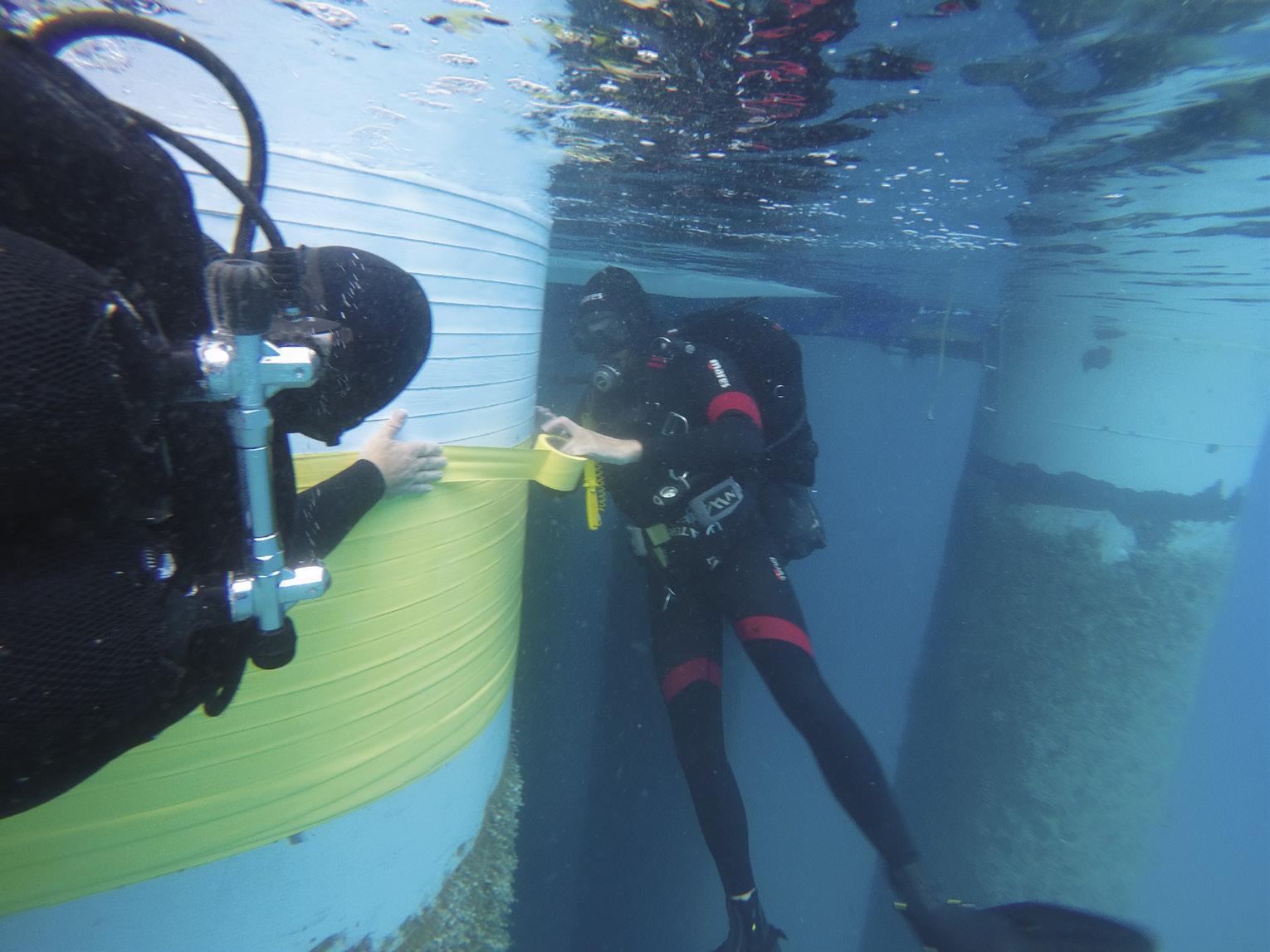
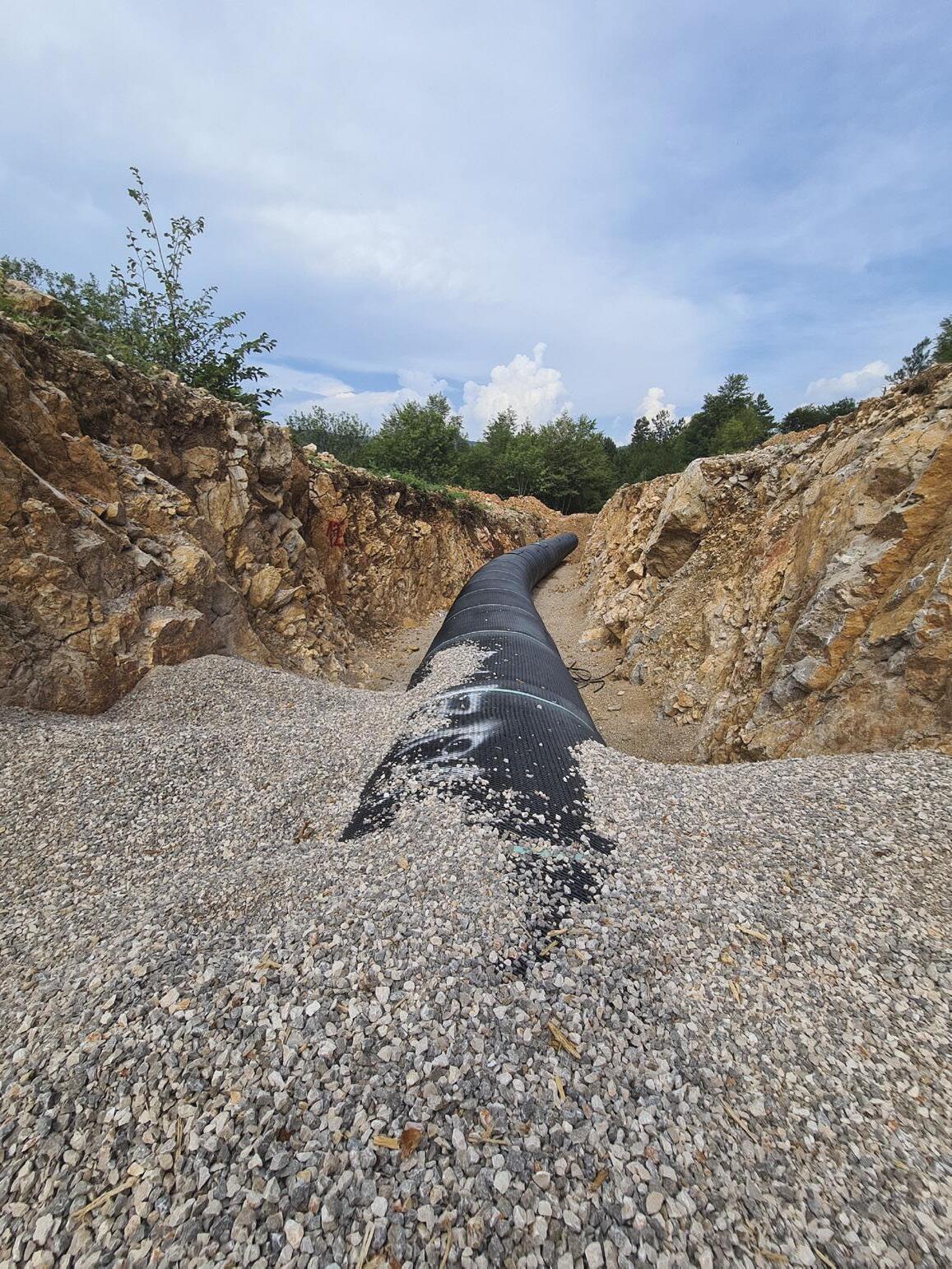
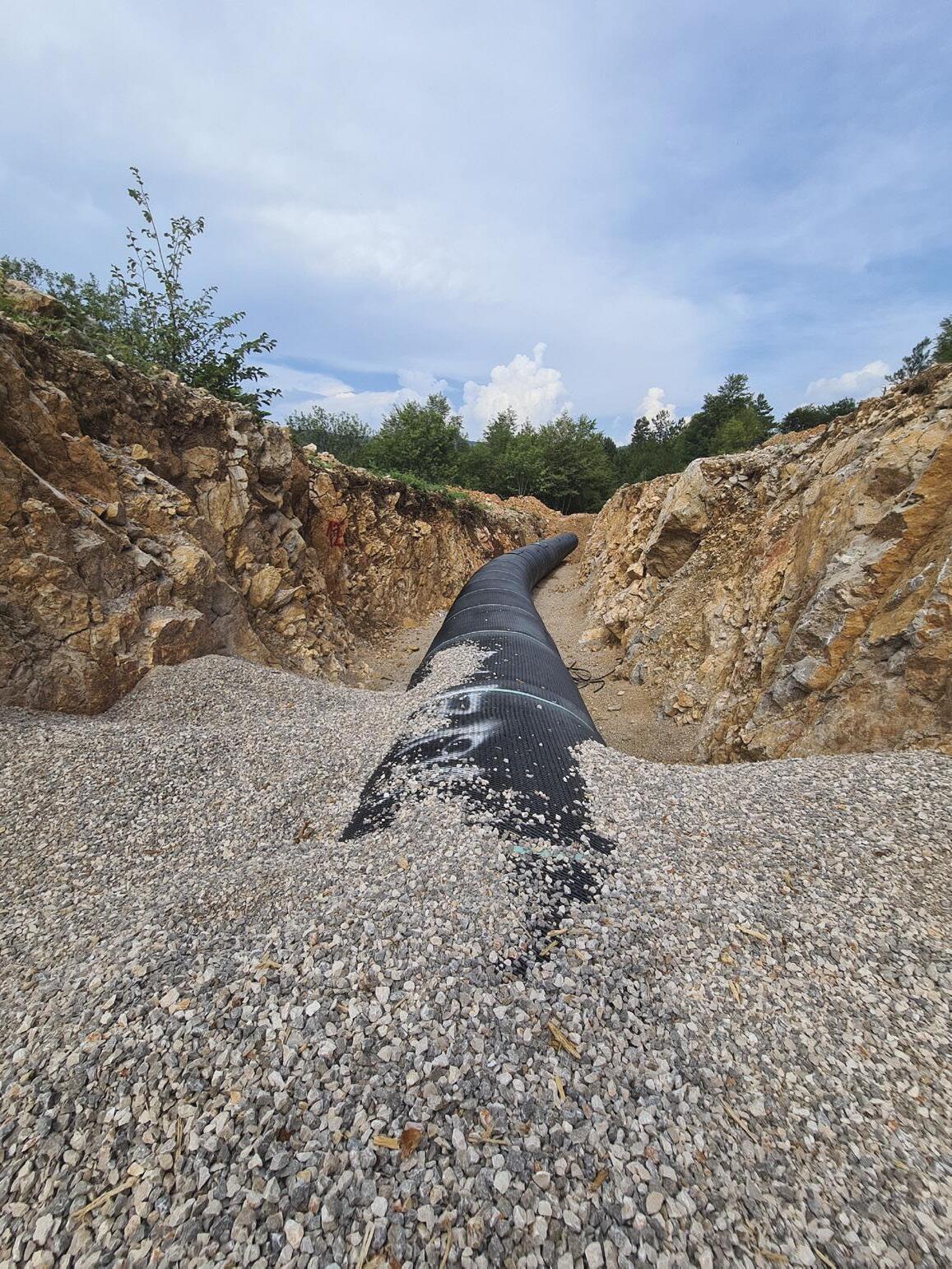
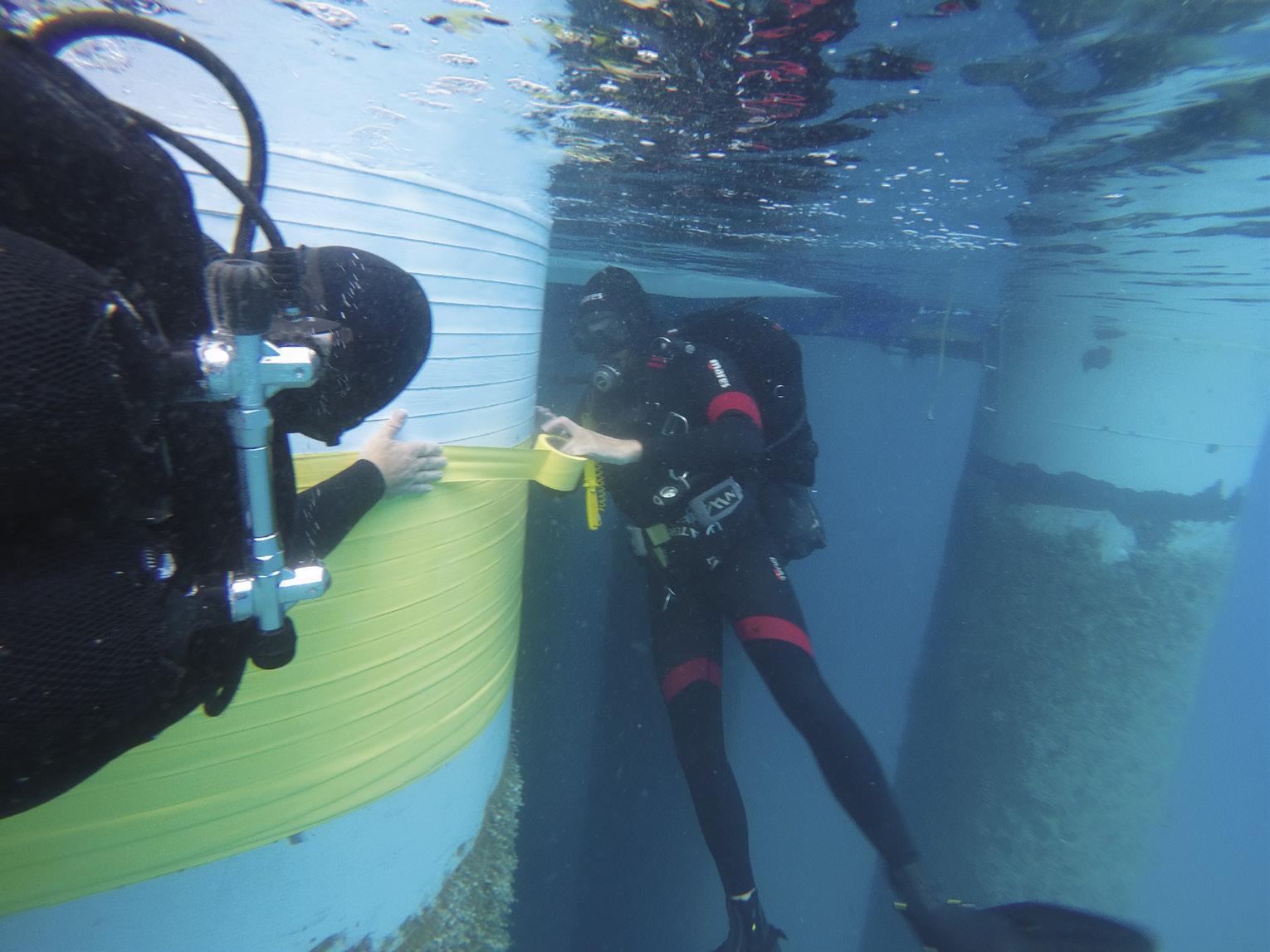

Elevate your asset integrity with unmatched data accuracy and unparalleled expertise
Our unique synergy of advanced inspection systems, cutting-edge analytics and human expertise allows us to transform data into knowledge. Knowledge enables smarter decision-making and delivers a comprehensive understanding of asset safety, lifetime, and performance.
KEYNOTE:
12. Helping ensure pipeline safety
Rick Dorsett, Vice President, ISN, asks: as
and
decline in the workplace, how can the pipeline industry stay vigilant?
17. Assuring technical competence
Andrew Hockey, ECITB, explores how a new initiative is helping to create a safer industry.
21. Off the map, on the monitor Alastair MacLeod, Ground Control, discusses how to prioritise lone worker safety in oil and gas pipeline operations.
DRONES AND AERIAL SURVEILLANCE
24. Bridging the methane detection gap James Aarestad, Vanguard Pipeline Inspection.
INTEGRITY AND INSPECTION
29. Ultrasonic testing in NDT Eugene Lo, EVIDENT.
PIGGING TOOL PERFORMANCE
35. Next generation inspection tools World Pipelines talks to Levi Porter, Dexon Technology, about inline inspection and high-resolution inspection tools.
39. Utilising urethane cups and discs Wilton Cardoso, Pigs Unlimited.
47. Changing the game Corey Richards, DarkVision.
PIPELINE SERVICES
51. Building an efficient hydrogen network Lewis Anderson, Luxfer Gas Cylinders.
METERING AND MONITORING
57. The evolving role of area and perimeter monitoring Brad Rister, Industrial Scientific.
EMISSIONS REDUCTION
63. Relieving the pressure Anand Palanivelu, Protectoseal.
SYSTEMS AND SOFTWARE
67. Transactional systems for pipelines Lindsey Saunders, Quorum Software.
71. When every second counts Sergej Arent, HIMA Group, and Michal Miklasik, HIMA Slovakia.
PUMPS
76. How to save a country's worth of electricity with better pump efficiency Manish Talwar, Sulzer Americas.
SUBSEA PIPELINES
80. The critical role of subsea pipeline integrity Jim Bramlett, Tracerco.
CAREERS IN PIPELINES
85 NDT jobs of tomorrow Garra Liming, ASNT.
Since 1924, BRADEN has conquered recovery challenges in the oil eld with products that are simple to install, use and service. Engineered to deliver unmatched durability and power, BRADEN winches are the preferred choice for equipment manufacturers and operators who demand performance under the toughest conditions.
MANAGING EDITOR
James Little
james.little@worldpipelines.com
EDITORIAL ASSISTANT
Alfred Hamer alfred.hamer@worldpipelines.com
SALES DIRECTOR
Rod Hardy rod.hardy@worldpipelines.com
SALES MANAGER
Chris Lethbridge chris.lethbridge@worldpipelines.com
SALES EXECUTIVE
Daniel Farr daniel.farr@worldpipelines.com
PRODUCTION DESIGNER
Amy Babington amy.babington@worldpipelines.com
HEAD OF EVENTS
Louise Cameron louise.cameron@worldpipelines.com
DIGITAL EVENTS COORDINATOR
Merili Jurivete merili.jurivete@palladianpublications.com
EVENTS COORDINATOR
Chloe Lelliott chloe.lelliott@worldpipelines.com
DIGITAL CONTENT COORDINATOR
Kristian Ilasko kristian.ilasko@worldpipelines.com
JUNIOR VIDEO ASSISTANT
Amélie Meury-Cashman amelie.meury-cashman@worldpipelines.com
DIGITAL ADMINISTRATOR
Nicole Harman-Smith nicole.harman-smith@worldpipelines.com
ADMINISTRATION MANAGER
Laura White laura.white@worldpipelines.com
Palladian Publications Ltd, 15 South Street, Farnham, Surrey, GU9 7QU, UK Tel: +44 (0) 1252 718 999
Website: www.worldpipelines.com Email: enquiries@worldpipelines.com
Annual subscription £60 UK including postage/£75 overseas (postage airmail). Special two year discounted rate: £96 UK including postage/£120 overseas (postage airmail). Claims for non receipt of issues must be made within three months of publication of the issue or they will not be honoured without charge.
Applicable only to USA & Canada: World Pipelines (ISSN No: 1472-7390, USPS No: 020-988) is published monthly by Palladian Publications Ltd, GBR and distributed in the USA by Asendia USA, 701C Ashland Avenue, Folcroft, PA 19032. Periodicals postage paid at Philadelphia, PA & additional mailing offices. POSTMASTER: send address changes to World Pipelines, 701C Ashland Avenue, Folcroft, PA 19032.
If the world’s economies are to continue pushing for digitalisation, then our global energy appetite is going to rapidly increase. Electricity grids are buckling under the weight of accommodating AI-driven computing power demands, not to mention bitcoin mining booms and the ever-expanding data centre sprawl that is cropping up in once-sleepy corners of the grid. For the pipeline sector, this is an emerging opportunity.
