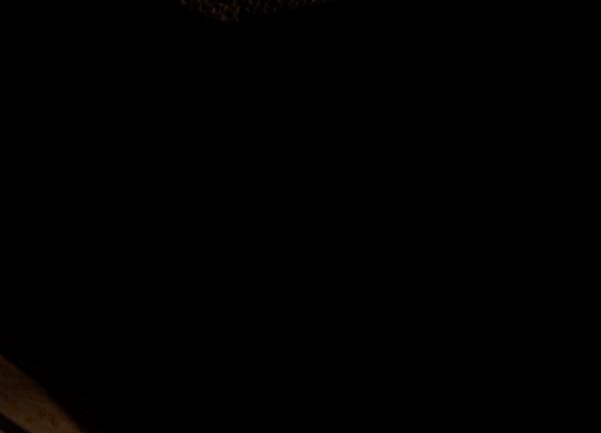


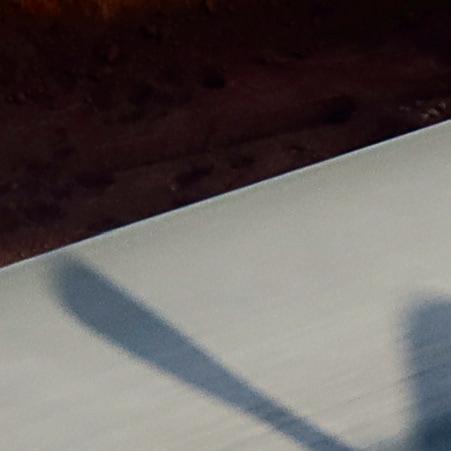
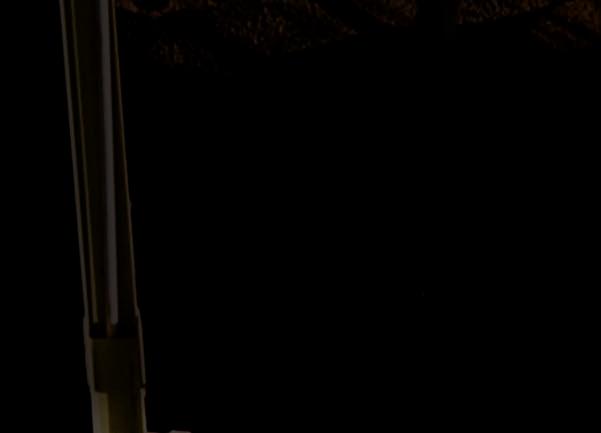
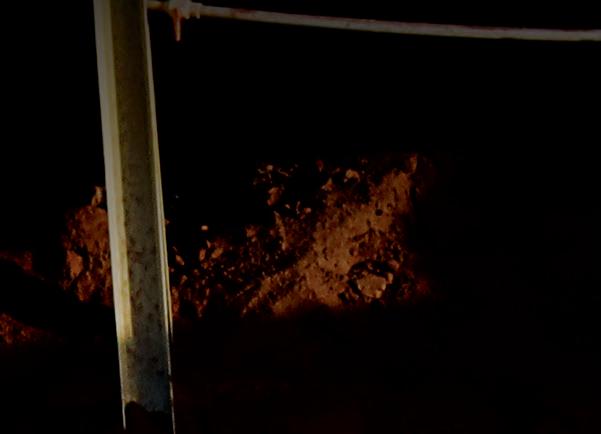
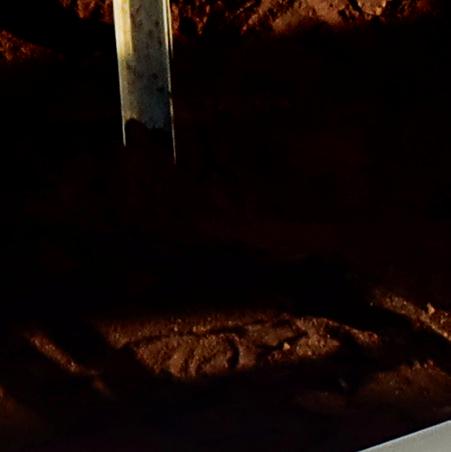
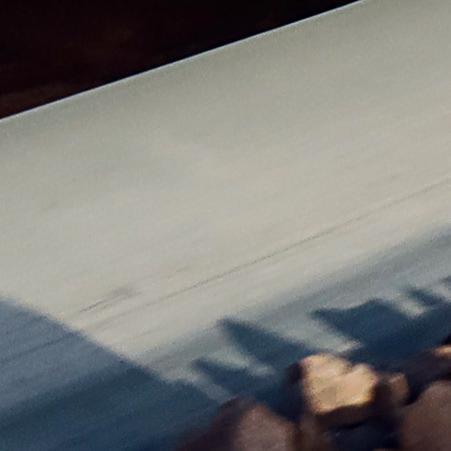
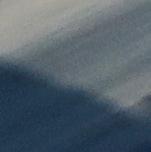
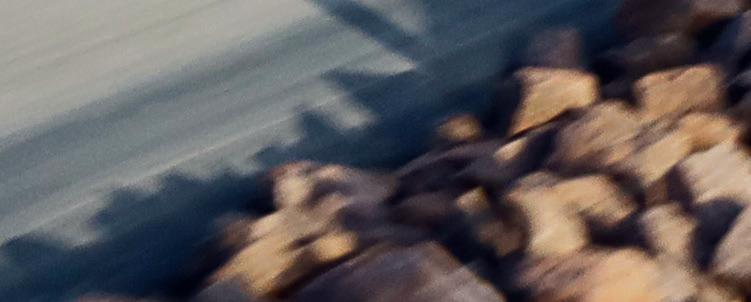
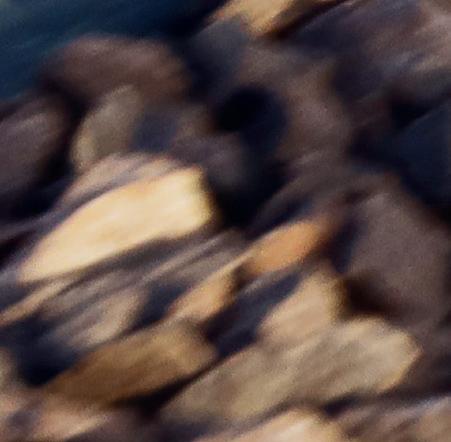
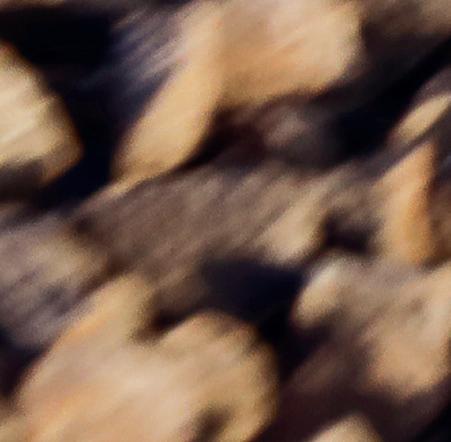
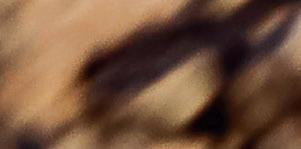
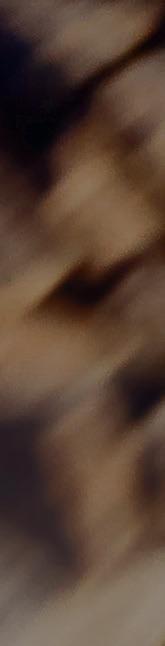


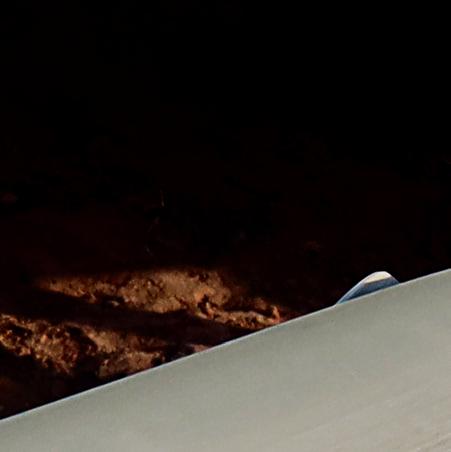
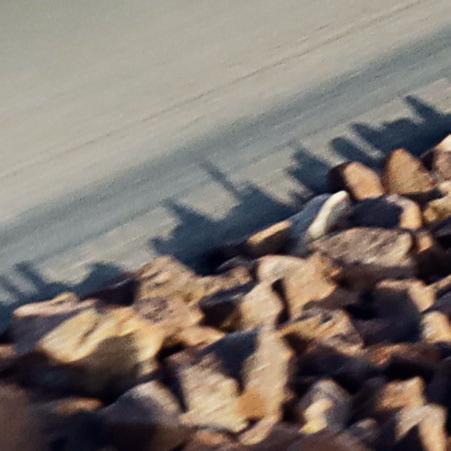
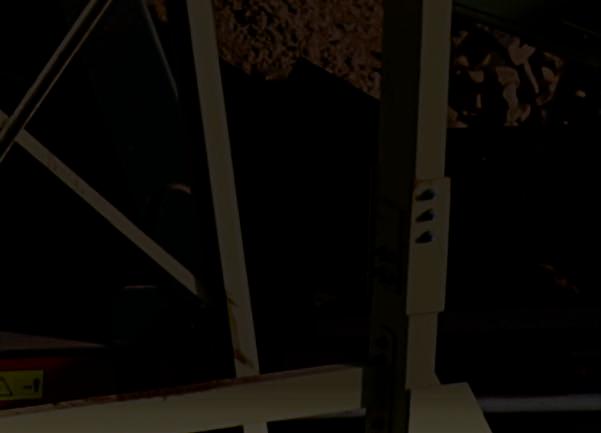
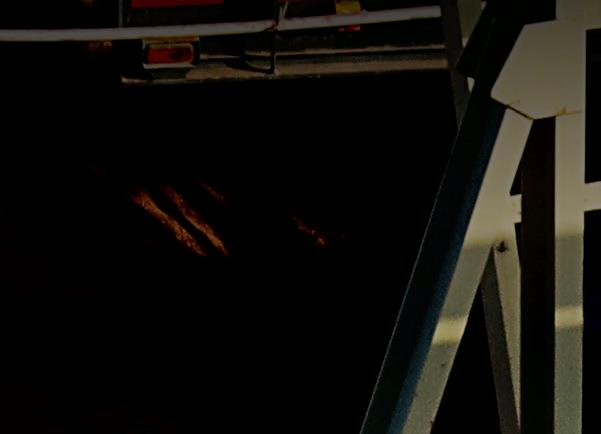

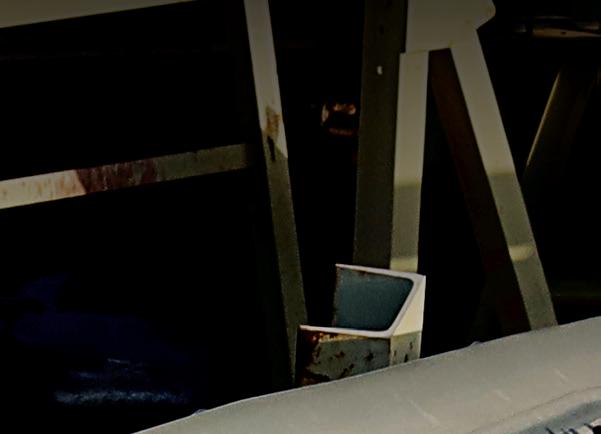
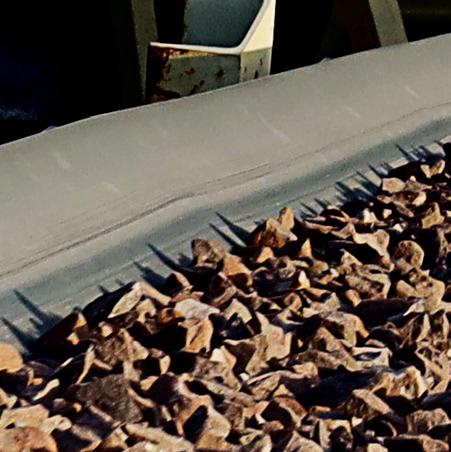
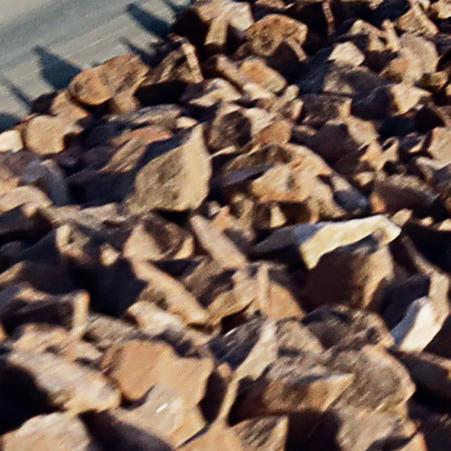
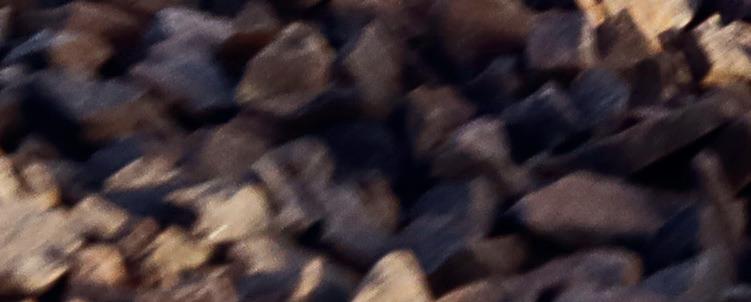

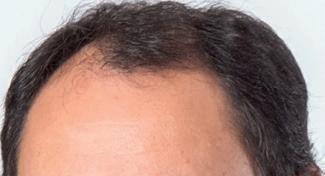
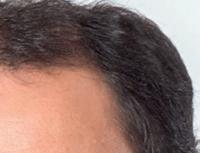
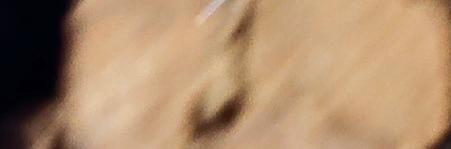
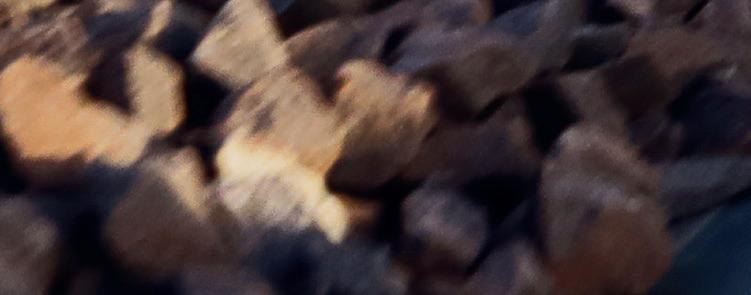
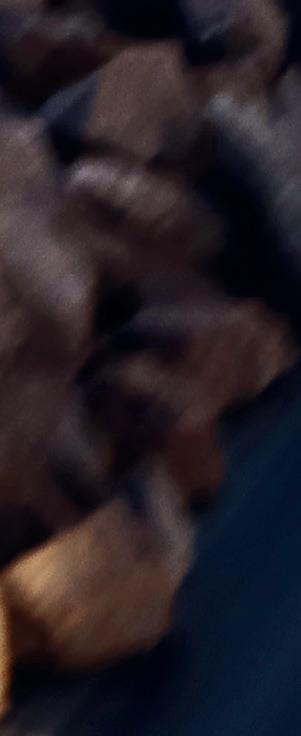

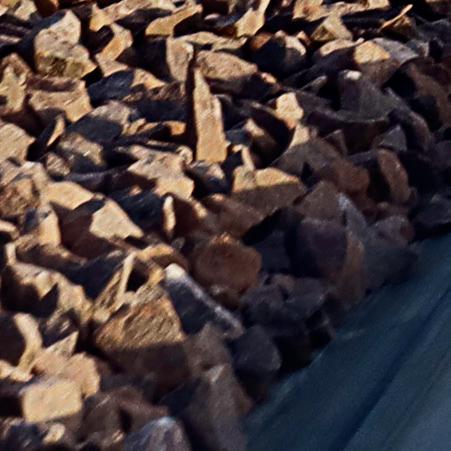
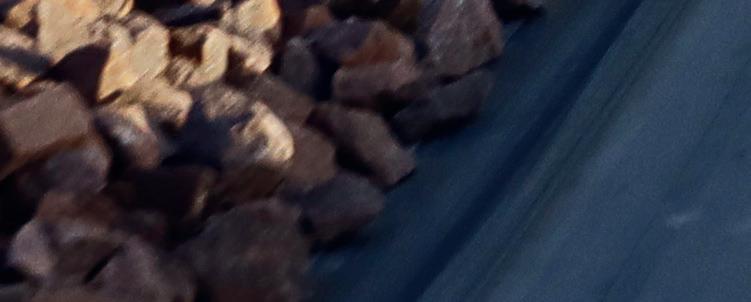



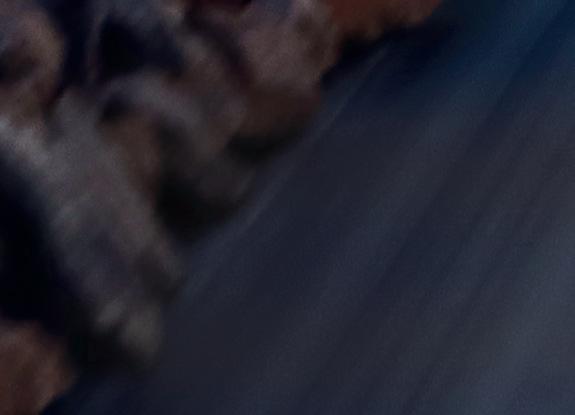
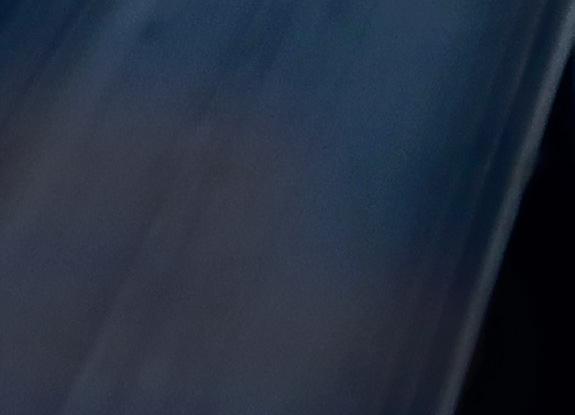
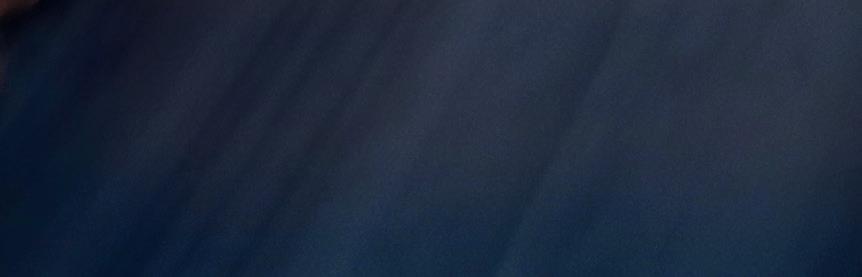

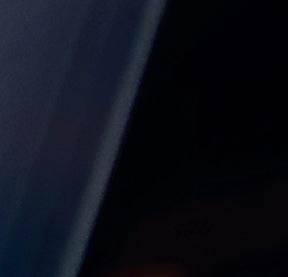
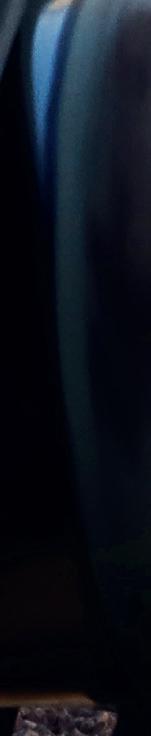
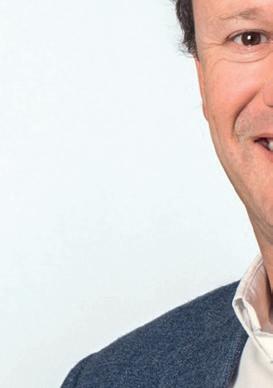

