Tadano reaches
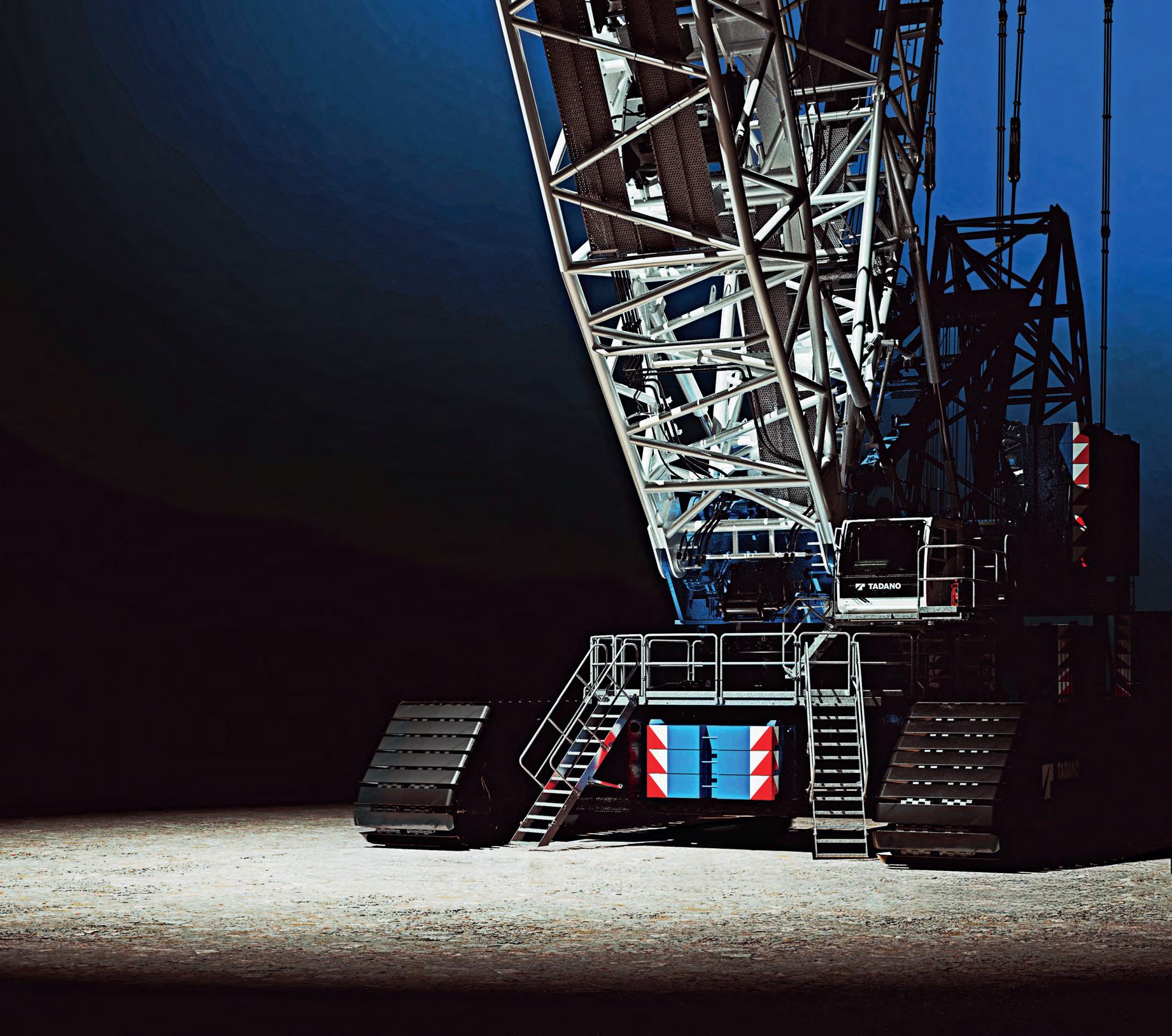

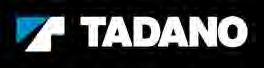
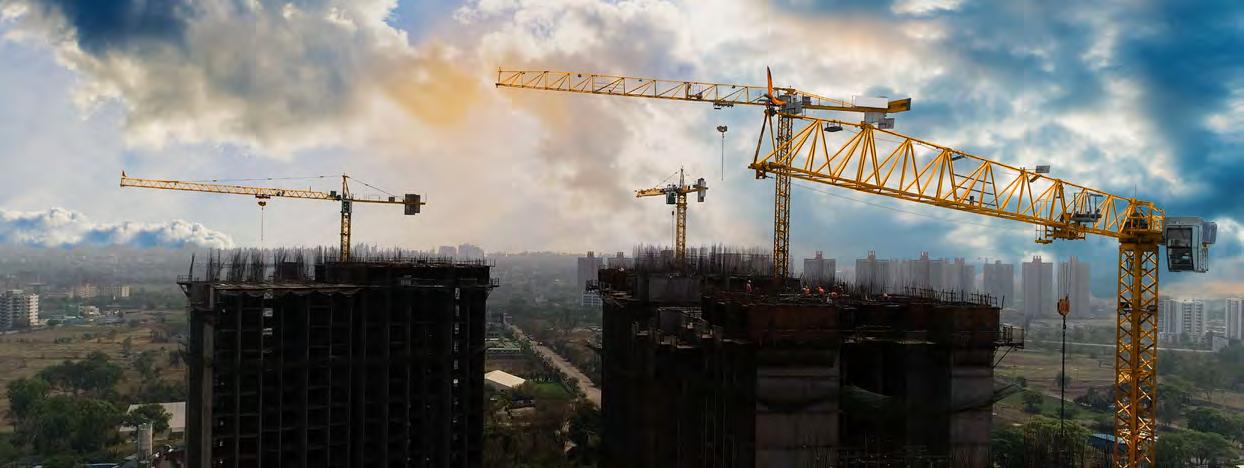
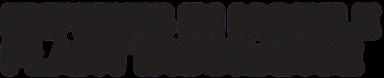
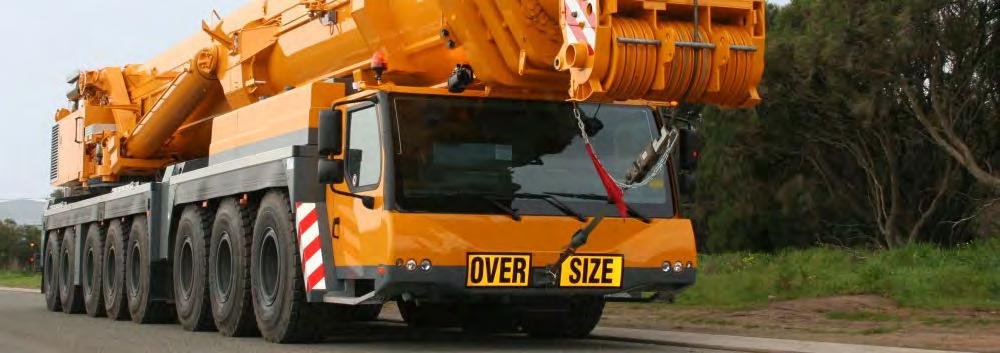
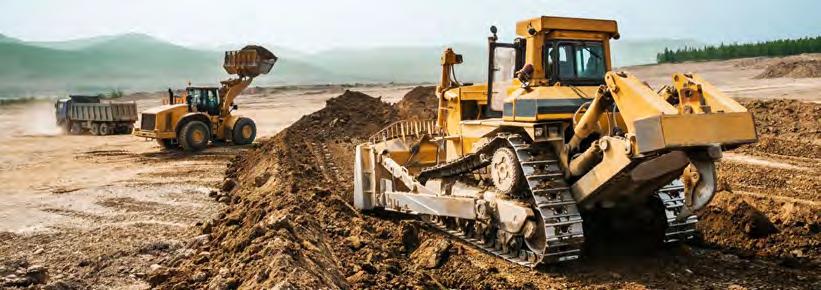
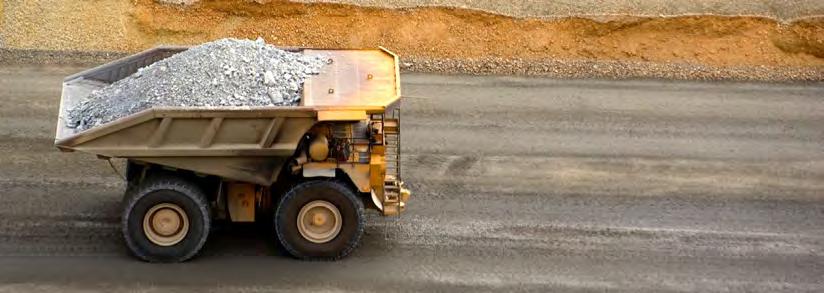
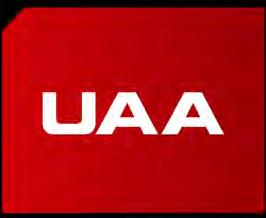
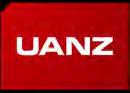
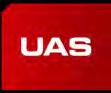
utt Bryant Group First Sany joins Membrey’s Transport &
Complete crane tyre and wheel service.
What’s behind the success of the brand.
TIDD PC28-3G exceeds Team ransport’s expectations.
Still lifting strong, three years on.
Niche insurance forges ahead.
Numerous new products launched
New Hybrids from Grove.
Sennebogen launch 200t tele crawler.
Published by:
industry is showing resilience as it is battered by large players going into administration and the scramble for labour as major infrastructure projects are undertaken around the country.
The latest construction league report,compiled by BCI Centra and powered by Hubexo, ranks Australia’s top construction firms by the total value of projects that commenced in 2024.
Based on live construction data tracked by BCI across thousands of projects, the report captures activity across sectors including commercial, community, industry, legal and military and multi-residential.
This year’s top 10 builders collectively delivered more than 272 projects valued at over $18.6 billion, showing the sector’s ongoing capacity for large-scale delivery despite the volatile climate.
The sector has also faced higher costs and interest rate pressures, as well as the lingering effects of the Covid pandemic, which interrupted supply chains and sent many subcontractors to the wall.
BESIX Watpac topped the rankings in 2024 with more than $3.45b in commencements across just 11 projects – averaging $314 million per build. In second place, Built continued its national dominance, launching 72 projects totalling $3.02b. None of this will surprise the crane sector as we continue to work closely with Tier One builders on projects across the nation.
This issue of the magazine includes our annual feature covering the Western Australian crane sector.
“This issue of the magazine includes our annual feature covering the Western Australian crane sector.”
We also look at bauma, covering some of the more significant procut releases and developments from the major OEMs.
As always, the team at Cranes and Lifting has worked hard to bring you what we hope is a dynamic and interesting magazine full of interesting content and we hope you enjoy the read.
Simon
Gould Editor, Cranes and Lifting
379 Docklands Drive, Docklands VIC 3008
T: 03 9690 8766
www.primecreativemedia.com.au
CEO John Murphy E: john.murphy@primecreative.com.au
Chief Operating Officer
Christine Clancy E: christine.clancy@primecreative.com.au
Publisher Sarah Baker
E: sarah.baker@primecreative.com.au
Managing Editor Lisa Korycki E: lisa.korycki@primecreative.com.au
Editor
Simon Gould
E: simon.gould@primecreative.com.au
T: 0404 865 109
Assistant Editor
Danny D’Cruze
E: danny.dcruze@primecreative.com.au
T: 0429 187 751
Business Development Manager
Emily Schlegel
E: emily.schlegel@primecreative.com.au
T: 0466 317 555
Client Success Manager Louisa Stocks E: louisa.stocks@primecreative.com.au
Art Director Bea Barthelson
Imaging Assistant Paul Breen
Subscriptions
Frank Rapone
T: 03 9690 8766
E: frank.rapone@primecreative.com.au
The Publisher reserves the right to alter or omit any article or advertisement submitted and requires indemnity from the advertisers and contributors against damages or liabilities that may arise from material published.
© Copyright – No part of this publication may be reproduced, stored in a retrieval system or transmitted in any means electronic, mechanical, photocopying, recording or otherwise without the permission of the publisher.
During BAUMA, a highlight from Tadano was the introduction of the CC 78.1250-1, the next generation of lattice boom crawler cranes.
of its predecessor, the CC 68.1250-1, this newest model incorporates significant advancements in performance, safety, efficiency, and transportability.
Designed to meet the evolving demands of heavy lifting applications, including the growing wind power sector, the CC 78.1250-1 achieves a maximum hook height of 224.5 metres when it is equipped with a 15-metre fixed jib. In this configuration it can lift an outstanding 140 tonnes. To improve its stiffness, the width of the base crane was increased to 3.5 metres. Furthermore, the two available crawler shoe widths – 2.0 metres and 2.4 metres – can accommodate varying ground pressure requirements.
“The CC 78.1250-1 represents a significant step forward in Tadano’s crawler crane development,” said Andreas Hofmann, Executive Vice President of Research & Development.
“Customer feedback played a crucial role in its design, ensuring that this crane delivers not only superior lifting capacity but also transport-optimised components and efficient assembly sequences.”
Tadano’s CC 78.1250-1 is designed to offer multiple redundancies maximising uptime and enhancing safety. The crane features a dual-engine arrangement with an optimised hydraulic system, allowing for single-engine operation at reduced speeds. Flexible user-friendly interfaces and an optional dual CAN BUS system contribute to increased reliability and operational flexibility. Additionally, the optional
auxiliary power unit enables cab systems, heating, ventilation, and air conditioning (HVAC), and lighting to operate using a compact 17 kilowatt diesel engine, reducing fuel consumption and emissions during standby operation.
SAFETY AND OPERATOR SUPPORT
Tadano prioritises safety, and the CC 78.1250-1 offers multiple features designed to enhance operator confidence and job site security. The crane is equipped with the Tadano Fall Protection System and incorporates protective access to the superstructure and the undercarriage including improved handrails, catwalks, and access ladders.
The cab design provides an expanded field of view, while an array of cameras and mirrors help the operator see the hoist drums and other blind spots around the crane.
ADD VERSATILITY WITH OUTRIGGERS
For job sites with uneven terrain, an optional Pedestal Crane (PC) kit replaces the crawlers on the undercarriage with outriggers enabling precise levelling at three different outrigger bases – 12m x 12m, 14m x 14m, and 16m x 16m –offering compatibility with existing foundations. This capability enhances setup efficiency while reducing both time and environmental impact.
SUSTAINABILITY AND SMART MONITORING
The CC 78.1250-1 features the IC-1 control system, which is standard on all Tadano crawler cranes and well accepted by operators.
The IC-1 also gives the operator real-time ground pressures on the rigging aids when erecting long boom systems. This system boosts efficiency with intuitive controls and precise configurations and provides essential information for safe and efficient operations.
The crane’s twin Mercedes-Benz engines are compatible with HVO (hydrotreated vegetable oil fuel), reducing carbon dioxide (CO₂) emissions without sacrificing performance.
Additionally, Tadano’s IC-1 Remote telematics solution enables real-time diagnostics and remote troubleshooting,
minimising downtime and optimising fleet management.
The CC 78.1250-1 has been designed for ease of transport, which includes accessible lifting points on components to make the assembly safe and efficient. Manufactured in Zweibrücken, a centre of excellence for mobile cranes, the crane adheres to worldclass safety standards and uses high-quality components from established partners.
In an ever-changing industry, Tadano remains committed to delivering lifting solutions that combine reliability, efficiency, and sustainability – ensuring customers can invest with confidence.
The first Tadano hybrid, the AC 4.070HL-1 is now available to order and is followed by the AC 5.120H-1 which features double the battery capacity.
The AC 4.070HL-1 is the market-ready version of the four-axle 70-tonne crane that the innovation leader showcased as a tech demo in 2022. Since then, the corresponding pre-production models have received an overwhelmingly positive response after both testing and real-life use.
The 120-tonne AC 5.120H-1 crane, which was developed on the basis of this experience, is the next model in the series.
These new hybrid crane developments are a result of Tadano’s ambitious “Tadano Green Solutions” (TGS) environmental protection strategy, which has the goal of reducing the company’s CO₂ emissions between 2019 and 2030 by 25 per cent worldwide.
Over the same period, Tadano aims to cut CO₂ emissions from the use of its products by 35 per cent. The goal is to be completely climate neutral by 2050.
One important step towards this goal is the hybrid crane solutions, which generate about 60 per cent less CO₂ than dieselpowered superstructures. Electric crane operation has a system efficiency of about 85 per cent, which represents more than double the energy efficiency of an efficient diesel engine.
Designed to meet the evolving demands of heavy lifting applications, including the growing wind power sector, the CC 78.1250-1 achieves a maximum hook height of 224.5 metres when it is equipped with a 15-metre fixed jib.
The first of Tadano’s AC 4.070HL-1 has arrived in Australia and is currently based in Western Australia with General Crane Services WA Pty Ltd .
A combination of conventional travel and fully electric on-site operation is made possible by the new Tadano AC 4.070HL-1 hybrid crane and the upcoming AC 5.120H-1.
More specifically, the diesel carrier engine is responsible for bringing the crane to its work site, where the engine can then be switched off for the duration of the job once the outriggers have been deployed.
Meanwhile, the high-voltage (HV) battery in the superstructure powers an electric motor, as well as the thermal management system and the superstructure cab’s air conditioning. The electric motor powers the hydraulic system used for crane operation, all with zero restrictions on the corresponding performance.
Tadano hybrid cranes can be operated both self-sufficiently with their own battery power and with the support of an external power source, such as temporary work site power. The latter not only extends a unit’s multi-hour electric runtime, but can also relieve the load on the HV battery. In
addition, these hybrid cranes remain fully operational even when the HV battery is fully depleted and no external power supply is available. This is thanks to a generator that is driven by a power take-off on the carrier’s diesel engine that charges the HV battery and allows for continued crane operation.
Finally, the hybrid cranes also feature a separate and time-tested 24-V vehicle electrical system that can be used for derigging in case of emergency.
The HV components and their accessories in the superstructure are housed in the packaging space that would normally correspond to the eliminated superstructure engine.
