
8 minute read
Controlling combustion for a cleaner future
Keith Warren, Servomex, UK, looks at the role that combustion measurements play in controlling carbon emissions.
With the increasing global focus on reducing and preventing harmful emissions, particularly carbon dioxide (CO2), many industries are looking for ways to minimise the environmental impact of their operations.
International action to reduce the impact of carbon emissions on climate, including the 2016 Paris Agreement, has intensified the implementation of ever more stringent environmental regulations. In response, industrial operators are increasingly adopting clean air and decarbonisation strategies designed to meet regulatory requirements and help them achieve carbon reduction targets.
Gas analysis plays an essential role in these efforts, not only by supporting the measurement of harmful emissions, but also by improving process efficiency, thereby ensuring fewer emissions are generated from the outset.
Combustion efficiency is one of the key stages in any effective clean air strategy. Taking control of this important process reaction allows operators to reduce emissions of key pollutants, lower fuel consumption, and improve safety.
In gas analysis terms, this control relies on accurate measurements of the relative concentrations of oxygen (O2) and combustibles (COe) in the reaction mixture to achieve the optimum ratio between fuel and air.
The combustion process
Combustion mixes fuel with O2 (traditionally from air, though some processes use recycled flue gases combined with enriched O2 to create combustion feeds) in a fired heater, creating heat energy for use in the process. This reaction typically requires a significant amount of fuel, creates potential safety hazards, and generates environmentally-harmful emissions.
Before the development of accurate combustion efficiency gas analyser technologies, fired heaters were typically run under inefficient conditions, with high excess air. This increased the level of fuel consumption, but avoided the creation of unsafe process conditions.
Any excess O2 in the process also combines with nitrogen and sulfur from the fuel to produce unwanted emissions such as oxides of nitrogen (NOx) and sulfur (SOx).
Accurate measurements of oxygen and combustibles, principally carbon monoxide (CO), allow the air-to-fuel ratio to be optimally balanced, controlling the combustion reaction and reducing fuel consumption. Emissions of NOx, SO x, CO and CO2 are also reduced.
Measuring oxygen with zirconia sensing
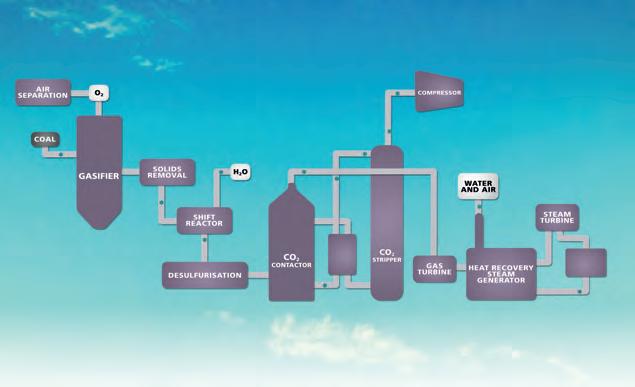
Figure 1. Pre-combustion carbon capture.
Figure 2. Post-combustion carbon capture. Zirconia-based sensing technology is a long-established and highly-trusted solution for O2 monitoring in combustion. It provides reliable, accurate measurements at ppm and % levels, and has a fast response to changing conditions.
Servomex’s version of the zirconia sensor consists of a cell made of ceramic zirconium oxide, stabilised with an oxide of yttrium to form a lattice structure. The measure and reference sections of the cell are covered with catalytic, porous, electrically-conductive coatings that serve as electrodes on both sides of the lattice barrier between sample and reference gas volumes.
At elevated temperatures, the lattice allows negatively-charged oxygen ions, formed at the catalytic electrodes, to pass at a rate that depends on the cell temperature and the difference in the O2 partial pressures of the sample gas and the reference gas. The passage of the ions generates a voltage across the electrodes. The size of this voltage is a logarithmic function of the ratio of the O2 partial pressures of the sample and reference gases. The partial pressure of the reference gas is predetermined, so the voltage produced by the cell can be used to determine the O2 content of the sample gas taken from the process.
Adding a combustibles sensor
A combustibles sensor can be added easily to a zirconia-based gas analyser, at a modest additional cost, to provide an all-in-one combustion control solution.
Calorimetry technology – also known as thick film catalytic sensing – can be used to achieve sensitive, accurate measurements of combustibles. A sensor using this technology measures COe based on its exothermic reaction with O2 over a catalytic platinum surface, which produces CO2. The heat generated is used to determine the COe concentration.
