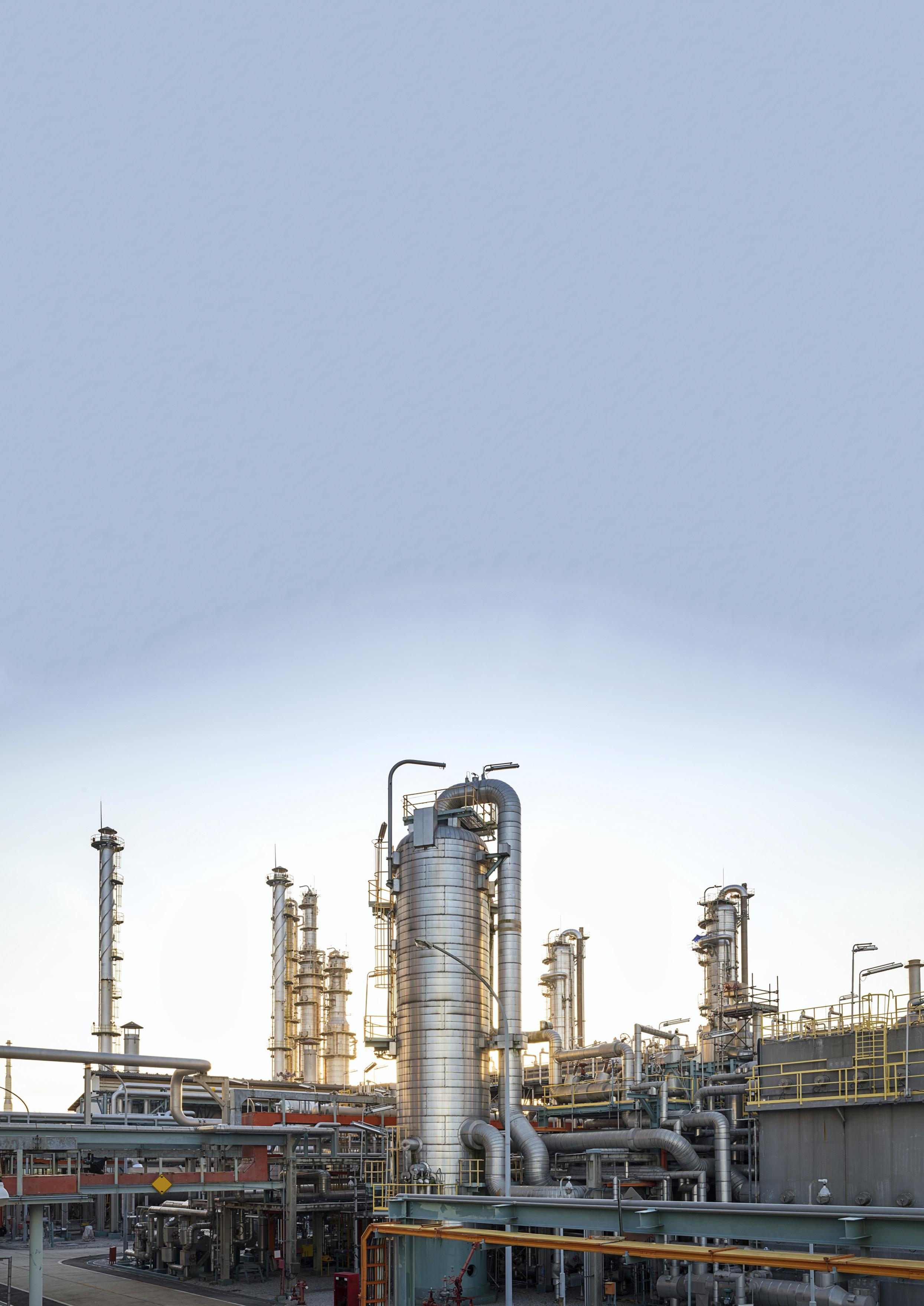
9 minute read
Delivering high-quality PTA
Rhys Jenkins, Servomex, UK, considers the role of gas analysis in purified terephthalic acid (PTA) production.
Purified terephthalic acid (PTA, sometimes referred to as polymer-grade terephthalic acid) is an important chemical component in the plastics industry. Together with ethylene, it is used to produce the high-demand plastic polyethylene terephthalate (PET), widely used as a polyester fibre and for recyclable food and drink containers, such as plastic bottles. There is a continuing and growing demand for PTA throughout the world, particularly in fast-expanding economies such as those found in Asia. Approximately 80 – 100 million tpy of PTA is produced, the vast majority coming from Asian plants, while China alone makes up 60% of the global demand.
