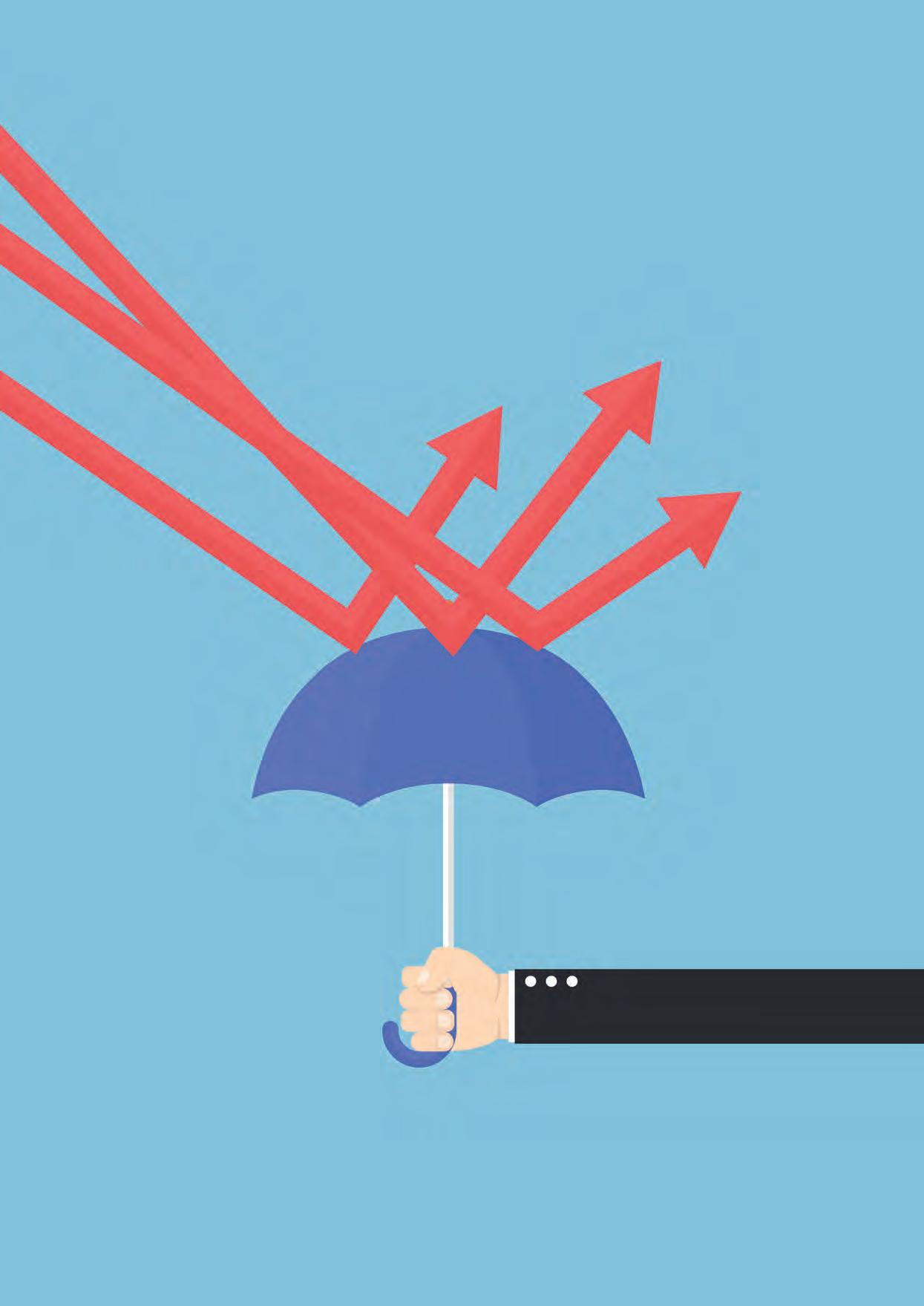
10 minute read
Manage to mitigate
Stephen Anderson, Daniel Walker and Andrew Jackson, Intertek,
examine how to manage the quality risks associated with LNG construction projects.
COVID-19 has had significant implications for construction projects and CAPEX programmes around the world. The pandemic has shown us how fragile our supply chains are and how quickly our well-laid plans can collapse. Project managers, contractors, subcontractors, labourers and suppliers have all been affected, resulting in capital project delays, loss of quality, lower efficiencies, and impacted costs.
