VRIJE MATERIAALKEUZE MECHANISCHE STERKTE INDUSTRIE KLEINE SERIE
3D-DRUKTECHNOLOGIE
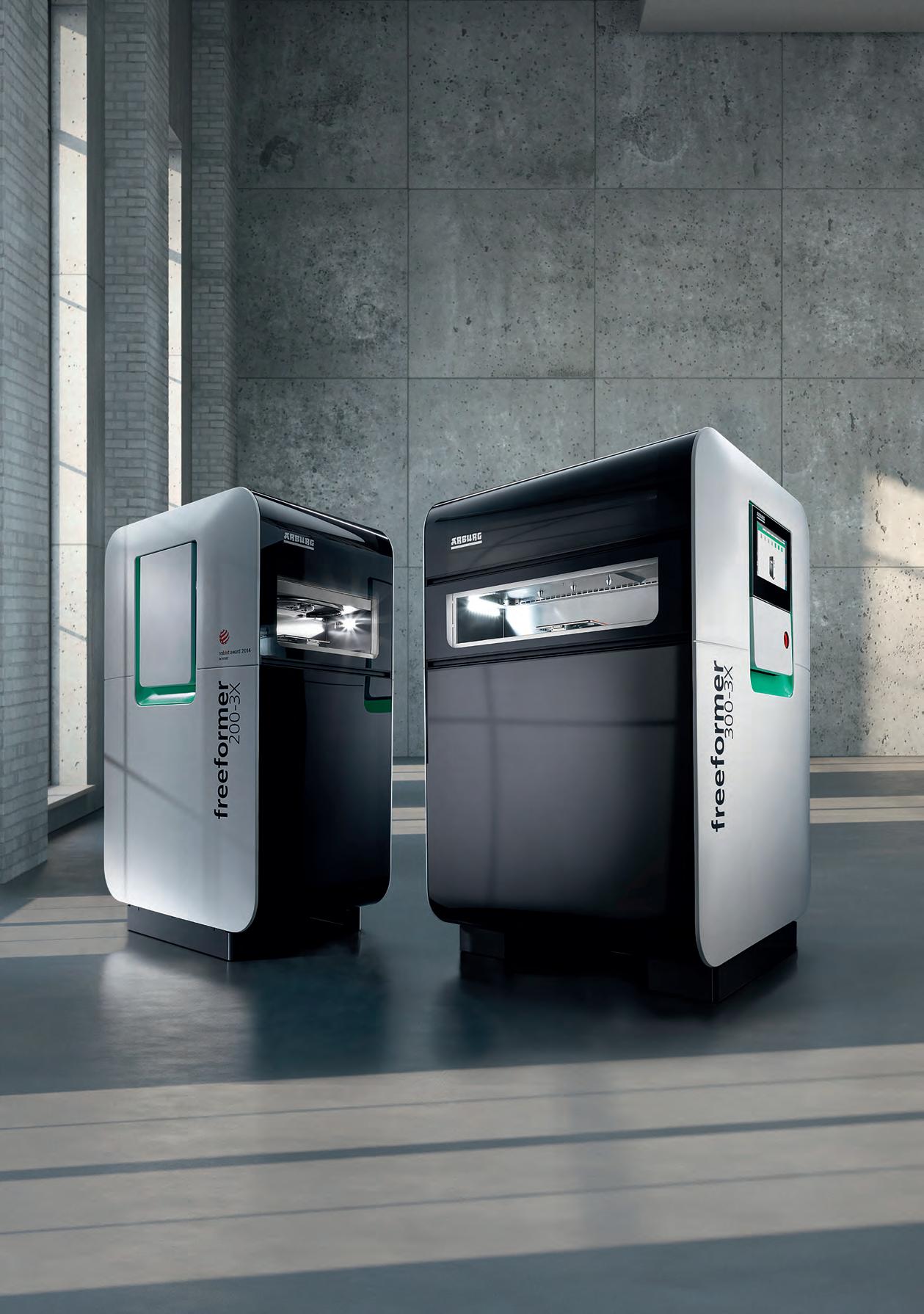
Is 3D-printen klaar voor de stap naar productie?

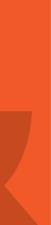
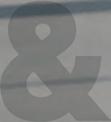
VRIJE MATERIAALKEUZE MECHANISCHE STERKTE INDUSTRIE KLEINE SERIE
3D-DRUKTECHNOLOGIE
Is 3D-printen klaar voor de stap naar productie?
Voor de verwerking van post-consumer afval (PE) en bloempotten (PP) zet Veolia Nederland-dochter Aufderhaar Kunststof Recycling in Vroomshoop vier grote WEIMA-shredders in voor de naversnippering. Het zo geproduceerde regranulaat wordt vervolgens hergebruikt voor de productie van verpakkingsmaterialen.
Nieuwste aanwinst is de W5.18. Productiemanager Sebastiaan Kok: “De oerdegelijke constructie, samen met de hoge prestaties van de aandrijving, hebben ons ervan overtuigd dat dit de beste keuze was voor onze eisen. En als er onderhoud nodig is, hebben we voldoende ruimte om te werken dankzij de directe toegang tot de rotor via een ruime opening.”
Nadat de geperste balen zijn voorgeshredderd, verkleint de W5.18 deze tot een homogene vlokgrootte. Daarna drukt hij het materiaal, afhankelijk van de belasting tegen de rotor. De vlokken worden vervolgens gewassen en geëxtrudeerd.
weima.com
Kunststof en Rubber
Uitgever: Arjan Stoeten
Redactie:
Maartje Henket
Tel. +31 570 504 302 m.henket@mybusinessmedia.nl
Kasper Weigand
Tel. +31 570 504 374 k.weigand@mybusinessmedia.nl
Robin Zander
Tel. +31 6 222 080 34 r.zander@mybusinessmedia.nl
Webredactie: Maartje Henket
Redactieadres: Postbus 58, 7400 AB Deventer redactie.kunststofenrubber@mybusinessmedia.nl www.kunststofenrubber.nl
Advertentieverkoop:
Marc Nühn
Tel. +31 6 536 301 20 m.nuhn@mybusinessmedia.nl
Alle advertentiecontracten worden afgesloten conform de Regelen voor het Advertentiewezen gedeponeerd bij de rechtbanken in Nederland.
Abonnementenadministratie
Abonnementen, bezorging en of adreswijzigingen:
MYbusinessmedia Holding bv, abonnementen Kunststof & Rubber, Postbus 58, 7400 AB Deventer Tel. +31 570 504 325 klantenservice@mybusinessmedia.nl
Abonnementstarieven
Jaarabonnement Nederland: € 275,-*
Jaarabonnement buitenland: € 299,-* Proefabonnement (drie edities): € 29,50*
KIVI-leden: 45% korting
Studentenabonnement: € 50,00* (inschrijvingsbewijs verplicht)
* Prijzen zijn exclusief 9% BTW Jaarabonnement geldt tot wederopzegging. Beëindiging van het abonnement kan schriftelijk en telefonisch (+31 570 504325) gebeuren, uiterlijk drie maanden voor het einde van de abonnementsperiode; nadien vindt automatisch verlenging plaats.
Druk: Drukkerij Roelofs, Enschede
Opmaak: Bureau OMA, www.bureauoma.nl
Hoewel de informatie gepubliceerd in deze uitgave zorgvuldig is uitgezocht en waar mogelijk gecontroleerd, sluiten de uitgever en de redactie uitdrukkelijk iedere aansprakelijkheid uit voor eventuele onjuistheden en/of onvolledigheid van de verstrekte gegevens.
MYbusinessmedia legt uw gegevens vast voor de uitvoering van de abonnementenovereenkomst. Uw gegevens kunnen door MYbusinessmedia of zorgvuldig geselecteerde derden worden gebruikt om u te informeren over relevante producten. Indien u hiertegen bezwaar hebt kunt u contact opnemen met de uitgever.
Met de Freeformer van Arburg is het mogelijk om met regulier spuitgietgranulaat te 3D-printen. Een artikel hierover stond in Kunststof & Rubber 6 van 2023.
Artikelen 3D-printen
AM
Rubrieken
De Kunststof en Rubber nieuwsbrief brengt u wekelijks (en gratis) op de hoogte van allerlei ins en outs uit de sector. Bedrijfsnieuws, materialen, machines, toepassingen, prijzen, vacature en human interest.
Aanmelden kan via www.kunststofenrubber.nl/ nieuwsbrief
Ik heb sinds kort een proefabonnement op Trouw. Uit nieuwsgierigheid, of noem het beroepsdeformatie, zocht ik in het archief van Trouw op het woord kunststof. Wat de krant schrijft over kunststof? Na een borstimplantaat en een hersenimplantaat van kunststof, kwam ik via kunststof damwanden en flexwoningen met kunststof muren uit bij een artikel over een nieuwe methode voor het recyclen van polyester kleding. In Denemarken zijn onderzoekers erin geslaagd katoen en polyester van elkaar te scheiden door textiel waarin beide zit, samen met een oplosmiddel en hertshoornzout te verwarmen tot 160 graden en het een dag te laten rusten. Daarna blijven polyester en katoen gescheiden van elkaar over en kan het opnieuw gebruikt worden. Hertshoornzout, wat is dat ook alweer, hoor ik u denken. Een oud huis-tuin- en keukenmiddeltje om brood mee te laten rijzen en onder de naam vlugzout geschikt om uw flauwgevallen metgezel weer mee bij bewustzijn te brengen. Maar nu dus uit de vergetelheid gehaald om textiel mee te recyclen. Hoog nodig want het doel van de EU om in 2030 75% van al het textiel te recyclen schijnt nog lang niet in zicht. De Deense methode is groener dan bestaande methodes dus alleen maar goed nieuws zou je zeggen. Nu alleen nog opschalen van het laboratorium naar de industrie. Hoe lang dat gaat duren? Geen idee.
Ik hoor de laatste tijd wel meer baanbrekende ideeen om grote problemen mee op te lossen. Zo zijn er grote hoeveelheden natuurlijk waterstof in de bodem gevonden. Genoeg om honderden jaren mee vooruit te kunnen, aldus een Amerikaanse overheidsdienst. Of wat te denken van de nucleaire batterij die 50 jaar meegaat zonder hem te hoeven opladen. Fantastisch. Maar laten we de technieken en methodes die nu al zijn toe te passen niet uit het oog verliezen. Want dat een Nederlandse recycler van kunststof op de fles gaat omdat virgin kunststof te goedkoop is, of dat EU-recyclaat wordt verbrand, omdat geïmporteerd recyclaat goedkoper is, dat lijken me dan weer hele slechte ontwikkelingen.
Kasper Weigand, redactie Kunststof & Rubber k.weigand@mybusinessmedia.nl
Volop aandacht voor zorgen van NRK en haar leden over ongelijk speelveld rond NCPN
‘Kunststofindustrie slaat alarm’, kopte het Financieele Dagblad onlangs.
‘Bijmengplicht duurzaam plastic nekt kunststofverwerkers’ kopte ABN AMRO recent in haar sector update. ‘De Nederlandse overheid kiest voor een Nederlandse aanpak binnen een Europees speelveld waarbij vooral de vervroegde invoering ervoor zorgt dat kunststofverwerkers in Nederland hun markt bedreigd zien, aldus de bank. Volop aandacht voor de zorgen van de NRK en haar leden over het mogelijk verdwijnen van een gelijk speelveld binnen Europa door de Nationale Circulaire Plastic Norm (NCPN).
Deze “bijmengverplichting”, start in 2027 met naar verwachting 15% en loopt op tot 25-30% in 2030. Nederland loopt daarmee vooruit op Europese wetgeving. Recent uitte de NRK al verschillende keren haar zorgen over de huidige invulling van de NCPN.
