making!
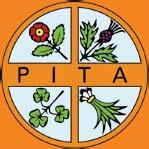
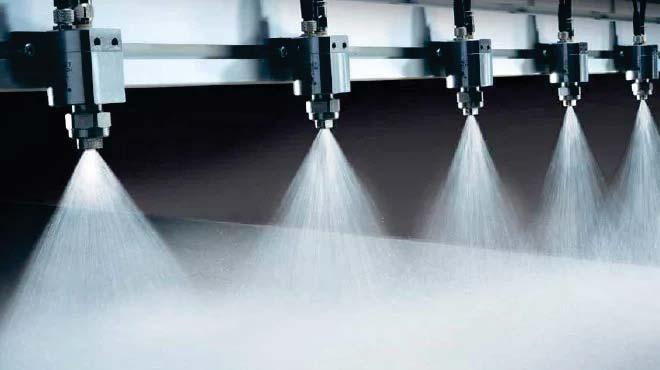


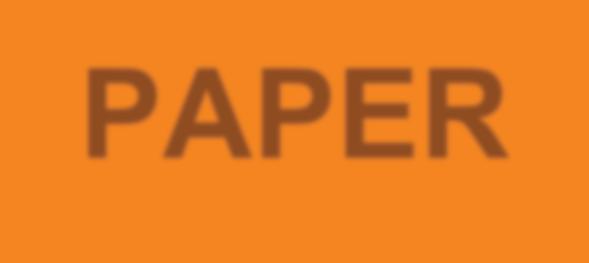
Volume 8,Number 3,2022
1. Papermaking: Cationic cellulose derivatives for filler flocculation.
2. Moulded Pulp: Review of moulded pulp use for disposable food packaging.
3. Decarbonisation:Review of sociotechnical developments and policy options.
4. Coated Paper: Cellulose nanofibers / PVOH blends as coating additives.
5. Biorefinery: LCA of a seaweed-based biorefinery.
6. Biopolymers: Plastic-free bioactive paper coatings for packaging applications.
7. Wood Panel: Review of agri-biomass use for particleboard manufacture.
8. Energy Recovery: Paper mill sludge biochar to enhance energy recovery.
9. Negotiation Tips:Top 10 tips on how to negotiate.
10. LinkedIn Etiquette: Top 10 tips to connect on LinkedIn like pro.
11. Goal Setting Tips:Top 10 tips for effective goal setting.
12. New Manager Tips:Top10 tips for new managers.
News / Products / Services:
Section 1 –PITA Corporate Members: ARCHROMA/ VALMET
Section 2 –PITA Non-Corporate Members
VOITH
BTG / MOISTTECH / TOSCOTEC
Events: PITA Courses & International Conferences / Exhibitions
Installations: Overview of equipment orders and installations since early Au gust2022
Research Articles: Recent peer-reviewed articles from the technical paper press
Technical Abstracts: Recent peer-reviewed articles from the general scientific press
The Paper Industry Technical Association (PITA) is an independent organisation which operates for the general benefit of its members –both individual and corporate–dedicated to promoting and improving the technical and scientific knowledge of those working in the UK pulp and paper industry. Formed in 1960, it serves the Industry, both manufacturers and suppliers, by providing a forum for members to meet and network; it organises visits, conferences and training seminars that cover all aspects of papermaking science. It also publishes the prestigious journal Paper TechnologyInternational® and the PITA Annual Review, both sent free to members, and a range of other technical publications which include conference proceedings and the acclaimed Essential Guide to Aqueous Coating.
Cationic polyacrylamides (CPAMs) are usually used as filler retention agents in papermaking formulations. However, increasing environmental restrictions and their non-renewable originhave driven research into biobased alternatives. In this context, cationic lignocellulosic derivativeshave been attracting considerable research interest as a potential substitute. In this work, distinctcationic celluloses with degrees of substitution of between 0.02 and 1.06 and with distinct morphol ogical properties were synthesized via the cationization of bleached eucalyptus kraft pulp, using adirect cationization with (3-chloro-2-hydroxypropyl) trimethylammonium chloride (CHPTAC) or atwo-step cationization, where the cellulose was first oxidized to form dialdehyde cellulose and wasthen made to react with Girard’s reagent T (GT). Fibrillated samples were produced by subjectingsome samples to a high-pressure homogenization treatment. The obtained samples were evaluatedregarding their potential to flocculate and retain precipitated calcium carbonate (PCC), and theirperformance was compared to that of a commercial CPAM. The cationic fibrillated celluloses, witha degree of substitution of ca. 0.13–0.16, exhibited the highest flocculation performance of all thecationic celluloses and were able to increase the filler retention from 43% (with no retention agent)to ca. 61–62% (with the addition of 20 mg/g of PCC). Although it was not possible to achievethe performance of CPAM (filler retention of 73% with an addition of 1 mg/g of PCC), the resultsdemonstrated the potential of cationic cellulose derivatives for use as bio-based retention agents.
information:
1 University of Coimbra, CIEPQPF, Department of Chemical Engineering, Pólo II, R. Sílvio Lima, 3030-790 Coimbra, Portugal
2 Forest and Paper Research Institute (RAIZ), R. José Estevão, Eixo, 3800-783 Aveiro, Portugal
2022,
The Paper Industry Technical Association (PITA) is an independent organisation which operates for the general benefit of its members –both individual and corporate –dedicated to promoting and improving the technical and scientific knowledge of those working in the UK pulp and paper industry. Formed in 1960, it serves the Industry, both manufacturers and suppliers, by providing a forum for members to meet and network; it organises visits, conferences and training seminars that cover all aspects of papermaking science. It also publishes the prestigious journal Paper TechnologyInternational® and the PITA Annual Review, both sent free to members, and a range of other technical publications which include conference proceedings and the acclaimed Essential Guideto Aqueous Coating.
JorgeF.S.Pedrosa 1, * ,LuísAlves 1 ,CarlosP.Neto 2 ,MariaG.Rasteiro 1 andPauloJ.T.Ferreira 1
1 UniversityofCoimbra,CIEPQPF,DepartmentofChemicalEngineering,PóloII,R.SílvioLima, 3030-790Coimbra,Portugal
2 ForestandPaperResearchInstitute(RAIZ),R.José Estevão,Eixo,3800-783Aveiro,Portugal
* Correspondence:jpedrosa@uc.pt
Citation: Pedrosa,J.F.S.;Alves,L.; Neto,C.P.;Rasteiro,M.G.;Ferreira, P.J.T.AssessmentofthePerformance ofCationicCelluloseDerivativesas CalciumCarbonateFlocculantfor Papermaking. Polymers 2022, 14,3309. https://doi.org/10.3390/ polym14163309
AcademicEditor:Francisco JavierEspinachOrús
Received:13July2022 Accepted:12August2022 Published:14August2022
Publisher’sNote: MDPIstaysneutral withregardtojurisdictionalclaimsin publishedmapsandinstitutionalaffiliations.
Abstract: Cationicpolyacrylamides(CPAMs)areusuallyusedasfillerretentionagentsinpapermakingformulations.However,increasingenvironmentalrestrictionsandtheirnon-renewableorigin havedrivenresearchintobio-basedalternatives.Inthiscontext,cationiclignocellulosicderivatives havebeenattractingconsiderableresearchinterestasapotentialsubstitute.Inthiswork,distinct cationiccelluloseswithdegreesofsubstitutionofbetween0.02and1.06andwithdistinctmorphologicalpropertiesweresynthesizedviathecationizationofbleachedeucalyptuskraftpulp,usinga directcationizationwith(3-chloro-2-hydroxypropyl)trimethylammoniumchloride(CHPTAC)ora two-stepcationization,wherethecellulosewasfirstoxidizedtoformdialdehydecelluloseandwas thenmadetoreactwithGirard’sreagentT(GT).Fibrillatedsampleswereproducedbysubjecting somesamplestoahigh-pressurehomogenizationtreatment.Theobtainedsampleswereevaluated regardingtheirpotentialtoflocculateandretainprecipitatedcalciumcarbonate(PCC),andtheir performancewascomparedtothatofacommercialCPAM.Thecationicfibrillatedcelluloses,with adegreeofsubstitutionofca.0.13–0.16,exhibitedthehighestflocculationperformanceofallthe cationiccellulosesandwereabletoincreasethefillerretentionfrom43%(withnoretentionagent) toca.61–62%(withtheadditionof20mg/gofPCC).Althoughitwasnotpossibletoachieve theperformanceofCPAM(fillerretentionof73%withanadditionof1mg/gofPCC),theresults demonstratedthepotentialofcationiccellulosederivativesforuseasbio-basedretentionagents.
Keywords: calciumcarbonate;cationiccellulose;fibrillatedcellulose;flocculation;laserdiffraction spectrometry;quaternaryammonium
Incertainpaperproductformulations,aportionofthecellulosefibersisoftenpartially replacedbymineralfillers(fromnowon,thesewilljustbereferredtoasfillers),suchas kaolinclay,talc,naturalgroundcalciumcarbonate(GCC)orsyntheticprecipitatedcalcium carbonate(PCC)[1].
Copyright: ©2022bytheauthors. LicenseeMDPI,Basel,Switzerland. Thisarticleisanopenaccessarticle distributedunderthetermsand conditionsoftheCreativeCommons Attribution(CCBY)license(https:// creativecommons.org/licenses/by/ 4.0/).
Fillers,initiallyappliedduetotheirlowerpricecomparedtocellulosefibers,arealso usedtoimprovearangeofproperties[2].Theuseoffillerscanimprovethebrightnessand opacityofthepaper,decreasethesurfaceroughness(especiallyaftercalendaring),enhance theprintingquality,improvetheformationofthepapermatrixbyfillingthevoidsbetween thefibersandalsoincreasethedimensionalstabilityofthepaper,astheytendtoremain inertwhenwetted,unlikecellulosefibersthatcanswellandretract[3].
Thesefillerspresentatypicalparticlesizesmallerthan4 μm[2],beingmuchsmaller thanthemeshsizeofthescreenattheformingsectionofthepapermachine.Infact,the screenswithameshsizerangingbetween40and100mesh(openingswithadiameterinthe 150to400 μmrange)[4],althoughsmallenoughtoretainalmostthetotalityofthecellulose fibers(withalengthofaround2–5mmforsoftwoodand0.3–1.5mmforhardwoods)[5], arenotsufficientlysmalltoretainthefillerparticles,resultinginmateriallosses.
,3309.https://doi.org/10.3390/polym14163309https://www.mdpi.com/journal/polymers
Althoughsomefillerscanpresentaslightlycationicsurface,mostofthecommercial fillerspresentanegativesurfacecharge,duetotheuseofdispersants[6].Withthecellulose fibersalsopresentinganetnegativecharge(mainlyasaresultoftheionizationofcarboxylic andsometimessulfonicacidicgroupsthatareintroducedontothefibersurfaceduring thechemicalpulpingandbleachingsteps)[7],cationicsyntheticpolymersareappliedin papermakingformulationsasretentionagentstominimizethelossesoffillersand/orsmall fibrousfragmentsandtotakeadvantageofthenaturalaffinitybetweenoppositelycharged particles.
Cationicpolyacrylamides(CPAMs)withhighmolecularweight(Mw),mediumto highchargedensity(CD)andlinearorbranchedchainsarefrequentlyusedasretention agents[8].AlthoughPAMsareconsiderednon-toxicintheirnativepolymericform,their non-renewableoriginandtheexistenceinthefinalproductofsomeresidualacrylamide monomers[9]poseenvironmentalandhumanhealthconcernssincetheyexhibitahigh degreeofneurotoxicity[10].Theseconcerns,togetherwithincreasingenvironmental restrictions,pavethewayforthedevelopmentofnewnatural-basedalternativestobeused asretentionsystems.
Inthepaperindustry,theuseofcelluloseasarenewableresourcethatcanserveasthe backboneforthedevelopmentofnewadditives,suchasretentionadditives,appearsto offeralogicalalternative.Overthelastfewdecades,lignocellulosicmaterialshavebeen functionalizedand/ordeconstructedintotheirhierarchicalsub-structurestoproducenew cellulose-basedproducts,suchasmicro-andnanofibrillatedcelluloses(MNFCs).Purer formsofcellulosecanbesynthesizedbysomebacterialspecies(referredtoasbacterial cellulose)andaretypicallyexploredforbiomedicalapplications[11].Someofthesenew productshavealreadybeentestedinpapermakingformulationsandhaveshowntheir positivepotentialasfillerretentionagents[12,13].
Fromthepublishedliterature,itispossibletoobservethatnonionicoranionic cellulose-basedproductsarefarmorecommonthantheircationiccounterparts,asobservedbyotherauthors[14].
Inmostrecentyears,thegraftofcationicgroups(typically,quaternaryammonium) intocellulosicmaterials,includinglignocellulosicresidues,hasbeenexploredasapossible alternativefortheproductionofbio-basedretentionagentsforthepaperindustry.However, thestudiespublishedarestillrelativelyscarceand,insomecases,inconclusive[15 19].
Diabetal.[17]studiedtheuseofcationicMFCinsingleanddualsystemswith bentonitefortheretentionofGCCinsheetsproducedwithsoftwoodandbagassepulps. Noimprovementswereobservedinthefillerretention,theresultsbeingattributedto thelowdegreeofcationization(0.27mmol/g).Onthecontrary,Lietal.[19]reported improvementsinGCCretentionbymodifyingthefillersurfacewithsolublecationic cellulose,withadegreeofsubstitution(DS)of0.52.
Forcellulosecationization,twomainstrategiesaretypicallydescribedintheliterature. Thefirst,thesimplestandmostappliedstrategy,comprisesthedirectreactionbetween celluloseandthereagentepoxy-propyltrimethylammoniumchloride(EPTAC)[20 22]. Pedrosaetal.[23]insteadusedtheprecursor(3-chloro-2-hydroxypropyl)trimethylammoniumchloride(CHPTAC)andconvertedittothemorereactiveformEPTAC,viaareaction withsodiumhydroxide.
Thesecondcationizationmethodisbasedonatwo-stepreactioninwhichcellulose isinitiallyoxidizedwithsodiummetaperiodate(NaIO4),causingtheconversionofthe twovicinalhydroxylgroupsattheC2andC3positionsintoaldehydegroupsandthe subsequentcleavageoftheC2–C3bond.Theresultingdialdehydecellulose(DAC)canthen reactwithGirard’sreagentTtoformastableiminestructurethatincludesthequaternary ammoniumgroups[23 26].
Thepolymericretentionadditivesworkthroughaprocessofchemicalflocculationby thedestabilizationoftheparticles(fillers)insuspension.Threedistinctmechanismsare typicallyreferredtoasbeingresponsibleforparticleaggregation.Chargeneutralization (orcoagulation)occurswhenasaltorlowMwpolymerneutralizesthesurfacechargeof
thesuspendedparticles,reducingtherepulsiveforcesthatseparatethem.Patchingoccurs bythecreationofpatchesonthesurfaceofthesuspendedparticlesofoppositecharge, creatingafewoppositelychargedzonesthatcaninteractwiththenon-patchedareasof otherparticles,resultinginflocculationviaelectrostaticforces.Thismechanismoccurs preferentiallybyusinglowormediumMwandhigh-chargepolymers.Finally,inthe bridgingmechanism,polymerswithhighMwandlowchargedensityarepreferablyused. Thepolymersadsorbonthesurfaceoftheparticlesinanextendedconformation,forming longtailsandloopsthatcanextendbeyondtheelectricaldoublelayeroftheparticles.The extendedbranchesofthepolymercanthenadsorbintootherparticles,formingpolymeric bridgesbetweenthem[5,7,27 29].
Thecoagulation-flocculationmechanismsandtheperformanceoftheretentionagents arehighlydependentonthepolymertype,thesuspendedparticlestobeflocculatedand theconditionsofthemedium[30],thisbeingthepredominantmechanismthatismainly dictatedbytheMwandCDofthepolymer[31].Forexample,Aguadoetal.[15]tested theuseofwater-solublecationicderivativesobtainedfrombleached Eucalyptusglobulus kraftpulp(BEKP)toflocculatedistinctfillers(kaolinite,GCCandPCC).Withthedosages tested(10or20mg/g),onlythederivativewiththehighestdegreeofpolymerization(DP) andCD(1703and5mmol/g,respectively)showedpromisingresults,butthiswasonlyfor kaolinflocculation.
Whendevelopingnewretentionadditives,itiscriticaltounderstandthedominant mechanisms,theflocculationkineticsandtheoverallstructureoftheformedflocs.For papermakingtests,theflocculationperformanceofanadditiveistypicallyassessedvia hydrodynamictechniques(thedynamicdrainagejartest),byevaluatingthedrainagetimes andfillerretention,andalsobymonitoringthezeta-potential(ZP)ofthesuspensions (whichismostimportantforthosemechanismsbasedonelectrostaticinteractions)[31,32].
Moresophisticatedalternativetechniquesbasedonlightscattering,suchasfocused beamreflectancemicroscopy(FBRM)[33,34]andlaserdiffractionspectrometry(LDS) [31,32], havealsobeenused,especiallyfortheircapabilityforreal-timemonitoringoftheflocsizes. LDSnotonlyallowsthedeterminationoftheflocsizedistributionateachmomentbutalso permitstheextractionofinformationaboutthefractaldimensionoftheflocsthatcanbe relatedtothecompactnessoftheflocsformed[31].LDShasalreadyproventobeavery usefultechniquebywhichtoassesstheflocculationperformanceofpolymersinrealtime, havingalreadybeenusedforthescreeningofsyntheticpolyelectrolytes[31,32,35],anionic MNFCs[12,36]andcationiccellulosepolyelectrolytes[15,37,38].
Inthepresentwork,twocationizationmethodswereappliedtoproduceseveral cationiccelluloses(CCs)withdistinctDSandmorphologicalproperties(fibers,micro/nanofibrillatedcellulosesandpolyelectrolytes)(Figure 1).LDSwasusedtoinvestigatethe effectofthecationiccellulosecharacteristics,flocculantdosageandcontacttimeonthe flocculationofoneofthemostfrequentlyusedfillersinpapermaking(PCC).
TheperformanceswerecomparedagainstacommercialCPAMandtheinitialnonfunctionalizedcellulosefibers.Thesamplespresentingthebestflocculationperformance intheLDStestswereincorporatedintopulpandfillerformulationsandthenanalyzedin adynamicdrainageanalyzer(DDA)toquantifytheeffectsondrainabilityandthemost effectivefillerretentioncapabilities.
Duetotheimportanceoffillerretentioninpapermakingandtheconstantlyincreasing healthandenvironmentalconcerns/restrictions,thepresentstudyaimstoshedsomelight onthepotentialuseofCCsasaretentionagentandasapossibleCPAMsubstitute.
Thecationiccelluloseswereproducedfromindustrialunrefinedandnever-driedBEKP (80–85wt%cellulose,14–19wt%xylan,0.3wt%ligninand0.4wt%extractives)[23].A commerciallinearCPAM(fromBASF,Ludwigshafen,Germany),withaMwof 3.7 × 106 DaandaCDof1.1mmol/g,wasusedasthereferenceretentionagent.Anindustrial scalenohedralformofPCCwithamediandiameter(d50 )of4.8 μm,determinedbyLDS, inaMastersizer2000(MalvernInst.,WorcesterCity,UK),andaZPof+9mV(atpH 10),measuredinawatersuspensionusingelectrophoreticlightscattering(ELS–Zetasizer NanoZS,MalvernInst.,Malvern,WorcesterCity,UK),wasusedasfillerintheflocculation tests.
Allchemicalsemployedinthecationizationofcellulosewereusedasreceived,without furtherpurification.The(3-chloro-2-hydroxypropyl)trimethylammoniumchloride(CHPTAC) 60wt%aqueoussolution,sodiumperiodate(SP)and(carboxymethyl)trimethylammonium chloridehydrazide(Girard’sreagentT–GT)wereobtainedfromSigma-Aldrich(Schnelldorf,Germany).Sodiumhydroxidepelletsandglacialaceticacid(AA)werepurchased fromVWR(Carnaxide,Portugal)andisopropanol(IPA)fromLabsolve(Lisbon,Portugal). Distilledwaterwasusedthroughoutthework.
Table1. ReactionconditionsusedforthecationizationofBEKPwithCHPTACandGT.
distinctdegreesofoxidation,werewashedwithwaterandcharacterizedfortheiraldehyde content,asdescribedelsewhere[39].TheDACsweredispersedinacidifiedwaterand acertainmolarratioofGT/aldehydewasadded.Thecationiccelluloseswerevacuum filteredandthoroughlywashedwithamixtureofisopropanol/water(9:1 v/v),withthe exceptionofsampleGT1.15_P.Thissample,duetoitshighdegreeofsubstitutionand consequenthighsolubility,waswashedinsuccessivecentrifugationcycles[37].
Theproducedcationiccelluloseswerelabeledaccordingtothecationizingagentused, withtheacronymsCHorGT,followedbythedegreeofsubstitution.
SomeofthecationiccelluloseswerefurtherprocessedtoproducecationicMNFCs. Forthatpurpose,theyweresubjectedtoapassat500barandasecondpassat700barina high-pressurehomogenizer(HPH;GEANiroSoavi,model:Panther115NS3006L).These sampleswerealsolabeledwiththeletterF(Fstandsforfibrillated).Moredetailsabout thepreparationofthesesamplesareavailableelsewhere[23].Thesamplesthatresultedin fullysolublematerials,duetotheirhighDSorthecombinationofcationizationwithHPH, werelabeledwiththeletterP(Pstandsforpolyelectrolyte).
TheCCswerecharacterizedbyelementalanalysis,potentiometrictitration,ZPmeasurements,FTIR-ATRandopticalmicroscopy[23].Elementalanalysiswasperformedin anEA1108CHNS-OanalyzerfromFisons(Italy)toquantifythenitrogencontentofthe samples,whichwasusedtocalculatethecorrespondingDSofthequaternaryammonium groups.TheCDwasassessedusingpotentiometrictitration.Inatypicaltitration,acationic cellulosesuspensionisadjustedtopH11withaNaOHaqueoussolutionandthentitrated with0.01MHCluntiltheinflectionpointofthepHversusHClvolumecurveisreached. TheZPofthedilutedCCssuspensions(ca.0.1wt%)wasdeterminedviaELSinaZetasizer NanoZSdevicefromMalvernInstruments.TheFTIR-ATRspectrawereobtainedona BrukerTensor27spectrometer,using128scansandaresolutionof4cm 1 ,intherange of650–4000cm 1 .Polarizedlightopticalmicroscopyimageswereacquiredusingan OlympusBH-2KPAmicroscopefromtheOlympusOpticalCo.,Ltd.,equippedwithan OlympusColorViewIIIhigh-resolutionCCDcolorcamera.
ThecationicMNFCswerefurthercharacterizedintermsoftheyieldoffibrillation (YF)andsolublefraction(SF).TheYFwasdeterminedviacentrifugationof40mLofCCs aqueoussuspensions(0.2wt%)at9000rpmfor30min,usingaUniversal32Hettich centrifuge.TheweightpercentageofCCremaininginthesupernatantwasconsideredas theyieldoffibrillation.TheSFwasdeterminedviathevacuumfiltrationof3mLofthe originalcationicMNFCssuspension(ca.1wt%)throughacelluloseacetatemembrane filterwitha0.2 μmporesize.TheweightpercentageofCConthefiltratewasconsidered asthesolublefraction.Moredetailedinformationregardingthecharacterizationofthese cationicMNFCsisavailableelsewhere[23].
Theweightaveragemolecularweight(avgMw)ofthecellulosepolyelectrolyteswas determinedbysizeexclusionchromatography(SEC)inanAgilent1260InfinityIIHighTemperatureGPCSystemthatwasequippedwithtwoPLaquagel-OHMixed-H8μm (300 × 7.5mm)columnsandaPLaquagel-OH8μm(50 × 7.5mm)guardcolumn[23].
ToaccesstheperformanceoftheproducedcationiccellulosestoflocculatePCC, theevolutionofthesizedistributionofthePCCflocswasmonitoredinaMastersizer 2000device(fromMalvernInstruments)equippedwiththeHydro2000module,ina similarwaytothatproposedbyRasteiroetal.[31,32,35]forthescreeningofsynthetic polyelectrolytes.
Previouslytothemeasurements,a1wt% aqueoussuspensionofPCCwassubjected tomagneticstirringfor30minandultrasonicatedfor15minat50kHztohelpdisaggregate thePCCparticles.Thesuspensionwasthenmaintainedundermagneticstirring.Forthe
flocculantstested(CPAM,BEKPandcationiccelluloses),0.1wt%ofaqueoussuspensions werepreparedandkeptundermagneticstirring.
Fortheflocculationexperiment,15mLofthePCCsuspensionwasaddedtothe equipmentdispersionunitvesselcontaining700mLofdistilledwater,resultinginaPCC concentrationofaround0.02wt%(alaser-obscurationlevelofnearly30%[32])andapH of9.Thepumpspeedwassetto1400rpm.
Inaninitialtest,afterthestabilizationofthePCCmediansize,acertainamountof flocculant(1mgofflocculant/gofPCC)wasaddedtothemeasuringvesseleverysingle minuteuntilamaximumof15mgofflocculantwasreached(15-mintest).
Althoughthisprocedureisnottypicalinflocculationstudies,andalthoughthatone minutebetweenthesubsequentadditionsofflocculantisnotenoughtimeforallthe flocculationsteps(mixing,adsorption,reconformationandaggregation)tooccur,ithas proventobeafasterandmoreefficientwayofscreeningthoseflocculantsthatofferthe bestpotential.Thismethodwasalsopreviouslyusedwithsyntheticflocculanttoaccess theoptimumdosage[32].Additionally,thisstrategyisquitecommonwhenprescreening flocculantsforflocculationineffluenttreatment,whereinofflinetestswiththecontinuous additionofconsecutivedosesoftheflocculantareconducted(jartests)[40],inorderto optimizetheflocculantdosage,thedifferencebeingthat,inthatcase,thenormalstrategy doesnotinvolvethesimultaneousmeasurementoftheparticlesize.
Forthesamplespresentingthebestperformanceintheprevioustest,asecondstudy wasconductedtostudytheevolutioninthesizeoftheflocsovertimeforafixedconcentrationofflocculant.Inthistest,aftertheadditionofthePCC,acertainamountofflocculant (1,2,4,8or10mg/gofPCC)wasaddedtothePCCsuspensionatonce.Theevolutionof thesizeoftheflocswasmeasuredeveryminutefor15min.Allthemeasurementswere performedintriplicate.AtestwithonlyPCC(noadditionofflocculant),whereinthesize wasmonitoredfor15min,wasperformedforcomparison.
Theminimumflocculantdosageconsideredinthisstudy(1mg/gofPCC)wasbased onthetypicalvaluesusedinapapermillfortheflocculationofmineralfillers.Otherauthors havetestedsimilardosagesofbioflocculantsfortheflocculationofdistinctminerals.As anexample,Sirviöetal.[25]testeddosagesofupto9mg/gofmineral,whileAguado etal.[15]testedtheadditionof20mg/gofmineral.Higherdosages,ofupto500mg/gof mineral,weretestedbyCampanoetal.[41].
Besidesthemeansizeandsizedistribution,LDSalsoallowsustoinferthestructure oftheformedflocsbymeansofmassfractaldimensions(dF )[31,42,43].ThedF expresses thedegreetowhichprimaryparticlesfillthespacewithinthenominalvolumeoccupied byanaggregate;thiscanbeusedasanindicationofthefluffiness/densityoftheflocs (Equation(1)):
m(R) ∝ Rd F (1)
Themass(m)ofanyfractalaggregateisdirectlyproportionaltoitsradius(R),raised totheexponent,dF [44].AdF valuetendingto1indicatesamorestringyandlessdense flocstructure,whileavalueapproaching3suggestsstrongeranddenserflocs[42].
AccordingtotheRayleigh–Gans–Debye(RGB)theory,thedF canbecalculatedfrom thenegativeslopeofthelog-logplotofthescatteredlightintensityversusthescattering wavevector(q)(Equation(2))[35,44]:
q=(4πn0 /λ0 )sin(θ/2)(2)
n0 istherefractiveindexofthedispersantmedium(1.33forwater), θ isthescatteringangle (between0.01◦ and40.6◦ fortheMastersizer2000equipment)and λ0 istheincidentlight wavelengthinvacuo(630nm).
ThevalidityoftheRGBtheoryisbasedontheassumptionthattheelementaryunits scatterlightindependently,thisbeingmoreappropriateforsub-micronsphericalparticles
withlowrefractiveindex[43]andapplicablewhentheregionofstudyismuchlargerthan theprimaryparticlesandismuchsmallerthantheflocaggregates(Equation(3))[45].
1/Ragg <<q<<1/Rpart (3)
Ragg istheradiusoftheaggregateandRpart istheradiusoftheprimaryparticle.
Forsystemswheretheflocculationisverypronouncedandthesizeoftheflocs (secondaryaggregationresultingfromtheaggregationofprimaryflocs)fallsoutofthe applicabilityrangeoftheRGBtheory,theinformationabouttheflocsisprovidedbythe scatteringexponent(SE)[43,46].TheSEcorrespondstothenegativeslopeofthelog-log plotofthescatteredlightintensity,versusqatlargelength-scales(lowdiffractionangles).
Inshort,structuralinformationabouttheflocsinacertainsystemcanbeobtained fromthedF forsmall-lengthscales(highdiffractionangles)andfromSEforhigh-length scales(smalldiffractionangles),asexemplifiedinFigure 2,correspondingtotheprimary andsecondaryaggregates,respectively.
Figure2. Exampleofthelog-logplotofscatteringlightintensityversusqforthedeterminationof thescatteringexponent,SE(firstregion),andthefractaldimension,dF (secondregion).
Thestructuralinformation(dF andSE)oftheflocsthatwereformedinthesecond flocculationstudy(best-performingsamples)wasobtainedbyoutputtingtherawdataof theLDSequipmenttoanexternalspreadsheet(providedbyMalvernInstruments)forthe offlineanalysisofthedataandforcomputingtheangleofeachdetectorandtheintensity oflightateachdetector.MakinguseofEquation(2),thedatawasfurthercomputedinto log-logplotsofscatteredlightintensityversusthescatteringwavevector(q)(Figure 2), wheneitherdF orSEcouldbeobtained.
DrainabilityandretentiontestswereperformedwiththecommercialCPAMandthe cationiccellulosesthatpresentedthebestperformanceintheLDSflocculationtests.
Beforecarryingoutthedrainagetests,suspensionsofthedifferentrequiredcomponentswereprepared.
ThesameBEKP(presentingarefiningdegreeof17◦ SR)thatwasusedtoprepare thecationiccelluloseswasusedforthedrainabilitytestsintheformofa1wt% solids contentsuspension.ThePCCwaspreparedasa1wt%solidscontentsuspension.The commercialCPAMandtheproducedcationiccelluloseswerepreparedas0.1wt%solutions/suspensions(asdescribedpreviouslyfortheflocculationtests).
Thedrainagetimeswererecordedinadynamicdrainageanalyzer(DDA,ABAkribi Kemikonsulter,Sweden)forformulationswithpulp,fillerandretentionagent(CPAMor cationiccellulose)[8].
Theformulationswerepreparedinordertoobtainsheetswithanominalfillercontent of20wt%.Forreference,testsusingonlypulpandPCC(80BEKP:20PCC)andwithouta retentionagentwereperformed.Contentsof0.02,0.2and0.4wt%ofcationiccellulose (correspondingto1,10and20mgofcationiccellulosepergramofPCC)weretestedand comparedtosampleswiththeadditionof0.02wt%ofCPAM.
ThepulpwasdisintegratedintheDDAvesselat1200rpmfor60s.Thefiller,preflocculatedwiththeretentionagentfor60sinanexternalbeakerwithmagneticstirring (700rpm),wasthenaddedtothepulpsuspensioninsidetheequipmentvessel,reachinga totalsolidsconcentrationof5g/Landafinalvolumeof500mL(extrawaterwasaddedto thepulpduringdisintegrationtoachievethefinaldesiredvolume).Thefinalsuspension waskeptat800rpmfor60sandwassubsequentlydrained.TheDDAvesselwasequipped witha60-mesh(250 μmporesize)screenandavacuumof30kPawasmaintainedinthe equipment.
Afterdrainage,theformedwetpadswereremovedfromtheformingscreenand driedat105 ◦ C.Thedriedpadsweresubsequentlycalcinatedat525 ◦ C(accordingtothe TAPPIstandard,T211)todeterminetheeffectivefillercontentandthecorrespondingfiller retention.
3.1.ChemicalAnalysis
Asmentionedbefore,cationiccelluloseswithdistinctmorphologiesandlevelsof cationizationwereobtainedbytheincorporationofquaternaryammoniumgroupsintothe BEKPstructureviadirectcationizationwithCHPTACorbyatwo-stepreaction(periodate oxidation+Girard’sreagentT)andthesubmissionofsomeofthesamplesfortreatmentin anHPH.ThesuccessfulcationizationwasconfirmedbytheZP(Table 2)andFTIR(Figure 3) results,andtheextentofthecationizationwasassessedbythedeterminationoftheDSand CD(Table 2).
Table2. CharacterizationoftheoriginalBEKPandcellulosescationizedwithCHPTACandGT. DS CD(mmol/g) ZP(mV) 1 YF(%)SF(%) avgMw(Da) 2,3 /PDI 4 BEKP- 0.14 ± 0.01 5 23 ± 5--CH0.080.08 ± 0.020.46 ± 0.04+29 ± 3--CH0.160.16 ± 0.000.92 ± 0.04+18 ± 4--CH0.13_F 6 0.13 ± 0.010.78 ± 0.01+26 ± 329.0 ± 0.40.0 ± 0.0GT0.320.32 ± 0.011.62 ± 0.09+21 ± 4--GT1.06_P1.06 ± 0.003.44 ± 0.00+35 ± 2-100.0 ± 0.0 2150 ± 12/1.01 ± 0.00 972 ± 8.5/1.02 ± 0.00 GT0.02_F 6 0.02 ± 0.010.23 ± 0.04+24 ± 26.4 ± 0.66.1 ± 1.0GT0.04_F 6 0.04 ± 0.010.32 ± 0.03+29 ± 511.5 ± 1.06.5 ± 1.6GT0.16_F 6 0.16 ± 0.010.90 ± 0.02+27 ± 298.4 ± 0.539.9 ± 1.4 1081 ± 3.5/1.11 ± 0.00 526 ± 0.5/1.02 ± 0.00 GT0.36_FP 6 0.36 ± 0.011.68 ± 0.04+30 ± 3100.0 ± 0.099.6 ± 0.4 1025 ± 43/1.06 ± 0.02 543 ± 4.5/1.01 ± 0.00
1 Determinedatca.pH7; 2 bimodaldistributions; 3 measuredforthesolublefractionofthesample; 4 polydispersityindex; 5 carboxylcontentoftheinitialBEKP,determinedbyconductometrictitration[47]; 6 Datafrom [23].
ThenegativeZP( 23mV)ofBEKPshiftedtopositivevaluesforalltheCCs,with theZPvaluesrangingbetween+18and+35mV,indicatingthesuccessfulincorporationof cationicmoietiesintothecellulosestructure.
Figure3. TheFTIR-ATRspectraoftheoriginalBEKPandcellulosescationizedwithCHPTACandGT.
ThechemicalmodificationsinducedinthecellulosewereanalyzedbyFTIR-ATR. TheFTIRspectraoftheoriginalBEKPandCCs,normalizedbythehighestpeakofBEKP (1028cm 1 ),arepresentedinFigure 3
ForthesamplescationizedwithCHPTAC,itwaspossibletoobservetheappearance ofashoulderat1473cm 1 relatedtothestretchingvibrationofthemethylgroupsofthe quaternaryammonium[48],alongwithasmallpeakat1638cm 1 duetotheincreased hydrophilicityandconsequentwateradsorption[49].Thechangesaremoreevidentforthe sampleknownasCH0.16,withthehighestDS.Forthesamplessubjectedtothetwo-step cationization,anewsetofdistinctpeaksisvisible(thisislessevidentforsamplesGT0.02_F andGT0.04_F,duetotheirlowDS).Theabsorbanceat1683cm 1 canbeassignedtothe stretchingofthecarbonylgroupontheGTstructure[50].Thebandat1558cm 1 confirms theformationoftheiminebondbetweenDACandGT[50].Thepeaksfoundat1473cm 1 and1414cm 1 arerelatedtotheasymmetricandsymmetricbendingofthemethylgroups ofGT,respectively[26].Thepeakat923cm 1 canbeassignedtotheasymmetricstretching oftheC–Nbond[26],theN–Nbond[50,51],ortothestretchingvibrationoftheC–C= bond[52]oftheGTgroups.
Theglucosering-openingandsubsequentoxidationofthehydroxylgroupsinto aldehydegroupsduringtheperiodateoxidationofcellulosecanjustifythedecreasein intensityobservedinthebandsat1158cm 1 and1052cm 1 [26,53].Theappearanceof
asmallpeakat868cm 1 canbeassociatedwiththeexistenceofhemiacetalbondsthat formedbetweentheremainingaldehydegroupsandnearbyhydroxylgroups[54].
Thecontentofquaternaryammoniumgroupsintroducedintothecellulosestructure wasquantifiedintermsofDSandCD(Table 2)viaelementalanalysisandpotentiometrictitration,respectively.ThesamplescationizedwithCHPTACpresentedaDSinthe rangeof0.08–0.16,whileforthosepreparedbythetwo-stepreactionwithGT,arangeof 0.02–1.06 wasobtained.TheCDoftheCCswasestimatedintherangeof0.23–3.44mmol/g.
Figure 4 displaysopticalmicroscopyimagesoftheoriginalBEKPandtheproduced CCs,allatthesamemagnification.ForthesamplesCH0.08andCH0.16,novisiblemorphologicalchangesareobservedinthecellulosefibers,keepingtheirstructureintactand similartothatoftheoriginalBEKP.TheHPHtreatmentoftheoriginalfibersledtothepartialdisruptionofthecellulosestructure,inducingtheformationoflongmicro/nanofibrils, asvisibleinsampleCH0.13_F.
Figure4. OpticalmicroscopyimagesoftheoriginalBEKPandcellulosescationizedwithCHPTAC andGT(*Residualcellulosefiberfragments).
Forthesamplesobtainedbythetwo-stepreaction,sampleGT0.32presentsfibers withanincreaseddiameterandtheappearanceofballoonsalongthefibers,withoutthe noticeablereleaseoffibrilsintothemedium,whilesampleGT1.06_P,revealsthattheinitial cellulosefiberswerealmostcompletelysolubilized(withtheexceptionofsomesmall, visiblefibersfragmentsremaining,probablyduetosomecross-contamination).
Theremainingsamples(GT0.02_F,GT0.04_F,GT0.16_FandGT0.36_FP)thatwere obtainedaftertheHPHtreatmentclearlyshowtheeffectofthemechanicaltreatment. SamplesGT0.02_FandGT0.04_Frevealthatthecellulosefibersbrokedownintosmaller fiberfragments,alongwiththeliberationofmicro/nanofibrilsintothemedium(which areshorterthanthosepresentinsampleCH0.13_F).SimilarlytosampleGT1.06_P,for samplesGT0.16_FandGT0.36_FP,onlyresidualsmallfiberfragmentscanbeseen,with allthecellulosefibersbeingconvertedtomicro/nanofibrilsandthenpartiallyortotally solubilized.
ThesamplestreatedintheHPHwerealsocharacterizedintermsofYFandSFto quantifythedeconstructionlevelsufferedbythecellulosefibers.SampleCH0.13_Fpresents aYFof29%andshowsnosolubilizationofcellulosefibers(SFof0%)(Table 2).Allthe samplesthatwerecationizedwithGThavesolubilizedcellulose,rangingfrom6.1%for GT0.02_Fto99.6%forGT0.36_FP.AsfortheYF,itincreasesfrom6.4%(sampleGT0.02_F) to100%(sampleGT0.36_FP).
FortheMwofthecationiccellulosepolyelectrolytes(GT0.36_FPandGT1.06_P)and forthesolublefractionofsampleGT0.16_F,abimodaldistributionwasobtained(Table 2), withsamplesGT0.36_FPandGT0.16_Fpresentingpeaksnear1000and500Daandsample GT1.06_Ppresentingpeaksat2150and972Da.
Theevolutionofthed50 ofthePCCflocsformedbythecontactofthePCCwiththe retentionagent(CPAMorCCs)asafunctionofthedosageoftheretentionagent,monitored byLDS,isplottedinFigure 5
Figure5. Themedianflocsizeasafunctionofflocculantdosage(the x-axiscorrespondstoboththe flocculantdosageandthetimeofflocculation).
WhennoretentionagentwasaddedtothePCCsuspension(blackline),thed50 of PCCsufferedasmallincreasefromtheinitial4.8 μmto5.8 μmafter15min,indicating
asmallnaturaltendencyforaggregation.Thereferencesyntheticcommercialretention agent(CPAM)presentsacurvedistinctfromthoseusingCCs.CPAMresultedinthe bestperformancefordosagesbelow5mg/gofPCC,alsoshowingthefastestflocculation kineticsuptoadosageof2mg/gofPCC(16.5 μm),fromwhichthesizeoftheflocsstarts tostabilize,levelingoffatca.40 μm.TheseresultsindicatethatadosageofCPAMabove 2or3mg/gofPCCdoesnotbringbenefitsintermsofflocculation.
WiththeadditionoftheoriginalBEKP,nochangeswereobservedintheflocculation ofPCC,withtheflocsachievingasizeof5.6 μmafterthefinaladditionof15mg/gofPCC (aswiththePCCsuspensionalone).SimilarresultsweredetectedforthesamplesCH0.08, GT1.06_PandGT0.36_FP,withflocsreachingafinalsizeof6.0,5.7and5.3 μm,respectively. SamplesGT0.02_F,GT0.32andCH0.16resultedinflocsizesthatwereslightlybiggerthan thoseofthePCCwithoutaretentionagent,withthefinalsizesrangingbetween6.6and 7.4 μm.
However,withsamplesGT0.04_FandGT0.16_F,anincreaseinflocculationperformancewasobserved,resultinginafinalflocsizeof11and20 μm,respectively;sample CH0.13_Fledtothebestflocculationperformance,exhibitinganaveraged50 of554 μm. Contrarytotheothersamples,theincreasedtendencyofthislattersampletopromote PCCflocculationalsoresultedinahighstandarddeviationofd50 ,clearlyvisibleafteran additionlevelof5mg/gofPCCandisindicativeofmoreheterogeneousflocculation.
Comparingthecurvesobtainedforthedistinctcellulosesamplesandconsideringtheir morphologicalandchemicalproperties,somemajortendenciescanbederived.Grouping thesamplescomposedofintactcellulosefibers(BEKP,CH0.08andCH0.16),itispossible toobserveasmallincreaseinflocculationperformancewithanincreasinglevelofcationization.SampleGT0.32,whereinthecellulosefibersstartshowingsignsofdegradation, ledtoaslightdecreaseintheaveragesizeoftheflocs.Thisbehaviorisanindicationthat thecationicchargeofthefibers(withaDSof0.32)isbecomingexcessive(comparedto CH0.16,withaDSof0.16)and,sincethePCCusedinthisstudypresentsaslightlypositive charge,thiscanleadtochargerepulsion.Anincreaseincationization(GT1.06_P)resulted inthecompleteabsenceofflocculation,furtherstrengtheningthehypothesisofexcessive cationicity.
ThepositiveeffectofHPHtreatmentandthedifferencebetweenthetwodistinctcationizationmethodscanbeobservedbycomparingsampleCH0.16withsamplesGT0.16_F andCH0.13_F.Withthefibrillationofthecellulosefibersandthesubsequentincreasein theavailablespecificsurfacearea,thefinald50 increasedbyca.3timesforGT0.16_Fand ca.75timesforCH0.13_F.AlthoughbothsamplespresentasimilarDSandweresubjected tothesameHPHtreatment,theyledtoverydistinctflocculationperformances.Such behaviorcanbeexplainedbythelengthdifferenceoftheobtainedfibrils,withsample GT0.16_Fpresentingamoredegradedstructureand,even,partiallysolubilizedcellulose,a consequenceoftheharshercationizationreaction,namely,thesodiumperiodateoxidation thatleadstotheopeningoftheglucoserings,asexplainedelsewhere[23].
ThefibrillatedsamplesobtainedbycationizationwithGTpresentedanincreased flocculationbehaviorfromsampleGT0.02_FuptosampleGT0.16_FwithhigherDS.An increaseinDSupto0.36(GT0.36_FP)resultedinthecompletesolubilizationofthesample andcompletelossoftheflocculationpotential.
Thetwobest-performingCCs(CH0.13_FandGT0.16_F)andCPAMweresubjectedto furtherflocculationtests.ThegrowthofthePCCflocswasrecordedovertime(15min)for afixeddosageoftheretentionagent(1,2,4,8and10mg/gofPCC),addedallatonceat 0min.TheobtainedflocculationcurvesareplottedinFigure 6.
Figure6. Medianflocssizeasafunctionofflocculationtimeforseveralconcentrationsofthebest flocculants.
TheevolutionofthesizeoftheflocsobtainedwithCPAM,forthevariousdosages tested,showsaverydistinctbehaviorcomparedtobothCCs.Independentlyofthedosage ofCPAM,theflocculationcurvesareverysimilar,withtheflocsreachingasizeofca.31 μm foradosageof1mg/gofPCCandasizeofca.43 μmforthehighestdosageof10mg/gof PCC.Althoughthehighestdosageultimatelyresultedinthelargestflocsizes,itispossible toverifyadeclineintheflocculationrate,attheinitialminutesofflocculation(1to7min), comparedtothelowerdosages.Suchbehaviorcanbeanindicationofanexcessofpolymer, resultinginslowerflocculationkineticsduetothechangeddiffusionbarriersandrepulsive forces[55].
WiththeCCs,thesizeofthefinalflocsseemstobeverydependentontheinitial dosageofpolymer.SampleCH0.13_Fpresentedaninitialflocculationpeakataroundthe 2-minutemark(similartoCPAM).Atadosageof1and2mg/gofPCC,theflocculation wasslowerthanwithCPAM,whereas,atadosageof4mg/gofPCCorabove,theopposite occurred.Withanadditionof1to4mg/gofPCC,therewasaninitialincreaseinthesize oftheflocsuntilthe2-minutepoint,withtheflocsizesstabilizingafterwarduntiltheend ofthetest(7to38 μm).Forahigherdosage(8and10mg/gofPCC)theflocscontinuedto increaseinsizeuntiltheendofthetest(ca.154and321 μm,respectively).
SampleGT0.16_Fshowedtheslowestflocculationkineticsamongthethreesamples. WhilebothCPAMandCH0.13_Fpresentedaninitialburstinflocculationforallthedosages tested,thesampleGT0.16_Fpresentedaslowandsteadyincreaseinthesizeoftheflocsat alowerdosage(1and2mg/gofPCC),withtheflocculationkineticsincreasingforhigher dosages.Forthetesteddosagesof1to10mg/gofPCC,afinalflocsizeofbetween8.5and 17.5 μmwasobtained.
Intheliterature,CPAMofhighMwandlowtomediumCDhavebeenutilizedto promoteflocculationviathebridgingmechanism(whichistypicallyassociatedwithafast flocculationrate)[32].
Thus,duetothelowCDandlongfibrils,bridgingisprobablythedominantmechanismforsampleCH0.13_F.Theexistenceofresidualcarboxylgroups(ionizedatpH9) inthecellulosefibers’structure,andtheirpossibleattractiveinteractionwithquaternary ammoniumgroups(andalsowiththeslightlypositivelychargedPCC),mayfavorthe entanglementofthelongfibrilsbetweenadjacentflocs;thistrendmayexplaintheextreme sizeoftheflocsobtainedfor8and10mg/gofPCC.
Ontheotherhand,sampleGT0.16_Fpresentedslowerflocculationkinetics.This reductionintheaveragesizeoftheflocs,comparativelytoCH0.13_F,isaresultofthe higherlevelofdegradationofthefibrils(shorterfibrils)andthepartialsolubilizationofthe sample(SFof40%).
Observingthevariousflocculationcurves,itispossibletoverifythatnotallthesystems wereabletoachieveasteadystate.Nevertheless,sincethefocusoftheworkistoexplore
thepotentialofcellulose-basedflocculantsforuseinpapermaking,andbecause,inthe papermakingprocess,theavailablecontacttimebetweentheflocculantandmineralfiller beforepaperproductionislowerthan15min,thereisnoneedtoextendtheflocculation testsfurther.Typically,theavailabletimecanbeevenlowerthan5min,andsothemost importantminutesaretheinitialminutesofflocculation.
ThedF andSEprofiles,calculatedfromthescatteringdatafortheflocculationtests presentedinFigure 6,areplottedinFigure 7.Aspreviouslyreferredto,ananalysisof thedF andSEcangivesomeinsightsregardingthestructure(density)oftheprimaryand secondaryaggregates,respectively.
Figure7. Evolutionofthescatteringexponent(SE)andmassfractaldimension(dF )asafunctionof flocculationtimeforseveralconcentrationsofthebestflocculants.
Inthisflocculationsystem,theprimaryparticlescanbeseenastheindividualsmaller PCCparticles.Forallthreesamples,thedF startedatca.2,droppingtoca.1.7after2min.
RegardingtheSEprofile,whichismorerepresentativeofthelargeraggregatesformed duringtheflocculationprocess,atthebeginningofthetest,asthesecondaryaggregates startedtoform,theypresentedaSEofca.0.5(lowdensity);astimeelapsedandflocculation progressed,thesecondaryaggregatesbecomemorecompactduetotheinclusionofmore particles,reachingsteadycompactness.
WhenusingCPAM,independentlyofthedosageused,SEincreasedrapidlyinthe initialminutes,coincidingwiththefastgrowthoftheflocs.After6min,theSEslowly stabilizedataround2.2.
TheflocsobtainedwithbothCCsbecamemorecompactwithincreasinglevelsof addition.
ForsampleCH0.13_F,adosageof1or2mg/gofPCCresultedinlowSEvalues (0.7and1.1,respectively).Adosageof4mg/gofPCCoraboveproducedflocswitha compactnesssimilartothatofthoseobtainedwithCPAM(SEofca.2.4).Asforsample GT0.16_F,atthelowestdosage,flocsthatwereslightlydenserthanthoseobtainedwith CH0.13_F(SEof1versus0.7)wereformed.Atadosageof2mg/gofPCC,similardensities wereobtainedforbothCCs(SEofca.1.1).Withafurtherdosageincrease,theflocsbecame morecompact,achievingamaximumSEofca.2atthehighestdosageof10mg/gofPCC (lowerthanthe2.2obtainedwithCPAMandCH0.13_F).
Thedrainagetimeandfillercontent/fillerretentionresultsforthepulpsuspension containingpre-flocculatedPCCarepresentedinFigure 8.AtestwithonlypulpandPCC (noretentionagent)wasperformedasareference.Consideringthepreviousflocculation resultsobtainedbyLDS,whereCPAMdemonstratedalmostthesameperformanceforall thedosagestested,onlythelowestdosage(1mg/gofPCCor0.02wt%addition)wasused intheDDAtests.ForbothCCs(CH0.13_FandGT0.16_F),threelevelsofadditionwere tested(1,10and20mg/gofPCC,equivalenttoanadditionof0.02,0.2and0.4wt%).
Figure8. Drainagetime,fillercontentandfillerretentionasafunctionofdosageofthebestflocculants.
ForthesuspensionwithonlypulpandPCC(referencetest),thedrainagetimewas 1.59s.Fromthetargetfillercontentof20wt%,onlyca.43%wasretainedduringdrainage (lessthanhalftheaddedamount),resultinginaneffectivefinalfillercontentof8.6wt%. WiththeadditionofCPAM(1mg/gofPCC),thefillerretentionincreasedtoca.73%, correspondingtoafillercontentof14.5wt%(anincreaseofca.70%versusthereference). Asaconsequenceoftheincreasedretention,anincreaseinthedrainagetimeto1.65swas alsoobserved.
ForbothCCs,anincreaseinfillerretentionwasalwaysdetected,whichretention directlyimprovedwiththelevelofaddition.Nevertheless,noneoftheformulationsledto betterretentionthanthatofCPAM.
SampleGT0.16_FledtoabetterfillerretentionthansampleCH0.13_Fat54.8,58.7and 61.6%against45.8,49.6and60.7%,foranadditionof0.02,0.2and0.4wt%,respectively.
Intermsofdrainability,sampleCH0.13_F,alwayspresenteddrainagetimesthatwere lowerthanthereferenceandthatdecreasedwiththeincreaseintheadditionlevel,with areductionofca.7%to1.48sforthehighestdosage.ForsampleGT0.16_F,thedrainage timesremainedslightlyhigherthanthereference.
ThedeclineinthedrainagetimeobservedforsampleCH0.13_Fwhenhigherdosages wereusedcanbeexplainedbytheexcessivetendencyofthissampletoflocculate(as observedbyLDS),promotingtheformationoflargeandporousflocsoffibers.Thesebig flocscanresultintheheterogeneityofthepad,whichleadstoregionswithfewerfibers thatpromotepreferentialdrainagechannelsandaconsequentdecreaseinthedrainage time.TheexistenceofthesechannelsmayalsofavorthelossofsmallPCCflocsthatare notproperlystucktothefibernetwork,whichmayexplainwhythestructureofsample CH0.13_F,althoughdemonstratingahigherflocculationperformancethanGT0.16_Finthe LDSflocculationtests,didnottranslateintoimprovedfillerretention.
Severalcationiccellulosederivativeswithdistinctmorphologies,namely,fibers,microandnanofibrillatedcellulosesandsolublecelluloses,withdegreesofsubstitutionranging between0.02and1.06,wereproducedbytheincorporationofquaternaryammonium groupsintothecellulosestructure.AdirectreactionwithCHPTACoratwo-stepreaction withGirard’sreagentTwasusedforcationization.Cationicmicro-andnanofibrillated celluloseswereproducedbysubsequenthigh-pressurehomogenization.
TheproducedsampleswereevaluatedbyLDSintermsoftheirpotentialtoflocculate PCC(intermsoftheaveragesizeofflocs)andwerecomparedagainstacommercialCPAM.
ThefibrillatedcelluloseswithaDSof0.13(CH0.13_F,obtainedbytheCHPTAC pretreatment)and0.16(GT0.16_F,obtainedbytheGirardTpretreatment)demonstrated thehighestflocculationpotential,beingthebestandsecond-bestperformingsamples, respectively.TheflocculationofsampleCH0.13_Fatdosagesabove4mg/gofPCCresulted inflocsizesgreaterthanthoseobtainedwithCPAM.ThesampleGT0.16_F,independently ofthedosageused(1to10mg/gofPCC),alwaysledtoflocssmallerthanwithCPAM addedatthelowestdosage(1mg/gofPCC).
Bothcationicsampleswerefurtherincorporatedintopulpandfillerformulationsand wereanalyzedinadynamicdrainageanalyzertoquantifytheireffectsonfillerretention. ComparedtothereferenceformulationofonlypulpandPCC(noretentionaid),wherea fillerretentionofca.43%wasobtained,bothcelluloseswereabletoincreasethelevelsof retentiontoca.61–62%(foranincorporationof0.4wt%),remaining,however,belowthe 73%achievedwithCPAM(foranincorporationof0.02wt%).
Thecationiccellulosesweredemonstratedtobeapromisingnewbio-basedretention agent,withthepotentialtoreplaceCPAMasaretentionagentinpapermaking,althoughthe resultsofthisworkindicatetheneedforfurtherstudiesinordertoachieveperformances similartoorbetterthanthoseofthefossil-basedretentionagentsthatareusedpresently, andwithequivalentcosts.
AuthorContributions: Conceptualization,J.F.S.P.,L.A.,M.G.R.andP.J.T.F.;fundingacquisition, P.J.T.F.;investigation,J.F.S.P.andL.A.;projectadministration,P.J.T.F.;supervision,C.P.N.,M.G.R.and P.J.T.F.;writing—originaldraft,J.F.S.P.andL.A.;writing—reviewandediting,J.F.S.P.,L.A.,C.P.N., M.G.R.andP.J.T.F.Allauthorshavereadandagreedtothepublishedversionofthemanuscript.
Funding: ThisworkwascarriedoutundertheProjectInpactus–innovativeproductsandtechnologies fromeucalyptus,ProjectN.◦ 21874fundedbyPortugal2020throughEuropeanRegionalDevelopment Fund(ERDF)intheframeofCOMPETE2020n◦ 246/AXISII/2017.Theauthorsalsowantto acknowledgetheStrategicResearchCentreProjectUIDB/00102/2020,fundedbytheFundaçãoparaa CiênciaeTecnologia(FCT),theProjectToxApp4NanoCELFI(PTDC/SAU-PUB/32587/2017,fromthe FoundationforScienceandTechnology,Portugal),andtheNetworkCYTEDNanocelia-Transferencia TecnológicasobreAplicacionesdeNanocelulosaenIberoamérica.J.F.S.P.alsoacknowledgesthePhD grantBDE05|POCI-01-0247-FEDER-021874.
InstitutionalReviewBoardStatement: Notapplicable.
InformedConsentStatement: Notapplicable. DataAvailabilityStatement: Notapplicable.
ConflictsofInterest: Theauthorsdeclarenoconflictofinterest.
References
1.Shen,J.;Song,Z.;Qian,X.;Liu,W.ModificationofPapermakingGradeFillers:ABriefReview. BioResources 2009, 4,1190–1209.
2. Thorn,I.;Au,C.O.(Eds.) ApplicationsofWet-EndPaperChemistry,2nded.;Springer:Dordrecht,TheNetherlands;London,UK, 2009;ISBN978-1-4020-6037-3.
3.Holik,H.(Ed.) HandbookofPaperandBoard;Wiley-VCH:Weinheim,Germany,2006;ISBN978-3-527-30997-9.
4. Biermann,C.J. HandbookofPulpingandPapermaking(SecondEdition);AcademicPress:SanDiego,CA,USA,1996; ISBN978-0-08-053368-1.
Polymers 2022, 14,3309
5. Hubbe,M.A.;Nanko,H.;McNeal,M.R.RetentionAidPolymerInteractionswithCellulosicSurfacesandSuspensions:AReview. BioResources 2009, 4,850–906.[CrossRef]
6. Hubbe,M.A.;Gill,R.A.FillersforPapermaking:AReviewofTheirProperties,UsagePractices,andTheirMechanisticRole. BioResources 2016, 11,2886–2963.[CrossRef]
7.Roberts,J.C. TheChemistryofPaper;RSCpaperbacks;RoyalSocietyofChemistry:London,UK,1996;ISBN978-0-85404-518-1.
8. Antunes,E.;Garcia,F.A.P.;Ferreira,P.;Blanco,A.;Negro,C.;Rasteiro,M.G.UseofNewBranchedCationicPolyacrylamidesto ImproveRetentionandDrainageinPapermaking. Ind.Eng.Chem.Res. 2008, 47,9370–9375.[CrossRef]
9.Joshi,S.J.;Abed,R.M.M.BiodegradationofPolyacrylamideandItsDerivatives. Environ.Processes 2017, 4,463–476.[CrossRef]
10.King,D.J.;Noss,R.R.ToxicityofPolyacrylamideandAcrylamideMonomer. Rev.Environ.Health 1989, 8,3–16.[CrossRef]
11. Fatima,A.;Yasir,S.;Khan,M.S.;Manan,S.;Ullah,M.W.;Ul-Islam,M.PlantExtract-LoadedBacterialCelluloseComposite MembraneforPotentialBiomedicalApplications. J.Bioresour.Bioprod. 2021, 6,26–32.[CrossRef]
12. Lourenço,A.F.;Gamelas,J.A.F.;Nunes,T.;Amaral,J.;Mutjé,P.;Ferreira,P.J.InfluenceofTEMPO-OxidisedCelluloseNanofibrils onthePropertiesofFiller-ContainingPapers. Cellulose 2017, 24,349–362.[CrossRef]
13. Lourenço,A.F.;Gamelas,J.A.F.;Sarmento,P.;Ferreira,P.J.T.AComprehensiveStudyonNanocellulosesinPapermaking:The InfluenceofCommonAdditivesonFillerRetentionandPaperStrength. Cellulose 2020, 27,5297–5309.[CrossRef]
14. Heinze,T.;Seoud,O.A.E.;Koschella,A. CelluloseDerivatives:Synthesis,Structure,andProperties;SpringerSeriesonPolymerand CompositeMaterials;SpringerInternationalPublishing:Berlin/Heidelberg,Germany,2018;ISBN978-3-319-73168-1.
15. Aguado,R.;Lourenço,A.F.;Ferreira,P.J.;Moral,A.;Tijero,A.CationicCellulosicDerivativesasFlocculantsinPapermaking. Cellulose 2017, 24,3015–3027.[CrossRef]
16. Aguado,R.;Moral,A.;Tijero,A.CationicFibersfromCropResidues:MakingWasteMoreAppealingforPapermaking. J.Clean. Prod. 2018, 174,1503–1512.[CrossRef]
17. Diab,M.;Curtil,D.;El-shinnawy,N.;Hassan,M.L.;Zeid,I.F.;Mauret,E.BiobasedPolymersandCationicMicrofibrillated CelluloseasRetentionandDrainageAidsinPapermaking:ComparisonbetweenSoftwoodandBagassePulps. Ind.CropsProd. 2015, 72,34–45.[CrossRef]
18. Korhonen,M.H.J.;Laine,J.FlocculationandRetentionofFillerswithNanocelluloses. Nord.PulpPap.Res.J. 2014, 29,119–128. [CrossRef]
19. Li,G.;Fu,Y.;Shao,Z.;Zhang,F.PreparingCationicCelluloseDerivativeinNaOH/UreaAqueousSolutionandItsPerformance asFillerModifier. BioResources 2015, 10,7782–7794.[CrossRef]
20. Hasani,M.;Cranston,E.D.;Westman,G.;Gray,D.G.CationicSurfaceFunctionalizationofCelluloseNanocrystals. SoftMatter 2008, 4,2238–2244.[CrossRef]
21. Kono,H.;Kusumoto,R.Preparation,StructuralCharacterization,andFlocculationAbilityofAmphotericCellulose. React.Funct. Polym. 2014, 82,111–119.[CrossRef]
22. Moral,A.;Aguado,R.;Ballesteros,M.;Tijero,A.CationizationofAlpha-CellulosetoDevelopNewSustainableProducts. Int.J. Polym.Sci. 2015, 2015,1–9.[CrossRef]
23. Pedrosa,J.F.S.;Rasteiro,M.G.;Neto,C.P.;Ferreira,P.J.T.EffectofCationizationPretreatmentonthePropertiesofCationic EucalyptusMicro/NanofibrillatedCellulose. Int.J.Biol.Macromol. 2022, 201,468–479.[CrossRef][PubMed]
24. Sirviö,J.;Hyvakko,U.;Liimatainen,H.;Niinimaki,J.;Hormi,O.PeriodateOxidationofCelluloseatElevatedTemperatures UsingMetalSaltsasCelluloseActivators. Carbohydr.Polym. 2011, 83,1293–1297.[CrossRef]
25. Sirviö,J.;Honka,A.;Liimatainen,H.;Niinimäki,J.;Hormi,O.SynthesisofHighlyCationicWater-SolubleCelluloseDerivative andItsPotentialasNovelBiopolymericFlocculationAgent. Carbohydr.Polym. 2011, 86,266–270.[CrossRef]
26. Grenda,K.;Arnold,J.;Gamelas,J.A.F.;Rasteiro,M.G.EnvironmentallyFriendlyCellulose-BasedPolyelectrolytesinWastewater Treatment. WaterSci.Technol. 2017, 76,1490–1499.[CrossRef]
27. Hubbe,M.A.FlocculationandRedispersionofCellulosicFiberSuspensions:AReviewofEffectsofHydrodynamicShearand Polyelectrolytes. BioResources 2007, 2,296–331.
28. Merayo,N.;Balea,A.;delaFuente,E.;Blanco, Á.;Negro,C.InteractionsbetweenCelluloseNanofibersandRetentionSystemsin FlocculationofRecycledFibers. Cellulose 2017, 24,677–692.[CrossRef]
29. Shin,J.-H.;Han,S.H.;Sohn,C.;Ow,S.K.;Mah,S.HighlyBranchedCationicPolyelectrolytes:FillerFlocculation. TappiJ. 1997, 80, 179–185.
