

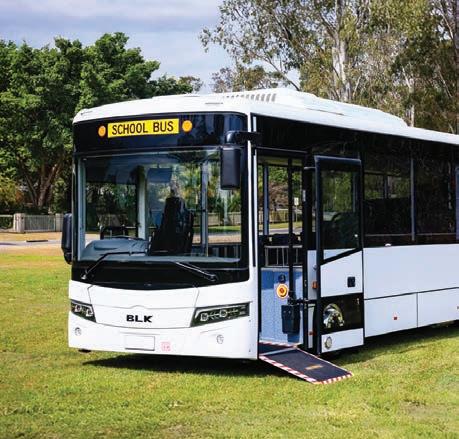
AUSTRALIAN OWNED, DESIGNED AND SUPPORTED.
By the time this edition of ABC hits the press, the federal election should have a date and there’s plenty the industry wants to see from the parties in the lead-up to voting
Never has a federal election been slated to come at such a pivotal time for Australia’s bus and coach industry. The continuing questions around the timeline for the sector’s zero-emissions vehicle transition means any party that wins power will need to come armed with a strategy to please the industry. The strategy will need to answer questions such as: When will operators be expected to transition their fleets fully to sustainable technology? What is the preference for the power source to be used? Who will help fund these large-scale transformations? And… is there a chance that the transition could include upgrades to low-emissions technology like Euro 6 diesel vehicles before operators have to purchase infrastructure to power zero-emissions buses?
Outside of the green transition, there are still so many issues facing the bus industry that demand government direction — whether it be the skilled driver shortage or the definition of what local content means for Australasia’s bus manufacturing market.
focus on safety systems onboard school buses.
Companies like SGESCO-MAX are moving quickly to meet this demand, with the brand’s variety of new ADR compliant and complete occupant safety solution products, as can be seen on page 46, ushering in a new era of security and protection.
Since first establishing its local presence in 2012, Yutong Australia has become a constant in the ever-growing zero-emissions bus market. On page 29, the international power discusses its history to date and what exciting chassis models it is preparing to welcome to operators.
Our March edition also comes with a servicing focus, with the likes of BSS – Bus Services & Solutions leading the way. Having only established its presence in Pakenham, Victoria a few years ago, the business’ growth underlines the value that repairs and service providers off er to the local industry.
There are still so many issues facing the bus industry that demand government direction — whether it be the skilled driver shortage or the definition of what local content means
All of this, of course, comes as the Victorian industry still grapples with the supply issue that is no closer to a resolution. Following the Bus Industry Confederation’s open letter to Victorian Premier Jacinta Allan in our February edition, this edition features a summary of the latest news on the issue and how it is aff ecting both safety and manufacturing. See page 26.
On the supplier side, businesses are already reacting to the change to upgrading rules and choosing to focus on diversifying their fl eet. As a leading Victorian based manufacturer, Volgren Australia has tapped into its global roots through parent company Marcopolo, bringing some Brazilian fl air to Australia in the form of the G8. Check out what this beauty will look like when it hits local roads and what it off ers for operators around the country from page 22.
When it comes to responding to recent developments, the release of the Australian Design Rule mandating seatbelt wearing monitoring technology has placed a fresh
Irizar’s latest service platform is further expanding the international brand’s capabilities in the a ersales game, while Wales Repairs is leveraging its wider network to continue evolving its Australian heavy vehicle repair operations.
All of this and more is included in another edition of ABC Magazine brimming with fresh stories and the latest news. We hope you enjoy the read.
Sean Mortell EDITOR, ABC
Sustainable. Efficient. Built for a Greater Tomorrow.
Whether you're navigating bustling city streets, arriving at schools, or operating on mine sites, the Yutong D7E delivers zero-emission performance without compromise.
With seating for up to 28 adults or 40 children, the D7E offers spacious comfort while eliminating tailpipe emissions. Advanced safety features—including a 360° camera and Yutong’s YESS Safety System—ensure every journey is secure. And with a full air suspension driver’s seat with lumbar adjustment, long drives are effortless.
In stock now for immediate delivery.
Discover the benefits of electric today—speak to our team about test drives and flexible finance options.
Image: EZPS/stock.adobe.com
06. editorial | ignition PREPARING FOR THE BALLOT
By the time this edition of ABC hits the press, the federal election should have a date and there’s plenty the industry wants to see from the parties in the lead-up to voting
10. news | all aboard
Check out the latest news from around Australia and the world
18. column | BIC PROMISES, PROMISES
With an election and the end of another financial year looming ever closer, the Bus Industry Confederation has dug its feet in on the issues that matter most to the bus and coach industry features
22. cover story | volgren SETTING THE BENCHMARK
Marcopolo is preparing to redefine coach travel in Australia when it launches the G8 to the local industry in September
26. feature | bus safety SILENCE ON BUS SAFETY QUERIES
Parents at a regional Victorian school are demanding answers as overcrowding on their school buses forces students to stand for long journeys at high speed
27. feature | victorian orders LACK OF PLANNING
The Victorian government is hinting at new brands entering the state while the industry disputes consultation calls over a four-year volume plan
29. feature | yutong ELECTRIC EXPERIENCE
Six decades of knowledge and technological development is allowing Yutong Australia to bring its leading electric chassis models to the local market
32. feature | bss NEW SENSATION
Blending international expertise with local innovation, Bus Service Solutions is redefining bus and coach maintenance through its unique approach
37. feature | irizar SERVICING YOUR NEEDS
Irizar’s iService portal is providing operators with a one-stop shop to help them stay on top of the maintenance of its buses
41. feature | challenger PARTS PERFECTION
Operators are at front of mind for Challenger Bus and Coach, its parts business ensuring operators get their buses back on the road in no time
44. feature | wales repairs ON TO BIGGER THINGS
With a renewed focus on expansion, innovation and customer service, Wales Heavy Vehicle Repair is setting the standard for heavy vehicle and bus repairs nationwide
46. feature | sgesco-max SAFETY AND SECURITY
In the wake of the unveiling of ADR 68/01, SGESCOMAX is upgrading its occupant safety system to keep school bus passengers safer than ever
48. column | qbic
A WORKFORCE ON THE BRINK
QBIC’s Jason O’Dwyer talks the current workforce crisis and the need for immediate action
51. competition | best bus LONG-LASTING LEOPARD
Bryce Pender’s terrific shot of a beautifully maintained 1979 Leyland Leopard has taken home ABC ’s Best Bus March
54. factory facts | bus deliveries FEBRUARY DELIVERIES
Check out the latest bus and coach supplier sales data collected and recorded for you to review and see how the market fared in February
58. back seat | women in the industry NEVER SAY NEVER
A er her time working in disability sector had ran its course, Rachelle Donnison decided to finally bite the bullet and get behind the wheel
EXECUTIVE GROUP
COO: Christine Clancy CEO: John Murphy
Head of Customer Experience: Regina Fellner
EDITORIAL & DESIGN
Managing Editor: Geoff Crockett
e-mail: geoff.crockett@primecreative.com.au
Editor: Sean Mortell
e-mail: sean.mortell@primecreative.com.au
Assistant Editor: Tiarna Condren e-mail: tiarna.condren@primecreative.com.au
Art Director/Design: Daz Woolley
PRINTING
Brougham Press
ADVERTISING
Sales Manager – South: Courtney Burton ph: 0481 736 890
e-mail: Courtney.Walker@primecreative.com.au
Business Development Manager – Bus: Adrian Kos ph: 0413 777 670 e-mail: Adrian.Kos@primecreative.com.au
SUBSCRIPTIONS
www.busnews.com.au/subscribe
ph: +61 (0)3 9690 8766
Mon-Fri 8am-4.30pm (EST) e-mail: subscriptions@primecreative.com.au mail: 379 Docklands Drive, Docklands VIC 3008 Australia
Annual subscription rates (12 issues): Australia: $99*
Overseas: $A170 (Australian air-mail only) *price includes GST
Cover image: Volgren
379 Docklands Drive, Docklands VIC 3008 T: 03 9690 8766 www.primecreativemedia.com.au
ISSN 1324-8634
A new era begins with the arrival of the long-awaited Marcopolo G8, set to redefine coach travel in Australia. With superior performance and ultimate comfort, it elevates every journey. Featuring an iconic design, the G8 is the future of Australian coach travel.
Visit us: www.volgren.com.au@volgrenaustralia MOVING PEOPLE, MOVING
Infrastructure Victoria’s dra strategy could see Victoria’s public transport looking very different
Extended public transport routes, reduced fares, lowered speed limits, increased service frequency and a revamped bus network form part of a dra 30-year blueprint to help Victoria’s infrastructure cope with the state’s growing population.
Released by Victoria’s independent expert advisory body, Infrastructure Victoria, the proposal is updated every three to five years and reflects insight from community and stakeholder feedback.
“If actioned, our recommendations will significantly reduce the costs to government of providing the infrastructure Victorians will need over the next three decades,” Infrastructure Victoria chief executive Jonathan Spear says.
“Action on these recommendations can generate at least $155 billion worth of benefits to Victorians over the next decade.”
A major focus in the dra strategy was improving the state’s current public transport system.
The proposal recommended that bus services across Victoria be given a makeover, redesigning bus routes to be more direct and starting services earlier and finishing later.
It suggested the government build a new rapid transit bus network on five routes including Tarneit to Maribyrnong, Point Cook to Watergardens, Melton to Broadmeadows, Huntingdale to Upper Ferntree Gully, and Endeavour Hills to Southland.
Running more buses in regional cities was a hot topic, starting with Shepparton, Wodonga, Mildura, Wangaratta, Horsham and Bairnsdale. It also suggested more buses that connect small towns to regional cities, starting with routes like Bendigo to Wangaratta, Geelong to Bendigo via Ballarat, and Wodonga to Kerang.
Fix Dandy Buses convenor Peter Parker says increasing bus operating hours across Melbourne would be
Above: The report includes a focus on reviewing regional bus networks. Image: John Lindsay, Victorian Department of Transport and Planning
a welcome change, referencing the report’s statement that “the most disadvantaged areas commonly have the least public transport”.
Parker says that this was particularly the case in Greater Dandenong, that had six bus routes that did not run seven days. In contrast, other outer areas like Craigieburn, Melton and Tarneit had all their buses operating seven days.
Long gaps between buses were also an issue in Greater Dandenong, with routes such as 804 having a two hour gap in the Saturday a ernoon timetable.
Parker says longer operating hours would improve bus connectivity in Greater Dandenong, which had routes like the 814 in Springvale and Noble Park North finishing as early as 1pm on Saturdays and the 802 not running on weekends.
“Seven-day service and longer hours for buses was a proven success in Dandenong with the outstanding patronage success of the Route 800 on Princes Highway that got upgraded last year,” Parker says.
Running more bus services will cost the government $550 million to $750 million each year to operate, which includes purchasing and maintaining the bus fleet and depot upgrades. The strategy plan outlines that public transport fares can help off set the operating costs of improved bus services.
Public transport fares influence travel behaviour, with the plan suggesting that Victoria’s fares can
be changed to encourage better use of the transport network and deliver the most benefit to Victorians. More people travel during peak hours than off-peak, placing pressure on roads and public transport.
“Lower off-peak fares can encourage motorists to catch public transport instead,” the proposal reads.
“There are many benefits including less congestion and fewer emissions. Cheaper off-peak fares can also help to defer costly infrastructure upgrades.”
A er upgrading the Myki ticketing system, the strategy suggests charging lower fares for off-peak travel on Victoria’s buses, trains and trams and reducing the number of regional fare zones.