Electricity blackouts are making headlines: in April, a major power blackout occurred across the Iberian Peninsula, affecting mainland Portugal and some of Spain for about 10 hours. The diagnosis pointed to a problem in the synchronisation of the power grid: The Conversation described it as “a perfect storm of poor grid management and inadequate connections of solar facilities to the grid, as well as other unknown faults”.1 At around midday on 28 April, most of Spain’s energy demand was being covered by renewable sources (solar and wind, as is usual at this time of the year), and nuclear plants were operating at half their usual capacity (as planned) to counteract high operating costs. A sudden drop in the Iberian electricity grid was registered just after 12:30. Here’s the breakdown: fluctuations were observed in the grid and there was a spike in wind power generation; France suddenly stopped importing electricity from Spain (likely because it had detected a problem in the peninsular grid); the few operating nuclear power plants received an overload signal and were shut down; then thousands of solar facilities were switched off automatically. The normal balance of supply and demand could not be restored, and the blackout ensued.
The incident served as a reminder that even grids flush with renewables are vulnerable without adequate storage, coordination, and backup power, especially in an era of unpredictable, tech-driven demand surges.
The Texas Observer reported recently on the energy drain of the digital boom, outlining Bitcoin mining’s voracious energy use and its impact on the grid in Texas, and beyond.2 The most famous of cryptocurrencies is reported to be rallying, which further drives the mining operations, placing more strain on the system.
ICF’s latest electricity report underscores this trend, showing how data centres and crypto operations could account for disproportionate spikes in regional demand.3
It’s a crisis, but also a crossroads. And the pipeline sector is uniquely positioned to step in as both a stabiliser and enabler in this situation.
In an article in the May 2025 issue of World Pipelines, Black & Veatch discussed how to shore up infrastructure resilience, explaining how natural gas midstream operators are helping power AI’s energy revolution, since gas offers a reliable, scalable and cost-effective fuel source to power generators. Expanding pipeline networks to accommodate data centre clusters makes geographical sense.
Private equity firms such as I Squared Capital are interested in assets that serve surging digital demand. Their investment in the Matterhorn Express Pipeline in May (described as critical to AI growth hubs) underlines the evolving interplay between traditional pipelines and the next-gen energy landscape. “This investment exemplifies our strategy of acquiring critical infrastructure assets that support the major re-industrialisation themes we see in the US economy today,” said Gautam Bhandari, Global Chief Investment Officer and Managing Partner of I Squared Capital.
Oil and gas pipelines can do it all: power generators, serve LNG terminals, and feed energyhungry industrial and digital economies. So the pipeline sector can no longer view digital demand as someone else’s problem. There are opportunities here to collaborate with renewable providers; focus on smarter pipeline routing, and monitoring; invest in hybrid infrastructure (hydrogen, CCS); and carry us into the future of powering modern life.
1. https://theconversation.com/spain-portugal-blackouts-what-actually-happened-and-what-can-iberia-and-europe-learnfrom-it-255666
2. https://www.texasobserver.org/the-crypto-racket/?src=longreads
3. https://www.icf.com/insights/energy/impact-rapid-demand-growth-us
Across energy and critical infrastructure, we bring expertise where complexity is highest. With globally local teams and proprietary technologies unmatched in the sector, we move projects forward, no matter the challenge.
We’re here to partner on how our specialist welding and coating solutions can help you power tomorrow.
B.C. First Nations to acquire an equity interest in Enbridge’s Westcoast Pipeline System
Stonlasec8 Indigenous Alliance Limited Partnership, an Indigenous-owned partnership representing 36 First Nations in B.C., has announced it has entered into an agreement to invest approximately CAN$715 million through a wholly-owned subsidiary to acquire a 12.5% interest in Enbridge Inc.’s Westcoast natural gas pipeline system. The agreement is subject to completion of required financing, closing conditions and customary closing adjustments. The transaction is expected to close at the end of 2Q25.
Stonlasec8 has also reached an agreement with Canada Indigenous Loan Guarantee Corporation (CILGC), a subsidiary of Canada Development Investment Corporation (CDEV), on a CAN$400 million loan guarantee to support the transaction. On closing, this historic equity investment will be the first major investment to receive a loan guarantee under the Canadian Indigenous Loan Guarantee Program, announced by
the Government of Canada last Spring.
“Today is a significant milestone for the First Nations involved in Stonlasec8 and we are incredibly grateful to have the Government of Canada’s strong support to bring this deal to fruition,” said Chief David Jimmie, President and Chair of Stonlasec8 and Chief of Squiala First Nation. “Our Nations can expect to receive sustained economic benefits from an asset that has operated within our traditional territories for over 65 years.”
“The agreement between Stonlasec8, Enbridge and the Government of Canada is truly ground-breaking,” added Justin Napoleon, Director of Stonlasec8 and former Chief of Saulteau First Nation. “The loan guarantee supporting the equity purchase transaction will bring increased economic prosperity to our communities, including funding for critical investments in housing, infrastructure, environmental stewardship, and cultural preservation.”
Tallgrass has announced the execution of anchor shipper precedent agreements for a new pipeline that will transport natural gas from multiple points of receipt in the Permian Basin to the Rockies Express Pipeline and other points of delivery. The firm transportation commitments under the already executed precedent agreements are sufficient to financially justify construction of the pipeline project, subject to customary regulatory and corporate conditions and approvals, with a target in-service date in late 2028.
An open season that will be announced subsequently will provide additional interested parties with an opportunity to subscribe to firm transportation service on the pipeline. The pipeline project is designed to be capable of up to 2.4 billion ft3 of natural gas transportation, with the ultimate capacity to be determined depending on the level of shipper commitments from
the open season.
The new pipeline project is unique in that it will enable affordable and plentiful natural gas to access markets across the US, including multiple major markets that are key hubs of activity for industrial, agricultural, and technological development and innovation, from re-shoring, policies to promote US agriculture, and AI-driven power demand.
Upon in-service, natural gas from the project will also be able to reach markets across Tallgrass’ approximately 800 mile decarbonisation pipeline network, so that consumers of new natural-gas-fired power generation and industrial consumers of natural gas will have an immediate and financially viable opportunity to supply their growing energy demand while decarbonising through CO2-capture and sequestration and the use of clean hydrogen.
ArcLight Capital Partners, LLC has announced its managed fund has acquired a 25% interest in Natural Gas Pipeline Company of America (NGPL), a strategic natural gas infrastructure system. As a result of the transaction, ArcLight will become the largest owner of NGPL with a 62.5% economic ownership interest, alongside its strategic partner Kinder Morgan, Inc. Kinder Morgan continues to own a 37.5% economic interest and operates NGPL.
NGPL is one of the largest interstate pipeline systems in the country, spanning nine states, supplying critical power and heating markets across its footprint and liquefied natural gas facilities in Texas and Louisiana. With ~9100 miles of pipeline, compressor stations totalling ~1 million hp, and 288 billion ft3 of storage, NGPL provides critical energy, access, reliability and supply from all major US natural gas basins.
“The US is seeing historic levels of power demand growth, from both electrification and AI, which we believe will continue well into the next decade. Critical infrastructure assets like NGPL
will be increasingly necessary to providing both reliability and the ability to help meet the growing infrastructure needs associated with these two investment mega trends,” said Dan Revers, Founder of ArcLight. “This acquisition builds on ArcLight’s deep history, dating back to 2001, of investing in critical gas infrastructure.”
“We believe NGPL represents a strategic natural gas infrastructure asset that cannot be replicated today and that has significant opportunities to help utilities, LNG exporters, data centre developers and hyper scalers meet their growing gas infrastructure needs,” said Lucius Taylor, Partner at ArcLight. “This continued investment in NGPL also reflects ArcLight’s ability to be a value-added partner and expands our strategic partnership with Kinder Morgan.”
Terms of the transaction were not disclosed. Barclays Capital Inc. acted as financial advisor and Latham & Watkins LLP acted as legal counsel to ArcLight on the transaction.
Audubon has announced a new development in NGL delivery for WhiteWater Midstream with EPC solution.
Denmark
Construction has begun on Greensand’s carbon dioxide transit terminal at Port Esbjerg.
Malaysia
Sarens is eyeing Malaysia as key site for upstream and pipelines.
India
GAIL completes laying over 97.6% of Pradham Mantri Urja Ganga.
Vallourec wins a new major line pipe contract for Brazil’s Buzios offshore field.
Perma-Pipe has been awarded several awards for data centre and industrial expansion projects in the US and Saudi Arabia.
Norway
STATS Group has developed mechanical pipe connectors for installation on titanium pipework.
Italy
Fox Innovation & Technologies (FOX) has acquired Sirio Solutions Engineering (SSE) S.p.A.
USA
US Transportation Secretary
Sean P. Duffy has advocated for enhancing pipeline safety in new advisory.
China is now the top buyer for Canadian crude on Trans Mountain pipeline.
Squared, MPLX, and Enbridge to acquire interests in Matterhorn
I Squared Capital, an independent global infrastructure investment manager, together with MPLX LP, and Enbridge Inc., has announced that it has agreed to acquire a significant equity interest in the Matterhorn Express Pipeline (MXP), a 2.5 billion ft3/d natural gas pipeline connecting the Permian Basin to key Texas demand centers and US Gulf Coast LNG export terminals.
“This investment exemplifies our strategy of acquiring critical infrastructure assets that support the major re-industrialisation themes we see in the US economy today,” said Gautam Bhandari, Global Chief Investment Officer and Managing Partner of I Squared Capital. “The pipeline benefits from a prime location and serves some of the fastestgrowing energy demand centers in North America, including LNG export terminals, industrial hubs, and rapidly expanding AI-driven data centers in the Austin and Houston metro areas. The WhiteWater team is a proven management team with a successful track-record of working with I
Squared. We are excited to partner with them, once again, to support the continued growth of this platform.”
Under the terms of the transaction, I Squared will acquire approximately 37% of Matterhorn InvestCo, LLC, alongside FIC and WhiteWater Midstream. MXP will be owned 65% by MXP HoldCo, 15% by ONEOK, 10% by MPLX, and 10% by Enbridge. WhiteWater Midstream will continue to operate MXP.
MXP is a newly constructed, 100% contracted natural gas pipeline in the heart of the Permian Basin. It was placed into service in November 2024 and has approximately 2.5 billion ft3/d of fully contracted capacity. The system transports natural gas from the Waha area in the Permian Basin with delivery capabilities throughout the greater Houston area.
The transaction is expected to close in mid-2025, subject to customary regulatory approvals and closing conditions. Kirkland & Ellis LLP served as legal counsel to I Squared in this transaction.
Tidewater enters into agreement to acquire North segment of Pembina Pipeline’s Western Pipeline System
Tidewater Midstream and Infrastructure Ltd. has announced that it has entered into definitive agreements with Pembina Pipeline Corporation and certain of its affiliates, through a wholly owned limited partnership, to acquire the North Segment of Pembina’s Western Pipeline System for total cash consideration of approximately CAN$1.2 million, as well as the assumption of certain future abandonment and reclamation obligations and liabilities estimated to be approximately CAN$30.0 million.
The Western Pipeline is an approximately 377 km crude oil pipeline originating in Taylor, British Columbia and terminating in Prince George, British Columbia. The Western Pipeline’s connection at Taylor, British Columbia is the key conduit tying the Prince George Refinery (PGR) into the northeastern British Columbia crude supply region. As part of the Transaction, Tidewater and Pembina will enter into an interconnection agreement upon closing which will allow Tidewater to continue to access existing crude sources at the terminal
located in Taylor, British Columbia for the next 25 years, which is expected to provide PGR with a reliable and cost-effective source of feedstock. The Transaction is anticipated to yield material run-rate cost improvements, compared to historical metrics, while further enhancing Tidewater’s ability to optimise its feedstock procurement at the PGR.
“We are excited to announce the agreement to purchase the Western Pipeline. The Transaction provides Tidewater with the opportunity to unlock meaningful cost savings and increased flexibility and control of our day-to-day refining operations at the PGR. We expect that the Transaction will allow us to significantly reduce the cost of feedstock flowing into PGR, which will improve product margins and will play a key role as we continue to focus on optimising our refining assets”, said Jeremy Baines, Chief Executive Officer of Tidewater.
The Transaction is expected to close on or before 1 September 2025 and is subject to customary post-closing adjustments and regulatory approvals.
PROTECTIVE OUTERWRAPS
Eni selects ABB as main automation contractor for one of the UK’s first industrial CCS clusters
10 - 12 June 2025
Global Energy Show 2025
Calgary, Canada
https://www.globalenergyshow.com/
25 - 26 June 2025
Carbon Capture Technology Expo North America 2025
Houston, USA
https://www.ccus-expo.com/about/registrationnorth-america
9 - 12 September 2025
Gastech Exhibition & Conference
Milan, Italy
https://www.gastechevent.com/visit/visitorregistration/
23 - 24 September 2025
Subsea Pipeline Technology Congress (SPT 2025)
London, United Kingdom
https://sptcongress.com/
21 - 23 October 2025
Carbon Capture Technology Expo Europe 2025
Hamburg, Germany
https://www.carboncapture-expo.com/
03 - 06 November 2025
ADIPEC 2025
Abu Dhabi, UAE
https://www.adipec.com/
03 - 07 March 2026
CONEXPO-CON/AGG 2026
Las Vegas, USA
https://www.conexpoconagg.com/conexpo-conagg-construction-trade-show
15 - 19 March 2026
AMPP Annual Conference + Expo
Houston, USA
https://ace.ampp.org/home
ABB has announced it has been selected by integrated global energy company Eni as the main automation contractor for HyNet, one of the UK’s first industrial decarbonisation clusters that forms part of the Government’s Track-1 carbon capture and storage CCS) commitment.
ABB’s Ability™ System 800xA® Integrated Control and Safety System (ICSS) will be deployed to manage the automation, telecoms and cyber security project scope for the transportation and storage of the captured carbon dioxide (CO2) emitted by heavy industrial plants in the North West of England and North Wales, to four depleted gas fields in the Irish Sea off the coast of Liverpool.
The project aims to reduce CO2 emissions
Dräger Marine & Offshore wins five-year contract with UK North Sea operator
Dräger Marine & Offshore (DMO), a provider of safety technology, has secured a long-term deal with a major North Sea oil and gas operator.
Due to run for five-years, with a further two one-year extension options, the extension of the existing supply contract means more than 10 UK North Sea assets will continue to benefit from Dräger’s industry leading portable gas detection and breathing apparatus systems.
Building on an existing decade-long relationship - which has previously covered the provision of products and training servicesthis partnership cements DMO’s reputation as a leading provider of essential safety equipment for the offshore oil and gas sector.
Lawrie Kerr, UK Sales Manager, Dräger Marine and Offshore, said: “This contract win is a testament to the expertise, dedication, and collaborative effort of our team and of our industry leading products. It further solidifies our position in the offshore sector, and I would like to thank our client for putting their faith in DMO to deliver this vital service up to 2029 and potentially beyond.
As DMO continues to expand its operations, this contract will serve as a foundation for business development and reinforces the company’s mission to provide cutting-edge safety-critical solutions to the industry.
by 10 million tpy by 2030, the equivalent of taking four million cars off the road and a quarter of the carbon dioxide currently emitted across the region.
“CCS has an important role to play within the current energy transition but navigating the complexities of operating an industrial cluster is highly technical and challenging,” said Per Erik Holsten, President of ABB Energy Industries.
“We are proud to support Eni on the exciting HyNet project by applying our integrated automation technology to accelerate decarbonisation in the UK and enable industries to outrun, leaner and cleaner.”
• Shell reportedly eyes BP acquisition
• SLB OneSubsea and Subsea7 awarded EPCI contract for bp’s Ginger Project
• Vaquero Midstream announces a 70 mile pipeline extension and gas processing projects in the Southern Delaware Basin
• Oil and gas companies add renewable fuels to low-carbon portfolio, says GlobalData
Follow us on LinkedIn to read more about the articles linkedin.com/showcase/worldpipelines
Fluxys and OQGN sign agreement to jointly develop Oman’s hydrogen transportation network
OQ Gas Networks SAOG (OQGN), the exclusive owner and operator of Oman’s natural gas transmission network, announced the signing of a Term Sheet Cooperation Agreement with Fluxys, the Belgian based global energy infrastructure group, to jointly develop the hydrogen transportation infrastructure in the Sultanate of Oman, where Fluxys intends to own and operate the hydrogen network as a minority shareholder, alongside OQGN.
OQGN and Fluxys share similar vision in leading energy transition activities, and with complementary infrastructure and aspirations, they say they are well positioned to enable rapid and efficient development of hydrogen infrastructure to cater to Oman’s need in line with Oman’s vision 2040 and hydrogen production targets.
This Cooperation Agreement solidifies the partnership between Fluxys and OQGN following the signing in September 2023 of a Memorandum of Understanding (MOU) between the two organisations to strategically collaborate in the hydrogen and CO2 network developments in Oman, as well as Fluxys’ acquisition of a 4.9% stake in OQGN as an anchor investor as part of the Initial Public Offering (IPO) of OQGN.
The partnership highlights OQGN’s commitment in enabling the timely development of decarbonisation infrastructure in Oman, as well as Fluxys’ strategy in investing in new low-carbon energy value chains with high renewable potential countries and connecting them to Belgium and Europe. This partnership also reflects their intention to exchange knowledge derived from their experiences and prior learnings.
Penspen wins HyNet CO2
Penspen, an international energy consultancy, has secured a multi-million-pound contract from United Living Infrastructure Services to advance the development of the HyNet CO2 transportation pipeline at Liverpool Bay.
Under this contract, Penspen will deliver the detailed engineering design for a project that will transform the northwest of England into a world-leading low carbon industrial cluster – and will shape the region’s low-carbon future for decades to come.
Penspen will lead the detailed engineering phase for the development of the onshore CO2 pipelines and above ground installations (AGIs), which will transport the captured carbon emissions from local industrial emitters in Stanlow to the Liverpool Bay CCS storage facility at Point of Ayr. CO2 will be transported through a combination of new assets and repurposed infrastructure.
Seventy of Penspen’s engineering specialists will deliver the project from a dedicated office at 280 Holborn, London, with 20 newly onboarded professionals for this scope of work. The project will also be supported by engineering disciplines from Penspen’s Aberdeen office, which has seen significant growth in the last six months.
Darren Bartlett, Director – Energy Transition at Penspen said: “This is a pivotal award that highlights Penspen’s reputation as specialists in supporting complex energy
The agreement was signed by Eng. Mansoor bin Ali Al Abdali, CEO of OQGN, and Mr. Pascal De Buck, Managing Director and CEO of Fluxys, at a ceremony held at the Mandarin Oriental Hotel, Muscat. The event was held under the patronage of H.E. Salim bin Nasser Al Aufi, Minister of Energy and Minerals.
Commenting on the agreement, Eng. Mansoor bin Ali Al Abdali stated: “We are very excited to work with Fluxys in jointly developing the hydrogen transportation network in Oman, and supporting Oman’s green hydrogen and decarbonisation initiatives. This cooperation is a clear signal of our commitment as the national energy infrastructure company in leading the development and deployment of green hydrogen infrastructure to support Oman’s energy transition goals and aspirations. Together with Fluxys, we will leverage our considerable joint experience and capabilities meeting Oman’s requirements for hydrogen transport infrastructure and realising the national agenda in a costeffective manner.”
Mr. Pascal De Buck added: “We are delighted to partner with OQGN in developing a new hydrogen transportation network in Oman. As a shareholder of OQGN, this collaboration is a pivotal step in our strategy to accelerating the energy transition and creating new value chains. By harnessing our combined expertise, we aim to bring renewable hydrogen to Belgium and Europe, while also significantly contributing to Oman’s sustainable energy goals. Together, we are committed to creating a brighter, greener energy future.”
transition projects, applying over 70 years of international engineering expertise to meet the challenge of decarbonising the UK’s industrial hubs.
“The HyNet North West project will be transformational for the UK’s energy network, and we are proud to be working with United Living to deliver this first-of-its kind project at Liverpool Bay. The development of this carbon capture facility will be critical in driving progress towards a cleaner energy future.”
HyNet North West is a UK-based project comprised of several different elements designed to decarbonise the industryheavy northwest of the UK around Liverpool Bay. Following the announcement of Government funding in October 2024, the project will implement carbon capture and storage and low carbon hydrogen infrastructure at large scale, utilising a hydrogen production plant, a hydrogen transport network and hydrogen storage, with carbon emissions captured and permanently stored in depleted hydrocarbon fields in the Irish Sea.