The compact electric motor is in the exact same position as the internal combustion engine it replaces, and runs with the same maximum speed. This makes it possible for the hydraulic unit used for crane operation to remain unchanged and in its original position – a plus when it
comes to maintenance and spare parts for the unit, which can be smoothly activated and deactivated. The HV battery is located above the electric motor, surrounded by battery thermal management system components and battery management system components. The HV components’ layout is optimised for short cable runs, good coolant flow to cooling elements, and ease of maintenance and repair.
The vehicle inlet for charging is on the right side of the rear end, leaving enough storage space to the left, as well as enough space for a trailer hitch in the centre. When selecting HV components, Tadano follows its tried-and-true strategy of using components that come from reputable suppliers and conform to industry standards. As a result, the HV battery has a modular design and can be accessed in a straightforward manner.
Best things first: Tadano hybrid cranes have the exact same lifting performance, lifting capacities and axle load capacities as their counterparts with two internal combustion engines, meaning that the slight increase in weight represented by the hybrid system is not tied to any loss of performance.
As with other electric vehicles, the purchase price is higher than that of comparable models with an internal combustion engine. However, these hybrid cranes pay for themselves as a result of their extra advantages. In fact, quiet and zeroexhaust-emission crane operation means that new applications and potential sources of revenue can be tapped into:
Tadano did not take any short cuts when it came to the software used to integrate the high-voltage system. The HV components are linked and controlled with in-house software developed internally by the company’s own IT resources, ensuring the hybrid cranes’ reliable suitability for daily use. The crane functions remain hydraulically powered, giving operators the same familiar, highly responsive control feedback, particularly since all HV-specific information has been smoothly integrated into the display solution.
Engineered for height, power and control, the Dieci Icarus 40.17 is the ultimate telehandler for large scale construction and industrial projects. With a maximum lift height of 16.6 metres and a 4,000kg capacity, this robust performer delivers exceptional reach without compromising on stability or safety. Its advanced hydrostatic transmission with inching control ensures pinpoint precision even under full load, while the spacious, soundproofed cab and 360° panoramic visibility keep operators comfortable and in command. Whether you’re lifting, loading or positioning at height, the Icarus 40.17 is built to outperform every time.
Max Capacity: 4,000 kg Max Lift Height: 16.60 m
Speed: 35 km/h
Power: 93 kW (125 hp)
Having just returned from two international trips where we had the privilege of representing CICA on the global stage, I’m feeling optimistic about the road ahead for our industry.
THE AUSTRALIAN CRANE SECTOR continues to earn respect internationally. More and more, we are being invited to join roundtables and forums to share our expertise, and it’s clear our collective voice is being heard. This recognition opens doors –not just for CICA, but for every one of our members. It gives us a platform to advocate for continued development, world-class safety standards, and longterm investment in our sector.
Back at home, the recent Federal election has ushered in another term for the Labor government. Their re-election comes with a bold agenda that has the potential to reshape the construction landscape in Australia, and with it, significant opportunities for our industry.
Here are some of the key initiatives and their implications for the crane sector:
• Ambitious housing targets: The commitment to build 1.2 million new homes over five years, including 100,000 dedicated to first-home buyers, will create a major pipeline of work for the construction industry. The government’s direct investment in enabling infrastructure and land development will support builders, developers, and the crane operators working alongside them.
• Support for new construction methods: $54 million allocated to boost advanced manufacturing, especially modular and prefabricated construction, with the objective of faster build times and greater
fast-tracking trade qualifications through the Advanced Entry Trades Training Program is timely. As our industry continues to face skilled labour shortages, this initiative will help bring experienced workers up to speed faster and CICA is wellplaced to advocate for a focus on
to support local supply chains. CICA will keep lobbying to ensure crane-related equipment, training, and infrastructure are part of this investment.
We’re committed to working with key departments on three critical areas – training, road access and ROVER. The
crane industry needs a coordinated response to address the skills shortage and ensure that crane importation, road access regulations, and infrastructure planning reflect the realworld needs of our members.
CICA is investing heavily in building the pipeline of future talent. Through the Launch into Work program and a series of upcoming careers expos across multiple states, we’re taking crane careers directly to the next generation.
We’re especially excited about our new high-spec crane simulator, now housed in a purpose-built trailer. This mobile experience will be a major drawcard at expos, giving tech-savvy job seekers a hands-on taste of crane operation and giving us the chance to introduce them to the diverse and rewarding roles available.
We’re also working on a major content project, filming across Australia to tell authentic stories from within our industry. From operators and engineers to logistics coordinators, project managers, and tech innovators, this campaign will showcase the full breadth of career paths in cranes. Keep an eye out for this inspiring content and don’t forget to share it across your social networks when it drops!
Finally, a reminder that registrations are now open for the 2025 CICA National Conference, being held in sunny Queensland from Wednesday 15 – Friday 17 October. With an exciting line-up of speakers, fantastic networking opportunities, and engaging social events, this is shaping up to be an unmissable event. Take advantage of early bird pricing and secure your spot at: https://conference. cica.com.au
Thanks again for your continued support and commitment to advancing the crane industry in Australia. I look forward to connecting with many of you over the coming months and seeing you in Queensland in October.
Stay safe, Brandon
CICA BOARD
Ben Pieyre – President
Marcus Ferrari – Vice President
Danny Adair – Director
Danny Black – Director
David Solomon – Director
Karli Sutherland– Director
Tom Clark – Director
Anthony Grosser – Director
Andrew Esquilant-Director
Brandon Hitch
Chief Executive Officer 0428 228 048 ceo@cica.com.au
Alice Edwards Road Technical Engineer 03 8320 0440 alice@cica.com.au
Patrick Cran
CICA Site Operations Advisor 0488 004 274 pat@cranesafe.com.au
Sharon Pearce
Crane Crew Competency Officer 0491 134 533 sharon@cica.com.au
Damien Hense
CICA Road Policy Advisor 0488 007 575 damien@cica.com.au
Thomas Webber Communications Coordinator thomas@cica.com.au
Kate Galloway Traineeship & Industry Engagement Coordinator
0491 047 118 kate@cica.com.au
Michelle Verkerk
Communications and Special Projects Advisor michelle@cica.com.au
Just ina Blackman
Member Events and Engagement 0403 717 626 justina@cica.com.au
Ashleigh Gould Office Operations Coordinator 0490 356 041 ashleigh@cica.com.au
Shane Coupe
CraneSafe & CrewSafe Administrative Assistant Officer 0491 047 134 shane@cica.com.au
Unit 10, 18–22 Lexia Place, Mulgrave Vic 3170
Phone: 03 9501 0078
Email: admin@cica.com.au
Website: www.cica.com.au
For information, please visit our website or call the CICA office.
WITH WORKPLACE FATALITIES ON THE RISE, it is more important than ever for employers to be aware of industrial manslaughter laws, which have now been enacted in all Australian jurisdictions.
Industrial manslaughter is a criminal offence where a person conducting a business or undertaking (PCBU) has recklessly or negligently failed to ensure the safety of workers or others impacted by their business or undertaking, resulting in a fatality.
Although the legal test differs across jurisdictions, essentially an individual or PCBU commits industrial manslaughter if the PCBU or person:
1. has a work health and safety (WHS) duty under the safety law;
2. engages in conduct that breaches a duty they owe under the WHS laws and that conduct causes the death of an individual; and
3. engages in conduct in circumstances knowing it is likely to cause the death or serious harm to an individual, or in disregard of that likelihood.
The adjacent image sets out the industrial manslaughter offences across Australia and when each state and territory introduced the offence. (See map top of opposite page). These offences carry serious consequences and should not be taken lightly by company directors or construction businesses as they carry significant maximum penalties, including imprisonment.
As at May 2025: (See table on the right.)
The Victorian Court of Appeal recently ordered that LH Holding Management Pty Ltd pay a fine of $3 million for breaching Victoria’s industrial manslaughter offence.
LH Holding is a stonemasonry business, solely owned and managed by Mr Hanna. The company regularly engaged
tipped, pinning him to the ground.
At the time of the incident, Mr Hanna was using the forklift to move an empty A-frame used to store stone slabs in LH Holding’s factory. Michael was on the ground, helping to steady the heavy load. Despite warning Michael to move, Mr Hanna manoeuvred the forklift sideways on the slope with the load suspended high above the ground – contrary to basic safe operating procedures.
It was found that this caused the forklift
on site used a second forklift to lift the mast off Michael and CPR was attempted. However, Michael could not be resuscitated and died at the scene.
LH Holding pleaded guilty before a judge in the Supreme Court to workplace manslaughter.
In the first instance, the Supreme Court ordered a $1.3 million fine on LH
Holding. In reaching this decision, the Court considered and weighed several factors, including:
• the fatality was caused by LH Holding’s negligence and the operation of the forklift across a slope with a high swinging load was contrary to basic safety rules
• Mr Hanna believed that Michael had moved away before he began to reverse the forklift
• the negligence occurred for a matter of seconds
• it would be very unlikely that Mr Hanna, LH Holding, or any future business he might establish, would ever be involved in a similar incident
• LH Holding continued to trade and had assets of between $300,000 and $400,000.
Mr Hanna was convicted and placed on a two-year Community Correction Order, with additional conditions that he complete 200 hours of unpaid community work and complete a course in forklift operation.
The Department of Public Prosecutions (DPP) appealed the decision, arguing that the sentences ordered were manifestly inadequate.
The Court of Appeal allowed the DPP’s appeal and increased the fine imposed on LH
Holding to $3 million, finding that the initial sentence was grossly inadequate.
In reaching this decision, the Court of Appeal considered and weighed several factors, including:
• the offending was not in the worst category
• the incident was a single act of unsafe conduct, rather than the result of ongoing, tolerated unsafe work practices
• Mr Hanna had, only a few months before the incident, completed a course on the safe operation of forklifts
• despite his recent training, Mr Hanna’s operation of the forklift involved a very significant departure from acceptable safety standards
• Mr Hanna was aware that Michael was near the forklift at the time
• the court is not prevented from ordering a fine that the offender is unable to pay. More importantly, an offender’s financial capacity cannot be a reason for a penalty that fails to reflect the objective seriousness of the offence or the need for general deterrence
• the imposition of a fine greater than $1.3
million will be “ruinous for the company” and will “very likely remain unpaid”. Although this is a Victorian case, the sentencing principles applied will likely be instructive to other jurisdictions.
This case serves as a stark warning to construction companies and their officers. Failing to comply with WHS duties by not taking reasonably practicable measures to protect the health and safety of their workers can lead to severe consequences. These may include substantial fines – potentially enough to bankrupt the company – and imprisonment for a serious offence.
The information in this publication is of a general nature and is not intended to address the circumstances of any particular individual or entity. Although we endeavour to provide accurate and timely information, we do not guarantee that the information in this article is accurate at the date it is received or that it will continue to be accurate in the future.
ON CONSTRUCTION SITES ALL AROUND
Australia, time is money and safety is paramount; so poorly planned lifts can lead to costly asset damage and serious injury, or worse.
One of the most overlooked risks comes down to something deceptively simple: failing to properly identify lifting points and load supports (gluts) before a lift or transport task begins.
Clear identification of lifting and support points is non-negotiable, not just for load security, but to protect equipment and people.
MORE THAN JUST A LUG
Designated lifting points must be engineered and clearly marked. These points – typically weld-on lugs, swivel eyes, or certified lifting rings – must be rated, tested, and labelled with their Working Load Limit (WLL), manufacturer, and identification number, in compliance with AS 4991:2004 and AS 1418.8.
Poorly placed or unidentified lifting points create significant risks, and an incorrect sling angle or undersized lug can result in overstress and failure. Ensure lifting points are:
• Certified and rated for the intended lift.
• Compatible with the hook or sling setup (to avoid side-loading).
• Inspected for wear, deformation, and weld integrity.
Using colour-coded or serial-numbered lugs that correspond with engineered lift plans helps teams in the field verify they’re lifting safely, before the crane even leaves the yard.
STABILITY STARTS AT THE BOTTOM
Gluts, also known as dunnage or bearers,
are critical for stable lifting, transport, and storage. These supports distribute weight, prevent damage to load components, and provide clearance for forklifts or slings.
In practice:
• Use only load-rated gluts (e.g., engineered plastic or hardwood).
• Avoid softwood or damaged timber, which can crush under load.
• Position gluts in line with structural support points, as shown in manufacturer diagrams or lift plans.
• Where possible, use full-width gluts to
minimise point loading and spread the footprint evenly.
Using gluts improperly, or not at all, can deform structural components or cause instability in transit. Proper placement also prevents machinery from rolling or tipping when parked on uneven ground.
Securing loads is more than throwing a strap over and hoping for the best. Chains, straps, and tie-downs must:
• Chain used for load restraint should comply with Australian Standard AS/ NZS 4344 specifications.
• Be matched in strength to the load’s mass and movement direction.
• Attach to certified anchor points (both on the load and the truck).
Each restraint device must be tensioned correctly. Friction aids like rubber mats or timber dunnage can increase load stability by increasing grip. Importantly, restraint devices must not interfere with or damage lifting points or crane components, which can be a common error when rushing to secure loads.
The Centre of Gravity (CoG) is a critical concept in lifting operations. It refers to the imaginary point in a body where the total weight can be considered to act. In practical terms, it’s the balance point, where mass is evenly distributed in all directions. Understanding and accounting for CoG is essential for ensuring machine stability, load control, and safe lift planning.
In crane operations, CoG affects how the load behaves when lifted, how the crane responds dynamically, and whether the lift remains within safe operating limits. A suspended load behaves very differently from a palletised or grounded one, primarily due to how the CoG shifts within the lifting system.
When a crane lifts a load, the load and crane effectively become a single, combined system. The total CoG of this system shifts depending on the boom angle, load position, and boom length.
For example, before lifting, the crane’s CoG is determined by the crane component configuration – boom, boom angle and length, counterweight, slew angle, etc . As the crane hoists a load from the ground, the CoG of the combined system moves both upward and toward the load the moment the load becomes suspended. This occurs because the suspended mass acts through the boom head rather than where the load’s CoG.
This effect is shown in Figure 1, where a six-axle mobile crane lifts a 10-tonne load at different boom lengths. Note how the CoG moves as the crane geometry changes:
The suspended load under the crane hook is free to tilt and move, in most simple lifts (not using any special equipment) the load will tilt or move until the CoG of the load is directly under the crane hook, and it will stay this way during the lift process until the load is placed on a supporting surface.
The CoG isn’t always where you think it is. Heavy components, fluid-filled chambers, or irregular shapes can create a hidden bias that causes the load to tilt or swing once airborne. Offset CoGs that aren’t planned for can unexpectedly uneven load slings, overload or sideload the crane, and result in load swing. These put workers and gear at risk, so accurately anticipating the CoG shift allows operators to maintain safe load charts, prevent overload, and reduce risk of instability.
Always refer to manufacturer load charts that account for boom position, radius, and lifting configuration, and conduct lift simulations where possible for complex picks.
Best practice:
• Always keep the crane hook directly above the CoG.
Finding the right position of the centre of gravity is more complex when the contents of the load have the potential to move.
• Use an adjustable spreader beam or different sling lengths to balance uneven loads.
• Conduct a short “test lift” to check level.
• Record CoG locations and sling setups in the lift plan for future repetition.
Lifting diagrams and rigging plans are essential tools – especially for heavy or irregular lifts. These should include:
• Load weight and CoG.
• Sling types and lengths.
• Attachment points (with labels or photos).
• Lifting angles and WLL calculations. Lift supervisors must ensure that what’s drawn matches what’s on the ground. That means verifying lug locations, checking against lifting certificates, and briefing the whole team
Machine specific checklists are in line with the CraneSafe program.
before starting the lift. Diagrams also serve as traceable documentation and are vital if something goes wrong or regulators come knocking.
Crane components are often overlooked in lift planning, but they’re just as vulnerable as the load itself. To prevent damage:
• Properly maintain the crane and running gear.
• Confirm hook latches are functional.
• Avoid shock-loading, swinging, or dragging the hook.
• Secure the boom, blocks, counterweights and tools during transit.
That means ensuring it’s not just working, but working without unnecessary stress, wear, or risk.
Clear lifting points. Proper gluts. Certified restraints. Balanced Centre of Gravity. Engineered diagrams. Protected cranes.
These are the fundamentals of every safe and successful lift and ignoring any of them risks not only your load, but your equipment, site schedule, and most importantly, your team.
Because it’s not just about getting the load from point A to point B, it’s about doing it without causing damage, injury, or downtime.
Under WHS regulations and AS 2550, the crane must be “maintained in a safe condition” and used “only for the purposes and loads it was designed for.”
Photos tell the story.
For more information on the CICA Member benefits, including access to Australian Standards and reduced pricing on the CICA Lift Supervisor Course, go to: www.cica.com.au
More than just a pre-start checklist
StartSafe is comprehensive tool designed to streamline your crane operations, enhance safety, and ensure accountability.
StartSafe streamlines the process for collecting pre-start information, with instant data retention to a central location for the crane owner to access.
When a faulty item is recorded by the operator, the maintenance team is notified of the issue by email, which includes photo evidence of the fault. This also assists with gathering major inspection data.
Machine specific checklists are in line with the CraneSafe program.
StartSafe streamlines the process for collecting pre-start information, with instant data retention to a central location for the crane owner to access.
Photos tell the story.
When a faulty item is recorded by the operator, the maintenance team is notified of the issue by
Guiding operators through the CICA Articulated Mobile Crane On-Road Course.
IN THE CRANE INDUSTRY, PRECISION, expertise, and safety go hand in hand, so making training accessible and engaging is essential. That’s why the Crane Industry Council of Australia (CICA) teamed up with one of the sector’s most trusted voices to simplify and support the verification of competency journey for articulated mobile crane operators across the country.
A brand-new, step-by-step instructional video has been produced to guide operators through every phase of the Articulated Mobile Crane (AMC) On-Road Course. From the initial sign-in to the adaptive learning module (Part 1), right through to the final practical component on CrewSafe (Part 2), this video is all about improving access, understanding, and ultimately, safety outcomes.