The production of PTA requires expert gas analysis for process control, efficiency and safety, as well as quality monitoring and environmental compliance.
In order to deliver this wide range of measurements, a variety of sensing technologies are required. Not only do these sensors have to be accurate and react quickly to changing gas
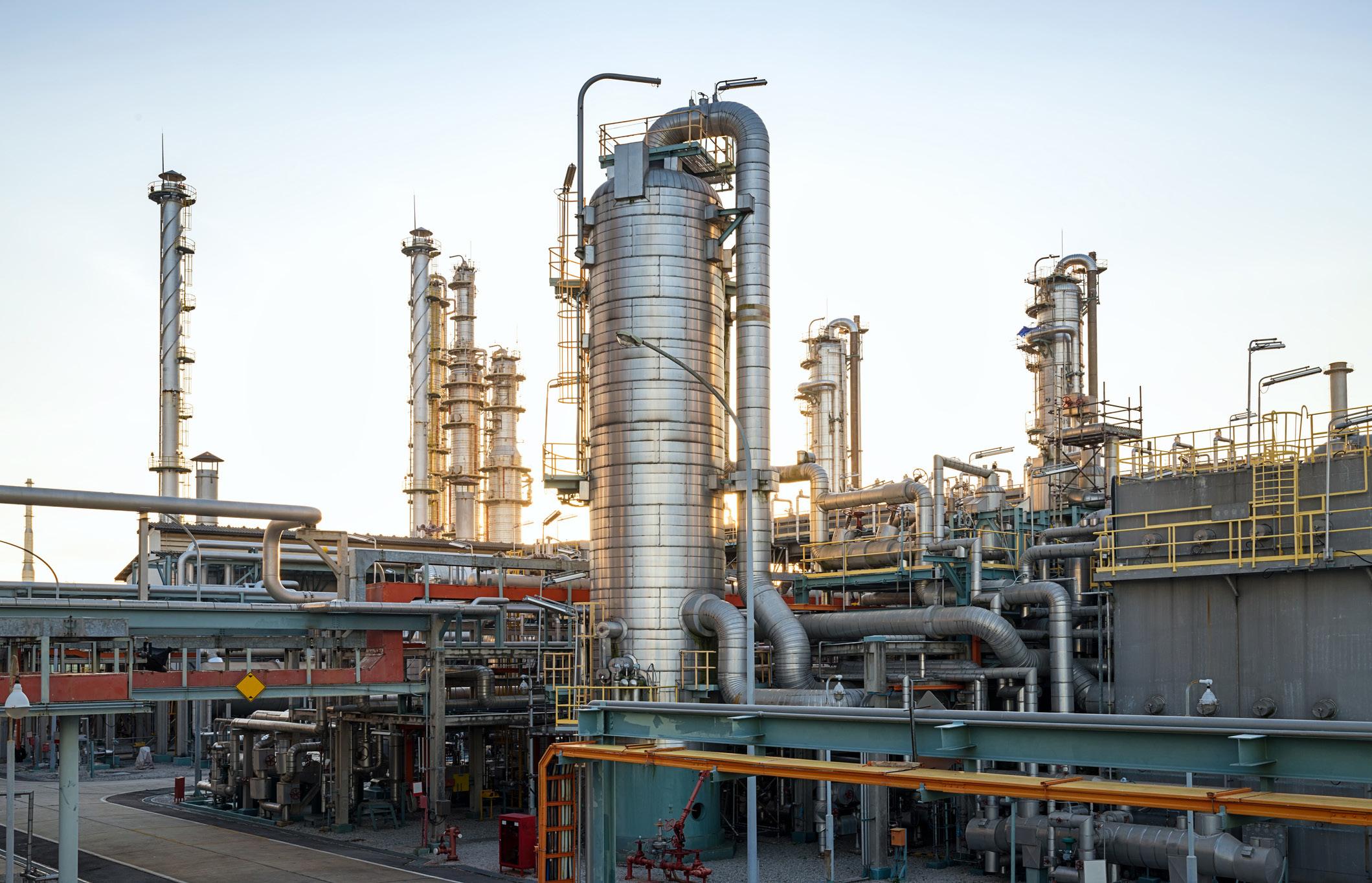
Figure 1. A PTA production plant.
concentrations, but they also have to be able to operate in the challenging – and often corrosive – conditions of the manufacturing process.
The PTA process and key gas analysis points
PTA is manufactured from the aromatic hydrocarbon p-xylene, which undergoes air oxidation in a reactor at high pressure and high temperature. Liquid acetic acid is used as the solvent for this reaction.