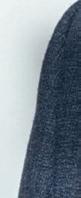
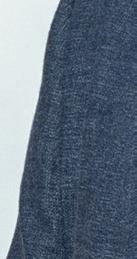
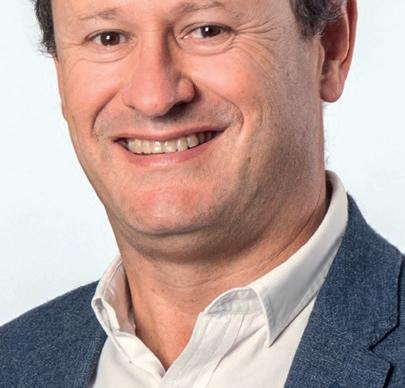
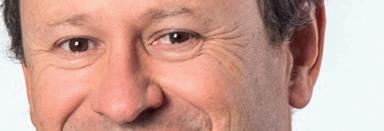
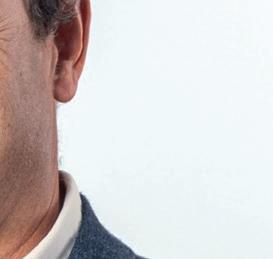
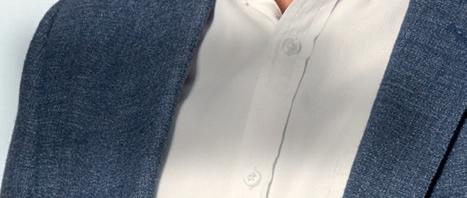
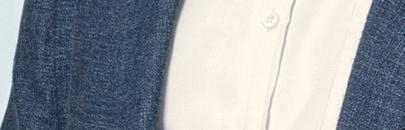
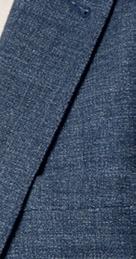
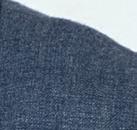
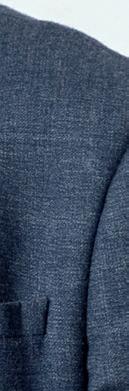
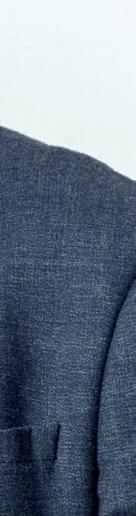
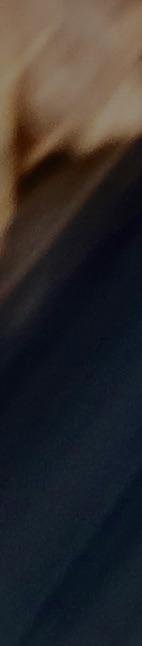

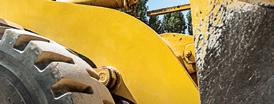

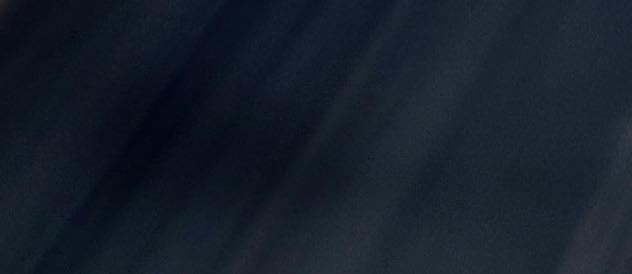

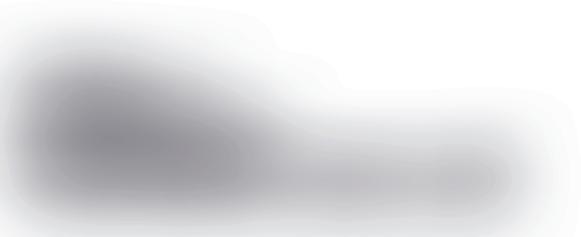
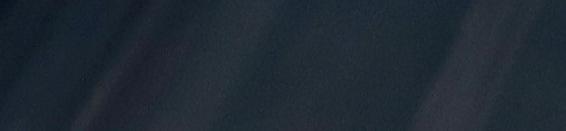
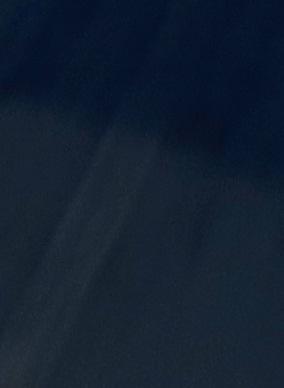
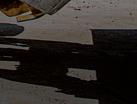

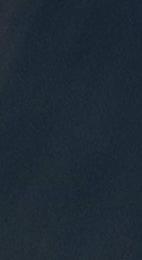
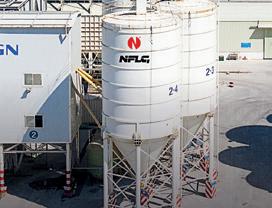
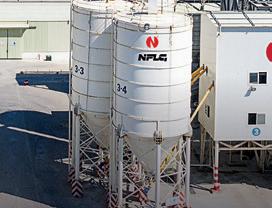

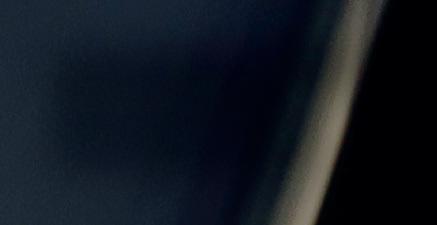
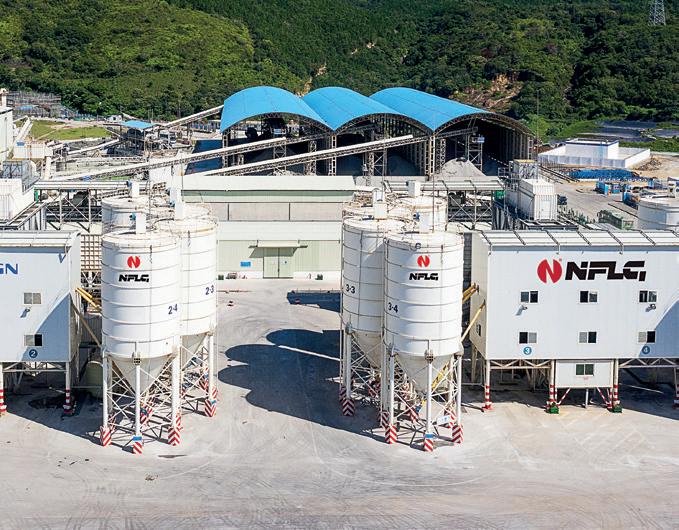
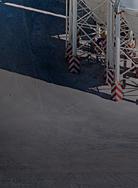
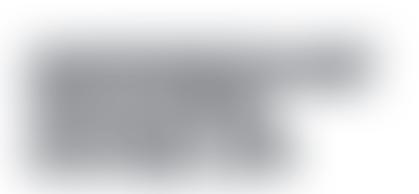

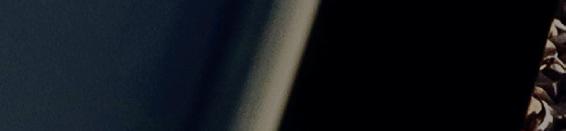
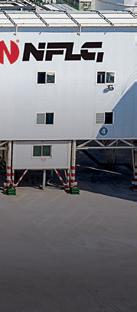