One of the largest areas of global capital investment is the LNG market, which is emerging as the hottest sector in the energy industry. This includes soaring demand for US LNG as global trade routes are upended and some long-stalled US export projects come back on track. However, rising costs for materials and labour threaten to slow these projects, but are not likely to halt new construction. Wall Street analysts now expect
four multi-billion-dollar plants to be approved in 2022, vs a previous projection of just two or three plants.1 As new LNG projects move forward, the pandemic has taught the industry to have good risk management programmes in place and to consider all eventualities, such as disruptions to the supply chain; potential insolvency and bankruptcy of suppliers and vendors; and delays in getting personnel to fabrication sites and obtaining permits.
To mitigate such challenges, risk-based data analytics tools can manage quality oversight and planning of LNG project vendors and supply chains in order to minimise procurement delays. Remote video inspections (RVI) can also help to alleviate personnel shortages and access issues. Finally, to minimise costs, modular units are being fabricated on LNG projects, and specialised dimensional control techniques can help to ensure modular quality and a single weld philosophy for piping.
Customised dashboards provided through risk-based data analytics tools can be utilised to provide procurement assurance, quality control tracking/transparency (live-time quality control access), and a foundation for the inclusion of construction and operations data such as commissioning and metrology. The assurance and control findings can be viewed in a ‘virtual’ environment for a full life cycle understanding of the asset construction and operation.
Intertek, a Total Quality Assurance provider to industries worldwide, is currently providing quality assurance services for many of the world’s major LNG projects. Such services help to ensure project efficiency, maximise quality, and improve safety – while minimising risk and costs. In addition to the company’s RiskAware analytical tool that provides advanced vendor and supply chain data, this article will also discuss LNG infrastructure and modular construction support (surveying, laser scanning, and dimensional control), as well as quality assurance services and RVI.
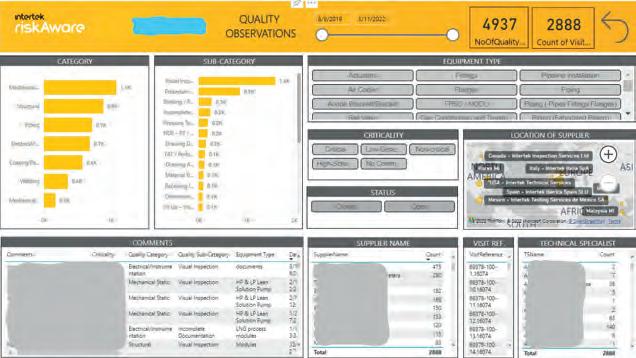
Figure 1. Supplier quality observation dashboard.
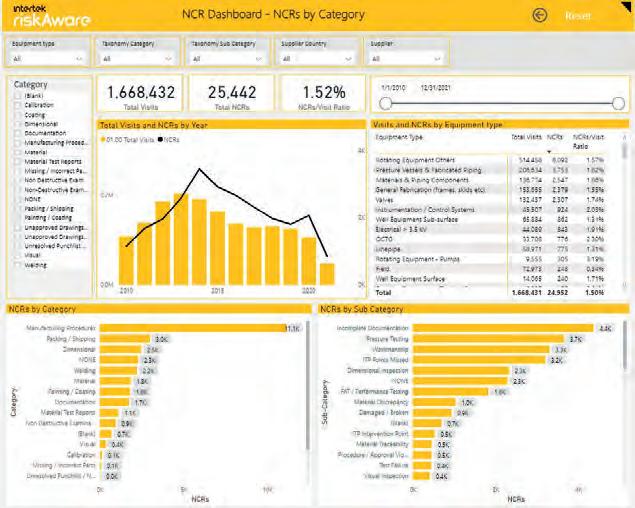
Figure 2. Supplier non-conformance summary dashboard.
