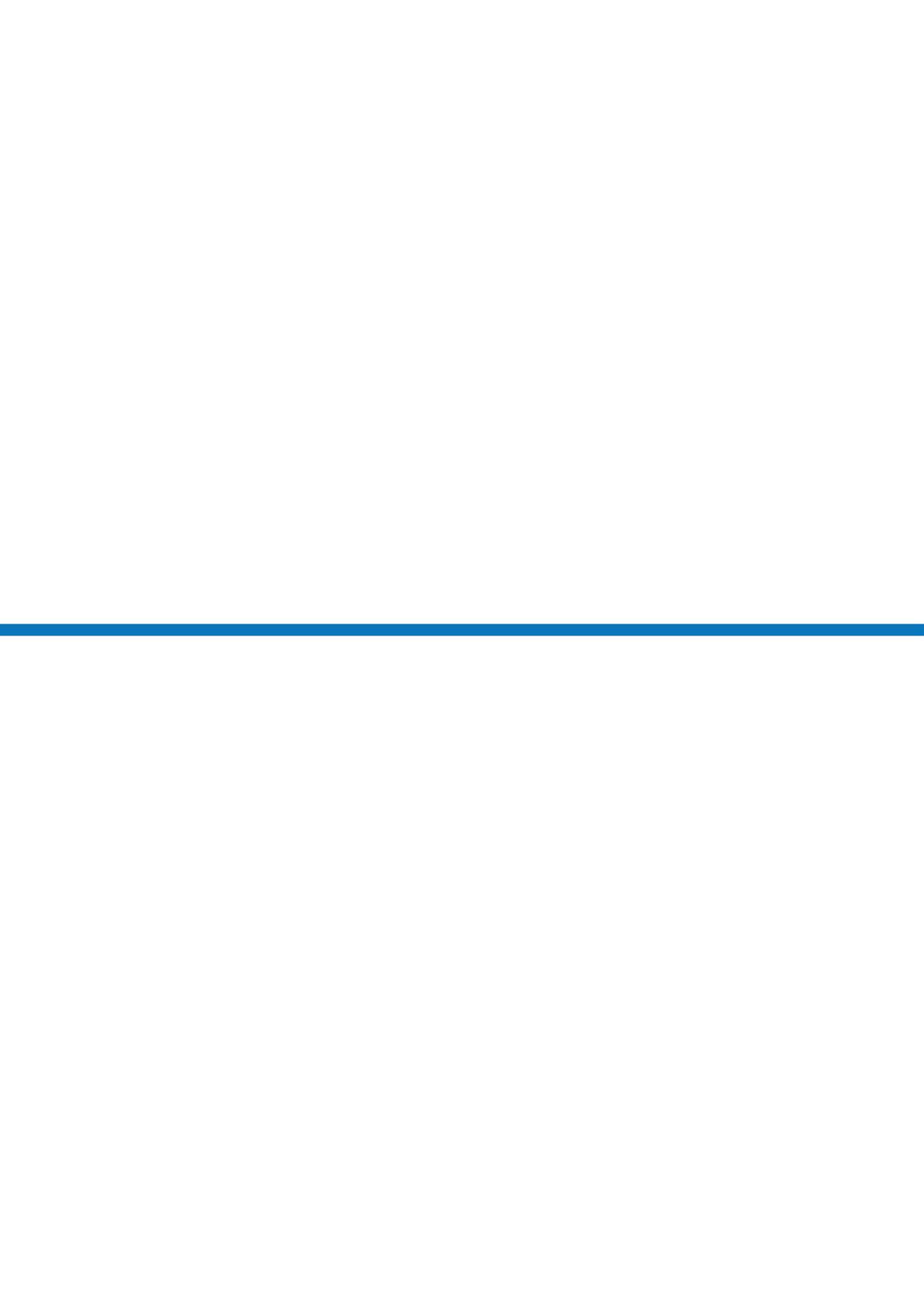
8 minute read
The secret to safety
There is nothing more important to US fuel refiners and petrochemical manufacturers than the safety of the people who work at the sites and live in neighbouring communities. Members of these industries invest significant resources in safety programmes and practices – all aimed at preventing process and occupational safety incidents or injury to employees; mitigating risk and impact; and coordinating with emergency responders and communities. Every person across these facilities plays a role in the American Fuel & Petrochemical Manufacturers (AFPM)’s collective mission to continually improve safety performance and risk management practices.