Import uit het buitenland is in het huidige wetsvoorstel namelijk vrijgesteld van deze nieuwe normering. Productie in het buitenland, die wordt geïmporteerd naar Nederland, hoeft niet aan de maatregel te voldoen. Daarmee worden Nederlandse producten duurder dan buitenlandse. Dit resulteert in economisch verlies en belemmert de beoogde CO2-verlaging, waardoor het klimaat altijd verliest.
Algemeen directeur van de NRK Harold de Graaf tegen ABN AMRO: “Wij onderschrijven de ambities van de Nederlandse overheid op het gebied van het terugbrengen van CO₂-uitstoot en de noodzaak daarvan
Er gebeurt veel branche breed: opleidingen, bijeenkomsten, bedrijfsbezoeken, noem maar op. Aan alles deelnemen gaat niet, maar alles overslaan is ook geen optie. Op deze pagina meldt Harold de Graaf van NRK nieuwsfeiten over actuele onderwerpen.
www.nrk.nl
voor onze aarde. De aankomende richtlijnen van de EU gelden per productsoort, terwijl de Nederlandse bijmengverplichting toegepast is op de verwerker en geldt daarmee voor alle kunststofproducten. Daarnaast is de bijmengverplichting nationaal georiënteerd. Vanwege de importvrijstelling geldt de norm niet voor buitenlandse aanbieders van kunststofproducten op de Nederlandse markt.” ‘De Graaf vreest voor ‘een exodus van productiebedrijven naar het buitenland’, zo viel te lezen in het FD.
Groen, Groener, Groenst? Pas op met duurzaamheidsclaims!
Al eerder berichtte NRK Verpakkingen over de beschuldigingen van ‘greenwashing’ die de Europese Consumentenorganisatie (BEUC) uitte aan het adres van producenten van plastic waterflessen. De BEUC stelt dat claims als ‘100% recyclable’ en/of ‘made of 100% recycled plastic’ misleidend zijn en in strijd met de Europese Richtlijn inzake oneerlijke handelspraktijken (2005/29/EC).
De flessenproducenten waren niet de enigen die op deze manier in de publiciteit kwamen. In oktober 2023 floot de Reclame Code Commissie (RCC) Shell voor de derde keer terug omdat het bedrijf de consument zouden misleiden met reclames over CO2gecompenseerd gas. Ook diende een aantal Amsterdamse studenten recent een klacht in tegen Colgate Palmolive. Volgens de RCC toonden de studenten aan dat de claims ‘100% recyclebaar’ en ‘fles en dop recyclebaar’ misleidend zijn. In Nederland is het de eerste zaak die aantoont dat
claims over de recyclebaarheid van plastic misleidend zijn. Colgate Palmolive is tegen de uitspraak in hoger beroep gegaan.
Als je in het uitsprakenregister van de RCC de zoekterm ‘duurzaamheid’ intypt, dan levert dat 142 hits op. Terwijl er dus al druk geprocedeerd wordt over duurzaamheidsclaims, werkt de Europese Commissie verder aan de Green Claims Directive die de regels voor het gebruik van milieuclaims verder moet harmoniseren. Bedrijven die een ‘groene claim’ willen hanteren, moeten volgens de voorgestelde regeling minimumnormen respecteren voor de onderbouwing en communicatie hiervan. Het voorstel is zowel van toepassing op expliciete milieuclaims van handelaren over producten als op handelaren in handelspraktijken tussen bedrijven en consumenten.
De aanstaande Green Claims Directive heeft verschillende doelen:
1. Het niveau van milieubescherming verhogen en bijdragen aan het versnellen van de groene transitie naar een circulaire, schone en klimaatneutrale economie in de EU;
2. Consumenten en bedrijven beschermen tegen greenwashing;
3. Consumenten in staat stellen bij te dragen aan het versnellen van de groene transitie door te zorgen dat ze weloverwogen aankoopbeslissingen kunnen nemen op basis van geloofwaardige milieuclaims en -labels;
4. Het verbeteren van de rechtszekerheid met betrekking tot milieuclaims en het gelijke speelveld op de interne markt;
5. Het vergroten van het concurrentievermogen van marktdeelnemers die zich inspannen om de ecologische duurzaamheid van hun producten en activiteiten te verhogen.
Op Europees niveau wordt nog druk gediscussieerd over de uiteindelijke tekst van de directive. In Nederland zijn echter al geruime regels van toepassing waarin veel aspecten terugkomen. Die regels zijn bijvoorbeeld terug te vinden in de Wet Oneerlijke Handelspraktijken, in de Code voor Duurzaamheidsreclame van de Stichting Reclame Code en in de Leidraad met betrekking tot duurzaamheidsclaims van de ACM. Voor de RCC vallen zowel milieu- als ethische claims onder duurzaamheid. Daarbij hanteert de RCC de vol-
gende definities: een milieuclaim is een claim die suggereert of op een andere manier de indruk wekt dat een product of activiteit een positieve, minder of geen invloed heeft op het milieu. Dat kan zowel gaan om het milieu in het algemeen als om bepaalde milieuaspecten, zoals lucht, water, bodem, ecosystemen, biodiversiteit of het klimaat. Een ethische claim is een claim die de indruk wekt dat de productie of de activiteit van een bedrijf heeft plaatsgevonden volgens bepaalde ethische standaarden, bijvoorbeeld ten aanzien van algemene arbeidsomstandigheden, dierenwelzijn of maatschappelijk verantwoord ondernemen.
De Autoriteit Consument & Markt (ACM) hanteert soortgelijke definities. Het is vaak lastig te bepalen of een bewering wel of niet binnen de regels past. Daarom geeft de ACM in haar Leidraad Duurzaamheidsclaims een aantal vuistregels met een toelichting die bedrijven moet helpen om de juiste duurzaamheidsclaims te formuleren:
1. Gebruik juiste, duidelijke, specifieke en volledige duurzaamheidsclaims;
2. Onderbouw deze met feiten en houd ze actueel;
3. Maak eerlijke vergelijkingen met andere producten of concurrenten;
4. Beschrijf toekomstige duurzaamheidsambities concreet en meetbaar;
5. Zorg dat visuele claims en keurmerken behulpzaam zijn voor consumenten en niet verwarrend.
In 2023 kwam het Kennisinstituut Duurzame Verpakken (KIDV) met een update van het Factsheet Milieuclaims, speciaal voor verpakkingen. Dit document schetst het wettelijk kader en maakt met praktijkvoorbeelden duidelijk hoe bedrijven bepaalde beweringen, zoals ‘recyclebaar’ of ‘100 % duurzaam’, moeten onderbouwen om niet het risico te lopen een claim aan hun broek te krijgen. Wilt u als bedrijf een groene bewering doen over een kunststofproduct? Wees u dan bewust van bestaande wet- en regelgeving en bespreek dit zo nodig met uw klant. Wat NRK Verpakkingen betreft geldt nog steeds ‘better safe than sorry’, zeker als het om duurzaamheid gaat.
Geslaagde Rethink Nieuwjaarsbijeenkomst
De Rethink Nieuwjaarsbijeenkomst van de NRK in het sfeervolle Spoorwegmuseum trok bijna 100 enthousiaste deelnemers. Met een scala aan sprekers en onderwerpen bood de bijeenkomst een waardevol inzicht in de uitdagingen en kansen die onze sector te wachten staan in het komende jaar. De aftrap werd verzorgd door Jan Willem Wieringa, voorzitter van NRK PVT, die met een boeiende terugblik op het jaar 2023 en een vooruitblik op de toekomstige ontwikkelingen de toon zette voor de rest van de middag. Zijn inzichten boden een solide basis om door te praten.
Harold de Graaf, algemeen directeur van de NRK, volgde met een analyse van waar de focus van de NRK lag in 2023 en waar de NRK haar leden zal ondersteunen in het komende jaar. Zijn presentatie bood een helder beeld van de richting die de NRK wil inslaan en welke initiatieven er op stapel staan. Rob Verhagen, voorzitter van NRK Verpakkingen, nam de aanwezigen mee door twee belangrijke dossiers: de CSRD en NCPN. De afsluitende presentatie van econoom Paul Schenderling bood een inspirerend perspectief op nieuwe duurzame economische modellen. Na de presentaties was er ruimte voor informele discussies en netwerken tijdens de borrel. De presentaties worden binnenkort naar alle leden gestuurd, zodat ook zij die niet aanwezig konden zijn, kunnen profiteren van de waardevolle inzichten die zijn gedeeld.
Blijf altijd op de hoogte van het laatste nieuws uit de branche via de LinkedIn pagina van de NRK.
www.linkedin.com/company/ nrk-nederlandse-rubber-en-kunststofindustrie-/
Arburg was als spuitgietmachinefabrikant lange tijd een witte raaf in de 3Dprintindustrie, maar tegenwoordig bouwt ook KraussMaffei 3Dprinters, net als Bosch. Is de technologie een volwaardige productietechnologie geworden?
Auteur: Franc Coenen
Degrote fabrikanten van 3D-printers voor kunststoffen hebben geen gemakkelijk jaar achter de rug. Context, een van de marktonderzoekers die elk kwartaal de wereldwijde verkopen van 3D-printers bijhoudt, berekende in een recent rapport dat de totale verkopen van industriële 3D-printers voor polymeren (kostprijs meer dan $100.000) in de eerste helft van 2023 is gedaald. De groei zat in het middensegment, de 3D printers met een prijskaartje tussen de $20.000 en $100.000 dollar. Met name Formlabs heeft het in dit marktsegment goed gedaan met een groei van het marktaandeel in SLS 3D-printen (Selective Laser Sintering) van 2% naar 17% in een jaar tijd. Opvallend, want nog niet zo lang geleden was je voor een poeder-
bed 3D-printer aangewezen op systemen zoals die van EOS (SLS), HP (Multi Jet Fusion) en Stratasys (SAF). Machines met zescijferige prijskaartjes. Niet alleen Formlabs heeft met de Fuse 1 lijn deze markt opengebroken, ook fabrikanten zoals Sintratec en Sinterit doen dit. De systemen lenen zich met name voor seriematige productie van bijvoorbeeld machineonderdelen, vaak geprint in PA11 of PA12.
Traditionele spelers
Het zijn niet alleen de scale-ups die aan het marktaandeel van gevestigde AM-bedrijven knagen. Opvallend is dat enkele nieuwkomers geen onbekenden in de kunststoffenindustrie zijn. Arburg is het oudste voorbeeld hiervan. Ondertussen bouwt echter ook KraussMaffei 3D-printers, twee modellen liefst. De powerPrint is bedoeld voor het printen van grote onderdelen en de precisionPrint voor nauwkeurige, kleine componenten. Het is de vierde pilaar onder het bedrijf, aanvullend op de andere activiteiten, niet als vervanging. KraussMaffei zet processtabiliteit bovenaan en kiest er daarom voor een complete oplossing aan te bieden: printtechnologie, software en materialen. In de powerPrint gaat het om grote componenten, tot 2 bij 2,5 bij 2 meter. Momenteel zijn vezelversterkte
Stratasys brengt met de F3300 een nieuwe generatie FDM-printers op de markt die vanaf de basis zijn ontwikkeld voor productie.
thermoplasten (granulaat) zoals ABS, PA6, PETG, PLA en ASA beschikbaar. TPU en PP compounds zijn op aanvraag leverbaar. De zelfontwikkelde extruders zijn bij deze groot formaat 3D-printer bevestigd op lineaire robots. In de configuratie met de grootste nozzle, kan de powerPrint tot 30 kg per uur printen. De precisionPrint is een SLA-printer (Stereolithografie) die gedetailleerde onderdelen print op basis van harsen. Vooral bij deze 3D-printer is merkbaar dat KraussMaffei ervaring heeft met industriële productiesystemen. Naast het feit dat meerdere lasers de productiviteit verhogen, automatiseert de fabrikant het wisselen van de tank waarin het hars zit. Hierdoor kan men direct op een ander materiaal omschakelen als een buildjob klaar is. Ook Bosch begeeft zich in de loop van 2024 in de 3D-printindustrie. De start-up Bosch Industrial Additive Manufacturing bouwt een 3D-printer die met standaard granulaat voor spuitgietmachines print omdat het hiermee de kosten per onderdeel laag kan houden. De door Bosch zelf ontwikkelde extrusietechnologie staat toe om met gevulde materialen te printen. Het eerste materiaal dat Bosch aanbiedt, is versterkt PA6 in spuitgietkwaliteit. Later volgen nog andere materialen zoals een versterkt PA66. De extruder kan temperaturen aan van 350 graden C. De Bosch 3D-printer kan men enkel per jaar huren (vanaf €28.000 per jaar inclusief één materiaal en zowel hard- als software updates!).
