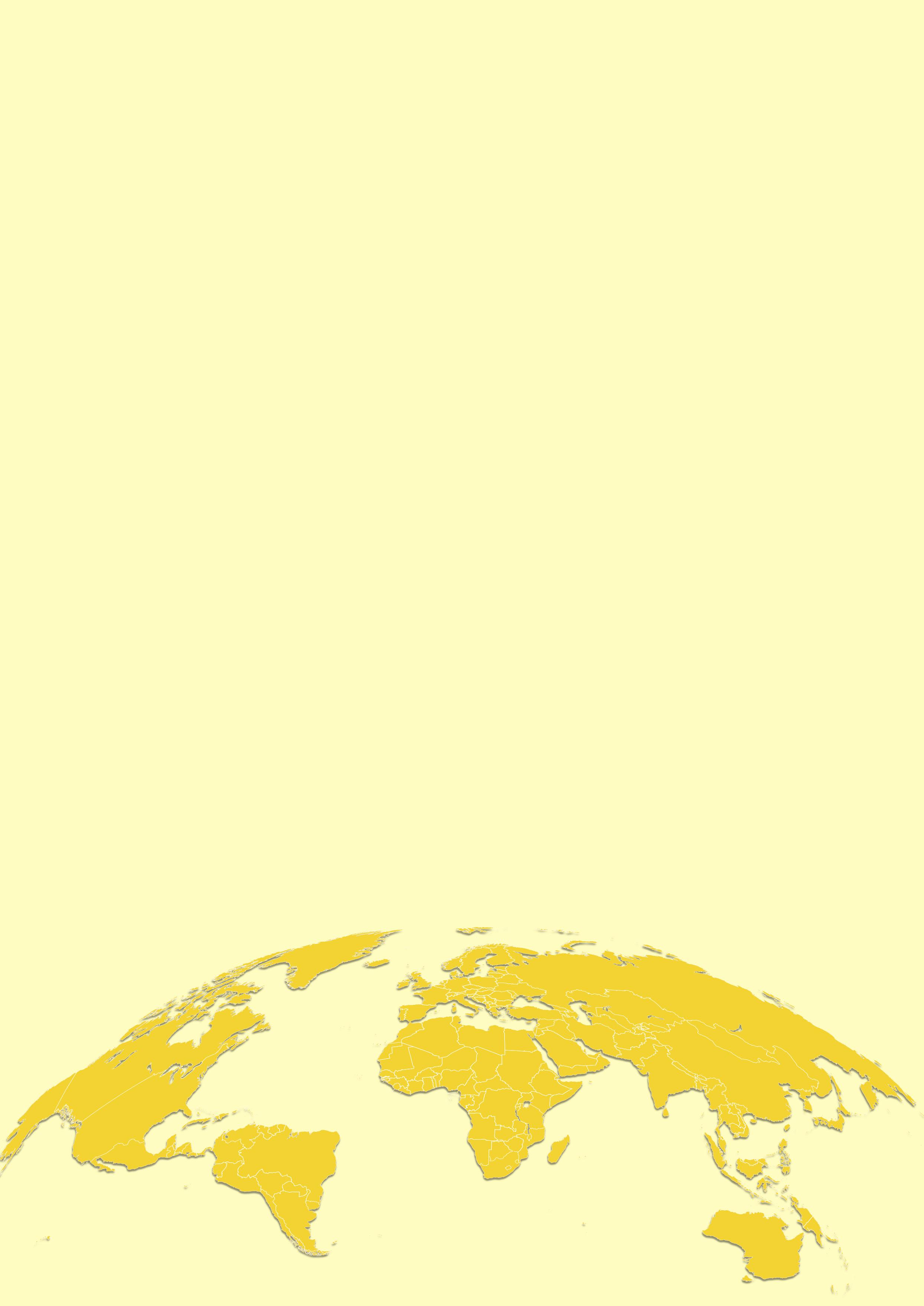
10 minute read
In a world made of sulfur
A.K. Tyagi, Nuberg EPC, India, explores the crucial role of sulfuric acid within the oil and gas industry, and places a spotlight on two projects that the company was involved in, in Saudi Arabia and Egypt.