The crystalline PTA product is separated off in crystallizer vessels, recovered and purified. The oxidation reactors and the crystallizers are key points for gas analysis in the PTA process.
At the beginning of the PTA manufacturing process, air is passed into the oxidation reactors. This oxidises the p-xylene to form terephthalic acid while also generating carbon dioxide (CO2) and carbon monoxide (CO).
Some oxygen (O2) is likely to remain unreacted – it is critical to monitor this residual O2 level in the off-gas to ensure that it stays between 4 – 5%. If the level gets too high, sudden runaway oxidation of all the flammable materials could occur, leading to an explosion.
However, if the level drops too low, insufficient oxidation occurs, reducing efficiency and lowering product yield.
Monitoring of the air inlet to the oxidiser, and the level of unreacted O2, can be reliably handled by paramagnetic O2 analysers.
Speed of response and reliable accuracy are critical at this point. As such, to ensure reactor safety, multiple analysers are typically used, installed in a voting system. A voting system uses multiple analysers and depends upon the measurement of the majority.
In a three-analyser system, for example, if one analyser detects a significant change, it is outvoted by the other two and no action is taken. However, if two (or all) of the analysers detect a change, this reading is seen as correct, and action may be taken, such as informing the operator or automatically halting the process.
This approach provides an extra layer of reliability for safety measurements, and also helps detect analyser problems at an early stage – if one device is continually giving a different result, it can be investigated and corrected.
Measuring the off-gas CO2 level offers more information about the progress of the oxidation. This can be accomplished using an infrared (IR) analyser configured for CO2.
Next comes the crystallizer stage, where acetic acid is driven off as the PTA product crystallises out of the solvent liquor.
This vapour is extremely flammable, so a measurement of residual O2 – again made possible by paramagnetic sensing – is essential to warn of any explosion risk.
Measurement of CO2 in the vapour also provides an indication of any post-oxidation reaction. IR gas analysis can be used for this application, and also to measure water in liquid acetic acid, helping to control the recovery and purification of the solvent before it is recycled back into the process.
The nitrogen inert blanket in the PTA product driers and storage bins should also be monitored for very low O2 levels, using a certified paramagnetic O2 analyser.
In addition, PTA plants may use auxiliary boilers for heating parts of the process – the combustion reaction within these boilers can be monitored for reaction efficiency, control and safety by a combustion analyser measuring both O2 and combustibles.
Key gas analysis sensing technologies
Paramagnetic
Ideal for reliable, accurate measurements in flammable or corrosive gas mixtures, paramagnetic technology provides fast, accurate and sensitive measurements of percentage levels of O2.
The paramagnetic sensor cell consists of two nitrogen-filled glass spheres, mounted within a magnetic field, on a rotating suspension, with a centrally-placed mirror.
Light shines on the mirror and is reflected onto a pair of photocells. As O2 is naturally paramagnetic, it is attracted to the magnetic field, displacing the glass spheres and causing suspension rotation, which is detected by the photocells.
A current is applied through a feedback coil present in the magnetic field to provide sufficient torque to return the suspension to its original position. The magnitude of this current is directly proportional to the O2 present in the sample gas mixture.
Unlike electrochemical sensing technologies, a paramagnetic cell never requires changing and its performance does not deteriorate over time, reducing ongoing maintenance requirements and delivering a long operational life.
Infrared
IR sensing is a flexible, widely-used measurement technology based on the unique light-absorbing properties of some gases. It delivers non-contact, real-time detection of the selected gas’ concentration in a mixture.
IR sensors focus an IR light source through a sample cell holding a continuously flowing sample of the gas mixture, and onto a detector after wavelength selection. The property of some gases to absorb unique light wavelengths can be used to detect the concentration of a selected gas in a mixture.
Depending on the intended application, this concept can be applied in two ways: single beam, single wavelength (SBSW) and single beam, dual wavelength (SBDW).
SBSW delivers fast, stable, and accurate real-time measurements with low maintenance requirements, and is used where a small transducer is required. The IR light source is electronically modulated, removing the need for a motor and rotating filters.
The SBDW method uses a pair of optical filters mounted on a rotating disc, which pass through a beam of IR light alternately. The measure filter is chosen to pass light only at a wavelength that the gas to be measured absorbs, while the reference filter has a light passed through it at a wavelength unaffected by the gas to be measured. The difference in absorbance is measured by the detector and provides a direct output of the gas concentration.
Gas filter correlation
Gas filter correlation (Gfx) technology is an enhanced version of the photometric analysis used in IR technologies. It is effective for applications where extremely accurate, low-level measurements are needed, or where background gases may interfere with the measurement.