30. Saritha,V.;Srinivas,N.;SrikanthVuppala,N.V.AnalysisandOptimizationofCoagulationandFlocculationProcess. Appl.Water Sci. 2017, 7,451–460.[CrossRef]
31. Rasteiro,M.G.;Garcia,F.A.P.;DelMarPerez,M.ApplyingLDStoMonitorFlocculationinPapermaking. Part.Sci.Technol. 2007, 25,303–308.[CrossRef]
32. Rasteiro,M.G.;Garcia,F.A.P.;Ferreira,P.;Blanco,A.;Negro,C.;Antunes,E.TheUseofLDSasaTooltoEvaluateFlocculation Mechanisms. Chem.Eng.Processing:ProcessIntensif. 2008, 47,1323–1332.[CrossRef]
33. Antunes,E.;Garcia,F.A.P.;Blanco,A.;Negro,C.;Rasteiro,M.G.EvaluationoftheFlocculationandReflocculationPerformanceof aSystemwithCalciumCarbonate,CationicAcrylamideCo-Polymers,andBentoniteMicroparticles. Ind.Eng.Chem.Res. 2015, 54,198–206.[CrossRef]
34.Blanco,A.;Fuente,E.;Negro,C.;Tijero,J.FlocculationMonitoring:FocusedBeamReflectanceMeasurementasaMeasurement Tool. Can.J.Chem.Eng. 2002, 80,1–7.[CrossRef]
35. Rasteiro,M.G.;Garcia,F.A.P.;Ferreira,P.;Blanco,A.;Negro,C.;Antunes,E.EvaluationofFlocsResistanceandReflocculation CapacityUsingtheLDSTechnique. PowderTechnol. 2008, 183,231–238.[CrossRef]
36. Lourenço,A.F.;Godinho,D.;Gamelas,J.A.F.;Sarmento,P.;Ferreira,P.J.T.CarboxymethylatedCelluloseNanofibrilsinPapermaking:InfluenceonFillerRetentionandPaperProperties. Cellulose 2019, 5,3489–3502.[CrossRef]
37. Grenda,K.;Arnold,J.;Gamelas,J.A.F.;Cayre,O.J.;Rasteiro,M.G.FlocculationofSilicaNanoparticlesbyNatural,Wood-Based Polyelectrolytes. Sep.Purif.Technol. 2020, 231,115888.[CrossRef]
38. Grenda,K.;Gamelas,J.A.F.;Arnold,J.;Cayre,O.J.;Rasteiro,M.G.EvaluationofAnionicandCationicPulp-BasedFlocculants withDiverseLigninContentsforApplicationinEffluentTreatmentFromtheTextileIndustry:FlocculationMonitoring. Front. Chem. 2020, 8,5.[CrossRef][PubMed]
39. Wei,J.;Du,C.;Liu,H.;Chen,Y.;Yu,H.;Zhou,Z.PreparationandCharacterizationofAldehyde-FunctionalizedCellulosicFibers throughPeriodateOxidizationofBambooPulp. BioResources 2016, 11,8386–8395.[CrossRef]
40. Grenda,K.;Gamelas,J.A.F.;Arnold,J.;Cayre,O.J.;Rasteiro,M.G.CationizationofEucalyptusWoodWastePulpswithDiverse LigninContentsforPotentialApplicationinColoredWastewaterTreatment. RSCAdv. 2019, 9,34814–34826.[CrossRef]
41. Campano,C.;Lopez-Exposito,P.;Blanco,A.;Negro,C.;vandeVen,T.G.M.HairyCationicNanocrystallineCelluloseasaNovel FlocculantofClay. J.ColloidInterfaceSci. 2019, 545,153–161.[CrossRef]
42. Bushell,G.ForwardLightScatteringtoCharacteriseStructureofFlocsComposedofLargeParticles. Chem.Eng.J. 2005, 111, 145–149.[CrossRef]
43. Liao,J.Y.H.;Selomulya,C.;Bushell,G.;Bickert,G.;Amal,R.OnDifferentApproachestoEstimatetheMassFractalDimensionof CoalAggregates. Part.Part.Syst.Charact. 2005, 22,299–309.[CrossRef]
44. Biggs,S.;Habgood,M.;Jameson,G.J.;Yan,Y.AggregateStructuresFormedviaaBridgingFlocculationMechanism. Chem.Eng.J. 2000, 80,13–22.[CrossRef]
45. Jarvis,P.;Jefferson,B.;Parsons,S.A.Breakage,Regrowth,andFractalNatureofNaturalOrganicMatterFlocs. Environ.Sci. Technol. 2005, 39,2307–2314.[CrossRef]
46. Im,W.;LaeLee,H.;Youn,H.J.;Seo,D.StructureCharacterizationofGroundCalciumCarbonateFlocsbyFractalAnalysisand TheirEffectsonHandsheetProperties. TAPPIJ. 2013, 12,17–23.[CrossRef]
47. Kekäläinen,K.;Liimatainen,H.;Illikainen,M.;Maloney,T.C.;Niinimäki,J.TheRoleofHornificationintheDisintegration BehaviourofTEMPO-OxidizedBleachedHardwoodFibresinaHigh-ShearHomogenizer. Cellulose 2014, 21,1163–1174. [CrossRef]
48. Song,Y.;Zhang,J.;Gan,W.;Zhou,J.;Zhang,L.FlocculationPropertiesandAntimicrobialActivitiesofQuaternizedCelluloses SynthesizedinNaOH/UreaAqueousSolution. Ind.Eng.Chem.Res. 2010, 49,1242–1246.[CrossRef]
49. Odabas,N.;Amer,H.;Bacher,M.;Henniges,U.;Potthast,A.;Rosenau,T.PropertiesofCellulosicMaterialafterCationizationin DifferentSolvents. ACSSustain.Chem.Eng. 2016, 4,2295–2301.[CrossRef]
50. Huang,X.;Dognani,G.;Hadi,P.;Yang,M.;Job,A.E.;Hsiao,B.S.CationicDialdehydeNanocellulosefromSugarcaneBagassefor EfficientChromium(VI)Removal. ACSSustain.Chem.Eng. 2020, 8,4734–4744.[CrossRef]
51. Otoni,C.G.;Figueiredo,J.S.L.;Capeletti,L.B.;Cardoso,M.B.;Bernardes,J.S.;Loh,W.TailoringtheAntimicrobialResponseof CationicNanocellulose-BasedFoamsthroughCryo-Templating. ACSAppl.BioMater. 2019, 2,1975–1986.[CrossRef][PubMed]
52. Liu,Y.;Yu,Y.;Wang,Q.;Xu,J.;Fan,X.;Wang,P.;Yuan,J.Biological–ChemicalModificationofCelluloseNanocrystaltoPrepare HighlyCompatibleChitosan-BasedNanocomposites. Cellulose 2019, 26,5267–5279.[CrossRef]
53. Zhang,L.;Yan,P.;Li,Y.;He,X.;Dai,Y.;Tan,Z.PreparationandAntibacterialActivityofaCellulose-BasedSchiffBaseDerived fromDialdehydeCelluloseandL-Lysine. Ind.CropsProd. 2020, 145,112126.[CrossRef]
54. Calvini,P.;Gorassini,A.;Luciano,G.;Franceschi,E.FTIRandWAXSAnalysisofPeriodateOxycellulose:EvidenceforaCluster MechanismofOxidation. Vib.Spectrosc. 2006, 40,177–183.[CrossRef]
55. Antunes,E.;Garcia,F.A.P.;Ferreira,P.;Blanco,A.;Negro,C.;Rasteiro,M.G.EffectofWaterCationicContentonFlocculation, FlocsResistanceandReflocculationCapacityofPCCInducedbyPolyelectrolytes. Ind.Eng.Chem.Res. 2008, 47,6006–6013. [CrossRef]
The paper provides a comprehensive review of moulded pulp production, properties and advantages over single-use plastics and bioplastics for food packaging. Bagasse, wheat and bamboo are replacing wood as the fibersources due to their cost effectiveness, wide availability and rapid renewability. Non-wood pulping and thermoforming processes have also advanced greatly which lead to improved fiber recovery, production efficiencyand product quality. Challenges include lengthy production cycles, high chemical and energy uses, competitionfrom bioplastics, and presence of toxic per-and poly-fluoroalkyl substances (PFAS). The industry is evolvingrapidly to overcome these challenges including new l aminated dry thermoforming processes, natural additives,customized fiber mixes, and PFAS-free products. Life-cycle assessments and provision of clear, viable green wasteand recycling pathways relative to plastic alternatives are still needed to establish and maintain the competitiveness of cellulosic bioproducts with plastics. Critical research areas are proposed.
Contact information:
1Department of Wood Science, The University of British Columbia, 2424 Main Mall, Vancouver, British Columbia V6T 1Z4, Canada
2Bioproducts Institute, Department of Chemical and Biological Engineering, Department of Chemistry and Department of Wood Science, The University of BritishColumbia, 2360 East Mall, Vancouver, British Columbia V6T 1Z3, Canada
3Application Engineering -Engineered Wood, Henkel Corporation, 10 Finderne Avenue, Bridgewater, NJ 08807, USA
Food Packaging and Shelf Life 33 (2022) 100908. https://doi.org/10.1016/j.fpsl.2022.100908
Creative Commons Attribution International License4.0
The Paper Industry Technical Association (PITA) is an independent organisation which operates for the general benefit of its members –both individual and corporate –dedicated to promoting and improving the technical and scientific knowledge of those working in the UK pulp and paper industry. Formed in 1960, it serves the Industry, both manufacturers and suppliers, by providing a forum for members to meet and network; it organises visits, conferences and training seminars that cover all aspects of papermaking science. It also publishes the prestigious journal Paper TechnologyInternational® and the PITA Annual Review, both sent free to members, and a range of other technical publications which include conference proceedings and the acclaimed Essential Guideto Aqueous Coating.
— ’
journal homepage: www.elsevier.com/locate/fpsl
’
’
’ ’ ’ ’
’ ’
’
’
’ ’ ’ ’ ’
≤ ’
–––––〈 = + + + = = = + + + = 〉 ’ ’ 〈 = 〉 〈 〉 〈 = = 〉
Ø –〈 〉 〈 〉
〈 〉 ´ ´ 〈 〉 〈 〉 “ ” 〈 〉 “ ” 〈 〉 〈 〉 〈 = 〉 〈 〉 〈 〉 〈 〉 〈 〉 〈 〉 〈 〉 ’ 〈 〉
“ ” Ø Ø ’ 〈 〉 〈 〉 〈 〉 〈 〉
’ ’ 〈 〉 〈 〉 –〈 〉
〈 〉 〈 〉 〈 〉 〈 〉 ’ ’
ø ø
〈 〉 〈 〉 ´ 〈 〉 〈 〉 ’
´ ´ 〈 〉 〈 〉
• 〈 〉 〈 〉
’ 〈 〉
〈 〉 〈 〉
Paper has shaped society for centuries and is considered one of humanity’s most important inventions. However,pulp and paper products can be damaging to social and naturalsystems along their lifecycle of materialextraction, processing, transportation, and waste handling. The pulp and paper industry is among the top fivemost energy-intensive industries globally and is the fourth largest industrial energy user. This industry accountsfor approximately 6% of global industrial energy use and 2% of direct industrial CO2 emissions. The pulp andpaper industry is also the largest user of original or virgin wood, with deleterious impacts on both human healthand local flora and fauna, including aquatic ecosystems. This critical and systematic review seeks to identifyalternatives for mitigating the climate impacts of pulp and paper processes and products, thus making the pulpand paper industry more environmentally sustainable. This study reviews 466 studies to answer the followingquestions: what are the main determinants of energy and carbon emissions emerging from the pulp and paperindustry? What are the benefits of this industry adopting low-carbon manufacturing processes, andwhat barrierswill need to be tackled to enable such adoption? Using a sociotechnical lens, we answer these questions, identifybarriers for the pulp and paper industry’s decarbonization, and present promising avenues for future research.
Contact information:
1Science Policy Research Unit (SPRU), University of Sussex Busi ness School, UK
2School of Chemistry and Chemical Engineering, Queen’s Universi ty Belfast, Belfast BT9 5AG, UK
3Center for Energy Technologies, Department of Business Development and Technology, Aarhus University, Denmark
4Department of Earth and Environment, Boston University, United States
5Khalifa University of Science and Technology, Abu Dhabi, United Arab Emirates
6Colorado School of Mines, Colorado, USA
7Department of Earth Resources and Environmental Engineering, Hanyang University, Republic of Korea
8School of Mechanical and Aerospace Engineering, Queen’s University Belfast, Belfast BT9 5AH, UK
9Civil, Structural, and Environmental Engineering, Trinity Coll ege Dublin, The University of Dublin, Ireland
Renewable and Sustainable Energy Reviews 167 (2022) 112706. https://doi.org/10.1016/j.rser.2022.112706
Creative Commons Attribution 4.0 International License
The Paper Industry Technical Association (PITA) is an independent organisation which operates for the general benefit of its members –both individual and corporate –dedicated to promoting and improving the technical and scientific knowledge of those working in the UK pulp and paper industry. Formed in 1960, it serves the Industry, both manufacturers and suppliers, by providing a forum for members to meet and network; it organises visits, conferences and training seminars that cover all aspects of papermaking science. It also publishes the prestigious journal Paper TechnologyInternational® and the PITA Annual Review, both sent free to members, and a range of other technical publications which include conference proceedings and the acclaimed Essential Guide to Aqueous Coating.
journal homepage: www.elsevier.com/locate/rser
’ ’ ’
’ ’
’
’ ’ ’ € ’ ’
’ ’
“ ” “ ”
”
“ ”
’
’ ’
◦ ◦ ◦
’ ’ ’ ’ ’ ’ ’ ’ ’ ’
’ ’ ’
’ “ ’
’ ’
’
’ ’
’ ’
“ ” ’ ’
’
’
’ ’ ’ ’ “ ” ’ ’
’ ’ ’ ’ “ ”
’
’ “ ”
’
–
’ ’ ’ ’
–´ –
’
’ ’ –
’ ´ ’ ´ ´ ´ –
’ ø ø ø ø ’ ´
–’
’ — ø ––
” –’ ” ø –’
´ –
’ “
The effect of cellulose nanofibers (CNFs)/polyvinyl alcohol (PVA) coating on the hydrophobic,oleophobic, and strength properties of paper were investigated. The results showed that the sizeof bamboo fibers (BFs) decreased significantly and the crystallinity increased signifi cantly afterbiological enzyme treatment. The average length of CNFs obtained by high pressure homogenization and the crystallinity was 63.63%. When the coating weightof PVA/CNF was 2.0 g/m2 and the CNF dosage was increased from 0.0% to 3.0%, the paper greaseresistance grade was increased from 7 to 9, the Cobb value was decreased from 22.68 ± 0.29 g/m2 to 18.37 ± 0.63 g/m2, the contact angle was increased from 67.82° to 93.56°, and the longitudinaland transverse tensile index were increased from 67.72 ± 0.21 N m/g and 37.63 ± 0.25 N m/g to68.61 ± 0.55 N m/g and 40.71 ± 0.78 N m/g, respectively. When the CNF dosage was 3.0% andthe coating weight of PVA/CNF was 4.0 g/m2 , the grease resistance grade of the paper was 12,the Cobb value was 21.80 ± 0.39 g/m2, and the longitudinal and transverse tensile indices were72.11 ± 0.43 N m/g and 42.58 ± 0.48 N m/g, respectively. In summary, the increase of CNFs caneffectivelyimprove the lipophobicity, hydrophobicity and tensile strength of the PVA coated paper.
information:
of Textile Science and Engineering (International Institute of Silk), Zhejiang Sci-Tech University, Hangzhou 310018, Zhejiang, China.
Jinchang Specialty Paper Co., Ltd., Quzhou 324404, Zhejiang,China.
Scientific Reports
The Paper Industry Technical Association (PITA) is an independent organisation which operates for the general benefit of its members –both
corporate –dedicated to promoting and improving the technical and scientific knowledge of those working in the UK pulp and paper industry. Formed in 1960, it serves the Industry, both manufacturers and suppliers, by providing a forum for members to meet and network; it organises visits, conferences and training seminars that cover all aspects of papermaking science. It also publishes the prestigious journal Paper TechnologyInternational® and the PITA Annual Review, both sent free to members, and a range of other technical publications which include conference proceedings and the acclaimed Essential Guide to Aqueous Coating
Grease-proof paper is a kind of paper with resistance to grease penetration and absorption, which is used in industrial, medical, food, and other packaging fields1. Most paper cannot prevent the decay and deterioration of goods by preventing grease, water, and oxygen transmission2. Therefore, plastic films such as polyethylene (PE) and polypropylene (PP) are used to improve the hydrophobic and oleophobic properties of paper3. However, most petroleum-based plastics are non-biodegradable, non-renewable, and have low recyclability4. Moreover, microplastics also threaten human health through the food chain5. In addition, fluorine-containing oil repellent is widely used in the production of grease-proof paper as an excellent grease-proof coating liquid6. But most fluorinated packaging materials release non-biodegradable perfluoroalkyl substances during the composting process, which are not only harmful to the environment but also to human beings7. Thus, safe, and environmentally friendly new fluorine-free oil-repellent materials have become a research hotspot, such as degradable polymers, nanocellulose, and chitosan, et al.8 10
The porous structure of paper is inherently oil-absorbing by means of capillary force, and cellulose surface is also oleophilic, therefore, surface coating is an effective method to prevent oil/grease from penetrating into the interior of the paper according to the pore blocking theory11. Polyvinyl alcohol (PVA) is a white water-soluble polymer compound with strong adhesion, smoothness, oil resistance, and solvent resistance12 14. It is an environmentally friendly functional material that can be degraded into water and carbon dioxide by bacteria and enzymes15. Therefore, PVA is widely used in papermaking as an environmentally friendly oil repellent material. The PVA coating can significantly improves the oleophobicity of paper, but the hydrophobicity of paper decreases due to the hydrophilicity of PVA. Shen et al.16 reported that the addition of alkyl ketene dimer (AKD) in PVA coating improved the hydrophobic property of paper, but the grease-proof property decreased. Therefore, the hydrophilic property of PVA limits its application as an oil repellent material.
12:16148
Nanocellulose is a cellulose particle with a size of less than 100 nm in one dimension, which is obtained by the chemical or mechanical processing of plant fibers. Research shows that nanocellulose products have great strength and function17. To realize the special application of nanocellulose, they are divided into various types, including microcrystalline cellulose (MCC), microfibrillated cellulose (MFC), cellulose nanofibers (CNFs), cellulose nanocrystals (CNCs), nanorods, and cellulose whiskers, etc.18 21. Compared with plant fibers, CNFs have greater advantages in aspect ratio and specific surface area, with a diameter of 2–100 nm and a length of 500–1000 nm22. Turbak et al.23 and Herrick et al.24 first used a high-pressure homogenizer to treat wood pulp to prepare CNFs with a diameter of less than 100 nm in 1983. The raw materials for preparing CNFs are not only wood, but also seed fibers, bast fibers, grasses, etc. The properties of CNFs prepared from different raw materials are also different. In order to obtain CNFs with a purer concentration, bamboo pulp fibers with less lignin content were selected as raw materials in this paper25.
Furthermore, Belbekhouche et al.26 demonstrated that CNF films are more beneficial than CNC films for barrier properties. Because the surface of CNFs contains a lot of hydroxyl groups, the CNF films have better barrier properties27. Wang et al.28 demonstrated that the CNF coating provided excellent hydrophobic properties to the paper. To further improve the hydrophobic properties of CNF coated paper, Mertaniemi et al.29 sprayed CNFs on the glass surface, and then used tridecafluoro-1,1,2,2-tetrahydrooctyl)trichlorosilane (FOTS) to modify it by fluorination. Studies have shown that CNF films also have certain oil/grease resistance30. Koppolu et al.31 used nanocellulose and polylactic acid (PLA) as coating raw materials to prepare barrier packaging paper with both hydrophobicity and oleophobicity. Therefore, the development of CNFs has offered a new alternative to the polymer coating to form a barrier layer32 33
Generally, CNFs were used as a coating to improve air resistance, oil resistance, surface strength, stiffness and tensile strength of paper, while Cobb index and roughness decreased34,35. In addition, there are several researchers about the use in combination of PVA and CNFs. Chaabouni et al.36 added CNFs to PVA to prepare adhesives and found that the viscosity and water resistance of the adhesives increased, and strongly enhanced the mechanical performance in wet conditions. Deng et al.37 prepared CNFs-PVA composite films and found that there are strong interaction and good compatibility between CNFs and PVA molecules. Furthermore, the light transmittance and thermal expansion coefficient of the composite films were decreased, while the tensile strength, Young’s modulus, glass transition temperature, and thermal stability were all improved compared with the PVA films38. CNFs and PVA are used in combination in some fields such as films, adhesives, and aerogels39,40. However, no researchers have studied the hydrophobic and oleophobic properties of PVA/CNF as coating.
In this study, we investigated the properties of CNFs and the effect of CNFs on the hydrophobicity, oleophobicity, and strength of PVA coated paper. CNFs were prepared from bamboo pulp fibers and mixed with PVA to prepare PVA/CNF coating solution. The hydrophobic and oleophobic PVA/CNF coated paper was obtained by a coating method, which was also degradable, recyclable, and environmentally friendly.
Bleached bamboo pulp (beating degree 13.5ºSR, wet weight 15.13 g) and base paper (110 g/m2) were obtained from Zhejiang Jinchang Specialty Paper Co., Ltd. (Quzhou, China). The bleached bamboo pulp composition: cellulose (94.37 wt%), hemicellulose (4.74 wt%), lignin (0.67 wt%), ash (0.10 wt%), and extractive (0.12 wt%). Bleached bamboo pulp Cellulase (enzyme activity 16,000 HCU/g) was obtained from Zhejiang Jinjiahao Green Nanomaterials Ltd. (Quzhou, China). Polyvinyl alcohol (analytical reagent (AR) grade), citric acid (AR grade), sodium citrate (AR grade), and other chemical reagents were purchased from Sinopharm Chemical Reagent Co. Ltd. (Shanghai, China).
Bamboo pulp was dispersed in water, then 60 U/g of cellulase and citric acid-sodium citrate buffer solution were added, and the reaction was carried out at pH 5.0 and temperature of 50 °C for 6 h, and the enzyme reaction was terminated at 90 °C. Then, the dispersed bamboo pulp was centrifuged at 8000 rpm for 15 min, and the undissolved part was precipitated, which was the enzyme-treatment bamboo fibers (EBFs). The EBFs were homogenized by a high-pressure homogenizer (AH-pilot2018, Shanghai Dibosi Biotechnology Co., Ltd., China) to obtain CNFs.
PVA and CNFs were fully dissolved and mixed in 90 °C water, and then dispersed in an ultrasonic cleaner (KQ-30DE, Kunshan Ultrasonic Instruments Co., Ltd., China), then the uniform CNF/PVA composite coating was obtained.
The prepared composite coating was coated on the surface of the base paper by a manual coater (ZAA 2300, Zehntner, Switzerland), and then dried at 80 °C to obtain the paper with hydrophobic and oleophobic properties. The preparation process and properties of PVA/CNF coated paper are shown in Fig. 1
The morphology of bamboo fibers (BFs) and EBFs were detected by fiber analyzer (LDAO2, OpTest, Canada) and optical microscope (S800T-930HD, Jiangxi Beitekar Photoelectric Technology Co., Ltd., China). The surface morphology of CNFs was observed by atomic force microscope (XE-100E, PSIA, Korea). The atomic force microscope images of CNFs were imported into Nanoscope analysis and Nano measurer software, and 50 CNFs were randomly selected to measure their length and diameter. In addition, the obtained data were graphed and analyzed using Oringin software. The length and diameter of CNFs were analyzed using Nanoscope analysis software. The microstructure of BFs, EBFs, and CNFs was analyzed by infrared spectrometer (Nicolet 5700, Thermo Fisher Scientific, USA) and X-ray diffractometer (ARL XTRA, Thermo
12:16148
Figure 1. The preparation process and properties of PVA/CNF coated paper.
ARL, Switzerland). The samples were scanned at 40 kV and 30 mA in a 2 h range between 10° and 40° using Cu Kα radiation (λ = 15.4 × 10–2 nm) at 1°/min41. The crystallinity index (CrI) was calculated according to the empirical method developed by Segal (1959) using the Eq. (1) 42
where I200 is the maximum intensity of the (200) plane (I200, 2θ = 22°) that represents the crystalline and amorphous material, and Iam is the minimum intensity between plane (110) and (200) (Iam, 2θ = 18°) that represents the amorphous material.
The viscosity and pH of the coatings were measured with a viscometer (ROTAVISC lo-vi Complete, IKA, Germany) and a pH meter (PHS-3E, Shanghai Yidian Scientific Instruments Co., Ltd., China). The oil/grease resistance of paper was measured using the TAPPI T559 standard. The contact angle of paper was measured according to ASTM D 724–1999 standard, using a surface contact angle tester (OCA40, Dataphysics, Germany). Water absorption of paper (Cobb test) was determined using Paper Cobb Water Absorption Tester (PWA-01, Sichuan Changjiang Paper Instrument Co., Ltd., China) according to TAPPI T441 standard. The tensile strength of paper was determined using a computerized tensile tester (TTM, Hangzhou Qingtong Boke Automation Technology Co., Ltd., China) according to the TAPPI T494 standard. The surface morphology of the paper was observed using a scanning electron microscope (Phenom pro, Phenom Scientific Instruments (Shanghai) Co., Ltd., China).
Morphology analysis. Figure 2 shows the optical microscope images of BFs and EBFs. Compared with BFs, the diameter of EBFs did no change significantly, about 20 μm. The average length of the EBFs was 0.4 mm, which was 1.1 mm smaller than the diameter of the BFs (Table 1). The reason for this phenomenon was that the amorphous region of cellulose was hydrolyzed by cellulase43. The reduction of fiber length was beneficial to the exfoliation of microfibrils from the fibers during the preparation of nanocellulose.
Figure 3a shows the image of CNF tested with the atomic force microscope (AFM). As shown in Fig. 3a, the CNF was a filamentous structure. And the length and diameter of CNFs were mostly distributed between 1–3.5 μm and 18–42 nm, with an average length of about 2.4 μm and an average diameter of about 28.7 nm (Fig. 3b,c).
FTIR spectroscopy analysis. Figure 4 shows the Fourier transform infrared (FTIR) spectra of BFs, EBFs, and CNFs. It could be seen from the figure that EBFs, CNFs, and BFs had similar characteristic peaks. They all con-
tained the characteristic peaks representing cellulose, such as the stretching vibration peak of –OH at 3425 cm−1, the stretching vibration peak of –CH at 2900 cm−1, and the bending vibration peak of –CH at 1375 cm−144. Compared with BFs, the absorption peaks of EBFs and CNFs were enhanced. The stretching vibration peak of –CO at 1030 cm−1 was enhanced, indicating that some of the cellulose of EBFs was hydrolyzed, and the content of primary hydroxyl groups increased45. The enhancement of the peak at 897 cm−1 was due to the breakage of some β-glycosidic bonds and the destruction of cellulose molecular chain46. In summary, EBFs and CNFs still maintained the basic chemical structure of cellulose.
X-ray diffraction analysis. Figure 5 shows the X-ray diffraction (XRD) patterns of BFs, EBFs, and CNFs. The diffraction overlapped peak at about 16° correspond to the (1–10)/(110) cellulose crystallographic plane, and the diffraction peaks of 22° and 34.5° correspond to the (200) and (004) cellulose crystallographic plane, respectively, which belong to the typical cellulose type I crystal47,48. Compared with BFs, the crystallinity of EBFs increased from 53.08% to 67.26%, which was
to the amorphous region of cellulose being destroyed by enzymes49. Compared with BEFs, the
homogenization has
of CNFs decreased slightly to 63.63%, which indicated that
effect on the crystalline region of cellulose.
Figure 4. FTIR spectra of BFs, EBFs, and CNFs.
Figure 5. XRD patterns of BFs, EBFs, and CNFs.
Table 2 shows the physical properties of the base paper. The Kit number of paper was 0, the Cobb value was 17.75 g/m2, and the contact angle was 95.21°, which show that the base paper had excellent hydrophobic properties, but had no oleophobic properties.
Table 3 showed that the viscosity of the PVA/CNF coating was 2032 ± 37 cP, which was 103.61% higher than of the PVA coating. Therefore, the CNF increased the viscosity of coating, which was consistent with the research results of Malucelli et al.50. The abundant hydroxyl groups on the CNF surface, which would absorb water and swell in water, thus increasing the internal friction of the coating when it flows. In addition, the formation of stronger hydrogen bond networks between PVA and CNF hydroxyl groups was also one of the reasons why the viscosity of PVA/CNF coating was significantly higher than that of PVA coating51
Figure 6 shows that the grease resistance grade of base paper was 0, which does not have grease resistance performance. The effect of CNF dosage on grease resistance of paper is shown in Fig. 7 When the coating weight was 2.0 g/m2, the grease resistance grade of PVA coated paper was 7. The grease resist-
Table 3. Coating properties. Note: The concentration of PVA was 10%, and the CNF dosage was 3.0% (relative to the mass of PVA).
Figure 6. Images of kit testing of (a) base paper,
b) PVA coated paper, and (c) PVA/CNF coated paper.
Figure 7. Effect of CNF dosage on grease resistance of paper.
ance performance was further improved with the addition of CNFs in PVA coating. When the CNF dosage was 3.0%, the grease resistance grade of the coated paper reached the highest value, which was grade 9, and then it was unchanged with the further increase of CNF dosage. When the coating weight was 4.0 g/m2 and the CNF dosage was 1.0%, the grease resistance grade of the PVA/CNF coated paper reached the highest level, which was grade 12.
Compared with base paper, the coated paper had better oil and grease resistance, which was due to the porous structure of base paper, that the liquid was easily absorbed and penetrated. After coating, the surface of the paper was covered with a continuous film, which greatly reduced the void size of paper, thereby reducing the penetration rate of liquids52. Furthermore, the addition of CNFs to the coating further improved the grease resistance of the coated paper, which was due to the CNFs increased the compactness of the coated film, preventing oil and grease from penetrating into the paper inside11
As shown in Fig. 8, with the CNF dosage increased from 0.0% to 3.0%, the Cobb value of the coated paper gradually decreased, indicating that the hydrophobicity gradually improved. When the CNF dosage exceeded 3.0%, the Cobb value began to increase, so the hydrophobicity began
to decline. It may be due to that the free hydroxyl groups of PVA are completely bound to CNF, and the hydrophilic hydroxyl groups of CNFs are dominant. When the coating weight was 2.0 g/m2 and the CNF dosage was 3.0%, the Cobb value of coated paper reached the minimum value of 18.37 ± 0.63 g/m2, which was 19.00% lower than that of PVA coated paper. When the coating weight was 4.0 g/m2 and the CNF dosage was 3.0%, the Cobb value of coated paper was 21.80 ± 0.39 g/m2, which was 19.31% lower than that of PVA coated paper.
As can be seen from Fig. 9, the contact angle of the base paper was 95.21°, the PVA coated paper was 67.82°, and the PVA/CNF coated paper was 93.56°. Figure 9 demonstrated that the hydrophobic properties of the base paper decreased significantly after PVA coating, while the PVA/CNF coated paper basically maintained the hydrophobicity as the base paper. Due to the presence of a lot of free hydroxyl groups in PVA, the hydrophilicity of the paper coating surface is enhanced. However, with the addition of CNFs, the network structure formed between CNFs and CNFs and the hydrogen bonds between CNFs and PVA reduced the free hydroxyl groups on the coating surface, resulting in a better hydrophobic performance of the PVA/CNF coating53
Figure 10 shows the effect of CNF dosage on the tensile strength of coated paper. As shown in Fig. 10, when the CNF dosage was increased from 0.0% and 3.0%, the tensile index of the coated paper increased significantly with the CNF dosage increased. However, continuing to increase the CNF dosage, the tensile index of the coated paper increased slowly. When the coating weight was 2.0 g/m2 and the CNF dosage increased from 0.0 to 3.0%, the transverse tensile index of the coated paper increased from 37.63 ± 0.25 N m/g to 40.71 ± 0.78 N m/g (Fig. 10a). Furthermore, when the coating weight was 4.0 g/m2 and the CNF dosage increased from 0.0% to 3.0%, the transverse tensile index of coated paper increased from 39.56 ± 0.22 N m/g to 42.58 ± 0.48 N m/g. As shown in Fig. 10b, the longitudinal tensile strengths of coated papers with 2.0 g/m2 and 4.0 g/m2 were 68.61 ± 0.55 N m/g and 72.11 ± 0.43 N m/g when the CNF dosage was 3.0%.
CNFs is rich in hydroxyl groups, which can combine with the fibers on the surface of paper by hydrogen bonding, and improve the bonding force between the fibers, thus improving the tensile strength of paper. In addition, CNFs and PVA form hydrogen bonds, forming a compact film on the paper surface, further improving the tensile strength of the paper54
Figure 11 shows the SEM images of base paper, PVA coated paper, and PVA/CNF coated paper. It can be observed from the Fig. 11a that the fibers of the base paper are crisscrossed, and there are a lot of gaps between the fibers. These gaps allow the liquid to penetrate the inside of the paper through capillary action, which is the main reason why the base paper does not have water and oil resistance. From the Fig. 11b,c we can observe that PVA and PVA/CNF coatings formed a smooth film on the surface of the paper, reducing the gap between fibers, thereby improving the ability of the paper to barrier oil/grease and water.
This study showed that the basic chemical structures of BFs, EBFs and CNFs were similar and belong to the cellulose type I crystal. In addition, the prepared CNFs have the smallest size, with an average length of about 2.4 μm, an average diameter of about 28.7 nm, and a crystallinity of 63.63%. This study also showed that the oleophobicity, hydrophobicity, and tensile strength of the coated paper increased gradually with the increase of CNF dosage in the PVA/CNF coating solution. When the PVA/CNF coating weight was 2.0 g/m 2 and the CNF dosage was increased from 0.0% to 3.0%, the paper grease resistance grade was increased from 7 to 9, the Cobb value was decreased from 22.68 ± 0.29 g/m2 to 18.37 ± 0.63 g/m2, the contact angle was increased from 67.82° to 93.56°, and the longitudinal and transverse tensile index were increased from 67.72 ± 0.21 N m/g and 37.63 ± 0.25 N m/g to 68.61 ± 0.55 N m/g and 40.71 ± 0.78 N m/g, respectively. Furthermore, with the increase of PVA/CNF coating amount, the hydrophobicity, oleophobicity and strength of PVA/CNF coated paper were improved. In summary, compared with the PVA coated paper, the hydrophobic and oleophobic properties of PVA/CNF coated paper are significantly improved, and the strength is maintained well. It is of great significance for the development of environmentally friendly oilproof packaging materials.
All data generated or analysed during this study are included in this published article.
Received: 17 July 2022; Accepted: 14 September 2022
1. Kjellgren, H., Stolpe, L. & Engstrom, G. Oxygen permeability of polyethylene-extrusion-coated greaseproof paper. Nord Pulp. Pap. Res. J. 23, 272–276. https://doi.org/10.3183/npprj-2008-23-03-p272-276 (2008).
2. Yook, S. et al. Barrier coatings with various types of cellulose nanofibrils and their barrier properties. Cellulose 27, 4509–4523. https://doi.org/10.1007/s10570-020-03061-5 (2020).
3. Zhang, H., Miles, C., Gerdeman, B., LaHue, D. G. & DeVetter, L. Plastic mulch use in perennial fruit cropping systems: A review. Sci. Hortic. 281, 109975. https://doi.org/10.1016/j.scienta.2021.109975 (2021).
4. Leja, K. & Lewandowicz, G. Polymer biodegradation and biodegradable polymers: A review. Pol. J. Environ. Stud. 19, 255–266 (2010).
5. Smith, M., Love, D. C., Rochman, C. M. & Neff, R. A. Microplastics in seafood and the implications for human health. Curr. Environ. Health Rep. 5, 375–386. https://doi.org/10.1007/s40572-018-0206-z (2018).
6. Aulin, C. et al. Wetting kinetics of oil mixtures on fluorinated model cellulose surfaces. J. Colloid Interface Sci. 317, 556–567. https:// doi.org/10.1016/j.jcis.2007.09.096 (2008).
7. Choi, Y. J., Lazcano, R. K., Yousefi, P., Trim, H. & Lee, L. S. Perfluoroalkyl acid characterization in US municipal organic solid waste composts. Environ. Sci. Technol. Lett. 6, 372–377. https://doi.org/10.1021/acs.estlett.9b00280 (2019).
8. Hubbe, M. A. & Pruszynski, P. Greaseproof paper products: A review emphasizing ecofriendly approaches. BioResources 15, 1978–2004 (2020).
9. Al-Gharrawi, M. Z., Wang, J. W. & Bousfield, D. W. Improving recycling of polyethylene-coated paperboard with a nanofibrillated cellulose layer. BioResources 16, 3285–3297. https://doi.org/10.15376/biores.16.2.3285-3297 (2021).
10. Frone, A. N. et al. Preparation and characterization of pva composites with cellulose nanofibers obtained by ultrasonication. BioResources 6, 487–512 (2011).
11. Aulin, C., Gallstedt, M. & Lindstrom, T. Oxygen and oil barrier properties of microfibrillated cellulose films and coatings. Cellulose 17, 559–574. https://doi.org/10.1007/s10570-009-9393-y (2010).
12. Gottberg, J. M., Lappalainen, T. & Salminen, K. Polyvinyl alcohol as foaming agent in foam formed paper. Tappi J. 18, 475–485. https://doi.org/10.32964/TJ18.8.475 (2019).
13. Baker, M. I., Walsh, S. P., Schwartz, Z. & Boyan, B. D. A review of polyvinyl alcohol and its uses in cartilage and orthopedic applications. J. Biomed. Mater. Res. B 100B, 1451–1457. https://doi.org/10.1002/jbm.b.32694 (2012).
14. Bolto, B., Tran, T., Hoang, M. & Xie, Z. L. Crosslinked poly(vinyl alcohol) membranes. Prog. Polym. Sci. 34, 969–981. https://doi. org/10.1016/j.progpolymsci.2009.05.003 (2009).
15. Pathak, V. M. & Navneet, R. Review on the current status of polymer degradation: A microbial approach. Bioresour. Bioprocess. 4, 15. https://doi.org/10.1186/s40643-017-0145-9 (2017).
16. Shen, Z. H., Kwon, S., Oh, K., Abhari, A. R. & Lee, H. L. Facile fabrication of hydrophobic cellulosic paper with good barrier properties via PVA/AKD dispersion coating. Nord Pulp Pap. Res. J. 34, 516–524. https://doi.org/10.1515/npprj-2019-0040 (2019).
17. Bendahou, D., Bendahou, A., Seantier, B., Grohens, Y. & Kaddami, H. Nano-fibrillated cellulose-zeolites based new hybrid composites aerogels with super thermal insulating properties. Ind. Crop Prod. 65, 374–382. https://doi.org/10.1016/j.indcrop.2014.11. 012 (2015).
18. Bandera, D. et al. Influence of mechanical treatments on the properties of cellulose nanofibers isolated from microcrystalline cellulose. React. Funct. Polym. 85, 134–141. https://doi.org/10.1016/j.reactfunctpolym.2014.09.009 (2014).
19. Anderson, S. R. et al. Enzymatic preparation of nanocrystalline and microcrystalline cellulose. Tappi J. 13, 35–42. https://doi.org/ 10.32964/TJ13.5.35 (2014).
20. Brinchi, L., Cotana, F., Fortunati, E. & Kenny, J. Production of nanocrystalline cellulose from lignocellulosic biomass: Technology and applications. Carbohydr. Polym. 94, 154–169. https://doi.org/10.1016/j.carbpol.2013.01.033 (2013).
21. Bilbao-Sainz, C., Bras, J., Williams, T., Sénechal, T. & Orts, W. HPMC reinforced with different cellulose nano-particles. Carbohydr. Polym. 86, 1549–1557. https://doi.org/10.1016/j.carbpol.2011.06.060 (2011).
22. Mishra, R. K., Sabu, A. & Tiwari, S. K. Materials chemistry and the futurist eco-friendly applications of nanocellulose: Status and prospect. J. Saudi Chem. Soc. 22, 949–978. https://doi.org/10.1016/j.jscs.2018.02.005 (2018).
23. Turbak, A. F., Snyder, F. W. & Sandberg, K. R. in J Appl Polym Sci Appl Polym Symp. 815–827.
24. Herrick, F. W., Casebier, R. L., Hamilton, J. K. & Sandberg, K. R. in J. Appl. Polym. Sci.: Appl. Polym. Symp. (ITT Rayonier Inc.).
25. Nechyporchuk, O., Belgacem, M. N. & Bras, J. Production of cellulose nanofibrils: A review of recent advances. Ind. Crop. Prod. 93, 2–25. https://doi.org/10.1016/j.indcrop.2016.02.016 (2016).
26. Belbekhouche, S. et al. Water sorption behavior and gas barrier properties of cellulose whiskers and microfibrils films. Carbohydr. Polym. 83, 1740–1748. https://doi.org/10.1016/j.carbpol.2010.10.036 (2011).
27. Kan, K. H. M. & Cranston, E. D. Mechanical testing of thin film nanocellulose composites using buckling mechanics. Tappi J. 12, 9–17 (2013).
28. Wang, J. W. et al. Moisture and oxygen barrier properties of cellulose nanomaterial-based films. Acs Sustain. Chem. Eng. 6, 49–70. https://doi.org/10.1021/acssuschemeng.7b03523 (2018).
29. Mertaniemi, H., Laukkanen, A., Teirfolk, J. E., Ikkala, O. & Ras, R. H. A. Functionalized porous microparticles of nanofibr illated cellulose for biomimetic hierarchically structured superhydrophobic surfaces. RSC Adv. 2, 2882–2886. https://doi.org/10.1039/ c2ra00020b (2012).
30. Kisonen, V. et al. Composite films of nanofibrillated cellulose and O-acetyl galactoglucomannan (GGM) coated with succinic esters of GGM showing potential as barrier material in food packaging. J. Mater. Sci. 50, 3189–3199. https://doi.org/10.1007/ s10853-015-8882-7 (2015).
31. Koppolu, R. et al. Continuous processing of nanocellulose and polylactic acid into multilayer barrier coatings. ACS Appl. Mater. Interfaces 11, 11920–11927. https://doi.org/10.1021/acsami.9b00922 (2019).
32. Li, J., Xu, Q. H. & Jin, L. Q. Advanced Materials Research Vol. 785, 440–443 (Trans Tech Publications Ltd., 2013).
33. Isogai, A. Wood nanocelluloses: Fundamentals and applications as new bio-based nanomaterials. J. Wood Sci. 59, 449–459. https:// doi.org/10.1007/s10086-013-1365-z (2013).
34. Afra, E., Mohammadnejad, S. & Saraeyan, A. Cellulose nanofibils as coating material and its effects on paper properties. Prog. Org. Coat. 101, 455–460. https://doi.org/10.1016/j.porgcoat.2016.09.018 (2016).
35. Aulin, C., Johansson, E., Wågberg, L. & Lindström, T. Self-organized films from cellulose I Nanofibrils using the layer-by-layer technique. Biomacromolecules 11, 872–882. https://doi.org/10.1021/bm100075e (2010).
36. Chaabouni, O. & Boufi, S. Cellulose nanofibrils/polyvinyl acetate nanocomposite adhesives with improved mechanical properties. Carbohydr. Polym. 156, 64–70. https://doi.org/10.1016/j.carbpol.2016.09.016 (2017).
37. Deng, Q., Li, J., Yang, J. & Li, D. Optical and flexible α-chitin nanofibers reinforced poly(vinyl alcohol) (PVA) composite film: Fabrication and property. Compos. A Appl. Sci. Manuf. 67, 55–60. https://doi.org/10.1016/j.compositesa.2014.08.013 (2014).
38. Wu, Y. et al. Mechanical and thermal properties of rice straw cellulose nanofibrils-enhanced polyvinyl alcohol films using freezingand-thawing cycle method. Cellulose 26, 3193–3204. https://doi.org/10.1007/s10570-019-02310-6 (2019).
39. Zhai, T., Zheng, Q., Cai, Z., Xia, H. & Gong, S. Synthesis of polyvinyl alcohol/cellulose nanofibril hybrid aerogel microspheres and their use as oil/solvent superabsorbents. Carbohydr. Polym. 148, 300–308. https://doi.org/10.1016/j.carbpol.2016.04.065 (2016).
40. Păduraru, O. M., Ciolacu, D., Darie, R. N. & Vasile, C. Synthesis and characterization of polyvinyl alcohol/cellulose cryogels and their testing as carriers for a bioactive component. Mater. Sci. Eng., C 32, 2508–2515. https://doi.org/10.1016/j.msec.2012.07.033 (2012).
41. Du, P. et al. The fluorine-free coating has excellent hydrophobic and oleophobic properties for porous cellulose-based materials. Cellulose 28, 6133–6146. https://doi.org/10.1007/s10570-021-03959-8 (2021).
42. Segal, L., Creely, J. J., Martin, A. E. & Conrad, C. M. An empirical method for estimating the degree of crystallinity of native cellulose using the X-Ray diffractometer. Text. Res. J. 29, 786–794. https://doi.org/10.1177/004051755902901003 (1959).
43. Ioelovich, M. Peculiarities of cellulose nanoparticles. Tappi J. 13, 45–51. https://doi.org/10.32964/TJ13.5.45 (2014).
44. Chen, Y., Fan, D. B., Han, Y. M., Li, G. Y. & Wang, S. Q. Length-controlled cellulose nanofibrils produced using enzyme pretreatment and grinding. Cellulose 24, 5431–5442. https://doi.org/10.1007/s10570-017-1499-z (2017).
45. Wang, S. et al. Fabricating cellulose nanofibril from licorice residues and its cellulose composite incorporated with natural nanoparticles. Carbohydr. Polym. 229, 115464. https://doi.org/10.1016/j.carbpol.2019.115464 (2020).
46. Duchemin, B. Size, shape, orientation and crystallinity of cellulose Iβ by X-ray powder diffraction using a free spreadsheet program. Cellulose 24, 2727–2741. https://doi.org/10.1007/s10570-017-1318-6 (2017).
47. Liu, Y. F. et al. A novel approach for the preparation of nanocr ystalline cellulose by using phosphotungstic acid. Carbohydr. Polym. 110, 415–422. https://doi.org/10.1016/j.carbpol.2014.04.040 (2014).
48. Abe, K. & Yano, H. Comparison of the characteristics of cellulose microfibril aggregates of wood, rice straw and potato tuber. Cellulose 16, 1017–1023. https://doi.org/10.1007/s10570-009-9334-9 (2009).
49. De Souza Lima, M. M. & Borsali, R. Rodlike cellulose microcrystals: Structure, properties, and applications. Macromol. Rapid Commun. 25, 771–787. https://doi.org/10.1002/marc.200300268 (2004).
50. Malucelli, L. et al. Grinding severity influences the viscosity of cellulose nanofiber (CNF) suspensions and mechanical properties of nanopaper. Cellulose 25, 6581–6589. https://doi.org/10.1007/s10570-018-2031-9 (2018).
51. Tyagi, P., Hubbe, M. A., Lucia, L. & Pal, L. High performance nanocellulose-based composite coatings for oil and grease resistance. Cellulose 25, 3377–3391. https://doi.org/10.1007/s10570-018-1810-7 (2018).
52. Syverud, K. & Stenius, P. Strength and barrier properties of MFC films. Cellulose 16, 75–85. https://doi.org/10.1007/s10570-0089244-2 (2009).
53. Svagan, A. J., Hedenqvist, M. S. & Berglund, L. Reduced water vapour sorption in cellulose nanocomposites with starch matrix. Compos. Sci. Technol. 69, 500–506. https://doi.org/10.1016/j.compscitech.2008.11.016 (2009).
54. Syverud, K., Xhanari, K., Chinga-Carrasco, G., Yu, Y. & Stenius, P. Films made of cellulose nanofibrils: Surface modification by adsorption of a cationic surfactant and characterization by computer-assisted electron microscopy. J. Nanopart. Res. 13, 773–782. https://doi.org/10.1007/s11051-010-0077-1 (2011).
This work was supported by the Key Research and Development Project of Zhejiang Province (2020C02043).
S.H., X.W, and X.X. wrote the main manuscript text and Y.Z., Y.M. and F.H. prepared Figs. 1 11. All authors reviewed the manuscript.
The authors declare no competing interests.
Correspondence and requests for materials should be addressed to X.X.
Reprints and permissions information is available at www.nature.com/reprints.
Publisher’s note Springer Nature remains neutral with regard to jurisdictional claims in published maps and institutional affiliations.
Open Access This article is licensed under a Creative Commons Attribution 4.0 International License, which permits use, sharing, adaptation, distribution and reproduction in any medium or format, as long as you give appropriate credit to the original author(s) and the source, provide a link to the Creative Commons licence, and indicate if changes were made. The images or other third party material in this article are included in the article’s Creative Commons licence, unless indicated otherwise in a credit line to the material. If material is not included in the article’s Creative Commons licence and your intended use is not permitted by statutory regulation or exceeds the permitted use, you will need to obtain permission directly from the copyright holder. To view a copy of this licence, visit http://creativecommons.org/licenses/by/4.0/
© The Author(s) 2022
Blue Economy is seen as an essential contributor to a sustainable development, and it is an important part of theEU Green Deal. Seaweed plays a key role in the Blue Economy as a source of food, feed, and feedstock forbiorefineries. Today, the largest part of global seaweed production is based in Asia, but there is also a growinginterest in seaweed production in Europe. However, more knowledge on the environmental impacts is needed toensure sustainable growth of the sector. Seaweed can be used in biorefineries to produce a variety of products forfood and non-food applications. The aim of this paper was to perform a life cycle assessment (LCA) of a seaweedvalue-chain, including seaweed cul tivation and production into sodium alginate, biodegradable materials,biogas, and fertilizer in a biorefinery setting. The LCA included 19 environmental impact categories but focusedon climate change. The seaweed Saccharina latissima was cultivated and processed in Ireland. Sodium alginatewas then extracted by means of ultrasound-assisted extraction, a novel extraction technology. Cellulosic residuesproduced after the extraction were used for the production of films used as a packaging material. Residues that remain after the production of the films were sent to anaerobic digestion to achieve a no-waste concept. Forseaweed cultivation, fuel use and drying of seaweed biomass were the main environmental hot spots; and for thealginate extraction process, the yield and purification after extraction were the main hot spots. Overall, theresults of this paper showed that the seaweed-based biorefinery has the potential to be sustainable, but severalimprovements are necessary before it is competitive with land-based systems.
Contact information:
1RISE Research Institutes of Sweden, Agriculture and Food, Frans Perssons väg 6, SE-402 29 Göteborg, Sweden
2Department of Food Chemistry and Technology, Teagasc Ashtown Food Research Centre, Dublin 15, Ireland
3School of Food Science and Environmental Health, College of Science and Health, Technological University Dublin, D07 ADY7 Dublin, Ireland
4Department of Food Quality and Sensory Science, Teagasc Ashtown Food Research Centre, Dublin 15, Ireland.
Algal Research 65 (2022)
Commons Attribution 4.0 International License
The Paper Industry Technical Association (PITA) is an independent organisation which operates for the general benefit of its members –both individual and corporate –dedicated to promoting and improving the technical and scientific knowledge of those working in the UK pulp and paper industry. Formed in 1960, it serves the Industry, both manufacturers and suppliers, by providing a forum for members to meet and network; it organises visits, conferences and training seminars that cover all aspects of papermaking science. It also publishes the prestigious journal Paper TechnologyInternational® and the PITA Annual Review, both sent free to members, and a range of other technical publications which include conference proceedings and the acclaimed Essential Guideto Aqueous Coating
journal homepage: www.elsevier.com/locate/algal
DryingofNa-alginate0%0%0%0%0%0% Electricity,separation0%0%0%0%0%0% Energy,alcoholrecovery5%6%6%2%0%0% CaCl2andHCl,separation0%0%0%0%1%0% Alcohol,precipitation58%9%9%2%0%0% NaCl0%0%0%0%0%0% Electricity,US6%6%6%2%0%0% Electricity,extraction1%1%1%0%1%0% NaHCO3,extraction2%2%2%1%2%1% Electricity,pretreatment1%1%1%0%1%0% HCl,pretreatment1%1%1%0%1%0% Seaweed25%25%1%1%1%1%
Hydrocarbon-derived polymers have been utilized in various packaging applications, such as pouches, films, foamed containers, rigid containers, andmultiple components for medical, food, and other uses. However, mountingenvironmental considerations increasedknowledge of the harmful consequences of greenhouse gas emissions, landfills,and disposal difficulties. Rising oil prices are forcing researchers and businesses to produce environmentally friendly packaging. These new sustainability requirementsare particularly suited to biomass-based products, instead of petroleum sources; sourcedfrom biomass entities. More functional and performance-oriented packagingis necessary despite the widespread usage of bio-based materials like paper.As a result, the transition to eco-friendly packaging will necessitate the improvement of existing bioderived packaging and the development of newbio-derived materials like biopolymer paper coatings. The goal of this briefstudy was to give a synopsis of the present status of bio-derived packagingand an insight into ongoing and prospective developments in sustainable next-generation paper coatings for the packaging industry.
Contact information:
1 Department of Polymer and Surface Engineering, Institute of Chemical Technology, Mumbai, India
2 Department of Microbiology, Savitribai Phule Pune University, Pune, India
Green and Sustainable Chemistry, 2022, 12, 9-27 https://www.scirp.org/journal/gsc
Creative Commons Attribution 4.0 International License
The Paper Industry Technical Association (PITA) is an independent organisation which operates for the general benefit of its members –both individualand corporate –dedicated to promoting and improving the technical and scientific knowledge of those working in the UK pulp and paper industry. Formed in 1960, it serves the Industry, both manufacturers and suppliers, by providing a forum for members to meet and network; it organises visits, conferences and training seminars that cover all aspects of papermaking science. It also publishes the prestigious journal Paper TechnologyInternational® and the PITA Annual Review, both sent free to members, and a range of other technical publications which include conference proceedings and the acclaimed Essential Guide to Aqueous Coating.
Green and Sustainable Chemistry, 2022, 12, 9-27 https://www.scirp.org/journal/gsc ISSN Online: 2160-696X ISSN Print: 2160-6951
1Department of Polymer and Surface Engineering, Institute of Chemical Technology, Mumbai, India
2Department of Microbiology, Savitribai Phule Pune University, Pune, India
H o w t o c
p ap er : Gadhave, R.V., Gadhave, C.R. and Dhawale, P.V. (2022) Plastic-Free Bioactive Paper Coatings, Way to Next-Generation Sustainable Paper Packaging Application: A Review. Green and SustainableChemistry , 1 12, 9-27. https://doi.org/10.4236/gsc.2022.122002
R e
d : January 17, 2022
: March 7, 2022
: March 10, 2022
Copyright © 2022 by author(s) and Scientific Research Publishing Inc.
is licensed under the Creative Commons Attribution International License (CC BY 4.0).
Hydrocarbon-derived polymers have been utilized in various packaging applications, such as pouches, films, foamed containers, rigid containers, and multiple components for medical, food, and other uses. However, mounting environmental considerations increased knowledge of the harmful consequences of greenhouse gas emissions, landfills, and disposal difficulties. Rising oil prices are forcing researchers and businesses to produce environmentally friendly packaging. These new sustainability requirements are particularly suited to biomass-based products, instead of petroleum sources; sourced from biomass entities. More functional and performance-oriented packaging is necessary despite the widespread usage of bio-based materials like paper. As a result, the transition to eco-friendly packaging will necessitate the improvement of existing bio-derived packaging and the development of new bio-derived materials like biopolymer paper coatings. The goal of this brief study was to give a synopsis of the present status of bio-derived packaging and an insight into ongoing and prospective developments in sustainable nextgeneration paper coatings for the packaging industry.
Biopolymers, Paper, Coatings, Starch, Itaconic Acid
Because it is compostable and fully safe for the environment, paper is often utilized in packaging. Paper is a low-cost, renewable material that can be used in place of plastics in situations where short-term use is preferred. Because of their fibrous structure, paper substrates are porous [1]. Furthermore, the cellulose
backbone chain contains hydroxyl groups, making the paper very hydrophilic [2]. Because hydrophilic hydroxyl groups and porous structures absorb water and grease substances, uncoated paper is less valuable when plastic replacement is required [3] [4]. However, there is a scarcity of hydrophobic and oleophobic developments in the paper packaging business. As a result, there is an urgent need to develop strategies for enhancing paper’s grease and water resistance while managing to stay recyclable and cost-effective [3] [5] [6]. High surface energy coatings also improved oil resistance due to a larger quantity of polar components, resulting in stronger grease resistance. After applying the coating, the mechanical characteristics of the paper improved as well. These naturally generated compounds provide an alternative to the fluoride-containing materials currently utilized in the market to increase paper wettability [7]. To address the aforementioned concerns, the coating industry today uses hydrocarbon-based polymers such as polyvinylidene chloride, low-density polyethylene, ethylene acrylic acid, and others to produce oil- and water-resistance paper via surface coating [8] Due to their low recyclability in current practices, alternatives to present procedures are in great demand [9]. Other extensively used coating techniques include fluorinated compounds, which negatively impact human health and aquatic habitats [10].
Given that, food and packaging containers account for around 45% of trash shipped to landfills, with papers and paper products accounting for the vast majority, these chemicals voice issues about microplastic contamination [11]. As health and environmental concerns regarding wax-based, fluorochemical-based, and extrusion-based paper coatings have grown, so has an interest in bioresorbable and repulpable substitutes for generating water- and oil-repellent coatings. This work describes a plastic-free, fluorine-free, and cost-effective grease and water-resistant paper coating process that uses novel chitosan-graft-polydimethylsiloxane copolymer and corn starch blends [12]. Scientists are presently focused on bio-based substances like chitosan, poly [lactic acid], wax-based, and protein-based (e.g., whey protein, and casein) and endow paper with specific properties like improved one’s liquid-repugnancy or gas-barrier performances. However, because of several complexities associated with modifying these materials while preserving water impermeability features, these attempts have had limited success, particularly in controlling water blocking capabilities and the high price of the alternatives available [9]
Global plastic manufacture has grown quickly since the 1950s, generating over 450 million tons of annual output. Despite the benefits and great value provided by plastics, environmental impacts over plastic waste have attracted international attention. Over 340 million tonnes of waste were generated worldwide, with the packaging industry accounting for approximately 46% of the total [13]. This waste is primarily the consequence of things with a shorter “in-use” life-
Green and Sustainable Chemistry
span, often six months or less, contrary to items used in the construction and engineering sectors, with an average lifespan of thirty years [14]. Even though plastic recycling rates have increased from 0% in the nineties to 19.5% in recent estimates, most packaging materials, particularly pliable packaged food, are nonrecyclable. Roughly 95% of conventional plastic wrapping materials made of polyethylene terephthalate and polyolefins are non-recyclable and end up in landfills after one use, causing a yearly economic loss of $80 - 120 billion to the world economy [15]. These difficulties are induced by polymers’ required characteristics, including lighter weight, specific strength, intricate structures, and contaminating from physical touch with foodstuffs [16]. Because of their ecologically favourable compostability, biodegradable polymers have sparked tremendous scientific and industrial interest. For the benefit of the market economy and recurrent environmental risks, biodegradable materials should play a larger part in plastic packaging, which today account for 60% of plastic items. The development of biodegradable polymers provides a solution to these problems by degrading such plastic into CO2, H2O, and biomass within six months; however, conventional synthetic plastic materials, even after burning or landfilling, remain for millennia. With the rise of processed foods in modern society, food packaging has played an essential part in the packaging sector. By 2025, the global market is anticipated to be worth USD 411.3 billion [17]. Because of its strong barrier and gas selectivity, plastic packaging provides food stability, shelflife extension, and safety and protection during transit and storage. Biodegradable polymers that can be degraded or composted after use are excellent substitutes for non-biodegradable packing. It can also work as a selective functional membrane or barrier against gas, humidity, and odour. Although several scientific research attempts to encourage the use of bio-based polymers in packing, few bio-based polymers in the market can meet modern society’s high demand for food packaging [18].
Because many bio-derived polymers are hydrophilic, their gaseous barrier properties and engineering capabilities are incredibly reliant on ambient humidity, limiting their usefulness as a packaging material compared to conventional polymers. Furthermore, their molar mass, rheological properties, and mechanical characteristics such as time-dependent crystallization behavior might cause problems and necessitate adjustments in processing techniques. As a result, bio-derived polymers should be blended with other polymer matrices or micrometers to nanometer-scale fillers to improve hydrophobicity and processing efficacy. The use of nanotechnology in papermaking science has been introduced in some areas. It has the potential to enhance the behavior of biopolymers and provide new capabilities to paper coatings. Currently, inorganic pigments [19], minerals [20], and ceramics [21] are the most often utilized nano-scale fillers in paper coatings, with bio-derived nanomaterial such as Nanocellulose [22] and
Green and Sustainable Chemistry
Nanoclays [23] being studied frequently. Antimicrobial paper [24], microfluidic paper devices [25], bioactive papers for drug delivery [26], flame-retardant papers, and self-healing characteristics for cotton fabric [27] are only a few of the fascinating functions achieved by using nanoparticles.
Paper is a biodegradable and hence ecologically beneficial material commonly utilized in packaging applications. The use of hydrocarbon derivatives as the coating, such as polyethylene, waxes, and fluor-derivatives, frequently regulates papers’ barrier resistance and wettability. Because of this coated layer, protective paper packaging loses its biodegradability and recyclability. Because of their poor recyclability and non-biodegradability, petroleum-based polymers account for most world trash. As an alternative, organically renewable biopolymers can be used as barrier coatings over paper packaging materials. Polylactide (PLA) is among the most promising polymers due to its bio-compatibility, bio-degradability, and ability to produce bio-based feedstocks [28]
It was suggested that polyvinyl alcohol (PVA)/Itaconic acid (IA)/acrylamide (AM) might generate a hydrophobic protective coating with a spatial structural framework on the paper’s surface, increasing the count of hydrogen bonds amongst the copolymer and the fiber. Further, when coated on the paper’s surface, the copolymer exhibited a superior film feature and a decreased penetration capacity through the paper compared to PVA. The strength of the paper reduces as the number of recycled paper increases. Surface scaling was widely recognized as the most efficient approach for improving the surface strength and hydrophobicity of paper and board [29] [30] [31] [32]. Starch and its derivatives were employed in the paper business for many years. Because of its low cost and ubiquitous availability, starch has indeed been recognized as among the most acceptable renewable biopolymer materials. Enzyme-modified starch, for example, is often employed to improve the interfacial strength of paper. Excess starch, on the other hand, may increase chemical oxygen demand (COD) and biological oxygen demand (BOD) during the effluent treatment process of the paper industry [33] [34] [35] [36] [37]. PVA was created as a biodegradable material by polymerizing vinyl acetate monomer. This provided the paper with large interfacial strength, low ink uptake, and exceptional film-forming capabilities. Nonetheless, the water-resistance of the bio-based PVA film had been lower than that of petroleum-derived polymers such as polyamide epoxy epichlorohydrin (PAE) [38] [39] [40] [41].
Meanwhile, PVA may easily infiltrate the inside of the paper. As a result, it limited PVA used in paper production. As a result, the weakness of PVA should be accounted for this through grafting with some other synthetic biodegradable
Green and Sustainable
polymers. Many chemical strategies have been discovered to increase PVA’s water resistance. The water-resistance of PVA has been enhanced via grafting of acrylonitrile monomer with PVA. Some studies developed PVA/polyacrylic acid mixtures to reduce PVA’s hydrophilic characteristic [42]-[52]. A cross-linked esterification process occurred between polyacrylic acid and PVA molecules. PVA molecules’ hydrophilic hydroxyl groups were transformed into hydrophobic groups. As a result, the water resistance of the PVA film was substantially enhanced. Biodegradable materials have gained popularity as a result of environmental concerns. One of the merits of IA is renewability. Furthermore, it has the potential to reduce people’s dependency on petrochemical products such as acrylic acid and maleic anhydride when picking raw materials for polymer synthesis [53]-[58]. This study used free radical polymerization to produce a PVA/ IA/AM copolymer having excellent water resistance and durability. PVA’s hydroxyl groups can create ester bonds with IA molecules’ carboxyl groups. It can increase the hydrophobicity of PVA. The double bond of itaconic acid may polymerize with an acrylamide monomer to form a structural matrix. Thereby, this could restrict PVA diffusion into the interior of the paper. Mini-table software was used to design the PVA/IA/AM copolymer experiment. It sought to enhance PVA’s hydrophobicity, increase surface strength, and decrease PVA penetration. PVA/IA/AM can establish additional hydrogen bonding with fibers and has better film-forming characteristics over PVA [59] [60]
Starch and its compounds have indeed been largely used in the paper industry because of its complete biodegradability, abundant availability, and relatively inexpensive. Surface coating of starch-derived goods is a well-established commercialized procedure for acquainting paper with desirable qualities. As a raw material, starch is exceptionally versatile. First, starch is a natural polymer with a large molecular mass that can be precisely depolymerized. It is also a hydrophilic polymer, meaning it dissolves in water and creates hydrogen bonds with cellulose fibers and pigment. Third, starch contains hydroxyl groups, which allow for a variety of substitution or oxidation methods to change its rheological characteristics and prevent retrogradation. Starch graft co-polymerization can generate innovative materials that combine the advantages of natural and synthesized polymers [32] [61]-[68]. Coated paper is a form of paper that consists of a base coat and a top layer. The coat color is applied to the base paper during the coating process to improve its qualities. Coat color is primarily made up of binders, pigments, and other additives. Binders are the second most common coating component after pigments [69]. Natural binders including starch and protein or synthesized latex such as styrene-butadiene, poly (vinyl acetate), and poly-acrylates are employed. When compared to synthetic latex, starch is a relatively lowpriced binder. However, nature-derived starch applications are restricted because of its insolubility in cold water, tendency to retrograde, and decrease in viscosity and thickening power during cooking and storage [70]. However, too
Green and Sustainable
much starch in a coating formulation might reduce drying rate [71] [72], reduce picking resistance [73], and maximize cracking area [74] [75]. The ultimate skill is finding a middle ground between quality and price. Starch grafted copolymers can be used instead of starch and synthesized latex. Graft co-polymerization is indeed a flexible method for combining the characteristics of starch and synthetic polymers [76] [77]
On the other hand, starch is a biopolymer with a large molecular mass and a high viscosity in an aqueous medium at low concentrations. The starch’s molecular weight must be decreased before it may be adequately grafted in co-polymerization [78]. Starch-based bio latex is a newly developed water-swollen, a cross-linked starch nanoparticle that commercially replaces synthetic latex [79] [80] [81]. Biolatex is sometimes referred to as starch-based bio-latex, biobased latex, bio binder, and a bio latex binder. Biolatex is a huge step forward in starch-based resins for paper coatings. On an industrial scale, bio latex can try replacing hydrocarbon-based synthesized latex by up to 50% or more [82]. For that reason, biolatex has enormous potential in the manufacturing of coated paper. A polymer blend is the physical mixing of two different polymers that may or may not interact chemically [83]. Compared to pure polysaccharide components, blends of multiple polysaccharides can form a new category of materials with improved mechanical and barrier properties. Starch/PVA mixes have been utilised to improve the characteristics of coated paper. A thin coating of starch/ PVA film was applied to paper. The coated paper demonstrated good organic solvent barrier characteristics. The better barrier properties are due to hydrogen bonding formed by hydroxyl groups of starch and PVA molecules. The hydrogen bonding on the paper surface form a tight thin layer, which increases the barrier characteristics of starch/PVA films [84]. Ethylene vinyl alcohol and starch mixture Ethylene vinyl alcohol (EVOH) copolymer is a semi-crystalline synthetic random copolymer composed of ethylene and vinyl alcohol units [85]. The vinyl alcohol molecule has good air barrier qualities, whilst the ethylene component has great damp resistance, thermal and mechanical properties, and easy handling [86] [87] [88]. Furthermore, EVOH is more biodegradable than normal PVA [89]. Blends of EVOH and hydrophobically altered starch may increase the permeability performance of flexible packaging paper.
