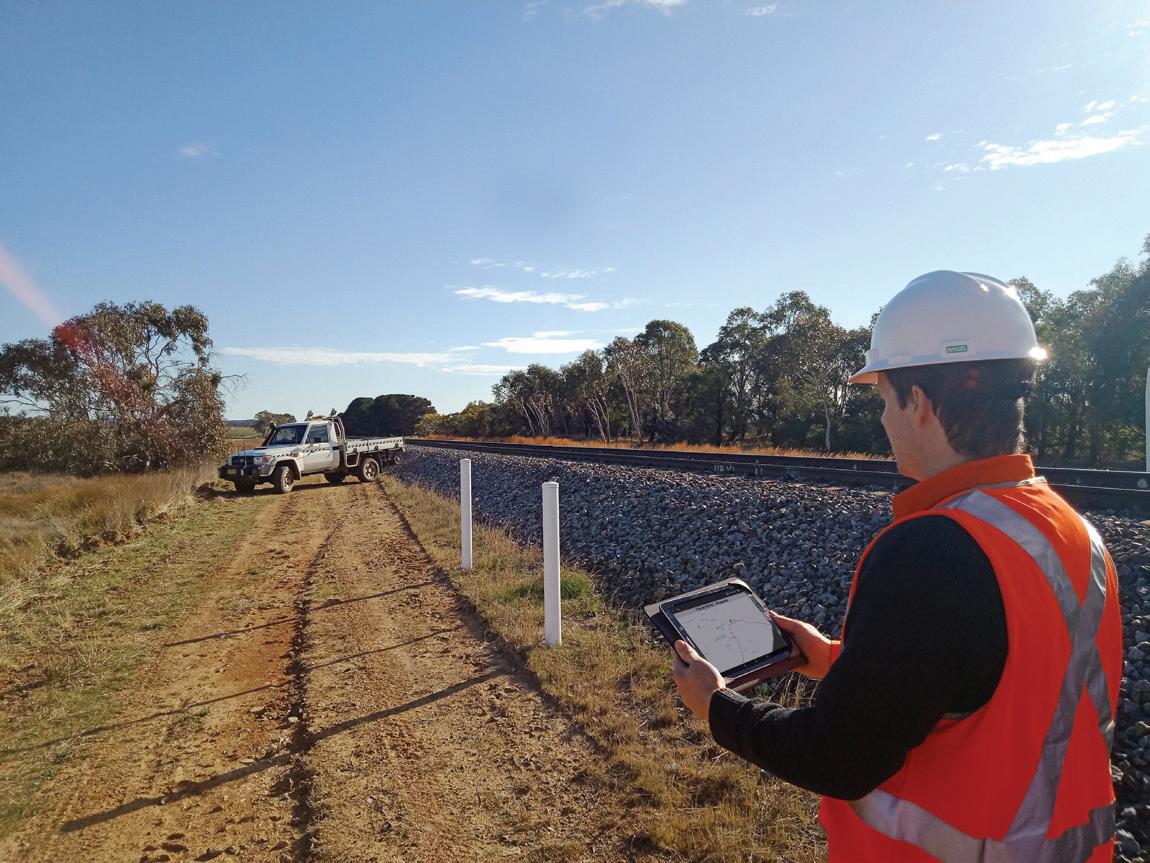
ACCESSING YOUR ON-SITE DEVICES FROM ANYWHERE
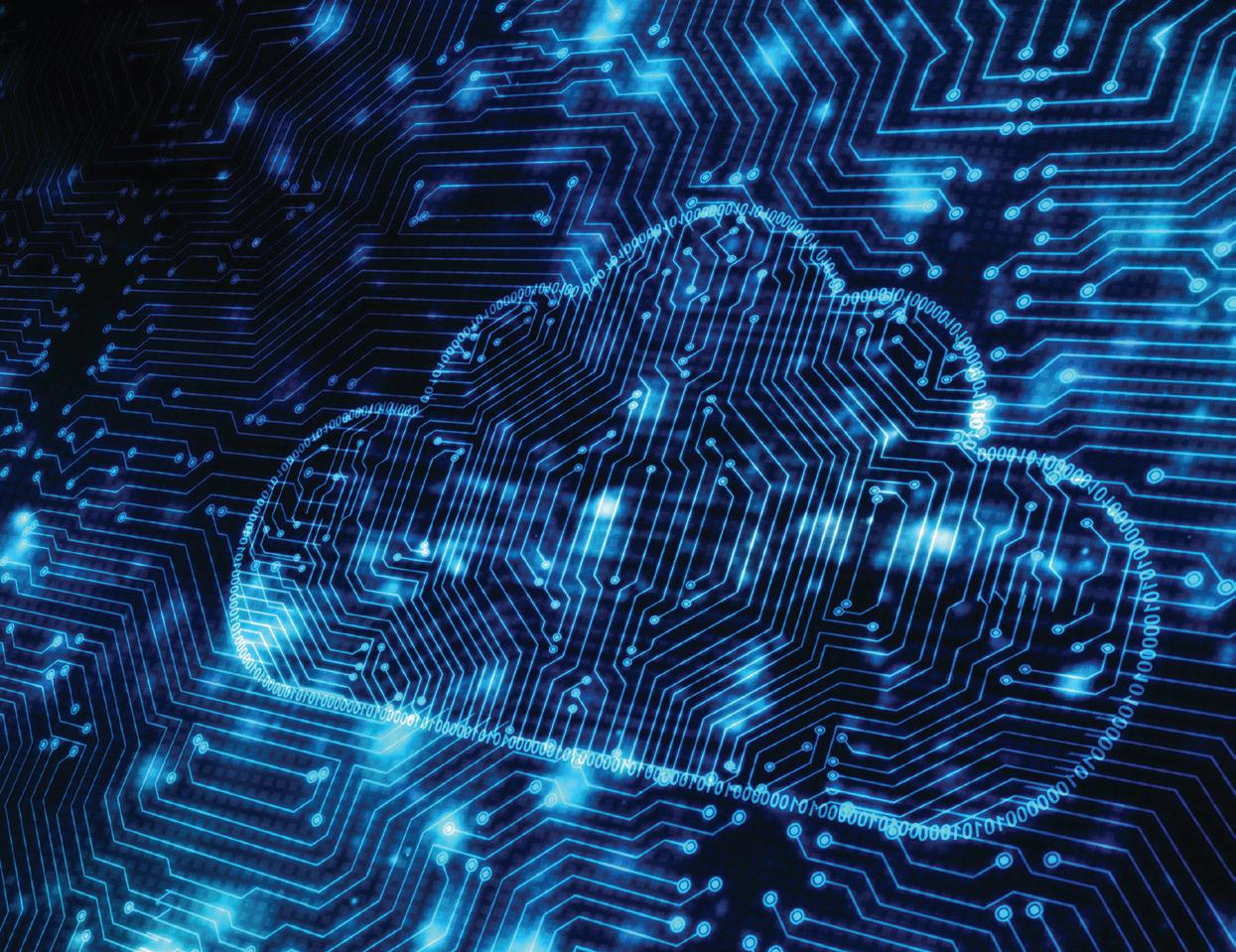
The workplace is changing, and this change requires us to be connected wherever we are. It requires us to be able to work from home, or on the road.
Imagine a device that helps you to work from home or wherever you are, that allows you to take control of worklife balance. A device that allows you to stay at home and be with your family and still be connected to the tools you need to run your business. For many workers, especially those in the utilities and infrastructure sectors, the ability to work seamlessly from home has been well and truly out of reach, until now.
In recent challenging times when normal working routines have been disrupted, InHand Networks offers a simple ‘plug and play’ service which enables you to access your devices anytime, from anywhere, and stay connected with your business.
The InConnect service builds secure remote networks from your machines, utilising a Software as a Service (SaaS) based solution. It features a user-friendly interface and offers users simple operation to keep you connected.
Key features of the InConnect service include: Convenient end-to-end remote access
With InConnect, you can access remote devices such as PLCs, HMIs and IPCs at multiple sites via PC/tablet/mobile phone. The InConnect supports various connections including user-to-device, site-to-site, device-to-device, one-to-one and multiple-to-multiple.
Network building with one click
With InConnect’s cloud connection service, networks can be built with just one click – no need for a data centre. You can access field devices anytime from anywhere.
Advanced security for data transmission
From firewall protections to encrypted data transmission, user authentication and access control, the InConnect service is fully secure for your applications. The client and the InRouter access the InConnect via CA authentication. Data is encrypted during transmission.
The InConnect service from InHand is a one-stop service integrating hardware and the cloud. It provides experience advanced security, management in the cloud, hassle-free plug and play, plus is highly scalable for IoT, and is free from operation and maintenance.
InHand has a wide range of products that support the InConnect service, including industrial cellular routers, edge gateways and vehicle terminals.
Madison Technologies is the exclusive agent for InHand in Australia and a B2B distributor of technology for commercial and industrial applications.
Simple and easy management for large scale M2M rapid deployment.

Control, monitor and automate with advanced security network services.
InHand offers industrial M2M cellular routers, gateways, Ethernet switches and IoT Management platforms to help critical infrastructure connect with remote assets.
9 Integrated 4G/LTE frequency bands to provide uninterrupted internet access
9 Enables access to remote assets for control, condition monitoring and automation
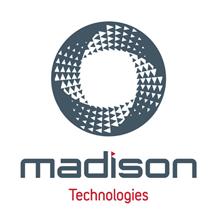
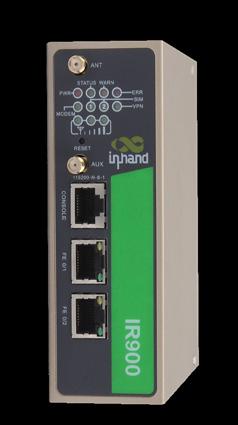
9 Suitable for fast large scale deployments
9 Python based OpenDevice programming platform
9 Plug & Play secure VPN connection available
Connect with confidence.
Madison Technologies is an exclusive distributor of InHand Networks in Australia. Our team is dedicated to ensuring our InHand Networks product portfolio is fully supported with an extensive range of hardware held locally across our national supply chain, and a team of InHand sales and technical support staff.
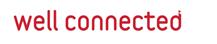
TIPS FOR RUNNING A SUCCESSFUL WEBINAR
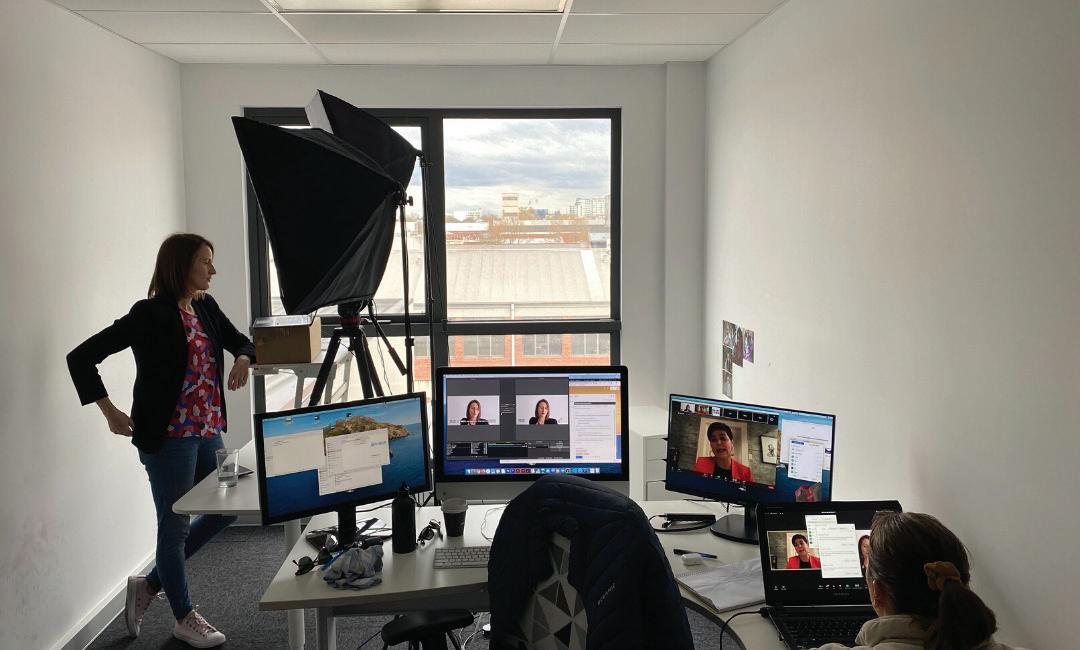
The uptake of webinars and Virtual Conferences has exploded since COVID-19 hit and all trade shows and face-to-face meetings were banned, and they aren’t going away anytime soon.
The pandemic has highlighted that webinars aren’t just a substitute for live events – they have their own benefits when it comes to branding, customer engagement and quality lead generation.
If you’re thinking about reaching potential customers with a webinar, here are five tips to help you better connect with your audience and for your event to run as smoothly as possible behind the scenes.
1. AUDIENCE: ARE YOU REACHING YOUR TARGET MARKET?
The main purpose of any webinar or Virtual Conference is to provide information to your target market – the people you want to engage with your product or service. So the first thing you need to decide is whether you will be talking to your existing audience or if you want to reach new people.
If you’re targeting your existing audience, you can directly promote your webinar to them and offer educational and/or interesting content.
If you want to reach a new market, the best way to find the most relevant people is through external marketing. This could include social media promotion or other channels like advertising in industry newsletters, allowing you to precisely track how many registrations it drives. Using social platforms like LinkedIn also allows you to identify a new audience based on factors such as job title and location, so you can find exactly who you want to attend your webinar.
Monkey Media Managing Editor, Laura Harvey, said virtual events also tend to attract a lot more people than a live event. Monkey Media has run several Virtual Conferences in 2020, including Digital Utilities, Disaster Management, Asset Management for Critical Infrastructure, Flow Technology, and Smart Cities.
“For example, at our Smart Cities Conference, we’d normally get around 300 people for a live event, but by making it a Virtual Conference, we had more than 1,000 people registering,” Laura said.
Once you’ve decided who your target audience is, it’s important to engage with them before and after the event to foster the relationships. Before the webinar, think about setting up an automated newsletter that sends them useful information on the topic. During the webinar, ensure they can participate in the conversation using Q&A chat functions to send questions to speakers, or through poll questions.
2. CONTENT: WHAT VALUE IS IT OFFERING?
The content of the webinar or Virtual Conference is what will get people to register, so you need to be offering high-quality information and engaging speakers. Think about what your identified target audience and potential customers would want to learn about and create a program around their interests and pain points.
Laura creates the programs for Monkey Media’s Virtual Conferences and said the choice of speakers can play a big part in the success.
“You need to decide if you will use an internal speaker from your own company, external experts, or both. A mix is often good as it provides broader program appeal and can look less promotional,” she said.
“The key with speaker selection is to first define the topics you want to address in your webinar, and then choose the speakers who are well regarded and best placed to address these topics, internally or externally.
“Speakers who have a high public profile, and who have their own broad networks that they can leverage to attract more delegates to your event are also beneficial.”
There’s been a huge number of new webinars popping up lately, so like anything else, there are good and bad ones. You want to make sure you’re not contributing to ‘webinar spam’. Don’t just do a webinar because everyone else is. You still need to have something useful to say.
3. FORMAT: MAKE IT FIT-FOR-PURPOSE
There is no set rule for how long a webinar or Virtual Conference should be, as the length of time should fit the content. If you’re turning a previously live event into a webinar, it’s important to not try to just jam in the existing content. For an event that was previously a one or two day conference, this could be compressed into a 3-4 hour webinar.
This is what happened with Monkey Media’s Digital Utilities 2020 Conference, as the COVID-19 lockdown and travel restrictions began less than a week out from the event.
Monkey Media Managing Director, Chris Bland, said the decision was made to move it online on Friday, with the event starting the following Thursday.
“This gave the production team only three work days to transform it into a completely Virtual Conference, including finding the best platform, and rejigging the program to work better in an online format, including working with all the speakers to ensure their presentations still had the same impact when delivered online,” he said.
“It was a steep learning curve and while it wasn’t perfect, we made sure to take the audience into account in terms of how they would be receiving the information presented.”
Most people also have short attention spans, so Laura said that generally webinars should go for a few hours, or if there are only one or two speakers presenting on a niche topic, keep it down to 45 minutes to one hour.
Take different time zones into account when choosing the optimal time, and make sure your speakers stick to their allocated times. Also, consider breaking up the event with a variety of presentation styles including panels and audience participation through Q&A sessions. Also, don’t forget to keep it visual – having powerpoint slides with illustrations or short videos is more interesting for viewers.
4. TECHNOLOGY: GET IT RIGHT
People are forgiving when there are technical issues, but it only takes a minute or two of dead air before you lose someone’s attention, so it’s important to get the technical basics locked down.
There are a number of webinar platform options available including GoToWebinar, On24, ClickMeeting and Zoom, with the choice depending on a number of factors, including price and the specific features needed.
Regardless of the platform, the key is to fine tune communication between the production team, speakers and the host/MC to ensure that everything is seamless on screen, said Monkey Media’s Marketing Account Manager, Harry Johnston.
Harry manages the technical components of all Monkey Media webinars through programs including the Zoom webinar platform and OBS Studio streaming software.
“We have set up websites through Zapier that allows people to automatically download Zoom when they register for a Virtual Conference, and also have several add-on programs such as a virtual camera attachment, so we’re not just using the one program,” Harry said.
“Since Digital Utilities, we’ve stepped up our production quality by using Adobe AfterEffects to custom-make our own graphics and animations to show who’s currently speaking and what’s coming up.”
While the webinar is running, it’s best to have a production team set up with different people managing different aspects, including one person to coordinate with the speakers and answer delegate questions that come through, and another to focus on the visuals and audio to ensure everything on screen is running smoothly.
“There’s a lot of dialogue behind the scenes, so my best piece of advice for all webinars is to do a practice run at least the day before to troubleshoot any problems. This ensures the speakers are comfortable and know what they need to do, and allows you to test the sound quality, backgrounds, and that slides or visual aids work,” Harry said.
Polls are also a great addition to a webinar or Virtual Conference as they keep people engaged but can also be used as lead generation, where people can opt in to receive more information on certain companies presented.

5. FOLLOW UP: KEEP THE CONVERSATION GOING
Some companies produce their own webinars, while others work with an agency or publisher to run something more hybrid, either under their own brand, or co-branded.
Sponsoring webinars and Virtual Conferences is another option and can include brand recognition through logos in event promotion, speaking slots or video presentations in the program, information sent directly to these lists before or after the event, and more.
These new contacts can opt in to receive more information about your product or service and if it’s a high-quality webinar, you will be associated with it and seen as an authority in the space.
If you’re hosting your own webinar, you will already have the leads, but it’s critical to continue to keep in touch with them in a useful way and provide them with continued value. This could be in the form of adding these contacts to an automated nurture track so they can be sent related information. It’s this ongoing engagement that allows you to get the most out of the webinars, long after they are over.
“Our conferences remain online after the live virtual event has concluded, so we continue to have people registering to watch our previous events on-demand, which extends the life of the webinar content we create,” Laura said.
USING SEAL COATS TO REDUCE URBAN HEAT
by Tanya Roe, Senior Consultant, Sustainability, City of Adelaide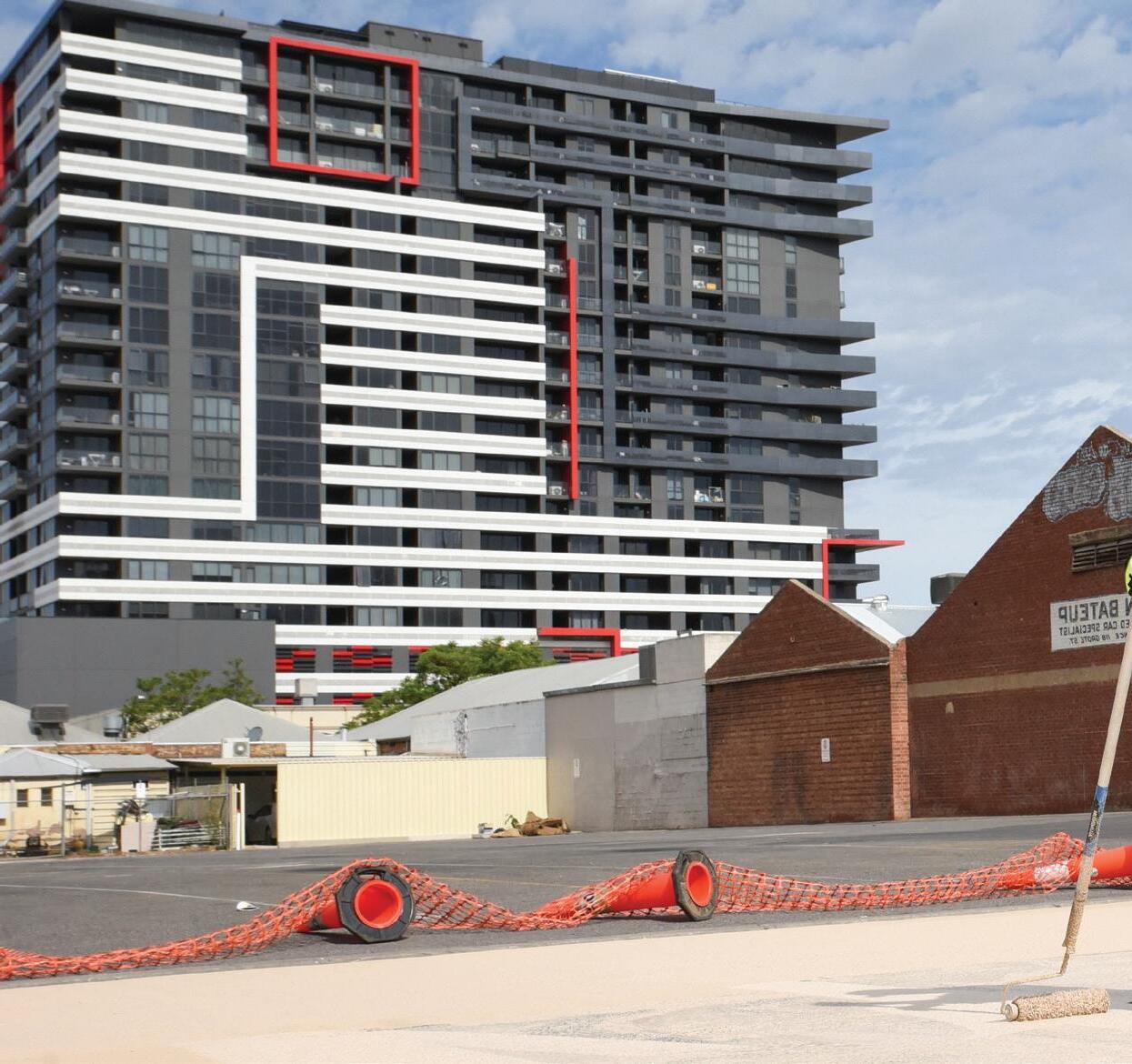
For the CBD and eastern Adelaide in South Australia, projections are:
♦ Annual average maximum temperatures to increase by 1.6ºC by 2050 and 2.3ºC by 2070
♦ Days over 35ºC to increase from 20 days per year to 47 (38-57) days per year by 2090
♦ Days over 40ºC to increase from 3.7 days per year to 16 (12-22) days per year by 2090
Bureau of Meteorology data indicates that 2019 recorded 38 days over 35ºC and 17 days over 40ºC. The urban heat island effect is prevalent in many Australian cities and has been shown to be exacerbated by climate change.
HEAT MAPPING OF LAND SURFACE TEMPERATURES
Due to urban ambient air temperatures being related to land surface temperatures, in 2018 the Resilient East climate change partnership (eight councils in central-eastern Adelaide plus the Government of South Australia), along with the City of Salisbury, commissioned The Collaborative Heat Mapping for the Eastern and Northern Adelaide Project. Graph 1 was taken from this study and depicts the average land surface temperatures of 1,100 locations across the study area, within 18 different land use type categories.
A key finding from the study was that non-shaded asphalt roads are 4ºC hotter than the average land surface day temperature, and they bank the heat and release it at night, becoming the hottest night-time surface.
The study findings are consistent with national and international research and the related map can be viewed along with those of greater Adelaide on the Urban Heat Mapping Viewer portal.
The City of Adelaide (CoA) is using this data to inform its planning and design. Residents and businesses can consult the tool to understand how heat exposed their properties and communities are.
Extreme heat kills more Australians than any other natural disaster and the number of extreme heat days is predicted to increase significantly for many areas of Australia. Climate-KIC Australia in partnership with the City of Adelaide (CoA) and South Australian Department for Environment and Water, are undertaking the Cool Road Adelaide project to test three heat reflective seal coats that may help combat urban heat now and in the future.
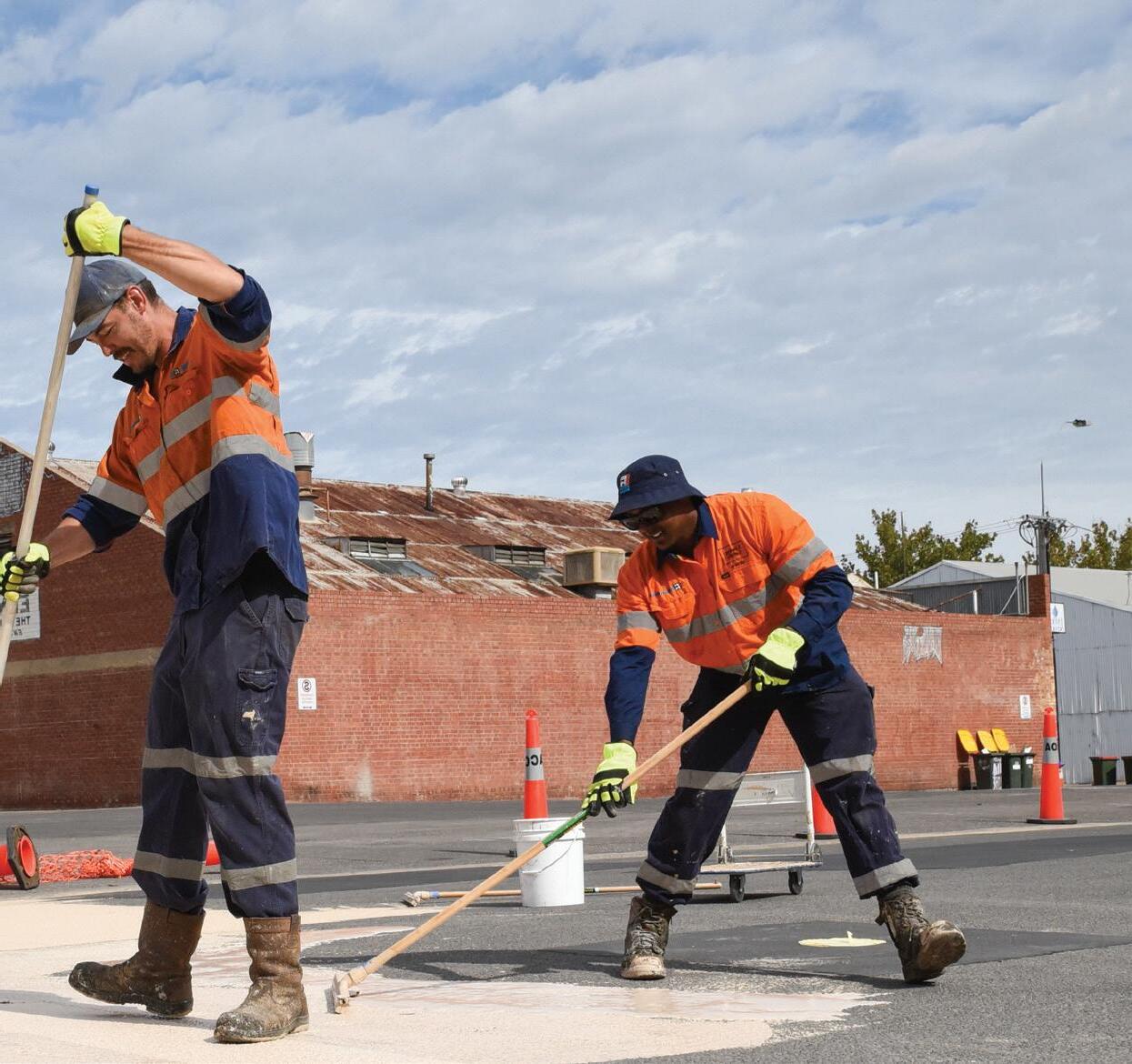
The CoA is responding to the predictions for climate change and knowledge of urban heat in a number of ways, such as developing a Climate Risk Profile, a Water Sensitive City Transition Plan, staff and community capacity building, increased greening, investigating more sustainable infrastructure renewals, and trialling cooler materials and infrastructure in the city.
IMPERVIOUS SURFACES
Hard surfaces typically account for the heat island effect in cities. Roofs typically account for 20-25 per cent and pavements 40 per cent of city surfaces, each absorbing 80 per cent of sunlight
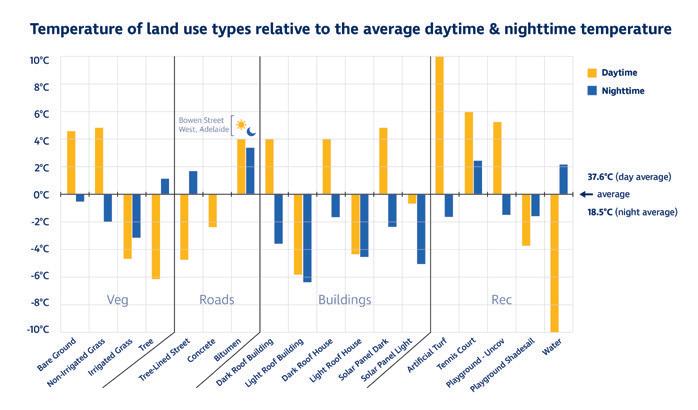
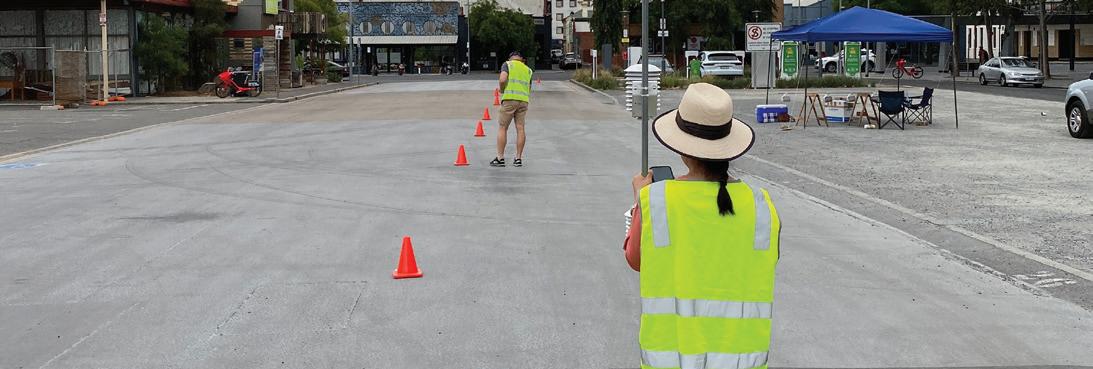
reaching them and converting it into heat. There’s a range of cool materials being used, trialled and developed, which include low heat conductivity (conducts heat less into its interior), low heat capacity (stores less heat in its volume), high solar reflectance (albedo) and a high level of embodied moisture to be evaporated or filtrated into the soil.
Asphalt roads, one of the consistently hot urban surfaces both day and night, cover a large area of our cities and are a local and state government asset. Conventional asphalt pavement can reach 50-65ºC. Alternative cooler options include heat reflective asphalt or concrete, heat reflective seal coats, permeable paving, foam/permeable concrete, resin-based concrete, permeable asphalt, block pavers and vegetated pavement.
As an example, the Tokyo Metropolitan Government has implemented 19km of water retentive pavements as an urban cooling strategy. An urban landscape is highly contested with road, parking, pedestrian access, underground services, aboveground power and signage and awnings, making tree planting challenging.
HEAT REFLECTIVE ROAD PAVEMENT SEAL COATS
In 2019, two local councils (the Cities of Charles Sturt and Salisbury) trialled a US manufactured cool road seal coat product, producing a 6.1ºC reduction in land surface temperature (City of Charles Sturt testing results). Adelaide Airport also trialled two locally manufactured products.
COOL ROAD ADELAIDE
The Cool Road Adelaide Project is trialling all three of the aforementioned cool road seal coats on the same piece of road, and has tested both land surface and air temperature.
The aim of the trial is to understand the advantages and disadvantages (from an urban heat, road preservation and community perception point of view) of the type of product overall, and comparing the three products to each other and a control patch.
Bowen Street West was chosen as an existing asphalt road, receiving a reasonably uniform heat profile, contributing to a night-time heat island (125m x 125m area) and a location site which would cause minimal impact to residents and traders within the CBD. The road is approximately 100m long, 11.5m wide and the road surface is over 20 years old.
The project patched potholed and cracked sections of the road approximately three months before the cool road surfaces were applied, conducted slip resistance (AS 4663:2013 and AS 4586:2013) and skid resistance (DPTI TP345:2-10) testing, and established a community information and consultation process.
The project conducted pre-application road temperature testing via a groundbased measurement platform in mid-December 2019 (after two days over 32ºC with clear skies) at both midday and early morning, to gather day and night-time temperatures.
The three cool road surface products were then applied in late January 2020 in patches approximately 24m long, 11.5m wide and 277m2.
The three products under trial are:
♦ JetBlocTM in Irish Cream by Fulton Hogan – a blend of epoxy modified and cementitious polymers that can be formulated in many colours including the most heat reflective Irish Cream option. It’s designed for high traffic and stressed asphalt pavements and can be sprayed on or hand applied
♦ JetCoolTM by Fulton Hogan – a premium bitumen emulsion with latex and sun reflective fillers which make it a light grey colour. It’s designed for asphalt roads and airport pavements, and can be sprayed on or hand applied
♦ CoolSeal by GuardTop® supplied by SuperSealing – a grey colour, waterbased asphalt emulsion. It has been used extensively in Los Angeles, as well as other US cities
POST-APPLICATION TESTING
The post-application temperature measurement occurred in February and March 2020 consisting of:
♦ Ground-based measurement of the entire road surface after two clear sky days over 32ºC. An average surface temperature and relative temperature values for over 100 individual points will be calculated and summary statistics provided
♦ Multiple temperature recordings on the air column directly above the different road surface types using a bluetooth Hobo (a weatherproof data logger with built-in temperature and relative humidity sensors), mounted on 2-3m high masts measuring air temperature to within 0.25-0.50ºC. Loggers mounted at 0.10m, 1m, 1.5m, 2m and 2.5m, and measured every 15 minutes 9am-11pm.
The results will also be used to determine a land surface temperature signal for the CRC for Water Sensitive Cities’ land surface temperature scenario modelling tool, and a series of scenarios modelled to determine an estimate of the day and night-time heat island mitigation benefits at a whole of CBD scale.
A report will be provided in July/August 2020 regarding the land surface and air temperature findings as well as the results of the community consultation. Road
preservation qualities will be assessed by CoA Road Asset Planners.
DENSE URBAN MICROCLIMATES
Heat reflectance qualities of materials will need to be considered on a caseby-case basis in different locations. Research is indicating these surfaces may be most useful on roads that are not abutted by high buildings. In highly built-up areas, the road may reflect heat onto surrounding buildings that absorb the heat, increasing the heat load of the building and/or reflecting the heat back into the street. Depending on the scenario and location, seasonal shading, misting, greening (particularly with canopy) and/or permeable pavements may be more effective at cooling a microclimate.
Project findings will be published on the Infrastructure website when released.
References
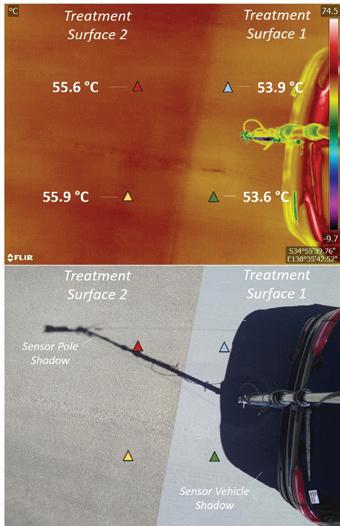
The Cool Road Adelaide project is a Climate-KIC Australia project delivered in partnership with the City of Adelaide and South Australian Department for Environment and Water. The project is also made possible with in-kind support from Fulton Hogan. More information is available at Your Say Adelaide yoursay. cityofadelaide.com.au/cool-road.
Post application temperature measurement using thermal imagery. Image credit – Edge Environment.
Coates, L., Haynes. K., O’Brien, J., McAneney, J. & Oliveira, F.D. (2014). Exploring 167 years of vulnerability: An examination of extreme heat events in Australia 1844–2010. Environmental Science & Policy, 42, 33-44. Commonwealth of Australia (2020). Bureau of Meteorology, Climate Data Online webpage http://www.bom.gov.au/climate/data/ C40 Cities Climate Leadership Group (2016). Good Practice Guide, Cool Cities Osmond, P & Sharifi, E. (2017). Guide to Urban Cooling Strategies, Low Carbon Living CRC, Sydney, N.S.W. Resilient East (2015). Climate Projections Report, prepared by URPS and Seed Consultancy Services as part of the Resilient East consultancy led by URPS, for the Eastern Region in association with the Government of South Australia and the Australian Government. Seed Consulting Services, EnDev Geographic and Monash University (2018). Collaborative Heat Mapping for Eastern and Northern Adelaide Report Prepared for the City of Unley on behalf of the Eastern Region Alliance of Councils and the City of Salisbury. Watkins, R., Palmer, J. & Kolokotroni, M. (2007). Increased Temperature and Intensification of the Urban Heat Island: Implications for Human Comfort and Urban Design. Built Environment, 33(1) Climate Change and Cities, 85-96.
Mobile Mapping
Taylors Mobile Mapping technology is a fast and cost effective way to manage assets such as bridges, buildings, roads, highways, and power stations. Taylors combines the latest in vehicle mounted and UAV technology to capture 360 degree geo-referenced imagery to document site conditions, asset capture and mapping.