Gfx sensing exploits the ability of gases to absorb unique light wavelengths in order to detect the concentration of a selected gas in a mixture. Two gas-filled cuvettes are mounted on a rotating disk, each passing through a beam of light alternately.
The measure cuvette is typically filled with nitrogen, while a second cuvette – the reference cuvette – is filled with a sample of the gas to be measured. Light is passed through the gas to be
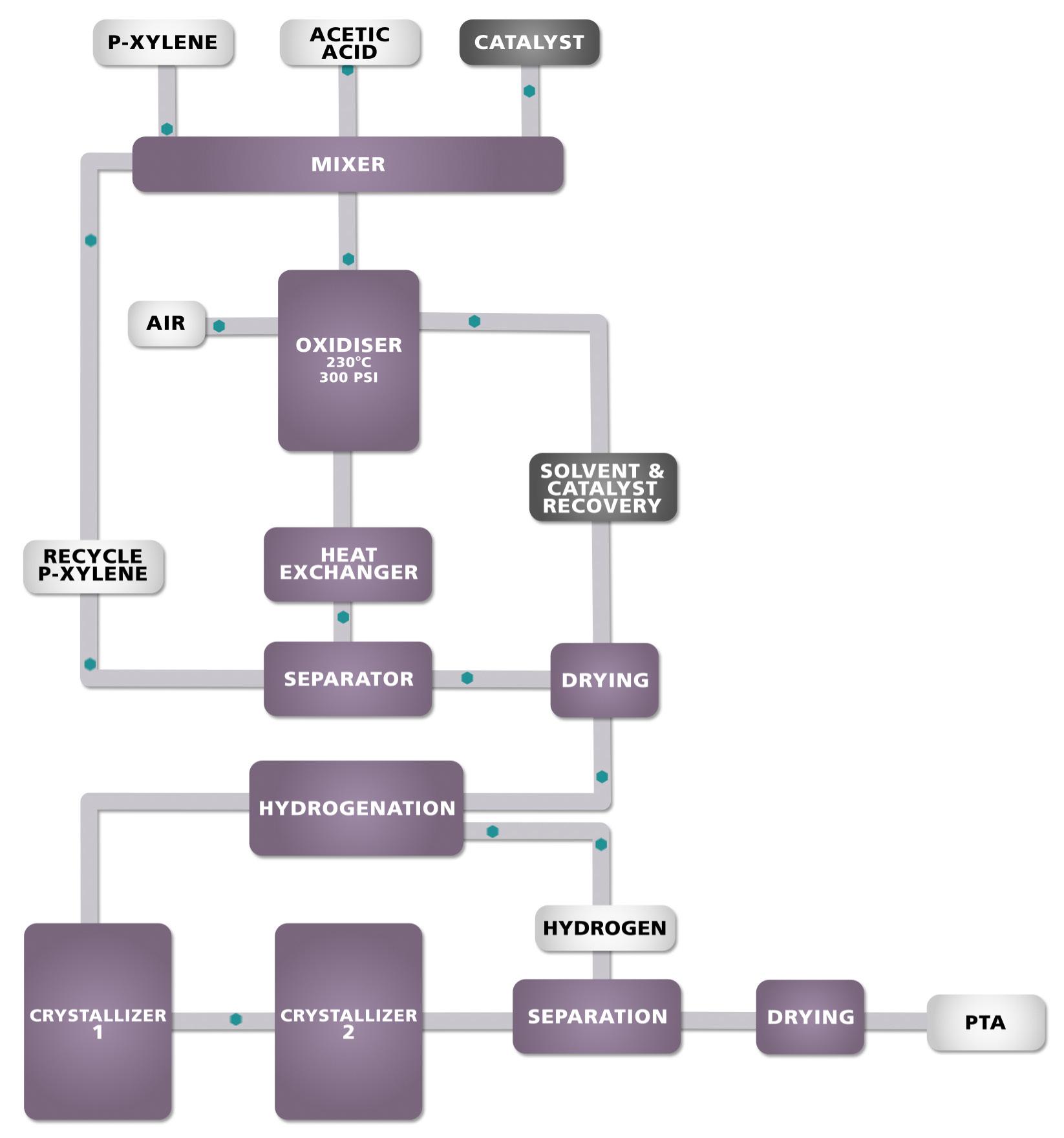
Figure 2. The PTA process.