The proposal also suggested reducing speed limits to 30km/h in “local streets”, starting with places that children o en visit including around schools, playgrounds, childcare centres and kindergartens.
So far, 30km/h speed limits have only been trialled in a few places in Victoria, including in Mildura in the state’s north-west and the Yarra council area in Melbourne’s inner-north.
“Victoria’s neighbourhoods should be safe for people to travel and for children to play. However, many roads are not safe for pedestrians or bike riders,” the strategy plan reads.
“An average of 35 pedestrians die each year in Victoria. Road trauma is a leading cause of death for children aged one to 14 in Australia. Nearly 300 children a year are seriously injured, mostly on local roads with speed limits of 50km/h.
“The Victorian government should update its speed limit policy and work with local governments to update speed limit signs.”
The Victorian government does not have to formally respond to Infrastructure Victoria’s report until next year.
Volvo’s Safety Zone technology gives Australian bus operators greater control over their fleet using advanced geofencing. By automatically adjusting vehicle speed in designated areas –such as school zones, depots, cafe strips, shopping centres, and busy city streets – it helps reduce risks for passengers, drivers, and pedestrians.
This intelligent system enables operators to create customised Safety Zones, enhancing compliance with local road safety standards while supporting smoother, more efficient operations. Investing in Volvo Safety Zones is a proactive step toward safer and more reliable public transport.
C Contact us today to learn more.
Services in Ballarat will now be running more frequently and align with new train schedules to reduce wait times
Public transport in regional Victoria is set for a significant upli , with the state government announcing major enhancements across key public transport services.
While the focus has largely been on increased train frequencies, regional bus services will also see substantial improvement, particularly in Ballarat where most weekend services will now run every 40 minutes to align with train schedules.
From April 13, weekend public transport connectivity in Ballarat will be stronger than ever, with trains on the Ballarat line now departing every 40 minutes between 8:00am and 9:00pm. Connecting bus services will follow suit, reducing wait times and improving overall service efficiency.
The increased services is part of a broader statewide investment in regional public transport. In addition to Ballarat, weekend train services on the Ararat, Warrnambool and
Bendigo lines will see a frequency boost, with 50 new or extended weekend services expected to kick in next month.
With the introduction of the regional fare cap last year, which has saved passengers over $114 million, demand for V/Line services has surged. Almost 40 million trips have been taken since the cap was introduced, and the latest service enhancements are designed to build on this momentum.
“We made regional travel more affordable for Victorian families through the regional fare cap and now we’re delivering more services to four regional rail lines,” Victorian Premier Jacinta Allan says.
Public and active transport minister Gabrielle Williams says the new services are building on a growth in demand, with more services expected to be added.
This means almost 150 of the 200 extra weekend services promised
by the state government at the 2022 election have now been delivered.
“More regional Victorians are choosing to take public transport than ever before thanks to our cheaper fares policy – so we’re catering to this extra demand with more trains, more o en,” Williams says.
The new funding takes the Australian government’s total contribution to the Brisbane Metro project to over $400 million
The federal government has announced that an extra $50 million has been allocated to the expansion of the Brisbane Metro to the city’s northern suburbs.
The move forms part of a $200 million investment in transport projects across Brisbane that aim to “revitalise” the city and reshape the way locals travel.
This newest investment builds on
$51.5 million of additional funding recently committed to Brisbane Metro to ensure the project’s delivery, taking the Australian government’s total contribution to the transformative public transport project to over $400 million.
“Better roads and better transport are critical to keeping Brisbane moving and we need all three levels of government working together
Le : The move forms part of a $200 million investment in transport projects across Brisbane.
Brisbane City Council to achieve this,” Brisbane mayor Adrian Schrinner says.
“With the Australian government’s support, we can now progress a rapid business case to progress the expansion of Brisbane Metro to Carseldine, Capalaba, Springwood and out to the airport.
“This funding will also help us progress a business case to ensure the Story Bridge continues to play a critical role in the national transport network for another 100 years.”
The Queensland government will also contribute to the development of business cases to improve important transport links and enhance infrastructure across the city.
Operation Solstice will see roadside inspections checking for safety issues, ensuring vehicles are mechanically safe and drivers are complying with fatigue laws
The National Heavy Vehicle Regulator (NHVR) has launched a national operation that will see buses across the country subject to roadside inspections and fatigue checks following an “alarming number” of bus crashes.
Operation Solstice is set to run for several weeks and aims to improve safety standards and reduce risks on Australian roads.
“The nation has witnessed an alarming number of fatal bus incidents over the past five years, which have had devastating impacts on families and communities,” NHVR COO Paul Salvati says.
“Tragically, from January 2020 to December 2024, there were 71 fatal crashes, and 84 lives lost in crashes involving a bus – this is deeply concerning, and it’s imperative that we do everything we can to prevent the further loss of life on our roads.
Above: The operation will run for several weeks across the country. Image: NHVR
“The NHVR is partnering with police across most states, as we o en do, to conduct Operation Solstice and safeguard bus passengers, drivers and other road users.
“This operation is more than just enforcement; it’s about making sure that everyone who boards a bus –whether it’s for work, school or leisure – returns home safely.”
New South Wales and Queensland have experienced the highest number of bus crashes in the past five years, with 40 and 21 lives lost respectively.
The safety blitz will see officers conduct roadside inspections on buses, checking for safety issues, ensuring vehicles are maintained and mechanically safe, and making certain drivers are fit to drive and are complying with fatigue laws.
The NHVR SCOs will focus their efforts on specific locations across the country that have been
pinpointed as high risk.
“Unfortunately, some bus operators and their drivers may not understand or be aware of their safety obligations under the Heavy Vehicle National Law, especially relating to fatigue,” Salvati says.
“An issue we are seeing is split shi drivers remaining at the yard instead of travelling home to have a proper rest break, particularly in urban areas.
“I would like to remind drivers that they are required to have adequate rest between shi s by law, and failing to do so can disrupt their ability to fully recharge between shi s and ensure they are fit to drive.
“Operation Solstice is a crucial step towards holding both operators and their drivers accountable, ensuring they are meeting critical safety obligations that are designed to keep all road users safe.”
The interim CEO has been with Keolis Downer for over 15 years, and will serve in the role until a permanent successor is appointed
Transport operator Keolis Downer has appointed Leila Frances as interim CEO, eff ective from March 17.
Frances will be taking over from current CEO Julien Dehornoy, who has le his role at Keolis to join the UK’s Network Rail as deputy regional managing director.
Frances has been with the Keolis Group for over 15 years, leading key international projects and commercial development across various countries, including Australia.
She also served as Chair of the Keolis Downer Board for five years until 2022 and is currently a non-executive board director in the UK’s transport sector.
Relocating to Melbourne, Frances will serve as interim CEO until a permanent successor is appointed.
“We are thrilled to welcome Leila back as interim CEO of Keolis Downer,” Keolis International CEO Laurence Broseta says.
“Her leadership and strategic insight will be invaluable to the company.
“Keolis Downer remains dedicated to expanding its presence in Australia, and Leila will play a crucial
role in shaping the right strategy, partnerships, and organisational structure to drive this growth.
“I would also like to extend my gratitude to Julien for his outstanding
leadership over the past five years; his contributions have had a lasting impact on our organisation, and we wish him all the best in his future endeavours.”
The Greens’ proposed plan would see a full time worker in Perth save around $46 a week and only cost the government $778 million in revenue
Despite a blossoming public transport system and pleas from the government, Western Australia residents aren’t taking full advantage of the services off ered to them.
O en opting for the car versus the train or bus, a large deterrent from jumping onboard is the transport fare prices. That’s why the Greens are proposing to make public transport free for all in WA.
Last year’s Summer of Free Public Transport led to a 42 per cent increase
in public transport use, taking pressure off the roads and people’s wallets at a time when so many were struggling to make ends meet.
The Greens’ plan would see a full time worker in Perth save around $46 a week, or $2,246 a year, but cost the state government just $778 million in revenue over the forward estimates, based on current usage.
If taking into account WA Labor’s commitment to cap fares at $2.80, the average full-time worker would
still save $28 a week, or $1,344 a year with the Greens’ proposed plan. The total cost would drop significantly to $446 million over the forward estimates.
WA Greens MLC Brad Pettitt says everybody in WA should be able to afford the basics, and that includes accessible transport.
“Nationally, there is a shi to reduce the cost of public transport for all which we acknowledge and support,” Pettitt says.
BIC
The Bus Industry Confederation (BIC) has responded to the Department of Infrastructure, Transport, Regional Development, Communications and the Arts’s (DITRDCA) intentions to harmonise with international standards, saying the task would be “complex”.
The Australian government commissioned an independent review of Australian Design Rules (ADRs) at the end of last year, looking at how closely Australia’s ADRs align with international standards, and how these can be better aligned.
The review engaged Dr Warren Mundy to conduct the review, and looked at the implications of streamlining the process of ADR harmonisation, as well as the risks and opportunities presented by taking United Nations standards and ‘converting’ them into ADRs.
Opening up the conversation to stakeholders and those in the various concerned industries, BIC has now responded with a submission that highlights how the bus industry is vastly different to other heavy vehicle industries.
In its submission, BIC outlines that it is not opposed to harmonisation where it is appropriate but highlights it would be a complex task that requires a lot of moving parts.
“Technology on buses can’t always be grouped in with trucks or cars or just le behind because there are lower volumes,” the submission reads.
“Buses are a unique category of their own and have unique technologies. We acknowledge the volume of buses are a fraction of cars or trucks, but buses have unique requirements to ensure the safe carriage of the general public to their destination.”
BIC says that the DITRDCA is under resourced to adequately support the bus industry, especially with the increase in and complexity of technology, and fast pace of
technology advancement.
“European ADRs are not subject to the same extent of jurisdiction and independent regulator laws, policies and regulations that are already in place to support the bus industry,” the submission reads.
“This is not a criticism, but the reality is that these parties, such as the National Heavy Vehicle Regulator (NHVR), National Transport Commission (NTC) and state jurisdictions, have been more agile in supporting changes and requirements affecting our industry.”
It goes on to say that the personnel in DITRDCA are generally very supportive, but there simply isn’t enough resources to support the fast pace of change or industry needs.
The submission also outlines that in regulation development, there hasn’t been enough focus on buses to adequately support the Australian industry requirements to manage technology changes.
Referencing the recent introduction of driver safety screens in multiple states, the submission called out how these changes were le to the industry to develop and manage, with little involvement from other agencies.
It also called out the bus safety working group set up by the DITRDCA,
which aimed to further improve safety at the regulatory level and was concluded a er completing only one of its 10 set objectives.
One of BIC’s major concerns with the DITRDCA’s plan was that this could hinder local manufacturing and create the need to comply with international standards already used by overseas suppliers.
“This has the potential to create an uneven playing field. Conversely, overseas manufacturers have invested in complying local models to meet local regulations,” it reads.
“Effectively this will lead to “recompliance” of local models to international standards which may lead to unintended consequences including industry waste and increased cost of production.”
Moving forward, BIC suggests that if harmonisation with international standards was to work, the DITRDCA would have to be sufficiently resourced to have a seat at the table at any international standards development.
It also suggested that Australian industry peak bodies and key stakeholders are informed and therefore can collaboratively support DITRDCA and the industry as a collective, and an equal playing field would have to be maintained.
Gemilang buses will soon be assembled at AMA Group’s current Wales heavy collision repair facilities across Australia
Australian collision repair and automotive supply business AMA Group has partnered with Malaysian bus manufacturer Gemilang to establish local bus assembly capabilities in Australia.
The collaboration aims to establish environmentally friendly bus body building solutions, with the two companies sharing a “vision to advance green mobility”.