Campbell Crawford, Managing Director, United Living Infrastructure Services said: “We are pleased to appoint Penspen to deliver the engineering design on this project. They have an exceptional track record in delivering complex detailed design for onshore pipelines, making them one of the few companies in the UK with the expertise to help us deliver this major energy transition project.”
Serious workplace injuries and fatalities are trending downward, potentially signalling the start of a longer-term decline as industries shift their focus toward higher consequence events.
ISN’s latest Serious Injury and Fatality (SIF) Insights white paper revealed a 16% decrease in SIF cases between 2022 to 2023. Notably, 2023 marked the lowest total of SIFs identified in ISN’s analysis since 2017. Still, sectors such as construction and transportation face elevated levels of serious and fatal incidents year over year, underscoring the persistent nature of risk in complex environments.
While an overall decrease in SIF rates is encouraging, sustaining progress across all industries hinges on forming proactive safety cultures. Organisations that continuously assess employee perceptions of workplace safety and design systems that allow
processes to fail safely can strengthen their ability to mitigate hazardous risks experienced by workers.
The frequency of SIFs in the workplace remains a critical concern across industries. According to the US Bureau of Labor Statistics (BLS), there were 5283 fatal work injuries reported in the US in 2023.
Yet, high-level incident data offers limited visibility into the patterns and trends around SIF rates. To gain additional insight, ISN extracted more than 132 000 recordable incidents from OSHA 300 logs submitted by US contractors between 2017 and 2023. From this data, approximately 19 900 incidents were identified as potential SIF cases.
Rick Dorsett, Vice President, ISN, asks: as serious injuries and fatalities decline in the workplace, how can the pipeline industry stay vigilant?
In 2023, ISN identified 2000+ unique SIF cases through this analysis, representing a 16% decrease from 2022 and the lowest total identified overall since the beginning of ISN’s seven year data set. These findings mirror national reports by OSHA and BLS, both of which recorded declines in serious injuries and fatalities between 2022 and 2023.
It is important to note that what qualifies as a serious injury often depends on the Client’s definition or the industry in which the scope of work is being completed. With this nuance in mind, ISN’s analysis integrates OSHA criteria and ASTM Level One injury classification system to enable a more detailed understanding of injury severity across a broader set of incident types.
Additionally, while a decrease in overall SIF rates is encouraging, it does not signal the elimination of risk altogether. More work must be done to advance system-level safeguards and proactive risk identification, which requires organisations to tap into safety culture insights.
Trends and variations in SIFs across high-risk industries
Operational and worksite risks vary widely across industries. Contractors working in the oil and gas sector face vastly different safety and environmental hazards than those in the food and beverage space, simply from the worksite conditions unique to their operations.
For example, construction is a high-hazard industry due to factors such as exposure to heavy machinery, work at heights, and struck-by injuries. ISN’s analysis reflects these risks, finding contractors in the construction sector experienced more than 1200 SIF cases in 2023. Contractors classified under construction North American Industry Classification System (NAICS) codes also accounted for over 40% of the total fatalities identified in 2023.
Similarly, ISN identified more than 1000 SIF cases tied to transportation activities in 2023 alone, alongside a nearly 30% increase in transportation industry SIF cases between 2021 and 2023. Operational pressures in transportation – such as long hours and tight delivery schedules – remain key drivers of roadway incidents and fatalities.
The oil and gas industry shares many of the same hazards found in construction, transportation, and other high-risk sectors such as renewable energy. Oil and gas workers contend with risks not often encountered by other industries, such as extreme weather conditions and extended periods of remote work.
Due to the safety-critical nature of pipeline operations, the Pipeline and Hazardous Materials Safety Administration (PHMSA) –an agency of the Department of Transportation (DOT) – requires pipeline operators to implement rigorous training programmes to protect against abnormal operating conditions.
However, even with regulatory oversight, internal commitment to proactive risk management is essential. Across sectors, many leading organisations are investing in robust cultural assessments and system design improvements to improve SIF mitigation.
A culture-driven approach to preventing workplace SIF
To continue driving down SIF rates, organisations are implementing a stronger focus on proactive safety cultures. These approaches are reshaping risk management for the pipeline industry and beyond.
Prioritise leading indicators and cultural insights
Incident reports and lagging indicator metrics are valuable sources to reveal where failures occurred. However, many industries are also emphasising leading indicators, such as company safety culture and energy-based safety practices, to determine where SIF potential still exists.
With regular safety culture assessments, organisations can gather feedback from internal employees and third-party contractors to better understand cultural strengths and risks. These insights offer a deeper understanding of safety culture maturity to help guide next steps when implementing frameworks such as energy-based hazard recognition, direct controls for high-energy hazards, and Human and Organisational Performance (HOP) principles.
Consistent feedback from employees and contractors is critical in environments with high worker turnover. In sectors such as oil and gas, where new employees frequently enter the workforce, capturing workers’ safety perceptions can offer early visibility into system-level gaps.
For more robust analysis, organisations can aggregate key data across functional groups and business units to benchmark progress against industry trends and target areas needing additional support.
Engage frontline workers in system and procedure design
Frontline workers are closest to the realities of day-to-day operations and often adapt processes in real time to meet worksite demands. This adaptation, while sometimes necessary, can introduce unrecognised hazards if not carefully understood.
Bridging the gap between “work-as-imagined” and “work-asdone” requires involving employees directly in designing work and standardising job procedures. Workers are often the first to recognise where standard processes break down under real-world conditions or when site demands require additional safeguards, such as enhanced transportation controls for lone worker situations common to pipeline operations.
By empowering workers to share where systems need adjustment, organisations can build safeguards that are grounded in operational reality. An environment where workers feel psychologically safe to report concerns and stop work when needed helps surface hazards before they lead to serious injuries or fatalities.
Sustain SIF reduction through proactive safety cultures
Over the past two decades, declines in serious injury and fatality rates lagged behind improvements in non-fatal injury rates. This disparity prompted organisations to change how they assess health and safety improvement. Today, leading companies recognise that strong performance depends on cultivating a proactive safety culture at every level – from leadership to the front line.
Particularly in high-hazard industries such as oil and gas, leveraging leading indicator insights and cultural assessments are critical to shift from reactive risk management toward an adaptive, worker-centred approach. Organisations that leverage data to address safety culture gaps can position themselves to better protect employees and hope to sustain a downward trend in serious injuries and fatalities.
Two Independent Plugging Modules. Zero Compromise.
The SmartPlug® Isolation System delivers true Double Independent Isolate and Monitor (DiiM) isolation—with independently anchored plugging modules that eliminate single points of failure. Rated up to 350 bar, it ensures safe, efficient, and high-integrity pipeline repairs with onboard control, bi-directional piggability, and remote pressure monitoring.
Andrew Hockey, Chief Executive of the Engineering Construction Industry Training Board (ECITB), explores how a new initiative is helping to create a safer industry.
ith the forecasted skills shortages the energy industry faces, the need to build safety resilience, increase workforce transferability across sites and sectors and ensure workers are technically competent has never been more important. Workers are always required to undertake basic safety training before being deployed to hazardous sites, but they do not necessarily demonstrate ongoing technical competence.
Incidents such as Piper Alpha, Bacton Gas Terminal and Deepwater Horizon were all avoidable. Serious managerial failures were attributed to all these events, including the lack of diligence around the recognition and assurance of competence standards. One of the biggest drivers behind the industry-led Connected Competence initiative is to help avoid workplace incidents like this. Put simply, assuring a base level of ongoing technical competence for all workers creates a safer working environment for everyone.
By requiring workers to demonstrate their ongoing technical competence every three to four years, Connected Competence assures a common approach to base technical competence required of site-based craft
and technician trades in the same way as sector-specific safety training is widely acknowledged. This helps build confidence that everyone is supporting a duty of care to their co-workers around them.
Supported and enabled by the ECITB, Connected Competence was developed in collaboration with some of
the UK’s largest contracting companies. Each has committed to working together to use standardised testing to create a safer, more competent and transferable workforce. The initiative was formally adopted as an industry-wide framework in 2021, focused initially on aligning base technical competence standards among oil and gas workers.
The initiative reduces the duplication of assessments and costs, speeds up the deployment of competent personnel between sites, but most importantly, increases safety through the recognition and ongoing assurance of base technical competence.
When the base standard has been achieved – either at site, as part of an employer’s competence management system or at a testing centre – candidates receive a digital badge. This gives them ownership of their skills, which is verifiable online and transferable across energy industry employers. By every site-based worker assuring their ongoing base technical skills, the industry is taking great strides towards a safer industry for everyone.
An investigation following an incident on an engineering construction site concluded that the employer could not prove the currency of technical competence of the workers concerned. Qualifications achieved many years ago or attendance certificates at training events do not prove workers’ current competence. Supply chain partners recognised they needed to address this. They also recognised the significant wastage and huge cost to industry in not recognising technical competence standards when workers transferred between organisations. The impact of this was that many workers were duplicating previous training and testing to demonstrate their technical competence to a new employer or to gain access to a new client site. Employers would often start competence profiles from scratch when workers transferred to different contracting organisations. This created significant duplication of training at a huge cost. It also meant workers had to re-do assessments with a knock-on delay to onboarding. With an increased demand for skilled workers, particularly during busy periods such as maintenance shutdowns, employers needed a programme that harmonised assessments and made records accessible online so that workers could transfer easily between companies and sectors.
Mark Wilson, HSE and Operations Director at Offshore Energies UK (OEUK), said: “Failing to recruit, retain and attract the necessary capabilities and expertise into the industry will jeopardise the UK’s ability to meet its energy security and climate goals. Connected Competence needs to be part of that solution. Supporting a recognised, transferable base level of technical competence will increase our safety resilience, establish common competence and reduce costs.”
Connected Competence employers have demonstrated outstanding commitment to safety in their collaborative actions to standardise a base level of technical competence for site-based trades.
In the last two years, the programme has grown significantly. Ten major contractors have now signed up to the scheme including Aker Solutions, Bilfinger, Boskalis, nexos, Petrofac, Ponticelli UK, Semco, Stork UK, Wood and Worley. Together, they employ more than 75% of the craft and technician workforce in the UK upstream oil and gas industry. The 20 clients that recognise and advocate the programme are Apache, bp, Centrica Energy Storage+, CNOOC, CNR International, Dana Petroleum, ENI, EnQuest, Equinor, Harbour Energy, INEOS Energy, Neo Energy, Neptune Energy, Repsol, RockRose Energy, Serica Energy, Shell, Spirit Energy, TAQA and TotalEnergies.
With the programme being designed to reduce the need for repeat training and testing, acknowledging existing certifications and supporting the Just Transition of the energy workforce, it has the backing of Unite the Union, GMB Union and the RMT. As a measure of good practice in managing safety and competence it is also supported by industry stakeholders including the Health and Safety Executive (HSE), the Scottish Government, Step Change in Safety, OEUK and NSTA, who have all contributed to the collaborative efforts of the scheme.
Craig Wiggins, CEO at Step Change in Safety, a memberled organisation which works to prevent incidents and injuries across the energy industry, said: “In our industry, we manage major accident risks every day. Each of us plays a role in ensuring that the barriers preventing these risks from escalating into serious incidents remain intact. It is vital that we have competent people in our operations who can install, operate and maintain the equipment that ensures safe operations. I see Connected Competence as a key tool in building a workforce that understands these risks and knows how they impact safety on our facilities. I encourage all personnel – both core crew and temporary staff – to take the opportunity to demonstrate their competency through Connected Competence.”
The impact of Connected Competence has been tangible since it was launched four years ago. Participating employers have shown a strong dedication to safety by working together to establish a standardised level of technical competence for site-based trades. Combined, their efforts have contributed to the recognition of ongoing technical competence, promoting a proactive commitment to safety among both employed and transient workers. This collaborative effort is facilitating the development of a transferable and more resilient skills pool throughout the energy industry. Connected Competence was recognised as an exemplar at the end of 2024 for the way its partners in the oil and gas industry were working together and delivering true sector collaboration. The initiative was named the winner in the Collaboration category at the Energy Industries Council’s World Energy Supply Chain Awards. The collaborative efforts have led to reduced duplication of assessments when workers have moved between sites and contractors, and increased cost efficiencies.
Connected Competence allows employers to share the same ongoing verification of workers’ technical competence. This means workers are verified against the same recognised and accepted standard for the applicable trade disciplines. This
can lead to significant savings when asset owners change the contractor responsible for a contract and when a TUPE process takes place. When both organisations use the same Connected Competence framework for the verification of ongoing base level of technical competence, the contract exchange is seamless. Contractors can save time and money in the actual processing of the transfer but, more importantly, there is minimal impact to the workers having to repeat assessments with their new employer. Trades to which this applies include pipefitters, platers, electrical technicians, mechanical technicians, instrument and control technicians, industrial coatings technicians, riggers, appointed persons for rigging and thermal insulators.
But the programme is not just about potential savings. By assuring all workers have the same base level of ongoing technical competence, it is increasing the safety on potentially hazardous sites and easing the mobilisation of workers between sites and sectors. This is essential if we are to meet the challenges of the energy transition. Employers hiring new starters who already hold Connected Competence digital badges has created a more efficient transfer of competent workers between companies with significant cost savings in management time, training costs and expenses.
A 2024 report by an impartial, external consultancy analysing the Connected Competence initiative confirmed the benefits delivered by the initiative will lead to improved safety standards, a reduction in lost-time incidents (LTIs), increased confidence of workers operating safely and reduced risk of business interruptions due to incidents or accidents. Two thirds (67%) of contractors expect reduction in waste, increased efficiency and productivity gains as a result of Connected Competence to be sustained in the long term. Further anticipated impacts are expected in the coming months and beyond, notably following the introduction of the Site Based Assessment scheme.
Jonathan Buchanan, Rope Access Painter Blaster at Bilfinger UK, is one of the many thousands of workers to benefit from Connected Competence already. He previously worked onshore as a rope access technician in various roles, but decided he needed change and wanted to go back offshore. Bilfinger, one of the leading industry providers, offered him that opportunity. He said: “Connected Competence is a means of gauging, testing and evaluating an individual technician’s personal skills, knowledge and ability in a given role. This is essential as every technician should have a good understanding of their role they are employed in, health and safety and being able to demonstrate that they are capable of doing said job. After my own technical tests, I came away not only satisfied with my own skill and ability, but also with some new knowledge gained from the process. The positive impact of Connected Competence has been an awareness of your own skills and abilities, and a better working knowledge in all. It has also created better working knowledge as a team. I can only speak for myself and my squad, but I do feel that there has been positive growth within the team due to the implementation.”
Alastair MacLeod, CEO, Ground Control, discusses how to prioritise lone worker safety in oil and gas pipeline operations.
t is sunrise, and Sam swings his truck into a layby, turns off the engine and steps into the crisp morning air. He grabs a gas detector and a weather-beaten tablet from the cab, knowing 4 km of right-of-way stand between him and an isolation valve whose failure could spill thousands of barrels of crude oil. A dozen paces from the back of the pickup, the last bar of cellular signal flickers out, and from that moment, Sam is entirely alone.
Scenes like this play out every day across the planet’s pipeline networks: technicians in deserts inspecting fibre-optic leak systems, corrosion specialists skimming swamps in airboats, hydrostatictest crews trudging tundra. For decades the midstream sector has relied on people such as Sam to be its eyes, ears and conscience along thousands of kilometres of buried steel. Yet the combination of vast geography, hazardous product and ever-thinner staffing has turned lone-worker protection from an operational worry
into a reputational and moral imperative. If an engineer slips on the permafrost, strikes his head and is left unconscious, a fully preventable emergency can spiral into tragedy long before anyone realises a routine check-in call was missed.
In the United Kingdom, the Health and Safety at Work etc. Act 1974 establishes a bedrock principle: employers, including pipeline operators, must do whatever is ‘reasonably practicable’ to safeguard their workforce. This duty of care applies equally to the lone employee trudging up a saturated embankment as it does to an entire shift team based at headquarters. And if your organisation is found wanting, the penalties under the Act can be severe, ranging from fines that run into the hundreds of thousands of pounds to criminal charges for senior managers.
Furthermore, legal and moral risks sow a reputational minefield that follows any serious workplace incident. In an age when environmental and social governance (ESG) metrics are increasingly under the spotlight, a lone-worker tragedy could tarnish your credentials in the eyes of investors, local authorities, and the broader community. One tragic accident can undo years, if not decades, of carefully nurtured goodwill, let alone damage investor relations and the balance sheet. The public does not soon forget an employer that places cost savings or expedience above the well-being of its people, particularly in sectors where safety is paramount.
For years, the industry’s approach to lone working was often limited to rudimentary methods: a phone call at the start or end of a shift, or a radio check-in at lunch. The assumption, one that was potentially lethal, was that silence meant everything was proceeding smoothly. If the technician didn’t phone to report trouble, it was assumed there was none. But what if the phone was dropped in a block valve pit, or the nearest signal mast was miles away?
As tasks grew more specialised and budgets tighter, the reliance on individual roving engineers or inspectors increased. Simultaneously, the potential scale of disaster loomed larger. A single slip near a raging sluice gate could become a fatal accident if nobody is there to witness it. A single mis-step while breaking out bolts on a high-pressure condensate line can turn fatal if no one is there to witness it. Waiting anxiously for a missed check-in could mean the window for rescue closes before it is even discovered that rescue is needed.
If moral duty and reputational risk are insufficient, the law leaves little room for doubt. The Management of Health and Safety at Work Regulations 1999 (Regulation 3) makes it crystal clear: each organisation must formally assess the risk to staff health and safety, including when they work alone. This is particularly acute in the water and dam sectors, where hazards multiply in remote settings: powerful water currents, heavy machinery, sudden changes in weather and ground conditions.
A question you might ask yourself: ‘If a worker faces a hazard in a certain area, does being alone amplify that hazard?’ If the answer is yes, and, in most pipeline environments, it often is, then additional controls are mandatory. This might mean bundling tasks in pairs or, more practically, providing high-grade safety gear and advanced communication technology to mitigate the absence of another pair of eyes.
Thankfully, the days of holding your breath until a lone worker ‘checks in’ are behind us. Advances in satellite communications, the Internet of Things (IoT) and ruggedised devices have revolutionised lone worker tracking. Indeed, technology now offers something closer to an active safety net, rather than the reactive approach seen in days past.
Now, many rugged satellite trackers are designed with waterand shatter-proof shells, extended battery life and an SOS function that operates in dead zones where your mobile won’t. An engineer cleaning debris from a dam outflow can carry a device that transmits location data and remains operational, irrespective of how hot or cold it is. If they require immediate attention, they can alert your control room with the click of a single button.
Furthermore, compact satellite units with two-way messaging are the Swiss-army knives of lone worker safety – portable, easy to use and able to handle remote communications where terrestrial signals are scarce. A technician inspecting a suspicious crack along the bank can not only send a distress signal, but can also receive instructions on how to proceed – turning a potentially frantic rescue operation into a coordinated response.
IoT plays a vital role with sensors fixed to gates or turbine housings that can relay real-time data about equipment health, water levels, or structural integrity. If a sensor flags an anomaly, your lone worker is immediately alerted and can investigate with caution rather than walking into a hidden danger. Meanwhile, control room operators remain in the loop, ready to intervene or send backup if the situation escalates.
All these measures do more than shield an individual from harm, they create a culture of safety that ripples through the entire workforce. Employees who know their employers have invested in modern safeguards often feel empowered to take initiative, raise concerns sooner, and adhere to best practice.
One might argue that outfitting every lone worker with advanced wearable tech and adopting new safety protocols seems costly. But consider the financial and human cost of a single major incident: lost time injuries, potential lawsuits, regulatory fines, project shutdowns, and a blow to your brand that can outlast a generation. For an industry as visible and critical as water management, where the public’s confidence is paramount, that is a gamble few can afford.
Moreover, robust lone-worker systems can dovetail seamlessly into broader operational improvements. Real-time data doesn’t just inform you about a worker’s whereabouts; it can reveal maintenance issues before they become breakdowns or highlight emerging structural concerns that might otherwise be overlooked. Efficient scheduling and resource allocation can follow, in turn potentially offsetting the initial investment.
The message is unmistakable: in pipeline operations, “off-grid” must never mean “off the radar.” When ground heave buckles a right-of-way, a prairie wildfire roars across a valve site, or a sudden pressure drop lights up the SCADA screen, crews linked by real-time connectivity can intervene before trouble spirals. In this business, preparedness and constant visibility remain the most valuable asset of all.