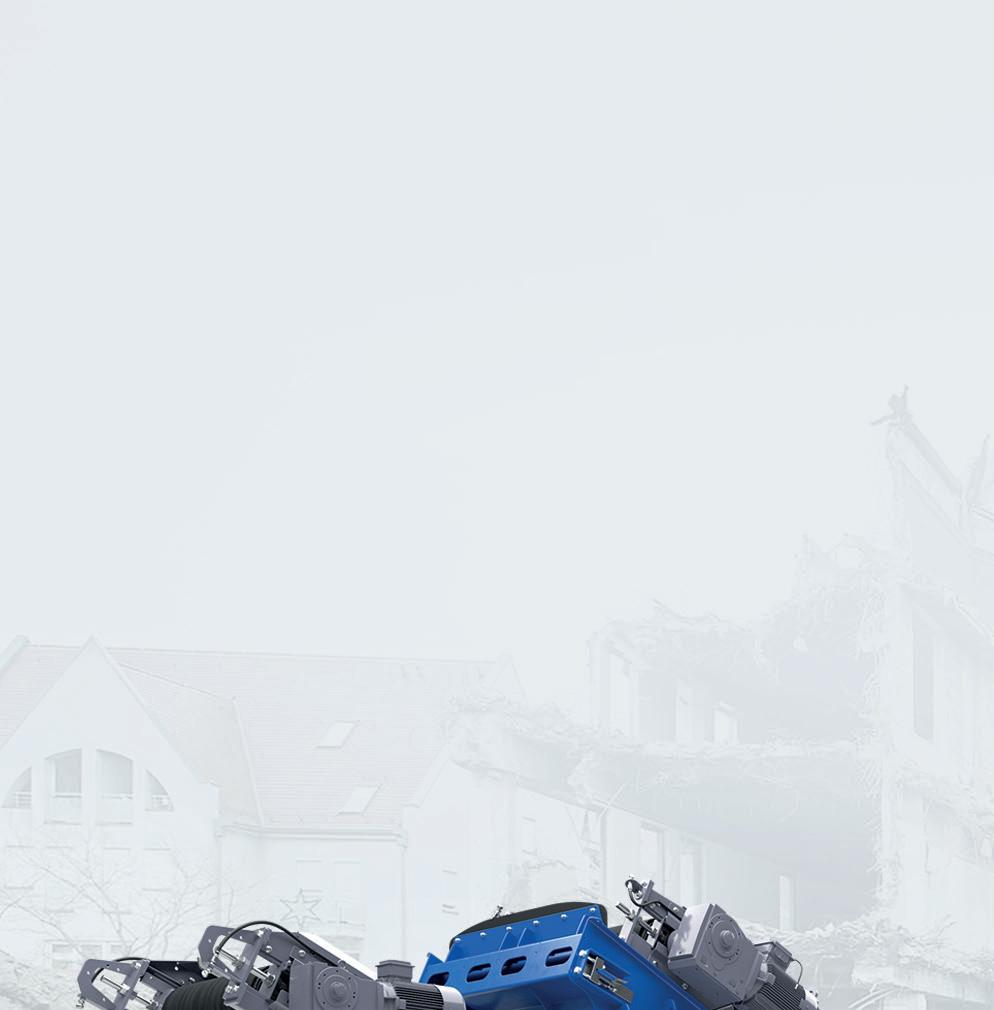
Effi cient when & where you need it – the MOBIREX MR 100 NEO mobile impact crusher! With its compact dimensions and low transport weight, this machine is amazingly fl exible, fast and versatile. The MR 100 NEO sets an all-new benchmark in the compact class – with highlight features such as automatic crusher gap adjustment or Lock & Turn Quick Access for tool-free, safe crusher opening in 30 seconds. Choose between two drive versions: the electric E-DRIVE or direct D-DRIVE. The MOBIREX MR 100 NEO: ready, set, crush!
www.wirtgen-group.com/mr-100i-neo-kleemann
Regulars 05 COMMENT
More eyes on the Central Asia prize? 50 EVENTS
All the key events in the quarrying and aggregates world.
Features 20 TYRES – 1
Making sustainable global tyre tracks
It’s load-up time in Europe. 26 SCREENING BUCKETS AND ATTACHMENTS
Big advances in the screening buckets and attachments market
Volvo CE unveils the A50 and other newgeneration articulated haulers.
CONVEYORS – 1
Conveying whole process benefits.
Aggregate Industries’ Kaziwe Siame Kaulule on the circular route to growth 42 CRUSHING AND SCREENING
Key OEMs invest heavily to gain US foothold. 46 CONCRETE PLANT
Delivering concrete certainty for customers
Eye-catching
SEPTEMBER 2025 23-25
As Australia’s longest running mining show, Asia-Pacific’s International Mining Exhibition (AIMEX) has a long, established history of showcasing and supporting the latest trends and developments in the industry.
AIMEX is relocating and will call South Australia home for the next 10 years, following market feedback and strong support from the local government and key mining players.
The move marks an exciting new chapter for the event and the region’s resource sector, with the state leading the way in future-focused mining.
AIMEX offers unparalleled opportunities to connect with Australia’s largest community of mining suppliers and professionals in an environment that stimulates innovation and collaboration.
HEAD OFFICE
Prime Global Publishing Capitol Square 4–6 Church Street Epsom, KT 17 4NR
EDITOR
Guy Woodford +44 (0) 7879 408 069 guy.woodford@primeglobalpublishing.com
ASSISTANT EDITOR
Adam Daunt adam.daunt@primeglobalpublishing.com
BUSINESS DEVELOPMENT MANAGER
Les Ilyefalvy +61 423 177 966 les.ilyefalvy@primeglobalpublishing.com
CHIEF EXECUTIVE OFFICER
John Murphy
CHIEF OPERATING OFFICER
Christine Clancy GROUP MANAGING EDITOR
Paul Hayes
CLIENT SUCCESS MANAGER
Janine Clements +61 432 574 669 janine.clements@primeglobalpublishing.com
ART DIRECTOR
Michelle Weston
COVER IMAGE CREDITS MMetso AfriSam BKT NFLG
SUBSCRIPTIONS subscriptions@primeglobalpublishing.com
No part of this publication may be reproduced in any form whatsoever without the express written permission of the publisher. Contributors are encouraged to express their personal and professional opinions in this publication, and accordingly views expressed herein are not necessarily the views of Prime Global Publishing. From time to time statements and claims are made by the manufacturers and their representatives in respect of their products and services. Whilst reasonable steps are taken to check their accuracy at the time of going to press, the publisher cannot be held liable for their validity and accuracy.
PUBLISHED BY
Prime Global Publishing
AGGREGATES BUSINESS USPS: is published six times a year.
PRINT: ISSN 2051-5766
ONLINE: ISSN 2057-3405
PRINTED BY: Warners (Midlands) PLC
hina has been a longstanding direct investor in the countries of Central Asia, including vast sums linked to Beijing’s megaprojects of all megaprojects, the US$1 trillion Belt and Road Initiative (BRI). Unveiled by President Xi Jinping in 2013, the project takes inspiration from the ancient Silk Road that connected China to the Mediterranean.
The BRI has created exciting new Central Asia commercial opportunities for quarrying equipment manufacturers and building material producers. G7 countries are now reportedly looking to invest up to US$200 billion in new infrastructure projects in the region consisting of Kazakhstan, Kyrgyzstan, Tajikistan, Turkmenistan and Uzbekistan. These countries are bound by the Caspian Sea to the southwest, European Russia to the northwest, China and Mongolia to the east, Afghanistan and Iran to the south, and Siberia to the north.
Bulk material handling solutions company Martin Engineering recently launched a new business unit in Kazakhstan, making it one of several Western-headquartered original equipment manufacturers (OEMs) that have expanded their Central Asian footprint in recent years. The business unit will be based in Almaty, the country’s largest city and commercial centre, in southeast Kazakhstan.
Martin Engineering said it chose Kazakhstan to start the new business unit as it will help the company support customers in the mining sector across Central Asia.
Oleg Glukhov, who has worked with Martin Engineering for the past seven years, will be the general manager of the new business.
“Kazakhstan is one of the world’s key sources of metals and industrial minerals,” he said. “Processing materials safely, ef ciently and pro tably is important, and that’s where Martin Engineering comes in – our market-leading products and services are proven to solve materials handling challenges for the world’s biggest mining and minerals companies.”
In a statement announcing its new Kazakhstan business unit, Martin Engineering noted that Kazakhstan is the world’s ninth-largest country by land area (approximately 1,000,000 square miles)
and has a diverse geology comprising a rich array of metal ores and mineral resources.
“Consequently, mining and minerals production is increasingly important in the Kazakh economy, with most materials exported,” the company said.
The announcement expands Martin Engineering’s presence in the country, which has previously included delivering innovative conveyor belt cleaning solutions to one of Kazakhstan’s largest copper producers.
Metso is another major OEM that has recently expanded its Central Asia footprint, signing a contract with Korund to distribute Metso solutions in Kazakhstan and Kyrgyzstan. Korund will distribute to aggregate segment customers, while Metso, through its direct sales and service organisation, will continue supplying minerals segment customers.
Elsewhere in Central Asia, reports suggest that Kyrgyzstan and Tajikistan are optimistic about new large investments from China, including in a multibillion-dollar China-Kyrgyzstan-Uzbekistan (CKU) railway.
Meanwhile, the European Commission reports that the ‘Stans’ countries of Central Asia, together with Southern Caucasus countries, Turkey and other partners, have teamed up with the European Union under the Global Gateway investment strategy to “ensure our paths continue to meet and protect our supply chains from disruptions”.
“The traf c currently building up on the Trans-Caspian Transport Corridor represents an opportunity for economic development in countries along the route, and it requires close intercontinental collaboration,” the European Commission website stated. “Corridor countries are leading in bridging transportation gaps by forging stronger ties with the European Union. Together with international partners, we are [so far] mobilising €10 billion to develop and modernise hard infrastructure and soft connectivity measures essential for the Trans-Caspian Transport Corridor.”
Is it time for more world aggregates industry eyes to take a fresh look at a very credible Central Asia trading prize? GW guy.woodford@primeglobalpublishing.com
The industry’s biggest players will soon descend on Munich to be part of bauma 2025. Aggregates Business looks at some of the key o erings at the major trade show.
One of the world’s largest industry trade shows is set to return to Munich in April, with bauma 2025 focusing on digitalisation and sustainability.
The show will see a mix of well-known original equipment manufacturers (OEMs) and emerging companies come together at the Munich Exhibition Centre from April 7–13. The show will welcome at least 150 companies for the first time alongside returning stalwarts such as Volvo, Wirtgen, McLanahan, and more.
The show will address some of the biggest issues facing today’s construction equipment and building materials industries, including climate neutrality, alternative drive concepts, networked construction, sustainable construction, and mining challenges.
Companies will also launch new products and services during the week-long event.
A significant focus of these new product launches is expected to be on sustainable construction, an emerging sector that contains 3D printing, serial construction, electric drives, and low-emission asphalt mixing.
The German Engineering Federation (VDMA) consultant for mining and minerals, construction equipment and plant engineering, Stephan Oehme, said these segments have demonstrated much potential.
“Sustainable construction is by no means limited to resource awareness, recycling of the materials used, and a smaller carbon
footprint,” he said. “The idea of recycling is now deeply etched in the DNA of the construction industry, demonstrated not least by the many extremely practical solutions.”
Here’s a look at some of the big industry players who will be at the show.
McLanahan returns as a bauma exhibitor, with the OEM exhibiting in hall C2, stall 439. Regional sales manager for Europe, James McShane, will be on hand to discuss potential solutions with new and existing clients.
The US-based OEM is exhibiting at bauma in hall B2, stall 113. The American manufacturer has been a major exhibitor at the trade show in the past, especially in 2019, when it debuted its Alliance Low Water Washer.
Kleemann will be showcased as part of the wider Wirtgen Group at bauma 2025. The company will display its diverse portfolio with Wirtgen, Vögele, Hamm, Kleemann, Benninghoven, Ciber, and John Deere equipment set to feature at booth FS.1011.
The company’s 13,000m2 exhibition space will revolve around the theme, “smarter, safer, and more sustainable”.
“The year 2025 revolves around bauma for the Wirtgen Group. We can’t wait to introduce you to our newest future-oriented
products and innovations, among other things,” Wirtgen said.
Haver and Boecker will feature its wares in hall B2, booth 149. The company has traditionally used the trade show to showcase its range of screening equipment. In 2022, Haver and Boecker Niagara gave a live demonstration of the Niagara T-Class free-swinging screening machine.
Telestack
Telestack will bring a range of equipment to its stand FN1219 at bauma 2025. The show has traditionally been a key showcase for the OEM. At the 2022 event, Telestack showed off three units from its zero-emission range – the LF520 Revolution, the TCL 1031 heavyduty tracked conveyor, and the TC421 battery tracked conveyor.
Attendees can visit BKT at bauma 2025 by attending its space in hall A6, stall 215.
Volvo Construction Equipment
Volvo CE will be at bauma 2025 alongside Volvo Group and dealers Robert Aebi and Swecon Baumaschinen in hall C6, booth 303/313, and block 60C.2 at the FM outdoor demo area.
“We will be showcasing our commitment to leading innovation and sustainability in the industry and look forward to meeting you there,” Volvo CE said.
Caterpillar
Caterpillar will continue its centennial celebration with a major exhibit at bauma 2025 to showcase “the next 100 years”.
Caterpillar will display 48 machines, including 17 new introductions or upgrades across its exhibit space of more than 9000m2.
“What we will show will be a fitting tribute to our heritage while demonstrating our commitment to building a safer, smarter and more sustainable world with our customers and dealers for the next 100 years,” Caterpillar group president of construction industries, Tony Fassino, said. “Alternative power sources, reduced-carbon options, and integrated technologies are the future, and Caterpillar is ready to deliver this in collaboration with our global dealer network.”
The conveyor belt manufacturer returns to bauma and will exhibit in hall B2, booth 127.
Smiley Monroe is set to preview its expanded ToughFlex range at the event which will be exclusive for attendees.
Smiley Monroe’s expanded ToughFlex range will include two new specifications with a reduced belt thickness and weight as the original while maintaining the same tensile strength. Smiley Monroe said the new specifications will provide “customers the opportunity to benefit from ToughFlex’s increased performance across their entire machinery range”.
Simex will bring a significant presence to hall C5, booth 325 alongside Italian dealer Capoverso Editrice.
“Our team is excited to connect with industry professionals, discuss new trends, and explore opportunities for growth,” Simex said.
Simex will be looking to carry on its success at other recent bauma showcases, including bauma China 2024 in Shanghai, where it showcased its latest innovations alongside Chinese dealer and importer ATE.
Following a successful presence in 2022, Triangle Tyre is set to return to bauma in 2025, reaffirming its status as a leader in off-the-road (OTR) tyre solutions. The renowned Chinese manufacturer will present its comprehensive product portfolio in hall A6, stand 39. The company will exhibit three flagship OTR products – crane tyre: 445/95R25 TB576 174F E2; wheel loader tyre: 29.5R25 three-star rating TL559S+ L5; RDT tyre: 27.00R49 TB599A E4 – and introduce its new Tyre Performance Monitoring System.
“Triangle remains committed to strengthening its position in Europe by further developing its product range to meet
the demands of both original equipment and replacement markets,” the company said.
Ammann
Visitors can find Ammann in the outdoor area south at stand FS.909 and FS.910, where it will showcase its asphalt and concrete plants and compaction solutions as part of its “green path forward” theme.
“Ammann is thrilled to announce our participation at bauma 2025 … as we showcase the future of sustainable construction technology, with innovations designed to boost productivity, efficiency and environmental responsibility,” Ammann said.
“Our displays will highlight how Ammann is shaping the future of infrastructure. Get ready for live demos, interactive experiences, and a chance to connect with our experts.” AB
Afrimat’s construction materials segment has delivered a solid performance in recent times.
On the back of rapid urbanisation, population growth and increased demand for sustainable infrastructure, many African governments are placing infrastructure at the centre of their development agendas.
While many African nations have traditionally relied on commodities to drive economic growth, governments across the continent have recently embarked on an ambitious infrastructure development drive.
Behind the newly found appetite for investment is a deep understanding among many African governments that infrastructure is the foundation for sustainable development and a critical lever for improving economic stability and enhancing trade across regions.
Marked by large-scale transportation and energy projects, the investment journey is underpinned by the quest to drive infrastructure-led growth across the continent. While a strong political will and strategic governance are apparent, population growth is one of the major drivers behind the rapid infrastructure development trajectory in Africa.
To provide context, Africa’s population expanded from 283 million in 1960 to more than 1.5 billion in 2024 – a more than fivefold increase. The United Nations projects the continent’s population to increase to reach 2.5 billion by 2050, a 63 per cent increase.
Africa’s share of the world’s population will be 28 per cent in 2050, up from 10 per cent in 1960. That means more than one in four people around the world will be African by 2050.
In addition, the rapid expansion of infrastructure development across Africa is primarily driven by the accelerated pace of urbanisation.
According to the United Nations, over half of Africa’s population will live in cities by 2050. As urban areas expand, so does the need for infrastructure, making construction one of the major sectors on the continent.
According to a Mordor Intelligence report, the African construction market is valued at US$61.09 billion. It is expected to reach $77.35 billion by 2029, growing at a compound annual growth rate (CAGR) of 4.83 per cent during the forecast period (2025 –30).
Corridor projects abound
According to business intelligence provider ABIQ Solutions, some 760 current infrastructure projects in Africa are worth almost US$620 billion. The largest share of those projects consists of 430 major road construction projects driven by regional corridors aimed at promoting regional trade. Several regional road corridor projects are underway, including the North–South Corridor, the Mtwara Corridor, the TransKgaladi Road Project, and the Abidjan–Lagos Corridor Highway.
The North–South corridor runs north from Durban, South Africa, connecting Zambia, the
Democratic Republic of Congo and western Malawi to Botswana and Zimbabwe. It also links to Durban’s port for imports and exports.
The Mtwara Corridor connects southern Tanzania to Zambia and crosses Mozambique towards the Malawi Lake border. The African Development Bank (AfDB) has financed road upgrades and a one-stop border post between Tanzania and Mozambique.
The Trans-Kgaladi Road Project aims to improve transport services, promote regional trade and diversify local economic activities among Southern Africa Development Committee (SADC) member states, mainly Botswana, Namibia and South Africa. It also aims to improve access to social services and reduce the cost of goods and services for roadside communities.
The Abidjan–Lagos Corridor Highway will link the cities of five major West African countries by 2030 and is set to become a powerful economic and industrial hub courtesy of the Spatial Development Initiative promoted by the AfDB.
The 1028km transnational coastal motorway will connect Côte d'Ivoire to Nigeria while crossing through Ghana, Togo, and Benin. Work is due to commence in 2026 and is earmarked for completion in 2030.
The toll-free motorway will have up to six lanes, with up to eight lanes in Lagos. After a drive of 82km through Nigeria, the road will cover 520km in Ghana, 144km in Cote d’Ivoire, 90km in Togo, and 127km in Benin. There are also plans to build 63 interchanges.
Construction is expected to generate up to 70,000 jobs, with most work carried out in public–private partnerships.
AfDB’s chief transport economist and project manager, Lydie Ehouman, said the project will link an urban population that is expected to reach 173 million people by 2050 and connect the most densely populated metropolitan areas in West Africa, from Abidjan, Takoradi and Accra to Lomé, Cotonou, Porto-Novo and Lagos.
“The Abidjan–Lagos highway will connect up with the West African transport corridors [airport, road and rail] and will link the inland regions of Mali, Burkina Faso and Niger to all eight ports in the corridor, as well as to the Abidjan–Dakar–Praia corridor,” Ehouman said.
In East Africa, Kenya is proving to be a true ‘construction site’ with several major projects, including roads and railways. One of the flagship projects is the Mombasa–Nairobi Expressway, a proposed four-lane toll highway.
The Kenya National Highways Authority has signed a project development agreement with Everstrong Capital, a US-based infrastructure investment manager, for the planned US$3.6 billion Nairobi–Mombasa Expressway project. The expressway would link the Kenyan capital of Nairobi to the Indian Ocean city of Mombasa.
On the back of this infrastructure drive, several construction materials suppliers in South Africa report increased demand for aggregates and related materials.
Despite enduring a protracted downturn, the construction sector in South Africa is optimistic, with several projects underway and strong projections for growth. In recent years, the South African National Roads Authority Limited (SANRAL) has demonstrated its investment appetite.
In the 2023–24 financial year alone, SANRAL spent around ZAR27.1 billion ($1.44 billion) on South Africa’s road infrastructure, including ZAR4.1 billion on toll roads and ZAR2 billion on non-toll road expenditures. According to the roads authority, ZAR12.3 billion of the ZAR23 billion was spent on capital, while ZAR10.7 billion was allocated to maintenance.
“The significant investments in toll and non-toll roads underscore our dedication to enhancing South Africa’s road infrastructure, ensuring safer, more efficient mobility for all,” SANRAL chief executive officer (CEO), Reginald Demana, said.
In September 2024, SANRAL announced major investments in critical road infrastructure for its northern region. At the time, Demana declared that the roads agency planned to invest ZAR50 billion in the South African economy through new tenders.
“I am happy to announce that we are currently evaluating 96 tenders worth ZAR35 billion, while 86 contracts worth ZAR15 billion have already been awarded since the start of the 2024–25 financial year on 1 April 2024,” Demana said.
Demana said the tenders currently under evaluation are spread across the country, but the majority falls under the northern region, which comprises Gauteng, Mpumalanga, Limpopo and North West provinces.
SANRAL’s northern region manages approximately 9500km of the national road network, making it the agency’s largest region.
Due to this infrastructure drive, several construction materials suppliers in South Africa report increased demand for their products.
In its results for the six months ending 31 August 2024, Afrimat, a leading construction materials and mid-tier mining company in South Africa, saw group revenue increase by 44.3 per cent, from ZAR2.8 billion to ZAR4.1 billion, including the newly acquired Lafarge South Africa business.
The construction materials segment (excluding cement) delivered a solid performance, increasing operating profit by 39.4 per cent to ZAR217.6 million from R156.1 million in the previous comparable period.
Afrimat CEO, Andries van Heerden, said this was largely due to the successful integration of the Lafarge quarries, fly-ash business, ready-mix batching plants, volume growth, and ongoing cost-saving initiatives.
Meanwhile, the Afrimat Construction Index (ACI), a composite index of the activity level within the building and construction sectors, recorded an upward trend in the third quarter of 2024.
Seven of the 10 constituent indicators comprising the index were in positive territory. These included the number of buildings completed, particularly in the metropolitan and larger municipalities, which was up by 23.3 per cent, employment in construction was up by 14.6 per cent, and sales values of building materials were up by 5.9 per cent.
Van Heerden is encouraged by the data in the ACI release.
“We previously indicated that across the construction landscape, the Construction Materials segment enjoyed slightly elevated volumes from road, rail and dam projects, and we continue to experience demand for our aggregates.”
Afrimat CEO, Andries van Heerden
“We previously indicated that across the construction landscape, the construction materials segment enjoyed slightly elevated volumes from road, rail and dam projects, and we continue to experience demand for our aggregates,” he said.
Elsewhere, Portland Group, one of the leading construction materials suppliers in the Western Cape Province of South Africa, has enjoyed high demand for aggregates and ready-mix concrete. Portland Group general manager, Martin Mostert, said the province has witnessed massive investment in construction activity in the last three years, anchored by road upgrades and commercial and residential building projects.
“We are fortunate to be located right in the thick of construction activity,” Mostert said. “One of the notable projects that we are currently supplying is the Vissershok road upgrade. Undertaken by H&I Construction, the project is on the doorstep of our Durbanville Quarry.
“The project – a major bypass off the N7 highway – is a significant infrastructure in the Durbanville area. To provide context, apart from all the G-products, we are also supplying in excess of 800,000 tonnes of overburden for backfilling purposes.”
Located to the south of Durban, AfriSam Coedmore has enjoyed high aggregate demand in the past few years, especially given its close proximity to SANRAL’s ongoing flagship N2/N3 road upgrades.
The upgrades, which form part of the national government’s Strategic Integrated Projects (SIP2): Durban-Free State-Gauteng Logistics and Industrial
Corridor, are expected to take eight to 10 years to complete.
One of the major project legs to which the quarry supplies materials is the upgrade of the EB Cloete Interchange on the N2.
Located 10km from AfriSam Coedmore, the EB Cloete Interchange is said to be the largest road infrastructure project in South Africa. With a project value of ZAR5 billion, SANRAL said it is the biggest single project undertaken by the roads authority to date.
“We are fortunate to be situated right at the doorstep of the many faces of the N2/N3 road upgrades,” AfriSam Coedmore manager, Lloyd Maringa, said.
“In the past few years, we have enjoyed high aggregates demand, initially supplying mostly base and sub-base materials during the early days of the projects. With the upgrades now moving onto surfacing, we are starting to move more high-value products such as roadstone and concrete aggregates.”
Demonstrating its confidence in the South African market, PPC, a leading supplier of cement and related products in southern Africa, has signed a memorandum of agreement with Sinoma Overseas Development Company (Sinoma) for the construction of a new ZAR3 billion stateof-the-art integrated cement plant in the Western Cape, South Africa.
The 1.5-million-tonnes-per-annum plant, which will replace and increase existing capacity, is planned for construction at one of PPC’s current sites. The new plant will
be equipped with the latest technology, including a fully dedicated solar generation system, enabling PPC to supply the lowestcarbon cement in the country.
PPC CEO Matias Cardarelli said South Africa’s changing cement market urgently requires modern, cost-efficient assets and environmentally conscious producers.
“By substituting existing capacity with a more efficient, environmentally friendly and larger plant, we are securing PPC’s competitiveness in a key market by delivering to our customers the best value proposition in the region,” Cardarelli said.
“This will better position PPC for sustained profitability for decades to come and will ensure the group’s long-term future.
“It also represents commitment and support of the national objective of economic growth and infrastructure development. The pursuit of this investment demonstrates the continued confidence in South Africa by the PPC board and management.”
Apart from South Africa, Angola is one of the hotspots for infrastructure development in the southern part of the continent.