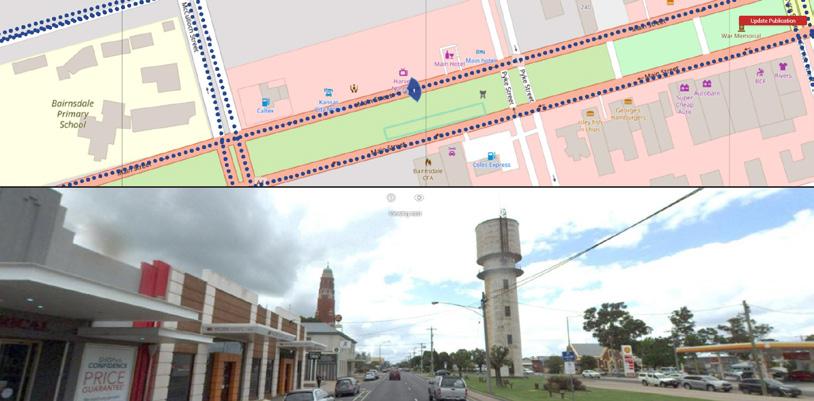
Bushfire Recovery
With the generous support of Ultimate Positioning Group, Taylors is assisting to document the Impact of the Bushfires throughout Victoria and New South Wales. Utilising the Trimble MX7 Mobile Imaging System, Taylors is collecting geo-referenced images which will help to document the impact of these bushfires. UAVs were also used to help in capturing data around areas where the impact of these bushfires cannot be seen by road. For Turn-key
Spatial & Digital Solutions
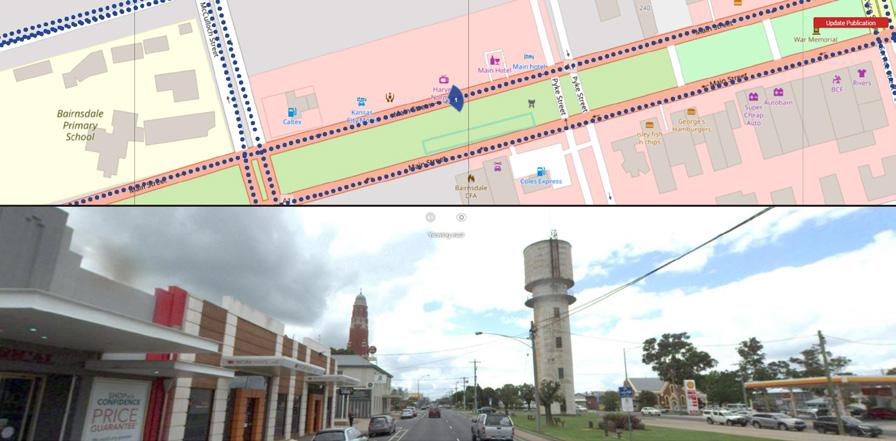
WHY CHANGING HOW WE PAY FOR TRANSPORT
IS A GOOD MOVE
by Michel Masson, Chief Executive Officer, Infrastructure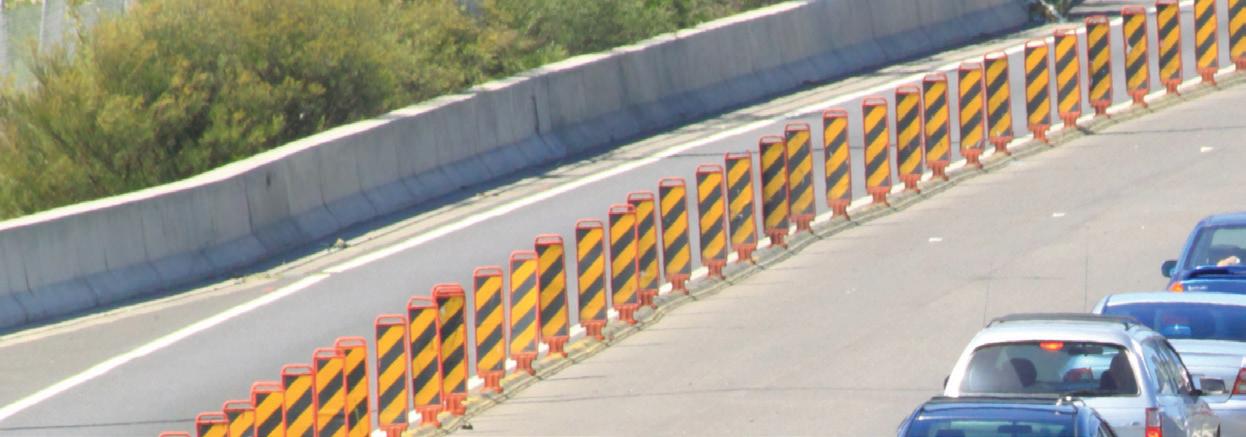
In both phases of COVID-19 lockdown in Melbourne, roads have been eerily quiet as numerous businesses, venues and attractions have been forced to close. But as we saw when restrictions initially eased throughout June, peak hour traffic jams re-emerged as more people opted for private transport to maintain social distancing.
Infrastructure Victoria recently released new research that looked at ways to ease the transport squeeze in the state. This work is even more relevant for supporting Melbourne’s crowded peak hour transport network with the short-term and long-term challenges resulting from COVID-19.
Our findings showed that by changing the way we pay for transport, we could reduce the amount of time people spend in congested peak traffic by eight per cent and increase traffic speeds by up to 25 per cent within inner Melbourne. In this example, up to 85 per cent of people could be better off, paying less than they do today for transport.
The report, Good Move: Fixing Transport Congestion, recommends changing how Victorians pay for roads, public transport and parking. While building new roads and rail can deliver needed transport services, analysis, evidence and experience demonstrates that they only relieve congestion temporarily.
Network-wide pricing reform has the potential to dramatically improve how we move around our cities, provide greater choice and make the best use of our existing infrastructure. It also offers the best prospects for managing the transport transition to a post-COVID-19 world.
WHY NOW?
While Melbourne is again in Stage 3 lockdown restrictions, at some point those will ease, and life and work will eventually settle into a new kind of normal. Governments and businesses
will again face the challenge of moving the workforce and tourists around our city safely. A return to commuters packed like sardines in peak hour is simply not an option given the requirement for social distancing. The need for change has come at a time when Melbourne’s transport system was already under pressure. Our modelling showed that if we don’t change, things will continue to get worse. By 2030, an additional 3.5 million trips would be made every day across Melbourne’s road and public transport networks alone, leading to the cost of congestion rising to $10.2 billion per year.
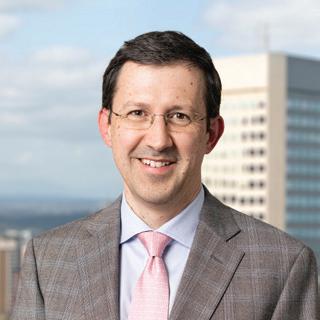
If social distancing requirements and heightened community concerns regarding mass transport continue, this is likely to mean more people will choose to travel by private vehicle. For many office workers across Melbourne, if the price they pay to travel is reduced during off-peak times then this will make it more attractive to travel off-peak. This will make it easier for workers to make better use of our transport system while maintaining social distancing.
WHAT ARE THE CHANGES?
Under the illustrative pricing scheme we modelled, annual charges like car registration would be scrapped and replaced with a per kilometre charge of 15.5 cents. Travel in Melbourne’s CBD area (inside a cordon – see Figure 1) during peak hours would be charged at an additional $1 per kilometre. Parking at train stations and park-and-ride facilities were also priced. Our modelling looked specifically at Melbourne, as that is where congestion is the biggest issue,
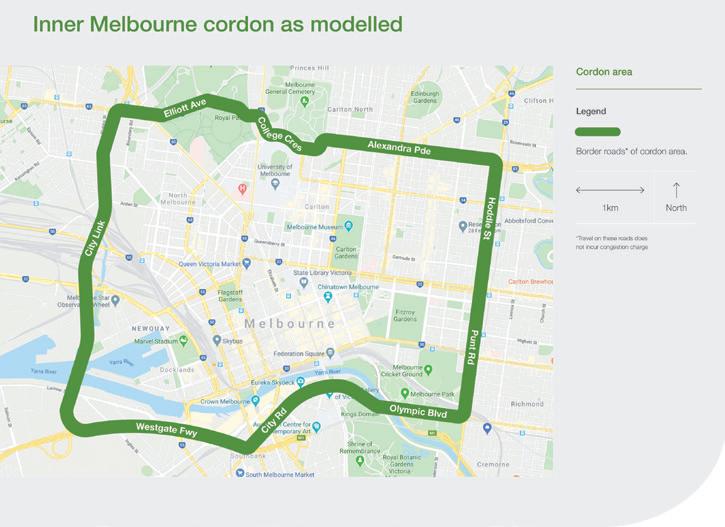
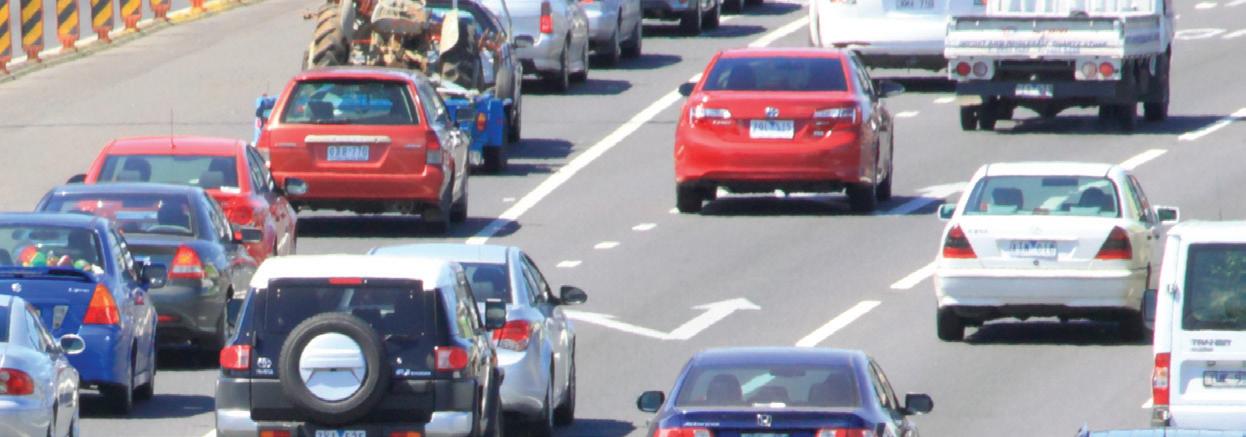
but people in regional and rural Victoria could also benefit from some changes.
Flat rates for public transport would also be replaced with fares based on time, distance and mode.
It would be cheaper to travel outside peak times, when there is spare capacity on the network, and cheaper to travel via bus or tram.
It’s important to note that this model is an illustrative example, and the actual cost of travel could change if a scheme like this were to be implemented in Melbourne. But the work we have done to develop this set of ideas and principles is based on economic modelling, best practice from other cities around the world who’ve successfully introduced pricing reform, and importantly, community views.
A broadly representative panel of community members told us that concessions and addressing locational disadvantage were crucial to a system like this being fair, and that service improvements would also be required to give people alternative transport options.
We modelled several measures to meet some of these concerns, including a $5 daily cap for concession holders and a discount for everyone else after the first $10 of charges. All Victorians would also be entitled to 20 free travel days a year. Compared to the pricing model without these measures, this system would cost roughly $1.4 billion more per year – a significant amount, but far less than the projected cost of congestion rising to $10.2 billion per year by 2030.
And what could these changes mean for our transport network? They would remove up to 168,000 car trips from Victorian roads every day. 110,000 people would make the shift to buses, as they would be the cheapest form of transport. More than 40 per cent of drivers would cease driving into the Melbourne city cordon, causing average speeds during the morning peak to rise by 25 per cent.
TRANSPORT NETWORK PRICING AROUND THE WORLD
We looked at where there have been major transport pricing reforms around the world, including London, Stockholm, Milan and Singapore, to see what we can learn. The first key design feature was that all road and parking reforms that were adopted at scale were location-based and designed to mitigate congestion. Another key feature was the use of cordons, or area charges. Charges applied to enter the designated area/s during peak times, but not during off-peak.
In London and Stockholm, additional public transport was introduced, at the same time as changes to pricing, to help provide greater choice for commuters.
And the impact is clear – in London, congestion has remained at similar levels over ten years, despite increases in population over that time. In Milan, in the first year of new pricing, traffic decreased by 30 per cent and average
speeds increased by about 12 per cent.
In Stockholm, traffic inside its city cordon decreased by about 20 per cent.
TRAVELLING AFTER COVID-19
Whether our transport system can adapt to restrictions around social distancing and meet future demand remains to be seen. But it is clear from our work that transport network pricing is the best solution to encourage Victorians to change their behaviour and make the best and safest use of our network.
Many office workers, particularly in the CBD, have already adapted to working from home in response to COVID-19. So changing when and how they travel in response to transport network pricing, will be easier than before. Providing these incentives through a change to how we pay will not only be easier, but essential, as people return to travelling when restrictions ease. This will be critical to avoid even worse problems with safety, congestion and crowding on our transport network.
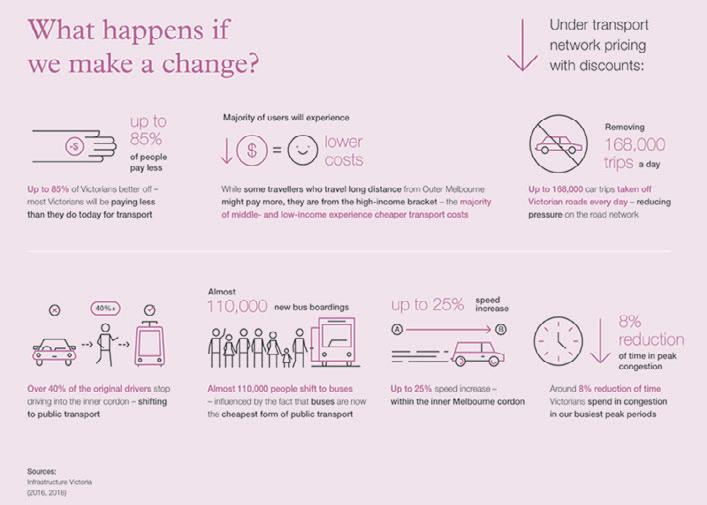
OPTIMISING TRAFFIC FLOW THROUGH DETECTION AND DATA
by Terry Parker-Jones, Armitage GroupOptimising traffic flow is a never ending challenge for traffic engineers with a myriad of variables entering the mix, such as peak hours, roadworks, delays due to accidents and more. As such, creating and maintaining traffic efficiency is a complex and multifaceted pursuit. The capture and analysis of traffic data is therefore critical to understanding the causes of congestion and implementing improvements.
From a functional perspective, the majority of current and historical traffic data has relied on presence detection from an inductive loop installed into the road surface. Where, unfortunately, there can be a degree of inaccuracy due to the need to detect metal content or distinguish the class of vehicles.
From an analytical perspective, the key to understanding congestion lies in detection and data. This highlights the importance of capturing multiple data points to build a multifaceted appreciation of factors that are influencing congestion. Where information around traffic patterns, travel and delay times, vehicle types, and occupancy periods can provide greater insight.
With the ability to detect up to 24 vehicle presence zones, with up to four lanes of coverage from one unit, a thermal imaging sensor such as the FLIR ThermiCam2 is a proven and cost-effective alternative to inductive loops or radar detection at the approaches to intersections. Being traffic adaptive, advanced detection and data algorithms can also be used to extend or reduce green light time based on congestion or demand.
With a ≥98 per cent accuracy in sensing, the incorporation of thermal imaging detection can result in better signal timing and increased traffic efficiency, with fewer false calls and missed detection events. Easily installed on existing infrastructure such as traffic poles, thermal detection provides highly accurate detection and data, providing traffic engineers with the insights they need to make improvements where they are needed most.
Thermal Detection + Data Collection
ThermiCam2 is an intelligent thermal traffic detector for intersections, capable of detecting vehicles, bicyclists and pedestrians. Incorporating integrated Wi-Fi technology that allows simultaneous thermal detection, data collection, travel time and delay time calculation. Able to operate through sun glare and in harsh weather conditions, day or night with 24/7 reliability.
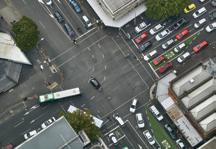
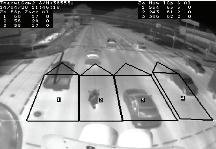
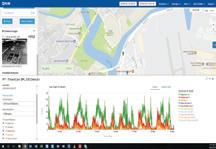