CICA has collaborated with Kieran Greham, Director of Kieran’s Training. With over 35 years of hands-on industry experience, Kieran is not only a seasoned crane operator and trainer, but also a familiar face with a strong YouTube presence and social media following. His approachable, no-nonsense style and deep respect for crane safety make him the ideal guide for this initiative. He speaks the language of the industry, because he’s lived it.
played a pivotal role in selecting the right person to front the video. Kieran brings not just expertise but credibility. His passion for lifting industry standards is evident, he is a strong ambassador for the message: respect the machine, respect the process.
“Simplifying complexity” was a core driver behind the video’s creation. The two-part structure of the AMC course, while comprehensive, had been flagged by some as a potential barrier. By visually demonstrating each step of the process, the video removes ambiguity and helps operators feel confident and in control of their learning experience. Just as importantly, familiarity and trust
Filming took place at Borger Cranes’ yard in Sydney on 24 and 25 March 2025, and CICA extends its sincere thanks to the Borger Cranes team for its support and hospitality, and to Kieran for his enthusiasm and professionalism throughout.
This project is funded by the National Heavy Vehicle Regulator’s Heavy Vehicle Safety Initiative, supported by the Australian Government.
By combining technical clarity with the voice of lived experience, CICA is proud to deliver a resource
A brand-new, step-by-step instructional video has been produced to guide operators through every phase of the Articulated Mobile Crane (AMC) On-Road Course.
that informs and gets alongside operators and those involved in crane operations, because crane safety is everyone’s responsibility.
To watch the video, scan the QR code, and for more information on the Articulated Mobile Crane On-Road Course and how to complete it, go to https://www.cica.com.au/The-CICAOn-Road-Course or contact Sharon Pearce, CICA Crane Crew Competency Officer on: admin@crewsafe.com.au or (03) 9501 0078.
The New Zealand crane industry, like much of the construction sector, continues to bear the brunt of prolonged government austerity measures. The uncertainty and delay in infrastructure and vertical build projects are having a real and measurable impact – not just on confidence, but on cashflow, capability, and the very survival of some of our members.
AS WE AWAIT THE MAY BUDGET, MANY in the industry are hoping for a signal that the government is ready to shift gears and invest decisively. But hope is not a strategy. What we are hearing from members across the country is that they are operating at the sharp end of a painful downturn, with far too many cranes parked in yards and not enough on sites. It’s not just a lull – it’s a crisis of momentum.
We are not alone in sounding the alarm. Engineering New Zealand, Civil Contractors NZ, and many others have delivered the same message: if the government waits too long to ignite the engine of capital spending, it will find the tank empty when it’s finally ready to move. The trades workforce is finite. Skilled professionals who down tools now may not be available when the calls
go out later. Recovery will be slower, harder, and costlier as a result.
This week, I had the opportunity to deliver this message directly to Minister of Building and Construction, Chris Penk, as part of a delegation convened by the Specialist Trades Federation – a group CANZ is proud to have recently joined. The minister was receptive, inquisitive, and showed a genuine willingness to listen. He acknowledged the critical issues we raised, including the need to act swiftly if we are to avoid losing capacity in our workforce and our industry.
We were encouraged to hear there may be movement coming in construction for the education and health sectors. However, what the government defines as “soon” rarely aligns with the financial runway available to crane
companies and other specialist trades. Businesses cannot wait indefinitely. The cranes are idle now. Our people are available now. What we need is not another promise, but a pipeline.
Of course, we recognise the economic constraints the government is grappling with. But this is not just a question of fiscal prudence – it’s one of economic foresight. Every delay in reactivating construction momentum pushes New Zealand further from recovery. Investment in infrastructure and public assets is not a cost to delay, but a catalyst to rebuild.
The Association will continue to advocate loudly and consistently. We are engaging not only with government but with industry partners, clients, and regulators to ensure our members’ voices are heard and their needs are understood. Because when the country is ready to build again, we will be standing by – skilled, prepared, and ready to lift New Zealand’s future into place.
· 288kwh large-capacity power battery with excellent endurance
· 215kW permanent magnet synchronous motor
· Zero emission and low noise
· 240kW DC dual-gun charging power is enables full charging in 1.5h only
· 40kW AC charging power, equipped with a 50-meter cable reel, compatible with mains electricity, and supports simultaneous charging and operation
· High-voltage interlocking (HVIL) technology
The fifth Global Lifting Awareness Day (GLAD) is set for 12 June 2025. From humble beginnings, this year is a significant event dedicated to addressing skills shortages and shaping the future workforce in the lifting industry. The theme, “Lifting Careers, Building Futures,” aims to attract new talent and inspire the next generation to explore careers in the lifting industry.
THE LIFTING INDUSTRY IS A VITAL PART of the global economy, worth billions of dollars annually. It encompasses a wide range of sectors including construction, oil and gas, mining, infrastructure, logistics, and entertainment.
The importance of lifting equipment and the professionals who operate and maintain this critical industry cannot be overstated. From cranes and hoists, to chains and ropes, lifting equipment is essential for moving loads safely and efficiently. However, the industry faces significant challenges, including a shortage of skilled workers and the need for continuous training and development to keep up with industry’s evolving needs.
While LEEA addresses these issues at a governmental level by highlighting the need to have occupations aligned to these roles, and educational pathways for industry professionals, we also need to bring people into our industry through schools and at grassroots level to develop talent from the ground up.
GLAD 2025 seeks to address these challenges by raising awareness of the incredible opportunities available in the industry and encourages individuals to consider this global industry, as one filled with diverse roles and enormous career potential.
The event will feature webinars, workshops, and live interviews, designed to showcase the diverse roles and career paths within the industry. Participants will have the chance to hear from industry experts, gain a broader understanding of lifting equipment, and explore the latest innovations and technologies.
One of the highlights of GLAD 2025 is the Australia and New Zealand industry Honour Roll, which showcases those who paved the way for the success of our industry. The lifting equipment industry is often overshadowed by more glamorous segments in our sector, but without the experience of those who came before us, we wouldn’t be in the strong position we’re in now.
We are the proud custodians of this industry today. An incredible industry, filled with opportunities. The roll will feature individuals and members who have made significant contributions to the lifting industry. It will demonstrate the wide range of career paths and opportunities available, and is a celebration of the professionals who have dedicated their careers to ensuring the lifting equipment industry is at the forefront of safety and best practice.
The honour roll also serves as inspiration for those considering a career in the industry. By highlighting the achievements of industry stalwarts, leaders and innovators, GLAD 2025 aims to attract new talent and encourage individuals to pursue careers in this dynamic and rewarding field.
The industry offers a range of opportunities for individuals with diverse skills and backgrounds, from technical and engineering roles to
management and safety positions. With the right training and qualifications, individuals can build successful and fulfilling careers.
In addition to the honour roll, GLAD 2025 will feature the inaugural LEEA Legend Award, which celebrates outstanding contributions to the industry and community and recognises individuals who have made a significant impact.
The LEEA Legend Award is designed to honour those who have demonstrated exceptional dedication, innovation, and leadership within the lifting industry and aims to inspire the next generation.
This inaugural industry legend has played a crucial role in advancing standards, has driven innovation, and promoted best practices within the sector. Their achievements in the lifting industry, but also their local community, serve as an inspiration for others and highlights the potential for growth and development within this industry.
GLAD 2025 also emphasises the importance of training and education in addressing the skills shortage within the lifting industry. The event will feature a range of educational activities, including the new inductees to the Certificate IV in Lifting Equipment Testing and Inspection, how LEEA’s TEAM Card certification program benefits Safe
Users of lifting equipment, and career development workshops.
These activities are designed to provide participants with the knowledge and pathways needed to succeed in the lifting industry and ensure the safe and efficient operation of lifting equipment.
Training and education are essential for maintaining high safety standards and ensuring the continued growth and development of the lifting industry.
By investing in training and education, the industry can attract new talent, retain skilled workers, and keep up with technological advancements.
GLAD 2025 aims to promote the importance of continuous learning and development and encourage individuals to pursue training and certification
equipment and automation to digital tools and data analytics, the industry is embracing new technologies to improve safety, efficiency, and productivity.
GLAD 2025 will showcase innovators and the people behind the lifting industry, providing participants with the opportunity to learn about this global industry and explore how they can be applied in their own careers.
Innovation is a key driver of growth and development within the lifting industry. By embracing new innovation and best practice, the industry can improve safety standards, increase efficiency, and create new opportunities for career growth and development.
GLAD 2025 aims to highlight the importance of innovation and encourage
skills shortages and shaping the future workforce in the lifting industry. With its focus on raising awareness about career opportunities, celebrating industry achievements, and promoting training and education, GLAD 2025 aims to attract new talent and inspire the next generation of lifting professionals.
The Australia and New Zealand industry honour roll and the inaugural LEEA Legend Award highlight the achievements of industry leaders and innovators, demonstrating the wide range of opportunities available within the lifting industry.
By showcasing the latest innovations and technologies, GLAD 2025 provides participants with the
When Wheeler Cranes made the move to a sprawling 22,000-square-metre facility in Hexham, New South Wales it wasn’t just the physical footprint that expanded – it marked a broader shift in how the business approached operations, technology, and efficiency.
FOR GENERAL MANAGER GLENN WILBOW, the shift to a new facility also led to a strategic decision to return to Visual Dispatch, a crane scheduling and logistics software platform that the company had first adopted more than a decade ago. “We initially took on Visual Dispatch
“We needed something that could handle electronic sign-on, digital job tickets, and cloud access,” said Glenn. “At the time, Visual Dispatch didn’t offer that, so we gave a couple of alternatives a shot. But, to be honest, they just didn’t cut it.”
The alternatives promised modern
In the end, Glenn said, the team’s frustrations led them full circle. “We went through two other systems before coming back to Visual Dispatch. Once they introduced the new cloud-based version –with sign-on-glass, better integration, and Australian support – it just made sense. And when I told the staff we were going back, they were ecstatic. It was like telling them they were getting their old tools back – just sharper and faster.”
For crane businesses managing multiple crews, cranes, and sites across tight schedules, dispatching is the nerve centre of the operation. Visual Dispatch’s drag-and-drop interface gives Glenn’s team a bird’s-eye view of all resources in real time.
“We used to need three screens open just to track jobs, crews, and compliance,”
Lara Roulston, Allocations Manager and Logan Flutey, Operations Coordinator at Wheeler Cranes’
You can’t just throw anyone into any job, it’ll tell you straight away what’s wrong.”
That level of automation is vital for a fleet of 30 cranes, ranging from 20-tonne to 250-tonne models, operating in a heavy industrial environment.
“We’re working in a high-risk sector where there’s no room for error. Visual Dispatch doesn’t just help us schedule, it helps us stay safe and compliant,” said Glenn.
Perhaps the most dramatic improvement has come in invoicing. “We’re currently doing around 40 to 45 jobs a day,” Glenn said. “And I’ve got just one person managing all the invoicing. That would’ve been impossible with our previous systems.”
As soon as a crew finishes a job and submits the digital docket, the system updates instantly.
“The job ticket changes colour on the screen so the allocators know it’s ready. They check the details, click complete, and it’s ready for invoicing. There’s no back and forth. No guessing.”
“Having everything – from job scheduling to servicing to compliance – on one platform is the dream.”
His team, particularly those in accounts, are seeing the benefits too. “My wife used to do all the invoicing,” he laughs. “She’s a fast typist, but even she was getting frustrated typing the same line 40 times a day. Now, the system remembers line items. You start typing, and it autocompletes. No typos. No duplication. No spelling mistakes. It saves hours.”
Mistakes in invoicing – what Glenn calls “rework” – are now rare. “Getting an invoice wrong and sending it to a customer is embarrassing. That’s just not happening anymore. Accuracy has gone through the roof.”
Wheeler Cranes is now working with the Visual Dispatch team to implement more features. Through the acquisition of Rapid Fleet, Visual Dispatch is integrating
pre-starts, fuel tracking, and service logs directly into the software.
“Having everything, from job scheduling to servicing to compliance, on one platform is the dream,” said Glenn. “I want my team to start their shift, swipe on at the fuel tank, record their hours, and have that data update the maintenance logs automatically. Visual Dispatch is getting us there.”
Even in its current form, Glenn sees the software as a long-term solution. “We’ve looked around. We’ve tested what else is out there. And honestly, Visual Dispatch is ahead of the pack by a country mile.”
For a business as fast-paced as Wheeler Cranes, the value of a reliable, intuitive software platform cannot be overstated.
“We’re not a software company, we lift heavy things for a living,” Glenn said. “We need systems that support that, not slow it down. With Visual Dispatch, we’ve found that balance.”
Dotmar Engineering Plastics offers high-performance load distribution materials tailored for the crane industry.
Our lightweight, durable solutions replace traditional steel and timber, delivering superior strength and reliability. Backed by engineering calculations, Dotmar products are designed to protect ground surfaces and support heavy lifting in all environments.
Engineered to perform. Trusted to support.
Polystone Confetti Grade Recycled UHMWPE
A sustainable and economical alternative that provides reliable strength and durability for everyday crane operations. Confetti grade plates are lightweight, corrosion-resistant and suited for general load distribution.
Ertalon/ Nylatron Nylon
A premium engineering plastic offering excellent mechanical strength and wear resistance. Nylon outrigger plates are ideal for applications requiring high load-bearing capacity, dimensional stability, and long service life under repeated use.
Both materials can be also used to manufacture stackable Dunnage Blocks , designed for ground levelling and height adjustment on uneven or sloped terrain, working alongside outrigger plates to ensure safe, stable footing.
Confetti Recycled
Nylatron
Safe working loads are per outrigger, based on the smallest contact area on flat, even ground. For application-specific calculations, contact Dotmar Engineering Plastics. Custom sizes available.
Select Plant is prepared to invest in the very latest technology, even if the market isn’t quite ready.
In an industry where precision, power, and performance are non-negotiable, staying ahead of the curve means more than just keeping up with technology – it means making the right investments at the right time.
At the forefront of this strategic evolution is Ruairi Mawn, Business Leader at Select Plant Australia. With a sharp eye on customer needs and a deep understanding of asset performance, Ruairi and his team are redefining how plant and equipment decisions are made – ensuring every dollar spent drives value, efficiency, and future readiness.
A subsidiary of a privately owned, global construction company, Select Plant Australia boasts a tier one pedigree.
“Although we provide solutions to several industries, the construction sector is our heritage. Select Plant Australia has been in operation in Australia for almost 18 years, so we are well and
truly established. Over that time, we have evolved into a solutions provider to numerous clients across many industry sectors,” said Ruairi.
“We continue to invest in a wide and diverse fleet of plant and equipment. The fleet includes cranes and lifting assets, but it also spans across material handling equipment, traffic management, offices on construction sites, fleet and heavy vehicles. With a diverse portfolio of fleet and equipment we can provide our customers with ‘turnkey’ solutions.”
Select Plant has four operation pillars: cranes and lifting, construction site office solutions, plant hire and logistics services. Each pillar has a different way
of approaching the market, said Ruairi.
“In some cases, we’ll provide our services through our supply chain partners but we also work directly with customers providing solutions for the challenges we know they face delivering major construction projects.
“Our heritage sets us apart in the industry because we truly understand the challenges that our customers face, particularly the major projects and very complex projects that get delivered in today’s world,” he said.
Select operates from a national footprint with a strong presence in Western Australia, New South Wales and a new facility in Victoria.
“In New South Wales, we operate two main and a couple of satellite facilities and it’s the same in WA with two main facilities in Malaga and Bassendean and a number of satellite. We’ve just moved into our new Sunshine West depot here in Melbourne which is a major step forward for us and it talks to the investment in our people and asset base. As out team grows, so does our commitment to providing a workplace that meets the high standards for health, safety and wellbeing.
“This new facility in Melbourne is almost triple the size of our previous premises and it confirms our intent to grow and invest in our facilities and our people. The reality is, we deploy plant, people and solutions nationally from as far north as Darwin down through Queensland to regional New South Wales and everywhere in between.”
Industries are evolving and sustainability is now a key topic across many sectors. Ruairi confirms Select’s commitment to a sustainable future.
“We’re invested in hybrid solutions and we are seeing these being deployed. Investing early in technology can mean a higher price point but what ’s been unanimous when we’ve deployed these assets is that people love using them.”
He sees it as a real point of difference and is a subject Select is very passionate about.
“I was in Europe recently and attended bauma which is the world’s leading trade fair for construction machinery and equipment. Original Equipment Manufacturers (OEMs) are examining what the future of electric plant will look like. But without people investing in the technology and providing feedback, the OEMs don’t know what the next iteration of innovation looks like and that’s where we are leading the way.
“We’ve invested heavily, whether it be the electric cranes, or the electric telehandler fleet, the batteries we’ve
invested in or the off-grid solar accommodation, we really are trying to push the boundaries of what’s possible and solve problems facing clients by deploying these assets.”
Ruairi said the investment in two Liebherr Unplugged 250t Electric Crawler Cranes is a classic example.
“The challenge we face with the early adoption of new technology is that people are not familiar with this equipment and change is not comfortable for them,” he said. “By leading from the front, we’re working with customers to come up with solutions on how to better use this greener and more sustainable equipment. We now use a portable
battery to recharge LR1250.1 Unplugged 250t crawler cranes, so it doesn’t need to operate close to a power source, you take the power to it. Our approach is to understand the challenges our customers face, invest in the technology and then work on the solutions around deployment of the asset.
“We invested in the first two electric cranes to come into Australia, which was a pretty bold move when you think that the technology hadn’t been deployed here before. One has been deployed on a project in WA and the second is currently operating on a site in New South Wales. The purchases confirm Select’s ambition to be different and challenge the industry and to really lead that way. We continue to do this across our general asset fleet.
“We recently added ten electric telehandlers into the fleet and a number large industrial battery units. We’re invested in hybrid solutions and we are
seeing these being deployed. Investing early in technology can mean a higher price point but what’s been unanimous when we’ve deployed these assets is that people love using them,” he said.
The Select crane fleet includes a mix of brands. Liebherr features prominently across the tele crawlers and lattice boom crawlers. There are several Tadano rough terrains and recently a number of Sany lattice boom and tele crawlers were added.