Life on Earth exists partly thanks to sulfur. It is one of the most prevalent chemical elements in nature. It is a pale yellow, tasteless and odourless brittle solid that is common in volcanic areas and hot springs. Its main source is as byproduct elemental sulfur recovered from natural gas and petroleum. Sulfuric acid (H2SO4), one of the most essential components that is utilised as an industrial raw material, is the most important derivative of sulfur. Dilute sulfuric acid, on the other hand, is formed naturally in the atmosphere when sulfur dioxide (SO2) is oxidised in the presence of atmospheric moisture. Sulfuric acid is in high demand as a result of its wide range of applications. Consequently, it is commercially produced through the contact process, which involves the reaction of sulfur trioxide (SO3) with water:
SO3 + H2O ⟶ H2SO4 (1)
Global production and the growing role of sulfuric acid
Sulfuric acid demand has fallen only once, during the global economic crisis in 2009. Between 2010 and 2012, however, there was a positive trend. Global sulfuric acid production currently exceeds 270 million t, with this figure expected to rise. China tops the list of sulfuric acid producers, with over 74 million t of production output. The US comes in second with over 37 million t, followed by India (16 million t), Russia (14 million t) and Morocco (7 million t). In total, these five countries account for approximately 61.5% of all sulfuric acid produced worldwide. The global sulfuric acid market was worth US$10 billion in 2016. This figure is expected to increase to US$15 billion by 2025. Similarly, global demand is expected to rise exponentially, necessitating an increase in production to keep up.
Production of elemental sulfur
India is one of the world’s leading sulfuric acid manufacturers. There is a positive relationship between a country’s sulfuric acid usage and its per capita income. The acidulation of rock phosphates and the generation of ammonium sulfate are both part of the process. Petroleum refining, steelmaking and other inorganic compounds are among its numerous industrial applications. In India, there are currently more than 65 sulfuric acid facilities.
Sulfuric acid is made from a variety of basic materials, including elemental sulfur, hydrogen sulfide (H2S), pyrites, etc. Nearly all Indian manufacturers rely substantially on elemental sulfur as a major raw material source.
On the other hand, the oil industry extracts sulfur from crude oil through the refining process. This is generally accomplished by hydrotreating, which produces H2S that is converted into sulfur in the sulfur recovery unit (SRU), thus limiting the SOX and NOX content as per regulations (typically a maximum of 8 mg/m3 of H2S).
Refineries’ design capabilities meet both low-sulfur and high-sulfur crude oils and, with an SRU, they can produce elemental sulfur (99.9% recovery) and meet emission norms. The unit consists mainly of the separation section, reaction section, tail gas treating unit (TGTU) and incineration section.
H2S + 1/2 O2 ⟶ 1/2 S2 + H2O (2)
In the separation section, the feed gas – which consists mainly of sour and acid gases (sometimes 80% or more H2S) – passes through drums with the assistance of a mist eliminator, to avoid liquid carryover.
The heart of the SRU is the reaction section and various options are available, sometimes with a high temperature reaction furnace to destroy ammonia, which generally creeps into the sour gases. The Claus reaction occurs in the reactor furnace at high temperatures (1300 – 1400°C). The sulfur produced is condensed and sent to storage. The exit gas from the condenser is reheated for the catalytic reaction stage, and the sulfur produced is again collected by condensing the gas. One can have multiple stages as well as a separate TGTU to accomplish product recovery.
The treated gas from the TGTU is burned in the incinerator. Heat integration of the SRU is carried out by passing the appropriate stream through heat exchangers and using a waste heat recovery system to produce steam. With robust process design and established technology, an estimated 99.9% recovery of sulfur in the product can be achieved. Process optimisation and heat recovery, for the lowest CAPEX and OPEX, is accomplished through available licensed software tools. Utilities typically include refinery fuel gases and boiler grade feed water (high-pressure steam production).
The future of the sulfur market
As per a report by Mordor Intelligence1, the sulfur market is predicted to grow at a CAGR of more than 5% from 2021 to 2026, with a market size of 61.88 million t in 2020.
COVID-19 has caused a disruption in sulfur supply and a drop in demand from a variety of end user sectors, including metal manufacturing and chemical processing. Furthermore, the pandemic has entirely interrupted manufacturers and supply networks, posing a short-term threat to the market. However, the situation is likely to improve, restoring the market’s development trajectory over the second half of the forecast year.
Sulfur in the oil and gas industry
A large amount of sulfur byproducts are produced as a result of oil and gas operations. For example, Qatar, which has the world’s third largest confirmed natural gas reserves, produces a lot of sulfur as a byproduct of its natural gas processing facilities. The amount of sulfur produced exceeds the amount that can currently be used in the country by a large margin. The Claus method is used to convert hydrogen sulfide in natural gas collected from Qatar’s North Field, to elemental sulfur. Across many nations that have oil and gas facilities, managing byproduct sulfur from natural gas processing is a critical part of economic development and environmental protection. As a result, new markets for sulfur must be discovered in order to avert disposal crises.