The buses will be assembled at AMA Group’s current Wales heavy collision repair facilities across Australia.
“Through this partnership, AMA Group is excited to bring its operational expertise to support the local assembly of next-generation fully electric buses in Australia,” AMA Group CEO Mathew Cooper says.
“By integrating Gemilang’s innovative aluminium bus body technology, we will assist in creating a strong and competitive presence for Gemilang’s technology in the Australian bus market.
Gemilang has been exporting buses and body kits for over 35 years, catering to over 15 markets worldwide. Widely recognised, over 1,000 units have been delivered to Singapore and 500 units to Uzbekistan.
The bus body brand also has a strong track record in the electric bus sector in Australia, having assembled and delivered over 100 BYD buses.
The partnership with AMA Group aims to meet the growing demand for sustainable transport solutions in Australia, supporting state governments’ commitments to reducing and neutralising carbon emissions.
“This partnership marks an exciting step forward in developing lightweight, corrosion free and cost-effective body solutions for electric buses,” Gemilang CEO Pang Chong Yong says.
“Our Switzerland-originated aluminium bus body superstructure technology, combined with the latest
industry advancements, allows us to work with any bus chassis brand, making it a versatile and reliable choice for the Australian market.
“This collaboration aligns perfectly with our shared vision to advance green mobility. In addition to a zero-emission chassis, a sustainable and efficient bus body is crucial for creating truly eco-friendly vehicles.”
AMA Group’s role in managing a er-sales services for Gemilang will ensure reliable support for customers, enhancing the overall value proposition of electric buses built through this partnership.
The operator also announced the acquisition of another New Zealand transport company in a post celebrating its success
Auckland Transport has awarded New Zealand bus operator Ritchies a nine-year $1.068 billion dollar contract to deliver expanded bus services in south and west Auckland.
The contract marks the largest ever tendered bus services contract in the country and will see 175 new electric buses introduced on the network.
Ritchies CEO Michele Kernahan welcomes AT’s decision as a vote of confidence and a reflection of the work that’s been put in to increase the quality of Ritchies offering.
She says she sees this contract as a credit to the entire Ritchies team for their hard work and dedication, whether they are driving buses,
contract marks the largest ever tendered bus services contract in New Zealand. Image: Ritchies
managing operations or cleaning and maintain fleets.
In a LinkedIn post celebrating the team’s success, the bus operator also announced the acquisition of
Pavlovich Coachlines Limited.
“We’re especially pleased that Pavlovich Coachlines is joining the Ritchies team,” the post reads.
“Together, we are not just building a better future for Ritchies, we’re delivering value for ratepayers and creating a more comfortable, connected and sustainable way to travel for the communities we serve.
“We have also used the opportunity of this new contract to further provide for the safety of our employees and passengers by committing to fitting our buses with advanced safety features including driver assistance systems, pedestrian and cyclist detection and fatigue management.”
New conditions have been set to determine whether buses in NZ are eligible to carry bike racks
Nelson Tasman’s eBus has been the first bus service to receive an exemption to the obstruction rule, which saw a complete restriction on front-mounted bike racks on buses across the country back in November 2024.
A 24/7 bike rack service returned in Nelson Tasman from February 21, in a move that acting mayor Rohan O’Neill-Stevens says is “fantastic news”.
“Nelson has the highest volume of residents cycling to mahi and kura, and a high percentage of recreational cyclists,” O’Neill-Stevens says.
“The removal of the bike racks was frustrating, so I am pleased to see this development. I thank Council officers and SBL who have worked towards this result since the initial announcement in November 2024.”
Bike racks were removed from buses across New Zealand on Friday,
November 8 as a precautionary measure implemented following concerns that the racks may partially obstruct bus headlights.
Most transport operators around the country have front bike racks on at least some of their bus services. These models, which can take two bikes and unfold and lock around the wheels, have had warning tape on them, preventing their use.
A working group comprised of councils, public transport operators
(PTO) and NZTA officers was set up to reach an agreed pathway to return the use of bike racks to buses. In mid-January 2025 this working group released a set of agreed conditions and steps.
Group Manager Infrastructure Alec Louverdis says the eBus fleet meets the new conditions.
“A diagram was issued to PTOs with a reference line. If the centre of the headlight is below the reference line, then it’s determined that the illumination is effective,” Louverdis says.
“eBus mechanics drew the reference line across headlights on our buses, which revealed that we would not be required to change our racks or buses.
“eBus mechanics worked through on Thursday, February 20 so we could carry bikes again on the morning of Friday, February 21.”
Hotard Coaches, a subsidiary of Kelsian Group, celebrated its second time running the football teams onto the field
While millions gathered around their televisions on February 10 to watch sweaty football teams battle it out for the 2025 Super Bowl, there was another team working tirelessly to ensure the event ran smoothly.
Hotard Coaches, which operates throughout Louisiana and Texas and is a subsidiary of Kelsian Group, took on one of the biggest jobs in transportation that day, shuttling the Kansas City Chiefs and the Philadelphia Eagles around New Orleans.
Hotard Coaches was contracted by SP+ GAMEDAY, a Metropolis Company, to support the event, a er having a longstanding history transporting NFL teams throughout the season.
Shuttling teams each week across
a league of its own.
the country, the team still maintain that the Super Bowl is in a league of its own, and meticulous planning was needed to pull it off.
Kelsian Group CEO Clint Feuerherdt says the achievement showcases the company’s global capabilities on one of the world’s largest stages.
“Having such a significant footprint in Super Bowl LIX logistics reflects our commitment to operational excellence and reinforces our international presence,” Feuerherdt says.
“The planning and execution by our team enhanced the passenger experience.”
Public transport conversations have begun to dominate conversations in Wellington, with multiple changes possibly on the horizon
Wellington’s public transport system could soon undergo some massive changes, with conversation stirring around cash-free buses, pets onboard and fares among public consultation topics in the dra Wellington Regional Public Transport Plan 2025-2035.
The plan aims to propose affordable investments that improve the passenger experience and encourage people away from using private vehicles.
“With 190,000 new residents expected in the Wellington Region over the next 30 years, upgrading our public transport network is critical for sustainable growth,” Greater Wellington chair Daran Ponter says.
“But given the high cost-of-living and reduced government funding, the plan strikes a balance by deferring the development of Porirua’s bus
interchange and slowing down the purchase of new buses.”
Greater Wellington transport committee chair Thomas Nash says to meet the needs of a growing population, the council is seeking submissions on the creation of a regional network of high frequency bus corridors.
“At a time when government funding is focused on multi-billion-dollar road tunnels, bus corridors can reduce traffic congestion and emissions while enabling faster, more frequent services
– all for a fraction of the cost,” Nash says.
“We currently depend on a single corridor through Wellington’s Golden Mile, which already has too many buses at peak times, causing bunching and delays.
“Combined with other bus priority improvements, a new corridor along the Wellington Harbour quays is projected to reduce peak time bus journeys by up to 10 minutes.”
The public is also being urged to have their say regarding parking charges at park and Rides. Despite millions of dollars being invested by Metlink to provide over 6,100 free car parks in Park and Rides at train stations across the region, they are frequently reaching capacity and leaving commuters struggling to find places to leave their cars.
With an election and the end of another financial year looming ever closer, the Bus Industry Confederation has dug its feet in on the issues that matter most to the bus and coach industry
Speaking for the industry, our focus on transitioning to sustainable transport, achieving low- and netzero, promoting manufacturing and supply, building a sustainable workforce and further enhancing bus safety form the pinnacle of what helps us prop Australian prosperity. We deliver economic and social value by connecting people to the essentials – employment, education and recreation.
Despite all this, bus transport is o overlooked in the grand public transit scheme, even when we’re the first-called, providing services to areas that rail, light rail and metro cannot reach. We are also the fastest, most cost-eff ective at improving surface transport networks, with service enhancements rolling out in a matter of months, not years.
A er speaking with many of you, we have put forward recommendations that address
1. The mode shi for a greener, more efficient future (ultimately improving public transport)
2. Transitioning to low and zero emissions (by adopting the bus industry policy position paper, Driving Towards Zero Emissions)
3. The bus manufacturing and supply crisis (by implementing a national local content policy that preserves our sovereign industrial capabilities)
4. Workforce recruitment and retention (upskilling ensures an efficient move to emerging technologies, practices and worker retention)
The first recommendation includes a federal incentive for the states to move away from car-centricism and expand public transport by improving bus service frequency and operating hours, optimising networks, regularly modernising
fleets, bettering passenger safety and promoting these changes via public relations campaigns.
As Enrique Peñalosa, former mayor of Bogotá, Colombia, said about bus transport: “An advanced city is not one where even the poor use cars, but rather one where even the rich use public transport.”
Secondly, we urge the government to adopt the recommendations outlined in the Bus Industry Policy Position Paper – Driving Towards Zero-Emissions.
Our industry is uniquely positioned to lead this transition, its highly scheduled nature making it an excellent capabilities and cost-eff ectiveness testing ground. And, as early adopters of technologies, we are ideally placed to demonstrate viability of the various alternative and hybrid fuels already in market.
Up next, we suggest the implementation of a national local content policy that all jurisdictions must follow, ensuring preservation of our sovereign capability to manufacture in Australia, along with a diverse supplier base able to import, assemble or manufacturing here. In October 2017, the last Aussie built car rolled off the production line in Adelaide. Currently, public transport buses are still made here, while coaches, long-distance buses and charter vehicles have largely shi ed overseas. If this trend continues, Aussie bus manufacturing could come to an end, costing a $5 billion loss to the economy, with another $1.5 billion in operational supplies and services. Finally, we promote the upskilling of the existing workforce, the professional recognition of those in bus and coach, and the efficient transition to emerging technologies and practices, while reducing costs and addressing challenges associated with recruiting, retaining and
Above: BIC is pushing the federal government to listen to its recommendations ahead of the upcoming election. Image: Anton Gorlin/ stock.adobe.com
training an entirely new workforce (referencing the Riding on the Same Bus – Policy Manifesto). According to Jobs and Skills Australia, bus and coach drivers across the country have gone from 49,300 in 2022 to only 38,000 in February 2024. The average age of our workforce is 58 years, compared to an all-industry average of 39 years. Bus and coach also suff ers poor gender diversity with only 12 per cent female participation.
All that said, it’s not all just about money and augmenting the economy. We also want to put across the reasons why most of us are still here, why our industry also stands to lead in environmental and safety innovation, how it has provided to and for a long-standing Aussie workforce and how it has always been there, helping to connect us… and moving people.
You can read about the strategies in our complete pre-budget submission, plus other publications mentioned, on the BIC website via bic.asn.au/
Marcopolo is preparing to redefine coach travel in Australia when it launches the G8 to the local industry in September. Tiarna Condren reports
For 75 years, Marcopolo has been at the forefront of bus and coach manufacturing, evolving from a small Brazilian operation into a global industry leader.
With 14 production facilities, three in Brazil and 11 overseas, the company produces up to 240 buses a day and has delivered more than 475,000 vehicles across 140 countries.
Marcopolo’s presence in Australia is anchored by its wholly owned subsidiary Volgren, the country’s largest bus manufacturer. Volgren, a 45-year-old company, plays a key role in adapting and supporting Marcopolo products for local operators, ensuring they
meet the demands of Australia’s transport networks.
Now, the duo is gearing up to bring one of Marcopolo’s much-loved models to Australian shores – the Marcopolo G8.