Alastair MacLeod is the chief executive officer of Ground Control, a group comprising three companies – Wireless Innovation, Rock Seven and Ground Control (US).
Alastair graduated from the University of York, England, in 1998 as an Electronic Systems Engineer, and has sat on various boards where his passion for innovation, technology and business growth has seen him be instrumental in increasing sales revenue from sub US$100 million to more than US$1 billion.
Alastair has a passion for deep tech and data, IoT, AI and M2M, with Ground Control specialising in satellite and cellular technology to connect people and things, particularly within hard to reach, remote areas – from wind farms to fishing fleets and first responders to forestry workers.
o appreciate the value of manned aircraft in leak detection, it’s important to first understand the roles and limitations of the existing technologies:
Equipped with methane detection instruments, satellites offer broad coverage and the ability to spot large leaks – typically those releasing over 100 kg/hr of methane. However, due to their
altitude and sensor limitations, satellites struggle to detect smaller but still significant leaks.
With their ability to fly at low altitudes and hover near infrastructure, drones are excellent tools for detecting small methane leaks with high precision. Yet their range is inherently limited by battery life, regulations, and the lack of infrastructure. Conducting large-scale inspections with drones is
James Aarestad, Vanguard Pipeline Inspection LLC, USA, describes how manned aircraft can bridge the gap between drones and satellites when it comes to methane detection.
to small, fixed winged aircraft or helicopters, for routine aerial inspections of pipeline, storage facilities, and oil well pads.
currently logistically complex and cost prohibitive. This is where manned aircraft enters the scene.
Every day, around the world, over 700 aircraft take to the skies for visual pipeline patrols. These flights are often mandated by federal regulations and primarily focus on identifying physical threats to pipelines – fallen trees, ground erosion, unauthorised construction, etc. Despite their ubiquity, very few of these aircraft are equipped with methane leak detection technology.
That’s precisely why Vanguard Pipeline Inspection developed its methane detection system for manned aircraft.
Vanguard’s system (the Falcon XL) is engineered with the everyday pipeline patrol operator in mind. It is compact, non-invasive, and plug-and-play. Installation on a standard Cessna aircraft or helicopter requires no aircraft modifications. Operators can be trained in just a few hours, making it easy to scale across existing patrol fleets.
Once installed, the equipment transforms a visual patrol aircraft into a sensitive methane detection platform. This hybrid capability allows for both threat identification and leak detection in a single flight: dramatically increasing the value of each patrol mission.
The core of the Falcon XL is a proprietary laser-based detection pod that uses spectroscopy to identify methane (CH4) concentrations above pipelines. The system emits laser beams and measures the amount of light absorbed by methane in the atmosphere. The more light that is absorbed, the higher the methane concentration.
These real-time readings are displayed for the pilot, allowing immediate reporting of leaks to pipeline operators. This real-time detection capability is critical in reducing response times and mitigating environmental and safety risks.
Complementing, not competing
It’s important to emphasise that the technology does not seek to replace satellites or drones. Rather, it complements them.
) When satellites flag a potential large-scale emission, our aircraft can be dispatched to confirm the leak and gather more granular data.
) When drones identify persistent issues in a localised area, our aircraft can provide broader context by surveying surrounding pipeline segments that are beyond the drone’s reach.
This layered approach: satellite for global awareness, aircraft for regional sensitivity and flexibility, and drones for hyper-local accuracy, creates a robust and cost-effective pipeline integrity programme.
One of the standout advantages of using manned aircraft is cost efficiency. Because the system integrates seamlessly with existing patrol operations, operators don’t need to add new aircraft, train entirely new personnel, or invest in expensive drone logistics.
This low barrier to entry means that operators can conduct more frequent and widespread leak inspections without significantly increasing operational costs. Catching leaks early not only conserves valuable product but also improves public safety and reduces greenhouse gas emissions – an increasingly important consideration in today’s regulatory and ESG-driven environment.
Vanguard works with multiple operators to deploy its system across hundreds of thousands of miles of pipeline. In one recent case, a client using our technology was able to detect and repair a mid-sized leak that had gone unnoticed by traditional patrols and was too small for satellite detection. The leak, although modest in scale, represented a significant loss over time and posed a potential safety hazard.
In another case, the Falcon XL was used to validate satellite-detected emissions, helping to prioritise maintenance efforts and verify the effectiveness of repairs. These real-world use cases highlight the system’s adaptability and practical value.
As methane regulations tighten and the industry moves toward net-zero goals, having a scalable, flexible, and cost-effective methane detection solution is no longer optional, it’s essential. Our manned aircraft-based technology fills a crucial niche, enabling operators to enhance their leak detection programs without overhauling their operations.
With hundreds of aircraft already flying daily pipeline patrols, the infrastructure is in place. All that’s needed is the right technology.
In the dialogue about methane detection, it’s time to give manned aircraft their due. Positioned between the high-level view of satellites and the ground-level precision of drones, aircraft equipped with our technology offer the best of both worlds: reach, sensitivity, and operational efficiency.
As we continue to refine our system and expand deployments, we’re proud to be a part of the solution; helping the industry detect leaks earlier, respond faster, and operate more responsibly.
Specialized, flexible, factory assembled
Cathodic Protection and AC Mitigation
+30 years proven in-service performance
Discover the ultimate AC mitigation electrode for pipelines and transmission lines, coupled with top-tier cathodic protection anodes for underground, in-plant, and storage tank systems. Your solution is here!
Eugene Lo, EVIDENT, emphasises the role of ultrasonic testing in safeguarding critical infrastructure, optimising safety, and reducing downtime.
ccording to a National Association of Corrosion Engineers (NACE) report, the global cost of corrosion is an estimated US$2.5 trillion – equivalent to 3.4% of global GDP. When corrosion control practices and technologies are properly implemented on a global level, the cost of corrosion can be reduced by a staggering US$375 billion to as much as US$875 billion (15% - 35% reduction in corrosion costs).1
Moreover, these figures do not consider benefits associated with the reduction of risk to human safety and the environment. While these corrosion statistics are not limited to only midstream assets, such as pipelines, US Department of Transportation Pipeline Hazardous Materials and Safety Administration (PHMSA) pipeline incident data reveals a more specific reality.
In the US, over a 20 year period from 2005 to 2024, there were a total of 12 674 pipeline incidents with a total cost of over US$11.3 billion. More tragically, these incidents resulted in over 250 fatalities and over 1000 injuries. These figures correspond to an annual average of 634 incidents, with individual incidents averaging US$566 million in damages and causing 13 fatalities and 53 injuries.2
In light of such data, the importance of pipeline integrity and corrosion control programs cannot be understated. A foundational element of a robust pipeline integrity programme is non-destructive testing (NDT), which is a combination of inspection methods, technologies, and processes used to evaluate the integrity of materials and components without causing damage. While a common NDT application is the detection and quantification of weld and other defects in pipelines, this article will focus on the inspection of corrosion as a preventative and predictive measure against component failure.
One of the most predominant NDT methods used to inspect for corrosion is ultrasonic testing (UT). This article
introduces UT, the primary application types where UT is deployed as an inspection method, and the critical role it plays in pipeline integrity, corrosion inspection and assessment, and in minimising the financial, human, and environmental impacts of unplanned downtime and accidents.
Ultrasonic testing instruments have been used in industrial applications since as early as the 1920s. The technique of propagating high frequency sound waves through solid materials has been used to detect hidden defects and internal discontinuities in metals and non-metals, as well as to measure thickness and analyse material properties. Ultrasonic testing is completely non-destructive, leaving the tested part intact and undamaged. Owing to this and other advantages, UT has become a preferred and well-established NDT method used in manufacturing processes and quality control processes, especially for the inspection of welds and structural metals.
The growth of ultrasonic testing largely parallels developments in electronics, and later in computers. Early work in Europe and the US in the 1930s demonstrated that highfrequency sound waves would reflect from hidden flaws or material boundaries in predictable ways, producing distinctive echo patterns that could be displayed on oscilloscope screens. Post-World War II sonar technology developments provided further impetus for research in ultrasonics. In 1945, US researcher Floyd Firestone patented an instrument he called the Supersonic Reflectoscope, which is generally regarded as the first practical commercial ultrasonic flaw detector. It used the technique referred to as ‘pulse-echo’ that is still commonly employed today. This would lead to the introduction of numerous commercial instruments in the years that followed. Among the leaders in the development of commercial ultrasonic flaw detectors, gauges, and transducers in the 1960s and 1970s were companies such as Panametrics, Staveley, and Harisonic.
By the 1970s, the introduction of precision thickness gauges brought ultrasonic testing to a wide variety of manufacturing operations that required thickness measurement of parts in situations where there was access to only one side, and corrosion gauges came into wide use for remaining-wallthickness measurements of metal pipes and tanks.
Modern advances in ultrasonic test instruments have been based on the digital-signal-processing techniques and inexpensive microprocessors that became available in the 1980s. Ongoing developments in these technologies have led to the latest generation of ultra-portable, highly reliable instruments and inline inspection systems for flaw detection, thickness gauging, and acoustic imaging.
Of all the applications of industrial ultrasonic testing, flaw detection is the oldest and the most common. UT data acquisition instruments process the echoes produced by high-frequency sound waves reflected off flaws, recording and displaying the signals for interpretation.
Sound waves are simply organised mechanical vibrations travelling through a medium, which may be a solid, a liquid, or a gas. These waves travel through a given medium at a specific speed or velocity, in a predictable direction, and when they encounter a boundary with a different medium, they are reflected or transmitted according to the basic laws of physics that underlie ultrasonic flaw detection.
All sound waves oscillate at a specific frequency, or number of vibrations or cycles per second (Hz), which humans experience as pitch in the familiar range of audible sound. Human hearing extends to a maximum frequency of about 20 000 cycles per second (20 kHz), while most ultrasonic flaw detection applications utilise frequencies between 500 000 and 20 million cycles per second (500 kHz to 20 MHz). At frequencies
in the megahertz range, sound energy travels efficiently through most liquids and common engineering materials.
The distance and velocity that an ultrasonic wave travels through a medium depends on its material properties. As a rule, materials that are hard and homogeneous transmit ultrasonic waves more efficiently than those that are soft and heterogeneous or granular.
Ultrasonic wavelength, which is the distance between any two corresponding points in the wave cycle as it travels through a medium, is directly related to frequency and velocity. Lastly, sound waves are defined by the direction in which they are propagated relative to the shape and position of the medium.
Ultrasonic flaw detection is a comparative technique. Using appropriate reference standards along with a knowledge of sound wave propagation and generally accepted test
procedures, a trained inspector identifies specific echo patterns corresponding to the echo response from good parts and from representative flaws. The echo pattern from a test piece may then be compared to the patterns from these calibration standards to determine its condition. Sound energy will travel to the far side of a part but reflects earlier if a defect or discontinuity is present in the material.
Ultrasonic thickness measurement is a widely used NDT technique for measuring the thickness of a material from one side. It is fast, reliable, and versatile, and unlike a micrometer or caliper, it requires access to only one side of the test piece.
On-line or in-process measurement of extruded plastics, rolled metals, and measurement of individual layers or coatings in multilayer fabrications are common manufacturing use cases. A common process industry application is measuring remaining material thickness when corrosion is present, as well as liquid levels and thickness of biological materials.
The fundamental theory and principles of UT for flaw detection also apply to UT for thickness measurement. That is, based on the frequency of the sound wave and specific material properties, sound energy is propagated in a pattern of organised mechanical vibrations traveling through a medium. Ultrasonic thickness measurement works by precisely measuring the elapsed time for an ultrasonic pulse introduced on the ‘near’ surface of a material to travel through the material and reflect back from the inner boundary, or ‘far’ surface. Because sound waves reflect from boundaries between dissimilar materials, this measurement modality is normally referred to as the ‘pulse-echo’ technique. In essence, a thickness measurement system ‘listens’ for the echo from the opposite side. In typical engineering materials, this time interval is only a few millionths of a second. The system is programmed with the material’s ultrasonic velocity, which it references to calculate the wall thickness.
It is important to note that the ultrasonic velocity of the test material is an essential part of this calculation. Ultrasonic velocity varies according to the material’s properties – for example, whether it is hard and homogeneous versus soft and heterogeneous – and it also changes significantly depending on material temperature. Thus, it is always necessary to calibrate an ultrasonic thickness measurement system to the actual material being measured.
In the broadest sense, a transducer is a device that converts energy from one form to another. Ultrasonic transducers convert electrical energy into high-frequency sound energy and vice versa. Typical ultrasonic transducers contain a piezoelectric element made of a ceramic, composite, or polymer material. When this element is excited by a high-voltage electrical pulse, it mechanically vibrates across a specific spectrum of frequencies and generates a burst of sound waves. Conversely, when vibrated by an incoming sound wave, it generates an electrical pulse. Because sound energy at ultrasonic frequencies does not travel efficiently through gases, a thin layer of ‘coupling’ liquid is normally used between the transducer and the material being inspected.
Modern ultrasonic thickness gauges are generally divided into two types: corrosion gauges and precision gauges. Corrosion gauges are designed to measure the remaining wall thickness of metal pipes, tanks, structural parts, and pressure vessels that are subject to corrosion on internal and inaccessible surfaces. Corrosion gauges are optimised to detect minimum remaining wall thickness on corroded components using specialised dual element transducers to compensate for rough surfaces.
Precision gauges using single element transducers are recommended for all other applications, including inspecting smooth metals, plastics, fibreglass, composites, rubber, and ceramics. Combined with the right transducer, precision gauges can be extremely versatile and, in many cases, can measure to an accuracy of ± 0.001 in. (0.025 mm) or greater, which is higher than the accuracy that can be achieved with corrosion gauges.
Pipeline integrity connotes the concepts of failure prevention, inspection and repair, and it also includes products, practices and services that help operators maximise their assets. With entire economies built on pipelines, pipeline integrity is receiving more attention than ever – from the composition of the tubular structure to the hightech methods for building, modelling, managing, monitoring, and repairing pipelines. It begins at the project conception stage, enabling risk mitigation and long-term optimised performance to be built into the final design.
Industry standards, such as the American Petroleum Institute’s API 579 Fitness-For-Service (FFS), make use of a three-level assessment process to evaluate the fitness for service of a particular component or system. Generally, a pipeline integrity management programme consists of various elements:
) A process for identifying the pipeline segments and failure modes that could affect a highconsequence area; a baseline assessment plan.
) An integrated analysis process using all available information about the integrity of the pipeline and the consequences of a failure.
) Criteria for repair actions to address integrity issues raised by the assessment plan and information analysis.
) A continual process of assessment and evaluation to maintain pipeline integrity.
) Identification of preventive and mitigation measures for protecting the high consequence area.
) Methods to measure the program’s effectiveness, personnel training, etc.
The availability of NDT data, particularly UT data, is crucial in enabling pipeline operators to identify high-risk areas, prioritise repairs, and implement proactive maintenance strategies, reducing the likelihood of leaks or failures while extending pipeline lifespan and ensuring safe, efficient operations.
Detects holidays, pinholes, and other discontinuities using continuous DC
n Lightweight, one-piece ergonomic design provides comfortable all-day use
n One wand covers the entire voltage range from 0.5 to 30 kV
n Up to 16 hours of battery life—powerful Li-ion batteries fit neatly within the compact wand handle eliminating the need for a separate battery box
n Built-in Certified Voltmeter and Voltage Calculator feature
n Industry standard connectors and adaptors provide compatibility with nearly all existing electrodes
As inspection technologies advance, data collected from UT systems is likely to play an even more significant role in ensuring pipeline safety and reliability. Integrating advanced UT data visualisation technologies, such as corrosion mapping overlays on 2D and 3D asset models and manipulation of data sets in augmented reality (AR), enhances the contextualisation of digital twins. The shift toward file format standardisation enables the integration of UT data analysis and data management software with operational and enterprise level asset performance management (APM) platforms, promotes the utilisation of cloud software, and facilitates the employment of machine learning algorithms for data analytics.
Such technology advancements could further enhance asset management and predictive maintenance capabilities, enabling faster decision-making, and thus significantly accelerating time-to-value for asset owners. By streamlining the lifecycle and orchestration of UT data and how it can be applied to pipeline inspection, this approach not only reduces the risk of accidents but also supports sustainability initiatives by minimising environmental impacts and ensuring compliance with constantly evolving industry regulations.
Conclusion
Ultrasonic testing is a cornerstone of modern pipeline integrity. The capabilities in UT flaw detection and thickness measurement enable proactive maintenance, extending asset lifespans while minimising risks of leaks or failures. UT’s precision and
non-invasive nature makes it an essential tool for safeguarding critical infrastructure, optimising operational safety, and reducing downtime – key priorities in asset management strategies for pipeline integrity and corrosion control.
References
1. Koch, Gerhard H., Michiel P. H. Brongers, Neil G. Thompson, Y. Paul Virmani, and J. H. Payer. International Measures of Prevention, Application, and Economics of Corrosion Technologies (IMPACT) Study. Houston: NACE International, 2016.
2. US Department of Transportation, Pipeline and Hazardous Materials Safety Administration (PHMSA). “Pipeline Data and Statistics: All Reported Pipeline Incidents (2005–2024).” Accessed April 7, 2025. https://portal.phmsa.dot.gov/ analytics/saw.dll?Portalpages.
About the author
Eugene Lo is the Senior Product Marketing Leader for the Americas at EVIDENT. He has worked in the nondestructive testing (NDT) industry for more than 10 years in both technical and management roles. Before joining EVIDENT, Eugene held positions in consulting and at a global original equipment manufacturer (OEM) of industrial equipment, where he led teams developing products in lean manufacturing, industrial IoT, and data analytics. Since taking on his first product management role in 2018, Eugene has been a dedicated practitioner and advocate of the discipline. He describes himself as a people enabler and a digital transformation proponent, collaborating with cross-functional teams to identify inefficiencies and implement improved processes and technologies.
Eugene has lived and worked in East Asia and is a proud veteran of the US Navy. He is based in Houston, Texas.
World Pipelines talks to Levi Porter, Dexon Technology Plc, about inline inspection and high-resolution inspection tools.
Levi Porter, Dexon Technology Plc
Levi brings over a decade of experience in ultrasonic inspection, starting his journey with well-known organisations such as IRISNDT and SpaceX. During those formative years, he developed a passion for UT, dedicating himself to learning everything he could and contributing to the field. For the past six years, he has contributed to Dexon as an ultrasonic researcher, designer, and enthusiast, working to improve inspection practices and share his knowledge with others.
Can you talk about how ILI solutions can help inspect pipelines that are transporting hydrogen or carbon dioxide?
Levi Porter, Dexon Technology: The solution begins with the problem. Hydrogen and carbon dioxide lines suffer from different weaknesses, and the solutions must address their particular challenges.
Hydrogen pipelines have two major issues: 1) tiny H2 molecules can leak through extremely small defects and 2) the heightened risks of cracking due to hydrogen’s properties. Both issues are resolved in a single solution: high-resolution crack detection tools. High-resolution is necessary because even extremely small
defects can allow hydrogen to leak, while crack detection must aggressively monitor cracks over the pipeline’s lifetime. Newer generations of tools must increase their precision to meet the needs of hydrogen pipelines.
Carbon dioxide pipelines have a single major issue: corrosion. When carbon dioxide reacts with water, it forms carbonic acid, which can rapidly corrode many metals. To counteract this, inspectors must develop better technologies that can more precisely and frequently monitor corrosion in pipelines. UT is typically slower and pricier but more precise – with some now able to operate in gas. MFL is often quicker and cheaper but lacks the precision of UT. The next generation of tools must increase efficiency and drive down costs to meet the rise in demand.
Can you discuss ILI methods (MFL + UT) and their different advantages?
Levi Porter, Dexon Technology: The biggest advantage of UT is precision. Unlike MFL, which uses comparative measurements to detect defects, UT uses direct measurements, examining the signals bouncing back to assess the line’s integrity. This technique puts greater strain on every aspect of the tool, from software analytics to the transducers, but it is also more accurate. UT’s high resolution detects tiny defects which might be overlooked by MFL, particularly cracks. This, in turn, allows operators to monitor and anticipate any repairs they must make with greater clarity.
The biggest advantage of MFL is its flexibility, as UT typically requires specific operating environments, such as a liquid medium to operate within. While UT tools gather higher resolution data, this can come at a premium in comparison to MFL. MFL can operate easily in a variety of conditions due to its use of magnetics. MFL runs at higher speeds, in a variety of mediums, is less sensitive to cleanliness, is less demanding on technical skill, and can identify nearly all defects – although typically without the precision of UT. These advantages translate into MFL being able to operate under a variety of conditions where UT would struggle or fail.