Nanocelluloses, which have lately been developed, have provided a new polymer coating option. Micro-fibrillated cellulose (MFC) is being used as a coating pulp for paper products. The MFC manufacturing technique was discovered and patented in 1983 by Herrick et al. [90] and Turbak et al. [91]. MFC, a cellulose fiber subdivision, has diameters of 10 - 50 nm and lengths of several micrometers [92] [93]. MFC had significant reinforcing potential and was employed in nano-composites because of its high aspect ratio, nano-scale dimensions, entangled network, and intrinsically good mechanical characteristics [92].
and Sustainable
Many researchers were intrigued by MFC’s capacity to manufacture films because MFC films’ barrier and mechanical properties are comparable with those of existing high-quality polymer matrices [94]. MFC coating and its mixture with petro- and bio-polymer films have attracted the attention of researchers by dramatically improving the barrier properties of the original films [95]. In contrast to these uses, the use of MFC with cellulosic materials is very new and remains uncommon. The first investigation of MFC coating onto paper was conducted in 2009 [94]. As ecologically friendly alternatives, many forms of cellulose nanofibres derived from cellulosic fibers have been used [96] [97] [98] [99].
Cellulose nanofiber (CNF) has been discovered to improve the properties of various composites and papers when used as a reinforcing element in wet-end applications [96]-[102]. Aulin et al. [103] demonstrated that utilizing CNF as a coating agent significantly reduces the air barrier capability of paper by generating a thick top layer. Hult et al. [101] investigated the mixture of CNF and shellac, deposited as a one-layer or multi-layer coating on paper products using a bar coater and a spray coating technique. The results revealed that paper permeability to water vapor, air, and oxygen decreased dramatically after coating. CNF improved the surface and barrier characteristics of coated sheets, according to Ridgway et al. [104]. The combination of CNF and clay improved the printing properties of paper, such as ink absorption rate and print density, according to Hamada et al. [105]. It was demonstrated that partially replacing NFC for the conventional co-binder carboxymethyl cellulose reduced the permeability of the coating material to water [106]. Andrade et al. studied the impact of several chemicals on the wettability of gelatin-derived edible coatings on banana and eggplant epicarps, discovering that cellulose-nanofibers increased coating wetting [107]
Papers made from recycled fibers have poor mechanical and barrier qualities due to insufficient inter-fiber bonding. The coating is a methodology of interest for creating appealing items from this type of paper. On 100% recycled paper, an oxypropylated lignin-based coating was investigated. Instead of propylene oxide, propylene carbonate, a non-volatile and biodegradable solvent, was employed as a reagent. One of them is the creation of lignin-based coatings for paper and paperboard applications, which is based on the hydrophobic property of lignin polymer [108] [109]. Some research has previously been conducted on bio-based coatings using cellulose derivatives, starch, and other polymers, [110] as well as a combination of lignin and cellulose nanocrystal or esterified lignin for paperboard use [110] [111] [112]. The subsequent research was of particular interest since they dealt with the esterification of lignin. Another method for lignin modification is oxypropylation, which has been extensively researched to produce novel polyol for polyurethane foam applications [112]. Lehnen et al. [113] investigated oxypropylation with propylene carbonate as a non-volatile and biodegradable solvent rather than propylene oxide, a possible human carcinogen.
An oxypropylated lignin-based coating was explored in this work to enhance the general characteristics of recycled paper. Propylene carbonate was employed as an oxypropylation reagent and a solvent in the coating formulation. This enables immediate use of the mixture at the end of the reaction, reducing the number of process stages to one.
Protein-based biopolymer films have been researched for usage as food wrapping and coating materials. They’ve been frequently employed in food systems like oil, gaseous, and mechanical barriers to extending processed foods’ shelf life [112] [113] [114]. Zein was used as an oxygen barrier layer in peanut products to avoid oxidation [115]. Casein coatings might also be utilized on less processed fruits to enhance their shelf life [116]. Trezza and Vergan [117] observed that zeincoated paper does have a high prospective for use as an oil-barrier paper bag in fast-food eateries. Isolated soy protein (ISP) also has a remarkable film-forming capacity [118] [119] [120]. Soy protein sheets have traditionally been used as a digestible covering for veg and meat mixtures that are then fried in oil. ISPbased films beat zein and wheat gluten-based films in terms of oxygen barrier performance [121]. Grease resistance is critical for packing items that include oils or fats.
Polyethylene and other polymers are considered effective grease barriers. On the other hand, the polyethylene content makes material segregation, recycling, and regeneration difficult [122] [123]. Papers coated with biodegradable polymers may meet packaging criteria as an oil barrier for commodities with a very short lifespan, like as fast-food restaurant sandwiches. ISP, a key by-product of soybean-oil extraction, on the other hand, is a low-cost natural polymer that competes against polyethylene. Mechanical and barrier performance of protein-based coatings are controlled by factors like plasticizer content and pH, solvent, and other additive choices [124]-[130]. As plasticizer content increases in wheat gluten films, flexibility improves while water vapor, oxygen barrier, and puncture strength qualities diminish [125] [126] [127]. Gennadios et al. [119] produced protein films from an ISP-wheat gluten blend. They investigated the impact of varying the pH of the produced film solution on properties such as water vapor permeability and mechanical strength. Brandenburg et al. [120] discovered that alkali-treated ISP films had enhanced film appearance and elongation characteristics. ISP films did not seem clear due to the inclusion of insoluble particles [128]. High pH and temperature treatments of ISP resulted in more soluble, hydrolyzed, and denatured chemicals [129]. Protein denaturation is known to change the structure of a protein from circular to extended chain geometry. Increased protein-protein linkages, in principle, would lower gas permeability while increasing tensile strength. Park et al. [130] revealed that different polyethylene glycol and glycerol plasticizer mixtures had a substantial influence on the mechanical properties and water vapor permeabilities of pro-
tein-based membranes.
Bio-polymer based coating on paper packaging materials are very important systems for the future improvement of food packaging. They have potential environmental advantages over conventional petroleum-based paper coatings. A literature survey indicates that bio-based polymers have a great potential for replacing hydrocarbon-produced synthetic polymers as a sustainable solution for paper coating applications. Not only can biopolymer paper coating provide biodegradability and renewability, but numerous methods for increasing the functioning of coated paper surfaces have been proposed. An appropriate mix of chosen ingredients (bio-derived polymer and fillers) and surface structure, according to the review, has the ability to offer an entirely impenetrable bio-based paper coating. From the presented review, appropriate bio-based polymers like starch, polylactic acid, itaconic acid, lignin, soybean protein and cellulose, provide a fully protective bio-based paper coating.
Finally, the difficulties associated with most biopolymers, such as hydrophilicity, crystallization behavior, brittleness, or melt instabilities, prevent their full industrial exploitation. This study cites investigations in which it was observed that mixing with other biopolymers, compatibilizers, and plasticizers might assist in alleviating this bottleneck. But extensively research will be needed in the paper packaging industry towards insubstantial materials for reduction of raw material use, conveying costs, minimizing the amount of waste and improvement in the performance properties of paper coatings. Interest in sustainable materials combined with improvement in performance properties of paper coating will continue to growth.
The authors declare no conflicts of interest regarding the publication of this paper.
[1]Rastogi, V. and Samyn, P. (2015) Bio-Based Coatings for Paper Applications. Coatings , 5 5 , 887-930. https://doi.org/10.3390/coatings5040887
[2]Samyn, P., Schoukens, G., Van den Abbeele, H., Vonck, L. and Stanssens, D. (2011) Application of Polymer Nanoparticle Coating for Tuning the Hydrophobicity of Cellulosic Substrates. JournalofCoatingsTechnologyandResearch , 8 8 , 363-373. https://doi.org/10.1007/s11998-010-9309-7
[3]Nair, A., Kansal, D., Khan, A. and Rabnawaz, M. (2021) New Alternatives to Single-Use Plastics: Starch and Chitosan-Graft-Polydimethylsiloxane-Coated Paper for Water- and Oil-Resistant Applications. NanoSelect , 3 3 , 459-470. https://doi.org/10.1002/nano.202100107
[4]Khwaldia, K., Arab-Tehrany, E. and Desobry, S. (2010) Biopolymer Coatings on Paper Packaging Materials. ComprehensiveReviewsinFoodScienceandFoodSafety , 9 , 82-91. https://doi.org/10.1111/j.1541-4337.2009.00095.x
[5]Gong, X., Zhang, L., He, S., Jiang, S., Wang, W. and Wu, Y. (2020) Rewritable Superhydrophobic Coatings Fabricated Using Water-Soluble Polyvinyl Alcohol. Materials&Design , 1 1 9 6 , Article ID: 109112. https://doi.org/10.1016/j.matdes.2020.109112
[6]Samyn, P., Deconinck, M., Schoukens, G., Stanssens, D., Vonck, L. and Van den Abbeele, H. (2012) Synthesis and Characterization of Imidized Poly(styrene-maleic anhydride) Nanoparticles in Stable Aqueous Dispersion. Polymers for Advanced Technologies , 2 23 , 311-325. https://doi.org/10.1002/pat.1871
[7]Tajeddin, B. (2014) Cellulose-Based Polymers for Packaging Applications. In: LignocellulosicPolymerComposites : Processing , Characterization , andProperties , John Wiley & Sons, Inc., Hoboken, 477-498. https://doi.org/10.1002/9781118773949.ch21
[8]Aday, M.S., Caner, C. and Rahvalı, F. (2011) Effect of Oxygen and Carbon Dioxide Absorbers on Strawberry Quality. PostharvestBiologyandTechnology , 6 6 2 , 179-187. https://doi.org/10.1016/j.postharvbio.2011.05.002
[9]Ahvenainen, R., Eilamo, M. and Hurme, E. (1997) Detection of Improper Sealing and Quality Deterioration of Modified-Atmosphere-Packed Pizza by a Colour Indicator. FoodControl , 8 8, 177-184. https://doi.org/10.1016/S0956-7135(97)00046-7
[10]Bai, H., Zhou, G., Hu, Y., Sun, A., Xu, X., Liu, X. and Lu, C. (2017) Traceability Technologies for Farm Animals and Their Products in China. FoodControl , 7 7 9, 35-43. https://doi.org/10.1016/j.foodcont.2017.02.040
[11]Han, J.-W., Ruiz-Garcia, L., Qian, J.-P. and Yang, X.-T. (2018) Food Packaging: A Comprehensive Review and Future Trends. Comprehensive Reviews in Food ScienceandFoodSafety , 1 1 7 , 860-877. https://doi.org/10.1111/1541-4337.12343
[12]Perpétuo, G.L., Gálico, D.A., Fugita, R.A., Castro, R.A.E., Eusébio, M.E.S., TreuFilho, O., Silva, A.C.M. and Bannach, G. (2013) Thermal Behavior of Some Antihistamines. JournalofThermalAnalysisandCalorimetry , 1 1 1 1 , 2019-2028. https://doi.org/10.1007/s10973-012-2247-0
[13]Tsakona, M. and Rucevska, I. (2020) Baseline Report on Plastic Waste-Basel Convention. United Nations, New York, 1-68. https://gridarendal-website-live.s3.amazonaws.com/production/documents/:s_docu ment/554/original/UNEP-CHW-PWPWG.1-INF-4.English.pdf?1594295332
[14]Geyer, R., Jambeck, J.R. and Law, K.L. (2017) Production, Use, and Fate of All Plastics Ever Made. ScienceAdvances , 3 3 , e1700782. https://doi.org/10.1126/sciadv.1700782
[15]World Economic Forum (2016) The New Plastics Economy: Rethinking the Future of Plastics. Ellen MacArthur Found, Cowes, 120. http://www3.weforum.org/docs/WEF_The_New_Plastics_Economy.pdf
[16]Wu, F., Misra, M. and Mohanty, A.K. (2021) Challenges and New Opportunities on Barrier Performance of Biodegradable Polymers for Sustainable Packaging. Progress inPolymerScience , 1 1 1 7 , Article ID: 101395. https://doi.org/10.1016/j.progpolymsci.2021.101395
[17]Reddy, M.M., Vivekanandhan, S., Misra, M., Bhatia, S.K. and Mohanty, A.K. (2013) Biobased Plastics and Bionanocomposites: Current Status and Future Opportunities. ProgressinPolymerScience , 3 3 8 , 1653-1689. https://doi.org/10.1016/j.progpolymsci.2013.05.006
[18]Zhang, H., Hortal, M., Jordá-Beneyto, M., Rosa, E., Lara-Lledo, M. and Lorente, I. (2017) ZnO-PLA Nanocomposite Coated Paper for Antimicrobial Packaging Application. LWT , 7 7 8 , 250-257. https://doi.org/10.1016/j.lwt.2016.12.024
[19]Hladnik, A. (2002) Characterization of Pigments in Coating Formulations for High-
Green and Sustainable
End Ink-Jet Papers. DyesandPigments , 5 5 4 , 253-263. https://doi.org/10.1016/S0143-7208(02)00050-5
[20]Kugge, C. and Johnson, B. (2008) Improved Barrier Properties of Double Dispersion Coated Liner. ProgressinOrganicCoatings , 6 6 2 , 430-435. https://doi.org/10.1016/j.porgcoat.2008.03.006
[21]Daoud, W.A., Xin, J.H. and Tao, X. (2004) Superhydrophobic Silica Nanocomposite Coating by a Low-Temperature Process. JournaloftheAmericanCeramicSociety , 8 7 , 1782-1784. https://doi.org/10.1111/j.1551-2916.2004.01782.x
[22]Dufresne, A. (2013) Nanocellulose: A New Ageless Bionanomaterial. Materials Today , 1 1 6 , 220-227. https://doi.org/10.1016/j.mattod.2013.06.004
[23]Sanchez-Garcia, M.D. and Lagaron, J.M. (2010) Novel Clay-Based Nanobiocomposites of Biopolyesters with Synergistic Barrier to UV Light, Gas, and Vapour. JournalofAppliedPolymerScience , 1 1 1 8 , 188-199. https://doi.org/10.1002/app.31986
[24]Cha, D.S. and Chinnan, M.S. (2004) Biopolymer-Based Antimicrobial Packaging: A Review. CriticalReviewsinFoodScienceandNutrition , 4 4 4 , 223-237. https://doi.org/10.1080/10408690490464276
[25]Guerrero, M.P., Bertrand, F. and Rochefort, D. (2011) Activity, Stability and Inhibition of a Bioactive Paper Prepared by Large-Scale Coating of Laccase Microcapsules. ChemicalEngineeringScience , 6 6 6 , 5313-5320. https://doi.org/10.1016/j.ces.2011.07.026
[26]Chen, S., Li, X., Li, Y. and Sun, J. (2015) Intumescent Flame-Retardant and SelfHealing Superhydrophobic Coatings on Cotton Fabric. ACSNano , 9 9 , 4070-4076. https://doi.org/10.1021/acsnano.5b00121
[27]Rong, M.Z., Zhang, M.Q. and Ruan, W.H. (2006) Surface Modification of NanoScale Fillers for Improving Properties of Polymer Nanocomposites: A Review. MaterialsScienceandTechnology , 2 2 2 , 787-796. https://doi.org/10.1179/174328406X101247
[28]Lopez-Rubio, A., Fabra, M.J., Martinez-Sanz, M., Mendoza, S. and Vuong, Q.V. (2017) Biopolymer-Based Coatings and Packaging Structures for Improved Food Quality. JournalofFoodQuality , 2 2 0 1 7 , Article ID: 2351832. https://doi.org/10.1155/2017/2351832
[29]Guo, Y., Guo, J., Li, S., Li, X., Wang, G. and Huang, Z. (2013) Properties and Paper Sizing Application of Waterborne Polyurethane Emulsions Synthesized with TDI and IPDI. Colloids and Surfaces A : PhysicochemicalandEngineeringAspects , 4 4 2 7 , 53-61. https://doi.org/10.1016/j.colsurfa.2013.03.017
[30]Brenner, T., Kiessler, B., Radosta, S. and Arndt, T. (2016) Processing Surface Sizing Starch Using Oxidation, Enzymatic Hydrolysis and Ultrasonic Treatment Methods—Preparation and Application. CarbohydratePolymers , 1 1 3 8 , 273-279. https://doi.org/10.1016/j.carbpol.2015.10.086
[31]Xiong, H., Tang, S., Tang, H. Zou, P. (2008) The Structure and Properties of a StarchBased Biodegradable Film. CarbohydratePolymers , 7 7 1 , 263-268. https://doi.org/10.1016/j.carbpol.2007.05.035
[32]Jonhed, A. andersson, C. and Järnström, L. (2008) Effects of Film Forming and Hydrophobic Properties of Starches on Surface Sized Packaging Paper. PackagingTechnologyandScience , 2 2 1 , 123-135. https://doi.org/10.1002/pts.783
[33]Domene-López, D., Guillén, M.M., Martin-Gullon, I., García-Quesada, J.C. and Montalbán, M.G. (2018) Study of the Behavior of Biodegradable Starch/Polyvinyl Alcohol/Rosin Blends. CarbohydratePolymers , 2 2 0 2 , 299-305. https://doi.org/10.1016/j.carbpol.2018.08.137
Green and Sustainable
[34]Ni, S., Zhang, H., Godwin, P.M., Dai, H. and Xiao, H. (2018) ZnO Nanoparticles Enhanced Hydrophobicity for Starch Film and Paper. Materials Letters , 2 2 3 0 , 207210. https://doi.org/10.1016/j.matlet.2018.07.075
[35]Li, W., Xu, Z., Wang, Z. and Xing, J. (2018) One-Step Quaternization/Hydroxypropylsulfonation to Improve Paste Stability, Adhesion, and Film Properties of Oxidized Starch. Polymers(Basel), 1 1 0 , 1110. https://doi.org/10.3390/polym10101110
[36]Du, Y., Liu, J., Wang, B., Li, H. and Su, Y. (2018) The Influence of Starch-Based BioLatex on Microstructure and Surface Properties of Paper Coating. Progress in OrganicCoatings , 1 1 1 6 , 51-56. https://doi.org/10.1016/j.porgcoat.2017.12.009
[37]Ondaral, S., Kurtuluş, O.Ç., Öztürk, G., Ergün, M.E. and Yakın, İ. (2018) Aldehyde Starch Complexes: Adsorption on Cellulose Model Film and Performance as a Strength Additive for Papermaking. BioResources , 1 1 3 , 4470-4483. https://doi.org/10.15376/biores.13.2.4470-4483
[38]Wang, Y., Chang, C. and Zhang, L. (2010) Effects of Freezing/Thawing Cycles and Cellulose Nanowhiskers on Structure and Properties of Biocompatible Starch/PVA Sponges. MacromolecularMaterialsandEngineering , 2 2 9 5 , 137-145. https://doi.org/10.1002/mame.200900212
[39]Fatehi, P. and Xiao, H. (2010) Effect of Cationic PVA Characteristics on Fiber and Paper Properties at Saturation Level of Polymer Adsorption. Carbohydrate Polymers, 7 7 9 , 423-428. https://doi.org/10.1016/j.carbpol.2009.08.029
[40]Liu, X., Fatehi, P., Ni, Y. and Xiao, H. (2010) Using Cationic Polyvinyl Alcohol (CPVA) to Improve the Strength of Wood-Free Papers Containing High-Yield Pulp (HYP). Holzforschung , 6 6 4 , 563-569. https://doi.org/10.1515/hf.2010.078
[41]Mittal, A., Garg, S., Kohli, D., Maiti, M., Jana, A.K. and Bajpai, S. (2016) Effect of Cross Linking of PVA/Starch and Reinforcement of Modified Barley Husk on the Properties of Composite Films. CarbohydratePolymers , 1 1 5 1 , 926-938. https://doi.org/10.1016/j.carbpol.2016.06.037
[42]Ismail, H. and Zaaba, N.F. (2014) Effects of Poly(vinyl alcohol) on the Performance of Sago Starch Plastic Films. JournalofVinylandAdditiveTechnology , 2 2 0 , 72-79. https://doi.org/10.1002/vnl.21348
[43]Zhai, M., Yoshii, F., Kume, T. and Hashim, K. (2002) Syntheses of PVA/Starch Grafted Hydrogels by Irradiation. CarbohydratePolymers , 5 5 0 , 295-303. https://doi.org/10.1016/S0144-8617(02)00031-0
[44]Garcia, P.S., Baron, A.M., Yamashita, F., Mali, S., Eiras, D. and Grossmann, M.V.E. (2018) Compatibilization of Starch/Poly(butylene adipate-co-terephthalate) Blown Films Using Itaconic Acid and Sodium Hypophosphite. JournalofAppliedPolymer Science , 1 1 3 5 , Article ID: 46629. https://doi.org/10.1002/app.46629
[45]Swain, S.K., Prusty, G. and Das, R. (2012) Sonochemical Compatibility of Polyvinyl Alcohol/Polyacrylic Acid Blend in Aqueous Solution. Journal of Macromolecular Science , PartB , 5 5 1 , 580-589. https://doi.org/10.1080/00222348.2011.609782
[46]Follain, N., Joly, C., Dole, P. and Bliard, C. (2005) Properties of Starch Based Blends. Part 2. Influence of Poly Vinyl Alcohol Addition and Photocrosslinking on Starch Based Materials Mechanical Properties. CarbohydratePolymers , 6 6 0 , 185-192. https://doi.org/10.1016/j.carbpol.2004.12.003
[47]Meng, F., Zhang, Y., Xiong, Z., Wang, G., Li, F. and Zhang, L. (2018) Mechanical, Hydrophobic and Thermal Properties of an Organic-Inorganic Hybrid CarrageenanPolyvinyl Alcohol Composite Film. CompositesPartB : Engineering, 1 1 4 3 , 1-8. https://doi.org/10.1016/j.compositesb.2017.12.009
[48]Kokhanovskaya, O.A. and Likholobov, V.A. (2018) Synthesis of Hydrophobic Aerogel
Green and Sustainable Chemistry
Heat Insulation Materials Based on Polyvinyl Alcohol/Carbon Black Composite. RussianJournalofAppliedChemistry , 9 9 1 , 78-81. https://doi.org/10.1134/S1070427218010123
[49]Zhang, R., Wan, W., Qiu, L., Wang, Y. and Zhou, Y. (2017) Preparation of Hydrophobic Polyvinyl Alcohol Aerogel via the Surface Modification of Boron Nitride for Environmental Remediation. AppliedSurfaceScience , 4 4 1 9 , 342-347. https://doi.org/10.1016/j.apsusc.2017.05.044
[50]Pan, Y., Shi, K., Peng, C., Wang, W., Liu, Z. and Ji, X. (2014) Evaluation of Hydrophobic Polyvinyl-Alcohol Formaldehyde Sponges as Absorbents for Oil Spill. ACS AppliedMaterials&Interfaces , 6 6 , 8651-8659. https://doi.org/10.1021/am5014634
[51]Pan, Y., Wang, W., Peng, C., Shi, K., Luo, Y. and Ji, X. (2014) Novel Hydrophobic Polyvinyl Alcohol-Formaldehyde Foams for Organic Solvents Absorption and Effective Separation. RSCAdvances , 4 4 , 660-669. https://doi.org/10.1039/C3RA43907K
[52]Maqueira, L., Valdés, A.C., Iribarren, A. and de Melo, C.P. (2013) Preparation and Characterization of Hydrophobic Porphyrin Nanoaggregates Dispersed in Polyvinyl Alcohol Films. JournalofPorphyrinsandPhthalocyanines , 1 1 7 , 283-288. https://doi.org/10.1142/S1088424613500028
[53]Bednarz, S., Wesołowska-Piętak, A., Konefał, R. and Świergosz, T. (2018) Persulfate Initiated Free-Radical Polymerization of Itaconic Acid: Kinetics, End-Groups and Side Products. EuropeanPolymerJournal , 1 1 0 6 , 63-71. https://doi.org/10.1016/j.eurpolymj.2018.07.010
[54]Duquette, D. and Dumont, M.-J. (2018) Influence of Chain Structures of Starch on Water Absorption and Copper Binding of Starch-Graft-Itaconic Acid Hydrogels. Starch Stärke , 7 70 , Article ID: 1700271. https://doi.org/10.1002/star.201700271
[55]Ko, S.Y., Sand, A., Shin, N.J. and Kwark, Y.-J. (2018) Synthesis and Characterization of Superabsorbent Polymer Based on Carboxymethyl Cellulose-Graft-Itaconic Acid. FibersandPolymers , 1 1 9 , 255-262. https://doi.org/10.1007/s12221-018-7837-9
[56]Huang, Z., Zhou, X., Xing, Z. and Wang, B. (2018) Improving Application Performance of in Situ Polymerization and Crosslinking System of Maleic Acid/Itaconic Acid for Cotton Fabric. FibersandPolymers , 1 1 9 , 281-288. https://doi.org/10.1007/s12221-018-7745-z
[57]Kasar, S.B. and Thopate, S.R. (2018) Synthesis of Bis(indolyl)methanes Using Naturally Occurring, Biodegradable Itaconic Acid as a Green and Reusable Catalyst. CurrentOrganicSynthesis , 1 1 5 , 110-115. https://doi.org/10.2174/1570179414666170621080701
[58]Yaman, S. and Öztürk, Y. (2017) Analyses of Particle Size and Magnetisation of Magnetic Nanoparticles via Minitab Statistical Software. Micro & Nano Letters , 1 1 2 , 784-786. https://doi.org/10.1049/mnl.2017.0101
[59]Shah, D. and Londhe, V. (2011) Optimization and Characterization of LevamisoleLoaded Chitosan Nanoparticles by Ionic Gelation Method Using 2(3) Factorial Design by Minitab® 15. TherapeuticDelivery , 2 2 , 171-179. https://doi.org/10.4155/tde.10.102
[60]Wang, D.X. and Conerly, M.D. (2008) Evaluating the Power of Minitab’s Data Subsetting Lack of Fit Test in Multiple Linear Regression. JournalofAppliedStatistics , 3 5 , 115-124. https://doi.org/10.1080/02664760701775381
[61]Maurer, H.W. and Kearney, R.L. (1998) Opportunities and Challenges for Starch in the Paper Industry. Starch Stärke , 5 5 0 , 396-402. https://doi.org/10.1002/(SICI)1521-379X(199809)50:9<396::AID-STAR396>3.0.CO; 2-8
Green and Sustainable Chemistry
[62]Chen, Q., Yu, H., Wang, L., ul Abdin, Z., Chen, Y., Wang, J., Zhou, W., Yang, X., Khan, R.U., Zhang, H. and Chen, X. (2015) Recent Progress in Chemical Modification of Starch and Its Applications. RSCAdvances , 5 5 , 67459-67474. https://doi.org/10.1039/C5RA10849G
[63]Zhu, F. (2015) Composition, Structure, Physicochemical Properties, and Modifications of Cassava Starch. CarbohydratePolymers , 1 1 2 2 , 456-480. https://doi.org/10.1016/j.carbpol.2014.10.063
[64]Kaur, B., Ariffin, F., Bhat, R. and Karim, A.A. (2012) Progress in Starch Modification in the Last Decade. FoodHydrocolloids , 2 2 6 , 398-404. https://doi.org/10.1016/j.foodhyd.2011.02.016
[65]Zia-ud-Din, Xiong, H. and Fei, P. (2017) Physical and Chemical Modification of Starches: A Review. CriticalReviewsinFoodScienceandNutrition , 5 5 7 , 2691-2705. https://doi.org/10.1080/10408398.2015.1087379
[66]Masina, N., Choonara, Y.E., Kumar, P., du Toit, L.C., Govender, M., Indermun, S. and Pillay, V. (2017) A Review of the Chemical Modification Techniques of Starch. CarbohydratePolymers , 1 1 5 7 , 1226-1236. https://doi.org/10.1016/j.carbpol.2016.09.094
[67]Khlestkin, V.K., Peltek, S.E. and Kolchanov, N.A. (2018) Review of Direct Chemical and Biochemical Transformations of Starch. CarbohydratePolymers , 1 1 8 1 , 460-476. https://doi.org/10.1016/j.carbpol.2017.10.035
[68]Niranjana Prabhu, T. and Prashantha, K. (2018) A Review on Present Status and Future Challenges of Starch Based Polymer Films and Their Composites in Food Packaging Applications. PolymerComposites , 3 3 9 , 2499-2522. https://doi.org/10.1002/pc.24236
[69]Lele, V.V., Kumari, S. and Niju, H. (2018) Syntheses, Characterization and Applications of Graft Copolymers of Sago Starch—A Review. Starch Stärke , 7 7 0 , Article ID: 1700133. https://doi.org/10.1002/star.201700133
[70]Holik, H. (2013) Handbook of Paper and Board. Wiley-VCH Verlag GmbH & Co. KGaA, Weinheim.
[71]Chen, G., Zhu, Z.J., Salminen, P. and Toivakka, M. (2014) Structure and Mechanical Properties of Starch/Styrene-Butadiene Latex Composites. Advanced Materials Research , 9 9 3 6 , 74-81. https://doi.org/10.4028/www.scientific.net/AMR.936.74
[72]Hallajisani, A., Hashemi, S.J. and Murray Douglas, W.J. (2011) Experimental Investigation of Industrial Coating-Drying Process Parameters. Drying Technology , 2 2 9 , 1484-1491. https://doi.org/10.1080/07373937.2011.575973
[73]Du, Y., Zang, Y.-H. and Sun, J. (2014) The Effects of Water Soluble Polymers on Paper Coating Consolidation. ProgressinOrganicCoatings , 7 7 7 , 908-912. https://doi.org/10.1016/j.porgcoat.2014.01.007
[74]Hashemi Najafi, S.M., Tajvidi, M. and Bousfield, D.W. (2018) Production and Mechanical Characterization of Free-Standing Pigmented Paper Coating Layers with Latex and Starch as Binder. ProgressinOrganicCoatings , 1 1 2 3 , 138-145. https://doi.org/10.1016/j.porgcoat.2018.07.009
[75]Zhang, S., Jiang, L., Zhang, M. and Wu, Y. (2010) Characteristics of Aramid Fibre/ Fibrids and Their Properties for Sheet Making. NordicPulp&PaperResearchJournal , 2 2 5 , 488-494. https://doi.org/10.3183/npprj-2010-25-04-p488-494
[76]Oh, K., Sim, K., Bin Jeong, Y., Youn, H.J., Lee, H.L., Lee, Y.M. and Yeu, S.U. (2015) Effect of Coating Binder on Fold Cracking of Coated Paper. NordicPulp& Paper ResearchJournal , 3 3 0 , 361-368. https://doi.org/10.3183/npprj-2015-30-02-p361-368
Green and Sustainable Chemistry
R. V. Gadhave
[77]Haroon, M., Wang, L., Yu, H., Abbasi, N.M., Zain-ul-Abdin, Z.-A., Saleem, M., Khan, R.U., Ullah, R.S., Chen, Q. and Wu, J. (2016) Chemical Modification of Starch and Its Application as an Adsorbent Material. RSCAdvances , 6 6 , 78264-78285. https://doi.org/10.1039/C6RA16795K
[78]Meimoun, J., Wiatz, V., Saint-Loup, R., Parcq, J., Favrelle, A., Bonnet, F. and Zinck, P. (2018) Modification of Starch by Graft Copolymerization. Starch Stärke , 7 7 0 , Article ID: 1600351. https://doi.org/10.1002/star.201600351
[79]Mange, S., Dever, C., De Bruyn, H., Gaborieau, M., Castignolles, P. and Gilbert, R.G. (2007) Grafting of Oligosaccharides onto Synthetic Polymer Colloids. Biomacromolecules , 8 8 , 1816-1823. https://doi.org/10.1021/bm061119o
[80]Bloembergen, S., Lennan, I., Lee, D. and Leeuwen, J. (2008) Paper Binder Performance with Biobased Nanoparticles. TAPPI J.-Pap. 360°. 3, 3.
[81]Klass, C. (2007) New Nanoparticle Latex Offers Natural Advantage. Paper360 Magazine , 2 2 , 30-31.
[82]Van Leeuwen, J. (2006) Paper Coating-SBR Latex Replacement Technology. TAPPI Coat. Graph. Arts Conf.
[83]Bloembergen, S., Mclennan, I.J., Leeuwen, J. and Lee, D.I. (2010) Ongoing Developments in Biolatex Binders with a Very Low Carbon Footprint for Paper and Board Manufacturing. 64th Appita Annual Conference & Exhibition , Melbourne, 18-21 April 2010, 363-369.
[84]Muthuraj, R., Misra, M. and Mohanty, A.K. (2018) Biodegradable Compatibilized Polymer Blends for Packaging Applications: A Literature Review. Journal of AppliedPolymerScience , 1 1 3 5 , 45726. https://doi.org/10.1002/app.45726
[85]Teodorescu, M., Bercea, M. and Morariu, S. (2018) Biomaterials of Poly(vinyl alcohol) and Natural Polymers. PolymerReviews , 5 5 8 , 247-287. https://doi.org/10.1080/15583724.2017.1403928
[86]Zhu, P., Kuang, Y., Chen, G., Liu, Y., Peng, C., Hu, W., Zhou, P. and Fang, Z. (2018) Starch/Polyvinyl Alcohol (PVA)-Coated Painting Paper with Exceptional Organic Solvent Barrier Properties for Art Preservation Purposes. Journal of Materials Science, 5 5 3 , 5450-5457. https://doi.org/10.1007/s10853-017-1924-6
[87]Mokwena, K.K. and Tang, J. (2012) Ethylene Vinyl Alcohol: A Review of Barrier Properties for Packaging Shelf Stable Foods. Critical Reviews in Food Science and Nutrition, 5 5 2 , 640-650. https://doi.org/10.1080/10408398.2010.504903
[88]Maes, C., Luyten, W., Herremans, G., Peeters, R., Carleer, R. and Buntinx, M. (2018) Recent Updates on the Barrier Properties of Ethylene Vinyl Alcohol Copolymer (EVOH): A Review. PolymerReviews , 5 5 8 , 209-246. https://doi.org/10.1080/15583724.2017.1394323
[89]Christophliemk, H., Johansson, C., Ullsten, H. and Järnström, L. (2017) Oxygen and Water Vapor Transmission Rates of Starch-Poly(vinyl alcohol) Barrier Coatings for Flexible Packaging Paper. ProgressinOrganicCoatings , 1 1 1 3 , 218-224. https://doi.org/10.1016/j.porgcoat.2017.04.019
[90]Zhong, Y., Godwin, P., Jin, Y. and Xiao, H. (2019) Biodegradable Polymers and Green-Based Antimicrobial Packaging Materials: A Mini-Review. Advanced IndustrialandEngineeringPolymerResearch , 3 3 , 27-35. https://doi.org/10.1016/j.aiepr.2019.11.002
[91]Harlin, A., Backfolk, K. and Laitinen, R. (2014) Process for the Production of Mcrofbrillated Cellulose in an Extruder and Microfibrillated Cellulose Produced According to the Process, US008747612B2.
Green and Sustainable Chemistry
[92]Siqueira, G., Bras, J. and Dufresne, A. (2009) Cellulose Whiskers versus Microfibrils: Influence of the Nature of the Nanoparticle and Its Surface Functionalization on the Thermal and Mechanical Properties of Nanocomposites. Biomacromolecules , 1 0 , 425-432. https://doi.org/10.1021/bm801193d
[93]Syverud, K. and Stenius, P. (2009) Strength and Barrier Properties of MFC Films. Cellulose , 1 1 6 , 75-85. https://doi.org/10.1007/s10570-008-9244-2
[94]Fukuzumi, H., Saito, T., Iwata, T., Kumamoto, Y. and Isogai, A. (2009) Transparent and High Gas Barrier Films of Cellulose Nanofibers Prepared by TEMPO-Mediated Oxidation. Biomacromolecules , 1 1 0 , 162-165. https://doi.org/10.1021/bm801065u
[95]Lavoine, N., Desloges, I., Dufresne, A. and Bras, J. (2012) Microfibrillated Cellulose—Its Barrier Properties and Applications in Cellulosic Materials: A Review. CarbohydratePolymers , 9 9 0 , 735-764. https://doi.org/10.1016/j.carbpol.2012.05.026
[96]Afra, E., Yousefi, H., Hadilam, M.M. and Nishino, T. (2013) Comparative Effect of Mechanical Beating and Nanofibrillation of Cellulose on Paper Properties Made from Bagasse and Softwood Pulps. CarbohydratePolymers , 9 9 7 , 725-730. https://doi.org/10.1016/j.carbpol.2013.05.032
[97]Rezayati Charani, P., Dehghani-Firouzabadi, M., Afra, E., Blademo, Å., Naderi, A. and Lindström, T. (2013) Production of Microfibrillated Cellulose from Unbleached Kraft Pulp of Kenaf and Scotch Pine and Its Effect on the Properties of Hardwood Kraft: Microfibrillated Cellulose Paper. Cellulose , 2 2 0 , 2559-2567. https://doi.org/10.1007/s10570-013-9998-z
[98]Djafari Petroudy, S.R., Syverud, K., Chinga-Carrasco, G., Ghasemain, A. and Resalati, H. (2014) Effects of Bagasse Microfibrillated Cellulose and Cationic Polyacrylamide on Key Properties of Bagasse Paper. Carbohydrate Polymers , 9 9 9 , 311318. https://doi.org/10.1016/j.carbpol.2013.07.073
[99]Afra, E., Yousefi, H. and Lakani, S.A. (2014) Properties of Chemi-Mechanical Pulp Filled with Nanofibrillated and Microcrystalline Cellulose. JournalofBiobasedMaterialsandBioenergy , 8 8 , 489-494. https://doi.org/10.1166/jbmb.2014.1462
[100]Taipale, T., Österberg, M., Nykänen, A., Ruokolainen, J. and Laine, J. (2010) Effect of Microfibrillated Cellulose and Fines on the Drainage of Kraft Pulp Suspension and Paper Strength. Cellulose , 1 17 , 1005-1020. https://doi.org/10.1007/s10570-010-9431-9
[101]Hult, E.-L., Iotti, M. and Lenes, M. (2010) Efficient Approach to High Barrier Packaging Using Microfibrillar Cellulose and Shellac. Cellulose , 1 1 7 , 575-586. https://doi.org/10.1007/s10570-010-9408-8
[102]Mashkour, M., Afra, E., Resalati, H. and Mashkour, M. (2015) Moderate Surface Acetylation of Nanofibrillated Cellulose for the Improvement of Paper Strength and Barrier Properties. RSCAdvances , 5 5 , 60179-60187. https://doi.org/10.1039/C5RA08161K
[103]Aulin, C., Gällstedt, M. and Lindström, T. (2010) Oxygen and Oil Barrier Properties of Microfibrillated Cellulose Films and Coatings. Cellulose , 1 1 7 , 559-574. https://doi.org/10.1007/s10570-009-9393-y
[104]Ridgway, C.J. and Gane, P.A.C. (2012) Constructing NFC-Pigment Composite Surface Treatment for Enhanced Paper Stiffness and Surface Properties. Cellulose , 1 1 9 , 547-560. https://doi.org/10.1007/s10570-011-9634-8
[105]Hamada, H., Beckvermit, J. and Bousfield, D. (2010) Nanofibrillated Cellulose with Fine Clay as a Coating Agent to Improve Print Quality. Pap. Conf. Trade Show 2010, Pap. 2010. 1, 854-880.
[106]Dimic-Misic, K., Ridgway, C., Maloney, T., Paltakari, J. and Gane, P. (2014) Influ-
Green and Sustainable
ence on Pore Structure of Micro/Nanofibrillar Cellulose in Pigmented Coating Formulations. TransportinPorousMedia , 1 1 0 3 , 155-179. https://doi.org/10.1007/s11242-014-0293-8
[107]Andrade, R., Skurtys, O., Osorio, F., Zuluaga, R., Gañán, P. and Castro, C. (2014) Wettability of Gelatin Coating Formulations Containing Cellulose Nanofibers on Banana and Eggplant Epicarps. LWT FoodScienceandTechnology , 5 5 8 , 158-165. https://doi.org/10.1016/j.lwt.2014.02.034
[108]Laurichesse, S. and Avérous, L. (2014) Chemical Modification of Lignins: Towards Biobased Polymers. ProgressinPolymerScience , 3 3 9 , 1266-1290. https://doi.org/10.1016/j.progpolymsci.2013.11.004
[109]Hambardzumyan, A., Foulon, L., Bercu, N.B., Pernes, M., Maigret, J.E., Molinari, M., Chabbert, B. and Aguié-Béghin, V. (2015) Organosolv Lignin as Natural Grafting Additive to Improve the Water Resistance of Films Using Cellulose Nanocrystals. ChemicalEngineeringJournal , 2 2 6 4 , 780-788. https://doi.org/10.1016/j.cej.2014.12.004
[110]Andersson, C. (2008) New Ways to Enhance the Functionality of Paperboard by Surface Treatment—A Review. PackagingTechnologyandScience , 2 2 1 , 339-373. https://doi.org/10.1002/pts.823
[111]Hult, E.-L., Koivu, K., Asikkala, J., Ropponen, J., Wrigstedt, P., Sipilä, J. and Poppius-Levlin, K. (2013) Esterified Lignin Coating as Water Vapor and Oxygen Barrier for Fiber-Based Packaging. Holzforschung , 6 6 7 , 899-905. https://doi.org/10.1515/hf-2012-0214
[112]Vartiainen, J., Vähä-Nissi, M. and Harlin, A. (2014) Biopolymer Films and Coatings in Packaging Applications—A Review of Recent Developments. Materials Sciences andApplications , 5 5 , 708-718. https://doi.org/10.4236/msa.2014.510072
[113]Araújo, T.S.L., de Oliveira, T.M., de Sousa, N.A., Souza, L.K.M., Sousa, F.B.M., de Oliveira, A.P., Nicolau, L.A.D., da Silva, A.A.V., Araújo, A.R., Magalhães, P.J.C., Vasconcelos, D.F.P., de Jonge, H.R., Souza, M.H.L.P., Silva, D.A., Paula, R.C.M. and Medeiros, J.V.R. (2020) Biopolymer Extracted from Anadenanthera colubrina (Red Angico Gum) Exerts Therapeutic Potential in Mice: Antidiarrheal Activity and Safety Assessment. Pharmaceuticals , 1 1 3 , 17. https://doi.org/10.3390/ph13010017
[114]Han, J.H. and Aristippos, G. (2005) Edible Films and Coatings: A Review. In: InnovationsinFoodPackaging , Elsevier, Amsterdam, 239-262. https://doi.org/10.1016/B978-012311632-1/50047-4
[115]Senturk Parreidt, T., Müller, K. and Schmid, M. (2018) Alginate-Based Edible Films and Coatings for Food Packaging Applications. Foods , 7 7 , 170. https://doi.org/10.3390/foods7100170
[116]Alexandre, E.M.C., Lourenço, R.V., Bittante, A.M.Q.B., Moraes, I.C.F. and Sobral, P.J.A. (2016) Gelatin-Based Films Reinforced with Montmorillonite and Activated with Nanoemulsion of Ginger Essential Oil for Food Packaging Applications. Food PackagingandShelfLife , 1 1 0 , 87-96. https://doi.org/10.1016/j.fpsl.2016.10.004
[117]Alparslan, Y., Yapıcı, H.H., Metin, C., Baygar, T., Günlü, A. and Baygar, T. (2016) Quality Assessment of Shrimps Preserved with Orange Leaf Essential Oil Incorporated Gelatin. LWT FoodScienceandTechnology , 7 7 2 , 457-466. https://doi.org/10.1016/j.lwt.2016.04.066
[118]Park, H.J., Kim, S.H., Lim, S.T., Shin, D.H., Choi, S.Y. and Hwang, K.T. (2000) Grease Resistance and Mechanical Properties of Isolated Soy Protein-Coated Paper. JournaloftheAmericanOilChemists ’ Society , 7 7 7 , 269-273. https://doi.org/10.1007/s11746-000-0044-2
Green and Sustainable
[119]Gorrasi, G. and Bugatti, V. (2016) Edible Bio-Nano-Hybrid Coatings for Food Protection Based on Pectins and LDH-Salicylate: Preparation and Analysis of Physical Properties. LWT FoodScienceandTechnology , 6 6 9 , 139-145. https://doi.org/10.1016/j.lwt.2016.01.038
[120]Falguera, V., Quintero, J.P., Jiménez, A., Muñoz, J.A. and Ibarz, A. (2011) Edible Films and Coatings: Structures, Active Functions and Trends in Their Use. Trends inFoodScience&Technology , 2 22 , 292-303. https://doi.org/10.1016/j.tifs.2011.02.004
[121]Chen, H., Wang, J., Cheng, Y., Wang, C., Liu, H., Bian, H., Han, W., et al . (2019) Application of Protein-Based Films and Coatings for Food Packaging: A Review. Polymers , 1 1 1 , 2039. https://doi.org/10.3390/polym11122039
[122]Hassan, B., Chatha, S.A.S., Hussain, A.I., Zia, K.M. and Akhtar, N. (2018) Recent Advances on Polysaccharides, Lipids and Protein Based Edible Films and Coatings: A Review. InternationalJournalofBiologicalMacromolecules , 1 1 0 9 , 1095-1107. https://doi.org/10.1016/j.ijbiomac.2017.11.097
[123]Hopewell, J., Dvorak, R. and Kosior, E. (2009) Plastics Recycling: Challenges and Opportunities. PhilosophicalTransactionsoftheRoyalSocietyB : BiologicalSciences , 3 6 4 , 2115-2126. https://doi.org/10.1098/rstb.2008.0311
[124]Álvarez-Castillo, E., Felix, M., Bengoechea, C. and Guerrero, A. (2021) Proteins from Agri-Food Industrial Biowastes or Co-Products and Their Applications as Green Materials. Foods , 1 1 0 , 981. https://doi.org/10.3390/foods10050981
[125]Cazón, P., Velazquez, G., Ramírez, J.A. and Vázquez, M. (2017) Polysaccharide-Based Films and Coatings for Food Packaging: A Review. FoodHydrocolloids , 6 68, 136-148. https://doi.org/10.1016/j.foodhyd.2016.09.009
[126]Wittaya, T. (2012) Protein-Based Edible Films: Characteristics and Improvement of Properties. In: StructureandFunctionofFoodEngineering , InTech, London, 43-70. https://doi.org/10.5772/48167
[127]Park, S.K., Rhee, C.O., Bae, D.H. and Hettiarachchy, N.S. (2001) Mechanical Properties and Water-Vapor Permeability of Soy-Protein Films Affected by Calcium Salts and Glucono-δ-Lactone. JournalofAgriculturalandFoodChemistry , 4 49, 2308-2312. https://doi.org/10.1021/jf0007479
[128]Cho, D.-Y., Jo, K., Cho, S.Y., Kim, J.M., Lim, K., Suh, H.J. and Oh, S. (2014) Antioxidant Effect and Functional Properties of Hydrolysates Derived from Egg-White Protein. KoreanJournalforFoodScienceofAnimalResources , 3 3 4 , 362-371. https://doi.org/10.5851/kosfa.2014.34.3.362
[129]Richert, M., Nejman, I. and Zawadzka, P. (2019) Characterization of Microstructure Coatings Used in Industry. JournalofSurfaceEngineeredMaterialsandAdvanced Technology , 9 9 , 11-27. https://doi.org/10.4236/jsemat.2019.92002
[130]Park, H.J. (1999) Development of Advanced Edible Coatings for Fruits. Trends in FoodScience&Technology , 1 1 0 , 254-260. https://doi.org/10.1016/S0924-2244(00)00003-0
PLA: Polylactide
PVA: Poly vinyl alcohol
IA: Itaconic acid
AM: Acrylamide
COD: Chemical oxygen demand PAE: Polyamide epoxy epichlorohydrin EVOH: Ethylene vinyl alcohol MFC: Micro-fibrillated cellulose CNF: Cellulose nanofiber
ISP: Isolated soy protein
FROM
8,Number 3, 2022
The use of alternative raw materials such as agricultural biomass and recycled wood wasteand by-products in particleboard production is a viable approach to respond to theincreased global demand for wood-based materials, and it is a key circular economyprinciple as well. W ood chips are the second most costly element after resin in particleboardproduction, where both elements accounting for more than 50% of the overall productioncost. Therefore, a significant cost reduction could be achieved by replacing woodchips with lignocellulosic agricultural wastes. Agricultural biomass exists in abundantpost-harvest and post-production processes and can be served as an ideal alternative forparticleboard manufacturing. This study aimed to review and evaluate the current stateof-the-art particleboard production using a wide variety of environmentally-friendlyagricultural biomass, recycled wood waste, and by-products. In this review, the agriculturalbiomass used for particleboard production was classified into seven different groups basedon the part of the plant which they are extracted from, i.e. straw, stalk, bagasse, seed/fruit,leaf, grass, and palms. Particleboards' properties of these raw materials were alsocompared in terms of their mechanical parameters. The last part of this review concludedthe challenges and future potential of using agricultural biomass and recycled wood waste.
Contact information: (see article –too numerous to list here)
Journal of Material Research and Technology, 2022: 2, 4630-4658 https://doi.org/10.1016/j.jmrt.2022.08.166
Creative Commons Attribution 4.0 International License
The Paper Industry Technical Association (PITA) is an independent organisation which operates for the general benefit of its members –both individualand corporate –dedicated to promoting and improving the technical and scientific knowledge of those working in the UK pulp and paper industry. Formed in 1960, it serves the Industry, both manufacturers and suppliers, by providing a forum for members to meet and network; it organises visits, conferences and training seminars that cover all aspects of papermaking science. It also publishes the prestigious journal Paper TechnologyInternational® and the PITA Annual Review, both sent free to members, and a range of other technical publications which include conference proceedings and the acclaimed Essential Guide to Aqueous Coating.
www.sciencedirect.com journalhomepage: www.elsevier.com/locate/jmrt
SengHuaLee a,*,WeiChenLum b,JiaGengBoon c,LubosKristak d , PetarAntov e,MartaPe˛dzik f,g,TomaszRogozinski g,HamidR.Taghiyari h , MuhammadAdlyRahandiLubis i,j,WidyaFatriasari i , SumitManoharYadav k,AujchariyaChotikhun l,AntonioPizzi m
a LaboratoryofBiopolymerandDerivatives,InstituteofTropicalForestryandForestProduct,UniversitiPutra Malaysia,43400UPMSerdang,Selangor,Malaysia
b InstituteforInfrastructureEngineeringandSustainableManagement(IIESM),UniversitiTeknologiMARA,40450 ShahAlam,Selangor,Malaysia
c FacultyofBioengineeringandTechnology,UniversitiMalaysiaKelantan,17600Jeli,Kelantan,Malaysia
d FacultyofWoodSciencesandTechnology,TechnicalUniversityinZvolen,96001Zvolen,Slovakia
e FacultyofForestIndustry,UniversityofForestry,1797Sofia,Bulgaria
f CenterofWoodTechnology, ŁukasiewiczResearchNetwork,PoznanInstituteofTechnology60-654Poznan,Poland
g FacultyofForestryandWoodTechnology,PoznanUniversityofLifeSciences,60-627Poznan,Poland
h WoodScienceandTechnologyDepartment,FacultyofMaterialsEngineering & NewTechnologies,ShahidRajaee TeacherTrainingUniversity,Tehran16788-15811,Iran
i ResearchCenterforBiomassandBioproducts,NationalResearchandInnovationAgency,Cibinong,WestJava 16911,Indonesia
j ResearchCollaborationCenterBetweenBRINandUniversitasPadjajaran,NationalResearchandInnovation Agency,Cibinong,WestJava16911,Indonesia
k DepartmentofForestProductandUtilization,ForestCollegeandResearchInstitute,Mulugu,Siddipeth,Telangana State502279,India
l FacultyofScienceandIndustrialTechnology,PrinceofSongklaUniversity,SuratThaniCampus,Mueang,Surat Thani,84000,SuratThani,Thailand
m LERMAB-ENSTIB,UniversityofLorraine,27RuePhilippeSeguin,88000Epinal,France
Theuseofalternativerawmaterialssuchasagriculturalbiomassandrecycledwoodwaste andby-productsinparticleboardproductionisaviableapproachtorespondtothe increasedglobaldemandforwood-basedmaterials,anditisakeycirculareconomy principleaswell.Woodchipsarethesecondmostcostlyelementafterresininparticleboardproduction,wherebothelementsaccountingformorethan50%oftheoverallproductioncost.Therefore,asignificantcostreductioncouldbeachievedbyreplacingwood chipswithlignocellulosicagriculturalwastes.Agriculturalbiomassexistsinabundant post-harvestandpost-productionprocessesandcanbeservedasanidealalternativefor particleboardmanufacturing.Thisstudyaimedtoreviewandevaluatethecurrentstateof-the-artparticleboardproductionusingawidevarietyofenvironmentally-friendly
* Correspondingauthor. E-mailaddress: lee_seng@upm.edu.my (S.H.Lee).
2022;20:4630 4658 https://doi.org/10.1016/j.jmrt.2022.08.166 2238-7854/© 2022TheAuthor(s).PublishedbyElsevierB.V.ThisisanopenaccessarticleundertheCCBYlicense(http:// creativecommons.org/licenses/by/4.0/).
Non-wood
Alternativerawmaterial
Environmentallyfriendly
agriculturalbiomass,recycledwoodwaste,andby-products.Inthisreview,theagricultural biomassusedforparticleboardproductionwasclassifiedintosevendifferentgroupsbased onthepartoftheplantwhichtheyareextractedfrom,i.e.straw,stalk,bagasse,seed/fruit, leaf,grass,andpalms.Particleboards' propertiesoftheserawmaterialswerealso comparedintermsoftheirmechanicalparameters.Thelastpartofthisreviewconcluded thechallengesandfuturepotentialofusingagriculturalbiomassandrecycledwoodwaste. © 2022TheAuthor(s).PublishedbyElsevierB.V.ThisisanopenaccessarticleundertheCC BYlicense(http://creativecommons.org/licenses/by/4.0/).
Particleboardisanengineeredwoodproductmanufactured fromwoodchipsbondedwithasyntheticresinoranother suitablebinderunderexposuretoahotpressatcertain pressureandtemperature.Particleboardisoneofthemajor wood-basedproductsinglobaltrade.Itsglobaldemandand productionhaveseenanupwardtrendinrecentyears.AccordingtoIMARCGroup[1],theglobalmarketforparticleboardreachedatotalvalueof21billionUSdollarsin2020.The groupanticipatesacompoundannualgrowthrate(CAGR)of 4.4%duringthenextsixyears.
In2020,theproductionquantityofparticleboardreached 96.01millionm3 worldwide(Fig.1),whichrepresentsa decreaseof4.7%comparedtothepreviousyear(100.74million m3).MainlandChinaproducedthehighestquantityofparticleboardin2020,amountingto29.43millionm3 involumeor 30.65%ofthetotalproductionquantityworldwide.Several EuropeancountriessuchasGermany,Poland,Italy,Austria, andFranceareamongtheleadingproducersofparticleboard. Asiaisthelargestproducerofparticleboard,followedby Europe,theAmericas,Africa,andlastly,Oceania(Fig.2).
In2020,thetotalimportvolumeofparticleboardwas22.04 millionm3.Germanywasthelargestparticleboardimporter withapproximately1.90millionm3,followedbytheUnited
StatesofAmericaandPoland(Fig.3).Europeancountrieswere thelargestparticleboardimporters(54.43%),followedbyAsia (26.51%),Americas(15.89%),Africa(2.83%),andOceaniawith only0.34%(Fig.4).
In2020,thetotalexportvolumeofparticleboardwasestimatedtobe21.97millionm3,whereThailandwasthemain exporterworldwidewith2.55millionm3 (Fig.5).Asshownin Fig.6,Europeancountriesarethelargestparticleboardexporters(69.95%),followedbyAsia(19.28%)andtheAmericas (9.77%).AfricaandOceaniaexportedaverysmallamountof particleboardin2020,whichamountedto0.72%and0.28%, respectively.
Thedatashowsthatthecountrieswiththehighestproductionofboardsarealsothelargestimporters.Themajor rawmaterialsusedinparticleboardproductionarewood chipsacquiredfromforestthinningandtimberwaste[3]. Commonly,medium-sizedandsmall-sizedsoftwoodsarethe preferredwoodspeciesforparticleboardproduction.However,anupwardtrendintheuseofhardwoodspecieshasbeen observedinrecentyearsincertaincountriesaroundtheworld [4].However,thedecreasingsupplyoftimbersfromnatural forestsmadeitdifficulttomeettheincreasingfuturedemand forparticleboard.Furthermore,woodchippriceswerereportedtohaveincreasedupto30%from2006to2011[5].The priceofthewoodchipswasreportedtobearoundRM300per tonasof2014,whiletheestimatedpricefortheplantresidues
isatleast50%belowthepriceofthewoodchips[6].Reforestationwoodssuchas Pinus spp.and Eucalyptus spp.arethe mostwidelyusedforcommercialparticleboard manufacturing[7].
InSoutheastAsia,rubber(Heveabrasiliensis)andsengon wood(Paraserianthesfalcataria)havebeenusedasthemain rawmaterialforparticleboardproductionastheyare medium-densityhardwoodswithanaturalwhitishcolor [8 11].Otherlessknownorunderutilizedwoodspecieshave alsobeenusedforparticleboardmanufacturing(Table1).
Theincreasedglobaldemandforwoodrawmaterials, growingenvironmentalconcerns,andrecentlegislativeregulationsrelatedtocascadingwooduseandprioritizingvalueaddedapplicationsofwoodresourceshaveposedcritical challengestothewood-basedpanelindustryintermsofwood supply.Strategiestoaddresstheseshortagesmaybevital, particularlyincountrieswithalowforestarea.Theoptimizationofavailablewoodandlignocellulosicrawmaterials,as
wellasthesearchforalternativenaturalfeedstocksderived fromabundantandrenewableagriculturalresiduesandwood by-products,toreplacewoodinparticleboardmanufacturing, isaviablestrategyforreducingthenegativeenvironmental impactandimprovingtheresourceefficiencyofthewoodbasedpanelindustry.Agriculturalwasteisahugepoolof untappedbiomassresourcesthatcanbeconvertedinvarious waysandmayevenrepresenteconomicandenvironmental burdens[23,24].Markedly,theutilizationofagricultural biomassinparticleboardmanufacturingshouldbeeconomicallyprofitable,andtheboardsproducedshouldmeetthe requirementsdescribedinthetechnicalstandards.
Thecostoftherawmaterialsused,namelyadhesiveand woodchips,constitutethemajorityofthecostofthefinal particleboardpanels(Table2).Thetotalmaterialcostrepresents40 60%ofthetotalproductioncost.Itwasreportedthat thecostofadhesiveamountedto30 50%ofthetotalmaterial costoftheparticleboardproduction,whiletheremaining
50 70%ofthematerialcostiswoodchips[25].Therefore,itis assumedthatadhesiveandwoodchipsrespectivelyrepresent 15 30%and30 40%ofthetotalproductioncost.Otherprimarycostcomponentssuchasenergy,manpower,andprocessingcostoftheparticleboardrepresentaround15 20%, 5 20%,and25 30%,respectively.IncontrasttoSoltetal.[25], whoreportedthatwoodchipsaremoreexpensivethanadhesive,vanDametal.[26]reportedthatadhesiveisslightly moreexpensivethanwoodchips.Accordingtotheauthors, materialcostsaccountfor66%oftotalproductioncosts,with adhesiveaccountingfor34%andwoodresourcesaccounting for32%.Meanwhile,accordingtoKlimekandWimmer[6], woodchipsarethesecondmostexpensivecomponentafter adhesiveinparticleboardproduction,accountingforroughly 20%oftotalproductioncosts.Thedisparitiescouldbeattributedtothehighvariabilityoftransportationcostsandcultivatedvolumes.Whateverthescenario,itisundeniablethat
thematerialcost,whichincludesthecostofadhesiveand woodchips,frequentlyaccountsformorethanhalfofthe totalproductioncost.Thecostofagriculturalbiomassis estimatedtobe50%lessthanthatofwoodchips[6].Asa result,replacingwoodchipswithalternative,non-woodraw materialscouldresultinsignificantcostsavings.
Thisstudyaimedtoreviewandsummarisethecurrent state-of-the-artparticleboardproductionusingvariousagriculturalbiomassandwoodby-productsasenvironmentally friendlyfeedstocks.Inthisreview,theagriculturalbiomass usedforparticleboardproductionwasclassifiedintoseven differentgroupsbasedontherespectiveplantpartsderived from,i.e.straw,stalk,bagasse,seed/fruit,leaf,grass,and palms.Thisstudycomparedtheexploitationpropertiesof particleboardsmadefromagriculturalbiomass(keepingthe divisionintogroups),processedwoodwaste,andby-products dividedintotwodensityranges.
Adhesiveandwoodparticles/chipsarethetwomajorcomponentsofparticleboard.Approximately95%ofthetotaladhesivesusedformanufacturingwood-basedpanelsarebased onformaldehyde.Theseresinsaremadebyreactingformaldehydewithotherchemicalssuchasurea,melamine,phenol, resorcinol,orcombinations[27].Urea-formaldehyde(UF), melaminefortifiedUF(MUF),melamine urea phenol-formaldehyderesin(MUPF),melamine-formaldehyde(MF), phenol-formaldehyde(PF),phenol urea-formaldehyde(PUF), polymericmethylenediisocyanate(pMDI),aswellasnatural, bio-basedadhesivessuchastannins,lignins,carbohydrates, andnaturalrubberlatexareamongthecommonlyusedadhesivesinparticleboardmanufacturing[27].Amongthese, aminoplasticresinsderivedfromnon-renewablepetrochemicalmaterialssuchasMFandUFarethemostprevalently usedadhesivesinparticleboardmanufacturing.Theseresins arenormallycharacterizedbyamolarratioofformaldehyde tourea(F/U)between1.00and1.10[28].UFresins,withan estimatedannualconsumptionofabout11milliontonsof
solidsworldwide,arethemostwidelyusedadhesivesystem inparticleboardproduction,accountingforabout85%ofthe totalvolumeduetotheirchemicalversatility,highreactivity, water-solubility,lowcuringtemperatures,shortpresstimes, colourlessglueline,andrelativelylowcost[29].
Inrecentyears,someexperimentsweremadetoimprove physical,mechanical,andbiologicalproperties,reducehotpresstime,andreduceformaldehydeemissionofUFresin byadditionofdifferentnano-fillers(suchasnanosilver,nano copper,andnano-mineralslikewollastonite)toproduce wood-basedcompositepanels[30 35].Thoughtheinitialresultswerepromisingbothatlaboratoryscaleandpilotbatch atfactories,theexperimentshavenotyetbeenusedatfull industrialscales.PFresinsarethesecondmostimportant typeofwoodadhesives,withanestimatedannualconsumptionofapprox.threemilliontonsworldwideareusedto producewater-andweather-resistantparticleboard.Meanwhile,polymeric4,4-diphenylmethanediisocyanate(pMDI)is mainlyusedformanufacturingexterior-gradeparticleboard [27],orinapplicationswhereconcernsabouttheharmfulfreeformaldehydeemissionassociatedwithUFadhesives,are present.pMDIhasexcellentadhesionpropertiesandcanbe usedinsignificantlylowerproportionsthanUF,PF,andMUF
resins.Duetotheirrelativelyhighprice,isocyanatesare mostlyusedinadhesivesystemsincombinationwithtraditionalformaldehyde-basedresinstoenhancetheirperformance.However,pMDIcouldalsobeusedtobindraw materialsthataredifficulttoglue,suchasbagasse,straw, leaves,orstraw[27].
propertiesandcancontributetotheparticleboard’smechanicalstrength,biologicaldurability,formationofchar,andultravioletdegradation[70,71].LertwattanarukandSuntijitto [71]statedthatlignincouldaidinsofteningtheparticles duringhotpressing,easingtheirresination[72].