The G8 is the latest evolution in the company’s lineup of premium coaches, designed with a focus on efficiency, safety and passenger comfort. Launched in 2021 amid the challenges of the COVID pandemic, the G8 introduced a new level of innovation to long-distance travel, reflecting Marcopolo’s decades of experience in bus manufacturing. Since its debut, nearly 4,000 G8 units have been delivered worldwide, serving a range of markets with
configurations from streamlined two-axle models to four-axle double-decker coaches.
“The Marcopolo G8 is the market leading product in basically every country where Marcopolo operates, which includes South America and now South Africa,” Volgren Australia chief executive officer Thiago Deiro told ABC
“This is the first time Volgren has been involved in bringing a coach product into Australia from Marcopolo and we had to jump through many hoops to make it a reality.”
As Brazilian regulations diff er greatly from those set out in the Australian Design Rule (ADR) requirements,
scratch” for local customers.
“We completely redesigned the model to ensure it would meet Australian regulations,” Deiro says.
“We also spent a lot of time talking to customers overseas to get feedback that was used to improve the model.”
While the G8 makes an immediate impression with its sleek, aerodynamic design, the internal structures of the model are even more impressive. Every detail is engineered with passengers, drivers and operators in mind.
“The main goal of the new design was to increase performance, lower fuel consumption and operational time while also focusing heavily on driver and passenger comfort,” Volgren chief commercial officer Yuri Tessari told ABC.
“The G8 comes with specific things you wouldn’t see in any other product.”
maintenance, the G8 introduces more than 60 patented innovations to boost comfort, reliability and operational
efficiency. The result is a coach that not only looks dynamic but delivers tangible benefits on the road.
“The G8 places significant emphasis on driver comfort and safety, recognising its crucial role in the vehicle’s operation,” Tessari says.
“The cabin’s ergonomics were redesigned, incorporating high-quality finishes such as injected parts for durability and ‘so touch’ surfaces that reduce internal noise and add a touch of sophistication.”
The driver’s space also features newly designed speakers and fibre-optic indirect lighting, off ering customisable light levels without compromising safety. The instrument panel has been revamped to ensure ease of use, with a new control interface that allows the driver to manage bus functions either through a 10-inch head unit or a set of intuitive keys located at the bottom of the panel, ensuring redundancy and seamless operation.
Driver safety and visibility were top of mind when designing the G8, including several key design enhancements. Blind spots have been eliminated, and the dashboard height has been lowered by 70mm to improve road visibility.
The rear-view mirrors have also been redesigned, now featuring a six per cent increase in reflective lens
width for a broader field of view.
For even greater safety, an optional indirect mirror system uses cameras to replace traditional mirrors, further eliminating blind spots and integrating infrared technology for enhanced night vision.
“We also ensured that passenger comfort was high on our priority list, with an advanced LED lighting system that adjusts in colour and intensity based on the time of day,” Tessari says.
For entertainment, the G8 off ers high-definition monitors and a new collective sound system,
with high-quality speakers ensuring a premium audio experience. Audio and video controls are easily accessible on the sides, and the system off ers four-channel digital sound, all manageable from the driver’s control centre.
The G8 also reimagines the onboard toilet for better passenger comfort and ergonomics. With internal support for added safety and convenience, the toilet features climate control with air conditioning, an automatic closing flat door, UV-C lighting and an Eco flush system for more sustainable operations.
Above:
The new design ensured that passenger comfort was high on Volgren’s priority list
Below:
The international model was re-designed to meet Australian regulations
For improved efficiency and odor control, the option of a vacuum suction system, similar to those used on airplanes, is available, ensuring a clean and comfortable environment.
“Seven decades of expertise have come together in the G8, a product born from Marcopolo’s relentless pursuit of innovation and reliability,” Tessari says.
“The company has invested more than 7,000 hours in virtual simulation testing and an additional
and road testing, simulating more than 11,000kms during the G8’s development to ensure long-term durability and performance.”
Going beyond standard simulations, Marcopolo conducted a physical crash test, achieving results 78 per cent better than the requirements set by the ECE R66 regulation from the Vehicle Certification Agency (VCA). Marcopolo also performed the first-ever rollover crash test on a double-decker coach as part of the G8’s validation process, setting a new benchmark in safety standards for the industry.
Coming standard with an exclusive full LED head light system, drivers can now see clearer than ever. The technology enhances visibility, extending up to 3.5 times further than traditional lighting systems.
The G8 also integrates Marcopolo’s Biosafe platform, a set of innovative solutions designed to enhance biosafety in public transport. This includes features such as disinfection systems, UV-C lights and antimicrobial surfaces, all aimed at reducing viral and bacterial contamination, making the G8 safer for passengers and operators.
“Beyond safety and comfort, the G8’s design focuses on reducing total cost of ownership,” Tessari says.
“Its unique aerodynamic shape, tested in wind tunnels, achieved an impressive coefficient of just 0.379, optimising fuel efficiency and reducing operational costs.
“Additionally, maintainability was a key consideration in the G8’s design, ensuring that operators can achieve greater business efficiency and performance, making the G8 not just beautiful, but a highly practical investment.”
The front grill system is designed for quick opening, off ering easy access for defroster maintenance, while the tilting wheel rim improves cooling and reduces tire wear.
Volgren, in partnership with Marcopolo, is set to launch the G8 to the Australian market in September 2025.
Available in two and three-axle configurations, the model is specifically designed to meet the
unique needs of Australian operators and passengers. This tailored approach ensures compliance with local regulations and suitability for both urban and long-distance travel across Australia’s diverse terrains.
“The introduction of the Marcopolo G8 marks a pivotal moment in the global push to modernise bus fleets, off ering superior comfort, safety and efficiency,” Deiro says.
“Its arrival in Australia is poised to set new standards in the coach travel industry, challenging other manufacturers and operators to raise their benchmarks.
“As the G8 begins operations, it is expected to transform passenger expectations and redefine bus travel in the region, marking the start of a new era in the Australian bus industry.”
BCI unveil a transformative partnership with Volvo® and Scania® Through this partnership, we’ve brought the next generation of buses to the road. Using the world’s most advanced technology chassis assembled with our cutting-edge design bus bodies, we continue to raise the bar, for sustainability, reliability and innovation. Contact our team for further information on 1300 289 224 or visit bcibus.com.au
Head Office Perth: 08 9353 9000
Melbourne: 03 8787 2100
Brisbane: 07 3275 6900
Adelaide: 08 8182 3888 BUS & COACH INTERNATIONAL
Parents at a regional Victorian school are demanding answers as overcrowding on their school buses
The new school year has got off to a rough start for students attending at least one regional Victorian school who have been forced to stand for more than 45 minutes on buses travelling at 100km/h while their school waits for government approvals to add more bus services.
Parents at the school have spoken out about the situation, which flies in the face of the Victorian government’s stated aim of having students seated and seatbelts fitted to all school buses for safety reasons.
ABC was contacted by a concerned parent a er the school told them the Victorian Department of Transport and Planning (DTP) allows students to stand on school buses if there are overcrowded services.
The school told parents it has “stretched the network” and “many of the buses will be overloaded” as students returned to school earlier this month — meaning some students may not have a seat on the bus and would be forced to stand for the journey.
The school says, “the Department of Transport does approve standing travel in these circumstances as a short-term measure”. It also told parents it is working closely with the department to ensure its application for additional school services was approved as soon as possible.
“Families live up to 45 minutes away and, without public transport options, rely on the school bus network to transport their school-aged children to their school,” a concerned parent told ABC
“Given the current inflation crisis, it is unacceptable to me that families are being told that they must take responsibility for transporting their kids to school in their own vehicles.
“Further, any student off ered a seat on a bus must be given a seat on that bus! Where buses are travelling on country roads at speeds up to 100km per hour, there should be no occasion for a student to have to stand.
“Compounding this, the
Above: A parent has raised the alarm about school kids being forced to stand on buses due to a lack of services being provided. Image: AGDER/stockadobe. com
announcement of extended life spans means that older buses with less safety features may be transporting students who are standing while travelling at high speeds.
“It is a universal right for children to have access to free education, but surely it is also a human right that they arrive to their school safely.”
In response, a spokesperson for the Department of Transport and Planning says safety is its top priority, as shown by its requirement for all new school bus program buses to be fitted with seatbelts.
“This requirement for seatbelts to be fitted still applies to any existing, or future, orders being placed under the school bus program,” the DTP spokesperson told ABC
However, the department did not respond to questions about this particular case or acknowledge that it endorses temporary provisions that allow students to stand onboard school buses.
On the Department of Education website it states:
“Students may be permitted to stand on a school bus once all existing seating has been allocated and only when:
• no student will be required to stand for more than 10 km
• the vehicle has a seating capacity of at least 25 adults
• the vehicle legal weight limit is not exceeded.”
The website information says the Department of Education must be notified by the coordinating principal where students regularly must stand in a speed zone above 80 km/h.
When asked about the parent’s concerns, the DTP spokesperson focused on Victoria’s school bus program which has seen seatbelt fitment rates on regional school routes rise from 43 per cent to more than 93 per cent.
The DTP spokesperson says the Department of Education has guidelines regarding standing on school buses and works with principals to monitor standing numbers.
“We continue to be informed by national safety guidelines and welcome the recent introduction of additional measures in the Australian Design Rules which will help ensure all passengers are reminded that if there is a seatbelt available on a coach or bus it must be worn,” the DTP spokesperson says.
The
Victorian government is hinting at new brands entering the state while the industry disputes consultation calls over a four-year volume plan
Victorian suppliers and operators have remained united in calling for the Victorian government to develop a plan that keeps jobs in the state’s bus industry following the recent deferral of orders.
The Victorian government says that bus manufacturers from outside of the state have expressed interest in moving into Victoria. It also provided a bare-bones four-year plan for bus orders in the state without going into details of what this will look like in the next year.
ABC reached out to the Victorian Department of Transport and Planning (DTP) seeking more clarity for the state’s bus industry as members continue to worry about the future of bus and coach manufacturing in the state.
In response, DTP told ABC the state government is still planning on following its Zero Emission Bus Transition Plan that it released in November last year.
“From July 2025, the Victorian government will commence transitioning the metropolitan and larger regional operator bus fleets with 250 low floor buses expected to be replaced over the next four years,” a DTP spokesperson told ABC
“The ZEB transition plan includes a staged approach based on direct feedback from industry that smaller operators need more time to transition.
“Smaller regional operators,
Victorian industry is expressing concern over a lack of a supply strategy in the state. Image:
through the Bus Association Victoria, told us they need more time to make the shi to ZEBs and the Department of Transport and Planning will work with these operators on the life extension of existing vehicles by up to five years, consistent with other jurisdictions.”
The DTP says this plan was informed by trials, industry engagement and consultation over three years with operators and manufacturers across the state, including regional businesses and associations like the Bus Association of Victoria.
In response, members of the state bus industry say they did support deferring the commencement of transitioning the regional and rural bus infrastructure to zero-emissions as of 2030, but at no stage did they call for or support stopping contracted bus replacement regimes. Members also confirmed they didn’t support the extension of working life for existing contracted buses.
“We have not been asked if there were any problems with introducing zero-emissions buses,” a Victorian bus operator told ABC
“The roadblock for the introduction of battery electric vehicles isn’t the vehicles themselves, but the inability of the state to create a workable system for purchasing, operating and maintaining the associated infrastructure.”
In its response to queries about the
four-year order plan and what that means for the state’s bus industry, the DTP told ABC it may look to brands currently not in the state to fulfil future orders.
“Several bus manufacturers have also shown interest in establishing a local presence, or growing their footprint here in Victoria, given the new opportunities this transition presents,” the spokesperson told ABC
“The transition off ers potentially significant new opportunities for local Victorian businesses in manufacturing zero-emission buses and ZEB components and constructing and fitting out ZEB depots.