Following its September 2023 appointment as the official Terex MPS dealer in Angola, Namibia and Botswana, Consulmet Equipment has successfully commissioned its first aggregate plant in Angola. Costa Blanca Angola, a construction, crushing and aggregate company, took delivery of the first plant and deployed it on one of its projects in Lobito, an infrastructure development hotspot in the Benguela Province.
Consulmet Equipment supplied a WC1150S wheeled cone crusher and screen combination, conveyors and a surge bin with a variable speed drive (VSD) pan feeder for the project. The client also purchased a wheeled CRC320 cone crusher plant and a wheeled CRS820H screen plant to complement the mobile crushing plants already available on site.
All equipment purchased was assembled, installed, and commissioned by the in-country Consulmet Equipment team, which was supported by TecProMic Lda and Terex MPS.
Consulmet Equipment’s Ken Bouch said he was encouraged by the hive of infrastructure
activity in Angola. To provide context, Consulmet Equipment is already negotiating for a larger 750-tonnes-per-hour (tph) plant for Costa Blanca’s Luanda quarry site, while equipment for another 600tph plant for the Lobito project is already in place and awaiting the arrival of conveyor belts and surge bins.
The new Lobito plant will service the required aggregates demand for the local construction industry and possibly for the Lobito Corridor project.
In September 2023, the US and the European Union made a joint statement announcing support for the corridor and that a Greenfield Rail Line feasibility study would be commissioned to explore establishing a new rail line from Angola through Zambia’s copperbelt region. The rail project is planned to conclude by 2029, and Costa Blanca is well positioned to supply aggregates.
Elsewhere, Costa Blanca is looking to boost capacity at its Luanda quarry, which has already supplied materials for the ongoing Barra do Dande Port project. The company has been contracted to supply backfill and aggregates for the construction of the port.
Portland Group, one of the leading construction materials suppliers in the Western Cape Province of South Africa, has enjoyed high demand for aggregates and ready-mix concrete.
The massive port is being developed through public–private partnerships with Sonangol, Angola’s national oil company.
The project entails constructing and installing 29 storage tanks, terminals for solid and liquid bulk materials, a container terminal, a multi-use terminal, and a petroleum support zone. It will see the construction of an 18.25km quay wall, a 10.5km² embarkment area, and a 4.68km² logistics support zone. The total cost of the port development is US$1.5 billion.
“For this project, we are looking at providing a 750tph plant to produce 0–40mm material as well as sized aggregates,” Bouch said.
“The front-end up to the secondary crusher will be modular, while the rest of the plant, from the secondary crusher, will be mobile. This layout will allow the client to ‘chop and change’ the layout as and when required to meet production requirements of certain material sizes.”
Bouch is excited about growth prospects in Angola, where he believes the infrastructure development prospects are massive. The country’s extensive coastline and natural resources provide opportunities for port expansion and maritime infrastructure.
Investment in road, rail and airport projects is planned in order to improve connectivity and trade. Furthermore, the energy sector is benefitting from investments in renewable energy sources and power generation to meet growing demand.
“Angola is an infrastructure and mining hotspot, and we believe that there is still so much more to come,” Bouch said.
Supply chain gains
Bunting, a global leader in magnetic solutions, is seeking to appoint capable distributors on the continent, with an initial focus mainly on South Africa, to capitalise
on the growth prospects in Africa. However, the company is also willing to consider opportunities in other regions.
Bunting’s wide range of equipment features magnetic separation products, metal detection devices, custom magnets and magnetic assemblies, in-stock neodymium magnets, and more.
“Our ideal partners would be existing suppliers of capital equipment – particularly crushers, screens and conveyors – to the mining and quarrying sectors in South Africa,” Bunting sales manager, Bradley Greenwood, said.
Greenwood said Africa is a strategic growth market for Bunting. The company sees potential and growth opportunities for its extensive line of magnetic solutions, especially in the extractive sector.
“We realise huge potential for growth and only see the market getting bigger on the back of a global shift towards a greener, electric world,” Greenwood said.
The energy transition so critical to meeting the Paris Agreement is heavily dependent on green minerals. Countries such as the Democratic Republic of Congo and South Africa are significant global players with substantial known reserves of green minerals in Africa.
Following the official local launch of the Liebherr TA 230 Litronic articulated dump truck (ADT) in June 2022, which marked Liebherr–Africa’s debut in the highly contested ADT market in southern Africa, several units are now hard at work in South Africa and Zimbabwe, where the ADT has proven its mettle in some of the toughest mining applications.
With several units already operating in the field, clocking about 35,000–45,000
market hours in the process, Liebherr–Africa general manager for earthmoving technology, Tendayi Kudumba, said he expects the sales of the Liebherr TA 230 to pick up steam due to increased enquiries in the region.
“The ADT market in southern Africa is very competitive, but we are very happy with the sales performance and enquiries of the TA 230 to date,” he said. “Several customers have shown immense interest in the machine, and we expect to put more units into the market soon.”
Having traditionally served the South African market, Beowulf Mining, a leading supplier of drilling consumables to the quarrying and mining sectors, has set its sights on expanding its footprint in Africa.
“Our African expansion drive started some five years ago, with initial focus on West Africa, particularly Burkina Faso and Guinea, where we have already secured business from two big mining houses,” Beowulf Mining director of sales, Riaan Theron, said.
“We have identified a big gap in terms of both quality product and good service in these markets. The expansion into West Africa complements our existing cross-border business in key markets such as Botswana, Zimbabwe and Namibia.”
After establishing itself as a household name in the South African tipper truck market, Powerstar, under Ever Star Industries (ESI) stewardship, has seen expanded growth in cross-border markets in recent years.
As part of its cross-border plans, ESI has fortified its aftermarket regime with a strong dealer footprint across southern Africa.
Following its official local launch in June 2022, the Liebherr TA 230 Litronic articulated dump truck has proven its mettle in some of the toughest mining applications in Southern Africa.
ESI senior head of sales, Rodney Selesnick, said the company currently ships out about 800 trucks per year, which is close to capacity for its current assembly infrastructure in South Africa. Between 200 and 300 units are destined for cross-border markets such as Zimbabwe, Mozambique, Botswana, Zambia and Namibia.
Given the increased demand, Selesnick said there are plans to increase the capacity of the assembly plant to 1500 units per year to cope with the growth in southern Africa.
As part of its growth in southern Africa, ESI has invested in its regional dealers and business partners. It has two dealer partners in Namibia who, according to Selesnick, are doing well. The same goes for Botswana, where the dealer appointed to manage that market is gradually increasing its sales.
ESI has a dedicated sales dealer and a separate service dealers in Mozambique.
The Eswatini dealer takes care of sales and service of the range, while Lesotho, currently a small market, is supported by ESI’s existing dealer in the Free State, South Africa.
The Zambian dealer and the Democratic Republic of Congo dealer are both part of the same group. The Democratic Republic of Congo is showing signs of renewed energy and growth.
Following the introduction of left-hand derivatives in its offering, ESI can now offer its Powerstar range to the Congolese market.
“Zimbabwe, supported by an extremely capable dealer, has been one of the more exciting markets in recent years,” Selesnick said. “To provide context, between 2015 and 2016 Zimbabwe only accounted for about 12 to 16 units per year. In 2023, a whopping 150 units were sold into this market. Over and above the spectacular product range lies an unrivalled aftersales support, which has been key to the Zimbabwean growth.” AB
The latest bauma CONEXPO India was held in Greater Noida in Uttar Pradesh State in December 2024, drawing 51,118 visitors from 83 countries and hosting 984 exhibitors in international pavilions from countries like Germany, Italy, China and South Korea.
The seventh edition of bauma CONEXPO India (bC India) may have been held at a time of relatively lower demand for Indian quarrying and construction equipment, but business confidence remained solid among exhibitors and visitors. Displayed next-generation technologies linked to aggregate extraction, loading and hauling and lowering infrastructure construction costs potentially able to generate a period of greater sales activity.
Among the key show highlights was the launch of the latest wheeled machines featuring new engines that meet new government BS V emission regulations standards that came into effect in April 2024.
Leading industry bodies such as Builders Association of India (BAI), Indian Concrete Institute (ICI), Tunnelling Association of India (TAI), and Central Road Research
Institute (CRRI) – Council of Scientific and Industrial Research (CSIR) held more than 30 knowledge-sharing sessions. The topics covered included ‘Charting India’s infrastructure growth journey’, ‘Innovative techniques in demolition and recycling’ and ‘Modern construction techniques in India’.
The event also incorporated the debut of Demtech India 2024, a dedicated show on demolition technology, as well as the NASSCOM Pavilion, which showcased innovations in construction technology.
Government of India's honourable union minister for road transport and highways, Nitin Gadkari, inaugurated the event and addressed the challenge of India’s reliance on fossil fuels, costing 22 lakh crore annually, and underscored the importance of transitioning to alternative fuels and biofuels to reduce the dependence on imported oils and mitigate pollution.
“When electric vehicles first emerged, the cost of lithium-ion batteries was $150 per kilowatt hour. Today, the cost has dropped to $110 per kilowatt hour and is expected to equal the cost of petrol and diesel vehicles within two years, making electric options more affordable,” he said.
Gadkari highlighted India’s growing manufacturing potential and noted the country’s ability to become a global hub for manufacturing and exporting construction equipment, given its pool of talented engineers and low production costs.
“India is becoming increasingly attractive to the global market. The construction equipment industry plays a vital role in development, driven by innovation, research and entrepreneurship.” Gadkari said.
The busy bC India 2024 showground.
Gadkari said the industry should develop cost-effective, pollution-free and indigenous solutions using alternative fuels. He believes such efforts would benefit India’s infrastructure projects and position the country as a global leader in the construction equipment sector.
JK Tyres launched advanced off-the-road (OTR) products in a major bid to strengthen its offering in the wheeled loaders, tipper trucks, and self-loading concrete mixers segments. These comprised the 17.5-25 VEM 63 L5 for wheeled loaders, 16.00-25 VEM 99D E3 for wide-bodied dump trucks, 12.00-24 VEM SMOOTH L5S for load haul dumpers, 300-15 JET LIFT for forklifts, and 10/75-15.3 MPT117 for self-loading concrete mixers. The company also displayed its TREEL tyre pressure and temperature monitoring solutions.
“The VEM 63 [L5 pattern] features an extra-deep tread for extended service life, enhanced by a sidewall protector, broad lugs for stability, and a tough nylon casing for load capacity. The VEM 99D (E3 pattern) offers superior handling with its chevron pattern, improved heat dissipation, and exceptional cut resistance,” JK Tyre & Industries president (India), Anuj Kathuria, said.
The VEM SMOOTH L5S ensures long tread life, stability and high-load endurance, which makes it suited for harsh operating conditions. The JET LIFT provides superior stability and wear resistance with a robust casing and silica-based compound. The MPT 117 offers enhanced durability and high load capacity for both on-road and off-road operations.
“Many existing and new wheeled loader manufacturers are getting CKD wheeled loaders in India for localised material handling activities with lower operating costs. We see this as a growing business area,” Kathuria said. “Self-loading concrete mixers are also witnessing phenomenal growth in India.”
Tata Hitachi showed its preparedness for the new BS V emission norms. Taking the opportunity to reposition its backhoe loaders in the highly competitive business segment, the company launched the upgraded Shinrai Prime CEV 5.
It exhibited its new BS V-based TL340H Prime CEV-5 8 and ZW 225 CEV-5 wheeled
loaders. Looking to leverage its position in electric solutions, it also showed its new indigenously developed 20-ton electric excavator concept – the EX 210LC Electric.
Tata Hitachi also displayed its EX 210 Value + excavator. Other products from the company's stable at the show included the ZAXIS 38U, NX 50, NX 80, EX130 Prime Tunnel, and EX350LC Prime models.
The company designed the EX130 Prime Tunnel to meet India’s tunnelling requirements, supporting critical connectivity, hydro-irrigation, and power generation projects.
Tata Hitachi showed its proven models to complement these launches, including the NX30, EX 215LC Prime, and ZAXIS 220LC Ultra excavators.
Tata Hitachi also showed a range of new attachments designed to enhance versatility and efficiency across various applications. These include the Tapered Ditch Bucket, ideal for precise ditching operations, and the Jaw Bucket, engineered for easily gripping and handling materials.
“The TL 340 three-ton class wheeled loaders and ZW 225 5-ton class wheeled
JK Tyre & Industries president (India), Anuj Kathuria.
loaders feature higher fuel efficiency and reliability levels,” Tata Hitachi Construction Machinery head of marketing, Siddharth Chaturvedi, said. “The hydrostatic transmission in the TL 350 unit makes it highly suitable for delivering lower operations costs. Most importantly, the machine is absolutely suitable for bigger-sized quarrying applications requiring frequent load transfers, loading, and stockpile arrangements. The higher capacity five-ton class also scores on similar parameters.
“The demand for wheeled loaders for block handling applications in granite and marble mining has been getting firmer in India. This has been due to the rising exports of the products and growing domestic demand, requiring rising demand for higher capacity wheeled loaders in the segment.
Our ZW 310 and ZW 550 class loaders are positioned to cater for the demand, which we have been doing quite successfully with strong product recall.
“Our new range of electric EX 210 LC excavators addresses the evolving needs of infrastructure development while maintaining a steadfast focus on significantly lower operations and maintenance costs and environment. It also reinforces a strong commitment to sustainability and environmental stewardship.”
Caterpillar India director of sales and marketing for the BCP Division, Amit Bansal, said its modified Hindustan wheeled loader was a key innovation.
“The Hindustan 2021 three-tonne class of wheeled loader has been our legacy product for over 50 years with very strong demand recall,” he said. “This is from the new and existing customers engaged in mining, quarrying, and other industry segments like ports.
“Based on the newer application requirements, Caterpillar India has always
looked to reposition the product with modifications. This was first characterised through the Hindustan 2021E.
“Catering to the new emission norms, we have equipped the machine with a BS V electronic engine, delivering better torque and penetration power to work on bulk material heaps easily.”
Caterpillar India showcased its updated 20-tonne class 320 DC GC hydraulic excavators which, according to the company, consumes just 11–13 litres of fuel per hour. It features new cooling systems that weigh 25 per cent less and use 50 per cent less power, optimised engine speed, a boom regeneration valve, and an improved hydraulic pump to deliver top performance.
The two power modes help manage fuel consumption. Power modes deliver maximum productivity in very high-demand applications, like truck loading and trenching. The Eco-mode automatically matches engine speed and hydraulic power to demand the highest fuel efficiency levels in any application.
The 320DC GC comes with an optional 1.8m³ general duty bucket, plus the option of 1m³ heavy-duty bucket.
The excavator features improved visibility. The glass area of the cab has increased by 25 per cent, giving the operators improved worksite productivity and safety. The convex profile glass profile enhances productivity. The low-effort joystick reduces safety features safety, further reducing blind spots.
Hyundai India is developing a long-term business plan for the Indian market.
“We plan to meet the emerging demand from the Indian construction sector through a wider range of equipment solutions. The market continues to be significant for us,” Hyundai India managing director, Seong Woo,
Shim said. “This is because, during 2024, Indian operations accounted for a third of our global sales.
“We are working on newer levels of longterm preparedness to address the evolving market requirements. This would essentially be through expanding the facility in 2025 for newer product verticals, making the Pune facility further world class in its entity.”
Hyundai India senior vice president, Rajeev Chaturvedi, said the company is prepared to meet rising national excavator demand.
“Hyundai India has an active fleet of 50,000 excavators in India. This gives us strong brand recall in a market with high levels of competition,” he said.
“We have a very strong position in the main 20-ton class demand segment with the R 215, 215L, and RT 230. We have special products for well digging, like 245 LR, a 24-tonne class excavator. These are in high demand from states like Maharashtra and Karnataka.
“Further, there are products to meet the quarry operations demand, even for bigger capacity quarries. Moreover, we have higher capacity products like the 36-ton HX 360 for mining and bigger quarries.”
LiuGong India exhibited the 22-ton 922 FE tracked excavator as part of its quest to expand its presence in the electric vehicle (EV) segment for construction equipment.
The machine features a 1m³ HD/1.25m³ general-purpose bucket for the infrastructure and quarry sectors. The 922 FE can be used to work in stockpiles to arrange the processed aggregates stocks and do the heaping job. It can also be used extensively for loading manufactured sand into rigid dump trucks. The 922FE’s electric system features an IPMSM motor that delivers a rated power of
JK Tyre & Industries had a major presence.
140kW, powered by an AC 380V working input voltage. Power is supplied to the excavator through a cable attached to a rotating pulley mounted on a temporary lattice tower. The cable draws power from the local grid arrangements. LiuGong provides the equipment set.
Continuing its new business strategy for EVs, Propel Industries (Propel), a south Indian crushing and screening manufacturing company, exhibited its new 470 eTR tractortrailer truck.
“The product is part of our new business quest for diversifying into the trucking EV business in India,” Propel president of EV Series marketing and services, Siddharth Kirtane, said. “Our strategy is to tap into the rigid dump trucks and heavy-duty trucks segment, which has not been addressed.”
“Our first initiative in this direction was launching the 6x4 45-ton GVW and 8x4 60-ton GVW tipper trucks for the mining and quarrying industries. Buoyed by the highly encouraging performance results of the products, with almost 80 units sold for various haulage applications, we have introduced the 470 eTR.”
Italian crushing and screening attachments manufacturer MB Crusher is upbeat about the Indian market's business prospects.
“Our business has been highly encouraging in India, and it continues to gain momentum,” MB Crusher India chief executive officer, Piero Guizetti, said. “Seeking a further foothold in the northeastern Indian market across seven states, we have appointed two dedicated dealers for our range of crushing and screening attachments. India has always
been among our important markets, and we have now drawn up long-term investment plans for the country.
“We are positioning our HDS line of shaft screens. This specialised attachment can easily screen wet, damp and organic material. This can also be used to crush soft materials like coal.
“The HDS 320–323 have been successfully used in Indonesia for coal crushing with close to 100–120 installations. The attachment is compatible with 20- and even for 14–45-ton-class excavators of any make. It can select materials directly on-site. This is suitable for large and small construction sites.”
The HDS shaft screens’ attachment is easy to maintain, and its optimal design and large loading volumes deliver high and optimal production rates.
“Based on the kinds of materials to be screened, the process to replace the shafts can be done easily in less time,” Guizetti said.
MB Crusher also highlighted its MB LS220 S2 and MB S14S4 screening buckets. The attachments can be fitted with excavators in the 9–20-ton class. The equipment attachment can be used before and after the crushing phase. The product, designed to pick up process material easily, features a loading strain control system that reduces strain on the attachment while loading the material.
The MB Crusher Bucket BF 90.3 S4 is designed to be an attachment for 21–32tonne excavators and is popular in India. Guizetti said the buckets are well suited to single-stage crushing of material in quarries, landfills, and urban and non-urban construction sites. The bucket’s manganese plates ensure minimal wear and tear during the product’s lifecycle.
Indian crushing and screening major Hailstone Innovations launched its new 200-tonne-per-hour track scalper and 350-tonne-per-hour cone crusher range. Its other new launches include the JC180 400 tonnes per hour jaw crusher.
“Our emphasis has always been to provide solutions to the customers for their. The new launches from our stable are testimony to that,” Hailstone Innovations managing director, RJ Williams, said. “Backed by the support of industry experts, we will continue to make larger interventions in the product design of our wheel-mounted plants.
“This will make the plants more mobile for their further ease of transportation and setting, as increasingly demanded by the present application needs of the road contractors and quarry owners. The higher performance of the machines will continue to be fully warranted through our complete in-house fabrication facility, which utilises high-tensile steel and finite element analysis.”
Generators and engine manufacturing company Greaves Cotton announced its foray into construction equipment, exhibiting new scissor lifts, boom lifts, hydraulic rock breakers, levellers, and micro levellers. It also displayed lever parts and wire harnesses from its acquired Excel Control business.
The business supplies Indian off-highway equipment industry majors, including Tata Motors, Ashok Leyland, and Mahindra.
“We will offer high-end quality products at cost-competitive prices, backed by superior product support,” Greaves Cotton head of sales, Piyush Bhargava, said. “Through our technical collaboration, we also offer 300kg, 500kg, and 1700kg hydraulic rock breakers.”
Action Construction Equipment (ACE) displayed its new AX 124 backhoe loader, featuring a vibrant olive-green colour scheme.
“The machine is powered by a 74hp BS V engine ... delivering 15 per cent better fuel efficiency and higher torque than competition products,” ACE head of the backhoe loader segment, Manish Handa, said. “The product has been given a complete facelift, including a newly designed cab. It is also more operatorfriendly and offers very high reliability and performance. We will soon introduce 90 and 49hp backhoe loader models with BS V engines, and continue to upgrade our backhoe loaders to meet evolving demand.” AB
Tirupati Stone Crusher said its state-of-the-art crushing plants, supplied by a major global quarrying equipment manufacturer, have enabled the company to supply huge quantities of aggregate for an Indian expressway megaproject.
Rajasthan state-based Tirupati Stone Crusher has been busy leveraging Metso's technology to meet the demanding aggregate requirement for the Delhi–Mumbai Expressway megaproject in India. The company is achieving signi cant production milestones, with ve Metso plants, exceeding 100,000 tonnes per month.
Tirupati Stone Crusher accelerated its growth in 2018 after acquiring its rst Metso Nordwheeler (NW) Rapid plant. Metso’s swift installation and reliable performance were pivotal, enabling Tirupati Stone Crusher to commence production in 14 days, far quicker than the industry standard. This eye-catching ef ciency accelerated project timelines and signi cantly bolstered revenue streams.
The versatility of the Metso NW Rapid plants is proving invaluable. They effortlessly adapt to Rajasthan’s varied rock abrasiveness, a challenge mitigated with robust support from the Metso team. From granular sub-base to speci c aggregate sizes, Tirupati Stone Crusher met every construction requirement.
With nearly 800,000 tonnes of aggregates produced in two and a half years, covering 70–80 per cent of its Delhi–Mumbai Expressway megaproject commitment, Tirupati Stone Crusher continues to set benchmarks in the industry. The company’s steadfast reliance on Metso’s hassle-free technology underscores its commitment to quality, ef ciency and seamless operations.
“We had a [project] target of 50,000–60,000 tonnes per month. After the [plant] upgrade and testing, we tried our best
and achieved 100,000 tonnes in a month,” Tirupati Stone Crusher owner Manoj Sharma said.