Risk-based data analytics
The RiskAware analytical tool helps global LNG equipment purchasers to minimise the total cost of quality by using the lens of data analytics to focus on high-impact quality and safety risks in their supply chain. LNG project purchasers require supplier inspection programmes to be efficient and transparent. By using risk-based data analytics to pinpoint risky areas within a quality programme, it is possible to optimise supply chain strategies. Risks arising from delays to production schedules, cost escalation and the late arrival of equipment can be mitigated through robust and proactive quality control programmes. This is complemented by vendor surveillance activities and overall assessment and monitoring of the supply chain suppliers. The programme produces optimised and integrated quality assurance and quality control (QA/QC) activities, which can be achieved most effectively by apportioning vendor inspection spend to higher-risk areas in comprehensive vendor assurance plans.
RiskAware provides the data and analysis that enables implementation of risk-based vendor assurance plans that minimise LNG project total cost of quality by avoiding costly and disruptive delays, significant rework costs and non-compliance issues. The cloud-based solution identifies quality and safety risks, which helps companies to optimise their quality and inspection programmes.
The programme provides a range of data analytics and reporting. Typically, this data is shown in dashboard format (see Figure 1), highlighting quality observations at hundreds of global suppliers. These observations are used to
proactively identify issues before they become non-conformances, especially non-conformances that could cause project delays due to the need for rework, repair or replacement.
In addition to proactive quality observations, Intertek uses historic and ongoing non-conformance report (NCR) counts (% rate per number of visits), which can then be analysed by country, supplier and NCR categories (see Figure 2). This analysis can be used not only as a historic data-based reference to give a high-level indication of supplier ‘risk’, but also to create risk-based vendor inspection plans.
Quality assurance of LNG modular units
For new LNG construction sites receiving components that have been fabricated as single modular units or in different geographical locations, dimensional control (DC) is an essential, accurate and efficient process that will provide certainty for problem-free fitting, or identifying potential dimensional issues that can be dealt with prior to installation activities.
The dimensional control process uses a calibrated total station survey instrument (accuracy 1/32 in.) with a built-in data capture facility to obtain the field data. The Intertek Data Integration Management Engineering System (DIMES) 3D Calculation and Cluster (Bundle Adjustment) software, supported by AutoCAD, facilitates the calculation and deliverable preparations.
For LNG modular build and installation, it is important to consider the following: n Experience shows that if the LNG plant construction philosophy is individual modular units, and a single weld philosophy is applied, this greatly increases the DC surveying scope of work. Building modular trains (as opposed to individual units) is the most cost and schedule efficient method available, and greatly condenses the amount of DC that is required. n Different fabricators have a variance within their DC experience, knowledge, abilities, instrumentation and software. Often, DC procedures are generic rather than project specific. It is important that the fabricator understands the tolerances and the overall objectives of the project. In addition, when fabricating outside, there can be challenges with the environment including deflection issues from the sun, and temperature expansion and contractions. This should be an area that is well covered within the DC procedure. n Do the design tolerances for fabrication, construction and installation ‘stack-up’? Do gauge tolerances match bolt-to-bolt hole design clearances? n The layout of modular datums is very important as they must relate to the structural frame as-built so that the built errors are split out and the best-fit datums are established. It is not practical to just accept that the steelwork is good enough to reference pipe dimensions.
A best-fit centre line (longitudinal and transverse) is very important in considering the global picture and not the single unit. n Depending on the site and modularisation design, pre-installation ‘clash checks’ around the outside parameter of each module would be useful, as this may identify hard clashes or close proximity concerns during the installation stage.
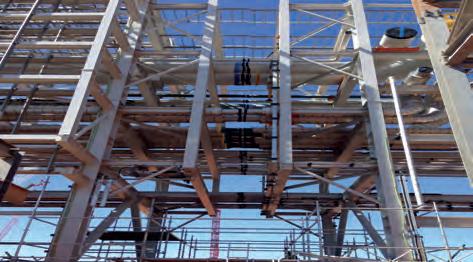
Figure 3. Scanned modular units being joined together using Intertek’s single weld philosophy.
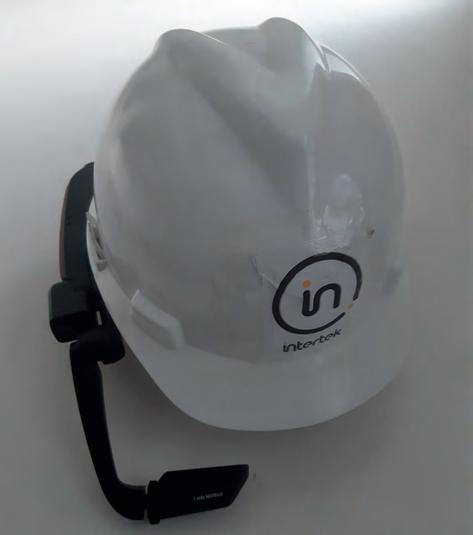
Figure 4. Intertek’s smart glass RVI solution.