A four-quadrant bridge track is over-glazed to shield the circuit from the sample gas, and two quadrants are then coated in a platinum catalyst. These quadrants form a Wheatstone bridge circuit, with the disc mounted in a cell heated to 300˚C (572˚F) or 400˚C (752˚F).
When the gas sample is added, any COe present in the sample will combust on the catalyst, heating the respective quadrant and altering the output voltage of the Wheatstone bridge. This output voltage will be directly proportional to the COe concentration, providing an accurate measurement for COe.
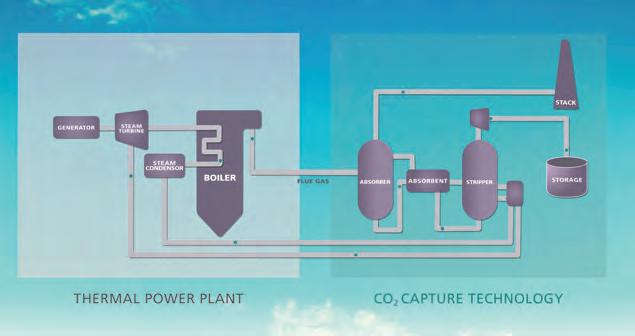
A combined solution for combustion control
Combining both zirconia and calorimetry sensing in one compact device, Servomex’s SERVOTOUGH FluegasExact 2700 combustion analyser delivers effective measurements of both O2 and COe in flue gases. Easy to operate and maintain, it meets the most demanding needs of combustion efficiency applications in the power generation and process industries, helping to improve combustion efficiency and reduce flue gas emissions.
Armed with an integral sampling system custom-designed for operation in some of the hottest and most extreme industrial environments, it is ideally suited to the control of a wide range of combustion processes, including process heaters, utility boilers, thermal crackers, incinerators and furnaces.
Aspirator interlocks prevent sampling while the analyser is heating or not up to optimum temperature, while the optional Flowcube continuous flow monitoring sensor enables positive flow conditions to be validated, aiding preventative maintenance.
Designed for high-temperature processes of up to 1750°C (3182°F), the FluegasExact 2700 uses an extractive measurement principle to protect both sensors from the harsh process environment, extending sensor lifespan. Typically, the zirconia sensor in the FluegasExact 2700 will operate effectively for at least seven to eight years.
The analyser is designed for safe areas, Zone 2/Division 2, and ATEX Category 3 hazardous-rated locations. It also offers both direct and remote mounting options to ensure easier, safer access for personnel, even if the desired measurement point is not freely accessible.
Servomex also offers a specially-designed, sulfur-resistant thick film catalytic sensor for the FluegasExact 2700. This is operated at a higher temperature to prevent sulfur from depositing permanently on the sensor.
Alongside the environmental benefits of maintaining efficient combustion reactions, the accuracy and reliability of the FluegasExact 2700 has been proven to save up to 4% of fuel costs per year. This is not only advantageous to the operator’s bottom line, but also aids their sustainability goals by reducing the consumption of non-renewable fuels.
An alternative combustion solution
Tunable diode laser (TDL) technology is a more recent sensing development, and provides an even faster measurement for this application, particularly in the case of CO. TDL analysers provide an average measurement across the measurement path, rather than the single-point result produced by a zirconia analyser. This ensures a better overall picture of conditions within the fired heater. However, since TDL sensing is highly specific to the gas being measured, separate analysers are required for O2 and CO.
Servomex’s SERVOTOUGH Laser 3 Plus Combustion TDL analyser, for example, can be configured to measure either O2 or CO. It can also be configured for a joint measurement of CO and methane to provide a rapid-response measurement for safety in natural gas-fired heaters and boilers.