The latest generation of tools, however, are pushing and blurring the borders between the two methods. Acoustic resonance technology (ART) allows UT to function in gas mediums, and the most advanced high resolution MFL technologies are able to identify cracks with greater precision.
How do you ensure the accuracy and reliability of your inspection results with pipelines in challenging terrains/ environments?
Levi Porter, Dexon Technology: Given the catastrophic costs of (dare I say it) getting a pig stuck in a line, inspectors can take no risks out in the field. This fear is especially true for lines that are challenging, but the principles of solid inspection do not fundamentally differ whether it be a typical 8 in. overground oil line or a subsea riser in turbulent seas. No one wants a stuck pig.
First, inspectors must gather comprehensive and accurate information about the line. Particularly in cases of challenging lines, small, easily overlooked details can spell failure and a costly re-run. Once inspectors understand the conditions, they can then customise their design and vigorously test it in analogous field conditions to ensure that it will be successful. Typically, these tests include multiple failures before landing on a solution that they are confident in.
In a recent job inspecting risers off Brazil’s coastline, Dexon dealt with high running temperatures (65˚C), a 3 in. diameter line, and 1.5D turns. The high temperatures required the electronic team to redesign circuit boards and heat sinks to deal with the heat without compromising data or increasing the tool’s size. These alterations are difficult at 3 in. Dexon tested it repeatedly in both the test yard and an oven running beyond operation temperatures. Although it took several iterations, the team finally hit on a solution that they knew would work – and rigorously tested it to remove all doubt. In the end, the run was a success.
What are the latest developments in ILI technology?
Levi Porter, Dexon Technology: For the absolute cutting-edge, you will have to wait until Dexon’s patent-pending tool comes out. The design will shake up the market and deliver some long-awaited capabilities. Until then, I can discuss what is on the market. One very recent development in UT technology (which Dexon helped pioneer) is using tip diffraction for crack detection and sizing.
The UT tip diffraction method uses an angled signal that bounces off the wall and is received by another transducer. Judging by how the signal changes, engineers can identify and size cracks. Think of it like someone observing waves in the ocean. If the waves rise back and forth in a typical pattern, you know that there is nothing underneath the surface, but if their pattern is even marginally disrupted, you can determine what is underneath the waves, including size and positioning.
The metaphor makes it sound simple, but it is extremely complex when a tool is running through a stainless-steel pipe at 2 m/sec. and attempting to pinpoint 1 mm cracks. It is a technically demanding task. These new UT tip diffraction tools require five times more transducers than conventional tools. In addition to increased transducer count, the transducers and the software used to analyse the large amounts of data are more advanced. The technology represents a jump in inspection quality and is of particular interest for crack-prone hydrogen lines.
We are running out of space...
Our inventory in sales & rental in pipeline equipment is out of this world. We have a huge amount of machines from all the big brands that are ready for worldwide delivery, or even further if you want...
You can build on BAUMA!
Wilton Cardoso, Electronic Development Engineer, Pigs Unlimited, underscores the role that urethane materials play in the sucess of long-range pigging operations.
he successful execution of an extensive 569 km pigging operation in a 20 in. natural gas pipeline from Nigeria to Ghana highlights the critical role of specialised urethane components. This article examines the contribution of long-range urethane cups and discs to the efficiency of the cleaning and inspection process.
Manufactured by Pigs Unlimited and conducted by Topline Limited and Pipeway Engenharia, the operation employed various pigging tools, including foam pigs, multi-disc brush pigs, caliper pigs, and magnetic flux leakage (MFL) pigs. The
focus is on how the properties of advanced urethane materials enhanced tool longevity, adaptability, and performance in a highly abrasive gas pipeline environment.
Introduction
Pigging operations in long-distance natural gas pipelines present significant challenges, particularly in terms of material wear, tool performance, and maintaining continuous flow efficiency. The abrasive nature of gas pipelines necessitates durable materials capable of withstanding prolonged exposure
to high-velocity particulate contaminants. This study explores the role of high-performance urethane cups and discs in mitigating these challenges, ensuring successful tool passage, and optimising cleaning and inspection outcomes.
The pipeline under discussion extends over a substantial distance of 569 km, presenting a complex operational environment. It functions under consistently high-pressure conditions and transports natural gas with variable compositions. These operational factors necessitated a comprehensive and carefully tailored pigging strategy to ensure efficiency, reliability, and tool longevity throughout the cleaning and inspection processes.
Achieving a successful pigging run over such a long pipeline required meticulous consideration of several key technical and operational challenges, including the following.
The sheer length of the pipeline significantly increases the distance over which pigs must maintain structural integrity and functionality. As pigs travel hundreds of kilometres, their components, particularly those in contact with the pipe wall, are subject to continuous friction. This leads to gradual material degradation, especially on the sealing and cleaning elements. Selecting materials capable of withstanding this prolonged wear was essential to ensure consistent performance from launch to receiver.
Over time, internal pipeline surfaces accumulate layers of particulate matter, such as dust, scale, and other solid residues. These contaminants not only restrict flow efficiency but also create an abrasive environment that can accelerate wear on pigging tools. The presence of sharp or granular debris increases the risk of damage to both the pig and the pipe. Addressing this challenge required tools that could effectively dislodge and remove debris while resisting abrasion.
Ensuring a reliable seal between the pig and the internal pipe wall is critical for propulsion, especially over long distances. Effective sealing ensures that the pig is pushed forward efficiently by the differential pressure of the gas behind it. Poor sealing can result in bypass, where gas leaks past the pig, reducing forward momentum and potentially leading to a stalled run. Achieving optimal sealing performance was a key design consideration, particularly given the pipeline’s internal variability due to scaling and diameter changes.
Pigs used in long-distance operations are continuously subjected to high pressures, fluctuating flow dynamics, and mechanical stresses. Over time, this exposure can lead to tool fatigue, manifested in component failure or reduced operational effectiveness. The dynamic environment within the pipeline, compounded by the abrasive nature of the internal
Dairyland’s PCRX is the most sophisticated decoupler on the market; offering the functions of standard decouplers while also eliminating capacitance delays during interrupted surveys. Unlike traditional decouplers, PCRX remains connected during testing, overcoming capacitive effects while maintaining protection for personnel and critical assets for the duration of the survey. This ensures accurate and timely potential measurements while still providing the rugged over-voltage protection, AC interference mitigation, CP isolation, and safety grounding expected from Dairyland decoupling products.
contaminants, can degrade conventional materials quickly. Tool resilience, therefore, had to be significantly enhanced to maintain structural and functional integrity throughout the run.
Urethane: material properties and performance benefits
Pigs Unlimited’s advanced urethane elastomers offer exceptional benefits in long-range pigging applications, including these things.
High abrasion resistance: Reducing material degradation over extended distances
Urethane’s inherent durability makes it particularly effective in environments where pig components are in constant contact with the internal pipe wall. As pigs travel through the pipeline, they encounter deposits, scale, and other abrasive materials. The high abrasion resistance of urethane minimises surface wear, allowing the tool to maintain its functional shape and edge definition for longer periods. This durability is critical when covering hundreds of kilometres without the opportunity for maintenance or replacement during the run.
Superior flexibility and resilience: maintaining consistent sealing despite pipeline irregularities
Pipelines often contain internal irregularities such as weld seams, diameter transitions, or slight bends. Urethane’s high flexibility allows pig components to conform to these inconsistencies while still maintaining a tight seal. Its resilience ensures that the material returns to its original form after deformation, preserving the sealing interface and preventing pressure bypass. This consistency helps maintain propulsion force and ensures complete coverage during cleaning or inspection passes.
Enhanced load-bearing capacity: supporting highpressure differentials without failure
In high-pressure gas pipelines, pigs must withstand significant forces acting on both sides of the tool. Urethane’s load-bearing capacity allows components like cups and discs to perform under these stresses without tearing, warping, or collapsing. This strength enables the pig to move steadily through the pipeline, overcoming resistance from debris and maintaining its trajectory even when faced with varying flow conditions or sudden changes in pressure.
Optimised friction coefficients: ensuring efficient propulsion while minimising energy loss
Urethane can be formulated to achieve specific friction characteristics, which play a vital role in how effectively the pig is propelled by the gas flow. Too much friction can slow or stall the pig, while too little can result in poor cleaning performance or tool instability. By balancing friction levels, urethane allows for smooth, efficient travel through the pipeline with minimal energy loss, enhancing overall operational efficiency.
To effectively address the multiple operational challenges presented by this long-distance, high-pressure pipeline, all pigging tools were equipped with specially engineered urethane components developed by Pigs Unlimited. These custom-developed materials were selected based on their proven ability to withstand wear, maintain elasticity under stress, and deliver reliable sealing performance in abrasive environments. Urethane’s adaptability and endurance made it the material of choice for ensuring the pigs could complete the full 569 km route without compromising their structural integrity or operational goals. The use of urethane was critical in achieving consistent cleaning results, minimising tool wear, and ensuring that each run met performance expectations without the risk of premature failure or tool degradation.
Since 1948, Tinker & Rasor has been a trusted name in holiday detection, relied upon by pipeline professionals worldwide. For over 76 years, our holiday detectors have set the benchmark for performance and reliability, ensuring the integrity of protective coatings by detecting coating flaws with precision. With a legacy of innovation and toughness, Tinker & Rasor continues to lead the industry, delivering cutting-edge solutions to safeguard pipeline coatings and maintain quality standards across the globe.
A variety of pigging tools were deployed, each benefiting from specialised urethane components manufactured by Pigs Unlimited for this project:
Foam pig
Employed during the initial pipeline sweeping phase, this pig utilises flexible urethane coatings that allow it to adapt effectively to varying debris levels, ensuring consistent contact and efficient removal of loose materials during earlystage cleaning.
Pig used: Pigs Unlimited heavy density criss cross foam pig. Note that the pig basket at the receiver was a little undersized and the pig got damaged by it. As you can see, most of the pig’s body is intact after the long run.
Multi-disc brush pig
Outfitted with multiple urethane-sealed discs and an integrated gauge plate, this tool is designed to detect internal pipeline restrictions and deformation, providing essential clearance verification to confirm safe conditions before deploying more sensitive inspection pigs. Pig provided by Pigs Unlimited.
Multi-disc pig with gauge plate
Outfitted with multiple urethane-sealed discs and an integrated gauge plate, this tool is designed to detect internal pipeline restrictions and deformation, providing essential clearance verification to confirm safe conditions before deploying more sensitive inspection pigs. Pig provided by Pigs Unlimited.
Caliper pig
Utilised for detailed pipeline geometry assessment, this tool relied on durable urethane cups to ensure stable movement through the pipeline and enable precise, highquality data collection throughout the inspection. Pig provided by Pipeway International with Pigs Unlimited’s polyurethane parts.
Based on the data presented in Table 1 and Figure 8, it’s evident that the urethane cups maintained most of their key properties and performance characteristics up to Kilometre 400. Beyond that point, however, we observed a noticeable increase in wear and tear, which began to affect the efficiency and structural integrity of the cups. This suggests that while the urethane components performed exceptionally well over the first 400 km, their ability to withstand the harsh operational conditions started to decline as the distance increased, highlighting the point at which more significant degradation occurred.
This tool is critical for the accurate detection of defects and corrosion within the pipeline, relying on precision-engineered urethane components to maintain consistent sensor alignment, mechanical stability, and reliable data acquisition throughout the inspection run. Pig provided by Pipeway International with Pigs Unlimited’s polyurethane parts.
The extensive pigging operation across the 569 km pipeline generated several important findings, highlighting the performance and reliability of the tools and materials used:
) Minimal component degradation: urethane cups and discs demonstrated exceptional longevity and durability, even under prolonged exposure to friction, pressure, and abrasive contaminants. The materials maintained their structural integrity throughout the run, enabling successful tool retrieval without any significant signs of wear or deformation.
) Enhanced sealing efficiency: the superior elasticity and flexibility of the urethane components effectively prevented gas bypass, allowing for sustained differential pressure across the pig. This ensured not only consistent forward propulsion but also optimal cleaning performance, especially in areas with variable internal diameters or minor pipeline irregularities.
) Operational continuity: the mechanical strength and resilience of the urethane-based elements significantly minimised the risk of tool failure or unplanned interruptions. This contributed to a smooth, continuous pigging operation with fewer delays, improving overall project efficiency and reducing operational downtime.
This case study clearly underscores the critical role that advanced urethane materials play in the overall success of long-range pigging operations. The exceptional performance characteristics of Pigs Unlimited’s urethane cups and discs – particularly their durability, adaptability to internal pipeline conditions, and sealing capabilities – were instrumental in overcoming the unique technical challenges presented by the 569 km gas transmission pipeline.
The collaboration between Pigs Unlimited, Topline Limited and Pipeway Engenharia, supported by the integration of innovative material solutions, serves as a strong example of best practices in modern pipeline maintenance, cleaning, and integrity assessment. The successful execution of this complex pigging project demonstrates how the right combination of engineering expertise and material science can lead to reliable and efficient outcomes.
Looking ahead, continued advancements in urethane formulations are expected to further enhance the effectiveness of large-scale pigging operations. These improvements will support even greater reliability in inspection and cleaning efforts, helping operators maintain optimal pipeline performance, extend asset life, and ensure the long-term safety and integrity of critical infrastructure. Visit our website: Follow us on :
nline inspection (ILI) technologies, despite their decades-long advancement, still fall short in addressing comprehensive anomaly detection and sizing needs today. These tools have become over-specialised, honing in on specific anomaly types at the expense of broader applicability. As a result, operators must conduct multiple inspections with varied tools, aiming to encompass a wide spectrum of anomalies and defects. This approach is not only cumbersome but also heavily reliant on prior knowledge or
assumptions regarding potential issues. Such dependence often results in unnecessary digs and persisting difficulties within integrity management. Furthermore, most ILI systems are built on indirect measurement techniques, such as amplitude-based sizing, which frequently yield ambiguous and unreliable results. This overreliance on indirect methods often leads to false positives and measurement inaccuracies, underscoring the need for an advancement in ILI tools that can deliver more precise and reliable outcomes.
Corey Richards, DarkVision, explores how triple-threat detection in a single pass is changing the ILI game.
A new tool
Kraken is a new, high-resolution direct measurement ILI tool built from the ground up to empower pipeline operators to detect, size, and understand the most challenging defects – pinholes, general wall loss, axial cracks, weld seams, interacting defects and changes in pipeline geometry – in a single run at full line speed.
Kraken harnesses the latest innovations from handheld inspection systems, medical imaging, and lab-grade nondestructive testing, to make a significant leap in resolution, detection, identification, and sizing accuracy. By providing 3D
defect visualisations with photographic clarity, it facilitates precise, targeted decision-making.
Already field-tested, this robust new ILI tool greatly improves the safety and integrity of pipeline operations by detecting and sizing smaller defects earlier (including those missed by other tools). This enables the discovery of more leading indicators versus lagging indicators thereby improving the monitoring of threat growth, de-risking operations and, lastly, improving dig planning while reducing false calls.
Tackling the hardest challenges in pipelines
Kraken is designed to simultaneously evaluate a variety of anomaly types down to 0.25mm (0.009 in.) resolution and a 3 m/sec. (6.7 mph) inspection speed, including:
) Wall loss from through-wall to sub-mm deep defects like pinholes, microbial induced corrosion, erosion, gouging, and corrosion.
) Axial cracks that are extremely short or shallow, hooked, mid-wall, grouped in colonies like SCC, in welds, and in heataffected zones (HAZ).
) Changes in pipe wall geometry like dents, ovality, weld misalignments, and deformations as well as coincident stress risers in the shoulders and peaks of dents.
) Interacting defects which can be analysed in a single dataset including cracks, selective seam weld corrosion, sloping laminations, and corrosion in dents.
Existing technologies rely on amplitude-based sizing correlations whereby the amplitude of a signal returned in the field is matched to the amplitude of a defect in a lab. This inferred measurement approach fundamentally limits the accuracy of a given system. In contrast to inferred measurements, Kraken captures measurements that are registered in 3D space. This point cloud of data can then be visualised in an intuitive, 3D manner, making it easier for operators and analysts to interpret.
Direct imaging is achieved by transmitting focused ultrasound waves, recording all the returning energy of the ultrasound waves and mapping where the energy came from with time-based and physics-based calculations. The exact position, contour, and size of anomalies are determined in 3D space from these calculations based on the trajectory of the signal. This highly accurate method enables clear identification, characterisation, and understanding of anomalies for both analysts and pipeline integrity engineers.
Recording all the returning energy over thousands of sensor elements across hundreds of miles results in massive, petabytesized datasets. Therefore, Kraken utilises cloud-based computing and advanced machine learning models to detect, identify and size anomalies. This approach leads to consistent and repeatable results and removes subjective interpretation.
The development of this high-resolution direct imaging tool involved rigorous validation processes, adhering to API 1163 standards. A continuous flow loop was designed to test the tool’s endurance and performance across a range of manufactured and real anomalies, including electrical discharge machined (EDM) notches and natural wall loss and cracks. The results were
PipePillos® were designed to support fully loaded pipelines in the trench but are also perfect for stringing, welding, integrity digs, fabrication and storage. Speed up your project, protect workers, and prevent ovality when you switch from cribbing, foam, sandbags, or pad dirt for in or out-of-trench applications to PipePillo® pipeline supports.
® Call PipeSak® Inc. at 1.866.747.3725 or visit www.pipesak.com to learn more
Support fully loaded pipes
Durable & versatile
Prevent ovality in-trench with permanent 90 degrees of support
Lightweight & easy to handle
Eliminates the need for cribbing, foam, sandbags, and pad dirt
Fast, safe & easily stacked
benchmarked against industry-standard tools such as metrologygrade laser scanners and phased-array ultrasound handheld devices. Validation demonstrated the tool’s superior detection and sizing accuracy, even in complex and interacting anomalies that often challenge traditional methods.
In 2024, a significant field test was conducted by deploying Kraken to inspect a 16 in. (406 mm) crude oil pipeline. Throughout the inspection, Kraken maintained a steady velocity of 1.3 m/sec. (2.9 mph), showcased excellent sensor performance, and efficiently managed challenges such as wax build-up. Its intuitive 3D visualisation of defects enabled the operator to accurately assess the severity and characteristics of the pitting, highlighting its superior ability to detail complex and localised corrosion.
This inspection effectively identified and measured multiple instances of pitting and corrosion on the pipeline’s inner surface and yielded three important outcomes:
) The tool performed well within mechanical design expectations and continuous flow loop validations.
) The tool recorded very high quality and high-fidelity data which enabled the identification, sizing, and profiling of pitting and corrosion found in the pipeline.
) Acoustic Imaging results compared well against Phased Array NDE in-ditch reports and inspection results from previous inspections of this pipeline. Compared to previous Magnetic Flux Leakage (MFL) inspections, which showed a ~15% error rate,
Midwestern’s M12H, M18H & M24H are the newest addition to our winch attachments. These winches are designed for hoisting purposes on excavators with lift capacities of 12,000/18,000/24,000 lb and attaches with a quick coupler to the excavator stick. The attachments use existing cab controls for all winch functions, ties into the auxiliary hydraulic circuit, and are easy to install. Make your equipment more versatile by adding on one of our hoist winches.
MIDWESTERN - built for the toughest jobs.
Kraken demonstrated a more accurate +/- 3% error margin, showcasing its capability to detect even minute anomalies.
Subsequent testing on the same pipeline demonstrated an impressive repeatability of measurements, with an average deviation of 0.76% in defect assessments between the two inspections. These assessments focused on pitting corrosion defects, typically measuring approximately 12.7 mm x 12.7 mm (0.5 in. x 0.5 in.), with depths ranging from 20% to 30%.
Capturing over two billion images, Kraken proved invaluable for early-stage corrosion detection, supporting proactive maintenance efforts. This successful field run not only validated the service’s capabilities but also prepared the groundwork for further assessments on various pipeline segments.
The introduction of high-resolution direct imaging marks a significant advancement in the field of pipeline inspection. Kraken’s ability to deliver accurate, high-resolution assessments of a wide range of anomaly types in a single run will serve beneficial to pipeline operators seeking to enhance safety and efficiency.