Schaalbare technologie
De stap van Bosch en KraussMaffei, evenals die van Arburg, geeft aan dat deze fabrikanten een markt zien voor 3D-printen als productietechniek. “De productie van een miljoen spuitgietcomponenten ga je nooit met
additive manufacturing doen. Maar voor kleinere series is 3D-printen inmiddels een goed alternatief”, zegt Andy Langfeld, Vice President EMEA bij Stratasys, een van de pioniers in de 3D-printindustrie. Stratasys speelt hierop in met de F3300, een nieuwe FDMprinter die vanaf de basis ontwikkeld is voor productie met 3D-printen.
Zo kunnen onder andere de printkoppen on the fly verwisseld worden. Een nieuwkomer die zegt klaar te zijn voor serieproductie is Inkit. Deze spin-off van MIT in Boston heeft de Vision Controlled Jetting
bouwt een 3D-printer die met standaard granulaat voor spuitgietmachines print
technologie ontwikkeld die nu ook in Europa leverbaar is. De technologie is afgeleid van de inkjettechnologie uit de 2D printwereld. 3D-vision meet de hoogte van elke druppel uit een van de duizenden nozzles tot op 20 micron nauwkeurig waarna de hoeveelheid materiaal in de volgende laag per nozzle afzonderlijk wordt bijgestuurd. Het resultaat is een glad oppervlak, de mogelijkheid fijne details te printen én men kan met de Inkbit Vista in één werkstuk tot vier verschillende materialen printen. Inkbit
3D-print met langzame uithardingschemicaliën die de polymeerketen nauwkeuriger opbouwen, waardoor de levensduur van de onderdelen langer is dan bij sommige andere printtechnieken. Op Formnext is een nieuw materiaal voorgesteld: TEPU 50A, een halfzacht elastomeer met een shore50A waarde. De kracht van de Inkbit Vista zit volgens Davide Marini, co-founder en CEO, in zowel de schaalbaarheid als het gebruik van was als supportmateriaal. Momenteel heeft de Inkbit Visa 16 printkoppen met elk 1.000 nozzles. “Dat kunnen we uitbreiden als we naar grotere productievolumes gaan”, zegt Davide Marini. Als supportmateriaal gebruikt men was die vloeibaar wordt bij een hogere temperatuur. Hierdoor kan Inkbit het uit de buildjob halen van de losse componenten automatiseren. De vloeibare was kan direct hergebruikt worden.
Technologie alleen zal echter niet genoeg zijn om de omslag op gang te brengen, meent Christian Alvarez, chief revenue officer bij Stratasys. De techniek moet meer plug and play worden. Daarnaast is standaardisatie in de workflow noodzakelijk. Stratasys heeft dat bijvoorbeeld voor de luchtvaartindustrie gedaan en kan een gecertificeerd proces aanbieden. Daarnaast zijn er oplossingen nodig voor post-processing van de onderdelen om de oppervlakte kwaliteit te verbeteren. Fabrikanten zoals Formlabs maar ook het
Nederlandse Leering Hengelo bouwen compacte stations voor het ontpoederen. Leering is partner van het Britse AMT Post-Proces, dat voor de kleinere SLS-printers inmiddels een compact systeem voor vapor smoothing heeft gebouwd. Vapor smoothing wordt steeds vaker ingezet om het enigszins ruwe oppervlak van ge-3D-printe thermoplastische onderdelen gladder te maken. Vapor smoothing is een chemisch proces waarbij een speciale vloeistof op het oppervlak van het werkstuk word opgedampt en daar de ‘dalen’ vult. Dit gebeurt doorgaans in een geautomatiseerd proces; bij de kleinere systemen moeten de onderdelen met de hand in de machine gehangen worden.
Kwaliteitscontrole
Een andere stap die tot nog toe amper geautomatiseerd is, is de kwaliteitscontrole. Het Nederlandse AM-Flow heeft de oplossing die het verleden jaar hiervoor ontwikkelde inmiddels verbeterd. Het nieuwe systeem kan praktisch onbemand per dag zo’n 20.000 onderdelen controleren. 3D-print servicebedrijven kunnen dus voortaan 100% kwaliteitscontrole bieden. Dat maakt ze volgens Stefan Rink, CEO, concurrerend met spuitgiettechnologie. “3D-print servicebedrijven kunnen nu concurreren met de Amazon ’s van deze wereld die alles op voorraad houden. Vandaag besteld, morgen geprint en overmorgen in huis met 100% kwaliteit.”
Nog één obstakel
Zijn hiermee alle obstakels voor 3D-print weggenomen? Fried Vancraen, oprichter en tot voor kort CEO van Materialise, denkt dat nog één belangrijke schakel ontbreekt. “Het is moeilijk opschalen als je niet de juiste software hebt om data uit te wisselen”, zo zei hij op Formnext, ’s werelds grootste 3D-printbeurs. Het gebrek aan data-uitwisseling door de hele procesketen is een van de knelpunten in de echte industrialisatie van 3D-printen. Dat erkent ook Siemens. De integrale procesbenadering ontbreekt, zegt Olivier Diegerick, bij Siemens verantwoordelijk voor de ontwikkeling van de AM-software. Dit maakt de integratie van 3D-printen in de bestaande productieketens moeilijk. Oplossingen die de 3D-printerfabrikanten ontwikkelen, zijn volgens zowel Materialise als Siemens onvoldoende. “Een productieomgeving kun je niet managen met allemaal propriëtaire software van de OEM’s. Industrialisering vraagt om een end to end oplossing”, aldus Diegerick. Materialise wil met het CO-AM platform (waarin onder andere Magics als printvoorbereidingssoftware geïntegreerd is) partijen samenbrengen en data-uitwisseling vergemakkelijken. HP erkent dit inmiddels en gaat met het Belgische bedrijf samenwerken aan een geïntegreerde end-to-end workflowoplossing. Hiermee kunnen bedrijven gemakkelijker de stap naar 3D-printen in hun productieomgeving maken. Niet als vervanging van, maar als alternatief voor.
Wat gebeurt er aan het einde van de levensduur van een rubber product? Op dit moment is er nog maar een klein aandeel ‘material recovery’; dat wil Circular Rubber Platform substantieel verhogen. Dit kan onder andere met ‘functionalised micronised rubber powder’ van Atlantis Rubber Powders, leverancier van de afbeelding en lid van het platform.
Netwerken, kennisdeling en toepassing
Nederland – en de wereld – is sinds kort een duurzaam rubberinitiatief rijker: het Circular Rubber Platform (CRP). Dit online platform heeft netwerken, kennisdeling en toepassing van circulair rubber als hoofddoel.
Auteur: Maartje Henket
Initiatiefnemers zijn Enrico Koggel en Jan Boomsma, twee rubber product engineers die tijdens hun carrières bij Angst+Phister gefrustreerd raakten over de onmogelijkheid om makkelijk duurzame materialen te vinden.
“Wij werkten beiden voor OEM’s en over het algemeen gebruikten we reeds beschikbare rubber compounds”, vertelt Koggel. “Rubber compoundontwikkeling kwam binnen onze vorige organisatie alleen voor bij grote projecten met complexe vereisten aan het eindproduct. Wij wilden echter rubber compounds kunnen kiezen, of mogelijk zelfs ontwikkelen, met een lagere carbon footprint dan voorheen. Hier bleek beperkt ervaring mee, dus vroegen we bij diverse bedrijven welke oplossingen zij al wel hadden, en noteerden dat in onze excellijsten. Intussen zijn we veel bekender met rubber compounding en de mogelijkheden. Bovendien
hebben we nu het netwerk om toepassingsvragen te stellen die we zelf niet kunnen beantwoorden. Dat willen we publiek maken, zodat iedereen het kan doen.” Koggel en Boomsma hebben Circular Rubber Platform een half jaar geleden opgericht. Het verdienmodel is dat leden er tegen betaling hun duurzame activiteit presenteren. “Dat zijn de bedrijven die circulaire materialen leveren en aangezien de circulariteit in het rubber zich nog in het beginstadium bevindt, zoeken die alle bekendheid die ze kunnen krijgen.” Het CRP centraliseert hun kennis.
Cursussen
Het CRP heeft een website (circularrubberplatform. com), maar ook fysieke en digitale bijeenkomsten. “We hebben die lijst waaruit mensen kunnen kiezen, maar in onze zoektocht zagen we ook dat mensen niet weten dat je rubber überhaupt kan recycleren. Dus dat moet
je ze dan eerst al vertellen. En dan kun je vertellen welke keuze hun product duurzamer maakt.” Artech Rubber en het ERT testlaboratorium (Elastomer Research Testing) geven wel cursussen, maar niet over compounderen met circulaire rubber grondstoffen. “Wij denken dat er over jaar vraag genoeg is. En in de VS wordt de cursus al gegeven, dus mogelijk kunnen we met hen samenwerken.”
Hoe kan je rubber verduurzamen?
De eerste mogelijkheid om rubber te verduurzamen is om je kersverse virgin rubber te maken met biobased materialen. Rubber bestaat uit vier hoofdbestanddelen: polymeren, vullers, vulkanisatiemiddelen en beschermende additieven. Naast het natuurlijk monomeer isopreen, worden nu ook andere monomeren zoals ethyleen en butadieen geproduceerd volgens het bio mass balance principe, welke voor deels biobased polymeren kunnen zorgen, bijvoorbeeld EPDM en SBR. Ook de vullers kunnen biobased worden gekozen. In sommige gevallen rijstvlies gebruiken, of bepaalde mineralen, of lignine. Een andere mogelijkheid is om gerecycled carbon black te kiezen. Er is een biobased vulkanisatiemiddel verkrijgbaar, namelijk Biobased Bisphenol A. En als verwerkingsoliën zijn soja-, koolzaad-, raapzaad, of castor olie geschikt (die laatste wordt ook wel wonderolie genoemd). “Wij laten zien welke materialen je waardoor kan vervangen – en waar je die dan koopt. Zo proberen we te helpen om een markt te creëren.”
Ook is het mogelijk om bestaande producten te recyclen. Daarin zijn er vijf hoofdlijnen:
1: Het product hergebruiken in een andere vorm (bijvoorbeeld boombeschermers van oude autobanden).
Waarom circulair rubber?
Rubber bestaat hoofdzakelijk uit grondstoffen die van olie gemaakt worden, behalve natuurrubberpolymeer. De oogst van dit natuurrubberpolymeer wordt echter bedreigd door klimaatverandering - en de bijmengverplichting komt eraan. Bedrijven moeten dus materialen gaan hergebruiken of alternatieve biobased grondstoffen gebruiken. Daarbij moeten grote bedrijven met ESG, CSRD en SDG’s aan duurzaamheidsrapportage gaan doen - en de impact van (rubber)materialen op de carbon footprint van een bedrijf kan erg groot zijn.
2: Vermalen en activeren. Deze methode wordt bijvoorbeeld gebruikt om sportmatten te maken van vermalen zolen van sportschoenen en polyurethaanhars.
3: Verpoederen. Het poeder kan je vervolgens bijmengen bij normaal rubber.
4: Pyrolyseren. Hierbij wordt het rubber ontleed bij relatief lage temperatuur en druk, tot olie, gas, en as. In deze as zit onder andere een mengsel van roet, silica en zinkoxide.
