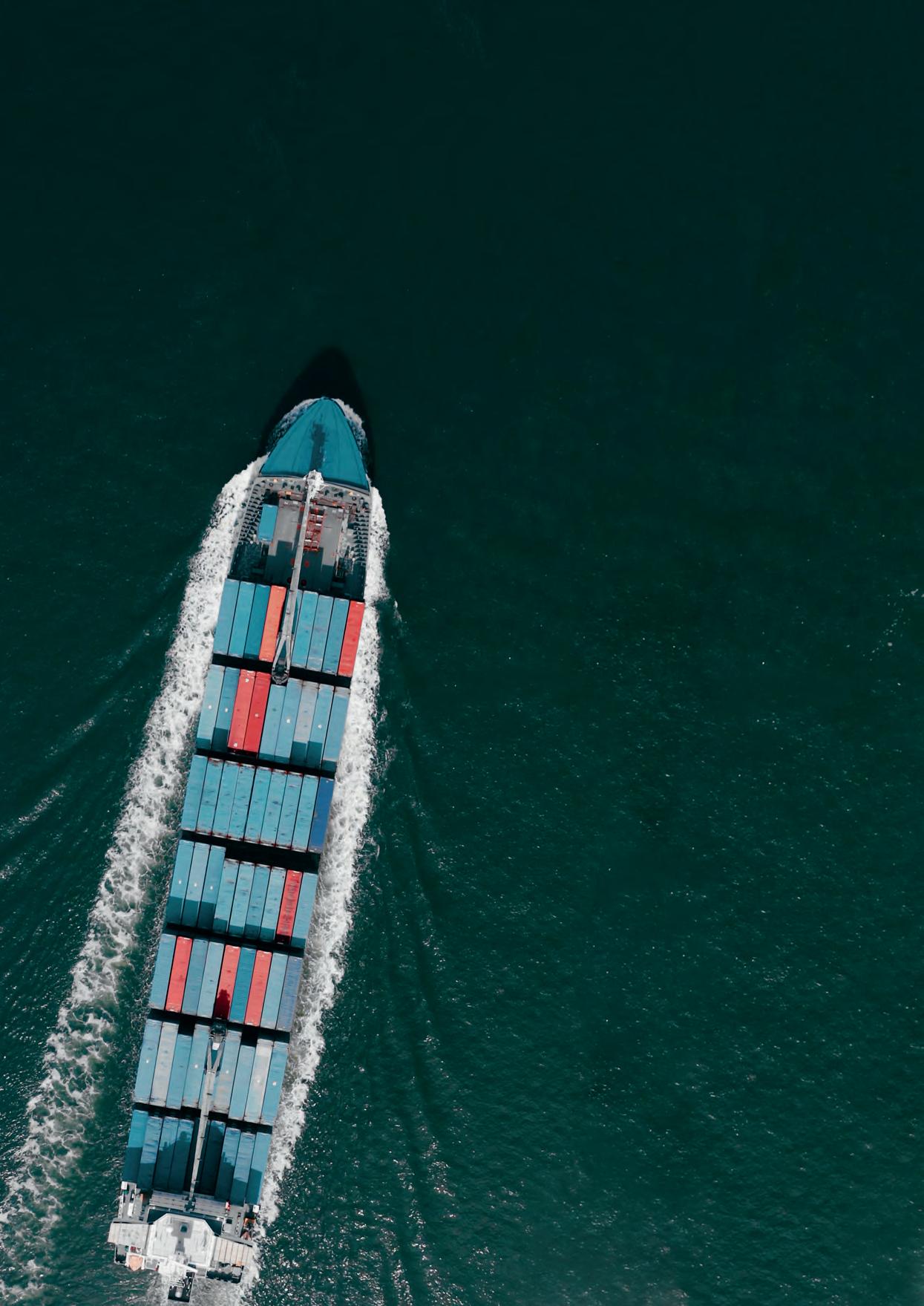
7 minute read
Shipping’s new scene
Giacomo Rispoli and Alessia Borgogna,
MyRechemical, Italy, discuss the use of low-carbon methanol from waste as a new fuel to help decarbonise the shipping sector.
Global emissions related to the transport sector accounted for 7.2 billion t of carbon dioxide (CO2) in 2020. The transport sector is indeed one of the most challenging sectors to decarbonise. Nevertheless, in the last decade, a strategy identifying the most suitable approach to addressing the environmental impact of different modes of transport has been shaped. For example, the sector is expected to move towards electrical mobility in the case of cars, as electric engine technology is able to maintain a similar standard as combustion engines for small vehicles. However, this option becomes unfeasible when applied to heavy cargo transport, as electric engines are still not suitable for vehicles of this size.