Some of the greatest process safety improvements that have been witnessed have occurred within the last 15 years. At both refineries and petrochemical facilities, there has been a more than 50% reduction in reportable process safety events; a key reason for this is cross-industry collaboration.
Efforts to formalise collaboration among the fuel refining and petrochemical industries, including launching a number of process and operational safety programmes, are making people and communities safer. In fact, over the past two decades, these industries have been ranked safest among all manufacturing sub sectors.
Safety is not proprietary
The AFPM’s commitment to collaboration across industry took on a whole new level of seriousness around 2010. Data at the time showed that individual member companies and facilities were making good improvements to their own operational safety performance, but there was a simultaneous uptick in serious incidents that was not acceptable.
Industry leaders saw the trend and wanted to turn it around. Jerry Wascom, ExxonMobil’s Americas Refining Director, reached out to AFPM to ask how to step up to better protect people. That conversation led to a paradigm shift in AFPM’s approach to safety, and it planted the seed for what has become an umbrella programme called Advancing Process Safety (APS).
Jerry Wascom was a fitting person to jumpstart the effort. He was 18 when he got his first job as a refinery operator and served in a number of roles at the facility level earlier in his career. One of Jerry’s first collaborators was Jim Mahoney, then Executive Vice President of operations at Koch Industries, and a future chairman of AFPM’s board.
Both men identified the existence of company and facility siloes in the safety space as a barrier to industry improvement. If facilities and process safety leaders could pool their knowledge and share how certain sites had achieved improvement and what tools were most helpful in driving results, Jerry and Jim knew that industry could take leaps forward in safety performance.
Data sharing would be at the core of this new approach. This is remarkable because the tendency in competitive businesses is to keep a lot of information proprietary,
Lara Swett, American Fuel & Petrochemical Manufacturers (AFPM), USA, explains why collaboration is a top driver of safety improvements in the oil and gas industry.
however it was decided that safety needed to be the exception. If the learnings from an incident at one site could be shared, other sites would be able to proactively review the details and assess any potential vulnerability of their own. They would then be able to affect change before problems developed, preventing other possible incidents from occurring and keeping people safe – both onsite and beyond the fence line.