EMPOWER ASSET PERFORMANCE MANAGEMENT AND DIGITAL TWINS
AI based solutionsexploiting ops data for
✓ Equipment health status awareness ✓ Early anomaly detection based on operative contexts ✓ Anomalies Correlation ✓ Fault Isolation ✓ Remaining Useful Life estimate

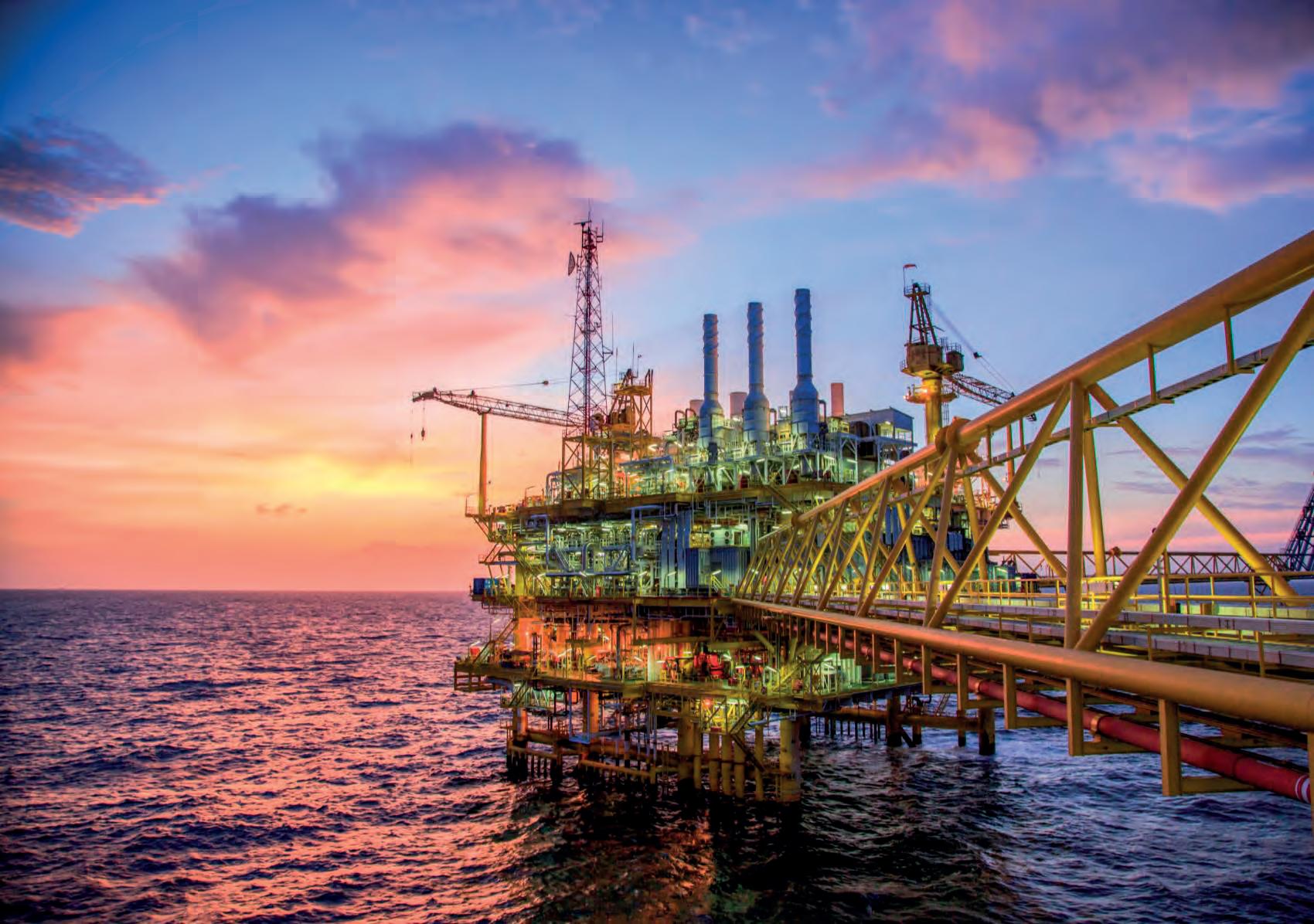
DIAGNOSTIC KERNEL MODULES™
S.A.T.E. Systems and Advanced Technologies Engineering S.r.l. www.sate-italy.com Santa Croce 664/a - 30135 Venezia -Italy info@sate-italy.com - ph. +39 041 2757634 30+ years experiencein Consulting Simulation services Modelling and diagnostic software for process plants and machines
Figure 3. Oxyfuel combustion carbon capture.
Part of a larger strategy
While combustion has been the primary focus of this article, it is important to note that it is just one part of a wider clean air strategy. Gas analysis can also be used in many applications to increase process efficiency. The more efficient the process reaction is, the fewer harmful emissions are likely to be generated.
It also plays an important role in gas cleaning – the removal of harmful substances from process gases that might otherwise be emitted by the plant. Typical examples of the many gas clean-up processes include DeNOx (ammonia slip) treatment, flue gas desulfurisation, and carbon capture and storage (CCS).
A further aspect of the strategy is the monitoring of flue gas emissions. This helps to determine the process efficiency and protect the environment, and demonstrates that plant operators are complying with the necessary regulations. To ensure compliance, a continuous emissions monitoring system (CEMS) is required to measure all of the necessary components of the flue gas. This must be capable of offering the highest sensitivity and accuracy when dealing with multiple measurements for pollutants. By combining these stages into a comprehensive strategy, operators can ensure more efficient processes, support the safe removal of pollutants, and monitor the remaining emissions that are output to the atmosphere.