“We’re continuing to work with bus operators and manufacturers to maximise the local benefits as we work through this transition and deliver a more sustainable bus fleet.”
The DTP says the 250 low-floor buses expected to be transitioned over the next four years are made up of a combination of replacement buses under the five Metropolitan ZEB Franchises (MZF) announced last year, the Metropolitan Bus Franchise (MBF) and the larger regional operator contracts in towns such as Geelong, Bendigo, Ballarat and Mildura.
It also says it’s looking at strengthening local manufacturing capabilities in high floor buses for its smaller regional operators.
At Wales, we know that every bus on the road is more than just a vehicle—it’s a lifeline for communities and businesses alike. With over 40 years of industry expertise, we specialise in restoring buses to their peak performance.
We’re not just a repair centre; we’re the trusted authority in bus restoration.
From dedicated assessment bays and fibreglass repair zones to precision paint booths and an optimised workshop flow, our facility is engineered for efficiency.
With our streamlined process, we get your fleet back on the road faster— because we know time is money.
Beyond repairs, we offer a full range of services, including accessories and maintenance support, to keep your fleet in top condition inside and out.
Grease Under Our Nails. Diesel in Our Veins. Pride in Our Craft.
For bus operators who demand the best, Wales Heavy Vehicle Repair stands ready to deliver precision, speed, and reliability.
When it comes to keeping your fleet moving, heavy is our duty. Contact us today at 1300 4 WALES (92537) or visit walesrepair.com and discover why we’re the bus repair experts you can trust.
Blending
Installs, modifications and repairs for your bus
Six decades of knowledge and technological development is allowing Yutong Australia to bring its leading electric chassis models to the local market
It’s been more than 60 years since Yutong was first founded as Zhengzhou Bus Repair factory.
The Chinese company took three decades until it was officially known as Yutong when Zhengzhou Yutong Bus was formed in 1993 with a sales volume of 689 units.
In the years since, Yutong has become a household name in the transport sphere, emerging as a global giant in the bus and coach manufacturing market.
Yutong’s rise to popularity took hold in 1997 when it became the first Chinese bus company to be publicly listed on the Shanghai Stock Exchange. Nowadays, Yutong buses are exported around the world, with a
global share of more than 10 per cent.
One of its emerging markets is in Australia, where Yutong has brought its might and quality to the country’s bus industry since first establishing a Sydney base in 2012.
“Yutong Australia has quickly become a cornerstone of the Australian transport industry,” Yutong Australia managing director Charles Hwang told ABC
“As a subsidiary of Yutong Bus, we bring decades of expertise and cutting-edge technology to the bus and coach industry.
“Over the past 12 years, Yutong Australia has reached a total delivery figure of more than 1,800 vehicles to date – serving as a testament to our
unwavering commitment to quality, reliability and customer satisfaction.”
There have been many international manufacturers who have tried and failed to set up Australian branches to serve the local bus and coach industry. What has made Yutong special in its endeavour to become a leading player in the Australian market is its willingness to collaborate with local partners, including its local dealer Vehicle Dealers International (VDI).
“VDI has become a driving force in the Australian bus industry, finishing 2024 in second position with 325 buses delivered to Australian operators, giving them a 17 per cent market share,” Hwang says.
“VDI is a proudly owned Australian company that distributes Yutong buses all around Australia. VDI’s partnership with Yutong, through state trials and collaborative partnerships with operators and governments, is allowing the brand to be at the forefront of the electric bus revolution in Australia.”
While Yutong has enhanced its capabilities to produce a variety
of bus models and types across its many global markets, its chassis have been its bread and butter. Since first launching its overseas market strategy in 2005 by becoming the first Chinese bus builder to export CKD parts, Yutong has supplied a range of diesel and electric chassis to many international regions.
Australia may be a growing arm for the brand, but it joins established
Le
Yutong segments such as in Latin America and Europe, where Yutong has become a leading chassis supplier. While Yutong Australia is looking at producing more options for local bodybuilders in future, the core content it will bring to Australia will continue to be its chassis varieties.
“From our diesel D7, C10 and C12 through to our battery electric D7E, C12E, E7S and E12, Yutong’s products portfolio can cover the major segments. In the future, we plan to bring more chassis options to Australia besides the E12,” Yutong director of e-chassis overseas Daniel Huo told ABC
“Our E12 chassis route service bus has become a leading option in Australia, with the lightweight model providing dual charge capabilities for operators.
“Supporting this fleet of chassis models is Yutong’s latest electrical technology, including its Yutong Electrical Safety System (YESS) and Yutong Electric Architecture (YEA) that it unveiled in the Asia-Pacific last year. YEA is the first electric vehicle specific platform in the commercial vehicle industry designed to integrate so ware and hardware onboard buses.”
At the core of this technology is the C architecture and YOS, which are both independently developed by Yutong. These latest technologies will be gradually applied to Yutong
electrical vehicles on sale or in planning.
In a local sense, Yutong Australia reached a milestone last year when it cooperated with local bodybuilder Volgren on the E12 model. The electric E12 chassis from Yutong has been paired with Volgren’s electric Optimus body to create a model ideally suited to new-age Australian operators.
The model came courtesy of Yutong’s international roots. At a global level, Yutong and Marcopolo are strategic partners, with Volgren being a wholly-owned subsidiary of the latter. A er both parties completed trial productions of the prototype E12/Optimus combination in Australia, the pair are hoping governments and operators continue to try the electric bus moving forward.
“The Australian chassis is a customised model derived from our leading option in the E12,” Huo says.
“Unlike standard city bus chassis, the middle section is a fixed design, which was jointly completed with Volgren. The battery placement is on the roof and in the rear of the bus, consistent with the design habits of other Australian bus body manufacturers.”
At a global level, this collaboration is not unusual for Yutong. It currently deploys its chassis in Brazil, Mexico, Spain, Portugal, Italy, Malaysia and South Africa, as well as throughout China. In Mexico, Yutong Group’s work with Marcopolo has shown the two companies can produce the latest technology in various regions with ease.
“Yutong, in collaboration with Marcopolo through a dual-brand strategy, delivered 45 units of 12m pure electric buses to the city of Monterrey in Mexico,” Huo says.
“Since these vehicles were put into operation, they have provided more than three months of efficient service and have received high praise from the local public transport system.
“Feedback from both the company’s management and the drivers have said that the Yutong vehicles off er excellent handling, great air-conditioning and superb acceleration performance.
“Yutong, with its solid capabilities, has played a key role in helping the local public transport system in Monterrey take a significant step towards achieving a green transformation.”
In Australia, Yutong’s view is that the increasingly stringent environmental protection policies in place means new energy vehicles have become the future of public transport. This means Yutong’s pure electric chassis can provide customisable solutions for the Australian market and promote low-carbon travel to achieve sustainable development goals.
Yutong has closely aligned its chassis technology it has introduced into the country with its green city planning and environmental protection goals, aiming to provide vehicles that improve urban transport efficiency and air quality. Covering the bus, highway, school bus and double-decker segments, Yutong’s fleet range from seven to 18 metres in length.
For operators wanting to check out the E12 and Yutong’s latest global technology that it is bringing to Australia, Yutong factory representative Alex says it has a prototype it is touring around Victoria currently.
“We invite Australian operators and industry experts to participate in our roadshow activities and conduct on-site test rides to gain a deeper understanding of our high efficiency
Below: Yutong’s local combination with Volgren is leading the way in Australia
and environmentally advantageous products,” he says.
“It’s not a product display, but an opportunity to try our technology and establish a long-term partnership with Yutong Bus. We’re inviting Victorian operators to see the demo, and we’re planning on bringing the bus to other states in future if operators want it there.”
Alex says the Volgren Optimus Yutong E12 represents the future of bus transport, with the model being the lightest electric bus in Volgren’s entire fleet.
With the potential for an electric school and tour bus model to arrive in Australia in the near future, Yutong Australia is preparing to expand its global power to another area as soon as possible.
“Yutong hopes to stand more closely with governments and operators in Australia to provide a variety of products and solutions, including complete vehicles, driveable knockdowns and chassis and local body solutions,” Hwang says.
“We want to allow each state, territory and operator to make more flexible choices based on their needs.
“In the meantime, Yutong will continue moving forward on the path of innovation and remains committed to providing the most advanced new energy technologies to the Australian market.”
Blending international expertise with local innovation, BSS - Bus Service Solutions is redefining bus and coach maintenance through its unique approach
Two years is barely a heartbeat in the Australasian bus and coach industry — the sector moves so quickly that it’s only a mere moment for most businesses to be able to simply find their footing.
For many entering the space, it could take two years to dra a business plan, two years to finally work out the logistics, two years to make that first sale.
Yet servicing and finishing business Bus Service Solutions (BSS) has defied every conventional timeline, transforming from a simple idea to a respected industry partner in just 24 months.
Born from a conversation between three industry veterans who saw a gaping hole in the market, the trio created a business that could truly meet the complex needs of bus and coach operators.
“I had been working for Irizar for more than eight years by the time I helped come up with the idea for BSS,” BSS co-founder and commercial director Anderson Souza told ABC
“I met Jonathan and then Thiago, and with our combined experience in the industry, we were able to pinpoint what we felt were pain points within the industry.
“That’s how BSS was born. We wanted to create a one-stop-shop for operators and bus manufacturers where they could come and get all of their work done.”
Wanting to save operators the hassle of jumping around to diff erent businesses for a variety of needs, BSS off ers a diverse range of services, including smash repairs, paintwork (full resprays), body modifications, Pre-Delivery Inspection (PDI), seat installation, wheelchair complete kits and local content fitments, ensuring that each bus operates at its best in terms of both performance and appearance.
“We have two main divisions at BSS. One is we off er smash repair services where we are working with the main insurance companies to get buses back on the road,” Souza says.
“And second is our service division. This is where we do pretty much everything else like modifications, inspections and panel beating –anything that the customer wants.”
In addition to these services, BSS provides custom-built products like bull bars, belt safety systems, bus toilets, bunks and destination panels, along with other specialised solutions that address the unique needs of the bus industry.
“We developed our own toilet that is able to fit any bus, regardless
of whether it is imported or locally made,” he says.
“That’s what we want to do – create products and off er services that are universal and suit a diverse range of vehicles.”
At the heart of BSS’s innovative approach lies its BSS Belt Safety System, a belt checking solution that aids operators in aligning with passenger safety compliance. With the federal government unveiling a new Australian Design Rule (ADR) that will require seatbelt wearing monitoring technology to be fitted to Australian buses and coaches, this new technology could provide the perfect solution to meet these new requirements.
“Our system is completely diff erent to everything the market is currently off ering,” Souza says.
“The system is incredibly simple and doesn’t require as much labour as some of the others. Designed to meet stringent government regulations around belt check systems, this proprietary technology requires minimal operational effort while delivering maximum safety assurance.
“The system is currently undergoing testing.”
In its effort to become a one-stop-shop for operators, the company also manages three separate divisions that off er more specialised services for customers: Inova Bus Services, BSS Moves and BSS Parts.
Inova Bus Services focuses on seat installation for indus-
Above: The company is focusing on training and upskilling new and existing employees
try-leading brands like Sege Seats Australia and StyleRide, while BSS Moves specialises in vehicle collection from the wharf and local and interstate movements.
BSS Parts off ers a growing range of local content products, including the BSS Bull Bar, BSS Belt Safety System and the company’s other products.
Despite the company’s young history, BSS already maintains strong, daily partnerships with leading bus manufacturers including Irizar, BCI, Higer, Volgren, Custom Denning, BLK, Yutong and others, both directly and through its customers.