5: Devulkaniseren. Daarbij verbreek je de vernetting* zonder de polymeerketen te breken. Dit kan mechanisch, thermisch, chemisch, of fysisch, of in een combinatie van meerdere methoden.
In tegenstelling tot kunststoffen, zijn rubbers elastisch. Dat komt doordat de molecuulketens op bepaalde contactpunten aan elkaar vast zitten in een chemische ver-
Circulariteit in de rubberindustrie is heel nieuw en informatie is erg versplinterd. Er zijn veel losse en kleine initiatieven, die CRP centraliseert en beter kenbaar maakt. “We verzamelen informatie over nieuwe en bestaande circulaire rubber grondstoffen (zowel gereycled als biobased) en recyclingstechnieken en koppelen die aan leveranciers wereldwijd, zodat ons netwerk daadwerkelijk aan de slag kan met circulair rubber.” Ook organiseert CRP 4x per jaar een digitale bijeenkomst voor kennisdeling en netwerken. “Veel engineers voelen zich persoonlijk betrokken met duurzaamheid, maar hebben geen idee waar te beginnen”, zegt Koggel. “Bovendien kost het ontwikkelen van circulaire grondstoffen en materialen tijd, en zijn er veel nieuwe leveranciers op de markt. Wij creëren de brug van de kleine initiatieven naar de markt en passen circulaire materialen daadwerkelijk toe. Door het netwerk kunnen we circulaire ketenprojecten opzetten, zoals voor polyurethaanrubber, schoen-tot-schoen recycling, nitril en latex rubberhandschoenen et cetera.”
ankering. Door toevoeging van bijvoorbeeld zwavel, peroxide, of bisphenol, kun je zorgen dat er nieuwe dwarsverbindingen ontstaan; zo maak je het rubber sterker (bijvoorbeeld voor autobanden). Dit proces heet vulkaniseren en het werkt middels vernetting. Die verbinding is de kracht van rubber – maar maakt het ook moeilijk te recyclen.
De klassieke techniek om de ketens weer te scheiden (devulkanisatie) is door het in een dubbelschroefs extruder mechanisch te kneden met een schuifspanning die te hoog is voor de eerder door vulkanisatie aangebrachte verbindingen, maar niet hoog genoeg om polymeerketens te verbreken. Koggel: “Dat is een hele dunne lijn. Als je te hard kneedt, of met een te hoge temperatuur, krijg je ketenverkorting. Maar als slechts een deel van de vernetting wordt verbroken, is je materiaal niet geheel gedevulkaniseerd en dus minder geschikt voor bijmenging met virgin materiaal.” Bij mechanische devulkanisatie ontstaat warmte door
Medewerker van Artech werkt een producten van gedevulkaniseerd rubber af.
Een pallet met gedevulkaniseerd rubber van de firma Tyromer. Devulkanisatie gebeurt al op industriële schaal en staat niet meer in de kinderschoenen. Het betreft echter nog maar een zeer klein aandeel in de totale rubberindustrie.
het kneden. Een andere mogelijkheid is om bij te verwarmen of koelen, of om chemicaliën toe te voegen. Dat laatste geschiedt nu nog alleen op onderzoekniveau. Ook zijn er bacteriën en schimmels die zwavel eten en zo waarschijnlijk kunnen devulkaniseren; ook deze methode heeft het lab nog niet verlaten. Dan is er fysisch devulkaniseren; dat geschiedt met behulp van magnetrontechnieken.
Training Design for Circularity
Tot slot, met betrekking tot training voor circulariteit, bespreekt Koggel het belang van ontwerpen met recycling in gedachten. Hierbij wordt uiteengezet hoe afval verminderd kan worden door minder materiaal te gebruiken, makkelijker te scheiden na gebruik, minder soorten materialen samen te gebruiken, materialen te kiezen die makkelijker te recyclen zijn (TPE’s in plaats van rubber bijvoorbeeld).
circularrubberplatform.com
Hoewel een nieuwe bundel over selective laser sintering (SLS) aanleiding was voor een bezoek aan het lectoraat kunststoftechnologie van Hogeschool Windesheim, mondde dit al snel uit in een breed gesprek over alle kansen die het lectoraat ziet voor AM in de kunststofindustrie. Onderzoekers Geert Heideman, Paul Dijkstra en Tommie Stobbe zien nog onbenut potentieel en bovendien bieden technologische ontwikkelingen ook weer nieuwe mogelijkheden.
Auteur: Kasper Weigand
Onderzoeker Paul Dijkstra is bezig met een bundel over SLS-printen. “Wanneer haakt additive manufacturing (AM) in op problematiek die ik als ontwerper tegenkom in mijn werk? Dat is denk ik een hele interessante vraag om te stellen. SLS is daar inderdaad één oplossing die al wel toegepast wordt, maar beter toegepast kan worden.” SLS is een poedergebaseerde 3D-print techniek. Een gedeelte van het poederbed wordt met een laser aan elkaar gesmolten. Het overgebleven poeder ondersteunt het materiaal wat je hebt gesmolten en is naderhand gemakkelijk verwijderbaar. “Dan kun je hele gekke vormen maken”, zegt Dijkstra terwijl hij een ge-3D-printe gamecontroller laat zien.
SLS
SLS is een volwassen technologie die ruim 15 jaar
industrieel wordt gebruikt. Het afnemen van onderdelen via service providers is heel gemakkelijk, maar het is niet eenvoudig om de proceskennis in huis te halen als je zelf geen SLS-printer hebt. “Dat merken we met elke printtechniek en dat betekent ook dat er nog wel weleens frictie is tussen wat er op de ontwerpvloer aan kennis aanwezig is voor een AM-techniek en wat ze aan kennis nodig zouden hebben om het ideale ontwerp te maken. Waardoor producten niet de kwaliteit hebben waarop gehoopt was, of de kosten onnodig oplopen.” Dijkstra hoopt met zijn publicatie daar een verschil te kunnen maken.
Bundel
Wat wordt de inhoud van de SLS-bundel die later dit jaar moet verschijnen? “Het begint heel basaal, wat is
Een CNCfreesmachine van Perron038 met rechts een geïntegreerde laserlaskop.
SLS en voorbeelden van hoe SLS in de industrie naar meerwaarde wordt benut. Vervolgens duiken we in de diepte. Wat bepaalt de verwerkbaarheid van een materiaal met SLS? Welke eigenschappen worden behaald? En hoe kan ik als ontwerper het maximale uit de technologie halen? Dan gaat het over zaken als procesparameters, wanddiktes, invloed van printoriëntatie”, vertelt Dijkstra.
Polyamide
Er werd tot voorkort eigenlijk alleen met polyamide 12 grade (PA12) geprint met SLS. “Zo heeft PA12 de juiste deeltjesgrootte en korrelvorm. Verder is sprake van een ‘gat’ tussen het smeltpunt en de kristallisatietemperatuur die het mogelijk maakt om naast elkaar een poederbed te hebben van niet gesmolten materiaal en een smeltbad dat onder de smelttemperatuur is afgekoeld maar nog niet kristalliseert. Hoe dichter dat op elkaar ligt, hoe lastiger het te verwerken is. Bij PA12 ligt daar voldoende ruimte tussen. Er zijn wel alternatieven, maar veelal niet goedkoper. PP is een goed voorbeeld: voor spuitgieten is het materiaal relatief goedkoop en uitstekend verwerkbaar. Voor SLS zijn de materiaalkosten vergelijkbaar aan PA12, maar is de verwerkbaarheid moeilijker en zijn de mechanische eigenschappen minder. Op dit moment is dus nog sprake van een niche, bijvoorbeeld voor chemische resistentie.”
Onderzoeken
Alle onderzoeken die het lectoraat Kunststoftechnologie het gedaan op het gebied van SLS-printen worden ook opgenomen in de bundel. Lange-duur eigenschappen, de invloed van hitte, of
van UV-licht, daar is allemaal onderzoek naar gedaan. “Warmtenabehandeling en ook de tribologische eigenschappen. Dat staat allemaal in de bundel.” Associate lector Geert Heideman vult aan: “Het gaat dus echt om de industriële toepasbaarheid helder te maken. Om bedrijven op weg te helpen.”
Grote aantallen
Als het om grote aantallen gaat is SLS, als poederbed AM-technologie de aangewezen keuze. “Voor kleinere producten zijn er al casussen bekend waarin SLS wordt gebruikt voor series in de tienduizenden, zelfs in de miljoenen. Dan hebben we het wel echt over hele kleine producten hoor, mascaraborstels”, zegt Dijkstra. Toch hameren de onderzoekers erop goed te kijken naar de voordelen van AM en het niet te zien als vervanger voor spuitgieten. “AM is bij uitstek geschikt bij maatwerk in grote massa. Als we iets hebben wat gebruikerspecifiek is in de zorg, of een machine die op maat gemaakt moet worden dan kan AM daar het antwoord bieden zonder een grote investering in tooling en bijbehorende levertijd. Die flexibiliteit heeft mensen de afgelopen tien jaar geïnspireerd en daardoor is de AM-markt ontzettend gegroeid. Het financieel aantrekkelijk maken van maatwerk is een van de sterkte punten van AM”, legt Dijkstra uit.
Flexibeler
Maar bedrijven moeten altijd goed nadenken waarom ze zouden willen gaan 3D-printen. Om de kosten te drukken waar conventionele productie ook volstaat? Dan vaak maar beter niet. “Wil je flexibeler zijn in je productie en doorlooptijden verkorten? Dan juist wel doen. Een bedrijf dat bijvoorbeeld 700 verschillende
De Minifactory 3D-printer bij Perron038, een industriële filamentprinter voor hoge-temperatuur materialen.
Hogeschool Windesheim heeft samen met brancheorganisaties NRK en Wavin het lectoraat Kunststoftechnologie opgericht om een brug slaan tussen industrie en onderwijs door praktijkgericht onderzoek. Binnen het lectoraat zijn vier programmalijnen: Duurzaam Produceren, Circulaire Economie, Hybride Ontwerp met kunststoffen en Industrieel Additive Manufacturing. Binnen deze laatste programmalijn wordt geprint met industriële machines en doet het lectoraat onderzoek om de inbedding van AM als productietechniek in de industrie te bewerkstelligen. Zo wordt er een bijdrage geleverd aan het concurrerend houden van de maakindustrie in de regio.
onderdelen op voorraad moet hebben en daarvoor een groot magazijn moet hebben kan misschien beter op aanvraag gaan printen”, illustreert hij.
Geprinte matrijs
Onderzoeker Tommie Stobbe gaat nog verder: “Ik denk ook dat je met je ontwerp die toegevoegde waarde van AM eruit moet halen, wil het echt zin hebben. Alleen als AM de enige manier is om een goed product te maken.” Als voorbeeld toont hij een ge3D-printe (metalen) matrijs. “De koeling in de hoeken was met het originele matrijsdeel problematisch. Er
“Start maar eens een spuitgietmachine op voor drie onderdelen”
was altijd een hotspot en zo kwam je nooit aan de juiste maatvoering van je product. De kanalen lopen nu dichter op de matrijswand en de afstand tussen de matrijswand en het koelkanaal is ook gelijkmatiger. Hierdoor krijg je een homogenere en een snellere koeling. Dat betekent betere procescontrole en een kortere cyclustijd. Dat kan uiteindelijk dus resulteren in een goedkoper en beter product en is een hele andere manier om met additive manufacturing in te haken op kunststofproductie.”