“Production is faster, which increases income. Metso works ef ciently, and the crusher was installed in the blink of an eye. With other brands, it can take up to three or four months Metso completed the project in 14 days, and we were able to start production.
“This is a huge achievement by Metso. When your production starts earlier, your income also comes in earlier.”
Metso India general manager of systems execution, Sanjeev Raina, said the original equipment manufacturer focused on supplying reliable equipment to support the “prestigious project”.
“Tirupati Stone Crusher got a challenging order, and the Delhi–Mumbai Expressway is a prestigious project for the government of India, so it’s a time-critical project,” he said.
“We supplied a two-stage wheeler plant to the customer, including an NW106 Rapid jaw crusher and an NW220GPS Rapid cone crusher.
“We also added some features and developed the [Tirupati Stone Crusher’s] old NW220GPD [plant], relaunching it after the upgrade as an NW220GPS Rapid. These additions have greatly improved reliability, ease of maintenance, and site operations.”
Raina said the Metso plant set-up is versatile when it comes to production.
“If a customer needs anything for road construction, like GSB [granular sub-base] or -40mm, -20mm or 8–10mm, they can produce it with this plant,” he said.
Sharma said the adaptability of Tirupati Stone Crusher’s Metso plant con guration in the company’s home state conditions has been impressive.
“Every 50km, there is a change in the abrasiveness of the rocks. Because of this challenge, Metso’s support was the most important thing,” he said,
“For the Delhi–Mumbai Expressway, we worked in six to seven packages. People say that [a plant throughput of] 250 tonnes per hour can only produce 50,000–60,000 tonnes of aggregates monthly. We produced 107,000 tonnes in one month with the NW Rapid plant at Runjhi.
“I only install Metso crushers. It’s hasslefree work. You install the crusher, and it works in auto mode. Metso provides service, sales and spares support, and whatever else you need.
“You only have to invest money, produce, sell, and keep earning. My overall experience with Metso is good, and the Metso team, from sales and service to the backend, is uni ed.” AB
The Delhi–Mumbai Expressway
The expressway stretches over 1350km through ve states –Haryana, Rajasthan, Madhya Pradesh, Gujarat and Maharashtra – and is set to be fully completed by 2026. It has eight lanes, including a separate lane for electric vehicles, and can be expanded to 12 lanes at peak times.
It starts at Gurgaon in Haryana and passes through Jaipur and Sawai Madhopur in Rajasthan. It then passes through Ratlam in Madhya Pradesh and Vadodara in Gujarat, ending in Mumbai in Maharashtra. On completion, the megaproject will halve the travel time between Delhi and Mumbai from 24 to 12 hours. The speed limit on the expressway is 120km. The Delhi–Mumbai Expressway will also signi cantly enhance road connectivity between different Indian states. India’s Ministry of Road Transport and Highways has also approved an expressway between Chennai and Surat that will connect to the Delhi–Mumbai Expressway at Surat.
The global o -highway equipment tyre market continues to seek sustainable growth.
In 2024, BKT consolidated and strengthened its position as one of the leading off-highway tyre manufacturers. It maintained a strong presence in the world’s major markets while also paving the way for new opportunities in other countries, not least through the appointment of two new original equipment manufacturer (OEM) managers for Asia-Pacific, Rishi Raj Singh, and Africa and the Middle East, Aniruddha Pandit.
BKT has also made further strides in innovation and technology through its research and development (R&D) to create more innovative products and sustainability initiatives that add to BKT’s position within the tyre industry.
A BKT spokesperson said the company’s EARTHMAX SR 50 and SR 53 lines, sized 26.5 R 25 and 29.5 R 25, respectively for loaders performing loading and grading operations in quarries or, as in the case of the EARTHMAX SR 53, for dozers and low-profile dump trucks, remain popular.
Both are All-Steel radial tyres designed to be fitted on vehicles operating in harsh conditions in rocky environments, including tasks in underground mines and at demolition sites. Their special compound is particularly cut-resistant, ensuring greater durability.
The spokesperson said BKT’s ROCK GRIP E4 tyre in the sizes 18.00 R 33 and 24.00 R 35 for rigid dump trucks is popular choice among quarry customer for on-site hauling activities. For use in tighter quarries and on more winding routes mainly fitted on articulated dump trucks, there are the EARTHMAX SR 41 tyres, typically in sizes 26.5 R 25 and 29.5 R 25 (E-4), which are ideal for transport, loading and levelling applications. The latter provides excellent puncture resistance and prolonged durability thanks to its steel construction and unique block design.
Tyre employment varies mainly according to the terrain type and conditions, which aligns with BKT's determination to respond to the specific needs of customers and operators.
“BKT remains focused on developing innovative, high-performance solutions as a response to the increasingly challenging industry needs, typically characterised by demanding terrains and complex operations,” the BKT spokesperson told Aggregates Business
“BKT's product portfolio, comprising more than 3600 SKUs [stock keeping units], includes purposefully designed and engineered tyres to meet such challenges. These are, therefore, highly durable and resilient to curb the potential risk of punctures or tears.
“This is exactly what BKT will leverage at bauma 2025 [Munich April 7–13], showcasing solutions suitable for various quarry applications, such as high-load capacity tyres or special tread patterns to provide greater traction and stability. In other words, it is a blend of innovations bringing together advanced performance, sustainability and digital technologies, thus responding to the needs of an increasingly competitive technological market.
“At AGG-1 [St. Louis March 25–27], we will showcase BKT’s EARTHMAX range of products at booth 408. Visitors will have the chance to discover EARTHMAX SR 45 M, an All-Steel radial tyre specially designed for rigid haul trucks; EARTHMAX SR 49, engineered for loaders and dozers operating in mining applications, loading and dozing activities. Finally, EARTHMAX SR 51 is ideal for severe operations requiring added cut resistance, sidewall protection and exceptional traction.”
The BKT spokesperson said the firm’s tyres have proven to be a game-changer for the US aggregates industry, performing in some of the most demanding environments. Known for being high quality, durable and reliable, the company’s tyres help operators maximise efficiency and reduce downtime in quarries and construction sites.
BKT plans to remain a trusted partner for tyre solutions as the industry evolves.
“Generally speaking, in 2024 the US tyre industry saw a fairly stable direction, although being influenced by a number of different factors according to the specific sector,” the BKT spokesperson said.
“As far as the market for mining tyres is concerned, forecasts suggest a modest growth in 2025, mostly driven by an increase in mining operations in fields such as aggregates, metals and coal, which will contribute to a greater demand for specialised tyres that can handle rough terrain and heavy loads.
“BKT’s presence in this market will remain strong, in line with this trend.”
At its carbon black plant in Bhuj, Gujarat, India, BKT has initiated a pallet recycling programme to enhance sustainability and resource management.
The company has significantly reduced plastic consumption and procurement needs by reusing and recycling plastic pallets for storing carbon bags.
BKT’s focus on sustainable practices is evident through this initiative, which supports the circular economy and reduces plastic waste, improving operational efficiency and contributing to environmental conservation.
As a responsible tyre manufacturer, BKT is the sole company in the sector with an in-house carbon black production facility able to fulfil 100 per cent of this requirement, ensuring self-sufficiency in this critical raw material.
“For the future, we have very ambitious growth and expansion plans to strengthen our extensive presence in the agricultural,
industrial and earthmoving sectors,” the BKT spokesperson said. “We have started to focus on expanding the company in the OEM channel, leveraging a well-defined plan that is apt for exploring new markets and new business and development opportunities.
Recent years have seen BKT has adopt a holistic approach towards sustainability, extending its commitment to sustainable innovation and social and corporate environmental responsibility. This has brought the company in line with the international standards of the Global Reporting Initiative (GRI), also verified by Bureau Veritas.
The company spokesperson said BKT has reduced non-renewable electricity consumption by 26 per cent and increased the use of renewable energy by six per cent, which has cut 28,000 tonnes of CO2 Moreover, 99 per cent of the waste generated has been recycled or reused, resulting in a 33 per cent increase in recycling and a 22 per cent reduction in plastic waste. Twentyfive thousand new trees were planted, while at the same time, water offtake in waterstressed areas has been reduced by 43 per cent. In addition, more than 91,000 tonnes of renewable materials have been used in BKT’s main products.
“This commitment, along with product quality and sustainability, enables BKT to compete at the top level in both the original equipment and after-market,” the company said.
BKT currently has a network of trusted distribution partners in 160 countries worldwide, all of whom help the business pursue its innovation plans following customer and end-user demands.
“Over the next 10 years, the off-highway tyre industry will experience significant evolutions in materials used and integrated technologies due to introducing new solutions related to digitisation and artificial intelligence,” the company spokesperson said.
“In particular, material research and innovation will continue to focus on increasing strength, durability and performance under extreme and complex usage conditions, as we can find in the mining and quarrying industries. Using recycled materials and greener processes will increasingly be a priority, reflecting corporate [and global] trends toward enhanced sustainability.
“Digitisation will likewise play a crucial role with the arrival of real-time monitoring systems on the market, enabling more efficient tyre management through sensors and the IoT [Internet of Things]. Collecting real-time data on pressure, temperature, wear status and other variables will provide operators with accurate information on tyre status, improving fleet management and optimising costs.”
Triangle Tyre, one of the biggest Chinese on- and off-the-road (OTR) tyre manufacturers and the world’s fourth-largest OTR tyre maker, told Aggregates Business that it expects a very busy 2025 as it looks to continue building on its strong global market presence.
Triangle Tyre will launch its first-ever Tire Performance Monitoring System (TPMS) at the world’s biggest off-highway machinery and linked technology showcase.
The company, which has its headquarters in Weihai, in China’s Shandong province and whose European subsidiary is based in Milan, Italy, is unveiling 11 new products for OTR customers in Q1 ahead of its appearance at bauma 2025.
Triangle Tyre’s appearance at bauma 2025 continues its long association with key global off-highway equipment industry exhibitions, including CONEXPO/CON-AGG (Las Vegas), MINExpo (Las Vegas), Intermat (Paris) and bauma China (Shanghai).
Triangle Tyre’s OTR director for Europe, Luca Mai, and marketing director for Europe, Angelo Giannangeli, estimated that the company has a double-digit market share in the European OTR market. It offers a range of options, including a 63-inch rim and a 1–4-star (load capacity) rated OTR tyre range. Triangle manufactures tyres for wheeled loaders, articulated dump trucks (ADTs) and rigid dump trucks (RDTs) for quarrying customers.
When asked about the company’s most popular OTR tyres for quarrying customers, Mai said Triangle Tyre’s 49-inch tyre for 100-tonne RDTs is a big hit in Russia and other key regional markets.
Mai and Giannangeli said the performance and longevity gap between premium and budget OTR tyres, the latter including those historically offered by Triangle Tyre, has significantly closed in recent years. They say more and more European quarrying customers are expressing interest in the company’s range for their site fleets.
Mai said it includes a multi-national building material major that has fitted many Triangle Tyre products on wheeled loaders, ADTs and RDTs operating at various European quarries. The company also offers custom-made OTR tyres to suit specific application needs.
Mai said that Triangle Tyre has for many years proudly received Caterpillar’s Supplier Excellence Recognition for the quality and
performance of its tyres fitted on machines manufactured by the world’s biggest off-highway machine maker. The company’s tyres are also supplied on machines made by other major OEMs, such as Komatsu, Hitachi, Hyundai, Volvo Construction Equipment, CNH, Develon, Terex, Liebherr and Sany.
Triangle Tyre strongly emphasises sustainability. Mai said the robustness of the brand’s OTR tyres, enhanced by continuous R&D and rigorous testing, helps extend their life, lowering quarry operators’ total cost of ownership (TCO).
The company has a large, state-of-theart manufacturing facility in Huasheng, Shandong province, producing around 400,000 OTR tyres annually.
Triangle Tyre was established in 1976, and its global market presence accelerated greatly after its 2016 listing on the Shanghai Stock Exchange. Triangle Tyre’s distribution network spans over 180 counties. Its sales and technical services branches are in China, Russia, the US (North America), India (South Asia), Singapore (Southeast Asia), Dubai (Middle East and Africa), Panama (Latin America), and Australia (Australasia and New Zealand). In addition, its Milan site serves customers in the European market.
With more than 30 years’ experience in the global OTR tyre industry, Mai said he is excited by Triangle Tyre’s market offer and growth plans.
“Our range is equal to the traditional premium OTR tyre manufacturers. From smaller construction to underground mining, we can fit our products on machines and quickly adapt to the market's needs,” he told Aggregates Business. “We are increasingly pushing to improve our OTR tyres. It is also very important for customers in the OTR tyre market to be able to monitor performance. As such, we are delighted to introduce our new Triangle TPMS officially at bauma 2025.
“We have been developing it for several years; it mainly monitors tyre pressure and temperature but also has a GPS tracker that can give useful information, store it and make it accessible via iCloud. I believe our device will be one of the best in the market. It is particularly aimed at big quarry and mining customers.
Giannangeli said that Triangle is “increasingly emphasising the OTR side of our business”.
“In 2024, we took all European OTR customers to China to see our production plant,” he said. “Speaking to them and spending time with them has reassured us that the Triangle brand has a premium tyre perception.
“The technological advancement in China has been enormous,” Mai said. “It’s the same when it comes to carbon emissions. In the last few years, the country has introduced strict policies to decrease them. One of the first in the world to do this.”
Mai said that changes to machine specifications and the customer operation of their machines are challenging OTR tyre performance and are among the key trends in the European quarrying market.
“The speed of load and carry operations has increased. Also, wheeled loaders that only had to transfer material short distances to a haul truck increasingly have to transport it longer distances on-site,” he said. “This places heavy pressure on the wheeled loader tyre for much longer. You need to find a new spec for your products. We sell more wheeled loader OTR tyres than ADT and RDT tyres combined – so it’s a crucial part of our OTR tyre business.”
Giannangeli said the Chinese manufacturer’s products had become increasingly in demand worldwide.
“The European off-highway market is increasingly asking for Chinese products, including OTR tyres, where the quality has become much better and more competitive than it used to be,” he said.
“We use the latest technologies, and our R&D intensively works to improve the expected performances of our tyres.
“Our modern manufacturing plant guarantees stable quality and high standards, and customers fully understand our product value.” AB
The All Steel radial tire EARTHMAX SR 53 is designed to provide traction and stability in any situation. As part of the OTR range, it has been developed for dozers, loaders, and low-profile dump trucks (LPDTs) moving through underground pit tunnels and offers excellent performance even in tight spaces. EARTHMAX SR 53 is extraordinarily resistant against cuts and punctures, so no worries on rocky grounds or debris on the site. Providing outstanding performance and durability – no matter your needs, the tire will handle it.
April 7th-13th, 2025 Hall A6 Stand 215 BKT’s latest solutions at
Volvo Construction Equipment has made a splash in Southeast Asia to boost customer e ciency, productivity and safety.
Volvo Construction Equipment (Volvo CE) has celebrated its biggest launch since Volvo Days 2024, unveiling its new-generation excavators, articulated haulers, wheeled loaders and more. The rollout of the new-generation excavators is already underway in Southeast Asian markets.
The first five excavator models in the new generation range – EC210, EC220, EC230, EC300 and EC360 – have been offered for sale across the region since January. Singapore hosted the first launch, with a customer event attended by more than 100 people on January 17.
The flagship 20-tonne new generation EC210 model was displayed alongside the L120 electric wheeled loader at the event. Further launch events are planned across the region, where customers can see the new range up close and in person.
The launch of the new generation excavators aligns with Volvo CE’s ‘Our EDGE to Success’ framework in Asia. The framework emphasises the company’s commitment to delivering customer success through competitive products, excellent services and a dependable distribution network.
The EDGE concept was first introduced during the Region Asia dealer conference
in September 2024 to underscore the importance of collaboration among Volvo, its dealers and its customers.
The Volvo engine in the new generation excavators provides higher power and torque to maximise performance, with 10 work modes for effectively using engine power across all segments and applications. The powerful engine, matched hydraulics and faster cycle times on a new generation EC210 can boost customers’ productivity, according to Volvo CE.
Due to the robust machine design and heavy-duty configuration, the new generation EC210 can be used across all
segments, no matter the application. The machines also increased the on-site safety for operators with three-point side access, emergency shutdown, rearview camera and anti-slip plates.
Operator comfort is ensured with more precise controls, a rollover protective structure (ROPS) cab, an ergonomically designed human–machine interface, and an improved operator environment.
The new generation Volvo excavators feature improved hydraulics that dramatically reduce fuel consumption. This is done by regulating engine speed and hydraulic flow rate based on the task at hand, leading to up to 15 per cent fuel economy improvement and lower operating costs.
Minimising downtime is key to protecting customers’ return on investment. The new generation excavators are designed for easy service access and longer service intervals to drive down maintenance costs and increase machine availability. A fuel shut-off valve also facilitates fuel filter changes, avoiding fuel spillage and further reducing costs.
“This new generation excavator series represents years of collaboration and innovation. We are excited to introduce these machines to customers in Region Asia, addressing the specific demands of the regional construction sector,” Volvo CE’s president of region Asia, Tomas Kuta, said
“Our customers are facing unique challenges, and these machines are designed to help them stay competitive in a rapidly changing market.” AB
Launching the new generation excavator series aligns with Volvo CE’s ‘Our EDGE to Success’ framework.
Norwegian contractor Grønseth Maskin AS purchased its first Hitachi wheeled loader in 2011 and has clocked over 11,000 hours. The contractor is now supported by the latest model, the ZW310-7, which is already making its mark in Gjemnes.
Oddmund Grønseth started his company at just 19, with a tractor and a few ditch-cleaning jobs, and Grønseth Maskin AS has expanded rapidly over the years. His sons, Kurt and Ole Jonny, run the business today, though Oddmund still operates machinery.
He said his first Hitachi loader, the ZW310, was purchased 13 years ago from Norwegian dealer Nasta AS.
“It met our needs perfectly, was well-priced and has required very few repairs. It’s been incredibly reliable,” he said. “It’s got many good hours left in it.”
Despite adding the ZW310-7 over a year ago, Grønseth Maskin AS continues to rely on the trusty ZW310.
“We need both wheeled loaders,” Grønseth said.
“The 25-tonne size is crucial for loading our trucks effectively, both in height and capacity.”
The older wheeled loader remains active at Høgset, while the ZW310-7 supports operations at the crushing plant on Averøya.
Grønseth has taken the new ZW-7 machine for a spin and noted some significant improvements.
“The cab is much quieter and the joystick control is great for comfort,” Grønseth said. “But I’ve always liked the old loader, too – it’s still a great machine.”
When he reflected on the most significant changes since he started working in 1970, Grønseth pointed to advancements in machinery.
“Back then, many machines didn’t even have roofs, and operators were freezing,” he said.
“The progress in technology has been incredible.”
Bucket attachments are helping construction material providers open up a whole new world in recycled products.
Bucket attachments can often be overlooked pieces of equipment, but they can solve the productivity jigsaw that is so often faced by the modern quarry.
If paired correctly with the machine, bucket attachments can significantly benefit construction material providers. The chance to increase productivity around the job site, even when it seems like a small improvement, can considerably boost a company’s bottom line.
More businesses are considering bucket attachments as potential additions to increase fleet productivity.
ALLU’s research and development project manager, Antti Rautamies, told Aggregates
ALLU was established more than three decades ago.
Business that the company has seen demand from emerging industries like recycled materials providers.
“I think that comes from increasing demand, as there is a need for recycled material that will take place more and more, especially as governments begin to look at this more,” he said.
“Contractors will need to adapt to this more and more. Recycled materials will have to be used, and that is where we’re at with our products.”
Established more than 35 years ago, ALLU has become a recognised name among bucket attachment manufacturers. ALLU specialises in serving customers in the 15–30-tonne excavator and wheeled loader range but has the product line to serve base machines starting from 1.5 tonnes up to 120 tonnes.
Rautamies said the company has been able to tailor its offerings to suit recent changes in key sectors in the global market.
“What is new is that we are targeting the small end because that is where more and more customers seem to be these days,” he said. “Not so much in the aggregates sector, but for soil and recycled materials or demolition waste contractors, that is what we’re seeing.“Being able to work with finer fragments and particles is something that is becoming requested more and more.”
One such example is the release of ALLU’s DC-Series and DL-Series screening buckets, which are designed for compact machines such as wheeled loaders and excavators.
The ALLU DC-Series is versatile enough for many applications but particularly well suited to mini excavators. A DC-Series Screening Bucket is capable of screening,
separating and crushing many materials including soil, compost and biomass.
The ALLU DL-Series Screening Bucket is capable of handling materials like sand, gravel and demolition waste due to its versatility. It provides an all-in-one solution to screen, crush, aerate, mix and load as a one-step operation. The DL-Series Screening Bucket has three sizes to suit excavators, wheeled loaders and skid steers.
““The smaller ALLU screening bucket ranges were launched because we wanted to bring ALLU screening power for all-sized base machines,” Rautamies said.
“It can apply to many industries and applications, including aggregates. In certain cases where it handles smaller amounts, it can act as an alternative method to a screening station or complement an existing set-up.
“I think the demand for these products has always been there, but I think more customers are becoming aware of different methods and the cost of different methods.”
One of ALLU’s recent developments has been the introduction of the ALLU Variable Drum, which features a shaft and easy locking system that enable operators to make quick blade replacements or adjust output sizes. ALLU designed the Variable Drum so these changes could all be made within hours, which gives any construction materials provider extra adaptability depending on their application.
For those working with a single ALLU Transformer screening bucket, the ALLU Variable Drum’s ability to change the frontend set-up can enable them to meet multiple job demands. The Variable Drum features a two-bolt drum attachment that enables
Top: ALLU has a wide range of screening bucket options for customers.
Right: The ALLU Screening Bucket range provides operators greater versatility from their machines.
easy changes and eliminates the need for operators to access the drive compartment, which saves on labour time and increases site safety.
“We’ve been highlighting since last year this VD [Variable Drum] that allows operators to easily change the drum or the screening or crushing plate from one to another,” Rautamies said.
“That is something that we have been pushing hard because it can work across many applications and enables the front end to have different set-ups easily.”
ALLU is likely to introduce several key products throughout the year. Rautamies said many of these new products were inspired by ALLU’s customers.