As the technology continues to evolve, ongoing validation and field testing will further assess its performance across different pipeline conditions and defect types. The potential to integrate this tool with cloud-based machine learning frameworks for even greater data analysis and insight promises a future where pipeline integrity management is more accurate, proactive and predictive.
Lewis Anderson, Luxfer Gas Cylinders, explores the role virtual gas pipelines can play in achieving the widespread adoption and integration of hydrogen networks, as the UK seeks to ramp up decarbonisation efforts.
s part of the UK’s net zero strategy, hydrogen has been identified as a zero-carbon fuel source that could drive the country towards its 2030 targets. In line with this, the government has set ambitious goals and pledged significant investment to position the UK as a leader in the global hydrogen economy.
At Luxfer Gas Cylinders, we believe that achieving these targets requires ongoing investment in innovation around hydrogen production, distribution, and consumption. While the country is making bold strides overall, the industry still faces challenges in maximising the distribution and use of hydrogen.
In fact, many hydrogen infrastructure initiatives and network expansion plans are still in development. This raises the question of how the gas can be safely and efficiently stored and transported to reach the businesses and operators that need it now.
For hydrogen to be widely adopted, the UK needs to develop proper storage facilities and infrastructure. Encouragingly, the country has identified 27 GW of potential hydrogen projects, but there is still much work to be done to build a fully accessible hydrogen network.
The UK is currently developing 0.025 TWh of salt cavern hydrogen storage, with two notable projects – HyKeuper in North West England and Aldbrough near the Humber – which is set to add a further 1.3 TWh and 0.5 TWh storage capacity, respectively.
These, however, will take a long time to build and, despite the UK having the right geology for salt cavern storage, there is simply not enough of it. Additionally, the locations suitable for salt cavern storage don’t necessarily geographically match up with current or future storage needs.
Of course, hydrogen can also be stored in liquid or solid state. The former, which requires it to be cooled to cryogenic temperatures to convert it to liquid, increases storage density. While effective, liquid storage requires significant energy for cooling and maintaining low temperatures, making it most suitable for specialised applications such as aerospace.
Hydrogen can also be stored by chemically bonding it to materials like metal hydrides or adsorbing it into high-surfacearea materials. This solid-state method is currently less mature and more expensive than other storage systems.
This leaves compressed gas storage – this simple and relatively mature method is currently the most practical and widely used solution as it is appropriate for a wide range of applications.
One approach is to repurpose the existing gas network to transport hydrogen from where it is produced to where it is needed. The UK has a world-leading gas network with around 300 000 km of gas pipes – enough to go around the world seven times!
Studies suggest that adapting the gas grid could be an efficient, low-disruption solution to supply hydrogen to large storage facilities and various end-users in sectors such as industry, transportation, and power.
However, while pipeline transportation of hydrogen will undoubtedly form part of the country’s long-term infrastructure, it requires a significant capital investment, takes time to build, and is limited in coverage. Additionally, according to a report by the Committee on Climate Change, the UK’s hydrogen pipeline network won’t fully serve industrial clusters until after 2030.1 This is due to several factors, including the need for significant investment in pipeline infrastructure and regulatory hurdles.
Bridging the gap with bulk gas transport
Where no gas networks exist, bulk gas transportation systems (BGT) offer a solution as ‘virtual gas pipelines’. They can bridge the gap between hydrogen production and consumption by linking the point of production and the point of use. Importantly, they serve as an interim measure until dedicated pipeline infrastructure is developed, offering temporary or long-term solutions to address delivery or capacity challenges.
Innovation in this area – enabling the easy and scalable deployment of hydrogen to various locations – has been driven by demand across different sectors, industries and markets, and Luxfer Gas Cylinders is among the companies pioneering in this space.
Our multiple element gas containers (MEGCs) –developed at a purpose-built alternative fuel facility in Nottingham – are designed specifically to meet the needs of large-scale requirements for hydrogen, allowing over 1 t of the gas to be safely stored and transported.
Available in 20 ft and 40 ft units, MEGCs offer maximum capacity and energy delivery, and are designed to optimise total cost of ownership by delivering over 1000 kg of hydrogen per load, significantly reducing vehicle movements
and the number of MEGCs on the road. Fewer trips mean lower operational costs, reduced fuel consumption, and decreased CO2 emissions, making hydrogen transportation more efficient and sustainable.
While MEGCs cater to large-scale hydrogen needs, high-pressure hydrogen gas cylinder bundles, or multiple cylinder packages (MCPs) offer a convenient and flexible storage solution, particularly for companies targeting cleaner and greener operations, but whose sustainability objectives are being curtailed by a lack of hydrogen infrastructure options. These systems, which consist of interconnected, horizontally stacked lightweight cylinders, can store gas in a smaller footprint compared to other available options. A key benefit is they can be easily transported by truck or other vehicles to remote locations, where traditional power sources are not available.
They are also particularly practical and efficient in situations where hydrogen is required to be fed at a consistent flow rate and pressure without interruption. Additionally, MCPs reduce the need to manage cylinder stocks and limit time lost in cylinder changeover and handling, as well as reducing gas wastage. This means less potential for operations to be delayed or interrupted.
These bundles can be tailored to meet the unique needs of different applications. The modular system is set in a lightweight, durable, high-strength frame that can be slotted into an existing structure and onto trucks and trailers seamlessly, making it a sound solution for transporting gases by road or rail. This mobility overcomes limitations imposed by pipeline infrastructure, crucially extending the reach of hydrogen.
MCPs also offer on-site storage solutions, providing immediate access to hydrogen for critical applications such as backup power systems or industrial processes. This on-site stock ensures business continuity and minimises downtime.
Alongside transportation, another crucial consideration is how hydrogen is stored. Here, cylinder choice plays a significant role, with Type 3 and Type 4 cylinders being the most widely used. Each has different core benefits, with product selection depending on the specific application.
On one hand, Type 3 aluminium lined cylinders are nonpermeable, robust and fill faster, which have made them a preferred choice of industry pioneers and OEMs for many years. Alternatively, plastic lined Type 4 cylinders deliver high storage volumes whilst remaining lightweight, offering a cost-effective hydrogen storage solution ideal for long range rail, boats and other vehicles.
While Type 3 cylinders are heavier, Type 4 cylinders often require hydrogen to be chilled before filling as the heat produced in a fast-fill system could cause issues with the internal liner. Each has its merits based on what is most critical to users’ operation. Drawing on decades of experience, we help customers select the most suitable option for their applications.
Hydrogen is a flammable, low-molecular-weight gas that requires stringent safety protocols for handling and storage. The potential for leaks, high flammability, and small molecular size makes hydrogen storage safety a top priority, particularly in high-pressure applications.
Due to its small molecular size, which can permeate through materials that other gases cannot, hydrogen is prone to leakage. To address this, advanced leak detection technologies, robust seals, and materials specifically designed to handle hydrogen are essential.
High-pressure hydrogen cylinders are designed to meet strict performance requirements and are tested against relevant regulations and engineering standards. It is vital that hydrogen gas cylinders undergo a stringent testing regime, including extreme temperature testing, drop and impact testing, gunfire testing, fatigue cycle, and burst testing.
The focus on safety is not only essential but is also a key differentiator for Luxfer Gas Cylinders. In fact, we were one of the first manufacturers to achieve approval for Regulation No. R134, a global safety standard which certifies that cylinders are safe for use in hydrogen-powered vehicles across a wide range of applications. Not all hydrogen cylinders in the market meet this benchmark.
Another challenge to greater hydrogen adoption is the absence of standardised regulations. For the UK to become a leader in the global hydrogen economy, more needs to be done to put codes and standards in place, supported by the necessary guidance and information for all manufacturers to safely build, maintain, and operate hydrogen equipment, systems, and facilities.
If concerns about safety are not addressed and clear, consistent guidelines and regulations are not established across the entire supply chain, it will be difficult to build confidence in hydrogen systems among companies interested in investing in greener, more sustainable solutions.
For the potential of hydrogen to be truly realised, the UK needs extensive and robust infrastructure. However, it will be a long time before physical pipelines are in place, making virtual gas pipelines critical in ensuring that sufficient hydrogen is available when and where it is needed by linking geographically diverse supply and demand.
But their value is not limited to the short term – virtual gas pipelines will play an important role in the medium and long term too. The creation of an efficient hydrogen network will involve a combination of physical and virtual pipelines, with each solution utilised to meet different needs across the supply chain. As such, virtual gas pipelines should be seen as a long-term investment that will remain relevant once a physical pipeline is established, especially for the first and final mile delivery.
References
1. https://www.theccc.org.uk/publication/net-zero-power-and-hydrogen-capacityrequirements-for-flexibility-afry/
No difficult-to-inspect pipeline should be left behind.
Whether you're dealing with short or extremely long pipelines, or you require ultra-high resolution, or high inspection speed.
Our Surveyor UT ILI family is designed to handle it all.
Explore what our ILI technologies can do for you.
Brad Rister, Industrial Scientific, highlights the need for pipeline operators to re-evaluate area monitoring as a solution for worker and community safety.
ipelines present a uniquely challenging environment where reliable gas detection is critical in protecting workers, maintaining compliance, and preventing serious incidents. A robust gas monitoring program protects workers, enables compliance with strict regulatory requirements, and provides crucial early warning in emergency scenarios.
Traditionally, fixed gas monitors and personal detectors formed the backbone of this strategy. But as pipeline operations become more dynamic, dispersed, and datadriven, traditional methods alone can fall short. Area monitoring, especially in the form of mobile or perimeterfocused gas detection, is quickly becoming a key layer in modern safety programs.
Area monitoring is a flexible approach to gas detection that uses portable, rugged devices to monitor the presence of hazardous gases in a defined area. Unlike personal monitors worn by individual workers or fixed systems hardwired into infrastructure, area monitors can be quickly deployed to where they’re needed most. This makes them particularly useful in temporary work zones, confined space entries, or maintenance turnarounds – all scenarios that are common in pipeline operations.
An area monitor also acts as a shared safeguard. Positioned near a worksite, it continuously samples the air and triggers alarms if dangerous gases are detected. Because it doesn’t rely on proximity to a single user, it can provide protection for multiple workers at once and add an additional buffer against potential threats.
Today, next-generation solutions like the Vector™ AM7 Area Monitor are expanding what’s possible in pipeline safety. Designed for ultimate versatility, the Vector AM7 supports up to seven gas sensors, offers extended runtime options with hot-swappable batteries and solar power compatibility, and delivers real-time connectivity through cellular and peer-to-peer networks. Its rugged, stackable design ensures it can be deployed rapidly in challenging environments without disrupting operations.
A specific and increasingly important form of area monitoring is perimeter monitoring. Here, the goal is to
place gas monitors around the edge of a hazardous or high-risk area – such as a process unit, compressor station, or excavation site. These devices form a virtual fence line, alerting safety teams if emissions begin to drift outside of expected boundaries.
According to the US Environmental Protection Agency’s Clean Air Act, oil refineries and petrochemical plants are required to monitor for benzene emissions at their fence lines, for example. Beyond regulation, perimeter monitoring offers real-world value: It helps teams detect problems early, protect surrounding communities, and prevent small leaks from becoming major incidents.
Area and perimeter monitors are commonly deployed during high-risk activities such as hot work, shutdowns, or maintenance near potentially leaking equipment. They’re also useful during construction activities, such as installing new pipeline infrastructure, where workers may be exposed to unknown gas sources.
These tools are equally important in emergency response scenarios. When hazardous gas releases occur, responders need fast, accurate information to assess risk and act. Area monitors, especially when networked together, can provide a complete picture of gas concentrations across a site in real time.
They’re also increasingly used to fill coverage gaps in facilities without permanent gas detection infrastructure. Because area monitors are portable and easy to reposition, they offer unmatched adaptability in dynamic environments.
Deploying area monitors effectively is about more than simply turning them on and walking away. A successful monitoring strategy requires careful consideration of environmental conditions and operational needs.
Sensor placement is crucial, as different gases behave differently. Some are lighter than air, others heavier, and some diffuse unpredictably. Monitors must be placed at the right height and distance for accurate readings. Environmental variables, such as wind direction and airflow, also affect gas movement and detection, requiring regular reassessment of monitor positioning.
Alarm notification is another key factor. Many of today’s area monitors offer loud audible alarms and bright lights, but advanced models also connect to wireless networks and personal monitors. This enables alerts to be transmitted across a worksite, or even to a remote safety office, in real-time.
To navigate these challenges, many organisations begin with a site survey
and build a perimeter monitoring plan. This helps ensure devices are strategically placed and that emergency response protocols are clear.
The rise of connected safety systems has significantly improved how area monitors function. Modern models now include cellular or peer-to-peer wireless communication, allowing them to form networks that share data instantly across devices.
This enhanced connectivity enables real-time situational awareness, as safety managers can view live gas readings from anywhere. It supports faster emergency responses by ensuring that alerts are shared instantly across teams, facilitating quicker evacuation or intervention. By integrating into cloud-based platforms, area monitors provide predictive insights, helping teams anticipate risks before they escalate. Additionally, centralised compliance data management simplifies reporting and audit readiness by storing all readings, events, and maintenance logs digitally.
For example, dynamic plume modeling software like Industrial Scientific’s SAFER One® can be integrated into connected gas detection systems like the Vector AM7. In the event of a gas leak, real-time weather data and sensor input can be used to model gas dispersion. Safety professionals can predict where the gas will travel, when it will arrive, and who may be affected, all within minutes.
Consider a pipeline crew tasked with installing new underground lines near existing pressurised gas infrastructure. The team sets up a perimeter of area monitors around the jobsite. These monitors are networked and positioned at varying elevations via tripods and wall mounts to account for different gas behaviors.
Throughout the day, the crew works safely, knowing they’ll be alerted immediately if gas levels change. Later that evening, after a minor bump into a valve, gas begins to leak into the trench. Because the monitor inside the trench is still active, it quickly detects the hazard. An alert is transmitted to both the on-site team and the control room.
Within seconds, the emergency response plan is activated. Using plume modelling software, responders assess how the gas is dispersing. They confirm that the community is not at risk and coordinate the safe evacuation of remaining personnel. Data from the incident is logged automatically, ready for post-event analysis.
Gas monitoring today isn’t just about detection – it’s about information. Manual logging is time-consuming and prone to errors. With dozens of monitors operating across different locations, trying to track exposures, alarms, and battery status by hand can be overwhelming.
This is where cloud-based systems like iNet® come into play. These platforms automatically collect and store
data from every monitor in the field. Safety professionals can check diagnostics, view trends, or see if devices need calibration from a laptop or mobile device. And because the system is automated, reporting is simpler and more reliable.
One of the challenges of implementing an area monitoring program is choosing the right ownership model. Not every project needs permanent equipment. In fact, for shutdowns or temporary maintenance jobs, renting or leasing may be the more cost-effective solution.
Rental options allow teams to access the latest equipment without a long-term investment. Leasing models take this a step further by managing all maintenance and repair. When a monitor shows signs of failure, a replacement is shipped automatically, often before the original unit is even returned.
For long-term, stable operations, purchasing equipment may be the most economical. In these cases, it’s important to consider interoperability – whether the monitors you invest in can be used across different sites, share components, or integrate with your broader safety ecosystem.
Newer area monitors are designed with these complexities in mind. They’re more portable, more durable, and more intelligent than ever before. Features like hot-swappable batteries, stackable housing, and extended run times (some offering up to 75 days with IR sensors) help teams stay focused on their work – not on device maintenance.
Mounting options have expanded too. Whether on a tripod, fence, I-beam, or wall, modern monitors can be placed wherever they’re needed without interfering with operations. Color-coded faceplates even allow for easy identification in large fleets.
The pipeline sector is undergoing a digital transformation – and area monitoring is part of that evolution. From enhanced coverage and real-time data to more flexible ownership models, these systems are enabling a more proactive and connected approach to safety.
What was once viewed as an add-on to personal monitors and fixed systems is now seen as an essential third layer of defense. When used strategically, area monitoring, especially perimeter-based setups, can reduce risk, improve operational efficiency, and provide peace of mind in some of the industry’s most challenging environments.
For pipeline operators seeking to modernise their safety practices, now is the time to rethink how area monitoring fits into the bigger picture. With the right plan, technology, and training, this adaptable solution can help both workers and communities stay safe today and tomorrow.
Subscribe online at: www.lngindustry.com/subscribe
Anand Palanivelu, Head of International Sales at Protectoseal, explains how pressure and vacuum relief vents are at the heart of transforming infrastructure, enhancing operational safety and efficiency while also supporting sustainable practices.
s global pressure mounts to reduce emissions and enhance industrial safety, the pipeline industry stands at a crossroads. Operators are rethinking traditional infrastructure in response to a number of challenges, ranging from tightening environmental regulations to the evolving demands of energy transition.
evolving landscape of the pipeline industry
The pipeline sector is critical in transporting fuels, petrochemicals, and speciality liquids that power economies and modern life, however it is now under increasing scrutiny. Regulators worldwide are introducing stricter emissions mandates, especially for volatile organic compounds (VOCs), a major contributor to ground-level ozone and smog. The public’s demand for safer, more sustainable industrial practices has never been greater, prompting energy companies to seek solutions that balance performance and responsibility.
At the same time, the operational environments for pipelines and storage tanks are becoming increasingly complex. Variations in geography, climate, product volatility, and pressure conditions demand flexible, high-performance venting systems. Manufacturers must bring expertise to the table and work closely with clients to provide engineered solutions that achieve industry-leading emission reduction and leak prevention while also meeting operational requirements.
Meeting emissions and safety goals head-on When it comes to storage tanks and pipeline infrastructure, managing internal pressure is not just a design consideration; it is a regulatory requirement. The storage and transportation of flammable or volatile liquids present a dual challenge: maintaining pressure equilibrium while preventing harmful vapour releases into the atmosphere.
Protectoseal’s team has been developing pressure and vacuum relief vents to address these challenges. The Series 56000 PIN-TECH™ Pressure Relief Vent is a ground-breaking product that redefines emissions control. This model, designed for low-pressure storage tanks, has no detectable VOC emissions (<500 ppm) during independent testing, making it a crucial benchmark for operators seeking to meet global emissions standards.
The Series 56000 ensures more than just regulatory compliance; it also promotes corporate responsibility, risk mitigation, and longterm viability in industrial operations. Working with products like these allows operators to confidently meet safety standards while actively contributing to environmental stewardship.
Protectoseal’s commitment to performance begins with smart design and its patented air-cushioned seating technology, which is used in many of its venting products. The technology uses FEP film to form a tight, ultra-low-leakage seal, lowering emissions to as low as 1 SCFH at 90% of the set pressure. This technology keeps vents closed until absolutely necessary, reducing product loss and fugitive emissions.
Take the company’s flagship Series 8540H End-of-Line Pressure and Vacuum Relief Vent, for example. It is the industry’s best vent and demonstrates how Protectoseal can balance high-flow performance with strict emission control. Engineered for both reliability and versatility, it gives operators peace of mind in a wide range of applications.
For more demanding environments, the company’s FAB Valve™ is the pinnacle of innovation. These valves combine multiple technologies, such as RE-Flow™ flame arresters, pressure and vacuum relief vents, and low-leakage seating, into a high-flow, emissionconscious package. They are ideal for operations that require safety and sustainability at scale.
The pressure and vacuum challenges that pipeline and storage tank operators face are not theoretical; they are daily realities with significant consequences. Overpressure events, caused by rapid thermal expansion, liquid transfers, or process upsets, can result in catastrophic tank failures or environmental spills. Furthermore, vacuum conditions caused by cooling temperatures or rapid liquid withdrawal can collapse storage vessels if not properly managed.
Another important consideration is increased VOC emissions, especially in hot climates where liquid vaporisation is naturally accelerated, as well as weight limitations, particularly on atmospheric tanks where venting devices must be both high-performing and lightweight.
Protectoseal’s products are tailored to meet these specific requirements. Customers can expect dependable pressure management from precision-engineered solutions that are not overly complicated. Our ProFlow™ sizing and selection software helps engineers and EPC contractors select the most efficient and cost-effective vent configuration based on actual flow rates and environmental parameters.
No two pipeline installations are identical. Geographic variation, from the freezing temperatures of Alberta to the scorching heat of the
Middle East, requires equipment that can adjust to thermal dynamics and atmospheric variability.
Effective vents must be designed for performance in both extreme heat and cold, but adaptability goes beyond temperature. Whether the system is intended for hydrocarbons, alcohols, acids, or custom chemical blends, Protectoseal provides materials and designs that are compatible with a wide range of fluid properties and corrosive conditions.