THE PLANS ARE IN PLACE, SO LET’S
GET TO WORK
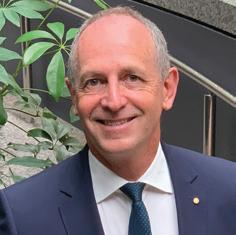
When the National Freight and Supply Chain Strategy was released a year ago, COVID-19 was not on anyone’s radar, much less something around which Australian households and businesses were busily redesigning their day-to-day activities.
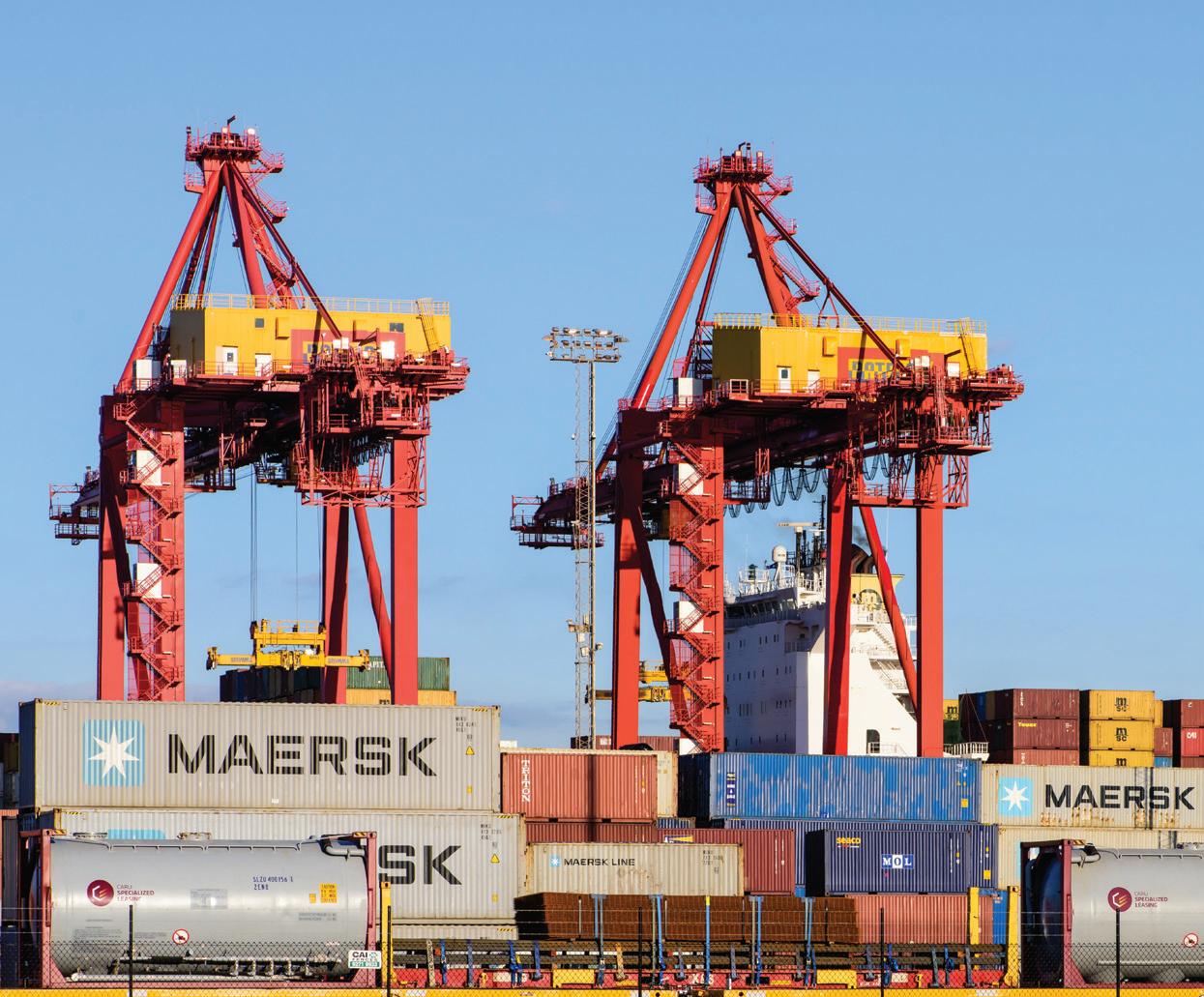
Yet now, with the pandemic’s curve seemingly flattened and government attention turning to how the economic recovery can be hastened, the good news is that a significant amount of work on that front has already been done.
Everything that political leaders have talked about as priority areas in the pursuit of economic recovery – enhanced infrastructure, regulatory reform, harmonisation, red tape reduction and ensuring the workforce is equipped with the right skills for the future – are explicitly addressed by the National Freight and Supply Chain Strategy (the Strategy).
At a meeting of the Transport and Infrastructure Council (TIC) in November 2019, governments were asked to present their implementation plans for the National Freight and Supply Chain Strategy. These documents were intended to move the Strategy into the next phase by setting out how jurisdictions would put their plans into action.
As ALC noted at the time, it was regrettable that there was not enough detail in several of the plans presented to give industry confidence that the measures will be pursued with a sufficient sense of urgency.
Certainly, the absence of clear deadlines for completing key actions – a basic requirement in being able to track and assess progress – was a deep concern.
Effective implementation of the Strategy was urgent before COVID-19 hit, but it is even more critical now.
INDUSTRY-LED ACCOUNTABILITY
The price we pay for consumer goods, our international competitiveness, continued growth in exports and the liveability of our communities are all inextricably linked to our ability to move freight efficiently, safely and cost-effectively.
The nation faces a far more challenging economic climate than that which prevailed at the time of the Strategy’s release, so opportunities to enhance national productivity and permit our exporters to compete more effectively on the international stage must be grasped quickly.
With so much at stake, it is essential that the implementation plans developed by governments be updated to reflect this new reality. In particular, it is essential that these plans clearly spell out how, when and by whom actions will be delivered, so that progress can be measured and jurisdictions can be held to account.
ALC also believes it is vital for industry to ensure that its needs are being actioned by governments by establishing an industry-led accountability measure that will provide a practical perspective as to how effectively implementation is occurring – and which areas need greater focus.
To that end, ALC is now working with our members to develop a ‘scorecard’ which will take into account the level of detail in each implementation plan, its alignment with the priorities contained within the Strategy, and the progress that has been made in implementing the commitments made in each jurisdictional implementation plan.
The scorecard will ‘grade’ each jurisdiction against a set of benchmarks. These benchmarks are currently being developed by members of ALC’s policy committees, which examine key policy areas including infrastructure, regulation, safety and technology.
This will ensure that the assessment criteria are being developed by those working in these key supply chain areas on a day-to-day basis, and accordingly will provide a realistic,
practical view of whether jurisdictional plans are actually being delivered in a way that meets the needs of industry.
NEW SKILL SETS FOR FUTURE FREIGHT WORKERS
A renewed focus on skills will also be vital in helping the freight and logistics industry be properly equipped for a post-COVID future.
The evolving nature of logistics and freight operations will require a very different skill set from the sector’s future workforce going forward. People will need to be comfortable operating sophisticated IT systems and equipment, in vehicles and in distribution centres and terminals, as customers demand greater visibility over freight as it moves through the supply chain. The influence of automation will also be felt, and those skilled in the operation and maintenance of robotics will be highly sought.
The sector will also increasingly need workforce participants that understand how to analyse and interrogate data sets. This will help companies to plan and coordinate more efficient supply chain operations and identify and address safety risks.
Although these efforts must be industry-led, there is certainly scope for governments to play a greater role in making certain the transport sector’s workforce is prepared for a changing world. Many industry participants continue to note that the transport sector has not received appropriate levels of attention when it comes to skills and training support, especially in comparison to the hospitality, retail and human services sectors.
The Federal Government began to develop a new Transport Sector Skills Strategy last year. In ALC’s view, this strategy must align the skills and ambitions of new workforce participants with the needs of a sector increasingly reliant on technology, and which requires workers with skill sets that enable them to work between multiple areas or tasks, depending on operational needs.
PRIORITISING THE STRATEGY’S GOALS
Our world has undoubtedly been changed by the COVID-19 experience – and the freight and logistics sector will see continued change as a result.
However, in an environment where providing economic stimulus and employment opportunities through infrastructure projects and regulatory reform are urgent priorities, the National Freight and Supply Chain Strategy now needs to be prioritised for what it is – a critical tool in driving Australia’s post-COVID economic recovery.
There’s been some encouraging signs in that respect over recent months, with all Ministers attending the COAG Transport and Infrastructure Council recommitting themselves to the implementation of the NFSCS.
Similarly, the Prime Minister’s announcement that the construction of Inland Rail would be expedited as part of the JobMaker initiative should be applauded because it also provides confidence for those looking to make complementary infrastructure investments along the alignment, including intermodals and logistics precincts.
Likewise, state and territory governments are now engaging with industry on issues like curfews and agreeing to explore how modern technology (including electric vehicles) can be deployed to make freight and logistics activities less intrusive, which would give operators the greater operational flexibility they have been seeking for many years.
A LONG-TERM STRATEGY
FOR SUPPLY CHAIN
by Port of MelbourneIn early 2020, Port of Melbourne received government approval for the major $125 million Port Rail Transformation Project to go ahead. The significant rail works form part of a larger future infrastructure strategy for the port involving plans to increase container handling capacity, port side road infrastructure, and a new liquid bulk berth.
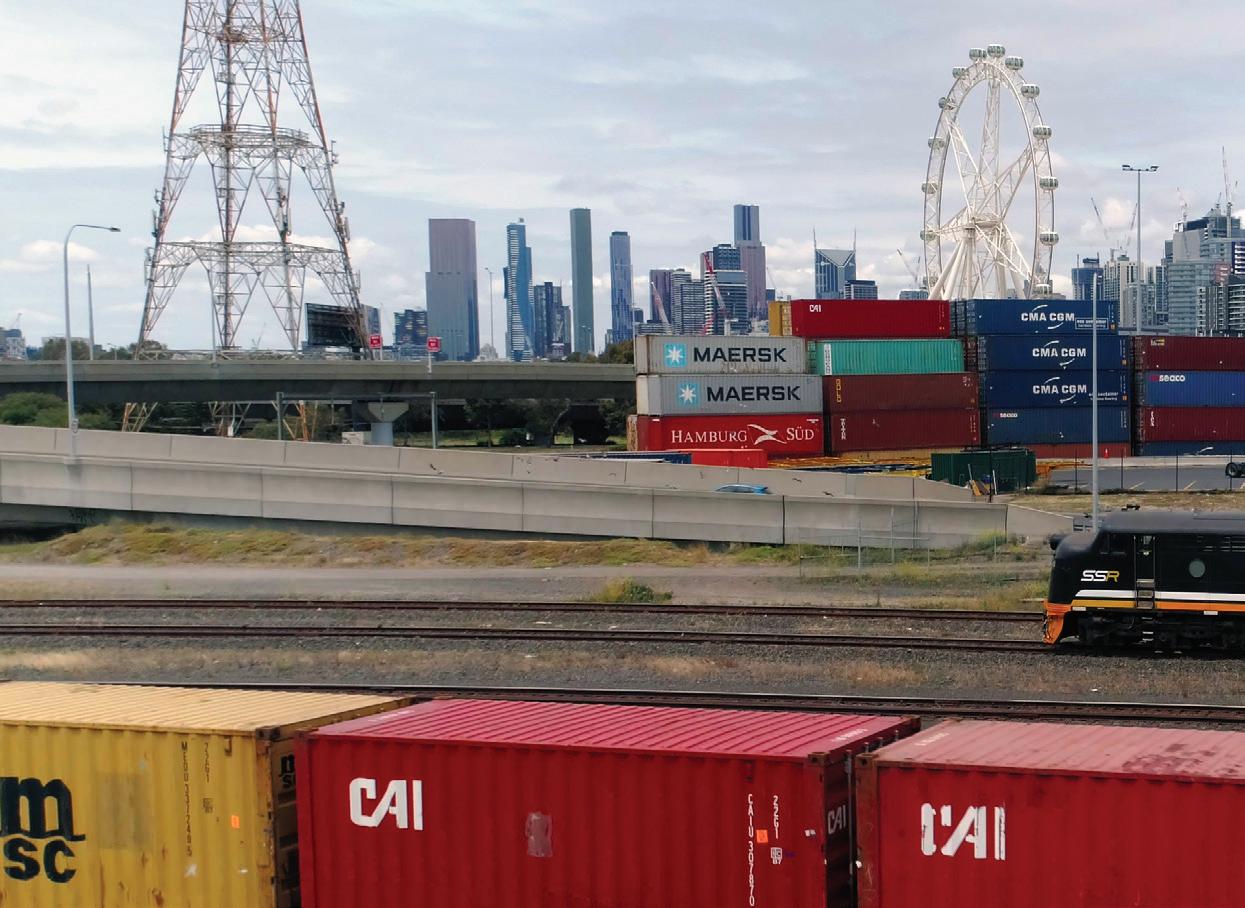
Just as Australia's ports have played a critical role in keeping Australia moving during the COVID-19 crisis, it's clear they will be the gateway to the nation's economic fortunes post-pandemic as we look to breathe new life into sectors, big and small. As our economy rebuilds and we begin thinking long term again, ports will play a pivotal role in Australia's economic future.
For Port of Melbourne, our task is threefold: optimise the efficiency and effectiveness of our port operations, facilitate Australia's vital link in the global supply chain, and continue to invest in infrastructure to meet our growth forecasts.
RAIL PROJECT GIVEN GREEN LIGHT
Earlier this year, the State Government gave the all-clear for our Port Rail Transformation Project (PRTP). It's an initiative many years in the making that will ease congestion for local communities, ensure an efficient supply chain for freight and business, and support Australia's economy through a productive Port of Melbourne.
Funded by a tariff on full import containers, the $125 million rail project will involve significant rail infrastructure works and a new rail operating framework inside the port.
The project involves:
♦ Development of a new on-dock rail terminal at Swanson Dock East to ensure a lower cost transfer of containers between rail and ships
♦ Restructuring the port rail land and asset commercial arrangements for port Rail Terminal Operators to provide rail land and assets on a similar basis it provides wharf and road assets and land
at most current and all future port rail terminals
The investment in PRTP is essential to maximising the port's capacity and improving landside transport connections for industry; and it's set to pay significant social, environmental and economic dividends. It will make our roads safer, reduce pollution, cut costs for exporters and, ultimately, allow Melbourne to maintain its competitive position within the national port freight system.
Our Port Rail Transformation is also a central part of our broader infrastructure investment plan which recognises the need for the port's land, and the infrastructure on it, to be used efficiently and productively over the next 30 years.
As our population grows and interstate and international trade increases, the demand for access to Melbourne's port will continue to grow. Our analysis shows that over the next 30 years, total container trade volumes will grow from three million TEU each year, to around 8.9 million TEU by 2050.
TO SUPPORT THIS GROWTH, WE NEED TO GET BUILDING
Infrastructure planning, approvals and delivery timeframes mean the next phase of port expansion needs to commence now, and we are committed to working with industry, government and all stakeholders to make it happen.
There are several projects in addition to our immediate investments in rail that will need to be delivered in the coming decade to support the forecast growth in trade and ensure our infrastructure can cater to growing demands.
First and foremost, we need to invest in terminal capacity
INFRASTRUCTURE

to support increased container freight. This means investing in container handling capacity at Webb Dock. As the precinct will cater for the significant growth in trade demand, Webb Dock must be directly connected to the state and national rail network via the Webb Dock Freight Link.
Investing in growth also means investing in port side road infrastructure. Currently, the port has adequate connections to Victoria's arterial road network. However, as the trade demand grows, our population and city is also set to grow, which will present a range of road network issues for port users and the local community.
In addition to our efforts to ensure more freight is carried by rail and our work with industry to get the best out of our network infrastructure, we are also committed to working with the relevant road agencies to explore road projects that will reduce traffic in Melbourne's inner west, maximise utilisation of the existing network, and ensure efficiencies in the road network connections around Swanson Dock and Webb Dock.
Infrastructure that will support demand on the bulk liquid pipeline network is another investment priority. While Port of Melbourne is currently well-serviced by the existing bulk liquid pipeline networks, in order to support anticipated liquid bulk growth, we're investigating options for the development of a new liquid bulk berth.
With a number of options under investigation, a new liquid bulk berth would be connected by new pipelines to the existing refined petroleum product storage and distribution facilities in Yarraville, Spotswood, Newport and Altona. Lastly, a range of specific and targeted improvements to port land are critical to our long-term supply chain infrastructure
planning. When the West Gate Tunnel opens, port land south of Somerville Road will be returned for port use. Port of Melbourne intends to put this land to market to identify the most optimal use, which could include liquid bulk storage and distribution, freight logistics and storage, or empty container storage.
LOOKING TO THE FUTURE
A strategic site for the port is the former Melbourne Wholesale Market Site in Dynon. The development of the former Melbourne Market site is critical to reducing the impact of congestion on supply chain costs and communities, and we’re exploring options for this precinct.
Whether it’s land development, rail transformation, terminal upgrades or road network management, our infrastructure investment plan is focused on ensuring Port of Melbourne can plan and develop port capacity and supply chain efficiencies that enhance the competitive position of Victoria and liveability of greater Melbourne.
Port of Melbourne Operations is a steward of the Port of Melbourne and works in partnership with our customers, industry, the community and government to ensure the right investment, at the right time to deliver the right outcomes for everyone’s benefit. Our 30 year Port Development Strategy sets the framework for this investment and ensures that we can work collaboratively with all stakeholders to achieve this outcome.
Optimising existing facilities and built infrastructure, combined with targeted delivery of new infrastructure, will enable the port to cater for Victoria’s growth and deliver for all Victorians well into the future.
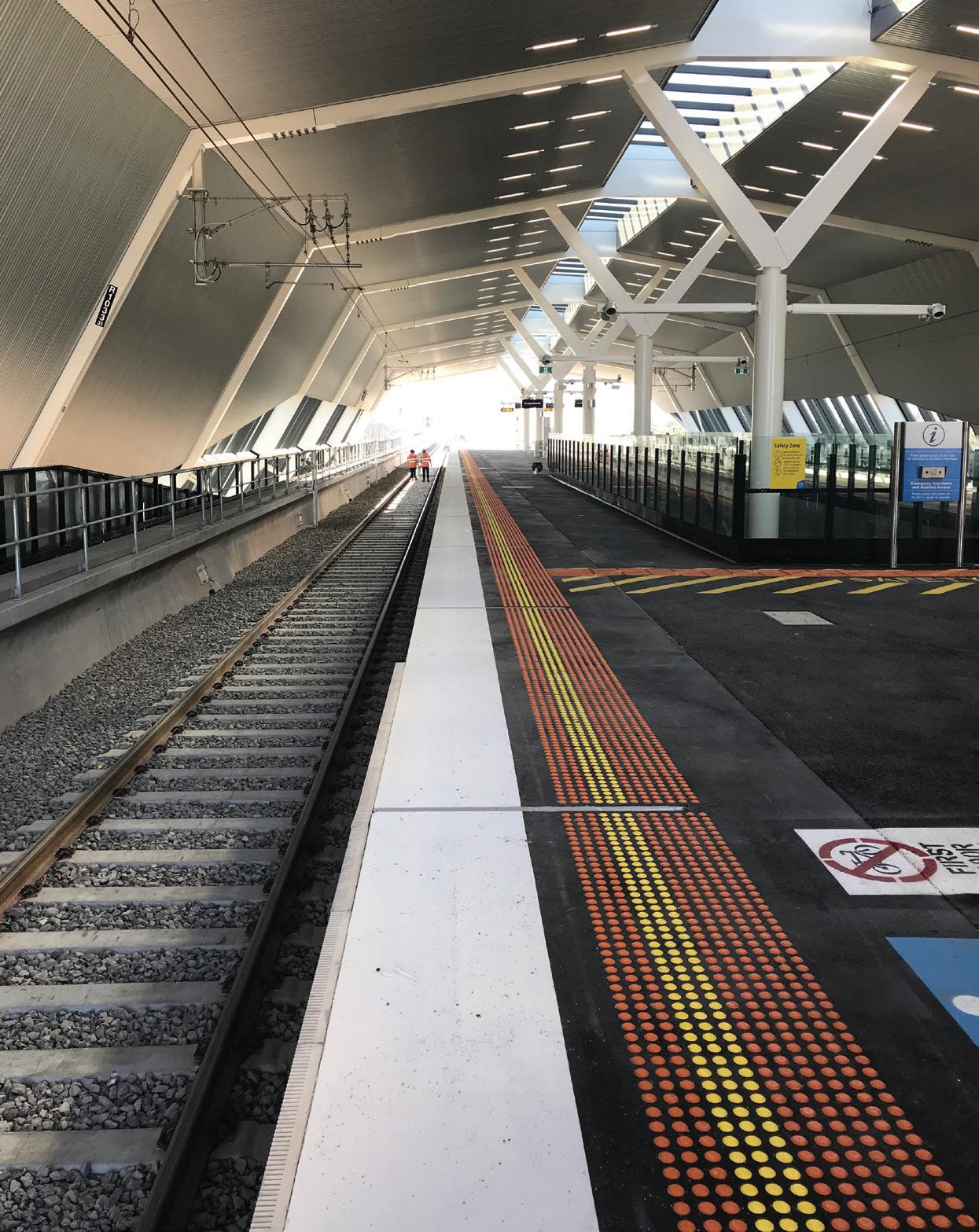
Roads made of glass bottles and crushed bricks will soon be business as usual, with the Victorian Government’s Recycled First policy dialling up the use of recycled and reused materials in construction.
USING RECYCLED MATERIALS IN MAJOR CONSTRUCTION PROJECTS
by Allen Garner, CEO, Major Road Projects VictoriaVictoria’s transport boom – with the delivery of close to 120 rail and road projects – came at a time when the state’s recycling system needed urgent reform.
The Andrews Labor Government responded with its circular economy strategy, Recycling Victoria, a ten-year plan to overhaul the state’s recycling sector.
A key part of the Recycling Victoria plan is to keep waste out of landfill and drive innovation in sustainability.
That’s where Victoria’s Big Build comes in, presenting an opportunity to optimise the use of recycled and reused materials on government projects.
The introduction of the Recycled First policy in March this year supports that commitment.
We are at a point where we must move from a “make-usedispose” model to a “make-use–reuse-repair-recycle” model.
The Recycled First policy will enable transport infrastructure projects to drive that change. Increasing demand for recycled resources will in turn create new prospects for local industry and technology development.
Companies interested in delivering major transport infrastructure projects will be required to demonstrate how they will optimise the use of Victorian recycled and reused materials that meet existing standards and specifications.
This will see recycled aggregates, glass, plastic, timber, steel, ballast, crushed brick, crumb rubber and reclaimed asphalt pavement take precedence over virgin materials.
The Victorian Government is working with construction and industry partners to identify and remove barriers to the use of recycled content.
Part of this is about dispelling myths, including the assumption recycled materials are more expensive and do not perform as well as virgin materials.
In many cases this is untrue, with recycled content often performing as well or better than virgin materials. Extra costs can often be mitigated by sourcing local content to reduce travel expenses or through economy of scale.
Ultimately, we need a comprehensive picture of the current state of the recyclables market so we can build capacity and generate data to improve acceptance and inform future project procurement.
Supporting and building a competitive and sustainable market will ensure recycled content is cost-competitive.
FROM AD HOC TO ORDINARY
The use of some recycled materials is already evident in Victoria’s transport projects, including the $1.8 billion Western Roads Upgrade, being delivered by Major Road Projects Victoria as a public-private partnership with Netflow.
More than 190 million recycled glass bottles are being used to build this project, including on Dohertys and Leakes Roads in Truganina, and Dunnings and Palmers Roads in Point Cook.
This material, together with asphalt and other recycled demolition material, was also used to build extra lanes along 24km of the Tullamarine Freeway. It was also used on sections
of the Monash Freeway and M80 Ring Road.
Up to 300,000 tonnes of recycled asphalt is also being used on the Western Road Upgrade to improve Palmers and Leakes Roads in Truganina, and Dohertys Road in Laverton North. Workers are also resurfacing 37 arterial roads in Melbourne’s west using recycled asphalt.
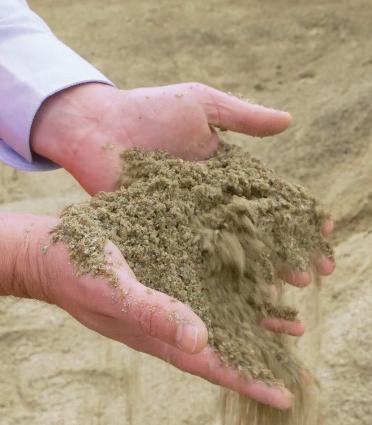
Victoria’s Big Build has also been reusing materials created by its own projects, with 14,000 tonnes of soil excavated from the Metro Tunnel site in Parkville used in pavement layers on roads in Point Cook.
This material weighs as much as 226 E-class Melbourne trams and would have otherwise gone to landfill.
The Chandler Highway Upgrade also used up to 40,000 tonnes of dirt excavated from the Queens Place skyscraper development in Melbourne’s CBD.
The Recycled First policy will transform this ad hoc approach into a uniform process that captures data and lessons learnt.
DRIVING INNOVATION
There is plenty to be learnt from research already underway, with the Victorian Government collaborating with construction and industry partners to drive innovation.
In an Australian-first trial into how crumbed rubber performs over time, a busy road in East Bentleigh has been paved using the equivalent of 1,600 old tyres.
Researchers have begun testing the use of crumbed rubber on a kilometre and a half section of East Boundary Road, with laboratory and field tests to be conducted over the next two years.
Four different asphalt mixes that incorporate crumbed rubber and two asphalt control sections were laid over several nights on the southbound carriageway between Centre Road and South Road.
The Victorian Government, Tyre Stewardship Australia and the Australian Road Research Board (ARRB) are conducting a $1 million study, which aims to incorporate more discarded tyres into the circular economy.
Australia generates the equivalent of 56 million car tyres every year, and it is estimated a third of these tyres end up in landfill or stockpiles. Only ten per cent of discarded tyres are currently domestically recycled.
Crumbed rubber in spray seals is already used to build roads in country Victoria and overseas, with the Department of Transport committed to reuse a million tyres in roadworks on regional roads every year until 2025.
This study aims to boost the opportunity to use crumbed rubber on metropolitan roads, by exposing it to high traffic volumes and testing the surface’s durability over time. A final report is due by mid-2022.
We’re determined to work closely with the construction industry to make recycled and reused materials the first choice where possible and pave a greener future for Victoria.
NEW VIRIBAR® 750 FITMENT IS SUSTAINABLE AND EASY TO SUBSTITUTE
InfraBuild Construction Solutions, Australia’s leading manufacturer and supplier of steel reinforcing, has recently announced the launch of Viribar®750, an innovative new range of high-strength steel fitments. The fitments are 33 per cent lighter than standard 500N fitments – and simple to substitute. Use of the fitments can unlock significant sustainability and other benefits for reinforced concrete construction projects.
The ease with which Viribar®750 high-strength steel fitments can be substituted for traditional 500N fitments has been proven at a new residential facility in Sydney. Structural engineering firm SCP Consulting specified InfraBuild’s new Viribar®750 fitments in its design for the new facility and found the product to be a straightforward replacement for the 500N standard fitments specified in original drawings.
Brad Wooster, Structural Engineer at SCP Consulting, said incorporating Viribar®750 into the design was a seamless process.
“InfraBuild was able to provide us with several documents showing the testing they’d done, the endorsement [that Viribar®750 had received] from Professor Stephen Foster of the University of New South Wales, and a step-by-step guide through each clause in the Australian Standards showing we had compliance in our designs,” he said.
The fitments conform to both AS/NZS 4671:2019 Steel for the reinforcement of concrete and AS 3600:2018 Concrete structures, as well as the Building Code of Australia (and hence the National Construction Code). Brad said the decision to swap Viribar®750 in place of the standard fitments was made easy by the simplicity of the substitution process.
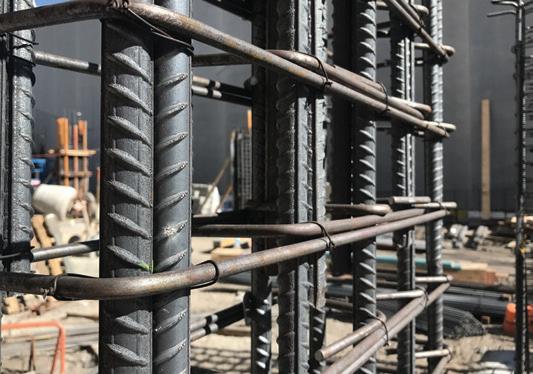
“We use finite element analysis software to determine design actions on the structure, and from there we are able to look at designing individual elements such as the columns,” he said. “The software provides an output for the size of fitments required and I was able to do a direct swap to the Viribar®750 fitments based on the diameter of the bar needed.
“We knew there would be considerable benefits in making the substitution,” Brad said. “Viribar®750 is a product that can slot straight in – and that’s a good thing.”
LESS RAW MATERIAL AND ENERGY TO PRODUCE
With 33 per cent less mass than its equivalent 500 MPa fitment, Viribar®750 uses less raw material and energy to produce. According to InfraBuild Construction Solutions Chief Engineer, Graeme McGregor, the use of less steel in the manufacture of Viribar® 750 means a reduction in carbon emissions of 25 to 35 per cent per tonne.
The reduced weight also brings other benefits in transport, craneage and handling.
“The product is more efficient to warehouse, freight and handle, and the customer and end users enjoy the benefits of a more sustainable product,” Graeme said. “It’s a win-win.”
Viribar®750 is recognised by both the Infrastructure Sustainability Council of Australia (ISCA) and the Green Building Council of Australia (GBCA) as offering sustainability benefits to projects that meet certain eligibility criteria.
A MORE SUSTAINABLE OPTION
Ultimately, it’s the sustainability benefits offered by Viribar®750 fitments that Brad said are its major attraction.
“As an engineer, I’m always looking to implement sustainable ideas where possible,” he said. “For example, when designing a structure, this means providing the most efficient structural system specific to that project, with the solution not only giving what is best for both client and architect, but also reducing the environmental impact of the structure through the reduction of material used.”
As for what the future holds, he said he hopes to continue to champion sustainability as a core concept on any project he is involved with.
“It’s an easy one for me; I’ll most definitely be specifying Viribar®750 when we next work with InfraBuild,” he said.
“It’s exciting to see innovation like this happening within our industry and I’m hopeful that InfraBuild will continue to introduce products like this in future.”
While Viribar®750 has been launched in the Sydney Metro area, InfraBuild Construction Solutions plans to commence manufacturing and distributing Viribar®750 in Melbourne and Brisbane in the near future.
Contact the nearest InfraBuild Construction Solutions branch for further details.