AccordingtoAlwanietal.[36],agriculturalbiomasscanbe classifieddependingonthepartoftheplantfromwhichthey areextracted.Agriculturalbiomasscanbedividedintowood andnon-woodbiomass.Woodbiomassincludeshardwood andsoftwoodspecies.Non-woodbiomasscanbecategorized intoleaf,grass,seed,fruit,stem,straw,andstalk[36].Most non-woodbiomassissmallindiameter,exceptforoilpalm trunksandbamboo.Thischaracteristichasrestrictedtheir practicabilitytobeprocessedintoveneer,lumber,orstrips [37].Therefore,non-woodbiomassissuitabletoserveasa feedstockforparticleboardproductionwherethesizeand dimensionsofthematerialsarenotemphasized.Inthisstudy, severalnon-woodbiomasseshavebeenidentifiedasraw materialsforparticleboardproduction.Forcomparisonpurposes,thesebiomasses,eitherdicotyledonousormonocotyledonous,wereclassifiedaccordingto Fig.7
Commonagriculturalwasteusedinparticleboardproductionisintheformsofstraw,stalk,shell,husk,leaves, stem,etc.Thesepost-harvestingandpost-productionwastes canserveasanalternativesourceforparticleboard manufacturing.Theresourcesofsomeselectedagricultural cropsworldwidearedisplayedin Table3.Staplefoodsuchas rice,maize,wheat,andbarleyhavethehighestharvestedarea (ha),andtheircorrespondingproductionquantity(tons)is alsoamongthehighest.Thefiguresin Table3 implythe abundanceofthebiomassgeneratedafterharvestingand processing.Therespectivepartsofthecropsusedinparticleboardproductionarealsolistedin Table3
3.2.Characteristicsofagriculturalbiomassfor particleboardmanufacturing
Summarisedinformationonthechemicalcomposition,i.e. celluloseandlignincontentofwoodandnon-woodbiomass asnaturalfeedstocksforparticleboardmanufacturing,is presentedin Table4.AccordingtoPedziketal.[4],agricultural wastegenerallyhasaslightlylowercellulosecontentthan softwoodandhardwood.Thismightrestrictthepotentialof agriculturalbiomassinparticleboardproductionascellulose isresponsibleforthestrengthanddimensionalstabilityofthe resultantboards.Stalk-basedbiomass,pineappleleaves,and bamboohaverelativelyhighercellulosecontentthanthe otherbiomass,whichmightmakethemfavorableforproducingparticleboardwithhighmechanicalstrength.Onthe otherhand,ligninisanamorphous,complexthreedimensionalaromaticbiopolymerwithhydrophobic
In2020,theproductionquantityofwheatwas760.93million tonsworldwide,precededonlybysugarcaneandmaize.With thishugeproductioncapacity,findingnovelmethodstoutilizetheremainingwheatstrawinvalue-addedapplications effectivelyisessential.Hanetal.[87]createdUF-bonded wheatstrawparticleboard,butitspropertieswereinferiorto thoseofcommercialparticleboard.Asimilarfindingwas madeforthereedstrawparticleboard.However,silane couplingagentswereusedtoimprovetheparticleboard's bondability.Thetreatmentwasfoundtoenhancethewheat strawandreedstrawparticleboardperformancetovarying degrees.Epoxidesilanewasfoundtobemoreeffectivefor reedstrawparticleboard,whileaminosilanewasfoundtobe moreeffectiveforwheatstrawparticleboard.Thesurface appearanceofstraw-basedparticleboardisshownin Fig.8
Despitetheresultantinferiorperformanceofstrawparticleboard,someresearchersfoundthatstrawcouldserveasa suitablerawmaterialforthesurfaceparticleboardlayer, providedpMDIresinoracombinationofUFandpMDIwere employed[88].Ricestrawwassuccessfullyusedasapartial substitutionofwoodparticlesupto20%withoutadversely affectingthemechanicalpropertiesoftheparticleboard [89,90].Lietal.[60]producedricestrawparticleboardbonded withpMDIandfoundthatitspropertiesexceededtheM-2 specificationoftheAmericanNationalStandardforWood Particleboard[ANSIA208.1][91].However,ricestrawishighin ashandsilicacontent,whichinterfereswithitsbonding abilityandleadstolowinternalbondingstrength.Hence,pretreatmentisnecessarytoremovetheexcessiveashandsilica content.
Rapeseedstraw,likewheatandricestraw,hasasimilar chemicalcompositiontowood,withlesscelluloseandlignin butmorehemicelluloseandextractives.Furthermore,rapeseedstrawhasbettergluabilitythanwheatstrawbecauseits chemicalsubstancesaredistributedthroughouttheentire mass,unlikewheatstraw.Rapeseedstrawcanbeeasilyglued evenwhenconventionalwoodadhesiveswasused.Dukarska
3.Agriculturalbiomassasrawmaterialfor particleboardmanufacturing
3.1.Classificationandavailabilityofagricultural biomass
etal.[92]manufacturedrapeseedstrawinfivedensities (450 650kg/m3).Withincreasingdensity,theparticleboard's bendingstrength(MOR),modulusofelasticity(MOE),andinternalbond(IB)valueincreased.Theparticleboardmetthe requirementsoftheP7type,i.e.,boardswithincreasedloadcarryingcapacityintendedforuseinhumidconditions,accordingtoEN312[93].Oneofthemostsignificantissueswith cerealstrawsasarawmaterialforparticleboard manufacturingistheirseasonalavailability,resultingin inconsistentsupplythroughouttheyear.Whitemustard (Sinapisalba L.),harvestedatdifferenttimesthancereals,isan excellentsubstitute.Whitemustardisahigh-yielding,fastgrowingcrop,anditsstrawcanbeusedasafeedstockin particleboardproduction[92].
Chilipepper[46],tobacco[67],cotton[94,95],sunflower[96], sorghum[78],Miscanthus[97],rapeseed[77],tomato[68], kenaf[98,99],topinambour[100],andcup-plant[72]haveall usedplantstalksasrawmaterialsforparticleboardproduction.Theirchemicalcompositionvariesamongagricultural biomassandsignificantlyimpactsthephysicalandmechanicalperformanceoftheresultingparticleboard. Fig.9 shows thesurfaceappearanceofstalk-basedparticleboard.
Thephysicalandmechanicalpropertiesofparticleboard madefromsomeselectedplantstalksaregivenin Table5 Underthesameprocessingparameters,i.e.UFresincontent 8%,pressingtemperature170 C,andpressingtime4min, particleboardmadefromchilipepperstalk[46]hadlower thicknessswelling(TS)andwaterabsorption(WA)values comparedtothatofitsrapeseedstalkcounterpart[77].This
mightbeattributedtothechilipepperstalk'shigherlignin contentthantherapeseedstalk(25.4%vs15.3%,respectively). Lignin,withrelativelyhigherhydrophobicity,isthemain contributortothelesswateraccessibilityofplants[101]. Nourbakhshetal.[102]alsofoundthatagriculturalbiomass withlowerlignincontenttendstohavehigherwateruptake. BothparticleboardsmadefromchilipepperstalkandrapeseedstalkachievedtheminimumrequirementsforMOR, MOE,andIB,accordingtotheKoreanStandardKSF3104forPB type8.0[KSF3104[103]].However,acertainamountofwood particlesorahigheramountofresincouldbeemployedto attainamoresatisfactoryoutcome[77].
Highholocellulosecontentintobaccostalks(~68%)isthe mainreasonforitsinferiordimensionalstability.Apartfrom that,itsanatomicalproperties,suchaslongfiber(1.23mm) withlargecelllumenwidth(15.4 mm),alsocontributedtoits dimensionalinstabilitycomparedtowoodparticles[67]. Markedly,particleboardmadefromtobaccostalkshasbetter termiteresistancethanparticleboardmadefrom P.falcataria L.Nielsen,asshownbyAcdaandCabangon[67].Afterexposureto Coptotermesgestroi Wasmann,particleboardmadefrom 100% P.falcataria experienced43%weightlosscomparedto only1.5%inparticleboardmadefrom100%tobaccostalk. Weightlosscausedbytermitesdecreasedastheproportionof tobaccostalksincreased.Incorporating25%tobaccostalkshas alreadyledtosignificantresistanceagainsttermites.Nevertheless,50%oftobaccostalksareneededfortheunderground fieldexposuretesttoprotectfromsubterraneantermites, Macrotermesgilvus Hagen.100%weightlosswasrecordedin theparticleboardmadefrom100% P.falcataria, whileonly 1.32%weightlosswasobservedforparticleboardmadewith 100%tobaccostalks,indicatingitshighresistanceagainst
Fig.7 Classificationofnon-woodbiomassusedinparticleboardmanufacturing.RawmaterialAreaharvested (000,000ha)
Partusedin particleboardproduction Source
Agavefibers0.060.047047Bagasse[38] Almonds,withshell2.164.1419,147Shell[39] Arecanuts1.231.8014,650Fiber[40] Bananas5.20119.83230,294Stem[41] Barley51.60157.0330,432Straw[42] Buckwheat1.861.819752Stalk[43] Cashewnuts,withshell7.104.185887Shell[44] Castoroilseed1.222.0516,776Cake[45] Chiliesandpeppers,green2.0736.14174,576Stalk[46] Coconuts11.5861.5253,148Pitandfiber[47] Dates1.249.45301,692Palmbranches[48] Eggplants1.8856.6213,637Stalk[49] Hazelnuts,withshell1.021.0710,562Shell[50] Hemptowwaste0.080.2532,068Hurd[51] Hempseed0.010.015164Shiv[52] Jute1.402.694900Stick[53] Linseed(flax)3.543.375392Shive[51] Maize201.981162.3557,547Cob[54] Manilafiber(abaca)0.170.116177Fiber[55] Pineapples1.0827.82258,056Leaves[56] Poppyseed0.040.026397Husk[57] Ramie0.030.0619,055Stem[58] Rapeseed35.5072.3820,390Straw[59] Rice,paddy164.19756.7446,089Straw[60] Rye4.4515.0233,781Straw[61] Seedcotton31.8483.1126,103Stalk[62] Sorghum40.2558.7114,585Bagasse[63] Sugarcane26.471869.72706,434Bagasse[64] Sunflowerseed27.8750.2318,020Husk[65] Tea5.317.0213,227Leaves[66] Tobacco,unmanufactured3.245.8918,188Stalk[67] Tomatoes5.05186.82369,798Stalk[68] Walnuts,withshell1.023.3224,989Shell[39] Wheat219.01760.9334,744Straw[69]
subterraneantermites.Theauthorsattributedthetermite resistancetothepresenceofnicotineintobaccostalks,which mightactasapotentinsecticidefortermites.Apartfromits chemicalandanatomicalproperties,Klimeketal.[72] demonstratedthattheadhesiveusedandloadinglevelduring particleboardproductionalsoplayavitalroleintheperformanceoftheresultantparticleboard.pMDIat4%and6% contentlevelsresultedinbettermechanicalandphysical propertiesthanUFresinat8%and12%content.Kenafstalks particleboard[104]hadhigherMORthantheparticleboard madefromtobaccoorsunflowerstalks,kiwipruning,grapevinestalks,andtealeavesresidues[105].However,itsIBwas inferiortotobacco,sunflowerstalks,vinestalk,andkiwi pruningboards,mainlyduetoitslessfibrousanatomical structureandbarkcontent[90].
Bagasse,alsocalledmegass,isthedrypulpyfibrousmaterial thatremainsaftertheextractionofthesugar-bearingjuice fromsugarcaneorsorghumstalks.Itisestimatedthat250kg ofbagassecouldbegeneratedfromeverytonofsugarcane. Thesugarcanebagasseisnormallyusedasfuelforsteam generationtosupplyenergy[65].Itcouldbenefitsocietyand
theeconomyifthissugarcanebagassewereconvertedinto panelproductssuchasparticleboardandotherfibercomposites[106,107].Sugarcanebagassehasbeenproventoproduceparticleboardwithacceptablephysicalandmechanical properties,withorwithouttheincorporationofwoodparticles[108,109].Particleboardmadeofsugarcanebagasseis shownin Fig.10.However,particleboardmadefromsugarcanehaslowermechanicalstrengthcomparedtothatofits eucalyptusandpinecounterparts[110].Therefore,insome cases,theincorporationofwoodparticlesisnecessaryto improvetheperformanceofparticleboard.AstudybyBuzo etal.[111]statedthatsugarcanebagasseparticleboardbonded withcastoroil-basedpolyurethane(PU)resincouldattainthe bestmechanicalandphysicalpropertiesaftertheincorporationof60%pineparticles.Asimilarobservationwasobtained byYanoetal.[112],whoreportedthattheincorporationof 50%industrialtimberresidueimprovedthemechanicalperformanceofsugarcanebagasseparticleboard.
Particleboardmadefromsweetsorghumparticles,onthe otherhand,haslowdimensionalstability,MOE,andIBproperties.However,thesedrawbackscanbeovercomebylayering surfacetreatment,asreportedbyIswantoetal.[63].Using citricacid(CA)andsucroseasabinder,sweetsorghum bagasseparticleboardwasfoundtohavesuperior
Table3 Globalresourcesofselectedagriculturalcrops[2]andtheirapplicationinparticleboardproduction.Table4
GroupRawmaterialCelluloseLigninReferences
WoodSprucewood45.428.2[72] Pinewood49.527.5[73] Eucalyptuscamaldulensis Dehn.49.6719.14[74] Softwood40 4425 32[75] Hardwood40 4418 25 StrawRapeseedstraw28.8321.35[76] Wheatstraw39.320.7[73] Whitemustardstraw36.721.6[73] StalkRapeseedstalk 15.3[77] Tomatostalk43.1112.29[68] Sunflowerstalk40.921.6[72] Topinambourstalk30.916.3 Cup-plantstalk38.621.4 Sorghumstalk45.917.2[78] Chilistalk 25.4
Bagassesweetsorghumbagasse34.7823.02[79] sugarcanebagasse35.222.2[80,81] Seed/fruitCoffeehusk19 2618 30 Coffeehull40 4933 35 Hazelnuthusk34.535.1[82] Cottoncarpel31.220.5 Macadamiashells29.540.1
LeafPineappleleaves66.24.28[83] GrassPerennialryegrass(Loliumperenne L.)29.2128.85[74] Vetivergrass 17.03[84] Petungbamboo(Dendrocalamusasper)43.4124[85] Wulungbamboo(Gigantochloaatroviolacea)45.1924.16 Apusbamboo(Gigantochloaapus)42.3822.71
PalmOilpalmtrunk39.46.64[86] Oilpalmfrond54.358.96 Emptyfruitbunch37.8212.16
dimensionalstabilityandMOEthanPFandpMDI-bonded sweetsorghumbagassebutlowerMORandIB[79,114].As shownin Table6,atthesamedensitylevelandresincontent, citricacid-bondedsugarcanebagasseparticleboardhad
inferiorMORandMOEvaluesthancitricacid-bondedsweet sorghumbagasseparticleboard.However,theIBstrengthand dimensionalstabilityofthesugarcanebagasseparticleboard werebetter[79,115].
Hullreferstotheoutercoveringofafruitorseed,whilehusk referstothedry,leafyorstringyexteriorofcertainvegetables orfruits,whichmustberemovedbeforeeatingthemeatinside.Sunflowerseedhuskandthehullaresuitablematerials forparticleboardmanufacturingastheyhavesimilarchemicalcompositionstowood[65].Thehusksofsunflowerseeds makeupto21 30%oftheirtotalweight;therefore,ahuge amountofresiduesareoftengeneratedduringsunfloweroil extraction[116].Gertjejansenetal.[117]investigatedthe performanceofparticleboardmadefrom100%sunflower hulls.Theyreportedthattheresultantparticleboardhad surpassedtheminimumrequirementsforMORandMOEas statedinCommercialStandard(CS)236-66[118].Nevertheless,theIBstrengthwasinferiorandadding50%aspenflakes wasrequiredtoimprovetheIBstrength.Cosereanuetal.[65] investigatedtheeffectsofparticlesizeandgeometryonthe performanceofparticleboardmadefromsunflowerseed husks.Twoparticlesizeswereused,namelycoarse(2 3mm) andfineparticles(0.5 1mm).Single-layerparticleboardmade fromfineparticleshasahigherdensityandperformsbetterin termsofWA,TS,MOR,andIBthanitscoarseparticle
counterparts.Fineparticlesareeasytopress,resultingin higherdensityandcompacterboardandcorrespondingly betterperformance.Particleboardproduceddisplayedgood thermalconductivitywithvaluesrangingbetween0.075and 0.079W/mK.ExceptforMOE,MOR,andTS,theparticleboard madefromsunflowerseedhuskfailedtomeettheminimum requirementsforparticleboardforgeneraluse(typeP1)and moistureresistanceparticleboard(typeP3).Itistherefore recommendedtobeusedforfurniturecomponentsorother structuralapplicationsthatarenotsubjecttoload-bearing.
Shellsofalmond,walnut,macadamia,andpeachnuthave beenutilizedinparticleboardproduction(Table7).Pirayesh etal.[39]producedwalnut(Juglansregia L.)shell-andalmond (Prunusamygdalus L.)shell-basedparticleboardbondedwith UFresin.Theresultsrevealedthatthe100%walnutshell particleboardhadthelowestMOR,MOE,andIBvalues. Markedly,particleboardmadefrom100%almondshell exhibitedbettermechanicalpropertiesthanwalnutshell particleboard.However,bothtypesofparticleboardwere inferiorcomparedtoparticleboardmadefromhornbeam (Carpinusbetulus L.)andbeech(Fagusorientalis L.)wood. Interestingly,particleboardmadefromwalnutandalmond
shellsexhibitedlowerTSandWAthanwood-based particleboard.
InastudybyWechsleretal.[121],macadamia(Macadamia integrifolia)nutshellsandcastor(Rı´cinoscommunis)oil-based resinwasusedtoproduceparticleboard.Evenwithamuch higherdensity(987kg/m3),theMORofmacadamiaparticleboardwaslowerthanpineparticleboard(691kg/m3)byhalf, whiletheMOEvaluewasalmostthree-timeslower.However, macadamiaparticleboarddisplayedbetterIB,TS,andWA thanpineparticleboard.Lowerabsorptionandwater-induced swellingofmacadamiaparticleboardcouldbeattributedto thesuperiormoistureresistanceofmacadamianutshells. Celluloseisresponsibleforthestrengthandstiffnessofthe agro-fibers.Therefore,lowerMORandMOEareexpectedfor macadamiashellparticleboardasmacadamiashellhaslower cellulosecontent(30%)thanpinewood(44%).Owingtotheir superiormoistureresistance,macadamianutshell/castoroil particleboardhasthepotentialforuseinhumid environments.
Barbuetal.[50]investigatedthefeasibilityofusingwalnut andhazelnutshellsinparticleboardmanufacturing.Theauthorsfabricatedvariouspanelsusingwalnutorhazelnut shellsbondedwithMUForPUresinandatargetdensityof 1000kg/m3 (Fig.11).MORandMOEvalueswere40 50%lower forMUFresinbondednutshellboardscomparedtospruce particleboardand65%higherwhenPUadhesivewasused. Whencomparedtospruceparticleboard,thedeveloped compositeshadsignificantlyhigherWAandTSvalues,aswell asclose-to-zerofreeformaldehydecontent,meetingtherequirementsoftheE0emissiongrade( 2.5mg/100g)forboth walnutandhazelnutshellrawmaterials,andofthesuperE0 category( 1.5mg/100g)whenPUresinwasusedENISO 12460-5[122].
Thepossibilityofmanufacturingparticleboardfrom groundnutshellandricehuskwastes,boundwithamodified adhesivesystem,wasevaluatedbyAkinyemietal.[123].The authorsinvestigatedtheeffectsoftheadditionofdifferent levelsofgroundnutshellsandricehusksinthecompositionof thepanels,i.e.30 70,70 30,50 50%,and100%foreachofthe wastematerials.Thedevelopedcompositesexhibitedsignificantlydeteriorateddimensionalstabilityvalues,failingto
complywiththestandardrequirements.Thehighestdensity andIBvaluesof0.98;0.97g/cm3 and0.24;0.23N/mm2 were determinedforthesamplesfabricatedwith30%rice husks þ 70%groundnutshellsand50%ricehusks þ 50% groundnutshells,respectively.Thebestmechanicalpropertieswereobtainedforthepanelsmanufacturedfrom30%rice husksand70%groundnutshells.
Owingtoitshighphenoliccontent,wasteleavesof Camelia sinensis L.areconsideredapromisingalternativematerialfor particleboardmanufacturing[66].AstudybyYalinkilicetal. [124]reportedthattealeaves,asasubstrateforgrowing mushrooms,resultedinverypoormycelialdevelopmentand almostnofruitbodyformation.Therefore,itisanticipated thatparticleboardmadefromwastetealeavesshouldhave superiorbiologicaldurability.Yalinkilicetal.[66]fabricated three-layerparticleboardfromwastetealeavebondedwith UFresin.Theboardswereexposedtobrown-rotfungus (Tyromycespalustris (Berk.etCurt)Murr.),white-rotfungus (Coriolusversicolor (L.exFr.)Quel.)andsubterraneantermites (Coptotermesformosanus Shiraki).Particleboardmadefrom wastetealeavesprovedbiologicallyresistantagainstdecay fungiandtermites.However,theboards' dimensionalstability andmechanicalpropertiesshouldbefurtherimproved.Apart fromitssuperiorityinbiologicaldurability,tannins,protein, andaminoacidthatexistsinabundanceintealeavescould activelyreactwithformaldehyde[125].Asaresult,lower formaldehydeemissionfromtheresultantparticleboardis expected.ThesameauthorsreportedhatheUF-bondedwaste
tealeavesboardsemittedsignificantlylowerformaldehyde comparedtoconventionalpoplarparticleboard,indicating thattealeavescouldactasformaldehydescavengers.
Oneofthewastetealeavesparticleboardissuesisits inferiormechanicalproperties.Boardwithhigherdensityor incorporationofacertainamountofwoodparticlesis necessary.Batiancelaetal.[126]incorporated10 80% P.falcataria (L.)Nielsenwoodparticlesinthewastetealeave particleboard.Comparedtowood,wastetealeavesareless hygroscopicastheyhaveasmalleramountofcelluloseand hemicellulose[127].Particleboardswith100%wastetea leaveshavesignificantlylowerTSandWAvalues.Inaddition, bladesoftealeavesconsistmainlyofthin-walledparenchyma cells,makingthemeasilycompressedduringmatconsolidationandresultingingoodIB[128].However,adding P.falcataria woodparticlesenhancedtheMORandMOEofthe boards.Particleboardproducedwithincorporationof20 50% woodparticlessurpassedtheminimumrequirementsofTS, WA,IB,MOR,andMOEforgeneraluseparticleboardsetbyEN 312-2.
Treeleavesareanotherunderutilizedbiomassthatcould beconvertedintoparticleboard[129].However,conventional UFresinisnotsuitabletobeusedasabinderforbondingtea leavesastheleaveshaveawaxyepidermalsurfacelayer[130]. Extractivessuchaswax,inorganicsilicon,andfatarefoundin thiswaxylayerandcouldinterferewithitscompatibilitywith awater-basedadhesivesuchasUF[131].Therefore,isocyanatessuchasMDIarecommonlyusedforbondingagriculturalresiduesthataredifficulttoglue.Acomparison betweenthephysicalandmechanicalpropertiesofleavebasedparticleboard,bondedwithUFresinandMDI,is
Table7 Physicalandmechanicalpropertiesofparticleboardmanufacturedfromselectedhulls,husks,andshells.
RawMaterialsAdhesive type Adhesive(%)Density (kg/m3) MOR (MPa) MOE (MPa) IB (MPa) TS, 24h(%) WA, 24h(%) References
HazelnuthuskUF10/8* 70011.9N/A0.50519.643.5[82] MUF10/870010.1N/A0.3929.347.7 PF10/870012N/A0.48216.244.5 UF10/86008.18N/A0.34922.164.2 MUF10/86007.7N/A0.33624.673.7 PF10/86008.49N/A0.34318.955.2 Ricehusksoybeanprotein108008.318750.2343.5888.67[119] SunflowerseedhuskUF166825.8217030.2410.255.4[65] 16/145555.3316450.189.253.4 PeanuthullUF10/85052.95710.1612.3494.88[120] 10/85915.247320.2214.0179.17 10/87068.5411900.316.6568.45 10/879610.414850.425.7177.57 11/95033.126540.1711.8397.85 11/96055.948140.2413.0983.81 11/96979.912740.3215.3467.85 11/979412.1417190.4121.0270.43
walnutshellUF11/97006.631208.90.26~7~20[39] almondshellUF11/9700~9~1400~0.35~11~45 macadamiashellcastoroilresin209874.33801.332.710.5[121]
Note: *
presentedin Table8.At4%MDIcontent,evenatalower densitylevel,leave-basedparticleboardhadhigherstrength propertiesthanits8%UF-bondedcounterparts.MDI-bonded sycamore(Platanusorientalis)leavesparticleboardwasproducedbyAghakhanietal.[132].Theparticleboardwasreportedtohaveachieveddesiredpropertiesforpartition,wall, andceilingpanelingapplications.Boarddensityandpressing timeisthemostinfluentialfactorsinthephysicalandmechanicalpropertiesoftheparticleboard,whiletheeffectof pressingtemperatureislesssignificant.Higherdensityand longerpressingtimeproducedparticleboardwithhigher mechanicalpropertiesanddimensionalstability.Woodparticlescouldbeaddedtoimprovetheperformanceofsycamore leavesparticleboard.Pirayeshetal.[133]reportedthatthe combinationof20%sycamoreleavesandindustrialwood
particlesresultedinparticleboardwithincreasedMOR,MOE, andIBvalues.
Fromtheliterature,grass-basedparticleboardisrelatively scarce.Thereareonlyfivegrassesidentifiedtobeconverted intoparticleboardbyseveralresearchers,namelyPerennial ryegrass(Loliumperenne L.),Reedcanarygrass(Phalarisarundinacea),Josetallwheatgrass(Agropyronelongatum),Vetiver grass(Chrysopogonzizanioides),andbamboo.Perennial ryegrass,alsocalledEnglishryegrass,winterryegrass,orray grass,isanimportantpastureandforageplantcultivated worldwide.Reedcanarygrassisatall,perennialbunchgrass thatmainlygrowsasornamentalplants.Itisregardedasan
invasiveplantinthewetland.Josetallwheatgrassisan introducedtall,cool-season,salt-tolerant,perennialbunchgrassplantedforgrazing,haying,orerosioncontrol.Vetiver grass,alsocalledkhus,isaperennialbunchgrassthatshares manymorphologicalcharacteristicswithotherfragrant grasses,suchaslemongrass.Therootsofvetivergrassareoilbearingandcanbeusedinperfumes.
Clippingsofperennialryegrass,togetherwith Eucalyptus camaldulensis Dehn.woodparticleshavebeenusedbyNemli etal.[74]intheproductionofUF-bondedparticleboard.The particleboardmadefrom100%grassclippingshadthelowest mechanicalstrength.Grassclippingscouldonlybeusedasa substitutionforwoodinarelativelysmallamount.Eucalyptus particleboardsubstituting6%and13%grassclippingswere reportedtoachievedesiredmechanicalpropertiesforgeneral usesandinteriorfitmentsandimproveddimensionalstability.Grasshasawaxylayeronthesurface;therefore,waterbasedUFresinisdeemedunsuitabletobeusedasabinder duringtheproductionofgrass-basedparticleboard.PanichnavaandNimityongskul[135]reportedthatpolyvinyl acetate-basedadhesiveisamoresuitablebinderforvetiver grassthanurea-formaldehydeandcornstarch.Althoughthe costofpolyvinylacetate-basedadhesiveisslightlyhigher thanthatofcornstarch-basedadhesive,itis,however,still 40%cheaperthanbagasseboards.Meanwhile,pMDIalso performedbetterinbondingvetivergrassparticleboardthan formaldehyde-basedresins(UFandPF)[136].pMDI-bonded SalineJosetallwheatgrassparticleboardalsoexhibitedbetterpropertiesthanitsUF-bondedcounterparts[137]. Isocyanate-basedadhesivessuchasMDI(diphenylmethane diisocyanate),pMDIorpolyurethane(PUR),PVA(polyvinyl alcohol),andPVAc(polyvinylacetate),andacryl-based
adhesivesaresuitableoptions[138,139]. Fig.12 showsthe imageofthereedcanarygrassparticleboard.
Bambooisaperennialwoodygrassoftenconfusedwith treesduetoitstree-likeappearanceandwoodyfeatures. Bamboosharessimilarcharacteristicswithalltypesofgrass asitsinternodalstemarehollow.Unliketrees,bamboodoes nothaveavascularcambiumlayerormeristemcellsatthe topofitsculm.Inaddition,bamboohasnobark[140].Allthese characteristicsmakebamboograss Informationonthe physicalandmechanicalpropertiesofparticleboardmanufacturedofdifferentbamboospecies,boundwith10%UF resin,ispresentedin Table9.Generally,thepropertiesofthe particleboardmadeofbamboodidnotdiffergreatlyasits chemicalcompositiondidnotvarymuchamongspecies.The densityoftheboardsisthemainfactorthataffectstheperformanceofbambooparticleboard.MORandMOEvalues increasedalongwithincreasingdensity.Incontrast,the dimensionalstabilitywasinverselyaffectedbyincreasing boarddensity.
Thecarbohydratecontentofoilpalmtrunk(OPT)ishigh, whilethelignincontentislow[145].Thecellulosecontentof OPTandemptyfruitbunch(EFB)iscomparabletothatof softwoodandhardwood.Incontrast,oil-palmfrondhasa highercellulosecontentthansoftwoodandhardwood.However,oilpalmbiomasseshavelowerlignincontentcompared tosoftwoodandhardwoodspecies[146].Formanyyears,oil palmtrunkhasbeenrecognizedasalignocellulosicmaterial suitableforproducingvalue-addedcompositepanels.Dueto thehighproportionofsoftparenchymatissuesinthecentral regionofthetrunk,onlytheouterpartoftheoilpalmtrunkis traditionallyusedduringthelumberproductionprocess[147]. AccordingtoBakaretal.[148],theunusedinnerpartcanaccountforupto70%oftotalweightandisfrequentlyconsideredwaste.Thesewasteshavethepotentialtobeanexcellent materialforparticleboardproduction.Particleboardmadeof OPF,OPT,andEFBisshownin Fig.13.
Becauseoilpalmtrunkhasalowerdensitythanrubberwood,usingitasthecorelayerofparticleboardcouldresultin ahighercompactionratio,accordingtoLeeetal.[9].Intheory, thehigherthecompactionratio,thelowerthedensityofwood materials.Highcompactionimprovesparticleboardperformance[149].However,inthestudyconductedbyLeeetal. [150],thiswasnotthecase.Thecorelayerofthethree-layer particleboardwastheoilpalmtrunk,andthesurfacelayers wererubberwood.Basedontheirfindings,theauthors concludedthatparticleboardmadeentirelyofrubberwood
RawMaterialsAdhesive type Adhesive (%) Density (kg/m3) MOR (MPa) MOE (MPa) IB (MPa) TS, 24h(%) WA, 24h(%) References
Bambusabalcooa UF1084915.71936.9N/A16.547.9[141] Bambusavulgaris UF1087317.72144.2N/A15.145.9
Gigantochloascortechinii UF1056112.5219590.4511.0745.75[142] UF1064117.9526840.7211.639.52 UF1072120.2129340.8812.6937.16
Bambusavulgaris UF1075413.85N/A0.6223.1N/A[143] Dendrocalamusgiganteus UF10630.747.481515.55N/A8.5848.23[144] Castoroil10705.294.76711.14N/A13.5358.84
outperformedmixed-speciesparticleboard.Despitehavinga highercompactionratio,oilpalmtrunkparticleboardhad lowerstrengthpropertiesthanpurerubberwoodparticleboard[9].Becausetheoilpalmtrunkhasalowerdensity,it takesupalargevolumeperunitweightinthecorelayer.At thesametime,itresultedinalargersurfaceareaperunit weight,makingadequateresincoveragedifficult.Asaresult, adequateparticle particlebondingwasnotpossible,negativelyimpactingtheboards' strengthproperties.However,the authorsconcludedthatifprocessingparameterssuchas pressingtemperatureandtimewerecarefullymanipulated, oilpalmtrunkhadapromisingpotentialasapartial replacementforrubberwoodinproducingparticleboard [9,150,151].Itwasalsoreportedthatbinderlessparticleboard madefromoilpalmtrunksmettherequirementsofJapanese IndustrialStandard(JIS)A5908type8(MOR8MPa)[152].
Asalignocellulosicmaterial,oilpalmfrondhasthepotentialtobeusedeffectivelyintheproductionofcomposite panels.Unfortunately,comparedtootherbiomasses,theuse ofoilpalmfrondsinparticleboardproductionisrelatively limited.Theoilpalmfrondisthoughttobeasuitablematerial fortheproductionofbinderlessparticleboard.Accordingto LaemsakandOkuma[153],thehemicellulosecontentofoil palmfrondsis1.5 3timesthatofwood.Asidefromthat, lignincouldberemovedfromthecellwallofoilpalmfronds usingsteam-explosiontreatment[152].Aftersteam-explosion treatment,agoodbondingstrengthcouldbecreatedbetween oilpalmfrondfiberandthesechemicalsubstancesduringthe hot-pressingprocess.Ligninandpolysaccharidesarethe mainchemicalcomponentscontributingtotheoilpalm frond'sabilitytoself-bind[154].
EFBproducesapproximatelyfourmilliontonnesoffiber peryear[155].TheuseofEFBasanalternativerawmaterialin manufacturingparticleboardisconsideredviable[156].EFB hasfiberstrengthcomparabletorubberwoodfiber.Becauseof itshightoughnessandcellulosecontent,EFBiswellsuitedfor compositeapplications[157,158].Previousresearch,however, hasshownthatcombiningEFBwithotherhardwoodspecies inparticleboardproductionisamoreviableoption[159]. WhencomparedtoitsOPTandOPFcounterparts,EFBparticleboardfrequentlyhasinferiorproperties.Zakariaetal.[160] preparedacitricacidsolutioncontaining12.5and25%wt tapiocastarch,whichwasthenusedasabinderforparticleboardmadefromoilpalmbiomass(emptyfruitbunch,oil palmtrunk,andoilpalmfrond).A12.5wt%tapiocastarch additionwasbeneficial,asevidencedbyimprovedmechanical
andphysicalproperties.Theparticleboardmadefromoil palmfrondandtrunkbondedwith87.5wt%citricacidand 12.5wt%starchmettheminimumMORrequirementfortype 8particleboardspecifiedinJapaneseIndustrialStandard(JIS) A5908.
Datepalm(Phoenixdactylifera L.),oneoftheoldestfruit cropsintheMiddleEastandNorthAfrica,hasalsobeenused inparticleboardproduction.Theadditionofpalmfrond pruningtotheMDFmatsignificantlyimprovedIBintheproducedpanels[161].Theperformanceofparticleboardmanufacturedfromdatepalmbranchesshowedthatthepanels' MOR,IB,andTSvaluesfulfilledthetechnicalstandardrequirements[162].Thedatepalm'strunkandrachisor brancheswereusedtoproduceparticleboardinthestudyby Amirouetal.[163].PF-andMUF-bondedparticleboardfabricationfromdatepalmtrunkandbranchesisdeemedviable. PF-bondedboardshavebetterperformancethanMUF-bonded boards.Ghofranietal.[48]recommendedthatbranchesofthe datepalmareagoodreplacementforfibrousmaterialfor particleboardproduction.Particleboardproducedissuitable forindoorapplications,includingabsorbingnoise,maintainingindoorlivingspaces' temperature,andpartiallyor completelysubstitutinginsulationboardsinwoodenconstructions.Betelpalm(Arecacatechu Linn.)isgrownforitsseed crops,afruitlocallycalledPinang.Thetrunksofbetelpalm werechipped,andparticleboardwasproducedfromit.Betel palmcanbeusedtomakevalue-addedpanelswithout significantlyaffectingboardproperties[164].
BinderlessparticleboardfromoilpalmhasalsobeenproducedbyHashimetal.[165].Thestudysuggestedthatcore parts,mid-parts,andfrondsoftheoilpalmtreescouldbeused toproducebinderlessparticleboardwithacceptableMORand IBof10.9N/mm2 and0.5N/mm2,respectively.Thegood propertiesofthebinderlessoilpalmparticleboardmightbe associatedwiththepseudo-plasticityandviscoelasticityof starch-richparenchymacellsfoundintrunks.Furthermore, thehemicellulosecontentofoilpalmfrondswas1.5 3times higherthancommonhardwoodspecies[153].Thismayresult inimprovedparticlebondingandleadtosatisfactorybending properties.Unfortunately,theWAandTSofthepanelsperformedpoorly.
4.8.Summary Basedonthefindingsoftheabovesection,itisnotedthat agriculturalbiomasscouldserveaspotentialrawmaterialsfor
Table9167
Thephysicalandmechanicalpropertiesofparticleboardproducedusingrecycledwoodwasteasrawmaterial.
Table10
IB (MPa)
MOE (MPa)
MOR (MPa)
AdhesiveVariableDensity (kg/m 3 )
Sources/TypeofWood Waste
AAAAA 14.2422480.65237.0392.47 BBBBB 13.2823570.51838.8940.79 CCCCC 12.1123430.37842.1044.17 DDDDD 13.1524020.50137.2038.78
650 680
-Urea-formaldehydeHydrothermal treatments -2bar/119 C/ 480min(A) -4bar/140 C/ 120min(B) -6bar/156 C/45min (C) -8bar/167 C/ 20min(D)
Recycledparticleboard madefrompoplar,fir, pineandotherwaste wood
50:5050:5050:5050:50 14.522100.2411.9 70:3070:3070:3070:30 16.922900.3111.3 100:0100:0100:0100:0 18.426500.346.4
800 830
PMDI/PFratio -50:50 -70:30 -100:0
-Phenolformaldehyde -PMDI
Recycledconstruction waste -Oak( Quercus spp.) -Lauan( Shorea spp.)
00000
[ 170 ] 8.958370.89 2525252525 6.316780.52
z 27(A), z 29(B), z 26(C)81.7(A),81.7(B),82.8(C) 5050505050 5.506450.44
z 31(A), z 24(B), z 20(C)83.9(A),78.9(B),79.7(C) 7575757575 4.716240.37
z 25(A), z 19(B), z 16(C)81.2(A),78.2(B),74.2(C) 100100100100100 4.376110.37
600
Wastepackagingwood boxesfrom-plywood -solidpine( Pinus sp.)wood -Urea-formaldehydeHeattreatment temperature( C) -180(A),200(B),220 (C) Proportionsof heat-treated particles(%) -0,25,50,75,100
z 26(A), z 15(B), z 10(C)83.6(A),70.2(B),55.1(C) * WAfor2h
ControlControl
ControlControl
177 ] 10.4209740101.5 BBBB 10.6218929.186.1 BSDBSDBSDBSD 10.7210427.984.5 PSDPSDPSDPSD 10.6224728.683.9 WPWPWPWP 8.0164529.786.0
Typeofliquefied woodwaste -Bark(B) -Beechsawdust (BSD) -Pinesawdust (PSD) -Woodpowder(WP) 643 652
-Urea-formaldehyde -liquefiedwoodwaste
Recycledwoodwaste -furniture,pallets,crates, baskets,packages
179
178
MDFMDFMDFMDFMDF
4.595970.1821.2773.62 MDPMDPMDPMDPMDP 6.4910130.7515.1644.41 PlywoodPlywoodPlywoodPlywoodPlywood 7.1212990.369.4279.40 TimberTimberTimberTimberTimber 9.6913920.965.0448.92 MixMixMixMixMix 7.1918910.765.4652.94
670 710
Constructionand demolitionofwoodwaste -Urea-formaldehydeTypeofwoodwaste -Mediumdensity fiberboard(MDF) -Medium-density particleboard (MDP) -Plywood -Timber
180
R1R1R1R1R1
10.6 14.72155 26660.55 0.7516.57 22.7649.23 60.02 R2R2R2R2R2
14.42194 28000.55 0.749.72 13.2933.46 43.43
-Urea-formaldehydeTypeofrecyclate -R1,R2 Ratioofrecyclate -0,20,50,100
-Freshsprucelog -Recycledhardboard,MDF board,pallet,oldfurniture (R1) -RecycledfaultyPB(R2)
Recycledwoodenpallet fromspruce
12.124710.7018.6750.95
12.422760.6827.8776.80 100100100100100 10.020120.6123.6756.77
particleboardmanufacturing.However,everytypeofagriculturalbiomasshasitsownissuethatpreventsittobeused effectively.Bagasseisamongthebestmaterialsforparticleboardmanufacturingasparticleboardmanufacturedfromit oftendisplayedsatisfactoryphysicalandmechanicalproperties.Still,insomecase,theincorporationofsomeportionof woodparticlesarenecessarytofurtherenhanceitsperformance.Straw-,leaves-andgrass-basedparticlessuffered fromthewaxysurfacelayerthatpreventstheeffective spreadingofwater-basedUFresinandinevitablyleadstopoor adhesionandbonding.Meanwhile,hull-,husk-andshellbasedparticleboardhaslowmechanicalstrengthduetothe lowcellulosecontentoftherawmaterials.Ontheotherhand, stalk-basedparticleboardhashighholocellulosecontentthat resultedinhighthicknessswelling.Palm-basedsuchasOPT andOPFhashighcarbohydratecontentbutlowlignincontent whileEFBhascomparablecellulosecontentbutlowerlignin contentwithhardwoodandsoftwood.Interventionshave beencarriedoutbymanyresearcherstoenhancetheperformanceoftheagriculturalbiomass-basedparticleboard.Most oftheminvolvetheincorporationofwoodparticlesorusing higherresincontent.Foragriculturalbiomasshavingwaxy surfacelayers,isocyanate-basedadhesivessuchasMDIand pMDIarerecommended.Polyurethane(PUR),PVA(polyvinyl alcohol),PVAc(polyvinylacetate),andacryl-basedadhesives aresuitableoptionstoo.Silanecouplingagentshavealsobeen usedtoimprovethebondabilityofstraws.
Asummaryofthephysicalandmechanicalpropertiesof particleboardproducedusingrecycledwoodwasteasraw materialsispresentedin Table10.Thesurfaceappearanceof thepost-productionparticleboardisshownin Fig.14.Most studieslookedattheeffectofdifferenttypesofwoodwaste, differentratiosofwoodwaste,anddifferenttypesofrecycled woodtreatmentsonthephysicalandmechanicalproperties ofrecycled-woodparticleboard.Themostcommonadhesives usedwereUFandPFresins.However,otheradhesivesystems suchasmixturesofliquefiedwoodbindersandUFandamix ofpMDIandUFwerealsoutilizedbyresearchers.
Thetreatmentstowhichthewoodparticlesandwood wasteweresubjectedpriortoparticleboardmanufacturing influencethemechanicalandphysicalpropertiesofthefinal products.LykidisandGrigoriou[166]conductedastudyto
investigatetheeffectsofhydrothermaltreatmentsofwood particlesonthephysicalandmechanicalpropertiesof recycled-woodparticleboard.Thehydrothermaltreatment wasutilizedtodegradethebondingofUFadhesiveinoldand faultyparticleboardtoretrievethedetachedwoodparticles fornewparticleboardproduction.Itwasrevealedthatthe MORvalueoftheboardsshowedasignificantreduction. Similarresultswerealsoreportedinotherliteratureandwere mainlyduetothethermaldecompositionofwood[167 169]. However,itisworthnotingthattheMOEvalueoftherecycledwoodparticleboardwassignificantlyhigherwhencompared tothecontrolparticleboard.Tofullyunderstandtheeffectof thermaltreatmentonthepropertiesoftheboards,theauthors suggestedthatachemicalcompositionanalysisofthetreated particlesbeconductedinfuturestudies.Theauthorsalso suggestedthattoproduceparticleboardthatmeetsrequirementsatthetime,amixtureofnewparticlesandrecycledwoodparticlestreatedwiththemilderhydrothermal conditioncouldbeusedintheproduction.
Fig.15 Modulusofrupture(MOR) densitychartforparticleboard(400 650kg/m3)madewithagriculturalbiomassand conventionalwood.
Andradeetal.[170]studiedparticleboard'sphysicaland mechanicalpropertiesfromdifferentproportionsofthermallytreatedrecycledpineparticles.Theauthorsalsoperformedachemicalcompositionanalysisforthethermaltreatedrecycledparticles.TSandWAvaluesofparticleboard madefromthermallytreatedparticleswerenotsignificantly lowerthanthoseofthecontrolpanels.However,conferences producedwithparticlestreatedat220 Cshowedasignificant reductioninWAcomparedtoothersamples.Thisresultwas inagreementwiththoseobtainedbyPauletal.[171].This phenomenonwasexplainedbythepartialdegradationof hemicelluloses,whichwasreflectedinthethermogravimetric analysisresults.Therelativecontentofligninandcellulose showedanincrement.TheIBdecreasedslightlybutcomplied withthespecification(0.10N/mm2)givenintheANSIstandard A208.1/99forlow-densityboards.ThemovementofextractivescausedIBreductioninthesurfaceoftheparticles,which wouldhinderwood-adhesivebonding[172].Generally, increasingtheproportionofheat-treatedparticlesresultedin adecreaseintheMORandMOEvaluesoftheboards.However, thereductionisinsignificant.TheMORandMOEdecreased withincreasingtreatmenttemperature,whichwasexpected ashightemperaturesdegradethestructureofthewood,thus resultinginlowermechanicalproperties[173 176].
Theadhesivesystemusedintheproductionofparticleboardalsoexertssignificantinfluencesonthepropertiesof theboardsproduced.Formaldehyde-basedadhesivesare someofthemostwidelyusedbindersinparticleboardproduction.However,othersuitablebindersarealsobeing exploredbutareoftenusedtogetherwithformaldehyde-
basedadhesive.Lietal.[52]conductedastudyinvestigating thepropertiesofparticleboardmadefromrecycledwood bondedwithpMDIandPFadhesivewithdifferentpMDItoPF ratios.Janiszewskaetal.[177]incorporateddifferentliquefied woodwastebindersintoaconventionalUFadhesivesystem toproducerecycled-woodparticleboard.
FortheparticleboardproducedwithdifferentpMDItoPF ratios,theauthorsfoundthatMORandMOEvaluesincreased withanincreasingpMDItoPFratio.Furthermore,theparticleboardproducedwithhigherpMDIcontentsalsoshowed higherIB.Thisresultwasincontrastwiththatreportedby Papadopoulos[182].However,acombinationofotherparameterssuchasmatmoisturecontent,pressingtemperature,pressingtime,andaddingotheradditivescouldcausea slightIBdifference.TheincreaseinIBwasexplainedbyBao etal.[183]thatpMDIcouldpenetratewoodcellsandtheintermediatelamellaebetweenthem,whereitcaninteractwith theaccessiblemoistureheldinthewood.Moreover,pMDI mayreactwiththechemicalcomponentsofthewood(the hydroxylgroupsinpolysaccharidesorthephenolicgroupsin lignin)toformurethanestructures,whicharelikelytofurther aidadhesion.Markedly,theTSvaluesreducedwhenthepMDI toPFratioincreased.
Janiszewskaetal.[177]investigatedthephysicalandmechanicalperformanceimpactofseveraltypesofliquefied woodwastebindersandrecycledwoodparticleboard.From theresultsobtainedfromtheexperiment,theauthors observedthattheMORandMOEvaluesofrecycled-wood particleboardbondedwithliquefiedwoodwasteandUFadhesiveweresimilartothoseofthecontrolparticleboard,
regardlessofthetypeofliquefiedwoodwastebindersused. TheslightreductioninMORandMOEintheparticleboard bondedwithliquefiedwoodpowderbinderwasattributedto therelativelylowdensityoftestedsamples(629kg/m3) comparedtothedensityofothersamplesofapproximately 650kg/m3.LiquefiedwoodwastebindersdecreasedtheTSand WAofallsamples.Nuryawanetal.[184]studiedtheeffectof liquefiedadhesivemadefromoilpalmstemparticleboard propertiesandreportedsimilarfindings.Thus,itcanbe concludedthatallrawmaterialsusedtomakeliquefiedwood wastebindershaveafavorableimpactontheTSandWAof theboards.
Thepropertiesofrecycled-woodparticleboardalsodepend onthetypeofrecycledwoodwasteused.Azambujaetal.[178] carriedoutresearchtodeterminethepropertiesofparticleboardmadefromdifferenttypesofwoodwaste,i.e.,medium densityfiberboard(MDF),medium-densityparticleboard (MDP),plywood,andtimberresidues.Theauthorsobserved thattheparticleboardmadefromrecycledtimberresidue displayedthehighestMOR,MOE,andIBvalues.Thisresult couldbeassociatedwiththehigherslendernessratioofthe recycledtimberparticles,resultinginbetterbendingstrength [29].Ontheotherhand,particleboardproducedfromMDF recordedthelowestMOR,MOE,andIBvalues.Asareference, theMOR,MOE,andIBofthecontrolpanelsmadefromfresh particlesfrompinelogswere8N/mm2,1378N/mm2,and 0.91N/mm2,respectively.RegardingtheIBofallsamples,only particleboardmadefromrecycledMDFparticlesdidnotmeet therequirementstatedinEN312.Toutilizeothertypesof recycledwoodwastedespitethereductionofmechanical
performancetheyinduced,theauthorssuggestedthatthose wastesbeusedastheinnerorcorelayerintheproductionof layeredparticleboard.Thestudyofotherprocessingparametersisrequiredtoimprovethemechanicalperformanceof recycledwoodparticleboardfurther.
Besidesthetypeofwoodwaste,theratioofwoodwasteto freshwoodparticlesalsoaffectsthepropertiesoftheboard manufactured.ThispromptedIzdinsky´etal.[180]toevaluate thephysicalandmechanicalpropertiesofparticleboardmade fromdifferentwoodwasteswithdifferentratios.Theparticleboardwasproducedwithparticlesfromthefreshspruce logandparticlesfromrecycledhardboard,MDFboard,pallet, oldfurniture(R1),andrecycledfaultyparticleboard(R2).The authorsobservedthatparticleboardproducedfrom100% freshspruceparticlesexhibitedthehighestMOR,MOE,andIB values.TheMOR,MOE,andIBofparticleboardspecimens madefromamixtureoffreshwoodparticlesandrecycled woodproductsshowedaslightdecrease.However,the physicalpropertiessuchasTSandWAofthespecimenmade fromrecycledwood,bothR1,andR2,demonstratedmajor improvement.Theauthorsconcludedthatalthoughthe additionofR1improvedtheTSandWAofthespecimens,the improvementwasconsiderednon-significant(r2, 0.0001 0.09).Ontheotherhand,theadditionofR2showeda significantpositiveeffect(r2,0.63 0.72)ontheTSandWA. SimilarresultswerealsoreportedbyAzambujaetal.[178]. Theresultsmightbeattributedtotheslowerwatermovement intotheparticleboardproducedwithfreshspruceandR2 particles.TheexistenceofcuredUFadhesivemoleculesonthe surfacesofR2particlesobstructsthewatermovement.
Fig.17 Modulusofelasticity(MOE) densitychartforparticleboard(400 650kg/m3)madewithagriculturalbiomassand conventionalwood.
InaseparatestudybyIzdinsky´etal.[181],amixtureof particlesfromtherecycledsprucepalletandthefreshspruce logproducedrecycled-woodparticleboard.Theresults showedaninterestingtrendwhichindicatedthattheTSand WAvaluesoftheparticleboarddecreasedslightlybelowthe controlvalueswiththeintroductionof20%particlesfromthe recycledsprucepallet,witha22%and25%reductioninTSand WAvalues,respectively.However,furtherincrementofparticlesfromarecycledsprucepalletat50%increasedtheTS andWAvaluesabovethecontrolvalue.Similarfindingswere foundinotherstudies[180,185].Theadditionofrecycled sprucepalletparticles,ontheotherhand,negativelyimpacted theboards' mechanicalproperties.Thereductionsobserved were32%(MOR),23%(MOE),and23%(IB).Thisresultcouldbe attributedtodeterioratedorpollutedwoodinparticleboard basedonrecycledsprucepalletparticles,asitiswellknown thatwoodattackedbydecayingfungioraggressivechemicals hasreducedmechanicalproperties[186].Laskowskaand Mamiski[185]alsoconcludedthatthetype,amount,and qualityofrecycledwoodparticlessignificantlyimpacted particleboardproperties.Despiteasignificantreductionin mechanicalproperties,alltheboardsproducedmeettheEN 312minimumrequirementofIB(0.35N/mm2)fortypeP2 particleboard.
InspiredbyKlimekandWimmer[6],MOR-densityandMOEdensitychartsforparticleboardmadefromdifferentagriculturalbiomassandconventionalwoodspeciesweredrawnand areillustratedin Fig.15, Fig.16, Fig.17 and Fig.18,respectively. Thechartscouldprovideaneasiervisualcomparisonofthe propertiesofparticleboardmadefromvarioustypesofagriculturalbiomassandconventionalwoodspecies.AsKlimek andWimmer[6]suggested,theMORofparticleboardfrom agriculturalbiomassdoesnotnecessarilyfollowthetrend wheretheMORincreasedalongwithincreasingboarddensity. Forexample,soybeanprotein-bondedricehuskparticleboard havingadensityof800kg/m3 andcastoroil-bondedmacadamiashellparticleboardhavingadensityof987kg/m3 didnot meettherequirementsoftheP2classinEN312.BagassebasedandbambooparticleboardhavehigherMORcompared totheothertypeofagriculturalbiomass.AsimilarobservationwasobtainedforMOE,asshownin Fig.17 and Fig.18
Irrespectiveofadhesivetypes,bagasse-basedparticleboard exhibitedsuperiorMOEthantheotheragriculturalbiomass.
ThestudybyOsmanetal.[187]alsodemonstratedthatboth bagasseandcottonstalksresultedinparticleboardswith relativelyhighermechanicalpropertiesthanparticleboards madefromstrawsandshells.
Lifecycleassessment(LCA)isanimportantandpowerfultool toassessthepotentialenvironmentalimpactsofaproduct system.However,LCAstudiesonagriculturalbiomassand recycledwoodparticleboardsarerelativelyscarce.Someof theavailablestudiesaresummarizedinthissection.
InastudybydosSantos[188],laboratory-fabricatedparticleboardsweremanufacturedusingsugarcanebagasseand pinewoodshavings.Generally,bagasseparticleboardshad lowerimpactsinallcategoriesthanpineshavingsparticleboards,exceptfortheconsumptionofenergyresources(CES), wherebagasseparticleboardsconsumed9.9%moreenergy thanpineshavingsparticleboards.Bagasseparticleboardshad 33.1%and32.4%lowerconsumptionofrenewableresources (CRR)andconsumptionofnon-renewableresources(CNR), respectively,comparedtopineshavingsparticleboards. Slightlylowerpotentialphotochemicalozonecreation(POC) andhumantoxicitypotential(HTP)wasproducedbybagasse particleboards.Intermsofglobalwarmingpotential(GWP), acidificationpotential(AP),andeutrophicationpotential(EP), bagasseparticleboardscompletelystandoutincomparisonto
pineshavingsparticleboards,withmorethan50%lowerimpactsinthesecategories.
However,thestudyconductedbydosSantosetal.[188]is oflaboratoryscaleandthereforeunabletoreflectthetrue scenarioatanindustrialscale.Followingthat,Silvaetal.[189] analyzedthelifecycleimpactsofbagasseparticleboardsatan industrialscale.Inthestudy,50%sugarcanebagassewasused tosubstitute50%woodparticlesintheproductionofUFbondedparticleboards.TheauthorscomparedtheenvironmentalperformanceofBrazilianconventionalparticleboards [190]andbagasseparticleboards.Bagasseparticleboards causedfewerimpactsonabioticdepletion(ADPe)andecotoxicity(ECP),mainlyduetothereductionintheuseof glyphosateinforestmanagementactivities.Otherimpact categoriessuchasAP,ecotoxicity(ECP),EP,GWP,ozonelayer depletion(ODP),photochemicaloxidation(POCP),human toxicity cancereffects(HTPC),andhumantoxicity noncancereffects(HTPNC)didnotdiffermuchbetween conventionalandbagasseparticleboards.ApplicationofUF resin,electricity,andheavyfueloilwerethemainreasonsfor thisfinding.Nevertheless,bagasseparticleboardscaused lowerland-useimpacts,indicatinglesslanddemandthan woodparticleboards.Therefore,bagasseparticleboardisa goodcandidatetosubstituteconventionalwoodparticleboard duetoitsbetterenvironmentalperformance.Finally,theauthorssuggestedthat75%sugarcanebagassecanbeadded duringparticleboardmanufacturingtoproducepanelswith betterenvironmentalperformance.
Ramosetal.[191]comparedtheenvironmentalperformanceandthermalbehaviorofcorncobparticleboard,
bondedwithtwotypesofadhesives,i.e.polyvinylacetate (PVA)andFabricolAG222(FAG222)asinsulationmaterials. Throughtheassessmentofimpactcategories,itwasfound thatEPShadahigherimpactonGWP,ODP,andHTP.Markedly,bothPVA-bondedandFAG222-bondedparticleboard showedsatisfactoryenvironmentalimpacts.However,the PVA-bondedpanelexhibitedbetterresultswhenlandfilling wasthepreferreddisposaltechnique.
Intheproductionprocessof1m3 particleboard,Shang etal.[192]discoveredareductionof40kgCO2 equivalent(CO2 eq)ofgreenhousegas(GHG)emissionbetweenstrawparticleboard(600kgCO2 eqGHGemission)andwoodparticleboard(640kgCO2 eqGHGemission).Ontheotherhand,straw particleboardconsumedlessnon-renewableenergy(2700MJ) thanwoodparticleboards(2800MJ).TheLCAresultsdemonstratedthattheenvironmentalimpactsofusingstrawfor manufacturingstrawparticleboardandcement-bonded particleboardweresignificantlyreducedby6%and10%, respectively,comparedwithusingwoodasafeedstock.The shareofwoodresourcesinprocessinganddryingoftheraw materialwithregardstonon-renewableenergyconsumption andGWPimpactwashigherthanstrawparticleboardsasthe moisturecontentofnaturalwoodishigher.Moreover,dueto theomittanceofthepeelingmachine,strawparticleboard consumedlowernon-renewableenergy.Theauthors concludedthatthestrawparticleboardistheoptimalscheme forrecyclingandreusingcropstrawresources.However, powerconsumptionduringformingprocessandstraw transportationdistancearethemainconstraintsthataffectits environmentalperformanceandshouldbeimproved.
Inthecaseofusingrecycledwoodwasteincement-bonded particleboardproduction,Hossainetal.[193]reportedthat recyclingwoodwasteatarateof10%couldsavearound11,016 tonnesofCO2 eqperyear.ThetotalsavingsofGHGsemissions forcement-bondedparticleboardproductioncouldreach 55,079tonnesofCO2 eqperyearif50%ofthetotalwoodwaste couldberecoveredandreutilizedyearlyfortheproductionof cement-bondedparticleboard.Reutilizationofwoodwaste reducedtheinducedemission,increasedcarbonsequestration,andavoidedemission,whichledtotheincreasedsaving ofGHGsemissions.Hoglmeieretal.[194]comparedthe environmentalperformanceofutilizingrecoveredwoodin cascadesversusprimarywoodinmanufacturingparticleboard.Overall,theenvironmentalfootprintcausedbythe cascadingsystemwasaround10% 25%lowerthantheprimarywoodsystem.Theauthorsconcludedthatthecascading effectsareminorcomparedtotheuseofprimarywood. However,whenconsideringlandoccupationandtransformation,cascadingprovedtobeanevenmorepreferable treatmentoptionforwastewoodasareductionof99.1%and 51.2%wasrecorded,respectively.Markedly,applyingagriculturalbiomassandrecycledwoodinparticleboard manufacturingprovidesenvironmentallybenignalternatives toconventionalwood.
Particleboardmanufacturersfaceaninconsistentsupplyof rawmaterials,andtheabsenceofanestablishedsupply
2022;20:4630
chain,particularlyintheAsiaPacificregion,isamajorchallenge[37].Manufacturersstillsticktoconventionalrawmaterialsforparticleboardproductionandhesitatetoadopt alternativefeedstocks.Itisamaliciouscyclewherethe manufacturersblametheinconsistentsupplyofrawmaterials.Atthesametime,theplantersarereluctanttoconvert theircultivationsbecausethereisnodemandforthem.This weaklinkmustbesolvedfortheagricultural waste-based particleboardtoflourish.Accumulatingagriculturalwastes withoutproperdiscardingmeasurescouldposeaserious environmentalthreattodevelopingcountries[195].Introducingrelevantpoliciesshouldenhanceawarenessand marketacceptabilityamongstakeholdersandthepublic.
Despitethescientificandtechnologicaladvances,thereare substantialchallengesregardingthewiderindustrialutilizationofagriculturalbiomassinparticleboardmanufacturing. Freshagriculturalbiomasshasahighermoisturecontent whichmakesitheavier,incurringhighertransportationand storagecosts[196].Moreimportantly,rawmaterialwithhigh moisturecontentislesscompressibleduringboardpressing. Adjustmentsintheprocessingparametersmightbenecessary.Inaddition,agriculturalbiomassgenerallyhasalower apparentdensitythanconventionalwoodparticles.Low densitycausesahighvolumeperunitweightofagricultural biomassthanwoodparticles[9].Therefore,asufficient compactionratiomightnotbeachievedwithinalimited pressingtime.Moreover,ahighervolumeofagricultural biomassrequiresmoreresinforsufficientcoveragetoattain adequatebonding.Usingthesameresincontentforagriculturalbiomassusedforwoodparticlesmeansthateveryparticleiscoveredwithlessadhesive,whichcouldadversely affectthefinalperformanceoftheresultantboards.
Anotherissueoftheparticleboardfabricatedofagriculturalbiomassisitsdeteriorateddimensionalstabilityand waterabsorption.Thisissueismoresignificantonthestraw-, stalk-,husk-andshell-basedparticleboardandcouldbe overcomebyaddinghydrophobicagentssuchaswaxduring theproductionprocess.Meanwhile,grass-andleave-based particleboardhaverelativelylowerTSandWAvaluesdueto theirwaxylayeronthesurfacesandlowercellulosiccontent. However,duetothewaxylayer,water-basedUFresinisunsuitableforuseasabinderduringgrass-andleave-based particleboardproduction.Bagasse-basedparticleboardgives satisfactoryphysicalandmechanicalpropertiescomparedto theotheragriculturalbiomasscounterparts.Nevertheless, mostagriculturalbiomass-basedparticleboardpanelshave relativelypoorermechanicalstrengththanthoseofwoodbasedpanels.Theincorporationofwoodyparticlesis deemednecessarytoimprovethestrengthofparticleboard.
Meanwhile,theintroductionofrecycledwoodparticlesin producingnewparticleboardshowspromisingresults.Nevertheless,itisinterestingtonotethatthecontentratioofrecycled woodparticleswasnotproportionaltothephysicalandmechanicalpropertiesvalues.Furtherstudiesonvarioustreatment conditionsanddifferentratiosofrecycledwoodparticlesare requiredtodeterminetheoptimumparameterstoproduce particleboardwiththebestphysicalandmechanicalproperties.
Animportantissuewithparticleboardandotherengineeredwoodproducts,fabricatedfromagriculturalwaste biomassand/orrecycledwoodwasteisthelackofsufficient
informationabouttheirfirecharacteristicsandreactionto fire.Thecombustionofwood-basedpanelssuchasparticleboard,widelyusedinthebuildingsector,isamajorproblem duetotherecentstringentfiresafetyregulations[28,197]. Somestudieshavebeencarriedouttoinvestigatethereaction tofireofwood-basedcompositesmadefromagricultural biomass[198 201],butpublicationsfocusedonthisproblem arestillratherlimited.Itwillbeaninterestingfieldtoexplore inthefuture.
Inmanycases,particleboardsmanufacturedfromalternative rawmaterialsexhibitsimilarorevenbettermechanical propertiesthanconventionalwood-basedparticleboards. Hence,boardsmadefromagriculturalbiomassandrecycled woodwastecouldensuresustainabledevelopment,which featuresthreekeyelements:economicgrowth,socialinclusionandenvironmentalprotection.Furthermore,thepressureonotherforest-basedresourcescanbesignificantly reduced,andadditionalemploymentopportunitiescanbe created.Thechangesinthecurrentrawmaterialstructurein particleboardtechnology,viatheapplicationsofalternative rawmaterials,willpositivelyimpactthecontinuedgrowth dynamicsofwood-basedparticleboardproduction.Complementingtheshortageofwoodrawmaterialsbyintroducingagriculturalbiomassandrecycledwoodasalternative rawmaterialscanensurethecontinuityofpanelproduction inamoreeconomicallyviableandenvironmentallyfriendly manner.