“Most likely, during the year we are going to be launching focused products to certain applications, some of them are related to recycling,” he said. “They will be clearly targeted to a specific need based on what we have learned from our customers.”
There has recently a greater push from construction material providers and original equipment manufacturers (OEMs) around the world to work within the recycled materials space.
OEMs like MB Crusher are beginning to focus heavily on the recycled materials sector and the clients who work in that space.
“Recycling materials like concrete isn’t just a responsible choice; it represents a fresh perspective on construction. It opens doors to new opportunities, cuts costs and offers an eco-friendly solution,” MB Crusher said.
“Concrete recycling is a key element in the process of ecological transition, bringing environmental benefits through proper management and reuse.”
As part of MB Crusher’s commitment to recycled materials, it has increasingly worked with businesses to implement these solutions into their operations.
An Italian client said it has saved time and money since using MB Crusher’s MB-C50 crusher bucket. The Italians ran the bucket on a mini excavator during a demolition job of a family home, which helped them recycle material further. The waste material from the old house was re-used on-site to fill the foundations of the new building and adjacent courtyard.
Elsewhere, a Spanish client has used MB Crusher’s BF90.3 bucket to expand its business. Before using MB Crusher’s equipment, the company had to send all its waste material to a landfill, which incurred high transport and disposal costs.
But thanks to MB Crusher’s BF90.3 crusher bucket, waste material can now be recycled on-site into reusable products for future construction projects.
“With MB Crusher, you do it directly on-site with your own machinery, cutting both costs and environmental impact,” MB Crusher said. “Thanks to recycled aggregates, you’ll always have material ready for immediate use.” AB
Volvo Construction Equipment has bolstered its suite of safe and productive solutions for the toughest worksites with a new line-up of articulated haulers.
Volvo Construction’s seven new generation articulated hauler models have revamped updates to the already proven A25, A30, A35, A40, A45, and A60 units.
The company has also introduced a new class machine, the 45-tonne A50. Designed to meet customers’ evolving needs, this range makeover marks the next wave in Volvo CE’s largest-ever product roll-out.
“Our haulers have always given our customers exceptional off-road performance, outstanding operator comfort and maximum uptime,” Volvo CE product manager for sales region Europe and International, Per Trozell, said.
“But now that we have updated them with our most exciting features yet for effortless operation, the best just got better.
“Our ability to maintain a world-leading position in this segment is a testament to our unwavering commitment to excellence, with quality, safety and environmental care firmly at its heart.”
Many new features have been included to help maximise productivity across the most challenging quarrying, mining and construction projects.
The Volvo drivetrain with Terrain Memory provides fuel efficiency without compromising power. It can also identify and remember any slippery road segments. Automatic drive combinations with 100 per cent differential locks and all-terrain bogie and hydro-mechanical steering also combine to provide unmatched traction, stability and precision control.
Volvo Dynamic Drive, with its predictive gear selection that adapts to operating conditions, downhill speed control function, and leading braking systems, further enhances efficiency, safety and comfort.
Volvo CE’s updated articulated haulers are equipped with in-cab information which is conveniently displayed on just two screens. This helps operators stay on top of what is happening on-site and to make informed decisions from the cabin,
The interactive, integrated Volvo Co-Pilot display offers control over essential functions such as media, camera settings, climate control, and machine status. This, combined with the dynamic instrument cluster positioned in front of the steering wheel, provides vital vehicle data at a glance.
The addition of adjustable seats, Bluetooth connectivity, USB ports, storage solutions, an ergonomic gear lever, and a noise-reducing cab design are designed with the operator in mind.
The operator’s visibility is improved thanks to redesigned cab panels and wider wiper coverage, resulting in a broad field of vision. Optional front and rear cameras and a standard entrance camera, all managed via Volvo Co-Pilot, further enhance visibility.
Entering and exiting the cab is simple and safe due to the repositioned door entrance, railings on both sides, and focused lighting on the stairs and platform.
The updated range has been engineered for durability, thanks to features such as reinforced axles that can withstand heavier loads and higher torque, resulting in superior stability and strength.
Safety is also a priority, with new harness anchor points in the cab that meet WorkSafeBC and OSHA regulations and can withstand up to 22kN of force.
With simplified servicing, longer change intervals and easy component access, servicing is quicker and easier than ever, while costs are reduced. The 250-hour greasing interval eliminates the need for daily or weekly greasing, boosting productivity and reducing downtime. According to Volvo CE, its articulated haulers require less fluid volume than comparable models, reducing operating costs.
Volvo also offers flexible service contracts tailored to operator needs. This service enables operators to receive service when they need it while still maintaining their uptime.
Customers can boost the performance of their articulated haulers even further by adding solutions such as Haul Assist with On-Board Weighing. Powered by Volvo Co-Pilot, this provides real-time payload data to prevent overloading and minimise carryback, maximising productivity and reducing fuel consumption and machine wear.
Digital and advisory tools such as Connected Map, Performance Indicator, and Site Optimisation can improve traffic flow, vehicle performance and on-site logistics.
The CareTrack telematics system is designed to help boost machine uptime and reduce repair costs.
The latest generation of Volvo articulated haulers features a new software architecture that allows customers to adapt to changing needs, seamlessly incorporate future upgrades and new smart solutions, and
ensure their equipment stays updated with the latest technology.
The updated models are planned to be introduced to international markets.
A Develon rst in Scotland
Cross Civils & Construction Services, located in Aberfeldy, Perthshire, Scotland, has acquired a new Develon DA30-7 articulated dump truck (ADT).
This ADT marks the company’s first from Develon and was supplied by James Gordon (Gordons), the brand’snewlyappointed
authorised dealer for Scotland, based in Castle Douglas.
Gordons is now solely responsible for the sales and servicing of the Develon crawler, wheeled and mini/midi excavator, wheeled loader, ADT, dozer, and attachment ranges in Scotland and Cumbria, England.
Since it was established six years ago, Cross Civils & Construction Services has specialised in various markets, including civil engineering, construction, pipe supplies, aggregates, and forestry equipment. The company facilitates large construction projects and sells pipe supplies, aggregate supplies, and forestry equipment for companies and individuals.
Cross Civils & Construction Services owner Kevin Cross has been impressed with Gordons’ level of expertise and professionalism.
“David Moir at Gordons, whom I’ve known for a long time, invited me over to try out the Develon DA30-7 ADT as a possible replacement for one of the machines in our fleet,” Cross said.
“David and Gordons showed impressive attention to detail and understanding of our business needs to ensure a very quick turnaround from placing the order to delivering the new machine.
“I was convinced about the DA30-7 right from the start. It has a shorter turning circle and is very stable, with a lower centre of gravity compared to other machines of its size on the market. The permanent six-wheel contact and drive offers excellent performance on all the surfaces we work on, such as soft ground, uneven surfaces, steep
slopes, tight turns, or a combination of these difficult conditions.”
The DA30-7 is one of three models in Develon’s ADT range, comprising the DA30-7 and DA45-7 6x6 models, complemented by a new 4x4 version of the DA45-7. The DA30-7 6x6 model has a payload of 28 tonnes and is powered by the Scania Stage V-compliant DC09 nine-litre diesel engine, which provides 276kW of power.
The DA30-7 and DA45-7 models feature an articulation hinge positioned behind the turning ring to distribute weight equally to the front axle even during maximum steer articulation. This, combined with a free-swinging rear tandem bogie, ensures equal weight distribution to each wheel and guarantees permanent six-wheel contact and drive for equal power distribution and excellent performance, particularly on all types of terrain.
The forward turning point, the unique tandem bogie and the sloping rear frame collectively result strong performance in rough and soft terrain.
Like all Develon ADTs, the DA30-7 is equipped with a modern cab and self-levelling front suspension that works independently to suit ground conditions and to give the operator a truly comfortable working environment.
The DA30-7’s features a dynamic look that stands out on the work site. The machine performs well with regard to load capacity, consumption, precision control, reliability, durability, operating costs, and low maintenance requirements.
“Due to work demands, the Develon DA30-7 became an addition rather than a replacement, bringing the number of different brands in our fleet to four,” Cross said,
“We utilise the DA30-7 in every part of our business, from our civils and housing development projects to working in our quarry, where we produce sand and gravel.
“Without doubt, the DA30-7 has proved itself to be the best machine we have, and this is strongly supported by the two drivers who normally operate the machine between them.” AB
Telescoping conveyors like the TeleStacker Conveyor can be equipped with PLCs that manage radial, height, and extension movements.
Investing in quality conveyors and conveyor belting is necessary for any quarry operator looking for optimal productivity and e ciency. Thankfully, major manufacturers have a lot new to o er in 2025.
As a leading endless belt supplier to premium material handling manufacturers globally, Smiley Monroe is on a mission to help customers protect the lifespan of their whole conveyor.
With close to 25,000 conveyor belts produced annually across Smiley Monroe’s three production sites, and more than 45 years of experience in the business, the experts at the company are regularly called on to troubleshoot common conveyor issues such as belt misalignment, spillage, or material build-up. Many of these issues, which lead to premature belt wear, roller damage and unplanned downtime, can be prevented by choosing the right conveyor components at the outset.
“Many people assume the key to successful, efficient conveying is simply down to using the correct belt for the correct application, and of course, this is important,” Smiley Monroe head of product support, Chris Jones, said. “We spend time speaking to our end user and manufacturing customers about the types of material the machine will be conveying, the belt speed, the expected output, and many other factors before choosing the right conveyor belt from our wide range of stock. However, we
also believe in protecting the belt’s lifespan and achieving efficient, safe conveying over a long period, so we offer a range of complementary conveyor components.”
For example, Smiley Monroe recommends that its customers fit skirting rubber, especially at loading zones, to prevent material spillage. Such spillage creates waste and can cause material build-up and damage to other conveyor components, such as rollers, causing wear to the belt.
Choosing a skirting rubber with lower shore hardness than the belt is also important. Skipping this step can cause the skirting rubber to damage the belt’s top cover over time. Smiley Monroe stocks a range of skirting rubber to suit many applications, and supplies CNC-cut parts ready to fit alongside other rubber, PE and PU parts such as gaskets, chutes and wear liners.
Belt misalignment is another common conveying issue that can be linked to straightness or improper tensioning. After ruling out these issues, fitting a Smiley Monroe GlideTracker can help prevent future misalignment problems, increase the lifespan of the belt, minimise spillage, and maximise the conveyor’s output.
Switching to Smiley Monroe’s Polymer Rollers also offers up to 40 per cent weight
reduction compared to steel rollers. According to Smiley Monroe, the polymer rollers will not rust in dusty, wet conditions, which can create sharp edges against the belt’s running side. The Polymer Rollers are designed with a triple ‘labyrinth’ seal, and the bearings are also protected from rust, dust and moisture, which often causes steel rollers to seize and fail.
Smiley Monroe will showcase its range of flat and chevron conveyor belts, including ZIP CLIP Replacement Belts and ToughFlex, alongside its entire range of conveyor components at bauma 2025 (Hall B2.127) in April. Throughout the show, it will offer package discounts for customers who enquire about complete conveyor ‘kits’, including belts and cut rubber or plastic parts, and welcome enquiries from new and existing customers.
Mitigating stockpile segregation
Material segregation within stockpiles remains a persistent challenge in aggregate production. Consistent product quality is critical for base materials, asphalt, and concrete applications.
Superior Industries (Superior), which designs and manufactures innovative material handling, crushing, screening, and
washing solutions, has developed advanced technologies to mitigate this issue. One is the TeleStacker Conveyor, a telescoping radial stacking conveyor known for its effectiveness in addressing segregation.
“Material segregation occurs when particles of different sizes separate within a stockpile,” Superior Industries aggregate applications specialist, Michael Dunne, said. “This can lead to inconsistencies that compromise the quality of asphalt or concrete products.”
Understanding the causes and solutions to this problem is essential for producers striving to meet stringent specifications and improve operational efficiency. Segregation typically begins during stockpiling and can worsen during handling and transport. Factors such as particle size variation, conveyor design, and environmental conditions like wind contribute to the issue.
“Segregation is most pronounced in materials with a range of particle sizes. Larger particles tend to roll to the edges, while finer particles settle in the centre, leading to uneven gradation,” Dunne said, Consequences go beyond aesthetic or structural concerns. Depending on whether it’s fine or coarse particles, a segregated aggregate product may result in stiff or runny concrete mixtures, compromising structural integrity and shortening the lifespan of roads and other structures.
Preventing segregation during stockpiling is more effective than attempting to correct it afterwards. Techniques such as layering and windrowing play a pivotal role in achieving uniformity. The windrow method involves depositing material in smaller, overlapping piles, which helps distribute particle sizes more evenly.
Superior’s TeleStacker Conveyor is capable of creating layered windrow piles.
“Combining constant movement radially with telescoping capabilities of the conveyor allows for building a stockpile layer by layer with precision,” Dunne said.
“This process significantly reduces the occurrence of overrun and ensures better material blending.”
Automation has changed stockpiling processes and provided operators with greater control and efficiency. The TeleStacker Conveyor can have
programmable logic controllers (PLCs) that manage radial, height and extension movements. These automated adjustments allow the conveyor to create fully desegregated piles with minimal operator intervention.
“By customising the conveyor’s movement, operators can eliminate overrun and produce a stockpile with consistent gradation. This not only improves product quality but also reduces labour and equipment costs,” Dunne said.
Superior’s TeleStacker Conveyor has advanced automation features to ensure each layer’s size and shape align perfectly. For example, as the pile grows, the conveyor’s discharge point adjusts to minimise material freefall, further reducing segregation.
Telescoping conveyors offer advantages beyond improved product quality. They allow producers to build customised stockpiles in various shapes and sizes, reducing the need for a dozer, which is valuable for sites with space constraints.
“When producers switch to automated telescoping conveyors, they see significant
Smiley Monroe is on a mission to help customers protect the lifespan of their whole conveyor.
Preventing segregation during stockpiling is more effective than attempting to correct it afterwards, according to Superior Industries.
savings in labour and equipment use,” Dunne said. “More importantly, they gain confidence in their ability to consistently deliver high-quality products.”
Superior Industries continues to help producers meet the demands of modern construction projects by providing equipment like the TeleStacker Conveyor.
“Stockpiling may seem like a minor step in the production process, but it’s a critical link that can make or break product quality,” Dunne said. “Superior’s TeleStacker Conveyor is designed to eliminate the challenges of segregation, allowing producers to focus on what matters most – delivering reliable, top-grade materials to their customers.”
The right tools and techniques allow aggregate producers to adopt advanced conveyor technology to overcome the challenge of stockpile segregation and achieve operational efficiency.
Martin Engineering process engineer, Dan Marshall, told Aggregates Business how quality conveyor belt return-side care can improve safety and efficiency.
“The return side of the conveyor may be the most deceptively hazardous part of a conveyor system,” Marshall said.
“With long gaps between rollers and carrying no cargo, there is an extensive list of injuries inflicted on workers from the return side of conveyors in the US Occupational Safety and Health Administration [OSHA] database.
“Caused by nip or shear points, belt contact and reach-in hazards from working around a running conveyor, these injuries stem not only from a lack of satisfactory protection of both the worker and system but also inadequate training.”
Marshall said many experts attest that efficiency and safety are inextricably linked. This means emphasising safety translates to reduced operating costs and increased production.
“Clean return systems using modern equipment mean less spillage and clean-up under and around the belt, which mitigates labour costs, downtime and exposure to work hazards,” he said.
“A well-maintained belt return yields less dust and fewer fouled rolling components. It also allows for a centred belt entry from the tail pulley into the loading zone.”
‘Nip points’, Marshall said, are created where a moving element of the conveyor machinery meets another rotating or moving component. Based on common belt speeds and average human reaction times, a shovel or other tool in an entrapment situation will pull the worker using the tool in with it before the person can even let go. The same applies to loose-fitting clothing or long hair when working beside or under a running belt.
‘Shear points’ can occur when the edges of two machine parts move across or close enough to each other to cut a relatively soft material. An example is when the belt quickly passes a stationary beam or component, which can trap a limb, abrading or severing it.
“The fugitive material hazards posed around the belt return begin with the discharge at the head pulley. An insufficiently cleaned belt can cause carryback to drop along the entire belt path and spill into walkways or on the return belt,” Marshall said.
“This produces a trip hazard and a possible violation. In addition, dust can get into cracks and divots in the belt, release along the belt path, and foul gears and bearings of rolling components, causing them to seize and creating a possible fire hazard.
“Inadequate cleaning technology and tensioning systems allow carryback to collect directly beneath the discharge zone. If not addressed, material accumulates quickly until the belt runs along the top of the pile, creating carryback across the entire profile. At the same time, abrasion degrades the belt face and frays the edges. In extreme cases, encapsulation can move carryback to the inside of the belt, fouling pulley faces and causing them to slip, leading to mistracking and component wear.
“Fugitive debris on the return side of the belt can rapidly reach the tail pulley. Once caught between the belt and the pulley, these material chunks can be recycled over and over, each time putting a new divot in the belt, and gouging and fouling the pulley face. This material can be ground into fine dust or ejected from the pulley. Plows are often used to clean the inside of the belt and protect the tail pulley and belt from damage.” [Figure 1]
Marshall said there were other equipment hazards of which operators needed to be aware when operating the equipment.
“Many operators focus on cargo side issues and neglect the return side, where belt tracking should be of pivotal concern. When left unchecked, the belt can drift into the structure, causing fraying and the potential for a fire hazard,” he said.
“Moreover, if the belt is off-centre on the tail pulley, it will likely enter the loading zone unevenly and cause the cargo to be loaded off-centre, exacerbating cargo-side belt tracking issues.
“While issues from fugitive material to belt tracking can cause a number of mechanical problems, each one also represents a safety hazard. If components are not functioning at 100 per cent, there is an increased likelihood of a situation that may put a worker in danger while trying to fix the problem.
“An operation’s interests are best served by taking actions intended to prevent the mechanical problems and the accompanying potential for injury, rather than just protecting the worker from hazards that will likely be present with guarding.”
Marshall said that according to OSHA, operators should adhere to the American National Standards Institute (ANSI) standards, which recommend detailed inspections of the entire conveyor mechanism. The first step is identifying potential problems before they occur [Figure 2 A&B].
The second step should emphasise training and enforcing strict lockout–tagout procedures for any activities on or around the conveyor system.
The third step is for operators to choose the proper equipment to minimise accidents. New equipment designs dispel the myth that conveyors are inherently dirty and need constant maintenance. Marshall said that today’s equipment is safer and easier to maintain, engineered to improve production and efficiency, and designed to reduce the cost of operation.
“In the past, belt cleaners were rigid, linear pieces of hardware made out of various materials from brick to plastic that earned the name ‘scrapers’ or ‘wipers’ because that’s what they did. They had a low operational life, broke or cracked often and significantly contributed to belt wear,” Marshall said.
“Modern primary cleaners are usually mounted at the head pulley and made from engineered polyurethane, which is forgiving to the belt and splice but still highly effective for dislodging cargo. Typically supported by mechanical or pneumatic tensioners designed to meet the application’s needs, the designs require significantly less monitoring and maintenance of blade tension.
“At least one modern primary cleaner design requires no tensioning at all after initial installation. Featuring a matrix of tungsten carbide scrapers installed diagonally to form a three-dimensional curve around the head pulley, it typically delivers up to four times the service life of urethane cleaners without needing re-tensioning.” [Figure 3]
Marshall said as conveyor speeds and cargo volumes increase to meet production demands, secondary belt scrapers are often installed immediately after the belt leaves the head pulley to address dust and fines that escape the primary cleaner.
Secondary cleaners are generally equipped with spring or air tensioners that easily adjust to fluctuations in the belt. They are particularly efficient for applications that produce wet, tacky or dusty carryback.
“In most applications, normal belt wear can yield valleys and depressions in the belt,” Marshall said. “Dust and fines that get into these blemishes often remain even after passing under primary and secondary belt cleaning blades, becoming dislodged by the impact of any return idler the belt meets [Figure 4]. This causes dust and spillage in areas away from the head pulley.
“In such cases, operations may choose to install a washbox cleaning system, which combines secondary cleaners with water spray bars enclosed in a self-contained unit that captures residue and drains wastewater safely away from the work area.” [Figure 5]
Marshall said that mistracking is another concern even on a clean belt, especially for operators of long conveyors.
“Previous belt tracking systems were reactionary pieces of equipment designed to help prevent belt contact with the mainframe. However, these designs have historically experienced problems with friction heat, edge degradation and belt curling. To avoid these expensive and hazardous consequences, operators can now specify modern tracking equipment designed for the belt return,” he said.
“Shorter single-direction or reversing conveyor systems may only require a crowned roller that uses a ribbed lagging made of durable polyurethane. The moment the belt wanders off-centre, the assembly tilts to the opposing side and steers it back toward the centre.”
Marshall said some longer systems may require modern upper and lower trackers hung from the mainframe every 21–50m and on the return run directly before the tail pulley. These designs utilise innovative multiple-pivot, torque-multiplying technology with a sensing arm assembly that detects slight variations in the belt path and
immediately adjusts a single flat rubber idler to bring the belt back into alignment.
“Tail pulley protection from build-up riding on the return side of the belt using a V-Plow or diagonal plow can extend the entire system's life by minimising fouling of the pulley face that can lead to mistracking,” he said.