In today’s regulatory environment, certification is not optional. Protectoseal’s products meet or exceed API 2000 and ISO 28300 requirements, as well as relevant national and regional codes such as fire safety and emissions management.
By adhering to these international standards, it ensures that products are accepted worldwide, allowing multinational companies to standardise solutions across their operations.
A venting system is only as effective as its ongoing performance. Even the most advanced vents require routine inspection and maintenance to ensure their continued effectiveness. Protectoseal’s team works to integrate service-friendly features such as swingbolt closures, which allow for quick, tool-free access to internal components for cleaning or inspection.
The company also provides field inspections for large and critical systems. Their technicians inspect vent integrity, evaluate emission performance, and provide actionable reports to help maintenance teams avoid unexpected downtime or compliance issues. This proactive support takes a comprehensive approach, assisting operators in optimising long-term performance.
The pipeline industry’s future lies in sustainable innovation. As alternative fuels, carbon capture systems, and green energy projects become more prevalent in the global energy mix, infrastructure will require smarter safety components that are compatible with new chemical profiles, operating pressures, and emissions standards.
Protectoseal is already anticipating these shifts and is focussing its research and development on key priority areas such as nextgeneration emission-free technologies and materials science breakthroughs, for compatibility with hydrogen, biofuels, and nextgeneration chemicals.
As decarbonisation becomes increasingly important, Protectoseal is assisting clients in making responsible and efficient transitions, ensuring that even legacy systems can meet modern sustainability expectations without sacrificing performance.
In today’s world, safety and sustainability are no longer mutually exclusive, they are interdependent requirements for the modern energy economy. By using the right products, operators can reduce their environmental impact, lower their operating costs, and ensure compliance with changing standards.
Whether you are upgrading an existing facility or designing tomorrow’s infrastructure, working with the right safety solutions provider can help companies across the sector do it not only safer and smarter, but also cleaner.
Galaxy Brushes is proud to unveil the Pit Hog, a cutting-edge innovation designed to take your pipeline cleaning to stellar heights, blasting through grime, one pipe at a time. With a powerful strip brush technique, this brush outshines traditional flat wire and pencil brushes, ensuring unparalleled cleaning efficiency.
Out-of-this-World Features:
Superior Cleaning Power: The Pit Hogʼs strip brush design maximizes wire contact with the pipe, delivering superior results in clearing out debris.
Custom Fit for Any Mission: Choose your wire diameter (ranging from 0.010" to 0.020") and tailor cleaning effectiveness to your needs.
Durable Materials for Any Terrain: Available in both carbon and stainless steel, the Pit Hog is built to withstand even the toughest pipelines.
Galaxy-Grade Quality: Backed by the legendary service and craftsmanship that make Galaxy Brushes the star of the industry.
Take your pipeline maintenance to the next level with the Pit Hog.
A podcast series for professionals in the downstream refining, petrochemical and gas processing industries
EPISODE 1
Alan Gelder, Senior Vice President of Refining, Chemicals and Oil Markets at Wood Mackenzie, provides a review of downstream markets in 2024 and looks ahead to what 2025 may hold for the sector.
EPISODE 2
Dr Klaus Brun, Global Director of Research & Development, Ebara Elliott Energy, discusses the progress that is being made towards adapting centrifugal compressors for high-speed hydrogen compression.
EPISODE 4
Rasmus Rubycz, Market Manager for New Energy at Atlas Copco Gas and Process, considers how heat pumps as an industrial technology are gaining greater attention as a result of the increased drive for sustainability and the challenges and opportunities of electrification of process heat.
EPISODE 3
Peter Davidson, CEO of the Tank Storage Association (TSA), outlines the essential role that the tank storage sector has to play in ensuring supply security and resilience, as well as in facilitating the energy transition.
Sponsored by
EPISODE 5
Mike Logue, Owens Corning Business Director – Specialty Insulation, delves into factors that can support the performance, safety and longevity of insulating systems installed in hydrocarbon processing environments, including cryogenic facilities.
EPISODE 6
Leakhena Swett, President, ILTA, and Jay Cruz, Senior Director of Government Affairs and Communications, ILTA, consider the importance of trade associations and industry collaborations.
Lindsey Saunders, Product Manager - North America Midstream & Measurement, Quorum
Software, explains how a secure transactional system can optimise capacity and improve the customer experience.
t’s easy to overlook great customer service in the name of maintaining a pipeline’s core functioning. Monitoring imbalances, managing contracts, keeping up with regulatory standards, and optimising a pipeline’s physical capacity should always take priority – but never at the shipper’s expense. That is why clear data insights and streamlined, paperless contract management are so valuable. A well-designed, secure transactional system doesn’t just simplify processes.
It builds trust, strengthens relationships, and elevates the entire shipper experience. When these relationships thrive, pipelines can scale their business like never before.
Time spent calculating capacity cuts in a typical gas day can easily steer any workload off course. Relying on spreadsheets or manual calculations adds unnecessary complexity and increases the risk of costly mistakes. Every cycle of a gas day has its limitations. Rushed timelines and hand calculations accelerate errors, doubling or even tripling time lost with adjustments. But with a robust scheduling module, what matters most stays in focus – efficiency, accuracy, and the ability to make proactive decisions.
A transactional system with a scheduling module can offer structured sets of rules that will optimise cut management at over-capacity locations, allowing a pipeline to make the most of every cycle. Automating these processes reduces errors and streamlines operations, replacing manual calculations with a more efficient and accurate approach.
A web-based system takes these efficiencies even further, providing real-time visibility into each cycle’s scheduled quantity data, accessible from any device, anywhere. It also enhances reporting capabilities, allowing pipelines to share scheduled quantity reduction information with shippers seamlessly.
As businesses expand, their systems must evolve to keep pace. Managing paper-based contracts becomes increasingly unmanageable, leading to inefficiencies that slow an operation. A modern system with paperless contract management allows shippers to even request their own contract terms from the pipeline. Take away the manual back and forth and you remove bottlenecks while strengthening the relationship between shippers and a pipeline. Clear records of contract, amendment, and rate change requests create transparency and trust, allowing both parties to thrive.
This healthy collaboration extends to multidepartmental approvals, which in the right system can be expedited through automated email notifications. This is especially beneficial for short-term contracts. Users can easily date-split existing agreements and create amendments as terms evolve, transforming contract management into a dynamic, adaptable process.
Because pipelines operate 24/7, 365 days a year, the ability to check data and submit changes from anywhere at any time is paramount for smooth business operations. Yet this level of insight can only happen with a web-based user interface (UI) optimised for mobile devices. Here shippers can access their data on a variety of dashboard views and reports with more transparency in their scheduled quantities, allocations, and imbalances, as well as any errors that may prevent data from being processed.
With the right system, pipelines can also email reports and notifications to shippers, alerting them to issues requiring attention for a given day or cycle. This proactive communication enables shippers to easily address errors and nomination quantity mismatches, reducing the need for prior period adjustments and increasing customer satisfaction.
When data is easier to find and interpret, pipeline schedulers can give shippers the context they need, allowing for more meaningful and efficient interactions. Web-based pipeline teams easily respond to shippers after hours as needed, reducing wait times for both shippers and operators.
When numerous service providers are supported by a single vendor software, shippers are already familiar with the software and can easily submit nominations across different pipelines, minimising training time for onboarding. This also fosters shared improvements: user communities drive continuous enhancement, ensuring both shippers and operators benefit from a seamless experience.
Choosing the right technology partner means pipelines don’t just implement software – they gain a strategic ally. The right provider ensures that every interaction is built on efficiency, transparency, and responsiveness, strengthening relationships and driving operational excellence.
Pipeline operations don’t stop for weekends, holidays, or system glitches – which means the underlying data infrastructure needs to support uninterrupted performance. A modern transactional system ensures that a shipper’s scheduled quantity and allocation data stay synchronised even during high-pressure moments. When data is centralised and accessible across teams, schedulers and commercial teams can respond quickly and consistently, without the bottlenecks caused by scattered spreadsheets or siloed files.
This continuity reduces friction between shifts and departments. Everyone works from the same source of truth, even when staffing changes or new team members come on board. From planned maintenance to unexpected outages, having a digital backbone for day-to-day processes ensures the business can operate with confidence and recover quickly.
For pipelines, regulatory compliance isn’t just a checkbox – it’s a constant. Regulatory frameworks require detailed records of contracts and capacity releases, available pipeline capacity, and locations. A transactional system that integrates compliance into its core functions helps operators meet these requirements without added manual effort.
Auditable trails of contracts, amendments, and nomination data can be automatically generated and stored, making it easier to respond to audits or regulatory requests. Standardised forms, submission protocols, and built-in validations improve accuracy while reducing the burden
on compliance teams. It’s not about adding extra steps – it’s about embedding compliance into the way people already work.
With the right software in place, pipelines gain more than real-time visibility – they build a foundation for strategic decision-making. Transactional systems that capture a rich history of nominations, contracts, and shipper data can support long-term forecasting and commercial modelling.
Seasonal trends, nomination cycles, and underutilised capacity become easier to spot and act on. This kind of insight helps operators fine-tune offerings, create more attractive short-term capacity packages, and plan future expansions more effectively. It also gives marketing teams the data they need to engage shippers with more personalised, relevant options based on usage patterns.
The move to web-based platforms brings flexibility – but it also demands a higher standard for cybersecurity. Today’s transactional systems are designed with this in mind, offering robust authentication protocols, user role controls, and encryption features to protect sensitive data.
Role-based access ensures that only the right people can view or edit critical information, while multi-factor
authentication helps prevent unauthorised entry. These protections are essential for both operators and shippers, who rely on secure systems to protect commercial interests and maintain trust. With proper access controls in place, pipelines can confidently offer remote functionality without compromising on security.
The long-term payoff: scalability and interoperability
As pipeline operators grow – whether through asset acquisition, expanding capacity, or diversifying offerings – the systems they rely on need to grow with them. A modern transactional system offers that scalability. It adapts to changes in volume, contract types, and operational complexity without requiring major overhauls or custom workarounds.
Just as importantly, these systems are built to integrate. They connect with multiple platforms – from measurement and SCADA to billing and accounting – so data moves seamlessly across the enterprise. This level of interoperability reduces duplication and unlocks faster reporting, cleaner reconciliations, and better cross-functional collaboration.
Looking ahead, the same data infrastructure that supports day-to-day efficiency can evolve to handle ESG reporting, carbon tracking, or other digital initiatives. With the right foundation in place, pipelines aren’t just reacting to the future – they’re ready to lead.
Fittings without limits
Outstanding material variety
Highest precision
From OD 20 to 3500 mm
Global logistics network
Sergej Arent, Director Applications, HIMA Group, and Michal Miklasik, Project Manager, HIMA Slovakia, explain how modern management and control solutions make pipelines safer, more efficient and more sustainable.
ipeline leaks are among the greatest risks in the operation of critical infrastructure – economically, environmentally and in terms of safety. With the increasing age of many networks, growing regulatory pressure and new challenges such as hydrogen transport, the need for precise, automated monitoring is increasing. Find out how a modular software solution combines different detection methods to achieve highly sensitive and at the same time fault-tolerant leak detection in real time.
It is a normal morning in the control room of a large pipeline operator. Countless operating data appear on the screens of the employees in the control room – everything seems to be running smoothly. But suddenly a message appears in the event display: ‘Suspected leak – northern sector, segment 17 – position 85 km north of the refinery’. No shrill alarm, no panic – just precise, data-based information that leaves no doubt.
What might have taken days to detect in the past – a passer-by smelling oil or a pressure drop at a remote measuring point – is now visible in a fraction of a second. That’s because the pipeline is part of a modern monitoring system equipped with an intelligent leak detection system that registers and evaluates even the smallest deviations in pressure and flow behaviour. In this case: FLOWorX® – a system that works in real time and localises with pinpoint accuracy.
A moment later, a team is on site. The leak can be sealed quickly and precisely before more damage occurs. Minimised environmental pollution, reduced critical product loss, no damage to the company’s reputation. What sounds like a routine operation was still a long way off just a few years ago. For many pipeline operators worldwide, this shift towards a digitalised, preventive safety architecture has long since become a necessity.
The invisible risk: why pipelines need to be monitored more than ever
Pipelines are the lifelines of industrial and urban infrastructure –but they are also risk factors with a high potential for damage. Theft, corrosion, micro-leaks, damage caused by third parties or extreme weather events can all affect them. In addition, cybercrime is increasingly coming into focus. The older a pipeline, the greater the risk – and worldwide, environmental protection and safety requirements are increasing. In addition to numerous local laws and regulations, international standards such as API 1130, API 1149, API 1175 and API 1160 must be taken into account. Modern
pipeline monitoring without intelligent, automated systems is hardly conceivable anymore.
But which technology is suitable for which infrastructure? Essentially, four approaches can be distinguished, which can be combined depending on the requirements:
) Classic inspection technologies: inline inspection (ILI), magnetic flux leakage (MFL) or ultrasound (UT) provide precise data on the condition of a pipeline. They show corrosion, material weaknesses or deposits – but they work selectively and reactively. Leaks can go unnoticed between inspections.
) Field instruments data solutions: sensors for pressure, temperature or flow register changes in real time and are easy to retrofit. However, they provide basic physical data and need further processing and calculations, as the data alone is not sufficient for making conclusions about leaks, especially in complex operating situations or with irregular flow rates.
) Centralised management systems (EPMS): enterprise Pipeline Management Systems combine monitoring, control and alerting. They integrate operating data and visualise processes. However, specialised modules or additional systems are required for leak detection.
) Computational pipeline monitoring (CPM): this is where model-based solutions come in: mathematical models such as real-time transient model, volume valance or pressure wave analysis simulate the pipeline and detect leaks reliably, even in complex scenarios – such as when pumps are started up or when there are flow fluctuations.
A modern all-in-one leak detection suite designed for oil, gas, water, chemical and hydrogen applications like FLOWorX® uses four different methods in parallel to ensure full coverage. It can be used as a stand-alone leak detection solution integrated into existing control systems or as part of a hybrid system with emergency shutdown (ESD) in a SIL 3-certified safety control system – for greenfield and brownfield projects. Unlike many solutions that rely on one or two methods, the leak detection suite combines four detection methods that work in parallel and independently of each other. This is crucial because real operating conditions vary greatly – with pressure fluctuations, temperature changes or changing flow rates. Systems with only one method quickly reach their limits in terms of accuracy and might overload the operator continuously generating false alarms.
) Volume balance method (VBL): this method permanently compares the incoming and outgoing volume flow of a pipeline. Additionally, it calculates
the amount of the product inside of the pipeline according to changes in temperature and pressure profile. If the difference exceeds a predefined threshold, the system triggers an alarm. The method is simple and very robust and suitable for all operating modes including transient conditions. It is sufficient to detect the presence of leaks; however, it lacks the ability to locate leaks.
) Enhanced pressure wave (EPW): when a leak occurs, a pressure wave propagates along the pipeline in fractions of a second. The leak detection system uses high-precision pressure sensors and sophisticated algorithms to detect these waves and quickly locate the leak. This enables an extremely fast response time in the event of sudden breaks or cracks. The algorithms have been specially developed to filter out background noise and measurement noise – an important advantage, especially for hydrogen pipelines.
) Pressure drop method (PDM): not every leak causes a dramatic pressure surge. Slow, creeping leaks – for example, due to material fatigue or corrosion – require a different strategy. This is where the pressure drop method comes in: it continuously monitors the absolute pressure curve and registers long-term deviations from the target curve. This ensures a high level of sensitivity even with very small, slowly developing leaks.
) Real-time transient model (RTTM): the core of the modern leak detection suite is the Real-time transient model. It precisely maps the pipeline in a mathematical model – including all dynamic influences such as pressure, temperature, flow velocity and specific media properties. HIMA has expanded this model specifically for hydrogen pipelines. The specific thermophysical properties of H2 – such as high diffusion rate and low density have been integrated into the calculation. RTTM enables the reliable detection of leaks even under transient conditions – i.e. when operating conditions change, when pumps are switched on and off, and when flow rates fluctuate.
The combined evaluation of all methods is a unique feature. If the system detects a small difference in volume without a pressure wave, for example, a pre-alarm is triggered – this allows real leaks to be sensitively detected and false alarms to be avoided. The Software detects leaks in seconds – even at just 0.3% of the flow rate – and localises them with an accuracy of up to 50 m. This requires high-quality measurement technology, which HIMA can supply on request, including sensors, controllers, telecommunications and SCADA.
The all-in-one leak detection suite FLOWorX® is based on a standardised product, but is customised individually. HIMA supports projects throughout their entire lifecycle – from the feasibility study to engineering and long-term support. The system’s strengths are particularly evident in brownfield projects: it can be flexibly integrated into existing infrastructures and offers future-proof solutions for operators worldwide.
The challenge of hydrogen: why H2 plays by different rules
Hydrogen introduces an entirely new set of challenges, and that requires the further development of the leak detection system for hydrogen pipelines. This is because H2 is not only the beacon of hope
OUR BALL VALVES GO BEYOND THIS DISPLAY AND YOUR EXPECTATIONS!
1/8’’ - 56 ‘‘
CLASS 2500 AND HIGHER
OIL, GAS, HYDROGEN, DISTRICT ENERGY & VARIOUS APPLICATIONS
for the energy transition, but also a challenge for any pipeline monitoring system:
) Hydrogen molecules are the smallest of all gases – and therefore particularly prone to diffusion.
) The gas is extremely volatile and highly explosive when combined with atmospheric oxygen.
) In addition, hydrogen attacks metallic materials over long periods of contact (hydrogen embrittlement).
All of this drastically increases the risk of leaks. HIMA has therefore specially adapted the thermodynamic model of the leak detection system for hydrogen. Sophisticated sensor technology and rapid data processing ensure that even the smallest deviations can be detected and isolated at an early stage. This is important for the rapidly growing market for hydrogen pipelines, which will grow by several thousand kilometres in the next few years.
Functional safety in the age of hydrogen: a new layer of protection
As hydrogen infrastructure expands rapidly, safety concerns are growing in equal measure. As said before, unlike traditional hydrocarbons, hydrogen presents specific technical challenges. These risks affect not only pipeline transport, but also production, storage, distribution, and end-use applications.
To address these risks comprehensively, functional safety systems are being applied across the full hydrogen value chain. These systems go beyond standard control logic, using
safety-rated hardware and software to detect dangerous process conditions and bring operations to a safe state in case of emergency. Their application spans a range of use cases:
) Electrolyser safety: large-scale hydrogen production systems are increasingly equipped with Emergency Shutdown (ESD) functions, often designed to Safety Integrity Level (SIL) 2 or SIL 3, depending on the production volume and associated risk. These systems monitor critical parameters such as pressure, temperature, and fill level to prevent overpressure, overheating, or gas escape.
) Storage and transport: hydrogen storage tanks and pipeline segments are exposed to high mechanical stress, temperature variations, and the risk of material degradation. Functional safety systems here may include pressure relief mechanisms, HIPPS (high-integrity pressure protection systems), and leak mitigation systems.
) Industrial and energy conversion applications: in sectors where hydrogen is used for re-gasification, combustion, or chemical processing, safety instrumented systems are employed to manage burner control, fire and gas detection, and shutoff sequences – particularly important in urban or high-density installations.
) Digital safety integration: with increasing digitalisation, safety systems are being designed within secure operational environments. This includes dedicated safety networks, hardened controllers, and segmented architectures that prevent interference from non-safety-critical systems.
These applications are built on established functional safety standards (such as IEC 61511 or IEC 61508) and are typically tailored to the specific operating environment. The goal is not only to protect assets and personnel, but also to support compliance, system availability, and public trust in hydrogen as a safe energy carrier.
As the hydrogen economy grows, functional safety is emerging not just as a compliance requirement, but as a strategic enabler – supporting scalability, investment protection, and public confidence in new energy systems. The integration of safety with digital technology is helping to define the operational backbone of a more resilient, decarbonised infrastructure.
Modern safety systems are being developed to adapt across diverse hydrogen applications – from production facilities and storage terminals to pipeline corridors and mobility hubs. These systems are typically based on certified platforms that conform to international safety and cybersecurity standards, ensuring reliability while enabling cross-sector interoperability.
Digitalisation plays a crucial role in this evolution. By combining functional safety with advanced monitoring, control, and lifecycle support, operators can ensure high availability, maintain regulatory compliance, and minimise engineering complexity. This includes secure communication networks, centralised diagnostics, and the ability to remotely manage and update safety functions over time.