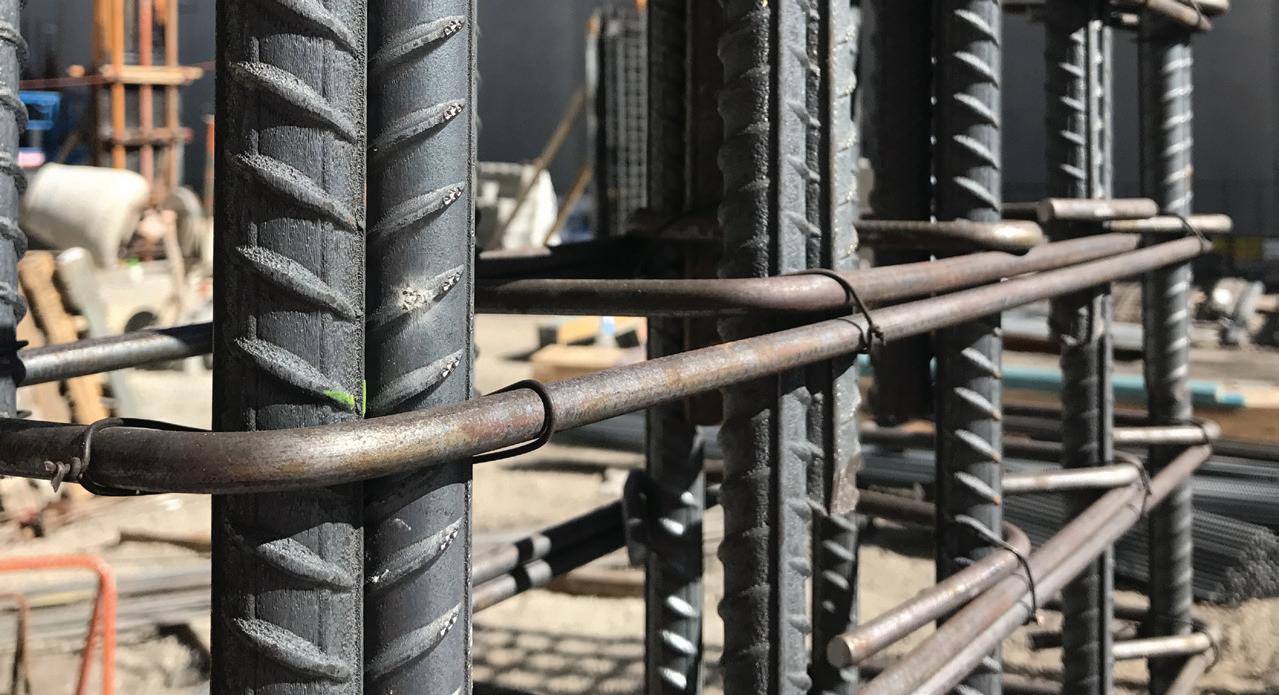
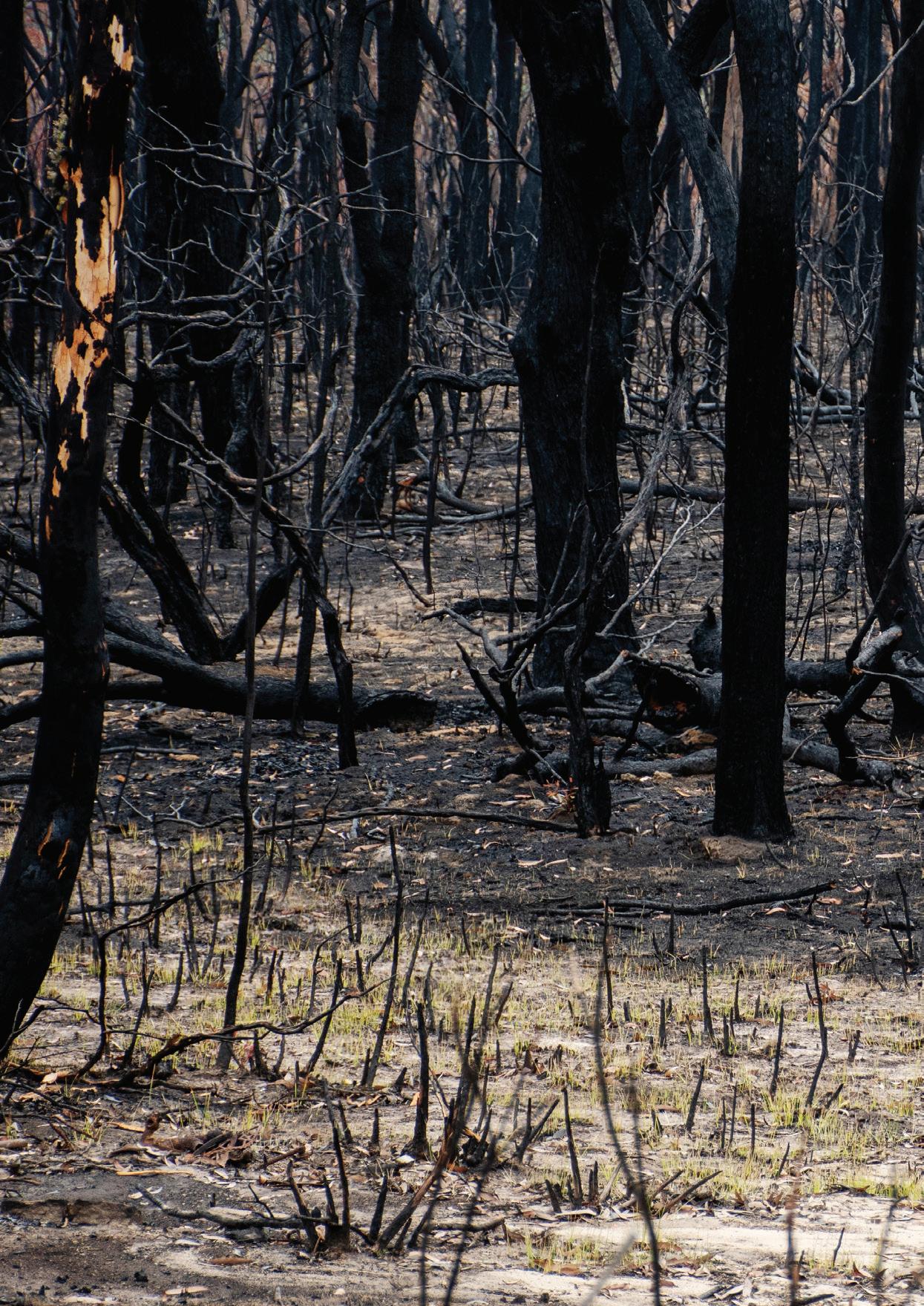
REBUILDING SUSTAINABLY AFTER THE BUSHFIRES
by Dr Sukhbir Sandhu,Senior
Lecturerin Sustainability and Ethics, University of South Australia, UniSA Business
With bushfires raging across 11 million hectares of Australia’s tinder dry landscape in January 2020, the Lucky Country moniker hung loosely. Here, Dr Sandhu explores some factors to consider as fire damaged communities look towards rebuilding.
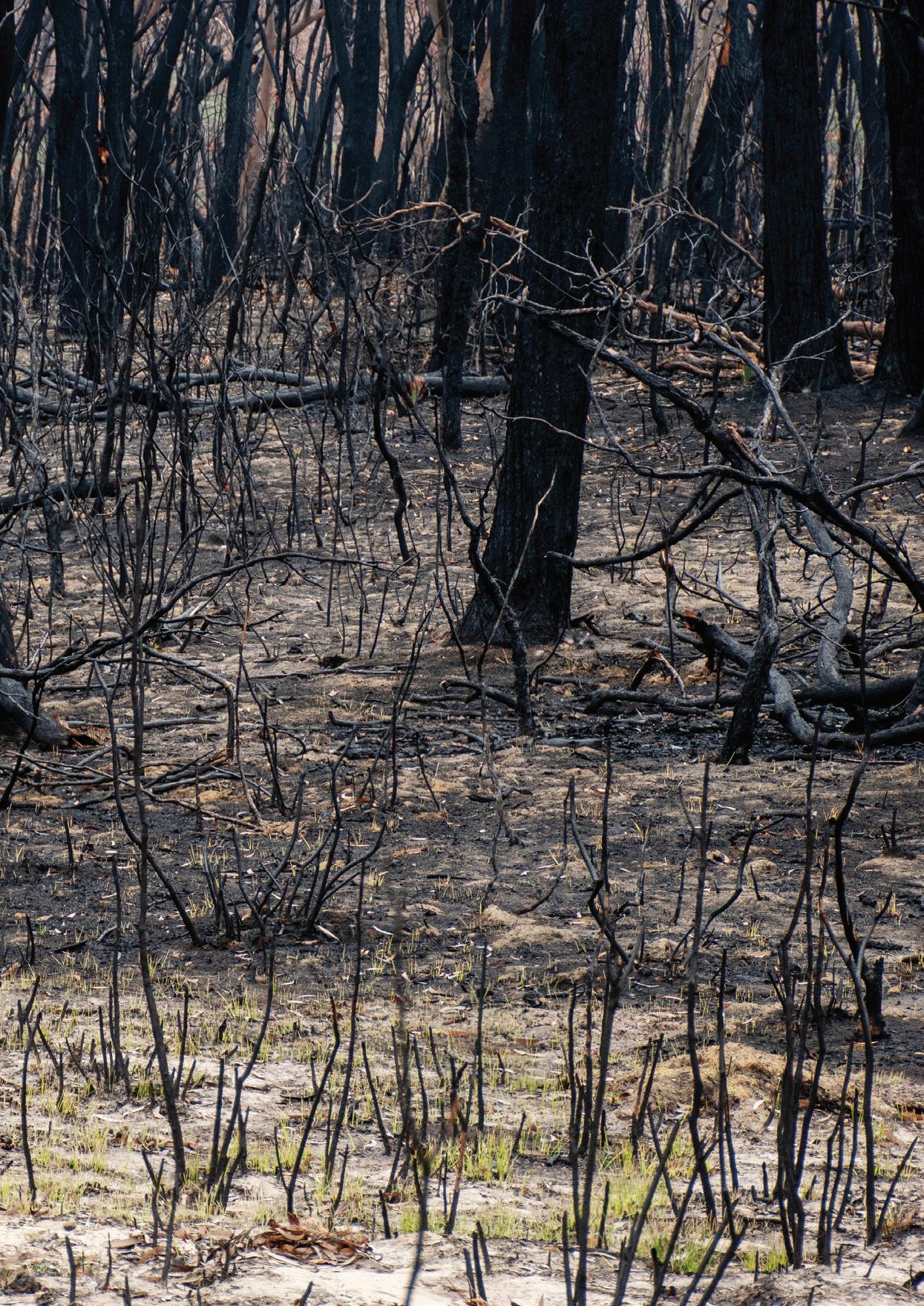
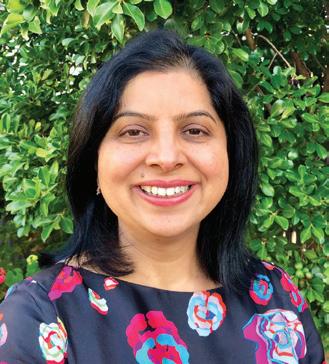
Nearly 2,500 homes were destroyed, and 26 people lost their lives in the recent bushfires. The economic damages have been calculated in the billions, and while the mental and emotional damages are harder to quantify, stories of heart wrenching loss continue to gradually unfold.
Forest fires have always been a part of Australia’s ecology (and indeed some native trees even need the bushfires to disperse their seeds), but climate change is creating a new reality. In 2019, Australia recorded its highest mean temperature (since recording began in early 1900) and it was the driest year on record.
Climate change means that bushfires in Australia have changed dramatically over the past decade. The frequency and the ferocity of our fires has changed – the fires are more brutal, and the fallout is extensive. As our world gets hotter and drier, the bushfire seasons are also changing. The fires are now starting much earlier and burning for longer, with the bushfires in the 2019/2020 summer starting way back in September and going well into February. This is reducing the time available for recovery and prevention.
The immense devastation, resulting from the fires, means policymakers are under pressure to identify strategies that will future-proof communities as they rebuild beyond the 2020 bushfires.
When the problem changes, our responses also need to change. Our old ways of dealing with the bushfires are becoming obsolete. Australia’s responses to the fires must change.
FIRE-LINES COULD HELP POLICYMAKERS
Australia should consider the establishment of a ‘fire-line’ – a bushfire demarcation line to identify high-risk areas not recommended for human habitation. In the same vein as Goyder’s Line of rainfall (created in South Australia in 1865 to map areas liable to drought and therefore unsuitable for planting crops), a fire-line would help people clearly recognise areas that are suitable, or not, for living.
As people rebuild their homes, and as governments invest in rebuilding schools, communities and the wider infrastructure, they need to be asking the question – is it actually safe to do so in these areas?
A fire-line will assist people and policymakers in dealing with this moral and economic dilemma. The bushfires have destroyed the livelihoods of far too
many people to be remedied by standard recovery and rebuilding strategies. And, with climate change, the blazes will keep burning; as bushfires continue to rage into residential areas, governments must consider something more ground-breaking in recovery.
It’s time for policymakers to take a strong stand where it is safe for communities to rebuild, and a fire demarcation line could help achieve this. Policymakers already have the basic tools to start such an initiative which, in conjunction with CFS aerial footage, satellite imagery and well-developed insurance company models (that not only identify areas susceptible to bushfires, but coastal flooding as a result of rising sea levels) would provide clear information for a new fire-line.
BUSHFIRE-RESILIENT CONSTRUCTION GUIDELINES
The fire-line strategy needs to be accompanied by compulsory bushfireresilient construction guidelines (especially in areas that are adjacent to fire-lines). We already have the technology to create homes with bushfire-resistant materials, and to enable houses with certain structural properties to serve as fire bunkers.
The Australian Standard for Building in Bushfire Prone Areas (AS3959) provides clear requirements for residential dwellings built in areas that pose a high risk of bushfires (ranging from ember attack to direct flame attack). Bushfire-resistant houses do not have to look bizarre or be unaffordable. Bushfire-resistant designs and materials can be incorporated into conventional houses.
Only about five per cent of the cost of the building goes towards meeting the BAL-40 requirements (one of the highest fire standards). But to date, there are no clear policies that support or promote these technologies for use in vulnerable areas.
If policymakers do not act, insurance companies will take the decision out of their hands. After the California fires, insurance companies lost nearly 24 billion dollars and have become unwilling to underwrite homes and infrastructure in fire prone areas.
Protecting our homes and infrastructure through fire-lines and fireproofing, however, do not replace the need to urgently focus on climate change. To ensure that our Lucky Country remains so, we need long-term, sustainable strategies to address the undeniable effects of climate change. Let us not let this crisis go to waste.
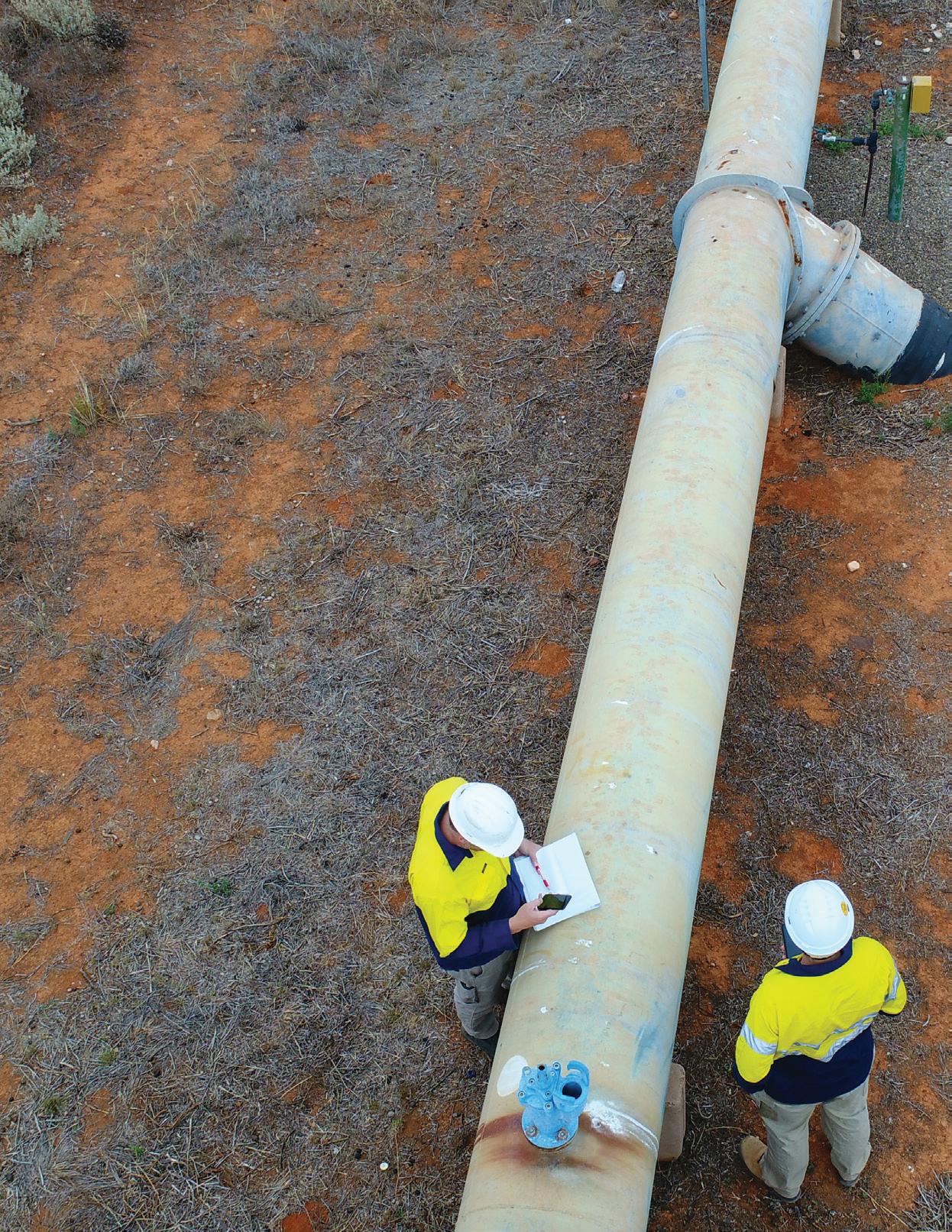
TO NEW WAYS OF LIFE ADAPTING ASSET MANAGEMENT
by Kim Ho, Journalist, Infrastructure magazineAs governments continue to work to get the COVID-19 crisis under control, critical assets must still be managed, monitored and maintained. Tammy Falconer, Director at KPMG Australia, argues that while the pandemic has confronted asset managers with once-in-a-career challenges, it also presents a unique opportunity for them to lead their teams, their sectors and the Australian community through this period of uncertainty.
The COVID-19 pandemic has transformed the world – impacting the ways we live, work, commute and communicate, and presenting major health risks and economic challenges. As much of Australia’s workforce took to working remotely, usage patterns for water, wastewater, electricity, internet and transport shifted in dramatic ways.
Speaking at the Asset Management for Critical Infrastructure Virtual Conference in May, Ms Falconer broke down some key findings from KPMG’s research and outlined the ways in which asset managers can continue working efficiently, manage maintenance backlog and –most importantly – turn disaster into opportunity.
A MARATHON, NOT A SPRINT
Spending the first part of her career in Darwin, Ms Falconer is no stranger to disaster management. Every year, she had to prepare for cyclone season, reviewing plans, testing disaster recovery systems, and ensuring a fast, coordinated response when the worst hit.
But a pandemic is different – not restricted to days or weeks, it requires a long-term approach to disaster mitigation. Asset managers must go through an elongated process: first reacting to the crisis, planning for ongoing operations, before hopefully returning to business as usual.
KPMG’s research into the challenges of COVID-19 in America revealed that US water, gas and electricity utilities typically planned in weeks for severe weather events, so they failed to anticipate the first-of-a-kind response of prolonged social distancing.
The research also yielded the following findings:
♦ Working remotely was a delicate balance for utilities, and while 50 per cent of corporate functions could be performed remotely, only 10-25 per cent of transmission and distribution functions were being performed remotely
♦ Utilities had not considered extreme conflated risks of two or more events occurring at the same time in their risk management plans
♦ Employee wellness was a near-term focus that may result in long-term changes including an increased emphasis on hygiene and personal care procedures
♦ The scale of the pandemic exceeded typical utility business continuity plans. The magnitude of potential lack of employee resources combined with technology restrictions to enable off-site working was not factored into plans.
♦ The expected shift in demand and workforce may result in regulatory changes with reduced revenue forecasts impacting financial plans for future regulatory decisions
FOCUSING ON FOUR HORIZONS
Even with the desire to update an organisation’s approach to disaster management, it can be difficult to determine where to focus energy and resources – especially with such an enormous, ever-changing situation and no clear end in sight.
To assist asset management professionals through this disruption, Ms Falconer proposed turning attention to four horizons:
1. Reaction: focusing on crisis management, essential supply and public safety
2. Resilience: working to secure the supply chain and focusing on essential maintenance and projects
3. Recovery: implementing sustainable set work practices with re-prioritised programs of work
4. New reality: planning for the transition into a new normal, and adapting to new expectations from staff, customers and stakeholders
USING CRITICAL INFRASTRUCTURE TO DRIVE ECONOMIC RECOVERY
Governments across Australia are recognising the key role that maintenance and capital investment can have in stimulating the economy, and fast-tracking smaller, ‘shovel-ready’ projects has become a key approach to the economic recovery. In this way, asset managers can play a critical part in getting Australia back on track.
“We all have a role to play in this crisis; but as asset managers of critical infrastructure, you can play an even bigger part, helping to address the economic impact of this crisis,” Ms Falconer said.
“You can make a difference to your community, your supply chain, and ensure your organisation is in the best position at the end of this crisis to continue to provide the valuable services to your customers.”
MAINTENANCE AND RISK
Asset managers should first focus on determining if the risk profile of asset maintenance has changed due to the pandemic.
Ms Falconer said organisations should ask themselves the following questions:
♦ How have our customers’ asset utilisation patterns changed?
♦ Has the risk profile of our maintenance task changed due to social distancing requirements?
♦ How can we keep our staff, contractors and the community safe?
♦ Has our supply chain risk changed?
♦ Do we have access to the services, tools and materials that we need to perform maintenance?
ADDRESSING YOUR MAINTENANCE BACKLOG
KPMG has heard from clients that a significant volume of noncritical maintenance was deferred due to pandemic restrictions.
“But how long can that last?” Ms Falconer asked. “Critical infrastructure needs to continue to reliably provide services to the community – we can’t indefinitely defer maintenance.”
Organisations must assess what risk this backlog might pose for assets and services, but also what opportunities it might provide to work differently.
Service-level risks may have financial and environmental impacts, but risks could be as significant as increased bushfire danger for electricity providers.
“Coupled with positive economic impact achieved through continuing work, there’s a compelling argument to continue establishing interim maintenance practices quickly.”
When addressing maintenance backlog, Ms Falconer suggested starting by analysing the impact of asset failures on service standards; establishing asset condition limits based on the organisation's tolerance for risk; identifying potential failure events; and using this information to prioritise the backlog.
Asset managers should review and adjust maintenance job plans to ensure social distancing measures are in place.
Technological advances may help accomplish more work with less physical contact. Ms Falconer prompted organisations to consider how drones, augmented reality, autonomous vehicles or robots could help maintain social distancing requirements.
Conducting maintenance also provides the opportunity to build trust with customers by optimising scheduling to take into account changes in asset utilisation patterns, communicating outages proactively, and noting the actions being taken to minimise impacts on them.
“Yes, this is a more complex environment we’re operating in, but could it be an opportunity for your organisation to really understand your assets and adopt new ways of working to benefit now, but also make your organisation more resilient in the future?” Ms Falconer said.
MANAGING SUPPLY CHAINS
This complex situation has placed financial pressures on supply chains, especially when relying on overseas suppliers for parts.
Ms Falconer urged asset managers to be responsive to the pressures, and use this time to cultivate a deeper understanding of their strategic operations and supply chain. This will help develop more collaborative and resilient relationships with critical suppliers – or identify where sourcing alternative suppliers is required.
One example solution was to follow the Victorian Government’s lead in fast-tracking supplier invoice payments, helping suppliers remain viable.
Clients may also be concerned with commercial and legal implications of COVID-19, fearing suppliers and contractors making claims against them due to delays.
“Developing a consistent strategy to manage these issues ahead of time will enable you to work proactively, rather than enter into multiple disputes with suppliers which will inevitably impact project delivery,” Ms Falconer said.
Staying on the front foot with stakeholder management and communication is also vital to keep government, suppliers, teams, customers and the public informed and reassured. Organisations’ remobilisation efforts should involve developing a transition plan, working closely with their supply chain to address any constraints, and ensuring they have any specialist skill sets that were previously sourced overseas.
Ms Falconer said an ‘all in this together’ approach for capital projects was vital to retain collaborative relationships with all stakeholders.
MAINTAINING A PRODUCTIVE WORKFORCE
Amidst this disruption, Ms Falconer said maintaining motivation and productivity was vital to efficient service delivery. Team leaders must calibrate employees’ expectations as the situation evolves; maintain enough visibility to evaluate performance; implement strategies to channel motivation; leverage the right technology to support remote work arrangements; check in on individuals’ mental well-being; and ensure their capability is aligned with capacity.
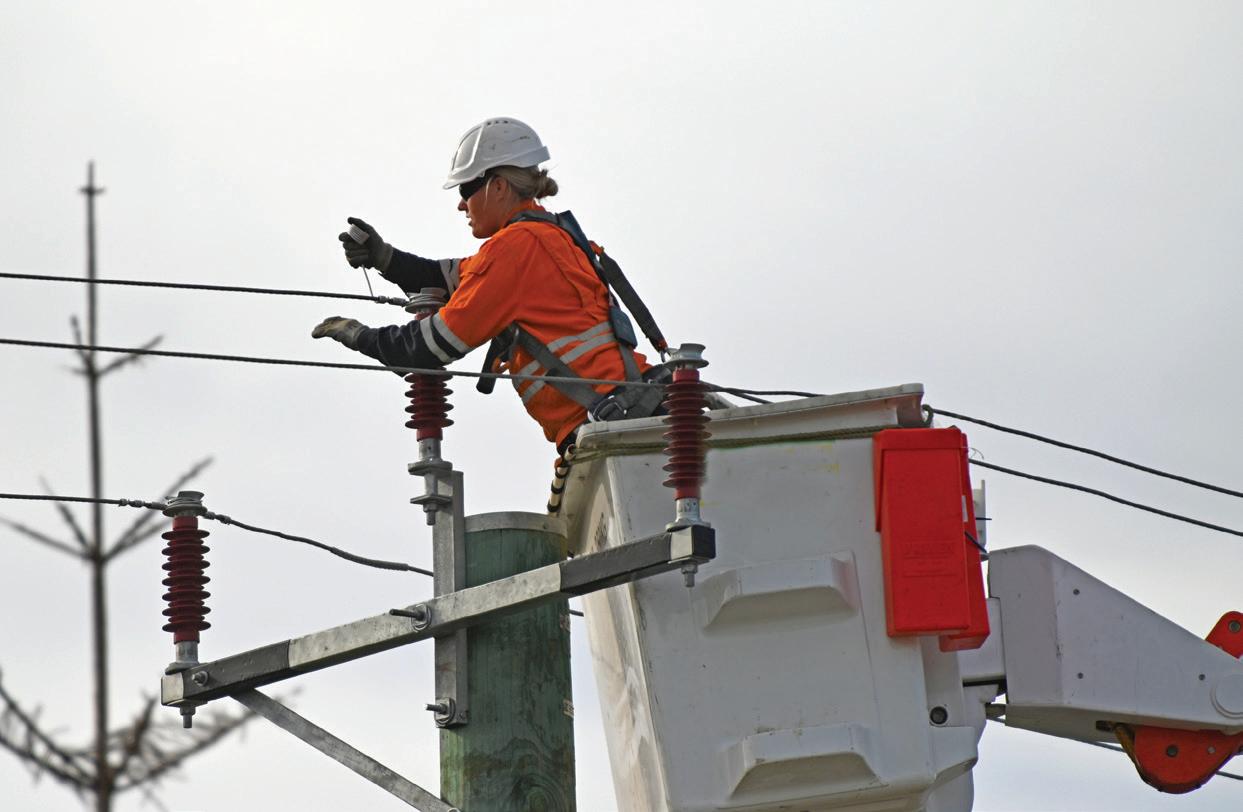
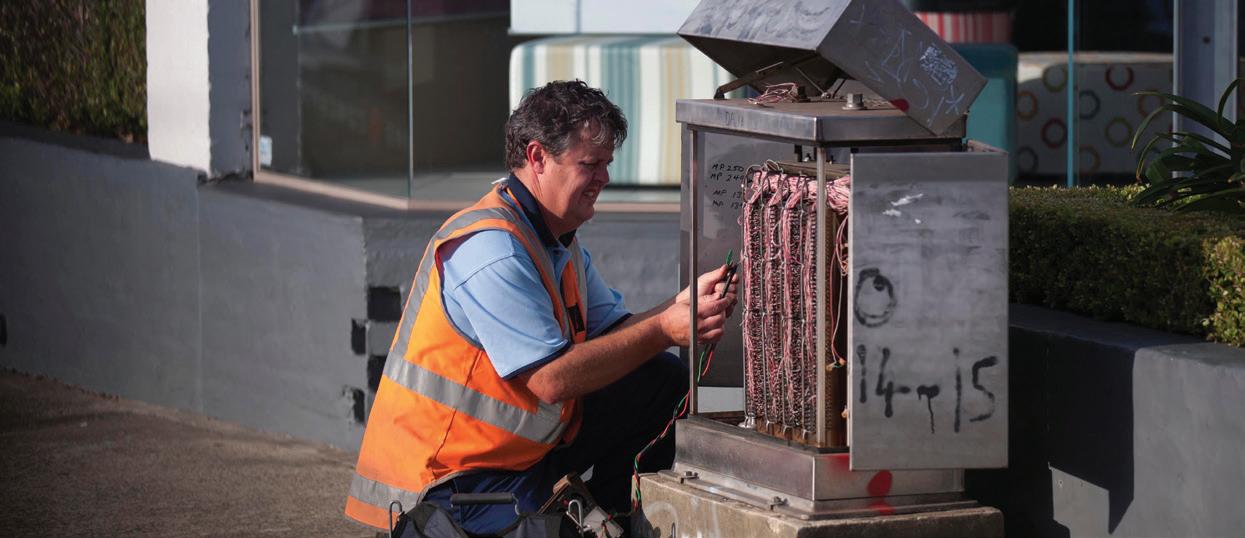
Ms Falconer knows the stakes of this crisis. If critical infrastructure organisations fail to take a risk-based approach to asset maintenance, delay delivery of key projects and neglect the front end of their value chains, this once-in-acareer challenge will only grow in scale.
“As asset management professionals, we know that effective asset management is a long-term game. If we don’t focus on the upstream parts of our asset value chain, we'll see productivity issues extend well past the end of this pandemic.
“Projects will not be planned, procurement will be delayed, and the risk associated with maintenance backlog will divert resources to unplanned work and away from planned work.”