ThisresearchwasfundedbytheFundamentalResearchGrant Scheme(FRGS2018-1),Referencecode:FRGS/1/2018/WAB07/ UPM/1,andHigherInstitutionCentreofExcellence(HICoE) (UPM/INTROP/100-13/9/3/6369113/H),providedbytheMinistryofHigherEducation,Malaysia.Thisresearchwasalso supportedbytheSlovakResearchandDevelopmentAgency undercontractNo.APVV-18-0378,APVV-19-0269,APVV-200004,andSK-CZ-RD-21-0100,alsobytheScientificGrant AgencyoftheMinistryofEducation,Science,Research,and SportoftheSlovakRepublic(grantnumberVEGA1/0714/21) andbyProjectNo.HИC-Б-1145/04.2021 “Development,Properties,andApplicationofEco-FriendlyWood-BasedComposites”,carriedoutattheUniversityofForestry,Sofia,Bulgaria. TheauthorsalsothanktheDeputyforStrengthening ResearchandDevelopment,MinistryofResearchandTechnologyintheNationalCompetitiveResearchgrantwiththe title “TheCharacteristicsofFire-ResistantWoodPanelCompositeBasedHomeComponents” FiscalYear2021(Grant number:95/UN5.2.3.1/PPM/KP-DRPM/2021).
Theauthorsconfirmthatthedatasupportingthefindingsof thisstudyareavailableonrequest.
2022;20:4630
Thisarticledoesnotcontainanystudieswithhumanoranimalsubjectsperformedbyanyoftheauthors.
Theauthorsdeclarethefollowingfinancialinterests/personal relationshipswhichmaybeconsideredaspotential competinginterests:LeeSengHuareportsadministrative supportwasprovidedbyPutraMalaysiaUniversity.LeeSeng HuareportsarelationshipwithPutraMalaysiaUniversitythat includes:non-financialsupport.LeeSengHuahaspatent NonependingtoNone.
Theauthorswouldliketothankthelibraryoftheirrespective Universitiesforprovidingfreeaccesstotheliterature.
references
[1]GroupI.Particleboardmarket:globalindustrytrends, share,size,growth,opportunityandforecast2021 2026. https://www.imarcgroup.com/particle-board-market [Accessed13January2022].
[2]FAOSTAT.Forestryproductionandtrade,2021.Available online: https://www.fao.org/faostat/en/#data/FO.[Accessed 16January2022].
[3] OdoziT,AkarantaO,EjikeP.Particleboardsfrom agriculturalwastes.AgricWastes1986;16:237 40
[4] Pe ˛ dzikM,JaniszewskaD,RogozinskiT.Alternative lignocellulosicrawmaterialsinparticleboardproduction:a review.IndCropProd2021;174:114162
[5] EastinI,BroseI,NovoselovI.Wood-basedpanelmarkets, 2011 2012.In:UNECE/FAOforestproductsannualmarket review.1;2012.p.67 77
[6] KlimekP,WimmerR.Alternativerawmaterialsforbiobasedcomposites.Alternativerawmaterialsforbiobasedcomposites.In:Proceedingsofinternational conference “woodscienceandengineeringinthethird millennium ” ICWSE2017;2 4November2017.Brasov, Romania
[7] DeAraujoVA,VasconcelosJS,MoralesEAM,SaviAF, HindmanDP,O'BrienMJ,etal.Difficultiesofwooden housingproductionsectorinBrazil.WoodMaterSciEng 2020;15(2):87 96
[8] LeeS,AshaariZ,LumW,AngA,AbdulHalipJ,HalisR. Chemical,physico-mechanicalpropertiesandbiological durabilityofrubberwoodparticleboardsafterpostheattreatmentinpalmoil.Holzforschung2018;72:159 67
[9] LeeSH,AshaariZ,LumW,H'ngPS,TanLP,ChowMJ,etal. Propertiesofparticleboardwithoilpalmtrunkascorelayer incomparisontothree-layerrubberwoodparticleboard.J OilPalmRes2015;27:67 74.
[10] HuaxuZ,HuaLS,TahirPM,AshaariZ,Al-EdrusSSO, IbrahimNA,etal.Physico-mechanicalandbiological durabilityofcitricacid-bondedrubberwoodparticleboard. Polymers2020;13(1):98
[11] HidayatW,AprillianaN,AsmaraS,BakriS,HidayatiS, BanuwaIS,etal.Performanceofeco-friendlyparticleboard
fromagro-industrialresiduesbondedwithformaldehydefreenaturalrubberlatexadhesiveforinteriorapplications. PolymCompos2022;43(4):2222 33
[12] ZhengY,PanZ,ZhangR,JenkinsBM,BlunkS.Propertiesof medium-densityparticleboardfromsalineAthelwood.Ind CropProd2006;23(3):318 26
[13] HizirogluS,HolcombR.Someofthepropertiesofthreelayerparticleboardmadefromeasternredcedar.Build Environ2005;40(5):719 23
[14] TrianoskiR,IwakiriS,DeMatosJ.Potentialuseofplanted fast-growingspeciesforproductionofparticleboard.JTrop ForSci2011:311 7
[15] RathkeJ,SinnG,HarmM,TeischingerA,WeiglM,MullerU. Effectsofalternativerawmaterialsandvaryingresin contentonmechanicalandfracturemechanicalproperties ofparticleboard.BioRes2012;7(3):2970 85.
[16] NelisPA,MichaelisF,KrauseKC,MaiC.Kiriwood (Paulowniatomentosa):canitimprovetheperformanceof particleboards?EurJWoodWoodProd2018;76(2):445 53
[17] RatulSB,RahmanK-S,HasanMAW,IslamMA,IslamMN, ShamsMI.Hybridparticleboardfromkadam(Anthocephalus chinensis)reinforcedwithdhaincha(Sesbaniaaculeata): effectsofparticlemixingratioonphysicalandmechanical properties.JIndAcadWoodSci2017;14(2):115 21
[18] LykidisC,GrigoriouA,BarboutisI.Utilisationofwood biomassresiduesfromfruittreebranches,evergreen hardwoodshrubsandGreekfirwoodasrawmaterialsfor particleboardproduction.PartA.Mechanicalproperties. WoodMaterSciEng2014;9(4):202 8
[19] MarashdehMW,TajuddinAA,BaukS,HashimR. DosimetricevaluationofRhizophoraspp.binderless particleboardphantomfordiagnosticX-rayenergy.Radiat PhysChem2017;136:23 9.
[20] AshoriA,NourbakhshA.Effectofpresscycletimeandresin contentonphysicalandmechanicalpropertiesof particleboardpanelsmadefromtheunderutilizedlowqualityrawmaterials.IndCropProd2008;28(2):225 30
[21] AbuarraA,HashimR,BaukS,KandaiyaS,TousiET. FabricationandcharacterizationofgumArabicbonded Rhizophoraspp.particleboards.MaterDes2014;60:108 15
[22] YusofMFM,HashimR,TajuddinAA,BaukS,SulaimanO. Characterizationoftannin-addedRhizophoraspp. particleboardsasphantommaterialsforphotonbeams.Ind CropProd2017;95:467 74.
[23] GontardN,SonessonU,BirkvedM,MajoneM,BolzonellaD, CelliA,etal.Aresearchchallengevisionregarding managementofagriculturalwasteinacircularbio-based economy.CritRevEnvironSciTechnol2018;48(6):614 54
[24]AurigaR,AurigaA,BorysiukP,WilkowskiJ,FolnalczykO, OchmianI.Lignocellulosicbiomassfromgrapevinesasraw materialforparticleboardproduction.Polymers 2022;14(12):2483. https://doi.org/10.3390/polym14122483
[25] Solt P,KonnerthJ,Gindl-AltmutterW,KantnerW,MoserJ, MitterR,etal.Technologicalperformanceofformaldehydefreeadhesivealternativesforparticleboardindustry.IntJ AdhesionAdhes2019;94:99 131
[26] VanDamJEG,vandenOeverMJA,KeijsersERP.Production processforhighdensityhighperformancebinderless boardsfromwholecoconuthusk.IndCropProd 2004;20(1):97 101
[27] DunkyM.Adhesivesinthewoodindustry.In:PizziA, MittalKL,editors.Handbookofadhesivetechnology.Boca Raton:CRCPress;2017.p.511 74
[28] MantanisGI,AthanassiadouET,BarbuMC,WijnendaeleK. AdhesivesystemsusedintheEuropeanparticleboard,MDF andOSBindustries.WoodMaterSciEng2018;13(2):104 16
[29] MolesmiAA.Particleboard.London:SouthernIllinois UniversityPress;1974.
[30] TaghiyariHR,RangavarH,FarajpourBibalanO.Effectof nano-silveronreductionofhot-pressingtimeand improvementinphysicalandmechanicalpropertiesof particleboard.Bioresources2011;6(4):4067 75.
[31] TaghiyariHR,HosseiniSB,GhahriS,GhofraniM, PapadopoulosAN.Formaldehydeemissioninmicron-sized wollastonite-treatedplywoodbondedwithsoyflourand urea-formaldehyderesin.ApplSci2020;10(19):6709
[32] TaghiyariHR,Moradi-MalekB,GhorbaniKookandehM, FarajpourBibalanO.Effectsofsilverandcopper nanoparticlesinparticleboardtocontrolTrametes versicolorfungus.IntBiodeteriorBiodegrad 2014;94:69 72
[33]KordB,MovahediF,AdlnasabL,AyrilmisN.Effectofnovel scavengersbasedonphenoliccompoundsonformaldehyde emissionandphysical-mechanicalpropertiesof particleboard.WoodMaterSciEng2021:1 11. https:// doi.org/10.1080/17480272.2021.1978542
[34] KristakL,AntovP,BekhtaP,LubisMAR,IswantoAH,RehR, etal.Recentprogressinultra-lowformaldehydeemitting adhesivesystemsandformaldehydescavengersinwoodbasedpanels:areview.WoodMaterSciEng2022:1 20
[35] BekhtaP,NoshchenkoG,RehR,KristakL,SedliacikJ, AntovP,etal.Propertiesofeco-friendlyparticleboards bondedwithlignosulfonate-urea-formaldehydeadhesives andpMDIasacrosslinker.Materials2021;14(17):4875
[36] AlwaniMS,KhalilHPSA,AsnizaM,SuhailySS, AmiranajwaASN,JawaidM.Agriculturalbiomassraw materials:thecurrentstateandfuturepotentialities.In: HakeemKR,JawaidM,RashidU,editors.Biomassand bioenergy.Cham:Springer;2014.p.77 100
[37] ParidahMT,JulianaAH,ZaidonA,KhalilHPSA.Nonwoodbasedcomposites.CurrForestRep2015;1(4):221 38
[38] Moreno-AnguianoO,Carrillo-ParraA,Rutiaga-QuinonesJG, WehenkelC,Pompa-Garcı´aM,Marquez-MontesinoF,etal. Chemicalcompositionof Luffa aegyptiaca mill., Agave durangensis gentryandPennisetumsp.PeerJ2021;9:e10626
[39] PirayeshH,KhanjanzadehH,SalariA.Effectofusing walnut/almondshellsonthephysical,mechanical propertiesandformaldehydeemissionofparticleboard. ComposBEng2013;45(1):858 63
[40] NurdinH,HasanuddinWaskito,KurniawanA.Particle boardmadefromarecafiberwithtapiocaadhesive.JPhys Conf2020;1594(1):012031
[41] JimmimAA,KhanMTA,RahmanMA.Fabricationand characterizationoflowdensityparticleboardsfrom pseudo-stemofbananaplant.AIPConfProc 2018;1980(1):030031
[42] Rojas-LeonA,Guzman-OrtizF,Boları´n-MiroA,OtazoSanchezE,Garcı´aF,FuentesTalaveraF,etal.Ecoinnovationofbarleyandhopewastes:aproposalof sustainableparticleboards.RevMexIngQuim 2019;18:57 68
[43] OhS-Y,LeeSS.UseofBuckwheatstalkinparticleboard bondedwithurea-formaldehyderesinadhesive.Cellul ChemTechnol2012;46:643 7.
[44] MariE,VillenaE.Propertiesofparticleboardfromwood wastesandcashewnutshellresidue.PhilippJSci 2016;145:1 8
[45] KurniatiM,FahmaF,KartikaI,SunartiT,SyamsuK, HermawanD,etal.BinderlessparticleboardfromCastor seedcake:effectofpressingtemperatureonphysicaland mechanicalproperties.AsianJAgricRes2015;9:180 8
[46] OhY,YooJ.Propertiesofparticleboardmadefromchili pepperstalks.JTropForSci2011;23:473 7
[47] LimJ,OngT,NgC,ChuaI,LeeY,YapZ,etal.Development ofparticleboardfromgreencoconutwaste.JPhysConf 2021;2120:012034
[48] GhofraniM,AshoriA,MehrabiR.Mechanicalandacoustical propertiesofparticleboardsmadewithdatepalmbranches andvermiculite.PolymTest2017;60:153 9
[49] GuntekinE,KarakusB.Feasibilityofusingeggplant (Solanummelongena)stalksintheproductionof experimentalparticleboard.IndCropProd2008;27(3):354 8
[50] BarbuMC,SeppererT,TudorEM,PetutschniggA.Walnut andhazelnutshells:untappedindustrialresourcesand theirsuitabilityinlignocellulosiccomposites.ApplSci 2020;10(18).
[51] Sam-BrewS,SmithGD.FlaxandHempfiber-reinforced particleboard.IndCropProd2015;77:940 8
[52] LiX,WangS,DuG,WuZ,GongY.Manufacturing particleboardusingHempshivandwoodparticleswithlow freeformaldehydeemissionurea-formaldehyderesin.For ProdJ2014;64(5 6):187 91.
[53] DasRN,DayA,PandeySN.Particleboardsfromjutestick. BiolWaste1987;20(4):309 13
[54] ScatolinoM,SilvaD,MendesR,MendesL.Useofmaizecob forproductionofparticleboard.CiencEAgrotecnol 2013;37:330 7
[55] CabaloV.UtilizationofcoconutcoirandAbacastripping wastefibersforcementbondedboard.JSci,EngTechnol 2015;3:183 8
[56] TangjuankS.Thermalinsulationandphysicalpropertiesof particleboardsfrompineappleleaves.IntJPhysSci 2011;6:4528 32.
[57] Kuc¸uktuvekM,KasalA,Kus ‚ kunT,ErdilY.Utilizingpoppy husk-basedparticleboardsasanalternativematerialin casefurnitureconstruction.Bioresources2016;12:839 52
[58] GuoY,XiaZ,XuJ,DaiX.Steaminjection-pressing preparationandformingmechanismofbinderlessramie stemparticleboardformodernfurniture.DEStechTrans EngTechnolRes2018;1:133 43
[59] DukarskaD,CzarneckiR,DziurkaD,MirskiR. Constructionparticleboardsmadefromrapeseedstraw gluedwithhybridpMDI/PFresin.EurJWoodWoodProd 2017;75(2):175 84
[60] LiX,CaiZ,WinandyJE,BastaAH.Selectedpropertiesof particleboardpanelsmanufacturedfromricestrawsof differentgeometries.BioresourTechnol 2010;101(12):4662 6
[61] MirskiR,DziurkaD,BanaszakA.Propertiesof particleboardsproducedfromvariouslignocellulosic particles. Bioresources2018;13(4):7758 65.
[62] GulerC,OzenR.Somepropertiesofparticleboardsmade fromcottonstalks(Gossypiumhirsitum L.).HolzalsRohWerkst2004;62(1):40 3
[63] IswantoAH,AritonangW,AzharI,SupriyantoS, FatriasariW.Thephysical,mechanicalanddurability propertiesofsorghumbagasseparticleboardbylayering surfacetreatment.JIndAcadWoodSci2017;14(1):1 8
[64] BritoF,Ju´niorG,SurdiP.Propertiesofparticleboardsmade fromsugarcanebagasseparticles.RevBrCienciasAgr.Univ FederalRuralPernambuco2021;16(e8783):16
[65] CosereanuCN,BrenciL-MNG,ZeleniucOI,FotinAN.Effect ofparticlesizeandgeometryontheperformanceofsinglelayerandthree-layerparticleboardmadefromsunflower seedhusks.Bioresources2015;10(1):1127 36
[66] YalinkilicMK,ImamuraY,TakahashiM,KalayciogluH, NemliG,DemirciZ,etal.Biological,physicaland mechanicalpropertiesofparticleboardmanufacturedfrom wastetealeaves.IntBiodeteriorBiodegrad1998;41(1):75 84
[67] AcdaMN,CabangonRJ.Termiteresistanceandphysicomechanicalpropertiesofparticleboardusingwastetobacco stalkandwoodparticles.IntBiodeteriorBiodegrad 2013;85:354 8
2022;20:4630
[68] TahaI,ElkafafyMS,ElMouslyH.Potentialofutilizing tomatostalkasrawmaterialforparticleboards.AinShams EngJ2018;9(4):1457 64
[69] MoX,HuJ,SunXS,RattoJA.Compressionandtensile strengthoflow-densitystraw-proteinparticleboard.Ind CropProd2001;14(1):1 9
[70] KarimahA,RidhoMR,MunawarSS,Ismadi,AminY, DamayantiR,etal.Comprehensivereviewonnaturalfibers: technologicalandsocio-economicalAspects.Polymers 2021;13(24):4280
[71] LertwattanarukP,SuntijittoA.Propertiesofnaturalfiber cementmaterialscontainingcoconutcoirandoilpalm fibersforresidentialbuildingapplications.ConstructBuild Mater2015;94:664 9
[72] Klı´mekP,MeinlschmidtP,WimmerR,PlinkeB,SchirpA. Usingsunflower(Helianthusannuus L.),topinambour (Helianthustuberosus L.)andcup-plant(Silphiumperfoliatum L.)stalksasalternativerawmaterialsforparticleboards.Ind CropProd2016;92:157 64
[73] DukarskaD, Łe ˛ ckaJ,SzafoniK.Strawofwhitemustard(Sinapis Alba)asanalternativerawmaterialintheproductionof particleboardsresinatedwithUFresin.ActaSciPolonorum, SilvarumColendarumRatioIndLignaria2011;10:21 8
[74] NemliG,DemirelS,Gumus ‚ kayaE,AslanM,AcarC. Feasibilityofincorporatingwastegrassclippings(Lolium perenne L.)inparticleboardcomposites.WasteManag 2009;29(3):1129 31
[75] DoelleK,BajramiB.Sodiumhydroxideandcalcium hydroxidehybridoxygenbleachingwithsystem.IOPConf SerMaterSciEng2018;301:012136
[76] PotucekF,GurungB,HajkovaK.Sodapulpingofrapeseed straw.CellulChemTechnol2014;48:683 91
[77] OhYS,JamaludinMA.Evaluationofrapeseedstalk particleboardbondedwithlaboratory-madeureaformaldehyderesin.CiencFlorest2015;25:515 21
[78] KhazaeianA,AshoriA,DizajMY.Suitabilityofsorghum stalkfibersforproductionofparticleboard.Carbohydr Polym2015;120:15 21
[79] KusumahSS,UmemuraK,GuswenrivoI,YoshimuraT, KanayamaK.Utilizationofsweetsorghumbagasseand citricacidformanufacturingofparticleboardII:influences ofpressingtemperatureandtimeonparticleboard properties.JWoodSci2017;63(2):161 72
[80] RezendeCA,deLimaMA,MazieroP,deAzevedoER, GarciaW,PolikarpovI.Chemicalandmorphological characterizationofsugarcanebagassesubmittedtoa delignificationprocessforenhancedenzymatic digestibility.BiotechnolBiofuels2011;4(1):54
[81] BekaloSA,ReinhardtH-W.Fibersofcoffeehuskandhulls fortheproductionofparticleboard.MaterStruct 2010;43(8):1049 60
[82] C ¸ opurY,GulerC,AkgulM,Tas ‚ c¸ıogluC.Somechemical propertiesofhazelnuthuskanditssuitabilityfor particleboardproduction.BuildEnviron2007;42(7):2568 72
[83] DaudZ,HattaMZM,KassimASM,AwangH,AripinAM. Exploringofagrowaste(pineappleleaf,cornstalk,and napiergrass)bychemicalcompositionandmorphological study.Bioresources2014;9(1):872 80
[84] KhanA,VijayR,SingaraveluDL,ArpithaGR,SanjayMR, SiengchinS,etal.Extractionandcharacterizationof vetivergrass(Chrysopogonzizanioides)andkenaffiber (Hibiscuscannabinus)asreinforcementmaterialsfor epoxybasedcompositestructures.JMaterResTechnol 2020;9(1):773 8
[85] WidyoriniR,UmemuraK,IsnanR,PutraDR,AwaludinA, Prayitno TA.Manufactureandpropertiesofcitricacidbondedparticleboardmadefrombamboomaterials.EurJ WoodWoodProd2016;74(1):57 65.
[86] ShrivastavaP,KhongphakdiP,PalamanitA,KumarA, TekasakulP.Investigationofphysicochemicalpropertiesof oilpalmbiomassforevaluatingpotentialofbiofuels productionviapyrolysisprocesses.BiomassConversion andBiorefinery2021;11(5):1987 2001
[87] HanG,ZhangC,ZhangD,UmemuraK,KawaiS.Upgrading ofureaformaldehyde-bondedreedandwheatstraw particleboardsusingsilanecouplingagents.JWoodSci 1998;44(4):282 6
[88] GrigoriouAH.Straw-woodcompositesbondedwithvarious adhesivesystems.WoodSciTechnol2000;34(4):355 65
[89] YangH-S,KimD-J,KimH-J.Ricestraw woodparticle compositeforsoundabsorbingwoodenconstruction materials.BioresourTechnol2003;86(2):117 21
[90] BarbuM,RehR,C¸avdarA.Non-woodlignocellulosic composites.IGIGlobal,ResearchDevelopmentsinWood EngineeringandTechnology;2014.p.281 319
[91] InstituteANS.ANSI208.1:2016,particleboard.American NationalStandardsInstitute;2016
[92] DukarskaD,BartkowiakM,Stachowiak-WencekA.White mustardstrawasanalternativerawmaterialinthe manufactureofparticleboardsresinatedwithdifferent amountsofurea-formaldehyderesin.Drewno 2015;58:49 63
[93] StandardizationECf,EN312.Particleboards specifications, Europeancommitteeforstandardization.2010.Brussels, Belgium.
[94] NazerianM,BeygiZ,MohebbiGargariR,KoolF.Application ofresponsesurfacemethodologyforevaluating particleboardpropertiesmadefromcottonstalkparticles. WoodMaterSciEng2018;13(2):73 80
[95] NazerianM,BeykiZ,GargariiRM,KoolF.Theeffectofsome technologicalproductionvariablesonmechanicaland physicalpropertiesofparticleboardmanufacturedfrom cotton(Gossypiumhirsutum)stalks,Maderas.CiencTecnol 2016;18:167 78
[96] GhofraniM,HaghdanS,NicKhahV,AhmadiK. Improvementofphysicalandmechanicalpropertiesof particleboardmadeofappletreepruningandsunflower stalkusingtitaniumoxidenanoparticles.EurJWoodWood Prod2015;73(5):661 6
[97] Klı´mekP,WimmerR,MeinlschmidtP,Ku´delaJ.Utilizing Miscanthusstalksasrawmaterialforparticleboards.Ind CropProd2018;111:270 6.
[98] XuJ,HanG,WongED,KawaiS.Developmentofbinderless particleboardfromkenafcoreusingsteam-injection pressing.JWoodSci2003;49(4):327 32
[99] XuJ,WidyoriniR,KawaiS.Propertiesofkenafcore binderlessparticleboardreinforcedwithkenafbastfiberwovensheets.JWoodSci2005;51(4):415 20.
[100] BalducciF,HarperC,MeinlschmidtP,DixB,SanasiA. Developmentofinnovativeparticleboardpanels.DrvInd 2008;59:131 6
[101] AchyuthanKE,AchyuthanAM,AdamsPD,DirkSM, HarperJC,SimmonsBA,etal.SupramolecularselfAssembledchaos:Polyphenoliclignin'sbarriertocosteffectivelignocellulosicbiofuels.Molecules 2010;15(12):8641 88
[102] NourbakhshA,BaghlaniFF,AshoriA.Nano-SiO2 filledrice husk/polypropylenecomposites:physico-mechanical properties.IndCropProd2011;33(1):183 7
[103] AssociationKS.KSF3104:2006,Particleboards.Korean StandardsAssociation;2006
[104] KalaycıogluH,NemliG.Producingcompositeparticleboard fromkenaf(HibiscuscannabinusL.)stalks.IndCropProd 2006;24(2):177 80
[105] GrigorovR,MihajlovaJ,SavovV.Physicalandmechanical propertiesofcombinedwood-basedpanelswith
2022;20:4630 4658
participationofparticlesfromvinesticksincorelayer. InnovWoodworkingIndEngDes2020;1(17):42 52
[106]SyahfitriA,HermawanD,KusumahSS,LubisMAR, WidyaningrumBA,IsmayatiM,etal.Conversionofagroindustrialwastesofsorghumbagasseandmolassesinto lightweightrooftilecomposite.BiomassConversBiorefin 2022:1 15. https://doi.org/10.1007/s13399-022-02435-y
[107]GillelaS,YadavSM,SihagK,LubisMAR,WibowoES,NegiA, etal.AreviewonLantanacamaralignocellulosefiberreinforcedpolymercomposites.BiomassConversBiorefin 2022:1 19. https://doi.org/10.1007/s13399-022-02402-7
[108] SilvaM,PinheiroR,ChristoforoA,PanzeraT,LahrF.Hybrid sandwichparticleboardmadewithsugarcane,Pı´nusTaeda thermallytreatedandmalvafibrefromAmazon.MaterRes 2017;21:e20170724
[109] FiorelliJ,SartoriDdL,CravoJ,SavastanoJH,RossignoloJ, NascimentoM,etal.Sugarcanebagasseandcastoroil polyurethaneadhesive-basedparticulatecomposite.Mater Res2013;16:439 46
[110] MendesRF,MendesLM,OliveiraSL,FreireTP.Useof sugarcanebagasseforparticleboardproduction.KeyEng Mater2015;634:163 71
[111] BuzoANA,SilvaS,AquinoV,ChahudE,BrancoL, AlmeidaD,etal.Additionofsugarcanebagasseforthe productionofparticleboardsbondedwithureaformaldehydeandpolyurethaneresins.WoodRes 2020;65:727 36.
[112] YanoBBR,SilvaSAM,AlmeidaDH,AquinoVBM, ChristoforoAL,RodriguesEFC,etal.Useofsugarcane bagasseandindustrialtimberresidueinparticleboard production.BioRes2020;15(3):4753 62
[113] FiorelliJ,BuenoSB,CabralMR.Assessmentofmultilayer particleboardsproducedwithgreencoconutandsugarcane bagassefibers.ConstructBuildMater2019;205:1 9
[114] KusumahSS,MassijayaSY,PrasetyoKW,SutiawanJ, LubisMAR,HermawanD.Surfacemodificationofecofriendlyparticleboardmadefromsorghumbagasseand citricacidsucroseadhesive.IOPConfSerMaterSciEng 2020;935(1):012054
[115] SyamaniFA,SudarmantoSubyakto,SubiyantoB.High qualitysugarcanebagasse-citricacidparticleboards.IOP ConfSerEarthEnvironSci2020;415(1):012006
[116] WanP,BakerG,ClarkS,MattockS.Characteristicsof sunflowerseedandmeal.CerealChem1979;56:352 5.
[117] GertjejansenR,HaygreenJ,FrenchD.Particleboardfrom aspenflakesandsunflowerhulls.Minnesota: AgriculturalExperimentStation,Universityof Minnesota;1972
[118] CS236-66.Mat-formedwoodparticleboard.1968
[119] CiannameaEM,MartucciJF,StefaniPM,RuseckaiteRA. Bondingqualityofchemically-modifiedsoybeanprotein concentrate-basedadhesivesinparticleboardsfromrice husks.JAmOilChemSoc2012;89(9):1733 41
[120] GulerC,U Buyuksarı.Effectofproductionparameterson thephysicalandmechanicalpropertiesofparticleboards madefrompeanut(ArachishypogaeaL.)hull.BioRes 2011;6(4):5027 36
[121] WechslerA,ZahariaM,CroskyA,JonesH,Ramı´rezM, BalleriniA,etal.Macadamia(Macadamiaintegrifolia)shelland castor(Rı´cinoscommunis)oilbasedsustainableparticleboard: acomparisonofitspropertieswithconventionalwoodbased particleboard.MaterDes2013;50:117 23.
[122] StandardizationECF.ENISO12460-5,wood-basedpanelsdeterminationofformaldehyderelease-Part5.Extraction method(calledtheperforatormethod).Brussels,Belgium: EuropeanCommitteeforStandardization;2015
[123]AkinyemiBA,KolajoTE,AdedoluO.Blended formaldehydeadhesivebondedparticleboardsmadefrom
groundnutshellandricehuskwastes.CleanTechnol EnvironPolicy2022;24:1653 62. https://doi.org/10.1007/ s10098-021-02270-1
[124] YalinkilicMK,AltunL,KalayHZ.Compostingofwastetea leavesaimedatutilizationforforestseedlingsasanorganic fertilizer.TurkJEngEnvironSci1996;1:28 32
[125] ShiJS,LiJZ,FanYM,MaHX.Preparationandpropertiesof wastetealeavesparticleboard.ForStudChina2006;8(1):41
[126] BatiancelaMA,AcdaMN,CabangonRJ.Particleboardfrom wastetealeavesandwoodparticles.JComposMater 2013;48(8):911 6
[127] RajannaL,RamakrishnanM.Anatomicalstudiesontwelve clonesofCamelliaspecieswithreferencetotheir taxonomicsignificance.IntJEngSciTechnol2010;2:5344
[128] JunX,DejiS,YeL,RuiZ.Micromechanismofultrahigh pressureextractionofactiveingredientsfromgreentea leaves.FoodControl2011;22(8):1473 6
[129] OrsY,KalayciogluH.Usingofwastetealeavesonthe particleboardindustry.TurkJAgricFor1991;15:968 74
[130] CampanellaA,WoolRP,BahM,FitaS,AbuobaidA. Compositesfromnorthernredoak(Quercusrobur)leaves andplantoil-basedresins.JApplPolymSci 2013;127(1):18 26
[131] ZhengY,PanZ,ZhangR,El-MashadHM,PanJ,JenkinsBM. Anaerobicdigestionofsalinecreepingwildryegrassfor biogasproductionandpretreatmentofparticleboard material.BioresourTechnol2009;100(4):1582 8.
[132] AghakhaniM,EnayatiSH,NadalizadehH,PirayeshH.The potentialforusingthesycamore(Platusorientalis)leavesin manufacturingparticleboard.IntJEnvironSciTechnol 2014;11(2):417 22
[133] PirayeshH,MoradpourP,SepahvandS.Particleboardfrom woodparticlesandsycamoreleaves:physico-mechanical properties,EngineeringinAgriculture.EnvironFood 2015;8(1):38 43
[134] HoffmammMartinsE,GuimaraesJrJB,ProtasioTDP, MendesRF,GuimaraesBMR.Evaluationofphysical propertiesofparticleboardproducedfromsugarcane leaves.KeyEngMater2016;668:270 4
[135] PanichnavaS,NimityongskulP.Developmentofparticle boardsfromvetivergrass.In:Proceedingsofthird internationalvetiverconference.China:Guangzhou;2003
[136] TongboonS,KiatkamjornwongS,PrasassarakichP, OonjittichaiW.Particleboardfromrubberwoodflakeswith polymericMDIbinder.WoodFiberSci2002;34:391 7
[137] ZhengY,PanZ,ZhangR,JenkinsB,BlunkS.Particleboard qualitycharacteristicsofsalinejosetallwheatgrassand chemicaltreatmenteffect.BioresourTechnol 2007;98:1304 10
[138] Trischler J,SandbergD.Monocotyledonsinparticleboard production:adhesives,additives,andsurfacemodification ofreedcanarygrass.BioRes2014;9:3919.3138
[139] TrischlerJ,NilssonJ,SandbergD.Reedcanarygrassas light-weightcoreinparticleboards.ProLigno 2013;9:469 76
[140]KetchumD.Isbambooagrassoratree?. https:// homeguides.sfgate.com/bamboo-grass-tree-81099.html. 2020.[Accessed15January2022].
[141] BiswasD,KantiBoseS,MozaffarHossainM.Physicaland mechanicalpropertiesofureaformaldehyde-bonded particleboardmadefrombamboowaste.IntJAdhesion Adhes2011;31(2):84 7.
[142] JamaludinK,JalilA,AhmadH,HarunJ,AshaariZ, MohmodA.Propertiesofparticleboardmanufacturedfrom commonlyutilizedMalaysianbamboo(Gigantochloa scortechinii).PertanikaJ.Trap.Agric.Sci.2001;24:151 7
[143] PapadopoulosAN,HillCAS,GkaraveliA,NtalosGA, KarastergiouSP.Bamboochips(Bambusavulgaris)asan
alternativelignocellulosicrawmaterialforparticleboard manufacture.HolzalsRoh-Werkst2004;62(1):36 9
[144] ValarelliI,BattistelleR,BuenoM,BezerraB,CamposC, AlvesM.Physicalandmechanicalpropertiesof particleboardbamboowastebondedwithurea formaldehydeandcastoroilbasedadhesive.Materia 2014;19:1 6
[145] TomimuraY.Chemicalcharacteristicsandutilizationofoil palmtrunks.JARQ1992;25:283 8
[146]Sudarmanto,JuwonoAL,SubyaktoBudimanI,LubisMAR, KusumahSS,KusumaningrumWB,etal.Effectofcoldwatertreatmentandhydrothermalcarbonizationofoilpalm-trunkfibersoncompatibilitywithcementforthe preparationofcement-bondedparticleboard.WoodMater SciEng2021:1 10. https://doi.org/10.1080/ 17480272.2021.1983871
[147] LohYF,ParidahMT,HoongYB,YoongACC.Effectsof treatmentwithlowmolecularweightphenolformaldehyde resinonthesurfacecharacteristicsofoilpalm(Elaeis quineensis)stemveneer.MaterDes2011;32(4):2277 83
[148] BakarE,FebriantoF,WahyudiI,AshaariZ.Polygonsawing: anoptimumsawingPatternforoilpalmstems.JBiolSci 2006;6:744 9
[149] VitalB,LehmannW,BooneR.Howspeciesandboard densitiesaffectpropertiesofexotichardwood particleboards.ForProdJ1974;24:37 45
[150] LeeSH,PaikSanHn,LumW,AshaariZ,BakarE, NurliyanaM,etal.Mechanicalandphysicalpropertiesofoil palmtrunkcoreparticleboardbondedwithdifferentUF resins.JOilPalmRes2014;26:163 9
[151] LeeSH,LumWC,ZaidonA,MaminskiM.Microstructural, mechanicalandphysicalpropertiesofpostheat-treated melamine-fortifiedureaformaldehyde-bonded particleboard.EurJWoodWoodProd2015;73(5):607 16
[152] BaskaranM,HashimR,SulaimanO,HizirogluS,SatoM, SugimotoT.Optimizationofpresstemperatureandtime forbinderlessparticleboardmanufacturedfromoilpalm trunkbiomassatdifferentthicknesslevels.MaterToday Commun2015;3:87 95.
[153] LaemsakN,OkumaM.Developmentofboardsmadefrom oilpalmfrondII:propertiesofbinderlessboardsfrom steam-explodedfibersofoilpalmfrond.JWoodSci 2000;46(4):322 6
[154] SuzukiS,ShintaniH,ParkS-Y,SaitoK,LaemsakN, OkumaM,etal.Preparationofbinderlessboardsfrom steamexplodedPulpsofoilpalm(Elaeisguneensis Jaxq.) frondsandstructuralcharacteristicsofligninandwall polysaccharidesinsteamexplodedPulpstobediscussed forself-bindings.Holzforschung1998;52(4):417 26
[155] AbdulKhalilHPS,IssamAM,AhmadShakriMT,SurianiR, AwangAY.Conventionalagro-compositesfromchemically modifiedfibres.IndCropProd2007;26(3):315 23
[156] RatnasingamJ,IorasF,MacphersonTH.Influenceof woodspeciesontheperceivedvalueofwoodenfurniture: thecaseofrubberwood.HolzalsRoh-Werkst 2007;65(6):487 9.
[157] JohnMJ,FrancisB,VarugheseKT,ThomasS.Effectof chemicalmodificationonpropertiesofhybridfiber biocomposites.ComposApplSciManuf2008;39(2):352 63
[158] SreekalaMS,KumaranMG,GeethakumariammaML, ThomasS.Environmentaleffectsinoilpalmfiber reinforcedphenolformaldehydecomposites:studieson thermal,biological,moistureandhighenergyradiation effects.AdvComposMater2004;13(3 4):171 97
[159] LeeSH,AshaariZ,AngAF,AbdulHalipJ,LumWC,DahaliR, etal.Effectsoftwo-steppostheat-treatmentinpalmoilon thepropertiesofoilpalmtrunkparticleboard.IndCropProd 2018;116:249 58
[160] ZakariaR,BawonP,LeeSH,SalimS,LumWC,Al-EdrusSSO, etal.Propertiesofparticleboardfromoilpalmbiomasses bondedwithcitricacidandtapiocastarch.Polymers 2021;13(20):3494
[161] TaghiyariHR,GhamsariF,SalimifardE.Effectsofadding nano-wollastonite,datepalmpruningsandtwotypesof resinsonthephysicalandmechanicalpropertiesof medium-densityfibreboard(MDF)madefromwoodfibres. BoisForTrop2018;335:49
[162] NemliG,KalaycıogluH,AlpT.Suitabilityofdatepalm (Phoenixdactyliferia)branchesforparticleboardproduction. HolzalsRoh-Werkst2001;59(6):411 2
[163] AmirouS,ZerizerA,PizziA,HaddadouI,ZhouX. Particleboardsproductionfromdatepalmbiomass.EurJ WoodWoodProd2013;71(6):717 23
[164] LinCJ,HizirogluS,KanSM,LaiHW.Manufacturing particleboardpanelsfrombetelpalm(ArecacatechuLinn.). JMaterProcessTechnol2008;197(1):445 8
[165] HashimR,WanNadhariWNA,SulaimanO,SatoM, HizirogluS,KawamuraF,etal.Propertiesofbinderless particleboardmanufacturedfromoilpalmbiomass. Bioresources2012;7:1352 65
[166] LykidisC,GrigoriouA.Hydrothermalrecyclingofwasteand performanceoftherecycledwoodenparticleboards.Waste Manag2008;28(1):57 63
[167] SalimanMAR,AshaariZ,BakarE,LeeSH,TahirPM, LeemonN,etal.Responsesurfacemethodologymodelof hydrothermaltreatmentparametersondecayresistanceof oilpalmwood.JTropForSci2017;29:318 24
[168] LeeSH,AshaariZ,AngAF,HalipJA.Dimensionalstabilityof heatoil-curedparticleboardmadewithoilpalmtrunkand rubberwood.EurJWoodWoodProd2017;75(2):285 8
[169] SchildA,CoolJ,BarbuM-C,SmithGD.Feasibilityof substitutingcorelayerstrandsinrandomlyOSBwith contaminatedwastewoodparticles.WoodMaterSciEng 2021;16(3):170 7
[170] AndradePI,Arau´joSdO,NeivaDM,VitalBR,Oliveira CarneiroADC,GominhoJ,etal.Strengthpropertiesand dimensionalstabilityofparticleboardswithdifferent proportionsofthermallytreatedrecycledpineparticles. Holzforschung2016;70(5):467 74
[171] PaulW,OhlmeyerM,LeithoffH,BoonstraMJ,PizziA. OptimisingthepropertiesofOSBbyaone-stepheatpretreatmentprocess.HolzalsRoh-Werkst2006;64(3):227 34.
[172] SernekM,KamkeFA,GlasserWG.Comparativeanalysisof inactivatedwoodsurfaces.Holzforschung2004;58(1):22 31
[173] JiangJ,LuJ,ZhouY,HuangR,ZhaoY,JiangJ.Optimization ofprocessingvariablesduringheattreatmentofoak (Quercusmongolica)wood.WoodSciTechnol 2014;48(2):253 67.
[174] Bal BC,Bektas ‚ I.Theeffectsofheattreatmentonthe physicalpropertiesofjuvenilewoodandmatureof Eucalyptusgrandis.BioRes2012;7(4):5117 27
[175] PolettoM,ZatteraAJ,ForteMMC,SantanaRMC.Thermal decompositionofwood:influenceofwoodcomponentsand cellulosecrystallitesize.BioresourTechnol2012;109:148 53
[176] WangS-Y,YangT-H,LinL-T,LinC-J,TsaiM-J.Fireretardant-treatedlow-formaldehyde-emission particleboardmadefromrecycledwood-waste.Bioresour Technol2008;99(6):2072 7
[177] JaniszewskaD,Fra ˛ ckowiakI,MytkoK.Exploitationof liquefiedwoodwasteforbindingrecycledwood particleboards.Holzforschung2016;70(12):1135 8
[178] AzambujaRR,CastroV,TrianoskiR,IwakiriS.Recycling woodwastefromconstructionanddemolitiontoproduce particleboards,Maderas.CienciaTecnol2018;20:681 90
[179] HongM-K,LubisMAR,ParkB-D,SohnCH,RohJ.Effectsof surfacelaminatetypeandrecycledfibercontenton propertiesofthree-layermediumdensityfiberboard.Wood MaterSciEng2020;15(3):163 71.
[180] Izdinsky´J,VidholdovaZ,ReinprechtL.Particleboardsfrom recycledwood.Forests2020;11(11):1116
[181] Izdinsky´J,ReinprechtL,VidholdovaZ.Particleboardsfrom recycledpallets.Forests2021;12(11):1597
[182] PapadopoulosA.Propertycomparisonsandbonding efficiencyofUFandPMDIbondedparticleboardsasaffected bykeyprocessvariables.BioRes2006;1(2):201 8
[183] BaoS,DaunchW,SunY,RinaldiP,MarcinkoJ, PhanopoulosC.Solidstatetwo-dimensionalNMRstudiesof polymericdiphenylmethanediisocyanate(PMDI)reaction inwood.ForProdJ2003;53:63 71
[184] NuryawanA,RisnasariI,SitumorangD.Applicationof liquefiedadhesivemadeofoil-palmstemforparticleboard binder.IOPConfSerEarthEnvironSci2020;454(1):012088
[185] LaskowskaA,MaminskiM.Propertiesofparticleboard producedfrompost-industrialUF-andPF-bondedplywood. EurJWoodWoodProd2018;76(2):427 35
[186] WilcoxW.Reviewofliteratureontheeffectsofearlystages ofdecayonwoodstrengthWoodFiber.Science 1978;9:252 7
[187] OsmanZ,PizziAP,AlaminIH.Comparativepropertiesof Agrofiberbasedparticleboardsusingnewlydeveloped bondingmaterials.JBiobasedMaterBioenergy2009;3:275 81
[188] dosSantosMFN,BattistelleRAG,BezerraBS,VarumHSA. Comparativestudyofthelifecycleassessmentof particleboardsmadeofresiduesfromsugarcanebagasse (Saccharumspp.)andpinewoodshavings(Pinuselliottii).J CleanProd2014;64:345 55
[189] SilvaDAL,LahrFAR,PavanALR,SaavedraYMB,MendesNC, SousaSR,etal.Dowood-basedpanelsmadewithagroindustrialresiduesprovideenvironmentallybenign alternatives?AnLCAcasestudyofsugarcanebagasse additiontoparticleboardmanufacturing.IntJLifeCycle Assess2014;19(10):1767 78
[190] SilvaDAL,LahrFAR,GarciaRP,FreireFMCS,OmettoAR.Life cycleassessmentofmediumdensityparticleboard(MDP) producedinBrazil.IntJLifeCycleAssess 2013;18(7):1404 11
[191] RamosA,Briga-SaA,PereiraS,CorreiaM,PintoJ,BentesI, etal.Thermalperformanceandlifecycleassessmentof corncobparticleboards.JBuildEng2021;44:102998
[192] ShangX,SongS,YangJ.Comparativeenvironmental evaluationofstrawresourcesbyLCAinChina.AdvMater SciEng2020;2020:4781805
[193] HossainMU,WangL,YuIKM,TsangDCW,PoonC-S. Environmentalandtechnicalfeasibilitystudyofupcycling woodwasteintocement-bondedparticleboard.Construct BuildMater2018;173:474 80
[194] HoglmeierK,Weber-BlaschkeG,RichterK.Utilizationof recoveredwoodincascadesversusutilizationofprimary wood acomparisonwithlifecycleassessmentusing systemexpansion.IntJLifeCycleAssess 2014;19(10):1755 66
[195] MadurwarMV,RalegaonkarRV,MandavganeSA. Applicationofagro-wasteforsustainableconstruction materials:areview.ConstructBuildMater2013;38:872 8
[196] DukarskaD,RogozinskiT,AntovP,KristakL,KmieciakJ. Characterisationofwoodparticlesusedintheparticleboard productionasafunctionoftheirmoisturecontent. Materials2021;15(1):48
[197]MartinkaJ,MantanisGI,LykidisC,AntovP,RantuchP.The effectofpartialsubstitutionofpolyphosphatesby
aluminiumhydroxideandboratesonthetechnologicaland firepropertiesofmediumdensityfibreboard.WoodMater SciEng2021:1 7. https://doi.org/10.1080/ 17480272.2021.1933175
[198] OsvaldovaL,GaspercovaS,MitrengaP,OsvaldA.The influenceofdensityoftestspecimensonthequality assessmentofretardingeffectsoffireretardants.WoodRes 2016;61(1):35 42
[199] MakovickaOsvaldovaL,MarkovaI,JochimS,BaresJ. Experimentalstudyofstraw-basedeco-panelusingasmall ignitioninitiator.Polymers2021;13(8):1344
[200]OsvaldovaLM,MitrengaP,Jancı´kJ,TitkoM,EfhamisisiD, Kosu´tovaK.Firebehaviouroftreatedinsulationfibreboards andPredictionsofitsfuturedevelopmentbasedonnatural agingsimulation.FrontMater2022;219. https://doi.org/ 10.3389/fmats.2022.891167.
[201] TurekovaI,IvanovicovaM,HarangozoJ,GaspercovaS, MarkovaI.Experimentalstudyoftheinfluenceofselected factorsontheparticleboardignitionbyradiantheatflux. Polymers2022;14(9):1648
Dr.LeeSengHua LeeisaresearchfellowintheLaboratoryof BiopolymerandDerivatives(BADs),InstituteofTropicalForestry andForestProducts,UniversitiPutraMalaysia.Hisresearchinterestsincludewoodcomposites,woodtreatments,woodadhesives,andpolymers.Email: lee_seng@upm.edu.my ResearchGate: https://www.researchgate.net/profile/Seng-Hua-Lee-2/research
Dr.LumWeiChen Lumisapost-doctoralresearcheratInstitute forInfrastructureEngineeringandSustainableManagement, UniversitiTeknologiMARA.Hismainresearchinterestsinclude engineeredwoodforstructuralapplications,wood-basedcomposite,andwoodfireproperties.Email: lumweichen@outlook. com,ResearchGate: https://www.researchgate.net/scientificcontributions/Wei-Chen-Lum-2073536997
Assoc.Prof.Dr.BoonJiaGeng BoonisaseniorlectureratFaculty ofBioengineeringandTechnology,UniversitiMalaysiaKelantan. Hismainresearchinterestsincludeforestproductsprocessing. Email: jia.geng@umk.edu.my,ResearchGate: https://www. researchgate.net/profile/Jia-Geng-Boon
Assoc.Prof.Dr.LubosKristak LubosKristakistheHeadof DepartmentofPhysics,ElectricalEngineeringandAppliedMechanics,FacultyofWoodSciencesandTechnologyinZvolen, Slovakia.HereceivedAssoc.Prof.titleinPhysics.Hisscientific interestisthephysicalpropertiesofwood,insulationsboard (fromthethermalandacousticpointofview),woodcomposites andwoodadhesives.Email: kristak@tuzvo.sk,ResearchGate: https://www.researchgate.net/profile/Lubos-Kristak-2
Prof.Dr.PetarAntov PetarAntovisanAssociateProfessor,PhDat theUniversityofForestry,basedinSofia,Bulgaria.Hismain researchinterestsareinthefieldofwoodtechnology,wood-based composites,biobasedwoodadhesives,formaldehydeemission, formaldehydescavengers,eco-friendlywood-basedcomposites, occupationalsafety,andhealthatworkinwoodindustryenterprises,ergonomicsandergonomicdesignoffurnitureproducts. Email: p.antov@ltu.bg, ResearchGate: https://www.researchgate. net/profile/Petar-Antov
Assoc.Prof.Dr.TomaszRogozinski TomaszRogozinskiisHeadof theDepartmentatDepartmentofFurnitureDesign,PoznanUniversityofLifeSciences.Hisresearchinterestsareinthefieldof woodcompositeandfurnituredesign.Email: tomasz.rogozinski@ up.poznan.pl,ResearchGate: https://www.researchgate.net/ profile/Tomasz-Rogozinski
MissMartaPe ˛ dzik MartaPe ˛ dzikisaPhDstudentatCenterof WoodTechnology,PoznanInstituteofTechnology.Herresearch interestsareinthefieldofwood-basedpanelsandcomposite. Email: marta.pedzik@itd.lukasiewicz.gov.pl,ResearchGate: https://www.researchgate.net/profile/Marta-Pedzik
Dr.HamidR.Taghiyari HamidR.TaghiyariisascientistfromWood ScienceandTechnologyDepartment,FacultyofMaterialsEngineering & NewTechnologies,ShahidRajaeeTeacherTrainingUniversity (SRTTU).HisareaofexpertiseisinWoodScienceandTechnology andPlantpathology.Email: htaghiyari@yahoo.com,ResearchGate: https://www.researchgate.net/profile/Hamid-Reza-Taghiyari
Dr.MuhammadAdlyRahandiLubis MuhammadAdlyRahandi LubisreceivedhisBScinForestryfromIPBUniversity(Bogor, Indonesia)in2011andintegratedmaster/doctoral,PhDinwood scienceandtechnologyfromKyungpookNationalUniversity (Daegu,SouthKorea)in2019.Hisresearchinterestincludeswood adhesives,woodadhesion,thermosettingresins,andpolymer composites.Email: marl@biomaterial.lipi.go.id,ResearchGate: https://www.researchgate.net/profile/Muhammad-Adly-Lubis
Assoc.Prof.Dr.WidyaFatriasari WidyaFatriasariisanassociate professoratResearchCenterforBiomassandBioproducts,NationalResearchandInnovationAgency(BRIN),Indonesia.The primaryresearchareasarebiomassconversion,bioenergy,biorefinery,lignin-basedbioproducts,cellulose-basedbioproducts, andwood/biomasschemistry.Email: widya.fatriasari@ biomaterial.lipi.go.id,ResearchGate: https://www.researchgate. net/profile/Hamid-Reza-Taghiyari
Dr.SumitManoharYadav SumitManoharYadavisanAssistant ProfessoratForestCollegeandResearchInstitute,Hyderabad, India.Hisresearchinterestsareinthefieldofbiocompositeand nanocomposite.Email: sumityadav@um.edu.my,ResearchGate: https://www.researchgate.net/profile/Sumit-Yadav-32
Dr.AujchariyaChotikhun AujchariyaChotikhunisasenior lectureratFacultyofScienceandIndustrialTechnology,Princeof SongklaUniversity,SuratThaniCampus.Hisresearchinterests areinthefieldofthermaltreatmentofwoodandwood-based composite.Email: aujchariya.c@psu.ac.th,Googlescholar: https://scholar.google.com/citations?
user
JGMscPUAAAAJ&hl
en
Prof.Dr.AntonioPizzi AntonioPizzicurrentlyworksatthe LERMAB-ENSTIB,UniversityofLorraine.A.Pizzidoesresearchin MaterialsChemistry,AnalyticalChemistryandPolymerChemistry.Themainfocusofhisworkisonpolycondensationresins, mainlybiosourcedandsyntheticwoodadhesives.Email: antonio. pizzi@univ-lorraine.fr,ResearchGate: https://www.researchgate. net/profile/Apizzi-Pizzi
Bio-oil and pyrolysis gas (py-gas) are two pyrolysis products available for potential energy recovery.Crude bio-oil, however, is typically corrosive and unstable, requiring special combustion equipment orcatalytic upgrading to produce drop-in-grade fuel. In contrast, py-gas is readily useable in standardequipment for energy recovery. Previous research revealed that Ca-impregnated biochar catalystimproved bio-oil to pygas conversion. Biochar produced from paper mill sludge (p-sludge) has very highCa content. In this study, the catalytic ability of p-sludge biochar was systematically evaluated for the firsttime in pyrolysis. P-sludge biochar resulted in higher py-gas yield (40 wt% of total pyrolysis products)and py-gas energy (8400 kJ of pygas per biosolids pyrolyzed) than other biochar catalysts (e.g. wood andcorn stover biochars) and mineral catalysts (e.g. calcined dolomite). Under some conditions (e.g. hightemperature and catalyst loading), catalysis completely eliminated the nonaqueous phase condensate. Alower catalyst-to-feedstock ratio was required using p-sludge biochar compared to other biochars forsimilar performance. P-sludge biochar also had a longer catalyst lifetime based on the effectiveness overfive reuse cycles. Bio-oil catalyzed by p-sludge biochar contained fewer organic constituents based onGC-MS and GC-FID analyses (e.g. toluene, ethylbenzene, styrene, phenol, cresol, and indole were notidentified after catalysis).
Contact information:
1Department of Physics and Engineering, California State University-Bakersfield, 9001 Stockdale Highway, Bakersfield, CA, 93311, USA
2Department of Mechanical Engineering, Marquette University, Milwaukee, WI, 53233, USA
3Department of Civil, Construction and Environmental Engineering, Marquette University, Milwaukee, WI, 53233, USA
4School of Economics, Shanghai University, Shanghai, 200444, China. Energy. 239 (2022) 121925. https://doi.org/10.1016/j.energy.2021.121925
Commons Attribution 4.0 International License
The Paper Industry Technical Association (PITA) is an independent organisation which operates for the general benefit of its members –both individual and corporate –dedicated to promoting and improving the technical and scientific knowledge of those working in the UK pulp and paper industry. Formed in 1960, it serves the Industry, both manufacturers and suppliers, by providing a forum for members to meet and network; it organises visits, conferences and training seminars that cover all aspects of papermaking science. It also publishes the prestigious journal Paper TechnologyInternational® and the PITA Annual Review, both sent free to members, and a range of other technical publications which include conference proceedings and the acclaimed Essential Guideto Aqueous Coating.
Energy239(2022)121925
Papermillsludgebiochartoenhanceenergyrecoveryfrompyrolysis: Acomprehensiveevaluationandcomparison
ZhongzheLiu a, *,MatthewHughes b,YiranTong c,JizhiZhou d,WilliamKreutter b , HugoCortesLopez a,SimchaSinger b,DanielZitomer c,PatrickMcNamara c, **
a DepartmentofPhysicsandEngineering,CaliforniaStateUniversity-Bakersfield,9001StockdaleHighway,Bakersfield,CA,93311,USA
b DepartmentofMechanicalEngineering,MarquetteUniversity,Milwaukee,WI,53233,USA
c DepartmentofCivil,ConstructionandEnvironmentalEngineering,MarquetteUniversity,Milwaukee,WI,53233,USA
d SchoolofEconomics,ShanghaiUniversity,Shanghai,200444,China
articleinfo
Articlehistory: Received23April2021 Receivedinrevisedform 25August2021 Accepted26August2021 Availableonline3September2021
Keywords: Biomass Bio-oil Catalyticpyrolysis Tarreduction Wastewatersolids Industrialwaste
Bio-oilandpyrolysisgas(py-gas)aretwopyrolysisproductsavailableforpotentialenergyrecovery. Crudebio-oil,however,istypicallycorrosiveandunstable,requiringspecialcombustionequipmentor catalyticupgradingtoproducedrop-in-gradefuel.Incontrast,py-gasisreadilyuseableinstandard equipmentforenergyrecovery.PreviousresearchrevealedthatCa-impregnatedbiocharcatalyst improvedbio-oiltopy-gasconversion.Biocharproducedfrompapermillsludge(p-sludge)hasveryhigh Cacontent.Inthisstudy,thecatalyticabilityofp-sludgebiocharwassystematicallyevaluatedforthe first timeinpyrolysis.P-sludgebiocharresultedinhigherpy-gasyield(40wt%oftotalpyrolysisproducts) andpy-gasenergy(8400kJofpy-gasperbiosolidspyrolyzed)thanotherbiocharcatalysts(e.g.woodand cornstoverbiochars)andmineralcatalysts(e.g.calcineddolomite).Undersomeconditions(e.g.high temperatureandcatalystloading),catalysiscompletelyeliminatedthenonaqueousphasecondensate.A lowercatalyst-to-feedstockratiowasrequiredusingp-sludgebiocharcomparedtootherbiocharsfor similarperformance.P-sludgebiocharalsohadalongercatalystlifetimebasedontheeffectivenessover fivereusecycles.Bio-oilcatalyzedbyp-sludgebiocharcontainedfewerorganicconstituentsbasedon GC-MSandGC-FIDanalyses(e.g.toluene,ethylbenzene,styrene,phenol,cresol,andindolewerenot identifiedaftercatalysis).
© 2021TheAuthor(s).PublishedbyElsevierLtd.ThisisanopenaccessarticleundertheCCBY-NC-ND license(http://creativecommons.org/licenses/by-nc-nd/4.0/).
Thermochemicaltreatmentisanefficientprocessthatcanbe usedtorecoverenergyandresourcesfromcarbonaceouswastes. Mainstreamthermochemicaltechnologiesincludeincineration, gasification,andpyrolysis[1 5].Pyrolysisisgainingattention becauseitcanproducecrudebio-oil(i.e.pyrolysiscondensate, hereafterreferredtoasbio-oil)andpyrolysisgas(py-gas)as renewablefuels,andbiocharasavaluablesoilamendmentproduct [6].However,allpyrolysistechnologies(i.e.fast,intermediate,and slowpyrolysisclassifiedbyheatingrates)producebio-oilwith undesiredpropertiessuchashighviscosity,watercontent,acidity,
* Correspondingauthor.
** Correspondingauthor.
zliu006@ucr.edu (Z.Liu), patrick.mcnamara@marquette.edu (P.McNamara).
journalhomepage: www.elsevier.com/locate/energy https://doi.org/10.1016/j.energy.2021.121925
andcorrosivenessthatrequiresspecialequipmentfordirectcombustionorcostlyupgradingtoproducedrop-in-gradefuel[7 9].In contrast,py-gascanmoreeasilybeusedinconventionalpower generatorssuchasinternalcombustionengines[10].Inparticular, forslowpyrolysis,thetargetproductisbiochar,whereaspy-gascan beusedforon-siteenergyrecoverytoprovideheattotheprocess. Thus,processesthatimprovepy-gasyieldwhileminimizingbio-oil productionarebeneficialforslowpyrolysisenergyrecovery.Catalyticpyrolysis,specifically,couldbeanefficientmeanstominimizebio-oilproductionwhileincreasingpy-gasyieldand maintainingbiocharproduction.
Organicwastewatersolidssuchasbiosolidsareamajor byproductfromwaterresourcerecoveryfacilities,andsolidsproductionhasbeenincreasing[11].Ourpreviousresearchshowed thatpyrolysisofdriedwastewaterbiosolidscanrecoverenergy [12].Biosolids-derivedbiocharwithsorbednutrientscanincrease grassgrowthratescomparabletothatofcommercialinorganic fertilizer[13].Moreover,biosolidspyrolysiscanremove
2021TheAuthor(s).PublishedbyElsevierLtd.ThisisanopenaccessarticleundertheCCBY-NC-NDlicense(http://creativecommons.org/licenses/by-nc-nd/4.0/
Z.Liu,M.Hughes,Y.Tongetal. Energy239(2022)121925
contaminantsofemergingconcernsuchastriclosan,triclocarban andantibioticresistancegenesaswellasreducetotalestrogenicity ofthesolidproduct[14 16].Therefore,biosolidspyrolysiscanbe favorableintermsofenergyrecovery,resourcerecovery,contaminantremovalandreleaseofcontaminantstotheenvironment[17]. However,biosolids-derivedbio-oilfromslowpyrolysisgenerally accountsfor40%ofthetotalproductmass[4].Also,Fontsetal.[18] statedthatfull-scaleimplementationofbiosolidspyrolysisis difficultduetotheloweconomicvalueofrawbio-oil[18].Thus, reducingbio-oilandincreasingcleanerpy-gasproductioncouldbe morepractical.Tothatend,catalyticpyrolysisdecomposesbio-oil resultinginhigherpy-gasproduction.
Previousresearchfocusedonpyrolysisvaporupgradingand decomposingtheresultingmixtureofhighmolecularweighthydrocarbons(i.e.,tar),whichisapredominantbio-oilcomponent [19],usingvariousheterogeneouscatalystsincludingacommercial catalyst(ZSM-5), fluidcatalyticcrackingcatalystandbiochar [20 22].Often,catalyticcrackingleadstodeoxygenationbyformationoflight-weightaqueousandgaseoushydrocarbonsaswell asincreasedpermanentgasproduction.Inparticular,ElRubetal. (2008)comparedtardecompositionusingtwobiochars(i.e.pinewoodandcommercialbiochars)tothatobservedusingtraditional catalysts(e.g.olivineanddolomite),concludingthattheformer twobiocharsweremorecosteffective[20].Inaddition,Liuetal. (2017,2018)foundCa-loadedbiochar(e.g.biosolidsbiochar)was moreeffectivewhenconvertingbio-oiltopy-gas[23,24].
IntheUnitedStates,over4milliondrytonsofwastewater sludgefromthepulpandpapersectorareproducedeveryyear[25]. Papermillsludge(p-sludge)oftenhasveryhighCacontentdueto theuseoflimeintherecausticizingcycle.Hence,theresultingpsludgebiocharalsohashighCacontent,whichcanbeapotential biocharcatalystforupgradingpyrolysisproducts.However,psludgebiocharhasonlybeenwidelystudiedforpollutantremoval [26 28].Researchhasnotbeenconductedregardingitscatalytic performanceduringpyrolysisprocess.
Therefore,themainobjectiveofthisstudywastoevaluatethe catalyticperformanceofp-sludgebiocharduringbiosolidspyrolysisintermsoftheyield,composition,andenergyofpy-gasand bio-oil.Thep-sludgebiocharwascomparedtotraditionalmineral catalystsandothertypesofbiocharthatoriginatefromcommon carbonaceouswastes.Theeffectsofcatalystloading(catalystto feedstockmassratio)andcatalystlifetime(thedurationforwhicha catalystcancontinuetoaltertheproductyieldscomparedtothe non-catalyzedcontrolyields)werestudied.Furthermore,possible factorsaffectingthecatalyticeffectiveness,suchasmetalcontent andsurfacearea,wereinvestigated.
2.1.Materialpreparationandpyrolysistest
2.1.1.Materials
Sixbiomassresidueswerechosenasprecursorstocreatebiocharcatalysts.P-sludgewasprovidedbyacommercialfacility producingrecycled fiberforthepaperindustryandfood-grade packaging(SustanaFiber,DePere,WI,USA).Otherresidueswere fromagriculture,bioethanolindustry,forestry,livestockindustry, andmunicipalwastewaterindustry,whichwerecornstover,dried distillersgrainswithsolubles(DDGS),pinewoodsawdust,cow manure,andwastewaterbiosolids,respectively.Cornstover, manure,andsawdustwerepurchasedfromDripTrap,HoffmanAH Inc.andHealthyPet,respectively.DDGSwasprovidedbyUnited Ethanol,LLC(Milton,WI,USA)andwastewaterbiosolidswerethe driedbiosolids(i.e.Milorganite®)fromtheMilwaukeeMetropolitanSewerageDistrict(Milwaukee,WI,USA).Biomassresidues
weregroundandscreenedtoanominaldiameterof1 2mm. Biomassresiduecompositiondataareshownin TableS1 inthe supportinginformation(SI).Proximateanalysiswasconducted accordingtoASTMD7582standardandultimateanalysiswas conductedusingVarioMicroCube(Elementar,Hanau,Germany). Theoxygencontentwascalculatedbydifference.Theresulting biocharcatalystswererepresentedbystover,manure,wood,DDGS, biosolids,andp-sludge.Theconventionalmineralcatalystsusedin thisstudywerecalcineddolomite(CaO$MgO)andsinteredolivine ((Mg,Fe)2SiO4),whichhavebeenextensivelystudiedbecausethey arewidelyavailableandefficientforreducingtarduringthermochemicalconversions[29].Thecalcineddolomiteandsintered olivinewerefromChemLimeCo.(Salinas,CA,USA)andMagnolithe GmbHCo.(Steiermark,Austria),respectively.Thedolomitecontained17%MgOand80%CaO(wt%,drybasis)andtheolivine contained48%MgO,39%SiO2,and11%Fe2O3 (7%Fe)(wt%,dry basis).