Productiecyclus
Heideman hoopt dat hoe meer ontwerpers weten van AM-techniek, hoe meer ze erin gaan denken. Hij merkt dat er nog veel vooroordelen spelen over AM: de eigenschappen zijn vast niet goed genoeg, is een bekend geluid. “Het is zeker belangrijk dat er meer kennis van komt. Dat komt er natuurlijk ook met een nieuwe generatie engineers. Gaan we AM steeds meer zien in de industrie? Daar zijn wij wel van overtuigd.” Maar niet als vervanging voor spuitgieten. Hij stipt voor alle stappen in de productiecyclus aan waar AM van nut kan zijn: “In de pre-production is er behoefte aan prototypes. Daarvoor is AM heel geschikt. Een probleem vaak is dat het prototype niet van hetzelfde materiaal is als het uiteindelijke product. Maar er zijn technieken om het met een echt spuitgietmateriaal te printen. Dat heb je bij de Freeformer gezien.” (Zie het artikel hierover in K&R 6-2023 of online -red.) In de productiefase zelf ga je grote aantallen spuitgieten met een matrijs. “Daar is AM interessant als je een afwijking hebt. Je maakt honderdduizend dezelfde producten, maar je hebt er eentje nodig met een speciaal bevestigingspunt. Daar kun je de matrijs niet voor aanpassen. Je kunt dan insert molding toepassen. Je print het specifieke onderdeel, dat plaats je in de matrijs en je spuit
eromheen.” Insert molding is ook onderzocht in het Freeformer-traject. “Daar is het wel belangrijk welke AM-techniek en materiaal je gebruikt.”
Reserveonderdelen
In de post-productie is AM interessant als het gaat om reserveonderdelen. “Sommige bedrijven moeten decennia lang reserve-onderdelen kunnen naleveren. Stel je krijgt een bestelling van drie onderdelen. Start maar eens een spuitgietmachine op voor drie onderdelen.” Dan is het dus heel interessant om die drie onderdelen te kunnen 3D-printen. “Voor een deel kan dat met SLS, maar lang niet altijd, want dat is bijna altijd met PA12 en soms wil je een ander materiaal gebruiken. De Freeformer van Arbug is een deel van het antwoord. En sinds kort heeft het lectoraat ook toegang tot een Minifactory 3D-printer bij Perron038, een industriële filamentprinter voor hoge-temperatuur materialen.
Een van de problemen bij het metaalprinten van matrijzen ten behoeve van kunststofproductie is de prijs ervan. “Conformal cooling heeft zich in de afgelopen tien jaar al wel bewezen vanuit het technologische oogpunt. Ge-3D-printe koelkanalen die de matrijsholte netjes volgen, zorgen voor een betere procescontrole en een kortere cyclustijd”, zegt Dijkstra. “Maar daar worden nog wel steeds metaalprinttechnieken toegepast die vrij kostbaar zijn. Het gaat om laser powder bed fusion. Dat geeft ontzettend hoogwaardige producten met hoog detail. Laser powder bed fusion vereist echter totaal andere machines, operators en andere ontwerpregels en manier van
denken dan conventionele metaalbewerking. Dat betekent onderaan de streep dat geprinte matrijsdelen met deze techniek heel kostbaar zijn.” Een ander probleem is dat de belanghebbende partij, de kunststofverwerker, meestal niet zelf de matrijs bouwt en de matrijzenbouwer zelf er niet per se belang bij heeft een duurder product te leveren. Als je nou alternatieve technologieën hebt, die goedkoper zijn, maar met hetzelfde effect, dan zou het een ineens heel stuk interessanter kunnen worden.
CNC-freesbank
“Er zijn andere metaalprinttechnieken waarvan de productiviteit nogal wat hoger ligt. En die gaan uit van het principe van boog- of laserlassen met metaaldraad. Ook zijn er dergelijke systemen die poeder gebruiken. Dit soort systemen zijn in sommige gevallen ook te integreren in een CNC-freesbank. Dan begin je met een deel van de matrijs, je freest vervolgens een deel weg, je brengt weer een deel aan en je gaat meteen nabewerken. Allemaal met weinig opspanningen in dezelfde machine”, legt Dijkstra uit. Heideman: “Ik denk dat dit veel potentie heeft omdat het heel dicht bij de metaalbewerker ligt.” Als je dit als extra feature integreert in een (vijf-assige) CNCfreesmachine, dan is dat nog steeds relatief betaalbaar. En het voelt vertrouwd, het is veel laagdrempeliger. Je gebruikt goedkoop lasdraad. Het gaat in ons geval om een vorm van laserlassen en dat kunnen we in de industrie wel. AM-metaal wordt zo veel toegankelijker voor een heel ander publiek”, verwacht hij.
www.windesheim.nl/onderzoek/lectoraten/ kunststoftechnologie
Lange gebruiksduur, duurzaamheid, circulariteit
Duurzaamheid is één van speerpunten bij 3D-printen op groot formaat. Doordat additive manufacturing een relatief nieuwe markt is, wordt deze nog zeer gedreven door snel opeenvolgende technische innovaties. Hierbij wordt geprint met zowel standaard kunststoffen die ook gebruikt worden bij het spuitgieten als met gespecialiseerde kunststof compounds. Dit terwijl je zou verwachten dat grootformaat 3D-printen echt andere eisen stelt aan de kunststofeigenschappen als ook aan de verwerking.
Auteur: Epco Blessing, Transmare CirQlair
Er is een belangrijke focus op de inzet van duurzamere dan wel circulaire of ‘groenere’ kunststof alternatieven. Voor het begrip duurzaamheid worden een mengelmoes van definities gebruikt, soms door elkaar heen. Wanneer is een materiaal nou duurzamer of groener? Wat mij wel duidelijk is geworden is dat het inzetten van consumentenafval oftewel post consumer recycled kunststoffen beschouwd mag worden als duurzaam. Deze gerecyclede materialen zorgen voor een aanzienlijke reductie in het verder belasten van het milieu (denk hierbij aan o.a. restafval, watergebruik, e.d.) als ook een lagere CO2-voetprint
gemaakt van duurzame grondstoffen als duurzaam bestempeld worden, ook de eindtoepassing heeft hier invloed op. Zo zal een langere levensduur van het eindproduct de milieubelasting nog verder reduceren met name bij gebruik van gerecyclede single-use plastics.
Grote objecten
ten opzichte van nieuwe, ‘verse’ grondstoffen. Toch zal niet iedere eindtoepassing nog
In de innovatieve markt van groot formaat 3D-printen verlopen materiaal- en procesontwikkelingen vaak simultaan en door elkaar heen. Hierbij volgen technologieën elkaar in rap tempo op. Zo zijn er momenteel meerdere technische concepten ontwikkeld waar er vanuit kunststof granulaten grote objecten geprint worden. Denk hierbij aan kunstobjecten, grote plantenbakken, (tuin)meubilair, tuinhuisjes, boten en zelfs bruggen en veerboten. Wat kenmerkend is voor deze eindtoepassingen, is dat ze zijn gericht op producten met een lange gebruiksduur waarbij duurzaamheid, circulariteit c.q. hergebruik belangrijke onderliggende thema’s zijn.
Door de innovatiedrift van de 3D-print markt, werd er al snel geëxperimenteerd met post consumer en post industrial recyclaat (PCR en PIR) en kwam men er aan de hand van dergelijke grote eindproducten achter dat PCRmateriaal een goed uitgangspunt kan zijn voor verschillende 3D-printtoepassingen. Een van de voordelen van PCR-kunststoffen, is dat het makkelijk print mits de juiste samenstellingen worden gebruikt. Hierdoor kan er gewerkt worden in een breed verwerkingsvenster en geeft het daarbij ook nog een goede laag-op-laag hechting in de Z-richting, wat sterkte biedt door de lagen heen.
Visueel aantrekkelijk
De juiste PCR-materialen bieden makkelijke verwerking, uitstekende technische eigenschappen, lange levensduur, zijn visueel aantrekkelijk en zelfs goed inkleurbaar. Daardoor zijn PCR-materialen een duurzaam alternatief voor de gangbare ‘nieuwe’ kunststoffen. Verwerking, hechting en krimp zijn de belangrijkste eigenschappen voor het makkelijk printen van een
‘Steeds meer 3D-print bedrijven kiezen voor speciaal voor hen ontwikkelde compound’
eindproduct. De kunststof krimp is wel een interessant discussiepunt, want de meeste 3D-printerbedrijven willen materialen met zo min mogelijk krimp. Helaas kunnen veel kunststoffen daar niet aan voldoen, zodoende werkt men er omheen of wordt er voor gezorgd dat het ontwerp en productietechniek hier minder ‘gevoelig’ voor zal zijn.
Krimp
Ondanks dat krimp lastig te beïnvloeden is, blijft het beperken ervan wel een belangrijke wens bij grootformaat 3D-printen. Technisch gezien zullen alle kunststoffen altijd wel een beetje krimp tonen. Met behulp van vulstoffen en andere additieven is het mogelijk om invloed uit te oefenen op deze eigenschappen. Echter zit hier wel een limiet aan. Het grote voordeel van 3D-printen met materiaal met een laag krimppercentage is, dat hierdoor gemakkelijker en strakker ontworpen maar ook geprint kan worden. Naast de wensen van weinig krimp zijn er afhankelijk
van de eindtoepassing natuurlijk ook nog andere eisen zoals UV/weersbestendigheid, vlamvertraging, uiterlijk als b.v. kleur, etc.
PP, PE en PET
Maar welke soorten gerecycled kunststoffen zijn er beschikbaar? Hierin is een onderverdeling te maken tussen: post consumer recycled en post industrial recycled. Bij het PCR zijn dat hoofdzakelijk PP, PE en PET, aangezien deze afvalstromen goed beschikbaar zijn vanuit het consumenten en ook industriële afval. Bij het PIR gaat het meer om productie uitval/afval en soms zijn dit fabrieksproductieresten en soms valt ook off-spec hieronder. In andere gevallen gaat het helaas zelfs om omgelabeld nieuw materiaal. Qua milieubelasting is post-consumer vrijwel altijd beter ten opzichte van post industrial, aangezien post-consumer er al een volwaardig leven op heeft zitten.
Technische kunststoffen
Naast de standaard gerecyclede commoditystromen wordt er ook gewerkt met gerecyclede technische kunststoffen. Deze zijn t.a.v. de commodity stromen vaak in relatief kleinere hoeveelheden beschikbaar, maar het wordt inmiddels al ingezet door verschillende verwerkers. Een aantal van deze technische kunststoffen moeten worden verwerkt op hogere temperatuur zoals bijvoorbeeld PC, PEI, PES, PPS en PEEK.
Industriële robot
De PCR-kunststoffen zijn vrijwel altijd ongevulde, onversterkte spuitgiet- of extrusiekunststof kwaliteiten en daarmee meestal niet direct geschikt voor 3D-printen. Dit wordt mede veroorzaakt doordat het verwerkingsproces bij 3D-printen anders is dan bij extrusie of spuitgieten. Zo wordt er ge-3D-print met verschillende machine setups waarbij bijvoorbeeld de extruder gekoppeld is op
een meerassige industriële robot of waarbij een extruder in een portaalframe staat of een stationaire extruder die via een meltpipe de nozzle (printkop) voedt op de robotarm en nog andere varianten. Daarnaast worden fibertapes en eventueel ook freesbewerkingen tijdens en na het printproces toegepast. Elke verwerkingsvariant én toepassing stelt daardoor net even andere eisen aan het materiaal en de verwerking ervan. Dit is ook de reden waarom steeds meer 3D-print bedrijven kiezen voor een speciaal voor hen ontwikkelde compound. Want naast de verschillen in verwerkingsmethodes zal bij het inzetten van de juiste kunststof en ook rekening moeten houden met andere eigenschappen als vloeigetal, thermische stabiliteit, verwerkingstemperatuur en temperatuurrange voor de laag-op-laag hechting e.d.
Zoals ik al aangaf, kenmerkt deze markt zich door diverse ontwikkelingen die simultaan plaatsvinden. Vandaar mijn advies: mocht je als 3D-print bedrijf een geschikte compound zoeken die aansluit bij jouw wensen, praat eerst eens met concullega 3D-printbedrijf, vraag naar hun materiaalervaringen of anders ga eens praten met jouw materiaalleverancier(s). Zij kunnen jou helpen met jouw specifieke eisen en wensen.
www.transmarecirqlair.com
Een veerpont van Holland Shipyards van 4 bij 9 meter met een ge-3D-printe romp van een speciale compound op basis van 100% post consumer recycled PP.