The company also collaborates with renowned international OEMs such as Scania, Volvo, Mercedes-Benz and MAN, off ering tailored solutions that cater to the needs of both local and international bodybuilders.
This close collaboration with top-tier manufacturers has allowed BSS to establish itself at the forefront of the industry in a short space of time, consistently delivering top-quality products and services that exceed customer expectations.
Below: BSS is actively exploring key partnerships in Queensland
One BSS customer is bus charter company Driver Bus Lines. Always taking great pride in the appearance of its fleet of 145 commercial
buses and its 20 preserved Driver Classics’ buses, trucks and cars, the charter company recently reached out to BSS to help with some projects.
Planning to restore an old 1984 Eagle Model 10, with colouring as a tribute to industry legend Russell Penfold, Driver Group Australia owner and director Gary Driver says the BSS team went above and beyond.
“To complete the Eagle Model 10 in a timely manner, we needed to find a body shop that could carry out the restoration task while meeting or exceeding our required standard,” Driver told ABC
“Anderson led the project from start to finish, with him encouraging me to visit on-site and monitor the progress. He was responsive to my requests and met all my objectives.
“I was extremely pleased with the quality and standard of the work that BSS did and would have no hesitation in recommending BSS. All of this was at a price that was fair and most reasonable.
“The shine on the Eagle’s paint work is a must see!”
Souza says the success of BSS is in its experienced team, boasting employees with decades of experience under their belts.
“This wealth of expertise ensures that every product and service meet safety standards while also providing long-lasting reliability for customers,” he says.
“One issue we are facing at the moment is recruiting more employees with these skill sets. That is why we have set up our training program.”
Souza believes that the success of a business relies heavily on the team, which is why BSS is investing in the training and upskilling of current and prospective employees.
“We want to replicate what we are doing in Melbourne in Queensland, and then eventually nationwide,” he says.
“Employing skilled technicians who have the customer’s best interests at heart is the way to do that.”
BSS has grown from a 500sqm premise to a nearly 4,000sqm space in just two years, boasting a staggering 600 per cent growth.
The company is actively exploring key partnerships in Queensland to strengthen its service capabilities and bring its industry-leading expertise closer to bus operators and manufacturers in the region.
This strategic expansion aligns with BSS’s mission to support the bus industry with innovative solutions, ensuring fleets across Australia receive top-tier service and products. It may be a newcomer to the local sector, but BSS is already proving it should be respected as an emerging presence for Australasian bus and coach companies.
“We have the space and capability to continue growing in a sustainable way,” Souza says.
“We will continue to grow our reputation, work with our partners and try out our hands in another state.”
Irizar’s iService portal is providing operators with a one-stop shop to help them stay on top of the maintenance of its buses
In the fast-paced world of the bus industry, bus operators face a constant challenge – keeping their fleets running smoothly and efficiently.
With a diverse range of vehicles, each with its own unique maintenance requirements, the task of managing a bus fleet can quickly become overwhelming.
However, Irizar has a powerful tool to help streamline this process and revolutionise the way bus operators approach fleet maintenance.
The iService portal is an advanced digital platform that revolutionises fleet maintenance, enhances a ersales support and empowers operators with technical data.
“Customers love the iService portal because it makes their lives easier when it comes to maintaining their buses,” Irizar procurement and spare parts manager Maiko Souza told ABC
“It’s basically a one-stop-shop for them, providing them with maintenance, technical and parts information in one place.”
This ensures that the portal is constantly updated with the latest technical data and maintenance requirements, providing customers with a comprehensive and up-to-date resource.
At the heart of the iService portal are three key pillars: technical documentation, spare parts catalogues and maintenance resources.
Accessing technical data of a particular bus is made easy, with operators able to retrieve mainte-
nance-critical information simply by entering the Vehicle Identification Number (VIN) or Body Number.
Customers can access the user manual for a particular bus, bringing up detailed guides on vehicle operation, system functionality and safety protocols.
There are also comprehensive specifications, component details and system performance metrics available within the portal, accessible with just the click of a button.
The platform includes step-by-step guidance for scheduled and preventive maintenance, tailored to the specific age and model of each customer’s buses. Customers can input their Vehicle Identification Number (VIN) or Body Number to see the recommended maintenance tasks and timelines, ensuring they stay on top of critical servicing and repairs.
“Once the customer inputs this information in the portal, they can check based on the age of the bus, which maintenance is required,” Souza says.
“For instance, during a 12-month maintenance cycle, customers receive a clear and detailed overview of the specific components that require
inspection, checking, cleaning, and replacement.
“It creates a customised schedule for what they have to do and when.”
A highlight for operators is also the bonus of accessing electrical, pneumatic and hydraulic diagrams. These detailed schematics aid in streamlining troubleshooting and repairs, reducing diagnostic time and improving efficiency.
Ordering the right replacement parts is o en complex, with each bus having unique requirements that can be difficult to navigate. iService simplifies this process by providing an intuitive digital parts catalogue.
The spare parts catalogue within the iService portal is a particularly valuable feature.
This integration between the technical data and the ordering process helps to minimise errors and ensure that the right parts are delivered in a timely manner.
The portal’s versatility caters to both large and small bus operators. Larger customers with their own workshops can use the iService portal to manage maintenance in-house, while smaller operators can rely on third-party maintenance providers who also utilise the platform.
The fully responsive iService Portal is accessible on desktops, tablets and smartphones, ensuring operators, technicians and fleet managers have instant access to essential data whenever and wherever they need it.
Above: iService Portal is accessible on desktops, tablets and smartphones
Below: Users can access technical documentation, spare parts catalogues and maintenance resources
Customers can search for and view detailed information on the specific parts installed in their buses, including part numbers, images and technical specifications. This allows them to quickly and accurately identify the parts they need, streamlining the ordering process.
“Customers can check all parts that they have installed in their buses through the iService portal,” Souza says. “They can see the part numbers and even the photos, which makes it much easier for them to order the correct replacement parts.”
With an intuitive interface and seamless navigation, the platform ensures that support is always at your fingertips, whether in the depot or on the road.
“Our goal was to develop a program that simplifies operations for bus operators,” Souza says.
“We recognize the challenges they face and the complexity of managing maintenance eff ectively.
By integrating iService into daily workflows, operators have a powerful tool that serves as a reliable guide, ensuring smoother and more efficient operations.”
But a properly fastened seatbelt will!
SGESCO MAX’s MAX-SAFE Seatbelt Warning System is a significant advancement in passenger and driver safety for the bus industry. The system not only protects individuals but also supports bus operators in maintaining high safety standards and compliance with road safety regulations, creating a more secure travel experience for everyone onboard.
Operators are at front of mind for Challenger Bus and Coach, with its parts business ensuring operators get their buses back on the road in no time
n an industry where downtime can mean the diff erence between profit and loss, bus operators across Australia know that reliable access to high-quality spare parts is essential.
Whether it’s a sudden breakdown on the side of the road or a routine maintenance schedule, having the right components on hand can make or break a fleet’s productivity and profitability.
That’s why Challenger Bus and Coach has made it a priority to ensure their customers can source critical spare parts quickly and cost-eff ectively.
Australasian Bus and Coach Parts stocks everything you need, off ering an extensive inventory of parts not just for Challenger vehicles, but for all major bus brands operating across the country.
“Challenger was created with operators in mind, so when establishing Australasian Bus and Coach Parts, we wanted to ensure operators needs were front of mind,” Challenger national sales and spare parts manager Mark Collins told ABC
“Parts are something that are always going to be required, and we know there’s nothing worse for operators than having a bus off the road and being unable to get parts.
“That’s why we hold a comprehensive range of critical parts right here in Australia, ensuring swi overall client support.”
Through Challenger CEO Greg Sloan’s connections, the parts business has been able to establish a network that can source spare parts of many brands quickly and at a good rate. Passing this onto customers, the business acts as a local connection.
Collins says Challenger customers are finding value in being able to talk to an Australian company to source international bus and coach parts. As inquiries and demand have grown,
Above/le : Australasian Bus and Coach Parts is a one-stop-shop offering an extensive inventory of parts
Challenger has sought to keep all Challenger parts in stock in Australia while also sourcing high volume, popular parts for other brands.
“And if a customer can’t find the exact part they need in stock? No problem,” Collins says.
“We can provide a guaranteed lead time and fixed price to get the part delivered straight to the customer’s door.”
Challenger’s deep relationships with national supplier networks, including industry leaders like Cummins, ZF and Allison, give it unparalleled access to a vast array of running gear components.
This allows it to provide customers with reliable access to everything from engines and transmissions to suspensions and brakes.
“We understand that most operators have buses from varied brands, and it can take a lot of time and patience to source particular parts for each,” Collins says.
“Instead of having operators bouncing around to diff erent shops and online, they can come and get everything directly from Australasian Bus and Coach Parts.”
But it’s not just the breadth of its parts inventory that sets Challenger apart. The company also off ers heavily discounted retail pricing on common service items like filters, belts, wheel bearings and brake linings. This helps operators keep their maintenance costs down and their buses on the road.
“We don’t want to charge operators an inflated cost and make their lives harder when there is already so much going on,” Collins says.
“We simply charge them what the part would cost us to buy.”
It’s this unwavering commitment to its customers that has earned Australasian Bus and Coach Parts a reputation as a true industry leader. By putting parts availability at the forefront of its business model, it is ensuring that bus operators across Australia can keep their fleets running smoothly, no matter the challenge.
“Customers have loved the service so far as it minimises downtime and allows operators to put their time and focus into other issues,” he says.
“Nobody wants to spend days running around tracking down parts.”
Opening its first depot in Melbourne back in 2017, Challenger now has locations in Perth, Brisbane and most recently Sydney.
“From starting small in Melbourne, we have now been able to grow our capabilities and off erings across the country,” Collins says.
“We’ve found success at the current depots, and it is encouraging us to continue to expand our reach.”
While the current depots are mainly used as spare parts holdings, the team hopes the time will come where they can off er a full suite of services.
“All depots are used to hold stock of buses and significant stock of
parts,” Collins says.
“We also use them to pre-deliver the vehicles, as offices and increasingly as show rooms where operators can come and view the vehicles and take them for a test drive.
“But hopefully, when the time is right, we would love to use the depots as multi-purpose shops for customers, off ering not only spare parts stock but repairs, maintenance, the whole lot.
“At the end of the day, our mission is to be a true partner to bus operators across Australia.
“If you are a er spare parts at super affordable prices, please reach out to us at parts@challegnerbusandcoach. com.au or call Mark Collins on 0431 705 566.”
With a renewed focus on expansion, innovation, and customer service, Wales Heavy Vehicle Repair is setting the standard for heavy vehicle and bus repairs nationwide
Wales Heavy Vehicle Repair began as a family-run workshop on the outskirts of Sydney, built on a foundation of hard work, skill and a deep respect for the transport industry. Local truck drivers trusted the team to keep their vehicles moving, knowing that every repair was done with care and precision. Through dedication, cra smanship and an unwavering commitment to keeping businesses on the road, Wales grew into a respected name in heavy vehicle repairs. Over time, the team recognised an opportunity to expand beyond trucks, applying their expertise to a growing demand for specialised bus repairs.
Now, with more than 40 years of expertise, Wales Heavy Vehicle Repair has evolved into a leading national network, combining industry heritage with cutting-edge repair solutions.
“Over the past nine months, we have focused on refreshing our brand – not just updating our name, but modernising our facilities, processes and service experience,” Wales Heavy Vehicle Repairs general manager Martin Dickinson told ABC
“This transformation reinforces our commitment to heavy vehicle and bus operators nationwide.”