“It’s interesting to note that two years ago, Liebherr was the only manufacturer offering an electric-powered large crawler but that’s changed with other OEMs examining the future of electric and hybrid technologies. We will continue to watch these developments and be ready to invest when the right opportunity presents,” said Ruairi.
Select is also recognised as a leading provider of turnkey construction solutions.
“Our project teams come together and plan the construction works, the site set up and site accommodation,” Ruairi said. “We also manage the logistics of the site which includes a technologyled solution.
“We are the Australian distributor for Datascope, a technology solution that streamlines logistics on construction sites. Datascope enables construction teams to manage everything from access control and plant and equipment tracking to material movement, delivery management, and on-site coordination. The strength of our business lies in our ability to draw on specialist expertise to support our customers in successfully delivering their projects.
“With a strong construction heritage, we understand the challenges that other Tier Ones and major contractors face and we have the ability to flex and provide the solutions to meet their needs.”
Cloud Solution • Quoting
• eTickets / eDockets • Payroll / Timesheets • Reporting / Dashboard • Purchase Orders
Invoicing
Fleet Maintenance
Storage
Visual, Drag and Drop Scheduling
Form Designer
ERP Integration
Inductions / Compliance
Operating the largest crane fleet in Australia, backed by 23 strategically located branches, this comprehensive network empowers a consistent safe delivery to meet and exceed on clients expectations.
FREO GROUP’S FLEET BOASTS OVER 480 modern and well-maintained crane units with an average age seven years and ranging from 3 tonnes to 800 tonnes in lifting capacity.
Freo Group invests over $40 million each year into new equipment, m aintenance and upgrades to ensure added reliability and to provide industryleading benefits for all clients.
Freo Group is committed to ensuring that all employees have access to learning and development opportunities to pursue their career goals.
The growth and development of
training opportunities, from technical training to career pathways, which include the purchase of high-risk work licences, specific external programs aligned to individual growth plans and a comprehensive suite of customised leadership development programs.
Freo Group’s dedicated national training and safety teams ensure employees are appropriately verified for competency to perform high-risk work and provide ongoing training and development opportunities to ensure all employees can perform their jobs safely and effectively.
Career pathways and leadership
Leadership Academy
Freo Groups Leadership Academy is a comprehensive leadership culturebuilding and behavioural change initiative, that will encompass all leaders within Freo Group. There are three
Freo Group invests over $40 million each year into new equipment, maintenance and upgrades to ensure added reliability and to provide industryleading benefits for all clients.
elevate our leadership capabilities and overall performance. This initiative aligns seamlessly with Freo Group’s strategic priority of ‘Developing teams with passionate leaders and coaches’.
Prior to commencing their leadership journey each leader completes a 180° Leadership Competency Evaluation to assess their current skills, knowledge and capabilities. As part of this evaluation an individual growth plan is developed in conjunction with their leader to identify areas to focus on as part of their leadership development journey. The 180° Leadership Competency Evaluation is repeated at the conclusion of the program to track improvements.
In addition to the 180° Leadership Competency Evaluation Freo Group has also invested in DiSC for every leader. DiSC is a personality profiling tool which helps to understand our own personality traits and the personality traits of others. DiSC will be used interchangeably throughout our Leadership Programs to assist leaders in understanding the needs of others to improve communication and relationships.
Freo Leadership Program for Supervisors
The Leadership Program for Supervisors commenced in July 2024, and approximately 60 supervisors will participate in this program over the next 24-36 months. This program is highly customised to Freo Group’s supervisor roles. There are a total of 14 modules clustered into 5 Learning blocks. Each learning block consists of pre work, two full days of face-to-face training and a workplace application task which is assessed.
After completing each successful learning block leaders receive a Credly Digital Badge which includes a digital summary of what they had to complete to achieve this.
Topics covered in this course include:
Emotional Intelligence, leadership shadow, adapting your leadership style, strategy, performance management, coaching, leadership safety, innovation and continuous improvement, change management, risk management, incident investigation, presentation skills and customer engagement.
Freo Leadership program for Managers
The Leadership Program for Managers commenced in June 2024, approximately 30 managers will participate in this
program over the next 24-36 months. This program is highly customised to Freo Group’s manager roles. There are a total of 16 modules clustered into six learning blocks. Each learning block consists of pre work, 2 x full days of face to face training, a workplace application tasks which is assessed and a 90-minute coaching session.
After completing each successful learning block, leaders receive a Credly Digital Badge which includes a digital summary of what they had to complete to achieve this.
Topics covered in this course include:
Emotional Intelligence, leadership shadow, adapting your leadership style, strategy, performance management, coaching, leadership safety, innovation and continuous improvement, change management, risk management, financial management, negotiation and contract management, incident investigation and presentation skills.
Freo Executive Leadership Program
The Executive Leadership Program commenced in March 2024, and 20 senior leaders will participate in this program over the next 12 months. This program is highly customised to senior leader roles and relevant to Freo Group.
There are a total of 15 modules clustered into 5 Learning blocks. Each learning block consists of pre work, 2 x full days of face to face training, a workplace application tasks which is assessed and a 90 minute coaching session.
After completing each successful learning block leaders receive a Credly Digital Badge which includes a digital summary of what they had to complete to achieve this.
Topics covered in this course include: Emotional Intelligence, leadership shadow, adapting your leadership style, strategy, performance management, coaching, leadership safety, innovation and continuous improvement, change management, risk management, financial management, negotiation and contract management and employee relations.
Rigger to Operator Career Pathway
Freo Group provides full-time and longterm casual employees with a structured Rigger-to-Operator Pathway, offering comprehensive training for riggers aspiring to become crane operators. This pathway includes a series of progressive training steps over a 3–4 year period, covering the acquisition of all High Risk
Work Licences (HRWL), truck licences, and extensive on-the-job training to develop the technical skills necessary for success as a crane operator.
The FAST Program was developed to address the industry-wide shortage of skilled riggers while ensuring safety and quality standards are upheld before new riggers are sent to worksites. This initiative stems from the relatively low barrier to obtaining a rigging ticket, often without substantial hands-on experience. The program’s primary goal is to instil in riggers the principles of the “Freo Way of Lifting,” emphasising Safe Hands lifting practices, a professional and thoughtful approach to high-risk rigging tasks, adherence to “fit-forwork” standards, and a commitment to excellence in all aspects of their work. This two-week program is a paid Freo Group learning experience and to get involved speak to Freo Group’s recruitment team.
Virtual Reality Training is one of Freo Group’s innovative initiatives
designed to enhance workforce training alongside traditional theoretical and practical programs. This value-added option in Freo Group’s training suite aims to inspire the next generation of crane operators by offering new team members an immersive learning experience. It provides employees with on-the-job training in a risk-free environment, covering the basics of rigging and allowing them to drive our cranes in realistic scenarios.
Why is Freo Group an ideal destination for e mployment?
The importance of successfully attracting high calibre personnel can be demonstrated by the many initiatives and programs implemented by the company to ensure Freo Group provides personnel with a positive work environment, pathways of progression and specialised training courses.
• Significant workload of Contracts over the next 18 months, across both East and West of Australia.
• Offer opportunities for growth and development, allowing employees to enhance their skills and advance in their careers.
• Focus on employee well-being and work life balance - Support from BSS for you and direct family, and with private health discounts rolled out in March 2025.
Freo Group takes a direct approach to advertising available positions, primarily through SEEK. Be sure to visit the careers section of the Freo Group website for the latest openings. You can also find career opportunities posted on LinkedIn. For those seeking a more personal touch, connect with our Branch Managers and Business Development Managers, who will be actively engaged at local Career Pathway Programs in Karratha, Port Hedland and Moranbah. Take this opportunity to inquire about potential job openings directly.
What began as a modest rigging company with a second hand Franna has grown into a formidable lifting and rigging force servicing Perth’s Tier One construction sector. Under the leadership of husband-and-wife team Kevin and Tanya Fitzgerald, Rigsafe Lifting Solutions is now marking its 10th year in business with more than 70 staff, a fleet of 17 cranes, and a new 10,000 sqm facility in High Wycombe, which is set to launch the company into its next phase of growth.
“WE STARTED OUT PREDOMINANTLY AS A rigging company focused in the construction space. Now, we’ve grown into a leading force in lifting and rigging,” Kevin said. “For the last 18 months, we’ve been working on significant Tier One projects like the Alua Elevated Rail project and new Perth Film Studios, where they’re going to make movies. It’s exciting.”
EVOLVING BEYOND RIGGING
While rigging remains a core strength, Rigsafe today delivers far more. The company offers an integrated service model that includes full equipment hire, access solutions, labour hire, experienced project managers, and crane lift specialists. This end-to-end approach allows clients to benefit from a single, coordinated provider across multiple scopes of work.
“We’re not just riggers – we’re a one-stop shop for lifting, access, labour and planning,” Tanya said. “Our clients come to us for solutions, and we have the capability, systems and people to deliver what they need, when they need it.”
THE EVOLUTION OF A CULTURE
Tanya credits the team and culture for Rigsafe’s evolution from subcontractor to trusted Tier One service provider.
“Over the years, we’ve built a team of high-calibre individuals who not only bring experience but also embody a positive, solutions-focused mindset. That culture –which we now call ‘The Rigsafe Way™’ –has become the backbone of our service,” she said.
It’s more than a catchphrase. Rigsafe has formally trademarked ‘The Rigsafe Way™’ to capture the values and behaviours that define every interaction with the company.
“From quoting and planning through to execution and invoicing, every touchpoint reflects our ‘can-do’ approach, where the client’s needs are always front and centre.”
Kevin explains that ‘The Rigsafe Way™’ is just as evident internally as it is to clients.
“Our communication is open, honest, and based on mutual respect.
“If something’s not right, it’s flagged early. We encourage 360-degree feedback,
and problem-solving is collaborative –not reactive.”
Before joining the business, every prospective employee receives a copy of Rigsafe’s mission statement and values, so expectations are clear from the outset.
“We’re crew-centric and client-centric, and people know that from day one. Our team wear the brand with pride – it means something to them, and they want to do a good job,” Kevin said. “Doing the right thing isn’t always the easy thing. But our values guide us, and we never shy away from a hard conversation when it’s in the best interest of the team or our clients.”
With every dollar over the past decade reinvested into the business, Rigsafe is now poised for its next chapter. Its new headquarters allow for a doubling of office staff capacity and supports an expanding equipment fleet.
Looking ahead, the company’s growth strategy includes expanding into the defence and mining sectors – two areas
where safety, precision, and reliability are paramount.
“Our systems, people and capabilities are well-aligned with the expectations of the defence sector, and we’re already in the process of aligning with key requirements like DISP (Australian Defence Industry Security Program) membership,” Tanya said. “Mining is another area of growth where our integrated service offering is a natural fit. We’re excited about what the next 10 years will bring,” Kevin added.
Rigsafe operates a modern and diverse fleet, including mobile cranes with lifting capacities up to 160 tonnes, a fleet of Magni rotating telehandlers, boom lifts reaching up to 150 feet, and a range of Maeda spider cranes. The fleet also includes scissor lifts with overwatch, mechanical rigging gear rated up to 100
Over the years, Rigsafe has built a team of high-calibre individuals who not only bring experience but also embody a positive, solutions-focused mindset. That culture’The Rigsafe Way ™’has become the backbone of the company’s service.
tonnes, and a suite of transport equipment such as prime movers, tilt trays, and mobile rigging utes – ensuring rapid deployment and full-service delivery across complex projects.
“We’ve kept our fleet consistent and modern, particularly with Tadano
Rigsafe a one-stop shop for lifting, access, labour and planning provides clients with the right solution, when they need it.
cranes, because operator familiarity boosts efficiency. With our own transport capability, we can manage logistics inhouse and deliver greater flexibility to our clients,” Kevin noted.
Rigsafe is triple-certified (ISO 9001, ISO 14001, ISO 45001) and a recognised leader in safety. In 2023, the business was awarded the WorkSafe Plan Platinum Certificate of Achievement and named Subcontractor of the Year at the Master Builders WA Excellence in Construction Awards.
In 2025, Tanya was honoured as a WA Business News 40 under 40 Award winner, taking out the Family Business category, further recognising Rigsafe’s values-driven leadership and long-term investment into building people, capability, and culture.
The company is also deeply committed to community impact. Rigsafe proudly supports initiatives such as:
• Mates in Construction (partnering to support mental health in construction)
• Toby FCC Charity (supporting children with cancer and research)
• Sponsorship of all six local football clubs, as well as staff children’s netball, swimming clubs, WA School Sports and the Special Children’s Christmas Party
“We’re here to lift our industry, prioritise solutions, and deliver exceptional service to our clients, crew, and community,” Tanya said. “That’s ‘The Rigsafe Way’™.”
Dotmar’s in-house machining capabilities include CNC routing and lathe operations –enabling quick turnaround on customised outrigger pads.
On crane sites across Australia, timber blocks and steel plates have long been the go-to for crane outrigger pads. But in Western Australia, a quiet transformation is underway, led by a team that believes engineered plastics can do the job better, safer, and for longer.
“WE’VE WORKED WITH ENGINEERED plastics for years,” says Ian Johnston, who heads up Dotmar in Western Australia, “and now we’re actively stepping into the lifting space with purpose-built solutions.”
Dotmar Engineering Plastics has spent more than 50 years supplying Australian industry with high-performance plastic components. Now, the team that includes the talented personnel at its Canning Vale site is drawing on that experience to deliver outrigger pads, wear parts and critical gear to the crane and heavy lifting sector– products designed not just to meet standards, but to raise them.
BACKED BY PLASTICS EXPERTISE
At the centre of Dotmar’s push into the lifting space is the POLYSTONE Crane
Support Pad, a lightweight, heavy-duty pad made from ultra-high molecular weight polyethylene (UHMWPE).
“The number one benefit is weight,” Ian explains. “One person can lift it. You’re not dealing with timber that cracks or warps, or steel that needs a forklift. These are designed to be strong, but manageable.”
Dotmar’s standard pad is 1200x250x 80 millimetre (mm) and comes with lifting handles. But the company also offers a range of custom options to suit different ground conditions and load requirements. “We’ve got the ability to machine pads in-house now, so we can be more flexible,” Ian said. “If someone needs a different thickness or a different profile, we can do it.”
Dotmar also offers jacking plates and custom wear parts made from polyamide
(nylon), designed to handle high load pressures with minimal flex. These are being used for off-the-road (OTR) tyre handling applications and have crossover potential into crane operations.
Despite industry advances, timber blocks are still common on many sites – a practice Ian hopes will change as more crane operators become aware of safer and more durable alternatives.
“We still see a lot of timber out there, and it just doesn’t make sense,” he said. “Timber absorbs moisture, breaks down over time, and you don’t know its exact capacity. With POLYSTONE, there’s consistency and durability.”
That durability makes a commercial difference too. “If these pads are looked after and not lost, you can get two years
of life out of them,” he adds. “That’s four times longer than timber in many cases.”
Dotmar’s pads are designed with real-world lifting conditions in mind. They don’t absorb water, they won’t splinter, and unlike steel, they won’t rust or damage other surfaces.
“They’re also easier to find on-site,” Ian noted. “Even though they’re black, they stand out more than timber when you’re packing down.”
The company’s approach is hands-on and responsive. “We talk to our customers about what they need, and then work backwards from the problem,” Ian said. “We’re not just selling off a shelf, we’re offering something that’s engineered for purpose.”
While many engineered components can be subject to long lead times, Dotmar is aiming to change that. “If I know someone’s serious, I’ll bring in stock,” Ian said.
“We’ve held 800 pads before and can do it again. What we need is to work with the right partners who want reliable supply.”
Dotmar’s ability to produce locally to a customer’s need quickly, as well as the ability to bring in dedicated (and even branded) product specifically for a customer, sets it apart.
Dotmar WA is already supplying pads to companies such as Mammoet and has recently fielded interest from Boom Logistics and Northfleet. Dotmar has eight locations across Australia and New Zealand, each fitted with a fullservice machining centre. Supported by distribution hubs in Queensland and Victoria, it is well equipped to rapidly address the needs of any project.
starting to ask those questions more. What are you doing to cut carbon? What’s your sustainability story?”
Even the company’s branding has shifted. “We’ve moved to a green underline in our logo to reflect that direction,” Ian said. “It’s not just a visual change, it’s a shift in mindset.”
As the lifting industry leans into sustainability, Dotmar is working to reduce the footprint of its products. One
From rigging pads, wire rope sheaves, and wear strips to jacking plates and beyond, Dotmar is proving that plastics have a serious role to play in the future of lifting.
“These aren’t throwaway parts,” Ian said. “They’re engineered, tested, and built to work. We just want people to know we’re here and we’re ready.”
With a legacy of over 50 years in the plastics industry, Dotmar is the largest distributor of semi-finished engineering thermoplastics and conveyor components throughout Australia and New Zealand. Its team of skilled engineers and industry experts enable it to bring ideas to life – whether a single prototype or large-scale production run.
Dotmar partners with some of the world’s most trusted and respected companies and organisations, including the Australian and New Zealand Defence Forces, Coca-Cola, Rio Tinto, Asahi Breweries, Arnott’s Group, BHP Billiton, and many more. For more information, visit www.dotmar.com.au or call 1800 170 001.
Base Marine’s new Humma 35T crane made its operations more flexible in Western Australia’s ports. The crane, known for its flexibility and mobility, is helping Base Marine grow across different sectors and services.
BASE MARINE IS A WEST AUSTRALIAN (WA) marine services company established in 2013 in the coastal town of Exmouth. The business began with just one crane and a forklift. Its founding goal was simple: to provide port and logistics services tailored to the booming oil and gas sector operating off the WA coast.
A decade later, Base Marine has grown into a diversified service provider operating across the state’s key ports, including Bunbury, Geraldton, and Ashburton. The company’s footprint has expanded beyond marine logistics to include stevedoring, landside operations, site services, decommissioning,
and specialised equipment and personnel hire.
As General Manager Nick Tutty puts it, “We’ve been through the ups and downs – from the oil price crash in 2014 to COVID, but we’ve kept adapting. That’s been the key to our survival and expansion.”