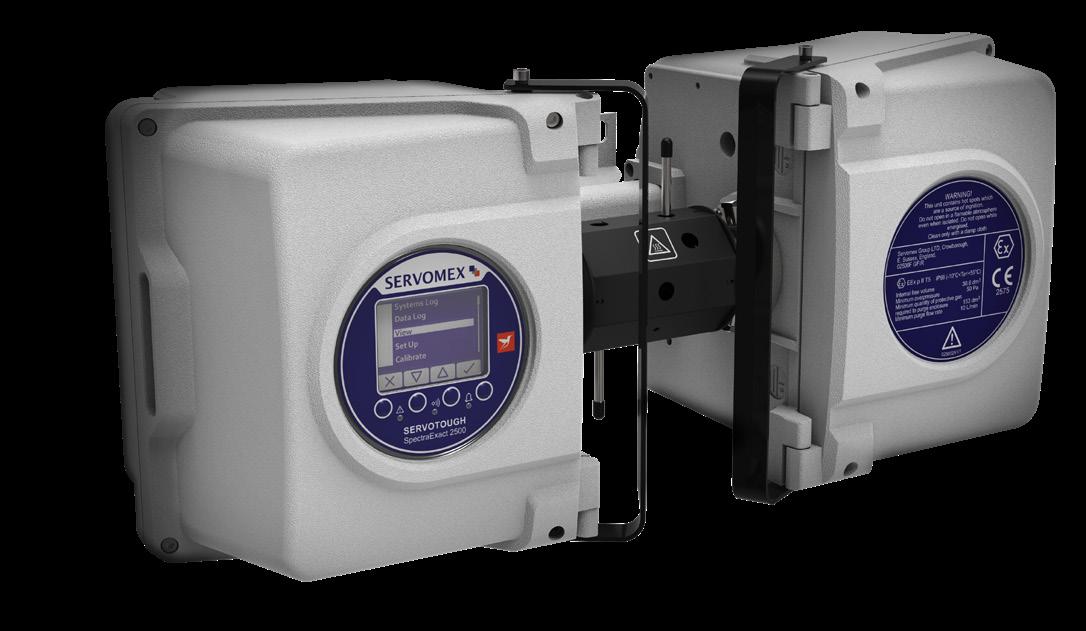
RUGGED RELIABLE READY MEET THE NEW BOSS
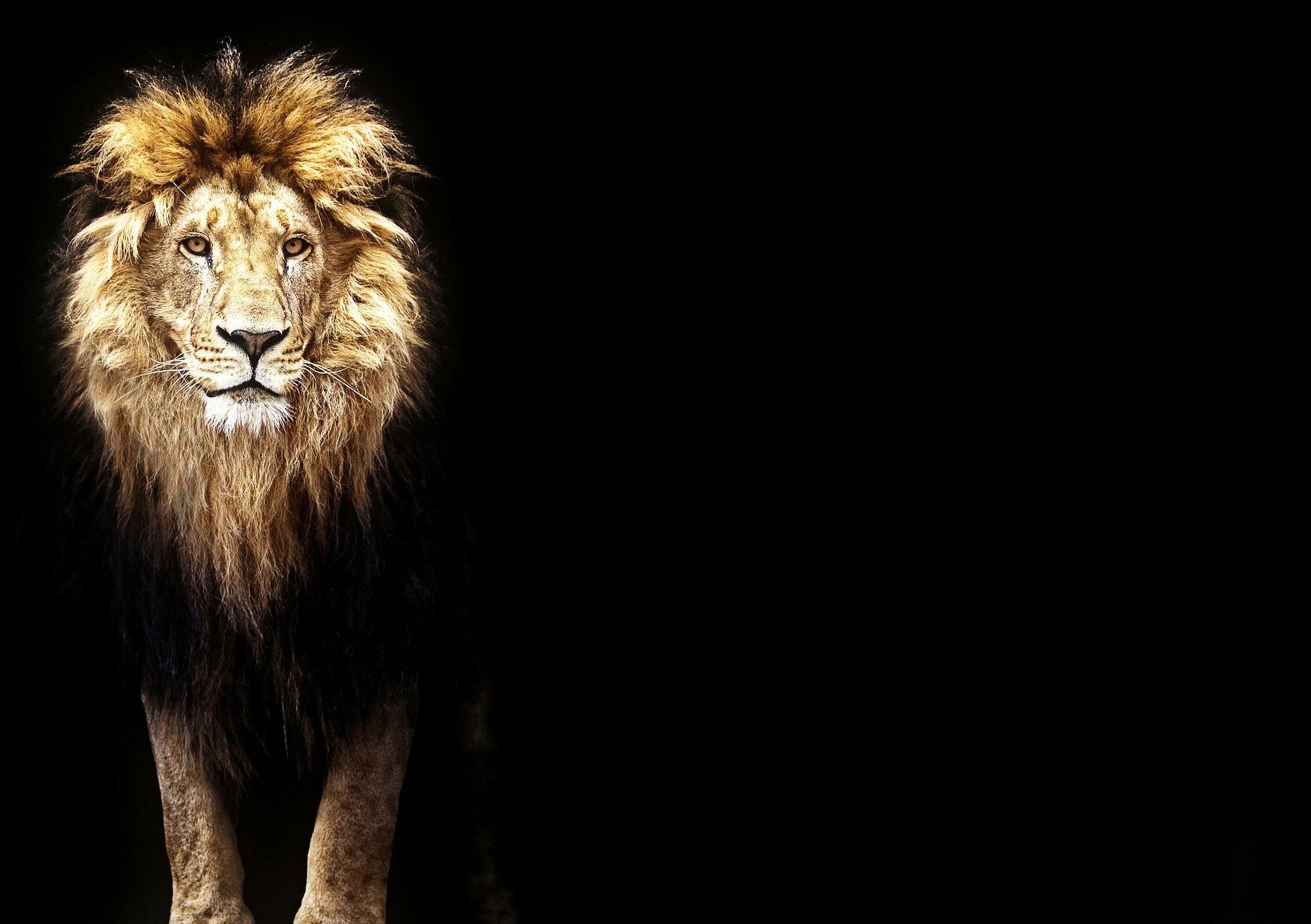
THE NEW SERVOTOUGH SpectraExact 2500
The new SERVOTOUGH SpectraExact 2500 upgrades the photometric gas analysis of its trusted predecessor, delivering an advanced solution to your process, in an easier-to-use package, leading the way for application solutions in a range of industries.
• Ethylene production • Carbon capture and storage • Ethylene dichloride • Direct reduction iron production
Get the latest launch news: servomex.com/signup
measured: the difference in absorbance is measured and provides a direct output of the gas concentration.
Gfx measurements provide a real-time measurement response, unaffected by background gases, and the technique is virtually immune to obscuration of the optics. This prevents sensor drift, reducing calibration frequency.
Case study
Servomex was selected by Jiaxing Petrochemical Co. Ltd to supply a complete analyser system for the second-phase development of its PTA production facility in Zhejiang province, China.
The plant was supplied with three SERVOTOUGH Oxy 1900 paramagnetic O2 analysers and three SERVOTOUGH SpectraExact 2500 IR gas analysers, all integrated into a bespoke analyser house.
The SERVOTOUGH Oxy 1900 uses paramagnetic O2 sensor technology to deliver accurate and stable measurements of O2. With a resilient enclosure for its transmitter unit, the analyser is optimised for hazardous applications including safety-critical oxidation, and meets Zone 1/Division 1 hazard ratings. A heated sample gas compartment improves measurement performance, while the non-depleting measurement technique means the analyser requires minimal calibration, ensuring a long lifetime of ownership and low maintenance costs.