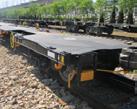
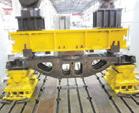

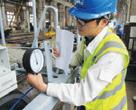
Despite the daunting path ahead, Ms Falconer is convinced that because maintenance and capital investment is so central to Australia’s economic recovery, the onus is on asset management professionals to lead Australia through the crisis.
“The critical infrastructure sector has the unique opportunity to stand up and provide leadership – the leadership your teams need to keep your teams safe, well and productive; the leadership your organisation needs to remain sustainable; but also the leadership that your country needs to minimise the economic impact of the pandemic on fellow Australians,” she said.
“This isn’t going to be easy, but it could be one of the biggest contributions that you will make in your career.”
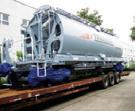
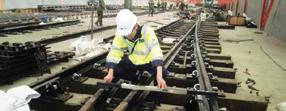
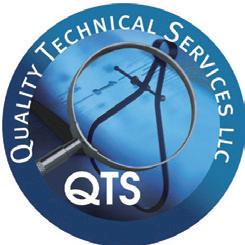
• Pre-award audits of manufacturers, subcontractors and suppliers
• Experienced, certified and qualified inspectors
• Verification of manufacturing and testing in accordance with AS standards
• Surveillance inspections throughout the entire manufacturing process
• Individual inspection and test of completed equipment
• Pre-delivery and ship loading inspections
• ISO 9001-2015 QMS certified company
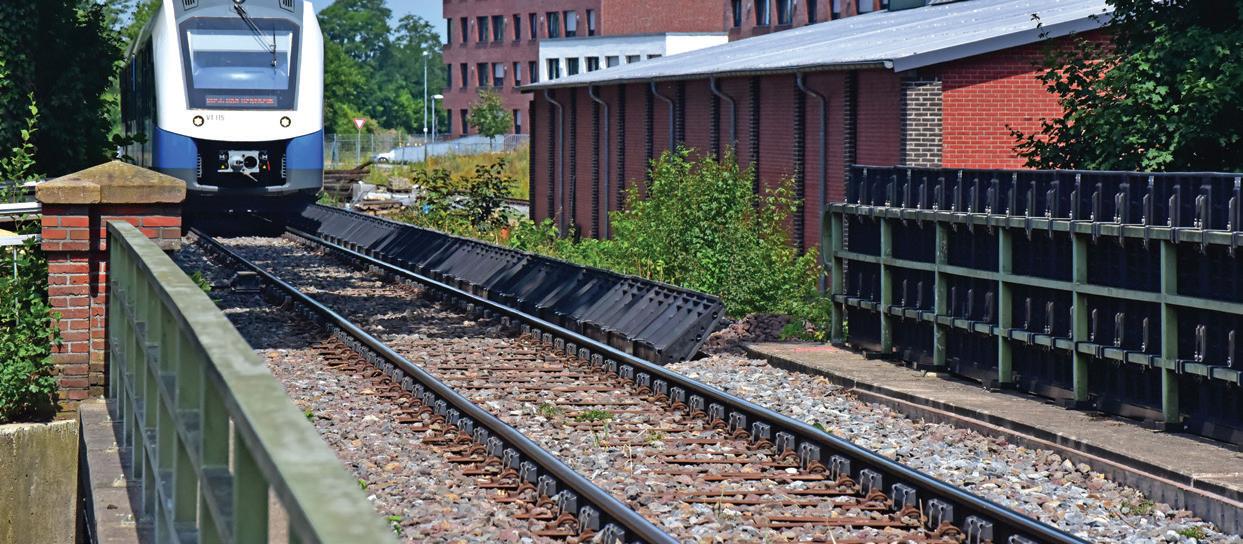
SOUND PROTECTION MEASURES AGAINST RAILWAY NOISE
by Andreas Göschl, Tittmoning, STRAILasticIn Germany, the tolerance threshold for railway noise and interference, e.g. in the landscape and the railway embankment biotope, is comparatively low. To counter high noise levels, metres-high, opaque sound barriers that flank the railway lines are often erected. These create a large visual blight on the landscape and restrict views from the trains. However, new sound protection systems from STRAILastic provide an alternative solution which, when used in combination, can reduce noise levels significantly without impacting the landscape and obstructing views.
FIGHT RAILWAY NOISE AT ITS SOURCE
Noise is most effectively reduced along the propagation path at the source. This is why modern sound protection systems are designed to get as close to the rail/wheel interface and clearance area as possible.
The sound protection products by STRAILastic comply with all prescribed minimum kinematic envelope dimensions and distances to maximise noise reduction whilst ensuring no operational impediments occur.
A special combination of high-quality UV and ozoneresistant rubber, with stable fibre reinforcement to counter the pressure and suction forces from rail traffic, allows these products to be installed at the shortest possible distance from the point of noise generation – the contact surface of wheel and rail.
THE REGIONAL RAILWAY LINE IN NORDHORN
On a section of the Bentheim railway line in Nordhorn in western Lower Saxony, Germany, a project undertaken in mid-2019 demonstrates how sound propagation from a railway embankment can be effectively limited by reducing noise without obstructing the view.
A sound protection solution was needed for a section of railway, adjacent to a still-to-be-developed construction area where a building permit had been granted. Due to a dense stock of trees, there was no direct line of sight between the railway and the construction site, but this would not provide sufficient noise protection in autumn when their noise insulating effect would be reduced by a loss of foliage.
Furthermore, the construction area was in the immediate vicinity of a bridge over the Nordhorn-Almelo canal, which needed to be taken into consideration when planning suitable noise measures.
According to a specially prepared noise report, there were two options for reducing noise: constructing a 6m-high sound barrier or installing the sound protection measures from STRAILastic.
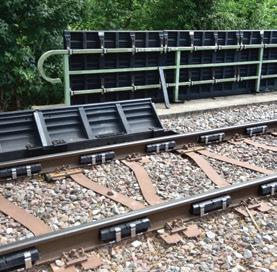
The solution was to combine three sound protection products from STRAILastic in the vicinity of the bridge and its access ramps on both sides of the track over a length of around 240m:
♦ STRAILastic_A inox 2.0 is the latest version of the STRAILastic_A rail web dampers, internationally proven for years
♦ STRAILastic_lP vertical panels create peace and quiet by using the existing structures. The infill panels can be mounted directly onto standard bridge railings and the reverse side of the panels can even be customised to perfectly blend into their surroundings
♦ STRAILastic_mSW is a mini sound protection wall 390mm high attached to the sleeper ends which gets closer to the source of noise than any other existing sound barrier
The combined solution met all of the client’s noise control requirements, while also perfectly blending into the landscape, with alumiuim patterned panels attached on the obverse side.
Importantly, a key decisive selection criterion for STRAILastic products was that in all cases no planning approval procedure is required for their use on the track. All products have been approved by the Federal Railway Authority (EBA) and they can be individually adapted during the planning phase, and within certain limits also during installation, as required.
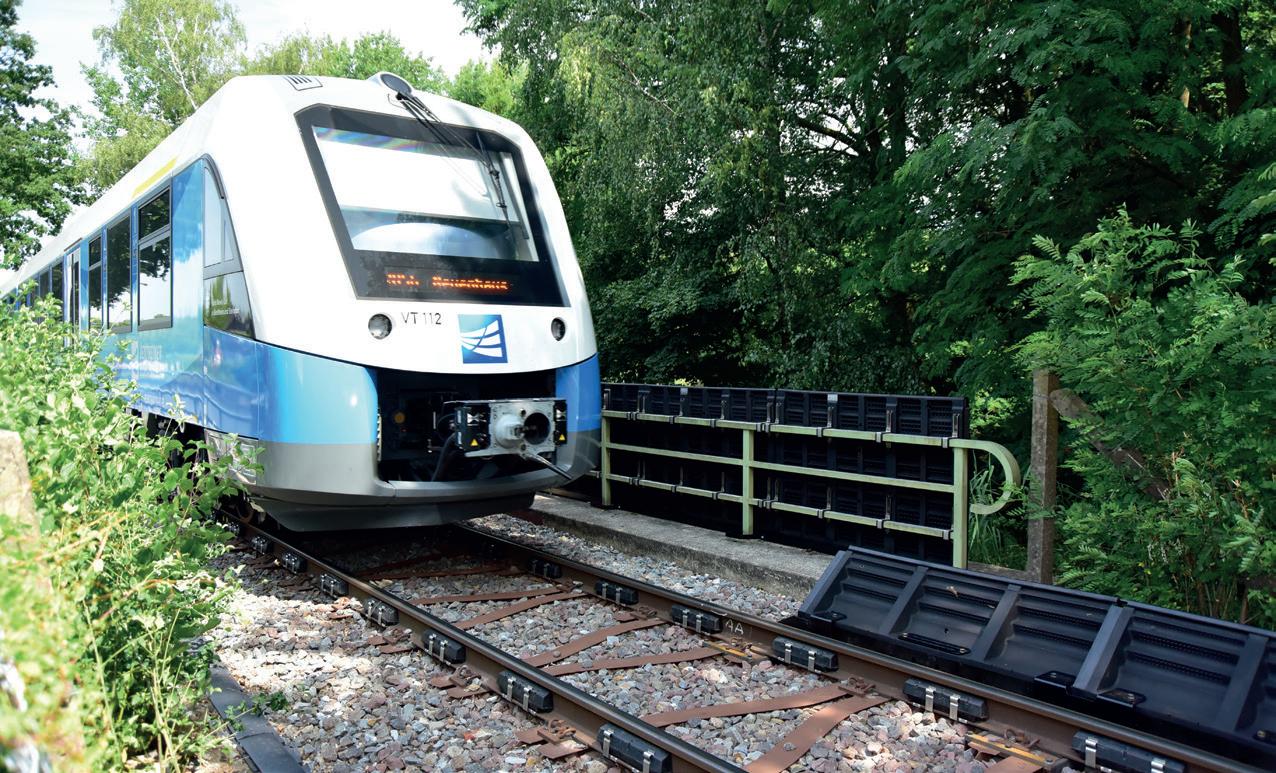
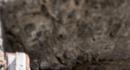
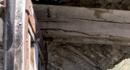

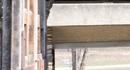
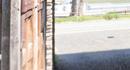

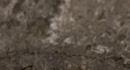
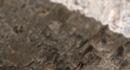
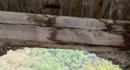
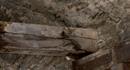

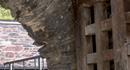
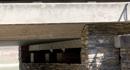
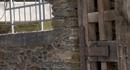
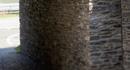
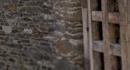
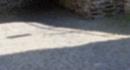
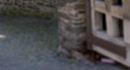
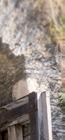
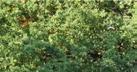

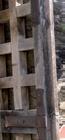
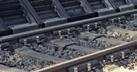
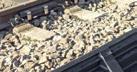
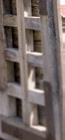
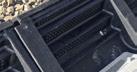
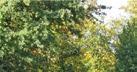
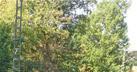
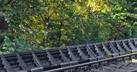


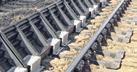
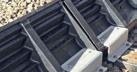

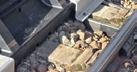



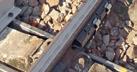
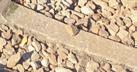
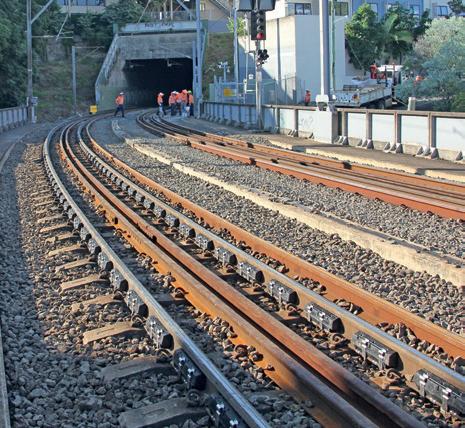
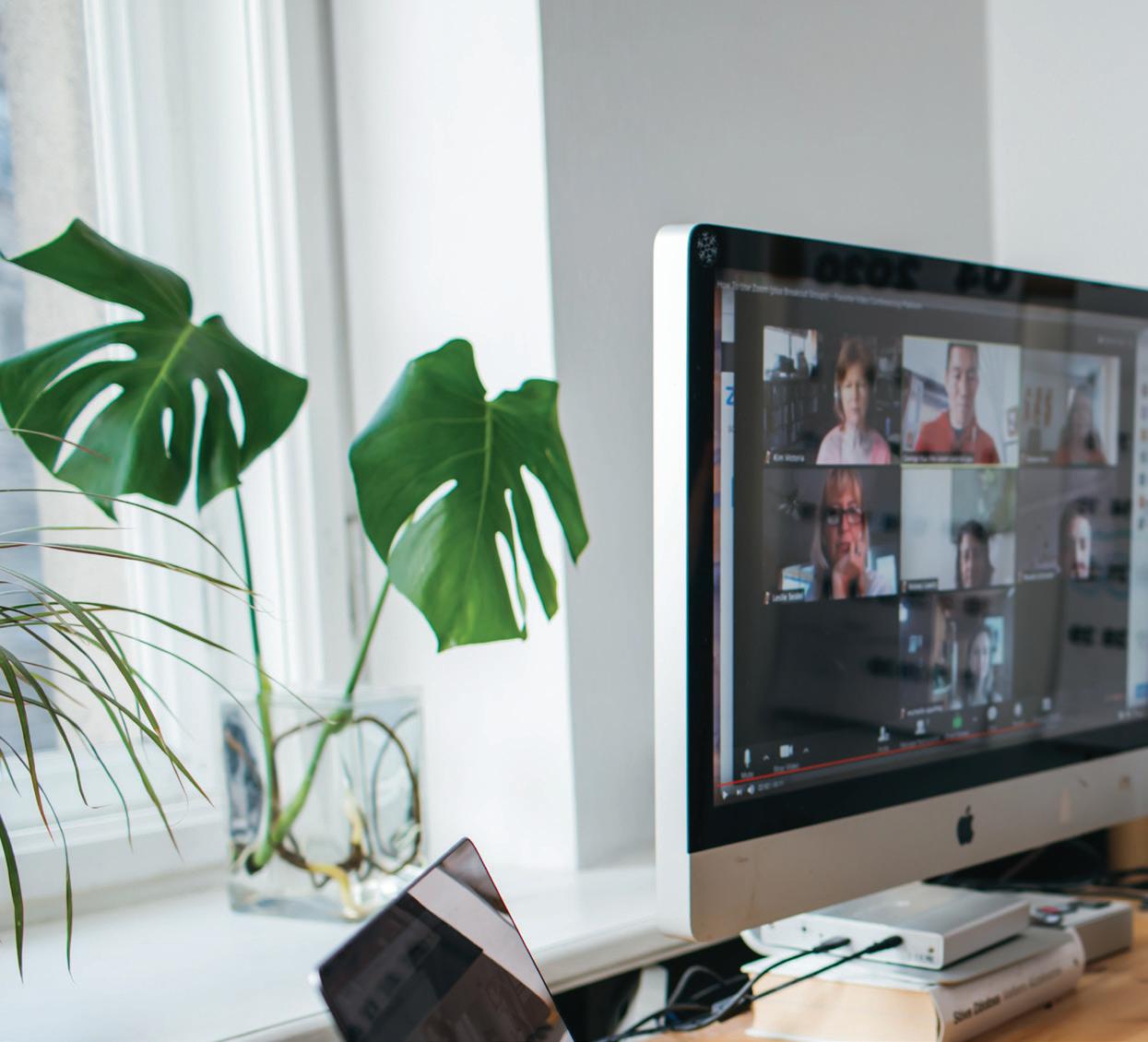
LEADING AN ASSET MANAGEMENT TEAM REMOTELY
‘Inever expected to be working remotely.’ Millions of people would share this sentiment in post-COVID 2020, but for me, that unexpected transition occurred more than a decade ago.
In late 2007, I left a secure job I’d held for 20 years and launched what felt like a small and rickety raft on the high seas of the gig economy. Yet after several weeks of searching for land, the adventure began. Project number one was an asset management contract with one of Australia’s largest maintenance service providers. Soon I was flying to sites all over the country and my client was talking about the need to prepare for a significant expansion, which would involve the incorporation of my company and the hiring of up to 20 employees.
The company was born…then the GFC hit. I got a call from the client who said I needed to put those employee plans on hold and that a freeze had been put on all discretionary spending. Suddenly, I was working from a dining room table.
But here’s the thing, I found that operating remotely works. And it works well. I wasn’t jet-setting any longer, but I was still connecting with my clients via email and phone, and meeting their expectations. We were still able to kick the same goals together.
So while you may not have planned to be at home, it’s totally do-able, and, in many cases, it allows you to work and lead more effectively than when you were at the office.
For our company in the years leading up to the COVID-19 crisis, internal contact between employees, and externally
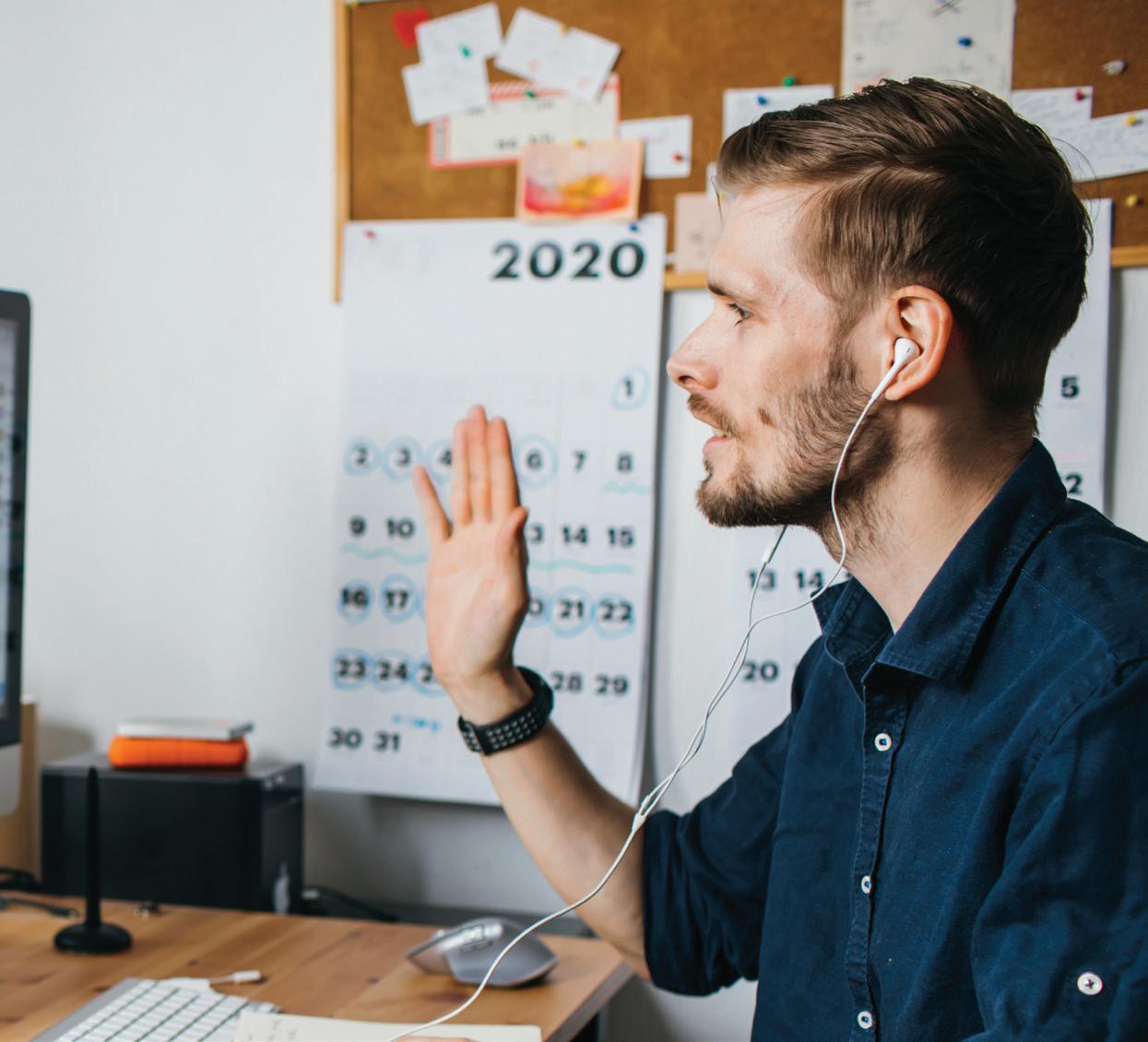
With many companies and asset management teams now having to work from home, here are three areas of focus that can help teams transition to new ways of working and create more opportunities.
with clients, has averaged around 70 per cent remote time over the total project time. I believe this is a key reason for the effectiveness and efficiency of our company’s services.
Let’s flesh this out a bit. Looking back on the years since I (accidentally) became a remote worker and then leader, I’ve learnt that there are three main focus areas which breed success. These are mindset, motivation and productivity.
MINDSET
It’s easy to arrive at the challenge of working remotely with a negative attitude. After all, it’s often unfortunate, uncontrollable circumstances that have brought us to that place. However, we need to shift gears and look at the opportunity it brings. There’s potentially greater productivity
and satisfaction to be found from working this way – for both you and your team.
Why is that the case? Firstly, it’s an opportunity for ‘deep work’, a term coined by best-selling author Cal Newport, who defined it as ‘the ability to focus without distraction on a cognitively demanding task’. Lack of distraction is the key here. Obviously, if we’re at home, there can be issues with family and establishing a physical workspace, but if those are managed, they can incur less of a drain on productivity than the often unnoticed and considerable time wastage that occurs in an office environment.
At the office it’s the norm to be bombarded with requests for small outputs or opinions on the half-developed thoughts of the colleagues around us. Three hours of deep remote work
can be more productive than eight hours at the office in my experience of both.
Another significant gain, perhaps the biggest one, is the shift to an outcome focus that tends to come almost automatically when we are working and interacting remotely. We’re not in an office where we need to look busy and occupy particular spaces within set times. Without these visible decoys, what really stands out is the outcomes you and your remote team makes. That is, the results of your activity and not the activity itself.
Here’s a simple results or ‘outcomes’ based production model. We have resources or inputs, which we arrange and deploy to maximise benefits and minimise (negative) impacts. Interestingly, this thinking aligns us with the systems approach that’s outlined in the international asset
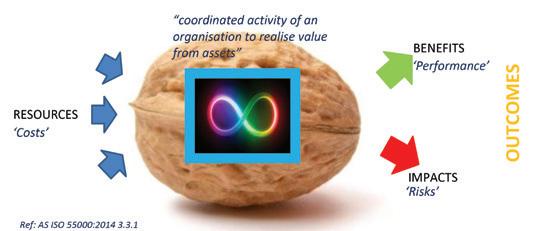
management standard ISO 55000. It’s about balancing ‘costs’ (inputs), risks (impacts) and performance (benefits) to achieve best ‘value for stakeholders’ (outcomes). Further, the standard’s definition for ‘asset management’ is ‘the coordinated activity of an organisation to realise value from assets’ (the way we arrange and do things).
For those familiar with ISO 55000, have a think about the asset management fundamentals outlined in the standard –value, alignment, leadership, assurance. They’re essentially all about outcomes.
In other words, working remotely will naturally push us towards the coordinated, outcomes-based approach that lies at the heart of good systems management. That’s an incredibly important and powerful mind shift.
MOTIVATION
Unlocking motivation is the second key to success as a remote leader and team. (Note: you’re not a ‘virtual’ team, you are a team, even if you’re physically separated).
Your team members will be inspired if they are selfmotivated, and self-motivation is stimulated by giving your team a sense of purpose, freedom and progress.
Purpose is about helping your people to understand the big picture and the significant part they have to play in making it happen. Freedom is about giving your team the space, within a framework, to work out solutions without being micromanaged. And progress is about creating an environment where team members feel that they are improving themselves or a situation; there’s a sense of advancement and growth, both individually and corporately.
"Your team members will be inspired if they are self-motivated, and self-motivation is stimulated by giving your team a sense of purpose, freedom and progress."
Beyond self-motivation, trust is critical if you want to build sustained enthusiasm and energy within the team. I’ve learnt a lot about trust in the consulting sphere, where you won’t be called back, or called in the first place, unless you have established confidence and a name for reliability.
There are three forms of trust.
There’s what might be called ‘the balance of interest’. You trust that your team will deliver for you and they trust that you’ll recognise that they have done so. Money, and value for money, are the obvious and tangible interests, but there are many other ways in which the balance of interest works.
Then there’s integrity and transparency, timeless values that mean precisely what they say – you’ll do what you promise, and you’re the same person when no one’s watching.
The third aspect of trust is that your colleagues will be sure that you’ll be working to lighten their emotional load, not add to it. You’re pulling together, not creating further drag.
PRODUCTIVITY
Anxieties around productivity are where a lot of would-be leaders fall down. We become fixated on results; we're not running a charity, there's a bottom line to meet. When there’s a glitch or dip, that’s often when tension spikes and the whip comes out. But we have a choice about whether to be a villain or hero.
The good news is that studies show the odds are in our favour. If your team is working remotely, you’re already pushing towards greater productivity. A Gallup analysis of January 2020 concluded that ‘the data is clear: remote work not only improves outcomes and employee branding but is a policy that the most talented employees desire.’ The authors noted decades of research showing that ‘performance soars’ when employees feel engaged and they found in 2020 that engagement was optimal when between 60 and 80 per cent of work was conducted remotely.
It’s striking that this study was released before the Coronavirus lockdowns, and at a time when several US government agencies were winding back their remote work programs. That’s at least one silver lining in the midst of this global disaster; many of us have been forced to do something that actually works better than what we were doing before. It reiterates what I’ve said about mindset and opportunity. Now, as we emerge from the worst of the restrictions, we can be looking to hit the 60-80 per cent sweet spot. That’s a huge opportunity.
BUSY V. PRODUCTIVE: UNDERSTANDING THE DIFFERENCE
Ok, but what about driving further productivity once you’ve plugged into the gains afforded by remote working? Well, I’ve found that an understanding of the distinction between ‘busy’ and ‘productive’ is critical. Picture a hamster on a wheel. Lots of visible, energetic activity, but no progress or real output. Now picture a rock climber. At times, movement and headway are impressive, at other times, it seems slow. There are also moments when the climber is completely stationary for 15 minutes while trying to solve a problem. Yet there’s genuine progress and, eventually, the summit is reached.
When you’re in an office, you can’t walk past someone’s computer screen and make an accurate judgement about how productive they are. It’s no loss that you can’t ‘monitor’ your team when they are at home, because it’s not minute-byminute scrutiny that brings productivity. Instead, encourage a positive mindset, do the things that stimulate motivation and work together at being productive rather than busy.
An example of the difference between the two, applied to an asset management context, might be the compilation of a procedure of many pages that regurgitates what’s already well known, versus a simple one-sheet decision tree which enables staff to make decisions on the spot without consulting a manager.
Even downtime can be enormously productive. It can give us the chance to stand back and reflect on the past, look at the present as part of its wider system, or brainstorm future opportunities. That’s not possible if we’re on the hamster wheel, obsessed with visible and frantic micro-activity.
PRACTICAL TIPS
Find ways of actioning the principles outlined above. Get inventive and discover what works in your unique situation. Experiment with tools that help you and your team connect and collaborate. In our company, we use online tools like Google sheets, Workflowy, Mindmup and Trello.
If you’re an asset manager, the asset management fundamentals – value, alignment, leadership and assurance –can be a great template or checklist for practical action. Refer back to them frequently as you chart your way forward.
Value:
♦ Know what it is to the stakeholders and make it clear
Alignment:
♦ Regularly check that every planned activity and effort points to higher level goals
Leadership:
♦ Lead by example, consistently
♦ Define expectations in the form of targets (regarding quality and timeframes)
♦ Be human and know that your team is too. Individualise where appropriate and support good mental health
Assurance:
♦ Openly track outputs and outcomes against agreed targets and goals
IT’S NOT COMPLEX
Every organisation and sector is different, and each of them have their own special challenges when it comes to remote work, but, in the last analysis, you can’t really fail if you apply the basics to the problem. If you lead your team with the right mindset, unlock motivation, build trust, understand the difference between busy and productive, and use appropriate practical tools, you’ll become an effective remote team leader.
The old adage, ‘necessity is the mother of invention’, is most apt in times of crisis. Just as the Second World War fuelled a multitude of innovations that are still with us, so too can the COVID-19 pandemic generate positive change to go with the negatives. A great leap forward in our ability to work remotely should be one of those. The scene is set like never before and it’s time for the hero to emerge.
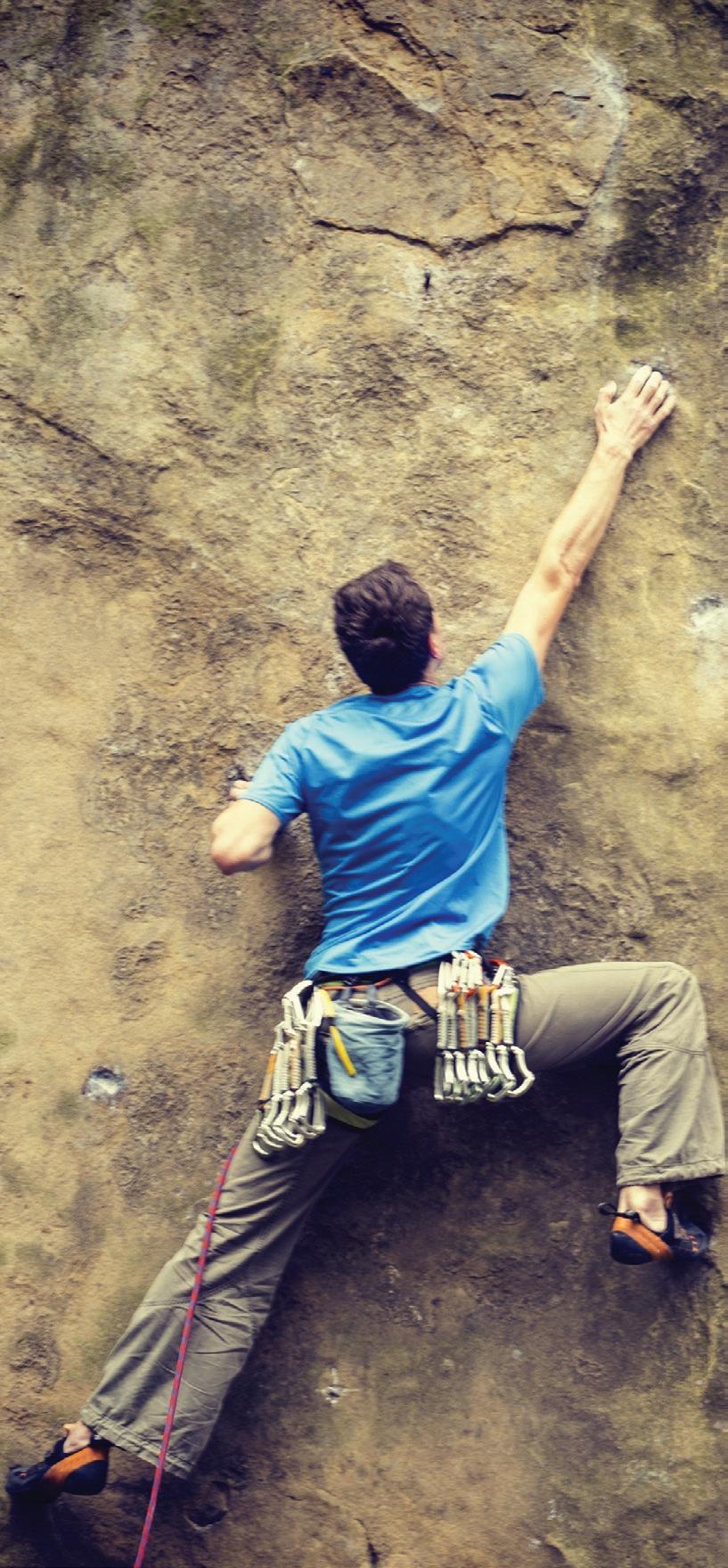
WHY IMPLEMENT RADIO FREQUENCY IDENTIFICATION ON RAILROADS?
Radio frequency identification (RFID) provides significant benefits for the preventive maintenance and monitoring of railways all over the globe, including asset tracking and reduced costs.
Hundreds of derailments occur on European railroads every year and according to the D-RAIL project, an average derailment has an impact of more than €800,000. Some of the major reasons for these accidents occurring include wheel, axle and suspension failures due to wear and tear, as well as incorrect loading.
To fix this several hundred million-euro problem, vehicle owners are investing significantly in preventive maintenance and monitoring systems. This requires a complex infrastructure of wayside train monitoring systems (WTMS) such as hot axle box detectors (HABD), axle load checkpoints (ALC) and other devices (ultrasonic sensors, high resolution cameras, etc.) along the rail tracks. These systems have already been in place for years.
The question now is, why add RFID into that process by tagging each train wagon with on-metal UHF RFID tags and mounting RFID long-range readers at the WTMS?
Well, the additional information of the unique RFID tag will enable a link between the critical measured values (detected failure) and the specific vehicle, wheel set, axle, brake and suspension.
Using RFID allows you to know in advance the specific part that requires rework. RFID also provides the following customer benefits:
♦ Reducing maintenance costs
♦ Reducing high-cost emergency maintenance
♦ Better planning due to real-time information about the vehicle’s condition
♦ Higher availability of rail vehicles and better reliability during operation