As energy systems evolve and hydrogen gains momentum, the requirements for pipeline monitoring and safety are shifting rapidly. Operators are no longer dealing with isolated challenges, but with a complex interplay of ageing infrastructure, environmental obligations, volatile media, and digital transformation.
To meet these demands, modern leak detection systems must go beyond isolated detection functions. They must operate intelligently, adapt to changing conditions, and integrate seamlessly with both legacy and next-generation infrastructure. The combination of multiple detection methods, model-based analytics, and high-precision instrumentation offers a powerful toolset for achieving fast, accurate, and reliable results.
At the same time, functional safety has emerged as a crucial framework for managing not just risk, but also operational continuity and regulatory compliance – particularly in hydrogen applications, where traditional safety margins no longer apply. The digitalisation of safety systems further strengthens this backbone by enabling secure, scalable, and remotely manageable architectures.
In this context, leak detection and safety systems are no longer optional extras. They are central to operational excellence, sustainability, and trust in a decarbonised energy landscape. Investing in resilient, future-ready monitoring and control strategies today will ensure safer pipelines – and safer societies –tomorrow.
As pressure mounts to reduce industrial energy consumption and improve sustainability, should pipeline operators refocus on pump energy efficiency? Manish Talwar, Head of Retrofits Americas at Sulzer, discusses.
riven largely by rising production in energy-intensive industrial subsectors, global energy consumption is growing, increasing the urgency for energy efficiency. According to the International Energy Agency (IEA), energy efficiency measures could contribute up to 50% of the CO 2 emission reductions needed by 2030, while also reducing energy bills by a third – but the pace of improvement needs to double.
How to save a country’s worth of electricity
Industrial pumps are installed in so many applications, yet often go unseen.This equipment represents a major energy efficiency opportunity, accounting for more than 20% of the world’s electricity demand. Even a 1% improvement in pump energy efficiency would save around 59 TWh –equivalent to New Zealand’s annual power needs – while also saving around 28 million t of carbon dioxide. The potential impact is immense – and in some instances the improvement could be as much as 20 - 30%. This is particularly the case for pipeline operators, whose networks often span thousands of miles and rely on hundreds of pumps that operate under highly variable conditions. Yet, many operators across oil and gas assume that if a pump is operating reliably, it is also efficient.
However, a recent sample of over 400 pumps monitored with Sulzer’s BLUEBOX™ predictive maintenance platform found that 68% were operating outside of their preferred operating region for over half the time, with 10% of pumps across upstream, midstream and downstream operations capable of saving over US$100 000/yr, if only they were operated more efficiently.
In addition, 56% of BB3 pumps, 26% of BB1 pumps and 25% of BB2 pumps across the sample were estimated to have potential energy efficiency savings of US$50 000 or more.
The data found that pipeline operators could make some of the largest savings among all pump users – potentially saving millions of dollars. This is due to several factors, including the large number of pumps required to operate a network of pipelines, the typical age of pipeline infrastructure and the variability of operating conditions that cause operators to throttle pumps or tolerate different temperatures and viscosities than originally designed for.
The research found that on average, a pipeline operator could save US$38 825/yr per pump by improving the efficiency of their main line or booster oil line pumps. If every pump across the entire network were to be improved, this could equate to hundreds of thousands, or even millions of dollars a year.
For example, one pipeline operator in the USA was found to have potential savings of over US$1 500 000/yr if it were to address the energy efficiency of its fleet of 38 BB1 pumps. Similarly, a pipeline operator in Pakistan could achieve up to US$500 000 in savings annually by improving the energy efficiency of just four BB3 multistage pumps. This was not an outlier; several pumps serving oil and gas operations within the analysis were identified as having the potential to achieve savings of between US$150 000 and US$465 000.
With a wide range of potential savings, operators should consider undertaking an energy efficient audit to gain a holistic view of their pump operations. Pipeline operators are also particularly strong candidates for energy efficiency improvements due to changes in fluid viscosity, additives and evolving fuel types – such as the blending of e-fuels to create more sustainable forms of aviation and maritime fuel.
As more fluid types and applications emerge, pipeline operators and pump manufacturers will need to continually adapt. For example, several countries including Japan, Australia, the USA, the UK, Denmark, Norway, Canada, the Netherlands, Belgium, and Germany are all pursuing projects to repurpose existing oil and gas infrastructure to support hydrogen transport and carbon capture and storage which will have implications for the efficient operation of pipelines.
Optimising pump efficiency offers substantial financial benefits – potentially into the millions of dollars in fuel saved.
However existing efficiency programmes tend to focus on ‘big ticket’ items such as boilers, turbines and other process critical equipment, overlooking the collective impact of high energy pumps. Some will only take a snapshot in time, without understanding the historic data. Others will not provide the after support required to ensure the savings are delivered as predicted or use the latest digital technologies to analyse and monitor.
Altogether, there is room for a new best practice standard of sorts that brings together the fundamental steps in achieving energy efficiency into one end-to-end process – from consultancy and retrofitting services through to ongoing monitoring. By combining digital analysis, machine learning and ongoing monitoring with hands on technical experience, there are many more benefits that can be unlocked in the process, such as improved reliability, reduced energy intensity and increased mean time between failure.
The first step is to establish a baseline to understand where improvements can be made. Historic data is collected and compared to the original pump design to understand whether it is running at its best efficiency point, and the pump’s hydraulic and mechanical properties are reviewed against modern, efficient design. Each pump can be analysed to
understand what carbon and cost savings are possible, and the work prioritised to address those that will have the most impact first.
Different retrofit options should be made available so that operators can balance their appetite for energy, carbon and potential tax savings against their OPEX, CAPEX, downtime and payback goals. Options could include re-rating pump hydraulics to match a plant’s current processing requirements, improvement of mechanical properties to reduce mechanical losses, and surface treatment of the pumps’ volutes/impellers to reduce friction. Any proposal presented should outline the target return on investment and payback period, alongside ESG metrics, for example carbon and fuel saved.
Finally, once installed, it is critical that the solution be monitored to ensure it continues to deliver the energy efficiency uplift that it said it would. Ideally, the work should be covered by an efficiency guarantee, and it is beneficial to take on a performance agreement so that the same vendor can ensure optimised reliability and efficiency.
As an example, an ambitious international oil company recently challenged Sulzer to reduce the energy consumption and emissions of four BB5 lean amine pumps at one of its European operations.
After collecting the data and completing an audit, a hydraulic upgrade was proposed with a new hydraulic
bundle designed to fit within the existing barrel. This allowed for the existing end covers, barrel closure, bearings, seal and drive coupling to be retained to minimise costs and downtime. A combination of PEEK and SUME coated wear parts were also proposed to achieve tighter running clearances.
To save time, the hydraulic bundle was manufactured in advance, enabling the upgrade to be performed as part of a planned overhaul. Once completed, site tests confirmed a more than 5% improvement in energy efficiency, leading to annual savings of €5.3 million in operating costs and 7751 t of carbon emissions.
Industrial pumps are a major source of potential energy efficiency, particularly for operators across oil and gas who have faced increasing energy costs of the last few years. A more proactive approach to their operation and maintenance that combines digital techniques with hands on expertise could lead to a significant uplift in a pipeline’s operational, environmental and financial performance. Through cumulative energy efficiency improvements, operators could achieve operational cost savings of millions of dollars while significantly reducing carbon emissions and improving the reliability of society’s critical infrastructure.
In this episode, Elizabeth Corner speaks to Matt Romney, Product Line Director for Pipeline Integrity, T.D. Williamson, about TDW’s perspective on the benefits of working with pipeline membership organisations.
This episode of the podcast covers:
• The value of membership associations for TDW.
• Examples of association impact.
• TDW’s approach to joint industry projects.
• Emerging industry challenges, and how associations can and do help.
• Exciting new technology and deepening collaboration with operators.
• And more!
Jim Bramlett, Commercial Manager – The Americas, Tracerco, describes managing flow assurance and corrosion risks through non-intrusive monitoring.
n the offshore energy sector, ensuring the long-term integrity of subsea pipelines remains one of the most pressing challenges for operators. As projects move into deeper and more complex waters, pipeline performance is increasingly affected by issues such as flow restrictions, corrosion, and limited access and options for inspection. These risks not only impact on operational efficiency but can also lead to significant financial and environmental consequences if not managed effectively.
Maintaining integrity over the full lifecycle of a subsea pipeline requires a multi-faceted approach, one that combines design foresight with practical, in-field diagnostics capable of identifying problems before they escalate.
Flow assurance is a critical focus for subsea operations, particularly in deepwater regions where long tiebacks and variable conditions increase the likelihood of restrictions forming. Common causes include hydrate formation, asphaltene, wax build-up, and scale accumulation, all of which can reduce flow rates, lead to pressure anomalies, or create complete blockages if left unchecked.
Pigging and other mechanical interventions, while often effective, are costly and can introduce additional risks or downtime. Moreover, not all pipeline systems are piggable, particularly when they are bundled, operating under specific design constraints, or the build-up in the pipeline is severe.
The inspection of partially buried pipelines or those housed within protective structures is another known difficulty in offshore operations. Inline inspection (ILI) is a critical process used in the pipeline industry to assess the structural integrity and condition of pipelines from the inside using intelligent tools – pigs.
This non-destructive testing (NDT) method involves sending the specialised device (pig) through a pipeline to detect metal loss, e.g. corrosion, cracks or fractures, dents or deformations, weld anomalies, changes in wall thickness, and geometrical issues.
ILI may be limited or impossible, due to the pipeline set up or known and unknown internal build up which makes it impractical or cost prohibitive. This makes the ability to monitor internal conditions non-intrusively increasingly valuable.
Technologies that allow operators to assess pipeline wall thickness, identify areas of suspected corrosion or under-deposit issues, and locate partial flow restrictions, without disrupting operations, are proving critical in environments where intervention is both complex and high-risk.
Non-intrusive inspection methods are enabling more informed decision-making in the offshore sector. Rather than relying on periodic intrusive testing or assumptions based on external conditions, real-time data is helping engineers understand what is happening within pipelines and to respond accordingly.
For example, in deepwater assets where access is limited and intervention costs are high, such diagnostics can support predictive maintenance strategies by providing early warnings of flow anomalies, density changes, or wall thinning. These insights can help prioritise inspection resources, defer unnecessary intervention, and extend the productive life of pipeline systems.
Jim Bramlett, Tracerco’s Commercial Manager for The Americas, said: “We are increasingly seeing a real shift in how operators approach subsea pipeline integrity. As offshore assets age and projects move into harsher environments, the tolerance for uncertainty is reducing. Operators are no longer waiting for failures or anomalies before acting – they want proactive intelligence that allows them to intervene early, cost-effectively, and safely.
“Non-intrusive diagnostics are giving them exactly that: clear, verified insights into the condition of their subsea infrastructure, even in cases where traditional inspection methods can’t reach. In deepwater operations, where access is limited and downtime is expensive, having this
kind of visibility can make the difference between a minor intervention and avoiding a major shutdown.”
A recent subsea inspection project in the Gulf of Mexico, conducted at a depth exceeding 4000 ft, involved scanning multiple jumpers, flowlines and SCRs for a life extension project. The operator, a major global energy company, was concerned they had build-up inside the piping system and required insights into the extent of deposition and wall loss on these critical components to inform future intervention strategies along with obtaining a permit extension.
Due to the complex geometry and the presence of internal deposition, the assets were considered unpiggable. The challenge was to determine whether the deposition could be cleaned or would require full replacement, and to assess the remaining structural integrity of the piping system.
Tracerco deployed Discovery TM at pre-selected external inspection points where deposition was suspected. This external non-destructive evaluation (NDE) method enabled precise imaging and wall thickness measurements without the need to remove protective coatings or interrupt production.
The inspection revealed up to 70% bore blockage in the well jumper due to scale, confirming the need for replacement. The SCR exhibited signs of external corrosion with 65% remaining wall thickness, data which helped the operator assess fitness-for-service and inform future maintenance planning.
This real-world application demonstrates how nonintrusive subsea diagnostics can provide operators with critical integrity data in otherwise inaccessible areas. The ability to quantify wall loss and deposition without halting production was highly beneficial for the major global energy customer – it supported informed decision-making, enabling proactive maintenance while reducing the risk of unplanned downtime and guided them on future decision concerning this system.
With pressure mounting to improve performance while minimising environmental risk and lifecycle costs, the ability to assess pipeline integrity safely and effectively is becoming a cornerstone of responsible offshore operations. Non-intrusive inspection techniques are offering a practical way to reduce uncertainty and help operators maintain flow assurance, without the need for disruptive access or invasive procedures.
As the offshore energy sector looks to align with broader Environmental, Social, and Governance (ESG) commitments and digital transformation goals, the adoption of non-intrusive integrity solutions is likely to accelerate. These technologies not only help reduce the environmental footprint of inspection by avoiding unnecessary vessel callouts and shutdowns, but they also support long-term reliability planning through higher-quality datasets and better risk modelling.
With further advancements in imaging resolution and real-time analytics, non-intrusive inspection is fast becoming an industry standard for safeguarding flow assurance and integrity in the world’s most challenging offshore environments.
Garra Liming, Director of Public Relations and Government Affairs at American Society for Nondestructive Testing (ASNT), talks about collaborating with the Jobs of Tomorrow docuseries, and how to build safer pipelines and stronger careers.
hat do you want to be when you grow up? It’s a question people have asked family members, friends and even themselves for generations. Though skilled trades offer immense opportunity for an exciting and lucrative career, it is not often the path people dream of first; though maybe they should. Consider, for example, working with pipelines in the oil and gas industry.
Oil and gas pipelines are the veins of our energy system. Like anything that is in constant use, pipelines need regular maintenance to remain reliable. That is why skilled trades, like nondestructive testing (NDT), are significant and should be considered by many as a potential career path. NDT specifically uses methods to analyse the materials and components making up pipeline structures and evaluate their integrity without interfering with their serviceability.
NDT keeps pipelines going by catching discontinuities before they become an issue, allowing operators to address any flaws or corrosion that develop over time to increase the pipeline’s lifespan and sustain safe and efficient industry operations. Technicians use advanced tools and technology to detect internal and external flaws without damaging the pipeline itself. From ultrasonic testing to radiography, they spot cracks, corrosion, or welding issues that could lead to leaks or major failures.
Think about the tragedies that have happened: San Bruno Pipeline Explosion in California in 2010, Colonial Pipeline Spill in North Carolina in 2020 or the Texas City Refinery Explosion in 2005. NDT prevents the occurrence of harmful incidents such as these from happening again.
Most NDT technicians in oil and gas use five common methods: ultrasonic testing (UT), radiographic testing (RT), magnetic particle testing (MT), and liquid penetrant testing (PT). UT involves the application of high-frequency sound waves to detect and evaluate cracks and defects in industrial components like pipelines. RT, or industrial radiography, uses radiation of X-rays or gamma rays to analyse the interior structure of a competent for flaws. MT involves the testing of ferromagnetic materials, requiring technicians to magnetise the material and apply fine particles to the surface to draw out cracks that disrupt the magnetic field and create a visible leakage field to indicate a discontinuity. PT requires the application of a specially formulated penetrant liquid to a component so it can fill into any surface-breaking defects and then the use of a developer to pull out the liquid and make the discontinuity visible.
Today, NDT methods and techniques are constantly evolving with the integration of innovative tools and technology. The application of varying testing methods for one component is necessary at times to explore the potential presence of different types of discontinuities in petrochemical infrastructure. Each method is valuable in its own right. However, most NDT technicians are only certified in a couple specific methods.
Today, the skilled trades workforce is in crisis, including in the field of NDT. The inspection industry needs talented, passionate individuals looking for rewarding careers who are willing to undergo training and certification. ASNT is the largest technical society of NDT professionals in the world, and it strives to attract individuals to explore a career as a technician by spreading awareness of NDT in new ways.
To accomplish this, ASNT collaborated with the Jobs of Tomorrow docuseries for its fifth season to help more people understand what NDT is and why it is so important.
Jobs of Tomorrow is a television series that explores the evolution of jobs in the modern era and shares an in-depth examination of the organisations and industry innovations shaping the future of the workforce. The fifth season, which was released earlier this year, focuses on NDT and the different sectors where technicians work to highlight the range of opportunities available.
Each episode touches on how NDT is shaping industries like petrochemical, aerospace, transportation, energy, and infrastructure. These are not abstract topics. These are real stories from real people about technicians out in the field, solving problems and preventing failures before they happen.
Most people have never heard of NDT, and it is often taken for granted every day. The docuseries provides a platform to raise awareness, tell real stories, and inspire the next generation of technicians, engineers, and industry leaders. By watching these episodes, more people can learn about NDT and its importance to maintaining reliability in various industries, as well as the various job opportunities available with a career in NDT.
Episode Three, Season Five of Jobs of Tomorrow, which is titled ‘NDT Keeps the Pipelines Flowing’, explores the importance of testing infrastructure like pipelines in the petrochemical industry. The episode explores how NDT technicians are the unseen heroes that perform crucial work to keep the oil and gas in pipelines flowing and prevent negative impacts on the environment and communities by protecting safe operations.
In the episode, real technicians illustrate how the petrochemical industry supports our way of life and how NDT makes it happen. NDT does not just keep energy moving – it prevents environmental disasters, protects workers, and ensures communities are safe. They also share their stories about how passion for music and the idea of using sound to create imaging led them to learn ultrasonic testing and begin a career in NDT; their experiences in the field and how everything is touched by NDT; and the need for ethics to direct technical decision-making and encourages anyone considering a career in NDT to have a passion for making the world a safer. They explain how it’s the best time for members of the next generation workforce to get involved in NDT due to the immense number of opportunities available and the industry’s constant evolution.
Since its establishment in 1941, ASNT has sought to advance the field of NDT with its vision of making NDT a highly respected professional field recognised globally for its role in creating a safer world. It establishes itself as an industry leader by setting inspection standards, helping people get trained and certified, and making sure NDT is part of the conversation when it comes to infrastructure, safety, and innovation.
NDT is not just a technical field. It is a career that offers real opportunity. It provides the chance for individuals to have a successful career, travel the world, work across different industries, and know that what they do makes a difference. The docuseries illustrates how NDT ultimately and simply keeps people safe. NDT is truly a job tomorrow, today.
NDT is the invisible work that protects everything we build and everything around us. It offers an alternative career path for everyone, from young people exploring higher education opportunities to seasoned professionals seeking a late career change. It requires commitment to develop strong technical skills that enable you to have a direct impact on ensuring the safety of public infrastructure.
There are opportunities available to those interested in pursuing a career in NDT and in other skilled trades today. As more skilled trades technicians retire, the gap between the need for trained professionals and the current availability continues to expand. There is a growing need for more technicians in the skilled trades, and it’s being recognised on a national level.
NDT is one of those hidden industries where the demand is high, the pay is competitive, and the work is meaningful. But too few people know it exists as a viable career, even for those without a four year degree. With the right training and certification, professionals can enter the field and begin building a career that offers growth, travel, and impact.
Many NDT technicians travel the world working on massive infrastructure projects. Others stay local, working in labs or plants. Some specialise in pipelines while others choose aerospace, renewable energy, or manufacturing. There are many options, and the need is growing quickly. As technology advances – with more automation, AI, and data analysis tools –the industry is evolving rapidly. Pipelines are ageing, regulations are tightening, and energy systems are under pressure to be more efficient and resilient. NDT plays a role in all of that. It is the safety net that makes sure everything else works.
The work of ASNT seeks to foster a growing interest from younger generations and to partner with community colleges, training centers, and workforce development programs to spread awareness of the NDT field. The organisation strives to lay the foundation for a nationwide workforce development programme that links schools with employers, supports apprenticeships, and opens doors to funding and grants.
Pipelines are crucial to the transportation of oil and gas resources, which power almost everything people do in today’s modern society. Regular inspection of oil and gas components like pipelines with NDT methodology ensures the safe and efficient operation and maintenance of infrastructure in the petrochemical industry and beyond. The work of skilled trades professionals is essential to keeping our society protected and supporting its ability to continue to evolve in the future. So, what do you want to be when you grow up?
Break free from bottlenecks. Vision, powered by GDi, slashes inspection time by up to 40%, clears backlogs with precision, and offers seamless integration into existing systems. Redefine what’s possible in maintenance and reliability.