Met kennis en visie verpakkingen ontwikkelen voor het middelgrote segment
Verpakkingsfabrikant Teamplast uit Heteren startte 2024 goed. Eind januari werd symbolisch de 50e spuitgietmachine afgeleverd. Een volledig elektrische SumitomoDemag IntElect 180-560. Bijna 30 jaar na de start van het bedrijf, met nog geen enkele machine, staan nu verschillende hallen vol met 24 uur per dag, 5 dagen per week, doorwerkende machines. En wordt het een hele uitdaging nog verder uit te breiden, want alle beschikbare ruimte wordt benut. CEO van Sumitomo-Demag Gerd Liebig en het team van machineleverancier Thiele & Kor Plastic Machinery waren er op deze feestelijke dag bij, om de nieuwe machine te onthullen.
Auteur: Kasper Weigand
Gerard van Amerongen en Gerhard Koning startten Teamplast in 1995 eigenlijk met niets. Ja, met kennis en een visie, maar verder niets. “Die visie die hebben we nog steeds”, zegt Van Amerongen. Klantspecifieke kunststof verpakkingen ontwikkelen en spuitgieten. “Dus niet blazen of extruderen. Alleen spuitgieten. En dan kom je al snel uit bij sluitingen, doppen, potjes, maar geen flessen. Onze visie was dat we in het middelgrote segment, qua aantallen, wilden produceren.”
Ontwikkelafdeling
Tussen de 500 duizend en 5 miljoen stuks per jaar. Daar zagen de beide heren mogelijkheden. In het grotere segment zijn de bedrijven vaak kapitaalkrachtiger
om te investeren in zaken als automatisering, matrijzen en ontwikkeling. Op het moment dat je producten gaat ontwikkelen dan zit er veel geld in het voortraject. In het middelgrote segment begint die ontwikkeling wel heel zwaar te drukken op die productprijs. “Wij wilden een eigen ontwikkelingsafdeling creëren die de ontwikkelingen doet voor dat middelgrote segment. Maar die kosten verdisconteren we in het grote geheel. Je wijst niet de ontwikkeling toe aan één product. Maar de kosten die wij daarvoor maken, worden als overhead in het geheel opgenomen. Daardoor open je deuren naar het middelgrote segment. Uiteindelijk geldt dat nog steeds tot op de dag van vandaag. De aantallen zijn wel wat toegenomen, maar we blijven nog steeds veel ontwikkelen en ook weer investeren in
nieuwe producten. We hebben ook geen eigen producten, geen catalogus. We hebben alleen maar ideeën. We proberen een oplossing te creëren voor de vragen van onze klanten”, legt Van Amerongen uit.
Groter geheel
Teamplast beseft goed dat het altijd onderdeel uitmaakt van een groter geheel. Zoals een dop onderdeel is van een fles. “En we moeten zorgen dat de dop op de fles past uiteraard”, gaat Gerhard Koning verder.
“Daarbij zijn we vaak in de lead. Wij maken dat dopje of dekseltje. Maar het gaat straks over een bestaande afvullijn, je moet ook verder kijken dan alleen wat je zelf doet.” Soms gaat het om standaard dopjes, soms wijkt het juist af. Of is er een hele nieuwe verpakking. “Maar het moet wel weer over die bestaande afvullijn.”
Maatwerk
“Het is bijna allemaal maatwerk. En dat vraagt ook heel veel van de organisatie”, vertelt Van Amerongen weer. “Dat is ook een van de redenen dat wij Teamplast heten”, zegt hij met de nadruk op team. “Het is niet alleen maar een team intern, maar ook een team met onze klant.” Daarnaast zoekt Teamplast ook de samenwerking in de keten. Teamplast met als kracht het ontwikkelingen en spuitgieten van kunststof verpakkingen. In die keten zitten ook de grondstofleverancier, de kleurstofleverancier, de machineleverancier, een ook de matrijzenbouwer. Langdurige, duurzame relaties en het liefst lokaal. “Hoe lokaler je werkt, hoe sneller je in staat bent om bepaalde problemen met elkaar op te lossen”, vult Priscilla Koning aan. Priscilla en Robin Koning vormen de jonge generatie binnen het directieteam en zullen uiteindelijk Teamplast overnemen.
De eerste machines waar Teamplast mee startte, worden langzamerhand allemaal vervangen. “En die wor-
Gerd Liebig is CEO van Sumitomo-Demag en was voor de officiële ingebruikname van de 50e Sumitomo-Demag spuitgietmachine door Teamplast overgekomen uit het Duitse Schwaig, waar het hoofdkantoor van het bedrijf staat. Hij heeft als geen ander zicht op de markt voor met name volledig elektrische spuitgietmachines. Hoe we het in Nederland doen op het gebied van elektrische spuitgietmachines? Goed! Nederland richt zich volgens hem meer op volledig elektrische spuitgietmachines dan andere Europese landen. “In Nederland wordt wat minder voor de automotive industrie geproduceerd en daar gebruiken ze over het algemeen grote machines. De limiet voor all electric is momenteel zo’n 800 tot 1000 ton. De markt in Nederland richt zich op kleine en middelgrote machines. Zeer nauwkeurige machines in het kleine en middelgrote segment die ook nog eens energie besparen. En daar hebben wij het perfecte antwoord voor”, zegt Liebig.
Sumitomo-Demag besloot zeven jaar geleden om zich voor het kleine segment volledig te richten op elektrische machines. Voor grotere machines is er nog steeds een limiet aan wat mogelijk is met volledig elektrisch. Is er nog veel ontwikkeling in de elektrische spuitgietmachines? Zeker! Of hydraulische machines helemaal zullen verdwijnen? Wie weet. Maar het is niet een vraag waar Liebig heel erg in is geïnteresseerd. Sumitomo-Demag is sterk in het kleine en middensegment en daar richten ze hun pijlen op. “Ik kan al wel zeggen dat we voor de volgende K-Show onze sluitkracht zullen uitbreiden. Maar onze focus blijft op volledig elektrische machines.”
De trend naar volledige elektrische spuitgietmachines begon in de medische sector, want dat was nodig voor cleanroomomgevingen. Toen kwamen de verpakkingen, nu de vastgemaakte doppen. “De sector voor vastgemaakte doppen gaat min of meer volledig over op elektrisch”, merkt Liebig. “Vanwege precisie en de hygiëne. En hetzelfde zien we nu voor consumentengoederen.” Dat is volgens hem ook de reden dat er in Nederland steeds meer volledig elektrische spuitgietmachines worden gebruikt. “Nederland is heel sterk in de consumentenmarkt. En daar realiseren ze zich de voordelen van volledig elektrisch. Hoe kleiner de machine, hoe groter het verschil.” Liebig denk dat in de Benelux 40 tot 45 procent van de totale markt volledig elektrisch is. “En Sumitomo-Demag neemt hiervan bijna 50% voor zijn rekening.”
De grote verandering die eraan zit te komen is die van digitalisering. Via MyConnect kan een klant de machine verbinden met Sumitomo-Demag. “Voor het eerst begrijpen we nu wat de klant precies doet met onze machines”, legt Liebig uit. “De afgelopen dertig jaar hebben onze ingenieurs componenten, machines en schroeven ontwikkeld. Maar niemand wist echt wat het doel van de klant was omdat we die data niet hadden. Nu hebben we grote hoeveelheden data en is de uitdaging hoe we die gegevens moeten gaan verwerken.” Doel is om van afstand, wereldwijd, problemen bij klanten op te lossen. En daarnaast inzicht in de machines te krijgen om slijtage en problemen goed te kunnen voorspellen en zo storingen voor te zijn.
Het directieteam van Teamplast met vanaf links Robin Koning, Gerhard Koning, Priscilla Koning en Gerard van Amerongen.
den vervangen voor volledige elektrische spuitgietmachines. Dat is een goede ontwikkeling”, vindt Gerhard Koning. Het bedrijf is merkvast en vervangt de oude Demag-machines voor nieuwe Sumitomo-Demag spuitgietmachines. Voor de toekomst liggen er nog uitdagingen genoeg. Verduurzaming is er één. Recycling een tweede. Over een aantal jaar wordt er een verplicht percentage recyclaat in alle kunststof producten afgedwongen door de overheid. Is dat iets wat speelt?
“Het speelt”, zegt Priscilla Koning. “Voor een deel zitten we in de voedingsmiddelen, waarvoor dat lastig is. Maar we hebben ook een aantal producten waarvoor dat prima zou kunnen. Het is wel altijd een wisselwerking met de klant. Want die bepaalt uiteindelijk, het is zijn product. Maar we stimuleren het, we doen proef-
CEO Sumitomo-Demag Gerd Liebig was voor de gelegenheid overgekomen naar Nederland.
spuitingen, we delen informatie.” De wetgeving in dit land zal ook helpen dit verder te ontwikkelen. “We worden steeds meer gedwongen recyclaat te gebruiken. Ook voedingsmiddelen zullen aan de beurt komen”, weet Gerhard Koning. “Dat duurt wat langer want dat heeft met voedselveiligheid te maken. Maar je ziet die ontwikkeling wel. Ook bij de granulaatproducenten. Die moeten ook.”
Toen QCP, Quality Circular Polymers, een aantal jaar geleden een plant voor gerecycled PP opstartte en testers zocht, sprong Teamplast daar bovenop. “Er werden tien potentiële afnemers gezocht en toen hebben we gelijk gezegd, ja dat doen we”, herinnert Van Amerongen zich. “We zijn gewoon op ons eigen gevoel producten gaan spuitgieten. Voor klanten waarvan wij dachten, dat is interessant. Dat heeft een hele lange adem gehad. En dat doen we nog steeds: stimuleren, promoten. En weer proefspuiten. Inmiddels zijn er een aantal producten van gerecycled kunststof die daadwerkelijk opgenomen worden. We zijn bezig met een aantal projecten die hopelijk dit jaar opgezet worden. Maar heel recent kreeg ik te horen dat een bepaald product dat de Duitse markt op gaat, alleen overgaat op post consumer recyclaat (PCR) als de Duitse overheid de verpakkingstaks voor virgin materiaal hoger maakt dan op PCR. Weer het klassieke prijsverhaal.”
Niet alleen
Robin Koning: “Het is eigenlijk een oproep dat als we vooruit willen, iedereen daarin mee moet. Of dat nou de verwerkers zijn, de producenten, de merkeigenaren. Laten we dat samendoen, ten koste van een klein beetje marge, dan kunnen we dat soort stappen zetten. Je kunt dat niet alleen dragen.” Teamplast produceert hoofdzakelijk voor Nederland en de omringende landen, Engeland, België en Duitsland. Priscilla Koning: “We hebben met leveren naar Engeland gemerkt wat voor impact regelgeving heeft. Iedereen weet waar hij aan toe is en waar de producten aan moeten voldoen. Dat helpt om de boel in beweging te
brengen.” Van Amerongen: “Onze Engelse klanten zeggen, kom met alternatieven want anders moeten wij 30% extra belasting betalen. Dan zie je dat er ineens concessies gedaan kunnen worden.” Dan moeten ze bij Teamplast nog wel aan de bak om een geschikt materiaal te vinden, want niet alles is zomaar beschikbaar.