The shipping sector alone accounted for the production of approximately 825 million tpy of CO2 in 2020. The European target is to reduce the shipping sector’s greenhouse gas (GHG) emissions by at least 75% by 2050. The solution that has been chosen is fuel substitution with low-carbon methanol. As evidence of this, one of the most relevant shipping companies has just declared the addition of eight large ocean-going container vessels that are capable of being operated with low-carbon methanol. Methanol has the potential to be a sustainable alternative fuel, blended into gasoline or used directly as it is, for fuel cells. It has been definitively selected as the most promising alternative marine transport fuel due to its following features: n It is essentially sulfur-free. n It has a high energy density, meaning that it is easily storable. n It emits a low quantity of CO2 per energy content. n It has much less impact on marine wildlife. To be as harmful as conventional gasoline, more than 5000 times its volume would be required (see Figure 1).
The main GHG and air pollution emissions reductions are also summarised in Figure 2. A clever solution for the production of low-carbon methanol is using waste and recovering the carbon and hydrogen that would have been disposed of. Specifically, the waste-to-methanol process converts non-recyclable waste into methanol. The main pioneering aspect of this process is the link between the waste and chemical industries, which are not traditionally connected to one another. Gasification converts solid waste into syngas – a gas mixture that is familiar to the chemical world. Tailored cleaning and purification sections allow for the management of the variable pollutants that are contained in waste in order to meet strict requirements related to chemical synthesis. A dedicated conditioning section is reserved to meet specific syngas composition requirements for methanol synthesis. The overall block scheme is depicted in Figure 3. The following section will introduce the technology in detail.
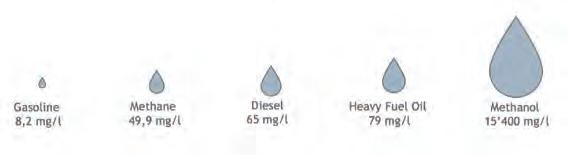
Figure 1. Fatal dose of different marine fuels for fish (source: Methanol Institute). Figure 2. GHG and emissions reduction (source: Methanol Institute).
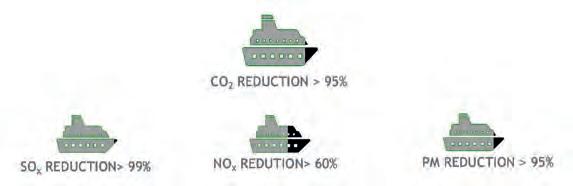
The waste-to-methanol process
High-temperature melting conversion is the core step in the process. This reactor is able to convert the
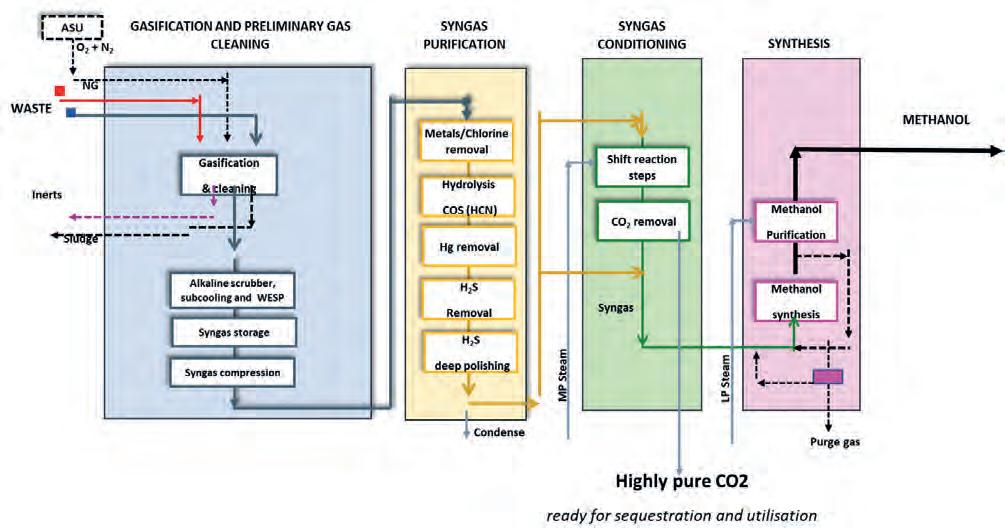
Figure 3. Block scheme of a typical waste-to-methanol process.
combustible fraction of waste into syngas and, at the same time, to melt the inert fraction (which is usually not negligible in waste materials). To this end, partial oxidation occurs by means of pure oxygen in order to reach higher temperatures rather than applying air. The reactor is composed of three zones (see Figure 4): n The melting zone: where oxygen is fed by promoting the exothermic oxidating reactions which convert the solid waste into gas, thus producing the heat required to reach a temperature higher than 1600°C, allowing for the melting of the inert fraction. n The partial oxidation zone: where the balance of gasification reactions results in the further conversion of the combustible fraction, as well as a reduction in the average working temperature (600 – 800°C). n The stabilisation zone: where gas flow – once produced by the lowest zones – is further oxidised in order to increase the temperature up to 1200°C, producing valuable syngas that is free of long chain characteristics of gasification processes (TAR) and far from the thermodynamic stability condition of some harmful compounds such as dioxins.