Combining gas filter correlation and IR sensing technologies, the SERVOTOUGH SpectraExact 2500 analyser is designed for a wide range of demanding process applications. Its robust sample cell is separated from the electronics, and is heated with solvent-resistant O-rings and calcium fluoride windows, making it suitable for the high-temperature, acidic environments encountered in PTA production.
For 2022, Servomex is releasing a new SpectraExact 2500, which will have upgraded electronics and a new user interface consistent with existing products in the company’s industrial process and emissions range. The all-digital design will have ATEX hazardous area certification (pending) and other global certifications.
Jiaxing Petrochemical Co. Ltd selected these analysers because of their strong track records in delivering accurate, stable results in challenging environments, such as those found in PTA production.
Servomex had also supplied a gas analysis system for the first phase of the Zhejiang project, and the reliability of this existing system – along with the service support offered in China – were major factors in the company being selected for the next stage of the development.
Conclusion
PTA plants require a comprehensive gas analysis solution, with project management from design to installation and commissioning.
To meet individual plant requirements for gas analysis, this may range from O2 sampling and analysis for quality and safety in the oxidation reactor, through to a complete solution for the plant that encompasses CO2 and CO process control analysis, combustion control and continuous emissions monitoring.
In this way, manufacturers can ensure that a high-quality PTA product is delivered in an efficient and safe manner, while meeting all necessary environmental regulations.