Collaboration was and is the most powerful thing that can be done to promote safety, and trade associations such as AFPM are in the perfect position to facilitate cross-industry engagement. For refiners and petrochemical manufacturers, safety is not proprietary, but rather a core value.
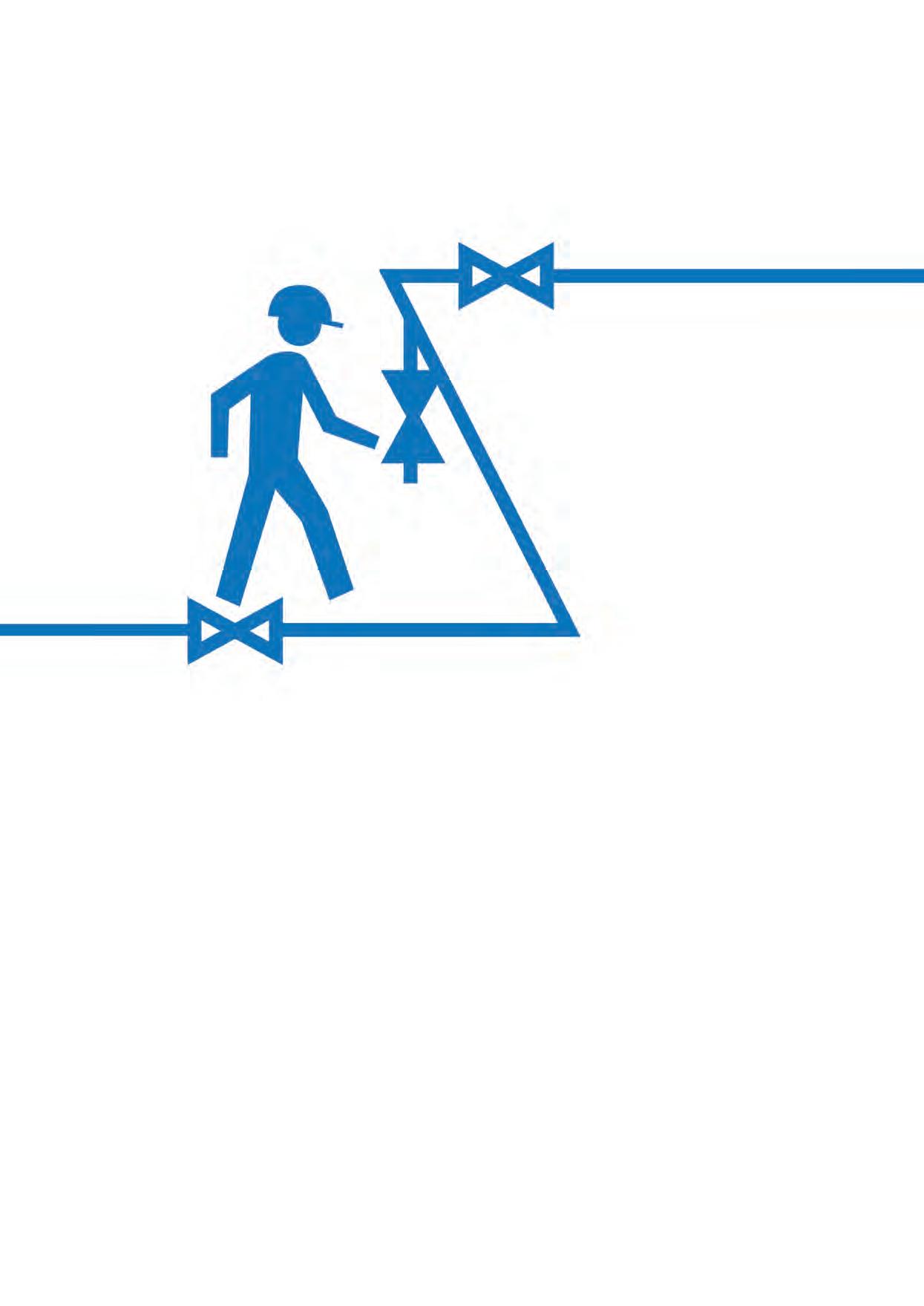
The evolution of advancing process safety
What began as a conversation between Jerry and AFPM, and then Jerry, Jim and AFPM, grew to a slightly larger group of 20 company representatives from throughout the refining and petrochemical industries. The group convened for the first time in 2010, kicking off APS and cementing the industry’s culture of collaboration on safety.
In subsequent meetings, the team took a more holistic look at industry process safety data, analysing it for macro trends and potential risk factors. To go from data to action required input from employees who manage safety on the ground at refineries and petrochemical sites. From there, resources and a library of good safety practices were developed to enrich facility programmes industry-wide.
In the years since that first meeting, the APS programme has been a resource for more than 200 companies. Over 3500 industry employees have directly taken part in APS programme activities and trainings. Today, APS is the umbrella for a number of sub-programmes that help refiners and petrochemical manufacturers to continuously improve their safety performance. These supporting programmes cover incident sharing, site assessments, and hazard identification tools, and present opportunities to share practices and more. The programmes include: n Walk the Line. n Process Safety Regional Networks. n Process Safety Site Assessment programme. n Hazard Identification/Practice Sharing Subgroup. n Mechanical Integrity Subgroup. n Human Reliability Subgroup. n Industry Learning and Outreach Group.
Figure 1. Iconography that often accompanies the Walk the Line programme.
APS at work: data reveals a need to ‘Walk the Line’
If you had to guess the number one cause of serious process safety events, do you know what you would answer? Mechanical failures? Natural disasters? What about honest human mistakes? Early APS data made clear that the last point regarding human organisational performance is the answer. About one-third of safety incidents at refineries and
petrochemical sites are due to operator error, often when ‘bleeders’ or valves are left open. More than half of serious safety events stem from similar mistakes.
Without the data check, it would have been easy for APS leaders to assume that training basics were in good shape and technical or mechanical improvements should be the focal point of combined industry efforts. The numbers said otherwise, and so it was clear that more resources needed to be fed into workforce training and safety fundamentals to limit future mistakes and the potential for mistakes to cause incidents.