A huge volume of sulfur is recovered each day by oil and gas corporations. The total amount of elemental sulfur produced across the globe in 2000 was 57.4 million t. Sulfur was collected at a rate of 103 000 tpd in January 2019, with Asia recording the highest rate. As more oil and gas is recovered from the ground, these figures are rapidly increasing.
The massive amounts of sulfur produced as a byproduct of the sector can be utilised in a variety of ways including fungicides, gunpowder, fertilizers, rubber vulcanisation, matches, pyrotechnics, fumigants, insecticides, the treatment of certain skin ailments, etc.
Sulfur has an extensive range of applications, and it has become a basic element due to its abundance, ease of extraction, and its ability to be directly mixed with most known elements.
Environmental effects of sulfuric acid production
Sulfur depositions in landfills and on the outskirts of cities are becoming a major health and environmental issue. However, with more research and development, sulfur’s abundance can be employed to solve a variety of problems, or as a novel additive that boosts efficiency while using less product. This should be both environmentally and health-friendly, as well as cost-effective.
Until now, industrial processes have been the primary cause of sulfuric acid related pollution. These include the manufacturing process, as well as its applications in metal smelting, petroleum refining, lead-acid accumulators and other operations. Sulfur dioxide is released into the atmosphere as a result of these processes, which can have disastrous consequences, such as acid rain. This can lead to the pollution of plant and animal life in the short-term. In the case of human contamination, sulfuric acid can cause significant burns if inhaled or absorbed via the skin. In contrast, recovery of sulfur by the SRU in refineries renders the flue gases more compliable to emissions standards.
According to a report released by Greenpeace on 19 August 20192, rising emissions have pushed India above China, which has surpassed Russia as the world’s second-largest emitter as a result of its progress in decreasing emissions. China lowered sulfur dioxide emissions by enforcing strict emission regulations and using technology such as flue gas desulfurisation (FGD).
Case studies
Since 1996, Nuberg EPC has successfully commissioned multiple sulfuric acid plants around the world, including Agrochem in Egypt and ADDAR in Saudi Arabia.
These case studies detail the learnings and obstacles encountered throughout the process.
Alexandria, Egypt
Agrochem contacted Nuberg EPC to express its ambition to build a new sulfuric acid plant in Egypt, with a capacity of 300 tpd (see Figure 1). With shop drawings and both basic and comprehensive engineering investigations of the proposed location, Nuberg EPC moved quickly. Following this, the company sought vendors in order to obtain the best supplies for the project. Process, technology know-how, basic and detailed engineering, design, procurement, production and supply of plant equipment – including complete installation, building, project management, commissioning and start-up – were all part of the project’s scope. The factory was successfully commissioned in 2012 after several months of hard labour, and it now uses double contact double absorption (DCDA) technology.
The sulfuric acid factory, which was completed in 2012, was Nuberg EPC’s first turnkey project in Egypt. The factory generates sulfuric acid (98%) using DCDA technology, which is mostly used in the fertilizer business in Egypt. Nuberg EPC’s plant engineering and construction services helped Agrochem to run a safe, reliable and environmentally-friendly facility.
Sulfuric acid is one of the world’s most widely utilised industrial chemicals. Fertilizers containing phosphates, such as diammonium phosphate (DAP), monoammonium phosphate (MAP), triple superphosphate (TSP) and single superphosphate (SSP), have fuelled expansion in the sulfuric acid market in recent years.

Figure 1. Sulfuric acid plant in Egypt.