This valuable composition is freezed as it is, by means of an evaporating quench, which ensures the abrupt change of temperature from 1200°C to 90°C. The quench is the first step of the syngas cleaning section, which is supplemented by two scrubbers working under different pH conditions, promoting the precipitation of mineral matters – including the potential contaminants still entrained into gas.
Electrostatic precipitators are also part of the cleaning section, and these ensure the removal of potential residual particles. A critical step is then reached, as the syngas is now cleaned but remains unsuitable for the chemical synthesis system as this requires a completely purified gas stream in order to not poison the catalysts. A tailored syngas purification section is therefore added into the scheme to achieve a very polished syngas as required by catalysts’ application. Syngas also has to be conditioned. In other words, syngas composition, in relation to the main components (i.e. hydrogen, carbon monoxide [CO], and CO2) has to be modified to meet the requirement set by the stoichiometry of the methanol synthesis reaction. By way of waste gasification, a syngas with a methanol module ([H2 - CO2])/[CO + CO2]) close to 0.5 is produced. Instead, a value of 2.1 is normally applied in industrial methanol synthesis. The target value can be reached by the combination of a water gas shift – which enhances the hydrogen content by converting CO in CO2 – and CO2 removal. By applying an amine separation system, pure CO2 is recovered, ready to be further applied, or liquified and then stored.
The proposed scheme allows for the production of approximately 1 t of low-carbon methanol for 2 t of waste. Compared to methanol produced by methane steam reforming, 270 kg of methane is avoided for each ton of methanol.
Additionally, the waste-to-chemical system avoids the disposal of waste via landfill or incineration. By using this solution, more than half of the carbon contained in waste is converted into a new product: methanol. According to the Renewable Energy Directive, the methanol produced from waste can be categorised as advanced biofuel (if the original carbon is biogenic), or recycled carbon fuel (if the original carbon is fossil-derived). The distinction between the biogenic or fossil origin of the feedstock can be retrieved by C14 analysis applied directly to the methanol produced. Refuse-derived fuel – a product of unsorted municipal solid waste – typically contains approximately 50% biogenic carbon and 50% fossil-based carbon. Approximately 50% advanced methanol and 50% recycled carbon methanol is produced from material that is literally wasted.
When continuous and green power is available at a cost of lower than €40/MWh, the methanol module can be adjusted by adding hydrogen from electrolysis, thus avoiding the shift of CO to CO2 and converting all of the carbon contained in waste into methanol. The advanced waste-to-methanol scheme has further benefits. First, the yield is doubled: from 1 t of waste, 1 t of methanol is produced. Furthermore, and most importantly, zero CO2 is produced.
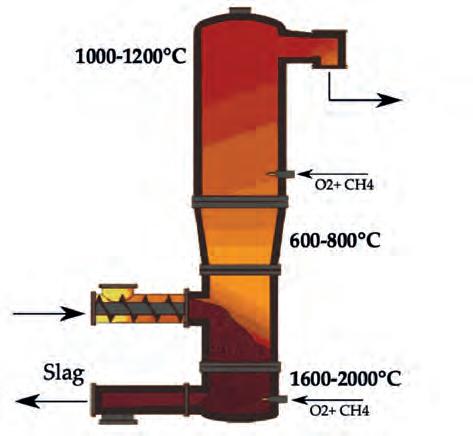
Figure 4. Longitudinal cross-section of the high-temperature converter.
Conclusion
The waste-to-chemical process is a tailored and elegant link between the world of waste conversion and chemical or fuel production. The technologies through which it is composed are already available and commercially-proven at industrial-scale. The waste-to-chemical process is, indeed, a ready-to-build alternative solution for non-recyclable waste management. Notwithstanding the novelty of the waste-to-methanol scheme, it is already an economically-attractive solution. The income for this process comes from both feedstock (waste) and product.
Furthermore, the methanol produced by this process is specially categorised, and is therefore able to access a sustainable methanol market, which ensures a significant additional remuneration. As such, it is possible to achieve a return on investment with this novel technology in a short period of time.
The fusion of waste disposal and methanol production in a unique overall process allows for the reduction of emissions related to each single process. This solution is already available and sustainable – both from an industrial reliability and economic point of view. Furthermore, the waste-to-methanol scheme integrated with green hydrogen will enable the conversion of waste, the production of methanol, and the storage of renewable power – without any CO2 emissions.