With this growth has come the need for a more flexible and capable crane fleet. While Base Marine began with a 150-tonne crawler crane, its fixed nature and high mobilisation costs eventually became a limitation. The team needed machines that could move quickly between sites, meet stringent compliance
standards, and handle a broad range of lifting jobs across both coastal and inland environments. Enter the Humma 35T.
Late in 2024, Base Marine added a 35-tonne Humma crane, designed and built by DRA Group in Perth, to its growing fleet. For a company that treats capital investment with caution, the decision followed rigorous evaluation.
“We ran a proper tender. We looked at all the usual players and put each model under the microscope,” said Nick. “In the end, the Humma came out clearly on top – both technically and practically.”
What won Base Marine over was the Humma’s superior articulation performance, especially under load.
“When you look at lifting charts, lots of machines seem similar at first. But once you start articulating the boom or while working at angles, their capacity drops away quickly. Humma maintains its strength without distortion from zero to 42 degrees.”
The Humma UV35-25 features four fully-powered fabricated booms
extending up to 20.9 metres, with no manual extension required. With the optional telescopic fly jib, operators can access over 26 metres of total reach. Its digitally compensated winch rope system ensures smooth and precise control during lifts, while the under-boom sliding hooks support low-clearance operations – ideal for ports and confined industrial sites.
“We need gear that can move fast, work hard, and get the job done without fuss. With the Humma, we’re seeing exactly that,” said Nick.
Mobility is a critical factor for any contractor working across Western Australia’s vast geography. One of the Humma’s most valued features is its ability to travel at highway speeds, up to 100 kilometre per hour (km/h). The three-tonne counterweight can be removed for easier transport.
The airbag suspension eliminates all shock loading and vibration through the crane chassis. This also leads to lower maintenance costs with no line boring of articulation or boom pivots required. Additionally, the suspension allows the crane to be stable at high speeds.
“Compared to other pick and carry machines, the 35-tonne Humma is in a league of its own on the road,” Nick said. “That speed and comfort – thanks to the airbag suspension – lets us respond quickly to shutdowns or mobilisation calls. It makes our business more responsive and more competitive.”
The climate-controlled cabin, fourcamera system, and separate digital gauge display add to the operator’s ease, safety, and visibility. These creature comforts, combined with the robust build, have earned positive reviews from Base Marine’s experienced operators.
“They’ve all worked across different machines,” said Nick, “and they’ve been impressed by the Humma’s power, control, and comfort – on site and on the road.”
Beyond performance, DRA Group’s commitment to quality and local service stood out.
“We were blown away by what we saw at their Perth facility,” Nick recalled. “The build quality, the longevity of their team, the pride in their work – it
reminded me of when we imported our straddle carrier from England. You could see generations of knowledge in the machine.”
That local manufacturing capability also aligns with Base Marine’s own values. “We have a strong local content policy. Buying from an Australianowned company that manufactures in WA fits perfectly with how we want to operate. And the after-sales support? It’s been outstanding.”
Even though the machine has had no major issues, the DRA team continues to check in post-delivery, something Nick said is rare in the industry.
The Humma’s impact was immediate. After passing all compliance inspections, including at Pilbara Port Authority and by major mining clients, the crane went to work on two high-profile projects.
“In its first week, it was working for two of our biggest clients. Since then, it’s been booked out constantly. We’re getting calls from new clients who specifically want that machine.”
Humma’s high compliance rating and mine site-ready safety systems has opened doors previously difficult to access. “It’s given our business development team something new to lead with.”
Lifting Solutions
Modern, zeroemission cranes. Expert planning. Seamless execution.
Logistics Solutions
Expert-led logistics. Tech-driven delivery. Safer sites. Total compliance.
Site Solutions
Tailored modular site compounds, facilities management & power systems.
Plant Hire
Compaction, lighting, material handling, traffic management, vehicles & more.
From a modest facility in Western Australia (WA), Protective Engineered Safety is quietly redefining how heavy equipment operators manage some of the most common and dangerous risks on construction and civil worksites.
ˆPROTECTIVE ENGINEERED SAFETY’S LINE of proximity detection systems, including its flagship Protective Shield and GoUpSafely (GUS) devices, is gaining momentum for the way it’s reshaping conversations around workplace safety, machine longevity, and insurance risk.
“We’re proud to be building this tech in Western Australia,” said Karl Rosewarne, Managing Director of Protective. “Everything is developed and manufactured locally – and we’re doing it not just for WA, but with WA in mind. The conditions out here are harsh, and if it can work here, it can work anywhere.”
The commitment to local design and production has been deliberate. Karl believes that WA’s mix of metropolitan construction, remote mining operations, and infrastructure challenges makes it
The company’s Protective Shield system, designed specifically for elevated work platforms (EWPs), uses ultrasonic technology to detect physical obstacles in real-time, alerting operators to potential crush hazards and preventing costly equipment damage.
“SHIELD doesn’t just stop someone from being crushed,” explained Jason Jordan, Business Development Manager at Protective. “It also offers a level of protection for the machine itself –whether it’s avoiding overhead beams in a tunnel or preventing a boom from striking a roof. That’s a huge benefit for companies trying to minimise downtime and repair bills.”
Protective’s other widely deployed solution called GoUpSafely (GUS) is a system that detects electrical fields on
alerting operators when they’re getting too close,” said Karl. “We had a guy at an event come up to us and tell us he pulled a power line down last week running a drill rig. He asked what our system costs – I said they start around four grand. He said that single mistake cost him over 30. That’s the cost of about six systems right there.”
Beyond power line protection and object detection, Protective is now closing in on a world-first: a system capable of detecting high-voltage DC infrastructure, a hidden hazard in tram networks and emergency response scenarios.
“We’re furiously working on DC detection,” Karl said. “We’re now in the prototype stage and to our knowledge will be the only organisation in the world to have achieved this.”
High-voltage DC, found in tram systems across Victoria, New South Wales, and other parts of Australia,
GUS technology can save operators from powerline strikes – often before they even realise the risk.
poses a lethal risk to emergency services and rail maintenance crews. Unlike standard AC systems, DC hazards are not commonly accounted for in most current safety protocols.
“We were approached by teams in Melbourne asking if we were doing anything in this space,” said Jason. “At the time, we weren’t ready to say yes. Now we are. Queensland Rail also showed early interest. We’re planning to re-engage once we have a deployable product.”
In a unique deployment during a Victorian tunnel project, Protective integrated both the SHIELD and GUS systems onto the same machine. The aim was to help operators navigate tight underground spaces with confidence, alerting them to both electrical fields and physical obstacles. “That was a real turning point,” said Karl. “Operators loved it. It gave
internationally, and it has been recognised for its potential,” Jason said.
“We’ve reached out to international regulatory board members to present our system, and we believe that once they see it in action, they will understand its necessity and push for its adoption. We are optimistic about similar advancements being adopted in Australia soon.”
For Karl, one of the most overlooked benefits of Protective’s systems is the potential to reduce insurance claims, both on equipment damage and personal injury.
“Besides safety, it’s about protecting assets and reducing incidents,” Karl said. “If you’re reducing the number of claims, you’re protecting the underwriters’ bottom line. It’s an obvious win for insurers.”
He sees a future where insurance companies could incentivise or subsidise the installation of such systems, much like how smoke alarms and dashcams are handled in domestic and auto sectors.
“We’ve reached out to international regulatory board members to present our system, and we believe that once they see it in action, they will understand its necessity and push for its adoption.”
them a complete sense of awareness, above and around. We haven’t advertised it much yet, but it’s proof we can combine the two technologies when needed.”
The global safety landscape is shifting. Karl said that from 2027, the European Union will mandate powerline detection systems on any construction equipment that can reach overhead lines.
“Australia won’t be far behind. When that happens, we’ll already be there –we’ve done the groundwork.
“Despite initial skepticism and the ambiguity of regulations, we’ve demonstrated our innovative system
“Everyone benefits,” Karl added. “Operators are safer. Machines last longer. Insurers face fewer payouts.”
The cost remains a significant selling point. The SHIELD pricing begins at $1450, while the GUS system starts at $4300, depending on the sensor configuration.
“That price point is deliberate,” said Jason. “We want this to be attainable. It’s not about milking clients. It’s about keeping people and gear safe. Ultimately, it’s about saving lives.”
While the technology is gaining traction, Karl says the bigger challenge is shifting the culture from reactive to proactive, from luck to logic.
The Lifting Company has been engineering some of Australia’s most complex lifting solutions. From supporting large-scale construction projects to solving niche engineering puzzles for museums and zoos, the company has been providing lifting, rigging and height safety products and solutions since 2001.
IN AN ENVIRONMENT WHERE INDUSTRIES are dominated by large groups and corporations, The Lifting Company (TLC) remains privately owned and locally operated. The owners of TLC are extremely hands on involving themselves with everything from engineering to deliveries where required, acting very much as part of the team. This earns them respect among both customers and employees of TLC and strengthens their positions as mentors and role models to the staff who rely on them.
“We specialise in the unique and unusual projects requiring a specifically designed solution,” said Matt Clarke, Director at The Lifting Company.
“If someone approaches TLC with a challenge that has not been undertaken before, we collaborate with the customer
and their project partners to engineer a solution.”
Located in the heart of Perth’s industrial zone, TLC operates from a fully stocked showroom in Kewdale and maintains an in-house fabrication facility. The company offers a full range of lifting and rigging equipment, forklift attachments, and height safety gear, but it’s the custom work that sets it apart.
“We do everything from basic rigging gear like synthetic slings and shackles to beams, lifting cages, personnel cages, custom fabricated lifting frames, our bespoke engineered solutions and conveyor belting maintenance products,” Matt said.
“A lot of our clients come in with specific needs – they might be lifting awkward shapes, working in tight spaces,
or dealing with unusual site restrictions. That’s when the TLC team gets to work.”
TLC’s sales team brings decades of experience. “Our sales manager has been in the game for over 30 years. Our technical guys have probably seen every lifting challenge you could imagine,” Matt noted.
In the engineering team, wisdom runs deep. “We had a 79-year-old part-timer who trained the entire team,” Matt said. “He is a legend in WA’s lifting industry. Our current engineering manager, James, was mentored by him and now leads our growing engineering team.”
With a five-person engineering team supported by seasoned fabricators, TLC can turn rough sketches into fully engineered solutions.
“We design, fabricate, test and certify everything in-house,” said Matt. “And obviously it’s all done strictly to relevant standards.”
Even in the workshop, experience counts. “Our testing supervisor and his brother, our warehouse manager, have both been in the industry for over 40 years. They’re mentoring the younger crew to keep quality and standards at the highest level and nurture new experience in this growing industry. With a focus on safety and training the younger team members have an invaluable opportunity to benefit from this wealth of knowledge and experience.”
Safety is a non-negotiable at The Lifting Company. It has robust internal quality assurance systems and procedures in place. As a National Association of Testing Authorities (NATA) certified laboratory, as well as being accredited by DNV and the Lifting Equipment Engineers Association (LEAA), the internal procedures run in strict compliance with these accreditations.
At a time when many suppliers are scaling back physical presence, TLC continues to invest in its showroom.
“A lot of companies have shut down their counter sales, but we still believe in face-to-face service,” Matt said. “Walkins are welcome. We’ve got two full-time staff at the counter helping everyone from farmers to construction crews.”
The showroom is stocked with products from leading brands including Linq Height Safety, Austlift, Kito Crosby, Pacific Hoists, Spanset, Rud Chains, Legend Lifting, East West Engineering and many more. “We also carry our own line of products including chain blocks, lever blocks and lifting magnets.”
Commitment to people is a strong focus for TLC. “Whether it’s a major customer or someone looking at towing a caravan, we treat every customer with the same level of care,” Matt said. “We’re not just selling equipment. We’re helping people lift smarter, safer, and with confidence.”
One standout project was at the Crown Towers Hotel in Burswood, where TLC installed nearly 100 chandeliers, including four enormous pieces in the main lobby. “There was no precedent,” said Matt. “We
had to design and install the mounting systems in the ceiling space with minimal headroom. Some of those chandeliers weighed two tonne.”
The WA Museum also turned to The Lifting Company for help moving a lifesized dinosaur exhibit into place. “We had to figure out how to lift and install it safely inside the building. It wasn’t your standard rigging job, but that’s what makes it interesting,” Matt said.
With a focus on improving safety across the lifting industry everywhere, Matt and the engineering team have designed an innovative, new generation spreader beam. The beam comes with revolutionary end lugs specifically engineered to eliminate bending stress from incorrect sling angles, thereby enhancing safety, reducing operator error, and maximising operational efficiency. A variety of different lengths
and capacities of these beams are in stock ready for the next lift.
Another interesting innovation that the TLC team has been working on is a range of hydraulically operated counterweight lifting beams. Used in situations where the load must be moved into areas of limited headroom or confined spaces, the beam remains in the horizontal position while the load is shifted into place. TLC has made up to 15-tonne single beams and 25-tonne for a pair of beams used in a dual lift.
The diversity continues into the area of conveyor belting maintenance equipment where TLC has established itself as world leaders with continual growth and innovation. Offering winches, winders, belt pullers and belt stands and ancillary tooling up to 100 tonne, the TLC range is supplied right across Australia and in overseas markets.
Western Australia’s Halifax Crane Hire recently took delivery of a new Franna AT40-2. It’s the latest addition to an already significant fleet of pick and carry crane brand.
“WE FOUNDED HALIFAX CRANE HIRE back in 1995 and for almost the entire time we’ve been in business, we’ve had a Franna in the fleet. We started with a 15 tonne capacity Franna some 27 years ago and we now have 11 in the fleet with capacities from 15t to the Mac 25s with 25t capacities, through to the original AT40 and now the AT40-2 with 40t capacities,” said Robyn.
“All of this time, we’ve experienced very little mechanical problems with the Frannas and when there have been issues, the product support and service from the team has been wonderful.”
Halifax Crane Hire operates in the south west region of Western Australia, with depots in Albany, Bunbury, Busselton, Bibra Lake, Collie and Greenbushes.
“We find Frannas to be very multifunctional in terms of the tasks we expect them to do. For us, they work really well in the mining sector and in the heavy lift industry, where they are ideal support cranes for mobilising and de-mobilising the larger, ‘heavy lifters’ we have in our fleet. They are also an ideal taxi crane moving from sites during a day conducting multiple lifts,” said Robyn.
“The new AT40-2 takes a significant step up in terms of roadability and we have been very impressed with the new safety features of the new model. Like all crane hire businesses, we are very focused on the wellbeing and safety of our team and the new AT40-2 takes a massive step forward in terms of the inbuilt safety systems,” she said.
Safety also remains an unwavering priority for Franna. The recent series upgrade to the range elevates safety standards by incorporating Franna’s patent-pending Safety Radar as a standard feature.
The Safety Radar system adds an additional layer of protection and awareness over the patented Dynamic LMI system, enabling the operator to plan their next move by viewing a colour contoured visual representation of the rated capacity for the entire working area of the crane. The operator can see the rated capacity of the crane before they move the load, hence well before any traditional rated capacity alarms or motion cuts.
“You’ve got a clear picture on the AT40 with the Safety Radar illustrating green, when you are operating within the designed limitations, yellow when you move from these limitations to red when the operator has taken the crane beyond its designed capabilities.
“You’ve
got a clear picture on the AT40 with the Safety Radar illustrating green, when you are operating within the designed limitations, orange when you move from these limitations to red when the operator has taken the crane beyond its designed capabilities.”
“There’s no reason for anyone to go out of those boundaries and if they do, well its as a result of human error and is not the manufacturer’s issue,” said Robyn.
Franna’s online Lift Planner has also been upgraded to include all current models – AT22, MAC25 and AT40. This allows precise rated capacity and front axle load calculations to be performed for various crane configurations and uneven ground conditions.
With last year’s introduction of new Australian Design Rules (ADR) compliance regulations, Terex Franna has taken the opportunity to incorporate new technology across the entire Franna range. Each model has received upgrades designed to minimise environmental impact and improve operational efficiency.
The upgrades start with the new Mercedes-Benz OM936 Engine
Stage V and Tier 4 Final compliant engine for cleaner emissions, ensuring seamless compliance with evolving environmental regulations.
This technology has been powering European all terrains and other special purpose vehicles for many years. While the technology has been implemented as a result of regulatory compliance requirements, Franna has taken opportunity to improve performance.
The OM936 is a proven 7.7 litre engine versus the outgoing OM906’s 6.4 litre displacement, power and torque are up across the range, up to 230 kilowatt (kW) and 1300 newton-metres (Nm) respectively. The OM936 boasts a wellestablished track record, having undergone more than a decade of refinements to achieve exceptional reliability.
For Halifax Crane Hire the new AT40-2 takes a significant step up in terms of roadability and the team has been impressed with the safety features of the new model.
Franna’s engineering team collaborated directly with the German manufacturer, MTU, in conjunction with Penske Power Systems, the authorised distributor of Mercedes Benz engines in Australia, to ensure seamless integration of the OM936 into the range. This collaboration included extensive emission reduction technologies, a power increase and finetuning of the gearbox providing optimal performance within the demanding environment of pick and carry cranes.
The OM936 engine is also fully compatible with HVO (hydrotreated vegetable oil) diesel fuels, enabling a reduction in carbon emissions by up to 85 per cent.
In addition, the OM936 is fitted with a ‘Jacobs’ style exhaust brake, giving effectively double the retardation over the existing OM906 engine. Franna selected the engine exhaust brake option rather than a transmission retarder as it has the advantage of providing additional retardation through every gear of the transmission selection.
The innovative design of the OM936 engine cooling system has been engineered to achieve a Limiting Ambient Temperature close to 50 degrees Celsius.
This was accomplished by incorporating an additional extraction fan into the cooling pack, ensuring the engine maintains optimal performance even in the most demanding environmental conditions.
Limiting Ambient Temperature refers to the highest ambient temperature at which the vehicle’s cooling system can effectively manage the engine’s heat output while allowing the engine to continuously operate at full power.