ASSET TRACKING – KNOW WHERE YOUR TRAIN IS
In addition to improving preventive maintenance, the second reason to implement RFID on railroads is the classical UHF use case: real-time asset tracking. This gives all involved parties (vehicle owner, railway undertaking, infrastructure manager, entity in charge of maintenance) the answers to the questions: what? where? when? and why?
For example, companies in cargo transport can finally have an answer when their customer asks, “Where are my goods/ cargo?”. There are also the additional benefits of better planning for vehicle availability and a reduction in unused capacities.
WHY USE SICK RFU630?
During work on a project with a leading European transport agency, the team at SICK learnt that the following features were significant to the success of the project:
Industrial design
1. Ruggedised housing EN 50125 (shock vibration)
2. Solid electronics compliant with rail norm EN 50121 (EMC)
3. Wide operating temperature range -30°C to +60°C (RFA630)
4. Outdoor IP67 protection class
Fast data processing
♦ Read tags > 200km/h
♦ Accurate time stamps
The SICK solution provided for the project is the SICK RFU630 – a UHF RFID read/write device combined with sensors that count the axles. This is necessary, not only to assign the tag to the vehicle/wheelset, but also to provide speed, direction of travel, orientation of vehicle, and order of vehicles within the train.
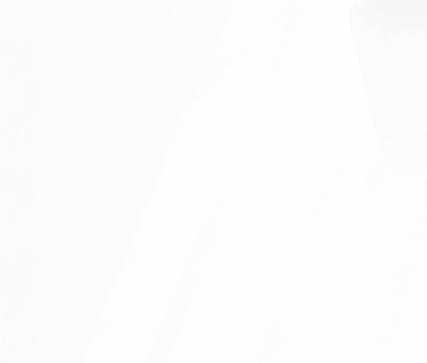
THE BAGGAGE CONNECTION.
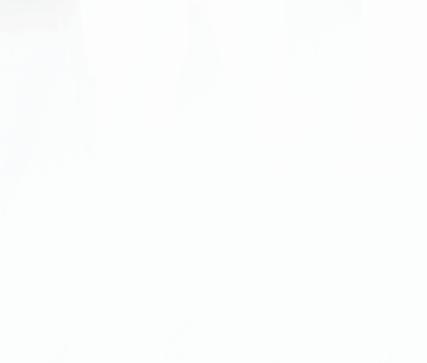
Where is the suitcase? Complete transparency is required in the transport chain ‒ also according to IATA Resolution 753. Martin is taking care of this with a partner who really knows what they’re doing: SICK. Being familiar with airport infrastructures all over the world, SICK also offers all three technologies for baggage identification ‒ laser, camera, RFID. So that every scan point is custom-fi t. No suitcase gets lost, read rates increase, handover errors are quickly identified. Martin is pleased. Thanks to SICK, he is connected to the baggage at all times and therefore more than ready for the future. We think that’s intelligent. www.sick.com/baggage-tracking
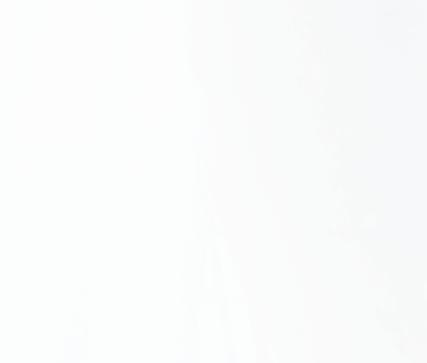
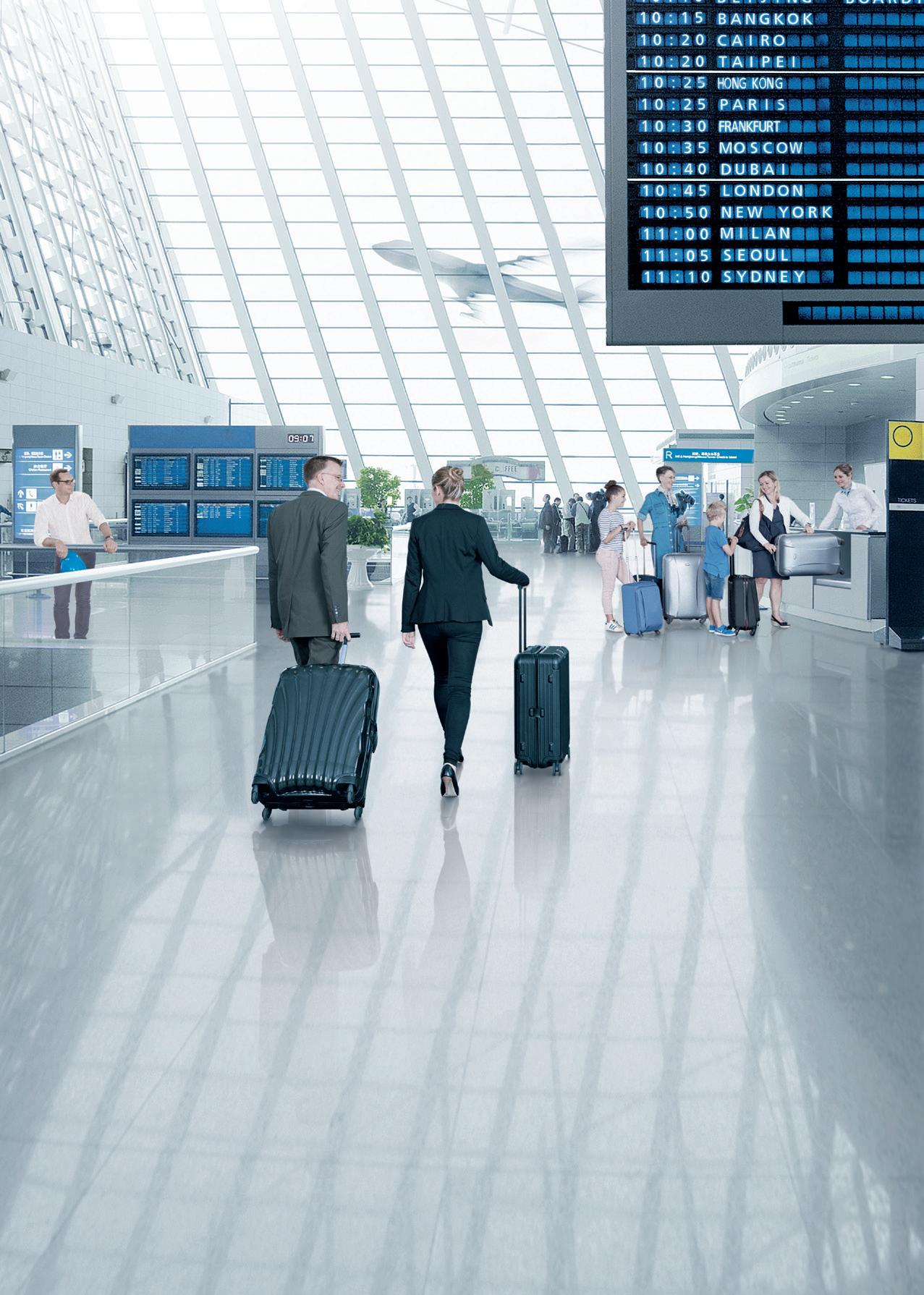
FIBRE OPTIC SENSORS MONITORING BRIDGES AND CRITICAL STRUCTURES
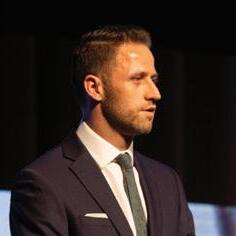
The way we manage and maintain bridges and other structural assets is set to be revolutionised by the adoption of embedded sensors, system analytics and AI, making asset monitoring more accurate, more efficient and significantly cheaper.
iBridge – an advanced structural health monitoring (SHM) solution – uses fibre optic sensors to collect and return real-time information about structural health, providing asset owners or operators with a wealth of knowledge to proactively assess asset condition, manage maintenance and optimise operations.
FiBridge grew from a VicTrack innovation project to improve asset monitoring and maintenance. Extensive trials conducted over two years proved FiBridge’s viability as an efficient and accurate asset monitoring system with strong commercialisation potential.
VicTrack owns Victoria’s transport land, assets and infrastructure, including more than 2,500 bridges, on behalf of the State Government.
VicTrack shares responsibility for keeping them all safe with rail operators V/Line and Metro Trains Melbourne (MTM). Our asset management program requires regularly taking stock of the structural health of bridges we manage and performing necessary maintenance. Until now, the only way to do that was periodic inspection by an engineer, usually twice per year – a huge undertaking considering the large number of bridges across the state.
Periodic inspection on such a large scale is expensive, laborious and inefficient. Those aren’t the only problems. Inspections are also prone to human error – some faults are not easily visible to the human eye – and can be disruptive to road and rail users if a bridge has to be closed for inspection.
We have thought for some time that there has to be a better way to monitor the structural health of Victoria’s bridge assets. We believe we’ve found it in FiBridge.
HOW FIBRIDGE IS A GAME-CHANGER
FiBridge uses tiny Industrial Internet of Things (IIoT) connected sensors attached to a bridge’s structure. The sensors measure and estimate parameters including structural strain, thermal response, bending moments, shear/impact loads, vibration and corrosion – all indicators of a bridge’s structural health.
Real-time data on the bridge’s performance is sent back to a remote single point for analysis. Bridge owners and operators are able to apply the diagnostic and prognostic information provided though physics-based system analytics and AI to manage assets, gaining efficiency and achieving cost reductions.
RIGOROUS TRIALS
The development of FiBridge kicked off in late 2017, funded by a $500,000 grant from the Victorian Government’s Public Sector Innovation Fund. VicTrack teamed up with Silicon Valley’s Palo Alto Research Center (PARC) – a Xerox Company – and Victorian Government partners including Department of Transport (now incorporating VicRoads and Public Transport Victoria) and Department of Environment, Land, Water and Planning (DELWP) – who manage thousands of bridges between them – Department of Premier and Cabinet, Office of Projects Victoria and education partners to test whether fibre optic sensing technology could be used to develop a costeffective and robust product for monitoring structural health in bridges.
PARC-designed miniature fibre optic sensors were first installed on a major Victorian highway bridge, which was then subjected to controlled tests. This included identifying the best locations on the bridge to attach the sensors. To validate our
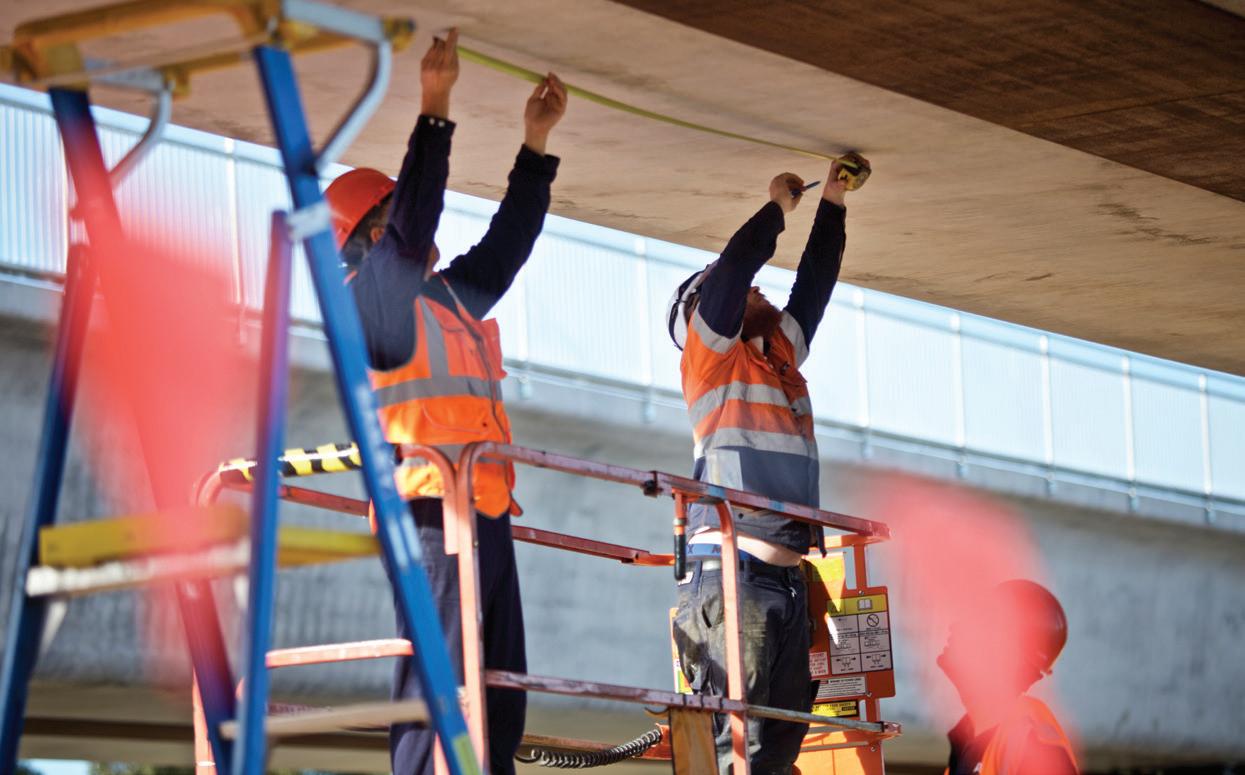
work, we compared outputs from the PARC sensors to those of traditional sensors used commonly for bridge assessment and qualification, as well as advanced computer simulation.
Once the proof of concept returned promising results, the pilot entered phase two with three more bridges added to the trial. They were fitted with hundreds of sensors to gather detailed and accurate data on the structural safety, performance and condition of each bridge over three months in 2019.
The sophistication of the data strongly indicated that this technology has the potential to revolutionise how we monitor and maintain our road and rail bridges. The technology was able to accurately detect, identify and map a range of different impacts on the bridge – all the way from a B-Double truck, train and tram, through to a pedestrian walking across it.
The trial proved FiBridge’s value in allowing asset owners to determine, in real time, where and when maintenance and repair is needed. FiBridge can also significantly reduce the need for routine scheduled checks on bridges, delivering significant cost savings when compared to standard monitoring technology.
AN END-TO-END APPROACH
Fibre-optic sensing technology for monitoring structural health is not in itself a new concept. However, to date there have been various obstacles to its widespread acceptance. These include an inability to establish true lifecycle costs and existing standards or regulations.
Other technology currently used in the structural health monitoring space include drones fitted with cameras, 3D imaging, and automatic feature recognition.
VicTrack officers had the opportunity to gain deep insights about other research being undertaken in the SHM space at leading international structural health monitoring conferences, asset management discussions and through detailed market studies.
We discovered that no one is currently offering a FiBridgestyle solution that takes an end-to-end approach using embedded sensors, IoT systems, AI, and edge/cloud smart system analytics in a cost-effective and scalable manner. We came away from the studies and industry engagements convinced there is a genuine need for a new solution like FiBridge that can provide low-cost, real-time monitoring. It provides a real opportunity to develop a tool for asset managers to use with minimal input from external parties.
FUTURE OPPORTUNITIES
Further research into future opportunities for FiBridge has identified a strong opportunity for FiBridge to become the technology of choice on bridges that are near end-of-life and high risk/performance bridges, as well as new bridges where installation can be seamlessly integrated as part of construction works.
While FiBridge was developed specifically with rail and road bridges in mind, the underlying technology can be used more broadly. It can be scaled for use in other classes of transport asset and in markets outside of Australia.
Other assets that could be monitored with FiBridge include critical structures such as airport runways, port structures, multi-storey car parks and rail or road tunnels. In effect, FiBridge, as a technology of the future, will convert our assets into smart structures of the future. For more information visit: https://victrack.com.au/fibridge
Resilience is the first thing that comes to mind when reflecting on the ports’ role through COVID-19. I empathise with the many industries struggling under the weight of the pandemic, many losing their workforce, supply, demand, or means to stay afloat. Representing Ports Australia, I’ve been fortunate to experience a sector that didn’t hesitate to adapt to ensure an uninterrupted supply chain which is evermore essential during these times.
Considering the maritime sector’s response to the pandemic holistically, ports and other members of the supply chain should be proud of their vigilance in banding together to share knowledge, establish new norms, and elevate industryrelevant concerns to the highest level. Ports Australia, with other industry leaders such as Shipping Australia and Maritime Industry Australia Limited, led an early push for establishing the Maritime Response group. Chaired by the Federal Department of Infrastructure, the group continues to meet weekly, bringing all corners of the Australian maritime industry together in response to COVID-19.
I couldn’t have anticipated in January just how imperative our industry’s presence in the forum would be given how fluid and aggressive the spread of the virus became domestically and abroad. The ports industry has stepped up through this group to manage concerns both reactively and proactively, whether through their own voice or through Ports Australia’s.
While government authorities around the country can be as vigilant as possible in managing the pandemic along the Australian supply chain, their ability to craft policy and protocols is only as strong as the knowledge pool boasted by the industry they serve. The same applies to us at Ports Australia; we are extremely fortunate yielding the ability to utilise the operational expertise of the personnel that make up our membership, expertise we’re constantly filtering up to government.
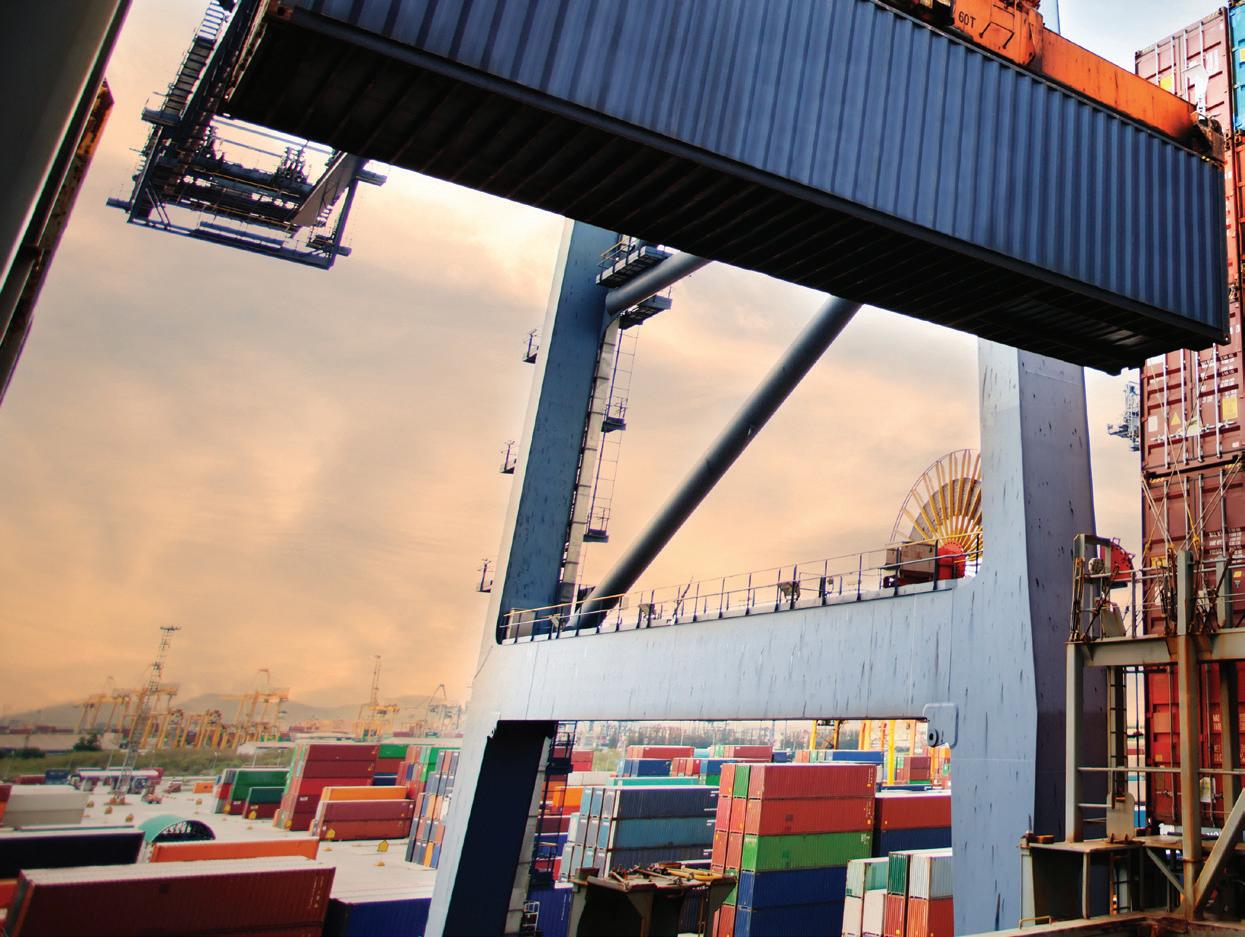
BUILDING RESILIENCE IN THE PORTS SECTOR
CONTINUED INVESTMENT AND EMPLOYMENT
While the future of COVID-19 and the resultant changes remain uncertain, it’s evident our ports still have their eyes locked on progress and sustainability given their continued investment in infrastructure. Many Australian ports have either announced, begun or continued with projects throughout the pandemic period, despite the many potential threats COVID-19 poses to trade.
Looking around the nation, there’s cruise terminals going up and being upgraded across Queensland; a Container Logistics Chain Study being conducted at the Port of Melbourne; continued construction at Port Botany in Sydney to double portrail connectivity; and lighthouses getting facelifts in Bunbury.
Investment extends beyond infrastructure too. Some weeks back, we highlighted on social media the number of ports posting job advertisements. While a job advertisement from Gladstone Ports Corporation for an operational role within the port may seem routine, we believe it's more important than ever in the context of the current world. It's important to remember that industries across the supply chain like ports are operational as ever, maintaining a sense of normality which means continuing the process of filling roles as per usual. Even more positively, filling those roles plays a strong part in building and strengthening the Australian workforce currently under the strain of COVID-19.
All projects, whether they come with a price tag or not, signify a desire of the ports to invest in a future beyond COVID-19, one where Australia will inevitably remain reliant on them as an indispensable link in the supply chain.
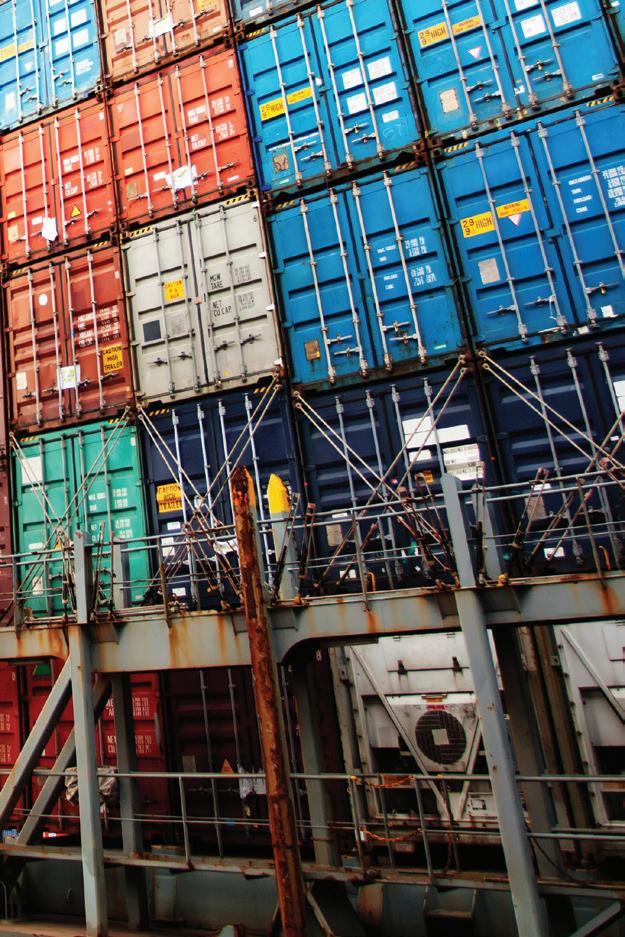
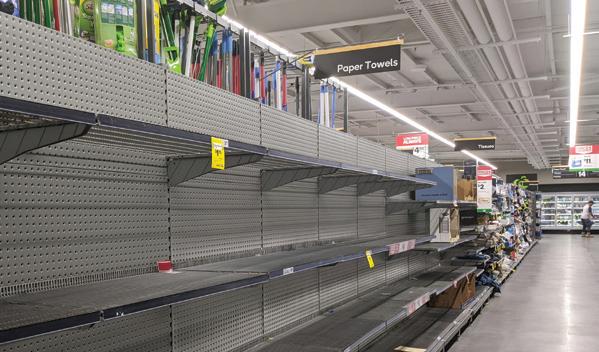
KEEPING MENTALLY HEALTHY
Resilience also comes in ways often forgotten when the focus is primarily fixed on physical safety and hygiene. The ports have equally turned their attention to the mental and social well-being of their staff and surrounding communities. While working from the isolation of one’s own home drastically reduces the spread of COVID-19, it also has the potential to socially isolate workers from their colleagues and workforce they ordinarily spend their days with, posing a threat to mental well-being.
The initiatives the ports have implemented are a creative way of taking the port to the workers when the workers cannot come to the port. To list a few: Flinders Ports further enhanced its mental health support services; Port of Portland assisted the local Mission to Seafarers prepare care packs for seafarers; Port of Townsville held an all-staff virtual lunch; and Fremantle Ports committed $10,000 to a local food relief emergency program.
POSITIVE SIGNS FOR FUTURE OPERATION
I acknowledge there’s no secret behind how throughput numbers and the operation of ports remain one of the most useful indicators to how Australia and its trade has reacted to COVID-19. It’s a privilege to report the fact that no port’s operation has had to be halted by government authorities due to concerns around COVID-19, and while throughput numbers across the numbers have been inevitably shaken, resilience prevailed and supermarket shelves have remained stocked.
Despite many of our international trading partners being squeezed even tighter than Australia by the grips of Coronavirus, our container ports’ statistics report a downturn of a far less significant measure than some may have initially expected. Even more positively, many of our major exporting ports have remained steady with their throughput, except for Pilbara Ports who hit record-breaking high numbers at the worst of COVID-19.
The consequence of these numbers transcends a mere success for the ports boasting them, they hold significance for an Australian economy needing every bit of support our resource-rich nation can muster. It’s certainly too early to ring the victory bell, but it’s important we celebrate deservedly.
To finish, I’ll reflect on the panic-buying saga when Coronavirus first hit Australian shores which saw toilet paper and food being snatched into trolleys in unprecedented quantities. While the panic brought about an unnecessary crisis, it crystallised three things: a lack of confidence from the public; the dire importance of supply chain continuity; and the evident need for balance between the two.
When COVID-19 ‘post-mortems’ begin analysing what worked and what didn’t, we must establish an agreed and transparent plan for the future that encompasses industry, government and the public. That way, our ports, supply chain and nation can stand up a nationally consistent and agreed plan when and if we need to move seamlessly to selfsufficiency and action once again.
ON TRACK TO SUPPORT NSW
by Marika Calfas, CEO, NSW Ports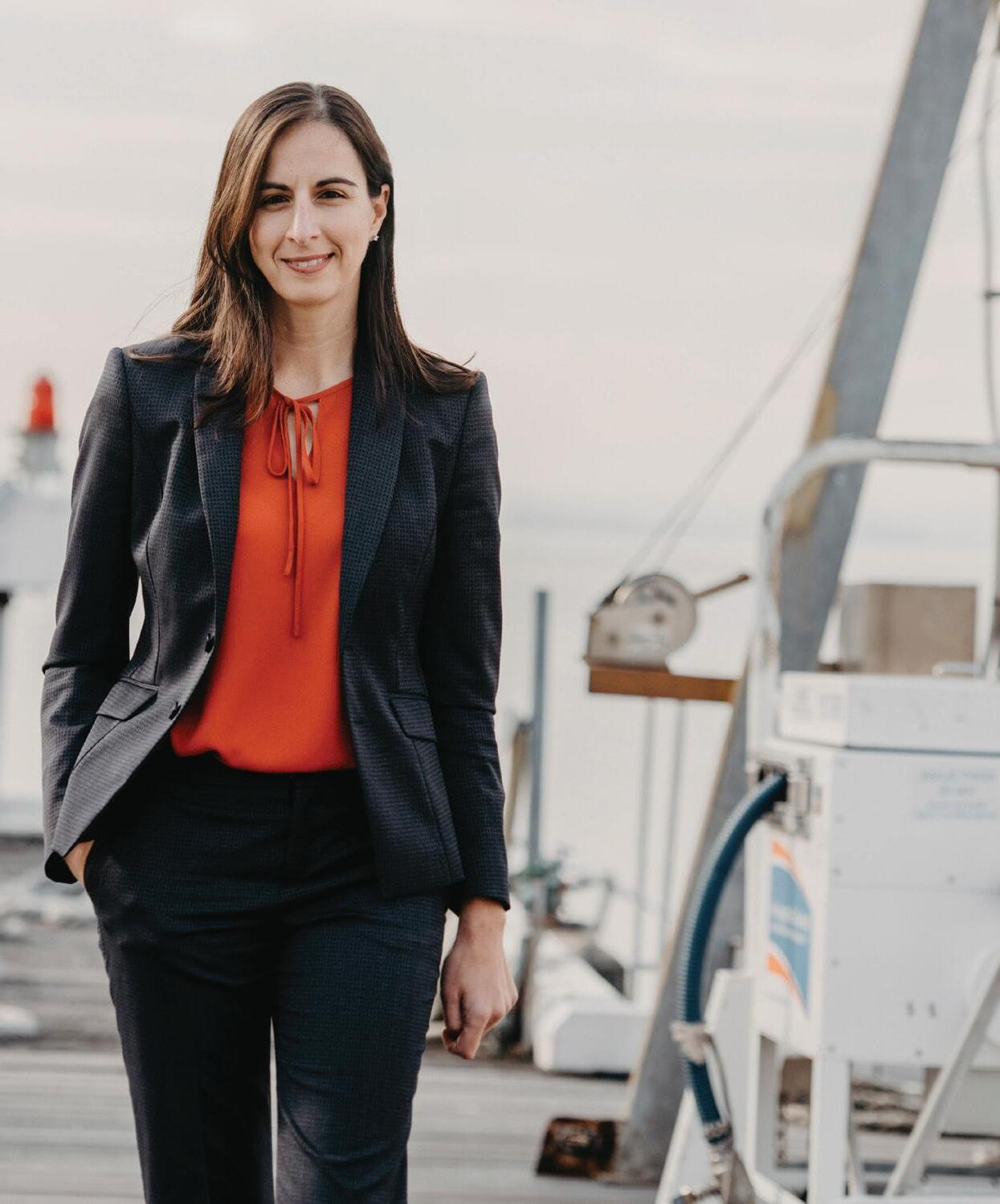
Australia is an island nation and the state of NSW has the largest population in the country. Connecting NSW and Australia with the global marketplace is the foundation of Port Botany.
Just 40 years ago, the port was built to enable NSW to handle containers – the new form of goods transport at the time. The construction was described at that time as “one of the biggest and most complex engineering projects ever undertaken in NSW”.
Today, Port Botany has cemented its position as Australia’s premier port and is inextricably linked to our lives and our lifestyles. Handling 99 per cent of NSW’s container volume, we rely on Port Botany to import goods for the people and businesses of NSW and to export goods to international customers. In fact, 42 per cent of all goods in a Sydney household have been imported in a container through Port Botany – everything from food, beverages, footwear and floor coverings, to mattresses, paints, fridges, televisions and toys. Port Botany also has Australia’s largest common user bulk liquids facility, handling fuel and gas.
PLANNING FOR NSW’S GROWING TRADE VOLUMES
In 2019 Port Botany handled 2.6M Twenty Foot Equivalent Units (TEUs)1 and has the highest volume of containers transported by rail of all ports in the country at 440,000 TEUs per year. NSW Government forecasts estimate that Port Botany could be handling over 7.3 million TEUs by 2056.
Our 30 Year Masterplan sets out how the port can handle these growing trade volumes. The key areas of focus include: ensuring efficient road and rail connectivity to our ports and intermodal terminals; growing the use of rail to transport containers; optimising the use of existing land and infrastructure assets; and protecting the ports from urban encroachment.
The use of data and technology will be fundamental to managing port assets. Whilst there has been considerable investment in port infrastructure over the last 40 years, there will need to be continued investment going forward.
In the next 40 years, NSW’s population is forecast to grow to 12.5 million, which includes an extra 3.8 million people living in Greater Sydney alone. Ensuring our port supply chains are able to efficiently cater for the growing trade needs to support this population growth is crucial to the economic vitality of the state.
INVESTING IN RAIL INFRASTRUCTURE
Rail is a fundamental part of our strategy to sustainably support container growth. While Port Botany is already directly connected to a network of Sydney metropolitan intermodal terminals and has dedicated freight rail lines into each of its three container terminals, we continue to invest in growing rail capacity to ensure efficient rail connections, which will keep supply chain costs low and reduce the cost of goods to families and businesses while keeping our exports competitive.
Our long-term goal is to move three million TEUs per year by rail, which will be about 40 per cent of future forecast container volumes. We therefore have a significant program of works underway to help us achieve this goal. This is supported by rail infrastructure investment by government and port and logistics operators. Some of the key projects include:
Port Botany on-dock rail
As the only port in the nation with on-dock rail at all three of its container terminals, Port Botany creates efficiencies and saves money for importers and exporters by removing the need for double handling of containers by trucks.
Together with the stevedores, we are investing in a staged program to increase ‘on-dock’ rail capacity to deliver a total of three million TEU rail capacity at the port.
The first stage involves $190 million investment at Patrick Terminals – Sydney
AutoStrad, with $120 million from NSW Ports to deliver on-dock rail infrastructure and $70 million from Patrick Terminals to deliver automated rail operating equipment. The project commenced in 2019 and when it is complete in 2023 it will double the existing Port Botany rail capacity to 1.5 million TEU.
The project will deliver significant benefits for importers and exporters, with 33 per cent faster train turnaround times and increased rail windows. Investment will follow at DP World Australia and Hutchison Ports Australia when the stevedores are ready to invest with NSW Ports.
Using rail, together with trucks, to move containerised freight will also reduce the growth of trucks on Sydney’s road network. For every one million TEUs moved by rail, the number of trucks around the port are reduced by 900 trucks per day.
Connectivity to intermodal terminals
Given 80 per cent of containers moving through Port Botany are delivered to locations within a 40km radius of the port, port rail shuttles are essential to help move more of the freight task to and from Western and South Western Sydney freight precincts. They also help reduce truck growth on Sydney’s roads.
For this reason, we are investing $250 million to develop the Enfield Intermodal Logistics Centre, including an intermodal terminal and logistics warehouses, connected by dedicated freight rail to Port Botany. The intermodal terminal,
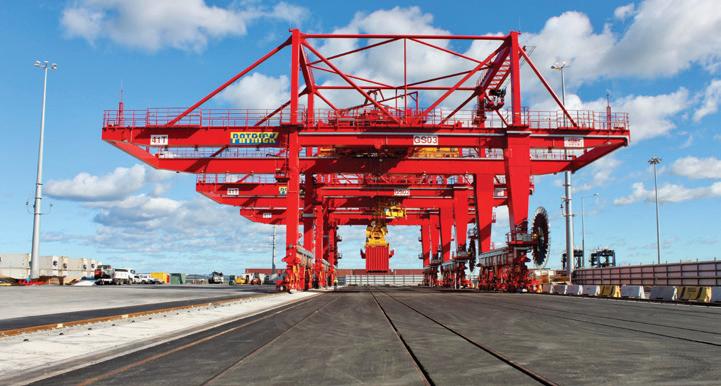
operated by LINX Cargo Care, and seven warehouses are now fully operational, with other warehouse precincts currently under construction. Enfield, together with other intermodal terminals such as Moorebank, provide logistics hubs for servicing Greater Sydney’s need for import goods and connecting regional areas.
Port Botany Freight Line Duplication
The Australian Rail Track Corporation’s (ARTC) $400 million project to complete the duplication of the Port Botany rail freight line (2.9km) and construct a new passing loop at Cabramatta on the dedicated freight line will further support increased volumes of containers being moved by rail to and from Port Botany. Now in the final stages of planning approvals, the project is funded by the Australian Government and should be progressed as a priority to deliver longterm port supply chain benefits.
The project will increase the resilience of the freight rail network and provide the capacity required to meet the forecast rail demand generated by the supply chain activities of regional NSW and existing metropolitan intermodal terminals, including Enfield Intermodal Terminal and Moorebank Intermodal Terminal, and future intermodal terminals in Western Sydney.
A SUSTAINABLE FUTURE
Looking to the future, sustainable operations and sustainable growth continue to be at the forefront of our approach to managing our port and intermodal assets. With ongoing investment in supply chain efficiency, sustainability, and a continued focus on optimising port and terminal capacity, Port Botany will be well equipped to support the state’s growing needs for the next 40 years and beyond.
CHANGE IN THE INCIDENT DATA
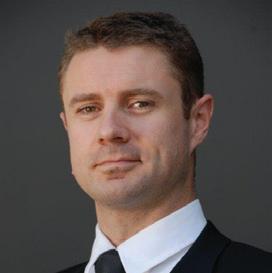
Until now, such data was considered too politically sensitive due to the complexity around determining root cause(s), legal liability, penalties, and outcomes. To overcome this issue and avoid interference with any ongoing investigations or reputational damage, the data has been de-identified and certain fields of information have been removed.
The information that remains is defined in broad categories and preliminary factual descriptions of equipment type, job type and incident type from which we can learn a surprising amount about what is really going wrong out there when an accident happens.
Worksafe Victoria has played a large part in not only unlocking the previous calendar year's data, but also securing the approval and paving the way for ongoing quarterly data instalments to be available to industry.
by John Humphries, VIC-TAS Safety Liaison Officer, The Crane Industry Council of AustraliaThe Crane Industry Council of Australia (CICA) and Worksafe Victoria have embarked upon a new collaboration involving the collection of raw incident data involving cranes and the construction industry dating back to January 2019, in an effort to increase site safety.
Two CICA Safety Bulletins have already been released focusing on topics that relate to the analysis and findings from this raw data and what these accumulating statistics point to. As time goes on, we will learn more and more about the nature of construction incidents involving cranes.
COLLECTING CRUCIAL DATA
This project follows the groundbreaking work of RMIT whose 2015 paper entitled Causes of Fatal Accidents Involving Cranes in the Australian Construction Industry studies a ten-year period from 2001-2013 during which 359 workers died in the Australian construction industry from work related causes. Of these, there are 258 ‘closed cases’ of which 22 involved a crane.
The work of RMIT focused on fatalities only, and as such, captured a limited number (22) cases that had run their course through our courts.