When using a wide range of different sensing technologies to ensure the best-fit and most cost-effective solution for each application, gas analysis plays an essential role in cleaner plant and refinery operations.
Additionally, it is certain that gas analysis technology will be essential to the production of current and future cleaner energy sources, helping plants and refineries to fully address the impact of their operations on the wider environment, and contribute to the creation of a world with cleaner air. For many power generation and hydrocarbon processing applications, the creation of that world will depend heavily upon maintaining and tightening the control of combustion efficiency.
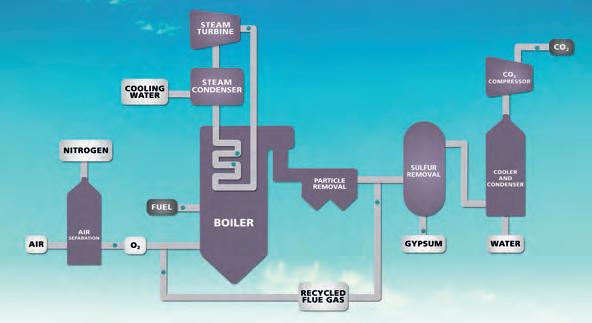
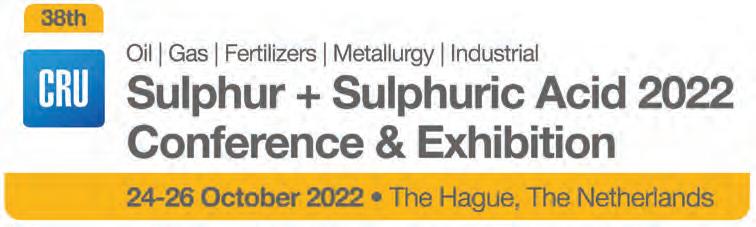
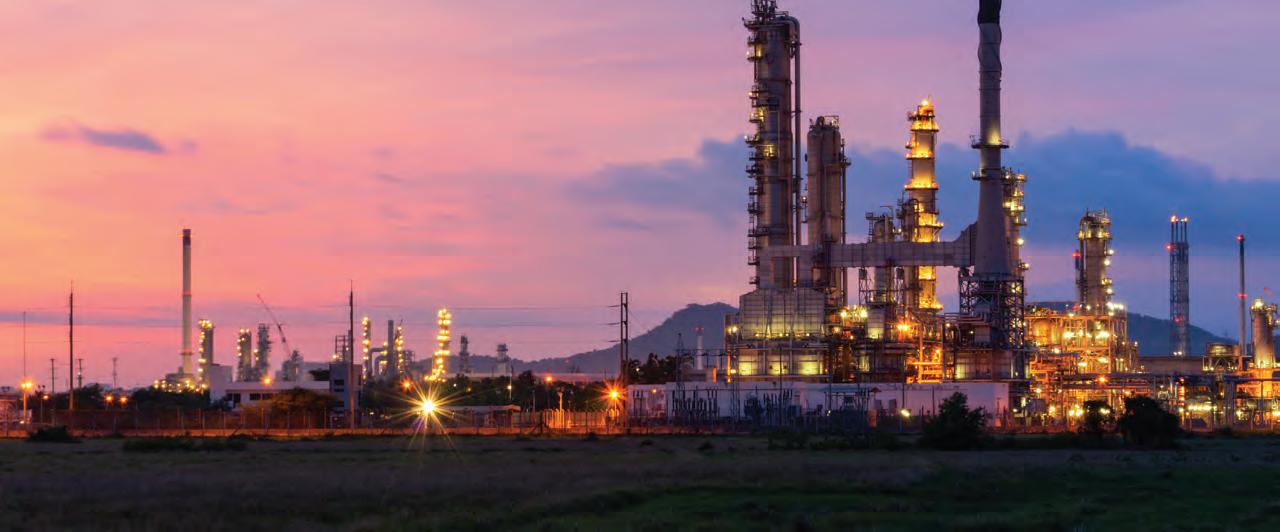
Technical excellence and operational improvement for the sulphur and sulphuric acid industries
Returning live to The Hague this October
Hybrid for 2022
Now in it’s 38th year, the event continues to be an essential annual forum for the global sulphur and acid community to learn, connect and do business. You can expect an expanded market outlooks agenda, including expert insights from CRU’s analysis teams on major supply and demand markets, including sulphur, sulphuric acid and phosphates, plus additional industry updates from key players from across the supply chain.