Achieving a high Limiting Ambient Temperature is crucial for ensuring the reliability and efficiency of the engine.
A rigorous testing process validated the cooling system’s capability, ensuring that the OM936 engine can deliver consistent performance under full load, even in ambient temperatures nearing 50 degrees Celsius. This breakthrough not only enhances the engine’s durability and reliability but also positions it as a leading choice for operators working in challenging environments where high temperatures are a critical factor.
The Series upgrade goes beyond just the new OM936 engine. Franna has implemented a series of additional enhancements across all models, designed to streamline customers’ lifting operations
enhancing useability, productivity and safety.
“Emissions is an increasingly important issue for our clients in the mining and renewables sectors as well as Tier One projects. The low emission Franna AT40-2 demonstrates how important our business is taking the reduction of our carbon footprint as we continue to invest in low emission technology,” said Robyn.
“Our operators really like the Frannas, they are very comfortable with them, having driven them for many years. As a business, we have found there is ‘no used by date’ with Frannas. We’ve still got the original motor in the 15 tonner we brought all those years ago and the service and parts availability from Franna has been exceptional.
“The new AT40-2 is an intelligent piece of equipment and the training for our crews was very important. Robin Ghosh, Crane Sales Manager at Terex Franna, went above and beyond during the sales and delivery processes as well as the training during the handover process.
“I don’t think any other supplier can match the levels of service and support that we receive from Terex Franna,” she said.
performance
Expanding a fleet with a new crane is a significant decision, and for Craig Membrey, Managing Director of Membrey’s Transport & Crane Hire, it’s about much more than just equipment. It’s about partnering with a business he can trust.
CRAIG’S FAMILY-RUN BUSINESS, established in 1962, recently decided to expand its fleet with a brand-new Sany 40 tonne telescopic boom crawler crane, choosing Tutt Bryant to make this significant addition.
Membrey’s Transport & Crane Hire has a long history of heavy haulage and lifting, tackling projects that range from infrastructure to industrial relocations. Craig explains how the business decided to acquire the new Sany SCC400TB.
Craig said, “It gives us the best of both worlds – the reach of a boom crane combined with the stability of a crawler. I needed something to fill the gap in the 40-tonne telescopic crawler crane range, and the Sany ticked all the boxes. The pricing was sharp, and seeing firsthand how they build the machines – it’s clear the quality has come a long way.”
The Sany SCC400TB, with its 40-tonne lifting capacity, fits neatly into a niche. Its telescopic boom extends to approximately 43 metres, giving operators considerable reach without the inconvenience of assembling lattice sections onsite. Additionally, because it’s mounted on crawler tracks, the crane can manoeuvre across uneven or muddy terrains.
Yet, purchasing a crane isn’t just about specifications and capabilities; it’s about trust and relationships. For Craig, working with Tutt Bryant wasn’t new territory. Craig said that over the years, Tutt Bryant became more of a partner than a mere vendor to Membrey’s. He said that this relationship made the buying process easy.
“In May 2024, Tutt Bryant provided me with an opportunity to tour the Sany factories in China, which gave
me valuable insight into the brand’s manufacturing quality,” Craig said. At a crane conference in Adelaide in October 2024, Craig sealed the deal for the new 40-tonne crane.
The team at Tutt Bryant provided detailed information, training, and support. Craig mentions the importance of their transparency and customer service: “Anytime we had a question, they answered immediately. It felt collaborative and supportive rather than transactional.
“We had the crane customised in our company colours, and the entire procurement process – from documentation to delivery – was smooth and professionally managed. The finish and paint quality were of a very high standard. The crane itself has performed well so far, and it’s now available for hire and ready to go. We’re
optimistic this won’t be the last Sany in our fleet – there’s definite potential for more as demand picks up,” Craig said.
For Membrey’s, another key factor in choosing Sany was Tutt Bryant’s after-sales support network.
“Our experience with Tutt Bryant has been nothing short of excellent. Being local certainly helps. So far, it’s been five-star service. Everything’s been handled exceptionally well.”
Craig said this isn’t the company’s first purchase from Tutt Bryant. “We also collaborate on projects and equipment support, so the relationship
works both ways. It’s a partnership that benefits both businesses,” he added.
Cost-effectiveness was another bonus. Craig describes the Sany 40t as a smart financial investment.
“The cost of the crane and its capabilities mean we’ll see strong returns. It provides high performance without the premium cost of some other brands,” he said.
In the 40-tonne class, not all machines deliver the same lifting capability – some fall short under pressure. Craig said, “One of the key reasons we chose the Sany was
the strength of its load chart. Not all 40-tonne cranes are built the same –some fall short when it comes to lifting performance. This one doesn’t. When you’re lifting day in and day out, that strength and reliability make a real difference.”
“It’s a smart addition to our 30-strong fleet. Industry feedback on the Sany brand has been overwhelmingly positive. In our line of work, people don’t mince words. If a crane underperforms, you’ll hear about it. But with the Sany, all we’re hearing is praise,” he said.
Membrey’s team has already had some hands-on time with the new Sany SCC400TB, and early impressions have been positive – especially from the next generation.
“The team’s had a chance to test it out, and they’re genuinely impressed.
“It’s a smart addition to our 30-strong fleet. Industry feedback on the Sany brand has been overwhelmingly positive.
In our line of work, people don’t mince words. If a crane underperforms, you’ll hear about it. But with the Sany, all we’re hearing is praise.”
My son, Jack Membrey, completed the full training on the crane and was enthusiastic about how intuitive the system is. The telecrawler’s operation is very straightforward, and he got the hang of it quickly.”
Now, with the Sany SCC400TB ready to get to work, Membrey’s Transport & Crane Hire is planning its first projects. Reflecting on the entire experience, Craig emphasised the significance of having trusted partners like Tutt Bryant. “When you have reliable partners, everything falls into place smoothly.”
P.A. Construction Equipment Pty Ltd (Pace Cranes) was established in 1987 to provide the construction industry with an independent Australian owned and operated crane sales, crane service and crane spare parts organisation.
For over 30 years Pace Cranes have offered premium quality equipment to the Australasian market with a dedicated and unrivalled service, supported by specialist technical advise across the full range of equipment sold.
Steve Bekker, Bridgestone Mining Solutions’ Regional Sales Manager East, explains how there is a lot more to Bridgestone’s service than simply selling quality tyres.
Bridgestone Mining Solutions has been supplying Australian industry with Off The Road Tyres (OTR) for over 40 years and has been focused on the crane sector for more than 20. Steve Bekker, Bridgestone Mining Solutions’ Regional Sales Manager East, explains how there is a lot more to Bridgestone’s service than simply selling quality tyres.
“BRIDGESTONE OPERATES 14 LOCATIONS around the country, with a presence in every state and territory, and a network of specialist OTR resellers and dealers nationwide. The overall service solution Bridgestone offers includes fitting of tyres to wheels and wheels to machines. We don’t just sell tyres and walk away, we follow up with after sales service and support,” said Steve.
“Every tyre is backed by Japanese warranties, allocated a serial number, and traced from manufacture. The tyre patterns we bring in for mobile cranes
are the VHS and VHS2. Recently, we had an upgrade of the VHS2 which saw the tyre manufactured with a more solid shoulder to give it better wear rate. The VHS has been used locally for many years and it’s tried and tested in the Australian market. It comes in two speed ratings, “E” (70km/h) and “F” (80km/h).”
Offering four sizes in the VHS and VHS2 range, Bridgestone is a trusted supplier, meeting 100 per cent of the mobile crane tyre needs of Liebherr and a leading crane hire business.
Stock of these tyres is readily available from Bridgestone facilities around the country as well as strategic resellers and dealers.
Steve explained some of the challenges around the supply of wheels. “It’s a difficult scenario when you factor in issues relating to weight. We are currently in negotiations with a wheel provider and waiting on updated specs on the low weight range they offer. It is difficult to fit tyres to single piece alloys. With Liebherr, we fit our tyres to their two piece alloys, which has
not been a problem. We are currently working on a holistic approach where we supply the complete tyre and wheel package making us a one solution provider for one of the biggest national crane operators.”
He highlights how Bridgestone manages the different conditions faced by crane hire businesses on the East Coast compared to the West Coast and the extreme temperatures tyres need to operate in.
“To ensure we are supplying the right tyre, we ask a range of questions starting with ‘what is the application? Will the tyre be carrying weight at creep speed or is it static? How far is the run? What geographical locations is it working in and what speeds is the
and Karratha for example, they’ve got to make sure the crane can sit at 80 kilometres an hour for a sustained period of time.”
Tyres are expensive but fundamental to the roadability and performance of a crane. Steve explains how a crane hire business can best maintain the quality of the tyre and the key factors to maintaining its integrity throughout its life.
“Research confirms that Bridgestone ‘tyre wear rates’ are far superior to anything on the market but maintaining tyre pressures are critical. If the air pressure is too low the shoulders will wear out much quicker, giving uneven wear which leads to reduced turnability. If the air pressure
so maintaining the cold inflation pressure is critical to the performance of the tyre.”
Any tyre 25 inches and over, including mobile crane tyres, must be changed by a fully qualified OTR tyre fitter.
“These tyres are under considerable pressure and our OTR tyre fitters, and those of our appointed service centres, are qualified to remove and inspect the integrity of the tyre and the wheel at the same time. For any inspection or changing to take place, tyres need to be completely deflated,” Steve said.
Wind farm construction and maintenance is an important industry sector for Bridgestone.
“I have been travelling through a
“Research confirms that Bridgestone ‘tyre wear rates’ are far superior to anything on the market but maintaining tyre pressures are critical.”
Tyres are under considerable pressure and Bridgestone OTR tyre fitters, and those from appointed service centres, are qualified to remove and inspect the integrity of the tyre and the wheel at the same time.
Rokewood in Regional Victoria, and there would have been at least 10 mobile cranes each running up to 32 tyres.
“The productivity of these cranes is critical to the success of each project, and we are talking to the crane owners about the cost of downtime as a result of tyre failure. How much does it actually cost their business if they go to a Tier Two or Three tyre supplier and buy on price, compared to the performance and quality of the products supplied and supported by a Tier One supplier like Bridgestone?”
“More often than not, wind farms are located in remote areas and if a tyre fails the crane owner will want the crane up and operating quickly. Tier Two and Three suppliers do not necessarily have the support capabilities to make this happen,” Steve said. “With Bridgestone, customers know they are buying a high quality product in the first place and if there should be an issue, they have the reassurance that there is a significant service and support network designed to fix the issue and have the crane up and operating as soon as possible, minimising the amount of downtime.”
SCAN QR CODE FOR MORE INFORMATION
The course instructors are seasoned professionals who will mentor course participants through real-life scenarios, preparing them for the challenges and responsibilities of a Crane Lift Supervisor.
Crane Lift Supervisors are in high demand globally. Completing this course enhances employability and opens doors to a wide array of job opportunities and career growth.
The curriculum covers a wide range of topics, including lift planning, load calculations, safety protocols, communication strategies, and legal compliance.
Scan the QR code to book in now
Melbourne 5-6 February 2025
Sydney 19-20 February 2025
Brisbane 5-6 March 2025
Perth 19-20 March 2025
Melbourne 4-5 June 2025
Brisbane 10-11 July 2025
Perth 16-17 July 2025
Sydney 17-18 September 2025
The advanced telescopic boom has a reach of 16.6m with load sensing and flow sharing distributors allowing for more simultaneous movements during operation.
Many in the construction sector recognise the hydraulic telescopic handler as a ‘multi tool’ asset which is one of the first pieces of equipment to arrive on a construction site and the last to leave. Bob Mules, National Sales Manager for Dieci Australia walks us through the features and benefits of the Dieci Icarus 40.17.
“WHEN IT COMES TO TELESCOPIC HANDLERS in the construction sector, there are many models and capacities to choose from. Dieci telehandlers range from 2.5 tonne to 23 tonne and feature fixed boom and rotational models. Fixed boom models have a pick up and carry capability which crosses over nicely to the crane industry,” said Bob.
The Dieci ICARUS 40.17 is a well established product with a track record of outstanding performance. The four tonne capacity Icarus is suitable for many jobs in the building and industrial sectors, thanks to its characteristics of great strength, power, and lifting heights.
The hydrostatic transmission combined with the “inching” pedal allows the Icarus to operate at slow speeds with the engine
at full throttle, ensuring extremely precise loading and maximum safety.
The Icarus also features great power, excellent handling with precision movement control, soundproofing for absolute comfort and three steering modes including 2WS, 4WS, and crab steering. The intelligently designed control layout makes the Icarus simple, intuitive and comfortable to use.
Dieci telehandlers have always provided a combination of comfort and functionality but they are also extremely rugged machines with exceptional loading capacities in all operating conditions, with the boom retracted or extended.
Independent outriggers with proportional controls and a transversal levelling device ensure the machine
is always working with the chassis in a horizontal position, even on uneven ground.
The advanced telescopic boom has a reach of 16.6 metres with load sensing and flow sharing distributors allowing for more simultaneous movements during operation. The Icarus responds to controls in a fluid way, with precision and promptness, providing exceptional work comfort in complete safety.
The Icarus can be fitted with a full range of accessories, making it an incredibly versatile machine.
The Icarus 40.17 is equipped with an integrated electric driver’s window, standard heater and a semi-automatic air conditioning system with six outlet vents. This setup allows air circulation inside the cabin for maximum operator comfort.
The Roll-Over Protective Structure-Falling Object Protective Structure (ROPS-FOPS) approved cab is designed with a safety cell to provide maximum safety to the operator at all times. Dieci telehandlers comply with AS1418.19 / AS10896.1.
A ‘Deadman Sensor,’ combined with the operator presence sensor in the seat, prevents accidental operation. The Load Limiter Device analyses vehicle stability
movements when the pre-set safety limits are reached.
Patented by Dieci, the Single Compensation Cylinder is located inside the lifting ram, ensuring that the load on the boom is balanced at all times, thereby improving durability.
Pre-arrangement for the man basket remote control enables boom and aerial platform operation directly from the basket, ensuring total autonomy and full safety. This function is compliant with Australian EWP standard AS 1418.10.
This is an essential control that allows travel speed to momentarily slow down or come to a stop while still offering maximum power to boom functions to increasing precision and productivity for delicate operations.
The Icarus is equipped with a side shift
carriage, making repositioning and stacking loads tightly, an effortless task.
The transmission is equipped with a servo controlled two-speed gear box and constantly varying hydrostatic drive, which guarantees top-end speed and low-end torque.
“The Icarus provides an ideal working environment for the operators with a fully-air conditioned cab, an air suspension seat and large curved windows providing 360 degree visibility. We have a fully proportional four-in-one joystick and simultaneous controls which also incorporates forward, neutral, and reverse,” said Bob.
“The operator has complete control of where they are placing the load or picking the load up from and the machine knows when the load is lifted. When the boom is telescoped in, the machine has the capability to pick and carry from one position to another.”
Over the years, the Dieci brand has built a solid reputation for reliability, designed with serviceability in mind.
“The Icarus provides an ideal working environment for the operators with a fully, air conditioned cab, an air suspension seat and large curved windows providing 360 degree visibility.”
“We have an 85 per cent commonality on our parts which makes for excellent parts availability. The Dieci brand continues to develop a reputation for reliability and is a significant reason why we have such a strong presence in the market,” said Bob.
“We support our growing population of machines with Dieci facilities in Brisbane, Sydney, Melbourne, Perth, and we are fully supported by our National Approved Parts and Service Agent (APSA), namely AWD Australia.
“Our Australia-wide network of regional APSA’s means you can be confident that we have you covered if you need after sales service, and support.”
When Kylie Wilkinson, General Manager at Team Transport & Logistics, first suggested venturing into pick-and-carry cranes, not everyone immediately shared her enthusiasm.
FOR YEARS, THE BRISBANE-BASED LOGISTICS
giant had built a sterling reputation handling “ugly freight”–those tricky, awkward loads that competitors often refused. Yet, despite an extensive fleet and diverse capabilities, one critical segment remained untouched: mobile pick-and-carry cranes.
“For a long time, we deliberately stayed away from larger cranes,” said Kylie. “The risks felt daunting, especially given the safety, insurance, and specialist skills required.”
However, Team Transport & Logistics has never been about standing still. Founded in 1979 as a family-owned business born
diversification has always been central to its strategy. Kylie, who joined in 1988 as a junior and rose to general manager, knew it was time to evolve once more.
The decision to move into pick-and-carry cranes was driven by both operational necessity and client demands. Long-standing contracts with clients such as Energex and Bunnings frequently involved lifting tasks Team Transport previously had to outsource.
“Outsourcing made me uncomfortable,” Kylie said. “We have skilled operators inhouse, and the demand was clearly there. I wanted us to offer the full package and deepen our relationships with key clients.”
This strategic insight led Kylie and the team to explore available options carefully, notably the TIDD PC28-3G and other competitors. After extensive research and demonstrations, Team Transport & Logistics
chose the TIDD PC28-3G by TRT for several strategic reasons.
The crane offers a maximum lifting capacity of 28 tonnes (t), utilising a four-section telescopic boom. The TIDD PC28-3G comes with a compact width of 2.5 metres (m) and a 44-degree articulation, which provides better manoeuvrability, allowing it to navigate and operate efficiently in tight spaces.
Kylie personally visited operators,
sought feedback, and conducted detailed evaluations. “We noticed younger operators gravitated towards the TIDD,” she said. “It seemed intuitive and modern, aligning with our need to attract and train younger staff.”
Beyond user preference, several practical factors favoured the TIDD PC28-3G. Its advanced safety features, including self-inflating tyres and stability systems, impressed Kylie.
The TIDD PC28-3G is equipped with Slew Safe, a system that significantly reduces the risk of rollovers by automatically moderating the crane’s steering and alerting the operator when a lift approaches unsafe parameters. The crane also features a dynamic Load Moment Indicator (LMI) with automatic cut-outs and overrides, which helps prevent overloads by monitoring the load and boom angle in real time.
These safety systems were a compelling differentiator. “The Slew Safe feature was something we hadn’t seen in older crane models,” Kylie said. “It gives our operators and our clients extra peace of mind, which is priceless. Safety is paramount. The visuals from the operator’s seat, the camera systems, and the advanced counterweight safety features were superior to other models we assessed.”