18 separate incidents that involved a crane in Q1-2020.
These incidents were also spread over a ten-year period, and during that time, equipment and technology have advanced immensely and standards/ best practices and training have evolved.
Where the RMIT paper proved immensely valuable, was the utilisation of the ‘Loughborough Model’ citing ‘immediate circumstances’, ‘shaping factors’, and ‘originating influences’, as well as specific details and breakdown of each incident, since this information was no longer legally suppressed.
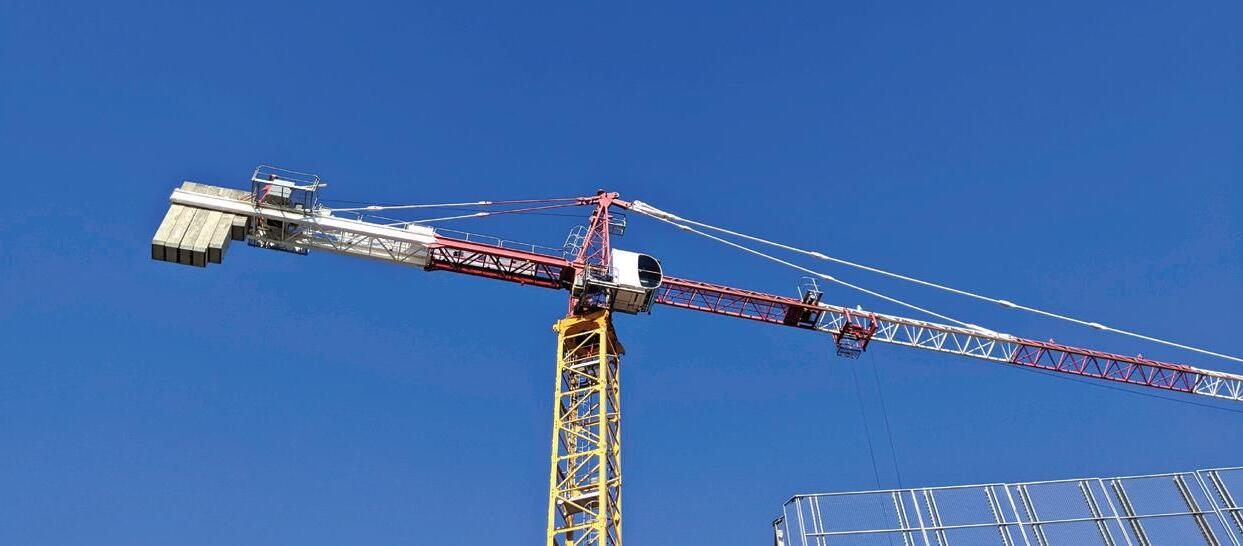
CRANE INDUSTRY PAVES WAY FOR
But what if we could capture all incidents involving cranes as soon as they occur and still legally gather enough information to indicate relevant causal/contributing factors? The CICAWorksafe data initiative treads the fine line between obtaining vital information from ground-zero while not implicating workers, employers or equipment manufacturers.
IMPROVING SAFETY
If we are in the business of improving safety, what does that mean exactly? Less incidents per calendar year? Fewer fatalities per incident? Fewer injuries and resultant property damage when an incident occurs?
As much as we would like to say, “all of the above”, the complexity and variability of incident type, contributing factors and causal factors means there is no one solution that will fix everything and make everyone safe. We need a ’multi-pronged attack’ and where the data is useful is in the breakdown and classification of incidents. This grants us a better understanding of where extra attention, awareness and training is needed, it will best equip our pitchfork with the right prongs for attacking the crane incident ‘beast’.
Fortunately, with construction incidents involving cranes, we are dealing with less than 100 annually and we can scrutinise each case while staying within the bounds of confidentiality. We can see where minor and major injuries happen, as well as examining the ‘near miss’ and ‘dangerous occurrence’ cases.
Another dimension to the data is the fact that it exists for all construction incidents filterable by plant type. This means we can tap into the excavator and concrete data and search for similarities or differences in the electrical contact incidents to understand if their learnings can be applied to cranes.
We can assess other equipment with stabilising outriggers and understand the differences and similarities of ground

bearing, failure related tip overs. We can examine scaffolding and access incidents to understand falling from height incidents and the effectiveness of fall protection. Maybe the other industries are doing something ours is not, or vice versa.
JUST A START
In one sense, this data is in its infancy. We retrieved data from January 2019 and at the time of writing this, are only weeks away from receiving Q2 2020. However, the 100 incidents analysed to date have already shown us the most common crane types and incident groupings combined, with some clear opportunities for raising awareness and increased training. We have identified common circumstances for hand crush injuries, the dangers of unstable loads, falling objects and the benefits of keeping the lifting path clear.
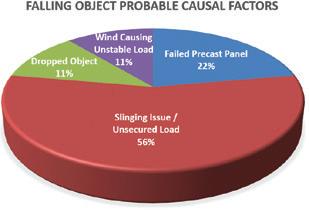
Falling object probable causal factors.
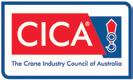
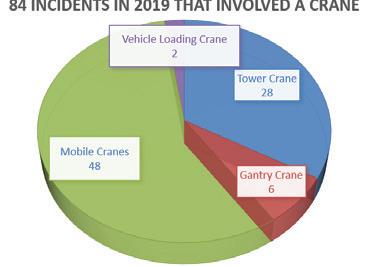
Construction work is usually very physical and there is a significant human factor in most, if not all construction related incidents. This is not a statement of presumed liability or blame and as workers, we are subjected to many challenges that life throws at us every day whether it be emotional stress, depression, anxiety, illness, minor injury, fatigue or distraction. High risk work is just that, and the decisions workers must make throughout their day often have severe consequences.
We need to use this data to understand how to keep our worksites safe and to empower us to better understand the common and consistent causal factors and circumstances that lead to incidents, so they can be engineered out of our work methods and procedures. Although the incidents are reviewed individually to be classified and allocated causal and contributing factors, this data analysis project is a statistical global approach to the challenge of reducing construction incidents involving cranes. The power of complete and factual data is the best weapon we have when it comes to keeping us all safe on-site.
For more information on crane safety, sign up to the monthly CICA Crane Safety Bulletins by emailing john@cica.com.au.
HOW TO CREATE SAFER, MORE EFFICIENT STORAGE FACILITIES
Worker safety is a top priority when it comes to handling and storing long, heavy or oversized product loads. Moving these types of items around warehouses can often be fraught with danger. However, by using the right equipment and storage options, companies can improve the safety of their facilities, enhance efficiency and increase storage capacity.
With forklift safety week falling in June in Australia, many companies were looking at how they can improve their safety best-practices and ensure the well-being of staff. One of the best ways to improve safety and mobility is to use the right kind of equipment to move and store these products in the safest way possible.
For Combilift, the largest global manufacturer of multi-directional forklifts and leaders in long load handling solutions, safety is at the heart of every one of its products. With a wide range of multi-directional forklifts, pedestrian stackers, straddle carriers, and Aisle-Master narrow forklifts, Combilift helps storage facilities optimise available space and efficiency, and ensure the safest environment for workers.
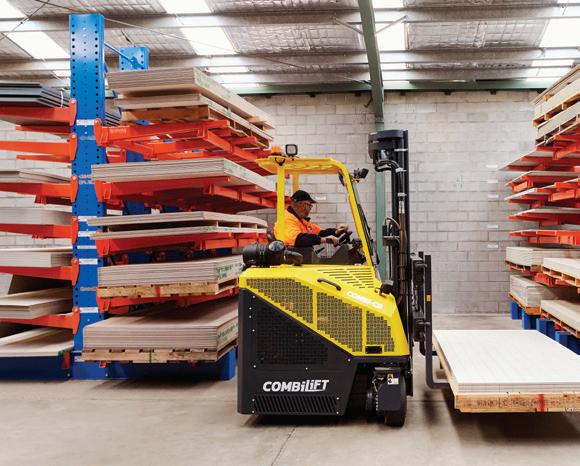
Combilift’s range of multi-directional forklifts are easy to use and combine the advantages of a counterbalanced forklift, side loader and very narrow aisle truck, into one vehicle. The pedestrian stackers also offer a safer option for lifting, especially in narrow and tight spaces by removing the user from dangerous crush points.
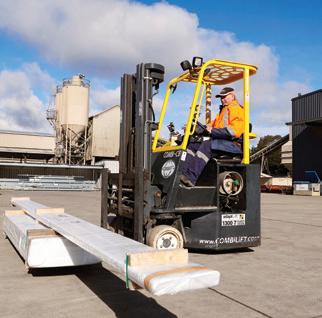
Combilift also offers free design and layout services for storage facilities looking to maximise and create more space in their warehouses. Using technology developed in-house, customers can send photos and videos of their facilities to Combilift who will then create 3D designs and animations outlining how the customer can make the most out of the space available, and make it safer and more efficient.
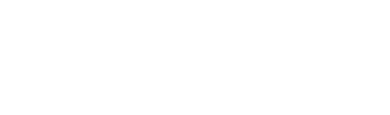

Safety | Storage | Efficiency
Manage your steel more safely, using less space and more productively with Combilift’s materials handling solutions