RVI
The COVID-19 pandemic exacerbated the problem of placing inspection personnel into LNG project and fabrication sites. One solution to this is the use of RVI. Intertek has experience working with RVI, and works with a range of smart glasses and augmented reality (AR) technologies. These glasses have several applications, including: n Supervision: senior inspectors can monitor technical specialists from one location via a video link to maximise their experience and product knowledge, resulting in a more streamlined inspection, and allowing materials to be expedited more efficiently. n Witnessing: live video stream of inspection and audits are available for clients to remotely attend the
inspection, following the technical specialist and directing them through each inspection step. Clients are able to interact with the technical specialist to ask questions and visualise the experience. n Evidence: recordings of the inspection process from the technical specialist’s perspective are available to be viewed at a later date by the client. This will allow for a more detailed visualisation of the inspection process and an invaluable enhancement of the auditing process. n Monitoring: in circumstances where the manufacturer agrees, remote inspections can be carried out with cameras positioned at the manufacturing location, with the technical specialist monitoring the activities from a remote location. This could reduce the overhead costs associated with the inspection process (such as travel costs), and would be beneficial for inspections carried out on lower criticality materials and equipment, as well as those with less inherent risk.
RVI provides inspection coverage worldwide where travel is either not permitted, or deemed unnecessary for low-criticality and non-complex equipment. Intertek uses an enterprise-ready, agnostic mobile application, which runs on supported wearable and/or mobile devices. This has built-in security features that enable connectivity – even at low bandwidth – to inspectors, customers and vendors all at the same time, via 3G/4G/5G or Wi-Fi. All users can access virtual rooms, share documents on screen, take photos/videos, and add annotations where necessary (see Figure 3). Hands-free wearable devices are supported and navigated using simple voice commands to control them. Inspections can be recorded where requested if participants are unable to attend in person.
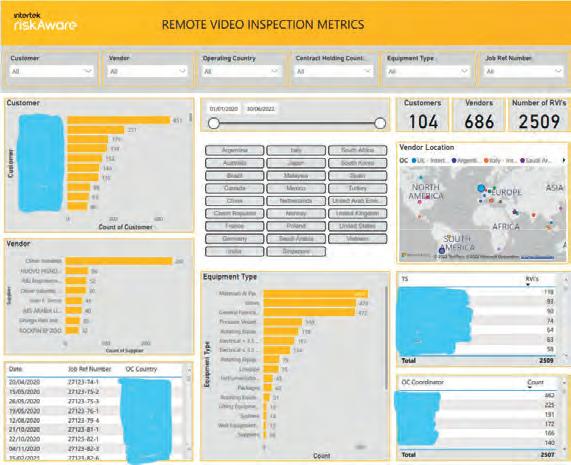
Figure 5. Global RVI dashboard.