Alab-scalepyrolyticsystemshowninSI(FigureS1)wasusedto producebiocharcatalystandconductcatalyticpyrolysistests.The systemconsistedofastainless-steelpyrolysisreactorvessel (360cm3),aceramicradiativeheater,agaspurgeandrelease system,astainless-steeltubularreactor(0.79cminnerdiameter, 27.9cmlong),anicebathforliquidcondensation,andapermanent gascollectionvalvewithaTedlar® bag.Biomassresidueswere pyrolyzedbypurgingthepyrolyticsystemwithargongasat15mL/ min.Theheatingratewascontrolledatapproximately10 C/min, andtheretentiontimeofeachtestwas30minafterthereactor reachedthedesiredpyrolysistemperature.Argon flowwasshutoff whenthedesiredmaximumretentiontimewasachieved.Pyrolysis vaporpassedthroughthetubularreactortocondensersinanice bathinwhichbio-oilandpy-gaswereseparated.Py-gaswas collectedinaTedlar® bagandbio-oilwascollectedintwocondensers.Biocharwasobtainedinthepyrolysisvessel.Themassesof biocharandbio-oilweremeasuredgravimetrically.Coke(i.e.solid carbonformedbycarbonizationordecompositionofheavyhydrocarbons)coulddepositonthebiocharcatalystsurfaceinthe tubularreactor.Thecokemassyieldwascalculatedfromtheweight difference(weightgain)ofthebiocharcatalystbeforeandafterthe test.Thepy-gasmasswascalculatedbydifference(i.e.initialbiosolidsmassminusthesumofbiochar,bio-oil,andcokemasses) basedonthemethodusedpreviously[23].Becausecokemass(<2% forallthetests)wasminorcomparedtobiochar,bio-oil,andpy-gas, thecokeyieldfractionwasnotpresentedintheresults figures.
Thebiocharcatalystswereproducedattemperaturesfrom 600 Cto800 Cinthepyrolysisreactorwithanemptydownstreamtubularreactormaintainedat500 C.Thetemperaturethat wasusedtoproducecatalystswasidenticaltotheexperimental pyrolysistemperature(e.g.,biocharcatalystmadeat700 Cwas usedfor700 Ccatalyticpyrolysisexperiments).Biocharand mineralcatalystshadanominaldiameterof0.5 1.5mm.
Incatalyticpyrolysisexperiments,wastewaterbiosolidswas usedforalloftheteststostudytheimpactsofdifferentcatalysts. Thetubularreactorwas filledwitheachbiocharormineralcatalyst (filledlengthwas26cmforeachcatalyst)andpreheatedtothe desiredtemperatureidenticaltothetemperatureofthepyrolysis reactorvesselinwhichbiosolidswaspyrolyzed(see Table1).Pyrolysistemperaturerangedfrom600 Cto800 C.Thecatalyst/ biosolidsmassratiowas0.33forallcatalystsandadditionallymass ratiosof0.2and1forwood,p-sludge,andbiosolidsbiocharswere employed.Upto fivecycles(i.e., fiveconsecutivebatchexperiments usingthesamebiocharcatalystsample)forthewood,p-sludge,and biosolidscharswereconductedtoobservecatalystactivityafter repeateduse.Allpyrolysisexperimentswereconductedin
Z.Liu,M.Hughes,Y.Tongetal. Energy239(2022)121925
Table1 Experimentaldesign. ReactorTemperature( C)DownstreamTemperature( C)DownstreamLoadingCatalyst/FeedstockMassRatio Catalytic 6006000.5 1.5mmcatalyst0.33 7007000.5 1.5mmcatalyst0.33 8008000.5 1.5mmcatalyst0.2a,0.33b,1a Non-catalytic(0S) 6006000.5 1.5mmsand0 7007000.5 1.5mmsand0 8008000.5 1.5mmsand0 Non-catalytic(0B) 600500Blank0 700500Blank0 800500Blank0
a Thecatalyst/biosolidsmassratiosof0.2and1wereonlyutilizedforwood,p-sludge,andbiosolidsbiochars.
b Wood,p-sludge,andbiosolidsbiocharswererecycledforupto fivetimesunder800 Cattheratioof0.33.
triplicate.Statisticalanalyses(ANOVA, a level ¼ 5%)wereperformedusingOriginLab(Northampton,MA,USA).
Twonon-catalyticbiosolidspyrolysistestswerealsoconducted ascontrols(see Table1).The firstnon-catalytictest(0S)employed inertsandwithnominaldiameterof0.5 1.5mminplaceofcatalyst inthedownstreamtubularreactor.The0Stestwasconductedto observeanysecondaryreactioneffectsamongpyrolysisvapor componentsathightemperature[30].Thesecondnon-catalytic test(0B)employedanemptydownstreamtubularreactormaintainedat500 Ctopreventpyrolysisvaporcomponentsfrom condensingduringtransitiondownstream(secondaryreactions wereminimized).
2.2.Characterizationofpy-gas,bio-oil,andbiochar
2.2.1.Characterizationofpy-gasandbio-oil
Py-gasconstituentconcentrations(i.e.H2,CH4,CO,C2H4,C2H6, CO2,C3H8)weredeterminedbygaschromatographywithathermal conductivitydetector(GC-TCD)(AgilentTechnologies7890A) describedpreviously[4].Gaschromatography-massspectroscopy (GC-MS)(7890B-5977A,AgilentTechnologies,USA)andgaschromatographywitha flameionizationdetector(430GC-FID,Bruker Daltonics,Inc.,USA)wereusedforthequalitativeandquantitative bio-oilanalyses.Thebio-oilcompositionanalyseswereconducted atIowaStateUniversity'sBioeconomyInstituteusingapublished analyticalmethod[31].
Thehigherheatingvalue(HHV)ofpy-gaswascalculatedbased onthecomponentconcentrationsandthecorrespondingcomponentHHVs.Thebiocharandbio-oilHHVsweremeasuredbybomb calorimetry(Parr1341,ParrInstrumentCompany,Moline,IL).By multiplyingeachpyrolysisproductyieldwithitscorresponding HHV(i.e.bio-oilyieldmultipliedbybio-oilHHV;py-gasyield multipliedbypy-gasHHV),theproductenergypermassofbiosolidspyrolyzed(kJ/kgbiosolids)wasobtained.
Surfacemorphologyandelementalcompositionofbothnew (i.e.pristine)andusedbiocharwereanalyzedusingascanning electronmicroscopeequippedwithenergydispersivespectroscopy (SEM-EDS)(JSM-6510LV,JEOLUSA,Inc.MA,USA).BiocharmicrostructurewasmeasuredusingaBrunauer-Emmett-Teller(BET) instrument(NOVA4200e,QuantachromeInstruments,Boynton Beach,FL).ThechemicalcompositionofbiocharwasanalyzedbyXray fluorescence(XRF-1800,Shimadzu).X-RayDiffraction(XRD) analysesofnewandusedbiocharaswellasrawp-sludgewere conductedusingBrukerD8DiscoverX-raydiffractometer(Cu anode).
Theusedp-sludgebiocharcatalysts(usedforonecycle,three
cycles,and fivecycles)wereanalyzedbytemperatureprogrammed oxidation(TPO)toquantifycokedeposition.TheTPOofnewpsludgebiocharwasalsoconductedforcomparison.TPOwasperformedinathermogravimetricanalyzer(TGA550,TAInstruments, NewCastle,DE)byheating2.5mgsampleata10 C/minto800 C withacontinuous100cc/minair flowanda finaldwelltimeof 10min.
3.1.Impactofp-Sludgebiocharandothercatalystsonmassyields andpy-gascomposition
P-sludgebiocharcatalystsignificantlyincreasedpy-gasyield andreducedbio-oilyieldathightemperatures(Fig.1a).At800 C, p-sludgebiocharresultedinthelowestbio-oilmassfraction (approximately20%)andthehighestpy-gasmassfraction(nearly 40%).Incomparison,bio-oilmassfractionswereapproximately 36%and31%inthe0Band0Scontrols,respectively.Hence,psludgebiocharplayedasignificantroleinfurtherdecomposingbiooilinadditiontotemperature(i.e.downstreamtemperature).At 700 C,bio-oilyieldusingp-sludgebiocharwasstillreducedto30% (wt%ofthetotalproductmass)whilethe0Bcontroltestyielded 36%bio-oil.
Atthelowertemperatureof600 C,productyieldsunderalltest conditionsweresimilar,indicatingthathighertemperaturesare requiredtoachievebiocharcatalyticactivity(Fig.1a).Bio-oilyield didnotsignificantlyvaryasaresultofdifferentdownstreamconditions(ANOVA, p ¼ 0.0752)at600 C,andwasapproximately35%.
Olivineanddolomitecatalystswerealsostudiedat800 Cfor comparison.Dolomitereducedthebio-oilyieldto20.5%,butolivine onlyreducedthebio-oilyieldto27.5%.Devietal.[32]alsofound thatcalcineddolomitewasmorereactivethanolivinewithrespect totardecomposition[32].Thecatalyticeffectofp-sludgebiochar onthebio-oilyield(21.5%at800 C)wascomparabletothatofthe traditionaltarreductioncatalyst,dolomite.
P-sludgebiocharcatalystalteredpy-gascompositionathigh temperatures(700 Cand800 C)(Fig.1b).Hydrogenwasthe predominantgascomponentinthecatalyzedpy-gas.P-sludge biocharincreasedtheH2 fractiontoover40vol%at800 C,which wassimilartoresultswithwoodandmanurebiochars.At600 C, though,theproductyieldsbarelychanged.P-sludgebiocharaltered thepy-gascompositionbyincreasingtheH2 concentrationtoover 35vol%.TheH2 increasemostlikelyresultedfromtarsteam reforming(tar þ H2O / CO,CH4,andH2),steammethane reforming(H2O þ CH4 # 3H2 þ CO;2H2O þ CH4 # 4H2 þ CO2), anddryreforming(CO2 þ CH4 # 2CO þ 2H2).
TheCO2 concentrationwasreducedtolessthan20vol%with biocharcatalystsathightemperatures(700 Cand800 C).TheCO2
Z.Liu,M.Hughes,Y.Tongetal. Energy239(2022)121925
Fig.1. Biocharandmineralcatalystsaffectmassyieldsandshiftpy-gascomposition.Theeffectofbiocharandmineralcatalystsatdifferentpyrolysistemperaturesontheproduct yields(a),andtheeffectonpy-gascomposition(b).Catalyst/biosolidsmassratiowasconstantat0.33andthepy-gascompositionwascalculatedon aninertcarrier-gas-freebasis. 0Bdenotescontrolwithoutcatalystorsandat500 Cdownstream;0Sdenotescontrolwithsandinplaceofcatalyst.Errorbarsrepresentonestandarddeviationoftriplicate experiments;someerrorbarsaresmallandnotvisible.
Z.Liu,M.Hughes,Y.Tongetal. Energy239(2022)121925
decreasewasostensiblyduetotherelativeincreaseofH2 andthe biocharenhanceddryreformingasproposedbypreviousresearchers[33].TheCOconcentrationwasstableat20vol%to25vol %whenusingcatalystathightemperatures.TheCH4,C2H4,C2H6, andC3H8 concentrationswerelower,buttheystillaccountedfora significantpercentageoftheHHVscomparedtoH2 andCO.These gasesaretypicallygeneratedbytarcrackingathighertemperatures [34].
Py-gasyieldincreasedasafunctionofbiocharcatalystloadingat 800 C(Fig.2a).Woodandbiosolidsbiocharswereselectedfor subsequentcomparisonwithp-sludgebiocharsincetheyproduced highpy-gasyield.Atthecatalyst/biosolidsmassratioof0.33,psludgebiocharandtheothertwobiocharcatalystsincreasedthe py-gasyieldtoapproximately37%;theyieldinthe0Bcontroltest wasonly22%.Withtheincreaseofcatalyst/biosolidsmassratioto1, py-gasyieldincreasedfurther.Inparticular,p-sludgebiochar resultedinthehighestpy-gasmassfractionof42%atacatalyst/ biosolidsmassratioof1.Thebio-oilyieldconcomitantlydecreased tothelowestvalueof18%.
Py-gascompositionwasalsoaffectedbycatalystloading (Fig.2b).TheH2 concentrationdidnotchangewhenusingp-sludge biocharbuttheH2 concentrationincreasedwhenusingwoodand biosolidsbiochars.P-sludgebiocharandtheothertwobiochar catalystsincreasedCOconcentrationwhenthecatalyst/biosolids massratioincreasedfrom0.2to1.Asaforementioned,theincrease inCOconcentrationwasmostlikelyduetothesteammethane reforming,dryreforming,andtarreformingprocessesandthe decreaseinCO2 concentrationwasaresultofthebiocharenhanced dryreformingandtherelativeincreaseofothergascomponents [33].
Catalyticactivityofthetestedwood,p-sludge,andbiosolids biocharsdecreasedover fivecycles(Fig.3),butp-sludgebiochar possessedverystablecatalyticcapabilitywithinfourcycles.There wasnoobviousdropinthepy-gasyield,andpy-gasfractionwas constantat39%.Thecorrespondingbio-oilyieldremainedat21%. Afterthe fifthcycle,thepy-gasyielddecreasedto33%,indicating thatthep-sludgebiocharcatalyticactivitydecreased.Thecyclicuse trendofwoodandbiosolidscharsweresimilarthroughfourcycles. However,woodbiochar finallylostallobservablecatalyticactivity after fivecyclesasindicatedbythesimilarpy-gasyieldat800 C0S controltest(29%).Thepy-gasmassfractioncatalyzedbybiosolids biocharwasslightlyhigherthanthatofthe0Scontroltestafterthe fifthuse,implyingalmostnofurthercatalyticeffect.P-sludgebiocharcouldbeusedtoprocessfourtimesasmuchfeedstock comparedtowoodandbiosolidsbiochars.
Asforpy-gascomposition,theH2 concentrationwasrelatively stableusingp-sludgebiochar,rangingfrom42vol%to45vol% (Fig.4).Incontrast,theH2 concentrationdecreasedfrom45vol%to 30vol%after fivecyclesusingwoodandbiosolidschars, approachingtheresultsofthe800 C0Scontroltest.
Sincep-sludgebiocharhadverygoodcatalyticcapabilityand stability,theresultingbio-oilsduringcyclictests(cycles1through
5)wereanalyzed.P-sludgebiocharalteredthebio-oilchemical composition(GC-MSandGC-FIDresultsareshownin Fig.5 and Table2,respectively).Onlyafewoforganicconstituentswere detectedandquantifiedbyGC-FIDwithin fivecycles,including3,5Dimethoxy-4-hydroxybenzeldehyde,ethylbenzene,andstyrene. Additionally,GC-MSanalysisshowedthatmanymajorpeakssuch astoluene,ethylbenzene,styrene,phenol,cresol,indole,and dimethylthiohydantoinweredetectedinthe0Bbio-oilbutwere notdetectedorhadmuchlowerpeakheightinthecatalyzedbio-oil within fivecycles,indicatinglowerconcentrationsoforganicconstituentsaftercatalysis.
(0Bdenotescontrolwithoutcatalystandwithoutsandat500 C downstream.)
Inadditiontothechemicalcompositionchange,theoptical propertieschangedduetop-sludgebiocharcatalyst(FigureS2).In particular,thedarkbrown,lightnon-aqueousphasewas completelyeliminatedbyp-sludgebiocharandonlyanaqueous phasewasproduced.Incontrast,thenon-catalyzedcontrol(0B) producedcondensatecomposedofalightnon-aqueousphaseas wellasanaqueousphasecontainingsolubleorganics,whilethe colorofcatalyzedbio-oilwasclear.Evenafterthreecycletests,the bio-oilcolorwasstillsemitransparent.However,duetothedeactivationofp-sludgebiochar,thedarkphaseformedagainafterfour cycles.Darkbio-oilcolorisassociatedwiththepresenceofunsaturatedhydrocarbons[35].Therefore,theopticalchangesalso indicatedthatp-sludgebiocharresultedinfewerunsaturatedhydrocarbonsinthebio-oilcomparedtothecontroltest0B.
Theusedp-sludgebiochar(cycle1)stillhadaporousstructure, whilethesurfacemorphologybecamemuchlessporousafterthe fifthuse(cycle5)(SEM-EDSimagesareshownin Fig.6),indicating cokedepositedonthesurface.MicrostructureanalysisbyBET verifiedthatthesurfaceareaandporevolumedecreasedfrom 10.21m2/gand0.025cc/g(cycle1)to7.12m2/gand0.018cc/g (cycle5),respectively.Thoughthesurfaceareaandporevolumeof usedp-sludgecharswerelowerthanthoseofnewp-sludgebiochar (52.3m2/gand0.033cc/g),thecatalyticabilitywasnotaffected substantiallywithinfourcycles(Fig.3).
Thestablecatalyticperformanceofp-sludgebiocharwasmost likelyduetotheexposedCaonthep-sludgebiocharduringcyclic use.Lime(CaO)iswidelyusedinthepulpandpaperindustryinthe recausticizingcycle[36].Thechemically-formedCaCO3 isalsoused asa fillertoimprovepaperquality[37].Therefore,thesettledpaper millsludgeduringpapermillwastewatertreatmentcontainsCaCO3 [38].XRDanalysisconfirmedtherawp-sludgeandthenewpsludgebiocharusedinthisstudyweremainlycomposedofCaCO3 (XRDimagesareshownin Fig.7).Withtheincreasinguseofpsludgebiochar(i.e.cycle1tocycle5),theCaOpeaksbecamemore predominant,indicatingsomeCaCO3 wascontinuouslydecomposedat800 Cineachcycle.SEM-EDSanalysisshowedthatCa wasstilldetectableafter fivecyclesonthep-sludgebiocharsurface. ThesurfacewithexposedCaostensiblyprovidedcatalyticsitesfor pyrolysisvaporupgrading.
CaOhasbeenextensivelystudiedontardecompositionandis capableofupgradingpyrolysisvaporbydestroyinghighmolecular weighthydrocarbons[39,40].Moreover,biocharthatcontainsCa provedtobeveryeffectiveinreducingbiosolids-derivedbio-oilin ourpreviouswork[23].SincesurfaceCawasnotcompletely coveredbycoke,p-sludgebiocharretainedsomecatalyticactivity afterthe fifthuse.
TheTG(thermogravimetry)andDTG(differential
Z.Liu,M.Hughes,Y.Tongetal. Energy239(2022)121925
Fig.2. Biocharcatalystloadingimpactsmassyieldsandpy-gascompositionat800 C.Theeffectofbiocharcatalystloadingsontheproductyields(a),andtheeffectonthepy-gas composition(b).0Bdenoteswithoutcatalystorsandat500 Cdownstream;0Sdenoteswithsandinplaceofcatalyst.0.2,0.33,and1denotecatalysttofeedstockmassratios.The py-gascompositionwascalculatedonaninert-carrier-gas-freebasis.Errorbarsrepresentonestandarddeviationoftriplicateexperiments;someerrorbarsaresmallandnot visible.
Z.Liu,M.Hughes,Y.Tongetal. Energy239(2022)121925
Fig.3. Theeffectofbiocharcatalystcyclenumberonproductyields(bio-oilandpy-gas)at800 C.0Sdenotescontrolwithsandinplaceofcatalyst.Errorbarsrepresentone standarddeviationoftriplicateexperiments;someerrorbarsaresmallandnotvisible.
Fig.4. Theeffectofbiocharcatalystcyclenumberonthepy-gascompositionat800 C.0Sdenotescontrolwithsandinplaceofcatalyst.Errorbarsrepresentonestandarddeviation oftriplicateexperiments;someerrorbarsaresmallandnotvisible.
Z.Liu,M.Hughes,Y.Tongetal.
Fig.5. GC-MSofbio-oilscatalyzedbyp-sludgebiocharfrom800 Ccyclictests.(QualitativeanalysisbasedonGC-MSlibrary.Catalyst/biosolidsmassratioisconstantat0.33.0B denotescontrolwithoutcatalystorsandat500 C.)
Z.Liu,M.Hughes,Y.Tongetal. Energy239(2022)121925
Table2 Bio-oilcompoundsquantifiedbyGC-FID(basedonselectedstandardcomponents).
Compounds(wt%,rawbasis)800 Cnon-catalytic (0B) 800 Cp-sludgecatalyzed(Cycle 1) 800 Cp-sludgecatalyzed(Cycle 3) 800 Cp-sludgecatalyzed(Cycle 5)
Aldehyde
Acetaldehyde0.03NDa NDND m-Tolualdehyde0.01NDNDND 3,5-Dimethoxy-4hydroxybenzeldehyde 0.010.270.270.28
Coniferaldehyde0.01NDNDND Vanillin0.01NDNDND
Ketone 40 -Hydroxy-30 -methoxyacetophenone0.02NDNDND 3,4-Dimethoxyacetophenone0.77NDNDND Guaiacylacetone0.05NDNDND 20 ,40 -Dimethoxyacetophenone0.44NDNDND 30 ,50 -Dimethoxy-40 hydroxyacetophenone 0.72NDNDND
Phenol
Phenol0.06NDNDND 2-Ethylphenol0.41NDNDND 3-Ethylphenol0.08NDNDND 2,5-Dimethylphenol0.16NDNDND 2,6-Dimethylphenol0.04NDNDND 3,4-Dimethylphenol0.41NDNDND 2,6-Dimethoxyphenol0.07NDNDND 4-Methyl-2,6-dimethoxyphenol0.01NDNDND o-Cresol0.11NDNDND m,p-Cresol0.11NDNDND 3-Methoxy-5-methylphenol0.02NDNDND Guaiacol
4-Ethyl-2-methoxyphenol0.02NDNDND 2-Methoxy-4-propylphenol0.35NDNDND 2-Methoxy-4-methylphenol0.04NDNDND 2-Methoxy-4-vinylphenol0.02NDNDND Ether
Anisole0.01NDNDND 2-Methylanisole0.44NDNDND 3-Methylanisole0.04NDNDND 4-Vinylanisole1.05NDNDND 1,2,3-Trimethoxybenzene0.02NDNDND 1,2,4-Trimethoxybenzene0.09NDNDND
Alcohol 1,2-Benzenedimethanol2.51NDNDND 2,5-Dimethoxybenzylalcohol0.03NDNDND OtherAromatics
Ethylbenzene0.040.260.230.27 p-/m-Xylenecomposite0.02NDNDND o-Xylene0.04NDNDND Styrene0.370.060.050.06 4-Ethoxystyrene0.99NDNDND 2,3-Dimethoxytoluene0.33NDNDND 3,4-Dimethoxytoluene0.02NDNDND a ND:NotDetected.
thermogravimetry)plotsofusedp-sludgebiochars(TGandDTG figuresareshownin Fig.8)havethreecharacteristiccombustion peaksstartingat375 C.Thesepeaksarelocatedbetween375 C and425 C,between425 Cand550 C,andbetween550 Cand 675 C,whichwereattributedtothecombustionsofcondensed lighthydrocarbons(e.g.aliphaticcompounds),coke(e.g.monoatomiccarbon,aromaticcompounds),andtheremainingcarbonaceousmatrix,respectively[41 43].Asforthenewp-sludge biochar,itsDTGcurveshowsasmall flatpeakbetween425 Cand 550 C,whichcouldbeduetoaverysmallamountofcokeformed onthep-sludgebiocharsurfaceduringbiocharmaking.Thenewpsludgebiocharhadthelargestpeakofcarbonaceousmatrix
combustionduetotheleastcokedeposition.
Withtheincreaseofp-sludgebiocharusecycles,theweightloss between425 Cand550 C(i.e.thecokecombustion)increased. Accordingly,smallerweightlossoccurredduringthecarbonaceous matrixcombustion.Theseresultsdemonstratedthatcokebuiltup duringcyclicuses,whichwasinaccordancewiththeSEM-EDS analysis.Moreover,becausethecatalyticactivitydecreased,the weightlossduringcokecombustion(between425 Cand550 C) increasedmuchlessafter fivecycleswhencomparedtocycle1and cycle3.
Z.Liu,M.Hughes,Y.Tongetal. Energy239(2022)121925
Fig.7. XRDofnewandusedp-sludgebiocharsandrawp-sludge(BecausetheCO2
partialpressureduringcatalystpreheatingandbiosolidspyrolysiswaslowerthantheCO2 equilibriumpressure(equilibriumwithCaCO3)of24kPaat800 C,calcinationhappenedduringrepeateduse.).
Z.Liu,M.Hughes,Y.Tongetal. Energy239(2022)121925
Fig.8. TPO-TGandTPO-DTGofnewandusedp-sludgebiochars(Morecokedepositedonthebiocharsurfaceafterrepeateduse.).
Fig.9. Theeffectofbiocharcatalystcyclenumberonthepy-gasandbio-oilenergydistributionat800
3.4.Impactofcatalystcyclenumbersonpy-gasandbio-oilenergy yields
Catalyticpyrolysisusingwood,p-sludge,andbiosolidsbiochars reducedbio-oilenergycontentcomparedtothebio-oilHHVinthe 0Btest(HHV figureisshowninSI, FigureS3).Thebio-oilHHV decreasewasduetotheaforementioneddecompositionofheavy hydrocarbonsandtheformationofwaterduringcatalysis[44].The bio-oilHHVslightlyincreasedafter fivecyclesofusingp-sludge
Cdownstream.0Sdenotes
biochar(from2300kJ/kgto2500kJ/kg),indicatingthestablecatalyticperformanceofp-sludgebiochar.Incontrast,duetothe graduallossofthecatalyticactivityofbiosolidsbiochar,thebio-oil HHVincreasedfrom2200kJ/kgto4300kJ/kgafter fivecycles.
Sincep-sludgebiocharwasmorestablecatalytically,thepy-gas HHVjustshowedanobviousincreaseafterthe fifthcycleofusing p-sludgebiochar.Whenwoodandbiosolidsbiocharswereusedfor threecycles,thepy-gasHHVincreasedgreatlybecausetheseused catalystsdecomposedlesshydrocarbonsresultinginlowerH2
*
Z.Liu,M.Hughes,Y.Tongetal. Energy239(2022)121925
Table3 Metalcompositionofnewbiocharcatalysts(wt%drybasis).
Element800 CBiocharCatalyst
Ca
K
Na
Ni
Cu
Zn ND0.01ND0.040.060.19
Mn NDND0.020.08ND0.36
Fe 0.110.020.01
Cr NDNDND0.03ND0.06
Ti 0.02NDND0.330.270.68
Zr NDNDND0.01ND0.06
concentrationrelativetothe firstcycle(Fig.4).H2 haslowvolumetricenergycontent,therefore,lowerH2 concentrationledto higherpy-gasHHV.Inthemeantime,theconcentrationsofhigh unitenergycomponentssuchasCH4 andC2H4 increased,leadingto theincreaseofpy-gasHHV.
Thepy-gasenergyyieldsperbiosolidspyrolyzeddecreasedas thecatalystcyclenumberincreased(Fig.9).Thoughpy-gasHHVs increasedafterthe fifthcycleforeachbiocharcatalyst,py-gas productionsdecreasedgreatlyatthesametime(Fig.3),leading tolowerpy-gasenergyoutputscomparedtocycle1.Specifically, thepy-gasenergywasonlyreducedby8%(from8400kJto7700kJ) fromcycle1tocycle5whenusingp-sludgebiochar,whilethepygasenergyreductionpercentageusingwoodandbiosolidschars were17%and19%,respectively.Meanwhile,thebio-oilenergy increasedgradually.Withthecatalystdeactivationduringcyclic uses,thepy-gasenergyyields finallyapproached0Spy-gasenergy, implyingthatonlythecatalytictemperatureandsecondaryreactionscausedtheenergyshifttopy-gas.
Inparticular,atcycle1,newp-sludgebiocharproducedapy-gas withenergyover8400kJ(almostthreetimeshigherthan0Bpy-gas energy).Thesignificantshiftfrombio-oiltopy-gasenergymaybe usefulforwaterresourcerecoveryfacilitiesthatalreadycombust anaerobicdigesterbiogasforincreasedon-siteenergyrecoveryby blendingbiogasandpy-gas.
Multiplepropertiesofbiocharcatalystscouldinfluencepyrolysisproductupgrading.First,somebiocharscontainmetalssuchas Mg,Ca,andFe.Thesemetalscanplayakeyroleincatalytic destructionofhighmolecularweighthydrocarbons(e.g.tar) [23,29,45,46].Forexample,p-sludgebiocharcontains39%Caand
Table4
800
Stover
biosolidsbiocharhas11%Fecontent(Table3).Thus,thegoodcatalyticperformanceofcertainbiocharssuchasp-sludgeandbiosolidsbiocharswasmostlikelyduetothespecificmetalspecies. However,ifthecatalyticmetalsarefullycoveredbycoke,thenthe biocharcatalyticeffectwilldecreaseorstop[47].
Second,pyrolysisvaporconstituentscaneasilyadsorbonto biocharandmetalsurfacesandthendissociatetoreactiveradicals suchasaromaticringfragments[48 51].Biocharitselfalsocontainsfreeradicalsviathedecompositionoforganicmatterduring pyrolysis[52,53].Therefore,free-radicalreactionsarefavoredunderhightemperatures,convertingvaporconstituentstosmaller moleculesandlighthydrocarbongases[48,54 57].Forexample, thoughwoodbiocharhasverylowmetalcontentwithsimilar microstructuretomanurebiochar(Table4),thecatalyticeffectof woodbiocharwasalwaysbetterthanmanurebiocharathigh temperatures(Fig.1).Thecatalyticperformanceofwoodbiochar wasevenclosetothatofbiosolidsbiochar(Fig.1).Theseresults indicatethatsomespecificradicalsinwoodbiocharcouldhave playedaroleinupgradingpyrolysisvapor.Theradicaltypeson biocharandradicalreactionsoverbiocharsurfacerequireadetailed investigationinfuturework.
Third,theporouscarbonstructureofbiocharactsasthesubstratesupportandactivesitesforhighlydispersedmetalsand radicalabsorptionenhancedreactions.Hence,biocharsurfacearea isanothercrucialfactortodeterminethecatalyticperformance. Poorbiocharmicrostructurereducescatalyticperformance.For instance,stoverbiocharandDDGSbiocharhaveverylowsurface areacomparedtootherbiochars(microstructuralanalysisisshown in Table4),sotheydidnotincreasepy-gasyield(Fig.1a).TheSEM imagesofstudiednewbiocharsareshownin Fig.10.Corresponding tothesurfacearea,themorphologyofnewp-sludgewasvery porous.Thismicrostructureprovidedenoughsitesforthecatalytic metalofCa.
Thisisthe firstreportthatp-sludgebiocharwasamoreeffective catalystcomparedtoothercarbonaceouswastebiocharstoincreasepy-gasyield(e.g.p-sludgebiocharresultedinthehighest py-gasmassfractionofnearly40%at800 C).Inaddition,the productionoflightnon-aqueousphasecondensatewaseliminated undersomecatalyticconditions(e.g.p-sludgebiocharresultedin thelowestbio-oilmassfractionofapproximately20%at800 C).Psludgebiocharresultedinthehighestpy-gasyieldandlowestbiooilyield,lowercatalystloadingrequirementsandlongerreuse times,andupgradedpy-gasandbio-oilcompositions.P-sludge biocharincreasedthepy-gasyieldbynearlytwo-foldcomparedto thecontroltest.Thecatalyticactivityofp-sludgebiocharwasstable andproducedthegreatestshiftinenergyfrombio-oiltopy-gas duringcyclicuses(i.e.thepy-gasenergywasonlyreducedby8%,
Z.Liu,M.Hughes,Y.Tongetal.
from8400kJto7700kJ,fromreusecycle1tocycle5whenusingpsludgebiochar).P-sludge-derivedbiocharisacost-effectivecatalysttoimproveenergyrecoveryinthewastewaterindustry.The usedp-sludgebiocharcanbeusedasasoilamendment.However, duetothechangeinmicrostructureafterbeingreusedseveral times,thebenefitsofusedp-sludgebiocharforagriculturalapplicationneedstobefurtherinvestigated.
Theauthorsdeclarethattheyhavenoknowncompeting
appearedtoinfluencetheworkreportedinthispaper.
LaboratoryassistancefromJohnKissel,MarkWendtland,Hui Liu,andErikAndersonisgreatlyappreciated.Wearealsograteful toDr.RobertBrownandDr.PatrickJohnstonoftheIowaState UniversityBioeconomyInstituteforprovidingGC-MSandGC-FID bio-oilanalyses.TheauthorsacknowledgetheuseofthethermogravimetricanalyzerfromMarquetteUniversity,fundedbythe
Z.Liu,M.Hughes,Y.Tongetal. Energy239(2022)121925
GHRFoundation.ThesupportforHugoCortesLopezfromthe CaliforniaEnergyResearchCenter(CERC),ChevronandtheInterdisciplinaryEnergyResearchProgramisalsoappreciated.
ZhongzheLiu: Conceptualization,Methodology,Writing originaldraft. MatthewHughes: Investigation. YiranTong: Formal analysis. JizhiZhou: Formalanalysis. WilliamKreutter: Formal analysis. HugoCortesLopez: Investigation. SimchaSinger: Formal analysis. DanielZitomer: Writing review & editing. Patrick McNamara: Supervision,Writing review & editing.
Supplementarydatatothisarticlecanbefoundonlineat https://doi.org/10.1016/j.energy.2021.121925
[1]LiuZ,NorbeckJM,RajuASK,KimS,ParkCS.Syntheticnaturalgasproduction bysorptionenhancedsteamhydrogasificationbasedprocessesforimproving CH4yieldandmitigatingCO2emissions.EnergyConversManag2016;126: 256 65. https://doi.org/10.1016/j.enconman.2016.08.008
[2]LiuZ,QianG,SunY,XuR,ZhouJ,XuY.Speciationevolutionsofheavymetals duringthesewagesludgeincinerationinalaboratoryscaleincinerator.EnergyFuel2010;24:2470 8. https://doi.org/10.1021/ef901060u
[3]McKendryP.Energyproductionfrombiomass(part2):conversiontechnologies.BioresourTechnol2002;83:47 54. https://doi.org/10.1016/S09608524(01)00119-5
[4]McNamaraP,KochJ,ZitomerD.Pyrolysisofwastewaterbiosolids:lab-scale experimentsandmodeling.ProcWaterEnvironFed2014:1 14. https:// doi.org/10.2175/193864714816196655
[5]PatrickJMcNamara,KochJD,LiuZ,ZitomerDH.Pyrolysisofdriedwastewater biosolidscanBeenergypositive.WaterEnvironRes2016;88:804 10. https:// doi.org/10.2175/106143016X14609975747441
[6]BridleTR,PritchardD.Energyandnutrientrecoveryfromsewagesludgevia pyrolysis.WaterSciTechnol2004;50:169 75. https://doi.org/10.2166/ wst.2004.0562
[7] LehtoJ,OasmaaA,SolantaustaY.Fueloilqualityandcombustionoffastpyrolysisbio-oils.VTTTechnol;2013
[8]OasmaaA,CzernikS.Fueloilqualityofbiomasspyrolysisoils-stateoftheart fortheendusers.EnergyFuel1999;13:914 21. https://doi.org/10.1021/ ef980272b
[9] SadakaS,BoatengA.Pyrolysisandbio-oil.2009
[10]BaratieriM,BaggioP,BosioB,GrigianteM,LongoGA.Theuseofbiomass syngasinICenginesandCCGTplants:acomparativeanalysis.ApplThermEng 2009;29:3309 18. https://doi.org/10.1016/j.applthermaleng.2009.05.003
[11] LuQ,HeZ,StoffellaP.LandapplicationofbiosolidsintheUSA:areview.Appl EnvironSoilSci2012
[12]McNamaraPJ,KochJD,LiuZ,ZitomerDH.Pyrolysisofdriedwastewater biosolidscanbeenergypositive.WaterEnvironRes2016;88. https://doi.org/ 10.2175/106143016X14609975747441
[13]CareyDE,McNamaraPJ,ZitomerDH.Biocharfrompyrolysisofbiosolidsfor nutrientadsorptionandTurfgrasscultivation.WaterEnvironRes2015;87: 2098 106. https://doi.org/10.2175/106143015X14362865227391
[14]HoffmanTC,ZitomerDH,McNamaraPJ.Pyrolysisofwastewaterbiosolids significantlyreducesestrogenicity.JHazardMater2016. https://doi.org/ 10.1016/j.jhazmat.2016.05.088
[15]KimbellLK,KappellAD,McNamaraPJ.Effectofpyrolysisontheremovalof antibioticresistancegenesandclassIintegronsfrommunicipalwastewater biosolids.EnvironSciWaterResTechnol2018. https://doi.org/10.1039/ C8EW00141C
[16]RossJJ,ZitomerDH,MillerTR,WeirichCA,McNamaraPJ.Emerginginvestigatorsseries:pyrolysisremovescommonmicroconstituentstriclocarban, triclosan,andnonylphenolfrombiosolids.EnvironSciWaterResTechnol 2016;2:282 9. https://doi.org/10.1039/C5EW00229J
[17]LiuZ,MayerBK,VenkiteshwaranK,SeyediS,RajuASK,ZitomerD, McNamaraPJ.Thestateoftechnologiesandresearchforenergyrecoveryfrom municipalwastewatersludgeandbiosolids.CurrOpinEnvironSciHeal2020. https://doi.org/10.1016/j.coesh.2019.12.004
[18]FontsI,GeaG,AzuaraM, AbregoJ,ArauzoJ.Sewagesludgepyrolysisforliquid
production:areview.RenewSustainEnergyRev2012;16:2781 805. https:// doi.org/10.1016/j.rser.2012.02.070
[19] VreugdenhilB,ZwartR,NeeftJ.Tarformationinpyrolysisandgasification. 2009
[20]AbuEl-RubZ,BramerEA,BremG.Experimentalcomparisonofbiomasschars withothercatalystsfortarreduction.Fuel2008;87:2243 52. https://doi.org/ 10.1016/j.fuel.2008.01.004
[21] PütünE,UzunB,PütünA.Rapidpyrolysisofoliveresidue.2.Effectofcatalytic upgradingofpyrolysisvaporsinatwo-stage fixed-bedreactor.EnergyFuel 2009
[22]StefanidisSD,KalogiannisKG,IliopoulouEF,LappasAA,PilavachiPA.In-situ upgradingofbiomasspyrolysisvapors:catalystscreeningona fixedbed reactor.BioresourTechnol2011;102:8261 7. https://doi.org/10.1016/ j.biortech.2011.06.032
[23]LiuZ,McNamaraP,ZitomerD.Autocatalyticpyrolysisofwastewaterbiosolids forproductupgrading.EnvironSciTechnol2017;51:9808 16. https://doi.org/ 10.1021/acs.est.7b02913
[24]LiuZ,SingerS,TongY,KimbellL,AndersonE,HughesM,ZitomerD, McNamaraP.Characteristicsandapplicationsofbiocharsderivedfrom wastewatersolids.RenewSustainEnergyRev2018;90:650 64. https:// doi.org/10.1016/J.RSER.2018.02.040
[25] BirdMichelleTJ.Wastestreamreductionandreuseinthepulpandpaper sector.2008
[26]IgalavithanaAD,ChoiSW,ShangJ,HanifA,DissanayakePD,TsangDCW, KwonJH,LeeKB,OkYS.Carbondioxidecaptureinbiocharproducedfrom pinesawdustandpapermillsludge:effectofporousstructureandsurface chemistry.SciTotalEnviron2020;739:139845. https://doi.org/10.1016/ J.SCITOTENV.2020.139845
[27]WangZ,MiaoR,NingP,HeL,GuanQ.Fromwastestofunctions:apapermill sludge-basedcalcium-containingporousbiocharadsorbentforphosphorus removal.JColloidInterfaceSci2021;593:434 46. https://doi.org/10.1016/ J.JCIS.2021.02.118.
[28]XuZ,LinYunqin,LinYuejin,YangD,ZhengH.Adsorptionbehaviorsofpaper millsludgebiochartoremoveCu,Znandasinwastewater.EnvironTechnol Innov2021;23:101616. https://doi.org/10.1016/J.ETI.2021.101616
[29] El-RubZA,BramerE,BremG.Reviewofcatalystsfortareliminationin biomassgasificationprocesses.IndEng2004
[30]SunQ,YuS,WangF,WangJ.Decompositionandgasificationofpyrolysis volatilesfrompinewoodthroughabedofhotchar.Fuel2011;90:1041 8. https://doi.org/10.1016/j.fuel.2010.12.015
[31]RoverMR,HallPH,JohnstonPA,SmithRG,BrownRC.Stabilizationofbio-oils usinglowtemperature,lowpressurehydrogenation.Fuel2015;153:224 30. https://doi.org/10.1016/j.fuel.2015.02.054
[32]DeviL,PtasinskiKJ,JanssenFJJG,vanPaasenSVB,BergmanPCA,KielJHA. Catalyticdecompositionofbiomasstars:useofdolomiteanduntreated olivine.RenewEnergy2005;30:565 87. https://doi.org/10.1016/ j.renene.2004.07.014
[33]MuradovN,FidalgoB,GujarAC,GarceauN,T-RaissiA.ProductionandcharacterizationofLemnaminorbio-charanditscatalyticapplicationforbiogas reforming.BiomassBioenergy2012;42:123 31. https://doi.org/10.1016/ j.biombioe.2012.03.003
[34]NamiokaT,SonYIl,SatoM,YoshikawaK.Practicalmethodofgravimetrictar analysisthattakesintoaccountathermalcrackingreactionscheme.Energy Fuel2009;23:6156 62. https://doi.org/10.1021/ef9006214
[35] SappokM,WagelsD.Methodforstabilizingheatingoilordieseloil,particularlyheatingoilordieseloilfromthedepolymerizationofhydrocarboncontainingresidues,orpyrolysisoil.USPat2013;8(394):264
[36] TechnicalAssociationofthePulpandPaperIndustry(U.S.),D.R..TAPPIKraft recoveryCourse.St.Petersburg,Florida,USA:TAPPIKraftRecoveryCourse, 2007.TAPPIPress,RedHook;2007.
[37]PaperPulpandPCC.URL http://www.carmeusena.com/markets/paper-pulpand-pcc (accessed1.10.18).
[38]KuokkanenT,NurmesniemiH,PoykioR,KujalaK,KaakinenJ,KuokkanenM. Chemicalandleachingpropertiesofpapermillsludge.ChemSpeciatBioavailab2008;20:111 22. https://doi.org/10.3184/095422908X324480
[39]GustaE,DalaiAK,UddinMA,SasaokaE.Catalyticdecompositionofbiomass tarswithdolomites.EnergyFuel2009;23:2264 72. https://doi.org/10.1021/ ef8009958
[40]SimellPA,LeppalahtiJK,BredenbergJB.Catalyticpurificationoftarryfuelgas withcarbonaterocksandferrousmaterials.Fuel1992;71:211 8. https:// doi.org/10.1016/0016-2361(92)90011-C
[41]Cordero-LanzacT,HitaI,VelosoA,ArandesJM,Rodríguez-MirasolJ,BilbaoJ, CorderoT,CastanoP.Characterizationandcontrolledcombustionofcarbonaceousdeactivatingspeciesdepositedonanactivatedcarbon-basedcatalyst. ChemEngJ2017;327:454 64. https://doi.org/10.1016/j.cej.2017.06.077
[42]IbanezM,ValleB,BilbaoJ,GayuboAG,CastanoP.EffectofoperatingconditionsonthecokenatureandHZSM-5catalystsdeactivationinthetransformationofcrudebio-oilintohydrocarbons.CatalToday2012;195:106 13.
Z.Liu,M.Hughes,Y.Tongetal. Energy239(2022)121925
https://doi.org/10.1016/j.cattod.2012.04.030
[43]WuC,WilliamsPT.Hydrogenproductionbysteamgasificationofpolypropylenewithvariousnickelcatalysts.ApplCatalBEnviron2009;87: 152 61. https://doi.org/10.1016/j.apcatb.2008.09.003
[44]RenS,LeiH,WangL,BuQ,ChenS,WuJ.Hydrocarbonandhydrogen-rich syngasproductionbybiomasscatalyticpyrolysisandbio-oilupgradingover biocharcatalysts.RSCAdv2014;4:10731 7. https://doi.org/10.1039/ c4ra00122b
[45] HayashiJ,IwatsukiM,MorishitaK,TsutsumiA.Rolesofinherentmetallic speciesinsecondaryreactionsoftarandcharduringrapidpyrolysisofbrown coalsinadrop-tubereactor.2002[Fuel]
[46] NordgreenT,LiliedahlT,SjostromK.Metallicironasatarbreakdowncatalyst relatedtoatmospheric, fluidisedbedgasificationofbiomass.2006[Fuel]
[47]DiStasiC,AlviraD,GrecoG,GonzalezB,ManyaJJ.Physicallyactivatedwheat straw-derivedbiocharforbiomasspyrolysisvaporsupgradingwithhigh resistanceagainstcokedeactivation.Fuel2019;255:115807. https://doi.org/ 10.1016/j.fuel.2019.115807
[48] MinZ,YimsiriP,AsadullahM,ZhangS,LiC.Catalyticreformingoftarduring gasification.PartII.Charasacatalystorasacatalystsupportfortarreforming. 2011[Fuel]
[49]ShenY,YoshikawaK.Recentprogressesincatalytictareliminationduring biomassgasificationorpyrolysis-areview.RenewSustainEnergyRev
2013;21:371 92. https://doi.org/10.1016/j.rser.2012.12.062
[50]TaralasG,VassilatosV,SjostromK,DelgadoJ.Thermalandcatalyticcracking ofn-HeptaneinpresenceofCaO,MgOandCalcinedDolomites.CanJChem Eng1991;69:1413 9. https://doi.org/10.1002/cjce.5450690626
[51] UddinM,TsudaH,WuS,SasaokaE.Catalyticdecompositionofbiomasstars withironoxidecatalysts.2008[Fuel]
[52] AmonetteJ,JosephS.Characteristicsofbiochar:microchemicalproperties. BiocharEnvironManag2009
[53]LiaoS,PanB,LiH,ZhangD,XingB.Detectingfreeradicalsinbiocharsand determiningtheirabilitytoinhibitthegerminationandgrowthofcorn,wheat andriceseedlings.EnvironSciTechnol2014;48:8581 7. https://doi.org/ 10.1021/es404250a
[54] LiC.Importanceofvolatile charinteractionsduringthepyrolysisandgasificationoflow-rankfuels areview.2013[Fuel]
[55] LiY,GuoL,ZhangX,JinH,LuY.Hydrogenproductionfromcoalgasificationin supercriticalwaterwithacontinuous flowingsystem.IntJHydrog.2010 [56]WestonPM,Sharifi V,SwithenbankJ.Destructionoftarinanovelcoandatar crackingsystem.EnergyFuel2014;28:1059 65. https://doi.org/10.1021/ ef401705g
[57] ZhangS,AsadullahM,DongL,TayH,LiC.Anadvancedbiomassgasification technologywithintegratedcatalytichotgascleaning.PartII:tarreforming usingcharasacatalystorasacatalystsupport.2013[Fuel]
Negotiation may conjure up images of trade delegations, hostage situations and large corporate mergers. However, the truth is that negotiation is also all around us, i t is a fundamental part of life and business. Knowing the basics will stand you in good stead, be it deciding your holiday plans or negotiating your salary. If you stick to these ten tips you will find that both you and the other side will walk away feeling like you’ve got a fair deal.
https://www.brightnetwork.co.uk/graduate-career-advice/key-career-skills/how-stand-out-graduate/top-10-tips-how-negotiate/
The Paper Industry Technical Association (PITA) is an independent organisation which operates for the general benefit of its members –both individual and corporate –dedicated to promoting and improving the technical and scientific knowledge of those working in the UK pulp and paper industry. Formed in 1960, it serves the Industry, both manufacturers and suppliers, by providing a forum for members to meet and network; it organises visits, conferences and training seminars that cover all aspects of papermaking science. It also publishes the prestigiousjournal Paper TechnologyInternational® and the PITA Annual Review, both sent free to members, and a range of other technical publications which include conference proceedings and the acclaimed Essential Guide to Aqueous Coating.
Good negotiation creates a deal that both parties feel good about. Win-win, not out to win. There have been many studies showing the benefits of a win win attitude, including game theory. Perhaps more importantly, your reputation will be far greater if you negotiate fairly and with respect.
The key to successful negotiation is truly understanding the other party's wants, needs and motivations. You can only do this by listening and drawing out information from what they tell you. The adage that 2/3rds should be spent listening and the other 1/3 speaking is a good one to follow.
Coinage is something that means a lot to the other party and not that much to you. Finding out the other party’s motivation can allow you to keep coinage for the latter part of negotiation. You may have even had this happen to you, for example salesmen “throwing in” a free warranty -it is most likely of a marginal cost to the salesman but may give you the piece of mind that you can return it if anything goes wrong.
Fail to prepare and prepare to fail. Co-ordinated negotiation i s key, especially if you’re in a team then you all need to make sure that you are on the same page. If you are by yourself you need to be clear on what your alternatives are. In trade negotiation this is called your BATNA, short for "best alternative to negotiated agreement” or put simply; what can you do if it doesn’t work out.
Surroundings and climate make a difference to negotiation. Choose the venue carefully as it will reflect how the negotiation may play out. For example, cold and informal boardrooms may inspire hostility, whilst a more informal setting may encourage warmth and agreement. Think of Camp David used by the US for the Israel and Palestine negotiations compared to the intimidating large boardroom’s of a major multinational.
At the beginning of a formal negotiation you should set out the terms of engagement. For example, everyone should agree to have a productive and respectful negotiation. This is useful for clarity but also allows you to anchor back if anyone deviates from the point. For example, if one person is becoming obtuse and playing the tough guy, you can remind them that they agreed to be respectful.
Bargaining power comes in many forms and you may often have more of it that you think. It is key to understand where your strengths and weaknesses lie. Bargaining power is not just the obvious metrics such as market power, but can be subtler, for example relationship power and time (for example deadlines).
Some negotiations may hit a brick wall. It may be a good idea to take a break and regroup, or to be open and discuss the impasse frankly. If all else fails, then perhaps the deal cannot be done. Some deals are not meant to be, new information may come to light, which changes the whole equation –there is nothing to be ashamed of.
Negotiation can be tense, drawn out and stressful. Learn how to turn it into an enjoyable experience and everyone will be thankful.
If there is any tip to take home it is win-win. Negotiating is about getting a good deal; aiming to destroy the other party will do you no favours.The long-term reputation cost may be very damaging.
Green and Sustainable Chemistry, 2022, 12, 9-27 https://www.scirp.org/journal/gsc ISSN Online: 2160-696X ISSN Print: 2160-6951
1Department of Polymer and Surface Engineering, Institute of Chemical Technology, Mumbai, India
2Department of Microbiology, Savitribai Phule Pune University, Pune, India
H o w t o c
p ap er : Gadhave, R.V., Gadhave, C.R. and Dhawale, P.V. (2022) Plastic-Free Bioactive Paper Coatings, Way to Next-Generation Sustainable Paper Packaging Application: A Review. Green and SustainableChemistry , 1 12, 9-27. https://doi.org/10.4236/gsc.2022.122002
R e
d : January 17, 2022
: March 7, 2022
: March 10, 2022
Copyright © 2022 by author(s) and Scientific Research Publishing Inc.
is licensed under the Creative Commons Attribution International License (CC BY 4.0).
Hydrocarbon-derived polymers have been utilized in various packaging applications, such as pouches, films, foamed containers, rigid containers, and multiple components for medical, food, and other uses. However, mounting environmental considerations increased knowledge of the harmful consequences of greenhouse gas emissions, landfills, and disposal difficulties. Rising oil prices are forcing researchers and businesses to produce environmentally friendly packaging. These new sustainability requirements are particularly suited to biomass-based products, instead of petroleum sources; sourced from biomass entities. More functional and performance-oriented packaging is necessary despite the widespread usage of bio-based materials like paper. As a result, the transition to eco-friendly packaging will necessitate the improvement of existing bio-derived packaging and the development of new bio-derived materials like biopolymer paper coatings. The goal of this brief study was to give a synopsis of the present status of bio-derived packaging and an insight into ongoing and prospective developments in sustainable nextgeneration paper coatings for the packaging industry.
Biopolymers, Paper, Coatings, Starch, Itaconic Acid
Because it is compostable and fully safe for the environment, paper is often utilized in packaging. Paper is a low-cost, renewable material that can be used in place of plastics in situations where short-term use is preferred. Because of their fibrous structure, paper substrates are porous [1]. Furthermore, the cellulose
backbone chain contains hydroxyl groups, making the paper very hydrophilic [2]. Because hydrophilic hydroxyl groups and porous structures absorb water and grease substances, uncoated paper is less valuable when plastic replacement is required [3] [4]. However, there is a scarcity of hydrophobic and oleophobic developments in the paper packaging business. As a result, there is an urgent need to develop strategies for enhancing paper’s grease and water resistance while managing to stay recyclable and cost-effective [3] [5] [6]. High surface energy coatings also improved oil resistance due to a larger quantity of polar components, resulting in stronger grease resistance. After applying the coating, the mechanical characteristics of the paper improved as well. These naturally generated compounds provide an alternative to the fluoride-containing materials currently utilized in the market to increase paper wettability [7]. To address the aforementioned concerns, the coating industry today uses hydrocarbon-based polymers such as polyvinylidene chloride, low-density polyethylene, ethylene acrylic acid, and others to produce oil- and water-resistance paper via surface coating [8] Due to their low recyclability in current practices, alternatives to present procedures are in great demand [9]. Other extensively used coating techniques include fluorinated compounds, which negatively impact human health and aquatic habitats [10].
Given that, food and packaging containers account for around 45% of trash shipped to landfills, with papers and paper products accounting for the vast majority, these chemicals voice issues about microplastic contamination [11]. As health and environmental concerns regarding wax-based, fluorochemical-based, and extrusion-based paper coatings have grown, so has an interest in bioresorbable and repulpable substitutes for generating water- and oil-repellent coatings. This work describes a plastic-free, fluorine-free, and cost-effective grease and water-resistant paper coating process that uses novel chitosan-graft-polydimethylsiloxane copolymer and corn starch blends [12]. Scientists are presently focused on bio-based substances like chitosan, poly [lactic acid], wax-based, and protein-based (e.g., whey protein, and casein) and endow paper with specific properties like improved one’s liquid-repugnancy or gas-barrier performances. However, because of several complexities associated with modifying these materials while preserving water impermeability features, these attempts have had limited success, particularly in controlling water blocking capabilities and the high price of the alternatives available [9]
Global plastic manufacture has grown quickly since the 1950s, generating over 450 million tons of annual output. Despite the benefits and great value provided by plastics, environmental impacts over plastic waste have attracted international attention. Over 340 million tonnes of waste were generated worldwide, with the packaging industry accounting for approximately 46% of the total [13]. This waste is primarily the consequence of things with a shorter “in-use” life-
Green and Sustainable Chemistry
span, often six months or less, contrary to items used in the construction and engineering sectors, with an average lifespan of thirty years [14]. Even though plastic recycling rates have increased from 0% in the nineties to 19.5% in recent estimates, most packaging materials, particularly pliable packaged food, are nonrecyclable. Roughly 95% of conventional plastic wrapping materials made of polyethylene terephthalate and polyolefins are non-recyclable and end up in landfills after one use, causing a yearly economic loss of $80 - 120 billion to the world economy [15]. These difficulties are induced by polymers’ required characteristics, including lighter weight, specific strength, intricate structures, and contaminating from physical touch with foodstuffs [16]. Because of their ecologically favourable compostability, biodegradable polymers have sparked tremendous scientific and industrial interest. For the benefit of the market economy and recurrent environmental risks, biodegradable materials should play a larger part in plastic packaging, which today account for 60% of plastic items. The development of biodegradable polymers provides a solution to these problems by degrading such plastic into CO2, H2O, and biomass within six months; however, conventional synthetic plastic materials, even after burning or landfilling, remain for millennia. With the rise of processed foods in modern society, food packaging has played an essential part in the packaging sector. By 2025, the global market is anticipated to be worth USD 411.3 billion [17]. Because of its strong barrier and gas selectivity, plastic packaging provides food stability, shelflife extension, and safety and protection during transit and storage. Biodegradable polymers that can be degraded or composted after use are excellent substitutes for non-biodegradable packing. It can also work as a selective functional membrane or barrier against gas, humidity, and odour. Although several scientific research attempts to encourage the use of bio-based polymers in packing, few bio-based polymers in the market can meet modern society’s high demand for food packaging [18].
Because many bio-derived polymers are hydrophilic, their gaseous barrier properties and engineering capabilities are incredibly reliant on ambient humidity, limiting their usefulness as a packaging material compared to conventional polymers. Furthermore, their molar mass, rheological properties, and mechanical characteristics such as time-dependent crystallization behavior might cause problems and necessitate adjustments in processing techniques. As a result, bio-derived polymers should be blended with other polymer matrices or micrometers to nanometer-scale fillers to improve hydrophobicity and processing efficacy. The use of nanotechnology in papermaking science has been introduced in some areas. It has the potential to enhance the behavior of biopolymers and provide new capabilities to paper coatings. Currently, inorganic pigments [19], minerals [20], and ceramics [21] are the most often utilized nano-scale fillers in paper coatings, with bio-derived nanomaterial such as Nanocellulose [22] and
Green and Sustainable Chemistry
Nanoclays [23] being studied frequently. Antimicrobial paper [24], microfluidic paper devices [25], bioactive papers for drug delivery [26], flame-retardant papers, and self-healing characteristics for cotton fabric [27] are only a few of the fascinating functions achieved by using nanoparticles.
Paper is a biodegradable and hence ecologically beneficial material commonly utilized in packaging applications. The use of hydrocarbon derivatives as the coating, such as polyethylene, waxes, and fluor-derivatives, frequently regulates papers’ barrier resistance and wettability. Because of this coated layer, protective paper packaging loses its biodegradability and recyclability. Because of their poor recyclability and non-biodegradability, petroleum-based polymers account for most world trash. As an alternative, organically renewable biopolymers can be used as barrier coatings over paper packaging materials. Polylactide (PLA) is among the most promising polymers due to its bio-compatibility, bio-degradability, and ability to produce bio-based feedstocks [28]
It was suggested that polyvinyl alcohol (PVA)/Itaconic acid (IA)/acrylamide (AM) might generate a hydrophobic protective coating with a spatial structural framework on the paper’s surface, increasing the count of hydrogen bonds amongst the copolymer and the fiber. Further, when coated on the paper’s surface, the copolymer exhibited a superior film feature and a decreased penetration capacity through the paper compared to PVA. The strength of the paper reduces as the number of recycled paper increases. Surface scaling was widely recognized as the most efficient approach for improving the surface strength and hydrophobicity of paper and board [29] [30] [31] [32]. Starch and its derivatives were employed in the paper business for many years. Because of its low cost and ubiquitous availability, starch has indeed been recognized as among the most acceptable renewable biopolymer materials. Enzyme-modified starch, for example, is often employed to improve the interfacial strength of paper. Excess starch, on the other hand, may increase chemical oxygen demand (COD) and biological oxygen demand (BOD) during the effluent treatment process of the paper industry [33] [34] [35] [36] [37]. PVA was created as a biodegradable material by polymerizing vinyl acetate monomer. This provided the paper with large interfacial strength, low ink uptake, and exceptional film-forming capabilities. Nonetheless, the water-resistance of the bio-based PVA film had been lower than that of petroleum-derived polymers such as polyamide epoxy epichlorohydrin (PAE) [38] [39] [40] [41].
Meanwhile, PVA may easily infiltrate the inside of the paper. As a result, it limited PVA used in paper production. As a result, the weakness of PVA should be accounted for this through grafting with some other synthetic biodegradable
Green and Sustainable
polymers. Many chemical strategies have been discovered to increase PVA’s water resistance. The water-resistance of PVA has been enhanced via grafting of acrylonitrile monomer with PVA. Some studies developed PVA/polyacrylic acid mixtures to reduce PVA’s hydrophilic characteristic [42]-[52]. A cross-linked esterification process occurred between polyacrylic acid and PVA molecules. PVA molecules’ hydrophilic hydroxyl groups were transformed into hydrophobic groups. As a result, the water resistance of the PVA film was substantially enhanced. Biodegradable materials have gained popularity as a result of environmental concerns. One of the merits of IA is renewability. Furthermore, it has the potential to reduce people’s dependency on petrochemical products such as acrylic acid and maleic anhydride when picking raw materials for polymer synthesis [53]-[58]. This study used free radical polymerization to produce a PVA/ IA/AM copolymer having excellent water resistance and durability. PVA’s hydroxyl groups can create ester bonds with IA molecules’ carboxyl groups. It can increase the hydrophobicity of PVA. The double bond of itaconic acid may polymerize with an acrylamide monomer to form a structural matrix. Thereby, this could restrict PVA diffusion into the interior of the paper. Mini-table software was used to design the PVA/IA/AM copolymer experiment. It sought to enhance PVA’s hydrophobicity, increase surface strength, and decrease PVA penetration. PVA/IA/AM can establish additional hydrogen bonding with fibers and has better film-forming characteristics over PVA [59] [60]
Starch and its compounds have indeed been largely used in the paper industry because of its complete biodegradability, abundant availability, and relatively inexpensive. Surface coating of starch-derived goods is a well-established commercialized procedure for acquainting paper with desirable qualities. As a raw material, starch is exceptionally versatile. First, starch is a natural polymer with a large molecular mass that can be precisely depolymerized. It is also a hydrophilic polymer, meaning it dissolves in water and creates hydrogen bonds with cellulose fibers and pigment. Third, starch contains hydroxyl groups, which allow for a variety of substitution or oxidation methods to change its rheological characteristics and prevent retrogradation. Starch graft co-polymerization can generate innovative materials that combine the advantages of natural and synthesized polymers [32] [61]-[68]. Coated paper is a form of paper that consists of a base coat and a top layer. The coat color is applied to the base paper during the coating process to improve its qualities. Coat color is primarily made up of binders, pigments, and other additives. Binders are the second most common coating component after pigments [69]. Natural binders including starch and protein or synthesized latex such as styrene-butadiene, poly (vinyl acetate), and poly-acrylates are employed. When compared to synthetic latex, starch is a relatively lowpriced binder. However, nature-derived starch applications are restricted because of its insolubility in cold water, tendency to retrograde, and decrease in viscosity and thickening power during cooking and storage [70]. However, too
Green and Sustainable
much starch in a coating formulation might reduce drying rate [71] [72], reduce picking resistance [73], and maximize cracking area [74] [75]. The ultimate skill is finding a middle ground between quality and price. Starch grafted copolymers can be used instead of starch and synthesized latex. Graft co-polymerization is indeed a flexible method for combining the characteristics of starch and synthetic polymers [76] [77]
On the other hand, starch is a biopolymer with a large molecular mass and a high viscosity in an aqueous medium at low concentrations. The starch’s molecular weight must be decreased before it may be adequately grafted in co-polymerization [78]. Starch-based bio latex is a newly developed water-swollen, a cross-linked starch nanoparticle that commercially replaces synthetic latex [79] [80] [81]. Biolatex is sometimes referred to as starch-based bio-latex, biobased latex, bio binder, and a bio latex binder. Biolatex is a huge step forward in starch-based resins for paper coatings. On an industrial scale, bio latex can try replacing hydrocarbon-based synthesized latex by up to 50% or more [82]. For that reason, biolatex has enormous potential in the manufacturing of coated paper. A polymer blend is the physical mixing of two different polymers that may or may not interact chemically [83]. Compared to pure polysaccharide components, blends of multiple polysaccharides can form a new category of materials with improved mechanical and barrier properties. Starch/PVA mixes have been utilised to improve the characteristics of coated paper. A thin coating of starch/ PVA film was applied to paper. The coated paper demonstrated good organic solvent barrier characteristics. The better barrier properties are due to hydrogen bonding formed by hydroxyl groups of starch and PVA molecules. The hydrogen bonding on the paper surface form a tight thin layer, which increases the barrier characteristics of starch/PVA films [84]. Ethylene vinyl alcohol and starch mixture Ethylene vinyl alcohol (EVOH) copolymer is a semi-crystalline synthetic random copolymer composed of ethylene and vinyl alcohol units [85]. The vinyl alcohol molecule has good air barrier qualities, whilst the ethylene component has great damp resistance, thermal and mechanical properties, and easy handling [86] [87] [88]. Furthermore, EVOH is more biodegradable than normal PVA [89]. Blends of EVOH and hydrophobically altered starch may increase the permeability performance of flexible packaging paper.
Nanocelluloses, which have lately been developed, have provided a new polymer coating option. Micro-fibrillated cellulose (MFC) is being used as a coating pulp for paper products. The MFC manufacturing technique was discovered and patented in 1983 by Herrick et al. [90] and Turbak et al. [91]. MFC, a cellulose fiber subdivision, has diameters of 10 - 50 nm and lengths of several micrometers [92] [93]. MFC had significant reinforcing potential and was employed in nano-composites because of its high aspect ratio, nano-scale dimensions, entangled network, and intrinsically good mechanical characteristics [92].
and Sustainable
Many researchers were intrigued by MFC’s capacity to manufacture films because MFC films’ barrier and mechanical properties are comparable with those of existing high-quality polymer matrices [94]. MFC coating and its mixture with petro- and bio-polymer films have attracted the attention of researchers by dramatically improving the barrier properties of the original films [95]. In contrast to these uses, the use of MFC with cellulosic materials is very new and remains uncommon. The first investigation of MFC coating onto paper was conducted in 2009 [94]. As ecologically friendly alternatives, many forms of cellulose nanofibres derived from cellulosic fibers have been used [96] [97] [98] [99].