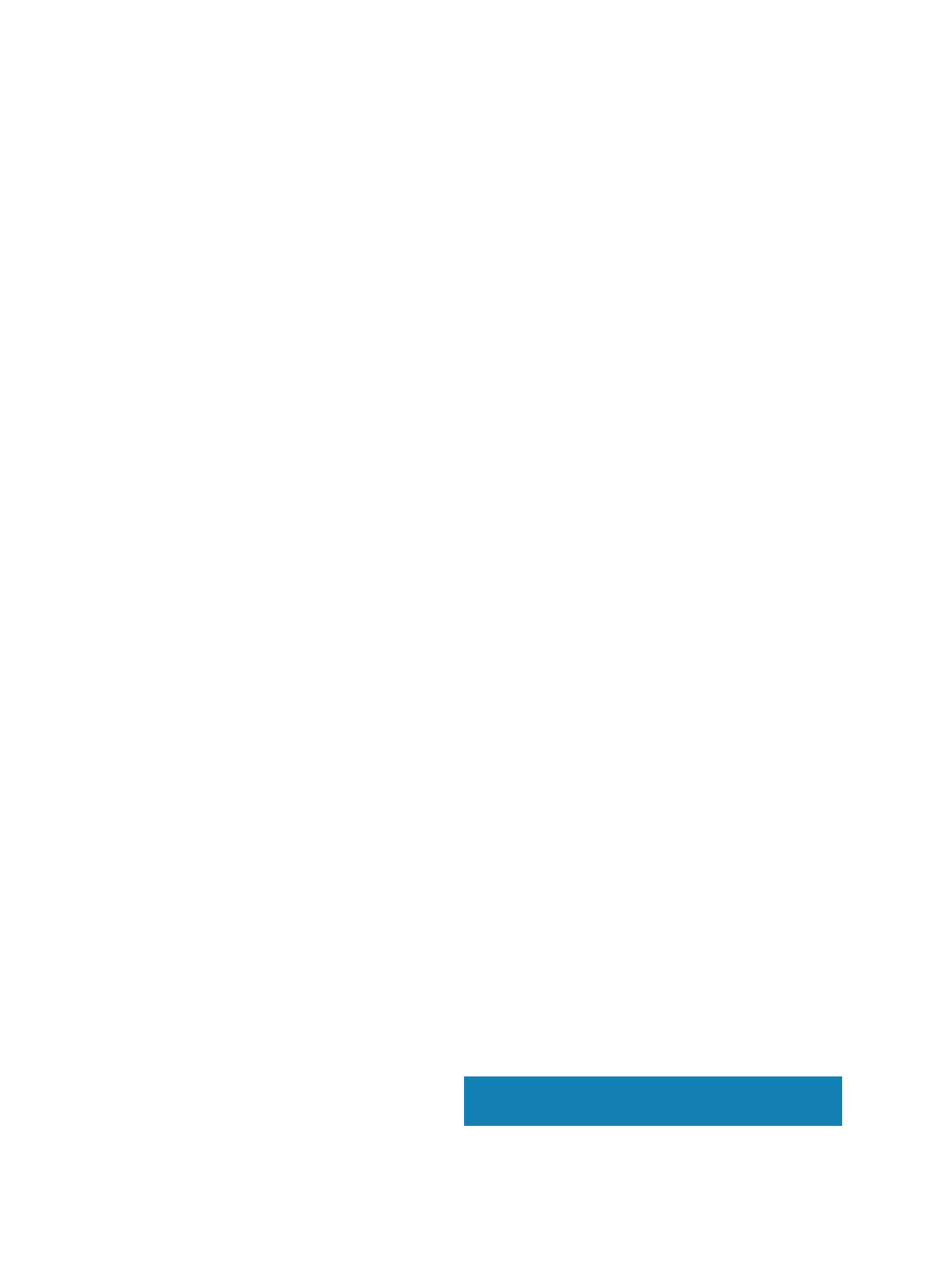
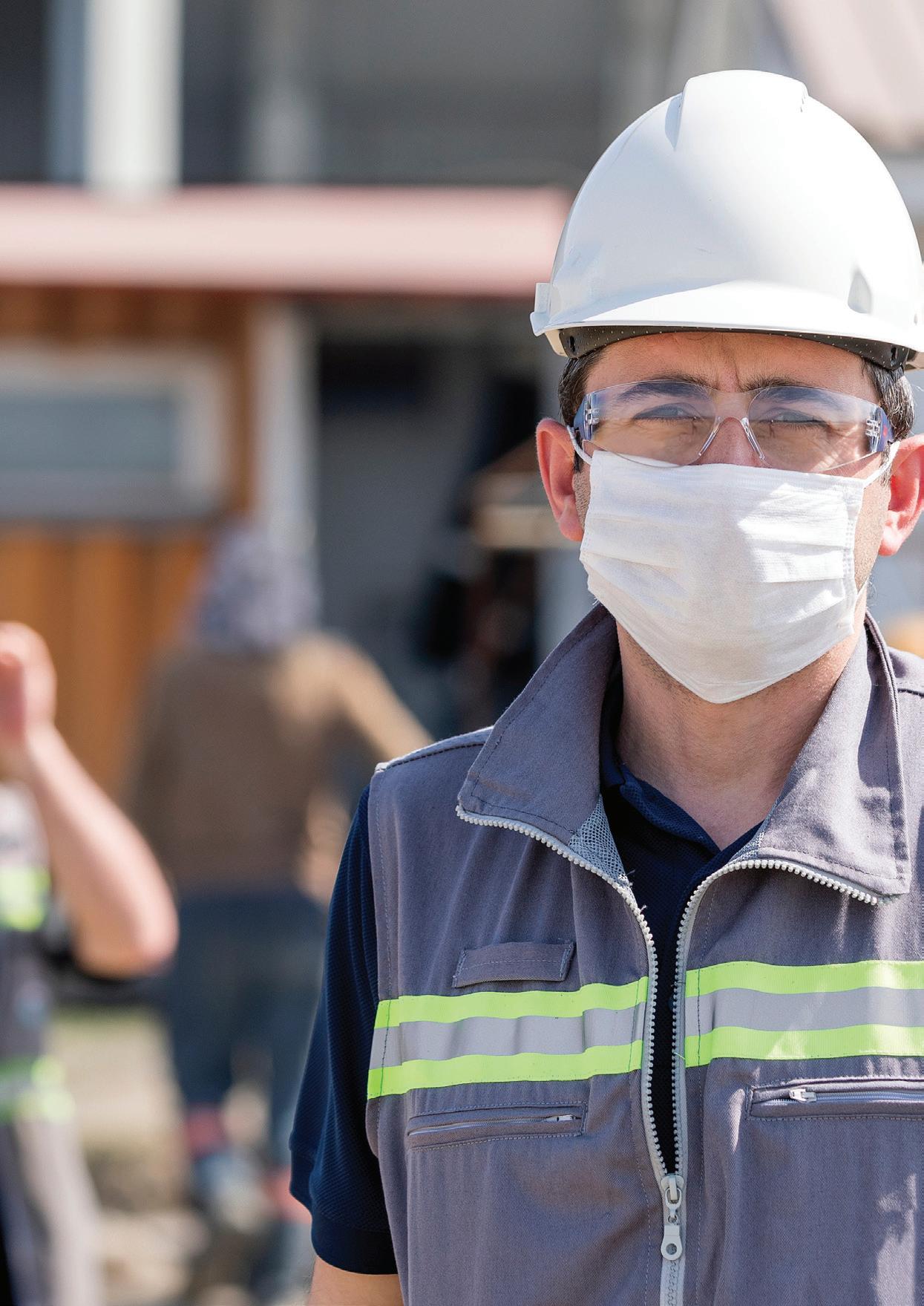
Under Australia’s model Work Health and Safety (WHS) laws, employers are required to protect the health and safety of workers and others at the workplace by eliminating or minimising risks arising from work.
Safe Work Australia has developed guidance to help employers in the construction and infrastructure industries understand how WHS duties apply during the COVID-19 pandemic and what you can do to keep your workplace as safe as possible.
ASSESSING AND MANAGING RISKS
Exposure to COVID-19 is a foreseeable risk that all businesses in the construction and infrastructure sector need to manage.
In consultation with workers and their representatives, it’s essential to undertake a COVID-19 risk assessment. Look at the way you work to understand and quantify the risks to health and safety from COVID-19. You can find tools to help you conduct a risk assessment on the Safe Work Australia website.
Once you have identified the risks, implement control measures to address those risks, and review them. While each workplace and business will be different, there are a few key control measures that will apply across the construction and infrastructure sector.
PHYSICAL DISTANCING
Physical distancing is a key measure to manage risks from COVID-19 because the most likely way of catching the virus is by breathing in respiratory droplets from an infected person. By ensuring there is at least 1.5 metres between workers where possible, you will reduce the likelihood of exposure to the virus.
You can put in place measures to maintain physical distancing in the workplace, including:
♦ Adjusting the workplace layout and workflows to enable workers to keep at least 1.5 metres apart
♦ Installing signage or wall or floor markings to identify 1.5 metres distance
♦ Using non face-to-face methods for meetings and training
♦ Minimising non-essential visitors
♦ Reducing the number of workers at the workplace or using common facilities at the same time, for example, by staggering start and finish times and meal breaks
♦ Ensuring each worker has their own equipment or tools
If physical distancing measures introduce new health and safety risks, for example if they impact communication or mean less people are doing a task, you need to manage those risks too.
CLEANING MEASURES
A key way to protect workers and others from the risk of exposure to COVID-19 is through cleaning and disinfecting measures.
Cleaning measures should include:
♦ Cleaning and disinfecting workplaces at least daily
♦ If the workplace operates in shifts, cleaning between shifts
♦ Cleaning shared equipment between uses, where practical
♦ Prioritising frequently touched surfaces, like door handles, lift buttons, tabletops, light switches, toilets and taps for cleaning and disinfection
♦ Directing workers to regularly clean personal items they use in the workplace, like glasses and phones, using disinfectant wipes
GOOD HYGIENE
Good hygiene reduces the risk of exposure to COVID-19. To minimise the risk of exposure at your workplace, require everyone to practice good hygiene and provide appropriate hygiene facilities. Ensure workers and others at the workplace:
♦ Don’t come to work when they are unwell
♦ Regularly wash their hands with soap and water for at least 20 seconds and dry them completely
♦ Cover coughs and sneezes with their elbow or a clean tissue, and no spitting
♦ Avoid touching their face, eyes, nose and mouth
♦ Dispose of tissues and cigarette butts hygienically, for example in closed bins
♦ Wash body, hair, facial hair and clothes thoroughly every day
♦ Have no intentional physical contact, for example shaking hands
You need to provide washroom facilities that are in good working order and are properly stocked with toilet paper, soap, water and drying facilities - preferably single-use paper towels. If handwashing facilities are limited, provide alcohol-based hand sanitiser at locations such as entry and exits.
OTHER THINGS YOU CAN DO TO KEEP WORKERS SAFE AND LIMIT THE SPREAD OF COVID-19
♦ Put up posters around the workplace on physical distancing and handwashing
♦ Review regular deliveries and request contactless delivery. Check systems for e-invoicing are in place
♦ Instruct workers to have meetings by phone. If not possible, require they meet in a large space and keep meetings short
♦ Instruct workers to tell you if they are displaying symptoms of COVID-19, have been in close contact with a person who has COVID-19 or have been tested for COVID-19.
♦ Develop a plan to ensure business continuity if there is a suspected or confirmed outbreak of COVID-19 in your workplace
Remember, you must consult with workers and their representatives, like health and safety representatives (HSRs), on health and safety matters relating to COVID-19, including what control measures to put in place in your workplace.
CHECKLISTS AND TEMPLATES
The Safe Work Australia website is the central hub of COVID-19 work health and safety information for Australian workplaces. Detailed guidance is available for the building and construction industry, covering 22 key topics including work health and safety duties, risk assessments, physical distancing, hygiene and cleaning.
A range of other resources including posters, checklists and templates are also available on the website in the COVID-19 business toolkit. To access the guidance and resources, go to safeworkaustralia.gov.au.
THE CHALLENGE OF SECURING REMOTE SITES
Remote sites are assets owned by a company that are dispersed over a large single area or geographic area. Companies with remote sites can include ports, airports, roads, utilities, and mobile phone networks, and they face significant ongoing challenges in managing access to these sites.
There are four main reasons why remote site access can be challenging:
1. Conventional master key systems provide no accountability and effectively become an everincreasing risk to security from the moment the first key is lost
2. Access control would be the logical solution, however, the geographic spread of the assets to be secured makes the prospect of hard cabling to install conventional access control cost prohibitive
3. Added to the cost of cabling, is that many remote assets are secured by padlocks or 3-point locking systems on cabinets that are not easily retrofitted with access control
4. Managing those who require access to the asset which includes the organisation's own staff, contractors and in many cases other companies and parties that share the site, can be difficult
However, these four key challenges can be used to help companies develop a wishlist for a system that is suitable to secure their remote sites. The main factors to consider when selecting a system to secure remote sites include:
Accountability
The system must be able to ensure accountability. This accountability would be a comprehensive audit trail that tracks all activity in the system including both valid openings and failed attempted openings.
Lost keys
Here, key refers to the device used to open the lock. It may be a key or access control media. The point is that any lost credential must be simple to delete or expire, so that a lost key does not pose an ongoing security risk.
Cost-effective
Security professionals know that cabling hundreds of doors is a major capital expense, even if they are in a single site. The potential costs are typically much greater if a remote site is to be cabled. To avoid this cost, the system must not require cabling. In addition, the locks placed on remote sites must not require regular service. To achieve this, they should not have batteries that need replacement. As an example, they should be powered by the key (imagine the cost of replacing batteries every year on a padlock located at every mobile phone tower for one of the Telcos!).
Retrofittable
The system must be suitable to fit into your existing hardware. Many remote sites are within a compound which is secured with a padlock or a roadside cabinet for traffic lights that have 3-point locks or even a conventional door lock. Padlocks are almost always located outside and must be IP68 rated without the need for additional weather covers. Why? Most users do not put the cover back after opening/closing the lock. If
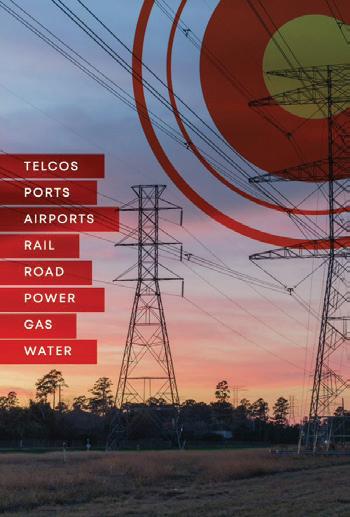
the system can be simply retrofitted, it again helps to reduce costs significantly.
Simple to manage and maintain
To make it simple, there needs to be a centralised management software that automates the process as much as possible, including a configurable administration hierarchy, being able to adjust for time zones across Australia, easy updates of access profiles on the fly (perhaps a mobile phone app that updates the key remotely), and finally a system that can integrate with lots of different systems such as contractor management or compliance systems.
The good thing is that there are products available that are designed to meet these challenges. The products are normally classified as Electromechanical Master Key Systems which are basically a hybrid that has combined the benefits of a conventional master key system with the functionality of an access control system.
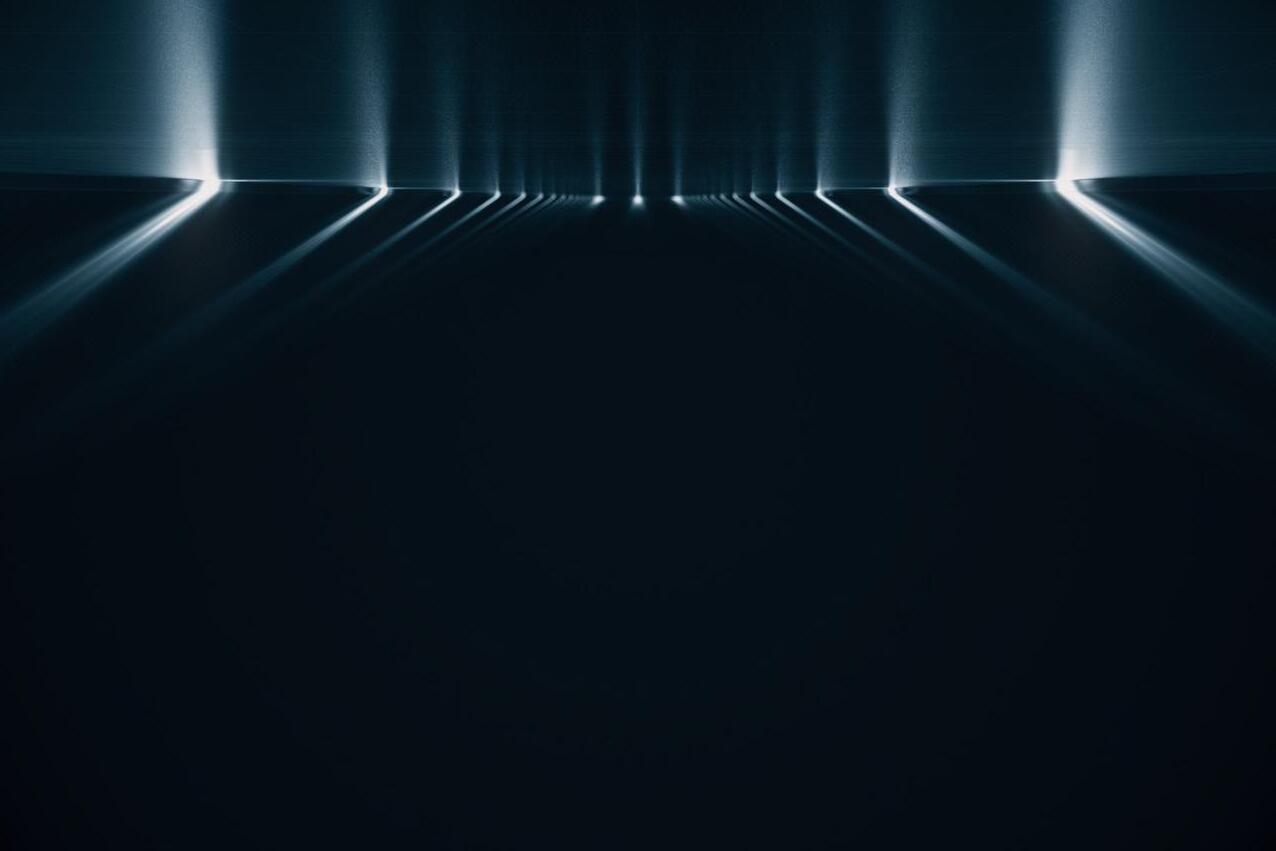
AWARD WINNING TECHNOLOGY
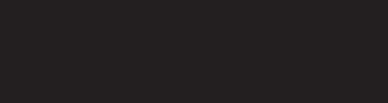
IP68 padlock with no weather shield required
Bluetooth CyberKey enables use with a smart phone app for virtual real time access control and updates of access permissions on the go
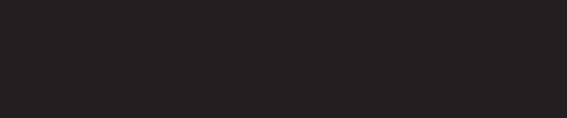
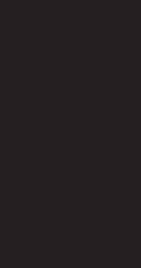
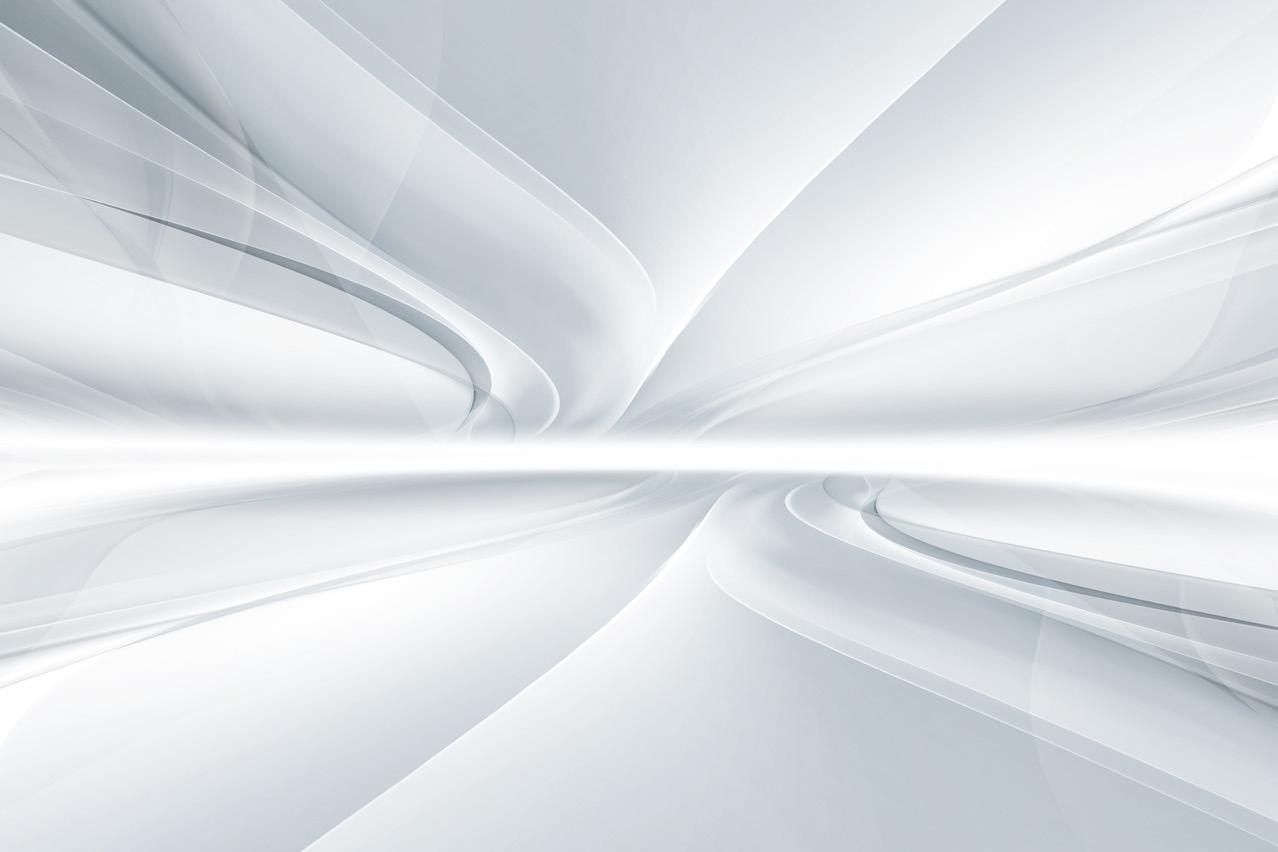
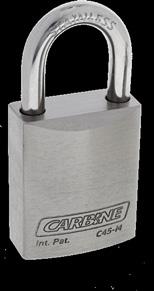
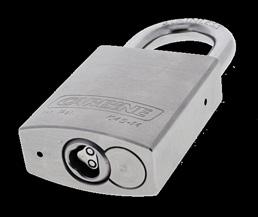
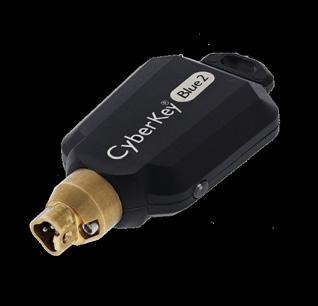
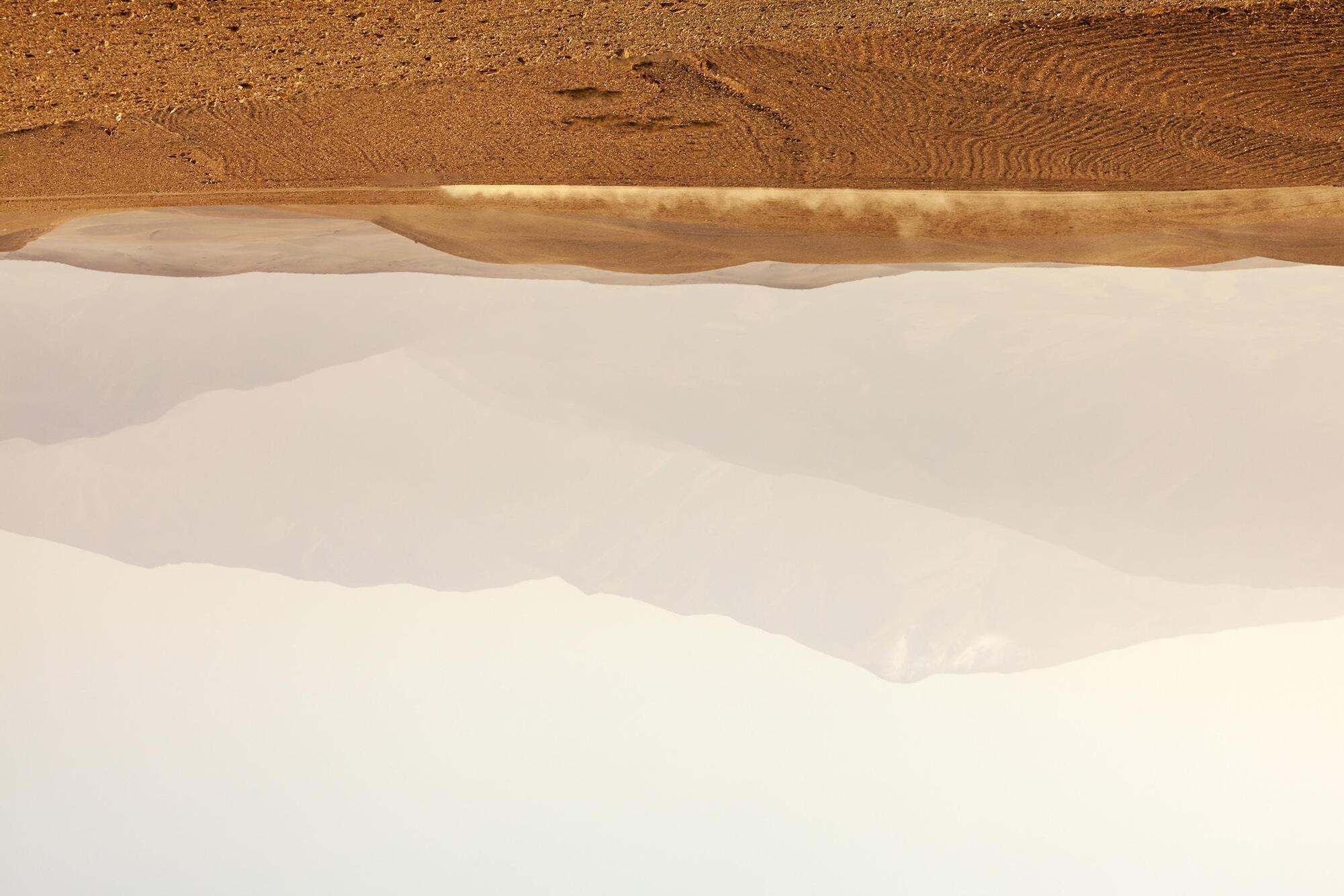
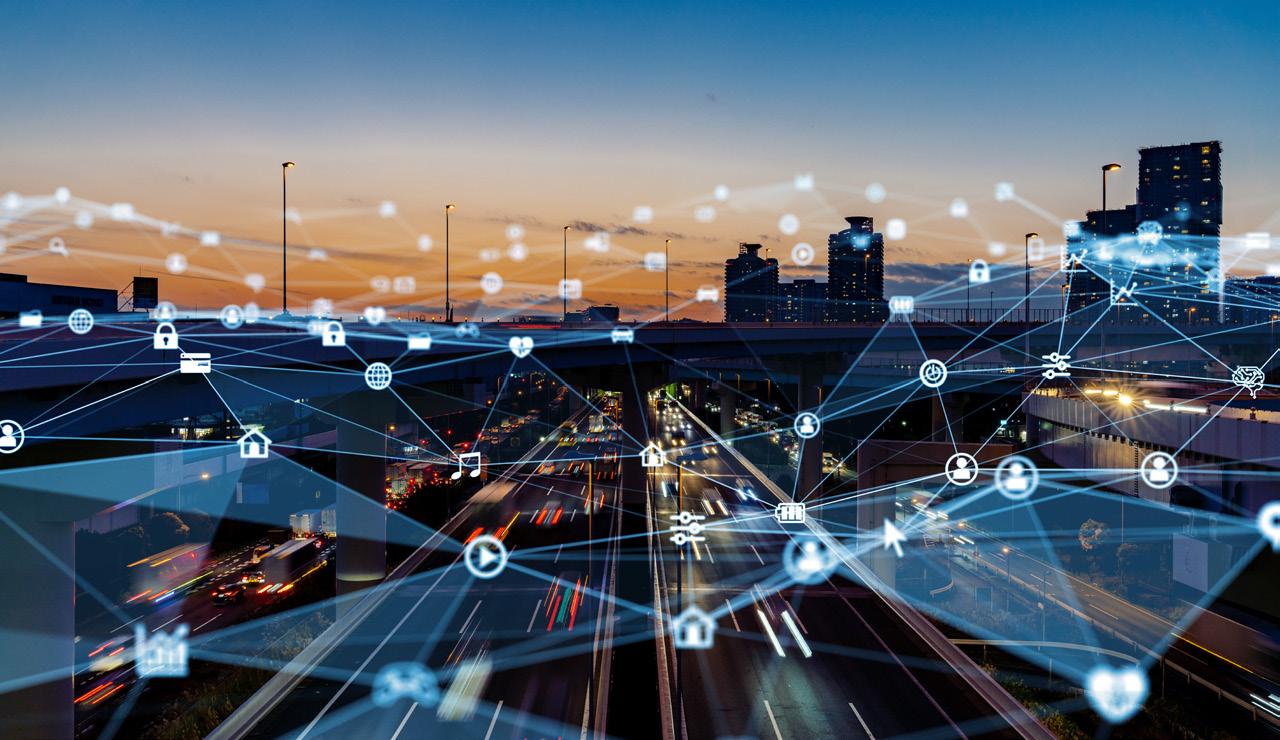
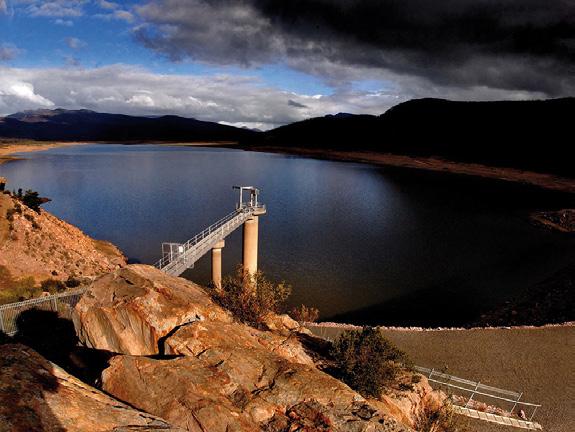
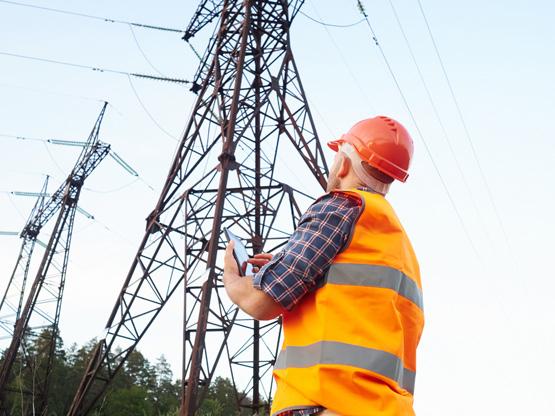
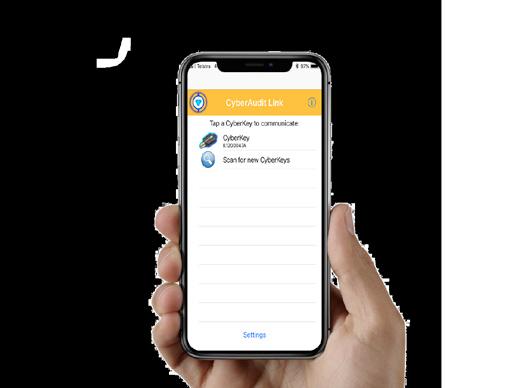
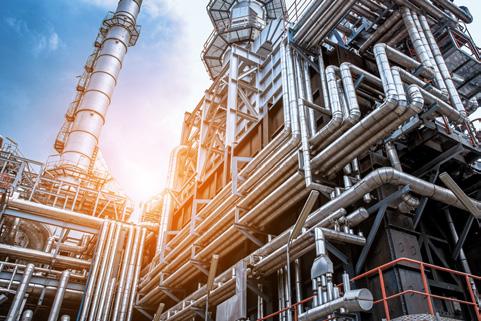
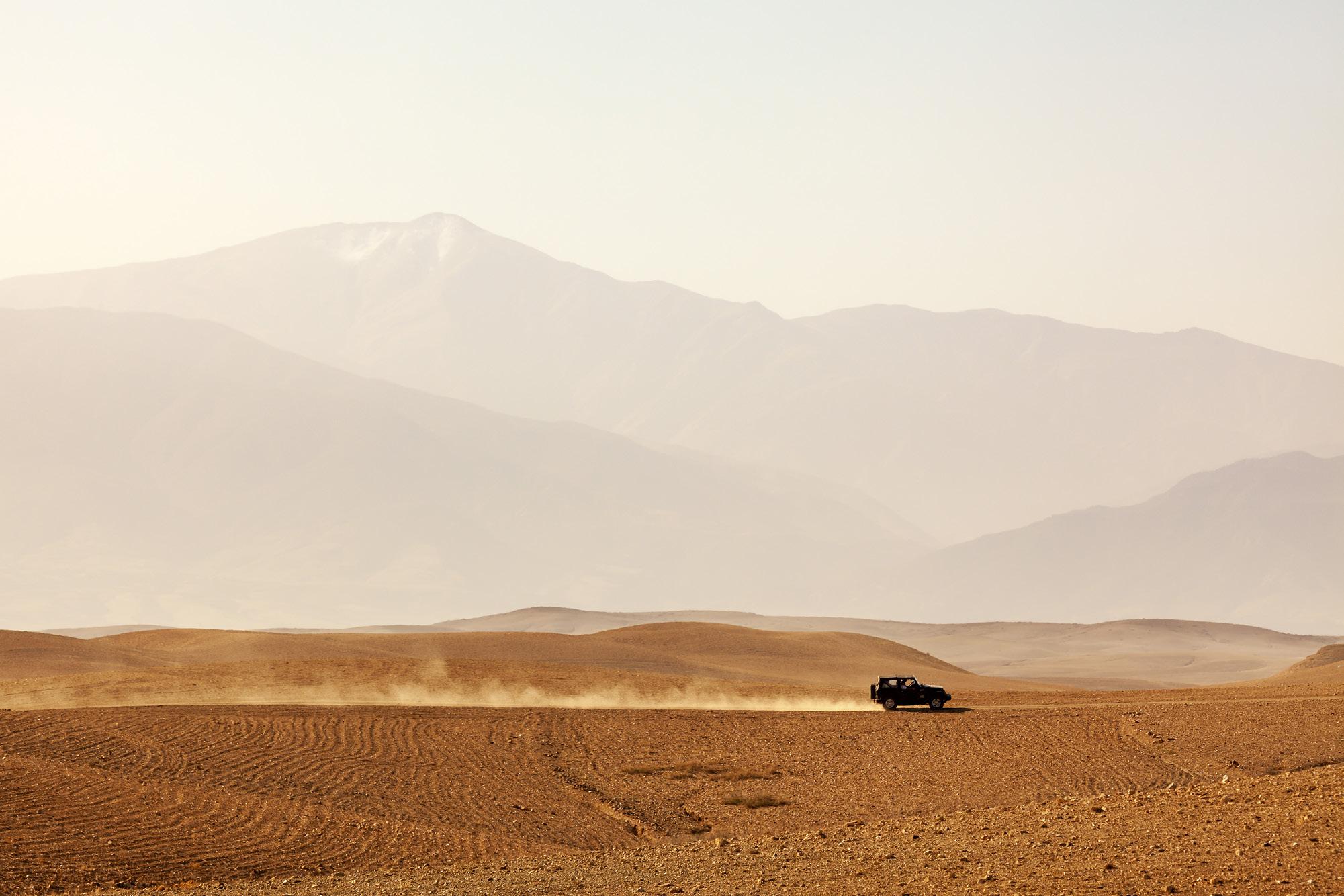
FEATURES SCHEDULE
November 2020 Deadline: 25 September 2020
AusRail Airports
IoT & cloud communication Tunnels
Corrosion Disaster management
Machine learning Recycling and waste management
Landscaping and vegetation management
DISTRIBUTION AUSRAIL SYDNEY BUILD EXPO
March 2021
Deadline: 8 January 2021
Road surfacing and design Spatial & GIS
Rail Equipment Training and skills
Signalling, tracking and control systems
Condition monitoring and maintenance
Software, communications and connectivity
DISTRIBUTION (TBC) SAFETY IN ACTION 2021 THE ITS ASIA PACIFIC FORUM LOCATE 2021
June 2021 Deadline: 9 April 2021 September 2021 Deadline: 9 July 2021
Smart cities Earthmoving outlook
Noise and vibration Bridges
Automated and electric vehicles
Urban development Intelligent Transport Systems (ITS)
Road surfacing and flexible pavements
DISTRIBUTION (TBC) CORE 2021
Road and Traffic Ports
Safety and risk management
Cranes & heavy lifting Freight and logistics
Sustainability Asset Management
Asset inspection & drones/UAVs
DISTRIBUTION TBC

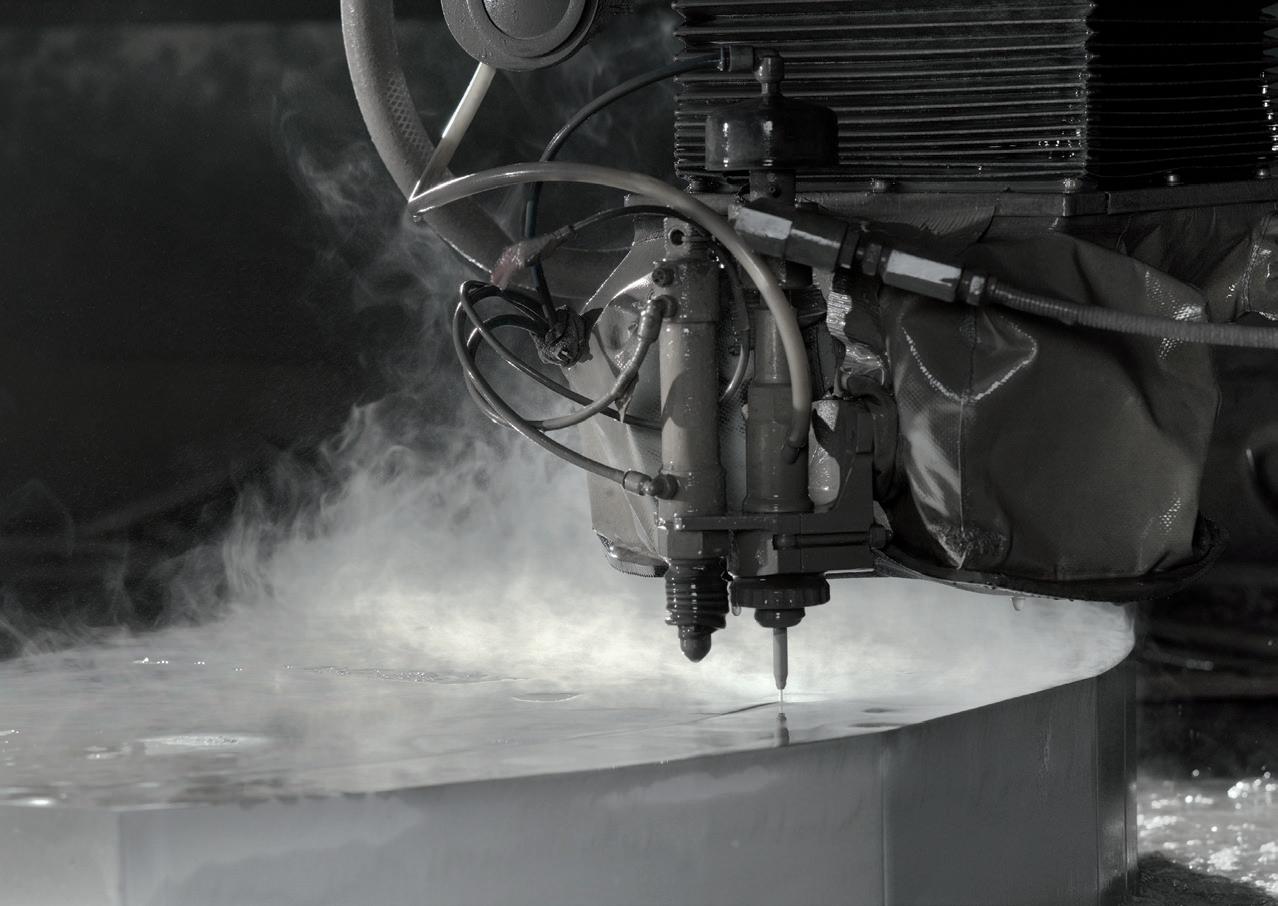
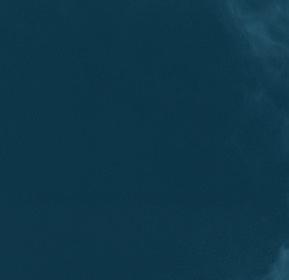
Reducing material cost through waterjet technology
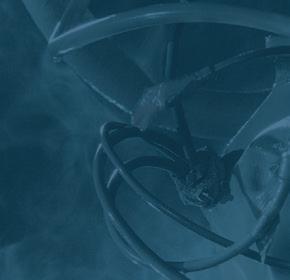
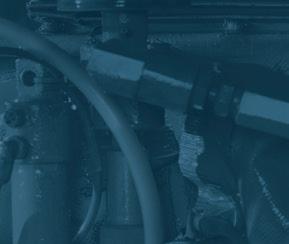
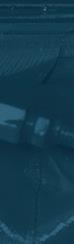





BUILDING AND CONSTRUCTION PARTS
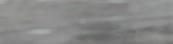
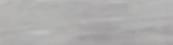





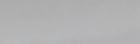
STRUCTURAL COMPONENTS DECORATIVE FACADES
Waterjet technology
Waterjet cutting is a process of precision cutting that utilises high pressure water.
We can process a wide array of materials. Heavy gauge plate, thin sheet stock and composite materials (i.e. carbon fibre, phenolics etc.). It is not uncommon for 6+ inch aluminium and titanium to be cut on waterjets to near final shapes. Edge quality of the parts can vary depending on customer requirements.
We can process anything from a very rough cut for hog-outs, to a very fine edge for precision, finished parts:
Cut up to 6 m x 3 m (20 ft x 10 ft)
Thickness up to 254 mm (10 in)
Improved yield and less waste material
Supplied close to net shape reducing customer machine time
Shorter lead times
Zero heat effected zone
Processing of customer supplied materials
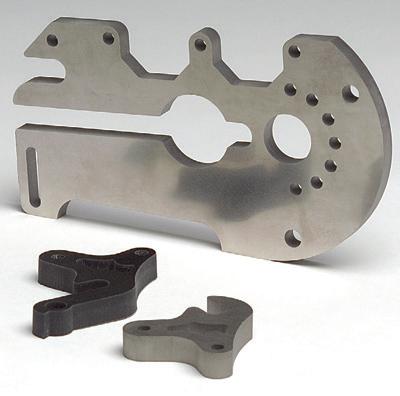