“Attached with dual steel crossbars bolted to the conveyor frame ahead of the tail pulley, the units employ a unique torsion
arm suspension system, which adjusts to fluctuations in belt tension to maintain consistent pressure for effective cleaning in all stages of wear. Lightly riding on the belt, the diagonal design deflects debris away in a specific direction, while the V-plow design deflects debris to either side.
“Where large lumps or broken idlers are getting on the return side of the belt, a tail protection plow designed for high impact is used, often in addition to or in combination with a return belt cleaning plow.”
Marshall said installing adequate guarding that encloses the system and has the correct
mesh size and mounting distance from the hazard also helps protect workers from fugitive material and reach-in injuries.
For systems considered ‘guarded by location’ (ie too high to reach), gates may not be needed, though most countries have standards that require guarding against falling bulk materials.
Marshall said return roller guards, though seldom seen except over roads and walkways, improve safety and meet the growing demands of government regulations. Build-up under the conveyor or on work platforms can negate the guarded by location criteria, so best practice is to guard all known hazards or eliminate the hazard by design.
“From head pulley to tail pulley, return side belt care is essential to maintaining an efficient and productive system,” Marshall said. “By installing modern equipment that helps remedy common return-side problems, operators reduce the time workers spend near the system servicing and cleaning it. This mitigates hazards, reduces downtime and improves compliance.
“In addition to resolving many mechanical problems, these improvements will help prevent injuries caused by incidental contact with a moving belt that can pull a worker into pinch and shear points. Hundreds of projects directly address return side issues using modern equipment, and operators have reported a quantifiable return on investment.
“Decreased labour hours for system cleaning and downtime for maintenance enable a lower cost of operation, translating into a return on investment in as little as
12–24 months. If an injury is prevented, the payback is instantaneous, but even without considering the cost, the improvements pay for themselves over time.”
Breaking transport barriers
Telestack, a global leader in material handling solutions, looks forward to presenting its latest innovation – the TSR40 Radial Telescopic Conveyor – at bauma 2025 (stand No FN.1219).
Designed to overcome the long-standing logistical challenges of transporting radial telescopic conveyors, particularly in regions with strict road permit regulations, Telestack said the TSR40 is set to transform efficiency, mobility and sustainability in the sector.
Radial telescopic units traditionally require complex and costly transportation methods – a they are shipped in Euroliners or containers, assembled on-site with cranes, and require additional labour for set-up.
“The TSR40 eliminates this issue entirely,” Telestack international sales manager, Carl Donnelly, said. “Unlike conventional radial telescopic units, it can be transported just like any standard RORO Tracked Mobile Unit.
“With transport dimensions of just 3m [9ft 10in] width, 3.5m [11ft 5in] height, and 23.2m [76ft 5in] length, it seamlessly navigates road networks, especially in areas with stringent restrictions, such as Europe.”
The TSR40 leverages the very best of Telestack’s technology. Its integrated PLC stockpiling system helps to ensure material quality is maintained throughout stacking, minimising segregation, degradation, contamination and compaction. Like its counterparts in the radial telescopic range, the TSR40 delivers up to 30 per cent larger stockpile capacity than traditional fixedlength conveyor systems while also requiring minimal civil works or planning permission.
Its lattice frame structure provides strength and enables fully automated stockpiling from secondary crushers, screeners and fixed conveyors.
Another feature is its all-electric drive system. In a world shifting toward greener operations, Telestack is a leader in low-emission, energy-efficient solutions. The TSR40 is equipped with an integrated dieselelectric generator, allowing it to operate entirely on electric power. If a three-phase power supply is available on-site, operators can further reduce their reliance on diesel, significantly cutting fuel consumption and minimising carbon footprint.
“With Europe spearheading the transition to electric-powered equipment due to increasingly stringent engine regulations, the TSR40 is a perfectly timed innovation,” Donnelly said. “Telestack has been designing and delivering electric-powered conveyors for over 30 years – long before sustainability became a widespread industry imperative.”
Original equipment manufacturers (OEMs) like Telestack are at the forefront of driving the move towards sustainability, delivering solutions that consume less fuel while moving more material. AB
As Aggregate Industries’ managing director of aggregates, Kaziwe Siame Kaulule is playing a key role in further enhancing the UK building materials company’s approach to circular construction, health and safety, and producing a more skilled and engaged industry workforce for today and tomorrow.
Kaziwe Siame Kaulule smiles broadly when talking about Ian White, known as ‘Speedy’, who left a lasting impression on him during an announced visit to one of Aggregate Industries’ quarries in the English Midlands.
“I decided to show up at this site around 4.00pm and found Speedy cleaning the workshop. I told him I found it very interesting that he was doing what he was doing when everyone else had clocked off,” Kaulule said.
“He then said something profound, ‘The job’s not done until all the day’s debris is swept from the floor’. That showed me the level of dedication he had to his work.”
Kaulule shared another experience, this time with a logistics shovel driver, which had a significant effect on him.
“I also met a logistics shovel driver at a company volunteering event,” he said.
“Gary Howell had been driving a shovel for 20 years, and I asked him what else he might want to do. He said all he wanted to do was drive a shovel.
“He said, ‘It’s the most mentally stimulating job you can have’. When driving, he said he was always thinking about whether there was someone around him to avoid when moving material and how he could work the most efficiently between different-sized material stockpiles.
“At the end of the workday, he asks himself, ‘What did I do today? What do I have to do tomorrow?’ Some studies show that shovel loaders thinking like this are 25 per cent more productive than ones that don’t. In a wider context, this type of thinking and planning is what all great leaders need to be doing.
“I get more inspired by meeting people like Speedy and that logistics shovel driver than any PowerPoint presentation. The teams that work in a quarry and walk the workshop floor are salt-of-the-earth people. They will tell you straight what is going on.
“I visit a quarry at least once, and often twice, a month, and also like to be out visiting customers as much as possible.”
A Zambian national, Kaulule, known to colleagues and friends as ‘Kaz,’ left his role as Lafarge South Africa’s chief executive officer (CEO) to join Aggregate Industries in November 2023, initially as group strategy and commercial growth director. He took up his current senior executive role at the nearly 4000-employee company, which is the UK subsidiary of Switzerland-headquartered Holcim, formerly known as LafargeHolcim and regarded as one of the world’s biggest building materials producers, in August 2024. With an impressive career spanning more than 20 years, Kaulule is a results-driven executive renowned for his inspirational leadership across diverse international landscapes, notably in Europe and Africa. His expertise encompasses operations, digital transformation, business development, mergers and acquisitions, and the achievement of commercial excellence.
Kaulule led Lafarge South Africa to unprecedented success in his time as its CEO. Within 18 months, he doubled the enterprise value and achieved profitability, reversing a trajectory of over five years of losses.
Joining the global construction sector in 2004, Kaulule has also held pivotal roles in LafargeHolcim Group audit in France and various senior marketing, commercial, and strategy posts across various southern African countries. He has also spearheaded digital ventures in the UK.
Kaulule brings academic rigour and practical experience to his work. He holds an MBA from the University of Oxford’s Saïd Business School, a Bachelor (Honours) of Commerce, and a Bachelor of Science from the University of Cape Town.
So what have his priorities been in his first year as Aggregate Industries’ managing director of aggregates?
“My aggregates role is people-facing. Do we have the right people and the right level of engagement for the ambitions we are setting for ourselves? More fundamentally, are we operating safely, given our business?,” Kaulule said.
“After that, it’s about the company being a UK leader in sustainability. Coming here from South Africa, I saw it as a big opportunity to drive forward circular construction at the scale that Aggregate Industries can offer. I would like us to have 20 per cent of our products being made from recycled materials. We are currently around seven per cent.
“Another key focus is being a commercially focused organisation that is easy to do business with. We are revamping how we approach the market and our intensity within it. We are looking at which sections to focus on and what products the market needs.
“One of the things you find when you’ve been in a business for a long time is that you produce the same type of products. We now want to bring our customers on the circular construction journey. To do that means our commercial people need to have different conversations. In some areas, we have had to introduce different commercial people to have the impact we’re looking for.”
While Kaulule acknowledges that circular construction-linked products generally cost more than traditional ones, he believes many customers are willing to pay a bit extra to gain added value in their business marketplace.
“When I first came to Aggregates Industries, and in my previous role, we were having conversations about recycling; some thought that recycled [building material] products should be cheaper, given they are recycled. That is not the case. You have to handle the used material and reprocess it carefully,” he said “It is about creating a value proposition. Part of that is not just that we recycle; our offer of external verification confirms what we are doing, and we have an ECOCycle brand that goes with that.
“The discussion with the customer has moved from one focused on price to one where the customer asks, ‘How can you make this a reality in my products?’ If you can make it a reality in their products, the customer reduces their carbon emissions, which can help them win contracts with municipalities.”
According to Kaulule, Aggregate Industries has been “walking the talk” about growing its circular construction business in recent years.
“We have been market-leading when it comes to ambition. We have made significant acquisitions in this space,” he said. “However, it’s not just about the acquisitions. We have been doing a lot internally on aggregate, asphalt and ready-mix [concrete], which has made a big difference given our scale.
“This means we can drive our ambitions downstream through the business. There is huge growth potential on that side. I would say that around 30–35 per cent of the materials we produce are used by our businesses in their work.
“What excites me even more is what we can do with our external customers around circular construction. We can change their business models.”
Among Aggregate Industries’ acquisitions linked to circular construction has been the Q4 2024 acquisition of Land Recovery, a leading supplier of primary and recycled construction materials.
Founded by the Beecroft family in 1982, Land Recovery has grown to become a leading supplier of construction and demolition materials.
The company supplies primary rail ballast, and handles and treats spent ballast, recycling a portion of it into new products for the rail network or brings it back into the value chain to create products such as ready-mix, precast concrete, and asphalt.
Another key acquisition related to circular construction was the Q3 2023 purchase of OCL Regeneration, a leading provider of highway waste recycling solutions. The integration of the Kent-headquartered business has further strengthened Aggregate Industries’ asphalt and surfacing operations, where it is a key player on National Highways and local authority contracts.
In Q4 2022, Aggregate Industries launched Your Carbon Report, the UK building materials industry’s first fully customisable carbon reporting tool.
Your Carbon Report offers customers accurate data by product or project. It produces a report using data from across Aggregate Industries’ business areas to provide a comprehensive cradle-to-site assessment. The tool looks at the whole manufacturing process, from raw material extraction to transportation, to provide a full and accurate carbon assessment of the products.
The report can be generated quickly, from request to supply, and allows customers the flexibility to interrogate the data to identify where future carbon savings can be made. To assure customers the solution includes all necessary material flows and is in line with industry best practices, all data in the carbon reporting tool is independently audited by Circular Ecology.
Aggregate Industries can produce up to 35 million tonnes of building materials annually. While unwilling to disclose exact current production numbers for commercial reasons, Kaulule offers his perspective on the present health of UK building materials demand.
“Everyone knows that the 2024 market has been challenging following another decline in demand in 2023,” Kaulule said.
“However, Aggregate Industries’ results have remained resilient.
“Part of that is by stressing that we are growing our business in a declining market through acquisitions, new recycled products and new brands. We have seen a lot more interest in our sustainable products like ECOCycle, and it’s the same when you go downstream with ECOPact for our readymix business and other brands for other business areas.
“We have seen the housing market decline substantially, so all the conversation needs to be around how to adjust UK planning regulations to get more houses built and built more quickly and address the reported labour shortage.
“We and the rest of the British building materials industry have the capacity to supply the materials required to meet the new government’s target of building 300,000 new homes a year for the next five years.
“What’s great is that we can now build sustainable housing. If 20 per cent of your aggregates are recycled, those houses are more sustainable. It’s the same as going down the value chain, having more ready-mixed concrete produced with recycled aggregates, and then you also have reduced cement content, further lowering emissions.”
Kaulule said everyone in the UK construction and building materials industry knows that changing planning laws to encourage more housebuilding “needs to be happening.” He fully supports the industry championing on this issue carried out by entities such as the Mineral Products Association (MPA), the London-based trade association for the aggregates, asphalt, cement, concrete, dimension stone, lime, mortar, and industrial sand industries.
Kaulule said that Aggregate Industries’ trading resilience has also been helped by falling interest rates and its ongoing supply of building products to major UK infrastructure works, including HS2 (high-speed rail network) and coastal renewable energy and protection projects.
Building materials for HS2 have mainly come from Aggregate Industries’ English Midlands sites. Building materials for the coastal projects have come from Aggregate Industries’ Glensanda ‘super quarry’, Europe’s largest granite quarry. It is situated on a remote peninsula north of Oban and is accessible only by sea.
Kaulule also reports a growth in commercial activity in southwest and southeast England, the latter largely linked to the Port of Tilbury on the River Thames at Tilbury in Essex. Aggregate Industries is building a state-ofthe-art grinding station and storage facility at what is London's principal port. This represents a significant investment to support the ambitious growth plans for the company’s cement business.
The Tilbury facility, which will be completed and fully operational in 2026, will allow the firm to supply customers with conventional, low-carbon and circular cementitious materials 24 hours a day from
five loading heads. The primary objective of this investment is to meet the increasing demand for sustainable building materials in an evolving market.
The development investment includes new plant equipment for manufacturing blended cements and lower-carbon cement components, including GGBS and alternative raw materials from construction demolition materials, as well as providing a major import hub.
In line with the company’s sustainability strategy, the project demonstrates Aggregate Industries’ ongoing commitment to lowercarbon construction. In particular, it boasts a significant commitment to circularity principles, ensuring that all potential construction demolition materials are reused or recycled wherever possible.
Aggregates Business reported in December 2024 that a key milestone had been reached in the project with the inflation of a groundbreaking dome silo that sits within the new multi-million-pound cement import, manufacturing and distribution facility.
The 45m-tall, 32m-diameter dome is designed to store up to 30,000 tonnes of cement to support local demand for building materials, which will be used in numerous construction projects in the region.
Once operational in 2026, this facility will allow Aggregate Industries to serve its customers 24–7 with conventional, low-carbon and circular cementitious materials from five loading heads.
During construction, over 25,000 tonnes of concrete from the existing site have been recycled and reused, and over 10,000 tonnes of recycled asphalt planings have been incorporated into new products. Aggregate Industries also incorporates lower-carbon materials every construction, including using the firm’s ECOPact readymix.
Local stakeholders and businesses are already seeing potential economic benefits, as the project is expected to stimulate demand for trade and materials in the region. More than 100 jobs are set to be created during the construction phase, with 30 full-time permanent positions to be generated once the site is operational.
Kaulule said continuing to innovate remained a key 2025 focus the 1300-employee-strong aggregates side of Aggregate Industries’ business.
“Given our emphasis on sustainability and circular construction, there is a lot of innovation and new ideas we need to bring to the table,” he said. “We need an engaged workforce whose working environment allows them to create good ideas.
“We also want to push up internally the use of sustainable products. There will be a big step-change in 2025, as we aim to produce three million tonnes of sustainable products for our internal and external works, up from two million tonnes in 2024.
“We also want to further integrate the recycled building materials businesses we’ve acquired. Through the Land Recovery
Aggregate Industries has seen much more interest in its sustainable products like ECOPact.
acquisition, we will be the first UK building materials business to certify the use of blended ballast, comprising 50 per cent virgin ballast and 50 per cent reprocessed.
“I want Aggregate Industries to be the UK’s most sustainable and profitable business. We’re on the right track to achieve that in 2025.”
After locking away previous acquisitions in 2024, Kaulule said the company will continue to look for opportunities to complement its existing strengths.
“We are always looking at good opportunities where there is complementarity,” he said. “The circular construction element of any potential deal is important. We are not done on the acquisitions front. We want to grow internally and with M&A [mergers and acquisitions].
“Our acquisitions in recent years have brought an entrepreneurial spirit to Aggregate Industries, which is great. From our side, we bring them a bigger playing field and the right level of [regulatory] compliance and rigour through our brands.”
Is there a danger that a very high percentage of recycled aggregate or ready-mix concrete and cement in construction works can negatively impact final-build quality?
“The quality of the recycled building material is based on the quality of the raw building material you are reprocessing,” Kaulule said. “We have examples from countries such as Switzerland where construction projects use 60 per cent recycled materials. It’s phenomenal, and legislation in that country allows for this.
“From a Holcim Group perspective, we were involved in an affordable housing project in France, and everything on the site used recycled materials, from aggregates to cement. It shows it can be done. By the end of 2025, you will see our recycled product brands very clearly in the marketplace.”
Kaulule said Aggregate Industries is keen to increase its embrace of digitalisation and artificial intelligence (AI)-inclusive technology.
“I was once the general manager for a digital business in the UK. We were building a digital solution called Lead Retail, which enabled users to order [clothes and other high street items] on their mobile phones,” he said.
“Holcim has adopted it, and it’s how most of our customers interact with us. We are in the process of rolling out several digital tools that are customer-facing and that make it easier for people to do business with us.
“One of the digital tools is called Rocks, and another is Click It. Rocks helps with internal logistics; Click It allows customers to place orders.
“We are using AI to improve [employee] on-site behavioural safety. When some of our loader drivers are loading and unloading materials, they wear goggles that track what is happening with their eyes. It records what is catching their attention, and you can analyse hot spot incidents and predict where safety issues must be addressed.
“We also want to do more with AI technology around predictive fleet maintenance. AI has not replaced anybody. Even with ChatGPT, its biggest benefit is helping you become a better version of yourself.”
Kaulule is based in Holcim’s central London office, which is about an hour’s commute from St Albans, a small city in Hertfordshire, just over 20 miles north of London. He lives there with his wife and three children.
“What I take from my working life in countries like South Africa and Zimbabwe is that industries can change rapidly due to political events or market shifts,” he said.
“It teaches you to be agile and adaptable in your business approach. It’s a strength I can lead on given the UK building materials industry is changing in its more focused approach to sustainability.”
Kaulule told Aggregates Business that he likes to balance empowerment with accountability as a leader.
“High [employee] empowerment but also high accountability for the results. I like to see a high support-high challenge environment in my teams,” he said.
“The biggest thing in any company is its people. I’m passionate about having the right people to deliver the best results. I like challenging the status quo and asking why we do this or that. I want to know how I can make the biggest positive impact on the business area I’m working in.”
Kaulule is also keen to develop Aggregate Industries’ young apprenticeship talent and identify future leaders who can drive the business forward.
“Our apprenticeship programme is crucial. The economic cycle does not come into play; it is a non-negotiable investment. I started as an intern in this business at Lafarge Zambia in 2004.
“The only reason I am where I am today is because I was allowed to grow. I strongly believe in investing in young talent, not because it’s a cliché, but because it works.”
The US is one of the global quarrying industry’s largest markets for equipment and materials, and the last year has seen key manufacturers invest heavily to secure a foothold in the region.
Despite being the third-most populous city in Arizona, after Phoenix and Tucson, and 36th-most populous in the whole country, Mesa is where one of the most recognised companies in global quarrying has its new training facility and expanded repair centre.
For Metso president of North and Central America, Giuseppe Campanelli, the reasoning is simple.
“Nearly five years ago, during the merger of Metso and Outotec, it became evident that the southwestern USA was underserved,” he said.
“Our customers, striving to optimise their assets and manage costs, highlighted the need for reliable alternatives to equipment replacement, especially due to lengthy lead times.”
Once the company identified the southwest as a target area, it began putting together a foundation to support the region’s customers with improved services. The cornerstone of this approach was announced in 2023: a new training centre to the company’s existing Mesa facility and an expansion to the service centre.
Metso’s investment of around €14 million enabled the company to increase its repair shop area by 60 per cent and support customers in crushing, screening, grinding, slurry handling and more.
The investment will add an extra 650m2 to the shop, as well as a new shipping and receiving area and a dedicated 650m2 training centre. The breakroom will be extended to double the original’s size, and a nearly 5m CNC vertical turning lathe with live tooling, a CNC horizontal boring mill and a submerged arc welding set-up will also be added.
The announcement marked the second expansion of the Mesa service centre since its opening in 2015. Metso’s commitment to the southwest heartland includes one of its largest warehouse operations globally, and the company is investing in additional energy efficiency improvements at the Mesa site.
“Our full-time employee count has nearly tripled since 2020, and we have nearly doubled the capacity and capabilities of our Mesa repair centre,” Campanelli said.
“However, attracting skilled individuals has been a significant challenge. To ensure long-term sustainability, we decided to establish a world-class training facility in the southwest to develop our workforce."
The challenge of recruiting new workers to replace an ageing workforce is not a unique problem to Metso, with examples being raised in the industry from Australia to the US, from quarry operators and original equipment manufacturers (OEMs).