Cellulose nanofiber (CNF) has been discovered to improve the properties of various composites and papers when used as a reinforcing element in wet-end applications [96]-[102]. Aulin et al. [103] demonstrated that utilizing CNF as a coating agent significantly reduces the air barrier capability of paper by generating a thick top layer. Hult et al. [101] investigated the mixture of CNF and shellac, deposited as a one-layer or multi-layer coating on paper products using a bar coater and a spray coating technique. The results revealed that paper permeability to water vapor, air, and oxygen decreased dramatically after coating. CNF improved the surface and barrier characteristics of coated sheets, according to Ridgway et al. [104]. The combination of CNF and clay improved the printing properties of paper, such as ink absorption rate and print density, according to Hamada et al. [105]. It was demonstrated that partially replacing NFC for the conventional co-binder carboxymethyl cellulose reduced the permeability of the coating material to water [106]. Andrade et al. studied the impact of several chemicals on the wettability of gelatin-derived edible coatings on banana and eggplant epicarps, discovering that cellulose-nanofibers increased coating wetting [107]
Papers made from recycled fibers have poor mechanical and barrier qualities due to insufficient inter-fiber bonding. The coating is a methodology of interest for creating appealing items from this type of paper. On 100% recycled paper, an oxypropylated lignin-based coating was investigated. Instead of propylene oxide, propylene carbonate, a non-volatile and biodegradable solvent, was employed as a reagent. One of them is the creation of lignin-based coatings for paper and paperboard applications, which is based on the hydrophobic property of lignin polymer [108] [109]. Some research has previously been conducted on bio-based coatings using cellulose derivatives, starch, and other polymers, [110] as well as a combination of lignin and cellulose nanocrystal or esterified lignin for paperboard use [110] [111] [112]. The subsequent research was of particular interest since they dealt with the esterification of lignin. Another method for lignin modification is oxypropylation, which has been extensively researched to produce novel polyol for polyurethane foam applications [112]. Lehnen et al. [113] investigated oxypropylation with propylene carbonate as a non-volatile and biodegradable solvent rather than propylene oxide, a possible human carcinogen.
An oxypropylated lignin-based coating was explored in this work to enhance the general characteristics of recycled paper. Propylene carbonate was employed as an oxypropylation reagent and a solvent in the coating formulation. This enables immediate use of the mixture at the end of the reaction, reducing the number of process stages to one.
Protein-based biopolymer films have been researched for usage as food wrapping and coating materials. They’ve been frequently employed in food systems like oil, gaseous, and mechanical barriers to extending processed foods’ shelf life [112] [113] [114]. Zein was used as an oxygen barrier layer in peanut products to avoid oxidation [115]. Casein coatings might also be utilized on less processed fruits to enhance their shelf life [116]. Trezza and Vergan [117] observed that zeincoated paper does have a high prospective for use as an oil-barrier paper bag in fast-food eateries. Isolated soy protein (ISP) also has a remarkable film-forming capacity [118] [119] [120]. Soy protein sheets have traditionally been used as a digestible covering for veg and meat mixtures that are then fried in oil. ISPbased films beat zein and wheat gluten-based films in terms of oxygen barrier performance [121]. Grease resistance is critical for packing items that include oils or fats.
Polyethylene and other polymers are considered effective grease barriers. On the other hand, the polyethylene content makes material segregation, recycling, and regeneration difficult [122] [123]. Papers coated with biodegradable polymers may meet packaging criteria as an oil barrier for commodities with a very short lifespan, like as fast-food restaurant sandwiches. ISP, a key by-product of soybean-oil extraction, on the other hand, is a low-cost natural polymer that competes against polyethylene. Mechanical and barrier performance of protein-based coatings are controlled by factors like plasticizer content and pH, solvent, and other additive choices [124]-[130]. As plasticizer content increases in wheat gluten films, flexibility improves while water vapor, oxygen barrier, and puncture strength qualities diminish [125] [126] [127]. Gennadios et al. [119] produced protein films from an ISP-wheat gluten blend. They investigated the impact of varying the pH of the produced film solution on properties such as water vapor permeability and mechanical strength. Brandenburg et al. [120] discovered that alkali-treated ISP films had enhanced film appearance and elongation characteristics. ISP films did not seem clear due to the inclusion of insoluble particles [128]. High pH and temperature treatments of ISP resulted in more soluble, hydrolyzed, and denatured chemicals [129]. Protein denaturation is known to change the structure of a protein from circular to extended chain geometry. Increased protein-protein linkages, in principle, would lower gas permeability while increasing tensile strength. Park et al. [130] revealed that different polyethylene glycol and glycerol plasticizer mixtures had a substantial influence on the mechanical properties and water vapor permeabilities of pro-
tein-based membranes.
Bio-polymer based coating on paper packaging materials are very important systems for the future improvement of food packaging. They have potential environmental advantages over conventional petroleum-based paper coatings. A literature survey indicates that bio-based polymers have a great potential for replacing hydrocarbon-produced synthetic polymers as a sustainable solution for paper coating applications. Not only can biopolymer paper coating provide biodegradability and renewability, but numerous methods for increasing the functioning of coated paper surfaces have been proposed. An appropriate mix of chosen ingredients (bio-derived polymer and fillers) and surface structure, according to the review, has the ability to offer an entirely impenetrable bio-based paper coating. From the presented review, appropriate bio-based polymers like starch, polylactic acid, itaconic acid, lignin, soybean protein and cellulose, provide a fully protective bio-based paper coating.
Finally, the difficulties associated with most biopolymers, such as hydrophilicity, crystallization behavior, brittleness, or melt instabilities, prevent their full industrial exploitation. This study cites investigations in which it was observed that mixing with other biopolymers, compatibilizers, and plasticizers might assist in alleviating this bottleneck. But extensively research will be needed in the paper packaging industry towards insubstantial materials for reduction of raw material use, conveying costs, minimizing the amount of waste and improvement in the performance properties of paper coatings. Interest in sustainable materials combined with improvement in performance properties of paper coating will continue to growth.
The authors declare no conflicts of interest regarding the publication of this paper.
[1]Rastogi, V. and Samyn, P. (2015) Bio-Based Coatings for Paper Applications. Coatings , 5 5 , 887-930. https://doi.org/10.3390/coatings5040887
[2]Samyn, P., Schoukens, G., Van den Abbeele, H., Vonck, L. and Stanssens, D. (2011) Application of Polymer Nanoparticle Coating for Tuning the Hydrophobicity of Cellulosic Substrates. JournalofCoatingsTechnologyandResearch , 8 8 , 363-373. https://doi.org/10.1007/s11998-010-9309-7
[3]Nair, A., Kansal, D., Khan, A. and Rabnawaz, M. (2021) New Alternatives to Single-Use Plastics: Starch and Chitosan-Graft-Polydimethylsiloxane-Coated Paper for Water- and Oil-Resistant Applications. NanoSelect , 3 3 , 459-470. https://doi.org/10.1002/nano.202100107
[4]Khwaldia, K., Arab-Tehrany, E. and Desobry, S. (2010) Biopolymer Coatings on Paper Packaging Materials. ComprehensiveReviewsinFoodScienceandFoodSafety , 9 , 82-91. https://doi.org/10.1111/j.1541-4337.2009.00095.x
[5]Gong, X., Zhang, L., He, S., Jiang, S., Wang, W. and Wu, Y. (2020) Rewritable Superhydrophobic Coatings Fabricated Using Water-Soluble Polyvinyl Alcohol. Materials&Design , 1 1 9 6 , Article ID: 109112. https://doi.org/10.1016/j.matdes.2020.109112
[6]Samyn, P., Deconinck, M., Schoukens, G., Stanssens, D., Vonck, L. and Van den Abbeele, H. (2012) Synthesis and Characterization of Imidized Poly(styrene-maleic anhydride) Nanoparticles in Stable Aqueous Dispersion. Polymers for Advanced Technologies , 2 23 , 311-325. https://doi.org/10.1002/pat.1871
[7]Tajeddin, B. (2014) Cellulose-Based Polymers for Packaging Applications. In: LignocellulosicPolymerComposites : Processing , Characterization , andProperties , John Wiley & Sons, Inc., Hoboken, 477-498. https://doi.org/10.1002/9781118773949.ch21
[8]Aday, M.S., Caner, C. and Rahvalı, F. (2011) Effect of Oxygen and Carbon Dioxide Absorbers on Strawberry Quality. PostharvestBiologyandTechnology , 6 6 2 , 179-187. https://doi.org/10.1016/j.postharvbio.2011.05.002
[9]Ahvenainen, R., Eilamo, M. and Hurme, E. (1997) Detection of Improper Sealing and Quality Deterioration of Modified-Atmosphere-Packed Pizza by a Colour Indicator. FoodControl , 8 8, 177-184. https://doi.org/10.1016/S0956-7135(97)00046-7
[10]Bai, H., Zhou, G., Hu, Y., Sun, A., Xu, X., Liu, X. and Lu, C. (2017) Traceability Technologies for Farm Animals and Their Products in China. FoodControl , 7 7 9, 35-43. https://doi.org/10.1016/j.foodcont.2017.02.040
[11]Han, J.-W., Ruiz-Garcia, L., Qian, J.-P. and Yang, X.-T. (2018) Food Packaging: A Comprehensive Review and Future Trends. Comprehensive Reviews in Food ScienceandFoodSafety , 1 1 7 , 860-877. https://doi.org/10.1111/1541-4337.12343
[12]Perpétuo, G.L., Gálico, D.A., Fugita, R.A., Castro, R.A.E., Eusébio, M.E.S., TreuFilho, O., Silva, A.C.M. and Bannach, G. (2013) Thermal Behavior of Some Antihistamines. JournalofThermalAnalysisandCalorimetry , 1 1 1 1 , 2019-2028. https://doi.org/10.1007/s10973-012-2247-0
[13]Tsakona, M. and Rucevska, I. (2020) Baseline Report on Plastic Waste-Basel Convention. United Nations, New York, 1-68. https://gridarendal-website-live.s3.amazonaws.com/production/documents/:s_docu ment/554/original/UNEP-CHW-PWPWG.1-INF-4.English.pdf?1594295332
[14]Geyer, R., Jambeck, J.R. and Law, K.L. (2017) Production, Use, and Fate of All Plastics Ever Made. ScienceAdvances , 3 3 , e1700782. https://doi.org/10.1126/sciadv.1700782
[15]World Economic Forum (2016) The New Plastics Economy: Rethinking the Future of Plastics. Ellen MacArthur Found, Cowes, 120. http://www3.weforum.org/docs/WEF_The_New_Plastics_Economy.pdf
[16]Wu, F., Misra, M. and Mohanty, A.K. (2021) Challenges and New Opportunities on Barrier Performance of Biodegradable Polymers for Sustainable Packaging. Progress inPolymerScience , 1 1 1 7 , Article ID: 101395. https://doi.org/10.1016/j.progpolymsci.2021.101395
[17]Reddy, M.M., Vivekanandhan, S., Misra, M., Bhatia, S.K. and Mohanty, A.K. (2013) Biobased Plastics and Bionanocomposites: Current Status and Future Opportunities. ProgressinPolymerScience , 3 3 8 , 1653-1689. https://doi.org/10.1016/j.progpolymsci.2013.05.006
[18]Zhang, H., Hortal, M., Jordá-Beneyto, M., Rosa, E., Lara-Lledo, M. and Lorente, I. (2017) ZnO-PLA Nanocomposite Coated Paper for Antimicrobial Packaging Application. LWT , 7 7 8 , 250-257. https://doi.org/10.1016/j.lwt.2016.12.024
[19]Hladnik, A. (2002) Characterization of Pigments in Coating Formulations for High-
Green and Sustainable
End Ink-Jet Papers. DyesandPigments , 5 5 4 , 253-263. https://doi.org/10.1016/S0143-7208(02)00050-5
[20]Kugge, C. and Johnson, B. (2008) Improved Barrier Properties of Double Dispersion Coated Liner. ProgressinOrganicCoatings , 6 6 2 , 430-435. https://doi.org/10.1016/j.porgcoat.2008.03.006
[21]Daoud, W.A., Xin, J.H. and Tao, X. (2004) Superhydrophobic Silica Nanocomposite Coating by a Low-Temperature Process. JournaloftheAmericanCeramicSociety , 8 7 , 1782-1784. https://doi.org/10.1111/j.1551-2916.2004.01782.x
[22]Dufresne, A. (2013) Nanocellulose: A New Ageless Bionanomaterial. Materials Today , 1 1 6 , 220-227. https://doi.org/10.1016/j.mattod.2013.06.004
[23]Sanchez-Garcia, M.D. and Lagaron, J.M. (2010) Novel Clay-Based Nanobiocomposites of Biopolyesters with Synergistic Barrier to UV Light, Gas, and Vapour. JournalofAppliedPolymerScience , 1 1 1 8 , 188-199. https://doi.org/10.1002/app.31986
[24]Cha, D.S. and Chinnan, M.S. (2004) Biopolymer-Based Antimicrobial Packaging: A Review. CriticalReviewsinFoodScienceandNutrition , 4 4 4 , 223-237. https://doi.org/10.1080/10408690490464276
[25]Guerrero, M.P., Bertrand, F. and Rochefort, D. (2011) Activity, Stability and Inhibition of a Bioactive Paper Prepared by Large-Scale Coating of Laccase Microcapsules. ChemicalEngineeringScience , 6 6 6 , 5313-5320. https://doi.org/10.1016/j.ces.2011.07.026
[26]Chen, S., Li, X., Li, Y. and Sun, J. (2015) Intumescent Flame-Retardant and SelfHealing Superhydrophobic Coatings on Cotton Fabric. ACSNano , 9 9 , 4070-4076. https://doi.org/10.1021/acsnano.5b00121
[27]Rong, M.Z., Zhang, M.Q. and Ruan, W.H. (2006) Surface Modification of NanoScale Fillers for Improving Properties of Polymer Nanocomposites: A Review. MaterialsScienceandTechnology , 2 2 2 , 787-796. https://doi.org/10.1179/174328406X101247
[28]Lopez-Rubio, A., Fabra, M.J., Martinez-Sanz, M., Mendoza, S. and Vuong, Q.V. (2017) Biopolymer-Based Coatings and Packaging Structures for Improved Food Quality. JournalofFoodQuality , 2 2 0 1 7 , Article ID: 2351832. https://doi.org/10.1155/2017/2351832
[29]Guo, Y., Guo, J., Li, S., Li, X., Wang, G. and Huang, Z. (2013) Properties and Paper Sizing Application of Waterborne Polyurethane Emulsions Synthesized with TDI and IPDI. Colloids and Surfaces A : PhysicochemicalandEngineeringAspects , 4 4 2 7 , 53-61. https://doi.org/10.1016/j.colsurfa.2013.03.017
[30]Brenner, T., Kiessler, B., Radosta, S. and Arndt, T. (2016) Processing Surface Sizing Starch Using Oxidation, Enzymatic Hydrolysis and Ultrasonic Treatment Methods—Preparation and Application. CarbohydratePolymers , 1 1 3 8 , 273-279. https://doi.org/10.1016/j.carbpol.2015.10.086
[31]Xiong, H., Tang, S., Tang, H. Zou, P. (2008) The Structure and Properties of a StarchBased Biodegradable Film. CarbohydratePolymers , 7 7 1 , 263-268. https://doi.org/10.1016/j.carbpol.2007.05.035
[32]Jonhed, A. andersson, C. and Järnström, L. (2008) Effects of Film Forming and Hydrophobic Properties of Starches on Surface Sized Packaging Paper. PackagingTechnologyandScience , 2 2 1 , 123-135. https://doi.org/10.1002/pts.783
[33]Domene-López, D., Guillén, M.M., Martin-Gullon, I., García-Quesada, J.C. and Montalbán, M.G. (2018) Study of the Behavior of Biodegradable Starch/Polyvinyl Alcohol/Rosin Blends. CarbohydratePolymers , 2 2 0 2 , 299-305. https://doi.org/10.1016/j.carbpol.2018.08.137
Green and Sustainable
[34]Ni, S., Zhang, H., Godwin, P.M., Dai, H. and Xiao, H. (2018) ZnO Nanoparticles Enhanced Hydrophobicity for Starch Film and Paper. Materials Letters , 2 2 3 0 , 207210. https://doi.org/10.1016/j.matlet.2018.07.075
[35]Li, W., Xu, Z., Wang, Z. and Xing, J. (2018) One-Step Quaternization/Hydroxypropylsulfonation to Improve Paste Stability, Adhesion, and Film Properties of Oxidized Starch. Polymers(Basel), 1 1 0 , 1110. https://doi.org/10.3390/polym10101110
[36]Du, Y., Liu, J., Wang, B., Li, H. and Su, Y. (2018) The Influence of Starch-Based BioLatex on Microstructure and Surface Properties of Paper Coating. Progress in OrganicCoatings , 1 1 1 6 , 51-56. https://doi.org/10.1016/j.porgcoat.2017.12.009
[37]Ondaral, S., Kurtuluş, O.Ç., Öztürk, G., Ergün, M.E. and Yakın, İ. (2018) Aldehyde Starch Complexes: Adsorption on Cellulose Model Film and Performance as a Strength Additive for Papermaking. BioResources , 1 1 3 , 4470-4483. https://doi.org/10.15376/biores.13.2.4470-4483
[38]Wang, Y., Chang, C. and Zhang, L. (2010) Effects of Freezing/Thawing Cycles and Cellulose Nanowhiskers on Structure and Properties of Biocompatible Starch/PVA Sponges. MacromolecularMaterialsandEngineering , 2 2 9 5 , 137-145. https://doi.org/10.1002/mame.200900212
[39]Fatehi, P. and Xiao, H. (2010) Effect of Cationic PVA Characteristics on Fiber and Paper Properties at Saturation Level of Polymer Adsorption. Carbohydrate Polymers, 7 7 9 , 423-428. https://doi.org/10.1016/j.carbpol.2009.08.029
[40]Liu, X., Fatehi, P., Ni, Y. and Xiao, H. (2010) Using Cationic Polyvinyl Alcohol (CPVA) to Improve the Strength of Wood-Free Papers Containing High-Yield Pulp (HYP). Holzforschung , 6 6 4 , 563-569. https://doi.org/10.1515/hf.2010.078
[41]Mittal, A., Garg, S., Kohli, D., Maiti, M., Jana, A.K. and Bajpai, S. (2016) Effect of Cross Linking of PVA/Starch and Reinforcement of Modified Barley Husk on the Properties of Composite Films. CarbohydratePolymers , 1 1 5 1 , 926-938. https://doi.org/10.1016/j.carbpol.2016.06.037
[42]Ismail, H. and Zaaba, N.F. (2014) Effects of Poly(vinyl alcohol) on the Performance of Sago Starch Plastic Films. JournalofVinylandAdditiveTechnology , 2 2 0 , 72-79. https://doi.org/10.1002/vnl.21348
[43]Zhai, M., Yoshii, F., Kume, T. and Hashim, K. (2002) Syntheses of PVA/Starch Grafted Hydrogels by Irradiation. CarbohydratePolymers , 5 5 0 , 295-303. https://doi.org/10.1016/S0144-8617(02)00031-0
[44]Garcia, P.S., Baron, A.M., Yamashita, F., Mali, S., Eiras, D. and Grossmann, M.V.E. (2018) Compatibilization of Starch/Poly(butylene adipate-co-terephthalate) Blown Films Using Itaconic Acid and Sodium Hypophosphite. JournalofAppliedPolymer Science , 1 1 3 5 , Article ID: 46629. https://doi.org/10.1002/app.46629
[45]Swain, S.K., Prusty, G. and Das, R. (2012) Sonochemical Compatibility of Polyvinyl Alcohol/Polyacrylic Acid Blend in Aqueous Solution. Journal of Macromolecular Science , PartB , 5 5 1 , 580-589. https://doi.org/10.1080/00222348.2011.609782
[46]Follain, N., Joly, C., Dole, P. and Bliard, C. (2005) Properties of Starch Based Blends. Part 2. Influence of Poly Vinyl Alcohol Addition and Photocrosslinking on Starch Based Materials Mechanical Properties. CarbohydratePolymers , 6 6 0 , 185-192. https://doi.org/10.1016/j.carbpol.2004.12.003
[47]Meng, F., Zhang, Y., Xiong, Z., Wang, G., Li, F. and Zhang, L. (2018) Mechanical, Hydrophobic and Thermal Properties of an Organic-Inorganic Hybrid CarrageenanPolyvinyl Alcohol Composite Film. CompositesPartB : Engineering, 1 1 4 3 , 1-8. https://doi.org/10.1016/j.compositesb.2017.12.009
[48]Kokhanovskaya, O.A. and Likholobov, V.A. (2018) Synthesis of Hydrophobic Aerogel
Green and Sustainable Chemistry
Heat Insulation Materials Based on Polyvinyl Alcohol/Carbon Black Composite. RussianJournalofAppliedChemistry , 9 9 1 , 78-81. https://doi.org/10.1134/S1070427218010123
[49]Zhang, R., Wan, W., Qiu, L., Wang, Y. and Zhou, Y. (2017) Preparation of Hydrophobic Polyvinyl Alcohol Aerogel via the Surface Modification of Boron Nitride for Environmental Remediation. AppliedSurfaceScience , 4 4 1 9 , 342-347. https://doi.org/10.1016/j.apsusc.2017.05.044
[50]Pan, Y., Shi, K., Peng, C., Wang, W., Liu, Z. and Ji, X. (2014) Evaluation of Hydrophobic Polyvinyl-Alcohol Formaldehyde Sponges as Absorbents for Oil Spill. ACS AppliedMaterials&Interfaces , 6 6 , 8651-8659. https://doi.org/10.1021/am5014634
[51]Pan, Y., Wang, W., Peng, C., Shi, K., Luo, Y. and Ji, X. (2014) Novel Hydrophobic Polyvinyl Alcohol-Formaldehyde Foams for Organic Solvents Absorption and Effective Separation. RSCAdvances , 4 4 , 660-669. https://doi.org/10.1039/C3RA43907K
[52]Maqueira, L., Valdés, A.C., Iribarren, A. and de Melo, C.P. (2013) Preparation and Characterization of Hydrophobic Porphyrin Nanoaggregates Dispersed in Polyvinyl Alcohol Films. JournalofPorphyrinsandPhthalocyanines , 1 1 7 , 283-288. https://doi.org/10.1142/S1088424613500028
[53]Bednarz, S., Wesołowska-Piętak, A., Konefał, R. and Świergosz, T. (2018) Persulfate Initiated Free-Radical Polymerization of Itaconic Acid: Kinetics, End-Groups and Side Products. EuropeanPolymerJournal , 1 1 0 6 , 63-71. https://doi.org/10.1016/j.eurpolymj.2018.07.010
[54]Duquette, D. and Dumont, M.-J. (2018) Influence of Chain Structures of Starch on Water Absorption and Copper Binding of Starch-Graft-Itaconic Acid Hydrogels. Starch Stärke , 7 70 , Article ID: 1700271. https://doi.org/10.1002/star.201700271
[55]Ko, S.Y., Sand, A., Shin, N.J. and Kwark, Y.-J. (2018) Synthesis and Characterization of Superabsorbent Polymer Based on Carboxymethyl Cellulose-Graft-Itaconic Acid. FibersandPolymers , 1 1 9 , 255-262. https://doi.org/10.1007/s12221-018-7837-9
[56]Huang, Z., Zhou, X., Xing, Z. and Wang, B. (2018) Improving Application Performance of in Situ Polymerization and Crosslinking System of Maleic Acid/Itaconic Acid for Cotton Fabric. FibersandPolymers , 1 1 9 , 281-288. https://doi.org/10.1007/s12221-018-7745-z
[57]Kasar, S.B. and Thopate, S.R. (2018) Synthesis of Bis(indolyl)methanes Using Naturally Occurring, Biodegradable Itaconic Acid as a Green and Reusable Catalyst. CurrentOrganicSynthesis , 1 1 5 , 110-115. https://doi.org/10.2174/1570179414666170621080701
[58]Yaman, S. and Öztürk, Y. (2017) Analyses of Particle Size and Magnetisation of Magnetic Nanoparticles via Minitab Statistical Software. Micro & Nano Letters , 1 1 2 , 784-786. https://doi.org/10.1049/mnl.2017.0101
[59]Shah, D. and Londhe, V. (2011) Optimization and Characterization of LevamisoleLoaded Chitosan Nanoparticles by Ionic Gelation Method Using 2(3) Factorial Design by Minitab® 15. TherapeuticDelivery , 2 2 , 171-179. https://doi.org/10.4155/tde.10.102
[60]Wang, D.X. and Conerly, M.D. (2008) Evaluating the Power of Minitab’s Data Subsetting Lack of Fit Test in Multiple Linear Regression. JournalofAppliedStatistics , 3 5 , 115-124. https://doi.org/10.1080/02664760701775381
[61]Maurer, H.W. and Kearney, R.L. (1998) Opportunities and Challenges for Starch in the Paper Industry. Starch Stärke , 5 5 0 , 396-402. https://doi.org/10.1002/(SICI)1521-379X(199809)50:9<396::AID-STAR396>3.0.CO; 2-8
Green and Sustainable Chemistry
[62]Chen, Q., Yu, H., Wang, L., ul Abdin, Z., Chen, Y., Wang, J., Zhou, W., Yang, X., Khan, R.U., Zhang, H. and Chen, X. (2015) Recent Progress in Chemical Modification of Starch and Its Applications. RSCAdvances , 5 5 , 67459-67474. https://doi.org/10.1039/C5RA10849G
[63]Zhu, F. (2015) Composition, Structure, Physicochemical Properties, and Modifications of Cassava Starch. CarbohydratePolymers , 1 1 2 2 , 456-480. https://doi.org/10.1016/j.carbpol.2014.10.063
[64]Kaur, B., Ariffin, F., Bhat, R. and Karim, A.A. (2012) Progress in Starch Modification in the Last Decade. FoodHydrocolloids , 2 2 6 , 398-404. https://doi.org/10.1016/j.foodhyd.2011.02.016
[65]Zia-ud-Din, Xiong, H. and Fei, P. (2017) Physical and Chemical Modification of Starches: A Review. CriticalReviewsinFoodScienceandNutrition , 5 5 7 , 2691-2705. https://doi.org/10.1080/10408398.2015.1087379
[66]Masina, N., Choonara, Y.E., Kumar, P., du Toit, L.C., Govender, M., Indermun, S. and Pillay, V. (2017) A Review of the Chemical Modification Techniques of Starch. CarbohydratePolymers , 1 1 5 7 , 1226-1236. https://doi.org/10.1016/j.carbpol.2016.09.094
[67]Khlestkin, V.K., Peltek, S.E. and Kolchanov, N.A. (2018) Review of Direct Chemical and Biochemical Transformations of Starch. CarbohydratePolymers , 1 1 8 1 , 460-476. https://doi.org/10.1016/j.carbpol.2017.10.035
[68]Niranjana Prabhu, T. and Prashantha, K. (2018) A Review on Present Status and Future Challenges of Starch Based Polymer Films and Their Composites in Food Packaging Applications. PolymerComposites , 3 3 9 , 2499-2522. https://doi.org/10.1002/pc.24236
[69]Lele, V.V., Kumari, S. and Niju, H. (2018) Syntheses, Characterization and Applications of Graft Copolymers of Sago Starch—A Review. Starch Stärke , 7 7 0 , Article ID: 1700133. https://doi.org/10.1002/star.201700133
[70]Holik, H. (2013) Handbook of Paper and Board. Wiley-VCH Verlag GmbH & Co. KGaA, Weinheim.
[71]Chen, G., Zhu, Z.J., Salminen, P. and Toivakka, M. (2014) Structure and Mechanical Properties of Starch/Styrene-Butadiene Latex Composites. Advanced Materials Research , 9 9 3 6 , 74-81. https://doi.org/10.4028/www.scientific.net/AMR.936.74
[72]Hallajisani, A., Hashemi, S.J. and Murray Douglas, W.J. (2011) Experimental Investigation of Industrial Coating-Drying Process Parameters. Drying Technology , 2 2 9 , 1484-1491. https://doi.org/10.1080/07373937.2011.575973
[73]Du, Y., Zang, Y.-H. and Sun, J. (2014) The Effects of Water Soluble Polymers on Paper Coating Consolidation. ProgressinOrganicCoatings , 7 7 7 , 908-912. https://doi.org/10.1016/j.porgcoat.2014.01.007
[74]Hashemi Najafi, S.M., Tajvidi, M. and Bousfield, D.W. (2018) Production and Mechanical Characterization of Free-Standing Pigmented Paper Coating Layers with Latex and Starch as Binder. ProgressinOrganicCoatings , 1 1 2 3 , 138-145. https://doi.org/10.1016/j.porgcoat.2018.07.009
[75]Zhang, S., Jiang, L., Zhang, M. and Wu, Y. (2010) Characteristics of Aramid Fibre/ Fibrids and Their Properties for Sheet Making. NordicPulp&PaperResearchJournal , 2 2 5 , 488-494. https://doi.org/10.3183/npprj-2010-25-04-p488-494
[76]Oh, K., Sim, K., Bin Jeong, Y., Youn, H.J., Lee, H.L., Lee, Y.M. and Yeu, S.U. (2015) Effect of Coating Binder on Fold Cracking of Coated Paper. NordicPulp& Paper ResearchJournal , 3 3 0 , 361-368. https://doi.org/10.3183/npprj-2015-30-02-p361-368
Green and Sustainable Chemistry
R. V. Gadhave
[77]Haroon, M., Wang, L., Yu, H., Abbasi, N.M., Zain-ul-Abdin, Z.-A., Saleem, M., Khan, R.U., Ullah, R.S., Chen, Q. and Wu, J. (2016) Chemical Modification of Starch and Its Application as an Adsorbent Material. RSCAdvances , 6 6 , 78264-78285. https://doi.org/10.1039/C6RA16795K
[78]Meimoun, J., Wiatz, V., Saint-Loup, R., Parcq, J., Favrelle, A., Bonnet, F. and Zinck, P. (2018) Modification of Starch by Graft Copolymerization. Starch Stärke , 7 7 0 , Article ID: 1600351. https://doi.org/10.1002/star.201600351
[79]Mange, S., Dever, C., De Bruyn, H., Gaborieau, M., Castignolles, P. and Gilbert, R.G. (2007) Grafting of Oligosaccharides onto Synthetic Polymer Colloids. Biomacromolecules , 8 8 , 1816-1823. https://doi.org/10.1021/bm061119o
[80]Bloembergen, S., Lennan, I., Lee, D. and Leeuwen, J. (2008) Paper Binder Performance with Biobased Nanoparticles. TAPPI J.-Pap. 360°. 3, 3.
[81]Klass, C. (2007) New Nanoparticle Latex Offers Natural Advantage. Paper360 Magazine , 2 2 , 30-31.
[82]Van Leeuwen, J. (2006) Paper Coating-SBR Latex Replacement Technology. TAPPI Coat. Graph. Arts Conf.
[83]Bloembergen, S., Mclennan, I.J., Leeuwen, J. and Lee, D.I. (2010) Ongoing Developments in Biolatex Binders with a Very Low Carbon Footprint for Paper and Board Manufacturing. 64th Appita Annual Conference & Exhibition , Melbourne, 18-21 April 2010, 363-369.
[84]Muthuraj, R., Misra, M. and Mohanty, A.K. (2018) Biodegradable Compatibilized Polymer Blends for Packaging Applications: A Literature Review. Journal of AppliedPolymerScience , 1 1 3 5 , 45726. https://doi.org/10.1002/app.45726
[85]Teodorescu, M., Bercea, M. and Morariu, S. (2018) Biomaterials of Poly(vinyl alcohol) and Natural Polymers. PolymerReviews , 5 5 8 , 247-287. https://doi.org/10.1080/15583724.2017.1403928
[86]Zhu, P., Kuang, Y., Chen, G., Liu, Y., Peng, C., Hu, W., Zhou, P. and Fang, Z. (2018) Starch/Polyvinyl Alcohol (PVA)-Coated Painting Paper with Exceptional Organic Solvent Barrier Properties for Art Preservation Purposes. Journal of Materials Science, 5 5 3 , 5450-5457. https://doi.org/10.1007/s10853-017-1924-6
[87]Mokwena, K.K. and Tang, J. (2012) Ethylene Vinyl Alcohol: A Review of Barrier Properties for Packaging Shelf Stable Foods. Critical Reviews in Food Science and Nutrition, 5 5 2 , 640-650. https://doi.org/10.1080/10408398.2010.504903
[88]Maes, C., Luyten, W., Herremans, G., Peeters, R., Carleer, R. and Buntinx, M. (2018) Recent Updates on the Barrier Properties of Ethylene Vinyl Alcohol Copolymer (EVOH): A Review. PolymerReviews , 5 5 8 , 209-246. https://doi.org/10.1080/15583724.2017.1394323
[89]Christophliemk, H., Johansson, C., Ullsten, H. and Järnström, L. (2017) Oxygen and Water Vapor Transmission Rates of Starch-Poly(vinyl alcohol) Barrier Coatings for Flexible Packaging Paper. ProgressinOrganicCoatings , 1 1 1 3 , 218-224. https://doi.org/10.1016/j.porgcoat.2017.04.019
[90]Zhong, Y., Godwin, P., Jin, Y. and Xiao, H. (2019) Biodegradable Polymers and Green-Based Antimicrobial Packaging Materials: A Mini-Review. Advanced IndustrialandEngineeringPolymerResearch , 3 3 , 27-35. https://doi.org/10.1016/j.aiepr.2019.11.002
[91]Harlin, A., Backfolk, K. and Laitinen, R. (2014) Process for the Production of Mcrofbrillated Cellulose in an Extruder and Microfibrillated Cellulose Produced According to the Process, US008747612B2.
Green and Sustainable Chemistry
[92]Siqueira, G., Bras, J. and Dufresne, A. (2009) Cellulose Whiskers versus Microfibrils: Influence of the Nature of the Nanoparticle and Its Surface Functionalization on the Thermal and Mechanical Properties of Nanocomposites. Biomacromolecules , 1 0 , 425-432. https://doi.org/10.1021/bm801193d
[93]Syverud, K. and Stenius, P. (2009) Strength and Barrier Properties of MFC Films. Cellulose , 1 1 6 , 75-85. https://doi.org/10.1007/s10570-008-9244-2
[94]Fukuzumi, H., Saito, T., Iwata, T., Kumamoto, Y. and Isogai, A. (2009) Transparent and High Gas Barrier Films of Cellulose Nanofibers Prepared by TEMPO-Mediated Oxidation. Biomacromolecules , 1 1 0 , 162-165. https://doi.org/10.1021/bm801065u
[95]Lavoine, N., Desloges, I., Dufresne, A. and Bras, J. (2012) Microfibrillated Cellulose—Its Barrier Properties and Applications in Cellulosic Materials: A Review. CarbohydratePolymers , 9 9 0 , 735-764. https://doi.org/10.1016/j.carbpol.2012.05.026
[96]Afra, E., Yousefi, H., Hadilam, M.M. and Nishino, T. (2013) Comparative Effect of Mechanical Beating and Nanofibrillation of Cellulose on Paper Properties Made from Bagasse and Softwood Pulps. CarbohydratePolymers , 9 9 7 , 725-730. https://doi.org/10.1016/j.carbpol.2013.05.032
[97]Rezayati Charani, P., Dehghani-Firouzabadi, M., Afra, E., Blademo, Å., Naderi, A. and Lindström, T. (2013) Production of Microfibrillated Cellulose from Unbleached Kraft Pulp of Kenaf and Scotch Pine and Its Effect on the Properties of Hardwood Kraft: Microfibrillated Cellulose Paper. Cellulose , 2 2 0 , 2559-2567. https://doi.org/10.1007/s10570-013-9998-z
[98]Djafari Petroudy, S.R., Syverud, K., Chinga-Carrasco, G., Ghasemain, A. and Resalati, H. (2014) Effects of Bagasse Microfibrillated Cellulose and Cationic Polyacrylamide on Key Properties of Bagasse Paper. Carbohydrate Polymers , 9 9 9 , 311318. https://doi.org/10.1016/j.carbpol.2013.07.073
[99]Afra, E., Yousefi, H. and Lakani, S.A. (2014) Properties of Chemi-Mechanical Pulp Filled with Nanofibrillated and Microcrystalline Cellulose. JournalofBiobasedMaterialsandBioenergy , 8 8 , 489-494. https://doi.org/10.1166/jbmb.2014.1462
[100]Taipale, T., Österberg, M., Nykänen, A., Ruokolainen, J. and Laine, J. (2010) Effect of Microfibrillated Cellulose and Fines on the Drainage of Kraft Pulp Suspension and Paper Strength. Cellulose , 1 17 , 1005-1020. https://doi.org/10.1007/s10570-010-9431-9
[101]Hult, E.-L., Iotti, M. and Lenes, M. (2010) Efficient Approach to High Barrier Packaging Using Microfibrillar Cellulose and Shellac. Cellulose , 1 1 7 , 575-586. https://doi.org/10.1007/s10570-010-9408-8
[102]Mashkour, M., Afra, E., Resalati, H. and Mashkour, M. (2015) Moderate Surface Acetylation of Nanofibrillated Cellulose for the Improvement of Paper Strength and Barrier Properties. RSCAdvances , 5 5 , 60179-60187. https://doi.org/10.1039/C5RA08161K
[103]Aulin, C., Gällstedt, M. and Lindström, T. (2010) Oxygen and Oil Barrier Properties of Microfibrillated Cellulose Films and Coatings. Cellulose , 1 1 7 , 559-574. https://doi.org/10.1007/s10570-009-9393-y
[104]Ridgway, C.J. and Gane, P.A.C. (2012) Constructing NFC-Pigment Composite Surface Treatment for Enhanced Paper Stiffness and Surface Properties. Cellulose , 1 1 9 , 547-560. https://doi.org/10.1007/s10570-011-9634-8
[105]Hamada, H., Beckvermit, J. and Bousfield, D. (2010) Nanofibrillated Cellulose with Fine Clay as a Coating Agent to Improve Print Quality. Pap. Conf. Trade Show 2010, Pap. 2010. 1, 854-880.
[106]Dimic-Misic, K., Ridgway, C., Maloney, T., Paltakari, J. and Gane, P. (2014) Influ-
Green and Sustainable
ence on Pore Structure of Micro/Nanofibrillar Cellulose in Pigmented Coating Formulations. TransportinPorousMedia , 1 1 0 3 , 155-179. https://doi.org/10.1007/s11242-014-0293-8
[107]Andrade, R., Skurtys, O., Osorio, F., Zuluaga, R., Gañán, P. and Castro, C. (2014) Wettability of Gelatin Coating Formulations Containing Cellulose Nanofibers on Banana and Eggplant Epicarps. LWT FoodScienceandTechnology , 5 5 8 , 158-165. https://doi.org/10.1016/j.lwt.2014.02.034
[108]Laurichesse, S. and Avérous, L. (2014) Chemical Modification of Lignins: Towards Biobased Polymers. ProgressinPolymerScience , 3 3 9 , 1266-1290. https://doi.org/10.1016/j.progpolymsci.2013.11.004
[109]Hambardzumyan, A., Foulon, L., Bercu, N.B., Pernes, M., Maigret, J.E., Molinari, M., Chabbert, B. and Aguié-Béghin, V. (2015) Organosolv Lignin as Natural Grafting Additive to Improve the Water Resistance of Films Using Cellulose Nanocrystals. ChemicalEngineeringJournal , 2 2 6 4 , 780-788. https://doi.org/10.1016/j.cej.2014.12.004
[110]Andersson, C. (2008) New Ways to Enhance the Functionality of Paperboard by Surface Treatment—A Review. PackagingTechnologyandScience , 2 2 1 , 339-373. https://doi.org/10.1002/pts.823
[111]Hult, E.-L., Koivu, K., Asikkala, J., Ropponen, J., Wrigstedt, P., Sipilä, J. and Poppius-Levlin, K. (2013) Esterified Lignin Coating as Water Vapor and Oxygen Barrier for Fiber-Based Packaging. Holzforschung , 6 6 7 , 899-905. https://doi.org/10.1515/hf-2012-0214
[112]Vartiainen, J., Vähä-Nissi, M. and Harlin, A. (2014) Biopolymer Films and Coatings in Packaging Applications—A Review of Recent Developments. Materials Sciences andApplications , 5 5 , 708-718. https://doi.org/10.4236/msa.2014.510072
[113]Araújo, T.S.L., de Oliveira, T.M., de Sousa, N.A., Souza, L.K.M., Sousa, F.B.M., de Oliveira, A.P., Nicolau, L.A.D., da Silva, A.A.V., Araújo, A.R., Magalhães, P.J.C., Vasconcelos, D.F.P., de Jonge, H.R., Souza, M.H.L.P., Silva, D.A., Paula, R.C.M. and Medeiros, J.V.R. (2020) Biopolymer Extracted from Anadenanthera colubrina (Red Angico Gum) Exerts Therapeutic Potential in Mice: Antidiarrheal Activity and Safety Assessment. Pharmaceuticals , 1 1 3 , 17. https://doi.org/10.3390/ph13010017
[114]Han, J.H. and Aristippos, G. (2005) Edible Films and Coatings: A Review. In: InnovationsinFoodPackaging , Elsevier, Amsterdam, 239-262. https://doi.org/10.1016/B978-012311632-1/50047-4
[115]Senturk Parreidt, T., Müller, K. and Schmid, M. (2018) Alginate-Based Edible Films and Coatings for Food Packaging Applications. Foods , 7 7 , 170. https://doi.org/10.3390/foods7100170
[116]Alexandre, E.M.C., Lourenço, R.V., Bittante, A.M.Q.B., Moraes, I.C.F. and Sobral, P.J.A. (2016) Gelatin-Based Films Reinforced with Montmorillonite and Activated with Nanoemulsion of Ginger Essential Oil for Food Packaging Applications. Food PackagingandShelfLife , 1 1 0 , 87-96. https://doi.org/10.1016/j.fpsl.2016.10.004
[117]Alparslan, Y., Yapıcı, H.H., Metin, C., Baygar, T., Günlü, A. and Baygar, T. (2016) Quality Assessment of Shrimps Preserved with Orange Leaf Essential Oil Incorporated Gelatin. LWT FoodScienceandTechnology , 7 7 2 , 457-466. https://doi.org/10.1016/j.lwt.2016.04.066
[118]Park, H.J., Kim, S.H., Lim, S.T., Shin, D.H., Choi, S.Y. and Hwang, K.T. (2000) Grease Resistance and Mechanical Properties of Isolated Soy Protein-Coated Paper. JournaloftheAmericanOilChemists ’ Society , 7 7 7 , 269-273. https://doi.org/10.1007/s11746-000-0044-2
Green and Sustainable
[119]Gorrasi, G. and Bugatti, V. (2016) Edible Bio-Nano-Hybrid Coatings for Food Protection Based on Pectins and LDH-Salicylate: Preparation and Analysis of Physical Properties. LWT FoodScienceandTechnology , 6 6 9 , 139-145. https://doi.org/10.1016/j.lwt.2016.01.038
[120]Falguera, V., Quintero, J.P., Jiménez, A., Muñoz, J.A. and Ibarz, A. (2011) Edible Films and Coatings: Structures, Active Functions and Trends in Their Use. Trends inFoodScience&Technology , 2 22 , 292-303. https://doi.org/10.1016/j.tifs.2011.02.004
[121]Chen, H., Wang, J., Cheng, Y., Wang, C., Liu, H., Bian, H., Han, W., et al . (2019) Application of Protein-Based Films and Coatings for Food Packaging: A Review. Polymers , 1 1 1 , 2039. https://doi.org/10.3390/polym11122039
[122]Hassan, B., Chatha, S.A.S., Hussain, A.I., Zia, K.M. and Akhtar, N. (2018) Recent Advances on Polysaccharides, Lipids and Protein Based Edible Films and Coatings: A Review. InternationalJournalofBiologicalMacromolecules , 1 1 0 9 , 1095-1107. https://doi.org/10.1016/j.ijbiomac.2017.11.097
[123]Hopewell, J., Dvorak, R. and Kosior, E. (2009) Plastics Recycling: Challenges and Opportunities. PhilosophicalTransactionsoftheRoyalSocietyB : BiologicalSciences , 3 6 4 , 2115-2126. https://doi.org/10.1098/rstb.2008.0311
[124]Álvarez-Castillo, E., Felix, M., Bengoechea, C. and Guerrero, A. (2021) Proteins from Agri-Food Industrial Biowastes or Co-Products and Their Applications as Green Materials. Foods , 1 1 0 , 981. https://doi.org/10.3390/foods10050981
[125]Cazón, P., Velazquez, G., Ramírez, J.A. and Vázquez, M. (2017) Polysaccharide-Based Films and Coatings for Food Packaging: A Review. FoodHydrocolloids , 6 68, 136-148. https://doi.org/10.1016/j.foodhyd.2016.09.009
[126]Wittaya, T. (2012) Protein-Based Edible Films: Characteristics and Improvement of Properties. In: StructureandFunctionofFoodEngineering , InTech, London, 43-70. https://doi.org/10.5772/48167
[127]Park, S.K., Rhee, C.O., Bae, D.H. and Hettiarachchy, N.S. (2001) Mechanical Properties and Water-Vapor Permeability of Soy-Protein Films Affected by Calcium Salts and Glucono-δ-Lactone. JournalofAgriculturalandFoodChemistry , 4 49, 2308-2312. https://doi.org/10.1021/jf0007479
[128]Cho, D.-Y., Jo, K., Cho, S.Y., Kim, J.M., Lim, K., Suh, H.J. and Oh, S. (2014) Antioxidant Effect and Functional Properties of Hydrolysates Derived from Egg-White Protein. KoreanJournalforFoodScienceofAnimalResources , 3 3 4 , 362-371. https://doi.org/10.5851/kosfa.2014.34.3.362
[129]Richert, M., Nejman, I. and Zawadzka, P. (2019) Characterization of Microstructure Coatings Used in Industry. JournalofSurfaceEngineeredMaterialsandAdvanced Technology , 9 9 , 11-27. https://doi.org/10.4236/jsemat.2019.92002
[130]Park, H.J. (1999) Development of Advanced Edible Coatings for Fruits. Trends in FoodScience&Technology , 1 1 0 , 254-260. https://doi.org/10.1016/S0924-2244(00)00003-0
PLA: Polylactide
PVA: Poly vinyl alcohol
IA: Itaconic acid
AM: Acrylamide
COD: Chemical oxygen demand PAE: Polyamide epoxy epichlorohydrin EVOH: Ethylene vinyl alcohol MFC: Micro-fibrillated cellulose CNF: Cellulose nanofiber
ISP: Isolated soy protein
If you're involved in business development or recruitment, you're already spending lots of time on LinkedIn. As a self-described LinkedIn junkie, everyone who knows me knows that as a result of all the time I spend there, I have strong opinions on LinkedIn etiquette, and have no qualms about calling someone out who violates rules that I consider sacred.
That being said, I also respect, appreciate and draw from the higher powers in the LinkedIn universe — people like Wayne Breitbarth, author of The Power Formula for LinkedIn Success, the seminal book on the subject, and Lindsey Pollak, a widely read blogger for LinkedIn. They and others regularly offer great etiquette and effectiveness advice that I continue to draw from. I should also add one caveat: I'm still learning from some of my own mistakes, and occasionally draw ri ghtful fire from other etiquette police. Mea culpa.
ByGreg Linnemanstons on September 4, 2018 https://www.weidert.com/blog/top-10-linkedin-etiquette-tips-to-connect-like-a-proThe Paper Industry Technical Association (PITA) is an independent organisation which operates for the general benefit of its members –both individual and corporate –dedicated to promoting and improving the technical and scientific knowledge of those working in the UK pulp and paper industry. Formed in 1960, it serves the Industry, both manufacturers and suppliers, by providing a forum for members to meet and network; it organises visits, conferences and training seminars that cover all aspects of papermaking science. It also publishes the prestigious journal Paper TechnologyInternational® and the PITA Annual Review, both sent free to members, and a range of other technical publications which include conference proceedings and the acclaimed Essential Guideto Aqueous Coating.
1. Complete as much of your profile as possible. You don’t need to share every little detail of your experience, but a description of your role at each stop in your professional career builds trust. And while we’re on the subject of trust...include a professional picture of yourself! “Faceless” profiles make it seem as though you’re hiding something. This is a social site, so if you are going to participate at all a picture is a must have.
2. Connect with people you know —or at least know of. Sounds obvious, but accepting invitations from unknowns makes little sense, nor is it appropriate to invite the same. My own decision rule is very simple: I accept invitations from people I’ve met and respect as professionals, and from people whose reputations precede them through trusted recommendations or public scrutiny
3. Respond politely. Whether or not you accept an invitation to connect, a direct, professional response is usually the best next step.
4. Say please and thank you. Frequently. What we all should have learned in kindergarten applies to LinkedIn as well. When you ask for something say please. When someone does something considerate, even if it's not invited, say thanks.
5. Keep updates interesting and professional. We want to know when you've accomplished something noteworthy, read something that's valuable, or discovered something you think should be shared. We (I) don't care what you had for lunch or what you're doing this weekend with your family. Save that for Facebook or Instagram.
6. Give recommendations to get recommendations. There's nothing wrong with asking for a recommendation. But the best way to ask is to first give one. W hen you think about it, the best recommendations should come from the people you know and respect the most, who naturally are the people you can most genuinely recommend.
7. Be honest. We've all experienced this. You find a former peer on LinkedIn and as you review their experience you see they've misrepresented a past role or the responsibilities they had. As a result you look at everything they claim to have done since then with a little more skepticism. Don't do anything that puts you at risk of harming your credibility.
8. Don't be a pest. You won't do yourself any good professionally if you annoy people. We all know someone who does. Don't be that person.
9. Participate. Kind of like when you go to a party: Don't go if you're not going to talk to people and add to the energy of the group. Same thing with LinkedIn. Be active, share information, interact with other people’s updates, grow your footprint, and be additive to the collective good.
10.Use video! Video influencers on LinkedIn are taking full advantage ofits popularity. Including video in your profile makes you more approachable/human. And don’t forget to use video messages to share, comment on, and like other content. Don’t just use the LinkedIn buttons either. Give good content a shout out in your message!
With more than 500 million users in hundreds of countries, LinkedIn is largest professional network in the world. The professional, collegial environment it represents are what users enjoy and what makes it such a special tool for business development, recruitment, and best practice sharing. It's up to all of us, through our behaviors and attitudes, to keep it that way.
Feeling overwhelmed? We understand the busy marketer. Learn how to become more productive by setting and sticking to your goals with these 10 tips.
I’m probably more passionate about goal setting than the average person. Since I have so much data to gather and analyze on a daily basis, I’ve come to realize that deciding on where to focus is key. As a leader, mentor and manager, I encourage others to be very clear about setting their own goals and developing action plans to achieve them. Because if you establish clear goals from the outset (whether it be personal, professional or marketing related), then you’re on a focused track to achieving them. Are you thinking this is easier said than done? Do you struggle with goal setting? If so, then my top 10 tips are for you!
Publish date: Jun 17, 2016 https://www.godfrey.com/insights/tips-for-effective-goal-setting
The Paper Industry Technical Association (PITA) is an independent organisation which operates for the general benefit of its members –both individualand corporate –dedicated to promoting and improving the technical and scientific knowledge of those working in the UK pulp and paper industry. Formed in 1960, it serves the Industry, both manufacturers and suppliers, by providing a forum for members to meet and network; it organises visits, conferences and training seminars that cover all aspects of papermaking science. It also publishes the prestigious journal Paper TechnologyInternational® and the PITA Annual Review, both sent free to members, and a range of other technical publications which include conference proceedings and the acclaimed Essential Guide to Aqueous Coating.
1. Know what makes a good goal. Goals should meet the criteria of SMART *:
S –Specific: Make them as clear as possible
M –Measurable: Develop a benchmark and a target so you know if you’re making progress
A –Attainable: It’s healthy to stretch, but ensure your goals are within reach so it’s worth the effort
R –Realistic: Create goals that are challenging enough to avoid underachievement and apathy
T –Time Bound: Assign deadlines to goals in order to create a sense of urgency, which fosters achievement
2.Do your homework. Look at past data and gather information in order to help you create goals. Without this insight, you can’t build on past successes or failures to know what worked and what didn’t.
3. Identify the rewards and consequences. Closely evaluate what you can gain or lose from not achieving your goal. Once identified, these factors can be powerful motivators.It’s important to be honest with yourself. If you genuinely care about it, you’ll make it happen.
4. List out the obstacles. By clearly identifying what’s holding you back from achieving your goals, you can minimize uncertainty and increase confidence. If roadblocks are identified, you can make plans to overcome them.
5. Brainstorm solutions for the obstacles. If you think through multiple ways to remove obstacles, you’ll be able to select the most effective solution for the situation.
6. Take action. Once you determine the most effective solution, identify the actions you need to take to achieve your goals. Also, establish deadlines for the actions and determine if you can delegate the task to someone else.
7. Get others on board with your goals. Gaining consensus and getting people to understand the why behind your goals is an important step in being able to achieve them. If people can get behind your motivations and your thinking, they will offer you support (whi ch will come in handy when you need to delegate!).
8. Check in frequently. Depending on the goals you set, make it a point to revisit your goals on a weekly, monthly or quarterly basis. How are you trending toward achievi ng them? Do you need to course correct?
9. Celebrate achievements. This is one we often forget. We need to be kind to ourselves and others and take the time to acknowledge that we’re on the right track. This helps us to continue on the path of motivation, energy, confidence and positive goal setting.
10. Say no to things thatdon’t fit within your goals. Yes, this is hard because we often are forced to give something attention based on the needs of others. The important thing is to allow your goals to focus you, and to ask yourself if this new item is in line with your goals. Don’t let anything distract you from what’s most important.
*Another version of SMART goals setting is WHYSMART . The WHY stands for Written, Harmonious and Yours.
Have you been promoted into a new managerial role? Perhaps you’re seeking best practice tips to be a better manager and leader at work.
Great leadership is possible, all it requires is mastering a new skill-set and being devoted to your craft.
Don’t worry, Live And Learn Consultancy’s top 10 ultimate leadership tips for new managers aim to get you started! As a new manager your primary role and responsibilities will involve;
Achieve individual objectives and specific team goals
Ensure your team reach their optimum performance and maintain morale.
A good manager doesn’t always make for a good leader. The main difference between management and leadership is;
Managers have people work for them and rely on control.
Leaders have people follow them and inspire through trust.
Here are 10 effective leadership tips for new managers to help increase your overall performance.
https://www.liveandlearnconsultancy.co.uk/leadership-tips-new-managers/
The Paper Industry Technical Association (PITA) is an independent organisation which operates for the general benefit of its members –both individual and corporate –dedicated to promoting and improving the technical and scientific knowledge of those working in the UK pulp and paper industry. Formed in 1960, it serves the Industry, both manufacturers and suppliers, by providing a forum for members to meet and network; it organises visits, conferences and training seminars that cover all aspects of papermaking science. It also publishes the prestigious journal Paper TechnologyInternational® and the PITA Annual Review, both sent free to members, and a range of other technical publications which include conference proceedings and the acclaimed Essential Guideto Aqueous Coating.
Open your mind to learning and growing as a manager.
Avoid making the mistake of more experienced managers who are set in their rigid ways of “my way is the only way”. You must be willing to adapt to changes andnew technological advances.
You will have worked hard for your promotion and have ample expertise in your chosen field, but you may find that you lack self-confidence in your ability to lead.
Be prepared to learn from others –including your new team.It wi ll help you grow into the role faster.
“A goal without a plan is just a wish.” One of the best management quotes to date.
Always keep your team fully informed of project goals, priorities and important deadlines.
When employees lack planning information, it can raise levels of distrust and anxiety.
Effective communication will be essential in both establishing your credibility and gaining the support of your team, so be sure to provide clear direction and always welcome questions and feedback from others.
Your team will look to you for setting standards.
When writing this blog on the ultimate leadership tips for new managers, management teams often forget to lead by example and demand too muchof their team. This will cause arguments as your team won’t feel yourdemands are justified if you are not following the demands too.
Demand from yourself the same level of professionalism and dedi cation that you expect from others. If you expect the team to be upbeat and friendly, then make sure you are!
Creating an environment where the energy is positive and ideas are heard are the core ingredients for a thriving team.
Have an open-door policy with your team. Being approachable is key.
Sometimes employees are unwilling to speak up about certain issues unless they are prompted, particularly if they fear losing their jobs.
Canvass for opinions on issues such as support, training, and resources while maintaining an open-door policy so that your team knows that you are willing to listen to their concerns and ideas.
By publicly recognising the efforts and achievements of your team, you not only build up their confidence, but also encourage future contributions and effort.
Praise does not always have to be formal –praising employees can be part of your day-to-day communication with your team.
When conducting monthly performance reviews with your team, thi s is a great opportunity to convey your thoughts but also listen to your staff concerns and challenges.
Many team leaders cancel appraisals when time is limited;make every effort to conduct a regular one to one employee interview.
6. Be decisive
Leaders who make decisions in a timely fashion build stronger trust with their team.
A quality leader needs to make decisions and stick to them. People do not feel comfortable with someone who changes his or her mind on a whim.
You only have to look at the public’s opinion of government U-turns to see how easily confidence in a leader can be weakened or lost altogether. Strive to be a decisive leader.
7. Help your team see the big picture
Your team will be working on the front-line which means they can’t always envision your goals as a manager. Remind them each week of the bird’s eye view and how they are performing.
Take time to explain to your team how their assignments and projects fit into the company’s larger goals and overall objectives.
This will help demonstrate that every task they complete can have an impact on the company’s reputation, success, and bottom line.
8. Create a learning and development environment
Managers who invest in training for their team are 80% more likely to see better performances.
The environment you create for your team dictates your chances of succeeding as a manager.
Encourage your team to explore new methods for reaching their individual and team goals. Be realistic, allow your employees to make mistakes and be sure to rewardnew and innovative ideas.
Treat your people like machines and eventually their output and productivity will decline. Poor managers make this terrible mistake.
9. Provide professional guidance
A good manager and leader will also be a mentor. Make yourself available to staff members and show interest in their career development within the company.
Don’t overlook the motivational power of positive reinforcement –your staff will appreciate your commitment to their progress.
10. Be patient with yourself
Developing strong team leadership skills takes time –especially as you adjust to your new position.
Avoid doing it all alone!
Seek guidance from colleagues, your line manager, or join a professional network on LinkedIn. If you are serious aboutenhancing your leadership abilities and making strides toward becoming a great manager, look for support.
While the above list of leadership tips is intended for new managers, you can share these tips with more seasoned managers to remind them of the basics and help them avoid derailing.
Be an open-minded manager who is willing learn and grow. Keep you team informed of latest news, projects and work deadli nes.
It’s your responsibility to set the standards.
Great managers are always approachable. Reward and recognise your teams great work. Don’t take too long to make important decisions. Remind your team of the bigger picture.
Create a winning environment through developing your teams’ ski lls. Positive reinforcements make your team as solid as a rock. Be patient with yourself and avoid being overly critical.
We hope our article Top 10 Ultimate Leadership Tips for New Managers has generated new team leading ideas, provided key reminders of what not to do and helped you in your quest to become a better manage in the workplace.
FROM
Volume 8, Number 3,2022
PITA CORPORATE SUPPLIER MEMBERS
Page 2 Archroma Appetan® NTR barrier chemistry
Page 3 Valmet Dryer section performance agreement
PITA NON-CORPORATE SUPPLIER MEMBERS
Page 4 Voith AiroGuide Tune Greenroll cover
Page 5 Voith
Page 6 Voith
C-bar HerculeXXupdated screen cylinder
OnQ FormingSensautomation solution
Page 7 Voith OnView.MassBalanceautomation solution
Page8BTGReelTime™automation solution
Page 9MoistTechmoisture measurement and control sensors
Page 10ToscotecTT Hydrogen Burner
The Paper Industry Technical Association (PITA) is an independent organisation which operates for the general benefit of its members –both individual and corporate –dedicated to promoting and improving the technical and scientific knowledge of those working in the UK pulp and paper industry. Formed in 1960, it serves the Industry, both manufacturers and suppliers, by providing a forum for members to meet and network; it organises visits, conferences and training seminars that cover all aspects of papermaking science. It also publishes the prestigious journal Paper TechnologyInternational® and the PITA Annual Review, both sent free to members, and a range of other technical publications which include conference proceedings and the acclaimed Essential Guideto Aqueous Coating
Archroma, a global leader in specialty chemicals towards sustainable solutions, today announced that its ground-breaking Appretan® NTR range based on 30% renewable raw material can now be applied to impart barrier properties to selected types of food packaging.
Consumers are increasingly frowning upon being served their fav orite street foods or fast foods in polystyrene or plastic based boxes and wrappings. Paper-based packaging can offer a much more sustainable alternative if they are not lined with a plastic film which can make them unsuitable for recycling and composting. The solution is to carefully select paper coatings and barriers solutions which are fit for purpose and that are designed to make food packaging both safe for food contact and more recyclable.
Archroma is well known for its innovations and sustainable solution systems aimed at helping packaging & paper manufacturers to optimize productivity and/or create value in their markets. Just a few months ago the company launched Cartaseal® VWAF, a PFC-free and ammonia-free* barrier for odorless paper-based food packaging, as well as in 2019, a ground-breaking binder, Appretan® NTR, made with 30% active content based on natural, renewable raw materials, designed for use in nonwoven articles such as tea bags and coffee filters.
In line with the principles of “The Archroma Way to a Sustainable World: Safe, efficient, enhanced, it’s our nature”, the paper & packaging R&D experts of Archroma decided to explore the properties of Appretan® NTR for paper-based packaging applications.
They investigated a new specific application aimed at providing a more sustainable barrier option for general food packaging used with a short contact time, such as burger or sandwich paper wraps.
The Appretan® NTR range is made with over 30% renewable raw mat erial component, allowing the reduced use of fossil fuel based resources without compromising on the needed performance of water, oil and grease resistance. It is a more sustainably responsible option for packaging manufacturers and food retailers willing to help tackle the impacts of our food consumption habits.
The Appretan® NTR range is therefore at the core of NATURE BITES, a barrier system just launched by Archroma. In this new system, Appretan® NTR can be combined with Cartacoat® primers suitable for food contact that will seal the paper surface for further increased performance.
“Consumers are increasingly questioning how products are made, and expecting them to be harmless for themselves and their loved ones, and the planet”, comments Andy Bell, Head of Competence Center Paper Chemicals, who adds: “That is why it is critical that major food and beverage brands and retailers have a close look at their packaging supplier, and ensure that they work only with leaders in sustainable innovations such as Archroma. Appretan® NTR and the NATURE BITES system illustrate once again the commitment of Archroma to drive sustainable innovation in everything we do. Because it’s our nature.”
As part of services offering for tissue producers, Valmet has developed a service agreement to improve the performance and safety of the Yankee cylinder, hood, and air system.
The dryer section consumes roughly 70% of all the energy usedin the tissue-making process, and it is the major CO2 producer in the process. A timely and correct maintenance plan as well as control of process parameters is essential for safety, end product quality and energy efficiency.
“By keeping the process at an optimal level, the risk of unplanned shutdowns due to Yankee failure is reduced by 99%, production efficiency increased by 1–2%, drying energy consumption and related CO2 emissions reduced by 3–10%,” says Raffaele Malutta, Agreement Manager, Tissue Service at Valmet.
The new agreement offers a systematic approach to improve the performance of the dryer section –its safety, reliability, availability, and energy consumption. An optimal length for the agreement is five years. Every agreement starts with a complete condition check and energy study. The rest can be tailored to the customer’s needs by adding the right combination of services, such as Valmet Industrial Internet solutions, remote support through Valmet Performance Center, improvement plans and maintenance guidance.
Valmet’s typical service agreements range from corporate-level frame agreements to milllevel partnership agreements. Valmet’s services offering forms the building blocks for customized agreements.
First guide roll cover certified according to DIN CERTCO for bio-based products
Successful step in the development of sustainable products as part of the Papermaking for Life program
Renewable raw materials reduce carbon footprint
Less wear of fabrics and reduced waste
With the AiroGuide Tune Green, Voith is setting a new standard in the field of papermaking products made of renewable raw materials. As the latest member of the AiroGuide guide roll cover family, AiroGuide Tune Green is certified according to the internationally recognized DIN CERTCO for bio-based products. The guide roll cover combines all the advantages of the proven AiroGuide technology while enabling the reduction of the carbon footprint. The new innovation aligns with Voith's long-time commitment and ambitious goals to accelerate sustainability for papermakers as well as in its own production
“With AiroGuide Tune Green, we are the first in the market to provide a DIN CERTCOcertified guide roll cover made with bio-based materials. We offer our customers a sustainable alternative and thus set a new milestone on the way to a more sustainable future of paper production.”Ralf Moser, Global Product Manager at Voith
AiroGuide Tune Green is a composite cover using bio-based raw material with mineral fiber reinforcement. It is particularly designed for the wet end and features improved corrosion protection with enhanced edge sealing to meet the corrosion requirements in humid areas.Its good stress resistance and high wear resistance result in less grinding and maintenance requirements compared to standard covers. Therefore, the roll cover leads not only to less wear of the fabrics and reduced waste but also contributes to important resource savings in paper production.
Due to the combined development of the AiroGuide Tune Green and SkyClean doctor blades, the machine can operate without additional lubrication showers –targeting less water consumption and reduced misting.