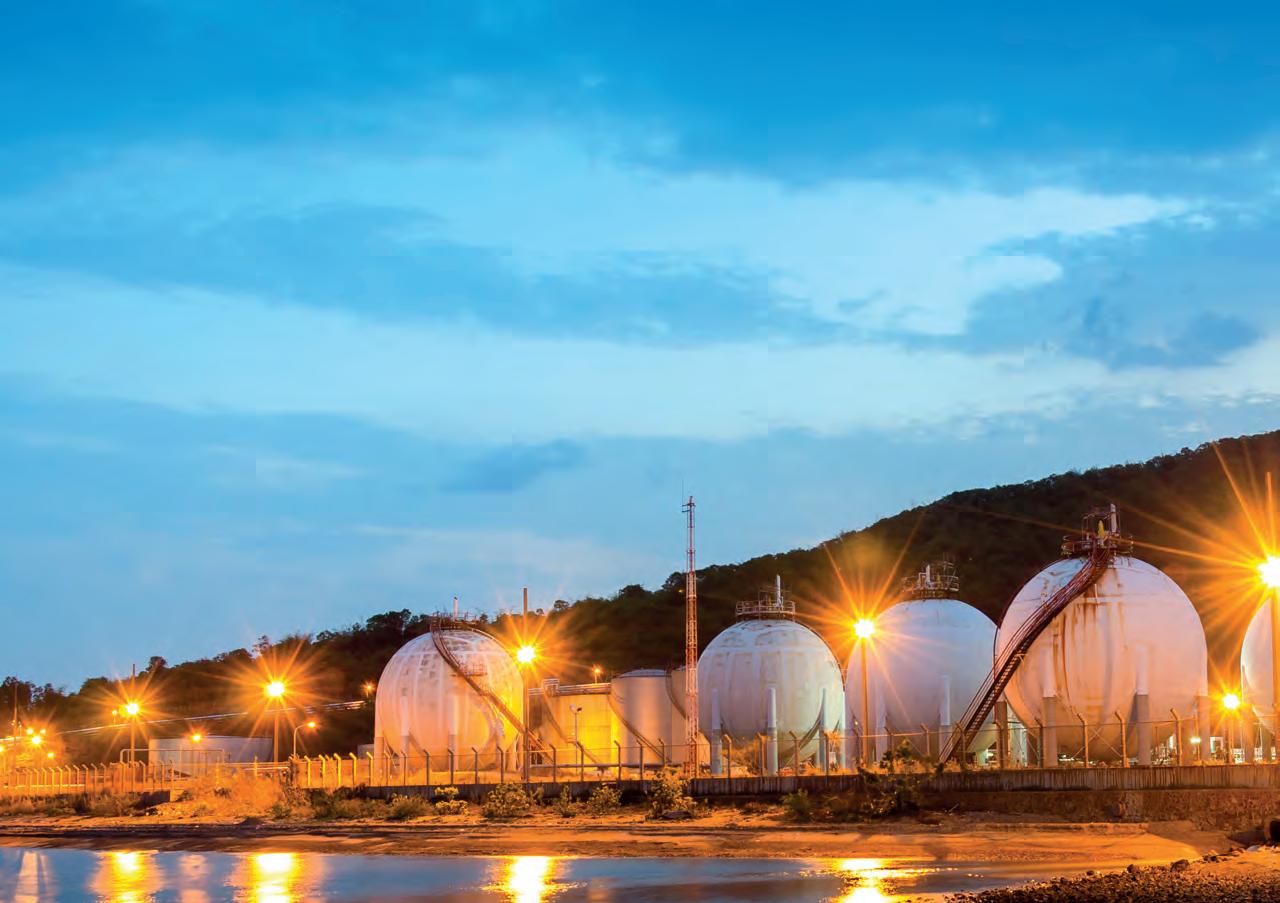
Benefits of RVI technology
n Cost reduction (for auditor or inspector travel expenses). n Improved auditor and inspector quality of life through reduced ‘burn out’ due to travel. n Validated audit or inspection integrity: the ability to validate via a recorded or live broadcast session. n Increased service quality through mentoring: shadow audits and inspections, witness audits, etc. n Business continuity: audits and inspections can still take place regardless of threat (weather, terrorism, travel delays). n Solution for clients with remote locations: potential to increase audit and inspection frequency with this approach.
When working on a recent global LNG project, Intertek calculated a saving of approximately US$100 000 in travel costs due to the use of RVI technologies. This also contributed to an overall reduction of the project’s carbon footprint. Intertek tracks its global RVI usage and key performance indictors (KPIs) using RiskAware to provide clients and managers with on demand analytical data.
Conclusion
There is currently tremendous worldwide investment in LNG and LNG facilities. The COVID-19 pandemic has highlighted the potential dangers and risks associated with these large capital projects. These risks include materials, personnel and regional supply chain issues. Intertek has provided quality assurance services for many of the world’s major LNG projects. As such, the company has developed a range of quality risk mitigation tools for the efficient and successful completion of such projects. The use of data analytics is key to identifying the risks related to manufacturers, vendors and regional supply chains. Understanding and managing these risks goes a long way in ensuring that projects stay on schedule.