De ontwikkelingen op de energiemarkt raken het bedrijf direct. Meer energie krijg je voorlopig niet. Dat dwingt het team om creatief naar de eigen processen te kijken. En dan loont het om een oude hydraulische spuitgietmachine te vervangen voor een veel zuinigere volledig elektrische machine. “We monitoren het energieverbruik per machine”, vertelt Van Amerongen. “Zo kun je heel gemakkelijk vergelijken wat een hydraulische machine doet van hetzelfde tonnage als een elektrische machine. We zijn zelfs zover gegaan dat we een matrijs op allebei de machines onder dezelfde omstandigheden hebben gespoten. Dan zie je dat je een energiebesparing van tussen de 50 en de 60% haalt. Niet op één machine, maar over de hele linie. En dan heb ik het nog niet eens over de betere cyclustijden, de hogere reproduceerbaarheid, dat je minder koeling nodig hebt. Het heeft echt heel veel voordelen. Als je wilt uitbreiden maar je krijgt niet meer stroom, dan lever je een oude machine in en dan zet je er twee nieuwe voor terug”, illustreert hij.
Personeel
Een ander veelgehoord probleem vandaag de dag speelt minder bij Teamplast: personeelstekort. “We groeien met de mensen uit ons netwerk”, legt Priscilla Koning uit. “Een leverancier die iemand weet. Een collega die een buurman heeft of een neef. Er werkt heel veel familie binnen Teamplast. Partners, broer en zus, ooms en neven en nichten, moeder/dochter. Best wel heel bijzonder. We hebben niet veel issues als het gaat om het vinden van personeel.” Daarnaast switch er soms een procesoperator van ploegendienst naar de dagdienst. Die kan zich dan ontwikkelen in een stuk techniek. “Het
Vlnr:
Gerhard Koning, Gerard van Amerongen en Gerd Liebig.
is ook kijken hoe je de mensen die je hebt, zo goed mogelijk kunt behouden. En op het moment dat je wilt uitbreiden, kijken hoe je je eigen netwerk kunt aanspreken. Maar er is in mijn ogen geen groter compliment dan een collega die een familielid aandraagt. Want dat doe je niet zo snel”, zegt ze tot slot.
www.teamplast.nl
www.sumitomo-shi-demag.eu
www.tkpm.eu
Spuitgieten met gerecycled kunststof
Stel, je bent een spuitgietbedrijf dat nog nooit iets met gerecycled materiaal heeft gedaan en je krijgt het gevoel dat 2027 met rasse schreden nadert. Wat doe je dan? Beginnen! Waarom nu al? Omdat je voor elk product het vrijgaveproces opnieuw moet doorlopen. Wij spraken ‘dame van het eerste uur’ Cristel Rijnen, directeur van Injection Point. “Je moet altijd eerst testen om te beoordelen of er qua maatvoering en functionaliteit en hetzelfde product uitkomt. Dus je kunt nooit in één keer je hele portfolio in gerecycled materiaal maken.”
Auteur: Maartje Henket
Rijnen, die Injection Point in 2011 oprichtte, merkte hoeveel er te recyclen valt toen ze kinderen kreeg. “Kleine kinderen ontwikkelen zich heel snel, dus ik had regelmatig nieuw speelgoed nodig. En het oude kon ik niet kwijt. Ook niet gratis. Dat was voor mij echt de eyeopener over de plastic afvalberg. En toen ben ik me gaan afvragen wat ik daar zelf aan kon doen.”
Injection Point maakt veel onderdelen voor elektrische apparaten en elektronica. Een markt bij uitstek waar hoge eisen worden gesteld aan de kwaliteit en continuïteit van onderdelen. “Mijn klanten zijn over het algemeen heel enthousiast over recycling, maar ze moeten aan de CE-keur voldoen en 5 jaar garantie geven. En een gerecyclede grondstof heeft zich nog niet door de tijd bewezen. Het moet nog CE worden gekeurd – en dat kost veel geld. Eén producteigenaar
gaat dat niet op zijn eigen houtje doen, zolang het niet echt moet. Vooral niet omdat de stroom van gerecycled materiaal uitputtend is. We hebben op dit moment niet voldoende om de gehele spuitgietproductie van Nederland over te zetten. Dus als je de CE-keur rond hebt, weet je vervolgens niet of je het recyclaat altijd kunt krijgen.”
Kinderziektes dus, die voorlopig nog wel even zullen blijven bestaan. Want recyclaars kunnen op hun beurt niet verder met ontwikkelen, omdat het onzeker is of de producten worden afgenomen. “Denk aan Umincorp. Dus totdat het inzamelen en scheiden veel verder is ontwikkeld dan nu, kan je geen garanties op beschikbaarheid geven.”
Echter, aan elk hoogtechnologisch product zit wel een dopje, knopje, of afdekplaatje dat je wel van gerecycled
De overgang van virgin kunststof naar gerecycled materiaal brengt aanzienlijke uitdagingen met zich mee. Het vereist niet alleen technologische inspanningen, maar ook samenwerking, planning en innovatie in de industrie. Bedrijven moeten bovendien proactief inspelen op veranderingen in regelgeving. Hier zijn enkele punten die de complexiteit van het proces benadrukken:
1. Tijd:
Het proces van overschakelen naar gerecycled materiaal vergt tijd. Het vinden van geschikte gerecyclede materialen, het uitvoeren van proefspuitingen, en het doorlopen van keuringsprocessen bij klanten vereist geduld en planning.
2. Stapsgewijze vervanging van artikelen:
Het vervangen van artikelen door gerecyclede varianten moet stapsgewijs gebeuren. Klanten hebben mogelijk niet de capaciteit om gelijktijdig meerdere producten technisch te beoordelen en goed te keuren, wat het proces vertraagt.
3. Versnippering van leveranciers en beperkt beschikbare data:
De versnippering van leveranciers in de markt maakt het complex om de juiste bron voor gerecyclede materialen te vinden. Dit vereist intensief zoeken en communiceren met verschillende leveranciers. Het gebrek aan een centrale database met gedetailleerde informatie maakt het moeilijk voor bedrijven om snel geschikte keuzes te maken. Er is behoefte aan een gestandaardiseerde informatiebron, vergelijkbaar met het Ides-platform, waarin alle materialen wereldwijd worden vermeld, met informatie over wie ze verhandelt. Dit kan helpen om een overzicht te krijgen van beschikbare stromen en scheelt een boel uitzoekwerk.
4. Kleurproblematiek:
Voor technische materialen zijn beschikbare gerecyclede stromen vaak zwart, terwijl de behoefte aan diverse kleuren hoog is. Het ontbreken van naturelle stromen maakt het moeilijk om aan deze kleurvereisten te voldoen.
materiaal kan maken, dus daar beginnen Injection Point en hun klanten mee. Terwijl intussen wordt voorgesorteerd op de veeleisende producten.
Circulaire projecten
Intussen heeft Injection Point al wel een aantal circulaire projecten tot een goed einde gebracht. Dat gaat eigenlijk een stapje verder dan het gebruik van gerecycled materiaal, omdat een producent dan de wens heeft om een bepaalde afvalstroom uit de eigen keten opnieuw te gebruiken. Injection Point maakte bijvoorbeeld antikreukneuzen van schoenzolen, brillenkokers van pasglazen en telefoonhoesjes voor de medewerkers van Renewi van de door henzelf ingezamelde oude koelkasten.
Antikreukneuzen van schoenzolen
Een antikreukneus, ofwel crease guard, heeft als functie de neus van een sneaker te beschermen tegen leerscheurtjes en verrimpeling. DFNS en MarcelvangalenDesign wilden graag een duurzame neus, gemaakt uit gerecyclede schoenzolen: een product dat als maalgoed verkrijgbaar is. De neus moet stevig zijn om scheuren te voorkomen, maar ook comfortabel om te dragen. Dat is op zich al een uitdaging, maar het begon pas echt toen bleek dat het maalgoed van de schoenzolen niet volledig bestond uit thermoplasten. Bij de eerste spuitgiettests zaten er stukken thermoharder in het product.
Rijnen zocht samenwerking met Korrels om het materiaal op spuitgietniveau te krijgen. Uit hun analyse bleek dat slechts 6 van de 10 korrels in het maalgoed
Het spuitgieten van een antikreukneus van gerecyclede schoenzolen bleek nogal een uitdaging. “In het begin kwam er een klonterig product uit. Bleek dat slechts 6 van de 10 korrels in het maalgoed thermoplasten waren.”
Ace & Tate, een bekende Europese brillenverkoper, voorziet zijn monturen van nepglazen voor het passen. Deze glazen, die later worden vervangen door glazen op sterkte bij de opticien, beschouwt het bedrijf als verpakking. Bij een zelfevaluatie ontdekte Ace & Tate dat maar liefst 50% van hun ecologische voetafdruk afkomstig was van verpakkingsmaterialen, niet van de verkochte producten zelf. Dit besef vormde de basis voor het idee om de brilglazen te hergebruiken en te transformeren tot een nieuw product: brillenkokers.
Wat deze case uniek maakt, in vergelijking met andere recyclingprojecten, is de uniformiteit van de materiaalstroom.
Ace & Tate kon zorgen dat de brilglazen in de winkels gescheiden werden gehouden van het andere afval en in bulk werden teruggenomen op het moment van nieuwe montuurzendingen. Toen bleek dat er glazen van drie verschillende materialen in omloop waren, heeft het bedrijf zijn leverancier geïnstrueerd om alleen nog pmma-glazen te leveren. De volgende uitdaging zat in de stickertjes met informatie over UV-bescherming en glastype. Die moeten voor verwerking worden verwijderd en het is niet makkelijk om het stickertje er inclusief alle lijmresten af te krijgen. In eerste instantie werd ervoor gekozen om glazen met stickers weg te gooien; vervolgens werd het stukje waar het stickertje zat eraf gezaagd. Nu heeft Injection Point aangeraden om te kijken of het ook mogelijk is om een lijm te gebruiken die oplosbaar is. Een gestructureerde aanpak en samenwerking kunnen zo leiden tot duurzame oplossingen.
thermoplasten waren. Om het te sorteren via de traditionele sorteerlijn, moest het maalgoed 3 à 4 keer over de lijn: veel te kostbaar. Micro-ionisatie bleek ook niet haalbaar, omdat er ook fluf in het mengsel zat, dat in de fik vloog. Uiteindelijk werd teruggegrepen op het vertrouwde sorteerproces, waarbij de schoenzolen meerdere keren door de sorteerlijn werden geleid.
“Bij micronising vloog het mengsel in de fik”
Dit roept vragen op over het ontwerp van schoenzolen zelf en de verwerking van het afgedragen product. Is het mogelijk om de zool uiteen te trekken in verschillende materialen voordat het wordt geshredderd? Of om schoenzolen te ontwikkelen die niet bestaan uit meerdere lagen, maar uit monomateriaal? Of, een andere vraag die je je kunt stellen: is het wel slim om antikreukneuzen te willen maken van maalgoed van schoenzolen? Het maalgoed wordt namelijk ook omgezet in kunststof sportvelden en dan doet het probleem zich niet voor.
Andersom denken
Dit voorbeeld laat zien dat de traditionele manier van werken bij circulaire projecten moet worden losgelaten. Normaal gesproken heb je een product in gedachten en daar koop je de ideale compound bij. Bij een circulair project, heb je een productwens en een beschikbaar materiaal – en die moet je op elkaar afstemmen. Dit komt wel vooral doordat we nog in de overgangsfase zitten. “Met deze projecten laten we zien dat het mogelijk is om nieuwe producten te maken van wat voorheen als afval werd beschouwd. Maar in de ideale toekomst heb je zoveel aanbod dat je weer net zo vrij bent als nu met virgin materiaal.”
Bij Injection Point is deze overgang een reis van constante aanpassing en leren. Het bedrijf investeert tijd en middelen in het experimenteren met de nieuwe materialen en het begrijpen van hun gedrag in het productieproces. Dat gebeurt met het hele team.
Dankzij de uniformiteit van de materiaalstroom was het maken van een brillenkoker relatief eenvoudig. “We hopen alleen nog op een oplosbare lijm voor de stickertjes.”