Operational readiness lapses and very preventable line-up errors involving pipeline valves were responsible for a number of safety incidents. Based on that, it was determined that operators working during equipment commissioning, draining, and loading and unloading activities would be most likely to benefit from additional training and safety practices. AFPM took it upon itself to address the industry-wide challenge together.
These efforts came to fruition in 2015 with the launch of the APS practice sharing sub-programme, ‘Walk the Line’. Jerry Forest, Senior Director of Process Safety at Celanese, led the early efforts to identify and source a pool of proven resources and practices to equip facilities, operators and front-line supervisors with a collection of trainings, exercises and tools designed to help operators be successful in their work, and reduce human error. The way it was seen was that if incident data sharing and analysis was able to help those in the industry to spot larger problem trends, Walk the Line would use that same data to provide key solutions.
At its core, Walk the Line reinforces the fundamental responsibility of every facility-level operator to know with 100% certainty that valves are in the correct position, that material in process units is where it should be, and that material will flow in the correct direction when a unit starts up. If there is any question on those points, operators need to ‘walk the line’ and check everything again.
With its robust and growing shared resource library and rigorous focus on mastering the basics, Walk the Line is about practicing what you preach. AFPM espouses a safety culture where errors are reduced and every operator and front-line supervisor has the tools and training that they need to readily collaborate and mitigate operational risks. Walk the Line is the toolbox, and to date, there are over 94 practices, trainings, exercises, presentations and videos available to the programme’s participants.
Each of the tools, recommendations and resources made available have been tested at actual facilities, and more than 500 safety professionals and experts have had input. These programmes work because they are operator-centric and customisable at the company and even site levels.
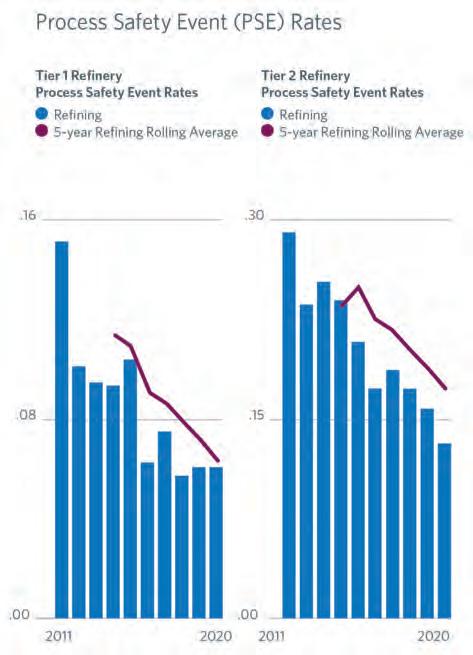
Figure 2. Both the fuel refining and petrochemical industries have made significant improvements in safety performance.
Collaboration beyond refining and petrochemicals
The learnings gathered across APS programmes are not restricted to just the fuel and petrochemical industries. AFPM shares information with the independent government agency in charge of investigating industrial incidents to foster smoother, more effective collaboration around the shared goal of keeping people safe.
Other industries and government partners are taking note of the success of AFPM’s safety programmes and are seeking to apply its good practices more broadly across the manufacturing sector. Over the course of the last year, AFPM has worked with organisations and government partners such as the American Gas Association, the American Petroleum Institute (API), the Center for Chemical Process Safety, the Chemical Safety Board, and the Occupational Safety and Health Administration (OSHA) to share good practices derived from these programmes.
Beyond what the industry does to advance safety within its facilities and through APS and its supporting programmes, refiners and petrochemical manufacturers work within their local communities to increase safety in a number of ways, ranging from donating equipment to volunteering and training emergency responders.
A continual pursuit of improvement
‘Process safety’ is not a status that sites achieve; it is a core value in our industries that requires every facility to commit to a continuous, daily cycle of safety improvement. Sites incorporate new tools and adopt different practices as technology improves, as sites learn from their own experiences and audits, and as information and learnings are shared by industry peers. Every refinery, petrochemical facility, and company is expected to play a part, because more can be accomplished by sharing.