Many LNG facilities are constructed as modular units, often coming from different geographical locations. As such, it is essential to understand dimensional tolerances and the use of the latest DC equipment and software tools. DC is an accurate and efficient process that provides certainty for problem-free fitting and identifying dimensional issues that can be dealt with prior to installation activities.
Finally, the shortage of qualified personnel, travel and access issues have highlighted the need for RVI to ensure project and equipment quality. RVI and testing complete a thorough risk-based quality assurance programme that ensures LNG project efficiency, maximises quality, and improves safety, while minimising project risk and costs.
Reference
1. ‘Rising Calls for U.S. LNG Revive Stalled Export Projects, but at
Higher Costs’, MarineLink, (21 April 2022), https://www.marinelink. com/news/rising-calls-us-lng-revive-stalled-export-495962
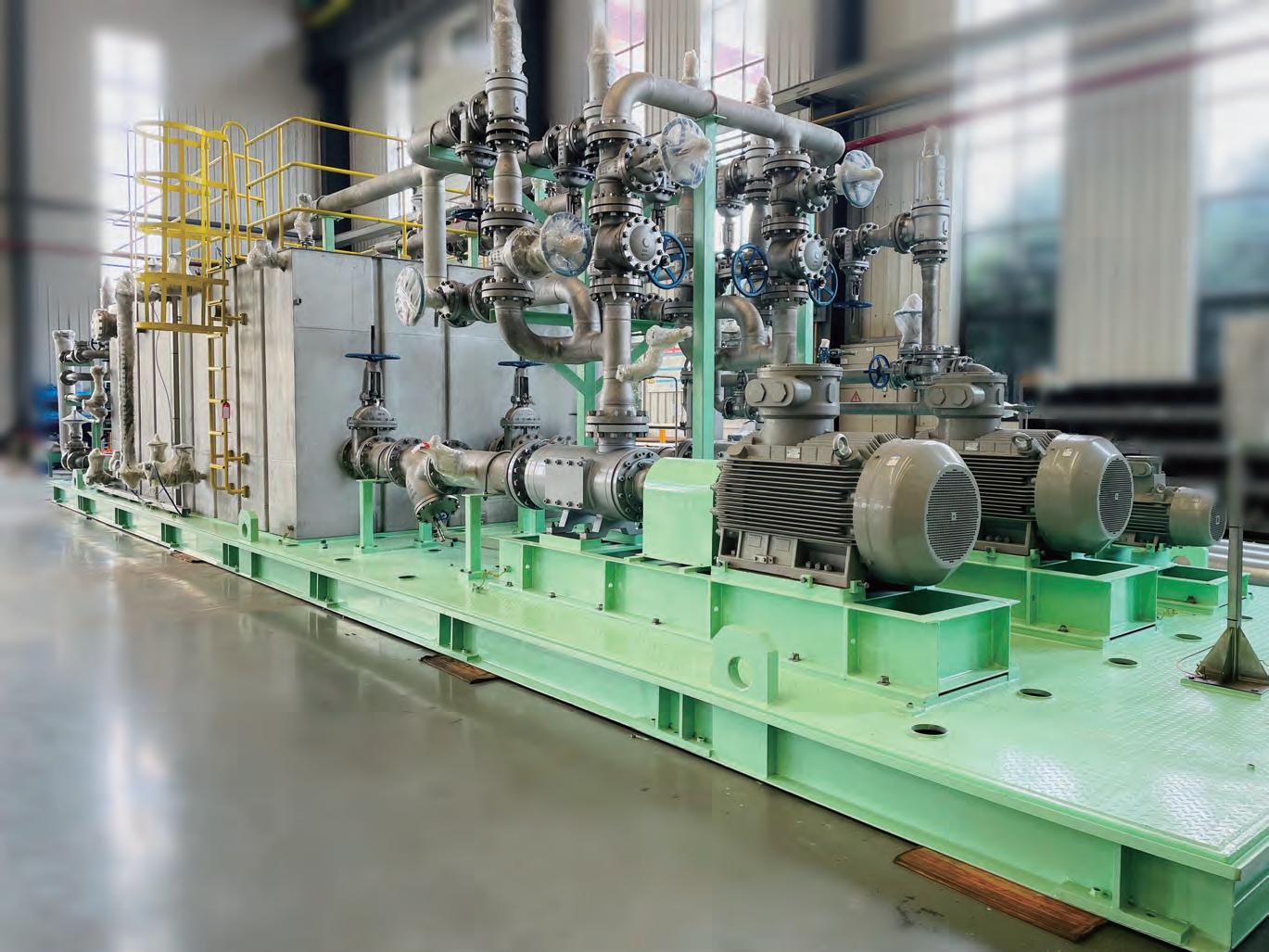
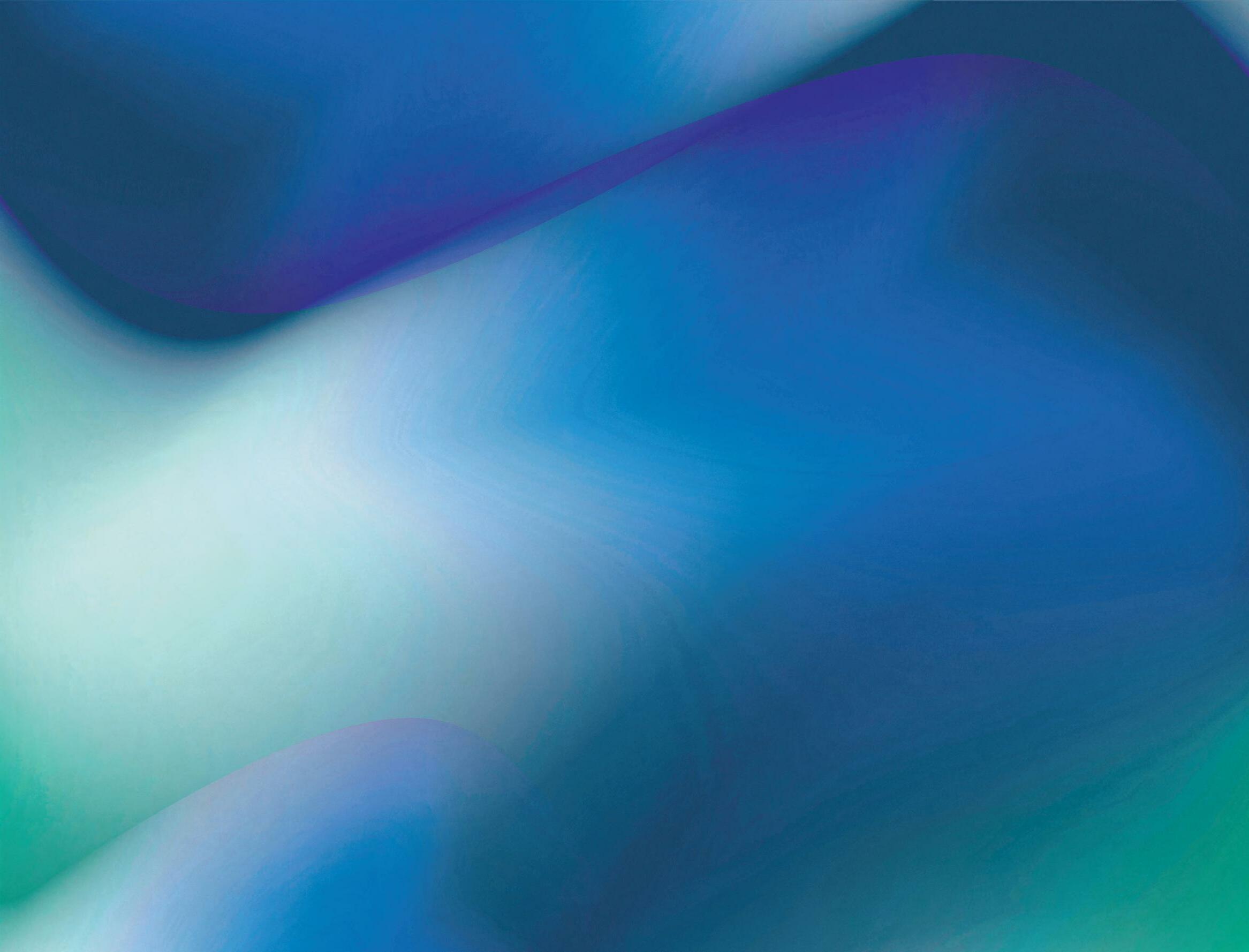