Infrastructure Australia, for example, noted in its 2023 Market Capacity Report that the country needed to increase its overall infrastructure workforce by 127 per cent to meet the demand across associated industries.
To that end, Metso has the Metso Academy, which has grown to support several training locations worldwide, but the Mesa Training Centre is new ground for the global OEM.
According to Metso, the training facility will feature modern simulators, digital training tools, classrooms and practical learning areas. Attendees can participate in tailored training programmes to increase their technical knowledge of parts, equipment and plants.
The new centre will be the first standalone training facility for Metso anywhere in the world. The company broke ground on the Metso Academy Training Centre in mid-December 2024, which senior manager for technical training, Nichole Pritchard, labelled “the beginning of a vision”.
"Training is no longer a nice-to-have or an afterthought. Today, it’s a must for our own company’s employees as well as our partners and customers,” she said.
“It is the beginning of a vision: a vision to empower the next generation of mining professionals, to enhance safety and efficiency in our operations, and to strengthen the backbone of an industry that fuels our modern world.”
Born in the USA
Mesa is part of a growing trend of OEMs expanding their presence within the North American region.
Although there are few similarities between Mesa, Arizona, and Morris, Minnesota, the two cities have become centrepieces for OEMs Metso and Superior Industries, respectively.
Superior Industries has had its headquarters in Morris since it was founded in 1972. The company has become almost synonymous with the town, as its HQ and facilities have delivered bulk processing equipment for more than five decades.
Superior expanded its footprint in the city by opening a new manufacturing facility dedicated to cone crushers and jaw crushers. Opened with a symbolic ribbon-cutting ceremony, the new facility will support Superior’s dealer network and producers in the North American market.
The facility features an integrated hydraulics assembly area, an inline test zone, and an expanded parts warehouse.
A render of Metso's new facility in Mesa, Arizona.
While the company’s other crush facility in Belen, New Mexico, will continue to manufacture impact crushers, including Vertical Shaft Impact (VSI) and Horizontal Shaft Impact (HSI) crushers, the addition expands Superior’s global manufacturing presence, which includes sites in South America and Asia.
“This new facility means more opportunities for everyone connected to Superior, from our dealers and producers to our team members and local communities,” Superior Industries’ president, Jason Adams, said.
“With more capacity and smoother operations, we’re able to stay true to our purpose of serving others by providing products that help our partners succeed.”
Regardless of the market in which quarry operators exist, being up to date on the latest methods of operation is crucial to success.
When it comes to screening, one of the most important parts of aggregate production, and that remains true in regards to operating a vibrating screen.
Many within the industry would be familiar with horizontal and inclined screens as the two main types of dry-screening applications. The two types are defined by the latter’s use of gravity to help with the material flow and conveyance.
According to McLanahan’s director of sales, Donal McNichol, the key factors to consider when choosing a screen include maximum tonnes per hour, gradiation of the feed material, type and weight of the material, desired size of separation, the material’s surface moisture, any special operation requirements.
By considering these factors, McNicholl said, businesses would be able to select the right screen for the job.
“Because they don’t rely on gravity to move the material forward, horizontal screens require higher energy and a larger stroke,” he said.
“These types of screens are ideal for low-profile applications where height requirements are limited, which makes them a great choice for portable plants. In stationary plants, they are often used as tertiary or finishing screens. Finer screening applications can greatly benefit from this type of screen.
“Known for their efficiency and reliability, horizontal screens offer more accurate particle sizing. The high G-forces required to
move the material ensure screen plugging is virtually eliminated, allowing for more continuous open area.
“Inclined screens are the most popular for aggregate applications. Since gravity helps to move the material, this type of screen requires low energy and low stroke.”
The modern vibrating screen comes in a wide range of set-ups that are often tailored to the operation. Manufacturers like McLanahan can tailor screens based on basic capacity, incline, deck, oversize, slots, shape, weight of material, and open area.
“Vibratory screens can be configured with one, two, three or four decks. Some fine
screening operations can even have as many as eight screening decks. Three decks are pretty common in the aggregate industry, but the number of screen decks depends on the number of products the site needs to make,” McNicholl said.
“In a typical application where multiple products are being made, the top deck of the screen makes the coarse cut, the middle deck makes a middle cut and the bottom deck make the fine cut.
“Each screen deck is covered with screen media containing the openings for the particles to pass through. Screen media comes in many different forms, and the type of screen media plays an important role in screening efficiency.”
With this in mind, choosing the right screen media is important for any quarrying operation.
Screen media is defined by the amount of open area or the amount of opening in the screen. It is important to understand the need to balance both the wear life and efficiency of screen media.
McNicholl said common types of screen media include woven wire, polyurethane, rubber and hybrid.
“Woven wire cloth is the most consistent, versatile performing media product. It averages 50–70 per cent open surface area in most configurations and provides the most flexibility for operations that need to make frequent media change-outs due to varying product specifications. Overall screening efficiency is good with this type of media,” he said. “Polyurethane is better suited for wet or wash screens and dry applications with highly abrasive materials. It provides 30–40 per cent less open area than wire cloth; however, polyurethane offers extended wear life over wire media.
“Rubber media is used for heavier, coarser materials that can damage standard wire screens. It is most often used for dry applications or abrasive materials. Rubber media has less openings than wire cloth, and
therefore less throughput; however, they last much longer than wire screens.
“Hybrid media combines wire screen with reinforced rubber or urethane strips to fit screen supports. It is highly popular in dry screening applications with high moisture materials and a high proportion of fines. This type of media works to eliminate blinding and pegging, which ends the need to stop production to clean the screen. It provides more open area than polyurethane and lasts longer than woven wire.”
McNicholl said manufacturers like McLanahan can use their team’s expertise to help quarry businesses choose the right screen and screen media for them.
Due to its demand, America will always remain among the top handful of key markets in the industry. However, the US market is tough to crack, especially when operators
face challenging conditions and need equipment to perform day after day.
Ridgeline Excavation faced such conditions during a recent job in Big Sky, Montana, building roads for a new residential area.
The task was simple enough: Ridgeline Excavation needed to crush blasted granite and quartzite into 75–100mm material. The challenge was to do this in an environment with an altitude of nearly 2500m and shifting weather conditions.
Access to the site was difficult. There was limited working space and workers had to contend with rain, snow and sleet. These conditions dampened the material containing sticky fines and clays, which could have made processing difficult. With an arduous task ahead, Ridgeline trusted Kleemann’s mobile jaw crusher MOBICAT MC 110i EVO2 to operate as a standalone machine.
“The flexibility and ability to easily move the plant to different locations in the quarry is a decisive advantage,” Ridgeline Excavation site manager, Lloyd Spanners, said. “Thanks to its mobility, the plant is very easy to move around the site. It also copes very well with the very sticky material we process here.”
The MOBICAT MC 110i EVO2’s doubledeck pre-screen with a slotted grate enabled Ridgeline to process the feed material effectively. The operators set a desired final grain size, and the machine screened the material so that corresponding grains bypassed the crushing chamber. This enabled greater throughput while lessening the impact on the crushing chamber.
“The pre-screen, with its ergonomic slotted grate, is really helpful in this application due to the wet, sticky material,” Spanners said. “On top of that, the consumption values are really manageable at approximately 19 litres of diesel per hour. The machine enables us to work efficiently and in an environmentally friendly manner.” AB
12-month partners get priority on the best branding opportunities.
Aggregates Business is a go-to source for up-to-date news and views on the European, American, Asian, African and Middle Eastern aggregates and building materials sectors. Our wide-ranging features line-up includes in-depth articles on the latest crushing and screening, loading and hauling machines.
A major Chinese manufacturer is targeting European market gains as premium concrete batching plants remain in demand worldwide.
Aplethora of European Union (EU)-funded projects are putting a Bulgarian business and an Ammann CBS 120 SL Elba concrete-mixing plant to work.
With an hourly output of 120m³, the Elba plant perfectly matches ATMIX’s needs in Zapaden.
ATMIX chief executive officer Ivan Achovski said plants of this size (2m³ to 3m³ mixers) are in great demand in Bulgaria.
“New infrastructure projects are being worked on that need to be supplied with high-quality concrete from this plant,” he said. “Many more will follow in the coming years.
“They are not too small, so construction projects are supplied with a decent delivery rate and match the work cycle. But it should also not be a highperformance system whose cost–benefit value overshoots the mark.”.
ATMIX operates multiple Ammann Elba mixing plants, and Achovski is “highly satisfied with their superiority and reliability”. His familiarity with the plants helped him decide on the new CBS 120 SL Elba.
Achovski and his ATMIX colleagues first saw the plant at bauma 2022, where it was exhibited in its latest configuration with the CEM 2660 S mixer. Investing in an Ammann solution was an easy choice for ATMIX, given the mixer, market needs, plant size, and Ammann’s product support history.
The CBS120 SL Elba stationary concrete mixing plant for ATMIX has a CEM 2660 S single-shaft compulsory mixer and a specially developed CEM 2660 S single-shaft compulsory mixer for 8m³ mixing vehicles. The set-up runs three batches until it is full.
The ATMIX plant also has a dust extraction filter system for the mixing plant and a CEL140/4 linear aggregate dosing bin (140m³ with four chambers at 35m³ each). The solution offers compact installation thanks to feeding the aggregate via skip track into the mixer, a galvanised skip, an additive dosing system with two 30-litre chambers, and four additive pumps, including control.
Customised features on the CBS120 SL Elba for ATMIX include a mounting frame for later plant enclosure, access stairs, surrounding platforms for the mixer and weighing platform, a by-pass for dosing water directly into the mixer, integration of the cement silos of the customer, upgraded with Ammann Elba silo equipment silos equipped with the latest filter and safety technology, integration of on-site silos and screw conveyors, and an interface cabinet for the connection of external control.
Achovski said Ammann’s exemplary product support continued after the most recent sale.
“Permanent customer contact was maintained during installation to achieve the best possible success,” he said.
Of course, the true test comes when the plant begins operation. In that regard, Achovski said the plant was “flawless and without any unfulfilled wishes”.
Chinese off-highway equipment
manufacturer NFLG (Next Forward Lead Global) is keen to make a big impression in the European market in 2025, and its concrete mixing plants are a crucial part of its growth strategy in the region.
The company came to Europe in 2007, making a notable impression with an innovative asphalt mixing plant. Meanwhile, its strategic partnership with European dry mortar mixing plant giants in the Chinese market has expanded globally.
“Our strategy for Europe focuses on exploring market and product adaptability over the next one to two years while preparing the entire sales chain, including establishing European spare parts warehouses and localised installation and service teams,” a company spokesperson told Aggregates Business
“After nearly 30 years of refining its technology, quality and cost-effectiveness in China’s diverse and challenging conditions, NFLG aims to provide the European market with a superior ‘Made in China’ alternative.
“The product portfolio includes all nine of NFLG’s lines: asphalt mixing plant, concrete mixing plant, dry mortar mixing plant, mobile
and static crusher and screen, aggregate shaping and sand-making plant, C&D waste recycling, washing plant, and residual sludge recycling plant.
“At bauma China [24–27 November 2024], European distributors recognised NFLG’s quality and products. We are currently in close communication with these potential partners.”
NFLG will be an exhibitor (booth C6. CNN – 100/1) at April’s bauma Munich 2025, the world’s biggest construction, quarrying, mining, and recycling equipment industry trade fair.
“We warmly welcome interested partners and customers to visit and connect with us at our booth. Due to the close timing of bauma Munich and bauma China, we will not display equipment this year. Instead, we will focus on brand promotion and introducing key products such as concrete mixing plants, asphalt mixing plants, dry mortar mixing plants, and mobile crushers and screens. For NFLG, the European and global markets represent more diverse opportunities,” a company spokesperson said.
A customised Lintec
“Currently, equipment for European customers is manufactured and assembled in China. As our business grows and the European strategy progresses, establishing local R&D [research and development] and supply chain facilities in Europe is a key part of NFLG’s strategic plan. This goal is expected to be steadily achieved by 2028.”
The NFLG spokesperson said the company’s founder, Fang Qingxi, constantly encouraged NFLG to manufacture futureoriented products and benchmark them against premium European brands.
“The business’s product development has consistently anticipated domestic market demands while exceeding industry quality standards,” the spokesperson said. “In 2001, NFLG became one of China’s pioneers in dry mortar mixing plant technology. The firm collaborated with an Italian asphalt expert a year later to develop China’s first hot recycling asphalt mixing technology. These innovations have been pivotal to our growth.
NFLG’s products are available globally, with markets in Asia, the Middle East, South America, and Russian-speaking regions. The company operates under a distributor model, and its distributor network maintains strong partnerships in key markets. Outside China, NFLG has offices in Moscow and St. Petersburg (Russia), Almaty (Kazakhstan), Kuala Lumpur (Malaysia), Singapore, Jakarta (Indonesia), and Riyadh (Saudi Arabia).
NFLG equipment is manufactured and assembled at its headquarters in Quanzhou, Fujian, and its production base in Xiantao, Hubei. It is exploring and localisation of non-core components in Southeast Asia and Russian-speaking regions.
“NFLG aims to enhance price competitiveness and localisation ratios by producing mature non-core steel components locally,” the company spokesperson said. “A dedicated team ensures strict quality control during localisation to maintain global supply chain standards and delivery quality.”
NFLG plans to accelerate product localisation and build a global supplier network that aligns with its expanding international business.
This global collaboration will “ensure superior quality, performance and pricing for customers worldwide”.
The NFLG spokesperson said the firm promotes sustainability in the manufacturing and operation of its product range.
“NFLG actively promotes sustainability by adopting green design principles in equipment manufacturing, focusing on energy efficiency, emission reduction, and enhanced environmental performance during production,” the spokesperson said.
“We also take a broader approach to low-carbon emission reduction and sustainable development across the industry chain. Our solid waste recycling and residual sludge recycling plant are designed to enable resource recycling, embodying the principles of low-carbon and sustainable development. Additionally, we have introduced a green building material processing and recycling system, transforming recycled aggregates into low-carbon products such as recycled concrete, mortar and asphalt.”
The company is committed to being part of the industry’s digital transformation regarding equipment operation.
“By leveraging intelligent technologies, we address carbon reduction and sustainability challenges through technological upgrades, achieving smarter energy efficiency, emission reduction, and low-carbon operations,” the spokesperson said.
Up to the multi-task Multi-Task, a prominent sub-contractor in Saudi Arabia, has acquired a Lintec UCP120 concrete batching plant to fulfil a critical road infrastructure project for Engineering for the Petroleum and Process Industries (Enppi). A a major road contractor in Saudi Arabia, Enppi is overseeing the ambitious development,
with the Lintec UCP120 playing a pivotal role in meeting the project’s requirements.
The UCP120 was sourced through Medco (Middle East Development Co. Ltd.), Lintec & Linnhoff’s distributor in Saudi Arabia, and began operations in the Eastern Province in December 2023. Known for high production capacity and advanced engineering, the plant is instrumental in ensuring the timely completion of the multi-year project.
Multi-Task’s choice of the Lintec UCP120 reflects its commitment to high-performance equipment tailored to complex infrastructure demands. High production capacity is a key feature of the UCP120, and plant can produce up to 120m³ of concrete per hour, ensuring smooth execution of large-scale roadworks.
The UCP120 has advanced automation features available through a computerised process control system that delivers precise batching and consistent concrete quality to meet project specifications. The plant’s adaptable design allows Multi-Task to tailor operations to specific project needs. The UCP120 has multiple aggregate bins and a central discharge belt conveyor system, minimising waiting times and maximising efficiency. The plant uses advanced German technology and high-quality materials, ensuring long-term reliability under demanding conditions.
Medco’s fast delivery timeline and reliable after-sales support also influenced the decision to invest in the Lintec UCP120. The plant’s rapid set-up allowed MultiTask to commence operations on schedule, allowing seamless progress on Enppi’s road construction initiative.
The Lintec UCP120’s deployment for this Saudi infrastructure project adds to its impressive track record, such as a customised version to handle unique requirements for the Mombasa port expansion in Kenya. UCP120 plants also supplied high-quality ready-mix concrete for diverse commercial developments
in the United Arab Emirates and various infrastructure works in large-scale developments in the Philippines, Malaysia, Vietnam and Sri Lanka.
As the Enppi project advances, the UCP120 continues to showcase its performance and reliability. This collaboration between Multi-Task, Enppi, and Lintec & Linnhoff demonstrates the importance of leveraging cutting-edge technology to achieve operational excellence in infrastructure development. The use of the UCP120 facilitates milestones and sets benchmarks for future road construction projects in the region and beyond.
On trak
Shannon Valley Group, one of Ireland’s leading civil engineering contractors, recently invested in the Rapid Trakmix, a trackmounted mobile continuous mixing plant, in response to a growing demand for ex-situ soil stabilisation projects.
Established in 1991 and headquartered in Drumshanbo, County Leitrim, Shannon Valley Group’s services include groundworks and civil engineering, commercial and housing site developments, controlled demolition, environmental, and recycling.
Trakmix is a valuable addition to Shannon Valley Group’s impressive machinery fleet. The new Trakmix continuous mixing plant offers total mobile flexibility via a selfcontained, track-mounted unit. This enables the company to undertake remote location projects easily and meet the growing demand for eco-friendly projects.
Ex-situ soil stabilisation involves using binders to improve weak soils geotechnically for construction purposes. This process produces a viable construction material suitable for reuse. Stabilised soils are often used as sub-bases for paving. Stabilisation increases the stability, impermeability, and load-bearing capacity of the sub-base.
Excavated screened material is mixed with the appropriate binder (cement, lime, etc) in Rapid Trakmix’s integral continuous mixer. The Trakmix’s aggressive, highvelocity mixing action, combined with the full weighing of all materials, ensures fully homogeneous outputs. The material is placed in its final point of deposition or stockpiled to cure before being finally deposited.
Ex-situ soil stabilisation uses raw materials more efficiently, limiting waste disposal and the use of virgin materials. As one of Ireland’s most progressive civil engineering groups, Shannon Valley Group is among the first in the market to offer ex-situ soil stabilisation using a mobile continuous mixing plant.
“We are always on the lookout for new technology. If there is a better way of doing things, we want to be the first to offer this solution to our clients,” Shannon Valley Group director, Michael English, said
“It’s simple: with Rapid, we get a job done faster and cheaper than our competitors. Mixing weak soils with binders for re-use on-site provides cost savings compared to traditional aggregates and muckaway methods.
“Our experience with the Rapid Trakmix 250 has been very positive so far. We are currently processing boulder clay material; we may not be getting 250 tonnes per hour [tph] because it’s a difficult material to work with, as it needs screening before treatment, but it still saves us time on the programme.”
Trakmix is a track-mounted, mobile, self-contained, fully-weighed, high-volume mixing plant. It is recommended for applications where all varieties of binders or neutralising powders are required in the mixing process, including road construction, road paving, groundworks or civil engineering, environmental stabilisation projects, aggregate recycling, and many more.
Trakmix was designed in response to the growing demand for a mobile continuous
mixing plant that provides easy, cost-effective transportation and eliminates the need for special transportation permits.
Customer demand also indicated a need for mixing technology that provides more output options on a different platform, offering flexibility for various site types and applications.
The addition of the Trakmix to the company’s fleet offers much-needed mobility and ease of set-up from project site to site. The machine possesses an entirely self-contained design mounted on tracks, including an on-board genset, providing mobile flexibility. Trakmix can be set up in minutes via remote control.
Trakmix includes several innovative features, including a modern control system that weighs all materials and a doublehopper cement weighing system. Other cutting-edge features include low-friction surface lining on hoppers, a bottom conveyor for easy cleanout, and an out-loading conveyor for easy discharge.
Trakmix offers outputs of up to 250tph via a high-volume continuous Rapid twinshaft mixer and 12m3 aggregate hopper, including a division plate for two aggregates. The Rapid-designed continuous twin-shaft mixer (pugmill) is one of the market’s largest and fastest continuous mixers. Its specially phased shafts and paddles ensure a homogenous mix for various applications within the concrete, construction and environmental industries.
Trakmix features full weighing capabilities via an integral, fully automated control system. Adjustable feeder gates from the aggregate bins and a variablespeed belt feeder to aggregate weigh belts are provided. Powders are thoroughly weighed via a twin hopper system with twin-screw discharge, and a flow meter measures the water. An integral 600-litre water tank and provision for admixtures are also included. AB
MARCH
12–13
SaMoTer Paving Show and Congress 2025 Verona, Italy
Organiser: Veronafiere
Tel: +39 045 8298 133 exhibitors@samoter.com samoter.it/en/paving-show-and-congress-2025
25–27
World of Asphalt 2025
St. Louis, MO
Organisers: NAPA, AEM & NSSGA
Tel: +1 (864) 208 3372 exhibitors@aem.org worldofasphalt.com
25–27
Agg1 2025
St. Louis, MO
Organiser: NSSGA
ST. LOUIS, MO
MARCH 25–27 BOOTH 1110
artin offers multiple primary belt cleaning solutions for diverse bulk material handling. Each cleaner features a rugged mainframe design with thick DOM tubing and a steel backbone. Application-specific, highperformance urethane blade s deliver superior cleaning effectiveness across various belt widths and speeds. These blades incorporate Martin’s patented Continuous Angle Radial Pressure design for consistent cleaning throughout their service life.
Tel: +1 (800) 867 6060 exhibitors@aem.org agg1.org
APRIL
7–13
bauma 2025 Munich, Germany
Organiser: Messe München
Tel: +49 89 949 11348 info@bauma.de bauma.de/en/trade-fair
us at Stand FN.1219 at Bauma 2025
Telestack are thrilled to participate at Bauma in Munich where we will be showcasing our latest innovation in material handling technology. The TSR 40 allows for up to +30% larger stockpile capacity when compared to conventional fixed length conveyor systems and with the added benefit of increased site mobility to that of the standard radial telescopic design.