Delayed Coking | Fluid Catalytic Cracking | Sulfur Production & Processing | Solvent Deasphalting
®REFCOMM
2022
Training, Conference, & Exhibition
May 9-13, 2022 • Galveston, Texas, USA
Returning to Galveston LIVE and in person
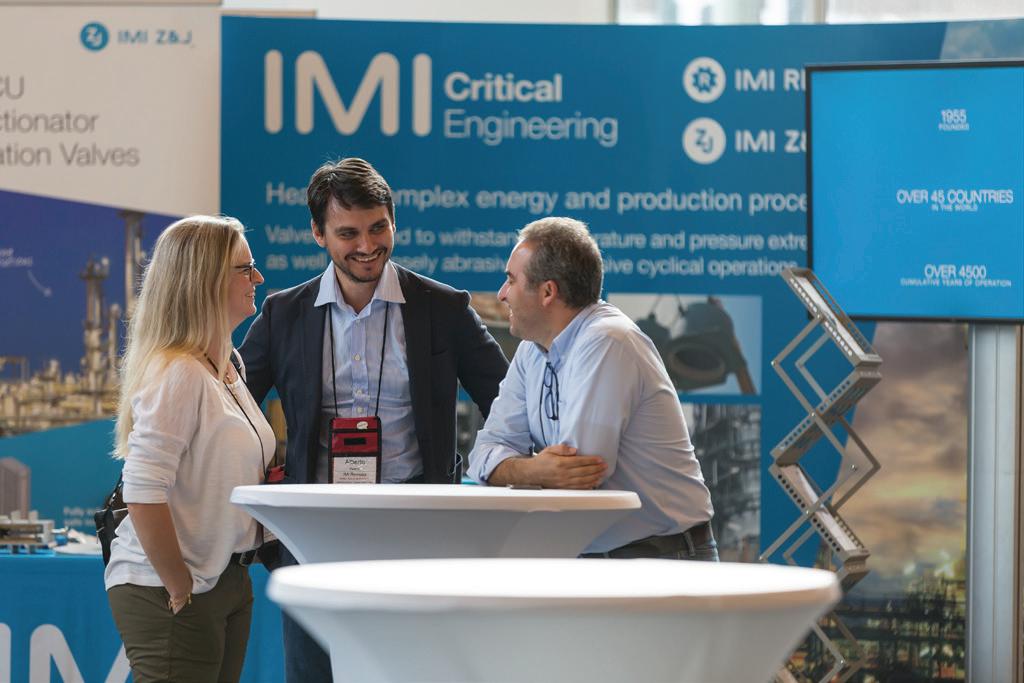
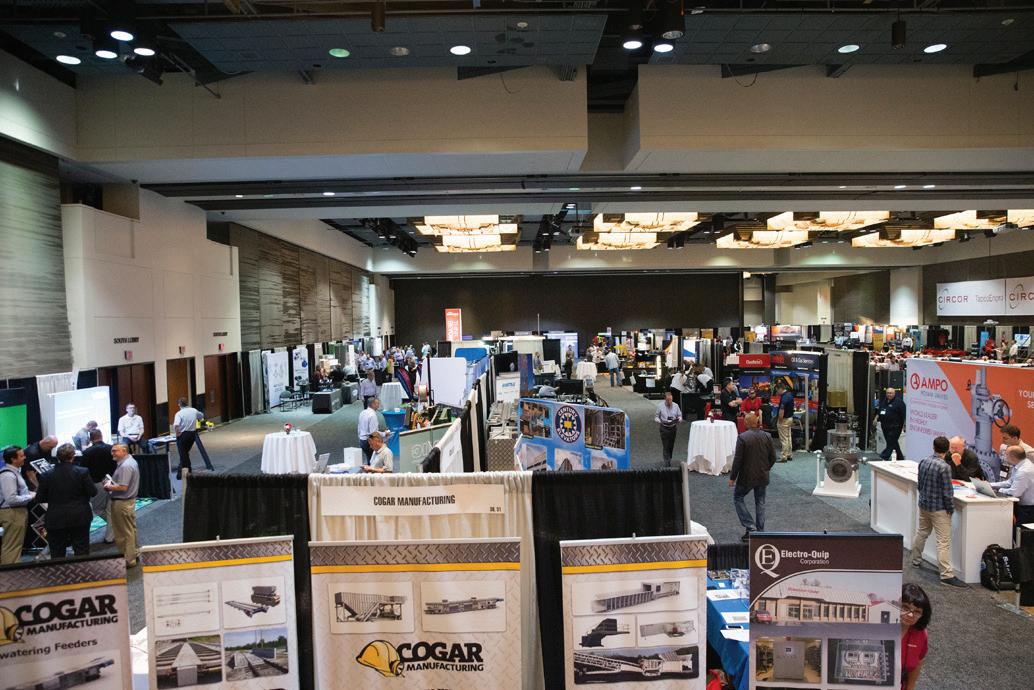
I picked up a lot of good information. I would definitely encourage those that are interested to participate and not to miss this conference.