Kylie’s team also appreciates the crane’s safety mechanisms.
Younger operators have embraced the safety-focused design, feeling secure without the need to override critical safety systems –common practice among operators of older crane models.
Team Transport & Logistics’ in-house mechanical team also found familiarity with the Cummins engine in the TIDD crane, simplifying routine maintenance and servicing tasks.
The TIDD PC28-3G is powered by a 6.7-litre Cummins ISB6.7 engine, delivering 238 kilowatt (kW) and meeting the stringent Euro 6 emission standards. This engine, coupled with the latest Allison Transmission featuring a retarder, enhances the crane’s safety and control by offering retardationstyle braking capabilities.
This transmission reduces operational costs through decreased repair and maintenance and ensures quieter operation in urban environments.
Since arriving late in 2024, the TIDD crane has become more popular and versatile than initially anticipated. “It’s been utilised far beyond our expectations in the first quarter alone,” Kylie said. Primarily supporting
Energex contracts across South-East Queensland, it quickly became the go-to tool for jobs requiring logistical solutions.
Recently, the crane moved a challenging boat delivery, showcasing its capability in handling complex tasks.
“Clients often approach us with the ‘impossible’,” Kylie said. “We tell them, ‘We’ve got you.’ The new TIDD crane elevates our capabilities, giving us the power to turn ‘impossible’ jobs into everyday success.”
Kylie is cautiously optimistic about expanding Team Transport & Logistics’ crane operations while monitoring performance and client satisfaction.
“We like to ensure we’re fully mastering new equipment and delivering exceptional service before growing further,” she said. “Given the early success, expanding our crane capabilities certainly looks promising, but we’ll do it thoughtfully.”
This strategic expansion highlights Kylie’s leadership philosophy – never rush growth but remain bold in seizing opportunities. “The TIDD crane isn’t just a new machine,” Kylie said. “It’s symbolic of Team Transport & Logistics’ continuous evolution. We’re lifting our business, literally and figuratively, and we’re excited about what’s next.”
Thursday 12th June
Tackling the growing skills shortage in the lifting industry
Promoting practical tools to attract new talent
Inspiring the next generation to explore lifting careers
Find out how you can get involved
Big Rhino Crane Hire’s significant move to buy a bigger crane was a game-changer for its plans to grow. CEO Marg Gravener wanted a crane that could handle larger and more complex projects without breaking the bank. Three years on, the crane has proven its worth.
“WE’VE HAD THE SANY 60T FOR OVER three years now and it has been a reliable and quality machine. There were minimal breakdowns. That’s something we’ve come to appreciate more as it continues to perform dependably on a range of jobs,” said Chief Executive Officer Marg Gravener.
Looking back at the purchasing process, Marg said, “We thoroughly evaluated various brands and models on the market, and the Sany 60T stood out in terms of performance, specifications, and overall value. It provided exactly the
capability we were after without exceeding our budget.”
The Sany 60T broadened Big Rhino’s operational capabilities. It provides an impressive maximum lifting capacity of 60 tonnes (t), a six-section telescopic boom extending to 50 metres (m), and an additional bi-fold swingaway jib, achieving a maximum tip height of approximately 66.5m. The crane’s jib is flexible, with angles of 0 degrees, 20 degrees, or 40 degrees, enabling adaptability across various lifting scenarios.
“Integrating the Sany into our fleet has undeniably opened new doors for us,” Marg said. “Projects we previously might have declined or subcontracted are now comfortably within our capabilities.”
Marg highlights how Big Rhino’s fleet evolution – from smaller city and pick-and-carry cranes to the robust 60T – was driven by client demand for heavier lifting capabilities.
One project where the crane notably excelled was at the new Bunnings development site in Oxley, where it remained active for five weeks.
“The client was extremely pleased with the crane’s performance. It facilitated the project seamlessly and without any operational concerns,” Marg said.
Comfort and user-friendliness have also proven standout features of the Sany 60T. “Our operators find the cabin notably comfortable, even over long operational hours,” said Marg.
Big Rhino’s operator, Ross Spreadborough, who brings more than 30 years’ experience across various crane types and sizes, confirms Marg’s views. He said that the crane is smooth to drive on and off the road, and the computer system is
detailed and effective once the operator gets familiar with it. In his experience, some safety aspects outdid the competitors.
“The downward vision system is an excellent safety feature, enabling operators to directly monitor winches in addition to the dogman’s observations,” he said.
“The cabin interior is specifically designed for comfort over extended operational periods, which significantly contributes to maintaining high safety standards by reducing operator fatigue.”
The Sany 60T comes with six steering modes, allowing for tight turns with a minimal steering radius of just 6.5 metres.
Its hydro-pneumatic suspension can adjust height by around 100 millimetre, which can factor into driving comfort, stability, and off-road capabilities. Fuel consumption is optimised at around 60 litres (L) per 100 kilometres (km) with the help of its load sensing and constant power control technologies.
Technical features further enhance the appeal of the Sany 60T. It comes with a Mercedes-Benz OM470 engine, the crane delivers 280 kilowatt (kW) of power at 1600 revolutions per minute (rpm), and meets Euro V emission standards.
The crane travels with a maximum speed of 80 km/h. Its Allison automatic transmission offers 12 forward gears and two reverse gears for different loads and conditions.
Marg also drew attention to the crane’s safety and technology features, including a Load Moment Indicator (LMI), boom-tip camera, wind-speed sensor, and additional aids designed to maximise operational safety and efficiency.
“Sany clearly prioritised operator comfort and safety, which gives us substantial peace of mind,” she said.
In terms of dimensions, the crane measures approximately 12m in length, 2.55m in width, and about 3.78m in height. This makes it suitable for transportation and operation on standard work sites. The Sany 60T is equipped with a standard 3.3t fixed counterweight, complemented by removable units totalling 9.7t, which increases its lifting capacity considerably.
“By having the fixed counterweights, it allows us the option to use it as 35T slew without having to cart the big counterweight everywhere. A very versatile option,” Marg said.
Operational efficiency is supported by its rapid-acting hydraulic systems, which allow the boom to fully extend in approximately 350 seconds and enable winching speeds of up to 130m per minute.
Marg sees continued growth in the future supported by investment in the Sany 60T.
“The crane has quickly become an essential part of our business. It has proven its reliability,” she said.
Today’s mobile plant and machinery landscape is evolving rapidly. Equipment is becoming more specialised, operational environments more complex, and client expectations around coverage and service much higher. UAA Group’s Marc Crossman, Executive General Manager, Distribution Strategy explains why deep practical industry knowledge matters more than ever in today’s plant and machinery insurance space.
“PRACTICAL INDUSTRY KNOWLEDGE ensures that insurers can accurately assess risk, structure coverage that genuinely protects the asset, and support clients when claims occur. Without that depth of understanding, there’s a real risk of insurers either underinsuring or mispricing risk, both of which can have devastating consequences for businesses that rely on these critical assets to operate,” said Marc.
Marc shares examples where a lack of specialist understanding – whether by a broker or an insurer – has led to poor outcomes for clients in the mobile plant sector.
“We’ve seen examples where mobile cranes were incorrectly insured under general commercial motor policies, rather than through tailored mobile plant policies – leaving critical lifting operations completely uninsured. Another common scenario is failing to recognise the operational differences between a dry-hired excavator and a wet-hired (operator-supplied) one, leading to claims disputes because the wrong liability cover was in place. These examples highlight that without specialist knowledge, even well-intentioned solutions can leave serious gaps that only become apparent when clients need to claim – by which time, it’s too late,” he said.
He goes on to explain how UAA’s specialist knowledge, such as understanding the various types of cranes, influences underwriting decisions.
“At UAA, our underwriters know that typically a pick-and-carry crane has a
different risk profile to a crawler crane for example, which provides stability on rough terrain for lifting heavy loads. This practical knowledge directly influences how we assess operational hazards, loss scenarios, and appropriate terms and conditions for coverage. It also impacts rating structures: for example, franna cranes may be more exposed to road risk, whereas crawler cranes are more exposed to load stability issues on site. That’s the level of nuance we bring to every decision – and it ensures clients get the right cover, at the right price, for the specific asset they operate,” he said.
intelligence: We regularly share industry insights, claim trends, and emerging operational risks specific to mobile plant, helping brokers anticipate client needs before they arise.
• Providing agile underwriting support: Our specialist underwriters are accessible and empowered to collaborate with brokers directly on complex risks, ensuring speed, flexibility, and technical depth in every interaction.
• Investing in digital capabilities: We are evolving our platforms
“For example, our involvement with crane and construction industry bodies provides direct access to real-world insights on lifting standards, operational safety practices, and evolving machinery technologies.”
From a distribution and market strategy perspective, Marc explains how UAA is equipping brokers to navigate increasingly sophisticated client demands in the mobile plant sector.
“UAA, proudly part of the wider UAA Group, recognise that brokers are facing clients who expect more tailored advice, deeper industry insight, and faster, more flexible solutions than ever before. Our strategy is built around partnering with brokers as an extension of their advisory teams, not just as a product provider.
“We equip brokers by:
• Delivering bespoke market
and broker tools to streamline submissions, quotes, and policy management, giving brokers faster turnaround times and greater visibility into the underwriting process.
• Focusing on specialisation: Through targeted training, field-based insights, and ongoing development of our internal expertise, we ensure brokers can offer clients not just insurance products, but true specialist advice tailored to the nuances of mobile plant operations.
“Ultimately, UAA’s approach is about empowering brokers to be
Crossman, UAA Group’s Executive General Manager Distribution Strategy.
with leading industry bodies across the construction, crane, and mobile plant sectors. By actively participating in associations and technical working groups, our underwriting and claims teams stay connected to frontline operational developments, regulatory changes, and emerging risks.
trusted industry advisors, equipped with the insights, speed, and technical depth needed to meet – and exceed – the growing sophistication of client expectations,” he said.
Marc explains where UAA sees gaps in industry knowledge that can lead to misaligned insurance solutions and UAA is working to close these gaps.
“One major gap is understanding how plant is operated rather than just what plant is owned. For example, whether machinery is used solely on private work sites, used in public road operations, or hired out under various agreements can all dramatically change the risk
profile – and therefore the insurance needs. We close these gaps by not only educating brokers, but by asking the right questions during underwriting. Our teams are trained to dig deeper beyond asset lists – into how, where, and under what conditions machinery is used – ensuring solutions are fully aligned with real-world operations,” he said.
Marc explains how UAA ensures its underwriting and claims teams gain practical, field-based insights into plant and machinery operations.
“UAA’s commitment to maintaining practical, field-based knowledge is closely tied to our strong involvement
“For example, our involvement with crane and construction industry bodies provides direct access to realworld insights on lifting standards, operational safety practices, and evolving machinery technologies. This active engagement ensures our underwriting and claims professionals bring not only technical insurance expertise but also an informed, practical understanding of how our clients work, resulting in more relevant coverage, smarter risk advice, and better outcomes for brokers and clients alike.”
Looking ahead, Marc explains how UAA will continue to deepen its niche expertise to support brokers and clients as plant and machinery technology evolves including automation and hybrid machinery.
“At UAA, we see ongoing collaboration with manufacturers, brokers, and industry associations as critical to staying ahead of technological change in the plant and machinery sector. As equipment evolves – with automation, hybrid drive systems, and advanced telematics becoming more common – we are working closely with industry partners to inform our product development, refine risk frameworks, and anticipate emerging coverage needs.
“By maintaining active involvement in technical forums, regulatory discussions, and operator training initiatives, we ensure our underwriting and claims strategies are shaped by real-world developments, not just theoretical trends.
“This collaborative, forwardlooking approach means that brokers and clients can continue to rely on UAA for specialist insurance solutions that keep pace with the operational realities of a rapidly changing industry,” said Marc.
The Crane Industry Council of Australia (CICA) recognises excellence and innovation in the Australian crane industry with the CICA Lift Of The Year Awards.
PROJECT OF THE YEAR
INNOVATION OF THE YEAR
LIFT OF THE YEAR –UNDER 20T
LIFT OF THE YEAR –OVER 20T
PROJECT OF THE YEAR WINNERSydney Gateway Project John Holland - Seymour Whyte JV.
LIFT OF THE YEAR MORE THAN 20 TONNES WINNERBMS Heavy Cranes Australia & CPB Contractors & John Holland Joint Venture. Girder GSR-08 Install of Bridge 80 of the West Gate Tunnel Project.
INNOVATION AWARD WINNERAlevro. LNG Compressors Jack Down with Jacking System.
BILL SHAW MEMORIAL CUP
WINNER - BMS Heavy Cranes Australia and CPB Contractors & John Holland Group Joint Venture.
LIFT OF THE YEAR LESS THAN 20 TONNES WINNER - John Holland and Johnson & Young Cranes. Relocation of the heritage-listed Nissen Hut.
600,000 visitors from more than 200 countries and regions, 3601 exhibitors from 57 nations. Corporate decision makers emphasise the relevance of bauma for sustainability, digitalisation and progress with significant growth among visitors from abroad.
bauma, the world’s leading trade fair for construction machinery, building material machines, mining machines, construction vehicles and construction equipment impressively demonstrated what the industry is capable of.
During bauma, Liebherr displayed a significant number of brand new models which are set to define the future of the crane and construction sectors. Hansi Nothacker, Liebherr’s, General Manager Mobile Cranes Australia and New Zealand, introduced Cranes and Lifting magazine to a number of the groundbreaking cranes.
A MAJOR DRAWCARD FOR VISITORS TO the Liebherr stand was the LG 18001.0, the successor to the highly regarded LG 1750 – a crane that came in for high acclaim thanks to the design’s combination of the mobility of a mobile crane and the load capacity of a crawler crane.
The LG 1800-1.0 possesses a maximum lifting capacity of 800 tonnes and, akin to its crawler relative in the Liebherr range, the LR 1800-1.0, holds a main boom option of up to 180 metres long and a main-boom-plus-luffing-jib combination providing a maximum hook height of 208m. The crane features a chassis width of three metres and is capable of climbing up gradients of 25 per cent making the crane “ideal” for the wind industry, according to Liebherr.
Further optimising the crane for the wind industry is the machine’s enhanced wind power boom systems that make it possible to work with a boom of 174m and
an 18m long lattice type fixed jib at hub heights of 180m, as well as the wind speed load charts with different permissible wind speeds of up to 13.4m/s.
Liebherr’s LG 1800-1.0 has also been designed to facilitate easier transport. Labelling the crane as “suitable for all markets” worldwide, Liebherr said the nine-axle vehicle features an axle-load of ten tonnes with all four supports, meaning the crane is accessible to public roads.
Additionally, transport of the mobile lattice-boom crane is possible with only two supports and a total weight of 70 tonnes, as well as completely without supports at around 50 tonnes. The crane comes with the latest in Liebherr technology too, such as V-Frame, VarioTray, ZF Traxon Torque transmission with EcoDrive, and the aforementioned WindSpeed Charts.
One of the major areas that the LG 1800-1.0 differs from the LG 1750 is that the folding beams on the new 800-tonne machine are not telescopic. The required support base of 13x13m is sufficient for the LG 1800-1.0 to achieve enormous load capacities with the derrick system and “very good” erectable lengths without the derrick system, according to the manufacturer.
Hansi had this to say.
“One of the largest capacity cranes on display here at bauma is our LG 18001.0, which was launched last year at Liebherr customer days. The LG 1800-1.0 is the successor of the LG 1750, which dominated the wind construction sector for 20 years.
“With the LG 1800-1.0 we’ve updated the complete chassis so instead of having an eight we now have a nine-axle chassis to make the crane road-legal in all parts of the world. We’ve upgraded the boom and derrick systems with a V frame, which allows you to infinitely adjust the derrick counterweight radius. The boom system allows us to erect wind turbines with hub heights up to 180 metres.
“We are showcasing the option for the X3-system on the machine. By putting these wide inserts into the main boom, we achieve lifting capacities above 140 tonnes at 165m hub height and max
system lengths of 174 metres plus 15 metres fixed jib, to enable the erection of newest generation wind turbines with hub heights of 165-180 meters. With the LG 1800-1.0 we are confidently prepared for the developments in the wind turbine construction sector for the next decade,” said Hansi.
Remote drive was a key feature of the Liebherr stand and visitors were able to remotely drive a Liebherr LTC 1050-3.1 which was three metres in the air. The LTC 1050-3.1 delivers the outstanding handling of a classic all-terrain crane. Its compact design also makes an ideal
hoisting tool for constricted sites. It shows all its strengths completing crane work in industrial buildings, old towns or in castles and palaces.
The LTC 1050-3.1 features the VarioBase® support system that enables outriggers to be extended to different lengths which means that constricted conditions are not a problem for this compact crane. It carries all its own equipment and ballast, thus significantly reducing the time required for jobs. The elevating cab delivers maximum safety by providing improved all-round visibility from the cab. The crane can also be manoeuvred with all controls from outside using RemoteDrive, ensuring the operator
has a perfect view of the constriction.
“All LICCON3 machines will feature the RemoteDrive option as a standard and we have LICCON3 models with capacities up to 300 tonnes. And what’s the idea behind it? This is our answer to various 360 degrees camera ‘birds eye view’ systems,” said Hansi.
“When the crane gets to a site with tight space tolerances, the operator is able to manoeuvre the machine remotely, walk around the machine to spot obstacles and move it into the spot where the crane needs to be to conduct the lift.
“It negates the need for an extra pair
of eyes or a sercond person like a dogman, because the operator has full control of the crane,” he said.
The crane display also included the Liebherr LTM 1150-5.4E mobile crane with electric drive. The LTM 11505.4E allows the crane movements to be performed emissions-free and with reduced noise pollution.
With an integrated battery, the crane can work autonomously for up to four hours without a power connection, and a low connected load on the construction
site is sufficient to utilise the crane’s full power, as the battery acts as an efficient buffer. The LTM 1150-5.4E meets the requirements of “Zero Emissions Construction Sites” and combines sustainability with maximum efficiency.