Rijnen: “Ja, het is een investering in tijd, testen en het doorlopen van onbekende paden. Het is een zoektocht naar een beter begrip van hoe gerecyclede materialen kunnen worden geïntegreerd in productieprocessen en hoe de industrie kan bijdragen aan een duurzamere toekomst. Het is een investering die misschien nu nog niet volledig rendeert, maar die cruciaal is om de overgang naar een circulaire economie te bewerkstelligen. En je kan het niet in één keer doen; de re-engineering van elk product vraagt zoveel tijd en aandacht, dat je maar een paar projecten tegelijk kan doorlopen. Dus met het oog op 2027 ben ik blij dat wij alvast een eind op weg zijn.” www.injection-point.nl
Het realiseren van een telefoonhoesje gemaakt van gerecycled materiaal van oude koelkasten klinkt goed, maar zoals bij elk innovatief project, zijn er technische obstakels te overwinnen. Bij het proces van Renewi en Injection Point om dit specifieke telefoonhoesje te ontwikkelen, werden verschillende uitdagingen geïdentificeerd en opgelost.
Renewi wilde een product maken van hun eigen afval, iets wat ze konden teruggeven aan hun personeel. Daarom wilde men het telefoonhoesje vervaardigen uit polystyreen. Dit ligt niet voor de hand, omdat polystyreen de benodigde flexibiliteit mist. Renewi koos er toch voor en wilde een hardcase om ervoor te zorgen dat de telefoon goed beschermd bleef, vooral omdat veel chauffeurs de telefoons dagelijks mee op pad nemen. Een softcase zou niet voldoende bescherming bieden in geval van een val.
De bescherming is goed bij polystyreen. Het hoesje is hard en klikt de telefoon veilig vast. Polystyreen is echter niet flexibel genoeg voor een hoesje dat er gemakkelijk op en af kan worden gedaan. De harde case vereist kracht om te bevestigen, wat betekent dat het niet geschikt is om er bijvoorbeeld pasjes in te bewaren, wat gebruikers wel gewend zijn. Het harde materiaal maakt het bovendien lastig om vingerafdrukken correct te scannen, wat voor sommige gebruikers tot frustratie leidde. Het ontwerp van een hardcase met een bolling maakte het bovendien lastig om het hoesje uit de matrijs te stoten zonder het te beschadigen. Het evenwicht vinden tussen duurzaamheid, bescherming en gebruiksvriendelijkheid bleek dus een delicate taak. Hoewel het telefoonhoesje uiteindelijk is ontwikkeld en gebruikt kan worden, moeten gebruikers rekening houden met enkele minpunten in termen van gebruiksgemak. Het is nu aan de gebruikersgemeenschap om te bepalen in hoeverre ze bereid zijn deze kleine ongemakken te accepteren voor een product dat is gemaakt van gerecyclede koelkastmaterialen en bijdraagt aan de missie van het verminderen van afval en het hergebruiken van grondstoffen.
Een antikreukneus moet hard genoeg zijn om rimpeling te voorkomen en zacht genoeg om draagbaar te zijn. “Met deze projecten laten we zien dat het mogelijk is om nieuwe producten te maken van wat voorheen als afval werd beschouwd.”
Een telefoonhoesje uit oude koelkasten is technisch geen logische keuze. “Het is gelukt, maar er zijn wel enkele minpunten in termen van gebruiksgemak. Het is nu aan de gebruikersgemeenschap om te bepalen in hoeverre ze bereid zijn deze kleine ongemakken te accepteren voor een product dat is gemaakt van gerecyclede koelkastmaterialen en bijdraagt aan de missie van het verminderen van afval en het hergebruiken van grondstoffen.”
Onderzoek polymer mixing in a single screw extruder
Met een enkelschroefsextruder kun je heel goed buizen of profielen extruderen. Maar hij is niet zo goed in mengen van meerdere componenten in je granulaat. Kun je de mengkwaliteit van enkelschroefsextruders verbeteren, dan leidt dat wellicht tot beter en goedkopere producten. Deze wens vanuit de industrie bereikte het lectoraat kunststoftechnologie van hogeschool Windesheim. En meteen ontstond er een nieuwe vraag: hoe kwantificeer je eigenlijk de mengkwaliteit van een extruder?
Auteur: Kasper Weigand
Met een dubbelschroefsextruder kun je heel goed mengen. Maar hij heeft beperkte drukopbouw. Een enkelschroefsextruder kan dat juist heel goed, maar die is dan weer slecht in mengen. Terwijl beter mengen wel zou kunnen leiden tot een beter en goedkoper product. Dan heb je bijvoorbeeld bij kleur toevoegen minder kleurstof nodig voor een homogene kleur. “Gebruikelijk nu is om eerst een masterbatch te maken met een hogere concentratie kleurstof dan wat je nodig hebt. Die meng je goed met een dubbelschroefsextruder. Vervolgens maak je je product in een enkelschroefsextruder, met toevoeging van je masterbatch aan je granulaat. Omdat deze al voorgemengd is, krijgt je product de juiste kleur”, legt projectleider Jakob Buist uit.
Pieken en dalen
Stel dat twee op de honderd granulaatkorrels masterbatchkorrels zijn. Die zijn er natuurlijk doorheen gemengd, maar je kunt je voorstellen dat er in het product uit je extruder niet overal exact evenveel kleurstof zit. “Als je beter mengt dan zijn er ook minder pieken en dalen in je kleur. En dat betekent dat je wellicht
Tijmen
Mateboer (links) en Jakob Buist.
minder kleurstof masterbatch nodig hebt”, vult onderzoeker Tijmen Mateboer aan. Het streven is een masterbatch met een hogere concentratie additief te gebruiken zodat je er minder van nodig hebt om toch dezelfde kleur te krijgen.
Bestaande mengmethodes
Er is gekozen voor het optimaliseren van bestaande mengmethodes. Aan het eind van de schroef in een enkelschroefsextruder zit, ook nu al, een mengelement. Die wordt ingezet voor het zogenaamde dispersief mengen en distributief mengen. Met dispersie mengen sla je grote korrels kapot, waarna je ze door distributief te mengen evenredig verdeeld. Een eerste aanpak in het optimalisatieproces was om CFD (Computational Fluid Dynamics) stromingssimulaties te doen. Want ga je mengkwaliteit met een echte extruder testen, dan moet je elke keer weer je schroef vervangen. Dat kost natuurlijk heel veel tijd. “Op het moment dat je met stromingsimulaties goed de mengkwaliteit kan simuleren, dan kun je in die simulatie heel veel variaties aanbrengen. We keken vooral naar het meng-element en de matrijs erachter. Dus telkens variaties aanbrengen in de geometrie van het mengelement en dan kijken of de mengkwaliteit beter werd”, vertelt Mateboer. “En dan heb je dus een methode om steeds de meer optimale versie te vin-
den.”
Pilotextruder
Het testen in de praktijk vond in eerste instantie plaats op een pilotextruder. Het nadeel daarvan was dat deze vrij groot was in vergelijking met een labextruder. “En die pilotextruders hebben vaak maar beperkte toegang tot metingen. Temperatuurmetingen, drukmetingen”, legt Buist uit. Ga je iets veranderen, dan is het wel even een klusje. Daarom is in de eerste fase
De labextruder met op verschillende punten de mogelijkheid tot het meten van druk en temperatuur.
van het project een numerieke methode ontwikkeld om mee te simuleren. “Daarna wilden we die valideren en dat hebben we gedeeltelijk gedaan op de pilotextruder. Maar uiteindelijk hebben we een labextruder aangeschaft”, vertelt Buist. Die hebben de onderzoekers zo ontworpen dat ze op verschillende punten de druk en temperatuur konden meten.
“We hebben één waarde voor de mengkwaliteit van het schroef-element”
Meting
Het doel was om de effectiviteit van het mengelement in de extruder te meten. Lastig was dat de schroef, die uit drie zones bestaat, ook voor enige menging zorgt.
Hoe weet je dan wat voor effect alleen het mengelement heeft? “Tussen de schroef en het mengelement kunnen we een drukmeting en temperatuurmeting doen. Maar dat gat kunnen we ook gebruiken om wat roet of masterbatch te injecteren, met een speciaal ontwikkeld extrudertje erbovenop. Dan weet je dus zeker dat de menging die je ziet, alleen van het mengelement komt”, legt Mateboer uit. “Dat kan natuurlijk nooit met een productiemachine.”
3D-printen
Een mengelement dat vaak wordt gebruikt, ziet eruit als een cilinder met een aantal pinnen erop. Er is getest met allerlei varianten. Je hebt ze met 3 pinnen in de omtrekrichting, maar ook met 6 pinnen. “Als uit de numerieke simulatie kwam dat een bepaalde geometrie een hele goede menging heeft, maar hij is niet te maken met conventionele productietechnieken, konden we die door te 3D-printen, toch produceren”, zegt Mateboer. Is er uiteindelijk een ultiem mengelement uitgekomen? Nee, maar dat was ook niet de intentie. Dat verschilt namelijk en heeft alles te
De schroef met daaronder vier verschillende soorten ge3D-printe mengelementen.
maken met wat je precies gaat mengen en met welk soort kunststof er in beginsel wordt gewerkt. “We hebben een methodiek ontwikkeld om mengelementen met elkaar te vergelijken zonder dat je ze ook echt fysiek moet gaan maken. Dat is het voordeel van numerieke simulaties. Als je eenmaal de simulaties hebt opgezet en gevalideerd, dan zie je wat je simuleert ook terug in de praktijk. Meestal niet één op één, maar je ziet wel dezelfde trend”, legt Buist uit. “Je ziet dan ook meer details, want je kijkt als het ware in de kunststof.”
Temperatuur
Voor iedere kunststof waar je mee gaat werken, kun je zo’n simulatie doen. Aan de ene kant moet je menging optimaal zijn. Maar je moet ook rekening houden met het feit dat bepaalde kunststoffen kunnen gaan degra-
Het onderzoeksthema Duurzaam produceren van het lectoraat kunststoftechnologie is gericht op het optimaliseren van huidige kunststofverwerkingsprocessen, zoals extruderen en spuitgieten, om ze voor de toekomst duurzamer te maken. Dit streven om duurzaamheid te bevorderen realiseert het door de bestaande machines te optimaliseren aan de hand van een drievoudige combinatie van expertise: Analyse op basis van diepgaande rheologische kennis en ervaring binnen de onderzoeksgroep. Geavanceerde simulaties van de productieprocessen met behulp van state-of-theart software, waaronder ANSYS CFD, MoldFlow en Moldex, om inzicht te krijgen in mogelijke verbeteringen en het uitvoeren van praktische experimenten met de extruders, spuitgietmachine en andere faciliteiten die beschikbaar zijn binnen het lectoraat.
deren als de temperatuur te hoog wordt. Dat is onderwerp van vervolgonderzoek. De temperatuurtoename door de wrijving van het mengelement moet niet boven een bepaalde waarde komen. Want dan kan het kunststof verbranden of degraderen.
Drie delen
Het gepubliceerde onderzoek bestaat uit drie delen. Het eerste deel is de ontwikkeling van een numerieke methode, de simulatie. Het tweede deel is het kwantificeren van de kwaliteit van de menging. “Het is gelukt om een kwantitatieve methode te bedenken voor de totale mengkwaliteit die het mengelement oplevert. We
“Tussen de schroef en het mengelement kunnen we een druk- en temperatuurmeting doen”
hebben één waarde voor de mengkwaliteit van het schroef-element. En dat moet natuurlijk een methode zijn die je zowel numeriek kunt toepassen als experimenteel kunt toepassen”, merkt Buist op. En het derde deel is de validatie. “Daarmee hebben wij de conclusie getrokken dat wij een ontwerpmethode hebben ontwikkeld die gevalideerd is met de experimenten en die dus toegepast kan worden in de industrie”, vult Mateboer aan. “Dat betekent dat als een bedrijf een situatie heeft met een slechte menging en iets aan het mengelement wil doen, het onze methode kan toepassen. Het is allemaal ontwikkeld in commercieel verkrijgbare software en beschikbaar voor de industrie.”
www.windesheim.nl/onderzoek/lectoraten/ kunststoftechnologie