As part of this evolution, Wales has rebranded all facilities under a single national identity, ensuring customers experience consistent, high-quality
repairs, no matter where they are in Australia.
“At Wales, heavy is our duty. That means we’re always pushing for better ways to serve our customers, minimise downtime and deliver precision repairs with every job,” Dickinson says.
Recognising that repairing heavy vehicles is about more than just fixing damage, Wales has invested in upgrading customer facilities and service innovations to enhance the experience. This included building enhanced customer lounge areas that provide a relaxed, professional environment and echo what Dickinson describes as an “OEM feeling”. The company has also
introduced a handover showroom where clients can personally collect their fully restored buses, allowing time for any customer questions and for the technicians to emphasise the quality and pride in their cra .
“Wales has also dedicated time to streamlining our internal processes, introducing dedicated assessment bays that make our quoting more efficient and ensure we maintain transparency in our service,” Dickinson says.
“We have also worked on improving workshop flow to reduce repair times and minimise customer downtime.
“We know that having a bus off the road is a major inconvenience for operators, so we’ve designed every step of our repair process to get them back in service as quickly as possible.”
As Australia’s transport industry transitions toward zero-emissions vehicles, Wales has invested in specialised electric and alternate-powered bus repair capabilities.
“Over the past 12 months, we’ve been training our teams nationwide to handle electric and hydrogen-powered buses,” Dickinson says.
“We’ve installed a dedicated EV charging station at our Smithfield site and are integrating advanced repair techniques to support the shi to green transport.”
By proactively upgrading its capabilities, Wales is positioning itself as the go-to repairer for electric buses nationwide, ensuring that operators can transition to new technologies with confidence.
Since joining AMA Group in 2019, Wales has expanded its national reach and broadened its capabilities to become a true one-stop shop for heavy vehicle repairs.
“Our partnership with AMA has given us the ability to service entire fleets, from light vehicles to trucks and buses under one trusted network,” Dickinson says.
This reach is further strengthened by AMA Group’s partnership with Malaysian bus manufacturer Gemilang, bringing local bus assembly to Australia for the first time in Gemilang’s history.
Gemilang executive general
manager Pan Jun Jie told ABC that AMA Group and Wales Heavy Vehicle Repair were the natural choice for this partnership.
“Gemilang chose AMA Group as its strategic partner due to AMA’s extensive expertise in the Australian automotive and heavy vehicle sector, particularly in bus repairs and refurbishment,” Jun Jie says.
“With a nationwide presence and well-established Wales heavy collision repair facilities, AMA Group provides the necessary infrastructure and skilled workforce to support local assembly, ensuring compliance with Australian standards and regulations.”
Through this collaboration, AMA Group will integrate Gemilang’s innovative aluminium bus body kits into its existing Wales heavy collision repair facilities nationwide, leveraging its extensive expertise in bus repairs to support local assembly.
Gemilang, which has more than 35 years of experience and has supplied bus body kits to more than 15 markets, including Australia, Singapore and the USA, sees this partnership as a key step in advancing sustainable transport solutions in Australia.
“By leveraging AMA’s operational capabilities and a er-sales service network, Gemilang can ensure the
seamless assembly, delivery and long-term support for its aluminium bus body solutions, strengthening its foothold in Australia’s growing electric bus industry,” Jun Jie says.
This collaboration will enable participation in government bus tenders across all Australian states and territories and aligns with national sustainability goals by advancing green mobility, reducing carbon emissions and ensuring reliable a er-sales support for electric buses built through the partnership.
Currently, Wales operates eight heavy vehicle repair sites across Townsville, Brisbane, Newcastle, Sydney, Victoria, South Australia and Perth, with dedicated bus and truck facilities also at Smithfield, NSW.
“While we started in Sydney, our services are now available nationwide,” Dickinson says.
With fully equipped facilities across the country, Wales is ready to support the growth of Australia’s bus industry, whether it involves large-scale fleet repairs, new vehicle assembly or electric bus servicing.
“At Wales, heavy is our duty –both today and into the future,” Dickinson says.
“We invite bus operators to partner with us as we set new benchmarks in repair excellence and sustainable fleet management.”
In the wake of the unveiling of ADR 68/01, SGESCO-MAX is upgrading its occupant safety system to keep school bus passengers safer than ever
For many parents around the country, it’s the little things that ease their doubts. As they hug their kids good-bye each weekday morning and guide them onto the bus to school, the safety of their little students is of the highest importance. It can be seen in the holding back of tears, the waiting for the bus to return in the a ernoon, the nagging desire each day to see their child return safely home from school.
In late January, the federal government took a major step to address safety concerns for school buses around the nation when it announced a new Australian Design Rule (ADR) that will require buses and coaches to feature seatbelt wearing monitoring technology. The ADR comes in the wake of the Hunter
Valley bus crash in June 2023 and other recent school bus incidents that have demonstrated the impact that fatal road crashes can have on families and wider communities.
From November 1, 2026, all new models of buses and coaches in Australia that have seatbelts fitted must also include this technology. From November 1, 2027, all new existing model buses and coaches with seatbelts must also have the technology installed. For heavy vehicle safety specialists like SGESCO-MAX, this new regulation provides an ideal opportunity to maximise the safety technology placed on school buses in the coming years.
“Occupant safety is our core solution that we off er the bus and coach industry,” SGESCO-MAX
Above: The new SGESCOMAX system will take occupant safety to the next level. Image: Cavan for Adobe/stock. adobe.com
managing director Scott McPherson told ABC
“On the back of the announcement of the new ADR, we’re looking at how our technology can help the industry comply with the requirements.”
As part of the regulation, the seatbelt wearing monitoring technology requires multiple facets. SGESCO-MAX’s latest technology that will adhere to ADR 68/01 –
Occupant Protection in Buses is set to provide both visual and audio alerts to remind students to wear their seatbelts correctly at all times.
“The detailed message will play when the door shuts and the bus starts to move. This system, along with visual alerts, is designed solely to meet the ADR and keep bus companies compliant with the new regulation.”
The latest technology will join a long
list of heavy vehicle safety systems that SGESCO-MAX offers. Its MAX-SAFE maximum safety range is currently installed on more than 22,000 vehicles to date, with the brand having a dealer and service partner network that spans most of Australia and New Zealand.
At the forefront of the seatbelt safety challenge that the local industry is currently addressing is SGESCO-MAX’s occupant safety system. A er first being introduced to the market nine years ago to promote safer mine transfers for companies like BHP, the system spans from the framework of the seat itself to the monitoring technology involved.
For its latest package that will adhere to the ADR, SGESCO-MAX’s occupant safety system will include all the usual protections as well as the audio and visual alert technology to ensure all passengers safely apply their seatbelts. The upgraded system will also include a passenger check solution as an additional option, forming a high-end occupant technology package for operators looking to maximise the safety of their passengers.
However, SGESCO-MAX is providing a level of flexibility with these latest upgrades. On top of the premium safety package, the brand is also offering just the seatbelt announcement technology for companies that simply want to comply with the ADR.
“Our system is designed to fully meet the ADR’s requirements, but one thing we wanted to ensure was that we also provided a more economical solution that complied with the regulation,” McPherson says.
“While our high-end occupant system is our premium package that can be built on and added to with the likes of voice announcements and passenger checks, the base solution can’t be added to and will solely meet the ADR.”
Within the local market, SGESCO-MAX is renowned for its seatbelt monitoring warning systems. McPherson is hoping the industry will cherish the latest upgrades to the system that will allow customers to add more features to
the occupant protection solution to create a customisable package for their fleets. If they don’t want this, then the ADR compliant base system will help ensure more seatbelted buses and coaches remain safer than ever before.
“Industry feedback has shaped what we are offering in the wake of the ADR announcement,” he says.
“Given the deadlines for the ADR, when buses need to comply with it, there will be a large market available that requires this technology to be fitted to its buses.
“The market has a need, and it’s in our wheelhouse, so we want to develop the solution that helps more fleets become safer for students.”
McPherson stresses the solution will come in multiple options, ranging from economical to including the latest enhanced safety technology.
Feedback from drivers and associations regarding the audio alerts and when they play has been incorporated into the new technology – the speaker can be tailored to play the seatbelt message both when the doors open and close, as well as when the bus begins to move.
“We also got asked to provide options that identify when people embark or disembark a bus, and we have a few concepts around that to develop,” McPherson says.
“It’s a balance between being economical and offering the best safety technology. We can do really smart things with AI cameras when it comes to counting passengers, so if we tie that in with when the speaker is triggered to play the safety message, it is a leading safety system.
“However, we are aware that it has to be economical for our customers, so we’re preparing to get industry feedback on our latest concepts.”
McPherson’s goal is to introduce the technology and its multiple packages in the first quarter of the new financial year, meaning the industry should prepare for the systems to hit the market between July and September. Due to the ADR announcement, it’s a high-priority product for the SGESCO-MAX team to develop and introduce to Australia’s bus and coach industry.
When it is unveiled, it’ll come as a great relief to both the legion of local operators running school services, and the many parents who send their kids to and from school each day on a bus. Alongside its various other solutions, SGESCO-MAX is most looking forward to the peace of mind it can provide many Australians.
“We’re just locking down what the final products will look like now – we’re known for our seatbelt safety solution and our anti-rollaway technology, so we’ll continue focusing on issues impacting the bus industry,” McPherson says.
“We’re trying to solve many diff erent problems while also increasing the level of safety technology onboard Australian buses and coaches.
“We understand the pressure that these rules may bring onto bus drivers, so we want to make the system easy to run. Our end goal is to empower companies to save lives, so we’ll work with the industry to help everyone with what they want and need.”
QBIC’s Jason O’Dwyer talks the current workforce crisis and the need for immediate action
The Australian bus industry is facing an imminent workforce crisis, with an aging driver and maintenance workforce presenting a major challenge to the sustainability of public transport services. The recent Bus Industry Confederation (BIC) National Conference highlighted this urgent issue, bringing to the forefront the need for immediate action. The Queensland Bus Industry Council (QBIC) has been proactively engaged in discussions on workforce recruitment, training initiatives and immigration policy reforms. While there have been some encouraging moves to streamline licensing processes for new drivers, a comprehensive and multi-tiered response is needed from both state and federal governments.
A key solution that should be implemented at the state level –particularly in Queensland – is the establishment of a Transport Skills Organisation. This initiative would allocate a small percentage of heavy vehicle registration fees towards industry-led programs that promote, identify and engage a broader cross-section of the community in transport careers.
To eff ectively address the workforce gap, this initiative must target underrepresented groups, including culturally and linguistically diverse (CALD) individuals, women and First Nations Australians. These demographics represent untapped potential in the transport sector and should be actively recruited and supported through dedicated training programs.
QBIC, in partnership with TAFE Queensland TMR and other stakeholders, is already working to address the barriers that prevent young apprentices and trainees from entering the industry. However, without a sustainable funding model, these initiatives will struggle to
have a lasting impact. By diverting a modest percentage of heavy vehicle registration revenue, the Transport Skills Organisation would ensure ongoing investment in skills recognition, employer incentives and industry training.