On and off-road, a 400 kW (544 HP) combustion engine with exhaust emission stage 5 provides for powerful drive. The motor is fully compatible with hydrogenated vegetable oil (HVO) and, compared to diesel fuel, reduces operational carbon dioxide emissions by up to 90 per cent.
The drive concept of the LTM 1150-5.4E builds on the proven technology of the Liebherr LTC 1050-3.1E compact crane, albeit with an important upgrade: an integrated battery pack.
This concept brings two key advantages. Firstly, the crane can be operated autonomously for around four hours without a power connection thanks to its battery. Secondly, even a low connected load, around 16 or 32 amps, is enough to unleash the crane’s full power since the battery acts as an efficient buffer.
The 99 kilowatt per hour (kWh) battery is securely installed in a box weighing around 1.5 tonnes at the rear of the crane. To enable driving on public roads, the ballast plates have been adapted accordingly – a carefully thought-out concept for maximum flexibility and efficiency on the construction site.
“The LTM 1150-5.4E is our answer to de-carbonising mobile crane operations. We achieve full net-zero emission crane operations by equipping the crane with a 100 kWh battery which weighs about 1.5 tonnes,” said Hansi. “To cater for this additional weight, the counterweight is reduced to 7.5 tonnes in road driving mode. With the battery pack and the additional electric motor, we can achieve four hours of crane operation from the battery which can be recharged when plugged into a 16 amp connection.
“Crane movements provide the same performance as a combustion engine, with net-zero and lowest noise emissions.”
From large-scale construction to civil and foundation work, Kobelco Crawler Cranes are designed to handle it all - big, small, and everything in between. As the exclusive Asia-Pacific agent, TRT delivers a comprehensive end-to-end solution. Service and parts support 24/7, 365 days a year during the entire life of your crane.
Talk to TRT today about your next Kobelco.
MAXbase Equipped
The GMK4080L is an outstanding four-axle taxi crane that, with its 60-meter-long boom, offers both the longest boom and the lowest gross vehicle weight in its class. Within 10 t per axle, the crane can carry 5.2 t counterweight and even 13.3 t counterweight with 12 t axle load.
•60 m boom length and capacity matches the 90-100t class (4.8 t @ 60 m)
•Main boom: 11,3m - 60m, 7-section
•Bifold swingaway jib: 8,7 m /15 m (optional)
•Minimum width 2,55 m and overall length 12,82 m
•Carrier cab: Latest generation of Grove carrier cabs
•Increased safety and flexibility with MAXbase variable outrigger system
•Faster Intuitive set-up with CCS (Crane Control System)
•Engine: Mercedes-Benz OM470LA, 300kW
•Capacity: 80 t
•Main boom: 60 m
•Maximum jib: 15 m (0°-40° luff)
•Maximum tip height: 77 m
•GVW: 48000 kg 3
many technologies that drew customers
Manitowoc launched two new Grove hybrid all-terrain cranes at bauma with the GMK5150XLe, taking centre-stage.
MANITOWOC LAUNCHED ITS FIRST EVER Plug-in Hybrid all-terrain cranes – the Grove GMK5150L-1e and GMK5150XLe. The GMK5150XLe, similar to its sister model, features much of the technology that excited customers three years ago when the GMK4100L-2 hybrid concept was unveiled.
The new models feature the existing 150 tonne capacity GMK5150L-1 and GMK5150XL cranes combined with a new, fully electrified superstructure resulting in more efficient, quiet, and environmentally friendly lifting operations.
At the heart of the new cranes is a battery pack that enables a solid day’s work as a taxi crane. With 180 kilowatt-hours (kWh) of energy, the Grove Plug-in Hybrid cranes can easily carry out several daily tasks. What makes them especially versatile is their ability to charge the battery from the grid (either AC or DC power supplies) or a 170 kW generator integrated into the carrier. This allows charging while driving and eliminates owner concerns about the availability of charging infrastructure. The cranes can even be operated while charging (providing there is infrastructure
for this at the jobsite).
The battery pack enables approximately eight hours of emissions-free lifting without compromising speed or capacity. When the crane is connected to the grid, the crane can operate continuously. This is more than enough functionality for a 150 t taxi crane, and when the day’s work is complete, the batteries are recharged while the crane is driven back to base, ready for the next working day. Another exciting feature is the E-Boost function. While accelerating the generator can be used as motor and gives an additional 800 Nm torque into the driveline.
“These new Plug-in Hybrid cranes deliver more sustainable lifting and boost owners’ environmental credentials. They can drive to the job site using HVO fuel to power the efficient Mercedes-Benz engine and reduce carbon emissions by up to 90% while simultaneously charging the batteries. Then, they can set up and use clean electricity to handle the lifting tasks. There’s also a massive reduction in noise pollution
– a great advantage when operating in a city center, especially in the very early mornings or in the evenings,” said Florian Peters, senior product manager for all-terrain cranes at Manitowoc.
Notably, adopting this more sustainable power source has no negative impact on lifting performance. Their operation is identical to the diesel driven cranes, just with considerably lower fuel consumption. Structurally, the 60 m main boom on the Grove GMK5150L-1e and 68.7 m main boom on the GMK5150XLe are identical to the diesel models, as are the load charts. This means the cranes will effortlessly handle their duties in day-to-day business.
Thanks to the carrier integrated generator the driveline, doesn´t require a retarder as it uses the braking energy to charge the batteries. This can be done in different modes where in ECO mode the batteries are being charges without additional fuel consumption. The remaining part of the driveline is maintained featuring the MEGATRAK® independent suspension system with disc brakes. There’s also Manitowoc’s efficient Crane Control System (CCS) with boom configurator mode and the flexible outrigger positioning system MAXbase™.
“Many cities and industrial sites are placing increasingly strict environmental requirements on machinery, so there is a need to provide customers with options to help them achieve their commercial and environmental goals. There was a lot of interest in the hybrid cranes and we were excited to unveil the GMK5150XLe at bauma 2025,” said John Stewart, VP Sales & Support, General Manager, Manitowoc Cranes Australia.
“When you examine the overall fuel consumption of a normal taxi machine, a hybrid crane can reduce the carbon dioxide (CO²) footprint by one third when it comes to the operational element of the crane. Obviously, getting the crane to site is where the majority of the diesel is consumed. Once on site the crane’s superstructure is powered by the battery and this can be recharged using renewable energy making it carbon neutral,” he said.
“The MCR 505 is due to be released in Q3 and we are expecting the same success with this model as we have had with the MCR305.”
“With hybrids, there will be savings in energy consumption but that by itself will not offset the price difference compared to a diesel-powered crane. Diesel is still too cheap, but it will certainly look different as the world moves forward and there is a price for carbon dioxide emissions,” said John.
Potain’s MR 309 luffing jib crane made its international debut at BAUMA in Munich. The MR 309 was announced last year and is part of Potain’s newest generation of luffing jib cranes.
Both the Potain MR 309 and its sister model, the MR 329, complete the latest generation of Potain luffing jib cranes. By integrating valuable customer feedback using Manitowoc’s Voice of the Customer (VOC) process, Potain engineered several notable benefits into the cranes, including quicker and simpler crane assembly and an enhanced overall user experience.
The MR 309 delivers class-leading
capabilities, offering maximum capacity variants of 16 t or 25 t; a 60 m jib; and a tip capacity of 3.4 t. It features a 2 m mast section connecting to the crane’s luffing section. There’s up to 49.2 m of freestanding height under pivot, and up to 4.3 t can be lifted at 55 m. The crane effectively addresses the demand for a significantly reduced out-of-service radius (9.5 m to 12 m) and minimizes anchorage frame requirements. These enhancements help improve efficiency and productivity on high-rise and congested construction sites where oversailing is prohibited.
“We’ve had such success with the Potain MCR305, that we embarked on a consultative process with Australian customers asking them what they wanted to see from Potain in terms of cranes best suited for our market.
“The feedback was passed back to the factory and collaboratively, we have designed the MCR505 which is tailored to meet the demands of our market. The
MCR 505 is due to be released in Q3 and we are expecting the same success with this model as we have had with the MCR305,” said Billy.
The MR 309 comes equipped with the Potain CONNECT™ telematics system, which uses a remote telematics platform to ensure higher uptime by enabling faster identification and resolution of issues. It also provides remote access to crane data for troubleshooting and fleet management, helping Potain customers get more from their machines.
The Potain MR 309 features a jib that can be mounted horizontally in one or two parts to minimize space requirements during erection. Accessible platforms and steps enhance worker security and efficiency, while the counter jib ballast is installed at working height, facilitated by built-in slinging points and a self-centering system.
A redesigned luffing mechanism further streamlines assembly, and an integrated jibend basket enables more secure installation, inspection, and maintenance. Additionally, the Potain CCS control system offers a range of advantages, including reduced commissioning time to help the crane get to work faster.
SENNEBOGEN set a new milestone in its crane technology at bauma 2025. With the introduction of the new 6203 E telescopic crawler crane, which has a maximum load capacity of 200 tonnes and a jib length of up to 78m, the company is expanding its range with what is now by far the largest and most powerful model in the series. A completely revised machine control system rounds off the new crane.
Sennebogen’s new 6203 E telescopic crawler crane, which has a maximum load capacity of 200 tonnes and a jib length of up to 78 metres.
Sennebogen and Prime Creative Media
international market, more and more contractors and crane hire companies are recognising the advantages and versatility of telescopic crawler cranes and are increasingly finding ways to use them.
“SENNEBOGEN has over 33 years of experience with telescopic crawler cranes and has been manufacturing material handling equipment and crawler cranes for 70 years. One market trend that we are now observing is the growing demand for large telescopic crawler cranes. To meet this demand, we are now expanding our range significantly upwards with the new 200t crane,” said Managing Director Erich Sennebogen.
The SENNEBOGEN 6203 E is the tenth telescopic crawler crane model in the manufacturer’s range and demonstrates its strengths above all when high capacities are required with varying radii and difficult construction site conditions.
The crane is powered by a 194 kilowatt (kW) Stage V diesel engine which, like all SENNEBOGEN cranes with Stage V engines, can be easily operated with HVO (hydrotreated vegetable oil) if desired. The main and auxiliary winches are driven by high-pressure-regulated variable displacement hydraulic motors, which give them an impressive pulling force of 135 kilo-newton (kN) each and rope speeds of up to 115 metres per minute. The machine is predestined for heavy precast concrete assembly, bridge and infrastructure construction and as an agile service and auxiliary crane for wind turbine construction.
The 6203 E has a six section Pin Boom that can be telescoped up to 56.4 metres. The Pin Boom telescoping system proves to be particularly
light and stable and achieves outstanding lifting capacities even with long boom lengths. On the 200-tonner, an additional pin point at 90 per cent extension on each telescopic section increases the rigidity of the boom, which means lifting capacities are impressive even at great lengths.
The 6203 demonstrates its capabilities with long boom lengths, but is extremely strong with short boom lengths and at angles of up to four degrees. This makes it particularly suitable for tasks on uneven construction sites or in pick-and-carry operation. The boom length can also be extended to up to 78 metres with a hydraulically adjustable jib – an option that makes it suitable for structural engineering.
To keep operation simple, the most effective boom configurations are preset with 16 ‘Extend Modes’. Switching between the extend modes is possible and saves valuable time when adjusting the boom length.
The telescopic crawler undercarriage
has a maximum track width of 6 metres, which can be reduced to up to 3.5 metres depending on construction site requirements.
Thanks to the robust design of the undercarriage and the high load capacities in the inclined position, the 200 tonne tele crawler is powerful, especially for pick and carry tasks, and can travel with 100 per cent of the specified load capacity on the hook. It can also slew the specified load capacities a full 360 degrees. The 1000 millimetre double grouser track shoes fitted as standard offer maximum stability and minimise floor pressure. For more sensitive surfaces, durable polyamide plates can also be used as an option to prevent damage.
Like all large SENNEBOGEN telescopic cranes, this telescopic crane is also equipped with the tried and tested Maxcab largecapacity cab, which can be tilted by 20 degrees as standard and therefore always offers the operator an optimum view of the
load. As an option, the cab can be raised hydraulically to a viewing height of 5.70 metres and tilted by 30 degrees. Cameras to the rear and to the right extend the driver’s field of vision to the entire safety and working area.
An absolute highlight in terms of driver assistance is the new SLC – Sencon Load Control machine control system. To make operating the crane as comfortable as possible for the operator, a separate control system with its own screen has been integrated into the cab in accordance with automotive standards. The new system is an addition to the existing Sencon (Sennebogen Control System) and provides all valuable data on the lifting process on a large, clearly organised display, in addition to the load moment limitation. The extend modes can also be conveniently set here.
There is also a floor pressure display calculated in real time. Operation of the large touch display is simple and intuitive and offers the driver valuable support when working with the machine. Diagnostic data on the machine and engine can still be found in the Sencon as usual.
The crane has a transport width of just three metres without the crawler tracks and can be transported in seven units. Once on site, the 200t crane, like all SENNEBOGEN telescopic cranes, is able to unload itself from a low loader and assemble itself in just a few steps.
In terms of service-friendliness, the crane shines with its tried-and-tested SENNEBOGEN technology, which avoids over engineering in line with the motto ‘keep it simple’. This means that hydraulics and electrics are still used where electronics offer no added value.
The clear arrangement of all maintenance and service points, as well as clear labelling of components, make orientation easy and ensure that the machine is quickly available again when servicing is required. State-of-the-art engine, drive and exhaust systems, as well as large-dimensioned lines and valves, ensure efficient operation and protect your wallet and the environment.
This new generation 175t class crawler crane SCX1800A-3 excels in all aspects from safety, user friendly, transportability, energy efficiency and many more. The SCX1800A-3 provides exceptional lifting capabilities with a compact body. The main boom and crane jib combination has a reach of up to 75m + 31m, covering a wide working area to further streamline operations on worksites. This crawler crane is powered with a clean-running Cummins engine, developed with high-pressure fuel injection and other features to lower emissions and comply with EU Stage III and US Tier 3 emissions regulations. Also available in a Stage IV and Tier 4 compliant engine.
bauma Germany 2025 highlights global appeal, advanced hybrid technology, and regulatory alignment for Oceania markets.
XCMG’S STANDOUT PRESENCE AT bauma Germany 2025, held from April 7-13 at Messe München, reinforced the company’s growing influence in the global crane industry. Showcasing its latest all terrain cranes and hybrid technology, XCMG attracted significant attention from European and Australian visitors, confirming its capability to meet both regional and international standards.
Stephen Broomfield, General Manager of XCMG Oceania Crane Center, reported strong demand, particularly for the 250-tonne all terrain crane with a 73-metre main boom and ADR (Australian Design Rules) compliance. Over 100 units were ordered during the event, including 40 units by a European dealer across the two, four, and five-axle range.
“The feedback we received on the 250-tonne crane was exceptional,” said Stephen. “It’s fully engineered to European standards and ready for the Australian market, where its dolly configuration now legally classifies as a trailer, making it more flexible and compliant.”
bauma 2025, the world’s largest construction equipment trade show, featured over 3500 exhibitors from 57 countries, and served as the perfect stage for XCMG to unveil its latest innovations – particularly in sustainable technology. The 60-tonne hybrid crane, equipped with a Tier Six, hydrotreated vegetable oil (HVO)-compliant engine and electric superstructure, impressed attendees with its ability to run on battery, mains power, or external E-pack systems. A standout feature was its battery-integrated counterweight, offering a unique design advantage for eco-conscious operators.
“All terrains now feature vario outriggers and vario ballasts, combined with operator-friendly components such as Wiki Herschmann computers, Kessler axles, and Mercedes or Allison engines,” Stephen explained. “We’re delivering cranes that not only meet technical standards but are also intuitive and familiar for operators.”
Interest in XCMG’s wind energy solutions was high, with European developers, especially from Poland, highlighting the need for high-capacity cranes like the XCMG 4000. Although not displayed at the event, the model drew attention for its capability to handle the taller turbine heights now common in wind farm construction– often exceeding 170 metres. These extreme heights demand cranes with exceptional reach and lifting capacity, which XCMG is well-positioned to deliver.
“When you see names like Sarens operating our cranes – and now partnering with us strategically – it’s a powerful endorsement of our quality and trustworthiness.”
Further reinforcing XCMG’s global momentum, the company signed a strategic cooperation agreement with Sarens, one of the world’s largest crane rental and heavy transport specialists, during bauma 2025. The agreement was signed by Jan L. Sarens, Board Member and Trade Director of Sarens, and Jianzhong Sun, Vice President and General Manager of XCMG’s Hoisting Machinery Division.
Both companies have agreed to establish a strategic partnership that emphasises commitment to quality, efficient, and personalised services.
“There’s a clear shift in Europe toward cost-effective alternatives that maintain safety and reliability,” said Stephen. “XCMG is positioned to deliver on that. When you see names like Sarens operating our cranes – and now partnering with us strategically – it’s a powerful endorsement of our quality and trustworthiness.”
As bauma 2025 underscored, XCMG’s combination of performance, regulatory compliance, and innovation continues to drive strong market adoption across both Europe and Australia.
Longest powered boom to 20.9m with 5.5m telescopic fly extends to 26m
All Models (25T, 35T, 55T) rated @ 1.4m boom position, highest boom strength available, fully fabricated
Air-spring suspension with shock absorbers eliminating cabin noise and vibration
High Stability at all positions to 42 degrees
Low centre of gravity with rigid chassis design, safest crane available
Dynamic Load Chart and Digital Rope Compensation
Safe road speed 90-100kph with 180 degree unobstructed front vision with four cameras to sides and rear
Humma Heavy Lift Crane design, specification with proven componentry has set the new Industry standard for performance. ONE FOOTPRINT FOR ALL MODELS.
Crane owners require low operating and maintenance costs, highest level of safety in both driving and crane mode, achievable on all Humma Models.
Patented Auto-leveller on Humma 55, the largest and safest Pick and Carry available.
Highest level of safety at all articulation positions to 42 degrees using Humma low twist chassis design.
Cabin rated the safest and quietest available at 65 decibels.
Remove the removeable counterweight from 35T and 55T and you have a heavy duty 25T and 35T.