Gregg Lorimor, Sr. Engineering Specialist, HollyFrontier Tulsa
Reasons to attend:
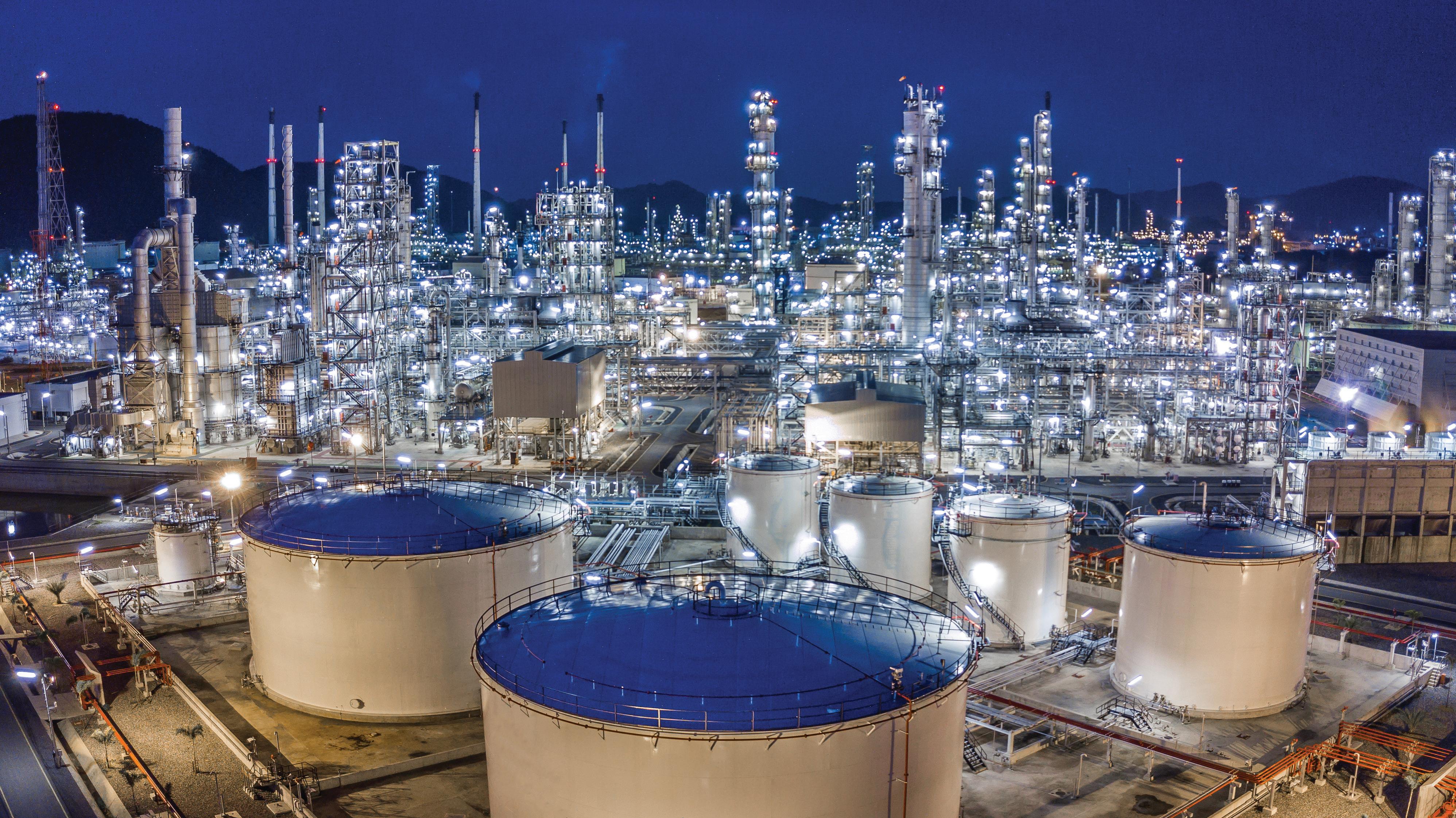
Learn from 50+ technical presentation in the multi-track agenda Agenda covers coking, cat cracking, sulfur and SDA Network with a large audience of refiners and technical experts Develop practical solutions for optimising your coking unit with our fundamentals and advanced training courses
500
ATTENDEES
180
REFINERS
*Stats from Galveston 2019
80
EXHIBITORS