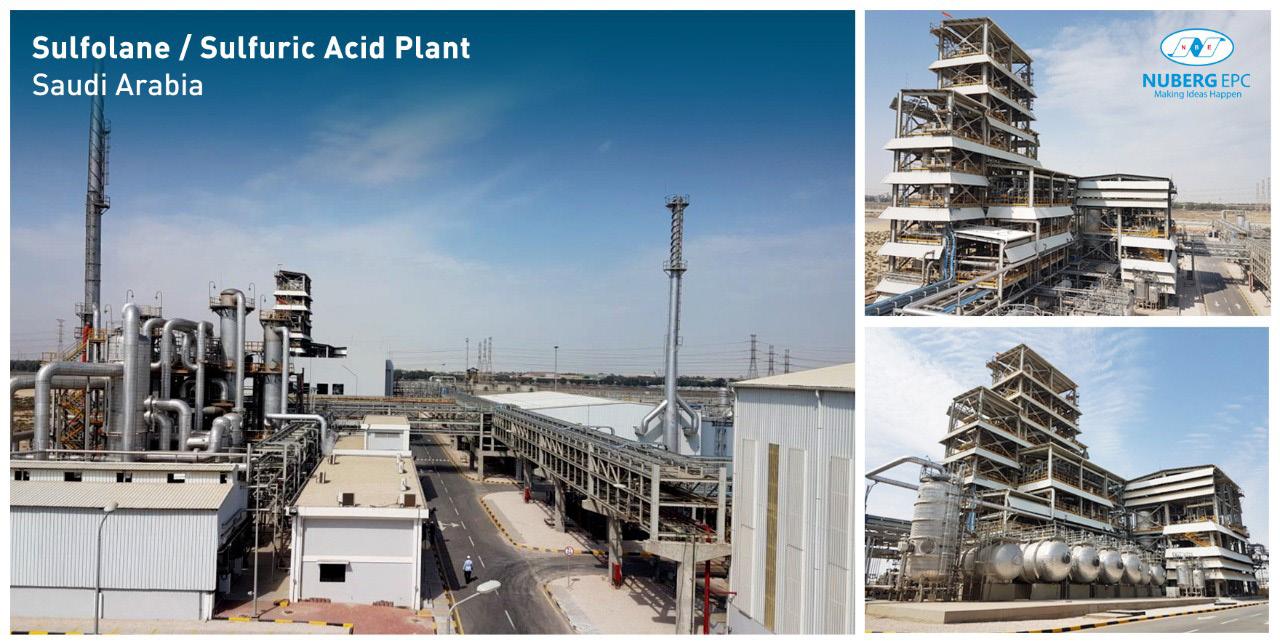
Figure 2. Sulfuric acid plant in Saudi Arabia. Jubail Industrial Area, Saudi Arabia
Nuberg EPC was hired by Addar Chemicals Co. to build a new sulfuric acid and sulfolane acid facility in Jubail (see Figure 2). The latter, which has a capacity of 6000 tpd, was Saudi Arabia’s first greenfield sulfolane production factory, with a capacity of 80 tpd.
As with the Agrochem project, process, technology know-how, comprehensive engineering, design, procurement, production and delivery of plant equipment, as well as installation, building, project management, commissioning and start-up of the plant, were all included in the scope of the project. The company complied with local standards set forth by the Royal Commission for Jubail and Yanbu (RCJY) and the Saudi Standards, Metrology, and Quality Organization (SASO).
The plant in Jubail was completed in November 2018 and commissioned by the Saudi Arabian firm. The facility generates sulfuric acid (98%), which is used to make ammonium sulfate and super phosphate of lime, among other things. The sulfuric acid business has risen in parallel with rising demand for organic compounds, with fertilizer production accounting for over 70% of total production today.
Conclusion
Sulfur is crucial for the existence of life on Earth. It has different derivatives, including sulfuric acid, which has an extensive range of applications in the oil and gas industry and is considered to be one of the most important industrial chemicals. Recently, COVID-19 has disrupted sulfur supplies and reduced its demand in a variety of end user industries. However, the situation is likely to improve as markets begin to recover and customers are express their ambition to build sulfuric acid plants. Nuberg EPC has signed multiple contracts amidst the pandemic. The 500 tpd Sprea Misr sulfuric acid plant project in Ramadan, Egypt, is one of them.
On the contrary, industrial processes have been the primary cause of sulfuric acid related pollution. This includes its applications in metal smelting, petroleum refining, lead acid batteries and other operations. However, with more research and development, abundant sulfur can be used to solve a number of problems, or as a novel additive that reduces product consumption and increases efficiency.
Supported by an international quality R&D centre for specialty chemicals, located in Sweden, Nuberg EPC has been improving its sulfuric acid technology. Since 1996, the company has effectively commissioned multiple sulfuric acid plant projects across countries such as Turkey, Egypt, Bangladesh and Saudi Arabia, and has maintained its commitment to providing safe, reliable and efficient facilities worldwide.
References
1. ‘Sulfur market – growth, trends, COVID-19 impact, and forecasts (2021 – 2026)’, Mordor Intelligence, (2021), https://www. mordorintelligence.com/industry-reports/sulfur-market 2. ‘Greenpeace analysis ranks global SO2 air pollution hotspots’,
Greenpeace, (2019), https://www.greenpeace.org/international/ press-release/23819/global-so2-air-pollution-hotspots-ranked-bygreenpeace-analysis/