At the federal level, two major policy changes are essential to securing the long-term viability of Australia’s bus industry workforce. Firstly, the government must allow aged pensioners to continue receiving their full pension while paying a marginal tax rate on any additional income they earn. Many experienced and capable retirees are willing to work part-time as bus drivers, yet current pension income thresholds discourage them from re-entering the workforce. By reforming pension rules, the government could harness the experience and reliability of older Australians to fill critical vacancies in the passenger transport industry. Secondly, the federal government must reclassify Passenger Transport as qualifying for skilled migration to streamline overseas pathways for skilled workers in the industry. The current visa system does not adequately reflect the need for skilled bus drivers and some maintenance staff, making it difficult for operators to recruit experienced workers from overseas. Recognising Passenger Transport as qualifying for skilled migration would help alleviate chronic
driver shortages, ensuring that Australia’s public transport systems remain operational and reliable particularly in rural and remote areas. Public transport is the backbone of Australia’s urban and regional mobility, and the consequences of workforce shortages will be severe if immediate action is not taken. Delays, service cancellations and reduced accessibility to transport services will disproportionately aff ect vulnerable communities, including the elderly, students and those in rural areas. Without a sufficient workforce, Australia’s ability to provide sustainable and efficient public transport is under threat.
The actions needed to build solutions are clear: an industry-led Transport Skills Organisation, federal pension reform and skilled migration policy adjustments. These measures, combined with industry-driven recruitment and training initiatives, will help build a resilient and diverse transport workforce capable of meeting future demands.
The time for discussion is over; action is required now. Our industry is ready to collaborate, innovate and implement solutions – but we need government policy change to turn these strategies into reality. A failure to act will not only jeopardise the future of the bus industry but also undermine the essential transport services that millions of Australians rely upon daily.
If buses are the unsung heroes of public transport, scheduling is one of the most critical components to get right and keep cities moving.
While innovative so ware has transformed the approach to modelling public transport networks, Australian integrated multi-modal transport operator Transit Systems says AI technology will be the next break through to shape the future of the industry, driven by transport planners and schedulers to ensure services are convenient, reliable and cost-eff ective.
Transit Systems executive general manager of service planning Richard Lizon says transport planners and schedulers are responsible for designing routes, managing timetables and adapting services to unpredictable challenges and circumstances.
“A transport scheduler’s role is to blend science and strategy. Their decisions aff ect thousands of commuters daily and play a vital role in keeping cities moving efficiently,” he says.
Transit Systems scheduling manager Giles Field says bus schedulers make critical decisions to keep public transport running smoothly. These include determining efficient routes
Be sure not to miss out on an opportunity to attend these fantastic in-person events
APRIL
APRIL 10–12
QBIC Annual Conference
APRIL 24
BusVic Regional Conference –Hamilton & Ballarat
APRIL 30–MAY 1
PTAANZ Melbourne Symposium
MAY
MAY 16–17
BusSA Annual Conference
MAY 30–31
TasBus Annual Conference
JUNE
JUNE 14
QBIC Regional Forum – Gympie
JULY
JULY 11
QBIC Future Leaders Luncheon
which best balance efficiency and accessibility.
“We analyse passenger demand, historical data and traffic patterns to create schedules that minimise delays and maximise service coverage and value,” Field says.
Real-time GPS tracking, predictive analytics and automated systems help schedulers make informed decisions.
“The quality of scheduling that is now possible is my favourite part of the role. We’re also increasingly using AI technology and incorporating so ware solutions to react to and predict outcomes, which will further improve the customer experience,” he says.
Lizon says great schedulers usually love a good jigsaw puzzle. The ultimate reward for a scheduler, he says, is getting passengers home or where they need to go, safely, reliably, efficiently and on time.
For those with a passion for logistics, technology, and urban transport, becoming a bus scheduler is a rewarding path with strong career growth, competitive salaries and the chance to be at the forefront of future transport solutions. To find out more, visit www.jointransit.com.au
AUGUST
AUGUST 2
QBIC Regional Forum – Chinchilla
SEPTEMBER
SEPTEMBER 11
QBIC Regional Forum – Gold Coast
OCTOBER
OCTOBER 22
PTAANZ Annual Conference and Gala Dinner – Brisbane
OCTOBER 29–31
BIC National Conference – Perth
NOVEMBER
NOVEMBER 14–15
QBIC Regional and Partner Forum – Cairns
NOVEMBER 22
QBIC Christmas Function
Bryce Pender’s terrific shot of a beautifully maintained 1979 Leyland Leopard has taken home ABC ’s Best Bus March
With each passing month comes yet another amazing photograph.
Following last month’s winning shot of a Ritchies 1129 Explorer bus hitting the town on New Year’s Day, March’s Best Bus winner has exceeded expectations.
While the ABC inbox was full of submissions this month, with each picture catching our eyes, it was ultimately Bryce Pender who took home Best Bus March a er he submitted a beautiful picture of an old 1979 Leyland Leopard.
It wasn’t an easy choice this month, with a number of photographs toughing it out for the top spot. Leo
Kriketos was quick to submit, his AAT Kings coach lapping up the sights at Uluru for a BBQ dinner tour.
James Mitchell surprised us with three special entries, one that had us smiling particularly hard and another two showing off some Auckland sights.
Michael Tran took us on a journey to Chapel Street in Melbourne, where the Ventura fleet shined against the bustling lights and nightlife.
Robert Bauer was a worthy finalist, sending through a stunning snap of a fleet of Firefly buses perfectly lined up. However, this month, none of these wonderful photos could surpass Bryce Pender and his shot of a vintage Leyland Leopard.
Above: Bryce Pender’s shot of a 1979 Leyland Leopard
“The bus is a privately owned 1979 Leyland Leopard PSU3E/2R used originally with Wellington City Transport (New Zealand) as fleet 454,” Pender told ABC
“The bus is now in preservation, with this picture being taken on February 13 2025 in Otaki.”
As the winner of Best Bus March, Pender has received a free 12-month subscription to ABC Magazine, while the winning photo is also being shown off as ABC ’s Facebook cover photo for the whole of the month.
Don’t forget to send through your Best Bus photos for April and throughout 2024 via email and keep an eye on our Facebook page for more details!
L: this one that had us smiling particularly hard
While the shorter month didn’t reap as many deliveries as in January, the industry is still motoring along at a fast pace
While the total number of deliveries for February may have fallen narrowly short of January’s high, it still highlights a sector that is producing and delivering new buses and coaches efficiently.
For February, 159 deliveries were recorded, falling five below the January number. Looking at year-on-year statistics, this year’s February deliveries still remain above the level of last year, where there were 135 units recorded in the same month.
In the chassis sector, Volvo returned to the top a er a slow start in January, with an even 60 deliveries recorded from the European giant. Sitting in second overall was Yutong with 27 deliveries for the month, with 10 of these being its D7 model, while Scania was next with the 22 deliveries. I-Bus made a mark in 2025 with the 15 deliveries, staying just ahead of Custom Denning and King Long, who couldn’t be split with 12 deliveries apiece. From there, BCI and MAN shared four deliveries each while Challenger (two) and BLK (one) wrapped up the chassis market for February.
Having nearly doubled its January deliveries, Volgren was a comfortable winner in the February bodybuilder market with the 42 units delivered. Yutong recorded the 27, with its 10 D7 deliveries allowing it to surge past Custom Denning with 17. BCI (16), I-Bus (15), King Long (12) and Irizar (12) all finished incredibly close in an even market, with the next best being Scania Higer (four) and Global Bus Ventures (three). The final 11 deliveries were split between six companies as the bodybuilder sector remained as competitive as ever.
There were no great surprises in the seating market as McConnell returned to the top of the three with 66 deliveries made in February. Sege claimed second spot with the 27 deliveries, while StyleRide (19) beat out APM (15) and Yutong (14) to finish third. Fainsa and King Long couldn’t be split with seven deliveries apiece, while Brazilian bodybuilder Marcopolo recorded four units delivered.
The air-conditioning market continues to be the tightest run sector in ABC ’s deliveries data, with Thermo-King (29) narrowly warding off Cling-Yutong (27) to claim
Above: Volvo returned to the top of the pack in the chassis and diesel delivery markets in February.
Image: Volvo Bus Australia
February honours. Sitting in third was Spheros (21) a er an impressive start to the year, while Coachair (17) snared fourth. From there, the likes of Songz (15), Hispacold (13), MCC (13) and King Long (12) all fought it out for the next best places, while the finishing touches went to Denso (five), Konvekta (four) and Valeo (three).
The state battle saw Queensland emerge as clear winners following a stunning February that saw the state record 55 deliveries. We go out west for second place, with Western Australia bringing home 38 deliveries, while Victoria (27) narrowly edged out NSW (24) for third place. Both South Australia and the ACT had the seven deliveries each, while the Northern Territory got on the board with the singular delivery.
When looking at the split between diesel and electric deliveries, there were 26 electric units sold in February compared to 133 diesel vehicles. In the electric space, Custom Denning (12) beat out Yutong (seven), Volvo (five) and King Long (two), while the diesel space saw Volvo (55) reign supreme ahead of Scania (22), Yutong (20), I-Bus (15) and King Long (10).
There were no great surprises in the seating market as McConnell returned to the top of the three with 66 deliveries made in February. Sege claimed second spot with the 27 deliveries, while StyleRide (19) beat out APM (15) and Yutong (14) to finish third.
Thermo-King (29) narrowly held off Cling-Yutong (27) to claim February honours. Sitting in third was Spheros (21) a er an impressive start to the year, while Coachair (17) snared fourth. From there, the likes of Songz (15), Hispacold (13), MCC (13) and King Long (12) all fought it out.
In the chassis sector, Volvo returned to the top a er a slow start in January, with an even 60 deliveries recorded from the European giant. Sitting in second overall was Yutong with 27 deliveries for the month, with 10 of these being its D7 model, while Scania was next with the 22 deliveries.
A er her time working in the disability sector had ran its course, Rachelle Donnison decided to finally bite the bullet and get behind the wheel
Some dreams manifest for people at a young age, knowing exactly what they want to do with their life before they even have the footing to do so.
For others, it can take years of trial and error, testing out different paths and experiences before ultimately landing on your feet.
Rachelle Donnison took the latter path with her career.
Working in the disability sector for close to a decade, Donnison says she always knew there was something else out there for her.
“I worked in disability for around eight years, and while I enjoyed my time in that industry, I knew it wasn’t what I was destined to be doing,” Donnison told ABC
“From a young age, I had always wanted to get a heavy vehicle license.
“It isn’t a typical story either, I didn’t grow up around people who were truck or bus drivers, I just saw it from afar and knew I wanted to get behind the wheel.”
With the passion fully instilled and roaring to get out, it wasn’t until she
came across the CDC Victoria Driven Women program that she started to consider it as a viable option.
“I had always had the confidence to do it, but I just didn’t know where to start,” she says.
“So when I came across the program, I just thought ‘challenge accepted’ and applied right away.”
The CDC Victoria initiative aims to increase, support and retain the female workforce by offering learning, training, development and employment across all roles, including drivers, mechanics, operations, administration or management roles.
“The heavy vehicle industries are o en dominated by men, and I think that’s why it took me so long to jump into it,” she says.
“I was always thinking, well what chance have I got?
“But because this program was with other women, I was more comfortable to put my hand up and know I would be surrounded by women wanting to do the same as me.”
The program saw Donnison undertake a 10-day training program with CDC’s partnered driving school,
working with trainers and two older diesel buses to learn the ins and out of bus driving.
“The buses were bigger than what I deal with now, and the steering was definitely a bit scarier,” she laughs.
“We had a ball, cheering each other on and giving each other confidence.”
Grouped with two other women, Donnison says she found more than just professional training.
“We’ve become such good friends, and we are still in contact now. The program created such an amazing experience that allowed us to learn and still be ourselves,” she says.
Donnison is now fully employed with CDC Victoria, completing roughly 13 runs around Sunshine.
“Everybody on the CDC team has just been incredibly supportive. During training and even now, I know I can go to anyone with any question or concern I may have, and they will help me with no hesitation,” she says.
“My advice to women trying to enter the industry is to just go for it. There will be ups and downs but never say never.”