“As part of our sustainability program Papermaking for Life, we are focusing on the entire product life cycle, among other things. The importance of this is also reflected in our customers' strategic orientation and diverse activities. This certification confirms that Voith, as a full-line supplier, provides products and services that support the global commitment to sustainable and resource-saving paper production.”Thomas Jäger, Senior Vice President Sales Fabric & Roll Systems EMEA
Highest stability and robustness for applications with extreme stresses
Sustainable reuse of end rings through innovative screw connection
Low maintenance costs and long service life increase savings potential and efficiency
Screen baskets are essential in paper production to remove contaminants from the suspension in the screening process. Since high stresses occur here, Voith developed the Cbar HerculeX screen basket in 2017, which combines maximum stability with the provenCbar technology. These screen baskets are characterized by their overlapping profile bar design that protects the slots from high wear and keeps the slot widths constant over the entire service life. Meanwhile, Voith is celebrating the success of 1,000 HerculeX screen baskets delivered and at the same time launches the newest member of the Voith screen basket family: the C-bar HerculeXX.
Due to its extreme stability and robustness, the new HerculeXX screen basket is particularly suitable for applicationswhere the stresses are even higher, such as in pulp production. Especially in the area where the screen cylinder is connected to the end ring, enormous forces prevail with extremely strong rotor pulsations and high stock consistencies. This requires screen baskets with maximum stability. In addition, the HerculeXX combines the hybrid technology of the HerculeX with an innovative screw connection of the end rings to the screen cylinder. The unique screw connection of the end ring offers papermakers the ability to reuse it when replacing a screen cylinder, which contributes to a sustainable material usage reduction.
Individual adjustments of slot widths and geometries enable the HerculeXX to sort particularly efficiently. In addition, the wear-protected material leads to a long service life and low maintenance costs. As a result, it contributes to the achievement of efficiency and savings targets.
“Since May 2020, the new C-bar Voith HerculeXX screen basket has been successfully in operation at our PM5. In the harsh application, the innovative design shows significantly improved lifetime compared to the previously installed screen baskets. The performance is outstanding and the efficiency, as you would expect from Voith, is on the highest level. Moreover, this HerculeXX was tested successfully in another application for six months before.”Özkan Aydin, PM 5 production manager at Modern Karton.
Based on many years of experience and profound know-how, Voith improves the design of OnQ FormingSens for optimized lifetime, reliability and operator friendliness
Thanks to real-time measurement, the operator continuously receives information about the dry content in the forming section and can optimize the v acuum settings
In combination with the OnC.Dewatering automatic vacuum control system, layer bonding in the forming section can be improved and energy requirements reduced
Compared to the previous OnQ FormingSens, the new generation features a significantly longer service life, flexible connectivity to existing process control systems and improved mechanical stability, enabling reliable measurement results. The focus of the new design is on a reliable, low-vibration construction, as well as a simplified electrical design.
OnQ FormingSens has a long track record of benefitting paper manufacturers of different grades, with more than 100 systems are already in use in the forming section worldwide. Thanks to microwave technology, the leading solution measures fluctuations in water weight precisely, reliably and in real time. Based on this information, papermakers can systematically improve their settings, achieve a stable dry content at the end of the forming section, and utilize the maximum dewatering capacity in the press section. At the same time, the optimized settings ensure less wear on the forming fabrics and ceramics. In addition, vacuum and drive energy usage can be reduced, which was confirmed, among others, by a Central European packaging papers manufacturer. Here, OnQ FormingSens reduces energy costs by around 130,000 euros per year and pays for itself in well under a year. For maximum user-friendliness and reliability, Voith experts have now further optimized the design of the solution.
“Compared to the previous OnQ FormingSens, the new generation has a significantly longer service life, flexible connection options to existing process control systems, and improved mechanical stability, thus enabling extremely reliable measurement results.”Jörg Spindler, Manager Actuator Development at Voith Paper
The new design focuses on a solid, low-vibration construction, as well as a simplified electrical design. Among other things, Voith'sexperts reworked the mechanical mount so that the operator can now fine-tune the penetration depth from outside the machine via waterproof mechanical gear. The sensor holder can be flexibly positioned on various existing dewatering elements in the former.Compared to hand-held measuring devices, the permanently installed application is characterized by higher safety, as no direct contact of the operator with the forming fabrics is necessary. An improved sensor housing ensures higher long-term stability. The new generation OnQ FormingSens is installed to a nearby terminal box, which can be serviced by Voith experts via a service connection. This allows the optimized solution to be better connected to customers' existing infrastructures, such as the process control system.
Based on the measurements of OnQ FormingSens, the control loop can be closed with the fully automatic dewatering control OnC.Dewatering. The control system defines and stabilizes thedry content of each layer produced and thus significantly increases ply bond on multi-ply machines.
OnView.MassBalance visualizes losses in stock preparation and thus enables operators to take appropriate countermeasures easily and at an early stage
Thanks to the digital solution, significantly more resource-efficient paper production is possible
Successful customer installations demonstrate a two percent improvement in total yield
The recycling process in paper production is complex. Fluctuations in fiber quality and the degree of contamination of the recovered paper bales have a dir ect influence on production output. At the same time, resource efficiency is more important today than ever before. However, with the current state of the art, it is hardly possible to determine the specific causes of losses and optimize them directly. Yield is usually only measured on a weekly or monthly basis –by the time paper manufacturers receive the information, the losses have already occurred. Furthermore, it is very difficult to estimate whether losses in individual stock preparation areas have increased or decreased compared to the last analysis. To address these issues, the leading full-line supplier Voith has developed OnView.MassBalance.
The innovative digital tool displays losses in stock preparation in real time to further increase the sustainability and efficiency of paper production. At a glance, the operator can locate the specific areas with optimization potential on the screen. For this purpose, a Sankey diagram maps each feed, accepts and rejects at each process step. As soon as a critical value is reached, OnView.MassBalance reports this to avoid high losses. In this way, standardized processes can be established that can be quickly and easily performed by operators across different shifts. Suitable countermeasures can be, for example, checking the pressure drop or the feed consistency of the last screening stage.
As there is less rejects to dispose of and at the same time more paper can be produced with the same amount of raw materials, the solution pays for itself in less than a year. Flavio Granito, Global Product Manager Fiber System 4.0 at Voith Paper,explains.
“The solution is already being used very successfully, for example in an OCC mill in France with an annual capacity of 250,000 tons. After the optimization phase, 600 tons of rejects, including raw material, could be saved per month. This corresponds to a two percent improvement in yield. OnView.MassBalance is another example of how digitalization can strengthen more sustainable and cost-efficient papermaking. As part of our major sustainability program Papermaking for Life, we have set the goal of optimizing recycling processes and minimizing fiber losses. We aim to achieve a 90 percent recycling rate by 2030.”
To calculate the mass balance in stock preparation, the innovative tool uses the signals from the sensors installed in the stock preparation plant. Voith experts identify the sensors required for this and develop a suitable concept together with the customer. Voith also separately offers the OnPerformanceLab (OPL) service. Based on bundled know-how,the OPL provides pragmatic support in analyzing losses, defining and implementing new countermeasures, and preparing monthly reports in close coordination with the respective paper technologists.
BTG’s ReelTime™ is the latest BTG solution aimed at tissue makers, targeting process variations from the pulper to the headbox, while at the same time predicting and impacting product quality in “real time”. The ReelTime solution combines innovative measurement, visualization and analytical software, supported by process and tissue-making expertise and knowledge.
“As tissue makers look towards self-regulating and autonomous papermaking, we believe implementing integrated digital solutions will provide the basis for achieving this. This is why we are so excited about the possibilities ReelTime represents for our customers”, comments Ian Padley, Global Solutions Manager for the tissue market.
A BTG ReelTimeproject usually delivers pay back within less than 12 months, and provides savings in the areas of fiber blending, productivity increases and energy consumption reduction.
MoistTech manufactures the diamond standard in moisture measurement and control sensors for both use directly on the production line and also for laboratory use. Providing the best solution in the industry, our near-infrared sensors can detect moisture levels within your product as well as thickness, and coat weight, oil, and fat/protein content with one unit. This allows our equipment to be a staple for a wide range of sectors and disciplines, including adhesives, biomass, chemicals, coatings, food, forest products, minerals, renewable energy, textiles and wood products.
Unsurpassed in performance, stability, reliability and cost of ownership, the MoistTech series of moisture analysis sensors can increase both the quality and efficiency of the manufacturing process. Product quality and consistency are forefront with MoistTech in the development of the IR3000 sensor to accurately provide moisture measurements throughout the process, yielding a consistent, quality product from lab to line that immediately reduces downtime,wasted energy and product loss.
Designed to provide accuracy and repeatability, the MoistTechtechnology is a ratio-based measurement with prime beam; this eliminates sensitivity due to distance, improves stability and accuracy. The technology captures hundreds of detailed, accurate measurements per second. The ability to pre-set the measurement rate to match the production rate is available on the technology and because there are no routine re-calibrations, this technology is low to zero maintenance which makes it an ideal solution for the manufacturing process.
The sensors are designed to be installed 4-12 inches above the production line so that it can continuously monitor the production process and can be incorpor ated into multiple environments including:
•Belt
•Conveying systems: screw, chute, roller, chain, drag, elevator and pneumatic
•Chutes,Cyclones, Bins
•Webs
•Pipelines
Insensitive to material variations such as particle size, material height & color, our moisture sensors provide continuous, reliable readings with zero maintenance and a one-time calibration with a non-drift optical design allowing operationa l personnel to confidently make immediate process adjustments based on real-time measurements.
Utilizing NIR Technology, which is a state-of-the-art, fast, non-destructive method of measuring and controlling moisture content, MoistTech is able to deliver multiple benefits to its clients -ranging from product quality monitoring, increased plant efficiency, lower energy costs and less waste, to precise dryer control, lower costs and higher accuracy. Instant ROI, low-to-zero maintenance andprocess optimization can also all be achieved through a MoistTech solution.
Toscotec launches TT Hydrogen Burner, a new generation of 100% hydrogen fueledburners designed and tested for Yankee hoods. Within the context of the energy transition from fossilbased to zero-carbon industrial operations, Toscotec developed this patented innovation to drive the conversion of paper manufacturing to clean energy.
TT Hydrogen Burner is an in-line burner featuring precisely controlled combustion and two safe operation modes. In carbon-free mode it runs on 100% hydrogen; in carbon-reduction mode it is fueled by a mixture of natural gas and hydrogen, where the percentage of hydrogen is accepted across a wide range.
TT Hydrogen Burner entirely matches the high performance of gas-fired burners, using a carbon-free fuel. In fact, hydrogen combustion does not emit carbon dioxide into the atmosphere. The key factor in the overall energy balance is that hydrogen fuel is produced from renewable energy sources. If this is the case, in the future hydrogen may possibly replace fossil fuels in all thermal processes associated with tissuemaking, including steam production and air system burners. In terms of its infrastructure, hydrogen can be stored in pressure vessels, or injected into the existing natural gas grid.
Stefano Pecchia, Energy Technology Director at Toscotec, says, “Tissue producers are asking for technological innovations that will allow them to work in full hydrogen mode. Whether they choose to replace their existing burners or install new tissue lines, tissue producers aim to be ready for when this fuel will be widely available, cost competitive and green. In response to this demand, Toscotec has invested in building a dedicated air system test bench to ensure guaranteed results according to the specific operating requirements of paper mills”.
The design of TT Hydrogen Burner is ready for industrial scale production because it has been successfully tested to operate under the same conditions of air speed, temperature, and humidity of the actual air system of a tissue machine. TT Hydrogen Burner is suitable for immediate installation.
Currently, hydrogen availability for tissue mills is limited, so the burner can be set to operate burning hydrogen mixed with natural gas in carbon-reduction mode, or even only natural gas if necessary. When hydrogen becomes readily available, in order to switch to full hydrogen mode, TT Hydrogen Burnersimply requires a nozzles replacement, which is a one-day easy procedure. This will guarantee the highest possible combustion efficiency based on 100% hydrogen gas.
PITA Introduction to Wet End Chemistry 9 10 Nov. 2022
PITA / Gernsbach Fundamentals of Papermaking 6 8 Dec. 2022
PITA / MCP Maintenance Planning & Scheduling 31 Jan. - 1 Feb. 2023
PITA Fundamentals of Wastewater Treatment 14 14 Mar. 2023
Technologie Kring Apeldoorn, The Netherlands 23 24 Nov. 2022
Paper One Snow Sharjah, UAE 21 23 Feb. 2023
Tissue World Düsseldorf, Germany 23-30 Mar. 2023
Paper Arabia Dubai, UAE 15-17 May 2023
Paper & Biorefinery Graz, Austria 24 25 May 2023
Zellcheming Wiesbaden, Germany 20 22 June 2023
The Paper Industry Technical Association (PITA) is an independent organisation which operates for the general benefit of its members both individual and corporate dedicated to promoting and improving the technical and scientific knowledge of those working in the UK pulp and paper industry. Formed in 1960, it serves the Industry, both manufacturers and suppliers, by providing a forum for members to meet and network; it organises visits, conferences and training seminars that cover all aspects of papermaking science. It also publishes the prestigious journal Paper Technology International® and the PITA Annual Review, both sent free to members, and a range of other technical publications which include conference proceedings and the acclaimed Essential Guide to Aqueous Coating.
The following pagescontain a summary of the various installations and orders from around the world of papermaking, wood panel and saw mills,and bio-power generation, received between early August2022 andearly November2022.
The Paper Industry Technical Association (PITA) is an independent organisation which operates for the general benefit of its members –both individualand corporate –dedicated to promoting and improving the technical and scientific knowledge of those working in the UK pulp and paper industry. Formed in 1960, it serves the Industry, both manufacturers and suppliers, by providing a forum for members to meet and network; it organises visits, conferences and training seminars that cover all aspects of papermaking science. It also publishes the prestigious journal Paper TechnologyInternational® and the PITA Annual Review, both sent free to members, and a range of other technical publications which include conference proceedings and the acclaimed Essential Guide to Aqueous Coating.
Ahlstrom-Munksjö
Aspa Bruk Sweden
SPMadvanced online system Intellinova Parallel EN to monitor the mechanical and lubrication condition of the mill’s pulp dryer and wood chipper
Anon Asia-Pacific region Valmetcoated board making line with automation and Industrial Internet solutions as well as spare parts and consumables packages
Anon Italy IMA TMCtwo palletizing lines for a customer active in the tissue rolls market
Anon Mexico ProJettwodryer fabric cleaners including a complete water recycling & treatment system
link
link
link
link
Anon Pulp Mill South America
Babcock & Wilcoxhighly efficient cooling technology (18 cooling cells for three wet towers)
link Arauco five Pulp Mills Chile
ABBremote supervision to ensure greater reliability and monitoring across all processes
Hergennew headbox (PM2) link
link Avelino Bragagnolo Faxinal dos Guedes SC Brazil
Bracell SP Celulose Ltda Lençóis Paulista São Paulo Brazil
Burgo Mosaico Lugo Paper Mill Italy
Andritzfour tissue production lines (design speed of 2100m/min and a working width of 5.68m) including DCS
link
SAELrenovation of paper laminator link
Canfor Corporation Southern Alabama USA
BID Groupstate-of-the-art sawmill complex (in collaboration with strategic partner Rockwell)
Cellmark & Total Fiber Recovery Chesapeake Virginia USA
Cheng Loong Binh Duong Paper Company Binh Duong Province Vietnam
Bulk Handling Systems (BHS)
recycled pulp production facility (capacity 300,000 tons of mixed paper and Old Corrugated Containers)
ProJettwo dry end tail cutters for BM23 (being supplied to OEM YueLi, Taiwan)
link
link Cartularia SPA Italy Pasabantwo new sheeter machines for premium FBB cardboard (converter)
link
link
Cheng Loong BinhDuong Paper Company
Binh Duong Province Vietnam
CMPC various sites Brazil
Valmetkey technology including approach flow systems, headboxes, a press section, a sizer, process air systems, a winder, automation systems and Industrial Internet solutions for new board machine (BM23)
SOSAto utilise open innovation capabilities to implement cuttingedge techsolutions that will optimise the efficiency and sustainability of CMPC's forestry supply chain (in collaboration with Brazilian National Confederation of Industry)
link
link
COBAP Ceara Northeast Brazil
Overmadeturnkey tissue line (PM7 ‘NICO project’) link
Hergenmodernisation of PM1 link Convertipap Mexico
Greenlam South Limited India
Dieffenbacherhigh-end particleboard mill including EVORIS, a new digital platform
ProJettail cutter (BM1) link
link Greif Board Milwaukee Wi. USA
Guangxi Sun Paper
Beihai
Guangxi Province China
Heinzel
Zellstoff Pöls Mill Styria Austria
Infinited Fiber Company Veitsiluoto Kemi Finland
ITC Limited PaperBoards & Specialty Papers Division Chandrahati site India
Jasztex Fibers Inc. Pointe Claire Quebec province Canada
Andritzfour stock preparation systems to process NBKP(Needle Bleached Kraft Pulp) and LBKP (Leaf Bleached Kraft Pulp) for tissue production
Valmetpulp technology equipment for a new pulp stream of unbleached kraft pulp
Andritzbasic engineering for key process areas for regenerated textile fibre production plant capacity 30,000tpy (reprocessing textile waste)
link
link
link
Voithto rebuild PM1 including stock preparation (décor machine) link
Andritzneedlepunch equipment (nonwovens) link
Kastamonu Entegre Kastamonu City
Türkiye
Siempelkampnew particleboard line link
Keryas Paper Oman ProJetdryer fabric cleaners (PM1) link
Kimberly Clark Tlaxco Mill Mexico
Kipas Söke Söke
Turkey
Klabin “Puma II”Project Brazil
KMK Paper Turkey
KMK Paper Turkey
ProJjetpower cleaner system (nonwoven line) link
Runtechvacuum system for containerboard line (PM3) link
ABBpower distribution system, drives and motors (through Valmet) link
AFTwet end rebuild including a complete POMapproach flow system for both plies (PM1)
Toscotecrebuild of packaging / board machine (PM1) from the forming section to reel, and to include new steel dryer cans
link
link
Lipy Paper Mills Ltd Bangladesh ValmetQCS link Mayr-Melnhof Group
FollaCell Pulp Mill Norway
Valmetnew baling line and flash drying rebuild link
Mercer Stendal Pulp Mill
Arneburg Germany
Valmetmodernise valves link Minhan Paper Joint Stock Company
Van Lam Hung Yen Province Vietnam
Valutecfive continuous kilns and control system link
Andritzcomplete OCC line from pulping to approach flow link Moelven (three sawmills) Norway & Sweden
MP hygiène Annonay Mill France
Oji Paper (various sites) Japan
Toscoteclow-carbon design tissue line (PM2) link
ProJetseven dryer fabric cleaners for various machines throughout Japan
link
Papeles y Conversiones de Mexico
Monterrey Nuevo Leon Mexico
AFTPOMapproach system for containerboard line (two POMp degassers, two POM Dynamix static mixers, two POMlock seal tanks, two POM headers, and two POM head tanks for PCM’s two-ply PM2, along with accompanying spare parts and system engineering)
link
Paracel S.A. Concepción
Paraguay
PF Nonwovens
Znojmo Czech Republic
RDM Group Blendecques Mill France
Saint Gobain/ ADFORS Litomysl Czech Republic
Shanying Suzhou Paper Zhongying Anhui Province China
Sichuan Huaqiao Fenghuang Paper Guanghan City Sichuan Province China
Sichuan Huaqiao Fenghuang Paper
Guanghan Deyang City Sichuan Province China
Sinaatec Spa Algiers Algeria
Smurfit Kappa Nettingsdorf Mill Austria
Sun Paper Nanning Nanning Guangxi province China
Andritzall process equipment and energy-efficient and environmentally friendly pulp production equipment for 1.8Mpty pulp mill
link
ProJeteight power cleaners for eight nonwoven lines link
A.Cellipaper rewinder link
ProJetCleaner for saturator belt (fibre glass mat manufacturer) link
Voithtwo paper machines for CCM products (PM71 and PM72)design speed of 1300m/min and a wire width of 9,300mm, total capacity 812,000tpy
A.Cellitwo 8m width rewinders to process fluting, testliner and kraftliner (PM6 line)
Andritzpatented combi-pulping system combining drum pulping, LC (low consistency) pulping, and HD cleaning in one innovative system (2200tpd capacity PM2)
Reifenhäuser Reicofil
two nonwovens lines (3.2m single-beam meltblown line and a 3.2m composite bico line)
link
link
link
link
IBS Paper Performance Group rebuild of forming section (PM6) link
A.Cellithree paper winders to process medium linerboard with a width of 6730mm and basis weights from 140 to 250gsm (PM8) and from 100 to 160gsm (PM9), at a design speed of 2500m/min
link
Uniboard Val-d’Or Quebec Canada
Vajda-Papír Budapest Hungary
VRG Dongwha Minh Hung Vietnam
Wakayama Gobo Biomass Power Plant G.K.
Wakayama Prefecture Japan
Whakatane Mill Limited North Island New Zealand
Welspun Advanced Material Telangana India
Yash Pakka Limited Ayodhya packaging production facility India
Dieffenbacherparticleboard line using new CEBRO small plant concept link
Voith digital documentation platform OnCare.eDocfor the comprehensive and user-friendly management of all the technical information of its new tissue line
Valmetchip washing and defibrating machine system (MDF plant) –capacity 700,000m3/y
Andritzhigh-efficiency circulating fluidized bed 50MW boiler (from Toyo Engineering Corporation)
Bellmerrebuild of board machine (BM3) to increase the production capacity of net paper by 60,000tpy up to over 200,000tpy
link
Yuen Foong Yu Consumer Products Co., Ltd. Chingshui Taiwan (Republic of China)
link
link
link
Andritzpredictive maintenance system (for spunlace line) link
AFRYbasic engineering assignment including a speciality paper machine of 100T per day to lead towards flexible packaging with furnish, utilising max strength of agro residue bagass, biofuel based 10MW of Cogen plant, pulp capacity enhancement by augmentation of Pulp Mill by another 75% as well as support infrastructure in line with increased output of pulp and paper machine.
Andritza complete production line (PM10) with design capacity of 112admt/d, a width of 3.65m and a maximum operating speed of 1650m/min. The scope of supply also comprises the stock preparation system, processing a mixture of NBKP (Needle Bleached Kraft Pulp) and LBKP (Leaf Bleached Kraft Pulp).
link
link
Most journals and magazines devoted to the paper industry contain a mixture of news, features and some technical articles. Very few contain research items, and even fewer of these are peer-reviewed.
This listing contains the most recent articles from threeof the remaining specialistEnglish language journals alongside one Korean journal and one Japanese journal, both of which publish original peer-reviewed research:
IPPITA JOURNAL(Peer-reviewed and other)
JAPAN TAPPI JOURNAL(English abstract only)
JOURNAL OF KOREATAPPI(English abstract only)
NORDIC PULP & PAPER RESEARCH JOURNAL
TAPPI JOURNAL
Notes:
1. IPPTA JOURNAL seems to have replaced IPPTA PAPYRUS 360° after only 2 editions of the latter, as of late 2021.
2. JAPAN TAPPI JOURNAL is a members-only journal that contains excellent research articles –abstracts are in English but articles are in Japanese.
3. JOURNAL OF KOREATAPPI is an excellentopen-access research journal–abstracts are in English but articles are in Korean.
The Paper Industry Technical Association (PITA) is an independent organisation which operates for the general benefit of its members –both individual and corporate –dedicated to promoting and improving the technical and scientific knowledge of those working in the UK pulp and paper industry. Formed in 1960, it serves the Industry, both manufacturers and suppliers, by providing a forum for members to meet and network;it organises visits, conferences and training seminars that cover all aspects of papermaking science. It also publishes the prestigious journal Paper TechnologyInternational® and the PITA Annual Review, both sent free to members, and a range of other technical publications which include conference proceedings and the acclaimed Essential Guide to Aqueous Coating.
1.A Chemical Free and biodegradable Cooking Enhancement program for efficient cooking andmercaptans reduction
2.Benchmarking of Pulping, Bleaching and Recovery Operations (W ood & Agro Based Mills
3.Cost reduction and Quality Improvement by Optimizing Cooking and Bleaching
4.Effect of Process Variables on Pulp Yield of Indigenous Raw Materials
5.Energy Consumption Benchmarking In Pulp & Paper Sector
6.Enhancing the pulp quality by optimization of pH of Chlorine Dioxide solution at the D-stageof bleaching process
7.Experience of Non-Condensible Gases Handling System inAPl
8.Kraft Mill variability and efficiency benchmarking
9.Non-Process Elements Leaching From Raw Materials and 95% Causticizing Efficiency
10.Process improvement in Agro pulping for enhanced productivity -Case studies
11.State of Art Vertical Lime KILN
12.Two Way Feeding And Condensate Sealing In Multiple Effect Ev aporation Plant
1.Paper, you and me
2.Paper is thread of Life “We Love Paper”
3.Paper -A Reflection of our progress
4.Paper -Natural & Sustainable
5.Paper -An inextricable bond with us
6.Paper the witness of our history
7.We Love Paper –In every step of our Life
8.Paper A boon to mankind
9.Paper : Emerging Trends
10.Intimacy of our feelings to Paper
11.Paper in our Lives
12.Importance of the Paper on Globe
13.What makes Paper so lovable among the masses?
14.A concise view of the Paper Making Process
15.A tool for creative expression
16.Paper is a great gift to all
17.Hamara Pyara Paper
18.Evolution of Paper
19.Paper -You cannot refuse “Yesterday, Today, Tomorrow” & Paper is recyclable
20.Achieving agenda 2030 of sustainable development goals through ”Paper”
21.Paper : Journey and Necessity
22.The secret of love with Paper
23.Paper -A friend forever
24.Why we love Paper?
25.Paper -A friend to our mother Earth
1. The High Efficiency Cooling Unit with a Thermo-Siphon HEX
2.Factory Equipment Optimization Solution based on Data Science
3.Energy-saving Technology for Public Water Treatment Energy-saving Rotary Blower “TBS/RSH series”
4.Energy Saving by Modifying Drainage System of Paper Machine 1
5.Energy Saving Case Study of Futatsuka Manufacturing Department, Chuetsu Pulp & Paper Co., Ltd.
6.Energy Saving of Chlorine Dioxide Generation System R8
7.New Challenge to Paperboard Machines with “AXISZ System”
8.Split Mechanical Seal for Agitator, and Auxiliary Seal
9.Recovery Boiler Online Ash Analyzer and Ash Balance Advisor Applications
10.Preparation of Antimicrobial -cyclodextrin Microcapsules containing a Mixture of Three Essential Oils as an Eco-friendly Additive for Active Food Packaging Paper
1.Conversion from Paper Pulp to Cellulose Nanofibers
Characteristics of Diverse CNFs, and Their Current R&D and Challenges
2.Recent Trends of Biorefinery in Scandinavia
3.Global Market Pulp Demand & Supply
4.Latest Trend about New Pulp Mill Projects in the World
5.Kiln Fuel Conversion Toward Carbon Neutrality
6.Advanced Technology to Counter the Increasing Foreign Matter
7.Operational Experience of MaxiTrasher and MaxiSeparator
8.Development of Online Pulp Color Dirt Observation Equipment
9.Preparation LC-Refining by Using Valmet Online Analyzer
10.Introduction of Sulfuric Acid Dilution System with Pump Control
11.Defoamerfor Kraft Pulp Manufacturing Process
12.Optimization of Liquor Recycling System
13.The Latest Pulper Detrash System. “S-PAL”
14.First step for Smart Factory, Operational experience and effectiveness of SKF Condition Monitoring System
15.Laboratory of Forest Resource Circulatory System and Laboratory of Chemistry of Biomaterial Utilization Division of Environmental Sciences, Graduate School of Life and Environmental Sciences, Kyoto Prefectural University
1.Report of the 26th Papermaking Technology Seminar
2.Installation Reference of Energy Saving & Recovery by Dryer Hood and Air System
3.Basic Technologies and Latest Trends for Paper Machine –Dryer to Size Press
4.Modification Example of Dryer and Size Press Part for Grade Conversion
5.Basic Concept of Drainage System and Possibility of Energy Reduction
6.Basic Technology of Tail Threading Equipment
7.SmartPapyrus® Approach to Optimizing Operations
8.Newly Canvas Cleaner ACE Cleaner
9.Otake Mill, Nippon Paper Industries Co., Ltd
1.Possibility of Digitalization Technology in Paper Machine
2.The Latest Thermal Spraying Technology to Solve Various Problems in the
3. -stick Thermal Spraying and Onsite Grinding Technology
4.Calender and Reel Part of Basic Theory and the Latest Trend
5.The Transition and Latest Technology of Dryer Fabric
6.Aikawa Canvas Cleaner
7.The SmartPapyrus Realizes Work Style Reform in Paper Mills
8.Quantitative Approach to Identify the Problematic Positions Causing Defects with SmartPapyrus
9.Laboratory of Timber Engineering, Research Group of Forest Science,Division of Fundamental Agriscience Research, Research Faculty of Agriculture, Hokkaido University
1.Apple nanofiber from apple-waste powder prepared by carboxymethylation and high-pressure homogenization
2.Optimization of a Multiple-Effect Evaporator Process by Simulation
3.Effect of Filling and Sizing Technique to Andong-po and Namhae-po Hemp Canvas on Painting and Fastness of Pigments
4.Effect of Application of Vinyl Acetate Ethylene Emulsion Binder and Type of Pigment on the Quality of Inkjet Paper
5.Effect of Vinyl Acetate Ethylene Emulsion Formulation and Poly (vinyl alcohol) Molecular Weight on the Quality of Inkjet Paper
6.Relationship between the General Properties and Compression Strength of Commercial Linerboard and Corrugating Medium
7.Impact of Carboxymethylation Pretreatment on the Rheology of Cellulose Nanofiber from Bleached Rice Hull
8.Effects of Zeolites and Carboxymethyl Cellulose Molecular Weights on the Quality of Coating Color and Inkjet Paper
1.Evaluation of the Physical Properties of Unbleached Kraft Pulp Produced from Persimmon Byproducts
2.Analysis of Ink Used in Ancient Documents Based on Printing Method
3.Application of Infrared Spectroscopy to Analyze the Degree of Substitution in Acetylated Wood Powder
4.Evaluation of the Physical Properties of CarboxymethylatedCellulose Nanofiber Derived from Red Algae Pulp
5.A Study on the Classification of European Copy Papers with Infrared Spectroscopy and Principal Component Analysis
6.Preparation of Lignin Derivatives Substituted with 3,4-dihydroxybenzylamine and Their Application as a Biomaterial with Antioxidant and Ultraviolet Light Blocking Properties
7.Soft Sensing and Multi-objective Optimization of Pulp Washing Process Based on Data-Driven Technology
8.Dissolution of HwBKP with [Bmim]Cl-DMF Solvent and Production of Cellulose Beads: Effect of the Cellulose Concentration and Syringe Needle Diameter
9.Influence of Wood Pulp Properties on the Efficiency of Carbox ymethylation
10.Dynamic Causal Relationships among Import Price, Import Quantity, and Ocean Freight Rate Index in the Chemical Pulp Market
11.Changes in Trade Structure of Paper Industry in Korea: Focused on Changes in Intra-Industry Trade
12.Utilization of Amino-Silane Modified Lignin Derivative as an Adsorbent for Cationic Dye Removal
1.Chemical pulping: Among-family variations of direct measurement values for chemical and pulp properties in 4-year-old Eucalyptus camaldulensis half-sib families in Thailand
2.Chemical pulping: Crosslinking of surface-sizing starch with cyclodextrin units enhances the performance of paper as essential oil carrier
3.Chemical pulping: Modeling a continuous digester extraction screen zone with an approximated flow model
4.Mechanical pulping: Advanced energy-saving optimization strategy in thermomechanical pulping by machine learning approach
5.Paper technology: Alternative method for determining basis weight in papermaking by using an interactive soft sensor based on an artificial neural network model
6.Paper technology: Fabrication of bio-based composite fillers based on the combination of crystallization and gelation
7.Paper chemistry: Kinetics of cellulose degradation in bamboo paper
8.Paper chemistry: Influence of DNA as additive for market pulp on tissue paper
9.Recycling: The recyclability and printability of electrophotographic printed paper
10.Nanotechnology: Production of cellulose nanofibers and sugars using high dry matter feedstock
11.Chemical technology/modifications: Comparison of fibers obtained from industrial corncob residue by two delignificationmethods and their application in papermaking
12.Miscellaneous: Effects on hand-sheet paper properties of pH in deinking process
13.Miscellaneous: Fiberspre-treatments with sodium silicate affect the properties of suspensions, films, and quality index of cellulose micro/nanofibrils
1.Editorial: A closer look at the 2021 TAPPI Journal Best Research Paper
2.Using bleaching stage modelsfor benchmarking softwood ECF bleach plants
3.On the usage of online fiber measurements for predicting bleached eucalyptus kraft pulp tensile index —an industrial case
4.Calender barring review with experiences
5.Investigation of the Cellulose-Water Relationship by the Pressure Plate Method
1.Editorial: Impacts from using recycled pizza boxes in furnish: TAPPI Journal’s runner-up to 2021 Best Research Paper
2.The runner-up to the 2021 TAPPI Journal Best Research Paper was “Incorporation of post-consumer pizza boxes in the recover Fiber Stream: Impact of grease on finished product quality."
3.A feasibility study of using the organic Rankine cycle for power generation from the flue gases of recovery boilers
4.Edge crush testing methods and box compression modeling
5.Causes of poor dregs settling in a green liquor clarifier
6.The Creep Properties of Paper
1.Editorial: Ravi Challabrings tissue, nonwovens, and operational expertise to TJ Editorial Board
2.Development of reinforced paper and mitigation of the challenges of raw material availability by utilizing Areca nut leaf
3.Economic and competitive potential of lignin-based thermoplastics using a multicriteria decision-making method
4.Fiber-based characterization of pulp refining
5.The Mechanism of Bonding
8, Number 32022
The general peer-reviewed scientific and engineering press consists of several thousand journals, conference proceedings and bookspublished annually. In among the multitude of articles, presentations and chapters is a small but select number of items that relate to papermaking, environmental and waste processing, packaging, moulded pulp and wood panel manufacture.The abstracts contained in this report show the most recently publisheditems likely to prove of interest to our readership, arranged as follows:
Page 2Coating Economics Energy
Page 3Moulded Pulp
Page 4Nano-Science
Page 5Packaging Technology Papermaking
Page 6Testing
Page 7Tissue
Page 8Waste Treatment
Page 10Wood Panel
The Paper Industry Technical Association (PITA) is an independent organisation which operates for the general benefit of its members –both individualand corporate –dedicated to promoting and improving the technical and scientific knowledge of those working in the UK pulp and paper industry. Formed in 1960, it serves the Industry, both manufacturers and suppliers, by providing a forum for members to meet and network; it organises visits, conferences and training seminars that cover all aspects of papermaking science. It also publishes the prestigious journal Paper TechnologyInternational® and the PITA Annual Review, both sent free to members, and a range of other technical publications which include conference proceedings and the acclaimed Essential Guide to Aqueous Coating
“Influence of pigment and binder composition on the dynamic water penetration and dried structure of precoatinglayers for double-coated paper”, Hye Jung Youn & Hak Lae Lee, Journal of Coatings Technology and Research,Vol.19, 931-938 (2022). The influence of precoating colors on the dynamic water penetration behavior of doublecoated paper was investigated using alaboratory coater equipped with two coating heads. Emphasis was placed on the effects of the pigment combination and binder type on dynamic water penetration. In addition, the latex content on the surface of the coating layer was examined by UV absorbanceanalysis. The amount of water that penetrated the base paper was found to be proportional to the square root of the contact time between the coating color and the base paper, regardless of the pigments and binders used. When a large amount of pigment witha fine particle size was used, or the starch binder content was increased, the low shear viscosity of the coating color increased, and the amount of water penetration into the base paper decreased. The UV absorbance analysis showed that higher water holding in the coating color increased the latex content on the surface of the coating layer. Increasing the viscosity or water retention of the coating color was found to reduce the amount of binder migration into the base paper.
“Analysis of the impact of circular economy over linear economy in the paper processing industry”, E.Sakthivelmurugan, G.Senthilkumar&K.N.Karthick, Materials Today Proceedings, Vol.66(3), 1446-1452(2022). In the present scenario, the linear economy principles are widely used in all fields. As per the linear economy concern once the product is utilized and treated as a waste. In the fut ure, the raw material requirement plays a vital role in many fields because of the lack of availability of resources. To meet the future demand, we need to focus on new techniques, methodologies, and principles for the effective utilization of resources. Given literature, the linear economy principles are replaced by the circular economy in many sectors. As per the circular economy concern, the waste product is again utilized as an input for making secondary products. In this paper, an attempt is made on the effective utilization of paper waste for making secondary products using circular economy techniques. The 9R model is used for the subjective study of various stages of paper-making processes. In addition to that, the fuzzy DEMATAL method is used for pairwise comparison of the linear economy, circular economy, and paper waste. Further analysis is carried out on how the solid waste and waste heat are treated as an input for making secondary products such as agricultural products, fuel, etc.
“Decarbonization of a tissue paper plant: Advanced numerical simulations to assess the replacement of fossil fuels with a biomass-derived syngas”, Lorenzo Giuntini, Rachele Lamioni, Luca Linari, Pietro Saccomano, Davide Mainardi, Leonardo Tognotti & Chiara Galletti, Renewable Energy, Vol.198, 884-893(Oct. 2022). Numerical simulations based on Computational Fluid Dynamic techniques are performed to analyze the possibility of feeding a biomass-deriv ed syngas into the combustion chamber upstream of the hoods for tissue-paper drying, to replace fossil fuels and thus decarbonize the plant. It was observed that, in the context of Favre-Averaged Navier–Stokes equations simulation, syngas requires detailed kinetics and finite-rate approaches, as the fast-chemistry ones, largely employed in the industrial practice for conventional fuels, lead to unreliable results. The actual chamber, originally designed to be fed with liquid petroleum gas, does not operate properly when fueled with syngas, with incomplete oxidation of carbon monoxide. Numerical simulations have proven how very
few modifications of the chamber can be devised to permit feeding efficiently the syngas, obtaining low pollutant emissions and meeting the desired requirements in terms of flow and thermal uniformity for the drying process. The solution proposed in the present study, with the effective use of a biomass-derived syngas to feed the drying section of a tissue paper plant, will allow saving approximately 8500 ton/y of CO2 emissions in comparison with today’s fossil fuel carbon footprint.
“Molded Pulp Products for Sustainable Packaging: Production Rate Challenges and Product Opportunities”, Mrittika Debnath, Roman Sarder, Lokendra Pal &Martin A.Hubbe, BioResources. Vol.17(2), 1-61(2022). Moldedcellulosic pulp products provide eco-friendly alternatives to various petroleum-based packaging systems. They have a long history of reliable usage for such applications as egg trays and the shipping of fruits. They have recently become increasingly used for the packaging of electronics, wine bottles, and specialty items. Molded pulp products are especially used in applications requiring cushioning ability, as well as when it is important to match the shapes of the packed items. Their main component, cellulosic fibers from virgin or recycled wood fibers, as well as various nonwood fibers, can reduce society's dependence on plastics, including expanded polystyrene. However, the dewatering of molded pulp tends to be slow, and the subsequent evaporation of water is energyintensive. The article reviews strategies to increase production rates and to lower energy consumption. In addition, by applying chemical treatments and processing approaches, there are opportunities to achieve desired end-use properties, such as grease resistance. New manufacturing strategies, including rapid prototyping and advances in tooling, provide opportunities for more efficient form factors and more effective packaging in the future.
“Press-forming Molded Pulp from Repulped Liquid Packaging Board: Role of Heat Input, Pressing Force, and Defect Formation”, Arvo Niini, Panu Tanninen, Ville Leminen, Ilari Jönkkäri&Mika Horttanainen, BioResources, Vol.17(4)(2022). Laboratory sheets were prepared from repulped liquid packaging board (LPB)for pressforming experiments and tensile tests to study convertibility and mechanical properties of molded pulp material developed from the repulped LPB. Maximum forming depth was utilized as a convertibility indicator, and defect formation in press-formed molded pulp samples was observed with a visual analysis. Female mold temperature and pressing force were altered among press-forming parameters. The results showed that the laboratory sheets had a limited convertibility. The fragile structure of the laboratory sheets was connected to negative effects from the presence of plastic particles in the material. Increased heat input and decreased pressing force improved the convertibility, and the defect formation during the press-forming was aggravated by flattening of the material in flange and bottom regions of the samples. The use of repulped LPB as the raw material in the manufacturing of molded pulp by press-forming was found viable, and the presented solution offers an ecological alternative to conventional recycling of LPB.
“Paper domus: The architectural potential of pulp”, Jimmy Örtendahl, Master’s Thesis, (2022). Cardboard and paper is a cheap and easily accessible material with a wide variety of uses ranging from packaging of products to furniture design and even structural building elements. Besides being versatile in its area of use the it also has a low environmental impact since it is mainly constructed from renewable sources containing cellulose. On top of that the material itself can be recycled, picked apart and reused for the production of more paper when it has reached its expected lifespan. Still only about half of the around 400 million tons of cardboard and paper being produced each year is recycled.
This means that approximately 200 million tons of cardboard leaves the recycle chain and ends up in landfills or is being incinerated which releases the stored carbon dioxide within the material. This thesis is aiming to make use of the cardboard and paper that is being wasted every year to be upcycled into architectural building elements. There are already projects that utilize cardboard as a building material. From using recycled paper tubes as pillars, to layering sheets of cardboard into building elements. The disadvantage of these methods isthat they rely on intact or newly produced cardboard instead of recycled. This paper however is exploring the method of molding with paper pulp in an architectural context. By combining shredded cardboard or paper, water and an adhesive agent the pulp canbe compressed or molded into solid elements that can be used to design building elements. Three different methods of working with the pulp is further investigated in this paper: compressive molds, rammed pulp, manually applied, and printing with pulp. In addition to these production methods a variety of additives will be used in the pulp to alter its material properties. These two variables is then combined to create discrete building elements made from paper pulp. Finally, these elements are put into context through a building proposal in Gothenburg entirely made with waste cardboard and paper.
“A Comprehensive Review of NanocelluloseModification and Applications in Papermaking and Packaging: Challenges, Technical Solutions, and Perspectives”, Mozhgan Hashemzehi, Beko Mesic, Björn Sjöstrand &Naqvi, Muhammad, BioResources. Vol.17(2), 1-63(2022). The increasing usage of petroleum-based compounds has prompted numerous environmental concerns. Consequently, there has been a steady rise in research on the synthesis of useful mater ials from natural sources. Paper technologists are seeking environmentally acceptable dry end and wet end additives. Among the bio-based resources available, nanocellulose is a popular sustainable nanomaterial additive in the paper industry because of its high strength, high oxygen barrier performance, low density, great mechanical properties, and biocompatibility.NC’s extensive hydroxyl groups provide a unique possibility to dramatically modify the hydrophilicity and charge of the surface in order to improve their potential applications in the paper industry. The current paper reviews two series of surface modifications, each with various subcategories, depending on why modified nanocellulose is added in the paper production: to improve barrier properties or to improve mechanical properties of packaging materials. The methods prese nted in this study use the minimumamount of chemically hazardous solvents to have the least impact on the environment. This review focuses on modifications of nanocellulose and their subsequent application in the papermaking. The knowledge and the discussio n presented in this review will form a literature source for future use by various stakeholders and the sustainable paper manufacturers.
“15 -Nanocellulose biocomposites in specialty papermaking” in Industrial Applications of Nanocellulose and Its Nanocomposites, Woodhead Publishing Series in Composites Science and Engineering, 353-374(2022). Nanocellulose is growing and getting attractive since a decade ago due to its capabilities in a wide range of areas and applications. It may be derived from any lignocellulosic-based natural materials. The nano-sized parts are isolated and will be added into the pulp slurry of papermaking stock. The great benefit of nanocellulose mostly regards its mechanical reinforcement function besides useful usage which meets the needs of certain specialty papermaking. Differingfrom typical paper, specialty paper carries its own niche property such as water and oil repellence, magnetic responsiveness, high durability, long-lasting food packaging, and more. This chapter aims to highlightthe potential and usage of nanocellulose in
making specialty papers dedicated to food packaging, high-durability papers, and printing papers. Nanocellulose has a bright future in terms of alternatives to petroleum-based packaging and environmental issues,but intensive research and development are still needed focally on reaching the commercial stage and, safety and security issues especially when dealing with foods.
“Study on the barrier properties and antibacterial properties of cellulose-based multilayer coated paperboard used for fast food packaging”, Fei-jie Wanga, Li-qiang Wang, Xin-chang Zhanga,Shu-feng Ma & Zhi-cheng Zhao, Food Bioscience, 46, 101398(April 2022). Some petroleum-based packaging materials have a series of safet y issues, and as a result, people are more inclined to use biodegradable and nontoxic packaging materials for foods. However, biodegradable alternatives often need to be modified to overcome their own shortcomings. In this paper, car boxymethyl chitosan (CMCS)/carboxymethyl cellulose sodium (CMC) + polylactic acid (PLA) nano zinc oxide (ZnO) nanoparticles (CMCS/CMC + PLA/ZnO NPs) multilayer coated paperboard was prepared to explore its potential use in food package applications. The multilayer CMCS/CMC + PLA coating reduced the oxygen transmission rate by 99% and doubled the barrier properties for soybean oil penetration and water vapor compared with a single PLA coating layer in a 23°C/50 RHenvironment. The oil resistance time of the multilayer CMCS/CMC + PLA coating also increased 28 times, and the water v apor barrier properties increased twofold compared to a single CMCS/CMC coating layer. The water vapor barrier properties increased by a factor of 3 even at 38°C/90 RH. Compared with the CMCS/CMC + PLA coating without nanoparticles, the barrier performance of the CMCS/CMC + PLA/ZnO NPs coating was further improved. The oxygen, water vapor, and heptane vapor barrier properties all doubled, and the oil resistance time reached 235 h. While a corona treatment reduced the polar component content in the CMCS/CMC coating and led to a slight decrease in the barrier properties of the coating to heptane, it was still a good oilrepellent coating overall. The antibacterial activity (A) toward Escherichia coli and Staphylococcus aureus exceeded 2, which meant that the multilayer coating with 1.5% added ZnO NPs reduced the growth of bacteria by more than 99%. The multilayer coated paperboard created here with the blended and modified materials significantly improved the barrier and antibacterial properties, suggesting that multilayer coatings prepared from degradable materials have good commercial prospects as fast food packaging.
“Wet Tensile Strength Development of PAE Wet-strengthened NBSK Handsheets by AKD Internal Sizing”, Antti Korpela, Aayush Kumar Jaiswal, Atsushi Tanaka& Jaakko Asikainen, BioResources,17(2), 3345-3354(2022). Polyamide-epichlorohydrin (PAE) is used in papermaking to increase the paper’s wet strength. High levels of PAE can make repulping of paper more difficult. PAE deposits can also impair paper machine performance by plugging the paper machine felts. The results of a preceding study indicated that the wet strength of paper containing a moderate amount of PAE (added amount 0.3 wt%) can be increased by utilizing internal alkylketene dimer (AKD) sizing. In the present study, the effects of an added amount of PAE and AKD on the wet strength of handsheets madefrom Nordic bleached softwood pulp (NBSK) were examined. The wet strength was measured after soaking the sheets in ion-exchanged water for up to 1 month. The improving effect of AKD sizing on the wet strength was long-lasting and it was apparent especially with a low and moderate added amount of PAE (0.15 and 0.45 wt%) resulting in higher wet strength than the highest added amount of PAE (1.35 wt%) alone. No clear sign of worsened repulpability was observed at low to moderate treatment levels.
The results suggest that use of small or moderate amounts of PAE with AKD can be a viable option for paper mills facing problems related to the high usage of PAE.
“Effect of Different Size Ratio and Filling Method on the Characteristics of Calcium Silicate-filled Paper”, Sheng Xu,Peng Xu,Pu-Qi Zhao&Yu-Ting Du, BioResources, Vol.17(3),4196-4205(2022). Process conditions were investigated relative to the use of the fly ash predesilication-alkali lime sintering method to extract calcium silicate, which is a by-product of alumina co-production technology, for use as paper filler. The ratio of different fiber raw materials, filler filling ratio, and filling method were studied, and papermaking experiments were conducted. The results showed that calcium silicate filler at a higher proportion (40%) paper can still maintain high mechanical properties. Under the same filling ratio and filling method of calcium silicate filler, the comprehensive performance of softwood pulp and hardwood pulp papermaking paper was found to be better than that of deinked pulp paper.
“Alternative method for determining basis weight in papermaking by using an interactive soft sensor based on an artificial neural network model”, José L. Rodríguez-Álvarez, Rogelio López-Herrera, Iván E. Villalón-Turrubiates, Jorge L. García-Alcaraz, José R. Díaz-Reza, Jesús L. Arce-Valdez, Osbaldo Aragón-Banderas &Arturo Soto-Cabral, Nordic Pulp & Paper Research Journal, Vol.37(3) (2022). Currently, there are two procedures to determine the basis weight in papermaking processes: the measurements made by the quality control laboratory or the measurements made by the quality control system. This research presents an alternative toestimating basis weight-based artificial neural network (ANN) modeling. The NN architecture was constructed by trial and error, obtaining the best results using two hidden layers with 48 and 12 neurons, respectively, in addition to the input and output layers. Mean absolute error and mean absolute percentage error was used for the loss and metric functions, respectively. Python was used in the training, validation, and testing process. The results indicate that the model can reasonably determine the basis weight given the independent variables analyzed here. The R2
2. Using the same dataset, the fine tree regression model showed an R2 of 2. Additionally, a dataset not included in the building process was used to validate the method’s performance. The results showed that ANNbased modeling has a higher predictive capability than the regr ession tree model. Therefore, this model was embedded in a graphic user interface that was developed in Python.
“Characterization of Paper Surfaces by Friction Profilometry”, Byoung Geun Moon, Na Young Park, Young Chan Ko&Hyoung Jin Kim, BioResources, Vol.17(4)60676078, (2022). Friction profilometryis a powerful technique that is suitable f or the surface characterization of paper products. In this technique, a stylus-type contact method that resembles papermaking processes is used for evaluating the quality attributes of products. The surface characterization requires both surface roughness and friction measurements. At present, however, few reports have been available regarding characterization of the friction by the surface profilometric method. The objective of this study was to provide guiding principles of a stylus-type contact surface profilometr y for determining the friction properties of paper. Another objective was to introduce the concept of the mean absolute deviation (MAD) from the average coefficient of friction as a new friction parameter.
“Relative permeability of barrier dispersion coatings applied on paper-based materials; mathematical modeling and experimental validation”, Gonzalo A. Martinez-Hermosilla, Beko Mesic & John E. Bronlund, Journal of Coatings Technology and Research,Vol.19, 543-558 (2022). Barrier dispersion coatings have been used to improve barrier properties of paper-based materials. Like other technologies such as thermoplastic composites, dispersion coatings include fillers to create obstacles that complicate the pathways for permeants through coatings. The development of these technologies has received significant attention where even predictive barrier performance models have been created. However, to the best of our knowledge, none of them are applicable to barrierdispersion coatings. This research proposed a mathematical model to predict the relative permeability of barrier dispersion coatings applied on paper-based materials based on Fick’s law. The uncertainty of the barrier properties due to variation in fillerorientation and spatial location was included through Monte Carlo simulation. Model validation against four models previously published by other authors, and water vapor transmission rate measured on three coating formations and two coating thicknesses was also conducted. The model predictions and experimental results showed that the increase in the amount of fillers reduces the relative permeability, and this reduction can be higher if the size of the fillers is larger. The predictions agreed with experimental results particularly at volume fractions below 10%. In most of the cases, the proposed model achieved better prediction in comparison with those already published. The model is useful to predict relative barrier performance of different coating formulations and can be used as a tool for future developments.
“Relating papermaking process parameters to properties of paperboard with special attention to through-thickness design”, Mikael Nygards, MRS Advances, online, (2022). A biaxial stress state has been proposed to formulate a failure criterion for paperboard during bending. About 100 paperboards have been splitted, such that top, middle, and bottom plies have been free-laid and tested in the machine direction, crossmachine direction as well as in out-of-plane direction (ZD). The purpose was to determine the failure stresses and its dependency of papermaking parameters: density, degree of orientation, and fiber length for each layer. A linear model to predict the geometrical strength of a plies was suggested. Analytically simulations of different paperboard structures behavior during bending were performed. The density of the middle ply affected the location of the failure position in ZD, as well as the maximum bending moment. The impact of orientation and degree of anisotropy was simulated, which can be used to optimize the ZD property gradient by tweaking the properties, and hence optimize paperboard performance.
TISSUE “Developing Alternative, High-Absorbency Brown Fibers: Tissue Paper from Upcycled Corrugated Packaging Waste to Meet New Consumer Trends”, Franklin Zambrano, Ronald Marquez, Ramon Vera, Hasan Jameel, Richard Venditti, and Ronalds Gonzalez, ACS Sustainable Chemistry & Engineering, 10, 40, 13343-13356 (2022). Consumers’ rising interest in brown tissue papers, perceived as sustainable, has increased the market share and selling prices of such products despite their limited performance. Meanwhile, the current excess of packaging waste in the US has created an opportunity for using old corrugated containerboard (OCC) as an alternative source of brown pulp, despite its inferior tissue-making characteristics relative to bleached fibers. Strength, water absorption capacity, and absorption rate are among the crucial properties of absorbent tissue products. Herein, we studied the feasibilit y of total chlorine-free treatments, namely, oxygen delignification, alkaline hydrogen peroxide, and ozonation, to
improve the tissue-making quality of OCC pulp. The processes ev aluated reduced the lignin content (kappa number from 89 to values as low as 55) and generated brightness gains as high as 8.8% ISO units. The strength of the sheets als o improved due to the delignification and increase in fiber swelling. Chemically treated OCCresulted in sheets with higher water absorption capacity and absorption rate and fiber slurries with higher freeness compared to sheets and slurries from mechanically refined OCC. Therefore, we demonstrate the application of treatments with low environmental impact to upcycle OCC into a high-quality brown pulp suitable for manufacturing high-performance tissue paper.
“To improve the disintegration potential of toilet grade tissue paper”, Sanjeev Kumar Jain, Olimpiya Biswas & Priyanka Pandey, Nordic Pulp &Paper Research Journal, online(2022). Disintegration potential of toilet grade tissue paper is one of the most important parameter keeping in mind the worldwide water scarcity faced by human race in current decade. The aim of this experimental study is t o improve the disintegration potential of toilet tissue. Softener is used as debonding material. The right amount dry strength required by Toilet tissue is maintained by controlled fiber refining. High fiber bonding would lower the disintegration potentialof the tissue paper, thus hampering the aim of study. The initial freeness of the pulp slurry was found 16°SR. It was then further 30°SR). Bulk, Strength properties along with disintegration time and softness of 15GSM hand sheets prepared from each set of pulp slurry was investigated. Turbidity test was done to check the cloudiness. Upon analysing, it was found that the paper developed at c/gm, breaking length 750 meter, softness 80 Hand feel units, and disintegration time 08 seconds was most suitable hav ing the better softness, optimum strength and higher disintegration potential as compared to the benchmarked samples.
“Strategies to improve membrane performance in wastewater treatment”, Shams Forruque Ahmed, Fatema Mehejabin, Adiba Momtahin, Nuzab a Tasannum, Nishat Tasnim Faria, M. Mofijur. Anh Tuan Hoang, Dai-Viet N. Vo & T.M.I.Mahlia, Chemosphere, Vol.306, 135527(Nov. 2022). Membrane technology has rapidly gained popularity in wastewater treatment due to its cost-effectiveness, environmentally friendly tools, and elevated productivity. Although membrane performance in wastewater treatment has been reviewed in several past studies, the key techniques for improving membrane performance, as well as their challenges, and solutions associated with the membrane process, were not sufficiently highlighted in those studies. Also, very few studies have addressed hybrid techniques to improve membrane performance. The present review aims to fill those gaps and achieve public health benefits through safe water processing. Despite its higher cost, membrane performance can result in a 36% reduction in flux degradation. The issue with fouling has been identified as one of the key challenges of membrane technology. Chemical cleaning is quite effective in removing accumulated foulant. Fouling mitigation techniques have also been shown to have a positive effect on membrane photobioreactors that handle wastewater effluent, resulting in a 50% and 60% reduction in fouling rates for backwash and nitrogen bubble scouring techniques. Membrane hybrid approaches such as hybrid forward-reverse osmosis show promise in removing high concentrations of phosphorus, ammonium, and salt from wastewater. The incorporation of the forward osmosis process can reject 99% of phosphorus and 97% of ammonium, and the reverse osmosis approach can achieve a 99% salt rejection rate. The control strategies for membrane fouling have not been successfully optimized yet and
more research is needed to achieve a realistic, long-term direct membrane filtering operation.
“Quorum sensing -a promising tool for degradation of industrial waste containing persistent organic pollutants”, Sonam Tripathi, Ram Chandra, Diane Purchase, Muhammad Bilal, Raja Mythili & Sangeeta Yadav, Environmental Pollution, Vol.292, Part B, 118342(1 Jan. 2022). Restoring an environment contaminated with persistent organic pollutants (POPs) is highly challenging. Biodegradation by biofilm-forming bacteria through quorum sensing (QS) is a promising treatment process to remove these pollutants and promotes eco-restoration. QS plays an important role in biofilm formation, solubilization, and biotransformation of pollutants. QS is a density-based communication between microbial cells via signalling molecules, which coordin ates specific characters and helps bacteria to acclimatize against stress conditions. Genetic diversification of a biofilm offers excellent opportunities for horizontal gene transfer, improves resistance against stress, and provides a suitable environment for the metabolism of POPs. To develop this technology in industrial scale, it is important to understand the fundamentals and ubiquitous nature of QS bacteria and appreciate the role of QS in the degradation of POPs. Currently, there are knowledge gaps regarding the environmental niche, abundance, and population of QS bacteria in wastewater treatment systems. This review aims to present up-to-date and state-of-the-art information on the roles of QS and QSmediated strategies in industrial waste treatment including biological treatments (such as activated sludge), highlighting their potentials using examples from the pulp and paper mill industry, hydrocarbon remediation and phytoremediation. The information will help to provide a throughout understanding of the potential of QS to degrade POPs and advance the use of this technology. Current knowledge of QS strategies is limited to laboratory studies, full-scale applications remain challenging and more research is need to explore QS gene expression and test in full-scale reactors for wastewater treatment.
“Removal of colour and lignin from paper mill wastewater using activated carbon from plastic mix waste”, V. Gupta, N. K. Bhardwaj & R. K. Rawal, International Journal of Environmental Science and Technology, Vol.19, 2641–2658 (2022). The study aimed at the use of char produced during pyrolysis of mix plastic waste. It further focused on producing activated carbon from char and also found its efficacy as efficient adsorbent for treatment of pulp and paper mill wastewater. The activated carbon was characterized in comparison with raw char for their physical, surface and adsorptive properties. Batch type adsorption experiments were carried out using 100 ml wastewater to observe the individual effectiveness using five different variables such as adsorbent dose (0.25–2.0 g), pH (6–10), time (5–24 h), agitation speed (100–200 rpm) and temperature (30–50 °C) by keeping other variables constant whic h helped to find out the effective range of all the variables. The competency was evaluated on thebasis of colour and lignin content of pulp and paper industry wastewater. Once the effective range of different variables was identified, the statistical analysis was conducted to monitor the mutual impact on the reduction in colour and lignin contents in wastewater. From the statistical design applied, the best result was obtained at activated carbon dose (1.25 g), pH (8.0), contact time (7 h), agitation speed (184 rpm) and temperature (40 °C). The study resulted in reduction of 96.48% in colour and 94.25% in lignin at optimized condition in comparison with 87.37 and 80.44%, respectively, at unoptimized conditions. A potential increase in reduction of 9.0% in colour and 14.0% in lignin content was achieved after optimization through statistical design thatconfirmed its usefulness.
“Comparative analysis of very volatile organic compounds and odors released from decorative medium density fiberboard using gas chromatography–mass spectrometry and olfactory detection”, Weidong Wang, Jun Shen, MingLiu, Wang Xu, Huiyu Wang & Yu Chen, Chemosphere, Vol.309, Part 1, 136484(Dec.2022). VVOCswith a retention range below C6 have become one of the main indoor pollutants that negatively affect human health. Most studies have focused on the emission of VOCs from furniture and decorative materials, seldom consider VVOCs. To close this gap, a 15-L environmental chamber, combined with multi-absorbent tube, was used for gas sampling.
Emissions of VVOCs and odors released from decorative medium density fiberboard (MDF) were measured using gas chromatography–mass spectrometry and olfactometry detection.The results demonstrated that multi-absorbent tubes had excellent capture capacity for low-molecular-weight VVOCs. Thickness and decorative materials had conspicuous effects on VVOCs and odor emissions. The total VVOCs (TVVOC) from 18mm decorative MDF was consistently higher than that of 8-mm samples. The major VVOCs from these decorative MDF were alcohols, esters and ketones, which were the major odor contributors with high odor intensity values. VVOCs concentration generally increased as thickness increased, but it decreased after decorative treatment. Fruity and alcohol-like were the main odor impressions of 8-mm MDF, whereas sweet and fruity were the major odor impressions of 8-mm polyvinyl chloride decorativ e MDF (PVC-MDF) and melamine impregnated paper decorative MDF (MI-MDF). Fruity was the main odor impression of 18-mm decorative MDF. The overall odor intensity increased and the major odor impression may differ when thickness was changed. Both the MI and the PVC decorative materials blocked some odor emissions but did so to a greater extent with the former than with the latter. Identification and analysis of the composition of VVOCs can supplement a database structure network of volatile pollutants and establish a novel and feasible method to investigate low-molecular-weight substances from wooden materials and their products.
“Multiscale analysis of water vapor diffusion in low density fiberboard: Implications as a building material”, Patrick Perré, Romain Rémond & Giana Almeida, Construction and Building Materials, Vol.329, 127047(25 Apr.2022). This work is devoted to diffusion mechanisms in low-density fiberboard (255 kg m ). Experiments were performed under unsteady state conditions (relative humidity step from 37% to 71%) with different thicknesses (half thickness ranging from 1 mm to 20 mm). The mass diffusivity was determined by inverse analysis from the experimental moisture content evolution, using a comprehensive macroscopic model of coupled heat and mass transfer. A clear failure of Fickian’s law becomes evident regarding the effect of thickness. A dual-scale model, based on the concept of distributed microstructure models with coupled heat and mass transfer at both scales, was used to simulate the experiments. The large number of dual-scale simulations proposed in this work were also analyzed by the inverse method. These dual-scale simulation results were successfullyconfronted to the experiment. The good fit with the experimental data is obtained for a diffusivity of the microscopic phase m2 s for a fiber radius of 20 μm. As the main recommendation, we advise that the dual scaleeffect can be neglected for this kind of fiberboard for a total thickness larger than some centimeters, depending on the panel density. This also means that this effect must be considered in material characterization or when capturing the buffering effectof the surface layers of the envelope.
“Combining X-ray CT and DIC to understand the bending strength of OSB”, Wanzhao Li, Donghu Li, Yanjun Duan, Changtong Mei,Jan Van den Bulcke & Joris Van Acker, Construction and Building Materials, Vol.354, 129125(7 Nov.2022). Oriented strand board (OSB) is an important engineered wood product manufactured through bonding of wood strands in cross-oriented layers. The bending strength, one of the crucial properties for loadbearing material, of OSBstrongly depends on its structural characteristics. To understand the bending strength of OSB, strain distribution was continuously monitored during a three-point bending test using digital image correlation (DIC) and internal structure was recorded before and after bending using X-ray computed tomography (X-ray CT) respectively. Specimens were cut either along the length (L specimens) or width (W specimens) of OSB panels. For all specimens, strain accumulation mainly seemed to occur in the top and bottom layers and then pr opagate along or across the central layer. Structural changes in the top and bottom layers of L specimens was either strand delamination or snap off, while only snap off is found in W specimens. This is the main reason of high modulus of elasticity (MOE) and modulus of rupture (MOR) of L specimens in comparison to W specimens. High MOR of the specimens is attributed to strain propagation along the central layer, which can absorb energy from loading. Strain propagation across the central layer causes low MOR, resulting from failure of small strands and delamination in the central layer. Different modes of structural change lead to large variability of MOE, MOR and deformation of the specimens even cut from a single OSB panel. Understanding the bending strength contributes to optimizing the production and application of OSB.
“Water vapour transmission properties of uncoated and coated wood-based panels”, Antonio Copak, Vlatka JiroušWood MaterialScience & Engineering, online (2022). Knowing the properties of wood-based building materials is essential for their proper use. Moisture transfer properties of building materials are crucial to proper building design and the prevention of moisture-related problems. In selecting materials for the building, it is important to know their water vapour transmission properties. In this research the water vapour transmission properties of uncoated and coated particleboard, oriented strand board (OSB) and birch plywood were studied using wet cup method and a moisture gradient in the samples was additionally measured. The water vapour transmission rate of free films of three commercial transparent coatings was also studied. Results showed that particleboard had thehighest water vapour permeability and that the coatings reduced the water vapour permeability of all tested wood-based panels. Moreover, sanding increased the water vapour permeability of uncoated particleboard and OSB. The moisture gradient in all testedwood-based panels was linear. The highest water vapour transmission rate was recorded for acrylic water-borne coating, followed by polyurethane water-borne coating and the lowest for polyurethane solvent-based coating.